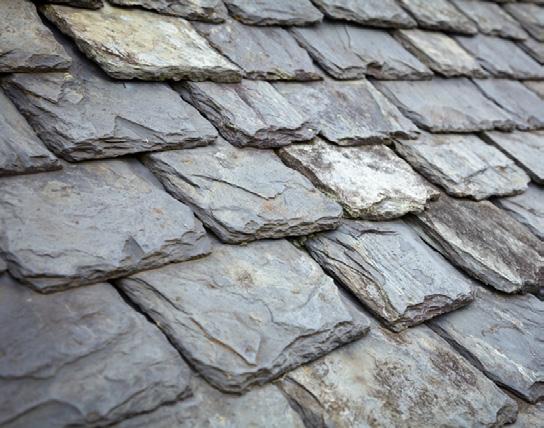
4 minute read
Technologies Position
Architectural Design Position & Technical Detail Study Purpose
Design Position
Advertisement
solid wall construction
My design position explores the reuse and conservation of existing Grade II listed structures & buildings. I want to be respectful to its materials and fabric. The redundant buildings form the backbone for the scheme whilst the new build is the heart of the structure. The main objective is to establish or test how to create a warm, dry and well ventilated environment between these two main elements i.e. the new and the old. The new extension will be a glass box that will house the equipment used in the distillation process which creates a lot of heat. So it is extremely important that there are controls and strategies in place so that the internal environment is kept at a constant and bearable temperature. Also, I chose glass as it would juxtapose the existing materials on site, which is preferred by conservationists currently.
Technological Responses
Climate Change
Exisitngbuilding Newbuild
Technological Artefacts
MATERIALS
My key choices of materials are:
GL ASS
Aesthetic appeal, allows for natural lighting which reduces the environmental impact of lighting systems, durable, sustainable, energy efficient and 100% recyclable.
TIMBER
Attractive, long lasting, natural, recyclable, durable, ensured to not be contributing to global forest destruction, PEFC (Pan European Forestry Certification) or SFI (Sustainable Forestry Initiative) also applicable.
SL ATE Durable, low maintenance, ecofriendly, recyclable, naturally insulating, non-porous and has a relatively low carbon footprint.
ALUMINIUM
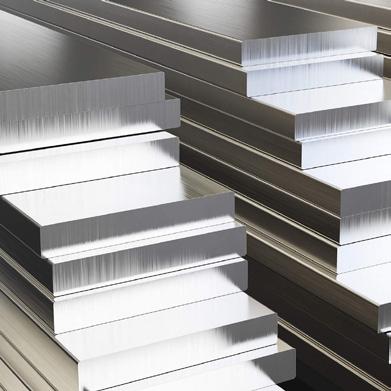
Recyclable, durable, lightweight, energy efficient, can withstand harsh weather conditions, resistant to corrosion, non-combustible and high fire resistance.
CONCRETE Long-lasting, high thermal mass (important in regulating internal environments), low maintenance and energy efficient.
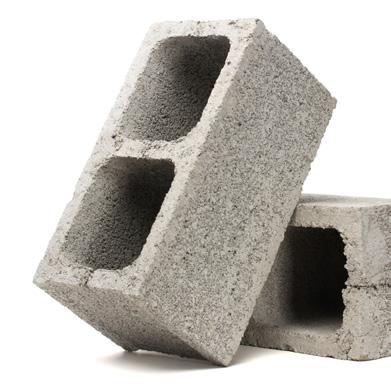
SIPs Energy efficient, fast construction, cost-effective, reduced waste, flexible and is made from renewable materials which can be recycled.
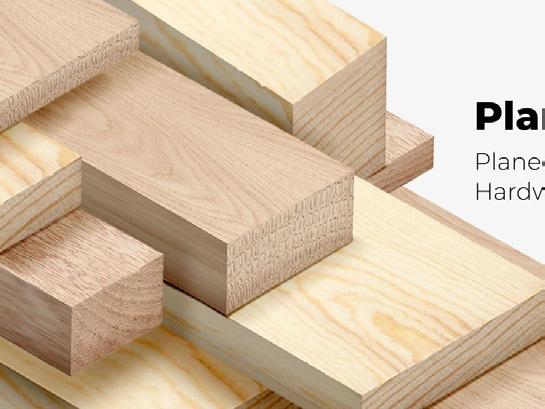
In addition to this, I will be looking at the thermal properties of various insulation materials. Consideration may be given to natural products such as granulated paper, hemp and the use of either vacuum or air cool façades.
