Journal of the Engineering Integrity Society
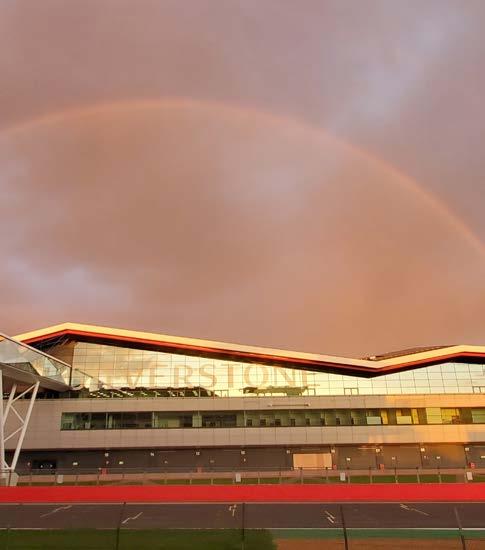
Journal of the Engineering Integrity Society
September 2023 | Issue No. 55
Overview of Profilometry-based Indentation: Plastometry and its Industrial Usage
ARTICLE: Novel Numerical Method for Real-Time Thermomechanical
Correction in Complex Load-bearing and Load-measurement Applications
FATIGUE 2024
|
Silverstone Wing, Silverstone Race Circuit
Tuesday 26 March 2024 10am-4pm
• 65 exhibitors from aerospace, automotive, motorsport, rail, off-highway, mechanical handling, civil engineering, industrial and power generation industries. The exhibitors offer a wide variety of modern instrumentation, measuring and modelling technologies
• Free Entrance to Exhibition and Mini Seminars
• Free Car Parking
• Complimentary Refreshments
To complement the exhibition there will be a number of mini seminars throughout the day.
To pre-register: info@e-i-s.org.uk | www.e-i-s.org.uk
Sponsored by:
Co-sponsored by:Structural analysis with HEAD acoustics –the new ArtemiS SUITE 12.5 software package makes modal and operational vibration analyses effortless, intuitive and effi cient. Ingeniously simple.
www.head-acoustics.com
If you would like to receive this journal electronically, please contact the Marketing & Events Manager: info@e-i-s.org.uk
Dr Spencer Jeffs
E-mail: s.p.jeffs@swansea.ac.uk
Rochelle Stanley
Tel. +44 (0)7979 270998
E-mail: managingeditor@e-i-s.org.uk
Sara Atkin
Engineering Integrity Society
6 Brickyard Lane, Farnsfield, Notts., NG22 8JS
Tel: +44 (0)1623 884225
E-mail: info@e-i-s.org.uk
WWW: www.e-i-s.org.uk
Engineering Integrity contains various items of information of interest to, or directly generated by, the Engineering Integrity Society. The items of information can be approximately subdivided into three general categories: technical papers, topical discussion pieces and news items. The items labelled in the journal as technical papers are peer reviewed by a minimum of two reviewers in the normal manner of academic journals, following a standard protocol. The items of information labelled as topical discussions and the news items have been reviewed by the journal editorial staff and found to conform to the legal and professional standards of the Engineering Integrity Society.
Copyright of the technical papers included in this issue is held by the Engineering Integrity Society unless otherwise stated.
Photographic contributions for the front cover are welcomed.
ISSN 1365-4101/2023
The Engineering Integrity Society (EIS) Incorporated under the Companies Act 1985.
Registered No. 1959979
Registered Office: c/o Hollis & Co., 35 Wilkinson Street, Sheffield S10 2GB
Charity No: 327121
‘Engineering Integrity’ is published twice a year
Black and White
1 insert 2 Inserts
Full Page £280.50 £506 annual
Half Page £174 £313.50 annual
Quarter Page £102 £192.50 annual
Full Colour
1 insert 2 Inserts
Full Page £489.50 £880 annual
Half Page £305.80 £550 annual
Quarter Page £176 £319 annual
Full Page 297mm (depth) x 210mm (width) and 3mm bleed
Half Page 255mm (depth) x 86mm (width) or 125mm (depth) x 180mm (width)
Quarter Page 125mm (depth) x 86mm (width)
Space is limited so place your order soon to avoid disappointment.
A copy of the latest issue of ‘Engineering Integrity’ is published on the website and includes all advertisements.
Loose Inserts £150 per A4 sheet (up to 160 gsm)
The principal activity of the Engineering Integrity Society is the arrangement of conferences, seminars, exhibitions and workshops to advance the education of persons working in the field of engineering. This is achieved by providing a forum for the interchange of ideas and information on engineering practice. The Society is particularly committed to promoting projects which support professional development and attract young people into the profession.
‘Engineering Integrity’, the Journal of the Engineering Integrity Society is published twice a year.
‘Engineering Integrity’ is lodged with the Agency for the Legal Deposit Libraries on behalf of the Bodleian Library Oxford University, the Cambridge University Library, National Library of Scotland, National Library of Wales and Trinity College Dublin.
films about space adventure. The Pragyaan rover will now explore the surface and I am excited to see the findings as they are reported.
Tata Group have announced investment of over £4 billion to build a UK gigafactory, their first outside of India. At 40GWh it would create up to 4,000 new jobs and thousands across the wider supply chain. It would be a huge boost to the UK automotive sector, and a significant step towards meeting the government 2030 target to end the sale of petrol and diesel cars. And with the expansion of Ultra-Low Emission Zones in London and across the UK, the demand for electric vehicles will only grow further and faster. On the other hand, Tata Steel are close to securing a £500 million package from the UK government to secure its long-term future, with a requirement to commit to building electric arc furnaces to reduce carbon emissions from steel production.
Firstly, a big thank you to all those involved in the Instrumentation, Analysis and Testing Exhibition which took place in May at the Silverstone Race Circuit, which was a huge success and attracted its highest visitor attendance to date. In other EIS events, Fatigue 2024 preparation is advancing with abstracts submitted and reviewed, keynote speakers announced, and the full programme being worked on. In addition, several EIS seminars have successfully taken place, one of which has led to the formation of a Net Zero Group that will aim to be a platform and catalyst for future innovations.
Throughout these last few months, we have seen wildfires, flooding and hurricanes across the globe with every increasing frequency and uncertainty around when these events will occur and what they may leave in their wake. Knowledge and understanding of how we can predict, mitigate and cope with such events is a serious challenge, one that engineering needs to be at the forefront of.
A technical failure of UK air traffic control for just a few hours took place one day in August and led to severe disruption with cancelled flights, stranded passengers and a knock-on effect that lasted several days with planes at locations they were not supposed to be. The cause was said to be from a single piece of data in a flight plan that was wrongly input. This highlights potential flaws within such automated systems and the serious consequences that can arise. In other flying news, although now flying in space, the Indian Space Research Organisation landed Chandrayaan-3's Vikram on lunar soil, the first to ever land near the lunar south pole. Particularly impressive when you consider the budget for the Chandrayaan-3 mission was much less than that of some Hollywood
University applicants have had their A level results, which have seen a steep fall compared to the last two years where they received teacher-assessed grades in the absence of taking exams. As always, I hope all those who have applied to university, whether their first choice, insurance choice or through clearing, have found a degree programme and university that is best for them. Universities themselves face certain challenges in terms of their funding, large inflation rises means that student fees are worth significantly less, approximately a £2,500 shortfall per student compared to the 2012 fee cap of £9,000. In addition, the loss of EU funds poses a real risk to research funding, jobs, collaboration and recruitment, and is something that must be addressed.
The technical paper in this issue provides an overview of profilometry-based indentation, which has the potential to offer real advantages in terms of providing bulk mechanical properties using limited material with increased turnaround times compared to conventional methods. A technical article on real-time thermal correction in complex load-bearing structures assessed using finite element modelling is presented, with a follow-up article revealing the experimental results due in a later Engineering Integrity publication. In addition, a piece on the importance of mastering and leveraging artificial intelligence gives some insight into its potential for enhancing productivity, efficiency and innovation.
Lastly, a huge thank you to Nick Richardson, who has stepped down from his role as a Trustee and Director of the EIS – we all wish him all the very best in retirement.
EXHIBITION | Advanced Engineering Show, NEC, Birmingham | 1–2 November 2023
COMPETITION | Peter Watson Prize Final, Makeney Hall, Derbyshire | 23 November 2023
EXHIBITION | Instrumentation, Analysis and Testing Exhibition, Silverstone Wing, Silverstone Race Circuit | 26 March 2024
CONFERENCE | Fatigue 2024, Jesus College, University of Cambridge | 19–21 June 2024
Thank you to HORIBA-MIRA and MIRA Technology Institute for hosting the June committee meetings and AGM.
One
Fast, precise, elegant, servo-hydraulic control. BIG or small, get your next project running more quickly than you thought possible.
Long-standing Director Nick Richardson has stepped down from his roles as a Trustee and Director to fully embrace retirement.
Nick has been a supporter of the EIS for decades and his commitment to the society and the valuable contribution he has made will be missed by his fellow Directors.
Nick will continue as a member of the Simulation, Test and Measurement Group.
axis or fifty; position, velocity, force, or position-pressure/force, look to Delta RMC Motion Controllers and graphical RMCTools software to make complex motion easier, smoother, and more precise.
10 August 1946 – 20 February 2023
John was born in Kingston-upon-Hull, in Yorkshire, UK, and attended Hull Grammar School. He then studied Metallurgy at Aston University, Birmingham, UK, obtaining a BSc Hons degree. An MSc course in physics of materials at Bristol University, UK, was followed by a CEGB-sponsored PhD at The Cavendish Laboratory, University of Cambridge, UK. His thesis was on the ‘Fatigue Mechanisms in Copper Single Crystals'.
On completion in 1973, he was invited to apply for a research officer position in the materials division at the CEGB research laboratories in Leatherhead, Surrey, UK, (known as CERL). He worked there, on a variety of power plant problems associated with cracking for nearly 20 years, until privatisation of the electricity supply industry in the late 80s led to a move to academia, where he took a professorial post in the engineering department at Sheffield City Polytechnic, UK.
He was a member of the International Co-operative Group on Environmentally Assisted Cracking (ICGEAC) from 1978 to 2008 (whilst at CERL, NPTEC and Sheffield Hallam University) and spent nine years as Chair of the Low Alloy Steels (LAS) Task Group, with duties on the Executive Committee.
Sheffield City Polytechnic were granted a university charter to become Sheffield Hallam University in 1993 and John was able to transfer some of his equipment at this time, as CERL was also closed down in 1993 by National Power. At Sheffield Hallam he had a busy life, developing teaching material on up to 15 modules at BEng and MSc level, as well as carrying out contract research on cracking issues for the relocated power companies.
Over a period of 15 years he generated a research/ consultancy income of £1m and helped to boost the 2001 RAE rating in materials from 3a to 5 of the university, equal at that time to Imperial College London. He supervised six PhD students to completion and, during Science Week, gave several public lectures in Sheffield on nuclear power issues.
John retired in 2015 and ceased his consultancy work within the power industries to pursue his hobby of restoring rusty old Porsche 356 cars and to spend time with his family – wife Sue, children Jane and Neil and five grandchildren.
Jane Gough (John’s daughter)John Atkinson was a respected voice in cracking, then later moved into academia where he advocated for quality research and supervised PhD students.
Back in 2022 when we chose the theme for International Women in Engineering Day 2023 (INWED) and our Top 50 Women in Engineering Awards (WE50), we couldn’t have predicted how important that theme would become.
In a world where the war in Ukraine sees no end, wildfires are continuing across the world, women’s safety concerns are still ignored, and the climate emergency continues to grow, our chosen theme of safety and security and INWED hashtag #makesafetyseen couldn’t be more appropriate.
posting on the day including Jessica Ashley (Miss England), Jodie Sloss (racing driver) and Bethany Holroyd (Top 100 Most Influential Women in Construction 2022).
• 25 community partners,
• Almost 30k visitors to the INWED website in June and
• A whopping 782m potential reach on Twitter!
Alongside the social media campaign, hundreds of events were held around the world all celebrating International Women in Engineering Day. There were podcasts and online events showcasing engineers from industries across the board including building, manufacturing, civil, structural and computing. Face-to-face events were held in locations as far and wide as Hong Kong, Korea, Australia and Africa all with a focus on the 2023 hashtag #makesafetyseen.
Keeping people safe is a key part of engineering, but often goes unnoticed. The women in this year’s WE50 list are a truly amazing group. Their work often goes unseen yet is key to keeping us all safe and secure. Winners were chosen from across the engineering industry. Through creating safer neighbourhoods via improved street design, improving body armour for women serving in the forces, or developing fire strategies for heritage buildings, the idea of safety and security encompasses all our lives.
Each year the judges are always amazed at the breadth and talent of the nominations. This year the judges were particularly impressed with how many of the women had overcome barriers both personally and professionally to forge a career in what is still a male-dominated environment. Many of our winners were mentors for other women, spending time actively challenging gender stereotypes and promoting diversity.
