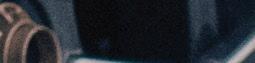
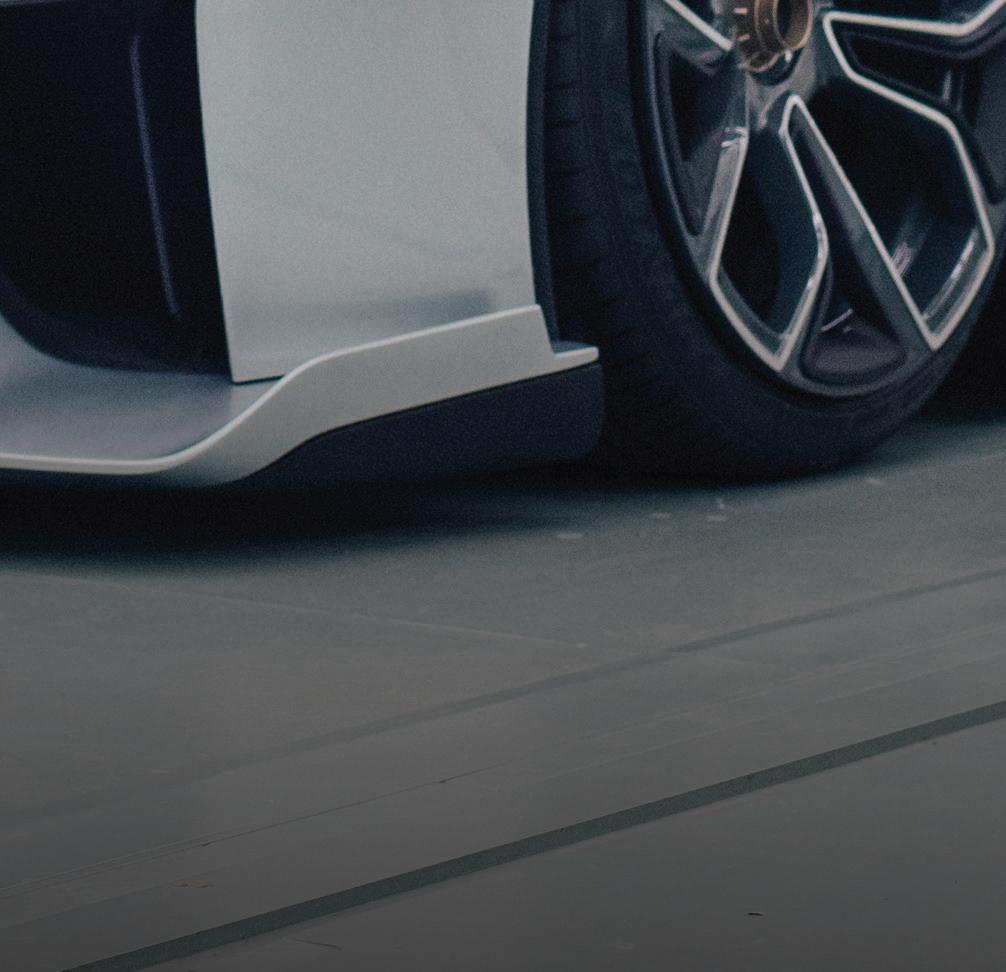
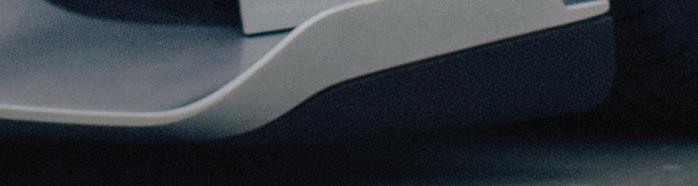



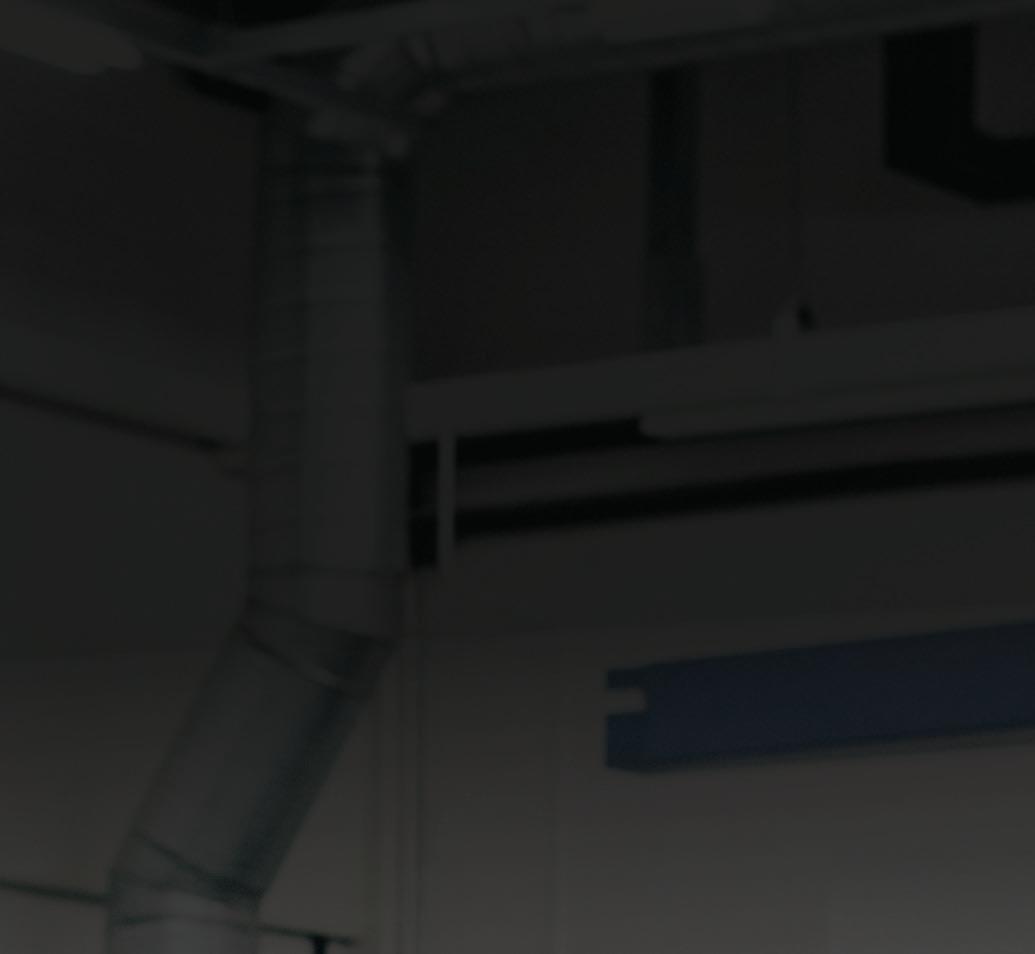
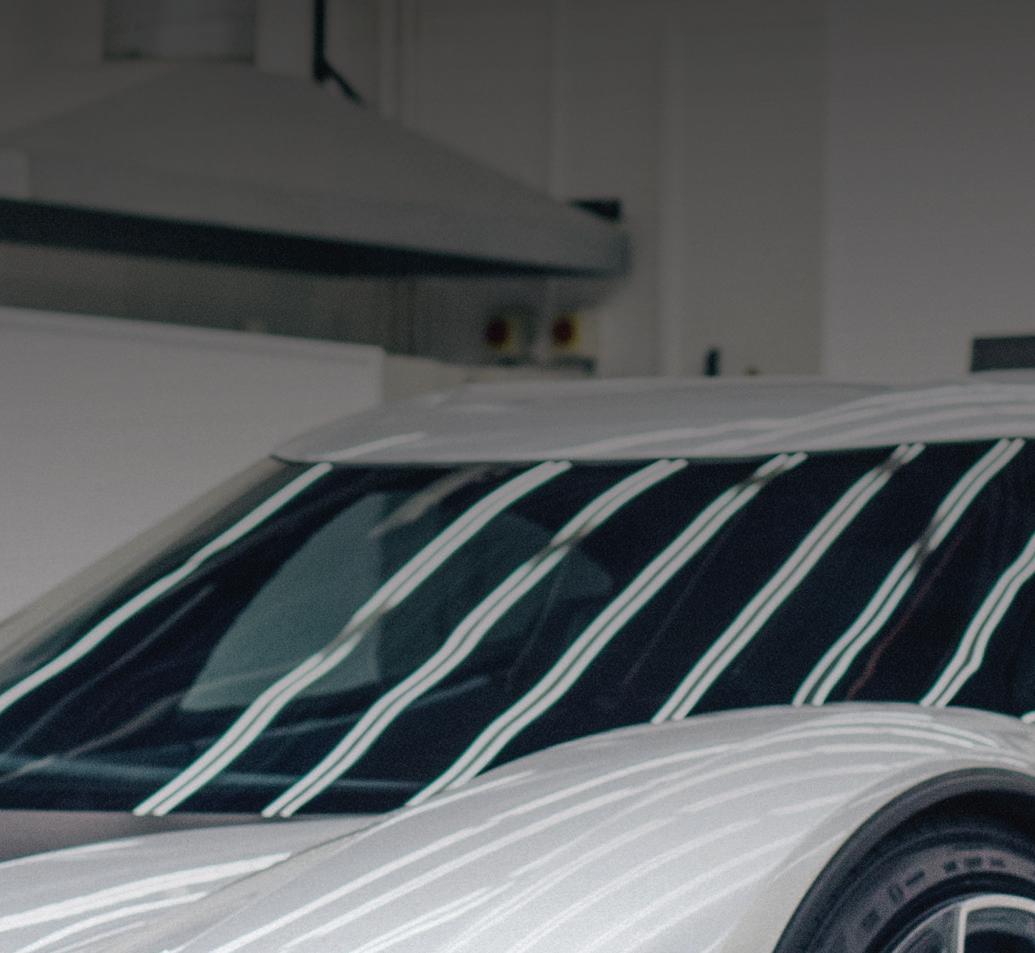
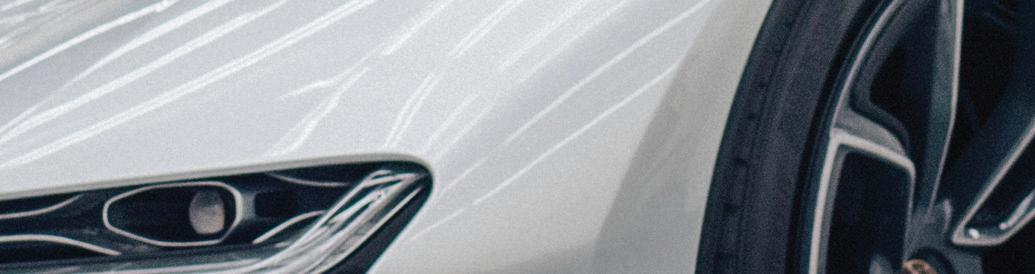
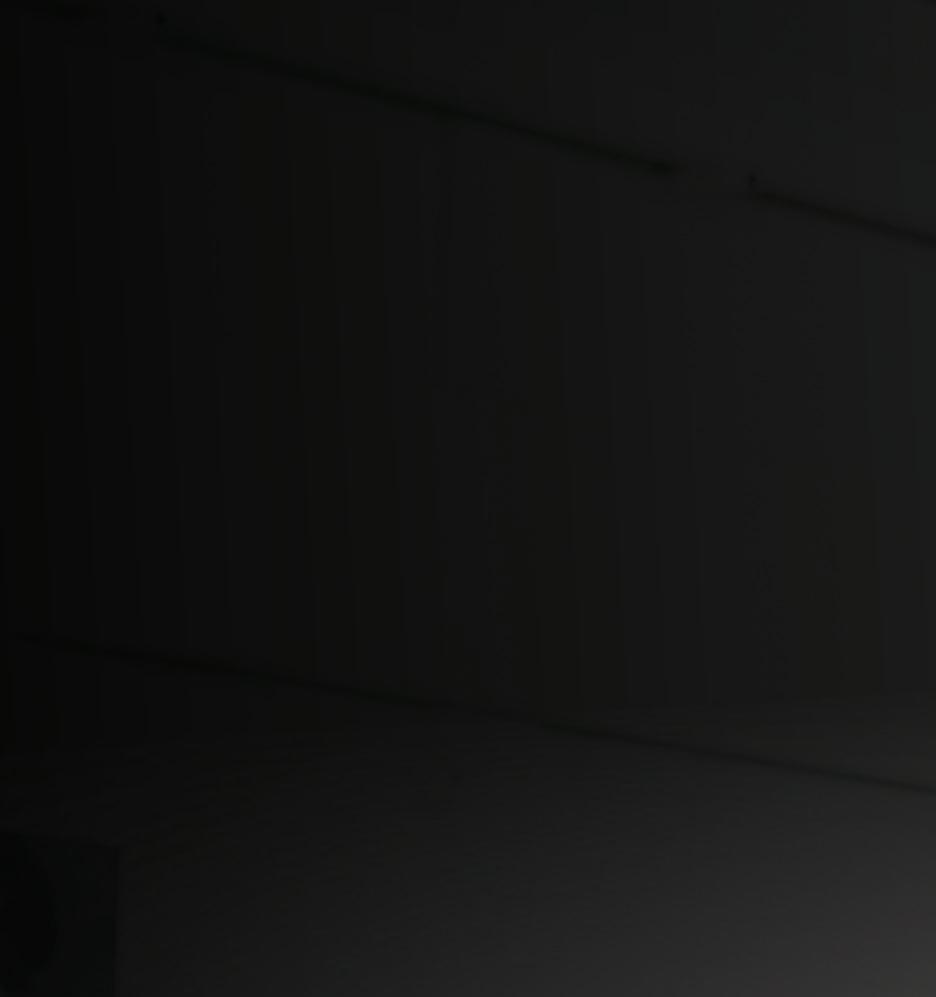
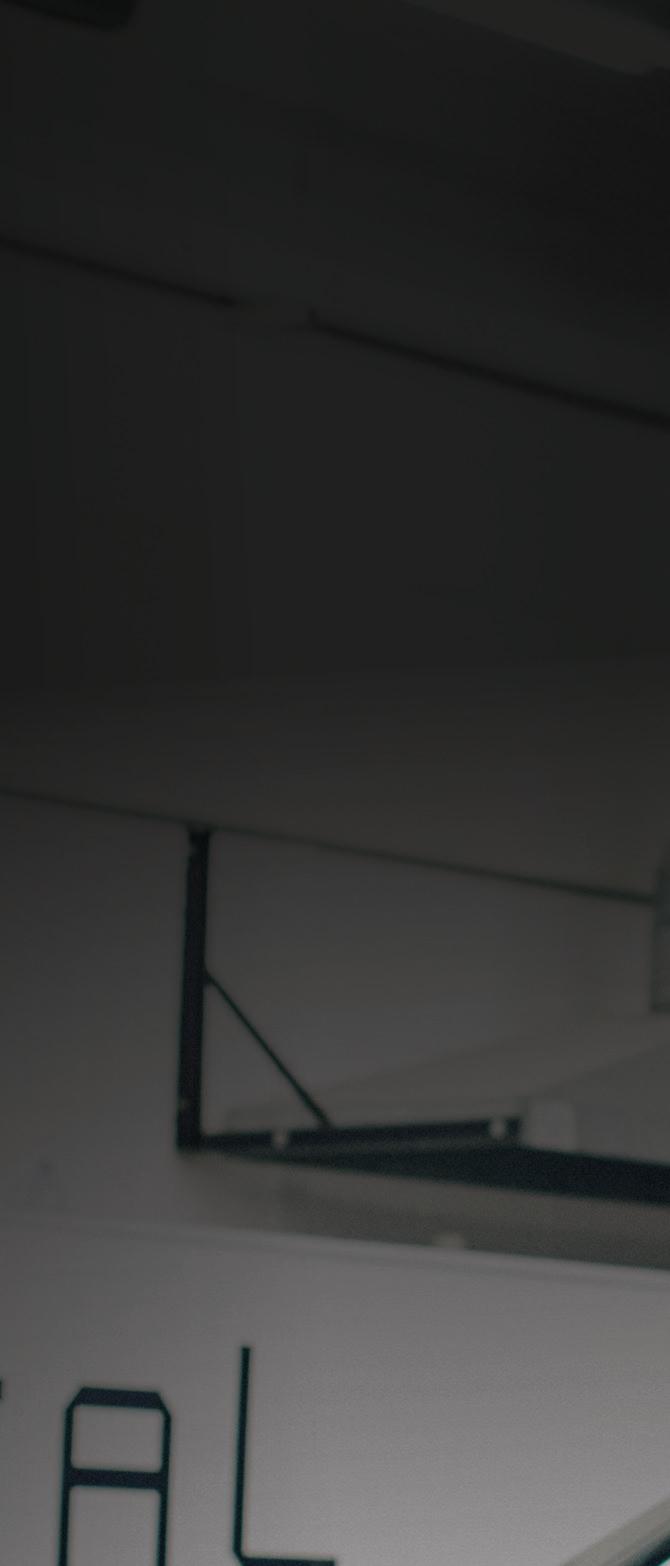



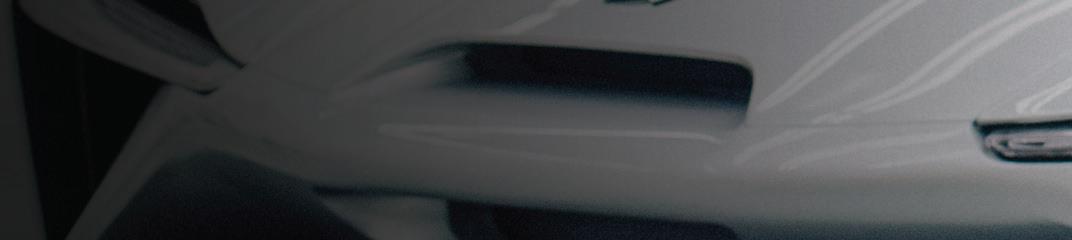
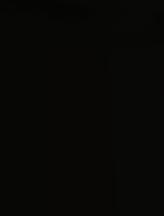

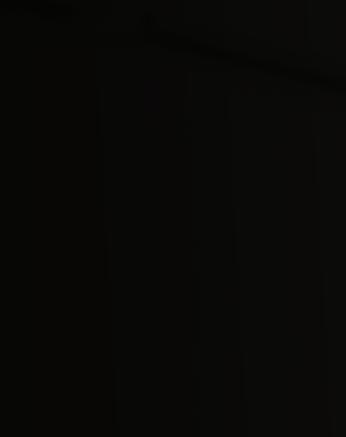
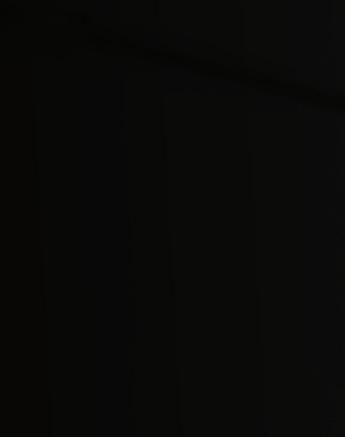
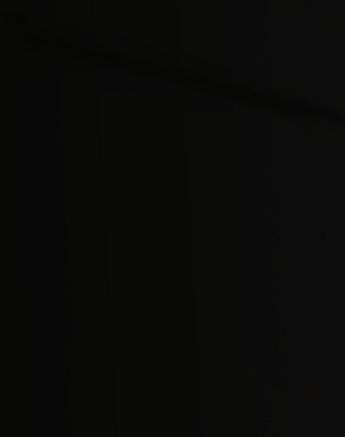
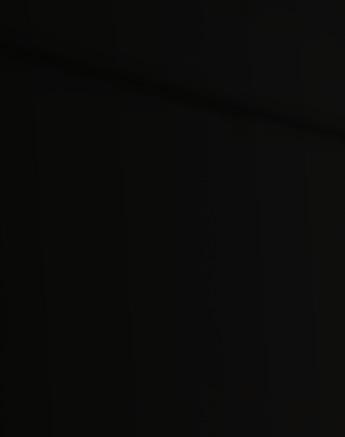
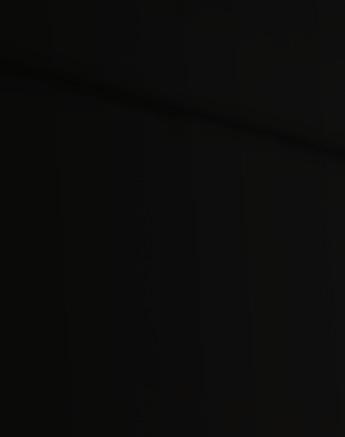
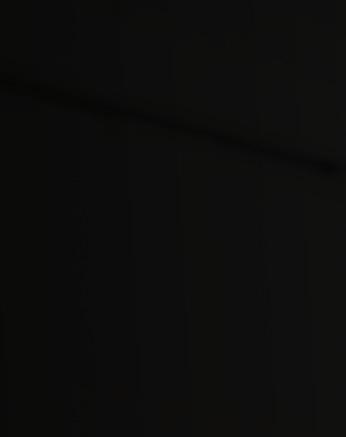
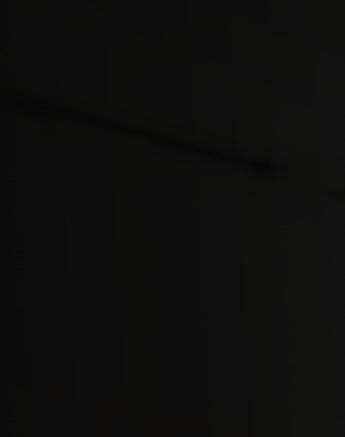
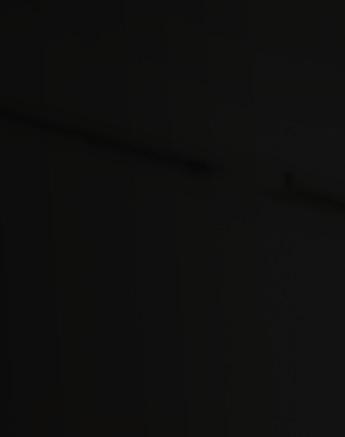
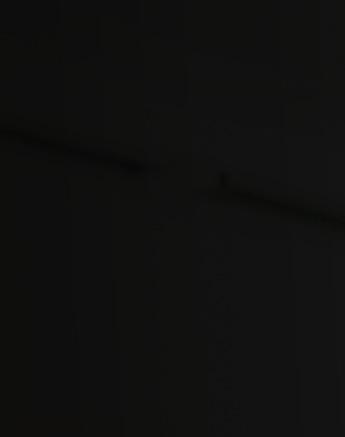
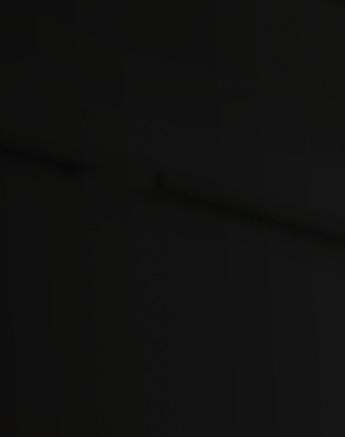
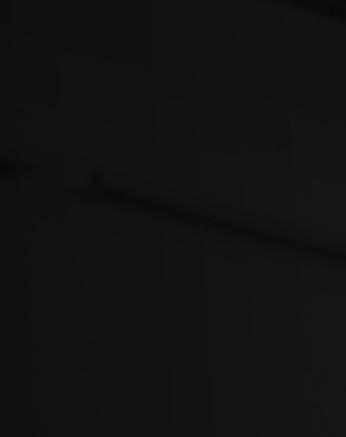

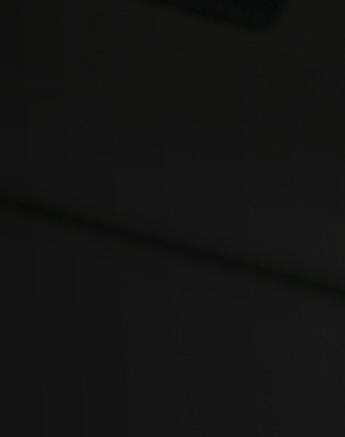
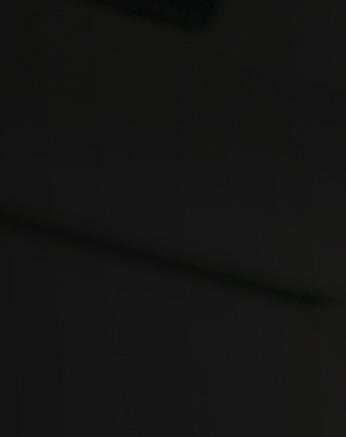
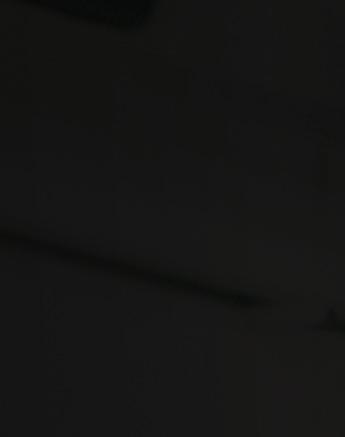
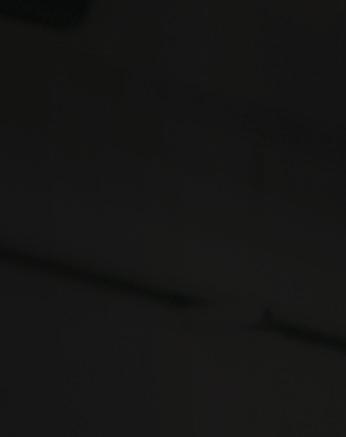
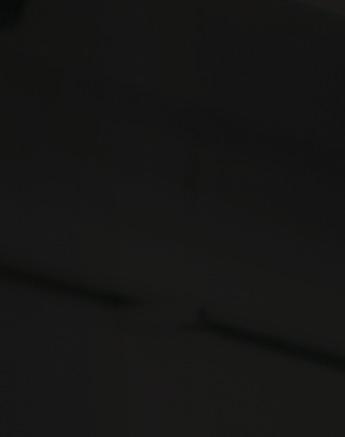
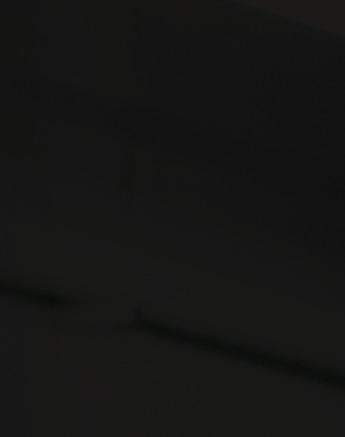

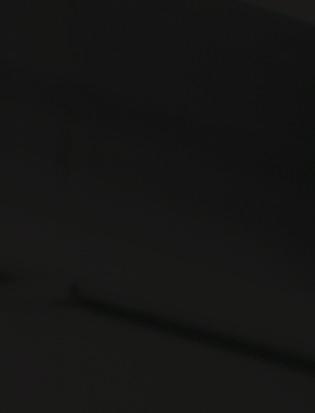
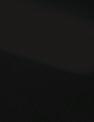
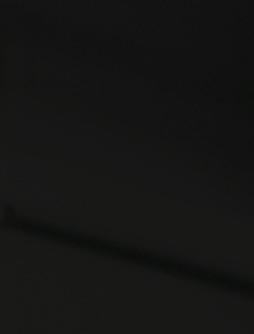
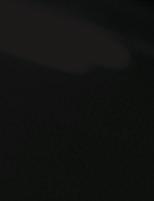

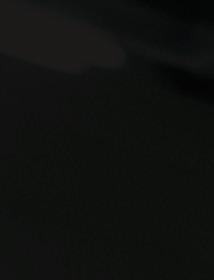



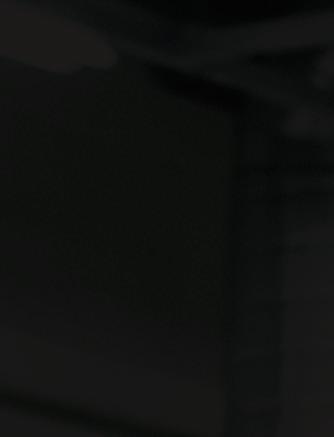
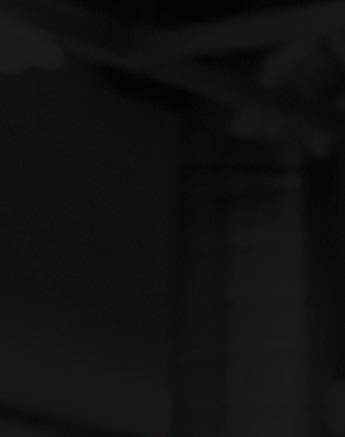
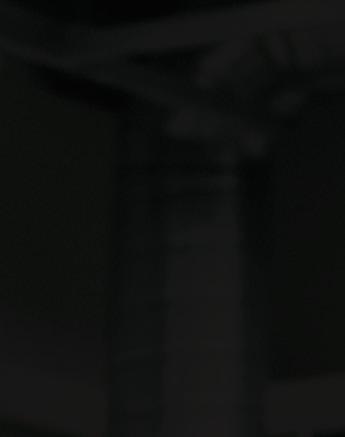
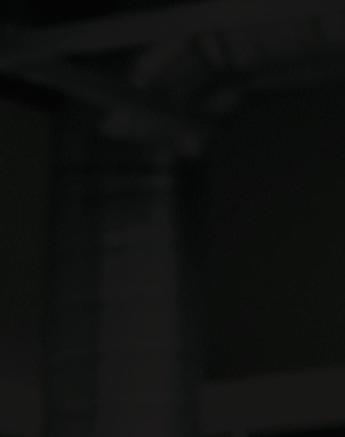
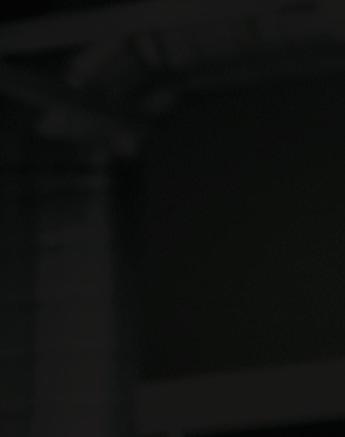
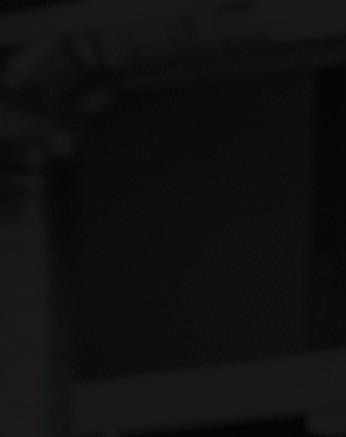
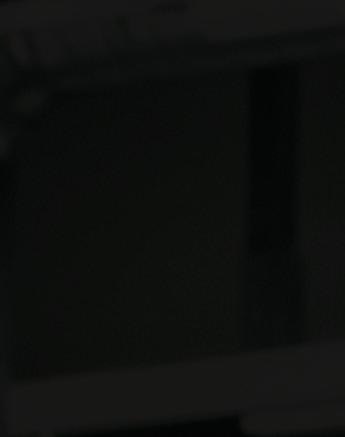
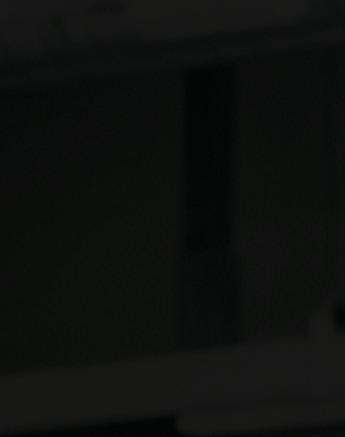

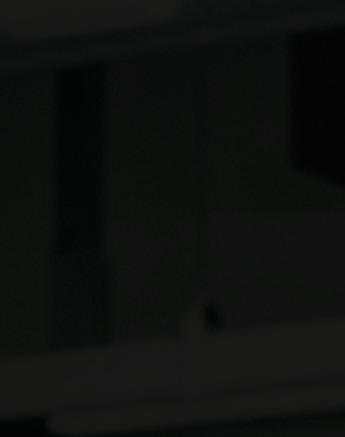
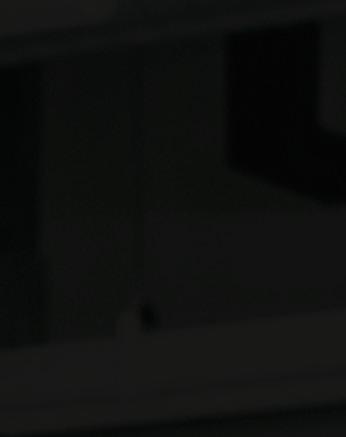
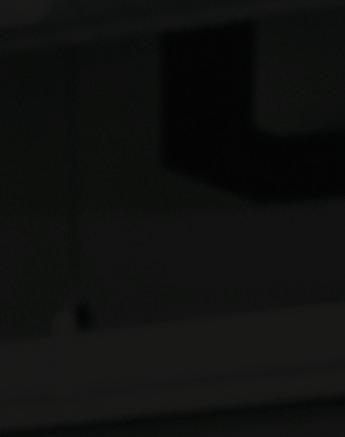
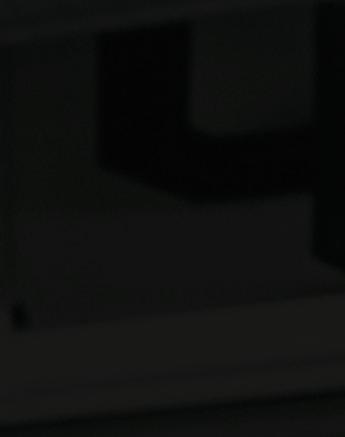

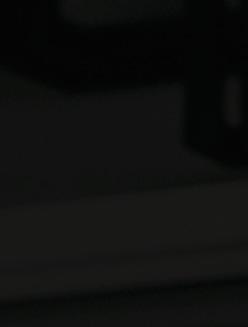
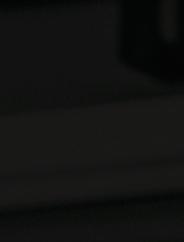



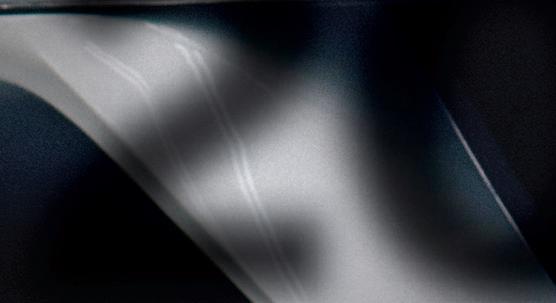
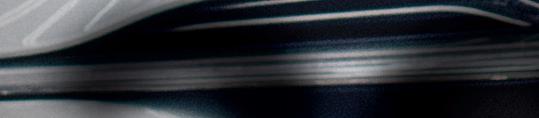
Partnering with 3D printing helps prosthetics developer create better products, gain workflow efficiencies, meet increasing demand, and shift to titanium 3D printing, all within in 6 months.
Point Designs is an innovator in the field of partial hand prosthetic design and provides artificial digit solutions through a combination of additive manufacturing (AM), mechanical design, and clinical care. Founded by researchers out of the Biomechatronics Development Laboratory at the University of Colorado, Point Designs needed manufacturing support when demand for its products outpaced in-house capacity.
With early access to lab resources at the University of Colorado, the company’s developers created its Point Digit solution with 3D printing in mind from the beginning.
The development team took advantage of the benefits of design for additive manufacturing (DfAM) by creating organic shapes, semi-hollow structures, and assemblies in situ. These types of features are uniquely enabled by AM and are a compelling reason for many to use the technology, enabling parts to be designed specifically for their intended function, at reduced weight, and with reduced assembly. However, achieving a successful 3D print can be tricky, especially when the final product entails detailed mechanisms that require strict tolerances. According to Point Designs CEO Levin Sliker, working with 3D Systems helped his team improve its designs to be optimized for the printing process.
The company’s team selected 3D Systems as its production partner to help solve its supply issue and advance its product development process. Through close collaboration with 3D Systems’ experts, the company changed from steel to titanium material in just six months, gaining workflow efficiencies and valuable knowledge to advance its portfolio.
