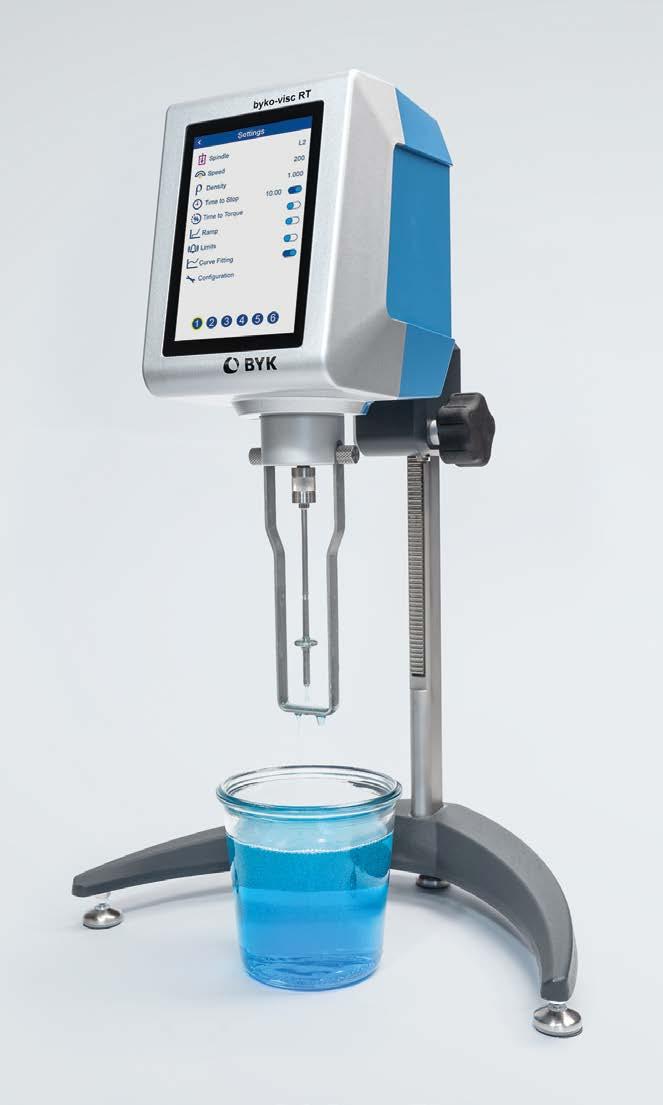
20 minute read
BRAND NEW
BYK-Gardner GmbH ha lanciato il nuovo viscosimetro rotazionale byko-visc RT
La nuova versatile linea di viscosimetri di BYK-Gardner offre misurazioni e ripetibilità affidabili.
© BYK-Gardner GmbH BYK-Gardner GmbH, il produttore di strumenti ed apparecchiature per il controllo della qualità di colore, aspetto e proprietà fisiche, ha recentemente annunciato di aver sviluppato il viscosimetro rotazionale byko-visc RT. La nuova soluzione consente risultati di misurazione precisi con ogni condizione di test registrata e offre analisi e revisioni dettagliate dei risultati. Il viscosimetro rotazionale è stato specificamente progettato per testare la viscosità di liquidi e paste in conformità alle norme ASTM D2196, ISO 2555 e ISO1652. È quindi adatto per testare la viscosità di lacche, vernici, primer, resine, lubrificanti, prodotti farmaceutici, creme, lozioni, saponi liquidi, bevande, condimenti e salse. Il prodotto è disponibile in due diversi modelli: byko-visc RT e byko-visc RT Lite. Entrambi sono caratterizzati da versatilità e compatibilità con tre diverse sensibilità e accessori opzionali. Inoltre, l’azienda fornisce un certificato di calibrazione ISO 17025 con ogni strumento, al fine di confermarne le prestazioni. Lo strumento offre una navigazione intuitiva grazie al display touch-screen a colori – che dispone di pulsanti preimpostati per richiamare rapidamente i parametri di misura più utilizzati – e diverse altre opzioni di controllo, che consentono di ridurre i tempi di funzionamento. Inoltre, include un facile attacco del mandrino a scatto per proteggere lo strumento e un supporto regolabile per consentire all’operatore di alzare e abbassare facilmente la testa del viscosimetro. La precisione della misurazione è ripetibile giorno per giorno e strumento per strumento, in quanto la nuova linea sviluppata dall’azienda è compatibile anche con molti altri modelli di viscosimetri rotazionali in termini di risultati, parametri di misura e accessori. Oltre al nuovo viscosimetro rotazionale byko-visc RT, BYKGardner offre anche un’ampia gamma di strumenti per la misurazione della viscosità, come tazze di flusso, viscosimetri a bolle, il viscosimetro digitale Stormer e viscosimetri a cono e a piastra.
Per maggiori informazioni: www.byk-instruments.com/en
La Dr.ssa Lan Deng è la nuova direttrice di ChemQuest
Deng si occuperà del miglioramento delle innovazioni e della crescita sostenibile di ChemQuest.
