NJR Construction LLC Building Bridges Across Conn., Western Mass.


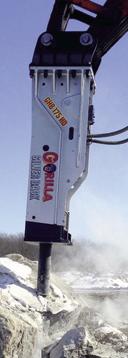

Nicholas Mancini Jr. grew up around his family’s construction business. In 2004, when they closed their doors, he picked from their best people and started NJR Construction LLC, specializing in small bridge building in the $1 million to $6 million range
Based in Torrington, Conn., with 20 to 30 employees,
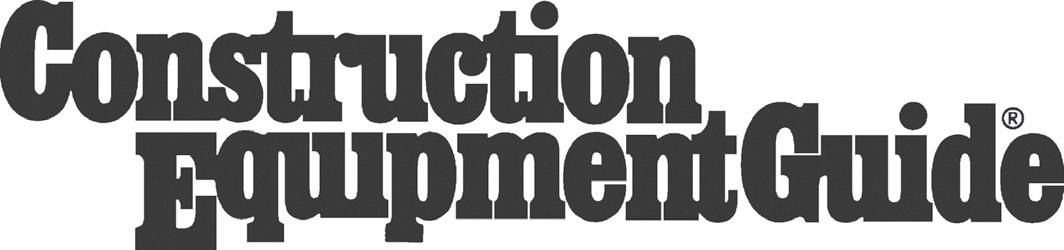
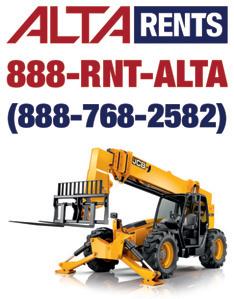
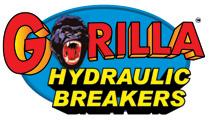
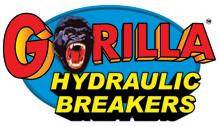
depending on the workload, the company does the majority of its work in Connecticut and western Massachusetts.
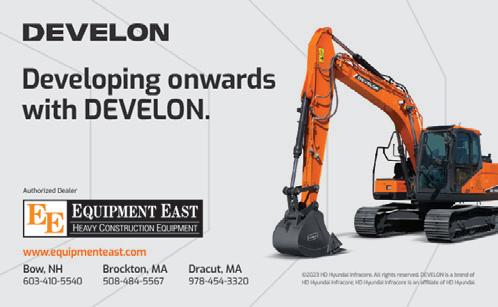
“We are generally a self-performing contractor,” Mancini said. “We sub out very little work. We do our own excavating, concrete, carpentry, and utility work. By and large we try
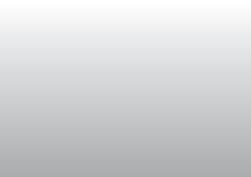
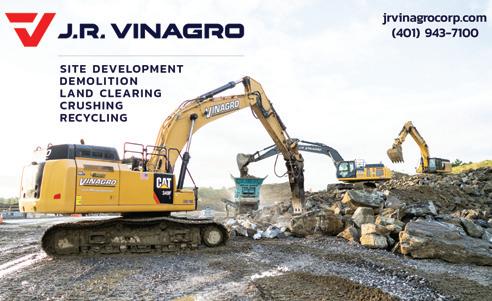
see NJR page 16
After Long Delay, Work Begins to Replace Bridge Over Maine’s Androscoggin River
The Maine Department of Transportation (MaineDOT) has begun onsite construction on the project to replace the Frank J. Wood Bridge, the agency announced July 26. The bridge carries U.S. Highway 201 over the Androscoggin River between the towns of Brunswick and Topsham, northeast of Portland.
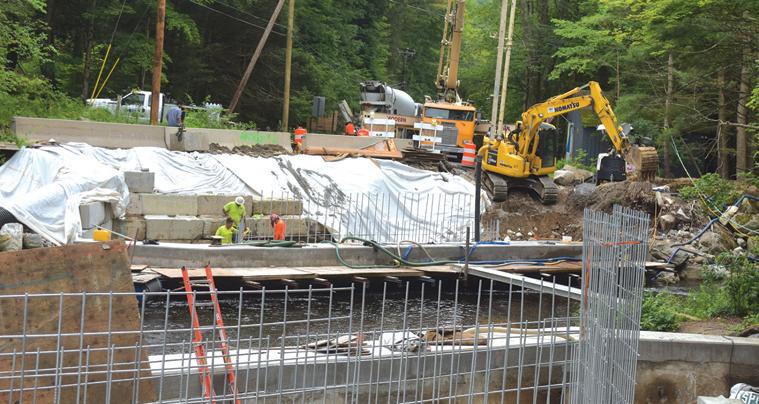
The new span in Maine’s coastal region is designed to be a newer, safer structure than the current bridge, which is more than 90 years old, and rated in poor condition, MaineDOT noted.
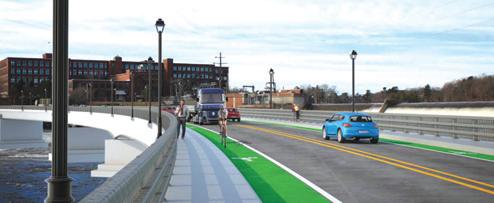
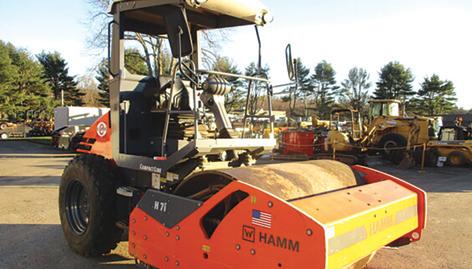
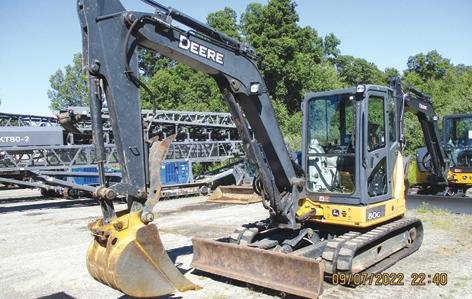
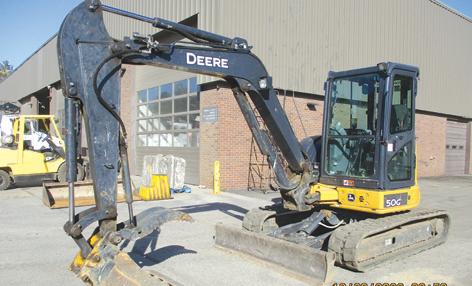
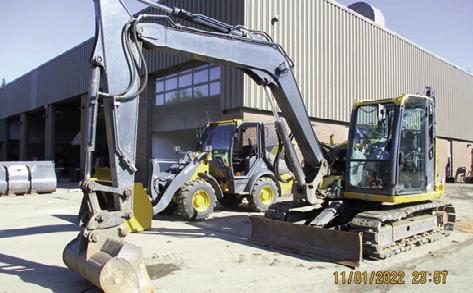
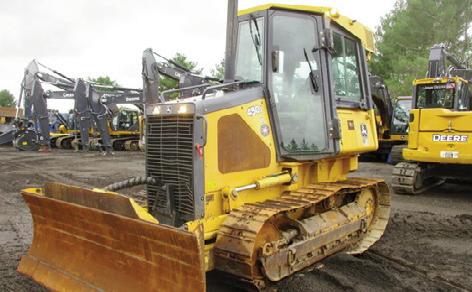

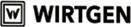

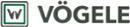


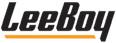

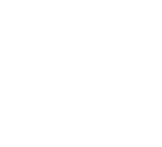
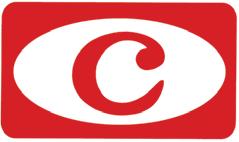
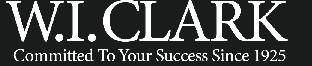
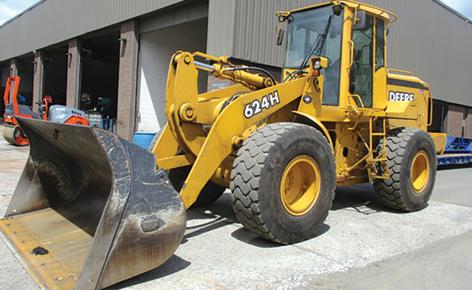

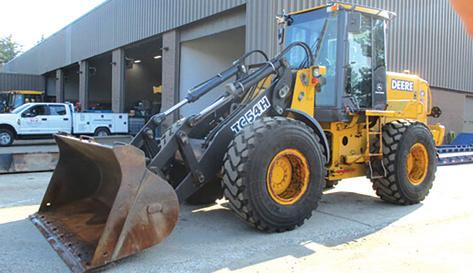
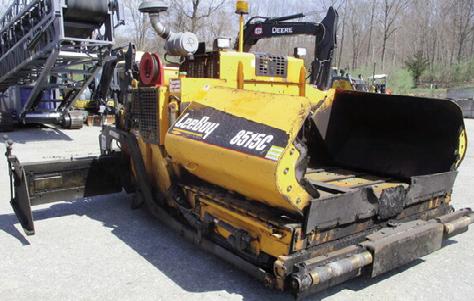
OPRROOVVEN U WITH UPTI



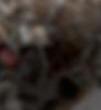
PTIME IME KITS



SENNEBOGEN, in kee philosophy to maxim created UPTIME Kits



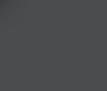

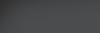

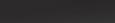
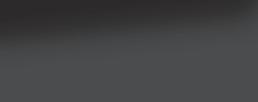












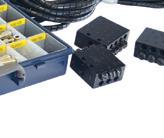

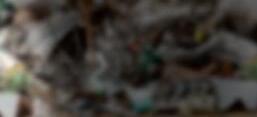
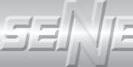
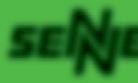
n-house or on the everything you e, maintenance place. They were ime and money. of related service d nuts to O-Rings omes easy with a o order and stock :kits
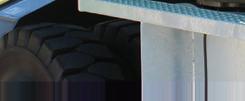






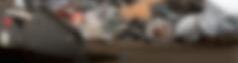




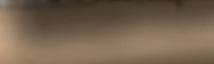
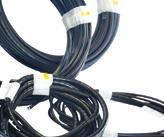

Easy e for (TCO) Ownership of thinki We’re equipment.



They are: rain e • T ervic ts • S Par




order and par ing • Application Special customer very to machine” the “beyond ng
stocking NEBOGENNN BOGEN SEN ctor suppor xible Financing lists • Fle









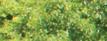



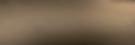





• Hydraulic service k
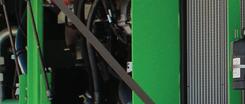
D T shops ols ervice owing kits system kits nance service kits its kits

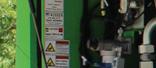
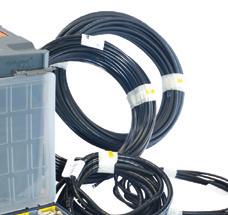
trucks Choose a uptime dependable deliver througho t ttachments • A
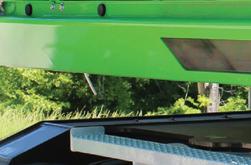




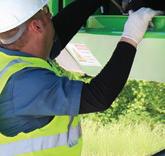
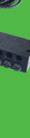
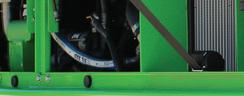


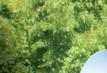

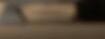
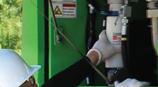