3D printing offers the ability to develop custom partial hand prosthetics.
One key AM-enabled feature that Point Designs uses is a live hinge, which is printed as an assembly in situ and allows rotation for more natural movement. Sliker says the ability to print this assembly in place is an incredible benefit because the hinge components are not only small, but they are internal components. “To assemble them any other way would be difficult, if not impossible,” says Sliker. “Not only would it be time-consuming, but you’d have to keep track of some really tiny parts. Printing everything in place with a live hinge really simplifies our assembly and manufacturing.”
Despite the short timeline to product launch, the development team had some design-related challenges to overcome when it started its work with 3D Systems, in particular when it came to part orientation. They had selected a build orientation to accommodate the critical dimensions and tight tolerances of its final parts. However, this orientation was not optimized for scaled production. Together, the 3D Systems team and the development team worked together to devise a new print strategy that would enable substantially more parts to be printed in a single build while taking downstream processes into account. To avoid support scarring on critical surfaces, the two companies worked together to come up with support structures that would be easy to remove, as well as post-processing techniques to deliver the desired finish on those surfaces.
When the development team was searching for a manufacturing partner, its primary concern was capacity. By selecting 3D Systems, Sliker says it gained titanium as a
bonus. But Point Designs is not the only one benefitting. Jeff Soelberg is an end-user of the Point Digit solution and has worn both the steel and titanium versions. With a 30% reduction in weight enabled by the new material, the difference was instantly noticeable. When wearing the steel device, Soelberg said it felt as if he was carrying around a small weight: “The switch to titanium feels so much lighter and much more natural,” he shared.
Beyond weight reduction, the material and design of these devices have earned a plethora of positive feedback from end-users because they offer strength, durability, and easy washing. Recipients can take them into any environment they would take their regular fingers. Soelberg said that with practice, he
Since working with 3D Systems we have really honed our design protocol in-house. 3D Systems has brought new perspective and knowledge about optimizing our designs for high volume 3D printing, improving postprocessing methods, and increasing the yield of high precision components from each build plate.
- Levin Sliker, Co-Founder & CEO, Point
is back to doing 95% of the activities he pursued prior to his accident.
In switching materials, 3D Systems helped the development team navigate titanium-specific challenges, sharing know-how that will translate to future projects. Primary among these was assistance in designing to accommodate titanium’s shrink factor.
“By working with the 3D Systems team we’ve definitely improved our design process for existing and future products, so that the next product will be easier to implement and quicker to achieve a frozen design file ready for mass production,” said Sliker.
The titanium Point Digit 2.0 solution is printed using 3D Systems’ direct metal printing (DMP) technology and LaserForm Ti Gr23 (A) material, which features best-inclass oxygen levels (<25 ppm) and an inert printing atmosphere, ensuring exceptionally strong and accurate parts with high chemical purity and repeatability. By using the same digital data package per part, the printing machines enable scalability of production by delivering the same outcome across all DMP machines with no global off-sets.
