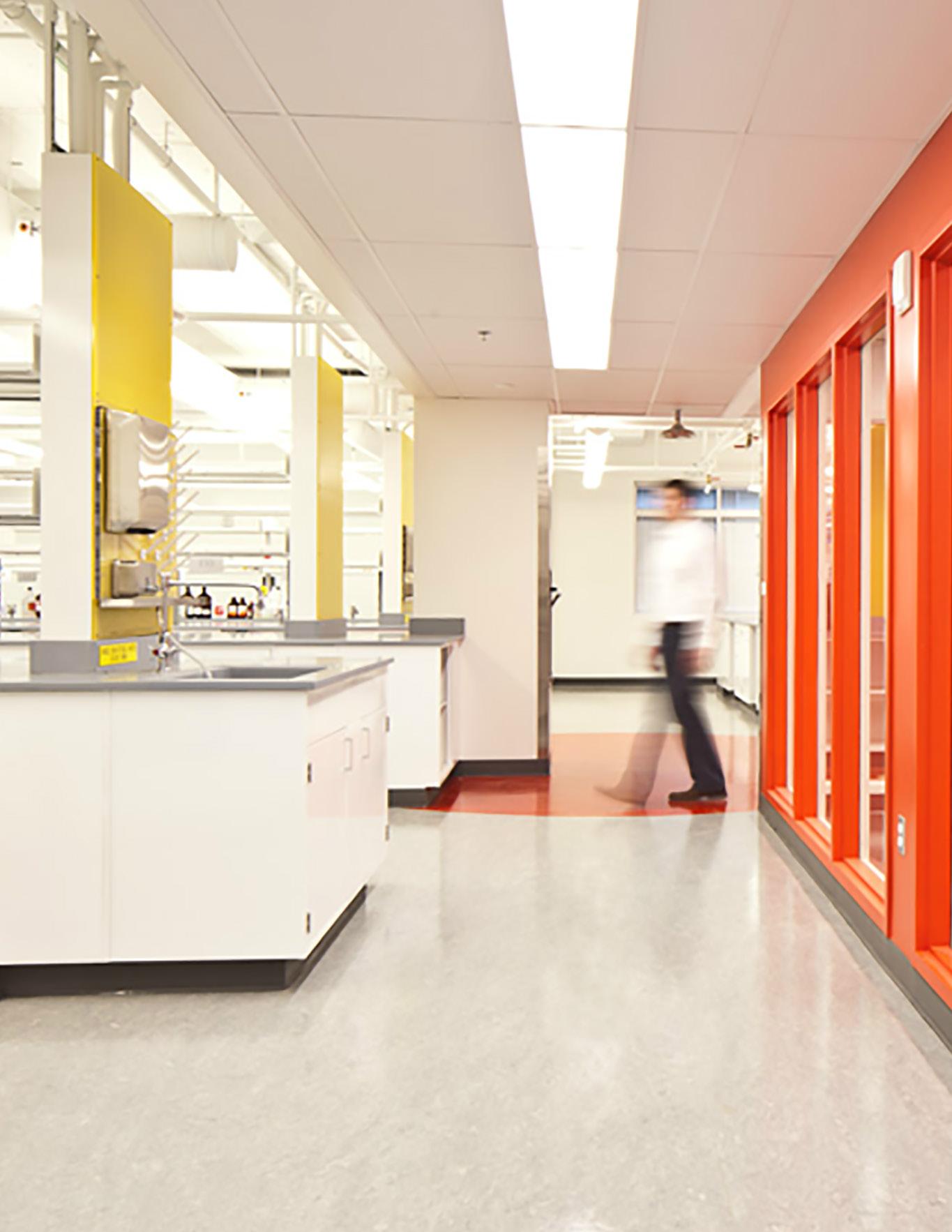
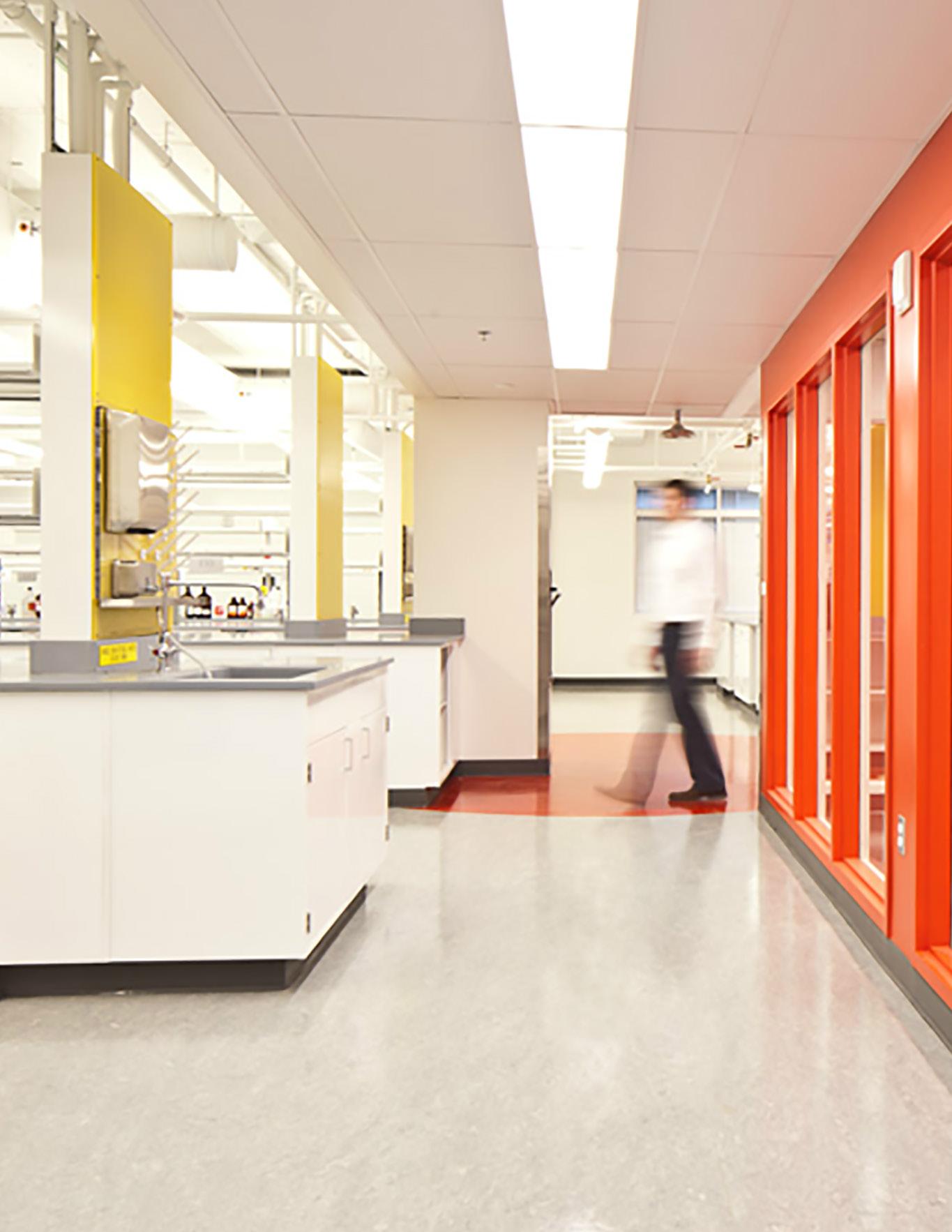
SERVING OTHERS SINCE 2005
COMMITTED TO INTEGRITY
WE ARE OneJTM
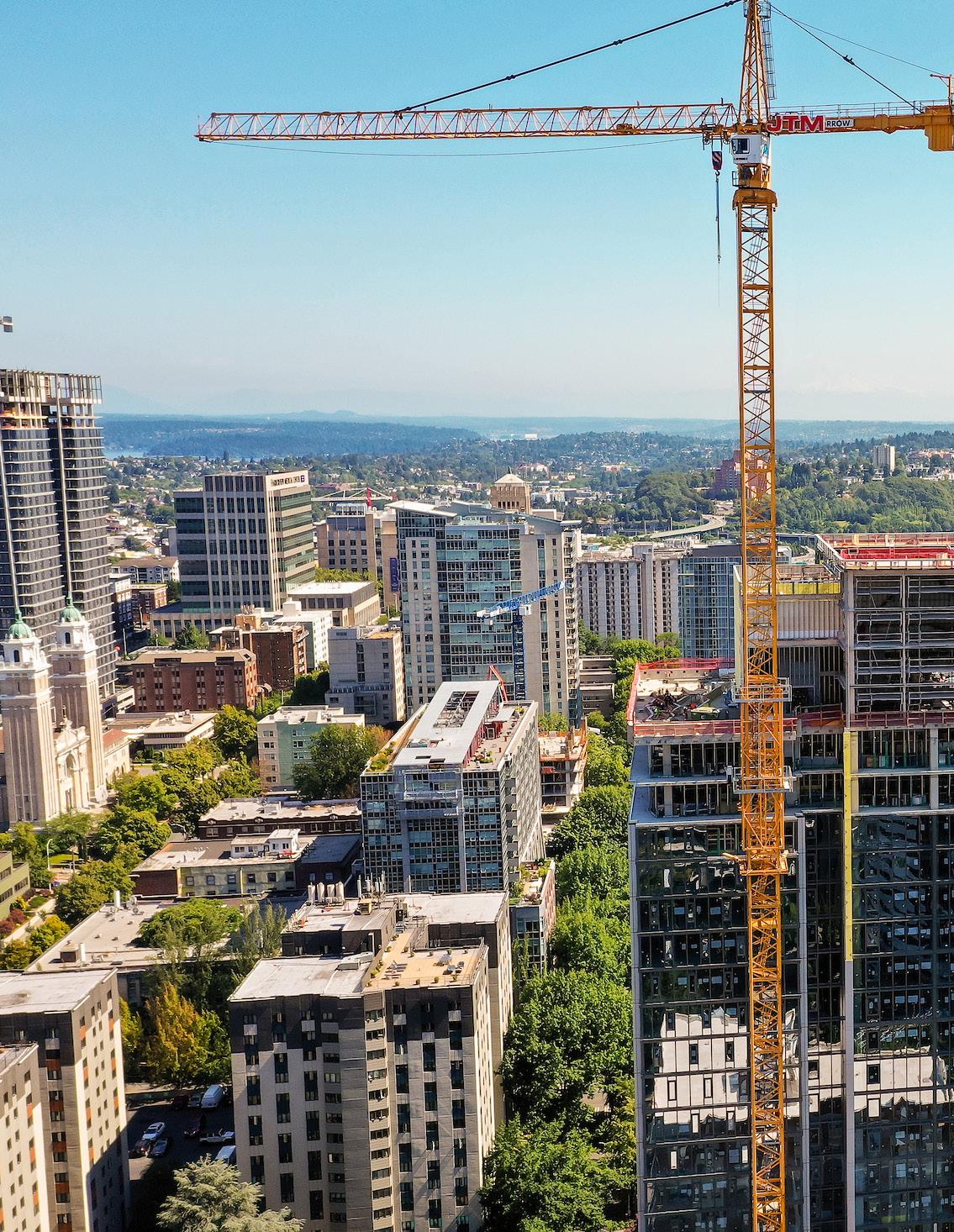
Formed in 2005, JTM was founded with the belief that outstanding project delivery should be the rule, not the exception. From the beginning, JTM has exceeded expectations, cultivated our hard-earned reputation for quality, and developed a proven foundation based on relationships, trust, respect, and performance. At JTM, we deliver on our commitments and our promises. Leadership is hands-on and actively engaged with all our projects, ensuring every team is set up for success while keeping our clients’ best interests at heart as we build their vision.
We are builders, focused on forming long-term client relationships, and committed to integrity in everything we do. The JTM team is passionate, energetic, innovative, and entrepreneurial. Our experience, size, and structure enable us to excel on construction projects of any size or complexity.

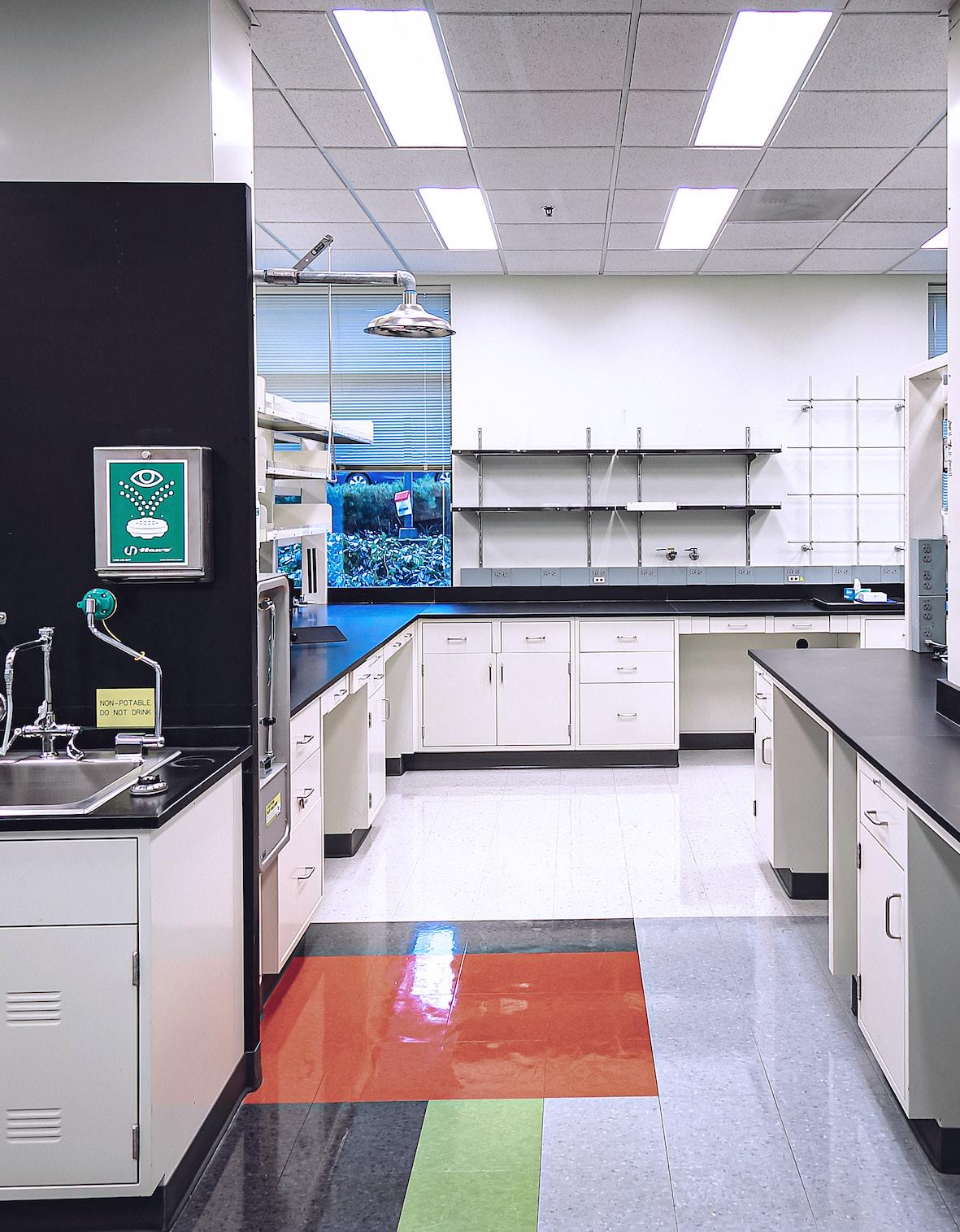
LOCATION
5900 Airport Way South, Suite 110, Seattle, WA 98108
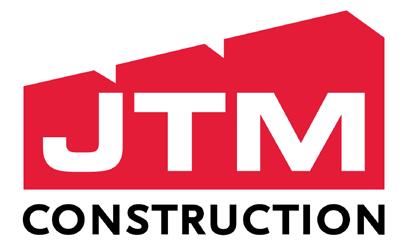
ABOUT JTM
JTM founders created our general contracting firm with over 100 years of combined experience in the construction industry. They founded the company upon their shared vision from the beginning: to create a company with a family-like culture that valued relationships and deep connections with everyone, and to always act with integrity.
