Recharging Resources Responsibly
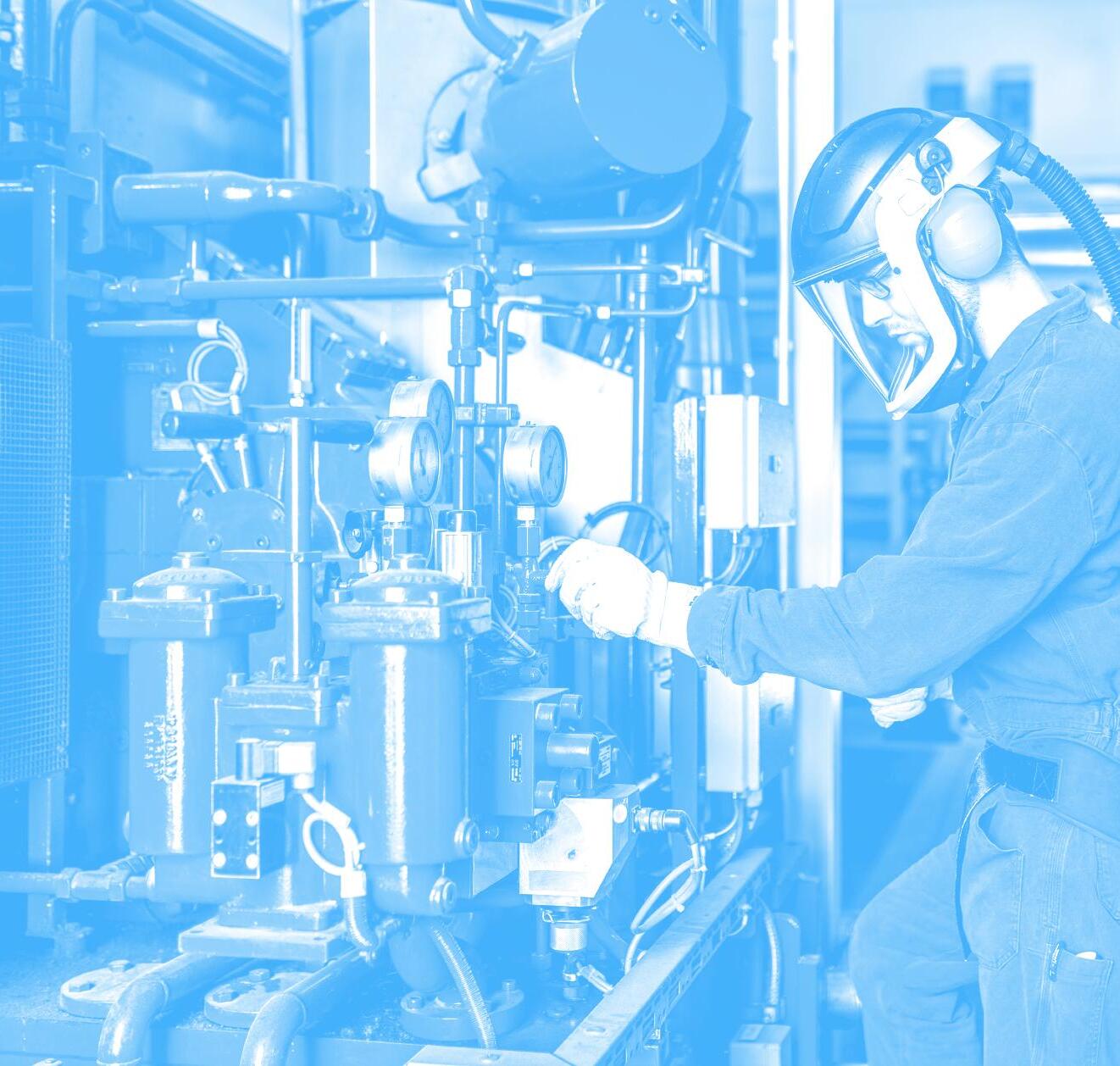
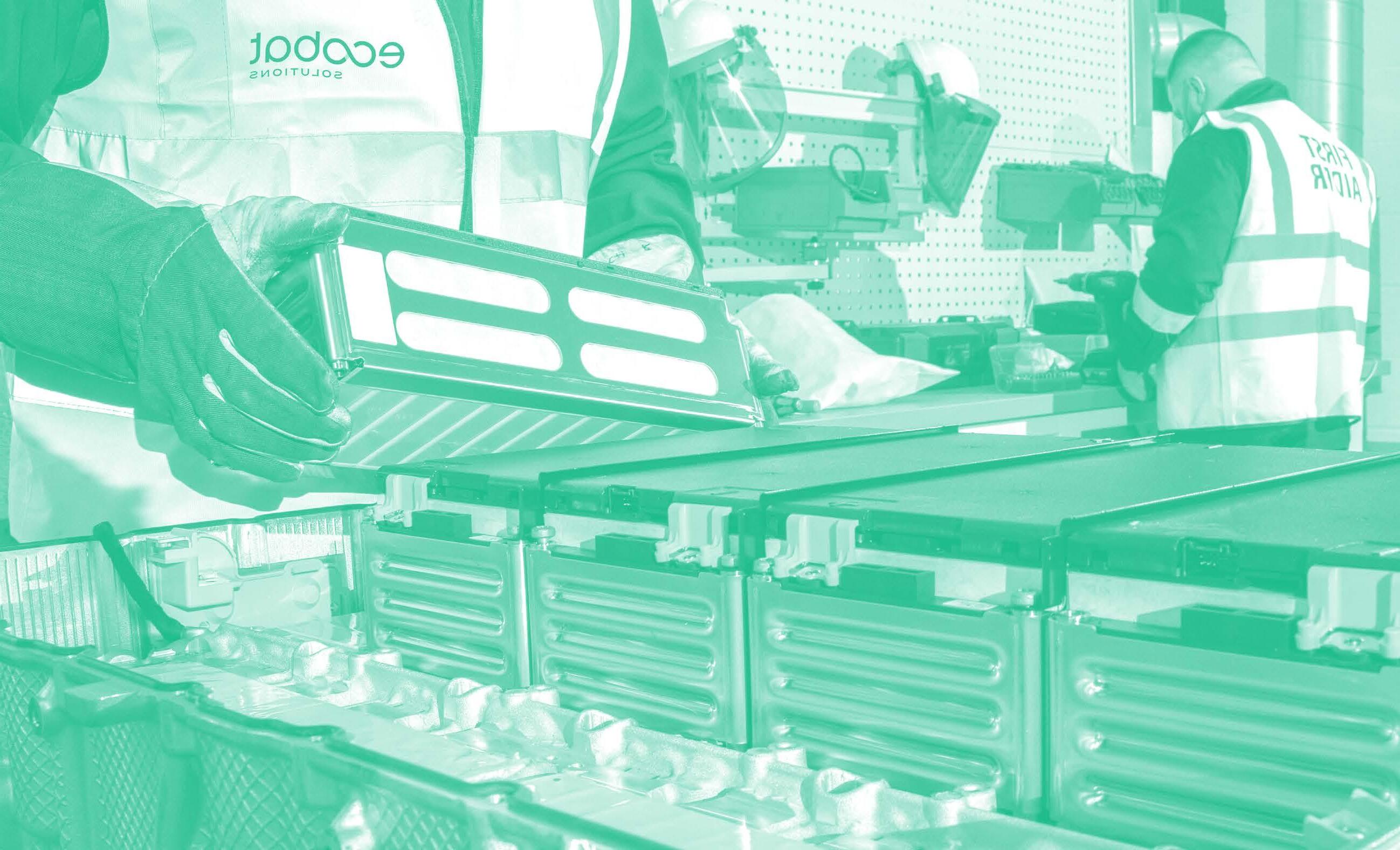
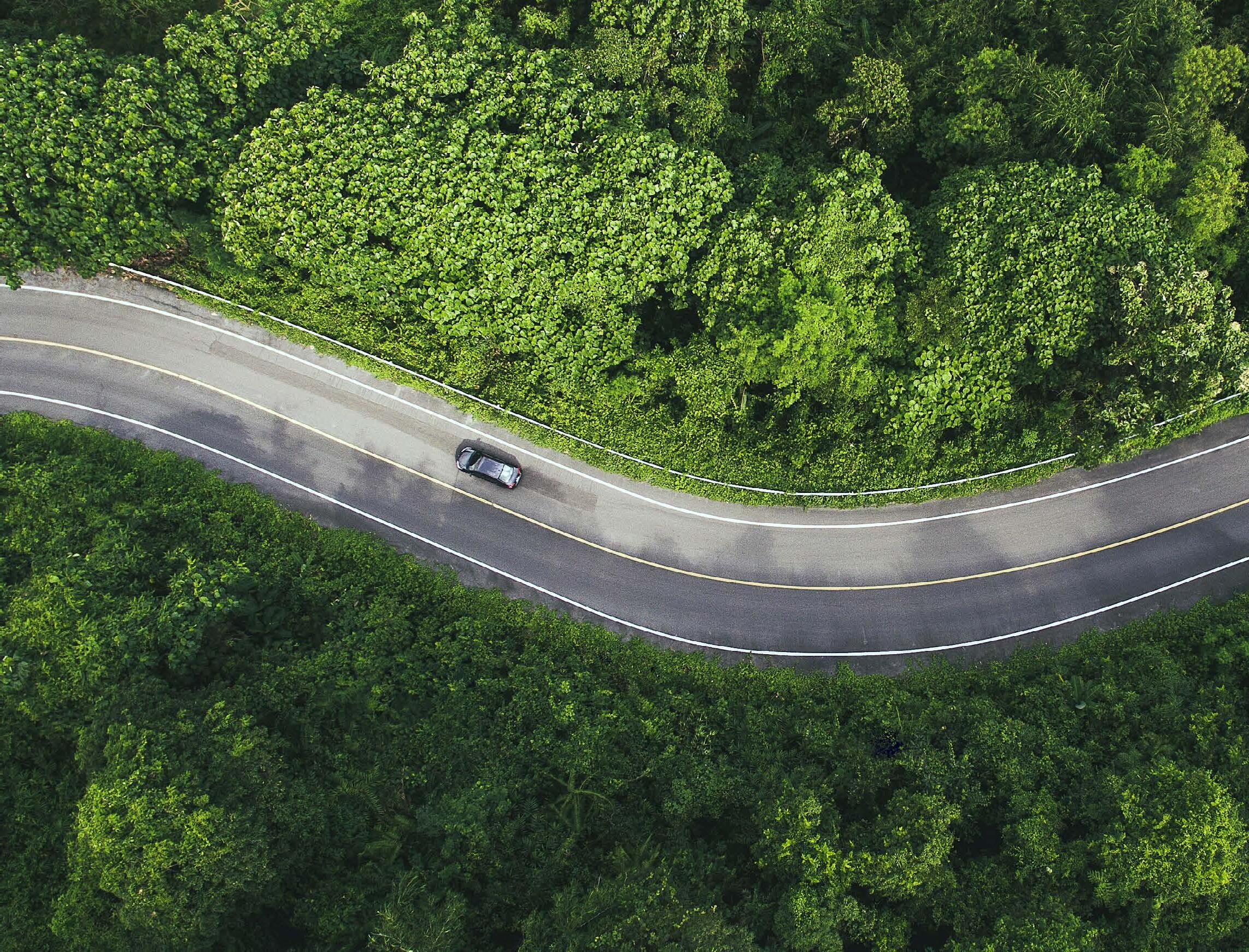
At Ecobat, we provide an essential service and value proposition to the world. We incorporate a business model that focuses on recycling in a circular environment. We strive to deliver products in a timely fashion that are designed for longevity and extended product use with exceptional quality and service.