Il Gruppo ChemQuest, una società internazionale di strategia aziendale e sviluppo tecnologico esterno focalizzata sui mercati delle Specialità Chimiche, ha recentemente annunciato di aver nominato Lan Deng come nuova direttrice. Deng ha ottenuto un B.E. in materiali polimerici e ingegneria presso l’Università di Scienza e Tecnologia della Cina e un dottorato di ricerca in chimica presso l’Università della California - Berkeley. Inoltre, è coautrice di sei articoli scientifici e detiene sedici brevetti. Più recentemente, ha ricevuto i premi R&D 100 e il Presidential Green Chemistry Challenge Award dell’EPA. La nuova direttrice di ChemQuest ha oltre quindici anni di esperienza nell’industria chimica, avendo ricoperto diversi ruoli dirigenziali in Dow Chemical, SherwinWilliams e PPG. Prima di entrare a far parte dell’azienda, è stata infatti direttrice tecnica globale della linea Automotive OEM di PPG, dove ha supervisionato lo sviluppo di prodotti per il pretrattamento, E-coat, primer e finiture, nonché adesivi e sigillanti. “La nostra società è a un punto in cui la prossima ondata di innovazione sta iniziando a prendere piede e ad accelerare. Ci sono enormi opportunità nell’assistenza sanitaria, nell’energia sostenibile e nella trasformazione digitale. Le aziende in grado di cogliere l’opportunità di cavalcare queste onde avranno vantaggi competitivi duraturi nei decenni a venire. In qualità di leader tecnologico, voglio aiutare le aziende pubbliche e private a cogliere e cavalcare queste onde. Voglio anche aiutare il mercato dei capitali a trovare la giusta opportunità di crescita, in modo che tutta la nostra economia possa trarne vantaggio”, ha affermato Deng. “ChemQuest può darmi l’opportunità di fare proprio questo. Non vedo l’ora di collaborare con i miei colleghi e clienti per apportare innovazioni e crescita sostenibile nella società”. “Siamo fortunati che si unisca al team qualcuno con una solida esperienza e capacità come la Dr. Deng. La sua passione per l’innovazione, la crescita e la creazione di posti di lavoro e la sua forza nel collaborare con i clienti per creare valore reciproco aiuteranno sia ChemQuest che i nostri clienti a creare vantaggi per tutti”, ha dichiarato anche Dan Murad, CEO di ChemQuest.
Per maggiori informazioni: www.chemquest.com
GLOBAL SOLUTIONS FOR WATER TREATMENT
with a complete service that includes system design manufacturing installation technical support chemicals
SPRAY BOOTHS WATER SLUDGE REMOVAL RESIN DEMINERALIZATION SYSTEMS REMEDIATION OF CONTAMINATED SITES BIOLOGICAL SYSTEMS BATCH TREATMENTS PHYSICAL-CHEMICAL SYSTEMS ADSORPTION FILTRATION REVERSE OSMOSIS MEMBRANE SYSTEMS EVAPORATORS BIOGAS BIOMASS SYSTEMS OIL SEPARATORS DESANDERS DESALINATION SYSTEMS PYROCHAR OTHER SYSTEMS CHEMICALS
La British Coatings Federation evidenzia l’impatto negativo della Brexit sull’industria delle vernici
Secondo l’ultimo report della British Coatings Federation, la Brexit ha avuto un impatto negativo sugli scambi commerciali con l’EU per il settore dei rivestimenti.
Secondo una nuova indagine della British Coatings Federation – che si proponeva di misurare l’esperienza delle sue aziende membri con l’accordo di commercio e cooperazione tra Regno Unito e Unione Europea (TCA) – mentre alcune aziende sono riuscite a mantenere o aumentare le esportazioni, la maggior parte degli intervistati ha visto diminuire le esportazioni verso l’UE negli ultimi 15 mesi.I membri hanno anche riferito di aver subito un aumento significativo dei costi operativi a causa delle varie nuove regole, procedure ed effetti a catena del TCA. Inoltre, ci sono stati ancora pochi segnali di compensazione della crescita del commercio in altre parti del mondo a causa dei nuovi accordi di libero scambio. In aggiunta, ci sono ancora sostanziali preoccupazioni per il futuro regime di regolamentazione delle sostanze chimiche nel Regno Unito, in particolare sul REACH britannico e come influirà sulla futura competitività delle imprese.
Alcuni dati Quasi un membro su 6 (59%) ha subito un aumento dei costi operativi di oltre il 4% a causa della Brexit, mentre quasi un terzo (32%) ha segnalato un aumento di oltre il 6%. Uno su 10 ha subito costi aggiuntivi superiori al 15%. Quasi 4 su 10 (39,5%) hanno riferito che le esportazioni verso l’UE sono diminuite, con una maggioranza che ha perso tra il 6 e il 10% delle esportazioni nell’ultimo anno – anche se alcune aziende hanno perso di più. La logistica rimane il problema più grande per i membri: disponibilità di trasportatori (69%), ritardi nelle spedizioni di materie prime in arrivo in UK (67%) e costi di spedizione (64%) sono i problemi causati dalla Brexit più comunemente citati. Quasi un quarto dei membri (23,1%) ha riferito che i fornitori dell’UE non vogliono più esportare in UK, rispetto al 19% dell’anno scorso. Guardando al futuro, le questioni normative sono ancora una preoccupazione per la futura competitività delle imprese. Le prime 3 citate sono state: costi aggiuntivi dovuti
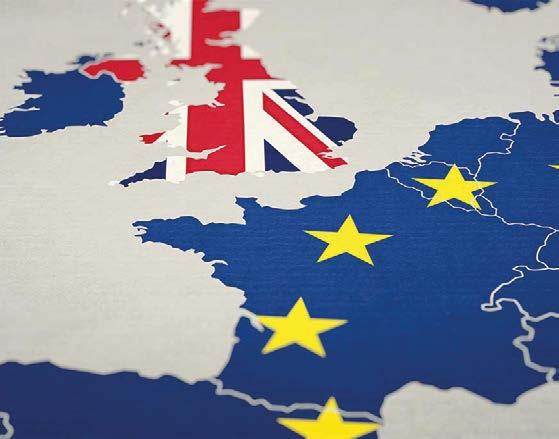
© Adobe Stock alle pratiche doganali (59%) l’impatto della futura divergenza del REACH britannico da quello europeo (59%) e l’impatto che potrebbe avere sui prezzi delle materie prime in UK (61%). “Il governo deve lavorare di più con le imprese per semplificare le esportazioni da e verso l’UE, cercando di migliorare i termini del TCA. Invece, sembra che le cose si stiano muovendo in direzione opposta, con la minaccia dell’articolo 16 del protocollo dell’Irlanda del Nord, che potrebbe far crollare l’intero accordo. Sarebbe un disastro per l’industria, soprattutto perché siamo nel mezzo della peggiore crisi globale delle materie prime e della supply chain della nostra generazione”, afferma Tom Bowtell, CEO della BCF. “Guardando oltre l’UE, c’è bisogno di un maggiore sostegno per le imprese britanniche che aumentano le loro esportazioni. Al momento, nonostante siano stati firmati e discussi nuovi accordi di libero scambio, sembrano esserci poche opportunità di sviluppo per il nostro settore. BCF farà la sua parte lavorando con il Dipartimento per il commercio internazionale, soprattutto attraverso un seminario sull’esportazione che si terrà a Manchester il mese prossimo”. “Infine, non dobbiamo distogliere lo sguardo dalla questione normativa. Il nostro sondaggio ha mostrato che i problemi e le preoccupazioni sul REACH britannico sono leggermente diminuiti rispetto allo stesso periodo dell’anno scorso. Ciò è probabilmente dovuto al fatto che il Dipartimento dell’ambiente, dell’alimentazione e degli affari rurali (Defra) sta esaminando un nuovo modello che, si spera, dovrebbe essere meno oneroso per l’industria. Tuttavia, queste preoccupazioni sono ancora sostanziali e incombono sulla futura competitività dei nostri membri. C’è bisogno che il Defra presenti rapidamente un nuovo approccio per il REACH britannico il più possibile, in modo da fornire alle aziende la certezza di cui hanno bisogno per pianificare e la capacità di accedere a una gamma completa di sostanze necessarie per aiutare l’innovazione futura”, conclude.
