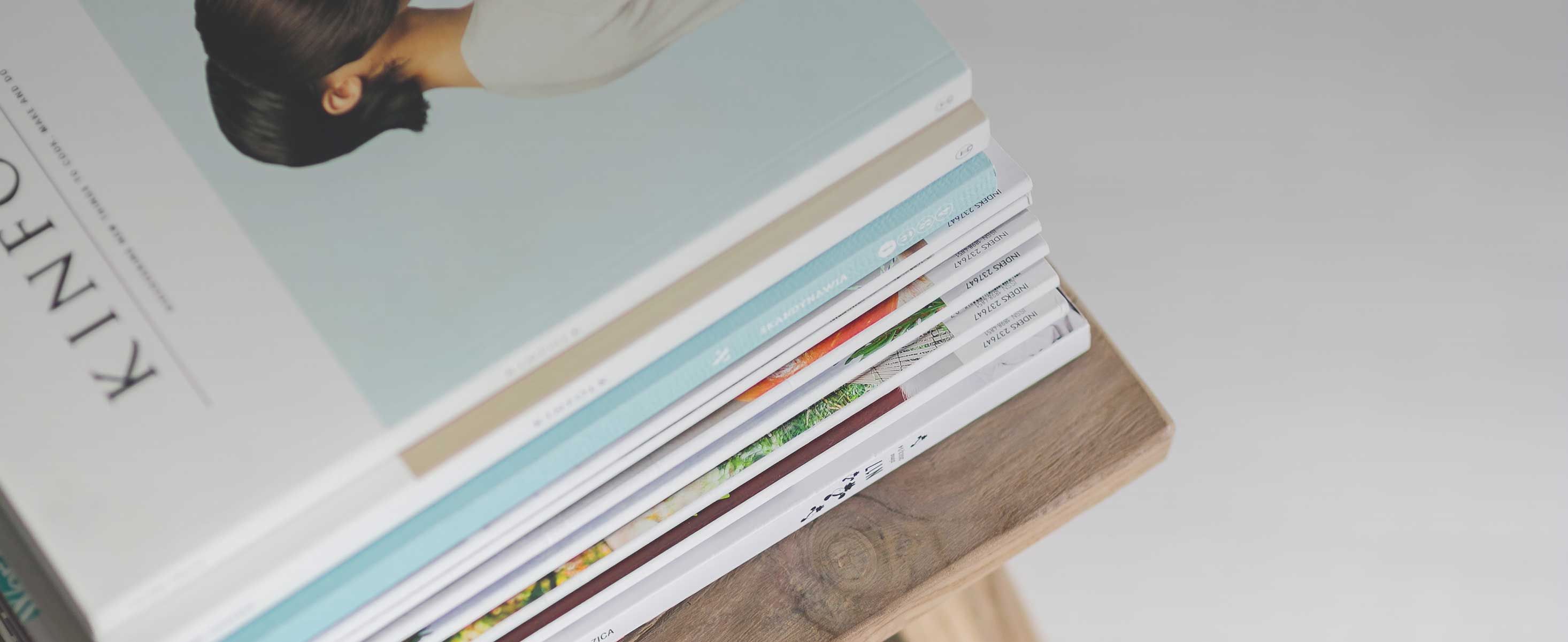
1 minute read
Smart Water Management – our holistic concept makes every drop count
Boiler water and cooling water systems are subject to heavy use day in day out as ships go about their business oiling the wheels of world trade. Just as we need clean water to live, ships need properly treated water to run smoothly. If left untreated, the integrity of equipment can be compromised over time through harmful scaling, mineral deposition, corrosion, and biofouling.
This becomes an operational pain point that can negatively impact operational efficiency. Poor heat transfer in the engine cooling system means the engine will not cool down properly, reducing vessel performance and eventually impacting CII ratings. Equipment problems can also be costly and time-consuming to fix should a failure or malfunction occur, translating into downtime and unscheduled delays.
Class society DNV records in a technical update that inferior water conditions due to poor equipment maintenance is still the number one cause of reported common boiler defects.
Operational Pain Point
Water can be a troublemaker
Water is one of the most essential elements used in critical equipment but can cause serious problems if treatment is inadequate. Water contamination is an ever-present risk. Distilled (demineralised) water should be the default as feedwater for boiler and engine cooling systems, combined with proper chemical treatment to limit unwanted scaling and corrosion.
Detrimental effects of poor maintenance on equipment
Water contamination either due to the use of low-quality feedwater and/or ingress of seawater or exhaust gas is the primary cause of hard scaling, deposition, and corrosion effects in boiler and engine cooling systems. Carryover in boiler systems refers to any contaminant (vapour, liquid, or solid) that is ‘carried over’ from the boiler in the service steam and can exacerbate scaling and corrosion.