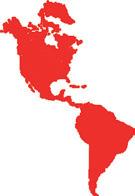
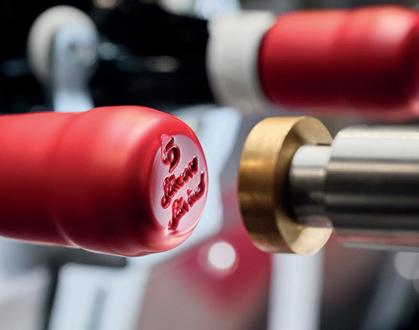
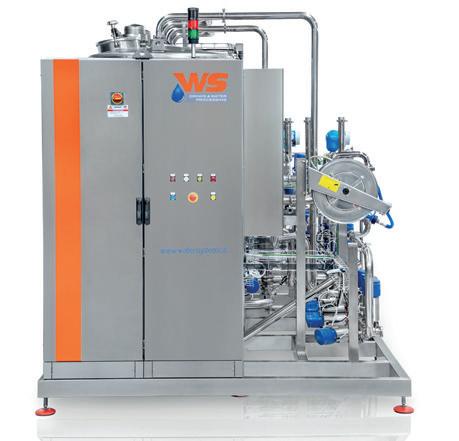
ITALIAN TECHNOLOGY FOR THE BEVERAGE INDUSTRY TECNOLOGÍA ITALIANA PARA LA INDUSTRIA DE BEBIDAS
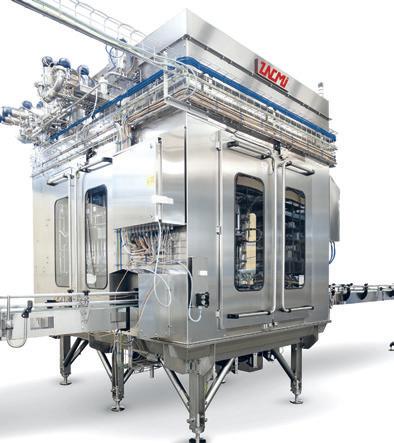
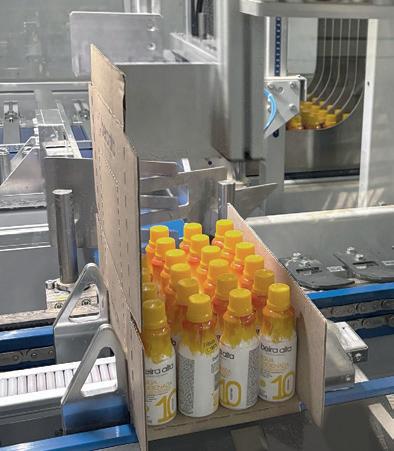
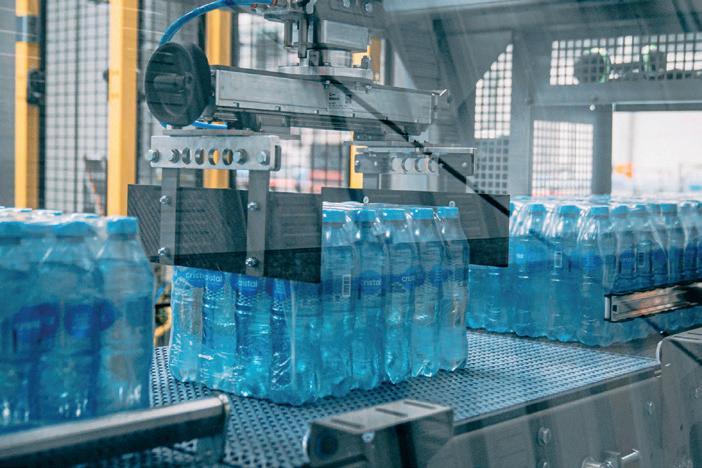
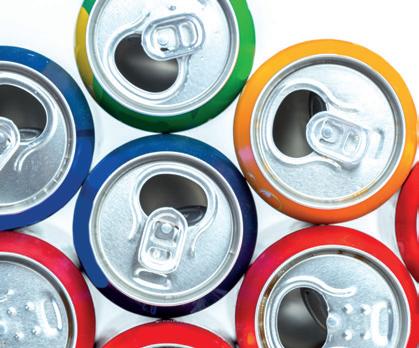
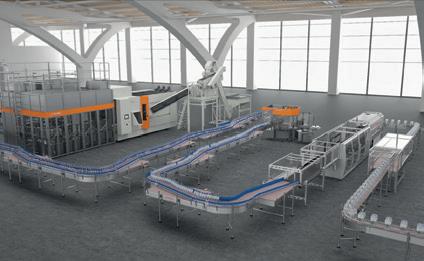
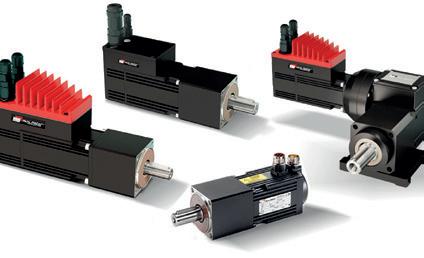
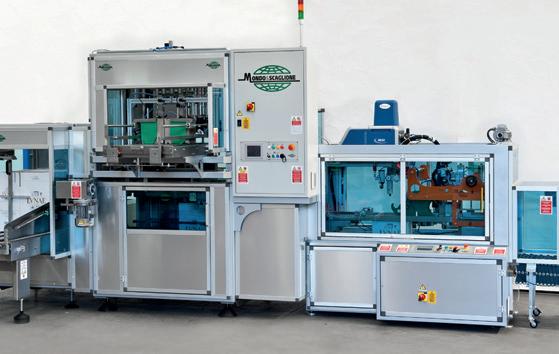
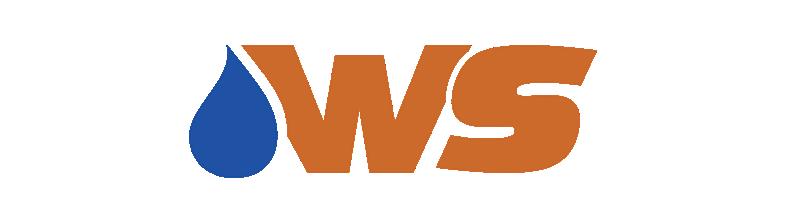
ITALIAN TECHNOLOGY FOR THE BEVERAGE INDUSTRY TECNOLOGÍA ITALIANA PARA LA INDUSTRIA DE BEBIDAS
PURIFICACIÓN DE AGUAS
DISOLUCIÓN DE AZÚCARES
PREPARACIÓN DE CONCENTRADOS
SALAS DE JARABES
PASTEURIZACIÓN
DOSIFICACIÓN Y MEZCLA
CARBONATACIÓN DE PRODUCTOS
MINERALIZACIÓN DEL AGUA
OZONIZACIÓN DE AGUA MINERAL LIMPIEZA Y ACLARADO
TUBERÍAS Y ESTANTES
SOLUCIONES LLAVE EN MANO
Como especialista experto en equipos de proceso para la producción de bebidas , WS puede suministrar una amplia y completa gama de tecnologías de proceso avanzadas que se pueden combinar fácilmente para crear una solución completa llave en mano : desde la fuente de agua hasta el producto listo para embotellar
A. WATER SYSTEMS srl C.so Piave 4 12051 Alba CN - ITALY
Operational Headquarters: Località Piana 55/D 12060 Verduno CN - ITALY
Tel. +39 0172 470235 Fax +39 0173 615633 info@watersystems.it
watersystems.it
TecnAlimentaria Supplement n. 6 June 2025 - Year XXX
Publisher: Fabiana Da Cortà Fumei
Editorial Staff & Design redazione@tecnalimentaria.it
Sabrina Fattoretto
Claudia Bosco
Elena Abbondanza
Marketing and Advertising
Anita Pozzi
anita.pozzi@edftrend.com
Franco Giordano franco.giordano@edftrend.com
Management and Editorial Office
Editrice EDF Trend srl
Corso del Popolo, 42 31100 Treviso – Italy Tel. +39 0422 549305 www.tecnalimentaria.it www.tecnamagazines.com
Printing: L’Artegrafica Srl
Member of:
Autorizzazione Tribunale di Forlì n. 5 del 19.01.1996
N° iscrizione ROC: 22054 (Registro degli Operatori di Comunicazione)
In questo numero la pubblicità non supera il 45%
Sped. in abbonamento postale 45%Art. 2 Comma 20/B Legge 662/1996 DCI-TV
All right reserved.
Reproduction in whole or in part without written permission is prohibited. The Publisher is not responsible for any materials, nor for writers’ nor contributors’ expressed or implied opinions.
Informativa ex D.lgs 196/03
Ai sensi dell’art.2 comma 2° del Codice Deontologico dei giornalisti si rende nota l’esistenza di una banca dati di uso redazionale presso la sede di Corso del Popolo, 42 - Treviso. Responsabile del trattamento dati è il direttore responsabile a cui ci si può rivolgere presso la sede di TrevisoCorso del Popolo, 42 per i diritti previsti dalla legge 675/1996.
AERAQUE SRL
A. WATER SYSTEMS SRL
ALTECH SRL
BEA TECHNOLOGIES SPA
GALIGANI FILTRI SRL
KOSME SRL
www.aeraque.com 13 Food & Beverage Industry
www.watersystems.it II^Cover, 9-11 Beverage Industry
www.altech.it 14-15 Food & Beverage Industry
www.bea-italy.com/it 55 Beverage Industry
www.galiganifiltri.com 4, 16-17 Beverage Industry
www.kosme.it 5, 19-21 Beverage Industry
MAGIC MP SPA www.magicmp.it 2, 23-25 Beverage Industry
MGM MOTORI ELETTRICI SPA
MINI MOTOR SPA
www.mgmrestop.com 26-27 Beverage & Food Industry
www.minimotor.com 3, 28-29 Beverage & Food Industry
MONDO & SCAGLIONE SRL www.mondo-scaglione.com 31-33 Beverage Industry
NEWTEC LABELLING SRL
SINCERA SISTEMI SRL
www.newteclabelling.it 34-35 Beverage Industry
www.sincerasistemi.it 37-39 Beverage Industry
SMI SPA www.smigroup.it 1, 41-45 Beverage Industry
SMIPACK SPA
www.smipack.it 47-49 Beverage Industry
TECHNO MIDA SRL www.technomida.com 54 Beverage Industry
ZANICHELLI MECCANICA SPA www.zacmi.com 51-53 Beverage & Food Industry
PURIFICACIÓN DE AGUAS
DISOLUCIÓN DE AZÚCARES
PREPARACIÓN DE CONCENTRADOS
SALAS DE JARABES
PASTEURIZACIÓN
DOSIFICACIÓN Y MEZCLA
CARBONATACIÓN DE PRODUCTOS
MINERALIZACIÓN DEL AGUA OZONIZACIÓN DE AGUA MINERAL LIMPIEZA Y ACLARADO TUBERÍAS Y ESTANTES
SOLUCIONES LLAVE EN MANO
Como especialista experto en equipos de proceso para la producción de bebidas , WS puede suministrar una amplia y completa gama de tecnologías de proceso avanzadas que se pueden combinar fácilmente para crear una solución completa llave en mano : desde la fuente de agua hasta el producto listo para embotellar
Operational Headquarters: Località Piana 55/D 12060 Verduno CN - ITALY
Tel. +39 0172 470235 Fax +39 0173 615633 info@watersystems.it
watersystems.it
Località Piana, 55/D - 12060 Verduno (Cuneo) Italy
Tel. +39 0172 47 02 35 - Fax +39 0173 61 56 33
info@watersystems.it - www.watersystems.it
Despite the name, WATER SYSTEMS is not only involved in water purification systems but is specialised in the production of complete solutions and plant designs for medium-large CSDs and juices projects as well.
All the steps involved in the production of mineral water, soft drinks and juices – from water purification, right through to syrup preparation, blending, carbonating, mixing and pasteurising and eventually including utilities supply as well for a real turnkey solution – are available from a single supplier at WATER SYSTEMS: this is clearly an important advantage allowing the bottler to save time during processing equipment design, project execution and equipment maintenance.
and hygienic aspects: CIP fluid paths are covering any part of the plant – including process water distribution lines – and the entire piping is tooled to avoid dead legs and minimize the number of weldings. In-house preassembled modules configuration allows plug and play quick installation granting customers an immediately available system. State-of-the-art technology for liquid mixing ensures that the sugar syrup, the flavours and all the required ingredients are optimally mixed and distributed to grant a perfectly homogeneous concentrated product and the best deaeration process; this benefits customers in three different ways:
• Shorter mixing and deaerating time corresponding to quicker production cycles;
WATER SYSTEMS recently installed and commissioned a new turnkey solution on a greenfield project in Nigeria with one of its historical partners in the beverage business: aimed to maximize sustainability thus minimizing energy consumption and water wastage, the entire scope of supply has been oriented to fulfil these goals; by the way the syrup room – probably the most automated unit present in an African beverages factory up to now, featuring more than 120 mixproof valves and conceived to maximise the efficiency of equipment regardless of the number or level of specialisation of operators – is the most representative part of this plant.
The market of beverages is very wide due to the growing diversification in terms of quality and variety of drinks (both alcoholic and non) required by consumers. Therefore, the producers, to answer quickly, need to process a wide range of ingredients (powder as well as liquid). In some cases, such ingredients might require a special treatment according to their features (texture, reaction, viscosity, solubility, temperature-sensitivity, flammability and so on).
The innovative design of the WATER SYSTEMS’ syrup room ensures automatic ingredients and CIP fluids loading as well as the automatic outlet through clusters of mixproof, single seat and butterfly valves dedicated to syrup tanks and ingredients preparators and sources. Syrup rooms provided by WATER SYSTEMS’ are designed on standard modules which are customised for each specific project according to specific needs. Furthermore, the equipment always features a non-compromising technology for what concerns cleanability
• Optimal low-shear mixing of low and high-viscosity fluids to prevent oxygen pickup and fruit’s cells damaging in case of pulpy ingredients;
• Lower energy costs through unique energy-saving impellers’ design.
