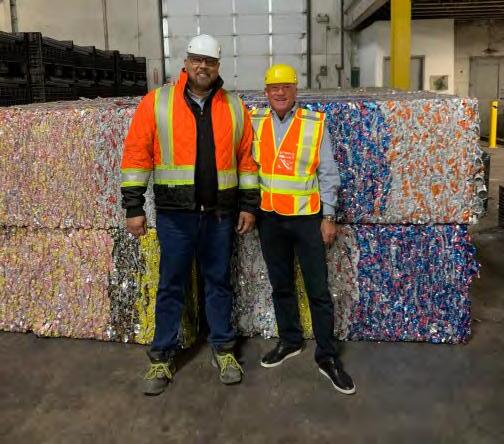
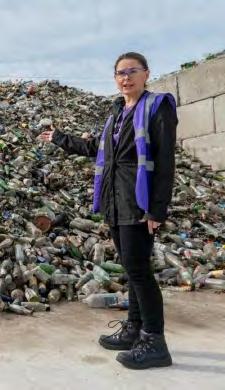
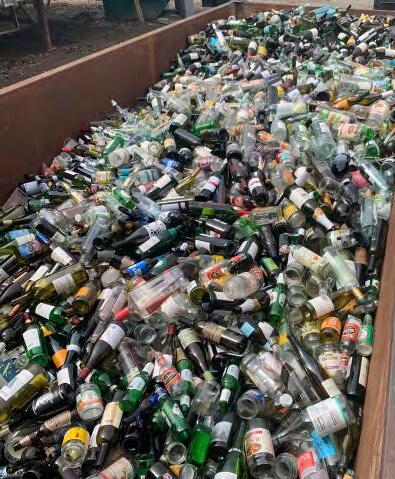
In 2022, we held ourselves to a higher standard with tangible goals in our product quality, creative collection methods and customer commitment. To that end, I’m proud of our glass warriors for holding their cullet quality acceptance rate to 99.95%, seamlessly integrating the Ripple Glass collection method into our portfolio and prioritizing our entire customer base as evidenced by our prestigious Supplier of the Year Award from fiberglass insulation leader Owens Corning.
These achievements are admirable, but we recognize the need to set the bar even higher. The U.S. recycling recovery rate for glass is about one third nationally, a robust recycling infrastructure is underdeveloped in Mexico, and opportunities to recycle more materials in Canada is within our reach.
Our focus is keenly on diverting more materials from the landfill benefiting our people, partners, and planet.
People: By optimizing our operations with better sorting technology and investments at key facilities, we increase efficiencies, improve work environments, and support communities where we operate. We are investing in the basics at all levels of the organization to not only create an enjoyable work environment for new and existing glass warriors, but also, to better educate how their work matters. We are focused on more training hours and maintaining our recordable rates well below industry averages.
Partners: We drive increased recovery for the entire value chain by innovatively solving complex challenges in glass collection and processing –there is not a one-size-fits-all solution when it comes to glass recycling. We recognize the need to be nimble. We are continuing our research & development for opportunities with new partners to accept new streams of glass for recycling.
Planet: As demand for furnace-ready recycled glass (cullet) in end markets reaches an all-time high, efforts to divert glass from landfill and return to the circular economy is vital for the industry and our planet. We are ready to help.
As an environmental leader, our mission is unwavering and simple: leave our planet better than we found it for generations to come.
Because of our glass warriors in 2022 we:
• Save nearly 2,177,794 tons of glass, plastic, aluminum and cardboard from the landfill
• Reduce more than 327,383 metric tons of CO2 emissions, a greenhouse gas directly linked to climate change. That’s roughly 391 metric tons of CO2 reduced per SMI employee
• Divert roughly 2.5 billion glass bottles from the landfill
Our success as a company is attributed to the talent and passion of our people. Cheers to another year of progress and our best days lie ahead!
CHRIS DODS PRESIDENT & CEOAs an environmental leader our mission is unwavering and simple: leave our planet better than we found it for generations to come.
Sherry D. Williams joined the company in January 2021 and previously served as vice president, deputy general counsel and global chief compliance and ethics officer for Jabil (NYSE: JBL), an American worldwide manufacturing services company, and as senior vice president and chief ethics and compliance officer for Halliburton Company, one of the world’s largest oilfield service companies.
Outside of SMI, she serves on the Board of Directors for several non-profit organizations, including Brown Girls Do Ballet, which promotes diversity in the arts by providing annual scholarships, a mentor network and community programs to empower young girls.
At SMI we act with integrity in all our dealings. The company has made considerable strides in the way we do business and how we treat others.
• TRIR was reduced by 43%
• Reduced workers’ compensation expenditures by 60%, with 20 fewer recordable injuries and an average reduction in medical costs of $5,000 per injury
• Production labor wages increased 12%
The key to our improvements have been the environmental, health and safety team partnering more closely with human resources to jointly focus on providing access to learning tools, effective safety training and continuous improvement.
No one is exempt from the values, policies and rules that govern our business. We will do the right thing, always.
At SMI we act with integrity in all our dealings. The company has made considerable strides in the way we do business and how we treat others.
Over the past year, we’ve developed and implemented robust policies and plans to ensure our corporate compliance is top tier. One example I’m proud of is our revised Code of Ethics & Business Conduct, which was finalized and publishing in both English and Spanish in 2023.
Our compliance focus has resulted in:
• Legal spend savings of 62.7% from the previous year
• 0 incidents of corruption
Whether you’re an employee of SMI or a third-party partner, if you see something, say something. Any inappropriate behavior or actions should be reported through our anonymous hot line, 1-877-217-4681.
We have made incredible progress in the last two years of my tenure. I’m looking forward to sharing our accomplishments in the future.