The two companies collaborated on four products, each comprised of multiple 3D printed components
and available in multiple sizes for a total of 17 SKUs and 107 unique components. Once the development team receives the printed parts from 3D Systems, they are assembled using a combination of off-the-shelf and custom components. Following assembly, the development team delivers its products to a prosthetist, who creates a custom prosthetic socket for each recipient.
“The fact that 3D Systems’ Application Innovation Group could support us through printing using its own technology was really enabling for us,” says Sliker. “The familiarity they have with the capabilities of their machines proved allowed this partnership to flourish.”
In terms of solving its supply issue, Griffin Drye, business development specialist at Point Designs, says that since working with 3D Systems, the companies have established a reliable production cadence and Point Designs hasn’t experienced any back-ordered products since, which is a meaningful and welcomed achievement. This has been possible through the close and open communication between the two companies,
allowing each to have visibility into the other’s timelines for accurate forecasting and planning. Following the successful launch of Point Digit 2.0, a Class I medical device, Point Designs is now pursuing numerous other prosthetic offerings which will leverage 3D Systems’ expertise.
The use of 3D printing has resulted in:
• 30% weight reduction for a better end-user experience
• greater DfAM know-how based on the guidance of AM experts
• product lauch in six months due to 3D printing
• elimination of back-orders thanks to an effective production schedule.
3D Systems
www.3dsystems.com
The scale of sizes that 3D printing machines can handle is impressive, from huge wind turbine blades to parts that are small, such as two microns. John Kawola, CEO of Boston Micro Fabrication discusses the microscale side of 3D printing.
Microscale 3D printing is the concept of making parts at millimeter scale or even sub millimeter scale. It’s a technology that has been available for five, maybe even 10 years. What’s new is that this technology is being commercialized for industrial use.
Boston Micro Fabrication (BMF) uses a microscale technology that is a variant of stereolithography. It is called projection micro stereolithography, or PµSL. A Boston MIT professor, Nick Fang, developed the idea. Fang had been working on micro fabrication techniques over the years.
A lot of those micro fabrication techniques are not 3D printing. These techniques include embossing, and etching and photolithography. But for 3D printed micro parts, applications include the semiconductor and the MIM space.
Fang’s idea was to try to move into the 3D printing/additive manufacturing space. The concept was to use the PµSL approach, which is similar to other DLP 3D printers in the market. The approach consists of a resin bath, with light to cure the resin. In BMF systems, the light source is focused down to a very fine resolution and the movement is controlled to ensure precision. Microscale 3D printing fits a market segment of high-value
industries that do product development, manufacturing, and production, but with resolution and dimensional accuracy requirements in the millimeter, and perhaps micron area in tolerances, such as electronic connectors.
Other small size production technologies exist, including photon lithography. One criticism of photon lithography is that it takes a long time to make a very small part. For example, a 20-millimeter size part might take a week to build.
