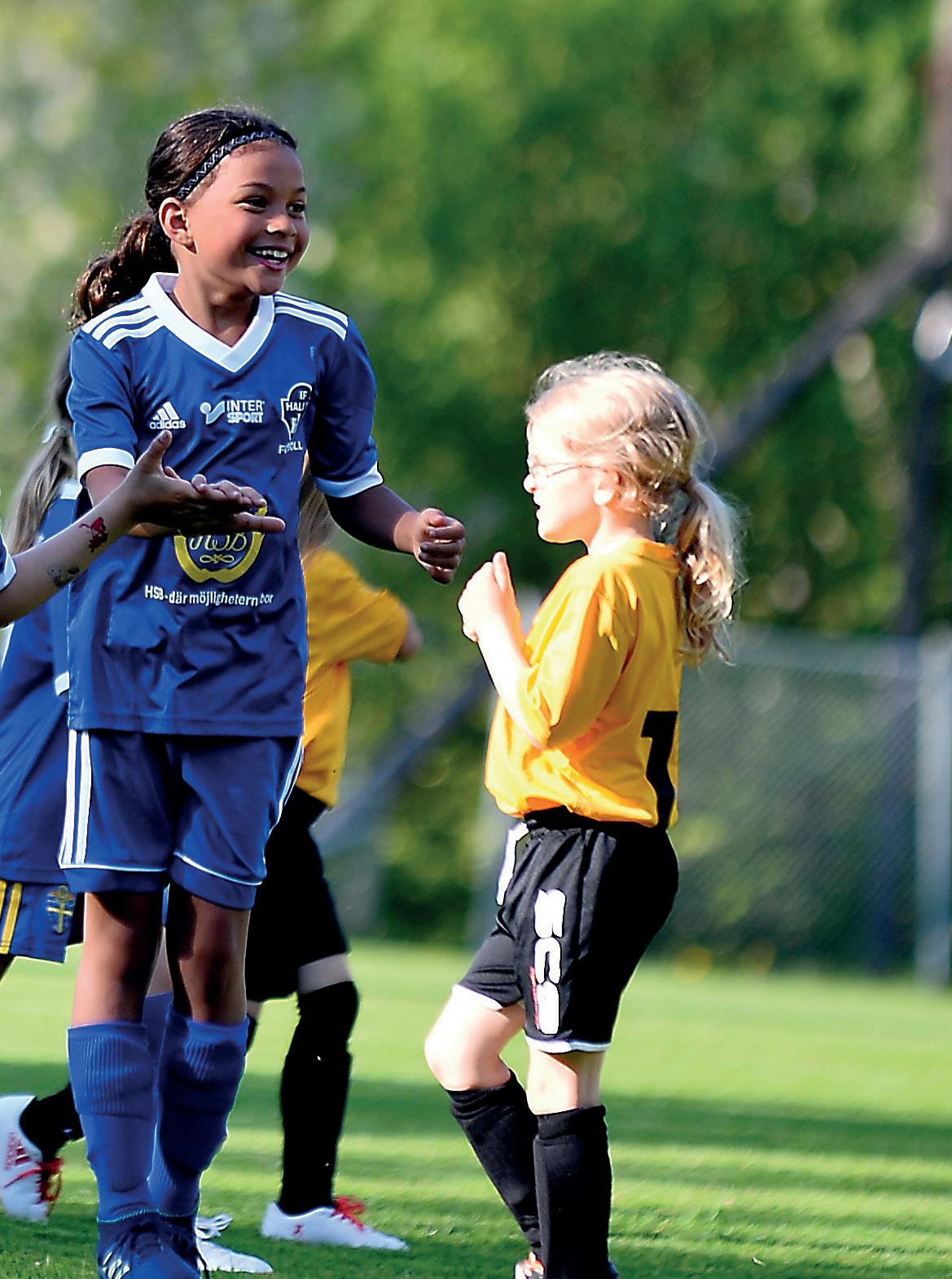
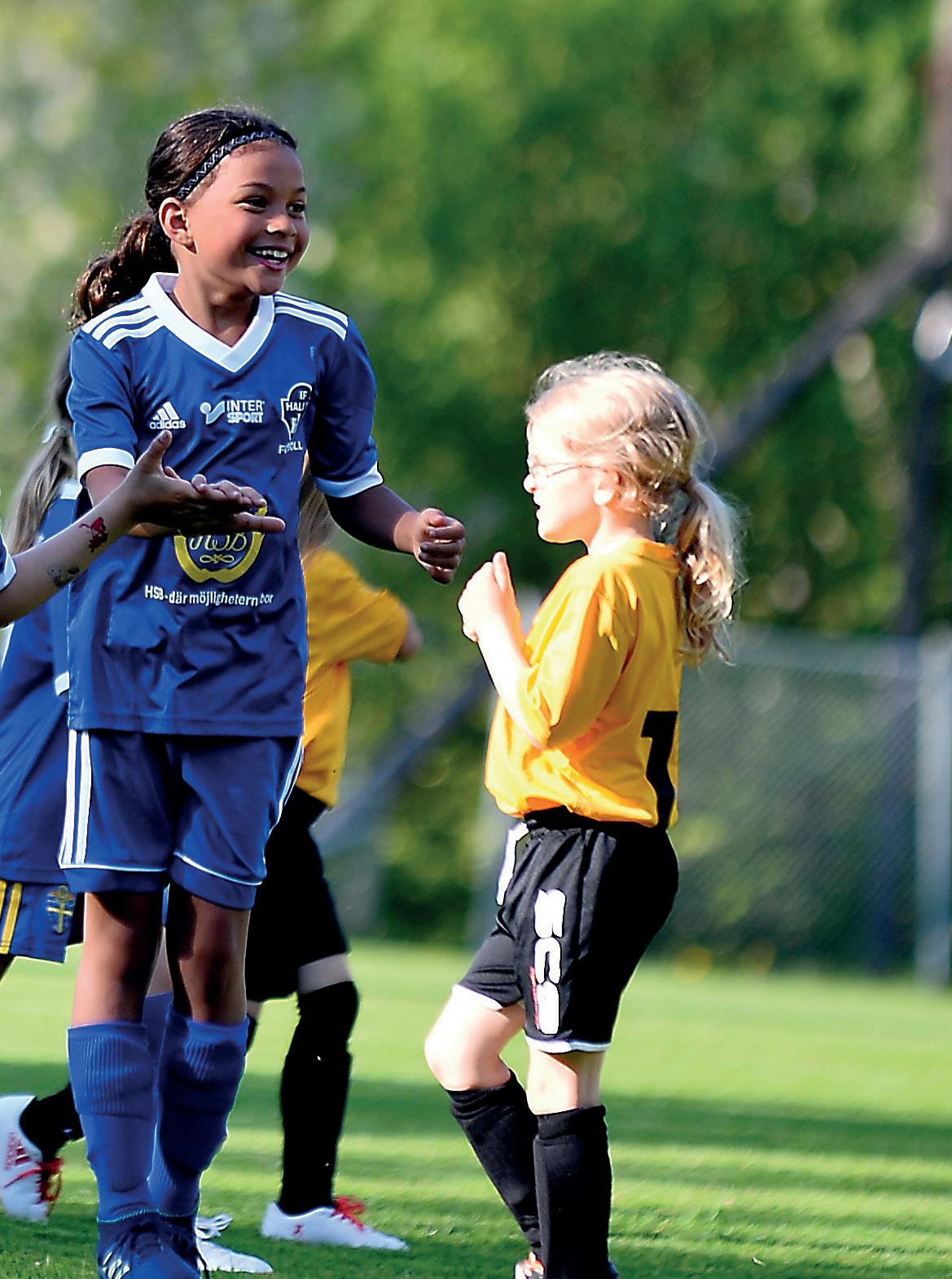
POSITIVITY
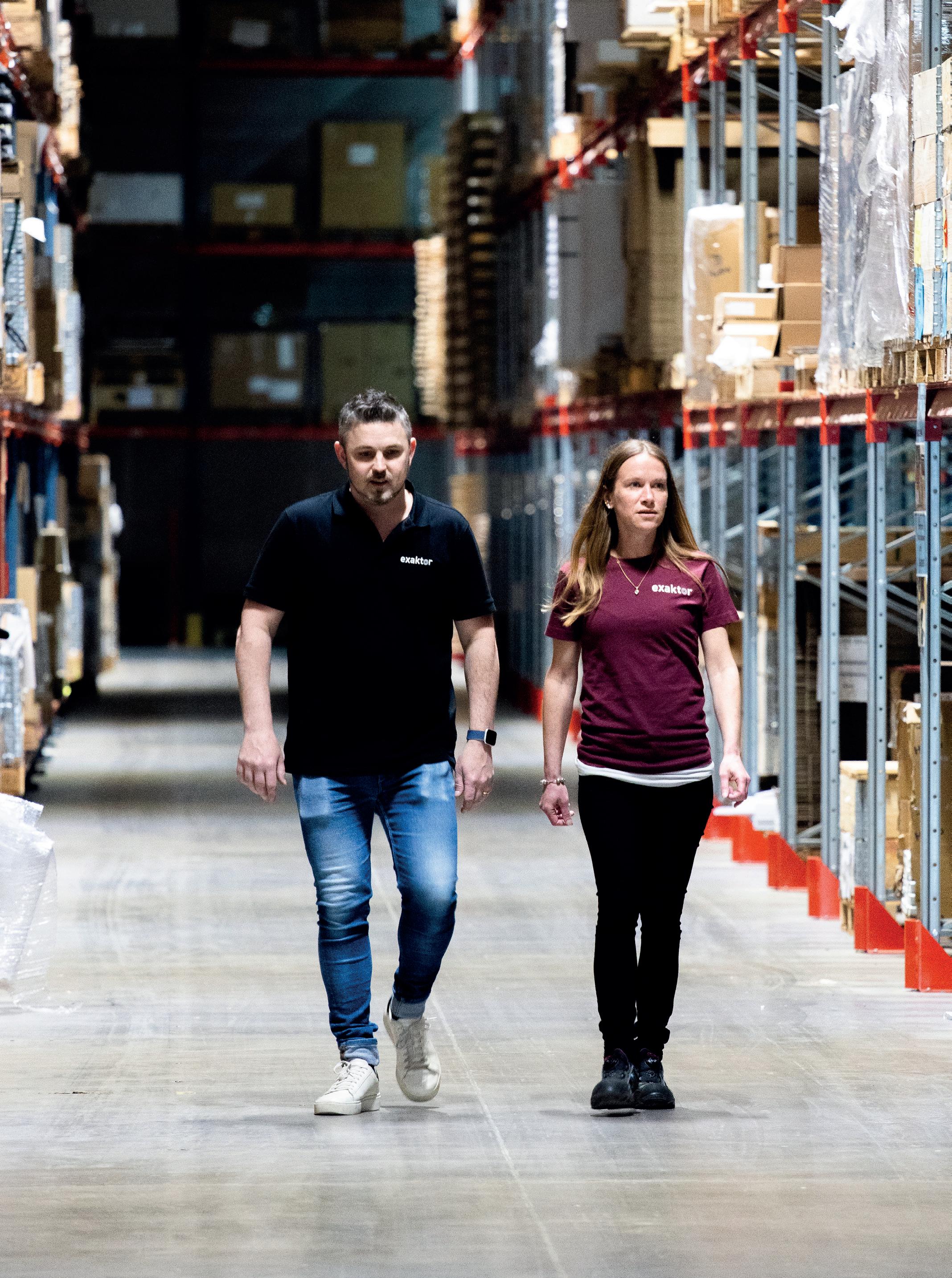
”
Proton stands for positive change. With clever industrial solutions we create meaningful jobs and conserve the earth’s resources.
Together we can contribute to a better world for the next generation.

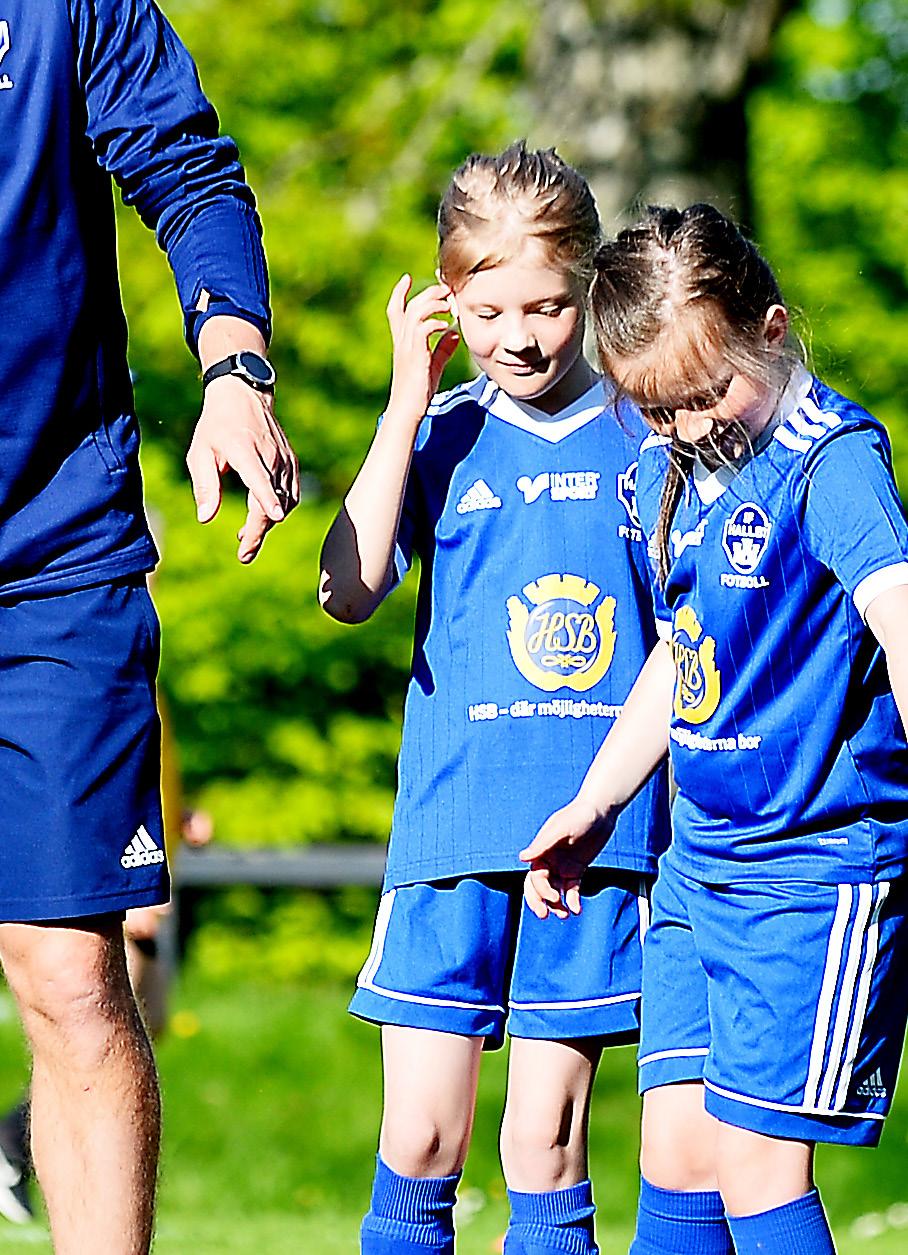
Photo: Martin Johansson, Martin Andersson, Anna Hållams, Erik Sundwall and IF Hallby
Proton Group is a family-owned group of companies with operations in six areas: surface treatment, pipe bending, machine safety, corrosion testing, pipe installations and lighting.
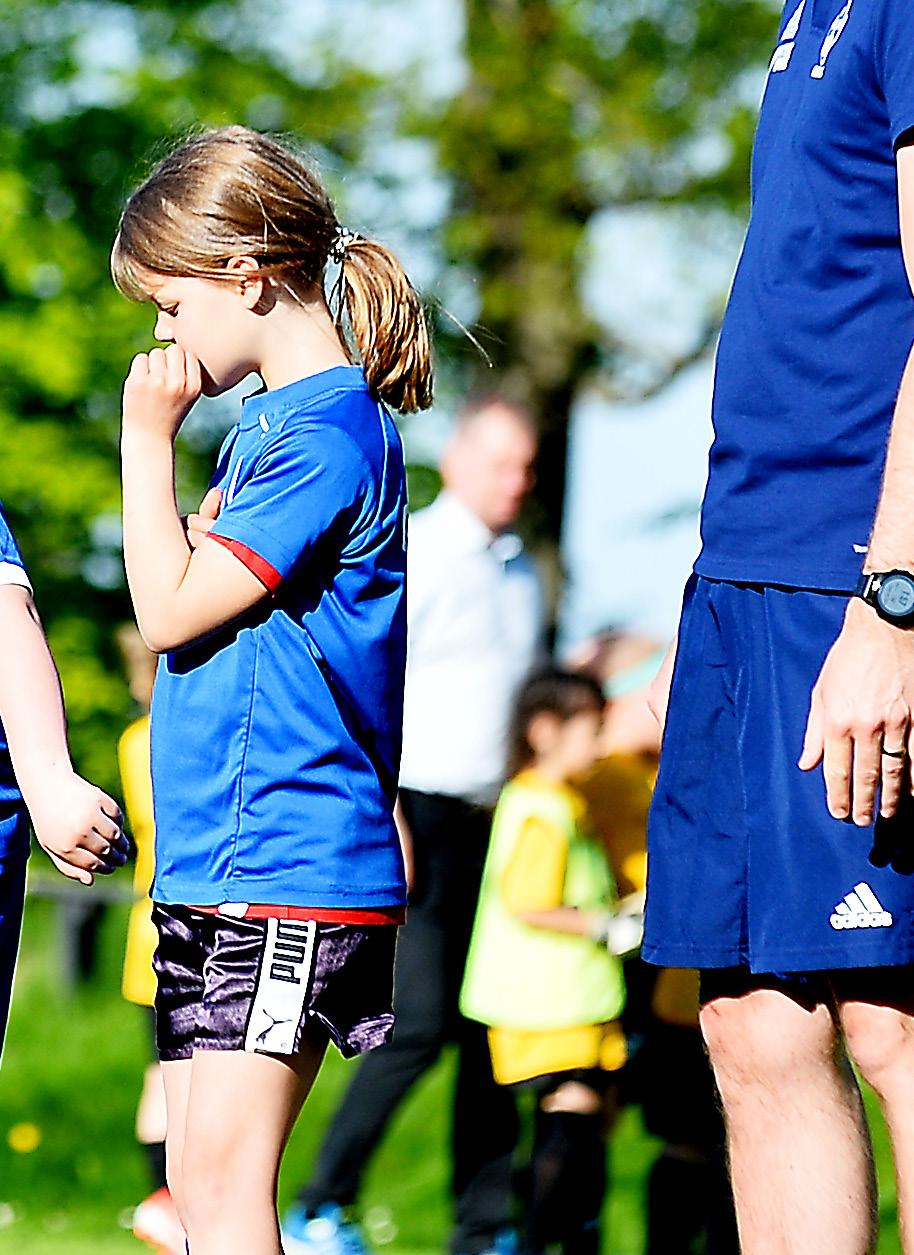
Climate calculations for the entire group are an important milestone in our sustainability work.

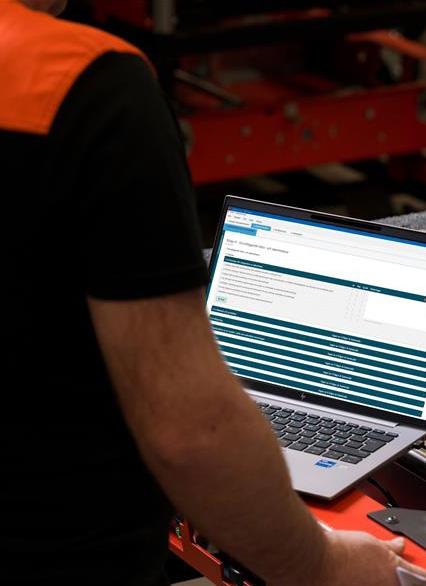
Cedoc works with its customers to make Sweden’s workplaces safer.
DAVID GUSTAFSSON, CEO OF THE PROTON GROUP
Our sustainability work aims to make a positive difference for future generations.”
Sustainability is no longer an option – it is a prerequisite for future business. For Proton Group, it is a natural way to take responsibility and drive development. We are convinced that both customers and employees want to make choices that are better for the environment, for people and for future generations, says David Gustafsson.
- It is in Proton’s nature to work with these questions. For us, everything we do, including our sustainability work, is about making a positive difference – and contributing solutions that are both profitable and sustainable in the long term.
By working in a structured and transparent way with sustainability, we can show that we are a partner to be reckoned with, now and in the future.
- Being able to offer products and services with reduced impact is not just something we want to do – we believe it will be crucial to winning business and building trust going forward. Our sustainability work gives us opportunities to find new circular solutions and to become even better at taking care of our employees. It can also help us win business.
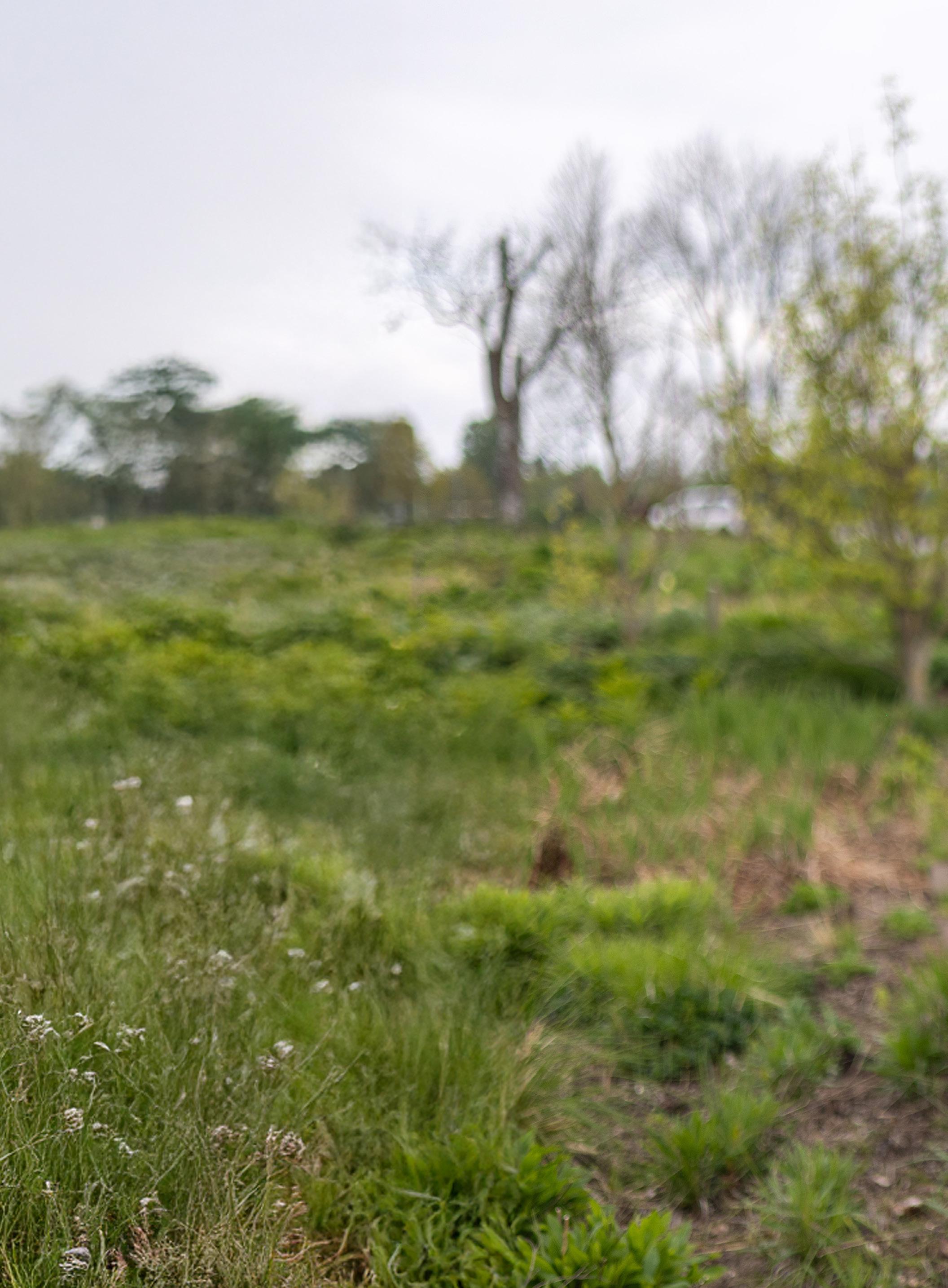
Proton Group focuses on growth by creating sustainable products and services. Is it really possible to combine growth with sustainability?
- Customers, consumers and stakeholders are increasingly demanding more sustainable solutions. Awareness has generally increased, and clear documentation of sustainability efforts is often a requirement for us to be considered for business. Being able to offer sustainability as part of the business model will be a prerequisite for companies that want to grow in the future.
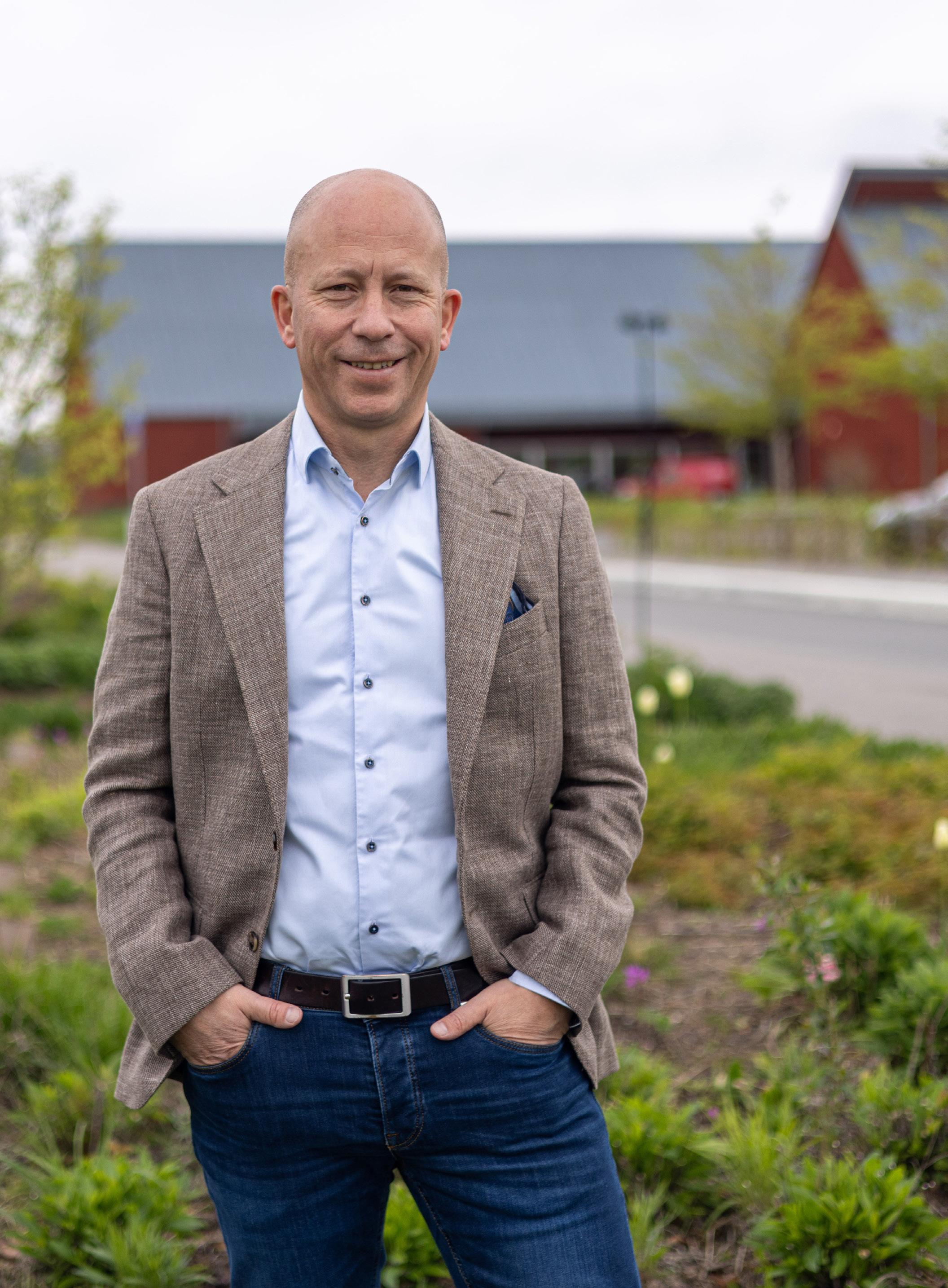
Proton conducts locally focused sustainability work in a global context. Caring for the people and environment in our neighbourhood is the first step in our contribution to a more sustainable world. The Vandalorum garden is one of the valuable natural areas in the local area that we enjoy and are proud of.
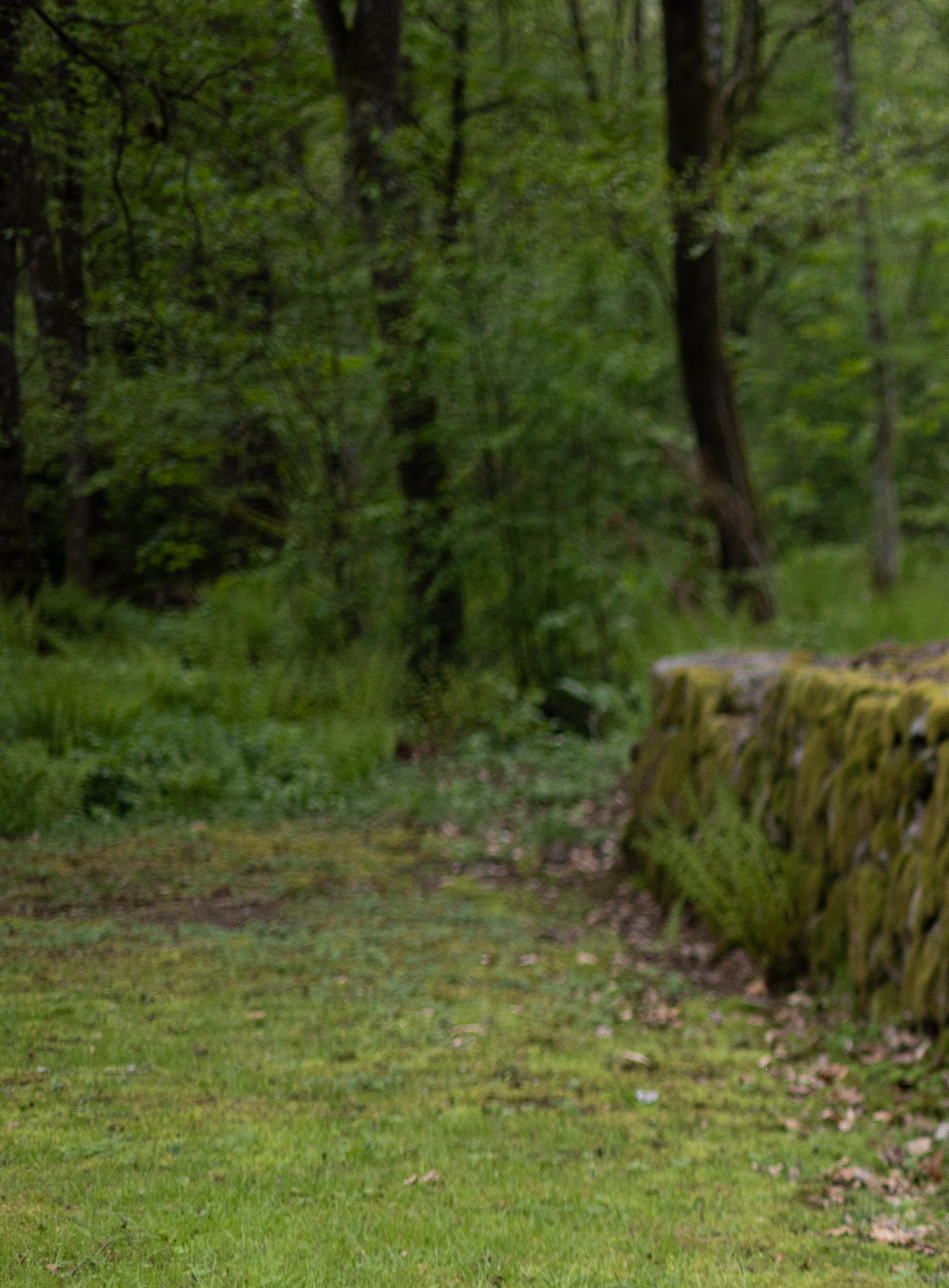
If we can develop a surface treatment method that has less impact on the environment but protects the details just as well, there is a good chance that customers will choose us. Then we will have contributed to a sustainable solution – while growing our business. To put it bluntly, it’s a matter of survival. If we can’t reverse the trend, there’s no tomorrow for any of us.
What is the main driving force behind your sustainability work?
- We are driving sustainability because we are convinced that it is the right way forward – for society, for our customers and for Proton. It is a natural part of how we want to build and develop our business. By integrating sustainability into our strategy at an early stage, we have laid the foundation for making a real difference. We have built up structures, expertise and insights that enable us to act with a long-term perspective, ambition and a clear direction.
A double materiality analysis has given us an even clearer picture of our impact and what we need to prioritise going forward. We are already in the process of developing action plans and targets based on the sustainability issues that are most relevant to us and our stakeholders.
- Discussions about reporting requirements and regulations do not affect our conviction. We choose to work in a forward-looking and trans-
parent manner, regardless of external requirements. For us, sustainability is about the mark we want to leave behind. The most important thing is to create value that lasts over time – for all people, our society and our planet.
What are Proton Group’s priority sustainability issues and how do you work with them?
- Our sustainability work is inspired by the Global Compact. The main reason for this is that the Global Compact is widely recognised and easy to communicate. This makes it easier to collaborate with our various stakeholders. We focus on three perspectives: People, Environment and Economy. By reducing emissions, working actively for a sustainable labour market and building long-term economic stability, we are creating the conditions for a future-proof business.
– We see great opportunities to make a difference locally. In both the long and short term, we can contribute to welfare by creating jobs, supporting people who are far from the labour market and offering development opportunities for our employees.
– At the same time, financial sustainability is an important part. When Proton was founded 35 years ago, there was already a clear diversification strategy, i.e. that we have operations in different industries. Another cornerstone is
”The big challenge is climate change and how we can create new, circular business models where everyone is prepared to contribute.
that we have a healthy debt level, which gives us freedom of action and security when the market fluctuates.
What challenges do you see within the framework of sustainability work?
- The biggest challenge we face is climate change and the need for circular business models. Another challenge is that the demands of different customer categories can vary quite a lot, and it is challenging to satisfy everyone’s interests. Authorities can also do more to simplify regulations and create stable conditions for investments in sustainable technology.
What are you most proud of achieving in the area of sustainability?
– We have carried out climate calculations for all companies in the Group. This has given us sharp insights and a clear direction for our sustainability work. I am also proud that we have long prioritised sustainability in practice – with an incredibly dedicated organisation, the right resources and new expertise in place. The fact that reduced emissions, a lower carbon footprint and smart energy savings now come directly

