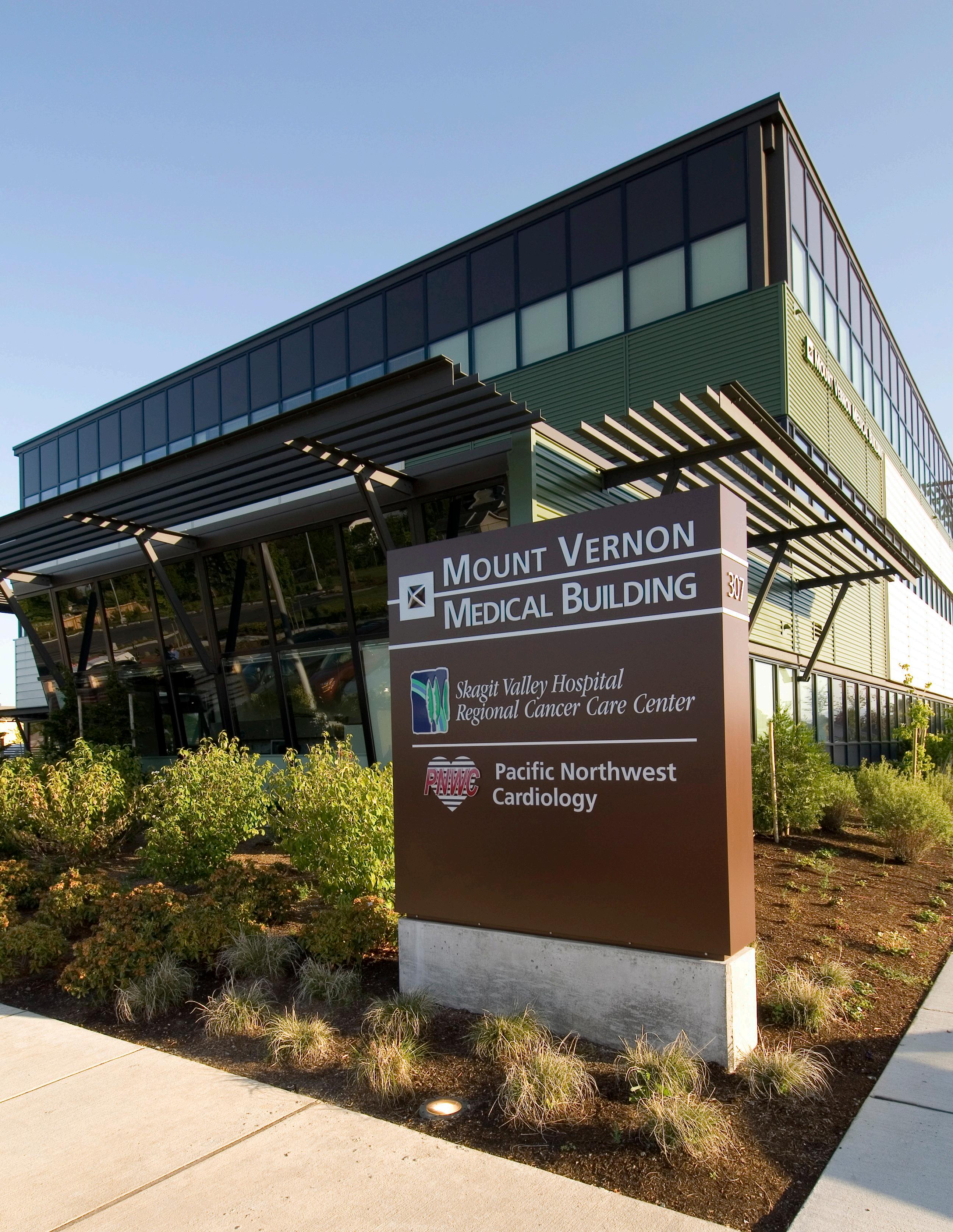
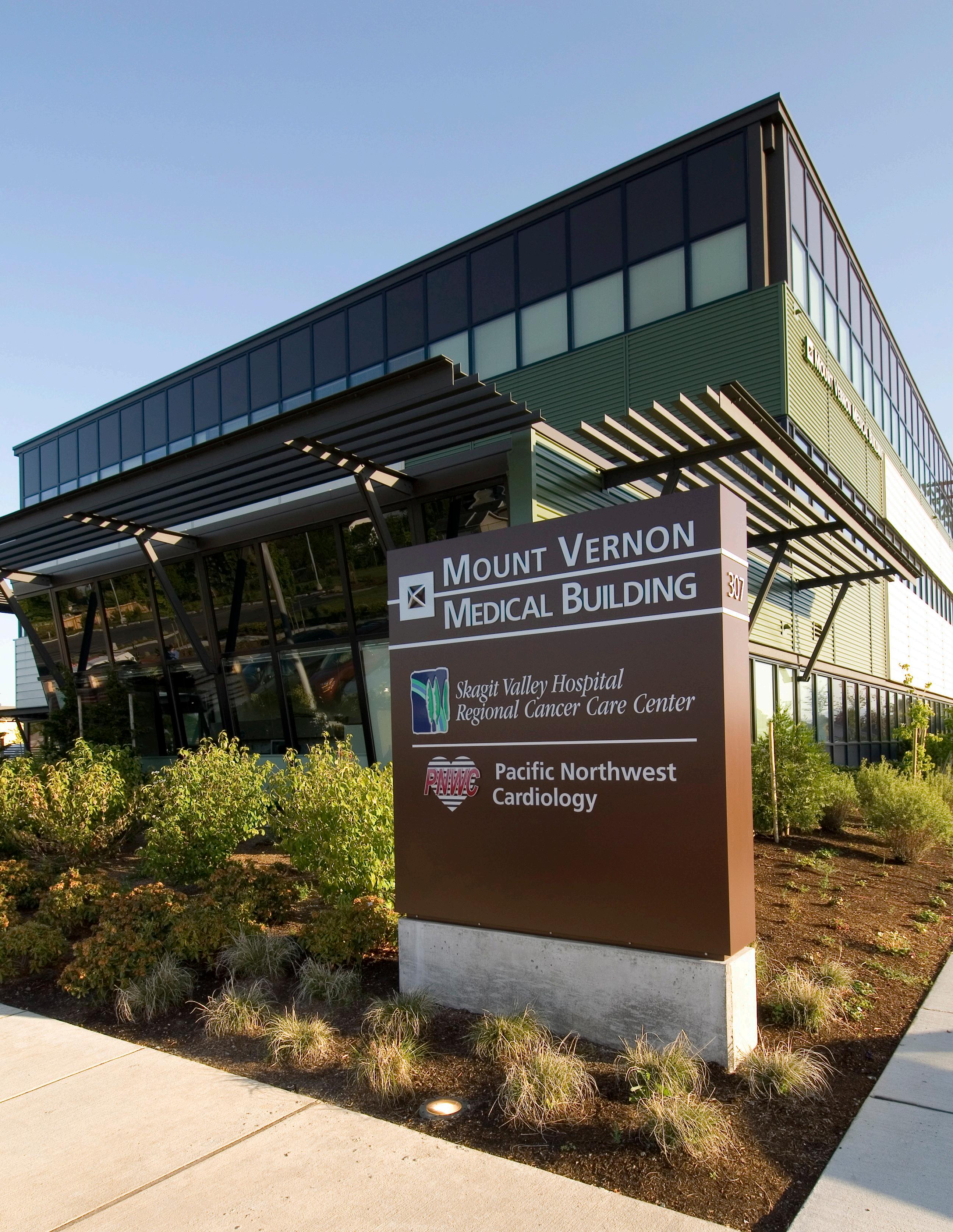
SERVING OTHERS
SINCE 2005
COMMITTED TO INTEGRITY WE ARE OneJTM
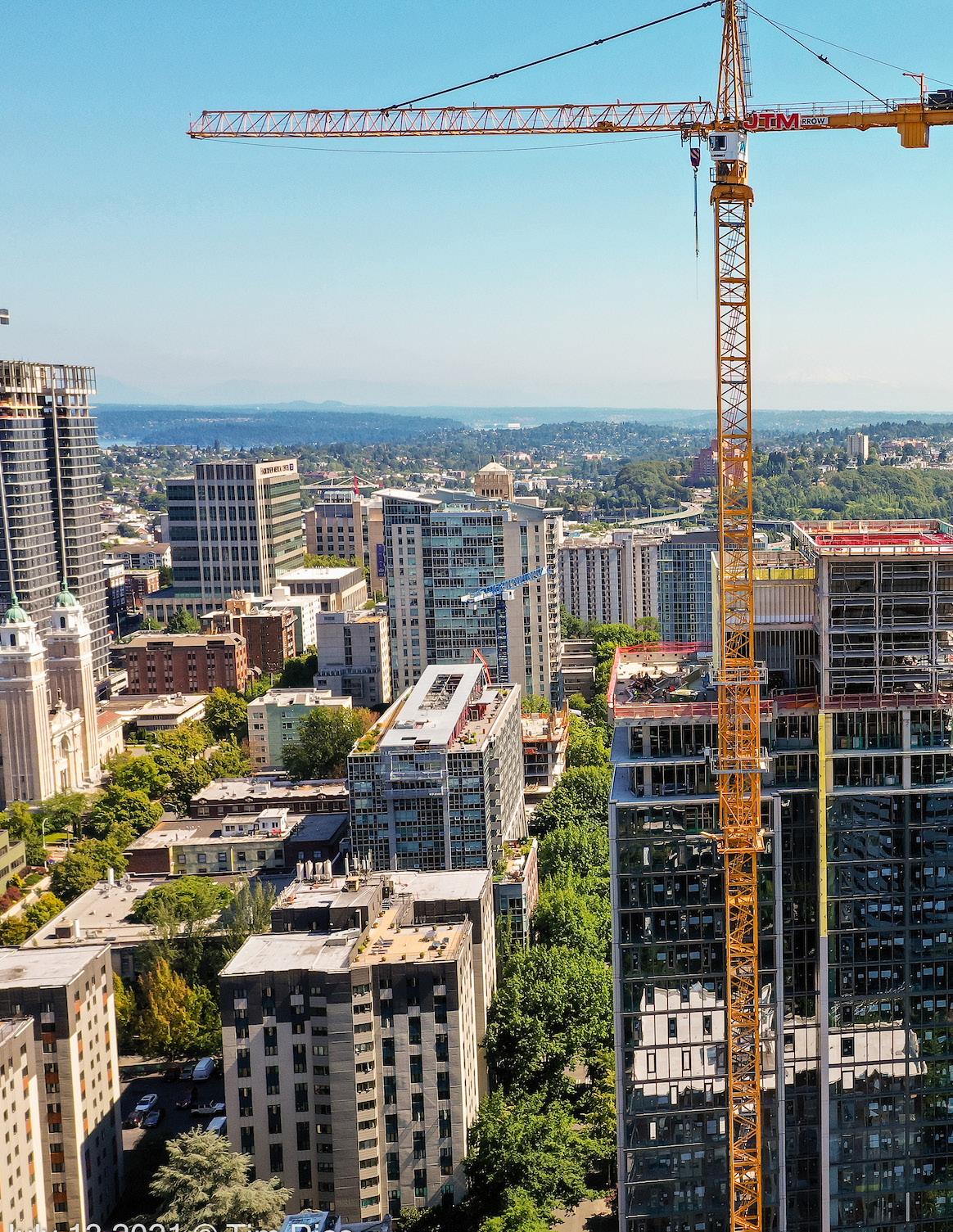
Formed in 2005, JTM was founded with the belief that outstanding project delivery should be the rule, not the exception. From the beginning, JTM has exceeded expectations, cultivated our hard-earned reputation for quality, and developed a proven foundation based on relationships, trust, respect, and performance. At JTM, we deliver on our commitments and our promises. Leadership is hands-on and actively engaged with all our projects, ensuring every team is set up for success while keeping our clients’ best interests at heart as we build their vision.
We are builders, focused on forming long-term client relationships, and committed to integrity in everything we do. The JTM team is passionate, energetic, innovative, and entrepreneurial. Our experience, size, and structure enable us to excel on construction projects of any size or complexity.
