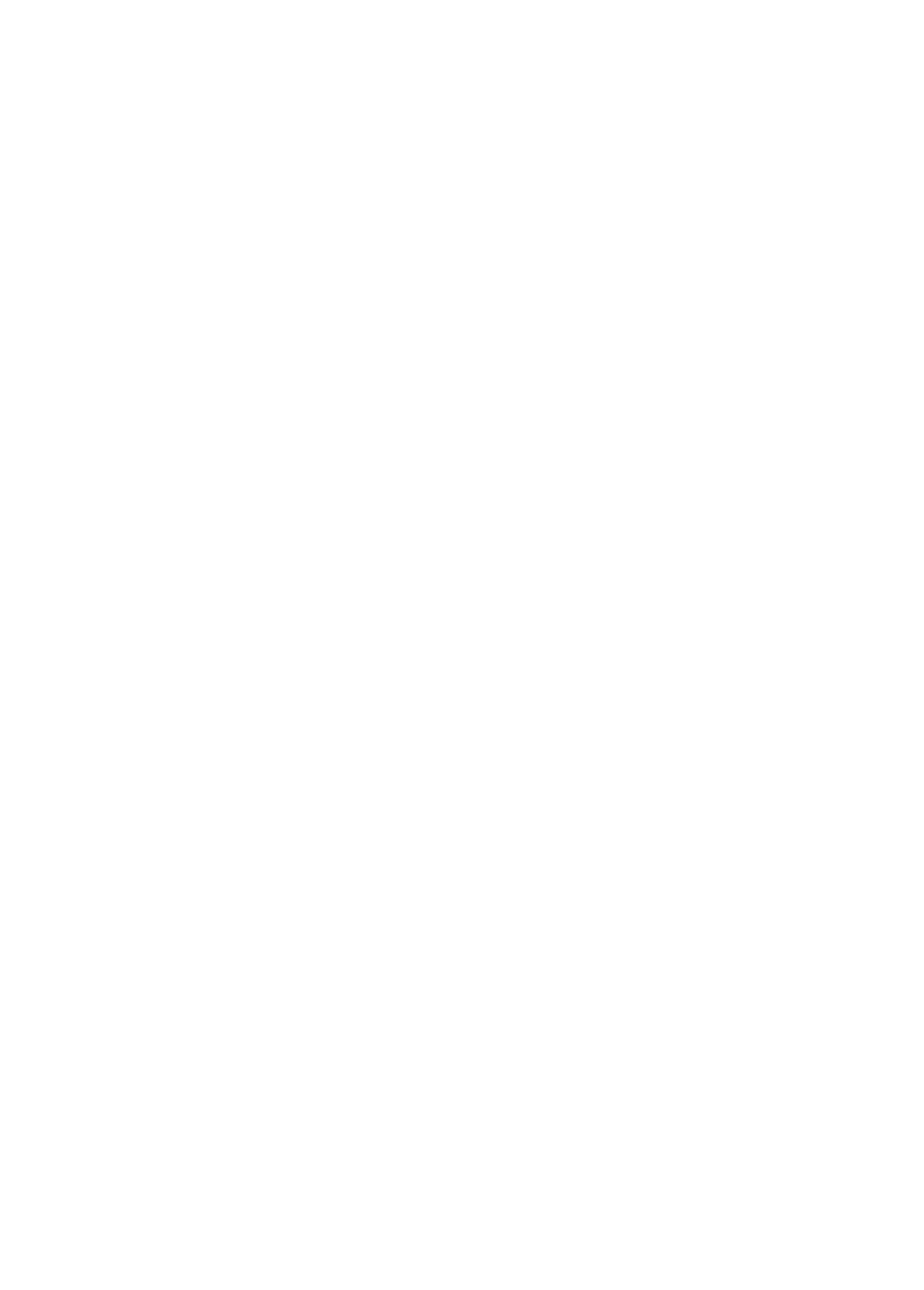
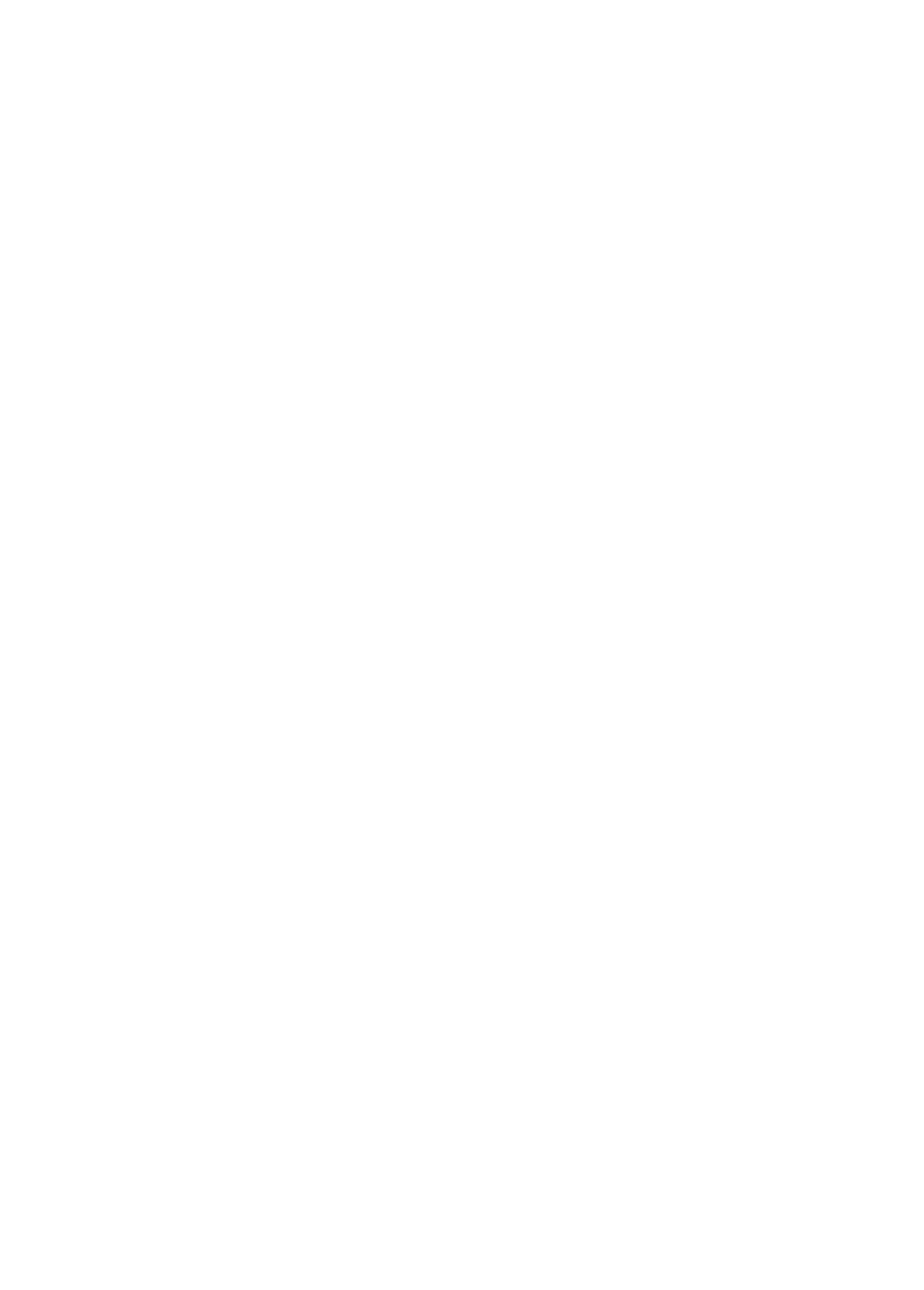
A new era
With one of the largest fleets in the country and exciting changes happening, the future is looking bright for Rail First. PAGE 12
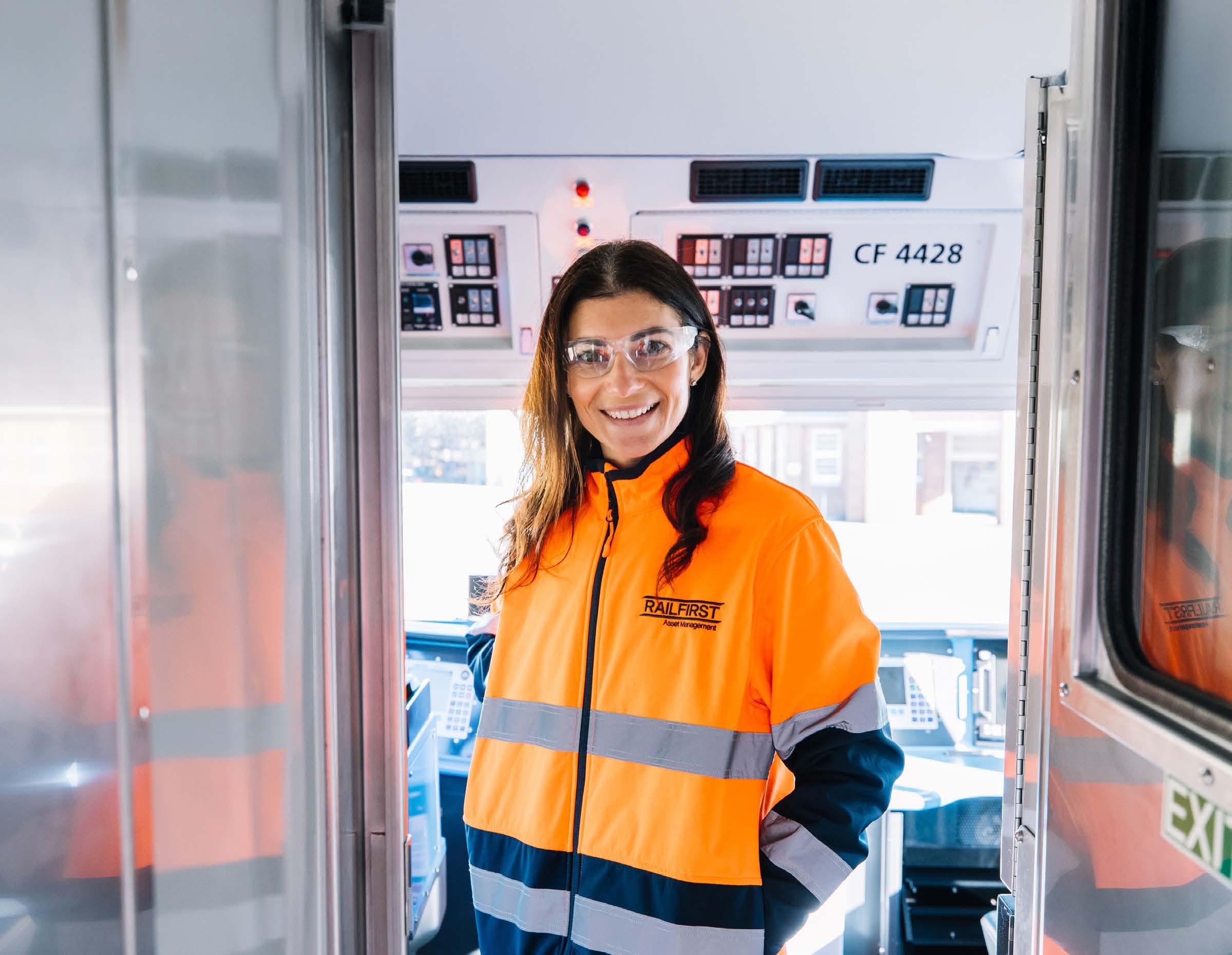
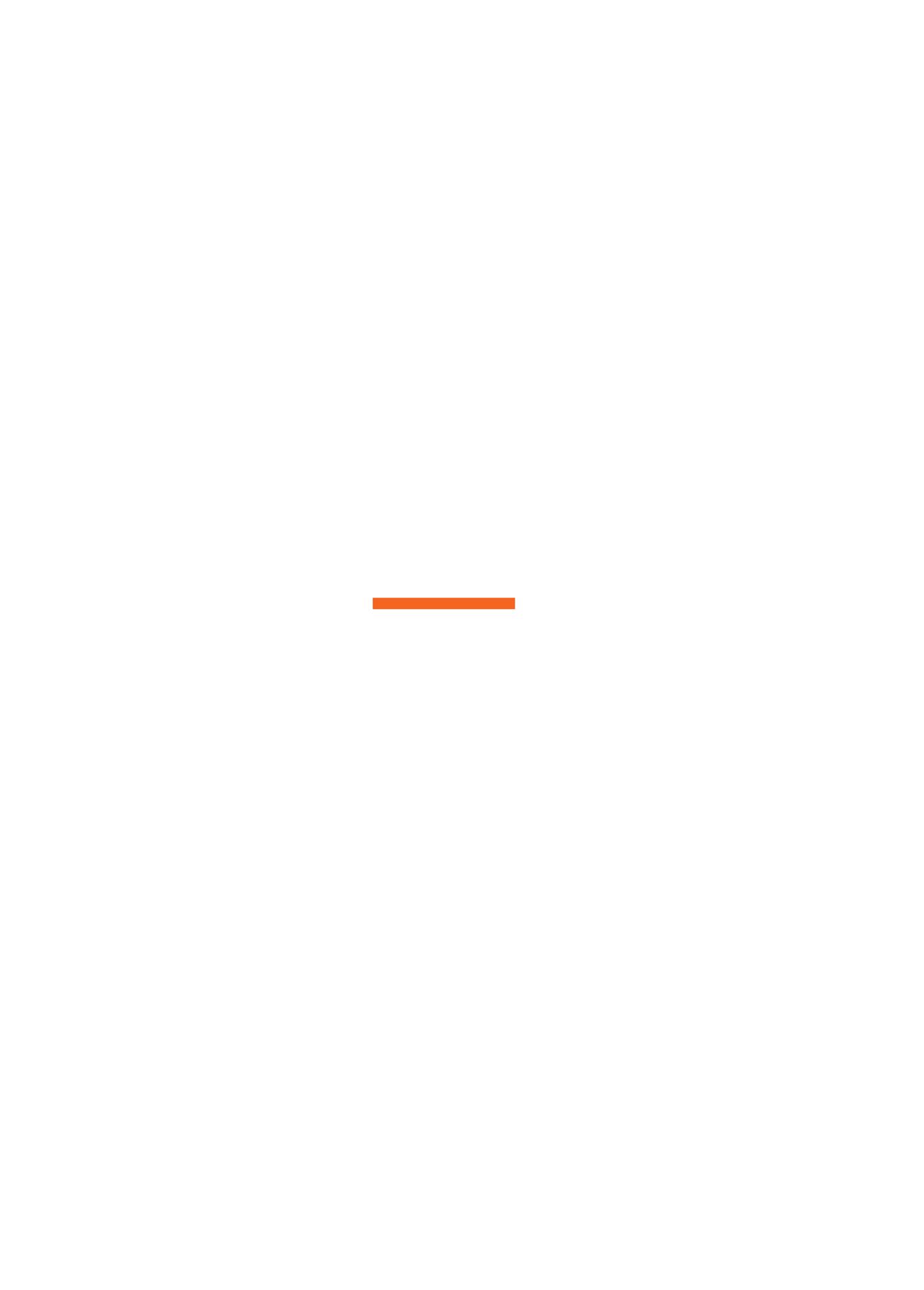
Innovating for solutions
PAGE 24
Battling the elements
PAGE 30
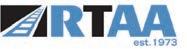

A major milestone PAGE 36
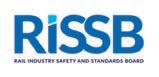


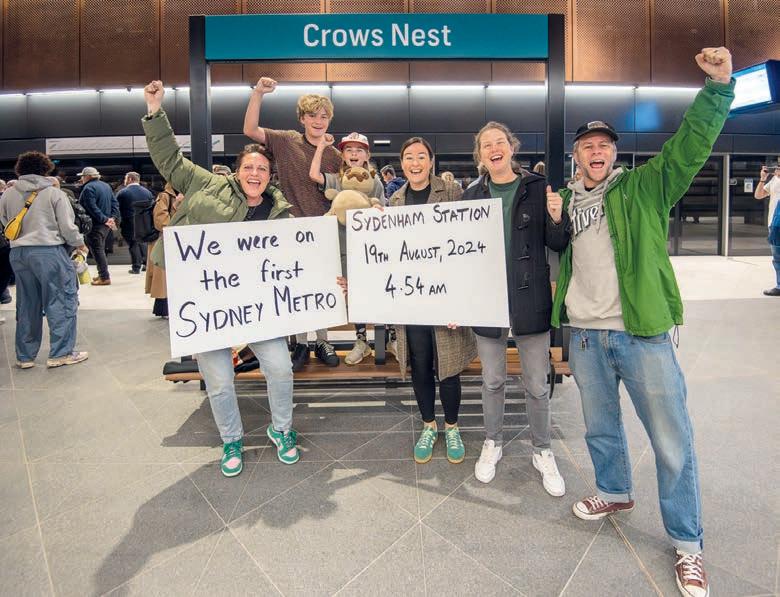
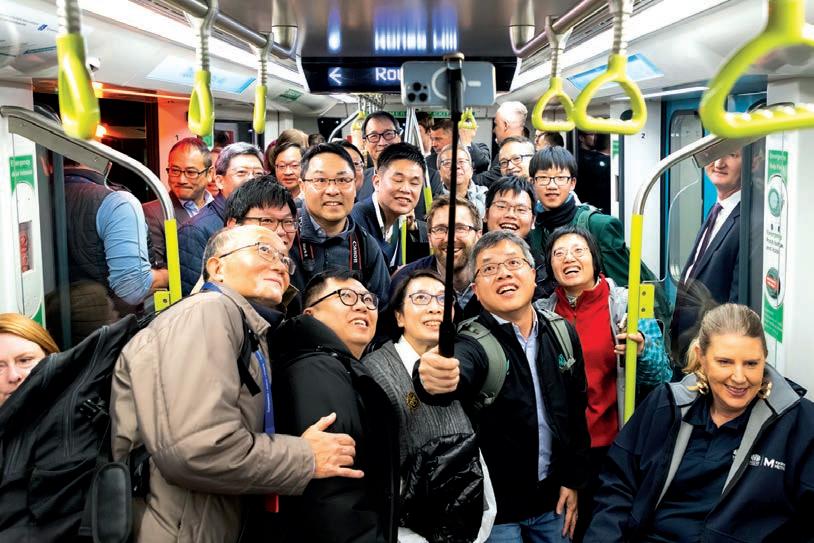
Sydney Metro is Australia’s first fully automated rail passenger system. As the Trains and Systems Integrator and Operator, MTR along with our partners are proud to be part of the team that is reshaping the way people move around our world-renowned city. Visit

