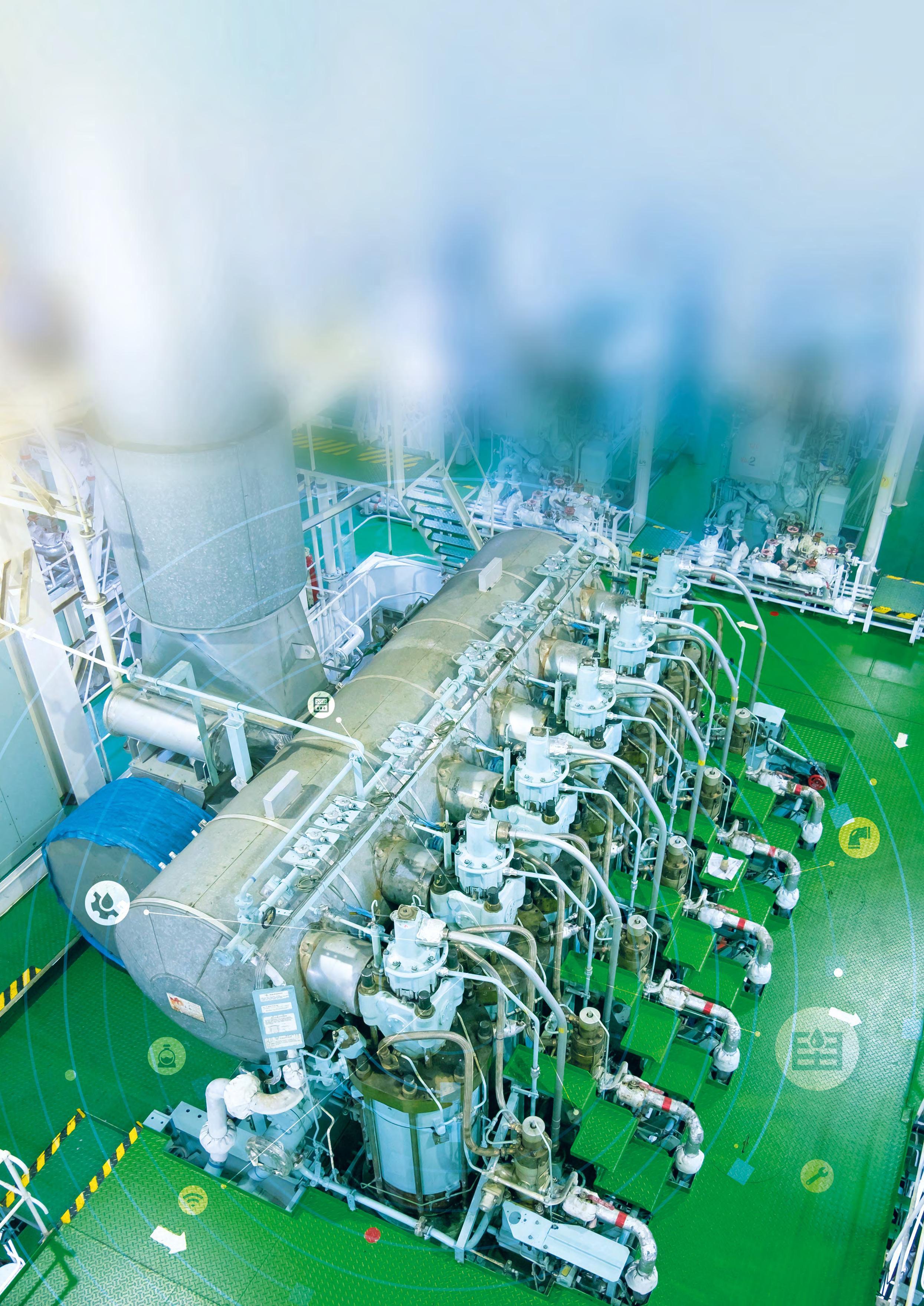
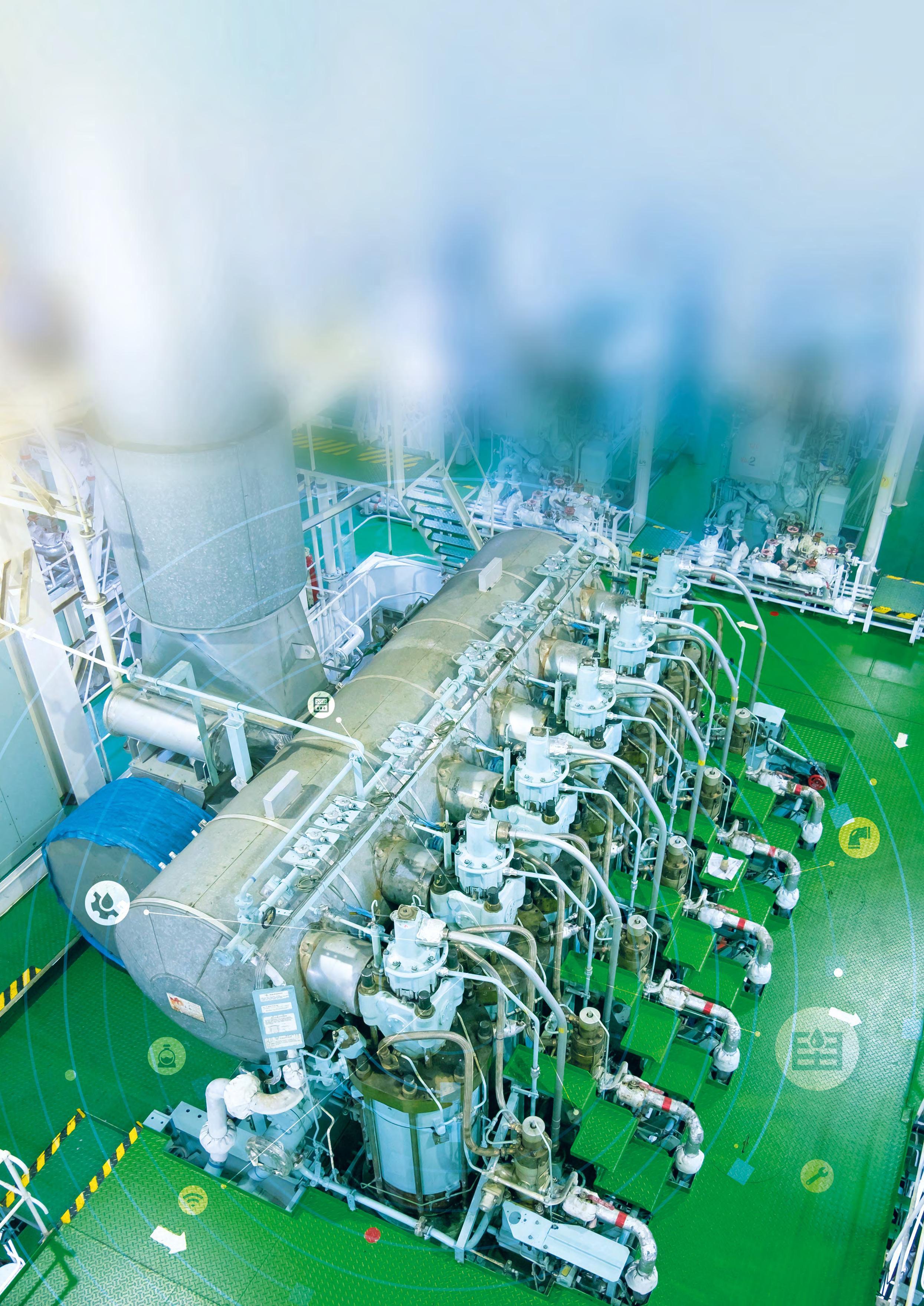
Smart Water Management – our holistic concept makes every drop count
Boiler water and cooling water systems are subject to heavy use day in day out as ships go about their business oiling the wheels of world trade. Just as we need clean water to live, ships need properly treated water to run smoothly. If left untreated, the integrity of equipment can be compromised over time through harmful scaling, mineral deposition, corrosion, and biofouling.
This becomes an operational pain point that can negatively impact operational efficiency. Poor heat transfer in the engine cooling system means the engine will not cool down properly, reducing vessel performance and eventually impacting CII ratings. Equipment problems can also be costly and time-consuming to fix should a failure or malfunction occur, translating into downtime and unscheduled delays.
Class society DNV records in a technical update that inferior water conditions due to poor equipment maintenance is still the number one cause of reported common boiler defects.
Operational Pain Point
As the vessel sails around the world,
Critical equipment such as boilers and pipes are in constant use.
