
7 minute read
ecosystem
Desktop Metal has been busy creating a portfolio of “Team DM” brands to make 3D printing accessible to companies of all sizes, helping them produce products more sustainably and closer to the point of end use. This portfolio offers a range of production capable 3D printers from binder jetting to digital light processing.
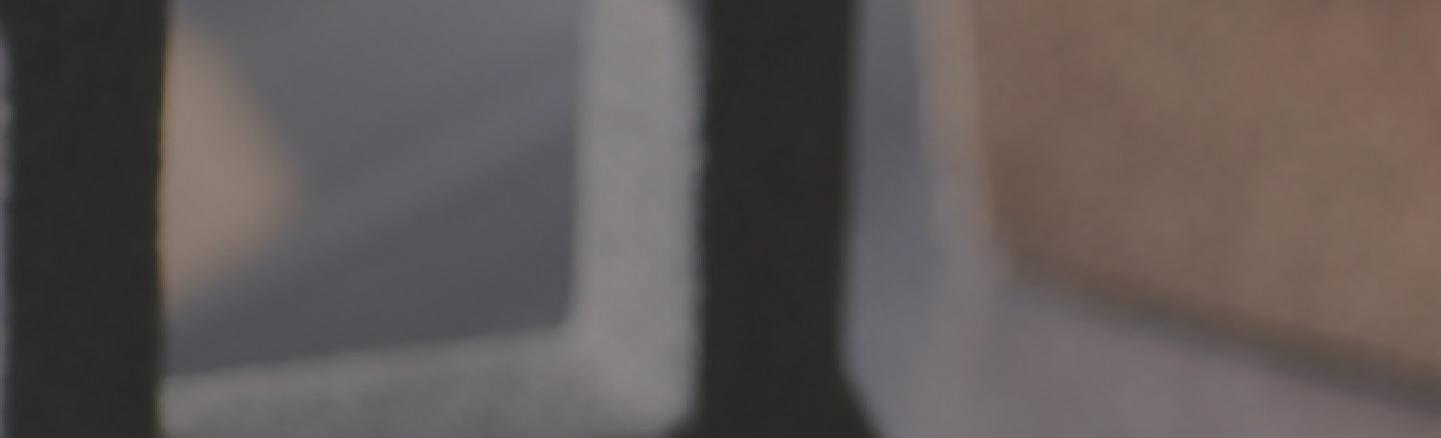
“The COVID pandemic exposed the weaknesses of our current manufacturing infrastructure,” said Ric Fulop, Co-Founder and CEO of Desktop Metal. “With today’s AM technologies, every country can have its own self-sustaining manufacturing industry with parts that can be shipped digitally and printed quickly.”


For Binder jetting, the S-Max Flex prints standard silica sand with furan binders and delivers final parts with dimensional accuracy of +/- 0.5 mm. The system comes with several accessories and safety features that are configurable to fit a variety of spaces.
A highlight of the portfolio is the Production System P-1, which was launched during the height of the COVID pandemic. A high-speed 3D printing system for end-use metal parts, the P-1 was designed as a gateway to the top-of-the-line Production System P-50 – one of the fastest systems to 3D print metal parts at scale. The P-1 shares the same patentpending Single Pass Jetting (SPJ) technology as the P-50, as well as common software and electronics for easy scalability.
The Production System is one of several Desktop Metal printing platforms that relies on binder jetting technology, which is widely regarded as one of the 3D printing methods likely to deliver mass production additive manufacturing at high speeds and competitive prices.