A FULL-SERVICE GC
YEARS OF OPERATION
18 Years
COMPANY SIZE
Informed by a deep well of experience, and supported by robust self-performing capabilities and innovative technological tools, we specialize in delivering exceptional preconstruction and construction services in a collaborative team environment.
Design-Build
MEP Expertise
Preconstruction
Project Management
Safety Management
Self-Perform
Special Project Groups
Survey + Scanning
VDC + BIM Technology
NOTABLE COMPANY RECOGNITION
PSBJ Best Places to Work
Washington’s Best Workplaces (2022, 2021)
Culture of Care Awareness
AGC (2021)
PROJECT RECOGNITION
35 + Awards
MARKET SECTORS
Life Science
Healthcare
Mixed-Use
Office | High-Tech
High-Rise
Special Projects
Tenant Improvements
Historic Renovation
Seismic Upgrade
Residential
Community Hospitality
Retail
Parking Garage
Visionary’ Award for Leadership
Seattle 2030 District Vision Awards (2016)
SAFETY RECOGNITION
Safety Excellence Award
General Contractor
250-500K Hours
AGC (2022)
National Construction
Safety Excellence Award
AGC EMR Award (2022, 2021, 2020, 2019, 2018, 2017)
Occupational Excellence Achievement Award
National Safety Council (2023)
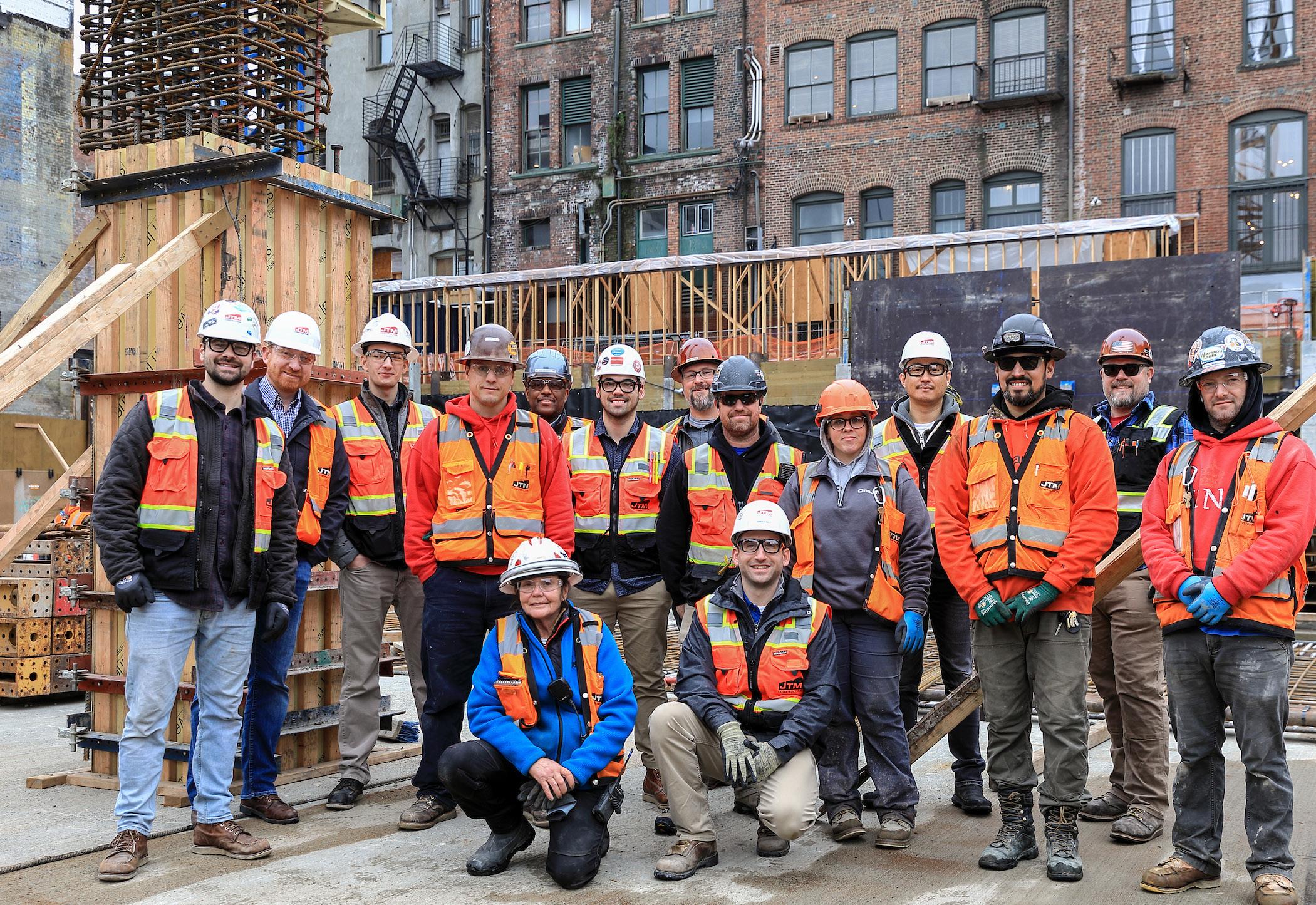
OUR VALUES
SAFETY
We protect our people and the community like family
INTEGRITY
We take pride in relationships built on trust and reinforced by our actions.
INGENUITY
We empower our people to challenge convention.
ENERGY
We bring passion and enthusiasm to our work and celebrate client, project, and individual successes.
ACCOUNTABILITY
We deliver on our commitments.
COMRADERY
We support each other as colleagues and friends.
WE ARE PASSIONATE, ENERGETIC, INNOVATIVE, AND ENTREPRENEURIAL.
WE BELIEVE IN OUTSTANDING PROJECT DELIVERY IS THE RULE AND NOT THE EXCEPTION.
WE AIM TO EXCEED THE EXPECTATION.
WE CULTIVATE OUR HARD-EARNED REPUTATION.
WE DELIVER ON OUR COMMITMENTS AND OUR PROMISES.
PROJECT
EXPERIENCE
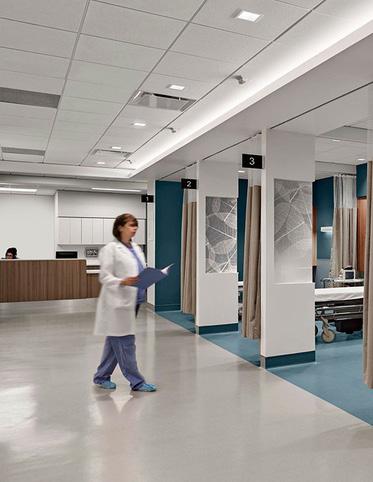
EXPERIENCE
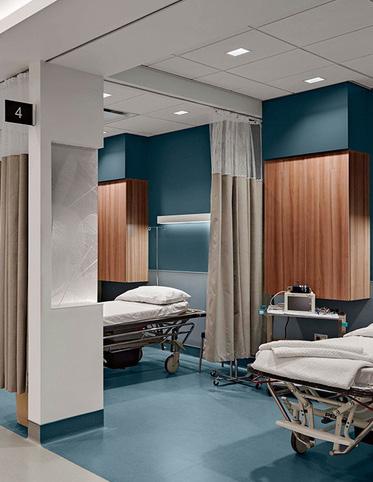
LIFE SCIENCES WORK
JTM has gained a strong presence in the life sciences market relatively quickly. This effort began six years ago when JTM committed to life sciences, brought on a life sciences veteran, Jimmy Craig, and filled out the team with talented individuals with hands-on experience. Below are highlights of several projects
Spaces must appeal to world-leading talent, and just as technology and procedures evolve, so must the spaces that house them. It’s about transformable facilities, collaborative research spaces, and engaging with clients early to create spaces tailored to their everevolving needs. In conjunction with the JTM values, this commitment has resulted in a dynamic Life Sciences team that has built lab spaces for several of the region’s best Life Sciences companies and campuses. LIFE SCIENCES
Light Sciences Lab TI
Philips Heartstream
Institute for System Biology TI/Vivarium
Puget Sound Blood Center TI/ Vivarium
Amgen Bothell Development Lab
Zymogenetics Microbial Manufacturing Facility
Gilead Lab 142
Inbios
1551 Eastlake S&C Improvements Zymeworks TI
B5 B6 Plaza
B6 Structural upgrade / Lab and office build-out
B1 & B3 Lab back fills
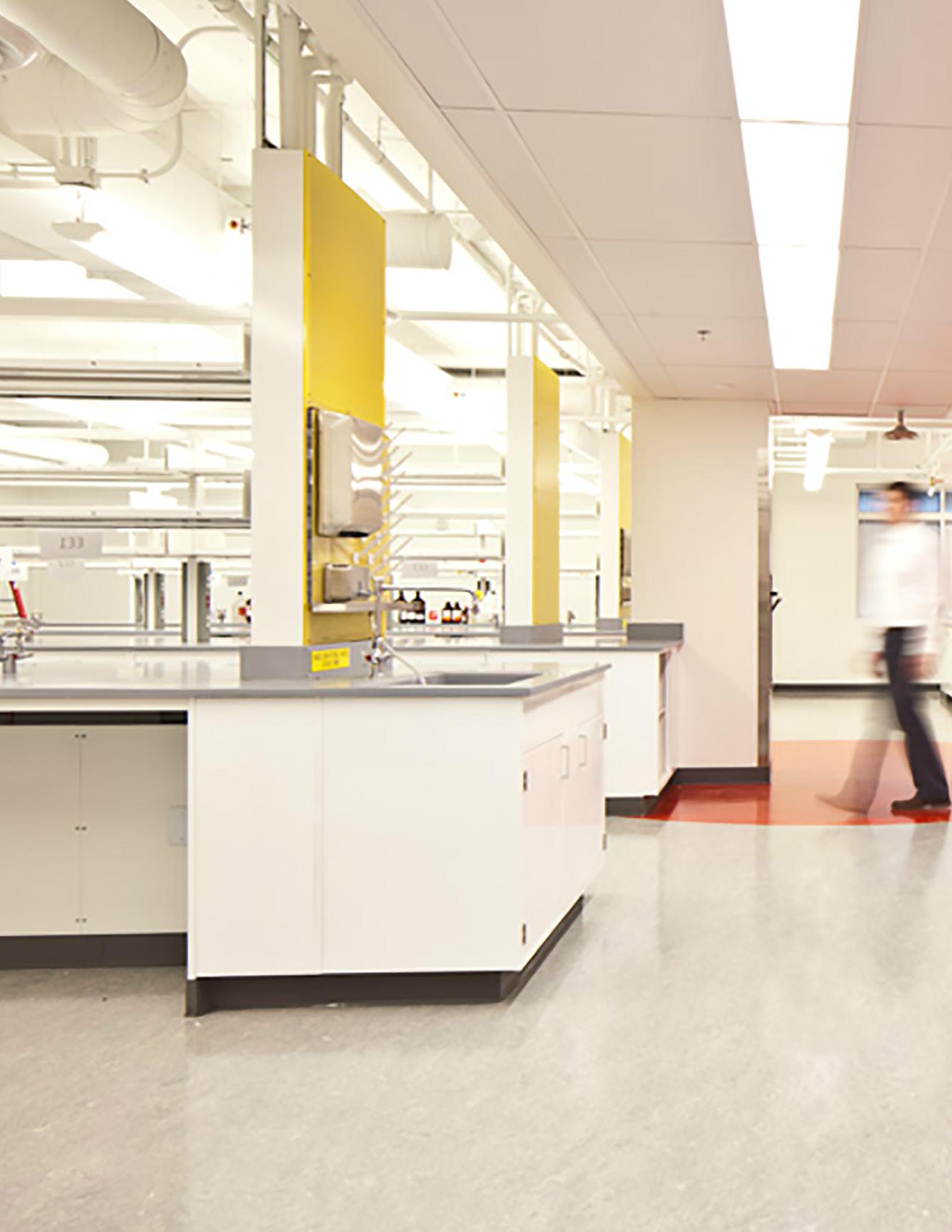
15 SEAGEN PROJECTS
8
HIGH-TECH + LABS PROJECTS
B2 War Room
B5 Structural upgrade / Lab & office build-out
B4 L1 Office build-out
B5 NMR Room Specialties Lab Vivarium
B1 Lab 264 upgrade
B3 PA Lab Build-Out
9 GILEAD PROJECTS

“
I HAVE ENJOYED WORKING WITH JTM ON MANY PROJECTS IN THE PAST THREE YEARS.
JIMMY AND HIS TEAM HAVE BEEN GREAT PARTNERS IN PROGRESS! THE PROJECTS ARE ALWAYS COMPLETED ON TIME AND AS BUDGETED. WHEN MY MANAGER OR I NEED A PROJECT COMPLETED, JTM IS STILL MY FIRST CHOICE.