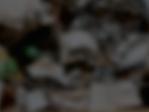





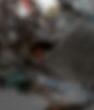



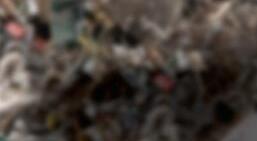

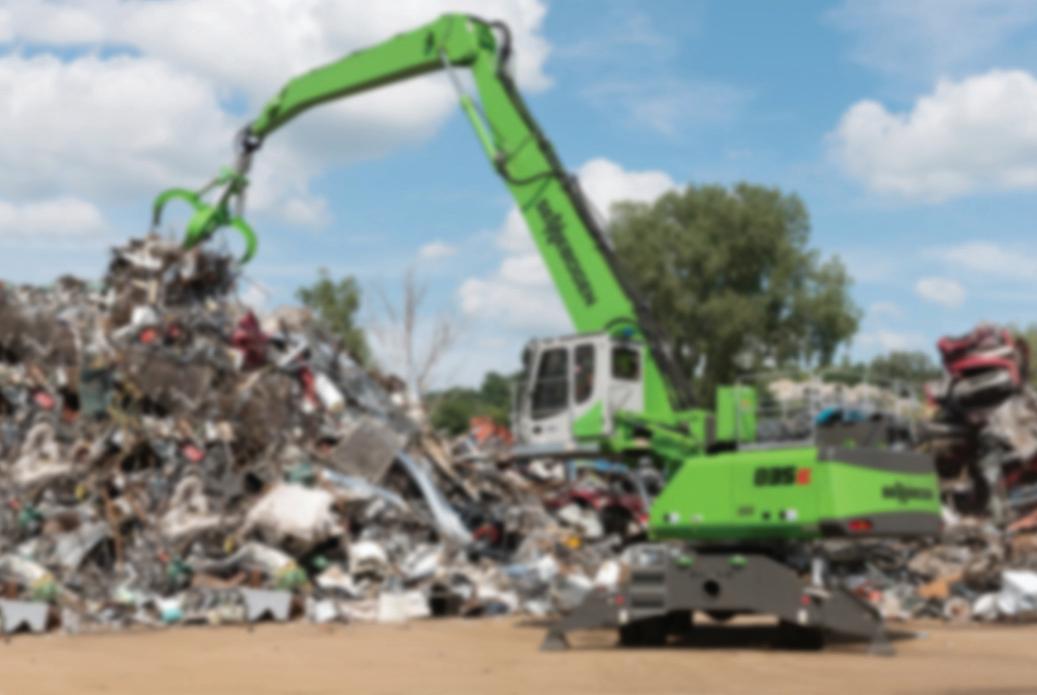
Cost Total lower and its of life the out
And the best thing is in stock and ready to built to match your m and series. Count on in-house. For more in UPTIME Kits, scan th a more Learn
N.H. to Replace Aged Bridge With One for Bicyclists, Pedestrians
Millions of dollars in federal funds coming to New Hampshire are earmarked for a major transportation infrastructure project that is not for motor vehicles at all.
The New Hampshire Bulletin in Concord reported in late June that the $20 million grant will go toward replacing the long-closed General Sullivan Bridge with a new two-girder superstructure to re-open as the only walking and bicycling access across Little Bay and provide a link between Newington and Dover.
The federal grant will be allocated through the Rebuilding American Infrastructure with Sustainability and Equity (RAISE) program.
When the General Sullivan Bridge replacement project is complete, the restored link between the two southeast New Hampshire communities is expected to see close to 500 new bicycle riders daily, in addition to pedestrians and fishermen.
The funding was announced by New Hampshire’s congressional delegation in Washington, including U.S. Sen. Jeanne Shaheen (D) — a senior member of the Senate Appropriations Committee — and Sen. Maggie Hassan (D), along with Reps. Annie Kuster and Chris Pappas.
Just last year, the state’s congressional delegation announced a similar RAISE grant for more than $19.5 million for an infrastructure project in Berlin. The 2021 Bipartisan Infrastructure Law (BIL), which Shaheen and Hassan negotiated, significantly increased funding for the RAISE program.
The New Hampshire Department of Transportation (NHDOT) will receive the money from the U.S. Department of Transportation (USDOT) to support the crossing project in Rockingham and Strafford counties.
“This is great news for New Hampshire,” said NHDOT Commissioner William Cass. “This $20 million grant will have a very positive impact on our state. Not only will it help ensure this long-awaited project to replace the aged General Sullivan Bridge with a new and modern bicycle and pedestrian bridge moves ahead to construction, but it will also help us solidify our highway program for the rest of the fiscal year.”
Old Bridge Long Past Its Expiration Date
The General Sullivan Bridge was constructed in 1934 and carried vehicular traffic until 1984. It closed completely in 2018 because of its deteriorating condition due to age and the harsh coastal climate.
The new 1,550-ft.-long structure — expected to cost $35.5 million — will be completely separate from vehicle traffic and located just upstream of the Little Bay bridges that carry U.S. Highway 4/Spaulding Turnpike both north and south. Without the General Sullivan Bridge, pedestrians and bicyclists are forced to take a 25-mi. detour to travel between Newington and Dover.
In his agency’s cover letter to U.S. Transportation Secretary Pete Buttigieg, Cass wrote the bridge replacement will improve safety by separating bicyclists and pedestrians from eight lanes of high-speed traffic. It also will reduce greenhouse gas emissions by encouraging a modal shift from automobiles for commuters and recreational users. And, Cass wrote, it will serve a diversity of users and connect nationally significant destinations.
New Hampshire’s application materials to the federal government pegged the General Sullivan Bridge project as

“an innovative response,” that addresses the growing demand for different transportation choices and improves efficiency of the regional transportation network.
In a statement released shortly after the grant was awarded, Sen. Shaheen said, “This project will enhance the quality of life for local residents and tourists, as well as ensure the continued economic vitality of New Hampshire’s Seacoast communities. I was happy to advocate on behalf of this project, and I look forward to seeing its positive impact on the Seacoast.”
Hassan Also Wants Attention Paid to ÂHigh-HazardÊ Dams
The Biden administration has placed a huge focus on infrastructure spending and has so far awarded funds from the BIL to nearly 35,000 projects, according to the White House.
With that in mind, New Hampshire Sen. Hassan also is requesting attention for another type of infrastructure. She has called on the Government Accountability Office (GAO) to review potentially hazardous dams operating under the authority of the U.S. Department of Agriculture’s Watershed Program and make safety recommendations.
The Bulletin reported there are currently 25 dams operated by the USDA in New Hampshire, and 75 percent of those are classified as “high hazard,” meaning their failure would cause significant property destruction and loss of human life.
“The safety of downstream communities is of serious concern when there is a risk of failure from high-risk dams, and coordination between federal, state and local governments is critical to protect against and mitigate those risks,” Hassan wrote in a letter co-signed by Wisconsin Sen. Ron Johnson.
Over the next five years, the Federal Emergency Management Agency (FEMA) will award $733 million through the BIL in dam safety grants to states and territories to enhance dam safety and rehabilitate or remove aging structures.
In June, New Hampshire Department of Environmental Services Commissioner Robert Scott said the state has $35 million in American Rescue Plan Act (ARPA) funds for high-hazard dams that are municipally owned.
Maine Contractors Busy Building a Variety of Projects
With summer being the busy season for construction in Maine, it is no surprise to see contractors of all sizes diligently working on infrastructure projects designed to make life easier for the state’s residents.
Every outdoor building project imaginable, including schools, hospitals, homes, offices, retail and roads and bridges, are currently moving along as contractors across the New England state work toward advancing, if not finishing, their job before the cold north wind blows in a few months.
Three of Maine’s top contractors each have multiple job sites progressing right now.
Landry/French Tabbed to Build $58M School
Landry/French Construction in Scarborough will kick off construction of Skowhegan’s $58 million Margaret Chase
Smith Community School elementary school with a groundbreaking ceremony scheduled for Aug. 17 for the Maine School Administrative District (MSAD) 54.

Waterstone Properties in Westbrook announced that next spring Landry/French would be managing the new $150 million medical center construction at Rock Row.
In addition, the contracting company is
nearing completion on the construction of the Avesta Porter Station in Portland, with a fall completion expected.
PM Construction Tackling Retail Projects
PM Construction in Saco, Maine, has started a full-scale renovation for Hannaford’s second Scarborough supermarket. The 58,000-sq.-ft. store on Payne Road was previously occupied by Shaw’s.
Work also is progressing on a renovation of the Hannaford supermarket in Winthrop. That store will remain open during PM Construction’s updates.
Additionally, the contractor has its crews building a multi-unit retail development in Scarborough, adjacent to the Marden’s lot, with Starbucks signed to be the anchor tenant. Port City and Sebago are part of the project team.
Consigli Busy in North, South
In Orono, Consigli Construction has been erecting steel on its ground-up construction of a site for Tyler Technologies.
Consigli also is busy in Portland, just blocks from its Maine headquarters, for the real estate developer East Brown Cow, with several projects in the works.
At One Canal Plaza, where the flagship tenant is KeyBank, Consigli is adding 24,000 sq. ft. of glass-fronted retail space on the ground floor, a grand staircase and redesigned lobby, and significant concrete work. The expected completion is sometime this winter.
At 178 and 184 Middle St. in Portland, the contractor will add 19 apartment units, shortterm “Urban Homes” marketed through the Docent’s Collection. Renovations on the
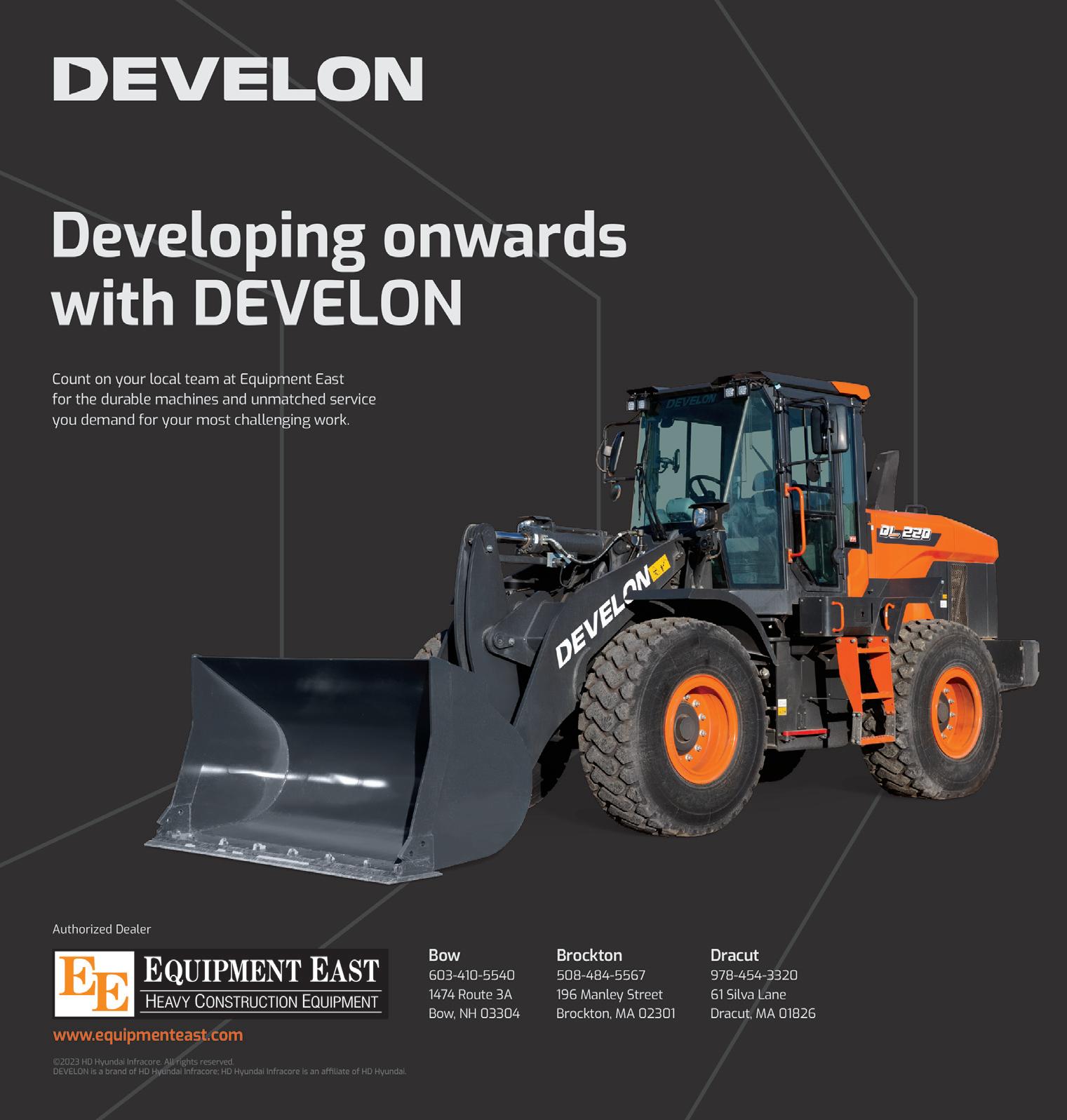
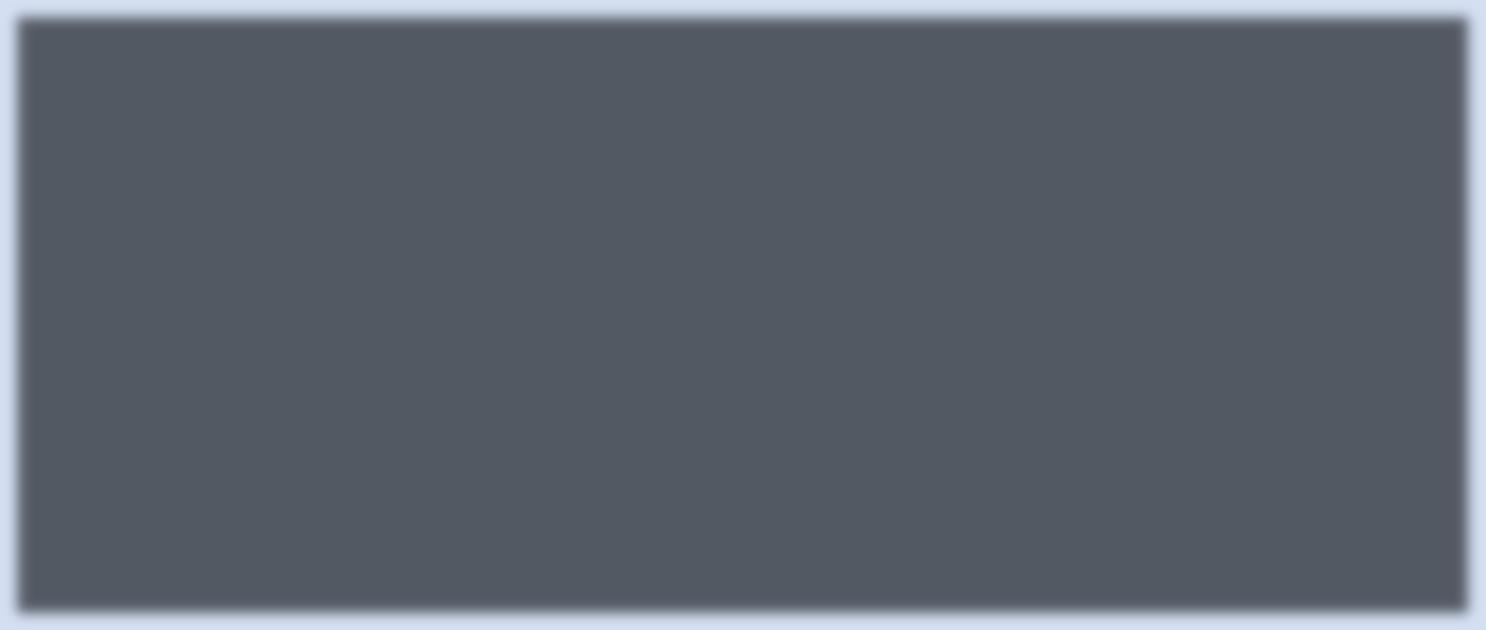
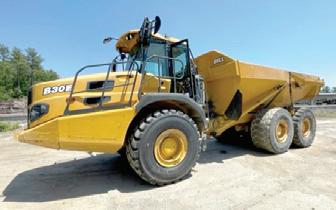
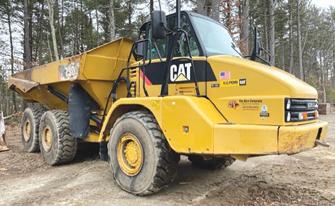
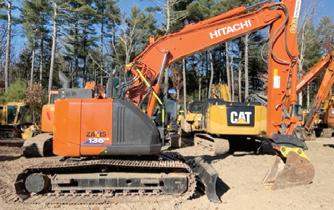
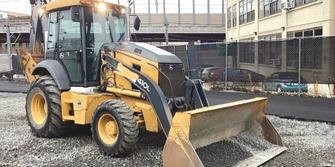
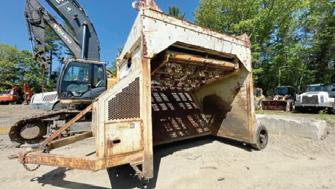
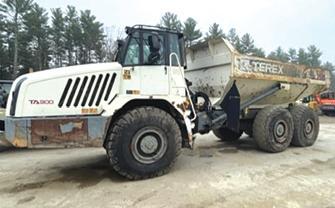
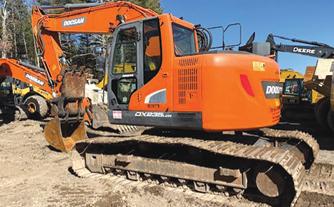
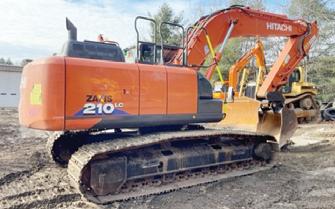
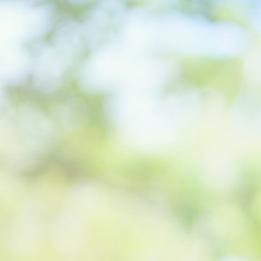
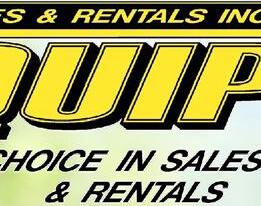