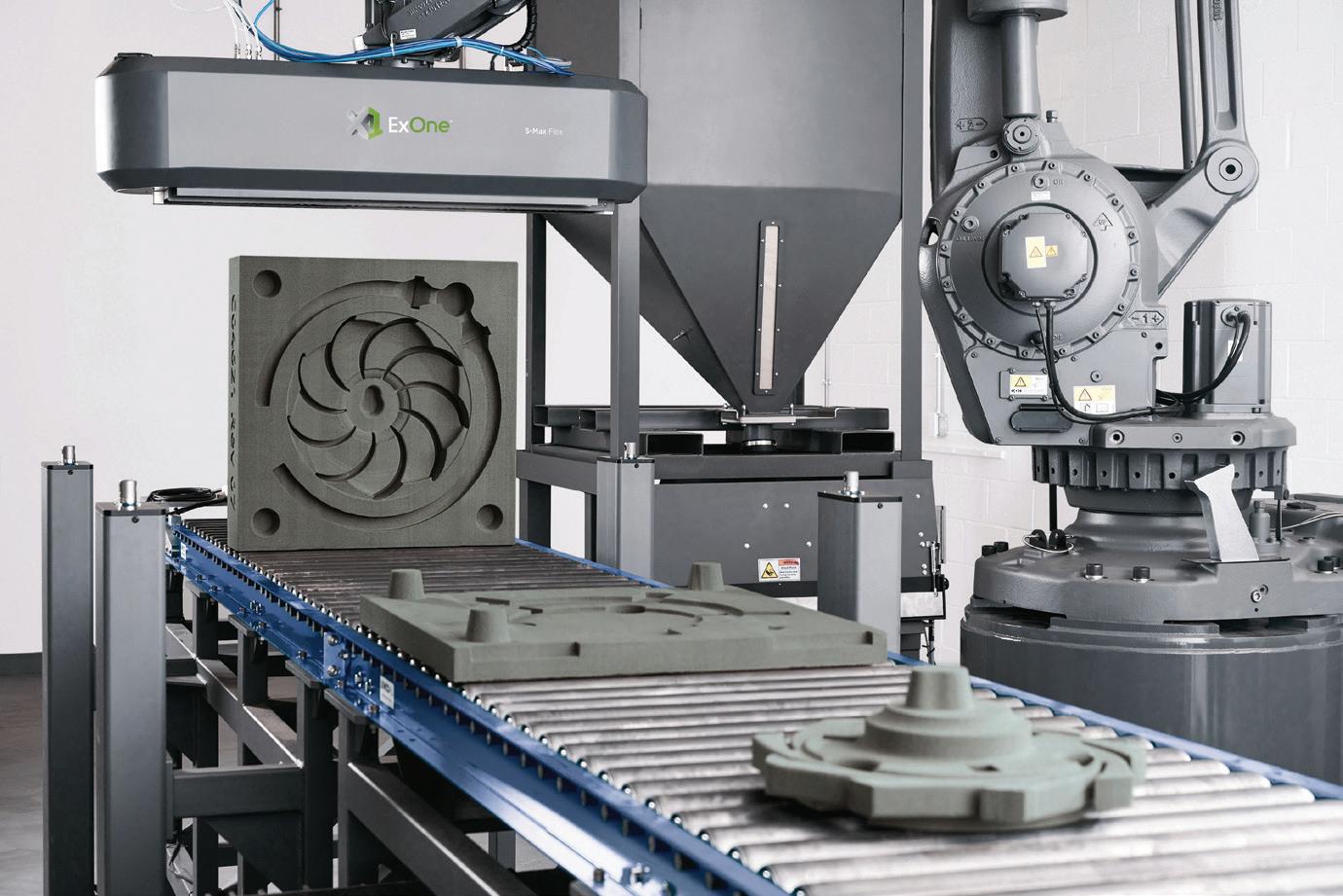
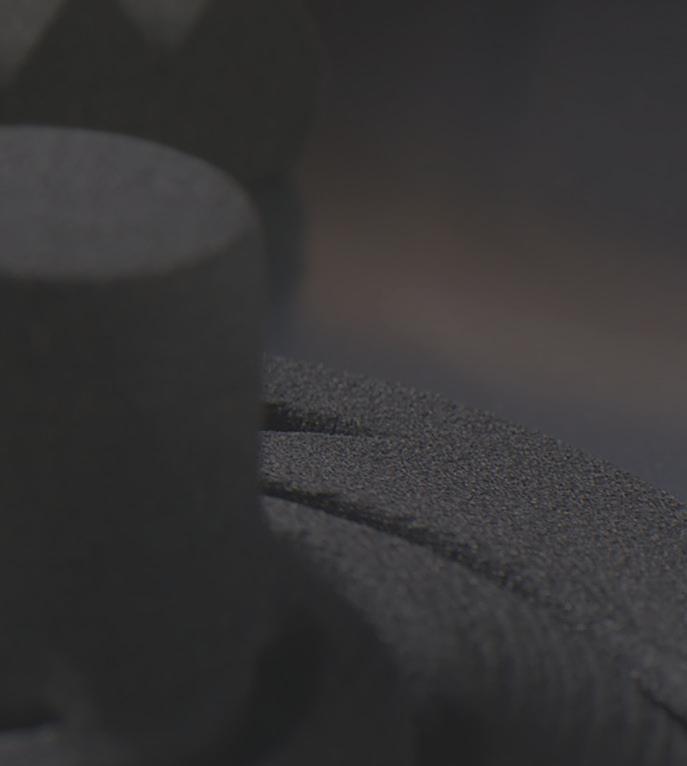
Nearly a dozen metals are now qualified for printing on the Production System P-1 and P-50 –delivering good part quality and surface finish, with sintered part mechanical properties that meet or exceed applicable industry standards, and final part densities up to or exceeding 99%. A partial list of qualified materials includes:
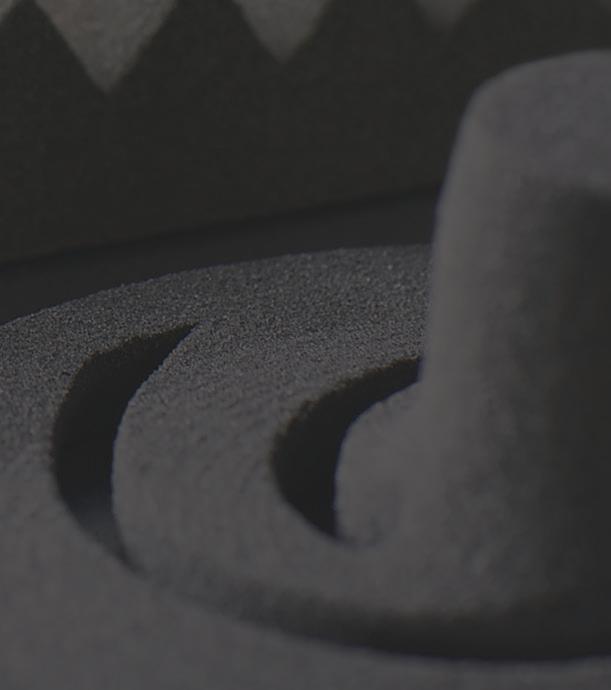
• Stainless steels, including 17-4 PH, 316L, 420, 440C, and DM HH SS
• Tool steels, including D2 and S7
• Low-alloy steels, including 4140
• Copper alloys
• Nickel superalloys, including IN625
• Precious metals, including silver and gold
• Ti64 and 6061 in development
Binder jetting
After years of contraction, the U.S. metal casting industry is experiencing growth as a result of supply chain changes related to the COVID-19 pandemic. This growth was one of the reasons
Desktop Metal bought ExOne and launched the ExOne S-Max Flex, a scalable, large-format binder jetting system that 3D prints sand tooling. Applications include sand casting complex metal designs for the aerospace, automotive, and energy industries.
