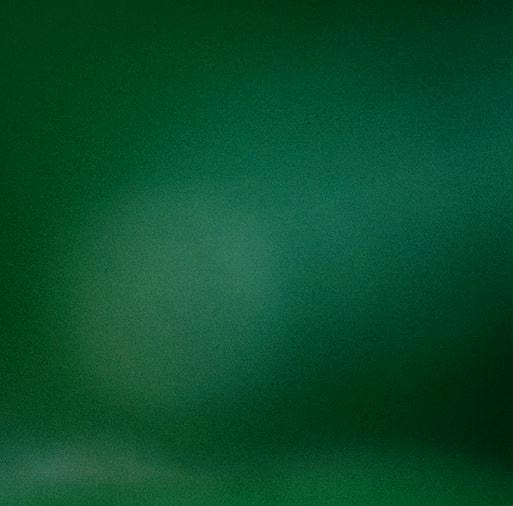
RELIABILITY BEYOND TOMORROW. SUSTAINABILITY REPORT 2021

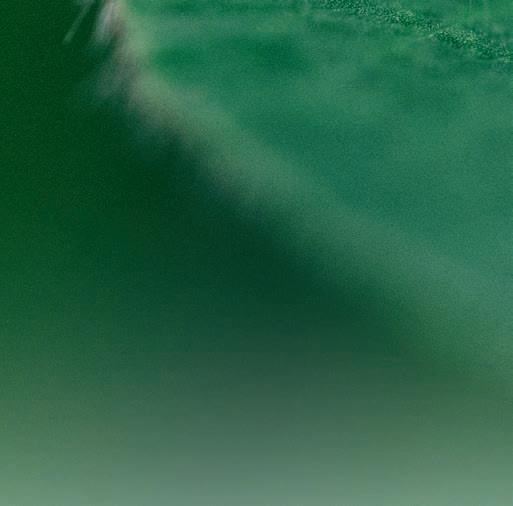
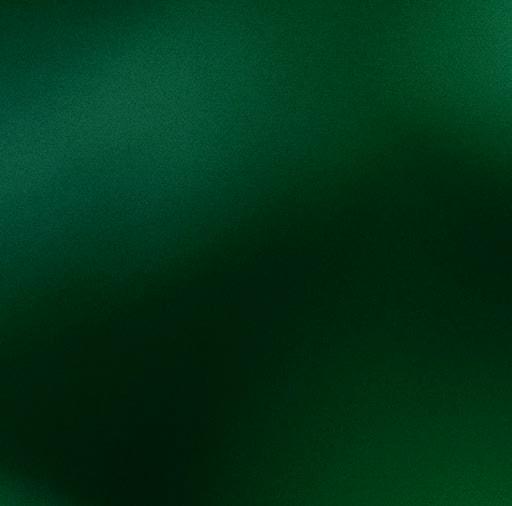
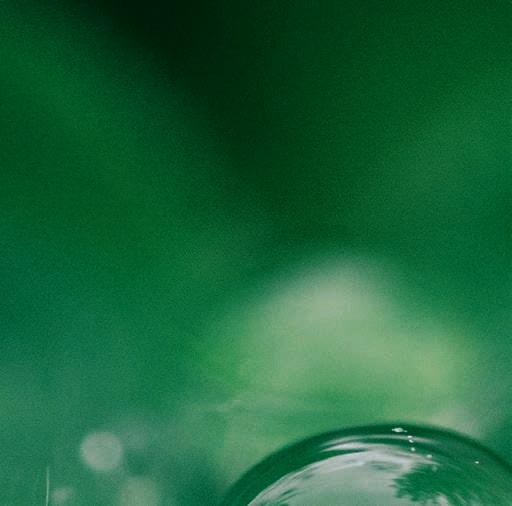
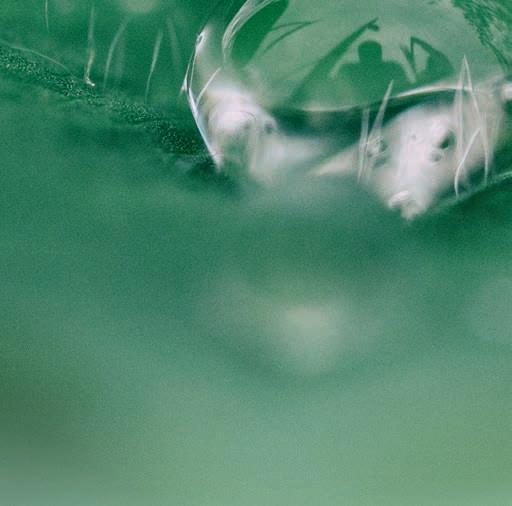
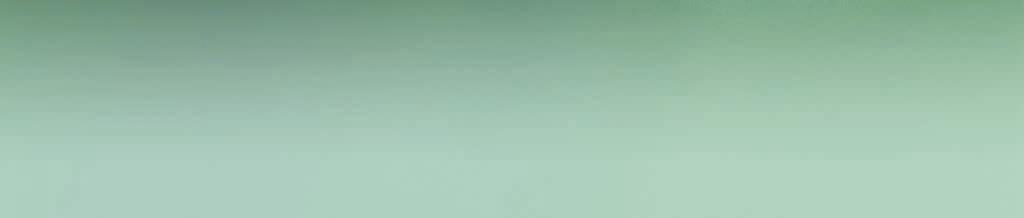

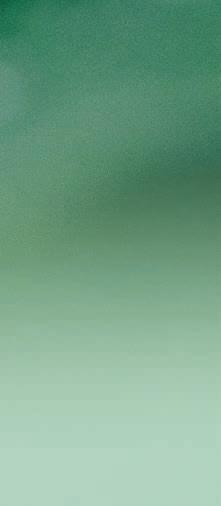
Reliability beyond tomorrow is not just the title of this report, it´s our company´s claim! Troyer, as supplier for the electromechanical equipment for hydroelectric power plants, deeply believes in substainability: hydroelectric power is environmentally friendly and it has an excellent environmental record, but our initiatives goes much further. Our plants reduce the ecological footprint and thus have an active role in preventing climate change.
We stand for reliability and trust. It is not only about reliability and trust in relation to our products and services, but about us as a company. We want to be the first point of contact for customers, employees, suppliers.
This report should not only be a document showing the steps towards sustainability of a company, it should also be a concrete proof of its philosophy! For this reason, we have decided to publish this document only in digital format! Dear reader, we kindly ask you not to print it out but to read it online.
Valentin Troyer founded the “Valentin Troyer – Elektromechanische Werkstätte” in 1934, which was renamed in 2010 to today’s Troyer SpA. The name has changed, the basic idea is the same: Quality and flexibility!
We always focus on the special needs and wishes of our customers and as a competent partner, we offer technical solutions in all areas (mechanical engineering, electrical engineering, automation) and are also on site with our service team after commissioning.
The evolution of the company over the years through its logo:
