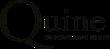

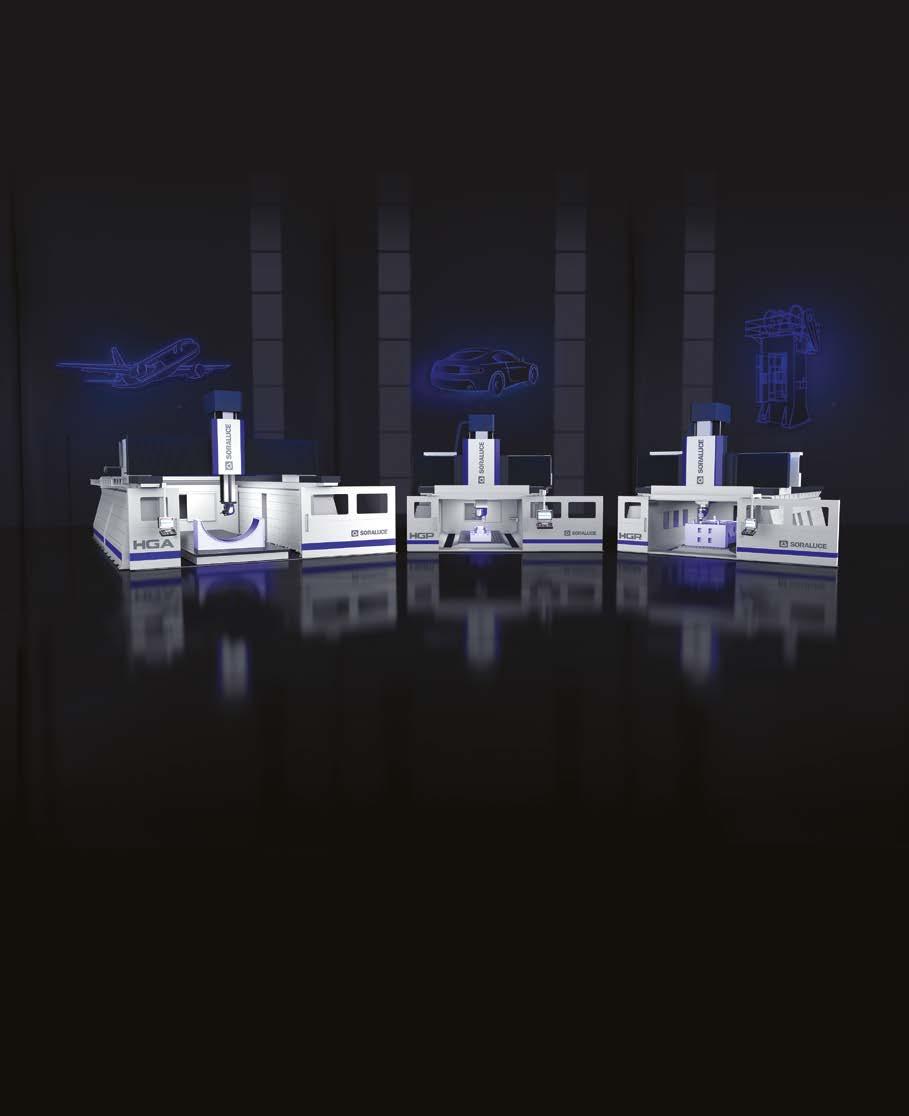
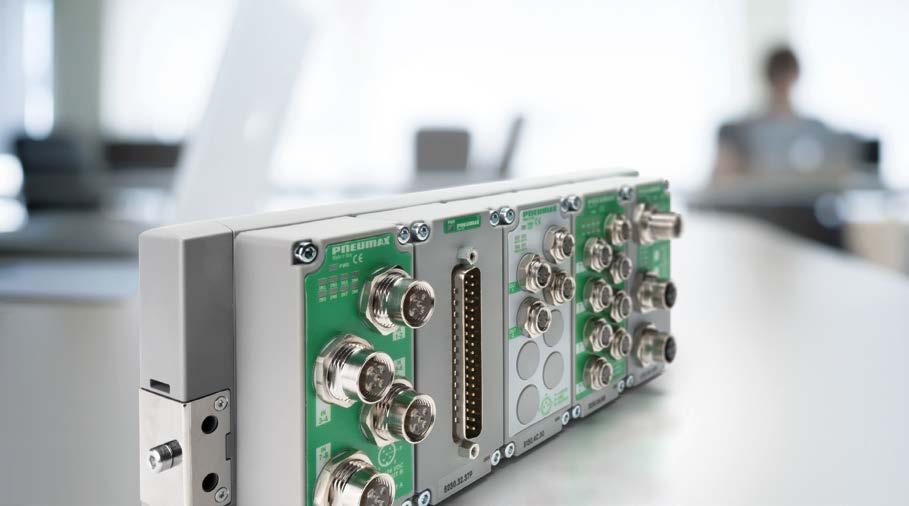
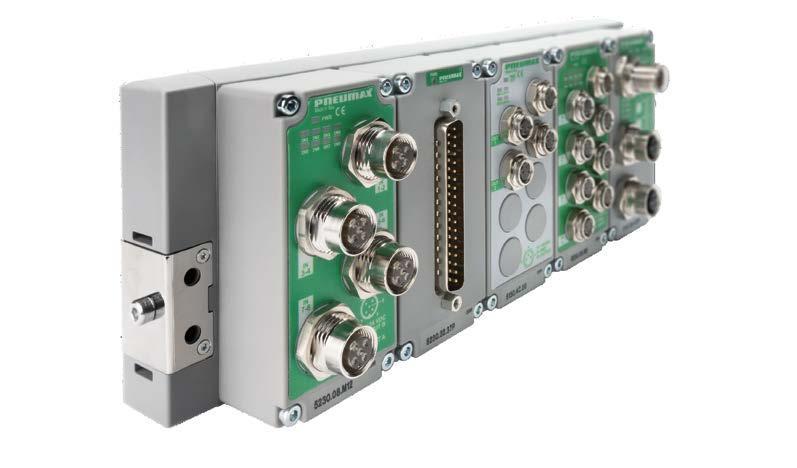
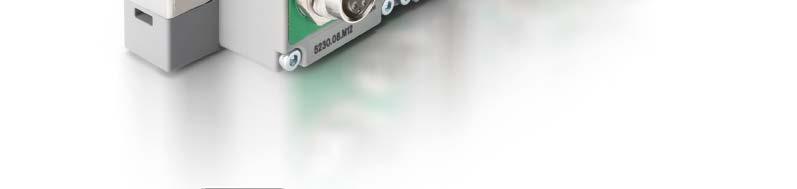
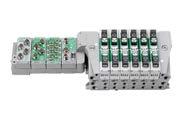
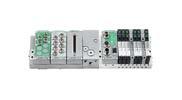

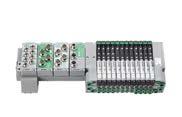
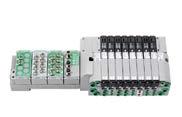

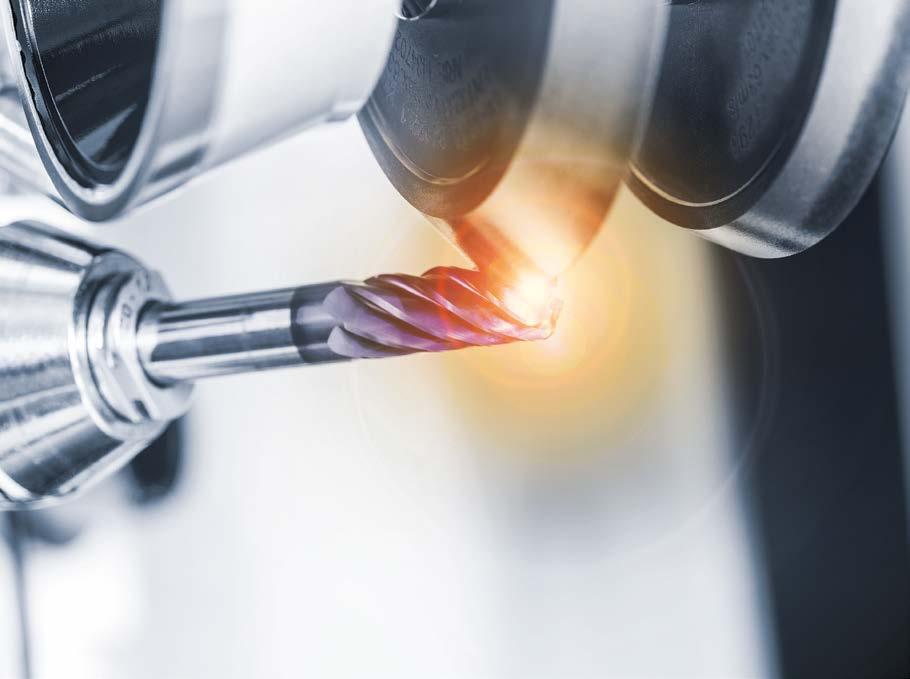

di Chiara Tagliaferri
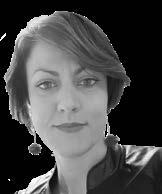
Perplessità, dubbio, incertezza… queste sono le reazioni che a volte si percepiscono quando si parla del lancio di un nuovo prodotto dichiarato più sostenibile. E vi confesso che, ben pensante di indole come sono, il dubbio si insinua sempre più spesso anche in me. Non tanto rivolto a mettere in discussione la buona fede di chi orgogliosamente dichiara lo sforzo e il perseguimento di una pratica sostenibile, ma piuttosto la pratica stessa. Quando dico ciò penso a tante delle nuove soluzioni adottate delle aziende negli ultimi anni. Siamo sicuri di sapere?
Se da un lato trovo assolutamente inconfutabile che la logica dell’usa e getta deve essere combattuta, non sempre mi convince quella del recupero o del riuso o quella dell’indubbio vantaggio dell’elettrificazione della mobilità, ad esempio.
Un collega ricercatore di LCA risponderebbe che faccio bene a dubitare, perché quasi tutto dipende dall’ impatto che un prodotto o un processo ha sul sistema circostante, ma che questo può e deve essere calcolato attentamente, prima di proclamare una scelta come sostenibile nelle sue diverse dimensioni. Ed infatti, figlia di questa perplessità, il parlamento europeo il 17 gennaio di quest’ anno, ha emesso una nuova direttiva molto più restrittiva del passato che cerca di combattere l’ormai noto fenomeno del green washing. Le aziende adesso, per usare determinate etichette come “carbon neutral”, devono dimostrare che lo è l’intero ciclo di vita del prodotto, con dati verificabili e “science based”. E qui inizia il vero dubbio e il fulcro del paradosso socratico, inteso come certezza di non conoscenza definitiva. Verificare con metodo scientifico vuol dire in primis avere consapevolezza e
alte professionalità a disposizione, poi riuscire nell’ intento e infine, nel caso delle aziende, perseguire la scelta anche a costi elevati ed essere pronti a verificarla successivamente adottandone un ulteriore modifica. E quanti posso dire di avere a disposizione tutti questi elementi? Perché, per esempio, riuscire a fare un prodotto con materiale riciclato, non è detto che sia un vantaggio assoluto, lo diventa, solo se, è tutto il ciclo ad aver avuto un minore impatto e il successivo fine vita replicherà il processo virtuoso. Ma bisogna avere competenze e dati scientifici raccolti nel tempo per dimostrarlo. E ancora, quel dubbio che muove il desiderio di colmare l’ignoranza si amplifica dopo aver letto alcuni dei trend di sostenibilità del rapporto Cysco. Dalla COP28 di Dubai è stato lanciato l’appello a triplicare la produzione di energia da rinnovabili e si prevede che entro il 2050 il 25% della domanda arriverà dai veicoli elettrici. Energia rinnovabile ma quanta? e con quali infrastrutture? E ancora, come si sosterranno i server necessari per lo sviluppo dell’AI? Se siamo indietro nella transizione green & digital e sappiamo che la componente sostenibilità è quella lasciata più indietro, forse è anche perché è quella più difficile da dimostrare con effetti economici per chi la persegue pari a zero se non peggiori?
So di non sapere e continuo a cercare ma ho la consapevolezza che fare bene e far del bene per costruire un futuro sostenibile rappresenta una responsabilità condivisa che costa, in termini di impegno economico e partecipazione collettiva.
chiara.tagliaferri@cnr.it
EDITORIALE
5 So di non sapere
CALEIDOSCOPIO
8 News e novità
PANORAMA
14 Calano gli ordini sul mercato interno
16 Hoffmann Group porta la logistica a un livello superiore
18 Le novità igus a Mecspe
20 L’importanza dell’automazione
22 Da Salvagnini, due nuove automazioni per il laser
DOSSIER MANIFATTURA
SNELLA E SOSTENIBILE
28 Un approccio olistico e innovativo per il futuro industriale
30 Nuova vita per modem e router con l’aiuto dei robot ABB
32 Statemonitor, il modem per ottimizzare la produzione
34 La movimentazione intralogistica snella e sostenibile nel futuro della produzione
38 È una questione di sensori
40 L’innovazione per un futuro sostenibile guidata da una visione sociale
42 Evoluzione tecnica e sostenibilità, in viaggio verso le zero emissioni
44 Produttività, flessibilità e sostenibilità: la pannellatrice è già nel futuro
48 Nuove sfide per un’industria sostenibile
50 Produzione efficiente con la massima qualità
54 Tecnologie intelligenti per la sostenibilità e il risparmio energetico
58 La rivoluzione della manutenzione predittiva e del condition monitoring
60 La visione di ORI Martin rispetto al Sustainable Manufacturing
TECNOLOGIE PER L’INNOVAZIONE
Pad.14 Stand D02
1973-2024
Da oltre 50 anni al vostro
Blo c caggi o
I Presidenti del Cnr Maria Chiara Carrozza e dell’ENEA Gilberto Dialuce hanno sottoscritto un accordo di collaborazione per la promozione e la realizzazione di progetti di ricerca e sviluppo congiunti a livello nazionale e internazionale. L’intesa, di durata quinquennale, ha inoltre come obiettivo la valorizzazione e divulgazione di conoscenze tecnico-scientifiche, la realizzazione, condivisione e promozione di infrastrutture di ricerca, la formazione avanzata e l’offerta di servizi, oltre al trasferimento di tecnologie, prodotti e know-how a soggetti terzi. Le iniziative riguarderanno in particolare i settori di produzione, trasporto e distribuzione di energia ma anche tecnologie e sistemi per il suo stoccaggio; nuove fonti e vettori energetici rinnovabili, tra cui l’idrogeno; smart grids e smart sector integration; tecnologie abilitanti e per la digitalizzazione; comunità energetiche rinnovabili; efficienza energetica; space e blue economy; sviluppo e applicazione delle biotecnologie; studi e applicazioni su atmosfera, oceani e dinamiche climatiche; sostenibilità e circolarità dei sistemi produttivi e territoriali; materiali e processi per la competitività del sistema industriale; fusione nucleare.Le modalità e le forme di collaborazione saranno regolate attraverso la stipula di specifiche convenzioni attuative. A livello operativo, è prevista l’istituzione di un Comitato di indi-
rizzo paritetico composto da sei membri per definire i temi programmatici oggetto dell’accordo stesso. “Sono particolarmente contenta di rinnovare la lunga e fruttuosa collaborazione di ricerca che ci lega all’ENEA e di indirizzarla all’esplorazione di ambiti scientifici e tecnologici così importanti per il futuro delle nostre società”, afferma la Presidente del Cnr, Maria Chiara Carrozza. “I settori individuati, infatti, rispecchiano le sfide che la ricerca deve affrontare per rispondere ai grandi cambiamenti globali. Abbiamo di fronte un percorso lungo, che sarà arricchito dall’unione di competenze e dalle sinergie che questo accordo intende consolidare”. “Questa alleanza fra le due maggiori istituzioni di ricerca a livello nazionale prevede una rafforzata cooperazione per individuare e sviluppare un portafoglio di progetti e iniziative di ricerca, sviluppo, innovazione, formazione e trasferimento tecnologico dei risultati e prodotti della ricerca”, ha dichiarato il Presidente dell’ENEA Gilberto Dialuce. “Come ENEA siamo particolarmente soddisfatti di quest’accordo che consente di mettere a fattor comune competenze, esperienze, infrastrutture, professionalità e know-how in settori strategici per la decarbonizzazione e la transizione ecologica e di promuovere la ricerca e l’innovazione tecnologica per favorire la crescita e la competitività del Sistema-Paese”.
IFP EUROPE, IL NUOVO MODO DI CONCEPIRE IL LAVAGGIO.
Il “nuovo” prende forma da un’estensione del “precedente” nella progettazione ergonomica, funzionale ed estetica nel lavaggio di minuterie e componentistica meccanica.
Il design si accompagna all’essenzialità e ad un minimalismo che ne facilita la manutenzione. Con tecnologia e responsabilità ambientale,
IFP Europe ridefinisce il modello imprenditoriale: un equilibrio tra economia di gestione, rispetto per l’ambiente e continua innovazione, tracciando nuove strade nell’ecologia industriale.
Quick Algorithm, startup deep tech italiana nata per democratizzare l’analisi avanzata dei dati e l’intelligenza artificiale in ambito industriale, vince il premio della giuria alla Startup Competition AI 4 Future 2024.
La finale si è svolta a Milano il 14 febbraio nell’ambito dell’AI Festival, il primo festival internazionale dedicato al presente e al futuro dell’Intelligenza Artificiale e organizzato dal WMF - We Make Future - che ha riunito professionisti, aziende, startup, stakeholder e player del settore per approfondire la rivoluzione apportata dall’AI non solo nel quoti-
diano, ma anche in ambito politico, sociale e lavorativo.
“Questo premio è un importante riconoscimento a tutto il team che quotidianamente lavora per rendere sempre più accessibile l’Intelligenza Artificiale e la tecnologia IoT alle aziende, con soluzioni di monitoraggio energetico e manutenzione predittiva pronte all’uso. Creare un’infrastruttura dati tipicamente richiede mesi, svariati interlocutori e budget molto elevati: attraverso Scops.ai, rendiamo questo processo cinque volte più veloce”, spiega Jacopo Piana, CEO e fonda-
tore di Quick Algorithm. “Con Quick Algorithm vogliamo espanderci a livello globale e allo stesso tempo contribuire concretamente al progresso italiano nel settore tecnologico dell’analisi dei dati e dell’Intelligenza Artificiale, avendo il Paese un grandissimo potenziale in ambito tecnologico e un tessuto industriale tra i più importanti in Europa, tuttavia con ampi margini di miglioramento in termini di applicazioni di analisi dei dati e Intelligenza Artificiale”. Grazie al premio della giuria Quick Algorithm prenderà parte al WMF - We Make Future 2024 - e sarà presente ad una tappa dell’International Roadshow del WMF.
Quick Algorithm ha conquistato la giuria proprio grazie alla sua soluzione all-in-one pensata per rendere accessibile ad ogni azienda tecnologie avanzate per il monitoraggio energetico Smart e la manutenzione predittiva: Scops.ai, infatti, è Plug and Play e attivabile in soli 20 minuti da qualunque azienda senza l’intervento di figure altamente specializzate, consentendo alle aziende di diventare Data-Driven in ottica 4.0 in modo semplice e veloce. Grazie alla combinazione di sensori IoT, connettività wireless a lungo raggio e software con Intelligenza Artificiale, Scops. ai consente di raccogliere in tempo reale dati sui consumi e le performance di macchinari ed edifici, analizzarli e generare allerte, portando le aziende a migliorare la propria efficienza energetica del 15% e ridurre i tempi di fermo impianto imprevisti del 40%, con benefici dal punto di vista della sostenibilità e della produzione. La natura della sensoristica IoT e l’infrastruttura cloud permettono di raggiungere risultati migliori rispetto a soluzioni tradizionali, con un quinto dei tempi e dei costi.
