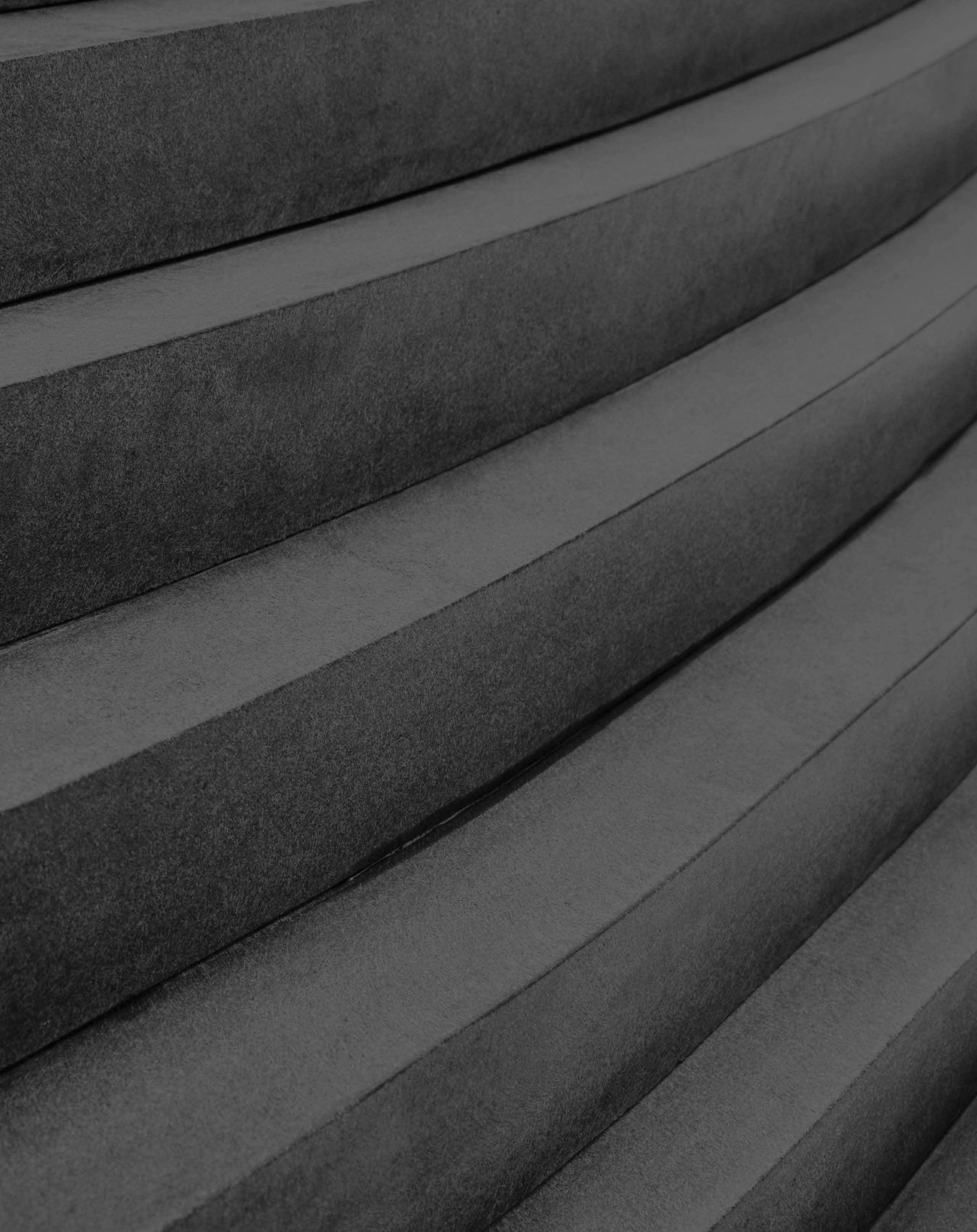
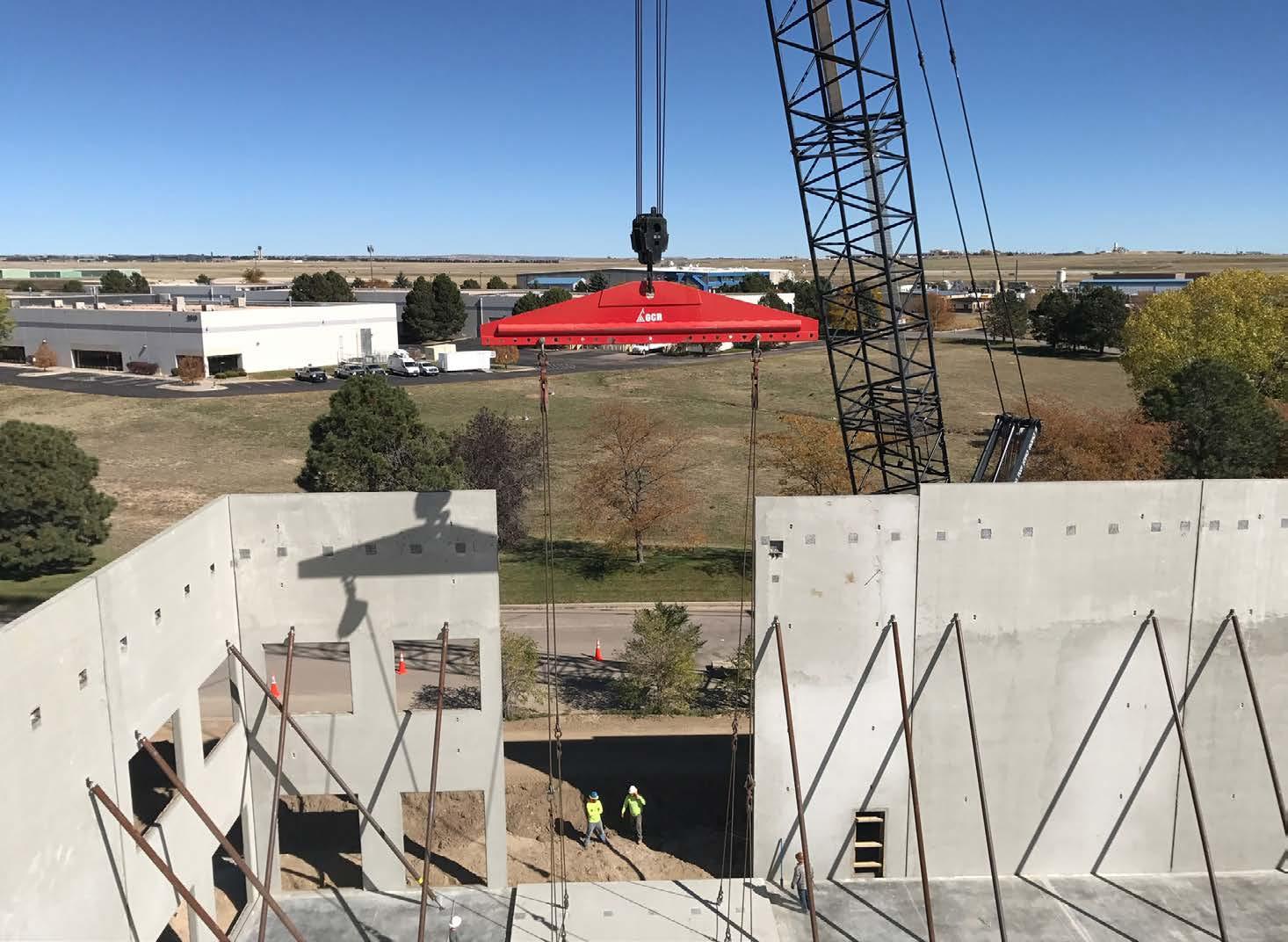
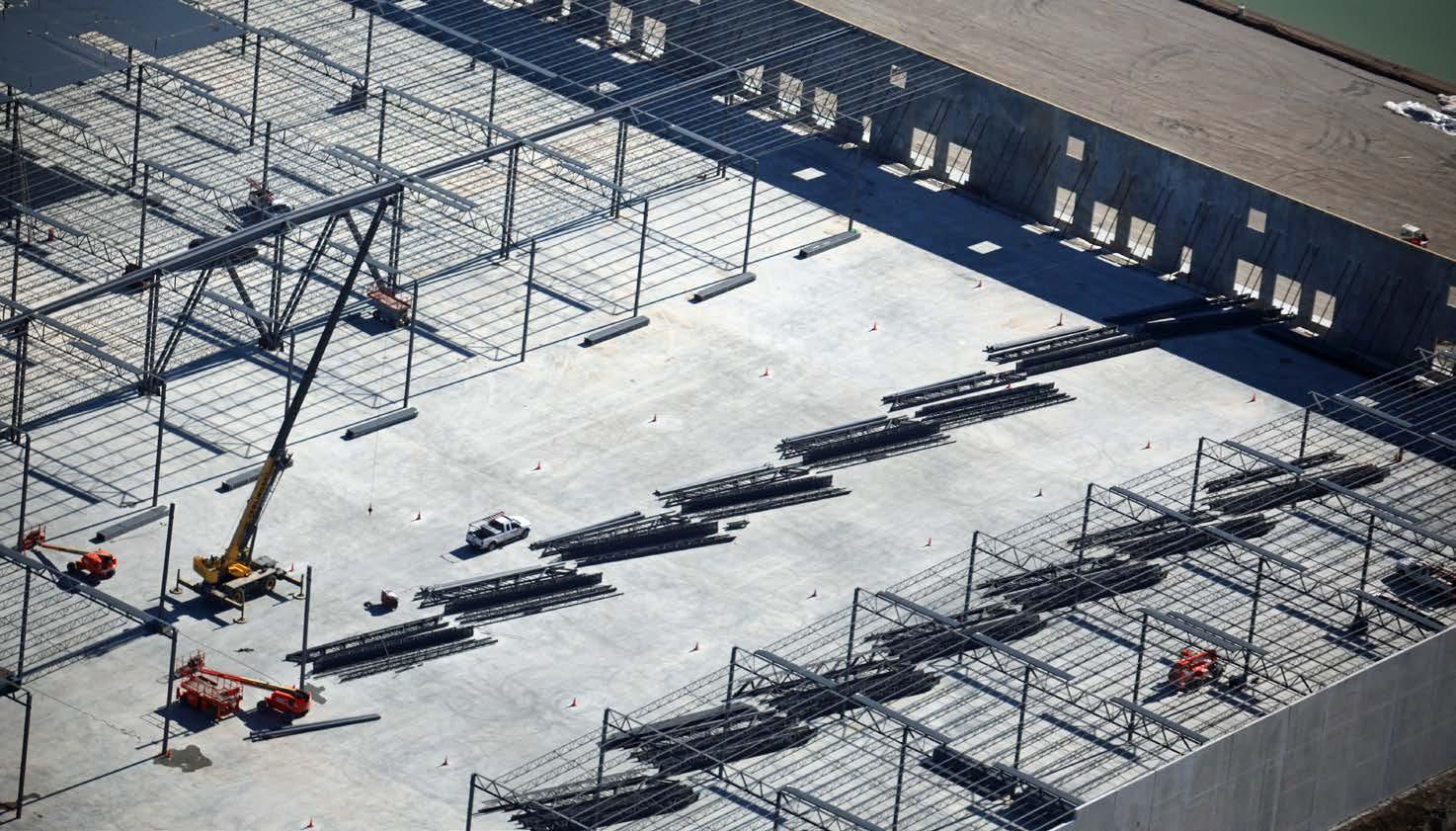
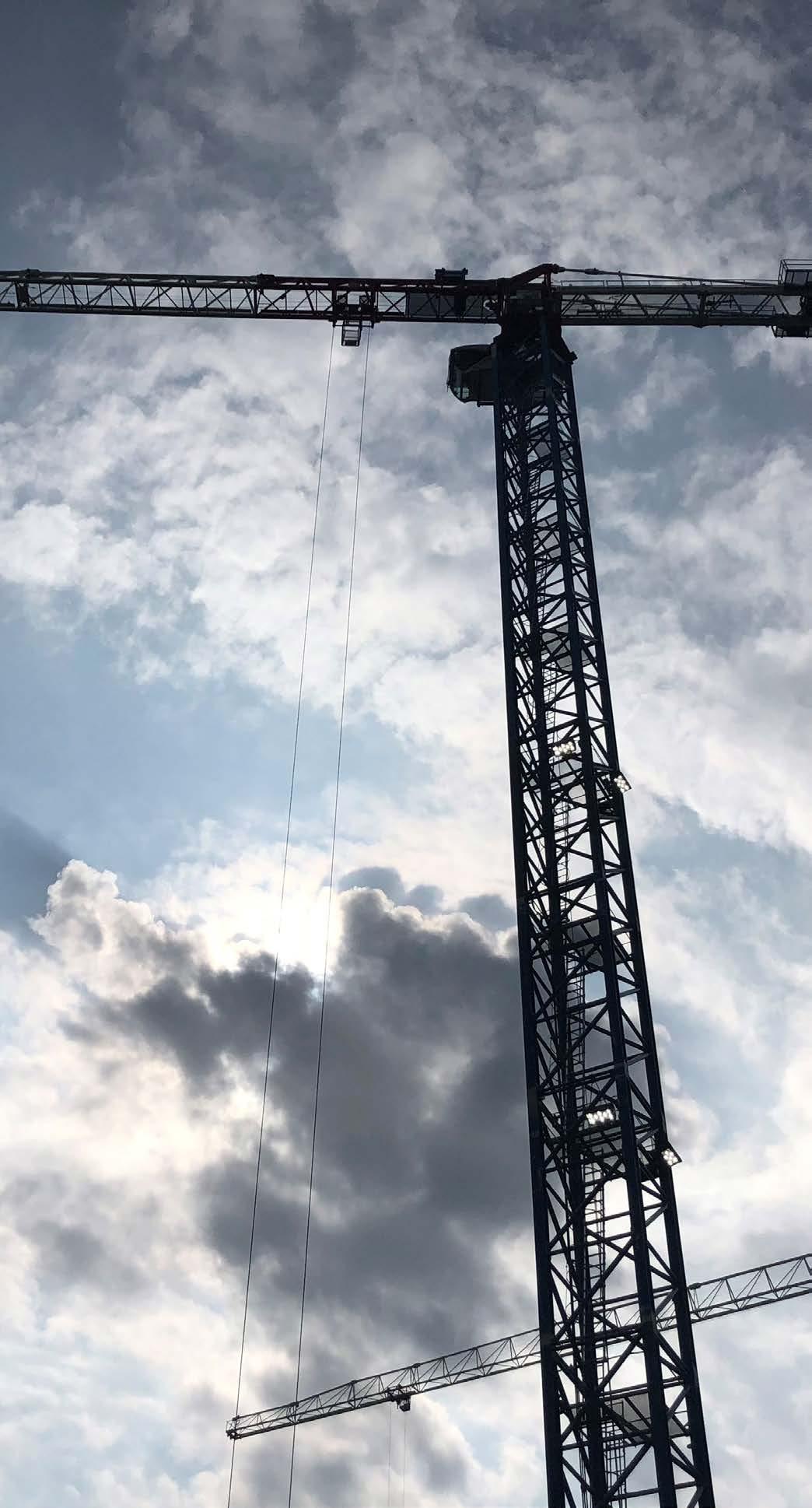
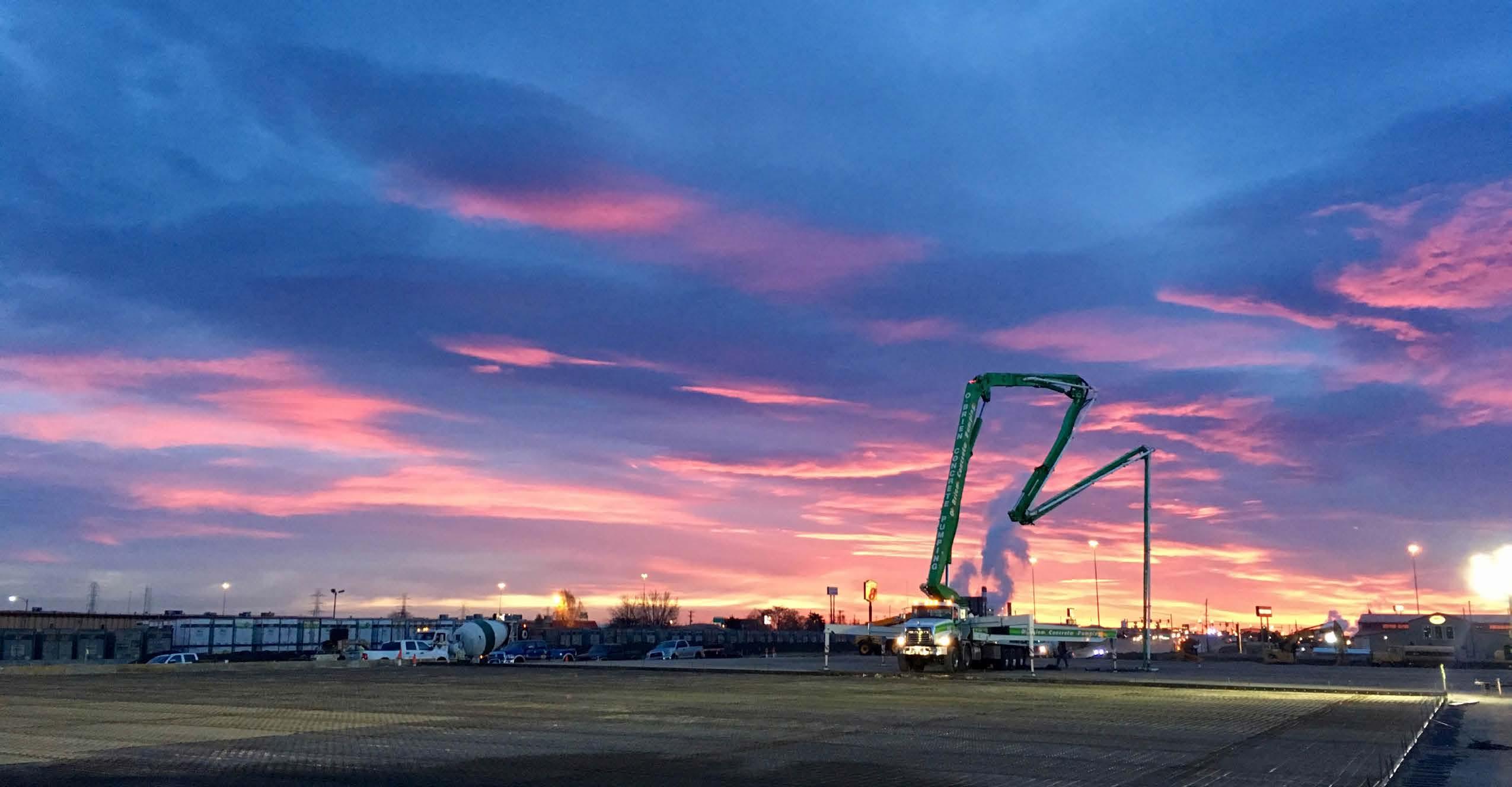
Brinkmann Constructors is the employee-owned, creative leader in the construction industry. We advocate for our clients through straight talk, unwavering integrity, and smart solutions that drive down costs, save time, and deliver value.
We share a passion for finding innovative opportunities to save our clients time and money throughout the construction process.
We go beyond the first right answer to take the second look. We see what others don’t.
We analyze every detail, from preconstruction to completion, to build success for our clients.
These aren’t just words; it’s what we practice on every project, every day.
Even when challenges arise, clients can count on us for straight talk, an even temperament, and unwavering integrity.
The majority of our business is based on repeat relationships that span decades. Our clients know us for consistent, creative solutions that save time and money. And we service each new relationship with the integrity and intelligence that keep our clients coming back.
You can feel confident knowing our team is always prepared and professional.
We’re not just here to lead your project — we’re here to build success, again and again.
We stand up and speak out on behalf of our clients. We have the tough talks and do what needs to be done. We tackle each project as if it’s our own, working in the interest of our clients and owners.
LOCATIONS
• St. Louis, MO (HQ)
• Denver, CO
• Kansas City, KS
• Phoenix, AZ
• Richmond, VA
• 2022 $1.35 B
• 2021 $825 M
• 2020 $760 M
“Our purpose is people. Our passion is building.”