from our own initiatives shows that we have the ability to drive change from within. I am extremely proud of that.
What do Proton’s stakeholders think about the work being done?
- We have been very clear that we see sustainability work as a way to make a positive difference for future generations. And I understand that this is something that is appreciated by many stakeholders, both customers and employees.
Doing something meaningful is not just about having a job here and now – it is about building a sustainable future.
Global growth – together
Organisation and business model
The Proton Group is a family-owned business group with the Malveholm family as the largest owners.The business is divided into six areas: surface treatment, lighting, pipe bending, pipe installations, machine safety and corrosion testing. They operate in a variety of industries that are all linked to industrial production. A number of companies operate within the framework of the various activities, all of which have the freedom to run their business and their sustainability work under their own responsibility. To support the operations, Proton Group has set up a special service company, Proton Services, which provides expertise in finance, HR, IT, marketing communications, sustainability and management.
In their specific fields of expertise, the companies in the five business areas have customers in an array of industries, which serve as suppliers, product owners or consultants to the automotive, construction, property and furniture sectors. Proton Group customers are primarily located in Europe, but some are in Asia, North and South America. Some long-term customers include names such as Ahlsell, Alfa Laval, Autoliv, Gunnebo Fastening, Hestra Inredningar, IKEA, Kockums Maskin, Koenigsegg, Kongsberg, MAN, Nevs, Renault, Rexel, Scania, Shiloh, Tesla, Thule, Volvo Trucks and Volvo Construction Equipment.
One of the core ideas of the Proton Group is that the business areas can benefit from each other’s strengths by working together on sustainability, sharing of skills and business development. The wide range of business activities also helps to make the group somewhat recession-proof and allows it to move sustainability investment funds between businesses where needed.
Strategic presence in the Nordics and Baltics
Skara
Gothenburg Hillerstorp
Anderstorp
Forsheda
SWEDEN
FINLAND
Eskilstuna
Bankeryd Skillingaryd
Värnamo
Proton Grouphead quarters
Vantaa
LITHUANIA
Klaipèda
Skövde
Growth strategy
The Proton Group pursues an active growth strategy with the aim of doubling sales every ten years. The sales target for 2030 is SEK 1.3 billion. This growth is to be achieved organically and through acquisitions, and through an increased global presence.
• We develop companies with unique abilities that are, or have reasonable potential to be, leading in their field.
• We invest in companies that have, or have the potential for, good dividends, long-term growth and limited risk.
• We have a healthy financial base that is stable in the long term.
• We are long-term owners with no ultimate time limit.
• We have operations in a variety of industries to reduce vulnerability and increase resilience.
• The dedication and knowledge of our staff are crucial to our development. This makes a decentralised organisation natural to us.
These strategies are steps towards these goals:
1. Strong business areas with their own, motivated management and clear focus on results.
2. Long-term resilient financial basis:
No single industry is to make up more than 1/3 of sales at the aggregate group level.
3. We actively seek new acquisitions based on our primary strategy.
4.The group supports the business areas and their subsidiaries with funding,analysis and resources in finance, HR, IT, marketing communications, sustainability and management.
History
The Proton Group was founded in 1990 when a number of stakeholders, including Leif Malveholm, bought out a group of ten industrial companies and delisted them from the stock exchange. The aim was to build an industrial group with several pillars to stand on. The existing base was the surface finishing companies that currently make up the company Proton Finishing. The strategy was to invest in environmental improvement measures, as the group owners expected that tighter environmental regulations would make it harder for smaller companies in the business to compete. Part of that strategy involved creating synergies between the surface finishing business and the construction business, which is now is the company Proton Engineering. Throughout its history, the Proton Group has faced both opportunities and setbacks, but it has always succeeded in offering stability to its customers and employees. The Proton Group has maintained an AAA credit rating for more than 25 years.
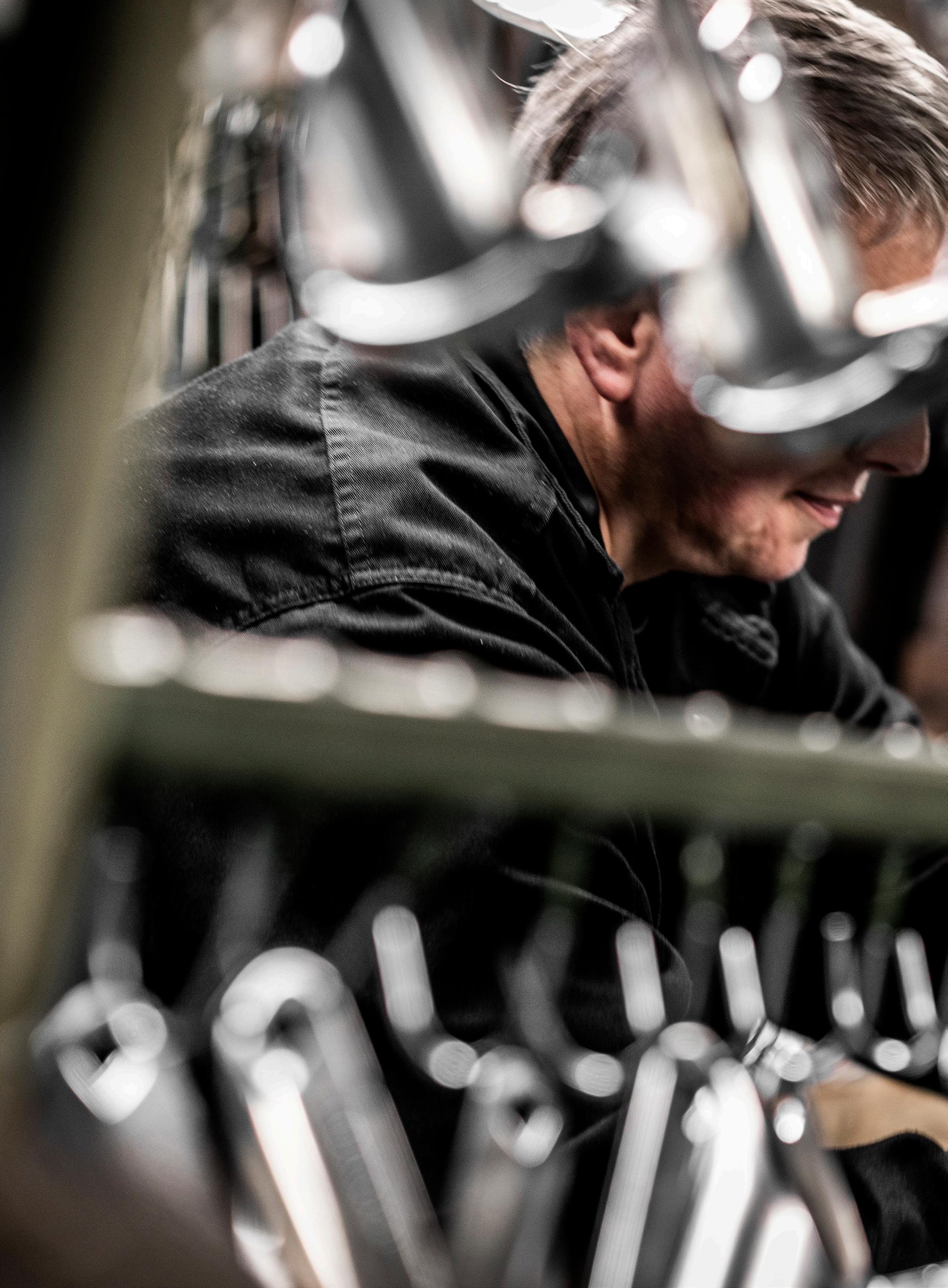
1990
The Proton Group is founded.
2012
Transition to buying fossil-free electricity.
2018
Transition from fossil natural gas to renewable biogas.
2011
Generational shift –ownership passes to Leif Malveholm’s children Daniel, Marcus and Sanna.
2017
TIA – incident management system for risks, incidents and accidents is implemented.
2018
Soil remediation of property in Markaryd where previous surface treatment business operated.
2019 Proton Group acquires JL Safety and CEDOC
2020
Proton Group acquires Gunnar Hansson Svetsteknik and Teknikrör i Kinna, which have now merged to form Weldin Gothenburg.

2020
Transition to purchasing environmentally declared hydropower.
2021
Proton Group acquires surface treatment company in Anderstorp.
2022
Proton Group publishes its first sustainability story.
2023
Producing our own renewable electricity through our first solar panel installation.
2025
Committed to Science Based Targets (SBTi) to set Near -term Targets
2022
Report of climate footprint, CO2 emissions from all surface treatment businesses
2023
JL Safety och Cedoc becomes separate companies.
2024
Climate footprint for the whole Group.
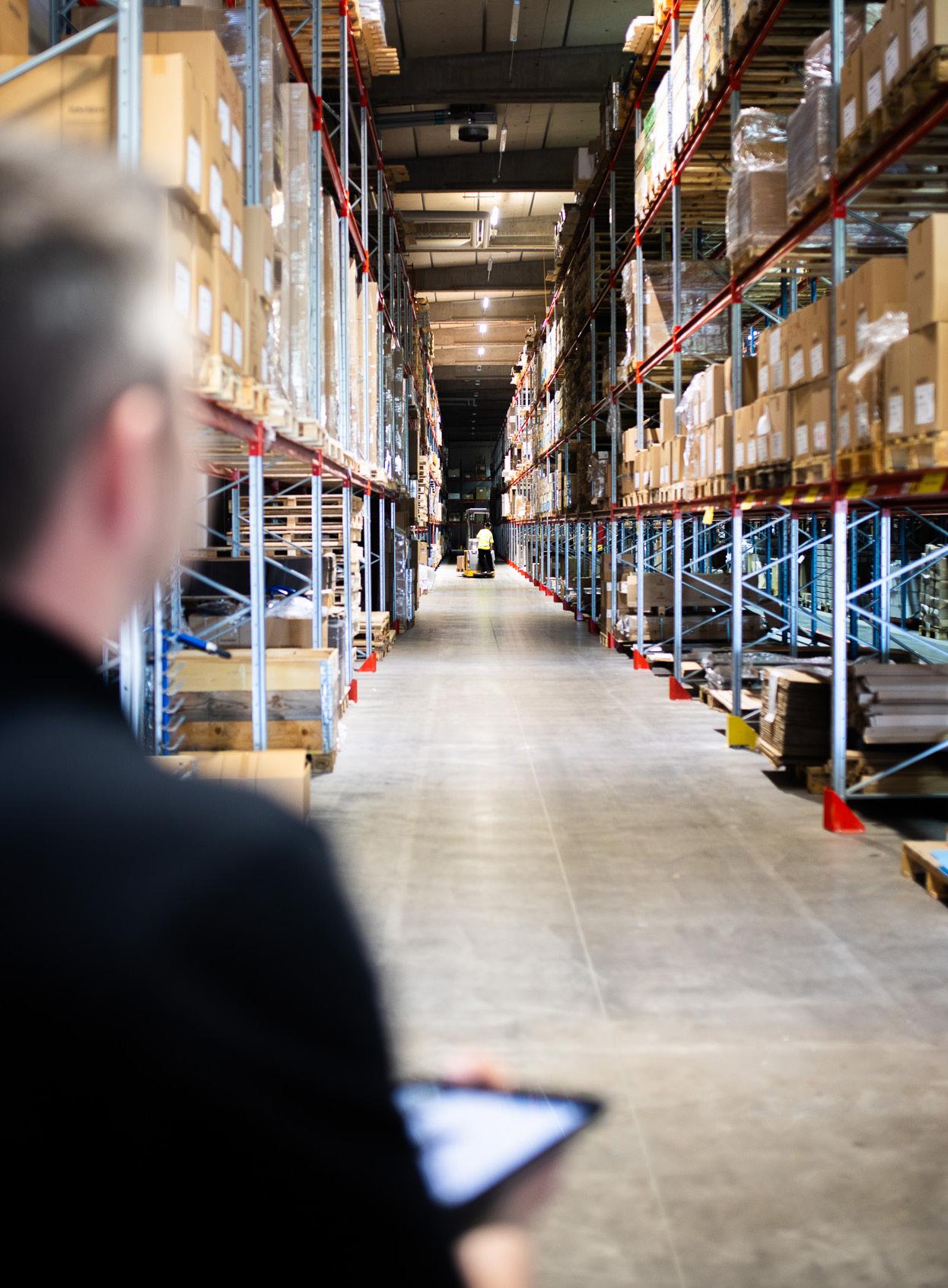
Exaktor Exlite
Lighting solutions for a sustainable society
Proton Lighting is one of Scandinavia’s most experienced suppliers of energyefficient lighting for healthy, productive environments. The luminaires are developed and manufactured with innovative light sources and lighting control to meet stringent demands for sustainability. The products are marketed under the brands Exaktor and Exlite.
COMPANIES
Proton Lighting, Värnamo
Proton Lighting, Helsinki, Finland
NUMBER OF EMPLOYEES 2024
TURNOVER 2024 (MSEK)
SUSTAINABILITY FROM A BUSINESS PERSPECTIVE
By offering energy-efficient LED lighting in combination with intelligent control systems, Proton Lighting can help its customers reduce their energy consumption and their carbon footprint. The current energy crisis and rising electricity prices also highlight clear business benefits from a financial perspective. In addition, more and more customers are demanding good ergonomic lighting for improved employee health, wellbeing and safety. Public environments with good, energy-efficient lighting also make people feel safer, which provides greater benefit from a societal perspective.
Värnamo
Vantaa

Proton Engineering
Supplier to leading automotive manufacturers
Proton Engineering focuses on high-quality components for the automotive and manufacturing industries. Currently the organisation consists of two companies: Proton Engineering in Skillingaryd and in Klaipèda. The companies perform pipe and tube bending, end forming and welding and have a long tradition of deliveries to leading vehicle manufacturers in Sweden and the world.
COMPANIES
Proton Engineering, Skillingaryd Proton Engineering Lithuania, Klaipèda, Lithuania
NUMBER OF EMPLOEES 2024
TURNOVER 2024 (MSEK)
SUSTAINABILITY FROM A BUSINESS PERSPECTIVE As a supplier to the heavy vehicle industry, Proton Engineering’s ability to deliver welldesigned, durable components is crucial to the life cycle of the finished vehicle. Proton Engineering’s sustainability measures create added value for its customers by providing resource and energy-optimised solutions and products that were created under good working conditions with stringent demands for suppliers both upstream and downstream.
Skillingaryd
Klaipèda
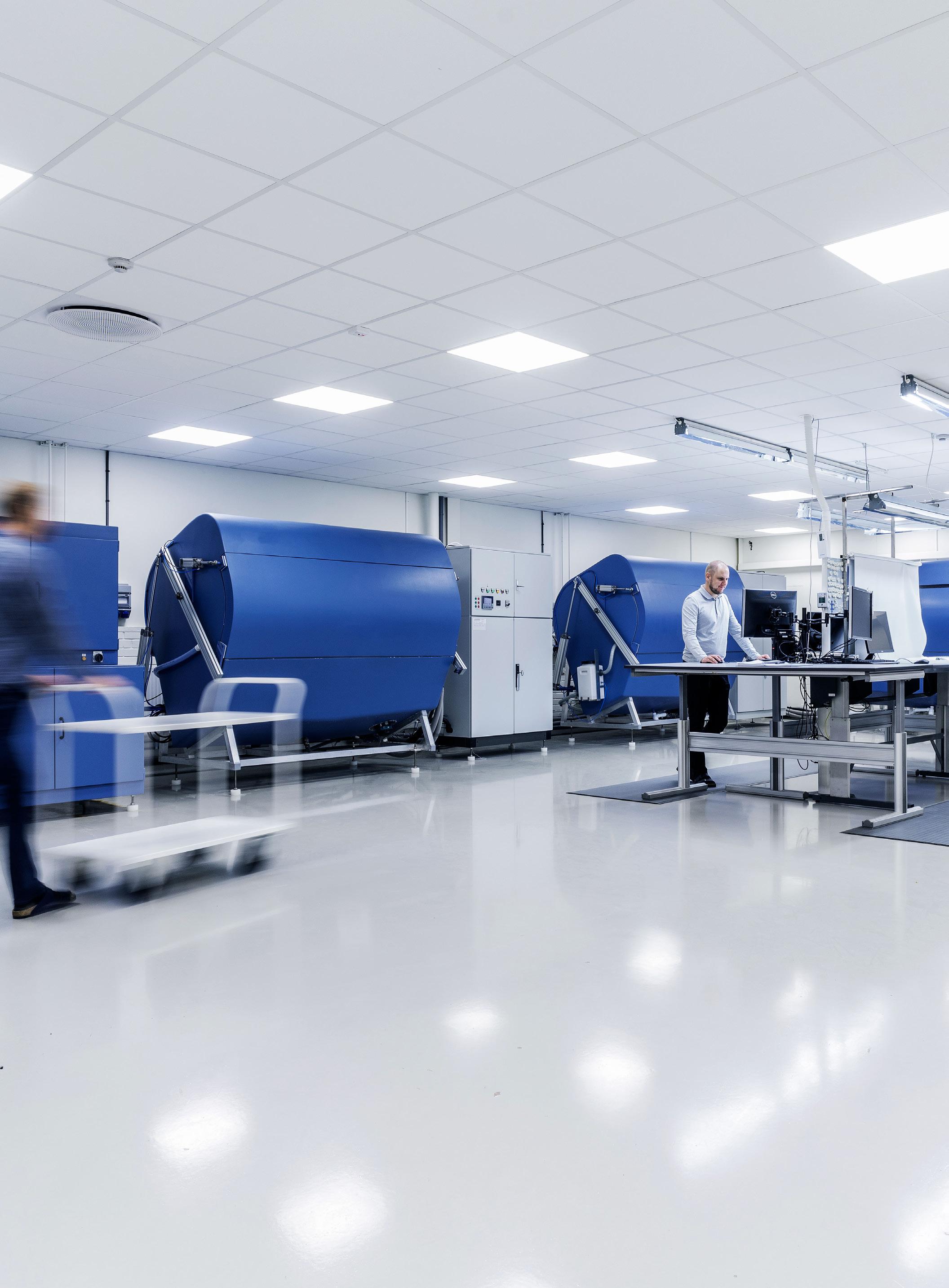
Cotec Labs
Specialist operations for an extended life cycle
Cotec Labs is a highly specialised company with a focus on quality. The company is a market leader in corrosion and surface testing for the international automotive and furniture industries.
COMPANIES
Cotec Labs, Bankeryd
NUMBER OF EMPLOEES 2024
TURNOVER 2024 (MSEK)
SUSTAINABILITY FROM A BUSINESS PERSPECTIVE
Cotec Labs’ services provide quality assurance of surface-treated parts, helping to extend the lifecycle of products reaching the market. Cotec Labs’ services are also strategically important in the development and quality assurance of new, more environmentally friendly surface treatment technologies.
Bankeryd

