FOOD & DRINK PROCESSING & PACKAGING
Issue 45 2023
Ishida weighers help hotel chocolat meet surging demand for velvetiser
Proseal marks a 25-year milestone


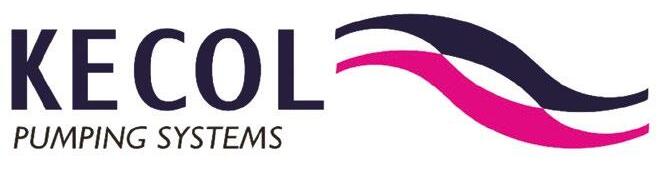
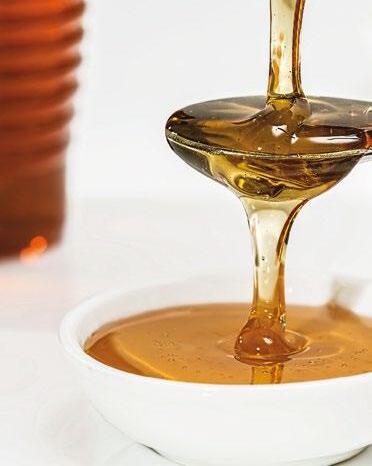
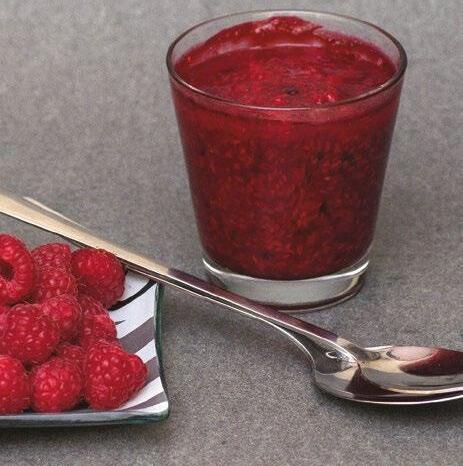
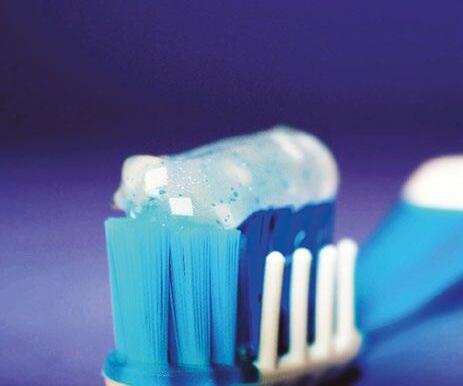

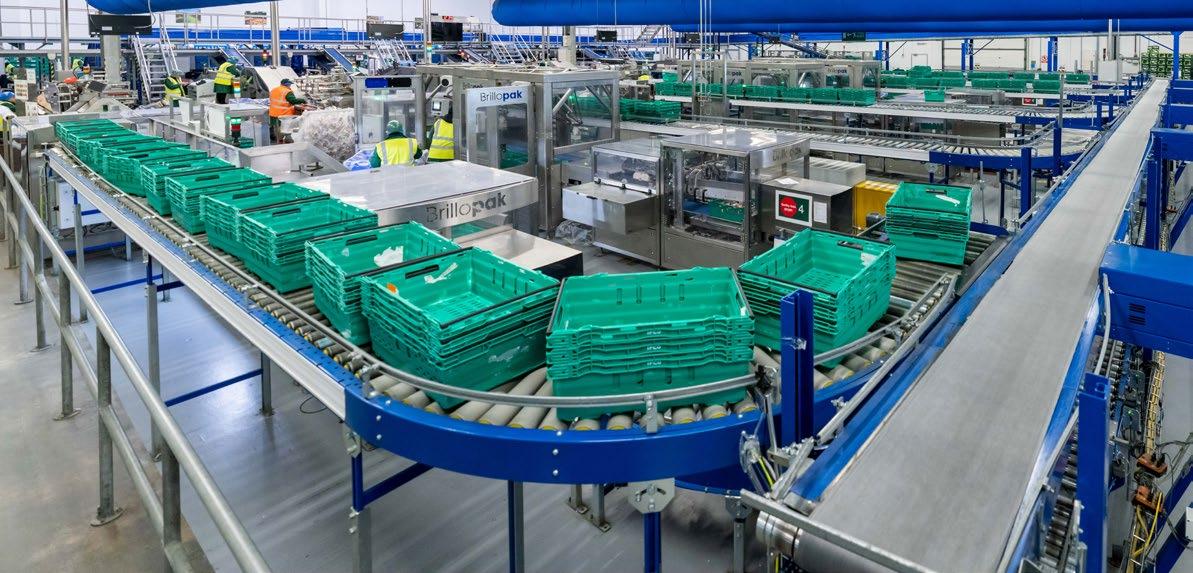
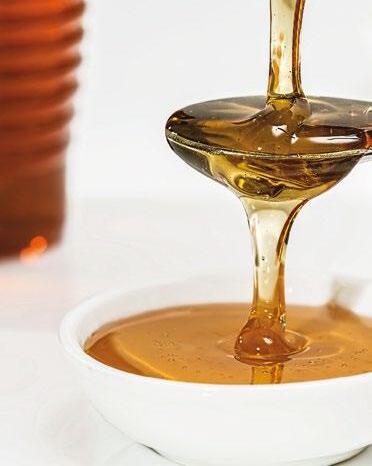
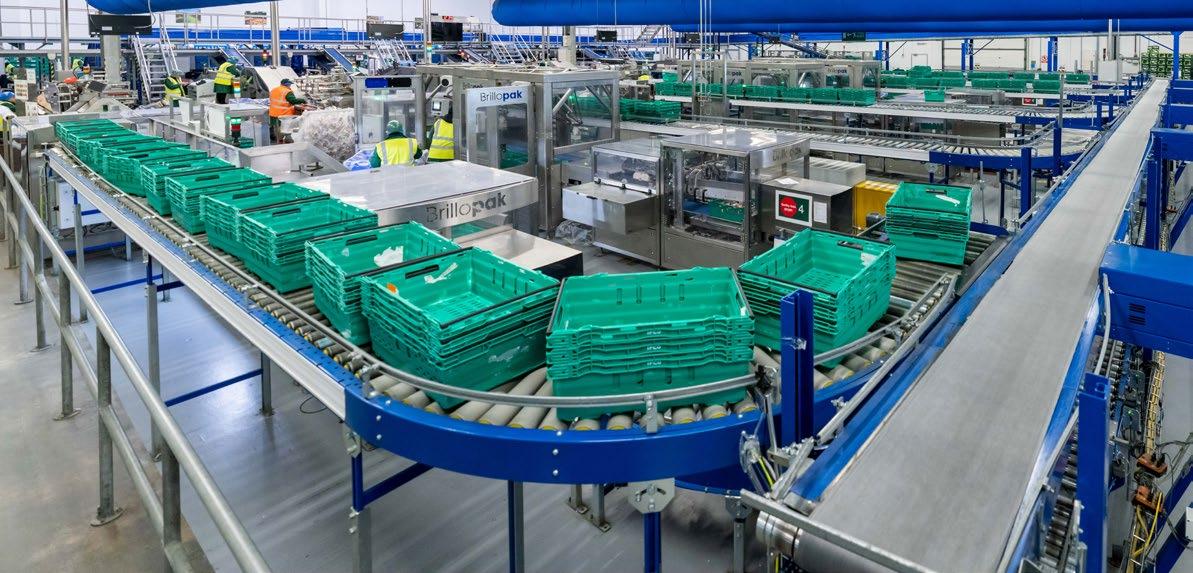
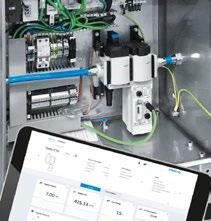
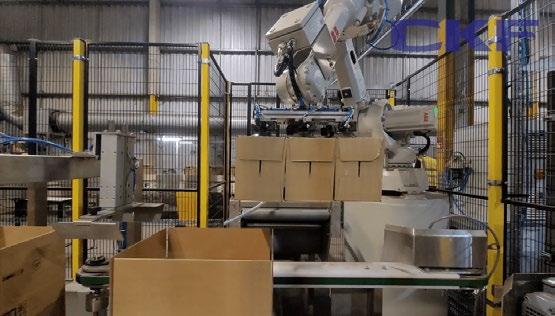
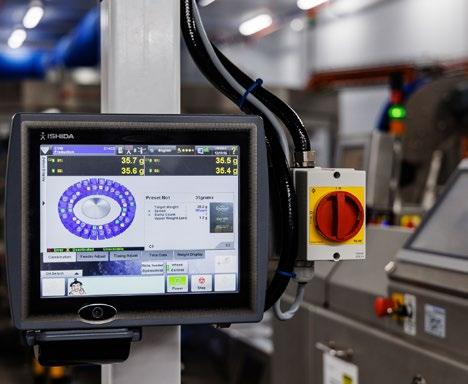
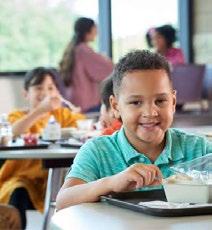
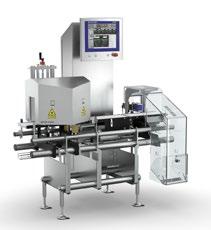
Issue 45 2023
Ishida weighers help hotel chocolat meet surging demand for velvetiser
Proseal marks a 25-year milestone
No matter whether consumers choose a pilsner, an ale, or another popular type of beer, there is a critical focus at nearly all breweries today on their production process’s energy (natural gas) costs and plant environmental compliance (waste gas emissions). Failing to pay attention to the efficiency of these processes at breweries or any other type of food/beverage plant can lead to cost competitiveness issues and hefty regulatory fines.
Today’s modern breweries must not only produce a popular refreshing product, but they also must continuously reduce costs and their carbon footprint by tightly controlling natural gas usage, residual CO2 levels and mixed waste gases. From fermentation vessel natural gas heating to waste gas recovery for co-gen electric power or combined heat and power (CHP) systems to stack flaring, the emphasis is on process efficiency and protecting the environment (Fig 1).
The plant team at a large craft brewery in Southern California’s San Diego County contacted FCI with concerns about its twin goals of (1) reducing natural gas consumption (cost) while also (2) lowering its waste gas emissions. Electric and natural gas energy costs in California are among, if not, the highest in the nation. The state is also well known for its environmental regulations, which can exceed national standards and those of many states.
According to a report published by the American Brewing Association, “There are
many best practices for energy efficiency and conservation that can be easily incorporated into daily operations, as well as solutions that can reach beyond greenhouse gas (GHG) reduction and lead to operating cost reductions, additional sources of income, and new community initiatives. These solutions help brewers save money and become industry leaders in sustainable practices.”
A guide produced by the American Brewing Association estimates the average energy input cost per barrel of beer from a craft brewer ranges from $3.34 to $4.26 each barrel. A craft brewer’s energy cost is higher than larger industrial type breweries.
There is one thing that all brewers have in common when it comes to controlling natural gas consumption and waste gas management. Whether they are micro, craft or large industry giants, all breweries depend on accurate and consistent air, natural gas and waste gas flow measurement instrumentation that must function under rugged and variable demand conditions. What isn’t accurately
measured can’t be controlled to optimize brew house process efficiency.
To reduce natural gas consumption, it is important that brewers and other plant engineers know and control the calorific value of the natural gas input of their gas feed for their boilers to produce steam used for heating brew kettles and to make hot water. To reach this goal, there are four key factors that plant engineers must consider when optimizing all heating processes involving brew kettles, boilers, etc.
The stoichiometric point in well controlled natural gas fired processes is where the mixture of fuel to air is optimal. Too little air, and the burner fire doesn’t achieve its full calorimetric heating potential and natural gas is wasted when it takes longer than necessary to achieve and sustain the required heating levels for vessel burners or steam boilers (Fig 2).
When the fuel mixture is too air rich, then there is the potential for excess nitrogen oxide (NOX) emissions, which are a highly
reactive gas and toxic pollutant. NOx often appears as a brownish gas (remember smog). It is a strong oxidizing agent and plays a major role in the atmospheric reactions with volatile organic compounds (VOC) that produce ozone on hot summer days.
Natural gas composition (Fig 3) differs somewhat around the world, as well as seasonally in very cold winters and hot, humid summer conditions. The primary energy components of natural gas are methane, ethane, propane, butane and condensates. The non-energy components are nitrogen, carbon dioxide, hydrogen sulfide and helium.
The mix of these components can affect gas density, the calorific value and then in turn plant instrumentation. Some thermal flow instruments, however, are available with multiple calibration groups, which can automatically switch seasonally or any time as inline gas analyzers indicate changes in the gas mixture to assure the proper air/gas ratio is maintained for heating efficiency.
Brewery and other food or pharmaceutical batch processes often operate at variable levels of production, which means the amounts of natural gas required for heating are also variable. Some of the reasons include processing multiple products on the same line, seasonal demand, wash-down cycles, planned maintenance, shift changes, etc.
For the most accurate gas and air flow measurement, a laboratory-like steadystate flow is generally the easiest to measure. That’s why in the real plant world it is important to understand the potential full flow range of the gas to be measured, also known as turndown range—from the lowest to highest flows and if the flow measurement accuracy expected will be available over the entire flow range (Fig 4).
In order to achieve the desired flow measurement accuracy level with confidence, the process or plant engineer must define the required process flow range, the desired flow measurement accuracy and the expected turndown ratio. For example, some processes require a rapid start-up with initially fast heating and then revert to a much lower steady-state
or standby function in between batches. The speed of these changes in gas flow can affect measurement accuracy.
The major natural gas flow meter technologies available (coriolis, differential pressure, thermal, ultrasonic, vortex) all vary in specified accuracy from ±0.5% and up depending on their turndown ranges from 1,000:1 to 8:1 (depending on sensing technology). For natural gas heating, thermal flow sensing offers the advantages of a broad flow range, wide turndowns and accuracy to ±0.75%).
For the San Diego County brewer and others concerned about natural gas cost control and waste gas emission levels, the ST75 Series Flow Meter from Fluid Components Internal (FCI) was a simpleto-make decision (Fig 5). It optimizes their complex fermentation tank steam heating
Today’s modern breweries must not only produce a popular refreshing product, but they also must continuously reduce costs and their carbon footprint by tightly controlling natural gas usage, residual CO2 levels and mixed waste gases.
processes by accurately measuring the ratio of boiler burner fuel gas to air for the most efficient combustion to lower gas consumption costs and emissions.
The CO2 gas that is also naturally produced during the brewing process and any additional CO2 gas necessary for finishing the beer also requires accurate flow measurement. Thermal flow meters such as this one, with its rugged, dependable thermal dispersion technology, are designed specifically for these small line size processes--from 0.25 to 2.0 inches (6 to 51 mm).
The San Diego County brewer’s plant team was pleased with how this thermal meter operates over a wide flow range, from 0.01 to 559 SCFM (0.01 to 950 NCMH). For their variable process conditions, the process engineers appreciated this meter’s wide turndown range, which can be preset by the factory from 10:1 to 100:1, with optional higher ranges are available on request.
Offering built-in temperature compensation, this thermal meter maintains consistent performance in rugged, hot industrial environments. The brew house’s engineers concluded that the meter’s standard accuracy to ±1% of reading with ±0.5% repeatability over varying temperatures would be adequate to achieve their process cost control improvement goals.
With a Vortab Flow Conditioner added as a spool piece, the Models ST75V or ST75AV meters are ideal for brew house installations with limited straight-runs and/or for operating in transitional flow ranges with accuracy of ±1% reading,
±0.5% full scale. Again, the brewer’s plant team appreciated the flexibility of the flow conditioner option for its pre-existing equipment layout.
Ideal for fermentation vessels or tanks, ovens, heat chambers, and furnaces, this meter features remote mounting capabilities for hazardous or crowded plant environments and includes major global Ex safety approvals. The remote mount transmitter, including a digital display, can be mounted 50 feet (15 meters) away from its flow sensor in the process piping and connected via two 0.50-inch FNPT or M conduit connections.
The meter’s fully scalable dual 4-20mA standard outputs are user assignable to flow rate and/or temperature and a 0-1kHz pulse output of total flow. The instrument can be ordered for input power with either 18 to 36 Vdc or 85 to 265
Vac, with or without a built-in LCD digital display.
Offering direct-flow measurement, the thermal meter eliminates costly additional pressure and temperature sensors, flow computers, or other devices that are required with orifice plates, Venturis, Vortex and other volumetric meters. The meter also requires virtually no maintenance for a low life-cycle cost, gaining the attention of the costconscious brewer’s plant team.
Energy efficiency goals set by brewers and other food/beverage plants typically start with monitoring energy bills. Sooner or later, however, the setting of key performance indicators (KPI’s) migrates down to the process instrumentation level to flow meters in the brew house.
Achieving heating process efficiency improvements can’t occur without more accurate, reliable flow meters to control the burn. This brewer’s plant team, like many others that rely on natural gas heating, is finding that upgrading to thermal flow meters pays for itself and keeps the energy cost savings flowing to drive future profits and dividends while protecting the planet. www.fluidcomponents.com
Figure 4Providing supreme accuracy, SATO printers are designed with high-speed data rates and right-first time tagging capabilities to meet the needs of the most complex business environment.
With improved flexibility, usability, connectivity and reliability, our flagship print engines are now equipped with next level SATO innovation, eclipsing all previous expectations
Efficient and accurate labelling using thermal transfer technology. Packaging materials can be integrated into existing lines, and have features like automatic label detection and variable data printing for traceability and safety.
Designed for the most demanding environments, the series is available inboth 4” and 6”, direct thermal/thermal transfer solutions. Ideal for printing text data, barcodes, RFID tags and labels. Its unrivalled versatility in performance is due to its excellent capabilities in emulation, PC-Less printing through Simple Stand Alone Mode or more complex AEP autonomous applications, alongside fast throughput and print speed
Book your demonstration today!
01255 240000
Address : Valley Road, Harwich, Essex, CO12 4RR
Mailbox : enquiries-uk@sato-global com
Website: www.satoeurope.com
Impact Handling is ready to solve any reach truck challenge, thanks to an expanded and upgraded line-up from Cat® Lift Trucks.
“The last two years have seen 11 extra models added – followed more recently by a fine-tuning programme for the existing reach trucks,” says Steve Shakespeare, Impact’s CEO. “We now offer a massive choice, with 26 base models and a long list of optional features. Whatever the customer’s operation, circumstances and preferences, we can find the ideal fit.”
Steve continues, “Our popular N2 reach trucks already covered most applications, but the additional N3 ranges allow for further possibilities. In our application surveys we first consider fundamentals like aisle width, racking height, and maximum load weight at each level. Next, we look at the specific demands of the driver’s job, which vary greatly between businesses. With that information, we can decide which model and set-up will optimise his or her performance.”
Both N2 and N3 offer top levels of ergonomics and comfort. N2 has particular advantages for drivers who get on and off the truck many times during a shift. Along with its lower step and seat height, it has an adjustable steering assembly which lifts up easily for obstacle-free entry and exit. It then returns quickly to the original preferred position.