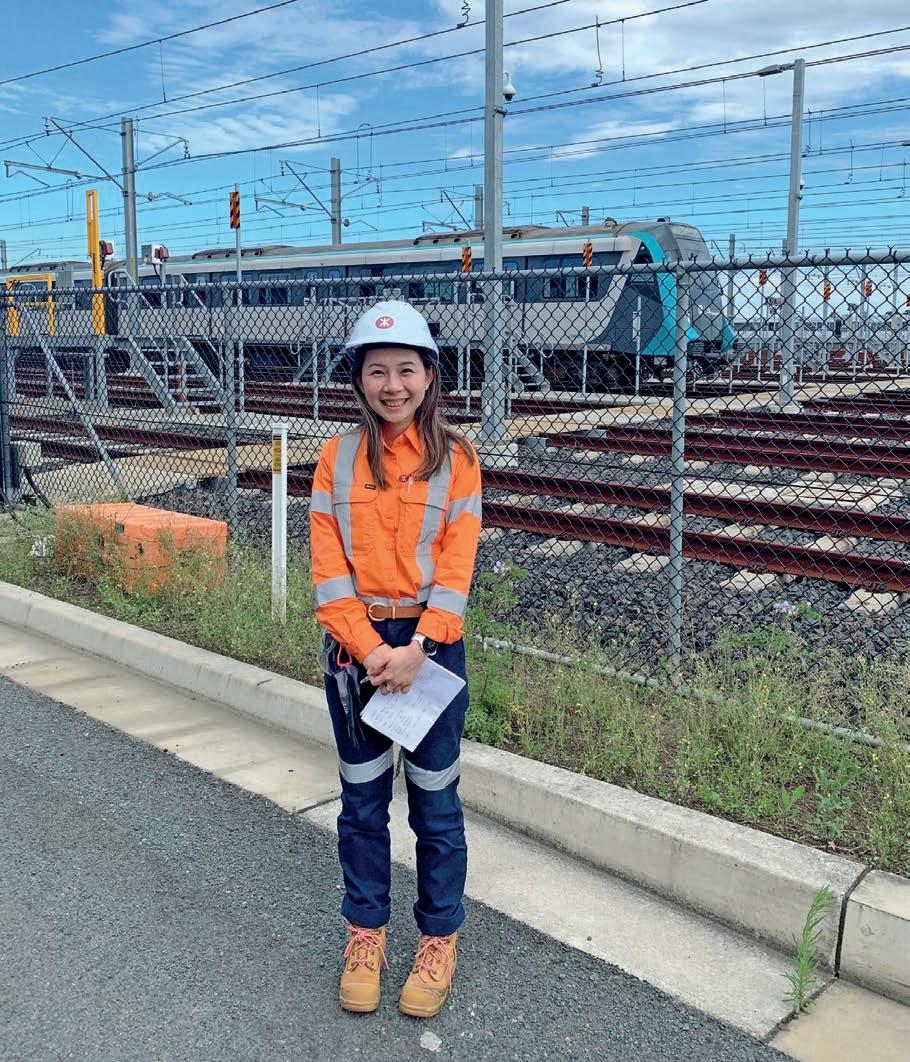
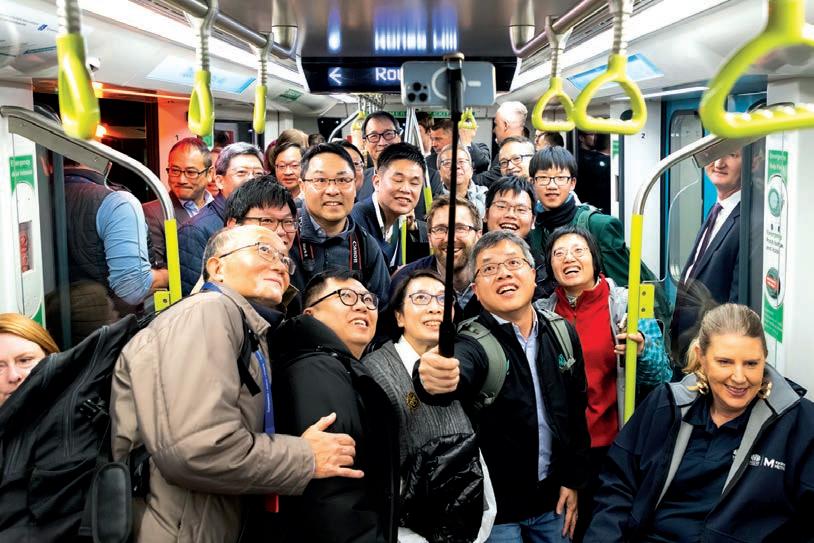
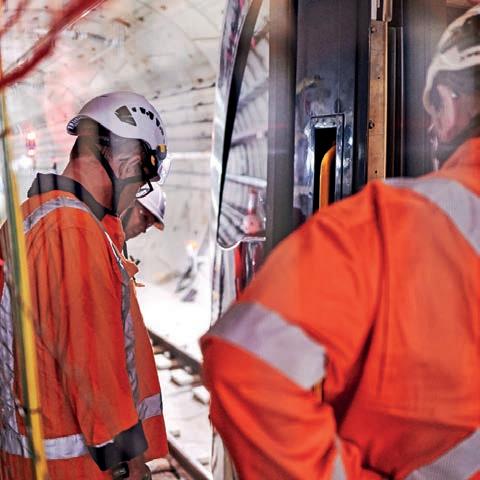
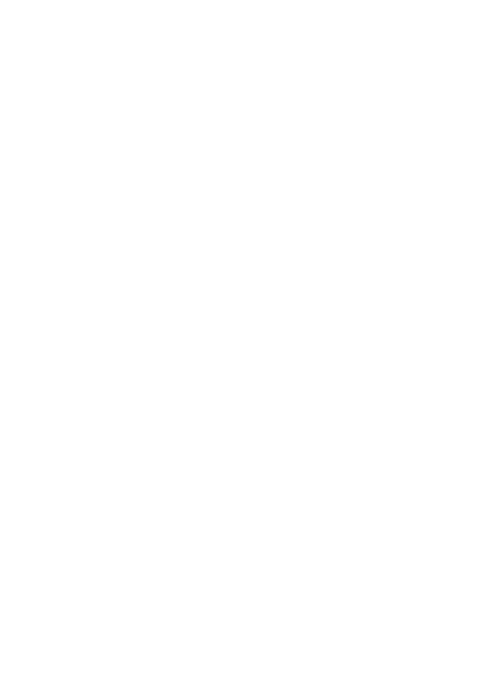
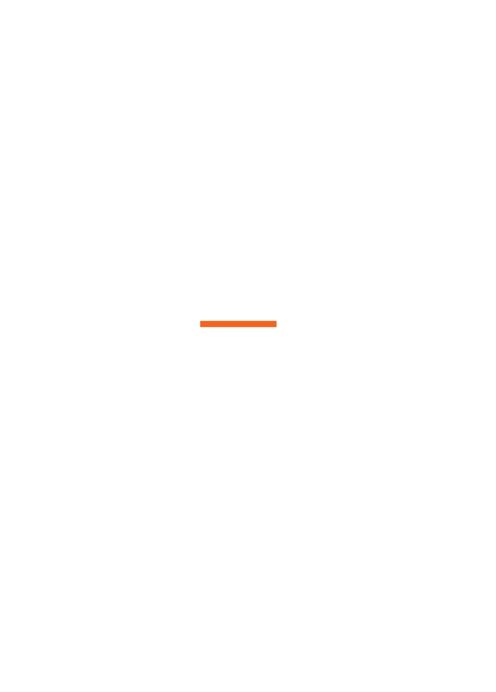
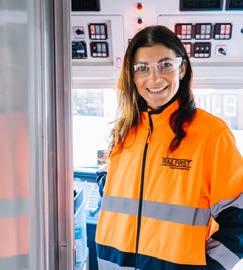
From the Editor
ISSUE 3 - APR 2025
Published by:
379 Docklands Drive
Dockalnds, VIC 3008
T: 03 9690 8766
www.primecreativemedia.com.au
Publisher John Murphy
E: john.murphy@primecreative.com.au
Chief Operating Officer
Christine Clancy
E: christine.clancy@primecreative.com.au
Managing Editor Lisa Korycki
E: lisa.korycki@primecreative.com.au
Editor Kayla Walsh
E: kayla.walsh@primecreative.com.au
Business Development Manager
Arron Reed
M: 0466 923 194
E: arron.reed@primecreative.com.au
Client Success Manager
Isabella Fulford
E: Isabella.fulford@primecreative.com.au
Head of Design Blake Storey
E: blake.storey@primecreative.com.au
Designer Apostolos Topatsis
Subscriptions subscriptions@primecreative.com.au
www.RailExpress.com.au
The Publisher reserves the right to alter or omit any article or advertisement submitted and requires indemnity from the advertisers and contributors against damages or liabilities that may arise from material published.
© Copyright – No part of this publication may be reproduced, stored in a retrieval system or transmitted in any means electronic, mechanical, photocopying, recording or otherwise without the permission of the Publisher.
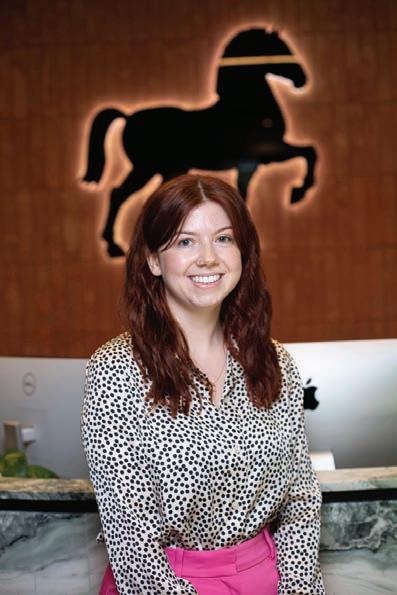
Kayla Walsh
Editor - Rail Express
Welcome to the April edition of Rail Express
The months are flying by in 2025, and so much has already been achieved across the rail industry.
Australia’s largest infrastructure project, Inland Rail, is hitting milestone after milestone as it edges closer to completion. Meanwhile regional New South Wales’s XPT fleet is getting an upgrade, and Canberra light rail is forging ahead with an extension from the city to Commonwealth Park.
The Federal Government has also announced some big investments in rail infrastructure, committing $2 billion to Melbourne’s Airport Rail project and $2.2 billion to the city’s Suburban Rail Loop. Brisbane’s public transport is set to get a boost too, with an extra $50 million towards the delivery of a business case to expand the metro line.
Big things are also happening for our April cover stars, Rail First. One of Australia’s leading providers of rollingstock solutions for the rail freight sector, Rail First has experienced some exciting changes recently, from new ownership and a new and diverse executive team to new spend in local manufacturing. The company recently invested $100 million to acquire 12 new energy-efficient UGL CF44 freight locomotives for its customer base, and we can’t wait to see what it does next.
In New Zealand, Auckland’s City Rail Link has moved into its next phase, with the first test trains travelling through the tunnels.
By the end of 2025, crews will have completed more than 8300 tests to be ready for passengers in 2026. We caught up with the team to get the latest on the project.
Queensland Rail crews have been hard at work after the North Coast and Mount Isa lines were damaged by severe flooding. We took a look at the post-flood recovery, and how new equipment and technology can help the process.
We also shone a light on digitalisation in the rail industry, with KeTech explaining how it’s ready to bridge the gap when it comes to realtime passenger information in Australia.
Siemens Mobility gave us some fascinating insight into the modernisation and extension of Line 14 on the Paris metro, while RATP Group discussed some of the impressive urban transport innovations it’s working on in collaboration with experts around the globe.
Transdiagnostics shared how its flagship product, Transend, is breaking new ground in digitalisation, offering 24/7 real-time rail monitoring and eliminating unreliable wayside detectors.
MTR Australia showcased some of the inspiring women behind the business, from the boardroom to the tracks, highlighting how companies can attract, support and retain female talent.
In this month’s column, the Australasian Rail Association sets out its current focus areas, from increasing rail’s freight mode share to addressing the workforce shortage, and the Permanent Way Institution celebrates achievements in the rail industry with a recap of its annual awards.
I very much enjoyed putting my first issue of Rail Express together and I hope you’ll enjoy reading it.
kayla.walsh@primecreative.com.au

Upgrades for ageing fleet
The New South Wales Government is undertaking upgrades to the XPT rail fleet which services Grafton and other regional centres across the state.
The XPT fleet has been in operation for more than 40 years and work is underway to ensure it “continues to provide passengers with a safe and comfortable service” until the next generation Regional Rail Fleet is ready.
The State Government has committed $40.3 million over five years to the XPT Life Extension Project.
The fleet upgrades will be carried out in by Sydney Trains and include extensive mechanical work to improve service reliability, new carpeting and refurbished seats, maintenance to improve operation of the air conditioning and toilets and a repaint and refurbishment of the power cars.
To allow for these upgrades, NSW TrainLink will operate two out of the six daily rail services between Grafton
and Sydney with “premium” coaches for about 12 months from mid-March 2025.
The remaining four daily rail services will continue to operate with XPT trains.
NSW TrainLink is going through a public tender process to secure a coach provider to provide wheelchair accessible vehicles for this service. This will provide travellers from Grafton the opportunity to choose between coach services or rail options, depending on their time of travel.
Minister for Regional Transport and Roads Jenny Aitchison said the State Government is committed to building a better transport system for regional New South Wales including the network of NSW TrainLink trains and coaches.
“To ensure passengers can continue to travel safely, comfortably and reliably in the longer term, over $40 million in essential upgrades are getting underway on the ageing XPT fleet now.”

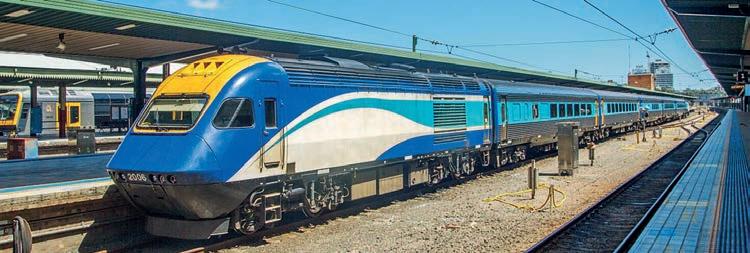
New future for Queensland station
A new lease has been signed for the historic Wallangarra station in Queensland, with plans to make the heritage buildings a “must-stop” food and beverage destination.
The Wallangarra railway closed in 1997, and the station has been closed to the public since 2023.
venue, café and restaurant, will undergo extensive renovations to restore them to their former glory.
The old train crew quarters onsite will also be renovated by the tenants in the future, to be used as an accommodation facility.
The new lease has been signed with local business Wallangarra Railway Café as part of Queensland Rail’s commitment to preserving
Regional, said the renovations will make the much-loved landmark a major tourist attraction in the region.
“At Queensland Rail we are all about connecting communities and we continue to work collaboratively with the local businesses to preserve and showcase important historical rail assets wherever possible,” he said.
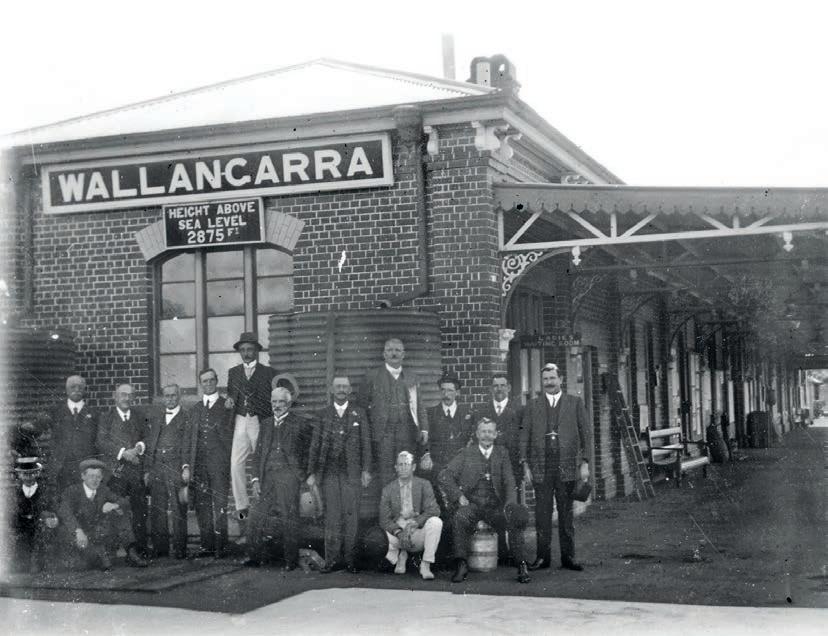
“We’re thrilled that the new tenants will breathe new life into the site with the plan to undertake restoration works and renovations.
“The station was [originally] built with a sizable refreshment room which operated for more than 80 years. It’s exciting that today’s travellers will be able to dine in the same location as travellers of the past.”
Wallangarra Railway Café owners LeeAnne Nichols and Greg Kentish added that they believe the Wallangarra Railway Café can become one of the region’s most iconic “must-stop” tourism destinations.
“The historic railway station offers an ideal canvas to create a unique and engaging hospitality experience for both the local community and travellers to enjoy and celebrate,” they said.
“The venue design will be reminiscent of the iconic refreshment rooms of years past.”

The XPT fleet has been in operation for more than 40 years.
Image: Transport for NSW
Image: Queensland Rail
Wallangarra Station opened in 1887, with a refreshment room that operated for 80 years.
Construction begins on Canberra light rail extension
Construction has begun on the expansion of Canberra’s light rail network from the city to Commonwealth Park.
Starting from Alinga Street, crews will build 1.7 kilometres of new rail line, with a new bridge over Parkes Way.
New stations will be added at Edinburgh Avenue, City South and Commonwealth Park as part of Stage 2A of the project.
Later this year, the first light rail tracks are expected to be laid and final testing and commissioning of the light rail vehicles will happen throughout 2027, with the new stops operational in 2028.
Once complete, Stage 2A will allow light rail services to connect Gungahlin and North Canberra to City West, the ANU, New Acton, Commonwealth Park and Lake Burley Griffin.
Stage 2B, which is currently in design, planning and approvals work, will extend Canberra’s light rail network to complete a north-south public transport link from Gungahlin, through the City Centre and on to Woden.
Canberra is one of Australia’s fastest growing cities, with the population predicted to approach 750,000 by 2050. The $577 million joint investment in Stage
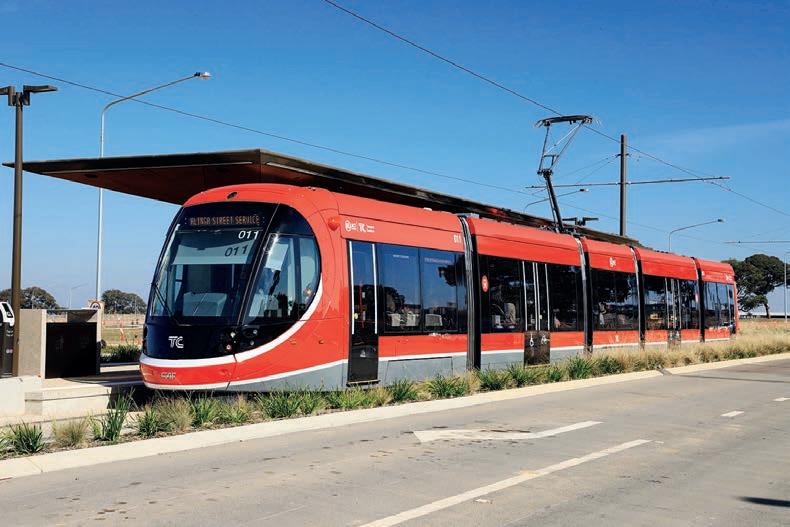
2A by the federal and ACT governments is intended to help prevent future congestion and provide greater ease of movement through Australia’s capital.
Federal Member for Canberra Alicia Payne said Canberra’s light rail is one of the most transformative infrastructure projects in the city’s history, and this next stage will make it even easier for people to get around.
“With construction now underway on Stage 2A, we are bringing light rail closer to the lake, unlocking new opportunities for housing and businesses, and ensuring our
growing city has the modern, sustainable transport it needs,” Payne said.
“This project is about making Canberra an even better place to live, work, and visit –now and for future generations.”
The Australasian Railway Association (ARA)’s Chief Executive Officer Caroline Wilkie also welcomed the official start of construction on the light rail extension.
“Canberrans can look forward to a city with world-class public transport, thanks to future-proof transport infrastructure that is safe, accessible and sustainable,” she said.

