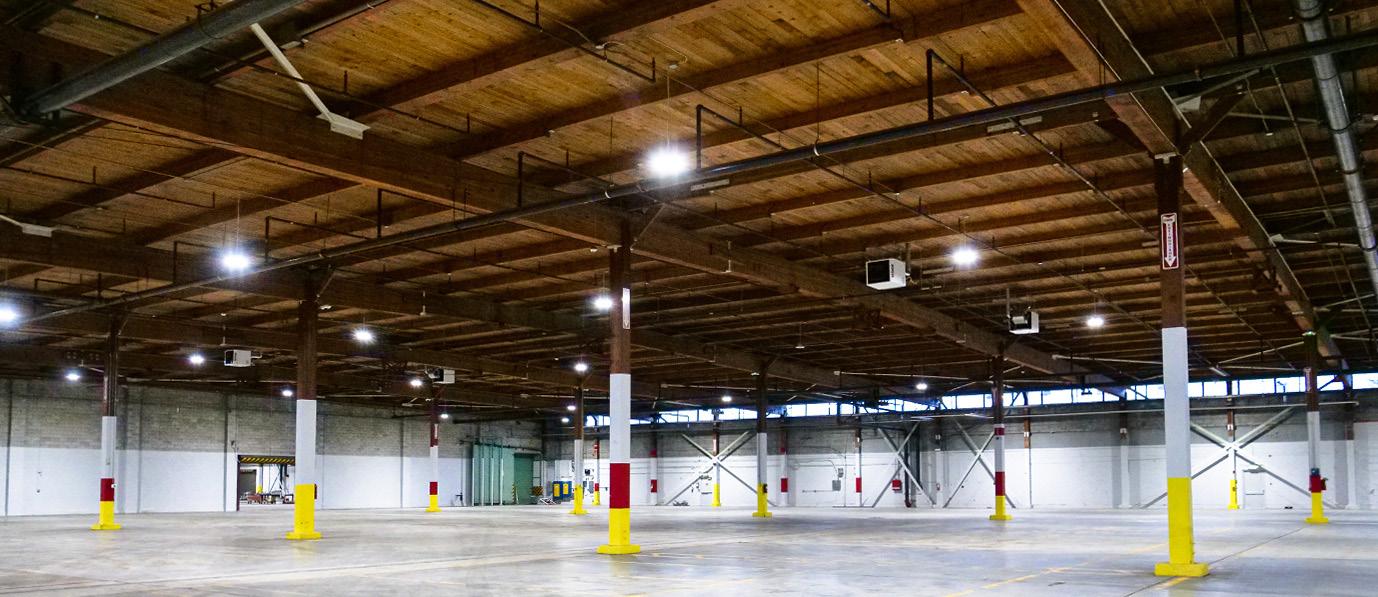
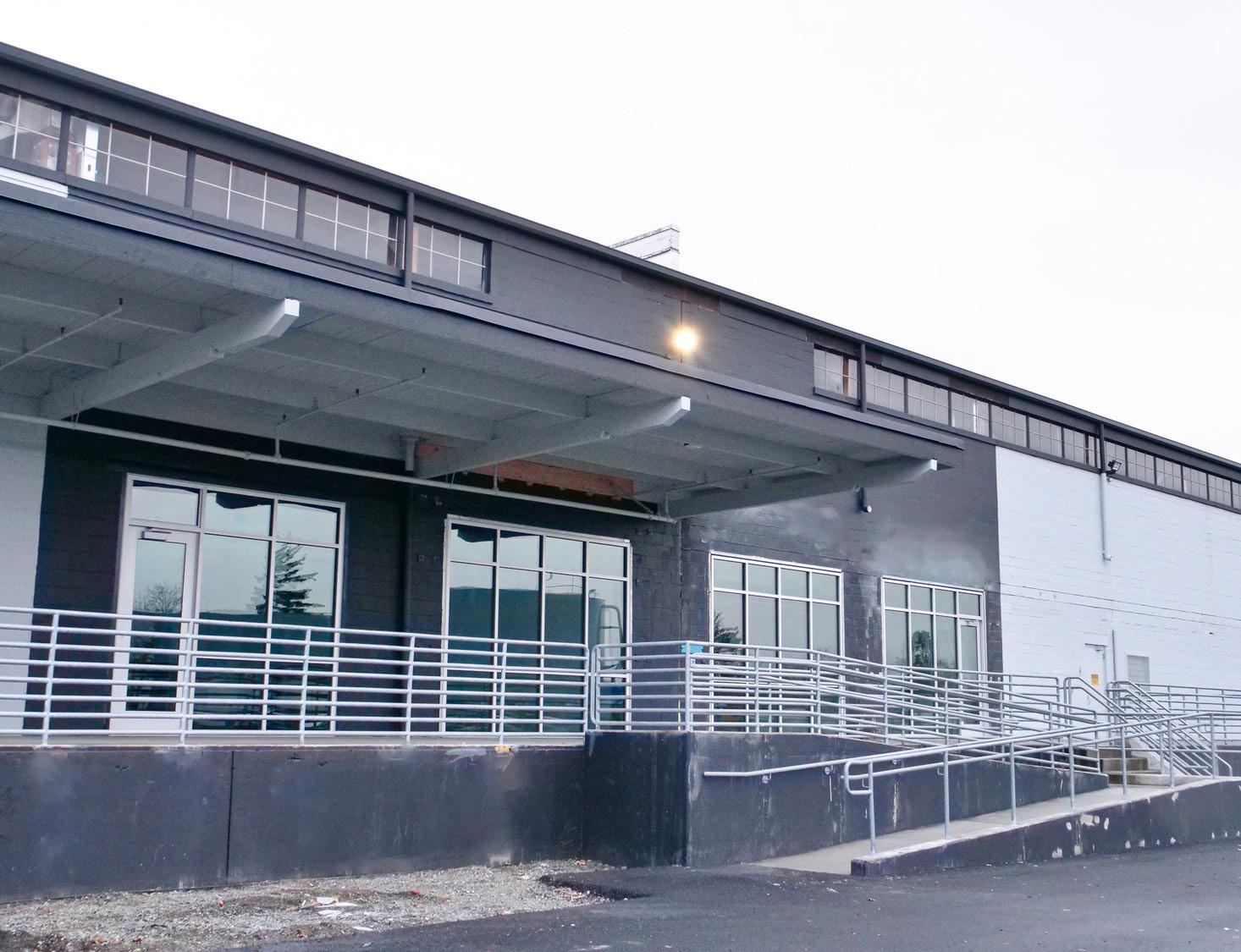
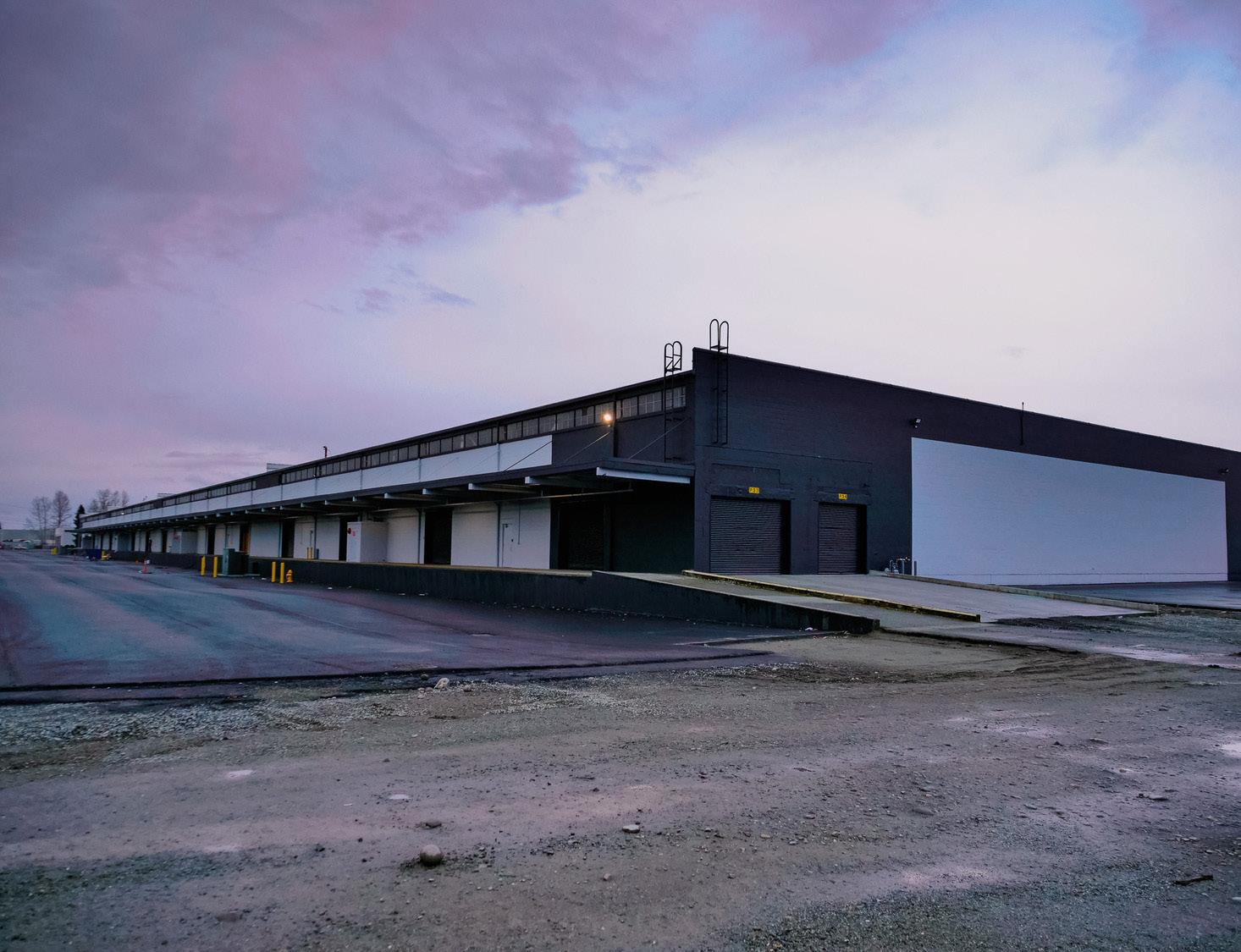
INDUSTRIAL & WAREHOUSE EXPERIENCE
INDUSTRIAL & WAREHOUSE EXPERIENCE
The JTM Founders created a Puget Sound Commercial General Construction company that focuses on building long term relationships, and building complex projects, through our broad qualifications, knowledge, and commitment to our core values.
Established in 2005, JTM Construction was founded with over a century of combined experience in the construction industry. Since its inception, JTM has grown into a trusted Seattle-based general contractor, renowned for delivering high-quality projects across project sectors including tenant improvements, office, warehouse and industrial, residntial, new developments, and community-based projects.
At JTM, we are builders dedicated to forming lasting client relationships and committed to integrity in everything we do. Passionate, energetic, and entrepreneurial, we approach every project with innovation and precision. Our experience, structure, and size allow us to excel on projects of any scope or complexity, ensuring success from start to finish.
We protect our people and the community like family.
We take pride in relationships built on trust and reinforced by our actions.