Executing our circular sustainability strategy is essential to our company, partners, and customers. By recharging resources responsibly, our business model aims to ensure that our customers receive high-quality, recycled products that support their economic, sustainability, and customer goals.
In 2023, we continued to rebound from macroeconomic headwinds of energy, inflation, and workforce pressures through focused enterprise risk management. We achieved an all-time lead production record internally. Restarted Italian operations focusing on a profitable business model and successfully divested Stolberg and South African operations to strengthen core business offerings and activities.
Ecobat’s focus on health extends from our fiscal responsibility to our dedication to our employees’ health, safety, and well-being. In 2023, we outperformed our 12-month rolling average blood lead improvement goals of 10% for the organization. Additionally, we recorded a 10% year-over-year improvement in employee engagement scores through the National Business Research Institute for our organization.
Since formalizing our sustainability programs in 2022, we have established goals that align with international standards and deployed business practices that support our commitment to striving towards exceptional lead, polypropylene, and lithium-ion battery transportation, collection, recycling, and distribution services. Our efforts were internationally recognized with the EcoVadis Gold Sustainability rating award, placing Ecobat in the top 5% of all participating companies.
We are proud of our story. We are proud to support a low-carbon future. We are proud of our continued effort to sustainability. No other material has a more efficient and prolific recycling story than lead. It is the premier standard of recycling demonstrated by our ability to take a waste product, recycle 99% of its components, and place these valuable commodities back into the supply chain for use
We look for Ecobat to maintain our focus on providing a superior product and look to continue our successes throughout 2024 and beyond.
Tom Slabe Chief Executive Officer
We hold ourselves accountable by measuring our efforts against these international standards, methodologies, and principles:
Sustainability Accounting Standards Board (SASB) and Global Reporting Initiative (GRI) Standards
We’ve looked to integrate these sustainability frameworks in our business processes since 2022.
EcoVadis Gold Medal Sustainability Rating
EcoVadis is an international organization that assesses environment, labor and human rights, ethics, and sustainable procurement performance. Ecobat earned this award in 2023, placing us in the top 5% of all organizations assessed by EcoVadis.
Our commitment to respect human and labor rights, safeguard the environment, and work against corruption in all its forms aligns with our product sourcing and production values and goals. Our approach to sustainability extends to our supply chain partners and customers, and it supports UNGC principles. We use an established assessment and review process to ensure our partner organizations align with Ecobat’s Code of Conduct expectations.
Metrics measure the success of our execution. Starting in 2022 and continuing in 2023, we developed our materiality tracking and reporting systems, supported by streamlined KPI tracking. With established processes and baseline data now in place, we have more confidence in the accuracy and scope of our data. And because we recognize the importance of shareholder confidence,
Nations Global Compact (UNGC) Participant
We’ve focused on embedding the Ten Principles of the UNGC into Ecobat strategies since 2023.
For the 2024 reporting year, we plan to increase transparency to our stakeholders through ISSB sustainability framework consistency.
we conduct third party limited assurance of key reporting metrics, such as our annual global greenhouse gas emissions (GHG) footprint. Metrics transparency reflects our commitment to embedding safe, responsible resource recycling procedures. This is fundamental to our story.
As sustainability practices develop worldwide, legislative and regulatory requirements evolve to keep pace. While we continue to concentrate on providing quality products to our customers, we are also actively engaged with trade organizations, symposiums, and peer organizations to stay up to date on any regulatory impact on our organization and our sustainability goals.
The enclosed information sets forth Ecobat’s global Sustainability Report. Transparency and accountability are crucial building blocks to achieving progress. Here, we showcase our efforts towards integrating sustainability throughout our company, processes, and products. All metrics represent 2022 and 2023 data and results.
This report has been prepared in alignment with the Sustainability Accounting Standards Board (SASB) and the Global Reporting Initiative (GRI). Furthermore, Ecobat's sustainability management and reporting are guided by our commitment to the United Nations’ Global Compact Sustainable Development Goals (SDGs).
We invite stakeholders to learn more about our approach to sustainability by visiting our website at www.ecobat.com . For more information, please contact info@ecobat.com
Lead is the primary focus of our business. We recognize that this 99% recyclable resource is an essential component of today’s commercial and consumer goods. We believe that a circular business model is the optimal way to bring this commodity to market.
Transportation, healthcare, telecommunications, agriculture, and consumer goods industries use lead as a primary energy source and product component. Lead has distinct advantages over other natural resources, including:
1 BORN RECYCLABLE
Lead is inherently recyclable - up to 99%and maintains undegraded performance post-recycling due to its long-lasting chemical properties.
2 SAFE AND COST EFFECTIVE
Lead offers a safe, cost-effective storage solution for industry and consumer goods.
3 STABILITY
Lead’s stable battery chemistry adds value to products it is used in.
Lead plays a critical role as both a primary energy source and a fundamental component in equipment and tools, driving essential sectors globally.
We believe that lead continues to be a solution for today and tomorrow. As the global need for energy accelerates, a diverse array of battery solutions must coexist. With electric vehicle (EV) adoption on the rise, we anticipate that the transition of the overall fleet to advanced battery chemistries will gradually progress. Despite the growth of lithium batteries, we expect that lead will continue to play a vital role in EV manufacturing and operation, powering electrical systems such as lights, windows, navigation, air conditioning, and airbag systems into the future. We estimate that by 2040, approximately 42% of the United States and European vehicles will continue to rely on leadacid batteries in internal combustion engine applications.
Lead batteries will likely also be required for alternative energy sources, including solar panels and wind turbines, as our society works to reduce its reliance on fossil fuels. However, solar and wind resources will still require batteries for a continuous 24-hour energy supply. With their stability, cost efficiency, and reliability, lead-acid batteries may prove ideal for expanding applications like energy storage.
Governments, including the European Union, are actively working to fortify circularity and sustainability regulations for batteries and waste Regulation (EU) 2023/1542 of the European Parliament and of the Council of 12 July 2023, with initiatives like the European Union Batteries Regulation. We believe that lead-acid battery recycling continues to be the model for circularity and efficiency for other products to emulate.
By leveraging our decades of lead-acid battery recycling expertise, Ecobat has expanded our offerings to recycle advanced battery chemistry waste, such as lithium-ion batteries. We recognize the pivotal role that advanced battery chemistries will play and look to meet the rising global marketplace demand for recycling services.
We also offer a key solution for vehicle original equipment manufacturers (OEMs) responsible for achieving EU Endof-Life Vehicles Directive recycled plastic requirements, Directive 2000/53/EC of the European Parliament and of the Council of 18 September 2000. We provide a second life for all battery components, including polypropylene. Offering recycled polypropylene is another way we plan to meet the needs of society and our customers.
We believe that our commitment to a circular business model, responsible collection and recycling, and safe business practices make us a global leader in sustainable lead production today and in the future.
The United Nations projects the world’s population will increase by nearly 2 billion people in the next 30 years, from the current 8 billion to 9.7 billion in 2050. We anticipate that with the growth, the demand for raw materials rises significantly. However, the supply of strategic and critical raw materials is limited. We believe that finite supplies of materials call for a departure from the traditional, take-make-consume-throw-away linear economic model.
Our goal is to demonstrate a different model of production and consumption, powered by the circularity model. We aim to extend the lifecycle of our products through our closed-loop recycling approach. We take end-of-life products and provide a second life, keeping their material circulating within the economy. This approach reduces waste and greenhouse gas emissions and creates further value, as the products can be used repeatedly. With a 99% recyclability rate, lead is the prime example of the success of circularity.