$2.2b for
Suburban Rail Loop
The Federal Government has released $2.2 billion in funds for Victoria’s Suburban Rail Loop, but there will be strict conditions attached.
Speaking to the media, Premier Jacinta Allan said the money can only be spent on “very specific things” including ground testing, utilities and land acquisition.
Building for the first stage of the project, SRL East, is already underway between Cheltenham and Box Hill in Melbourne.
Twin tunnels stretching 26 kilometres will connect six new underground stations, and the government said each station will enable around 70,000 new homes to be built in these areas by the 2050s.
SRL East is expected to cost between $30 billion and $34.5 billion, with an estimated completion date of 2035.
Plans are also in place for the wider SRL project to later include north, airport and west sections, however construction has not
yet started on any of these sections. So far, the Victorian Government has committed $11.8 billion to the project, and is hoping the Federal Government will provide a third of the overall cost.
The final third is expected to come from “value capture”, a way of funding infrastructure through taxes, levies or charges associated with increases in the value of land.

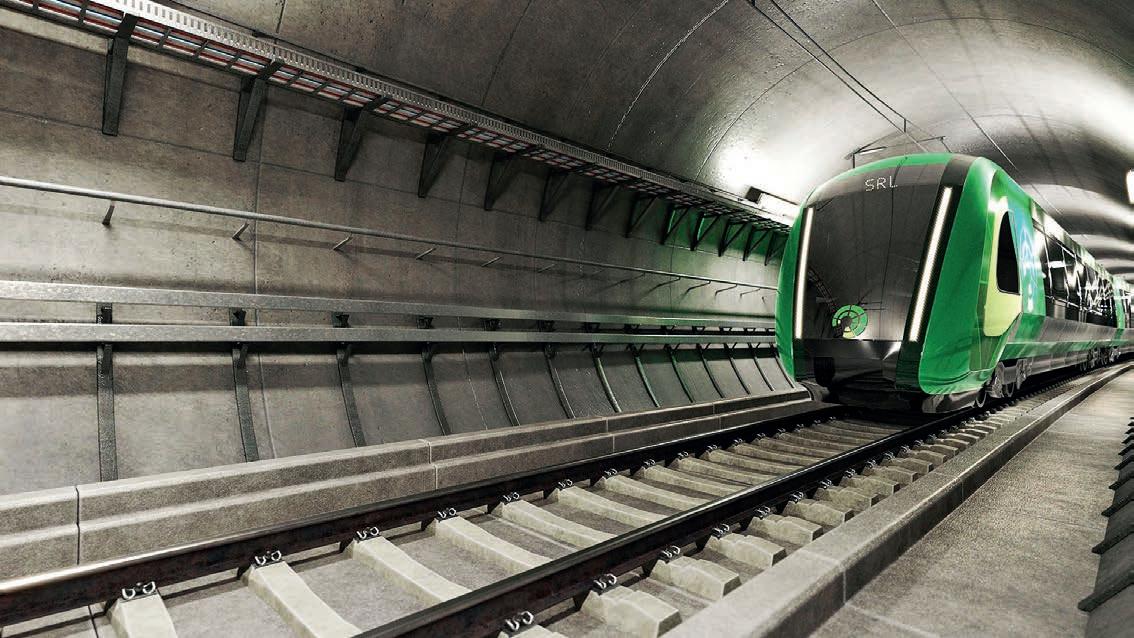
SRL East is expected to cost between $30 billion and $34.5 billion in total.
Canberra light rail will be extended to Commonwealth Park, with three new stations added.
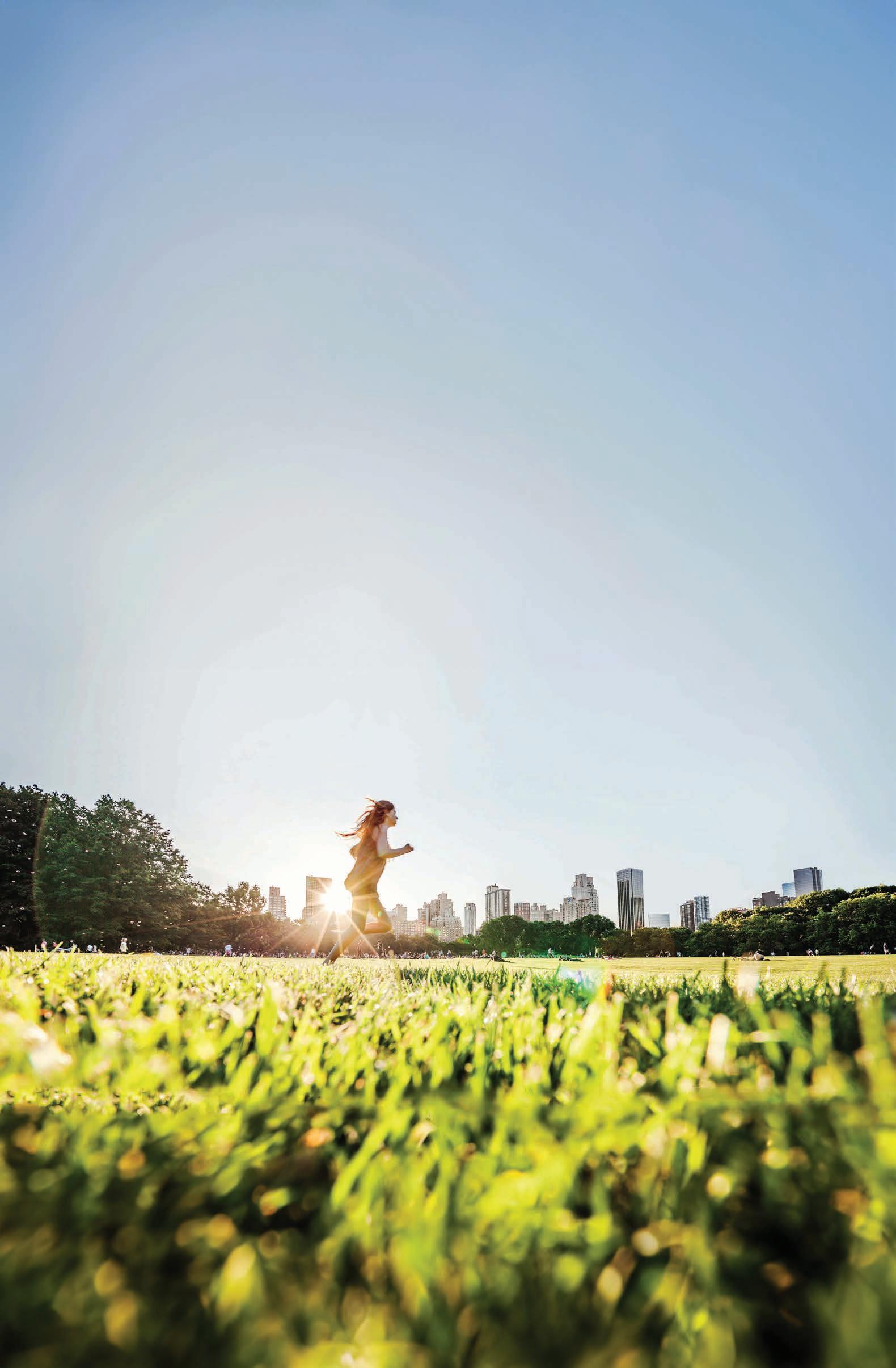
ratpdevaustralia.com.au
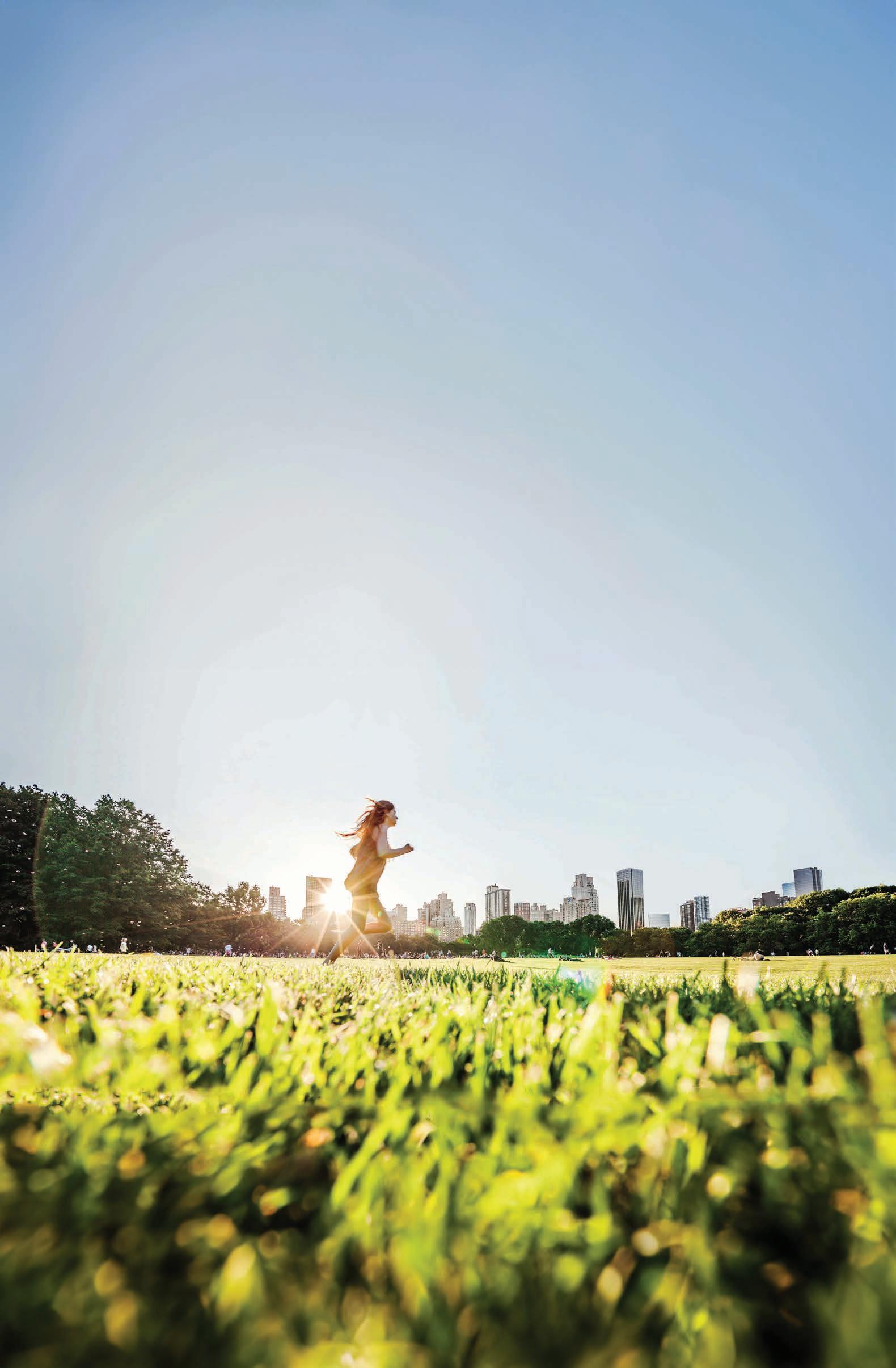
Remutaka Tunnel reopens after overhaul
Trains between Masterton and Wellington in New Zealand are back in service following the complete overhaul of the 70-year-old railway line inside the Remutaka Tunnel.
KiwiRail had a 150-strong crew working around the clock inside the tunnel from 26 December, 2024 to finish the renewal project ahead of the first passenger service on 10 February.
The project involved the installation of almost nine kilometres of new track, more than 15,000 sleepers, over 10,000 tonnes of ballast, and 47 days of bus replacements.
KiwiRail’s Chief Planning and Asset Development Officer Dave Gordon said the new rail infrastructure means this important connection between Wairarapa and Wellington is here to stay.
“It is a mighty milestone,” he said.
“This is the first time the tunnel has had any significant work done on it since first opening in 1955.
“It is now equipped with modern composite sleepers and 50 kilograms of rail that will easily cater to increased services, and ensures the future resilience of the line.”
At 8.8 kilometres long, with a confined space and limited access, engineering innovation has been a big part of the project.
An industrial-sized conveyor system was purpose built early on to test a different way to efficiently remove large quantities of old ballast (gravel) from inside the tunnel.
A digital ‘tunnel simulator’ that mimics the environment inside the tunnel was also key to engaging the crew in crucial health and safety planning.
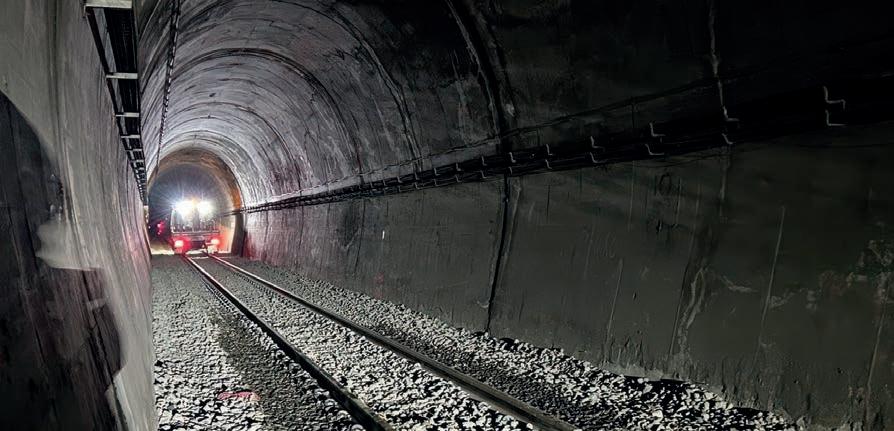
“The environment inside New Zealand’s second longest tunnel is tough, and the work has thrown up plenty of challenges along the way – extremely dry conditions at the tunnel’s most central point was one,”
There was also no way to get standard excavators or transporters in or out of the confined space, which presented another challenge.
“I’m extremely proud of the team who planned and practiced throughout the year, and then used innovation to problemsolve their way to a successful outcome,”

Work underway to remove level crossings
Work has started to pave the way for the removal of two railway level crossings and improved safety at key locations along the Inland Rail project corridor, near Parkes and Illabo in regional New South Wales.
Once these works are complete, there will be capacity for double-stacked train movements up to 1.8 kilometres long.
Level crossings on the Newell Highway at Tichborne and on the Olympic Highway at Harris Gates will be removed and replaced using grade separation as either overpasses or underpasses.
Geotechnical investigations, biodiversity studies and Aboriginal cultural heritage surveys of the Tichborne site and surrounds began on Wednesday 12 February.
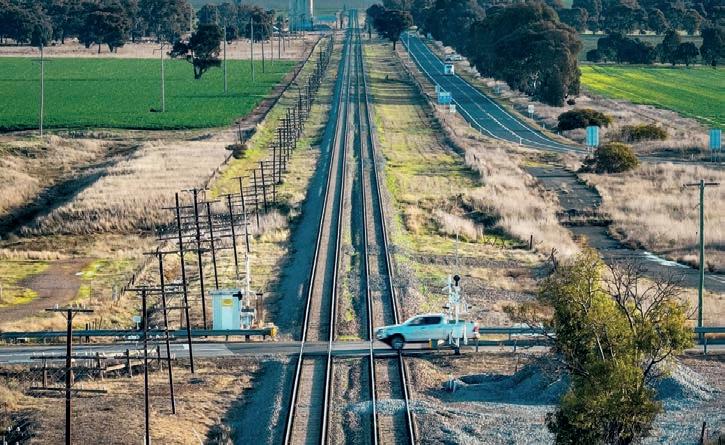
The geotechnical investigations at the Tichborne site will be followed by similar work at the Harris Gates intersection in the
The Federal Government is investing $280 million in the project, while the State Government is contributing $70 million.
The Federal Government contribution is part of a broader $450 million commitment to grade separating Inland Rail interfaces with roads across New South Wales.
The governments said the project will improve road and rail safety while allowing freight to be delivered faster and
Senator for New South Wales Deborah
O’Neill said the development of Inland Rail will be a boost for regional areas of the state, creating thousands of jobs and helping to move goods between Melbourne and Brisbane via inland New South Wales more efficiently.
“Inland Rail is an investment in better connecting regional business, manufacturers and producers to national and global markets while enhancing national freight and supply chains networks,” she said.
New South Wales Regional Transport and Roads Minister Jenny Aitchison said that by grade separating road and rail at these locations, the risk of a crash will be “eliminated”.
“This investment will improve safety at two key intersections on the Inland Rail route while realising the project’s potential to expedite the movement of freight on our road and rail networks,” she said.
“Crashes at level crossings have the potential to cause major trauma and even fatalities, which have devastating impacts on families and local communities.”