5900 Airport Way
South, Suite 110, Seattle, WA 98108
PSBJ WA Best Places to Work (2024, 2023, 2022, 2021)
Excellence in Innovation
AGC Build Washington Awards (2023)
Culture of Care Awareness, AGC (2021)
Visionary Award for Leadership
Seattle 2030 District Vision Awards (2016)
Occupational Excellence
Achievement Award
National Safety Council (2023)
Safety Professional of the Year, AGC Safety Excellence Award (2023)
GC 250k-500k Worker Hours
AGC Safety Excellence Award (2023)
Grand Award, AGC Safety Excellence Award (2023)
General Contractor 250-300K Hours
AGC Safety Excellence Award (2022)
National Construction Safety
Excellence AGC EMR Award (2022, 2021, 2020, 2019, 2018, 2017)
We empower our people to challenge convention.
ENERGY
We bring passion and enthusiasm to our work and celebrate client, project, and individual successes.
ACCOUNTABILITY
We deliver on our commitments. COMRADERY
We deliver on our commitments.
The senior leadership team comprises individuals who are all local, ensuring a deep understanding of the community and its unique needs. This local expertise enables us to make informed decisions that will have a significant impact on your project. With our decision-making capabilities centralized in one place, we can streamline the process and ensure the efficient execution of your vision. Our team’s collective knowledge and experience empower us to navigate any challenges that may arise, ensuring the success of your project. Trust in our local ownership and decision-making prowess to bring your project to fruition.
BEN COFFMAN PRESIDENT
WARREN JOHNSON DIRECTOR OF BUSINESS DEVELOPMENT
ROSS MCKENZIE DIRECTOR OF SPECIAL PROJECTS
MARTIN O’LEARY LEED AP CEO
KYLE NEVILS LEED AP BC+D VICE PRESIDENT OF PROJECT MANAGEMENT
JENNI COX CHIEF FINANCIAL OFFICER
JUSTIN PARIS VICE PRESIDENT OF FIELD OPERATIONS
TROY BLOEDEL CHIEF OPERATING OFFICER
KYLE DAVIS DIRECTOR OF PRECONSTRUCTION & ESTIMATING
DIRECTOR OF SAFETY, HEALTH & ENVIRONMENT
At JTM Construction, we have a proven track record of delivering high-performing warehouse and industrial facilities that prioritize efficiency, durability, and scalability. Our team brings deep expertise in complex infrastructure upgrades, ensuring that each facility meets the unique operational needs of our clients.
With a focus on cost-effective scheduling, safety, and long-term performance, JTM collaborates closely with owners, design teams, and trade partners to optimize workflow, maximize space utilization, and deliver projects on time and within budget.
JTM has successfully completed warehouse and industrial projects that support the growth and productivity of businesses across the region. Our experience ensures seamless execution, allowing clients to focus on operations while we handle the complexities of construction.
The project involves improvements to existing vacant warehouses on a 162-acre site, built in 1940, in preparation for new tenants.
FEATURES INCLUDE:
» Demolition of select structures and alterations to canopies
» New interior offices along with vehicle and truck ramps to improve access
» Improved lighting, updated HVAC systems, plumbing, and energy systems
» New loading docks, ramps, and rail systems to facilitate operations
» New overhead doors and storefronts, as well as enhanced envelope/siding
CLIENT: Avenue 55
The project involves improvements to existing vacant warehouses on a 162-acre site, built in 1940, in preparation for new tenants.
FEATURES INCLUDE:
» Interior configurations to function as a gallery for showcasing stone slabs
» Three overhead industrial cranes in the back three structural bays
» New columns and beams to support the cranes, running east to west across the space
CLIENT: Avenue 55
ARCHITECT: Nelson Worldwide
The first tenant improvement of a 17,638 square-foot vacant suite in a newly constructed industrial warehouse for Electric Era Technologies.
FEATURES INCLUDE:
» A 2-hour fire-rated battery storage room to ensure safe testing of electrical components
» New electrical transformers and sub-panels along the perimeter to power R&D operations
» A staff break area with kitchen amenities
CLIENT: Museum of History and Industry
ARCHITECT: Burgess Design
This project involved the conversion of an existing building supply office and warehouse into a storage facility.