Per maggiori informazioni: www.coatings.org.uk
Anton Paar costruirà un nuovo centro tecnologico
La sede di Anton Paar a Graz (Austria) sarà ampliata per includere un nuovo centro tecnologico.
Anton Paar, produttore di strumenti e tecnologie di misurazione, ha annunciato l’intenzione di espandere la sede aziendale di Graz-Straßgang (Austria) per includere un nuovo centro tecnologico. Il nuovo centro tecnologico occuperà un’area di 26.800 m2 e includerà tutte le unità aziendali, nonché il dipartimento centrale di ricerca e sviluppo, mentre i tre edifici più antichi del sito sono già stati demoliti. Il nuovo centro sarà caratterizzato da un concetto open-space per favorire la ventilazione naturale e comprenderà anche due atri che consentiranno agli ambienti interni di essere alimentati con luce naturale. “La pianificazione del nuovo centro tecnologico è iniziata nel 2014. L’obbligo di un piano di sviluppo e le restrizioni sull’altezza dell’edificio hanno ritardato il progetto di anno in anno, ma finalmente nel 2024 oltre 650 dipendenti si trasferiranno nel nuovo edificio tecnologicamente all’avanguardia, che ci garantirà più spazio per la crescita”, ha affermato Dominik Santner, COO di Anton Paar e responsabile del progetto di costruzione. Attualmente ci sono circa 1.400 dipendenti nella sede di Graz, ma l’ampliamento consentirà di ospitare altri 1.000 posti di lavoro. Il 25 aprile 2022 Anton Paar ha celebrato l’inizio dei lavori di costruzione da 60 milioni di euro, che saranno eseguiti dallo studio di architettura KFR ZT GmbH e che dovrebbero essere completati entro la fine del 2023. Il sistema di accumulo dell’energia termo-solare e del ghiaccio Il nuovo centro tecnologico di Anton Paar utilizzerà un innovativo sistema di accumulo di energia dal ghiaccio con pompe di calore per coprire la metà del fabbisogno di raffreddamento e riscaldamento del sito. È composto da un bacino sotterraneo del diametro di 19 metri e profondo 6, corrispondente ad un volume d’acqua di circa 1,7 milioni di litri. Prima dell’estate, l’acqua viene ghiacciata. Il calore necessario per la sua fusione e poi l’acqua fredda sono utilizzati per raffreddare il sito, con le pompe di calore che trasferiscono il calore dall’edificio al serbatoio di accumulo, il quale si riscalda nel corso dei mesi. All’inizio della stagione fredda, il serbatoio di accumulo è quindi caldo e può essere utilizzato per riscaldare l’edificio, fino a quando ghiaccerà nuovamente alla fine dell’inverno. Inoltre, l’azienda disporrà di impianti fotovoltaici e termosolari installati sul tetto.
Per maggiori informazioni: www.anton-paar.com
© Anton Paar
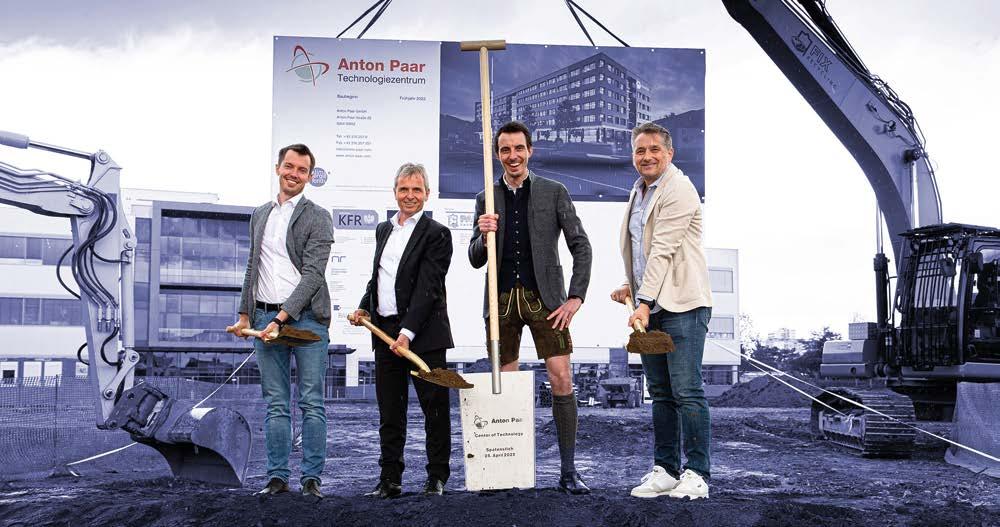
GEINSA fornisce la cabina di verniciatura per i veicoli della metropolitana di Bangkok
GEINSA ha fornito a Design&Project una cabina di verniciatura per il rivestimento dei veicoli della Metro di Bangkok.