Water can be a troublemaker
Water is one of the most essential elements used in critical equipment but can cause serious problems if treatment is inadequate. Water contamination is an ever-present risk. Distilled (demineralised) water should be the default as feedwater for boiler and engine cooling systems, combined with proper chemical treatment to limit unwanted scaling and corrosion.
Detrimental effects of poor maintenance on equipment
Water contamination either due to the use of low-quality feedwater and/or ingress of seawater or exhaust gas is the primary cause of hard scaling, deposition, and corrosion effects in boiler and engine cooling systems. Carryover in boiler systems refers to any contaminant (vapour, liquid, or solid) that is ‘carried over’ from the boiler in the service steam and can exacerbate scaling and corrosion.
Causing the captain to lose sleep over lost money, downtime, and constant calls from the ship owner.
If left untreated, equipment can be compromised by corrosion and deposit formation,
Common damages and defects – awareness is the key to mitigating risks
Regular monitoring and maintenance can help the ship crew detect the problem areas and issues early before they cause structural damage to the system.
Challenges affecting Boiler Water Systems
There are three key challenges associated with Boiler Water Systems – corrosion, scaling/deposition, and carryover. These need to be guarded against to ensure proper and efficient functioning of the equipment.
Corrosion
Corrosion describes loss of metal resulting from chemical oxidation of the metal in the presence of electrolytes in the surrounding environment. The multitude of causes; improper pH control, contaminated feedwater, and incorrect operating temperature can all cause corrosion in the Boiler Water System over time.
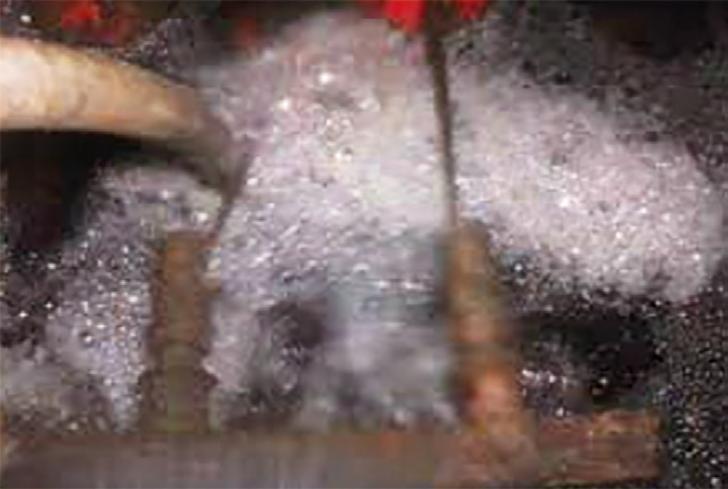
Scaling/deposition
Mineral scaling such as calcium and magnesium can restrict boiler water circulation, increasing drag, accelerating deposition, and potentially causing overheating. Over time, deposits and scaling can lead to localized overpressure and premature equipment failure, including ruptured pipes.
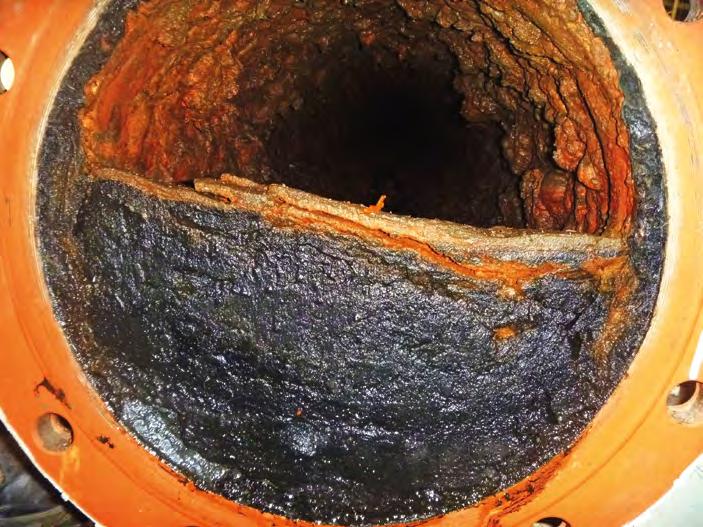
Carryover
Boiler carryover occurs when water and steam are carried over from the boiler drum into the system piping. This typically happens when there is a surge in steam demand, improper boiler level control, or excess dissolved solids or organic matter in the boiler water.