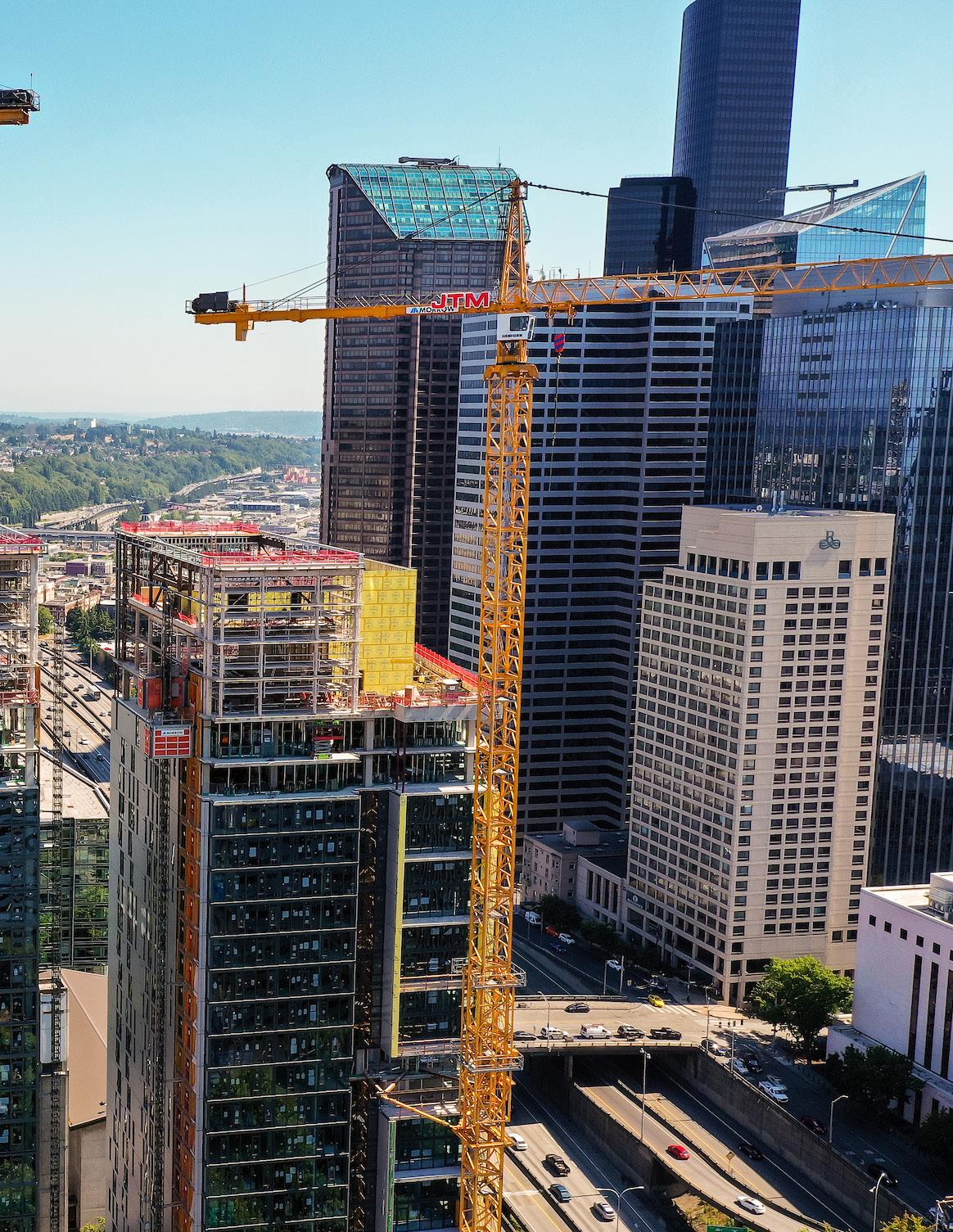
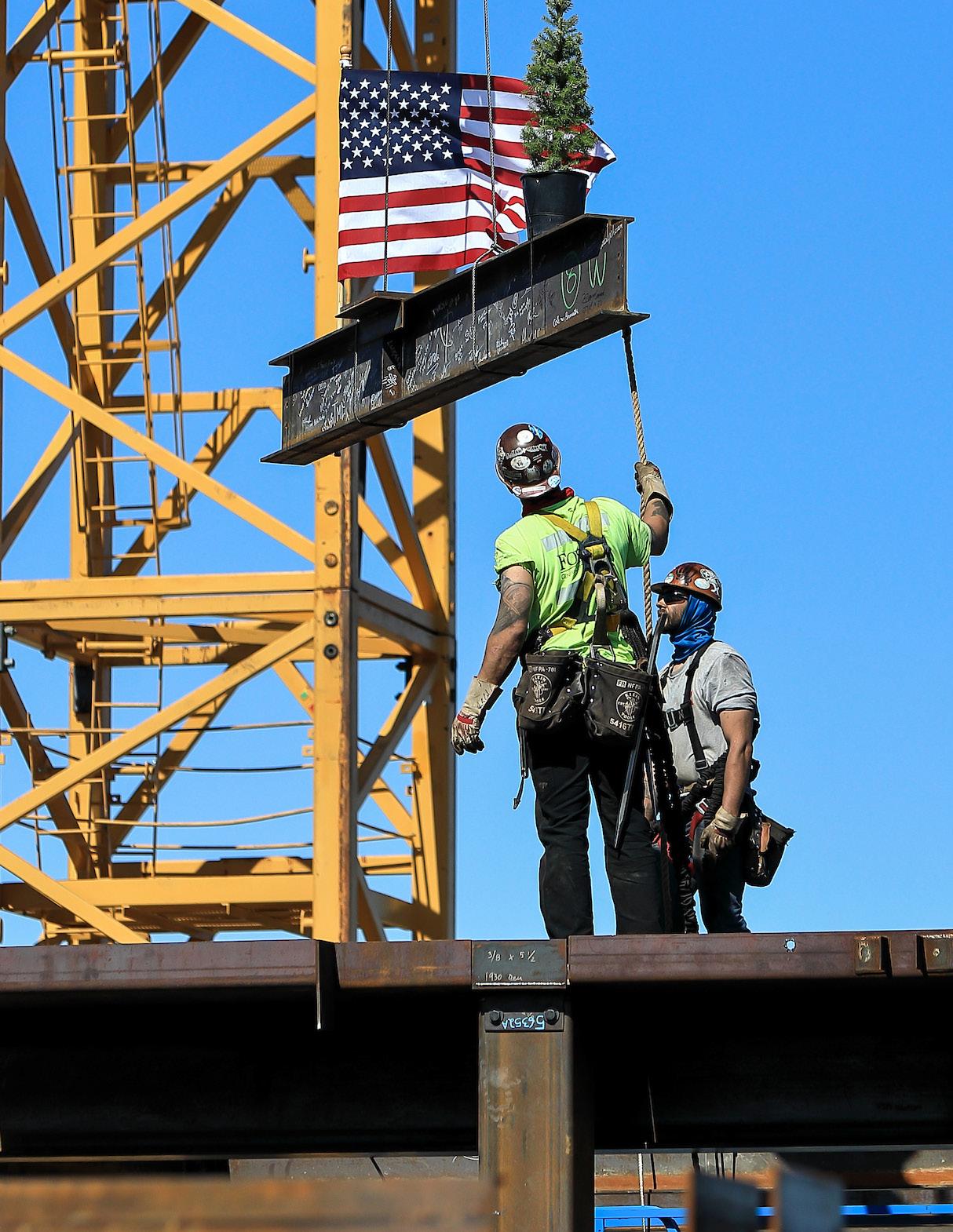

FUELED BY A PASSION TO BUILD
ABOUT JTM
The founders of JTM established our general contracting firm, which has drawn from over 100 years of combined experience in the construction industry. From the outset, they set out on a shared vision to cultivate a company culture akin to a family, placing high value on relationships and meaningful connections with all stakeholders while upholding principles of integrity in all actions. Backed by extensive expertise, strong self-performing capabilities, and cutting-edge technological resources, our focus lies on providing outstanding preconstruction and construction services within a collaborative team setting.
OUR VALUES
SAFETY
We protect our people and the community like family.
INTEGRITY
We take pride in relationships built on trust and reinforced by our actions.
INGENUITY
We empower our people to challenge convention.
ENERGY
We bring passion and enthusiasm to our work and celebrate client, project, and individual successes.
ACCOUNTABILITY
We deliver on our commitments.
COMRADERY
We support each other as colleagues and friends.
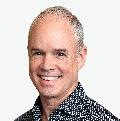
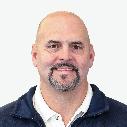

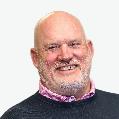
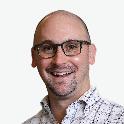
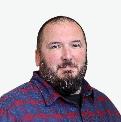
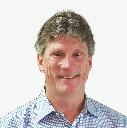
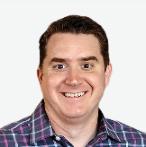
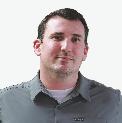
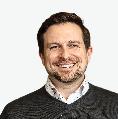
KYLE M. DAVIS Dir. of Preconstruction & Estimating Construction Technology
Preconstruction
JAMES HARBIN Dir. of Construction Tech
Precon Managers
Survey Superintendent VDC / BIM Manager
Estimators
Survey Team VDC Coordinators
JUSTIN MOLOCZNIK Dir. of HR and Safety
Safety Managers Safety
Sr. Safety Manager
Safety Engineers
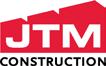
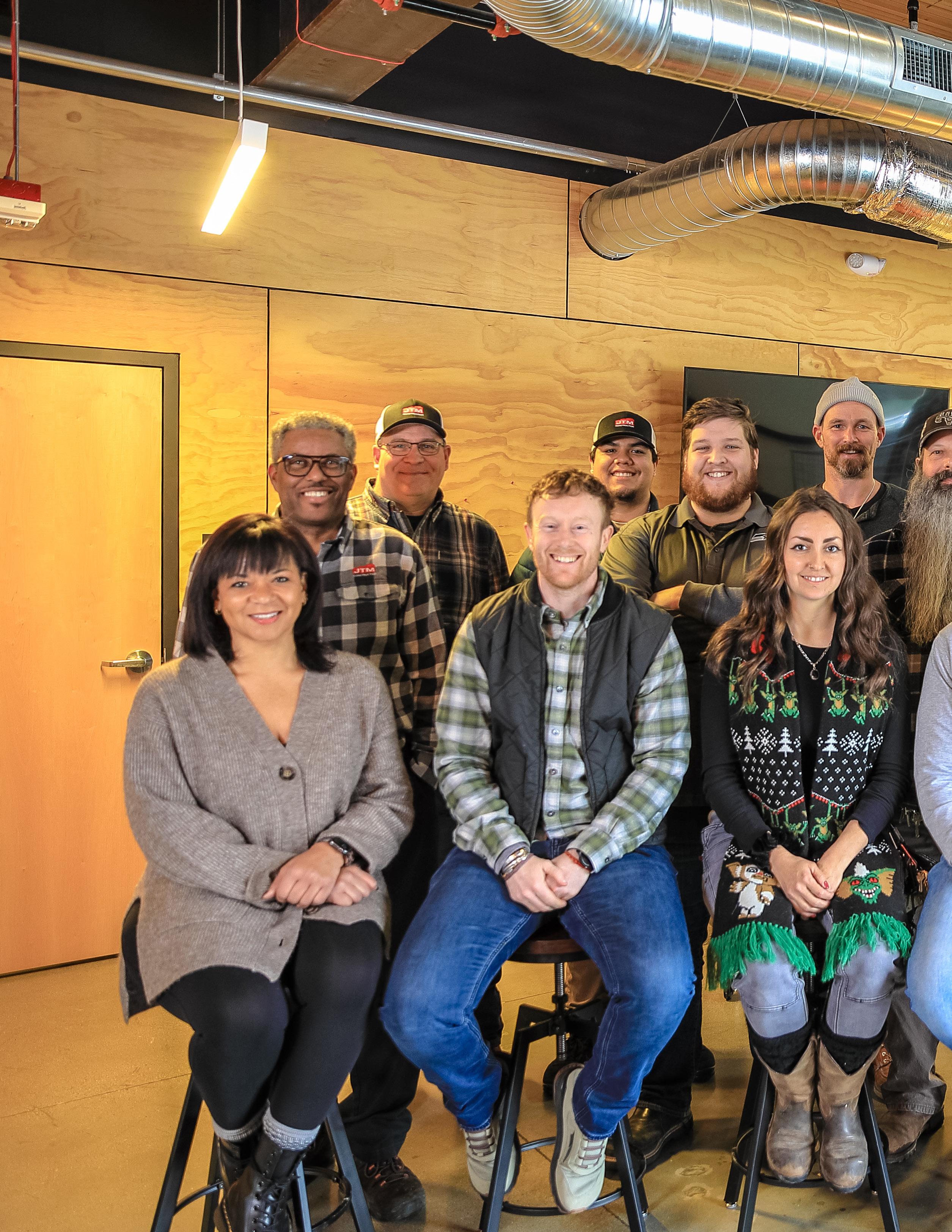
OUR TEAM HAS THE KNOWLEDGE
AND SKILL SET TO EXECUTE COMPLEX WORK IN CRITICAL AND OCCUPIED ENVIRONMENTS
At JTM Construction, we prioritize the quality and experience of our project teams as key drivers of project success. Our firm is dedicated to ensuring senior leadership remains actively engaged in every project phase, facilitating seamless coordination between the preconstruction and construction stages. Drawing on their wealth of experience, our team members work diligently to achieve project budget and constructability objectives.
Our builders at JTM embody extensive industry experience and have successfully navigated some of the Puget Sound region’s most intricate construction sites. With a team of long-serving employees, we bring knowledge to each project we undertake. Our teams are well-equipped to fulfill our commitments and tackle any challenges that may arise. Each team member possesses a unique skill set and disposition that aligns perfectly with the needs of our clients. Whatever your project demands, we are confident that our team members have the expertise to meet and exceed your expectations.