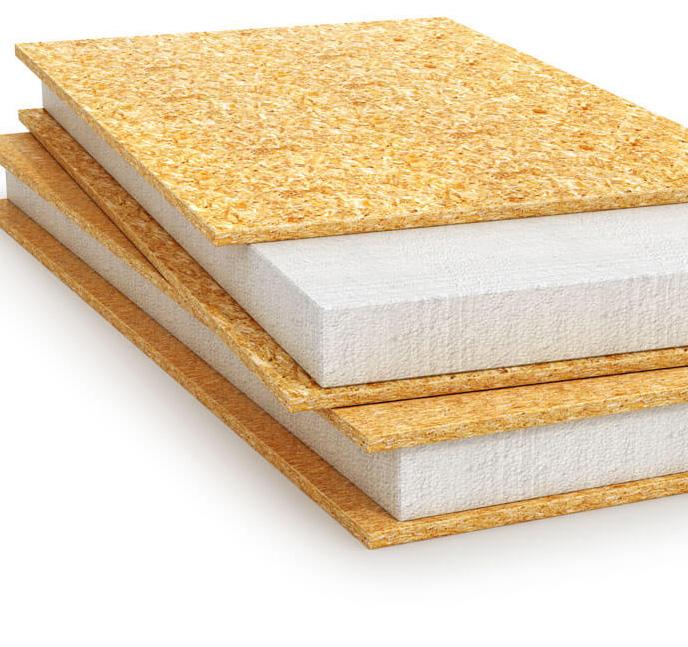
In light of climate change, the reuse of existing buildings holds significant value as it reduces the carbon footprint associated with new material production and construction. This approach entails utilizing at least 30% of existing materials on site. To enhance the buildings’ performance, retrofit measures such as improved insulation, the use of low carbon materials, and upgrading fenestration are incorporated. Manchester’s natural climate, with an average humidity of 70%, proves advantageous for both the malt conversion process and the barrel storage. My intervention involves constructing a new glass building between the two existing buildings. To create a suitable internal environment that is warm and dry, a buffer zone is necessary. Achieving this with the lowest possible carbon footprint is my goal. My strategy encompasses carefully selecting facade materials and insulation for the buffer zone, utilizing a heat source pump to warm the stills, and

BUILDING & LIFE SAFETY
The principle designer role is to look at these elements in order to meet the construction CDM regulations of 2015. The amount of in pre-construction information should be sufficient to ensure that risks can be anticipated.
Constructibility
In order to construct the building in the most efficient manner to the Latham report where recommendations were made to utilise modern methods of construction (MMC). The recommendations included using off-site manufacture to minimise on-site works so that the more higher risk elements, like working with toxic and dangerous materials, heat and at height , can be performed in an controlled internal environment. I have looked at how we can use elements like SIPs, cassettes of facade materials and pre-fabricated components such as roofing to arrive in panels, and then be interconnected and interlaced on site. The majority of the works for the new build elements will be manufactured in this way where our requirement for site works will be minimised to the work for the foundations and floor slabs alone. Examples of this include new housing schemes as well as the roll out schemes by McDonalds.