N3 may have the edge in operations where drivers spend long hours in the seat and rarely leave the truck
except for breaks. Its Palm Steering and multifunctional joystick, both on adjustable armrests, allow a relaxed driving position and enable control with minimal movement. A tiltable seat minimises strain when viewing loads at height, while the floor can be electrically raised or lowered to suit the driver.
“Often it comes down to what the customer or the drivers prefer,” Steve adds. “We find, for example, that
those who operate Cat counterbalance trucks as well as reach trucks like the familiarity of the N2’s controls and displays. They include a more conventional steering wheel and an armrest-mounted fingertip hydraulic control unit. We can change things around though. For instance, if you wish, you can now have an N2 with dual joysticks and a dual pedal that incorporates direction change. It’s up to you.”
As well as standard N2 and N3 models, there are high-performance (H) variants for heavier loads and/or higher lifts. Extra-high lifting (X) models allow the highest lifts of all – up to 13 metres in one case. N2 standard, H and X trucks, featuring poweRamic masts, are the class leaders for residual capacity. Compact (C) models are adapted for use in drive-in racking.
Straddle (S) models are another variant to consider. They can retract pallets up to 1,000 mm wide between their load legs – without first having to lift them above load leg height. There’s no need
for a beam under the lowest pallet in the racking, as the truck can lift from floor level. In addition, this solution is useful when clearance between the top of the load and the lower edge of the beam above is limited. It also helps in situations where bagged materials bulge over the edges, making the load wider than a pallet.
For applications in which a reach truck is used for less than two hours per shift, light (L) models are a cost-effective option. They are designed for light and medium duties with lift heights up to 7.5 metres, depending on model and mast choice.
The Cat reach truck portfolio is completed by multidirectional (M) models. These are highly specialised for handling exceptionally long loads in narrow aisles. You can choose between the N3 four-way and N2 multi-way ranges. Four-way trucks move forwards, backwards and from side to side. They can also rotate on the spot. To those, the multi-way models add diagonal and other modes for the ultimate in versatile mobility.
Steve Shakespeare concludes: “We truly have a reach truck for every situation. Each comes with a generous standard specification, to which we can make jobspecific changes and additions. Popular options include telescopic forks, pre-set height selectors, transparent overhead guard roofs and insulated cabins. Most models also offer a choice between lithium-ion and lead-acid batteries.”
Finally, Steve stresses that each product benefits from Cat quality and Impact customer care. “You can expect high levels of power, performance, and advanced control technology, along with cost-saving efficiency, durability and low maintenance requirements. What’s more, our first-class, nationwide service and support will keep your business moving, for maximum productivity and profit.”
For more information on the extensive Cat Lift Trucks range, visit www.impact-handling.com
We now offer a massive choice, with 26 base models and a long list of optional features. Whatever the customer’s operation, circumstances and preferences, we can find the ideal fit.
Heat transfer specialist Fulton will be using BeerX to promote how its classleading fuel-fired and electric steam boilers and portfolio of aftercare solutions can help with a brewery’s or distillery’s decarbonisation strategy and put your company on the Road to Net Zero.
While Fulton will continue to promote the many features and benefits of its Classic and award-winning VSRT vertical steam boilers the company will, at a time when fuel costs are soaring and efficiency is vital to an organisation’s on-going strategy, also be promoting its range of electric steam boilers.
Some believe that electric steam boilers are superior to fuel-fired steam boilers in many ways, believing that using electric boilers may be less expensive than using a fuel-fired boiler in the long term, whilst also possibly being more environmentally friendly.
Using Fulton’s portfolio of electric steam boilers as an example, including Compack, Electropack and Europack models, less ancillary equipment is required than a traditional steam boiler, therefore helping to reduce the installation costs that come with a fuel-fired boiler. Electric boilers also generally have a smaller footprint and can therefore fit into smaller areas thanks to the way they are constructed and the lack of ancillaries that a fuel-fired boiler needs to operate. Additionally, because no flue system nor fuel supply is required, electric steam boilers can sometimes be located closer to the process, which reduces pipe work losses and improves steam system efficiencies.
However, this doesn’t mean the end for fuel-fired boilers which, given the correct infrastructure and process requirements, will play a huge role in a company’s decarbonisation strategy.
Beyond its product portfolio, the company will also be showcasing the many solutions on offer from its aftercare division, which can support Fulton’s own installations and those from other boiler manufacturers.
As well as offering boiler spares and repair service for all makes and types of heat transfer equipment, Fulton’s aftercare portfolio also includes accredited boiler operator training to INDG436 and BG01-R2, technical boiler house risk assessments, boiler and water treatment service contracts, water treatment training to BG04 and EN12953, steam trap surveys, site mass balance assessments and system design, etc.
For further information on Fulton’s heat transfer and aftercare solutions, visit stand 85 at BeerX, call +44 (0)117 972 3322 or click www.fulton.co.uk.
Reducing energy costs and energy intensity of operations is vital to customers and stakeholders. Strong ESG performance is crucial to your competitive advantage.
We take practical steps to reduce the kWh consumed and to generate low-carbon power, tailored to each business.
Ask about our zero-capital outlay, off-balance sheet energy partnership model.
Unfamiliar with the term leakage (residual*) current ? This is the current that leaks to earth from live conductors and electrical equipment. Leakage current is an indicator of the health of an electrical system (heartbeat / pulse). Increases in leakage current indicate developing problems with the electrical system and or electrical equipment - an early warning!
In the production environment, leakage current problems are normally associated with a fuse, circuit breaker or residual current device tripping and disconnecting the electrical supply. Why wait until the production line has stopped? You do not for example wait for pressure to exceed a critical level and shut down the production, you monitor it constantly. So why not monitor electrical leakage?
Efficient and effective production is synonymous with the health of the production line. We monitor changes in temperature, vibration, pressure, sound etc to identify developing issues. Enabling early assessment and maintenance scheduling i.e. predictive maintenance. The cost benefits of monitoring leakage current (Residual Current Monitoring), compared to the cost of lost production due to sudden power loss, damage to electrical equipment and personal safety are easy to quantify for individual sites.
Main reasons for not monitoring leakage currents:
1 – Unaware - acceptance of lost production due to electrical issues.
2 - Aware - but did not know how to
monitor, solve the issue.
3 – Issues of an electrical nature passed to the electrician to deal with.
4 - Limited knowledge of complex leakage currents associated with modern production
All electrical systems will leak electricity to earth, this is unavoidable. This is due to the nature of electricity and electrical insulation. Leakage currents associated with electronic equipment such as speed control invertors, EMC filters, motion control for positioning and robots, are significantly higher in value than conventional electrical equipment and more complex. This requires specific types of monitoring and residual current protection device. Increases in operational leakage current above the
norm (design level), indicate a change in electrical insulation quality e.g. a developing fault in electrical equipment, motors, EMC filters, cabling, junction box.
Periodic electrical inspections, including simple insulation tests give a basic snapshot of the electrical health of the production line at the time of the tests. The electrician completes these tests with the power switched off. Consequently they do not reflect what is happening when the production line is running or between tests.
In this example picture, total production line supply leakage current measured with a clamp meter is 20A i.e. the sum of all the individual leakage currents associated with the production line running. Questions to ask: Is this normal? Is it higher or lower than last week, yesterday or has it just increased by 25% in the last few minutes? What is the distribution of the leakage current associated with individual manufacturing cells, robots ? Is there a developing problem which will result in
a protection device tripping, leading to a partial or complete production stoppage?
Developments in predictive maintenance, associated with shared data, IIoT, ML, AI (Industry 4) at the top end, are enablers for high level management and control through condition monitoring and installation forecasting regarding future installation behaviour. Existing production line automation may not fully embrace the Industry 4 benefits, without major upgrades to hardware and software.
Product developments such the e. Guard residual current monitoring system from Doepke, enable the adoption of a fully scalable bundle, with 5 levels of performance:
Basic Level 1, using free Doepke software enabling clear visualisation of the complex leakage currents within a system, offering evaluation and monitoring of < 20 RCMs on a PC, plus alarm email messaging.
Moving through the levels adds additional features e.g. Level 5 – bespoke software incorporating machine learning, customer meta data, hyperparameters,
developed in conjunction with the Customer’s Engineering and IT project team.
e. Guard (from Doepke The residual current protection expert)
e. Guard permanently monitors the residual currents in electrical installations and therefore offers comprehensive surveillance of their status. Smart residual current sensors positioned at critical points in the system, manufacturing cells and or items of equipment, enable the early identification of issues within specific locations.
This results in timely and planned intervention by electrical staff to conduct essential checks and repairs. The aim, reduce downtown, catastrophic equipment failures and associated production line losses. For further information please contact Doepke on sales@doepke.co.uk.
www.doepke.co.uk
Efficient and effective production is synonymous with the health of the production line.
Titan Enterprises offers a range of high-performance flowmeters in food grade materials where both food hygiene and precision flow measurement are required.
Flow measurement is a critical tool for food and beverage manufacturers, the industry having a diverse range of processes that require the precise control of liquid flow rates. Production processes including filling of vessels or bottles, measuring liquid ingredients, and controlling cleaning processes, require varying degrees of complexity and accuracy to ensure consistent product yield and minimise wastage. Although there are a wide variety of general flowmeters on the market, only a few high-performance measuring devices will ensure the high levels of hygiene and precision are maintained for applications in the food and drinks sector.
“The physical properties of the liquids themselves lend additional complexities to the choice of flow measuring equipment,” says Neil Hannay, Senior Development Engineer at Titan Enterprises. “Consideration of whether the liquid is viscous, volatile, corrosive, flammable, or contaminated with particles, for example, or needs to be maintained at a high temperature, are key factors in deciding a suitable flow meter.”
Flow monitoring of high viscosity liquids, such as cooking oils, sauces and syrups (e.g. syrup injections in beverage lines) require devices such as Titan’s oval gear flowmeters, which provide highly accurate flow measurement. Unlike other flowmeters, measurement accuracy of oval gear flowmeters
improves as the liquid viscosity increases, from a nominal 1% to around 0.1% of flow rate at higher viscosities.
Whereas for low viscosity liquids such as water, beer, wine and spirits, Titan’s NSF-approved 800-series and beverage flowmeters provide a low-cost drink dispensing solution. Designed to give high performance over 6 flow ranges from 0.05 to 15 l/min, these devices have totally non-metallic NSF-approved wetted components making them ideally suited for applications where both food hygiene and precision flow measurement are required.
In processes where ingredients need to be maintained at high temperatures – chocolate for example – a flowmeter designed for applications requiring precise flow measurement at elevated
in the
temperatures would be needed. Capable of operating up to 110°C, Titan’s inline non-invasive Atrato® ultrasonic flowmeter is largely immune from viscosity and offers excellent turndown and repeatability.
Titan Enterprises offers a range of oval gear flowmeters in food grade materials for viscous products such as sauces, oils and syrups, as well as NSF-approved mini-turbine flowmeters for drink dispensing. As an experienced OEM supplier, Titan develop customised flow meters for specific customer applications within the food and beverage industry.
To discuss an optimised flow measurement device for your OEM application please contact Titan Enterprises on +44 (0)1935 812790 or email sales@flowmeters.co.uk. Or visit our website for further information.
Although there are a wide variety of general flowmeters on the market, only a few high-performance measuring devices will ensure the high levels of hygiene and precision are maintained for applications
food and drinks sector.
Smart-Space is the UK’s largest independent supplier of instant buildings and has designed and installed all kinds of warehouses, factory spaces, workshops and storage facilities. They’re something of an authority on instant buildings having been in the sector for over thirty years. Utilising some of that knowledge, here are a few things to consider if you’re thinking of going for an instant building:
1 RESPONSE TIMES: From order to handing over the key, it should only be a few short weeks.
2 PLANNING: Ask about planning – it’s hardly ever a ‘one solution fits all’ answer. With its own planning department SmartSpace can advise.
3 FIT FOR PURPOSE: The different uses for a building determine the type of building you need and you should be offered exactly the right solution for your needs.
4 OFF-HIRING: Smart-Space requires 7-days’ notice to off-hire at any point during the contract believing that there is no point holding a customer to an agreement that no longer suits them.
5 HIRE OR BUY: If you are hiring and this becomes a longer term prospect, make sure
you can switch to purchase if it makes better sense.
6 SUPPLY CHAIN: Smart-Space supports buying British as relationships are easier to build and maintain and they can source stock and support customers on demand.
7 SITE SURVEYS: Don’t accept a project proposal unless the supplier has visited you to assess the site, make suggestions and check your utilities and groundworks.
8 PREVIOUS WORK: Ask to see case studies on completed projects and find out what kind of expertise your supplier has in your sector.
9 WORKFORCE: Ask if the installation team is directly employed. If they are subcontracted you’ll shoulder complete liability.
10 GOOD TO DO BUSINESS WITH: And finally, are your instant building suppliers good to work with? Are they pro-active and communicate every stage of the process with you? If the business relationship feels right, it probably is.
www.smart-space.co.uk
Talk to our friendly, professional, experienced team - we can advise on the best options from a range of solutions. Our British supply chain and directly employed teams means we are quick and reliable. We are also completely flexible: you can hire or purchase (or switch whenever you like) and you can off-hire at any time. We do everything - from building only to turnkey solutions (and everything in between).
Brillopak’s five-year phased automation roadmap accelerates packing efficiency at Morrisons fresh-produce operations in Thrapston
Packing automation success is all in the planning. Embarking on a mission to reconfigure its fresh-produce packing hall at Thrapston, the Morrisons Centre of Excellence - which prepares and delivers 130 million packs of fruit every year to 82 stores - has succeeded in its automation vision and ambition.
British automation specialist Brillopak supported Thrapston at every phase of the five-year programme. In total,
Brillopak installed 11 fully integrated fresh-produce packing lines comprising around 40 machines, with equipment and capital investments split across three defined phases.
Rather than piecemeal different technologies together, Thrapston’s site manager at the time, Matthew Peczek, sought a cohesive automation investment approach to increase efficiency, achieve packing consistency and optimise produce quality.
Taking the decision to completely redevelop the factory layout in 2017, Matthew was resolute that all
machinery would be designed and placed linearly, with everything coming from the chillers and out to the back end for distribution, in one continuous flow. His linear vision has since been realised. Now, every part of the line faces in the same direction throughout the packing hall.
Having seen the possibilities accomplished when managing the Morrisons Rushden depot, Matthew, now Head of Operations for produce at the company, was confident that Brillopak director David Jahn and his engineering team would see the bigger picture and deliver these
transformational benefits. Most importantly, Brillopak was completely aligned to the investment roadmap that assisted Thrapston in reaching its end point.
In 2016, Brillopak delivered stage oneoptimising the manual packing of apples into crates. Thrapston commissioned five of Brillopak’s award-winning and ergonomic PAKStations to replace less efficient manual packing and turntable operations. This was the first step to automation and enabled the site to get familiar with the automation.
To support these apple-packing lines and eliminate any potential bottlenecks, two Crate DESTAKers, five bale arm closers and five double stackers for palletising were also introduced. The result was five integrated packing lines that maintained a consistent packing pace, each feeding out onto the main track to an existing palletising system.
This first phase was intentionally designed as a holding pattern in Thrapston’s automation plan, allowing for the subsequent robotic machines that were to follow. “As a result of the
fast payback due to labour efficiency, enhanced produce quality and reduced complaints, the plan was always to replace the PAKStations within two years. Swapping out with three fully automated UniPAKer robotic crate packing systems in phase two,” reflects Matt. It was, he affirms, always central to their produce strategy of improving quality and process efficiency and reducing costs and waste.
Having got the measure of the design requirements and long-term goals at the outset, Brillopak’s Automation Architecture meant that the innovative firm had already factored in the available real estate. The team built the framework of the PAKStations to match the dimensions of the UniPAKer machines, as well as the conveyor infeed and outfeed heights; enabling a seamless
and simple swap over, to mitigate any packaging disruption.
“We literally pulled out the UniPAKer machines and inserted the robotic machines into the apple lines,” affirms David. Local power requirements and access points, as well as feeds to the main conveyor track for each line had already been considered at the initial due diligence planning phase. Craig Savage who project managed the entire programme, affirms that the devil really was in the detail. “It involved multiple simulations to define the best approach.”
New access doors and platforms were inserted and refrigeration doors were moved. Approximately one fifth of the main track was removed along with the overhead crate feed track. To optimise efficiency a two-tiered conveyor track was proposed. Now, the lower level feeds all the clean empty crates to the 11 packing lines, while the top tier transports filled fresh produce crates to the palletiser.
Another key advantage of this modular line design and phased introduction of machinery was that Brillopak was able to retain and redeploy the existing conveyors, which previously transferred crates to the PAKStations. “From a sustainability perspective, where components can be repurposed, we do, as it boosts the ROI even further,” adds David.
The robotic packing solutions that Brillopak builds are extremely intuitive to operate and very reliable.
Applying the best practice gained from phases one and two, in 2021 Thrapston completed its full-scale automation transformation with the roll out of six new linear packing lines. Handling a range of flow-wrapped and traysealed fresh produce, including pears, tomatoes, apricots, blueberries and grapes, Brillopak delivered a further five UniPAKers, one PAKstation, six bale arm closers, two Crate DESTAKers and six double stackers.
With 40 individual Brillopak machines now on site and running continuously, Matt upholds the value of working with a single and reliable integrator. One that can factor in all the unknowns and deliver innovative yet easy to operate ‘plug and play’ machines that talk seamlessly to each other. In particular, Matt appraises Brillopak’s foresight and deep integration knowledge. “We had a clear vision of how the linear Thrapston packing lines would ultimately look and partnered with the Brillopak engineering team throughout every phase of the process.”
This collaborative teamwork approach is a result of the personal relationship the Morrisons’ fresh produce team, site managers and engineering experts share with Brillopak. Matt expands: “The robotic packing solutions that Brillopak builds are extremely intuitive to operate and very reliable. As testament, our robot potato lines in Gadbrook continue to run as efficiently as the day they went in seven years ago. We know they are always going to work and maintain their efficiency and presentation consistency.”
The smoother and gentler handling of fresh produce has been proven to reduce complaints by over 30 percent and almost instantly, reports the Head of Operations.
However, for Matt, the real Brillopak value comes from dealing with one machinery supplier. “There’s definitely something to be said for Brillopak’s amenable and accommodating approach. Integrating with other suppliers’ equipment is probably the hardest aspect. Yet, this
is something I entrust to David and the engineers.
“Brillopak will often go above and beyond during the handover to ensure all their machinery is seamlessly integrated with conveyors, downstream camera graders and other equipment. Even when it’s not technically their responsibility. I don’t know of many other integrators that would undertake this level of meticulous service and support before, during or post install,” notes Matt.
Since embarking on the first automation project with Morrisons fresh produce almost 6 years ago, Matt is adamant that this trusting collaboration with Brillopak has helped to accelerate and optimise its packing efficiency.
With all five fresh produce sites now kitted out with end-to-end Brillopak machinery, a side-line benefit is how much the manufacturer has been able to streamline its stockholding of spares and components. “Dealing with one automation provider formed part of our produce directive. From a maintenance and ongoing service perspective, dealing with one or two machinery suppliers, versus liaising with multiple contacts is evidentially more straightforward. Being able to pre-plan projects and roll automation platforms out in phases as part of a wider, aligned plan certainly helps to mitigate investment risks,” ends Matt.