As a foundational component of the European Green Deal focusing on sustainable growth, the EU adopted the Circular Economy Action Plan (CEAP). The CEAP establishes measures to achieve a climate-neutral, sustainable, toxic-free and fully circular economy by 2050. To achieve 2050 targets, the EU will introduce tighter recycling and binding targets for material use and consumption by 2030, European Commission, Directorate-General for Communication, Circular economy action plan - For a cleaner and more competitive Europe, Publications Office of the European Union, 2020.
We believe Ecobat is uniquely positioned to advance these emerging legislative initiatives, which will only grow in importance with global raw material and resource pressures. Recycling and resource recovery comprise more than 80% of our business. We believe we will supply vital resources necessary in the global energy supply as the next generations of low-emission technologies develop and mature.
Ecobat’s Circularity Model is shown to the right.
With over 90 years of experience, Ecobat’s extensive history in the lead-acid battery recycling market provides a tremendous marketplace advantage. Decades of technical acumen, practical experience and operational excellence drive our focus on sustainable processes and practices for safe, effective lead handling. Our operations’ scope and breadth allow us to capitalize on transferable advantages, including vast logistical knowledge, strategic geographic positioning, and industry contacts. We believe that managing the responsible production and recycling of lead gives us a distinct competitive advantage.
We aim to provide customers with global, best-in-class recycling, logistics, and distribution services. We recognize the importance of meeting our customers’ needs in the low-carbon transition. That’s why we extended our capabilities to include lithium-ion battery recycling. Moving forward, we strive to provide the same best-in-class services for advanced battery chemistries, complementing our core business expertise in lead and lead-acid battery recycling.
Ecobat Resources
Ecobat Resources is one of the leaders in the responsible recycling and production of resources essential to modern life. Backed by an international network of smelters, we are the world’s largest producer of lead and lead alloys used in energy storage solutions and a range of other industrial and commercial applications. Alongside our lead production and recycling operations, Ecobat Resources also manages the reclamation of polypropylene used in the development of premium polymer solutions and other commodities.
Headquarters
Ecobat Resources
Ecobat Logistics
Ecobat Battery
Ecobat Solutions
Ecobat Logistics manages the collection of end-of-life batteries as part of our commitment to supporting the closed-loop management and recycling of energy storage solutions. We provide collection services for the markets we operate in through our 11 smelting facilities, a collection truck fleet, and 65,000 battery collection points, aiming to offer a seamless service for battery collection and recycling in Europe. Our Logistics locations geographically complement our European Resources and Solutions operations. In addition to lead batteries, we also manage the collection and handling of other battery chemistries, including, but not limited to, lithium batteries.
Ecobat Battery manages the procurement and sale of energy storage solutions. We supply batteries for a wide range of uses, including automotive, commercial vehicle, marine and leisure, motorcycle, and industrial applications. We are the sole European license holder and distributor of Lucas and Rolls batteries and a key distributor for Exide, Varta, US Battery, Trojan, Optima,
Sonnenschein, Tab and more. In addition to our vast portfolio of products, we offer various services to our industrial customers, including battery maintenance contracts, installation, and repair.
Ecobat Solutions leverages our extensive technical experience and international team to bring innovative products and solutions to market in the advanced battery chemistry space. We also work to drive innovation within our company and industry as part of our commitment to sustainability and environmental stewardship, in the development of technologies and processes for recycling and resource recovery for lithium-ion and other battery chemistries. We have capabilities for collection, dismantling, diagnostics, and crushing/sorting to derive black mass for advanced battery chemistries. We also support research and partner with universities, trade organizations, and government entities to develop safe, more efficient energy storage solutions.
As the world continues to evolve in the transition to a lowcarbon future, Ecobat remains steadfast in progressing our program and operational practices with sustainability in mind. Material changes to the business, marketplace, and regulation will drive our strategy and response.
We believe that our model, which aims to provide safe, environmentally responsible product recycling helps drive the future of the low-carbon transition. We’re proud of the essential role we have the potential to play in the circular economy not only today but also in the future of recharging resources responsibly.
Ecobat’s Relevant Documents Supporting This Section:
• Global Code of Conduct
• Delegation of Authority Matrix
• Ethics & Confidential Helpline Guidelines
• Whistleblowing Procedure
• Anti-Bribery and Corruption Procedures & Guidance
• Antitrust & Competition Compliance Procedures and Guidance
• Ecobat Conflict Minerals Policy Statement
Every day, it is estimated that billions of people benefit from the technologies that use and rely on lead. It provides efficient energy storage solutions in transportation, medicine, telecommunications, agriculture, and clean energy. Lead is a crucial resource that connects us to modern life today and tomorrow. Our commitment to the well-being of our team members, partners, communities, and the planet guides us in our practices, and we continually look for new ways to enhance our efforts.
To lead in the responsible collection, recycling, production and distribution of resources essential to modern life.
As a market leader, we drive advancement within our industry and work to develop innovative and sustainable products that help our customers succeed, protect our environment and improve our communities while meeting the ever-growing need for more efficient, reliable energy storage solutions.
• Ecobat Modern Slavery & Human Rights Statement
• Prohibited Parties Compliance Guidelines
• Group Enterprise Risk Management Policy
We’re Proud
We find a deep sense of pleasure and satisfaction in the work achievements and qualities we share.
We’re Engaged
We aim to be consistent, precise, and purposeful in the way we conduct our business.
We’re Rigorous
We gather and review the facts before we engage. If you want to get involved with us, we will make sure you’ve done your homework.
We’re Operationally Excellent
We look to embrace principles and tools that produce efficient outcomes.
We’re Caring
We aim to prioritize the wellbeing of our people, each other, and the planet, and we seek to be intentional about making a positive impact.
We’re Collaborative
We believe we produce effective and efficient outcomes because we work together as a team.
In 2022, we refined Ecobat’s Environmental, Social, and Governance (ESG) strategy based on a comprehensive materiality assessment that included extensive research, benchmarking, and key stakeholder engagement. We plan to continue to conduct materiality assessments every three years, using a Materiality Matrix to visually highlight key focus areas.
Materiality Matrix data comes from surveys and interviews with 45 internal and external stakeholders, gathering feedback and expectations. Next, we prioritize and rank the list of issues, visually representing them in the Materiality Matrix shown below. The data in the matrix represents annual data for 2023 used to support and validate progress against identified issues.
Material Topic
2022 Sustainability Report
Published Targets
Energy & Greenhouse Gas Emissions
Environmental Protection
• In 2023, establish inventory baseline per GHG Protocol
• In 2024, set emissions target
• Scope 1 & 2 Inventory data available for years 2021, 2022, and 2023.
• After establishing GHG emissions data years 2021, 2022, and 2023, Ecobat is on track to set an emissions target in 2024.
Engaging with key stakeholders helps Ecobat stay abreast of emerging issues and areas for improvement. We typically follow a routine cadence, shown below, to interact with internal and external parties to ensure Ecobat addresses their material ESG concerns. The table below outlines the frequency and focal points of our ESG engagement.
Waste Management
• In 2023, further improve data collection to monitor lead, cobalt, and nickel releases to air, soil, and water, globally
• In 2024, set a quantitative target
• In 2023, improve data collection to break out hazardous vs nonhazardous while assessing the potential impact of reduction initiatives
• In 2024, set a quantitative reduction target
• Ecobat has aligned data collection procedures globally to allow for consistency in methodology and comparisons of information. Internally, 2023 data collected in alignment with procedures has been reviewed to validate process. Quantitative target will be set in 2024.
• Ecobat has aligned data collection procedures globally associated with hazardous and non-hazardous waste generation. Internally, 2023 data collected in alignment with procedures has been reviewed to validate this process. Quantitative target will be set in 2024.
Responsible Materials Sourcing
• In 2023, establish a Responsible Materials Sourcing Policy and Questionnaire for Suppliers and Vendors
• In 2024, establish compliance targets
• Continue to report on Ecobat’s internal HSE metrics of Total Case Incident Rate (TCIR) and blood lead
Workforce Health & Safety
• In 2023, mature high severity program
• In 2024, set target for Solutions
• Average Blood Lead < 6 μg/dL by 2025
• Ecobat has established a Responsible Materials Sourcing Policy and has implemented the associated questionnaire for Supplier and Vendors and is on track to establish compliance targets in 2024.
• We continue to report Ecobat's internal HSE metrics of Total Case Incident Rate (TCIR) and blood lead.
• Established continuity of terminology in Risk Matrix methodology for severity categories. Updated Incident Investigation Program to align reporting and investigations requirements for 2024.
• We continue to improve our biological testing regime for Solutions occupational exposure in 2023 and 2024 in process.
Management/ Internal Leadership
Executive Committee
Board
Monitoring of targets and progress; budgeting
Customers
• Average 12-month rolling average of 6.72 μg/dl for its leadexposed populations in 2023. Stakeholder
Quarterly or monthly, depending on topic
Presentation on targets and progress; oversight Biannual
Presentation on targets and progress; oversight Annual
Investors Individual meetings on targets and progress Annual
Responses to data requests; two-way discussions on ESG best practices
Trade
Associations
As needed data sharing; annual discussions
Participation in requests for comment on new program development; two-way discussions on ESG best practices Ad hoc program development; bi-annual discussions
Local Communities Public meetings, facility tours, etc.
