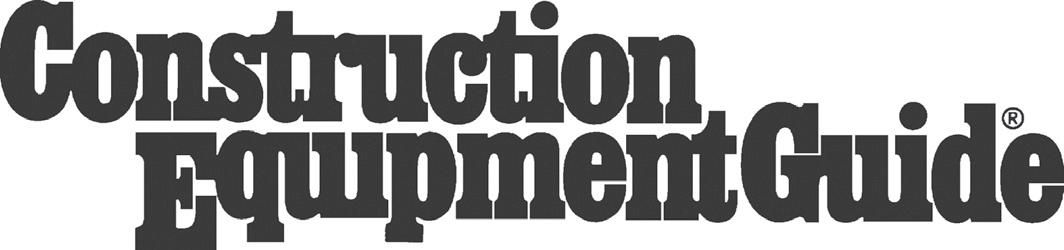
“The Nation’s Best Read Construction Newspaper… Founded in 1957.”
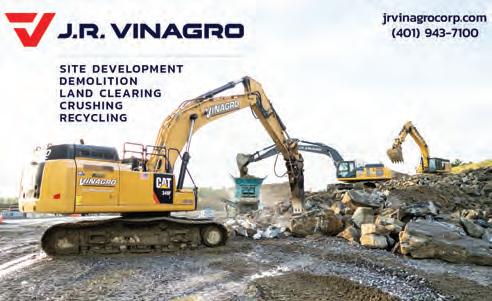
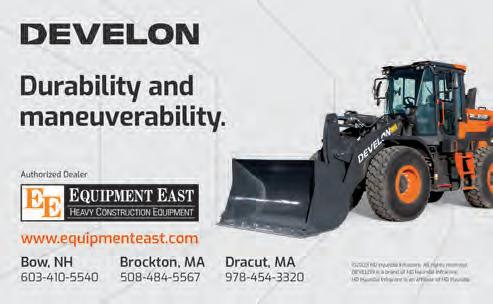
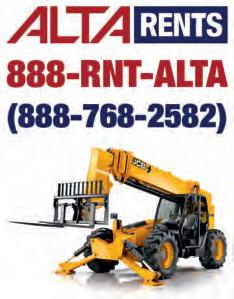
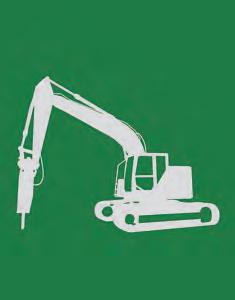
Services, Inc. www.tibbitseq.com 802-479-9696

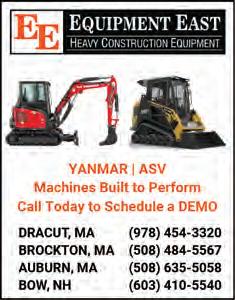
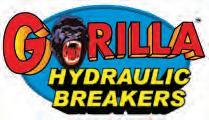

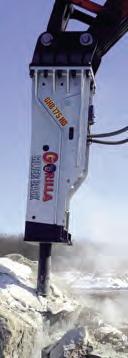
“The Nation’s Best Read Construction Newspaper… Founded in 1957.”
Services, Inc. www.tibbitseq.com 802-479-9696
From lifting timber beams in rural Vermont to raising towers on military bases in New York and dam infrastructure in Georgia, Classen’s Crane Service has spent the past three decades growing into one of the region's most versatile and trusted crane service providers.
With headquarters in St. Johnsbury and operations spanning al of New England and beyond, the family-owned business now boasts the largest taxi crane fleet in Vermont.
Owen Palmer (L), Woods CRW sales representative, and Ben Classen, vice president of Classen’s Crane Service.
“We started with a Stinger 12-ton boom truck back in 1981,” said Ben Classen, vice president and co-owner of the company. “We worked seven days a week, setting trusses, palleting fieldstone, whatever it took.”
Classen’s Crane Service was founded by Ben’s father, Mike Classen, who bought his first crane in 1981. Ben Classen has grown up in the family business. He was known to sneak into the cab of a crane as young as 12 years old. He became one of the principals of the company in 2012.