The S-Max Flex combines ExOne’s sand printing expertise in process and materials with the SPJ technology to deliver a build rate up to 115 l/h. The goal is to make good sand 3D printing accessible to every foundry.
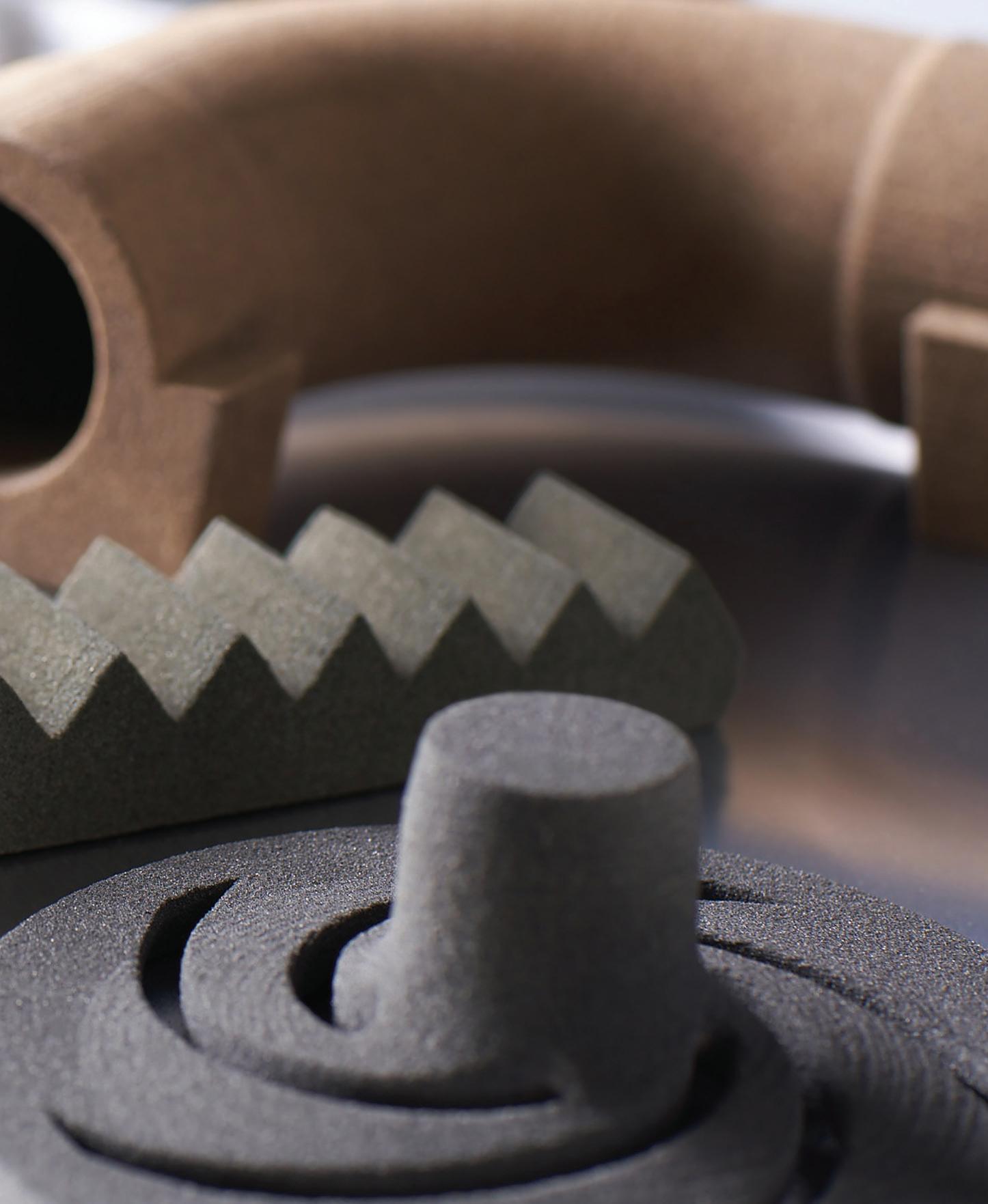
It pairs an affordable industrial robot with an end effector printhead design that deposits binder into a 1900 x 1000 x 1000 mm (74 x 39 x 39 in.) telescoping build box that grows as the parts are built layer by layer. Additional build box sizes are available up to 4700 x 1000 x 1000 mm (185 x 39 x 39 in.), with taller versions available up to 1000 x 2500 x 2400 mm (39 x 98 x 94 in.).
The S-Max Flex prints standard silica sand with furan binders and delivers final parts with dimensional accuracy of +/- 0.5 mm. The system comes with several accessories and safety features that are configurable to fit a variety of spaces.
Industries beyond metal casting are also set to take advantage of the S-Max Flex’s large form factor and ability to binder jet a variety of powders. Infiltrated sand tooling for plastic thermoforming, composite layup, and sacrificial tooling applications are printed on S-Max machines, along with infiltrated sand consumer products, such as those offered by Sandhelden and Deeptime. Desktop Metal’s Forust brand, which upcycles byproducts of the wood waste stream into consumer designs, will also leverage the new system to print large form factor wood parts at scale cost-effectively. Additional projects are underway printing reclaimed concrete and other materials.
Another binder jet 3D printing system is the X-Series line for metal and ceramic powders in a range of particle sizes. Like the S-Max Flex, this line of printers is derived from the acquisition of ExOne.
The X-Series line offers a differentiated approach to binder jetting enabled by patented Triple ACT — an advanced compaction technology for dispensing, spreading, and compacting powders during the binder jet printing process. This flexible, open material platform architecture can bind together a range of powders with a D50 of 3 to 100 microns.
Three X-Series models are available:
• InnoventX, an affordable, entry-level binder jet system for academic, R&D, and low-volume production applications.