Summary of operational pain points that crews should be aware of:
Corrosion and scaling/deposits reduce heat exchange and performance of the Boiler Water System while increasing fuel consumption, costs, and emissions.
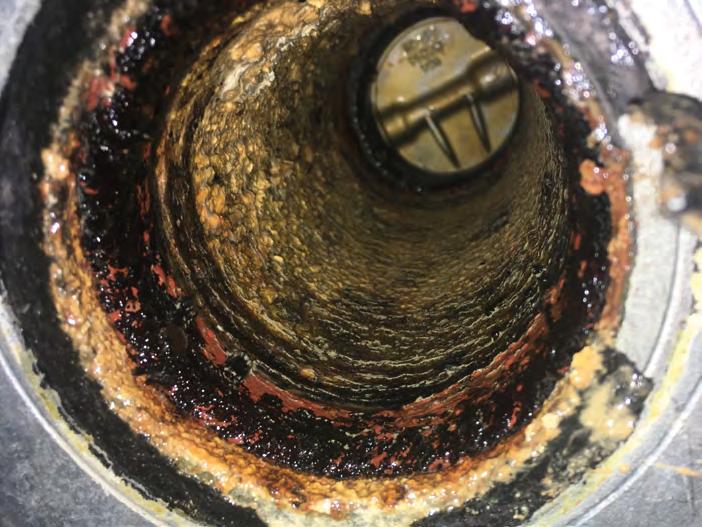
Defects can lead to a higher required boiler temperature endangering the boiler structure while also reducing efficiency.
Deposits restrict boiler water circulation, potentially leading to overheating and premature failure of equipment.
Carryover of contaminants in boiler steam can infect connected systems again reducing overall efficiency.
Challenges affecting Engine Cooling Water Systems
The same challenges of corrosion and scaling/deposition are found in Engine Cooling Water Systems, with the addition of biofouling. It is crucial to safeguard against all three issues to ensure efficient equipment performance over time.
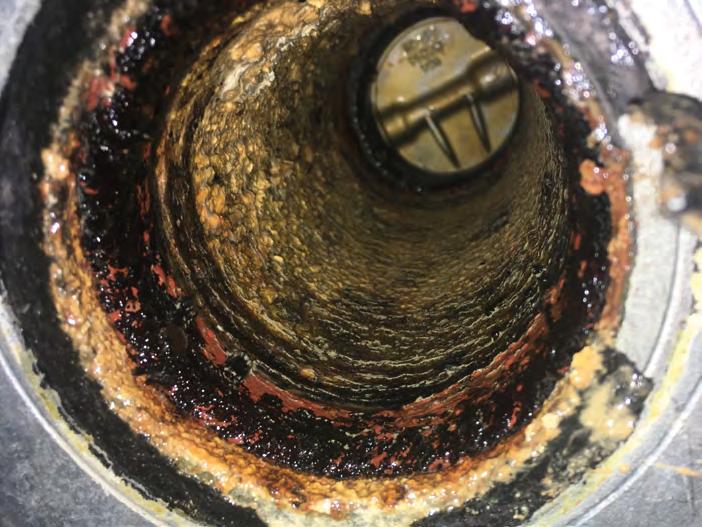
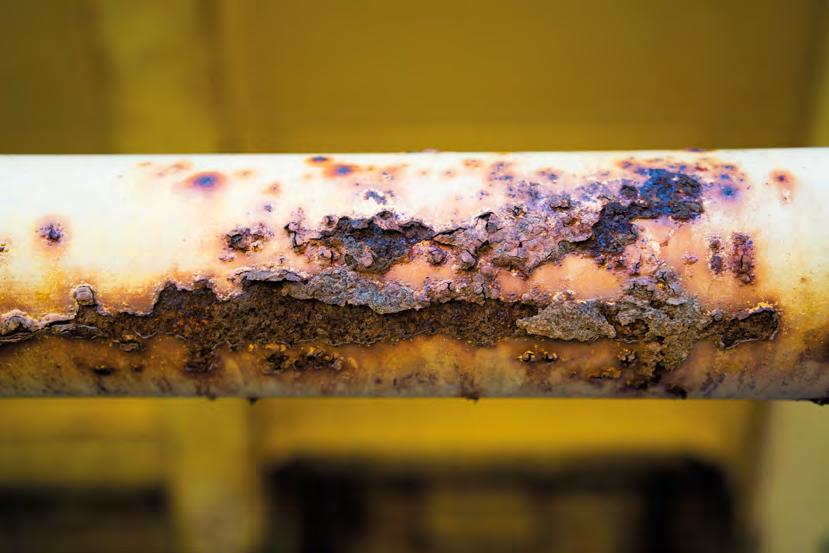
Corrosion
Corrosion describes loss of metal resulting from chemical oxidation of the metal in the presence of electrolytes in the surrounding environment. Seawater in the Engine Cooling Water System can lead to corrosion of equipment components.