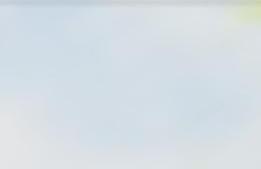





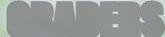
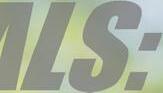
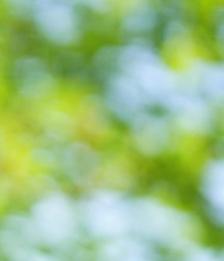

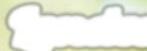
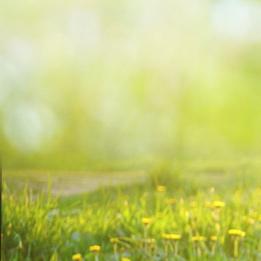
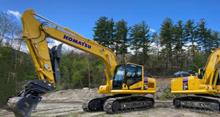
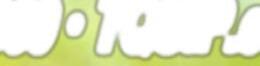

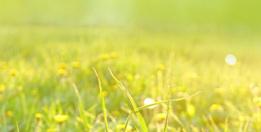
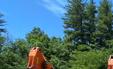
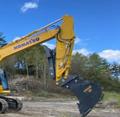
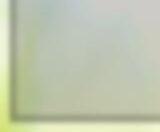

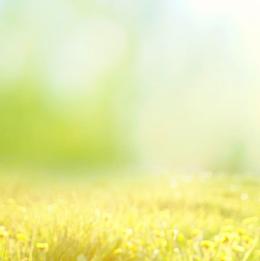
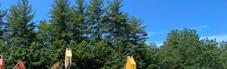


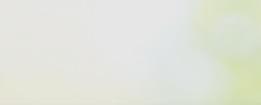
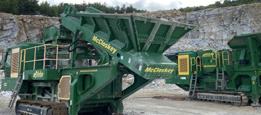
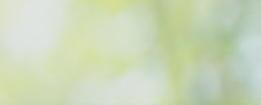
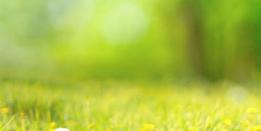
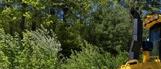

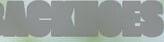
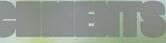
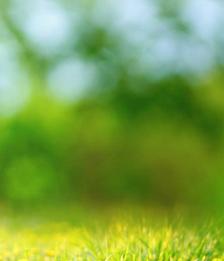
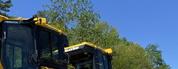
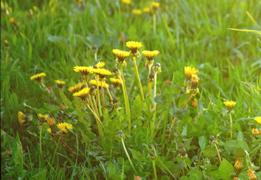

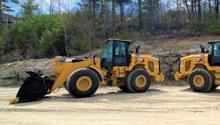
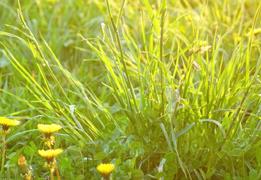
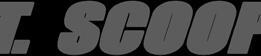

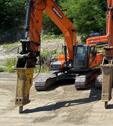

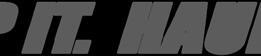
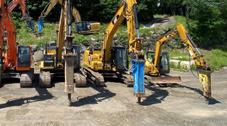
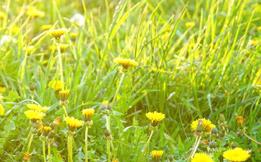
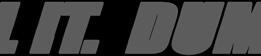
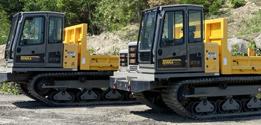
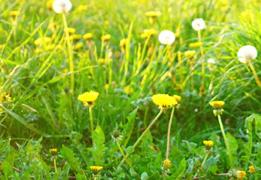
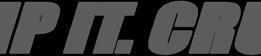
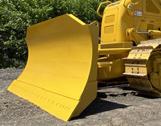
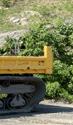
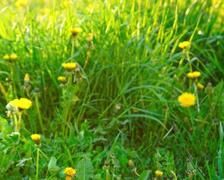
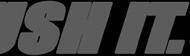
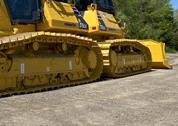

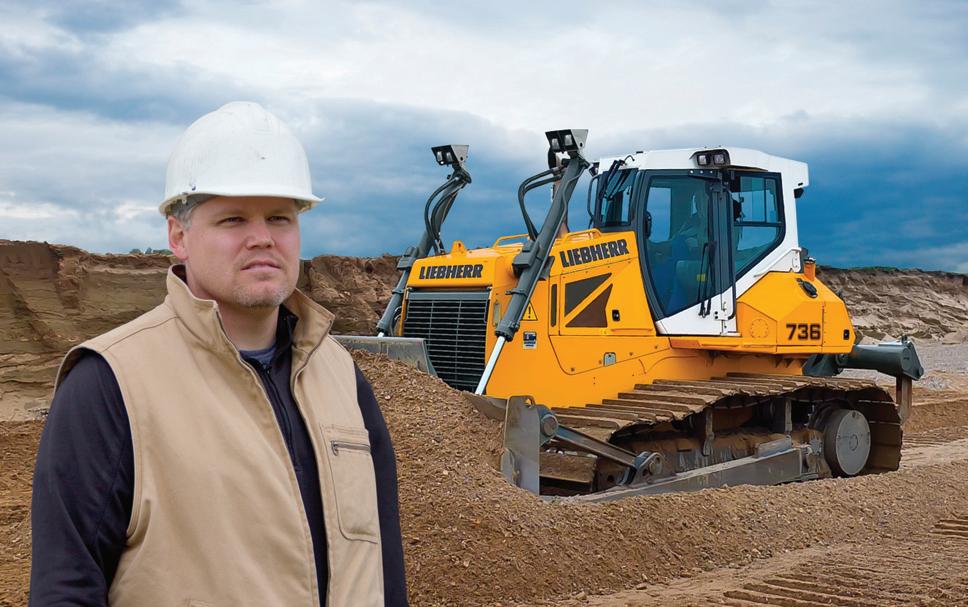
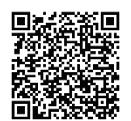
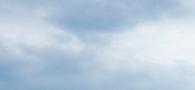

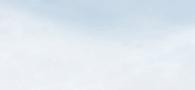
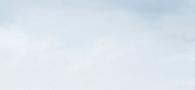
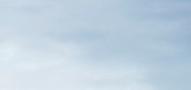
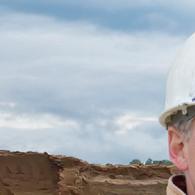


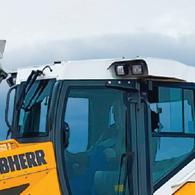
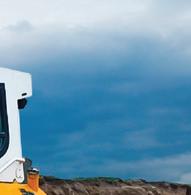
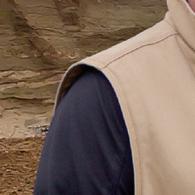
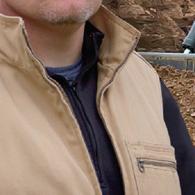

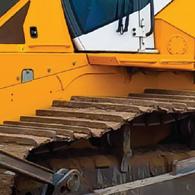
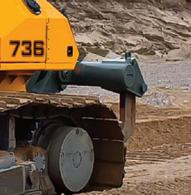
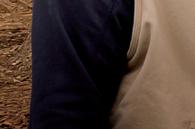
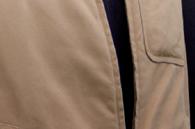
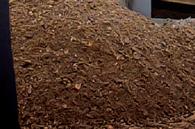
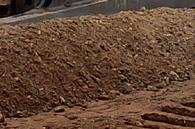
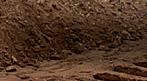

