Link
IN FOCUS
Passion and craftsmanship
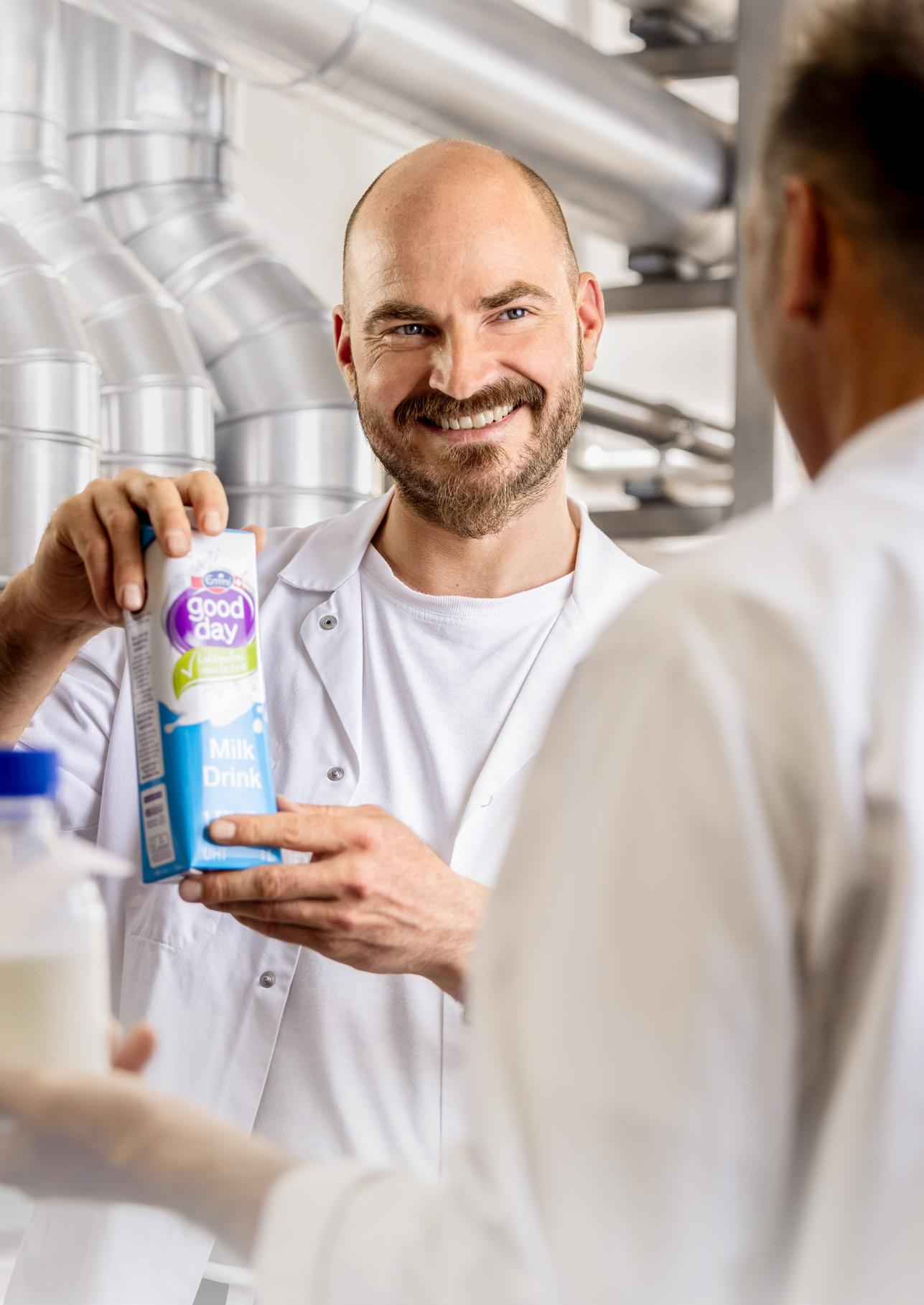
Dear Colleagues,
Our commitment to creating heartfelt indulgence unites Emmians all over the world. We dedicated this year’s first issue of ‘Link’ to our roots. For more than four generations now, Emmi has been a passionate producer of high-quality dairy products, driven by a great tradition and sense of responsibility. We are committed to working together to create the best dairy moments. And we go the extra mile to make that happen, constantly developing and making the impossible possible. For 20 years, we’ve been bringing cold coffee to Europe with Emmi Caffé Latte. Under brands like Good Day, Kaiku Sin Lactosa and Surlat Sin Lactosa, we create lactose-free moments of indulgence for customers in the northern and southern hemispheres. And our cheese from the sandstone cave in Kaltbach delights cheese lovers around the world.
