JUNE 2018 ISSUE 005 £3.75
SITE REPORT –XXXXXXXXXX XXX XXXXXXX
Page 16
FEATURE: A future for construction p12
AUDITS: Benefits for scaffolding contractors p19
HEALTH & SAFETY: Investigate accidents –improve safety p20
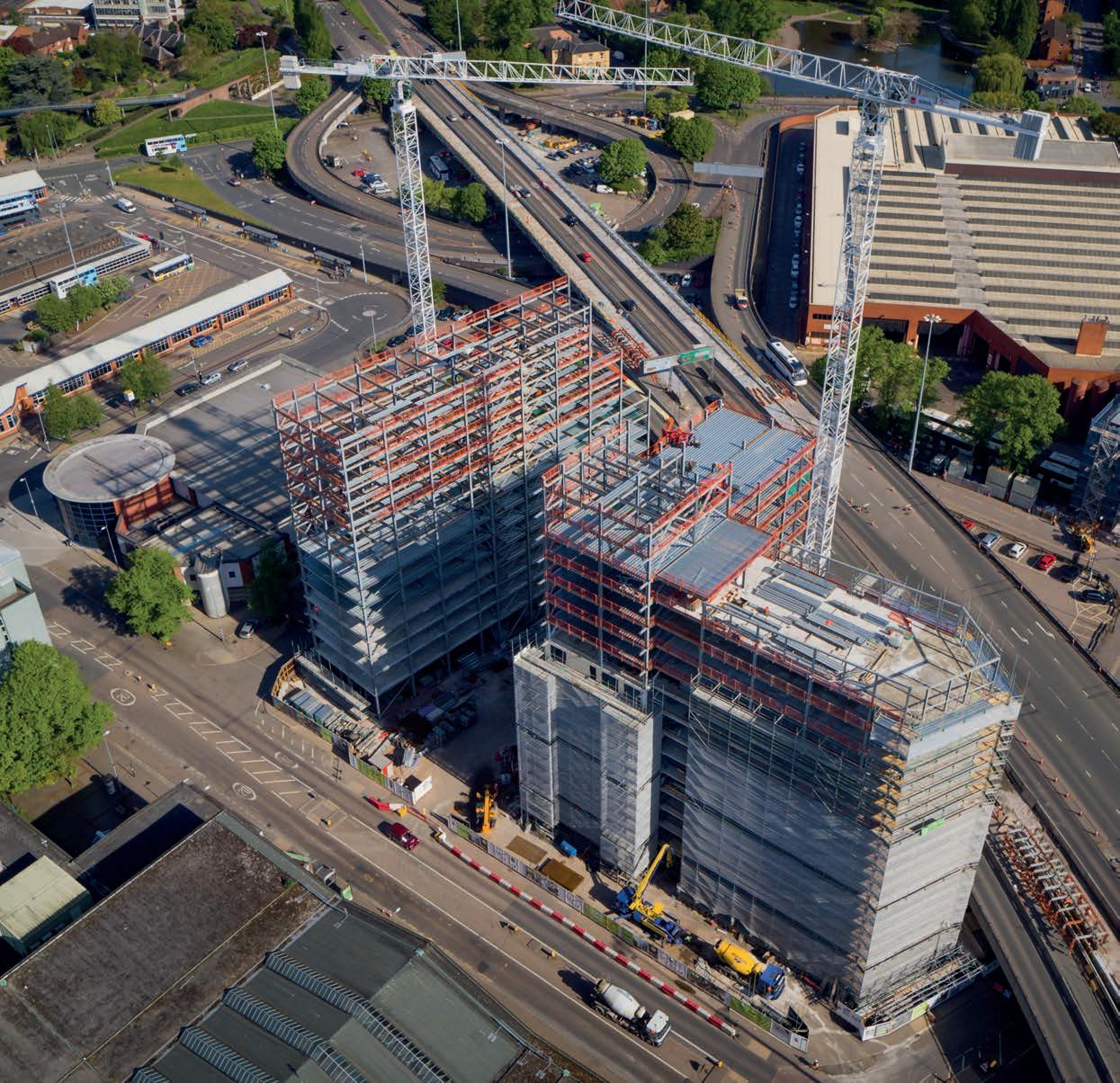
JUNE 2018 ISSUE 005 £3.75
SITE REPORT –XXXXXXXXXX XXX XXXXXXX
Page 16
FEATURE: A future for construction p12
AUDITS: Benefits for scaffolding contractors p19
HEALTH & SAFETY: Investigate accidents –improve safety p20
04 Voice of the sector: The must-listen-to voice of scaffolding
05 Opinion: Confidence and trust at the centre of quality control
10 Commercial: New court case on payment rights
11 Site Story: Scotti fittings
12 Feature: A future for construction
14 Technical: Embracing change in scaffold design?
15 Site Story: P&M Scaffolding
16 Site Report: XXXXXXXXXXXXXX XXXXXXXXXXXX
18 Trade: Updates from the FLTA and FASET
19 Audits: What ’s in it for the scaffolding contractor?
20 Health & Safety: Investigating incidents to improve safety
21 Market Analysis: Update on the construction sector
FRONT COVER:
Cranes towering over Coventry on the City´s tallest new building where Godiva is responsible for scaffolding services for the 1,192-bedroom student accommodation complex.
A report looking at the role that technology will play in the construction industry in the future has revealed that 3D-printed walls, drones and a roof made from recycled plastic bottles from the ocean will all be possible by 2025, thanks to advancements in technology.
The report from futurologist Dr Ian Pearson BSc DSc(hc) and commissioned by Colmore Tang Construction and Virgin StartUp has also revealed that carbon foam, which is lighter than air, will make possible the creation of floating buildings or apartments by 2050.
By 2025, drones will be able to carry large materials up construction sites and, even more remarkably, plastic bottles recovered from the world’s oceans will be recycled to create biometric buildings, or even a roof shaped in the form of a wave.
Over the next decade, artificial intelligence (AI) will be commonplace, linking to sensors
and cameras around construction sites, ensuring that buildings are being developed according to the architect’s plans. Humans will work alongside AIs and will see these robots as not only clever tools but also colleagues, and even friends, as they start to develop unique relationships.
Dr Pearson said: “By 2025, we will already see huge changes in the construction industry thanks to technology with drones, AI and 3D printing all becoming commonplace.”
The report was launched by Colmore Tang Construction, which has partnered with Virgin StartUp to deliver a £10m innovation fund that is open to entrepreneurial companies in a construction industry-first technology accelerator programme called ‘ConstrucTech’.
Turn to page 12: A future for construction
The Scaffolding Association continues to grow and announced in April record membership levels with more than 300 companies now joined in the pledge to raise standards in the access and scaffolding industry.
Association chief executive Robert Candy said: “This continued growth is extremely encouraging and the success demonstrates the sector´s absolute commitment to achieving the very highest safety standards. This is something we at the Association,
EDITORIAL
Editor: Adrian JG Marsh
Assistant Editor: Jenny Gibson
Telephone: 01926 420 660
Email: newsdesk@accesspoint.org.uk
AccessPoint, Althorpe Enterprise Hub
Althorpe Street, Leamington Spa CV31 2GB
Design: Matthew Glover
SUBSCRIPTIONS
AccessPoint is distributed to members of the Scaffolding Association and other selected access and scaffolding businesses. If you wish to receive a copy of AccessPoint or would like to amend or cancel your subscription, please contact either info@scaffolding-association.org or call 01386 764 905.
ADVERTISING
Advertising enquiries:
Adam Turner Tel: 01926 420660 adam.turner@campbellmarsh.com
Scaffolding Association
Tel: 01386 764 945 www.scaffolding-association.org
Email: info@scaffolding-association.org
ISNN: 2055-2033 (Print)
AccessPoint magazine is published on behalf of the Scaffolding Association by Campbell Marsh and the views expressed in this journal are not necessarily those held by the Scaffolding Association or the publishers. The publishers shall not be under any liability in respect of the contents of the contributed articles. The Editor reserves the right to edit, abridge or alter articles for publication.
and our members, are passionate about.