WATER SYSTEMS’ syrup rooms can be flexibly extended thanks to modularly arranged skids: the design always take into consideration future customer’s expansion plans and the maximum allowed number of bottling lines that can be fed is four; the syrup output flow rate can be individually adjusted to suit each bottling line need.
All instruments and regulation systems dedicated to the control of individual syrup and product components are characterised by the highest precision in the processing in order to grant accurate ingredients blending and to minimize product wasting during circuits emptying.
Using the new pulse and burst technology for valves cleaning, trials have revealed that up to 90% of CIP liquid can be saved – significantly lowering the operating costs compared to the traditional (PLC) timer-controlled seat lift; further information are available at: https://food.alfalaval.com/thinktop-rethought-burst-seat-clean
WATER SYSTEMS’ syrup rooms are conceived to ensure and safeguard the perfect ingredients blending and always aim to meet the needs of all the customers who are looking for high-quality product.
For more information and to discover the range of products visit the site: www.watersystems.it
Località Piana, 55/D - 12060 Verduno (Cuneo) Italy
Tel. +39 0172 47 02 35 - Fax +39 0173 61 56 33
info@watersystems.it - www.watersystems.it
pesar del nombre, WATER SYSTEMS no solo ofrece sistemas de purificación de agua, sino que también está especializada en la producción de soluciones completas y diseños de plantas para grandes y medianos proyectos de CSD y jugos.
Todos los pasos involucrados en la producción de agua mineral, refrescos y jugos - desde la purificación del agua hasta la preparación de jarabe, mezcla, carbonatación, mezcla y pasteurización y, finalmente, incluyendo el suministro de servicios públicos, así como para una solución llave en mano real - están disponibles en un solo proveedor en WATER SYSTEMS: esto es claramente una ventaja importante que permite al embotellador ahorrar tiempo durante el diseño del equipo de procesamiento, ejecución de proyectos y mantenimiento de equipos.
WATER SYSTEMS recientemente instaló y puso en marcha una nueva solución llave en mano en un proyecto greenfield en Nigeria con uno de sus socios históricos en el negocio de bebidas: con el objetivo de maximizar la sostenibilidad minimizando así el consumo de energía y el desperdicio de agua, todo el alcance del suministro se ha orientado a cumplir con estos objetivos; por la forma de la sala de jarabe - probablemente la unidad más automatizada utilizada en una fábrica de bebidas africana hasta ahora, con más de 120 válvulas mixproof y concebido para maximizar la eficiencia de los equipos independientemente del número o nivel de especialización de los operadores - es la parte más representativa de esta planta.
El mercado de bebidas es muy amplio debido a la creciente diversificación en términos de calidad y variedad de bebidas (tanto alcohólicas como no) requeridas por los consumidores. Por lo tanto, los productores, para responder rápidamente, necesitan procesar una amplia gama de ingredientes (en polvo y líquido). En algunos casos, estos ingredientes pueden requerir un tratamiento especial según sus características (textura, reacción, viscosidad, solubilidad, sensibilidad a la temperatura, inflamabilidad, etc.).
El innovador diseño de la sala de jarabe de WATER SYSTEMS garantiza la carga automática de ingredientes y fluidos CIP, así como la salida automática a través de grupos de válvulas mixproof, de asiento único y de mariposa dedicadas a tanques de jarabe y preparadores de ingredientes y fuentes.
Las salas de jarabe proporcionadas por WATER SYSTEMS están diseñadas en módulos estándar que se personalizan para cada proyecto específico según las necesidades específicas. Además, el equipo siempre cuenta con una tecnología de máxima compatibilidad con limpieza y aspectos higiénicos: Las trayectorias de fluido CIP cubren cualquier parte de la planta - incluidas las líneas de distribución de agua de proceso - y toda la tubería está equipada para evitar puntos muertos y minimizar el número de soldaduras. La configuración de módulos preensamblados internamente permite una instalación rápida, que brinda a los clientes un sistema disponible inmediatamente.
La tecnología de última generación para la mezcla de líquidos garantiza que el jarabe de azúcar, los sabores y todos los ingredientes necesarios se mezclen y distribuyan de manera óptima para garantizar un producto concentrado perfectamente homogéneo y el mejor proceso de desaireación; esto beneficia a los clientes de tres maneras diferentes:
• Un tiempo de mezcla y desaireado más corto que da como resultado ciclos de producción más rápidos;
• Mezcla óptima de fluidos de baja y alta viscosidad para evitar recolección de oxígeno y daño en las células de la fruta en el caso de ingredientes pulposos;
• Reducción de costos de energía a través del diseño especifico de los impulsores.
Las salas de jarabe de WATER SYSTEMS se pueden ampliar de forma flexible gracias a skid dispuestos modularmente: el diseño siempre tiene en cuenta los planes de expansión
del futuro cliente y el número máximo permitido de líneas de embotellado que se pueden alimentar es de cuatro; el caudal de salida de jarabe se puede ajustar individualmente para adaptarse a las necesidades de cada línea de embotellado.
Todos los instrumentos y sistemas de regulación, dedicados al control del jarabe individual y de los componentes del producto, se caracterizan por la máxima precisión en el procesamiento para garantizar una mezcla de ingredientes precisa y minimizar el desperdicio de productos durante el vaciado de los circuitos.
Utilizando la nueva tecnología de pulsos y ráfagas para la limpieza de válvulas, los ensayos han revelado que se puede ahorrar hasta el 90% del líquido CIP - reduciendo significativamente los costos operativos en comparación con el sistema elevador de asientos controlado por temporizador tradicional (PLC); se puede obtener más información en: https://food.alfalaval.com/thinktop-rethought-burst-seat-clean
Las salas de jarabe de WATER SYSTEMS están diseñadas para garantizar y salvaguardar la mezcla perfecta de ingredientes y siempre tienen como objetivo satisfacer las necesidades de todos los clientes que buscan productos de alta calidad.
Para más información y para descubrir la gama de productos visite el sitio www. watersystems.it
Viale De Gasperi, 70 - 20008 Bareggio (Milano) Italy
Tel. +39 02 90 36 34 64 - Fax +39 02 90 36 34 81
info@altech.it - www.altech.it
ALTECH is one of the major European producers of self-adhesive label applicators for product decoration, coding and identification. Today, the company distributes its systems all over the Italian territory through a network of direct sales, while the commercial distribution for Europe and overseas takes place in more than 50 countries through a network of 80 qualified resellers and 3 subsidiary companies in the United Kingdom, the United States and South America. Its range encompasses the following products: ALstep – low-cost applicator featuring modular and flexible configuration.
ALritma – high-performance label applicator, which can be easily integrated in packaging lines. It is also available with thermal transfer printing group in the ALritmaT version, for print/apply applications.
ALcode – real-time print-apply systems which apply labels immediately after printing, in any position, on both stationary and moving products (even at high speeds).
A specific pallet labeling version, ALcode P, is able to print and apply A5 format labels on two consecutive sides of a pallet (normally front and side, per EAN 128, or even three sides on request).
ALTECH es uno de los principales fabricantes europeos de sistemas de etiquetado autoadhesivo para la decoración, la codificación y la identificación de productos y materiales en general.
En la actualidad, la empresa distribuye sus sistemas en toda Italia a través de una red de ventas y servicio posventa directo, mientras que la distribución comercial para Europa y fuera del continente se lleva a cabo en más de 50 países a través de una red de 80 distribuidores cualificados y 3 subsidiarias, a saber en Gran Bretaña, Estados Unidos y Sudamérica.
La gama de etiquetadoras ALTECH incluye: ALstep – aplicador económico con configuración modular y flexible.
ALritma – aplicador de alto y altísimo rendimiento que se puede integrar fácilmente en las líneas de envasado. También está disponible equipado con una unidad de impresión por transferencia térmica en la versión ALritma T para aplicaciones de impresión/aplicación (empresa).
ALcode – sistema de impresión y aplicación de etiquetas en tiempo real, que aplica la etiqueta recién impresa en cualquier posición en productos inmóviles o en movimiento (incluso a altas velocidades).
Una versión específica, ALcode P, para el etiquetado de palets, es capaz de imprimir y aplicar etiquetas de formato
A5 en dos lados consecutivos de palets (normalmente en posición frontal y lateral, según el estándar EAN 128, pero a pedido también en tres lados).
ALbelt – simplified linear system that is open, compact, and particularly economical. It can be configured for wraparound, c-wrap, top, bottom, top and bottom, top and side labeling of various products, cylindrical or flat. It’s ideal for labeling cases, boxes, trays, jars and cans. Its simple and solid main structure houses a conveyor and one or more labeling heads (choice of ALstep, ALritma or ALcode model).
ALline – complex linear system able to apply selfadhesive labels to a wide range of product shapes, constructed with the most reliable materials and
components on the market to offer the highest levels of performance and production.
The modular design incorporates ALstep and/or ALritma heads, and can be configured on the basis of customer requirements, allowing application of labels of any shape and size for front/back or wrap-around labeling and seal application to food, cosmetics, chemical and pharmaceutical products.
For further information: sales@altech-us.com – www.altech-us.com info@altech.it – www.altech.it
ALbelt – sistema lineal simplificado, abierto, compacto y particularmente económico. Se puede configurar para etiquetado envolvente, c-wrap, superior, inferior, superior/ inferior, superior/lateral de varios productos, tanto cilíndricos como planos. Es ideal para etiquetar cajas, bandejas, botes y latas.
Su estructura principal simple y sólida contiene un transportador y uno o más cabezales de etiquetado (a elegir entre los modelos ALstep, ALritma o ALcode).
Bottle labeling machine with seal
ALline – sistema lineal complejo capaz de aplicar etiquetas autoadhesivas en productos de varias formas, fabricada con los materiales y componentes más fiables disponibles en el mercado, que aseguran un nivel considerable en términos de rendimiento y de producción. Su diseño modular integra los cabezales ALstep y/o ALritma, y se puede configurar de acuerdo con las necesidades del cliente, permitiendo la aplicación de la etiqueta en productos de cualquier forma y tamaño para el etiquetado frontal/posterior y envolvente y el precintado de productos alimenticios, cosméticos, químicos y farmacéuticos.
Para más información: sales@altech-us.com – www.altech-us.com info@altech.it – www.altech.it
Strada Provinciale Colligiana, 50 53035 Monteriggioni (Siena) Italy
Tel. +39 0577 30 50 04 - Fax +39 0577 30 50 19 info@galiganifiltri.com - www.galiganifiltri.com
Galigani Filtri is a leader in the design and construction of filter presses and relevant filtration systems.
Since 1958, the company has boasted over 3,000 installations in 5 continents, created with skill and professionalism, in order to offer a high-quality product and a support service for users, installers, and designers. The company is based in Italy, located in a modern facility in the heart of Tuscany, where it makes use of the most modern systems of research, study, and design so as to
best solve the problems of each individual application, as well as provide adequate pre- and post-sales assistance through its qualified technicians.
Furthermore, the company is also equipped with a laboratory for filtration testing on samples supplied by clients to determine all the necessary parameters required for sizing the filter press that is most suitable for their needs. Production includes filter presses and pumping units that feed the filter presses.
The wide range of filter presses varies from manual discharge machines to fully automatic machines run by modern PLCs.
Galigani Filtri es una empresa líder en el diseño y fabricación de filtros prensa y sistemas de filtración relacionados.
Desde 1958 hasta la actualidad, la empresa puede preciarse de más de 3000 instalaciones presentes en los 5 continentes realizadas con competencia y profesionalismo para ofrecer un producto de alta calidad y un servicio de atención al cliente dirigido tanto a usuarios como a instaladores y diseñadores.
La empresa tiene su sede en Italia y está ubicada en una moderna fábrica en el corazón de la Toscana, donde utiliza los más modernos sistemas de investigación, estudio y diseño a fin de resolver de la mejor manera los problemas de cada aplicación individual, así como proporcionar un buen servicio pre- y posventa gracias a sus propios técnicos calificados.
La empresa cuenta con un laboratorio para realizar pruebas de filtración en muestras suministradas por los clientes para determinar todos los parámetros necesarios para el dimensionamiento del filtro prensa más adecuado.
La producción incluye filtros prensa y unidades de bombeo para alimentar los filtros prensa.
La amplia gama de filtros prensa varía desde máquinas de descarga manual hasta máquinas totalmente automáticas gestionadas por modernos PLC.
Galigani Filtri fabrica filtros prensa para cada aplicación: alimentaria, química, farmacéutica, para entornos explosivos (ATEX), para la depuración de aguas residuales, para la filtración de ácidos, inertes, para el sector minero, las industrias galvánicas, las industrias de reciclaje, etc. Todas las máquinas están equipadas con los dispositivos de seguridad más avanzados.
Los filtros prensa y los sistemas de filtración construidos por Galigani Filtri realizan una filtración “mecánica”, con lo cual el líquido no sufre alteraciones químicas.
Galigani Filtri manufactures filter presses for all types of applications: food, chemical, pharmaceutical, explosive atmospheres (ATEX), purifying waste water, acid filtration, aggregates, mining, galvanic industries, recycling industries, and so on. All machines are equipped with the most advanced safety devices.
The press filters and filtration systems that are manufactured by Galigani Filtri carry out “mechanical” filtrations, and therefore the liquid does not undergo chemical changes.
Filtration can occur on the synthetic filter cloth, which retains solid particles up to 1 micron, or on cardboard for particles that measure less than or equal to 1 micron. When it comes to the most technologically advanced systems that Galigani Filtri can provide for filtration and clarification before bottling, the Diatom and the Clearness systems are in the forefront.
The Diatom system is comprised of a filter cloth for the filter press and is equipped with all the necessary parts (tanks, pumps, valves ...) that are required for filtration processes using various aids (fossil shell flour or cellulose flour, perlite...).
The Clearness system is a filter press with an Aisi304 or Aisi316 structure, which uses cardboard filters and a plate pack that is entirely sealed and protected from contact with the external environment.