Now, in the second issue of ‘Link’, we want to celebrate our craftsmanship and our passion. Every day, almost 10,000 Emmians are working across a wide variety of areas, demonstrating their unrivalled knowledge, superb craftsmanship and immense passion. For us, craftsmanship is more than just a professional activity; it’s an expression of our identity and culture. Because craftsmanship unites people
through shared work and creates products of inestimable value that provide moments of indulgence for generations of people. And in a world that is moving ever faster, craftmanship is also an ancor. It reminds us that beauty and indulgence lie in the details. It’s about choosing the best materials and handling them with skill, care and dedication. Craftsmanship never stands still; it is constantly evolving and combines tradition with innovation and passion. That’s exactly how it is at Emmi.
This issue of ‘Link’ shows how we are constantly developing our craft, ourselves and our organisation, and how we never stop learning – at the Finance Academy, for instance, or at the international workshop of the Global Research and Development Programmes for plant-based products and yogurt. The new Sensorikum in Emmen, Switzerland is another prime example of how Emmi is constantly honing its craft. And we also show you how you can grow by taking on new challenges.
I hope you enjoy reading this issue. Thank you all very much for your craft and your passion. They are what makes us strong and unique.
Ricarda Demarmels, CEO Emmi Group
Global Research and Development Programme: Birchermuesli for Chile?
06 Finance Academy: the first pilots have taken off!
08 Farewell to Matthias Kunz: an Emmi pioneer takes a step back 11 Emmi General Meeting 2024: with a record number of visitors
14 Location profile: Emmi Roth in Seymour USA FOCUS
16 Emmi: heartfelt indulgence –passion and craftsmanship
22 The Sensorikum in Emmen: a prime example of our ongoing development
24 CEO Ricarda Demarmels and neuroscientist Dr Barbara Studer in conversation about passion, innovation and willingness to learn
26 Employee development: learning through experience
Three days of transnational networking, exchanging experiences and an insight into the latest projects: the Global Research and Development Programmes for plant-based products and yogurts show how.
“Ihave touched snow for the first time in my life,” Hanene Chemek beams, her face lighting up. Hanene heads up the Research and Development department, or R&D for short, at Vitalait, our Emmi subsidiary in Tunisia. At the end of April, together with 23 colleagues, she enjoyed a fine dinner at the top of the snow-covered Alpgschwänd in the canton of Nidwalden (Switzerland) at 1,216 metres above sea level. A successful end to the day after an intensive exchange of expertise amongst Emmi R&D experts from Spain, Chile, Tunisia, Austria, the UK, Italy, the USA and Switzerland.
Global knowledge transfer, exchange of experience and networking
Jasmin Riedweg and Ladina Michel, project managers at R&D International, initiated the three-day
workshop in Lucerne (Switzerland). “Since summer 2022, we have been organising quarterly meetings where we present our ongoing product developments to each other and share our experiences with new technologies and processes,” explains Jasmin. So far, the 20 or so participants from the R&D departments of Emmi subsidiaries in the plant-based and yogurt programmes have only exchanged ideas virtually. “That makes it even nicer that we’re all getting to know each other personally now,” says Ladina. “And the on-site meetings also have another big advantage: we can introduce and taste each other’s own products and those of our local competitors. ”
Strawberry yogurts from six countries
Such as strawberry yogurt from six different countries. “Our Vitalait strawberry yogurt has more flavour and stabilising agent than Emmi Pure Swiss Yogurt,” says Hanene. And Alvaro Aravena, Head of R&D at Quillayes Surlat Chile, asks the others which of the six yogurts would be sold in the premium segment. A good question, which sparks off a lively conversation about ingredients such as sugar, protein, fat, starch and fruit content.
“The Birchermuesli –I’m taking it with me to Chile! ”
Alvaro
Aravena, Head of R&D at Quillayes Surlat
Product tasting on the third workshop day with the Global R&D team: Everyone benefited from exchanging experience and knowledge in person.
And what particularly impressed Hanene and Alvaro during those three days? “I really appreciated the face-to-face interaction. I’m also inspired by the vegan product line. Vitalait has nothing of that kind
yet,” says Hanene. And Alvaro enthuses about the excitement of networking and the new technologies, which he also saw during the company tour at the various Emmi sites. He was particularly impressed by an Emmi product from Switzerland: “The Birchermuesli – I’m taking it with me to Chile! ”
For Günter Englmeier, Head of R&D in Switzerland and programme sponsor, the three-day workshop was more than worth it: “The first face-to-face meeting was very important for our collaboration with the Global R&D team. They all networked intensively and shared their experiences and best practice examples. Finding joint solutions for product development and technologies: everyone benefits from this, and our innovations enable us to reach the market faster and more effectively. ”
“I’m inspired by the vegan product line. Vitalait has nothing of that kind yet.”
Higher, faster, further: the Finance Academy pilot group began its learning journey at the start of January 2024.
20 pilots were on board, working with a great deal of energy and enthusiasm to deepen their financial skills.