Sample measurements in only 5 seconds: Moisture, Fat and Oil, Protein, Degree of Brownness, Degree of Roast.
■ Replace time-consuming laboratory methods
■ Deliver deeper process insight for consistent production output
■ Reduce company’s operational expenditure (OPEX)
Leverage the power of Nordson infrared technology
Simultaneously measures the key constituents: Moisture, Fat, Protein and Color.
■ Meet product quality demands and efficiency goals
■ Increase productivity
■ Realize immediate and long-term value
Sometimes you just need to look from a different perspective to achieve your goals, and “We didn’t know that” is a phrase that IKO UK & Ireland’s technical sales engineers are greeted with on a regular basis.
Alinear rail and carriage system is many a design engineers first choice for transporting a load, and for good reason. It provides a rugged and precise solution that is inherently self-aligning, offers high load handling capabilities, and can operate in some of the most challenging environments. But the temptation to over-engineer a system can add significant cost to a project, while asking a vendor to supply a non-standard arrangement can dramatically lengthen the lead time.
For example, the company was asked to solve an issue a customer was suffering with where excess food particles were causing contamination of its current linear bearing arrangement.
This is where IKO Nippon Thompson’s in-house design and adjustments service becomes invaluable, with the UK team of applications engineers able to suggest design amendments that can reduce lead times from months to days, and/or remove significant cost from a project. Mark Ross, technical sales engineer at the company’s Milton Keynes UK headquarters, says: “There are a wide range of things we can do at local level, from the everyday to the more unusual, to deliver an application-specific solution, providing a key service that can save UK customers time and money.”
our various global locations, and we can tap into that free stock and have it delivered within a couple of days,” says
stroke length, but then bumped up the rail and carriage dimensions to accommodate the required load? Perhaps they’ve even ended up with a design that
sions, we can often find a much more cost-effective ucts or better cost products,” he continues. “We can play
The customer had a production line which traversed over a 40m length, & in this case, the carriages needed to pass over multiple joints where each rail, laid end to end, met. The customer was unaware that, due to the rail manufacturing process, the existing product had 45-degree chamfers at each end. When placed end to end, this arrangement created a crevice where debris could gather. These unwanted deposits unfortunately then transferred to each carriage’s rolling elements and raceways as they passed over these areas, eventually causing premature bearing failures.
length at the simplest level, or changing the e-dimension –the measure from the end of the rail to the first mounting hole. “As standard, this e-dimension would be half the normal hole pitch, but that might not suit the application,” Mark explains.
A prime example is the company’s ability to assess the key parameters in a project, and look at what can be easily amended without compromising the performance criteria, so that the project can be serviced from the company’s free stock. “For any supplier, manufacturing a system to order is going to take time, but IKO Nippon Thompson will always have standard products available as free stock at
Such adjustments and amendments can be important time savers for customers, particularly when they are building a prototype as proof of concept. But IKO Nippon Thompson’s design services can also save customers significant amounts of money, for example when it is clear that the design engineer has over-specified the project, perhaps as a belt and braces approach to meeting particular lifespan requirements.
“We can quickly drill down to the customer’s most important considerations and then look at how that impacts on the rail and carriage dimensions,” says Mark. “By talking through load and stroke requirements, that might lead us to propose alternative carriage lengths. For example, has the designer opted for a shorter carriage to increase
IKO’s rails, like with all of its linear products, are triple-ground, and every part of the rail and carriage is inspected fully before final assembly. In addition, IKO can offer rails with squaremachined faces that will sit flush, with minimal to no gaps at all (butt joints). This significantly reduces the chance of contaminants or deposits building up in these regions, and of course that reduces the risk of premature failures in the carriages.
with parameters such as preload to see if this provides a better way to meet specific application criteria. Or we can butt together standard rails to deliver longer, non-standard lengths at given profile dimensions without impacting precision.
“In addition, we can add seals and scrapers to protect the rolling elements on some product types, as well as offering different coating options to protect against rust or to alter the products’ aesthetic appearance if that’s a requirement too. The addition of rail caps can also be a further simple (yet cost-effective) way to increase the longevity of the system, and is something which, whilst basic, is often overlooked.”
All of this comes hand in hand with the capability to provide CAD drawings and models, and to port those designs straight into customers’ models.
IKO Nippon Thompson is conscious, too, of the cost of logistics for its customers, and so can supply pre-packaged sets to reduce packaging, handling and stock management. And then there is the company’s on-site training in addition to its telephone and web video support.
“It’s all part of a service that means we are much more hands-on with our customers than perhaps other suppliers are willing or able to be,” concludes Mark. “We want to be more involved because it benefits all of us – we get to
We talk to the experts at IKO Nippon Thompson about how linear rail and carriages can be easily adjusted and modified, and how projects can be redesigned around standard products, to save customers time and money
To bolster this defence against contamination, IKO also proposed the use of its MX range fitted with its patented RC sealing system. The MX range is IKO’s roller type linear rolling guide, offering the brand’s highest level of rolling performance in terms of load capacity, rigidity, friction and accuracy.
The RC seal consists of scrapers (to deal with larger deposits), c-wiper (to add lubrication to the rail surfaces), end seals, inner seals, and even under seals (to protect the rolling elements even further).
environment.
This simple, yet effective, switch, combined with the MX carriages fitted with RC seals, drastically improved the life of the carriages, from around 3-4 months previously to more than 12 months, with no intervention or need for additional maintenance.
In this case, as in so many others, IKO worked with clients to look at the issues at hand, the current bearing arrangements, and specific application requirements before then going through a review of what was possible technically and what the best solution would be.
Contact IKO UK & Ireland today to discuss your motion control requirements.
Email: enquiries@iko.co.uk
Tel: 01908 566144
www.ikont.eu/en
IKO UK & Ireland prides itself in being not just a supplier, but also a true business partner. It is always looking to give customers the best possible service and the best technical support, no matter what the
Peterborough based, Hydromarque Ltd have 30 years’ experience providing specialist pump solutions to food processing companies.
Hydromarque’s expert engineering team understand the important role food handling pumps play in today’s marketplace and the need for pumps capable of transporting even the most delicate food products.
Pumping food products has an overriding issue – any food product damage can result in degradation to the final product and profit losses for food processing plants. Continuous and trouble-free pumping operation is critical.
Hydromarque ltd are the sole UK and Eire agent, stockist and service provider for Cornell hydro-transport and hot oil pumps. Unlike solids handling pumps that are sometimes used in the food industry, the Cornell P and PP series pumps are designed and manufactured with the sole
purpose of pumping food products. Cornell food process pumps have the lowest product damage rates in the industry and are the pump of choice for food processors around the world. Their innovative single port impeller configuration with unique offset volute* provides the end user with a food handling pump capable of transporting even the most delicate food products.
Hydromarque are proud to supply Cornell’s hot oil pumps offering enhanced vapour handling and improved sealing technology. This prevents entrained steam from impacting pump head and flow which is central to Cornell’s innovative cooking oil pump developments.
Working alongside many larger potato chip, potato crisp, fried snack and vegetable processing companies, Hydromarque have extensive experience providing tailored solutions to improve food processing pumping.
Whether you make potato products, process vegetables, produce ready meals, snacks or process poultry or other livestock, the Hydromarque team will recommend the best solution to enhance your efficiency and reduce your production downtime.
To find out more about how our specialist pumps can help you, get in touch 01733 370545 or sales@hydromarque.com
One of the main risks to employee health within food manufacturing facilities is the quality of the air.
Research proves that flour dust can act as an irritant which causes short-term respiratory, nasal and eye problems for workers, as well as potentially triggering asthma among those who suffer with the condition - flour dust is the UK’s second most common cause of occupational asthma according to the Health and Safety Executive. Exposure to high levels over a prolonged period of time can also lead to longer-term illnesses including allergic rhinitis.
What can employers do?
Using Local Exhaust Ventilation (LEV) to reduce flour dust is an approved way of minimising the risk to employees as well as guaranteeing companies are operating within the legal emissions limits.
Once an appropriate LEV system is installed, visual checks should be regularly undertaken to ensure the system is performing as intended, and it should be thoroughly tested by a competent person
at least once every 14 months under HSE guidelines.
It’s the duty of employers to ensure that the health and safety of employees is protected.
How we can help
Filtermist’s dedicated systems division includes experienced design and contracts engineers who have delivered a wide range of customised air movement and pollution control systems for many leading food producers including Cadbury, Halo Foods, Taylors of Harrogate, Weetabix and Ryvita.
Dustcheck from Filtermist
Filtermist’s Dustcheck brand includes dust
control products specifically designed for use in food environments and all of our filters and dust collectors can all be adapted to meet the European Hygienic Engineering & Design Group (EHEDG) hygiene requirements of the food industry and Good Manufacturing Practice (GMP) in the food industry.
Dustcheck Product Manager, Andy Darby, comments, “Dustcheck products are used in a number of applications in the food industry. Our standards of construction vary from mild steel with standard or special paint finishes to stainless steel with finishes from standard sheet with welds as laid, to special crack and crevice free polished finishes.
“All of our filters come with ATEX rated options meaning potentially explosive and volatile products, such as flour, can be handled safely. They can also be built to comply with Dangerous Substances and Explosive Atmospheres Regulations (DSEAR) where applicable.”
For more information visit www.filtermist.co.uk, call 01952 290500 or email sales@filtermist.co.uk
Swiss technology group Bühler has announced the launch of a new 8-inch TUBO tubular push conveyor. With the new solution customers in malting and brewing, milling, coffee, oat flakes, and animal feed processing industries can benefit from an increase of 80% of throughput capacity, reaching up to 43 tons per hour.
“The new addition builds on the success of the revolutionary TUBO system with push technology. With the new 8-inch tubes we offer a system for an even broader range of applications with higher capacity requirements,” says Stefan Anshelm, Product Manager Grain Quality & Supply at Bühler. Up to now, the system has been available with tubes in 5-inch and 6-inch diameters with a throughput ranging from 12 tons per hour to 24 tons per hour. The new TUBO with 8-inch tubes allows for capacities of 40 to 43 tons per hour. The system transports products gently over distances of up to 50 meters in all directions. “With lighter loads and fewer bends in the system’s configuration this can be increased to 70 meters,” says Markus Huber, Product Engineer at Bühler.
Like previous releases the new 8-inch TUBO follows the simple and effective principle of pushing instead of pulling. Loose pusher elements called TUBITs are pushed inside the tubular construction moving material gently from inlets to outlets.
“The TUBO concept has many advantages over conventional pneumatic systems or mechanical conveyors such as bucket and chain conveyors. These conventional
systems require more space, more conveying components to transport material in different directions, and additional explosion protection such as decoupling devices,” says Anshelm.
The TUBO significantly lowers energy consumption through reduced friction in the conveying process and offers maximum flexibility and efficiency in the setup and retrofit of plants. Its unique push technology allows configurations in three dimensions. Thanks to its modest space requirements TUBO also reduces investments in building costs.
Thanks to the modular construction and low weight of individual components the system can be easily assembled by a small
team. The plug and play TUBO comes equipped with its own controls and is fully operational within a minimum of time.
Low transportation speeds prevent damage to the conveyed goods. The TUBO transports sensitive materials at speeds as low as 0.2 to 0.3 meters per second. This is ideal for sensitive products such as coffee.
Conveying products with TUBO ensures a system free of residues. As some dust can build up over time, a specially designed drive station enables the removal of particles during operation. This is particularly important for operators that use one conveying line for different products and need to avoid contamination.
TUBO has proven its reliability in operation at many plants around the world. Offering great cost savings, flexible design, gentle product handling while maintaining highest sanitation and safety standards, TUBO helps operators in several industries to improve the efficiency of their production lines.
“With the option for greater capacity, the TUBO is now available for even more applications in the brewing and malting, milling and related food and feed industries,” says Anshelm. “This means that even more customers can benefit from cost savings and unparalleled efficiency and flexibility.”
www.buhlergroup.com
With the option for greater capacity, the TUBO is now available for even more applications in the brewing and malting, milling and related food and feed industries
CKF have recently designed, installed and commissioned a new robotic case packing system for an international third party logistics company. Situated within one of their many UK facilities, the new system is the latest robotic automated installation to be successfully completed on this site.
CKF are leaders in automated robotic solutions with more than 30 years’ experience supporting different industries including Food & Beverage, Logistics, Pharmaceutical and Automotive. This is the latest robotic system to have been delivered and commissioned by the experienced engineering team at CKF, aiding the clients drive for the improvement and automation of operations within its packing and distribution facility.
The branded pet food products within shelf-ready cardboard cartons are delivered to the automated cell on CKF modular belt conveyors, the system being designed to handle a number of product formats to meet the customer
CKF are leaders in automated robotic solutions with more than 30 years’ experience supporting different industries including Food & Beverage, Logistics, Pharmaceutical and Automotive.
specification. An automatically formatted collation of cartons is presented to the robot at the pick area, ready for placing into an outer case. Outer cases are delivered from a case erector, preconditioned and tracked in the robot place zone via variable speed twin side drive belts, providing positional accuracy for the robot placement.
An ABB IRB2600 robot with custom vacuum tooling has been used to pick and place the cartons into the cardboard outer cases. The CKF team opted to use positional tracking to enable the
case throughput to meet the clients’ specification. The robot cell has been designed to handle 25 cartons per minute.
The system is driven via the ABB IRC5 Controller, with the controller housed adjacent to the robot system. The robot cell is configured to fit within a designated area within the clients’ facility and is protected with a safety enclosure using a TROAX safety guard system. Operator access into the robot cell is gained through a Fortress interlocked, access door.
Installed and commissioned by the CKF engineering team, with minimal disruption to the customers operation, the automated case packing system has been delivered to meet the clients’ specification and performance. It has provided the client with the opportunity to re-allocate staff from what has been a repetitive task and enabled improved operational efficiency.
Depending on the products manufactured, many food and beverage processing facilities consume a lot of water. Beyond the actual processing usage, the facilities need water for a variety of utility purposes, including cleaning, heating and cooling systems, irrigation, and more. Decades ago, food and beverage processing facilities were less concerned with the volume of water or steam they were using so long as it didn’t impact production.
However, as water costs rise and sustainability becomes more in focus, many facilities are urgently trying to measure and manage their utility fluid usage. In the process, they are running into a variety of challenges to reliable and accurate liquid and steam fluid measurement. Below are seven common challenges food and beverage processing facilities face and their potential solutions.
LIQUID MEASUREMENT CHALLENGES
1. Aging meters. No meter lasts forever Replacing a full-bore mag meter can
be complex and time-consuming. Personnel must stop the pump, drain the system, unbolt the old meter, and bolt the new one into place – a four to six hour job.
A full-profile insertion (FPI) mag meter has multiple sensors extending across the full pipe. Each sensor takes a measurement and they are averaged to determine flow rate.
This allows the FPI mag meter to take accurate readings even near bends and valves.
McCrometer’s Full-Profile Insertion (FPI) mag meter can be installed in under two hours and does not require
the removal of the old meter. Hot tapping means they can be installed under full pressure without shutdown. If there is a subsequent issue with the meter, removal takes just a few minutes. Should it need to be replaced, a new meter can be inserted in its place without having to create a new tapping point. Installing an FPI mag meter means installing a metering point for the life of the facility.
2. No instrumentation where required. Many processing plants either have insufficient measurement points or don’t have them in effective locations. This could be due to original instrumentation omissions or because of internal changes/reconfigurations. While full-bore mag meters are considered the go-to technology, these devices are difficult to install retrospectively. Processes must be stopped, lines drained, pipes cut, and flanges welded, before the new meter can be bolted in place.
FPI mag meters solve this problem extremely well for main line sizes above 6”. FPI meters solve the same issues whether the line is 4” or 120” and are certainly more cost effective at the larger line sizes. These meters are hot tapped, which requires minimal welding and, most importantly, can be done on a live process. The full-profile sensor measures multiple points across the pipe, accounting for turbulence and facilitating accurate
measurements regardless of the amount of or proximity to bends and valves.
3. Achieving sustainability goals/saving money. When it comes to water usage, sustainability and corporate savings boil down to the same basic challenge: measuring water in versus water out. Using FPI meters, food and beverage processing plants can measure incoming water with ±0.5% accuracy which is the highest of any hot-tapped meter. The easy hot-tap installation means that these meters can be placed in nearly any location. With enough meters, plants can use data to reduce waste via repaired leaks and discover areas where water can be reused rather than dumped, and more.
4. Long straight pipe requirements. Measuring steam imposes similar but distinct challenges and very different technological solutions. Firstly, there is the need for long straight runs prior to the meter. Orifice plate differential pressure (DP) meters, a decades-old industry standard for steam measurement, requires about 30’ of straight pipe. Orifice plates are very sensitive to turbulence, which can cause puddling, inhibiting proper measurement.
V-Cone DP meters conical shape resolves this by pushing turbulence to the outside of the device (Top image). This eliminates the
need for long straight runs, allowing the V-Cone to be installed anywhere in the system and still maintain a ±0.5% accuracy.
5. Tighter control on low flows. Steam is an expensive commodity. Unfortunately, orifice plates often fail to read at low flow rates, making it difficult to control the amount of steam being used. Another advantage of V-Cones is that they have a sensor opening about the size of the inner pipe diameter, which allows it to operate lower in the flow range than orifice plates. Its ±0.5% accuracy further improves the level of control and reduces expensive waste.
6. Too much maintenance. Orifice plate meters must be checked and sometimes replaced every few years. Their design forces the steam over the rim of the plate, which mars the edges and, over time, reduces the effectiveness of the device. V-Cones’ conical shape changes the friction dynamic , gently directing the steam to the outside of device, as opposed to presenting a flat obstruction. As such, they are known to last around 25 years without maintenance.
7. Off-the-shelf solutions won’t work. Whether it’s an unusual pipe diameter or another challenge, sometimes a standard solution won’t suit the application. V-Cones can be customized based on specific application needs, including exotic materials, end connections, taps, and more.
When it comes to water usage, sustainability and corporate savings boil down to the same basic challenge: measuring water in versus water out.The conical shape of the V-Cone differential pressure (DP) meter gently pushes steam around the outside of the meter, which allows the device to take accurate readings even amidst turbulence. Thus, the V-Cone can be placed anywhere in the pipe network without regard for straight runs.
The detection of foreign body contaminants is part of the critical quality assurance process to improve food safety standards. X-ray inspection has long been a key technology in this process, but there are different types of x-ray detection with which food manufacturers can inspect their products, depending upon the nature of the application.
Traditionally, manufacturers have used single energy x-ray detectors, but dual energy technology is becoming more commonplace, and is more powerful, effective, and easy to use than ever before. It works using the concept of ‘material discrimination’, with dual x-ray beams of different energy able to identify materials of different densities. Advances in detection sensitivity mean that dual energy x-ray is now even more discerning, allowing ever-smaller contaminants to be detected in a wider range of applications.
