Scaffold design –know your responsibilities
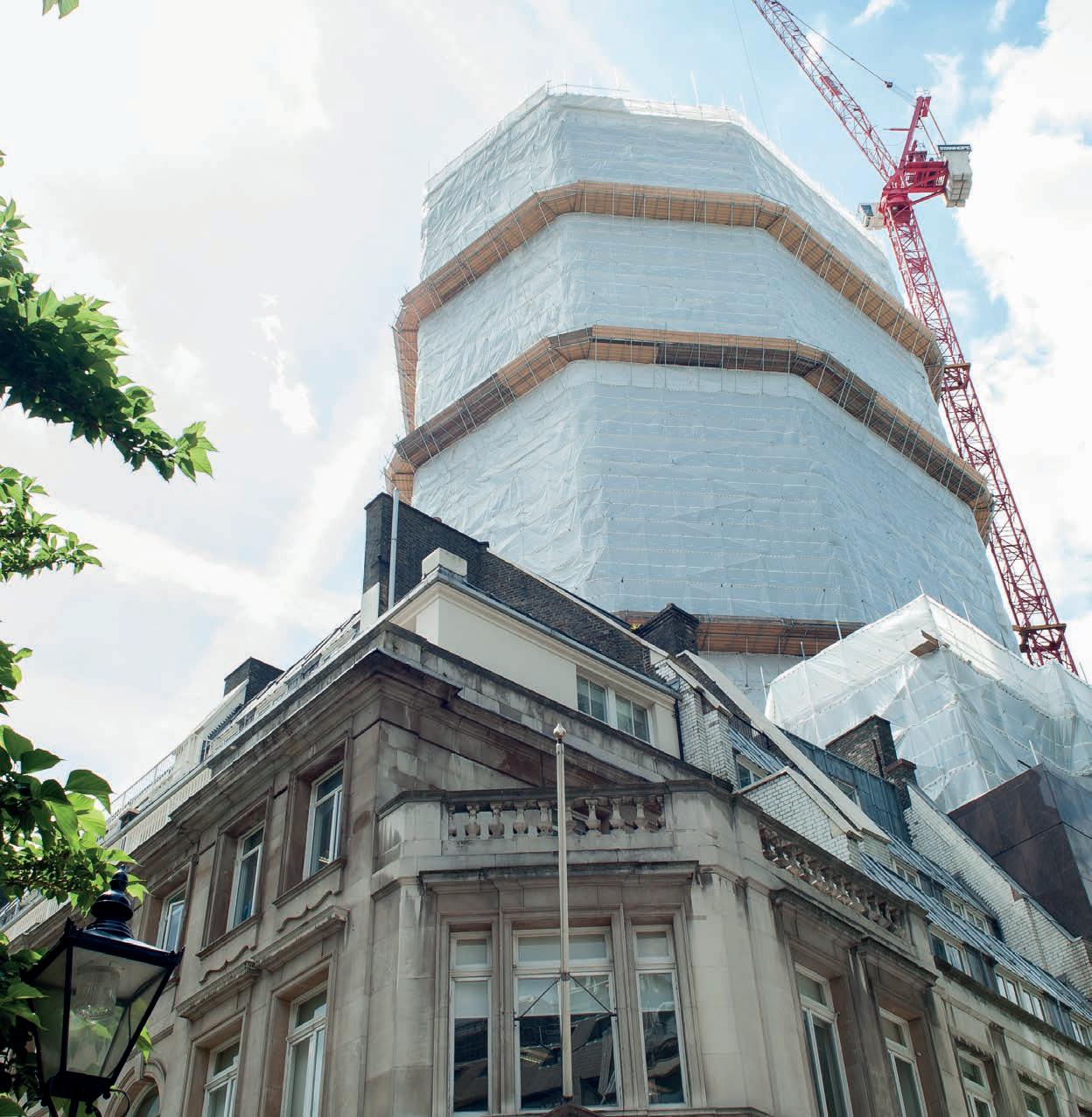
04 Voice of the sector: Raising standards – together
05 Opinion: Dropped objects
10 Commercial: A standout case on contractual obligations and the law
12 Feature: When does scaffold build become scaffold design from an insurance perspective?
14 Technical: Considering limit state design philosophy
16 Site visit: Tiger Scaffolding take on a complex brief for North Yorkshire County Council
18 Safety: A look at new loading bay gates
19 Edge Protection: Direction on access platform decking
20 Trade: Pre-qualification audits for scaffolders
21 Health & Safety: The invisible risk – mental health
22 Association News: Updates from the Scaffolding Association and members
FRONT COVER: Angel Court in the City of London where Alandale was contracted for the scaffolding works by main contractor Mace.
From 1 July 2017, CISRS will be introducing a two-day Continuing Professional Development (CPD) course which will become a mandatory requirement prior to either a Scaffolder or Advanced Scaffolder card being renewed but there have been calls for more flexibility in how courses are delivered.
Industry sources told AccessPoint that safety must not be compromised but a more flexible approach to the way CPD scaffolding courses are delivered would be more effective. The course content is said to cover areas many scaffolders don’t require and that two days out of work is too long.
CISRS has said it is making changes to course content following two CPD refresher pilot courses which were held at NCC Midlands. Dave Mosley, CISRS scheme manager, said: “The pilot schemes have proved to be a huge success and have given us the opportunity to fine tune the two-day course content before the July roll-out.
The event equipment hire market is forecast to increase by a further 2 per cent in 2017 to reach a value of around £600m according to a new report published by AMA Research. However, growth has been restricted by its highly competitive nature which has tended to increase pressure on prices.
The UK has a well-developed infrastructure of event destinations, venues and service suppliers, with estimates of around £40bn annual income from UK events, which provides good opportunities for the event equipment hire market. There is no universally accepted definition of the ‘event hire’ sector, but AMA’s definition includes the key product groups of staging & structures, portable buildings, audio-visual, power generation and climate control, interiors, traffic & crowd control, security, signage & portable access solutions and access & other plant hire.
It is difficult to quantify the product mix as no two events are alike, but it is estimated that the largest equipment hire sectors are ‘staging, structures & seating’ and ‘portable buildings & sanitation’ – with a combined share of around 50 per cent of the market according to AMA estimates.
Andrew Hartley, director of AMA Research, said: “Whilst future growth rates can be significantly affected by changes in the climate in any given year, the underlying rate of growth is set to be positive.”
Events that should have a positive impact on the market include the 2017 World Athletics Championship in London and the 2019 Cricket World Cup.
“Some had initially been sceptical due to comments made on social media and the internet about costs, duration and content. But having attended, [delegates] felt it was worthwhile and that they had been reminded of information they’d forgotten since they last attended a centre, whilst also being brought up to date on current industry guidance.”
Robert Candy, chief executive at the Scaffolding Association, said: “We welcome moves to make our industry safer. Our members have told us that they would like to see more continuous assessment as part of a comprehensive renewal process. We advocate regular training on an ongoing basis rather than two days every few years. The wider industry could then benefit from a move ultimately designed to make us all safer in our work.”
