
11 minute read
Mistři a roboti
by MTX Group
AL INVEST Břidličná: Tavení
Dánský fyzik Hans Christian Ørsted se proslavil nejen svým bádáním v oblasti elektromagnetismu, ale také tím, že v roce 1825 izoloval hliník. Ačkoliv hliník patří k prvkům, které jsou nejvíce zastoupeny v zemské kůře, nebyla jeho výroba do doby, než pokročily technologie, snadná. V Česku se můžeme pochlubit dlouhou tradicí zpracování hliníku, která má kořeny ve 30. letech minulého století, a to v Břidličné u Bruntálu, kde se dnes vyrábějí hliníkové desky a fólie nejvyšší kvality pro průmyslové zákazníky i další hliníkové výrobky. Třeba ty, které možná máte v ruce při každé snídani v podobě víček od jogurtových kelímků.
V Česku se jedná o unikátní provoz a v Evropě jsou maximálně tři výrobci, kteří se věnují celému výrobnímu procesu, tedy od tavení hliníku až po výrobu finálních hliníkových produktů. Jak vysvětluje Daniel Ujházy, jenž má v Břidličné jako ředitel divize výrobu hliníku, hliníkových desek i fólií na starosti, je unikátní, že si sami po modernizaci a investicích vyrábějí top kvalitní hliníkové bramy (desky), které dále opracovávají. A také to, že sami zpracovávají veškeré odpady z výroby a takřka každou hliníkovou třísku vracejí do výrobního procesu.
Právě tavírna je podle Plant Managera Vincenta Hrubého, který zastává také funkci Group Director of Aluminium Technology Development, tepajícím srdcem závodu. Seznamujeme se se Zdeňkem Vránou, mistrem hutní výroby, který letos slaví ve firmě 30 let práce. Společně s ním míříme do tavírny. Být tavičem si žádá opravdové chlapy. Není to práce pro někoho, kdo hledá sterilní prostředí a jasně nalajnované procesy. Taviči jsou mistři řemesla, které je kreativní, něco zajímavého jim vzniká pod rukama a celá fabrika navazuje na jejich kvalitní práci. Na jeřábech převážejících těžký materiál v tavírně pracují i ženy.
Taviči pracují s tekutým kovem lesklé stříbrné barvy, ve slévárně celý výrobní proces začíná. Je tu horko od dvou rozpálených plynových pecí, kde teplota přesahuje 1 000 °C. Na začátku procesu je v tavírně hliníkový materiál nakládán do pecí a na konci z tavírny vycházejí hliníkové bramy vysoké kvality (která se průběžně hlídá v laboratoři), připravené na další zpracování a finálně pro zákazníky. Za 24 hodin taviči vyrobí zhruba 50 tun v případě větší ze dvou pecí a 42 tun v případě menší pece.
Co vlastně v tavírně znamená mistrovství? Dosažení nejvyšší kvality v rychlosti výroby, vzhledu ingotů, v kvalitě materiálu i v produktivitě práce. „Vyučení v oboru už neexistuje. Vše je potřeba se naučit a trvá to roky, aby byl člověk v řemesle skutečně dobrý a nic ho nepřekvapilo. A stejně ho překvapí, protože práce s kovem je živý mechanismus,“ říká Daniel Ujházy o dovednosti, jejíž detaily se špatně vysvětlují a radost i satisfakce přicházejí s tím, když na ně člověk praxí přijde. „Jsou za tím hodiny dřiny,“ upozorňuje Daniel. „A litry potu,“ dodává Zdeněk.
AL INVEST Břidličná
Hliníkové produkty se v Břidličné vyrábí už více než 90 let, od 30. let minulého století. Firma je významným evropským a jediným tuzemským výrobcem hliníku, vyrábí hliníkové desky, obalové materiály, fólie i válcované polotovary. Velké úsilí závod věnuje inovacím a modernizaci výroby, a to nejen z technologického, ale i z ekologického hlediska.
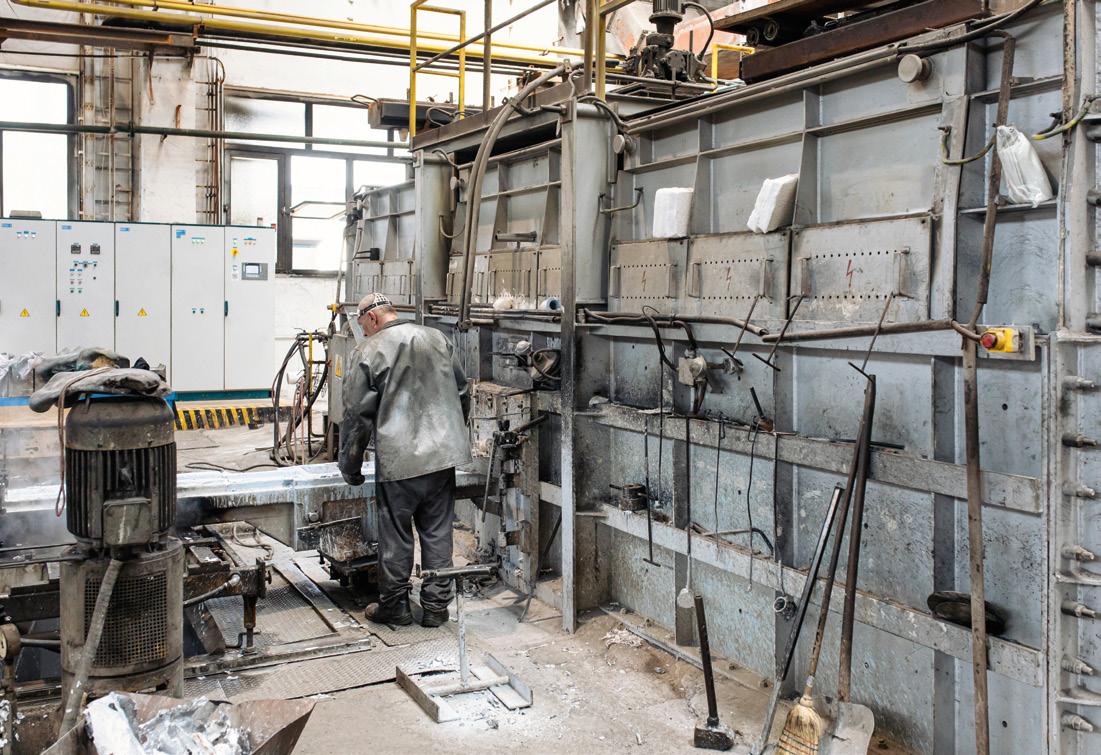
01 Roztavený hliník vytéká z pece a následně po zchlazení tuhne do podoby hliníkových ingotů.
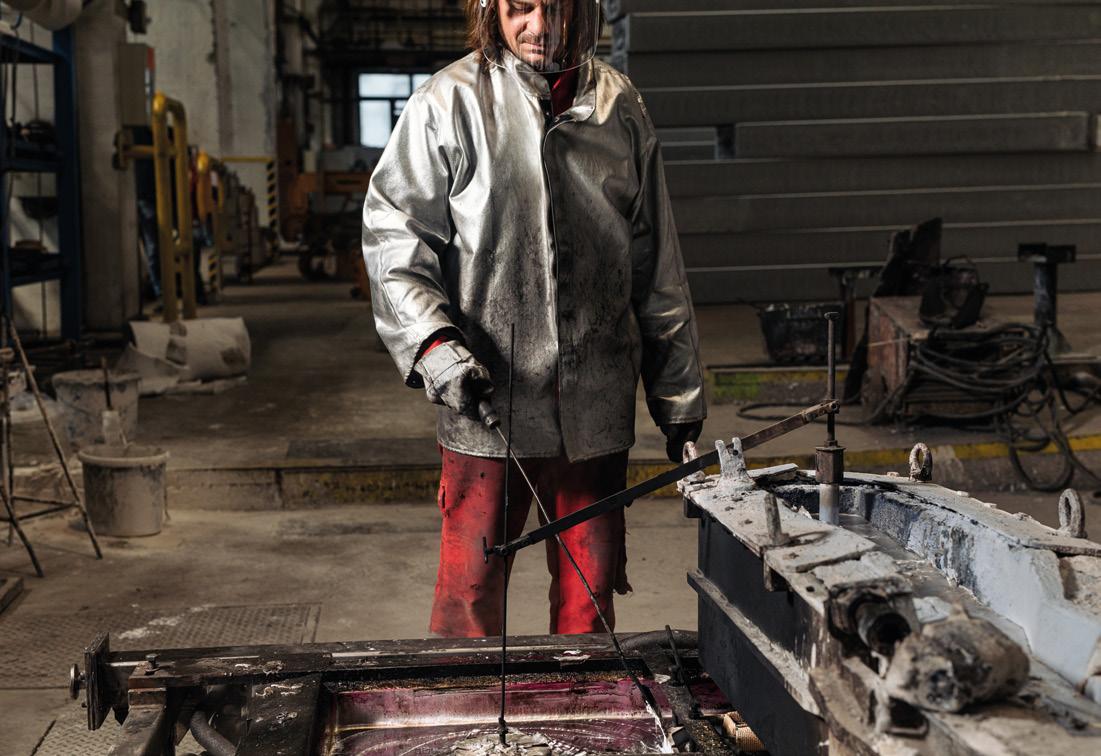
02 Přes veškerou modernizaci a inovace práce v tavírně stojí a padá se samotným materiálem – hliníkem – jehož kvalita se průběžně sleduje v laboratoři.