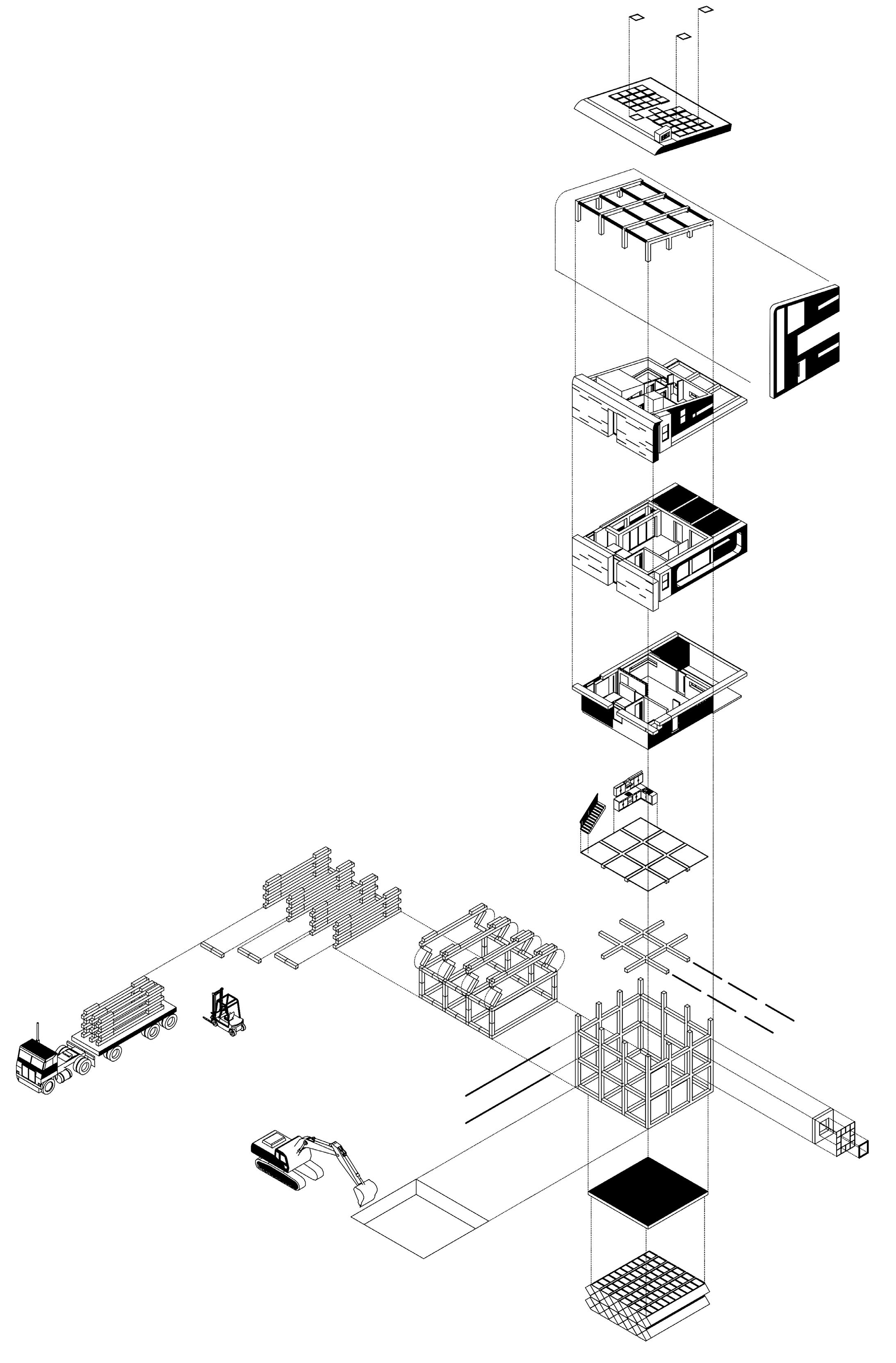
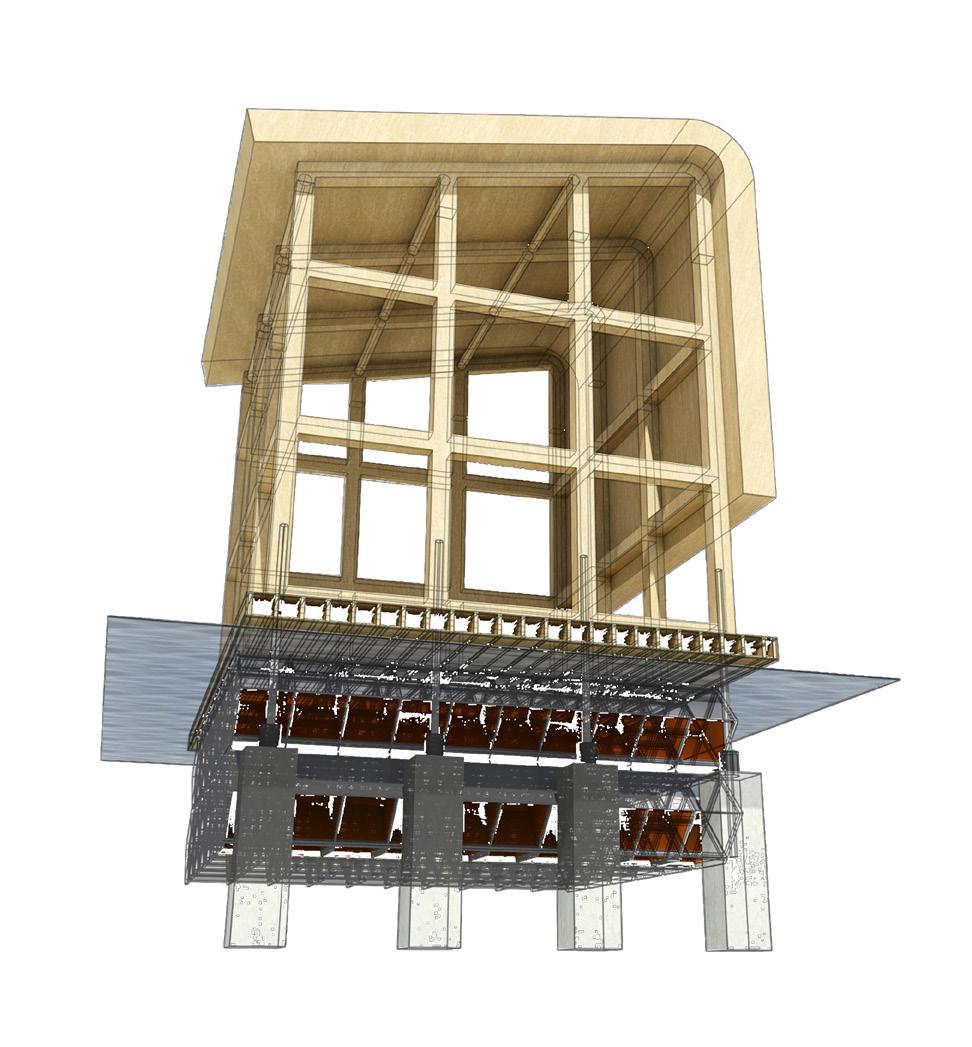
Construction process:
1. Loading from factory
2. Delivery of off-site materials
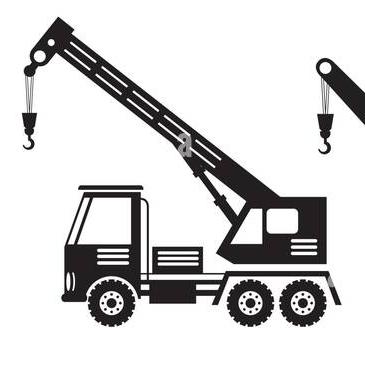
3. Assembly of pre-fabricated elements
4. Assembly of interconnecting components
5. Fixed elements (stairs & equipment)
6. Primary internal finishes e.g. walls
7. Secondary internal finishes e.g. ceilings
8. Plant (air handling unit - M&E equipment)
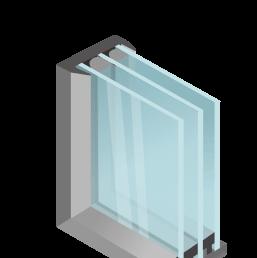
9. Roof structure
10. Lay roof on top
11. Apply external cladding
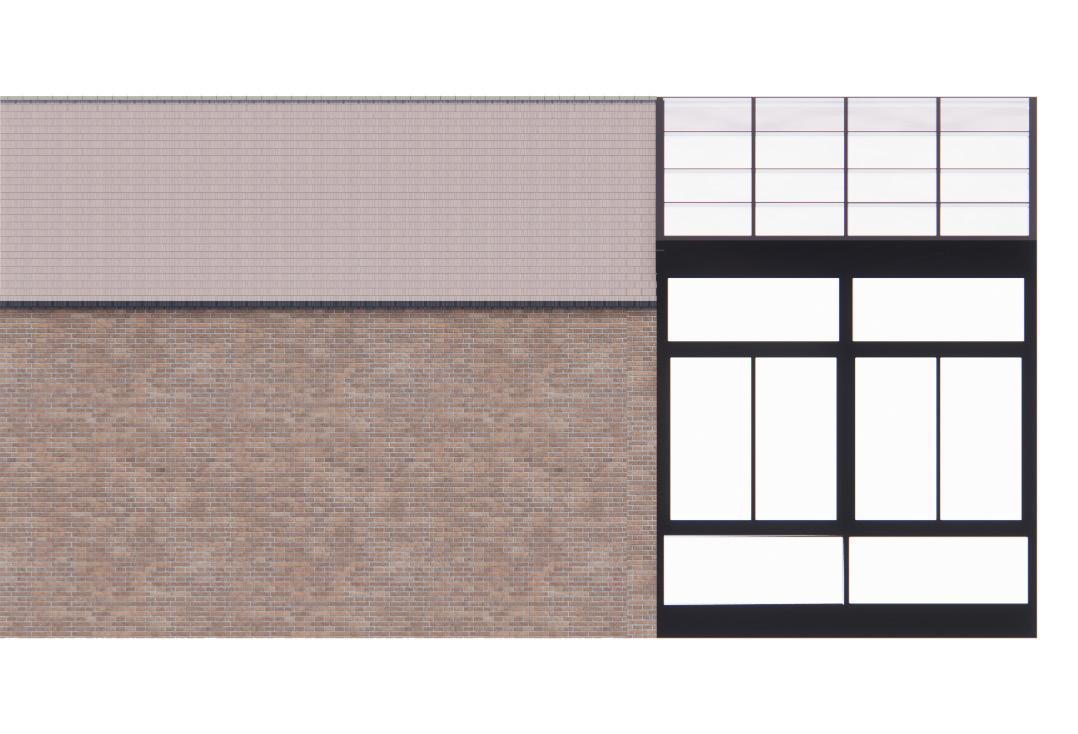
Site works:
A. Ground work
B. Foundation slabs
C. Floor slabs
D. Primary structure employing an air handling unit to distribute air, heat, and excess moisture throughout the site as needed. Water will be drawn from on-site ponds, serving as balance pools and supplying water for the whiskey process. This minimizes reliance on external energy sources, thus increasing carbon efficiency. However, it’s important to acknowledge that the distillation process