Design&Projects International è un’azienda specializzata nella fornitura di progetti di manutenzione ferroviaria e ha acquisito da GEINSA una cabina di verniciatura per Min Sen Machinery, leader nella distribuzione di macchine utensili in Thailandia, per il progetto della linea rossa della metropolitana di Bangkok. Il processo di verniciatura e asciugatura dei veicoli della metropolitana viene effettuato nella cabina in dotazione. La cabina ha una dimensione di 30 metri in lunghezza, 5 in larghezza e 5 in altezza ed è dotata di piattaforme pneumatiche per i verniciatori, attrezzature per l’applicazione e un laboratorio di preparazione della vernice. Dispone di illuminazione con tecnologia LED e inverter di frequenza nei motori ad impulso ed estrazione. Chi è GEINSA
GEINSA è stata fondata nel 1967 e ha sviluppato tecnologie avanzate in più di 2000 installazioni in tutto il mondo. La sua attività consiste nel servizio di progettazione, realizzazione, montaggio e assistenza tecnica di impianti e cabine per il trattamento superficiale e successiva verniciatura. Fornisce: la progettazione e l’ingegneria, sia nella pianificazione che nella produzione, assemblaggio e post-vendita, e in ciascuna di queste fasi tutto il personale fa parte del team di GEINSA.