FIND OUT MORE
www.cisrs.org.uk
More than £1 billion of cash is estimated to be owed to the UK’s top 12 construction companies according to analysis carried out for leading construction representative body the Specialist Engineering Contractors’ (SEC) Group. This figure was ascertained from the fact that nine of the top 12 that published separate figures for retention were owed more than £800 million.
SEC Group also found that the money owed to the construction companies was then, in turn, owed to their supply chains, the overwhelming majority of whom are SMEs. In one case the research even showed that the cash retention held against the company in question’s supply chain was significantly greater than the amount withheld against it by its clients.
Robert Candy, chief executive of the Scaffolding Association, said: “As a trade association that is proud to represent a high number of SMEs it worries us that such a large amount of money is owed to such companies. The analysis comes at a time when we await a government review of the retentions system and we watch with hope that this brings further protection of SMEs via legislation or ring-fencing of cash retentions.”
He added: “More often than not, the cash being held in retention by these large companies is the difference between making a profit or not on any given job for SMEs. The Scaffolding Association would certainly welcome any legislation that ensures all our members receive all cash owed to them for work completed.” FIND
This month sees the introduction of the government’s new Apprenticeship Levy on large construction firms. This is due to have a big impact on the opportunities available to those looking to start a career in construction.
Currently, two thirds of apprenticeships take place within SMEs and this new levy is designed to encourage more large construction companies to become involved.
More apprenticeships could also prove to be good for business according to research from the Federation of Master Builders (FMB). The research showed that almost two thirds of those that responded thought more highly of companies that trained apprentices.
Robert Candy, chief executive of the Scaffolding Association, said: “The construction industry is highly competitive and so reputation is paramount. The research by FMB reiterates the fact that apprenticeships are undoubtedly good for business.
“We look forward to the launch of the government’s Apprenticeship Levy this month and hope that our members seize the opportunity to both help get more people into our industry and, in doing so, increase their desirability to potential clients.”
www.scaffolding-association.org
Kent-based CCS Scaffolding is celebrating after becoming an Audited Member of the Scaffolding Association.
Edward Farrell, health and safety executive at CCS, said: “We saw many benefits to becoming an Audited Member but what really stood out for us was the opportunity to undertake an annual audit which is currently not offered by any other association.
“Becoming an Audited Member of the Scaffolding Association means we are confident that our methods and procedures are fully compliant to industry standards and we are working in the safest possible way.”
Welcome to our very first issue of AccessPoint
Our aim is to promote achievement and successes in the access and scaffolding sector. We want to be able to praise good news yet also question initiatives that could benefit from a different approach. We live and work in a changing world and the sector’s supply chain will inevitably be flexible and open to new ways of working.
Change is an integral part of any organisation and change is certainly high on the agenda within the access and scaffolding industry. Workload among contractors continues to hold up and demand for skilled and qualified labour is strong. So, is it sustainable?
Well, that’s the challenge for any sector, and it’s no different for access and scaffolding. But what’s also a challenge is how to protect the integrity of the service that is provided. Skilled resources are crucial for the long-term success, and maintaining hard-won improvements in safety is critical.
This summer sees the introduction of the CISRS CPD refresher courses. This is a major step forward and CISRS should be congratulated for its commitment to raising and maintaining standards. However, is sending an operative back to the classroom for two days every five years the best solution? Or has an opportunity been missed?
Inside this issue there are some fine examples of innovation and forward thinking. On page 18, we see how one business has developed a testing process that means it can deliver loading bay gates that will raise safety standards within the industry. While our first site visit (turn to page 16) discovers how an integrated project team can come up with new ways of working to deliver technical excellence.
And congratulations to FASET for working with major suppliers and trainers in the sector to agree common training and test standards for platform decking. Go to page 19 to find how it has successfully agreed a training and certification scheme which will result in a Skilled CSCS Card specific to the trade.
All really positive and exciting. A lot has happened during the last 12 months and no doubt continuing change will bring more challenges for the skills and capabilities of those active in the sector. The new era is only just beginning.
Adrian JG Marsh EditorHere it is – a new magazine for the sector, AccessPoint!
This is the first issue of what we hope will help to boost awareness and understanding about the skills and capabilities of businesses active in the access and scaffolding industry.
It’s a great time to bring AccessPoint to you. Scaffolding Association membership is at record levels – and growing – and some of our members are successfully completing the audit process right now to become Audited Members. We hear from CCS Scaffolding on page 23 about the stringent audit process they went through and what their new member status means to them, both for now and the future. Congratulations to everyone at CCS on achieving Audited Member status.
Large clients are starting to look for wider-reaching procurement routes, and our audit process is being welcomed in this respect. There are different levels of audit available to scaffolding contractors needing to pre-qualify (we talk through these on page 20) and our Audited Membership category sits at Level 1 in the PAS 91 Three Assurance Level Model. It’s the highest and most-comprehensive audit level you can go for and involves an independent two-stage audit, desktop and on-site, by IQ Verify, who are UKAS accredited. Just ask us if you want to know more or read the details on the Membership Levels page on www.scaffolding-association.org
Our holistic approach to the sector is paving the way for a more joined up and progressive industry – one we can be very proud of. We continually hear of scaffold contractors receiving prestigious accolades, demonstrating their commitment to raising standards and improving the image of our industry.
One aspect of the sector – and of construction as a whole – that’s important to keep focused on is making ‘health’ a priority by helping to support colleagues with mental health issues and tackling the stigma surrounding it head on. We read statistics on mental health and wellbeing in construction every week and it is such an important topic that entire summits are dedicated to raising awareness of health issues in construction and discussing ways to encourage more openness around the topic. We know it’s impossible to remove workplace stress completely, but where we can find ways to minimise the risks of harm caused by stress and mental health issues, let’s do so at every opportunity.
Another area we’ll be focusing on as an association is the temporary works process within BS 5975, which is still an area of weakness within the industry. Areas we’ll be looking at include the information that should be included within a Design Brief, the role of the Temporary Works Co-ordinator and the levels of supervision required through the temporary works process, and raising awareness of the temporary works process by improving client and contractor understanding.
So, it just leaves me to say… happy reading!
Robert Candy Chief executive Scaffolding Association• Store required equipment and tools securely
• Stagger ladder hatches
• Install protection fans
• Build a pavement gantry
• Create exclusion zones with barriers and safety signs
• Tether tools and equipment
• Prevent ‘hemping’ of long tube
HSE statistics for the 2010–2015 period have identified that 10 per cent of construction RIDDOR reportable injuries were as a result of being struck by dropped or moving objects. This data has to be interpreted with care because it is well known that non-fatal injuries are significantly under-reported.
A dropped object is any item or object that falls, or has the potential to fall, from its position. Dropped objects fall into two categories: Static Dropped Objects and Dynamic Dropped Objects.
A Static Dropped Object is an object that falls from its position under its own weight, such as an inadequately secured fitting. Whereas a Dynamic Dropped Object is one that falls from its position due to applied force, such as severe weather.