JTM HAS BEEN AMAZING TO PARTNER WITH. THEY DO HIGHQUALITY WORK AND COMMUNICATE WELL THROUGHOUT EACH PHASE OF THE PROJECT. THEY HAVE ALWAYS MET TIMELINES AND BUDGETS FOR OUR PROJECTS AND PRIORITIZED OWNER SATISFACTION AND SAFETY. I CAN’T RECOMMEND THEM ENOUGH.
Travis Duncan, Mirabella Retirement HomeTROY BLOEDEL CHIEF OPERATING OFFICER
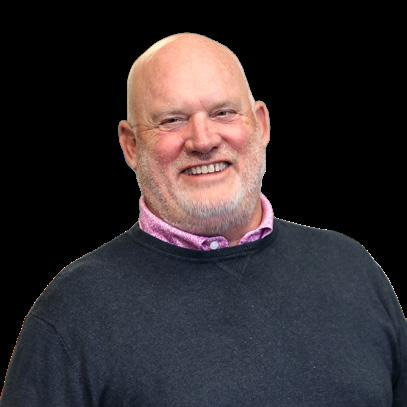
EDUCATION | CREDENTIALS
Studied Construction Management & Mechanical Engineering, University of Portland
As COO, Troy is a builder at heart. He brings 35 years of experience to all projects, from preconstruction to construction, and he has proven expertise in the healthcare field. Troy is well-versed in budget management, timeto-market strategies, and constructability and is knowledgeable in alternative delivery methods such as design-build, VDC, and BIM.
KYLE NEVILS VP OF PROJECT MANAGEMENT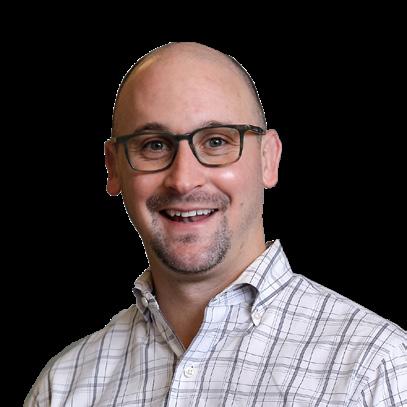
EDUCATION | CREDENTIALS
BS Construction Management, Washington State University
Kyle’s outstanding track record of delivering large, complex, ground-up projects can be attributed mainly to the partnerships he has formed over his 15-year career with our clients and design team members to work in unison through all project phases. He focuses on each team member’s definition of a successful project and uses those definitions to help drive meaningful decisions.
JIMMY CRAIG ASSOC. DBIA, LEED AP CRITICAL ENVIRONMENTS DIVISIONS MANAGER

EDUCATION | CREDENTIALS
BS Construction Management, University of Washington
Jimmy manages fast-paced schedules and budget-driven projects. He built the critical environments group to be agile and flexible, able to scale up and down to meet the client’s objectives. As a leader with over 15 years of experience, he brings his personal attention to the client and their project, identifying potential problems and working through the solutions.
PROJECT EXPERIENCE
» Virgina Mason University Village Medical Center, Seattle, WA*
» Discovery Hall, Bothell, WA*
» First Hill Medical Pavilion, Seattle, WA*
» ICHS Bellevue Clinic, Bellevue, WA*
» Meridian Center for Health, Seattle, WA*
* Experience prior to JTM
PROJECT EXPERIENCE
» UW Valley Medical Center, Renton, WA
» Valley Medical Center Radiation Oncology Shielding, Renton, WA
» Tacoma General Hospital Center Utility Plant, Tacoma, WA
» Weyerhaeuser HQ at 200 Occidental, Seattle, WA
» Stadium Place, The Nolo & The Wave, Seattle, WA
PROJECT EXPERIENCE
» Seagen B5 Assay Lab, Bothell, WA
» Valley Medical Center Radiation Oncology Shielding, Renton, WA
» Inbios Clean Room Expansion, Seattle, WA
» Zymeworks Lab TI, Seattle, WA
» Zymogenetics Microbial Manufacturing Facility Bothell, WA
» MHSC UW RR Wing Neurological Surgery Remodel, Seattle, WA
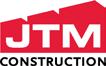
KYLE M. DAVIS ASSOC. DBIA, LEED AP DIRECTOR OF PRECONSTRUCTION AND ESTIMATING
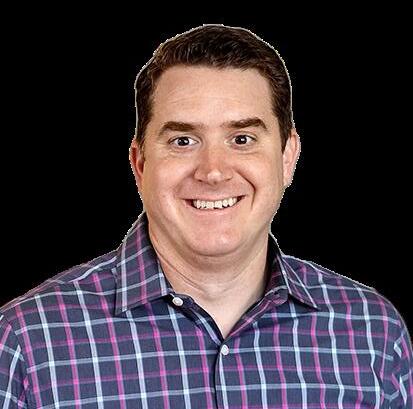
EDUCATION | CREDENTIALS
BS Construction Management, University of Washington
Kyle brings our clients 20 years of experience and best-in-class preconstruction services through constructability, market research, and detailed estimates. He leverages his expertise to successfully tee up projects before the shovel hits the ground to the GMP, completing the project and working hard and creatively with the owners and design team to complete the project successfully and on budget.
RESPONSIBILITIES
» UW Medical Valley Medical Center, Renton, WA
» Scripps Mercy Cancer Center and Garage, San Diego, CA*
» UCSD Thornton Hospital Frozen Section, San Siego, CA*
» Scripps Chula Vista 4th Floor, Chula Vista, CA*
* Experience prior to JTM
BRYDEN MATHIS PROJECT MANAGER
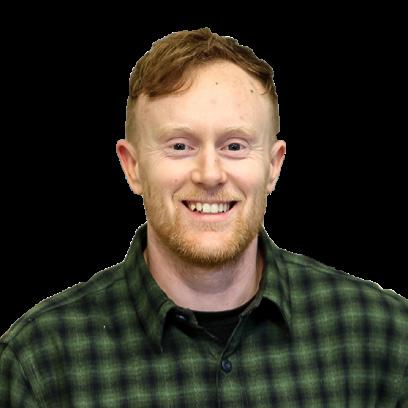
EDUCATION | CREDENTIALS
Bryden is a detail-oriented, client-focused, results-driven project manager. Over his 10-year career, he has successfully constructed multiple projects of varying sizes, from shell and core, tenant improvements to occupied buildings, life science, health work, and interior build-out work, ensuring each meets client requirements and is completed on time and within budget.
BS Engineering, North Carolina University
UW BIM Certification; CITCWA Electrical; CPES Certification CMBES Certification; PMP Certification
COREY WOLLASTON SUPERINTENDENT
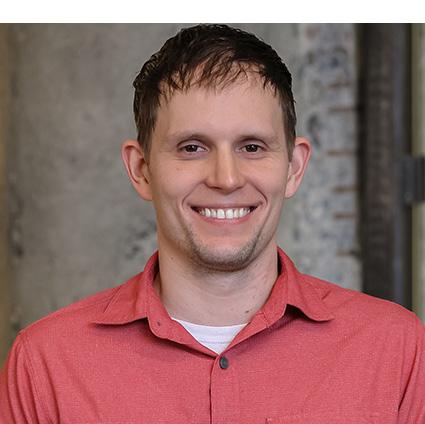
EDUCATION | CREDENTIALS
BA Business Administration, Central Washington University
Corey’s extensive office building experience and working in occupied buildings have prepared him to complete any project. He works closely with the team, trade partners / subcontractors, and the client to ensure the project is completed efficiently and on time. Corey brings his attention to detail, planning, thoroughness, excellent communication skills, and commitment to exceeding the client’s expectations of every project.
PROJECT EXPERIENCE
» Valley Medical Center Radiation Oncology Shielding, Renton, WA
» MHSC UW RR Wing Neurological Surgery Remodel, Seattle, WA
» Multicare Covington Campus, Covington, WA*
» Zymeworks Lab TI, Seattle, WA
» Seagen B5 Assay Lab, Bothell, WA
» Inbios Lab Tenant Improvement, Seattle, WA
* Experience pior to JTM
PROJECT EXPERIENCE
» MHSC UW RR Wing Neurological Surgery Remodel, Seattle, WA
» Zymeworks Lab TI, Seattle, WA
» Inbios Lab Tenant Improvement, Seattle, WA
ALLEN WEST SUPERINTENDENT
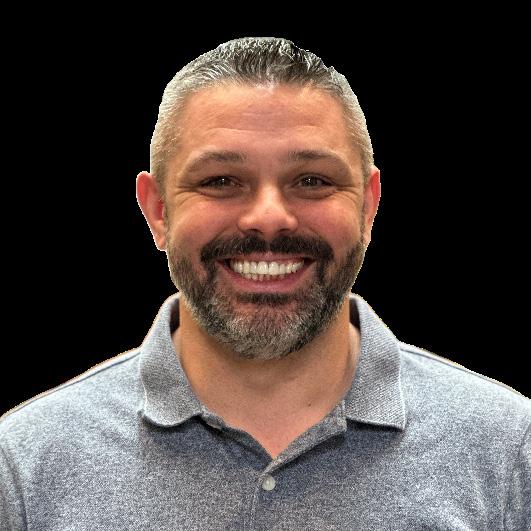
EDUCATION | CREDENTIALS
OSHA 30
ICRA Training Wabo certified
Allen has built strong client relationships and has experience in life science, healthcare, office, new construction, and tenant improvements. His skill set, including scheduling, developing site logistics plans, working in occupied environments, and safety, makes him ideal for jobs with complex finishes and fast-track schedules. Allen is directly responsible for quality control, field cost control, and coordination of all trades while providing strong field team leadership to deliver exceptional outcomes for owners.
PROJECT EXPERIENCE
» Franciscan Health St. Josephs ED Observation Unit, Federal Way, WA*
» Swedish Medical Center Vascular Clinic Renovation, Seattle, WA*
» OHMC Infusion Department Remodel, Bellevue, WA*
» Swedish Cancer Clinic, Arnold Pavilion, Seattle, WA*
* Experience prior to JTM
JUAN ALVARADO STSC SUPERINTENDENT
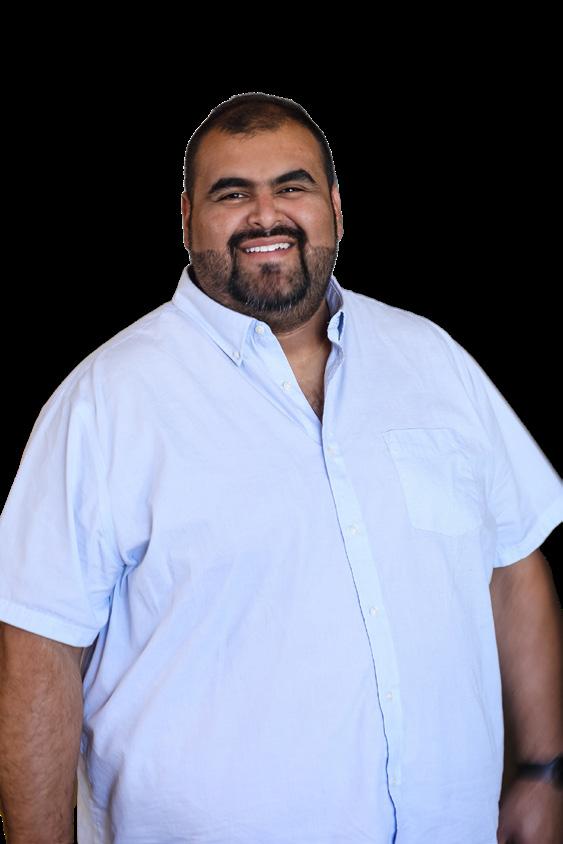
Juan is a client-oriented superintendent who loves building the most intricate and challenging projects. His natural leadership skills and 13 years of field experience allow him to supervise, sequence, coordinate, and monitor all fieldwork to ensure it is completed to the highest quality standards. His communication style goes the extra mile to help the field, clients, and trade partners complete projects with high quality, safely, on time, and within budget.
PROJECT EXPERIENCE
» VA Puget Sound Health Care Hospital Expansion, Seattle, WA*
» Juno Therapeutics Expansion, Seattle, WA*
» Providence Health & Services, Expansion, Everett, WA*
» UW Medical Center, ER Expansion, Seattle, WA*
» Swedish Issaquah, Hospital & Mob, Issaquah, WA*
* Experience prior to JTM
EDUCATION | CREDENTIALS
Construction Management Certificate, WA State Carpenter App Certificate, Building Inspection Certificate, Civil Construction Management Inspection Certificate
THOMAS GRIFFITH SUPERINTENDENT
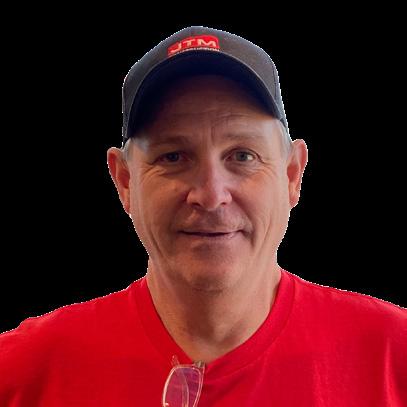
EDUCATION | CREDENTIALS
37 Years Industry Experience
OSHA 30 Certified
Thomas’s 37 years of experience covering healthcare and life sciences and working in occupied buildings have prepared him for any project. He works closely with the team and is the point-of-contact between the trade partners and supervisors. His responsibilities include the creation of the project schedule in collaboration with trade partners, maintaining a safe site, serving as the main point-of-contact for field leadership, and ensuring close coordination with the team to ensure quality.