Beautiful recently dedicated the newly installed mosaic art column “Serenity” in Gastonia, North Carolina. Our SMI facility in Wilson, NC, was honored to donate all the recycled glass material to the project!
99.95%
QUALITY ACCEPTANCE RATE
GREENHOUSE GAS EMISSIONS AVOIDED
327,383
METRIC TONS
2,518,300,000 BOTTLES DIVERTED FROM LANDFILL
$155,020 CHARITABLE CONTRIBUTIONS
HAZARDOUS WASTE RECYCLED
PROGRAM BEING EXPANDED TO INCLUDE ENHANCED ONBOARDING, NEW IMPROVED UNIFORMS, AND A MILESTONE RECOGNITION PROGRAM
TRAINING HOURS
OWENS CORNING SUPPLIER OF THE YEAR AWARD
Strategic Materials, Inc. (“Strategic Materials”, “SMI”, or the “Company”) is proud to publish this 2022 report highlighting the Company’s commitments, progress, and initiatives within each of our focus areas: People, Partners, Planet. SMI has identified these themes to reinforce the commitment to sustainability practices and purpose, mission, and values.
This report describes the Company’s impacts based on the most material topics as identified via a materiality analysis conducted in 2022. The materiality analysis consisted of industry research and stakeholder engagement efforts including interviews with senior leadership and a materiality survey distributed to employees, suppliers, customers, and recycling organizations. The results of the stakeholder engagement efforts highlighted the societal and environmental topics that SMI impacts most.
Information and data collected for this report were consolidated across each location through centralized databases in the United States, Canada, and Mexico.
Strategic Materials, Inc. has reported in accordance with the GRI Standards for the period from 1 January 2022 to 31 December 2022.
This report was published on July 2023.
For questions about this report, contact: info@smi.com
With over a 125-year history, Strategic Materials Inc. (SMI) is North America’s most comprehensive glass recycler. SMI is a privately held company headquartered in Houston, Texas, USA, and is comprised of 46 locations in the United States, Canada, Mexico. The company continues to be focused on operational excellence and collaborative partnerships.
SMI is a trusted advocate for cleaner and more efficient glass production, providing customers with economical and environmentally viable solutions for recycling.
Container: Food & beverage containers are made from materials that include sand, soda ash, limestone and recycled glass (cullet).
Fiberglass Insulation: Use of cullet by fiberglass insulation manufacturers continues to rise each year.
Highway Bead: Cullet offers a more cost-effective alternative to virgin glass in highway bead manufacturing.
Crushed Glass Abrasives: Crushed glass is manufactured for the surface preparation industry under the trade names TruAbrasives ® and WhiteBlast®
Decorative Glass / Glass Aggregate: The leading U.S. manufacturer of glass aggregate for decorative uses such as countertops, terrazzo flooring, landscaping, fire pit glass under the American Specialty glass trade name.
Construction: Supply recycled glass feedstock to light-weight foam glass and concrete manufacturers
Plastics: Nexcycle, a SMI company, recycles select post-industrial plastics in Canada.
Purpose: We recycle glass to unite the interests of our people, our partners, and our planet.
Mission: Through the passionate advocacy, operational excellence, and collaborative partnership, we recycle glass for the world.
See Through the Customer’s Eyes
Internal: Support each other to serve the customer
External: Listen actively, act in the customer’s interest
Integrity Guides Every Decision
Internal: Work to earn teammates’ respect and trust everyday
External: Honesty and accountability lead to strong relationships
Be Passionate About the Progress We Make
Internal: Focus on our goals for each other, our customers, and the planet
External: Care deeply about the outcomes
Embrace and Drive Change
Internal: Commit to finding better ways
External: Accept the challenge to think differently
Create Positive Energy
Internal: Find joy in our journey
External: Be the partner with whom customers want to work
Created in 2021, the SMI sustainability committee continues to drive the Company’s sustainability efforts, monitor progress, and create new opportunities for the company to expand sustainability practices. Overseen by President and CEO, Chris Dods, the sustainability committee is responsible for maintaining and implementing the sustainability plan focused on delivering meaningful changes to business initiatives connected to SMI’s material topics. The cross-functional sustainability committee was created to implement sustainability initiatives as well as track progress toward goals, targets, and aspirations. The committee is comprised of senior management across the organization, representing the following business functions: Human Resources, Finance, Environmental, Health and Safety (EHS), Communications, Quality, and Procurement.
• Plan, execute, and manage sustainability initiatives
• Enhance organizational understanding of sustainability and ensure stakeholder buy-in through all levels of the company
SMI’s senior leadership team (SLT) functions as the company’s highest governance body and is comprised of a crossdisciplinary team of eight leaders who provide strategic and operational direction to the company. The SLT is responsible for the development, approval, and update of SMI’s purpose, value statement, mission statement, strategies, policies, and goals related to economic, environmental, and social topics.
The SLT is equipped to lead the Company into a sustainable future due to its vast background in material recycling, waste processing, business management, and sustainability. The SLT is selected and hired into strategic positions based on qualifications regarding education, prior experience, core competencies, and leadership ability. The team’s effectiveness is monitored by regular, internal, self-assessments.
To further drive the company’s commitment to sustainability a new position was created for the company: Senior Vice President of Sustainability and Corporate Affairs. The Company appointed its very own Laura Hennemann, who previously held Vice President of Marketing and Communications role during her six years with SMI. Before joining the company, Hennemann held positions with Harsco Environmental, a $1B division of Harsco Corporation (NYSE: HSC), supporting post-industrial by-product management and commercialization in 32 countries.
The Senior Vice President of Sustainability and Corporate Affairs leads the company’s sustainability, inbound material (supply), marketing & communications, and government affairs departments, reporting to President and CEO Chris Dods.