A number of factors can contribute to a dropped object incident. These include:
• Inadequate risk assessment
• Human factors
• Inadequate work processes
• Failed fixtures and fittings
• Poor housekeeping
• Inadequate inspection and maintenance
• Environmental factors
Dropped objects are a fundamental hazard of working at height, and there should be a clear system in place to identify, prevent and manage the associated risks. Policies should detail the
appropriate inspection and control mechanisms that are implemented to identify, assess, eliminate or manage the risks from dropped objects. Preventative and mitigating controls should be detailed within safe systems of work and method statements.
The risks associated with potential dropped objects should be reduced to the lowest reasonably practicable level in line with the hierarchy of controls. Effective task planning and risk assessment will eliminate, reduce, isolate and control hazards.
In the first instance, potential dropped objects should be eliminated at source with the following actions:
• Remove any unnecessary equipment and tools
• Mechanise lifting equipment where possible
• Stop work during adverse weather conditions
• Install toe boards
• Use solid barriers and brick guards to close any open edges
• Install board gap fillers
• Close ladder hatches
Where potential dropped objects cannot be completely eliminated, it is important to assess the likelihood of a potential fall and determine the severity of the consequence. From this, the following measures can be devised and put into place to reduce the distance of fall and prevent personal injury:
• Ensure all operatives are competent to work at height
• Regularly undertake dropped object Toolbox Talks and safety meetings
Although having a robust management system in place is the primary tool in preventing dropped objects, there is a fundamental requirement for all personnel on-site to remain vigilant of the associated hazards, by:
• Being aware of the hazard and associated risks, and being prepared to stop work if the conditions or actions are unsafe
• Recording and reporting all incidents
• Removing potential dropped object hazards
• Controlling tools and equipment which have the potential to become a dropped object hazard
• Designing the work environment and selecting suitable tools and equipment which mitigate the risk of potential dropped objects
• Undertaking regular worksite inspections
This article details just some of the important considerations and solutions when preventing dropped objects. However, it is not exhaustive and should always be supplemented with additional checks and processes specific to the individual location, task and environment.
John Steven SimonsJS Safety Associates
www.jssafetyassociates.com
In this first AccessPoint Opinion column, John Steven Simons, of health, safety and scaffolding advisors JS Safety Associates, considers the topic of dropped objects, highlighting the many contributing factors and how dropped objects can be eliminated or prevented on-site.
A new app from Avontus Software lets users ‘travel’ through scaffold drawings in a virtual reality (VR) environment.
Users of the new Scaffold VR app can view and rotate 3D scaffold drawings in VR from a smartphone using Google Cardboard – a simple and inexpensive VR viewer. Even without a viewer such as Google Cardboard, the Scaffold VR app allows users to navigate through a rendered 3D environment and view the scaffold design from any direction on a Windows desktop.
By virtually walking through a design, users can explore the scaffold step by step without having to put up a single bay on-site. This walk-through will provide the opportunity to catch planning mistakes and ensure the scaffold is designed correctly, avoiding costly rework from delays and cost overruns.
The Scaffold VR app is available for iPhone or Android smartphones, or a Windows desktop.
www.avontus.com
The TAMER toe board clip eliminates the inherent gap from the working platform that occurs with the ReadyFix type of scaffolding.
This simple, cost-effective solution exceeds the requirements of BS EN 12811 for toe board installation by replacing the more typically used single coupler to secure the toe board. Its design allows the toe board to sit either directly onto the transom tube or on top of the working platform boards without reduction of side loading capacity.
The unique way in which the toe board is held away from the standard has led to the adoption of the TAMER with various types of system scaffolding, as it allows traditional timber scaffold boards to be used as toe boards without fouling the ring or cup. When using scaffold boards to form the working platform on the above systems, the TAMER unifies the platform in a way that was unattainable previously.
Take a first look at the TAMER on YouTube: search ‘TAMER toe board clip’. All test data and prices are available from Metal Spraying (UK) Ltd.
www.ms-uk.co.uk
Loading bay gates developed by VR Access Solutions in conjunction with the Scaffolding Association are set to raise safety standards in the industry.
These redesigned gates not only comply with the requirements of BS EN 12811-1-2003 and BS EN 13374:2013 but far exceed existing industry standards.
Read more about how the unique design of the new VR Access Solutions loading bay gates improves safety on-site. Turn to page 18.
www.vrscaffold.com
KLAWZ, a new innovative ‘Double on Double’ scaffold fitting, is helping scaffolders to reduce the amount of tube required and erect scaffolding faster than traditional methods.
Available exclusively from Forgeco’s nominated distributors, KLAWZ is fully tested in accordance with BS EN 74-1:2005. KLAWZ exceeded Class B requirements in all tests, with a slip load of over 30kN, more than double the requirement for a normal Class B Fitting.
This unique engineering allows scaffolding schemes to be designed with high load bearing for both ledgers and transoms. The patented spacing means the ledger and transom sit together easily, allowing the scaffold to be boarded out on a single level whilst maximising strength, removing the need for supplementary structural transoms.
KLAWZ also perfectly complements the widely used Prefabricated Structural Transom unit, and has been extensively tested with the Metal Spraying (UK) supplied ReadyFix transom. KLAWZ allows seamless transfer between sections of scaffolding constructed with transom units and traditional tube and fitting. Double and triple standards necessitated by extra leg loading requirements can be added at any point of a build. Deadmen can be installed with a single fitting, and beam installation time can be cut by up to 50 per cent by using KLAWZ instead of traditional methods.
www.klawz.co.uk
Our experienced customer driven team provides a seamless service from product development, supply chain management, production, quality control, delivery and local engineering support available for fast, effective solutions where required.
VR Access Solutions has launched a Readylok Transom User Guide. The new guide, which can be downloaded from the company’s website, covers aspects including component details and load capacities, deck arrangements, bracing and tying, safe working heights, and storage and maintenance.
VR Readylok is a mobile transom system that prefabricates a transom tube and four fittings to produce a rigid unit that speeds scaffold erection. Readyloks are designed to be used in conjunction with standard scaffold tubes and ledgers, or extendable transoms, to form 5, 4 or 3 board wide system access scaffold.
www.vrscaffold.com
Complete scaffolding solutions company AT-PAC is increasing the scope of its UK operation with a new Aberdeen branch, which opened in March, and the relocation of its Birmingham branch to a larger operation, which happens on 1 May. Both operations offer the AT-PAC Ringlock system, a quality assured product, engineered with consistent quality with the highest ultimate loadings for any ring system in the UK. Ringlock is available for hire or sale from AT-PAC along with a full engineering service that provides clients with both innovation and cost savings.
Alongside Ringlock, all AT-PAC branches offer the full range of access products including tube, fittings, boards and ancillaries.
www.at-pac.com
A Bellway Homes development has overcome time pressures and increased safety by using Sayfa Systems’ RhinoDeck load deck platform and trestle system.