The connector market, worldwide, is valued at $100 billion dollars. And connectors are getting smaller all the time. New markets, such as AR/VR for glasses are emerging that suit this technology. Design efforts continue to try to miniaturize in the optics and photonics market. In the medical device market, things are getting smaller, whether they’re sensors or drug delivery devices, or implantable devices. There’s a trend around industries wanting to get smaller.
Design challenges with microscale parts are not much different than those for macro parts. If it’s a connector, it needs to have certain features to be a connector, same with chip packaging. It needs to have certain characteristics to hold a chip, or a lens holder, but there are always considerations about how are you going to make it, including how to mold, machine, and/or stamp the part. One of the realities is the manufacturing processes for these smaller parts are more difficult and much more expensive.
For example, if you’re molding something like a computer mouse, that’s not that hard to do. The injection mold for that mouse is maybe tens of thousands of dollars, maybe $25,000. But if you’re making something really small, that
Microscale 3D printing is the concept of making parts at millimeter scale or even sub millimeter scale. It’s a technology that has been available for five, maybe even 10 years. What’s new is that this technology is being commercialized for industrial use.
injection mold may no longer be $25,000. It might be $250,000 because you need to machine that mold to get all the tolerances that you need, and you need to be able to build in the ports and all the dynamics that go into an injection mold, but at a very small scale.
Most users of these micro 3D printing machines are using them for prototyping. Until about two years ago, affordable micro 3D printers were not available for this application. Users could not get the resolution and detail they wanted one for one.
Today, about a third of users are doing some production. Users are testing materials, their design and then looking into production quantities. Some are finding out it’s less expensive to let the 3D printer handle the mold than to machine or stamp them. The mold materials are predominantly resin-based, with some ceramic materials.
What goes into the development of a macro 3D printer
BMF’s chief technology officer, Chunguang Xia, came from the semiconductor industry. One of the challenges was ensuring high tolerance, to create a platform when people are looking to get tolerances in the plus or minus five-micron area. At this level, measurements are done using technologies similar to a CT scanner.
“We needed to have a platform that could image onto the resin and create the part,” says Kawola. “If you’re making a larger part, our platform actually moves to be able to image in certain sections. All of that had to stack up. You’re also dealing with material shrinkage, so you’ve got all these variables that you’re trying to get to a place where you’re plus or minus whatever that tolerance is. I think it’s just a lot of good engineering by our team here to recognize that’s the target.”
For the DLP system, high precision optics were needed. “We’re really focusing down to a certain pixel size,” Kawola continued. “When we talk about,
let’s say 10-micron optical resolution, that’s actually the size of the pixel that’s being imaged onto the liquid. Most DLP systems in the market are upside down, so they’re coming out of the liquid. That has a lot of advantages. We are top down. We do that for a couple reasons. One is we need to control layer thickness. The thicknesses of our layers are in the 10-to-20-micron range, so we need to be able to highly control that. Two, all DLP systems, all resin-based systems, when that light comes down and polymerizes the resin, that’s a reaction and there’s heat. Most 3D printing systems, there’s heat being generated and that’s one of the challenges, actually, for a lot of DLP platforms.
“A company in Chicago, Azul, has some new breakthroughs in how to control that heat and try to cool that process as it goes, but it’s a challenge and heat is bad for trying to maintain dimensional accuracy. That’s another reason why we are top down because when you’re bottom up, you only have a thin layer of resin. There’s heat there and that can build up. When the system is top down and you have a vat, it acts as a heat sink, so you don’t really have that buildup of heat that affects most other technologies.”
An ecosystem for materials has been evolving for about five years. BMF is an open platform. “For prototyping, arguably the materials don’t matter that much. They need to be close enough and most people can be pretty happy, but when you get into manufacturing, they need to be really close or exact. I think the collective wisdom of more companies coming into the 3D printing material space, in my opinion, has significantly moved the industry forward over the last five years, at least.
“Now, it’s not just the 3D printing companies with their material science departments within each company. Now you’ve got Henkel, and Covestro, and BASF and Evonik and all these big companies coming in and developing materials to help push that along. We’ve tried to take advantage of that. We’ve tried to shop around and see what’s available and partner with as many people as we can. I think what’s attractive also in that open business model is if resins work on some other DLP printer, and have proven to be successful and attractive to customers, they will probably work on our platform too. We can take things that have been developed. We need to modify them a little bit, primarily because our layers are thinner. We have to tune them essentially, but then we can offer that wider range of materials for the customers.
“The other important thing that we believe in for the open materials model is if big customers are really going to go into production, they’re going to want to have more control over the material supply chain. That’s our opinion. They’re going to want to be involved. I mean, we even see it when we work with some of them. We’re still a small company and when we go to a big chemical company and ask them to do something for us, they’re polite, but they don’t jump, but if we go there with a customer that is already one of their customers on the thermoplastic side, who already buy tons of plastic pellets, they are more willing, I think, to think about working together to develop 3D printing materials for that customer.”
There’s been a significant improvement in materials over the last ten years for nearly all 3D printing platforms.
A key trend now is to make sure that all the systems, the materials, and the software are designed with manufacturing in mind so that the systems can be put into a factory and put in series or parallel with other manufacturing technologies, and can work with the quality management system that the company may have. Users are realizing that for most 3D printing technologies, the very large majority of the cost is not the labor. It’s the amortization of the machine, it’s the materials and the labor’s a relatively small component.
The automation piece is important when it adds real value, but it should be balanced with the cost and flexibility that comes with a person. “A person’s pretty flexible. If he drops something on the floor, he picks it up. If the robot drops something on the floor and it didn’t mean to, it doesn’t know how to pick it up. There’s that balance there. I’ve been in injection molding houses and I’ve been in 3D printing service bureaus where there’s 20 machines running and there’s one or two people. I think the automation will help, but I think there’s still lots of room to go in terms of getting the machines to the point where they may need more automation.”
Kawola thinks that for all of 3D printing, whether it’s resin-based, or filament-based or powder-based, the key is to get those additive manufactured materials, those 3D printing materials to be sufficiently the same as molding materials or machine materials.
“Our challenge and the industry’s challenge is to try to get that part to be close enough to the thermoplastic to be suitable for the application.”
Boston Micro Fabrication
www.bmf3d.com
Additive hardware continues to improve in productivity, accuracy, and in ease of use. Now, the focus is on software to improve additive functions and capabilities, and to take additive to the next level. Hardik Kabaria, the director of Software Engineer focused on R&D at Carbon, offers insights.
Kabaria notes that more engineers are involved in some way with 3D printing/ additive manufacturing. Reports from ASME, for example, estimate that about 88% of the engineers use 3D printing, whether it’s for prototyping, bridge manufacturing, or actual manufacturing of the
parts. More engineers view 3D printing as a toolkit, so more design tools are emerging to support them.
These tools support engineers to make amazing parts and to take advantage of 3D printing’s design and manufacturing capabilities.
With its manufacturing capabilities, each process is different, for example between plastic and metal materials, and every process underneath that.
Software is making it easier to place different mechanical functions in specific areas of a part. A bike saddle, for example, can be made aesthetically pleasing, as well as comfortable. If you create many different types of foam, layered into a bike saddle, it’s possible to reduce pressure for greater riding comfort. But then it will create a nightmare in terms of manufacturing cost and assembly. Shifting to a lattice design achieves the same comfort, but with less assembly and less cost.
Software programs are also working on robustness. An issue that often occurs is that the data for a 3D printable part will have gaps in the data. The triangle measure is not clean, for example. Thus, software developers are looking to create tools that are more robust in handling these issues, as well as being easier to use.
“So, there is a lot of opportunity to create amazing software in the CAD and CAE world to help these engineers create products,” says Kabaria. “I think as the processes mature more parts are going out as production parts (rather than prototypes) through these processes.”
“Additive manufacturing is, in my mind, still in a very early stage because amazing innovations continue to develop on the software side allowing users to create amazing designs. Lattices are one particular innovation. We had to innovate. But we just didn’t innovate on how to draw lattices on all the different type of lattices available. We innovated on the
software that underlies this type of software.
“Once it gets to a mature state, the next stage is making these tools easier in terms of accessibility. That means any engineer who may not have a lot of background on 3D printing can at least use these tools easily. They should be able to make some parts, and then come the ideas of all the things one would have to do to optimize those designs for any particular
manufacturing process. That in my mind is sort of the middle stage, continues Kabaria.
“And then the final stage is when everything is workflow optimized. That means the users are not going through three different tools. Everything is connected, often with plugins. But I still think we are far from that. We are in the place where we are innovating on the core technology about what lattices are, how to generate lattices and
how to help users pick the right lattices with the minimum design iterations. Can the simulation software handle performing mechanical simulations on these lattices? I would say we are in that stage. And it’s exciting because there are a lot of unsolved problems and it can lead to amazing parts using this new way to manufacture things. So, that’s where we are all trying to create impact.”
A design that uses lattices can have 10 to 40,000 different primitives. This factor is significantly higher than the number of primitives typically seen in designs made for traditional manufacturing. Some developers of lattice software are innovating how to represent the primitives more efficiently—not just by representing them as triangles, for example.
Software programs are also working on robustness. One area this affects is custom manufacturing. When you have custom manufacturing, data are captured in some way, whether it’s from an iPhone scan or dental labs scanner. An issue that often occurs is that the data will have holes. The triangle measure is not clean. Thus, software developers are looking to create tools that are more robust in handling these issues, as well as being easier to use.
“At Carbon, we are able to deal with the parts that have holes. That means we have a way to create a meaningful out of a non-meaningful input. I think there is active innovation here, algorithms being developed. I would say the state of the art is changing every month.
A challenge, however, involves handling all of that data.
“Can we use GPU (graphics processing units) to make the processing faster? I think that’s a great question,” says Kabaria. “We at Carbon are working on that idea. That type of innovation is what is going to take us to the middle age, where it is easy to use these tools for any engineer who may not have background in innovating.”
Tools integrate with CAD software
Improvements in working with established CAD programs are on the way. For most, though, it’s not an optimized flow, yet.
Notes Kabaria, there are several reasons for this situation. One is because the tools are still emerging. It’s difficult to create a full ecosystem today, but it will improve. Plugins are one solution for now.
“Everybody’s thinking about this,” says Kabaria. Our philosophy at Carbon has been that before we create workflow optimization, we make sure that the parts being designed on Design Engine are good enough in terms of business or performance logic. So, it’s going to be painful in the
short term, but you still get benefit out of it. That means at the end our customers are putting a kick ass product in the market that they feel proud of, and know they cannot make any other way. And hence maybe that pain is worth it because we did enable to create a superior product. And the examples are countless from helmets to saddles.
“Let’s say we wanted to achieve a particular energy absorption performance. For a helmet, you want to do that by keeping the helmet volume the same. You don’t want to make a heavier helmet, but you want to achieve better energy absorption. Then you could use lattices, especially alongside elastomers because lattices and elastomers could create a competing metamaterial together that would outperform foam.
“Imagine you want to achieve a sort of cushioning response. That means you have a bike saddle and you don’t want to just create a bike saddle with 3D printing so it looks aesthetically cool. But you also want to reduce the peak pressure at the SIT bones. Academia has explored this quite a bit to understand that if you create many different types of foam, layered into a bike saddle, it’s possible to reduce that pressure. But then it will create a nightmare in terms of manufacturing cost and assembly. Shifting to a lattice design achieves the same comfort, but with less assembly and less cost.
“The business logic aspect comes in two ways because you are designing on the means of manufacturing. That means you are designing parts, let’s say using lattice structures and elastomer materials for Carbon, and you’re printing on a Carbon machine during the prototyping phase. So, you create this design, you test it
Increasingly, software for additive manufacturing is developing an ecosystem for engineers, helping them find more applications that they can put in production.
out, you can do this fast because you are not needing to create a mold to test three or four different foam molded designs. Over the course of 18 months, you can do 70 integrations in three months. So the product development cycle is shorter and it is shorter for two reasons.
“One is, of course, you are using printed prototypes. And the same printer at Carbon is available to do manufacturing. And the second is the design is digital. That means you change your lattice parameters by a click of a button and you get a slightly different design. Yet, the workflow between designing the primitive and the CAD on Solidworks and generating lattice is going to be painful, but it’s still faster. And we have showcased that with our customers, that you can reduce the product conceptualization of the prototype and manufacturing time significantly. So that means you are able to put more product in the market faster if you utilize these technology platforms and that is your business logic. Second, you can add more skews, you are not restricted to offering just three sizes, you can offer five. There’s a whole scale between one or three t-shirt sizes to 50 skews.
“In my mind that is the business logic; let the product company be in the decision and driving seat to figure out what’s right for its customer segment. And this certainly helps in the medical device segment as well as consumer products. So, you don’t necessarily have to generalize too much and have sort of one size fits all approach.”
Based on customer demand, more companies are developing opensource software.
According to Kabaria, Carbon will offer general availability of its lattice software at some point. “That means you can design a lattice structure in the Design Engine Pro and download the STL file and you can choose to put it on any printing process of your liking. We are becoming more agnostic and we are certainly proud of that because we believe not every material, not every process needs to be tied up to a particular machine. But at the same time, we are being cautious. If a user wanted to use the Design Engine Pro and extended capability for a metal AM part, we are happy to jump on call and help you figure out all the areas where you may run into problems, because we certainly want to enable you to do that.
For Kabaria, applications are a motivating force. “I think the software is a tool to accelerate the product design needs to manufacturing. And I’ll give an example that has still to date astonished me because I’ve been working for Carbon since 2015. I didn’t have an additive manufacturing background before, but since then I have been sort of living, breathing lattice structures in one form or another. But that means I’m also always on the lookout for places where you could apply lattice structures. During COVID we all ran into the shortage of COVID 19 swabs. Swabs were something I would have never in my dreams imagined being made with 3D printing. Yet, the shortage and breaking of the supply chain sort of demanded that need.
We played a role in it. We were able to design the swab. And within 20 days we did a clinical trial at Beth Israel Deaconess Medical Center at Harvard, at Stanford. We proved that the swab is as good
as the gold standard swab. And it was in use at hundreds of clinical institutions and it was produced using the same printer using the same design engine and the same materials that are already validating. So, in my mind, at least for me, the moral of the story is there are more applications out there than any one human or one organization can ever think of. Everybody has realized that the faster you do the product development, the more applications you can reach.