Jacopo Piana CEO di Quick Algoritm
La Fritz Studer AG, fondata nel 1912, è una fra le aziende leader del mercato e sotto il profilo tecnologico per quanto riguarda la rettifica universale, esterna, cilindrica interna e non cilindrica. Con oltre 25’000 impianti prodotti, STUDER è da decenni sinonimo di precisione, qualità e durata.
studer.com
Il passaggio alla mobilità elettrica sta rivoluzionando il settore dei trasporti, determinando lo sviluppo di tecnologie di alimentazione sempre più avanzate e di nuovi processi produttivi, più efficienti, sicuri e sostenibili. In questo contesto, l’innovazione tecnologica è un fattore determinante per permettere di realizzare veicoli performanti con costi sempre più accessibili - elemento essenziale per la diffusione dei veicoli elettrici. Una necessità incentivata dalle politiche europee, sostenute anche da altre organizzazioni internazionali, che per soddisfare gli obiettivi del Green Deal, che puntano a ridurre entro il 2030 le emissioni di CO2 dei trasporti su strada del 55%, per arrivare a raggiungere entro il 2035 il traguardo delle “emissioni zero”. Per riflettere su questi temi Stefania Ferrero, Chief Marketing Officer di Comau, selezionata per il ruolo di “Ambasciatore dell’Innovazione”, ha partecipato alla tavola rotonda “Mobilità sostenibile: tecnologie, scelte e strategia”, organizzata durante la Fiera A&T. Ferrero, nel corso del suo intervento, ha sottolineato l’impegno dell’azienda nella progettazione e realizzazione di tecnologie e sistemi avanzati per la produzione di energia rinnovabile nel campo della mobilità e in numerosi settori chiave dell’industria. Una scelta strategica che, negli anni, ha portato Comau ad investire nello sviluppo di conoscenze e competenze dedicate, partendo da un forte e consolidato know-how, maturato nel campo Automotive, per creare team altamente specializzati, pronti a rispondere in modo efficace alle nuove necessità produttive. Secondo diversi studi di mercato analizzati da Comau, nel periodo 20232030 il mercato globale della mobilità sarà caratterizzato da una crescita superiore al
15%. Nello stesso arco temporale, i veicoli elettrici venduti sul mercato saranno il 50% in più di quelli attuali, portando così ad un aumento del 600% della domanda di celle per batterie agli ioni di litio. Una situazione di mercato che richiederà ai produttori l’adozione sempre più elevata di soluzioni robotizzate e automatizzate, per ottimizzare i processi produttivi. Inoltre, puntualizza Stefania Ferrero, l’adozione di fonti di energia rinnovabile, sarà spinta dalla richiesta di tecnologie per la produzione di idrogeno verde, per cui si stima una crescita del 1000% nel medesimo periodo di riferimento.
“ Gli oltre 50 anni di esperienza maturati
nell’Automotive hanno permesso a Comau di essere pioniere di nuove tecnologie all’avanguardia nella mobilità elettrica e in altri settori, come la logistica di magazzino, il farmaceutico e l’alimentare, le energie rinnovabili e la cantieristica navale, solo per citare alcuni esempi di comparti industriali dove la richiesta di automazione è in costante crescita. – afferma Stefania Ferrero, Chief Marketing Officer di Comau -. Grazie allo sviluppo di processi produttivi più sicuri, più efficienti e sempre più sostenibili, siamo pronti a supportare i nostri clienti e partner di fronte alle sfide di un mercato in continua trasformazione.’’
INFORMAZIONE DAL MONDO TECNOLOGICO
NEL QUARTO TRIMESTRE 2023, L’INDICE DEGLI ORDINI DI MACCHINE UTENSILI ELABORATO DAL CENTRO STUDI & CULTURA DI IMPRESA DI UCIMU-SISTEMI PER PRODURRE SEGNA UN CALO DEL 31,1% RISPETTO AL PERIODO OTTOBRE-DICEMBRE 2022. IN VALORE ASSOLUTO L’INDICE SI È ATTESTATO A 92,1 (BASE 100 NEL 2015) a cura della redazione
Il risultato negativo è frutto della riduzione della raccolta ordinativi sul mercato interno; l’estero invece mostra capacità di tenuta. In particolare, gli ordinativi raccolti oltreconfine risultano in calo del 2,9% rispetto allo stesso periodo dell’anno precedente. Il valore assoluto dell’indice si attesta a 100,9.
Sul fronte interno, gli ordini hanno segnato un arretramento del 69,1%, rispetto al quarto trimestre del 2022, per un valore assoluto di 79,4. In ragione d’anno, l’indice ha segnato un calo del 24,7% rispetto alla media del 2022 (90,5 indice assoluto). -48,4% l’indice interno (74,6 indice assoluto); -11,3% l’indice estero (102,8 indice assoluto).
Barbara Colombo, presidente UCIMU-SISTEMI PER PRODURRE:
“I dati elaborati dal Centro Studi & Cultura di Impresa confermano le nostre attese: il 2023 segna una evidente riduzione della raccolta ordinativi da parte dei costruttori italiani sul mercato domestico a cui si contrappone una generale tenuta dell’attività sui mercati esteri. Nel complesso,
nonostante il segno negativo, le nostre aziende stanno lavorando intensamente grazie alla coda di ordini che ancora devono smaltire”.
“Con riferimento particolare al mercato interno, la riduzione della raccolta di nuove commesse sull’intero anno è anzitutto fisiologica e corrisponde ad un generale ridimensionamento della domanda dopo il boom dell’ultimo periodo. Se invece stringiamo lo sguardo all’ultimo trimestre, il calo risente anche e soprattutto dell’effetto di attesa per le nuove misure di incentivo che si aspettavano, e tuttora si aspettano, per il 2024”.
“La discussione aperta negli ultimi mesi dell’anno da Governo e Parlamento in merito alla possibilità di introdurre nuovi incentivi 5.0 ha certamente spinto le aziende a sospendere le decisioni di acquisto in attesa di chiarezza”.
“In pratica - ha aggiunto la presidente di
UCIMU - è accaduto l’opposto di ciò che si verificò l’anno scorso quando vi fu la corsa ad investire nell’ultimo trimestre dell’anno per poter sfruttare l’aliquota del credito di imposta al 40% prima che venisse dimezzata con l’anno nuovo”.
“Al momento siamo in attesa dei decreti attuativi relativi ai provvedimenti 5.0 che dovrebbero tramutarsi in un credito di imposta per la formazione e per gli investimenti in progetti di innovazione finalizzati alla twin transition ovvero alla sostenibilità digitale”.
“In questo modo le aziende manifatturiere italiane potrebbero così disporre di un sistema modulare di incentivi fiscali, combinabili e cumulabili, maggiormente premianti per chi investe in nuove macchine ove la digitalizzazione è anche abilitatore di sostenibilità. Tutto ciò in risposta alla necessità dell’industria del paese di proseguire con la transizione digitale che, anche in linea con le nuove direttive europee, deve considerare rispetto dei criteri legati al tema della sostenibilità e della green manufacturing”.
“Considerati i tempi e tutte le procedure per rendere operativi i nuovi provvedimenti - ha affermato Barbara Colombo - possiamo immaginare che questi primi mesi dell’anno saranno ancora caratterizzati da una certa cautela nella definizione degli acquisti in nuovi macchinari, per poi sbloccarsi a partire dall’inizio del secondo trimestre”.
“Nel frattempo, un indicatore ulteriore della ancora buona predisposizione del mercato italiano ad investire è data dall’andamento di adesioni alla BI-MU, la biennale della macchina utensile, robotica e automazione, in programma il prossimo ottobre a fieramilano Rho che, al momento, ha raccolto un numero di adesioni decisamente superiore a quello che aveva ottenuto, pari periodo, per l’edizione 2022”. “In ogni caso - ha concluso Barbara Colombo nel suo commento alla situazione del mercato italiano - alla luce di quanto sta accadendo, probabilmente, sarebbe utile sganciare alcuni provvedimenti dalla temporaneità delle Leggi di Bilancio così da garantire alle aziende un set di strumenti fiscali strutturali che possano permettere loro di pianificare gli investimenti nel lungo periodo. In questo modo si permetterebbe al mercato di distribuire in modo più omogeneo la domanda favorendo, tra l’altro, l’attività dei costruttori che potrebbero meglio programmare la propria produzione”.
“Sul fronte estero - ha affermato Barbara Colombo - la raccolta ordinativi è risultata sostanzialmente stazionaria confermando il trend di lungo periodo che evidenzia un andamento più regolare delle commesse ottenute dai costruttori oltreconfine rispetto a quelle conseguite sul mercato domestico ove gli incentivi disponibili nel corso degli anni hanno dato luogo a marcate oscillazioni della domanda”.
“In particolare, i costruttori italiani hanno da sempre negli Stati Uniti un partner di eccezione e, in questo momento, la prima area di destinazione dell’export. La vivacità della domanda nordamericana, che ci attendiamo resti tale anche nei prossimi mesi, ha sostanzialmente bilanciato la debolezza di quella asiatica ed europea”.
“Ora l’auspicio è che l’Europa e soprattutto la Germania tornino a lavorare come in passato o anche di più, considerato che il fenomeno del reshoring può avvantaggiare i costruttori italiani già presenti nelle catene del valore tedesche. Questo auspicio diviene oggi ancora più accalorato, se si considera la grande incertezza che grava sul mercato internazionale ove le numerose crisi geopolitiche aperte rendono l’attività economica sempre più complicata”.
Con riferimento alla Germania, nel periodo gennaio-settembre 2023 (ultimo dato disponibile) le vendite di made in Italy di settore sono risultate pari a 244 milioni di euro, il 10% in più rispetto allo stesso periodo dell’anno precedente. Nonostante ciò, occorre considerare che il valore dell’export italiano lì destinato risulta decisamente più contenuto rispetto al periodo precedente al 2018 e rispetto al record segnato nel 2008 quando raggiunse la cifra di 465 milioni di euro.
“Questi dati ci dicono che possiamo e dobbiamo fare di più. Per tale ragione - ha concluso la presidente di UCIMUl’associazione ha presentato al Ministero degli Affari Esteri e della Cooperazione Internazionale una proposta di azione e collaborazione per il biennio 20242025, dedicata agli operatori del settore, costruttori italiani e costruttori e utilizzatori tedeschi, con l’obiettivo di avviare, insieme a loro, un dialogo su un possibile piano di azioni comuni volte a rafforzare e valorizzare le peculiarità delle due industrie e le possibili partnership in mercati di interesse condiviso”.
Grandi industrie e piccole e medie officine meccaniche richiedono approvvigionamenti veloci, precisi e sicuri. Hoffmann Group lo sa bene, per questo ha compiuto l’investimento più grande nella sua storia aziendale: LogisticCity. Un centro logistico a Norimberga, nel cuore dell’Europa, che può gestire fino a 100.000 posizioni e 40.000 pacchi ogni giorno
“La logistica è la nostra passione” ha dichiarato Andreas Meissner, Direttore di LogisticCity. Ma non solo, è il più
ingente investimento realizzato da Hoffmann Group nella sua storia lunga oltre un secolo. Ben duecento milioni di euro sono stati investiti dal fornitore di utensili e attrezzature industriali per realizzare LogisticCity, il centro logistico più moderno d’Europa, e assicurare approvvigionamenti veloci, precisi e sicuri a oltre centotrentacinque mila clienti in tutto il mondo, di cui otto mila solo in Italia.
UNA NUOVA ERA NELLA LOGISTICA DEGLI UTENSILI
LogisticCity sorge a Norimberga, in un’area di oltre duecento mila metri
quadrati, l’equivalente di trenta campi da calcio, e dispone di un’area logistica di cento mila metri quadrati. Per la sua costruzione, sono state impiegate dodici mila tonnellate di acciaio e posati ottocento chilometri di cavi. All’interno dell’area sono stoccati circa ottanta mila articoli, tra utensili da taglio, sistemi di serraggio, strumenti di misura, utensili manuali e dispositivi di protezione individuale.
Con quattrocento persone impiegate e un elevato livello di automazione –sono cinquecento mila le posizioni di stoccaggio dei contenitori completamente automatizzate, trenta mila quelle
LogisticCity di Hoffmann Group a Norimberga, il centro logistico per utensili più moderno d’Europadei pallet anch’esse completamente automatizzate e quattordici i chilometri di trasportatori di contenitori e pallet – il centro logistico può gestire fino a cento mila posizioni e quaranta mila pacchi al giorno, spedendoli il giorno stesso dell’ordine
Tutto ciò grazie anche al centro nevralgico di LogisticCity: il magazzino a navetta estremamente all’avanguardia che si estende fino a trenta metri di altezza. Più di quattrocento veicoli navetta viaggiano su sessantasei livelli tra cinquecento mila posizioni di stoccaggio dei contenitori, rendendo tecnicamente possibile movimentare quindici mila contenitori all’ora
Con il nuovo centro logistico, non solo Hoffmann Group garantisce il 99% di capacità di consegna, ma anche il 99,9% di accuratezza lungo l’intera catena di fornitura, grazie alla combinazione
In ognuna delle 32 postazioni di lavoro è possibile prelevare fino a 350 articoli all’ora
Il magazzino automatizzato a scaffalature alte conta 30.000 postazioni di stoccaggio pallet
Il sistema di trasporto di container e pallet di LogisticCity si estende per ben 14
tra tecnologia di scansione delle merci in entrata, controllo della pesatura sul sistema di trasporto, movimentazione delle merci completamente automatizzata e “goods-to-man” tramite contenitori di stoccaggio non miscelati.
L’impegno di Hoffmann Group per una maggiore sostenibilità continua anche in LogisticCity, ad esempio attraverso la riduzione delle confezioni che necessitano di materiale di riempimento, che comunque è stato sostituito da carta riciclata. La riduzione delle emissioni di CO2 e l’ulteriore aumento dell’efficienza lungo tutta la catena logistica è infatti considerata da Hoffmann Group una sfida fondamentale.
IGUS RINNOVA LA PARTECIPAZIONE A MECSPE, FIERA INTERNAZIONALE DI RIFERIMENTO PER L’INDUSTRIA MANIFATTURIERA (BOLOGNAFIERE, 6/8 MARZO 2024), DOVE SARÀ TRA I PROTAGONISTI DELL’AREA DEDICATA ALL’AUTOMAZIONE E ALLA ROBOTICA (PAD. 30 – STAND D24), AL FIANCO DEI BIG DELLA MECCATRONICA.
di C.G.
Mecspe è da sempre un appuntamento imprescindibile per igus che quest’anno punta a consolidare i rapporti, già ben saldi, con la clientela italiana del comparto manifatturiero, un settore sempre più consapevole dell’importanza di innovazione e digitalizzazione. “Il nostro obiettivo è quello di ampliare ulteriormente il target, rivolgendoci sempre più ad aziende e realtà di piccole e medie dimensioni che sono alla ricerca di soluzioni tecnologiche che possano contribuire a dare nuovo slancio alla propria attività”, afferma Marcello Mandelli, country manager di igus Italia. “A loro proponiamo una gamma di prodotti e servizi ad alto tasso di innovazione, in grado di potenziare il con-
tenuto tecnologico delle loro applicazioni, ottimizzando processi e costi di produzione”.
Allo stand igus, dunque, troveranno spazio le più recenti novità del vasto catalogo che lo specialista delle motion plastics offre al mercato italiano, sia in ambito di prodotti, sia di servizi messi a punto per semplificare i lavori di progettazione e ingegnerizzazione. Tutte proposte accomunate da massima affidabilità ed eccellenza qualitativa, assicurate anche dalle garanzie più lunghe del mercato.
igus, infatti, ha recentemente annunciato il prolungamento del periodo di garanzia per l’intera gamma chainflex - che comprende oltre 1.350 tipologie di cavi, da quelli entry level a quelli di fascia alta - portandolo alla durata record di 4 anni. Un vantaggio
significativo per i clienti, sia in termini di sicurezza funzionale, sia di pianificazione, reso possibile dai test effettuati negli ultimi dieci anni nel laboratorio di igus a Colonia.
In ambito di prodotto, riflettori puntati sulle nuove guide lineari miniaturizzate della serie drylin W nella dimensione di installazione 06. Estremamente compatte ed esenti da lubrificazione, sono ideali per l’utilizzo in spazi ridotti e possono essere fornite pronte per l’installazione e/o con componenti personalizzati. Tra le novità della serie, anche i carrelli lineari miniaturizzati drylin WW-06-20-T415-AL con un alloggiamento in alluminio anodizzato resistente alla corrosione, progettati per essere installati su una guida a doppio albero, anch’essa in alluminio anodizzato.
In mostra a Mecspe anche le più recenti soluzioni firmate igus per l’utilizzo in camera bianca, tra cui Clean SCARA, il nuovo sistema di alimentazione per robot SCARA progettato per guidare cavi e tubi nelle applicazioni in cleanroom ad alta velocità. Ideale per la produzione di dispositivi elettronici, questa esclusiva soluzione, presentata in anteprima italiana, è realizzata in plastica ad alte prestazioni tribologicamente ottimizzata e funziona senza rilasciare particelle secondo ISO
Classe 2, anche con i movimenti più dinamici. Clean SCARA rappresenta, inoltre, una valida alternativa ai classici tubi flessibili corrugati, garantendo, oltre alla compatibilità con l’impiego in camere bianche, anche interessanti vantaggi in termini di resistenza e semplicità di utilizzo.
In fiera ci sarà spazio anche per l’ampia gamma di strumenti messi a punto da igus per semplificare i lavori di progettazione e ingegnerizzazione, tra cui il servizio di stampa 3D online per la realizzazione di componenti
resistenti all’usura, al di fuori della gamma standard, recentemente potenziato con nuove funzionalità. Oltre al calcolo istantaneo del prezzo e all’analisi di fattibilità, infatti, il tool online fornisce in tempo reale una stima della durata d’esercizio prevista per i singoli particolari personalizzati da realizzare tramite produzione additiva, agevolando così la scelta del giusto materiale. Dopo averlo identificato, sarà sufficiente caricare il file STEP o STL e ordinare il pezzo, che verrà spedito entro tre giorni.
MITSUBISHI ELECTRIC LANCIA UNA CAMPAGNA DI SENSIBILIZZAZIONE GLOBALE SULL’IMPORTANZA DEI SISTEMI DI AUTOMAZIONE INDUSTRIALE a cura della redazione
Mitsubishi Electric ha avviato una campagna di sensibilizzazione a livello globale utilizzando una serie di narrazioni illustrate, ciascuna accompagnata da un’immagine di grande impatto, rivolta a un pubblico vasto, non solo appartenente al mondo dell’automazione industriale. L’obiettivo è trasmettere ai lettori l’importanza dell’automazione industriale nella loro quotidianità, oltre a fornire ai produttori una visione di come sarà il loro futuro.
Il soggetto principale ha come titolo “Realizziamo ciò che conta per te”. Attraverso l’utilizzo di un razzo, la campagna mostra come, in futuro, la progettazione, la produzione e la logistica saranno personalizzate in base alle esigenze di ciascun individuo.
Il secondo soggetto è incentrato sul modo in cui le tecnologie digitali guideranno la produzione avanzata in futuro ed è intitolato “La digitalizzazione per moltiplicare il potenziale della tua produzione”. Spiega come la tecnologia digitale e l’utilizzo dei dati
favoriscano la creazione di un mondo senza vincoli, in cui la produttività e la qualità aumentano, eliminando sprechi ed errori. Il terzo e ultimo soggetto, intitolato “Rendere sostenibile la produzione”, si concentra su come la produzione sostenibile supporterà la creazione di un mondo più green. Spiega che, ad esempio, l’efficienza non è solo un modo per incrementare il proprio business, ma permette anche di avere un minore impatto sull’ambiente. I tre soggetti, le loro spiegazioni e le immagini chiave, sono tutti volti a rendere il tema dell’automazione industriale “comprensibile” a tutti gli individui della società. Ad esempio, la ripetizione in tutti i visual della “bambina con il vestito rosso” e del braccio robotico evidenziano come l’automazione sia in grado di supportare e aiutare gli esseri umani nel raggiungimento dei loro obiettivi, aiutando a creare il prodotto o il servizio desiderato, personalizzandolo in base alle singole esigenze e garantendo che il processo abbia un impatto minimo sull’ambiente. Questo approccio si inserisce all’interno dell’impegno dell’azienda nei confronti della società per rimanere sostenibile attraverso l’occupazione e le contromisure per l’invecchiamento della forza lavoro, la necessità di flessibilità e agilità nella produzione, pur rimanendo redditizia, e un maggiore uso dei progressi tecnologici che offrono benefici per la vita. Per saperne di più sull’impegno per la sostenibilità di Mitsubishi Electric Factory Automation vistare il sito.
