
10 minute read
Un“pockerd’assi”insintoniacon efficientamentoerisparmioenergetico

Frigosystem: i quattro nuovi equipaggiamenti presentati al K di Düsseldorf Un “poker dʼassi” in sintonia con eff icientamento e risparmio energetico
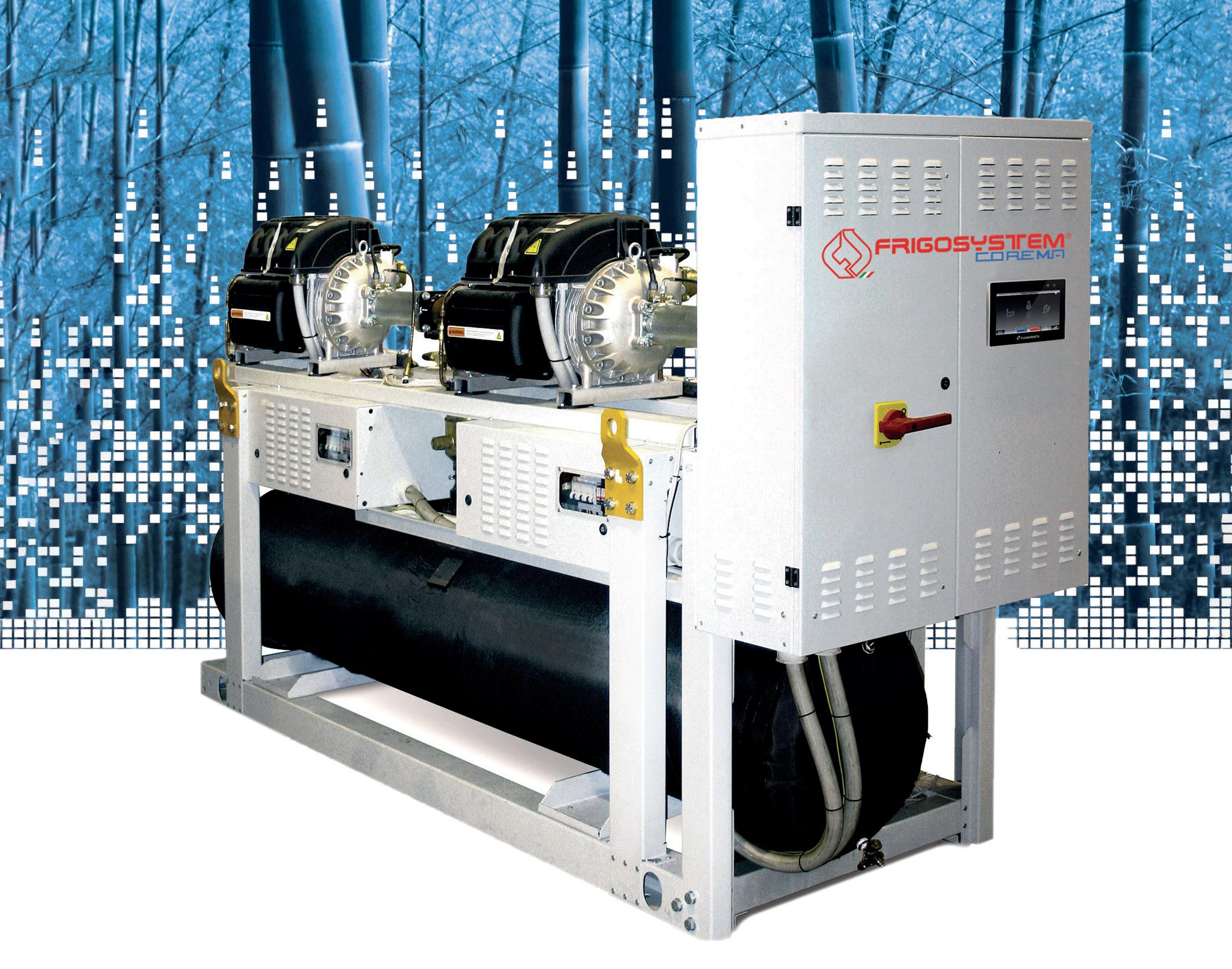
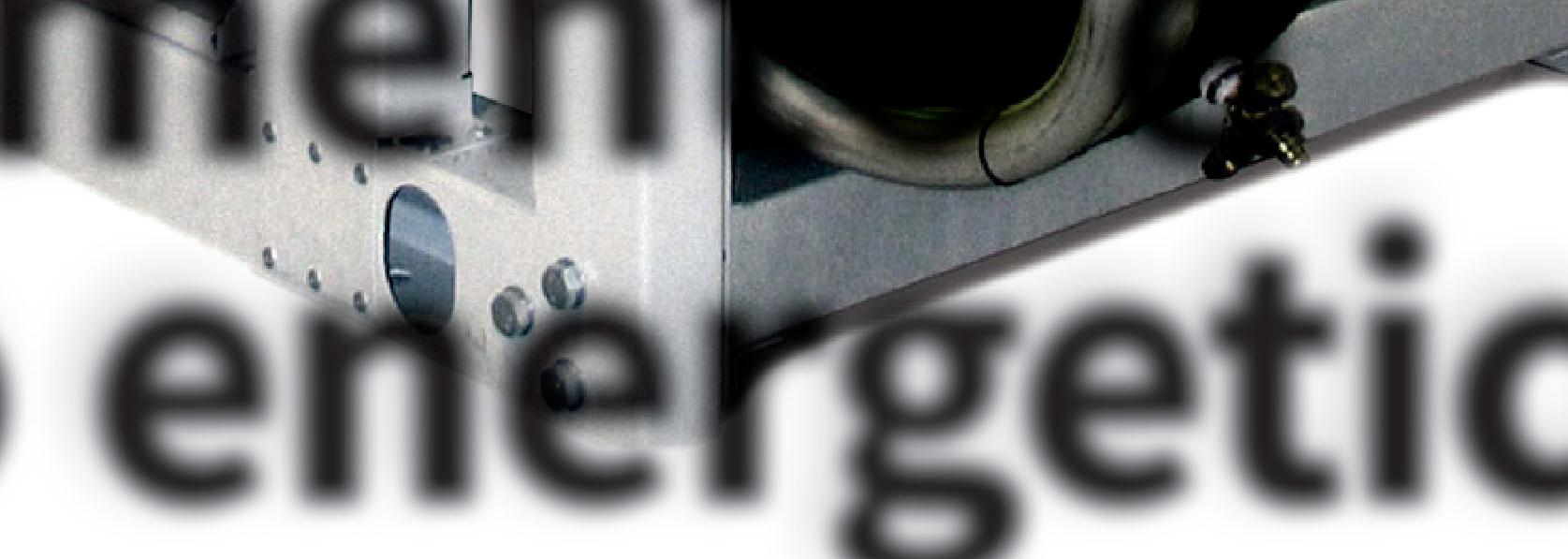
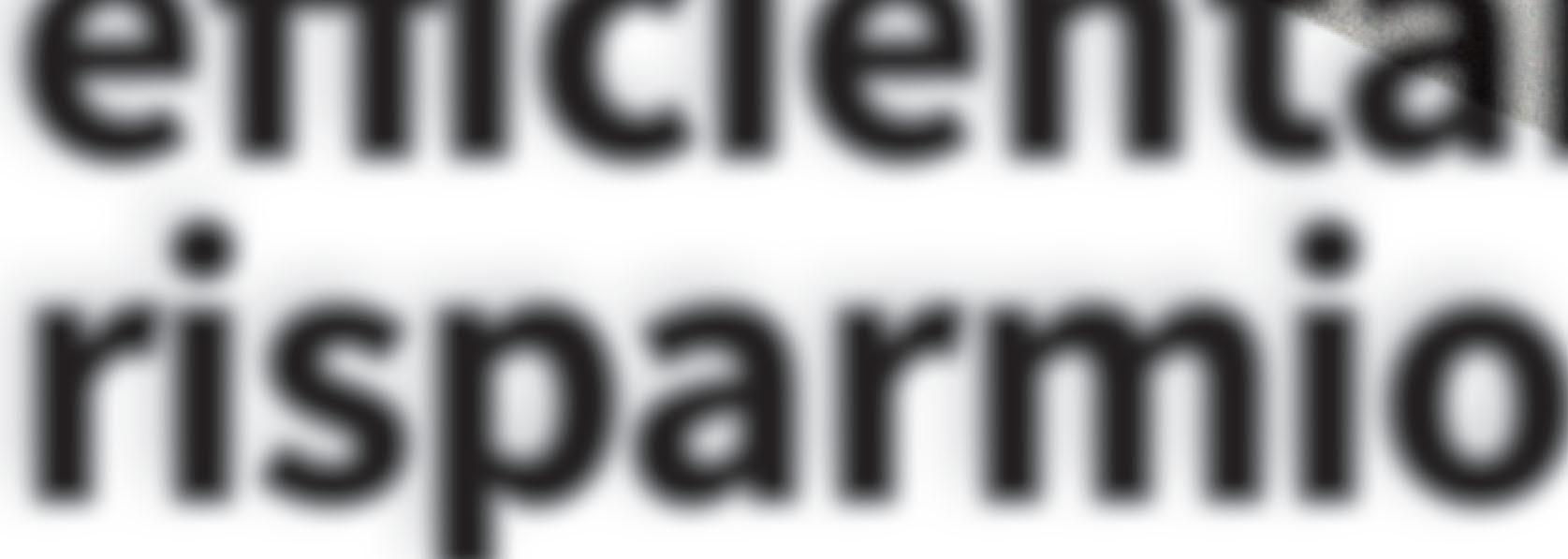