All
At least one touchpoint annually, additional as needed
Published sustainability report Annual
With over 125,000+ companies rated across 160 countries, EcoVadis is a globally recognized platform that provides reliable industry sustainability ratings. EcoVadis supplies benchmarks for ethical and environmental standards across many industries in four key categories: environmental impact, labor and human rights standards, ethics, and procurement practices.
Earning an EcoVadis medal or badge acknowledges achievement relative to other assessed companies across the EcoVadis database. To be eligible for a medal, a company must achieve a minimum score of 30 in each of the four themes: environment, ethics, labor and human rights, and sustainable procurement.
In 2023, Ecobat received the Gold Badge from EcoVadis, earning a minimum performance score of 70 across all categories and ranking in the 95th percentile across all firms EcoVadis evaluated. This achievement recognizes our successful efforts in the areas of environment, ethics, labor and human rights, and sustainable procurement.
Ecobat is committed to striving to achieve the highest international standards and holds almost 60 International Standards Organization (ISO) certifications, including ISO 9001 (Quality), ISO 14001 (Environmental Management), ISO 45001 (Occupational Health and Safety), ISO 50001 (Energy Management) and ISO 17025 (Testing and Calibration Management). We leverage these certifications to help advance performance through continuous improvement.
The UNGC and SDGs form the basis of our sustainability framework and help us strategically address pressing global challenges. Our strategy embraces the 10 UNGC Principles as well as 9 SDGs. The SDGs allow us to frame our business into a broader perspective that considers social and environmental impacts, embracing their interconnected and mutually dependent nature.
We have aligned our management system and sustainability efforts to adhere to internationally recognized sustainability best practices, such as the Global Reporting Initiative and SASB Standards. We also consistently work towards contributing to the SDGs in our business operations and strive to embody the UNGC 10 principles.
In developing our people and planet aims, we used the UN sustainable development goals to inform our thinking. Although our business activity touches the majority of the SDGs, we are focusing our efforts on those that align with our aims in order to sustainable development and for people over the next decade.
We strive to:
Enhance wellbeing
Enhance the health and wellbeing of our employees, contractors and local communities.
Sustainable purchasing
Develop a more sustainable supply chain.
Advocating
More actively advocate for policies that support circularity, including material recycling rates.
Greater equity
Support greater diversity, equity and inclusion for our workforce and customers.
Promote circularity
Unlock enterprise of value through circularity.
Transparency leader
Be recognized as an industry leader for the transparency of our reporting.
Just transition
Support a just energy transition that advances human rights, environmental stewardship, and education.
Aligning associations
Set new expectations for our relationships with trade associations around the globe.
Enable clean energy
Provide an essential material to aid in the low-carbon transition through battery applications.
Incentivizing employees
Incentivize our global workforce to deliver on our aims and mobilize them to become advocates for circularity.
Ecobat’s Relevant Documents Supporting This Section:
• Avoidable Loss Reporting
• Travel and Expense Policy
• Delegation of Authority Policy
• Cost Accounting
• Trade and Other Payables
• Cost of Sales
• Lease Accounting
• Bank Accounts
• Foreign Currency
• Intergroup Sales & Transfers
• Intercompany Loans
• Inventory
• Property, Plant & Equipment
• Revenue Recognition
• Derivatives Use & Hedging
Ecobat’s governance framework aims to ensure efficient and effective use of resources and aligns closely with stakeholder interests. The framework requires custodial accountability and balances our economic and social goals. We believe our governance enhances the stability and equity of our communities.
Ecobat, LLC is a limited liability company whose corporate governance is subject to the requirements, rights, and obligations set out in its formation documents, including its governing LLC agreement. Ecobat’s Board is comprised of 12 individuals appointed by unitholders. Board members have a varied and expansive depth of experience in financial sectors, with members adding expertise in global industries, manufacturing, and service.
• Financial Reporting
• Income Tax Filing
• Indirect Tax Filing
• Intercompany Transfer Pricing
• IT Change Management Policy
• Acceptable Usage and Mobile
Device Management Policy
• IT Governance Policy
• Cybersecurity Policy
• Data Privacy Policy
• IT Business Continuity & Incident Response Policy
• Health, Safety, Environmental & Sustainability Policy
The Board charter spells out the responsibilities of the Board and delegates authority to the Chief Executive Officer. The charter also gives the Board the authority to add management positions to further reinforce its commitment to good governance. The charter includes Legal and Health, Safety and Environment (HSE) positions.
The Board retains decision-making capacity and authority for the annual budget and oversees significant and exceptional decisions. The Board has four committees to provide structured oversight and governance: the Audit Committee, Capital Expenditures Committee, Health, Safety, Environmental and Sustainability Committee, and the Governance and Compensation Committee.
Each committee has its own charter, and these are the governance documents. The Board charter requires four board meetings per year at minimum and additional meetings as required to ensure Board alignment with management.
The Ecobat Enterprise Risk Committee (ERC), comprised of Ecobat’s Executive Leadership team and the Director of Audit and Risk Services (ARS), is a management-level risk committee accountable for enabling Leadership to understand, evaluate, and mitigate the risk that may negatively impact enterprise value and prevent the achievement of Company goals and objectives.
The annual Enterprise Risk Assessment (ERA) evaluates Ecobat’s broader portfolio of operational, commercial, strategic, financial, technological, legal/ regulatory, and human capital risks. It creates a priority list of the most critical enterprise-level risks. The ARS team further formulates the annual audit project plan based on the outputs of the ERA to reduce risks to an acceptable level. In addition, the ERC meets quarterly to review risk owners’ response plans to Ecobat’s top risks and discuss any emerging enterprise risks, shifts in risk priorities, and high priority audit recommendations.
Ecobat monitors business ethics through the Annual Enterprise Risk Assessment, quarterly enterprise risk committee meetings composed of the Executive Team, internal reporting through the SpeakUp hotline, and internal avoidable loss reporting.
% of the total workforce across all locations who received training (e.g. e- learning) on business ethics issues
% of all operational sites for which an internal audit & control concerning business ethics issues has been conducted
% of all operational sites for which a risk assessment concerning business ethics issues has been conducted
Public legal cases regarding corruption brought against the organization or its employees during the reporting period and the outcomes of such cases
Legal actions for anti-competitive behavior, antitrust, monopoly practices
Number of legal actions pending or completed during the reporting period regarding anti-competitive behavior and violations of anti-trust and monopoly legislation in which the
identified as a participant
*Corruption is defined as making a payment, offer or promise (or the authorization of a payment, offer or promise) of anything of value directly or indirectly to a foreign public official for the purpose of obtaining or retaining business for reporting purposes.
Building on the successes in 2022, Ecobat continued our focused efforts to enhance business ethics in 2023. We:
We enhanced global ethics and compliance tool platforms launched in 2022. We strengthened on-demand reporting to Human Resources and Audit with self-service options for employees, promoting engagement, accountability, and access.
• EthicsPoint - EthicsPoint is an internal hotline for all global employees to report alleged incidents of unethical or otherwise illegal activity. It has continued to evolve and grow in our culture. The SpeakUp hotline allows employees to report business ethics concerns via web, email or telephone and anonymously correspond with investigators. To ensure consistency in the investigation process, the SpeakUp hotline has a Whistleblowing Procedure. This was developed alongside an investigation handbook, tool manual development, and global investigations training.
• PolicyTech - This is a centralized hub where all employees can access global company policies and procedures.
• Engage - This compliance training platform provides all employees with vital competition and antitrust training.
We created an internal Data Privacy Committee to ensure data privacy is a business priority. The committee oversees the application of data privacy cross-company in compliance with applicable laws.
We are guided by fiduciary responsibility. The DOA Matrix directs Ecobat’s monetary approval authorities and guides various areas of responsibility for each function. The process starts with our Executive team and extends to the various functions in the submatrices. The Matrix is used company-wide to communicate the clearly defined functional and financial responsibilities of our team members. The Matrix specifies upper limits on approval authority, describes the required action of each team member to organize the business, streamlines the decision-making process, and elaborates upon Ecobat’s corporate matrix structure.
We brought together members from across functions and countries to ensure diverse viewpoints to collaboratively champion compliance throughout our business.
We established a global training calendar for employees via The Terminal, our Intranet site. Managing Directors are provided with a quarterly reporting tool for team training visibility. A biannual compliance newsletter was created to communicate compliance trends that could affect employees. We also published and shared an enterprise-wide compliance program for all employees through the Terminal.
Ecobat’s supplier and customer partnerships are critical to our success. Relationships with organizations who do not share Ecobat’s values and have known ethics violations and governance concerns pose risks to our business. So, in 2023, we invested in a platform that looks to provide end-to-end visibility of the supply chain. From a risk mitigation control perspective, this onboarding and sanctions monitoring tool aims to ensure our partnerships align with our organizational values. During the new onboarding process, each third party must be reviewed prior to conducting business with Ecobat. We share our Third-Party Supplier Code of Conduct requirements and suppliers are required to note acknowledgment.
We use this supply chain platform to:
• Assess all suppliers, customers, and employees through a standardized watchlist
• Send external questionnaires for additional clarification
• Demonstrate a level of due diligence for the company
• Evaluate affiliated persons
• Evaluate parent or subsidiary companies
• Indicate past standard sanctions applied to the specific entry
• Conduct a questionnaire on Health, Safety, and Environmental program
• Analyze Environmental, Social and Governance Program
• Communicate and confirm conformance to Code of Conduct expectations
Ecobat recognizes that digitization and sustainability are intrinsically linked, and that successfully managing its impacts requires credible and secure data measurements and inputs. Therefore, Ecobat has developed a digital strategy that is pivotal to attaining its sustainability goals.