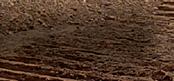
Developer Proposes Using Mass Timber for New Apartment Complex in Hartford
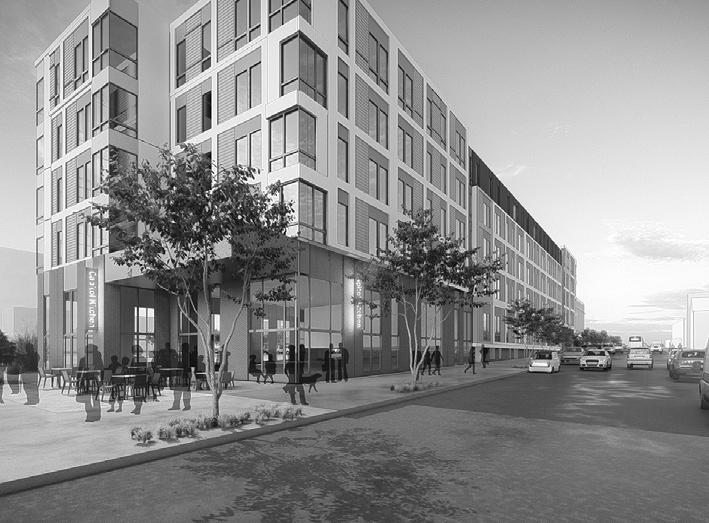
A developer presented plans for a high-end apartment complex built with compressed wood “mass timber” for a parcel in the Bushnell South area of Hartford, Conn., on June 15 to upgrade both the area’s housing stock and environmental bona fides.
Laminated wood beams would form the skeleton of the new buildings, designed by Anthony Amenta on behalf of the Michaels Organization. The developer, which has its East Coast headquarters in Camden, N.J., was chosen by Connecticut’s Capital Region Development Authority (CRDA) last year to develop a parcel across from the State Capitol Building, near The Bushnell theater in Hartford.
The $100 million project would result in 233 apartments in two newly built mid-rise buildings designed “to push the envelope on the marketplace,” CRDA Director Michael Freimuth said in speaking to the Connecticut Post.
Mass timber technology allows for the buildings to rise to eight stories, instead of the five-story limit for traditional “stick-built” construction.
Massive structural beams composed of compressed wood would be visible on the building’s ground floors, highlighting the sustainable material. The project’s developer is currently completing preliminary work with plans to refine plans over the summer, said Geoff Lewis, director of development for the Michaels Organization.
Amenta told the Post that mass timber would allow for not only taller buildings, but greener finishes and more housing.
“For this particular site, we wanted to see if we could do something different, particularly on the key corner there across from The Bushnell,” he explained. “We spent a good amount of time looking at mass timber… and what this means is the entire structure of a building of this type could be made of a renewable resource.”
The proposed complex is part of a major project designed to create a new neighborhood south of Hartford’s downtown. Mayor Luke Bronin told the City Council in May that public subsidies in the form of tax-fixing agreements would be needed to com-
Gordon Contractors Leads U.S. 1 Project in Searsport, Maine
first floor will support retail spaces while work on the upper floors will convert office space to hospitality units. That project is scheduled to finish next spring.
Also in Portland, at Two Canal Plaza, Consigli is adding a glass entrance and performing lobby renovations, with work winding up next winter; and at 121 Middle St., the builder will convert office space into seven Urban Homes to the Docent’s Collection. That work is slated to be done by next spring.
MaineDOT Revitalizing U.S. 1 in Downtown Searsport
The bustling downtown area of Searsport is undergoing a remarkable transformation as the Maine Department of Transportation (MaineDOT) started on a major construction project along U.S. Highway 1 in June.
plete the redevelopment.
New Haven is the home of Connecticut’s first mass timber project, a 69-unit apartment complex now under construction on Dixwell Avenue. That complex also is said to be the first affordable housing project in the United States to use the environmentally friendly material.
More developers are choosing mass timber as the technology evolves and customers demand sustainability, Amenta said.
“I do believe [mass timber] will be taking over a good deal of the marketplace, because [it] allows the beauty and aesthetics of wood to be shown within some of the unit types,” he elaborated, adding that structures utilizing the timber “have a very rapid construction time.”
Bringing Vibrancy Back to Bushnell South
Michaels, a national leader in residential real estate, will redevelop a now mostly unused three-acre surface parking lot current surface parking lot along Capitol Avenue east of the renovated State Office building.
The development will include not only new housing, but green spaces and commercial and retail space as well.
“This important neighborhood has so much potential, and we are excited to work with [Hartford] and the CRDA to transform it into an area where peo-
ple can live, work, shop and play,” said Jay Russo, Michaels’ vice president of development.
Hopes are that the new development will help transform Bushnell South into a bustling residential and commercial area, connecting both sides of the neighborhood currently being divided by the vacant parking lots, and marking Bushnell Park as the center of the city.
Michaels was awarded the development project through a competitive bidding process and was ultimately chosen for its strong understanding of public financing and urban development strategies.
“The Bushnell South plan is critical for not only the State Capital and the city, but also for the neighborhood,” explained Mike Freimuth, CRDA’s executive director. “Having a national developer such as Michaels investing in the project demonstrates that all the development that has occurred over the last 10 years has led towards Hartford realizing its full potential as a major city. CRDA is looking forward to working with Michaels. It has experience with public private urban development projects and understands the unique strategies, problems and consequences that come with such projects.”
The Michaels Company said in a news release on its website that it plans to work closely with surrounding neighborhoods and the various stakeholders throughout the development process.
According to Today Maine, the construction work will span nearly 2 mi., starting from Savage Road and extending northward to Station Avenue in the mid-coastal town. With a projected completion timeline of two years, the construction activities will be in full swing until the arrival of winter.
To ensure a smooth flow of traffic and minimize disruptions, an alternate route will be implemented until Oct. 15. Southbound traffic will be temporarily detoured onto Black, Union and Mortland Roads, allowing commuters and residents to navigate through the area seamlessly.
The focal point of the project entails the addition of a center left-turn lane between Trundy Road and Station Avenue. This crucial enhancement aims to alleviate congestion and improve traffic flow, providing motorists with a safer and more efficient driving experience.
In addition to the road improvements, the construction plans also include the enhancement of sidewalks and the installation of pedestrian lighting. These upgrades, MaineDOT said, will create a more pedestrian-friendly environment, encouraging residents and visitors to explore the vibrant downtown area of Searsport on foot.
The state agency’s ambitious project aims to revitalize downtown Searsport, unlocking its full potential as a thriving commercial and cultural hub. By prioritizing the needs of both motorists and pedestrians, the construction endeavor seeks to strike a balance between efficient transportation and a vibrant streetscape.
Gordon Contractors of Sangerville, Maine, is the contractor on the U.S. 1 reconstruction project in Searsport. The contract amount is $17.75 million and is boosted by $9.2 million in congressional spending.
As the construction crews continue with their work, the town eagerly anticipates the positive impact the transformation will have on the local economy and quality of life, Today Maine reported. The revitalized U.S. 1 promises to attract more visitors, enhance accessibility and provide a renewed sense of pride for the residents of Searsport.
MaineDOT said that with a long-term vision in mind, it remains committed to completing the U.S. 1 project diligently and efficiently. While construction activities may present temporary inconveniences, the long-term benefits will undoubtedly make downtown Searsport a more dynamic and inviting destination for all.
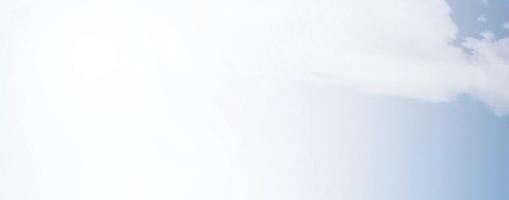
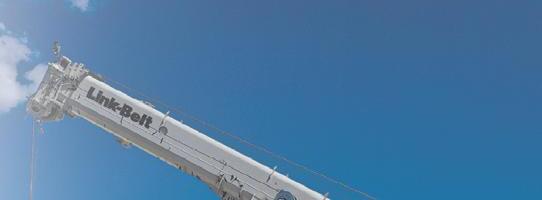
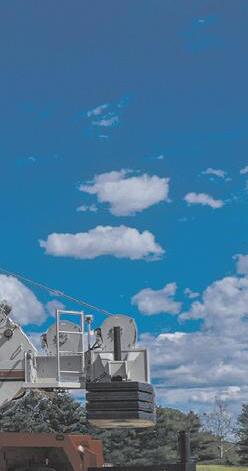
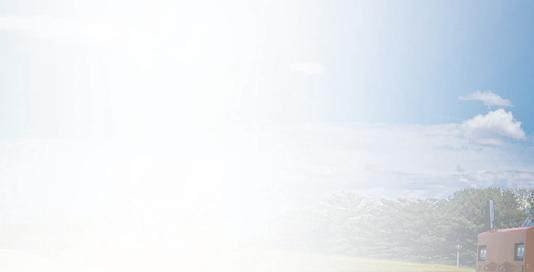

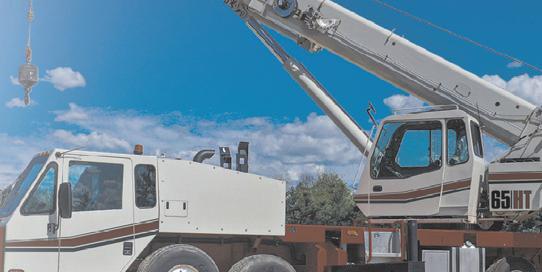

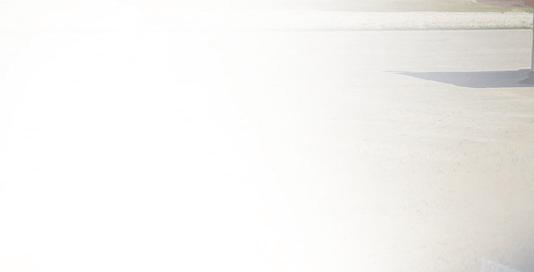

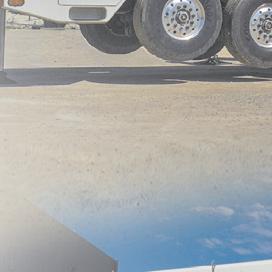
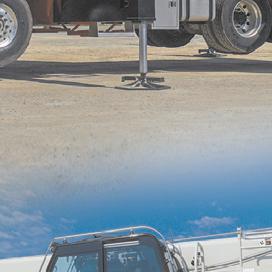

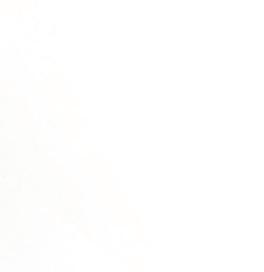





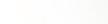


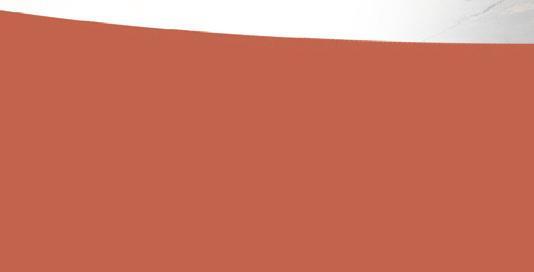
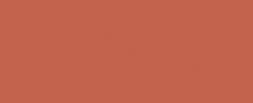
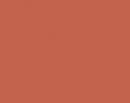
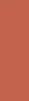

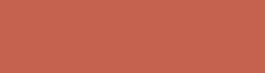

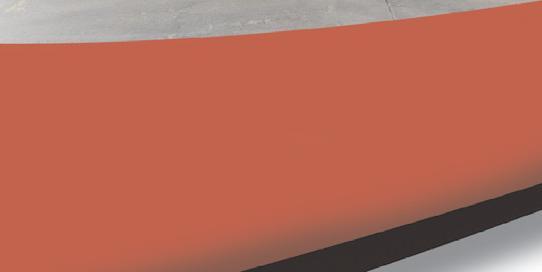
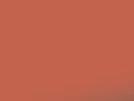

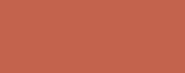
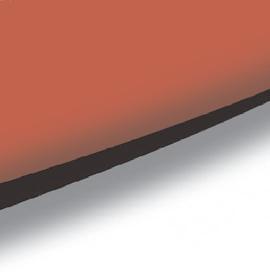
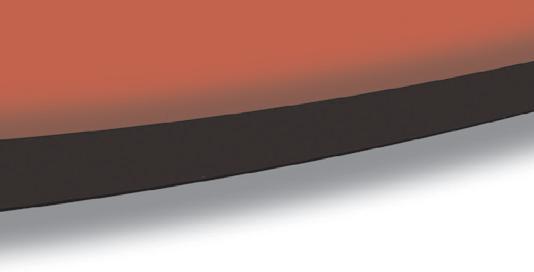