La filtración puede tener lugar sobre una tela filtrante de material sintético para retener partículas sólidas de hasta 1 micrón o de cartón para partículas de 1 micrón o menos. Entre las instalaciones tecnológicamente más avanzadas que Galigani Filtri puede ofrecer para la filtración antes del embotellado, destacan los modelos Diatom y Clearness.
El sistema Diatom consta de un filtro prensa de tela, dotado de todos los dispositivos necesarios (depósitos, bombas, válvulas, ...) para realizar la filtración con adyuvantes (tierras de diatomeas o de celulosa, perlitas, ...).
El modelo Clearness consta de un filtro prensa de cartones cuya estructura está íntegramente realizada en Aisi304 o Aisi316, con un paquete de placas completamente cerrado y protegido del contacto con el exterior.
Via dell’Artigianato, 5 - 46048 Roverbella (Mantova) Italy
Tel. +39 0376 75 10 11 - Fax +39 0376 75 10 12 kosme@kosme.at - www.kosme.it
Engineering excellence across the Americas:
Innovations in home & personal care and liquid food production
From Canada to Argentina, the Americas represent a diverse and rapidly evolving market for Home & Personal Care and Liquid Food products. In this dynamic environment, Kosme delivers engineering excellence through integrated, sustainable, and customer-focused production solutions tailored to regional needs.
Smart line design for a diverse market
Kosme specializes in designing flexible, high-efficiency production lines that integrate its proprietary technologies with those of the Krones Group and other partners. These systems are built to handle the wide variety of packaging formats and product viscosities found across the Americas—from shampoo bottles in Brazil to dairy alternatives in the U.S. and sauces in Mexico.
Advanced line automation and sensor-driven conveyors ensure seamless machine communication and smooth product transitions. Kosme’s engineering teams adapt each layout to local space constraints, labor availability, and regulatory requirements, ensuring optimal performance across vastly different production environments.
Efficiency and sustainability at the core
Kosme enhances production efficiency through:
• Energy analysis and consulting to reduce consumption and optimize reuse of water, steam, and electricity.
• Flexible machines to ensure efficient productions.
• Simulation tools that model line behavior, predict performance, and help customers avoid costly downtime. These practices are especially valuable in regions where energy costs are high or infrastructure is limited, such as parts of Central America or remote areas in South America.
Tailored solutions for home & personal care
The demand for personal hygiene, skincare, and household cleaning products is growing across the continent. Kosme’s lines are designed to handle:
• Viscous and foaming liquids with precision filling systems.
• Flexible packaging formats, including refill pouches, pump bottles, and sustainable containers.
• High-speed changeovers to accommodate frequent product variations and seasonal demand.
Liquid food: From dairy to dressings
Kosme’s hygienic and modular systems are ideal for the growing liquid food sector, including:
• Dairy alternatives and plant-based beverages in North America.
• Fruit juices and nectars in Central America.
• Sauces, dressings, and edible oils in all Americas. Kosme’s solutions support returnable and large-format packaging, helping producers reduce environmental impact and meet sustainability goals.
Regional market highlights
• North America: High demand for automation, sustainability, and flexible packaging. Kosme supports large-scale operations with advanced simulation and energy recovery systems.
• Central America: Growing need for compact, costefficient lines that can adapt to limited space and infrastructure. Kosme’s modular designs are ideal for this
: A mix of traditional and modern production needs, especially in Brazil, Argentina, and Chile. Kosme provides scalable solutions that support both export and local consumption.
Kosme’s approach is rooted in collaboration and customization. By working closely with clients, Kosme develops solutions that reflect local market realities and long-term business goals. Simulation tools, real-time data collection, and continuous feedback loops ensure that each line evolves with the customer’s needs.
Looking ahead
Kosme proudly champions the advancement of the Home & Personal Care and Liquid Food sectors throughout the Americas, from the vibrant markets of Canada to the dynamic landscapes of Chile. With a steadfast commitment to innovation, sustainability, and customer-centric solutions, Kosme empowers producers to navigate today’s challenges while seizing the opportunities of tomorrow.
At the same time, Kosme remains deeply rooted in the industries that have long defined its legacy—wine, spirits, beer, and beverages of all kinds. These traditional markets continue to be a cornerstone of the brand’s identity, reflecting decades of expertise and trusted partnerships. By blending forward-thinking strategies with a respect for tradition, Kosme is uniquely positioned to support a diverse range of industries with tailored solutions that drive growth, efficiency, and long-term success.
Excelencia en ingeniería en toda América: Innovaciones en la producción de cuidado personal y alimentos líquidos
Desde Canadá hasta Argentina, América representa un mercado diverso y en constante evolución para los productos de Cuidado Personal y Alimentos Líquidos. En este entorno dinámico, Kosme ofrece excelencia en ingeniería mediante soluciones de producción integradas, sostenibles y centradas en el cliente, adaptadas a las necesidades regionales.
Diseño inteligente de líneas para un mercado diverso Kosme se especializa en el diseño de líneas de producción flexibles y de alta eficiencia, que integran sus tecnologías propias con las del Grupo Krones y otros socios estratégicos. Estos sistemas están diseñados para manejar la amplia variedad de formatos de envases y viscosidades de productos presentes en América: desde botellas de champú en Brasil hasta bebidas vegetales en EE. UU. y salsas en México.
La automatización avanzada de líneas y los transportadores con sensores garantizan una comunicación fluida entre máquinas y transiciones suaves de productos. Los equipos de ingeniería de Kosme adaptan cada diseño a las limitaciones de espacio locales, disponibilidad de mano de obra y requisitos normativos, asegurando un rendimiento óptimo en entornos de producción muy variados. Eficiencia y sostenibilidad como ejes centrales Kosme mejora la eficiencia de producción mediante:
• Análisis energético y consultoría para reducir el consumo y optimizar la reutilización de agua, vapor y electricidad.
• Máquinas flexibles que garantizan producciones eficientes.
• Herramientas de simulación que modelan el comportamiento de la línea, predicen el rendimiento y ayudan a evitar costosos tiempos de inactividad. Estas prácticas son especialmente valiosas en regiones donde los costos energéticos son elevados o la infraestructura es limitada, como en partes de Centroamérica o zonas remotas de Sudamérica.
Via dell’Artigianato, 5 - 46048 Roverbella (Mantova) Italy
Tel. +39 0376 75 10 11 - Fax +39 0376 75 10 12
kosme@kosme.at - www.kosme.it
Soluciones a medida para cuidado personal y del hogar
La demanda de productos de higiene personal, cuidado de la piel y limpieza del hogar está creciendo en todo el continente. Las líneas de Kosme están diseñadas para manejar:
• Líquidos viscosos y espumosos con sistemas de llenado de alta precisión.
• Formatos de envases flexibles, incluidos sobres recargables, botellas con bomba y envases sostenibles.
• Cambios rápidos para adaptarse a variaciones frecuentes de productos y demandas estacionales.
Alimentos líquidos: De Lácteos a Aderezos
Los sistemas higiénicos y modulares de Kosme son ideales para el creciente sector de alimentos líquidos, incluyendo:
• Alternativas lácteas y bebidas vegetales en América del Norte.
• Jugos de frutas y néctares en Centroamérica.
• Salsas, aderezos y aceites comestibles en toda América. Las soluciones de Kosme admiten envases retornables y de gran formato, ayudando a los productores a reducir el impacto ambiental y alcanzar sus objetivos de sostenibilidad.
Panorama regional del mercado
• América del Norte: Alta demanda de automatización, sostenibilidad y envases flexibles. Kosme respalda
operaciones a gran escala con sistemas avanzados de simulación y recuperación de energía.
• Centroamérica: Necesidad creciente de líneas compactas y rentables que se adapten a espacios e infraestructuras limitadas. Los diseños modulares de Kosme son ideales para este mercado.
• Sudamérica: Mezcla de necesidades tradicionales y modernas, especialmente en Brasil, Argentina y Chile. Kosme ofrece soluciones escalables que respaldan tanto el consumo local como la exportación.
Innovación centrada en el cliente
El enfoque de Kosme se basa en la colaboración y la personalización. Trabajando estrechamente con sus clientes, desarrolla soluciones que reflejan las realidades del mercado local y los objetivos empresariales a largo plazo. Herramientas de simulación, recopilación de datos en tiempo real y ciclos continuos de retroalimentación aseguran que cada línea evolucione junto con las necesidades del cliente.
Mirando hacia el futuro
Kosme se enorgullece de impulsar el desarrollo de los sectores de Cuidado Personal y Alimentos Líquidos en toda América, desde los vibrantes mercados de Canadá hasta los paisajes dinámicos de Chile. Con un firme compromiso con la innovación, la sostenibilidad y la satisfacción del cliente, Kosme capacita a los productores para enfrentar los desafíos actuales y aprovechar las oportunidades del mañana.
Al mismo tiempo, Kosme mantiene un fuerte vínculo con las industrias que han definido su legado: vino, licores, cerveza y bebidas en general. Estos mercados tradicionales siguen siendo un pilar fundamental de la identidad de la marca, reflejando décadas de experiencia y asociaciones de confianza.
Al combinar estrategias visionarias con un profundo respeto por la tradición, Kosme está en una posición única para apoyar a una amplia gama de industrias con soluciones personalizadas que impulsan el crecimiento, la eficiencia y el éxito a largo plazo.
Via Giancarlo Puecher, 24 - 20842 Besana in Brianza (Monza Brianza) - Italy
Tel. +39 039 23 01 096 - Fax +39 039 23 01 017
customercare@magicmp.it - www.magicmp.it
Industrial machines, the future is now! Magic has presented during the Open House in November the revolutionary fully electric accumulating machine with patented head and clamping.
Even the field of industrial machines have been revolutionized, the innovative ideas of Magic will give its clients enormous benefits in terms of profit and process. Principal benefits:
• Reduction of consumption equal to -53%,
• Maximum precision of the movements. Consequent efficiency equal to 99% with a perfect repeatability of the working cycles, potential reduction of the working cycle and potential reduction of the weight of the articles to be produced,
• Reduction of the maintenance costs equal to -52%,
• Machine completely oil free,
• Very silent machine since it is free of hydraulic pumps. Magic MP S.p.A. is an Italian company founded in 1959, specialized in the conception and construction of extrusion blow moulding machines (EBM) and injection, stretch e blow moulding machines (ISBM) of plastic materials.
Thanks to its constant orientation to innovation Magic has become an excellence of the Made in Italy and a
Industrial Machine, model MET T80 double station for containers up to 280 litres
Máquina industrial, MET modelo T80 de doble estación para piezas grandes de hasta 280 litros
worldwide reference point for all the operators of this field.
MAGIC has been the first company in the world to conceive fully electric machines, revolutionizing the field of plastic and tracing a new technological greener and more sustainable road.
The clients recognize in the MAGIC machines patented technological benefits, which turn into real process improvements and consequent profit increases. Investments and efforts to give to their actual and future clients a unique and solid contact point in the production of bottles: machines, moulds and packaging solutions. Everything is internally developped and produced and commercialized with the best value for money on the market.
These investments confirm the continuity of principles, values and skills that has been distinguishing Magic Group for more than 60 years.
With his words reported below the President of the Magic Group, Mr. Ferruccio Giacobbe, devotes the moon’s landing of his company on the planet of industrial machines and he does it always in an innovative and futuristic way.
“Innovation is and always will be the engine that fuel growth and development of Magic. Up to date no one in the world has ever built a completely electrified accumulator head of big size, Magic, which always looks ahead and, driven by this philosophy, has understood that even in the field of industrial machines the complete electrification will become a determining and indispensable factor. We did it in the past with the continuous extrusion technology for machine up to 60 Tons for the production, per example, in 6+6 cavities for 5 litres containers; we do it today
also with the industrial machines for containers up to 280 litres. Soon we will do in fact a second Open Day to show the world the new transfer machine with all electric technology of 80-100 Tons for containers up to 280 litres. This machine will have an incredible saving for our clients in terms of energy consumption equal to almost 180.000 Euro per year. We are led to think that electrification is all about the necessity of the energetic economy. But this is one of the aspects, even though very important. The electric motor means also more precision and repeatability in the execution of the movements, that impacts on the efficiency of the machine, in lighter articles and shortest working cycles and with less wastes. It will be easy for our clients to understand how advantageous and innovative is to produce with a machine which consume 50-60% less, that thanks to its stability allows shortest working cycles and allows to produce lighter articles and even more with reduced maintenance costs of 50%.”
We are sure that orientation to ’Green”, to be effectively implemented, must bring to our clients even advantages in terms of profit. In fact, in 25 years and 1800 electric machines sold as well as having “saved” almost 3 billions of Kg in CO2, our clients have saved more than 500 million euro in electric energy. To these many various millions must be added for the economy in maintenance costs. We want our clients, with our patented technology, win the complex challenge of the market; we aspire to become their partner, grow with them and become their reference point in the field.”
Máquinas industriales, ¡el futuro es ahora! Magic presentó durante la jornada de puertas abiertas de noviembre la revolucionaria máquina con acumulador totalmente eléctrica, con cabezal y cierre patentados.
El sector de la maquinaria industrial también se ha revolucionado; las ideas innovadoras de Magic aportarán a los clientes enormes ventajas tanto en términos de beneficios como de proceso.
Las principales ventajas:
• Reducción del consumo en un -53%.
• Máxima precisión de movimientos. Eficacia consiguiente del 99% con perfecta repetibilidad de los ciclos de trabajo, reducción potencial del ciclo de trabajo y reducción potencial del peso de los artículos que deben producirse.
• Reducción de los costes de mantenimiento en un -52%.
• Máquina totalmente exenta de aceite.
• Máquina muy silenciosa ya que no tiene bombas hidráulicas.
Magic MP S.p.A. es una empresa italiana fundada en 1959, especializada en el diseño y la fabricación de máquinas de extrusión y soplado (EBM) y de inyección, estirado y soplado (ISBM) de plásticos.
Gracias a su constante apuesta por la innovación, Magic se ha convertido en una excelencia Made in Italy y en un punto de referencia mundial para todos los operadores del sector.