Speed and simplicity of installation as well as the provision of a stable work platform both saved time and increased safety on-site. Contractor Vision Access & Safety Systems recommended the high-load RhinoDeck work platform to Bellway for its The Chase development, located between Winchester and Eastleigh.
The Rhino Load Deck System is designed for use inside a building during construction. Because the system is self-supporting, it doesn’t require contact with walls and can therefore be installed before the mortar is fully set with no risk of damage to the structure.
It provides a safe working height of up to 3m and can support an evenly distributed load of 600kg per m2. The Rhino Load Deck system has been fully tested to test procedures set out by the British Standards Institute and wholly complies with the following standards: Temporary Works Equipment BS EN 12811-1:2003, section 6.1.3 6.0kN/m2, 6.2.2.3 and 6.2.2.4.
Mark Lowes, site manager at Bellway Homes, said: “This is the first time I have used RhinoDeck but I have no reservations – I won’t be using anything else in the future.”
www.sayfasystems.co.uk
Shrink-wrap from Tufcoat has helped a Plymouth housing project for at-risk adults to deliver “business as usual” during a major refurbishment.
Plymouth House, a supported housing project that is home to a large community of vulnerable individuals in Plymouth, is undergoing a major refurbishment with the aid of Tufcoat’s printed shrink-wrap installation service.
Along with Westward Housing and JEM scaffolding, Tufcoat have installed their first-of-its-kind printed wrap to display partner logos across the Plymouth skyline, crucially enabling the doors to remain open to those in need during the refurbishment.
Over 750m2 of printed film was installed in just six days, ensuring the job site was weather-proof as per the schedule. All material used to seal the building will be recycled upon project completion.
Jill Moore, the services manager at Plymouth House, said: “It is business as usual here while the work carries on. Having a newly refurbished building will do wonders for the self-esteem of those who live here.”
www.tufcoat.co.uk
KLAWZ is a new innovative ‘Double on Double’ scaffold fitting, that helps scaffolders to reduce the amount of tube required and erect scaffolding faster than traditional methods.
The unique engineering of KLAWZ allows scaffolding schemes to be designed with high load bearing for both ledgers and transoms. The patented spacing means the ledger and transom sit together easily, allowing the scaffold to be boarded out on a single level whilst maximising strength, removing the need for supplementary structural transoms.
KLAWZ is fully tested in accordance with BS EN 74-1:2005. KLAWZ exceeded Class B requirements in all tests, with a slip load of over 30kN, more than double the requirement for a normal Class B Fitting.
Barrister Professor Rudi Klein discusses a standout legal case from 2016 regarding contracts and the law.
Once made, contracts are meant to be adhered to. That has always been the attitude of the law. The role of the courts, therefore, is to uphold the agreement entered into by the parties, even if that agreement turned out to be a poor bargain for one of the parties. In 2016, this principle was illustrated in a very graphic way in the case of Balfour Beatty Regional Construction Ltd v Grove Developments Ltd.
Balfour Beatty (BB) had been engaged by Grove Developments (Grove) to design and construct a hotel and serviced apartments for a sum in excess of £121 million. The contract was the standard JCT Design and Build Contract 2011, designed for construction projects where the contractor carries out both the design and the construction work.
When they entered the contract,
the parties’ intention was that stage payments would be made (in accordance with one of the two options in the standard contract). The contract contained rules for calculating the stage payments. Unfortunately, the parties were not able to agree a list of stages.
Instead they agreed to a schedule of monthly interim payments that was to take them up to 22 July 2015 – the date specified in the contract for practical completion. This schedule included dates for applications (which were to be the third Thursday of each month), valuations, and issue of payment certificates and for payment.
Twenty-three interim payments were envisaged under the schedule. Up to July 2015, both sides managed the payment process in accordance with the agreed schedule. But trouble was brewing.
By May 2015, it had become apparent that the project was in
serious delay. In fact, practical completion of the whole project was not achieved until a year later, in July 2016.
BB sought to extend the schedule beyond July 2015 but the parties couldn’t agree on the dates for applications, valuations and payments. Nonetheless, BB issued a payment application (number 24) on 21 August 2015.
On 28 August 2015, Grove issued a payment notice followed by a pay less notice on 15 September. This indicated a deduction of £2 million, leaving £439,503 as due to BB; Grove paid this on 18 September 2015. BB immediately challenged the correctness of these dates and the validity of the pay less notice. Further efforts were made to resolve
future dates for interim payments. Eventually, relying on independent advice, Grove asserted that BB had no entitlement to receive further interim payments after July 2015 and sought a declaration from the court to that effect.
The trial judge granted Grove’s declaration. The schedule was an agreed amendment to the contract. It envisaged 23 interim payments in accordance with the specified dates. There was no further provision for interim payments.
BB appealed to the Court of Appeal:
• The schedule did – expressly or impliedly – provide for interim payments to be made between August 2015 and the actual date of practical completion.
• In any event, the schedule did not comply with section 109, Housing Grants Act 1996 (which provides for a statutory right to interim payments).
• If the above arguments were to fail, there was a fresh agreement for monthly interim payments arising during discussions/ correspondence after July 2015.
Identification of the dates for valuations, payment notices and pay less notices was essential to the operation of the contract. If Grove served notices out of time, the consequences could be draconian.
The express words used by the parties clearly indicated that they were only agreeing a regime of interim payments up to the contractual date for practical completion (July 2015).
Furthermore, there was no implied term providing for interim payments after valuation 23. There would only be a need to imply such term to make the contract workable; but here it was perfectly workable without such term.
Section 109 of the Act states “A party to a construction contract is entitled to payment by instalments, stage payments or other periodic payments for any work under the contract…”
BB’s case had been that interim payments had to be applied to all the work envisaged by the contract. Therefore, after the contractual date for practical completion, the fall-back provisions in the Scheme for Construction Contracts would apply (meaning that a regime of interim payments would be incorporated into the contract).
The Court of Appeal disagreed. “Any work” in section 109 did not mean “every single piece of work”. This section simply provides a general entitlement to interim payments; the frequency of interim
payments and their timing is left up to the parties. (However, the court felt that a contract providing for one interim payment “of an insignificant amount” would not comply with the section and the Scheme would apply.)
The court concluded that there was no evidence of a separate agreement having been concluded.
For BB this was a costly error; they had to do without interim payments for the best part of a year. In fact, the court’s judgement may also have been rather harsh. Some of the delays had been caused by Grove. BB had obtained a two-month extension of time but there was still a dispute over responsibility for the delays. To some extent, therefore, Grove had profited from delays it had brought about; Grove didn’t have
to make interim payments for the period of the delay it had caused.
Lord Justice Jackson said: “This [was] a classic case of one party making a bad bargain.” He was echoing another statement made by Lord Neuberger in a recent Supreme Court case on the approach to be adopted when interpreting commercial contracts. He had said: “When interpreting a contract, a judge should avoid re-writing it in an attempt to assist an unwise party or to penalise an astute party.”