Brinkmann Constructors provides Construction Management, Design/Build and General Contracting services nationwide.
billion
1.2 million SF warehouse and built-to-suit (BTS) for a confidential client. Improvement utilizes the “Box in a Box” approach to create a cold storage distribution center for a national grocery chain. Although typically separated, this project combines freezer and cooler operations under one roof for speed-to-market. The build out adds the following spaces to the building:
• Cooler and Processing (includes Produce Room, Cheese Room, RTE, Commissary and Battery Charging Room): 259,961 SF
• Conditioned Space (includes Ripening Room): 145,974 SF
• Ambient Vent and Heat (includes Battery Charging Room): 320,392 SF
• Consolidation: 118,880 SF
• Freezer: 202,812 SF
• Cold Dock: 65,853 SF
• Turkey Room: 7,886 SF
• Ice Cream Room: 7,637 SF
• Office Space: 25,885 SF
• Engine Room: 3,021 SF
• Maintenance Bldg: 6,261.1 SF
• Dock Positions: 160
• Detached Vehicle Maintenance Facility: 6,180 SF
Brinkmann is currently converting a one million SF spec warehouse into a 600,000 SF industrial drycleaning, laundry, office, and distribution facility for Nuuly (Urban Outfitters Subscription Rental Company). Building improvements include separating the additional 400,000 SF for possible operation expansion or other tenant use. Also, adding boiler, chilled water, custom modular central plant, and chemical storage buildings to support operations, and effectively control hazardous conditions away from plant personnel. Expedited schedules with preordering long lead equipment to support 8 month building tenant improvement upgrades.
OVERALL BUILDING SIZE 1,000,000 SF
MAIN FACILITY 600,000 SF
CHEMICAL STORAGE 4,800 SF
BOILER ROOM 3,300 SF (3) Fulton VMP-150 Steam Boiler System
CHILLER SYSTEM 1,000 SF ( Pump Room) with (8) 80 Ton Chillers
CUSTOM MODULAR CENTRAL PLANT (2) 400 Ton Water Cooled Chillers, Chemical water treatment system, (3) 5,000 MGH high efficiency condenser boilers, with redundancy pumps for all chilled water loop, hot water, secondary hot water, and condensate system.
WASHER & DRYING EQUIPMENT (26) Wet Cleaning Washers, (26) Gas Dryers, (3) Automatic Steam Tunnels, (18) Alternate Solvent Dry Cleaning Equipment
CLOTHING CAROUSEL State of the art 2,000,000 garment automated carousel system
VALUE
$26 million
DEVELOPER/OWNER
URBN
ARCHITECT
New Studio Architecture, LLC
This production, warehouse, and office facility is located in California’s Mohave Desert, serving as the bottler’s center for western U.S. distribution. The structure’s loadbearing, tilt-up concrete exterior is finished with reflective, textured paint.
The project interior combines 544,000 SF of warehouse, supported by 44 truck docks with 267,000 SF of production area containing five bottling lines, and 40,000 SF of office space, and auxiliary appendage buildings. A total management system controls the evaporative coolers, RTUs and occupancy sensors, maximizing the building’s efficiency.
Collaboration between several teams for the design, shell protection, building construction and processing work resulted in successful partnerships and a quality project.
SIZE
851,000 SF, 57 acres
VALUE
$30 million
DEVELOPER/OWNER
Dr. Pepper/Snapple Group
ARCHITECT
GMA Design - St. Louis, MO
GENERAL CONTRACTOR
Brinkmann Constructors as part of a joint venture with ARCO National Construction
“You knocked it out of the park!” _JEFF TURK, VP Development Services, Van Trust Real Estate
This design/build project was the first food production job for Brinkmann. A fast-track schedule included a phased permitting plan to both design and build the plant in 10 months. This project included many unique aspects, including a caustic system, acid PH neutralization system for wastewater, a process water system, compressed air piping, a walkable ceiling and a tank farm design with snow melt glycol system.
This project was designed to LEED Silver Standards to receive tax credits. The Brinkmann team got the owner in on time to allow them to start pretzel production.
DEVELOPER/OWNER
VanTrust Real Estate
ARCHITECT
Gray Design Group
This new aircraft interiors facility for Collins Aerospace focuses on engineering, new product development, unique manufacturing process, and a maintenance repair and overhaul service area. It more than doubles the square footage of the previous facility and has space for future expansion.
