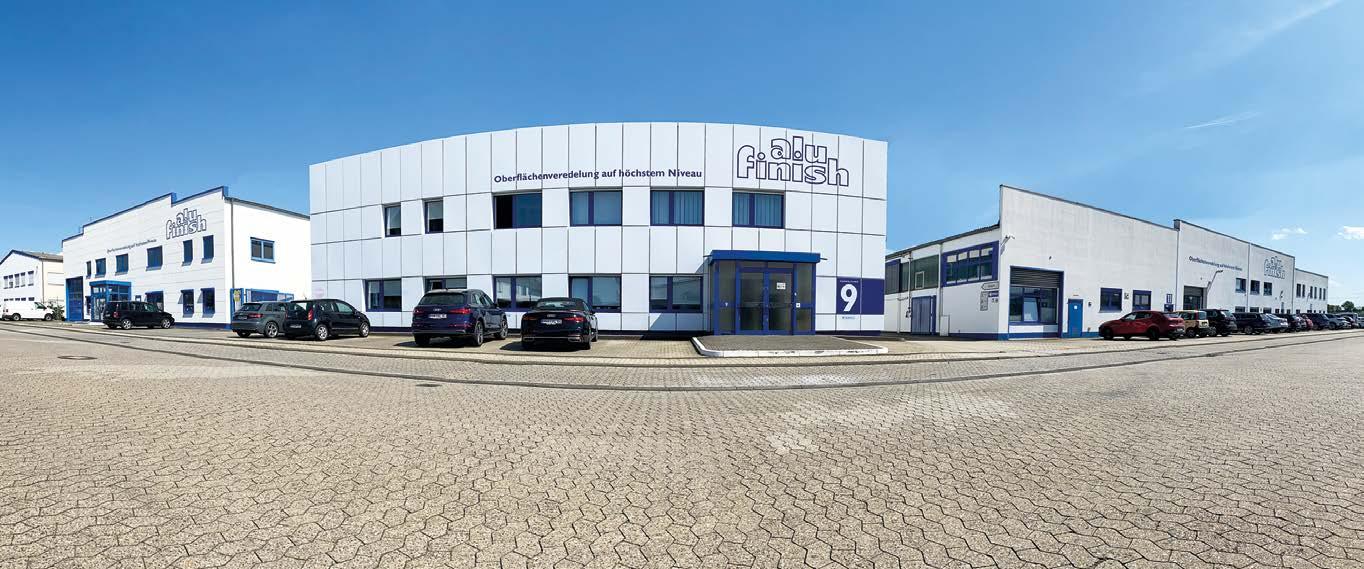
16 minute read
HIGHLIGHT OF THE MONTH
Da azienda a conduzione familiare a fornitore internazionale di prodotti per il pretrattamento: cooperazione e partnership come pilastri aziendali
Intervista con Nils Monreal e Stephan Zegers
Alufinish GmbH & Co. KG – Andernach (Germania)
Cooperazione, partnership globali e flessibilità: sono questi gli elementi fondamentali che hanno permesso ad Alufinish, sviluppatore tedesco di prodotti per il trattamento delle superfici, di avere successo nel proprio settore. Durante le celebrazioni del 50° anniversario della fondazione, abbiamo intervistato gli amministratori delegati Nils Monreal e Stephan Zegers per comprendere meglio la strategia di crescita dell’azienda.
Gli anniversari sono una celebrazione gioiosa e sono anche un buon momento per riflettere sia sul passato sia sul futuro. Ciò è particolarmente vero per l’anniversario di fondazione delle aziende, che può trasformare la celebrazione in un’opportunità per fornire una panoramica sui risultati passati e per pianificare il futuro. Alufinish GmbH, sviluppatore e produttore di prodotti e processi di pretrattamento chimico per superfici in alluminio, acciaio e zinco con sede ad Andernach (Germania), festeggia il suo 50° anniversario. Nell’ultimo numero di questa rivista abbiamo dedicato un articolo alla storia dell’azienda. Questa volta siamo invece andati in visita allo stabilimento tedesco per intervistare Nils Monreal – il genero di uno dei fondatori originali – e Stephan Zegers, gli amministratori delegati di Alufinish GmbH & Co. KG. Entrambi hanno fornito interessanti osservazioni sulle strategie che hanno assicurato il successo di Alufinish, gli sviluppi attuali dell’industria del trattamento delle superfici e le tendenze future previste dall’azienda.
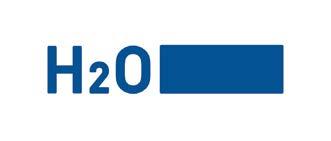
Come ci si sente a pensare al 50° anniversario di Alufinish? Lo considerate un avvenimento molto importante?
“Ci si sente vecchi” scherza Stephan Zegers, il primo che ha iniziato a rispondere alle nostre domande. “Ma seriamente, penso che sia un grande risultato per un’azienda privata, cosa piuttosto rara di questi tempi. Il fondatore Otmar Monreal ha capito che il pretrattamento delle superfici metalliche necessitava di prodotti e processi di qualità, perché questo settore offre molte opportunità per diversi mercati. Così, cinquant’anni fa è entrato in questa nicchia di mercato e ha cercato di fornire le migliori soluzioni disponibili in quel momento. La celebrazione di questo anniversario significa che le sue azioni e la sua visione hanno avuto successo. Ne siamo molto orgogliosi”.