La Linea Hercules offre soluzioni per il trasporto e la distribuzione di energia elettrica a bassa, media e alta potenza nei settori industriale, commerciale e terziario.
I condotti a sbarre in alluminio o rame di alta qualità e dal design innovativo garantiscono elevata resistenza meccanica e alla corrosione per un’installazione facile e veloce Le soluzioni sono tutte conformi alle normative CEI EN 61439-6, che certificano le qualità Made in Italy.
PIERANDREA BELLO, PRODUCT MANAGER PER LE TECNOLOGIE LASER IN SALVAGNINI, SPIEGA COME MASSIMIZZARE L’EFFICIENZA DEL TAGLIO LASER SU FORMATI DI LAMIERA FINO A 6 METRI DI LUNGHEZZA di Sofia Rossi
Nel mondo dei sistemi laser l’automazione gioca un ruolo sempre più rilevante, migliorando l’efficienza delle fasi di carico/scarico. Salvagnini produce macchine per il taglio piano della lamiera da metà anni 90. “Alcuni dei vincoli che limitano l’efficienza dei laser in taglia 3 e 4 metri hanno un impatto ancora più evidente su quella dei laser di grandi dimensioni”, spiega Pierandrea
Bello, Product Manager per le tecnologie laser in Salvagnini. “Negli ultimi anni, il mercato ha acquisito in misura sempre maggiore la consapevolezza che il vantaggio dell’automazione non consista soltanto nella riduzione di manodopera, ma anche e soprattutto in un incremento di efficienza. In generale, che sia a causa della delicatezza e del formato del foglio o del peso e dello spessore del materiale da movimentare, possiamo considerare vera l’equa-
zione per cui a maggiori dimensioni della lamiera corrispondono sempre maggiori tempi di gestione, sia nelle fasi che precedono il taglio sia in quelle che lo seguono”, afferma Bello. “Oggi, inoltre, si riscontra una tendenza ad aumentare le dimensioni dei formati di lamiera anche nei settori industriali del sottile e medio-sottile, ad esempio, nelle cabine di verniciatura, nei banchi frigo, pannelli per facciate, HVAC ecc., e questo comporta molti più cambi
foglio che necessitano di manodopera per la movimentazione della lamiera e delle parti tagliate. Con formati più grandi l’automazione assume un ruolo ancora più rilevante; è una tendenza che rileviamo anche per la pannellatrice, prodotto distintivo di Salvagnini, e che ha portato le taglie delle macchine ad aumentare negli anni. Sfruttando i dati raccolti da LINKS, la soluzione IoT Salvagnini che monitora le prestazioni dei sistemi, abbiamo valutato l’efficienza delle varie configurazioni, analizzando le numerose variabili che entrano in gioco come, ad esempio, tipologia e peso della lamiera utilizzata, movimentazione dei materiali, tempi di attesa. L’analisi ha fornito risultati davvero interessanti: le soluzioni stand-alone hanno un’efficienza media di circa il 60%, mentre i sistemi con automazione hanno valori di efficienza medi di gran lunga superiori, che raggiungono l’80% o addirittura il 90% se prendiamo in considerazione il nostro magazzino a torre LTWS”, spiega Bello. Attualmente, oltre il 70% dei sistemi di taglio laser che è prodotto e venduto da Salvagnini è dotato di automazione e circa il 35% è dotato anche di sorting automatico, grazie al quale è possibile recuperare efficienza non tanto nelle fasi di taglio, quanto in quelle di lavorazione a valle del taglio. “È bene precisare –ricorda Bello - che intorno al taglio della lamiera ruotano tante attività a basso valore aggiunto, che hanno un costo in termini di ore uomo non trascurabile. Incrementare la competitività passa anche
dall’automatizzazione di queste attività”. È questo il motivo che ha convinto Salvagnini a sviluppare il dispositivo di carico/scarico ADLU e quello di sorting automatico MCU in taglia 6020, per la lavorazione di formati di lamiera fino a 6 metri di lunghezza. Sono automazioni dedicate al laser L3-6020, introdotto da Salvagnini nel 2017.
Il ruolo dell’automazione di carico/scarico ADLU e del sorting automatico MCU
Il dispositivo ADLU automatizza il carico delle lamiere da pacco e lo scarico delle lastre lavorate con tempi ciclo molto rapidi, di circa 60 secondi, eliminando tutte le fasi intermedie di manipolazione solitamente a carico dell’operatore.
“ADLU è quindi una soluzione di interesse per una platea di settori industriali più ampia, sia per chi lavora con grandi spessori che con lamiere più sottili. Inoltre, è una soluzione flessibile anche in termini di layout, perché la sua struttura a terra è modulare e può
adattarsi agli spazi disponibili in officina”, afferma Bello.
I motivi per investire in un dispositivo di sorting automatico sono diversi. I più evidenti sono i benefici che derivano dall’eliminazione delle attività manuali: la riduzione dei costi operativi, dei problemi di disponibilità della manodopera e di infortuni, cui si somma la riduzione degli scarti collegati al danno da manipolazione, che può essere più o meno frequente durante la separazione. Altrettanto
prevedere in modo estremamente preciso i tempi di sorting, che con un dispositivo automatico sono costanti e ripetibili, e la possibilità di separare il materiale prodotto in eventuali turni non presidiati. Il sorting automatico
perché rende più rapidamente disponibile il materiale per l’invio alle stazioni di lavoro a valle, e semplifica la tracciabilità delle parti raggruppandole per commessa, per kit o per stazione di lavoro successiva. “Questa è una possibilità particolarmente attraente perché, rispetto ai formati più piccoli, il 6 metri permette di mescolare un maggior numero di parti, aumentando la complessità della tracciatura in modo proporzionale rispetto alle dimensioni della lamiera”, spiega Bello. “Il dispositivo
di sorting automatico MCU impila agilmente parti con geometrie, dimensioni e pesi differenti. Oltre alla strategia di sorting standard, può lavorare in modalità full multigripping, permettendo di prelevare in sequenza più parti con lo stesso organo di presa attivando individualmente le ventose o i magneti necessari, o double picking, riducendo i tempi destinati al prelievo dei pezzi”.
La struttura ad aeroplano per il Laser L3 in configurazione 6 metri Una delle caratteristiche distintive dei laser Salvagnini è la cosiddetta struttura ad aeroplano: si tratta di una struttura a trave portante con manipolatore ad aeroplano alleggerito, che assicura numerosi vantaggi: elevata rigidità, rapidità, precisione di posizionamento e accessibilità a tutto il campo di lavoro.“È la struttura tipica di L3 in taglia 3 e 4 m, con due porte scorrevoli, una a destra e l’altra a sinistra, e consente all’operatore di avere una buona accessibilità a tutta l’area di lavoro. Per la taglia 6020, aggiungendo un ulteriore gantry centrale siamo riusciti a mantenere la stessa rigidità che caratterizza le macchine di taglia inferiore e ad aggiungere altre due porte, per non rinunciare all’elevata accessibilità all’area di lavoro”, spiega Bello.
Le caratteristiche di MCU
MCU ha pochi limiti: è in grado di prelevare spessori tra 0.5 e 12 mm e pesi fino a 65kg per ciascun manipolatore, che diventano 130kg quando i due organi di presa lavorano in coppia. La flessibilità e l’estrema mobilità dei manipolatori, che possono ruotare sull’intero arco dei 360°, annullano i vincoli geometrici: gli organi di presa possono prelevare parti di un’estrema variabilità di forma e dimensioni. “Le dimensioni minime – precisa Bello - sono di 100x200mm, ma per superare l’ostacolo dimensionale nello scarico di parti sotto i limiti ufficiali ed evitare che il sorting automatico finisca per ridurre la resa della lamiera, Salvagnini ha reso disponibile la funzionalità smart cluster che consente di micro-giuntare tra loro i particolari in modo semplice e veloce, senza utilizzare una cornice di taglio e senza appesantire la programmazione in ufficio, per ridurre i tempi complessivi di scarico”.
Un software per ridurre il rischio d’errore e gestire scenari di produzione diversificati
MCU si programma con il software NEXUS. Semplice e facile da usare, NEXUS elabora automaticamente i programmi di sorting che l’operatore, se necessario, può modificare in modalità interattiva. Permette il totale controllo
del processo, sia dell’intera sequenza di produzione che della singola lamiera in precisi momenti del ciclo produttivo, e una sua verifica puntuale grazie al simulatore 3D integrato. “Il software – afferma Belloconsente al dispositivo sorting MCU di impilare agilmente parti con geometrie, dimensioni e pesi differenti, anche in modalità multigripping, permettendo di prelevare in sequenza più parti con lo stesso organo di presa.. Così facendo, il sorting automatico agevola notevolmente l’attività degli operatori, che possono prelevare i pezzi già impilati senza doverli separare, riducendo notevolmente i tempi di attesa tra la fine della fase di taglio e l’inizio di quella successiva. NEXUS permette di non scegliere in fase progettuale una strategia produttiva definita, e può risolvere esigenze diverse, grandi lotti, piccoli lotti, kit, lotti unitari perché è estremamente flessibile nel gestire scenari di produzione diversificati”. Queste caratteristiche fanno di NEXUS il software di sorting ideale, sia per il terzista che per il produttore OEM.
Particolare attenzione alla riduzione dei consumi
Strizzando l’occhio alla sostenibilità, sia ADLU che MCU sfruttano la tecnologia AVC, Adaptive Vacuum Control, un sistema di attivazione del vuoto intelligente: tramite dei sensori viene monitorato quindi il grado di vuoto presente nelle ventose in presa e la generazione di vuoto è attivata solo quando necessario. La riduzione dei consumi di aria compressa supera il 90%. “Anche in questo caso, aumentando le criticità all’aumentare delle dimensioni, il risparmio in valore assoluto è superiore nei fogli di dimensioni maggiori. Per ridurre l’impatto energetico degli organi in movimento, inoltre, Salvagnini ha dotato i sistemi di automazione di motori ad alto rendimento e le tavole idrauliche per il carico/scarico del materiale di attuatori ibridi”, conclude Bello.
Con StateMonitor di HEIDENHAIN, non occorre presidiare costantemente la macchina utensile. Rileva l’operatività del parco macchine e lo rappresenta in tempo reale su PC, laptop, tablet o smartphone.
BASATA SULLA RIDUZIONE DEGLI SPRECHI E L’OTTIMIZZAZIONE DELLE RISORSE, LA MANIFATTURA SNELLA E SOSTENIBILE CONSENTE DI CREARE UN AMBIENTE PRODUTTIVO EFFICIENTE E, AL CONTEMPO, SOSTENIBILE DAL PUNTO DI VISTA AMBIENTALE E SOCIALE
La manifattura snella e sostenibile rappresenta un paradigma innovativo nell’ambito industriale, unendo l’efficienza operativa alla responsabilità ambientale. Questo approccio si basa sui principi della produzione snella, noti anche come “Lean Manufacturing”, e li integra con l’obiettivo di minimizzare l’impatto ambientale e promuovere la sostenibilità.
In un contesto in cui le preoccupazioni ambientali sono sempre più al centro dell’attenzione, la manifattura snella e sostenibile si propone di ridurre gli sprechi e ottimizzare le risorse, contribuendo così a una produzione più efficiente ed ecocompatibile. Uno dei principi fondamentali è la riduzione degli sprechi, che include non solo gli sprechi di materiale e risorse, ma anche quelli di energia e tempo lavoro.
La manifattura snella ha le sue radici nel Giappone degli anni ‘50 e ‘60. Il concetto fu sviluppato principalmente presso la Toyota Motor Corporation come risposta alle sfide economiche dell’epoca e alle pressioni competitive del mercato automobilistico. La Toyota ha cercato di affrontare le limitazioni delle metodologie di produzione tradizionali, sviluppando un sistema che minimizzasse gli sprechi e ottimizzasse l’efficienza operativa. La manifattura snella ha iniziato a guadagnare attenzione oltre i confini giapponesi negli anni ‘80, quando le pratiche e i principi adottati dalla Toyota furono studiati e applicati in occidente. Da allora è stato ampiamente adottato in molte industrie in tutto il mondo e, oggi, il sistema di produzione Toyota, guidato allora da figure chiave come Taiichi Ohno e Shigeo Shingo, viene considerato il precursore della manifattura snella, continuando a evolversi e a influenzare le pratiche aziendali, fungendo da modello per un’efficienza operativa sostenibile e orientata al valore.
Un elemento chiave della manifattura snella è la creazione di un ambiente flessibile e reattivo. Ciò si traduce in una produzione guidata dalla domanda effettiva, evitando la sovrapproduzione e riducendo al minimo gli stock di magazzino. Questo non solo ottimizza i processi, ma riduce anche il consumo di risorse e l’emissione di gas serra associati alla produzione e allo stoccaggio eccessivo.
Un altro aspetto cruciale è la promozione dell’innovazione continua. Attraverso la collaborazione interdisciplinare e l’adozione di tecnologie avanzate, le aziende possono migliorare costantemente i loro processi, riducendo al contempo l’impatto ambientale. L’implementazione di tecnologie sostenibili, come l’uso di energie rinnovabili o l’adozione di materiali riciclabili, è un passo fondamentale verso una manifattura più sostenibile.
Sposando l’efficienza operativa con un impegno profondo verso la sostenibilità, la manifattura snella e sostenibile si erge come faro guida nel panorama industriale moderno. Questo approccio innovativo
porta con sé una serie di vantaggi significativi che vanno oltre la mera ottimizzazione dei processi. In primo luogo, concentrandosi sulla riduzione degli sprechi e ottimizzando i processi produttivi, comporta un miglioramento tangibile dell’efficienza operativa, con una produzione più rapida, costi ridotti e una maggiore competitività sul mercato.
Riducendo sprechi di materiali, tempo e energia, la manifattura snella preserva le risorse naturali limitate del nostro pianeta. Questa pratica mira a un utilizzo oculato delle materie prime, contribuendo alla sostenibilità delle risorse.
L’approccio snello favorisce la flessibilità operativa, consentendo alle aziende di adattarsi rapidamente alle mutevoli esigenze del mercato. Questa agilità non solo migliora la capacità di rispondere alla domanda del consumatore, ma riduce anche il rischio di sovrapproduzione e stoccaggio eccessivo.
La cultura della manifattura snella promuove l’innovazione continua. Attraverso l’adozione di nuove tecnologie e pratiche avanzate, le aziende possono non solo migliorare la qualità dei loro prodotti, ma anche sviluppare soluzioni più sostenibili e orientate al futuro.
La manifattura snella e sostenibile non è solo un modello operativo avanzato, ma un catalizzatore per un cambio di paradigma nell’industria. Questi vantaggi, tra efficienza e responsabilità ambientale, trasformano le aziende in pionieri di un futuro industriale sostenibile e prospero. Adottare la manifattura snella e sostenibile può conferire alle aziende anche un vantaggio competitivo in termini reputazionali. I consumatori sempre più orientati verso la sostenibilità sono propensi a premiare aziende che dimostrano un impegno concreto per la responsabilità ambientale, migliorando così la reputazione aziendale.
La manifattura snella e sostenibile non si limita solo alla produzione, ma si estende anche alla gestione delle catene di approvvigionamento, promuovendone una gestione etica. Collaborare con fornitori che condividono valori sostenibili contribuisce a creare una rete di produzione responsabile, che evita il ricorso a materiali provenienti da fonti non etiche o non sostenibili. Trasparenza e tracciabilità diventano elementi chiave per garantire che ogni componente del processo produttivo rispetti gli standard ambientali e sociali.
In conclusione, la manifattura snella e sostenibile rappresenta un approccio integrato che mira a coniugare efficienza operativa e responsabilità ambientale. Le aziende che abbracciano questo modello non solo riducono i costi operativi, ma diventano anche attori attivi nella costruzione di un futuro industriale più sostenibile e consapevole. Buona lettura!
GRAZIE AD UNA CELLA CON UN ROBOT ABB, È STATO AUTOMATIZZATO IL PROCESSO
DI COLLAUDO DEI MODEM PER IL RICICLO DEI DISPOSITIVI, MIGLIORANDO LA PRODUTTIVITÀ E GARANTENDO UNA QUALITÀ COSTANTE ALL’INSEGNA DI UNA
ECONOMIA CIRCOLARE
L’industria delle comunicazioni via Internet ha un enorme giro d’affari di apparecchi elettronici di rete come modem e router. Quando gli utenti ricevono offerte speciali dai fornitori di servizi, spesso ricevono un nuovo modem che possono utilizzare solo per pochi mesi prima di restituirlo alla scadenza del contratto.
Riciclare questi dispositivi per poterli rimettere in uso, evita di mandarli in discarica, eliminando la creazione di ulteriori rifiuti e risparmiando il consumo di energia e materiali aggiuntivi che sarebbero necessari per produrne di nuovi. Riuscire ad automatizzare il processo di collaudo dei modem per poterli riutilizzare per i clienti finali, consentirebbe di liberare personale per altre mansioni, migliorando la produttività e garantendo una qualità costante del processo.
Un’azienda italiana che si occupa di smaltimento di rifiuti sta ottenendo esattamente questo risultato utilizzando i robot ABB per testare i dispositivi modem e assicurarne il funzionamento, consentendo così di reinserirli nel flusso di fornitura dei clienti.
SEVal S.r.l. è il leader italiano nel mercato dei RAEE (Rifiuti di Apparecchiature Elettriche ed Elettroniche), con stabilimenti in tutto il Paese. L’azienda ricicla tutti i tipi di apparecchi elettronici, sia domestici che aziendali, tra cui stampanti, cellulari e modem. Nel 2021 l’azienda ha raccolto oltre 155.000 tonnellate di rifiuti elettronici da riciclare e recuperare.
Le fasi del processo di verifica
Il recupero di modem e router funzionanti viene effettuato per il secondo fornitore di servizi di telecomunicazione in Italia, che vuole riutilizzare il più possibile i dispositivi per evitare le spese aggiuntive per l’acquisto di nuovi articoli. Il processo di verifica prevede diverse fasi. La prima è una fase manuale, in cui il dispositivo viene esaminato per vedere se è conforme agli standard estetici richiesti. Gli articoli vengono rimossi dal processo se sono graffiati, rotti o deturpati in qualsiasi modo.
La fase successiva è quella di “accensione e ripristino” per garantire
che gli articoli rotti non vadano oltre. Il terzo passo è un test approfondito per confermare che il dispositivo è completamente funzionante. Una volta eseguiti questi passaggi, la fase finale prevede che il modem venga pulito, reimpacchettato e restituito alla rete.
Un compito ripetitivo adatto ai robot
La seconda fase del processo, in cui il modem viene acceso e resettato, viene ora eseguita da un robot ABB. “Il compito è molto ripetitivo e richiede molto tempo. Utilizzavamo due persone in due turni. Con un totale di quattro persone, potevamo trattare 800 dispositivi al giorno. Ora, con il metodo robotizzato, possiamo lavorare 900 pezzi al giorno. Il personale è stato spostato ad altre mansioni più varie e gratificanti, come la pulizia dei modem e l’imballaggio per la spedizione. I lavoratori sono felici di vedere che stiamo investendo per dare loro altre mansioni e compiti da svolgere”, spiega Stefano Spavioli che dirige il reparto che ricicla i dispositivi e ha collaborato con ABB per sviluppare la soluzione robotizzata.
Il processo di collaudo pone delle sfide
L’azienda ha iniziato le indagini e la pianificazione del progetto nel marzo 2021 e il robot è stato installato nel novembre 2021.
Il robot è stato programmato con l’aiuto di RobotStudio®, lo strumento di simulazione offline di ABB che consente di valutare e mettere a punto l’applicazione del robot prima di collocarlo nell’area di lavoro reale. Per facilitare il prelievo degli apparati elettronici, questi sono disposti orizzontalmente in scatole di plastica. Il robot trova il modem grazie a un sistema di visione. Prende l’apparecchio e lo posiziona su una stazione di prova, quindi cambia l’utensile di presa e ruota il modem per eseguire la scansione di un codice a barre. La cella è collegata a un database che contiene informazioni sul modem e tutti i dettagli necessari per controllare il test. Un dato essenziale da acquisire è il numero di volte che il modem è tornato indietro dalla rete: se è tornato indietro più di una o due volte, probabilmente non è un buon dispositivo e dovrà essere scartato.