So, what excites me the most is as these tools go out the door, I think they will enable an ecosystem of engineers to find more applications that they can put in production, whether it’s once in a year or it’s a recurring product for tens of years, it doesn’t matter. We just want to enable engineers to put more products in manufacturing on any additive manufacturing platform.
Many AM vendors are developing additive ecosystems that offer more complete approaches to the use of additive technology for manufacturing. Here’s a look at what one company is doing.
Desktop Metal has been busy creating a portfolio of “Team DM” brands to make 3D printing accessible to companies of all sizes, helping them produce products more sustainably and closer to the point of end use. This portfolio offers a range of production capable 3D printers from binder jetting to digital light processing.
“The COVID pandemic exposed the weaknesses of our current manufacturing infrastructure,” said Ric Fulop, Co-Founder and CEO of Desktop Metal. “With today’s AM technologies, every country can have its own self-sustaining manufacturing industry with parts that can be shipped digitally and printed quickly.”
For Binder jetting, the S-Max Flex prints standard silica sand with furan binders and delivers final parts with dimensional accuracy of +/- 0.5 mm. The system comes with several accessories and safety features that are configurable to fit a variety of spaces.
A highlight of the portfolio is the Production System P-1, which was launched during the height of the COVID pandemic. A high-speed 3D printing system for end-use metal parts, the P-1 was designed as a gateway to the top-of-the-line Production System P-50 – one of the fastest systems to 3D print metal parts at scale. The P-1 shares the same patentpending Single Pass Jetting (SPJ) technology as the P-50, as well as common software and electronics for easy scalability.
The Production System is one of several Desktop Metal printing platforms that relies on binder jetting technology, which is widely regarded as one of the 3D printing methods likely to deliver mass production additive manufacturing at high speeds and competitive prices.
Nearly a dozen metals are now qualified for printing on the Production System P-1 and P-50 –delivering good part quality and surface finish, with sintered part mechanical properties that meet or
exceed applicable industry standards, and final part densities up to or exceeding 99%. A partial list of qualified materials includes:
• Stainless steels, including 17-4 PH, 316L, 420, 440C, and DM HH SS
• Tool steels, including D2 and S7
• Low-alloy steels, including 4140
• Copper alloys
• Nickel superalloys, including IN625
• Precious metals, including silver and gold
• Ti64 and 6061 in development
Binder jetting
After years of contraction, the U.S. metal casting industry is experiencing growth as a result of supply chain changes related to the COVID-19 pandemic. This growth was one of the reasons
Desktop Metal bought ExOne and launched the ExOne S-Max Flex, a scalable, large-format binder jetting system that 3D prints sand tooling. Applications include sand casting complex metal designs for the aerospace, automotive, and energy industries.
The S-Max Flex combines ExOne’s sand printing expertise in process and materials with the SPJ technology to deliver a build rate
up to 115 l/h. The goal is to make good sand 3D printing accessible to every foundry.
It pairs an affordable industrial robot with an end effector printhead design that deposits binder into a 1900 x 1000 x 1000 mm (74 x 39 x 39 in.) telescoping build box that grows as the parts are built layer by layer. Additional build box sizes are available up to 4700 x 1000 x 1000 mm (185 x 39 x 39 in.), with taller versions available up to 1000 x 2500 x 2400 mm (39 x 98 x 94 in.).
The S-Max Flex prints standard silica sand with furan binders and delivers final parts with dimensional accuracy of +/- 0.5 mm. The system comes with several accessories and safety features that are configurable to fit a variety of spaces.
Industries beyond metal casting are also set to take advantage of the S-Max Flex’s large form factor and ability to binder jet a variety of powders. Infiltrated sand tooling for plastic thermoforming, composite layup, and sacrificial tooling applications are printed on S-Max machines, along with infiltrated sand consumer products, such as those offered by Sandhelden and Deeptime. Desktop Metal’s Forust brand, which upcycles byproducts of the wood waste stream into consumer designs, will also leverage the new system to print large form factor wood parts
at scale cost-effectively. Additional projects are underway printing reclaimed concrete and other materials.
Another binder jet 3D printing system is the X-Series line for metal and ceramic powders in a range of particle sizes. Like the S-Max Flex, this line of printers is derived from the acquisition of ExOne.
The X-Series line offers a differentiated approach to binder jetting enabled by patented Triple ACT — an advanced compaction technology for dispensing, spreading, and compacting powders during the binder jet printing process. This flexible, open material platform architecture can bind together a range of powders with a D50 of 3 to 100 microns.
Three X-Series models are available:
• InnoventX, an affordable, entry-level binder jet system for academic, R&D, and low-volume production applications.
• X25Pro, a mid-sized system for volume production with a build box of 400 x 250 x 250 mm (15.75 x 9.84 x 9.84 in)
• X160Pro, as large metal binder jet
P-1 is a high-speed 3D printing system for enduse metal parts. It uses the same Single Pass Jetting (SPJ) technology as the P-50, as well as common software and electronics for easy scalability.
system with a build box of 800 x 500 x 400 mm (31.5 x 19.7 x 15.8 in).
The X-Series printers repeatably deliver tight dimensional tolerances and densities of 97-99% or greater — in line with or surpassing metal injection molding or gravity castings. Surface roughness values as low as 4 µm (Ra) can be achieved directly out of the furnace.
When Desktop Metal bought EnvisionTEC, it rebranded the 3D printing line as ETEC. This line uses digital light processing (DLP)
Stainless Steel (DM HHSS) is a custom stainless-steel alloy that combines high strength and hardness with corrosion resistance. A key application is its use to make offset sockets.
technology, and the goal is to bring high-speed, photopolymer 3D printing to volume manufacturers of consumer and industrial products.
These 3D printers offer extreme levels of accuracy and surface finish and have been used in the healthcare, dental, medical and jewelry industries since 2002. Another result of the EnvisionTEC acquisition was the launch of Desktop Health to focus on healthcare and dental customers.
Through a partnership with Adaptive3D, another subsidiary of Desktop Metal, ETEC offers a broad portfolio of photopolymer 3D printing materials, including Elastic Tough Rubber 90 (ETR 90), which is one of the highest tear strength elastomers on the market. ETR can be found in products on store shelves, including power tool adapters and recoil pads.
When it comes to materials, Desktop Metal has released several, including DM HH Stainless Steel (DM HH-SS), a custom stainlesssteel alloy that combines high strength and hardness with corrosion resistance, for use on the Production System platform.
DM HH-SS is a custom, heat treatable-alloy that combines the tensile strength, ductility, and corrosion resistance of 13-8 PH stainless steel with hardness comparable to low-alloy steels, such as 4140. These attributes may help companies eliminate the use of low-alloy steels, which also require a subsequent plating step for applications needing corrosion protection. DM HH-SS is also suitable for conformally cooled injection tool core and cavity applications, where millions of injection strokes per year are required.
An example of a key DM HHSS application is the offset socket,
often used for manufacturing tooling in scenarios where space is limited and a traditional tool would not be able to access a bolt. Instead of maintaining an inventory of a variety of tools to accommodate multiple socket sizes for each bolt size, users can maintain a digital warehouse of each socket size and print quantities of different sizes together in a single build.
Another material finding greater use in 3D printing is copper. Desktop Metal announced it has qualified commercially pure copper (> 99.95% purity) for use on the Production System platform.
With its thermal and electrical conductivity, commercially pure copper suits applications that require heat or electricity transfer, such as cold plates, pucks and manifolds, heat sinks, heat exchangers, and bus bars used in power-intensive electrical applications. It is the third-mostconsumed industrial metal in the world.
Desktop Metal’s materials science team has qualified and fully characterized commercially pure copper (C10300) printed on Production System technology. Liquid cooling plates, which are used to regulate temperature on microprocessors, are an example. Coolant flows through the fins, which provide a large surface area to transfer heat from the passing fluid to the heat sink to cool the chip attached to the outer body. These cooling geometries typically require capital-intensive, long lead time, and skilled laborintensive production processes, such as skiving and machining, given the challenges associated with achieving precision and repeatability in such a small form factor. In addition, these commonly used conventional manufacturing processes are subtractive and
produce excess scrap material, greatly increasing the associated part costs. Binder jetting on the Production System can produce a liquid cooling plate as a single component.
D2 tool steel is a versatile highcarbon, high-chromium air-hardening tool steel characterized by its hardness and compressive strength after heat treatment. This tool steel is wear resistant, dimensionally stable, and resists corrosion in the hardened condition, a key benefit for conformal cooling applications. D2 is used for a variety of cold work tools that require a combination of wear resistance and moderate toughness, such as coining and sizing tool members, blanking and forming dies, shear cutting tools, gauges, burnishing tools, and other wear parts. An example application is rotating cams.
Cams are used in oil and gas or chemical processing applications to convert rotary motion into reciprocating linear motion in a machine. Typically, these parts require multiple manufacturing steps, beginning with CNC machining, followed by broaching of the spline on a separate machine. Binder jetting enables the production of cams in a single printing step, reducing both the cost and lead time of the part, while also supporting the production of different cam sizes in one build.
D2 tool steel suits this application because of its hardness and corrosion resistance, which ensures a longer lifetime as the cam mechanically interacts with a sliding pin. In addition, because these components are often integrated into machines operating in harsh environments, the corrosion resistance provided by D2 ensures that the parts will perform as intended and not deteriorate.
Vital Auto was founded by three friends who got together, quit their jobs, and decided to set up a shop in a garage. One of the first contracts the company took on was for the NIO EP9 supercar concept, which set the team on a course to produce extremely realistic vehicular prototypes.
Located in the heart of the UK’s auto industry, Vital Auto is an industrial design studio with expertise in automotive design. The company’s clientele includes many of the major automotive manufacturers, such as Volvo, Nissan, Lotus, McLaren, Geely, TATA, and more.
“Clients typically come to us to try and push the boundaries of what’s possible with the technology available,” said Shay Moradi, Vital’s VP of Innovation & Experiential Technology. When manufacturers don’t have time for experimentation themselves, they rely on Vital Auto with any kind of challenge to turn ideas, initial sketches, drawings, or technical specifications into a fully realized physical form.
Vital Auto was founded in 2015 when three friends got together, quit their jobs, and decided to set up a shop—fittingly—in a garage. One of the first contracts the company took on was for the NIO EP9 supercar concept, which instantly set the team on a course to produce
extremely realistic vehicular prototypes.
Today, depending on the client request, the team will start anywhere from simply a sketch on a piece of paper to an already designed vehicle. They develop cars from a blank sheet, design all the mainframes, all the exterior and interior elements, open/closings, and interactive elements. With five to 30 people working on a single concept, a typical project could take anywhere from three to 12 months.
In this time, a typical show car goes through up to a dozen core design iterations, and within those, there can be further iterations of smaller components until the design meets the expectations of their customer.
“It’s all well in our industry to look at virtual properties as a means of evaluating a product before it goes to market. However, I think there’s always going to be a place for physical manufactured objects as well. There’s nothing that beats the sensation and feeling of holding an object in your hands with the correct weight, with the correct proportions, and the dynamics of how the physical environment changes your perception of that physical object,” said Moradi.
“Most of our customers will come to us with an innovative idea, something that’s never been done before. So, the challenges for us are new every single day and they’re endless,” said Anthony Barnicott, Design Engineer in charge of additive manufacturing. “These challenges can range from, how can we produce this number of parts in this amount of time to, how can we make a sustainable product or how can we make a part that achieves a particular weight while still achieving a particular performance.”
While traditional show cars are normally made from milling clay, the team also uses three- and five-axis CNC milling, hand forming, hand clay
modeling, and GRP composites. These traditional processes are, however, often not ideal for producing the custom parts required for one-off concepts.
“We’ve used 3D printing from day one. We wanted to introduce it to our manufacturing processes, not only to reduce costs, but to give the customer more diversity with their designs and their ideas,” said Barnicott.
Today, Barnicott runs a whole 3D printing department, including 14 largeformat FDM printers, three Formlabs 3L large-format SLA printers, and five Fuse 1 SLS printers.
“In terms of capacity, all those printers have run 100%, 24/7, pretty much since day one. We use these printers for all areas of our concepts and designs. Typically, we would use the Fuse 1s for our production-based parts and we
The team mainly uses the Fuse 1s for mechanical parts, such as door hinges, door handle inners, door internals, and structural applications. They can use these parts straight off the printer, with minimal finishing.
we moved to the White material to produce a production-ready part.”
This air vent was based on a proprietary design. 3D scanning technology was used to create a digital file of the vent. Then, software was used to create a custom external skin for customer approval. Once done, the designers went on to product a production ready part.
would use our Form 3Ls for our conceptbased parts,” said Barnicott.
“We use the Form 3L machines for anything that is an A-class finished surface. So typically, in an automotive interior where you have parts that are not being trimmed with leather or Alcantara or some sort of cloth material. Formlabs materials give us a nice, smooth finish for our painters to work with; we can use these parts straight out the printer, straight onto a vehicle,” said Barnicott.
“What interests me most about the Form 3L machines is their versatility, the ability to do a material change in less than five minutes and the variability of those materials going from a soft, flexible material to a hard and rigid material for us is priceless,” said Barnicott.
The team uses the Form 3L’s with multiple materials for a wide array of applications from air vents to door seals.
Customers will often approach a highend auto manufacturer with a proprietary product that they want to encase in their own design.
“One customer, for example, approached us with a proprietary air vent from another vehicle that they wished to have inside their own interior. We used 3D scanning technology to reproduce this part digitally and then created an external skin. We first produced this in the Draft material to test out the design and allow the customer to verify it. From there,
“When working with incredibly intricate designs, such as small switch packs, what we’re able to do is use multiple materials to achieve a mechanical product that not only functions correctly, but can be used in a real-world environment. [For these switch packs], we combined harder materials, such as the Tough 2000 for the top surface, with the lighter, more cost effective materials for the internals.”
“Typically, door seals for automotive applications can be incredibly costly to produce. there’s simply no other way other than extrusion molding to produce them. This comes at, not only a very large tooling cost, but also a long lead time as well. We were able to experiment with one of Formlabs’ newest materials, the Flexible 80A. The Form 3L enabled us to produce sections of this door seal overnight to test various geometries and was printed within 50 microns of the actual design.”