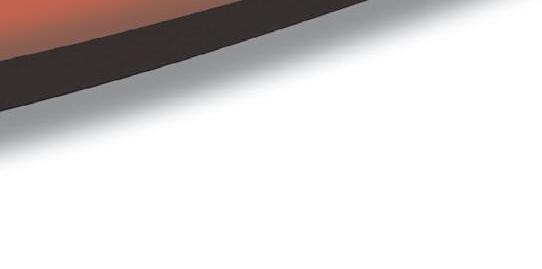




JCB 35Z excavator
Lease special payments as low as $812 a month!*
Operating Weight: 7,840 lb
Max Dig Depth: 11' 5"
Max Dump Height: 11' 7"
Engine Power: 24.7 hp
Tailswing: Zero
Diesel T4F
JCB 50Z excavator
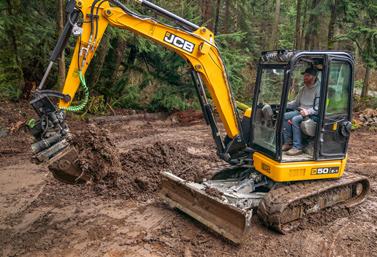

Lease special payments as low as $999 a month!*
Operating Weight: 11,089 lb
Max Dig Depth: 11' 11"
Max Dump Height: 13' 5"
Engine Power: 48.3 hp
Tailswing: Zero
Diesel T4F
JCB Loadall 509-42
Lease special payments as low as $2,023 a month!*
Max Lift Capacity: 9,000 lb.
Max Lift Height: 42'
Max Engine Power: 74 hp
Lift Capacity at Full Height: 6,000 lb
Lift Capacity at Full Reach: 1,800 lb
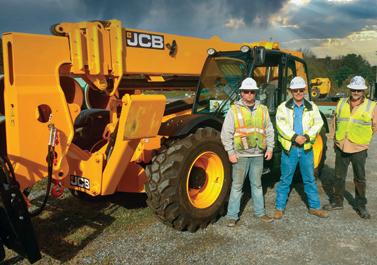
Max Speed: 15.5 mph
JCB Loadall 510-56
Lease special payments as low as $2,594 a month!*
Max Lift Capacity: 10,000 lb
Max Lift Height: 56'
Max Engine Power: 74 hp
Lift Capacity at Full Height: 4,000 lb
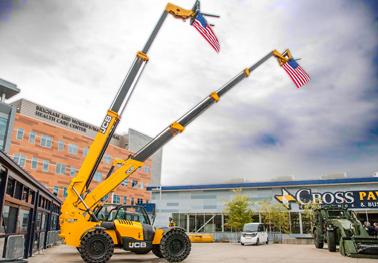
Lift Capacity at Full Reach: 3,000 lb
Max Speed: 15.5 mph
steer (wheeled): $19
JCB 215T skid
d steer (tracked): $1
JCB 270T skid
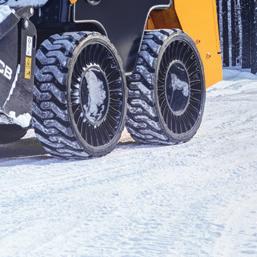

d steer (tracked): $1
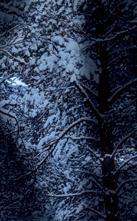
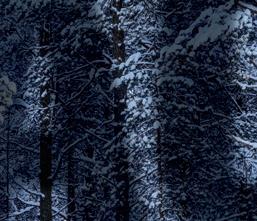

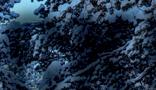
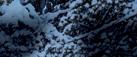




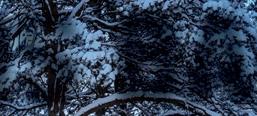
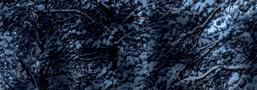
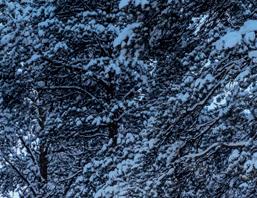
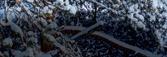

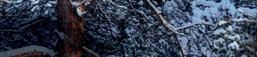


Teeleskid 3
3TS-8W (wheeled): $
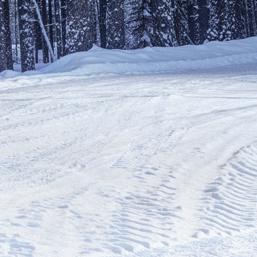
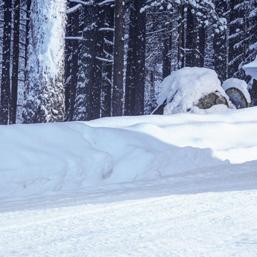
Teeleskid 3

3TS-8T (tracked): $1
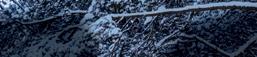
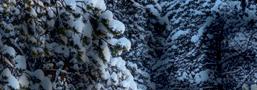

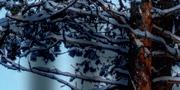
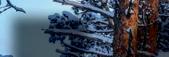
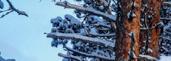
JCB 409 comp
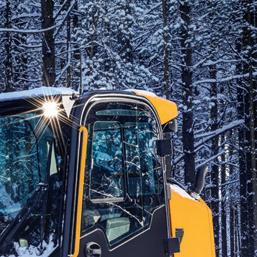
pact

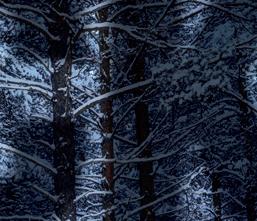
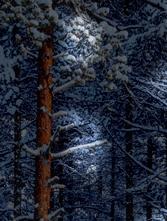
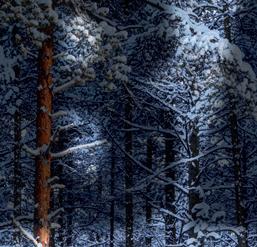
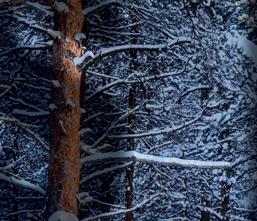
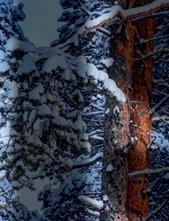
ths a year/ $1,731 a m

nths a year / $2,133 a m
nths a year / $2,139 a m
months a year / $2,159 a
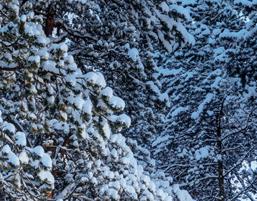
nths a year / $2,729 a m
onth for six months a y month for six months a y month for six months a y month for six months a month for six months a


























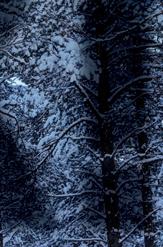

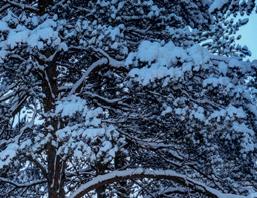
onths a year / $2,797 a
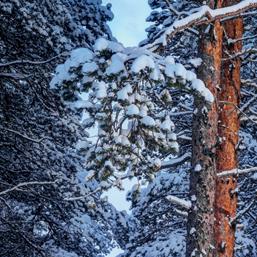
er year. Contact an Alta Equipm
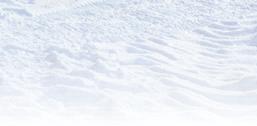
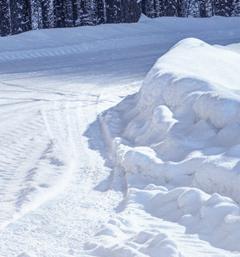
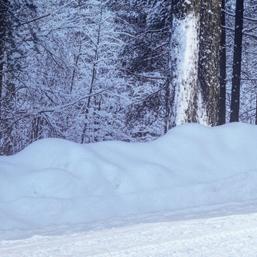
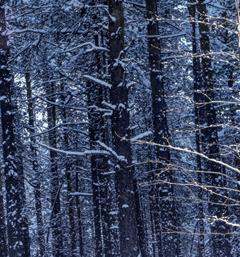

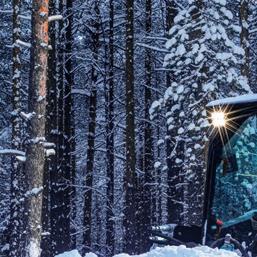

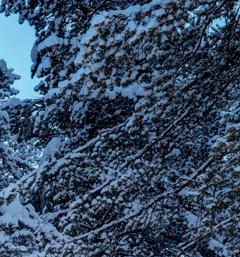

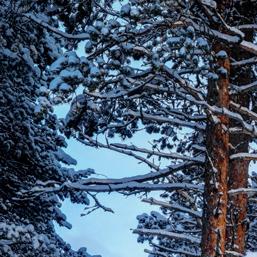
year.* year.* year.* a year.* year.* a year.*
ent Company representative f
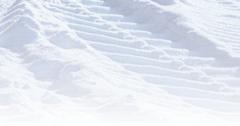