JL Safety Cedoc
Services in machine safety and risk assessment
The machine safety business area comprises two highly specialised companies focusing on risk assessment and machine safety. JL Safety specialises in machine safety and CE marking and helps manufacturing companies to ensure safe workplaces. Cedoc develops software for risk assessment and documentation of machines.
COMPANIES
JL Safety, Skara Cedoc, Skövde
NUMBER OF EMPLOYEES 2024
16
TURNOVER 2024 (MSEK)
21
SUSTAINABILITY
FROM
A BUSINESS PERSPECTIVE
Within their respective businesses, JL Safety and Cedoc contribute to creating safer and healthier working environments and reducing the risk of injury in industry.
Skövde
Skara
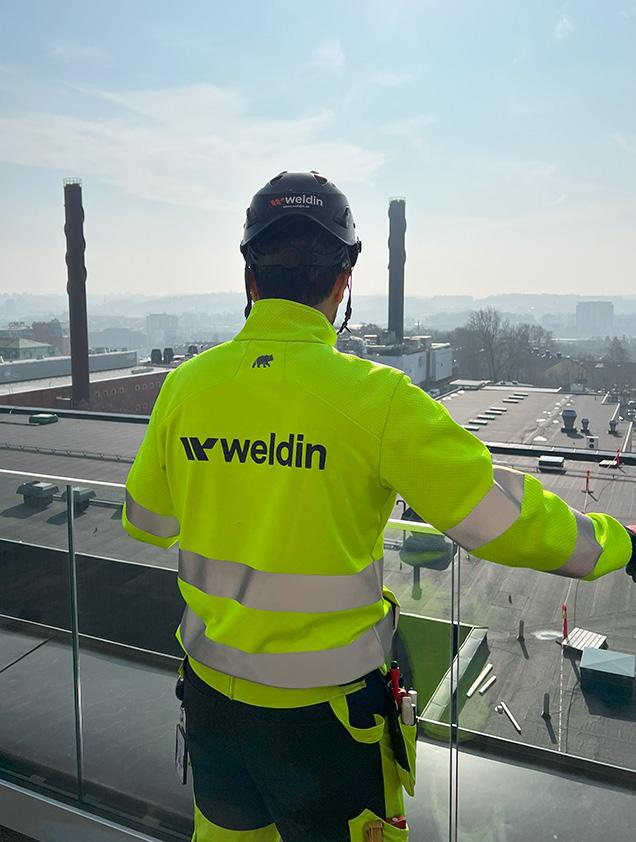
Building the industrial infrastructure of the future
Weldin Gothenburg, develops safe, efficient infrastructures for the distribution of materials and media. The company represents unique expertise in advanced pipe and tube installations for industries such as pharmaceuticals, food and the process industries.
COMPANIES
Weldin Gothenburg, Gothenburg
NUMBER OF EMPLOYEES 2024
TURNOVER 2024(MSEK)
Gothenburg
SUSTAINABILITY FROM A BUSINESS PERSPECTIVE
As consultants for companies in fields such as food, process industries and chemical industries, the company in this field of operation is part and parcel of these customers’ transition to more energy and resource-efficient production. Many customers are building new or completely renovating their facilities to meet future demands for sustainable production, and Weldin Gothenburg assists them with providing complete solutions, from planning and design to construction.
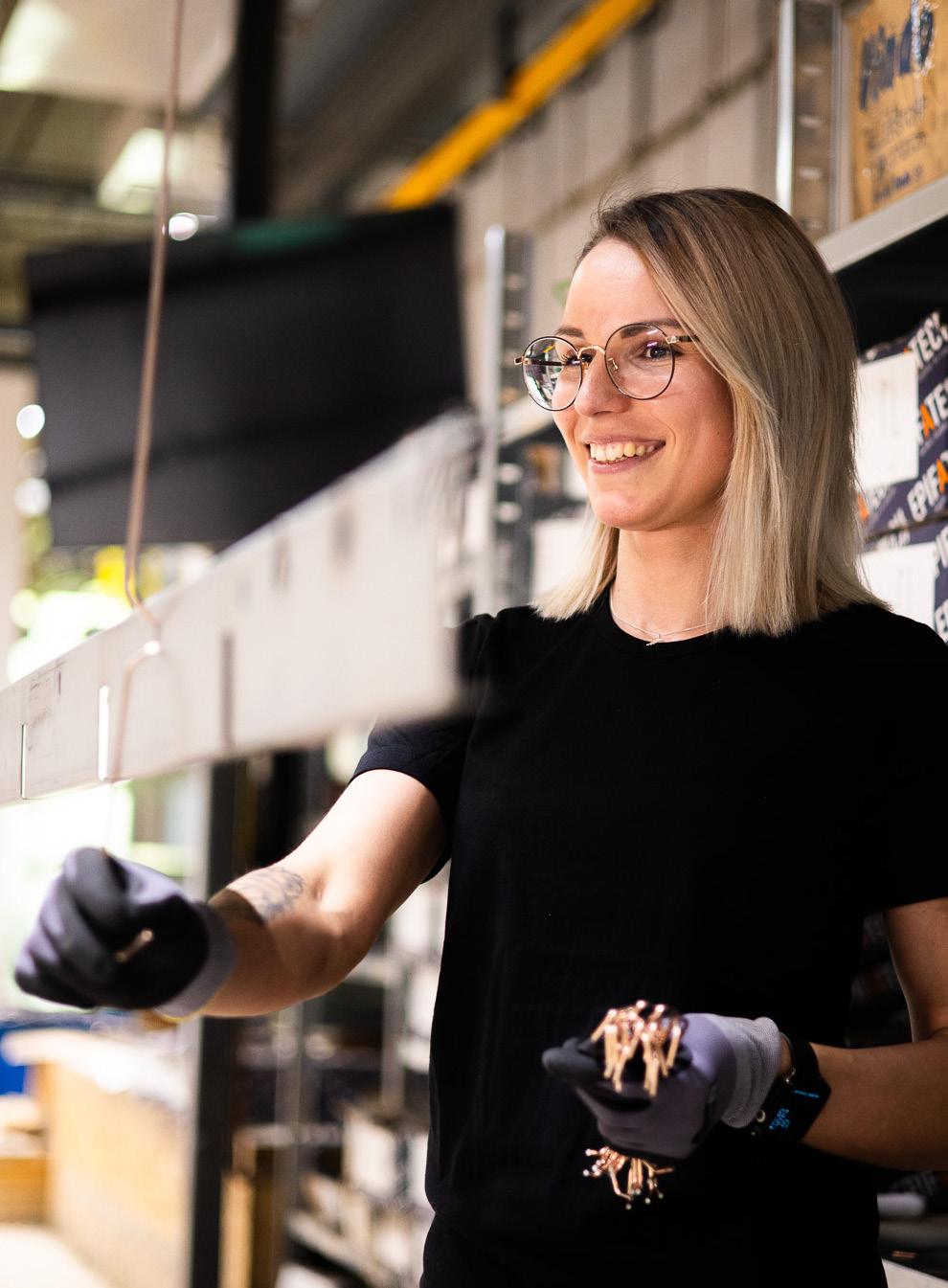
Proton Finishing
SURFACE TREATMENT
Experts in surface treatment
Proton Finishing consists of six companies that specialise in various surface treatment processes – primarily in the form of corrosion protection, but also decorative coating for customers in the automotive, construction, furniture and other industries.
COMPANIES
Proton Finishing, Forsheda
Proton Finishing, Hillerstorp
Proton Finishing, Eskilstuna
NUMBER OF EMPLOYEES 2024
Proton Finishing, Anderstorp
Proton Finishing, Anderstorp, Stans 1
Proton Finishing, Anderstorp, Stans 8
Eskilstuna
TURNOVER 2024 (MSEK)
Hillerstorp Anderstorp Forsheda
SUSTAINABILITY FROM A BUSINESS PERSPECTIVE
Surface treatment is an industry that involves extensive handling of chemicals that are hazardous to humans and the environment. By developing new, sustainable processes for reduced environmental impact, and by pursuing active personal safety measures, the companies in Proton Finishing can be seen as innovative, attractive business partners as sustainability becomes an increasingly important aspect in procurement.
THAN A STRATEGY
Sustainability work is part of our identity”
Sustainability has become an increasingly important issue for companies in today’s society, and at Proton Group, efforts to reduce our climate footprint and ensure sustainable supply chains have long been an integral part of our business strategy.
- We at Proton have come a long way in our sustainability work and are excited to continue developing,’ says Maria Thom, Sustainability Manager at Proton Group.
A long-term commitment to sustainability
Maria Thom has been working with environmental and sustainability issues in industry for almost 20 years. She began her journey at Proton Finishing in 2014 as Quality and Environment Manager and now has strategic responsibility for the entire group’s sustainability work.
‘What drives me is the opportunity to contribute to longterm thinking, for Proton of course, but also for my family, my children, my friends and my community – and yes, even for myself,’ she says.
In recent decades, sustainability issues have become increasingly important, not least because of growing expectations from the outside world.
“The most important change is that demands have increased from a range of different stakeholders. It is not only legislators who care about the environment today, but also customers, suppliers, the media and the general public,” says Maria.
CSRD – strengthening what we already do From 1 January 2025, the Proton Group will be covered by the CSRD (Corporate Sustainability Reporting Directive), a new EU directive that sets requirements for how companies report their sustainability work. For Proton, however, it is not a question of “starting” – but of systematising and highlighting the sustainability work that is already integrated into
the business.
‘We will report our strategies and goals in a transparent and detailed manner, but also how we are succeeding in achieving them. For us, it’s a way to become even better at something we are already actively working on,’ says Maria.
The directive is linked to a standard called the European Sustainability Reporting Standards (ESRS), which governs the content of the reporting.
At the same time, discussions are ongoing within the EU regarding the so-called Omnibus proposal, which may affect the scope of the reporting requirements.
“We are following developments closely, but we don’t want to stand still and wait for a decision. For us, this is important regardless – it is a natural part of our strategy and identity,” says Maria.
Making sustainability work visible can also contribute positively to business.
‘It can mean that we gain increased momentum in transition issues, that we find new circular solutions and that we become even better at taking care of our employees. It can also help us win business,’ says Maria.
Focus on climate emissions and supply chains
One of the biggest sustainability challenges for Proton Group is to reduce carbon dioxide emissions.
“Our stakeholders are clear that they want to see concrete
progress in how we reduce our climate footprint.
Another challenge is to ensure sustainability throughout the supply chain. Proton has complex flows, and it is crucial that sustainability requirements are met throughout the value chain. At the same time, there are great opportunities.
– There is a strong drive and commitment within the organisation and among the owners. We have already gained a head start in certain areas, such as surface treatment, and the entire Proton Group supports this work. In fact, our group is well prepared for CSRD.
– We are humble in the face of this task, because it really is a huge undertaking. But the fact that we have a management team that prioritised sustainability early on means that we have a stable foundation to build on. Proton has been producing a comprehensive sustainability report for several years, which gives us a good starting point.
The new reporting also requires a double materiality analysis –something Proton has already carried out. Based on this, work is underway to develop relevant targets and action plans for the most material sustainability issues.
Scientifically based climate targets with SBTi
As part of its sustainability work, Proton Group has applied to join the Science Based Targets initiative (SBTi). The organisation offers independent third-party verification of companies’ climate work and helps them set scientifically based emissions targets.
Several of our customers require us to join in order for us to be an attractive business partner. SBTi will become one of the most common ways of validating climate work in the future.
Looking ahead: continued learning and development
To stay one step ahead, Proton Group plans to produce a pilot report as early as 2025.
‘We want to have time to test processes and tools well in advance of delivering our first official report in 2026. It’s an exciting time and we look forward to developing our work further. This will give us a solid foundation for real and important improvement work going forward,’ says Maria.
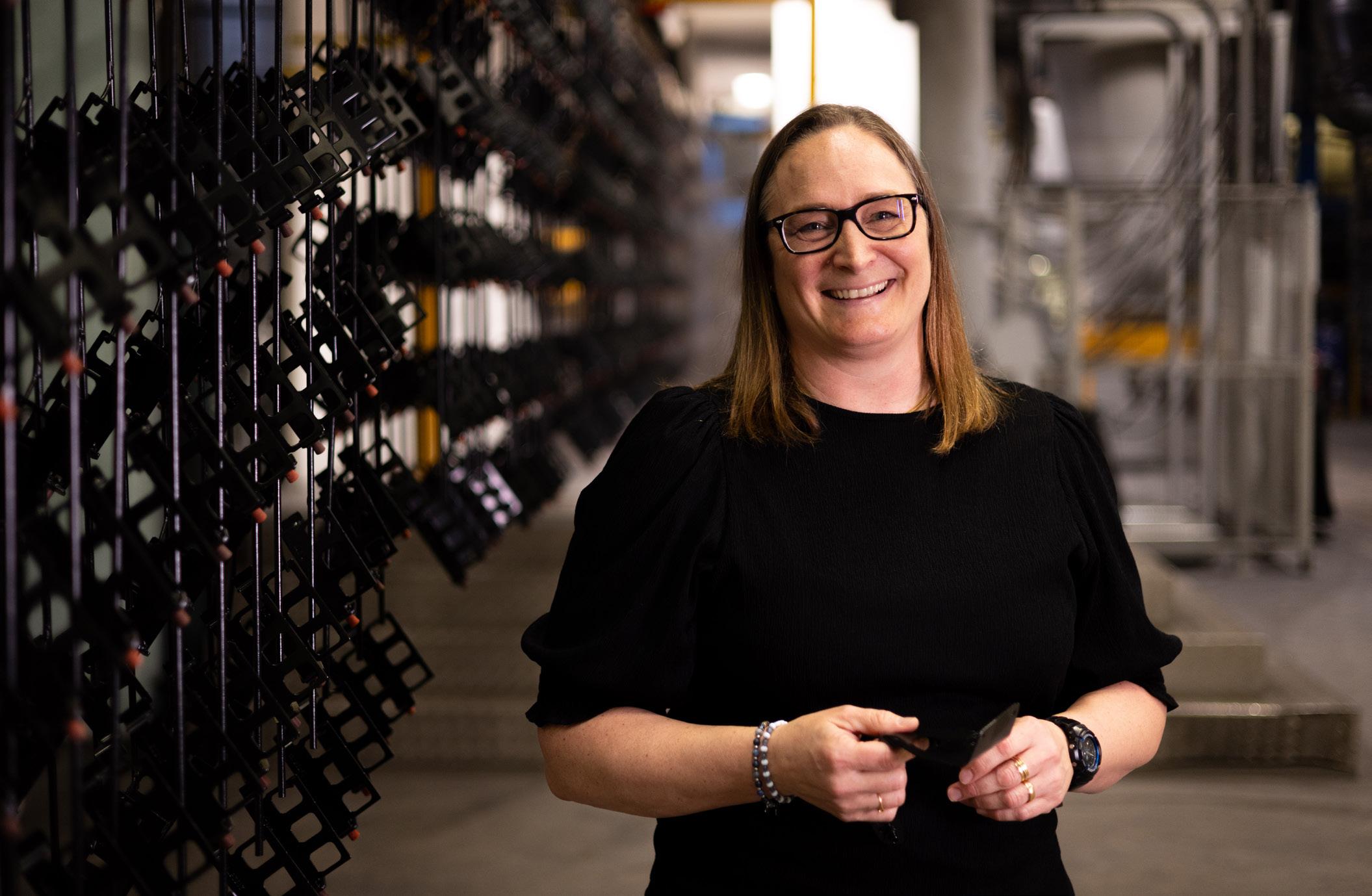
”What drives me is contributing to long-term change –both for Proton and for future generations”

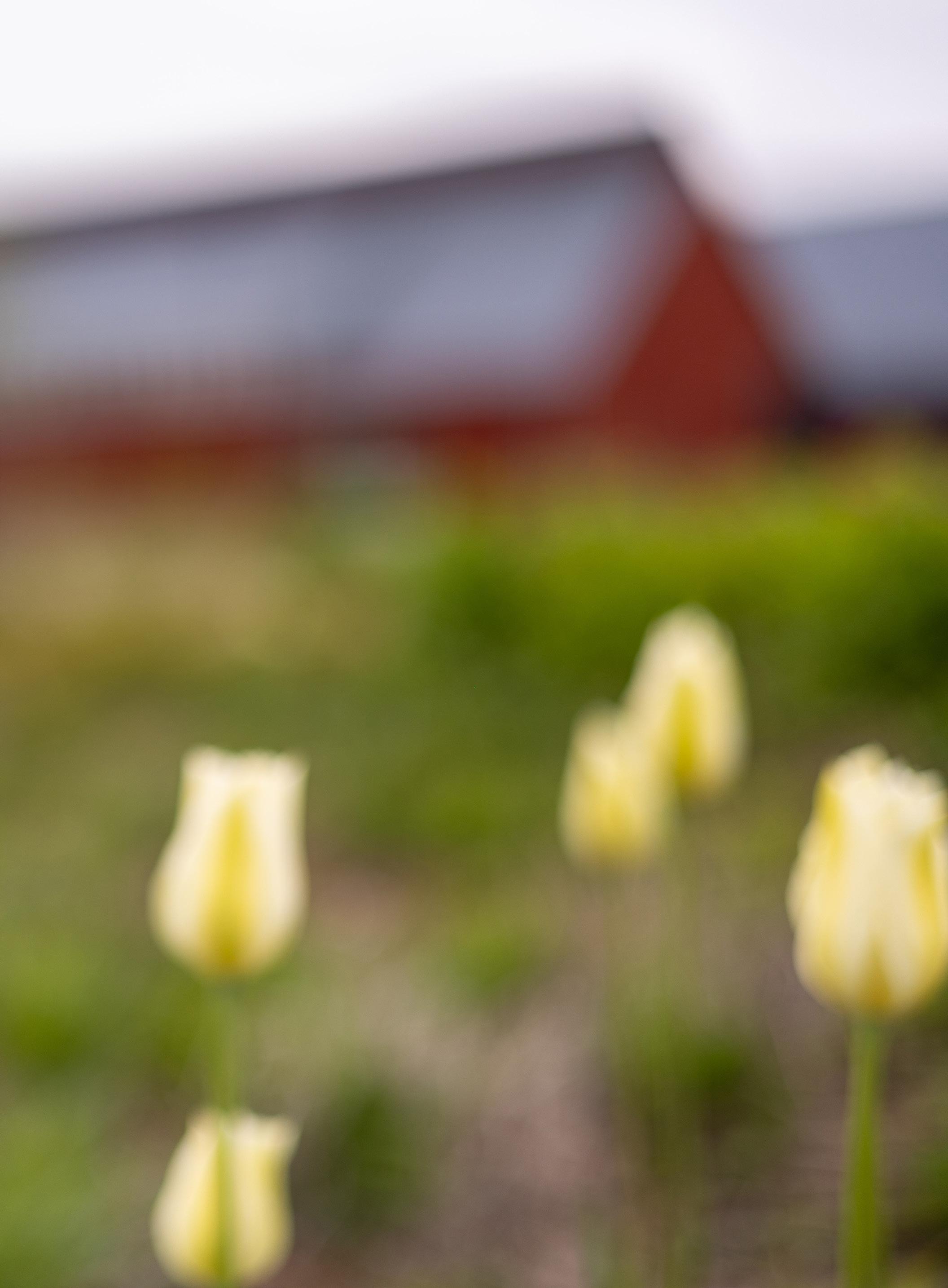
Sustainability policy
For Proton Group, sustainability means that we take active responsibility for the impact our operations have on society. Being a sustainable company is fundamental to the long-term development of our operations and business. Our ambition is to develop solutions that contribute to a sustainable world for future generations.
Proton Group sees sustainable business as a social, ethical, environmental and economic responsibility where we in all our businesses work purposefully to live by our core values of being proactive, working as a team, challenging ourselves and collaborating. We transparently assess and report our impact on society.

Enjoy succeeding together
Collaboration
Challenge
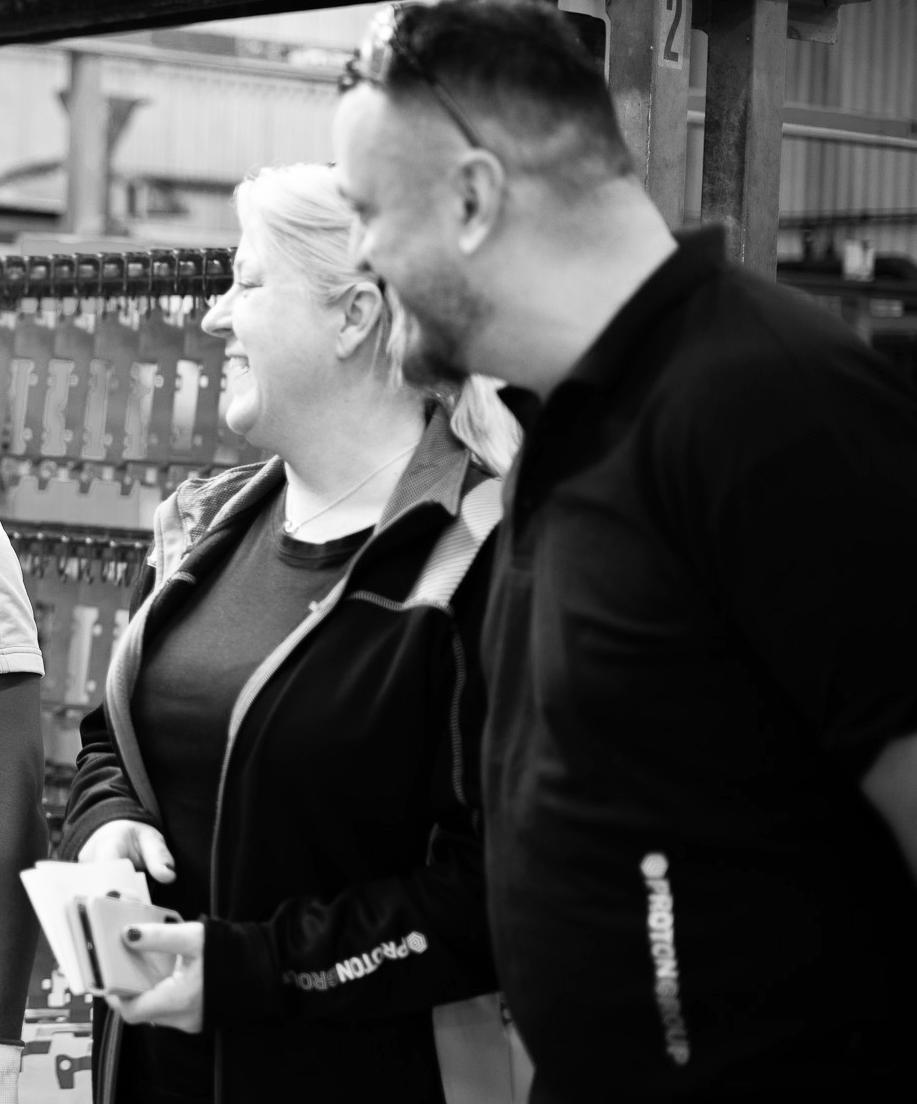
Independent individuals knitted together by one strong belief: that real success is created through collaboration. The journey towards the goal, the challenges along the way and our pride in our everyday work are the things that motivate us.
Proton’s Sustainability Strategy
Employees
We want to contribute to safe, secure working environments that allow our employees to grow. We want to make it possible for people with different backgrounds to work under good conditions. Through our products and services, we also contribute to greater safety for our customers’ employees.
ANSTÄNDIGA
SOCIA
Society
We want to contribute to a community where children and young people have meaningful free-time activities and where we can help young people to get an education, internships and jobs. So we participate in many activities with schools and associations. We also want to ensure a good working environment and consideration of the environment in our value chains, including the supplier and customer links.
ANSTÄNDIGA
Climate impact
We want to contribute to the Paris Agreement by reducing our climate footprint. As our first step, we are doing climate calculations on each part of our operations, after which we will establish a plan for how to achieve our goal of being climate neutral by 2045.
BEKÄMPA
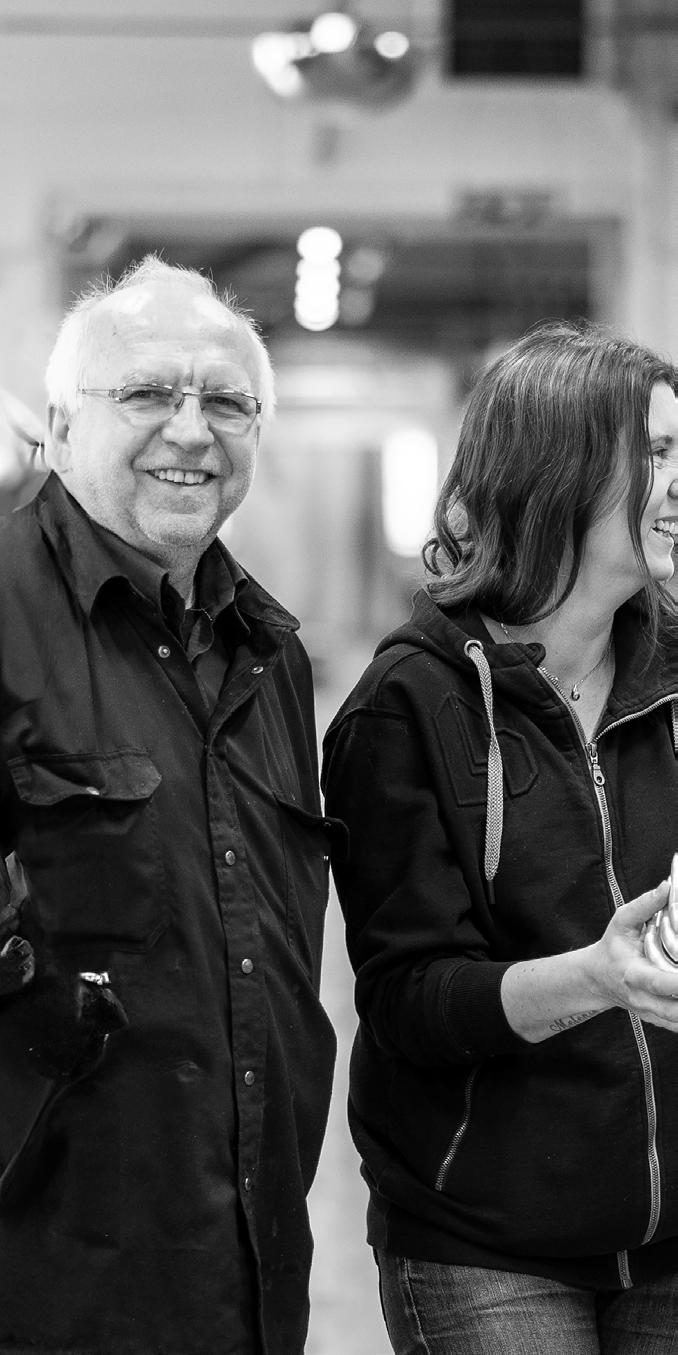
ENVIRONMEN
Our sustainability strategy is based on three perspectives: Social, Environment and Economy. Within the frameworks of each perspective, we have two focus areas where we work towards clear goals, which we monitor using key figures. The choice of perspective and focus areas is based on a risk and materiality assessment.
Development