Alongside the WE50, another highlight of the WES calendar is the INWED campaign, which continues to grow with women and allies all over the world joining in on social media.
The statistics show how big a campaign this has become:
• #INWED23 trended at number 1 on Twitter in the UK.
• Almost 84k impressions on @inwed1919 Twitter, an increase on 2022.
• 276,550 impressions across all INWED social platforms.
• 25 social media ambassadors from around the world
Seeing how many organisations and individuals were keen to get involved shows just how important this campaign is not only in inspiring the next generation of engineers but also in supporting women working in industries where they are still in the minority. Women still struggle to break into what is perceived as a maledominated industry and the barriers to women entering and staying in engineering are hard to break down. A lack of flexible working, incorrectly fitting PPE, and unequal pay are all issues that women engineers face today and need to be addressed.
That’s why campaigns such as INWED are still so relevant today and why as an organisation we continue to champion our vision of an engineering industry that employs the diversity of the society it serves to solve the biggest societal issues of our time.
In the dynamic world of engineering, where innovation propels industries forward, the annual Instrumentation, Analysis, and Testing Exhibition has emerged as a pivotal event, drawing professionals from various sectors under one roof.
A unique platform showcasing the latest in testing and analysis technologies, this exhibition has evolved into a hub of ideas, contacts and advancements. With a diverse array of exhibitors spanning automotive, aerospace, motorsport, rail, off-highway, mechanical handling, civil engineering, industrial, and power generation, this year's show, held at the iconic Silverstone Wing in May 2023, was an unmissable rendezvous for engineering professionals.
An added attraction was the thought-provoking mini seminars, centred around the theme "Test and Measurement: The Road to Virtualisation." Attendees were treated to a series of enlightening presentations that delved into various facets of this crucial topic. The response from the audience was overwhelmingly positive, indicating a desire for knowledge and exploration of the transformative journey toward virtualisation in testing and measurement. As plans for the 2024 exhibition take shape, organisers eagerly welcome fresh ideas from members for future seminar topics, ensuring a dynamic and relevant experience for all participants.
Outside the Silverstone Wing, a showcase awaited visitors, featuring two exceptional vehicles that embodied the spirit of engineering excellence. Morris Commercial's iconic J-type van and White Motorcycle Concept's First Responder Hybrid Police Bike captured the attention of attendees, offering them the chance to engage directly with the visionary creators behind these groundbreaking vehicles. Visitors were able to delve into the intricate technical details of these innovative machines, further enriching their understanding of the evolving landscape of automotive engineering.
Following the resounding success of the 2022 show, the return to the Silverstone Wing was met with anticipation, and the turnout exceeded all expectations, marking the highest visitor attendance to date. The demand for exhibition tables was unprecedented, selling out at a record rate. Throughout the day, the space hummed with energy as industry delegates engaged in insightful conversations with exhibitors, fostering a rich exchange of ideas and forging valuable connections.
The anticipation for the upcoming 2024 event is already building. Set to take place on March 26, 2024, at the Silverstone venue, the exhibition promises yet another immersive experience. A day filled with knowledgesharing, inspiration, and connection awaits, so save the date!
Plastometrex Ltd, 204 Science Park, Milton Road Cambridge CB2 0GZ, UK.
Author correspondence: j.campbell@plastometrex.com
Abstract
This paper includes a review of the current state-ofthe-art in a technique for extracting the (quasi-static) stress-strain relationship of a metallic sample from an indentation experiment, as well as an industrial case study using the technique to map the stress-strain properties of a forged part. The technique, called profilometry-based indentation plastometry (PIP), uses a large (either 1 mm or 0.5 mm radius) spherical indenter to create a residual indent under relatively high applied loads (kN range). The indent profile is measured, and iterative finite element method (FEM) simulation of the indentation is carried out to converge on the true stress-strain curve of the indented material (with the indent profile as the target outcome). Commercial products are now available that automatically complete indentation, profilometry and convergence upon Voce plasticity parameter values, which describe the full stress-strain curve within a few minutes. The review covers the technique’s advantages as an indentation-based technique, firstly in the mapping of samples and secondly in giving insight into the direction and sense of anisotropy from the breakdown in radial symmetry. The case study demonstrates the application of the technique in both of these areas for characterising a forged part, comparing the results from PIP to conventional uniaxial testing. It is shown that the scale of PIP unveils local inhomogeneity unable to be detected by tensile testing, where these differences can be linked to the prior plastic strains introduced during forging. Additionally, anisotropy is detected by PIP relating to aligned FeNiAl precipitates that give a sense of the strength and direction of the anisotropy.
Keywords: Indentation; Stress-strain curves; Profilometry; Inverse FEM.
Attempts to extract meaningful plasticity characteristics from indentation tests on metals have a long history. These characteristics are fully described by the relationship between the applied stress and the resultant plastic strain, which is conventionally obtained via a uniaxial tensile test, or in some cases via a uniaxial compression test. However, while this relationship also dictates the outcome of an indentation test, inferring the former from the latter is far from simple. The stress
and strain fields are naturally much more complex, and evolve substantially, during an indentation operation, compared with the situation during a uniaxial test. However, progress has been made recently and a viable methodology has been developed. Known as profilometry-based indentation plastometry (PIP), the methodology involves measurement of the residual indent profile and then iterative finite element modelling (FEM) of the indentation operation, to infer the stress-strain relationship that is most consistent with that profile. While this is relatively simple in principle, the methodology must be optimized in several respects if accurate stress-strain curves are to be obtained in an efficient and robust manner. It may also be noted that most early attempts to implement this kind of approach were based on use of the loaddisplacement plot as the target outcome [1–6] but this approach suffers from a lack of uniqueness where different stress-strain curves produce identical loaddisplacement curves. It has now become clear that using the residual indent profile offers a number of important advantages[7–10], including alleviating the uniqueness issue.
Other requirements include the need to deform a relatively large volume of material that is representative of the bulk. This requires the effects of all the microstructural features that contribute to the plasticity response to be captured, i.e. the indent must be large relative to the grain size. In addition, the indent must generate relatively large plastic strains to ensure that the range of strains of interest in a conventional tensile test are covered during indentation. There are also a number of important advantages[3–5, 11, 12] in using a spherical indenter. These include ease of manufacture, reduced risk of damage and a high sensitivity to the detection of anisotropy in the material via a lack of radial symmetry in the indent profile. In terms of practical usage, it is clear that an integrated facility is needed, in which creation of the indent, measurement of its profile and the iterative FEM are under automated software control and are completed within a short period (a few minutes). An example of such a facility is shown in Figure 1. It incorporates a stylus profilometer, has a load capability of about 10 kN and 'uses interchangeable silicon nitride spheres of either 0.5 mm or 1 mm radius. Samples with a yield stress of up to about 2.5 GPa can be tested[13], with software protection in place to abort any test started on a material with values in excess of this limit. This allows testing of virtually any metal used for structural engineering purposes.
The key issues involved in implementation of the PIP procedure are covered in a recent review article[14]. One point to note is that the elastic constants of the material and the indenter, the Young’s modulus and Poisson ratio, are required for the FEM simulation. While the focus is on plasticity, elastic deformation takes place during the test and does affect the outcome (residual indent shape). For the indenter, the elastic constants are defined by the indenter material and for the specimen, the sensitivity to these elastic constants is relatively small and they need only be specified to a precision of about 10–15%. Furthermore, since the modulus is determined by the electrostatic interactions between the atoms in the structure and shows very little sensitivity to microstructure (unlike plasticity, which is strongly influenced by microstructure) all that is required is knowledge of the base metal.
Once the elastic constants have been specified, indentation has been carried out, the profile has been measured and the iterative FEM algorithm has been implemented, the “solution” is obtained as a true stress –true plastic strain relationship, in the form of a set of three parameter values in a constitutive law. For PIP testing, the Voce law is used, as shown in Equation (1) where σ is the (true) stress, ε is the (true) strain, σY is the yield stress, σ s is a saturation stress and ε0 is a characteristic strain (for the approach of the stress to its saturation level). When implemented in the FEM model, these stresses and strains are von Mises values.
A typical comparison between experimental and bestfit modelled indent profiles is shown in Figure 2 for as-received and annealed copper (with two different penetration depths in each case – i.e. two different applied loads). A corresponding comparison is shown in Figure 3 between the nominal stress – nominal strain plots obtained by tensile testing these materials and those from the indentation-derived true stress – and true strain relationship (with FEM simulation needed to obtain the post-necking part of the curve).
4, which shows two maps of yield stress and ultimate tensile stress (UTS) across parent-weld transition regions.
Such information cannot be obtained via tensile testing and, while it would be common to carry out hardness tests on this type of scale, hardness numbers are just semi-quantitative indicators of the resistance to plastic deformation and should not be used in any quantitative way. In contrast to this, these PIP-derived stress-strain relationships (as a function of location) can be used in FEM simulation of how the weld region would respond under service conditions.
It is quite common for metallic samples to exhibit at least some (plastic) anisotropy – i.e. for the stressstrain curve to be different when tested in different directions – for example, in the two in-plane directions and the through-thickness direction of a rolled plate. This commonly arises from crystallographic texture – a non-random distribution in the orientations of individual grains. One attraction of PIP is that it has a high sensitivity to the detection of in-plane anisotropy, in the form of a lack of radial symmetry in the indent. Indent profiles are routinely taken in more than one direction and any significant differences between them are automatically flagged to the operator. An example[16] is shown in Figure 5.
PIP testing offers many advantages over conventional uniaxial testing. These include a capability for the mapping of properties on a relatively fine scale. The deformed region is typically a disk of about 0.5 mm radius and a thickness around 0.2 mm, so mapping on a scale of mm is feasible. An example[15] is presented in Figure
The two SEM micrographs of the indent (in transverse and parallel planes relative to the growth direction of an additively manufactured superalloy component) do show that one of them is not radially symmetric. Rather more sensitively, the profiles are noticeably different for the asymmetrical case, with the pile-up height greater in the “softer” direction – which in this case is the growth direction. The PIP-derived stress-strain curve is effectively a direction-averaged one, lying between those obtained via tensile testing in the two principal directions. Although it is not at present possible to obtain stressstrain curves for different directions from a PIP test, the presence and sense of the anisotropy can be detected. Since the monitoring of anisotropy is often very difficult via uniaxial testing, this is a valuable capability.
It is common for components to have large variation in properties due to their processing. This is widely seen in all industries, for example when large plastic strains are imposed during forming, or when there are localised differences in thermal histories such as near a weld. When the scale of such inhomogeneity is smaller than the scale of a tensile test, such that the variations have little effect, it becomes difficult to fully characterise a component. Often hardness testing would be used instead, but this gives only a semi-quantitative indication of a material’s plasticity properties. For the purposes of making confident engineering decisions, such as predicting component life as part of an engineering critical assessment (ECA) where plasticity properties are required, a different method is needed for characterisation, which can give localised plasticity parameters. PIP testing is able to bridge this gap, giving a full stress-strain curve from an indentationbased test, and is therefore ideally suited to characterising parts with localised plastic inhomogeneity. The objective of this case study was to detect localised variations in the plasticity parameters of a section of an aluminiumbased forging, pictured in Figure 6. Traditional uniaxial testing, both tensile and compressive, was carried out and compared to PIP testing on a sectioned slice of the forging.
Microstructures were examined using optical and SEM microscopy, with EDX for compositional analysis. An investigation was also made into the phases present, using a Philips X’Pert PW3020 X-ray diffractometer, in combination with the Highscore programme, and the Inorganic Crystal Structure Database (ISCD) was used to identify phases formed on the free surfaces. The Highscore search was limited to phases containing Al, Ni and Fe.
Uniaxial testing was carried out both in tension and compression for the Al-based forging. Figure 7 shows a photo of a section of the forging, indicating the approximate locations from which tensile and compression samples were cut, and the corresponding numbering system. The numbers for the compression samples are also used to indicate the locations of indents. Round tensile samples were machined in accordance with ASTM E8, and compression samples were 5 mm diameter by 5 mm height. All tests were carried out on an Instron 3367 conventional mechanical testing frame. Full details of the conditions used for tensile and compressive testing are available in previous publications[5, 10, 17, 18] .
PIP results were measured using a PLX Benchtop Plastometer, pictured in Figure 1. Multiple indents were carried out, and the compression sample locations in Figure 7 give a rough indication of their location. The input Young’s modulus of the forging was taken to be 69 GPa, and the Poisson’s ratio to be 0.3.
After preparation to P2500 grit using silicon carbide paper, and polishing using 1 μm diamond paste, the sectioned Al-forging was placed on the load cell of the plastometer. A 1 mm diameter indenter ball was used to indent the material in several locations with a fixed load of 1.5 kN. A contacting stylus profilometer, with a depth resolution of about 1 μm, was used to carry out profilometry of the indents.