“I’m convinced that this initiative will help us progress as a company. ”
Rico ter Voert, Sales Export Manager at Bettinehoeve
Successful take-off in the Netherlands: employees of Emmi Benelux, Bettinehoeve and Emmi Nutritional Solutions expanded their financial knowledge with the e-learning modules before taking part in the interactive team workshop in Tiel in March. “I am convinced that this initiative will help us progress as a company and it has also helped me a lot personally – we had a great time,” says Rico ter Voert, Sales Export Manager at Bettinehoeve. The other participants are also very enthusiastic. Thanks to the good preparation and everyone’s active participation, the two-day workshop was not only very informative, but also entertaining. Larissa Haltiner, Brand Manager at Emmi Benelux, encourages all Emmi colleagues: “Don’t be afraid of the Finance Academy. On the contrary: you can look forward to this learning experience! ”
“Don’t be afraid of the Finance Academy. On the contrary: you can look forward to this learning experience! ”
Larissa Haltiner, Brand Manager, Emmi Benelux
Following the successful launch in the Netherlands, more pilots took off at Emmi Dessert Italia (EDITA) and Emmi UK in mid-March. Switzerland followed in April, and Spain, Germany and Emmi Austria in May. The rollout will continue in the second half of the year at all other Emmi Group companies.
The Finance Academy increases financial literacy throughout the entire organisation. Not only are employees better prepared for an ever-changing world, they are also able to grow and develop both professionally and personally, which strengthens Emmi as an international group worldwide.
Text Carolina Yepes and Raphaela Heim Photos zVg
Three questions for …
Sacha D. Gerber, CFO
1 Why did Emmi launch the Finance Academy? Financial knowledge and corporate success are closely linked. Companies where employees have a high level of financial knowledge are more successful – and it makes no difference what their job titles are.
2 How do you feel about this in your role as CFO? We all carry out tasks or make decisions that are financially relevant. For me as CFO, it is important that there is no longer any distinction between “ finance” and “business”. The Finance Academy provides all employees with a basic knowledge of financial contexts, as well as financial terms and concepts. This promotes mutual understanding and makes collaboration easier. And of course it is also an opportunity for each and every one of us to develop.
3 Which book from the world of business would you recommend to Emmi employees?
“ No Rules Rules: Netflix and the Culture of Reinvention”, written by Reed Hastings, the co-founder and former CEO of Netflix. The book explains Netflix’s unique and efficient corporate culture, which is characterised by a high degree of freedom and responsibility and a low level of bureaucracy.
TO MATTHIAS KUNZ
Few people have shaped Emmi’s international orientation as strongly as he has: Matthias Kunz, Head of the business division Americas until the end of 2021. The 64-year-old Emmian is now taking his well-deserved retirement. A look back at more than two decades of Emmi, combined with a big thank you.
There the two men stood surrounded by green hills, 200 km north of San Francisco, overlooking the rough ocean. But far and wide – no goats. But Matthias Kunz, Head of Emmi International at the time, and Konrad Graber, former Chairman of the Board of Directors, had flown to California especially because of goats’ milk production – to get an impression of the “Cypress Grove” dairy. Well, Matthias found at least one old goat while he was there, and that trip later led to an investment in an own goat farm. This was by no means the only adventure Matthias had on his countless trips abroad for Emmi.
Growing up in the tranquil, traditional Swiss valley of Emmental, the young farmer’s son decided to study agricultural sciences at ETH Zurich. After spending time in many countries, including a long spell in the USA, the trained agronomist joined Toni International AG in 1997. Following the acquisition of Swiss Dairy Food, Matthias joined Emmi in 2002. Here, as Head of Emmi International and a member of Group Management, he held responsibility for the international cheese business.
“Urs, the day after tomorrow we’re going to Italy to take a look at an Italian dessert company. ”
Matthias Kunz
Former Executive Vice President Americas
Thanks to his entrepreneurial, cosmopolitan nature and his outstanding international contacts, Matthias soon heralded the first steps towards expansion at Emmi. Urs Riedener joined Emmi as CEO in 2008, and together the two sought out potential subsidiaries abroad. This call from Matthias, for example, is one he has never forgotten: “Urs, the day after tomorrow we’re going to Italy to take a look at an Italian dessert company.” And Matthias and Urs still laugh today about some of the interesting situations they ended up in, such as the fishing trip with hosts in Chile, which went on until late at night. Matthias is
particularly proud of the development of Siggi’s, the pioneer of skyr in the USA. The shares held by Emmi were sold at a large profit.
As Executive Vice President Americas for many years, Matthias Kunz managed acquisitions and restructurings and successfully positioned Emmi on the international market with a great deal of vision, straightforwardness and a strong sensitivity towards people. In 2022, Matthias gradually handed over responsibility for the fast-growing business division Americas with its 13 subsidiaries in seven countries to his successor Jonas Leu. Matthias is now taking his well-deserved retirement. And those who know him will be curious to see what Matthias’ great entrepreneurial heart will beat for in the future and what his tireless pioneering spirit will discover next.