But what are the applications in which dual energy x-ray excels compared to the more commonplace single energy detection systems? In simple terms, there are two key aspects of a product that make it suitable for inspection by dual energy x-ray. The first is where there is a large degree of overlap within the package, or where there are variations in thickness. Examples of the types of packs where products overlap include packs of pasta, rice, nuts, and frozen goods such as French fries or potato wedges. Packs with variations
in product thickness include chicken breasts and other fresh cuts of meat. Both scenarios produce an x-ray image with high levels of contrast.
The second type of application where dual energy x-ray is most suitable is
where the likely contaminant in a food product is a low-density material, such as glass, plastic, rubber and calcified bone.
If a product application has one or both of these aspects, then a case can be
With certain products, food manufacturers can realise great benefits from using dual energy x-ray detection. Mike Pipe, Head of Global Sales of Mettler-Toledo Safeline X-ray, explains how the technology can improve both inspection and business performanceFront view of Mettler-Toledo X36 X-ray Inspection System
made for dual energy x-ray. However, it is important to understand how this technology works. Here, the key concept is material discrimination.
Dual energy x-ray works by using high and low x-ray energy levels to discriminate between materials of different densities. Software algorithms enable the material that is the food product to be removed from a noisy x-ray image, leaving behind any material identified by the second energy level. This is most likely to be a contaminant.
The most advanced dual energy technology available today features an enhanced detector that collects detailed data about the product being inspected. When this is combined with sophisticated image analysis software, the result is even clearer, higher resolution images that enable the best levels of contaminant detection possible today.
Mettler-Toledo dual energy x-ray systems can detect more than eight times as many difficult-tofind contaminants as single energy x-ray systems. To ensure that a manufacturer’s application is best suited to dual energy x-ray manufacturers should look for a “Test Before You Invest” service.
The general rule of thumb is that dual energy is best suited to applications where some or all of these factors exist:
• the product being inspected is one with high contrast, caused by overlapping products or products with variable thicknesses
• the expected contaminants are low
density materials such as glass, rubber, plastic and calcified bone • the packaging material used is low density, allowing low energy x-rays to pass through and inspect the product inside
Improving the effectiveness of contaminant detection with dual energy x-ray that is optimised to the product application is clearly beneficial to food quality and consumer safety standards, but it also helps the food manufacturer’s business.
Consider, for example, the degree to which the sensitivity of a single energy x-ray system would have to be finetuned to detect very small contaminants such as 0.8mm pieces of stainless steel in packs of nuts. The sensitivity required for such an application would very likely cause many false rejects, which would result in a great deal of product throwaway. Turning down the sensitivity to reduce the false reject rate might mean that contaminated products pass undetected, leading to a product recall and damage to reputation. Using dual energy x-ray would very likely enable the manufacturer to optimise detection around this application, without the resulting surge in false rejects and wasted products. In turn, this makes the business case for dual energy x-ray much stronger.
Food manufacturers have to balance a range of factors, including budget constraints, when deciding upon investments and improvements to their production line capabilities, and product inspection is only one of their considerations. It is a critical one though since it is the guardian of food safety.
With dual energy x-ray, everything depends upon the application, including the nature of the product, the possible contaminant, and the packaging. If operating on a tight budget, a single energy x-ray system might seem superficially more attractive. However, the more advanced contaminant detection capabilities of dual energy make more accurate inspection of challenging applications possible, and can quickly provide a return on investment, when set against the mounting costs of waste through false rejects and potential product recalls.
For more information, please click www.mt.com/xray-de-wp-pr
Mettler-Toledo dual energy x-ray systems can detect more than eight times as many difficult-to-find contaminants as single energy x-ray systems.Detection of 6 pieces of 2mm low mineral glass contaminants in a bag of pasta with Mettler-Toledo DXD technology Mettler-Toledo DXD technology detects 6 pieces of 2mm rubber contaminants in a potato wedges pack
High-resolution reader decodes multiple symbologies simultaneously at high speeds, even at short package gaps
Cognex Corporation has released the DataMan® 580 fixed-mount barcode reader, designed for five- and sixsided Modular Vision Tunnels.
The new logistics tunnel solution gives an edge to companies that want to increase sortation throughput and decrease processing times for e-commerce and store fulfillment. All tunnels are pre-configured with pre-built reader modules and can be set up within a day, greatly minimising downtime and delivering fast ROI at inbound, outbound, and sortation areas.
The DataMan 580 barcode reader optimises logistics processes by enabling higher-speed operations while improving traceability. Patented algorithms simultaneously decode multiple 1D and 2D codes at top line speeds while the nine-megapixel area scan imager enables greater field-of-view.
“The DataMan 580 adds significant performance gains for high-speed logistics tunnels,” said Matt Moschner, Vice President of ID Products and
The DataMan 580 adds significant performance gains for high-speed logistics tunnels.
Platforms. “The system’s algorithm decodes multi-symbology labels up to three times faster than conventional methods. And, because the DataMan 580 system actively tracks packages throughout its field of view, users can
reduce the space between boxes and process more items.”
In contrast to linear scanning systems, the DataMan 580 ensures more robust code reading by deciphering highperspective labels on irregular objects. The system’s innovative HDR+ imaging algorithm significantly reduces exposure times needed for high-resolution images, delivering crisp, clear images even in lowcontrast environments.
The DataMan 580 can be enhanced with Edge Intelligence, Cognex’s device management and performance tool, to track real-time system performance and optimize operations downstream. Additionally, pairing DataMan 580 Modular Vision Tunnels with Cognex 3D vision systems enables logistics operations to identify label placement and dimensions in real time, helping validate label compliance.
For more information, visit http://www.cognex.com/dataman-580 or call +44 121 296 5163.
BST are proud to be the original pioneers in metal detectable plastic technology and are the driving force in the UK combatting the issue of plastic contamination in food production worldwide. We specialise in metal detectable, x-ray visible, shatter resistant, and antimicrobial food safe products, utilised across all food sectors to reduce the risk of foreign body contamination.
Brain S Teasdale (BST) founded the company in 1985 and initially focused on providing engineering supplies to UK bakeries, before inventing the concept of metal detectable products and the world’s first detectable pen. BST remains a family business, now headed by John S Teasdale since Brian’s retirement in 2002.
Detectable products are now an integral part of food safety and HACCAP procedures
worldwide. As new regulations and legislations have highlighted the necessity for detectable, food safe products in the food industry, it is becoming increasingly important to show due diligence in the prevention of plastic and rubber contamination. BST focus on producing high quality detectable products, less susceptible to wear and therefore less likely to end up contaminating food in production. Should a BST detectable item break or be dropped into food production, fragments as small as
5mm³ can be detected by metal detection or x-ray inspection systems and automatically be rejected from the production line.
The food industry aside, BST products are high quality, ergonomic, and a wide range of the products are antimicrobial and so are also suited to environments of highrisk cross infection such as medical areas, reception areas, open plan offices, and call centres.
www.bst-detectable.com
Since 1985 BST have refined our materials to increase both performance and the range of products available to the food industry.
BST detectable products are developed using highly advanced food grade materials, tested on x-ray inspection and metal detection systems, produced in hygienic environments and migration tested to the FDA and EU standards for food contact.
Our products are designed to be as safe as possible for food production environments and if we don’t have what you need, then we can use our stocked materials to make it for you, through our network of injection moulders, machinists, and extruders.
One of the UK’s leading suppliers of prepared fresh vegetables has seen a significant increase in capacity since completing a multi-million pound investment.
Fenmarc has enjoyed the benefits of additional throughput and efficiency at its Wisbech factory since installing a complete new multiple line weighing and packaging plant.
The new lines feature the latest in multi-head weighing technology along with four GIC3100 high speed vertical form fill and seal packaging machines, which now give Fenmarc higher speeds, greater accuracy and a lower cost of ownership.
“The previous three lines had been running 18 hours a day, seven days a week since 2015,” says Terry Holland, Head of Engineering at Fenmarc. “We decided to see how we could become more efficient for several reasons. The lines were showing their age and needed more frequent expensive maintenance; some parts had become obsolete and were no longer supported; and new machinery offered better accuracy and performance.”
Phase one of the project was completed in 2020, and included the installation of two GIC3100s along with new high specification multi-head weighers and a new complex product feed and mixing system.
The new plant requirement was for each GIC3100 to handle over 100 packs per minute, with pack weights ranging from 100g to 800g.
The GIC3100, which features a 10-inch HMI colour touch screen and the latest specification Rockwell Allen Bradley Servo Drives, is ideal for all high-speed applications to a maximum of 250mm
wide, such as pillow, gusseted and block bottom. The GIC3100 boasts a robust mechanical design with a new counterbalance system for higher speeds.
“The weighers and GIC vertical form and fill packaging machines installed in phase one proved to be so much
more flexible, faster and more accurate than the previous set-up,” says Terry. “That’s why we decided to commission an additional two lines, which were installed in August 2022.
“In the six months since the additional lines were commissioned, we’ve increased our capacity significantly, allowing us to expand our range with both new and existing customers.
“Since deciding to work with GIC back in 2019, when we visited their facilities, we have been very impressed with the efficiency of the GIC3100 machines and the after sales back-up and support received. We are
The new plant requirement was for each GIC3100 to handle over 100 packs per minute, with pack weights ranging from 100g to 800g.
also pleased with the overall low total cost of ownership.
Fenmarc’s four GIC3100 machines bring the total number of GIC machines operating in the fresh produce sector to in excess of 300 machines. “We are very pleased to have reached this milestone,” says Andy Beal, GIC’s Managing Director. “We pride ourselves on delivering high quality, well-built and efficient packaging machines and providing the best levels of after-sales support to our customers that we can. It’s great to know that our vertical form
fill and seal packaging machines can help increase our customers’ capacity and play a part in helping them win new business.”
GIC was established more than 30 years ago in Gainsborough, Lincolnshire, and employs over 30 people. The company manufactures an extensive range of vertical bagmakers, producing a wide range of finished bag sizes from 100mm to 600mm wide in both intermittent and continuous motion variants. All GIC machines offer lowcost ownership, robustness, reliability and exceptional build quality.
GIC’s machines integrate seamlessly with upstream equipment such as multi-head weighers, cup fillers and counters. The company offers efficient and cost-effective after-sales to all its customers in fresh and frozen foods, cereals, snacks, confectionery, pasta, powders and pulses, industrial hardware and liquids.
For further information about GIC, email info@gic.uk.net or call 01427 611885.
www.fenmarc.com
GIC’s machines integrate seamlessly with upstream equipment such as multi-head weighers, cup fillers and counters.
The most critical requirements in the high-volume manufacturing of folding cartons is consistency and repeatability of the folding and opening forces. When problems occur they often stem from variations in crease geometry between impressions. This is why Cerulean acquired the design for the Laboratory Carton Tester (LCT) and improved it with the aim to help producers and end-users fight against variations in the crease and fold performance. These variations present serious supply chain problems as well as costly machine downtime.
Cerulean was approached by a company making cake products. They had two packaging suppliers, both competing for the supply of the same carton box design for the highspeed packing of cake products. They noticed a significant difference between the 2 suppliers’ product. Traditional analysis methods could not establish the reasons behind the failures.
Whilst supplier A did not suffer any rejects, Supplier B had a batch of two million cartons rejected. In an effort to understand the problems, two cartons from the four impressions from each supplier were tested using the LCT in a blind test process.
The results have shown that supplier A’s products (purple curves) had a wide range of crease forces but no folding errors were reported. On the other hand, supplier B (red curves) had more consistent crease forces but suffered from occasional creasing failures associated with cartons from the first of the four die impressions which resulted in rejected batches of two million cartons.
As you can see from the graphs, Supplier A did not have effective control over the creasing process but did not have any rejected products. However, supplier B who had much
To resolve these problems, supplier B used an LCT on their site to aid the machine setter in setting up the die. It was found that a 30-micron adjustment of the creasing knife allowed the production of a crease within tolerance. The difference in torque of 0.04 Newton per metre of crease had been previously undetectable when tested by hand. After testing and making adjustments, a batch of two million cartons was then produced by supplier B and sent to the end user and there were no further rejects.
Accurate and exhaustive tests are performed by the LCT – the only instrument available that tests complete cartons and plots torque for every degree of deflection.
www.cerulean.com
The Cerulean Laboratory Carton Tester (LCT) is a test instrument designed for testing and measuring the folding resistance of creased carton board, corrugated board and complete cartons and boxes.
The LCT comprises four instruments into one machine, with the instrument recording the measurements for Fold, Form, Spring Back and Friction. Offering benefits to its end users through improved running efficiency on form-and-fill lines whilst also offering converters a reduction in rejected cartons leading the less wastage along the production line.
World-wide support; we are your global, local supplier.
Food processing plants must balance rigorous hygiene requirements with the need to improve productivity, leaving many plant managers unsure of the best investments regarding conveyor systems. Here Enrico Visconti, Head of Industry Segment Food at hygienic conveyor belt manufacturer Habasit, shares some advice on how to improve conveyor belt sanitation in food processing applications.
Conveyor belts in food processing are key focus areas for cleaning as they are in direct contact with food products. The biggest challenge they face is cross contamination, where food products are
contaminated by foreign bodies. This can either be physical contamination or microbiological contamination, caused by biofilm build-up on the line.
Biofilms typically consist of water, lipids, proteins, polysaccharides, and microorganisms and are particularly challenging for food processing sanitation operators to remove. Essentially, biofilm structures create bacterial colonies and single-cell groups that adhere to surfaces. These are preserved by a protective dome of polysaccharide meshing, making them difficult to remove and clean. Therefore, hygienic design features
that prevent biofilm build-up from occurring in the first place are crucial for ongoing hygiene in food processing plants.
A critical area for modular belting is the hinges, where, if not properly cleaned, product debris might accumulate and biofilm grows. Therefore, hygienic belt design must limit the surface area of hinges and provide easy access to belting from all sides, allowing sanitation workers to inspect, clean, and validate belts quickly and effectively. Belts must also facilitate the flow of water and cleaning agents
The key design features that will increase profitability in the food processing industry by improving sanitation and productivity
to the most hidden parts and the rods connecting the belts, so they cannot become breeding grounds for harmful bacteria.
Overcoming this challenge led to the development of Super HyCLEAN, a plastic modular belting range designed to improve cleaning efficiency and food safety. These belts have a completely flat belt surface, including on the running side, where the hinge and rod area have been minimized. The hinges have been placed on the outer sides of the belt, resulting in a flat bottom surface, significantly reducing any areas at risk of debris collection and biofilm accumulation. Furthermore, the dynamic open hinge allows water flow to reach the hinges and the rods, facilitating debris removal.
Independent third-party testing and industrial trials in the most hygienically demanding applications in poultry, fish, and red meat processing concluded that cleaning operation time and water usage can both be reduced by over 50 per cent because they trap less debris. Further testing using UV-tracers found that, after only five rinsing cycles, there was up to 4.1 times less soil residue on Super HyCLEAN compared to other commonly used hygienic plastic modular belts. Furthermore, microbiological swab tests and CFU testing showed the belts developed 20 times fewer bacterial colonies compared to commonly used hygienic modular belts.
The next way hygiene of food processing conveyors can be improved is by using modern cleaning in place (CIP) units ꟷ spray cleaning bars fitted to conveyor frames to increase cleaning effectiveness. The functional use of CIPs is clear, they improve cleanability and reduce the time required for cleaning, therefore improving productivity. However, most food conveyor systems are not equipped with CIP units and it is
often overly complicated to install them as aftermarket.
This perception is changing thanks to new plug-and-play hygienic CIP units that can be easily installed on any conveyor system. This allows industry to retrofit CIP units onto any system without requiring costly and disruptive engineering work, improving plant-wide cleanability and reducing the cleaning window, improving plant productivity.
Another way to improve hygiene in food processing is by installing components that allow removal of belts from conveyor frames without using tools, such as Saniclip. This facilitates easy cleaning of conveyor frames without requiring specialist engineers, drastically cutting the time required for cleaning and improving productivity.
To find out more about how Habasit can help improve sanitation programs in food processing plants, visit https:// www.habasit.com/en/Industries/Foodand--Beverage
Conveyor belts in food processing are key focus areas for cleaning as they are in direct contact with food products.
Handling an abrasive or viscous liquid is often one of the most demanding applications a pump can experience.
The inability of such fluids to flow well under gravity, suspension of sharp particles which can cut seals or gaskets creating leaks and solid concentrations which can reduce pumping efficiency, often mean that only a handful of pump technologies exist to handle such a requirement.
Whilst often there can be more than one solution for transferring an abrasive or viscous solution, selecting the right pump for the process application can often mean the difference between lowest life time cost, or a lifetime of problems!
A client approached us with an application to transfer ceramic resin from containers to machines. This was a new process and they wanted to ensure any unit supplied could handle sharp solids without experiencing wear or failure as part of a robust manufacturing process.
The customer had various existing pumps on site, but were concerned that when handling the ceramic resin, premature damage may be incurred to the pump or internal parts.
We worked with the customer to obtain an overview of the process and once the specifics of the process were understood we determined that a peristaltic pump which transfers fluids at low speeds via a reinforced natural rubber hose was the correct solution. With a maximum operating speed of only 29 revolutions per minute, it would ensure that ceramic particles would not be given enough energy or velocity to cause damage to either internal parts, pipework or seals.
Peristaltic pumps not only operate at very low speeds, but as they are seal
The pump will transfer ceramic resin which is around 1000cst at up to 800Litres an hour, well within the pumps performance range meeting process requirements.
less there are not prone to leaks when handling abrasive media as is found with other pump designs.
The pump will transfer ceramic resin which is around 1000cst at up to 800Litres an hour, well within the pumps performance range meeting process requirements.
4 Reasons why a Peristaltic Pump was the best solution:
1. Slow pump operation ensured sharp particles were not transferred at high velocities which could damage pipework or the pump.
2. Variations in viscosity means flow rates would not be affected due to its positive displacement design.
3. The Unit can run dry or with higher
concentrations of solids without damage.
4. As the unit is seal less and contains a single wearing part, maintenance can be performed with ease, with very little experience, and only 1 spare part is required – a hose.
Additionally, the pump was supplied with 2 spare reinforced hoses, ensuring should maintenance be required in the future, they are on hand for maximum reliability in a hazardous environment.
If you have a process requiring the pumping of abrasive solid laden fluids, or have aging process equipment that is holding back your plant, contact us on 01773 302 660 or visit www.northridgepumps.com to see how we can help.
Optimise performance with specialist support
Whether you’re dealing with clogging, separation, downtime, or other issueit’s costly. Time wasted troubleshooting and lower production mean missed targets and less profit. A sanitary pump is the solution but choosing the right one feels like stepping into a minefield. You know what you need it to do but with so many options, it’s difficult to know which is best for your process and parameters.
+ Accelerated stator wear
+ Clogging
+ Changes to fluid consistency
+ Clean-in-place and sterilise-in-place hygiene issues
+ Crushing of sensitive products
+ Inconsistency in finished product
+ Inaccurate transfer of flavourings or ingredients
+ Liquid separation
+ Seal wear or failure
We’ve been engineering sanitary pumps for sectors such as distilling, brewing, food manufacturing/processing, and more, for 20+ years. We understand industry-specific processes and know what it takes to optimise performance through better-suited pump design - giving you complete peace of mind.