FEATURES INCLUDE:
» High-density and high-pile racking systems for efficient storage
» Chilled photo storage areas to preserve sensitive materials and large artifact storage areas
» Office and administration areas for operational needs
CLIENT: Pepsi Company
ARCHITECT: Transystem
The project involves a 34,000-square-foot warehouse addition to the Pepsi Northwest production plant located in Tumwater, WA.
FEATURES INCLUDE:
» New loading dock, concrete tilt structures, and a metal buildingNew interior offices along with vehicle and truck ramps to improve access
» Major utility re-routing involved both public and private storm, sanitary sewer, and water systems
» A 2,100-square-foot wood structure with brick veneer, designed to accommodate employee meetings and serve as a break room
CLIENT: Clay Lacy Aviation
ARCHITECT: N/A
The project features a full-service Fixed Base Operator (FBO) and hangar facility at Boeing Field in Seattle.
FEATURES INCLUDE:
» 40,000-square-feet of hangar space for enhanced aircraft storage
» Designated maintenance area
» Upgraded aircraft refueling location and office for aircraft support
CLIENT: Georgetown Brewing
ARCHITECT: Olson Kundig
The project features a complete build-out of a 38,000-square-foot production facility for Georgetown Brewing.
FEATURES INCLUDE:
» Seismic retrofit
» 3,000-square-foot cold storage unit for kegs
» 1,500-square-feet for laboratory testing, shop space, and offices
CLIENT: O'Boy Oberto
ARCHITECT: Craft Architect
The scope of work for this project included partial consolidation of the 170,000-square-foot Oh Boy O’Berto Kent plant.
FEATURES INCLUDE:
» Relocation of mechanical, electrical, and fire protection systems
» Consolidation and reorganization of food processing equipment
» Installation of IMP panel walls and soffits
» Construction of concrete curbing
CLIENT: Lincoln Properties
ARCHITECT: N/A
This project involved the renovation of two existing warehouse facilities, including interior office space, to align with industry standards and attract potential tenants.
FEATURES INCLUDE:
» Exterior & Site Upgrades: New landscaping, exterior paint, new fencing, and upgraded exterior lighting for both properties.
» Interior & Structural Improvements: Interior warehouse and office repainting, demolition and removal of existing offices and exterior finishes, including abatement work.
» Building System Enhancements: Roof reseal and new flashing, installation of new exterior skylights, and a new HVAC unit.
JTM combines the efficiency, agility, and vast resources of a large contractor with the personalized attention that small construction projects require. Drawing on our extensive experience across both large and small-scale projects, we offer cost-effective and innovative solutions tailored to your unique needs.
Our team collaborates closely to ensure each project is delivered with precision and care. At JTM, we treat every build as if it were our own, setting us apart other construction firms and ensuring results that exceed expectations.
» SAFETY
» PROJECT
» MANAGEMENT
» PRECONSTRUCTION
» SELF-PERFORM
» VIRTUAL DESIGN
» CONSTRUCTION
» QUALITY CONTROL
JTM Construction’s focus is that our team members return home safely every night as a general contractor assumes responsibility for the care, custody, and control of each project we build. With safety a foremost priority, JTM has developed a dynamic safety management approach with a comprehensive Safety Management Program.
JTM has a comprehensive safety program that protects all employees, subcontractors, Owner personnel, site visitors, and the public on ALL of our projects. Our goal is to eliminate property damage and occupational injuries by providing a safe work environment and supporting safe work behaviors. Establishing programs that promote safe work planning and practices and providing leadership that encourages, guides, instructs, and insists upon compliance from ALL employees, subcontractors, and site visitors to ensure our documented safety policies and procedures are strictly adhered to by all. JTM has been a 10+ year member of the AGC’s Safety Team, we make a safe workplace a top priority, and we have successfully created a safetyconscious culture at JTM.
JTM EXPERIENCE MODIFICATION RATE FIVE YEAR HISTORY
OUR TEAM WORKS HARD TO ENSURE A SAFE WORKPLACE. WE’RE PROUD THAT BOTH OUR LOST-TIME INCIDENT RATE AND EMR CONSISTENTLY OUTPERFORM THE INDUSTRY AVERAGE.