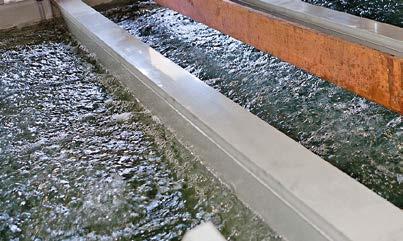
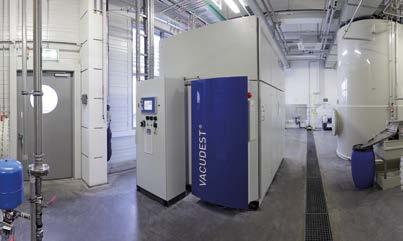
Quali ritenete che siano stati i principali successi ottenuti dall’azienda negli ultimi 50 anni?
“La nostra azienda ha stabilito il suo successo su svariate piccole attività che ne hanno assicurato la crescita nel corso di cinquant’anni. Abbiamo iniziato come una piccola azienda a conduzione familiare che realizzava prodotti standardizzati attraverso processi standardizzati e, nel tempo, abbiamo innovato e siamo cresciuti sempre di più. Fino a raggiungere la diffusione globale e le capacità produttive di oggi”, ha continuato Zegers. “Non c’è stato un singolo successo chiave, anche se siamo molto orgogliosi dei nostri risultati come i miglioramenti nella qualità dei prodotti, il loro impatto ambientale e i nostri processi di produzione efficienti ed ecologici. Il nostro più grande successo è quindi una combinazione di tutte le attività che ci hanno permesso di diventare ciò che siamo oggi”, ha aggiunto Nils Monreal.
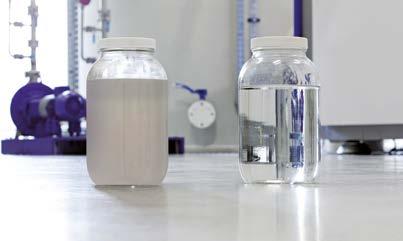
Sia il mondo sia l’industria dei trattamenti superficiali sono cambiati molto dalla fondazione di Alufinish. Come sono cambiati i vostri servizi negli ultimi cinquant’anni?
“Non sono cambiati, questo è un altro aspetto importante. Mi spiego meglio: abbiamo saputo anticipare l’evoluzione del mercato, abbiamo innovato e modificato i nostri processi produttivi, abbiamo migliorato la nostra organizzazione interna e adattato il business alle esigenze e alle nuove richieste dei clienti, ma il fulcro dei nostri servizi è rimasto lo stesso”, ha chiarito Zegers. “Le aspettative dei nostri clienti sono diventate sempre più alte, quindi abbiamo agito di conseguenza. Quando abbiamo iniziato le operazioni, consegnavamo i prodotti in bicicletta”, ricorda Monreal. “Oggi abbiamo una rete globale di fornitori e spediamo in tutto il mondo, quindi ora ovviamente ci affidiamo a processi logistici più sofisticati. Ma la nostra mission aziendale e, quindi, i nostri servizi sono gli stessi: fornire le soluzioni migliori e più performanti per il pretrattamento di qualità delle superfici metalliche”.
Tuttavia, presumiamo che sia Alufinish sia il settore abbiano dovuto affrontare diversi ostacoli e sfide. Come li avete superati?
Zegers: “Ci sono state senza dubbio alcune difficoltà, come la crisi economica mondiale del 2008 o il recente aumento del costo delle materie prime e la loro carenza, ma i nostri due pilastri aziendali ci hanno permesso di superarle. Innanzitutto, abbiamo deciso di differenziare la produzione e offrire soluzioni per diversi settori. Quando il mercato automobilistico è crollato, ci siamo concentrati maggiormente sui servizi legati all’architettura, poiché eravamo specializzati anche nei processi per facciate in alluminio con ENVIROX NR. In secondo luogo, abbiamo considerato il capitale umano come la risorsa più importante della nostra azienda. La sfida più grande che abbiamo mai affrontato è stata creare una squadra di successo e mantenerla. Pertanto, siamo stati in grado di ottimizzare la nostra pipeline. La comunicazione e il flusso di dati tra i team è eccellente e le fasi di produzione sono perfettamente interconnesse, quindi ogni aspetto è attentamente pianificato ed eseguito: dalla fase di sviluppo e progettazione alla produzione, dal controllo qualità all’assistenza post vendita. Ciò non riguarda solamente il nostro personale presso la sede di Andernach, ma anche i nostri fornitori”. Monreal: “...o dovremmo dire partner. Rispondere alle nuove richieste dei clienti in modo rapido ed efficiente è molto difficile, quindi ci affidiamo a una rete globale di partner che distribuiscono i nostri prodotti ma che ci aiutano anche a rimanere in contatto con i clienti, ad ascoltarli e ad agire tempestivamente quando hanno bisogno del nostro aiuto. Per avere successo sul mercato non basta solo fornire prodotti, bisogna anche interagire con i clienti, capire i loro processi e sviluppare insieme le soluzioni più adatte”.
Your Leaders in Zero Liquid Discharge
Industrial Wastewater Treatment
Simple Principle
Effective Result
Leading companies rely on vacuum distillation systems for the sustainable treatment of industrial wastewater.
Do you want to benefit from a zero liquid discharge production with VACUDEST aswell?
Visit us at IFAT Munich! Hall A2, stand 147
© Alufinish
Stephan Zegers (a sinistra) e Nils Monreal.