EXPERT GUIDANCE:
Our expert engineers understand your process and guide you through the options, so you can confidently select the most suitable sanitary pump.
Want to optimise performance sooner? Speak to one of our specialists.
EXAMPLE PRODUCTS:
+ Abrasive mixtures
+ Creams, milk & ice cream
+ Edible oils & fats
+ Fish & meat
+ Fruits eg. cooked apples, plums, berries, grapes
+ Grains & seeds
+ Pastes & purees
+ Syrups, juices & alcohols
+ Vegetables & peelings
+ Waste eg. trimmings, packaging & offcuts
+ Sheer sensitive liquids
+ Solid laden or viscous mixtures
As a brand synonymous with quality and innovation, Hotel Chocolat uses only the best ingredients – a factor that extends to the production equipment at its manufacturing base in Huntingdon. So when the company invested in a dedicated plant for its Velvetiser drinking chocolate brand, two Ishida CCW-RV multihead weighers have become an integral part of the packing line solution.
The Velvetiser brand, launched in 2018, is one of Hotel Chocolat’s greatest successes, enabling the creation of drinking chocolate using sachets of pure chocolate flakes. In order to meet huge consumer demand, Hotel Chocolat took the decision to convert existing warehouse space into a dedicated production line for the flakes, enabling a four-fold increase in capacity.
Offering a diverse range of sizes, from retail packs to larger variants aimed at
cafés and businesses, and over a dozen distinct flavours, weighing accuracy was a critical requirement for the success of the new packing lines.
Simon Wood, Head of UK Manufacturing Projects at Hotel Chocolat, had used Ishida in a previous food production role
and knew its multihead weighers had the hygienic design, reliability, performance and precision to deliver.
“Chocolate is understandably temperature-sensitive, the flakes used in the Velvetiser are small but non-uniform in size, and there’s always a residue of
cocoa dust created during production,” Simon explained. “Our choice of weigher had to cope with these factors, as well as delivering the required speed, accuracy and ease of changeovers during 24-hour operation.”
The two Ishida 28-head CCW-RV range multihead weighers with 500 cc hoppers are ideal for Hotel Chocolat’s requirements
to handle smaller target weights at high speeds. This is made possible thanks to improved feeder technology, using pulse width modulation and an integrated AFD (Automatic Feeder Drive) system that ensures precise control of product flow through the weigher.
The weigher’s unique triple combination calculation software is able to calculate three optimal weight combinations, double check them and then select the one nearest to the target weight – all in a single cycle. This delivers highly accurate weighing for Hotel Chocolat at speeds of up to 210 weighments per minute.
The Ishida CCW-RVs are part of a multilevel system for Velvetiser flakes, installed
and commissioned during 2021 against the backdrop of the COVID-19. For Hotel Chocolat, Ishida’s advice, service and support during this challenging project was just as important as the quality of the weighing machines.
“The Ishida weighers sit at the centre of a three-level facility, created from scratch in what used to be a warehouse,” explained Sylwia Zmuda, Manufacturing Site Manager, Velvetiser. “On the top floor, the chocolate is mixed, extruded and chilled, before being broken into flakes by rollers.
“The flaked chocolate is conveyed to the middle level, where the Ishida CCW-RVs weigh them into the required portion sizes, before they drop down to ground level to be bagged and inspected,” she said.
Given the high production volume, the conveying system is able to transfer the chocolate flakes to two Ishida weighers in order to provide additional capacity, as well as uninterrupted production in the event of machine maintenance.
“It’s a highly efficient system and Ishida provided exceptional training to help our team get the best out of the weighers,” commented Snieguole Kaikaryte, Operations Shift Manager.
“This has been a major investment by Hotel Chocolat, and one that is paying off in terms of the high standards of throughput and quality achieved by the flaked chocolate production line. Ishida’s involvement in the project has been an integral part of this success, allowing us to treat our global customers to high-quality drinking chocolate,” confirmed Simon Wood.
For Hotel Chocolat, Ishida’s advice, service and support during this challenging project was just as important as the quality of the weighing machines.
SVTS B series slip ring assemblies from Servotecnica offer machine builders a continuously rotating electrical joint with a working life that can extend to 100 million revolutions at high speeds. The range is aimed at demanding industrial applications in high throughput production machinery where gold alloy multifibre brushes and precious metal rings in IP65 fully sealed ABS/aluminium/ stainless steel housings ensure the highly reliable transfer of electrical power and instrumentation signals through rotating structures. A variant, the 70 mm diameter SVTS B 03, is particularly aimed at transferring power to the rotating heatsealing blades in flow wrapping machines as well as handling temperature signal output to the machine controller.
Available with full sales and technical support from Heason Technology, Servotecnica’s UK distribution partner, this variant is equipped with three 400V/20 A circuits as well as two 240V/2A signal circuits. Its 22 mm diameter through-hole allows direct mounting on the drive shaft of the rotating blade via four M3 set screws. Available in two versions that facilitate machine washdown use: fully housed and IP65 sealed or part-housed for IP65 when installed - both feature sealed cable gland electrical connection with lower power and customer specified number of slip ring ‘ways’ available. Servotecnica’s SVTS fibre bundle technology has lower friction and provides exceptionally longer life when compared to the traditional wear-prone carbon brush designs used by other manufacturers.
The multi-fibre bundles require no lubricants and produce only negligible
debris which significantly reduces the need for routine servicing or frequent brush replacement. Highprecision stainless steel support bearings also help ensure long working life and a specified nominal speed capability of 400 rpm enables use on high-throughput machinery. Other benefits include improved signal quality as the (up-to ten) individual gold-alloy strand brushes ensure multiple point contact with the slip ring as well as a much higher capacity for handling high transient loads in addition to better resistance to shock and vibration. Other versions of the SVTS - B series have faston-type male terminal connectors where sealing is not required.
Servotecnica’s considerable range of slip rings and rotary joints include standard and customised models with specifiable multiple channels for power and signal transmission as well as Ethernet, radio, fibre optic and fluidic transfer – available as housed or part housed, explosion proof, highly ruggedised, open type, and pancake slip ring assemblies. As well as packaging machinery and industrial
manufacturing plant, other industries served include wind turbine, crane & hoist, process control, medical and pharmaceutical production machinery, amusement equipment, machine toolsand more.
Heason Technology is on hand to add machine customisation using Servotecnica’s slip ring assemblies. As a systems integrator with its own inhouse design and production facilities and distribution partnerships with selected global automation component suppliers, Heason also supplies and supports motion control equipment from component level to complete systems including stepper and servo motors and drives, motion hardware and software, gear units, linear bearings, mechanical positioning mechanics and more.
For further information on Servotecnica and Heason Technology visit www.heason.com, call +44 (0) 1403 792 300 or email sales@heason.com.
At OMEX we understand the importance of keeping the wastewater treatment facility at optimum performance. Below our Technical Director, Dimitris Theodoridis, highlights the key points to achieve the best performance from your WWT plant:
For the plant to function, the first area to look at is ensuring the biology is "happy". Keeping the biology in working condition enables the plant to work, so this should usually be the first point to check on any site managers checklist. If the biology isn't getting all the necessary elements it needs, such as adequate food, aeration and nutrition, the plant will subsequently fail and lose performance, this can in turn lead to wastewater being discharged with certain measured parameters being out of consent.
The best way to assess the biology in the plant is to analyse it. OMEX offer full technical support and provide facilities to assess the performance of the bacteria in the plant. The fully accredited OMEX labs can offer an in-depth analysis and treatment of all the possible problems which can occur within the wastewater treatment industry. OMEX
technical staff will collect a set of samples to establish the status of the biological process.
Once a full nutritional analysis of the plant has been undertaken, results should be analysed and discussed with a technical expert, who is able to advise on the best course of action to improve and optimise the process. The OMEX technical sales team are able to assess the plant via lab analysis and in-depth discussion with the site operator/ manager to gain a thorough understanding of any issues the plant is experiencing. Once this process is completed a tailored product
programme is put together, along with recommendations and appropriate dosing rates to achieve the desired outcome.
OMEX offer a full range of products to help with the optimisation of the wastewater treatment process, including:
• Magmex - an environmentally friendly pH neutraliser. In addition, Magmex contains certain compounds that are beneficial nutrients needed by the biology within the plant
• Nutromex N&P (Plus)- strengthens the biology, stabilises performance and enables a more effective breakdown of the organic content in the raw wastewater
• Micromex - when the plant is lacking in the number of microorganisms needed to process, Micromex augments the biology cultures, effectively breaking down the unwanted organics
• Anomex - in activated sludge processes there is a risk of hydrogen sulphide in the sludge storage tank, Anomex is used to minimise the risk of sludge becoming septic
www.omexenvironmental.com
The fully accredited OMEX labs can offer an in-depth analysis and treatment of all the possible problems which can occur within the wastewater treatment industry.
In any business world, data is reshaping the landscape. Food processing is no exception. If we consider the next big technology development, it will inevitably be a non-incremental, non-organic, move away from human labour and towards automation. In food production humans generally perform two subtasks for each primary task. In virtually every case, one of these sub-tasks is checking/quality control.
After biological contamination, label related defects are cited as
the second most common cause behind costly and brand-damaging product withdrawals and retailer returns. There are several powerful reasons to ensure that the labelling of food products is correct. From the perspective of a food processor, the reasons broadly fit into three categories – improved production efficiency, waste reduction and regulatory compliance.
Automated label verification has a huge part to play in increasing production line efficiency in food
factories. Many applications which were previously deemed uneconomic to automate are now being automated based solely on the unavailability of a skilled workforce.
Using technology to verify the label offers far greater benefits compared to manual inspection. Given today’s production speeds, it’s impossible for one human to accurately read and process all the data for an entire shift. Let alone check all elements of the label integrity, use by dates, country of origin, special promotions and cooking time. Operative fatigue swiftly kicks in. A few minutes is more realistic.
Having decided to automate the two main questions that follow are “How to go about it?” and soon after “what’s the risk?”. Most automation tasks should be achievable and contacting organisations such as BARA can help guide projects.
Among some of the many automation risks, one of the most significant is removing the final visual check due to labour shortages. For instance, a food operative putting meat steaks into a retail tray will inevitably check a multitude of critical factors, such as general appearance, colour, fat content etc. as they pick up and place the steaks into the tray. However, inspecting established quality parameters in each piece of meat on processing lines can be further enhanced with the use of automated vision solutions. Machine vision companies can almost replicate (and in many cases outdo) a human operative. It is non-destructive, easy and quick.
It is entirely feasible that inspection processes on meat and poultry processing and packing lines will be dominated by cameras in the next decade.
In the case of checking the label is correct, the case for automation is much stronger. The label not only identifies the product but contains critical variable information such as “use by” dates and pricing. A welldesigned label verification system should be able to verify 100% of the data on 100% of the products against validated source production data. Typically via the factory MRP system, not from a production line operative. As well as guaranteeing its accuracy, having this complete audit trail provides proof that all data or labels are verified.
A study by climate action NGO WRAP titled “Quantification of food surplus, waste and related materials in the UK grocery supply chain” calculated that approximately 1.7 million tonnes of food were wasted in the UK prior to it reaching the consumer, almost half of which was preventable.
A further study by Rentokil determined
that mislabelling was the second most common cause of food recalls in the US, and the third in the UK. A welldesigned label verification system would be able to detect not only that an incorrect label was being used but also any incorrect data necessitating a recall.
Food labelling errors fall in to two categories, systematic errors, and random errors. A systematic error is where the label and/or data is manifestly incorrect. Random errors are generally a problem relating to the vagaries of the production process, such as a foreign body becoming attached to a printer. Label verification facilitates this full end of line automation and is critical to the whole quality control picture. JentonDimaco label verification systems are the only ones that meet all UK labelling requirements and provide the data to prove it.
Almost all aspects of food production are subject to strict legal and customer compliance regulations.
Food labelling requires that many parameters must be checked, from the basics of is it the correct packaging, to
Using technology to verify the label offers far greater benefits compared to manual inspection.
the more complex of weights, prices and country of origin. Typically, this information is recorded at intervals (often every 30-60 minutes) on paper check sheets with labels then affixed as proof.
Companies that have stuck with a manual approach to label verification are often tethered to a system that generates little, if any, benefit to themselves over and above meeting their compliance obligations.
A fully automated label verification system should offer several benefits over a manual system.
• 100% of the data is verified
• 100% of the packs are verified
• The label data is verified against a known correct standard
• Both systematic errors (incorrect data) and random errors (e.g., misplaced label / missing label / print head contamination) are captured.
Additionally, these systems provide:
• Proof of compliance
• Facilitates fast audit responses
• Tracks manual overrides against individual user and time/date
• Easily allows the data to be fed back as part of continuous improvement programs.
An automatic label verification system should provide the data not only for compliance but to help guide the business.
An automated label verification can deliver multiple benefits to a food producer. It can increase efficiency, reduce staff count, reduce waste, and improve compliance.
To achieve these significant benefits, care and attention must be taken when designing and implementing the system. Simply attaching a smart camera and entering data into a local terminal will not deliver anything close to the same benefits. For example, if a lineside
operator sets a printer up to print a use-by date of “Feb 30” and sets the smart camera up to verify “Feb 30”. Guess what? The so called, verification system passes all the packs!
In label verification there are no shortcuts to success. Yet, for those businesses prepared to make the investment there is the prospect of numerous benefits. Everything always circles back to one thing – It’s all about the data!
An automated label verification can deliver multiple benefits to a food producer. It can increase efficiency, reduce staff count, reduce waste, and improve compliance.
In 2021 a large European foodservice business supplying fresh, refrigerated, and frozen food products, as well as non-food products and supplies, to foodservice customers were facing increased demand for their services and needed to hire for large numbers of roles. With customers ranging from large leisure, pub, restaurant, hotel and contract catering groups to smaller businesses, including independent restaurants, hotels, fast food outlets, schools and hospitals, they needed an RPO that understood their needs and could deliver both HQ and high-volume roles.
Seeking a strategic partner to implement a streamlined recruitment process while delivering highly qualified and skilled candidates, RP01 were selected as their partner of choice. Tasked to deliver a vertical RPO solution to meet their demand, RP01 also proposed bespoke digital candidate attraction solution which provided distinct added value.
RP01 supplied a complete resourcing service and redefined their talent strategy for HQ roles. This allowed for ‘switch on’ recruitment services for warehouse, logistics, HQ and corporate roles across the whole of the UK. The service included:
• Immediate lead time
• Digital candidate attraction for high volume roles
• Dedicated talent partner
• Support of our Morson recruitment specialists
• Feature page hosted on www.morson.com
• Social media advertising
• Review of job specifications to maximise value positioning
• Application of EDI best practice
• Ex forces recruitment consultancy
• Performance management of second tier and indemnifying further costs
RP01’s bespoke vertical RPO solution completed go live in only 5 days. The customer benefited from a dedicated recruitment team and RP01 successfully onboarded 70 candidates within 4 months, in an extremely buoyant and
competitive market, and had a 100% direct fill rate. Beyond just filling roles we supported ED&I efforts and recruitment of under-utilised talent pools such as ex-forces through a coordinated social media campaign and landing page created for ex-forces events that was accessible via QR code and led to increased applications from veterans. We also provided market insight around salary inflation to ensure that roles were competitive.
“Part of our RPO solution was an ex-forces candidate engagement programme to support all levels of hiring needs. We’ve quickly demonstrated our commitment to operating at pace underpinned by a strong social value campaign.”
Seeking a strategic partner to implement a streamlined recruitment process while delivering highly qualified and skilled candidates, RP01 were selected as their partner of choice.
A complete talent solution that wraps around your brand today, tomorrow & for the future.
Facing a surge in demand?
Losing candidates to your competitors?
Have difficulty forecasting or controlling spend?
Have an inconsistent candidate attraction process?
Lacking insight into the demands of today's workforce?
We exist to solve your end-to-end talent challenges RP01, the boutique RPO brand of Morson Group, adds value throughout the entire recruitment journey with custom made solutions that enrich your business with insight, talent and capability, for today, tomorrow and the future
Our team is your team; your ambitions are our ambitions. Let’s achieve them together.
e: hello@rpo-one.com
w: www.rpo-one.com
Ishida Europe has further consolidated its position as the leading manufacturer of complete snacks packaging solutions with the launch of a new vertical form fill seal (VFFS) bagmaker. With 30% increase in speed compared to previous models, the INSPIRA Boxmotion is particularly effective for food manufacturers that want to reduce costs and ensure an error-free production whilst maintaining a flexible operation to meet the everchanging customer needs.
According to Euromonitor International, value sales of snacks are expected to show higher growth rates during 2022 to 2026 than in 2020 and 2021, and healthy snacks are projected to see the highest CAGR. Innovation will continue to drive the sector with emerging trends including the introduction of sustainable packaging, diverse world food flavours, functional foods, on-the-go snacks and a greater
range of packaging sizes and formats to satisfy consumer demands.
Rising energy costs, skilled labour shortages, and supply chain issues are just some of the challenges facing our snacks customers today.
To meet these challenges and market requirements, snacks manufacturers are seeking exceptional levels of adaptability and future proofing from their packaging equipment.
The Ishida INSPIRA Box Motion bagmaker can operate in both continuous and intermittent motion modes. This enables it to handle the widest variety of both product and pack formats, including the introduction of recyclable film and paper packs, while maintaining excellent seal quality and integrity.
Box motion technology enables the sealing jaw motion to operate in both vertical and in/out horizontal planes. This means more uniform pressure is applied over the entire area of the jaws, whereas rotary jaws can only make a single point of contact as they rotate together. As well as ensuring a more consistent and reliable seal, box motion technology can handle all the latest pack formats which, in addition to pillow packs, include side gusset, block bottom, chain packs and flat bottom.
The INSPIRA Box Motion features a new splice table light-bar for easier and faster automatic film splicing overcoming the challenges associated with manual intervention. Capable of completing a film splice cycle in just 20 seconds, this great addition allows operators to manage more machines per head and can result in huge operational cost savings.
With increasing consumer demand to enhance and expand flavours and portion choice, production runs for many snacks can be shorter, making changeover time a bigger factor in maximising throughput.
Switching between continuous and intermittent motion can be carried out through pre-settings on the machine with no change parts or operator intervention required. Similarly intelligent, automated features for centring film, managing air fills and adjusting tensions ensures faster changeovers with minimal operator intervention reducing human error, film and product waste and increasing production consistency and profitability.
With an energy saving design INSPIRA Box Motion uses 17% less energy when in operation and 25% less energy on standby than previous models. The bagmaker’s open structure also allows easy access to key components such as the forming tube, film spindle and tension roller. A large menu-driven Human Machine Interface (HMI) screen provides performance data and diagnostics, with multi-level password access to ensure data integrity.