PROJECT EXPERIENCE
» Harborview Medical Center West Wing Addition, Seattle, WA*
» OHSU Center For Health And Healing Lab Addition Portland, Or*
» Providence Regional Medical Center, Everett, WA*
» Swedish Medical Center, Issaquah, WA*
» UW Medical Center Wing Addition And Remodel, Seattle, WA*
» Arlington Medical Office Building, Arlington, WA*
» Camp Pendleton Naval Hospital, Oceanside, CA*
* Experience prior to JTM
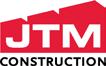
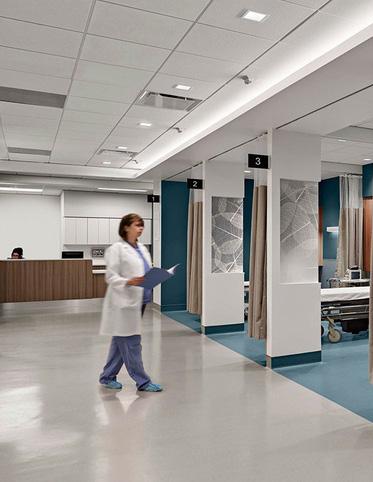
EXPERIENCE
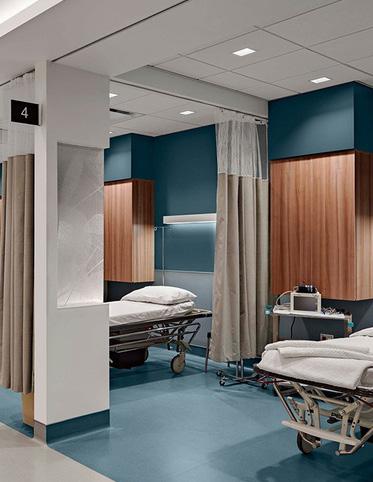
MT. VERNON MEDICAL OFFICE
BUILDING, MT. VERNON HEALTHCARE, OFFICE
The Mount Vernon Medical Office Building is a threestory, multi-use medical building. JTM successfully completed four separate contracts, including the medical building shell and core, Skagit Valley Hospital Regional Cancer Care Center, Pacific Northwest Cardiology, and a VA outpatient clinic. Delivering the latest medical services, the cancer care center features the most recent developments in high-tech equipment, including two state-of-the-art linear accelerators used for radiation treatment, each enclosed in 3’–6’ thick concrete shielding walls. A private outdoor healing garden surrounds the building, providing a serene environment for healing.
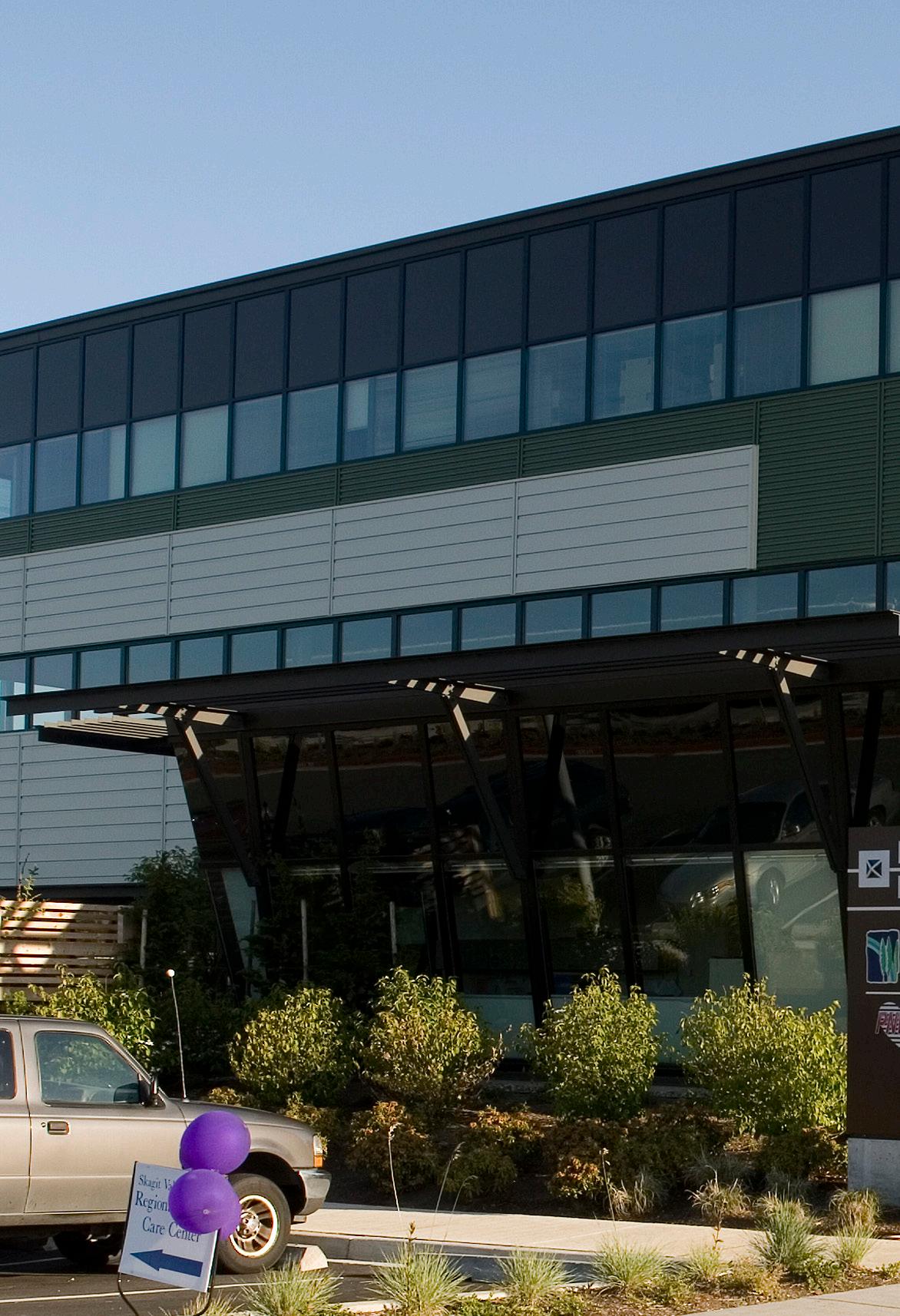
SIZE
53,000 SF
CLIENT Capstone Partners
PROJECT ARCHITECT Mahlum Architects
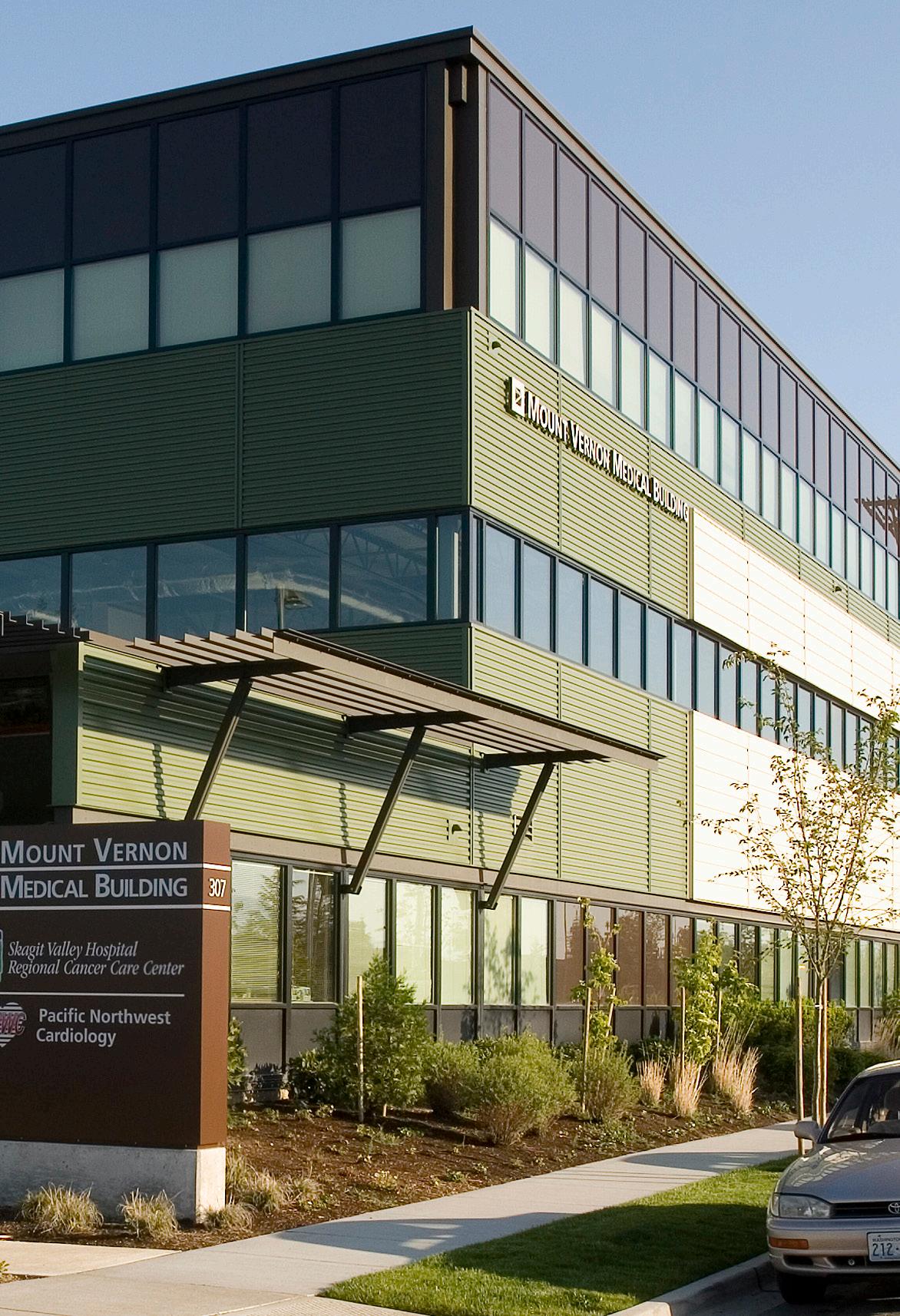
CASE STUDIES
SHELL AND CORE CONSTRUCTION
During preconstruction planning, JTM developed an unorthodox schedule sequence that strategically and proactively mitigated schedule and cost impacts for our client. We knew the building permit would be issued in the early summer months during dry weather and that the site was susceptible to rainy conditions, making a typical construction sequence very expensive and adversely impacting the project schedule. Therefore, we developed a schedule to expedite all site work, install dry and wet site utilities, and place base rock and asphalt treated base (ATB) to cap the site to eliminate the impacts of wet weather on-site conditions. In collaboration with our site trade partner, we authorized them to increase their crew size, mobilize additional equipment, and work all Saturdays to complete the site work through the placement of the ATB layer in 5 weeks instead of 9 weeks. We beat the rainy weather by two weeks, saving the owner extra costs and schedule impacts. This is an excellent example of JTM “living” one of our core values of “Ingenuity.”
BUILDING TENANT IMPROVEMENTS
Skagit Valley Hospital Cancer Care Center (SVH CCC) was the first tenant improvement build-out within the Mount Vernon Medical Office Building. JTM collaborated with the architect to design the linear accelerator with 3’6” thick shielding concrete walls in the most cost-effective manner possible. JTM crews self-formed all the concrete work for the two linear accelerator rooms’ concrete foundations, walls, and ceilings to control quality, costs, and schedule. In addition, on behalf of SVH, JTM coordinated and assisted in procuring the two linear accelerators and related equipment, and we coordinated and oversaw the vendor installations. JTM incorporated the equipment installation activities into their master schedule and seamlessly completed the work within the overall construction schedule.
PACIFIC NW CARDIOLOGY AND VA HOSPITAL COMMUNITY-BASED OUTPATIENT CLINIC
We completed these two tenant improvements after the SVC CCC project. Completing these tenant improvements coincided with the operation of the CCC. JTM coordinated all of our scheduled activities with SVH facilities and nursing staff members to mitigate and eliminate any adverse impacts on the CCC’s patients and operations staff.
The procedures we implemented to complete these two tenant improvements included:
» Constant communication with CCC staff to eliminate any surprises
» Completing any noisy or dusty work during off hours
» Scheduling material deliveries off hours and loading large materials through a removed window adjacent to a back-of-house staff lunchroom.