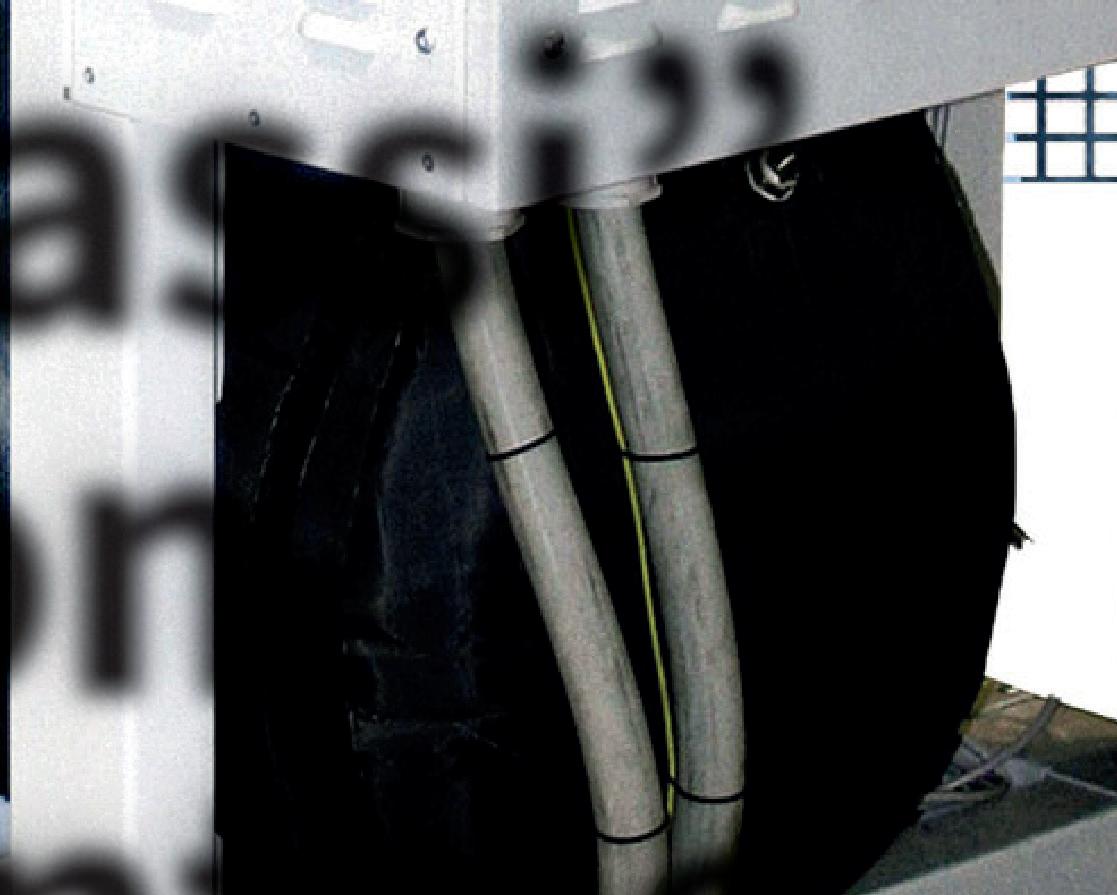
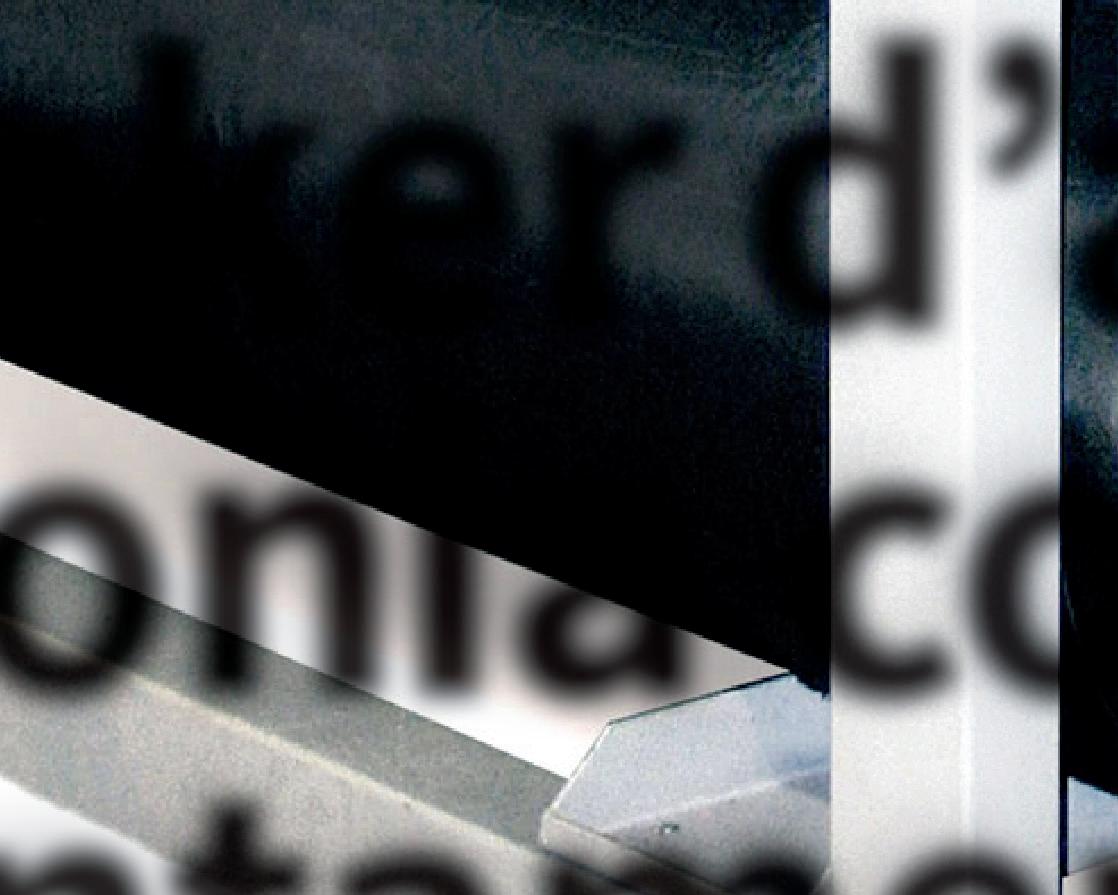


Dal 19 al 26 ottobre scorso, sul suolo tedesco, la casa italiana ha presentato quello che è lo stato dell’arte in materia di termoregolazione industriale racchiuso in quattro unità dove gli alti standard qualitativi e innovativi fanno la differenza soprattutto in ambito di estrema efficienza energetica
DI ERMANNO PEDROTTI E LUCA MEI
Nella lavorazione di materie plastiche e gomma, come anche nella produzione di materiali speciali, il controllo della temperatura e la termoregolazione sono funzionalità a dir poco indispensabili per ottenere i requisiti fisici e tecnici riportati nelle specifiche degli articoli processati. E questo è un primo dato oggettivo.