Scaling/deposition
The accumulation of scale, rust and sludge can lead to blockages and ‘clogging’ in heat exchangers, reducing efficiency and causing equipment malfunction. Scaling/ deposition results in poor heat transfer of metal surfaces thereby increasing cooling water temperature leading to an overheated engine.
Biofouling
Biofouling refers to the gradual build-up of marine microorganisms and macro-organisms within the Engine Cooling Water System. This can lead to increased friction and reduced water circulation causing the engine to overheat. Biofouling also impacts heat transfer efficiency and can trigger corrosion leading to metal loss.

Summary of operational pain points that crews should be aware of:
These problems, either individually or combined, can lead to financial losses due to vessel downtime, repair costs, as well as increased fuel consumption and emissions.
Biofouling that is not addressed can also result in equipment failure.
Mismanagement of water quality and equipment can lead to corrosion within the Engine Water Cooling System.
Smart Water Management in practice
Smart Water Management rests on the four foundational pillars: good products, a user-friendly digital platform, great service, and reliable automation. Combining these pillars will provide an optimal preventative maintenance programme for your vessel(s) ensuring your equipment runs smoothly and for longer. Avoid unexpected repair costs and downtime caused by the detrimental effects of poor maintenance.
Smart Water Management is designed to bring peace of mind so vessel crews and shore managers can focus on other important tasks and priorities.
Customer Pain Points
Smart Water Management
Product Solution
(Chemicals & Test Kits)
Proper water treatment and routine testing are essential to reduce the possibility of unwanted critical equipment failures.
Digital Solution (Waterproof)
Using our digital platform, Waterproof, as part of your vessel ISM/SMS protocol ensures that testing is performed regularly and systematically, with all tests results safely stored ensuring a good treatment record.
Protecting your assets onboard
Services (PSE Visits)
Our Port Service Engineers can conduct inspections/ surveys on your vessel. They can advise the crew on proactive water management and best practice, with each visit report stored in Waterproof.
Automation (Equipment & Pumps)
Use an automated dosing system that introduces the chemicals in a consistent way and maintains the boiler passivation layer. Water treatment systems can maintain consistent water quality, reduce the risk of corrosion and scaling, and optimize system performance.
Get in touch with your local representatives to find out how our integrated approach to water management can help you.
Scan or click the QR code for more information.
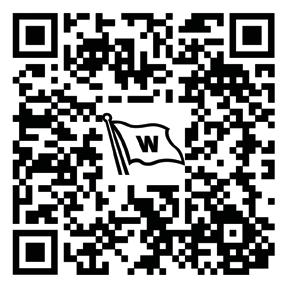
Waterproof by Wilhelmsen – making safe water management easy
Most boiler defects are caused by poor water quality. Each incident costs on average more than 100,000 USD in direct repair cost, and can put the vessel out of operations for up to a week. In most cases this is completely avoidable.
Correct testing and treatment
Small mistakes done onboard can quickly become a serious problem. Frequent testing and correct dosing and maintenance can be complicated and requires dedicated focus and competency.
Focus where it matters
Knowing what vessels need attention and support is impossible without access to transparent data and insight. If potential problems are not addressed early the risk of serious issues increases.
Fragmented records
Making sure all information and records are available when you need it is crucial. When the information is spread across systems and hard copies onboard this requires a lot of effort to maintain.
Making sure critical systems like boiler and engine cooling systems are protected and monitored are important to avoid costly repairs and accidents. Easy access to the vessel data is crucial to detect potential problems early and document the routines and conditions. Waterproof by Wilhelmsen makes it all accessible in one system on the vessel and onshore.