“By having such broad membership that include clients, scaffold erectors, designers, and health and safety professionals, we have been able to assist in creating new opportunities that allow our members to leverage greater value and standards in the scaffolding industry.”
FIND OUT MORE
www.scaffolding-association.org
The Specialist Engineering Contractors’ (SEC) Group is urging the government to act on the lessons from the Carillion debacle and it has drawn up a four-point plan for action.
The joint report from the House of Commons Business and Work and Pensions Select Committee has highlighted Carillion’s abuse of its supply chains. They were treated with “contempt”, said the report.
SEC Group, which represents the largest sector of UK construction by value, welcomed the Committees’ report. Commenting, SEC Group’s chief executive, Professor Rudi Klein, said that the Carillion saga has shone a light on the dark underbelly of construction, adding, “Unfortunately, Carillion is not alone. Payment and contractual abuse is rife in the construction industry.”
SEC Group’s four-point plan for action
includes calls for all public sector projects to use project bank accounts so that everybody is paid within short timescales from the same ‘pot’. It also states that Public Contracts Regulations 2015 should be amended to mandate 30-day payments on all public sector contracts and sub-contracts, and suppliers failing to pay within these timescales be excluded from public sector works.
Retention monies should be ring-fenced in a protected scheme, and the Small Business Commissioner should have the power to fine large companies for poor treatment of their supply chains.
“Unless we act now,” said Professor Klein, “the risk is that we’ll end up with more Carillions.”
Sayfa Systems has created a separate company – RhinoDeck Ltd – to meet big demand from housebuilders for its RhinoDeck work and load platform.
The housebuilding industry is continually looking for better and faster building methods and, according to Sayfa Systems, its new RhinoDeck company will focus on increased service levels for customers.
RhinoDeck provides a safe and stable work platform that also accepts loads up to 600kg/m2. The platform enables easy access to the point of work with tools and working materials close at hand, in complete safety. The modular system is quick to install and has minimal components, meaning it can be adapted to a variety of layouts.
In addition to on-site training, RhinoDeck courses lead to a recognised CSCS qualification, with the card itself endorsed as proof that the worker is qualified to install RhinoDeck correctly.
FIND OUT MORE www.sayfasystems.co.uk
Are you working on an interesting project that you’d like to share with AccessPoint readers? Or, are you working on something unusual or quirky that you’d like to shout about to members of the UK’s fastest growing trade association? Then we’d love to hear from you! Send us your story with any relevant images to newsdesk@accesspoint.org.uk
Essex Scaffolding has successfully completed the process to become an Audited Member.
The scaffolding contractor was the first member of the Scaffolding Association, and for director Mike Worrell, the decision to go for Audited Membership was all about confirming ability and compliance. He said: “We wanted to become an Audited Member to demonstrate to existing and future clients that Essex Scaffolding is fully compliant and experienced within the scaffolding sector.”
The audit process for Essex Scaffolding, which employs over 50 people, took two months from initial enquiry to completion in April. Mr Worrell added: “The Association was very helpful and quick to respond. We found the whole process easy to follow.”
Payment remains the top priority for specialist contractors. Many are only too aware of the stain on our reputation that poor payment records have brought and the damage caused. Without the steady and reliable flow of payments for work done, businesses can grind to a halt, and could potentially crash.
Thumbs up, in principle, for government plans to ban slow-payers from public contracts. However, how will slow-payers be defined? We all know that Carillion were awful payers, and there are others with similar reputations, but before Carillion went bust they were adamant that they paid the majority of their bills on time and that they were nice to subcontractors. Umm…I’m not sure MPs in parliament agreed with them (see page 2).
Herein lies the challenge to legislators; we don’t know just how many construction contracts end in dispute, but it’s plain to see the sector is far more prone to legal wrangling than other spheres of business, and delaying payment until disputes are settled puts the supply chain under immense pressure. Anything to encourage a new payment culture is very welcome.
Inside this issue, barrister Rudi Klein reviews a very recent court case which has implications for scaffolding contractors (turn to page 10). There has been an increase in incidence of adjudications relating to the true value of the work or threats to adjudicate. Procedures can be complicated and the unwary business owner needs to tread carefully in order to protect their position.
We also take a look into the future (see page 12). Drone and 3D printing technology are really changing the world and construction is beginning to embrace it.
The market analysis feature (page 21) shows that the work opportunities are beginning to tighten. Being able to demonstrate that your business is superior to competitors is very import to attracting and retaining clients. Third party endorsement helps to prove this and the audit process (see page 19) indicates the positive client-facing messages that a successful audit brings.
This issue also features some wonderful projects that demonstrate some of the best in class. Access and scaffolding contractors are vital components for clients, but they are so often the Cinderella of the construction and facilities sector. Our top priority is to shout louder with more examples, so please send us details of your recent projects we can feature so that we can do just this.
Adrian JG Marsh EditorWhen the Scaffolding Association was formed in 2013, our aim was to become a voice for scaffolding contractors who felt disenfranchised and not listened to. At that time the industry was dominated by major players and did not reflect, or respect, the significant role that SMEs play within the supply chain.
Well, five years on, and the scaffolding community has woken up and has recognised the benefits of the Scaffolding Association. During the last 12 months, membership levels have boomed and burst through the 300 barrier in the first quarter of 2018 (see news on page 2). This makes the Association the largest trade body in access and scaffolding, with more members than any other trade body.
A key component of our strategy has been to offer support to the whole of the industry, and by adopting an inclusive approach, we have been able to embrace a broad cross section of companies. While this brings challenges, it certainly creates opportunities.
We have begun to break down barriers to change by promoting a collaborative approach. We have worked hard with our procurement partners, and other interested parties and government agencies, to ensure that the right information is available to enable the safe commissioning of scaffolding projects. And we have been rewarded for this as more property owners, developers and contractors have accepted Scaffolding Association members onto their tender lists.
The Audited Member status is now recognised as one of the highest levels of third party accreditation in the construction industry. Regulating the standards in the access and scaffolding sector in this way gives our customer base greater confidence in the competence of Association members who may need to demonstrate higher standards when pre-qualifying and undertaking complex and challenging contracts.
The Association is also encouraging manufacturers and distributors to clearly demonstrate the quality and standards of their products so that the right product or fitting that designers and installers use are suitable for the job. We see independent auditing as the way forward.
Equally, training and skills development are vital ingredients if our members are to succeed. The advent of the Access Industry Training Scheme (AITS) is a new initiative that will help to increase capacity. The access and scaffolding sector needs to deliver a workforce that is trained and qualified to do the job, and AITS is responding to the needs of our members and the wider industry.
In a post-Grenfell era, as an industry, access and scaffolding specialists must re-double their efforts to ensure that designs and specifications are complied with, and that those responsible for installation have the necessary skills and can clearly demonstrate competencies to complete tasks safely.
Expanding the pool of professional scaffolding specialists is helping to create healthy competition, and stimulate service and quality improvements, right across the construction sector. The Scaffolding Association has developed a voice that clients and other interested parties want to listen to, and these people understand – and support – our aim to deliver a fully qualified workforce, raise standards, deliver quality and improve safety.
Robert Candy Chief executive Scaffolding AssociationKnowing that what you are buying is fit for purpose is a fundamental requirement of the supply chain and no more so than when scaffolding contractors are sourcing tube, fittings and system. Donald McGrath of VR Group outlines the importance of trust in quality.
Commercial pressures are a temptation to purchase a cheaper look-a-like or clone that just does not perform as you would expect.
But temptation may soon be a thing of the past because the Hackitt Report into the Grenfell Tower disaster could fundamentally change the construction industry’s attitude towards design and construction, not just from a fire safety issue, but right across the construction life cycle and including access and scaffolding.