“I am honored to step into this position. I’ve been passionate about sustainability and mission-driven work since a very young age. Although the company is arguably one of the first environmental leaders in the U.S., the level of importance given to these initiatives today is inspiring.”
—Laura Hennemann , SVP Sustainability & Corporate Affairs
In 2021, SMI engaged stakeholders to identify the topic areas with the largest impact on society and the environment. As part of this engagement, SMI conducted 18 interviews and analyzed 143 responses from an administered materiality survey engaging senior leadership, employees, suppliers, customers, and recycling organizations. The results of this assessment were analyzed to better understand the concentration areas of SMI impacts or with the potential to impact most significantly.
In 2022, SMI conducted a review of the previously defined material topics and identified Diversity, Equity, and Inclusion (DEI) as a topic area which merits additional focus and resources. Therefore, the Company added DEI to the list of material topics. In the upcoming years, SMI will be refreshing the materiality assessment to ensure focus is maintained on the most important material topics and properly assessing the impact on internal and external stakeholders.
The material topics drive the company’s sustainability goals and create ownership of those goals with the appropriate members involved. SMI will continue to use material topics to refine and continuously improve sustainability aspirations and quantitative targets.
PEOPLE: Employee health and safety, ethics and integrity, diversity, equity and inclusion, and employee engagement.
PARTNERS: Customer service, product offering and scale and quality.
PLANET: Recycling and material recovery, waste generated and diverted, and GHG emissions.
Stakeholder engagement is integral to SMI’s sustainability strategy and business. Providing regular, transparent communication with employees, customers, trade associations, suppliers, investors, regulators, and communities is part of every day life. Communication is disseminated through newsletters, social media, memos, monthly meetings, and the annual sustainability report.
Continuing to strengthen connections with stakeholders in the communities where the company operates with proactive communications from local team members is valuable. The company shares regular updates to keep stakeholders informed on significant developments and to encourage interactions with the company.
As a special initiative of the UN Secretary-General, the United Nations Global Compact is a call to companies everywhere to align their operations and strategies with ten universally accepted principles in the areas of human rights, labour, environment and anticorruption, and to take action in support of UN goals
SMI is committed to making the U.N. Global Compact and the Ten Principles part of its strategy, culture, and day-to-day operations, and to engage in collaborative projects that advance the broader development goals of the United Nations, particularly the Sustainable Development Goals (SDGs).
The company recognizes a key requirement for participation in the U.N. Global Compact is an annual submission of a Communication on Progress (CoP). SMI supports public accountability and transparency and commits to reporting annually on company progress. This report is intended to serve as SMI’s CoP.
Icon image credit: U.N. Global Compact Guide to Corporate Sustainability
Principle 1: Support and respect the protection of internationally proclaimed human rights.
Principle 2: Ensure that business practices are not complicit in human rights abuses.
Principle 7: Adopt a precautionary approach to environmental challenges.
Principle 8: Conduct environmentally responsible activities.
LABOR
Principle 3: Uphold the freedom of association and the effective recognition of the right to collective bargaining.
Principle 4: Eliminate all forms of forced and compulsory labor.
Principle 5: Abolish child labor.
Principle 6: Eliminate discrimination in employment and occupation.
Principle 9: Encourage the development and diffusion of environmentally friendly technologies.
Principle 10: Fight corruption in all its forms including extortion and bribery
The United Nationals (UN) General Council declared 2022 the International Year of Glass through the approval of a joint application by the International Commission on Glass (ICG), the Community of Glass Associations (CGA), and ICOM-Glass. The year celebrates the essential role glass has in society. Kicking off the celebration was an opening ceremony in February, featuring 30 world-class speakers who highlighted the latest thinking on how glass can aid the development of more just and sustainable societies, the most recent scientific and technical breakthroughs, its influence on art and history, and finally, the role of museums.
The International Year of Glass was a result of scientists’ and industry leaders’ advocacy for the use of glass and its direct support of the UN Sustainability Development Goals. As part of their support, advocacy groups cited lifesaving medical care, integration with clean energy, and reducing carbon emissions as examples of how glass can advance a more sustainable world.
SMI is a proud supporter of this initiative and shared its mission with stakeholders through communications platforms.
The United Nations Sustainable Development Goals (“SDGs” or the “Global Goals”) were created by the United Nations in 2015 to help advance sustainable development practices across the world. SMI is a strong advocate in supporting the global community to reach these aspirational goals. SMI’s sustainability practices are aligned with and in support of the SDGs.
Recycling glass provides a workforce that extends the life of glass and critically supports the entire value chain. SMI has an environment where this workforce is provided with safe, humane, working conditions – providing decent work and economic growth.
Glass pushes industries forward - from serving as a container for life-saving medications to creating the most resilient buildings, glass has been the driving force behind these innovations. SMI supports this goal by providing cullet to customers who responsibly manufacture new products. Example: The Baltimore Aquarium project on page 30.
Industries that consume recycle glass are participating in responsible consumption because glass can be recycled endlessly, and does not pose a health risk to employees, consumers, or wildl ife. Recycled glass also provides an opportunity for responsible prod uction compared to virgin glass. Manufacturers who use recycled glass reduce their greenhouse gas emissions, since less energy is used in melting the glass. SMI contributes by providing material to markets for m ore responsible and sustainable manufacturing.
Climate change is the code red warning for humanity, as described by the United Nations. However, glass is shattering how we think about it. Glass is creating processes that are more environmentally-friendly, products that can have an infinite life cycle, and reducing consumption and waste. SMI’s cullet is taking climate action in fiberglass insulation market by creating a product that reduces consumer energy consumption, and similarly in the container market by creating a more sustainable process and reusable product for customers. SMI employees are also taking climate action by attending conferences, events, and producing media that engage the public and policymakers. Read more about how SMI is engaging in climate action on page 38.