ECONOM
We want to contribute to inclusive industrialisation and promote sustainable innovations. By developing sustainable solutions, we can add value to our customers’ sustainability measures. With our own innovative development projects, we can also make our own operations more circular.
We want to contribute to sustainable growth, where we can continue to invest in new technology, develop new products and services and develop our employees’ skills through profitable operations.
We want to contribute to a better use of resources by reducing our use of materials and preventing, reducing, reusing and recycling our waste. We also work to handle chemicals responsibly to reduce negative consequences to human health and to the environment.
Local footprint
Risk analysis
Risk area/description
Climate impact (CO2 emissions)
Our operations contribute to CO2 emissions, which have a negative impact on the climate. It would be a business risk not to reduce our CO2 emissions, because of increased demands from our customers.
Reource use
Reckless use of raw materials, electricity and water negatively impacts the environment and the economy. These risks also embrace the raw materials used, waste in production and the handling of waste in manufacturing and end use.
Materials and chemicals
Exposure to certain materials and chemicals during use can occur throughout the value chain and impact the natural environment, the working environment and people’s living environments.
Reduced faith in the brand
Not living up to legal requirements, our Code of Conduct and our stakeholders’ expectations in sustainability matters can harm our brand and our stakeholders’ faith in us.
Risks in the working environment
Within our business operations, there is a risk of accidents, injuries and illness among our employees. This can negatively affect our employee brand and our ability to recruit skills.
Culture of silence
The existence of a culture of silence creates a risk that employees don’t dare to discuss problems or report breaches of policy or our core values.
Hazardous emissions
Our operations generate noise and emissions of pollutants into the air, water and soil, which are subject to specific conditions through permits from authorities. At incidents there is a risk that we will iolate these permits.
Decline of biodiversity
In and around our properties are land areas that risk constraining biodiversity and nature’s provisioning capacity if they are not used properly.
Climate-related consequences
Heavy rain can lead to a risk of flooding of production facilities, leading to a risk of long-term production loss.
Business with countries at war
Conducting business with companies in countries at war leads to both social and financial risks throughout the value chain.
The risk analysis shows risks that have great impact on individuals, the environment and our ability to conduct business. The identified risks are general for our business and apply to the whole Proton Group. The individual companies in the group are each responsible for making detailed risk analyses of their own operations.
Risk level* Risk management
We work with tools such as our sustainability policy, climate calculation, energy audits, renewable electricity and supplier assessments.
We work strategically and practically with sustainable solutions and reduced use of resources through our sustainability policy, purchasing policy, various labels and certifications, permit terms and conditions and management systems.
We work with tools such as chemical management systems, risk assessments, replacing materials and chemicals, and supplier assessments. We also demand information on chemical content based on IMDS, REACH and SCIP.
We monitor legislation and maintain continuous dialogues with suppliers and customers.Tools such as our core values, supplier assessments and ranking, our sustainability policy, business strategy and Code of Conduct help us in this.
We continuously develop our health and safety policy and systematically develop our routines, risk analyses and assessments, safety rounds, incident reporting, employee satisfaction surveys, employee appraisals, internal training and key figure monitoring.
We use tools such as our core values, Code of Conduct, NMI tools with action plans and a reporting tool for whistleblowing.
Our operations are subject to authorisation, which means that we follow a control programme, emergency routines and a non-conformance system with regular audits and inspections.
We work in the framework of our sustainability policy, but we currently have no established routines for working in this area.
We work with risk analyses, preventive measures, emergency preparedness and crisis scenarios.
Opportunities
Opportunities to reduce climate impact through choice of materials, energy solutions, transports, suppliers and increased resource efficiency and circularity.
Opportunities to reduce our own use of materials, increase circularity and ensure long life cycle of our products.
Opportunities for increased dialogue with customers and suppliers and offer more sustainable products and processes.
Opportunities for further development of a sustainable business strategy. Cataloguing of the value chain as regards to sustainability criterias. Clearer supplier agreements and monitoring. Training of employees.
Opportunities for continuous improvement.
We use tools such as our core values and our Code of Conduct, which includes business ethics.
Opportunities for continuous improvement.
Opportunities for continuous improvement.
Opportunity to analyse how we can contribute to increasing biodiversity.
Opportunities to update risk analyses with climate-related risks for all facilities.
Opportunities for continuous improvement.
Stakeholder analysis & Stakeholder dialogue
Stakeholders
Customers
Employees
Owners & board
Type of dialogue
Sales organisation and customer support, annual customer satisfaction index (CSI), customer meetings, customer reviews, development projects, trade fairs and customer events, annual reports, interim reports, the sustainability story, website, web portals and social media, Protonen magazine.
The annual employee satisfaction index (ESI), annual performance reviews, various meeting forums in the business, safety inspections and safety committee, intranet and the Ernest business system, annual report, interim reports, the sustainability story, Protonen magazine.
Board meetings and regular reporting.
Suppliers & partners
Orders and supplier meetings, annual supplier assessments and ranking, industry associations and network meetings, customer surveys, inspections and audits, trade fairs and customer events, annual reports, interim reports, the sustainability story, the website, web portals and social media, Protonen magazine.
Authorities
Local community
Verification and reporting based on permit requirements, inspections and information transmissions, projects, workshops and seminars, regulations and updates of regulations, agreements and permits, inquiries and surveys, annual reports, interim reports, the sustainability story, web portals.
Discussions when needed, sponsorship activities, internships, study visits and open houses and events in the local area. Annual reports, interim reports, the sustainability story, website, web portals and social media, Protonen magazine.
The stakeholder analysis was conducted based on all of the Proton Group’s business activities. The prioritisation of the stakeholders takes into account both how we influence the stakeholders and how they influence us. In the coming year, we plan to conduct several stakeholder dialogues focusing on sustainability, to collect comments and expectations from our stakeholders. For businesses covered by ISO certification -Cotec Labs, Proton Engineering, Exaktor, Exlite och Proton Finishingstakeholder analyses are done for each business.
Essential questions
Industry and business requirements, fulfilment of requirements and expectations, business ethics and the Code of Conduct in the supplier chain, improvements and development, climate impact, life cycle and life time, partnership and long-term relationships, competence and knowledge sharing.
Satisfaction, fellowship and activities, the attractiveness of the workplace, various benefits and work-life balance, environmental and health-and-safety issues, skills enhancement, professional and personal development, employee spaces, tools, equipment and clothing, community involvement and security through stability and a long-term perspective.
Strategic direction, development and change, competence, growth, profitability and cash flow, satisfied workers and customers and ambassadorship, business ethics.
Sustainable value chains, long-term thinking and partnership, financial stability for the reduction of financial risks, active collaboration for improvements and development, business ethics through the Code of Conduct.
Sustainable value chains, long-term thinking and partnership, financial stability for the reduction of financial risks, active collaboration for improvements and development, business ethics through the Code of Conduct.
Adherence to laws and permits, improvements and development, long-term thinking and stability, sustainable operations and conservation of resources, measurement data and statistics.
Good to know about our sustainability story
MATERIALITY ASSESSMENT
In 2021, we worked on structuring our sustainability work. Among other things, we conducted a risk analysis (see page 34) and a stakeholder analysis (see page 36). Together with the work we have done within the framework of our work environment, environmental and quality efforts, these have formed the basis for the design of our sustainability strategy (see page 32). Our sustainability work is based on three perspectives: people, the environment and the economy. Within these, we have identified six focus areas based on our impact and stakeholder expectations. Our sustainability strategy contains long-term goals for each focus area with a link to the global goals. Short-term goals are set on an ongoing basis within the framework of each business area’s business plan.
ORGANISATION AND GOVERNANCE
Proton Group’s sustainability work is based on the company’s sustainability policy and code of conduct, both of which have been adopted by the company’s board of directors. The Code of Conduct covers areas such as business ethics, anti-corruption and human rights. Work on the working environment is systematic and based on a common working environment policy. There is also a policy on equal treatment. Most of the Group’s policies are common to all businesses. However, each business area has an environmental policy based on its own operations. Work within the Proton Group is governed and monitored on the basis of certified management systems (ISO 9001 and 14001). This governance and monitoring structure also includes sustainability work, and a sustainability forum was established
SUSTAINABILITY-RELATED POLICIES:
• Sustainability Policy
• Code of Conduct
• Health and Safety Policy
• Environmental Policy
• Equal Treatment Policy
• Guidelines for Purchasing and Procurement
• Company Car Policy
• Sponsor Policy
CERTIFIED TO:
• ISO 9001
• ISO 14001
• IATF 16949
• ISO/IEC 17025
• Safe Water
• ISO/IEC 17020 C
• SS-EN ISO 9606-1
• SS-EN ISO 14732
in 2022.The main purpose of the sustainability report is to highlight and communicate the Group’s sustainability work to stakeholders and, through structured and strategic sustainability work, to be able to report on sustainability work based on the requirements set by legislators and customers, among others. During the year, we have been working hard to prepare for sustainability reporting in accordance with CSRD, where we now need to find our way to use this to drive our sustainability work forward despite fluctuations within the EU.
Apladalen är en välkänd natur- och hembygdspark i Värnamo som vi är mycket glada och stolta över.
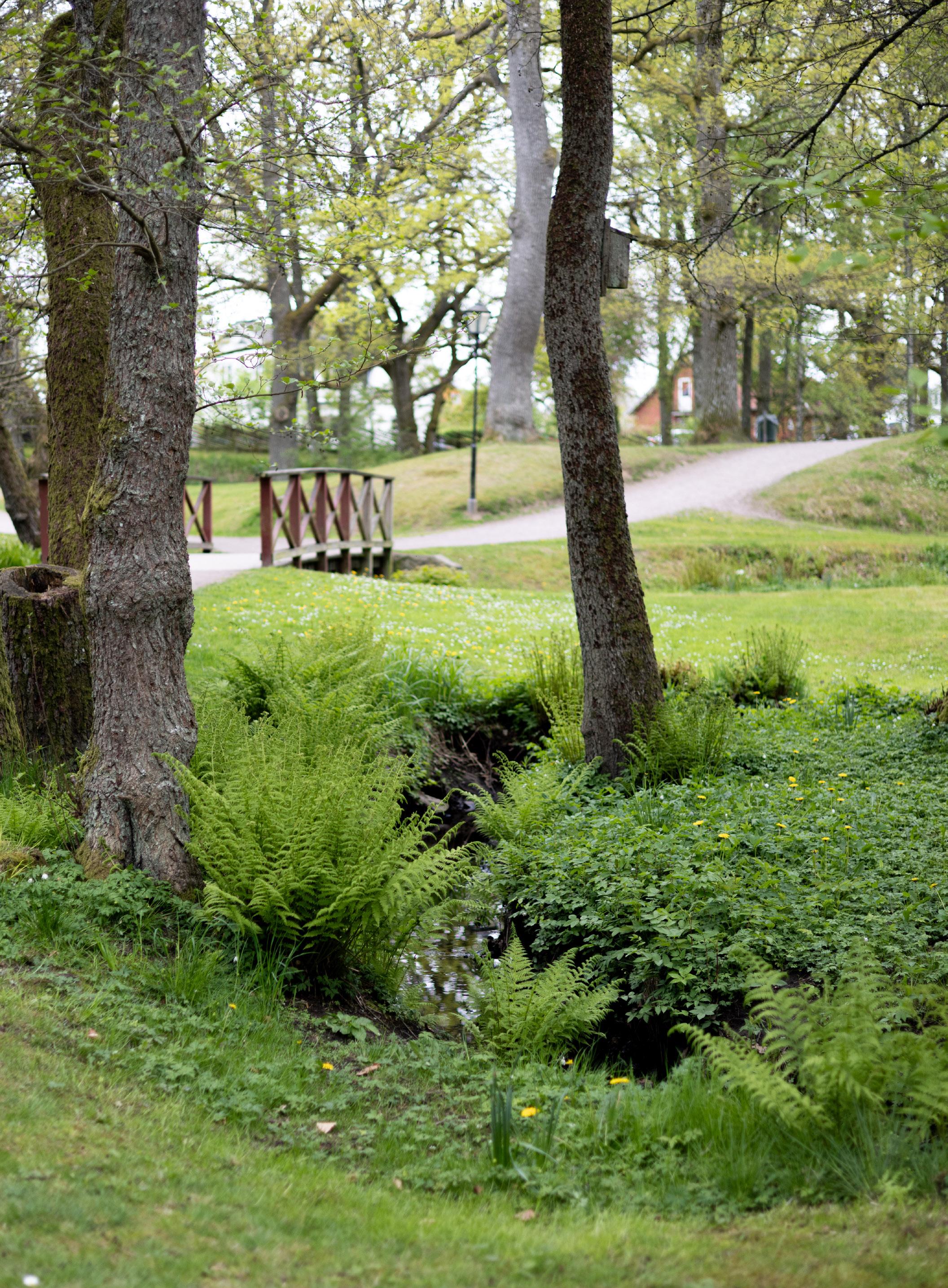
” Sustainability offers a fantastic opportunity to develop a company
David
Gustafsson, CEO
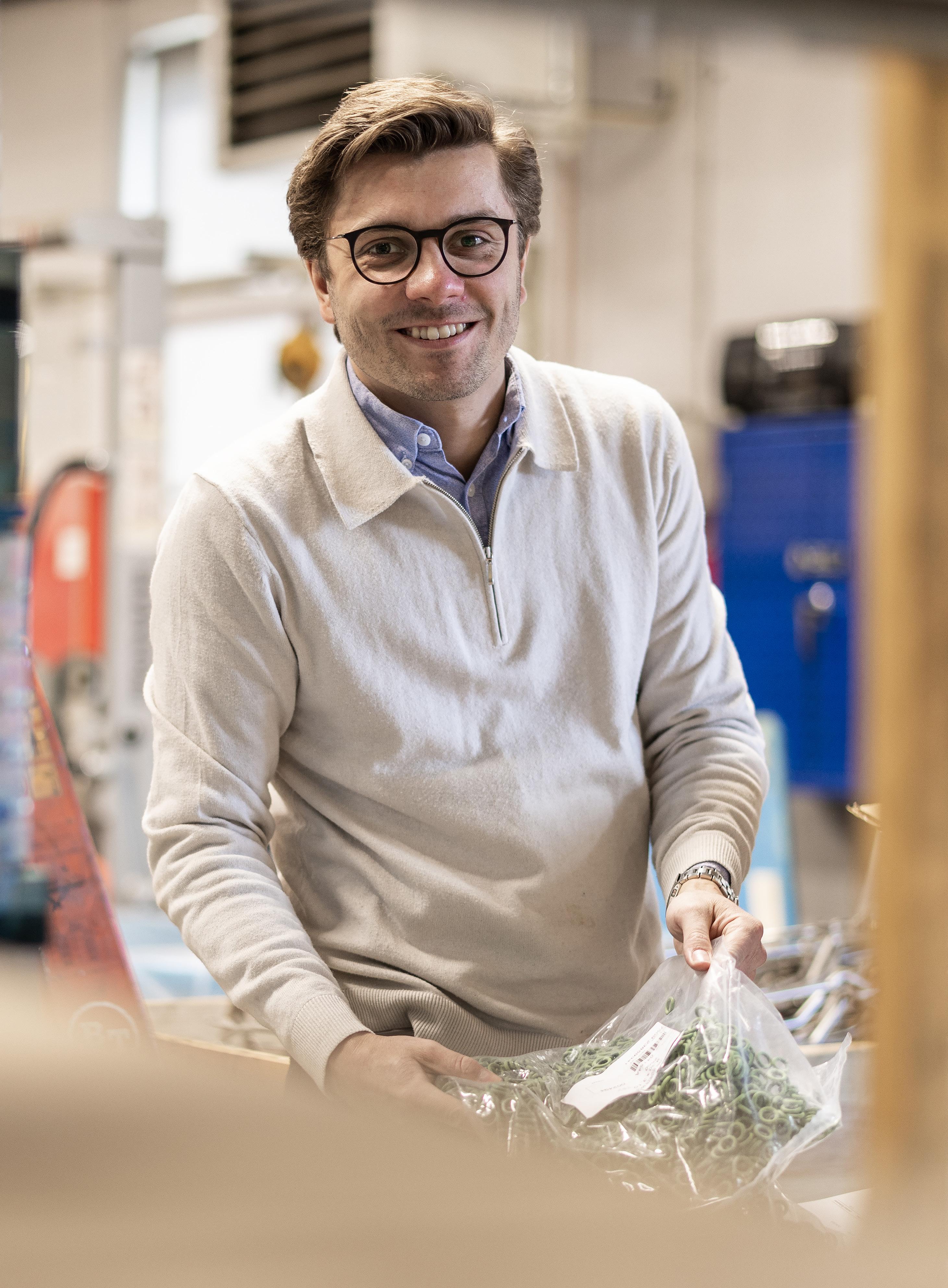
SOCIAL
Within this perspective, we work actively with ethical and social issues, primarily from a local perspective, as this is where we are able to have an influence. Our employees are important to us, and their commitment and wellbeing is a necessity for us to develop and contribute to sustainable growth. We also care about the society where we operate, and we want to be a credible actor that provides jobs and activities that enhance the quality of life for many. A large part of this is simply good common sense and is a requirement for finding the right employees and selling our products and services.
Employees
We want to contribute to safe and secure working environments that give our employees opportunities to develop. We want to enable people from different backgrounds to find work with good conditions. Through our products and services, we also contribute to increased safety for our customers’ employees.
OUR OBJECITVE
Ambassadors. By 2030, we will have satisfied employees corresponding to a score of 25 eNPS in the employee survey.
Safe workplace. The goal is to have no accidents resulting in absences. By 2030, we will have achieved 10 risk observations per incident.
Personal developmen By 2030, all employees will be offered 16 hours of training per year.
Whistleblowing. Our long-term goal is to have no deviations that lead to whistleblowing.
GOVERNANCE AND MONITORING
Our work is governed by our policy documents: sustainability policy, code of conduct, work environment policy and equal treatment policy, as well as by our management system. The CEO and business area managers are ultimately responsible, and each manager is responsible for ensuring that the work is carried out at their organisational level. We currently use our annual employee survey and employee interviews as tools for follow-up, as well as regular follow-ups in the form of audits and key performance indicator follow-ups in scorecards. The work environment is monitored on a daily basis in the form of safety rounds, risk assessments and incident reporting, which are summarised once a month via key performance indicators.
COMPLETED ACTIVITIES AND EVENTS
In recent years, we have built a solid foundation to ensure the development and well-being of our employees. We have reviewed and updated our Code
of Conduct to ensure that it is clearly aligned with our sustainability policy. In connection with a companywide leadership development programme launched in 2023, our core values were revised, resulting in four new value words. As part of our work on core values, we provide training and discuss our core values, code of conduct, harassment and whistleblowing. The CEO and business area managers are ultimately responsible, and each manager is responsible for ensuring that the work is carried out at their organisational level. We currently use our annual employee survey and employee interviews as tools for follow-up, as well as regular follow-ups in the form of audits and key performance indicator follow-ups in scorecards. The work environment is monitored on a daily basis in the form of safety rounds, risk assessments and incident reporting, which are summarised once a month via key performance indicators.
CHALLENGES AND OPPORTUNITIES
As industrial production accounts for a large part of our operations, there are risks of workplace accidents and exposure to chemicals. We work continuously to identify and implement improvements to create a good physical working environment for our employees. For example, we are systematically upgrading our fleet of forklift trucks to improve safety for both drivers and other employees in the vicinity. Being a multicultural organisation with many different nationalities also presents social and ethical challenges, where we must constantly work to create a common understanding and be attentive to language challenges and cultural differences. The ability to work persistently with both the physical and psychosocial work environment is a challenge. Making employees aware of these issues and generating commitment within the organisation requires time and energy. To strengthen the conditions for a healthy and developing culture in our companies, we have an extensive leadership development programme in place.
AMBASSADORS
eNPS (Net Promoter Score) measures a company’s attractiveness, brand and popularity among employees by answering the question: On a scale of 0 to 10, how likely are you to recommend the organisation as an employer to a friend or acquaintance? Index from -100 (worst) to 100 (best).
PERSONAL GROWTH
SAFE WORKPLACE
Accidents and risk observations, where the number of risk observations is seen as a tool for reducing the risk of accidents.
Society
We want to contribute to a local community where children and young people have meaningful leisure activities and where we can help young people get education, internships and jobs. That is why we participate in various activities with schools and associations. We also want to ensure a good working environment and environmental considerations.
OUR OBJECTICE
Contribute resources to social development. The goal is that by 2030, we will contribute to or participate in 100 different social development activities per year. Sustainable value chains. We will define a goal for our work with sustainable supply chains. Work is underway to find a way to evaluate and measure performance in the supply chain that is suitable for the Proton Group. This work has been delayed due to the introduction of CSRD legislation and ongoing changes. Nevertheless, the goal is to have a working method in place by 2026.
GOVERNANCE AND MONITORING
Our work is governed by our policy documents: sustainability policy, code of conduct, work environment policy, sponsorship policy and equal treatment policy, as well as by our management system. The CEO and business area managers have ultimate responsibility, and each manager is responsible for ensuring that the work is carried out at their organisational level. Certain environmental issues related to the local community are partly governed by our environmental policies and the audits and inspections linked to our permits. At present, we do not have any established systems for measuring and monitoring our targets in the focus area Society. Therefore, no key figures are reported for these. In 2025, we plan to design a system to measure the number of community engagement activities and the value of these contributions. The work of ensuring a good working environment and environmental consideration in our value chains requires us to review our value chains and identify the system we will work according to. This is a long-term effort that will span several years.
COMPLETED ACTIVITIES AND EVENTS
The various businesses within the Proton Group already have a strong commitment to the local community. Primarily, we sponsor various types of activities that benefit children and young people, both at group and business level. We have also supported those in need in Ukraine through contributions to the UNHCR. We also actively collaborate with universities, vocational training programmes and primary schools by offering opportunities for internships and thesis projects of various kinds, participating in teaching and getting involved in the planning and design of training programmes. For example, we are collaborating with Vandalorum Design School for children and young people, where participants get to visit Proton and learn about and try out various work tasks in the manufacturing industry. Cotec Labs collaborates with the IF Hallby association and its active work to make football accessible to all children and young people, regardless of their circumstances. Proton Lighting has a well-established collaboration with Samhall, where people who would otherwise find it difficult to enter the labour market are offered jobs in production. Through employee initiatives, both our employees and the Proton Group have supported Hela Människans work for vulnerable children, ‘Hjärta för barn’ (Heart for Children), with money and Christmas presents at Christmas time and a clothing collection. Proton’s commitment to Campus Värnamo’s production development programme was recognised with the award for ‘Collaborative Company of the Year 2024’, presented by Värnamo Näringsliv.
CHALLENGES AND OPPORTUNITIES
The fact that Proton Group is seen as an active and valuable force in society strengthens our brand among customers and stakeholders and makes it easier to find attractive employees. To strengthen its ability to take environmental, social and ethical responsibility, Proton has already developed a double materiality analysis in connection with the business’s work to adapt to the new sustainability legislation (CSRD). This identifies risks and opportunities from a sustainability perspective throughout the value chain, which provides a good basis for improvement activities within our various operations and for our stakeholders.
ASSOCIATIONS AND ORGANISATIONS THAT PROTON GROUP IS INVOLVED IN OR CONTRIBUTES TO
• IFK Värnamo’s Soccer school
• Vandalorum’s Design school
• Värnamo Hockey
• Hjärta för barn
• Värnamo Tennis Club
• Värnamo Gymnastics Club
• Skara Hockey
• Ardala Soccer Club
• Skara Handball
• Lundsbrunns Golf Club
• IF Hallby Soccer Club
• Götaström’s Golf Club
• Gislaved Hockey
• Lion’s Club
• Active School
• Lidköpings Riding Club
• Värnamo Södra FF Soccer Club
• Smålandsstenars Swimming Club
• International Friens
• Production development Campus Värnamo
• Värnamo Wrestling Club
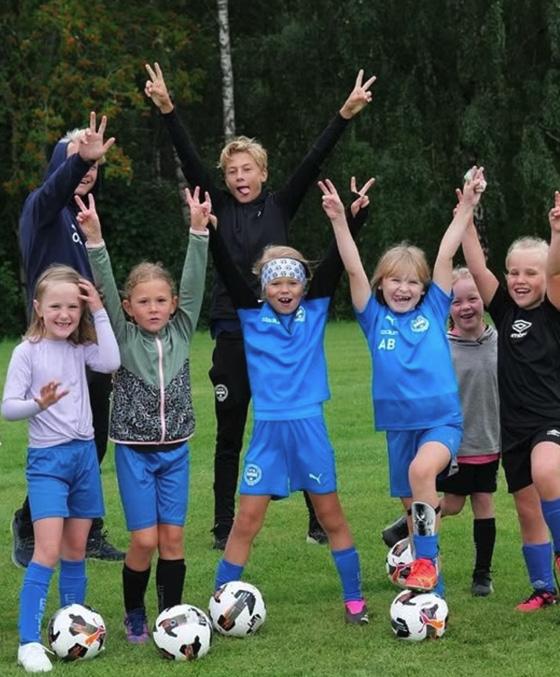
• Smålandsstenars GoIF Soccer Club
• Värnamo Golf Club
• The Confederation of Swedish Enterprise
• SYF (The Swedish Electroplaters and Surface Finishers Society)
• FKG (The Scandinavian Automotive Supplier Association)
• River Lagan water conservation association
• Forsheda business association
• The Hillerstorpare community association
• River Nissan water conservation association
• Anderstorp business association
• NCA (Nordic Coating Association)
• Halland’s entrepreneurs’ network
• El-kretsen
• Swedish electrical wholesalers’ network
• SIS Standards Institut
• Värnamo Näringsliv business association
• Säker vatten (Safe water)
• NPA - The Swedish Business Producer Responsability
• Skövde University
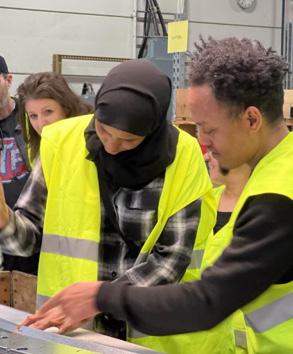
As a
For the twelfth year, Proton is the main sponsor of IFK Värnamo’s football school for children and young people.
corporate friend of International Friends, we create opportunities for new arrivals to integrate into Swedish working life.
Values that drives us forward Culture, leadership and the courage to change
How do you build a strong corporate culture that lasts – even when the world around you is changing rapidly? For us, the answer began with what many would call soft values, but which we believe will have a decisive effect on leadership, collaboration and growth. With a new set of values, concrete training and strong commitment from the entire organisation, we have embarked on a cultural journey that is already influencing everyday life, conversations and people’s development.
Almost two years ago, work began on developing a new set of core values for the entire Proton Group. All operations have been involved in defining the values and behaviours that will carry us forward – with a view to achieving the ambitious growth targets we have set. ‘The core values are strongly linked to our vision. By living them, I am convinced that we are moving closer to our ambition – to build a culture of growth where
both people and the business develop,’ says David Gustafsson, CEO of Proton Group.
When the work began, all the leaders in the group gathered to identify four values – Proactive, Team Spirit, Challenge and Cooperation – with clear behaviours linked to each word. Together, they form PLUS, our new compass for everyday life. A positively charged particle – just as we want Proton to be.
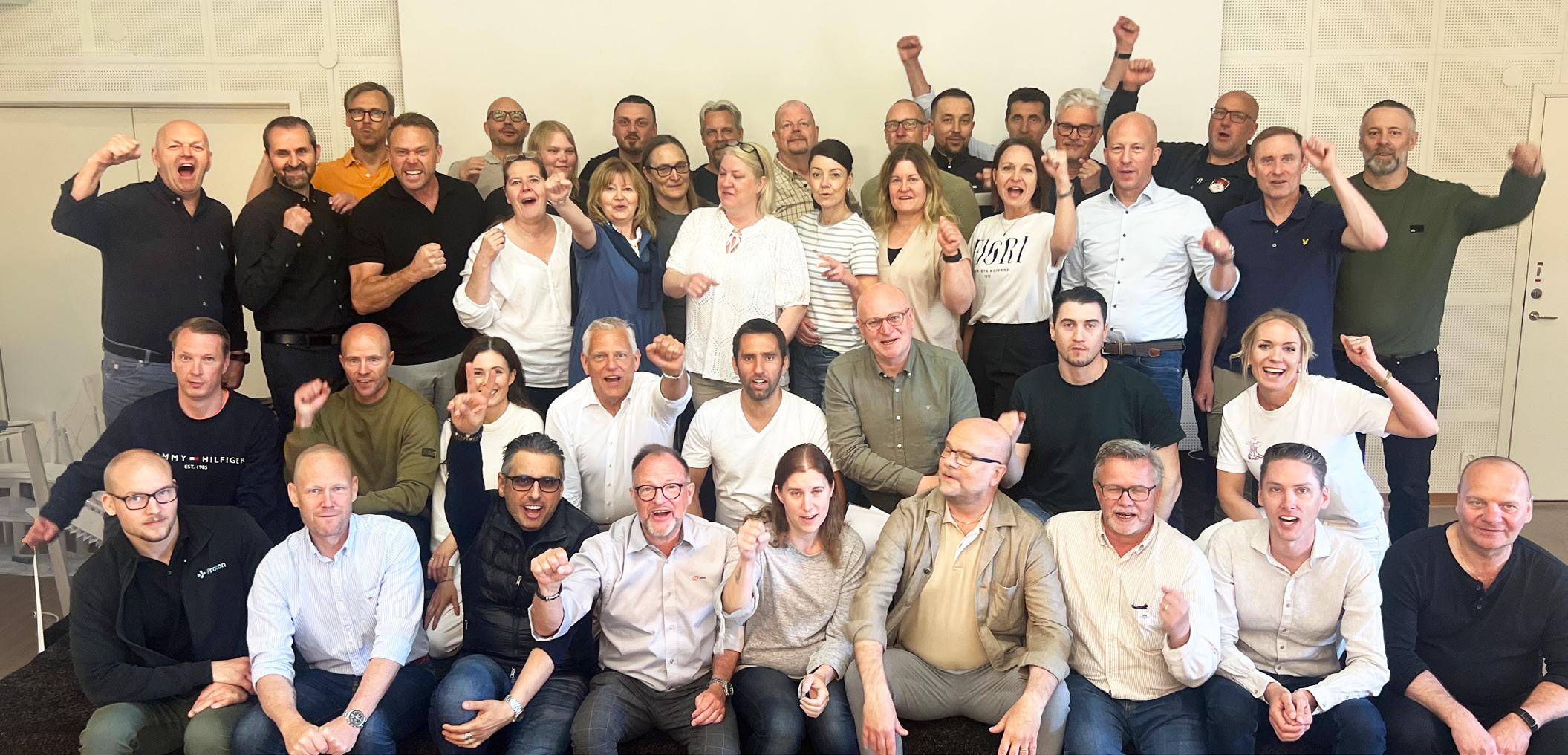
Proactive, Team work, Challenging. Cooperation - our leaders live PLUS every day!
‘What got us here won’t take us further. We need a new way of thinking and acting. That’s why it was important for all managers to be involved in the development process. But this is a joint journey – which is why all employees are highly involved in bringing our core values to life,’ says Mari Lundqvist, HR Manager.
From insight to tools – development in practice
The work on core values has gone hand in hand with a comprehensive leadership development programme, in which all managers have received both education and practical training. The focus has been on strengthening self-leadership, developing a coaching approach and creating security in the leadership role. Through concrete exercises in areas such as reflection, feedback, communication and team building, managers have been given tools to lead not only others, but also themselves. The training has also provided time and space to build relationships and learn from each other across company boundaries, which further contributes to increased consensus and cooperation throughout the Group.
“We have succeeded in getting the content and level right. Many have grown both in their leadership roles and as people. Several have really come to the fore. We have built bridges between the companies where everyone can help each other. It is clear that real development is taking place when we put what we have learned into practice.
From project to process – and beyond
“What power there is when you bring together so much expertise and commitment! This is not a temporary initiative, it is a process we will live every day,” Mari continues.
And that is precisely what is noticeable – that the core values are actually used in everyday life.
“I hear employees talking about our behaviours, and also when we have not really lived up to them. That’s when we know it’s really starting to take root.
And the fact that our core values are part of everyday
life is something that is noticeable.
– Sometimes I hear people talking in the corridors about our core values and the behaviours we want to promote – and also about when we may not have lived up to those values. That’s how it should be – alive and present in our culture.
The next step
The need for continued development is clear.
– As a person and a leader, there are always things to develop. The journey doesn’t end here; we are planning many different types of initiatives. For example, we have worked to strengthen our leaders in fundamental areas such as the code of conduct, labour law and the work environment. But work is also underway to create more targeted initiatives that leaders encounter in their everyday work. Examples include how we create a sustainable work environment for everyone and how we recruit and work with skills development initiatives in a professional manner, says Mari.
– What has made the biggest impression? The positive attitude. So many people really want to develop – and we have created a safe environment where people dare to grow together. That gives incredible strength!
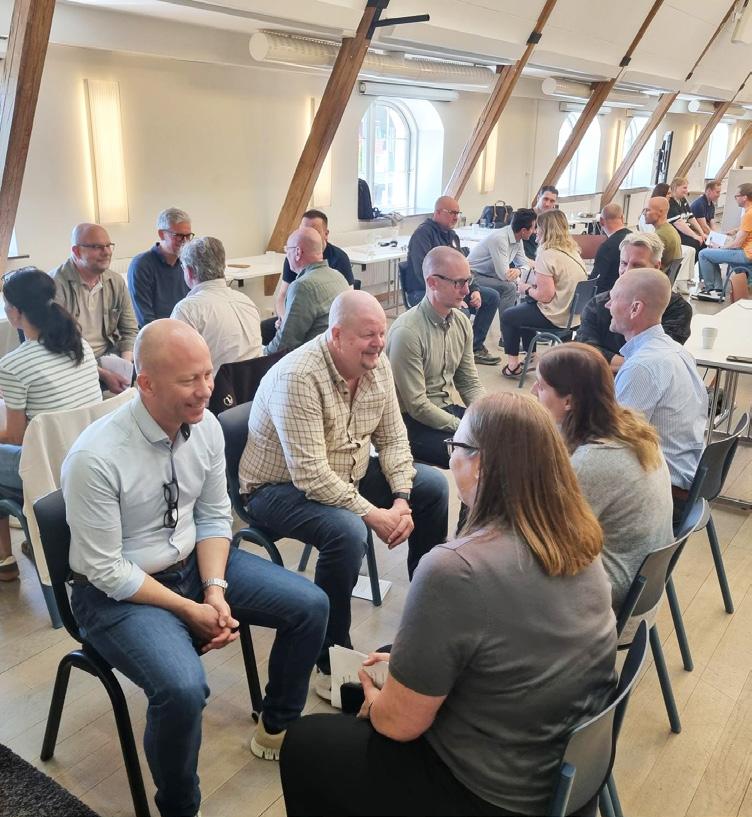
Giving and receiving feedback requires confidence, and is an important step in building the culture we want to live every day.
The children in our hearts When caring makes a difference
Proton Group takes wholehearted responsibility for creating long-term impact through local roots and a focus on children and young people. By strengthening local influence, children’s development and safety in the community, we strive to build a sustainable future in the places where we operate. With a broad local focus, we want to make a difference – and we are convinced that a better world starts with investing in the next generation.
Proton Group has a strong social commitment that permeates everything we do. Our commitment to children and young people is about more than just one-off initiatives. We work with schools and associations to give young people the opportunity to participate in activities, learn new things and find meaningful leisure activities. Many children lack the resources to participate in sports, culture or other leisure activities – sometimes for financial reasons, but also because of other obstacles such as mental or physical ill health. Through our initiatives and partnerships, we want to help give more children that opportunity.
Employee initiatives that bring hope and joy
But it’s not just about financial support. It’s also about creating connections and relationships. Proton Group also supports initiatives that promote
safety and inclusion. Many children and families in vulnerable situations do not get to experience the magic of Christmas that so many of us take for granted. That is why, in Christmas 2024, we started a Christmas gift collection for Hjärta för barn (Heart for Children), part of Hela Människan – LP Finnveden in Värnamo. The organisation works to support children and young people in families living in various forms of vulnerability and offers a safe place where they can get help, support and opportunities for change. The Christmas gift collection was a completely voluntary initiative where employees within the Group had the opportunity to contribute to a brighter Christmas for these children by spreading kindness and value to the families who need it most.
”It really warms the heart to be able to contribute to Hjärta för Barn and their work with children and young people. Our Christmas gift collection initiative is a way for us to spread hope and joy to those who
need it most, especially during a time that should be characterised by community and caring. Seeing the commitment of our employees and knowing that together we have made Christmas a little brighter for these families is something that really touches us. We hope that our support will inspire more people to get involved in this important work,” says Emma Ohliw, Marketing and Communications Manager at Proton Group.
The Christmas gift collection was the start of something bigger. The strong commitment among our employees led to a fundraiser that was donated to Hjärta för Barn – a contribution that made a real difference to families in our local area.
But it didn’t stop there. The fundraiser inspired us to continue supporting the organisation in other ways. In the spring of 2025, we therefore launched a joint clothing drive. The need for clothing is great, and through this initiative, we hope to further support
vulnerable families and give them a safer and easier everyday life.
Everyone is important
A safe adult – whether a teacher, leader, neighbour or volunteer – can make all the difference in a child’s life. We are proud of the commitment shown by our employees and look forward to continuing to show our support for Hjärta för Barn and other important organisations around us.
At Proton, we do what we can to create improvements that make a real difference. We are committed to a better future for children and young people and want to encourage more people to get involved, to see the children around us and to help give them a brighter future.
Together, we make a difference!