La prima fase del test consiste nel collegare la presa di alimentazione. Si tratta di un compito impegnativo per il robot, poiché il jack è un collegamento molto piccolo che deve entrare in un piccolo foro. Il robot accenderà e spegnerà il modem come parte del processo di test.
Una sfida è stata quella di
programmare la cella in modo che potesse rilevare il colore del LED del modem, consentendole di riconoscere lo stato del modem e di inviare questa informazione al robot.
In seguito, il modem viene resettato, il che comporta il posizionamento di un foro di connessione ancora più piccolo, la cui posizione può variare. I modem che superano il test vengono inseriti dal robot in una scatola specifica per essere trasportati alla fase successiva, mentre le unità non funzionanti vengono inviate alla rottamazione. I trituratori aprono e rompono gli involucri, mentre le schede dei circuiti vengono recuperate per ricavarne materiali di valore.
La messa a punto porta al successo Con l’aiuto di ABB e del suo software di programmazione offline RobotStudio®, l’azienda è stata in grado di affrontare una serie di sfide. “All’inizio abbiamo avuto bisogno di diversi aggiornamenti della programmazione per tenere conto delle condizioni di illuminazione, che causavano al robot alcuni problemi nella lettura del nome dell’apparecchio. Abbiamo anche sperimentato l’ottimizzazione delle procedure, la sequenza delle operazioni e il tempo che il robot dedica al controllo del dispositivo. Inizialmente, il robot riusciva a produrre 600 pezzi al giorno. Modificando i parametri di temporizzazione, siamo riusciti a ottimizzare le prestazioni fino a raggiungere i 900 pezzi al giorno”, spiega Spavioli. Un’altra sfida è stata rappresentata dal fatto che il fornitore di telecomunicazioni ha cambiato la forma, il peso e il modello dei modem, che ora hanno la forma di cilindri del peso di 2 kg, anziché la forma più piatta e simile a una scatola del tipo precedente. “Sia ABB che il robot avevano bisogno di flessibilità per adattarsi al nuovo modello”, afferma Stefano. Il sistema presenta enormi vantaggi in termini di costi per il fornitore di servizi di telecomunicazione: ogni modem riciclato costa tra il 60 e l’80% in meno rispetto all’acquisto di una nuova unità. Per SEVal, il processo automatizzato migliora la sua reputazione di riciclatore hi-tech che svolge un ruolo importante nell’economia circolare. “Il supporto fornito da ABB nello sviluppo della cella robotizzata è stato fondamentale per il progetto. ABB è un’azienda affidabile, con un approccio professionale e in grado di fornire le prestazioni promesse. Mi hanno aiutato con la programmazione per impostare correttamente la cella - so di poter contare sul supporto e sull’aiuto di ABB”, conclude Spavioli.
Il successo del progetto ha portato l’azienda a studiare altri processi di riciclo che potrebbero essere adatti all’automazione robotica.
Per dare visibilità in tempo reale ai processi produttivi. Con #StateMonitor si stabilisce sempre se la macchina è in lavorazione, in attesa oppure se si è verificata un’anomalia.
CON STATEMONITOR DI HEIDENHAIN È POSSIBILE RILEVARE, VISUALIZZARE E ANALIZZARE NEL DETTAGLIO I DATI MACCHINA
QQuando si vuole ottenere una panoramica a 360° dell’officina, le soluzioni software della Fabbrica Digitale HEIDENHAIN sono la risposta giusta. Sono in grado di rappresentare interamente la catena di processo di ogni attività con macchine utensili CNC – dalla commessa alla manutenzione.
StateMonitor è il software di monitoraggio HEIDENHAIN che consente di combinare su misura esigenze e ambiente produttivo, personalizzando le impostazioni secondo le necessità della propria officina. La connessione macchine avviene tramite le interfacce HEIDENHAIN DNC, Modbus TCP, OPC UA o MTConnect, assicurando la possibilità di collegare tutto il parco macchine, anche in presenza di controlli numerici di marche diverse e se si tratta di
macchine a taglio laser o alesatrici. È inoltre possibile connettersi a un reporting database esterno per una pratica gestione dei dati macchina rilevati anche con l’utilizzo in soluzioni software esterne. La gestione utenti è personalizzabile tramite autenticazioni; il software è disponibile in ben 23 lingue diverse ed è possibile impostare una lingua diversa per ogni operatore.
StateMonitor consente di consultare in tempo reale lo stato di produzione di macchine utensili CNC. Rileva l’operatività del parco macchine e lo rappresenta con chiarezza sul PC, laptop, tablet o persino sullo smartphone. La videata di stato fornisce informazioni sull’operatività delle macchine: in produzione, non in produzione, in manutenzione o non in uso. Si può sorvegliare perfettamente
l’andamento della produzione e individuare le potenzialità di ottimizzazione, analizzando indici e tempi di esecuzione del programma. E con Messenger si possono anche ricevere e-mail per eventi predefiniti: ad esempio quando la macchina si arresta, se il livello di refrigerante è basso o se un programma è completato.
Le altre soluzioni offerte
StateMonitor integra altre opzioni per permettere di analizzare e quindi comprendere a fondo l’operatività nella vostra officina.
L’opzione software JobTerminal consente di creare o assegnare commesse o cicli di lavoro, prenotare manualmente o automaticamente tempi di attrezzaggio e di produzione, salvare i dati delle commesse e definire le sequenze di lavorazione. Permette di avere sempre e ovunque sott’occhio tutte le informazioni sulle commesse pianificate,
La Fabbrica Digitale: trasparenza, efficienza e sicurezza di processo StateMonitor è uno dei tasselli della Fabbrica Digitale HEIDENHAIN che riunisce hardware, software, consulenza e servizi. È possibile realizzare la digitalizzazione dell’intero ambiente produttivo, con combinazioni su misura secondo le vostre necessità specifiche, senza essere vincolati al cloud e indipendentemente dalle dimensioni dell’azienda. In base al know-how HEIDENHAIN sull’ambiente di produzione, la Fabbrica Digitale offre una visione digitale a 360° di tutte le fasi di processo: dalla formulazione dell’offerta al controllo qualità e alla consegna. Tra le proposte più apprezzate, il Digital Twin ricopre sicuramente una posizione di spicco: si tratta della riproduzione realistica della macchina su una stazione di programmazione per disporre in ufficio di cinematiche effettive, parametri e funzioni della macchina, permettendo di eseguire la lavorazione virtuale proprio come sulla macchina vera e propria. Si garantisce così che i programmi NC creati sul sistema CAM o sulla stazione di programmazione vengano eseguiti senza errori anche dal controllo numerico in macchina. Ciò consente di contenere i tempi di attrezzaggio e simulazione come pure di apportare più velocemente migliorie al programma in officina, con conseguente incremento della sicurezza di processo e aumento della produttività.
Con le soluzioni di automazione supplementari e i servizi online di HEIDENHAIN, la fabbrica si trasforma in un ambiente produttivo altamente efficiente.
in corso e completate. I dati operativi vengono rilevati con rapidità e chiarezza a livello centrale, diventando un utile “database” per una precisa valutazione delle commesse. JobTerminal supporta inoltre l’operatore nel rilevamento e nel calcolo consuntivo dei tempi delle commesse.
L’opzione aggiuntiva MaintenanceManager permette di definire le manutenzioni sulla base di diversi intervalli. Oltre all’organizzazione e alla documentazione delle manutenzioni, con MaintenanceManager è possibile rilevare anche guasti e fornire informazioni in modo mirato. Infatti, StateMonitor segnala e registra anomalie come pure informa tempestivamente i responsabili, potendo così risparmiare tempo prezioso in fase di risoluzione dei problemi.
L’opzione “5 Signals” utilizza i segnali PLC per rappresentare dati macchina speciali (come ad esempio valori di temperatura oppure il livello del refrigerante) e consente anche di creare analisi statistiche e grafici. Se i livelli rilevati variano oltre i limiti settati, StateMonitor manda un avviso via mail dando così il tempo di reagire e di evitare che si possano verificare problemi che fermano la produzione.
E infine l’opzione “5 Machines” permette di interconnettere diverse macchine all’interno di uno stesso ambito produttivo.
StateMonitor contribuisce a realizzare una visione digitale e green dell’officina. Infatti sulla base dei dati raccolti si possono rivedere i processi e produrre in modo più efficiente risparmiando risorse preziose. Un esempio? Con StateMonitor è possibile ottimizzare il consumo energetico del parco macchine. Infatti, è possibile rilevare i periodi di inattività e intervenire con contromisure mirate. Ad esempio tramite regolazioni automatizzate, dopo due ore di inattività lo stato della macchina viene registrato come “macchina inutilizzata”. Se i periodi si susseguono, è possibile ridefinire la sequenza delle fasi di lavoro per renderle contigue, ottendendo un sensibile risparmio in termini di energia e di costi.
Un altro esempio è legato all’opzione MaintenanceManager che contribuisce a diffondere la logica di Predictive Maintenance nell’officina. È dimostrato che una strategia di manutenzione definita in base all’elaborazione dei dati raccolti ha un impatto diretto sui KPI aziendali e, più nel lungo periodo, sulla sostenibilità della produzione.
LEAN E GREEN SONO UN OBIETTIVO DELLA PRODUZIONE E L’INTRALOGISTICA È
UN’AREA OPERATIVA TRASVERSALE AD OGNI COMPARTO PRODUTTIVO. L’OBIETTIVO È
DUNQUE CONDIVISO ANCHE NELLA MOVIMENTAZIONE INTERNA AI SITI PRODUTTIVI. NE
PARLA CLAUDIO CARNINO, MANAGING DIRECTOR DI INTERROLL ITALIA
“Lo sviluppo di tecnologie e organizzazioni produttive snelle nel mondo dell’intralogistica come in quello dell’asservimento alle macchine di produzione richiede un approccio strategico che integri l’efficienza operativa con la tecnologia avanzata. Il focus è sulla minimizzazione degli sprechi, l’ottimizzazione dei processi e l’implementazione di soluzioni tecnologiche che supportino un flusso di lavoro fluido e continuo”. Claudio Carnino, managing director di Interroll Italia affronta quotidianamente il tema della movimentazione intralogistica affiancato ai concetti della produzione snella e sostenibile. L’argomento è sviluppato insieme ai system integrator, principali interlocutori della
multinazionale svizzera.
“La base della discussione quando si affronta un nuovo progetto per un cliente finale è sempre quello dell’offerta di soluzioni operative che siano tecnologicamente avanzate, integrabili, scalabili, flessibili per assecondare ondulamenti di mercato del tutto imprevedibili”.
Secondo Claudio Carnino prima di implementare qualsiasi cambiamento, è fondamentale comprendere i processi attuali. “Questo accade con l’identificazione e l’analisi dei processi e delle tecnologie in essere per attivare tutte quelle soluzioni che possono migliorare in termini assoluti la produzione”.
Lo sviluppo di progetti industriali è un lavoro di team. La coesione e la professionalità dei componenti della squadra che discute e sviluppa progetti è cementata soprattutto dall’orientamento al cliente. È necessario immedesimarsi non solo nell’attività del cliente finale ma penetrare il suo mercato per prevederne gli sviluppi.
“In termini generali il mondo produttivo è pesantemente influenzato da una mutata modalità commerciale. L’e-commerce influenza sia il mondo consumer sia quello B2B. La modalità digitale, alla quale così rapidamente si sono adeguate le imprese produttive, influisce su strategie industriali di crescita e di ottimizzazione”.
Se l’obiettivo comune è quello di rendere il sito produttivo più produttivo e sostenibile, è necessario pensare a soluzioni che sostengano l’obiettivo sia nell’immediato sia nel tempo.
“Interroll ha sviluppato una strategia che si è rivelata estremamente efficace per le esigenze del mercato. La tecnologia del motion intralogistico di Interroll si basa su piattaforme che consentono lo sviluppo di soluzioni di movimentazione flessibile, intelligente, sostenibile ed efficace”.
MCP, la piattaforma modulare per trasportatori
La capostipite dell’innovazione di Interroll, rappresentata dal concetto di piattaforma, è la MCP, Modular Conveyor Platform o Piattaforma Modulare per Trasportatori.
Una soluzione che rappresenta la sintesi dell’eccellenza dei componenti unita alla visione della semplicità d’uso e flessibilità di applicazione Il concetto di piattaforma nasce dalla volontà di offrire ai clienti un elemento per la movimentazione delle merci e degli oggetti in un ambiente produttivo che sia facilmente inseribile e gestibile, semplice da manutenere e che possa essere parte di un sistema di movimentazione espandibile o modulabile La MCP è un sistema motorizzato con Roller Drive 24V di Interroll ed ha una struttura decentralizzata, non essendo dotata di un gruppo motore centrale, ma i motori si trovano in ogni singola zona di trasporto. Grazie a questa struttura è possibile attivare o disattivare ogni singola zona di trasporto. Ne deriva che il sistema è in movimento soltanto se è presente il materiale da trasportare. Vengono azionati solo i
Roller Drive necessari per un passaggio ottimale dei materiali da trasportare.
Questa soluzione Interroll rappresenta per system integrator e clienti finali non irrilevanti vantaggi.
“Soluzioni anche complesse, in ambienti difficili, possono essere risolte con agilità e flessibilità. Il sistema di movimentazione, in una fabbrica, in un magazzino, in un centro di smistamento o di movimentazione, diventa componibile come con i mattoncini di un gioco di costruzione. La manutenzione è facilitata, il controllo è agevolato e i consumi sono sotto controllo. La logica della piattaforma porta direttamente all’incremento della produttività con la contemporanea crescita della qualità e il decremento dei consumi e degli errori produttivi”, sottolinea Claudio Carnino.
MPP, la piattaforma modulare per il convogliamento di carichi pesanti
Il concetto della piattaforma è fondamentale per lo sviluppo di soluzioni agili, snelle e pulite. Lean e Green mettono nel mirino la minimizzazione degli sprechi, l’ottimizzazione dei processi e l’implementazione di soluzioni tecnologiche che supportino un flusso di lavoro fluido e continuo.
“Alla MCP segue la MPP, Modular Pallet Platform, un’innovativa piattaforma modulare per il convogliamento di carichi pesanti. Questa soluzione è un trasportatore di pallet particolarmente versatile, che si contraddistingue per la struttura altamente flessibile e modulare. Insieme al collaudato sistema di stoccaggio dinamico Pallet Flow di Interroll, questa piattaforma per il trasporto pallet rappresenta la base ideale per realizzare soluzioni di ogni tipo di trasporto e stoccaggio di pallet e di movimentazione in magazzino”.
La MPP rappresenta un sistema per il trasporto motorizzato dei pallet. A seconda dello scenario applicativo, l’azionamento avviene tramite motoriduttori o Pallet Drive, per cui è possibile realizzare anche linee di trasporto prive di accumulo. Nella gestione di un’impresa sono obbligatori tempi sempre più ristretti e certi per quanto attiene la movimentazione tra ingresso e uscita merci o tra magaz-
zino, produzione e aree di picking in azienda. L’obiettivo è ottenere la massima efficienza attraverso l’automazione – e tutto questo con processi di pianificazione snelli, bassi costi di montaggio e flessibili opzioni di espansione.
HPP, la soluzione per il trasporto modulare dei pacchi
Sulla scia dei successi internazionali del concetto di piattaforma, Interroll ha sviluppato una soluzione per il trasporto modulare dei pacchi. L’HPP (High Performance Conveyor Platform), che integra le diverse soluzioni di smistamento dell’azienda, consente di aumentare in modo significativo la produttività, la capacità e l’efficienza energetica dei centri di distribuzione grandi e piccoli. La globale strategia di piattaforma prevede principalmente l’utilizzo di prodotti
tecnologici già collaudati che hanno dato prova di affidabilità ed efficienza in centinaia di migliaia di applicazioni.
Il cuore della tecnologia di movimentazione sviluppata da Interroll è anch’essa basata sul concetto di piattaforma. La Interroll DC Platform consente di realizzare straordinarie soluzioni di movimentazione perfettamente integrate nel concetto di agilità e sostenibilità. La piattaforma in corrente continua, a 24 e 48 Volt, con l’innovativo RollerDrive EC5000 (anche in diametro 60mm e “IP66” e “Deep Freeze” per ambienti fino a -30°C) aumenta la flessibilità anche nella potenza di uscita meccanica. I rulli motorizzati, da 20 W, 35 W e 50 W, soddisfano le più diverse esigenze di trasporto, leggere e pesanti. Interroll EC5000 è disponibile anche con interfaccia Bus basata sullo standard CANOpen. In connessione con la scheda Interroll Multicontrol, che gestisce i protocolli di comunicazione PROFINET, EtherNet/IP e EtherCat, si visualizzeranno sullo schermo infinite informazioni e funzionalità tramite PLC o piattaforma Web. L’interfaccia Bus del RollerDrive EC5000 consente la realizzazione di funzioni di comando specifiche per l’automazione. Accelerazione, velocità e frenatura sull’impianto sono ancora più precisi, e gli oggetti saranno posizionati millimetricamente sulla linea di trasporto. Un prerequisito per l’interazione continua delle soluzioni di trasporto con robot o bracci di presa automatizzati.
UN PROCESSO PRODUTTIVO LEAN E GREEN È SEMPRE PIÙ INDISPENSABILE A TUTTA
LA FILIERA INDUSTRIALE. COME SI OTTIENE? CON LA SENSORISTICA ADEGUATA CHE
AIUTI IL PROCESSO PRODUTTIVO IN FABBRICA E NEI MAGAZZINI AD INCREMENTARE SOSTENIBILMENTE LA PRODUZIONE, LA QUALITÀ E LA SICUREZZA. LO ASSICURA
ANTONIO BELLETTI, AMMINISTRATORE DELEGATO DI LEUZE ITALIA
LLean e Green Manufacturing sono due filosofie di gestione della produzione che mirano a ottimizzare l’efficienza e a ridurre gli sprechi, ma con focus leggermente diversi. La produzione lean si concentra sull’eliminazione degli sprechi per migliorare l’efficienza operativa. Questo include la riduzione dei consumi di tempo, di materiali, di risorse. Il Green Manufacturing si concentra principalmente sulla riduzione dell’impatto ambientale della produzione. Questo include la riduzione del consumo di energia, l’uso di materiali sostenibili, il riciclo e la riduzione delle emissioni. L’obiettivo è produrre beni in modo più sostenibile. Secondo Antonio Belletti, amministratore delegato di Leuze Italia, vi sono delle strategie che integrano sia la sostenibilità sia la prodizione snella. “Partirei dalla ottimizzazione della supply chain in un’ottica pratiche sostenibili ed efficienti. Penserei poi al «design for environment». Progettare impianti che siano rispettosi dell’ambiente e ideati affinché si evitino sprechi è fondamentale. Come è fondamentale migliorare l’efficienza energetica degli impianti di produzione riducendo il consumo di energia e l’impatto ambientale. Infine una costante analisi dei processi per arrivare ad un miglioramento continuo per ottimizzare l’efficienza operativa e la sostenibilità complessiva.
L’implementazione di queste strategie richiede un approccio olistico e può coinvolgere investimenti in nuove tecnologie, formazione dei dipendenti, e cambiamenti nei processi di produzione. L’obiettivo finale è creare sistemi di produzione che non solo siano efficienti dal punto di vista operativo, ma che siano anche responsabili dal punto di vista ambientale”.
Sensoristica, automazione e sicurezza: 3 elementi fondamentali per la sostenibilità
Parlare di produzione snella significa parlare di tecnologie e soluzioni in grado di ottimizzare gli ambienti produttivi, che non significa solo la fabbrica ma anche i magazzini, che oggi trasversalmente rappresentano una parte fondamentale del processo produttivo di ogni settore.