The easiest solution would have been to state in the schedule that interim payments would continue after July 2015 (to cover any period by which the works might be delayed). A timeline could have been agreed enabling applications to be submitted on the third Thursday of each month and specifying the number of days (rather than actual dates) thereafter for valuations, payment notices and final dates for payment.
that
enthusiasm
industry
means that you can trust Amicus to not only find the best insurance to protect you, your business and your employees, but that you can also rely upon us to do it at the most competitive price.
Once made, contracts are meant to be adhered to.
In this increasingly litigious world, protecting your business from legal action can be a full-time occupation. In this series of articles, scaffold insurance specialist Amicus will explore some of the hidden pitfalls that you need to watch out for and provide some tips and advice in areas that scaffolding companies can take to protect themselves. Amicus director Richard Evans talks us through the first topic: scaffold design.
drawings then obtained from the designer), you, the scaffolder, can become legally responsible for this new design.
In the event of a problem, you can be sure that everyone who has had any input to the design will potentially be ‘in the frame’ and if you have made an alteration that has not been signed off by the designer, then it will be you, and not the scaffolding designer, who can be held liable for this failure. This can even occur when the failure relates to an item that you did not specifically alter.
Even though you may end up proving that you were in no way negligent, the defence costs in contesting a claim against you could cripple your business. Your standard public liability policy will not cover you against issues raised by undertaking design work.
By simply understanding how a liability can incur, you will have gone a long way to managing your risk.
Most scaffolding is designed by professional designers, so why would you have any responsibility for any mistakes in the design of the scaffold. You just build it… don’t you?
Well, as we all know, designs on paper that are handed down from the principal contractor or designer cannot always reflect the true situation on the ground and so minor
adjustments and modifications to drawings sometimes must be made to reflect localised ground conditions, or to bridge drainage pipes and such like that only become apparent when you are on-site.
But this is where you need to tread very carefully, because if you amend the drawings and they are not then re-submitted and re-approved by the principal (and, in some cases, new
If you think that it could be argued that you have had some input into the design of the scaffolding, then you need to look into how to reduce your risk by transferring it back to the designer/principal. They will have insurance to cover themselves.
Make suggestions and improvements by all means, but ALWAYS obtain an updated set of drawings or a written variation from the designer or your principal.
If that is not possible, then you need to consider whether you should purchase professional indemnity insurance (PI) to cover you when undertaking design work.
You will probably have never considered covering PI and have relied on the fact that your firm does not provide plans and drawings as part of your standard range of services. However, as you can now see, you can unwittingly incur a liability, even when you have not charged for the service.
Although the instances that I describe may be unusual, the consequences may be devastating. So, understanding what you are exposing yourself to when you change or alter a scaffold drawing is so important. If it is something that you do need to do, you should look into obtaining some basic
PI insurance to protect yourself (it need not be particularly expensive but could end up saving you a small fortune).
Finally, a reminder to always check the insurances of anyone who is providing designs and plans for you. Any reputable scaffold designer will almost certainly have professional indemnity insurance to cover them in the event of an error or omission with their drawings. You may need to rely on this insurance if there is a problem, but if you have altered their plans then they may be able to argue that they are not responsible. Having your own PI policy “just in
case” may be worth looking into.
Next time, we shall be exploring fees for intervention (HSE) insurance and some common pitfalls that arise on liability policies sold to scaffolding companies.
Is there a topic you’d like us to discuss in this section? Or do you have an insurance query we can help with? Please get in touch with Richard Evans or Adam Scott.
GET IN TOUCH 0208 669 0991
richard.evans@amicus-insurance.com adam.scott@amicus-insurance.com
The ‘basis of design’ employs calculations to check that the stresses due to loading at critical points have a very low chance of exceeding the material strength. This ensures that the safety of a structure is never compromised and that inherent redundancy is present in the design and in the final structure.
The scaffold engineering sector generally uses Permissible Stress Design for structures, whereas all other structural engineering branches have now switched to the Limit State Design method.
The two different design philosophies have their own advantages and disadvantages when considered with respect to the design of scaffolding. However, it is evident in comparison that the
advantages of limit state design far outweigh the benefits of permissible stress design.
The scaffold engineering sector traditionally always adopts the permissible stress method for the added reason that site personnel generally do not understand the concepts of the limit state approach, while they do understand the terms ‘allowable’ and ‘safe working load’.
It is of my opinion that site personnel do not need to understand the concept of limit state design; they just need to know what load can be applied to the structure before the factors are applied – the serviceable load.
The terminology is just slightly different but can be portrayed in the same manner. The serviceable load
(design working load) is something which is indicated on the design and is managed on-site by the principal contractor. Therefore, site personnel and scaffolders do not have to consider the inner workings of the basis of design; they just need to know the load permitted.
I don’t believe that understanding of ‘allowable’ or ‘safe working load’ is a founded reason for not adopting limit state design as site personnel do not often understand the concept of either kilo-Newton per square metre or kilo-Newtons and do not need to if a design is produced.
A good way of viewing this argument in a different light is considering permanent works construction. If permanent works operatives do not understand the concept of limit state design, then why should a scaffolder? Would a steel fixer understand how the reinforcement bar had been calculated and derived? It is irrelevant as to whether or not the site personnel understand the basis of design because they just need to know the specification of the materials. Therefore, I see no reason why it cannot be adopted in temporary works design.
The other reason why scaffold engineers believe that limit state cannot be adopted is that all materials and components are stated in terms of ‘permissible’. However, in order to obtain the permissible, an ultimate value
has obviously been obtained through testing.
All scaffolding products will be tested to failure with 95 per cent confidence limits. If the factor of safety is known, then the characteristic / ultimate value of resistance can be obtained by multiplying the permissible by the factor of safety. In addition, some manufacturers state both ultimate and permissible values. The ultimate value can be obtained directly from the manufacturer or the relevant British Standard.
The limit state approach is much more comprehensive and provides a much more versatile basis of design, where design can lead to more efficient structures, resulting in reduced construction costs. This, in addition to all other engineering sectors adopting limit state design, all codes requiring limit state design and the possible downsides of not adopting limit state design, means that the permissible stress method should remain a thing of the past. As scaffold engineers, we should move into a new era and embrace the change with open arms. I am sure that the change would cause some trepidation by the sector but this would soon be overcome when the benefits to be had are seen.
The ‘thinking process’ before the ‘analytical process’ is essential in ensuring the correct design decisions are made by the scaffold engineer. Ryan Berry from Creator Scaffold Designs considers the critical comparison between the permissible stress and limit state approach.
It’s not every day that you see scaffolding suspended from a temporary roof surrounding a building more than 100 years old. But, this is just what has been created at the North Yorkshire County Council (NYCC) Hall in Northallerton by contractors Tiger Scaffolding. Faye Callaghan visited the site for AccessPoint to take a closer look.
The NYCC building has been home to North Yorkshire County Council since 1974 but the building itself is more than 100 years old. The building is a stunning example of turn-of-thecentury architecture and celebrates Grade II listed status.