Detto questo, le moderne tecnologie di termoregolazione industriale possono contribuire a raggiungere nuovi traguardi in tema di efficienza energetica grazie al recupero del calore di scarto. Piuttosto che dissipare quell’energia termica nell’ambiente, la si può infatti recuperare per reimpiegarla nel riscaldare i fluidi coinvolti in altre fasi del processo produttivo o nel riscaldare ambienti e acqua per uso sanitario, portando così benefici in termini di riduzione dei consumi dell’energia primaria. E questo è un secondo dato oggettivo.
Un’azienda che ben conosce l’uso intelligente dell’energia e del calore di scarto negli impianti industriali è Frigosystem di Caronno Pertusella (Varese): “È dal 1970 che progettiamo e costruiamo unità di refrigerazione, termoregolazione e centrali frigorifere pronte per essere collegate agli impianti dei clienti”, ci ha raccontato Alessandro Grassi, amministratore unico dell’azienda lombarda, che aggiunge: “Non paghi del fatto che la nostra gamma di equipaggiamenti già soddisfi ampiamente sia le normative europee sull’efficienza energetica sia la legislazione Fgas sui gas a basso impatto ambientale (GWP - Global Warming Potential), un serrato working progress svolto dai nostri ingegneri del reparto R&D ha permesso di alzare ancora di più l’asticella dell’efficientamento e del risparmio energetico. Risultati che, con grande orgoglio, abbiamo presentato l’ottobre scorso al K di Düsseldorf tramite quattro nuove macchine: talune esposte all’interno del nostro stand e molte altre presso stand di clienti sia italiani sia esteri, queste ultime tutte in funzione live, tra cui il chiller monoblocco più potente mai esposto in
funzione al K ossia un chiller da 1500kw di potenza frigorifera a servizio di una linea di produzione stretch film”.
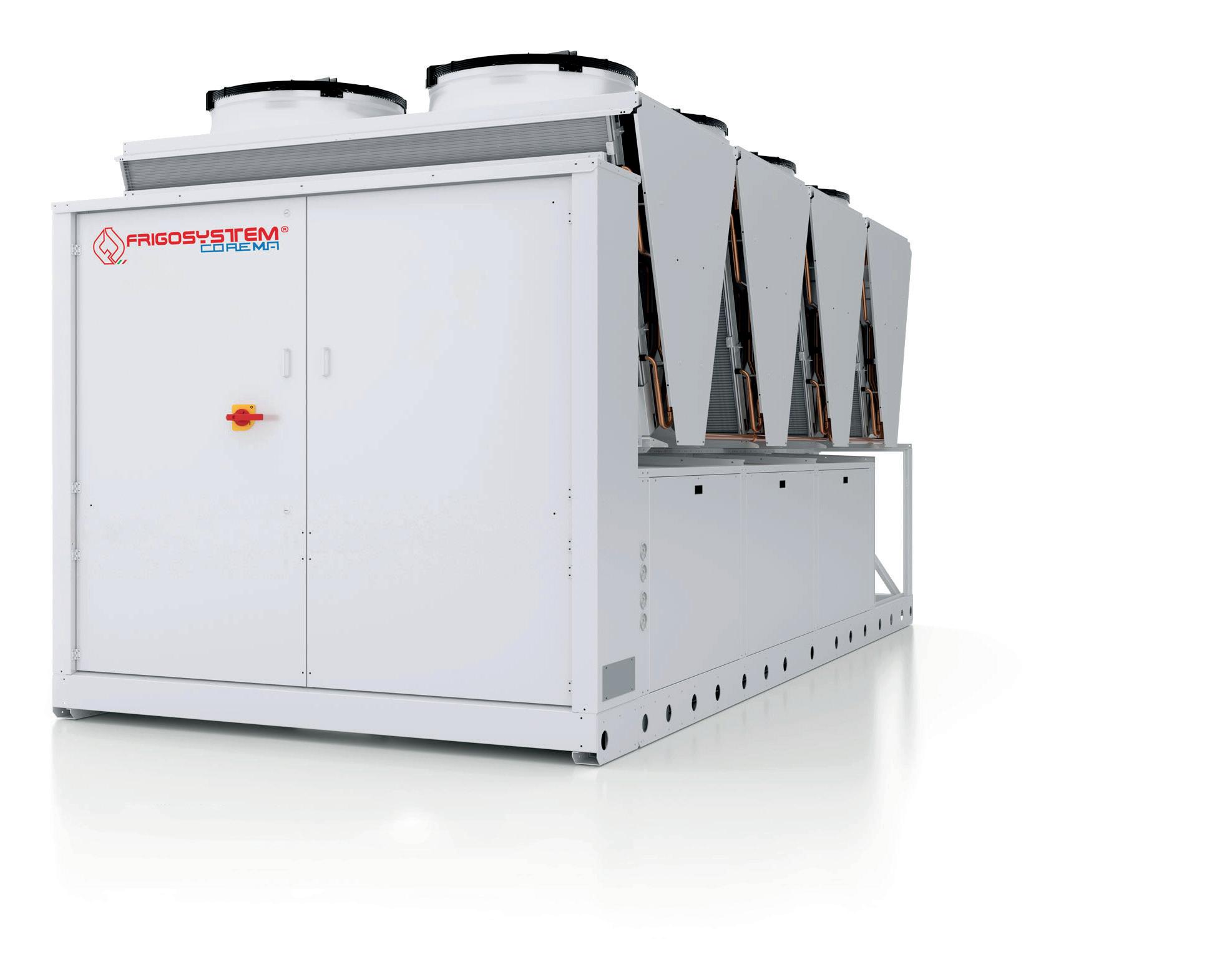
Identikit delle quattro macchine esposte in Germania
Il “poker d’assi” calato l’ottobre scorso da Frigosystem in Germania rappresenta un unicum in tema di risparmio energetico e innovazione destinato a non passare inosservato agli occhi degli addetti ai lavori che, a vario titolo, si occupano di trasformazione delle materie plastiche. La prima soluzione è rappresentata dalle varianti D e D-HT della serie Raca Plus Energy e rappresenta l’evoluzione di un refrigeratore-riscaldatore già intravvisto al Plast 2018 di Milano, allora ancora in fase sperimentale. “In termini di ricerca e sviluppo è da tempo che noi affrontiamo l’apparente paradosso per cui chi produce freddo produce caldo”, ha ripreso Grassi, “nel senso che in base al tipico circuito inverso della pompa di calore, da un lato l’impianto frigorifero produce del freddo e, dall’altro, produce del caldo. Concetto banale e scontato, in fisica. Con questo voglio dire che il busillis stava nello svincolare una fonte dall’altra. È noto che, per esempio, a fronte della domanda di 100 kW di freddo la centrale frigorifera, di default, ne produce circa 115kw di caldo; se non di più. Parimenti è noto che quel caldo lo si può buttare in ambiente o riutilizzare, ma se lo si riutilizza lo si deve fare in toto per evitare che l’equilibrio della macchina frigorifera si sbilanci e non funzioni più a dovere, questo fino ad oggi è stato il grande limite del recupero di calore. Ed è proprio lì che i nostri ingegneri hanno ragionato sull’uso di compressori scroll ad alta efficienza in versione con motore brushless DC e azionati da inverter, come pure sull’interfacciamento con elettroniche molto spinte per poter riutilizzare quel calore dallo 0 al 100% in modo progressivo