Per Antonio Belletti sono tre gli elementi da prendere in particolare considerazione quando si parla di produzione snella e sostenibile. “La sensoristica, l’automazione e la sicurezza negli impianti di produzione e nei magazzini rappresentano tre componenti fondamentali nell’industria moderna, che contribuiscono significativamente all’efficienza operativa, alla precisione e alla sicurezza del lavoro, dunque alla sostenibilità”.
I sensori sono gli occhi e le orecchie degli impianti di produzione e dei magazzini. Rilevano una vasta gamma di parametri, come temperatura, pressione, umidità, movimento, e presenza di oggetti o persone. Questi dati vengono poi utilizzati per monitorare le condizioni operative, prevenire malfunzionamenti e ottimizzare i processi.
“L’offerta di sensoristica Leuze è riconosciuta per precisione, affidabilità e durata. Offriamo al mercato una gamma completa di soluzioni che va dai sensori ottici, ai sensori induttivi, a quelli di posizione, ai sensori di sicurezza e ai sistemi di visione industriale. Grazie ad una ricerca e sviluppo in costante attività, siamo in grado di sviluppare costantemente soluzioni innovative che trovano applicazione in molteplici ambiti, dal rilevamento di oggetti alla misurazione di distanze e velocità, fino al monitoraggio di condizioni ambientali e di sicurezza”, specifica Antonio Belletti.
la sicurezza in ogni tipo di magazzino automatizzato”. Le innovazioni in questo specifico settore sono di particolare impatto nell’ottica della produzione snella e sostenibile. Soltanto per fare un esempio le soluzioni di posizionamento lineare, Leuze AMS300 e BPS300i contribuiscono alla precisione e alla velocità operativa, rendendo così la funzionalità all’interno di un magazzino fluida e ampiamente sostenibile.
Il ruolo dei sensori e dell’automazione per un ambiente di lavoro più sicuro
Un altro aspetto cruciale nella produzione snella e sostenibile è il concetto di sicurezza.
Un ruolo chiave nell’incremento della produttività e nella riduzione dei costi operativi è ricoperto dall’automazione. Robot, bracci meccanici, e sistemi di trasporto automatizzati sono esempi di come l’automazione sia implementata negli impianti di produzione. Essi non solo eseguono compiti ripetitivi con maggiore precisione e velocità rispetto ad operatori umani, ma possono anche operare in ambienti pericolosi o insalubri, riducendo il rischio per i lavoratori.
Belletti sottolinea come anche in quest’area Leuze abbia un ruolo da protagonista. “Uno dei mercati principali in cui Leuze opera è quello dell’automazione industriale. Qui, la nostra sensoristica trova applicazione per l’ottimizzazione dei processi di produzione, per l’incremento dell’efficienza delle linee di assemblaggio e per la contemporanea garanzia della sicurezza dei lavoratori. I sensori Leuze sono impiegati in varie fasi della produzione, dalla manipolazione dei materiali al controllo di diversi parametri, fino al packaging e all’intralogistica”.
Proprio l’intralogistica riveste una particolare importanza per Leuze. “Nel mondo del warehousing, i sensori sono fondamentali per la gestione efficiente dei flussi delle merci. Vengono utilizzati per il tracciamento dei prodotti, la gestione degli inventari, l’automazione dei processi di picking e
Con l’aumento della complessità delle macchine e dei sistemi, cresce anche il bisogno di proteggere chi vi lavora intorno. Qui, la sensoristica e l’automazione svolgono un ruolo vitale. I sensori possono rilevare situazioni potenzialmente pericolose e attivare sistemi di allarme o di spegnimento automatico. I sistemi di sicurezza automatizzati, come le barriere ottiche e i sistemi di arresto d’emergenza, sono fondamentali per la protezione dei lavoratori da infortuni. E proprio la ricerca costante della massima protezione dagli infortuni che eleva la produzione ad uno status di qualità superiore e contribuisce a classificarla come snella e soprattutto sostenibile. Oltre all’impatto fisico sul lavoratore, da evitare in assoluto, la mancanza di sicurezza impatta anche sul conto economico a causa di potenziali fermo impianti, manutenzioni straordinarie, revisioni e quant’altro.
“In sintesi, sensoristica, automazione e sicurezza sono interconnessi e fondamentali per il moderno ambiente industriale e produttivo. Mentre la sensoristica fornisce i dati necessari per il monitoraggio e il controllo, l’automazione utilizza questi dati per ottimizzare i processi e migliorare l’efficienza. Allo stesso tempo, entrambi contribuiscono a creare un ambiente di lavoro più sicuro, riducendo il rischio di incidenti e garantendo la protezione dei lavoratori. Leuze è protagonista grazie ad innovazioni tecnologiche che portano costantemente più automazione, efficienza e sicurezza negli impianti di produzione e nei magazzini contribuendo così ad aumentare il tasso di sostenibilità e di agilità produttive delle imprese.” conclude Antonio Belletti.
PER OMRON SOSTENIBILITÀ SIGNIFICA SOSTANZIALMENTE “MIGLIORARE LA QUALITÀ DELLA VITA E CONTRIBUIRE AL BENESSERE DELLA SOCIETÀ”
II sistemi e le tecnologie Omron mirano a realizzare un’“innovazione guidata dalle esigenze sociali” disegnando scenari di crescita basati su quello che in Omron viene definito un “near-future design”, che è una rappresentazione concreta della visione sociale a cui l’azienda sta puntando.
Per Omron il raggiungimento della sostenibilità della società equivale a quello della propria sostenibilità aziendale, contribuendo a risolvere le questioni sociali con soluzioni uniche che uniscono i tre approcci Omron all’innovazione nell’automazione: “integrato (evoluzione del controllo)”, “intelligente (sviluppo dell’intelligenza attraverso le TIC)” e “interattivo (nuova armonizzazione tra persone e macchine)”.
“Il numero di applicazioni innovative che abbiamo sviluppato utilizzando questa tecnologia di automazione è cresciuto fino a oltre 290, impiegandole per risolvere problemi e apportare miglioramenti in molti plant dei nostri clienti. Di recente abbiamo incorporato anche tecnologie avanzate di digitalizzazione, come la virtualizzazione e la simulazione 3D, per accelerare continuamente la creazione di
applicazioni innovative”, spiega Chiara Rovetta, Field Communication Coordinator Italy di Omron.
“Sulla base delle nostre esperienze in fabbrica e del feedback dei clienti, utilizziamo il nostro patrimonio di conoscenze accumulato (competenze e know-how) per mantenere e migliorare i siti produttivi dei nostri clienti, offrendo cinque diversi programmi di assistenza e mantenendo attiva una rete assistenziale che comprende più di 150 sedi in circa 40 Paesi e regioni del mondo, oltre a 36 Centri di Automazione (ATC) dove è possibile verificare e dimostrare l’idoneità delle nostre soluzioni per i problemi dei clienti utilizzando apparecchiature reali”, chiarisce Rovetta. “Gli esempi di utilizzo “lean & green” della nostra tecnologia si possono trovare in molti campi”.
Cobot assistant: l’ultima soluzione per la produzione di dispositivi farmaceutici
L’industria dei dispositivi farmaceutici produce molti sottocomponenti piccoli e delicati, la cui manipolazione è fondamentale. Un’altra sfida è rappresentata dal fatto che alcune
attività del processo di produzione dei componenti sono molto noiose e, di conseguenza, i produttori possono registrare tassi di turnover più elevati.
In quest’ottica la ripetibilità e l’affidabilità sono capacità intrinseche della maggior parte dei robot, che possono contribuire a creare una soluzione molto robusta per la manipolazione di pezzi delicati con visione integrata, sensori di forza e altri strumenti aggiuntivi.
I cobot (robot collaborativi) possono ad esempio aiutare a risolvere non solo i costi associati a un’ispezione di qualità non corretta, ma anche a ridurre i costi di formazione dei nuovi operatori e i costi successivi di ogni nuovo assunto.
“Un caso è quello di Kraus Maschinenbau, azienda produttrice di attrezzature specializzate per la stampa e il confezionamento, che ha unito le forze con Omron per sviluppare un innovativo progetto di robot collaborativo (cobot) per il suo ambiente di confezionamento. Un elemento chiave di questo progetto è il cobot TM12 di Omron, utilizzato per ottimizzare l’alimentazione automatica dei libretti nelle confezioni farmaceutiche. Il cobot TM12 di Omron è stato scelto come soluzione più adatta in grado di ridurre la necessità di lavoro manuale, aumentando l’efficienza e riducendo al minimo gli errori”, racconta Rovetta.
L’automazione alla guida della fabbrica alimentare del futuro
Le aziende del settore F&B future-ready stanno valutando sempre di più le opportunità e le possibilità offerte dalla robotica innovativa, dalla tecnologia dei sensori e dagli approcci olistici all’automazione, in considerazione di fattori quali la forza lavoro (dipendenti), qualità dei prodotti e del packaging, flessibilità della produzione e sostenibilità.
In questo contesto, per automazione non si intende solo la robotica o l’intelligenza artificiale, ma una struttura complessiva ben congegnata di robotica fissa, collaborativa e mobile, oltre a tecnologie di monitoraggio e controllo, sensori e tecnologie di visione adattate ai rispettivi requisiti di produzione. Inoltre, le varie parti interessate e i driver di mercato non devono essere considerati isolatamente, ma nel
loro insieme e integrati nella futura strategia di produzione.
“Un esempio viene dalla nuova incartonatrice orizzontale per pasta lunga di Ricciarelli, che utilizza i sistemi di visione Omron per verificare l’effettiva chiusura della confezione e la perfetta marcatura OCR/OCV. Offrono la possibilità di controllare tutte le variabili dall’HMI e di integrare i dati di produzione direttamente dal sistema di gestione aziendale; ma i vantaggi della nuova soluzione sono evidenti anche per gli operatori. Il sistema di visione Omron garantisce un funzionamento più semplice grazie alla diagnostica avanzata integrata e a una maggiore trasparenza dei potenziali guasti che potrebbero causare malfunzionamenti”, afferma Rovetta.
Packaging sostenibile: l’imballaggio flessibile
Una delle strategie per una maggiore sostenibilità nel settore degli imballaggi consiste nel ridurre la quantità di plastica, soprattutto se vergine. Una tattica chiave per farlo è il passaggio dall’imballaggio rigido a quello flessibile. Pareti più sottili, formati più piccoli, cuciture più strette e pesi più leggeri sono un buon modo per ridurre la quantità di plastica vergine utilizzata nel contenitore primario. A ciò si aggiunge l’uso di monomateriali, di carta e biopolimeri, nonché l’aumento della percentuale di materiale riciclato negli imballaggi principali, protettivi e di trasporto (imballaggio primario, secondario e finale). Tutto questo ha implicazioni per i processi e le tecnologie in fabbrica, che devono essere rivisti: le aziende devono ad esempio verificare la compatibilità delle loro attrezzature e regolare le impostazioni, se necessario. Le linee devono essere flessibili per passare a nuovi materiali. È necessario collegare e gestire le nuove informazioni macchina-macchina, oltre a controllare le prestazioni delle macchine nelle nuove condizioni ed evitare il più possibile gli sprechi.
“Omron offre una soluzione completa per l’automazione sostenibile delle linee di confezionamento che aiuta le aziende a diventare più efficienti ed ecologiche, utilizzando le loro macchine per nuovi materiali riciclabili e garantendo la qualità del prodotto. Sysmac è una piattaforma di automazione integrata che fornisce un controllo e una gestione completi dell’impianto di automazione. Al centro di questa piattaforma, la serie Machine Controller supporta il controllo sincrono di tutti i dispositivi della macchina e offre funzionalità avanzate quali motion, robotica e connettività con database. Questo concetto multidisciplinare consente di semplificare l’architettura della soluzione, ridurre lo sforzo di programmazione e ottimizzare la produttività.
La serie NX7 Sysmac realizzata da Omron, in particolare, è una CPU ad alte prestazioni con due core di movimento sincronizzati in grado di controllare fino a 256 assi. Vanta una funzionalità che consente un utilizzo in tempo reale del modello di machine learning e una libreria IA di manutenzione preventiva che garantisce apparecchiature senza interruzioni”, conclude Rovetta.
NX7 SysmacPER RIDURRE L’IMPATTO DELLE PROPRIE ATTIVITÀ, RENISHAW HA RIDOTTO LE EMISSIONI DEI SUOI STABILIMENTI PRODUTTIVI. MA NON SOLO. GRAZIE A SOLUZIONI CHE AIUTANO LE AZIENDE A PRODURRE DI PIÙ, CONSUMANDO DI MENO SOSTIENE I PROPRI CLIENTI NEL PASSAGGIO A MODELLI PIÙ SOSTENIBILI
LLa temperatura globale è in costante aumento e i periodi di siccità diventano sempre più frequenti. In questo contesto è indispensabile trovare metodi di produzione più sostenibili per ridurre l’impatto ambientale sul nostro pianeta. Renishaw ha iniziato il proprio viaggio verso la sostenibilità con la definizione di una serie di obiettivi chiari, da perseguire all’interno dell’azienda: raggiungimento di Net Zero Scope 1 e 2 entro il 2028 e Net Zero completo al massimo entro il 2050. La strategia aziendale è stata allineata agli obiettivi di sviluppo sostenibile delle Nazioni Unite, anche per quanto riguarda consumi e produzioni responsabili. “Quest’avventura ha avuto inizio molti anni fa, ma oggi i nostri sforzi si sono moltiplicati e abbiamo costituito uno speciale team dedicato, per supportare l’implementazione dei cambiamenti all’interno dell’azienda e su tutta la nostra catena del valore”, spiega Ben Goodare, responsabile del reparto Sustainability di Renishaw. La sostenibilità riguarda una serie di problematiche molto più ampia di quanto generalmente non si creda. Oltre alle criticità ambientali, come ad esempio le emissioni di gas serra, bisogna prendere in considerazione anche argomenti come equità sociale, diritti umani e divario retributivo di genere. “Gli obiettivi di sostenibilità di Renishaw abbracciano tutti questi aspetti – afferma Goodare - cercando di migliorare le condizioni di vita delle persone con cui interagiamo e al tempo stesso di ridurre al minimo l’impatto ambientale della nostra catena del valore. Riuscire ad
avere un impatto positivo su entrambi questi aspetti, senza perdere di competitività è la chiave per creare un’attività realmente sostenibile”.
Non si diventa sostenibili da un giorno all’altro. Per risolvere tutte le criticità ci vuole tempo, ma è indispensabile intervenire subito. La strada verso la sostenibilità è diversa per ogni impresa, ma è essenziale riuscire a trovare un modo efficace per creare una cultura sostenibile. “Nel settore della meccanica operano molti professionisti esperti nel risolvere problemi, quindi trovare nuove vie per accrescere la sostenibilità delle aziende e dei fornitori diventa un obiettivo raggiungibile. Il settore meccanico e le aziende manifatturiere sono in grado di sviluppare tecnologie e processi più sostenibili. I prodotti Renishaw possono contribuire ad aiutare i produttori a ridurre i consumi di energia e di materie prime. Una maggiore sostenibilità dell’intero settore meccanico può portare benefici straordinari ed è importante definire percorsi e obiettivi chiari per arrivare a questo traguardo”, sostiene Goodare.
Le tecnologie Renishaw rendono le aziende più produttive e sostenibili
La gamma di soluzioni industriali Renishaw aiuta le aziende manifatturiere di tutto il mondo ad abbreviare i tempi di inattività, eliminare gli scarti e ridurre il consumo complessivo di energia elettrica. Grazie ai sistemi di metrologia industriale Renishaw è possibile aumentare la
produttività e la sostenibilità dell’azienda. Le tecnologie per misure di precisione e controllo dei processi aiutano a prevedere, identificare e correggere gli errori, prima ancora che si verifichino. In questo modo, si potranno eliminare gli scarti, con una conseguente riduzione degli sprechi di energia, tempo e materiali.
Con l’automazione delle operazioni è possibile accrescere l’efficienza e la produttività, senza bisogno di macchinari aggiuntivi. Le soluzioni di ispezione Renishaw per l’automazione dei processi di lavorazione tramite CNC consentono di sfruttare al massimo le macchine, mantenendole in funzione 24 ore su 24, 7 giorni su 7. L’installazione di tecnologie per l’automazione dei processi permette di implementare procedure volte ad aumentare la produttività e a ridurre scarti e consumi energetici.
di lavorare in sedi più piccole, con consumi energetici minori. Grazie al sistema di misura a 5 assi REVO si possono utilizzare in una singola CMM ben sette sensori diversi e intercambiabili. I sensori offrono una vastissima gamma di funzionalità: scansioni, ispezioni a contatto e a visione, finiture di superficie e misure a ultrasuoni. Le funzioni multisensore aumentano la flessibilità della CMM ed eliminano la necessità di disporre di apparecchiature ridondanti, liberando spazio prezioso in officina. L’utilizzo delle teste a 5 assi assicura una maggiore velocità di acquisizione dati e permette di mantenere lo stesso livello produttivo con un numero minore di macchine di misura.
La sonda a ultrasuoni RUP1
Maggiore durata delle batterie con la serie QE
I tastatori pezzo per macchine utensili sono diventati una delle tecnologie indispensabili per l’automazione dei processi. La possibilità di disporre di dati inerenti alle condizioni dei pezzi e degli utensili, alle prestazioni delle macchine, ai trend dei processi, agli interventi e agli effetti di temperatura e umidità consente di tenere sempre sotto controllo gli elementi critici del processo produttivo. I dati possono essere analizzati e corretti automaticamente in base all’usura e alla deriva degli utensili. In questo modo, si garantisce la produzione di pezzi sempre conformi, eliminando gli scarti, le rilavorazioni e gli interventi manuali da parte degli operatori. Gli innovativi sistemi di ispezione QE a trasmissione radio sono altamente affidabili e forniscono funzioni automatiche di presetting e verifica dell’integrità utensile, di impostazione e verifica dei pezzi.
L’app Probe Setup semplifica le procedure di impostazione e diagnostica a distanza delle sonde radio. Le nuove elettroniche e un sistema di trasmissione radio all’avanguardia prolungano la durata delle batterie del 400%. Se le sonde vengono utilizzate con l’interfaccia RMI-QE, le batterie possono durare in media fino a 5 anni. “Andiamo molto fieri delle innovazioni tecnologiche offerte da questo sistema di nuova generazione e siamo altrettanto orgogliosi del nostro attuale progetto atto a migliorare l’efficienza ambientale dei nostri prodotti. Prolungando la durata della batteria, e con le recenti migliorie apportate alle sonde a trasmissione ottica OMP40 e OSP60, stiamo dimostrando nei fatti il nostro impegno a ridurre l’impatto ambientale dei nostri prodotti”, afferma James Hartley, Industrial Metrology Software Marketing Manager di Renishaw.
Il sistema REVO® aiuta a ottimizzare lo spazio in officina
In questo importante percorso, anche la sala metrologica assume un ruolo fondamentale ad esempio attraverso il sistema di misura multisensore REVO, il quale può rivelarsi molto utile perché consente di svolgere una grande varietà di ispezioni utilizzando una singola macchina di misura ed eliminando quindi la necessità di disporre di più CMM dedicate. L’azienda fornisce anche una serie di dispositivi multifunzione per CMM, che operano in modo rapido e accurato liberando spazio prezioso in officina. Ciò consente di avere spazio per altre macchine o
La sonda a ultrasuoni RUP1 accresce le capacità multisensore del sistema REVO e permette di utilizzare gli ultrasuoni per effettuare ispezioni dello spessore. A differenza di molti altri sistemi a ultrasuoni, RUP1 assicura una buona trasmissione del segnale anche senza vasche d’acqua o gel di accoppiamento. Utilizza invece un’innovativa punta a sfera con elastomeri che garantisce un accoppiamento eccellente fra la sonda e il materiale. Di conseguenza, la sonda non richiede la presenza di operatori specializzati e capaci di interpretare le informazioni visualizzate sull’oscilloscopio e permette anche di liberare spazio in officina, perché vasche di immersione e CMM per fori profondi non sono più necessarie.
Le sonde RVP (REVO Vision Probe) vengono utilizzate anche per aiutare le aziende del settore automotive a rinnovare le loro metodologie produttive in preparazione di un futuro più elettrico e sostenibile. RVP è la sonda ideale per ispezionare gli statori dei motori di veicoli elettrici.