» Scheduling any building system shutdowns with SVH facilities nd completing these shutdowns off hours.
The goal was to make the construction activities invisible to the patients. All of our intentional and strategic procedures were effective.
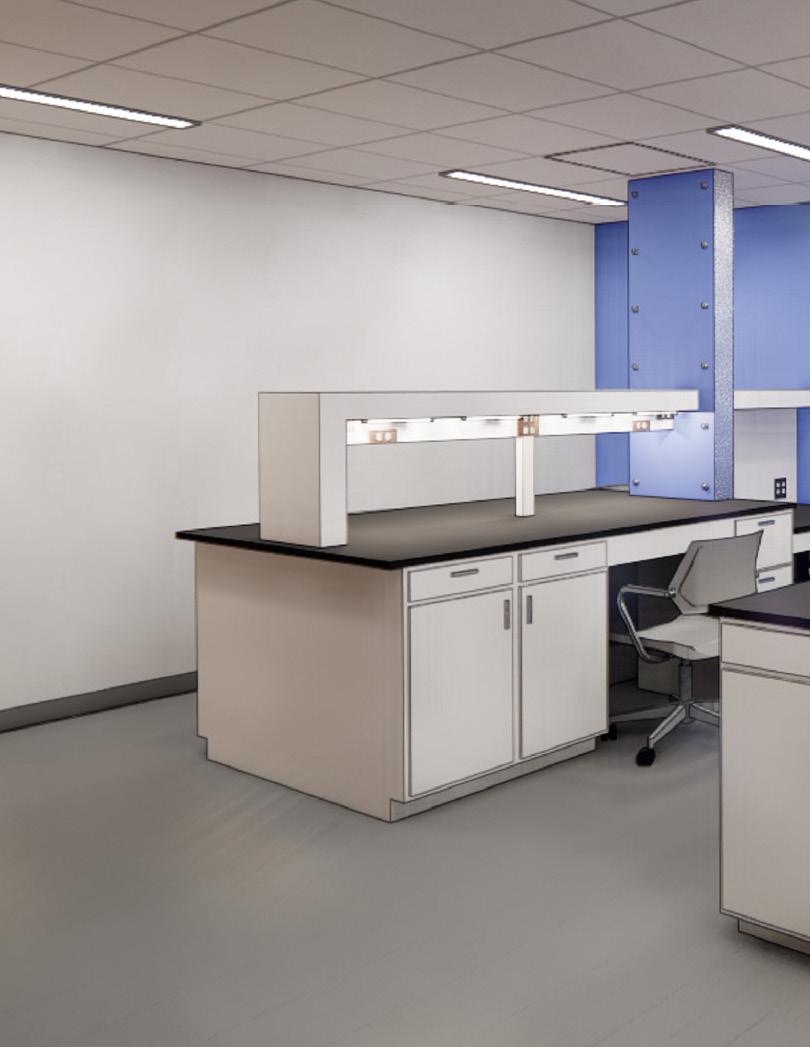
MHSC UW RR WING NEUROLOGICAL SURGERY REMODEL, SEATTLE
HEALTHCARE, TENANT IMPROVEMENT
The MHSC RR-Wing Neurological Surgery Remodel at the University of Washington Medical Center consisted of a complete interior demo and reconfiguration of the 7th floor. The programming goal was to renovate the existing outdated and underutilized lab, storage, and office spaces into the reconfigured lab, meeting, and support rooms with the addition of single-occupant and open office space.
The 1,854-square-foot renovation includes complete abatement, demolition of interior partitions, doors, lab casework, fume hoods, finishes, mechanical, plumbing, and electrical infrastructure, installation of new non-load-bearing partitions, doors, finishes, lab casework, fume hoods, biosafety cabinets, lighting, and reconfiguration of electrical, mechanical, and plumbing systems.
SIZE
1,854 SF
CLIENT
UW Neurological Surgery
PROJECT ARCHITECT
SHKS Architects

CASE STUDY
CHALLENGE
The contract documents indicated that an existing fume hood would remain in place and be reused with the new build-out. Unfortunately, this could not be accomplished due to the existing conditions of the fume hood and the revised wall layout. What made it more complicated was that the University of Washington had to purchase a new fume hood and verify the correct power was in place. This building is 60 years old, and the electrical as-builts were unreliable. As such, JTM and our electrical trade partner spent multiple days troubleshooting and tracing down electrical pathways to verify. It was paramount that we got this right as we could not allow shutting down power and did not know what it might impact downstream in other parts of the facility. JTM accomplished this verification task effort off hours to minimize impacts to the end user and without UW facilities support. Lastly, we provided this added service at no additional cost to the owner.
SOLUTION
The architect’s specifications seemed comprehensive. However, once we got into the project, we quickly realized that the University of Washington standards sometimes conflicted with the specifications. We quickly learned that we must trust and verify the architectural specifications sooner and vet them with the facility’s construction standards. This would have minimized construction administration efforts during project execution.
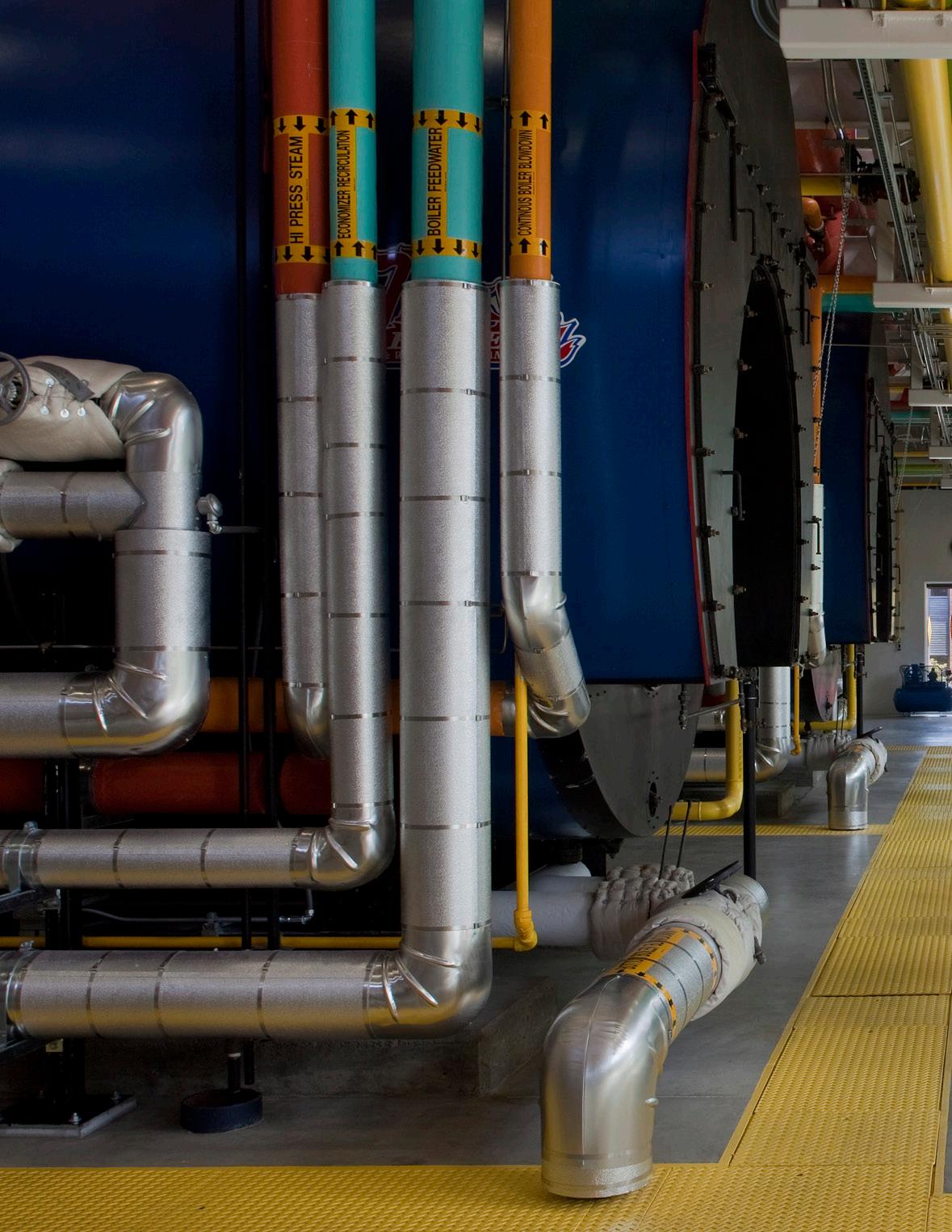
TACOMA GENERAL HOSPITAL CENTRAL UTILITY PLANT, TACOMA
HEALTHCARE
This 20,000-square-foot central utility plant houses three steam boilers, three emergency power generators, and electrical switch gear to support the emergency and normal power distribution. An 80,000-gallon backup underground fuel oil tank is located on-site. The building also contains a control room, offices, lockers, a maintenance shop, and a medical gas tank farm. The steel-columned structure with massive concrete shear walls is engineered to withstand a severe earthquake and remain operational.
The project also entailed rerouting a steam pipe through the entire operational facility. Extensive coordination and the use of ICRA barriers were utilized to successfully complete this phase of the project.
SIZE 20,000 SF
CLIENT MultiCare Health Systems
PROJECT ARCHITECT
Giffen Bolte Jurgens
KEY FEATURES / AWARDS + CERTIFICATIONS
2009 Northwest Construction Best of the Best Regional Award — Best Industrial Project; 2009 McGraw-Hill National Award — Best Industrial Project; 2010 ACEC National Track Silver Award — Energy Category

CASE STUDY
CHALLENGE
During the preconstruction phase of the $20 Million ground-up project, it was determined that the existing steam piping distribution throughout the facility needed to be replaced. After establishing the GMP, JTM worked with our Mechanical Contractor to identify this new scope and collaborated with the client on appropriate phasing and sequencing. Since this steam piping replacement was located in critical environments throughout the facility, ICRA barriers and safety isolation plans were established and assumed in our base Change Order Request. As often occurs in hospital settings, end-user requirements shifted, and the scope grew from 8 phases into 22 phases.
SOLUTION
As a collaborative partner, JTM found creative solutions to approach the work to maintain the initial change order amount. By excluding added phasing requirements and extra ICRA isolation barriers, we saved the client money. By strategically placing the ICRA barriers in the various phases and utilizing our JTM-owned Edge Guard ICRA barrier product, we eliminated waste on panels. We saved the client time and resources on the 22 phases required.

VALLEY MEDICAL CENTER SHIELDING UPGRADES, RENTON HEALTHCARE
This project entailed replacing the current linear accelerator system and upgrading the shielding around the room to align with the new equipment with the operational class IV medical facility. Additionally, minor finish upgrades were provided to improve the overall aesthetics and functionality of the facility. This comprehensive initiative aimed to modernize the medical facility, enhance patient care, and advance the medical staff’s capabilities.
SIZE
22,633 SF
CLIENT
UW Medicine Valley Medical Center
PROJECT ARCHITECT
CollinsWoerman
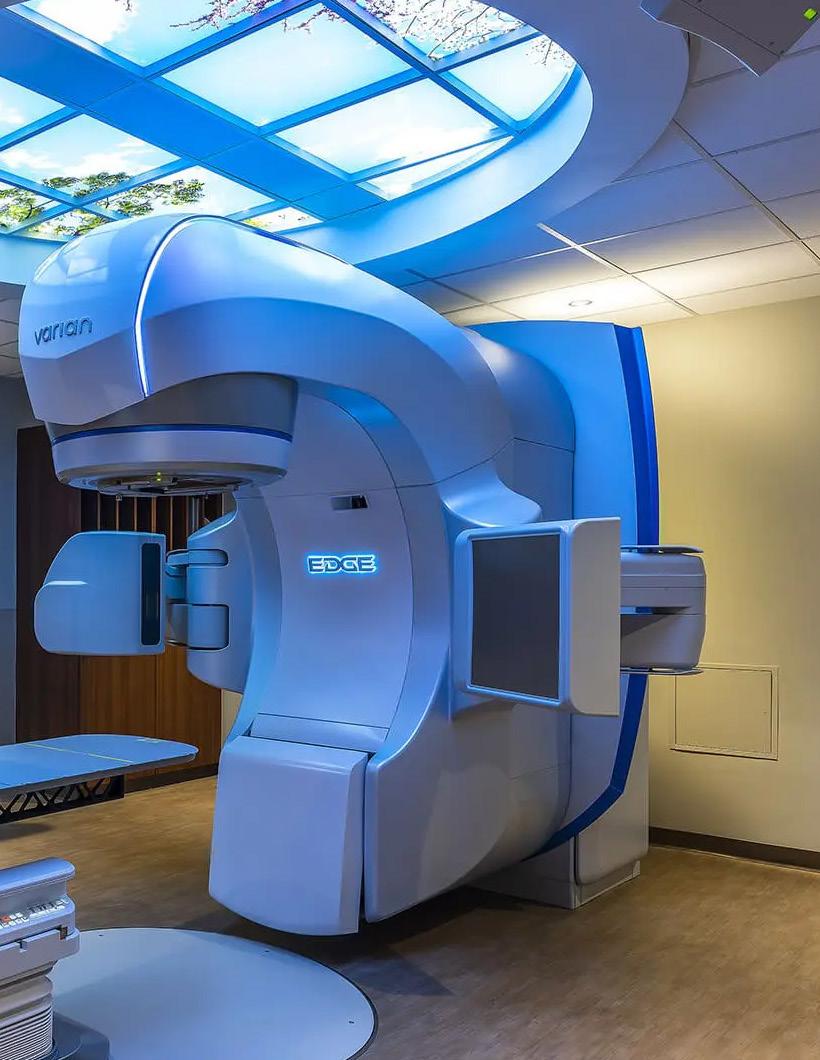
CASE STUDY
CHALLENGE
During the bid process and the preconstruction phase, the working hours were established and agreed upon with Valley Medical Center. JTM was to conduct early starts for noisy and disruptive work, then transition to daytime work with less impactful construction activity. Unfortunately, Valley Medical Center’s secondary Linac tool unexpectedly went down, and they had to continue to utilize the Linac tool in JTM’s construction work zone. JTM had to be nimble and flexible with the end user and project management staff and quickly adjust our work hours to almost completely night shifts on a one-week notice for the project duration. JTM accommodated these requests with our internal staff and subcontractors at no additional cost to the owner.
