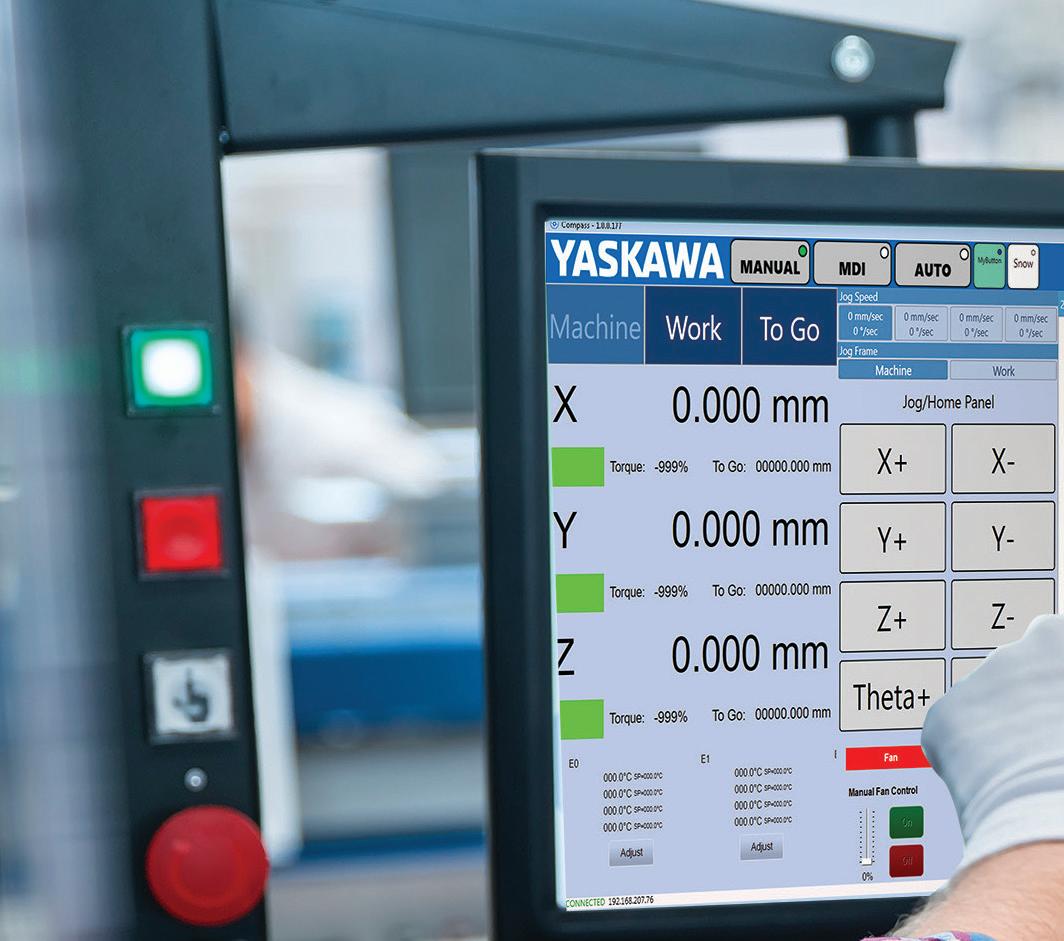
2 minute read
Additive technology
“Now, it’s not just the 3D printing companies with their material science departments within each company. Now you’ve got Henkel, and Covestro, and BASF and Evonik and all these big companies coming in and developing materials to help push that along. We’ve tried to take advantage of that. We’ve tried to shop around and see what’s available and partner with as many people as we can. I think what’s attractive also in that open business model is if resins work on some other DLP printer, and have proven to be successful and attractive to customers, they will probably work on our platform too. We can take things that have been developed. We need to modify them a little bit, primarily because our layers are thinner. We have to tune them essentially, but then we can offer that wider range of materials for the customers.
“The other important thing that we believe in for the open materials model is if big customers are really going to go into production, they’re going to want to have more control over the material supply chain. That’s our opinion. They’re going to want to be involved. I mean, we even see it when we work with some of them. We’re still a small company and when we go to a big chemical company and ask them to do something for us, they’re polite, but they don’t jump, but if we go there with a customer that is already one of their customers on the thermoplastic side, who already buy tons of plastic pellets, they are more willing, I think, to think about working together to develop 3D printing materials for that customer.”
The future of micro 3D printing
There’s been a significant improvement in materials over the last ten years for nearly all 3D printing platforms.