Hydroelectric power has been part of our name for over 85 years. Valentin Troyer founded the “Valentin Troyer - Electromechanical Workshop” in 1934, which was mainly concerned with the repair of electric motors and small turbine systems. In 1938 Valentin married Maria Weissteiner, who actively supported him in his workshop. They had three children: Herbert, Ernst and Maria Luise, and Marlene was taken in as a foster daughter. All the children worked in the business: Herbert joined the company in 1954 at the age of fifteen and soon became workshop foreman. Maria Luise took over the company office in 1966. Ernst studied electrical engineering at the Technical University in Graz and was responsible for technical and project planning from 1975.
Over the years, the workshop turned into an industrial company and it became more and more important to increase productivity as well as the company’s success through innovation. From this moment, the basic idea became “everything from one source”: the company covered every task from design, production, assembly and installation.
The increasing number and size of orders brought the production to its capacity limits, so that in 2001 the decision was made to build a production hall in the industrial zone “Unterackern” and to found the “Turbinenbau Troyer GmbH”. Already in 2010, the second plant was completed and Turbinenbau Troyer GmbH became “Troyer AG”.
In 2011, the company management was handed over to the 3rd generation of the family: Norbert Troyer (son of Herbert), Stefan Troyer (son of Ernst) and Simone Bressan (son of Maria Luise) are now the owners of the company. 2016 the third plant was blessed.
Today, Troyer employs over 140 people and delivers its complete electromechanical equipment for hydroelectric power plants all over the world.
The 13 themes we have selected symbolise the goals we have set ourselves: while some are by their nature closer to our core business or more easily aligned with the characteristics of our company, others represent a more ambitious goal for us to pursue in order to further improve our products and services, our commitment to employees and our actions to protect the environment.