Riduzione dei consumi energetici con gli encoder incapsulati FORTiS™
Renishaw offre anche una serie completa di sensori di movimento per macchine di diverso tipo. Gli encoder della serie FORTiS™ sono stati sviluppati per ottimizzare le prestazioni delle macchine utensili, massimizzare affidabilità e tempi produttivi e accrescere l’efficienza delle operazioni di assemblaggio, manutenzione e assistenza, tutti fattori che incidono in modo sensibile sulla produttività e sui consumi energetici.
Il sistema di sigillatura avanzato di FORTiS riduce enormemente i consumi e le perdite di aria, con un significativo beneficio in termini di costi operativi e longevità. I consumi del getto d’aria sono inferiori del 70% rispetto a quelli di altri encoder ottici incapsulati, con una sensibile riduzione dei costi energetici nell’arco di vita della macchina. “Le innovative guarnizioni DuraSeal™ sono state sviluppate e messe a punto dopo cinque anni di stress test svolti in condizioni estreme e offrono un’incredibile resistenza all’usura e ai lubrificanti della macchina. Inoltre, hanno un’ottima capacità sigillante e garantiscono una protezione di classe IP64 se affiancati da un sistema con getto d’aria”, conclude lan Eldred, Principal Mechanical Engineer di Renishaw.
ELEVATO CONTENUTO TECNOLOGICO E RIDOTTI CONSUMI ENERGETICI, SENZA DIMENTICARE PRODUTTIVITÀ E FLESSIBILITÀ FANNO DELLE PANNELLATRICI SALVAGNINI, LO STRUMENTO PER RIMANERE COMPETITIVI IN UN CONTESTO PRODUTTIVO SEMPRE PIÙ DINAMICO E SFIDANTE
CCon oltre 4000 installazioni in 80 paesi, il più grande stabilimento europeo dedicato alla produzione di pannellatrici e più di 40 anni di esperienza e competenze nell’ambito della piegatura automatica, Salvagnini è portavoce autorevole della pannellatura 4.0, un processo flessibile come mai prima d’ora i cui confini applicativi sono ormai estesi anche a settori ed ambiti considerati, da sempre, poco adatti a questa tecnologia.
La pannellatrice è la macchina che più di ogni altra rappresenta lo spirito del Gruppo, perchè capace di combinare tecnologia all’avanguardia, sostenibilità, produttività e flessibilità. Una macchina
che, a partire dal primo modello di P4 ideato nel 1977, non ha mai smesso di evolvere, diventando, oggi, una soluzione di comprovata affidabilità: una macchina automatica sotto tutti i punti di vista, ideale per una moderna smart factory. La gamma Salvagnini comprende 4 pannellatrici - P1, PX, P2 e P4 – caratterizzate da tre capisaldi comuni: produttività, adattatività e sostenibilità.
Produttività: ogni pannellatrice Salvagnini, indipendentemente dal modello scelto, realizza mediamente 17 pieghe al minuto. Un risultato raggiunto grazie a cicli automatici di piegatura e agli utensili di piega universali. Inoltre, non richiede riattrezzaggio: lama superiore
e inferiore, controlama e premilamiera sono utensili universali in grado di processare tutto il range di spessori e materiali lavorabili. Ciascuno dei 15 modelli disponibili può essere configurato e personalizzato con numerose opzioni, per rispondere alle più diverse esigenze produttive.
Adattatività: ogni pannellatrice integra al suo interno sensoristica evoluta che misura lo spessore reale e le dimensioni effettive del pezzo da lavorare, rilevando eventuali deformazioni legate alla variazione della temperatura. I dati alimentano in tempo reale la bending formula che definisce la forza corretta da applicare alla lamiera, garantendo precisione, ripetibilità e qualità del prodotto finito.
MAC, l’insieme di tecnologie integrate – sensori, formule ed algoritmi – che rende la pannellatrice intelligente, azzera gli scarti e riduce le correzioni, poichè rileva in ciclo e compensa automaticamente eventuali variabilità del materiale in lavorazione. Grazie al software proprietario OPS, con cui comunica con l’ERP di fabbrica gestendo in base alle necessità la produzione di sequenze di parti differenti, la pannellatrice risponde immediatamente alle richieste grazie agli utensili di piega universali e all’allestimento automatico in ciclo.
Sostenibilità: le pannellatrici Salvagnini utilizzano solo attuatori elettrici e sono prive di impiantistica idraulica. I cilindri piegatori sono azionati da motori brushless a tutto vantaggio di una ridotta usura e deperibilità dei componenti che non sono più, come avviene in altre tecnologie similari, sottoposti a forze puntuali continue ed esasperate. Le cicliche in tempo mascherato e i cablaggi degli azionamenti permettono di utilizzare al meglio tutta l’energia assorbita. La sostenibilità non è solo nella tecnologia delle macchine Salvagnini. Tutta la filiera produttiva ha sposato una filosofia più sostenibile. Gli stabilimenti Salvagnini dove le pannellatrici sono prodotte, con il rinnovamento degli impianti di illuminazione e climatizzazione,
hanno ridotto il proprio impatto ambientale annuo di più di 160 tonnellate di CO2
Pannellatrice P2, non solo produttività e flessibilità
P2 è senza dubbio uno dei modelli di pannellatrice Salvagnini di maggior successo. Produttività, flessibilità, precisione, elevato contenuto tecnologico, consumi energetici ridotti e layout compatto sono le caratteristiche che l’hanno sempre contraddistinta e resa particolarmente attraente, anche grazie ad un’ampia gamma di opzioni in costante evoluzione che ne ha via via ampliato gli orizzonti applicativi.
Per rimanere competitivi in un contesto produttivo dinamico e sfidante come quello attuale non basta più essere molto veloci nel realizzare un singolo pezzo, occorre garantire efficienza produttiva, intesa come capacità di ridurre lead time e dimensioni dei lotti mantenendo marginalità. Questo significa passare da un codice di produzione a quello successivo riducendo al minimo i tempi di attrezzaggio, indipendentemente dalle caratteristiche geometriche e meccaniche del foglio di lamiera caricato e da numero e sequenza delle pieghe da realizzare. Un contesto ideale per le pannellatrici Salvagnini.
La P2 di Salvagnini – disponibile in tre versioni, con lunghezza massima di piegatura fino a 2500 mm e altezza massima di piegatura fino a 254 mm – combina nativamente produttività, grazie a cicli automatici di piegatura e manipolazione realizza mediamente 17 pieghe al minuto, e flessibilità, grazie agli utensili di piega universali. Come tutte le pannellatrici Salvagnini non richiede riattrezzaggi. Il premilamiera automatico adatta la lunghezza dell’utensile in funzione delle dimensioni del pezzo da produrre, in ciclo, senza fermi macchina o riattrezzaggi manuali. Quindi, P2 è davvero una soluzione perfetta
per produzioni in kit o a lotto unitario.
P2 offre la garanzia di una produzione zero scarti adattandosi in modo totalmente automatico al variare delle caratteristiche meccaniche e geometriche della lamiera in lavorazione, oltre che a quelle dell’ambiente esterno. La sua sensoristica evoluta misura lo spessore reale e le dimensioni effettive del pezzo da lavorare, rilevando eventuali deformazioni legate alla variazione della temperatura. MAC3.0 le permette di adattarsi al materiale in lavorazione misurandone in tempo reale la resistenza alla trazione: se le caratteristiche meccaniche sono comprese nel range ±25% del valore di riferimento, la compensazione è totalmente automatica perché P2 ricalcola la forza necessaria a ottenere le pieghe previste. Se la variazione eccede il range del ±25%, MAC3.0 permette di definire nuovi materiali in modo semplice e intuitivo. La resistenza della lamiera rilevata può essere memorizzata come valore di riferimento per un nuovo materiale – che potrà essere richiamato in pochi clic, ogni qualvolta sarà necessario: la pannellatrice rimodulerà di conseguenza la forza di piegatura ed eviterà di lavorare fuori parametro. La rilevazione delle caratteristiche meccaniche del materiale – circa 3 decimi di secondo – e l’eventuale correzione dei parametri di piegatura sono talmente rapide da risultare sostanzialmente ininfluenti su tempi ciclo e indici di produttività.
Tra i molti highlights di P2 a vantaggio della sostenibilità c’è anche Impacts, il nuovo prodotto che misura il consumo puntuale di energia elettrica e aria compressa della pannellatrice, presentato a Blechexpo 2023. È il primo passo per arrivare a calcolare i volumi di CO2 equivalenti di ciascun singolo componente prodotto. Impacts permette di monitorare i propri consumi, ottimizzarli e ridurli. Aumenta la profittabilità, perché ridurre i consumi significa ridurre i costi operativi.
AQC, il dispositivo automatico che certifica la precisione
Per rispondere alle sempre più numerose richieste di uno strumento per semplificare e velocizzare il controllo di qualità, lo scorso anno alla fiera internazionale Blechexpo di Stoccarda, Salvagnini ha presentato l’opzione AQC, acronimo di Angle Quality Control. AQC è un dispositivo automatico che misura ed eventualmente corregge l’angolo di piega e certifica la precisione raggiunta in un report. AQC è facile da usare, risolve alcuni vincoli nella misurazione – ad esempio nel caso di pieghe particolarmente strette, difficili da misurare – e non richiede un arresto della produzione per completare la propria analisi, riducendo
Plafoniera riprogettata con il servizio Rethinks. Il costo di produzione della plafoniera, considerando solo le attività di piegatura e assemblaggio, è passato da 10,64€ a 2€ con una riduzione oltre l’80%.
il tempo ciclo. AQC disintermedia il controllo qualità perché non richiede interventi dell’operatore né nella fase di misurazione né in quella di invio dei dati: la misurazione e l’invio dei dati su MES/ERP sono completamente automatici, azzerando il rischio di errore umano e garantendo un controllo qualità affidabile. ACQ non è un’alternativa ma un dispositivo complementare a MAC3.0 utile in settori, come quello dell’automotive o dell’aerospaziale, che sono particolarmente esigenti per applicazione o per motivi di accoppiamento e assemblaggio. Ma è utile anche per tutti quei processi produttivi che prevedano, a valle della pannellatura, fasi successive di lavorazione automatizzate o robotizzate.
Rethinks, il servizio per rivoluzionare la produzione
Passare da tecnologie produttive tradizionali a tecnologie produttive evolute e sfruttarle al massimo del proprio potenziale significa spesso cambiare approccio e guardare al processo produttivo in modo completamente differente. Rethinks significa ripensare, riprogettare; con Rethinks, Salvagnini mette la conoscenza e la competenza dei propri specialisti a disposizione dei clienti, per permettere di sfruttare al massimo il potenziale dei loro sistemi. È la proposta ideale per chi vuole ottimizzare il processo di produzione di un prodotto migliorandone la qualità e l’efficienza, riducendo le fasi di lavoro, l’uso di materiale e i costi. Di Rethinks fanno parte servizi diversi: un corso di design dedicato ai progettisti, creato in base alle configurazioni dei sistemi Salvagnini a loro disposizione, e un servizio di supporto alla progettazione, con cui i progettisti Salvagnini mettono la propria esperienza e competenza a disposizione dei progettisti dei clienti. Efficientando i processi produttivi e migliorando la qualità dei prodotti, Rethinks assicura maggior profittabilità.
SEW-EURODRIVE È IMPEGNATA NELLA PROMOZIONE DI UN CAMBIAMENTO CULTURALE
NELLE AZIENDE MANIFATTURIERE CHE PORTI ALLO SVILUPPO DI PROCESSI E TECNOLOGIE SEMPRE PIÙ EFFICIENTI E SOSTENIBILI
L’impegno delle aziende verso l’ambiente è ormai uno dei fattori principali che influenza la percezione del brand sul mercato, a cui si aggiunge la necessità di dover contrastare il riscaldamento globale e i cambiamenti climatici.
Ci troviamo davanti a un’evoluzione che introduce il tema ambientale nel risk-management aziendale e viene trasmessa di conseguenza alle politiche aziendali. Un vero e proprio cambio di paradigma: mentre negli scorsi anni veniva perseguita maggiormente una strategia di profittabilità ora viene ricercata una sostenibilità a tutto tondo, che si fonda su tre principali pilastri: sviluppo economico, sociale e ambientale.
“Anche se si tratta di un percorso che deve necessariamente abbracciare tutta la catena del valore di un’azienda, i primi passi verso la sostenibilità si possono compiere già a livello di fabbrica, attraverso la riduzione degli sprechi, l’ottimizzazione degli asset, delle risorse coinvolte nei processi aziendali e delle stesse linee produttive. Da questo punto di vista, le tecnologie 4.0 abilitano una maggiore visibilità su tutti gli asset e i processi aziendali: la digitalizzazione degli asset utilizzati nei processi, e dell’intero impianto, rappresenta la condizione di partenza per misurare le performance e i consumi al fine di compiere uno slancio concreto verso sostenibilità ed efficienza”, spiega Francesco Di Pasquale, Chief Supply Chain Officer di SEW-EURODRIVE Italia.
Efficienza energetica e affidabilità dei prodotti
SEW-EURODRIVE già da diversi anni è particolarmente sensibile al tema della sostenibilità. “Anzitutto, l’azienda promuove la produzione di componenti a basso assorbimento energetico e ad alto rendimento: far consumare poca elettricità ai clienti genera loro benefici in termini economici e di emissioni di gas effetto serra, richiesta che molte aziende oggi esprimono chiaramente alla propria catena di fornitura”, precisa Francesco Di Pasquale. In aggiunta, SEW-EURODRIVE da sempre si occupa di fornire soluzioni che abbiano una lunga durata, puntando appunto sull’affidabilità che è un elemento imprescindibile quando si deve garantire la continuità del funzionamento delle linee industriali. Allungare la durata della vita di un prodotto ha una grande valenza per la sostenibilità ambientale, oltre che sociale, in quanto comporta una riduzione del consumo di materie prime e risorse, specializzando sempre di più le risorse umane nella manutenzione e riparazione.
In questo contesto si inserisce il programma di remanufacturing Up To Next di SEW-EURODRIVE, che consente di estendere il ciclo di vita dei motoriduttori SEW mediante un processo di rigenerazione che prevede la sostituzione di parti e componenti usurati che influiscono sulle prestazioni o sulla vita utile del motoriduttore. La riparazione avviene in soli sette giorni e il motoriduttore rigenerato ha una garanzia di due anni.
“Il remanufacturing è una delle strategie chiave dell’economia circolare. Si tratta di un modello di business in forte crescita negli ultimi anni, che, se implementato correttamente, è capace di generare valore per l’impresa e per il pianeta, grazie al risparmio di risorse e materie prime. La rigenerazione è, infatti, una strategia cruciale in un mondo in cui la crescente domanda di materie prime sta determinando il progressivo esaurimento delle stesse”, commenta Francesco Di Pasquale. Dando nuova vita ai motoriduttori per riportarli alle prestazioni originali attraverso la sostituzione delle sole parti usurate e il rimontaggio di tutti gli altri componenti, SEW-EURODRIVE intende offrire un contributo concreto alla protezione dell’ambiente e delle risorse naturali, in linea con i valori di responsabilità sociale e sviluppo sostenibile che da sempre ispirano l’attività dell’azienda. Infatti, il programma Up To Next consente di ridurre l’utilizzo di materie prime e le emissioni di CO2 che si genererebbero con il diretto smaltimento di prodotti mal funzionanti e la produzione di nuovi motoriduttori. Il remanufacturing di SEWEURODRIVE differisce dalla riparazione standard e da altre forme di recupero di componenti usurati per la sua completezza, perché consente una totale rigenerazione del motoriduttore, che viene rimesso a nuovo per restituire tutte le caratteristiche originali in termini di qualità, prestazioni e affidabilità.
Gestione intelligente degli asset
“Grazie a un portfolio di tecnologie, prodotti e servizi completo e
innovativo, SEW-EURODRIVE è in grado di aiutare le aziende ad abilitare una gestione davvero intelligente di asset, processi e risorse, che consente di ridurre gli sprechi, efficientare le operazioni e promuovere la sostenibilità all’interno degli impianti”, continua Francesco Di Pasquale. A cominciare da DriveRadar®, piattaforma che consente di integrare componenti, macchine, sistemi e interi stabilimenti oltre i confini aziendali in una rete digitale. Accanto a questa e altre tecnologie che aiutano le aziende a sfruttare, nel segno dell’efficienza, tutto il potenziale dei dati, SEW-EURODRIVE ha sviluppato una soluzione di gestione intelligente dell’energia: Power and Energy Solutions (PE-S). “Si tratta di un sistema basato sulla piattaforma MOVI-C® che permette di ridurre i picchi di potenza nella rete elettrica, oltre che di recuperare e rigenerare energia dalle movimentazioni di alcune applicazioni nelle fasi di rallentamento o di frenatura. L’energia viene immagazzinata in supercondensatori che vengono dimensionati in funzione della necessità di potenza dell’applicazione o degli impianti”, aggiunge Di Pasquale.
Bilancio di sostenibilità per un approccio condiviso
Un cambiamento determinante delle politiche aziendali è quello di mutare il proprio punto di vista e invece che orientarsi solamente agli shareholders, come è stato negli ultimi decenni, vi è la necessità di allargare agli stakeholders, cioè a tutte le figure che hanno interesse nell’azienda. “Non solo gli investitori e i clienti, quindi, ma anche i dipendenti, i fornitori, la comunità locale, e in generale tutti coloro che traggono valore dall’azienda. L’obiettivo è quello di recuperare un senso di comunità che possa far evolvere l’ecosistema industriale in un contesto dove persone e ambiente sono al centro delle scelte strategiche delle aziende”, precisa Francesco Di Pasquale. Coerentemente con le linee guida dettate dall’Unione Europea, a partire dall’anno 2021 SEW-EURODRIVE Italia si è impegnata nel redigere annualmente il Bilancio di sostenibilità, documento nel quale vengono raccolte la strategia, i progetti e i risultati concreti espressi attraverso gli indici GRI (Global Reporting Initiative). Il bilancio di sostenibilità viene poi condiviso con tutti gli stakeholder, i quali sono informati in modo trasparente dell’impegno attuale e futuro che SEW-EURODRIVE si assume relativamente ai pilastri della sostenibilità: economia, ambiente e sociale.
L’efficienza dei processi produttivi è legata all’efficacia totale dell’impianto di produzione. Siemens offre, grazie al proprio portfolio di prodotti Software e Hardware, una suite completa per la verifica, l’ottimizzazione e l’incremento della produttività, garantendo la massima qualità.
Attraverso “Machinum”, che comprende l’intero portflio di digitalizzazione Siemens per aumentare la produttività e la sostenibilità dedicato alle macchine utensili, è possibile analizzare e ottimizzare le macchine utensili e le aree di produzione. Machinum combina la moderna IT (Information Technology) con la moderna OT (Ope-
ration Technology). È parte integrante di Siemens Xcelerator, la piattaforma digitale aperta che comprende un portfolio di software e hardware abilitati all’IoT, un ecosistema di partner e un marketplace.
L’integrazione smart con sistemi tipo Scada, MES e ERP è essenziale per la valutazione dei dati provenienti dalle macchine: grazie al portfolio Machinum e la suite Mcenter con i software Manage MyResources è possibile ottenere una produzione efficiente con la massima qualità.
Tale efficienza è legata all’integrazione di automazione, come la gestione dei robot. Il CNC Sinumerik ONE, in particolare, gesti-
sce direttamente il robot all’interno dello stesso CNC dedicato alla macchina utensile, permettendo all’operatore macchina di conoscere un solo linguaggio di programmazione e alla manutenzione di avere uno stesso fornitore come interfaccia tecnica.
Soluzioni per un monitoraggio intelligente
Il monitoraggio in real-time dei parametri fisici di macchina è essenziale per ottenere una fotografia reale delle condizioni meccaniche, al fine di prevedere eventuali fermi macchina che inciderebbero negativamente sulla produttività. L’intelligenza artificiale è già presente in diverse applicazioni disponibili sul CNC Sinumerik ONE, attraverso un’offerta di software dedicati alla maggiore produttività/ qualità e alla manutenzione predittiva.