The building has been undergoing renovations and repairs since August 2016 provided by William Birch & Sons Ltd and work is due to continue until August this year. As part of the extensive restoration project,
Whitby-based Tiger Scaffolding was enlisted to provide scaffolding services to allow for the roof and external building to be repaired and rejuvenated.
Due to the delicate nature of the building and its listed status, the brief for the contract was both detailed and complex. It specified that no weight could be placed on the roof and that no scaffold could be tied into the building. Additionally, the scaffolding also had to be constructed while still
allowing for vehicle access to the site at all times.
Barry Brown and Mark Parkin, Tiger’s managing directors, explained more about the process of ensuring the client’s needs were met. Mr Parkin said: “The client came to us with very specific requirements around the type of structure they would need on this project,” he told me. “We collaborated closely with our design team to produce drawings and calculations that would ensure
the safety and suitability of the structure. We then worked with our component suppliers to ensure that we were selecting the appropriate products for the temporary structure so that the integrity of the existing building would be protected at all times.”
Tiger ’s solution to this complex brief is impressive.
At its heart, a unique free-standing structure has been created. It wraps around the entire building without coming into contact with it at any point, and still allows for site access. This free-standing structure then provides the base on which a temporary roof has been constructed, meaning the building’s existing roof is completely protected.
The temporary roof then provides the basis for what is perhaps the most fascinating aspect of this complex build. Here, Tiger has created a 17m² scaffold which is completely suspended from the temporary roof. This scaffold
provides tiered access platforms around the building’s roof to enable contractors to undertake their specialist repair and restoration work safely.
A free-standing structure on this scale is rare, particularly one that supports both a temporary roof and suspended working platforms. As testament to the complexity of the job, the list of components used during the build is also fairly impressive. The completed structure contains nearly 145,000 feet of scaffold tube, more than 30,000 scaffold fittings – with around half of those being recently developed KLAWZ fitting – nearly 50,000 feet of wooden scaffold planks and almost 500 metres of structural X beams.
Mr Brown told AccessPoint that rather than being daunted by the project at hand, his team revelled in the challenge. He commented: “This project saw a range of specialist work being undertaken and it was vital that we helped ensure the safety of everyone working on-site, as well as maintaining the integrity of the Grade II listed building.”
And it seems the project not only presented a welcome challenge to the team at Tiger but also struck a chord with those involved. “This project has been special to us for a number of reasons,” Mr Brown added, “because the building itself is steeped with history and it is always a privilege to work in one of our home counties.”
While the overall project is ongoing, William Birch & Sons Ltd at NYCC has been seriously impressed by Tiger’s dedication to the part they’ve played. Site manager Jason Ware said: “Understandably, we are extremely protective of the building’s heritage and so we had to be very specific with our requirements. It was a pleasure to work with a contractor who was as dedicated to the specialist nature of the job as we were and we’ve been extremely pleased with the solution that was delivered.”
My visit to the NYCC Hall was both fascinating and inspiring. It’s reassuring to see contractors working hard to be innovative, forward thinking and proactive, striving not only to deliver customer satisfaction and quality workmanship but also to
ensure the health and safety of everybody involved in the project. This project was exacting and complex in its nature and provided a showcase for just what the scaffolding industry can produce when put to the test.
“This project saw a range of specialist work being undertaken and it was vital that we helped ensure the safety of everyone working on-site, as well as maintaining the integrity of the Grade II listed building.”
By adopting the use of the innovative KLAWZ fitting, Tiger was able to reduce the amount of tube by more than 25 per cent at Northallerton and erect the scaffolding 25 per cent faster than with traditional methods. This led to reduced labour costs thanks to a shorter installation time with less labour required to erect the structure within the agreed programme. Using fewer materials also reduced lorry movements to get tube and fittings to and from the site leading to lower transport costs and reduced environmental impact.
VR Access Solutions has teamed up with the Scaffolding Association to develop a testing process that has meant they can deliver loading bay gates that will raise safety standards within the industry.
The process allowed VR Access Solutions to rigorously review and enhance its existing product range and the resulting redesigned gate now far exceeds any existing industry standards. VR employed a chartered engineer and a UKAS accredited test house, to further help in the development of the product and the relevant testing process.
The result is the new VR Access Solutions loading bay gates, which have been designed to comply with the requirements of BS EN 128111-2003 and BS EN 13374:2013.
Their unique design allows the safe and easy retrieval of materials in the loading area, without the risk of working near an exposed edge and falling from height.
The loading bay gates are also self-counterbalanced with a smooth one-man operation and are the first to include gate locks to prevent the inadvertent opening of the gate in the open and closed position.
To reduce manual handling and work at height concerns, the gate can be pre-assembled at floor level and lifted into position by mechanical means, and the gates are designed to fit any loading bay width ranging from 2.5m to 3.7m wide.
By using a Scaffolding Association Audited Member, employers can be confident that they are prequalifying and awarding work to contractors who have undertaken a rigorous independent assessment of their experience and capabilities and bring greater choice to employers.
Access platform decking must be inspected daily prior to use, and the system and its components must be inspected every seven days and, in addition, after any incident, alteration or adverse weather conditions where structural integrity may have been compromised.
FASET can also assist here. The FASET Platform Decking Committee has also agreed a training course for those managing and inspecting platform decking systems on their sites. This training will result in a FASET Platform Decking training certificate.
FASET is the international trade association and training body for the safety net rigging and temporary safety systems industry, including access platform decking. FASET is also a founder member of the Access Industry Forum (AIF), which is the industry alliance for access when working at height.
By providing collective access at eaves height, access platform decking enables builders to work both inside and outside of a structure, combining ease of installation with strength. This allows users to safely access, work from and load the decking with materials.
FASET has been working with all the major suppliers and trainers in the sector to agree common training and test standards in the industry, and has successfully agreed a training and certification scheme which will result in a Skilled CSCS Card specific to the trade: endorsed ‘FASET Platform Decking Installer’. This is a first for the industry.
Technically, platform decking systems must conform to BS EN 12811, and if made from plastic type materials, be tested to ACR (M) 001: 2014. Where additional handrails are incorporated, they must conform to BS EN 13374.
In addition to a safety checklist and component schedule, all system manufacturers are obliged to supply a complete and comprehensive installation guide for their respective products. No work should be undertaken without adherence to this guide.
It must include, among other things, details of the PPE required for installers, the
limitations of the system, guidance on load capacity, assembly instructions, step-by-step images of the assembly sequence, information on the maximum gaps permissible under current legislation, a post-installation checklist and guidance on dismantling.
Importantly, all manufacturers must provide, upon request, evidence of load testing, which must have been carried out by a recognised, independent UKAS-accredited test house based in the UK. They must also provide details of the load capacity that their system is rated to under BS EN 12811.
They must undergo a post-erection inspection and handover by a competent installer. This must be formally recorded and state the load capacity of the system.
The highest level of Scaffolding Association membership is the Audited Membership category. This sits at Level 1 in the PAS 91 Three Assurance Level Model, which is the highest and most-comprehensive audit level.