• X25Pro, a mid-sized system for volume production with a build box of 400 x 250 x 250 mm (15.75 x 9.84 x 9.84 in)
• X160Pro, as large metal binder jet
The Production System
P-1 is a high-speed 3D printing system for enduse metal parts. It uses the same Single Pass Jetting (SPJ) technology as the P-50, as well as common software and electronics for easy scalability.
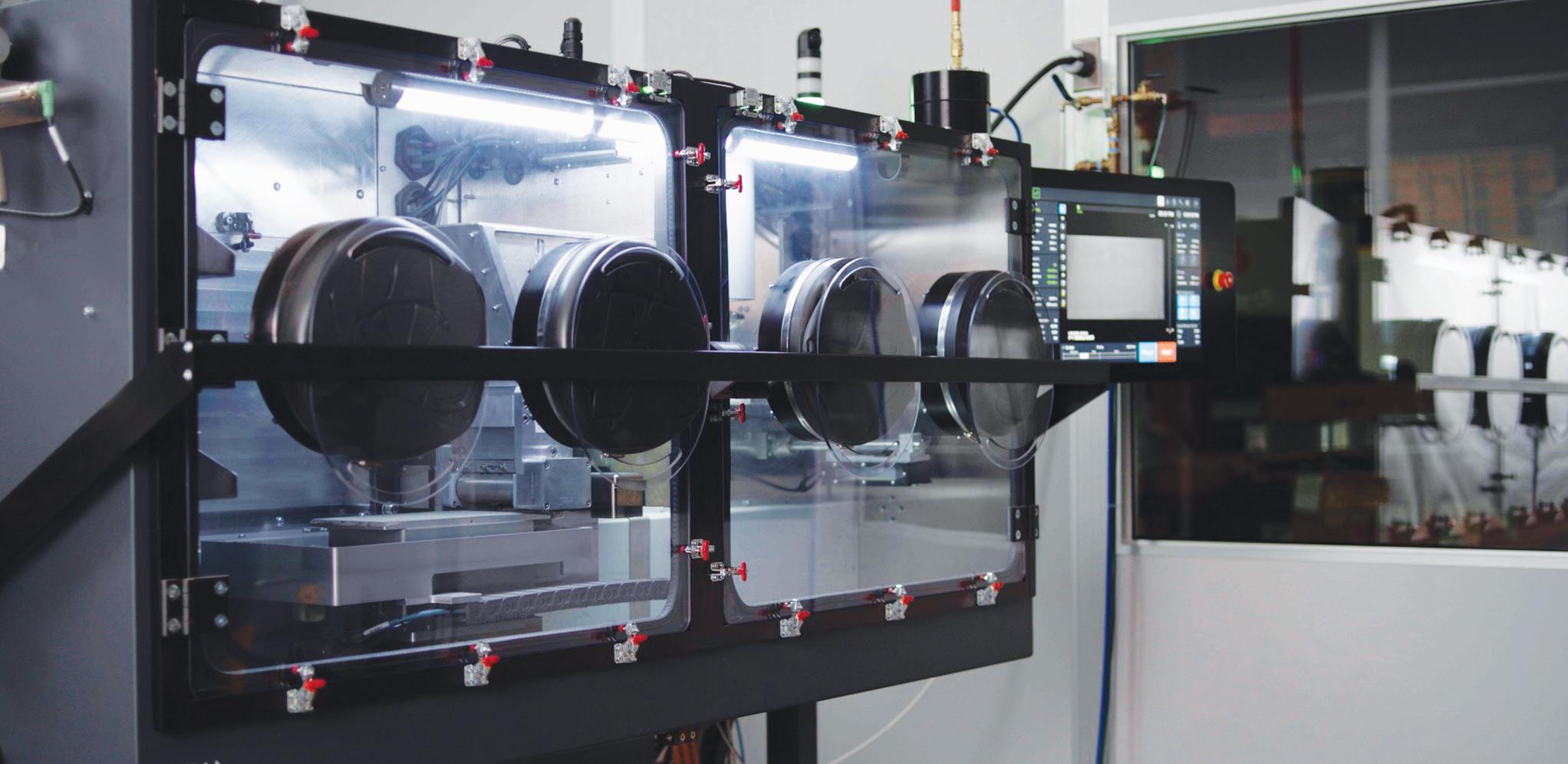

system with a build box of 800 x 500 x 400 mm (31.5 x 19.7 x 15.8 in).