“Aggiungo un altro aspetto essenziale: il signor Monreal ha giustamente affermato che apprezziamo davvero gli sforzi del nostro team. Infatti, ci concentriamo anche sul miglioramento del know-how di tutti i soggetti coinvolti. Quando, ad esempio, un tecnico ha intenzione di andare in pensione, lo affianchiamo a un operatore più giovane non per un paio di mesi, ma per anni. Vogliamo fornire il naturale trasferimento di competenze. In questo modo anche i clienti si troveranno a proprio agio con il nuovo staff di Alufinish. Lo stesso accade con i nostri partner. Lavoriamo insieme da diversi anni, condividiamo preziose informazioni e conoscenze e continuiamo ad aggiornarci a vicenda. I vari paesi che serviamo hanno leggi, regolamenti, materiali, climi, temperature e qualità dell’acqua diversi. Ovviamente, un singolo sviluppatore di prodotti non può conoscerli tutti, quindi la cooperazione è estremamente importante”, ha spiegato Zegers.
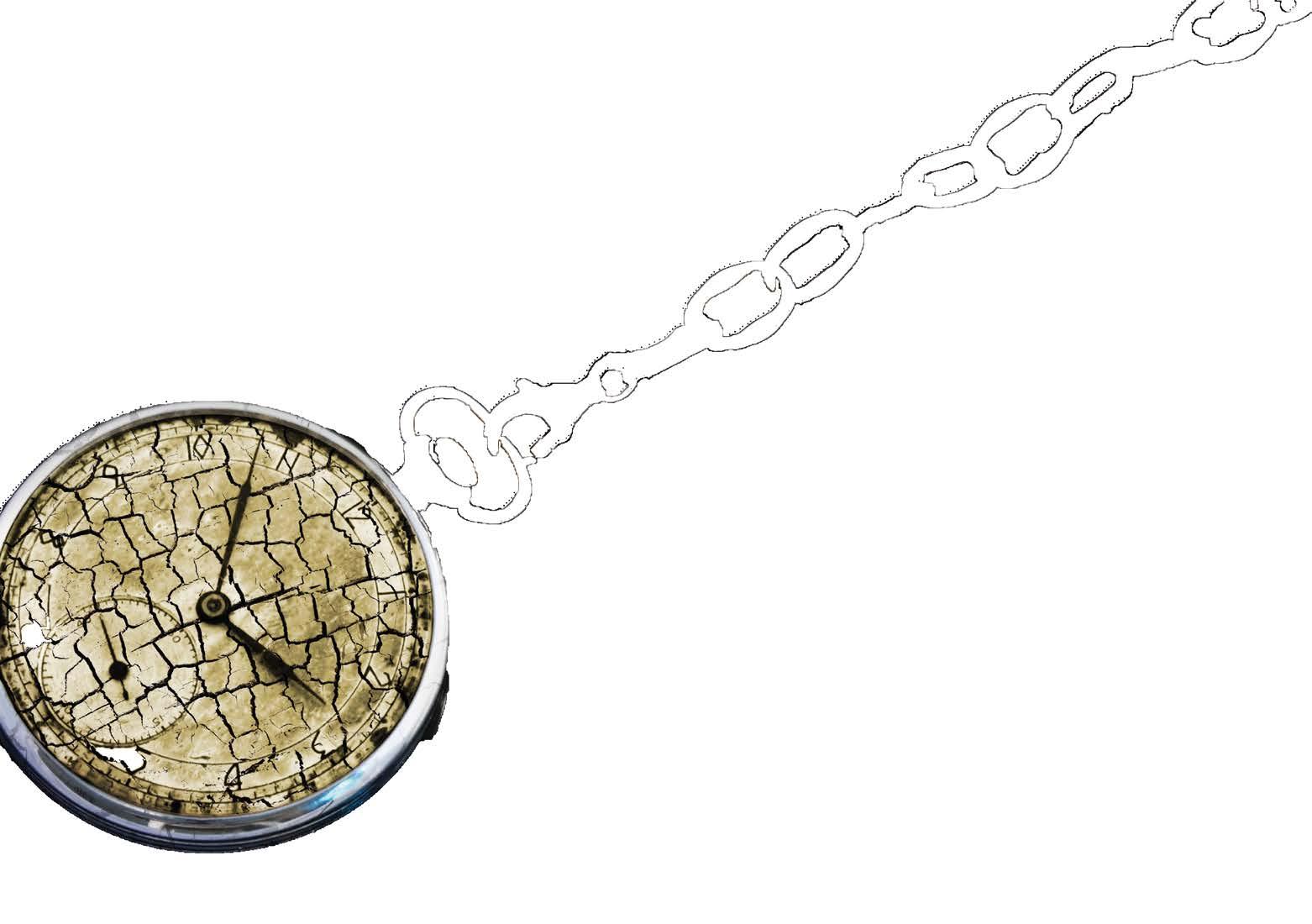
Abbiamo parlato del passato, ora concentriamoci sul futuro: come pensate cambierà il settore del trattamento superficiale dell’alluminio nei prossimi 5-10 anni?