Tilt correction functions were applied to the raw data, based on the far-field parts of the scan being parallel. Iterative finite element analysis is then applied to obtain the true stress-strain curve, by optimising for three plasticity parameters in a constitutive law. Confidence intervals are also presented based on how unique the experimental residual indent profile is. These procedures are carried out automatically under software control. Comparisons with the uniaxial testing data related to nominal stress v. nominal strain curves, for which simple analytical conversions from the true form were used. These are only valid while the stress and strain fields within the gauge length are uniform, which is the case up to the onset of necking (the UTS).
The microstructure of the forging was unusual and varied between different locations within the component. The grain structure was relatively fine (~30150 μm) throughout, although there were certainly local variations in grain size and shape. More striking was the presence of a significant volume fraction (~7 %) of the second phase in the form of relatively coarse (~5-10 μm) precipitates. These showed a strong tendency to: (a) align so that their longer axis is in a particular direction and (b) be collected into parallel sets of “stringers”, as can be seen in Figure 8.
This kind of structure is strongly indicative of the effect of relatively large plastic strains being imposed in the direction concerned. It is likely that the component was produced in a two-stage process, being initially cast to a suitable shape, and then plastically deformed during a forging process, with the magnitude and directionality of the plastic strain varying between different locations.
The composition of the second phase was obtained using EDX in the SEM, with the beam focused on individual particles. The overall average composition of the alloy was obtained similarly, with the beam scanned over a large area. Both sets of compositions are shown in Table I, where it can be seen that the second phase mainly contains Al, Fe and Ni. It was identified by X-ray diffraction as Fe0.7Ni1.3Al9, with a typical spectrum shown in Figure 9. (This phase has a complex crystal structure, giving many low intensity peaks: those at high Bragg angles are virtually impossible to identify, but several at lower angles are indexed in Figure 9 and it seems likely
that only this phase is present, apart from the Al matrix, or other phases present at levels below 1%.) The (relatively low) intensity of the second-phase peaks is consistent with it being present at a level of about 7 vol%.
This alloy is thus effectively a particulate reinforced MMC. The FeNiAl phase is both stiffer and harder than the matrix, so a significant increase in both stiffness and hardness of the material is expected to result from its presence[18]. Furthermore, the alignment evident in Figure 8(a) is expected to create some (in-plane) anisotropy. In addition, differences in the magnitude of the plastic strain in different parts of the forging are also expected to affect the mechanical properties, with work hardening of the matrix expected to raise the yield stress in parts subjected to higher strains. Care is, however, needed here, since it is possible that recrystallization, leading to marked softening, could have occurred after forging, depending on the thermal history.
There is clearly interest in exploring variations in microstructure between different parts of the forging. Some information of this type can be seen in Figure 10, which shows several optical micrographs, together with an indication of their location on the section shown. The alignment of the FeNiAl precipitates allows the broad nature of the plastic flow field during forging to be visualized, giving at least some idea of the probable distribution of plastic strain. Most regions have clearly been subjected to relatively high strains, although there appears to be a region in the lower central part of the section (near image 27) that may have been a “dead zone” that remained relatively undeformed from the original cast structure.
Tensile stress-strain curves are shown in Figure 11(a), with the labels corresponding to the locations shown in Figure 7. These curves are all very similar, with a yield stress of around 420 MPa and a UTS value of about 450 MPa. It is also evident that there is little or no systematic difference between the individual curves. This is in fact unsurprising in view of the information in Figure 10. While there are certainly indications there that some locations had been subject to different plastic strains during manufacture, these tensile tests were interrogating relatively large volumes of material, over which such local variations would probably have had little effect.
Illustrative compressive stress-strain curves are shown in Figure 11(b). These relate to two pairs of samples, both from the base region, one from a location near the inner surface and one near the outer surface – see Figure 7. Even on the relatively coarse scale of the compression samples, significant variations are apparent. The yield stress is noticeably higher for the outer region (samples 9 and 10), which may be associated with that region having experienced higher prior strains during manufacture. This type of relevant information is lost in the tensile test results of Figure 11(a).
PIP tests were carried out in different locations, with significant differences between some of the outcomes. Variations were observed from point to point, consistent with observed differences in local microstructure. As an example, derived plots are shown in Figure 12 for two locations, compared in each case with the tensile curves of Figure 11(a). While there are locations for which the indent profiles reflect the tensile test outcomes, and these were in the majority, in other locations the outcome indicated a slightly different response with a higher yield stress. This outcome highlights the capability of PIP testing to obtain stress-strain characteristics on a much finer scale than is possible by conventional tensile or compressive testing.
PIP testing also detected marked anisotropy, although it varied from point to point and was not systematic across the component. The anisotropy in this component does not arise from texture, but from preferential alignment and inhomogeneous distribution of a hard “reinforcement”. It could be regarded as a (metal matrix) composite material and in general composites often exhibit strong anisotropy.
The kind of effect that can arise during indentation of such material is illustrated by the SEM micrograph of an indent shown in Figure 13. The alignment of the “stringers” in this case is from top left to bottom right. Small “undulations” have been created around the rim of the indent, which are primarily associated with the anisotropy (possibly influenced in some cases by a relatively large grain size in these regions – there is some rotation of individual grains in the rim area during indentation). Variations such as these have the potential to influence measured indent profiles. This is illustrated by Figure 14, which shows four profiles across another indent, oriented at four different angles. Such variations are not normally observed. An average can be taken of such profiles, and this is likely to lead to a direction-
anisotropy, without the need for machining separate samples.
The ability to generate accurate stress-strain curves from a simple indentation test opens many applications for PIP testing. As has been shown, it can be used to map properties over inhomogeneous components such as forgings or those containing welds. It can also be used for quality control or quality assurance purposes, as a replacement for tensile testing or hardness testing, as well as for rapid quality checks during manufacture to optimise further processing on the component. The turnaround times are significantly lower than for tensile testing, where the requirement for CNC machining often leads to days or weeks of a delay, and therefore the cost per test is also significantly lower.
As an indentation-based technique, an added advantage is that it can be applied to high-value assets in the field for in-situ monitoring of properties. Applications in this space include the assessment of properties in oil and gas pipelines, especially if such assets are to be repurposed for example for the transport of hydrogen. In this context, it can be used as a non-destructive test method to support engineering critical assessments.
The following points can be noted regarding PIP technology:
a) Integrated facilities are now commercially available, with the complete set of operations under automated control, so an understanding of their capabilities and features is starting to become highly significant. It seems likely that usage of the technology will expand considerably over the next few years.
b) If “bulk” properties are required, then it is important to mechanically interrogate a “representative” (manygrained) volume, and to create plastic strains in the approximate range of up to several tens of %. These requirements lead, in turn, to a need for an indenter radius of around 0.5–1 mm, a penetration depth of a few hundred μm and a load capability in the kN range.
c) Using the profile of the residual indent as the target outcome, rather than the load-displacement plot, offers many advantages. It is easier from an experimental point of view, its sensitivity to the stress-strain curve is greater and it allows detection and exploration of sample anisotropy.
averaged stress-strain curve that will be acceptably accurate. However, such variations can already be used to obtain information about local anisotropy, for example the direction parallel to the “stringers” is hardest as its profile has the lowest peak pile-up. In this way, a single indent has identified the presence and sense of
d) PIP can be applied to a wide range of industrial scenarios, offering capabilities such as mapping of properties over surfaces and detecting anisotropy. Some examples are presented here. Such information cannot be obtained using conventional uniaxial testing. In addition, the cost of a PIP test is significantly lower and the turnaround time significantly faster than the conventional tensile test where coupons must be prepared through subtractive manufacturing.
[1] C. Heinrich, A.M. Waas & A.S. Wineman, Determination of material properties using nanoindentation and multiple indenter tips, Int. J. Solids and Structures, 46 (2009) p.364–76. https://doi.org/10.1016/j. ijsolstr.2008.08.042.
[2] J. Dean, J.M. Wheeler & T.W. Clyne, Use of QuasiStatic Nanoindentation Data to Obtain StressStrain Characteristics for Metallic Materials, Acta Materialia, 58 (2010) p.3613–23. https://doi. org/10.1016/j.actamat.2010.02.031.
[3] D.K. Patel & S.R. Kalidindi, Correlation of spherical nanoindentation stress-strain curves to simple compression stress-strain curves for elastic-plastic isotropic materials using finite element models, Acta Materialia, 112 (2016) p.295–302. https://doi. org/10.1016/j.actamat.2016.04.034.
[4] J. Dean & T.W. Clyne, Extraction of Plasticity Parameters from a Single Test using a Spherical Indenter and FEM Modelling, Mechanics of Materials, 105 (2017) p.112–22. https://doi.org/10.1016/j. mechmat.2016.11.014.
[5] J.E. Campbell, R.P. Thompson, J. Dean & T.W. Clyne, Experimental and Computational Issues for Automated Extraction of Plasticity Parameters from Spherical Indentation, Mechanics of Materials, 124 (2018) p.118–31. https://doi.org/10.1016/j. mechmat.2018.06.004.
[6] H. Xue, J.X. He, W.N. Jia, J.L. Zhang, S. Wang, S. Zhang, HL Yang & Z Wang, An approach for obtaining mechanical property of austenitic stainless steel by using continuous indentation test analysis, Structures, 28 (2020) p.2752–9. https://doi. org/10.1016/j.istruc.2020.11.001.
[7] J. Lee, C. Lee & B. Kim, Reverse analysis of nanoindentation using different representative strains and residual indentation profiles, Materials & Design, 30 (2009) p.3395–404. https://doi. org/10.1016/j.matdes.2009.03.030.
[8] W.Z. Yao, C.E. Krill, B. Albinski, H.C. Schneider & J.H. You, Plastic material parameters and plastic anisotropy of tungsten single crystal: a spherical microindentation study, Journal of Materials Science, 49 (2014) p.3705–15. https://doi.org/10.1007/s10853014-8080-z.
[9] M.Z. Wang, J.J. Wu, Y. Hui, Z.K. Zhang, X.P. Zhan & R.C. Guo, Identification of elastic-plastic properties of metal materials by using the residual imprint of spherical indentation, Mat. Sci. & Eng. A, 679 (2017) p.143–54. https://doi.org/10.1016/j. msea.2016.10.025.
[10] J.E. Campbell, R.P. Thompson, J. Dean & T.W. Clyne, Comparison between stress-strain plots obtained from indentation plastometry, based on residual indent profiles, and from uniaxial testing, Acta Materialia, 168 (2019) p.87–99. https://doi. org/10.1016/j.actamat.2019.02.006.
[11] P. Hausild, A. Materna & J. Nohava, On the identification of stress-strain relation by instrumented indentation with spherical indenter, Materials & Design, 37 (2012) p.373–8. https://doi. org/10.1016/j.matdes.2012.01.025.
[12] G. Pintaude & A.R. Hoechele, Experimental analysis of indentation morphologies after spherical indentation, Materials Research, 17 (2014) p.56–60. https://doi.org/10.1590/S151614392013005000154.
[13] J.E. Campbell, M. Gaiser-Porter, W. Gu, S. Ooi, M. Burley, J. Dean & T.W. Clyne, Indentation Plastometry of Very Hard Metals, Adv. Eng. Mats., (2022) p.2101398. https://doi.org/10.1002/ adem.202101398.
[14] T.W. Clyne, J.E. Campbell, M. Burley & J. Dean, Profilometry-based Inverse FEM Indentation Plastometry (PIP), Adv. Eng. Mats., (2021) p.21004037. https://doi.org/10.1002/adem. 202100437.
[15] W. Gu, J.E. Campbell, Y.T. Tang, H. Safaie, R. Johnston, Y. Gu, C. Pleydell-Pearce, M. Burley, J. Dean & T.W. Clyne, Indentation Plastometry of Welds, Adv. Eng. Mats., (2022) p.2101645. https://doi.org/10.1002/ adem.202101645.
[16] Y.T. Tang, J.E. Campbell, M. Burley, J. Dean, R.C. Reed & T.W. Clyne, Use of Profilometry-based Indentation Plastometry to obtain Stress-Strain Curves from Anisotropic Superalloy Components made by Additive Manufacturing, Materialia, 15 (2021) p.101017. https://doi.org/10.2139/ssrn.3746800.
[17] J.E. Campbell, T. Kalfhaus, R. Vassen, R.P. Thompson, J. Dean & T.W. Clyne, Mechanical properties of sprayed overlayers on superalloy substrates, obtained via indentation testing, Acta Materialia, 154 (2018) p.237–45. https://doi.org/10.1016/j. actamat.2018.05.043.
[18] T.W. Clyne & P.J. Withers, An Introduction to Metal Matrix Composites. Cambridge Solid State Science Series, ed. E. Davis and I. Ward. 1993, Cambridge: Cambridge University Press.
BSI’s standards committee area for engineering design, specification and verification, TPR/1 (Technical product realization) – whose Subcommittee for the BS 8887 standards on Design for Manufacture, Assembly, Disassembly and End-of-life processing (MADE) is chaired by Professor Brian Griffiths – has been as busy as ever so far this year.