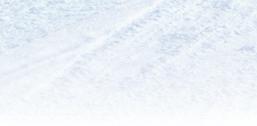



for six months a for complete details.
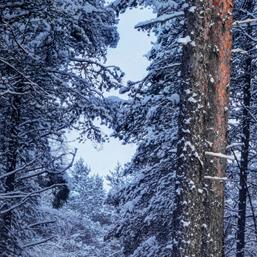
New $82M Martha’s Vineyard School On Track for ’24 Finish
Walking through the construction zone of the Tisbury School on Martha’s Vineyard, it is easy to see the vision that the project is building toward: Starting on the first level — which currently has a dirt floor, no insulation and an open-floorplan — the towering ceilings, grand windows and history still lend an academic air.
The goal of the $82 million project is to bring the school up to modern health, accessibility and environmental standards. It is intended to address space needs for current and future students, increase accessibility for students and community members with impaired mobility, and work to meet Tisbury’s Green Community pledge by eliminating the use of fossil fuels.
But building plans also are intended to preserve iconic features of the original 1929 structure, like its brick exterior and tall, arching windows.
Construction on the Tisbury School has been ongoing since last year.
“Right now, things are going quite well, and we know we will come in at budget, but our hope is that we’ll come in under budget,” Amy Houghton, chair of the Tisbury School Committee, told the Times during a recent tour.
Houghton acknowledged there are another 12 months of construction ahead, the Times reported, so it is hard to say what the final cost of the project will be. But, she added, the building effort is progressing according to plan, and work is expected to be complete by August 2024 — just in time for students arriving for the fall semester.
School Rid of Hazardous Waste, Has Internal Frame Rebuilt
The Tisbury School improvement project is operating with a “Construction Management at Risk” contract. W.T. Rich Company, in Natick, Mass., is responsible for overseeing the building process and hiring all subcontractors needed for an agreedupon, maximum-guaranteed price.
The first part of construction at the school site was demolition. Steve Brenner, senior superintendent of W.T. Rich, said his company spent approximately five weeks with its demolition contractor removing all hazardous material from the building, including lead paint and asbestos. The hazardouswaste removal was carried out by a thirdparty hygienist consultant, he told the Martha’s Vineyard Times.
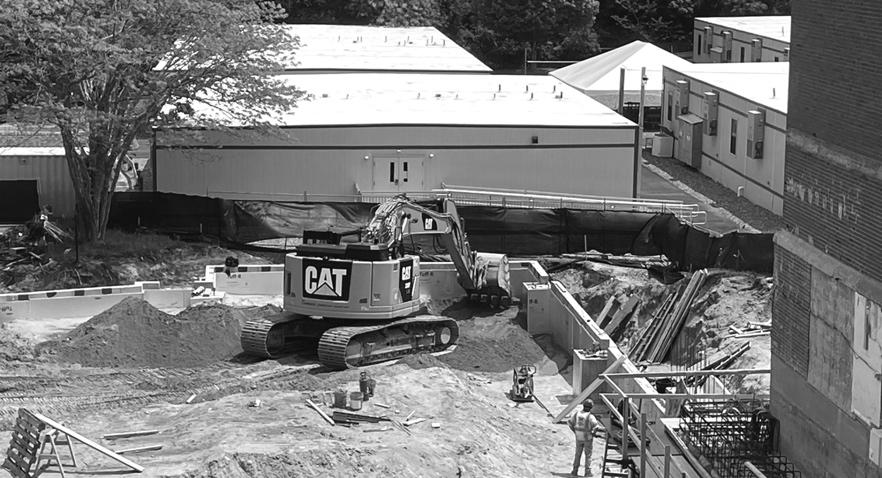
“One of our primary goals was for it to no longer have toxins,” said Michael Watts, a member of both the All Island and Tisbury school committees on Martha’s Vineyard. “It
was a more extensive demo because we needed to do that.”
He added that school officials on the island were aware of asbestos and lead in the building due to previous encapsulation work.
Apart from the hazardous materials that had made their way into the school, many of the original floorboards on the second and third floors were rotted, thinning and full of holes, Brenner explained. There also were some poorly fastened building joints, including a roof that was not secured to meet today’s hurricane standards.
The good news, he said, is the building should last at least another 100 years after the new construction is finished.
List of SchoolÊs Issues Carefully Checked
All the problems Brenner mentioned that needed to be repaired at the Tisbury School were on a list that he maintained, as well as the next major phase of the project: A new addition, which will house the cafeteria, gymnasium, locker rooms and a performance space.
“The old gym was basically a couple of squares of concrete with some wood posts on them,” Watts said in describing the school’s former indoor athletic facility.
He added that the gym only had dirt underneath it, but with no foundation; in fact, it was not even a regulation-sized gymnasium.
When the Tisbury School building was first constructed 94 years ago, it originally welcomed grades K-12. By mid-century, the island’s high school kids moved to another location when Tisbury became a
K-8 facility.
Reality Bested Nostalgia to Get Voters Behind New School
Due to the old facility’s age and history, the people of Tisbury, prior to voting on the school renovation and addition in the last few years, had strong feelings about preserving the building.
“I think people had a lot of misperceptions about the construction and the quality of this building,” Houghton said. “It had sentimental value, but as you get into the building, you realize it should have been torn down [much earlier]. We’re honoring the will of the people and building it the way people voted on, but had people known how diminished the situation was in here, they may not have voted the way they did.”
In April, there were about 35 to 40 workers laying the foundation for the new addition. Following that, work in the school’s main building involved installing plumbing and new bathrooms. Today, the number of crews has increased as the work ramps up, with an average of 100 to 120 people on the job every day, Brenner told the Martha’s Vineyard news source.
Walking through the exposed bare bones of the school, one senses that even in its current state, it has an historic and academic air. Among the things to admire in the lightfilled structure are the Tisbury School’s high, vaulted ceilings, its steel beams, fresh floors and arching antique windows.
The finished product will include classrooms off a central hallway, small “breakout” rooms where students can work in groups, and a sparkling new, three-story multimedia library accessible on every floor
via its new elevator.
Until then, Tisbury School students will continue to learn in modular buildings set up adjacent to the new school’s construction. The temporary structures are equipped for all seasons with heat, air conditioning, electricity, multi-stall bathrooms, classrooms with whiteboards and administrative offices.
The school also uses a small, outdoor-campus area with tables under a tent as well as a makeshift playground/outdoor classroom with short stumps that serve as both seating and platforms for balancing exercises.
When the school is ready for students, according to Houghton, the entire construction project will still not be completely finished.
“Once they are in here, we anticipate there will be additional work that will have to be done on the site, like landscaping and cleaning up where the modular classrooms were,” she explained. “But our hope is to have them in the building for the start of the 2024 school year.”
School Designed to Be Friend to Environment
Houghton told the Times that the goal for the new facility is to be completely emission free. In accordance with that, the school will no longer run on fossil fuels but will instead be powered by electricity and solar power.
Watts pointed to another green upgrade to the property: a 40-ft.-long, 30-ft.-wide and 12-ft.-deep retaining system for stormwater runoff from the school to help mitigate flooding at five corners downhill from the building.
The main drainage system tank is estimated to hold up to 107,000 gal. of rainwater. The massive cistern has been installed and will be located beneath the playground to collect excessive rainwater and runoff. From the retaining system, the water then percolates down into the ground.
There are also two smaller tanks — one in the front of the building, and a second on its east side — to assist the town with stormwater runoff.
Between eliminating the old boiler room, utilizing solar, installing the stormwater drainage systems and making the building as safe and energy efficient as possible, the committee is trying to meet future standards, the Times noted.
On the island, Martha’s Vineyard’s Climate Action Plan, “The Vineyard Way,” has set a goal to reduce fossil fuels to 50 percent by 2030, and to eliminate fossil fuel use entirely by 2040.
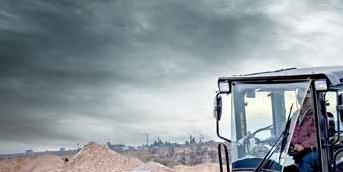
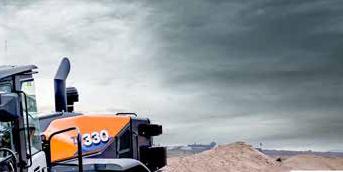
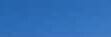

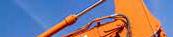
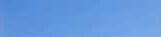
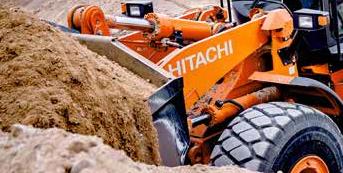

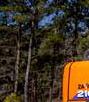


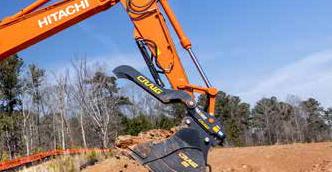




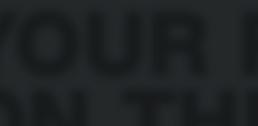

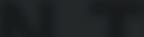



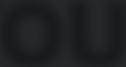
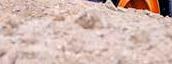
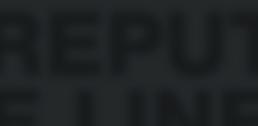


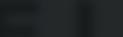






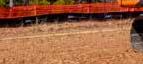




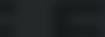





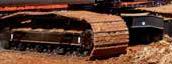
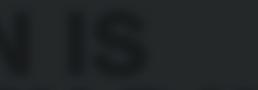




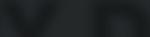

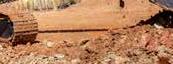
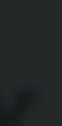







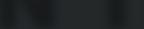

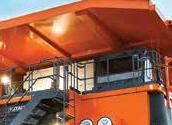



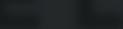
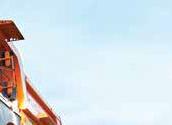




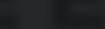
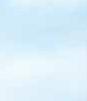






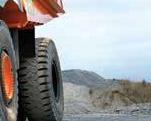

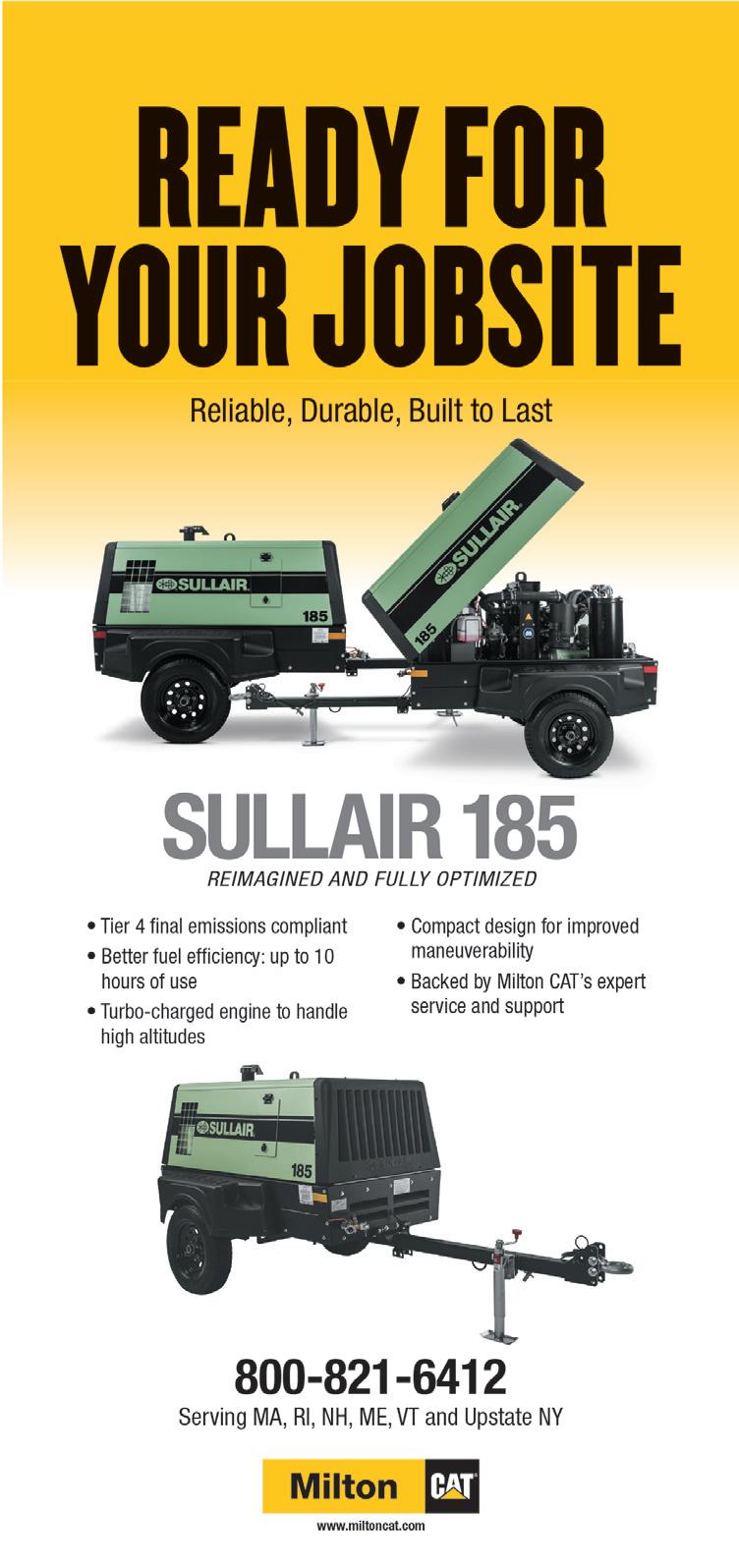
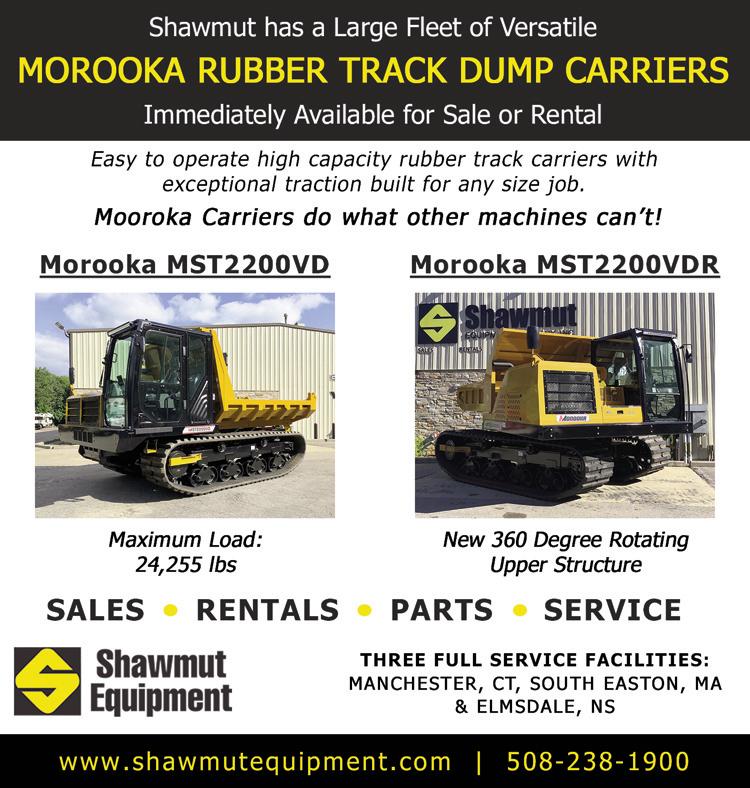
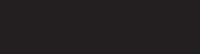
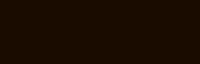
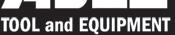
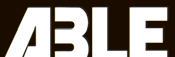
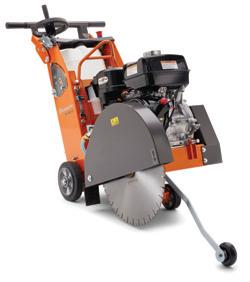