Glass is inert. Glass will not leach into the product it’s holding an d will not leach into waterways, should it end up in streams. Unlike a m aterial like plastic, wildlife will not ingest glass. Over time, glass will degr ade back to sand. Glass is a great alternative to other materials for the se reasons and SMI works to educate and motivate others to choose glass to help protect the environment.
Glass recycling brings communities together and gives ownership of an individual’s impact on climate action - some even go beyond and can be used as a source of education and highlight the beauty within the community. Example: Ripple Glass art bins on page 34, and the Gastonia, NC, art installation on page 36.
Glass brings people together, through art, design, and history. Glas s is a part of each person’s everyday life. SMI creates meaningful, sustain able partnerships with customers, suppliers, employees, and the public to achieve the Sustainable Development Goals.
Employee health and safety continues to be the number one priority for SMI. Overseen by the environmental health and safety (EHS) Director, all employees are covered through the company’s health and safety management system, policies, and actions. Therefore, no employee is excluded from being protected on the job. Additionally, all full-time employees are offered health benefits packages.
SMI performs routine facility assessments and internal safety audits as a critical measure in identifying potential safety hazards in the workplace; Additionally, SMI conducts a job safety analysis audit (JSA) annually; And completes facility assessments at each location at least once per year; All employees are actively encouraged to report any potential workplace hazards to their supervisors or plant managers.
In 2022, the environmental health and safety team introduced an enterprise tracking system to document recordable incidents, assign tasks, and monitor compliance within each facility. Furthermore, the new system allows for consolidated and standardized root cause analysis. This, along with the additional monitoring and reporting opportunities, has been instrumental in the identification and management of workplace hazards across all locations.
The adoption of a new safety systems provides the ability to analyze safety performance data and target the most impactful prevention strategies. The main types of work-related injuries in SMI’s operations include puncture, strain, and caught-in or between injuries. SMI works mitigate more
frequently occurring injuries by providing appropriate training and personal protection equipment.
SMI set an annual target for total recordable incident rate (TRIR) under 1.25. This meant a 1.4 reduction in 2022 compared to 2021. The company fell short of the goal by .25 but it still impressive progress of a 43% reduction. The strides made across the health and safety of SMI operations is admirable and will continue to improve safety metrics in future years and in part, with help from the newly implemented tracking system and additional safety initiatives.
To maintain and strengthen high ethical standards, SMI created an ethics training program for employees which emphasizes the importance of business ethics and integrity in the workplace.
Additionally, SMI has developed an updated Code of Ethics and Business Conduct with enhancements to integrity and safety. These improvements provide more concise guidance on preventing integrity breaches and reporting them if they do occur. The updated Code is set to be distributed across all SMI employees in mid-2023.
SMI maintains an anonymous whistle-blower hot line for all stakeholders to report incidents of wrongdoing and noncompliance. Any reported incidents are reviewed and appropriately handled by the human resources department. The hot line promotes accountability and ensures stakeholders have a mechanism to report ethical concerns.
All ethics and integrity matters are overseen by the Chief Legal Officer and Senior Vice President of Human Resources.
In conjunction with the Company’s commitment to the Ten Principles of the UN Global Compact, SMI complies with all laws regarding freedom of association, privacy, collective bargaining, immigration, work hours and wages, forced, compulsory, and child labor, human trafficking, corruption, and discrimination.
SMI strives to ensure employees feel valued and engaged at work Employee ownership of work helps to uphold a shared mission. Employee engagement programs and initiatives are implemented and monitored by the human resources and communications teams and are overseen by the sustainability committee.
SMI provides employees with biannual performance reviews that measure employees’ performance toward goals determined at the beginning of each year by employees and their managers. These goals are tied to corporate strategy, safety, and sustainability goals. Employee reviews serve as a way to evaluate pay increases and promotions while providing feedback on performance.
Employees are also encouraged to submit an annual satisfaction survey, where they can provide feedback on compensation and benefits, health and safety, job satisfaction, career training and advancement, and management’s performance. The company
utilizes this information to implement meaningful changes to better support glass warriors on and off the job. The results of the survey are reviewed by the human resource department.
The “buddy” program established last year has successfully carried into 2022. The initiative provides new employees with a senior team member as their mentor for onboarding. The program enhances the leadership skills of the mentor and improves acclimation for the mentee. It is a important contributor to improving employee retention and safety metrics while making the employee feel welcome and included.
In 2023, SMI plans to carry out an employee parental leave policy and define an employee engagement council that will be comprised of employee representatives across facilities. The council will meet to discuss potential improvement opportunities in areas like diversity, equity, inclusion, health, safety, and overall employee engagement.
As a result of increased attention and programming, SMI has seen an improvement in employee turnover rates. Compared to 2019, SMI has realized a 25% reduction in annual turnover rate.
SMI Indianapolis, IN: The SMI team in Indianapolis enjoy participating in quarterly raffles and cook-outs, celebrating overall team attendance, going above and beyond expectations, and most importantly, being safe. Pictured: Plant Manager, Joe Merchant, and team Employee Education: President of Latin America operations, Javier Lopez-Portillo, graduated from the University of San Diego with a Master of Science in Global Leadership. Javier has been with SMI since April 2018 and maintained a commitment to the company while earning his degree. He is responsible for developing and growing Mexico and Latin American operations, as well as building and maintaining relationships with customers and suppliers. Congratulations, Javier!