The railway line has had its first major upgrade since it opened in 1955. Image:
$2 billion for Airport Rail
Prime Minister Anthony Albanese has announced $2 billion in funding for Melbourne’s long-awaited Airport Rail project.
The money will go towards creating a new rail “Superhub” at Sunshine, which has to be built before tracks can extend to the airport.
Sunshine will get two new dedicated regional platforms and an extended concourse, and will be able to support more than 40 train services per hour, creating capacity for additional services for the growing west and to the airport.
The new rail hub will allow travellers on V/Line regional services from Geelong, Bendigo and Ballarat to bypass the city and go directly to the airport.
The Prime Minister also promised a $300 million cash injection to boost rail services in the Melton growth corridor. The line to Melton will eventually be electrified
New
as part of the Airport Rail project. Other works planned between West Footscray and Albion includes three new rail bridges, new and upgraded tracks, new signalling technology and realigned passenger and freight lines.
The Victorian Government will also deliver a new modern Albion Station, featuring an accessible concourse with lifts and stairs.
Following its budget in 2024, the government had announced the timeline for the Airport Rail link would be delayed by at least four years.
Speaking to the media, Victorian Premier Jacinta Allen said the new funding will bring forward the Sunshine section of the project and it is expected to be completed by 2030.
estimated completion date for
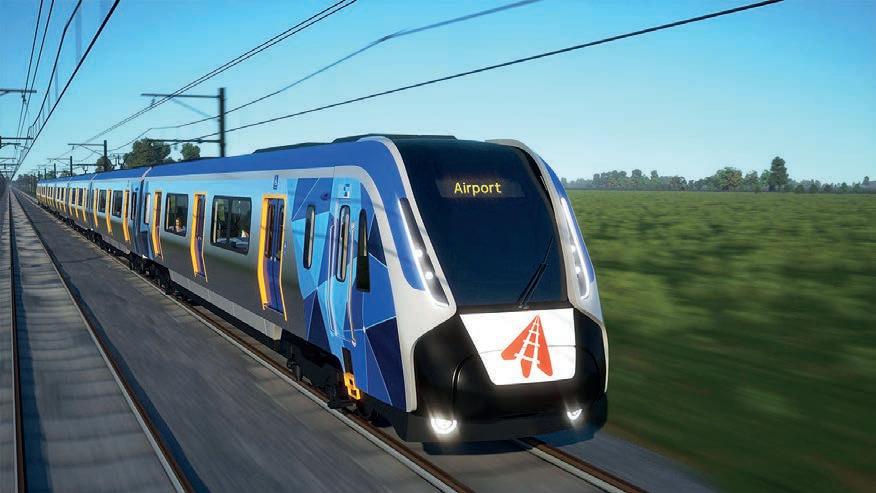

However, the completion date for the Airport Rail project is still unknown and is likely to stretch into the next decade.
tech keeping trains moving
New technology is keeping trains moving in Melbourne with state-of-the-art motion sensors and CCTV cameras on rail bridge beams.
Some of Metro’s 180 rail bridges over roads are struck on average almost every week, so the new technology was installed at three bridge strike hotspots – Racecourse Road in Newmarket, Huntingdale Road in Jordanville and Warrigal Road in Holmesglen.
When an overheight vehicle touches one of the bridges, the motion sensors
and CCTV cameras are triggered, alerting Metro’s Security Operations Centre and Infrastructure Department of the incident and time of impact and sending images from the scene.
This allows Metro’s Infrastructure team to immediately review the incident, including the type of vehicle that has hit the bridge, and decide whether trains need to be slowed or stopped until an on-site assessment of the damage can be undertaken. Previously, the notification of bridge strikes was solely
reliant on an incident report being filed by the person who caused the incident, a member of the public, emergency services, or a Metro team member.
Bridge Inspector Liam Fetherston said that travelling to a site for a bridge inspection, assessment and clearance would normally take up to an hour, but this can now be done in 10 to 15 minutes.
“This technology has saved hours of time and less disruption for thousands of our passengers,” he said.

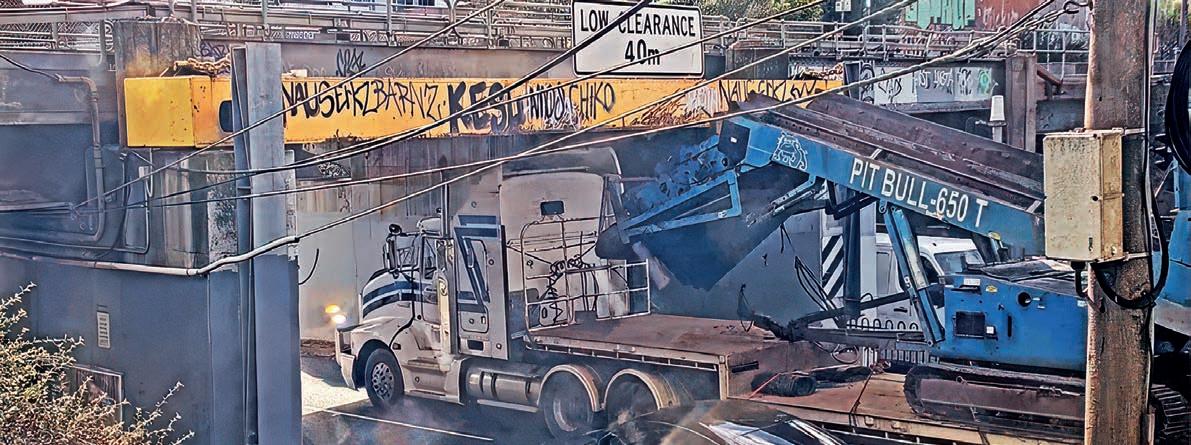
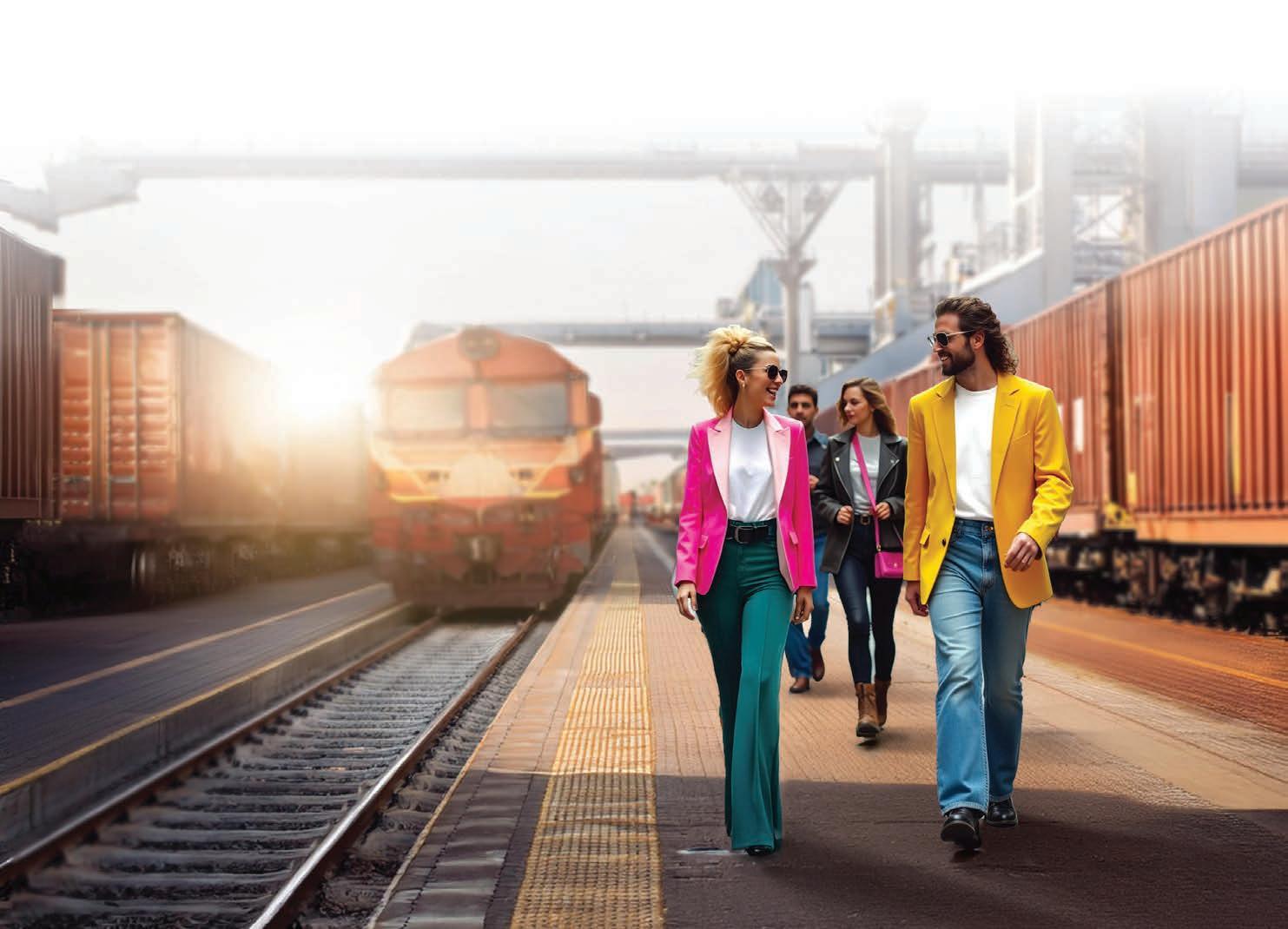
An
the Airport Rail link is still unknown.
When an overheight vehicle touches one of the bridges, it triggers the motion sensors and CCTV.
Works ramp up on Ballarat Station upgrade
Work has ramped up to make Ballarat Station in Victoria more accessible, as crews prepare for the installation of a new pedestrian overpass, lifts and stair access to both platforms.
Along with a new ramp and landscaping at the northern station entrance, the upgrade will make it easier for people with a disability, prams and luggage to get around the station.
Fencing, concrete paving and a section of roof sheeting have been removed between the bus interchange and northern platform to make space for the lift shaft and stairwell.
Crews have also carried out works to create space for the overpass and lift shaft in a section of the southern station building. A section of roof canopy has been temporarily removed and will be reinstated after the overpass has been lifted into place. Temporary supports have been installed to reinforce the southern building while works are underway.

Site offices and temporary fencing had already been established at Ebden Street Reserve and at the northern station, while bus services have temporarily relocated to Lydiard Street North.
From March onward, piling will progress
THE 80S WERE FAMOUS FOR MANY INNOVATIONS
FREIGHT RAIL SAFETY WASN’T
ONE OF
THEM
to form the foundations for the new overpass and crews will continue relocating services and communication infrastructure. Works to upgrade the station will continue throughout 2025, with the new overpass opening in 2026.