Brinkmann used Building Information Modeling (BIM) allowing for better projection coordination, efficient workflows, and 3D visualizations during the planning process, setting the project up for success early on. This tactic allowed Brinkmann to develop and coordinate with MEP subcontractors, integrate owner-provided equipment and provide walk-throughs of the project. Finalizing the detail area layouts early allowed for large quantities of prefabricated equipment, racks, support, and misc. components that accelerated schedule and lowered the overall project costs.
The facility includes a 42,000 SF class 4 clean room for oxygen tank assembly, and 7,500 SF of climate chamber rooms designed to keep relative humidity below 2%, with prefabricated double insulated aluminum walls/ceilings, rapid roll-up interlocked doors and 420 stainless duct work.
246,000 SF office & manufacturing facility
DEVELOPER/OWNER US Capital Development
ARCHITECT
Workplace Architecture + Design
German cleaning technology manufacturer Karcher, moved its North American headquarters and manufacturing center to Aurora, Colorado, with the construction of this 23-acre facility, and added 350 jobs to the area.
Brinkmann was able to save the client more than $275,000 in value engineering solutions by reconfiguring the space to make it more efficient.
375,000 SF, 21 acres
$28 million
DEVELOPER/OWNER
SunCap Property Group / Karcher North America
ARCHITECT
Ware Malcomb
This best-in-class engineering, research and development and laboratory space houses the majority of Leonardo DRS business unit’s development and platform systems integration activities. Brinkmann constructed this 171,000 SF warehouse, office, research facility including all sitework and interior tenant improvements.
After several design meetings and a deep review of each light fixture, the Brinkmann team was able to cut the initial $1.4 million lighting spec in half to $700,000. A code consultant was hired to reduce the original design of the fire walls to not only reduce cost but also accelerate the schedule at the full height demising walls, leading to a savings of $48,000.
This project was finished two weeks ahead of schedule, even with COVID-19, last minute changes from the tenant, and the need for a phased schedule to allow for the Leonardo DRS to start furniture install before the building was complete. This took a lot of additional work by the crew onsite to coordinate with the local AHJ’s to get TCO’s for each phase, which then released DRS to start with their furniture for that phase.
The Brinkmann team communicated regularly at all levels and with all teams to reach the same goal AND deliver the project ahead of schedule.
This cast-in-place, concrete tilt-up warehouse and logistics facility is leased by General Motors and doubled the size of the previous facility GM occupied. It has eighty-four, 11-foot dock doors and six, 14-foot drive-in doors. The bottom of deck elevation is 34 feet above the floor. The parking lot consists of 1.6 million SF of 9-inch concrete.
The MEPs are design/build. Throughout the project, Brinkmann coordinated with General Motors for installation of their equipment for the new parts processing center
1.1 million SF, 146 acres
DEVELOPER/OWNER
NorthPoint Development/General Motors
ARCHITECT
Powers Brown Architecture
These projects are design/build trucking sales and service facilities for Murphy-Hoffman Company.
ALVARADO, TX
SIZE
65,000 SF
VALUE
$15 million
EL PASO, TX
SIZE
97,000 SF
VALUE
$18.7 million
KNOXVILLE, TN _UNDER CONSTRUCTION
SIZE
75,000 SF
VALUE
$21.5 million
CHEYENNE, WY _UNDER CONSTRUCTION
SIZE
65,000 SF
VALUE
$17.5 million
DEVELOPER/OWNER Murphy-Hoffman Company (MHC Kenworth)
ARCHITECT Finkle + Williams Architecture
Lewisville, TX
This project is a new parts and service dealership for JCB Equipment. Brinkmann challenged the paradigms of the client regarding the building type which resulted in a more durable full concrete tilt-up building for the same cost as a pre-engineered metal building. The project is the first of a national program.
SIZE
13,000 SF VALUE
$6 million
DEVELOPER/OWNER JCB, Inc.
ARCHITECT Praxis3
This project consists of a 41,000 SF medical marijuana cultivation grow facility on eight acres.