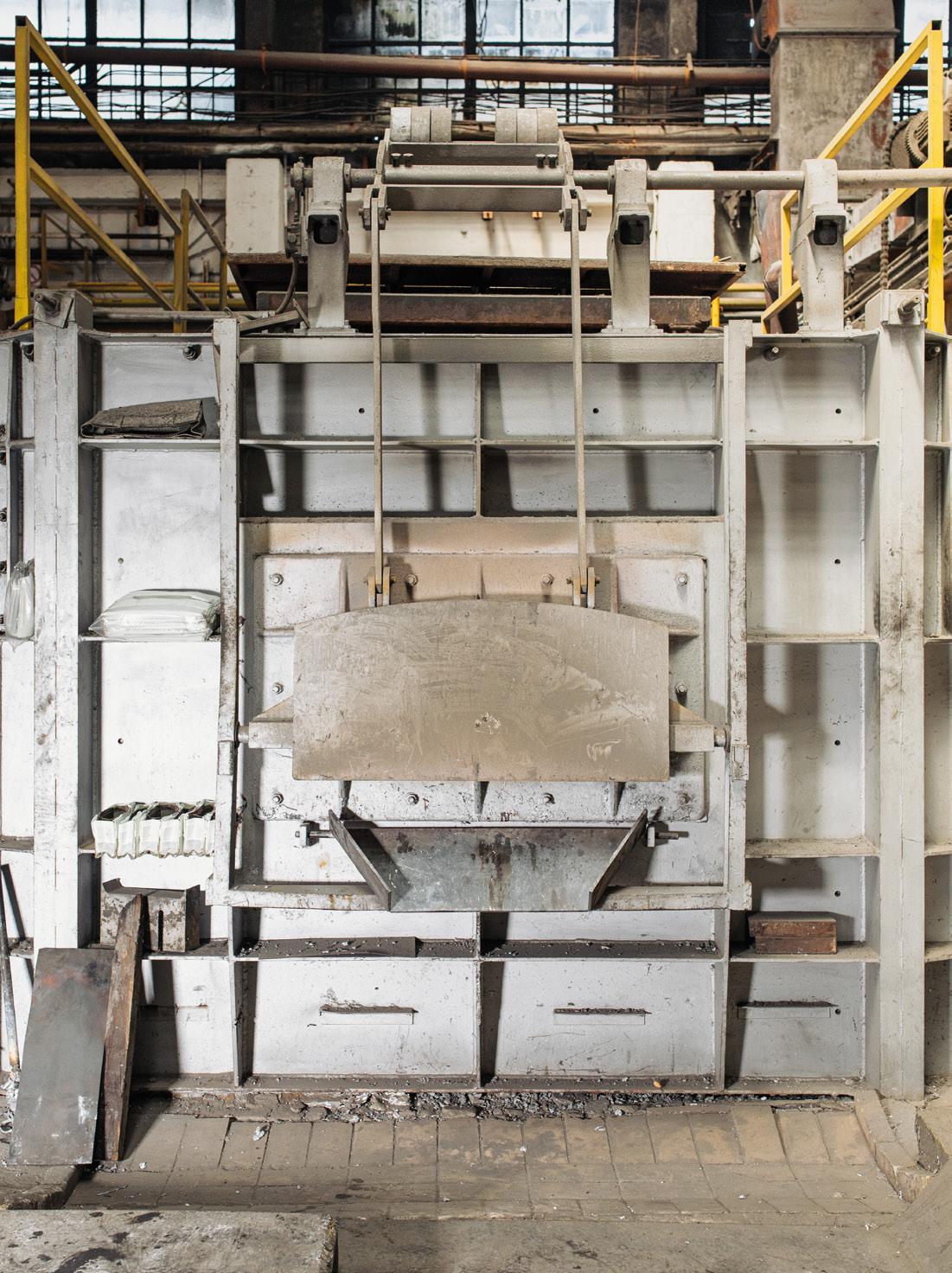
03 Dvě tavicí pece v nepřetržitém provozu jsou středobodem tavírny.
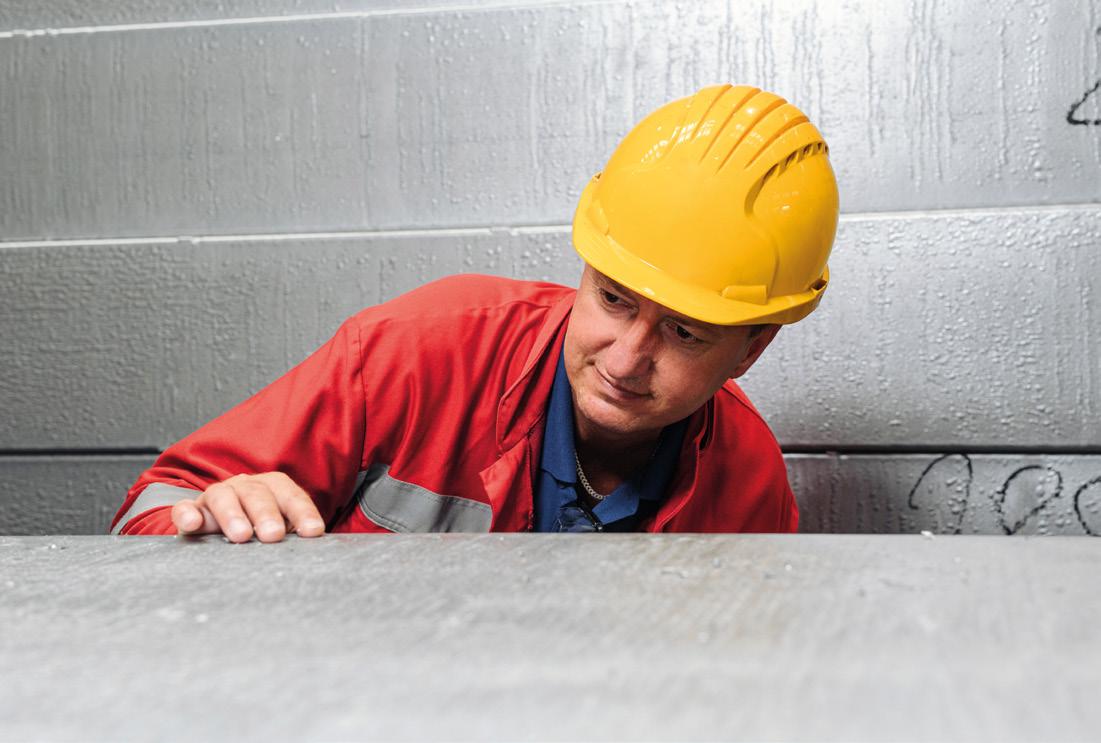
04 Zdeněk Vrána prohlíží zatím neopracované hliníkové bramy, desky, které jsou svou špičkovou kvalitou chloubou závodu.
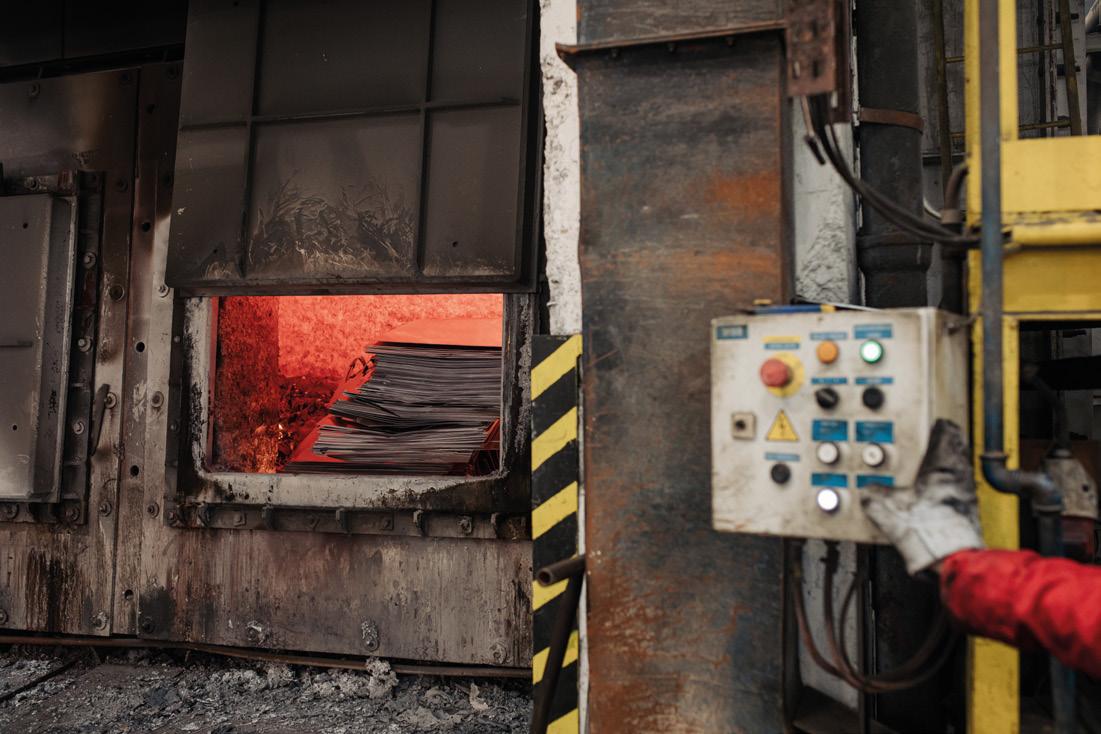
05 U plynových pecí, které je potřeba naložit materiálem, práce v tavírně začíná.
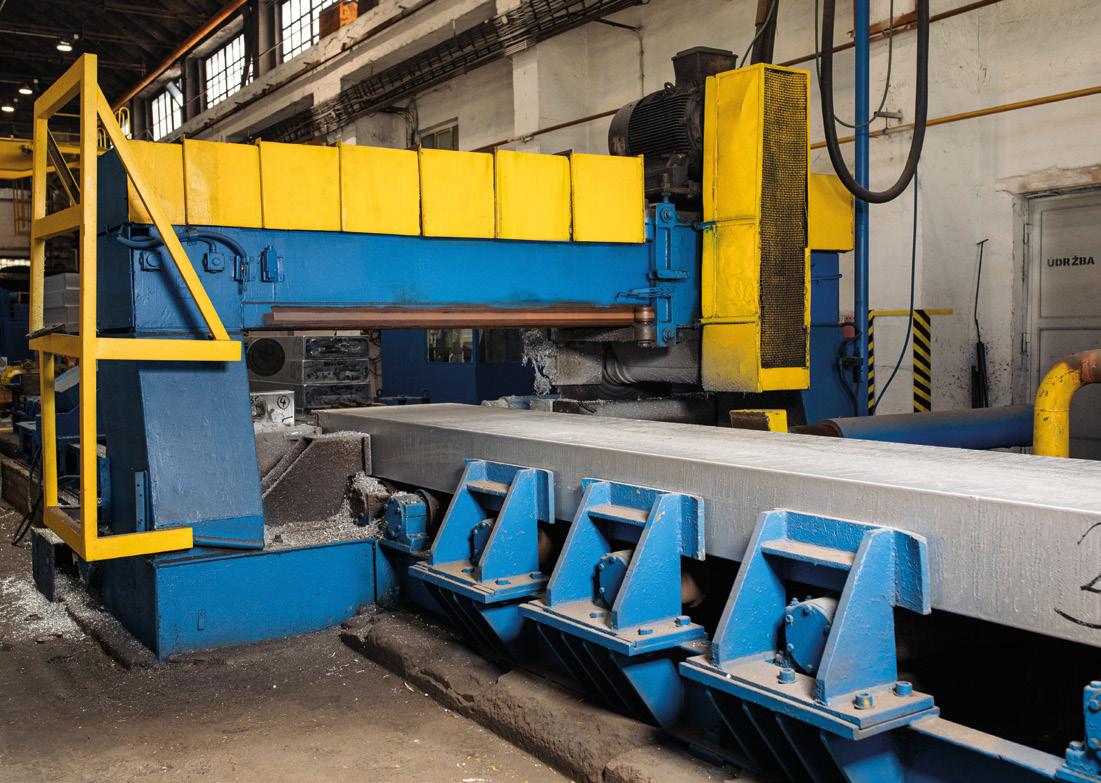
06 Než hliníkové bramy opustí tavírnu, frézují se a řežou do požadované podoby.