Per maggiori informazioni: www.geinsa.com
© GEINSA
Vista all’interno della cabina di verniciatura installata a Min Sen Machinery, Bangkok. Immagine 3D della cabina di verniciatura.
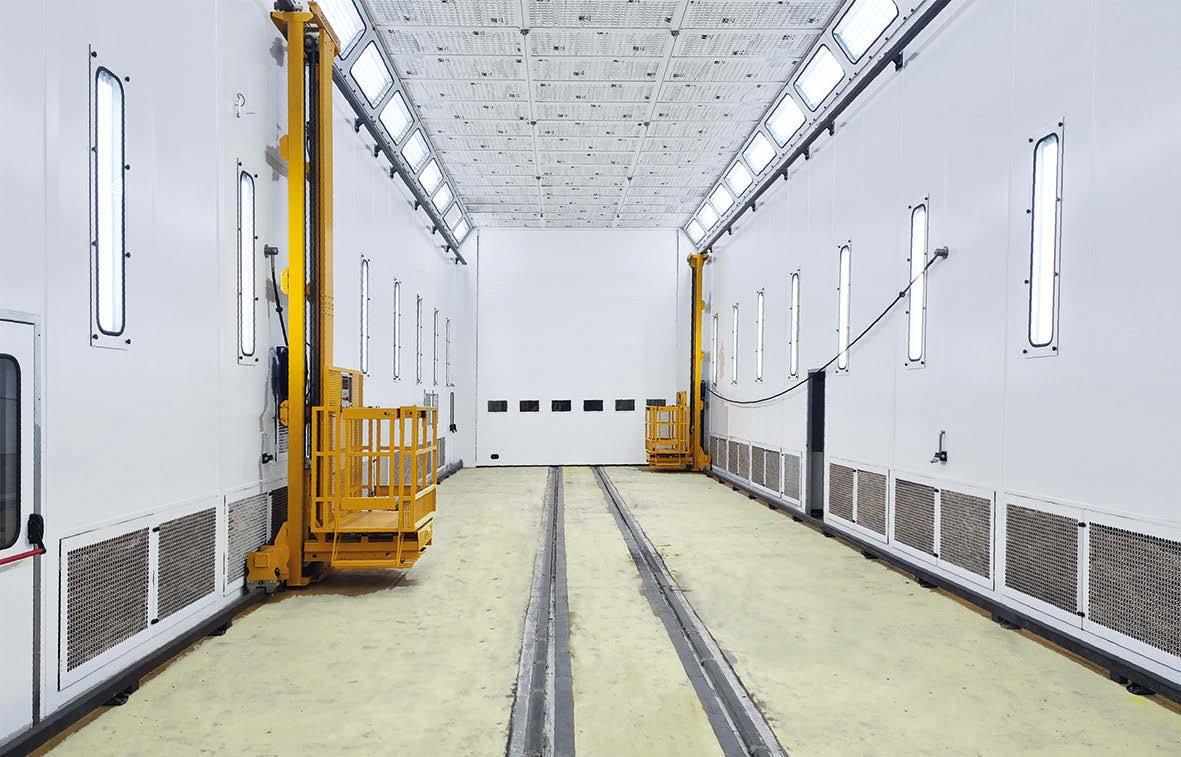
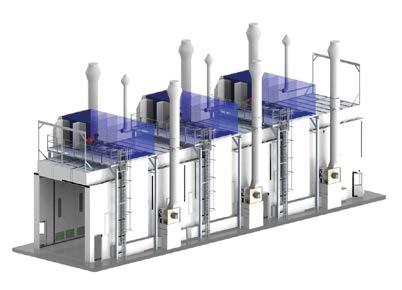
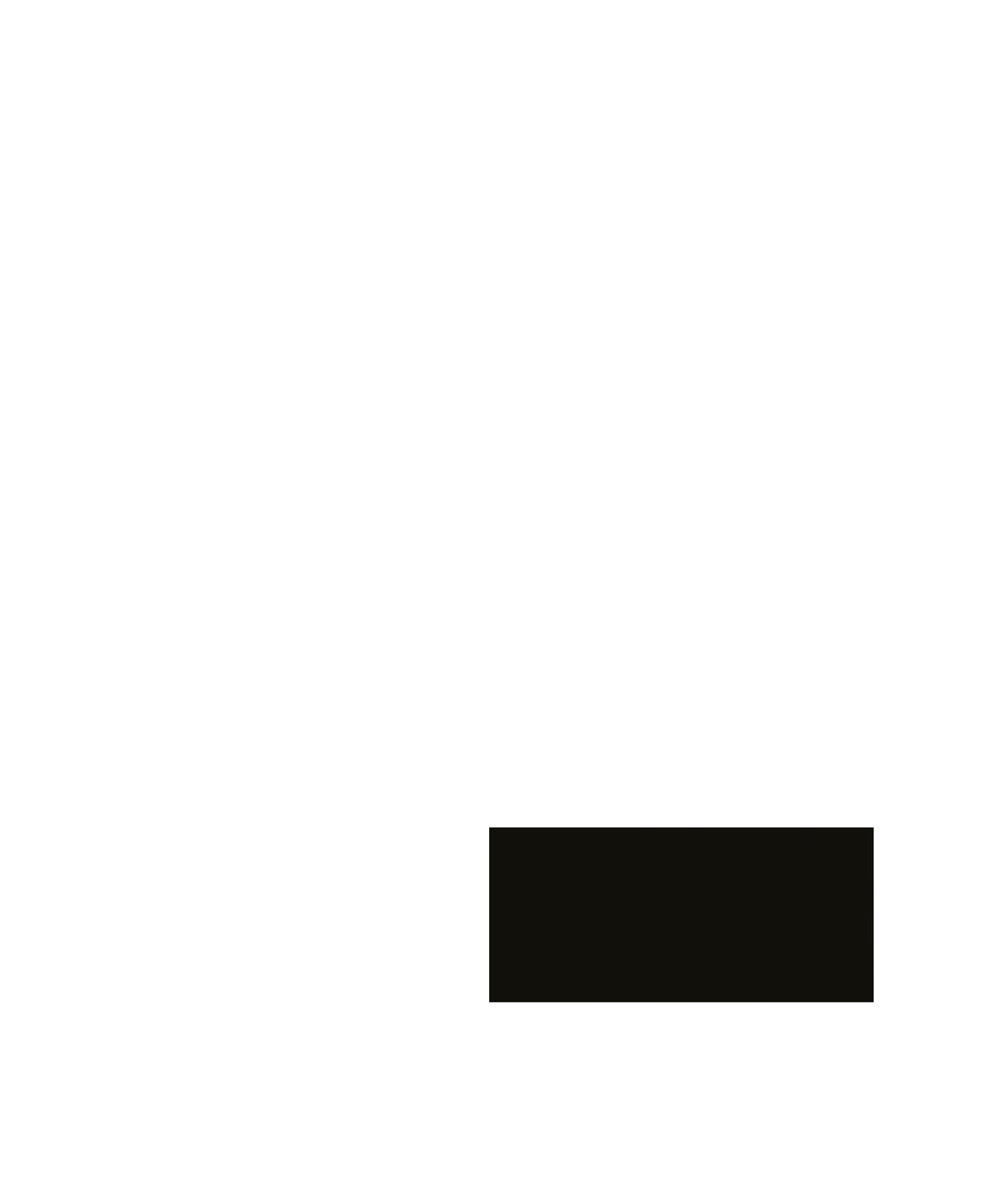
Future-proof and reliable overhead and floor MONORAIL and P+F

CONVEYOR systems that can be perfectly integrated into your production processes.
We take care of all your requirements and create a tailor-made and cost-optimized concept for you.
Ridurre al massimo: un impianto di verniciatura 3 in 1 per i componenti degli orologi meccanici
Il più prestigioso produttore tedesco di orologi meccanici ha esigenze elevate per la soluzione di verniciatura dei piccoli e delicati svariati componenti di orologi. Anche l’impianto deve funzionare come un orologio. Deve offrire un’estrema precisione pur rimanendo flessibile e facile da utilizzare. Per cercare un concept impiantistico adatto, le due aziende storiche Hermle e Venjakob hanno unito le forze.
© Venjakob
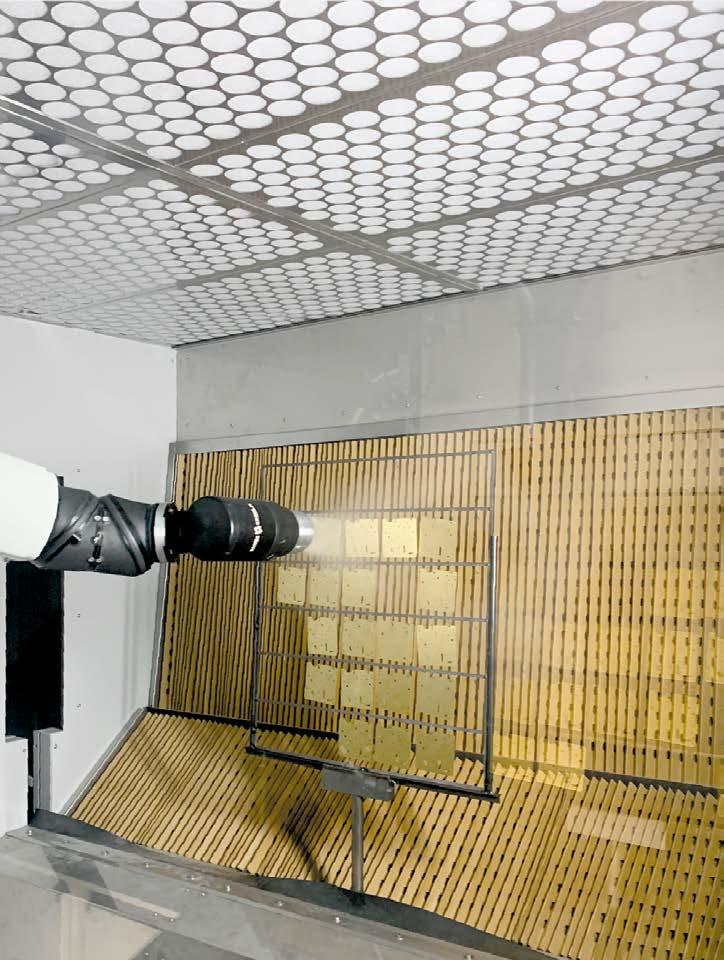
Vista dell’impianto di verniciatura completamente automatico e compatto con robot e trasportatore a pavimento con sistema rotante per la verniciatura a 360° in un unico passaggio.