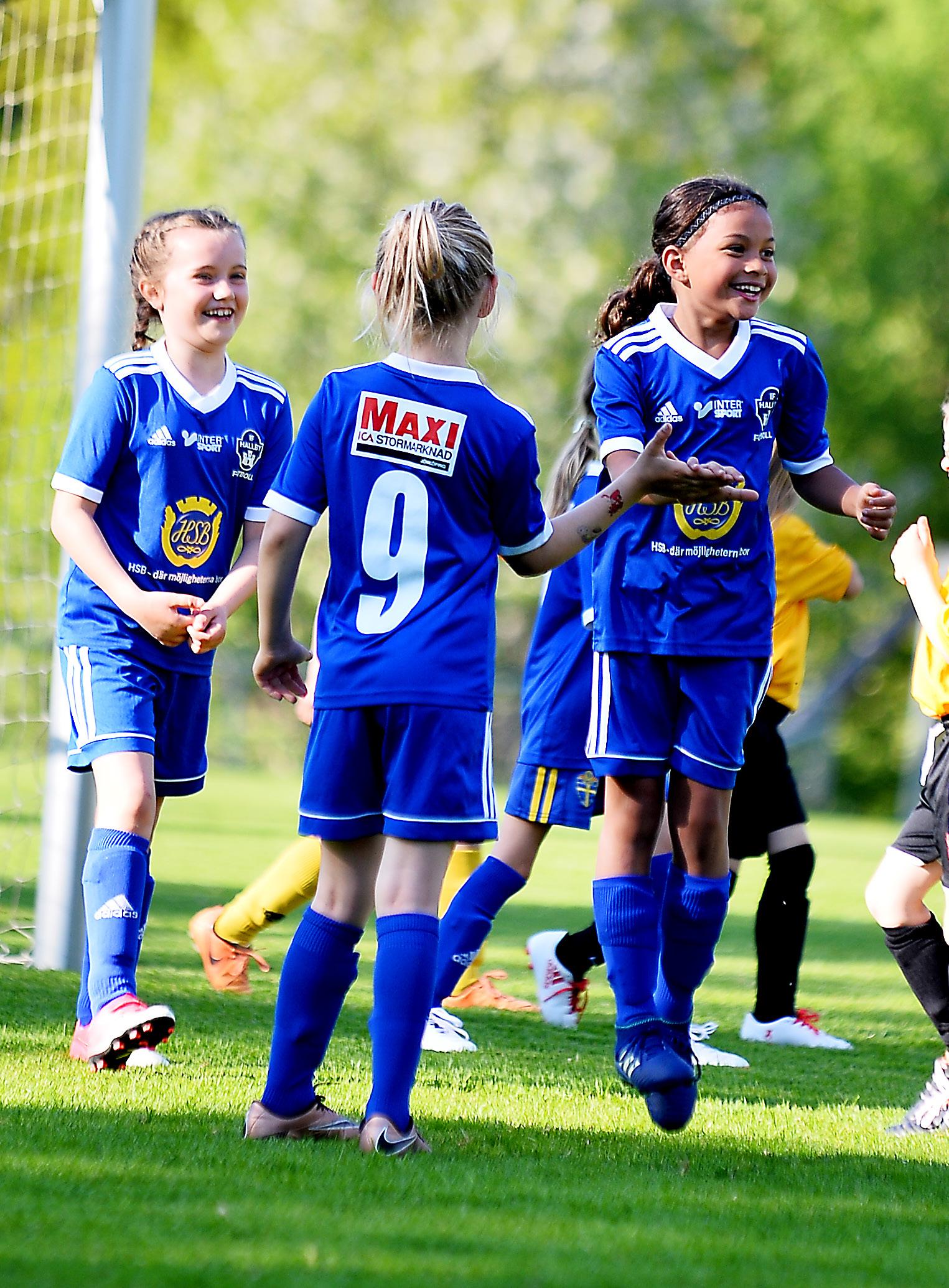
COTEC LABS
The future starts with fair play
Creating sustainable communities is about people. About children who dare to grow, young people who are allowed to develop – and environments where everyone feels included. That is why we are proud of Cotec Labs’ sponsorship and commitment to IF Hallby Fotboll and their initiative Blå vägen (The Blue Path) –a policy document and a direction for the future that permeates the entire organisation with security, respect and inclusion. By supporting IF Hallby Fotboll, we can contribute to just that: a safer environment where children and young people can develop – both as footballers and as fellow human beings.
IF Hallby Fotboll is one of Jönköping’s largest clubs. With over 750 active players in 26 teams, nearly 150 dedicated leaders, and a clear focus on children and youth activities, Hallby is a role model in Swedish grassroots sports. Everyone should feel welcome here, regardless of their background, circumstances or level of ambition.
Clear guidelines for leadership, values and safety
In 2019, the club adopted Blå vägen (The Blue Path), a policy document that permeates all youth activities. The document sets guidelines for leadership, values, training and safety. It is based on a child rights perspective, recommendations from the Swedish Sports Confederation and Bris, and the club’s own experiences. Safety, respect, joy and community are the cornerstones here. It is clear that everyone is equally valuable, that everyone has the right to develop at their own pace – and that leaders have a responsibility to create a safe, drug-free and respectful environment. ‘We want to ensure the quality of the experience for children and young people at IF Hallby. Here, you should feel safe – as a player, leader or parent,’ says
Joakim Ekström, senior coach for women’s football and Marketing and Sales Manager at Cotec Labs
For every child’s right to participate Football is a sport for everyone. But for some families, training fees, camps or tournaments can be a barrier. The Hallby Fund was established so that no one has to be left out. It is a support fund that enables children to play, regardless of their financial circumstances. It is an important piece of the puzzle in the club’s work to promote inclusion. It’s not all about football. It’s just as much about seeing each individual. Listening, understanding and helping them grow.
To feel secure - every day
The Blue Way is implemented in everyday life. Through leadership training, daily dialogue and clear expectations, a safe environment is created where children support each other – not complain. Where leaders are role models, not just coaches. Where Fair Play is more than words: it is a culture.
“It actually works. The children feel better. Team spirit is strengthened. And when something goes wrong – a bad attitude, a transgression – there are tools and a
willingness to quickly rectify the situation. It’s not just a club. It’s a community,” continues Joakim.
Everyone can participate – on their own terms
Cotec Labs has supported IF Hallby Fotboll for over five years. The logo adorns the left sleeve of over 900 match shirts – from the 4-year-olds’ football games to the women’s and men’s senior teams. But our support is more than just visibility. It’s a concrete way to contribute to social sustainability at the local level.
We are particularly proud that our support also makes initiatives such as Bollkoll possible – an inclusive training programme for young people with functional variations. Here, everyone can participate on their own terms.
- When local businesses step in and take responsibility together with clubs, we build strong communities. That’s real sustainability, says Mattias Flodin, chairman of IF Hallby Fotboll.
Security, joy and community
Club life in Jönköping is driven by volunteers, local businesses and a big heart. IF Hallby helps out when the city needs volunteers, coaches are trained with support from sponsors, and children get more than just training – they get security, friends and hope for the future.
For Cotec Labs and Joakim, the partnership with IF Hallby Fotboll is a no-brainer.
‘We’re not just sponsoring a football club – for us, it’s an investment in community and inclusion.’
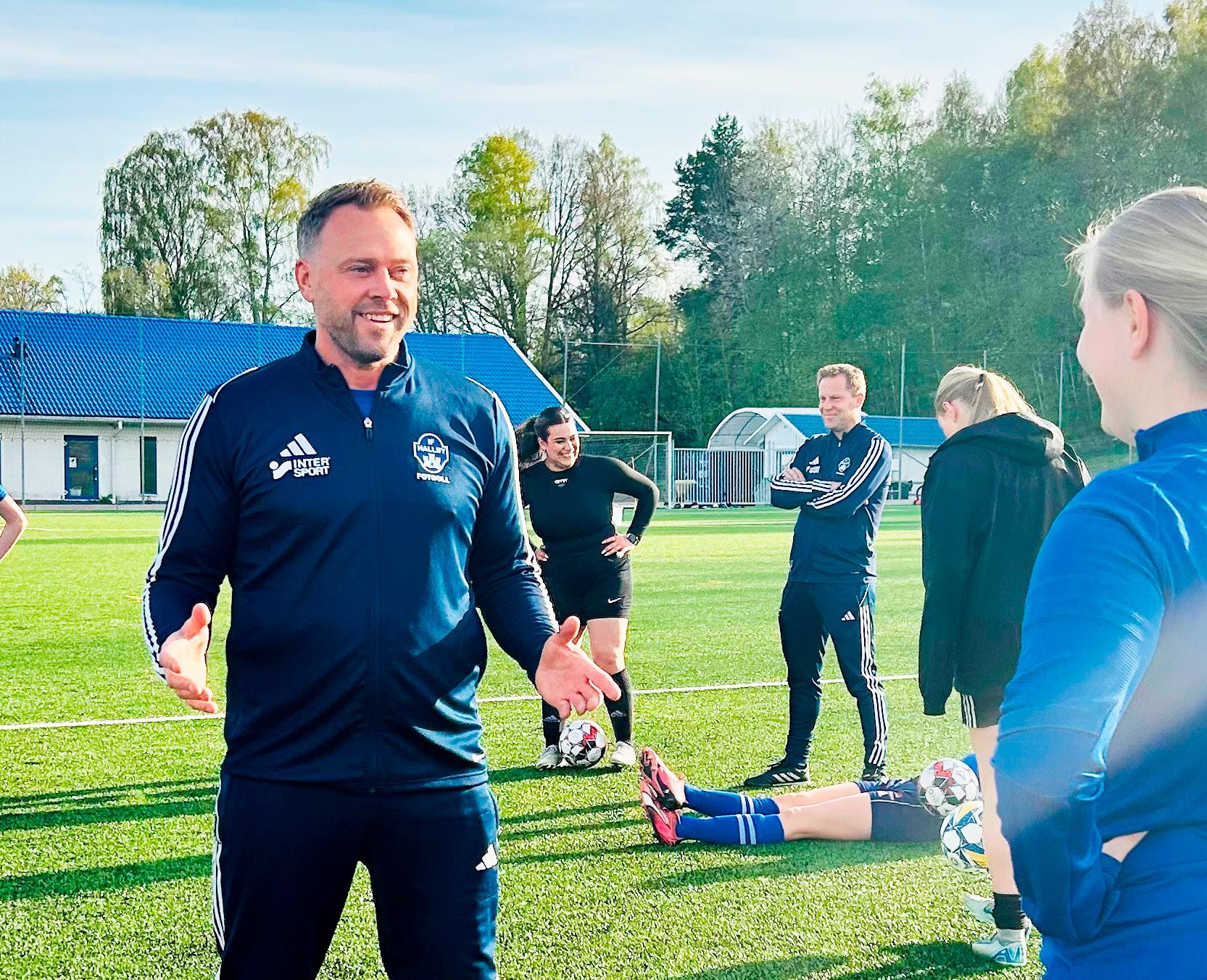
Joakim Ekström, Sales and Marketing Manager at Cotec Labs, is senior coach for IF Hallby’s women’s team and has been involved with the club for many years.
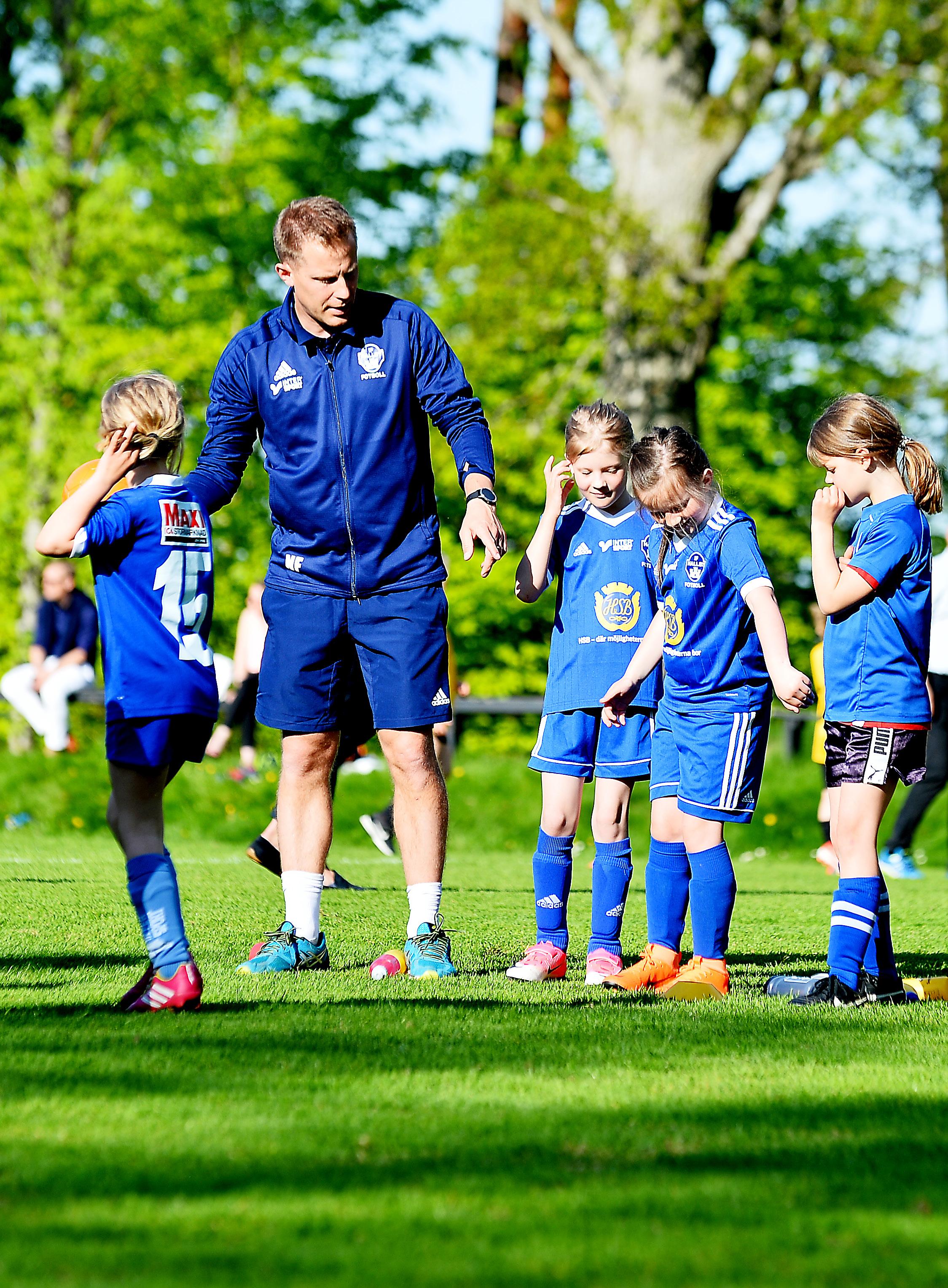
As a leader at IF Hallby, you are involved in supporting, inspiring and showing the way both on and off the pitch.
CEDOC and EAB make Sweden’s workplaces safer
Under the motto ‘Built to last’, EAB supplies warehouse interiors, doors and steel buildings to customers all over the world. But it’s not just the robustness of the products that’s important. Offering a long-term sustainable and safe workplace is priority number one. That is why they have chosen to work with CEDOC.
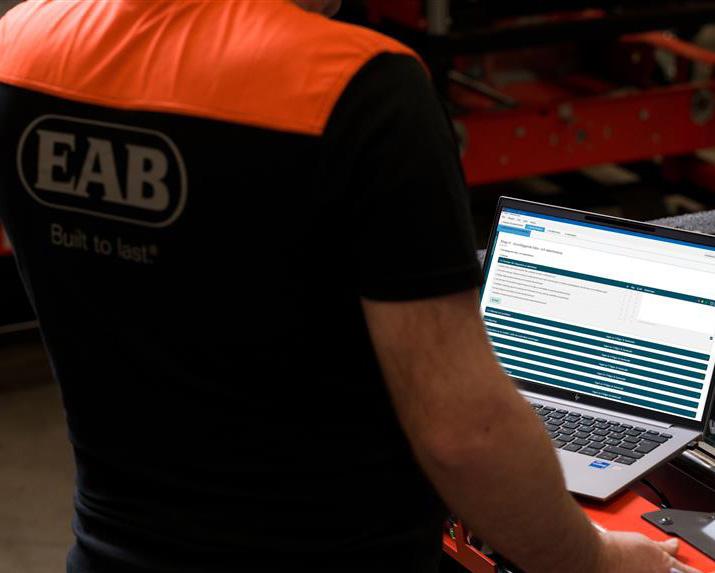