Monreal: “Questa è una domanda molto interessante. Penso che il settore dell’alluminio amplierà il suo mercato in nuove aree del mondo, poiché l’alluminio può essere un materiale molto utile per diverse applicazioni sostenibili. Per un’azienda operante nel settore del pretrattamento, la chiave per un’espansione industriale di successo sarà identificare ciò che sarà incluso nei settori del trattamento delle superfici nei prossimi anni: potrebbero esserci nuove materie prime a base biologica, nuove soluzioni per il packaging, nuove tecnologie di processo. Sarà importante rimanere aggiornati sulle evoluzioni. Inoltre, anche l’efficienza energetica e il tasso di riciclo (secondo e persino terzo utilizzo di materiali) giocheranno probabilmente un ruolo molto importante”. Zegers: “Il settore deve anche trovare modi efficienti per gestire l’approvvigionamento e la spedizione, al fine di avere effetti positivi sull’intera impronta ambientale. Per fare ciò, è importante sviluppare relazioni commerciali di successo con i fornitori e tutti gli altri partner. La creazione di una rete affidabile può aiutare a gestire meglio tutti gli aspetti delle operazioni aziendali. Dall’approvvigionamento delle materie prime alla spedizione dei prodotti e all’assistenza post vendita”.
Ecco perché il motto di Alufinish è “Costruire sulla fiducia”, giusto?
Zegers: “Esatto. Se costruiamo insieme il futuro, possiamo affrontare con successo tutte le sue sfide. Apprezziamo molto la fiducia che i nostri partner ci hanno conferito: credono che le nostre attività e i nostri prodotti siano le migliori soluzioni per trattare le superfici ed eccellere in questa industria. Ascoltiamo sia i nostri partner sia i clienti finali, quindi siamo in grado di migliorare i processi coinvolti e garantire risparmi sui costi per tutti. Il valore fondamentale che rappresentiamo è che siamo più di un semplice fornitore, siamo il partner su cui puoi fare affidamento: orientato ai servizi, flessibile e adattabile. È una grande responsabilità, quindi la cooperazione è essenziale”.
Infine, potete introdurre ai nostri lettori gli ultimi sviluppi di Alufinish?
Monreal: “Ci stiamo concentrando su prodotti ecologici a base di titanio e zirconio privi di cromo e boro, adatti non solo per alluminio ma anche per acciaio e superfici zincate a caldo, nonché su nuove e ottimizzate proprietà di gestione e pulizia. Stiamo anche lavorando per aiutare i nostri clienti nel settore dell’anodizzazione a migliorare i loro processi di decapaggio con i nostri additivi, che garantiscono un migliore drenaggio e una bassa formazione di schiuma, e abbiamo aumentato i nostri sforzi per prodotti sigillanti più rispettosi dell’ambiente in quanto privi di nichel, cobalto e metalli pesanti. Dal 2018 abbiamo anche avviato una partnership con un fornitore per una gamma completa di coloranti organici, molti dei quali sono anche privi di metalli pesanti.
L’impianto di verniciatura a polvere in continuo dei coil di alluminio.
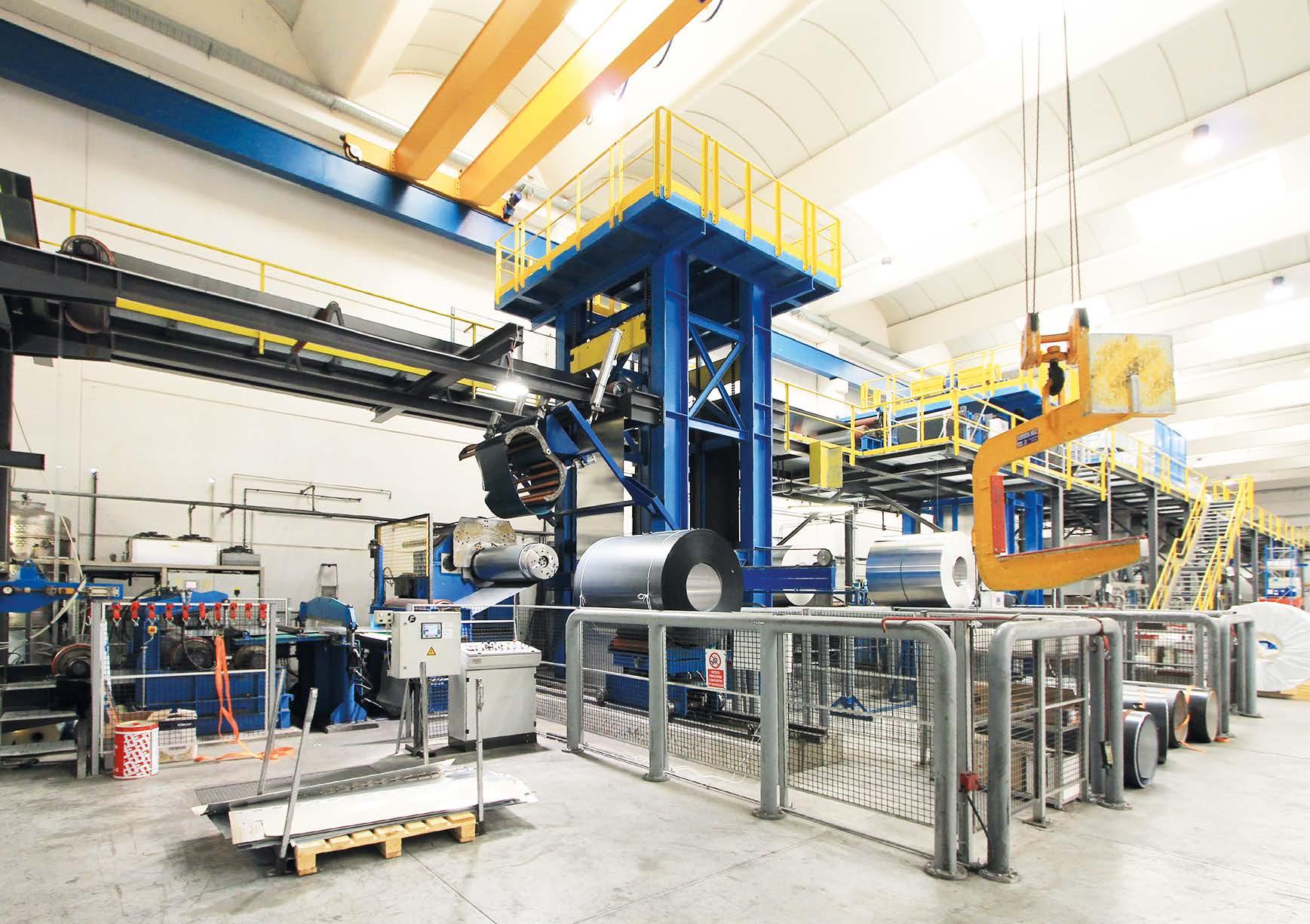
FOCUS ON TECHNOLOGY
SPECIAL ISSUE ON ARCHITECTURE & DESIGN
AluCoating sceglie la tecnologia IR catalitica per velocizzare la verniciatura a polvere dei coil in alluminio
Monica Fumagalli ipcm®
Compattare la linea di coil coating grazie alle innovazioni impiantistiche più evolute: AluCoating, azienda specializzata nella verniciatura a polvere dei coil in alluminio, ha scelto la tecnologia IR catalitica sviluppata da Infragas Srl per velocizzare il processo senza ampliare oltremodo l’impianto.