In questo luogo il tempo sembra non fermarsi mai. Il sito produttivo e la sede dell’azienda a Reichenbach am Heuberg, nello stato tedesco del Baden-Württemberg, è il luogo in cui l’azienda familiare di medie dimensioni Hermle, che vanta 100 anni nell’orologeria, produce i suoi orologi meccanici. Hermle gestisce uno degli impianti per la produzione di orologi più moderni al mondo ed è uno degli ultimi produttori di orologi rimasti. Hermle è rimasto l’unico fornitore al mondo di una gamma completa di meccanismi meccanici per orologi di grandi dimensioni.
La richiesta di un sistema compatto su misura
Il produttore di orologi voleva una nuova soluzione per la verniciatura dei componenti degli orologi meccanici da installare negli stabilimenti costruiti a Reichenbach nel 2021. Il progetto prevedeva la sostituzione con un nuovo impianto delle macchine utilizzate in precedenza, ormai datate, tra cui un banco di spruzzatura manuale per i componenti speciali, un impianto automatico di verniciatura con trasportatore aereo per il rivestimento dei telai degli orologi e trasportatore rovesciato per il rivestimento a rotazione simmetrica dei componenti degli orologi. “Idealmente, il nuovo impianto dovrebbe combinare tutte le diverse soluzioni che utilizzavamo prima”, questa la richiesta del cliente. Ma Heiko Dreher, Purchasing Manager di Hermle, aveva solo una vaga idea di come potesse essere una simile soluzione 3 in 1. Dopo discussioni dettagliate, Kornelius Berg, il responsabile vendite di Venjakob per Hermle, ha presentato tre diversi concept del nuovo impianto, ognuno dei quali presentava funzioni diverse. “Abbiamo raggiunto rapidamente un accordo”, afferma Berg. Le principali differenze riguardavano il sistema di trasporto. Heiko Dreher sembrava preso dall’idea e dai precisi dettagli dei concept. Alla fine, Hermle ha scelto il concept con un impianto di verniciatura piccolo, compatto e completamente automatico attrezzato con un robot ABB e un trasportatore a pavimento con sistema rotante. Il convogliatore ospita i telai che trasportano i componenti degli
orologi ed è destinato alla movimentazione in serie attraverso ciascuna delle stazioni di processo.
Configura, installa e parti
Tra i criteri di scelta vi era anche lo spazio disponibile. Le funzioni e il design dell’impianto sono stati adattati alle dimensioni del futuro sito di installazione. Per facilitare un rapido avvio - che rappresentava un’altra delle richieste del cliente - l’impianto di verniciatura è stato consegnato in pochissimi pezzi separati. In questo modo è stato necessario collegare solo la piattaforma per l’aria di ingresso e uscita e la cabina di spruzzatura. “Il cliente ha anche accettato di rimuovere due pareti dal locale per consentire il trasporto dell’impianto al luogo di installazione nel minor numero possibile di pezzi”, riferisce Kornelius Berg di Venjakob. Questo piccolo aneddoto rimarrà sicuramente impresso per molto tempo nella mente di tutte le persone coinvolte.
Programma master speciale per il funzionamento autonomo
Il concept impiantistico sviluppato da Venjakob consente a Hermle di verniciare la più grande varietà di piccoli componenti in un’unica stazione e con un unico sistema di trasporto. Il carrello portapezzi è saldamente installato sui binari. La capacità della macchina è stata adattata all’applicazione (con un tempo ciclo di 5 minuti per portapezzi) ma può essere ancora aumentata del 20% circa. L’intero impianto è progettato per essere flessibile e il più possibile semplice da usare. Gli ingegneri informatici di Venjakob hanno programmato una speciale interfaccia di ingresso per il controllo del robot di verniciatura, offrendo al cliente l’opzione più semplice possibile per creare ricette proprie. “È sufficiente copiare la ricetta e inserire poi i diversi parametri, come le dimensioni del componente, la velocità o l’angolo della pistola”, spiega Kornelius Berg. La facilità di utilizzo e di adattamento alle esigenze del cliente si applica all’intero impianto. Un sistema operativo centrale viene utilizzato per controllare la macchina, inclusa la tecnologia del trasportatore. Allo stesso modo, la formazione dell’operatore della macchina ha richiesto solo un corso di formazione base per la manutenzione e l’assistenza del robot da parte del produttore ABB.
Sequenza delle funzioni e fasi di processo
L’impianto di verniciatura trasporta i manufatti in senso antiorario, la stazione di carico e scarico si trova nello stesso luogo. I componenti

© Venjakob
Veduta nel cuore dello stabilimento: la cabina di verniciatura. Lo speciale programma master di Venjakob è sinonimo di elevate prestazioni della linea e consente di creare facilmente ricette per l’ampia varietà dei pezzi di orologeria.