The Scaffolding Association’s Audited Membership is specifically for scaffolding contractors to enable them to demonstrate that they operate to the highest standards. It offers an independent two-stage audit – desktop and on-site – undertaken by IQ Verify, a UKAS-accredited certification body.
The audit process has been developed to reduce the burden on both clients and contractors by increasing understanding and building on the widely applicable range of standards within the industry to provide a Scaffolding Specific Procurement Process. This audit demonstrates a contractor’s ability to safely manage and undertake work and assesses it against criteria which are specific to the scaffolding industry. The process consists of two stages:
Stage One: Desktop – Remote review of documentation, including policies and procedures, training records and a company’s incident reporting system, against a Scaffolding Specific Procurement Standard to establish compliance.
Stage Two: ‘On-site’ – Verification of the documentation implementation on-site against the Scaffolding Specific Procurement Standard.
Once the audit has been successfully completed, contractors are issued with a copy of the audit report, certification from IQ Verify detailing compliance and an Audited Membership certificate from the Scaffolding Association.
Pre-qualification is an essential aspect of tendering for a scaffolding contract. And to be eligible for pre-qualification, scaffolding contractors need to demonstrate that they possess, or have access to, what’s required to undertake work and deliver services for potential buyers.
PAS 91 is a publicly available specification (PAS) that sets out the content, format and use of questions that are widely applicable to pre-qualification for construction tendering. There are three types of assessment – from Level 1 at the high end to Level 3 at the low end – that can be carried out to assess that a potential tenderer meets the requirements of PAS 91.
This includes an audit typically involving on-site verification and outcome assessment, before accepting the supplier as meeting the requirements. This is the most certain option for buyers but potentially the most complex for pre-qualifying contractors. It is preferable where high levels of assurance are essential or simply sought by the buyer.
Within this assessment level, activities include, for example, obtaining copies of certificates
and gathering details of company procedures. This commonly includes what is referred to as ‘desktop’ assessment. This level provides more certainty for buyers than the minimum assessment offered by the self-assessment approach of Level 3.
Level 3: Self assessment
To be assessed at this level, the supplier completes a questionnaire and makes statements about their work and certifications. Minimal verification activity is carried out. Although this is the cheapest solution, it is the least-certain option for buyers.
The move by the Scaffolding Association to offer an Audited Membership level for scaffolding contractors has been welcomed by house builders, local authorities and major contractors who now recognise the benefit of Association members on their tender lists and construction sites.
Clugston Construction’s health and safety manager, Mark Atkinson, commented: “By using Audited Members of the Scaffolding Association we can be confident that we are procuring contractors that have demonstrated their skills, knowledge and experience through a trusted process.”
Increasingly to prove competence, contractors must undertake multiple pre-qualification processes depending on client preference, with PAS 91 being the specification that the majority of pre-qualification questions are based on. Stacey Underhill from the Scaffolding Association takes a look at the different levels of audit available to scaffolding contractors needing to pre-qualify.
Stress and mental health issues can have enormous negative impact on employee wellbeing. They are a huge drain on productivity and thought to be a strong contributor to absenteeism, yet they can still pass unnoticed and unmanaged by many organisations.
There are many sources of stress in the workplace: job-related anxiety, workplace conflict or bullying, high workloads, heavy pressure and more. Stress and anxiety often go undiagnosed or unreported, particularly in the “macho” environment of construction sites. And as a result, some construction companies claim they have never had an employee suffering from mental health problems, but national statistics tell a different story.
The Centre for Mental Health estimates that 91 million working days are lost each year because of mental health conditions, costing employers nearly £26 billion. In addition, stress and anxiety can lead to lower morale in the workforce, physical illnesses in individuals, accidents and injuries, and, in extreme cases, self-harm or suicide.
All employers have legal responsibility under the Health and Safety at Work Act 1974 to ensure the welfare (physical and mental) of their employees. This includes minimising the risk of stress-related illness or injury.
In January, the Health in Construction Leadership Group (HCLG) held its second summit. Following the success of its inaugural 2016 event, which discussed the importance of raising awareness of health issues in the construction industry – focusing initially on respiratory disease – this year’s summit reflected on progress to date as well as bringing a focus to the growing issue of mental health within the industry. The 300 delegates were presented with a variety of tools and techniques to apply with their teams.
This included the launch of the Mates in Mind programme (see www.matesinmind.org), set up with the support of the British Safety Council. Mates in Mind aims to raise awareness and understanding of poor mental
health in the construction sector by bringing the industry together to openly talk and address the stigma associated with mental health through employer support and sharing of information.
Dealing with any health and safety issue is not just about jumping through legislative hoops. Good health and safety management is about creating win-win situations between workers and employers. When stress is managed at work, it will no longer be a cause for absenteeism, and employees will be happier and more productive.
The HSE publishes Management Standards for work-related stress (see www.hse.gov.uk/stress/ standards). Simply monitoring the six identified sources of stress in your organisation is a powerful first step to promoting organisational and individual health and wellbeing. But monitoring the risk factors should be followed up with stress management plans.
There are plenty of ideas that can be implemented to reduce stress and to show concern for your employees’ mental wellness. Simply saying “Thank you” and asking “How are you?”, and listening sincerely to the answer, can
go a long way. Making sure that your employees’ work is meaningful and providing adequate down-time for your employees to rest and socialise are also very important.
Speaking at the HCLG summit, Clive Johnson, one of the founding members and chair of the HCLG and Group Head of Health, Safety and Security at Land Securities, said: “With suicide causing ten times more deaths than accidents on sites, it is imperative that the industry is truly aware of the deeply impactful consequences of unaddressed mental health issues.
“In raising this issue today with over 300 industry leaders, we have set the foundations to addressing mental health openly, confidently and honestly within the construction industry; not just by ‘starting the conversation’ but by providing delegates with the skills and knowledge to go back into their workplace and address this issue head on.”
Scaffolding Association chief executive Robert Candy said: “It’s impossible to remove all types of workplace stress, and this is especially true of the construction industry. And, of course, some employee stress will come from sources that are outside your control.
“Having said all that, it’s incredibly important to control and minimise the risks of harm that stress and mental health issues present, wherever it’s possible to do so.”
When managing your organisation’s health and safety, don’t forget about the issue that affects one in four people in the UK at some time in their life. Jenny Gibson reports.
“It’s incredibly important to control and minimise the risks of harm that stress and mental health issues present, wherever it’s possible to do so.”
www.accesspoint.org.uk
Keep an eye out for our latest events at www.scaffolding-association. org/events
Scaffold VR Demonstration and Scaffolding Association
Roadshow
Jurys Inn, Aberdeen
25 April 2017
Edinburgh Capital Hotel, Edinburgh
26 April 2017
Jurys Inn, Glasgow
27 April 2017
Scaffolding Association AGM Union Jack Club, London
19 June 2017
UK Construction Week NEC, Birmingham
10–12 October 2017
CASS was awarded the contract by Galliford Try Partnerships to provide all the scaffolding for the new Stoke Gifford Retirement Village, north of Bristol, in October 2016.