Having the Form 3L empowers the team to produce multiple iterations of parts in most cases within 24 hours. They ended up buying three different machines so they could produce up to three different iterations of a part at the same time, even using three different materials. They can then pass on the cost savings to the customer or offer more value by showcasing multiple design options for the same price.
“One of the beauties of using additive manufacturing is the compression of a timeframe. So what do you do in that span of time that you have freed up? We sort of see it as extending the possibility space into imagining alternatives, into adding more iteration loops in the process,“ said Moradi.
“There are many products we
Small switch packs are incredibly intricate parts. Designers and Vital Auto used multiple materials to achieve a mechanical product that functions correctly and can be used in a realworld environment. The engineers combined harder materials, such as the Tough 2000 for the top surface, with the lighter, more cost-effective materials for the internals.
produce that we simply wouldn’t be able to without our Form 3Ls. With some of the most advanced manufacturing techniques, such as seven-axis CNC machining, we’d be able to produce these parts, but it would come at a huge compromising cost,” said Barnicott.
“The Fuse 1 one was our first venture into SLS technology. As a small business, this is a technology we thought we would never be able to have on site. With the Fuse 1, not only do we have one of the machines, but we actually have five of the machines on the site. What these machines enable us to do is produce structural mechanical parts quickly, not only for testing but for physical applications in most of our concepts. This process would have typically been done by CNC machining, either on our site or off site, depending on the geometry, and we would have to wait two to four days to get the parts in our hands. The Fuse 1 enables us to cover all of this on site and have parts in our hand in most instances, less than 24 hours,” said Barnicott.
The team mainly uses the Fuse 1s for mechanical parts, such as door hinges, door handle inners, door internals, and structural applications. They can use these parts straight off the printer, with minimal finishing. Some of the applications where the team used the Fuse 1s include an air duct.
“A lot of automotive interior parts can be incredibly tricky to produce without going down the
traditional injection molded route. Items such as internal air ducts and vents, items that are never seen, but yet require a large cost to produce. We use the Fuse 1 to produce these parts. It allows us to be much more versatile with the designs we put in the vehicle without incurring the large costs that they would typically have.”
“3D printing has allowed us to combine both the SLA and SLS materials to work our way through design iterations on a specific project. This allows us to quickly produce multiple iterations, combining both processes, using them for their specific properties, to achieve a final design. This can be anything from mechanical parts to clear parts to check their optical quality and output.”
While it’s often said that additive manufacturing is here to replace subtractive manufacturing, the Vital Auto team sees benefits in combining different technologies to leverage their best qualities.
“We use the two processes together to help support each other. We have many parts
where we would use subtractive manufacturing and then use additive manufacturing to produce all the finer details. This allows us to have a much more cost-effective way of producing a lot of our concept models,” said Barnicott.
“The progression in technology and 3D printing over the last 10 years is phenomenal. When I first started, producing low volume, niche vehicles, some of the products that we produce today would simply have been inaccessible. And not only am I able to produce these parts today, but I’m also able to produce them cost-effectively, quickly,” said Barnicott.
3D printing not only helps the team create better products faster, but also to attract new business. They found that many of their customers turn to them because they want to have access to the latest technologies and they want to have their components made using the latest cutting edge materials.
“There are certain things that you just can’t class as emerging technologies anymore. 3D printing is one of those things. It’s advanced to a point where everything that we produce is good enough for use in the final presentation stage with all the layers of making that we apply on top of that. 3D printing has gone from almost a novelty to becoming an absolutely inseparable part of what we do,“ said Moradi.
Formlabs | www.formlabs.com
Many automotive interior parts can be tricky to produce without using traditional injection molding. Internal air ducts and vents may never be seen, yet they are costly to produce. Formlabs Fuse 1 was used to produce these parts, enabling more versatility with the designs without incurring large costs.
Additive manufacturing continues to evolve. Here’s a look at how Wayne Davey, Global Head of Sales and Goto-Market for 3D Printing Solutions, HP Inc., sees the latest developments in this industry.
Q: Over the last few years, various commentators have discussed the need for designers to think differently when designing for additive manufacturing versus machining and injection molding. Where do you see the design thinking now, and where does it need to get to in order to take full advantage of AM?
Davey: The manufacturing industry is seeing the benefits of reframing the design process to better suit additive manufacturing. With a fresh perspective to product structure and design, manufacturers are able to create unique, cost-effective and, most importantly, commercially useful products. Engineers developing products which cannot be manufactured today is one element of 3D printing realizing its full potential. To take 3D printing to the next level, however, means looking towards mass scale production. For that, we need to pair 3D printing with other innovative technologies like AI and machine learning. Using data-driven insights, manufacturers can push the boundaries even further and create complex, high quality parts that are also sustainable.
A great example of this is HP’s partnership with Cobra Golf and Parmatech where a first of its kind, limited edition, 3D printed putter is being manufactured commercially using HP Metal Jet. The KING Supersport-35 putter features a thin exoskeleton braced by lattice beams—entirely different from traditional putters made with solid chunks of metal. Cobra Golf is also leveraging HP’s Multi Jet Fusion platform for three oversized models in the King 3D Printed Series – the GrandSport-35, the SuperNova and the Agera – producing a nylon lattice cartridge to optimize weight distribution for high moments of inertia and stability. And just last month, Cobra Golf announced that it is expanding its collection of KING Putters with new options for personalization, like different shapes and colors.
Cobra Golf and so many others are showing the world what can be achieved when 3D printing platforms and design tools are seamless. As the industry continues to leverage breakthroughs in automation, software, and data, customers will be better equipped to understand the entire end-to-end lifecycle, from supply chain to the useful life of a part, so that better parts can be printed with improved design.
Q: Are there new applications emerging as a result of additive’s capabilities? What are they?
Davey: The ability for increased customization has broken down the barriers of what is possible for new and emerging applications. Take healthcare for example. Through the evolving capabilities of AM, the health and wellness industry is poised to greatly benefit from the advanced design and manufacturing. According to HP’s Digital Manufacturing report, 55% of those surveyed predict the medical industry will see the most innovation. AM has the capabilities to deliver
personalized and customized care of specific aliments. Consider as an example, a blend of advanced 3D printing and cloud-based software that allows podiatrists and orthotists to capture 3D renderings of a patient’s foot, fine-tune and prescribe personalized orthoses for their patients in less than five minutes.
The automotive industry is also investing heavily in AM. They are taking parts and redesigning them using metal binder jetting for structural components for the first time. While the pieces or functionalities might not be an emerging application, the way in which they are designed and created are a first for a heavily regulated industry.
A strong example of this is HP’s collaboration with GM and GKN Forecast3D. GM recently turned to HP’s Multi Jet Fusion printing technology to produce a spoiler closeout seal, which typically goes through a standard finishing process. In three weeks, together with GM and GKN Forecast3D, we were able to design, create, and implement a viable value stream
for the rear spoiler seal, with speed and flexibility that would have not been possible with traditional manufacturing models. The result was an accelerated production schedule, creating and polishing the required 60,000 parts over the span of five weeks for use on approximately 30,000 parts for fullsized SUVs.
Q: Scaling additive technology is becoming a more frequent subject. What do users of AM need to understand to convince management to invest in AM now, and what does management need to understand about AM scale to have more confidence in this technology?
Davey: The value proposition for AM investment today is threepronged:
Manufacturers are seeking greater supply diversification with an emphasis on localized, ondemand production to build more resilient supply chains
Consumers want the goods they purchase to be tailored specifically to them—hyper personalized—
an expectation filtering in from their experiences interacting and consuming in the digital world.
Sustainability mindset, consumers are actively making calculated purchasing decisions that are also better for the planet. These market moving trends are all intertwined by one common factor – traditional manufacturing methods are inefficient and costly at addressing all three, especially at once. The opportunity cost of not evolving with the new manufacturing paradigms facing us today is a risk that can no longer be overlooked. And it’s not just one industry being impacted. Across the board, automakers, health and wellness brands, sports equipment manufacturers and so many more are looking for new processes and technologies like 3D printing that help them meet these demands quickly, economically, and at a mass scale.
3D printing’s capabilities are unmatched. It offers economic viability removing cost implications of part inventories, expedites iteration and speed to market, and is less resource intensive. These
COBRA Golf, a leader in golf club innovation, used 3D Printing technology on its KING Supersport-35 putter. This putter has been in collaboration with COBRA engineers and the teams at HP and Parmatech. It features a fully 3D printed metal body with an intricate lattice structure to optimize weight distribution and deliver the highestpossible MOI in a blade shape. In addition to the 3D printed design, the putter features a face insert designed in partnership with SIK Golf, which uses their patented Descending Loft Technology (DLT) to create the most consistent and accurate roll on every putt.
The COBRA’s LE 3D-printed Supersport-35 Putter represents a revolutionary advancement in the way golf clubs are designed and manufactured. Born out of a forward-thinking philosophy, COBRA selected HP as its partner to pioneer 3D printing in golf due because of HP’s Metal Jet Technology. With its quick processing time and design adaptability, COBRA engineers were able to design, prototype, and test multiple iterations and bring the product to market faster than using
COBRA and HP began working together in early 2019 and, by early 2020, the team had created thirty-five different design iterations over the course of eight months using the HP Metal Jet.
The Supersport putter, which comes in an oversized blade shape, features SIK Golf’s Patented Descending Loft technology reengineered into an aluminum face insert. This insert design strategically saves weight from the front of the putter to be repositioned heel-toe and tunes the feel to a slightly softer feel than a traditional all-steel SIK putter face. Their signature face design uses four descending lofts (4°, 3°, 2°, 1°) to ensure the
are all factors that can improve a company’s bottom line. As the ability to scale increases, so does that reality of mass-personalization through additive manufacturing.
Q: There’s a lot of discussion about the supply chain. What are some of the better applications for additive in a supply chain system today? What could they be in the next few years? What will it take to get there?
Davey: Companies are actively looking for ways that 3D printing can strengthen their supply chains,
enabling them to become more agile, creating more innovative product development and manufacturing strategies. We saw firsthand during the pandemic that 3D printing can be a solution to a distributed supply chain, helping manufacturers develop, iterate and manufacture goods at a challenging time. Through 3D printing, manufacturers can create parts needed for goods that may have been backlogged due to the supply chain – enabling a quicker time to customer journey.
But it’s not just in times of crisis that additive will bring benefits to the supply chain system. 3D printing enables both short and long-term solutions capable of near-instant
responses to market changes. What once worked in traditional manufacturing models are not conducive to today’s environment. For example, older models were not built for shorter runs or minimized inventory. Localized production will continue to be prioritized. This is an unparalleled competitive advantage for companies, but customers and the world around us see benefits as well.
most consistent launch conditions for every putting stroke.
HP Metal Jet 3D printing delivers excellent part quality and requires minimal post-process finishing. The entire putter body is printed using 316 stainless steel, and then sintered at a high temperature to bind the metal and form the final head part. Due to the capabilities of Metal Jet printing, engineers printed an intricate lattice structure within the body – a manufacturing feat that wouldn’t be possible using traditional casting or forging methods. The lattice fine-tunes feel and optimizes the distribution of weight within the putter head to create the highest MOI without the need for additional fixed weights. During the final step of the manufacturing process, the surfaces of the putter are precision milled using a
Computer Numeric Controlled (CNC) machine to ensure precise shaping and detail while adding the finishing touches to the cosmetic. The Supersport features a high MOI heel-toe weighted design for maximum stability, and a plumber neck hosel with a 35-degree toe hang suitable for slight arc putting strokes.
The lattice structure removes weight from the center of the putterhead and pushes significant amounts of weight to the perimeter. The result is superior MOI levels and massively increased stability and forgiveness.
The final product is a celebration of a major revolution in golf club manufacturing in the form of a high-performance putter that will appeal to golf purists seeking a clean look and feel but is packed with advanced technology to improve the quality of a golfer’s short game.
Among the many benefits of using 3D printing is how it effects sustainable efforts in design and production. Here are highlights from an interview with Nadav Goshen, president and CEO at MakerBot on 3D printing developments in this area.
The subject of sustainability and 3D printing covers a range of issues. Goshen and MakerBot are focused on changing the way we make things, specifically around overall production. Changes to the production process can be enormous, covering initial design phases through manufacturing.
“In each part of the journey from a design to a part, 3D printing brings a lot of value into sustainability,” he says. For example, there’s a cost to maintaining a number of parts somewhere for future use. One aspect of storing the parts is they must be stored properly and then transported back and forth, all of which has a cost associated with it.
3D printing/additive manufacturing can eliminate those costs by producing the part where it is needed, when it’s needed.
“Because of the way industry typically fabricates things, we are constrained by the need to have parts ready, not necessarily when they’re needed. But 3D printing can change that. The digital element of additive manufacturing and 3D printing can really take all of this waste out of the system and make sure that we are more considerate about the resources we use when we build things.”
On the design side, there’s more opportunities to really, for example, cut cost and waste from the manufacturing process. When you design with sustainability in mind, or when you get to the production side of things, you have much more efficiency on that side.”
The quality of desktop professional grade 3D printers continues to improve. “Once more designers and engineers have more access to such 3D printers, they can really experiment with the technology. And that brings new design thoughts into a process of engineering product. So, we see that trend coming.
“In some industries, we see that subtractive design is eliminating possibilities, because you need to do multiple parts. Thus, you have multiples of tools, fasteners, etc. to produce and assemble the multiple parts. You also have double the waste. Once you think in additive, though, then you can combine two parts into one. And then you cut almost in half the overall environmental cost to produce a part. So, we see that trend coming.
Once you think in additive, then you can combine two parts into one. And then you cut almost in half the overall environmental cost to produce a part.
The way industry typically fabricates things requires that parts be available before they are needed. 3D printing can change that. The digital element of additive manufacturing and 3D printing can take wait and waste out of the system and ensure greater consideration about the resources used when building things.
“We see a number of economical drivers, but sustainability by itself needs to be fueled by the industry to make it more, I would say, embedded within companies’ P and L statements and the way they think about process.
“We see that for example in aviation and aerospace, where that kind of additive thinking really translates into less complicated and also lighter parts. When you have that, then it translates immediately into less or better fuel economy.