Today, the company operates a fleet of nine cranes, including the only 175-ton Link-Belt all-terrain crane in New England at the time of purchase. Most of the company’s
see CLASSEN page 4
At the Burlington International Airport project, Classen’s Crane Service is using both its Link-Belt 120ton and 175-ton cranes, depending upon the phase of the construction.
Thompson Equipment recently hosted a two-day demonstration event at Bridgewater Raynham Sand and Stone (BRS), aimed at showcasing the capabilities of RUBBLE MASTER’s mobile impact crushers.
The event drew a steady stream of potential customers and contractors from the southern New England region to see the RUBBLE MASTER RM 120X in action.
“This demo was all about showing people what RUB-
BLE MASTER machines can do,” said Steve Ferris, Vice President of Thompson Equipment. “These crushers are extremely efficient, easy to transport and produce a really clean product — especially important in recycling and reclaimed asphalt applications.”
Thompson Equipment became a RUBBLE MASTER dealer approximately a year ago as part of its expansion see THOMPSON page 6
SENNEBOGEN, in kee philosophy to maxim created UPTIME Kits
eping with their mize uptime, has Whether you are a service technician i road, these kits have need for every service and PM task in one p created to save you t Managing hundreds o parts, from belts and and special tools bec single part number to n-house or on the everything you e, maintenance place. They were ime and money.
They are:
• Easy to order and ea t d t ockst asy to s l dow NO I th Norour intspar om c with omerscust
• Ideal for stocking se and trucks
Choose from the follo
• Central lubrication
• Preventive mainte
• O-Ring kits
• Electrical service k
• Hydraulic service k
Hydraulic service k : kits shops ols ervice owing kits system kits nance service kits its kits
And the best thing is in stock and ready to built to match your m and series. Count on
in-house. For more in UPTIME Kits, scan th
s that these kits, go, are custommachine model SENNEBOGEN nformation on he QR code.
e orf ) OCT(Ownership of
of related service d nuts to O-Rings omes easy with a o order and stock C OND YBE E H HE HIN T MA virtua lI entim lose llyt
xim ma ommitmentc h about e morad ontract Demolition C parepairtsinsthavether andvirtuinanothermachineI onttoback.If very e ctomehavea Theyechnician machine, wntim w American o-shiptady- of oriesinventplete orf uptime izes aftersale achine”M he yond “Beour ow , Bloomfield Hills, MI or theunitbackquickly. kIg losedonoSinctheey ally Ihaveasituation,[they]bringjust ogooverthroncougheamontht wntime… ock.get theSENNEBOGEN y-t t act OGEN f tor ained technicians tr ned tec cians components and too
equipment has been sourced through Woods CRW, with whom it shares a business relationship dating back to 1994.
“We’ve purchased over 20 cranes from Woods since then,” Classen said. “It’s all about service. If something breaks down, they’re there. Day, night, weekends — they’ve always shown up. I have always been impressed that they will answer their phone and respond to our needs. We lost our in-house mechanic, so we have increased our use of Woods’ service department. Just the other day their service rep showed up at our job site at 3 p.m. on a Friday and stayed until 8 p.m. when the crane was up and running.”
Classen’s Crane Service is known for its adaptability. The company has supported ski resorts from Lake Placid to northern Maine, replacing haul ropes and terminals. One job at Whiteface Mountain involved lifting a 120,000-lb. reel of rope.
Another recent standout project took the company to a hydro dam site for Green Mountain Power. Its team used four cranes working in tandem to install a 200-ft. inflatable rubber bladder system. The job required precision, coordination and power.
“That dam job really proved what we could do with the 175,” Clasen said. “It was a six-month project and kept us running over 40 hours a week.”
The company also was involved in the construction of a
In the world of heavy lifting, skill and precision are non-negotiable — and so is proper training.
For Ben Classen, vice president of Classen’s Crane Service in St. Johnsbury, Vt., ensuring that operators are not only qualified but also confident in their craft became more than a business necessity — it became a mission.
That mission now has a name: Green Mountain Crane and Training.
Housed within the Classen Training Service facility, Green Mountain Crane and Training emerged from a practical need Classen encountered firsthand.