itself generates CO2 and other by-products (not considered in this analysis). The buffer zone’s primary purpose is to establish a controlled environment within the distillation area, necessitating the selection of locally produced materials with low carbon footprints. When materials with higher carbon footprints are unavoidable, they will be employed only to offset the overall carbon impact of the construction.
Spider cranes, also known as mini cranes or compact cranes, are versatile machines used in glass construction. They are compact and can access tight spaces, making them suitable for manoeuvring glass panels in challenging areas or indoors.
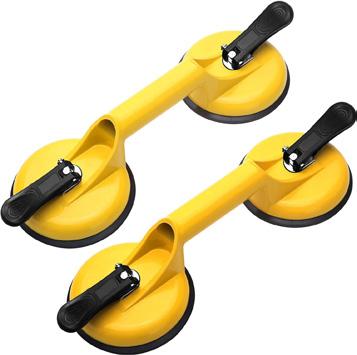
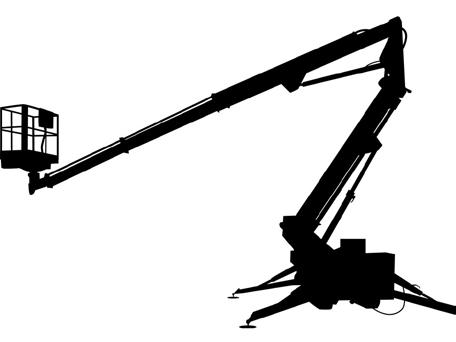
Aerial work platforms, such as scissor lifts or boom lifts, are utilized for glass installation at elevated heights. These platforms provide a stable and secure working surface for workers to install glass panels with ease.
Processes
Glass transport trailers are specialized trailers designed to transport large glass units. They often have adjustable racks, protective padding, and securing mechanisms to ensure the safe transportation of glass panels from the manufacturing facility to the construction site.
Caulking guns used to apply sealants and adhesives around the edges of glass panels to create a watertight and airtight seal. They help in ensuring the structural integrity and weather resistance of the glass building.
The fragment I am exploring forms a buffer between the existing buildings and enables that to be reused efficiently, therefore extending its life cycle whilst also improving its current U-value, energy usage etc. The biggest benefit to the circular economy of this scheme is the reuse of the existing buildings, thus maximising the benefits from reduced waste, carbon footprint and use of natural resources. We benefit from pre-fired clay from the bricks etc. - essentially. The materials that we are adding to the existing building are to be sourced from both ethical and carbon neutral sources where possible.
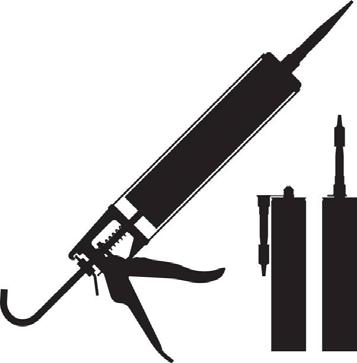