MAGIC fue la primera empresa del mundo en diseñar máquinas Full Electric, revolucionando la industria del plástico y abriendo un nuevo camino tecnológico más ecológico y sostenible.
Los clientes reconocen las ventajas tecnológicas patentadas de las máquinas MAGIC, que se traducen en mejoras reales de los procesos y el consiguiente aumento de los beneficios.
Inversiones y esfuerzos para ofrecer a sus clientes actuales y futuros, un socio sólido en la producción de botellas: máquinas, moldes y soluciones de envasado. Todo ello desarrollado y producido internamente y comercializado con la mejor relación calidad-precio del mercado. Estas inversiones confirman la continuidad de los principios, valores y competencias que distinguen al Grupo Magic desde hace más de 60 años.
Con sus palabras, que se pueden leer a continuación, el presidente del Grupo Magic, Sr. Ferruccio Giacobbe, consagra el aterrizaje de su empresa en el mundo de las Máquinas Industriales y, como siempre, lo hace de forma innovadora y futurista.
“La innovación es y será siempre el motor que impulsa el crecimiento y el desarrollo de Magic. Dado que hasta la fecha nadie en el mundo ha fabricado un gran cabezal de almacenamiento totalmente electrificado, Magic mira siempre hacia delante y, guiada por esta filosofía, se ha
Via Giancarlo Puecher,
24 - 20842 Besana in Brianza (Monza Brianza) - Italy
Tel. +39 039 23 01 096 - Fax +39 039 23 01 017
customercare@magicmp.it - www.magicmp.it
dado cuenta de que incluso en el campo de la maquinaria industrial, la electrificación total se convertirá en un factor decisivo e indispensable.
Lo hicimos en el pasado con la tecnología de extrusión continua para máquinas de hasta 60 toneladas para la producción de, por ejemplo, 6+6 cavidades para envases de 5 litros; y lo hacemos hoy con máquinas industriales para envases de hasta 280 litros. De hecho, pronto celebraremos una segunda jornada de puertas abiertas para mostrar al mundo la nueva máquina Transfer con tecnología totalmente eléctrica de 80-100 toneladas para envases de hasta 280 litros. Esta máquina supondrá un ahorro increíble para nuestro cliente en términos de consumo de energía de unos 180.000 euros al año.
Uno se inclina a pensar que la electrificación viene dictada por la necesidad de ahorrar energía. Sin embargo, éste es sólo un aspecto, aunque sea muy importante. La motorización eléctrica también implica una mayor precisión y repetibilidad en la ejecución de los movimientos, lo que repercute en la eficacia de la
máquina, en artículos más ligeros y en ciclos de trabajo más cortos, con menos residuos. Será fácil para nuestros clientes comprender lo ventajoso e innovador que resulta producir con una máquina que consume entre un 50 y un 60% menos de energía, que gracias a su estabilidad permite ciclos de trabajo más cortos y habilita la producción de artículos más ligeros, y además con unos costes de mantenimiento un 50% inferiores. Estamos seguros de que la orientación “verde”, para aplicarse eficazmente, también debe reportar beneficios a nuestros clientes. De hecho, en 25 años y con 1.800 máquinas eléctricas vendidas, además de haber “ahorrado” unos 3.000 millones de kg de CO2, nuestros clientes han ahorrado más de 500 millones de euros en electricidad. A esto hay que añadir los varios millones de euros ahorrados en costes de mantenimiento. Queremos que nuestros clientes, con nuestra tecnología patentada, superen los complejos retos del mercado; aspiramos a convertirnos en su socio, crecer con ellos y ser la referencia del sector”.
S.R. 435 Km. 31 51034 Serravalle Pistoiese (Pistoia) Italy
Tel. +39 0573 91 511 - Fax +39 0573 51 81 38 mgm@mgmrestop.com - www.mgmrestop.com
For over 75 years M.G.M. Motori Elettrici S.p.A. has been a global leader in the field of brake motors, with a solid presence in Europe, America, Asia and the Middle East. The heart of the company is located in Serravalle Pistoiese (PT), where its main production facility is based. In Italy the company is also present in Assago where it has a warehouse with commercial offices. Its global influence extends through subsidiaries in Montreal, Detroit, Chennai and Izmir, as well as a network of distributors for sales and assistance covering over 75 countries worldwide.
M.G.M. is synonymous with quality, innovation and reliability. The range of brake motors the company offers can be used in a wide variety of applications. The motor shaft heights range from 71 mm to 355 mm and the power outputs are between 0.09 kW and 250 kW. The brake motors can be supplied with a brake unit powered
Dby either alternating current or direct current. Additionally the company is able to meet customer needs by providing customized products.
The company has always been at the forefront of technological innovation, with much of what we now know as AC brake motors having originated from M.G.M.’s research and laboratories. Since 2008 the energy efficiency of its products has been continually evolving: the average amount of energy required for the operation of M.G.M. products has consistently decreased. All single-speed motors comply with the new European energy efficiency regulations and improvements in the electromagnets of the brakes - both AC BA series and DC BM series - have led to reduced energy consumption and a significant increase in performance.
The future of M.G.M. Motori Elettrici is focused on sustainability and environmental respect. With the goal of reducing environmental impact the company has committed to several initiatives. The geothermal system for air conditioning, the reduction of plastic consumption and the ongoing search for solutions to reduce potable water consumption and the energy required to produce brake motors, along with a consequent reduction in greenhouse gas emissions, are just some of the actions undertaken.
In particular M.G.M.’s photovoltaic system, which originally covered 100% of the energy needs of the facility and offices, has recently been expanded to meet the growing demand for energy, partly due to the transition of
esde hace más de 75 años M.G.M. Motori Elettrici S.p.A. es una referencia mundial en el sector de los motores con freno, con una fuerte presencia en Europa, América, Asia y Oriente Medio. El corazón palpitante de la empresa está en Serravalle Pistoiese (PT), donde se encuentra la principal planta de producción. En Italia, la empresa también está presente en Assago, donde dispone de un almacén con oficinas de venta.
Su influencia mundial se extiende a través de filiales en Montreal, Detroit, Chennai e Izmir y una red de distribuidores de ventas y servicios que abarca más de 75 países de todo el mundo.
M.G.M. es sinónimo de calidad, innovación y fiabilidad. La gama de motores freno que ofrece la empresa puede utilizarse en una amplia variedad de aplicaciones. Las alturas de eje de los motores oscilan entre 71 mm y 355 mm y las potencias entre 0,09 kW y 250 kW. Los motores freno pueden suministrarse con un grupo de frenado alimentado con CA o CC. Además, la empresa es capaz de responder y satisfacer las necesidades de los clientes ofreciendo también productos personalizados.
La empresa siempre ha estado a la vanguardia de la innovación tecnológica, hasta el punto de que gran parte de lo que hoy conocemos como motores freno de CA es fruto de la investigación y los laboratorios de M.G.M.. Además, desde 2008, la eficiencia energética de sus productos no ha dejado de evolucionar: el consumo medio de energía que requieren los productos M.G.M. Motori Elettrici para su funcionamiento ha disminuido constantemente. Todos los motores de una velocidad cumplen la nueva normativa europea de eficiencia energética, y las mejoras introducidas en los electroimanes de los frenos -tanto en los motores de CA de la serie BA como en los de CC de la serie BM- han
the company’s vehicle fleet from combustion engines to electric motors. This commitment represents a concrete response to the energy and environmental challenges of our time.
M.G.M. Motori Elettrici not only makes eco-friendly choices within its own plants but also promotes sustainable practices with its suppliers and partners worldwide. It is only through collective effort that a greener and more sustainable future can be achieved. The company strongly believes that awareness and global collaboration are essential to making tangible change.
M.G.M. Motori Elettrici is not just a leader in the production of brake motors: it is a company looking to the future with a concrete commitment to technological innovation, energy efficiency and sustainability, ensuring cutting-edge solutions for a more sustainable world.
permitido reducir el consumo de energía y aumentar considerablemente el rendimiento.
El futuro de M.G.M. Motori Elettrici se centra en la sostenibilidad y el respeto por el medio ambiente. Para reducir su impacto ambiental, la empresa ha emprendido varias iniciativas. El sistema geotérmico para la climatización, la reducción del consumo de plástico y la búsqueda continua de soluciones para reducir el consumo de agua potable y la energía necesaria para la fabricación de motores autofrenantes, con la consiguiente reducción de emisiones de gases de efecto invernadero, son algunas de las medidas adoptadas.
En concreto, el sistema fotovoltaico de M.G.M., que originalmente cubría el 100% de las necesidades energéticas de la planta y las oficinas, se amplió recientemente para satisfacer la creciente demanda de energía, un aumento debido en parte a la transición de la flota de vehículos de la empresa de motores de combustión a motores eléctricos. Este compromiso representa una respuesta concreta a los retos energéticos y medioambientales de nuestro tiempo.
M.G.M. Motori Elettrici no sólo toma decisiones respetuosas con el medio ambiente en sus propias plantas, sino que también promueve prácticas sostenibles entre sus proveedores y socios de todo el mundo. Sólo mediante el compromiso colectivo es posible contribuir a un futuro más ecológico y sostenible. La empresa cree firmemente que la concienciación y la colaboración a escala mundial son esenciales para lograr un cambio tangible.
M.G.M. Motori Elettrici no es sólo un fabricante líder de motores autofrenantes: es una empresa que mira al futuro con un compromiso concreto con la innovación tecnológica, la eficiencia energética y la sostenibilidad, garantizando soluciones de vanguardia para un mundo más sostenible.
Via E. Fermi, 5 - 42011 Bagnolo in Piano (Reggio Emilia) Italy
Tel. +39 0522 95 18 89
info@minimotor.com - www.minimotor.com
Mini Motor: 60 years of innovation towards the new frontier of wireless technology
A lot has happened since 1965, when Gianfranco Franceschini embarked on his entrepreneurial adventure.
Today, Mini Motor is a company with almost 100 employees and a global network that allows the brand to be present in 60 countries.
Innovation is the keyword that has guided the company over the last fifteen years and has allowed it to consolidate its role as a partner with some of the major players in strategic sectors for Italy. From packaging to ceramics, with a growing share in the food sector, Mini Motor has been able to take on the challenges of each sector and translate them into features for its products.
Compactness and mechanical performance
With the same footprint, Mini Motor solutions guarantee higher torques and longer life cycles. The selection of materials, process-oriented design, and vertical integration of the supply chain ensure a stable quality standard over time that is recognized internationally. All Mini Motor lines—Brushless/DBS, Gear, Clean, FC/FCL— allow configurations with drives or integrated drives and digital communication. 97% of components are produced in-house or by selected suppliers with established
Mrelationships, allowing direct control over the quality and traceability of each unit manufactured. This focus on quality translates into thorough control over the reliability and performance of each product, which is individually tested and inspected.
ini Motor: 60 años de innovación hacia la nueva frontera de la tecnología inalámbrica
Se ha recorrido un largo camino desde 1965, cuando Gianfranco Franceschini inició su aventura empresarial. Hoy en día, Mini Motor es una empresa con casi cien empleados y una red global que le permite estar presente en 60 países. La innovación es la palabra clave que ha guiado a la empresa en los últimos quince años y que le ha permitido consolidar su papel como socio de algunos de los principales actores de sectores estratégicos para Italia. Desde el embalaje hasta la cerámica, con una cuota en crecimiento en el sector alimentario, Mini Motor ha sido capaz de afrontar los retos de cada sector y traducirlos en características para sus productos. Compacidad y rendimiento mecánico
Con el mismo tamaño, las soluciones de Mini Motor garantizan pares superiores y ciclos de vida más prolongados. La selección de materiales, el diseño orientado a la
Integration and simplification of system architecture
Mini Motor solutions are designed to integrate with the main fieldbus protocols (Profinet, EtherCAT, Ethernet/ IP, Powerlink, Modbus, CanOpen). The integrated drive eliminates the space required for electrical panels, reducing wiring and installation time.
The use of drivers allows for standardized management of the entire power transmission range and is an advantage in hybrid topologies or mixed architectures.
In addition, the implementation of advanced logic configurations—such as Safe Torque Off (STO), digital outputs, and software parameter setting—allows for a high degree of customization based on the required behavior.
Wireless communication: a new design option
Mini Motor has introduced solutions that support wireless communication between the motor and the control system. The goal is to offer a concrete alternative to traditional wiring in applications where space constraints, mobility, or harsh environments make radio transmission a good choice.
Wireless technology simplifies installation on moving axes, reduces maintenance downtime, and improves the accessibility of operational data. It is an enabling technology for modular and flexible architectures geared towards interconnection and remote management.
calidad de los procesos y la verticalización de la cadena de suministro garantizan un estándar de calidad estable en el tiempo y reconocido a nivel internacional. Todas las líneas de Mini Motor (Brushless / DBS, Gear, Clean, FC/FCL) permiten configuraciones con accionamiento integrado y comunicación digital. El 97 % de los componentes se fabrica internamente o por proveedores seleccionados con relaciones consolidadas, lo que permite un control directo de la calidad y la trazabilidad de cada unidad fabricada. La atención a la calidad se traduce en un control exhaustivo de la fiabilidad y el rendimiento de cada producto, probado y comprobado individualmente.
Integración y simplificación de la arquitectura del sistema
Las soluciones Mini Motor están diseñadas para integrarse con los principales protocolos de bus de campo (Profinet, EtherCAT, Ethernet/IP, Powerlink, Modbus, CanOpen). El accionamiento integrado permite eliminar el espacio ocupado por los cuadros eléctricos, reduciendo el cableado y los tiempos de instalación.
La adopción de los controladores permite una gestión estandarizada de toda la gama de transmisión de potencia y supone una ventaja en presencia de topologías híbridas o arquitecturas mixtas.
Además, la implementación de configuraciones lógicas avanzadas, como Safe Torque Off (STO), salidas digitales y ajuste de parámetros mediante software, permite un alto grado de personalización en función de los comportamientos requeridos.
Comunicación inalámbrica: una nueva opción de diseño
Mini Motor ha introducido soluciones capaces de soportar la comunicación inalámbrica entre el motor y el sistema de control. El objetivo es ofrecer una alternativa concreta al cableado tradicional en aplicaciones en las que las limitaciones de espacio, la movilidad o los entornos difíciles hacen que la transmisión por radio sea ventajosa.