CONTINUED
Volunteering in Ukraine: Alexander John, embodies what it means to be a glass warrior. Before joining the SMI team in 2017 and becoming a supervisor at our Ashland City, TN, plant, he served in the U.S. Army as an 11B and was stationed at 101st 1-502 C Company. During the initial conflict in Ukraine in early 2022, Alex took time off at SMI to volunteer in Ukraine as a humanitarian, helping set-up a field hospital in Kiev. He also helped train locals in the area in combat first aid. When asked why he decided to go, he stated, “I served because I wanted to do something bigger than myself. I wanted to help.” SMI is inspired by veterans like Alex, today and every day.
743 Full-time Employees
2 Part-time Employees
93 Temp Employees
SMI creates a workplace where every employee feels valued and accepted. The Company’s Diversity, Equity, and Inclusion (DEI) goals, initiatives, and metrics are implemented and monitored by the human resources team and overseen by the sustainability committee. SMI is a second chance and equal opportunity employer.
Several new initiatives were introduced in recent years to create a more diverse and inclusive workplace, where employees feel empowered to express themselves. Some examples include an interview requirement, mandating a female employee be present during all operational-level interviews to prevent unconscious bias and a formal opportunity for all employees to express preferred pronouns within email signatures. Additionally, SMI conducted a pay equity assessment that will be presented to leadership to determine the next steps in closing the gender pay gap.
SMI spotlighted glass warriors in honor of Hispanic Heritage month throughout September and October. These highlights acknowledged employees from across our company and from all levels of service.
Looking forward, the Company plans to provide additional training on DEI-related topics and are investigating conducting an inclusivity survey to identify the most important DEI topics for employees.
IMPACT STORY: DELANO S. STEWART AWARD — Chief Legal Officer, Sherry D. Williams, was honored with the 2022 Delano S. Stewart Award from the George Edgecomb Bar Association. The George Edgecomb Bar Association is the Tampa Bay area’s largest predominantly AfricanAmerican voluntary bar association.
Williams demonstrates a sustained, long-term commitment to encouraging and increasing diversity in the legal profession, with a specific focus on diverse recruitment, retention and advancement. Additionally, she demonstrated the impact of addressing issues of access and bias in the legal profession and increased advancement opportunities for lawyers who have been historically underrepresented.
Sara has been with SMI for over 12 yrs. Sara plays a vital role in plant operations scheduling trucks, data entry, ensuring inventories are accurate and replenished, handling all new hire paperwork, and attendance.
Sara is a focused team player who comes in early or works late regularly to ensure customers are satisfied. Every day Sara demonstrates her dedication to SMI and her co-workers.
Sara has a great rapport with vendors, trucking companies, and customers. Sara has been described as the right-hand person and the go-to person for the team..
Ana has been a key person in the Latin America organization to support growth. She is responsible for all the inbound and outbound transportation and always looking for ways to save costs for the company and suppliers.
Claudia is responsible for the testing and reporting of all inbound materials. Since her arrival, the plant has maintained 100% compliance with material testing.
Yvonne has been with SMI for over 15 years, working the scale house and providing accurate data reporting. She manages the work environment very well and ensures on-time communication with all inbound and outbound transactions, creating seamless and accurate processes. Yvonne is happy to help whenever asked. She is a dedicated, hardworking, and passionate team member at NexCycle Guelph. Her attention to detail and devotion are unmatched.
Kayleigh follows through on every task quickly and efficiently. She is very knowledgeable and always goes the extra mile when needed. She is a pleasure to work with and her coworkers say, “We definitely need more people like her!”
Sheila has been a versatile and impactful glass warrior. Throughout her tenure, she has worked every possible shift, in every department. She enjoys coming to work daily and leads her shift with passion and enthusiasm. Her work ethic and dependability are valued by her managers and serves as a standard of value to being an SMI team member.
Robbie spent four years in the U.S. Navy on board the USS John L. Hall as a Logistics Specialist 3rd Class Petty Officer (LS3). He was part of the VBSS team (Visit, Board, Search, and Seizure) - which is the onboard SWAT team that captured enemy vessels and conducts customs inspections as well as a part of a Damage Control Team (ship firefighter), - managing the onboard warehouse along with all classified equipment, Robbie spent seven months on a Mediterranean and Black Sea deployment, which resulted in port visits to 14 different countries that spanned over three continents. Today, Robbie serves as a procurement analyst for the company and is a valuable contributor to the Company’s success.
Eugene enlisted in the United States Marine Corps in January 1982 as a 3072, Aviation Supply Clerk. His basic training took place at Parris Island, SC, and he was selected for OCS (Officer Candidate School). Upon learning the length of service requirements, he opted out of that program but was selected as a cost accountant for the MAG-31 (Marine Air Group-31 based in Beaufort, SC) which included H&MS-31, VMFA-115, VMFA-251, VMFA-333, and VMFA-451. His duty stations were Parris Island, SC - Basic training; NAS Meridia, MS – Aviation Supply School; and MCAS Beaufort, SC. Eugene attained the rank of E-4 meritoriously in 15 months and was awarded an expert shooting badge, a good conduct service medal, several letters of appreciation, and an honorable discharge from active duty in January of 1986. He remained on inactive duty until January 1988. Eugene has built an extremely strong team that has a laser focus on customer needs and fulfilling them daily. His leadership has been instrumental to the success of SMI and its partners.
SMI plays an vital role in advocating for and supporting the glass recycling industry. Dedicating time and resources to develop community and non-profit relationships around glass recycling are important for societal good. SMI views relationships in the supply chain as partnerships - whether it’s providing a high quality product or technical assistance with glass clean up systems at the material recovery facility (MRF) level - helping each other achieve business goals is critical to broader success.
SMI is a proud member of the following organizations, promoting and advocating for robust recycling programs across the value chain and the planet.