La produzione in serie di grandi lotti o piccole serie può essere monitorata da parametri dinamici di lavoro della macchina utensile attraverso un algoritmo di intelligenza artificiale che viene allenato con la lettura di parametri ad alta velocità (1 KHz), provenienti dalla macchina utensile stessa e confrontati in automatico tra le lavorazioni dei pezzi lavorati in sequenza. Questo tipo di controllo garantisce la qualità dei prodotti lavorati, grazie a un set di parametri all’interno di un range stabilito e alla tracciabilità dei pezzi lavorati stessi.
Per quanto riguarda la manutenzione predittiva, dalla lettura di parametri fisici provenienti dalla macchina e dalla lettura di sensori esterni, viene garantito lo stato di salute meccanico, grazie ad una continua valutazione e al confronto con dati “campione”.
L’utilizzo di Siemens Industrial EDGE - Edge Computing, permette un modello di calcolo distribuito nel quale l’elaborazione dei dati avviene il più vicino possibile a dove i dati vengono generati, ovvero alla macchina utensile, gestendo gli algoritmi dedicati senza sgravio di performance del CNC.
Soluzioni software per l’ottimizzazione e l’efficienza dei processi produttivi
Il portfolio Machinum con la suite Mcenter dedicata all’ottimizzazione dei processi contempla diversi software. Manage MyResources/Programs, per la gestione centralizzata dei partprogram, è un server connesso al parco macchine, il quale si occupa non solo dell’invio del partprogram dedicato alla singola macchina ma, al termine dell’esecuzione, consente di richiamare lo stesso partprogram e confrontarlo con l’originale, segnalando su un file di log eventuali modifiche apportate dall’operatore macchina.
Manage MyResources/Tools, per la gestione centralizzata degli utensili macchina, stazioni di presetting e tool room, crea una visibilità sulla disponibilità e posizione non solo del singolo utensile, ma anche delle parti che compongono il singolo utensile, avendo tutti i magazzini macchina, tool room e stazioni di presetting connessi centralmente, permettendo così di ottimizzare le scorte nel magazzino e pianificando gli acquisti nel momento di un numero residuo inferiore a soglie definibili.
Analyze MyPerformance /OEE, è stata studiata per il calcolo dei principali fattori dell’impianto, come disponibilità, efficienza e qualità. La macchina di produzione rappresenta la sorgente centrale dei dati e attraverso Analyze MyPerformance /OEE è possibile aiutare la capacità produttiva ad essere più efficiente. L’applicazione
permette di individuare importanti indicatori per aumentare la produttività eliminando eventuali punti di bottlenecks, visualizzando i dati relativi alla produzione. I KPI visualizzati possono essere personalizzati, attraverso formule per ottimizzare i processi, e utilizzati come termine di confronto con ciò che è stato pianificato.
Il portfolio di Drives Siemens, destinati alle macchine produttive all’interno della famiglia Sinamics, offre alimentatori in grado di restituire la tensione in linea, al posto di trasformare l’energia in calore attraverso resistenze di frenatura. Il portfolio di motori della famiglia Simotics risponde alle attuali classi di efficienza sino a IE4, e garantisce la massima efficienza energetica.
Il CNC Sinumerik ONE include il Control Energy: attraverso la pressione dei tasti CTRL+E è possibile attivare il menù nel quale sono disponibili 8 differenti livelli dedicati a operazioni di spegnimento di automazioni, luci e organi divoratori di energia, in situazioni dove la macchina utensile non produce.
L’utilizzo del software SIMATIC Energy Manager PRO, in abbinamento al multimetro digitale Sentron Pac/ ET200SP Energy Meter, permette di avere sotto controllo non solo il consumo della singola macchina utensile ma anche quello di tutto il plant.
Attraverso funzioni specifiche, il CNC Sinumerik ONE permette la modifica dinamica dell’accelerazione mandrino, in base al posizionamento degli assi di lavoro terminato il movimento in G0 (rapido), garantendo la vita cuscinetti mandrino più longeva.
La sostenibilità nei processi produttivi
In linea con i propri obiettivi di sostenibilità, delineati nel Report Sustainability 2023, Siemens mette a disposizione per il prodotto Sinumerik ONE “Environmental Product Declaration” in accordo con ISO 14021, dove viene condiviso l’impatto ambientale: dalla produzione, alla distribuzione sino al termine vita del prodotto stesso.
Siemens con il CNC Sinumerik ONE continua lo sviluppo di Software dedicato sia all’utilizzatore finale che al costruttore di macchina, rendendo nel primo caso l’utilizzo dell’HMI Sinumerik Operate sempre più intuitivo e user friendly per l’operatore, nel secondo caso la messa in servizio sempre più automatizzata; entrambi hanno il fine di ridurre il time to market sia del prodotto lavorato che del commissioning della macchina utensile. L’attenzione verso l’operatore macchina viene evidenziata aumentando la qualità di lavoro attraverso alcune novità, tra le quali l’esecuzione grafica in 3D del pezzo lavorato, la possibilità di utilizzare il DXF reader, l’avere sotto controllo in un’unica pagina tutti i parametri di lavoro e non per ultimo l’utilizzo del powerride, nato dall’evoluzione del semplice override per regolare la velocità assi/mandrino, un vero strumento di lavoro con funzionalità di Start/Stop e retroazione tattile al movimento impostabile. Il CNC Sinumerik ONE nativo digitale nasce prima come gemello digitale per poi essere utilizzato in officina. Il Digital Twin della macchina utensile migliora ulteriormente la qualità del lavoro, permettendo ai tecnici di testare i part program in ufficio, lasciando la macchina reale in produzione, ottenendo un tempo di lavorazione identico alla macchina reale, la verifica di collisione con un report dettagliato e il bilanciamento degli utensili necessari alla lavorazione stessa. Inoltre, il gemello digitale viene utilizzato per svolgere training al nuovo personale.
La sostenibilità nei processi produttivi è coadiuvata dal supporto del gemello digitale della macchina stessa, garantendo di azzerare i tempi necessari al test in macchina di nuovi part-programs, la ricerca degli utensili necessari alla produzione stessa e check di collisione
per eventuali posizionamenti causati da errori di programmazione o la non valutazione corretta della lunghezza degli utensili.
Il gemello digitale viene sempre più richiesto al costruttore macchina, in quanto strumento riconosciuto e valutato necessario nelle aziende per abbattere i tempi non produttivi.
Il CNC Sinumerik ONE e il suo Digital Twin con 8 differenti versioni, 4 dedicate al cliente finale e 4 dedicate al costruttore macchina, copre l’intera gamma di richieste di mercato inerenti alla produttività, affidabilità e risparmio energetico.
Sinumerik Operate, la superficie operativa per la diagnosi della macchina in produzione
Attraverso la superficie operativa Sinumerik Operate, il CNC Simunerik One offre una diagnosi dettagliata sull’intera macchina in produzione. Equipaggiato di 4 processori dedicati all’interpolazione, PLC, Drives e superficie operativa HMI, permette di tenere sotto controllo lo stato del CNC e allarmi o messaggi che provengono dal campo, correlando informazioni di dettaglio sull’errore o avviso e sulle possibili soluzioni, immagini e procedure operative.
La diagnostica può essere attivata anche da remoto attraverso il software di telediagnosi “Manage My Machine/Remote”, dove il costruttore o il Technical Support di Siemens, può effettuare una diagnosi approfondita, evitando così interventi in loco e lunghi fermi macchina. Il software “Manage My Machine/Remote” è disponibile in forma pay per use, ovvero attivato se e solo se la macchina presenta una necessità o un’anomalia, senza aggravare le spese per il resto del ciclo di vita della macchina stessa.
Precisione.
Il nostro filo conduttore è “Fresare meglio”. Ogni problema che riusciamo a risolvere, ogni modifica e ogni ottimizzazione che apportiamo contribuisce a rendere il risultato migliore, più preciso e disponibile più velocemente. Non per noi, ma per il successo dei nostri clienti, che con i nostri centri di lavorazione ottengono i risultati migliori.
www.hermle-italia.it
Maschinenfabrik Berthold Hermle AG, info@hermle.de
Ergonomia per l’operatore e ottima visibilità delle lavorazioni con la massima sicurezza
Da sempre SORALUCE, azienda di riferimento nel settore delle tecnologie di fresatura, alesatura e tornitura verticale per il mercato italiano, considera lo sviluppo sostenibile e il rispetto dell’ambiente fattori chiave indiscutibili per il futuro. In particolare, il primo aspetto, cioè lo sviluppo sostenibile, per SORALUCE è un principio guida nella collaborazione con i propri clienti per la progettazione e lo sviluppo di un’ampia varietà di soluzioni sostenibili di fresatura, alesatura e multitasking.
Con un approccio di sostenibilità strutturato e proattivo, l’azienda parte di Danobatgroup, la divisione macchine utensili della Corporación Mondragón, una delle holding più importanti d’Europa, ha messo in atto un piano d’azione a breve e medio termine per migliorare il proprio sistema di gestione della sostenibilità perseguendo impegni, politiche e azioni tangibili sulle principali questioni con informazioni dettagliate sull’attuazione, seguite da una rendicontazione di sostenibilità significativa sulle azioni e sugli Key Performance Indicators. A tal fine, si impegna continuamente nella riprogettazione dei propri prodotti e processi, riducendo il consumo di energia e lubro-refrigeranti, introducendo materiale riciclabile, inserendo sostenibilità e responsabilità sociale nella cultura e nei processi aziendali.
Responsabilità verso l’ambiente: il sistema ECO DESIGN
L’azienda ha creato una nuova generazione di macchine a portata d’uomo, progettata per ridurre al minimo il consumo energetico e i materiali di consumo. In accordo con le normative ISO 14006, SORALUCE realizza macchine con il sistema ECO DESIGN e con la più recente ed innovativa tecnologia per ridurre l’impatto
ambientale e allo stesso tempo aumentare la produttività della macchina. SORALUCE è infatti la prima società nel settore delle macchine utensile ad ottenere, nel 2010, la certificazione per il Design di Prodotto e lo Sviluppo del Sistema di Gestione dei Processi (ECO DESIGN). Questa certificazione garantisce una riduzione dell’impatto ambientale totale delle macchine SORALUCE pari al 18%. Per diminuire l’impatto ambientale, gli aspetti più significativi nel ciclo di vita delle fresatrici sono la riduzione del consumo energetico, del materiale durante la fase di produzione dei vari pezzi di macchina, dei componenti idraulici e l’utilizzo di un sistema di cambio utensile automatico. L’attenzione riposta nei confronti di questi aspetti, ha portato ad una riduzione dell’11% dei consumi nella produzione, del 16% dei consumi di elettricità e lubrificante, rispettivamente, durante l’uso e ad un risparmio annuale dei consumi della macchina del 16%, avendoli portati da 187, 2 MW/h/anno a 156 MW/h/anno. La new generation di macchine SORALUCE è progettata tenendo conto di questi aspetti, rispettando e sostenendo lo sviluppo dell’ambiente, esempio di efficienza e garanzia per il futuro.
L’innovazione in un’ottica di ecosostenibilità rientra nel piano di sviluppo a lungo termine di SORALUCE, con criteri di progettazione studiati affinché i prodotti siano più eco-efficienti, quindi più competitivi e rispettosi dell’ambiente. I modelli delle macchine sono stati ottimizzati riducendo il consumo energetico fino al 65% negli ultimi 30 anni.
Il programma di sviluppo eco-sostenibile di SORALUCE comprende:
• Pacchetto Risparmio Energetico (EF) che garantisce un risparmio energetico del 30%;
• Certificazione ISO 14006 dal 2010;
• Ecodesign con il quale SORALUCE riduce il consumo energetico del 15%;
• Riduzione delle dissipazioni energetiche;
• Utilizzo delle guide lineari a ricircolo di rulli;
• Lubrificazione a grasso delle guide lineari a ricircolo di rulli, viti a ricircolo di sfere e insieme cremagliera pignoni;
• Componentistica idraulica minimizzata;
• Motorizzazione premium più efficiente;
• Minor quantità di lubrificanti necessari;
• Macchina intelligente dotata di:
• SLEEP mode (riduzione fino all’80% del consumo energetico della macchina quando il sistema è attivo);
• Data System (SORALUCE Monitoring I4.0);
• Controllo Adattativo;
• SORALUCE vuole contribuire a ridurre l’impatto ambientale derivante dalle emissioni di C02 generate dalla propria attività produttiva e, a tal fine, ha adottato una politica a zero emissioni.
L’innovazione è al primo posto in tutti i prodotti e le soluzioni che l’azienda sviluppa e molte delle tecnologie che guidano il settore della macchina utensile sono state sviluppate da SORALUCE. L’atteggiamento innovativo, caratteristica distintiva dell’azienda, è accompagnato da un impegno e una vocazione costanti per fornire un servizio alla società. Grazie ai continui sviluppi tecnologici,
SORALUCE migliora la efficienza, la produttività, la precisione e la capacità di adeguamento ai processi concreti di produzione dei propri clienti, avendo cura, durante il processo, di tutti gli aspetti e fornendo tecnologie intelligenti in continua evoluzione, rispondendo oggi alle domande di domani.
L’incremento della produttività della macchina
Nei differenti settori merceologici, oggi più di ieri sempre più esigenti, lo sviluppo di soluzioni di produzione tecnologicamente avanzate, che riducono i tempi di lavorazione e offrono elevata disponibilità e precisione, è la chiave per affrontare le diverse sfide di produzione. Le soluzioni devono inoltre ridurre al minimo i tempi di fermo macchina, i tempi di carico/scarico di pezzi o le operazioni accessorie, ottimizzando così i tempi di cambio teste e utensili. Inoltre, devono consentire la produzione non presidiata, dove l’intervento dell’operatore è minimo, ma l’affidabilità è garantita. SORALUCE offre un’ampia gamma di soluzioni per la realizzazione di pezzi con differenti morfologie e dimensioni, in grado di soddisfare le esigenze dei vari settori, totalmente focalizzate sul raggiungimento della massima produttività e sulla garanzia di un’estrema precisione in lavorazione. Grazie allo sviluppo tecnologico di soluzioni di fresatura e alla sua competenza ed esperienza nell’ingegneria meccanica, la società è in grado di fornire soluzioni personalizzate e adattate alle esigenze di produzione del cliente, progettate per rispondere ad ogni specifica applicazione. Le sue attrezzature di produzione consentono di ottimizzare i tempi di lavorazione, riducendo i tempi morti e con il minimo intervento
dell’operatore. Le soluzioni SORALUCE sono molto affidabili ed efficienti, oltre ad essere macchine estremamente precise e di semplice gestione.
Fresatrice SORALUCE TA35
Esposta a MECSPE 2024, la fresatrice SORALUCE mod. TA35 della nuova Performance Line è dotata di elevata ergonomia e flessibilità, per garantire la massima produttività, ottima rigidità e stabilità meccanica e, come tutte le macchine prodotte da SORALUCE, presenta una struttura interamente in ghisa ampiamente nervata e dimensionata. La fresatrice ha un motore mandrino in-line (potenza 38kw, 725Nm) e un’elevata capacità di asportazione truciolo.
È dotata di controllo numerico HEIDENHAIN con monitor touch screen da 24” e presenta corsa longitudinale di 3500 mm, corsa verticale di 1.500 mm e corsa trasversale di 1200 mm, che permettono di caricare pezzi fino a 10 ton. Grazie alla sua flessibilità può essere configurata anche con tavole girevoli e teste differenti. In particolar modo, il modello TA35, esposto in fiera, presenta una testa birotativa automatica da 6.000 rpm e ha la possibilità di applicare sul piano di lavoro da 3.700x1.000 mm una tavola girevole avente superficie 1.000x1.000mm e portata 4 ton. È dotata di magazzino utensili a 60 posti con un braccio di cambio utensile motorizzato orizzontale-verticale, guidato da servomotore elettronico controllato da CNC, che permette di ridurre il tempo di cambio utensile. La fresatrice TA35 è inoltre provvista di Teleservice, software che permette all’assistenza tecnica di SORALUCE ITALIA e
SORALUCE di collegarsi direttamente alla macchina, offrendo un servizio di assistenza tecnica immediato ai propri clienti.
Grazie alla sua struttura totalmente in ghisa abbinata all’utilizzo delle guide lineari a ricircolo di rulli, le fresatrici della serie TA hanno ottime prestazioni anche durante lavorazioni gravose.
Sono macchine dotate di grande ergonomia, in quanto permettono l’accesso dell’operatore al piano di lavoro sia frontalmente che dal lato posteriore della macchina, garantendo la massima sicurezza per l’utilizzatore e, allo stesso tempo, un’ottima visibilità dell’area di lavoro. La facile manutentabilità, unita all’ergonomia e alla struttura stessa della macchina hanno valso alla fresatrice SORALUCE TA il titolo di Total Machine, ovvero una macchina costruita per l’operatore in un’ottica di risparmio energetico e di sostenibilità ambientale.
Per il raggiungimento della sostenibilità, SORALUCE è stata premiata con la Silver Medal 2021 dall’ente di certificazione indipendente Ecovadis; un riconoscimento che attesta, una volta di più, quanto l’azienda sia attenta ai temi della sostenibilità e quanto sia attiva sul fronte della responsabilità sociale.
EcoVadis, affidabile piattaforma per le valutazioni della sostenibilità aziendale all’interno delle catene di approvvigionamento globali, valuta ogni azienda in base a criteri di prestazione ambientale, sociale ed etica. La metodologia di valutazione include la valutazione della qualità del sistema di gestione della sostenibilità di un’azienda attraverso le sue politiche, azioni e risultati.
L’automazione industriale continua a evolversi e, con essa, emergono nuovi metodi per mantenere ottimale il funzionamento delle macchine. La manutenzione predittiva e il condition monitoring si stanno affermando come strumenti cruciali in questo ambito, offrendo soluzioni innovative per ridurre i tempi di inattività e aumentare l’efficienza.
La manutenzione predittiva differisce notevolmente dalla manutenzione preventiva tradizionale, basata su calendari e stime generali forniti dai produttori. Invece di affidarsi a piani standard, la manutenzione predittiva utilizza dati in tempo reale forniti dalle
macchine stesse. Questo approccio permette di anticipare le esigenze di manutenzione in modo molto più accurato, riducendo tempi di inattività non pianificati e costi relativi.
Il cuore di questo sistema è il condition monitoring, una tecnica che monitora le condizioni delle componenti cruciali delle macchine, come motori e cuscinetti. Questo monitoraggio si rivela fondamentale nel rilevare i problemi prima che diventino gravi. Ad esempio, un aumento delle vibrazioni in una macchina può essere un indicatore precoce di componenti sbilanciati, disallineati, allentati o usurati. Rilevare questi problemi in anticipo può prevenire
danni maggiori e costosi tempi di inattività.
Basti pensare che, a seconda dei settori, il costo di fermo macchina (total downtime cost – TDC) può variare da medie di 4mila euro all’ora, a 30mila euro all’ora. Perché per l’azienda il costo di fermo macchina equivale alla somma di tutti i costi sostenuti durante la sospensione della produzione oltre alle risorse necessarie per risolvere la causa del problema. Con l’avvento dell’IIoT (Internet Industriale delle Cose), il condition monitoring è diventato più sofisticato e accessibile.
Turck Banner, azienda nata dalla joint venture tra la tedesca Hans Turck GmbH & Co. KG e la statunitense Banner Engineering Corp, specializzata nella produzione di sistemi, prodotti e soluzioni per il mondo dell’automazione industriale, offre un ampio portafoglio di soluzioni per la raccolta dati, il monitoraggio industriale e la manutenzione predittiva.
Soluzioni di manutenzione predittiva e condition monitoring degli impianti
I sensori di vibrazione e temperatura sia wireless che con cablaggio tradizionale di Banner Engineering sono esempi di come questa tecnologia sia stata adattata per monitorare l’efficienza delle macchine. Questi sensori, che possono essere facilmente installati su diverse componenti, fungono da “spia del motore”, fornendo dati essenziali in tempo reale.