A key trend now is to make sure that all the systems, the materials, and the software are designed with manufacturing in mind so that the systems can be put into a factory and put in series or parallel with other manufacturing technologies, and can work with the quality management system that the company may have. Users are realizing that for most 3D printing technologies, the very large majority of the cost is not the labor. It’s the amortization of the machine, it’s the materials and the labor’s a relatively small component.
The automation piece is important when it adds real value, but it should be balanced with the cost and flexibility that comes with a person. “A person’s pretty flexible. If he drops something on the floor, he picks it up. If the robot drops something on the floor and it didn’t mean to, it doesn’t know how to pick it up. There’s that balance there. I’ve been in injection molding houses and I’ve been in 3D printing service bureaus where there’s 20 machines running and there’s one or two people. I think the automation will help, but I think there’s still lots of room to go in terms of getting the machines to the point where they may need more automation.”
Kawola thinks that for all of 3D printing, whether it’s resin-based, or filament-based or powder-based, the key is to get those additive manufactured materials, those 3D printing materials to be sufficiently the same as molding materials or machine materials.
“Our challenge and the industry’s challenge is to try to get that part to be close enough to the thermoplastic to be suitable for the application.”
Boston Micro Fabrication www.bmf3d.com
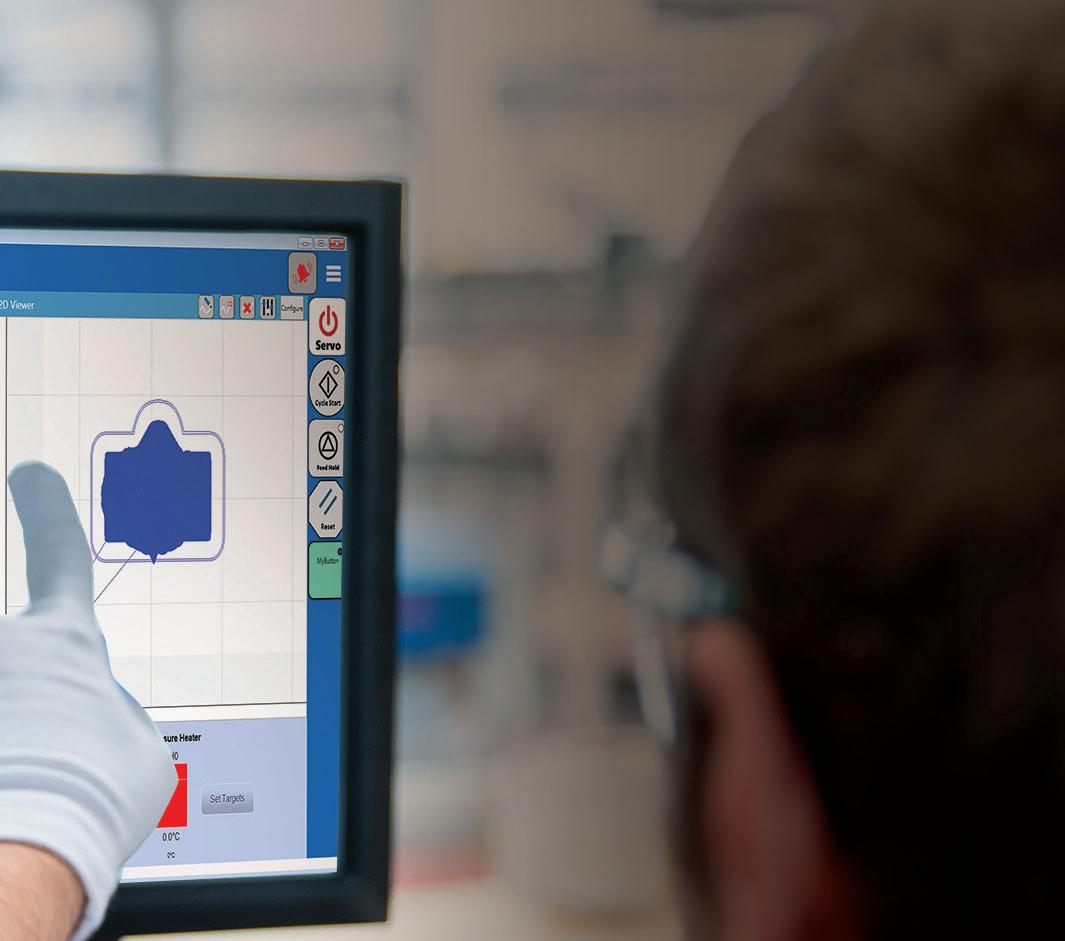

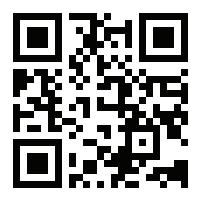