“Five years ago, I started doing licensing and training,” he said. “Because of that, I had to go get trained to be a federal examiner, so I can do NCCCO licensing and training right at our facility.”
Today, the school operates as a separate but closely connected arm of the family-run crane business, which maintains a fleet of nine cranes and serves clients across New England and as far as Georgia and Oklahoma.
The training center offers both certification and real-world readiness — backed by Classen’s experience in the field and the resources of Classen’s Crane.
helicopter hanger at Fort Drum in N.Y. And Classen’s also has been extensively involved in cell tower construction all across New England.
At the Burlington International Airport, Classen’s Crane Service is currently placing structural glulam beams and ceiling panels for a terminal expansion. The ceiling panels weigh up to 7,000 lbs. each just to give an idea of the types of picks happening at the airport site. This phase of the project calls for the company’s new 120-ton Link-Belt while earlier phases of the project called for the Link-Belt 175-ton crane.
“We had to bid it hourly — crane time, counterweights, transport. It’s been a hybrid effort between the Link-Belt 120 and the Link-Belt 175. We were uniquely positioned to take it on.”
For Classen, who started running cranes at age 12, the work is second nature. Now a seasoned operator and executive, he attributes the company’s success to its long-standing employees and a commitment to craftsmanship.
That makes Green Mountain Crane and Training a rare public access point for NCCCO crane certification, drawing aspiring operators from far and wide
“I’ve had people from 500 miles apart in each class,” Classen said.
The demand is evident — and growing.
As Classen’s Crane Service continues to expand its reach on job sites, from ski mountains and hydro dams to airports and industrial facilities, Green Mountain Crane and Training is lifting up the next generation of operators to meet the industry’s rising standards. With a strong foundation in hands-on expertise, a deep commitment to safety and the rare distinction of being the only public facility of its kind in the region, this training center is more than a school — it’s a launchpad for careers in crane operation.
Equipment East has = job the compact machine to ell do w one.
ork modes pl and w us one of the highest
THOMPSON from page 1
into Massachusetts, Rhode Island and Connecticut. According to Ferris, this move was driven by growing demand for compact, mobile crushing units that meet strict transportation laws in the region.
“Massachusetts has tough DOT restrictions when it comes to equipment transport,” Ferris said. “We chose to bring in RUBBLE MASTER models like the RM 90, RM 100 and RM 120X because they stay within those limits. You don’t need special permits, and they’re still powerful, productive machines.”
The RM 120X, RUBBLE MASTER’s largest impact crusher, was the centerpiece of the demonstration. Despite its production capacity, the machine remains compact — approximately 9 ft. wide and 60 ft. long when fully folded for transport.
“It’s small but mighty,” Ferris said. “We’ve got a competitor’s unit here on site that the customer owns, and I believe they’ve already seen that the RUBBLE MASTER is outperforming it.”
All RUBBLE MASTER units in the demo lineup are closed-circuit horizontal impactors, equipped with single-deck screens and return conveyors. The RM 120X was processing granite countertop waste during the demonstration, turning it into a clean inch-and-a-half-minus gravel product.
“The machine can comfortably handle up to a 12 to 14-inch input,” Ferris said. “Any larger and you’d want to pre-crush with a jaw, but for most demo debris and C&D materials, this thing just eats it up.”
THOMPSON page 8
All functions of the crusher can be operated via remote control by the excavator operator, making this a oneperson project.
After screen processing, a highly desirable granite product is produced from the granite counter tops.
THOMPSON from page 6
A highlight of the RM 120X is its hybrid power system, which combines a John Deere diesel engine with both hydraulic and electric drive components. While the hydraulics handle the tracks, electric motors power the conveyors.
“The hybrid system is a major advantage,” said Ferris. “Electric motors are incredibly efficient — they provide 100 percent torque at zero RPM, and they eliminate issues like hose leaks or dry rot. Plus, they save a lot on fuel, which is a major concern for anyone running a crusher all day.”
Ferris emphasized that cost per ton is the key metric in crushing, and RUBBLE MASTER delivers.
“These are well-built Austrian machines with smart engineering,” he said. “They’re
Oversized materials are conveyed back to the impact crusher to be reprocessed to meet specific requirements.