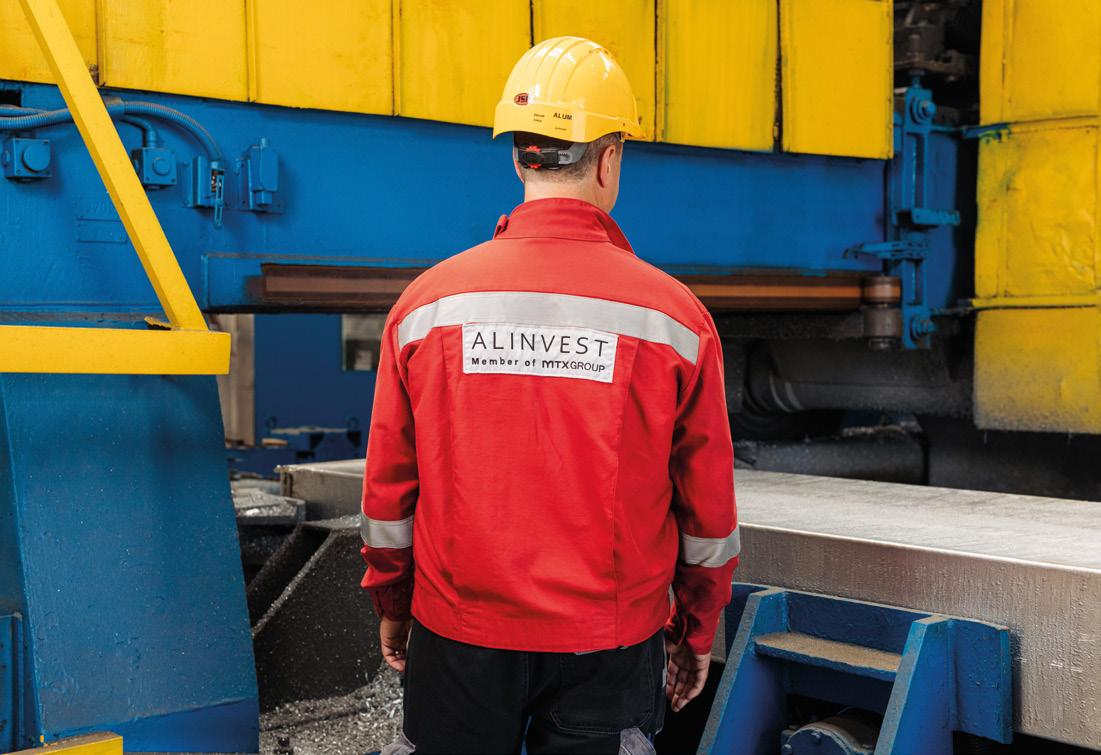
07 Bramy se dále zpracovávají, jak ukazuje Zdeněk Vrána.
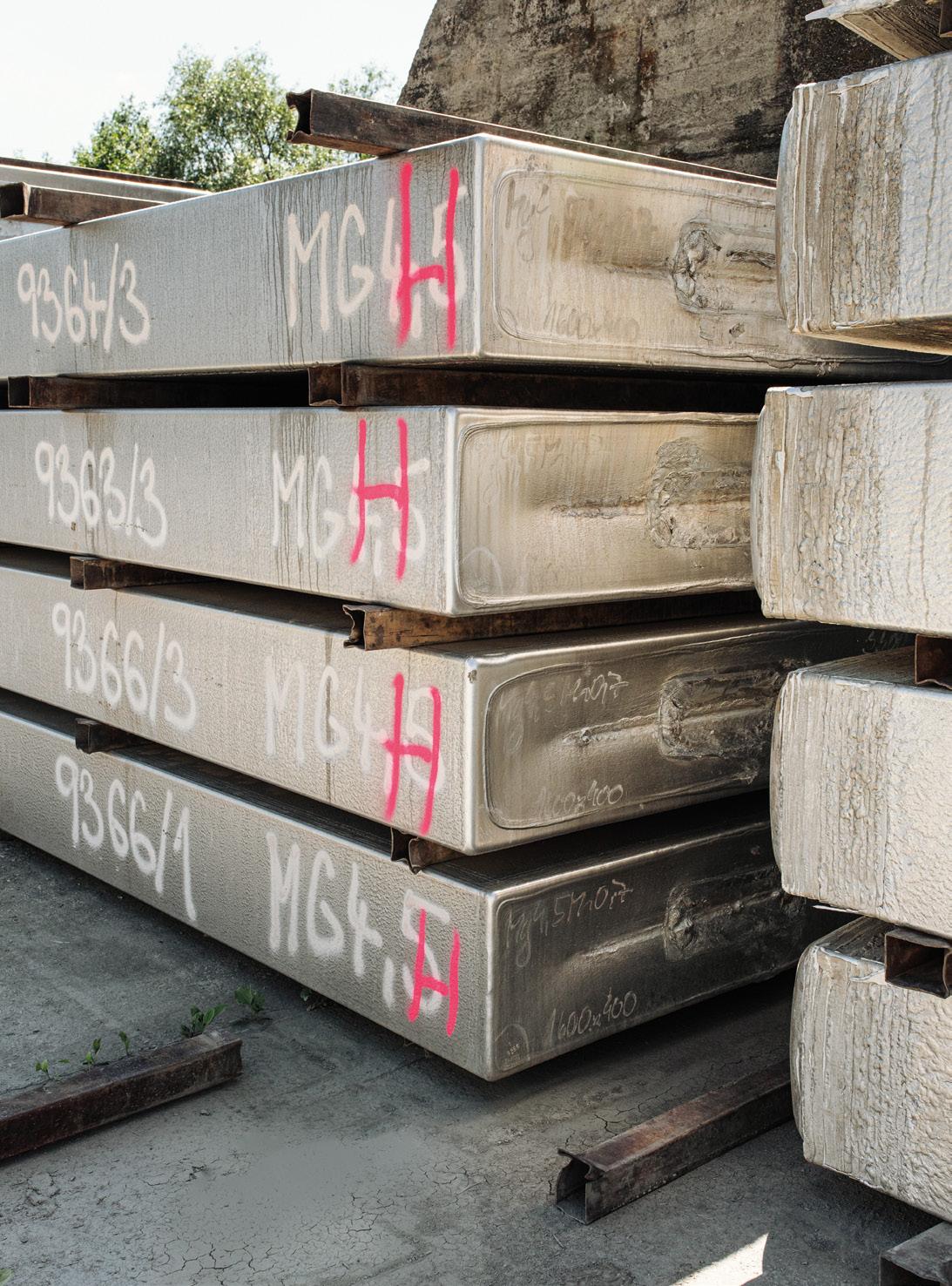
08 Na začátku byl surový materiál, na konci jsou hliníkové desky, na něž jsou v Břidličné hrdí.
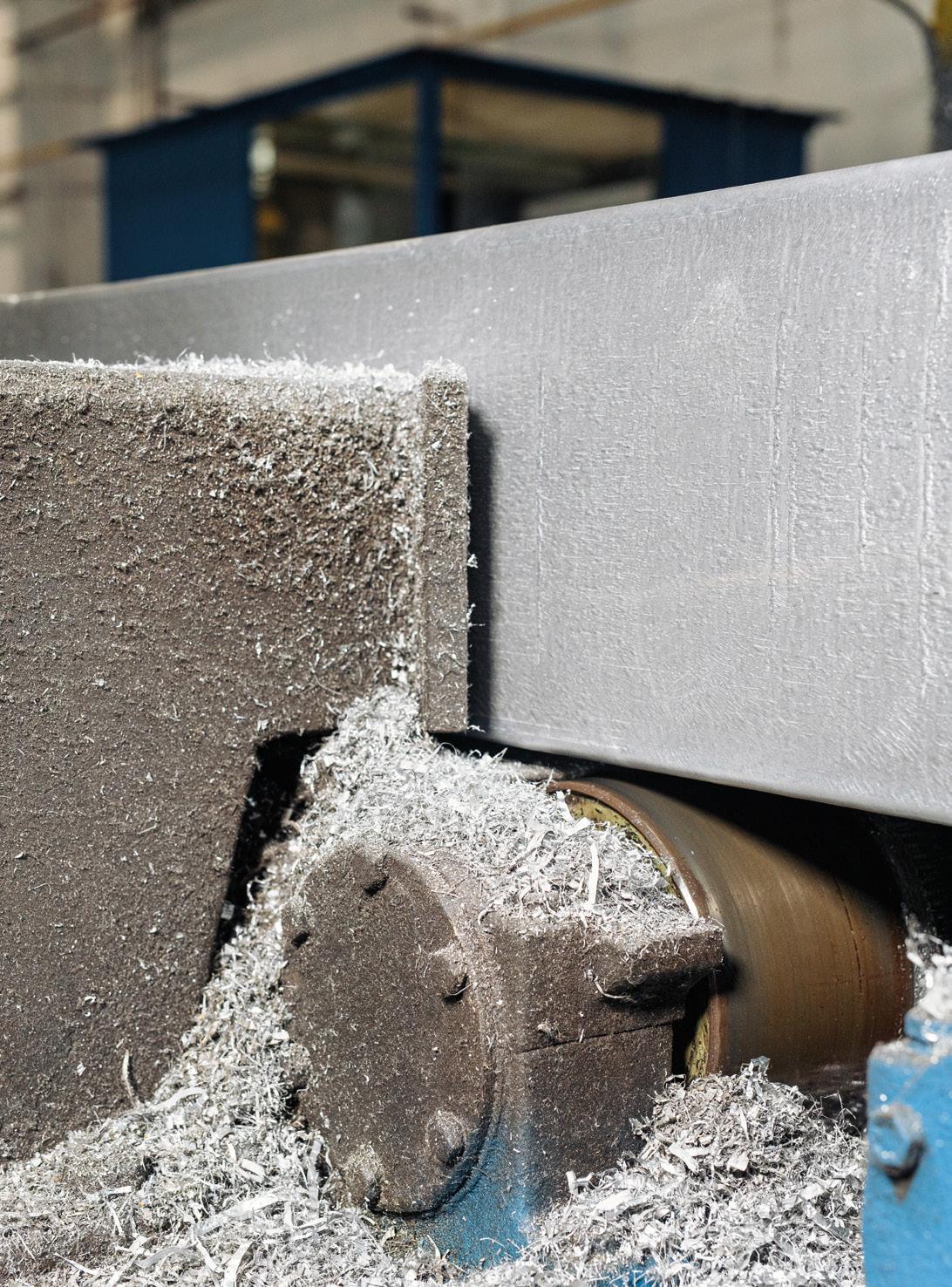
09 Veškerý hliníkový odpad včetně pilin z frézy se v tavírně opět vrací do výrobního procesu.
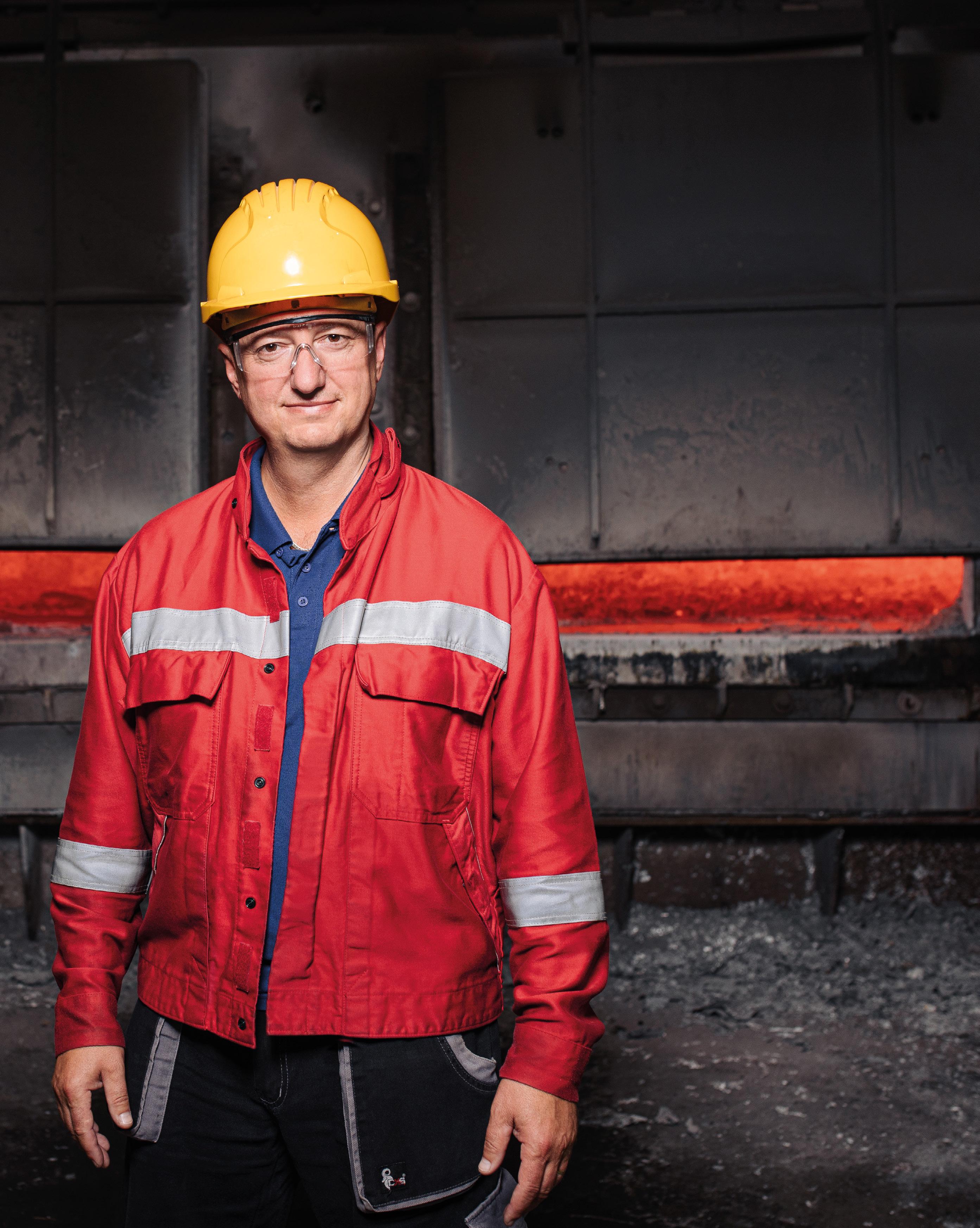
Mistr hutní výroby
Mistr hutní výroby Zdeněk Vrána je zodpovědný za chod tavírny, má na starosti obsazení směn, péči o to, aby měla tavírna k práci dostatek materiálu, stará se o vzdělávací akce i o to, aby měli všichni zaměstnanci k dispozici veškeré informace, které při práci potřebují. Tavírnu zná podrobně a do detailů má zvládnutý celý technologický postup. Ve 21 letech tu totiž začínal jako 3. tavič a začal se řemeslo učit od píky. Mistrem je rok a letos slaví 30 let od chvíle, kdy získal hned po vojně v Břidličné zaměstnání.