”With CEDOC we get the
support
we need. We
know
that
we have checked all the points and thus fulfil the legal requirements of the Machinery Regulation.”
The family business EAB was founded in 1957 and has since grown as steadily and stable as its solutions. The head office and production are located in Smålandsstenar and the group has over 400 employees. Europe, North America and Asia are EAB’s main markets and about a quarter of production is exported.
Important part of sustainability
In terms of production, it is a classic engineering industry with a focus on pressing, cutting and welding,’ says Anders Olsson, CE coordinator at EAB.
- We have a strong focus on a safe working environment as part of our sustainability work, and machine safety is an important part of this. We
are careful to follow up all our machines to ensure that they are safe and meet the requirements of the Machinery Directive, both in connection with commissioning and during ongoing production. For the past five years, the EAB has been working with the CEDOC risk assessment and documentation software.
- With CEDOC we get the support we need. We know that we have checked all the points and thus fulfil the legal requirements of the Machinery Regulation. Of course, the fact that we get the documentation on the purchase makes it much easier and makes the work more efficient, says Anders Olsson.
Anders Olsson, CE coordinator at EAB.
”By working in a structured way with machine safety, you can avoid many accidents that can have consequences for both the individual employee and the company.
Safety culture in the organisation
Anders Olsson emphasises that legal requirements are not the main driver for risk assessment work at EAB. The job is just part of life and EAB’s employees should feel confident that they will come home safe to their families in the evening.
- For us, employee safety is the ultimate goal. Complying with the Machinery Directive is a very good foundation, and on top of that we are working to spread a safety culture in the organisation. I think we have built a good general understanding of
how important these issues are,’ says Anders, who believes that knowledge of machinery safety is still limited in large parts of society.
- Unfortunately, I believe that there are some gaps in our knowledge about the demands placed on us in industry. If you work in a structured way with machine safety, it is possible to avoid many accidents that can have consequences for both the individual employee and the company.
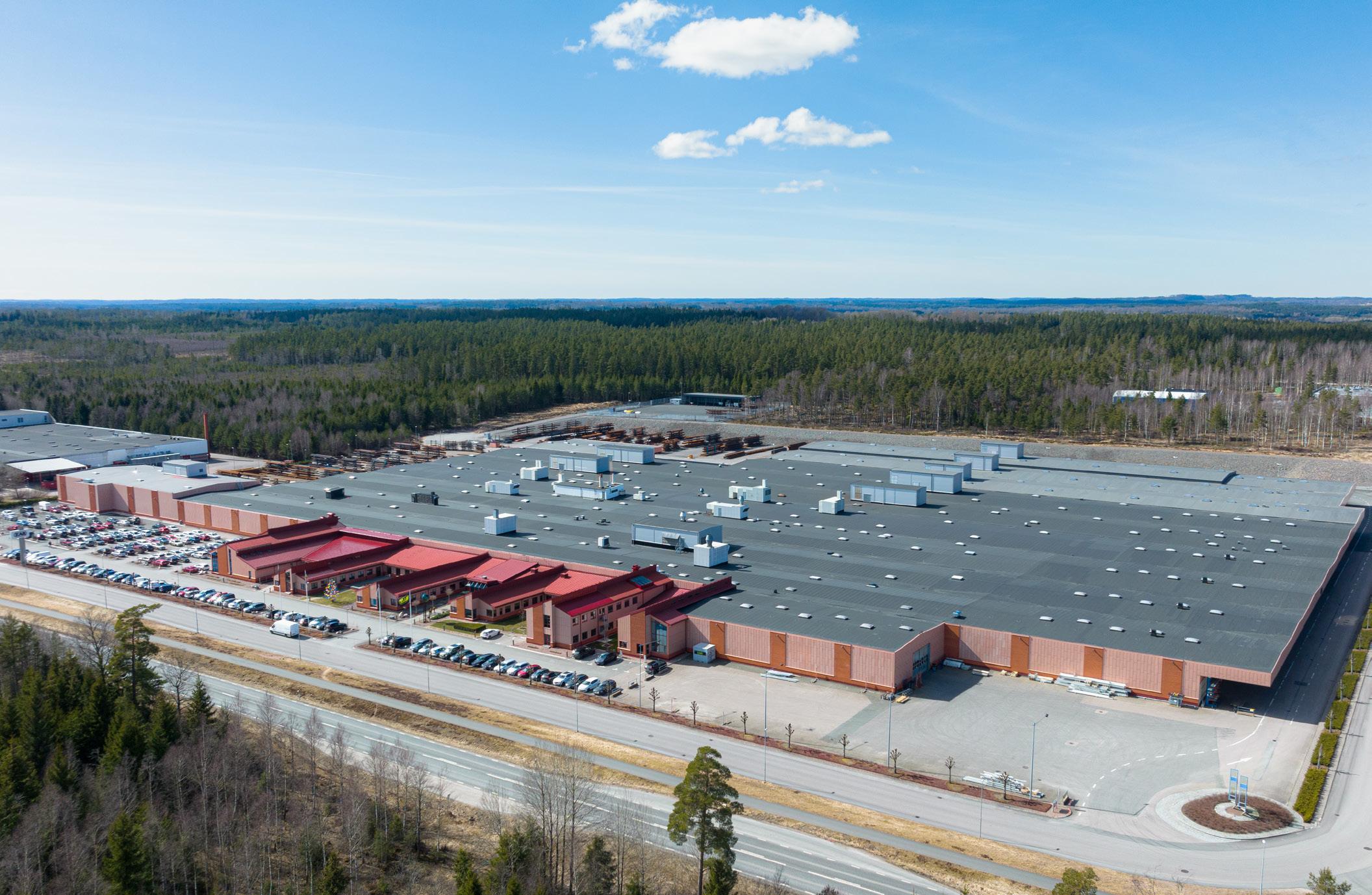
EAB has both headquarters and production in Smålandsstenar.
Test pilot in development
Using CEDOC in risk assessment work is a good way to lower the thresholds for those who find it difficult to structure safety work. That is why EAB and Anders Olsson have also chosen to participate as test pilots in the further development of the software. A way of contributing both to their own organisation’s security - and to that of others.
- We are currently evaluating the latest version and have provided some input and requests for further improvements,’ says Anders Olsson, who recently signed a new three-year contract for the software.
For Max Dahlbom, sales manager at Cedoc, EAB’s involvement is a source of inspiration in the work of spreading knowledge about machine safety.
- The fact that EAB thinks long-term about its sustainability work and is involved in developing our software in this way is very valuable. We will be releasing even more features that we are happy to develop together with our customers. We all have an important task to contribute to safer machines and workplaces.
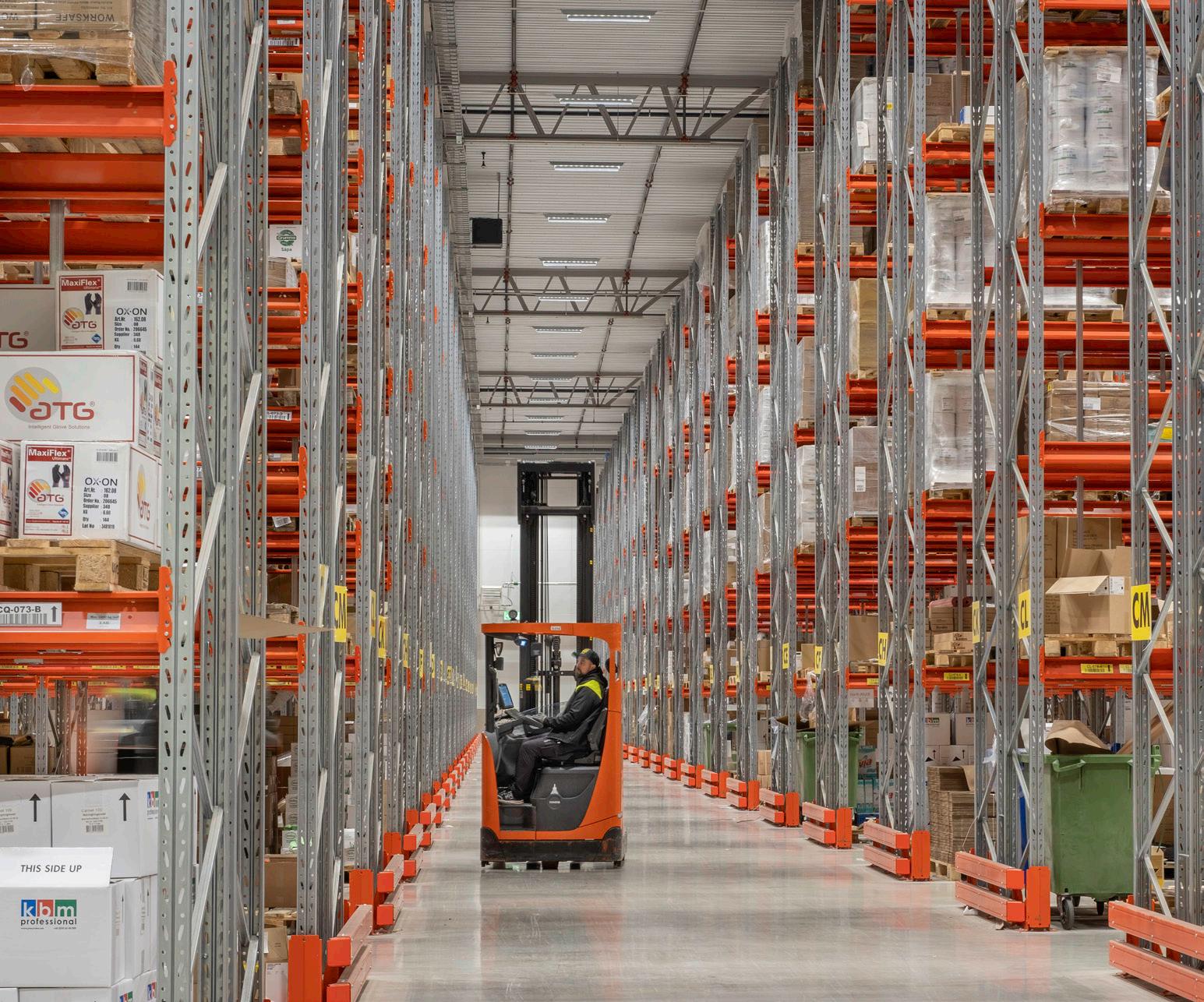
EAB supplies warehouse equipment, steel doors and steel buildings to customers all over the world.

ENVIRONMENT
If we destroy the earth and deplete our natural resources, entrepreneurship and growth will be meaningless. Within the confines of this perspective, we have chosen to focus on our climate impact for the obvious reason that it is crucial to the future of mankind. The climate is also the single most important question to our stakeholders. If we do not take our responsibility, then we won’t do business. In the near perspective, we are working on our local footprint and what we can influence in our local environment, with the aim of reducing the negative effects of our operations and creating positive change. We are sweeping in front of our own door.
Climate impact
We want to contribute to the Paris Agreement’s goals by reducing our climate footprint. As a first step, we are conducting climate calculations for the various parts of our business. We will then draw up a plan for how we will achieve our goal of becoming climate neutral by 2045.
OUR OBJECTIVE
Climate neutral. Climate neutral. Our goal is to become climate neutral and reduce our CO2e emissions by 90% according to scope 1 (direct emissions) and scope 2 (indirect emissions from electricity) by 2035. By 2045, we also aim to be climate neutral according to scope 3 (indirect greenhouse gas emissions outside the scope of our operations). Target achievement is measured using the key figure CO2e emissions per working hour
Energy consumption: The proportion of purchased electricity must be reduced by 40% by 2035. Thetarget is measured using kWh purchased per working hour.
GOVERNANCE AND MONITORING
Our work is guided by our policy documents: Sustainability Policy and Environmental Policy, as well as by our management system. The CEO and business area managers are ultimately responsible, and each manager is responsible for ensuring that the work is carried out in their organisations. We use key performance indicators as a tool for follow-up, which are reviewed annually, although the intention is to do this at shorter intervals. The key performance indicators for energy consumption and carbon dioxide emissions are mainly based on purchasing data. The intention is to perform climate calculations for all operations within the Proton Group. We will then draw up an action plan for how we will achieve our goal of becoming climate neutral.
COMPLETED ACTIVITIES AND EVENTS
In cases where we can control our own electricity purchases, the entire Proton Group has been using only fossil-free electricity since 2012, and since 2020, all electricity comes from renewable sources. In 2022, Proton contributed to the signing of a new agreement for renewable electricity for Alsab and in 2025 for Cedoc (operations in rented premises). In 2024, the Group’s first own electricity production was commissioned in the form of a solar cell facility at one of the Anderstorp companies. In 2018, all natural gas was replaced
with biogas. Energy audits have been carried out at Group level and for operations with significant
energy consumption. We have installed charging stations for electric cars outside most of our operations to facilitate the use of electric cars for both employees and visitors. A first very important step in our climate work is the climate calculations that have been carried out and completed for all of Proton Finishing’s operations. This has provided a good basis for improvements and the ability to report our climate footprint to customers per surface area treated. The lessons learned from this work then formed the basis for the implementation of climate calculations for all Proton companies in 2024, which will be completed in the first half of 2025 for the two financial years 2023 and 2024. Proton Group has also begun its journey towards scientifically based climate targets and action plans that align with the Paris Agreement through a commitment to develop Near-Term Targets with SBTi (Science Based Target initiative). In 2024, a strategic supplier change was implemented for the group’s zinc purchases, resulting in a reduction in the climate footprint associated with these purchases by just over 50% per kg of zinc purchased.
CHALLENGES AND OPPORTUNITIES
Climate emissions from our operations account for the lion’s share of our negative environmental impact, but this is also the area where we have the greatest potential for change. The energy transition is a major challenge, and at Proton Finishing in Forsheda, we have shut down the most energy- and power-intensive flakes production during the first quarter of 2025. This creates excellent opportunities for alternative energy supplies going forward. At Proton Finishing in Eskilstuna, a decision has been made to convert from LPG to biogas. Energy meters have been installed at Proton Engineering, Proton Finishing and Proton Lighting to identify energy efficiency opportunities, and work is underway to implement system support for analysing data from these measurements to simplify improvement efforts. Based on the climate calculations that have been carried out, clear action plans will be drawn up during the year to reduce the Group’s total climate footprint, and reducing the climate footprint in our value chains will be a major challenge. At group level, we will introduce guidelines for sustainable investments and future climate compensation.
Key figures
CO 2 e -FOOTPRINT (CLIMATE NEUTRALITY)
CO2 e-footprint, emissions per work hour.
8,1* 5,6
OUTCOME 2021 kg CO2e per work hour** (Scope 1 and 2) 0 5,1
OUTCOME 2022 kg CO2e per work hour** (Scope 1 and 2)
OUTCOME 2023 kg CO2e per work hour** (Scope 1 and 2) 5,1
OUTCOME 2024 kg CO2e per work hour** (Scope 1 and 2)
*Adjusted value from previous 6.7 due to new knowledge regarding biogas emission factor ** Operations in corrosion testing and machine safety not included
GOAL 2035 kg CO2e per work hour** (Scope 1 and 2)
ENERGY Energy, purchased per working hour
* Starting position 2021: 68 kWh per working hour
Local footprint
We want to contribute to better use of resources by reducing our material consumption and preventing, reducing, reusing and recycling our waste. We also work with responsible management of chemicals to reduce negative consequences for human health and the environment.
VÅR OBJECTIVE
Waste. Our goal is to have operations that do not generate waste for landfill or energy recovery by 2035. Instead, we will be able to extract materials, recycle, reuse or eliminate waste.
Candidate chemicals Our goal is that no listed substances will be included in the chemical products we use or in the products we sell by 2035.
Company cars . Our goal is that all purchased company cars will be electric or hybrid (not purely fossil fuel-powered).
GOVERNANCE AND MONITORING
Our work is guided by our policy documents: Sustainability Policy and Environmental Policy, as well as by our management system. The CEO and business area managers are ultimately responsible, and each manager is responsible for ensuring that the work is carried out at their organisational level. We use key performance indicators as a tool for monitoring, which are reviewed annually, although the intention is to do this at shorter intervals. Governance also takes place through checks and supervision of compliance with various environmental permits from the authorities.
COMPLETED ACTIVITIES AND EVENTS
A large part of the activities carried out to date have been within the framework of Proton Finishing. This is because Proton Finishing has an energy- and chemical-intensive business, but also because the company is very active in change management with the ambition of transforming the entire industry. Measures implemented include soil remediation of a former property in Markaryd that has now been sold, renovation of treatment plants and improvements in process and treatment plant management. A process involving only passivation in the drum for cast zinc goods has been established, which means fewer process steps for the goods, resulting in reduced resource
consumption and waste. Investments in more resource-efficient membrane technology in the plating baths in the hanging lines in Forsheda have resulted in a process with lower resource consumption and reduced waste. Optimisation of the process at the treatment plant in Forsheda has been carried out, which has meant that more water streams can be handled in the internal treatment plant instead of being sent away as hazardous waste. A collaborative project is underway with a supplier regarding treatment equipment for our ZnNi rinses, which are currently sent as hazardous waste. Further fine-tuning and adjustments are ongoing, which will lead to a significant reduction in hazardous waste. The Group’s policy on the use of company cars has been adjusted with new conditions to increase the proportion of electric cars and plug-in hybrids. Smaller measures are also important. For example, JL Safety and Cedoc have digitised their training materials for customers to reduce paper consumption.
CHALLENGES AND OPPORTUNITIES
The major risks in this focus area are linked to chemical management in the operations of Proton Finishing and, to some extent, Proton Lighting and Proton Engineering. However, we have made some progress in creating even more efficient processes and control systems. Among other things, we will inventory the use of listed substances in these three business areas and work on substituting them. For example, work is underway to replace all remaining cobalt-containing passivations with cobalt-free ones and to shut down the painting operations at Proton Lighting in order to outsource the painting to Proton Finishing. The flake process in Forsheda is also being shut down, which means that the consumption of solvents there will be almost eliminated and PFAS-containing flake products will be phased out. To bring about change, it is important that we are persistent and continuously implement projects that take us forward. Among other things, we have initiated a project in collaboration with researchers in which willow has been planted on historically contaminated land to purify the soil of contaminants (phytoremediation). We are continuing to work hard to be able to purify additional water streams in our treatment plants, recirculate streams back into the processes and increase the performance of the treatment plants to reduce emissions, reduce the amount of hazardous waste and lower water consumption.
CANDIDATE CHEMICALS
An important milestone in our sustainability work Climate calculations for the entire group
Since 2021, Proton Group has taken major steps to map and understand its climate footprint. It started with a pioneering initiative at Proton Finishing and has now grown into a group-wide project in which all companies calculate their climate emissions according to international standards.
Proton Finishing as a pioneer and leader
It was in the winter of 2021 that Proton Finishing in Forsheda completed its first climate calculation, thereby laying the foundation for the structured sustainability work we are engaged in today. Joel Pierre, process developer and team leader, described it at the time:
- Not only did we get a clear picture of where to implement measures, we can now provide our customers with detailed information about how the surface treatment they choose affects the climate.
Since 2023, all units within Proton Finishing have been offering climate calculations – information that is used in customer dialogues, quotations and as a basis for decisions on internal improvements. This work also created a structure and methodology that the rest of the group has been able to build on.
From pilot project to group-wide initiative
When we decided to roll out climate calculations to other parts of the group, we started with two of our larger companies: Proton Engineering and Proton Lighting. These became pilot projects where we could benefit from the lessons learned from Proton Finishing. We started with materiality analyses, mapping which parts of the business generate emissions and which
data was important to collect. The management teams were then involved to establish both the analysis and the approach.
The work then continued with our smaller companies, where representatives such as the CEO participated in the preparation of the underlying data. All data was entered into a calculation model, and the result was a comprehensive climate profile for each company and for the group as a whole.
For our large companies in the group, the purchase of materials is the largest item, with raw materials, chemicals and zinc accounting for a large proportion of emissions. Within Proton Finishing, this has already led to concrete changes, such as changing the supplier of zinc balls to reduce emissions.
Commitment, insights and next steps
After all companies had presented their climate results, we discussed several potential measures, such as improving the proportion of recycled materials, choosing suppliers with better climate performance and making smarter choices in our purchasing.
For Proton Lighting, the work of developing climate calculations is extremely valuable.
”We now have a completely different level of control over our climate impact. Instead of basing our decisions on assumptions, we base them on facts. This allows us to direct our resources where they really make a difference. Right now, for example, we are looking at better shipping options, opportunities with new and more sustainable materials, and increasing the proportion of recycled materials in our products,” says Johanna Gustafsson, Environmental and Sustainability Manager at Proton Lighting.
Elsewhere in the group, climate calculations have also been directly linked to business. At Weldin, they describe how this work has become a requirement –but also an advantage:
- Climate calculations are absolutely crucial for us at Weldin. Several of our industrial customers require us to be affiliated with EcoVadis, for example, and to work in accordance with SBTi – otherwise we are not even allowed to participate in tenders. This work is therefore not only important, it is critical to our business,‘ says Peter Fahar, CEO at Weldin. ’Our customers operate in a segment that is far ahead in terms of sustainability issues, compared to the construction industry, for example. This makes our commitment a clear competitive advantage.
We win business from players who have not come as far, and we strengthen our credibility as a partner. Producing climate data is not just something we have to do – it is an active choice that makes us better equipped for the future.
Several management teams within Proton have committed to this, and the work has become an integral part of our strategic governance. We now have climate calculations for both 2023 and 2024, which gives us a good basis for comparison to further develop our models and data quality.
Towards science-based climate targets
The next step is to develop targets and action plans in line with the Science Based Targets initiative (SBTi). After submitting a commitment to them, the next step is to submit our targets and action plans for validation – and then translate them into concrete measures in our operations.
Measuring and understanding your climate footprint is not easy – but it is necessary. By combining data, dialogue and concrete initiatives, we can take the next step towards a sustainable future – together as a group.

Maria Thom and Johanna Gustafsson work proactively and closely together to advance sustainability efforts.
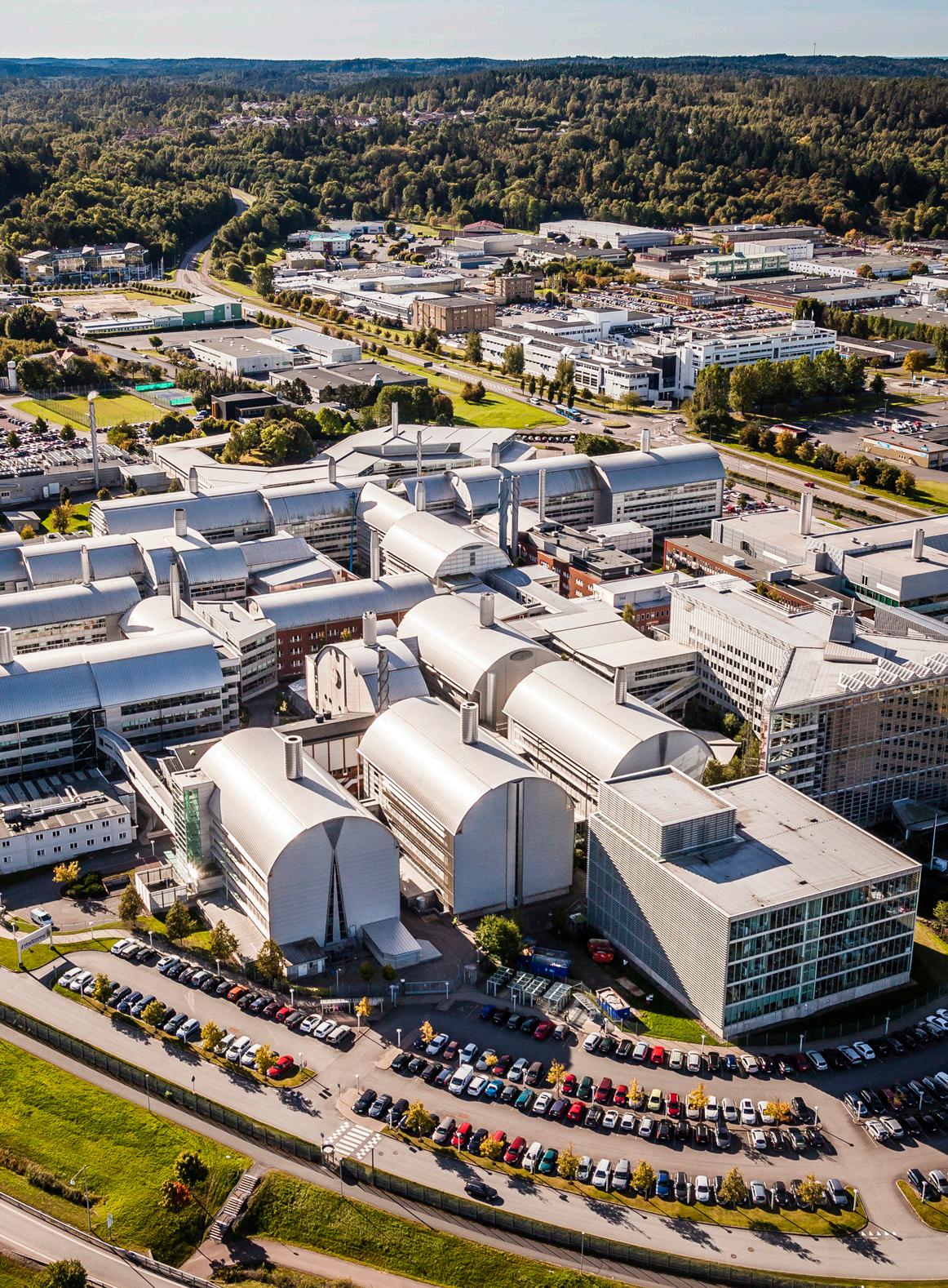
”It is extremely important to us that our suppliers work actively with sustainability issues and that they, in turn, place demands on their suppliers. It may sound a little harsh, but by putting pressure on each other, we create a positive chain reaction.
Astra Zeneca’s R&D facility in Gothenburg
WELDIN
Weldin builds sustainable infrastructure for the process industry
A new cooling system is currently being installed at AstraZeneca in Gothenburg, and Protonägda Weldin has been commissioned to install the system. Weldin’s affiliation with the sustainability initiatives SBTi and EcoVadis was a requirement.
With many years of experience in delivering comprehensive solutions for pipe installations, Weldin is a reliable partner for installing a modern, efficient and reliable cooling system at one of the world’s leading research and development facilities for pharmaceuticals.
Weldin’s assignment is to be responsible for the pipe installations in the facility, including cooling machines and pumps.
‘Since all the work is done on site in the existing facility, we focus heavily on preparing the solutions so that the work can be carried out quickly and with high quality without disrupting normal operations more than necessary,’ says Martin Svensson, project manager at Weldin.
”The fact that we have enjoyed long-term trust from AstraZeneca means a lot, as it has given us the opportunity to get to know the business and thus plan effectively. Our employees’ knowledge and experience of the customer makes it easier to deliver according to the customer’s requirements.
The world’s leading R&D centre AstraZeneca in Gothenburg is a global research and development facility with the ambition of becoming one of the world’s leading R&D centres. The facility employs 3,100 people. Here, medicines are developed for cardiovascular diseases, lung diseases, kidney diseases and cancer.
Dedicated teams work on formulating medicines, developing medicine packaging and producing technical aids and solutions.
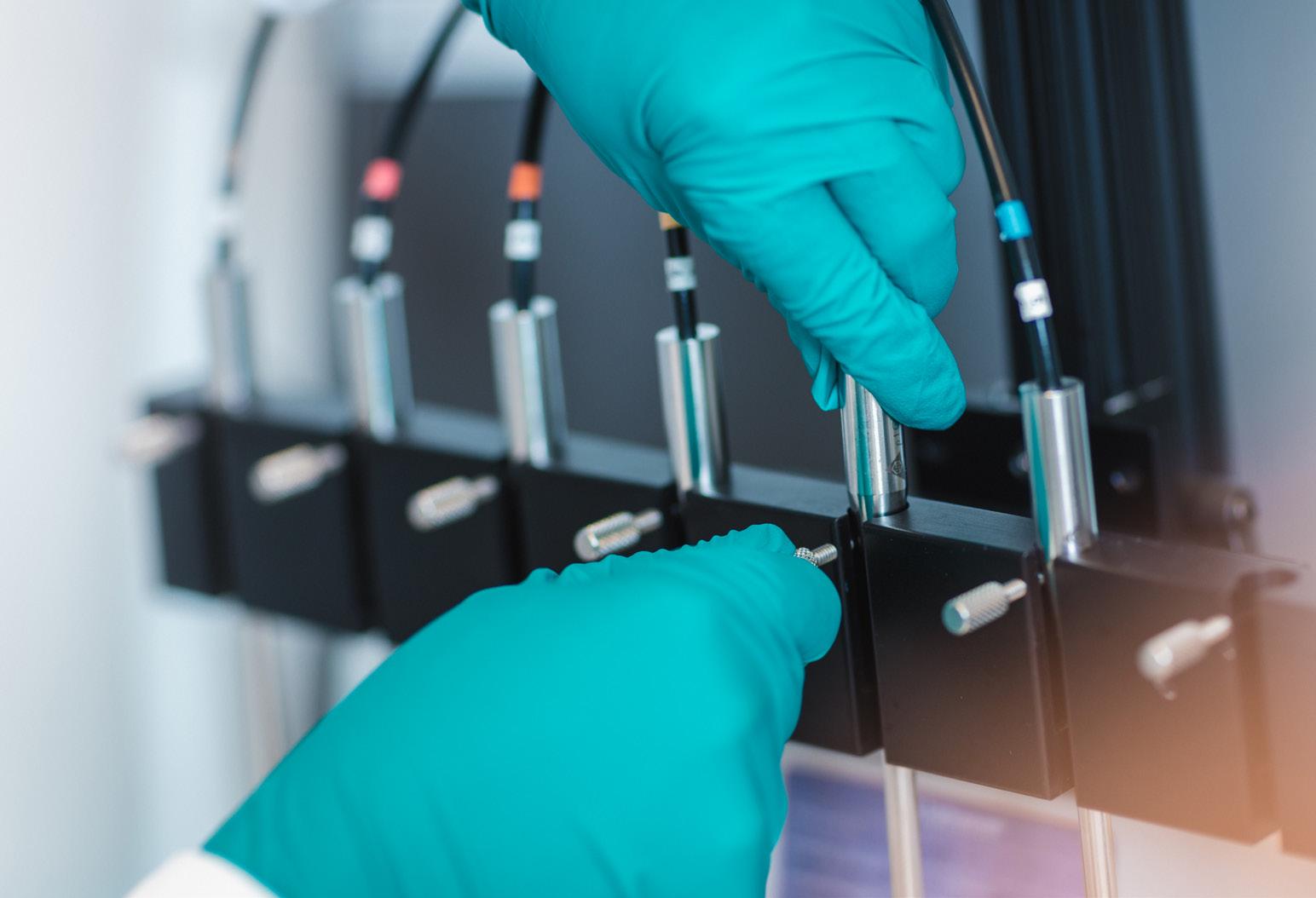
”The fact that we have enjoyed long-term trust from AstraZeneca means a lot, as it has given us the opportunity to get to know the business and thus plan effectively.
Cooling is a very important part of the site, which is why AstraZeneca has its own cooling plant that produces cooling water.
By rejuvenating the machine park and replacing the older cooling machines, efficiency is increased and investments are made in both economic and environmental sustainability.
The new cooling machines have low GWP values and are much more energy efficient.
‘Our labs actually look like most people imagine them to be. Fume cupboards, safety goggles and white coats – the difference is that we have much more advanced machines and lab equipment,’ explains Jonas Lundgren.
A chain reaction
Weldin is affiliated with the sustainability initiatives SBTi and EcoVadis, which is a requirement from AstraZeneca when procuring suppliers, says Jonas Lundgren.
AstraZeneca’s environmental and climate impact is partly through the goods and services we buy. So, it’s super important for us that our suppliers are actively working on sustainability issues and that they, in turn, set requirements for their suppliers. It might sound a bit harsh, but by putting pressure on each other, we create a positive chain reaction.
WHAT DOES IT MEAN THAT WELDIN HAS BEEN AWARDED A GOLD MEDAL BY ECOVADIS?