e indipendente dalla fonte fredda. Detto questo, i primi risultati li avevamo, in effetti, anticipati a Plast 2018 di Milano. Due, all’epoca, gli ambiti applicativi. Il primo riguardava i tipici grossi stampi che necessitano stazioni di preriscaldo in attesa d’essere inseriti in macchina, per non inficiare i tempi di avvio ciclo. Applicazione tutt’oggi in essere, ma pur sempre di nicchia che ha comunque abbattuto per i clienti che ne hanno fatto uso l’85% del costo energetico nelle stazioni di preriscaldo. Il secondo caso riguardava i lavaggi a valle delle macinazioni di scarti plastici; processo che ben si sposava con le versioni più recenti dei nostri chiller, non fosse altro perché allora l’economia circolare era proprio di nicchia”. Nicchia sì, ma fortunatamente destinata a durare poco. Con l’impennata della green economy tanti riciclatori hanno potenziato i loro impianti di lavaggio per, in soldoni, avere più qualità e più margine. Lì Frigosystem ha capito che era giunto il momento di “pigiare l’acceleratore” sull’incremento d’efficienza. “Prima del 2019-2020 il lavaggio delle scaglie di plastica post macinazione era fatto con acqua fredda”, ha puntualizzato Grassi, “anche con due problematiche non banali: le colle insite negli imballi non venivano ben rimosse e l’acqua usata era tantissima. Vero è che in breve tempo i produttori di colle ne hanno messo a punto alcune meno difficili da rimuovere, a patto di usare non più acqua fredda bensì tiepida. Il mix di colle meno aggressive e l’uso di acqua a 45°C ha dato buoni risultati; non solo le scaglie erano più pulite, ma il consumo di acqua è precipitato. Se a ciò

aggiungiamo che con le tecnologie di Frigosystem l’acqua la si riscalda praticamente a costo zero, è possibile affermare che il cambio di passo ottenuto è stato a dir poco eclatante”. Dato che “l’appetito vien mangiando”, poco più di un anno fa Frigosystem ha ritenuto che quel refrigeratore-riscaldatore poteva “dare ancora di più”. Detto fatto: i tecnologi della casa lombarda hanno partorito il Raca Plus Energy D-HT che a Düsseldorf così tanto ha impressionato i visitatori. “Il mondo della termoregolazione, parlo cioè del puro riscaldamento, è sempre stato approcciato tramite resistenze elettriche”, ha spiegato ancora Grassi. “Questo perché quei 45°C dell’acqua citati poco fa erano sì allineati ai bisogni degli impianti di lavaggio, ma oltre non si andava proprio, cosa che ci stava stretta. Abbiamo quindi deciso di affidare a un pool d’ingegneri della ricerca e sviluppo il compito d’interrogarsi sulla possibilità, o meno, di poter superare quel limite. Dopo poco più di un anno di elucubrazioni, con nostro immenso stupore, quel pool è riuscito non solo a portare l’acqua fino a 80-85°C, ma è stato pure in grado di stabilizzare alla perfezione la costanza nel tempo di quelle temperature. Il che consente di coprire l’80% delle applicazioni industriali dove serve acqua calda, svincolando la gene-
Il modello D-HT della serie Raca Plus Energy
RACA PLUS ENERGY D e DHT
Una nuova tecnologia per recuperare il calore libero dal raffreddamento di processo
Utilizzatore 1 100 % Riscaldamento libero
Utilizzatore 2
30% versione D +60°C (140°F) 70%versioneDHT +80°C(176°F)
Schema di funzionamento dei sistemi Raca Plus Energy D e DHT
KBFC Tropcal: l’ultima “carta” calata da Frigosystem al K 2022 riguarda un nuovo sistema di raffreddamento per linee in bolla in ambienti molto umidi
Una veduta dello stand di Frigosystem al K 2022 con i prodotti in esposizione
Alessandro Grassi, amministratore unico di Frigosystem