Employees & society
• Occupational and health safety
• Clearly defined organisational structure
• Staff training and development
• Work-life balance
• Equal opportunities
• Diversity
• Corporate values
• Open and transparent communication
• Contribution to society
Economy
• Customer satisfaction
• High product quality
• Everything from one source
• Sustainable company
• Family business (continued existence of the company)
• Acting in accordance with laws and standards, ethically, environmentally friendly and resource-saving
• Selective choice of suppliers
• State-of-the-art technology
• Increase in company performance
• Environmental protection in the company and on construction sites
• Energy-efficient factory operation
• Supply of energy-efficient products and services
• Raising awareness of environmental protection
• Energy efficiency contact
• Minimising environmental impacts
Employees
Troyer not only has an influence on the country’s economy, but also promotes cultural and social projects as a sustainably operating company. In this way, we set impulses and inspire our employees, customers, partners and public interest groups to follow this example.
• collegial and supporitive working atmosphere
• Everyone has an influence on the achievment of goals
• united team
• professional and personal development
• competent partner
• exceeding expectations
• optimal solutions
• all from one source
• highest quality
• absolute reliability
• innovation
• progress and further development
• honest and responsible work
• transparency
• thinking and acting beyond tomorrow
With Legislative Decree No. 231/2001, the administrative responsibility in Italy has been extended to legal individuals. This means that in addition to the civil and penal liability of the physical person who committed the offence, the company itself is also held responsible with its capital.
The Code of Conduct and Ethics provides a framework of orientation, and represents a union of values and guidelines. It describes the principles that apply to our conduct and is the basis of an open, appreciative and legally compliant corporate culture to which we are committed and which we fill with life every day anew. Our claim to offer our customers the best possible quality and fair, trustworthy dealings with our partners are the benchmarks of our actions. We want to be perceived as a trustworthy partner - by our customers, business partners and employees as well as by authorities, institutions and the society. Every single employee of the company contributes to this through personality, performance and behaviour.
We supply the full electromechanical equipment for hydroelectric power plants. Our area of expertise comprises the construction of Pelton, Kaplan and Francis turbines as well as electrical engineering, control and automation, revitalization and service.
We offer full, individual support for each power plant, from comprehensive advice and planning, project engineering and complete construction through to regular maintenance services. Our portfolio ranges from the engineering, mechanical and electrical production, to development of automation software to the final service and maintenance.
The subsidiary Troyer Suisse AG has been taking care of all projects in Switzerland since 2013. For several years, the company has already been focusing on customer care and service.
The subsidiary in India was opened in 2021. Troyer Hydro Pvt. Ltd. is based in New Delhi and is the direct contact for all projects in Asia.
In addition to our two subsidiaries in Switzerland and India, we have established a network of partners and representatives in several countries around the world to provide direct support. Our local partners have a long time experience of the national markets and are available to provide direct assistance. Through the collaboration with our partners, we offer local support to the customer: we will be present to provide advice and assistance from the first contact until the project completion and beyond.
25.875.498
1.3.7
We are already shaping the future of our planet today. The way a society lives today determines how future generations will live tomorrow. A major focus in Troyer’s mission statement is to raise awareness of energy and resource efficiency. As a reliable partner in the hydropower sector, we contribute with our competence and experience in energy topics, trying to reduce both direct and indirect environmental impacts. Our actions are guided by the requirements and expectations of internal and external stakeholders as well as our social and ecological environment. Based on this responsibility, we develop, produce and sell products and services that have as little impact as possible on the environment during production, use and disposal. It is our top priority to reduce the consumption of resources and the environmental impact of the activities and products we carry out, or to compensate where elimination is not possible.
An open and transparent communication is a prerequisite for mutual trust and acceptance. Only by involving all stakeholders a sustainable dialogue is possible.
By stakeholders, Troyer includes all parties who have an interest in the future development of the company. Based on ISO 9001, 14001 and 45001, internal and external issues as well as requirements and expectations are analysed in a continuous process.
“Water is fluid, soft, and yielding. But water will wear away rock, which is rigid and cannot yield. As a rule, whatever is fluid, soft, and yielding will overcome whatever is rigid and hard. This is another paradox: what is soft is strong.” Lao Tzu
Covid 19 pandemic turned in 2020 our known and accustomed way of life upside down. It forced us to rethink our usual habits and adapt to new circumstances and regulations as quickly as possible.