• Associated Recyclers of Wisconsin (AROW)
• CalRecycles
• Carolina Recycling Association (CRA)
• Container Recycling Institute (CRI)
• Georgia Recycling Coalition
• Glass Recycling Coalition
• Glass Packaging Institute (GPI)
• Glass Recycling Foundation (501c3)
• Indiana Recycling Coalition (IRC)
• Institute of Scrap Recycling Industries (ISRI)
• National Recycling Coalition (NRC)
• Northeast Recycling Council (NERC)
• National Waste & Recycling Association (NWRA)
• Ontario Waste Managers Association
• Southeast Recycling Development Council (SERDC)
• Solid Waste Association of North America (SWANA)
• Tennessee Recycling Coalition
• State of Texas Alliance for Recycling (TX STAR)
• Washington State Recycling Association (WSRA)
• Missouri Recycling Association (MORA)
• Kansas Organization of Recyclers (KOR)
• Nebraska Recycling Coalition (NRC)
• Arkansas Recycling Coalition (ARC)
• Missouri Recycling Association (MORA)
• Kansas Organization of Recyclers (KOR)
• Nebraska Recycling Coalition (NRC)
• Arkansas Recycling Coalition (ARC)
• Iowa Recycling Association (IRA)
SMI is proud to serve on the executive board for and donate to the Glass Recycling Foundation, 501c3 nonprofit, to help fund glass recycling solutions across the country. glassrecyclingfoundation.org
SMI’s partnership with O-I provided expanded collection sites for glass collection in Waco, Texas. Although, a drop-off program existed through SMI, O-I’s facility in Waco donated large Glass4good containers to increase the number of locations available for local residents to recycle their glass and divert it from landfill. Glass4good is a recycling program created by O-I to address accessibility issues surrounding glass recycling. The program enhances local recycling infrastructure and provides the potential of generating local charitable donations in the communities where O-I employees live and work.
In April 2022, Chemical & Engineering News (c&en) spotlighted SMI for our innovation relating to automotive glass recycling. The article quoted our Vice President of National Accounts, Mark Nelson, detailing the process and benefits of using cullet for automotive glass recycling.
SMI partnered with the National Aquarium in Baltimore, MD, to limit their waste to landfill during renovations to the South American Rainforest Exhibit.
The 684 glass windowpanes that were original to the building were recycled with SMI.
In August 2022 fiberglass insulation leader, Knauf Insulation, became the official glass recycling partner of the Big Machine Music City Grand Prix – making SMI the recycling partner for all glass collected from the event. Knauf Insulation deployed a multi-faceted glass recycling engagement and collection program. The glass collected at this event was sent to the local SMI facility to be recycled back into products like fiberglass insulation that supports a more energy-efficient, sustainable, and comfortable environment.
In 2022, SMI celebrated The Beer Store’s partnership with the Liquor Control Board of Ontario (LCBO) with the return of the five billionth container under the Deposit Return Program for wine, spirit, and beer containers sold in the province of Ontario. SMI partners with The Beer Store to recycle their non-refillable containers, including aluminum, other metals, and select plastics. Annually, The Beer Store recovers an average of 1.8 billion containers under deposit return programs.
In Williams Bay, Wisconsin, SMI glass warriors aided in education and resource recovery at Yerkes Observatory. Since the reopening of the Yerkes Observatory in Spring of 2022 they have been focusing on educating the public on the benefits of glass recycling. To show support, SMI partnered with Yerkes Observatory to help create the world’s tallest glass Christmas tree. Using community recycled glass, artists Rob Elliot and Jason Mack created a 31-foot tree topped with an unforgettable 4-foot star on top. In total, the tree stood 35 feet tall and was constructed of 3,000 pounds of recycled glass.
Visit
worldstallestglasstree.com
SMI is proud to be a reliable and trustworthy partner for customers, providing high-quality products they can rely on. This sentiment is formalized in the Company’s core value to “See Through the Customer’s Eyes.” To ensure continuous improvement, SMI distributed an anonymous customer satisfaction survey. Topics included product quality, volume, delivery, order fulfillment, and communication. SMI received a response rate of approximately 39%. Key leadership and internal stakeholders met to discuss results and develop action items to address any concerns regarding the survey topics.
AWARD:
SMI was a proud recipient of the prestigious Owens Corning Supplier of the Year Award - 2022 for quality and safety. The SMI Midlothian, Texas, team is pictured with the award.
SMI is consistently in search of increasing not only material recycling but also expanding supported industries and product offerings. This is an ongoing, conscious effort to make glass recycling more accessible for individuals during a time when many municipalities have “curbed” or eliminated glass recycling. To improve the recycled glass supply, SMI implemented non-traditional collection methods or “creative collections” in conjunction with or in lieu of curbside program partnerships. Creative collections, such as drop-off programs, are part of a wider solution for glass recycling, giving residents and businesses more convenient ways to recycle glass.
In addition to a traditional cullet products, SMI has launched several glass products to continue to expand the scope of the organization and the overall positive impact on society. The expansion of the offerings allows for market flexibility and pioneer glass and plastic product circularity needs.
Glass Warrior Monika from Southern Pines, North Carolina, collected over 400 lbs. of glass for recycling from her neighbors and local church.
We partner with the glass warriors at Cheers to Recycling to recycle glass in Cobb County, Georgia. Cheers to Recycling provides monthly food and beverage-grade glass pick-up and our College Park, GA, facility.
TruAbrasives are a high-quality, 100% recycled glass air blast abrasive. Abrasive media is required for the surface preparation industry in steel, concrete, wood, and other substrates. The term “sandblasting” has come from the use of virgin, mined sand. SMI introduced TruAbrasives to the marketplace as an alternative to sand and other materials such as slags, not only for environmental benefits, but also, worker health benefits. Although glass is made from sand, it is considered a low-free silica material in comparison to sand with 99% crystalline silica – and performs extremely well on a variety of substrates.