“So, all of this process is making a full circle from the possibilities we have to
the economic value and then to the process of manufacturing.”
For the C-Suite, working with innovation imposes a risk. Engineers are more comfortable with innovation because they are closer to the technology and can get hands-on experience with it. The C-level is a bit further away from innovative technology. Thus, executives can have a gap of knowledge and experience where they potentially view that
technology, such as 3D printing, as a higher risk than what it should be. Such an approach was common sense during the early days of a technology, but after a decade, it’s time for a new perspective. Part of changing the habitual perspective involves how to communicate to the C-level executive that the technology has matured and is less risky, and that there are use cases across the world. Hopefully, we won’t rely on events such as pandemics to bring greater awareness to the C suites about how useful 3D printing can be, especially with supply chains.
Another part of the issue is the cost of insurance. You don’t understand the cost of not having something unless you have “insurance” for it. This insurance covers situations we are not really prepared for. And again, the pandemic proved that if we are not putting some type of thought, action and policies in place, i.e., insurance, when the time comes, then there is a big cost to not being prepared.
Additive manufacturing and 3D printing is insurance for supply chain
Additive manufacturing and 3D printing is insurance for supply chain shortages and to everything that might happen. In many cases, these economic factors were not really put into the overall calculation of reasons to use 3D printing.
shortages and to everything that might happen. In many cases, these economic factors were not really put into the overall calculation of reasons to use 3D printing.
“I think both perspectives are changing now. The risk averse nature is changing and the need to understand or the understanding that the need to invest in a different way to manufacture and to have a supply chain strategy is also something that companies are investing in. The actual hidden costs in the supply chain have made the C-executive really consider their strategy around supply chain, manufacturing, and overall engineering.”
Another factor that will help the C-Suite re-evaluate 3D printing is the price of this technology. The investment that is needed to get 3D printing technology into your organization is lower. Systems that are capable, that are engineering grade, are being sold for a few thousand dollars, which is
potentially affordable on a designer’s discretionary budget. Then if you want to move up to more advanced additive manufacturing technology based on a proven use case, your company can invest to get a manufacturing grade machine.
“I think this is what we need to do because if your sales pitch is too theoretical, then it becomes less tangible for the C-executive,” continues Goshen.
A highly innovative technology, like 3D printing, brings enormous possibilities for addressing design and manufacturing challenges. But it comes with an inherent “trap” that what it can deliver is real. It’s easy for C-suite executives to lose confidence in the practical engineering that this technology can bring to their own day to day challenges.
“I’m C-suite. I know my challenges. They’re not in the conceptual world. They’re in the
practical world. And what I need to get a decision about investing in something new is, how does that translate into pragmatics? Let’s see more executive P and L contribution to my business,” says Goshen.
Desktop 3D printers can play a key role in demonstrating pragmatic benefits. With a very low investment, engineers can eventually change the way products are made and change the way their company handles the supply chain. A desktop 3D printer can help engineers make their ideas, their concepts tangible in the minds of their bosses.
As Goshen notes, technology needs to shift from being inspiring to being practical for executives to buy into it.
“We need that transition from an inspiring technology into practical technology, aside from innovation to engineering. And I think what is really happening is what happened in the computing industry maybe 20 years ago, for example, where it
A product needs to serve a specific purpose. We are now in the stage where we can take this technology into different applications.
became more accessible.”
Goshen compares the adoption of 3D printing to that of the early adoption of personal computers. Computing, to Goshen, is a crosstechnology product. A 3D printer, on the other hand, is a combination of chemistry and embedded computing, and all of it has to work together.
“3D printing is a much more complex process to control versus electric circuits on boards. So, I think this is what is affecting how this technology’s been spread. While it’s easy to get a part, it’s less easy to tune the printer. And that’s a challenge.
“I think there are many desktop machines, but they are not practical because they get to the point where they print the part, but it’s not repeatable. It’s not dimensionally accurate. And it’s really not easy to use and it’s not reliable. And when you have this, and this we had in the last few years, then it contributes to the confusion and also to the frustration of users.
So, we need to get the technology into the stage where it’s reliable and repeatable and it’s really engineering grade. This is the journey. It’s different between desktop and engineering grade machines. We need to make sure that we have engineering grade machines in the hand of anyone that has a practical use to it. I think that’s what is happening right now.”
The additive technology is still quite fragmented with people grouping brands and systems together. One example is what MakerBot calls engineering grade desktop versions. Desktop 3D printers and engineering grade desktop 3D printers are similar in size. Maybe the cost is double the desktop one, but it offers features such as in-process tuning that is required to get these engineering
grade machines accepted.
“In computing, I think that inprocess tuning was built in because its electronics. In 3D printing, it’s a combination of... I wouldn’t get into the details, but every engineer knows that taking a solid, liquefying it, and then getting it back to solid involves a micro-level accuracy and involves a complex system to make sure that you can control it and you can maintain the same results.
Three general categories
The range of 3D printing features and functions is wide. That fact is also contributing to the reluctance of some to invest in this technology. One category is the hobbyist market, or the maker market. This market was the origin of the desktop movement. “It’s a great market. I’m a user. But it’s a market where users have the skills in trying to get something to work and the willingness to participate in the result process. It means that I’m involved in the process of making, because I’m a maker. I enjoy that process of making it successful. But it’s not a professional use case,” notes Goshen.
The second category is education, which has different needs because of the use of technology for learning purposes. They use 3D printing to make learning more immersive. It ties into STEM education in many ways.
“The third category is what I call entry level engineering, which we are operating in, which is an accessible and affordable engineering grade machine. But it is still aimed at the individual engineer. It brings to the table a well-tuned, reliable engineering grade device that can be used for professional purposes to design and engineer parts.
“A subset of this category is the shared office 3D printer, which is a larger than an individual printer,
often a floor model. That is a natural expansion of that individual printer,” says Goshen.
And then, on top of this, comes various levels of scalability in terms of materials and manufacturing focused printers. And then it becomes more specific. Then you move from the prototyping and small plastic production part to manufacturing. And this is another world by itself.
“All of this is using the same technology. But they’re not the same products. All of them use the same underlying technology, but classifying them together is probably not accurate and could contribute to the confusion that we already have in this fragmented industry,” notes Goshen.
Goshen sees the industry shifting since it’s early days when people expected we’ll have a 3D printer at each house without thinking about the basics of what products are.
“A product needs to serve a specific purpose. There has been confusion between the technology and the applications and the product translation of that technology. Which is something common with hype cycles. We are now in the stage where we can take this technology into different applications.
“I think that’s the cost that you’re paying today. We can reduce the cost today if we just change the way we think about manufacturing in general,” he says.
One of the changes engineers can expect is to have greater control and empowerment at the point of need with 3D printers.
As AM becomes more accepted as part of a manufacturing supply chain, it is altering the way engineers work and develop products. We recently had a conversation with Daniel Lazier, product marketing manager at Markforged. Here are highlights from the interview.
One of the changes engineers can expect is to have greater control and empowerment at the point of need with 3D printers.
“Back in the day when I was a design engineer, the nature of my job was to create a design and then rely on
We now see engineers, technicians and point managers alike, all converging on the point of the manufacturing line that needs that critical part and locating a printer as close to that, pushing that printer as far forward into that manufacturing challenge as possible.
on great manufacturing platforms. Now it’s sort of reverted back to this reality where I am directly in control of creating that part, pulling it right off the printer and getting that hands-on feedback as to how my design worked out.
a completely different and distinct set of resources, often outside of my business entirely, to make the part. And that might take weeks or months, depending on what the part was and what processes it was beholden to. I recall how frustrating that could be when the reality of your job, your timetable, and even your cost structure is dictated by someone completely outside of your business and outside of your control.
“The very nature of that job and that role changes when you’re empowered with equipment right on your desk,” continues Lazier. “In addition, the kind of components and parts that you rely on now can be produced right where you need them. And as an engineer, you are actually specifically involved with the creation of that part.
With 3D printing, designers can qualify a part all the way from prototype to production at a design lab or geographically distinct office, and then push that design to production where it may be pulled down by production resources somewhere completely different across the planet. This process is happening for a specific and growing band of use cases and applications, especially with printers
like the Markforged Digital Forge, and other cloud manufacturing capabilities.
With 3D printing, you have more choice about how hands on you want to be with a design, depending on the organization, the individuals involved with manufacturing, and the roles and responsibilities of those individuals.
“What I thought engineering would be before I went to college, I assumed I would be involved in the process of actually creating my object. But the reality was, at least in 2015, when I started my career as an engineer, it was really hands off. I could go walk through the factory, and go see how the parts were being created. But when I was actually doing my job, it was all behind a computer screen.
“And the beauty of 3D printing today is I’m sitting in a room that’s like 10 by 12, and I have three 3D printers sitting behind me. Even as I’ve transitioned to a role that has less to do with engineering, the process of actually creating physical parts, and every little detail that goes into that, are completely under my control. And by extension, the people who make great designs and made those great designs, create it
Engineers can be involved in the manufacturing process. If you’re a concept development engineer that’s making prototypes, you are interacting with the folks that are involved with mass production use cases in that you need to reflect manufacturability in the design of your final part. If you are, by contrast, directly involved with the creation of those manufacturing processes, then the nature of your very job is on that manufacturing line.
“And the trend we’re seeing is this emergence of humongous, gargantuan manufacturing plants of 9, 10 million square feet, where it could take almost an hour to walk from one end to the other. It doesn’t just matter that you have a 3D printer at the factory itself, it actually matters where in that factory you are, because it could take a while to walk that part from one place to another.
“We now see engineers, technicians and point managers alike, all converging on the point of the manufacturing line that needs that critical part and locating a printer as close to that, pushing that printer as far forward into that manufacturing challenge as possible.
“The biggest difference we see is in the role and the response. I talked a lot about the transition of the role and responsibilities of the individual engineer. The reality of the technician’s role and responsibilities change as well, where there’s less time doing the manual processes of clamping, fixturing, programming, doing all the things that it takes to get a successful part out of the CNC mill, and spending more time actually making parts, managing
things from the digital level where those individuals are now empowered to make more parts for more people, solve more problems, which is a great transition to see as well.”
“One of the challenges we’re all facing right now is coordination of distinct supply chains. There’s a small but growing wedge of production parts that can be produced on a 3D printer today, at least in economic and logistically feasible means. The challenge becomes, how do I get the rest of this part or this assembly or this add product produced at the point of need? And the really exciting part and trend we’re seeing emerging out of the pandemic is, manufacturers are by nature parallelizing their supply chains so that more parts are available in distinct, shorter supply chains.
“And while that may be potentially more expensive in the short run, it ends up being far more beneficial for manufacturers in the long run when they have the ability to more flexibly balance load, demand on specific discrete components of their supply chain, and then rely on the flexible components of the supply chain like 3D printing, additive manufacturing to fill in the gaps.
The supply chain, after the pandemic
Will the changes experienced with the supply chain over the last two years continue, or it return to how it operated pre-pandemic?
“I think over the next few years, as we transition from pandemic to endemic, we right size the really critical links of global supply chains, like shipping, trucking, warehousing, and we get to a new point of equilibrium where we’ve got the right resources to solve the right problems in manufacturing. I think we’ll see a sort of asymptotic releveling to something that looked a lot more like what it looked like in 2019.
“I think that said, manufacturers are going to clamp down on the specific use cases where we all mutually have found it’s more beneficial, both from a cost and lead time, to parallelize and have this flexibility. And something that might cost a little more in the short term to spool up, and in fact, things that people are investing in now that you can’t just throw in the garbage can, like in a new factory, we’re going to find new and more powerful ways to use these things and produce products with more flexibility, more customization, and ultimately more acceptance at the end-customer level. And I think those advantages are going to be here to stay and they’re going to be enduring.
Additive manufacturing is influencing the supply chain. At the extreme level, look at the U.S. military and how its supply chains have evolved.
“Even before the pandemic, they had some of the most austere supply chain challenges that you could imagine, needing to get a specific part or bracket somewhere in some desert in the middle of Kuwait where there are no roads, how do you get a part there? And we saw the
military really treat 3D printing almost like, their terminology, not mine, 3D duct tape. I’m making something that’s sort of going to take the form of the object I need.
“In the case of Markforged, they were making really strong parts that conventionally could only be made of metal, but sort of coming in as this, I love that metaphor of this duct tape. The thing that solves the problem cheaply, quickly and efficiently that I can make at any time, at any point where it’s needed with the portability of the printers.”
3D printers can be rugged and work in hostile environments, as the military example shows.
“I did a little science experiment a while back. I actually wanted to see if I could 3D print while driving to a customer location. I was running a little under the gun and I needed to show them a demonstration part. At the time I was living in Los Angeles and I was driving down to Orange County, about a two hour drive down a pretty, I’ll say bumpy Interstate 5 freeway. I hooked the printer up to my car battery. The printers are just so robust, reliable, and it bears mentioning, power efficient, that throwing the thing in the back of my Honda Accord and getting a successful printout was really a no muss or fuss experience. Mileage may vary on the 3D printing on the road, I should probably disclaim.”
Markforged
Recently, the World Economic Forum, in collaboration with ETH Zurich and Fraunhofer IGCV, IPT and IAPT, released a report on the current state of additive manufacturing (AM) and its future. Their goal was to provide a realistic understanding of what AM can deliver today and why some are achieving that potential while others are not, as well as define the most probable near-term future production scenarios and what needs to happen to make those scenarios a reality. Pat Carey, Senior Vice President of Strategic Growth for Stratasys addresses this subject.
Q: What are some of the roadblocks along the value chain that AM can address?
A: According to Carey, additive technology helps in several areas of the value chain including local production, the iterative process, and bureaucracy.
“The ability to produce a part locally is a big deal, especially when we’re all dealing with parts on boats coming from China,” notes Carey.
Also, companies are shifting to a more personal, mass production model that favors additive manufacturing over other manufacturing technologies.
The Stratasys F770 3D printer will build large parts. It features the longest fully heated build chamber on the market and a generous build volume of over 13 cubic feet (372 liters). The system, priced under $100,000, is designed for prototyping, jigs and fixtures, and tooling applications requiring standard thermoplastics.