- Jeffery Price, NC Facilities Supervisor, Life Science Market
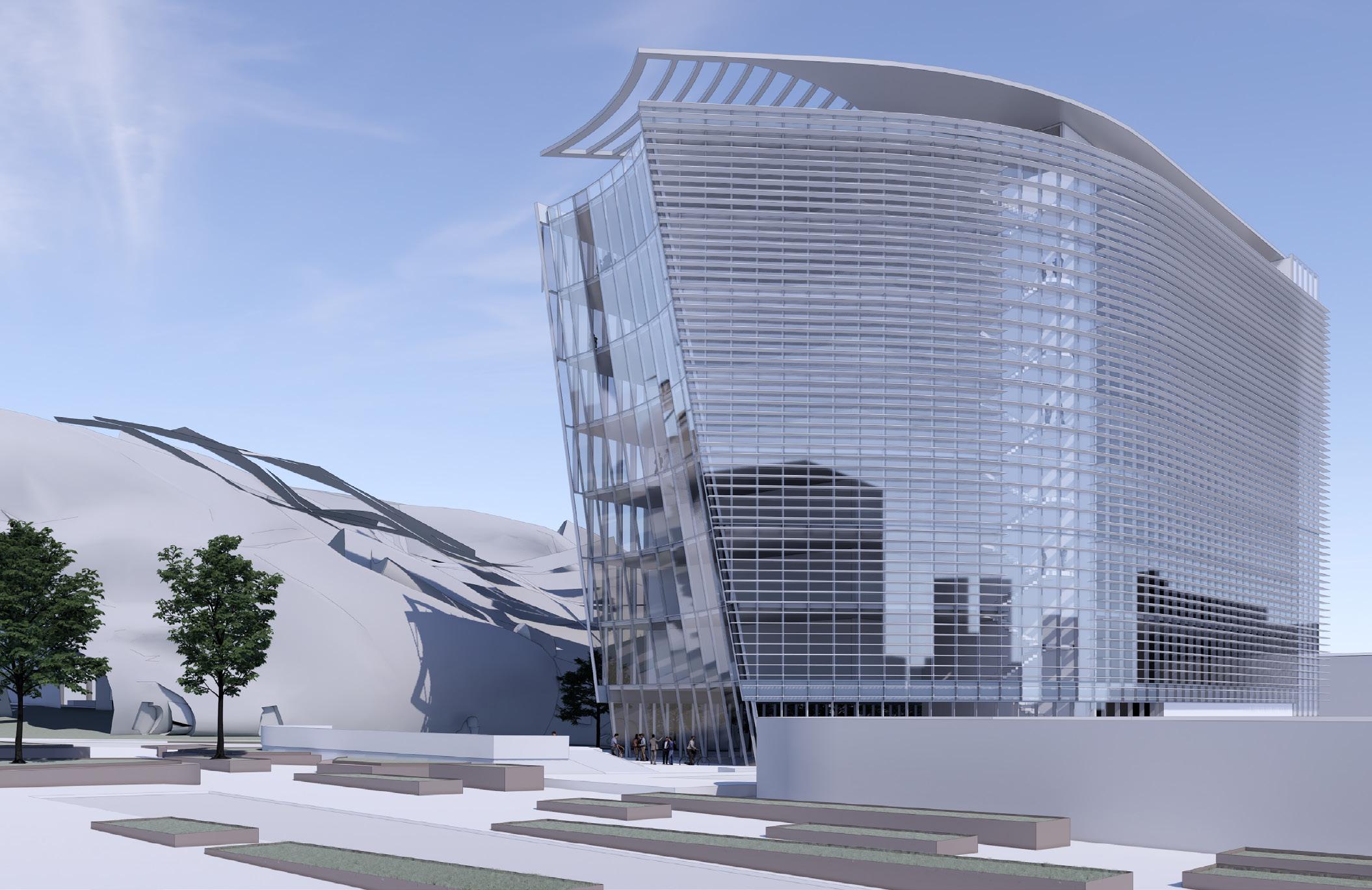
FIFTH & BROAD, SEATTLE
LIFE SCIENCES, SHELL & CORE, OFFICE, HIGH-RISE
This life science-ready office space will occupy 197,000 square feet on floors two through nine across the street from the Space Needle. The project aims to bring roughly 180,000 square feet of high-performance research space to the market. In addition, ground floor retail uses, indoor and outdoor rooftop amenities space, amenity space along the building’s south face, and three to four levels of below-grade parking for approximately 185 stalls. The unique rooftop will feature an extensive vegetated green roof and a hardscape roof patio.
SIZE
197,000 SF
CLIENT Urban Visions
PROJECT ARCHITECT
Perkins&Will
KEY FEATURES/AWARDS + CERTIFICATIONS
LEED 4.0 Gold, WELL Building
Standard Gold Certified, Salmon-Safe Accredited
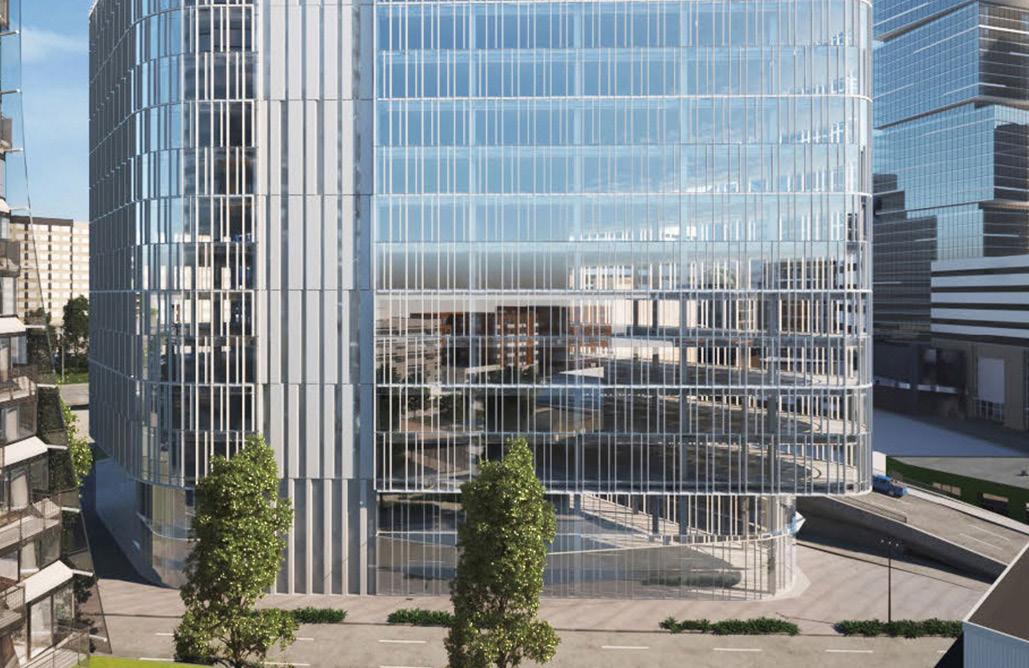
1305 STEWART, SEATTLE
LIFE SCIENCES, SHELL & CORE, OFFICE, HIGH-RISE
PMB’s 1305 Stewart is a 13-story, life science-ready core and shell building at the corner of Denny Street and Stewart Street, right off South Lake Union. This 340,000-square-foot project will include 15-foot floor-to-ceiling heights, PT concrete curtain wall glazing, a large rooftop amenity area, two test-fits built with shell and core floors, and four below-grade parking levels with approximately 270 parking spaces available. Construction schedule 25-month duration.
SIZE
340,000 SF
CLIENT PMB
PROJECT ARCHITECT
Perkins&Will
KEY FEATURES/AWARDS + CERTIFICATIONS
LEED 4.0 Gold
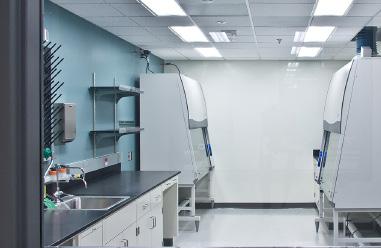
SEAGEN B5 ASSAY LAB EXPANSION, BOTHELL
LIFE SCIENCES, LAB RENOVATION, TENANT IMPROVEMENT
Seagen’s Assay Lab expansion required converting an adjacent room and working on a four-month design-assist preconstruction effort before launching into construction. Opportunities in preconstruction included supporting the client on the mechanical equipment selection. Careful examination of room pressurization requirements and the existing structural capacity of the roof were required to evaluate options for the new rooftop unit.
JTM partnered with our HVAC trade partner to provide multiple options to the Owner to make the most cost-effective and schedule-conscious decisions. This expansion space hosted highly critical equipment to support the adjacent active NMR Room. JTM developed strategic phasing plans to maintain the operation of this equipment and eliminate impacts on Seagen’s essential research processes.
As an operational occupied facility, this project required intense pre-planning to ensure our high-impact activities did not disrupt the end-users. Activities like saw cutting/trenching, a crane picks, and significant utility tie-ins were coordinated closely with the client months before execution.
SIZE
1,200 SF
CLIENT
Seagen
PROJECT ARCHITECT
SABArchitects
KEY FEATURES/AWARDS + CERTIFICATIONS
RODI Tie In and Building Flush / Roof Top Crane Pick
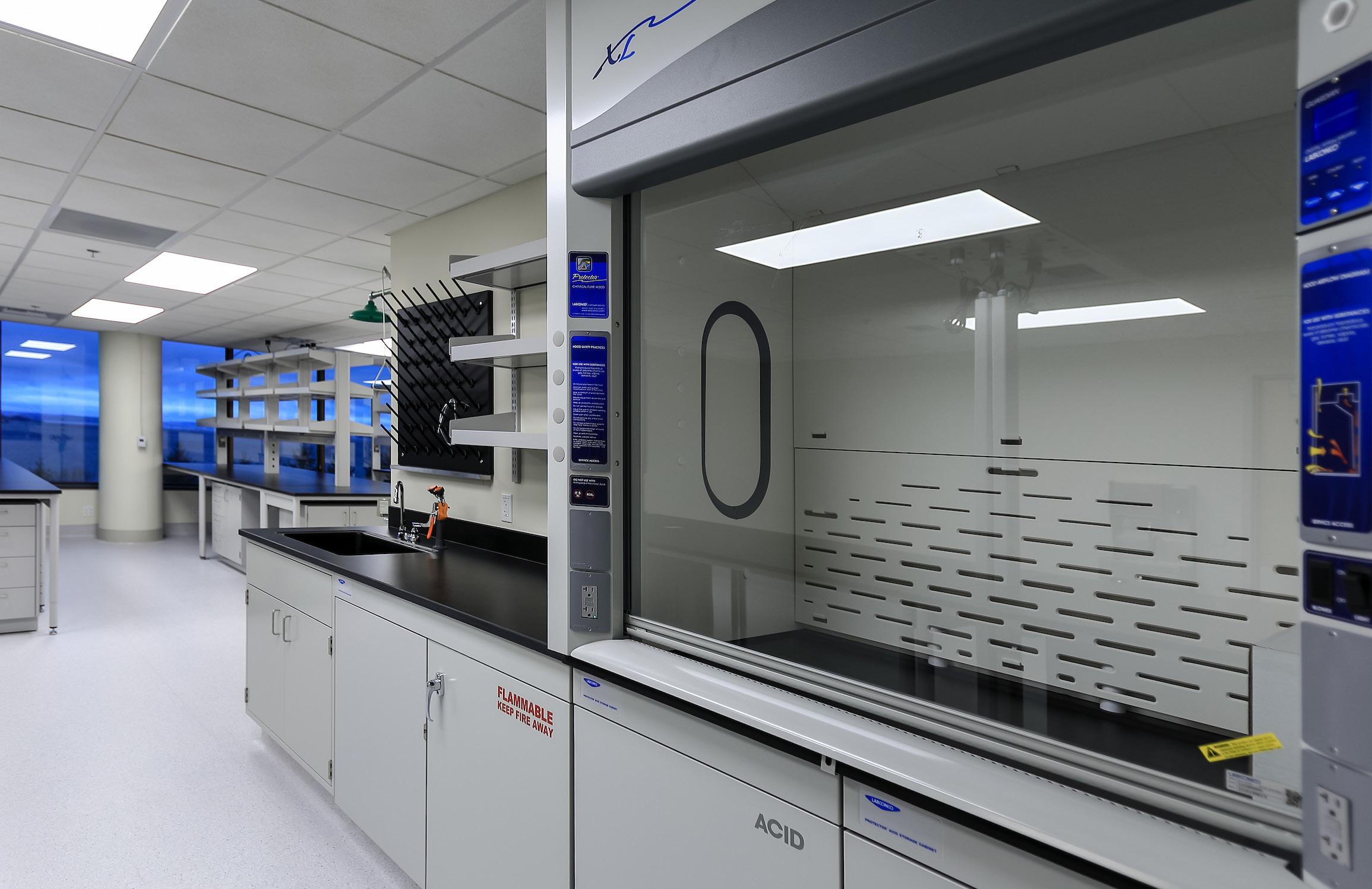
ZYMEWORKS LAB TENANT IMPROVEMENT, SEATTLE
LIFE
SCIENCES, LAB RENOVATION, TENANT IMPROVEMENT
This clinical-stage biopharmaceutical company, developing multi-functional biotherapeutics, Zymeworks expanded its current lab and office spaces into the Seattle area with this 6,750-square foot build-out of Suite 204—the first lab tenant improvement in the 3005 First Avenue building for Beacon Capital.
Initially, the space was programmed as a spec suite, but soon after the award and commencement, Zymeworks finalized their lease, and quickly this project evolved into a build-to-suit project. Zymeworks required significant design changes to meet the tenant requirements, and JTM had to provide “thinkoutside-the-box” solutions to meet the project schedule.
Executing this complex project on an aggressive timeline provided insights for Beacon Capital and its multiple scheduled lab improvements. The shell and core upgrade to the building took place concurrently with the Zymeworks improvement, adding a layer of complexity and sequencing for the build-out.