La tecnología inalámbrica permite simplificar la instalación en ejes móviles, reducir los tiempos de inactividad relacionados con el mantenimiento y mejorar la accesibilidad de los datos operativos. Se trata de una tecnología habilitadora para arquitecturas modulares y flexibles, orientadas a la interconexión y la gestión remota.
Since 1965, Mini Motor has been designing and manufacturing brushless motors and servomotors for industrial automation, with a constant commitment to quality, innovation, and reliability
Today, 60 years after our establishment, we continue to be more than just a supplier: we are technology partners and offer tailor-made solutions for every sector.
In-house design, total quality control, a 100% in-house supply chain and maximum integration guarantee excellent performance.
Advanced technology, people and passion: the driving force behind our growth.
Regione San Giovanni, 19 - 14053 Canelli (Asti) Italy
Tel. +39 0141 824206
sales@mondo-scaglione.com - www.mondo-scaglione.com
Innovative technological solutions that involve many packaging and packing aspects
Mondo & Scaglione was founded in Canelli (the capital of Asti Spumante) in 1969, since then the company has been designing and building packaging machines.
At the beginning, Mondo & Scaglione worked especially for local wineries producing sparkling wines around its area (Gancia, Riccadonna, Cinzano, Martini & Rossi…); these companies needed a local manufacturing company able to build case packers, case erectors, and palletizers, the so-called “end of line” machines as an alternative to German machine manufacturers that were dominating the market at the time.
After a few years from its establishment, Mondo & Scaglione spread its presence not only all over Italy but also to the foreign markets. Today, Mondo & Scaglione has customers all over the world and exports more than 85% of its manufactured machines. Thanks to this success, it has widened its market presence addressing not only its core business (wine and spirits) but also the beverage, food and chemical markets with machines that feature innovative technological solutions.
Mondo & Scaglione designs and manufactures all its machines entirely in-house, starting from the mechanical and electronic engineering, right through parts and components manufacturing for final assembly.
Besides the Design Office and the Electronic Office, Mondo & Scaglione has also a Welding Department to build in-house machine frames, and a Tooling Machines Department for the manufacturing of all the components that will be assembled on the machines.
Moreover, Mondo & Scaglione has also an important Electrical Department to create electrical cabinets and to completely wire in-house the machines, as well an assembly department that enables assembling the mechanical parts of the machines before testing and start-up before shipments.
In general, installation, start-up and commissioning of Mondo & Scaglione machines are operated by its specialized service engineers.
The company has also an after-sales and spare parts department suitable to help the customers worldwide supplying the necessary parts and components it keeps in its inventory or supporting them by phone, e-mail or via remote access to the machines PLC.
Mondo & Scaglione is a dynamic company that does not only build standard machines for its customers, but it also tries to understand customer’s requirements as to propose a tailored technological solution upon the product to handle, space available, and required production speed.
Flexibility is for sure one of the major features that Mondo & Scaglione is recognized on the market for, and for this
reason it often manufactures “special” machines upon its customers’ needs.
That requires a strong “team effort” with engineers constantly exchanging ideas, as well as the considerable experience that Mondo & Scaglione can count on as a company that has been on the market for more than 50 years, a peculiarity that is hardly to be found in other companies of the sector.
In a few words, thanks to its experience and know-how gained in more than 50 years, the flexibility and strong motivation to always find new technical challenges, Mondo & Scaglione sees its future bright always looking for new market opportunities.
Soluciones tecnológicas innovadoras que abarcan múltiples aspectos del envasado y embalaje
Mondo & Scaglione se fundó en Canelli (capital del Asti Spumante y el Moscato d’Asti) en 1969, y siempre se ha dedicado al diseño y la construcción de máquinas de envasado y embalaje.
En sus primeros años, Mondo & Scaglione trabajó principalmente a nivel local para importantes productores de vino espumoso de su zona (Gancia, Bosca, Riccadonna, Cinzano, Martini & Rossi...) que sentían la necesidad de encontrar un fabricante local de máquinas para el estuchado y la paletización (el llamado “final de línea”) con el fin de disponer de una alternativa a las máquinas de los fabricantes alemanes, en aquel momento los únicos productores de este tipo de equipos.
Poco después de su creación, Mondo & Scaglione amplió sus límites geográficos de operación, inicialmente a nivel italiano y posteriormente a nivel mundial. Hoy en día, la empresa tiene clientes en todo el mundo (las exportaciones representan el 85% de su facturación total) y, gracias a su éxito, ha ampliado su gama de producción, dejando de dirigirse únicamente al mercado del “vino y los licores” para empezar a abastecer a los sectores de las bebidas, la alimentación y la química, tratando de
Regione San Giovanni, 19 - 14053 Canelli (Asti) Italy Tel. +39 0141 824206
sales@mondo-scaglione.com - www.mondo-scaglione.com
ofrecer soluciones tecnológicas innovadoras que abarcan múltiples aspectos del envasado y el embalaje. Mondo & Scaglione diseña y construye las máquinas internamente, empezando por el diseño mecánico y electrónico y pasando por la construcción de las distintas piezas y componentes que integran la máquina. Cuenta con departamentos técnicos mecánicos y electrónicos; un departamento de carpintería que permite la construcción de cimientos; un departamento de máquinas herramienta que incluye tornos paralelos visualizados, fresadoras visualizadas, tornos de control numérico y centros de mecanizado de control numérico. Dispone de un departamento eléctrico que permite construir y montar los cuadros eléctricos y el cableado “a bordo de la máquina”, así como de un departamento de montaje que permite ensamblar las piezas mecánicas que constituyen las propias máquinas y, a continuación, realizar pruebas de funcionamiento y ensayos en el taller antes del envío.
La instalación, el montaje de la máquina y la aceptación por parte del cliente corren a cargo de los técnicos especializados de Mondo & Scaglione.
La empresa cuenta con un departamento de servicio posventa y piezas de repuesto que puede proporcionar a los clientes asistencia a distancia o enviar técnicos especializados; también puede enviar piezas de repuesto
rápidamente gracias a su almacén interno de piezas de repuesto que mantiene un número adecuado de piezas en stock.
Mondo & Scaglione es una empresa muy dinámica que no se contenta con construir máquinas estándar, sino que trata de comprender las necesidades del cliente para proponerle una solución tecnológica “a medida” en función del tipo de producto que deba procesar, el espacio disponible y la velocidad de producción requerida.
La flexibilidad es sin duda una de sus características más importantes, por lo que a menudo se construyen máquinas “especiales” siguiendo especificaciones precisas del cliente.
Esto implica un gran trabajo en equipo en el diseño y la implantación del sistema, así como la oportunidad de aprovechar un caudal de conocimientos y experiencia difícil de encontrar en otras empresas del sector.
En resumen, Mondo & Scaglione, gracias a su experiencia y saber hacer adquiridos a lo largo de más de 50 años de historia, a su flexibilidad a la hora de abordar nuevos proyectos y a su fuerte propensión a buscar nuevos retos al no conformarse con sus logros, se orienta hacia un futuro de crecimiento en términos de mercado geográfico y, sobre todo, de nuevos sectores de productos que puedan acoger y apreciar bien su oferta tecnológica.
Via I. Giordani, 10 - Z.I. Postumia - 46044 Goito (Mantova) Italy
Tel. +39 0376 689 707 - Fax +39 0376 68 96 44 info@newteclabelling.it - www.newteclabelling.it
Automatic labelling machines
Newtec Labelling Srl was founded in 1982 in Goito (Mantua), designs and produces linear and rotary labelling machines suitable for all user requests both in terms of production speed and type of packaging. Each model, thanks to the customization of the design, has specific characteristics designed to give maximum performance in every type of production. The result of a very long experience and constant updating of technologies, each model is designed to guarantee high production rates, absolute packaging precision and low operating costs. The materials used and the construction technologies allow these machines to support very heavy workloads. Thanks to their reliability and ease of use they are also successfully used in small and medium-sized businesses.
Panther is a high-level multi-label machine, ready to work with all application technologies: self-adhesive, hot melt, roll fed and wet-glue. Equipped with a complete control system for quality control, rejecting defective products and remote management.
Etiquetadoras automáticas
Newtec Labelling Srl, fundada en 1982 en Goito (Mantua), diseña y fabrica etiquetadoras lineales y rotativas adecuadas para todas las exigencias de los usuarios, tanto en términos de velocidad de producción como de tipo de envase. Cada modelo, gracias a un diseño personalizado, cuenta con características específicas pensadas para ofrecer el máximo rendimiento en cada tipo de producción. Fruto de muchos años de experiencia y de constantes actualizaciones tecnológicas, cada modelo está diseñado para garantizar altos índices de producción, absoluta precisión de envasado y bajos
costes de funcionamiento. Los materiales utilizados y las tecnologías de construcción permiten a estas máquinas soportar cargas de trabajo muy pesadas. Gracias a su fiabilidad y facilidad de uso, también se utilizan con éxito en pequeñas y medianas empresas. Panther es una máquina multietiqueta de gama alta, preparada para trabajar con todas las tecnologías de aplicación: autoadhesivo, hot melt, roll fed y wet-glue. Equipada con un completo sistema de control de calidad, rechazo de productos defectuosos y gestión remota. Giotto es una etiquetadora Roll Fed de última generación, compacta y muy sencilla de instalar, usar y mantener.
Giotto is a latest generation Roll Fed labeller, compact and very simple to install, easy to use and maintain in perfect working order.
The modular structure of the machines, based on direct drive servo motors, is designed to help dramatically reduce all running costs. In addition to Panther and Giotto, the company also offers other models of rotary or linear labelling machines, for the application of paper labels with cold glue, for the application of wrap-around labels in paper or plastic materials with hot glue, and for selfadhesive labels.
The company is present all over the world with its own agents and participates in the most important exhibitions in the sector.
La estructura modular de las máquinas, basada en servomotores de accionamiento directo, está diseñada para ayudar a reducir drásticamente todos los costes de explotación. Además de Panther y Giotto, la empresa ofrece otros modelos de etiquetadoras rotativas o lineales, para la aplicación de etiquetas de papel con cola fría, para la aplicación de etiquetas envolventes en papel o materiales plásticos con cola termofusible y para etiquetas autoadhesivas.
La empresa está presente en todo el mundo con sus propios agentes y participa en las ferias más importantes del sector.
Via della Scienza, 13 - 37139 Verona - Italy
Tel. +39 045 51 17 941
estero@sincerasistemi.it - www.sincerasistemi.it
Sincera Sistemi Srl, over the last decade, has become the leading player in a movement of technological renewal that has involved a sector traditionally bound to craftsmanship, such as that of winebottle sealing with wax. The company has turned its motto ‘Technology in Tradition’ into its leitmotiv, thus pursuing a project focused on innovation and quality, where the customer is always at the very heart; Sincera Sistemi’s machines, although born from a standard base, are then adapted to customers’ needs, thus becoming in fact tailor-made.
Customers, being rather heterogeneous in terms of geographic origin, product quality placement and company size, have contributed, through their own sector-specific needs, to the widening of Sincera Sistemi’s product range. The Company has established from the outset a deep connection with all major realities in the wine industry, expanding its customer portfolio over the years to also include breweries, distilleries, vinegar and oil manufacturers. Generally, the Company can follow from micro-producers to large wine groups with millions of bottles per year, never lacking in punctuality, following a precise logic of quality and service tailored to the real needs of the customers.
From the very beginning, the aim to ease the craftsman’s work has been a powerful reason to keep searching for an innovative solution, which would not depart completely from the centuries-old tradition of wax sealing.
The sealing process has grown from being almost out of fashion to being increasingly used by manufacturers who have seen renewed potential in it. It is a fairly simple process to do, but depending on the number of bottles involved, it can be quite time- and money-
consuming, not to mention the danger of accidents due to the rather precarious condition of the techniques in use until the introduction of new technologies, such as those of Sincera Sistemi.
The product range includes several machines, starting from the manual up to the full automatic one.
Sincera1 manual machine, the entry-level device, perfectly conjugates easier operation and no exceeding money effort. It’s small but very sturdy and can process bottles (mainly bordelaise/burgundy) ranging from 0.75 up to 5lt, by simply adjusting or changing supports. For those interested in higher throughput, Sincera2 and Sincera 4 represent bestselling products of the company worldwide. Both devices are semiautomatic, which means that the operator should just arrange loading/unloading of bottles, but the whole cycle is automatically performed by the machine itself. Technologically speaking, they are user friendly thanks to the touchscreen which allows setting most features such as temperatures, times, stamping option (if available) and even a preheating process. This option is useful when scheduling production over the week because operators can have the machine ready for operating at a specific hour of the day, without wasting time. These two models now feature an all-stainless steel design; an interactive LED system helps the operator to immediately identify the status of the machine, through the different colours of the Plexiglas protective panels. In terms of operation, both models are equipped with a slide-out system of the tank, thus allowing easier maintenance.
Increasing customer demands led to the development of Sincera SL14, the automatic machine, suitable for both inline positioning and as a stand-alone solution; its average production is approx. 1200 bottles per hour, but it may vary according to bottle dimensions.
The solutions offered by Sincera Sistemi are not only limited to the models currently on the market, but also include additional accessories or bespoke machinery to suit each customer’s needs.
Nonetheless, the real innovation, beyond machinery, has been to introduce the use of a more reliable and flexible product such as soft wax, capable of combining superior quality and better performance on the bottle.
Waxing bottles is a choice that has a major impact on the quality of the final product, either a bottle of wine or a prestigious spirit. On a cost level, it has more or less the same value as high-quality capsules, although market fluctuations and the recent supply chain crisis have caused the price to rise steadily and delivery dates to lengthen. Since wax is sold per kilo, companies can purchase only the quantity needed for the production of a given product, without incurring the effort of purchasing many pieces that is often required with capsules.
The technological solutions offered by Sincera Sistemi therefore allow customers to innovate without leaving their tradition behind.