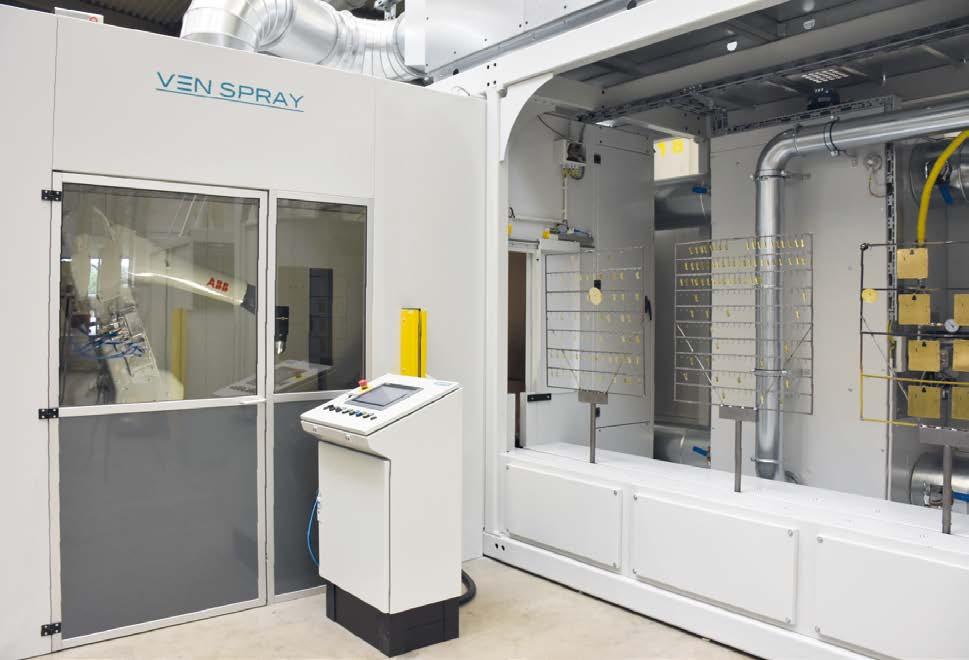
degli orologi da verniciare sono fissati manualmente ai telai portapezzi. Questi vengono quindi posizionati in modo da bloccare il pezzo sul carrello del trasportatore a pavimento e possono essere scaricati rapidamente al termine del processo. Prima del processo di verniciatura, la ricetta desiderata viene selezionata sul pannello di controllo dell’impianto e trasmessa ai comandi. I controlli di sistema contengono i parametri per la lavorazione dei pezzi secondo ciascuna ricetta. Dopo la selezione della ricetta desiderata, una semplice pressione del pulsante start sul pannello di comando avvierà il sistema. Il trasportatore a pavimento conduce il portapezzi nella cabina di verniciatura. Una volta che il primo lato del manufatto è stato verniciato dal robot, il portapezzi ruota automaticamente grazie al dispositivo rotante per consentire la verniciatura dell’altro lato. La fase successiva è l’evaporazione. L’area di evaporazione può contenere due portapezzi contemporaneamente. Dopo un periodo di evaporazione di 10 minuti, i portapezzi sono trasportati nel tunnel di asciugatura. La temperatura di essiccazione è compresa tra gli 80 e i 120 °C. La lunghezza dell’essiccatore a passaggio consente l’asciugatura simultanea di sei carrelli portapezzi. I portapezzi entrano qui per 5 minuti e vi rimangono ad asciugare per 30 minuti. Il successivo processo di raffreddamento dura 10 minuti e si svolge all’esterno del tunnel a temperatura ambiente. Successivamente i portapezzi vengono semplicemente scaricati dalle aste del trasportatore a pavimento nella zona di scarico.
Per ulteriori informazioni: www.venjakob.com
L’insolito legame tra uno squalo e una monoposto di Formula 1
L’artista Alastair Gibson, dopo aver lavorato in Formula 1, ha iniziato a creare sculture in fibra di carbonio di vari esemplari marini che sono verniciate tramite un processo molto complesso direttamente nello stabilimento della scuderia Mercedes AMG Petronas.
Ad una prima analisi, la fauna marina e le monoposto di Formula 1 non sembrano avere molti punti in comune. Eppure Alastair Gibson, l’ideatore di particolari sculture in fibra di carbonio, sostiene che ci siano molteplici similitudini: “Per esempio, le vetture di Formula Uno e gli squali hanno linee centrali ben definite e sono ambedue straordinariamente simmetrici. Sono creature magnifiche che si muovono sinuosamente nello spazio: le macchine sono aerodinamiche e gli squali sono idrodinamici. Per questo motivo ho deciso di utilizzare maestosi animali marini come soggetti delle mie opere”. Abbinando ispirazione artistica, attenzione ai dettagli, interesse per i colori e competenze ingegneristiche, Alastair Gibson crea infatti delle sculture in fibra di carbonio che incorporano parti di vetture di Formula Uno – ciascuna con un numero di produzione che rimanda a macchine e gare specifiche. Per rendere queste sculture più vivaci, sono verniciate con i prodotti Spies Hecker, il brand di Axalta Coating Systems dedicato allo sviluppo di pratici sistemi di verniciatura per carrozzerie di automobili. Originario del Sudafrica, lo scultore ha iniziato la propria carriera nell’ambito degli sport motoristici. Dopo aver lavorato come meccanico e ingegnere per sette anni in alcune serie minori, ha esordito poi in Formula 1 come capo meccanico del Team Benetton. Nei suoi quindici anni nel massimo campionato automobilistico, ha inoltre ricoperto il ruolo di capo meccanico in ambito gara per i team BAR e Honda Grand Prix. Essendo però appassionato anche di arte, nel 2008 Gibson prese
© Alastair Gibson
Gli squali sono uno dei soggetti preferiti dallo scultore Alastair Gibson.
la decisione di perseguire la propria passione e diventare uno scultore a tempo pieno. “Iniziai giocando con frammenti scartati di fibra di carbonio e pezzi delle vetture nei momenti di pausa prima e dopo la stagione di gare, perché era tutto ciò che avevo a portata di mano in quel momento. Capii quindi che attraverso questi scarti era possibile creare nuovi e bellissimi oggetti. Non avevo la minima idea che qualcuno poi avrebbe voluto acquistarli!” racconta scherzosamente Gibson. La realizzazione delle sculture richiede molto impegno, tempo e pratica. L’artista inizia incidendo a mano nel legno di balsa un modello in scala 1:1 della propria opera. Poi utilizza il software CAD per decidere il posizionamento di dettagli come occhi, branchie o pinne. Dopodiché posiziona precisamente i sottili fogli di fibra di carbonio negli stampi, il cui numero dipende dalla tipologia di scultura che si appresta a realizzare. “Questa è una fase particolarmente complicata, perché in alcune delle mie sculture la trama della fibra di carbonio è visibile attraverso la vernice trasparente. Perciò è fondamentale collocare il materiale in modo corretto ed essere certi che non vi sia nulla tra lo stampo e la fibra di carbonio”. Gli stampi ricoperti di fibra di carbonio sono dunque sottoposti a un processo di de-bulking in ambiente pressurizzato e posti in un’autoclave per creare una perfetta sezione finale della scultura. Una volta assemblate, le opere sono portate nella carrozzeria di MERCEDES AMG
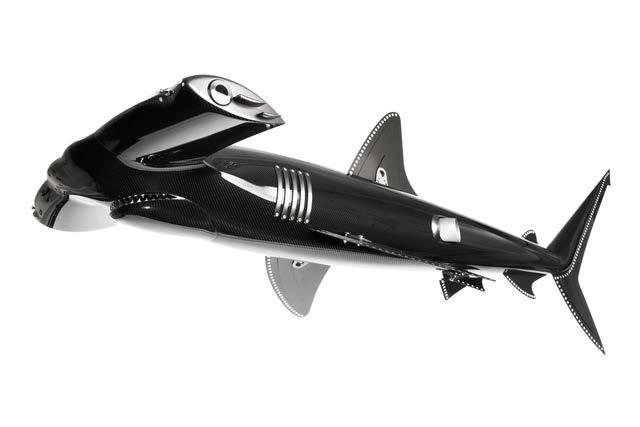
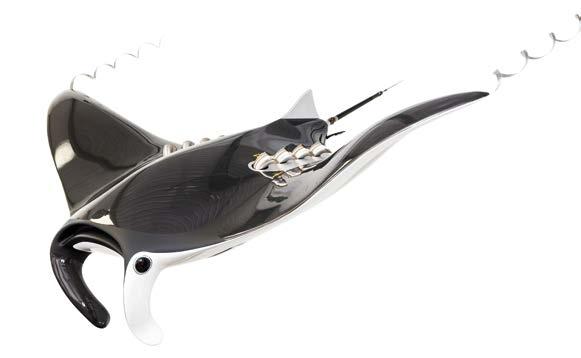
Aero Manta, una scultura lunga un metro ma che ha richiesto 25 ore per essere verniciata.