One area of Ecobat’s digital strategy that presents an opportunity for sustainability is Artificial Intelligence (AI). AI provides a measure by which Ecobat can leverage state-of-the-art technology to achieve its environmental and social goals. Ecobat actively invests in AI across a number of initiatives to ingest data, train models, analyze forecasts, and ultimately predict, respond, and mitigate future trends across its operations. Some examples of how Ecobat aims to use AI for sustainability are:
• AI-powered energy management systems that aim to optimize energy consumption and reduce greenhouse gas emissions.
• AI-enabled predictive maintenance that reduce downtime, improves efficiency, and should extend the lifespan of equipment.
• AI-facilitated health and safety monitoring that is designed to detect hazards, alerts workers, and prevent accidents and injuries.
Another aspect of Ecobat’s digital strategy that supports its sustainability goals is the transformational implementation of S4 HANA Cloud ERP across its operations. This strategic initiative gives Ecobat more visibility into its supply chain and recurring operating costs, making it easier through analytics to identify opportunities for improvement. Ecobat’s single, global cloud-based ERP (SAP) enables it to combine, connect, and link financial and non-financial metric views into one holistic reporting. A single source of truth for data contributes to giving Ecobat clear visibility for performance management and internal and external disclosure requirements. Some benefits of Ecobat’s cloud ERP for sustainability are:
• Cloud ERP reduces the need for physical infrastructure, hardware, and maintenance, which lowers Ecobat’s environmental footprint and operational costs.
• Cloud ERP enables real-time data collection, integration, and analysis, which should improve Ecobat’s decision-making and transparency.
• Cloud ERP facilitates the tracking and reporting of Ecobat’s sustainability performance, which helps Ecobat communicate its progress and achievements to its stakeholders.
Cloud ERP supports the alignment of Ecobat’s sustainability goals with its business strategy, which aims to ensure Ecobat’s long-term viability and competitiveness. Ecobat’s digital strategy is a key enabler for its sustainability goals, as it provides the tools and capabilities to measure, manage, and improve its environmental and social impacts. By investing in AI and cloud ERP, Ecobat demonstrates its leadership and innovation in the battery recycling and metal production industry, and its commitment to creating a circular economy for battery materials. Ecobat’s digital strategy aims to promote sustainability by improving waste reduction emissions source tracking and reporting, and transparency.
We recognize that digital transformations present security and privacy concerns. We are committed to upholding the privacy of employee, client, and customer data through an Information Security Policy, put in place to effectively communicate to stakeholders how their data is processed and stored.
Controls include:
• Data Privacy Committee
• Engaging a third party as the single, global data privacy officer (DPO)
• Security reviews on new vendors
• Contractual clauses encompassing data privacy elements
• Whistleblower procedure in place to allow employees to report any information security concerns
• Additional precautionary password protection steps to protect data privacy, including multi-factor authentication
• Employee education through Fair Business Practices Awareness Training about the risks related to data breaches and the importance of preventing information security breaches
Security control monitoring and testing includes:
• Deploying real-time monitoring of Ecobat networks
• Deploying a Managed Security Services Provider and primary cyber security platform
• Performing email phishing testing and awareness training for employees
In addition, we monitor critical KPIs through dashboards that display specific cybersecurity effectiveness and awareness. These measures help our team members quickly address outstanding issues that impact information security operations and business continuity concerns.
Ecobat Information Security program aligns with:
Cybersecurity Framework
ID.AM-6, ID.GV-2, DE.DP-2, SP 800-37 3.3, SP 800-53 AT-3.2, CA-3.4, PS-3.16
APO01.02, APO01.11, APO07.03, APO07.05, APO10.01, APO13.02, DSS04.05
alignment with 108 Subcategories
(0) Open Critical & High Severity Vulnerabilities exposed to the internet
0 of 32
• Completed 3rd Party Penetration Test
• Completed BYOD (Bring Your Own Device) in U.S.
1. Integrate Ecobat Battery (Emrol acquisition) networks into Corporate Footprint
2. Simulated Phishing
3. Password Phrases
Ecobat depends on our talented, diverse workforce to succeed in a competitive market. To ensure we attract the right talent, we rely on recruiters, recruitment tools, and search engines that promote our employment opportunities. We also remain focused on a diverse pipeline of applicants. Additionally, our employment practices and training programs support work and social protections, helping to improve our employees’ experiences at their jobs and in their personal lives. Our commitment to our values drives us to ensure our employees receive fair pay and treatment for their contributions to our global success.
In 2023, Ecobat was awarded the National Business Research Institute (NBRI) Circle of Excellence Award for the significant improvements made over our 2022 Employee Engagement Survey results. This prestigious award demonstrates our dedication to the highest levels of employee experience.
Ecobat’s Relevant Documents Supporting This Section:
• Global Code of Conduct
• Working Conditions Policy
• Pension and Post-Retirement Benefits Policy
• Leave Policy (USA Only)
• Anti-Bribery and Corruption Guide for Third-Parties
• Parental Leave - Minimum Global Standards
• New Employee Referral Program
• US Employee Handbook
• Marketing: Brand Standards Communication Toolkit
• Ethics & Confidential Helpline Guidelines
• Ecobat Conflict Minerals Policy Statement
• Ecobat Modern Slavery & Human Rights Statement
• Prohibited Parties Compliance Guidelines
• Sustainable Procurement Policy
Ecobat Resources UK achieved the prestigious Investors in People Gold status, a testament to our commitment to employee development and organizational excellence. Notably, the Investors in People program recognizes only one award higher than Gold: Platinum.
Ecobat’s UK operations emphasize the significance of investing in the success of all employees, recognizing it as the cornerstone of organizational success. As a program, it provides a comprehensive framework for organizations to evaluate and enhance their people management practices. A three-year accreditation cycle lets us strategize and implement initiatives aimed at continuous improvement and addressing identified opportunities for growth.
In 2023, we focused on enhancing employee experience, development and enrichment in the following ways:
• Introduction and implementation of Ecobat company values
• Successful union contract negotiations in California, United States operations
• Conducted Employee Engagement focus groups across North American plants and Battery Division to drive action and engagement
• Developed a job mapping and alignment tool to drive salary standardization and align employment terms across the organization
• Execution of Accelerate My Potential Leadership (AMP) course with approximately 180 participants with a survey rating of 4.7 out of 5.0 across the program
• Developed and piloted the Emerging Supervisor Program for 2023 engagement
• Implementation of the Ecobat 360 Coaching Program
• Deployed the TalentGuard program for enterprise performance management and individual development planning
• Created a Refinery Training Program for competency assurance
• Deployed LMS365, a tool to manage training curriculum and tracking to streamline and integrate training platforms and offerings
• Conducted the first Functional/Talent Assessment Reviews
• Supported the Leading the Charge initiative with quarterly development webinars and led the 2023 Women’s Virtual Conference
• Updated the Retirement Plan Committee charters for 401(k) and pension plan for improved governance and to ensure compliance
• Launched financial planning and well-being workshop and seminar series
The health and safety of our workforce is integral in achieving our mission “To lead in the responsible collection, recycling, production, and distribution of resources essential to modern life.” We recognize that we can’t meet the needs of our customers and partners without a safe and healthy workforce. The success and sustainability of our organization depends on it. With that in mind, Ecobat has the following Health and Safety program and process controls:
Health and Safety Emergency Action Plan
• Emergency Response, Crisis Communication, and Business Continuity have been identified in our Enterprise Risk Management (ERM) corporate focus areas. We also implement an internal auditing schedule for emergency action plan reviews.
• Written, site-specific Emergency Action Plans are in place and reviewed annually. We typically hold annual drills to test these procedures.
• Engineering controls include ventilation, compatible material design, tank spill control, and similar procedures
• Training, Standard Work Instructions, internal and third-party audits, emergency response drills, and air quality monitoring
• Administrative Controls, Safety Data Sheets, Hazard Communication Program
• Personal Protective Equipment appropriate for job task, including a written compliance plan
Employee Health and Safety Risk Assessment
• Routine Job Risk Assessment (JRA’s)
• Non-Routine JRA’s
• Behavioral Based Safety (BBS) Observations
• TRACE and “Stop and Think” program
• Annual PPE risk assessment review and signoff by managers and employees
• Annual hazardous assessment program review and signoff by employees
• Stop Work Authority Program
• Annual LOTO procedure reviews
Repetitive Strain Injury Prevention
• Training
• Proper tool selection and equipment design
• Job rotation where required
Equipment Safety Inspections or Audits
• Pre-use, weekly, monthly, quarterly and annual equipment safety inspection
• Weekly, monthly, and quarterly inspections of emergency response and other safety equipment
• Critical Control Behavior Safety Observations by Supervisors/Managers and HSE
• Monthly supervisors’ safety reports and inspections
• Third-party audits annually
Employee Complaint Procedure for Reporting Occupational Incidents, Risks and Concerns
• SpeakUp hotline and Safety Committees
• Near Miss reporting, tracking and corrective actions
• Job Risk Assessment
Health and Safety Training for Subcontractors Working On Premises
• Contractor Visitor Safety Program
Respiratory Protection Program
• Training
• Behavior-based observations
• Management of Change Review Process
• Chemical Hazard Assessment Reviews
Noise Exposure Prevention
• Documented Hearing Conservation Program for all employees
• Annual employee audiogram
• Annual review of our ‘Noise Reduction Efforts’ (part of Engineering and Administrative Controls)
Health and Safety Risk Training For All Employees
• Annual employee and refresher safety training
• Daily Crew Briefs
Actions to Address Stress and Promote
Psychological Well-Being
• Ecobat provides resources and training
• Ecobat Employee Assistance Program (EAP) counseling and services
The health and safety of our employees is a measure of our success. We aim to use our established programs and controls to continuously evaluate and improve the health and safety of our workforce.