LESSON LEARNED
Extensive owner surveys were completed prior to being awarded the project to identify where the lead shielding should be located around our Linac room, specifically on the roof. JTM’s major lesson learned is to trust these surveys but verify them. If JTM had completed our 3D scanning overlay of the roof and the room, we could have identified discrepancies in the design during the preconstruction phase and not during the construction phase.
EDMONDS PROFESSIONAL CENTER, EDMONDS HEALTHCARE, OFFICE
This 18,500-square-foot expansion to an existing Edmonds Professional office building comprises a cardiology suite, a pharmacy, a family practice clinic, and multiple medical specialty offices. The expansion extended the clinic’s second floor over a new, covered ambulance pick-up and drop-off zone and parking. The latest addition was a steel structure with a stucco exterior and significant mechanical and electrical systems upgrades to match the existing exterior. The clinic was completed in phases to minimize patient and staff impacts and remained open for the project’s duration.
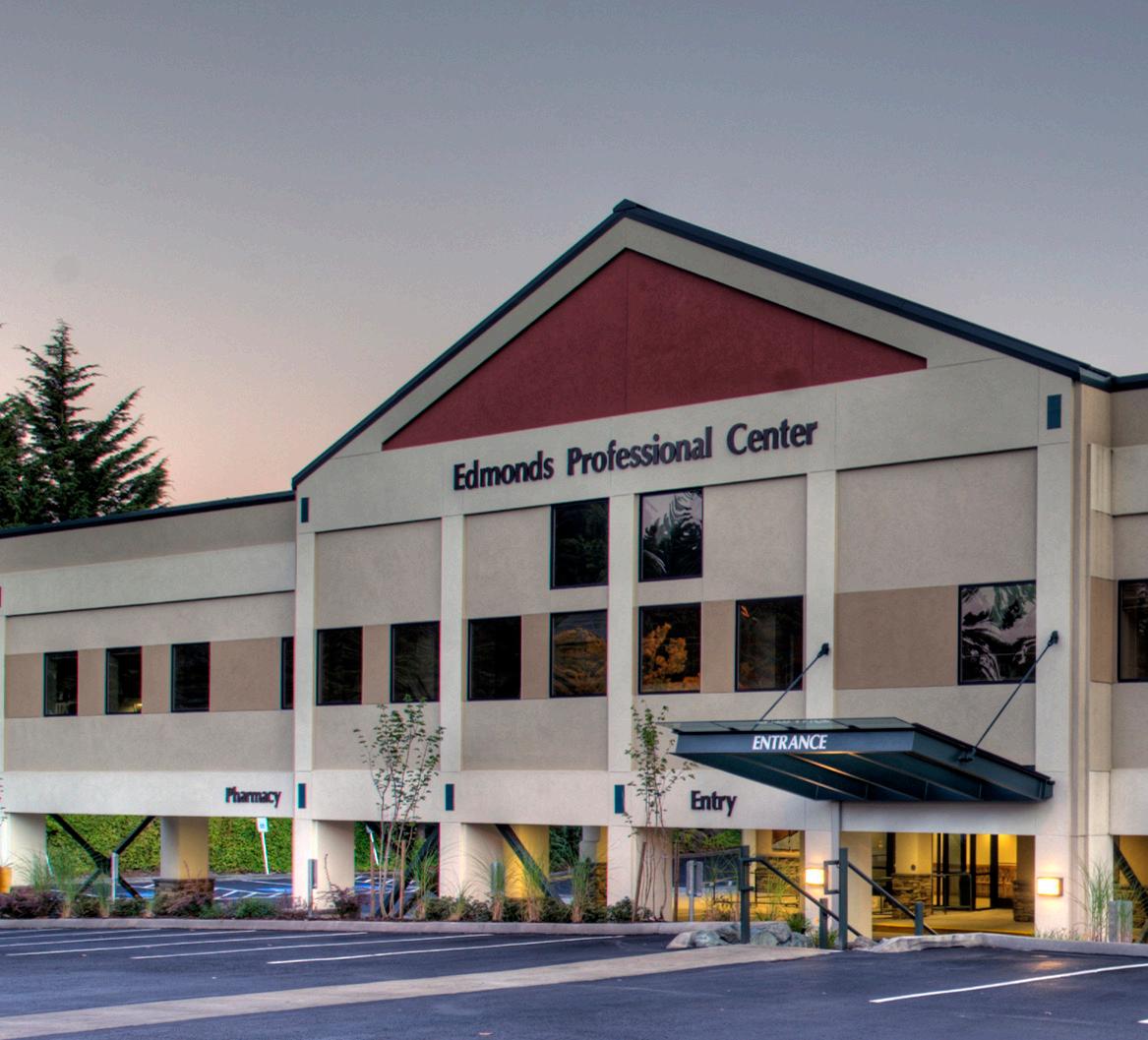
SIZE: 18,500 SF
CLIENT: EDMONDS PROFESSIONAL CENTER
ARCHITECT: PPE / SALMON BAY DESIGN
EVERGREEN NEUROSCIENCE INSTITUTE, KIRKLAND HEALTHCARE, OFFICE, TENANT IMPROVEMENT
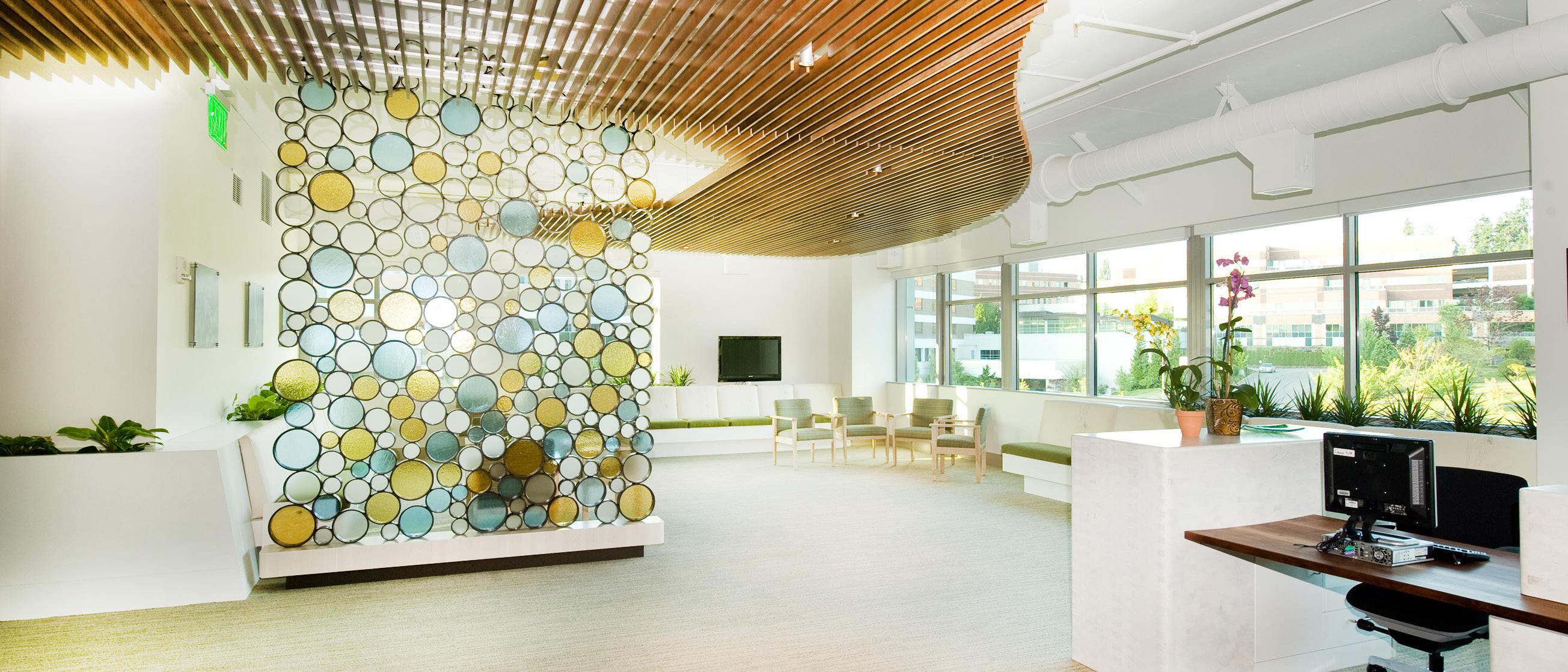
SIZE: 30,935 SF
CLIENT: EVERGREEN HEALTHCARE
ARCHITECT: SKB ARCHITECTS
Evergreen Hospital Medical Center is a complete build-out of 30,935-square-foot tenant improvements on the second and third floors of the DeYoung Pavilion. The project primarily included consult and exam rooms, office and waiting spaces, an employee gym, and cardiac / neuroscience rehabilitation spaces. Unique finishes are featured throughout the project, including a flowing contour ceiling throughout the lobby. The mechanical system was specifically engineered to reduce noise, and all partitions were acoustically insulated and sealed.
SKAGIT VALLEY CANCER CARE CENTER, MT. VERNON HEALTHCARE, TENANT IMPROVEMENT

SIZE: 16,276 SF
CLIENT: SKAGIT COUNTY PUBLIC HOSPITAL DIS. 1
ARCHITECT: MAHLUM ARCHITECTS
This 16,276-square-foot tenant improvement was completed on the first floor of the Skagit Valley Hospital. The Skagit Valley Regional Cancer Care Center delivers state-of-the-art cancer diagnosis and treatment in Mount Vernon. The Cancer Care Center features the most recent developments in high-tech equipment—two state-of-the-art linear accelerators used for radiation treatment. The two linear accelerators and the PET / CT scanner required substantial set-up and calibration timelines, resulting in a fast-track completion and turnover of this portion of the project for equipment installation.
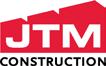

JTM HEALTHCARE BEST PRACTICES
BUILDING MEDICAL FACILITIES TAKES A DIFFERENT APPROACH THAN TRADITIONAL BUILDINGS
Many mechanical and electrical systems are unique to medical facilities: medical gas, pneumatic tube systems, nurse call systems, etc. These systems require acute and accurate coordination during the preconstruction phase to assure efficient routings that also support ongoing operation and maintenance.
Also, medical facilities typically utilize specialized equipment such as MRI machines and X-rays, which all require spaces that have unique tolerances and mechanical / electrical requirements. Room containment systems, such as lead-lined walls, glass, and doors, are also highly important to the function of the equipment spaces and require intense coordination with finish details.
During the preconstruction phase, we will work with all end users, PMO leads, building engineers and medical equipment providers to fully understand the programming needs for each space and identify all critical systems, specifications, and materials required to ensure all aspects of the project adhere to the programming requirements.
OPTIMIZING INFRASTRUCTURE
In the current medical infrastructure landscape, efficiency is needed to enhance the growing demands of these healthcare facilities. The following are considerations for optimizing resources and improving healthcare delivery methods.
ADVANTAGES
» Increases technology infrastructure day-one to allow for every progressing technological enhancements
» Data-driven planning to understand the evolving patient care environment
» Implementation of long-term goals around future funding
» Build in flexibility day-one to reduce future rework and patient impact, lowering infection and complication rates
» Implementation of life safety measures such as barriers, fire suppression, and emergency lighting to enhancement of safety
» Build with future needs in mind. This requires preplanning to determine financial priorities
OTHER CONSIDERATIONS
» SUPPORT FUNCTIONS Understanding key roles is essential for cross disciplinary implementation and collaboration.
» REGULATORY REQUIREMENTS Compliance means accreditation.
» SUSTAINABILITY INITIATIVES Implementing sustainable initiatives reduces environmental impact and operating costs. Energy-efficient designs and renewable resources contribute to a greener healthcare infrastructure.