“Thank
“Heart first … that is Matthias all the way! ”
Pamela Dressler, MD, Cypress Grove Cheese
“Heart first … that is Matthias all the
way!
Add in smarts, patience, curiosity and a dash of boyish charm and you’ve got the recipe for a terrific boss and colleague. ”
you for the Emmi moments around the globe.”
Jonas Leu, Executive Vice
President Americas
“Thank you Matthias for your incredible generosity, your inspiring leadership and the countless Emmi moments we have shared around the globe. It is a great honour for me to continue and develop your legacy. ”
“You
have not only laid stone upon stone, but moved whole mountains! ”
Ricarda Demarmels, CEO Emmi Group
“Thank you from the bottom of my heart for your vision, your courage and your magic, Matthias – with a lot of charm, great strength and humanity you have not only laid stone upon stone, but moved whole mountains! ”
“Matthias has made a significant contribution to Emmi’s strong international position today.”
Urs Riedener
Chairman of the Board of Directors
“No matter which continent we were on together, Matthias always impressed me with his keen sense for very different people, cultures and companies. Thanks to his entrepreneurial, solution-oriented and persistent manner, he has made a significant contribution to Emmi’s strong international position today. ”
“He had a unique gift for attracting people to Emmi.”
Natalie Rüedi, Chief Human Resources Officer
“Matthias had a unique gift for attracting people to Emmi. His many years of personal investment in many relationships have helped make Emmi what it is today. ”
“We have been a ‹dream team› for 26 years.”
Britta Würgler, Assistant to the business division Americas “We have been a ‹dream team› for 26 years. I would like to sincerely thank Matthias for many years of enjoyable and appreciative collaboration. ”
“A unique leader and a great friend.”
Eduardo Urrutia, President of Kaiku
“Matthias has positioned Emmi on the international markets with great ambition. He made decisions with extensive expertise, always keeping an eye on local markets and supporting his teams. A unique leader and a great friend. ”
Recorded by Petra Troxler
The Lucerne exhibition hall in Switzerland was full to the rafters on 11 April: 1,794 shareholders voted at the 31st Annual General Meeting.
Bright spring weather greeted Emmi shareholders upon their arrival at the exhibition hall. The motto of our umbrella brand, “Heartfelt indulgence”, followed the guests throughout the AGM. And not just visually – you could taste its influence too. Even outside the entrance, guests tasted the finest Emmi cheeses – 13.5 kg of Luzerner Rahmkäse and 10 kg of Luzerner Rustico were eaten in total – and indulged in 1,500 cups of Emmi Caffè Latte. In the hall, the shareholders dived further into the world of Emmi before quickly finding themselves seats at one of the 70 tables. →
Urs Riedener opened the official part of the AGM. He looked back on his first year as Chairman of the Board of Directors with satisfaction: “Once again, Emmi has proven itself to be a reliable partner and achieved solid business results, even in a challenging market environment.” The shareholders also listened with interest to CEO Ricarda Demarmels’ remarks on the past financial year. Ricarda Demarmels emphasised that, in addition to clear and focused strategic direction, it was above all the people who put their heads, hands and hearts into Emmi’s work. CFO Sacha D. Gerber then highlighted the financial and sustainability aspects of the past financial year.
“Once again, Emmi has established itself as a reliable partner. ”
Urs Riedener, Chairman of the Board of Directors
Why, though, is there a need for an AGM? As a listed company, Emmi AG is required to publish financial reports, disclose information on compensation to the Executive Board and the Board of Directors and convene an Annual General Meeting. The AGM is the supreme body of every listed company, at which shareholders vote on published agenda items. At the Emmi AGM in 2024, there were seven agenda items, all of which were approved. Last but not least, the AGM provides an excellent opportunity to engage in direct dialogue with shareholders. Guests can also experience the world of Emmi and taste products.
After the official part of the General Meeting, most attendees stayed for the popular dinner. A total of 4,000 portions of raclette were served and 1,800 little pots of Emmi coffee creamer were enjoyed with coffee. The last guests left the exhibition grounds at 9 pm – all with happy faces and a coveted Emmi bag filled with a multitude of moments of indulgence. An all-round success for the Emmi AGM 2024, once again thanks to the many employees who worked hard both in advance and on the spot to create unforgettable Emmi moments.