Nel settore del coil coating, dove i volumi dei materiali da trattare sono estremamente elevati, la velocità della linea è fondamentale. Per capire l’importanza che questa riveste all’interno del ciclo produttivo, dopo un anno esatto dalla nostra precedente visita1, siamo tornati in AluCoating Srl, la società di Corzano (Brescia) che è stata tra le prime aziende a specializzarsi nella verniciatura a polvere di coil in alluminio. “Verniciamo i nostri coil alla velocità di 7 m/min e puntiamo ad aumentarla ulteriormente” – afferma Paolo Di Massimo, titolare di AluCoating. “Uno dei colli di bottiglia che però riscontriamo per farlo è legato alla fase di asciugatura dopo il pretrattamento e alla fase di polimerizzazione della polvere applicata, per cui le dimensioni del forno che sarebbero richieste per adattarsi alla velocità della nostra produzione non sono accettabili per gli spazi che abbiamo a disposizione. Questo ci ha spinti a cercare una soluzione che ci garantisce fasi di asciugatura e di polimerizzazione molto rapide, senza però ampliare la lunghezza della nostra linea con l’introduzione di forni di dimensioni importanti, e l’abbiamo identificata nei pannelli catalitici IR di Infragas Srl (Mappano, Torino), che ottimizzano il trattamento termico dei coil verniciati a polvere”.
1 https://www.ipcm.it/en/open/ipcm/2021/69/52-58.aspx Una linea compatta di coil coating
Il reparto produttivo di AluCoating è attrezzato con un moderno impianto in continuo per la verniciatura a polvere di coil in alluminio e di una linea di spianatura e di taglio in diversi formati del prodotto finito. La linea compatta prevede il seguente processo di trattamento: • spianatura mediante macchina a 17 rulli sestupla; • pulizia superficiale del nastro mediante pretrattamento a spruzzo con prodotti alcalini e acidi per la preparazione dei nastri alle successive lavorazioni; • conversione mediante chem coater con applicazione di prodotti no rinse e chromium free (fluotitanazione e fluozirconatura); • applicazione elettrostatica di vernici in polvere studiate appositamente per il processo di post-bending; • polimerizzazione della polvere mediante irraggiamento IR catalitico a gas; • applicazione del film autoadesivo UV resistant trasparente o bianco/nero per la protezione della superficie verniciata durante le successive fasi di lavorazione e di installazione. “A partire dalle prime fasi di lavorazione fino alle ultime in cui prepariamo i coil preverniciati per la spedizione ai clienti – sottolinea Di Massimo – ogni stazione è studiata per ridurre al minimo il volume di ingombro delle apparecchiature e degli impianti, pur mantenendo la massima efficienza del processo. Fin dal pretrattamento abbiamo cercato di mantenere
© ipcm
La piattaforma traslabile con le due cabine Gema.