Our success also depends on protecting our workforce from the impact of lead exposure. Ecobat is proud of our industry-leading blood lead level (BLL) performance, which we achieve through effective engineering controls, personal hygiene protocols, and personal protective protocols. These measures are critical to the safety of our employees and our ongoing success.
We developed a Global Blood Lead Standard to set standards and ensure a consistent approach across all our operations. Our program addressed blood lead sampling requirements, sampling populations, minimum Blood Lead Reduction program elements, and mentorship expectations.
In 2023, we implemented consistent practices to ensure that employee BLL stay within acceptable ranges, including:
• Mandatory training and mentoring programs to educate and monitor employees’ actions, ensure compliance with best practices, and answer questions.
• Bi-weekly, monthly, and quarterly employee-driven BLL improvement teams ensure improvement of existing protocols.
• Quarterly testing of blood levels for identified employees. If levels exceed established thresholds, additional testing is required. The employee may be reassigned to work in a nonexposure area.
• Mandatory monthly testing for new employees to monitor transitioning into a work environment exposed to lead.
BLL performance is shared across all levels of the organization, including the Board of Directors, to ensure appropriate risk management.
Our commitment to protecting employees requires us to stay up to date on new and changing Occupational Exposure Limits (OEL) regulatory requirements. Globally, Ecobat Resources achieved a 12-month rolling average of 6.72 μg/dl for its lead-exposed populations. This metric represents our best performance to date as an organization. We continue to look for opportunities to advance the protection of our exposed populations and protect the health and safety of our workforce.
Ecobat offers a comprehensive portfolio of programs intended to create a good working environment for our employees. They include:
Employee Benefit Programs
U.S. employees who work either full or part time and work more than 30 hours per week are eligible for Ecobat’s comprehensive benefit programs under a costsharing program. Benefits include:
• Medical and prescription drug plans
• Health Savings Account (HSA)
• Flexible Spending Account (FSA)
• Tele-health
• Dental and vision coverage
• Basic and voluntary AD&D
• Short and long-term disability programs
• Supplemental benefit programs
• Parental leave
• 401(k) retirement savings accounts, including company-matching funds
• Employee Assistance Program (EAP)
• Identity theft protection
• Financial wellness program
• Consumer insurance programs via Gallagher Marketplace
Family-Friendly Programs
Starting in 2023, U.S. non-union employees were given enhanced vacation and maternity leave, and we introduced paternity leave. Programs were democratized for salaried positions.
Additionally, family protection programs were offered at no cost to employees. Programs included home and renters insurance and extended vehicle warranties.
In March 2023, we implemented a Pay Grade Framework to define pay levels for employees. Through the Pay Grade Framework’s leveling criteria, jobs were assigned to grade levels within broad work categories (e.g., Executive Management, Middle Management, Professional & Sales, and Business and Technical Support). Each grade level was aligned to a pay range. The guide is also to establish benchmarking across similar positions at companies we compete with to attract talent.
We ensured transparent communication by sharing a guide with employees detailing the new program and how they would be impacted, including contact information for the Compensation Team if they had any questions.
Ecobat grants family and medical leave in accordance with the requirements of applicable federal and state law in effect at the time the leave is granted. Employees will be eligible for the most generous benefits available under applicable law.
We believe in every employee’s right to paid time off away from work, individual and family-related illness and other types of leave. Eligible U.S. non-union employees have access to vacation, sick leave, and paid parental leave (including primary and secondary caregiver leave where appropriate).
Ecobat has specific policies that describe employee union / non-union and exempt / non-exempt employment status. Policies for each Ecobat location outline specific guidelines for pay periods, regular and shift premium pay, holiday and vacation pay, overtime pay, personal days pay, jury duty pay, as well as pay policies for bereavement, safety related, Leadman, stipend, and mentors.
If there are discrepancies between our policies and/or documents and applicable law, the law applies.
Every fall, we conduct the annual employee engagement survey to encourage employees to provide anonymous feedback about their experience at Ecobat. Additionally, exiting employees are invited to share employment feedback during their exit interview with an onsite local HR representative.
Ecobat is continuously focused on building a more diverse, equitable, and inclusive environment for our employees. Here, we’ve outlined our efforts to ensure we create a space where all employees feel supported.
Our SpeakUp hotline allows employees to anonymously report workplace concerns, including allegations of discrimination and workplace harassment. Additionally, all employees are required to participate in Code of Conduct training, which outlines our anti-harassment and anti-discrimination workplace environment.
Ecobat’s women’s initiative, Leading the Charge, launched in 2022. It was created to build awareness and development opportunities for women. DEI indicators on the annual engagement survey are one of the top three rated areas across the organization.
We adopted fair wage practices by appropriately and effectively benchmarking pay scales from industry-leading compensation survey organizations.
Managers and supervisors are required to complete mandatory e-learning for DEI via the PowerUp tool.
Employees who believe they have been victims of discrimination or harassment can report substantiated concerns via the SpeakUp hotline, either by phone or email. HR has processes in place to begin investigating the claim and address any substantiated concerns of discrimination or harassment.
Ecobat has appropriate agreements in place in the U.S. and European locations to ensure a positive social dialogue.
Ecobat has labor union contracts in the U.S. (California, New York, Indiana) and European Work Councils contracts (Austria, France, Germany, Italy, United Kingdom). Agreements cover various time periods and employee groups as appropriate.
All locations have employee representatives. In the U.S., they are called Union Stewards, and they have special rights and protections. In Europe, Ecobat employees sit on the Works Councils and have special rights and privileges. The number of Union Stewards and Works Councils members varies by the facility’s location and size.
We strive to ensure our employees are positioned well for future career opportunities while being properly trained for their current position. Our efforts include:
• Promoting career mobility. This includes identifying high potential talent and necessary skill development, along with socializing succession planning with leadership.
• Individual performance assessments. Performance check-ins are a progressive, dynamic way to provide employees with performance feedback and help them progress toward goals.
• Individual career plans and development. Ecobat’s Talent Management HR function allows employees to create and discuss comprehensive career plan development.
• Resource planning. Leadership must approve all additions to headcount, frequently requiring resource planning to ensure functions are not over-sourced.
• Transparent recruitment process. Ecobat aims to provide all local recruiters with tools and resources (i.e. LinkedIn, Career Site, Indeed) to consistently attract talent.
• Skills development training. Ecobat’s Emerging Supervisor (ESP) and Accelerating My Potential (AMP) Programs provide new and current leaders with comprehensive management and leadership development. Additionally, we adopted a training methodology for frontline roles (Tell, Show, Do, Review) with the launch of the Refinery Training Program.
% of the total workforce across all locations who are covered by formal collective agreements concerning working conditions
Minimum number of weeks notice typically provided to employees and their representatives prior to the implementation of significant operational changes that could substantially affect them
For organizations with collective bargaining agreements, report whether the notice period and provisions for consultation and negotiation are specified in collective agreements
across all
elected employee representatives
Hours of
*Investments in a learning management system provided better visibility and reporting on completed training for the organization in 2023.
We take seriously our commitment to ensuring that our operations and our business partners refrain from using child labor, forced labor, or human trafficking. We’ve put the following policies in place to support our efforts:
Grievance Mechanism on Child Labor, Forced Labor and Human Trafficking
Employees can air grievances and concerns via the anonymous SpeakUp hotline. This mechanism provides action to protect young workers. HR representatives work directly with employees to listen and act on any concerns. The SpeakUp investigatory process addresses the following areas:
• Remediation procedure in place for identified victims
• Stakeholders consultation
• Monitoring of internal controls to ensure no child labor
• Impact assessment
Awareness Training
Training is provided to identified populations of corporate, office, management, and supervisory roles to identify human trafficking and modern slavery concerns.
While job candidates do not have to provide proof of age, all employees must provide ID documents and proof of residency, which includes their birth date, to prove they can work legally in each country.
Ecobat has a robust screening tool to promote sustainable procurement. Responsible Materiality sourcing involves integrating social, ethical and environmental performance factors into the process of selecting suppliers. From a Risk Mitigation control perspective, we use a supply chain monitoring tool to promote responsible material sourcing for our operations. During the new onboarding process, the aim is for all third party partners providing materials and services be reviewed before they can do business with us. Suppliers are required to acknowledge Ecobat’s Third-Party Supplier Code of Conduct, provide annual attestations, and are subject to regular monitoring and periodic auditing based on their risk profile. We address responsible material sourcing in the following ways:
• Supplier CSR Code of Conduct
• Supplier assessment on environmental and social practices
• Integration of social and environmental clauses within contracts
• Worker voice surveys or other supplier monitoring practices
% of all operational sites that
While Ecobat operates globally, we also act locally by building relationships and investing in our communities. We focus on employee engagement, job creation, economic growth, and outreach to ensure we positively impact the communities we operate in.
Our external stakeholder engagement principles guide our interactions with local communities. We commit to using Community Relations resources to monitor and respond to stakeholder requests to ensure we capture valuable feedback. In addition, we have facility-specific, region-specific, and scope-specific engagement strategies based on the five qualitative pillars of stakeholder analysis:
Positive community relationships are a result of our actions, including our charitable contributions. Locally, we contribute to Boys and Girls Clubs, sports, academics, Science, Technology, Engineering, Arts, and Mathematics (STEAM) sponsorships, community health fairs, blood drives, toy and food drives, and other local events. Our community involvement, with help from the employees who participate in them, ensures that these organizations have a positive local impact.