Text Cornelia Stupf
Photos André Scheidegger
More than 10,000 shareholders have a financial stake in Emmi. This includes both private and legal entities such as companies and associations. Some own only one share, others own many. Emmi’s majority shareholder is the Genossenschaft der Zentralschweizer Milchproduzenten [Central Switzerland Milk Producers Cooperative], ZMP Invest AG. It holds 53.2 % of the shares (as at 31 December 2023). The cooperative is not only our largest shareholder, it was also there with us at the beginning of Emmi’s history and is a reliable partner. The second-largest shareholder is an American investment fund, which has been closely associated with Emmi for a long time. Other organisations with significant shareholdings include the Zentralschweizer Käsermeister Genossenschaft [Central Switzerland Master Cheesemakers’ Cooperative], at 4.0 %, and the MIBA Genossenschaft [MIBA Cooperative], at 3.2 %.
On 17 April, Emmi paid out a dividend of CHF 15.50 per share to its shareholders. Through the shareholding of ZMP Invest AG, the dairy farmers also participate indirectly in Emmi’s business success. ZMP pays a refund to its members from the dividends it receives from Emmi. In 2023, ZMP paid out an average of CHF 9,005 to each farm from the dividends it received.
The unmistakable blue cheese is in high demand among Americans. That’s why we’re taking a look at the production site of our subsidiary Emmi Roth in Seymour, Wisconsin, which produces this aromatic, premium-quality speciality cheese.
Founded
1976, part of Emmi Roth since 2019
In charge
Marvin Jones – Plant Manager at Emmi Roth since 2022
Team Around 72 people
Centrepiece
Blue cheese, available as whole wheels, in pouches or in pots from retail outlets such as Wholefoods or Target, as well as in diners and restaurants
Interesting to know
Second largest producer of “blue cheese crumbles” in the USA
The second largest producer of “blue cheese crumbles” in the USA is headquartered in Seymour. The small town in Wisconsin is about three and a half hours north of Chicago and has a population of around 3,500. The production site of our subsidiary Emmi Roth is the third-largest company in this small town, where blue cheese is produced with great love and passion.
Significant production facility
More than 43,300 pounds of creamy cheese are produced every day on an area of over 500 square metres – equivalent to around 19,600 kg. A total of 4.2 million kg of blue cheese is planned to be produced this year. Whole wheel, in pouches or pots. From 110 g pots and 2.2 kg pouches to 2.7 kg wheels, we produce very different quantities according to requirements.
Important mould
Mould is an important component of blue cheese (known in German as Blauschimmelkäse). The non-toxic fungus permeates the cheese and gives it a unique taste. Blue cheese is very popular with Americans: whether with a salad, on pizza or as a dip with spicy chicken wings, this cheese is a must.
Full of positive energy
Operations Manager Marvin Jones is proud of his employees: “Each and every one of us is always committed and passionate about our work. We are all proud to contribute to this outstanding blue cheese. ” You can feel this when you’re there, he says.
“It fills everyone with pride that they are contributing to this outstanding blue cheese. ”
This energy is also reflected in the fact that processes are continuously being improved and optimised. For example, a lot of packaging was done by hand in the past. Since 2022, packaging has been automated, meaning that between 13,000 and 23,000 kg of cheese are now packaged by machine every day.
Marvin is on the factory floor every day and the door to his office is always open. Transparency is important to him and motivates his teams. He points out:
“Personal interaction is the be-all and end-all, whether with employees or my superiors.” As the newly opened headquarters of Emmi Roth in Stoughton is only three hours’ drive away, Emmi Roth MD Tim Omer can also be seen in person on a regular basis. A big plus, because both sides benefit from the exchange.
Day in, day out, Emmi employees use craftsmanship, passion and innovation to create moments of indulgence to high quality standards. In this issue, we shed light on our passion and craftsmanship. A glimpse of our production facilities in Suhr and Emmen (Switzerland), where Emmi employees use their extensive expertise to produce high-quality dairy products.
No dust clouds the smooth surfaces, everything is neatly in its place and there is a strong air of concentration on that Monday at 1:45 pm in the company laboratory in Suhr (Switzerland). At the heart of the action: Fabienne Mentil. The trained dairy technologist moves almost silently from her lab bench to the fridge, from which she takes a chilled milk sample. Add two pipettes, a test tube and a petri dish – the testing is ready to begin. With a practised grip, Fabienne opens the milk sample, takes three drops of milk and starts the laboratory test for quality control.
Fabienne has been working at Emmi for 13 years, starting as an apprentice. “I already knew at the beginning of my apprenticeship that I wanted to work in the company laboratory after my
training.” And that’s exactly what happened: she started in the company laboratory in Dagmersellen (Switzerland) and, after five years, switched to the one in Suhr (Switzerland), where she now gets a lot of enjoyment from pursuing her ideal job, which she had been dreaming of since the beginning of her apprenticeship.