2023 has seen a number of national committee initiatives in the TPR/1/7 area move forward. One in particular – new national work with the lighting sector on the remanufacture of luminaires – has been formally accepted onto the BSI work programme. The proposed new British Standard, a code of practice BS 8887-221, will be moving through its formal standards development stages over the course of the rest of the year.
National Subgroup TPR/1/7/4, which brings together leading UK lighting remanufacturers, lighting industry trade associations and professional bodies, as well as relevant academic institutions, will refine the document and see it through its public comment, committee approval and publication stages.
Also on remanufacturing – which is the process by which a previously sold, worn, or non-functional product can be rebuilt, recovered or reused – another national Subgroup, TPR/1/7/5, has been meeting with the medical devices sector in order to explore options for new standards on sustainable product design and sustainable manufacture. The discussions are still at the exploratory stage but TPR/1/7/5 reports growing interest from across the healthcare sector.
On the international standards front, TPR/1/7 was pleased to welcome the publication of ISO 8887-2, the international vocabulary for MADE. The new standard sets out the terms and definitions across the ISO 8887 area allowing for future parts of the series to be developed at the international level. ISO/TC 10 WG20, which is converting a number of parts of the national BS 8887 series into international (ISO) standards, is run by the UK and chaired by Brian Griffiths.
The first part of the series, ISO 8887-1, was published in 2017. New work is currently under way to convert BS 8887-3 – guidance on the selection of an appropriate end-of-life design strategy – into a new international standard, ISO 8887-3.
And finally, back to the national standards work programme. Brian Griffiths’ TPR/1/7 main Subcommittee will be meeting in the autumn to review and discuss all of the standards and projects under its remit. The aim of the meeting – which will be a workshop-style event at BSI’s offices in Chiswick, West London – will be to flesh out future standards needs as well as allocating responsibilities for existing and ongoing work items and initiatives.
With all of this ongoing work and activity, the TPR/1area committees are always looking for new committee members and experts to join its standards drafting groups, national committees, and international working groups. Further general information on taking part in BSI’s standards work can be found at:
https://www.bsigroup.com/en-GB/about-bsi/uknational-standards-body/how-to-get-involved-withstandards/
If you would like more detailed information on any of TPR/1’s projects or work programme – or if you would like to get involved in any way in the committee’s activities – please contact Sarah Kelly, Lead Standards Development Manager and Committee Manager for TPR/1 at BSI on sarah.kelly@bsigroup.com.
2023 saw the UWR Formula Student team transition into the second phase of the Wolf VII project. With the 2022 event having provided valuable knowledge regarding the static events, the team felt well prepared to tackle the 2023 competition as a Formula Student class entry.
The competition itself took place at Silverstone immediately after the F1 Grand Prix weekend, from the 27th to the 30th July. Four long days that saw some of the worst July weather for years challenged the 60+ university teams that brought either petrol or EV cars to the contest.
Thursday brought the first challenge of the week; static events. Cost & Manufacturing was the first judged session of the day, which was immediately followed by the Engineering Design event. Costing and engineering design were both a success, with good feedback on the team’s approach to costing structure, price-based design choices and general design aims and understanding. We also received useful feedback regarding our designs and where they could be improved or iterated upon.
Taking the feedback from the judges in our stride, the car was swiftly brought to scrutineering, the first of which being tech scrutineering. This initial stage is usually very difficult to overcome, as there is a vast array of rules and compliances the car must adhere to. However, Wolf VII passed this stage in our second attempt (with many teams needing four or more visits to scrutineering), and
Sponsored by the EIS
all other static scrutineering stages were completed on the first run. After the car was weighed, coming in at 221kg, the dynamic scrutineering took place. Tilt, noise, and brake tests were all passed first time, with flying colours, and the car was fully approved to compete in dynamic events by Friday afternoon.
Three dynamic events took place on the Saturday: Acceleration, Skidpad and Autocross. Mixed conditions were forecast for the day, so the call was made to exploit the dry start of acceleration and skidpad. UWR were the second car out to the acceleration area and put in a solid baseline time of 5.2 seconds, then smashed this first time with a 4.7 second run. We were the first team under the 5-second barrier and secured a spot in the run-offs. To make the best of the conditions, the car was swiftly wheeled to the skidpad area, and a solid time of 7.1s was put into the books. Just before the autocross laps, the car went out for the run-offs in wet conditions. A mechanical error resulted in a missed gearchange, unfortunately not gaining any extra points. Autocross was completed in very wet conditions, with a best time of 1:20.4, placing the team 12th in that event.
Sunday saw the final dynamic event of the weekend, endurance. This event is a 28-lap test of reliability and teamwork, with a driver change requiring solid coordination and communication. Wolf VII went first of the qualified cars and rocketed to a fast start. The first stint went very well, and the pace was looking very
good for the remainder of the event. Unfortunately, the car ran out of fuel with 8 laps to go, resulting in a DNF
for endurance. As is the nature of the competition, the team went into full diagnostics mode, and determined a poor sensor reading to be the culprit. We were justifiably heartbroken with the endurance result, but the team have taken it on the chin and are now in the planning stage for Wolf VIII, with the aim of making an even bigger comeback for the next competition!
UWR Formula Student placed 17th of 64 FS-Class entries, with a best dynamic event finish of 4th position (acceleration). This is our second-best performance in 7 years of competitions, and our best result since our 11th place finish in 2017. We are incredibly proud of the car that has been produced in this project and are immensely thankful for the support received from the Engineering Integrity Society and all the sponsors who made Wolf VII possible.
As the world becomes increasingly driven by technology, the role of artificial intelligence (AI) in shaping the future of engineering cannot be overstated. Engineers stand to benefit greatly from mastering AI skills. However, there can be some doubt around how it can exactly be integrated to the day-to-day workflows of engineers.
AI has the potential to revolutionise mechanical engineering by enhancing productivity, efficiency and innovation. Its applications are diverse, ranging from design optimisation and predictive maintenance to autonomous systems and robotics.
To effectively build AI models and systems, engineers need a range of skills and knowledge, including digital skills, maths and domain/business expertise. Traditional research in any field applies techniques from mathematics and statistics to a certain domain or problem. Machine learning in its simplest form is statistical and numerical problems solved iteratively with computational mathematics. Software engineering is about solving a domain or business problem with the help of computers and custom developed tools. However, by combining these skills, engineers can work with data in ways that have given rise to the field of data science – which also includes AI model development. Data science is a multidisciplinary field that involves extracting insights and knowledge from data using various techniques and methodologies. It combines elements of mathematics, statistics, computer science and domain expertise to analyse and interpret large and complex datasets.
Engineers of tomorrow can also be data scientists without having to leave the engineering field behind. Most engineering problems involve working with data in spreadsheet tools like Excel. This often involves running mathematical calculations on this data, such that certain values are calculated for solving design, maintenance, or operational problems. What sets engineers with data science skills apart is their deep domain expertise and strong mathematical background. This gives them an advantage, allowing them to create AI tools that don't exist yet or work with engineering datasets that data scientists from another field may not be able to use. However, to unlock this potential, engineers need to learn new skills and work with more tools.
While engineers can certainly use tools like Excel for various tasks, it is not the most suitable tool for building complex AI models. Excel has limited computational and data processing power and does not provide any tools for building AI models. In these cases, programming languages like Python are necessary for engineers to handle complex or large
datasets. The main point to takeaway is engineers need a diverse skill set that includes digital proficiency, mathematical aptitude, and domain expertise. By combining these skills, engineers can delve into the field of Data Science, extracting valuable insights from complex datasets. By embracing AI and honing their digital and programming skills, engineers can position themselves at the forefront of innovation, shaping the future of their field. The engineers of tomorrow have a unique opportunity to leverage the power of AI, driving advancements and making a significant impact in the increasingly technology-driven world.
Ali Parandeh CEng IMechE Trainer www.imeche.orgThe National Adaptation Programme (NAP3) has been launched.
Dr Laura Kent, Public Affairs and Policy Advisor at the Institution of Mechanical Engineers said: "The National Adaptation Programme (NAP3) published today is a step in the right direction amidst the alarming increase in temperatures and other extreme weather events both nationally and worldwide. The urgency to adapt has never been more evident. We are pleased with the establishment of a new coordinating body within the Cabinet Office and the collaborative efforts with the Met Office to enhance accessibility to climate data. This is a vital move to effectively plan and retrofit our building stock as well as a wide range of vital infrastructure assets, to ensure their resilience to future higher temperatures and increasingly frequent, prolonged and severe heatwaves. The time for action is now, and we must swiftly implement comprehensive strategies across a wide range of sectors to safeguard lives, livelihoods and productivity."
Commenting on publication of NAP3, IMechE Fellow Dr Tim Fox, Chair of the Climate Change Adaptation Working Group said: “The Institution of Mechanical Engineers and wider engineering profession are focused on helping government, academia, industry and civil society develop solutions to the challenges of adapting to climate change. The record-breaking temperatures being experienced in many parts of the world at the moment put a sharp focus on the urgent need to deliver these solutions. We stand ready to work with the new cross-government Climate Resilience Board to help support the continued health, comfort, safety, food and nutritional security, productivity and economic well-being of the nation.”
Headline Sponsor Sponsors:
The conference will take place at Jesus College, Cambridge, UK. Set in 24 acres of gardens in the heart of Cambridge, it provides a beautiful setting for events in a purpose-built conference centre.
As engineering modelling and simulation tools become ever more powerful and sophisticated there still remains the challenge of correlating the virtual world with both idealised laboratory testing and the wide, and potentially unexpected, range of service conditions experienced by machines and structures. These challenges are compounded by the advent of new materials, new ways of manufacturing components, new applications and new test, measurement and characterisation techniques.
At Fatigue 2024 we will seek to explore not only the latest developments in engineering modelling and simulation, new test, measurement and characterisation techniques, innovations in manufacturing and developments in materials science, but also the complex interrelations between all these topics that give rise to improvements in fatigue performance, durability and structural integrity.
Established in 1496 on the site of the 12th Century Benedictine nunnery of St Mary and St Radegund it is protected from the noise and bustle of the town. The College has many notable buildings dating as far back as the 12th Century and the spectacular Hall with its vaulted ceilings provides a unique dining venue for our conference dinner.
There will be an accompanying exhibition of material testing systems, durability software tools and engineering services where delegates will have the opportunity to discuss the latest developments in the field of fatigue and durability.
Hotel standard accommodation is available at Jesus College and student standard accommodation is available at Wesley House subject to availability. Please select the accommodation option on the booking form. Prices include bed and breakfast.
The nearest airports are Stansted and Luton. Cambridge is easily reached by train. Jesus College is located about ¾ mile from the railway station and is served by regular buses and taxis.
www.fatigue2024.com
www.e-i-s.org.uk
EIS as organiser is not liable for any changes in the programme due to circumstances beyond their control. The organisers are not liable for any losses, accidents or injuries to persons or damage to property of any kind. Participants must arrange their own insurance if considered necessary.
VISA
Visa applications must be applied for in your country of origin.
The booking form available at www.fatigue2024.com should be completed and emailed to the conference secretariat, Sara Atkin: info@e-i-s.org.uk
With over 80 presenters from across the globe the conference will offer a full programme across the three days. The full provisional programme including list of speakers will be at: www.fatigue2024.com.