Povrly Copper Industries: Válcování
Podobné je to s profesí valcíře, se kterou se seznamujeme v Povrly Copper Industries nedaleko Ústí nad Labem. Válcovnou nás provází Jiří Štofčo, 1. valcíř na kvartu (a také ostřílený dobrovolný hasič). Zkušenosti začal ve fabrice sbírat už v roce 1994, kdy nastoupil na místo 4. valcíře. Ještě se stihl v oboru vyučit, což už dnes nejde a vše je třeba se učit praxí.
Než se vydáme do válcovny, setkáváme se s ředitelem firmy Davidem Kozlem. „Naše specifikum tkví v materiálu. Jako mosazná huť jsme jediní v České republice, a i v celé Evropě je podobných firem málo, jednotky. Ve válcovně je naše unikum právě kombinace s materiálem, kterým je nyní především mosaz,“ vysvětluje.
Mosaz je slitina, výrobní proces začíná nákupem čisté mědi a čistého zinku i mosazných a měděných odpadů. Materiály tu roztaví zhruba na teplotu kolem 1300 ºC, odlijí bramu, nahřejí ji a za tepla vyválcují, čímž vznikne první forma svitku. Svitek se pak frézuje a už za studena válcuje do přesné tloušťky. Následně se upravují mechanické vlastnosti, svitek se vyžíhá, vymoří, na povrchu vyčistí a podélně nastříhá na šířky, jaké zákazníci požadují. „Drtivá většina naší produkce směřuje do výrobků pro průmyslové aplikace. Zhruba polovina produkce jde k zákazníkům, druhou polovinu zpracováváme v naší kalíškárně, což je lisovna, která vyrábí polotovary. Veškeré technologické odpady, které při výrobě vznikají, se vrací do pecí,“ zasvěcuje nás David Kozel. Produkují zhruba 1100 tun výrobků měsíčně, za posledních 2,5 roku zvedli kapacitu výroby cca o 30 %.
Investice do modernizace je v Povrlech, kde stojí fabrika mezi řekou a železniční tratí u obytných domů, téma, výhled modernizace mají na 10 let. Modernizace strojů, jež jsou dnes řízeny počítačem, klade čím dál vyšší nároky na lidi, kteří s nimi pracují. A to platí i pro válcovnu. „V jádru je stále tradiční řemeslo, ale pořád se zdokonaluje, zpřesňuje, modernizace strojů reflektuje vzrůstající tlak na efektivní využití materiálů a energetickou náročnost. Dokonalá znalost materiálu je však základ, na kterém stavíme,“ říká s tím, že právě Jiří Štofčo má díky dlouholeté praxi dokonalou znalost materiálu a prošel také velkým profesním vývojem.
Když David Kozel mluví o investičním výhledu, znamená to obrovský kus práce. „Je to přesně to, co mě a většinu mých kolegů na práci baví – že můžeme firmu rozvíjet, aby rostla a nepropouštěla, protože cítíme odpovědnost k místním lidem,“ vysvětluje. Úcta k lidské práci a know-how zdejších profíků jsou pro něj důležité. „Teď se nám povedl fantastický kus – člověk, který tu byl zaměstnaný přes 40 let, zaškolil před odchodem do důchodu na svou práci svého vnuka,“ sdílí jeden z firemních příběhů.
Povrly Copper Industries
Historie hutnictví v Povrlech sahá do roku 1898. Firma je dnes neustále se modernizujícím výrobcem válcovaných a lisovaných produktů z mosazi. Průmyslové aplikace, kalíšky a rozety vyrábí také ve své kalíškárně. Je významným zaměstnavatelem Ústeckého kraje a její výrobky míří do celého světa.

01 Jiří Štofčo prošel za svou dlouhou praxi velkým profesním posunem. Dnes ho často najdete ve velíně, kde precizně řídí kvarto přes počítač.