SIZE
6,750 SF
CLIENT
Beacon Capital / Zymeworks
PROJECT ARCHITECT
SABArchitects
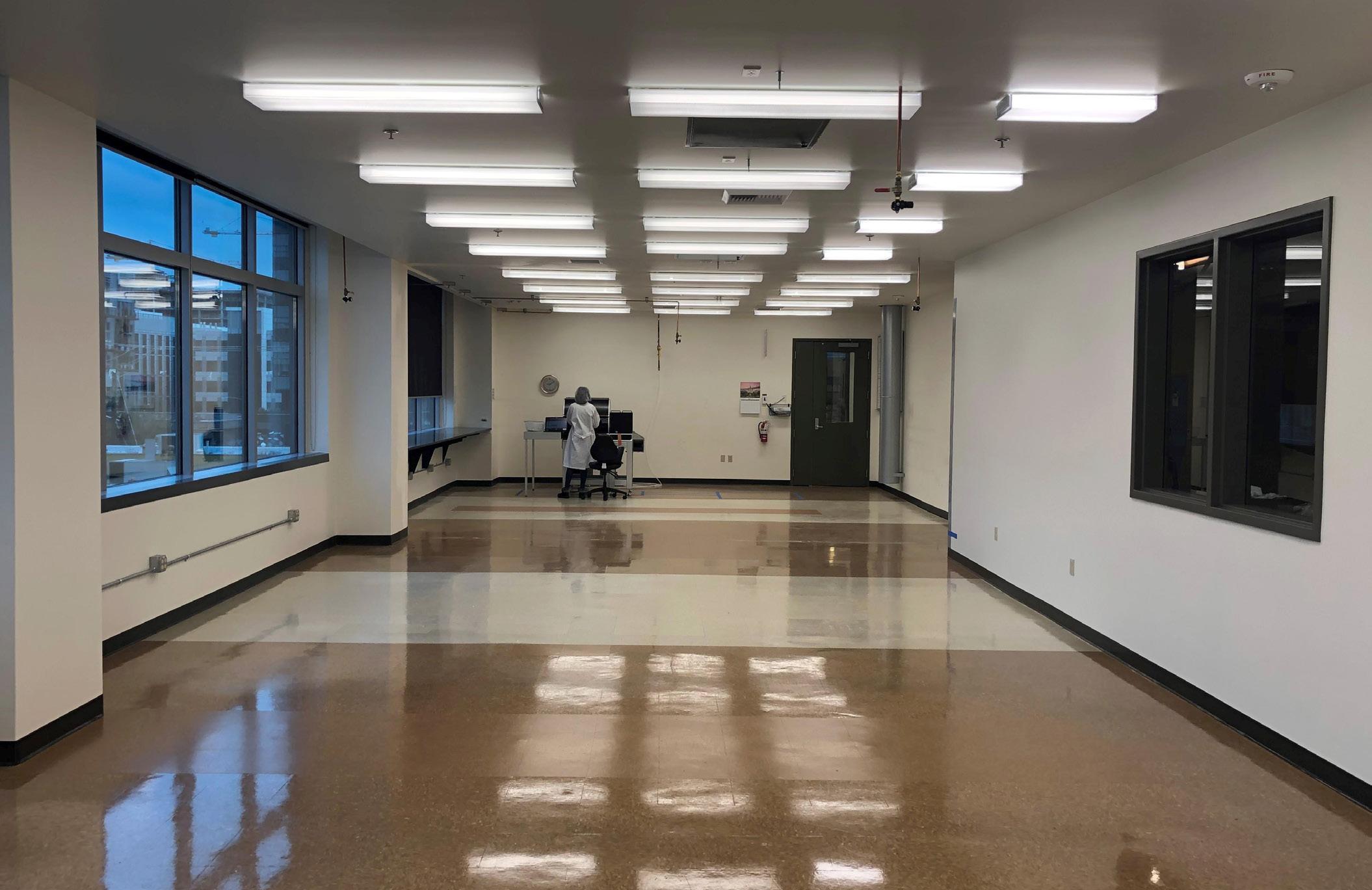
INBIOS LAB CONVERSION, SEATTLE LIFE SCIENCES, LAB RENOVATION, TENANT IMPROVEMENT
This conversion of existing R&D Labs supported a new cleanroom for specialized testing equipment. This project included furnishing and installing new doors, frames, GWB, framing, ACT grid, paint, and specialty window film. The lab “scale-up” was completed two weeks ahead of schedule to allow them to open a dry lab extension for use while keeping the existing dry lab operational for COVID-test kit production throughout the construction of the extension. Close coordination with the Chief Building Engineer required scheduling with the owner-direct contractors on an aggressive construction timeline.
SIZE
1,492 SF
CLIENT
InBios International
PROJECT ARCHITECT
Sheldon Architecture
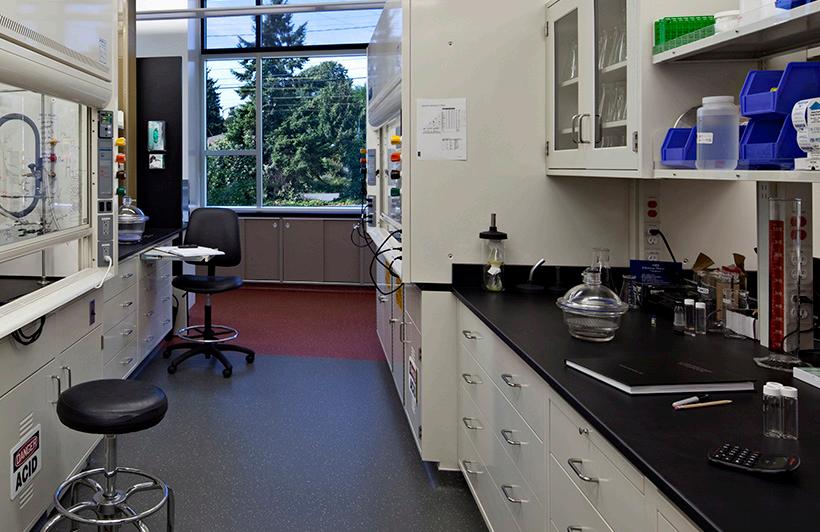
GILEAD LAB 142 TENANT IMPROVEMENT, SEATTLE
LIFE SCIENCES, LAB RENOVATION, TENANT IMPROVEMENT
Interior consolidation of two lab spaces into one larger R&D Chemistry research room. The 1,200-square-foot lab tenant improvement had to be executed directly adjacent to highly sensitive research. They were eliminating impacts to their facility paramount to the owner. Extensive pre-planning and coordination with the design team, owner, and facilities were key to the successful delivery of the project. The project also introduced five new recirculating fume hoods, new metal lab casework with epoxy countertops, and umbilical chasing to support new lab gases and MEP systems.
SIZE
1,200 SF
CLIENT
Gilead Sciences
PROJECT ARCHITECT
SABArchitects
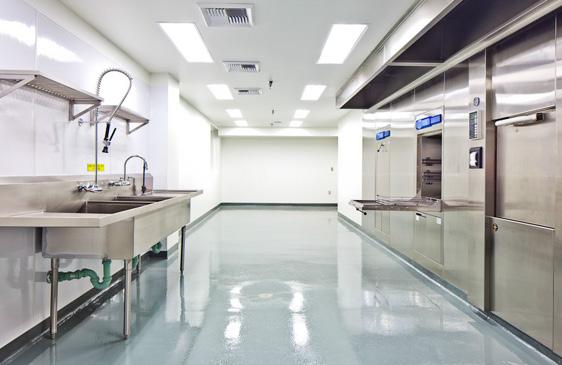
1551 EASTLAKE S&C LIFE SCIENCES UPGRADES, SEATTLE
LIFE SCIENCES, LAB RENOVATION, TENANT IMPROVEMENT
Work on the existing three-story building with basement include retrofitting of existing office spaces into lab and research facilities. This required all new mechanical and electrical systems, including new hot water boiler plant, steam boiler, air handlers and chillers to serve the new lab space and fume exhaust system.
SIZE
80,000 SF
CLIENT
Alexandria Real Estate
PROJECT ARCHITECT
Perkins&Will

ZYMOGENETICS MMF, BOTHELL LIFE SCIENCES, LAB RENOVATION, TENANT IMPROVEMENT
This $25 million project in Bothell, Washington, consisted of the complete renovation of an existing tilt-up structure for ZymoGenetics. This new 25,000-square-foot drug manufacturing facility required significant structural upgrades and new underground utilities. The phased delivery process assisted in delivering the project within the client’s schedule.
SIZE
25,000 SF
CLIENT ZymoGenetics
PROJECT ARCHITECT Perkins&Will

SEAGEN B5 BUILDING RENOVATION, BOTHELL LIFE SCIENCES, TENANT IMPROVEMENT
This $26 million, the 48,000-square-foot single-story tilt-up building was a half lab, half office tenant improvement. It required a complete interior demo and substantial structural upgrades, including building a full second-floor interstitial level to support mechanical systems. The lab consisted of high potency, ASSY, NMR, and mass spectrometer labs. Support systems included glass wash, processed chilled water system, and RODI.
SIZE
48,000 SF
CLIENT
Seagen
PROJECT ARCHITECT
Stock and Associates
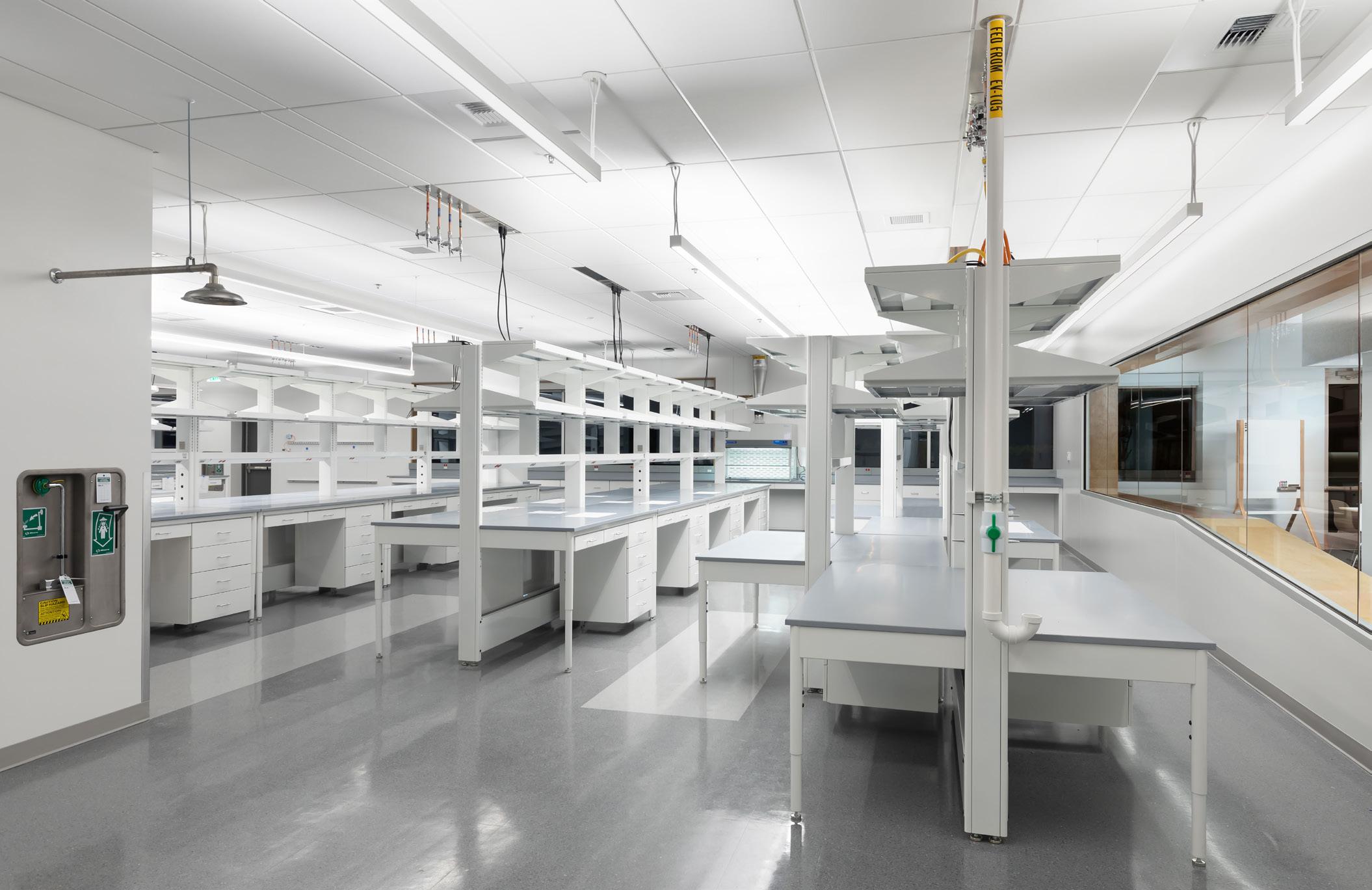
SEAGEN B6 BUILDING RENOVATION, BOTHELL LIFE SCIENCES, TENANT IMPROVEMENT
Seagen B6 implemented the updated campus standards for this halflab, half-office tenant improvement. A $36.5 million, the 48,000-squarefoot single-story tilt-up building required a complete interior demo and substantial structural upgrades, including building an entire second-floor interstitial level to support mechanical systems. B6 introduced state-ofthe-labs implementing mobile casework with ceiling service panels for electrical and gas connections and high-end finishes.
SIZE
48,000 SF
CLIENT
Seagen
PROJECT ARCHITECT
Flad Architects
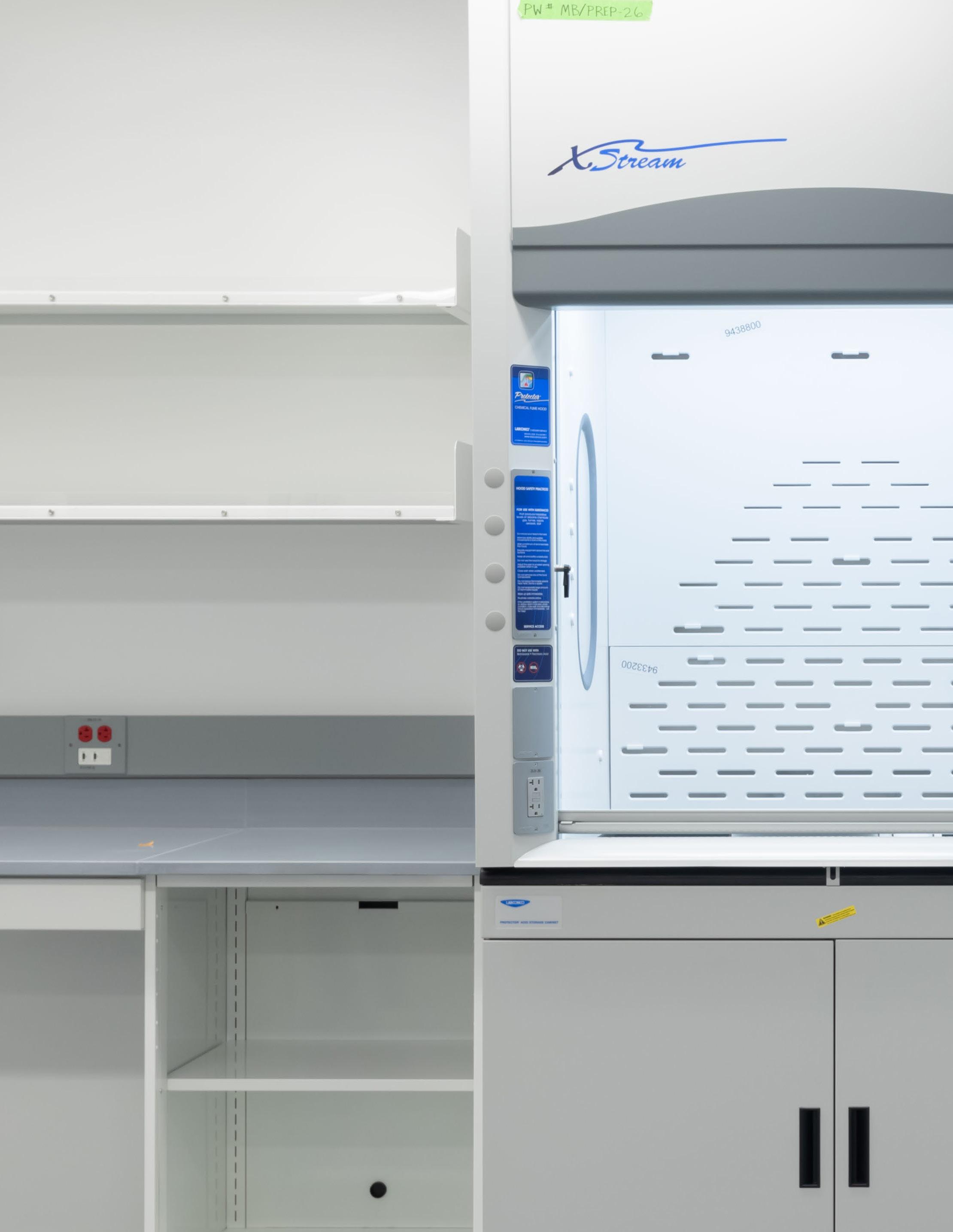
JTM LIFE SCIENCES TEAM
OUR TEAM HAS THE KNOWLEDGE AND SKILL SET TO EXECUTE COMPLEX WORK IN CRITICAL AND OCCUPIED ENVIRONMENTS
JTM Construction believes that the project team’s quality and experience is the most significant factor contributing to a project’s success. We are committed to continuous senior leadership involvement in all aspects of our projects. This involvement provides seamless continuity between the preconstruction and construction phases. Leveraging their extensive experience to ensure the project budget and constructability goals have been obtained.