Fabienne is one of six Emmi employees in Suhr (Switzerland) who give an insight into their work that Monday. Professional pride is clearly palpable amongst all interviewees, and their identification with Emmi and its products runs like a recurring theme through their explanations. And so it soon becomes clear: here are six true Emmians, pursuing their craft with great passion. →
“As team leader, I am responsible for the milk and cream intake in Suhr (Switzerland). Maintaining direct contact with farmers and drivers and ensuring milk quality – connecting these worlds fascinates me. In my work, you not only need a good understanding of the raw product and the equipment, you also need to be able to handle people well. As I come from a farming background, I know what it means for farmers to deliver milk of the desired quality. I can also understand the situation of the drivers: the next trip is often already waiting for them. They therefore appreciate it very much and feel understood when I explain to them why, on rare occasions, they have to wait longer until we have completed the milk inspection. After all, an average of 500,000 litres of milk and up to 10 different types of label are delivered to Suhr (Switzerland) every day. ”
“I have already completed my apprenticeship as a plant operator at Emmi. I’ve been working as a shift coordinator for two years. This means that I not only work directly on the machines, but also prioritise the deployment of the technical service, coordinate scheduling with our skilled workers and record how the shift progressed for the machine operator. A very good understanding of technology and good communication are crucial for my job. I’m thrilled at how close I am to the heart of it all: I get to know about all the technical innovations, learn something new every day and work with products that hit the market quickly and end up on families’ dining tables. What’s more, I’m usually on site and find out first-hand what’s on the front-line employees’ minds. All of this gives my work a great sense of purpose. ”
Fabienne Mentil, 29, laboratory technician, at Emmi since 2011
“As a stand-in, I am used wherever I am needed. Sometimes I don’t find out which area of our plant lab I’m going to be working in until the evening before. This uncertainty is just the thing for me. I’m flexible and adaptable. Conditions like this spur me on. Thanks to my varied assignments, I can now draw on a wealth of experience and knowledge. I learn the most from my best friend, who I met at Emmi and who also works in the company laboratory in Suhr (Switzerland). I benefit from her both on an interpersonal level and from a work point of view, for which I am very grateful. Chemical and bacteriological analyses have become more demanding in recent years, as there are more milk alternatives available than before. We also process more samples per day. At the end of the day, however, we are always proud of what we have achieved. ”
Ivan Vrabel, 32,
“The interplay of technology is unique here at Emmi. Since no two days are the same, I’m constantly learning something new. As an industrial electrician, I look after the equipment, some of which has been in operation for 40 years, but I also deal with new technologies just as often. Whether it’s sensors that need to be replaced, a robot that won’t move into position, or electric doors that don’t close properly: since I’m deployed all over the site, I can’t fix everything at once and have to set priorities. That challenges me. I used to work as an electrician on a construction site. It works the same everywhere, on all construction sites –there was a lot of routine involved. The variety at Emmi suits my nature much better. ”
Howthaman Loganathan, 22, logistician, at Emmi since 2018
“ As a logistician in the control centre, I am at the heart of logistics and have to approve orders, analyse processes and sometimes temporarily hold back and inspect pallets. This gives us the certainty that the goods will reach the customer as ordered. It gives me great satisfaction that my work contributes to trouble-free operations, and that I can ensure quality. To achieve this, it is essential to work in a very focused manner. As an early bird, I prefer to be on the morning shift between 5 am and 2:30 pm. In the autumn, I’ll be starting my further training to become a logistics specialist, which goes a little deeper than the three-year logistics apprenticeship that I’ve already completed. I’m very happy that I can develop myself further and that we have a good team spirit. ”
“I’m very happy that I can develop myself further. ”
Howthaman Loganathan, logistician
Emmi trains young people in 14 different occupations. In 2023, there were a total of 130 apprentices across Switzerland. In order to continuously develop its employees and their technical expertise, Emmi also invests in the further training of its staff. In 2023, 57 % of all Emmians had a personal development plan.
Sarah Lanz, 24, road haulage specialist, with Emmi since 2020
“I particularly enjoy driving at night, I like the peace and quiet. Also, I’m my own boss during those hours. Almost half of all our trips start at night. Many people think you just have to be able to drive a truck, but working as a lorry driver requires a lot of logical thinking. In traffic I have to be proactive, and it’s the same when loading the lorry; the dispatcher can’t always foresee everything. My job involves so much more than just driving: I am the first point of contact for customers when they receive supplies. I like representing Emmi in this way – especially since our Emmi lorries not only look good, they also have modern equipment. ”
Developing a new product, refining recipes or ensuring consistent quality: these things require testers with a strong sense of taste. The new Sensorikum [sensory centre] in Emmen (Switzerland) enables internal product testing under controlled conditions – a prime example of the ongoing development of Emmi’s craftsmanship.
Nothing in this room is left to chance. No rays of sunlight penetrate, no distracting sounds, no external smells... The arrangement of the 12 seats, which are separated from each other like cabins, also enables concentration. In this way, the testers’ undisturbed attention can be focused on the palate, and on their senses of smell and sight. We find ourselves at the Sensorikum in Emmen (Switzerland), which has only recently become operational. Here, employees can taste and evaluate products based on their aroma, texture, smell and appearance.