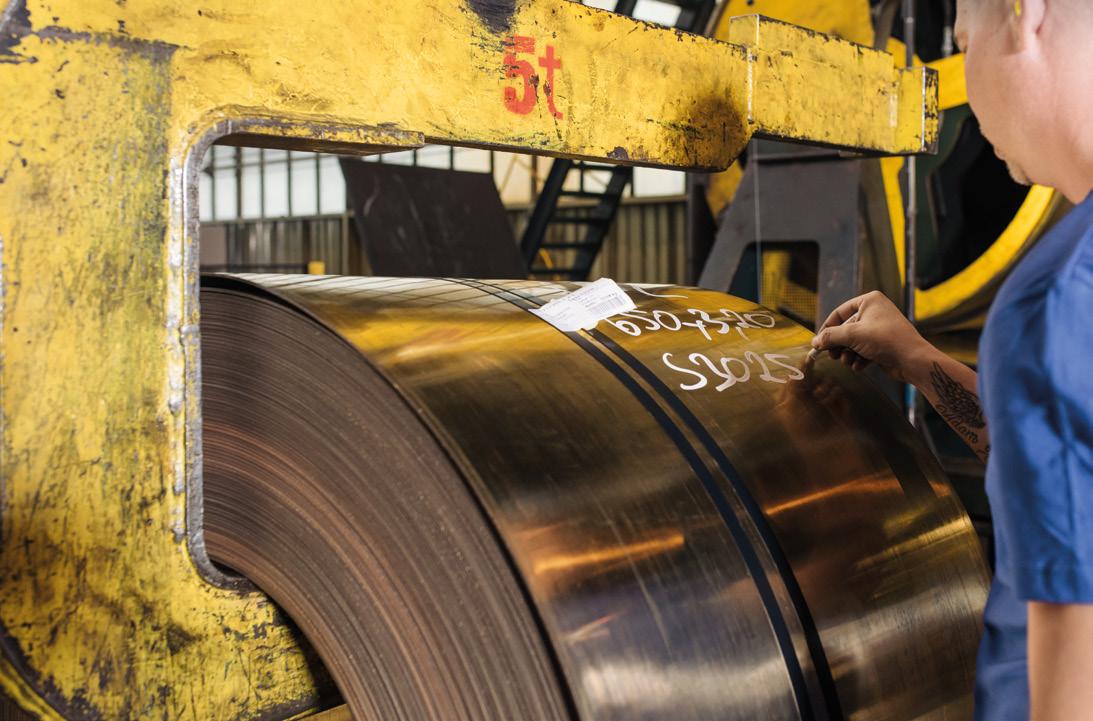
02 Z kvarta vycházejí mosazné svitky požadované tloušťky, kterou má zkušený valcíř přesně v oku.
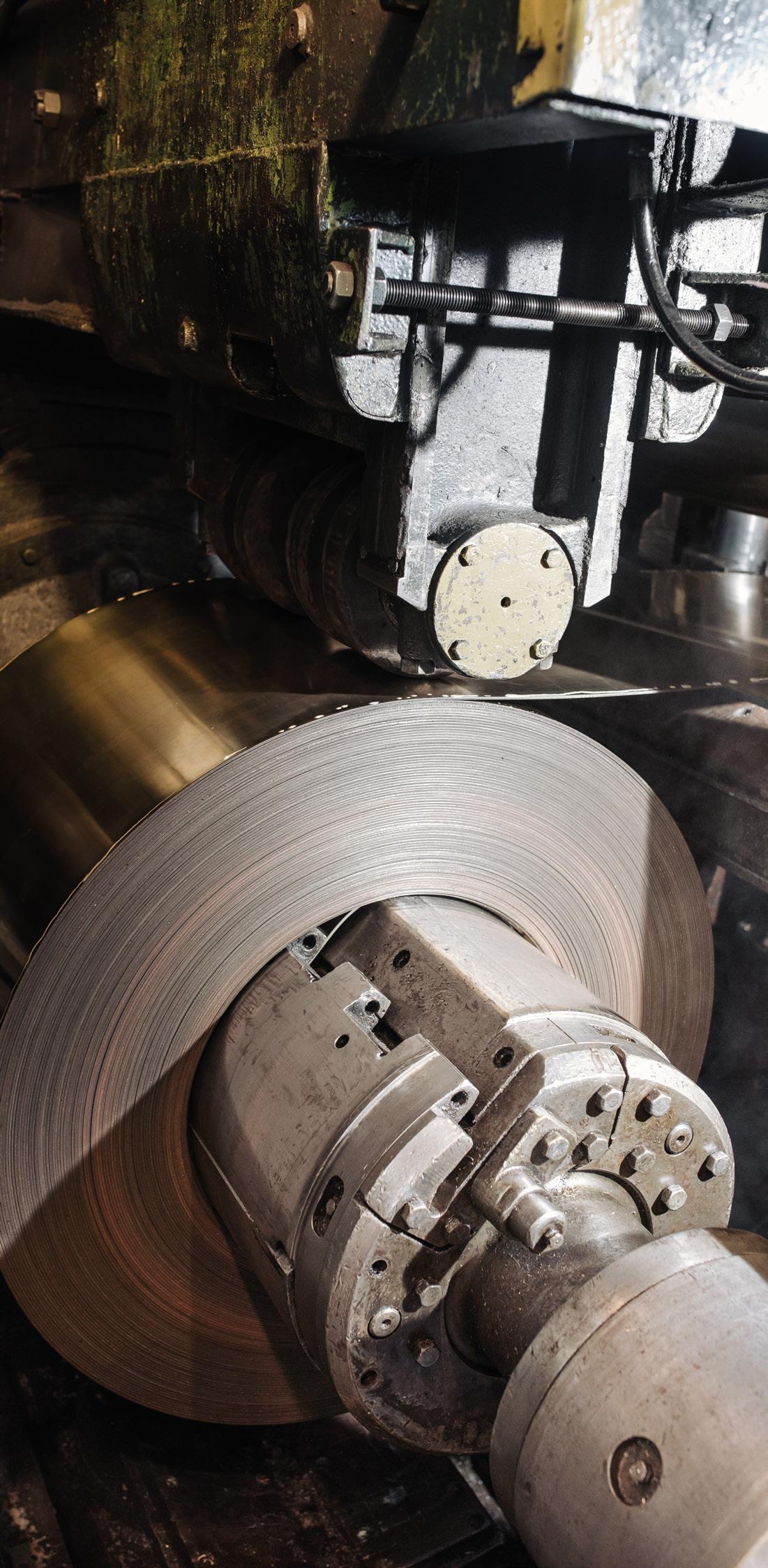
03 Nitro masivního válcovacího stroje.
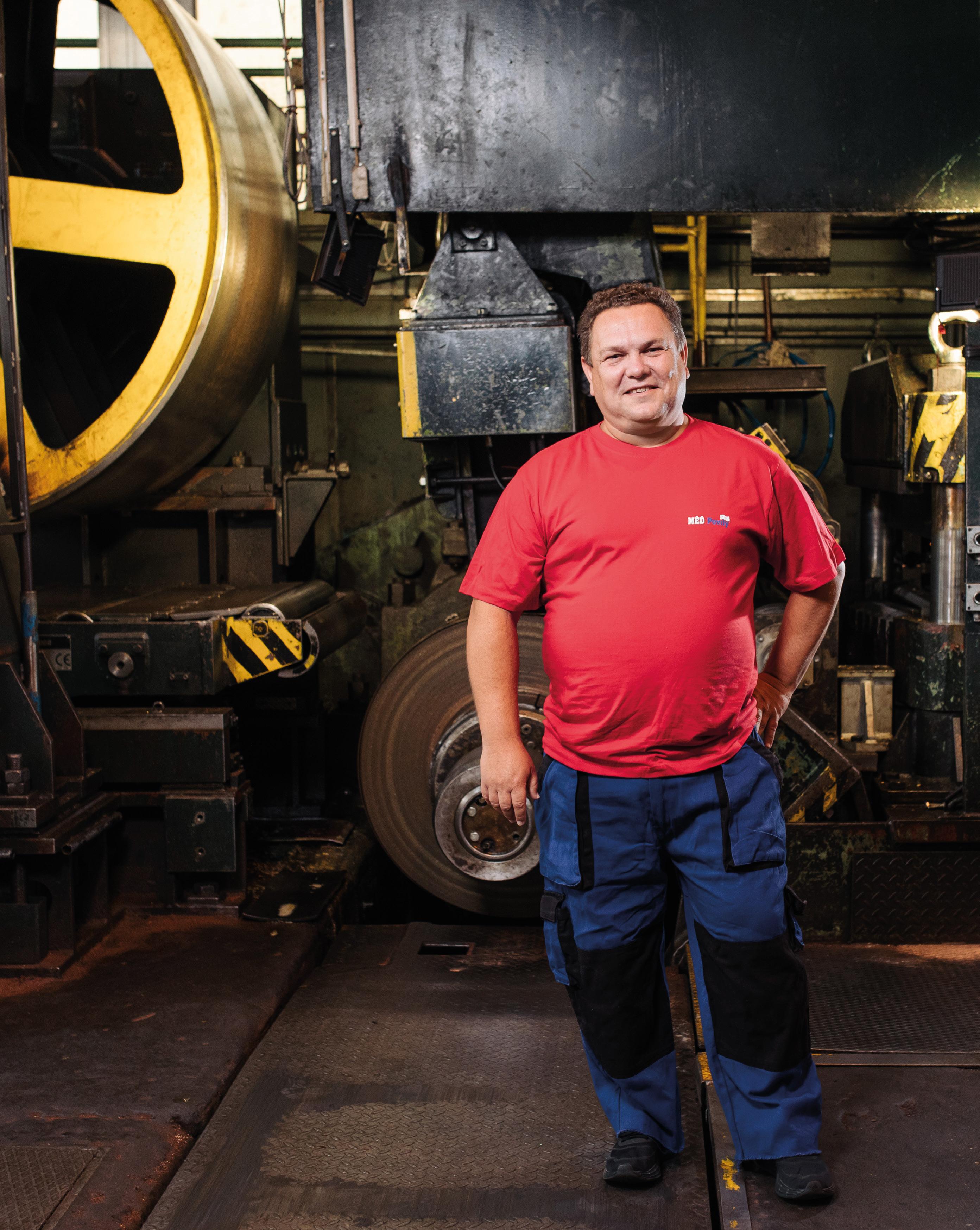
Jiří Štofčo
Valcíř
1. valcíř Jiří Štofčo pracuje ve firmě od roku 1994, když se předtím pro fabriku vyučil valcířem neželezných kovů. Šel ve stopách rodičů, kteří v závodě také pracovali. Dnes má ve firemní laboratoři manželku, v partě svého synovce a jeho syn přes léto brigádničí na vrátnici. Jiří nastoupil na formátovací linku, pak šel na vojnu. Vrátil se na kvarto, tedy válcovací stroj se čtyřmi válci, na místo 3. valcíře, asi po deseti letech přešel na novou válcovací stolici. Po pár letech šli starší parťáci z kvarta do důchodu, na kvarto se tedy zase vrátil a postupně se zaučil až na 1. valcíře. Trpělivost, rozvaha a smysl pro zodpovědnost jsou přednosti, které využije nejen v práci, ale i jako povrlský dobrovolný hasič.