“I’ve been working with a number of product design firms that were following a traditional process of product design,” notes Carey. “Prototypes were a challenge …. with all the supply chain issues. …. Many of them have switched to using additive manufacturing. They wanted to change their processes, but changing processes in big companies is difficult. …. So, we’re seeing a number of large companies entertain new design processes which include faster iteration or skipping whole steps of iteration. One of the fun complaints I’ve heard from some customers is that the additive product process is faster than their bureaucracy can keep up with. So, it’s interesting to hear that from customers, ‘Pat, your technology is really helpful, but it’s so fast that the paperwork can’t keep up.’”
The recent acquisition of Origin One enables Stratasys to take advantage of its new approach to the additive manufacturing of end-use parts.
Origin One uses Programmable PhotoPolymerization to precisely control light, heat, and force, among other variables, to produce parts with exceptional accuracy and consistency.
The design process has always aligned with the manufacturing process. Designers know in advance whether a part will need to be manufactured through injection molding or machining. And they know the limitations of each process. Now, as designers turn to additive processes, they are beginning to question why they make certain design decisions because additive enables different decisions and approaches.
“The design process is very different and it has to do with both the customization, iteration, design, those three needs are really not separated for a lot of companies right now,” adds Carey. “They’re saying, ‘I can actually do this. I can have an idea and have a part or a product that looks and feels just like it in the customer’s hands in a week,’ which for them is nearly unbelievable.”
Additive manufacturing allows you to skip some or many of the typical steps of iteration.
Traditional manufacturing technologies often require the use
of defined steps for prototyping, depending on the part or object. Prototypes range from the initial stage where it’s a white or gray prototype, to the how-does-it-feel prototype, to the how-does-it-look, how-does-it-fit-into-a-package prototype.
“Some customers were going through all these processes and some of those processes were decades old and they’d always done it that way. Well, the supply chain challenges, COVID challenges, Trump trade wars, all this stuff blew that up.”
The realization that companies could not do what they used to do set in. They had to deliver products to the marketplace. They were forced to change.
“I tell people from a 3D printer perspective COVID’s been great. A lot of choices have been eliminated.”
To get product to market, companies had to do something. “So, we saw people adopt stuff and like, “Wow, this is really interesting. This really works. Why are we doing it the old way?”
Q: What kind of industrialization steps are needed for AM to reach its full potential?
A: Part of the issue is that prototyping has been done on the side. Early versions of 3D printers were standalone systems. To move into manufacturing, they now need to be inline—meaning they need to be part of the manufacturing line.
“And we know the manufacturing line is a complex software and data driven process nowadays. Millions and probably billions of dollars have been spent making these manufacturing lines that way, because we need to know what’s going in and what’s going out.”
For a number of industries, including aerospace and automotive, collecting data on the part and storing that data for warranty or
other issues is a big deal.
Thus, the next steps for the additive industry are the connectivity part--to continue to give the 3D printer data, get data in return, and store that data in a standard format.
“Those are big processes that need to be adapted and a lot of the 3D companies are just starting that.
“Another issue is what I call serviceability. If I go on a factory floor with a printer, I need to match its serviceability with that of all the other products on that floor. And that means either train company operators to fix it or have a response time to fix it, especially if it’s key to a product. If it’s key, the downtime of the printer is a big deal. This is a big challenge for 3D printing.
“Users can go online, depending on the printing company, and find the answer on a blog. Well, that’s not going to work on a factory. So those types of challenges around serviceability, reliability, and then repeatability are some of the challenges around industrialization that we’re seeing the industry take on, … get together and have discussions on.”
The questions to discuss and answer revolve around: Will it make the same part over and over exactly the same like injection molding or machining does?
“I don’t think we need to pave any new ground because we can watch what everybody else in the factory’s done. And to be honest, the customers tell us what we need to do. They say, “If you want to be here, you need to do this, this, this, this, this.” It’s just, how do we adapt to it? And then how do we, as an industry start to agree that this is what we’re going to do.”
Q: Is 3D printing additive manufacturing too disruptive to manufacturing right now?
A: “I don’t think so. A lot of it’s going to be driven by the materials. So, if we’re bringing a material to manufacturing that they already know, nylon is the easiest one to talk about. Also, Polycarbonate. So, no, I don’t think so. We’re seeing this, to be honest, we’re seeing the advantages outweigh the effort, the gap.”
Q: Can additive manufacturing be advanced or developed to the point where it fits in with traditional manufacturing processes, the way the manufacturing people want it to do so?
A: “Yes, but one of the common discussions I have with executives revolves around how it’s not a replacement for traditional manufacturing. You can’t take one out and put AM in its place.
Designing for additive at the very beginning of the process has been a key part of making this technology economically viable. Mass production brings in new challenges. Simply taking an older part and trying to duplicate it on an additive system
Jigs and fixtures are common tools when manufacturing a part. They are also used when a part undergoes secondary processes, such as finishing, and may be known better as masking fixtures. The FDM Fixture Generator lets users 3D print these fixtures. The module came about as a result of a collaboration between Stratasys and nTopology. Users can generate and 3D print custom fixtures with a few clicks.
usually doesn’t work economically. And it doesn’t take advantage of additive.
“That’s a caution I always tell people. But if we start up front, back to the earlier discussion on COVID and how additive helped because we had a time problem, that became a key element. Especially for large companies that introduce products on a monthly basis. When you’re not introducing new products to consumers, they get bored. During the pandemic lockdown, consumers had a lot of time on their hands. So, there was a lot of pressure to introduce new products and companies couldn’t do it with traditional methods.
“That changed the world a little bit and made it an advantage for additive. And I think we’ll see that on the manufacturing floor as well. When we think about automotive, going from making millions of the same car to tens of thousands of the same car. Personalization.
Customization. As a company processes change, it makes additive more favorable, more appealing than in the past. If a company needs to make two million of a part identically, well, we’re not going to compete with an old process for that. But the markets are changing I think, to our (additive) advantage.
Q: What efforts are underway to address the current criticisms of post-production with AM to make that process more efficient and more cost effective?
A: “I think it is a fair criticism. We’ve spent a lot of decades actually, we’re over 30 years old as Stratasys, getting reliable parts out of the printer. And when it was just prototypes, we mostly did sanding and some painting. There was not a lot of thought put into post processing. But now that we’re going into production environments, there’s an expectation of durability and quality. So if I’m a manufacturer, I’m making a consumer device that somebody’s going to have in front of them, in their hand, the quality of the device is part of the brand. And a 3D printed part needs to carry that level of quality.
The expectation’s going way up, and so there’s more focus on postproduction, as well as with some of the newer technologies like powder effusion, DLP as those parts ramp up in production. Post-processing is a big factor because postprocessing can really slow down the additive process and it can either add a lot of value or detract a lot of value. We are, as Stratasys, experiencing a big focus on post processing. It is a fair criticism and it’s a big opportunity in my view.”
Q: What’s your prediction for the future of post processing?
A: “I think there will be many new processes in additive postprocessing. The big trend will be integration with the printer, though. Can I pass information from the printer about the parts to the postprocessing and then customize this?
“Post-processing can be customized. In a lot of cases really, in the old world, it’s just a tank of something, water, glycol, or alcohol to clean the parts. It’s basically a dumb tank. Now we’re starting to see the post-processing process actually gather information and develop information around those parts and be able to pass that information along with the part. So a part goes on an airplane or in a car, it’s possible today to trace back where was that made. Where was it post-processed? What was happening in post-processing?
“And we’re in the polymer space. So heat has a lot to do with polymerization. So what happened heat wise or what happened to the surface? And did that surface make it more or less biocompatible, more or less food grade? All as additive goes into new industries, there’s new sets of requirements, FDA requirements, and so on. Post processing can help or hinder a lot of that.
“I also see a lot more tracking of and storing of the data. I’m seeing control systems put in post processing machines. So rather than being a tank, literally with a drain, it’s actually a smart box that knows what’s going on. We’re starting to see that.”
Q: Could you say that additive is driving digital manufacturing or is additive adapting to digital manufacturing?
A: Carey sees both options. Traditional manufacturing technology is being altered to become more digital, that’s a lot of what efforts such as IoT are about. But additive is inherently digital, so it’s ahead of traditional manufacturing technology.
For Carey, materials are key. “Either metal or polymer, the materials are the most important thing. We’re going to start to see an area where the materials are developed to fit the product. Customers come to us, ‘Can you make a material that looks and feels like this?’ That’s going to start to happen where the end product will drive the chemistry, not here’s ABS now figure out what you can make with it. Before, the material drove the product. Now the product will drive the material and we’ll be able to make materials on the fly or change the materials or affect the materials on the fly. That’s what’s going to start happening. And that will be true digitization.
“And we’ve done some experiments. We’ve had some of these demonstrator systems out there over the last three or four years. We’re able to mix the materials at the point of jetting. And we’re talking to customers who have requirements about putting different materials at different places in a part. Because this place undergoes a different stress and needs more something here or less something there.” And medical is making similar requests.
“We talk to a lot of universities and in the bio space. We get questions such as ‘Can I put down a material that looks like bone, or looks like skin, or looks like cardiac or nerve material?’ We’re starting to see that around jetting.
“Many limitations are being removed. And then the smart customers start to do stuff with it. I tell people, we make a tool. It’s amazing what humans can do with the tool. We don’t make a product, we make a tool that we give to humans and then see what they do with it. That’s what’s going to be cool about 3D printing.
“And we’re starting to see bio materials come in. I’m seeing more and more focus on materials that are sustainably made from current plant-based fibers.”
Q: What do you think is going to be the next phase for AM? Are we going to go back to more technological developments or are we going to continue in more of a business development phase?
A: Carey sees a key trend being ecosystems. “I think a lot of the players are established as we look at the industry. I spent a lot of time in Silicon Valley over the last decade. Many of innovative startups had one or two innovations; they tend to get grouped into multiple innovation companies. And then those multiple innovation companies start to form ecosystems because they can’t innovate any faster and can’t do everything. When I mentioned connectivity, that’s really networking. So, when a printer goes onto a factory floor, it’s networking.
Well, if I need to network my device to somebody else’s, I better have a common language. I better have a common data format that requires an agreement, which is an ecosystem.
We’re starting to see ecosystems. 3D printing is a relatively tiny industry. And to be honest, we’re mostly friendly with each other. And we’re seeing a lot of ecosystems and partnerships develop. It’s kind of exciting to see at this time of a
35-year-old industry, but it’s very small and everybody wants to be successful. And we’ve watched how technologies progressed over these years. I think we can follow that building ecosystems, building standards, agreeing how to do stuff.
“It’s an exciting time right now in additive, we went through the hype period of 2013, 2014. We went through the financial hype period of 2021. And now it’s all out there. We can all see how each other is doing, growing, shrinking. It’s not just about press releases anymore. We can look at each other’s numbers. And I think there will be a period of rationalization in the next six months to a year that will really help to market go ahead.”
Stratasys
www.stratasys.com
3D Platform is the trusted source for industrial-strength, large-format 3D printers. Based in Roscoe, Illinois, USA, the 3D Platform team is focused on driving advancements in technology to innovate, design, and build next-generation equipment for additive manufacturing. Our approach to 3D printing focuses on four clear industry demands:
Scalability and increased throughput from high-flow extruders allows smart manufacturers to shed legacy product development cycles and small-scale models for full-size prototypes and production.
Open market-enabled solutions allow users to go bigger with 16 times the speed of competitors’ extruders for faster printing and exceptionally strong parts.
• Quick-Swap dual extruder heads deliver high quality 3D prints.
Affordability of equipment and materials allows SMB’s and Fortune 100 companies to tailor 3D printing to their needs, and quickly develop new products and bring them to the market.
Robust industrial technology stands up to harsh environments and the excessive demands of rapid manufacturing using the world’s leading linear motion mechatronics, reliable motors, and sophisticated control systems.
•
• Modular design accommodates variable nozzle and filament sizes Nozzle flexibility for fine layer resolutions or faster printing and strength.
To learn more about 3D Platform, visit www.3dplatform.com.
3D Platform 6402 E. Rockton Road Roscoe, Illinois 61073 USA +1.779.771.0000 3dplatform.com
marketing@3dplatform.com
sales@3dplatform.com
CS Hyde Company is your source high performance tapes, polymer films, fabrics, and silicone. For over 20 years we have been supplying almost every industry with performance materials for all types of applications. Our product line is composed of a variety of materials with properties associated with additive manufacturing/3D printing including low friction, nonstick release, and high temperature resistance. As a polymer film supplier of engineering grade thermoplastics and PTFE Fluoropolymers, we have grown to be a premiere source for custom printing surfaces. Common materials include ULTEM® PEI, and Optically Clear FEP tape or film. FDM printers using PEI benefit from a surface with durability and a surface that will hold filament in place and remove cleanly when cooled. Our PEI sheets are also pre-laminated with high temperature 3M™ adhesive that adhere to spring steel or glass build plates. FEP film is a great release material for resin vats found on DLP, Laser, LCD or as a release layer for tensioned “drum” style resin vats. Our custom cutting capabilities allow us to cut these materials to exact dimensions of any build plate or resin tray. Common sizes are available on our online catalog for click and ship availability.
Bring new precision and performance to every stage in your additive machine development with Yaskawa motion control
Rise above the desktop: Shaky, imprecise desktop machines become robust industrial performers with motion control that overcomes vibration, boosts speed and gets you ready for tomorrow's hybrid technologies.
Advance the industry standard: Industrial quality printers benefit from Yaskawa's smooth and precise motion, plus worldwide support that distinguishes your machine in a crowded marketplace.
Restate the state of the art: Top tier manufacturers need new ideas, plus the engineering support to make them work. Yaskawa supplies both, using the latest linear and robotic motion systems and Singular Control to create a seamless, supportable development environment.
Our motion control technology also prepares you for new frontiers in additive manufacturing:
• Robotic systems that produce curvilinear motion for true 3D deposition
• Additive/Subtractive technology which combines the benefits of 3D printing and traditional routing/machining
Yaskawa servos provide smooth, precise motion for additive manufacturing, while the G-code compatible MP3300iec controller can operate any motion device to implement the latest advances in hybrid manufacturing. Couple these with Yaskawa Compass™, our customizable user interface software package, to bring new precision, performance, and creativity to your additive machines.