Only those who pass the taste perception tests and successfully complete the internal sensory training will be considered as testers. After all, this work is not about personal taste, but whether you can differentiate between different roasted aromas or the degree of bitterness, for example. “Everyone needs to be guided by the same standards. This is the only way to achieve measurability that shows us how we can develop a product in the desired direction,” explains food scientist Claudia Zimmermann, who heads the Sensorikum.
“We use the Sensorikum to make taste more measurable. ”
Claudia is currently setting up a panel of around 20 employees who are available to carry out testing and regularly undergo sensory training. The composition of each team, which consists of a maximum of 12 people per test, depends on the project and product. The area in which they work at Emmi is irrelevant. So if you’re testing a cheese, you don’t have to be a cheese developer. “On the contrary, we want a really broad-based panel. ”
It goes without saying that products used to undergo appropriate sensory tests in the past as well. But until now, each department used to do its own testing. “With the new Sensorikum, we have both standardised conditions and trained test personnel at our disposal,” explains Claudia. In future, Emmi will be able to carry out sensory tests internally that were previously performed externally, for a fee. In addition, it is now possible for Emmi to professionally assess its own products and those of competitors.
The standardised conditions even include the selection of the appropriate light. For example, if cheeses of different shades of yellow are to be tasted, the light can be adjusted so that they do not differ visually. “This means that the testers are not influenced in their perception of taste.” In addition, keeping control of environmental influences enables the products to be evaluated under the same neutral conditions each time.
New sensory software is currently being tested that should enable the products to be assessed even more precisely. Claudia puts it in a nutshell: “We use the Sensorikum to make taste more measurable and reduce the arbitrary and subjective aspects of taste perception.” This is not only a great help when it comes to testing new products, but also when it comes to refining existing recipes and reducing sweetness, for example. Last but not least, the tests also aim to ensure consistent taste quality for existing products.
Text Manuela Specker
1 The light can also be adjusted so that products are visually indistinguishable.
2 In the Sensorikum, the testers’ undisturbed attention is focused on the palate, and on their senses of smell and sight.
Our CEO, Ricarda Demarmels, spoke to Dr Barbara Studer, a neuroscientist at the University of Bern (Switzerland) and CEO of Hirncoach [Brain Coach].
A fascinating conversation about passion, innovation and the willingness to learn.
Ricarda Demarmels: What sets us apart at Emmi is our craftsmanship and our passion. How do you think passion develops in a team, Barbara?
Dr Barbara Studer: The key element is a shared vision that increases the sense of community and personal commitment. A common understanding of goals activates the emotional centre in the brain. That makes us feel inspired and ready to make a personal and energetic contribution. With this attitude, the successes of the company are seen as personal successes. The reward centre in the brain is activated, which in turn leads to more motivation and stamina, and ultimately also to passion.
As a neuroscientist, how do you explain passion?
Passion is a strong emotional involvement. It is shaped by personal values and interests as well as by neurochemical processes in the brain: when we do something emotionally fulfilling, our brain releases dopamine and noradrenaline. This triggers a feeling of
“When managers involve all team members, actively provide information and also ask for their opinions, their sense of appreciation increases. ”
Dr Barbara Studer, neuroscientist
reward and satisfaction. Endorphins and oxytocin are also released. These are happiness hormones that are associated with positive emotions and social bonding. We feel happy and are motivated to continue investing in this activity, relationship or object.
What is the best way for a team to develop a shared vision?
An effective vision cannot simply be adopted, but must be “felt” by the person themselves. It should be defined in such a way that each person in the team can contribute their own personal part to this vision. They need to ask questions such as: “What do I find particularly rewarding about the goal we are working towards together? How can I use my personal strengths to help me achieve those goals? ”
How do managers foster passion in a team?
The essential thing is a team culture that is characterised by empathy and trust. When managers involve all team members, actively provide information and also ask for their opinions, their sense of appreciation increases. That, in turn, motivates them to actively contribute to challenges.
And what else does it take to become passionate about work?
In addition to meaningfulness, experienced autonomy, i.e. the ability to act independently and make decisions, is beneficial. Every employee should be able to say: “I can be effective and help shape things myself.” This is known as self-efficacy, and it enables team members to unleash their passion for their work.
How is our Emmi culture bound up with our innovative strength?
Creativity can flourish and innovation is encouraged in a supportive and collaborative working environment where ideas are valued and successes recognised. Opportunities for creative exchange are important, where you challenge each other, contribute ideas and develop solutions together.
Innovation always requires a willingness to change – but this is something that many people find difficult.
Thinking in the usual way requires less energy and offers security. Since change is associated with insecurity – you don’t know what’s coming or how to react to it – many people experience inner resistance to it, even amounting to stress. Our brain then goes into a state of alarm and tries to identify possible dangers.