CASS started work on-site within weeks of the contract win, with the management team, supervisor and operatives worked closely with site management to develop a very positive working relationship.
Galliford Try Partnerships named CASS supervisor Jon Wingren as Employee of the Month earlier this year, recognising Jon’s high standards of safe working and support of Galliford Try’s ‘Challenging Beliefs, Affecting Behaviour’ programme.
Howard Evans from Galliford Try Partnerships said: “Jon has been recognised for his hard work on this site, but this could have a greater impact if this good practice is transferred to all other contractors and sites that Galliford Try Partnerships are managing. Well done to Jon and to CASS.”
The team at Hampshire-based Hampton Scaffolding are keeping busy putting on fantastic charity events. General manager Jamie Phillips is organising a charity ‘international friendly’ between England and Holland at Aldershot Town FC on Friday 12 May – 7pm kick off – on behalf of his son Chase and the Cystic Fibrosis Trust. Entry is free and everyone is welcome.
Lizzy Hampton, one of Hampton’s owners, organised a hugely successful Grand Prix Ball in October last year, raising over £15,000 for charity Enabling Asher.
Asher is a happy young boy who has the condition spastic cerebral palsy, which followed on from him being born 10 weeks early with three holes in his heart. Funds raised help to buy life-changing equipment that makes a huge difference to Asher’s development.
FIND OUT MORE
www.justgiving.com/fundraising/Englandvholland www.justgiving.com/fundraising/enablingasher
Congratulations to Scaffolding Association members WellMax Scaffolding Limited, Tiger Scaffolding Limited and KLAWZ Limited for being recognised as finalists at this year’s Construction News Specialist Awards.
These construction industry awards celebrate the outstanding achievements of the very best specialist contractors in the UK, so making it to the shortlist is fantastic.
Both WellMax Scaffolding and Tiger Scaffolding were finalists in the Access & Scaffolding Specialist of the Year category.
A number of prestigious projects in and around central London for WellMax Scaffolding, in addition to impressive business growth, put them on the shortlist.
And it was Tiger’s complex project in Northallerton for North Yorkshire County Council’s Grade II listed building that caught the judges’ attention both in the Access & Scaffolding Specialist of the Year category and in the Project of the Year (subcontract up to £1m) one. Read more about this challenging brief for Tiger in our Site Report on page 16.
In the Business Innovation of the Year category, KLAWZ stood out for its recently developed KLAWZ Scaffolding Fitting. This category is all about ideas that improve construction efficiency, and the new KLAWZ is a specially designed Class B-tested fitting with a theoretical safe working load of 18.2 kN – double that of any standard Class B fitting.
Well done to you all. A great achievement!
Apex Scaffolding Services Swindon Limited www.apexscaffoldingservices.co.uk
B&C Scaffolding Limited www.bandcroofing.co.uk
Chelsea Scaffolding Access Limited www.chelseascaffolding.co.uk
Conker Nation Limited www.conkernation.co.uk
Finningley Scaffolding Limited www.scaffolding4yorkshire.co.uk
Infrastructure Site Services Limited 07947 372139
Masons Scaffolding Limited www.masonsscaffolding.com
Morris’sons Scaffold Services Limited 01495 246233
PDC Scaffolding Limited www.pdcscaffoldingltd.co.uk
Pinnacle Access Services Limited www.pinnacleaccess.co.uk
Scafftech Scotland Limited www.scafftech.co.uk
South West Scaffolding Limited www.swscaffolding.co.uk
Summit Scaffolding Limited www.summitscaffolding.co.uk
Trueform Scaffolding Limited www.trueformscaffolding.co.uk
TWO Tone Scaffolding Limited 07939 400167
PRODUCT MANUFACTURER Sayfa Systems UK www.sayfasystems.co.uk
INSURANCE COMPANY
Berns Brett Limited www.bbicover.com
CCS Scaffolding, based in Gravesend, Kent, is celebrating after becoming an Audited Member of the Scaffolding Association. The company, which employs more than 40 people, has been a member for 11 months but made the decision to become audited from the moment it gained membership.
Edward Farrell, health and safety executive at CCS, said: “We have always been dedicated to complying with both industry standards and our client’s own safety processes to ensure our scaffolding is erected in the safest manner and our employees’ safety.
“We saw many benefits to becoming an Audited Member but what really stood out for us was the opportunity to undertake an annual audit which is currently not offered by any other
association. Also, the fact the association uses an independent UKAS-accredited auditing company is important as it means auditing will be undertaken thoroughly and will help us continually improve our processes as we grow as a company.
“The process of becoming audited was extremely thorough and covered all aspects of the scaffolding industry from our start of shift briefings and tool box talks to harness inspections and a recording of our findings. We also had to demonstrate our working gangs to see whether, as a company, we were following best practice.
“Becoming an Audited Member of the Scaffolding Association means we are confident that our methods and procedures are fully compliant to industry standards and we are working in the safest possible way. We know that
London-based M R Scaffolding has had its commitment to public safety and high-quality workmanship duly recognised with a Gold Award from the City of London Considerate Contractor Scheme.
The scheme encourages all building and civil engineering contractors working in the City to carry out their operations in a safe and considerate manner, with regard to pedestrians and road users.
M R Scaffolding is a second-generation family-owned business, established in 1974 by Michael and John Trayfoot and now managed
by the founders’ sons, Matthew and John Jnr, alongside Frank Pickford as contracts director. A new modern and agile management style, coupled with strict quality controls and a continuous improvement programme, has seen the business grow in recent years.
Matt Trayfoot, M R Scaffolding’s health and safety director, said: “We take public safety and quality of workmanship very seriously and so we are thrilled to be selected as a Gold Award winner this year.”
FIND OUT MORE www.mrscaffolding.com
scaffolding is a high-risk industry but with the Scaffolding Association’s knowledge behind us, CCS Scaffolding is implementing every possible control measure to ensure employees are safe at work, and, by undertaking an annual audit, we will always be up to date and following best practices year in, year out.”
FIND OUT MORE
www.scaffolding-association.org/membership
Do you have a story to share in the next edition of AccessPoint? We’d love to hear about your latest projects, business developments, examples of best practice and whatever else you’re doing that might interest AccessPoint readers!
We just need around 100-150 words and a good quality photograph. Please email your news to newsdesk@accesspoint.org.uk
SYSTEM SCAFFOLDS
LATTICE BEAMS
ACCESSORIES
TEMPORARY ROOFING PROPS-STRUTS
FALL PREVENTION
TRADITIONAL SCAFFOLD READYLOKS
LADDER BEAMS VR Access Solutions is a manufacturer and supplier for access solutions and scaffolding products. VR Access Solutions has established a strong market position and it is committed to delivering quality and innovation.
The new VR Access Solutions loading bay gates, which have been designed to comply with the requirements of BS EN 12811-1-2003 and BS EN 13374:2013 demonstrate how innovation can help contractors improve both safety and quality. Their unique design allows the safe and easy retrieval of materials in the loading area, without the risk of working near an exposed edge and falling from height.