JTM builders are composed of long-tenured employees, including four of its 15 shareholders. They have extensive vertical construction experience on some of the city’s most complex building sites. Our team also has the Life Science experience necessary to design and build a world-class facility that will attract the region’s best Life Science tenants.
Our project teams are ready to take on any challenge that may arise and have the experience to deliver on our promises we make. Each team member has a unique skillset and temperament that we believe makes them the perfect fit for the client. Whatever your needs, we are confident these team members can meet them.
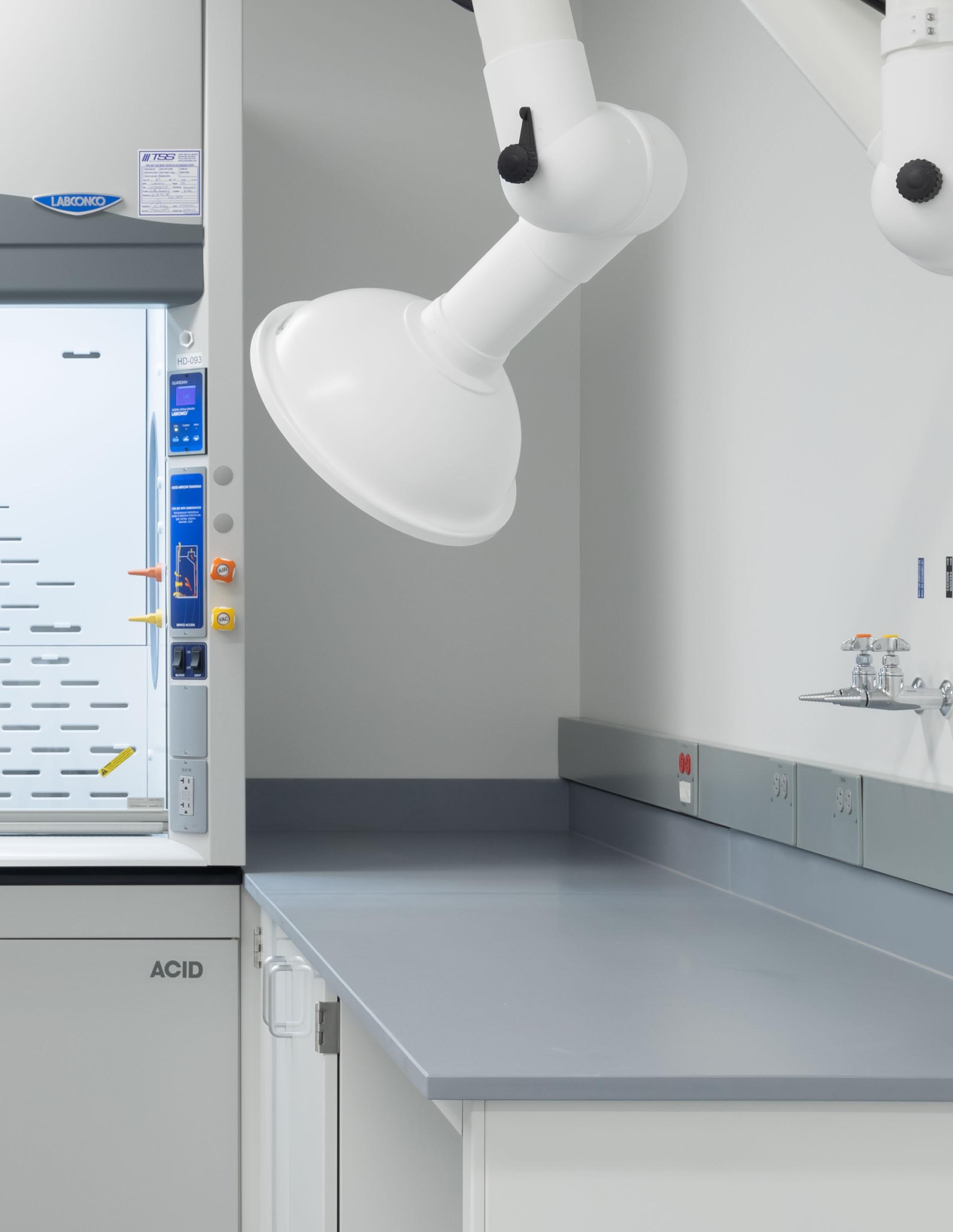
“
JTM WORKS COLLABORATIVELY AND IS ALWAYS EAGER TO FIND SOLUTIONS THAT WORK FOR THE DESIGNERS AS WELL AS THE OWNER.
JTM HAS CONSISTENTLY EXECUTED
PROJECT CONSTRUCTION IN A HIGH-DESIGN ENVIRONMENT WITH A COLLABORATIVE APPROACH.
CONSTRUCTION ALWAYS IS AN ARDUOUS TASK, HAVING A CONSTRUCTION TEAM THAT COMES TO THE TABLE WITH COLLABORATIVE SOLUTIONS MAKE THIS PHASE OF THE PROJECT MORE STRAIGHTFORWARD AND PRODUCTIVE!
— Victor Malerba Jr. AIA,NCARB, LEED GA Associate Principal MG2
JIMMY CRAIG ASSOC. DBIA, LEED AP SPG DIVISION MANAGER & LIFE SCIENCES SPECIALIST
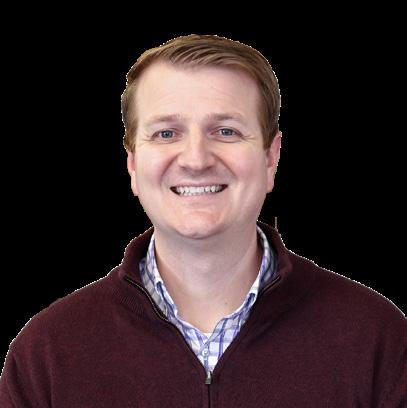
As JTM’s Life Sciences Specialist, Jimmy has successfully managed life sciences tenant improvements and two cGMP Facilities since 2007. Life sciences projects rely on intense pre-planning, deep knowledge of MEP systems installations, keen understanding of clean build protocols. Clients include Institute for Systems Biology, Amgen, Seattle Genetics, Gilead Sciences, and Zymeworks.
EDUCATION | CREDENTIALS
BS Construction Management, University of Washington
DREW CARLSON SUPERINTENDENT, LIFE SCIENCE S
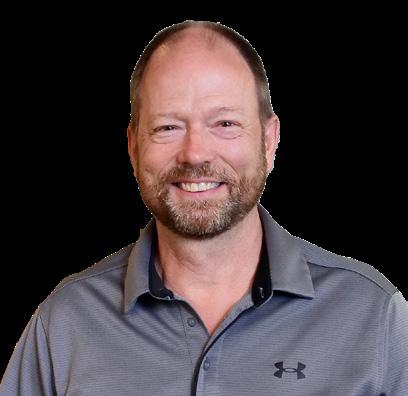
REFERENCES
Scott Lofton, Alexandria Real Estate 206.408.1550
PROJECT EXPERIENCE
» Seagen Clia Lab, Bothell, WA
» Zymeworks Lab Tenant Improvement, Seattle, WA
» Zymogenetics Microbial Manufacturing Facility Bothell, WA
» Bothell Development Lab, Bothell, WA
Bob Vizenor, SABArchitects 206.229.2779
Cody Pettersen, Gilead Sciences 206.228.1889
With over 30 years of commercial construction experience, has primarily included life science projects and expertise in ground-up, tenant improvement, office, education, high-tech, and retail. His collaborative winwin leadership style goes the extra mile to help the field, clients, and partners complete projects with high quality, on time, within budget, and safely.
EDUCATION | CREDENTIALS
Bellevue Community College Western Washington University Carpenters Apprenticeship Program
REFERENCES
Kyle Murdock, PCS Structural Solutions, 206.292.5076
PROJECT EXPERIENCE
» Seagen B5 Potency Lab, Bothell, WA
» Seagen Assay Lab Expansion, Bothell, WA
» Seattle Genetics B6 Structural Upgrade Lab & Office Build-out, Bellevue, WA*
» Seattle Genetics Specialties Lab Vivarium, Bothell, WA*
Dave Philips, Seagen 206.920.1233
Dan Seng, Perkins&Will 206.579.7503
ANNIE THOMAS
PROJECT MANAGER, LIFE SCIENCES
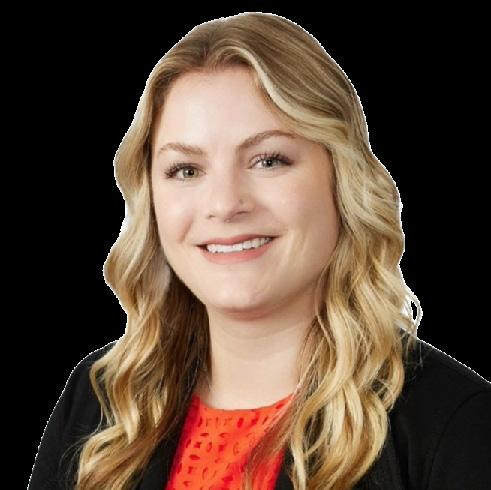
Annie is a top-tier construction project manager. Annie’s intelligence, analytical acumen, and clear communication make her an invaluable asset. She consistently delivers exceptional outcomes, fosters collaboration, and navigates complex challenges adeptly. Annie’s leadership and expertise make her an excellent choice for any project.
EDUCATION | CREDENTIALS
MA, Business Management, Sustainability
Focused & BA, Phychology & Sociology, Seattle Pacific University
OSHA 30 Certified
REFERENCES
Dan Wrenn, AGC Biologics 206.251.2683
PROJECT EXPERIENCE
» Adaptive Biotech HQ, Seattle, WA*
» Silverback Therapeutics, Seattle, WA*
» AGC Bio, B4 Maintenance Shop, Bothell, WA*
» AGC Bio B1 UPD Ambr Lab, Bothell, WA*
» AGC Bio B1 CLD Mol Bio Upgrades, Bothell, WA
Michael Riha, Unico Properties
773.230.7051
Priya Konduru, AGC Biologics 919.534.65862
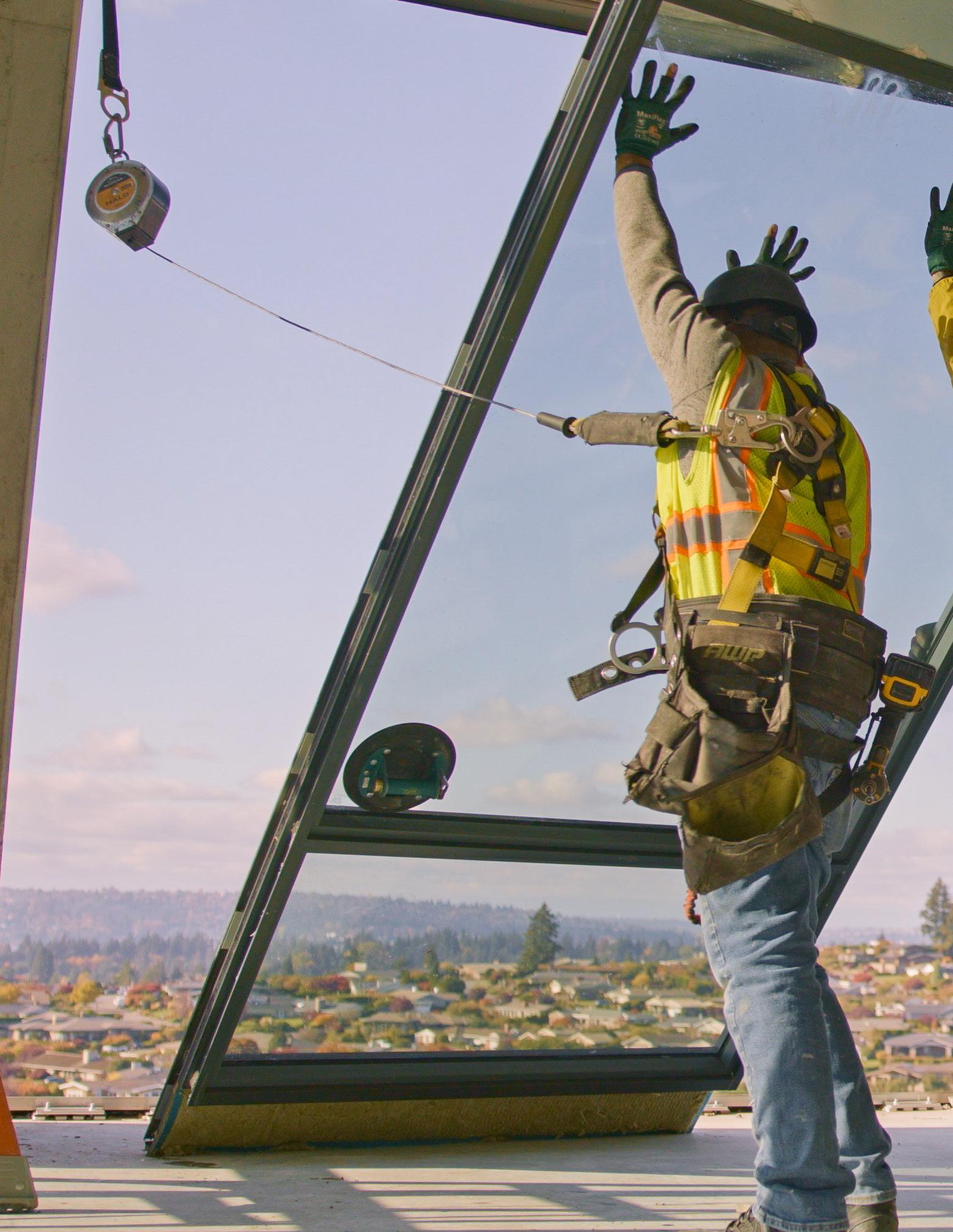
ENSURING A SAFE WORKPLACE
JTM has a comprehensive safety program that protects all employees, subcontractors, owner personnel, site visitors, and the public on ALL of our projects. Establishing programs that promote safe work planning and practices and providing leadership that encourages compliance from all to ensure our documented safety policies and procedures are strictly adhered to. JTM has been a 10+ year member of the AGC’s Safety Team. We make a safe workplace a top priority and have successfully created a safety-conscious corporate culture at JTM, proven by receiving AGC’s Low EMR award for the past 6 years.