It is absolutely vital that clear measures are taken to ensure that in future any building product, including non-mechanical construction equipment, is compliant with appropriate standards and backed by valid test certificates.
Access and scaffolding products demand the highest integrity. Having trust in component quality gives contractors the confidence to use
those components that they know are fully tested and manufactured to a safe standard. So-called ‘value engineering’ has a lot to answer for, as this can push clients and contractors to drive out cost, creating unintended consequences.
Companies spend many thousands of pounds on auditing and testing to demonstrate that what they are manufacturing and erecting meet the standards required. A substandard component, or a poorly fitted one, can lead to catastrophic results.
Demonstrating that suppliers’ products have been manufactured to the correct standard demands rigid quality control procedures and constant checking and verification.
Every month at VR, we take delivery of thousands of system components from our
production plants in the UK and China. It is essential we can prove to our customers that what they are buying meets the appropriate standard.
Every month at VR, we take delivery of thousands of system components from our production plants in the UK and China. It is essential we can prove to customers that what they are buying meets the appropriate standard. Our rigid quality control procedure means we can trace every component from when it was manufactured to who it was sold to. Critical features are inspected and tested on a random selection at independent testing facilities.
Being able to rely on independent test data gives clients confidence that a product can be trusted. In today’s litigious world, such a high level of traceability and testing gives wholesalers and contractors an assurance in the quality of the tube, fittings and system they’re using.
Donald McGrath VR Group www.vrscaffold.comAll that expertise, enthusiasm and industry knowledge means that you can trust Amicus to not only find the best insurance to protect you, your business and your employees, but that you can also rely upon us to do it at the most competitive price.
your language!
www.amicus-insurance.co.uk
Faction Health and Safety Group has launched a new digital risk assessment tool designed to facilitate risk assessment for scaffolding contractors.
The new RAMs (Risk Assessment and Managing Safety) app is a simple piece of software which assists in the creation of risk assessments and method statements, COSHH assessments, manual handling assessments, and HAVs and noise assessments.
Presco Ltd have introduced a new specialist scaffolding fitting developed in conjunction with product designer Phil Holdsworth of West Yorkshire scaffold contractor My Install Ltd.
The new Lay Flat Fitting means scaffolders can lay all scaffold boards flat on a return, removing the need for overlapping and getting rid of trip hazards. Using this Class B fitting, which has been tested to 9.1 KN, also increases the structural integrity of the return while enabling the full scaffold board to be used, gaining useful additional working space. And there’s no need to cut any tube or boards for this fitting to work.
Mr Holdsworth, a scaffolder for over 30 years and director of My Install Ltd, said: “The Lay Flat Fitting is really versatile because it works with double arm scaffolds as well as a traditional fitting. I’ve had the product idea for a very long time and know it will be cost-effective for contractors and improve safety on-site.
“It’s exciting to see the idea come to reality and I’m pleased to be working with a manufacturer such as Presco to be able to bring this to the industry.”
www.presco.co.uk
Forgeco reached a milestone mark in the first quarter of 2018 with the sale of its two-millionth scaffold fitting.
Built upon quality with fittings that are traceable to less than one in 3,000 and adhere to the latest standards, both Forgeco’s standard fitting range and innovative patented fittings are used on many projects around the UK.
Forgeco-supplied fittings include Scotti Fittings, which bypass the need for Deadmen and support contractors with enhancing health and safety on-site while saving time and equipment needed. By helping to alleviate the amount of kit needed to erect a scaffold, Scotti Fittings reduce the possibility of dangerous drops.
The innovative Klawz fitting saves time and adds an extra dynamic to erecting a scaffold. There are many uses for Klawz including reducing the kit needed on normal tube and fit scaffold, or for spacing out beams on system scaffolding where the rosettes or cups can get in the way.
www.forgeco.co.uk
Loaded with over 350 pre-populated risk assessment templates based on key hazards and hazardous activities and over 550 COSHH assessments, the content is in line with current legislation and best practice – and has been developed by an advanced scaffolder.
Over 80 toolbox talks are also available within the app, ready to be downloaded and delivered to the workforce as an effective way to engage them and develop understanding on specific aspects of health and safety.
A free trial version of the app is available from www.rams-app.co.uk
www.factionhsg.co.uk
SpanSet, which provides work at height, load control and lifting solutions, is continuing to run its popular Technical Day programme in 2018 with regular events scheduled throughout the year at its Middlewich Training Centre.
The free half-day events can provide valuable training and guidance on a range of SpanSet’s solutions for people with health and safety responsibilities.
SpanSet Technical Day events are free to attend and Scaffolding Association members are welcome to join.
height-safety.spanset.co.uk/technical-days or jfielding@spanset.co.uk
An integrated access system from scaffolding and access system provider SGB has been used on a major new residential development in Manchester.
A total of 71 mastclimbers have been provided by SGB for the creation of the Clipper’s Quay project, which has been built by Sir Robert McAlpine in Salford Quays.
Clipper’s Quay comprises five blocks of between nine and 11 storeys, incorporating various commercial spaces and over 600 residential units –it is believed to be one of the largest private rented sector developments outside London.
SGB’s business development manager, Karl Hancock, said: “Scaffolding access was originally considered for this project, but a mastclimber solution proved to be much more cost effective.
“We have worked with Sir Robert McAlpine on previous projects, so they were aware of our capabilities in servicing a large project such as this and knew we could supply a range of mastclimber solutions and associated equipment to suit different requirements.
“SGB created a system which included a combination of single and twin mastclimbers, and this proved to be an extremely practical and cost-effective solution.”
www.sgb.co.uk
Worldwide scaffolding, weather protection and stair tower manufacturer
HAKI Scaffolding has unveiled its new global website: www.HAKI.com
The new multi-language website replaces the old versions which featured separate HAKI domains in different languages for different markets. These are all now housed under one user-friendly .com site, with translations into English, French, Danish, Norwegian and Swedish easily available.
HAKI.com provides users with advanced functionality and is fully optimised, regardless of the choice of desktop, mobile or tablet viewing device. The new website showcases the growth of the HAKI brand, its proud 60+ year heritage, the latest business news, project reports from across the globe and a plethora of product information.
New system scaffolding products including the HAKI Bridge System (HBS), Public Access Staircase (PAS), UTV slim stair tower and the MK2 of the brand’s established HAKI Stair Tower system take pride of place in the products section.
The website also features a packed downloads section – offering informative user material, technical data and product information for HAKI clients and prospective buyers alike – and the contact section enables users to easily locate the HAKI sales, training and technical/product support networks nearest them.
www.haki.com
SCP Group has been supplying builders’ trestles, also referred to as Tubular Trestles, for over 20 years. The manufacturer supplies Tubular Trestles in the highest-quality red finish and fully tested to BS 1139-4 with a safe working load of 460kg.
These Tubular Trestles can be combined with SCP’s Trestle Form Easi Clamp Handrail Bracket to create a safe working lift where scaffolding or towers are not suitable.
Available from stock in three sizes, to cover heights from 464mm up to 1,673mm, Tubular Trestles are pre-assembled. Size 3 trestles (1,673mm) can be ordered as a pallet of 90.
www.scp-props.co.uk
VR Access Solutions, working in partnership with GKR Scaffolding and Loughton Plant, has revealed plans to produce a new multi-use fitting – the Saddle Fitting – for use with both tube and fitting and system scaffolds.
The new Saddle Fitting provides scaffold contractors with numerous applications and is being described as a replacement to the structural (Aberdeen) transom.
Applications for this multi-use fitting include use as a one-piece tie with drilled anchors, with guardrail puncheons, and with load-bearing birdcages and scaffolds. Additional uses include with gantry scaffolds, loading bays, temporary roofs, sheeted and debris-netted scaffolds, and guardrails without protruding bolts.
www.vrscaffold.com
Hertfordshire-based ADS Security Installations now holds the National Security Inspectorate (NSI) approved accreditation, meaning the company can provide scaffold alarm installations to NCP115, the NSI Code of Practice for the Design, Installation and Maintenance of Scaffold Alarm Systems.