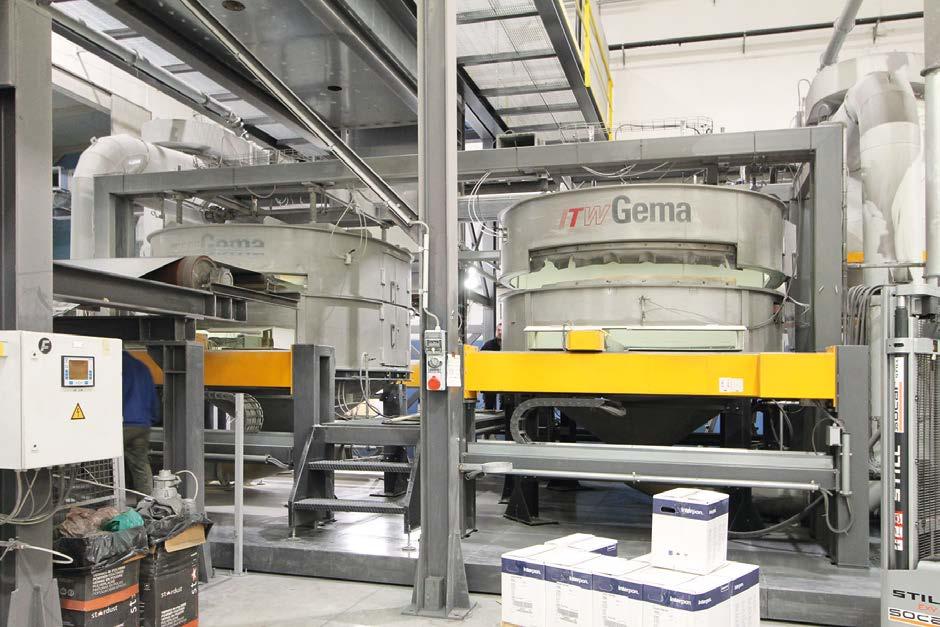
© ipcm
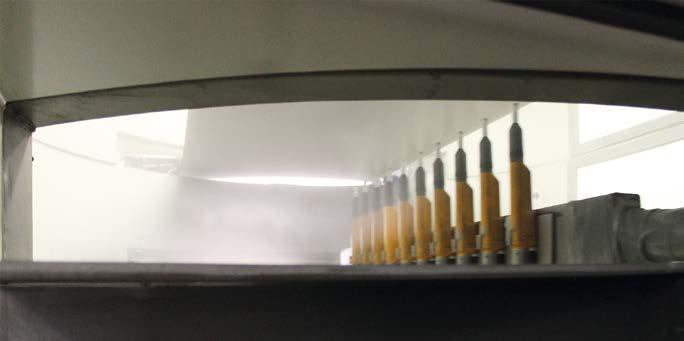
© ipcm

© ipcm le caratteristiche di massima compattezza e efficienza dell’impianto raddoppiando i risciacqui per ottenere risultati di pulizia più efficaci. Eseguiamo quindi un primo lavaggio seguito da 2 risciacqui per rimuovere i residui di grasso, segue un lavaggio acido per eliminare gli ossidi superficiali rimasti sulla superficie dopo l’intervento di laminazione, gli ultimi 2 risciacqui (uno con acqua di rete e l’altro con acqua demi) e l’ultima fase di conversione mediante chem coater. Le acque reflue sono filtrate e re-immesse in circolo dal sistema di trattamento acque a circuito chiuso e i fanghi smaltiti ogni 3 mesi”.
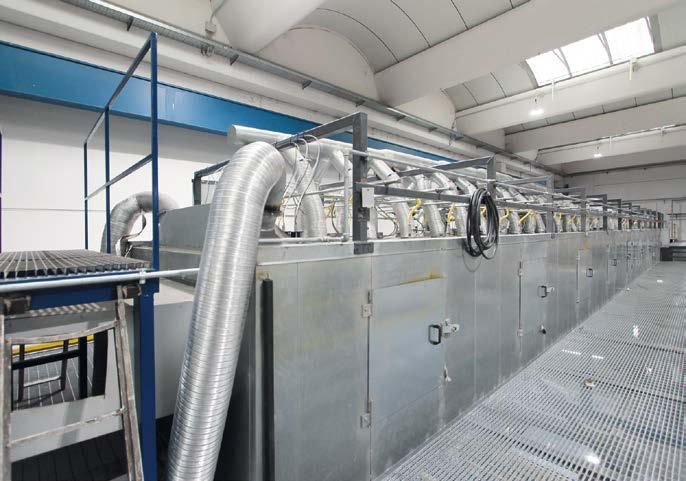
Verniciatura a liquido e a polvere a confronto
“Come già avevamo anticipato nel corso dell’incontro dello scorso anno” – continua Di Massimo – “è ancora in piena evoluzione quel passaggio dalla verniciatura a liquido dei coil a quella a polvere che rappresenta il trend di questi ultimi anni. Contemporaneamente sta avvenendo lo sviluppo di nuovi sistemi applicativi e di polimerizzazione delle polveri, che non compromettano la struttura compatta degli impianti di coil coating con sistemi per il trattamento termico di dimensioni eccessive”. La fase di essiccazione della vernice liquida applicata sui coil è molto diversa rispetto a quella della vernice a polvere. “Nel caso della liquida – precisa Di Massimo - è possibile gestire i parametri relativi alla portata e alla pressione dell’aria al fine di ottenere uno scambio termico ottimale con tempi di asciugatura che corrispondono a 30 secondi, proprio in virtù delle temperature più alte. Con le polveri il discorso è diverso, perché con l’aumento della portata dell’aria il rischio è quello di rimuovere parte della vernice applicata, trattandosi di un prodotto molto volatile. In questo caso, quindi, i due parametri devono attestarsi intorno a valori più bassi, ma questo comporta il prolungarsi delle tempistiche di processo. Abbiamo cercato una soluzione che consentisse il trasferimento più rapido del calore alla parte superiore del coil e l’abbiamo trovata nei pannelli catalitici IR di Infragas che sono stati installati sia per la fase di asciugatura dopo il pretrattamento, che avviene a temperature pari a 70 °C, sia per la polimerizzazione a temperature pari a 240 °C per un tempo di cottura corrispondente a 2 e ½ min., che avviene in un forno della lunghezza di 20 m”.
Dall’alto: La batteria di erogatori all’opera, il modulo generatore di azoto con il powder center, il forno di cottura.