“The snacks market is being driven by ongoing product and packaging developments, and remains fiercely competitive,” said Andrew Green, Snacks Business Unit Manager, Ishida Europe. “Our new INSPIRA Box Motion has been designed to allow manufacturers to continually adapt to the latest market trends while offering a new level of automation and efficiency. This minimises the chance of human error and helps to consistently produce quality bags while cutting costs and increasing profitability.”
www.ishidaeurope.com
The Ishida INSPIRA Box Motion bagmaker can operate in both continuous and intermittent motion modes
Looking back to 2021, it was easy to consider compressed air as something of a ‘free’ resource. Energy prices were low and manufacturers generating compressed air for one area of their factory could utilise it in another area for next to zero marginal cost. However, since energy prices began their upwards journey, compressed air is no longer the cheap commodity it once used to be.
In 2022, the British Compressed Air Society (BCAS) conducted research into the extent of compressed air use in UK industry. They found that 70% of UK industry uses compressed air in some form or another and that on average, 30% of a business’s entire energy costs could be attributed to compressed air generation.
Using figures from the (then recent) UK Energy-related products policy study, conducted by ICF in May 2021, they calculated the combined energy usage for the mid-point of all industrial compressor technologies over their lifetime at 11.71 TWh. Based on the current UK average non-domestic electrical unit cost of 12.49p/kWh at the time, the figures were substantialequating to £1.475 billion being spent by UK companies to generate the compressed air their businesses rely on.
Add to this the fact that on average 32.9 per cent of this energy was being wasted through leaks and inefficient practices - equivalent to £485.43 million in wasted electricity spend - and we began to understand the extent of which this presents a problem for UK manufacturing.
Skip forwards to today and the Department of Business, Energy and Industrial Strategy (BEIS) has recently published its figures for UK average nondomestic electricity costs for the final
quarter of 2022. This figure now stands at 24.56p/kWh according to statistics, but it is estimated that many industrial tariffs are now reaching as high as 50.73p/kWh as of January 2023.
If we use the Government’s current published figures as a starting point and adjust the BCAS research for today’s prices, we find that £2.943 billion is being used to generate compressed air in the UK. At a loss rate of 32.9%, that’s almost £1 billon of wasted energy every year in the UK, equivalent to £2.62 million every single day.
This staggering figure may come as a surprise to many of the UK’s manufacturers who have until recently worked on an ‘out of sight, out of mind’ policy when it comes to monitoring exactly what is going on within their compressor houses. It’s with this in mind that industry veterans Thorite recently launched their ‘Behind Closed
Doors’ campaign, urging businesses to gain a better insight into what their compressors are actually doing for them. From scheduled leak testing to automatic shut off valves, datalogging to flow control and monitoring, the options for saving energy are numerous and the results are astonishing.
While energy savings in the past might have been outweighed by the cost of fixing leaks, thanks to the latest energy prices, the return on investment to combat inefficiencies is now months, not years. Not to mention the opportunity to reduce carbon emissions by up to 3.2 tons per year - a consideration that companies can’t help but be aware of.
With all things considered, isn’t it time your company found out what is happening behind closed doors?
Hart Door Systems, the original British manufacturer of the high-speed door concept, is confident that there are considerable prospects for another successful year for the Speedor brand.
“Our management team led by Nick Hart as managing director and David Mason as sales director has just delivered a very good year when there have been many uncertainties in the UK economy and wider afield.
“In that challenging business environment, we have had many successes at home and abroad not just through the Speedor range of highspeed doors but through our range of high-quality shutters. Both these leading brands have had additional variants introduced such as Speedor ECO and our Typhoon shutters,” says Doug Hart, chairman, Hart Door Systems.
“The breadth of offer created by the choice of solutions for industry and commerce has cemented our presence in the UK market and globally. The fundamentals delivered by Hart are quality throughout manufacture to installation as well as service back-up to comply with changing national and international safety standards.
“We are also cognisant of Climate Change issues and the need to keep both Hart’s and our clients’ carbon footprints to a minimum by using the latest manufacturing technology to streamline the manufacturing process. Where possible we would use recyclable materials.”
Looking more closely at Speedor ECO, this high-speed door complements Hart’s very successful Speedor Storm, Speedor Mini and sub brands such as Speedor Conveyor and Speedor Cleanroom, further
strengthening Hart’s overall high-speed door offer.
Speedor ECO is a new mid-range variant suitable for external use up to Class 3 and available up to 5m x 5m size whereas the Speedor Mini is for internal use only to a maximum 4m x 4m size. The focus with these two Speedor options is on lower price and high-speed doors that can be tailored to meet clients’ budgets.
Mr Hart says: “With the new Speedor ECO being a mid-priced high-speed
door variant with state-of-the-art direct drives and controls which are BSEN safety compliant, the ECO offers single or variable speed motor, heavy fabric and hand chain operation if necessary.
This adds to ECO’s many other features such as safe operation, reliability, and ruggedness. “We have always had quality as our prime driver and our success with new variants, not just in high-speed doors but shutters such as our new Typhoon range, the fundamentals are quality throughout manufacture to installation and service
to comply with changing national and international safety standards,” says Mr Hart.
“Without doubt there is demand for a mid-priced high-speed door variant such as ECO and given our considerable experience, we are the ones to deliver it,” he adds. “ECO will appeal to companies requiring a high-speed door solution but within a tight budget. It is for frequent use, high traffic situations where low maintenance is a priority.
“In all cases across our range of brands, we comply with the new code of practice announced by the DHF Door Hardware Federation and we are ever mindful of post installation maintenance costs. So, while Mini and ECO cater for less demanding environments, Speedor Storm’s increasing success is based on its improved, rugged, design predominately for external use up to 8m x 6m/6m x 8m) often in robust operating conditions with high wind loads.
“We have always had quality as our prime driver and our success with new variants, not just in high-speed doors but shutters such as our new Typhoon range, the fundamentals are quality throughout manufacture to installation and service to comply with changing national and international safety standards.”
Hart Door Systems, now in its 75th
year, is a global business supplying a range of door and shutter systems to sectors such as automotive, agriculture, communications, consumer foods, energy, environment, exports, food, logistics, manufacturing, power, sport, transport and utilities.
Contact www.hartdoors.com
t: 0191 214 0404
sales@hartdoors.com
Without doubt there is demand for a midpriced high-speed door variant such as ECO and given our considerable experience, we are the ones to deliver it.
The versatile Citadel range offers a costeffective solution to the secure housing of equipment. Available in five industry standard sizes, the cabinets can be supplied with or without vents for IP56 rated protection.
Citadel steel cabinets provide protection and security for electrical equipment, metering and monitoring devices. Manufactured in plastic coated steel with a 2mm stainless steel chassis and featuring all-round double skinned insulation and reinforced door, Citadel cabinets are strong and resilient.
Designed with a forward sloping roof that will prevent liquids and debris from collecting on the top of the cabinet, Citadel will efficiently protect your equipment.
Citadel cabinets require minimal maintenance without the need for coating or painting during their long service life.
For more information, visit our website www.glasdon.com or contact our sales team enquiries@glasdon-uk.co.uk Tel: +44 1908 373927
Offer consistent product quality at the point of use for a wide range of applications, guide rails position the IBC and the mixer is raise and lowered into the IBC with a push button operated electrical actuator.
Fixed or mobile mixing stations are supplied complete with a control panel and safety interlocks.
Standard IBC mixing stations can be adapted to integrate with systems on site including pumps, valves, weighing and measuring instrumentation and controls to meet specific site requirements.
Safer Safety began trading in 1985 when the owner was granted a patent for the world’s first ever Metal Detectable Earplug, “DETECTAPLUG”. Mass food processing was at its height and product contamination, whether accidental or malicious, was a big worry for the leading manufacturers of the time.
Employees hated wearing bulky, often uncomfortable, traditional earmuffs but earplugs were thought to be too risky to use on the production line for fear of them falling into the produce undetected. Detectaplug incorporated a metal tagged connecting cord and later a ball bearing in each plug which would trigger any metal detector usually found on such lines. Later versions went one stage further and are now made from a special metal impregnated material for both the plug and the connecting cord making them 100% detectable even if broken up. Low-cost disposable foam earplugs called DETECTAFOAM were introduced also incorporating a detectable cord and metal insert and
the company are proud to be the only UK based company still manufacturing these to this day. Another first for Safer Safety was the development of high-performance ANTI-SLIP footwear, also used extensively in the food industry where slips account for a high proportion of accidents. Since 1999 we helped develop several US brands before designing our own “GRIP” brand of footwear in 2017. This range offers amazing grip even on wet and greasy floors by combining a special rubber compound with a unique tread pattern designed to expel liquid as you walk.
Another world first are the tread wear indicators on our shoes, similar to those found on car tyres, making
it easy for employees to know when to change their footwear. From sturdy steel toecap boots to very trendy lightweight trainers for both men and women, the Grip range of Anti-Slip footwear is leading the way in reducing slips in the workplace while providing comfortable, attractive footwear. As an active member of the world renowned UK Slip Resistance group, our owner is proud to be involved in helping to reduce the overall number of slip fall accidents in the workplace and will continue to develop new ideas to minimise this risk wherever possible.
www.safer-safety.com
Detectable
Safer Safety Ltd - Unit 3
Langham Industrial Park Mansfield Road - Chesterfield
Packing Options
Derbyshire - S41 0GG - United Kingdom Tel: 01246 201 666 www.safer-safety.com
Detectaplug are the world's most detectable earplugs made from attenuation across the speech frequencies making it easier to communicate whilst cutting out harmful noises. They are easy to fit and very comfortable to wear for long periods.
Detectaplug are the world's most detectable earplugs made from metal impregnated rubber. They also have a metal tagged connecting cord for extra security. They provide very flat attenuation across the speech frequencies making it easier to communicate whilst cutting out harmful noises. They are ea fit and very comfortable to wear for long periods.
Metal Impregnated Cord
Cotton Cord with metal tag
Dispenser
Reuseable SNR 29dB FREQUENCY (Hz) 63 125 250 500 1K 2K 4K 8K Mean Attenuation (dB) 27.6 29.1 28.8 31.0 28.9 35.4 37.6 40.0 Standard Deviation (dB) 5.1 4.6 4.1 5.0 4.0 5.2 8.6 6.8 Assumed Protection (dB) 22.5 24.5 24.7 26.0 24.9 30.2 29.0 33.2 Tested to EN352-2: 2002 (DIN EN 352-2:2003)
Detectafoam earplugs are made from soft polymer foam that expands slowly once inserted into the ear canal. They have a hidden metal insert and the connecting cord is metal impregnated
Cotton Cord with metal tag
with Packing Options Performance Packing Options
Detectafoam earplugs are made from soft polymer foam that expands slowly once inserted into the ear canal. They have a hidden metal insert and the connecting cord is metal impregnated
Detectafoam earplugs are made from soft polymer foam that expands slowly once inserted into the ear canal. They have a hidden metal insert and the connecting cord is metal impregnated
Code with Packing Options Performance
Cord Options Product Code Cord Packaging H313 CottonB = Boxes P = Polybags H517 Metal Impregnated B = Boxes P = Polybags
EARPLUGS
Detectafoam earplugs are made from soft polymer foam that expands slowly once inserted into the ear canal. They have a hidden metal insert and the connecting cord is metal impregnated
Tested to EN352-2: 2002 (DIN EN 352-2:2003)
FREQUENCY(Hz) 125 250 500 1K 2K 4K 8K Mean Attenuation (dB) 30.3 32.1 34.7 35.1 36.8 43.0 45.8 Standard Deviation (dB) 8.2 6.9 6.8 5.2 6.1 3.8 3.0 Assumed Protection (dB) 22.1 25.2 27.9 29.9 30.7 39.2 42.8
SNR = 29dB H = 29dB M = 26dB L = 26dB Tested to EN352-2: 2002 (DIN EN 352-2:2003) SNR = 33dB H = 33dB M = 30dB L = 27dB EARPLUGS Detectable • Reuseable • Disposable Safer Safety Ltd - Unit 3, Langham Industrial Park, Mansfield Road, Chesterfield, S41 0GG Tel: 01246 201 666 | www.safer-safety.com | sales@safer-safety.com
SNR = 29dB H = 29dB M = 26dB L = 26dB Tested to EN352-2: 2002 (DIN EN 352-2:2003) SNR = 33dB H = 33dB M = 30dB L = 27dB
New product inspection solutions to be shown for the first time in Europe, including new X2 x-ray inspection platform and an entry-level X12 x-ray system, alongside comprehensive portfolio of inspection technologies integrated with ProdX™ data management software.
Mettler-Toledo Product Inspection will bring a message of productivity and integration to the Interpack trade fair in May 2023. The company will be showing a wide range of smart product inspection systems – some of them on display for the first time in Europe. All solutions are positioned to help food manufacturers tackle the increasing need for digitalization in the marketplace, as well as helping combat rising manufacturing costs.
Under the banner theme of “Boost Your Productivity”, the Mettler-Toledo booth, A60 in Hall 11 at the Messe Düsseldorf, Germany, will comprise several different themed “islands”. These will include areas dedicated to checkweighing, metal detection, x-ray inspection, vision inspection, track & trace and combination product inspection systems, in which more
than one product inspection technology is integrated within a single frame.
The “Boost Your Productivity” theme will be truly brought to life by the integration of many of Mettler-Toledo’s newest technologies in an integrated loop that is connected to Mettler-Toledo ProdX™ data management software. Visitors will be able to see a practical demonstration of how connectivity delivers a range of digital productivity and security benefits.
Interpack will provide Mettler-Toledo with the opportunity to unveil the X2 x-ray inspection platform. The X2 platform is designed for the inspection of small and medium packages with a belt width of 300mm and 400mm. X-ray inspection solutions within the platform are positioned to consistently deliver high
performance detection capabilities for ensuring the safety and quality of food products.
As part of the X2 platform, the X12 entry-level x-ray inspection solution will be showcased for the first time in Europe at Interpack. This x-ray solution is ideal for brand owners requiring cost-effective contaminant detection with added integrity checks. A key feature of the system is ContamPlus™ software which enhances detection capabilities to identify a wide range of contaminants, including glass, metal, mineral stone, calcified bone, dense plastic and rubber compounds.
Another new innovation to be shown for the first time is the X32 x-ray system. Part of the X2 Series, this x-ray inspection solution consists of an advanced detector
and optimum power generator to achieve outstanding detection performance.
Also shown on the stand is the modular X32 x-ray system, which is part of the new X2 platform and provides users with a strong level of flexibility in how they configure their x-ray system.
On the metal detection side, Mettler-Toledo will show several machines, including the versatile M31R StandardLine, which is suitable for dry and wet applications and the M33R GC and M34R GC PlusLine metal detection systems which offer a stepchange in performance and sensitivity for dry or deep frozen and wet or metalized film-packed products inspected via a conveyor. With the latest SENSETM software enhancements, all these metal detection solutions help to support sustainability initiatives with paperless record-keeping, boost productivity through simplifying essential tasks, and make compliance easier to achieve. Visit the stand to discover a new range of software upgrade packs that give the M31R StandardLine metal detectors PlusLine functionality and see ProdX™ automated record-keeping in action.
Also available on the Mettler-Toledo stand is the retailer-recommended Automatic Test System (ATS) for throat and gravity fall systems. Visitors will be able to discover how this award-winning innovation (Innovation Award for Quality Health, Safety and Environment, CFIA Show 2019) can significantly increase operator productivity.
A new vision inspection system – the V13 Flat Pack Label Inspection System – will be launched globally at Interpack. This system performs inspection from the bottom up with a unique line scan camera, to inspect
labels on the underside of flat packs at speeds of up to 300 packs per minute. This system completes the portfolio of Label Inspection solutions from Mettler-Toledo that carry out 100% label inspections from all directions, for all package shapes and for all label quality and data defects. The systems are modular and can be configured to match the customer application and are available as kits, stand-alone or combination systems.
Two new standardised combinations systems are also launched at Interpack, integrating 100% label inspection with checkweighing and optionally also metal detection. These combination systems offer advanced quality control for all product shapes.
Also available on the Mettler-Toledo stand are the advanced checkweighers featuring the new FlashCell™ EMFR technology, enabling precision weighing at speeds of up to 800 packs per minute, as well as Washdown checkweighers, designed for harsh production environments that support intense and frequent cleaning whilst offering reliable accuracy.
“We are looking forward to bringing new product inspection technology and positive messages to our customers and prospects in the food sector at Interpack,” said Rainer Mundt, Head of Marketing at Mettler-Toledo Product Inspection, Germany. “Amid rising manufacturing costs and pressures from the supply chain, manufacturers need product inspection solutions that can make them more productive while making no compromise on food safety. We will be showing a range of systems and software that take them towards a digitalized and sustainable future; systems that will boost their productivity performance to dynamic levels.”
Visitors to the exhibition booth will be able to meet with Mettler-Toledo experts, discuss a comprehensive range of service options, and relax a little over light refreshments. Mettler-Toledo is also offering free Interpack show tickets for guests who register their interest in advance.
For more information, visit www.mt.com/interpack-pr
All solutions are positioned to help food manufacturers tackle the increasing need for digitalization in the marketplace, as well as helping combat rising manufacturing costs.
KHD specialises in providing conveyor belt steam cleaning solutions for the Food Industry. With 25 years experience of developing portable and fixed conveyor belt steam cleaning systems, KHD has the most useful and effective product range available. KHD systems are in use by big brand names around the world. KHD machines are powerful tools that work within existing cleaning regimes to enable operators to do their job better, faster and more effectively.
KHD provides environmentally responsible solutions, producing designs that have the widest possible use within a factory. Portable solutions quickly adjust so they can be used on multiple conveyors in a factory. KHD devices clean primarily with steam and without chemicals, harnessing industrial steam power that uses very little water, typically 15-30 litres of tap water per hour.
The Fixed Conveyor Belt Cleaning Systems use steam and vacuum to clean and sanitise conveyor belts and are suitable for use during production. The lightweight cleaning heads are quick and easy to remove for cleaning. Designed for use in conjunction KHD portable 3-phase steam generators, the systems are also suitable for use with factory steam supply. Available for both single or double sided cleaning this innovative and flexible system can be fitted to a wide range of existing or new conveyor belts.
KHD Technology is a design led company. Alongside standard products KHD also provides bespoke solutions, selling direct to end users and to OEMs including conveyor equipment manufacturers.
Why choose industrial dry steam cleaning over other cleaning methods? You need to have a rigorous cleaning regime in place, opting for an innovative dry steam cleaning approach offers greater benefits.
It’s quicker, easier and cheaper Traditional cleaning methods tend to involve consumables in the form of chemical cleaning agents, and require a lot of labour and time. The amount of time cleaning takes has a direct impact on productivity – the longer a conveyor line is out of action for cleaning, the less product can be processed and dispatched.
It’s better for the environment (and you) Avoiding the use of chemical-based cleaning products, which can be toxic to the environment has additional benefits to cost saving. The quantity of water needed (and the energy required to
heat it) to use and wash away chemical cleaners is excessive compared to the amount of water required for steam cleaning. Visit KHD
The Fixed Conveyor Belt Cleaning Systems use steam and vacuum to clean and sanitise conveyor belts and are suitable for use during production.
Conveyor belt systems are mostly designed as a bespoke solution to fit specific factory requirements. The design therefore needs to address a complex array of factors, including: food type, physical factors, speed, duty cycle, materials, local environment, original manufacturer.