The NSI is recognised as the leading certification body for the security and fire protection sectors in the UK. Its approval of ADS now means scaffold companies and building contractors have choice when adhering to a specification that stipulates the installation of NCP115, NSI-approved scaffold alarm systems.
Scaffold alarm services provided by ADS include hardwired scaffold alarms (standard), wireless mains-powered alarms with remote keyfobs, battery-powered alarms, and 24-hour alarm monitoring.
www.adssecurity.co.uk
The team at Spirafix recently worked on a project of a different kind for the ‘Breaking Badly’ episode of Amazon Prime series The Grand Tour, featuring Jeremy Clarkson, Richard Hammond and James May.
Spirafix’s challenge was to securely fix a jet engine to the ground at Huddersfield International Airport, where, in usual style, The Grand Tour trio were causing mayhem and creating laughs.
The stunt itself was no laughing matter, and the Health & Safety team were, quite rightly, watching every move to ensure compliance with safety regulations. The production crew needed 12 tonnes of force to fix the 6 tonnes of thrust from the turbine, safely and securely to the ground.
Using the biggest anchors currently in production, the team installed 6 x 75mm anchors and 12 x 40mm anchors using a combination of ratchet straps and brackets.
Paul Clatworthy, operations director and joint owner of Spirafix, said: “It was a top-secret project that was, as you’d expect, a lot of fun but with a very serious health and safety brief.
“It all looks like chaos when you watch the programmes and the Grand Tour team are really entertaining – but we had a pretty serious job to do. Our unique ground anchors proved their capabilities.”
www.spirafix.com
By law, scaffolding contracts must have the following basic requirements:
• all contracts must indicate the due dates for payment; this is essential since all the other requirements depend on this;
• within five days of the due payment dates, the contract must provide for one or other side to issue a notice stating:
• the sum considered to be due at the payment due date, and
• the basis on which the sum has been calculated; (usually the contract specifies that the paying party is to issue the notice.)
• contracts must state the final dates for discharge of each interim payment and final payment;
• contracts must prescribe a period prior to the final dates for payment during which a pay less notice may be issued (in practice this ‘period’ is likely to be one day prior to the final date for payment).
All these requirements are provided for by the Construction Act.
If the paying party fails to issue a payment notice and/or a pay less notice, the consequences are potentially severe. If the scaffolding contractor has issued an application, the amount stated in that application must be paid by the final date for payment. This is subject to a couple of caveats. The application must have been issued strictly in accordance with any contractual requirements, such as where it is to be sent or the time within which it must be issued. Furthermore, it must set out how the sum was calculated (which can be done by attaching a spreadsheet listing the items of work done and values attached to each).
Over the last three years or so there have been complaints from paying parties about ‘smash and grab’ adjudications. Take this example. A scaffolding contractor has submitted an interim application for payment of £50,000. The application is issued in accordance with the contract and sets out how the £50,000 was built up. The final date for payment is 60 days from the due date. By the 60th day, there hasn’t been a valid payment or pay less notice issued by the other party. In fact, there was a pay less notice, but the calculation was not shown. The £50,000 is now due. The contractor immediately refers the matter to adjudication and the adjudicator confirms that there were no valid payment notices and this amount is due with interest and must be paid immediately. This has been labelled a ‘smash and grab’ adjudication.
A recent decision of the Technology and Construction Court has applied a brake to these so-called ‘smash and grab’ adjudications. This was the case of Grove Developments Ltd v S & T (UK) Ltd. The case related to a design and
build contract for the building of a new Premier Inn at Heathrow. An interim application in the sum of £14m had been submitted by the contractor. The judge had to answer the following question: “Can a paying party pay the sum stated as due in an interim application (following an adjudicator’s decision that there was no valid payment or pay less notice) and then start another adjudication to obtain the true value of the sum due?”
The judge answered yes to the question. He gave a number of reasons. The contractor could go to adjudication to challenge an underpayment by the employer. So, why can’t the employer challenge an overpayment?
Going back to our example involving the scaffolding contractor, the first adjudication was concerned with the validity of the notices. In the Grove case, the judge explained that the dispute referring to the second adjudication was about the true value of the works covered by the application. The second adjudication, therefore, concerned a different dispute.
The decision goes against earlier judgements in the Technology and Construction Court. These judgements indicated that the paying party should only have the right to challenge in adjudication the true value of the work at the stage of final payment (or, possibly, beforehand by simply recovering an overpayment in subsequent payment cycles). How does this impact on the scaffolding contractor? There may be an increased incidence of adjudications relating to the true value of the work or threats to adjudicate in cases where the contractor’s application has been upheld by an adjudicator because of the lack of valid notices.
sites. He said: “My role is to assess and evaluate that we are using our resources to the best of our capabilities, ensuring the client and our business are looked after. The time, space and weight savings with using Scotti fittings are quite unbelievable.”
Richard Buhlman, KAEFER’s contracts manager, added: “This product is fantastic for use within our FME areas, where we have to log all material in and out of the controlled clean-condition areas. Therefore, reducing material will certainly reduce risk.
“The nature of many scaffolds means there are a lot of inside edges, so the Scotti fittings not only replace the materials required for a Deadman, but they also reduce materials required for handrails.”
Demonstrating an innovative approach to improving best practice and a keenness to respond to lessons learned from a previous contract helped German-based KAEFER to secure a contract with gas plant owners Uniper for 500 scaffolds over 26 weeks at its Grain Power Station in Kent.
Scotti fittings – available as Ledger Ties, Transom Ties and Aberdeen Ties – are simple fittings which allow for the removal of Deadmen, saving materials, time and weight, and helping to improve safety.
KAEFER’s line manager, Gary Hewitt, said: “One of our contracts managers came across the fittings, and they were a perfect solution for removing Deadmen.”
Aaron Gray, managing partner of Scotti Co, said: “The main issue surrounding Deadmen is that it can be difficult to spot if certain installation methods have not been adhered to, and this can mean there is a potential risk of falling tube.”
Mr Gray, along with Scott Wesson, Scotti Co’s innovation director, worked alongside KAEFER at Uniper’s immaculate Grain Power Station to see how using the fittings could reduce risks, especially as there were a high number of inside edges within the scaffold construction.
Graham Woresley, lean manager at KAEFER, outlined plans to run a lean exercise programme to demonstrate best practice across all KAEFER
This new approach has helped the project to take strides towards better health and safety. Although the selection of fittings is the contractor’s main decision, Uniper has expressed praise for the product, and their contractor.
Uniper plant manager Bill Cliff said: “Any innovation which our contractors want to bring to our site will always be listened to. It was immediately clear that Scotti fittings would help with time and safety, two of my main priorities.”
Future-gazing can give an insight into how the future of the UK construction industry could look, and a report looking at the role that technology will play makes for an interesting read. Adrian JG Marsh reports.
open to entrepreneurial companies in a construction industry-first technology accelerator programme called ‘ConstrucTech’.
The fund will be provided to those companies that can successfully show how their innovation and technology could improve the sector’s productivity, sustainability and skills issues.
Futurologist Dr Pearson said: “By 2025, we will already see huge changes in the construction industry thanks to technology with drones, AI and 3D printing all becoming commonplace.
“By 2050, we could see floating buildings or apartments that could save the housing crisis using carbon foam that’s lighter than air – the possibilities for this really are endless.”
In this technology-based report into the construction industry of tomorrow, 3D-printed walls, drones and a roof made from recycled plastic bottles from the ocean are all detailed as possible developments by 2025, thanks to advancements in technology.
