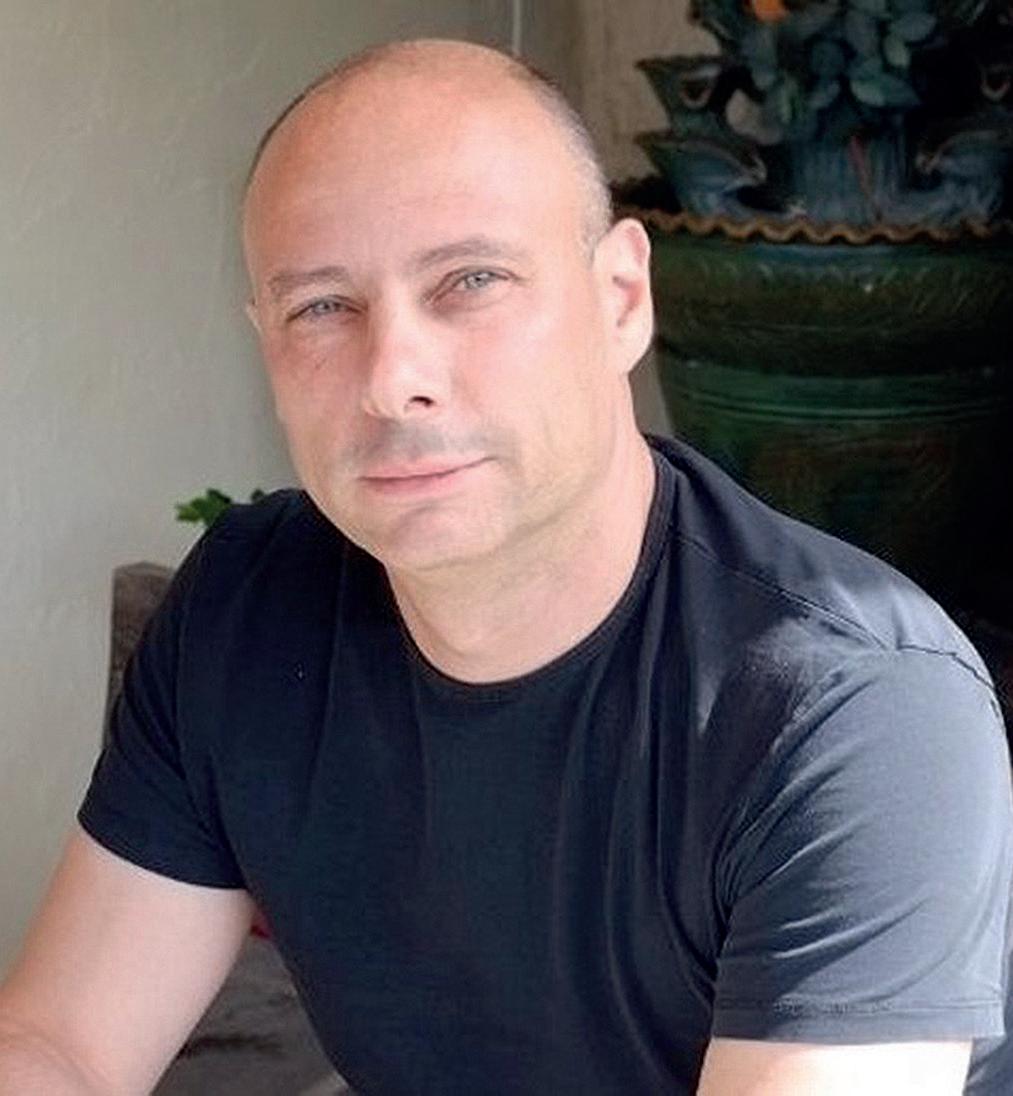
5 minute read
Rassegna internazionale di scienza e tecnologia
Più di dieci riviste esaminate
Ventunesima puntata della rubrica dedicata agli articoli di stampa estera selezionati dal comitato di redazione di Elastica, composto da Fabio Bacchelli, Rino Gilotta e dal team di Cerisie, coordinati da Maurizio Galimberti
INDAGINI PER MIGLIORARE LA CALANDRATURA DI COMPOSITI ELASTOMERICI ALTO VISCOSI Testata: Kautschuk Gummi Kunststoffe, 4, 22 (2022) Titolo: Investigations to improve calendering of high viscous rubber compounds Autori: Oliver Krieger, Benjamin Klie, Ulrich Giese
A CURA DI FABIO BACCHELLI
La calandratura è un processo comunemente utilizzato nell’industria della gomma per produrre lastre di alta qualità con elevata precisione geometrica e basso spessore. Una calandra è costituita da coppie di rulli disposte coassialmente, che ruotano in direzioni opposte e sono trattenute da un’intelaiatura. I rulli della calandra possono essere regolati alla temperatura di lavorazione desiderata e ogni rullo può essere impostato individualmente con una velocità di rotazione definita per creare attrito. Le mescole ad alta viscosità mostrano frequentemente difficoltà di lavorazione durante la calandratura. L’inefficiente comportamento Tack della mescola porta al distacco prematuro della lamiera calandrata e provoca raggrinzimento e formazione di bolle e intrappolamento d’aria. A causa della bassa precisione dimensionale che ne risulta, i requisiti di qualità non vengono raggiunti. In precedenti pubblicazioni è stato affrontato lo sviluppo di una nuova metodologia di calandratura per lavorare mescole di gomma ad alta viscosità in lastre di alta qualità con altezza fino a 2 mm, attraverso l’uso di un composto adesivo (tackifier). Viene qui proposta una ulteriore tecnica alternativa, basata sui concetti di “frictioning” e skimming”. La sperimentazione è condotta utilizzando una mescola a base NBR, caricata con 135 phr di silice silanizzata, priva di plastificanti e contenente il sistema vulcanizzante a zolfo. La viscosità Mooney del compound è 115, ML (1+4) a 100 °C. La calandra, da laboratorio, è del tipo a 4 rulli. Il rigonfiamento del compound alle condizioni di processo viene determinato separatamente utilizzando un modello semplificato a 2 rulli. In questo esperimento i “roll nips” 2 e 3 vengono utilizzati come una sorta di zona di calibrazione, con tolleranze modificate ad hoc rispetto al numero 1, sfruttando il fatto che un maggiore attrito tra rulli 2, 3 (e 4) impedisce al foglio di gomma di raggrinzirsi e formare bolle. Un altro effetto di questa configurazione è che la velocità di rotolamento ridotta dei rulli 1 e 2 porta a una migliore alimentazione del compound. A causa della bassa adesività di lavorazione della mescola, la velocità circonferenziale dei rulli di alimentazione 1 e 2 è il fattore limitante della linea di calandratura. Un foglio di gomma così prodotto ha un’elevata precisione geometrica di ± 0,02 mm senza difetti superficiali. Con un’altezza della lastra compresa tra 1 e 2 mm non si verificano intrappolamenti di gas capaci di influire sulla qualità, nel senso che il diametro dei difetti occasionali, inferiore a 1 mm, si
Fabio Bacchelli, direttore tecnico Tyre di Versalis
risolve durante la vulcanizzazione. Aggiungendo al compound 4 phr di una resina fenolica tackifier il comportamento in alimentazione può essere migliorato in modo significativo con una qualità del foglio costante e una migliorata stabilità del processo. Per trasferire i risultati della prova su una calandra in scala industriale, devono essere considerati alcuni fattori e limitazioni. In generale, all’aumentare del diametro del rullo, la pressione di contatto risultante aumenta di un fattore che può essere calcolato. Ne consegue che la velocità massima della linea dovrebbe essere ridotta rispetto ai modelli con rulli più piccoli. Il principale fattore limitante è un peggioramento del comportamento in alimentazione del compound nel punto di contatto 1 della calandra.