That is why we offer a range of belt cleaners to tackle multiple types of conveyor belts, to ensure we have a solution for almost every scenario, and almost every customer.
KHD Technology has the largest steam-based conveyor belt cleaner range anywhere in the world. Our range of innovative belt cleaners are used globally in various types of production facilities and factories. From dedicated fixed systems to portable belt cleaners, we have a system to handle the widest range of jobs.
The careful use of saturated steam is at the core of every KHD conveyor belt steam cleaning system. KHD understands how to manipulate and deliver steam in dry or wet form to maximise efficiency and effectiveness, without requiring harsh chemicals. Simply hook up the cleaner to a steam generator and start cleaning. Using as little as 10-30 litres of tap water per hour, KHD solutions are designed to be environmentally friendly, and can even be used during food production. We aim to make it quick and easy to slot a KHD system into your existing regime. Our no-compromise approach means we can tailor our steam conveyor belt cleaners to your unique needs. Every system supplied by KHD Technology has been built to the highest design standards, and we are constantly developing new exciting applications and adding to our product offering.
Plastic-wrap, or Shrink-wrap as it is commonly known, features in highly in quick effective securing of many loads, that otherwise, would have stability issues when being moved. Is there an answer to reduce or even possibly eliminate the use of once only plastic wrap?
Historically, pallet straps were used and re-used prior to the advent of plastic-wrap. This is still a potential solution for some, however the use of shrink-wrap is very quick and efficient, but certainly not good when it comes to disposal, especially in current times, when we all trying to make our carbon footprint as neutral as possible, whilst still trying to use an efficient method to secure loads to move about.
Whilst you can put measures in to control the waste generated in your environment, what you may not be able to do is control the waste once it has left your premises.
We produce Elasticated pallet bands, that are a multi-use band, and operates to hold together items in the same manner as plastic-wrap. The use of one or more pallet bands are just as effective in holding uniform loads in position whilst moving otherwise unstable loads, both in the warehouse, and also for use in delivery vehicles. Pallet bands can come in various tensions, and are made to length to suit the application so that there is no compromise. Once removed, they can be re-used for as long as the band is in good working condition. Usually, the webbing is 50mm wide (other widths available up to 70mm), and any circumference loop can be made, using webbing with a 50% or up to 90& stretch. A good example of how tough they are is the deployment in White Goods manufacturing, where they are used to secure 4 x washing machines on one pallet to move around areas of the warehouse as required.
The use of recycled securing products can also reduce the impact on the environment. For instance, we are working with other industry professionals, to offer recycled webbing, that offers close to 100% of its original strength properties, and the production of load rated webbing straps can be rated to offer the same strength as new non-recycled webbing.
Another Eco-friendly product is the highly successful GACK (acronym for our Gas Activated Cargo Keeper) bar. It can be used vertically, or horizontally and has its own rubber feet for maximum versatility for suitable vehicles. That, coupled with the constant pressure applied by the gas strut, keeps the GACK bar in place by applying 120Kg of constant force, to avoid the bar from being dislodged during the course of the vehicle journey Other forms of load restraint bar, get used until they become damaged, and then the whole bar is replaced. The GACK bar has a full complement of spares to keep the bar serviceable for as long as possible. This bar is very popular in the Fresh Produce Market, but can be used anywhere where there is a need to use it in a vertical direction for floor to ceiling security, or used in the horizontal plane in all suitably strengthened (normally refrigerated) box vehicles or trailers.
We manufacture a range of quality Gravity & Pneumatic conveyor products, from lightweight Aluminium channels with 25mm diameter Nylon rollers, to Stainless steel channels using a mixture of Nylon or Steel 50mm diameter roller solutions. Our pneumatic modules can also act as pop up roller conveyor, breaking into an existing conveyor line to pull products off the line to work on or inspect, and then re-introduction onto the main after wards to continue its journey. These can be either from our current range, or made to your specification, tailored to suit your requirements. Whilst we cannot currently offer much in the way of ecofriendly improvements on these particular products, we can make them to a very high standard to aid robustness, thus ensuring that the maximum return of service to avoid premature replacement.
The use of recycled securing products can also reduce the impact on the environment.
Infor®, the industry cloud company, today announced that Oliver Packaging & Equipment Co. — a leading manufacturer of premium food equipment and meal packaging systems — is leveraging its integrated Infor CloudSuite Industrial and artificial intelligence (AI) solution to help provide critical food supplies to senior meals programs (including Meals on Wheels America), healthcare organizations, schools, grocery stores and more.
The integrated solution enabled Oliver Packaging, headquartered in Walker (Grand Rapids), Michigan, to optimize its inventory 30 times faster while boosting customer and employee satisfaction.
“The pandemic created greater demand for packaged meals, combined with supply chain challenges,” said Mitch Summerfield, president of Oliver Packaging. “With Infor CloudSuite Industrial in place, we were able to
We now have a system that has greatly improved our operations, and we’ve seen significant margin improvement simply because we’re able to better project what products we need.
meet these challenges and improve our business significantly across the board — margins, NPS[1] (Net Promoter Score), on-time delivery, and employee satisfaction. Now, with Coleman AI integrated into some of our key processes, we can stretch them even further simply because we’re able to better project what products we need.”
With customer purchase patterns continually changing, Oliver Packaging knew there had to be a better way to
detect these changes so that the right products were delivered at the right time — to improve the bottom line and customer experience.
Leveraging integrated Infor Coleman AI services with Infor CloudSuite Industrial, Oliver Packaging implemented anomaly detection algorithms to identify abnormal customer orders and amounts quickly and more accurately. Daily processing of these anomalies, using machine learning, is delivered to the Oliver Packaging team in a userfriendly dashboard, where it reviews and analyzes the variances for sales and operations to make critical, real-time business decisions.
Implemented in less than 90 days, the AI solution has helped Oliver Packaging realize the following business benefits, in addition to optimizing its inventory 30 times faster to keep pace with shifting customer demand:
• 90 percent reduced employee workload in identifying customer order anomalies
• $1.3 million in revenue variance (across 15 percent of its customers, where the ordered amount was less or more than normal) identified in just two months
• Lower costs by reducing the need to ship more expensive, alternative solutions or to expedite delivery when the right item is not in stock
• Better customer retention, with sales able to quickly contact customers to address new requirements
• Improved customer satisfaction by providing the right product instead of shipping alternative solutions
Oliver Packaging could implement the solution in less than 90 days because the Infor OS technology platform enabled the company to automate the process of collecting, analyzing and consuming data. Customer orders from Infor CloudSuite Industrial are automatically collected and managed in the Infor Data Lake, with integrated services to build, deploy and consume AI-driven insights. The Infor OS platform includes tools for data integration, data management, reporting and analytics, and enterprise performance management, as well as tools for machine learning and AI solutions, so that Oliver Packaging can deploy data-driven applications in weeks instead of months.
As a data-driven company, Oliver Packaging has been closely tracking the company’s return on investment in moving to the cloud with Infor CloudSuite Industrial.
“Every ERP integration has its challenges, but what’s critical is ensuring that you have the right partner with industry expertise to work through those issues,” Summerfield said. “We now have a system that has greatly improved our operations, and we’ve seen significant margin improvement simply because we’re able to better project what products we need. This company is light years from where it was four years ago.”
Four years ago, Oliver Packaging worked with Infor and its implementation partner, Decision Resources, Inc. (DRI), to move to the cloud. Since then, both customers and employees are happier because customers can get the right products at the right time and employees can take advantage of the operational efficiencies now in place. This has resulted in Oliver Packaging achieving:
• A 55 percent increase in on-time deliveries
• A 15-point increase in its Net Promoter Score (NPS)
• A 15-point increase in employee engagement
Watch this video to see how Infor CloudSuite Industrial with Infor Coleman AI is helping Oliver Packaging optimize inventory via anomaly detection and forecasting, while improving customer service, productivity and margins.
Learn more about Infor enterprise artificial intelligence solutions.
Learn more about Infor purposebuilt ERP solutions for industrial manufacturing.
www.infor.com/products/cloudsuiteindustrial
The matt white synthetic paper is suitable for use with all large format, wide edge leading, linerless applications mainly in the dairy, meat and fish industries
Innovia Films has recently extended their linerless label range, and produced a specialist matt white coated BOPP film, Rayoface™ AWPMatt. The film is available in a thickness of 92 micron and has a unique matt white printable surface on one side, and an adhesive receptive coating on the other.
AWPMatt has enhanced stiffness, so is suitable for use with all large format, wide edge leading, linerless applications. From Top & Side, C-wrap, D-wrap labels, through to full wrap and skin pack labels.
“The market for trays made from PE or foam for example is growing globally. Given their ability to shield food from many contaminants, trays are anticipated to see a rise in demand. They serve as a barrier to avoid food waste.” Explains
Alasdair McEwen, Global Product Manager – Labels & Graphics at Innovia Films. “these trays have to be labelled to not only help market the product on the shelf but to provide mandatory information like nutrition facts and recycling guidance.
The enhanced coating technology of Innovia Films means AWPMatt has a matt, paper like surface finish, but the
film gives all the benefits that a high performance BOPP label needs for these demanding applications. AWPMatt has outstanding moisture and water resistance, making it perfect for labelling products such as dairy, meat or fish, which will be part of wet or frozen supply chains.
The print performance of the matt white coating means that the finished label and pack can give the brand a premium on-shelf appearance. This film has already undergone in-depth trialing and shown excellent results throughout the linerless supply chain and is available immediately.
To find out more email labels@innoviafilms.com www.innoviafilms.com
The market for trays made from PE or foam for example is growing globally. Given their ability to shield food from many contaminants, trays are anticipated to see a rise in demand.
DMN-WESTINGHOUSE has invested in a new Rotor Welding Cell (RWC) to modernise production through automation, digitalisation, and optimisation. The cell consists of several robots that can assemble parts into rotors by fully automated welding. This leads to three main advantages for you:
1. Quality: the automated process improves quality repeatability and raises the standard with robot accuracy, leading to great benefits in the next steps of the workflow process.
2. Lead time: several welding steps are combined for labour-intensive product lines, reducing lead time by a week for these rotors.
3. Innovation: this investment opens up improvements in current designs and increased the design flexibility for future product lines.
Watch our video to find out more: https:// www.youtube.com/watch?v=s3hf-eI0olk
Call for inquiries +44 1249 818 400 or email us at dmn.uk@dmnwestinghouse.com www.dmnwestinghouse.com
Maximize your industry output, while maintaining the highest possible standards of safety, hygiene, and cleanability. With our latest MZC-series rotary valves, you can outperform yourself and your competition on any level.
Choose the compact MZC-I for any duty and use its easy-access single opening to keep it clean. Does your industry require the highest possible standards of hygiene? The MZC-II offers you ultimate cleanability through double-sided access to the rotor and valve body. Install the future of safety, hygiene, and cleanability today.
Our MZC-I and MZC-II rotary valves are CE, UKCA, ATEX and UKEX-certified for both dust and gas.
Feldschlösschen is Switzerland’s leading brewery and largest distributor of beverages. The company’s ZERO Accidents strategy aims to reduce the yearly number of safety related incidents to zero by 2030. In order to achieve this, Feldschlösschen and its MHE supplier Jungheinrich decided to install ELOKON’s radio-based proximity detection and warning system ELOshield.
The production facility at the company HQ in Rheinfelden is spread across a number of locations including a basement, meaning that a mix of employees on foot as well as those driving forklifts work in close proximity. The high level of human and motorised traffic poses a heightened risk of accidents, particularly in areas with limited visibility such as thoroughfares and entrances to transfer aisles.
Warehouse Manager Martin Waldmeier: “we wanted to use the latest technology to ensure the highest level of safety in our logistical operations. We chose ELOKON as a partner due to its wealth of experience in the beverage sector which enabled us to offer optimum protection for our workforce. As the products are also OEM-independent, we have been able to retrofit them to our entire forklift fleet.”
The various functionalities of ELOshield were individually configured according to the requirements of specific hazardous zones. If a forklift enters these areas, the ELOshield vehicle module triggers a warning signal and automatically reduces the vehicle‘s speed. Personnel wear or carry personal transponders, which emit acoustic and vibration warning signals whenever a forklift or industrial vehicle approaches. The ultra-wideband technology (UWB) ensures unobstructed
protection as people and vehicles can be promptly detected and alerted in blind spots and through obstacles.
“The ability of ELOshieldSPEED to automatically reduce vehicle speed was particularly important for us,” explains Waldmeier, and adds: “with some of our forklifts moving loads of up to 3.5 tonnes, this not only increases the risk to our staff but can result in costly damage to goods and infrastructure in the case of a collision. We were also very impressed with the ELOshield variants which
allow customised security concepts for different areas.”
Matthias Merklinger, Key Account
ManagerAfter Sales at Jungheinrich sums up: “from initial consultation to commissioning, the ELOKON team was always there for us whenever we needed them. The systems are working perfectly and as a result we have been able to successfully prevent operational accidents.”
As the products are also OEM-independent, we have been able to retrofit them to our entire forklift fleet.”
It’s even safer at Feldschlösschen thanks to ELOKON
PACE Mechanical Handling has been appointed as the first UK representative for Innova’s Stretch Hood pallet wrapping system.
Established in 2001 and headquartered in Castellón, Spain, Innova Group specialises in end-of-line strapping and wrapping, packaging machinery including its Stretch Hood system.
Unique to the UK market, the Stretch Hood system guarantees total protection against humidity, rain and dust due to the tightness of the wrapping and properties of the Stretch Hood film, which envelopes palletised products from above to the base.
As well as being the only system that delivers completely waterproof protection, Stretch Hood uses the minimal amount of film possible, reducing material and energy costs.
Until now, Innova has focused on North America, Mexico and Brazil but turned its attention to the UK after another Spanish packaging machinery manufacturer - TMI Sl - introduced the company to Nick Cesare at PACE Mechanical Handling.
“We have been representing TMI in the UK since June 2022. I think Innova was impressed with how we’ve gone about introducing TMI’s ILERBOX system to the UK and thought we
might be able to do the same with the Stretch Hood system,” says Nick. “Stretch Hood is unlike anything else available in the UK, and we are confident it will replace traditional stretch wrappers due to the way it protects products and reduces both film and energy use. We think it will be popular with packers of all sizes across several sectors, including agriculture, food and beverages, chemicals and cement.
“Stretch Hood complements our range of robotic and automated packing lines in the same way as ILERBOX does, so we are very excited to be appointed as the sole representative for Innova in the UK.” Commenting on PACE’s appointment, Sergio Llido, CEO of Innova Group, says: “For Innova, the UK is a strategic market, and we needed an experienced partner to work with. We chose PACE for their experience, technical team,
market know-how, and all their expertise in packaging and end-of-line projects. Nobody understands the needs of English customers in packaging better than PACE.”
Stretch Hood is the only system that prepares the film precisely to the size of the load to be packaged. The tubular film is slightly smaller than the contour of the load as the Stretch Hood machine stretches and applies the film to fit the dimensions of the load, sealing it completely.
Innova says that the film used by the Stretch Hood system is one of the most advanced materials available, being a multilayer LLPDE polymer composition, offering waterproof protection and exceptional stretching capabilities.
PACE Mechanical Handling has been at the forefront of robotic and automated end-of-line packaging solutions since 1996. The company, based near Spalding in Lincolnshire, specialises in designing and integrating robotic handling solutions to increase productivity.
Thanks to its long-standing partnership with Motoman of Japan, PACE Mechanical Handling offers a wide of robots, from pick and place up to specialist heavy lifting models. With its own fabricators and software engineers and extensive experience in designing and installing complete production lines, Nick and his team can deliver everything from a small automated packing robot to a complete turnkey solution.
For further information about Innova Group and Stretch Hood, visit https://en.innovamaquinaria.com/ stretch-hood/, and to learn more about PACE Mechanical Handling, visit www.robotpalletizing.co.uk
We chose PACE for their experience, technical team, market knowhow, and all their expertise in packaging and end-of-line projects.
When it comes to the Food and Beverage industry, no half measures can be made when it comes to safety and hygiene standards. Tech giants Murrelektronik took this on board when they designed the MVP12 steel distribution box. PIF spoke with Murrelektronik engineers, experts in decentralization installations, about the IP69K stainless steel distribution box and its many advantages.
The MVP12 Distribution Box is extremely hygienic for many different reasons. Firstly, it is made from top-quality stainless steel which makes it easy to clean. It is also resistant to corrosion from high-pressure cleaners and harmful detergents, which is vital within the food processing industry.
Furthermore, the Food and Beverage Distribution Box was designed with no cavities, groove or other small spaces where mold or bacteria can build up, making it even easier to maintain its cleanliness.
Another impressive hygiene-preserving aspect of the Murrelektronik Stainless Steel Distribution Box is that it has a very high IP rating. Whichever stage of the cleaning process you are in, the rating of IP66K, IP67, IP68, IP69K (96 hours) mean that the system will not fail you when you require it the most.
For easy maintenance, look no further than the MVP12 Steel Distribution Box with its LEDs connected right at the ports. Forget about endlessly checking every wire to locate the source of the problem, and save your time especially when working with large systems.
As we mentioned previously, the lack of indentations or grooves in the MVP12 distribution box makes the product extremely easy to keep clean, but the benefits of the design don’t stop there:
• 4-, 5-, 8-, 12-pole
• A-, B-, D-coded models available
• 0.34mm² (AWG22) PP wires
• 0.2m, 0.5m, 1.0m standard wire lengths
• Anti twist protection ensures easy assembly
• IP69K rating
The Food and Drug Administration (FDA) is in charge of the regulations involved in food safety and the hygienic standards that food processing companies are required to meet.
Murrelektronik’s TPE-S, TPE-V M12 Steel and MVP12 Steel cables have been granted this accreditation, highlighting the reliability and prestige of these products.
The hygienic benefits of the Murrelektronik Stainless Steel Distribution Box continue with the revelation of the M12 sealing concept. The connectors, created within a grey mold to make contamination easy to identify, contain a gasket in the MVP12 Steel range that initiates a closed unit.
The connector is then sealed in both an axial and radial direction. This second precautionary level means that the likelihood of any foreign matter penetrating the port is highly unlikely. Murrelektronik goes above and beyond when it comes to hygienic standards, which has earned the company both ECOLAB and UL/CSA accreditations for the MVP12 Steel range.
For more information on the MVP12 Stainless Steel Distribution Box or any of Murrelektronik’s products, give them a call on 0161 7283133 or email them at info@murrelektronik.co.uk.
Machine components and installations in the F&B industry have to be easy to clean. Routing cables to meet the requirements for cleanliness often requires a lot of effort. The MVP12 Steel distribution box is the new benchmark for simplified installations. Its hygienic design and stainless steel housing
meets F&B industry requirements. The built-in spacer enables easy and quick cleaning while the FDA compliant homerun cable replaces up to eight individual cables. Murrelektronik also offers connectors specifically for the F&B industry that are made with your choice of stainless steel or gray molding.