The report, written by renowned future gazer Dr Ian Pearson BSc DSc(hc) and commissioned by Colmore Tang Construction and Virgin StartUp, also revealed that carbon foam, which is lighter than air, will make possible the creation of floating buildings or apartments by 2050.
By 2025, drones will be able to carry large materials up construction sites and, even more remarkably, plastic bottles recovered from the world’s oceans will be recycled to create biometric buildings, or even a roof shaped in the form of a wave.
Over the next decade, artificial intelligence (AI) will be commonplace, linking to sensors and cameras around construction sites, ensuring that buildings are being developed according to the architect’s plans. Humans will work alongside AIs and will see these robots as not only clever tools but also colleagues, and even friends, as they start to develop unique relationships.
Looking more than 50 years into the future, Dr Pearson suggests that by 2075 self-assembling
buildings under AI control will allow a new form of structure – kinetic architecture – where a structure is literally thrown into the sky and assembled while gravity forms the materials into beautiful designs.
However, it is 3D printing that will steal most of the construction headlines in the immediate future, according to the future-gazer. Cheap homes, built quickly using 3D printing, will essentially put an end to the housing crisis.
The report was launched by Colmore Tang Construction, which has partnered with Virgin StartUp to deliver a £10m innovation fund that is
Andy Robinson, Group CEO of Colmore Tang, said: “This forward-thinking report has shown that technology is set to have a hugely positive impact on the construction industry. However, we need to discover those exciting and innovative start-ups whose products and services could deliver the technologies and innovations that will be the key to future success.”
Colmore Tang Construction and Virgin StartUp hope the £10m innovation behind ConstrucTech will be the spark to improve lacklustre productivity levels and also begin addressing the need to re-skill over half a million construction workers to suit the industry’s future. Interested start-ups can apply to be part of ConstrucTech.
An aerial view of the future Drones have emerged as a highly viable commercial tool with applications in numerous sectors, most notably construction. This isn’t surprising, as their benefits range from enhancing on-site safety to achieving a level of project monitoring not previously possible.
In the construction industry, drones provide easy access to large or difficult sites as well as complex or tall structures. They can gather aerial data, mapping information and images.
As of spring 2018, the UK government released a new set of regulations concerning the use of drones. The Bill’s intention is to increase overall drone safety while ensuring that Britain remains at the forefront of drone tech development. These measures also seek to expand the use of drones with businesses and infrastructure.
If you are considering using a drone in your business, the Civil Aviation Authority (CAA) will be able to provide information on ensuring safety on-site.
www.caa.co.uk
design, resulting in very little knowledge of the process and no driving force for change. For this reason, rather than promoting change, this knowledge gap just halts it.
I believe this to be the largest contributing factor as to why the change has not been made, although there is little proof of this apart from experience within the industry.
order to obtain the permissible, an ultimate value has obviously been obtained through testing.
All scaffolding products will be tested to failure with 95 per cent confidence limits. If the factor of safety is known, which an engineer would always want to know, then the characteristic/ultimate value of resistance can be obtained by multiplying the permissible by the factor of safety.
Scaffolding is not often directly seen and managed by a client and the professional team because it’s the principal contractor who manages the construction phase and hence manages the scaffolding and temporary works – including design. Therefore, it’s essential that the appointed scaffold engineer adopts a design philosophy that is focused on contract safety and efficiency.
Clients, architects and contractors should view the roles and responsibilities of a scaffold engineer, and the ways in which they are employed, as professional engineers who employ the correct design philosophy – sometimes the correct philosophy is overlooked by the need for a ‘quick design’.
The typical stages within the scaffold design process follow the Association of Consulting Engineers’ (ACE) conditions of engagement, Agreement B. The ‘thinking’ stages in the pre-construction and feasibility phases enable imagination – rushing into something head first does not produce the most innovative or efficient design but could create a headache.
Imagination is the consideration of how members will interact in a 3D plane and what loading they will be subjected to. It is imagination that provides solutions to engineering problems which are cost effective, save on time and improve on safety.
The analytical stage comes
second – this stage obviously requires ‘thinking’. However, it is more focused on a thorough understanding of the codes of practice used in design.
Where the design process employs calculations, this will ensure that the safety of the structure is never compromised and that inherent redundancy is present in the design and in the final structure.
The scaffold engineering sector currently adopts the Permissible Stress Design whereas all other structural engineering branches have now switched to the Limit State Design.
The two different design philosophies have their own advantages and disadvantages when considered with respect to the design of scaffolding. However, it is evident in comparison that the advantages of limit state design far outweigh the benefits of permissible stress design.
So, why has the transition not been made and the potential benefits of adopting a new basis of design – the way forward seems extremely obvious to me. The biggest contributing factor is largely down to the scaffold engineer’s unfamiliarity with the limit state design and a certain affinity with permissible stress design.
This ‘knowledge’ gap is largely due to scaffold engineers being trained in-house; the vast majority of engineers trained pre limit state
Another reason why the scaffold engineering sector traditionally adopts the permissible stress design method is that site personnel do not generally understand the concepts of the limit state approach, whereas they do understand the terms ‘allowable’ and ‘safe working load’.
Site personnel do not need to understand the concept of limit state design; they just need to know what load can be applied to the structure before the factors are applied – the serviceable load. The terminology is just slightly different but can be portrayed in the same manner. One reason why scaffold engineers believe that limit state cannot be adopted is that all materials and components are stated in terms of ‘permissible’. This is very true; however, in
Many believe that limit state approach is much more comprehensive and provides a much more versatile basis of design, resulting in more efficient structures and reduced construction costs.
We as scaffold engineers should move into a new era and embrace the change with open arms. I am sure that the change would cause some trepidation by the sector, but that this would soon be overcome when the benefits are seen.
Ryan Berry MSc (Eng) BSc (Hons) Managing Director / Principal Engineer Creator Scaffold Design and Temporary Works Consultantswww.creator-scaffolddesigns.co.uk
In an extract from his book The Application of Limit State Design to Temporary Works, Ryan Berry from Creator considers what design philosophy contractors and their clients should follow when carrying out an engineering design role in scaffolding.
Highlighting some of the challenges, Lee Roberts, contracts director of P&M Scaffolding, said: “To minimise the footprint of the scaffold on the terrace to enable enough space for works to be carried out efficiently below, we set the scaffold out on the terrace wall above the ever-busy Duke St below and spanned the roof back to a supporting beam tied into an existing concrete slab.
“Noise reduction escaping into the work environment was also a main consideration, and we addressed this by installing acoustic panels to the inside perimeter and underside of the temporary roof covering.”
Also important within the brief was ensuring the building retained its aesthetically pleasing look, for both the public and Selfridges. This was achieved by ensuring the scaffold was built exactly to design specifications and then shrink wrapped in a Portland Stone-effect sheeting to provide a tight and smooth finish. This not only helped to retain the building’s attractive aesthetics during the renovation works but also ensured the store remained watertight throughout.
P&M Scaffolding, working for main contractor ISG, has completed the installation and removal of scaffolding as part of a 22-week renovation project of the 4th Floor Corridor at Selfridges London.
The scope of works consisted of providing a temporary roof covering to the floor’s terrace while the existing roof was exposed and the corridor external wall removed. The store and offices remained live during the works.
Mr Roberts added: “We carried out all of this work under the pressures of knowing that our scaffold had to be built safely over the busy London streets below and knowing that we were responsible for ensuring that the exposed area of one of Britain’s most famous stores remained watertight and protected.
“A team of four operatives from P&M worked on this scaffold construction and we have received great feedback on our approach to the project.”
CCS Scaffolding is well underway with a year-long contract to provide scaffolding for significant improvements to the A14 – currently the UK’s biggest road construction project. Jenny Gibson spoke to Edward Farrell, health and safety executive at CCS, to find out more.