Sincera Sistemi Srl, en la última década, se ha convertido en el principal protagonista de un movimiento de renovación tecnológica que ha involucrado a un sector tradicionalmente ligado a la artesanía, como el sellado de botellas de vino con cera. La empresa ha convertido su lema “Tecnología en la Tradición” en su leitmotiv, persiguiendo así un proyecto enfocado en la innovación y la calidad, donde el cliente siempre está en el centro. Las máquinas de Sincera Sistemi, aunque nazcan de una base estándar, luego se adaptan a las necesidades de los clientes, convirtiéndose en productos fabricados a medida. Los clientes, siendo bastante heterogéneos en términos de origen geográfico, calidad del producto y tamaño de la empresa, han contribuido, a través de sus propias necesidades específicas del sector, a la ampliación de la gama de productos de Sincera Sistemi. Desde el principio, la empresa ha establecido una conexión profunda con todas las principales realidades de la industria del vino, ampliando su portfolio de clientes a lo largo de los años para incluir también cervecerías, destilerías, fabricantes de vinagre y aceite. En general, la empresa puede atender tanto a microproductores como a grandes grupos vitivinícolas con millones de botellas al año, sin dejar de ser
Via della Scienza, 13 - 37139 Verona - Italy
Tel. +39 045 51 17 941
estero@sincerasistemi.it - www.sincerasistemi.it
puntual, siguiendo una lógica precisa de calidad y servicio adaptada a las necesidades reales de los clientes. Desde el principio, el objetivo de facilitar el trabajo del artesano ha sido una poderosa razón para seguir buscando una solución innovadora que no se alejara por completo de la centenaria tradición del sellado de botellas con cera. El proceso de sellado ha pasado de estar casi pasado de moda a ser utilizado cada vez más por fabricantes que han visto un renovado potencial en él. Es un proceso bastante sencillo de hacer, pero dependiendo del número de botellas involucradas, puede ser bastante consumidor de tiempo y dinero, sin mencionar el peligro de accidentes debido a las técnicas precarias utilizadas hasta la introducción de nuevas tecnologías, como las de Sincera Sistemi. La gama de productos incluye varias máquinas, desde la manual hasta la completamente automática. La máquina manual Sincera1, más simple y básica, combina perfectamente una operación más sencilla y un esfuerzo económico adecuado. Es pequeña pero muy resistente, y puede procesar botellas (principalmente burdeos/borgoña) que van desde 0.75 hasta 5 litros simplemente ajustando o cambiando los soportes. Para aquellos interesados en un mayor rendimiento, Sincera2 y Sincera 4 representan los productos
más vendidos de la empresa a nivel mundial. Ambos dispositivos son semiautomáticos, lo que significa que el operador solo tiene que encargarse de cargar/descargar las botellas, pero todo el ciclo se realiza automáticamente por la máquina misma. Tecnológicamente hablando, son fáciles de usar gracias a la pantalla táctil que permite configurar la mayoría de las funciones, como temperaturas, tiempos, opción de sellado (si está disponible) e incluso un proceso de precalentamiento. Esta opción es útil cuando se programa la producción durante la semana, ya que los operadores pueden tener la máquina lista para operar a una hora específica del día, sin perder tiempo. Estos dos modelos ahora cuentan con un diseño totalmente en acero inoxidable; además un sistema interactivo de LED ayuda al operador a identificar de inmediato el estado de la máquina a través de los diferentes colores de los paneles protectores de plexiglas. En cuanto a la operación, ambos modelos están equipados con un sistema deslizante del tanque, lo que permite un mantenimiento más sencillo. Las crecientes demandas de los clientes llevaron al desarrollo de Sincera SL14, la máquina automática, adecuada tanto para la posición en línea como para soluciones independientes; su producción promedio es de aproximadamente 1200 botellas por hora, pero puede variar según las dimensiones de la botella.
Las soluciones ofrecidas por Sincera Sistemi no se limitan solo a los modelos actualmente en el mercado, sino que también incluyen accesorios adicionales o maquinaria personalizada para adaptarse a las necesidades de cada cliente.
No obstante, la verdadera innovación, más allá de la maquinaria, ha sido introducir el uso de un producto más confiable y flexible como el lacre sintético, capaz de combinar una calidad superior y un mejor rendimiento en la botella.
Encerar las botellas es una elección que tiene un gran impacto en la calidad del producto final, ya sea una botella de vino o un destilado prestigioso. En cuanto al costo, tiene más o menos el mismo valor que las cápsulas de alta calidad, aunque las fluctuaciones del mercado y la reciente crisis en la cadena de suministro han provocado un aumento constante en el precio y un alargamiento en las fechas de entrega. Dado que la cera se vende por kilo, las empresas pueden comprar solo la cantidad necesaria para la producción de un producto determinado, sin tener que hacer el esfuerzo de adquirir muchas piezas, como suele ser necesario con las cápsulas.
Las soluciones tecnológicas ofrecidas por Sincera Sistemi permiten a los clientes innovar sin abandonar su tradición.
Via Carlo Ceresa, 10
24015 San Giovanni Bianco (Bergamo) Italy
Tel. +39 0345 401 11 - Fax +39 0345 402 09 info@smigroup.it - www.smigroup.it
SMI solutions for Bepensa Bebidas Seas with transparent waters and white sandy beaches; archaeological sites, which preserve and protect the remains of ancient Mayan civilizations; parks and natural beauty all to be admired. Welcome to Cancun, a fascinating city in Mexico, which boasts the presence of cutting-edge companies such as Embotelladora Bepensa Cancun, a division of Bepensa Bebidas, an important bottler of The Coca-Cola Company brands. The company, in order to respond to the growing market demands for Cristal bottled water, recently turned to SMI and ENOBERG for the supply of a complete line for bottling and packaging in 0.335 L / 0.5 L / 0.6 L / 1 L and 1.2 L PET bottles.
A solid relationship of trust thanks to flexibility, timeliness and efficiency
The line installed in Cancun is the first of three lines for bottling and packaging the Cristal brand natural water supplied by SMI and ENOBERG to Bepensa Bebidas; the second was installed at the Merida plant, also in Mexico, and the third at the Dominican Republic plant.
The line installed in Cancun is the first of three lines for bottling and packaging the Cristal brand natural water supplied by SMI and ENOBERG to Bepensa Bebidas; the second was installed at the Merida plant, also in Mexico, and the third at the Dominican Republic plant. The collaboration between Bepensa Bebidas, SMI, ENOBERG and the Mexican subsidiary Smicentroamericana is the result of a long-standing strategic partnership that allows
Bepensa to have high-tech machines and equipment and to make use of timely and efficient technical, commercial and after-sales consultancy.
The project that led Bepensa Bebidas to purchase 3 new bottling and packaging lines for Cristal natural water focused on a few simple aspects, first of all the need for an efficient and extremely flexible line solution to process 5 different formats of PET bottles within the same production line, followed by the speed of format changes and the timeliness in the delivery and installation of the systems. The new line supplied to Embotelladora Bepensa Cancun, intended for the bottling of Cristal water, includes an integrated ECOBLOC® ERGON system consisting of a compact EBS 10 KL ERGON stretch-blow moulder by SMI and an electronic volumetric filling system for natural water HEVF/ECO 60/94-12/94 by ENOBERG; for secondary and tertiary packaging, the Mexican company has chosen a solution that includes a CSK 40 F ERGON film-only shrinkwrapper and an APS 1570 ERGON palletising system, both produced by SMI.
Water: resource of the universe
Water is a source of life, a right for everyone, it is a nonrenewable and potentially exhaustible good. Hence the importance of the behaviour of bottling companies, as Embotelladora Bepensa, in adopting sustainable and virtuous production systems.
The company is constantly striving to improve the water efficiency of its plant’s operations and reduce water consumption in relation to the litres of beverage produced;
a key element in the pursuit of these objectives are the continuous investments in technological innovation, which also include the SMI and ENOBERG machinery recently installed in Cancun, Merida and the Dominican Republic for the bottling of Cristal water. The latter is packaged in bottles made up of 100% other bottles, thanks to recycling technologies and processes that transform PET safely; The result is a completely recycled and recyclable blue-toned bottle that maintains the quality and freshness of the water.
Focus on the Bepensa world
Bepensa is a Mexican business group founded in 1946 in Mérida, in the Mexican state of Yucatán, by Fernando Ponce G. Cantón; today it is a multinational industrial company consisting of 40 companies grouped into five divisions (Beverages – Industrial – Motor – Capital and Spirits), which can count on a workforce of over 15,000 people.
In terms of sales volume, the Bepensa Bebidas S.A. de C.V. division is the third most important bottler in Mexico and the United States and the fifth in Latin America; this important industrial reality produces, markets and distributes a portfolio of 35 brands of The Coca-Cola Company, in particular soft drinks, water and ready-todrink drinks.
SMI and ENOBERG solutions for Embotelladora Bepensa
Bepensa Bebisas is constantly committed to meeting the needs of consumers by offering high quality products packaged in practical package formats.
Recent investments for the installation of three new production lines within the Cancun, Merida and Dominican Republic plants focused on the need to have extremely flexible multi-format systems to quickly switch from one production batch to another; a demanding challenge, considering that Bepensa’s traditional production system has always been based on single-format lines. Another request from the company to SMI and ENOBERG, was to be able to quickly have the new systems available to meet the growing market demand for Cristal bottled water.
Great teamwork between the customer and suppliers has made it possible to achieve all the objectives set, thanks to which Bepensa has obtained the required market competitiveness and preserved the quality of bottled and packaged products.
Rotary stretch-blow moulder EBS 10 KL ERGON for stretch-blow moulding of 0,355 L / 0,5 L / 0,6 L / 1L and 1,2 L bottles in PET at max. speed of 24,000bph
• Simple and fast format changes, essential for quickly switching from one bottle format to another within a multiformat production line
• Compact design thanks to the preform heating section integrated with the stretch-blow moulding section
• Reduced transport costs
• Quick and easy installation and start-up
• Reduced energy consumption: the stretch-blow moulding carousel is equipped with motorised ironing rods controlled by electronic drives, which do not require compressed air. In addition, the current consumption is lower than linear motor solutions.
• High-performance valves and low dead volumes (-50%) that ensure reduced preblowing and blowing times and better quality of the bottles produced
• Reduced tunnel consumption: optimised chain pitches according to the preform diameter.
• Highly efficient preform heating due to uniform heat distribution
• Reduced mechanical intervention: the servo motor automatically adjusts according to the production speed.
• Simple and intuitive HMI
• Less wear and greater precision of handling of the blow moulding machine: handling of the grippers based on springless preform/bottle grippers equipped with desmodromic cams.
• Easy management and maintenance.
HEVF/ECO 60/94-12/94 filling and capping monobloc in ECOBLOC® configuration with stretch-blow moulder
• Filling system with high-precision flowmeters installed near each tap
• Frame entirely made of AISI 304 stainless steel
• Isolation of the filling chamber from the external environment, thanks to gaskets installed on the doors, the upper cover and an air blowing system that allows to generate an overpressure of sterile air inside the work environment, protecting it from external agents and allowing air recirculation
• Machine table inclined towards the drainage points: this solution ensures the drainage of liquids from the filler to the outside in order to avoid stagnation with a consequent higher level of hygiene
• The parts in contact with the product are made of AISI 316 stainless steel
• Quick and “tool-less” bottle format changes
• Dummy bottles (for CIP washing of pipes) with automatic insertion: a solution that allows a higher level of hygiene and considerable time savings for the preparation of the machine for CIP washing
• Easy access to all parts of the filler for complete and efficient maintenance.
CSK 40 F ERGON shrink wrapper to pack PET bottles in format in film only
• Machine equipped with a motorised system of oscillating guides at the infeed, which facilitates the correct channelling of loose containers on a conveyor belt equipped with chains in thermoplastic material with low coefficient of friction
• Grouping of bulk containers in the desired format carried out continuously by means of electronically synchronised rungs and separator bars
Via Carlo Ceresa, 10 24015 San Giovanni Bianco (Bergamo) Italy
Tel. +39 0345 401 11 - Fax +39 0345 402 09 info@smigroup.it - www.smigroup.it
• Film cutting unit with a compact design, where the blade is managed by a brushless motor with direct “direct-drive” transmission that makes the cutting operation more precise and simplifies maintenance
• New ICOS motors, equipped with integrated digital servo-drive (driver), able to simplify the wiring of the machine and ensure greater energy efficiency, less noise and reduced wear of the components
• The shrink tunnel installed in Bepensa is equipped with a metal chain and lubrication capable of ensuring better sealing of the film under the pack
• The tunnel efficiently and homogeneously manages the distribution of hot air flows over the entire surface of the pack being formed
• Reduced energy consumption and maximum environmental compatibility of production processes
• Optional system for automatic format change adjustments
• Machine equipped with additional optional devices to ensure high quality of the final pack, such as the additional 1,150 mm belt placed at the tunnel exit for rapid cooling of the packs.
• Single-column system with two Cartesian axes, extremely flexible and easily adaptable to the logistical conditions of the end-of-line area
• System consisting of different modules that can be individually configured according to palletizing needs
• The palletser installed at Bepensa packs bundles in film only, but the system is also suitable for palletising cartons, trays and packages in general
• Reduced maintenance costs and low energy consumption, thanks to the mechanical simplicity of the machine and the use of robotically derived components
• Simple and intuitive automation and control system.
Via Carlo Ceresa, 10
24015 San Giovanni Bianco (Bergamo) Italy
Tel. +39 0345 401 11 - Fax +39 0345 402 09 info@smigroup.it - www.smigroup.it
Soluciones SMI para Bepensa Bebidas
Mares de aguas transparentes y playas de arenas blanquísimas; yacimientos arqueológicos que preservan y protegen los restos de antiguas civilizaciones mayas; parques y bellezas naturales para admirar. Bienvenidos a Cancún, una ciudad fascinante de México que cuenta con la presencia de empresas de vanguardia como Embotelladora Bepensa Cancún, una división de Bepensa Bebidas, importante embotellador de las marcas de The Coca-Cola Company.