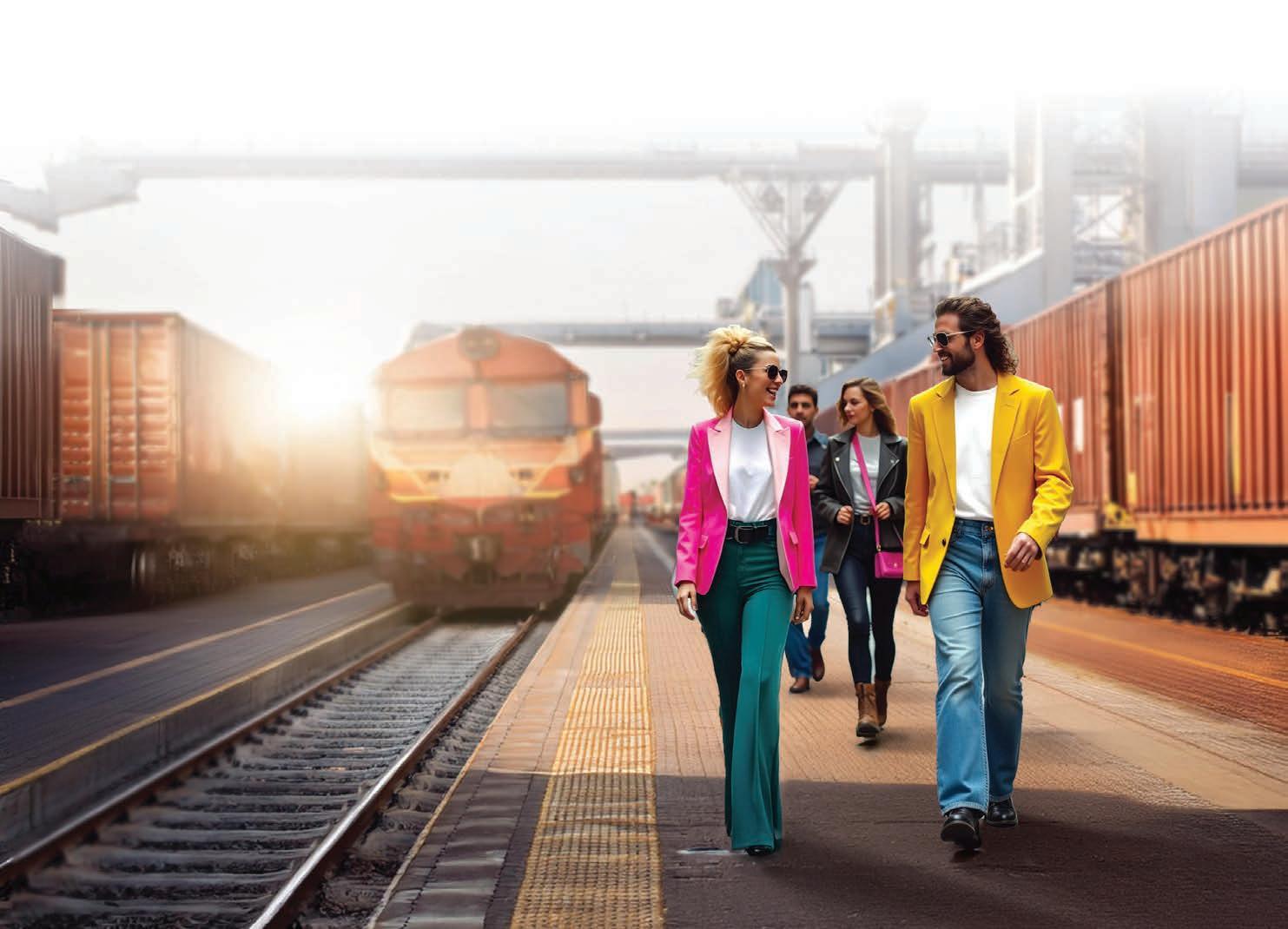
Most freight rail operators rely on safety devices developed in the 1980s. They are unreliable and are directly linked to catastrophic derailments.
Transend ® is the pioneer in real-time wireless monitoring of the full range of safety indicators across all classes of freight trains.
Contact us to learn how you can keep your freight and your trains safely on track.
www.transdiagnostics.com/transend
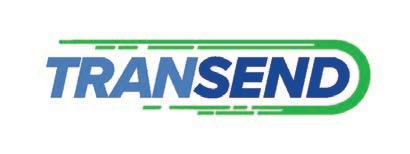
Site establishment works underway in Ballarat.
Image: Victoria’s Big Build
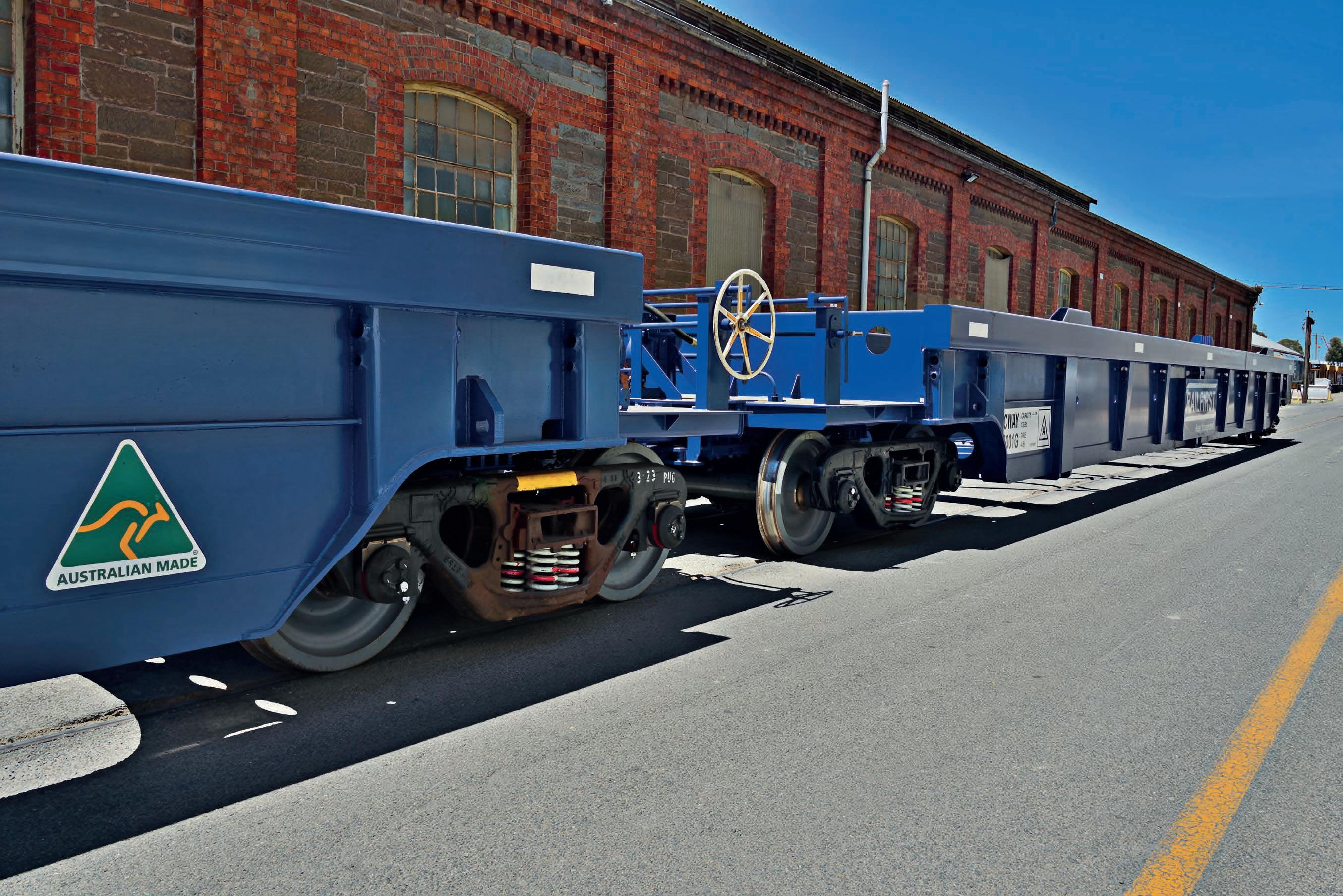
New era in rollingstock solutions
With one of the largest fleets in the country and exciting changes happening, the future is looking bright for Rail First.
New ownership, a new and diverse executive team, new leasing offerings for customers, and investment in new local manufacturing is the start of a new era for Australia’s leading providers of rollingstock solutions for the rail freight sector.
Formerly known as Chicago Freight Car Leasing Australia (CFCLA), Rail First is now backed by global investors CVC DIF and CBRE Investment Management.
Beata Lipman, Rail First Chief Executive Officer, noted that pandemic-induced constraints in global and domestic supply chains and recent geopolitical tensions surrounding world trade have shone a spotlight on Australia’s ability to efficiently service complex freight and logistics networks.
“Shortages of essential products during the Covid crisis exposed Australia’s lack of local manufacturing – in a 2021 submission to the Senate Economics References Committee, the Productivity Commission reported manufacturing accounts for less than 10 per cent of the Australian economy,” she said.
“Rail First is therefore immensely proud to be the only domestic manufacturer of rail container wagons in the country, in addition to being the only provider
of rail freight leasing services in the country.
“Today our company has one of the largest fleets in the country with approximately $500 million in assets, including 80 freight locomotives and 1400 wagons.”
Rail First provides leasing and manufacturing services to a variety of customers, including rail operators, rail infrastructure owners and managers, and cargo owners.
“These are some of the leading freight and logistics companies in Australia,” Lipman continued. “Rail First also plays a pivotal role in maintaining and overhauling rollingstock – both locomotives and wagons – for many Australian rail freight operators.”
FUTURE FREIGHT GROWTH
Lipman said Rail First was well-positioned to benefit from forecast growth in the domestic freight task, notably the haulage of containerised freight via well wagons which enable the double-stacking of interstate intermodal train services.
“To help customers meet demand capacity in the containerised market, Rail First recently developed a new 48-foot intermodal well wagon which recently
completed successful operating trials between Penfield and Flinders Port in South Australia.
Rail First is therefore strategically positioned at the junction of solid underlying intermodal containerised volumes, strong forecasted TEU growth, and state and federal government programs and projects designed to help shift more freight from road-to-rail and create greater resilience and reliability in rail freight networks.”
In terms of containerised freight volumes in Australia, in 2022-23, the Bureau of Infrastructure and Transport Research Economics reported about nine million TEUs were exchanged at the five principal container ports in Melbourne, Port Botany, Brisbane, Adelaide and Fremantle.
“To add to our diverse and growing customer base, our company also builds and leases hopper wagons used in the haulage of loose bulk commodities and materials like iron ore, grain, and track ballast,” Lipman said.
NEW TEAM OFFERS NEW SOLUTIONS
In recent years, new ownership and management at Rail First has helped create a new culture at the company – including more women in executive roles – with
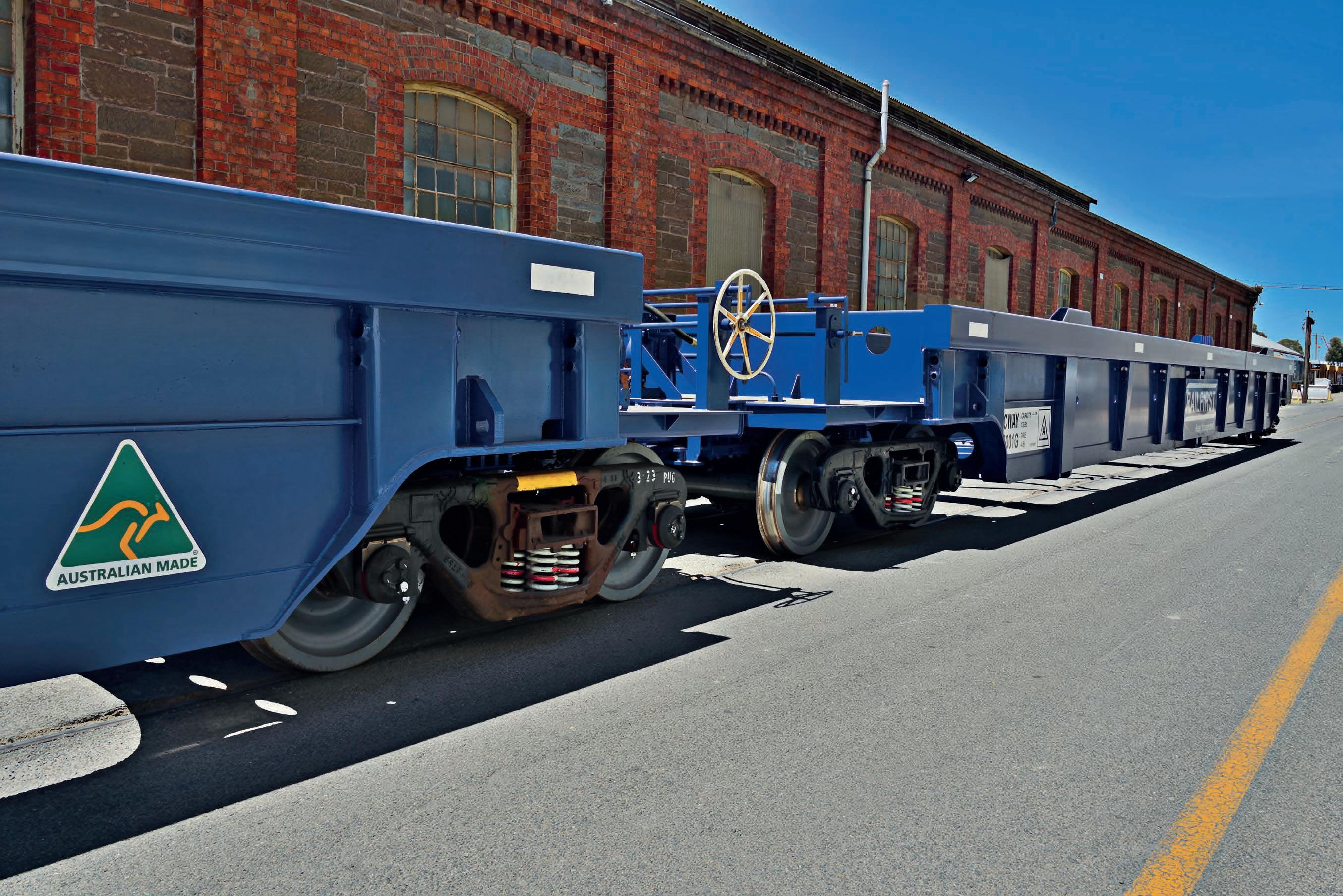
a core focus on offering market-leading long-term solutions to customers. Lipman said greater diversity in the six-member executive team, with each executive having 20 to 30 years of expertise in transport and logistics, rail supply chain operations, manufacturing, construction and/or commercials, is putting customer needs at the centre of every decision.
“For example, two new offerings called ‘Purchase to Long Term Lease’ and ‘Manufacture to Long Term Lease’ have been designed to provide Rail First customers with the option to use and maintain the latest modern freight locomotives and rail wagons, allowing customers to allocate capital to other projects and business initiatives.
“These new products provide Rail First customers with the ability to rapidly ‘flex up’ their locomotive and rollingstock capacity, notably when new rail haulage contracts come to market or renewal of existing contracts are in play. In contrast, overseas companies have limited ability to quickly respond to these market dynamics.
“As part of long-term leases, Rail First customers also benefit from having full control of assets and favourable pricing discounts for longer lease periods and increased volumes.”
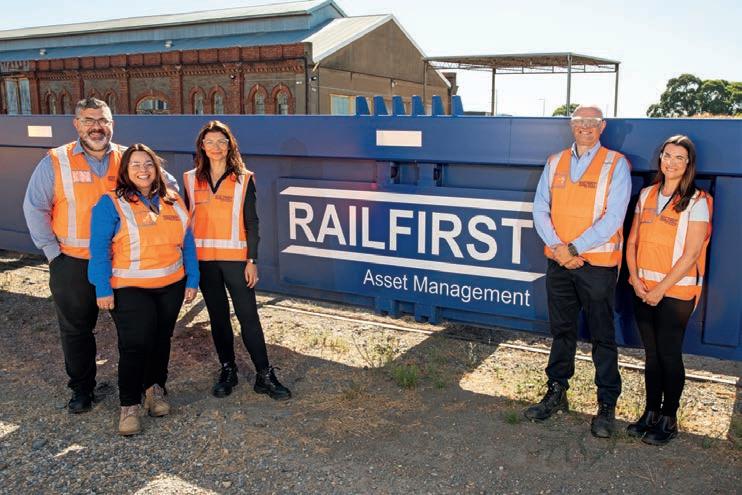
ROAD-2-RAIL
Rail First is the only Australian manufacturer of 40-foot and 48-foot two-pack intermodal well wagons which cater for double stacking of containers used in the national freight and logistics market.
Lipman said a key objective of the future Melbourne–Brisbane Inland Rail project is to facilitate the deployment of doublestacked freight trains, up to 1800 metres in length.
“Customer demand for well wagons on double stack trains is also increasing on the critical east-west rail freight corridors between Adelaide–Perth and Parkes–Broken Hill–Adelaide–Perth.
“Well-wagons provide Rail First customers with the capability to ‘move more boxes with less’. The increase in productivity and cost efficiency helps to shift freight from road-to-rail. In doing so, our sector can act as a powerful agent in helping to reduce
CEO Beata Lipman leads a new and diverse executive team at Rail First.
Images: Rail First
Rail First is the only manufacturer of 48-foot 2-pack intermodal well wagons in Australia.
traffic congestion, vehicle emissions, and road accidents.”
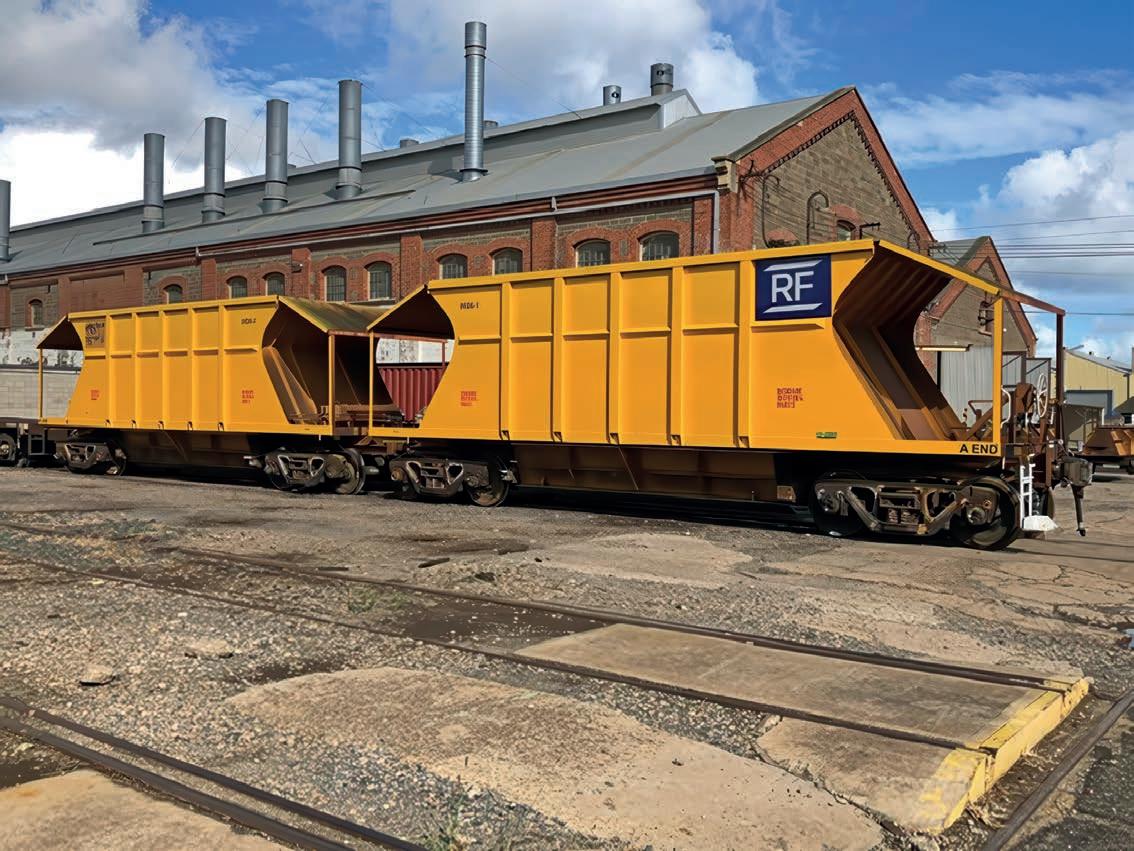
interstate intermodal marketplace is the $1 billion-plus Network Investment Program jointly funded by the Australian Government and the ARTC.
“The Network Investment Program will help deliver critical upgrades to enhance the national rail network,” said Lipman.
“The result of these governmentsponsored projects and funding initiatives is that Rail First and its customers will benefit from a broader reform agenda supporting rail freight networks and operations.”
LOCALLY MANUFACTURED ROLLINGSTOCK
With the Australian Government implementing the Future Made in Australia and National Rail Manufacturing plans, Rail First is a prime example of what can be achieved in cut-throat global markets with a focused and skilled workforce.
Lipman said the benefits to Rail First customers of leasing locally manufactured rail rollingstock are many and varied, including the important role of helping to support and build critical trade and engineering skills in Australia.
“Rail First sources steel for the manufacture of its rail freight wagons from the BlueScope Port Kembla Steelworks via a South Australian company called Adelaide Profile Services,” she said.
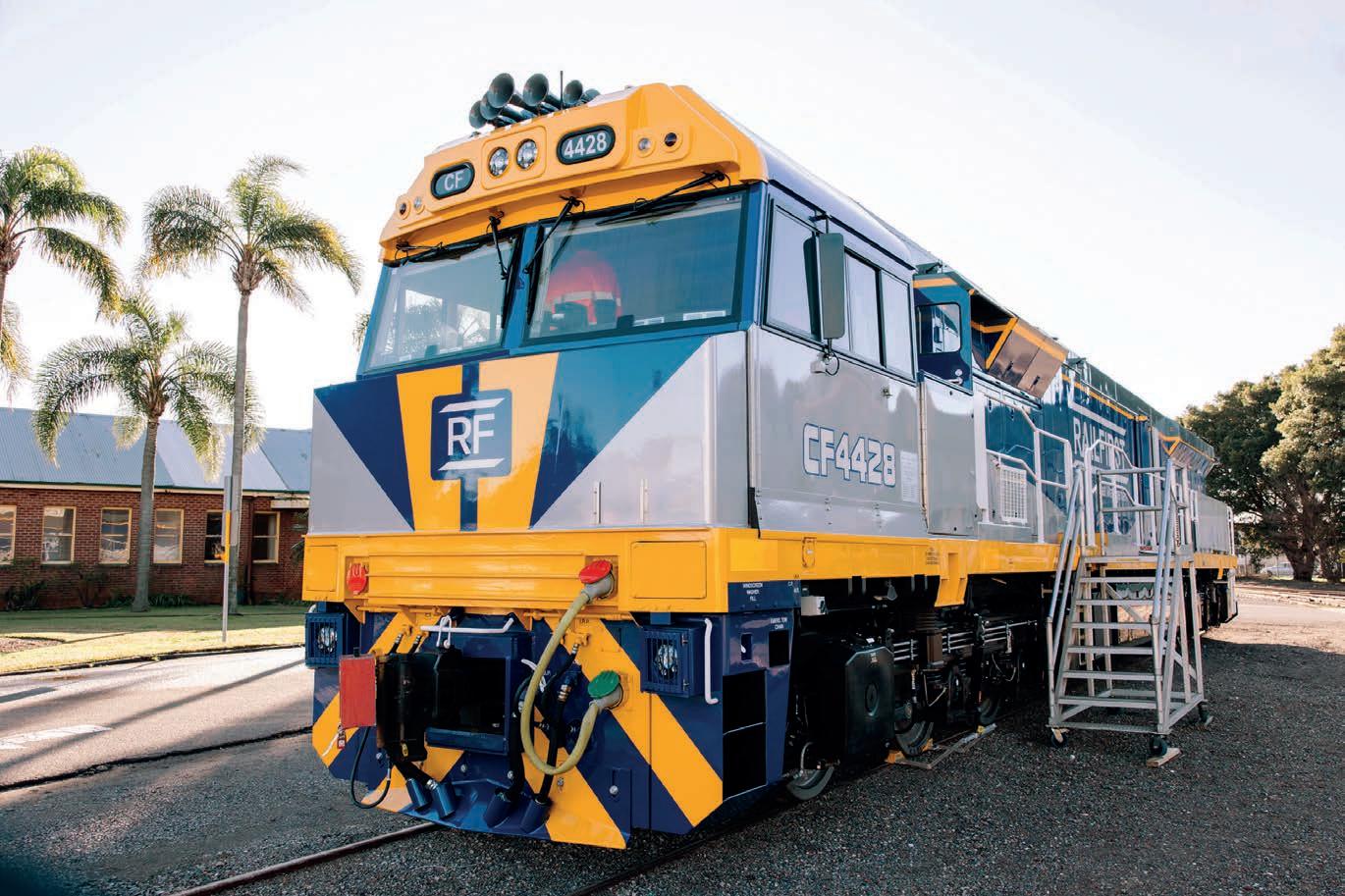
emissions than offshore manufacturing, and better visibility of safety standards and quality control during the production process for customers.”
Lipman said local manufacturing of rail rollingstock also generates skilled jobs in the Australian supply chain and helps to support other domestic industries like the steel sector.
“For example, it requires approximately 45 tonnes of steel and 1200 work hours
metal fabricators, electricians and spray painters.
“In total, Rail First employs 140 essential workers, including staff based in regional New South Wales in Goulburn, involved in the maintenance and overhaul of rail rollingstock.”
250TH WAGON DELIVERED
In 2024, Rail First hit the milestone of manufacturing its 250th 40-foot intermodal
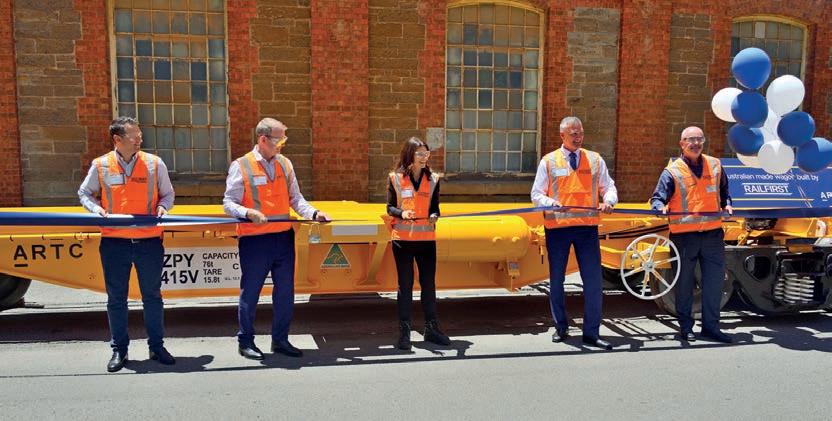
In December 2024, Rail First delivered its 250th rail wagon to the ARTC – locally manufactured by skilled workers and tradespeople at the company’s facility in Islington, Adelaide.
Rail First also builds and leases hopper wagons used in the haulage of loose bulk commodities and materials such as iron ore, grain, and track ballast.
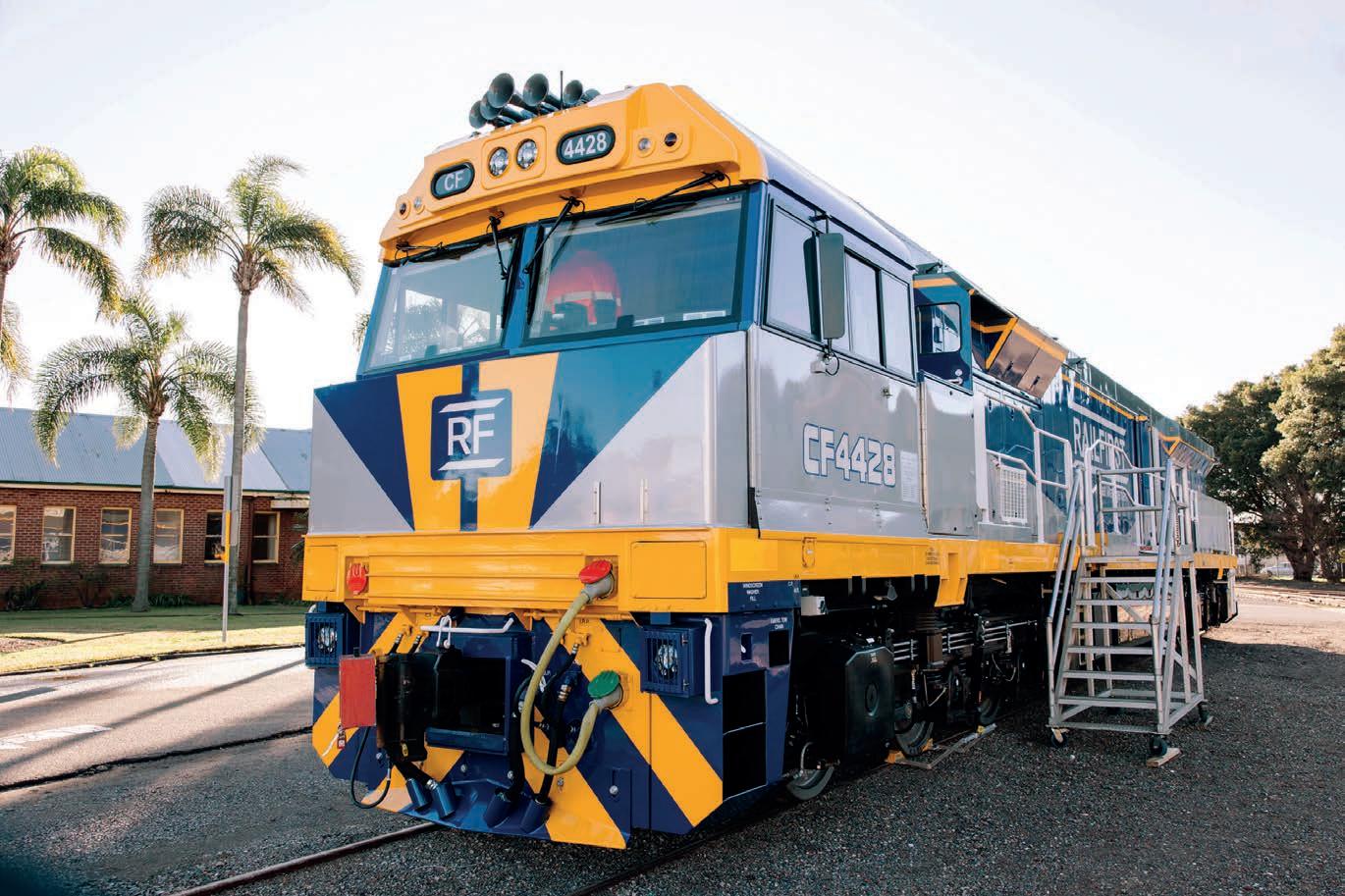
wagon – with the ARTC taking delivery of the rail wagon at Islington.
Lipman said in line with the ARTC’s ongoing commitment to continuously maintaining and upgrading its vast interstate and Hunter Valley networks, the government enterprise is rolling out a fleet of 36 modern 40-foot ‘skel’ wagons from Rail First to haul long lengths of rail steel.
“A distinct advantage the ARTC saw in supporting the local manufacture of rail wagons is that the typical lead time for delivery of the final product is only six months.
“Overseas companies struggle to match both the speed and standards of our manufacturing and delivery processes.
“Additionally, Rail First provides its customers with strategically located maintenance facilities in New South Wales and South Australia for rollingstock needing repair or overhaul.”
NEW $100 MILLION INVESTMENT
Recently Rail First invested $100 million to acquire 12 new energy-efficient UGL CF44 freight locomotives for its customer base. Under a lease agreement with Rail First,
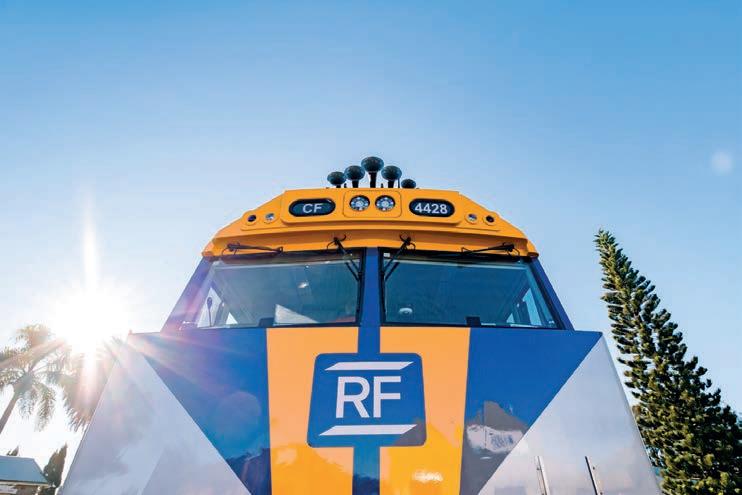
Rail First has invested $100 million to purchase 12 new energy-efficient freight locomotives for its customer base.
Melbourne-based SCT Logistics, the country’s largest private freight operator, has taken delivery of six of the new CF44 locomotives.
Lipman said the locomotives are being used by SCT Logistics to help increase rail freight capacity between the east and west coasts and grow interstate volumes on north-to-south rail lines between Melbourne, Wodonga and Brisbane.
At the time of the announcement of the leasing deal, Managing Director of SCT Logistics Geoff Smith said the company is looking to an expanded fleet of new energy-efficient locomotives to help meet the country’s goal of net zero emissions by 2050, and the company’s decarbonisation objectives, which includes transitioning freight from road to rail.
“A key advantage to these locally manufactured locomotives is that SCT Logistics can continue expanding its distribution network, grow its freight volumes and remain focused on reliability,” Smith said.
The new Australian-made UGL CF44 freight locomotives have one of the most fuel-efficient engines in the market, with each locomotive capable of hauling a rake of wagons 1800 metres in length – equivalent to removing approximately 160 large trucks from the road.
“Transport is the third largest source of national emissions and rail is 16 times more carbon efficient than the road equivalent,” Smith said.