How can this defensive attitude be counteracted?
It is worthwhile to learn a “change-affirming”, curious mindset: there is a lot of exciting potential for growth outside what we’re used to. In fact, it actually makes our neural networks grow inside our heads! By saying yes to change and innovation, we develop both ourselves and our craftsmanship further.
Can openness and curiosity be learned?
Yes, of course. We can cultivate our curiosity in everyday life by continually engaging in new things and consciously trying out new methods or techniques. If we do not avoid challenges, we are always strengthened and delighted by the experience that even difficult hurdles can be overcome. In concrete terms, this means breaking the routine, talking to people who hold different opinions and taking on tasks that require you to leave your own comfort zone.
Does this keep your brain fit?
Yes, our brains love to learn. We get to know ourselves better when we tread new paths. We suddenly find new skills that we had no idea about before. We develop our potential instead of standing still. This strengthens the brain and ultimately makes all of us, including companies, fit for the future. Here’s to lifelong learning!
Finally, what advice can you give us Emmians in an increasingly fast-moving world?
Your brain is challenged, so calm and strengthen it by giving it breaks every so often. For example, with mindful walking, eating or “forest bathing”, i.e. by spending time in nature. It is also important to set healthy boundaries in order not to feel stressed by constant availability and pressure. Plan time for self-reflection and strengthening activities such as friendships, sport, music, etc. And last but not least: cultivate gratitude, in thoughts and words. That means you’re giving your brains soothing massages, so to speak.
Dr Barbara Studer
Neuroscientist and speaker Barbara Studer is CEO of Hirncoach AG, which offers programmes for the holistic promotion of mental fitness and health – scientifically, effectively and beneficially. The hybrid programmes are intended for private individuals as well as for companies and schools. More information at www.hirncoach.ch and www.studertalk.ch
SUSTAINABILITY: FOCUS ON EMPLOYEE
DEVELOPMENT IN 2024
Whether at home or at work – we all learn from the experiences we have every day. By trying new things, we develop ourselves and our skills further. The fact that it is precisely this type of learning that has great potential is unfortunately often forgotten.
When we think of “learning and development” in the context of work, we often link these topics with further education and training. The 70-20-10 learning model, developed by researchers Morgan McCall, Robert Eichinger and Michael Lombardo, shows that it doesn’t have to be this way. It indicates that our development and learning are divided up as follows:
• 70% occurs during our day-to-day work , when we try out (new) things and acquire new skills and knowledge as a result,
• 20% is achieved in dealing with and exchanging ideas with others, for example when we take part in coaching sessions, expert discussions or feedback discussions,
• 10 % takes place formally, through courses or further training.
It is therefore important to have a working environment with a range of learning opportunities in which all employees feel valued, inspired and encouraged to grow. But how can we do this? Three practical examples from the Emmi world:
In the “InLoW” programme, employees from Emmi Logistics Switzerland take on a new role in a different department for a period of six months. For example, a driver becomes a transport scheduler, or an employee switches from Logistics to Requirements Management. There are many winners: employees develop both professionally and personally, and value the trust placed in them. The new department benefits from their expertise, skills and the breath of fresh air they bring in. And the department that sends the employee looks forward to their return as a more mature personality, with a rucksack full of new skills and knowledge.
2 Pasticceria Quadrifoglio, Italy: feedback culture and job rotation
“We need a coordinated and committed team in order to grow together.” Thanks to this insight, our subsidiary Pasticceria Quadrifoglio has launched the “BELIEVE” initiative in Italy. The goal is to align all managers and employees with the strategy, including the vision, mission and values that go with it. To achieve this, they aim to improve understanding of the company as a whole. One measure to achieve
this is job rotation on a voluntary basis, i.e. interested employees change jobs for one day and work with colleagues from at least two other departments. The insight they get into a new department promotes awareness of higher-level processes and the needs of other departments. The company also invests in a feedback culture by holding weekly feedback meetings with constructive discussions. Each meeting results in immediate measures to improve collaboration. The initiative is already having an impact: initial feedback shows that group cohesion is stronger, communication is better and everyone’s view of the bigger picture has improved.
3 Emmen production site, Switzerland: additional tasks and roles
At the production site in Emmen (Switzerland), employees have various development opportunities in their day-to-day work: in addition to existing tasks and areas of responsibility, they are introduced to new shifts, trained on new lines, machines or equipment, or act as stand-ins. They can participate in projects and thus contribute their practical knowledge, represent the interests of the department and at the same time become familiar with new methods and ways of working. By taking on additional roles, such as practical trainers or key users, employees face new challenges and acquire additional skills.
Emmi Landenbergstrasse 1
CH-6002 Lucerne Switzerland
info@emmi.com www.emmi.com