SINCE 2015
Experience Modification Rate (EMR) substantially impacts a construction company. Insurance companies use this number to gauge the past cost of injuries and future chances of risk. The lower the EMR, the lower the worker compensation insurance premiums, which benefits the client in the form of reduced cost. JTM has an EMR of 0.60, which is significantly lower than the industry average. We have maintained an EMR of less than 1.0, which is the industry average.
JTM Construction provides collaborative and thorough preconstruction services to ensure your project process is seamless. JTM provides valued input early and often in the process, helping the team make informed decisions quickly.
SERVICES INCLUDE:
• Cost estimating, budget control, and value engineering
• Analyze alternate building systems and present findings
• Constructibility reviews
• Develop and analyze Site Logistics Plans
• Strategize and develop comprehensive and thorough bid packages
• Project scheduling and the development of phasing plans
• Assess sustainability options
• Envelope systems analysis
• Mechanical and electrical system choices
• Actively participate in all project team meetings and produce meeting note documentation
Known for expert project management, exceptional client and subcontractor relationships, and meticulous attention to detail, JTM goes beyond the traditional general contractor’s role. We aggressively manage the project budget and drive the schedule to ensure our client’s goals are achieved. Through active engagement and management—we help clients make the best decisions, closely managing costs while maximizing efficiency and always delivering excellence beyond expectation.
Initiated on day one and sustained throughout the project, ensuring excellence from start to finish.
Our top core value, with a commitment from everyone to ensure every team member returns home safely each day.
We lead the process, leveraging the collective expertise of the entire project team to maximize value.
Every decision, from preconstruction to completion, is guided by our commitment to stretch every dollar and treat the owner’s budget as our own.
The self-perform capabilities of our general contracting team are one of JTM’s most robust tools for meeting and overcoming those challenges. Our experienced crews deliver greater safety, efficiency, early and continuous cost certainty, schedule and budget control, and a higher quality of work.
By self-performing these scopes of work. JTM effectively manages critical-path items in a schedule and safety and quality control for the entire project—all advantages that create greater value for our clients. our craft professionals take pride in their work, which leads to a higher quality of construction and a better end product.
At JTM Construction, we leverage Building Information Modeling (BIM) to drive efficiency, accuracy, and collaboration across all project phases. By integrating detailed 3D models, we enhance coordination between design, engineering, and construction teams, reducing conflicts and minimizing costly rework.
BIM allows us to identify and resolve clashes early, streamline system integration, and optimize scheduling and logistics. This proactive approach ensures seamless project execution, improved cost control, and enhanced building performance, delivering a smarter, more efficient construction process for our clients.
We utilize Virtual Design & Construction (VDC) to enhance project planning, coordination, and execution. By integrating detailed digital models with real-world construction workflows, we optimize logistics, scheduling, and resource allocation before work begins on-site.
Our VDC approach enables proactive clash detection, improves coordination, and enhances cost and time efficiency. Through advanced visualization and simulation tools, we provide clients with greater project insight, ensuring seamless execution, reduced risk, and improved overall project outcomes.
Our in-house scanning and survey capabilities provide precise, real-time data to enhance project accuracy and efficiency. Using 3D laser scanning and advanced surveying technology, we capture detailed as-built conditions, ensuring seamless integration with BIM and VDC workflows.
This approach enables early clash detection, precise site verification, and improved coordination between trades, reducing rework and minimizing delays. By leveraging our scanning expertise, we deliver projects with greater precision, efficiency, and confidence, setting the foundation for seamless execution and long-term success.
We prioritize environmental responsibility in every project. As stewards of the environment, our integrated approach streamlines design and build decisions, reducing administration while enhancing project efficiency and quality.
We believe responsible design benefits all stakeholders— employees, clients, trade partners, and communities. By collaborating, we ensure our clients’ goals are met with smart, sustainable solutions.