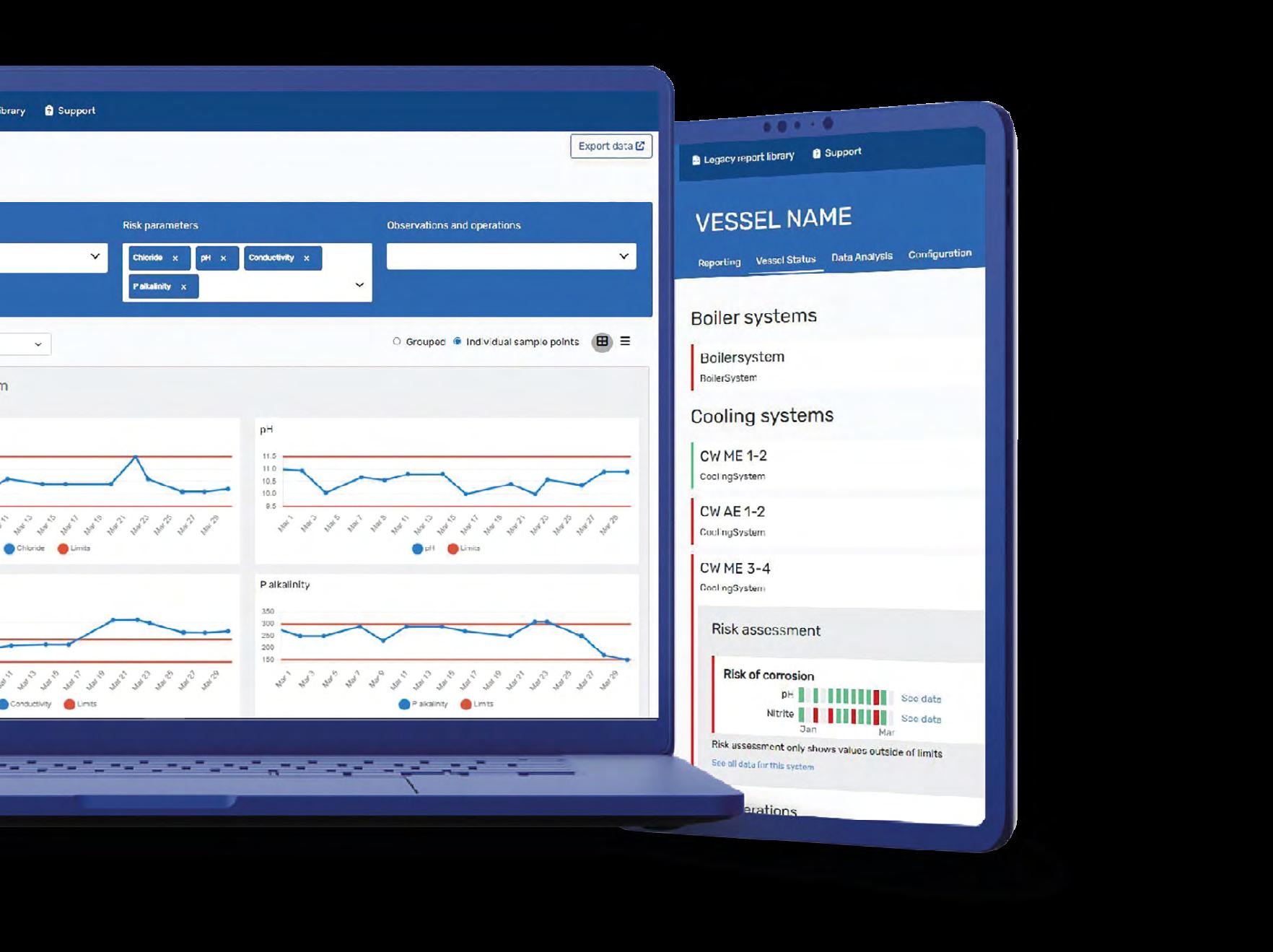
Contact us
Waterproof@wilhelmsen.com
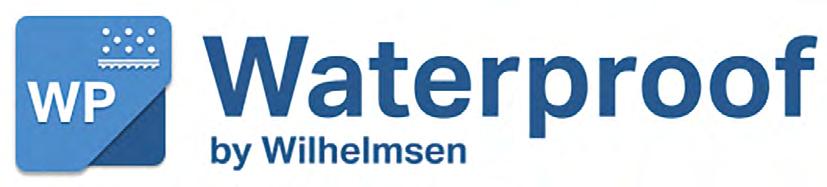