SAFETY AWARDS
JTM Construction was honored to recieve three awards from the AGC at the Annual Build Washington Awards:
» Safety Excellence for a General Contractor (250k-500K Hours Worked)
» Safety Professionall of the Year
» Grand Award for Safety Excellence
These awards reflect how our company embraces its role and contributes to making our workplace safe.
JTM EXPERIENCE
MODIFICATION RATE
(EMR) PAST THREE YEARS
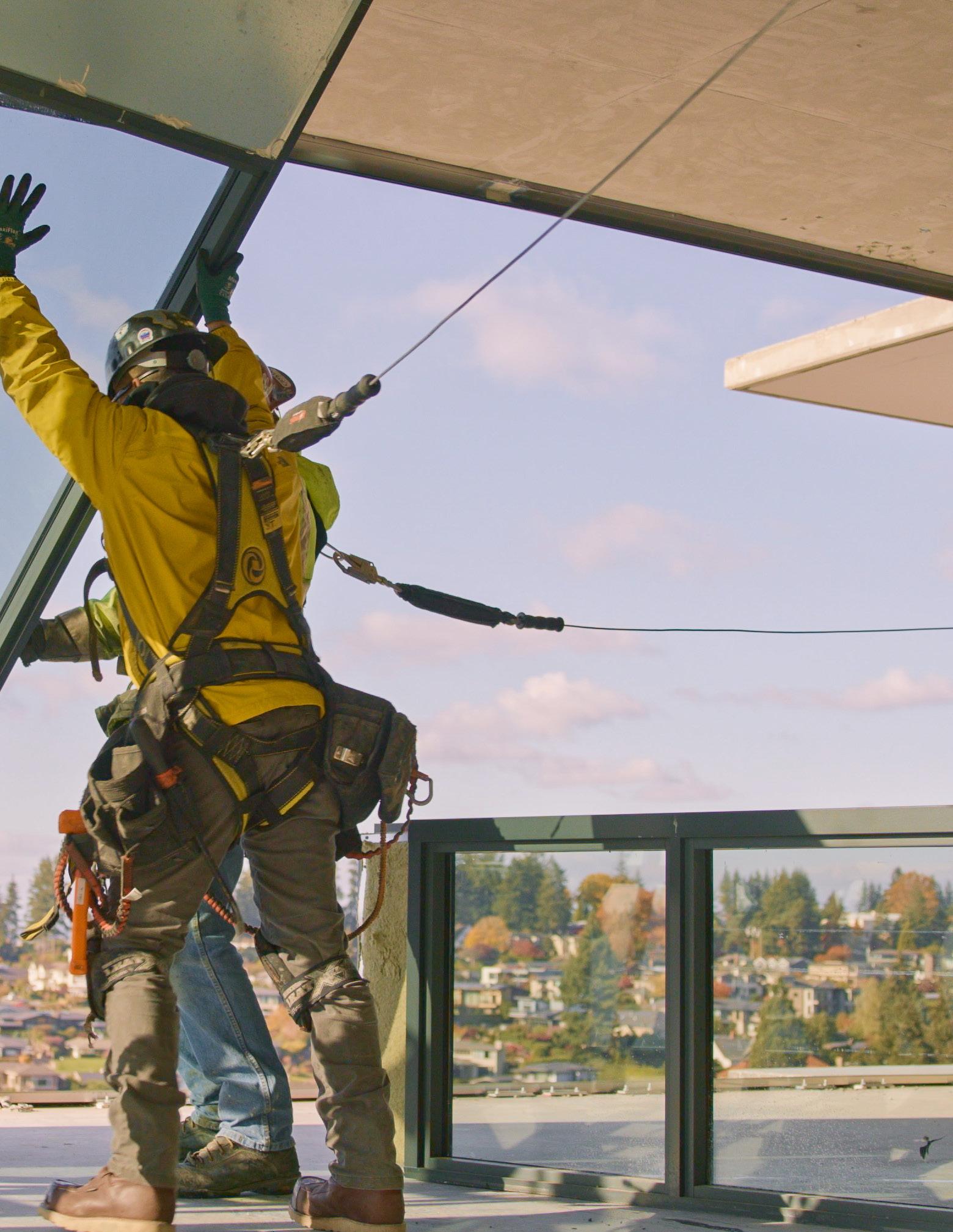
JTM has an EMR of 0.60, which is significantly lower than the industry average. We have maintained an EMR of less than 1.0, which is the industry average.
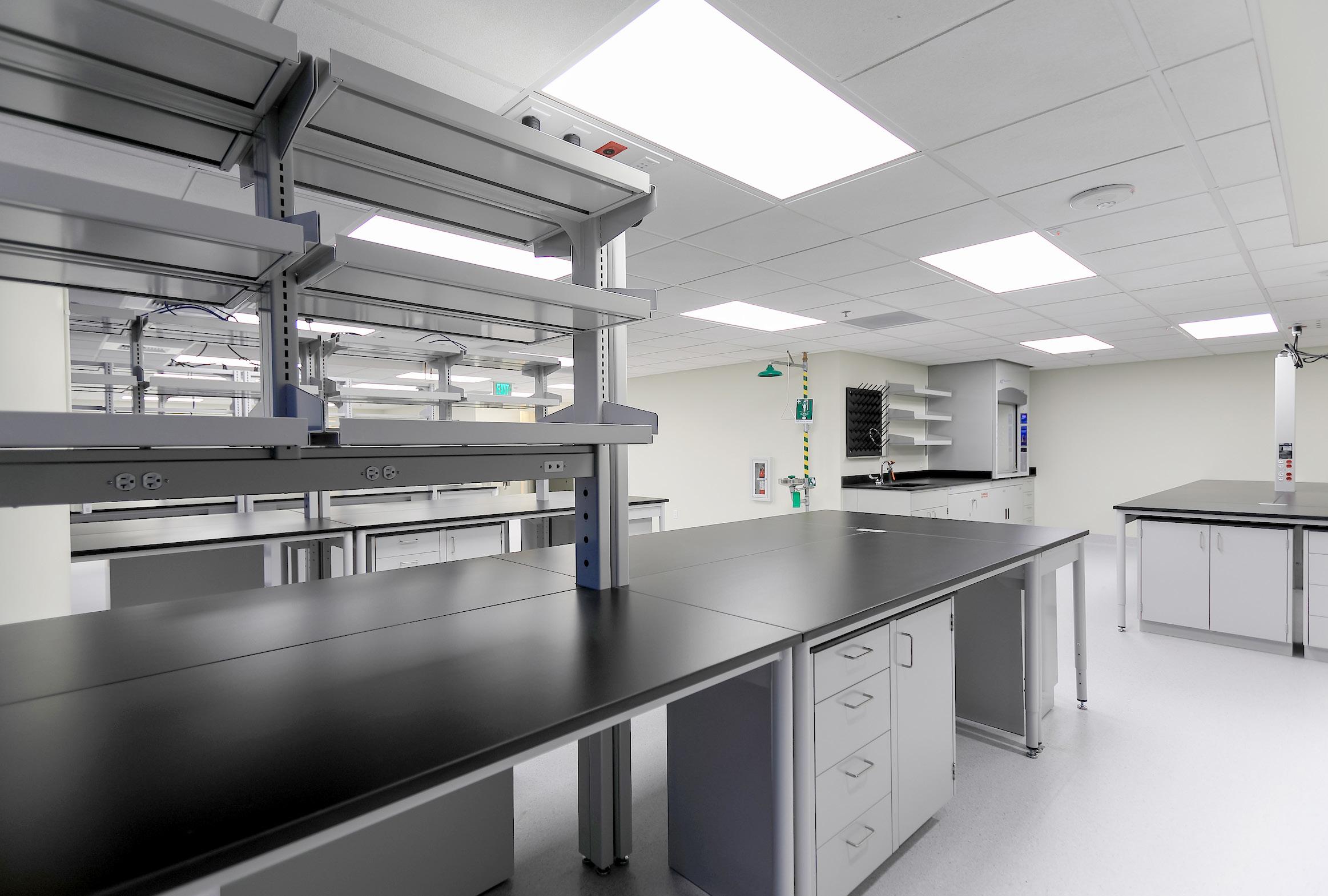
JTM LIFE SCIENCES BEST PRACTICES
BUILDING LABS TAKES A DIFFERENT APPROACH THAN A TRADITIONAL BUILDING
Labs demand complex mechanical systems, carry specific power requirements, and due to the increased air changes per hour in the ventilation system, must minimize potential chemical exposure. In addition, every discovery has the potential to take research in a different direction and could require the introduction of new lab equipment into a recently completed lab.
Consider the installation of specialized equipment, how that particular room, and critical research fits into the master plan of the entire facility. For these buildings to facilitate world-class care and cutting-edge research, unique construction considerations are essential, with extreme attention to detail and highly technical procedures.
BUILDING STRUCTURE DECISIONS
Lab and research buildings must be designed with higher live loads, increased vibration mitigation / reduction (measured in MIPS), and taller floors than their office and tech office cousins. The structural frame options are the same, but those distinguishing factors make the structure selection even more important for lab buildings.
STEEL & CLT PROS
» More future flexibility (easier to saw cut/core drill if needed in the future).
» Faster construction schedule.
» Lower building weight equates to smaller foundation. CONS
» Significant cost increases if a lower MIPS rating desired.
» Thicker deck assembly means lower lab ceilings or taller floor-to-floor heights (which could mean fewer floors depending on maximum allowable height).
» Late design changes are more impactful (more pressure on early design coordination).
MECHANICAL SYSTEMS APPROACH
The amount of air required by labs and the evolving energy code requirements equate to a significant amount of mechanical equipment. Where you plan to put all that equipment is a very important decision that will fall into one of two categories – rooftop or floor-by-floor. Here are the key considerations associated with each approach.
FLOOR-BY-FLOOR PROS
» Flexibility to significantly reduce day one building cost (lab ventilation equipment could be installed with the initial build or deferred to the tenant build-outs).
» Flexibility to provide separate systems for lab and office ventilation creating energy code compliance opportunities.
» Less shaft space is required up through the building.
» Significantly less space is required on the rooftop allowing more flexibility for things like amenity space, PV panels, and base building lab upgrade equipment.
» Less reliant on the decision-making process and pre-planning that occurs throughout the design.
» Overall, less expensive (Day One + Day Two).
» The ability for tenants to pay for what they need vs. potentially having to pay a premium for a system that’s larger than they.
» Ability to “right size” equipment for each tenant.
CONS
» Mechanical rooms on each floor reduce leasable square footage.
» Increased noise and vibration considerations/ mitigation throughout the building.
» Increased impact to existing tenants to build-out new spaces, and when maintaining equipment.
» Significantly more louvers are required in exteriors.
MINIMIZING IMPACT
F UTURE-PROOFING ON MEP SYSTEMS
» FUME EXHAUST INFRASTRUCTURE | If fume exhaust is a requirement in the future, considerations of placing a slab block out or welded stainless steel duct during initial construction could pay dividends in the long run. It’s much easier to place those elements now than in occupied labs.
» AIR HANDLER SIZING | Developing strategies to oversize the air handler’s day one, taping into existing duct runs, and rebalancing a system is more efficient than upsizing AHU on day two. Added structural work and replacing central ductwork could create significant facility impacts.
» LAB UTILITIES / GASES | Creating an intelligent initial design on the lab utilities can create minimal impacts for the future. One can significantly minimize the lab utility shutdown impacts on each floor by utilizing lab gas piping loops off the mains and valving both ends and midpoints of the loop.
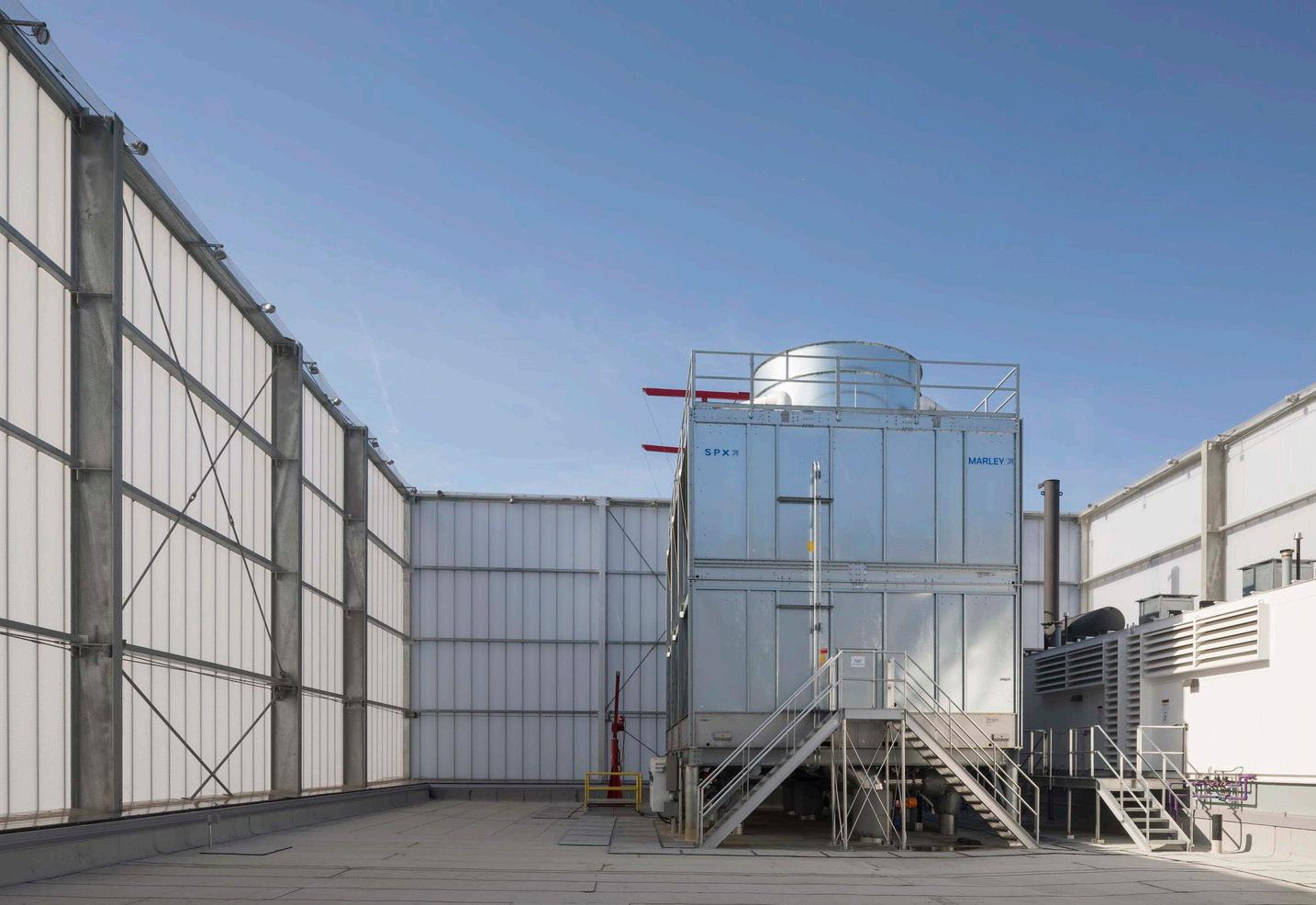
» RODI/PURE WATER SYSTEMS | By adding valves and short spools to a RODI or other clean piping systems, an owner can save money by sanitizing the new section locally, not having to disrupt the service the entire building.