Le due stazioni con tecnologia IR
Le due stazioni con tecnologia IR sono state installate per l’asciugatura dopo la conversione con chem coater e per la polimerizzazione dopo l’applicazione della polvere. “Dopo la conversione e prima dell’applicazione del primo strato di vernice” - prosegue Di Massimo - “il nastro viene asciugato tramite la tecnologia IR. E, dopo l’applicazione della polvere, abbiamo installato il secondo sistema di Infragas: in questo modo è possibile ridurre notevolmente i tempi di asciugatura e polimerizzazione”. “I dispositivi installati presso AluCoating – interviene Francesca Marabotti, marketing manager di Infragas – fanno parte della serie Boostercat 25K, il modello potenziato (Booster) della famiglia dei pannelli IR catalitici Infragas caratterizzato dal sistema di ventilazione incorporato posizionato sul retro del bruciatore. Si tratta, infatti, di pannelli infrarossi catalitici a gas completi di flange posteriori che si collegano alle tubazioni per l’immissione aria sulla parte posteriore al fine di potenziare l’ossidazione del gas e combinare l’effetto infrarosso con l’effetto convettivo. La densità di potenza dei
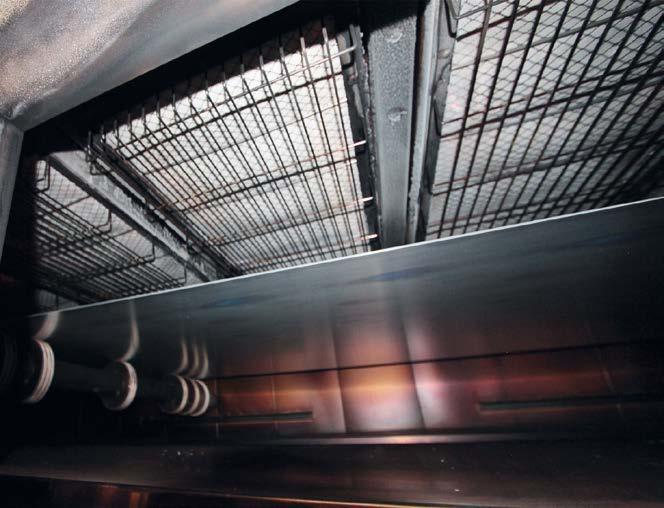
© ipcm
I pannelli infrarossi posizionati dopo l’ingresso nel forno di cottura.
ALUMINIUM vertical and horizontal plants over 60 years of experience in surface finishing lines
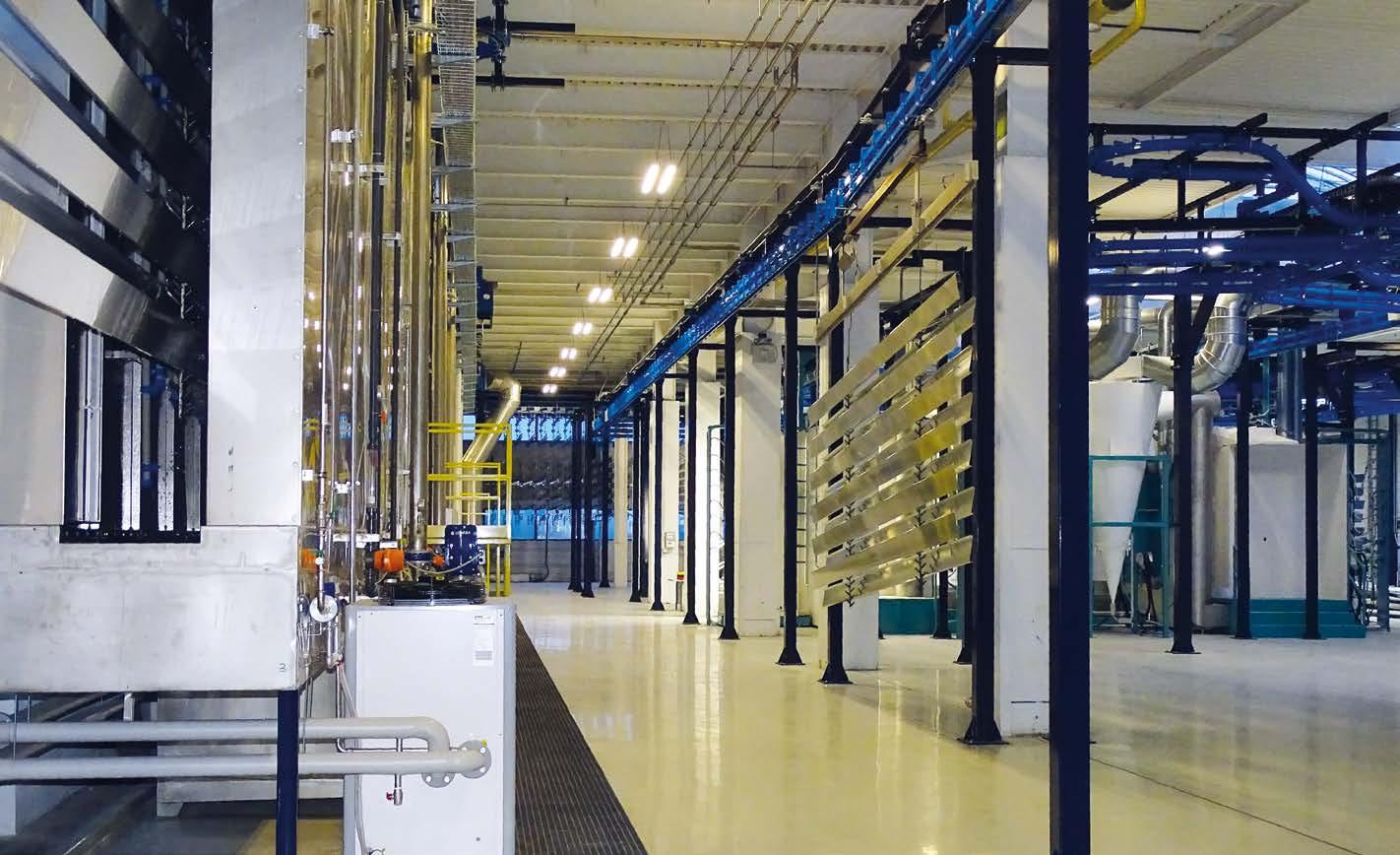
Boostercat è di 30kW/m2 e la temperatura massima di superficie è di 650 °C”. Uno dei vantaggi derivante dall’installazione di questi pannelli è l’uniformità del trattamento termico sulla superficie dei coil. “Abbiamo dotato i pannelli con 3 ingressi per il gas in modo da espandere la capacità di immissione e uniformare il più possibile la superficie di irraggiamento di tutti i lati del coil” – continua Marabotti. “La vernice in polvere è ideale per questa tecnologia, perché il materiale organico assorbe molto bene i raggi infrarossi. Inoltre, un ulteriore benefit è dato dal fatto che con la tecnologia catalitica IR il coil non si surriscalda e può essere sottoposto al rolling finale subito dopo la polimerizzazione, senza la necessità di attenderne il raffreddamento”.