Granite countertop scraps are stockpiled and ready to be recycled at the Bridgewater Raynham sand and stone pit.
reliable, fuel-efficient and simple to operate. For a contractor or recycler trying to make product profitably, that makes all the difference.”
The event underscored Thompson Equipment’s commitment to supporting the RUBBLE MASTER line across southern New England. With a product offering that fits the region’s transportation and regulatory environment, and high-performance machines, Thompson sees a bright future with RUBBLE MASTER.
“We’re excited to grow with RUBBLE MASTER, Ferris said. “This event showed the kind of results these machines can produce — and that’s what customers really want to see.” CEG
(All photographs in this article are Copyright 2025 Construction Equipment Guide. All Rights Reserved.)
Concord, NH Berlin, CT
Middleboro, MA
Scarborough, ME
Zero percent financing for 60 months on JCB skid steers including wheeled, tracked, and even the revolutionary Teeleskid!
Zero percent financing for 60 months on JCBcompact excavators including the 19C, 50Z, 55Z, 85Z, and 86C!
Zero percent financing for 72 months on JCB35Z!
Zero percent financing for 60 months on the JCB3CX and 4CX backhoe loaders!
Zero percent financing for 60 months on JCB411, 417, 427, 437, and 457wheel loaders!
Oh... and don’t forget to ask about our 5-year/3,000 hour warranty!
The
“We’ve had guys with us who’ve been here 18 to 22 years,” he said. “Our rigging foreman’s been with us for 14. That kind of loyalty isn’t easy to find.”
Classen’s Crane Service also has built a robust rigging and machinery-moving division with forklifts, trailers and specialized equipment to support manufacturing expansions and relocations.
The Classen fleet includes a variety of machines tailored to the wide range of work the company tackles. Classen’s Cranes can be seen restoring an old barn, setting a modular home, building a cell tower or working at an airport expansion, all on the same day. The company’s crane fleet consists of:
• National 16-ton knuckle boom
• National 30-ton fixed cab boom truck
• National 33-ton swing cab with 127 ft. of main boom
• Link-Belt 50-ton rough-terrain with 110 ft. of boom and a 51-ft. jib
• Link-Belt 40-ton lattice crawler
• National 55-ton with 151 ft. of main boom
• A 65-ton truck crane used locally
• A recently added Link-Belt 120-ton truck crane
• And the flagship Link-Belt 175-ton all-terrain crane
“Link-Belts have the best capacity-to-weight ratio in the market,” Classen said. “They’re operator-friendly, and for the kind of work we do — everything from ski lift terminals to hydro dams — that makes all the difference. All of the Link-Belts have been sold and maintained by Woods CRW.
Service a unique footprint size that has put the crane in very
Another key reason that they are our primary crane provider is that they have locations all across New England and Upstate New York. Generally speaking, anywhere we go they are there to support us. We added the 175-ton crane to fill a specific niche in the market. It seems that most crane services fleets, jump from 100 tons to 200 tons. The 175-ton machine has put us in a great position for bidding specific projects where that size is best suited.”
Classen explained why the company continues to go with Link-Belt cranes.
“In 2006, I was at ConExpo, and I sat in every make and model at the show, and compared Link-Belt to all of its competitors,” he said. “Chart-wise, Link-Belt cannot be beat. They have the best capacity for counterweight and machine size in the market. Link-Belt also gives us the creature comforts that our operators are looking for. The controls for swing in the machine are uniquely engineered. It is the tightest operation available on the market. When I visited the company headquarters in Lexington, Ky., last year I was amazed to see that almost the entire machine is manufactured in the USA. Also, as a result of our visit to Lexington, I was able to develop a line of communication directly with some of the factory people whose assistance has been extremely valuable.”
When Classen’s Crane Service needed to expand its fleet, Classen didn’t just look for more capacity — he looked for smarter features. That search led him to the 175-ton LinkBelt all-terrain crane, now the company’s largest and most versatile piece of equipment.
One standout feature that helped seal the deal was the tilting operator cab, a seemingly simple innovation with major ergonomic benefits.