During this time, we took responsibility in order to minimize the impact of the Corona virus on our staff and stakeholders, as well as on the environment in which we operate. Through rapid and transparent communication, we have managed to respond efficiently, quickly and to act in a clear and structured manner at all levels. The crisis also offers opportunities and points to possibilities for improvement, which are being tackled by everyone with courage and curiosity.
2 COMPANIES ARE MADE BY PEOPLE FOR PEOPLE
The constant grow of the company over the years led to many changes: different procedures, organized working methods that allows a good management.
We are proud to say, that one thing did not change since 1934: the human relationship! Valentin Troyer used to have this direct personal relationship that enhances a person; this part of the founder´s character is today a corporate value.
Every employee of the company is obliged to carry out his or her work responsibly, to the best of his or her knowledge and belief, in compliance with environmental, health and safety regulations. All irregularities and incorrect occurrences in their area of responsibility must be reported to their superiors.
Employees are involved in all levels of health and safety. For us, this means providing time, training and resources to those involved.
Employees by department (July 2021)
On average, our employees stayed with the company for 12,01 years.
Two of our men have worked for the company for 39 years.
One employee reached the record of 43 years of service in the company.
All Troyer employees attend a large number of training courses every year. The health and safety training courses, which are mandatory in Italy, represent a significant part of the training. These vary according to competence and field of application:
In 2017, Troyer launched the “ Work and Family” project to make the workplace more pleasant and attractive. The focus is not only on the classic mother/father role, but also on all employees. This is because the compatibility of private and professional life is not an either/or decision, but a both/and solution. Our employees work in various associations or take care of a family member requiring care at home. Family-friendly working conditions promote motivation, increase performance and productivity and reduce carelessness and even accidents.
Sector Risk Training in work safety
High
• Basic course in work safety
• (Supervisor (Preposto)
• First aid course
• Fire protection
• Driving industrial cranes
• Driving industrial forklifts
• PPE III. cat
Combination of office and construction site work
• Basic course on work safety
• Supervisor (Preposto)
A selection of the most important benefits
Various part-time models
Smart working 2nd shift work in summer: Friday only until 5 p.m.
LunchTime also for part-time
Health fund
Mutual Help (contribution paid in full by company)
Fresh fruits and vegetables (twice a week)
Staff events and celebrations
Social fund (interest-free loan) Troyer Club
Mainly office work
• Basic course on work safety
All employees of Troyer have access to various training opportunities and everyone has the possibility to attend internal courses, external subject-specific seminars, lectures and trade fairs. The focus is on social and professional skills. The know-how of the employees should be maintained, shared and further developed in the future by strengthening the internal training courses. In particular, the exchange between generations and departments will be promoted and internal turnover will be strengthened. Our employees are also involved in the succession planning for their positions.
Family-friendly offers, flexible work schedules and various social offers have a positive impact on the satisfaction of our employees. In 2018, we conducted an employee satisfaction survey. Around 100 closed statements were evaluated using a scale from 1 (almost never true) to 5 (almost always true). 82.9% of the employees participated in the survey.
The feedback supports the top management to improve work processes, organisations and the environment.
Our company contributes to improving the quality of life in the Wipptal Valley within the scope of its possibilities:
Answer options 2018
The key statement is rated as follows:
5 almost completely true
4 mostly true
3 partly/partially
2 mostly do not apply
1 almost does not apply at all
0 no answer
total answers
total answers 4 and 5
Percentage of answers
In addition, annual meetings between managers and employees are obligatory. Every employee is also free to approach his or her supervisor or the executive board at any time.
Financial support and, where possible, support through cooperation, assistance, ecc… to clubs and associations both in the world of sport and in the world of culture is our company’s commitment to support leisure activities outside of work.
We cooperate with local and professional school in our province. Visit of our factory, stages for students during summer, trainees and much more are part of our activities in order to have the best job offer for young students entering the world of work.
There are many non-profit associations and lots of social projects offering help to people in need on a local and international level. The company is committed to supporting various associations that work to help, especially at local level. This principle of helping is reflected in the actions of employees, who also organise private fundraising events to make a further contribution.
A high priority in our mission statement is to increase awareness of energy and resource efficiency. As a competent partner, we contribute our expertise in energy issues and thereby seek to reduce both direct and indirect environmental impacts. Our actions are “oriented towards the requirements of internal and external interest groups (...) as well as our social and ecological environment. Based on this responsibility, we develop, produce and sell products and services that (...) have as little impact as possible on the environment during production, use and disposal”.