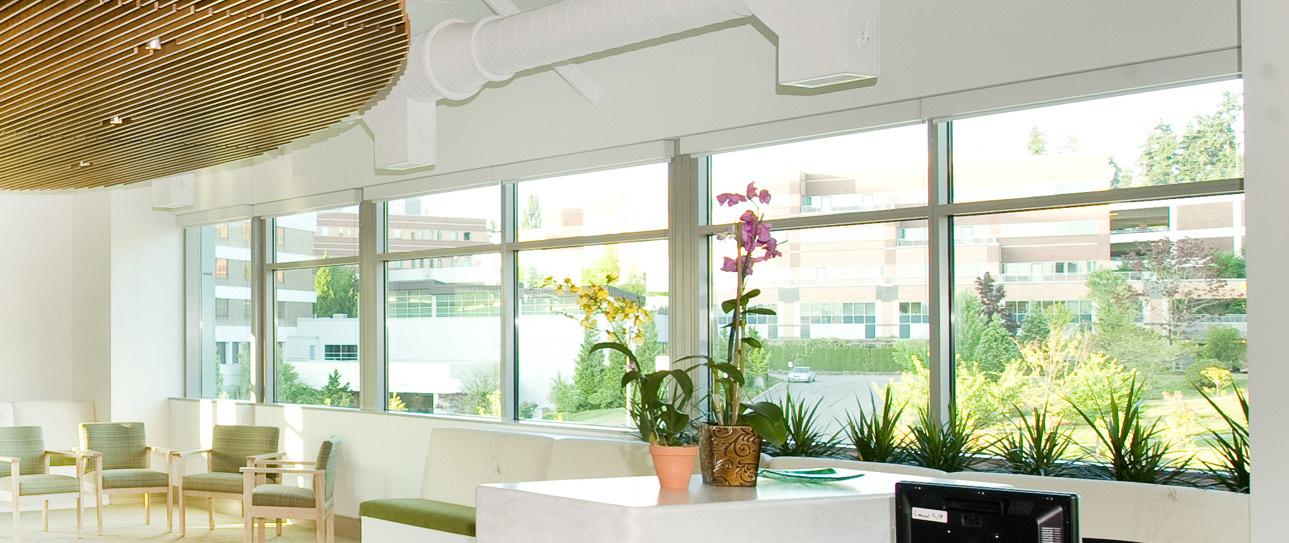
RULE NUMBER ONE - PATIENT SAFETY
As a contractor, our primary goal is to maintain patient safety. This idea is what drives all of JTM’s and the project team’s decision-making processes. To expand further, we can break down patient safety into many categories. This could mean assuring a clean environment during construction to eliminate patient health risks. Or it could indicate the need for eliminating utility interruptions to the facility so that patients can use medical equipment and feel confident that they are receiving care when they need it most. We strive to ensure that our presence and activities do not disrupt the critical healthcare services being provided to patients. The facility type will dictate the hours of operation. It is unlikely that work can be done in a hospital without some sort of shutdown / interruption. The key here is planning, communication, and more planning. Each hospital is unique in its shutdown process, and flexibility is key to meeting the hospital’s needs. We understand that we cannot interrupt / impact any healthcare services being provided. We should not be seen or heard. It is crucial to maintain the smooth functioning of healthcare facilities without causing any disturbances. Moreover, it is worth noting that the majority of healthcare projects take place within existing facilities that operate 24 hours a day.
Below are some examples of the measures we take during the pre-planning phase to ensure a healthy and safe environment throughout the project lifecycle.
» Construction flexibility through the course of construction
» Coordination with key support functions and personnel
» Communication plans and training procedures
» Maintaining patient confidentiality
» Minimizing construction footprint
» Elite quality assurance processes
» Material and man power moving / travel optimization.
» Extensive protection of existing equipment
» Risk assessments
» Strategic phasing and sequencing
» Upholding patient privacy and safety
» Cost saving strategies without compromising quality
» Reduce modifications to routing as much as possible to increase efficiencies.
» Maintaining life safety egress 24 / 7
» Clean and concise construction signage / notices
» Aligning security measures for eliminating unwanted access
» AHJ coordination for ensuring alignment with facilities emergency response plans
» Maintaining ADA accessibility during construction
» Regulatory compliance coordination and quality assurance
» Maintaining life safety branch systems.
» Planning construction to create the least number of shutdowns to the facility critical components
» Coordinate material handling outside of heavily used stairwells and elevators
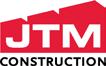
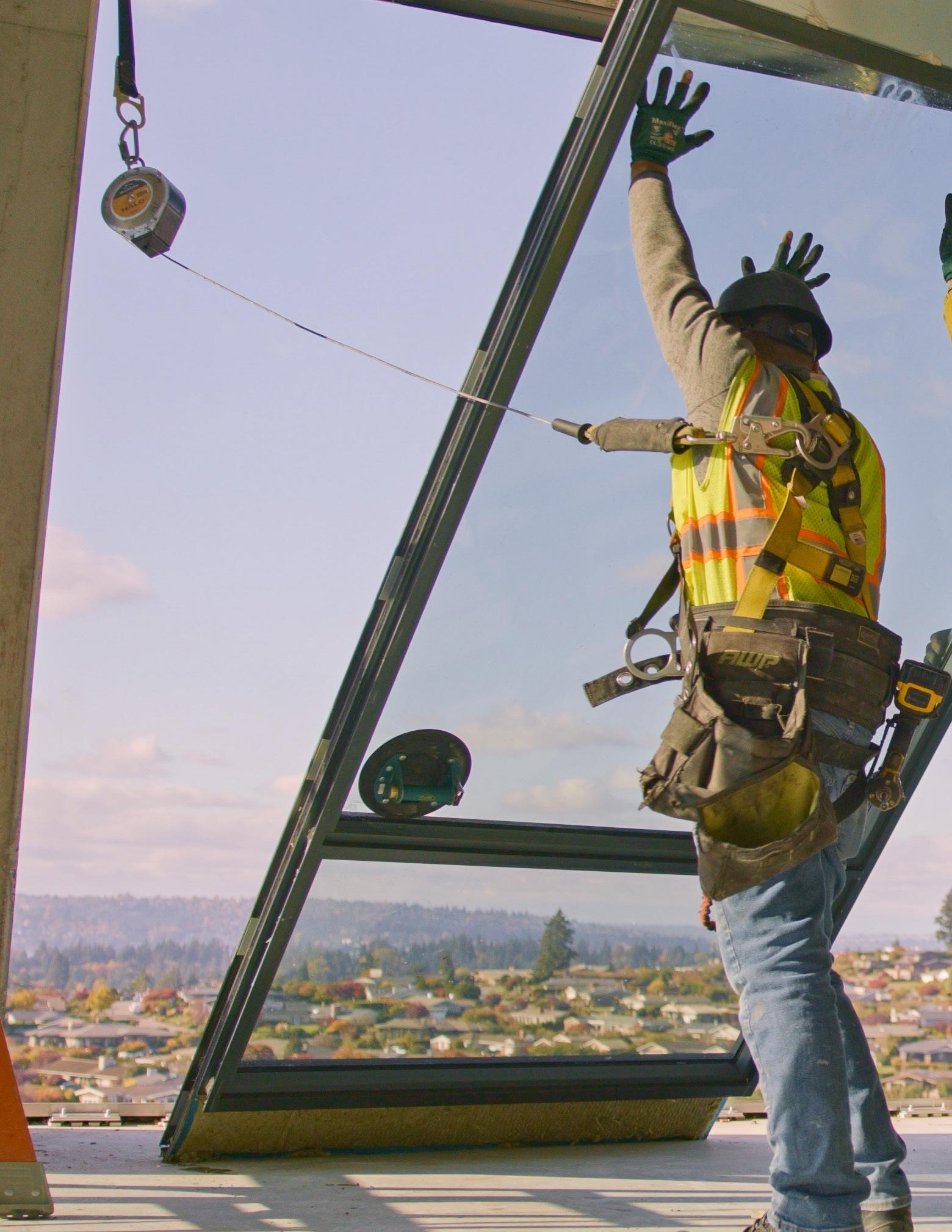
ENSURING A SAFE WORKPLACE
JTM has a comprehensive safety program that protects all employees, subcontractors, owner personnel, site visitors, and the public on ALL of our projects. Establishing programs that promote safe work planning and practices and providing leadership that encourages compliance from all to ensure our documented safety policies and procedures are strictly adhered to. JTM has been a 10+ year member of the AGC’s Safety Team. We prioritize a safe workplace and have successfully created a behavioral-focused corporate safety culture at JTM, which has been proven by receiving AGC’s Low EMR award for the past six years.
A dedicated safety professional oversees the day-to-day safety performance on each project and conducts job site safety meetings, audits, and inspections to ensure compliance, evaluate performance, identify corrective action, and implement follow-up assessments. The on-site safety officer executes and conducts preventative care, safety, and compliance training programs.
DAY TO DAY RESPONSIBILITIES INCLUDE:
» Project safety inspections, on-site safety assessments, and documentation
» Review of subcontractor safety plans
» Development of safety training and site emergency plans
» Ensures state and OSHA compliance
SAFETY AWARDS
JTM Construction was honored to receive three awards from the AGC at the Annual Build Washington Awards:
» Safety Excellence for a General Contractor (250k-500K Hours Worked)
» Safety Professional of the Year
» Grand Award for Safety Excellence
These awards reflect how our company embraces its role and contributes to making our workplace safe.
JTM EXPERIENCE

JTM has an EMR of 0.60, which is significantly lower than the industry average. We have maintained an EMR of less than 1.0, which is the industry average.
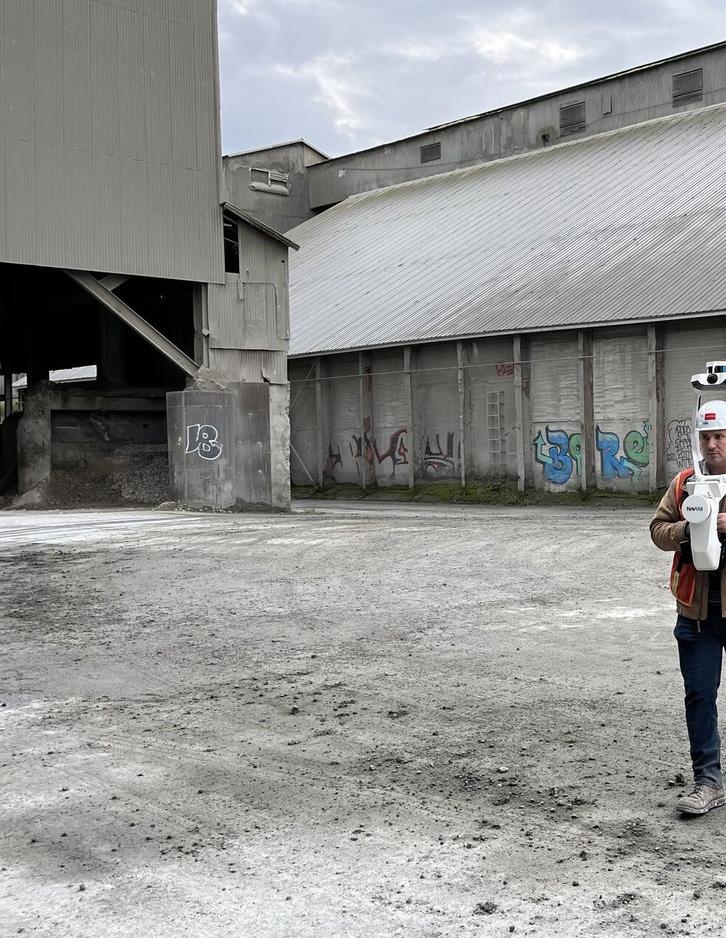
SCANNING & SURVEY CAPABILITIES
REVIZTO
√ Cross-team collaboration
√ Integration with Procore allows tracking of BIM clash logs
√ Early engagement reduces RFI’s and field impacts
LIDAR SCANNING
√ As-built our work prior to final cover
√ Capturing this data allows us to compare it against the coordinated model
√ When the project is complete, we have detailed as-built information that can guide future TI work to success.
JTM’S AS-BUILT DELIVERABLE
√ Utilizing our coordination software, Revizto, we can host all our as-builts and coordinated content in one place
√ We know where everything in our projects is placed, from in-deck PT cables and rebar to in-wall MEPF locations
√ In-slab penetration verification
We can start and finish a project using the best technology in the industry. From scanning a project space and delivering as-built data within 24 hours to modeling from that scan data to create an accurate as-built model, our team has the tools and knowledge necessary to make our healthcare projects successful.