razione di calore dall’uso delle resistenze elettriche o di bruciatori a gas. Una vera rivoluzione in termini di risparmio energetico. Avendo infatti le resistenze elettriche un’efficienza di 1:1, per ottenere 12 kW di caldo assorbono 12 kW d’energia, mentre per gli stessi 12 kW di caldo la nostra unità consuma solo 2,5 kW in caso stia solo scaldando, ma se la stessa macchina stesse fornendo acqua fredda ad altra applicazione come un estrusore per riciclo, allora il consumo si ridurrebbe a 1kw con un risparmio di oltre il 90%”. Non paghi di queste prime due macchine, a Düsseldorf Frigosystem ha pure portato un chiller (serie I-RES) con compressore a levitazione magnetica di terza generazione. A titolo di cronaca, vale la pena ricordare che la levitazione magnetica è un metodo con il quale un oggetto è sospeso su un altro oggetto senza altro supporto che un campo magnetico, appunto. Seppure il teorema dell’inglese Samuel Earnshaw (1805-1888) abbia provato definitivamente che non è possibile far levitare stabilmente un oggetto utilizzando solo i campi elettromagnetici “classici”, esistono tuttavia diversi modi per rendere possibile la levitazione violando i presupposti di tale teorema: per esempio, mediante l’uso di una stabilizzazione elettronica o di materiali diamagnetici. “In tema di risparmio energetico applicato ai processi di raffreddamento, al K abbiamo presentato una nuova versione della ns linea con compressore a levitazione magnetica in grado di raggiungere un’efficienza SEPR pari a 12” (efficienza stagionale annuale indica 1 kW energetico speso = 12 kW di raffreddamento resi), ha specificato Grassi. Dal 2018 a tutti i produttori di chiller e trattamento aria, le normative europee impongono un’etichetta relativa alla classe energetica. Di fatto si tratta di una “conditio sine qua non” per poter proseguire il business. In tale logica il SEPR citato da Alessandro Grassi - acronimo di Seasonal Energy Performance Ratio - è un indice energetico per il raffreddamento che vale solo per l’acqua, non per l’aria. In altre parole, vale solo per chiller industriali con potenze nettamente alti. “Mediamente un chiller tradizionale si attesta su un indice energetico per il raffreddamento pari a 4, nel senso che con un kW di energia produce 4 kW di freddo. In virtù di un non banale lavorio di ricerca e sviluppo che ha portato i nostri tecnologici a sviscerare applicativi ad hoc in ambito elettronico, con un kW di energia la nostra nuova linea con compressori a levitazione magnetica raggiunge il citato indice energetico 12”, ha spiegato Grassi. L’ultima “carta” calata da Frigosystem a Düsseldorf riguardava un nuovo sistema di raffreddamento per linee in bolla da usarsi in ambienti molto, ma molto, umidi. “L’unità in questione si chiama KBFC Tropical”, ha chiosato Grassi, “e fa parte di una nuova gamma di scambiatori per il raffreddamento dell’aria in uscita dall’anello o dal dispositivo IBC (Internal Bubble Cooling), concepita per linee per l’estrusione di film in bolla. Alla base del KBFC Tropical c’è una tecnologia, in attesa di brevetto, che consente di abbattere l’umidità in sospensione dopo il raffreddamento, rendendo così possibile lavorare in ambienti a 35-40°C e con elevati tassi di umidità tipici dei paesi tropicali senza, questione niente affatto banale, diminuire la capacità produttiva della linea. Con KBFC Tropical c’è la certezza di poter lavorare sempre al massimo anche nei periodi dell’anno decisamente più umidi: anche questo aspetto non banale se si pensa ai recenti sconvolgimenti climatici”.