Advanced Concepts on Fatigue and Fatigue-Crack
Growth of Metallic Materials
Prof James Newman, Mississippi State University
Characterising fatigue crack tip deformation states in nickel base superalloys: slip character, strain accumulation and oxidation effects
Prof Philippa Reed, University of Southampton
Design & Manufacturing Challenges for High Pressure Disc rotors in Aircraft Engines
Dr Mark Hardy - Rolls Royce
Roberto Cipolla, Professor of Information Engineering, Cambridge University
PRESENTING AUTHOR £495+VAT
EIS MEMBER (3 DAY) £520+VAT
EIS MEMBER (2 DAY) £440+VAT
EIS MEMBER (1 DAY) £280+VAT
NON MEMBER (3 DAY) £650+VAT
NON MEMBER (2 DAY) £550+VAT
NON MEMBER (1 DAY) £350+VAT
STUDENT/RETIRED PERSONS £350+VAT
POSTER PRESENTER £425+VAT
info@e-i-s.org.uk
Alan Hellier (Australia)
Alberto Campagnolo (Italy)
Alfredo Navarro (Spain)
Ali Fatemi (USA)
André Galtier (France)
Andrea Carpinteri (Italy)
Andrea Spagnoli (Italy)
Barbara Rossi (UK)
Chris Hyde (UK)
Christophe Pinna (UK)
David Nowell (UK)
Ken Wackermann (Germany)
Fabien Lefebvre (France)
Filippo Berto (Norway)
Francesco Iacoviello (Italy)
Francisco A Diaz (Spain)
Frank Walther (Germany)
Harry Bhadeshia (UK)
Hellmuth Klingelhoeffer (Germany)
Hossein Farrahi (Iran)
James Marrow (UK)
James Newman (USA)
Jan Papuga (Czech Republic)
Johan Moverare (Sweden)
Liviu Marsavina – (Romania)
Luca Susmel (UK)
Marc Geers (The Netherlands)
Mark Whittaker (UK)
Martin Bache (UK)
Matteo Benedetti (Italy)
Matteo Luca Facchinetti (France)
Mike Fitzpatrick (UK)
Miloslav Kepka (Czech Republic)
Muhsin J Jweeg (Iraq)
Neil James (UK)
Pablo Lopez-Crespo (Spain)
Paul Bowen (UK)
Phil Withers (UK)
Philippa Reed (UK)
Reinhard Pippan (Austria)
Rob Ritchie (USA)
Robert Akid (UK)
Sabrina Vantadori (Italy)
Shahrum Abdullah (Malaysia)
Svjetlana Stekovic (Sweden)
Takashi Nakamura (Japan)
Thierry Palin-Luc (France)
Veronique Doquet (France)
Wim de Waele (Belgium)
Yee Han Tai (UK)
Yoshihiko Uematsu (Japan)
Youshi Hong (China)
Yukitaka Murakami (Japan)
Dr Amir Chahardehi
Andrew Blows
Assoc Prof Chris Hyde
Dr Emilio Martínez-Pañeda
Dr Fabien Lefebvre
Dr Farnoosh Farhad
Prof Filippo Berto
Prof Francisco A Diaz
Dr Hassan Ghadbeigi
Dr Hayder Ahmad
Dr Hollie Cockings
Dr John Yates
Prof Mark Whittaker
Dr Mohamed Bennebach
Dr Pablo Lopez-Crespo
Paul Roberts
Dr Peter Bailey
Robert Cawte
Dr Spencer Jeffs
Assoc Prof Svjetlana Stekovic
Yi Gao
CONFERENCE CONVENOR
Dr John Yates
DEPUTY CONVENOR
Dr Hollie Cockings
CONFERENCE SECRETARIAT
Sara Atkin
Engineering Integrity Society
6 Brickyard Lane, Farnsfield
Nottinghamshire, NG22 8JS, UK
Tel. +44 (0)1623 884225
Email: info@e-i-s.org.uk
Website: www.fatigue2024.com
The National Metrology Skills Alliance (NMSA) was established in 2021 on the back of work started by the Midlands Centre for Data Driven Metrology (MCDDM), which had identified the need for a national framework outlining skills and knowledge in the field of metrology.
From that work, a cross-industry group was formed, with the primary aim to develop and promote a recognised standard for professional metrologists.
The NMSA was formalised as an official InstMC Special Interest Group (SIG) in 2022 with representatives from academia and industry including MCDDM, Jaguar Land Rover, Coventry University, BAE Systems, AWE, Suriflo, Reliance Precision, Sellafield, NPL and Rolls-Royce. Working groups were set up to focus on drafting the core standard and the subject specific annexes covering topics including core, flow, manufacturing, control and force.
With regular SIG meetings and cross-industry collaboration throughout 2023, the core standard documents were created and have now been put through the process of both alpha and beta testing. This has resulted in the standards and subject/sector-based annexes being split into three sections:
NMSA 1 – Core Metrology Skills – with four categories aimed at different skill levels: Foundation (for nonmetrologists), Level 1 (Practitioners, Technical/Skilled), Level 2 (Senior Technician/Team Leader/Skilled) and Level 3 (Approver, Managing/Expert).
NMSA 2 – Subject/Industry Sector Skills – split into the following sectors: Manufacturing, Flow, Force, Control and Future.
NMSA standards are structured to help both individuals and organisations. Individuals can use the standards to look at their own skills in relation to their work objectives as part of their career development. Perhaps using it to create a gap analysis, identifying where skills need to be further developed. Organisations can utilise the standards to monitor the skills of their teams. They could also use the information to create role profiles, either for existing staff or to help construct job adverts to recruit externally. Internal training can also be tailored according to the standards, in line with specific learning outcomes that are recognised by industry.
Earlier this year, a call went out for volunteers to assist with beta testing the standards, prior to publication. The NMSA invited contribution from a range of companies, organisations and universities and were delighted with the high volume of responses. Support was voiced from industry, manufacturing, research centres, measurement OEMS and manufacturers as well as users, all expressing their willingness to be involved and how the standards could work for them.
Following a successful testing phase, the Core, Manufacturing & Flow Standards are now close to publication and will be available, ready to use, later in the year through the InstMC website.
A working group for ‘Qualifications’ (NMSA 3) is currently being set up and is open for volunteers who would like to take part and offer their expertise.
If you have any questions or would like to get involved in any aspect of the NMSA, please email NMSA@instmc. org. For all the latest information on the NMSA, visit https://www.instmc.org/sigs/national_metrology_ skills_alliance.
IAAPS, Bristol & Bath Science Park | 27 April 2023
Engineers, researchers and experts gathered at the Institute of Advanced Automotive Propulsion Systems (IAAPS) for a groundbreaking seminar focused on "Net Zero Vehicle Powertrain Engineering Design and Development Technology." The event, held on April 27, delved into the unique challenges and advancements in vehicle powertrain engineering for achieving net zero emissions.
The seminar presenters showcased novel technologies, research findings and case studies related to powertrain dynamics, integration and design for net zero vehicles. The event's keynote speaker, David Hudson from ePropelled, opened the seminar by addressing the critical question, "The Second Age of Electric Vehicles: Are our tools fit for purpose?" His thought-provoking talk set the tone for the day's discussions.
The seminar underscored the importance of collaboration, innovation, and knowledge-sharing in driving advancements in net zero vehicle powertrain engineering. As the automotive industry continues its journey towards a sustainable and environmentally friendly future, events like this play a crucial role in shaping the path forward.
Delegates also had the chance to tour IAAPS' stateof-the-art experimental propulsion research facilities. The tour provided a closer look at the cutting-edge testing labs and facilities, with knowledgeable guides offering detailed explanations and insights.
The day concluded with a discussion panel session where attendees had the opportunity to interact with
the speakers and ask questions. The lively discussions generated valuable insights and potential avenues for future research and collaboration. As a result of the event's success and the importance of the topic, the Engineering Integrity Society has announced the formation of a new Net Zero group to further focus on this critical area).
In July, the Warwick Manufacturing Group (WMG) hosted an EIS seminar on "Latest Innovations in Battery Design & Testing." The well-attended seminar drew engineers from various sectors together to discuss battery technology amid the global push towards electrification.
The crucial role of batteries in the electrification movement cannot be overstated, and the seminar offered a platform to address the pressing demand for smaller, lighter, and more powerful energy storage solutions. With sustainability and emissions targets in focus, the event underscored the urgency for innovative breakthroughs in battery design to meet the evolving needs of various industries.
Battery design is pivotal to achieving costeffectiveness, power and energy density while ensuring uncompromised safety. The seminar delved into the heart of these challenges, facilitating discussions on a range of critical topics including Li-ion testing, pressure, temperature and vibration testing, as well as thermal management and future safety.
Attendees also experienced a guided tour of the Battery Innovation Centre to see the world-class facilities that are dedicated to research, development and innovation in the field of battery technology. Feedback from delegates was excellent, highlighting the immense value in facilitating this type of seminar.
The EIS is forming a Net Zero Group to support the engineering community in meeting net zero challenges, bringing together engineers across all engineering disciplines, and providing the opportunity for webinars and seminars where ideas can be shared and discussed, and new connections made.
In a world driven by the urgency to combat climate change, the EIS has taken a crucial step by establishing the Net Zero Group, a platform dedicated to accelerating the transition towards a sustainable and net zero emissions future. From energy generation and storage to product electrification, the engineering community is under mounting pressure to lead the charge in identifying and implementing solutions that align with the global net zero goal.
As the demand for net zero solutions intensifies, engineers face a set of unique challenges. These hurdles include the need for advanced tools and technologies to model and design net zero products and processes. The successful achievement of net zero also hinges on the seamless integration of engineering tools and interdisciplinary models. There’s also a need to provide engineers with the education and support necessary to cultivate interdisciplinary skills, empowering them to drive innovation across diverse fields.
With its extensive network of individual and corporate members, the EIS is ideally positioned to play a pivotal role in driving the transition towards a net zero world. The society has already been focused on this area, hosting a series of webinars and seminars on net zero solutions. This has included events on topics such as hydrogen and energy storage, net zero powertrain engineering and battery technology. These events have not only showcased cutting-edge advancements but have also encouraged meaningful discussions and connections within the engineering community.
Recognising the pressing need for collaboration and knowledge sharing, the EIS has established the Net Zero Group. This initiative aims to unite engineers across various disciplines, providing them with a platform to collectively address the challenges associated with achieving net zero emissions. The intention is to ignite innovative ideas, facilitate thoughtful discussions, and establish new connections that will be instrumental in propelling the transition to a net zero world.
For more information about the Net Zero Group and upcoming events, visit the Engineering Integrity Society's official website. Together, engineers are shaping a net zero world that future generations will be proud to inherit.
In a historic moment for the British automotive sector, Tata Group, the parent company of Jaguar Land Rover (JLR), has announced plans to invest £4 billion in building a state-of-the-art battery gigafactory in the UK. The new facility, located in Somerset, is set to become one of Europe's largest battery cell manufacturing sites.
Tata Group's investment is expected to create around 4,000 jobs at the gigafactory itself, and thousands more in the broader supply chain. This much-needed boost to the domestic automotive industry comes at a critical time for the UK, as the country prepares for its ban on the sale of new petrol and diesel cars by 2030.
Prime Minister Rishi Sunak said: "With the global transition to zero-emission vehicles well underway, this will help grow our economy by driving forward our lead in battery technology whilst creating as many as 4,000 jobs, and thousands more in the supply chain."
While exact details of the UK Government’s financial involvement in the project remain undisclosed, it is understood that it has offered subsidies in the form of cash grants, energy cost discounts, and research funding. The facility is expected to produce high-quality, highperformance, and sustainable battery cells and packs for various applications within the mobility and energy sectors.
The gigafactory is committed to optimising its renewable energy sources, aiming for a 100 percent clean power supply. To achieve this, the plant will leverage innovative technologies and resource-efficient practices, such as battery recycling, to recover and reuse all the original raw materials. This approach will create a truly circular economy ecosystem. With production scheduled to commence in 2026, Tata Group aims to supply not only JLR’s battery electric models, including the Range Rover, Defender, Discovery and Jaguar brands, but also other car manufacturers.
www.jaguarlandrover.com
A new agreement between University of the Arts London (UAL), acknowledged to be one of the world’s top arts and design universities, and leading, international research and technology organisation (RTO) TWI, will see the two parties establish a unique centre for creative textile and materials engineering technologies called
the University of the Arts London Innovation Lab.
The collaboration between UAL and TWI aims to expand the field of design research and technology innovation in textile and fibre-based materials science and engineering with creativity at its core. The innovation lab will focus on delivering new applications, tools and processes that will advance the knowledge and expertise of the partners and, importantly, contribute to wider technological development across industries that use textiles within their supply chain.
The core focus areas include circular and bio-inspired design, material and environmental sciences, creative computing, additive manufacturing (AM) technologies and Industry 5.0, offering a holistic approach. The combination of scientific, technical and design expertise will establish the University of the Arts Innovation Lab as a centre of excellence for novel, sustainable solutions for the twenty-first century.
www.arts.ac.uk
www.twi-global.com
As Extreme E produced a spectacular opening X Prix of Season 3 on-track, off-track it delivered a successful first test of a new and innovative mobile fuel cell system provided by ENOWA, the championship’s Green Hydrogen Power Partner.
As a more portable energy source, with a strong capability to store power, the Hydrogen Fuel Cell system will be a green power provider in the region of NEOM. During the Desert X Prix, the fuel cell was in operation for its first ever time, where it charged the Championship’s fleet of electric racing vehicles.
ENOWA is the engine room for renewable energy, water and hydrogen at NEOM and, since 2022, has been a part of a pioneering and multi-year relationship with Extreme E. The core aim of the partnership has been to showcase the use of green hydrogen power as part of the race site, and also be a platform for the promotion of hydrogen as a more widespread sustainable solution.
Green hydrogen is widely seen as the most promising energy carrier in the push for positive climate action. This technology supports the transportation of renewable energy over long distances and the decarbonisation of major industries and infrastructure..
www.extreme-e.com
www.enowa.neom.com
Technology being developed by a global consortium of companies and academic institutions could revolutionise the use of industrial additive manufacturing – also known as 3D printing – in the UK, bringing the advanced manufacturing of high-value components for key industries to the country for the first time.
The Evo One ‘large-format additive manufacturing’ (LFAM) project – which involves 3D printing experts Evo-3D; the National Manufacturing Institute Scotland (NMIS) operated by the University of Strathclyde and part of the High Value Manufacturing Catapult (HVMC); Rolls-Royce; materials supplier Filamentive; software developer AI Build; and energy technology company Baker Hughes – are developing a 3D printer system that could make UK manufacturers more competitive than their international peers. The initiative has received £1.1 million in funding from Innovate UK, the UK’s innovation agency.