American Specialty Glass specializes in decorative glass aggregate applications including landscaping/xeriscaping, countertops, terrazzo flooring, and fire pit glass. American Specialty Glass products are made in the USA from 100% recycled glass and help to offset quarried materials such as granite or other stone.
Strategic Materials, Inc. announced the acquisition of Ripple Glass in September 2022. Ripple Glass, based in Kansas City, Missouri, has provided a solution for local glass recycling since 2009. Before Ripple Glass, Kansas Citians threw away 150 million pounds of glass. Since its launch, Ripple Glass has more than quadrupled the rate of glass recycling in the Kansas City metropolitan area and has collected glass from more than 100 municipalities throughout the Midwest. Ripple Glass achieves glass recovery goals by expanding glass collection and glass recycling facilities. The two companies’ missions and values align closely making the partnership a natural match. All Ripple Glass employees were retained during this process, as they are an invaluable addition to the SMI team.
World Conservation Day, July 28th, 2022, was the “Glass Breaking” on ten new glass collection bins for Ripple Glass. Ripple Glass coordinated the launch of the new bins. Each bin is an artistic representation of the vibrant Kansas City community and was created by local artists to highlight the rich culture and treasured landmarks of their beautiful hometown.
The consistent quality of products elevate SMI as a premier partner. For three consecutive years, SMI achieved a quality acceptance rate of over 99%. This level of quality can be attributed to a refined and optimized process and sophisticated operating systems.
Supply: SMI receives feedstock glass from a variety of streams. Single-stream or curbside glass is typically known as 3-mix because all the colors of glass are mixed together and includes some nonglass residuals or contamination such as plastic, paper, metal, or non-recyclables. SMI also accepts automotive glass like windshields, windows, borosilicate, and heavily laminated glass at select plants.
Pre-Process: This part of the process removes non-glass residuals using air classification to remove lightweight material.
Second Cleaning: The remaining glass, heavier plastics, and other materials not removed from the pre-cleaning line run through a series of conveyors and screens to remove all non-glass items.
Optical Sort Line: Removes ceramic, stone, and porcelain, and large pieces of plastic or other contaminates.
Color Sorting Line: We sort the glass by colors, primarily flint (clear), amber (brown), and emerald (green).
Sent to Finished Product Bunker: The glass now meets customer specifications and is ready to be loaded into a truck and delivered to customer.
The Strategic Materials Operating System (SMOS) is built on a broad application of lean fundamentals and Six Sigma tools. It drives the business and gives Strategic Materials a true competitive advantage over competition. The SMOS is comprised of 12 elements that measure the production system, management system, and organization design. By standardizing, measuring, and driving results, this system focuses on both application and human interaction.
• Build the foundation of SMOS with a focus on standard work (operator and processes), preventative maintenance, and 5S
• Capture Yield Improvement best practices and transfer them to other plants
• Deploy virtual metrics and tracking to improve information availability and accuracy
• Train and certify more LE Blackbelts in the company
• Help the organization gain Six Sigma expertise
• Develop a formal mentoring and coaching process with Lean Six Sigma Green belts
• Integrate customers and suppliers into the operating system
Resource recovery is the nature of SMI’s business and take pride in the ability to recycle postconsumer products and reintroduce them into the value chain. SMI’s contribution reduces the need for mining or extracting virgin materials and helps close the material loop. For every ton of glass that is recycled and processed through SMI facilities, 1,300 pounds of sand, 410 pounds of soda ash, 380 pounds of limestone, and 160 pounds of feldspar are conserved. SMI’s role in the circular economy is vital for our customers to meet their sustainability goals.
In 2022, SMI proudly supported the recycling needs and community education on the importance and beauty of glass recycling. In Gastonia, North Carolina, SMI partnered with “Keep Gastonia Beautiful,” an organization dedicated to beautifying their community. “Serenity,” commissioned by local artist Carlos González García. The column is a creative showcase of the town’s beautiful history, a piece of education on their “Beetopia” initiatives, and a physical symbol of their commitment to sustainability. The vibrant geometric structure was constructed with recycled glass all donated by our SMI facility in Wilson, North Carolina.
Percentage of RECYCLED CULLET used to manufacture the organization’s primary products and services. 100% 100% 100%
Percentage of RECYCLED INPUT MATERIALS used to manufacture the organization’s primary products and services. 100% 100% 100%
Percentage of RECLAIMED PRODUCTS and their packaging materials for each product category. 100% 100% 100%
SMI’s goal is to realize a circular economy society that generates minimal waste to landfill. To achieve this goal, the Company advocates for and supports the proper classification and handling of the materials that enter the facilities and suppliers’ facilities. All loads that enter a SMI facility are tested for contamination. If materials received are not processable, the Company takes measures to ensure that these materials are responsibly disposed of. We will only landfill materials if there is no other recycling option available. One example material found in the inbound glass supply is batteries. Due to the hazardous nature of batteries, SMI has implemented specific procedures to mitigate negative environmental impacts. These additional procedures help to maintain high-quality standards, reduce waste at the secondary processor level, and help the environment by ensuring batteries are properly recovered. To ensure batteries are properly handled, along with any other potential hazardous waste, SMI utilizes a specialized third-party recycler to transport and recycle.
Water Bottle Program: To reduce internal waste generation, SMI discontinued purchasing singleuse plastic water bottles at our Wilson, NC, facility. Instead, the Company installed refillable water stations that are easily accessible and provide clean drinking water for all employees. Due to the program’s success, SMI plans to install a third water refill station in 2023. This program has provided a cost savings of about $1,000 and has reduced nearly nine pallets of plastic water bottles generated by the facility each year.