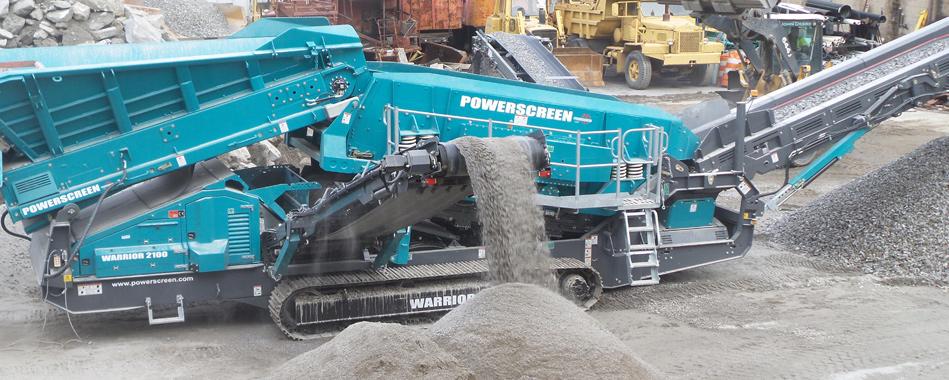
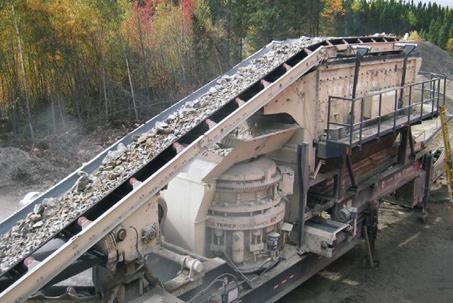
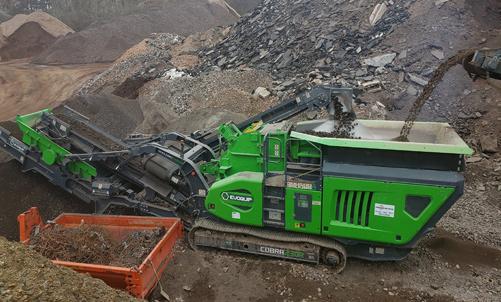



Able Tool Provides Pumping Power in T-Storm Aftermath
to handle all items of work ourselves. This way we can maintain control over our projects.”
According to Mancini, typical projects are bridges with a span of 120-ft. or less that are cast-in-place or precast or culvert bridges.
Currently, the company is finishing up a $2.5 million bridge that is actually two bridges under one contract in Colebrook, Conn. One small bridge is being rehabbed and the other bridge is completely new construction.
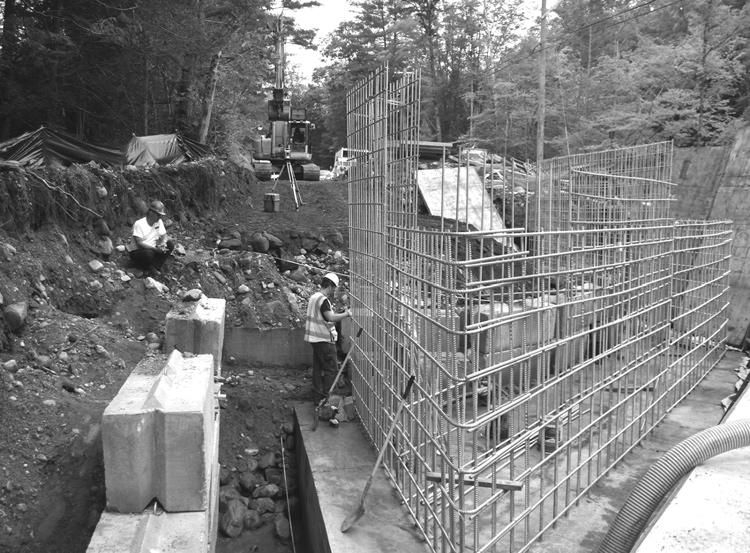
In describing the project Mancini said, “This bridge is founded on ledge with castin-place spread footings and abutment walls, wing walls, all cast-in-place and a steel I-beam bridge with a cast-in-place bridge deck. The bridge is 110-feet long and 30-feet wide.”
The project was started April 3, 2023, and is scheduled for completion in November 2023; NJR Construction is currently running ahead of schedule.
When Construction Equipment Guide visited the site, NJR was pouring the abutment #2 spread footings with approximately 80 yds. of concrete being put in place. As is the case in any bridge construction over moving water, the project has had its challenges with water level fluctuations.
“We got flooded out and had to pump all day to get the site back to the water level that it was at the day before,” Mancini said. “This river is a relatively small body of water, but the water level fluctuates quite a bit. Fortunately, Able Tool & Equipment was able to respond to us very quickly
and get additional pumps to us that could handle the additional influx of water that we were dealing with. Once we were able to get the site under control again, we rescheduled our pour and we are on schedule to complete the pour by the end of the day.
“During the course of this project, we have had two or three freak thunderstorms that have quickly dropped 2 or 3
inches of rain in a short period of time. Fortunately, our key rental partner, Able Tool & Equipment, has quickly dispatched plenty of pumping power to our site to get things back under control with 2 and 3-inch water pumps.”
The major excavating equipment on the site is primarily
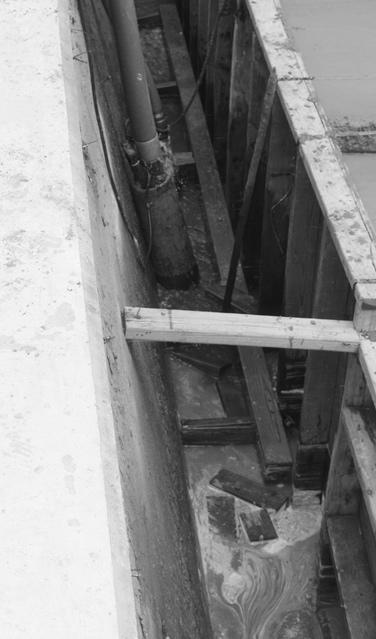

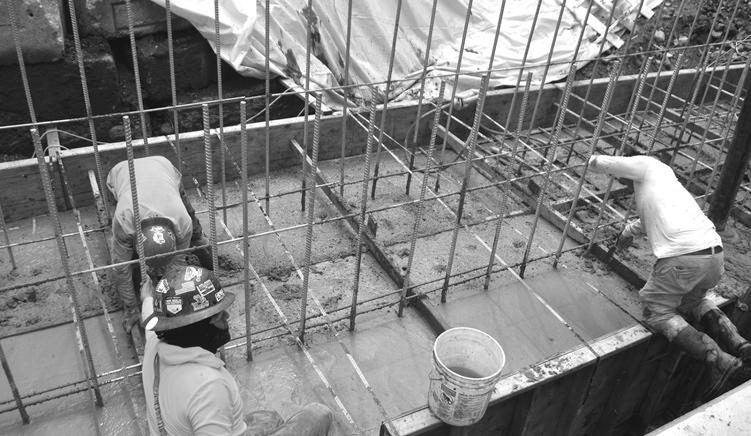
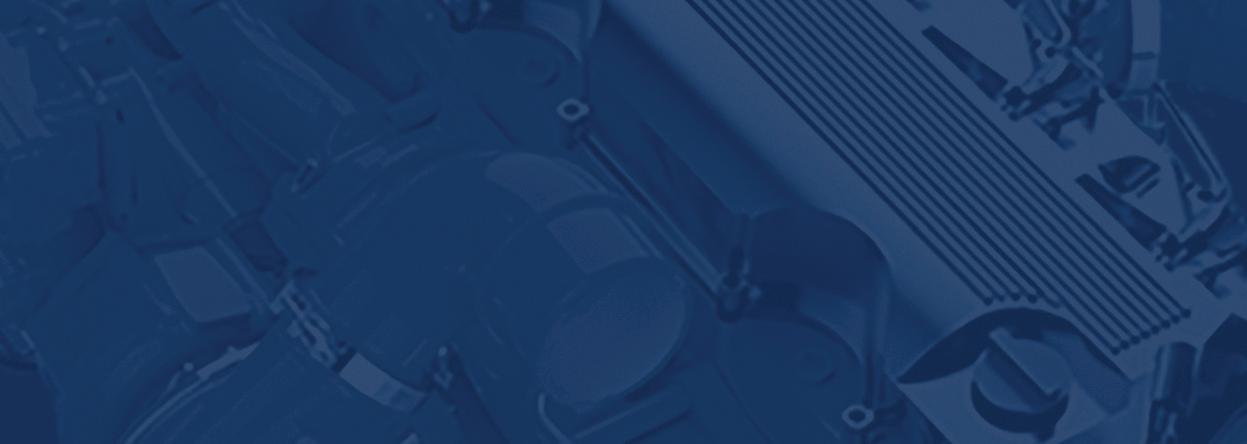
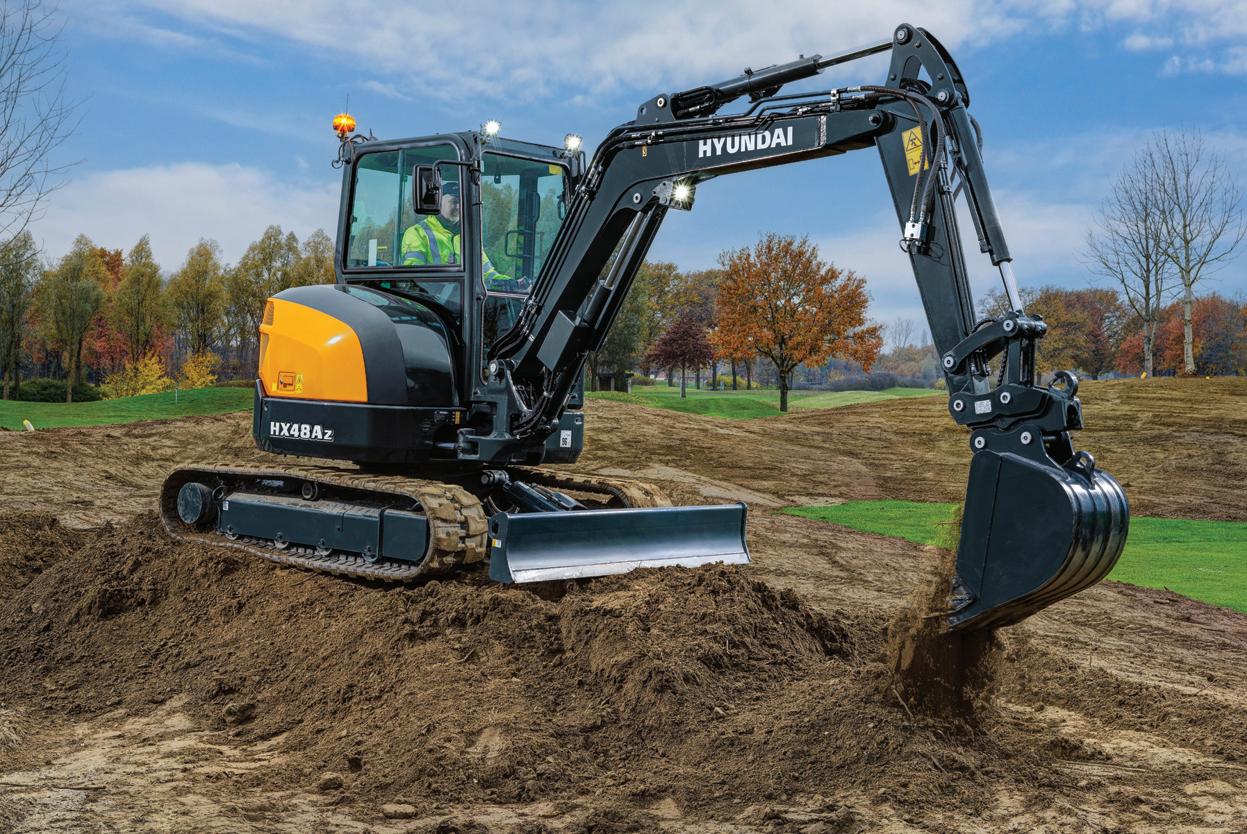

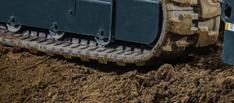

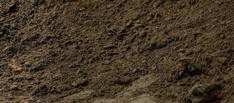
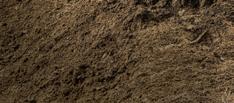

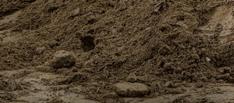


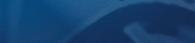
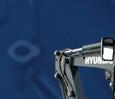
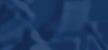
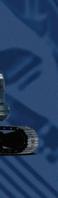
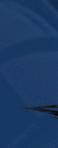



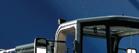
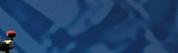
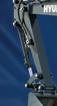