Troyer’s top priority is to reduce the consumption of resources and the environmental impact of the activities carried out to zero or to compensate where elimination is not possible.
Due to the extensive evaluation within the framework of the preparation of the environmental report, environmental impacts are evaluated in a separate form. The CO2 calculation is an inventory taken as of the cut-off date of 31.12 each year. The following sources are taken into account, which are necessary for the production of the hydropower plants:
Direct environmental aspects
are caused by activities whose process can be directly influenced at the site.
At Troyer, these include
Indirect environmental impacts
arise from interaction with third parties (customers, suppliers, service providers) and for this reason cannot be fully influenced. These include:
The quantity is converted with CO2 equivalents and thus the CO2 emission in tonnes is determined, for 2020 this is 770.56 t CO2
Hydropower is one of the most environmentally friendly forms of energy generation: kinetic energy (flow) and potential energy (the difference in altitude) are converted into usable energy through the use of turbines and generators.
According to a publication by the Fraunhofer Institute, a run-of-river power plant saves 0.723 kg per kilowatt hour per year. Thus, for an installed capacity of 66.5 MW and an assumed operating time of 4,000 hours, there is a saving of 93,700.8 t CO2
The positive balance of CO2 production per year
Hydropower plants with an installed power of
770,56 t
93.700.800 kg CO2
Troyer therefore saves over
92.930 t of CO2 per year. CO2 generated during production in 2020
The evaluation of environmental impacts is a systematic, process-oriented questioning of the direct and indirect environmental aspects triggered by our activities.
The risk is divided into three classes, with 1 corresponding to the highest and 3 to the lowest level. The risk is determined by the probability of occurrence and the extent of damage.
Early detection and prevention of environmental impacts by our operations makes it easier to plan and implement concrete measures to improve the company’s environmental performance.
The life cycle assessment evaluates the environmental impacts of the individual process and life phases of a hydropower plant, for example the selection and use of materials/raw materials, production, transport, (dis)assembly/commissioning and disposal.
Energy (electricity, heat)
Energy sources
(gas, fuels, oils)
Raw materials
Water
• Products and services
• Emissions (noise, air)
• Waste water
• Valuable materials (hazardous and non-hazardous)
• Purchasing
• Planning and dimensioning
• Production
• Storage and transport
• (Dis)assembly and commissioning
• Use and service
• Recycling and valuable substances/recyclables
It is not only about reliability and trust in relation to our products and services, but also about us as a company. We want to be the first point of contact for customers, employees, suppliers and society when a reliable and trustworthy partner is required.
A major focus of Troyer’s mission statement is to increase awareness of energy and resource efficiency. As a competent partner, we contribute with our expertise in energy issues and thereby try to reduce both direct and indirect environmental impacts. Our actions are “oriented towards the requirements of internal and external interest groups (...) as well as our social and ecological environment. Based on this responsibility, we develop, produce and sell products and services that (...) have as little impact as possible on the environment during production, use and disposal”.
Troyer’s top priority is to reduce the consumption of resources and the environmental impact of the activities carried out to zero or to compensate where elimination is not possible.
We do not use rare raw materials and try to buy the necessary quantities locally and from certified suppliers.
Plastic is only used in production in very small quantities as an auxiliary material (cable sheathing or switch cabinets). 95% of the components are painted in the in-house varnishing cabin, so that floor and air contamination is avoided.
The varnishing cabin, sandblasting cabin and welding department have a suitable filter and exhaust air system to reduce air emissions to zero.
Furthermore, we use the environmentally friendly hydraulic oil Panolin and environmentally friendly cooling liquids in the machining center (does not flow into the end product).
Thanks to the design departments in mechanical and electrical engineering, long delivery times can be taken into account only for non-standardized products and production can be influenced in the long term.
Energy consumption and personnel deployment in the machining processes are optimally planned with software support. Materials and finished products are transported directly to production in Vipiteno, to the processor or to the construction site (e.g. generator, transformer).
Hazardous substances such as varnishes, stains, oils, silicones and diesel are used to 95% in production operations, so that soil or water contamination on the construction site is avoided.
Recyclable materials are reused as far as possible, for example packaging from deliveries from suppliers (cardboards or plastic packaging).
All construction site waste is already sorted on site, brought to Vipiteno at the end of assembly and disposed of properly.