Offrono livelli di precisione ineguagliati nella misurazione della velocità RMS, un indicatore affidabile dello stato di salute delle macchine rotanti, e dell’accelerazione RMS ad alta frequenza, che segnala l’usura precoce dei cuscinetti. Integrati con sistemi come il DXM100 il gateway di con trollo, questi sensori trasmettono dati preziosi che possono essere utilizzati per analisi più dettagliate e decisioni di manutenzione informate. “L’implementazione della manutenzione predittiva e del condition monitoring nelle industrie non è soltanto una questione di installazione di nuove tecnologie, ma richiede anche un cambio di mentalità. I responsabili degli impianti devono passare da un approccio reattivo a uno proattivo, utiliz zando i dati raccolti per anticipare e prevenire problemi prima che si verifichino”, afferma Giuliano Collodel, Amministratore Delegato di Turck Banner.
Il vantaggio più significativo di questi sistemi è la riduzione dei tempi di inattività. Una mac china che si guasta inaspettatamente può causare ritardi significativi e perdite economiche. Attra verso la manutenzione predittiva, è possibile pro grammare interventi di manutenzione quando sono
meno intrusivi e più convenienti, mantenendo così la produzione in costante funzionamento.
Dal modello reattivo a quello proattivo
In conclusione, la manutenzione predittiva e il condition monitoring rappresentano un passo avanti fondamentale nell’evoluzione dell’automazione industriale. Forniscono agli operatori gli strumenti per mantenere le macchine in condizioni ottimali, riducendo i costi e migliorando l’efficienza complessiva. Mentre il settore continua ad evolversi, questi metodi si dimostreranno sempre più indispensabili per le industrie che cercano di rimanere competitive in un mercato in rapida evoluzione. Collodel sottolinea l’importanza di questo cambiamento: “La manutenzione predittiva e il condition monitoring non sono solo progressi tecnologici, ma rappresentano una rivoluzione nella gestione delle risorse e nell’efficienza operativa. In Turck Banner, abbiamo visto come l’adozione di questi sistemi abbia trasformato il modo in cui i nostri clienti approcciano la manutenzione, passando da un modello reattivo a uno proattivo. Questo non solo aumenta la longevità delle macchine ma ottimizza anche il ciclo di produzione, portando a significative riduzioni di costi”. Evidenziando il ruolo cruciale dell’integrazione tecnologica, Collodel aggiunge: “Integrare tecnologie come i sensori di vibrazione e temperatura nel cuore delle operazioni di fabbrica non è solo una questione di aggiornamento tecnico, ma di adattamento strategico. In un mondo dove l’efficienza e la rapidità sono essenziali, la capacità di prevedere e prevenire i problemi diventa un fattore chiave per il successo aziendale”.
LA STORIA DI ORI MARTIN HA INIZIO NEGLI ANNI ‘30, CON L’AVVIO DELL’ATTIVITÀ
PRODUTTIVA DELLA FERRETTI & MARTIN. ATTRAVERSO UN PROCESSO DI CRESCITA E TRASFORMAZIONE DURATO OLTRE MEZZO SECOLO, L’ATTUALE COMPLESSO INDUSTRIALE DI SAN BARTOLOMEO, SITUATO A NORD DI BRESCIA, PRENDE FORMA DALL’INTRECCIO DELLE DUE REALTÀ AZIENDALI, AVVIANDO
UNA SIGNIFICATIVA PRODUZIONE DI ATTREZZI AGRICOLI UTILIZZANDO FERRO RICAVATO DA ROTAIE DISMESSE di Maurizio Zanforlin, Luca Piedimonte, Antonio Lucarelli – ORI Martin; Martina Imarisio
– AFIL
Dopo pochi anni, gli impianti vengono raddoppiati con l’acquisto di un maglio dotato di forno a nafta. In aggiunta a tale maglio, viene introdotto un primo laminatoio per trasformare il materiale lavorato. Durante la Seconda Guerra Mondiale, il laminatoio viene smontato per precauzione, ma la produzione continua con attrezzi agricoli, mantenendo la tradizione dei magli bresciani. Dopo la fine della guerra nel 1945, inizia la ripresa economica e sociale del Paese. La disponibilità abbondante e a basso costo di materiali come rotaie, ordigni bellici e travi, spinge all’adozione di tecnologie per la loro trasformazione in prodotti commerciali.
Negli anni ‘50, ORI Martin installa il primo forno elettrico da tre tonnellate, seguito da un nuovo forno da dodici tonnellate e un impianto di laminazione con forno di riscaldo a metano. Il laminatoio, con sette gabbie e operazioni di serpentaggio eseguite manualmente dagli operai, diventa un punto di riferimento nell’industria siderurgica. Oggi, ORI Martin è un gruppo industriale leader nella produzione di acciai speciali per il settore automotive e meccanico, con una presenza consolidata in numerosi Paesi europei e una significativa attività di esportazione anche verso Asia e America.
Innovazione Industriale per lo Sviluppo Sostenibile: il contributo di ORI Martin
Nel corso degli ultimi anni, ORI Martin ha abbracciato con impegno i principi dell’Agenda Globale per lo Sviluppo Sostenibile al 2030, concentrando i propri sforzi nell’adottare modelli sostenibili di produzione e consumo. Questo impegno riflette la consapevolezza che la lotta contro la
povertà debba essere accompagnata da strategie volte a promuovere la crescita economica e a soddisfare una vasta gamma di bisogni sociali, tra cui istruzione, salute, sicurezza sociale e opportunità lavorative, mentre contemporaneamente si affrontano le sfide del cambiamento climatico e si protegge l’ambiente.
ORI Martin si allinea in prima battuta all’Obiettivo 12 dell’Agenda 2030 per lo Sviluppo Sostenibile delle Nazioni Unite, il quale enfatizza l’importanza di promuovere l’efficienza delle risorse e dell’energia, oltre alla creazione di infrastrutture sostenibili e all’accesso ai servizi di base e a lavori dignitosi e rispettosi dell’ambiente. La sua messa in pratica contribuisce non solo alla riduzione dei futuri costi economici, ambientali e sociali, ma anche al miglioramento della competitività economica e alla riduzione della povertà. ORI Martin adotta un approccio che integra l’innovazione, la competitività e la sostenibilità come pilastri fondamentali della sua attività produttiva, promuovendo così una visione che colloca al centro l’uomo e l’ambiente.
Questo impegno si manifesta concretamente nel progetto “Acciaio 4.0”, nato in collaborazione con Tenova, grazie anche al ruolo di promotore della Ricerca e Innovazione nel settore della Manifattura Avanzata rivestito da AFIL - Associazione Fabbrica Intelligente Lombardia, a cui entrambe le aziende sono associate. Attraverso il lavoro delle proprie Strategic Communities, AFIL, Cluster Tecnologico per il Manifatturiero Avanzato della Lombardia, ha favorito lo sviluppo di un modello di Economia Circolare dell’acciaio nella regione, capace di diffondere tecnologie e modelli produttivi innovativi.
Grazie proprio alle tecnologie abilitanti dell’Industria 4.0, “Acciaio 4.0” ha elaborato un’integrazione completa e trasversale di tutto il processo produttivo dell’acciaio, rendendolo più efficiente, flessibile e sostenibile. Il progetto ha portato alla creazione di una “Cyber Physical Factory” ed è stato anche uno dei primi quattro Lighthouse Plant selezionati dal Cluster Fabbrica Intelligente, con il supporto di AFIL, per conto del Ministero dello Sviluppo Economico. Tra i tanti aspetti tecnologici sviluppati nell’ambito del progetto alcuni hanno permesso una connessione tra dati, ambiente e produzione, come ad esempio il sistema automatico di classificazione del rottame e il sistema di calcolo dinamico del Life Cycle Assessment (LCA).
Il primo sistema, messo a punto da Tenova, si basa su un algoritmo di Intelligenza Artificiale per la gestione ottimale delle informazioni e delle immagini del materiale in ingresso e la costruzione di ricette di carica ottimali per una gestione oculata del rottame riciclato, elemento caratterizzante il processo di fusione elettrico a basso impatto ambientale.
In collaborazione con l’Istituto di Ricerca STIIMA CNR di Milano, è stato messo a punto un progetto di ricerca per il calcolo Life Cycle Assessment (LCA) dinamico degli impatti ambientali dei prodotti, sino alla loro rappresentazione integrata in sistemi di gestione aziendale. Questa valutazione del ciclo di vita rappresenta uno degli strumenti fondamentali per l’attuazione di una politica ambientale: si tratta infatti di un metodo oggettivo di valutazione e quantificazione dei carichi energetici ed ambientali e degli impatti potenziali
associati ad un prodotto, ad un processo o ad un’attività lungo l’intero ciclo di vita, dall’acquisizione delle materie prime al fine vita (“dalla Culla alla Tomba”). Il Life Cycle Assessment (LCA), del resto, rappresenta un supporto fondamentale allo sviluppo di schemi di Etichettatura Ambientale.
Il progetto di ORI Martin mira a sviluppare uno strumento per fornire un supporto dati alle decisioni e alla politica aziendale sulla sostenibilità, culminando nello sviluppo di una dashboard per il monitoraggio a lungo termine dell’impatto ambientale del ciclo di produzione dei prodotti core business dell’azienda.
Quanto realizzato è uno strumento altamente innovativo per la valutazione dell’impatto ambientale ed è stato affiancato da ulteriori progetti relativi alla gestione e all’analisi dei dati per l’impatto ambientale. L’obiettivo di dotarsi di piattaforme digitali, in grado di gestire e analizzare i dati relativi alla sostenibilità ambientale dei processi produttivi, ormai è diventata una primaria esigenza per l’intera industria siderurgica.
L’eterogeneità di questi tipi di dati mette in grande crisi gli attuali sistemi informativi di fabbrica dedicati alla gestione della produzione spingendo la tecnologia IT verso nuovi tipi di architetture con un sempre maggiore livello di flessibilità, scalabilità e sicurezza informatica. La dotazione di sistemi digitali innovativi specifici per tale ambito rappresenta ormai un punto significativo per la competitività aziendale in termini di risposta alle esigenze di mercato e di pianificazione degli investimenti per la decarbonizzazione della produzione.
ORI Martin è inoltre impegnato in un grande progetto di ampliamento del monitoraggio dei consumi energetici di stabilimento, finalizzato all’ottimizzazione dei consumi attraverso soluzioni IoT dedicate. La capacità di analizzare sempre più in dettaglio i consumi legati alla produzione consente di individuare nuove situazioni di spreco di energia, spingere verso il riutilizzo di questa ed ottimizzare le pratiche operative per avere prodotti di altissima qualità con il minor impatto ambientale possibile.
I due esempi del progetto “Acciaio 4.0” sono precursori della visione ambientale e produttiva che porta verso l’Industria 5.0, dove la trasformazione digitale e l’innovazione sono il motore di uno sviluppo sostenibile e inclusivo e di un necessario rinnovamento delle imprese. Ciò deve saper coniugare bene tecnologie e persone verso un senso di responsabilità nei confronti delle risorse, ben rappresentato dalla definizione di sostenibilità coniata nel 1987 dal Rapporto Brundtland (Our Common Future), che fa sempre bene ricordare e che cita testualmente: “lo sviluppo sostenibile è uno sviluppo che soddisfa i bisogni del presente senza compromettere la possibilità delle generazioni future di soddisfare i propri”.
Con questo nuovo paradigma nasce l’opportunità di valorizzare i dati applicati alla possibilità di rendicontare, rendendo quindi sempre più possibile comunicare in modo chiaro (nell’ottica di riduzione dei rischi di greenwashing) cosa vuol dire concretamente realizzare una produzione sostenibile, efficiente ed efficace; mostrare a clienti e investitori cosa significa attuare processi e prodotti sostenibili, dare quindi vita a un contesto capace di favorire un consumo più sostenibile attraverso il quale recuperare risorse, energie e materiali (ad esempio con le logiche della cosiddetta Circular Economy). Questa capacità di far parlare i dati permetterà sempre di più di monetizzare i vantaggi di questa trasformazione.
ORI Martin sta lavorando anche nell’integrazione di robot antropomorfi in acciaieria e nei laminatoi in collaborazione con la società BM Group Polytec. Un robot dedicato ai campionamenti di acciaio in Electric Arc Furnace (EAF), mediante un apposito strumento, provvede all’ispezione dell’interno del forno fusorio, al fine di anticipare l’ordinaria sostituzione della carpenteria
dell’EAF se necessario, di prevenire interventi di manutenzione gravosi se effettuati in loco interrompendo il normale esercizio della macchina e, fondamentalmente, di prevenire incidenti dovuti allo sversamento dell’acqua di raffreddamento in forno. Il sistema di monitoraggio del EAF si integra con la piattaforma di monitoraggio dell’acciaieria iMeltshop, al fine di avere un’integrazione completa tra le richieste del processo produttivo e le performance dello stesso. L’intera piattaforma iMeltshop è orientata nell’ottica di soddisfare i requisiti dell’Obiettivo 8 dell’Agenda Globale
2030: lavoro dignitoso e crescita economica. Anche le linee di laminazione di ORI Martin sono dotate di robot antropomorfi che provvedono all’etichettatura del laminato. I robot sono integrati con il sistema di tracciatura della produzione (tracking), in modo da rendere automatica l’etichettatura e di evitare al personale dedicato alla supervisione di questa fase di produzione di applicare manualmente l’etichetta al collo prodotto riducendo gesti ripetitivi e in condizioni ostili.
L’Intelligenza Artificiale ed i robot stanno cambiando il mondo del lavoro, e la
siderurgia non fa eccezione. Il futuro vedrà sempre più persone e Intelligenza Artificiale lavorare assieme. La sfida sarà dunque far in modo che la collaborazione uomo-macchina sia quanto più proficua possibile, aumentando la sicurezza, produttività, e la qualità del lavoro.
AFIL – Associazione Fabbrica Intelligente Lombardia – è il Cluster Tecnologico per il Manifatturiero Avanzato ufficialmente riconosciuto da Regione Lombardia. Attraverso le Strategic Communities, ovvero gruppi di lavoro formati da grandi imprese, PMI, start-up, associazioni, università e centri di ricerca che lavorano su tematiche strategiche per il manifatturiero lombardo, AFIL accompagna i suoi associati in un percorso collaborativo di crescita attraverso incontri tematici, workshop, webinar, matchmaking, missioni internazionali, favorendo lo sviluppo di progettualità di filiera e promuovendo la R&I anche a livello interregionale.
Le Strategic Communities di AFIL ad oggi sono 6: De- and Remanufacturing for Circular Economy, Digital Transformation, Advanced Polymers, Additive Manufacturing, Secure and Sustainable Food Manufacturing, Smart Components.
Per maggiori informazioni sulle attività di AFIL e per le modalità di adesione al Cluster, si invita a visitare il sito www.afil.it oppure a scrivere all’indirizzo comunicazione@afil.it
Interroll ha disegnato il futuro dell’intralogistica con l’innovativo concetto di piattaforma. Qualità, semplicità di funzionamento e di design, risparmio energetico e sostenibilità. Per ogni peso, per ogni mercato, per ogni esigenza.
interroll.com/it
Redazione Direttore Responsabile
Giorgio Albonetti
Coordinamento Editoriale Area Industry
Marco Tenaglia –marco.tenaglia@quine.it – cel. 3298490024
Direttore tecnico
Chiara Tagliaferri
Segreteria di Redazione
Cristina Gualdoni cristina.gualdoni@quine.it – cel. 3477623887
Hanno collaborato a questo numero
Patrizia Ricci, Maurizio Zanforlin, Luca Piedimonte, Antonio Lucarelli
Martina Imarisio Neviani
Pubblicità Costantino Cialfi | Direttore Commerciale c.cialfi@lswr.it - tel. +39 3466705086
Elena Genitoni | Ufficio Traffico
e.genitoni@lswr.it – tel. 0289293962
Servizio abbonamenti abbonamenti.quine@lswr.it
Abbonamento annuale € 49,99
Costo copia singola € 7,07 (presso l’editore)
Produzione Antonio Iovene | Procurement Specialist
a.iovene@lswr.it | Cell. 349.1811231
Grafica e Fotolito: Fabio Castiglioni
Stampa: FAENZA PRINTING
Peschiera Borromeo (MI)
Registrazione del Tribunale di Milano n. 653 del 21.09.2005.
Iscrizione al R.O.C. n. 12191 del 29/10/2005 Tutti gli articoli pubblicati su m&a meccanica &automazione sono redatti sotto la responsabilità degli Autori. La pubblicazione o la ristampa degli articoli deve essere autorizzata per iscritto dall’Editore. Ai sensi dell’art. 13 del D.Lgs. 196/03, dati di tutti i lettori saranno trattati sia manualmente sia con strumenti informatici e saranno utilizzati per l’invio di questa e di altre pubblicazioni e di materiale informativo e promozionale. Le modalità di trattamento saranno conformi a quanto previsto dall’art. 11 D.Lgs. 196/03. I dati potrebbero essere comunicati a soggetti con i quali Quine S.r.l. intrattiene rapporti contrattuali necessari per l’invio delle copie della rivista. Il titolare del trattamento dei dati è Quine S.r.l. - via Spadolini, 7 - 20141 Milano Tel +39 02 864105 Fax +39 02 72016740, al quale il lettore si potrà rivolgere per chiedere l’aggiornamento, l’integrazione, la cancellazione e ogni altra operazione di cui all’art. 7 D.Lgs. 196/03.
Ai sensi dell’art. 13 Regolamento Europeo per la Protezione dei Dati Personali 679/2016 di seguito GDPR, i dati di tutti lettori saranno trattati sia manualmente, sia con strumenti informatici e saranno utilizzati per l’invio di questa e di altre pubblicazioni e di materiale informativo e promozionale. Le modalità di trattamento saranno conformi a quanto previsto dagli art. 5-6-7 del GDPR. I dati potranno essere comunicati a soggetti con i quali Edra S.p.A. intrattiene rapporti contrattuali necessari per l’invio delle copie della rivista. Il titolare del trattamento dei dati è Edra S.p.A., Via G. Spadolini 7 - 20141 Milano, al quale il lettore si potrà rivolgere per chiedere l’aggiornamento, l’integrazione, la cancellazione e ogni altra operazione di cui agli articoli 15-21 del GDPR.
Testata associata
Limitatori di Coppia
Serie SKH | 0,1 - 2.800 Nm
Chiedi una consulenza. Insieme troveremo la soluzione.
I limitatori di coppia con fissaggio a morsetti scomponibili rappresentano componenti fondamentali nelle trasmissioni meccaniche.
Mozzo di Serraggio in alluminio o acciaio.
Limitatore di coppia a sfere con molle a tazza degressiva con montaggio radiale.
Robusti, Compatti e Precisi
#restaconnesso
Aumenta la produttività con i dispenser Tork Performance®
I dispenser Tork Performance® sono progettati per essere collocati esattamente dov’è più necessario: presso le postazioni di lavoro.
La gamma completa di dispenser Tork comprende formati versatili, diverse opzioni di montaggio e vari tipi di panni adatti a ogni attività.
74%
dei lavoratori prende più panni del necessario per evitare di doverne andare a prendere altri*
* Ricerca Tork sugli operatori di macchine (luglio 2019)
come la MX – Machining Transformation aumenta la vostra produttività, migliora il flusso di lavoro, crea nuove opportunità e riduce il consumo energetico.
Combinate più processi in un’unica macchina utensile per ottenere maggiore produttività ed efficienza.
Incrementate la produttività, la qualità e le attività 24 ore su 24, 7 giorni su 7.
Rivoluzionate il vostro flusso di lavoro, scoprite infinite possibilità, aumentate l’efficienza e promuovete la sostenibilità riducendo il consumo energetico, ottenendo allo stesso tempo un forte vantaggio competitivo.
I processi integrati aumentano la produttività, riducono al minimo il consumo energetico e massimizzano la redditività.
Vieni al nostro stand e scopri come Tork si impegna a migliorare la produttività con i dispenser Tork Performance®
I dispenser Tork Performance® sono progettati per essere collocati esattamente dov’è più necessario: presso le postazioni di lavoro. La gamma completa di dispenser Tork comprende formati versatili, diverse opzioni di montaggio e vari tipi di panni adatti a ogni attività.
Scopri di più su:
Il
20 volte algiorno