© Alastair Gibson
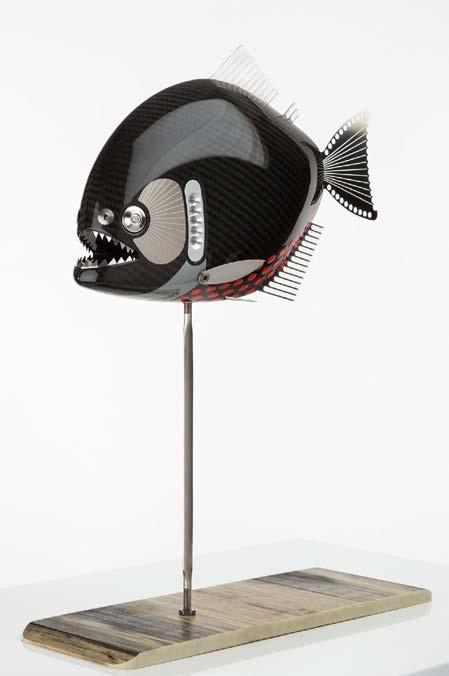
Racing Piranha.
PETRONAS, dove sono verniciate con prodotti Spies Hecker – le stesse vernici utilizzate anche dalla scuderia. Oltre alle vernici trasparenti, a volte sono applicati anche i colori Permahyd® Hi-TEC Basislack 480 e Permasolid® HS Optimum Plus Klarlack 8650, che permettono di ottenere un’elevata brillantezza. Per garantire che le sue visioni artistiche possano essere realizzate, Gibson si confronta con Andrew Moody, Responsabile Paint and Graphics del team, che si affida allo spettrofotometro ColorDialog di Spies Hecker per individuare i colori e gli effetti più adatti. “Adoriamo questo tipo di sfide, anche se richiedono molto tempo. Per la verniciatura della manta ci sono infatti volute 25 ore, mentre per uno dei racing piranha ci solo volute circa 10 ore. Ma verniciare qualcosa di completamente diverso è molto avvincente”, racconta Moody. Le sculture verniciate sono infine inviate nuovamente allo studio di Gibson, dove l’artista aggiunge gli ultimi dettagli come le pinne in acciaio inossidabile foto-inciso o i denti in lega di bismuto. Le sculture sono state esposte in innumerevoli mostre britanniche ed internazionali, oltre ad essere anche state acquistate da collezionisti. “Prendo ispirazione da molte cose che mi circondano e metto grande passione nella creazione di queste sculture e nel fare in modo che le finiture siano perfette. Spero che tutto ciò venga percepito dalle persone che le guardano,” conclude Gibson.
towards the future
SOLUZIONI ROBOTIZZATE DI
ROBOTIC PAINTING SOLUTIONS VERNICIATURA
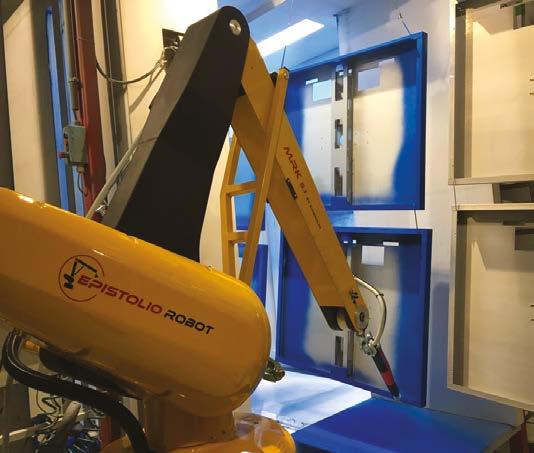
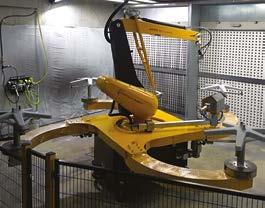

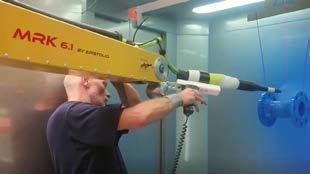
Epistolio Srl.
Via Piemonte 120 21100 Varese (VA) ITALY Ph: +39 0332 212692 Fax: +39 0332 223666 info@epistolio.com www.epistolio.it
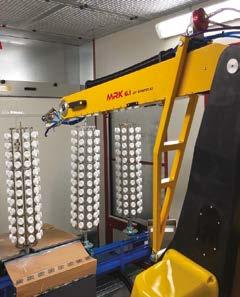
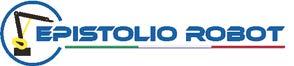