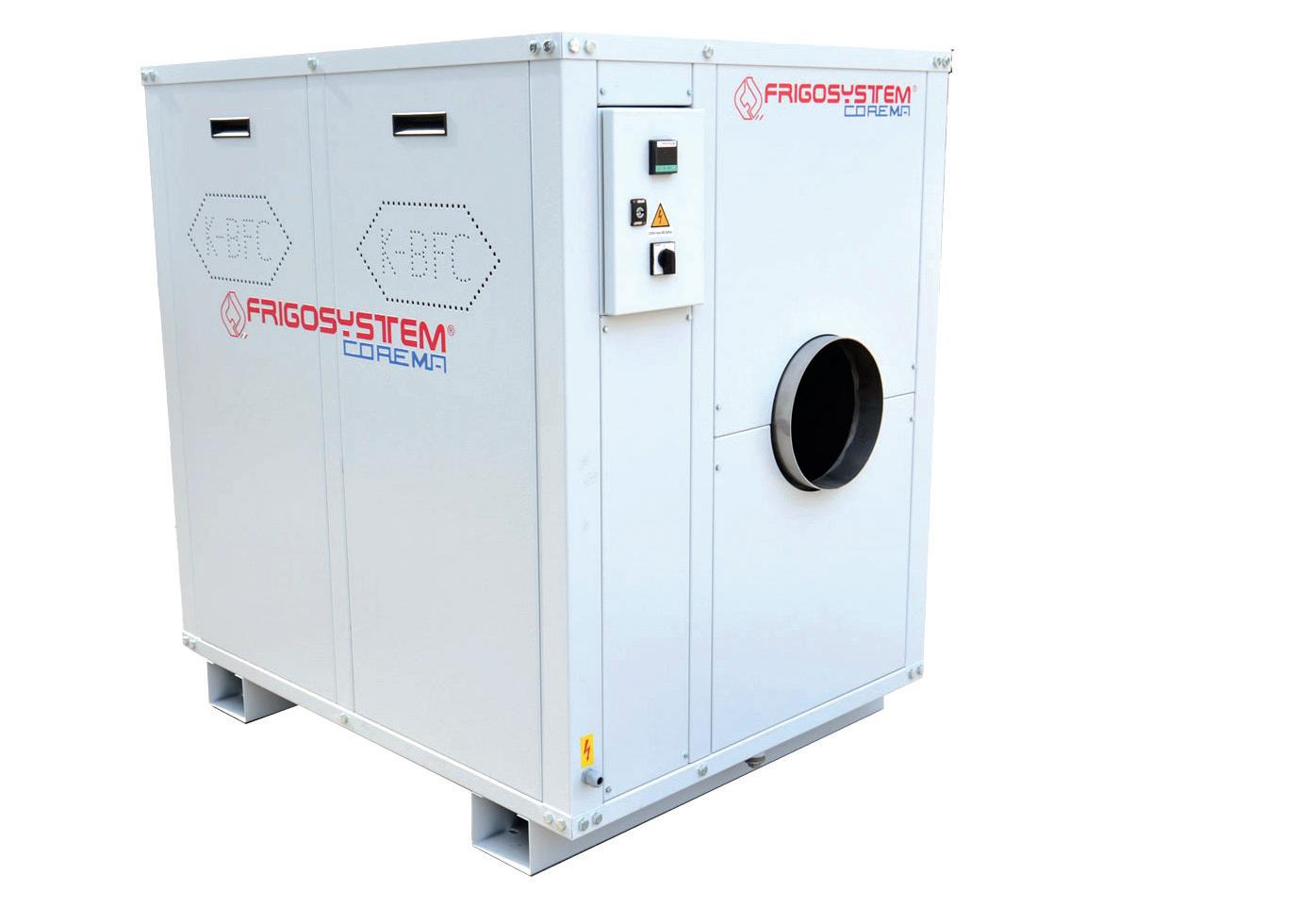
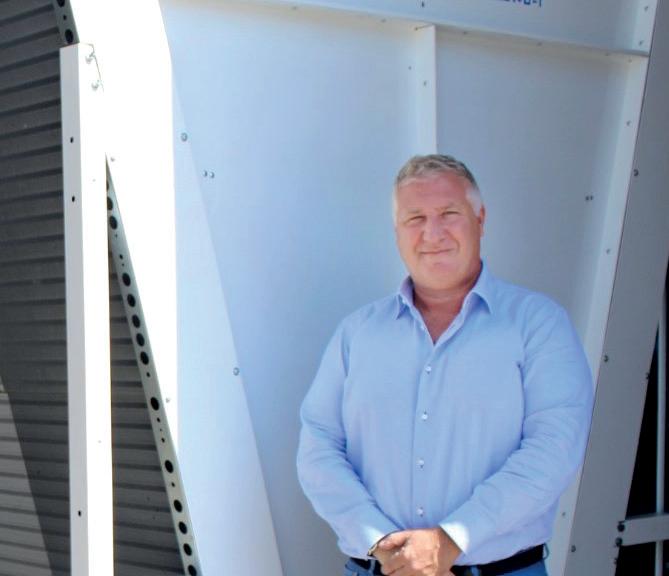
Quando l’innovazione parte dalle “retrovie”
In fase di commiato, l’amministratore unico della casa lombarda ha tenuto a dire che l’efficientamento e il risparmio energetico insiti nel poker d’assi visto a Düsseldorf è frutto, anche, di significative migliorie strutturali e operative compiute in seno all’azienda di Caronno Pertusella. In tal senso già il 2020 aveva visto il raddoppio della superficie dei reparti produttivi che, da 3000 metri quadrati, era salita a 6000 metri quadrati. Inoltre, entro la fine del 2022 è prevista l’ultimazione di altri 2000 metri quadrati pensati nell’ottica di un potenziamento della logistica di magazzino. Non paghi, sempre entro la fine del 2022 entrerà in funzione un sistema fotovoltaico che garantirà 400 kW di energia a zero emissioni di CO2. In tal modo Frigosystem sarà indipendente dalla rete elettrica, eccezion fatta per quando dovrà svolgere i collaudi di macchine molto grosse. In tal caso, Grassi ci ha spiegato che, quell’eccezione si riduce a tre-quattro ore nel corso di una settimana quando, in effetti, dalla rete si dovrà “succhiare” il delta mancante dall’energia autoprodotta.