On a 21-mile stretch of the A14 between Cambridge and Huntingdon, a 2,200-strong construction team is busy upgrading the dual carriageway to three lanes, including the creation of a new 17-mile bypass south of Huntingdon that will have four lanes in each direction. This much-anticipated and much-needed infrastructure project will add additional capacity, boost the local and national economy, and cut journey times by up to 20 minutes.
Kent-based CCS Scaffolding, along with sister company Sian Formwork, is one of the many subcontractors helping to deliver this upgraded road system, which is due to open to traffic by the end of 2020.
on many occasions previously – to remove time pressures and allow CCS and Sian Formwork to concentrate on other aspects of the project.”
On appointment, CCS’s site manager attended programme and progress meetings to ensure materials and labour resources were on-site as required to meet the project’s programme objectives.
Mr Farrell continued: “The interaction between the scaffold design team and the client’s temporary works team helped to make sure that the designs for some bridge abutments were fully approved, and ready for when the structure was released to us.
“This avoided delays and meant our scaffolders could help to keep the programme on schedule.”
The specific contract awarded jointly to CCS Scaffolding and Sian Formwork is for Section 2 of this A14 Highways Project. The award, given by the A14 Integrated Delivery Team on behalf of Highways England, involves the construction of various abutments and piers for the required bridge works.
CCS’s health and safety executive, Edward Farrell, described the tender process. He said: “From the outset we had to take into consideration the planning, the materials and the complexity of the structures required, along with the specific deadlines all aspects needed to be complete by.
“Given the largescale structures and multiple bridges, we decided to work with a dedicated scaffold design company – one we’d worked with
The structures across Section 2 of the A14 project were all generic abutments and wing walls, all tasks that CCS and Sian Formwork had performed as a joint venture many times before. The BN03 structures had three separate sets of abutments all around 60 metres long, 8 metres high and 1.8 metres thick. This scale required multiple boarded lifts and for all structures to be freestanding with buttresses installed at regular intervals, and with high amounts of kentledge, to ensure the safety and structural stability of the scaffold for Sian Formwork and other contractors needing to install bearing pads and large heavy duty steel bridge beams.
CCS used a system scaffold solution to increase production rate and enhance safety processes while erection, adaption and dismantle occurs at BN05 structures.
For one of the BN05 sections, pre-set formwork shutters were made for sets of three round columns for the bridge sections to sit on. Mr Farrell explained: “Once we’d started the section and we were erecting scaffolding for the circular piers, we soon came to the conclusion that by
using a system scaffold approach there was a quicker and safer way to erect these specific shaped columns.
“This also meant we were able to overcome any safety issues with regards to working at height by installing our guardrails via our advanced guardrail tools.
“This had the benefit of saving a large amount of labour and time resources by not using tube and fitting and not needing to install half lifts
or installing edge protection via scaffold steps,” he explained. CCS has an average of 20 scaffolders on-site and commenced the contract in March last year. As a whole team with Sian Formwork, there are around 60 operatives working on this A14 project.
Our experienced customer driven team provides a seamless service from product development, supply chain management, production, quality control, delivery and local engineering support available for fast, effective solutions where required.
FASET enjoyed a successful three days at the Health & Safety Event, which was held at the NEC in Birmingham in April, spreading the latest safety netting and temporary safety systems guidance to many of the 6,000 visitors.
The packed event – billed as ‘Three Days to Save a Life’ –featured 48 conference and seminar sessions and 45 different industry speakers, along with 200+ exhibition stands. FASET was represented on the Access Industry Forum (AIF) stand by managing director Tony Seddon and Becky Clutton.
Hundreds of event delegates attended the stand to talk netting, edge protection, stair
towers, training and temporary safety systems and to look at FASET’s freely available safety guidance. And FASET also played a part in the launch of the new ‘No Falls Foundation’ during the event, which aims to have a work at height industry with zero falls.
Mr Seddon said: “It was a very productive three days, helping us spread the safer work at height message wider, with a lot of genuine enquiries.
“In fact, the event was such a success, we are now looking to be part of these events in Manchester and Glasgow later in the year.”
www.faset.org.uk
The Fork Lift Truck Association (FLTA) is helping to overcome confusion regarding what constitutes ‘fair wear and tear’ of fork lift trucks – a long-standing issue for the industry –with the creation of its Fair Wear and Tear Guide.
Businesses that rely on rented lift trucks are urged to take good care of them. Failure to do so, warns the FLTA, places them at risk of large end-of-contract repair bills.
“Disagreements between customers and dealers can quickly lead to costly court cases and damaged reputations all around,” explained FLTA chief executive Peter Harvey MBE.
“At the end of a typical five-year contract, some degree of deterioration is expected. But, as you would expect when using a leased car, any damage caused by carelessness or neglect – be it a hole in a seat or a cracked mirror –
must be paid for.”
The FLTA advises that ‘fair wear and tear’ refers to the degradation of components consistent with manufacturer’s recommended use, and that dealers and customers need to agree what condition a lift truck should be returned in and what damage is acceptable before equipment is leased out.
Mr Harvey MBE added: “Damage caused by carelessness or improper use, for example scratched bodywork or a dented overhead guard, is simply not ‘wear and tear’.”
The Fair Wear and Tear Guide – available through FLTA members –uses photographic examples of real lift trucks returned at end of contract to show what is and is not acceptable damage.
It’s a good question, with lots of very good answers.
An audit ascertains adequacy and competence of an organisation to work within a given industry against set criteria that assess and measure performance. This sentence alone points to the many benefits of being audited.
For contractors, an audit is an essential part of pre-qualification to tender for a contract. Within the access and scaffolding sector, PAS 91 (PAS stands for ‘publicly available’ specification) is the specification that the majority of pre-qualification questions are based on. Being audited to the highest level – Level 1 – of the PAS 91 Three Assurance Level Model is a way for scaffolding contractors to demonstrate their competence as a supplier.
Alongside the client-facing benefits of having been audited come the benefits of verifying internally that a company’s methods and procedures are in line with industry best practice.
The audit process developed by the Scaffolding Association is linked to Audited Membership status. Specifically for scaffolding contractors, this membership level enables contractors to demonstrate that they operate to the highest standards.
Membership offers an independent two-stage audit certified by a UKAS-accredited certification body.
The audit process reduces the burden on both clients and contractors by increasing understanding and building on the widely
applicable range of standards within the industry to provide a Scaffolding Specific Procurement Process. This audit demonstrates a contractor’s ability to safely manage and undertake work and assesses it against criteria which are specific to the scaffolding industry.
Stage One: Desktop – This consists of a remote review of documentation, including policies and procedures, training records and a company’s incident reporting system, against a Scaffolding Specific Procurement Standard to establish compliance.
Stage Two: On-site – Verification takes place against the Scaffolding Specific Procurement Standard looking at how the company’s documentation is implemented on-site. This part of the audit will focus on (but is not limited to) Work at Height, Temporary Works, Construction and Design Management (CDM) Regulations 2015, Control of Contractors, Hazardous Substances and Personal Protective Equipment (PPE).
Once the audit has been successfully completed, contractors are issued with a copy of the audit report and certification from the certification body detailing compliance along with an Audited Membership certificate from the Scaffolding Association.
The time period from initiation to completion is typically three months and certification is available to any company interested in becoming an Audited Member of the Scaffolding Association.
“Becoming an audited member of the Association will lift the profile of Formark as a bona fide scaffolding contractor. For many potential clients, such as main contractors and public authorities, this could be a key to acceptance on their tender list. Audited Membership provides a level of comfort to all our clients that we take health and safety very seriously and endeavour to continue upgrading our policies and procedures regularly.”
Mark Coote Snr, managing director at Formark Scaffolding, Surrey“The process of becoming audited was extremely thorough and covered all aspects of the scaffolding industry from our start of shift briefings and tool box talks to harness inspections and a recording of our findings. We also had to demonstrate our working gangs to see whether, as a company, we were following best practice.”