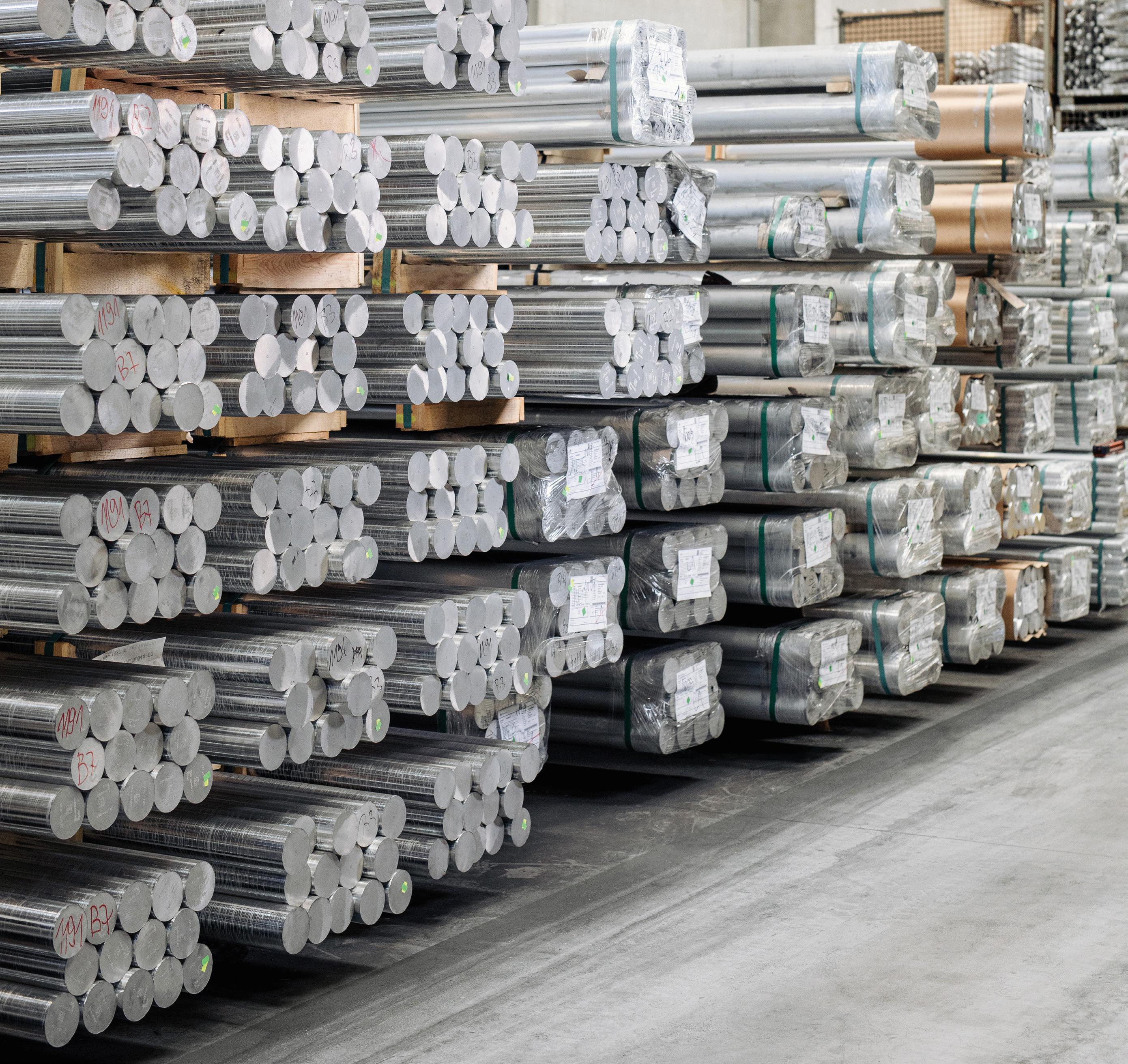
01 Hliníková tyč je výchozím materiálem pro další zpracování.
Strojmetal Aluminium Forging Kamenice: Kování
Ve Strojmetalu ve středočeské Kamenici, kde z hliníku a hliníkových slitin vyrábějí především kované podvozkové díly do automobilů světových prémiových značek, míříme s Janem Žídkem do obrobny. Jan Žídek, absolvent Vysokého učení technického v Brně, nastoupil do Strojmetalu před dvěma a půl lety jako technolog obrábění, v obrobně řešil různé projekty, pracoval jako projektový manažer, zastupoval šéfa a dnes obrobně sám šéfuje. I v obrobně se lidé základy řemesla naučí, hlavní je zápal a přístup k práci. Jan Žídek hodně dá na osobní agilitu, kdy má každý možnost hledat způsoby, jak práci v obrobně zlepšit a posunout kupředu svými nápady či zpětnou vazbou. „Baví mě, když je měsíc od měsíce v naší práci vidět pokrok,“ říká. Obrobna je v provozu zhruba šest let, kdy pro ni také vznikly v areálu podniku zbrusu nové prostory. Její kapacitu navýšila dvě nová obráběcí centra a také dvě kompletně automatizované výrobní linky, potřebné pro kapacitně velké projekty. Stačí sem vložit polotovar a roboti se postarají o konečný výrobek. Obrobna pracuje s polotovary, které sem putují z kovárny, z nich vyrábí i montuje finální výrobky. A také tady využívají cenný materiál do mrtě, včetně třísek, které smetou z podlahy.
„Strojmetal je v Evropě významný kovář, v kování máme velké know-how a kompetenci. Zákazníci dnes už ale nechtějí jen vykovaný díl, chtějí ho mít také obrobený. Obrábění je pro nás relativně nová kompetence a naše díly získávají vyšší přidanou hodnotu, nehledě na to, že díly pro zákazníky také rovnou smontujeme,“ vysvětluje ředitel Strojmetalu Robert Smutný, proč nás nasměroval právě do obrobny, která je vybavena sofistikovanými technologiemi pro obrábění a montáž výrobků, včetně moderních automatizačních prvků. Firma díky obrábění získává nové prestižní projekty a kvalitativně se posouvá, dodává díly i pro exkluzivní auta. „Čím specifičtější auto je, tím víc je díl jiný a komplikovanější, což je výzva i dobrý byznys s velkou přidanou hodnotou,“ říká.
Satisfakce v práci přichází třeba s tím, když se po roce i dvou letech příprav úspěšně podaří náběh projektu. „Je skvělé, když si ověříme, že se naplnily naše předpoklady spojené s výrobou nového dílu. Radost máme i z toho, jak se rozjela obrobna, a těšíme se i z naší nové kovací linky, kterou jsme v září spustili v Bruntále,“ říká Robert Smutný a připomíná, že automobilový průmysl dnes čelí mnoha výkyvům způsobeným externími vlivy. „Proto máme pestrou práci, jinou než dřív, kdy fungovaly zaběhané dodavatelsko-odběratelské řetězce. Přitom se nám stále daří plnit přání zákazníků,“ uzavírá s tím, že příležitosti firmě přinášejí i změny spojené s rozvíjející se elektromobilitou.