“If he was down flat, he’d be staring at a beam,” Classen said. “Now he’s tilted up. He has a clear line of sight at his work, so he can see what he’s doing better. And if you’re going to be in there eight or 10 hours a day, the last thing you want is your neck wrenched.”
For crane operators working long shifts on demanding jobs, that comfort translates directly into productivity.
Another important feature for Classen is the air ride suspension, a newer system designed to mimic the smoothness of a traditional all-terrain (AT) rig.
“The old ones could shake you up a little bit,” said Classen. “This one’s a lot softer for the operators and drivers. And with the air brakes and suspension, it’s just a better ride overall.”
Although the road speed topped out at 52 mph — a slight trade-off from the company’s previous 100-ton machine — Classen considers the comfort and performance gains well worth it. With 49,000 lbs. of counterweight, most highway moves require just a single truckload to offload and rarely need escort vehicles, adding to the crane’s operational efficiency.
As the skilled trades see renewed interest from younger generations, Classen is optimistic.
“One of my newest operators isn’t even 30, and I trust him with a brand-new 120-ton machine," he said. “He learned the ropes with a veteran who’d been with us for 18 years. This type of employee depth and new employee development will be key to our future growth.”
CEG
(All photographs in this article are Copyright 2025 Construction Equipment Guide. All Rights Reserved.)
Two Connecticut airports were recently granted a combined $8.7 million in federal funding from the U.S. Department of Transportation (USDOT) for necessary improvements to their infrastructure.
Bradley International Airport (BDL), located in Windsor Locks, north of Hartford, was awarded the lion’s share of the grant when it received $8.5 million for an ongoing expansion project of its terminals, CT Insider reported July 2, 2025.
“The construction at Bradley International Airport has been years in the making,” said Michael W. Shea, executive director of the Connecticut Airport Authority (CAA). “We are pleased to see the first of these key projects nearly completed. [BDR’s upgraded] exit corridors, and the other ongoing construction, are part of our long-term strategy to really optimize the flow and functionality of the terminal and ensure we are meeting the demands of current and future air travel growth at Bradley.”
The two-year-long, $250 million infrastructure improvement project at the Hartford-area airport has so far received over $113 million in federal funding through the Federal Aviation Administration (FAA) Airport Improvement Program, the Transportation Security Administration and
the Bipartisan Infrastructure Law.
According to the CAA, the quasi-public agency that runs Bradley and other airports in the state, the rest of the project’s funding will come from passenger facility charges and the authority’s airport revenue.
Ground first broke on Bradley’s terminal expansion in April 2023, CT Insider noted, and in June 2025, the project reached a milestone with the opening the airport’s east concourse corridor. When complete, there will be two exits providing faster and more direct access to airline baggage claims, car rentals, ground transportation and shuttles on the airport’s arrivals level.
To the southwest near the ConnecticutNew York state line, Danbury Municipal Airport (DXR) also is receiving a $225,378 grant to replace its existing airport lighting vault equipment.
“More than $8.7 million of federal investment for Connecticut’s airports will deliver important infrastructure upgrades at Bradley International Airport and Danbury Municipal Airport,” the state’s congressional delegation in Washington said in a joint statement. “Bradley is receiving additional federal funds for a much-needed terminal expansion — greatly improving the passenger experience and satisfying safety standards.
“We’re proud to have secured this funding for our state and will continue to fight for the federal resources needed to upgrade and elevate Connecticut’s infrastructure.”
The federal grant received by Bradley International Airport is in addition to $30 million in FAA funding already allocated for its terminal expansion and renovations.
The Windsor Locks air facility also provided an update on a couple of its major construction projects.
Besides the unveiling of BDR’s exit corridor in its east concourse, airport officials told WFSB-TV in Hartford at the end of June that the west concourse corridor was still under construction but will likely open to the traveling public later this summer.
When both corridors are completed, the terminal will have a new pair of exit points as well as two new meet and greet locations, while the old exit corridor will be reconfigured into an expanded security checkpoint.
In addition, an airport spokesperson said the facility will provide faster and more direct access to baggage claims, vehicle rentals, ground transportation and shuttles.
A second construction project at Bradley will bring a new 80,000-sq.-ft. inline baggage screening facility on line that will be designed to house the airport’s explosivedetection machines.