When purchasing equipment, raw materials, manufacturing and support materials or services, we pay attention to ecological aspects. A more ecological alternative will be preferred, especially if the quality is the same and the price is the same.
Where possible, the purchasing department takes into consideration the eco-labels, because these guarantee us
• products and services with a high environmentally friendly quality
• reduction of environmental impact
• environmentally friendly production and a recycling of valuable materials (recycled paper, deposit bottles, etc.).
We also try to raise the environmental awareness of our employees through various activities/purchases:
• the fruit and vegetables box for healthier eating
• the water dispenser to reduce plastic waste
• coffee cup instead of plastic cup
• environmentally friendly cleaning products
• paper used is FSC or PEFC certified: we only use paper produced from wood from sustainably managed forests.
We return the recyclable materials properly to the cycle. Troyer guarantees disposal by specialist companies, return to cycle (iron, cables, ...) and recycling, as well as possible reuse after repair (welding on impellers).
• In manufacturing most of the waste produced is metallic. The different types of metal are collected separately and fed into the secondary recycling cycle.
• Packaging material from suppliers is used for our own packaging purposes as far as possible. Packaging that cannot be reused is recycled.
• All recyclable materials are collected separately in designated containers at defined locations and disposed of or recycled by authorised waste management companies (Südtirolfer, Ekos) or at the local recycling centre.
• Disposal or recycling of the plant: partly out of our control if the customer himself disposes of the plant or parts of it.
Quantitative development of hazardous and non-hazardous waste and recyclables (as of 31/12/20)
kg
kg
kg
kg
kg
kg
At Troyer, renewable energy and environmental awareness is everything. We have been certified according to the ISO 14001 environmental management standard for 20 years. Through the cooperation of each individual, we can achieve a sustainable ecological way of working. Every employee is aware of his or her actions and their effects on the environment and is responsible for them in his or her area of work.
Switch off the light when leaving the office and the PC and monitor in the evening.
Print only what is necessary and, if possible, in black and white and double-sided. Use incorrectly printed paper as a scratch sheet.
Form car pools
Cycling to work
Use public transport as much as possible: this is particularly suitable for training courses, as they are usually held in a central location with good transport connections.
Some tasks cannot be carried out by individual employees, but require the cooperation of the management, executives or even entire departments:
According to our motto “quality before quantity” we use environmentally friendly products wherever possible
In the case of electronic equipment, we pay attention to a long service life and a low consumption of resources in production and use.
Use LEDs for lighting fixtures
Increased digitalisation in order to reduce paper
Replace “notice boards” with screens
Use district heating in all three plants
If everyone gives a small contribution, the sum adds up to something big. Or as an African proverb says:
Troyer has a modern fleet of around 50 vehicles that meet the latest environmental standards. Average fuel consumption has been continuously reduced since 2018:
Ø Fuel consumption per car per 100km
Troyer not only stands for hydropower: as an environmentally conscious company, it supports the sensible use of electrical energy.
Troyer has a photovoltaic system on the roof of plant 3, and the electricity produced by system can be used for free by employees to charge their electric cars. For this purpose, three charging stations were already set up at specially marked parking spaces in 2015. In 2020, an electric car was also purchased as a pool car, which is used as a shuttle car for employees from Bolzano.
Our products already make a big contribution to reducing environmental impact: hydropower is probably the most environmentally friendly way to generate electricity. We also actively strive to reduce our environmental impact within the company itself: by using environmentally friendly products or avoiding waste. For this purpose, various measures have been implemented to make everyday life at the company more “ecological”. In 2017, water automats were installed and the coffee machines were adapted for the use of a cup.
“If many small people in many small places take many small steps, they will change the face of the world.”
Eduardo Galeano
• In-house Sustainability Day
• Education on waste separation on construction sites
• Publication of 10 sustainability tips
• Work group to improve environmental measures within the company
Increase knowledge and competence on sustainability
Greenhouse gas emissions/air emission
• Increasing the use of electric cars
• Controlling business trips and optimising vehicle deployment
Reduction of fuel consumption
• Working group on the reduction/ replacement of hazardous substances
Reduction and avoidance
Purchasing
Gender Pay Gap ISO
Increase the percentage of ISO 14001 certified suppliers
• Weekly training Employees Health
Equal opportunities and equal treatment
• Calculation of the GPG 2021 and setting of reduction measures