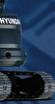

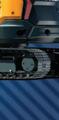

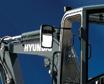





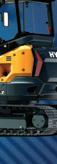

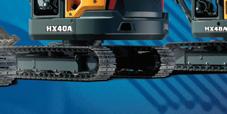
NEW ENGLAND SUPPLEMENT ADVERTISER INDEX
NJR Construction LLC Credits
Crew for Continued Success
NJR from page 16
Komatsu, which NJR has purchased from C.N. Wood. But, the majority of its smaller support equipment comes from Able Tool & Equipment, including small and large generators, water pumps, light towers, concrete equipment and demolition tools.
“Just about anything in that size category comes from Able Tool & Equipment,” said Mancini. “If it is standard pieces that are commonly used on most of their projects they purchase, and specialty equipment is rented. If you walk around any of our sites you will see a lot of Able Tool & Equipment stickers on many of the machines. We really depend on them; they are a primary supplier and that is because their service is excellent. I am fortunate to deal directly with the owner, Derek Bauer. You can’t find a better standup, honest person.”
Employees Key to Success
“I have some fantastic employees that have been with me for a long time,” Mancini said. “My project manager, Ryan Giguiere, has been with me for 13 years. He does an excellent job setting up and managing our projects, often managing multiple sites at one time. It’s not unusual for us to have four to eight projects going simultaneously.
“I’ve got a fantastic concrete crew,” he added. “My concrete foreman, William Sanchez, does an excellent job, as well. When you surround yourself with good people, the end result is good workmanship, and good people and good workmanship has given us a great reputation.” CEG
(All photographs in this article are Copyright 2023 Construction Equipment Guide. All Rights Reserved.)
Reed & Reed Inc. Leads Bridge Replacement Project in Maine
BRIDGE from page 1
Since November 2021, the state transportation department has prohibited all commercial traffic from using the current bridge due to its being “fracture critical.”
While bridges are normally inspected every two years, the Frank J. Wood bridge is inspected every six months by MaineDOT structural engineers to allow for more frequent analysis of its condition and the potential need for further traffic or weight restrictions.
The replacement bridge will improve safety and reliability for the surrounding communities, according to MaineDOT. It will be located on a curved upstream alignment and feature enhancements requested by a local design advisory committee.
Planned to last for at least 100 years, the new bridge will have sidewalks and wider shoulders on both sides (including pedestrian viewing bump-outs), parks on each end, special railings, lighting and other design details as well as unobstructed views of the natural and architectural features of the surrounding Pejepscot Falls site on the Androscoggin River.
Almost 10 Years Passed From Planning to Construction
The state started considering options for the bridge in 2014 and last January
announced that it was ready to accept bids for the construction work after getting the green light from federal officials.
Reed & Reed Inc. of Woolwich, Maine, is the contractor on the replacement bridge project, which is budgeted at just under $50 million.
Subject to inspections and restrictions of the existing Frank J. Wood Bridge, the new crossing project is not expected to have any significant impacts on motorists until 2025. If the work proceeds as planned, MaineDOT noted, all work associated with the construction contract is scheduled to be finished in late 2026, but the new bridge is expected to be open to traffic earlier than that.
The work to replace the bridge comes after years of delays and legal wrangling by some who wanted to preserve the historic structure.
The Friends of the Frank J. Wood Bridge sued state officials in an attempt to stop the project, saying that the old span should be rehabilitated — rather than replaced — and that MaineDOT had failed to accurately estimate the replacement costs.
“I think it’s a good idea,” Bowdoin resident Tim LaCount told WGME-TV in Portland. “This bridge right here is too dangerous. I mean, if you look underneath, the concrete is all chipped and ready to go. And it looks like the design on the new bridge [is] a good modern design.”

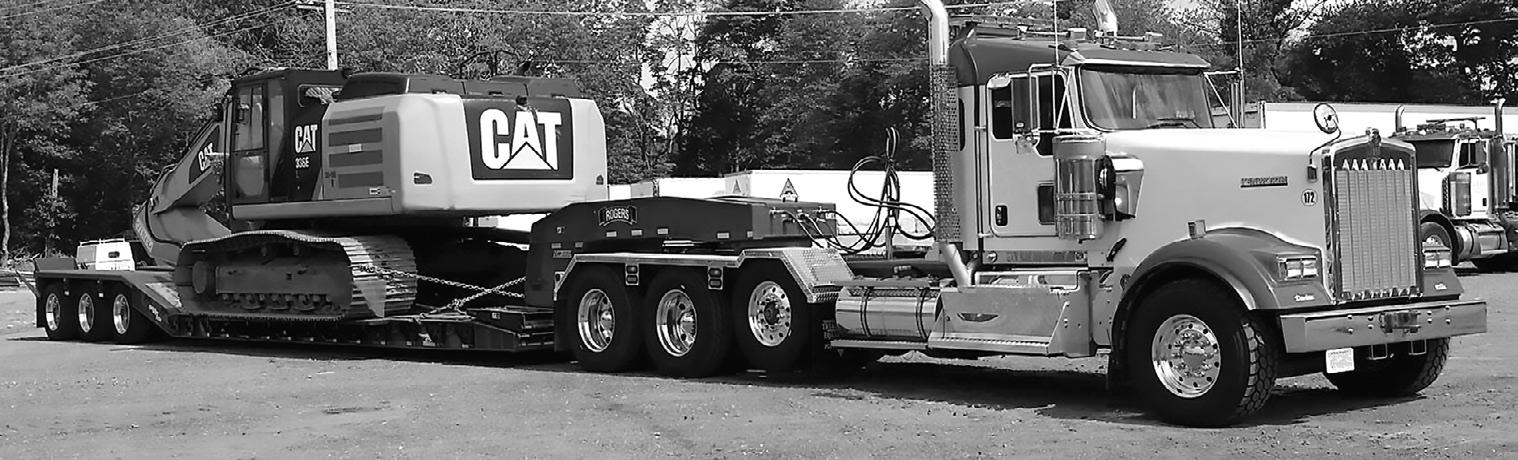
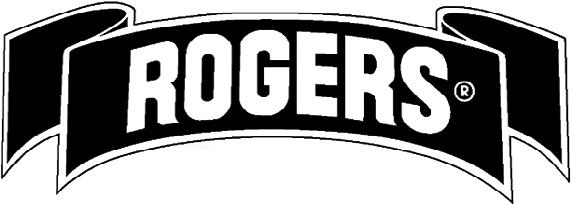

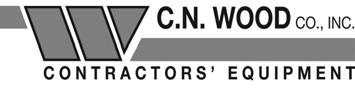
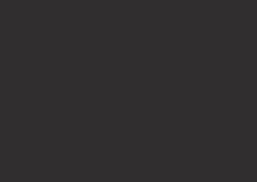
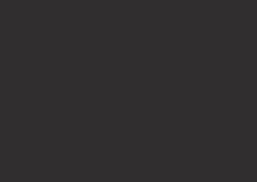
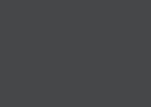
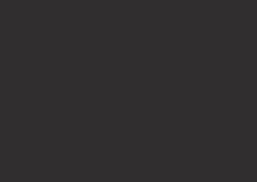
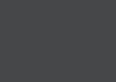
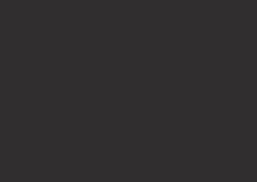
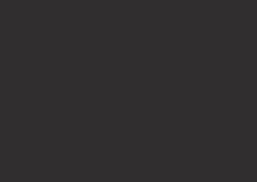
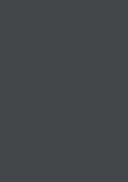



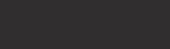







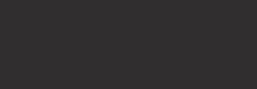

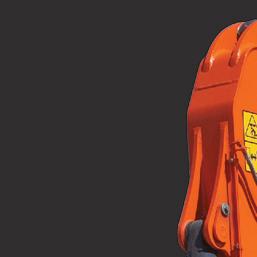
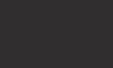
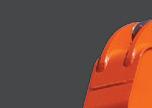
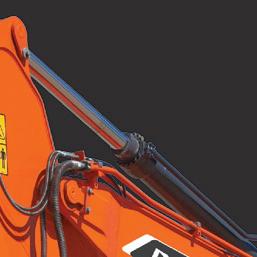
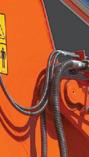
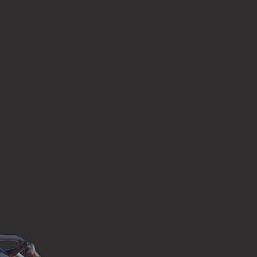
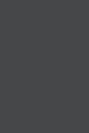

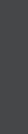


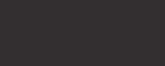

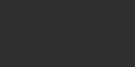

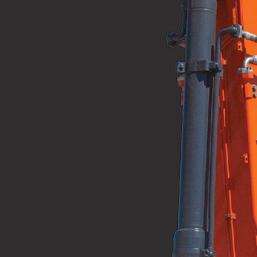
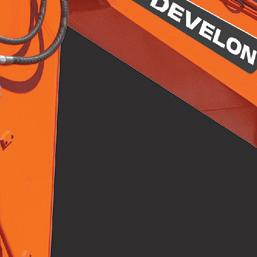
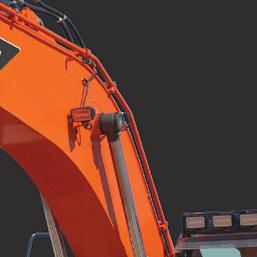
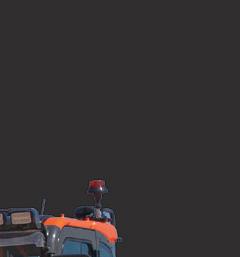


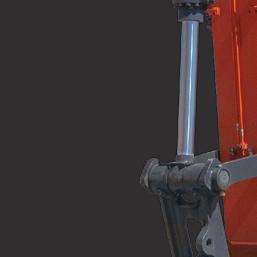
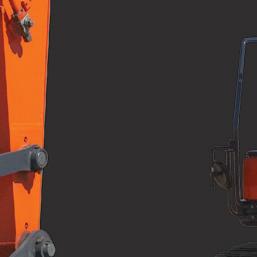

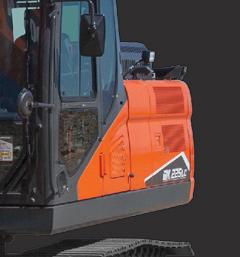

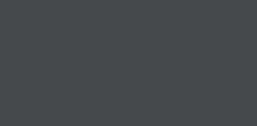
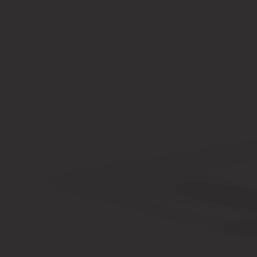
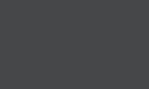

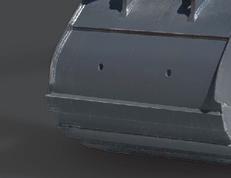
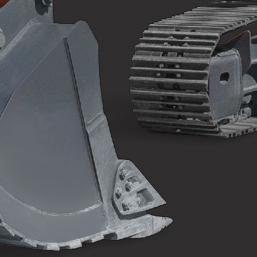

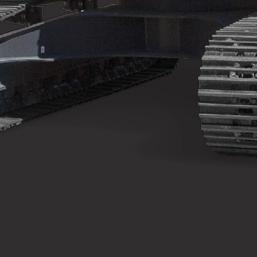

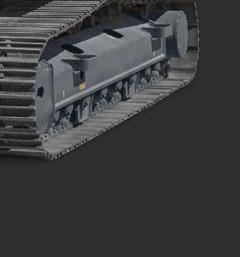



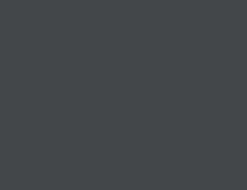
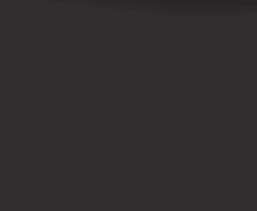

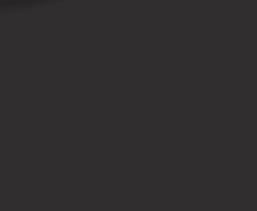

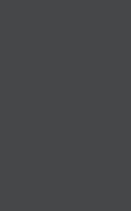
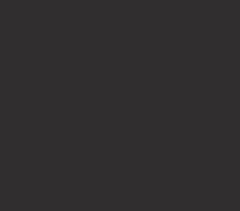