The new locomotives are each capable of hauling a rake of wagons 1800 metres in length.
Revitalising Paris Metro Passenger Rail
Siemens Mobility and RATP have completed the first-ever migration of an operational driverless metro line to an advanced Communications-Based Train Control (CBTC) system.
The Paris Metro Line 14 has been successfully modernised and extended thanks to a collaboration between Siemens Mobility and RATP (Régie Autonome des Transports Parisiens).
This significant project has resulted in enhanced efficiency, reliability, and increased capacity for passengers across Paris. It also marks the first migration of an automated driverless (GoA4 – Grade of Automation) metro line to the latest generation GoA4 system, ‘Trainguard MT CBTC’.
CONNECTING PARIS LIKE NEVER BEFORE
Line 14 was built in 1998 and was the first metro line to be built in Paris in half a century. It was also the first fully automated driverless line in Paris – which at the time was already equipped with a Siemens Mobility signalling solution.
In 2018, Siemens Mobility was awarded contracts to overhaul the line’s automation, replacing the 26-year-old ‘METEOR’ system
building a new Operations Centralised Control Station (OCC), equipping 72 new trains, and extending the automation by 14 kilometres to connect Orly Airport to central Paris, effectively doubling the line’s length to 28 kilometres.
With a headway of 85 seconds along the entire 28-kilometre route, Line 14 is now one of the most reliable and high-performing lines in the Paris Metro network, transporting 40,000 passengers every hour, in every direction. It will eventually accommodate over one million users daily.
The expansion accommodates the growing demand for public transportation in the Paris metropolitan area, providing a faster and more reliable service for commuters. The line now links Orly Airport to central Paris in just 20 minutes and connects Saint-Denis Pleyel’s northern business districts to Orly Airport in 40 minutes.
With its improved capacity, reliability,
system, connecting to the future lines 15, 16, 17 and 18 of the Grand Paris Express network.
SEAMLESS INTEGRATION WITH CBTC TECHNOLOGY
One of the key highlights of this project is the seamless integration of the new CBTC system while maintaining passenger services.
Over six years, more than 250 Siemens Mobility engineers contributed, dedicating over 500,000 hours of engineering. The project faced several challenges, including the need to complete it in time for the Paris 2024 Summer Olympics.
The upgrade was meticulously planned and executed to ensure minimal disruption to passenger services. Siemens Mobility engineers worked during off-peak hours and overnight to install and test the new CBTC system. This approach allowed the line to remain operational during the day, ensuring that passengers could continue to use the
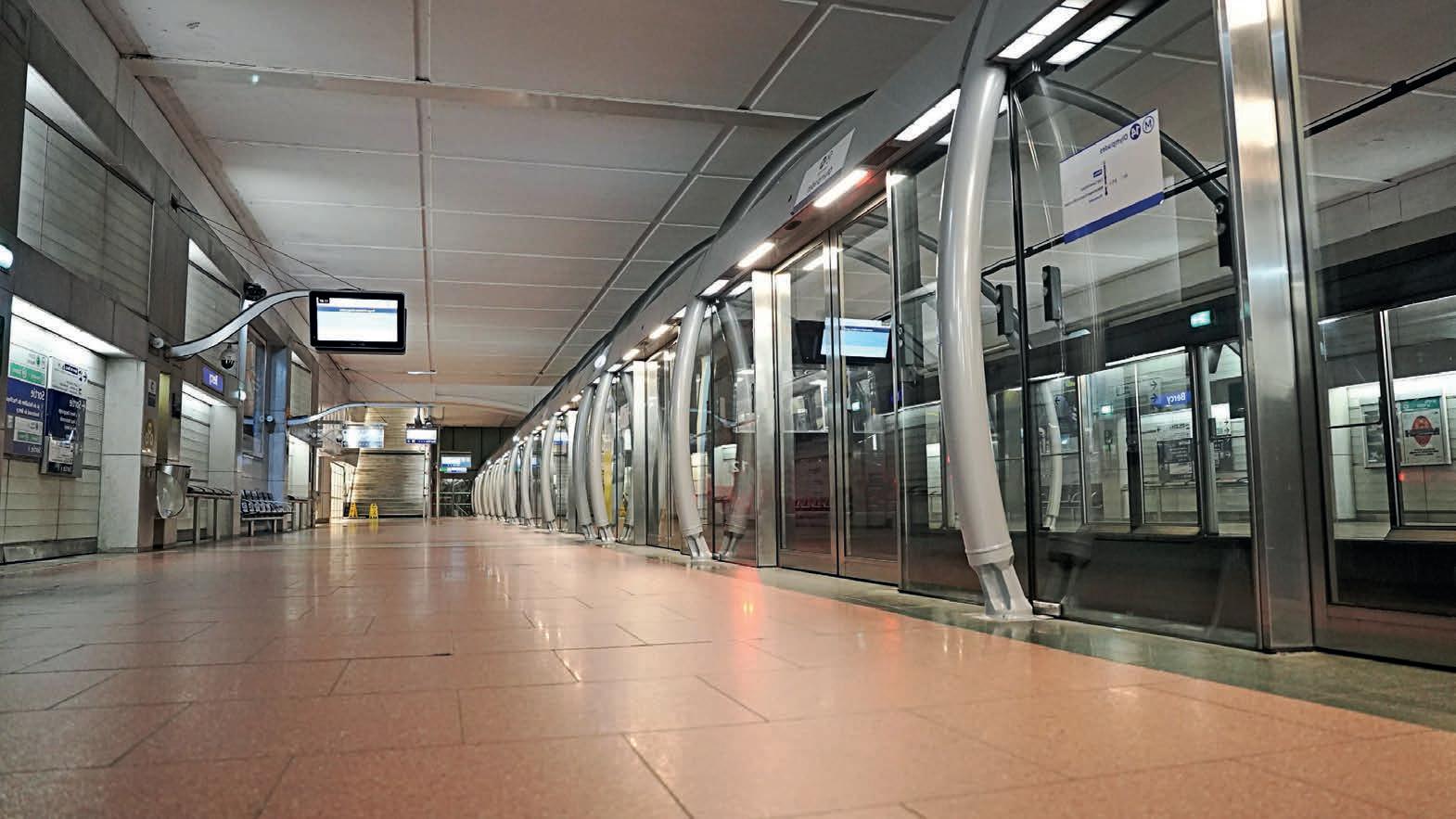
Line 14 was the first fully automated driverless line in the Paris Metro.
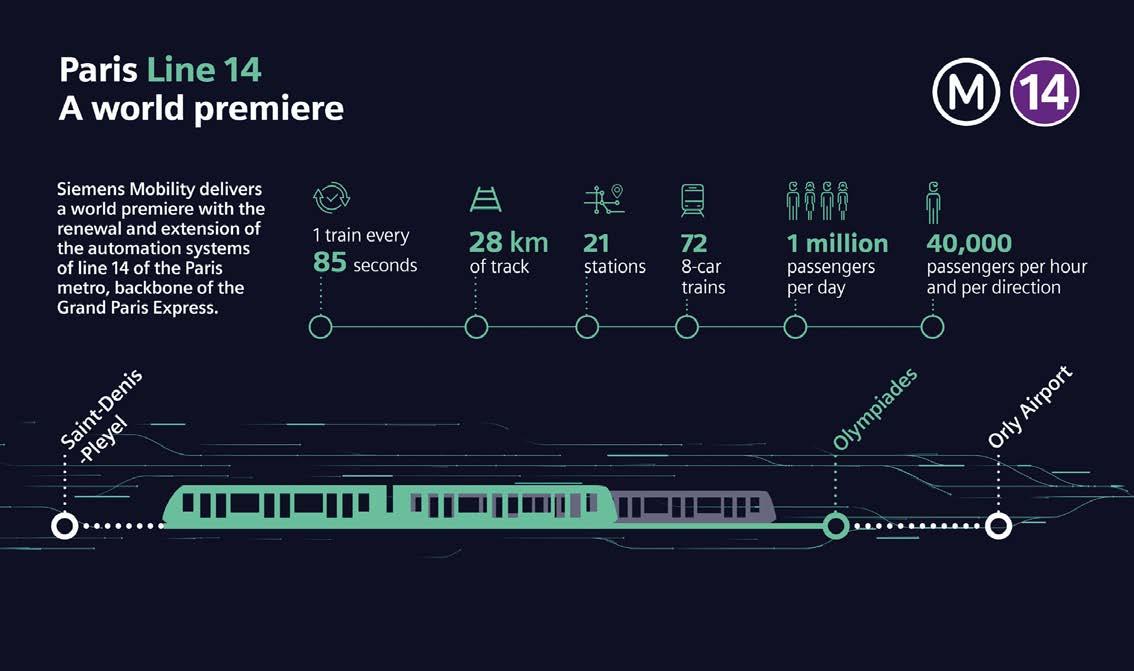
Business Unit director at Siemens Mobility France, said the successful integration of the new system on an existing line while maintaining passenger services is a testament to Siemens Mobility’s expertise and commitment to delivering highquality solutions.
“The extension and modernisation of line 14 is a truly unique project. It is the first time in the world that an automated driverless (GoA4) metro line has migrated to a new,
The CBTC technology enables highfrequency, driverless train operations that optimise train spacing and speed, reducing wait times, increasing passenger capacity, enhancing safety through real-time monitoring and control of train movements, and reducing human error to ensure reliable service.
Additionally, the project incorporates energy-efficient technologies and sustainable practices, aligning with global
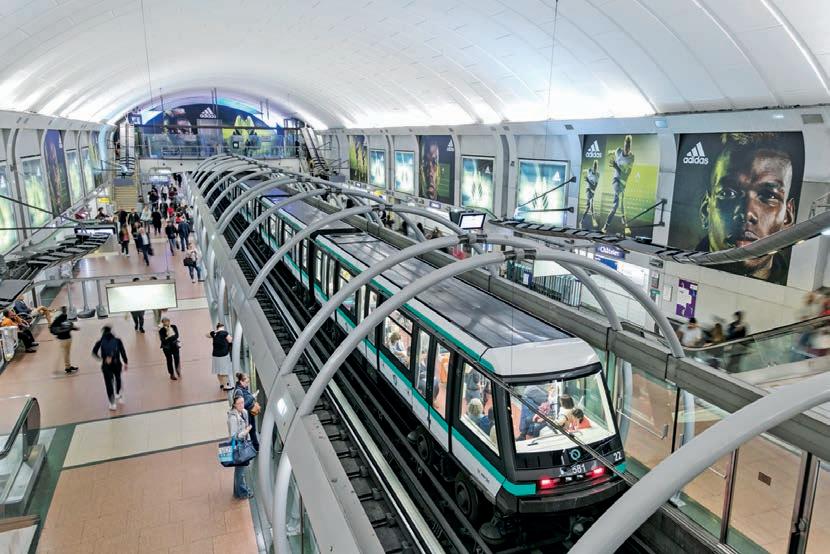
The system upgrade was meticulously planned and executed to ensure minimal disruption for passengers.
promote green transportation.
Siemens Mobility’s GoA4 CBTC system means that the trains are fully automated and operate without any staff on board.
This system, which is the highest level of train automation, transfers all train controls, including starting, stopping, and handling emergencies, to the train control system.
Siemens Mobility will also implement the GoA4 CBTC system to equip future lines of the Grand Paris Express, a new 200-kilometre automatic metro network currently under construction in the Île-deFrance region.
This will further enhance connectivity and efficiency in the Paris metro system while delivering an advanced, large-scale rail solution that meets the demands of a modern urban transit system.
A COLLABORATIVE SUCCESS FOR URBAN MOBILITY
The collaboration between Siemens Mobility and RATP has resulted in the modernisation and extension of Line 14, which improves the daily commute for millions of passengers and contributes to the overall efficiency and sustainability of Paris’ public transportation system.
The partnership demonstrates the power of collaboration and how advanced technology can transform urban mobility for everyone.