Embotelladora Bepensa, para satisfacer la creciente demanda del mercado de agua embotellada bajo la marca Cristal, recientemente se ha dirigido a SMI y ENOBERG para el suministro de una línea completa para el embotellado y envasado en botellas de PET de 0,335 L / 0,5 L / 0,6 L / 1 L y 1,2 L.
Una sólida relación de confianza gracias a la flexibilidad, actualidad y eficiencia
La línea instalada en Cancún es la primera de las tres líneas para el embotellado y el empaquetado de agua natural de la marca Cristal, suministradas por SMI y ENOBERG a Bepensa Bebidas. La segunda se ha instalado en la planta de Mérida, también en México, y la tercera en la planta de la República Dominicana.
La colaboración entre Bepensa Bebidas, SMI, ENOBERG y la filial mexicana Smicentroamericana es el resultado de una histórica y duradera asociación estratégica que permite a Bepensa contar con máquinas y equipos de elevado contenido tecnológico y beneficiarse de una asesoría técnica, comercial y de posventa ágil y eficiente. El proyecto que llevó a Bepensa Bebidas a adquirir tres nuevas líneas de embotellado y empaquetado para el agua natural Cristal se centró en pocos pero fundamentales aspectos: la necesidad de una solución de línea eficiente y extremadamente flexible para trabajar con cinco formatos diferentes de botellas de PET en la misma línea de producción, seguida por la rapidez en los cambios de formato y la celeridad en la entrega e instalación de las plantas.
La nueva línea proporcionada a Embotelladora Bepensa Cancún, destinada al embotellado del agua de la marca Cristal, incluye un sistema integrado ECOBLOC® ERGON compuesto por una estiro-sopladora compacta EBS 10 KL ERGON de SMI y un sistema de llenado volumétrico electrónico para agua natural HEVF/ECO 60/9412/94 de ENOBERG. Para el empaquetado secundario y terciario, la empresa mexicana ha optado por una solución que incluye una enfajadora de solo film CSK 40 F ERGON y un sistema de paletización APS 1570 ERGON, ambos fabricados por SMI.
Agua, recurso universal
El agua es una fuente de vida, un derecho de todos; es un bien no renovable y potencialmente agotable. De aquí la importancia del comportamiento de las empresas embotelladoras al adoptar sistemas de producción sostenibles y responsables. Embotelladora Bepensa se encuentra constantemente comprometida en mejorar la eficiencia hídrica de las actividades de su planta y en reducir el consumo de agua en relación con los litros de bebida producidos; un elemento clave en la consecución
de estos objetivos son las inversiones continuas en innovación tecnológica, que incluyen la reciente instalación de maquinaria SMI y ENOBERG en Cancún, Mérida y la República Dominicana para el embotellado de agua de la marca Cristal. Esta última se envasa en botellas compuestas al 100% de otras botellas, gracias a tecnologías y procesos de reciclaje que transforman el PET de manera segura; el resultado es una botella azul completamente reciclada y reciclable que mantiene la calidad y frescura del agua.
Bepensa en foco
Bepensa es el tercer grupo embotellador de Coca Cola en Mexico. Fundado en 1946 en Mérida, en el estado mexicano de Yucatán, por Fernando Ponce G. Cantón. Hoy en día, es una realidad industrial multinacional activa en el sector automotriz y de bebidas, compuesta por 40 empresas agrupadas en cinco divisiones (Bebidas, Industrial, Motriz, Capital y Spirits), que cuenta con una fuerza laboral de más de 15,000 personas. En términos de volumen de ventas, la división Bepensa
Bebidas S.A. de C.V. es el tercer embotellador más importante en México y Estados Unidos, y el quinto en América Latina. Esta importante realidad industrial produce, comercializa y distribuye un portafolio de 35 marcas de The Coca-Cola Company, en particular refrescos, agua y bebidas listas para beber.
Soluciones SMI y ENOBERG para Embotelladora Bepensa
Bepensa Bebidas está constantemente comprometida en satisfacer las necesidades de los consumidores, ofreciendo productos de alta calidad en prácticos formatos de embalaje.
Las recientes inversiones para la instalación de tres nuevas líneas de producción dentro de las fábricas de Cancún, Mérida y República Dominicana se han centrado en la necesidad de contar con instalaciones multi-formato
sumamente flexibles para poder cambiar rápidamente de un lote de producción a otro; un desafío complicado, considerando que el sistema productivo tradicional de Bepensa siempre se ha basado en líneas mono-formato. Otra solicitud de la empresa a SMI y ENOBERG ha sido la de contar rápidamente con las nuevas instalaciones para responder a la creciente demanda del mercado de agua embotellada Cristal.
Un gran trabajo en equipo entre el cliente y los proveedores ha permitido alcanzar todos los objetivos establecidos, gracias a lo cual Bepensa ha conseguido la competitividad de mercado requerida y ha preservado la calidad de los productos embotellados y empaquetados.
Estiro-sopladora rotativa EBS 10 KL ERGON para estiro-soplado de botellas PET de agua natural de 0,355 L / 0,5 L / 0,6 L / 1 L y 1,2 L a una velocidad máxima de 24.000 botellas/hora
• Cambio de formato sencillo y rápido, fundamental para pasar rápidamente de un formato de botella a otro dentro de una línea de producción multiformato;
• Estructura compacta, gracias a que la sección de calentamiento de preformas está integrada con la sección de estirado-soplado;
• Reducción de costos de transporte;
• Instalación y puesta en marcha de la máquina de manera simple y rápida;
• Reducción del consumo energético: la rueda de estirado-soplado está equipada con varillas de estirado motorizadas controladas por accionamientos electrónicos, que no requieren aire comprimido. Además, el consumo de corriente es inferior al de soluciones con motores lineales;
• Válvulas de alto rendimiento y bajo volumen muerto (-50%) que garantizan tiempos reducidos de pre-soplado y soplado, así como una mejor calidad de las botellas producidas;
• Consumo reducido del horno: pasos de cadena optimizados en función del diámetro de la preforma;
• Calentamiento de preformas de alta eficiencia, gracias a una distribución uniforme del calor;
• Menor intervención mecánica: el servomotor se ajusta automáticamente según la velocidad de producción;
• Interfaz HMI simple e intuitiva;
• Menor desgaste y mayor precisión en la gestión del soplador: manipulación de las pinzas basada en pinzas de preforma/botellas sin muelles, dotadas de levas desmodrómicas;
• Fácil gestión y mantenimiento.
Llenado y tapado monobloque HEVF/ECO 60/94-12/94 en configuración ECOBLOC® con la estiro-sopladora para llenado y taponado de botellas PET de agua natural cristal
• Sistema de llenado con caudalímetros de alta precisión instalados cerca de cada grifo;
• Estructura completamente fabricada en acero inoxidable AISI 304.
• Aislamiento de la cámara de llenado respecto al ambiente exterior, gracias a juntas instaladas en las compuertas, la cubierta superior y un sistema de soplado de aire que permite generar una sobrepresión de aire estéril dentro del entorno de trabajo, protegiéndolo de agentes externos y permitiendo la recirculación del aire;
• Superficie de la máquina inclinada hacia los puntos de drenaje: esta solución garantiza el drenaje de líquidos desde la llenadora hacia el exterior, evitando estancamientos y logrando un mayor nivel de higiene;
• Las partes en contacto con el producto están fabricadas en acero inoxidable AISI 316;
• Cambios de formato de botella rápidos y sin herramientas;
• Botellas falsas (para el lavado CIP de las tuberías) de inserción automática: solución que permite un mayor nivel de higiene y un considerable ahorro de tiempo para la preparación de la máquina para el lavado CIP;
• Fácil acceso a todas las partes de la llenadora para un mantenimiento completo y eficiente.
Enfajadora CSK 40 F ERGON para botellas de PET en formato en película
• Máquina equipada con un sistema motorizado de guías oscilantes en la entrada, que facilita el correcto encauzamiento de los envases a granel sobre una banda transportadora con cadenas de material termoplástico de bajo coeficiente de fricción;
• Agrupamiento de los envases a granel en el formato deseado realizado de manera continua mediante pletinas y barras de separación sincronizadas electrónicamente;
Via Carlo Ceresa, 10 24015 San Giovanni Bianco (Bergamo) Italy
Tel. +39 0345 401 11 - Fax +39 0345 402 09 info@smigroup.it - www.smigroup.it
• Unidad de corte de película de diseño compacto, donde la cuchilla es accionada por un motor brushless de transmisión directa “direct-drive”, lo que hace más precisa la operación de corte y simplifica el mantenimiento;
• Nuevos motores ICOS, dotados de accionamiento digital (driver) integrado, que simplifican el cableado de la máquina y aseguran una mayor eficiencia energética, menor ruido y reducción del desgaste de los componentes;
• El túnel de contracción termal instalado en Bepensa cuenta con una cadena metálica y lubricación capaz de asegurar una mejor unión de la película por debajo del paquete;
• El túnel gestiona de manera eficiente y homogénea la distribución de los flujos de aire caliente sobre toda la superficie del paquete en formación;
• Consumos energéticos reducidos y máxima compatibilidad ambiental de los procesos productivos;
• Sistema opcional de ajustes automáticos para el cambio de formato;
• Máquina equipada con dispositivos adicionales opcionales para garantizar una alta calidad del paquete final, como la banda adicional de 1.150 mm dispuesta en la salida del túnel para el rápido enfriamiento de los paquetes.
Sistema automático de paletización APS 1570 ERGON
• Sistema monocolumna de dos ejes cartesianos, extremadamente flexible y fácilmente adaptable a las condiciones logísticas del área de final de línea;
• Sistema compuesto por diversos módulos configurables de forma personalizada según las necesidades de paletización;
• El paletizador instalado en Bepensa empaqueta los fardos en solo film, pero el sistema también es adecuado para la paletización de cartones, bandejas y paquetes en general;
• Reducción de costos de mantenimiento y bajos consumos energéticos, gracias a la simplicidad mecánica de la máquina y al uso de componentes de origen robótico;
• Sistema de automatización y control sencillo e intuitivo.
Via Piazzalunga, 30
24015 San Giovanni Bianco (Bergamo) Italy
Tel. +39 0345 40 400 info.smipack@smigroup.net - www.smipack.it
Beira Alta: Brazilian cosmetics. Quality, innovation, and sustainable packaging
Founded in 1969, Beira Alta Cosméticos is a Brazilian company based in Guarulhos, São Paulo state, that has established itself in the professional cosmetics industry. Located in one of Brazil’s most dynamic and industrialized regions, Guarulhos is part of the São Paulo metropolitan area, a city known not only as the country’s economic heart but also for its vibrant cultural and creative scene. Beira Alta’s wide range of products, ranging from hair treatments to skincare items, reflects a constant commitment to quality and innovation. In recent years, the company has embarked on an increasingly eco-friendly journey, adopting responsible practices throughout production, including the choice of more eco-compatible packaging solutions. With the support of SMI DO BRASIL, one of the SMI Group’s branches, Beira Alta Cosméticos has recently integrated two SMIPACK WPS 600R wrap-around case packers into its production lines. Wrap-around technology: Efficiency and environmental responsibility
Beira Alta Cosméticos choice of WPS 600R case packers is a concrete example of how companies in the beauty sector can combine production efficiency and environmental sustainability, responding to a market increasingly aware of the ecological impact of industrial processes. The WPS 600R wrap-around case packers allow products to be wrapped with extended cardboard, minimizing waste and reducing scraps. This technology allows for packing up to 25 packs per minute in compact spaces, working with micro-flute, corrugated, and kraft cardboard. The integration of these machines into Beira Alta’s production lines has enabled the company to enhance operational efficiency while promoting an eco-compatible packaging process.
WPS Series: Flexibility and sustainability for the beauty sector
The WPS series case packers offer numerous advantages for beauty sector companies:
1.- Efficiency and flexibility in automatic packaging
They combine automatic wrap-around technology with a storage capacity ranging from 300 to 900 cartons, optimizing production flow. Their design allows them to work with cartons of various sizes, making them a versatile option for packaging products of different shapes and volumes.
2.- Eco-friendly design and use of sustainable materials
Designed to use cartons of varying thicknesses, including eco-friendly options like kraft, these machines enable the use of recyclable and biodegradable materials, helping to reduce waste and the environmental impact of packaging.
3.- Smart automation and precise control
Equipped with the Flxmod® control system and a color touchscreen interface, as well as management through gear motors and servomotors, these packers offer high automation and precision, simplifying the management of the entire process. These features enhance safety and efficiency in the packaging line while reducing the possibility of errors that can lead to waste.
4.- Industry 4.0 compatibility
Being compatible with Industry 4.0 standards, the WPS machines enable companies to integrate their processes with advanced technologies such as the Internet of Things (IoT), optimizing production monitoring, management, and energy efficiency.
SMIPACK S.p.A. – Innovative and technologically advanced packaging solutions
Since 1997, SMIPACK S.p.A. has established itself as a leader in advanced and highquality packaging technology. The Italian company, a subsidiary of the SMI Group, offers a wide range of solutions including: shrink tunnel machines, L-sealers, flow pack systems, bar-sealing and film-launching shrink wrappers, and wrap-around case packers. The combination of innovative technologies, strong investment in research and development, and a constant focus on customer needs has enabled SMIPACK to produce over 4,300 units annually, becoming a global reference point. Its presence across various industrial sectors and its commitment to eco-sustainability highlight the company’s ability to offer versatile solutions, setting a new standard in the packaging industry.
BEIRA ALTA: cosmética brasileña. Calidad, innovación y packaging sostenible Fundada en 1969, Beira Alta Cosméticos es una empresa brasileña con sede en Guarulhos, en el estado de São Paulo, que se ha consolidado en el sector de la cosmética profesional.
Ubicada en una de las regiones más dinámicas e industrializadas de Brasil, Guarulhos forma parte del área metropolitana de São Paulo, una ciudad reconocida no solo por ser el corazón económico del país, sino también por su vibrante escena cultural y creativa.