EcoVadis is a global independent platform that evaluates companies’ sustainability efforts in the areas of the environment, working conditions and human rights, business ethics and sustainable procurement.
Being awarded a gold medal means that the company is among the top five per cent of all companies evaluated globally. It is proof of systematic, transparent and ambitious sustainability work – and an important signal to customers, suppliers and other stakeholders that sustainability is an integral part of the business.

At Astra Zeneca’s R&D facility in Gothenburg, 3,100 people are working to make life a little better for people all over the world.

ECONOMY
Having a healthy financial base is a necessity for us to pursue our sustainability measures. This is why we work with developing our operations and services from a economic perspective to make them more circular and attractive on the market. Having sustainable growth with expanding operations and finances is also a necessity for us to offer secure, rewarding jobs, contribute resources to society through taxes and fees, and last but not least, have the muscle to pursue change projects to benefit the environment and climate.
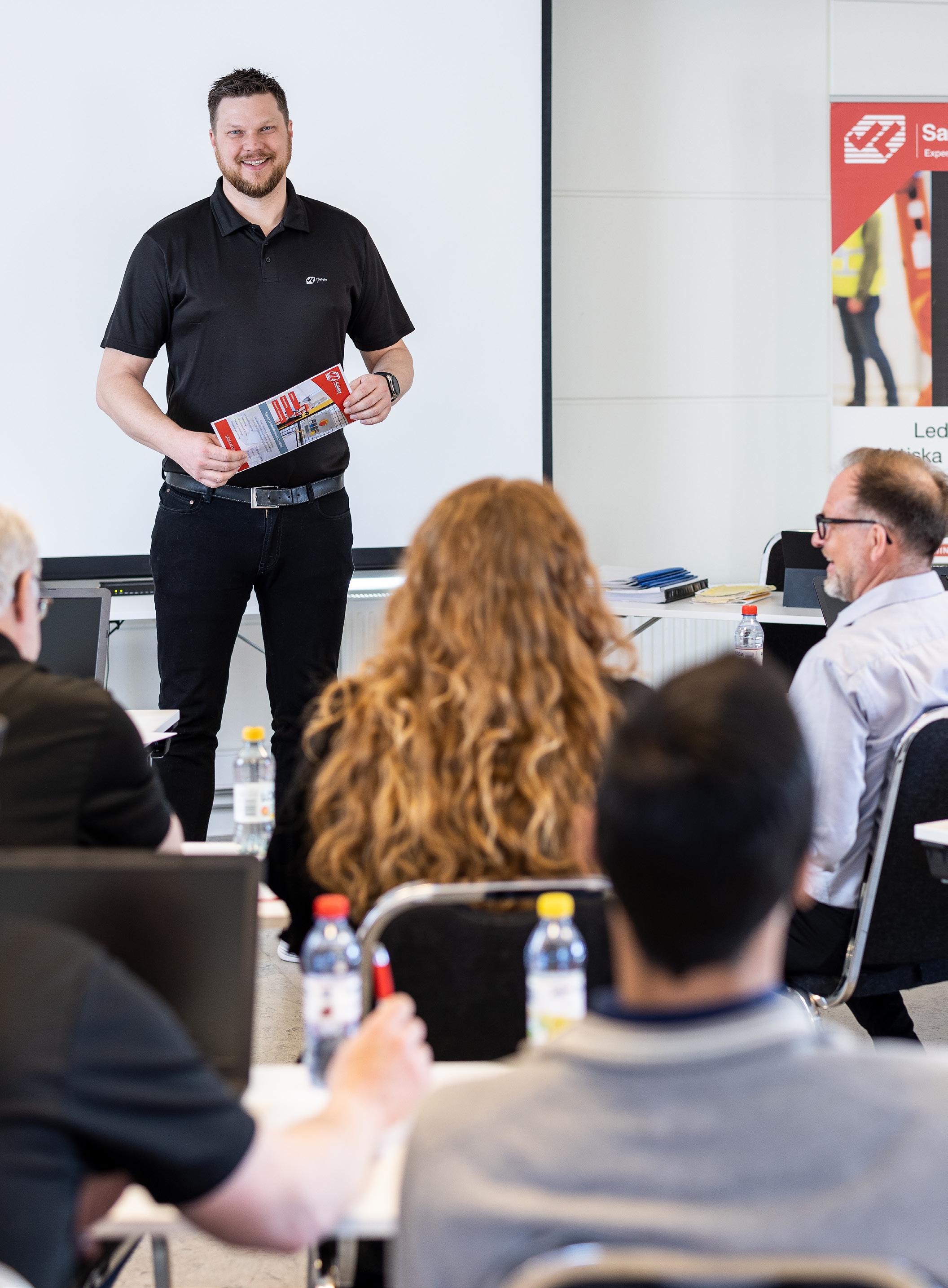
Development
We want to contribute to inclusive industrialisation and promote sustainable innovations. By developing sustainable solutions, we can add value to our customers’ sustainability efforts. With our own innovative development projects, we can also ensure that our own operations become more circular.
OUR OBJECTIVE
Sustainable producs and services. By 2030, the products and services we offer will be sustainability declared (100%).
Sustainability-promoting development projects from a brand and business perspective By offering our customers circular solutions, sustainability work becomes a natural part of our business development.
GOVERNANCE AND MONITORING
Through internal development and improvement projects, we can contribute to increased sustainability for both our customers and our employees. With more circular, resource-efficient and ergonomic solutions, we can integrate the sustainability perspective into our business concept and create sustainable growth for ourselves and others. However, we are currently unable to report key figures for any of the focus areas as we lack the tools for systematic follow-up. The goal is to capture the internal information flows that already exist at management level in the various business areas and see how far we can build on these. One example is Proton Lighting, which currently performs light and energy calculations for its customers, demonstrating in concrete terms the link between development, customer benefit and climate impact.
COMPLETED ACTIVITIES AND EVENTS
Proton Group’s operations currently have many established activities in this area. Proton Engineering’s development team supports automotive customers in the development of new solutions for fuel conversion, while Proton Finishing’s development team has been created to design new solutions for sustainability in all areas of the business. As a result of this initiative, Proton Finishing’s customers can now see the climate footprint of their surface treatment directly on their quotation. A collaborative project with a supplier has resulted in the installation of purification equipment for our ZnNi rinses, which are currently sent as hazardous waste, leading to a significant reduction in hazardous waste. Within
Proton Engineering’s operations, a new washing process has been implemented to enable new business opportunities. Proton Lighting is running development projects on more ergonomic and energy-efficient working environments through lighting control combined with innovative LED products, which effectively saves energy for customers. Within the framework of JL Safety’s operations, we offer safer working environments and machine safety, as well as a concept called Safety Concept, which gives customers an overview and a comprehensive approach to the journey towards safe machines. Cotec Labs, a leader in corrosion testing, ensures through its work that customers can develop products with better resistance and longer service life, which in the long term can contribute to reduced material consumption and better resource management. Weldin helps its customers with solutions for energy conversion and energy and raw material efficiency. The new brand strategy decided for the group has been implemented during the year. To further strengthen the group’s sustainability work, the organisation has been strengthened in recent years with sustainability managers in Finishing, Lighting, Engineering and the Group.
CHALLENGES AND OPPORTUNITIES
Being able to declare the sustainability of products and services is a strong competitive advantage. We will therefore begin work on developing sustainability declarations within the various operations. Examples of individual activities include Exaktor’s further development of lighting control for lower energy consumption and increased comfort, and work on developing products with a more circular approach. Proton Finishing intends to develop a more environmentally friendly pre-treatment for ED powder and a process involving only passivation in the drum for cast zinc goods. In parallel, Proton Finishing will also implement automation and AI projects for a more sustainable business process. Within the framework of Proton Engineering’s operations, we intend to introduce requirements for recycled materials in metal raw materials and increase prototype activities in order to take on new business. To equip the entire group for future challenges, we are in the process of switching to Microsoft’s Dynamics business system. During the year, we have been working hard to prepare for sustainability reporting in accordance with CSRD, where we now need to find our way to utilise this to drive our sustainability work forward despite fluctuations within the EU.
Growth
We want to contribute to sustainable growth where, through profitable operations, we can continue to invest in new technology, develop new products and services, and develop the skills of our employees.
OUR OBJECTIVE
Profitability. We have a profitability target of 6-8% over the economic cycle.
Growth. Our annual growth target is at least 7.2%.
Solidity. Our solidity target is at least 35%.
Ambassadors. We will measure customer satisfaction in all our business areas and aim to have a cNPS* of 25 by 2030.
GOVERNANCE AND MONITORING
Our profitability is measured monthly, with operating profit measured for the current month and accumulated value for the year. In the future, we will measure all figures monthly, but on a rolling basis. Until now, growth has been measured via a monthly report compared with turnover and the budget for the previous year. From January 2023, we will measure growth on a rolling basis against the last twelve months and in relation to the group strategy’s vision of doubling turnover every ten years. The equity ratio is measured once a year.
COMPLETED ACTIVITIES AND EVENTS
During 2019-2020, Proton Group made a number of acquisitions with the aim of driving the group’s growth by broadening its offering to customers. These included the acquisitions of JL Safety and Cedoc, which specialise in consulting and software for machine safety, and Alsab, which is now part of Proton Finishing. With the acquisitions of Teknikrör in Kinna and Gunnar Hansson Svetsteknik, we entered a completely new business area, focusing on advanced pipe installations and infrastructure for the process industry. We believe that demand for qualified services in this area will increase as customers rebuild their facilities and reorganise their processes as part of their sustainability efforts. In 2023, the two companies merged to form Weldin Gothenburg AB to create better conditions for growth. In 2021, Proton Group launched a project in collaboration with the University of Gothenburg and growth researcher Jonas Fasth to actively drive and develop the group’s growth efforts. The Group’s management team and business area managers have participated in workshops and strategy development, and work is now underway to implement the lessons learned in
the organisation. Our key figures for growth and solvency in 2021 require comment as they must be viewed in the context of the pandemic. Growth in 2021 is strong in relation to the targets but should be seen in light of the loss of revenue in 2020 and the recovery that took place the following year. The strong financial strength in 2021 can also be related to the pandemic, which included a government-imposed dividend freeze, which had a positive impact on financial strength. Projects have been carried out together with customers and end customers to jointly identify opportunities for better solutions and growth. Proton Finishing’s customer event “Sustainable Together” was a successful activity that we are continuing to develop.
CHALLENGES AND OPPORTUNITIES
Proton Group’s strategic growth target is to double its turnover every ten years, which we cannot achieve on our own. This shift must be made in collaboration with our customers. Our challenge right now is therefore to get closer to our customers in order to develop new offerings that support them in both their profitability and their sustainability development. Among other things, we need to get involved earlier in our customers’ product development process in order to meet and satisfy their needs through development. To gain an understanding of how well we are meeting customer expectations, we will conduct customer satisfaction surveys via cNPS* in all companies. In order to grow and develop, we need to strengthen our sustainability profile through, for example, increased information and communication via customer meetings, social media and events. Based on the dialogue with our customers, we will then allocate the development resources necessary to move forward with our growth-promoting measures. Sustainable growth will not be achieved individually, but through collaboration and partnership. To succeed in this, we will continue to invest in our employees. All sales staff have undergone internal sales training, and everyone with customer contact within Proton Finishing has been trained in sales communication –initiatives that strengthen our ability to understand customer needs and communicate our offering more clearly. A challenge going forward will therefore be to find more partners in many different areas to strengthen our opportunities for sustainable solutions, products and services. The Group’s new brand strategy will make our offering clearer and create better conditions for growth.
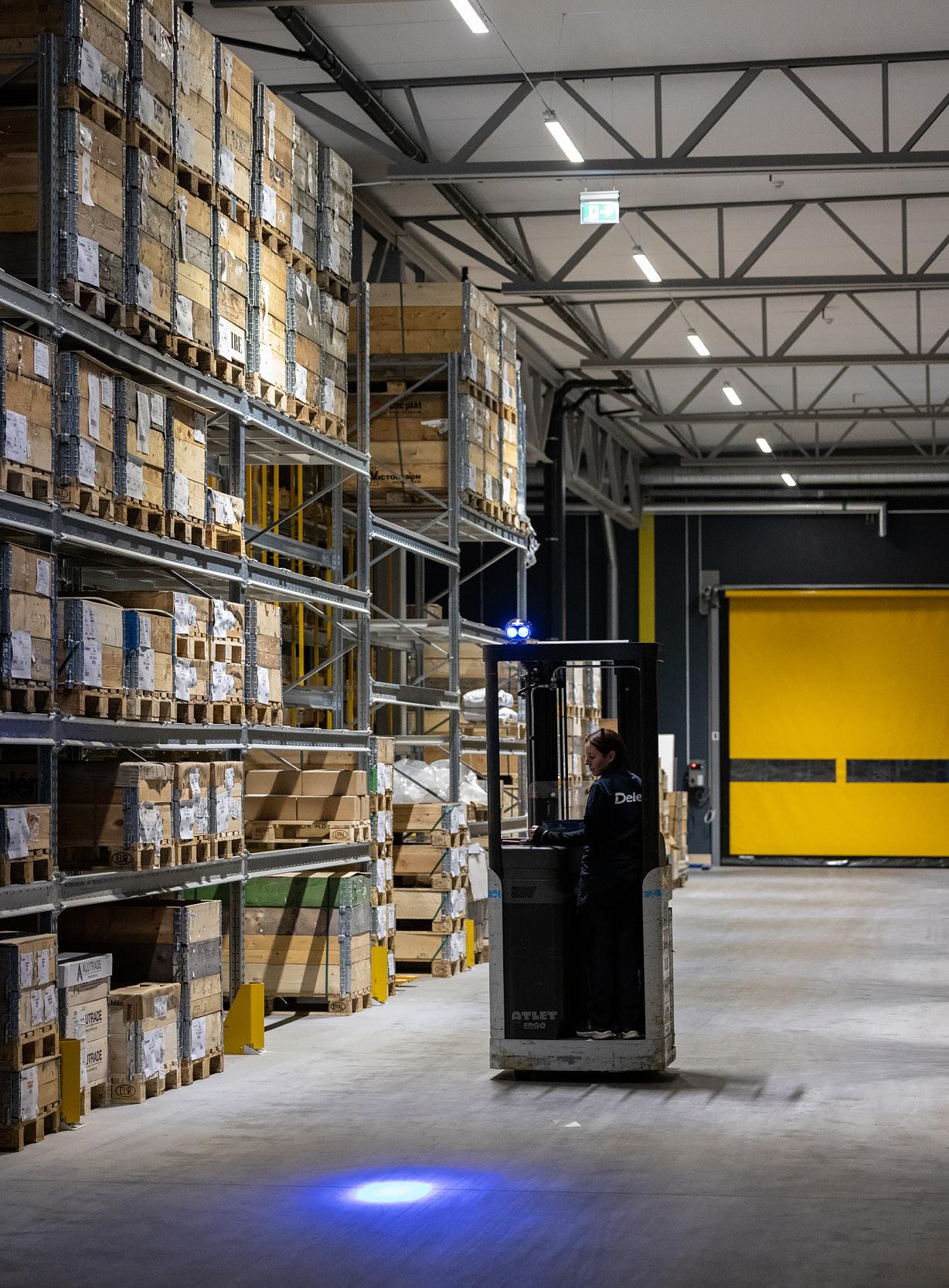
”It’s all about having the right light, in the right place, at the right time –nothing more.”
Brilliantly efficient and sustainably designed with smart control
As the need for energy-efficient solutions increases, BTDA (Bluetooth DALI) has established itself as a leading technology in lighting control. BTDA is an advanced system that enables lighting to be controlled directly at the luminaire level and is a solution that saves both energy and resources by optimising lighting in premises based on needs and presence – which is a concrete measure for sustainability.
Market demand – a solution for energy efficiency Initially, the need for BTDA was primarily to reduce energy consumption in buildings and facilities. However, over time, the system has proven to have several other advantages. By programming the luminaires to only shine at full brightness when people are actually in the premises, it is possible to dramatically reduce the number of hours the lighting is in operation. This not only leads to energy savings but also to a longer service life for the luminaires and a reduced impact on the environment.
In many properties, the lighting is often left on unnecessarily, and by adjusting the light to only shine when someone is present, we save on both luminaires and energy while reducing our climate impact. Exaktor has seen that warehouses, for example, which previously had up to 12 hours of lighting per day, have now seen a drastic reduction in energy consumption and are only used for 5 hours a day.
‘It’s about having the right light, in the right place, at the right time – and nothing more. With BTDA, our customers get a solution that is both energyefficient and future-proof,’ says Anders Schultz, Sales at Exaktor.
A new dimension of flexibility and sustainability BTDA differs from previous lighting control technologies in that control takes place at the luminaire level. This offers great flexibility, especially in environments where traditional solutions have not worked. In the past, lighting systems were often inflexible due to obstacles such as robots or other objects that needed to be illuminated. With BTDA, we can switch off sensors that cause false detection and control the luminaires much more precisely.
With increased demands for energy efficiency and sustainable investments, BTDA has become a natural choice for companies that want to combine smart technology with environmental responsibility. For many businesses, it is also a concrete way to work towards their environmental goals, reduce carbon dioxide emissions and at the same time future-proof their properties. By not keeping entire premises lit all the time, and only illuminating the parts of the premises that are in use, energy consumption is reduced. In addition, the system has more sensors that allow the lighting to be kept at a lower level where possible, which further reduces operating time.
What does ‘smart lighting’ mean?
The term ‘smart lighting’ means that the luminaires are connected to a network and can be programmed to automatically respond to various parameters, such as presence and daylight. The BTDA system offers a range of features that make lighting both more efficient and sustainable.
These include presence control, daylight compensation, scheduling, timer functions and integration with other systems, such as ventilation and compressors. It is this comprehensive solution that makes BTDA so effective.
90% energy savings despite halving the number of luminaires
BTDA has been installed in a wide range of buildings, from factories and schools to car parks and walkways. One example of a successful project is a factory in Värnamo, where Exaktor installed BTDA and managed to reduce energy consumption dramatically, by almost 90%. Before installation, the facility consumed 116,000 kWh per year, while after installation it only uses 12,523 kWh per year. The number of luminaires was halved from 320 to 160,
while light quality and efficiency were improved.
This installation not only led to significant energy savings, but also to a reduction in CO2 emissions of 10,348 kg per year. This is a clear example of how smart lighting can contribute to both economic and environmental gains.
The control system plays a central role in optimising energy use in buildings. By adapting the lighting to specific activities and the needs of the premises, Exaktor can ensure that the right light is used in the right place at the right time. For example, it is possible to have 300 lux in storage areas and 500 lux in production areas – but only when people are present.
When no one is in a specific area, the lighting is reduced to a minimum level, and after a certain period of inactivity, the lights are turned off completely. This type of control makes it possible to significantly reduce energy consumption while maintaining the right light levels in areas where it is really needed.
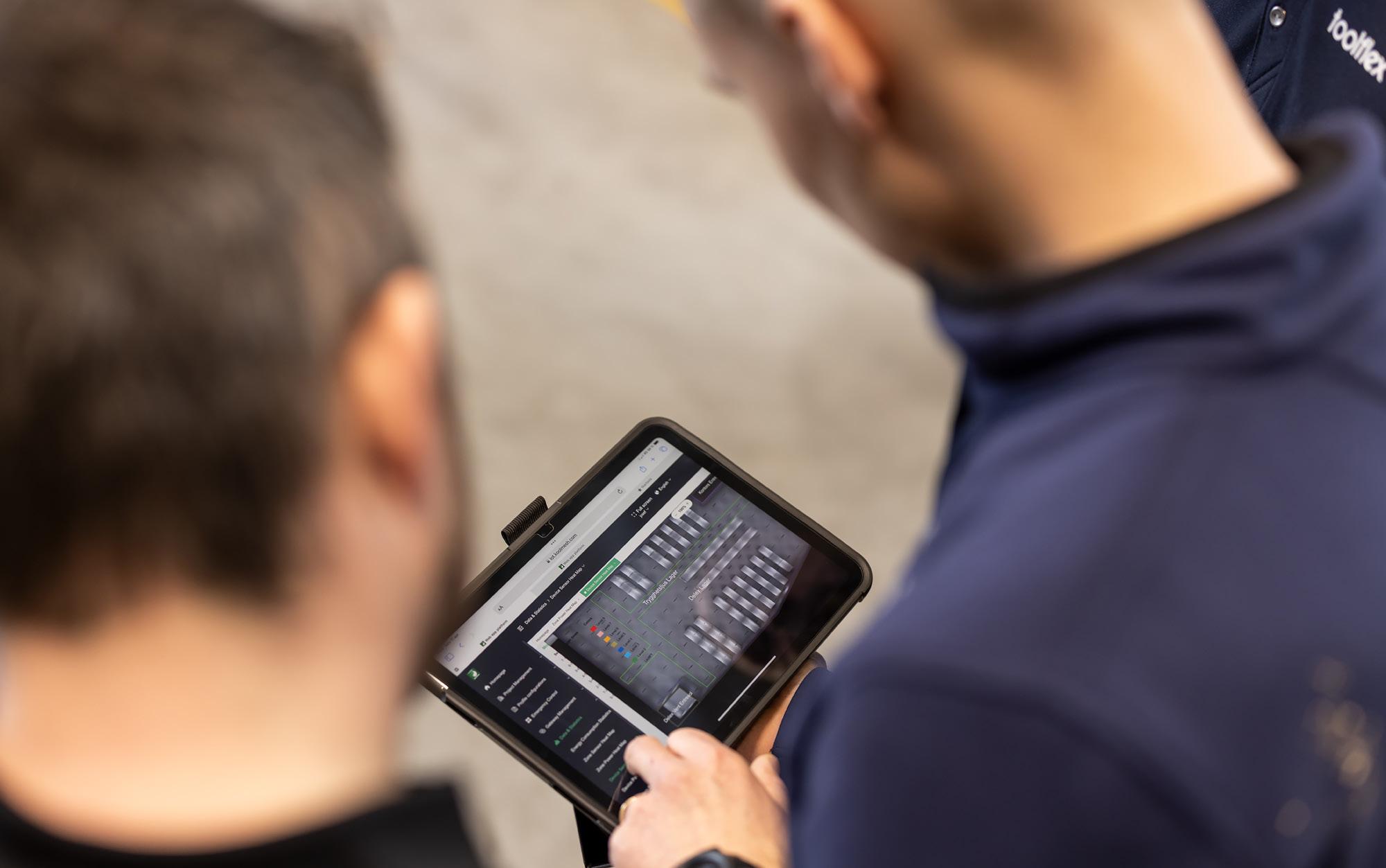
By programming the luminaires to only shine at full brightness when people are actually in the premises, you can dramatically reduce the number of hours the lighting is in operation.
Climate impact and sustainability beyond energy consumption
In addition to reducing energy consumption, BTDA also contributes to increased sustainability by extending the service life of luminaires. By not keeping the lighting on at full power when no one is there, we reduce the load on the luminaires and the need for frequent maintenance. This leads to a longer service life for the luminaires, which both saves resources and reduces the amount of waste. Exaktor also works to use recyclable materials in its luminaires. For example, Exaktor has used recycled plastic in the end caps of its luminaires and provides recycling instructions on how to sort and dispose of the luminaires when they are no longer in use.
The future of smart lighting
The future of smart lighting looks promising. As more and more companies and organisations realise the significant benefits of controlled lighting, the use of systems such as BTDA will continue to grow. Exaktor expects more advanced sensors to be developed to distinguish between people and machines, enabling further optimisation of lighting and reducing energy consumption. It will also become more common for different sustainability systems to work together, with lighting, ventilation and heating being controlled together to optimise energy use. This would create smart buildings that are not only energy efficient but also more sustainable and comfortable for those who use them.
BTDA is a clear example of how technology and sustainability can go hand in hand to create a more energy-efficient and environmentally friendly future. By continuing to develop and implement smart lighting control systems, we can contribute to the green transition and create more sustainable and efficient buildings for the future.
‘BTDA is not just a control system. It is an investment in both sustainability and long-term economy,’ concludes Anders.