The line now links Orly Airport to central Paris in just 20 minutes.
Diversity and Inclusion
Women in Rail – from the boardroom to the tracks
Three MTR employees open up about the importance of gender equality in the rail industry – and share their advice for anyone hoping to follow in their footsteps.
Women make up just 24 per cent of the Australian rail industry workforce, according to the latest figures from the Australasian Railway Association (ARA Gender Diversity Report Survey, 2022).
While this is an improvement on the 17 per cent reported back in 2014, there is still a long way to go until gender equality is achieved in the sector.
Jeshree Gaundar, Head of People & Culture at MTR Australia, said one way of attracting more women, not just to pursue a career in rail but to stick around and rise up the ranks, is by showcasing female success stories.
“We also make a concerted effort to facilitate women’s career growth through mentorship and networking opportunities, flexible working arrangements, career development plans and more,” she said.
Here, three successful women at MTR Australia share how they got where they are today and what they think needs to be done to improve the gender equality in the rail industry.
RENEE LEUNG, RESILIENT SYSTEM INTERFACE ENGINEER AT MTR
Ever since she was a child, Renee Leung has wanted to fix things.
“My dad was an industrial engineer and he built the little toys that you get with Happy Meals at McDonald’s,” she said.
“When I was a kid, I would see my dad bringing these toys home and reassembling them, trying to fix any problems.
“That’s when I got the idea that fixing things was interesting!”
Later, Leung decided she wanted to follow in her father’s footsteps and study engineering – but he wasn’t too keen on the idea.
“Dad wasn’t very supportive,” she said. “He asked some of my female relatives to guide me towards studying something else, like commerce.
“Being an engineer himself, he knew how male-dominated the industry was and thought it would be tough for any female.”
Despite her father’s reservations, Leung pursued her dream. At the age of 17, she
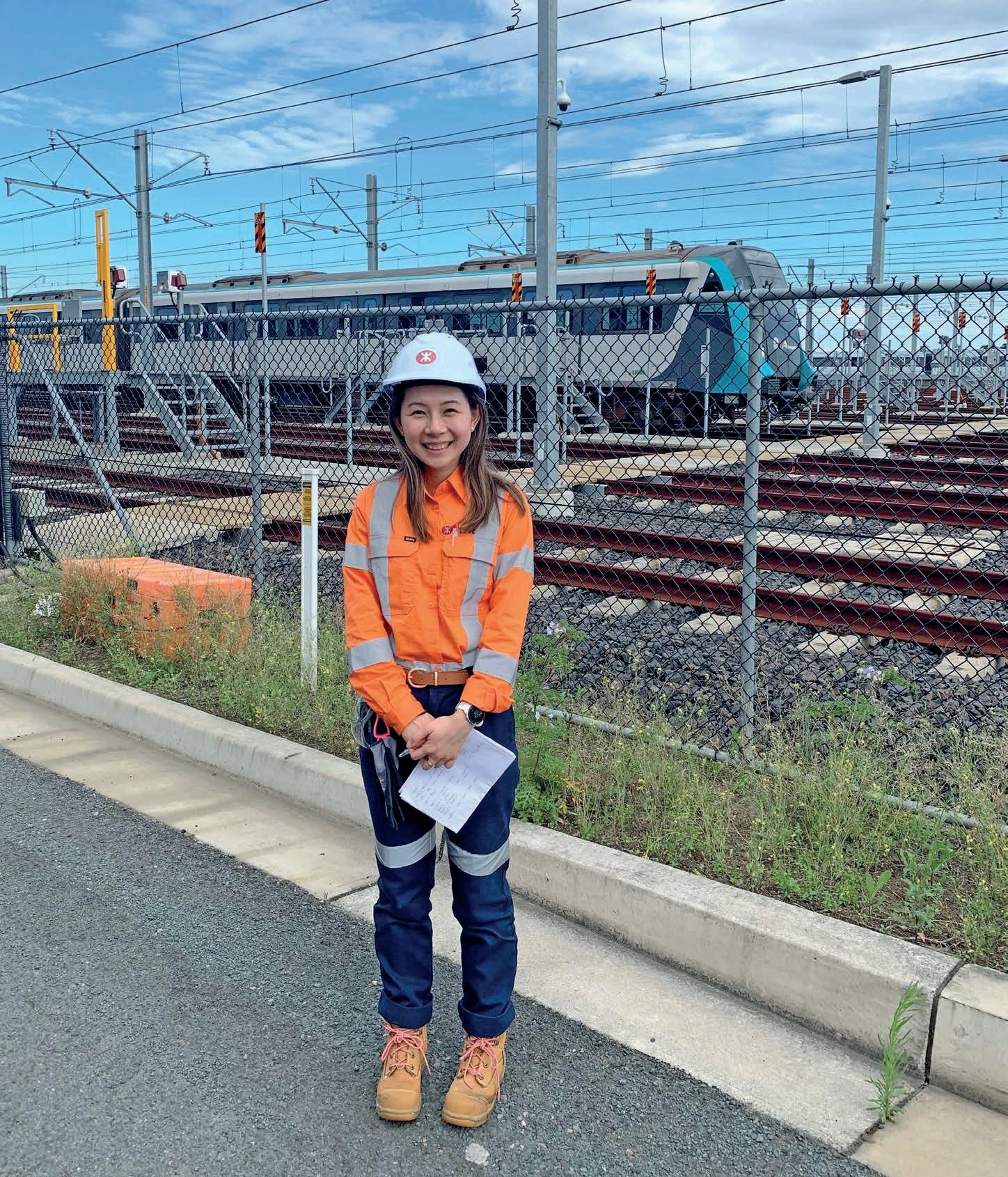
Renee Leung has been involved in crucial infrastructure projects over the course of her work with MTR.
Image:
Renee Leung
trains, or I’m asked to lead a major meeting at work, I don’t panic. I always remember my motto, and I hope to make my dad proud.”
Leung wants to inspire more women to enter the construction and rail industries, and said it’s important to have female role models in leadership roles.
“For a while, I worked for [financial, software, data, and media company] Bloomberg, and there were actually a lot of female leaders there,” she said.
“I could see women who were both mothers and leaders at their workplace, and that helped me imagine how I might balance work with becoming a mother in the future. You need to see so you can become.
“In the construction and rail industries, this is more uncommon, but MTR is doing great work to change that.”
One of the ways MTR is promoting female leadership is by running a mentorship program for women in the workplace.
“There was a matching process where I put in my interests and my requirements from a mentor, and I was matched with a director or a senior manager, and we have a catch up each month,” Leung said.
“I was also matched with a group of five females from other companies and we have regular catchups as well.
“From there, I really found my role model and got to see different leadership styles and how they manage their work while having successful relationships with their loved ones.”
Leung has also benefitted from various workshops regularly run by MTR, aimed at empowering women in the workplace.
In addition, a personalised development plan has been formulated by MTR to help her grow her career.
“Before, I never thought I had the skills or personality to go beyond being an engineer,” she said.
“But because of all the mentoring I have received and the inspiring female leaders I have met, I now believe I will be able to achieve what they have.”
Sharing her advice with other women who are interested in a career in the rail industry, Leung said: “If you’re passionate about it, don’t let yourself be discouraged by rejection or criticism. Keep moving, believe in yourself and you will find your way.”
CARMELA PELAEZ – SENIOR PROJECT ENGINEER AT MTR
For MTR’s Sydney-based Senior Project Engineer Carmela Pelaez, female leadership adds diversity and another perspective in terms of problem solving, driving project delivery and leading teams.
“I believe diversity contributes to positive impacts in projects, bringing varied strengths and skillsets,” Pelaez said.
“I often feel inspired when witnessing females excel in driving outcomes, leading teams, and contributing to achieving milestones in complex projects.”
In Pelaez’s view, having strong female representation in the rail industry encourages more young women to get on board.
“It also demonstrates to females in other industries that rail and engineering is a potential area for their growth as there are many transferrable skills,” she said.
“There are plenty of opportunities for young professionals, females and males alike, to excel in this industry.”
Pelaez said companies can support, mentor and retain female talent through on-the-job mentoring and buddy systems, as well as through growth, performance and succession plans. This can help ensure that female talent is “engaged, challenged and able to see a promising future”.
When it comes to getting a start in the rail industry, Pelaez recommends chatting to people currently working in rail and asking them about their roles.
“Ask them what they love about working on rail projects. This may lead to opportunities and a foot in the corridor!”
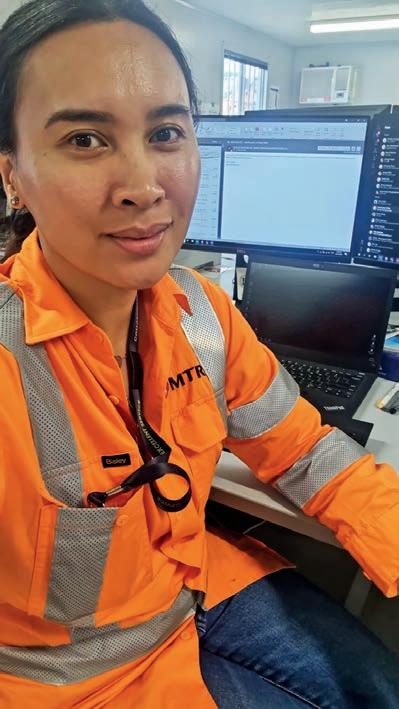
BELINDA MOVERLEY, SENIOR COMMERCIAL MANAGER AT MTR
Belinda Moverley has worked in the construction and rail industries for over three decades, and has spent the past seven years at MTR.
As a Senior Commercial Manager, Moverley gets exposure to the most senior level in the Australian business.
She’s played a pivotal role in numerous major projects, from early works on the Sydney Light Rail to station upgrades and more.
“I’m currently managing our contract with Sydney Metro, which is a massive project,” she said.
“I’m part of a team of 14 and we manage our rights and obligations under the contract, as well as finance, risk, opportunity and other similar matters.
“I also have a full-time job at home with three children and a husband and a dog!”
When Moverley started out 30 years ago, the Australian rail and construction industries had very few women in the workforce.
“They still are male-dominated industries, absolutely, but nowhere near what they used to be,” she said.
“It was a bit intimidating at the very start, but I think once you’ve learnt your skills and you prove yourself, the men go ‘Oh, you can actually do this!’
“You build your confidence and then you know you can conquer anything.”
Moverley said it’s crucial to have female leaders at all levels in the rail industry because they act as role models to others.
“Women leading the way is a success story which will inspire other women and help demonstrate that gender is not a barrier to success,” she said.
“It encourages newcomers to our industry, promotes retention, provides pathways for career advancement and allows stereotypes to be challenged and perceptions to be changed.
“There is an underlying assumption in our industry that rail and construction work is men’s work. It is hazardous, it is dirty and involves a lot of heavy lifting. This is outdated and needs to be changed. By having more women in leading roles at all levels of a business, we can quash this myth.”
Moverley said women bring many beneficial qualities to the workplace, from empathy to adaptability to strong communication and creativity.
“Men and women are different,” she said. “Our brains differ, and we think and process information differently. Our bodies differ –
Carmela Pelaez thinks having strong female representation in the rail industry encourages more young women to get on board. Image: Carmela Pelaez
we see differently and move differently. But these differences are not limitations. Men and women are complimentary, and we need to leverage off this.”
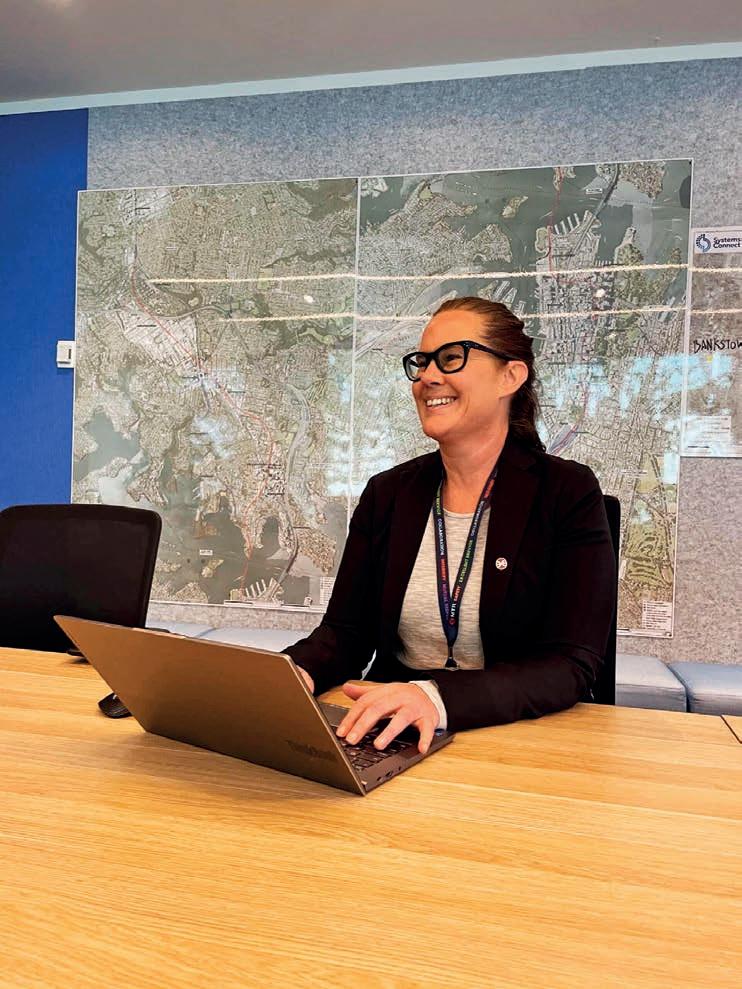
creating a workplace that is welcoming to women, culture is everything.
“Understanding and promoting the criticality of women in the workplace must come from the top,” she continued.
“An organisation must achieve ‘buy in’ from the executive and senior leadership teams, as it is these people who build the foundational architecture of a business.
“By creating non-toxic environments where women feel supported and respected, companies can foster a sense of belonging for all workers.”
Outside of defining an inclusive culture, she said there are many initiatives businesses can (and should) implement. These include removing the gender pay gap and equalising bonus opportunities between men and women, appointing “Champions of Change”, equalising prospects for career progression and promotion, and celebrating its female success stories.
“They can implement mentorship programs, which is something that MTR Australia has recently implemented,” she said.
“They can also ensure that they have the right policies in place, like parental leave, flexible working, wellness leave etc – which MTR also does.
such as the Australasian Railway Association or the National Association of Women in Construction.
“Through sharing best practices and aligning policy and strategy, businesses can leverage their collective intelligence and influence to foster an inclusive culture for both their own organisations and the wider industry.
“We need to work together to make this the norm.”
Sharing her advice to women who want to build a career in rail, she suggested joining a rail industry association.
“These associations can provide valuable resources, support and networks to help inform and connect people and businesses, and in my view is a sensible place to educate
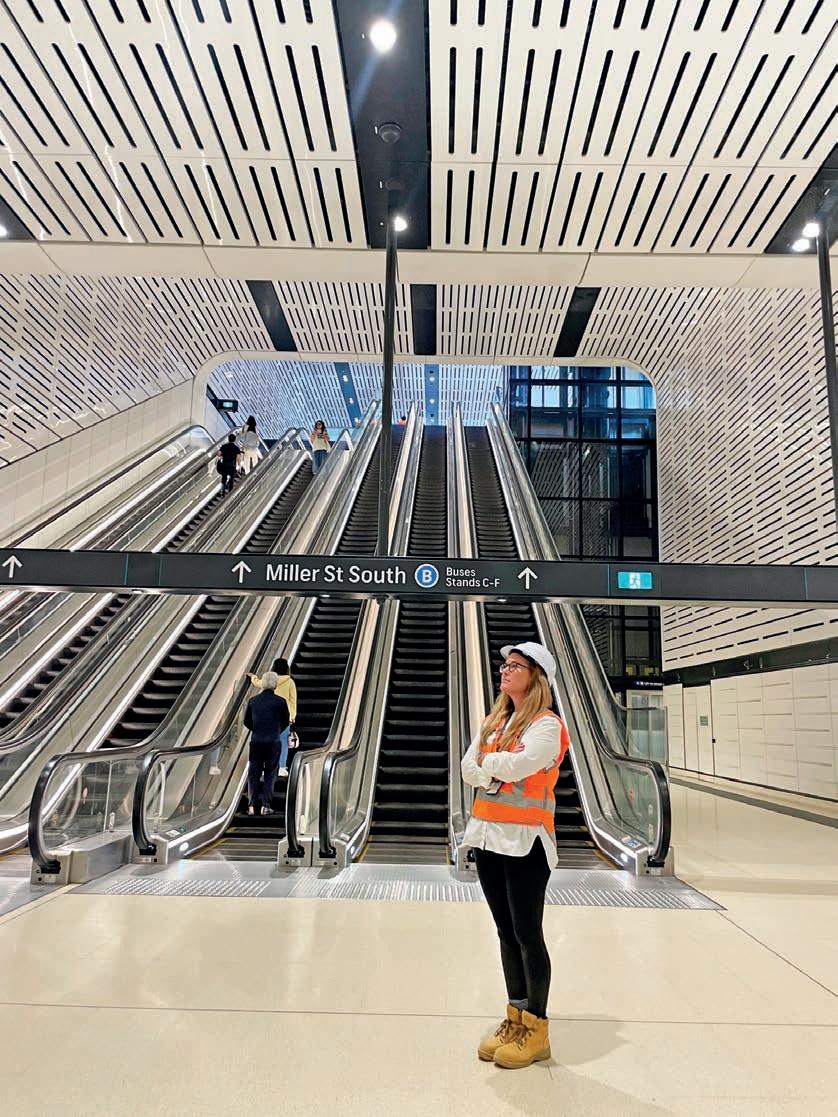
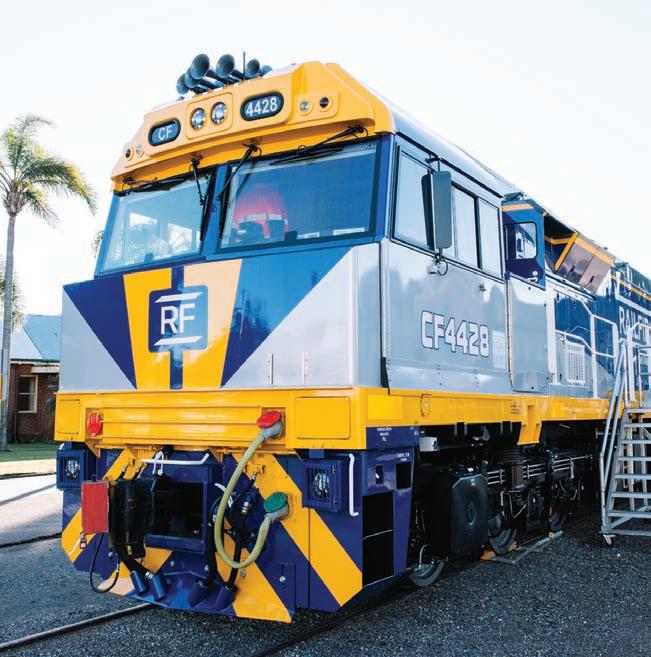
As a Senior Commercial Manager, Belinda Moverley gets exposure to the most senior level in MTR Australia.
Belinda Moverley is currently managing MTR’s contract with Sydney Metro.
Images:
Belinda Moverley
New era in rollingstock solutions for Australian rail freight
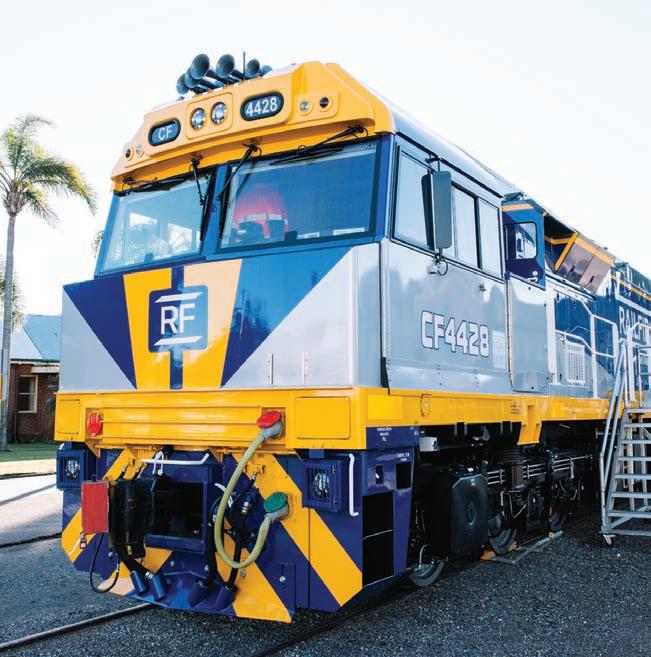
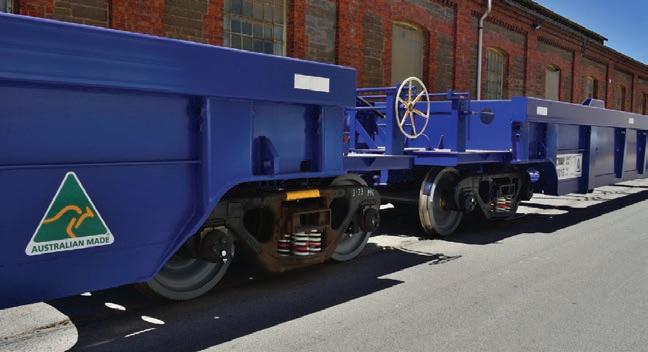
To register your interest in the above-mentioned leasing products and locally manufactured rollingstock, please contact Rail First’s Chief Commercial Officer Vic Regina: vic.regina@railfirst.com.au
New and diverse leadership team
Each executive has 20 to 30 years of expertise in transport and logistics, rail supply chain operations, manufacturing, construction and/or commercials
Core focus on offering market leading long-term solutions to customers
New leasing options for customers
Purchase to Long Term Lease
Manufacture to Long Term Lease
Provides customers with flexibility to allocate capital to other business initiatives
Favourable pricing discounts for longer lease periods and increased volumes
New locally manufactured rollingstock
48-foot intermodal well wagons and 40 -foot intermodal skel wagons
Hoppers for bulk commodities
Crew vans
Local manufacturing provides shorter lead times in customisation and delivery
Better customer visibility of safety standards and quality control during production
Less embedded carbon emissions than that of offshore manufacturing
New $100 million investment in energyefficient locomotives
Australian-made UGL CF44 freight locomotives feature one of the most fuel-efficient engines in the market
Helping customers to reduce emissions in rail supply chain operations
Real-time info: Empowering passengers and operators
The future of passenger communication is real-time, and KeTech is ready to help bridge the information gap in Australian rail.
In today’s fast-paced world, passengers expect instant access to reliable and accurate information. Whether checking real-time departure updates, service disruptions, or platform changes, access to up-to-the-minute travel information is no longer a luxury – it’s a necessity.
In Australia, there is a growing opportunity to enhance rail networks with real-time passenger journey information systems, whether that’s at stations and platforms or on board trains, both of which have the potential to improve passenger experience and operational efficiency.
The rail industry in the United Kingdom defines systems on stations and platforms as Customer Information Systems (CIS) and systems on board trains as Passenger Information Systems (PIS).
Unlike their European and North American counterparts, Australian rail networks predominantly rely on scheduled timetables and manual updates for passenger communication. While this approach has served the industry for decades, it no longer meets modern expectations.
According to research conducted by the International Association of Public Transport (UITP), passengers rank real-time information as one of the most critical factors in their overall journey satisfaction. A separate 2023 study by Transport Focus in the United Kingdom found that 86 per cent of passengers believe access to realtime updates significantly improves their travel experience.
A 2024 report published in the Journal of Public Transportation highlights that there is a knowledge gap in the Australian rail industry regarding passenger perceptions when it comes to design features on stations. The report, Train passengers’ perceptions and preferences for different platform and carriage design features, highlighted that 77 per cent of the Melbourne Metro passengers surveyed agree that the introduction of real-time carriage occupancy data would be helpful to decide which carriage to board.
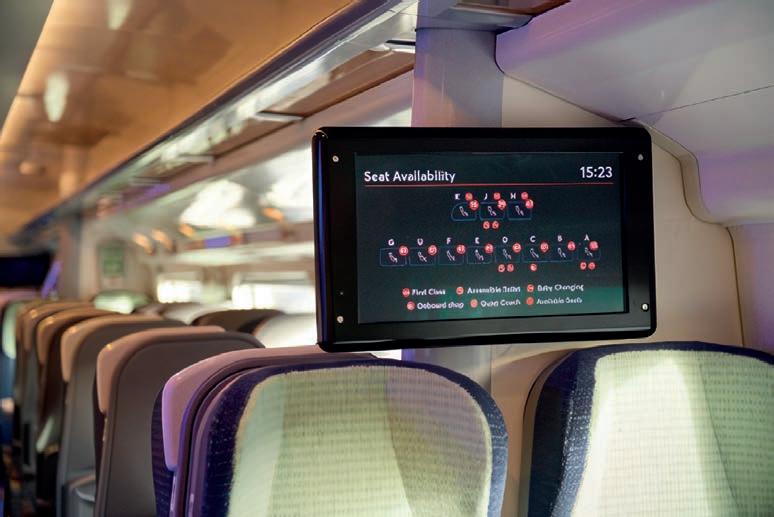
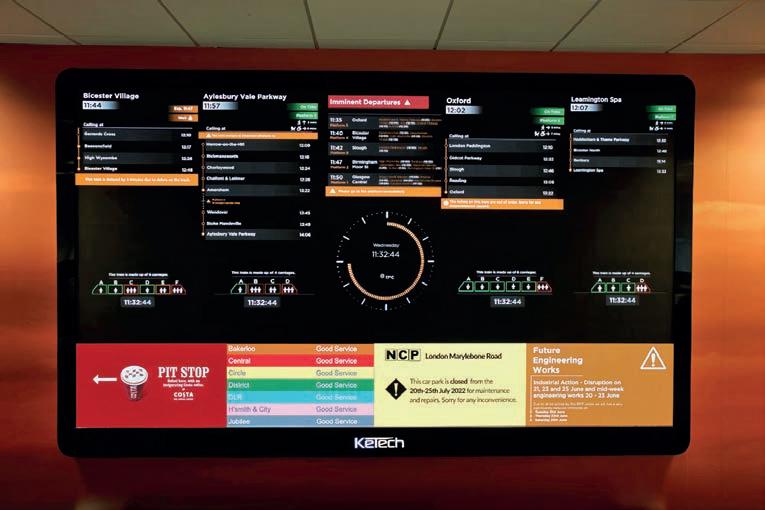
This finding emphasises that introducing new features such as real-time carriage occupancy data may improve passengers’ journey experience.
The demand for accurate, timely information on station is clear, but
the demand for a system that can also solve other challenges is apparent, and Australian passengers are no exception.
A real-time CIS provides instant, dynamic updates on train movements, service disruptions, and platform changes,
KeTech provides on-board passenger information on Avanti West Coast trains in the United Kingdom.
KeTech’s systems provide consistent real-time data. Images:
ensuring passengers always receive the most current information. This not only enhances customer satisfaction but improves operational efficiency by reducing congestion, mitigating confusion, and optimising passenger flow. Realtime CIS also supports accessibility by providing clear, consistent information across multiple channels, including station displays, mobile apps, and onboard systems.
Beyond passenger convenience, realtime CIS can also support rail operators by improving decision-making and reducing pressure on station staff. Instead of relying on manual announcements or outdated schedules, operators can dynamically adjust and communicate changes in real time, improving overall network performance.
Operators have the option to both manually send ad-hoc messages and schedule messages and notices remotely to specific stations, fleets or individual trains.
Rail technology company KeTech has back-end tools that allow operations teams to record, edit and schedule longline Public Address (PA) announcements. The system also allows operations staff to monitor equipment and third-party feeds using digital twin technology. The system has various configuration options for user management, allowing operators to set different access levels for staff.
KeTech specialises in delivering fully integrated real-time CIS solutions that bridge the gap between legacy infrastructure and modern passenger expectations.
Paul Warren, Sales Director at KeTech said: “With decades of experience across the United Kingdom and international rail markets, we have successfully implemented real-time information systems that seamlessly integrate with existing equipment.
“Our expertise in data fusion allows us to consolidate multiple data sources into a single, cohesive system, ensuring passengers receive the most accurate updates possible.”
KeTech’s CIS has intelligence built into its core and can do more than just provide accurate, real-time departure information. KeTech provides CIS to a single United Kingdom train operator at over 470 stations, 26 of which have antisocial behaviour issues.
Multiple studies have shown that playing classical music discourages criminal behaviour. KeTech tailored its system to play classical music at 26 of the train operator’s stations to prevent loitering, vandalism and graffiti. After only a few weeks, the rollout was classed as a success, with customers calling for an encore, saying they felt safer at those stations because large groups had stopped gathering there on a regular basis and causing a nuisance, particularly during the school holidays. The system can schedule certain times of the day for music to be played and at different volumes as to not affect local residents, or it can be controlled manually.
Feeling safe when travelling on public transport is essential for mobility, and fear of crime can be a larger problem for passengers than crime itself. A 2022
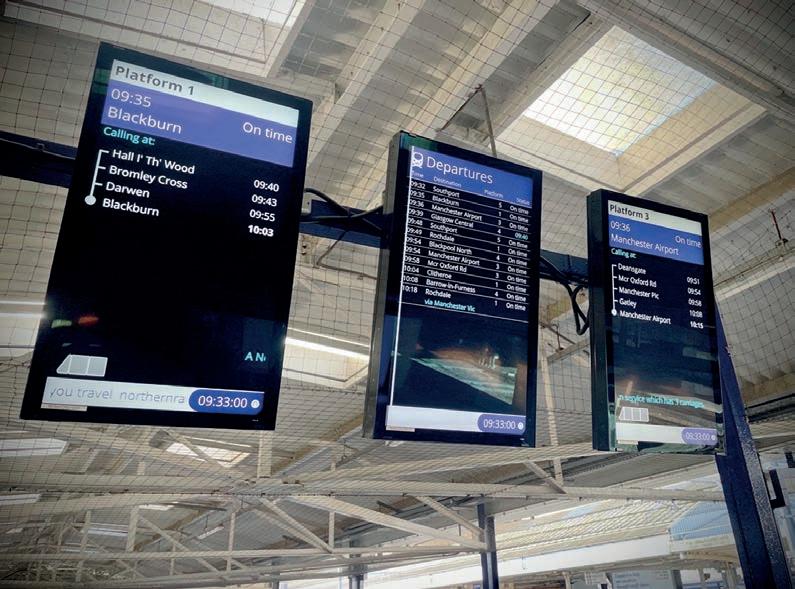
report states that Australian passengers value surveillance such as Closed-circuit Television (CCTV), and agree it is one of the most important factors when it comes to passengers perceived safety when travelling by train. However, the passenger only values CCTV if they can verify or have some kind of confirmation that it is active and in use.
KeTech provides on-board passenger information in the United Kingdom on Avanti West Coast trains via its Passenger Information System. Here, the system displays a live feed of the CCTV in the carriages. This provides confidence for passengers that they are being monitored live and aims to deter criminal behaviour. As KeTech’s systems are modular, its CIS has the same capabilities as its PIS and the relevant CCTV feed could be integrated to the CIS.
A key advantage of KeTech’s technology is its ability to integrate with both new and legacy equipment. Many rail networks face the challenge of modernising outdated systems without significant infrastructure overhauls. KeTech’s solutions are designed to work within these constraints, offering a cost-effective and scalable approach to upgrading Customer Information Systems.
Deploying a real-time CIS is only half the battle – ensuring its continuous reliability is just as critical. KeTech provides roundthe-clock support, 365 days a year, ensuring that rail operators always have the technical assistance they need.
“Our commitment to system resilience means that our solutions remain operational even under high-demand conditions, offering unparalleled reliability to both operators and passengers,” Warren said.
As Australia’s rail networks continue to expand and evolve, the need for real-time passenger information will only grow stronger. Implementing a robust, realtime passenger information is not just an enhancement, it’s an essential step toward meeting passenger expectations and improving overall network performance.
KeTech’s experience in delivering realtime CIS solutions has transformed rail travel in the United Kingdom. KeTech’s CIS is installed on about 500 stations – each with additional features that have been tailored to meet specific passenger and operator needs in different regions.
Warren said: “By integrating seamlessly with existing infrastructure, providing 24/7 support, and delivering industry-leading reliability, KeTech is ready to help bridge the information gap in Australian rail.
“The future of passenger communication is real-time and the time for change is now.”