Il beneficio energetico
La capacità della tecnologia catalitica di non riscaldare l’aria e concentrare la propria azione sul pezzo da verniciare permette di evitare qualsiasi spreco energetico. “Una delle più importanti esigenze dell’ultimo periodo” – afferma Marabotti – “è proprio quella relativa al consumo energetico, ma l’IR rappresenta da questo punto di vista proprio un’ottimizzazione del trattamento termico del metallo”. “In fase di pre-polimerizzazione – conferma Di Massimo - presenta anche il vantaggio di “bloccare” la polvere sulla superficie, evitando la contaminazione tra un coil e l’altro: un aspetto da non sottovalutare in un settore che sta diventando sempre più esigente in termini di spessori e qualità superficiale”. Recentemente il sistema IR di Infragas è stato potenziato con bruciatori radianti a gas RHT, Radiant High Temperature, per velocizzare ulteriormente la fase di polimerizzazione del coil. “Si tratta di sistemi premiscelati a infrarossi che raggiungono una temperatura superficiale di 950°C e presentano una densità di potenza 10 volte superiore a quella dei pannelli catalitici che presentano 30 kW/m2 di potenza, mentre quella dei RHT è di 180 kW/m2. Questa soluzione richiede diverse prove al fine di trovare l’equilibrio perfetto dei parametri di riscaldamento, ma con velocità sostenute come quelle di AluCoating potrebbero rappresentare la soluzione ideale per un settore come quello del coil coating sempre alla ricerca della massima velocità della linea”.
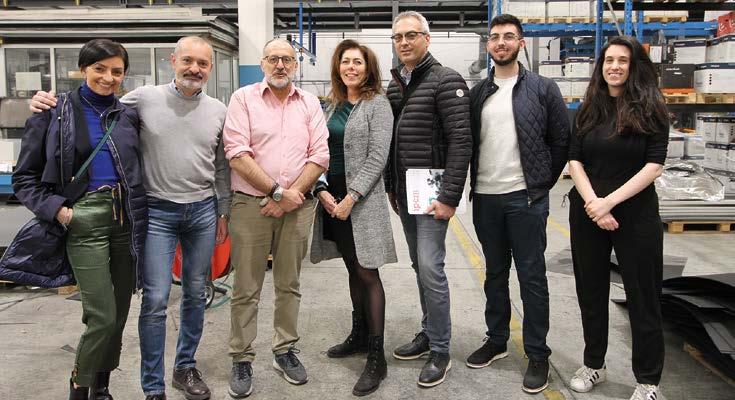
Caratteristiche tecniche BOOSTERCAT 25K con flange posteriori
Dimensioni: 492 x 1841 x 311 mm Assorbimento elettrico per il pre-riscaldamento: 1210 W Tensione alimentazione pre-riscaldamento: 230 V Controllo pre-riscaldamento: termocoppia tipo K cavo lunghezza 2 m Tempo pre-riscaldamento: 10’ Potenza: 25.0 kW max – 15.0 kW min Pressione gas naturale: 20 – 8 mbar (200 – 80 mmH2O; 2 – 0.8 kPa) Consumo gas naturale: 2.5 m3/h max – 1.5 m3/h min Pressione Propano: 37 – 15 mbar (370 – 150 mmH2O; 3.7 – 1.5 kPa) Consumo Propano: 1.87 kg/h max – 1.12 kg/h min
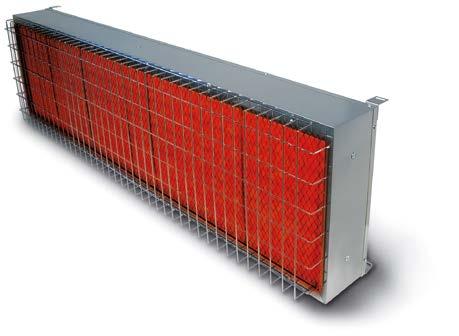
© ipcm