OTHER CONSIDERATIONS
» INTERSTITIAL FLOORS | Significant day-one cost increase but allows for ultimate future flexibility.
» OVERSIZED DOORS | Allowing for larger equipment to be installed on day two.
» LOADING DOCK SIZING | Don’t make this your facility pinch point.
» HIGHER CAPACITY FREIGHT ELEVATORS.
JTM GIVES BACK TO OUR COMMUNITIES
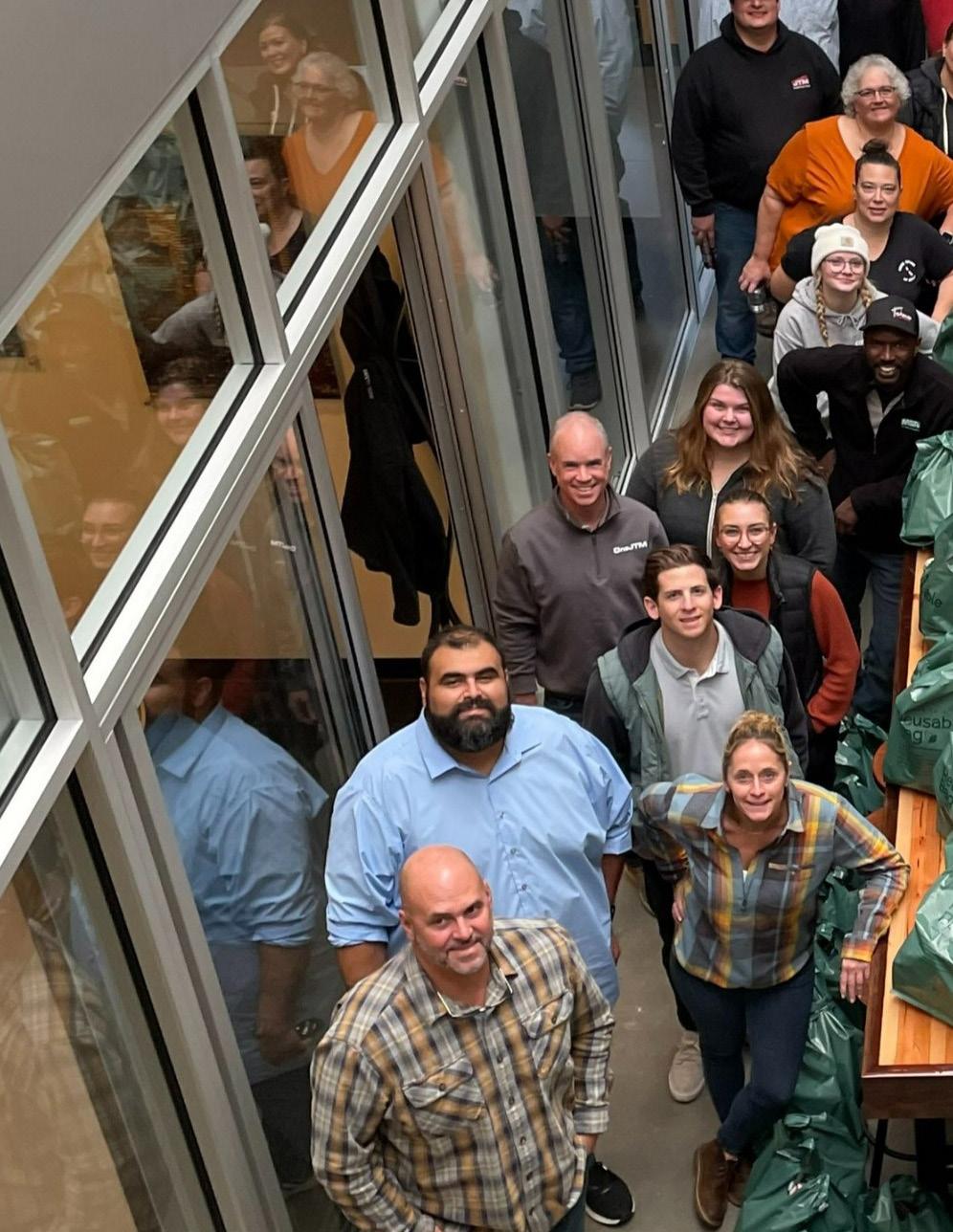
At JTM Construction, it’s our culture to give back to the communities in which we live and work. We support our team members and organizations doing great things.
SAFETY NET
We are supporting health, wellness, and those in need.
ENVIRONMENT
Maintenance and enhancement of the resources that surround us are essential.
COMMUNITY FUTURE
Encourage efforts to participate in non-profit organizations of their choice.
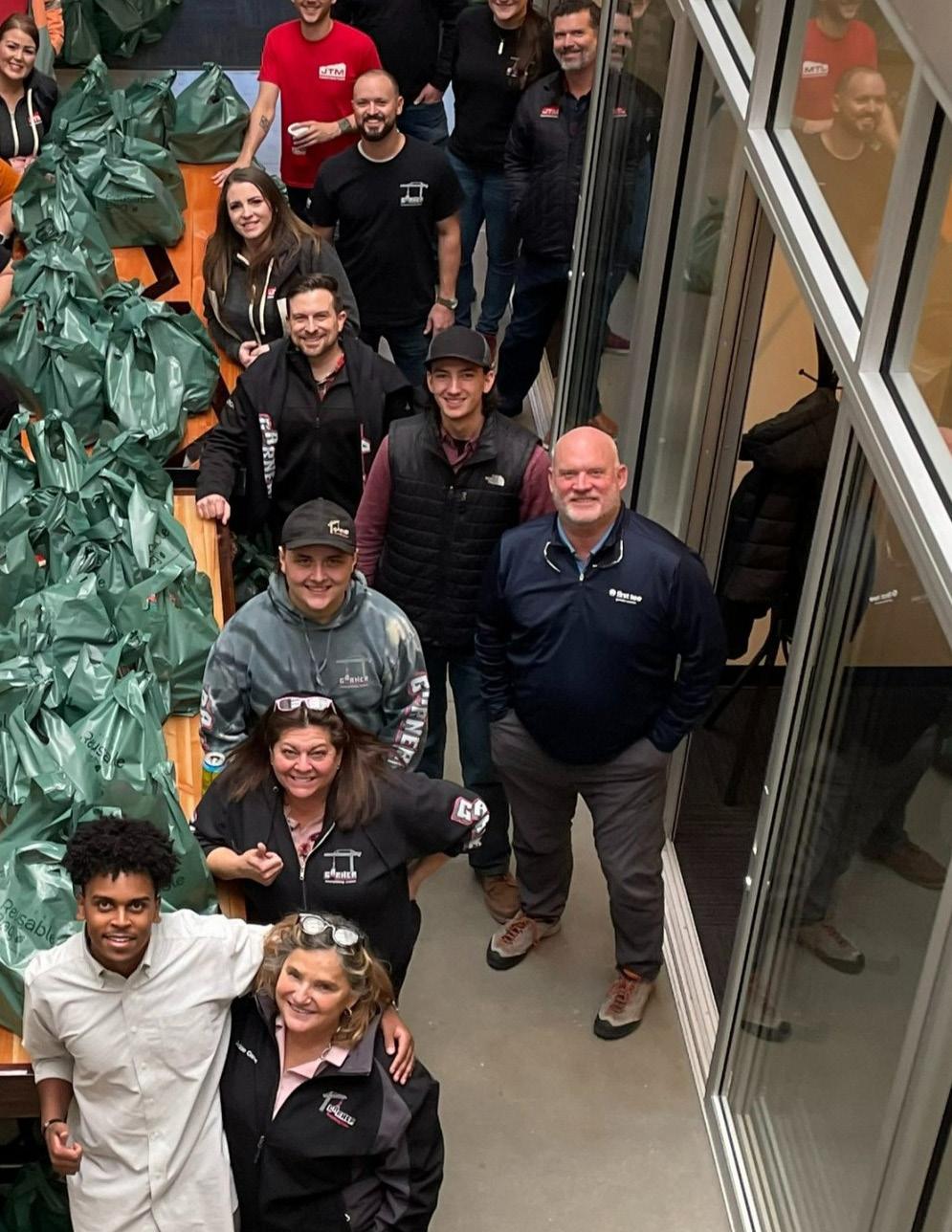
ORGANIZATIONS WE SUPPORT
» American Heart Association
» Childhaven
» Community Turkey Drive
» Construction For Change
» Culture of Care
» Cycle Therapy
» Farestart
» Food Lifeline
» Goodwill
» InvestED
» Juvenile Diabetes Research Foundation
» KidsQuest Children’s Museum
» Mary’s Place
» NAIOP Community Enhancement
» Northwest Carpenters Union
» Raven Rock Ranch
» The First Tee of Greater Seattle
» United Way of King County
» YouthBuild
LEVERAGING VDC FROM PRECONSTRUCTION THROUGH CONSTRUCTION
JTM leads and manages the VDC/BIM process on all of its commercial projects from preconstruction through construction. JTM’s in-house VDC/BIM team has developed a robust “JTM Construction Collaborative Construction and Design Execution Plan” implemented on all JTM commercial projects.
During the various phases of the design and construction, JTM has multiple tools to identify, provide insight, and recommend solutions for:
√ Site’s logistical complexities
√ Scope clashes
√ Design conflicts
√ As-built condition verification
√ Quality Control for future elements
√ Schedule challenges
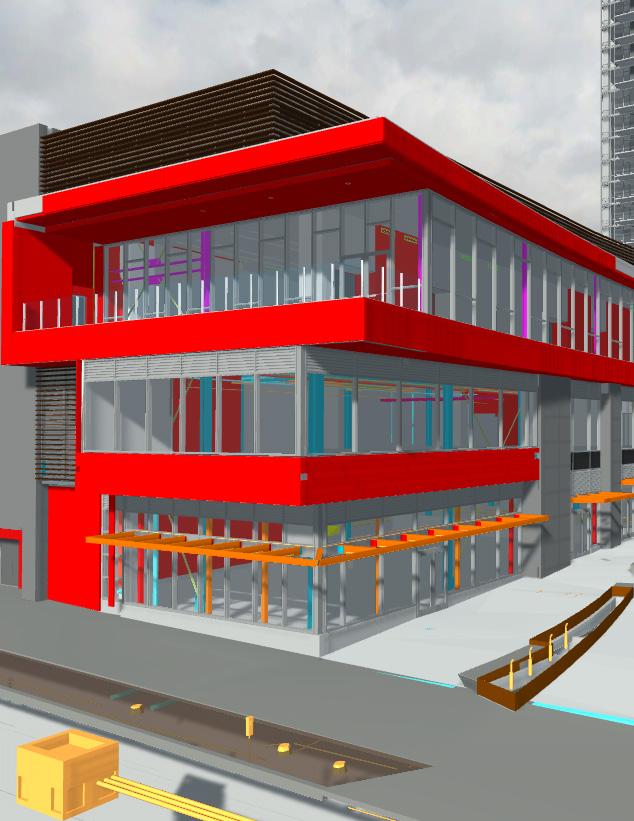
OUR VDC TEAM HAS BEEN A PART OF THE COORDINATION AND DESIGN PROCESS OF SOME OF THE INDUSTRY’S MOST COMPLEX, MISSION-CRITICAL BUILDING TYPES, RANGING FROM RESIDENTIAL AND OFFICE HIGH-RISES, DATA CENTERS, MEDICAL OFFICE BUILDINGS, LIFE SCIENCES LABS, HOTELS, AND EVERYTHING IN BETWEEN.
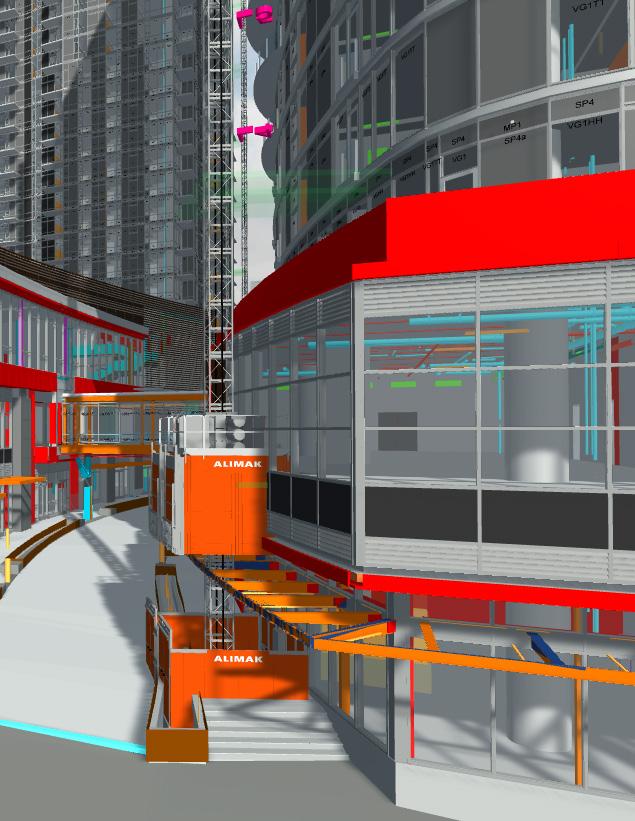
“
JTM IS FIRST AND FOREMOST A PARTNER. THROUGHOUT PRECON AND CONSTRUCTION, THEY LOOK FOR OPPORTUNITIES TO HELP US ACHIEVE OUR PROJECT GOALS, AND THEY HAVE A SCRAPPY, OUTSIDE-THEBOX MENTALITY THAT HELPS THEM FIND UNIQUE SOLUTIONS TO PROJECT CHALLENGES.
— Sean O’Brien | Urban Visions
JIMMY CRAIG ASSOC. DBIA, LEED AP SPG DIVISION MANAGER & LIFE SCIENCES SPECIALIST
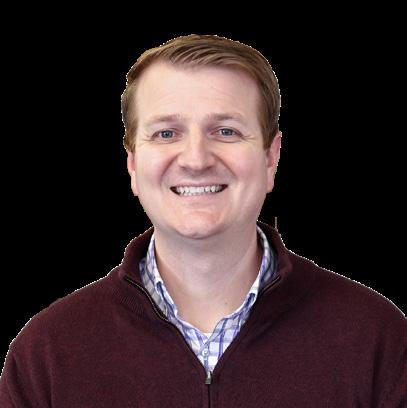
As JTM’s Life Sciences Specialist, Jimmy has successfully managed life sciences tenant improvements and two cGMP Facilities since 2007. Life sciences projects rely on intense pre-planning, deep knowledge of MEP systems installations, keen understanding of clean build protocols. Clients include Institute for Systems Biology, Amgen, Seattle Genetics, Gilead Sciences, and Zymeworks.