The X-Series printers repeatably deliver tight dimensional tolerances and densities of 97-99% or greater — in line with or surpassing metal injection molding or gravity castings. Surface roughness values as low as 4 µm (Ra) can be achieved directly out of the furnace.
For photoploymers
When Desktop Metal bought EnvisionTEC, it rebranded the 3D printing line as ETEC. This line uses digital light processing (DLP)
Dm Hh
Stainless Steel (DM HHSS) is a custom stainless-steel alloy that combines high strength and hardness with corrosion resistance. A key application is its use to make offset sockets.
technology, and the goal is to bring high-speed, photopolymer 3D printing to volume manufacturers of consumer and industrial products.
These 3D printers offer extreme levels of accuracy and surface finish and have been used in the healthcare, dental, medical and jewelry industries since 2002. Another result of the EnvisionTEC acquisition was the launch of Desktop Health to focus on healthcare and dental customers.
Through a partnership with Adaptive3D, another subsidiary of Desktop Metal, ETEC offers a broad portfolio of photopolymer 3D printing materials, including Elastic Tough Rubber 90 (ETR 90), which is one of the highest tear strength elastomers on the market. ETR can be found in products on store shelves, including power tool adapters and recoil pads.
Materials
When it comes to materials, Desktop Metal has released several, including DM HH Stainless Steel (DM HH-SS), a custom stainlesssteel alloy that combines high strength and hardness with corrosion resistance, for use on the Production System platform.
DM HH-SS is a custom, heat treatable-alloy that combines the tensile strength, ductility, and corrosion resistance of 13-8 PH stainless steel with hardness comparable to low-alloy steels, such as 4140. These attributes may help companies eliminate the use of low-alloy steels, which also require a subsequent plating step for applications needing corrosion protection. DM HH-SS is also suitable for conformally cooled injection tool core and cavity applications, where millions of injection strokes per year are required.
An example of a key DM HHSS application is the offset socket, often used for manufacturing tooling in scenarios where space is limited and a traditional tool would not be able to access a bolt. Instead of maintaining an inventory of a variety of tools to accommodate multiple socket sizes for each bolt size, users can maintain a digital warehouse of each socket size and print quantities of different sizes together in a single build.
Another material finding greater use in 3D printing is copper. Desktop Metal announced it has qualified commercially pure copper (> 99.95% purity) for use on the Production System platform.
With its thermal and electrical conductivity, commercially pure copper suits applications that require heat or electricity transfer, such as cold plates, pucks and manifolds, heat sinks, heat exchangers, and bus bars used in power-intensive electrical applications. It is the third-mostconsumed industrial metal in the world.
Desktop Metal’s materials science team has qualified and fully characterized commercially pure copper (C10300) printed on Production System technology. Liquid cooling plates, which are used to regulate temperature on microprocessors, are an example. Coolant flows through the fins, which provide a large surface area to transfer heat from the passing fluid to the heat sink to cool the chip attached to the outer body. These cooling geometries typically require capital-intensive, long lead time, and skilled laborintensive production processes, such as skiving and machining, given the challenges associated with achieving precision and repeatability in such a small form factor. In addition, these commonly used conventional manufacturing processes are subtractive and produce excess scrap material, greatly increasing the associated part costs. Binder jetting on the Production System can produce a liquid cooling plate as a single component.
D2 tool steel is a versatile highcarbon, high-chromium air-hardening tool steel characterized by its hardness and compressive strength after heat treatment. This tool steel is wear resistant, dimensionally stable, and resists corrosion in the hardened condition, a key benefit for conformal cooling applications. D2 is used for a variety of cold work tools that require a combination of wear resistance and moderate toughness, such as coining and sizing tool members, blanking and forming dies, shear cutting tools, gauges, burnishing tools, and other wear parts. An example application is rotating cams.
Cams are used in oil and gas or chemical processing applications to convert rotary motion into reciprocating linear motion in a machine. Typically, these parts require multiple manufacturing steps, beginning with CNC machining, followed by broaching of the spline on a separate machine. Binder jetting enables the production of cams in a single printing step, reducing both the cost and lead time of the part, while also supporting the production of different cam sizes in one build.
D2 tool steel suits this application because of its hardness and corrosion resistance, which ensures a longer lifetime as the cam mechanically interacts with a sliding pin. In addition, because these components are often integrated into machines operating in harsh environments, the corrosion resistance provided by D2 ensures that the parts will perform as intended and not deteriorate.