Hygienic Design
• FDA® compliant cable
• V4A housing
• Application-specific design
Lasting protection
• IP69K Rated
Quicker Installation
• Plugged connections
• Factory tested products
• Cable routing requires less effort
Environment Social Governance (ESG) is part of the Leuze company strategy. For Leuze, growth means taking responsibility - for the environment and society, too. In this context, The Sensor People have achieved an initial goal that they were aiming for: the company is CO2 neutral in Germany since 2022.
As part of their growth strategy, Leuze had set the target to become CO2 neutral in Germany by the end of 2022. To do so, the company first examined its direct emissions and on this basis, it optimized the issues that were identified: thanks to comprehensive investment in new buildings and the modernization of existing buildings, it was possible to achieve a substantial reduction in energy consumption. Leuze was also able to significantly improve its energy efficiency in production: this was due to a massive expansion of its own renewable energy generation using photovoltaics, among other measures. As a result, The Sensor People were able to reduce last year the purchase of electricity from external sources by about half. Leuze has been using 100% green electricity by external electricity for years. Some of this is supplied by Leuze’s own, leased hydroelectric power stations. The vehicle
fleet has also been optimized: hybrids and fully electric company cars are already in use. And more will follow. In addition, Leuze provides charging stations to its customers and employees. The company also offers its employees “Job-Rad” (bicycle to work), and opportunity to charge e-bike batteries at the company.
In order to avoid direct CO2 emissions, Leuze supports an international forest protection project in northern Brazil on approx. 148,000 hectares. This is not related to reforestation but is a project that supports the preserve the rainforest as a natural CO2 store. The forest protection project saves emissions by avoiding the deforestation of the jungle.
Sustainability remains firmly on the agenda For Leuze, it is not enough to avoid direct emissions. As an international
company, The Sensor People also want to make a contribution to more sustainable management worldwide. Therefore, it also includes checking the indirect mission in the supply chain. With most companies, these make up a large part and are more difficult to implement. In this context, the question arises: where do the components come from? How and in what conditions are they manufactured? Do these reflect Leuze’s ethical and ecological ideas? What does this mean in terms of competition?
In order to get answers and initiate improvements, Leuze carries out regular audits, not only in Germany but also in manufacturing countries such as Asia.
Further, Leuze also plans to become CO2 neutral on the product side. For this purpose, individual new sensor series are already being considered in the sense of the “cradle to cradle” approach. In this context, The Sensor People check to what extent a specific product contributes to CO2 emissions and what this means for system operators with Leuze sensors.
In order to avoid direct CO2 emissions, Leuze supports an international forest protection project in northern Brazil on approx. 148,000 hectares.
Goals 2022 achieved: thanks to improved energy efficiency, Leuze has taken the step to become a CO2- neutral company in Germany. Indirect emissions in the supply chain will also be examined going forward.
ViSWIR Hyper APO Features:
• Capable of fully corrected focus shift in visible and SWIR range (400nm - 1700nm)
• Achieves spectral imaging with a single sensor camera by simply syncing the lighting
Floating design adjusts focus for different wavelengths
8mm, 12mm, 16mm, 25mm, 35mm* and 50mm* (*2023)
ViSWIR Lite Features:
• High transmittance at whole wavelength of 400nm - 1700nm by adopting hyper wideband AR coat
Outstanding cost-performance for single-wavelength lighting & narrow-band imaging Compact design
5mm, 8mm, 12mm, 16mm, 25mm, 35mm, 50mm
MORE THAN 70,000 STANDARD COMPONENTS
THE BIG BOOK GREEN
n Get your copy of THE BIG GREEN BOOK easily online.
n More than 70,000 standard and operating parts from one place: simply ordered - delivered immediately.
info@norelem.co.uk
www.norelem.co.uk
Live event scheduled 9th March 2023 will discuss the damaging nature of glass-in-glass contamination for food manufacturers and how x-ray inspection can help to mitigate these risks
Mettler-Toledo Product Inspection is running a live webinar on 9th March 2023 (08.00 and 14.00 GMT) to explain how advanced x-ray inspection systems can detect a wide range of foreign body contaminants in glass-packaged products. Experts will describe how x-ray technology can detect glass within glass packaging resulting in improved consumer protection and less costly product recalls for manufacturers.
The free webinar – titled “Glass-inGlass Detection with X-ray Inspection”–will be presented by Adam Green, Market Manager, X-ray Inspection, Mettler-Toledo. Green explains the importance of the webinar, “Glass packaging is a common choice for food and pharmaceutical manufacturers, but a single shard of glass can lead to devastating consequences. That’s why it’s vital to protect your product by selecting the right x-ray inspection system for optimum contamination detection. This will be an informative session, packed with the solutions manufacturers require, alongside realtime demos, to help alleviate some of the risks facing their businesses”.
In the webinar, Green will look at the basic principles of x-ray inspection technology and how they can help in significantly reducing the risk of glass-in-glass and other foreign body contamination. He will also discuss the importance of choosing the right x-ray beam technology for your application, while giving a live demo of the MettlerToledo X3750 X-ray Inspection system.
The webinar will look specifically into six key areas among glass-in-glass detection, including:
• Risk of Glass in Glass - the significant safety risk imposed and the effects of glass-in-glass contamination
• Challenges with Detecting Glass in Glass – the issue with how foreign bodies and potential contaminants can “hide” anywhere in glass
• Test Piece Importance – the importance to understanding the different test piece types
• X3750 Benefits & Live Demonstration – from adjustable angle inspection beam to an FDA Approved Modular
Conveyor, an in-depth look at what makes the X3750 a viable solution for manufacturers
• Factory Integration – new software methods and easy connectivity
• Service & Warranty – a look at the different care packages and warranties on offer
A live, interactive Q&A session will bring the webinar to its conclusion. To register for the webinar: click here
Experts will describe how x-ray technology can detect glass within glass packaging resulting in improved consumer protection and less costly product recalls for manufacturers.
Wavelength: 525nm
Power out of the ber: 1W 4W
Fiber: core 105μm, NA=0.22, detachable, connector FC/SMA905
External beam homogenizer: optional
Operating temperature: -40degC + 55degC
Dimensions: max 72mm x 44mm x 21mm
Applications: Remote illumination, Target designation
Eye-safe passively Q-switched
High peak energy up to 700μJ
Miniature dimensions: 21 ~ 35mm x 8mm x 7mm
Applications: laser range-nding, laser imaging, surveying equipment
Wavelength: 520nm, 555nm, 577nm
Power output: 5mW 1W
Dimensions: Ø18mm x length 55mm
Operating temperature: -40degC + 50degC
Applications:
Industrial: pointing, alignment, semiconductor inspection
Biomedical: photoluminescence microscopy, intravital imaging
Clinical Medicine: robotic surgery, endoscopy
Wavelength: 520nm
Output power: 850mW
Dazzling distance: adjustable, 3m to 30m
White LED tactical light incl.
Rechargeable battery with 5000mAh
Operating temperature: -20degC + 50degC
Protection standard: IP65
Weight: 800gr
Application: Dazzling equipment for police, special forces and border patrol
1998: the Google search engine was launched, Cher’s Believe was the UK’s best-selling single of the year, Arsenal won the Premiership title – and tray sealing specialist Proseal produced its very first machine.
Since then, the company has grown to become the world leader in tray sealing technology and an expert in the design and installation of complete packing line solutions. Today Proseal has nearly 600 employees worldwide and alongside its near 250,000 sq ft manufacturing headquarters in Adlington, UK, has manufacturing facilities in the USA and Australia and a worldwide network of distributors. The company became part of the JBT Corporation in 2019.
Founded by Steve Malone and Robbie Hargreaves in a small unit in Bollington, Proseal launched its first tray sealer, the PR30, now known as the GTR, in May 1998. This was the start of a series of ground-breaking tray sealing solutions
from the company that revolutionised the top sealing of trays in a variety of sectors including ready meals, meat and poultry, petfood, plant-based protein and, most notably, soft fruit. Indeed, the company estimates that as much as 95 percent of top-sealed trays in this sector in the UK are sealed on Proseal machines.
In the past 25 years, Proseal has developed a comprehensive range of products to meet all types of customer and market requirements, diversified its offering into complementary equipment including conveyors and case packers, and introduced a variety of technical innovations, such as its unique E-sealing
and Pro-Motion technologies, alongside a number of patented developments.
To date, the company has manufactured 6,000 machines for nearly 3000 customers worldwide. Staggeringly, if all the Proseal machines produced to date were placed on top of each other, they would stand at a vertical height of around 12,500 metres – nearly one and a half times the height of Mount Everest.
Alongside its technical expertise, a key reason for Proseal’s success has been its commitment to exemplary customer service. The company’s ability to deliver customised solutions to meet the individual requirements of every customer has been supported by its comprehensive support services, with engineers on hand 365 days a year, 24 hours a day, to provide a fast response whenever needed to avoid unnecessary downtime and ensure packing lines can continue to operate to maximum efficiency.
More recently, this has seen the introduction of the company’s innovative preventative maintenance programme, PRoCARE.
Proseal has also supplied nearly 200,000 spare parts and undertaken over 50,000 service visits.
The company has always been quick to adapt to changing market trends. For example, the future proof designs of its tray sealers mean that the machines can be easily adapted to handle trays in different formats and materials, in particular the switch from plastic to board and pulp alternatives, allowing Proseal to be at the forefront of sustainability movements.
Other innovations have included the launch of the Proseal Test Kitchen. This provides customers with access to a wide variety of testing machinery, allowing them to carry out shelf-life trials and seal integrity testing in order to facilitate smooth product launches without the need to invest in their own materials
and equipment. Since inception, The Test Kitchen has already hosted over 3,000 customer trials since it was first established in 2018.
“A huge congratulations to the entire Proseal team on reaching this 25year milestone,” says David Wright at Kershaws Frozen Foods.
“As Proseal’s longest-standing customer, Kershaws Frozen Foods was the very first company to invest in the Proseal PR30, back in 1998. Two and a half decades later and our partnership remains strong, as Proseal continues to deliver the same quality and efficiency to our production and packaging operations as it has done since day one.”
Dubbed Proseal’s ‘Number 1 Customer’, David says it has been an honour to witness Proseal’s growth over the years and invest in the company’s marketleading equipment.
Proseal’s expertise has also been acknowledged over the years by a number of award wins. These include the prestigious Queen’s Award for Enterprise in 2018 and last year, the AgTech Breakthrough Awards for Food Tech Equipment of the Year, beating more than 1,600 nominees across the global agricultural and food technology industries with the introduction of the case packer family of products.
“One of the main reasons behind Proseal’s success has been its determination to remain true to the values of technical and service excellence that were the foundations on which the business was first established,” said Jon Garner, President, JBT Packaging Group.
“The 25th anniversary is a testament to the company’s unparalleled expertise and innovative talents within the business. We congratulate each and every member of the team on their unique contribution in helping us to reach this milestone. We will continue to drive the business forward to further success and growth, working in partnership with our customers in the development of high-quality packing equipment to meet the changing needs of the many different markets and countries we serve.”
Proseal will mark the anniversary with a special open day at its UK headquarters this summer for both customers and team members, past and present.
www.proseal.com
One of the main reasons behind Proseal’s success has been its determination to remain true to the values of technical and service excellence that were the foundations on which the business was first established,
LogiDrive is an energy-efficient, service-friendly and standardised modular system for many different requirements and purposes Image: NORD DRIVESYSTEMS
With the LogiDrive solution space, NORD DRIVESYSTEMS offers a wide portfolio of perfectly matched drive solutions, which meet many different requirements and purposes – be it energy efficiency, variant reduction, cost-effectiveness or flexibility.
LogiDrive is a standardised modular system. Depending on the demand, different NORD products are combined into one drive solution, which is 100% tailored to the respective industry standards and application requirements. The extended LogiDrive solution space is intended for conveyor applications in the fields of post & parcel, airport and warehouse, and comprises one advanced variant with IE5+ synchronous motor technology and a basic variant with IE3 asynchronous motors.
All LogiDrive systems are extremely easy to maintain and install thanks to plug-and-play technology. The entire system has a modular design, so that that all components of the drive technology can be individually serviced. This minimises maintenance and repair costs. All connections are made using simple plug connections while integrated maintenance switches and manual control switches ensure a high level of userfriendliness.
The compact design saves space and is light in weight thanks to the aluminium housing. Due to the motor design and the frequency inverter operation, the same motor variant can be universally used worldwide.
DuoDrive: Seamless integration of gear unit and motor The patented DuoDrive from NORD DRIVESYSTEMS is a revolutionary integrated gear unit/ motor concept that covers power ranges of up to 3 kW. It combines the high-efficiency IE5+ motor and a single-stage helical gear unit in one housing.
The seamless integration of the gear unit and motor into one drive system is a quantum leap and sets new standards with regard to user-friendliness and efficiency.
Not only in times of rising energy prices is energy efficiency one of the most important goals of industry.
Highly efficient components from
NORD DRIVESYSTEMS help to reduce the energy consumption of drive systems. Additionally, the drive specialist offers its customers energy-related advice. “We help our customers to save energy”, is how Jörg Niermann, Head of Marketing, sums up one of the major guidelines of NORD DRIVESYSTEMS. NORD sets new standards with the IE5+ synchronous motor, integrated into the DuoDrive system, which achieves an efficiency of up to 95% – one of the highest efficiencies in this power class in the market.
NORD DRIVESYSTEMS will present these and more drive solutions from 25 to 27 April 2023 at LogiMAT in Stuttgart. You will find the company at Stand 3C41 in Hall 3
User-friendly plugand-play technology
All LogiDrive systems are extremely easy to maintain and install thanks to plug-and-play technology.
NotCo, a global foodtech company and key player in the plant-based food sector, has announced its partnership with SIG and is launching NotCreme and NotMilk High Protein products in SIG carton packs. The partnership with SIG strengthens the company’s expertise and flexibility in the plant-based food sector. NotMilk Original, zero-sugar, semi-sugar and chocolate milk products will also be available in aseptic carton packs from SIG.
NotMilk High Protein products in the flavours chocolate, vanilla with coconut and peanut butter, all with 15g of protein, are filled in SIG’s combismile 250 ml aseptic carton packs. The combismile carton pack offers a convenient drinking experience. With its curved, modern shape and easy-grip corners, combismile is easy to use onthe-go, and is designed to stand out on retail shelves. NotCreme is available in combiblocMini 200 ml.
Renata Kasahara, Head of Marketing
America South at SIG: “With our agile and flexible filling system, we are able to offer high flexibility combined with speed. Our customers can respond efficiently to any trends that are shaping the market. Both NotCo and SIG are strongly committed to sustainable innovation and constantly looking for solutions that cut the environmental impact of food and beverage packaging even further”.
SIG’s high-speed filling lines are highly flexible with waste rates of less than 0.5% and offer high productivity – aspects that contribute to the sustainability strategies of both companies. Both are committed to
ensuring healthy and safe food with less impact on the environment through technology and innovation.
SIG works in partnership with customers to bring food products to consumers around the world in a safe, sustainable and affordable way. This includes many brands in the plant-based beverage sector, a product category that is experiencing strong growth in many regions of the world, as a result of increasing consumer demand for healthier products with a lower environmental impact.
According to the research “Plant Based Foods Poised for Explosive Growth”, published by Bloomberg Intelligence, plant-based foods are expected to account for 7.7% of the global protein market by 2030, valued at US$162 billion.
Visit us on www.sig.biz or on our blog at sig.biz/signals
With its curved, modern shape and easy-grip corners, combismile is easy to use on-the-go, and is designed to stand out on retail shelves.
NotCo expands product portfolio with carton packaging solutions from SIGPhoto: SIG
Engineers and technicians working in the food and drink processing and packaging industries are well aware of the possible consequences of tools going missing. Foreign object damage (FOD) is a threat in any manufacturing or line maintenance workplace, especially those where food or drinks are being produced.
Keeping track of every tool and item of equipment presents a major challenge, making professional tool storage and management more important than ever. Snap-on Industrial’s Level 5™ automated tool management system constantly tracks every tool, advising with voice announcements which tools have been removed or when they are returned, ensuring greater protection against FOD.
It also enables engineers and technicians to find every tool they need quickly, saving time and easing stress.
Major benefits of the system include:
• No individual tool scanning required;
• No RFID tags to install or replace;
• No limitations on tool size: from ¼” screwdriver bit upwards;
• Intuitive interface, via touchscreen;
• Audible voice confirmation of tool removal and replacement;
• Automatic locking for maximum security;
• Errors announced and displayed to indicate incorrect tool position or advise when a drawer is not closed.
Says Richard Packham, Director UK & Europe for Snap-on Industrial: “Snap-on’s automated system takes tool management to an entirely new level. The ability to monitor several boxes from one central computer offers managers a huge time saving advantage.”
For more information visit: www.snapon-industrial.co.uk; call (01536) 413904 or e-mail: indusrialuk@snapon.com
Parker Bioscience Filtration – part of Parker Hannifin, the global leader in motion and control technologies –has launched a portable filter testing solution, Valairdata 4, which verifies the integrity of sterile gas filter systems and supports the food and beverage sector in reducing the risk of airborne contamination.
Valairdata 4 is a fully automated, aerosol challenge integrity test unit that has been developed to provide fast and reliable filter integrity testing in-situ, enabling operators to quickly identify any filter failures with minimal disruption to aseptic process operations. It is the latest in the series of Valairdata solutions developed by Parker and features updated software and functional design enhancements to improve ease of use.
The new version is lightweight and portable, with a long battery life. It has been ergonomically designed to allow users easy access to connection ports and includes a handle that can be folded away during testing. Valairdata 4 has multi-language menu availability and is supplied in a carry case for portability, enabling it to be deployed throughout a facility.
The Valairdata 4’s aerosol challenge is fully correlated to aerosolized bacterial and viral challenges and has been designed as an accurate, reliable method for detecting gas filter integrity. Test details are securely stored within the unit in accordance with FDA 21CFR part 11 requirements. Test results from the Valairdata 4 aerosol challenge are available within seconds and the filter can be introduced back into process immediately after testing, with no flushing or drying required. Once testing
is complete, the results are easily transferred from the unit via a USB data stick for easy tracking, storage and transfer of test data. A stand-alone printer has also been introduced to the Valairdata 4 solution, which can help users save time on data transfer.
Mark Richardson, Product Manager –Food and Beverage, of Parker Bioscience Filtration, said: “We are excited to be introducing Valairdata 4 to the market. Valairdata 4 builds on the success of its predecessor, Valairdata 3. Several improvements have been made
which improve both its useability and portability, and its design utilizes more than 50 years of experience in the provision of sterile air and gas filtration solutions.”
Richardson continued: “It will help operators in the food and beverage sector to ensure that production can run without contamination from airbourne sources, and help them meet production standards, eliminate wastage and increase profitability, for increased process control and protection.”
With five decades of experience in working with the international food and beverage sector, Parker Bioscience Filtration offers a wide range of filtration solutions that ensure product quality, while maintaining the lowest cost of ownership.
For more information about Valairdata 4, please visit www.parker.com/v4
It has been ergonomically designed to allow users easy access to connection ports and includes a handle that can be folded away during testing.
We look forward to this April when the industry comes together at the UK Food & Drink Shows, encompassing Foodex Manufacturing Solutions, Farm Shop & Deli Show, Food & Drink Expo and National Convenience Show.