LFAM is a commercial 3D printing technique that creates large volume polymer components, used in a variety of industries including aerospace, automotive, energy, and marine. While countries like the USA, Germany and China have embraced this approach, there are currently no manufacturers of large-format 3D printers in the UK and the country only accounts for around 5% of the global additive manufacturing market, which the UK government aims to increase to 8% by 2025.
Access to the right technologies will be a crucial part of achieving that aim, but existing LFAM systems have their limitations. These include slow build times, being unsuitable for high-value or high-integrity parts, operational complexity, use of unsustainable materials, and being unaffordable to small- and medium-sized companies.
The new product being developed through Evo One LFAM will address the challenges associated with these systems and cater to the specific needs of the UK market. The system’s design team is aiming to make it 60% more reliable, achieve a 50% increase in productivity, reduce training and maintenance costs by 30%, and cut material waste by 80%, among a range of other improvements.
On the project’s completion, Evo-3D will launch a spin-out business to commercialise the system, called RapidFusion, creating the UK’s first original equipment manufacturer (OEM) in LFAM. Its development would also create the foundation on which a new supply chain can be built, re-shore critical manufacturing capabilities, and help more UK manufacturers take advantage of the opportunities presented by Industry 4.0 – the fourth industrial revolution.
www.evo3d.co.uk
www.nmis.scot
(SOC) in just under 90 seconds
The hofer powertrain battery team developed a fully functional high-voltage battery using a market-leading BMS system and fast-charging CCS DC wallbox available on the market at the time. The initial proof of concept (POC) involved installing it in a racing kart and subjecting it to a series of complex tests under load and with real road resistance, which significantly exceeded expectations. By simulating various driving situations with the highvoltage charging system, it was possible to determine the battery's and system's functionalities as well as the overall performance within the powertrain system, where all measurements confirmed the groundbreaking charging curve. The hofer powertrain BlueFire battery demonstrated extremely high cycle stability. In less than 90 seconds, the battery could be recharged successfully from 5–85% SoC (State of Charge). The LTO cells used for this purpose have proven to be particularly suitable for applications that require fast charging and discharging with high charging currents and have opened new possibilities for the future.
During this initial pilot project in pre-development, it became apparent that the new battery is ideal for 24-hour endurance races that rely on extremely short charging times. In addition, it can be variably scaled to fit different applications.
In the meantime, initial discussions with interested parties and investors have started with excellent responses. The engineers are currently focusing on increasing the already very high energy density in the cells of the BlueFire battery considerably while at the same time reducing the weight of these cells.
www.hofer.de
A new technology that offers a cost-effective way to produce synthetic gas and pure hydrogen with nearly zero direct carbon dioxide emissions will be developed and delopyed by an international team of scientists, led by The University of Manchester. The RECYCLE (REthinking low Carbon hYdrogen production by Chemical Looping rEforming) project will construct and test a fully integrated innovative hydrogen production pilot unit based at the University.
The technology uses special reactors called fixed bed reactors to convert different materials into hydrogen gas. The process also effectively captures and separates carbon dioxide. It offers a competitive solution for the production of low-carbon hydrogen using both natural gas, biobased streams and waste materials to provide low-cost hydrogen.
The £5.1 million collaborative project is funded by the Department for Energy Security and Net Zero as part of the Net Zero Innovation Portfolio (NZIP), and involves five world-leading industrial partners in the area of engineering for sustainable development, including Johnson Matthey, TotalEnergies, OneTech, Kent, Helical Energy and Element Energy.
In the recently published Powering Up Britain: Energy Security Plan, the UK government expects to have two gigawatts of low-carbon hydrogen production capacity in operation or construction by 2025 and 10 gigawatts in 2030, subject to affordability and value for money. The final demonstration of the project is planned for
the second half of 2024 in the pilot area of the James Chadwick Building at The University of Manchester.
www.manchester.ac.uk
Advanced surface coating technology company, Hardide Coatings has been awarded funding from Innovate UK to further study the flexural behaviour of the Hardide chemical vapour deposition (CVD) coatings under high static and cyclic loading conditions.
The funding has been awarded under Innovate UK’s Analysis for Innovators (A4I) Round 9 programme and will enable the company to understand better the influence of key coating characteristics on performance when subject to high static and cyclic loading conditions. This will enable the optimisation of the coating to solve technical challenges encountered in the power generation and hydrogen production and distribution sectors. In turn, this will support the UK’s net zero ambition while reducing waste generation and pollution through the development of longer-lasting equipment resistant to hydrogen attacks and reduced servicing, downtime and part replacement.
The study will be carried out in collaboration with the National Physical Laboratory (NPL) and is expected to be completed by spring 2024.
Leclanché revolutionary battery pack is selected by Socofer to equip brand new hybrid maintenance locomotives in the Channel Tunnel
Leclanché, a world leading provider of energy storage solutions, has been chosen by Socofer to equip its maintenance locomotives for the Channel Tunnel. The Leclanché INT-53 battery pack, currently used by rail manufacturers in Europe and North America for railway traction applications in both fully electrified and hybrid configurations, was selected by Socofer due to its quality, safety features, and compliance with international standards.
The INT-53 battery pack meets all safety requirements for use in demanding environments such as the Channel Tunnel, including the standards of no flames, no explosions, and no battery components projected out of the pack. Additionally, the battery pack fully complies with all norms related to thermal propagation. Leclanché's expertise in containing any thermal runaway event within the battery was also a significant factor in Socofer's decision to choose the INT-53. Socofer is supplying Eurotunnel with 19 hybrid locomotives, which will be used to pull maintenance wagons on the railroad line linking the UK and France under the English Channel.
www.leclanche.com
www.socofer.com
The UK’s EV rapid charging network is under significant pressure – but new software could significantly reduce charging time and cut queues at motorway services.Elysia, the pioneering new battery intelligence company offering from WAE Technologies (WAE), draws on WAE’s unrivalled experience in high-performance batteries, gleaned from the sole supplier of batteries to ground-breaking electric motorsport series, as well as the design and development of batteries for road cars, electric hypercars and 1.4 MWh packs for 250 tonne mining trucks.
Its suite of algorithms can safely unlock extra performance from an electric vehicle battery, bringing a host of benefits for plug-in car makers, which in turn can be passed on to consumers, such as faster charging. With an estimated 12.6 million journeys set to be made by holidaymakers per week in summer, a significant number of which will be electric cars – EVs made up 17.9 per cent of new car sales in June, with last month showing a 40 percent increase in volumes over this time last year – charging demand is likely to exceed supply at points during holiday peaks.
However, Elysia estimates that a typical electric vehicle could rapid charge 25 per cent faster if it was equipped from the factory with its intelligent software, reducing the time spent on a charger by 10 minutes, alleviating queues and resulting in much more efficient use of the rapid charging network.
www.elysia.co
Contributions to Industry News may be emailed to managingeditor@e-i-s.org.uk. The nominal limit for entry is 200 words.
Young engineers are invited to submit an entry for the 2023 EIS Peter Watson Prize which will be held at a special event at Makeney Hall near Derby on 23 November 2023. The prize is named after our founding President, Dr Peter Watson, who passed away in 2015. It was created to support young engineers at the start of their career, a cause Peter keenly supported throughout his working life.
Interested engineers should submit an application form and a one page abstract summarising the presentation they would like to give. The presentation should be relevant to the interests of the EIS and should be based on work that the
A prize of £400 will be presented to the young engineer who has delivered the best presentation as determined by the judges.
A prize of £200 will be presented to the individual who the judges would like to highly commend.
applicant has undertaken themselves. Suitable topics include: durability, fatigue, NVH, sound and vibration, simulation, test and measurement. Applications will be assessed by a panel and the shortlisted candidates will be invited to present at the Final.
Please see our website for full details including terms and conditions and entry form.
Finalists will be invited to make a ten minute presentation at a special EIS event. Presenters will also have five minutes to take questions from the panel, who will assess the candidates and their presentations for technical content, presentation quality and handling of questions.
Entrants should meet at least one of the following criteria:
- A person working in industry below the age of 28 on submission
- A post-doctoral worker with a maximum of three years’ experience since completing a PhD/EngD
- Any currently registered undergraduate or postgraduate student
CLOSING DATE: Applications must be received by 30 September 2023 by emailing info@e-i-s.org.uk www.e-i-s.org.uk
Once again, the annual Instrumentation, Analysis and Testing Exhibition will take place in 2024 in the Silverstone Wing at Silverstone Race Circuit. This is slightly earlier than this year’s event but brings us back in line with our traditional March date which was altered due to the pandemic.
The exhibition attracts visitors from across the UK and is seen by many as the go-to event for testing and analysis technologies. With 70 tables of exhibitors from sectors including automotive, aerospace, motorsport, rail, off-highway, mechanical handling, civil engineering, industrial and power generation, the exhibition is an excellent opportunity to see the latest equipment and technologies as well as being a great meeting point for the exchange of ideas and contacts.
Attendance is free and visitors receive complimentary refreshments along with free parking. To complement the exhibition there will be a series of mini seminars throughout the day. The series of presentations throughout the day will cover a wide range of topics from well-respected engineers across several different sectors. Further details of the presentations will be announced in the coming weeks and closer to the event the exhibitor guide will be published with full details of products and services offered by the exhibiting companies.
The Instrumentation, Analysis and Testing Exhibition opens at 10 am on 26 March 2024. More information is available at www.e-i-s. org.uk. Tables are likely to sell out quickly so exhibitors are advised to book early to avoid disappointment.
Author correspondence: hbdeiwi@ara.co.uk, slawson@ara.co.uk
Temperature variations within complex structures can present daunting engineering challenges in a wide range of applications and industries affecting safety and reliability of operations and the ability to achieve objectives. Advanced aeronautical research is no exception, and one particularly important topic is the requirement to obtain high-quality, reliable load data for novel flight vehicle development programmes using wind tunnel tests. This has motivated ARA to find a solution using the latest mathematical, computational and experimental techniques currently available, and will be the focus of this article.
Wind tunnel testing commonly involves the measurement of forces and moments on the test article using a strain gauge balance. This measures the strain of structural beams within the balance using strain gauges. A mathematical model relates the strains to applied forces and moments. Wind tunnel balances are mounted internally within the wind tunnel model and typically measure up to six components, consisting of forces and moments about three axes on the model. Loads can be measured on complete aircraft models, half models, control surfaces, stores and blown nozzles. The following analysis relates to an ARA-designed balance, used to measure forces and moments on a nozzle with air flowing through the internal structure as well as the external surfaces.
Temperature-related effects are the most common causes of error in strain measurements with
strain gauge balances used for wind tunnel load measurements. Ideally, wind tunnel (WT) balances equipped with of a number of strain gauges measure strain only in response to applied aerodynamic loads. However, strain gauge material, the lead wiring, as well as the balance material to which the strain gauge is applied, also respond to changes in temperature, which affects the strain measurement accuracy. Empirical
methods commonly used to minimise the steadystate temperature sensitivity include optimising the toplogy of the beams and gauge layout and by tuning the inter-gauge wiring. Nevertheless, these steady-state conventional methods based on a uniform temperature do not completely remove the thermally induced strain errors, which are often due to thermal gradients and changes of temperature with time.
Besides conventional methods that are used to minimise thermal effects on balance measurement readings, modelling can also be employed to gain a better understanding of the structural state of the balance induced by thermal changes.
At ARA, a novel thermal error reduction technique has been developed and employs computational analysis. The approach approximates the balance thermal and structural states for the purpose of real-time thermally induced strain prediction for balance operations during a wind tunnel test, providing a reasonable balance between accuracy and computational cost. For investigation and validation, the numerical thermal correction method was applied to an ARA bespoke balance (illustrated in Figure 1) for the testing of a dual-stream jet propulsion rig, where the balance measures aerodynamic loads of engine nozzles powered by high pressure air[1]
In the first phase of the research and ahead of the balance experimental test taking place in the ARA facility in summer 2023, the thermal correction method was assessed and verified using a finite element (FE) simulation of a realistic physical experiment. The FE model of the balance, shown in Figure 2, is built by importing the CAD model into the FE software ABAQUS CAE[2].
The FE balance model is made of UDDEHOLM RAMAX HH steel described in Table 1. Figure 3 depicts the boundary conditions and the thermal load applied to the FE balance.
The FE balance is clamped at its left side, called the “earth”, and is subjected to a time-dependant temperature distribution at the right side, or the “live”, in order to induce thermomechanical error. The physical WT balance includes a number of temperature sensors and strain
gauges. In real WT conditions, the thermal correction method uses the temperature values measured by the temperature sensors as inputs and outputs the thermally induced strain at each of the balance beams.
These strains are then further processed and translated into forces. Here, the temperature values were extracted from the FE analysis at the locations of the temperature sensors and utilised as inputs for the thermal correction method. Figure 4 compares the thermomechanical strain generated by the thermal correction method (solid line) with the FE results, (dashed line) at two different beams. Overall, the thermal correction method very closely follows the trend of the FE data over time, in particular
at the time = 1s where the absolute value of the applied temperature gradient is the highest (about 10 K).