Another of its planned features is a milelong conveyor belt that BDR said will carry an estimated 2 million checked bags that the airport moves annually from the airline ticket counters directly to the new screening facility.
That building is expected to be completed by the end of 2025, WFSB-TV reported.
Loved for the features. Trusted for the performance.
Do more without feeling like it in Hyundai’s easy to own, easy to operate, skid steer and compact track loader.
Standard features include:
• LED front and rear work lights
• Auto leveling bucket
• Ride control
• Review camera
• Two speed travel
• AM/FM bluetooth radio
• Free Hi MATE telematics access for 5 years
Greenfield Savings Bank held a groundbreaking event July 2, 2025, to mark the development of a new Easthampton branch located on Massachusetts Highway 10. The facility is envisioned as a secondary base of operations for the bank in the western part of the state.
Approximately 40 people attended the kickoff ceremony for the office’s construction, as well as view the design of the planned Greenfield Savings branch, at 9397 Northampton St. The site is located within the new, 33-acre Sierra Vista Commons commercial development.
“It’s not really just a branch, this is really going to be our southern headquarters so we can continue to do business into Hampden County as well as Hampshire County,” Thomas J. Meshako, the bank’s president and CEO, said during his remarks at the event.
The new Easthampton office of Greenfield Savings brings the company’s total number of branches to nine — all in Hampshire and Franklin counties. Other Hampshire County locations can be found in Northampton, Hadley and Amherst; in Franklin County, the bank maintains fullservice offices in Greenfield, Turners Falls, Shelburne Falls, Conway and South Deerfield.
“The bank has seen — over the last few years — a lot of growth with commercial lending specifically in Easthampton and that was really the catalyst for us making the decision to come down here,” said Greenfield Savings Bank First Vice President Kevin De Rosa, who is overseeing the branch expansion effort. “We’re excited to come into Easthampton. We don’t just have branches; we engrain ourselves in the community.”
Greenfield Savings serves more than 400 customers in Easthampton and holds nearly 1,000 loan and deposit accounts locally. After its planned opening late this year, the branch will provide access to experts in wealth management and trust services, commercial lending and mortgage services, according to a news release from the bank.
Construction at the site will begin in July 2025, after the removal of several underground clay clusters, according to the Daily Hampshire Gazette in Northampton, Mass. If all goes to plan, the new building will be
completed by Dec. 15, 2025, followed by a public grand opening in January 2026.
The branch will sport a modern, twostory design, Meshako told the Gazette.
Easthampton Mayor Nicole LaChapelle also was in attendance to welcome Greenfield Savings to the community, noting that the new branch is part of a much larger development for the city.
“This is a part of the biggest mixed-use development Easthampton has ever seen since a mill has been built,” she said.
“Greenfield Savings is not a stranger to Easthampton,” LaChapelle added while describing the bank’s involvement in the community. “The branch has grown bigger, and we’re delighted to be your southern hometown location.”
The Greenfield Bank branch project in Easthampton marks the first vertical construction within Sierra Vista Commons, also known as the Tasty Top Development LLC. It represents the first step of a plan to invest an estimated $26 million to $30 million into the site.
Frank DeMarinis, owner of SAGE Engineering & Contracting Inc. of Westfield, Mass. bought the property for $2.2 million in 2022, the Gazette noted.
Greenfield Savings reached out to DeMarinis after eyeing Sierra Vista Commons as an ideal location for the new bank branch.
“This is where we think the growth in Easthampton really is,” Meshako said.
Future construction within Sierra Vista Commons will occur in phases, DeMarinis told the Northampton news source.
In approximately six months, SAGE plans to begin building an approximately 9,000-sq.-ft. Roots Learning Center and a 7,000-sq.-ft. Roots Gymnastic Center.
After they are complete, other projects will begin with no set construction date, he said, including 188 apartments — 54 of which would be affordable housing units — spread across 10 mid-rise buildings.
In addition, a sit-down restaurant, a small, stand-alone retail building, two 7,400-sq.-ft. mixed-use warehouses and one mixed-use building with ground floor retail/commercial use and 14 apartment units above are on the drawing board.