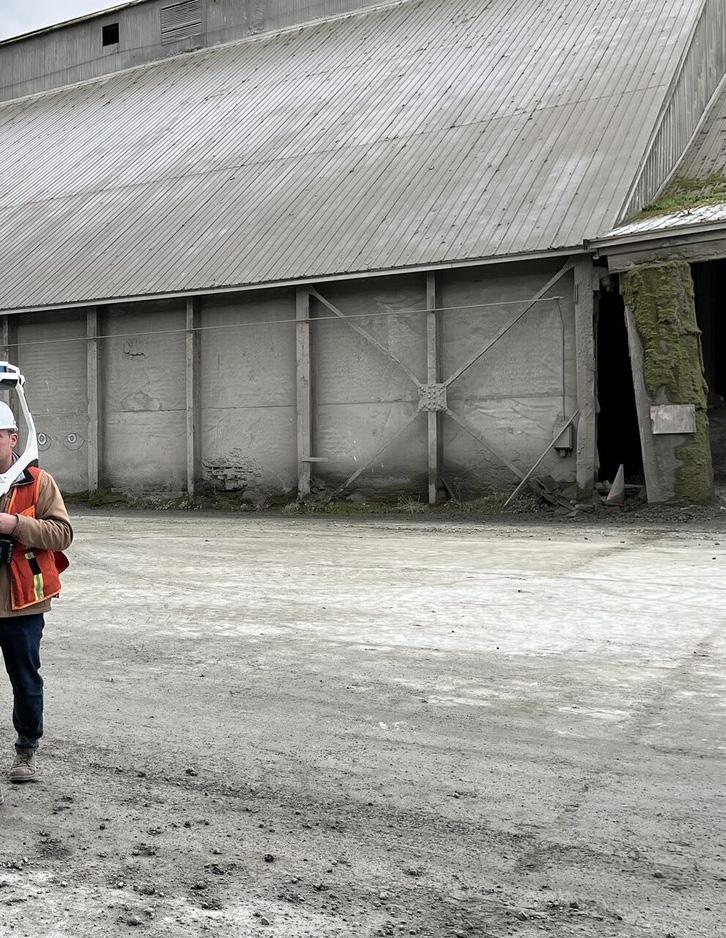
AT JTM, OUR CONSTRUCTION TECHNOLOGY TEAM IS STRIVING TO BE AT THE FOREFRONT OF INNOVATION AND PROJECT SUPPORT. WITH THE COMBINED ASSETS OF IN-HOUSE SURVEY AND BIM-VDC DEPARTMENTS, WE PROVIDE SERVICES QUICKLY AND EFFICIENTLY.
WE HAVE DEVELOPED SYSTEMS AND PROCESSES THAT ALLOW US TO OFFER A RANGE OF SERVICES TO OUR HEALTHCARE TEAMS AND CLIENTS, INCLUDING:
√ 3D As-Built Scanning
√ In-Field Surveying and Staking
√ 3D Model Site Coordination and Work Packages
√ Scan to BIM Modeling
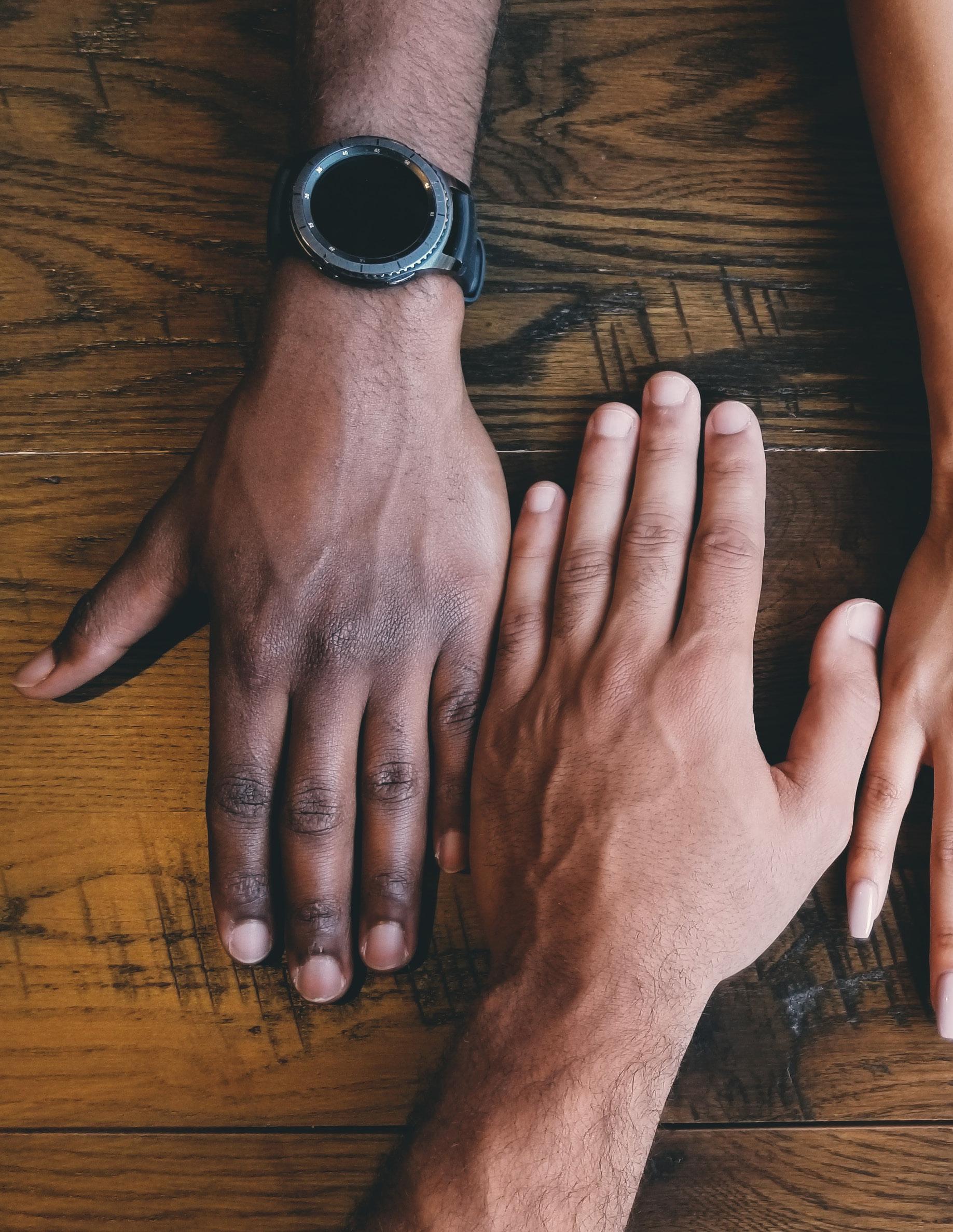
HONORS OUR DIFFERENCES, LIVE THE VALUES
ENHANCING OPPORTUNITIES IN THE COMMUNITIES WHERE WE LIVE AND WORK
JTM supports diversity and inclusion in the communities in which we live and work. This is part of our OneJTM culture and one of our core values. Maximizing diverse participation in everything we do is as familiar to us as maximizing quality and minimizing accidents; it’s just part of our culture.
JTM is proud of our overall current work-in-progress contracts. We have achieved over 21% participation, equating to over $156m for diverse businesses in our community. Our commitment goes beyond projects with stated goals and requirements - we measure across all our work.
“
JTM ACTIVELY COMMITS TO BUILDING BETTER LIVES THROUGH REPRESENTATION, EMPLOYEE WELLNESS, SAFETY, AND OPPORTUNITY THROUGHOUT OUR BUSINESS PRACTICES. A CULTURE OF OPPORTUNITY AND INCLUSION IS AT THE HEART OF JTM’S VALUES AND BUSINESS APPROACH.
— ONEJTM’S DIVERSITY, EQUITY, AND INCLUSION (DEI) MISSION STATEMENT
KEY STRATEGIES WE IMPLEMENT

Leveraging
Parnerships & Relationships
Promote the Project Buy-out Strategies
Project Specific Outreach
Mentorship & Support for Success
OUTREACH EFFORTS INCLUDE:
√ Project Specific Open House’s
√ Industry Outreach
√ Pre-Bid Workshops
Measure with Progress Tracking

SUSTAINABILITY IS GOOD BUSINESS
JTM believes in building with a sense of environmental responsibility. We take care of the environment and know that our comprehensive approach helps clients make informed decisions about design and construction, with a team that has expertise in procurement and construction methods. That translates into minimizing administration processes while maximizing the efficiency and quality of the finished project. Responsible design and construction affect all stakeholders—our employees, clients and developers, trade partners, and communities.
Minimizing administration processes while maximizing the efficiency and quality of the finished project is the right thing to do. The most impactful step to be taken, from a sustainability perspective, is hiring JTM Construction. Being a local contractor is incredibly important to us. We know the local suppliers, installers, and inspectors, and we will make a difference. Responsible design and construction affect all stakeholders—our employees, clients and developers, trade partners, and communities. Clients seek cost savings through sustainable strategies and energy efficiencies that meet their objectives. JTM collaborates with all stakeholders— our employees, clients, developers, trade partners, and communities—to make the best project decisions and achieve all our client’s goals.
DELIVERING PROJECTS WITH MEANINGFUL MATERIALS
» LEED
» Build Green
» Salmon-Safe
» Living Building Challenge
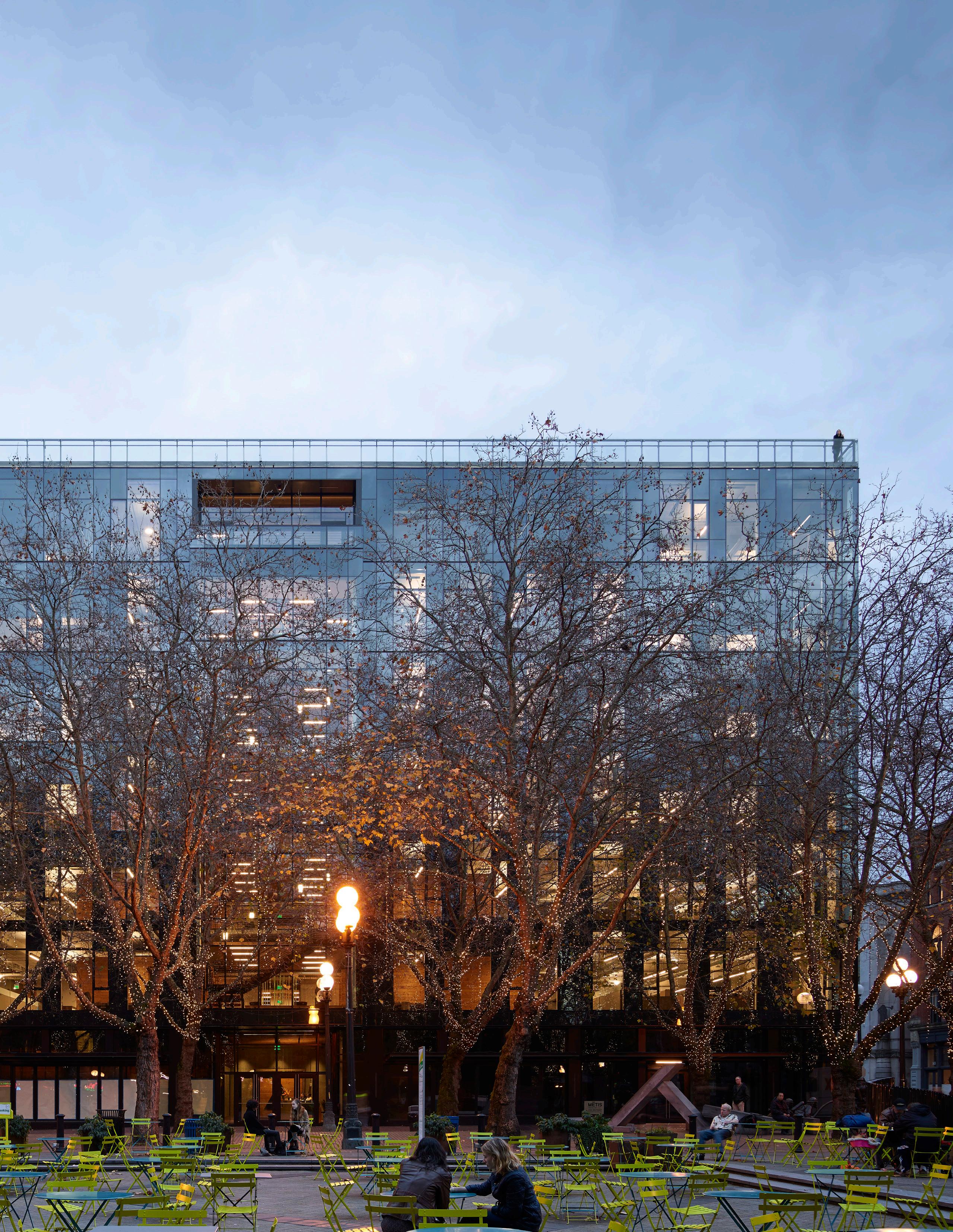
WE AIM TO CONTRIBUTE TO A MORE SUSTAINABLE FUTURE, REDUCE OUR CARBON FOOTPRINT, AND INSPIRE POSITIVE CHANGE WITHIN THE INDUSTRY. JTM BELIEVES THAT BY WORKING TOGETHER, WE CAN SIGNIFICANTLY REDUCE EMBODIED CARBON FOR THE BETTERMENT OF OUR FUTURE.