Finally, we recognize that our operations affect our communities. It’s essential to remain committed to our sustainability principles with this in mind. We actively evaluate, measure, and manage our community impact to ensure the safety of the people and environment.
We strive to prioritize our ongoing efforts to ensure the health and safety of the environment and our neighbors, in addition to providing charitable contributions. We aim to engage with our local communities in these areas:
• Safety procedure engagement
• Community health initiatives
• Educational programs about Ecobat’s role in the industry
• Neighborhood improvement projects, including partnering with local organizations
This approach keeps Ecobat accountable to our external stakeholders and communities.
Environmental stewardship aligns with our core value of prioritizing the well-being of our people and planet. To stay true to our values, we use best practices and internationally recognized industry standards to protect the environment, improve our operational efficiency and resource management to sustain economic growth, and reduce negative environmental impact. We continue to work towards preserving our natural resources through recycling, not mining, with the goal of capturing 99% of the inherent properties of lead-acid batteries through our operations.
We set our standards appropriately high, focusing on increasing our energy efficiency, in turn reducing air emissions, energy consumption and carbon dioxide generation, lowering water consumption, and reducing waste generation per ton produced. Eighty four percent (84%) of our facilities are certified under ISO 14001. Thirty five percent (35%) are certified for energy management under ISO 50001. Aspiring for operational efficiency, employing best practices, and monitoring our progress make up the foundation of our environmental stewardship.
We strive to diligently manage our energy consumption and greenhouse gas emissions in the following ways:
• Improvement of energy efficiency through technology or equipment upgrades
• Use of waste heat recovery system or combined heat and power units
• Purchase or generation of renewable energy
• Training of employees on energy conservation/climate
• Fuel switch to achieve higher energy efficiency and lower carbon emission intensity
• Energy or carbon audit
• Managing the lifecycle of our GHG performance, includes understanding our Scope 3 emissions. In 2024, we look to validate our Scope 3 methodology approach for future reporting.
^This metric was assured by ERM CVS in 2024. Reference Independent Limited Assurance Statement to Ecobat, LLC for details.
*South Africa, Stolberg, and Peru entities not including in reporting. Stolberg asset divestiture in 2022 with South Africa asset divestiture finalized in 2023.
**Updates in methodology have improved accuracy and is reflected to align figures for consistency across reporting years.
***Total Energy Consumption figures have been updated from 2021 reporting and now include all stationary combustion, mobile combustion, and purchased energy.
Decreasing energy consumption supports the environment and the communities where we operate, contributing to Ecobat’s operational efficiency. Our Indianapolis, Indiana, facility set out to reduce energy consumption, leveraging engineering consulting expertise to review primary sources of electrical demand within the plant. By analyzing use cases and power bills and modeling energy savings scenarios, the plant discovered they could modify their equipment start-up procedures and install variable speed drives. The Indianapolis plant now expects to reduce its energy consumption between 5-7% by modifying procedures and equipment.
We look to mitigate air and noise pollution through strategic measures and proactive initiatives to safeguard public health. This includes:
• Work processes and technology implemented to mitigate emissions of VOC, SO 2, NOx or heavy metals
• Work processes and technology implemented to mitigate emissions of dust and particular matter
• Actions to prevent emission of atmospheric pollutants and other environmental nuisances (noise, odor, vibration, road, light)
• Work processes implemented to mitigate odor
• Work processes implemented to mitigate noise
• Periodical analysis on the volumes of major air pollutants or ambient air quality monitoring
We remain committed to protecting our employees and the environment from the impact of hazardous materials. Steps we take to work toward reducing this impact include:
• Specialized treatment and safe disposal of hazardous substances
• Training employees to safely handle and manage hazardous substances
• Prescribed actions for labeling, storing, handling and transporting hazardous substances
• Process optimizations that reduce material consumption
• Use of recovered input materials
• Environmental emergency measures in place
Although lead remains integral to our future, we have the opportunity to use our vast recycling expertise and deep experience handling lead batteries to provide solutions for emerging advanced battery chemistry recycling.
Our operational expertise is a key differentiator. Capabilities include sorting, shredding, and separating battery materials to produce black mass. Our lithium recycling footprint includes: Hettstedt, Germany, Casa Grande, AZ, United States, and a third in Darlaston, United Kingdom with commissioning in 2024.
We’re confident of our expansion into the lithium battery recycling market and of our ability to leverage our proven expertise in this marketplace in the management of hazardous materials.
We strive to conserve and protect our water resources using these protocols:
• Technologies to recycle or reuse water
• Wastewater quality assessment
• Water accounting or audit
• Adoption of a cooling system with reduced or recycled water consumption
• Control of wastewater generated in finishing operations such as quenching or demurring
We have procedures in place to reduce and limit where possible the waste we produce, including:
• Internally sorting and disposing of waste according to waste streams
• Training to raise employee awareness of waste reduction and sorting
• Reducing internal waste through material reuse, recovery or repurposing
• Mapping of waste streams
Ecobat’s Bazoches-les-Gallerandes, France plant recently achieved remarkable improvements by focusing on removing the waste, gypsum, from their smelter feed. Gypsum is a byproduct of electrolyte neutralization with lime, but by isolating the gypsum from the lead paste, the plant can increase the capacity of the smelters by 5%. This results in an additional 3,000 tons of lead production and an approximate 25% reduction in energy consumption and CO2 hazardous materials at this site.
We continue to review the following KPIs with the aim of tracking performance year-on-year. For some of the following metrics, we are in the process of establishing targets which the business should strive to meet. Such targets are subject to change, and no assurance can be given that such targets will be met.
% of the total workforce across all locations who received training (e.g. e-learning) on business ethics issues
% of all operational sites for which an internal audit & control concerning business ethics issues has been conducted
% of all operational sites for which a risk assessment concerning business ethics issues has been conducted
# confirmed incidents of corruption and actions taken
number and nature of confirmed incidents of corruption
number of confirmed incidents in which employees were dismissed or disciplined for corruption
Total number of confirmed incidents when contracts with business partners were terminated or not renewed due to violations related to corruption
Public legal cases regarding corruption brought against the organization or its employees during the reporting period and the outcomes of such cases
Legal actions for anti-competitive behavior, antitrust, monopoly practices
Number of legal actions pending or completed during the reporting period regarding anti-competitive behavior and violations of anti-trust and monopoly legislation in which the organization has been identified as a participant
% of all operational sites with an information security management certification (ISO 27001)
Minimum number of weeks notice typically provided to employees and their representatives prior to the implementation of significant operational changes that could substantially affect them
For organizations with collective bargaining agreements, report whether the notice period and provisions for consultation and negotiation are specified in collective agreements
% of all operational sites that have been subject to human rights reviews or human rights impact assessments*
*Identified populations providing operational site oversight; including, corporate, office, management, and supervisory roles.
has gone through a CSR
% of suppliers in line with our Code of Conduct & Supplier Code of Conduct
% of suppliers with recognized High-quality products/services
*Investments in a learning management system provided better visibility and reporting on completed training for the organization in 2023.
% of suppliers with an Environmentally efficient policy and plan
% Locally based
% of suppliers in Compliance with Health and Safety measures
% of suppliers which present high level of Reliability
not currently tracked
not currently tracked not currently tracked
RR-FC-130a.1 (1) Total Energy Consumed, (2) Percentage grid electricity, (3) Percentage renewable
RR-FC-320a.1 (1) Total recordable incident rate (TRIR) and (2) fatality rate
RR-FC-320a.2 Description of efforts to assess, monitor, and reduce exposure of workforce to human health hazards
RR-FC-410a.1 Average storage capacity of batteries, by product application and technology type Contact info@ecobat.com
RR-FC-410a.3 Average battery efficiency as coulombic efficiency, by product application and technology type
RR-FC-410a.5 Average operating lifetime of batteries, by product application and technology type
Contact info@ecobat.com
Contact info@ecobat.com
RR-FC-410b.1 Percentage of products sold that are recyclable or reusable Contact info@ecobat.com
RR-FC-410b.2 Weight of end-of-life material recovered, percentage recycled Contact info@ecobat.com
RR-FC-410b.3 Description of approach to manage use, reclamation, and disposal of hazardous materials 36-37
RR-FC-440a.1 Description of the management of risks associated with the use of critical materials 36-37
1 We support and respect the
Our commitment to the well-being of our team members, partners, communities, and the planet guides us in our business practices, and we strive to look for new ways to enhance our efforts by embracing quality education, gender equality, decent working conditions and good health and wellbeing.
We are proud to say that we supply key resources necessary to our global energy supply, and that we help develop and produce the next generation of low-emission technologies. Managing the production and recycling of lead responsibly is essential to making this possible. At Ecobat, our operations are centered around sustainable processes and practices for the safe, effective handling of lead in accordance with industry standards. Recycling and resource recovery comprise more than 80% of our business.
Our closed-loop recycling approach helps us maintain the supply of lead while reducing the overall environmental footprint of lead.
Principle 2 We make sure that we are not complicit in human rights abuses by applying our policies and procedures.
Principle 3 We uphold the freedom of association and the effective recognition of the right to collective bargaining. Principle 4 We are committed to the elimination of all forms of forced and compulsory labor and apply legislation where we operate.
Principle 5 We are committed to the effective abolition of child labor; and
Principle 6 the elimination of discrimination in respect of employment and occupation.
Principle 7 We support a precautionary approach to environmental challenges.