SIZE 41,000 SF on 8 acres
VALUE
$11.4 million
DEVELOPER/OWNER
LSL Management
ARCHITECT
TR,i Architects
Houston, TX
Boomerang Tube was a manufacturer of off-shore drill stem tube. The project involved complete revitalization of a 50+ year old manufacturing plant constructed from a pre-engineered metal building. The structure was taken back to the steel skeleton and structural modifications were made to raise the finish floor elevation by four feet - lifting it up out of the flood plain, as well as brining the structure up to modern building codes.
SIZE
510,000 SF VALUE
$17 million
DEVELOPER/OWNER
Boomerang Tube, LLC
ARCHITECT
Holleran Duitsman Architects
Colorado Springs, CO
This project tripled Fed EX’s Colorado Springs footprint with a build-to-suit distribution and sorting facility that includes 8,300 SF office area, 225,000 SF warehouse area, and 257 SF remote toilet rooms on a 27 acre site. The distribution warehouse has the capacity to serve up to 153 trucks at a time.
Brinkmann completed full development of site utilities and infrastructure, as well as extension of off-site utilities along the city-owned street improvements in this corridor. The sitework involved concrete paving for the warehouse storage yard and two truck scale platforms.
SIZE
234,000 SF │ 27 acres
VALUE
$16 million
DEVELOPER/OWNER
SunCap Property Group
ARCHITECT
TR,i Architects
This is the second ground facility Brinkmann has built for this client. The facility is 479,000 SF including a 21,000 SF office.
This design/build project had more than 1.5M SF of pavement alone.
SIZE
479,000 SF
VALUE
$42 million
DEVELOPER
Scannell Properties
ARCHITECT
Powers Brown Architects
Brinkmann Constructors acted as a turn-key design builder for this regional distribution and office facility. Half of the tilt-up concrete building was to receive sloped floors with trench drains where the box trucks drive into the facility for loading. This created a sequencing challenge as the sloped space could not be easily used as a casting bed for the tilt-up walls. By applying other sequencing approaches, the team successfully navigated this challenge.
This project also had a complex MEPF systems including vehicle exhaust system, CO2 monitoring, combination of wet & dry fire sprinkler systems, and coordination with owner provided conveyor equipment.
$16.6 million
DEVELOPER/OWNER Confluent Development
ARCHITECT Ware Malcomb
WAREHOUSE
The 99,000 SF CertainTeed warehouse is situated on 33 acres and features six overhead doors and two high-speed doors with an interior rail car pit, office area, break rooms, and meeting rooms.
The sitework involved concrete paving for the warehouse storage yard and two truck scale platforms.
MANUFACTURING FACILITY
This facility is a 143,000 SF steel structure with metal siding. The 122-foottall process tower holds equipment that handles the materials used in asphalt shingle manufacturing. Three electrical rooms were constructed of masonry and structural framing around the perimeter to house electrical switchgear and panels.
2 buildings:
$20 million
DEVELOPER/OWNER
CertainTeed Corp.
ARCHITECT
TR,i Architects, Cooper & Associates
The bioenergy plant is for converting cow manure into biogas via anaerobic digestion. The Dexter plant is surrounded by multiple dairies. The cow manure from the dairies is loaded onto trucks and delivered to the biogas plant. This particular plant will produce approximately 20 million CF per year of biogas.
After it’s processed, approximately 82 million gallons per year of nutrient liquid will be returned via pipelines to the dairies to be used as irrigation. Approximately nine miles of pipeline will be installed to carry the nutrient liquid back to the grazing land.
DEVELOPER/OWNER
Kolb Bionergy NMI, LLC
ENVIRONMENTAL ENGINEER
CHFour Biogas
Riesel, TX
The Sandy Creek Power Plant is one of the largest coal-fired energy facilities in the U.S. Brinkmann Constructors completed the build-out and interior finishes for seven buildings on the 1,000-acre site including complete buildout of 40,400 SF office building, and a 9,720 SF control center. Work also included the fireproofing and construction of fire-rated drywall shaft walls at five stair towers.
SIZE
Build out of 7 buildings VALUE
$3.8 million
DEVELOPER/OWNER
Sandy Creek Power Partners
ENGINEER
Black & Veatch Corp
TAMMY CARR Director of Business Development tcarr@brinkmannconstructors.com
6991 E. Camelback Road C-340 Scottsdale, AZ 85251
t 480.908.7930
c 602.390.0458
BrinkmannConstructors.com