The axial and side forces resulting from the thermal strain match the FE predictions, as shown in Figure 5. The method offers good approximation of timedependant loads and proves to be reliable in correcting balance measurements affected by thermal strain. In summary, a novel balance thermal correction method has been developed in order to correct balance
measurement readings due to temperature gradients during a WT test. In the first stage of the investigations, it was assessed using an FE analysis simulating a possible experimental scenario. The numerical method successfully predicted load errors induced by the thermal strain by only considering temperature inputs while balancing speed and accuracy. Coupled with calibration methods, the thermal correction method appears promising in providing insight into the balance thermal and strain state for live balance measurement corrections during WT tests. While the results presented give cause for cautious optimism, the problem of real-time thermal correction in complex load bearing structures is very challenging as it demands capturing thermally induced strain variations of an order of magnitude of 10-6 making the method sensitive to discrepancies in the exact positions of the temperature sensors and strain gauges and the accuracy of the time-dependant temperature measurements. In the second stage of the research, experimental tests on the balance will be conducted at ARA and the proposed thermal correction method will be validated against experimental data. The outcome will be reported in a follow-up article in this publication in the near future.
[1] A. Gomariz-Sancha, C. Sheaf and C.O. Marquez Gutierrez, "Development of a Dual Stream Jet Propulsion Rig for Test and Evaluation of Engine Nozzles in a Transonic Wind Tunnel," in AIAA SCITECH 2023 Forum, no AIAA 2023-2009, June 2023.
[2] SIMULIA, "https://www.3ds.com/products-services/ simulia/products/abaqus/abaquscae/" [Online].
Introducing the EvoS cann® P16-D. The most advanced miniature true-differential 16 channel digital pressure scanner available.
Ÿ 0.1% Full Scale Accuracy
Ÿ Data output directly in engineering units
Ÿ Lightweight - <45g (including 1m cable)
Ÿ Small - dimensions: 50 x 32.4 x 10mm
Ÿ True-differential measurement , shared static reference
Ÿ Lightweight carbon fibre external construction
Ÿ Integral microprocessor
Ÿ CAN-FD output
Whilst the title of this journal update could quite happily be the title of a sitcom, it does nicely capture the focus of my STEM outreach for the past six months.
Out of the blue I received an email from a colleague based in Turkey who wanted to provide STEM outreach to communities local to the Rolls-Royce offices in Antalya. Approximately 10 years ago a number of 3D jigsaws were designed and machined from aluminium by the apprentice academy in Derby, which are a collection of seven pieces that represent the modules from a jet engine. At events such as careers or STEM roadshows, the engines can be used to talk to students about the jet engine and they can have a go at constructing the engines against the clock or their friends and family. The engines have proved very successful and are in regular use.
been used for the shaft that holds all the pieces together and I also embedded some retaining metal nuts. The aluminium versions were quoted at around £400 each and whilst it is nice to hold something metal, the 3D printed equivalents cost just £15 each (most of which is the metal threaded rod).
Our first test of the engines was at an RAF family day in late July where they were used as if they were the original metal versions. Not only did they function as the metal ones do, but we were able to also introduce the concept of 3D printing at the same time and the potential benefits we can unlock for aerospace materials and manufacturing.
In parallel I have been hosting cohorts of work experience students now that schooling has returned to normality after the pandemic. Historically much of the experiences have had to be talking about the work rather than allowing them to do any (due to health and safety); however recently we have been working on some more practical examples for the students to undertake themselves during the week.
The offices in Turkey wanted to enquire about manufacturing the engine puzzles locally and, after some quotes received in the UK for metal conventional manufacturing of them, I had a brainwave: Why do they need to be machined from metal? Wouldn’t it be cheaper, just as a effective and cooler to 3D-print them?
I set about modifying the CAD files to make the engines printable (as some of the tolerances and fits needed to be changed) and we then manufactured two test engines from silver PLA. For longevity a bit of metal has
A particular favourite of the students is Charpy testing of chocolate bars and biscuits, which they are allowed to do themselves. We can demonstrate in a mildly destructive way the ability of a material to absorb deformation under a fixed set of impact criteria. The students also get to experience a shortened failure investigation to establish the series of events that led to a catastrophic overload of a paperclip.
As ever, if anyone is interested in knowing more about how they can get involved in STEM please do not hesitate to contact me or your local STEMnet contract holder.
Grant Gibson EngD BEng (Hons) Materials Technologist, Surface Engineering Rolls-Royce plc grant.gibson@rolls-royce.com 07469375700Game-changing robotics technology to provide remote medical treatment to casualties in high-risk emergency environments has been developed by researchers at the University of Sheffield.
Using medical telexistence (MediTel) technology, researchers from the university’s Advanced Manufacturing Research Centre (AMRC), Sheffield Robotics and Department of Automatic Control and Systems Engineering, have successfully created a mobile, robotic-controlled uncrewed ground vehicle (UGV), which boasts virtual reality (VR) capability, to enable medics and operators to assess critical casualties in hazardous environments, allowing them to perform a remote triage while also ensuring their safety.
The first-of-its-kind, fully integrated medical telexistence solution was developed in just nine months. It features two robotic arms that can effectively remotely operate medical tools to perform a critical initial assessment of a casualty within 20 minutes, including: temperature, blood pressure and heart rate checks; carry out a palpation of the abdomen and administer pain relief through an auto-injector – all while streaming real-time data to the remote operator.
The project was led by David King, Head of Digital Design at the AMRC and Sanja Dogramadzi, Professor of Medical Robotics and Intelligent Health Technologies at the Department of Automatic Control and Systems Engineering and Director of Sheffield Robotics.
www.amrc.co.uk
With the new M-THERMO3 16 temperature measurement module, IPETRONIK is ushering in a new generation of devices. As the first module in the "M3 family", the M-THERMO3 16 sets standards in modular measuring technology. Its 16 channels, which can be selected independently of the thermocouple type, offer a high degree of precision and flexibility with a highresolution 24-bit analogue to digital converter (ADC). The M-THERMO3 16 is ultra-compact, robust and boasts a new wireless and magnetic connection concept –which saves time during installation and offers the best possible security for the data connection.
Its applications are: validation of long-term strength under various ambient conditions (thermal safeguarding of vehicle components), function testing of the climate control (interior air conditioning), verification of
maximum permitted temperatures (cooling of safetyrelevant assemblies), monitoring of thermal limits in closed-loop systems (thermal management system optimization), detection of temperature arrays at the system inlet and outlet (cooling capacity determination). Further applications for the M-THERMO3 16 are in the e-mobility sector like determination of temperature parameters of auxiliary units for system optimization and optimization of temperature distribution in the passenger compartment. It can also be used in the aerospace sector for altitude tests of engines in flight operations or for validation of fuel consumption and maintenance intervals of engines.
www.ipetronik.com
Scientists may have finally found a solution to effectively harvesting energy from humans into electrical energy. Researchers from the Institute of Thin Films, Sensors and Imaging (ITFSI) from the University of the West of Scotland (UWS) explored the use of the 3D graphene foam material Gii™ by Integrated Graphene as an active layer in an energy generator. The investigation aimed to transform mechanical energy wasted in nature into electrical energy that could be used to power small electronic devices and sensors in the booming global market for Internet of Things (IoT) technologies.
The research, published in ScienceDirect, shows that the force of a human footprint on a pressure-sensitive mat, equipped with Gii-TENG sensors, can produce enough energy to anonymously identify people entering or leaving a room. As well as providing a low-cost and energy-efficient solution to monitoring building occupancy, the mats could also help to optimize energy resources by, for example, controlling room temperature upon entrance or exit.
Mechanical energy is one of the most abundant and versatile energy sources available in nature. For around 20 years, triboelectric nanogenerators (TENGs) have been investigated as a technique for converting mechanical energy from our daily actions into usable electrical energy that can power both small IoT electronic devices
and sensors but also more power-hungry items such as electric cars and drones.
However, efforts to develop a commercially viable TENG have, to date, been hampered by issues relating to low durability, limited energy output and inefficiency. The addition of Gii™ to TENG has opened up a whole new world of possibilities due to its unique properties, including high surface area, porosity, light weight, and superior electrical properties. The energy autonomous, pressure-sensing nature of Gii-TENG has the potential to transform various aspects of our lifestyles, society and economy including, for example:
• Harvesting energy from sports such as golf, running, and tennis to power smart devices which generate performance data.
• Self-powered wearable biosensors for early diagnosis of health conditions including cardiovascular disease, gout and diabetes.
• Harvesting energy from cars on roads and people walking in the creation of smart cities.
• A smart energy solution for Industry 4.0.
• Extending the hovering time of drones, allowing transportation of parcels – and even people in the future – for longer distances and longer times.
www.integratedgraphene.com
PCB Piezotronics (PCB) has released a new lowoutgassing ICP triaxial accelerometer, called the Model 356A19. The solution is the company’s latest addition to its portfolio of miniature, triaxial accelerometers and has been developed to enable accurate high-frequency measurements to 13kHz (±5%).
(10.2mm) cubical housing with a 1.5m integral cable to a four-pin ¼-28 pin connector. A 1.5m mating extension cable to the BNC plug termination is a supplied accessory.
www.pcb.com
Apex Dynamics UK we have recently expanded their range to include hypoid gearboxes. This is a natural progression to enhance their offering to customers, providing a wider range of products and potential performance applications. Their new high efficiency BKM Series of high-precision hypoid gearboxes offers high torque, superior accuracy, excellent radial load capacity and low backlash, all in a compact design that is fully compatible with any motor.
Hypoid gearboxes are a type of spiral bevel gearbox. In contrast to traditional bevel gearboxes, they have nonintersecting axes, meaning they are not parallel, but rather are offset from one another. This provides them with hyperbolic rather than conical geometry.
Due to the tooth design, there is a greater contact area, meaning higher torques and gear ratios are possible, delivering greater precision. Hypoid gearboxes are compact and also offer smoother running properties, have quiet operation and can achieve lower backlash ratings than traditional bevel or worm-type gearboxes. They tend to be used where speeds exceed 1000 rpm, or for lower speed applications that demand extreme smoothness or quietness.
Although hypoid gearboxes are currently a relatively small segment of the overall precision gear market, it is likely to grow faster than the general rate as a range of industries continue to see the benefits of the technology. This includes high-growth sectors such as robotics and automation. Recent research by industrial automation market specialist Interact Analysis forecasts the precision gear products market will expand by a compound annual growth rate of 7.7% between 2022 and 2027, climbing from $3.6 billion to $5.2 billion.
Key applications include the automotive industry, industrial machinery, robotics and automation, renewable energy systems, and power tools.
The transducer electronic data sheet (TEDS), which complies with IEEE 1451.4, is located within the sensor and includes data such as the serial number, sensitivity and last calibration date.
Due to its small size and wide frequency range, the 356A19 is well suited for modal and structural analysis, vibration testing in thermal vacuum environments, ESS and HALT/HASS testing of satellites, automotive internal combustion engine and electric vehicle powertrain development, vehicle systems NVH, and vibration testing in confined spaces or on small, lightweight objects.
The 356A19 features a hermetically sealed, 0.4in
With a variety of mounting, input and output options, the expansion was a natural step for existing and new customers that allows Apex to become even more competitive and keep up with market trends. Anyone purchasing a hypoid gearbox from Apex Dynamics UK is able to take full advantage of their five-year warranty, excellent lead times and high levels of customer service. www.apexdynauk.com
Over recent months a large part of our energies in the Durability and Fatigue Group have been devoted to preparations for the forthcoming Fatigue 2024 conference, in Cambridge. We are very pleased and excited by the programme which is coming together.
Over 100 papers are already confirmed but, at time of this publication, there is still space for just a few more, even though the abstract deadline is officially passed. There are also opportunities to sponsor and exhibit, so please get in touch with our Marketing & Events Manager if you are interested.
Meanwhile, the group continues to run a mixture of virtual and in-person meetings, aiming to find a good balance for ease of participation. Fatigue issues within the renewable sector continue to be a topic of discussion, as does durability in joining technologies, in which regard we are working towards a seminar on bolted joints.
Peter Bailey ChairmanIn March’s journal, I started off by saying how keen the EIS is to understand how people want to attend future events; that said, we still believe it’s important, more than ever, to offer the ability for people to attend events in person, rather than just online. Offering interesting locations and live demonstrations is something we are keen to do, and seminars are usually best experienced in person rather than virtually.
We want to ensure that seminars are not just click and listen but interactive, two-way forums that stimulate conversation and build communities of like-minded people, keen to learn from others and grow with the future! To keep the seminars stimulating, we will be exploring old and new techniques and are always keen to hear the hot topics you feel should be included.