La amplia gama de productos de Beira Alta —que abarca desde tratamientos capilares hasta cuidado de la piel— refleja un firme compromiso con la calidad y la innovación. En los últimos años, la empresa ha asumido una dirección cada vez más orientada hacia la sostenibilidad ambiental, adoptando prácticas responsables en todas las etapas de producción, incluida la elección de soluciones de empaque más ecológicas.
Gracias al apoyo de SMI DO BRASIL, una de las filiales del Grupo SMI, Beira Alta Cosméticos ha integrado recientemente dos encartonadoras automáticas wraparound modelo WPS 600R de SMIPACK en sus líneas de producción.
Tecnología wrap-around: eficiencia con conciencia ambiental
La elección de las encartonadoras WPS 600R por parte de Beira Alta Cosméticos es un claro ejemplo de cómo las empresas del sector belleza pueden combinar eficiencia operativa con responsabilidad ambiental, respondiendo a la creciente demanda de procesos industriales más sostenibles.
Las encartonadoras WPS 600R envuelven los productos utilizando cartón envolvente, lo que minimiza el desperdicio y reduce los residuos. Esta tecnología permite encajonar hasta 25 paquetes por minuto, ocupando un espacio reducido y trabajando con cartón microcorrugado,
Via Piazzalunga, 30 24015 San Giovanni Bianco (Bergamo) Italy
Tel. +39 0345 40 400
info.smipack@smigroup.net - www.smipack.it
ondulado o kraft. La incorporación de estas máquinas ha permitido a Beira Alta optimizar su productividad y adoptar un proceso de empaque más amigable con el medio ambiente.
Serie WPS: flexibilidad y sostenibilidad para la industria de la belleza
Las encartonadoras wrap-around de la serie WPS ofrecen múltiples ventajas para las empresas del sector cosmético:
1.- Eficiencia y flexibilidad en el encartonado automático
Combinan tecnología de envoltura automática con una capacidad de almacenamiento de cartones de entre 300 y 900 unidades, optimizando el flujo de producción. Su diseño permite trabajar con diferentes tamaños de cartón, lo que las hace ideales para productos de diversas formas y volúmenes.
2.- Diseño ecológico y uso de materiales sostenibles
Están diseñadas para utilizar cartones de distintos grosores, incluidas opciones ecológicas como el kraft, permitiendo el uso de materiales reciclables y biodegradables, lo que contribuye a reducir el impacto ambiental del empaque.
3.- Automatización inteligente y control preciso
Equipadas con sistema de control FLXMOD®, interfaz touch screen a color y gestión de componentes mediante motorreductores y servomotores, ofrecen un alto nivel de
automatización y precisión. Estas características mejoran la seguridad y eficiencia de la línea, y disminuyen errores que podrían generar desperdicio.
4.- Compatibilidad con los estándares de la Industria 4.0
Compatibles con los requerimientos de la Industria 4.0, permiten la integración con tecnologías avanzadas como el Internet de las Cosas (IoT), optimizando el monitoreo, la gestión de la producción y la eficiencia energética.
SMIPACK S.p.A. – Soluciones de empaque innovadoras y tecnológicamente avanzadas
Desde 1997, SMIPACK S.p.A. se ha posicionado como líder en el desarrollo de tecnologías de empaque de alta calidad. La empresa italiana, parte del Grupo SMI, ofrece una extensa gama de soluciones, que incluyen: selladoras tipo campana, angulares, sistemas flow pack, enfardadoras con barra de soldadura o film retráctil, y encartonadoras wrap-around.
La fusión de tecnología de vanguardia, una fuerte inversión en I+D, y una atención constante a las necesidades del cliente, han llevado a SMIPACK a superar las 4,300 máquinas producidas al año, consolidando su presencia global. Su participación en distintos sectores industriales y su firme compromiso con la sostenibilidad demuestran su capacidad para ofrecer soluciones versátiles que establecen nuevos estándares en la industria del packaging.
Via Mantova, 65 - 43122 Parma, Italy
Tel. +39 0521 490211 - Fax +39 0521 243701
zacmi.info@promachbuilt.com - www.zacmi.com
ZACMI: Advanced solutions for the food and beverage industry
Established in 1954, ZACMI (Zanichelli Meccanica) is an Italian industrial firm headquartered in Parma, specialising in the design and manufacture of filling and seaming machinery for the food industry
In 2024, ZACMI joined the ProMach Group—a global leader with over 50 brands offering solutions across the entire production line—further strengthening its position in the international market.
With a rich history of success, ZACMI is committed to delivering innovative and technologically advanced solutions tailored to meet customer needs and enhance production efficiency. The company’s highly skilled team is dedicated to providing top-tier service, embodying a forward-thinking vision that ensures clients receive optimal support
Machinery and solutions
ZACMI’s success is built on a foundation of extensive research and development, with the help of a highly specialized R&D department. Leveraging decades of expertise, the company offers a wide range of advanced machinery, from standalone units to fully integrated processing lines.
Filling
ZACMI’s filling machines are designed to deliver precision, efficiency, and versatility:
• Piston fillers: Perfect for accurately dosing liquid and viscous products, with or without suspended solids, ensuring uniform distribution and the total absence of dripping, thanks to a patented dosage system.
• Vacuum fillers: Airtight filling preserves product quality and freshness, ideal for topping up containers pre-filled with solid products or for completely filling containers with thick products.
• Telescopic fillers: Suited for rapid and precise filling of bottles, cans, and other containers, these fillers minimise waste while maximising efficiency. Their specialised design and instrumentation achieve the highest standards of filling accuracy.
• Monoblocks: Compact systems integrating rinsing, filling, and closing, optimising space and enhancing productivity.
Seamers
In 2024, ZACMI introduced a new seaming machine designed to improve industry standards. With a compact design, simplified maintenance, and reduced operational costs, this innovative seamer enhances flexibility and efficiency while maintaining ZACMI’s hallmark of robust
performance. Its modular design minimises downtime, simplifies spare part management, and ensures faster maintenance—setting a new benchmark in seaming technology.
Other standout models include:
• Clean design seamers: Fully washable systems that meet stringent hygiene standards, reduce handling costs, and facilitate maintenance.
• Vacuum seamers: Advanced solutions that prevent contamination, preserve product integrity, and extend shelf life.
Additionally, ZACMI seamers offer flexible configurations to adapt to specific customer requirements, ensuring highquality productivity.
One of ZACMI’s flagship solutions is the Synchronised Group, which combines a piston filler with a patented vertical valve and a high-performance seamer. Together, these machines operate in perfect harmony, achieving production speeds of up to 1,200 cycles per minute for the filler and 1,600 cycles per minute for the seamer. This system offers exceptional versatility, waste minimisation, and ease of maintenance, making it a standout solution for high-volume operations.
ZACMI also offers complete solutions for essential food industry processes, such as pasteurisation. The machines deliver precise thermal disinfection, eradicating harmful bacteria and microorganisms without compromising the product’s organoleptic properties. Advanced technology ensures energy efficiency and compliance with strict food safety standards.
ZACMI’s Global Service offers tailored support to customers worldwide, available both on-site and remotely through augmented reality tools. The services include smooth installation processes, proactive maintenance to prevent issues, and rapid-response troubleshooting, all aimed at minimising downtime and optimising machinery efficiency.
Customer Care Portal
The ZACMI Customer Care Portal is an innovative online platform designed to simplify customer support. Key features include:
• Access to detailed machine documentation, including technical manuals and schematics.
• Personalised remote assistance and real-time technical support.
• An online spare parts catalogue for easy and accurate ordering, with rapid delivery to minimise downtime.
This user-centric platform is designed to streamline operations, enhance productivity, and reduce costs, ensuring a seamless customer experience.
Global presence and trade fairs
ZACMI actively participates in the world’s leading packaging and food and beverage trade fairs, showcasing its cuttingedge technologies and engaging with industry professionals across the globe.
For over seven decades, ZACMI has delivered innovative solutions to meet the evolving needs of the food and beverage industry. By continuously investing in research, technology, and customer support, ZACMI has established itself as a trusted global partner.
For more information, please visit website: www.zacmi.com
ZACMI: Soluciones avanzadas para la industria alimentaria y de bebidas
Fundada en 1954, ZACMI (Zanichelli Meccanica) es una empresa industrial italiana con sede en Parma, especializada en el diseño y la producción de maquinaria de llenado y cierre para la industria alimentaria
En 2024, ZACMI pasó a formar parte del Grupo ProMach -líder mundial con más de 50 marcas que ofrecen soluciones para toda la línea de producción-, reforzando aún más su presencia en el mercado internacional.
Con un historial de éxitos, ZACMI se compromete a proporcionar soluciones innovadoras y tecnológicamente avanzadas adaptadas para satisfacer las necesidades de los clientes y aumentar la eficacia de la producción
El equipo altamente cualificado de la empresa proporciona un alto nivel de servicio, encarnando una visión de futuro que garantiza a los clientes una asistencia óptima
Maquinaria y soluciones
El éxito de ZACMI se basa en una amplia labor de investigación y desarrollo con la ayuda de un departamento de I+D altamente especializado. Con décadas de experiencia, la empresa ofrece una amplia gama de maquinaria avanzada, desde unidades autónomas hasta líneas de proceso totalmente integradas.
Llenado
Las máquinas de llenado ZACMI están diseñadas para ofrecer precisión, eficacia y versatilidad:
Via Mantova, 65 - 43122 Parma, Italy
Tel. +39 0521 490211 - Fax +39 0521 243701
zacmi.info@promachbuilt.com - www.zacmi.com
• Dosificadoras de pistón. Perfecta para dosificar con precisión productos líquidos y viscosos, con o sin sólidos en suspensión, garantizando una distribución precisa y un funcionamiento totalmente antigoteo, gracias a un sistema de dosificación patentado.
• Rellenadora al vacío. El llenado hermético preserva la calidad y frescura del producto, ideal para llenar envases prellenados con productos sólidos o para llenar completamente el envase con productos densos.
• Llenados telescópicos. Ideales para el llenado rápido y preciso de botellas, latas y otros recipientes, estas llenadoras minimizan los residuos y maximizan la eficacia. Gracias a un diseño específico y a la elección de las herramientas, la llenadora telescópica alcanza los más altos niveles de precisión de llenado.
• Monobloques. Las fases de enjuague, llenado y cierre están perfectamente integradas en estos sistemas compactos, optimizando así el espacio y maximizando la productividad.
Cerradoras
En 2024, ZACMI introdujo una nueva máquina cerradora diseñada para mejorar los estándares de la industria. Con su diseño compacto, mantenimiento simplificado y costes de explotación reducidos, esta innovadora cerradora aumenta la flexibilidad y la eficiencia, manteniendo al mismo tiempo el sólido rendimiento que caracteriza a ZACMI. Su diseño modular minimiza el tiempo de inactividad, simplifica la gestión de piezas y garantiza un mantenimiento más rápido, estableciendo un nuevo estándar en la tecnología de cierre.
• Cerradoras clean design. Sistema totalmente lavable que cumple las normas de higiene más estrictas, lo que reduce los costes de funcionamiento y facilita el mantenimiento.
• Cerradoras al vacío. Soluciones avanzadas que evitan la contaminación, preservan la integridad del producto y prolongan su vida útil.
Además, las cerradoras ZACMI ofrecen configuraciones flexibles para adaptarse a los requisitos específicos del cliente, garantizando una productividad de alta calidad. Tecnología del grupo sincronizado
Una de las soluciones estrella de ZACMI es el Grupo Sincronizado, que combina una dosificadora de pistones con una válvula vertical patentada y una cerradora de alto rendimiento. Juntas, estas máquinas funcionan en perfecta armonía, alcanzando velocidades de producción de hasta 1.200 ciclos/minuto para la dosificadora y 1.600 ciclos/minuto para la cerradora. Este sistema ofrece una versatilidad excepcional, minimización de residuos y facilidad de mantenimiento, lo que lo convierte en una solución excepcional para operaciones de gran volumen.
Procesos
ZACMI también ofrece soluciones completas para procesos cruciales de la industria alimentaria, como la pasteurización. Las máquinas garantizan una termodesinfección precisa, eliminando bacterias y microorganismos nocivos sin comprometer las características organolépticas del producto.
Las tecnologías más avanzadas garantizan la eficiencia energética y el cumplimiento de estrictas normas de seguridad alimentaria.
Servicio posventa y atención al cliente
Servicio mundial
El Servicio Global de ZACMI ofrece a los clientes de todo el mundo asistencia personalizada, disponible tanto in situ como a distancia mediante herramientas de realidad aumentada. Los servicios incluyen procesos de instalación sin complicaciones, mantenimiento proactivo para evitar problemas y rápida resolución de problemas; todo ello para minimizar el tiempo de inactividad y optimizar la eficiencia de las máquinas.
Portal de atención al cliente
El Portal de Atención al Cliente de ZACMI es una innovadora plataforma en línea diseñada para simplificar la atención al cliente. Las características principales son:
• Acceso a documentación detallada de la máquina, incluidos manuales técnicos y hojas de datos.
• Asistencia remota personalizada y soporte técnico en tiempo real.
• Catálogo de piezas de repuesto en línea para pedidos fáciles y precisos, con entrega rápida para minimizar el tiempo de inactividad.
Esta plataforma de usuario está diseñada para mejorar las operaciones, aumentar la productividad y reducir los costes, garantizando una experiencia de cliente sin complicaciones.
Presencia mundial y ferias comerciales
ZACMI participa activamente en las principales ferias mundiales de envasado y alimentación y bebidas, aportando sus últimas tecnologías e interactuando con profesionales de todo el mundo.
Durante más de setenta años, ZACMI ha proporcionado soluciones innovadoras que satisfacen las necesidades cambiantes de la industria de alimentación y bebidas. Gracias a su continua inversión en investigación, tecnología y servicio al cliente, ZACMI se ha consolidado como un socio global de confianza.
Para más información, visite www.zacmi.com
“ANTI-STICKING”
Coating recommended for elastomer polymer and rubber injection moulding
ITALIAN TECHNOLOGY FOR THE BEVERAGE INDUSTRY TECNOLOGÍA ITALIANA PARA LA INDUSTRIA DE BEBIDAS