Edward Farrell, health and safety executive at CCS, Kent
“What really impressed us about the Association’s audit process is that it combines a paperwork check with the all-important ‘boots on the ground’ approach. Safety is what’s most important in scaffolding, so seeing what actually happens on-site as part of the independent audit process is a must.”
Phil Griffin, commercial director at SBBS Building & Scaffolding, West MidlandsAn ‘audit’ is a systematic review or inspection, and it’s easy to see why an audit might not be immediately welcomed. But there are many benefits to going through an audit, not least the positive client-facing messages that a successful audit brings. Stacey Underhill of the Scaffolding Association highlights what Audited Membership with the Association is all about.
For any organisation to effectively manage its health and safety risks, it needs to have a robust and proportionate incident investigation procedure. The benefits of investigating an incident robustly can’t be overstated.
An investigation:
• provides a true picture of how work takes place.
• ensures root causes are dealt with effectively to prevent reoccurrence.
• protects your business both financially and reputationally by mitigating or defending any claims.
• demonstrates your commitment to effective health and safety management.
While you can’t predict when an incident might occur, you can have robust procedures in place to dictate what happens when an incident (inevitably) does happen. But what makes an effective investigation?
In my view, there are two main elements: evidence and analysis.
At the heart of any incident investigation is the strength of the evidence collected. For an effective investigation, you need to consider what the evidence shows through an independent and rigorous process. For most accidents, there is no knowing where they might end up, i.e. in a claim, in someone making a complaint. Therefore, you need to be assured that what you have identified is correct. In the most part, with training, this can be carried out internally. However, sometimes there is a case for oversight, review or the use of an independent party. Investigating accidents should be a high priority; an important metric of organisational culture is the speed at which it responds to an incident. Incidents should be acted upon as soon as possible because doing so demonstrates a willingness to improve and could prevent a reoccurrence elsewhere in the organisation. Remember: people’s memories fade, evidence is lost and the impetus to make changes can be missed. For these reasons, an instruction from senior management is required that ensures speed of response (and monitoring this speed).
When collecting evidence, consider the following:
• Photos, phone footage, CCTV – a picture really is worth 1,000 words.
• Drawings and diagrams – these can often capture the scene in great detail, adding clarity, especially if there are language barriers.
• First-hand statements – timeliness is key to prevent information being lost and forgotten. Statements needn’t be complicated or long, and using or referencing photos, diagrams, etc. can help avoid confusion.
• Measurements – if possible, photograph or record these in a statement to demonstrate context and ensure the evidence can’t be refuted later.
• Paperwork – training records, RAMS, induction sheets, technical data sheets, qualifications, records of inspection, correspondence (between parties, etc.) should be stored and kept in an investigation folder.
These steps will ensure that the main sources of evidence are preserved with integrity and can be interrogated to provide the best possible platform to analyse.
Without interrogating the evidence and providing analysis, the value of an incident is lost. Each incident should be treated as an opportunity to learn and improve from.
There are many ways of identifying the root cause of an incident, but one of the most simple is to harness the power of your inner toddler and keep asking “why?”! The ‘Five Why’ technique is a simple and effective way of identifying root cause issues. By relying on you asking “why?” to statements relating to an incident, the technique enables an organisation to reach a conclusion.
In this example, John is seen on the scaffold without wearing a harness. Why? Because it was left in the van.
Why? Because it was damaged and was no use to him and hadn’t been replaced.
Why? Because the inspections hadn’t been carried out.
Why? Because Dave, who carries out the inspections, didn’t have time and didn’t have a record of when they should be carried out.
Why? Because Dave is the only person trained and was busy doing other things.
Without proper analysis, this simple scenario could have stopped at point one, the first “why?”. The company could have disciplined the worker for not wearing the harness and leaving it in the van. But using the ‘Five Why’ technique effectively not only draws out the root cause issues but also highlights a series of problems – i.e. lack of trained harness inspectors, no log, lack of inspections – that could be identified and rectified from just one near-miss incident.
An effective incident investigation allows us to learn from our mistakes and improve. By sticking to the fundamentals of ensuring good evidence and analysis of evidence, risk gaps can be identified and closed and your organisation will reap the safety rewards.
The ‘Five Why’ technique is an effective way to get to the root cause of a near-miss incident and identify issues to be rectified. Craig Varian, a consultant for Consalium, gets into the details.
The Office for National Statistics’ (ONS) figures show that construction output decreased during the first quarter of 2018. The fall was broad-based but was led by a decline in public house building activity and a reduction in public non-housing work. Allan Wilén, Glenigan’s economics director, reviews the latest ONS data.
Construction activity continued to weaken during the three months to February according to official ONS output data, with the volume of construction output falling 0.8 per cent against the preceding three months. Output was 1.2 per cent down on the same period a year ago.
The slowing in construction activity follows the decline in the value of projects starting on-site reported by Glenigan during 2016 and 2017 which has fed through to a reduction in on-site construction activity over the last year.
The decline in construction output has been widespread, affecting most construction sectors. The weakening in industrial and public new housing sectors has been especially marked, with output in the three months to February falling by 6 per cent and 3 per cent respectively against the previous three months. There were small declines in public non-housing and commercial output against the preceding three months, but output was significantly lower than a year earlier.
In contrast, private new housing work remains a growth sector, although the pace of growth has moderated.
Glenigan project data and CIPS survey data both provide a more up-to-date assessment of construction activity to the end of March, with both sources pointing to a continued weakening in construction activity. However, poor weather in March and the collapse of Carillion will have been short-term, temporary contributors to the declines.
Glenigan data has recorded a weakening in the development pipeline since mid-2017. The latest Glenigan Index shows that value of work starting on-site in the three months to March was unchanged on a year ago, but on a seasonally adjusted basis, starts were 5 per cent lower than during the three months to December.
The upturn in private housing starts seen in the final quarter of 2017 has petered out. Private residential starts during the three months to March were 17 per cent down on the final quarter of 2017 on a seasonally adjusted basis, although starts were still 4 per cent ahead of the same period a year ago. The smaller, social housing sector was 18 per cent down on October to December on a seasonally adjusted basis, but 9 per cent up on a year ago.
Overall, non-residential projects were 1 per cent higher than a year ago, but down 16 per cent against the three months to December on a seasonally adjusted basis. The decline against the final quarter of 2017 is largely due to a sharp retrenchment in hotel & leisure sector starts. Year on year, a weakening in hotel & leisure, office and health projects was outweighed by growth in industrial, retail and educations project starts.
Civil engineering starts were 18 per cent down on a year ago. The fall was due to declines in both infrastructure and utilities work.
Looking ahead, the latest project starts data indicates that construction output volumes will continue to soften this year. Non-residential building work is expected to be particularly weak: private commercial sector work is forecast to weaken, while the public non-residential sector output will
be disrupted by the recent drop in project starts. Cooler conditions in the wider housing market are expected to constrain new house sales and dampen private housing project starts as developers focus on building out existing sites.