Automatizovaná kovací linka
Od loňského roku funguje ve Strojmetalu další automatizovaná kovací linka. Jak říká výrobní ředitel Jiří Rokos, právě tato linka primárně zásobuje obrobnu polotovary. Vyrobí až 1 kus za 1,5 sekundy, tedy až kolem 55 tisíc kusů denně, takže je ve výrobě významně rychlejší než ostatní linky. Nabízí širokou škálu kovacích pozic, až sedm nástrojů v rámci jedné sady v lisu, transferové překládání dílů i kompletní tepelné zpracování. Do linky vstupuje na jedné straně kovová tyč, na druhé straně vystupuje výrobek připravený pro obrobnu. „Je to jiný technologický postup, který nám umožňuje výkonně a ekonomicky vyrábět daleko větší množství produktů, než jsme byli schopni vyrábět dodnes,“ shrnuje ředitel Strojmetalu Robert Smutný. Firma teď žije i výstavbou nové automatizované kovací linky v Bruntále, opět ve spolupráci s firmou Schuler. Jede od září letošního roku a dále rozšíří výrobní kapacitu. V horizontu čtyř let a zejména ve spolupráci s ICE Industrial Service, která dělá kompletní automatizaci a programování řízení celé linky, se v Bruntále počítá ještě s dalšími dvěma automatizovanými kovacími linkami.

01 Obrábění je pro Strojmetal relativně nová kompetence, díky němu se dostává k zajímavým a prestižním zakázkám. Zajišťují ho stroje napojené na informační systém a pracují zde také roboti, lidská práce má však v provozu klíčové místo. Automatizované pracoviště umožňuje vyšší kapacitu výroby. Roboti se postarají o kompletní obrobení i montáž výrobku.
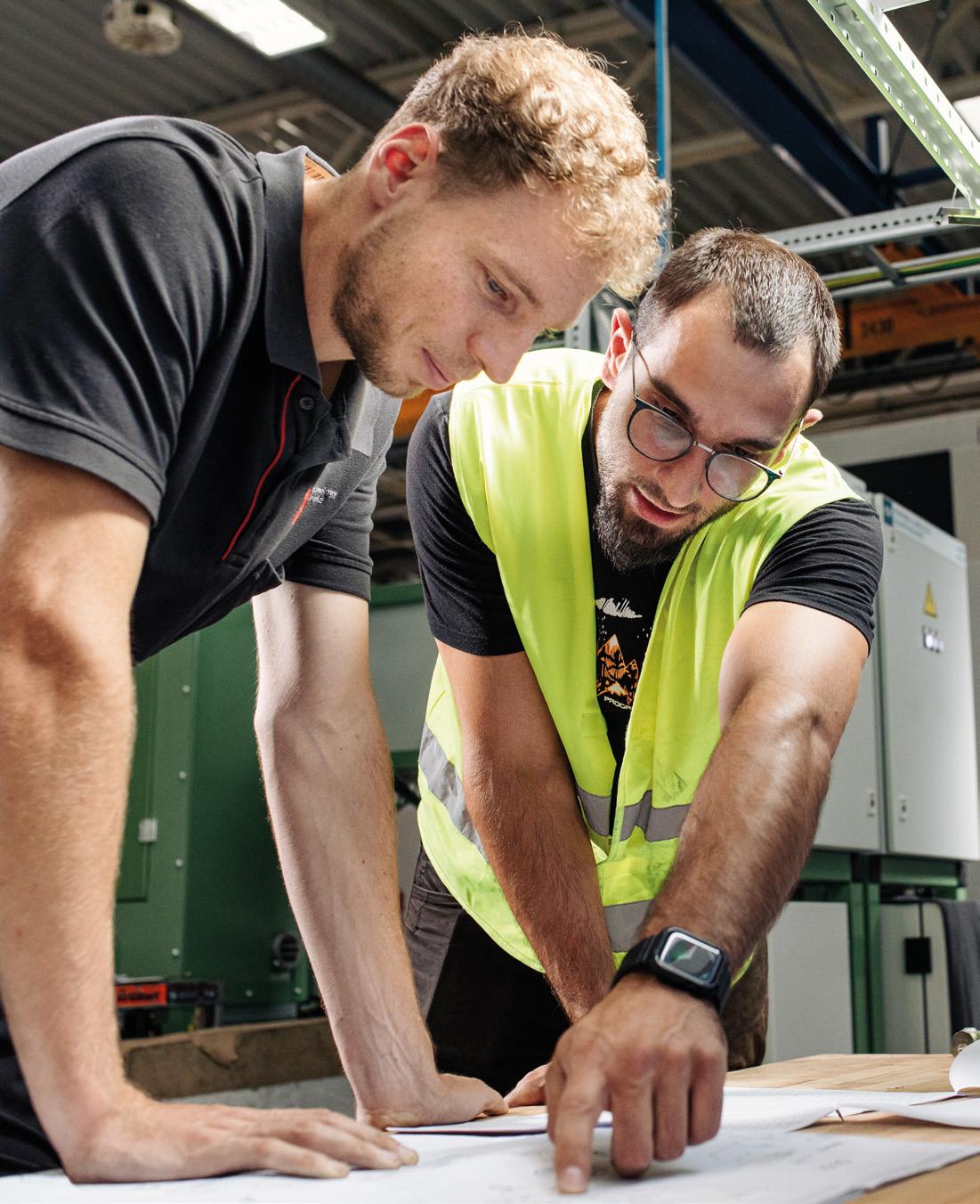
02 Setkání nad plány, výsledný produkt musí přesně odpovídat požadavkům zákazníka
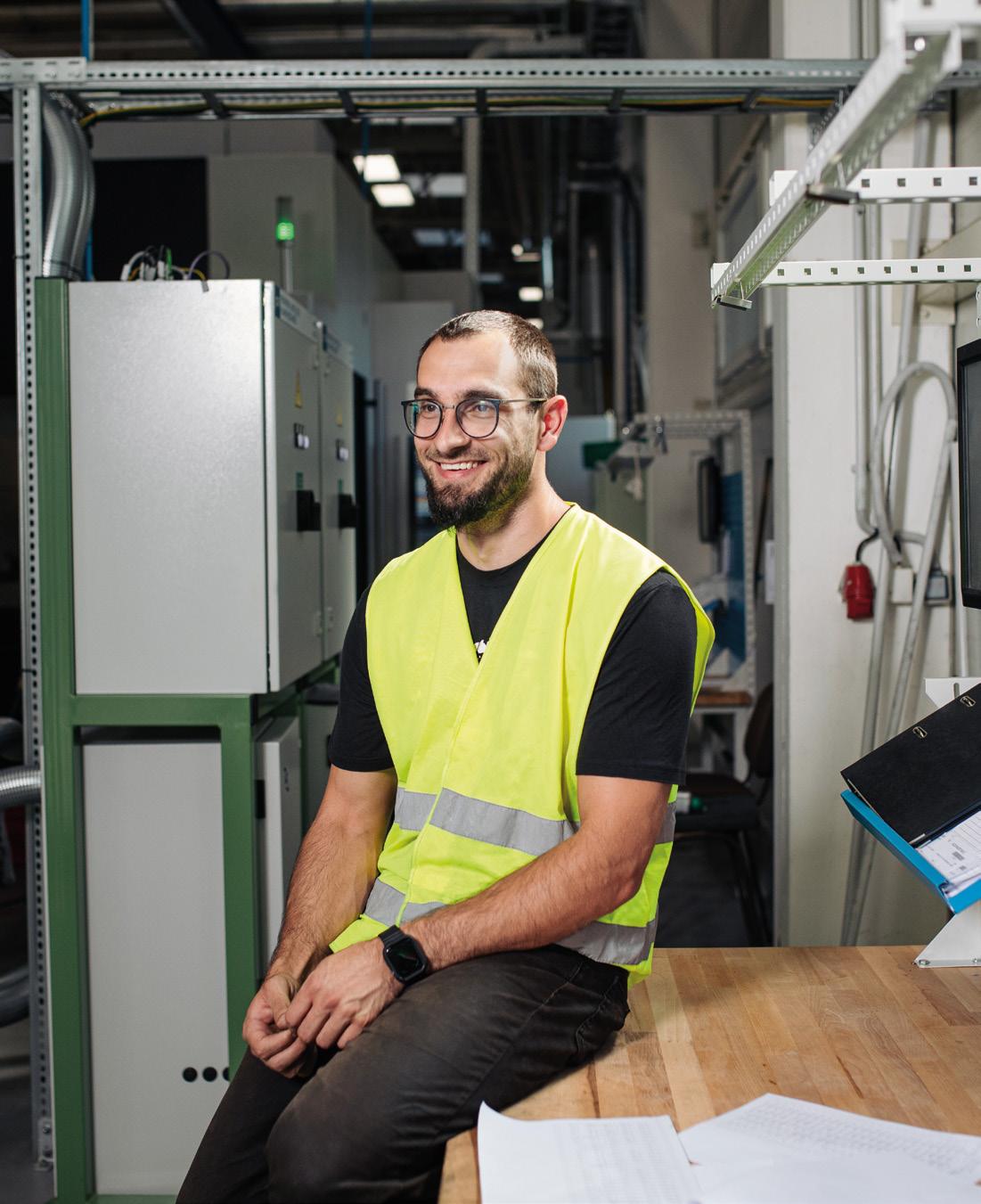
03 Jan Žídek v práci u kolegů oceňuje nápady a iniciativu. Rád s lidmi v obrobně zapáleně řeší, jak práci zlepšovat a posouvat kupředu.
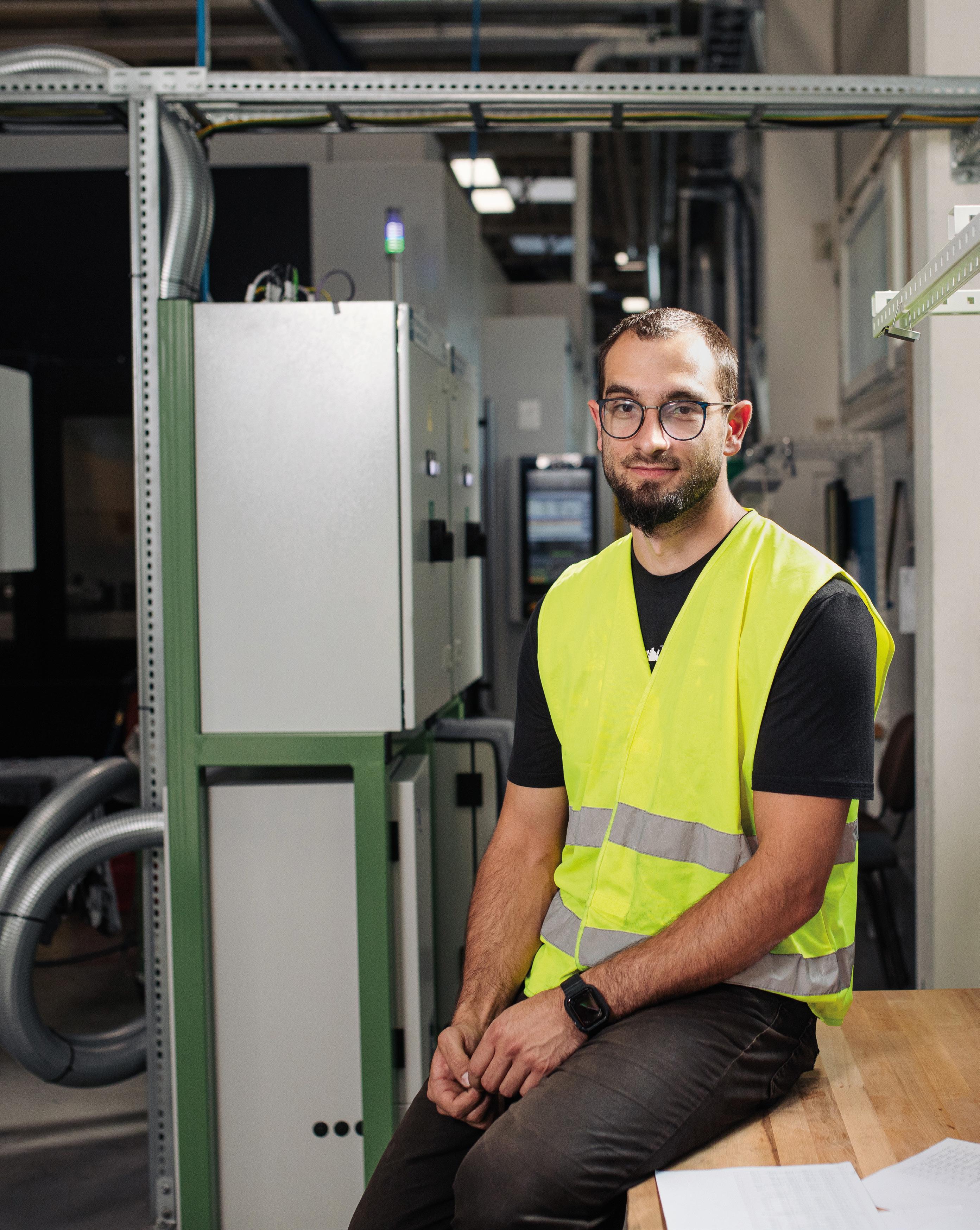
Šéf obrobny
Jan Žídek pracuje ve Strojmetalu 2,5 roku, nyní šéfuje obrobně. Vystudoval Vysoké učení technické v Brně, obor strojírenské technologie a průmyslový management. Jeho práce teď hodně spočívá v setkávání s kolegy během schůzek, které jsou na denním pořádku, ať už napříč firmou, nebo přímo v obrobně. Jeho snahou je zavést v obrobně kaskádovité řízení, aby získali větší roli a zodpovědnost mistři. Někdy má víc práce na počítači, na jeho pozici je nezbytné také sebevzdělávání. Je rád, že to, co se naučí, může hned aplikovat v praxi.