Strategic Materials is committed to managing, reporting on, and reducing GHG emissions. In 2022, the Company’s GHG emissions totaled 18,686 MT CO2e Scope 1 emissions and 31,866 MT CO2e Scope 2 emissions. Compared to the 2021 baseline, SMI reduced emissions by 7%, largely due to a decrease in diesel fuel consumption. Furthermore, using tons of product sold as the denominator, we realized a 3.8% reduction in GHG emission intensity.
The GHG emissions sources include diesel fuel, gasoline, purchased electricity, welding gas, natural gas, and propane. In future reporting, SMI will improve data collection process, and report on Scope 3 GHG emissions associated within the supply chain. Furthermore, the Company will set GHG emissions reduction targets aligned with the Science Based Target Initiative.
All GHG emissions calculations were conducted using the Greenhouse Gas Protocol’s Corporate Accounting and Reporting Standard. All facilities under operational control were included in the inventory.
The GHG emissions material topic is managed by the sustainability committee and any planned initiatives are implemented by the facility.
2-24
GRI 2: General Disclosures 2021 (Continued)
2-25 Processes to remediate negative impacts
2-26 Mechanisms for seeking advice and raising concerns
2-27 Compliance with laws and regulations
Ethics and Integrity, Pg. 22
Ethics and Integrity, Pg. 22
Ethics and Integrity, Pg. 22
2-28 Membership associations Partnerships, Pg. 29
2-29 Approach to stakeholder engagement
Stakeholder Engagement & Communications, Pg. 15
2-30 Collective bargaining agreements Employee Engagement, Pg. 22 GRI 3: Material Topics
Pg. 14
GRI 205: Anticorruption 2016 3-3 Management of material topics
205-1 Operations assessed for risks related to corruption
and Integrity, Pg. 22
We currently do not track this information, however, we will be investigating opportunities to do so in the future.
205-2 Communication and training about anti-corruption policies and procedures Ethics and Integrity, Pg. 22
205-3 Confirmed incidents of corruption and actions taken
and Integrity, Pg. 22
GRI 305: Emissions 2016
301-1 Materials used by weight or volume
301-2 Recycled input materials used
301-3 Reclaimed products and their packaging materials
3-3 Management of material topics
305-1 Direct (Scope 1) GHG emissions
305-2 Energy indirect (Scope 2) GHG emissions
305-3 Other indirect (Scope 3) GHG emissions
305-4 GHG emissions intensity
305-5 Reduction of GHG emissions
305-6 Emissions of ozone-depleting substances (ODS)
305-7 Nitrogen oxides (NOx), sulfur oxides (SOx), and other signi ficant air emissions
GRI 306: Waste 2020 3-3 Management of material topics
306-1 Waste generation and significant waste-related impacts
and Resource Recovery, Pg. 36
Recycling and Resource Recovery, Pg. 36
Greenhouse Gas Emissions, Pg. 38
Greenhouse Gas Emissions, Pg. 38
Greenhouse Gas Emissions, Pg. 38
SMI is actively investigating opportunities to expand GHG emissions reporting to include Scope 3 emissions.
Greenhouse Gas Emissions, Pg. 38
Greenhouse Gas Emissions, Pg. 38
We currently do not track this information, however, we will be investigating opportunities to do so in the future.
We currently do not track this information, however, we will be investigating opportunities to do so in the future.
Waste Generated and Diverted, Pg. 37
Waste Generated and Diverted, Pg. 37
GRI 306: Waste 2020
(Continued)
306-2 Management of significant waste-related impacts
306-3 Waste generated
306-4 Waste diverted from disposal
306-5 Waste directed to disposal
GRI 401: Employment
2016
3-3 Management of material topics
401-1 New employee hires and employee turnover
401-2 Benefits provided to full-time employees that are not provided to temporary or part-time employees
401-3 Parental leave
GRI 403: Occupational Health and Safety
2018
3-3 Management of material topics
403-1 Occupational health and safety management system
403-2 Hazard identification, risk assessment, and incident investigation
403-3 Occupational health services
403-4 Worker participation, consultation, and communication on occupational health and safety
403-5 Worker training on occupational health and safety
403-6 Promotion of worker health
403-7 Prevention and mitigation of occupational health and safety impacts directly linked by business relationships
403-8 Workers covered by an occupational health and safety management system
403-9 Work-related injuries
403-10 Work-related ill health
GRI 405: Diversity and Equal Opportunity
2016
3-3 Management of material topics
405-1 Diversity of governance bodies and employees
405-2 Ratio of basic salary and remuneration of women to men
Waste Generated and Diverted, Pg. 37
Waste Generated and Diverted, Pg. 37
Waste Generated and Diverted, Pg. 37
Waste Generated and Diverted, Pg. 37
Employee Engagement, Pg. 22
Employee Engagement, Pg. 22
Health and Safety, Pg. 20
SMI currently does not track data for this disclosure.
Health and Safety, Pg. 20
Health and Safety, Pg. 20
Health and Safety, Pg. 20
Health and Safety, Pg. 20
Health and Safety, Pg. 20
Health and Safety, Pg. 20
Health and Safety, Pg. 20
We currently do not track this information, however, we will be investigating opportunities to do so in the future.
Health and Safety, Pg. 20
Health and Safety, Pg. 20
Health and Safety, Pg. 20
Diversity, Equity, and Inclusion, Pg. 25
Diversity, Equity, and Inclusion, Pg. 25
Corporate Governance and Sustainability, Pg. 12
Diversity, Equity, and Inclusion, Pg. 25
© 2023 Strategic Materials, Inc. All Rights Reserved.