The group is working hard to bring you interesting and relevant seminars that will hopefully resonate with all. AI, alternative fuel and autonomous vehicles are on the horizon, and this is an opportunity to revisit some previously covered topics with a fresh focus. It will be interesting to explore and discover; will products be changing what they are doing faster than we can measure it?
The question posed at the last EIS STMG meeting was whether we thought running more seminars on measurement carried value. The answer was a unanimous yes. In the current simulation-heavy climate, it is arguable that quality data collection is more important than ever before, as a simulation is only as good as the physical data that you feed it. AI systems will also run based on data collected, so data collection is as relevant as ever, despite the move to relying more heavily on simulation.
As a result, the EIS is currently looking at a series of seminars/webinars focused on first principles and basic understanding of measurement, which I hope will be finalised in the forthcoming months. I look forward to sharing this soon. We are also looking at presenting a series of case studies, successes and failures to Young Engineers with perhaps a panel of engineers to answer questions and provide help and guidance.
We are also aware we are dominated by members in the automotive sector and want to increase our membership to include other sectors.
Finally, as always, I wrap up the September journal with a thanks to all those who supported the Instrumentation, Analysis & Testing Exhibition, which once again was very well-attended with excellent exhibitor feedback. This year saw the largest number of attendees to date and it was great to bump into so many old friends at the Silverstone Circuit. Next year’s event will take place on 23 March 2024 and we hope to see many of you there.
Steve Payne ChairmanSince the last journal issue in March 2023, the SVPP Group successfully held a seminar in April at the Institute of Advanced Automotive Propulsion Systems on the subject of Net Zero Vehicle Powertrain Engineering Design and Development Technology. More information on this seminar and future initiatives can be found on page 30, but suffice to say that
this was a very successful event with overwhelming support for further seminars in the future.
Consequently, there will be more offerings and activity from the EIS over the coming months and years, in what is a rapidly developing engineering field with some of its own unique challenges and technologies.
Alongside the Net Zero seminar the SVPP Group committee has also been working on ideas for a Sound Quality-themed seminar for 2024. Many years ago the SVPP would quite often run sound quality seminars and workshops based around aspects of the internal combustion engine and its loudness, harmonic content and impulsiveness etc. Many metrics and techniques evolved at the time to support the development of the internal combustion engine noise character and level, which were explored at numerous EIS seminars and workshops at the time.
As the automotive sector transitions to electric vehicles, there has been a re-emergence in interest in this subject, albeit with new designs and technologies. In general, the
environmental acoustic impact on human health from a range of noise sources is well-documented. In the progression towards net zero products and use of renewable energy generation, the soundscape in the environment is changing and in some respects significantly deteriorating. This presents an engineering challenge across a range of product sectors.
In bringing together engineers from industry and academia through seminars and workshops, we intend to facilitate the understanding and know-how to address the future netzero soundscape.
If you are interested in supporting our activities in the future, whether through the Net Zero or Sound Quality initiatives then please let myself or Sara Atkin (EIS Marketing & Events Manager) know.
Dave Fish ChairmanThe following companies are corporate members of the Engineering Integrity Society. We thank them for their continued support which helps the Society to run its wide-ranging events throughout the year.
AcSoft
AMETEK Vision Research
Aircraft Research Association
Axiometrix Solutions
CATS3
CentraTEQ
Correlated Solutions
Darvick Ltd
Dassault Systemes
Data Acquisition and Testing
Services Ltd
Data Physics
Datron Technology
Delta Motion
Dewesoft
Frazer-Nash Consultancy
HBK
HEAD acoustics
HORIBA-MIRA Instron
Intrepid
Interface Force Measurements
iPetronik
Kistler
M&P International
McLaren Applied
Mecmesin
Micro Measurements
Micro-Epsilon
Moog
Nprime
PCB Piezotronics
PDS Hitech
Polytec
Prosig
Rutherford Appleton Lab
Sensors UK
Servotest
Siemens
Star Hydraulics
Strainsense
Stress-Space Systems Services
Technica Engineering GmbH
Techni Measure
THP Systems
Torquemeters
UTAC
Yokogawa
ZEISS
ZwickRoell
Directors
Peter Bailey, Instron
Robert Cawte, HBK
Dave Fish, JoTech Ltd
Graham Hemmings, Engineering Consultant
Alex O'Neill, Siemens
Jamie Shenton, JCB
Norman Thornton, Engineering Consultant
John Yates, Engineering Consultant Chairman
John Yates, Engineering Consultant
Vice-Chairman
David Fish, JoTech
Marketing & Events Manager
Sara Atkin
Communications Sub Committee – ‘Engineering Integrity’ Journal of the EIS
Honorary Editor
Spencer Jeffs
Managing Editor
Rochelle Stanley
Chairman
David Fish, JoTech
Deputy Chairman
Keith Vickers, HBK
Members
Dave Boast, DB Engineering Solutions
David Bryant, Bradford University
Mark Burnett, HORIBA-MIRA
Pierfrancesco Cacciola, University of Brighton
Max Chowanietz, Aston Martin
Martin Cockrill, RLE International
Paul Francis, JCB
Paul Jennings, Warwick University
Jonathan Joy, UTAC
Amir Khan, Bradford University
Andrew McQueen, Siemens
Alexander Shaw, Swansea University
Tony Shepperson, HEAD acoustics
Jason Truong, UTAC
James Wren, Spectral Dynamics
Ying Yi, University of Southampton
Chairman
Steve Payne, HORIBA-MIRA
Deputy Chairman
Alex O'Neill, Siemens
Members
Jack Allcock, Tata Steel
Carl Barcock, Data Acquisition & Testing Services Ltd
Dan Bailey, Instron
Gian Matteo Bianchi, Jaguar Land Rover
Connor Bligh, JCB
Marc Brown, Vibration Research
Darren Burke, Servotest
Steve Coe, Data Physics (UK)
David Copley, Consultant
David Ensor, Engineering Consultant
Robin Garvie, Airbus
Graham Hemmings, Engineering Consultant
Richard Hobson, Engineering Consultant
Jerry Hughes, Moog
Ben Huxham, Prosig
Shak Jamil, Techni Measure
Chris Johnson, Wacker Neuson UK Ltd
Virrinder Kumar, Engineering Consultant
Trevor Margereson, Engineering Consultant
Tim Powell, MTS Systems
Anton Raath, CATS3
Gary Rands, Siemens
Nick Richardson, Servotest
Paul Roberts, HBK
Raul Rodriguez, Hyster Yale
Jarek Rosinski, Transmission Dynamics
Norman Thornton, Engineering Consultant
John Wilkinson, Engineering Consultant
Darren Williams, UTAC
Scott Williams, Williams F1
Rob Wood, ZEISS
Jeremy Yarnall, Data Acquisition and Testing Services Ltd
Chairman
Peter Bailey, Instron Secretary
Jamie Shenton, JCB Members
Hayder Ahmad, Safran
Martin Bache, Engineering Consultant
Andrew Blows, Jaguar Land Rover
Robert Cawte, HBK
Amir Chahardehi, Kent Energies
Hollie Cockings, Swansea University
Richard Cornish, Birmingham City University
Farnoosh Farhad, Northumbria University
Hassan Ghadbeigi, Sheffield University
Lee Gilbert, Element
Oliver Greenwood, Rolls-Royce
Karl Johnson, ZwickRoell Group
Angelo Maligno, IISE, University of Derby
Andrew Mills, Siemens
Giovanni De Morais, Dassault Systèmes Simulia
Mahmoud Shafiee, University of Kent
Giora Shatil, Darwind
Niall Smyth, Coventry University
John Yates, Engineering Consultant
Committee members can be contacted via the Marketing & Events Manager, Tel: 01623 884225.
Unit 115, Gibson House, Ermine Business Park, Huntingdon, Cambridgeshire, PE29 6XU
Tel: +44 (0)7395 285065
Email: uk-sales@axiometrixsolutions.com
Website: www.axiometrixsolutions.com
Contact: Philippa Wolfarth
Axiometrix Solutions is a leading provider in test and measurement. Our global customer base can be found in most technology-intensive industries including electronics, aerospace and automotive.
Axiometrix Solutions consists of a strong group of well-established brands. Our three main product lines are industry-leading brands in their respective segments: Audio Precision, GRAS Sound & Vibration, and imc Test & Measurement.
Unit 4 Gainsborough Close, Gainsborough Business Park, Long Eaton, Nottinghamshire, NG10 1PX
Tel: +44 (0)1332 875450
Email: enquires@datsltd.com
Website: www.datsltd.com
Contact: Jeremy Yarnall
Data Acquisition & Testing Services provides data acquisition, test and measurement, instrumentation, analysis and engineering consultancy services across a wide spectrum of industries, from aerospace to rail. Based near Derby, with field engineers available nationally and outside the UK.
Additionally, we provide sales and service of the latest digital data collection equipment, with a full calibration facility for instruments and sensors. Hire of dataloggers, sensors and cables is also offered. Vibration and durability testing is provided in our in-house laboratory.
1 Appley Court
Appley Wood Corner
Haynes, Bedfordshire MK45 3QQ
Tel: +44 (0)1234 381 261
Email: sales.uk@dewesoft.com
Website: http://www.dewesoft.com
Contact: Andy Hathway
Dewesoft supply flexible modular data acquisition systems, for laboratory and mobile applications, with sample rates up to 1MS/s and signal conditioning for any type of sensor. Systems are also offered with IP67 rating for extreme environmental conditions. Dewesoft instruments are supplied with turnkey data acquisition software addressing a wide range of measurement applications, including power analysis, NVH, combustion analysis, road load data and many more.
Dewesoft supplies systems to all industries, including automotive, aerospace, defence, power and energy and transportation.
Unit 8, The Cobalt Centre
Siskin Parkway East Coventry, CV3 4PE
Tel: +44 (0)1582 711 670
Email: info@polytec-ltd.co.uk
Website: www.polytec.com/uk/
Non-contact optical measurements.
Polytec manufactures a wide range of laser vibrometers that are the acknowledged gold standard for noncontact vibration measurement. No matter your measurement need in research, development and production or even for long-term monitoring, there is a Polytec system to provide the answer. Laser-Doppler vibrometers analyse samples of different sizes, from entire car bodies, large aerospace parts over engines and actuators to micron-sized MEMS or delicate HDD components, even biological samples.
Polytec also provide non-contact velocimeters for industrial process length and speed measurements, as well as optical profilers for surface metrology applications using the latest advances in white light interferometry.
The Coach House
303 Willington Road
Kirton End, Boston
PE20 1NR
Tel: +44(0)1205 724242
Email: stephen.barrett@systemsservices.co.uk
Website: www.systems-services.co.uk
Contact: Stephen Barrett | Tel: +44 7836 607414
Since 1982, Systems Services have offered a complete service for fluid power motion control systems, ranging from a single channel to multiaxis, multi-channel, interactive, full-scale systems. Our range of services includes consultancy, training, associated servicing and calibration, calibration management, commissioning, gasloaded accumulator management and related technical procurement services. We offer a range of customised training courses for all users of fluid power systems and have trained over 720 delegates.
West Haddon Road
Ravensthorpe, Northamptonshire
NN6 8ET
Tel: +44 (0)1604 770232
Email: sales@torquemeters.com / info@torquemeters.com
Website: www.torquemeters.com
Contact: Geoff Robinson – Sales & Marketing Director | Peter Rogers – Business Development Manager | Jane Davies – Sales Administrator
Pioneers in the design, manufacture and support of torque measurement systems for high-speed and highpower rotating applications, Torquemeters is a provider of specialist torquemeters, couplings, flywheels, spindles and turnkey test rigs. A key partner to the major aero engine, automotive, industrial machinery and industrial gas turbine manufacturers, Torquemeters has over 2,500 systems installed worldwide. At the forefront of testing the next generation of e-motor and e-propulsion systems, recent projects include a 2MW 30,000rpm regenerative test-stand system for starter/generator testing.
Leopoldstr. 236
D-80807 München
Germany
Tel: +49 89/200 07 24-10
Email: Thomas.fone.ext@technicaengineering.de
Website: www. technica-engineering.de
Contact: Thomas Fone
The Pioneers of Automotive Ethernet.
As a leading technology company, we support our customers from E/E Architecture design to vehicle validation. We are working with multiple well-known OEMs on their presentday and next-generation E/E architectures. As creators and experts of Automotive Ethernet, we can cover every aspect of modern communication networks.
Technica Engineering is part of the KPIT Group.
Worcester Six Business Park
Clayfield Road
Worcester
Worcestershire
WR4 0AE
Tel: +44 (0)1568 615201
Email: Daniel.Jones@zwickroell.com
Website: www.zwick.co.uk
Contacts: Daniel Jones
ZwickRoell is a leading, global supplier of advanced materials and component testing equipment. We offer a wide range of both electro-mechanical and servo-hydraulic testing products and controller/ software modernisations to give older generation systems a new lease of life.
We supply standard and bespoke testing solutions and collaborate with an extensive range of industrial customers and academic establishments where Zwick equipment is used for both teaching and research purposes.