EDUCATION | CREDENTIALS
BS Construction Management, University of Washington
DREW CARLSON SUPERINTENDENT, LIFE SCIENCE S
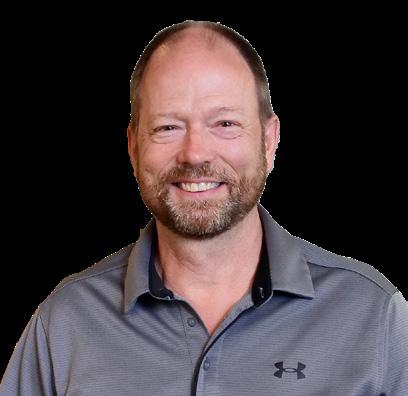
REFERENCES
Scott Lofton, Alexandria Real Estate 206.408.1550
PROJECT EXPERIENCE
» Seagen Clia Lab, Bothell
» Zymeworks Lab Tenant Improvement, Seattle
» Zymogenetics Microbial
Manufacturing Facility Bothell
» Bothell Development Lab, Bothell
Bob Vizenor, SABArchitects 206.229.2779
Cody Pettersen, Gilead Sciences 206.228.1889
With over 30 years of commercial construction experience, has primarily included life science projects and expertise in ground-up, tenant improvement, office, education, high-tech, and retail. His collaborative winwin leadership style goes the extra mile to help the field, clients, and partners complete projects with high quality, on time, within budget, and safely.
EDUCATION | CREDENTIALS
Bellevue Community College Western Washington University Carpenters Apprenticeship Program
BRYDEN MATHIS PROJECT MANAGER, LIFE SCIENCES
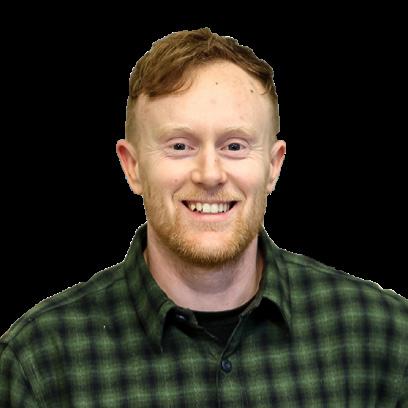
REFERENCES
Kyle Murdock, PCS Structural Solutions, 206.292.5076
PROJECT EXPERIENCE
» Seagen B5 Potency Lab, Bothell
» Seagen Assay Lab Expansion, Bothell
» Seattle Genetics B6 Structural Upgrade Lab & Office Build-out, Bellevue*
» Seattle Genetics Specialties Lab Vivarium, Bothell*
Dave Philips, Seagen 206.920.1233
Dan Seng, Perkins&Will 206.579.7503
Bryden is a detail-orientated, client-focused, results-driven project manager. He has successfully constructed multiple projects of varying sizes, from shell and core, tenant improvements, to occupied buildings, coordinating lab renovation and interior build-out work ensuring each meets client requirements and is completed on time and within budget.
EDUCATION | CREDENTIALS
BS Engineering, North Carolina University
UW BIM Certification, PMP Certification
REFERENCES
Herbert Baker, SABArchitects 206.957.6400
PROJECT EXPERIENCE
» Multicare Covington Campus, Covington*
» Zymeworks Lab Tenant Improvement, Seattle
» Seagen B5 Assay Lab, Seattle
» Inbios Lab Tenant Improvement, Seattle
Kayln McClure, Beacon Capital 206.386.5387 Joe Dixon, Swenson Say Faget 206.443.6212
BENJAMIN COFFMAN LEED AP PRESIDENT
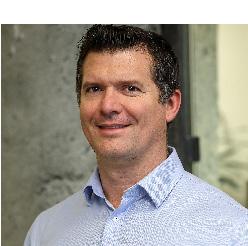
Ben has established a reputation as a premier builder over his career at JTM, managing its most significant and complex projects. He is a natural leader who actively engages with his team and clients. As Vice President, Ben challenges his teams to think outside the box, improve processes, and look for solutions that benefit the client, the project, and JTM.
EDUCATION | CREDENTIALS
BS Civil Engineering, University of Colorado
Certificate Commercial Real Estate, University of Washington
KYLE NEVILS LEED AP BC+D VICE PRESIDENT OF PROJECT MANAGEMENT
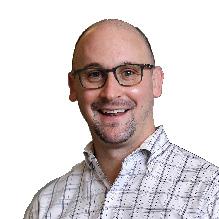
REFERENCES
Greg Smith, Urban Visions 206.262.2880
PROJECT EXPERIENCE
» Ovation Apartment Towers, Seattle
» F5 Tower at 5th & Columbia, Seattle
» The Jack, Seattle
» Weyerhaeuser HQ at 200 Occidental, Seattle
» South Hill Business & Technology Center, Puyallup
Brad Hinthorne, AIA, LEED AP BD+C, Perkins&Will, 206.381.6019
Bryan Zagers, Coughlin Porter Lundeen, 206.343.0460
Kyle is one of JTM’s most experienced and trusted managers. His track record of delivering large, complex, ground-up projects is attributed to the partnerships he creates with our clients and design team. Kyle’s attributes include strong estimating and scheduling technical skills and a willingness to dive into the details without compromising the relationships with the team and subcontractor community.
EDUCATION | CREDENTIALS
BS Construction Management, Washington State University
REFERENCES
Dan Shieder, Quarterra
206.683.2966
PROJECT EXPERIENCE
» Ovation Apartment Towers, Seattle
» 6100 Building, Seattle
» Weyerhaeuser HQ at 200 Occidental, Seattle
» Stadium Place, The NOLO & THE WAVE , Seattle
» O2 Apartments, Seattle
Broderick Smith, Silent Water Real Estate, 425.241.6155
Ian Klein, Westlake Consulting Group, 206.255.7828
TORREY DAVIS LEED AP BC+D
PROJECT EXECUTIVE
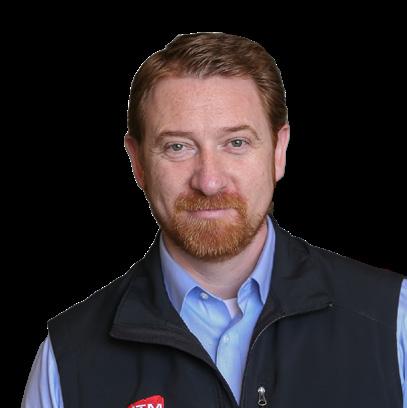
Torrey is a jack of all trades with a vast experience in various commercial building types, whether it is office, life science, or residential, there are very few things Torrey has not seen before. He applies his experience to his project, providing the team with the confidence and creativity necessary to complete the most complex challenges.
EDUCATION | CREDENTIALS
BS Construction Management, University of Washington
KYLE M. DAVIS ASSOC. DBIA, LEED AP DIRECTOR OF PRECONSTRUCTION
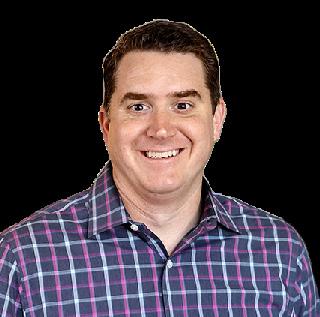
REFERENCES
Sean O’Brien, Urban Visions 206.507.5050
PROJECT EXPERIENCE
» The Jack, Seattle, WA
» Stadium Place, The NOLO & THE WAVE , Seattle, WA
» O2 Apartments, Seattle, WA
» Russell Investments Tower, Seattle, WA
Max Blume, Blume Development 206.327.6150
Garo Pehlivanian, Coughlin Porter Lundeen, 206.343.0460
& ESTIMATING
Kyle brings his best-in-class preconstruction for our clients through constructability, market research, and detailed estimates. He leverages his experience to successfully tee up projects before the shovel hits the ground to the GMP, taking the project to completion, working hard and creatively with the owners and design team to complete the project successfully and on-budget.
EDUCATION | CREDENTIALS
BS Construction Management, University of Washington
REFERENCES
Scott Holbrook, KG Investments
206.423.8463
PROJECT EXPERIENCE
» USCD Jacobs Cardiac Wellness Lab, La Jolla, CA*
» Scripps Mercy Cancer Center, San Diego, CA*
» UCSD Thornton Hospital Froze Section, San Diego, CA*
» Dignity St. Johns Camarillo Hospital Addition, Camarillo, CA*
Mike Nelson, Trammell Crow
206.708.6152
Luis Martinez, Gemdale USA
206.949.9064
SEAN SORAN
PROJECT ENGINEER
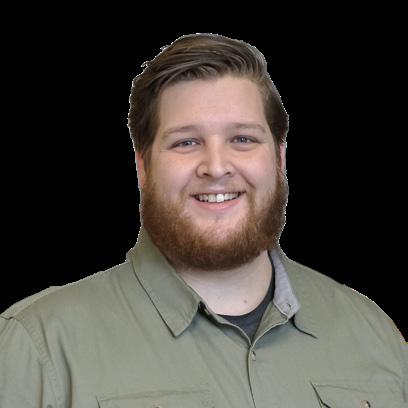
Sean’s experience in life science and technology industries aligns well with his estimating, project management, and material procurement responsibilities. He focuses on practical, effective, and timely communication — his dedication to excellence and commitment to exceeding expectations ensure the project’s success.
EDUCATION | CREDENTIALS
BS Aviation Professional Pilot , Central Washington University
REFERENCES
Christopher G. Anthony, InBios Inc., 425.503.6960
PROJECT EXPERIENCE
» Zymeworks Lab Tenant Improvement, Seattle, WA
» Seagen Sustaining Campus, Bothell, WA
» InBios Tenant Improvement, Seattle, WA
» Biomed Realty Sustaining Campus, Seattle, WA
Elizabeth Dickey, BioMed Realty 858.472.1977
Jeffey Price, Seagen 425.626.0238
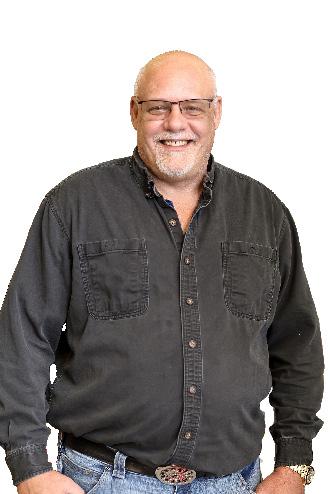
Jim thrives on utilizing his experience and delivering complex and challenging projects. His leadership and communication skills allow him to provide high-quality work and maximize his strengths throughout pre-planning, value-engineering solutions, and logistics plans for the site and supporting the field staff. Project schedules emphasize safety and efficiency, keeping an eye on the bottom line.
EDUCATION | CREDENTIALS
Lead Awareness Training; Army Corp of Engineering Quality Control; Lockout / Tagout Control of Hazardous Energy; OSHA 30
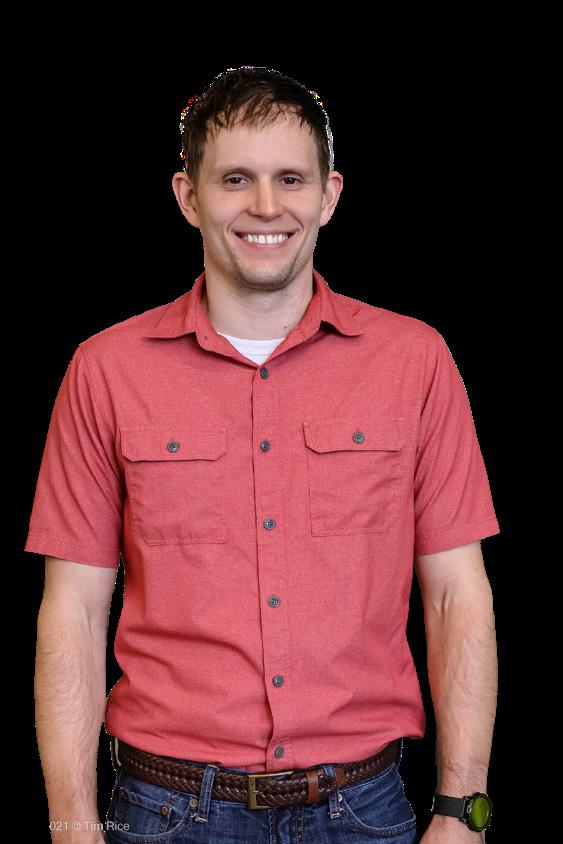
REFERENCES
Mike Hubbard, Capstone Partners 206.652.3364
PROJECT EXPERIENCE
» Esterra Park Block 3, Redmond, WA
» F5 Tower at 5th & Columbia, Seattle, WA
» Dexter Station, Seattle, WA
» Kirkland Urban Campus, Kirkland, WA
Mike Duffy, Duffy DevelopmenT, 206.406.9148
Michael Petersen, LMN Architects 253.377.1830
Corey’s extensive life sciences experience and working in occupied buildings have prepared him for any building challenges. Corey brings his attention to detail, planning, excellent communication skills, and commitment to exceeding the client’s expectations. He works closely with the team, trade partners/subcontractors, and the client to ensure the project is completed efficiently and on-time.
EDUCATION | CREDENTIALS
BA Business Administration, Central Washington University
REFERENCES
Christopher G. Anthony, InBios, Inc., 425.503.6960
PROJECT EXPERIENCE
» Zymeworks Lab Tenant Improvement, Seattle, WA
» Seagen b5 assay lab, Bothell, WA
» InBios Tenant Improvement, Seattle, WA
» gilead lab 142 tenant improvement, Bothell, WA
Lauren Hammond, Alexandria Real Estate, 206.375.1287
Emma Gaulke-Janowski, Gensler 206.654.2106
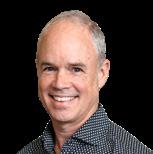
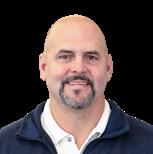

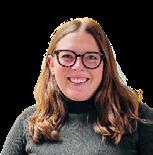
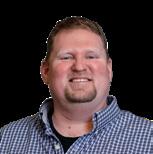
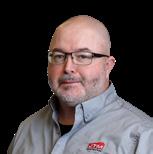
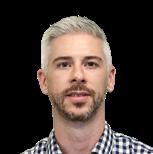
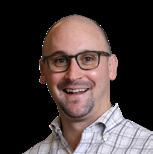


JENNI COX
MARTIN
KYLE NEVILS
JESSICA BARRY Controller
COHEN MORRIS Dir. Project Controls
DUSTIN SCOGGINS Yard Manager
JUSTIN SCOTT Dir. of IT
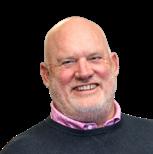
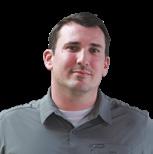
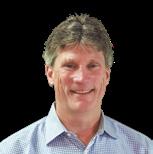
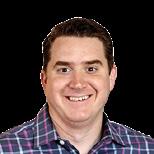
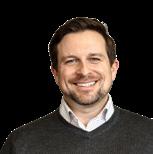