Principle 8 We undertake initiatives to promote greater environmental responsibility; and
Principle 9 encourage the development and diffusion of environmentally friendly technologies.
Principle 10 We work against corruption in all its forms, including extortion and bribery.
ERM Certification & Verification Services Incorporated (“ERM CVS”) was engaged by Ecobat, LLC (“Ecobat”) to provide limited assurance in relation to the selected information set out below and presented in Ecobat 2023 Sustainability Report (the “Report”).
Engagement summary
Whether the 2022 and 2023 selected KPIs are fairly presented in the Report, in all material respects, in accordance with the reporting criteria.
GHG Emissions:
Scope of our assurance engagement
Total Scope 1 GHG emissions [metric tonnes CO2e]
Total Scope 2 GHG emissions (location-based) [metric tonnes CO2e]
Total Scope 2 GHG emissions (market-based) [metric tonnes CO2e]
Our assurance engagement does not extend to information in respect of earlier periods or to any other information included in the Report.
Reporting period
1st January 2022 to 31st December 2022 1st January 2023 to 31st December 2023
Reporting criteria
Ecobat’s reporting criteria as explained in footnotes in the Report
WMSCD/WRI GHG Protocol (2004, as updated January 2015) as relevant for the Scope 1 and 2
Assurance standard and level of assurance
We performed a limited assurance engagement, in accordance with the International Standard on Assurance Engagements ISAE 3000 (Revised) ‘Assurance Engagements other than Audits or Reviews of Historical Financial Information’ issued by the International Auditing and Assurance Standards Board.
The procedures performed in a limited assurance engagement vary in nature and timing from and are less in extent than for a reasonable assurance engagement and consequently, the level of assurance obtained in a limited assurance engagement is substantially lower than the assurance that would have been obtained had a reasonable assurance engagement been performed.
Our conclusion
Ecobat is responsible for preparing the Report and for the collection and presentation of the information within it, and for the designing, implementing and maintaining of internal controls relevant to the preparation and presentation of the Report
ERM CVS’ responsibility is to provide a conclusion to Ecobat on the agreed scope based on our engagement terms with Ecobat, the assurance activities performed and exercising our professional judgement.
Based on our activities, as described below, nothing has come to our attention to indicate that the 2022 and 2023 data and information for the disclosures listed under ‘Scope’ above are not fairly presented in the Report, in all material respects, in accordance with the reporting criteria.
Our assurance activities
Considering the level of assurance and our assessment of the risk of material misstatement of the Report a multi-disciplinary team of sustainability and assurance specialists performed a range of procedures that included, but was not restricted to, the following:
Evaluating the appropriateness of the reporting criteria for the selected disclosures
Interviewing relevant staff to understand and evaluate the management systems and processes (including internal review and control processes) used for collecting and reporting the selected disclosures;
Reviewing of a sample of qualitative and quantitative evidence supporting the reported information at a corporate level;
Performing an analytical review of the year-end data submitted by all locations included in the consolidated 2022 and 2023 group data for the selected disclosures which included testing the completeness and mathematical accuracy of conversions and calculations, and consolidation in line with the stated reporting boundary;
Conducting one in-person and one virtual site visit to the Ecobat facilities in Middletown, New York, USA and Arnoldstein, Austria to review source data for 2022 and local reporting systems and controls;
Conducting two desk-based reviews for the Ecobat facilities in Middletown, New York and Arnoldstein, Austria to review source data for 2023 and local reporting systems and controls ,
Evaluating the conversion and emission factors and assumptions used;
Reviewing the presentation of information relevant to the scope of our work in the Report to ensure consistency with our findings.
The reliability of the assured information is subject to inherent uncertainties, given the available methods for determining, calculating or estimating the underlying information. It is important to understand our assurance conclusions in this context.
ERM CVS is an independent certification and verification body accredited by UKAS to ISO 17021:2015. Accordingly we maintain a comprehensive system of quality control, including documented policies and procedures regarding compliance with ethical requirements, professional standards, and applicable legal and regulatory requirements. Our quality management system is at least as demanding as the relevant sections of ISQM-1 and ISQM-2 (2022).
ERM CVS applies a Code of Conduct and related policies to ensure that its employees maintain integrity, objectivity, professional competence and high ethical standards in their work. Our processes are designed and implemented to ensure that the work we undertake is objective, impartial and free from bias and conflict of interest. Our certified management system covers independence and ethical requirements that are at least as demanding as the relevant sections of the IESBA Code relating to assurance engagements.
ERM CVS has extensive experience in conducting assurance on environmental, social, ethical and health and safety information, systems and processes, and provides no consultancy related services to Ecobat in any respect.
Heather I. Moore Partner, Corporate Assurance
Manhattan, New York
June, 7 2024
On behalf of:
ERM Certification & Verification Services Incorporated www.ermcvs.com | post@ermcvs.com
References to environmental, social and governance (ESG) matters, including with respect to sustainability, refer to the current initiatives and commitments of Ecobat. Discussion of such factors have been included for purposes of illustrating that Ecobat also expects to take into account certain ESG factors when making business decisions. While Ecobat expects that in many cases the ESG strategy may align with the business and financial objectives of the company, Ecobat generally does not intend for ESG considerations to be determinative when making business decisions. There can be no guarantee that we will be able to successfully consider ESG factors while achieving our business strategy. The information provided herein is intended solely to provide an indication of the ESG or impact-related initiatives and standards that Ecobat strives to apply when seeking to evaluate and/ or improve the characteristics of its business as part of a larger goal of maximizing financial objectives (howsoever they may be measured). There are also significant differences in interpretation of what positive ESG outcomes mean by region, industry and topic, as well as the interpretation of their scope, severity, remediability and materiality. Interpretations and decisions made by Ecobat are expected to differ from others’ views and could evolve over time. ESG practices are evolving rapidly and market pressures, including the potential adverse reactions by investors and other participants to the application of ESG factors to investment processes, could result in tensions, conflicts of interest or other potential issues as companies navigate how to balance competing interests with respect to ESG considerations. There is also a growing regulatory interest across jurisdictions in improving transparency regarding the definition, measurement, management and disclosure of ESG factors. The ESG practices maintained by Ecobat could become subject to additional regulation in the future, and we cannot guarantee that our current approaches will meet future regulatory requirements or predict the manner in which any such future requirements (including any enforcement with respect thereto) could affect our business, including with respect to future administrative burdens and costs.
It should not be assumed that any ESG or impactrelated initiatives, standards or metrics are applicable to us. Methodologies for measuring ESG metrics may also differ across industries and asset classes. While we seek to integrate certain ESG factors into our business and operational processes in accordance with our ESG strategy and subject to our fiduciary duty and any applicable legal, regulatory or contractual requirements, there is no guarantee that our ESG strategy will be successful or that it will create a positive ESG impact. ESG risk factors are only some of the many considerations that we take into account when making business decisions, and other considerations can be expected in certain circumstances to outweigh those considerations. In addition, applying ESG factors to business decisions is qualitative and subjective by nature, and there is no guarantee that the criteria utilized by Ecobat, or any judgment exercised by Ecobat, will reflect the beliefs or values of any particular person or industry participant. In connection with such determination, we may rely to a large extent on the due diligence, reporting and other materials provided by consultants, accounting firms and other third parties. There can be no assurance that Ecobat or these third parties will accurately evaluate the potential or actual ESG or impact-related outcomes of business decisions. Further, a focus on one or more ESG outcomes may come at the expense of others.
Ecobat is permitted to determine in its discretion that it is not feasible or practical to implement or complete certain of its ESG initiatives, policies, and procedures based on cost, timing, or other considerations. Statements about ESG or impact-related initiatives or practices related to Ecobat’s business do not apply in every instance and depend on factors including, but not limited to, the relevance or implementation status of an ESG or impact-related initiative to or within its business; and other factors as determined by management teams, subsidiaries, and/or businesses on a case-by-case basis.
Certain information contained herein relating to any ESG, impact, or other similar industry frameworks is subject
to change, and no assurance can be given that Ecobat will remain a supporter, or member of such initiatives or other similar industry frameworks. Similarly, information contained herein relating to any goals, targets, intentions, or expectations and related timelines, is subject to Ecobat’s fiduciary duty and subject to change, and no assurance can be given that such goals targets, intentions, or expectations will be met. Descriptions of any ESG or impact-related achievements or improved practices or outcomes are not necessarily intended to indicate that Ecobat has substantially contributed to such achievements, practices, or outcomes.
There is no guarantee that any ESG measures, targets, programs, commitments, incentives, initiatives, or benefits will be implemented or applicable to the investments managed by Ecobat and any implementation of such ESG or impact-related measures, targets, programs, commitments, incentives, initiatives, or benefits may be overridden or ignored at the sole discretion of Ecobat at any time.
In addition, anti-ESG concerns have been raised across the U.S., with several states and Congress having proposed or enacted “anti-ESG” policies, legislation or initiatives or issued related legal opinions. Additionally, companies have been subject to recent scrutiny related to ESG-focused industry working groups, initiatives, and associations, including organizations advancing action to address climate change or climate-related risk. Such anti-ESG policies, legislation, initiatives and scrutiny could expose Ecobat to the risk of litigation, antitrust investigations or challenges and enforcement by state or federal authorities, result in injunctions, penalties and reputational harm and require certain investors to divest or discourage certain investors from investing in Ecobat. Ecobat could become subject to additional regulation, regulatory scrutiny, penalties and enforcement in the future, and Ecobat cannot guarantee that its current approach or its investments will meet future regulatory requirements, reporting frameworks or best practices, increasing the risk of related enforcement.