IL PROCESSO DI DEVULCANIZZAZIONE HSM, UNO STUDIO PRATICO Testata: Gummi Fasern Kunststoffe, 5, 25 (2022) Titolo originale: The HSM devulcanization process - a practical study Autore: Rodrigo Diaz
A CURA DI FABIO BACCHELLI
Oggi lo smaltimento e il trattamento dei rifiuti di gomma rappresentano una delle più grandi sfide di settore. Per ragioni di marketing, di consapevolezza ambientale o di rispetto delle nuove normative, i produttori di gomma stanno cercando di individuare soluzioni per riciclare tipologie di rifiuti, che andrebbero altrimenti smaltite mediante incenerimento o pirolisi. Idealmente, il riciclo della gomma dovrebbe essere mirato alla devulcanizzazione, cioè alla rottura del network di vulcanizzazione preesistente, in modo tale che il materiale di riciclo possa essere nuovamente inserito nel ciclo di lavorazione. Le tecniche sviluppate fino a ora rientrano generalmente in due categorie. I processi chimici comprendono tutti quei metodi in cui composti chimici o microrganismi vengono utilizzati per attaccare e rompere il network di vulcanizzazione. I processi fisici sfruttano invece procedimenti meccanici o termomeccanici, microonde e ultrasuoni. Un processo di devulcanizzazione fisica come quello qui illustrato sfrutta le diverse energie di legame: un legame C-C è più forte di un legame C-S, che a sua volta è più forte di un legame S-S. L’idea è quella di fornire alla gomma una certa quantità di energia per rompere selettivamente i legami S-S e C-S del network, ma non i legami C-C che appartengono alle catene polimeriche. Il processo HSM (High Shear Mixing) consiste nell’esporre la gomma vulcanizzata a elevate sollecitazioni di shear e deformazione, in modo da disgregare selettivamente i legami costituenti il network a zolfo. Questo viene fatto con l’aiuto di un’apparecchiatura costituita da due coni metallici coassiali, dotati di scanalature e posti a una certa distanza fissa (gap). La gomma viene introdotta tra questi due coni e lavorata con una combinazione di vari parametri quali gap, velocità di rotazione, senso di rotazione. Durante il processo HSM, che consente una lavorazione in continuo del materiale, la gomma tende a riscaldarsi e, per evitare un aumento incontrollato della temperatura viene utilizzato un sistema di raffreddamento composto da due circuiti indipendenti all’interno dei coni. Utilizzando questo processo, è stato condotto uno studio con tre diverse tipologie di gomma (AEM, FKM, NR). Per ciascun materiale, una mescola di riferimento costituita esclusivamente da gomma fresca è stata confrontata con una versione corrispondente contenente il 10-20% di materiale devulcanizzato via HSM. Tutti i campioni non vulcanizzati mostrano una viscosità maggiore rispetto a quella dei riferimenti, senza tuttavia influenzare significativamente il test di iniezione. I tempi di vulcanizzazione rimangono sostanzialmente invariati, mentre la durezza risulta leggermente inferiore a quella dei compositi di riferimento. L’introduzione di prodotto riciclato HSM riduce il carico a rottura nel caso di compositi a base AEM e, in modo meno importante nel caso di FKM e NR. Il confronto di campioni con identica percentuale di gomma trattata, ma diversa granulometria, mostra che ci si avvicina meglio alla prestazione del riferimento utilizzando particelle più piccole. Nel complesso, le deviazioni misurate sono tali da consentire il rispetto dei requisiti associati al materiale di riferimento e lasciano spazio, nei casi meno soddisfacenti, a un procedimento di correzione formulativa attraverso strategie tradizionali (oli, plastificanti, agenti vulcanizzanti, ecc.).