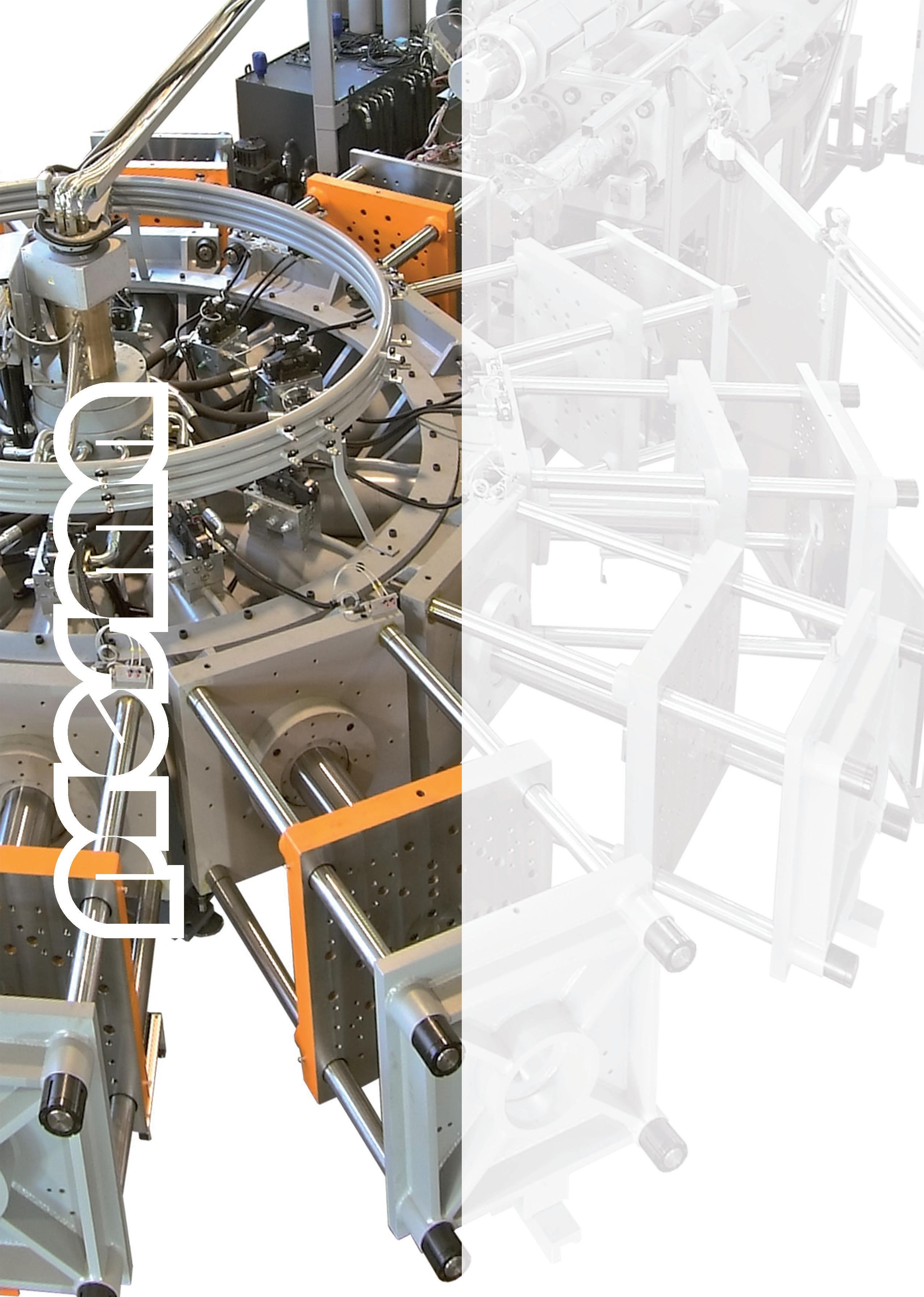