”BTDA is an investment in both sustainability and long-term economy.
Knowledge of surface treatment creates added value
How can increased knowledge about surface treatment contribute to better sustainability, quality and economy – throughout the entire value chain? That was the question when Proton Finishing and Thule invited guests to a theme day dedicated to surface treatment.
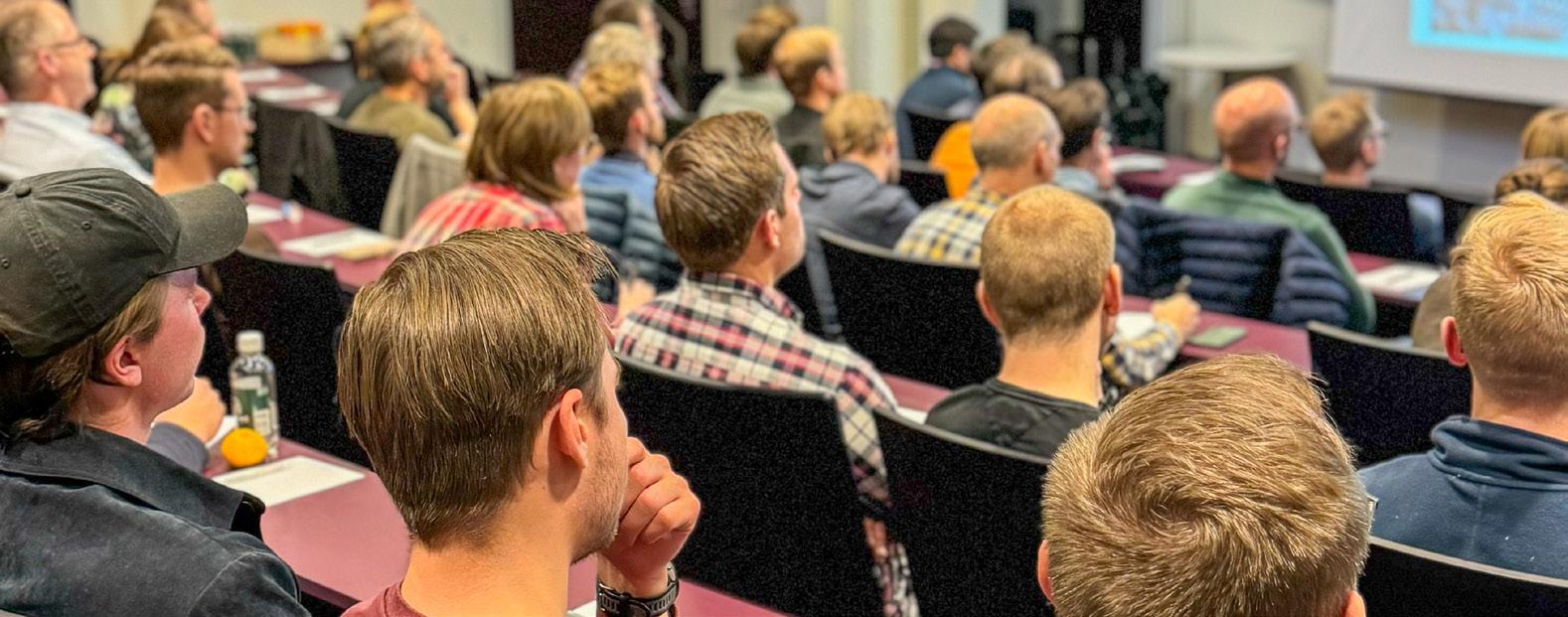
It all started when Anders Olsson, sales manager at Proton Finishing, and Niclas Tjäderborn, development engineer at Thule, came up with the idea of spreading knowledge about surface treatment to a wider audience. With its slogan ‘Bring your life’, the Hillerstorp-based company is one of the world’s leading lifestyle companies whose products make it possible to transport equipment: roof racks, roof boxes, bike and ski carriers are among Thule’s bestknown products. Many of them have to withstand tough conditions with rain, snow and salt. The right choice of surface treatment, carried out with quality, is essential.
Participants from across the chain ‘Niclas and I started talking about how everyone in the value chain could gain a better understanding of surface treatment and, not least, that they should all have the same knowledge,’ explains Anders Olsson.
Previously, shorter training courses were held for Thule employees. But this year, it was decided to invest heavily in a joint training day at the rubber factory in Värnamo. Under the name ‘Thule with friends’, both Thule’s suppliers and the organisation’s own employees from the development and production sides were invited to a knowledge-filled and inspiring day on the theme of surface treatment. A total of around 70 people took part in the training, which was led by Åsa Svanholm from Win3.
A stronger partnership
Organising an event like this is no easy logistical feat, but we received really positive feedback from the participants, says Martina Ny, Communications & Sales at Proton Finishing, who was responsible for the event:
”By offering our customers added value in the form of knowledge, networking and new types of forums, we are creating a stronger partnership, which is incredibly important to us. Our events over the past three years have not only been appreciated by our customers, but have also contributed to new business. This shows us that we are investing in the right things.
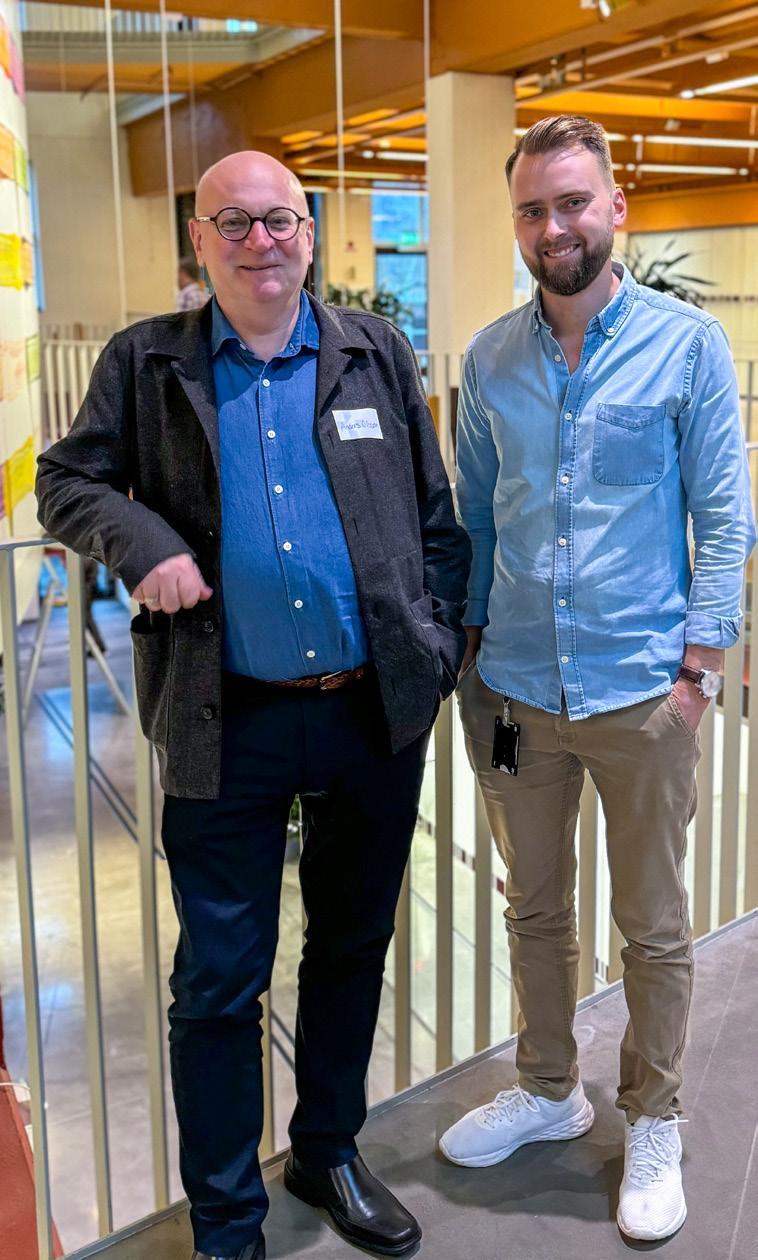
This view is shared by Niclas Tjäderborn and his colleagues at Thule:
”Our aim for the day was to increase the knowledge of designers, technical managers, test engineers and purchasers regarding technical surface treatment. We turned to Proton because we know that they have a high level of expertise in this area. I found the day very rewarding, and Åsa, as an expert in the field, went through both important aspects of surface treatments of interest and what needs to be taken into account in the design process in order to be successful.
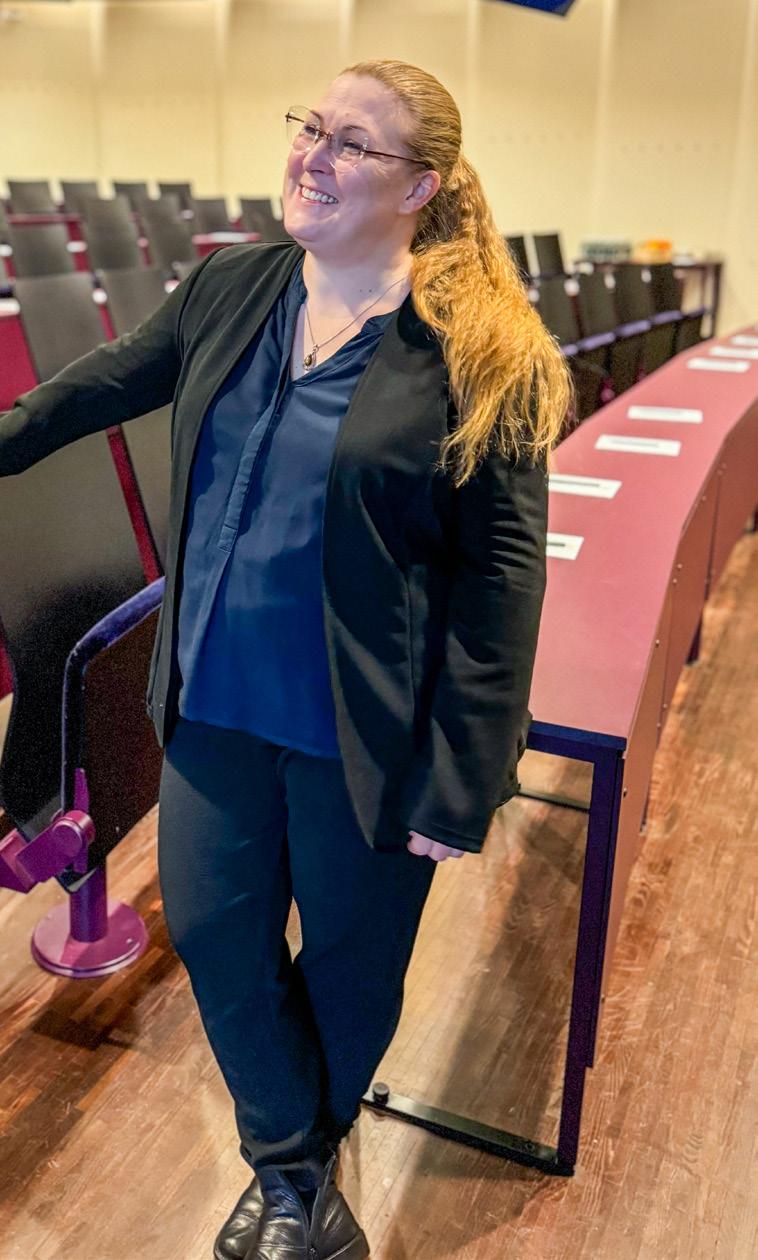
The training was led by Åsa Svanholm from Win3. Åsa is a specialist in surface treatment with extensive experience in the automotive industry, including Scania.
Anders Olsson, Sales Manager at Proton Finishing, and Niclas Tjäderborn, Development Engineer at Thule, are the initiators of ‘Thule with friends’.
Cotec Labs makes waves
With advanced corrosion testing that makes products and vehicles last longer, Cotec Labs contributes to better material management worldwide. Together with its Italian partner MaterialScan, Cotec Labs is making waves.
Cotec Labs is one of the market’s leading laboratories for corrosion testing. In its advanced testing environment, more than 200 different tests can be carried out in accordance with various industry standards and customer requirements. The laboratory simulates conditions that can cause corrosion, such as high temperatures and high humidity, cold, salt or other substances that can have a negative impact on materials and surfaces.
“Putting pressure on development”
Globally, corrosion damage is estimated to account for around three per cent of a country’s GDP. Replacing these parts naturally has a major environmental impact. Through its customers in the automotive, engineering and furniture industries, Cotec Labs can contribute to lower material consumption, reduced environmental impact and a better global economy.
–Our customers are found at every stage of the supply chain, and we carry out tests on behalf of both the manufacturers themselves and their subcontractors. Our tests ensure that the products released onto the market are of good quality and durable. Quite simply, you get better resource utilisation with a longer service life, while using fewer spare parts,” says Joakim Ekström, Sales and Marketing Manager at Cotec Labs.
”When major brands and manufacturers demand quality and sustainability, it puts pressure on development at all levels. The pressure from above helps to make the entire chain more sustainable, and Cotec Labs plays a natural role in verifying the effect. We help to spread the ripples.
Cooperation leads to development
As a Scandinavian company, Cotec Labs has experience of testing in harsh climates – knowledge that makes the company’s offering attractive to large parts of Europe.
‘Our goal is to develop our international relations. If we can work together, the overall impact will be better,’ says Joakim Ekström.
MaterialScan is Cotec Labs’ partner in Italy. The company has extensive experience in supporting customers in their development projects and provides them with technical and commercial support in the choice of test methods. ”Since we work with corrosion treatment, extending service life through verified surface treatment methods is our absolute focus. With our expertise and services, we aim to contribute to increased service life and reliability, as well as reduced maintenance.
Through our collaboration with Cotec Labs, we can help Italian companies gain easier access to
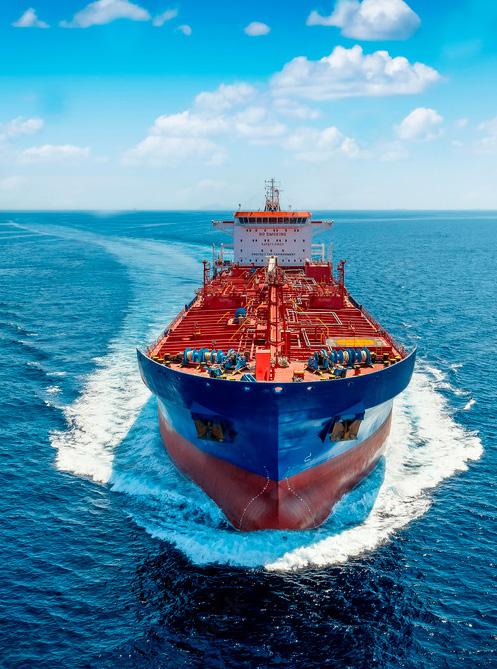
”Globally, corrosion damage accounts for approximately three per cent of a country’s GDP.
corrosion testing and surface analysis. We also recommend our customers to use Cotec Labs in the development of new circular and sustainable surface treatment methods,” says Alessio Ferluga, CEO of MaterialScan.
Increased focus on service life
In recent years, Italian customers have become more aware of sustainability.
”Historically, there has been a lot of focus on the manufacturing process itself: recycled materials, renewable energy and hazardous substances. But now we are noticing that people are also starting to look at the service life of products and mechanics. We also believe that ESPR (Ecodesign for Sustainable Products Regulation) will have a significant impact in the future.
By working closely with customers, MaterialScan and Cotec Labs can contribute to development in the right direction.

”It’s very much about strengthening the customer’s confidence in sustainability-related development issues.
We provide advice and support throughout the entire test cycle, from the collection of technical data and enquiries to marketing and after-sales follow-up, says Alessio Ferluga.
Cleaner seas
Through this collaboration, Cotec Labs has been given the opportunity to contribute its expertise in new industries.
–In our region, we have a very strong shipbuilding industry, a sector in which we have a natural commitment. Many shipbuilders use paint as their main anti-corrosion method, which means that its effectiveness must be verified. It is also an industry with a major impact on sustainability issues, as the maritime industry is highly focused on developing technologies that can help reduce marine pollution,” says Alessio Ferluga.
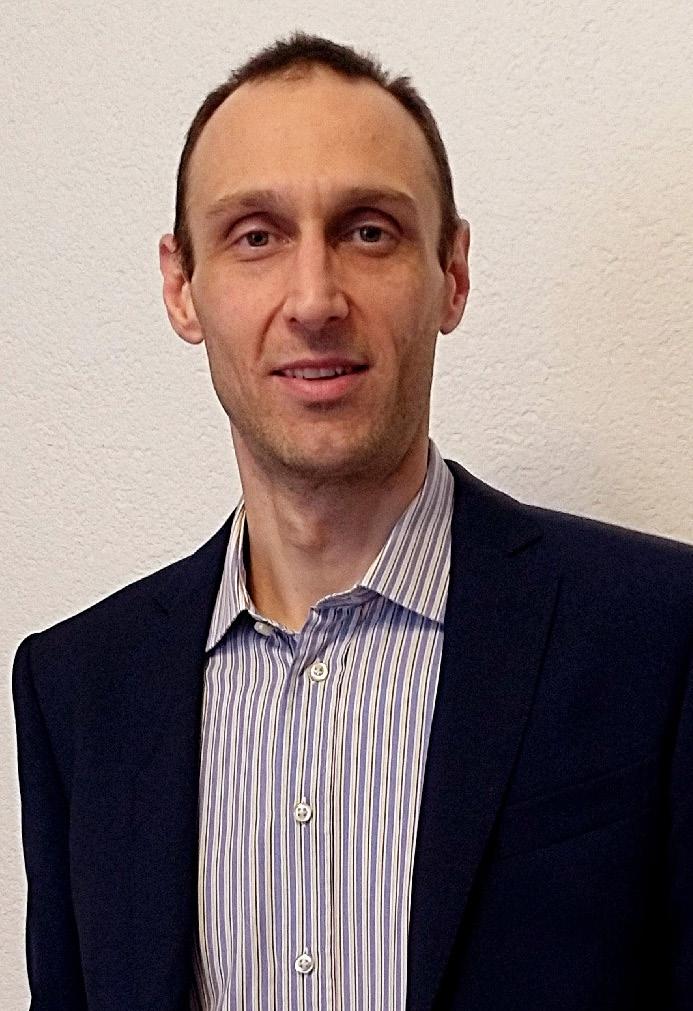
Joakim Ekström is Marketing and Sales Manager at Cotec Labs.
Alessio Ferluga is CEO of MaterialScan, Cotec Labs’ partner in Italy.
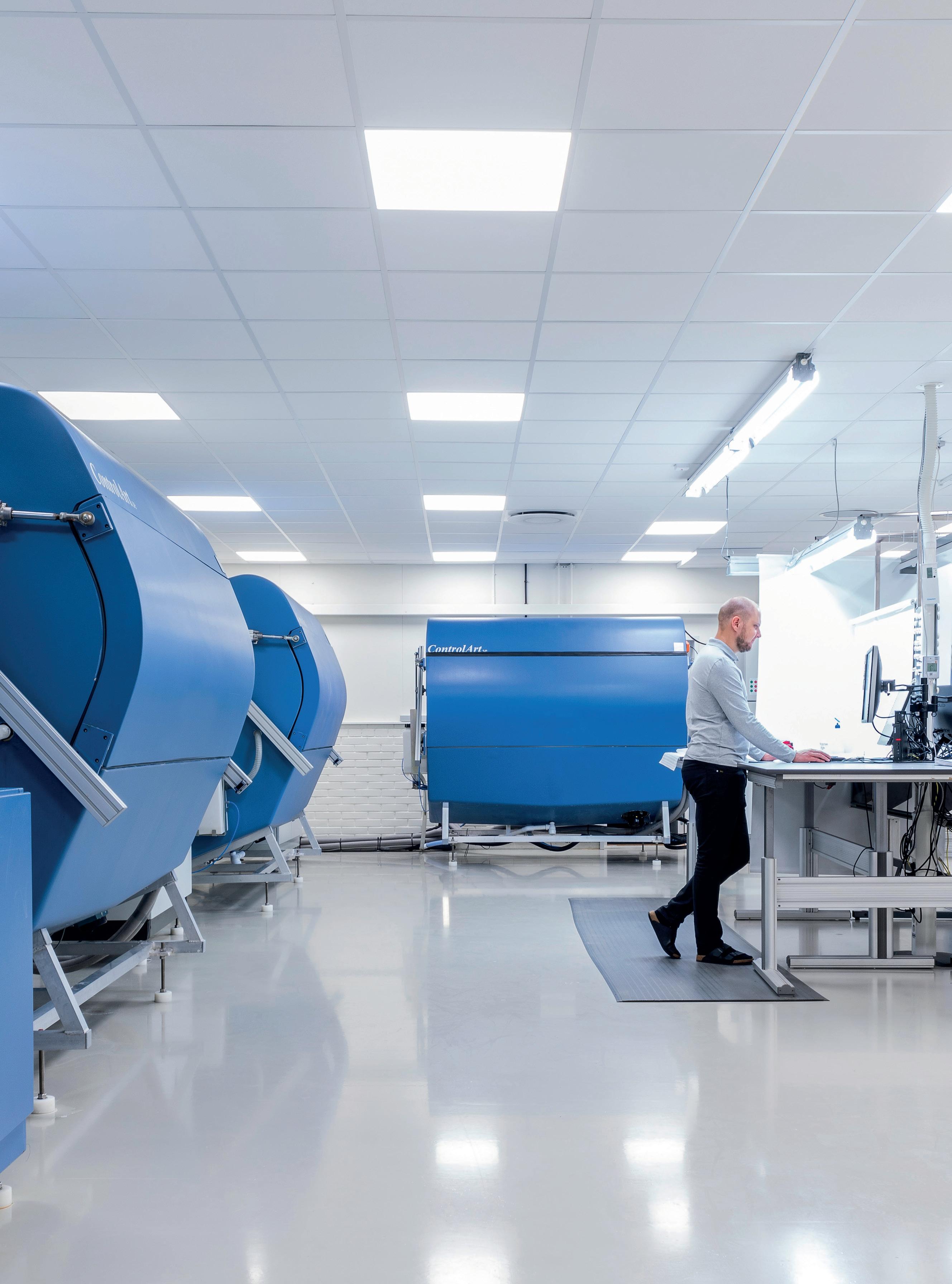
With advanced corrosion testing that makes products and vehicles last longer, Cotec Labs contributes to better material management worldwide. Together with its Italian partner MaterialScan, Cotec Labs is making waves.
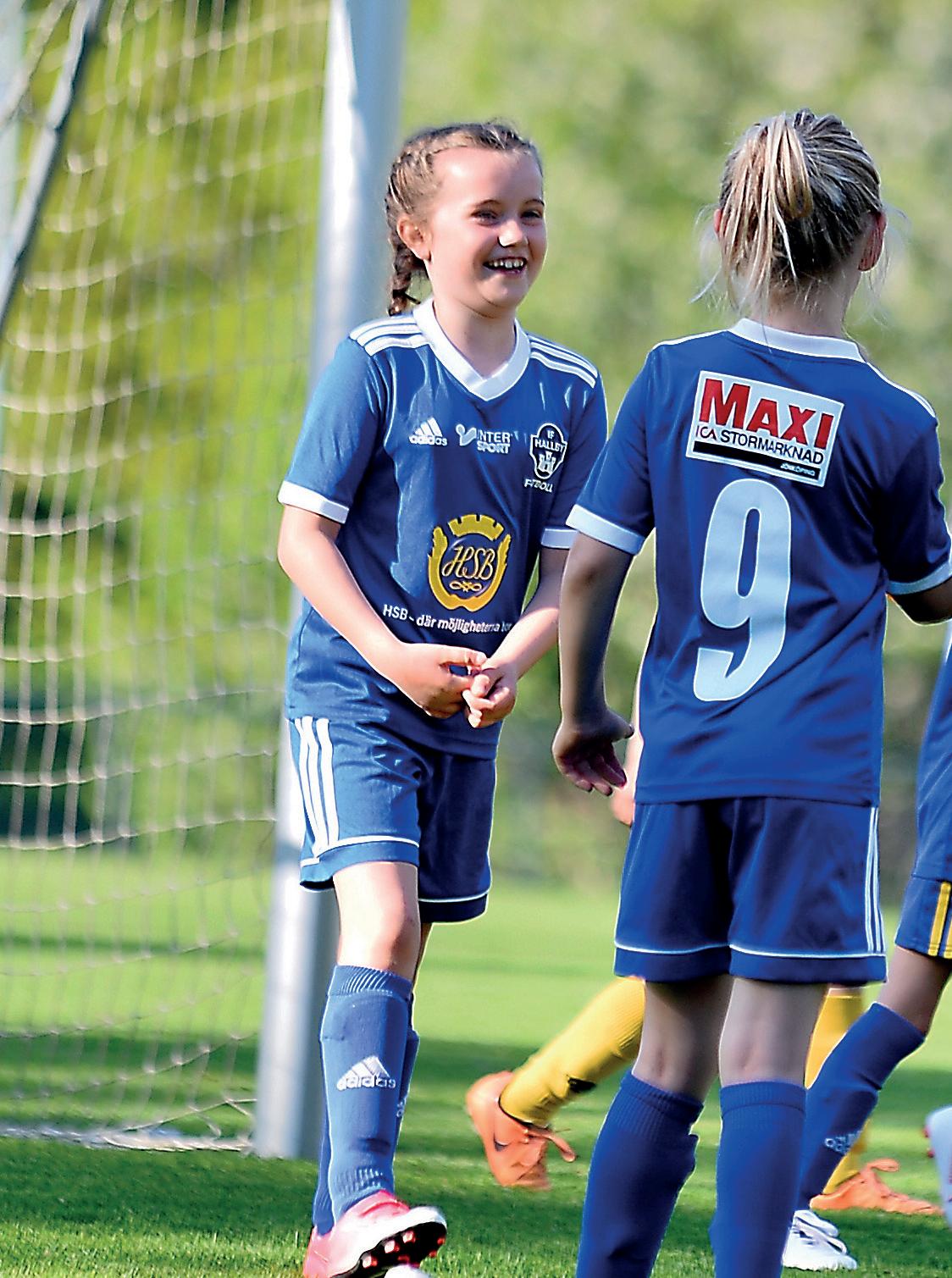
Box 1002, 331 29 Värnamo, Sweden +46 370-69 56 20, info@protongroup.com protongroup.com