In contrast, despite the current dip in project starts, the infrastructure sector will benefit from the upturn in civil engineering starts during the second half of last year and will be further boosted as work gathers momentum on several major projects, including HS2, Hinckley and Thames Tideway.
www.accesspoint.org.uk
AAA Scaffolding (Lincoln) Limited
XXXXX XXXXXXXX
Aerial Scaffolding Limited
www.aerialscaffolding.com
Allscaff (SW) Limited
www.allscaff.co.uk
Aspire Scaffolding Services Limited
www.aspirescaffolding.co.uk
Atrium Access Limited www.atriumaccess.co.uk
Attleborough Scaffold Hire
www.attleboroughscaffoldhire.co.uk
Bearings Scaffold Services
www.bearingsscaffolding.co.uk
Burns Scaffolding Limited
www.burnsscaffolding.co.uk
Conxim Limited
www.conxim.com
Creed Scaffolding Limited 0800 1216570
Extreme Scaffolding Services Limited
www.extreme-scaffolding.com
Force Scaffolding Limited
www.forcescaffolding.co.uk
Gorilla Scaffolding
www.gorillascaffolding.com
HighScaff Limited
www.highscaff.co.uk
Inner City Scaffolding Limited www.innercityscaffolding.co.uk
JJ Scaffolding Limited www.jjscaffoldinglimited.co.uk
JTL Scaffolding Limited www.jtlscaffolding.co.uk
JTL Special Projects XXXXX XXXXXXXX
KGK Scaffolding Limited www.kgkscaffolding.co.uk
Lysander Scaffolding Limited www.lysanderscaffolding.co.uk
MAN Scaffolding Services Limited XXXXX XXXXXXXX
Mattison Scaffolding Limited www.mattisonscaffolding.com
MB Scaffolding 07387 100514
MW Scaffolding UK Limited www.mwscaff.co.uk
PKS South East (Scaffolding) Limited pksscaffolding.co.uk
Radford Scaffolding Limited www.radfordscaffolding.co.uk
Rose System Scaffolding Limited www.rosessl.co.uk
Scaffold Contracts Limited www.scaffoldcontractsltd.co.uk
Scaffrite Limited www.scaffritescaffolding.co.uk
South Western Scaffolding Limited www.southwesternscaffoldingltd.co.uk
Streamline Scaffold Solutions Limited
001 407 443 4799
SCAFFOLD
28 June and 3, 5 and 11 July
Regional Member Forums (see below)
19-21 June
Safety & Health Expo (SH&E) Excel, London
18 September
Scaffolding Association AGM Union Jack Club, London
9-11 October
UK Construction Week NEC, Birmingham
The Scaffolding Association recently held its inaugural Membership Forums in four locations around the UK (London, Birmingham, Leeds and Bristol). These events were well-attended by numerous contractors, designers, suppliers and industry stakeholders.
Chief executive Robert Candy opened the Forums with an update on the Association and outlined the Access Industry Training Scheme. He then introduced Ray Gold, of RDG Engineering, who gave an interesting and thoughtprovoking presentation on Temporary Works before ending with a question and answer section, resulting in a useful and friendly debate among the audience.
Opportunities for networking before and after the event were very well-received and attendees gave extremely positive feedback.
Tickets can be booked for forthcoming Scaffolding Association Regional Member Forums via Eventbrite. They all begin at 3pm:
• Thursday 28 June in Birmingham –Arden Hotel, B92 0EH
• Tuesday 3 July in Bristol – Bristol Golf Club, BS10 7TP
• Thursday 5 July in Leeds – Thorpe Park Hotel, LS15 8ZB
• Wednesday 11 July in London –The Union Jack Club, SE1 8UJ
Formark Scaffolding is celebrating the successful certification of its first female apprentice scaffolder.
Charlie-Lauren Whitear
gained her CISRS Labourer Card after achieving the COTS Site Safety Plus Certificate and passing the CITB Health, Safety and Environment test.
After joining Formark as an office administrator in 2015 and giving as good as she got when bantering with the scaffolders about site work, Charlie decided to go one step further – and join them.
“A lot of people were very apprehensive when I said what I was going to do. When I got a chance to qualify as a labourer, they were equally supportive and now I have got the Labourer Card, the scaffs treat me as one of the team.”
Charlie still works in the office at Formark’s yard and has already been on-site. She continued: “It was very challenging and different but made a nice change from the office. I intend to mix working in the office with site work – and I haven’t ruled out becoming a qualified scaffolder one day.”
“Once Charlie got started, there was no stopping her,” said Mark P Coote, director of Formark Scaffolding. “We were delighted to support her through the process and look forward to seeing where this new qualification will take her next.” FIND
Alliance Intelligent Scaffolding has scooped two major awards at the Hertfordshire Building and Construction Awards.
Alliance firstly picked up the much-coveted Health and Safety Award for its commitment to exercising the most stringent health and safety standards across the business. And the company was also awarded the evening’s top prize, the Judges’ Special Recognition Award for Outstanding Commitment to the Hertfordshire Built Environment Sector. Jointly, directors Justin Wall and Daniel Yorke commented: “We are delighted to have won two fantastic awards at this, our first, construction industry event.
“Each award recognises the efforts of the entire team at Alliance, who work relentlessly to raise the standards across all areas of our business in order to offer our clients the safest and most efficient service possible.”
www.scaffolding-association.org
The team at St Helens Plant has been called upon to fabricate a bespoke metal solution for a client’s exhibit at this year’s RHS Chelsea Flower Show.
St Helens Plant was approached by Tendercare Nurseries to provide fabrication of a specialised network of stillage-type steel metal bins as part of the Wuhan Water Garden, a display designed to mesmerise, depicting purity, beauty and a multitude of foliage masterpieces.
The Wuhan Water Garden is described by Chelsea Flower Show as being inspired by the historic ability of Wuhan, also known as China’s City of 100 Lakes, to manage and control the flood waters of the Yangtze River.
As made-to-measure steel specialists, this was another interest project for the team at St Helens Plant! FIND
Elite Scaffolding has commenced works at the Shell Tower on London’s Southbank.
During the five-month project, Elite will install 14 independent access scaffolds to facilitate asbestos removal and encapsulation by the Erith Group, on behalf of contractor Overbury.
Lee Mayhew, Elite Scaffolding’s operations director, said: “This is a notifiable job working under our ancillary asbestos licence.
“One scaffold crew of five to eight operatives will carry out all works under licence restrictions and out of normal working hours. All scaffolders on-site have full asbestos training, medicals and face-fit certificates, and the manager is asbestos management trained.
“We are delighted to be the chosen access provider on this prestigious contract.”
FIND OUT MORE www.elitescaff.co.uk
The Scaffolding Association will be hosting a panel discussion on working at height at this month’s Safety & Health Expo (SH&E) at Excel, in London.
Linked to the recent call for submissions from the All Party Parliamentary Group (APPG) on Working at Height, the panel discussions will take in a review of the existing regulations for working at height, the primary reasons for falls, and whether enhanced reporting would lead to better understanding of the causes of/ help reduce falls from height.
In addition, panel speakers will consider whether the current definition of ‘competence’ for working at height is appropriate, any necessary measures to prevent falls/falling objects not currently required by law and what more industry can do to avoid falls.
The panel discussion will be hosted by construction industry journalist Adrian Marsh, who is editor of AccessPoint magazine and PR/marketing consultant at Campbell Marsh Communications.
Adrian will be joined by industry specialists including Craig Varian, consultant and chartered member of IOSH at Consalium; Paul Reeve, head of working at height sub group – Construction Industry Advisory Network (CONIAN); Simon Mitchell, training and technical support manager at SpanSet; and Robert Candy, chief executive of the Scaffolding Association.
SH&E runs from 19-21 June, with the Working at Height panel discussion taking place on 21 June from 1-1.45pm in the Keynote Theatre.
FIND OUT MORE
www.scaffolding-association.org
• HIRE
• SALES
• MANUFACTURING
• DESIGN AND SAFETY
VR Group embraces the manufacture, supply, hire and design of scaffolding and associated non-mechanical access products. The Group has considerable industry expertise and its operations are driven by a total commitment to safety, quality and innovation. The Group’s VR Design and Safety consultancy complements the Group’s portfolio of services and offers a full temporary works scaffolding design service with the aim of delivering high-quality scaffold designs to meet the demands of BS EN 12811-1, TG20:13 and EN1991-1-4:2005.
VR’s signature system scaffolding, Turnlok 460, exceeds technical specification and compliance to EN 12810, EN 12811 and TG20:13 and the system is the strongest known product on the market. Turnlok is a fast, simple and conventional scaffolding system with ongoing innovative improvements. The system has only four component fastenings and compliance and quality audits are carried out by UKAS external bodies to ensure products are made to the highest of standards.