KeTech has decades of experience across the United Kingdom and international rail markets.
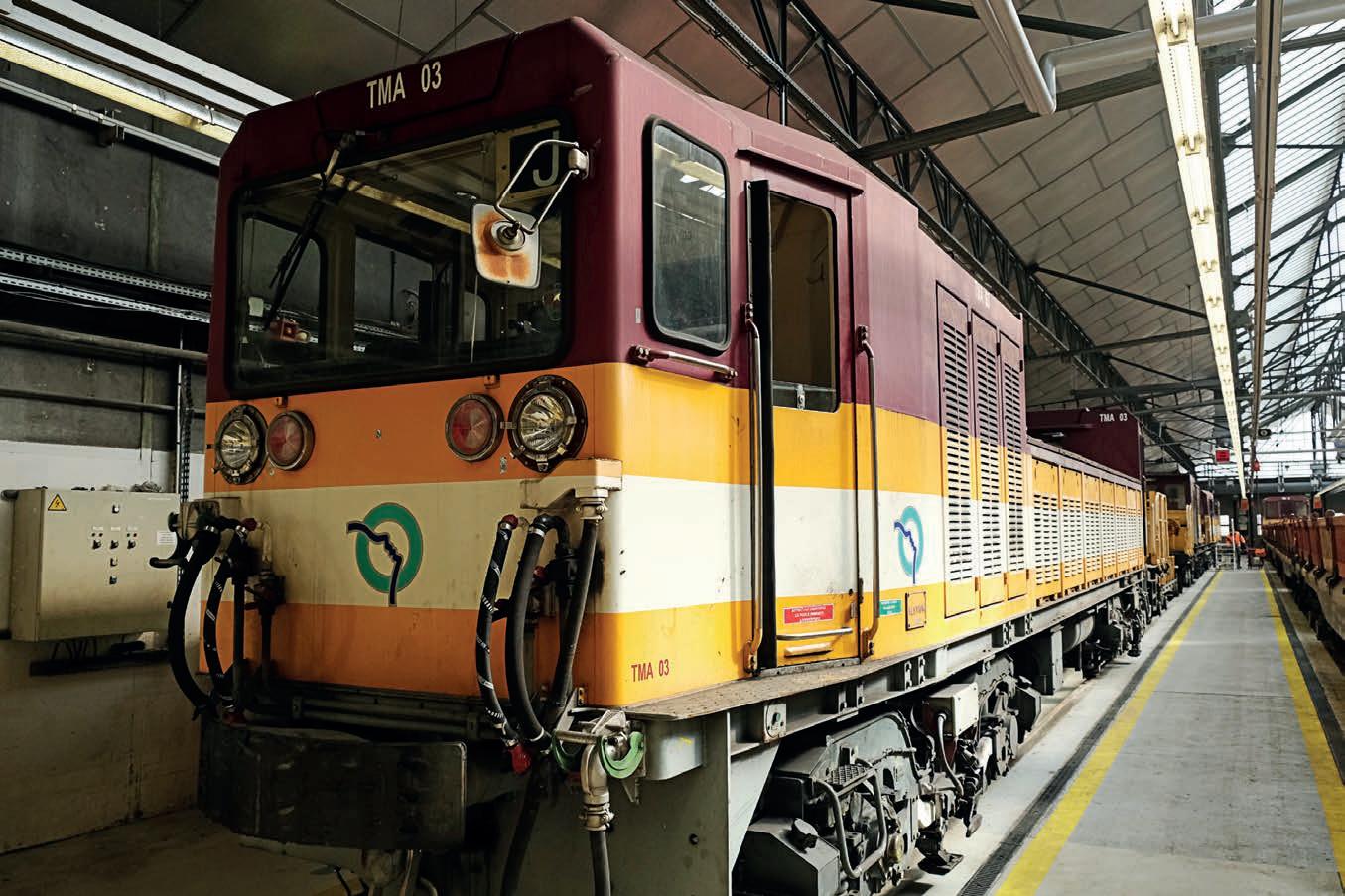
Innovating for better solutions
RATP Group is working with experts around the world to improve urban transport solutions, innovating and experimenting to improve its passengers’ experience.
RATP Group is a global leader in highcapacity urban rail, with operations and maintenance in more than 100 cities and 16 countries.
In Australia, its international subsidiary, RATP Dev, is leaning on RATP Group’s 125 years of experience and operations from international networks to develop solutions and bring innovation.
Innovation is of key importance to the group, especially when it comes to digitalisation, from modernising systems to developing digital tools for asset maintenance.
LEADERS IN AUTOMATION SYSTEMS
RATP Group has been a leader in metro operations – including successfully delivering the first fully-automated line on the Paris network, Line 14.
The group has also applied its knowledge to commuter rail in the French capital, with the installation of the Automatic Train Operation (ATO) system on the commuter rail line RER A (one of the five lines in the Réseau Express Régional, a hybrid commuter rail and rapid transit system serving the city and suburbs of Paris) when the time
came to renew the SACEM system. SACEM is an abbreviation of the French “Système d’Aide à la Conduite, à l’Exploitation et à la Maintenance” – or “Driver Assistance, Operation, and Maintenance System” in English. It’s a digital driving assistance system on the central section of RER A, developed by RATP at the end of the 1980s.
SACEM allows traffic to be regulated throughout the line, through fixed blocks used for train spacing. It was designed to reduce the practical interval between trains from two minutes and 30 seconds to two minutes, increasing the line capacity by 20 per cent to 30 trains per hour.
RATP Group has studied, designed and proposed an automatic control system to maximise and homogenise train speed in the central section equipped with SACEM. With the ATO system, the driver supervises the passengers’ ascent and descent, closes the doors and sets the train in motion, and the train is then driven by the automated system to the next station. Automatic piloting would thus make it possible to save two minutes of travel time and achieve the target of 30 trains per hour in the central section.
RATP Group committed to having a functional automatic control system on the central section of RER A, to improve train operation and journey times. To do so, the existing SACEM system and the rollingstock had to be updated. The ATO system was first installed on RER A trains in April 2017 and all trains were equipped by March 2018.
The Automatic Train Operation system enabled more regularity on the line. Coupled with new timetables and a unified command centre, the line punctuality increased from 89.3 per cent in 2018 to 93.47 per cent in 2024.
These initial findings highlight the benefits of the Automatic Train Operation mode. The provisional schedule was followed without impacting traffic, and with no negative effect on operations during the deployment. Finally, the main result of the project is the deployment of a viable technical solution, building on existing infrastructure and systems, which improved the service provided to travellers.
In 2030, in conjunction with the opening of lines 15 and 16 of the Greater Paris metro network at Noisy-Champs, it is planned to extend the SACEM zone, with automatic
RATP Group is a world-leading urban transport operator.
piloting from Val de Fontenay to Noisy Champs stations.
More recently, the full automation of Line 4 again showcased the Group’s capacity to modernise assets and its expertise in automated metro. This shows how RATP Group is always at the forefront of innovation to modernise assets for better operations and maintenance.
RATP Dev has also developed a digital tool for asset maintenance aimed at leveraging data to optimise and predict maintenance and offer improved quality of service to its passengers.
DIGITAL TOOLS FOR ASSET MAINTENANCE
Maint’Up is an in-house digital maintenance solution from RATP Dev that collects, centralises and analyses the data available from all equipment to optimise maintenance and facilitate the work of teams on a daily basis.
Maint’Up has been developed to be tailored specifically for each network. It has one single, streamlined interface for all equipment, including trains, bus, tram, stations, infrastructure, and signalling, to ensure the data can be understood by all teams, from operators and maintenance staff to data experts and management. With a dashboard showing contractual and operational KPIs at their fingertips, teams can monitor operational performance with ease.
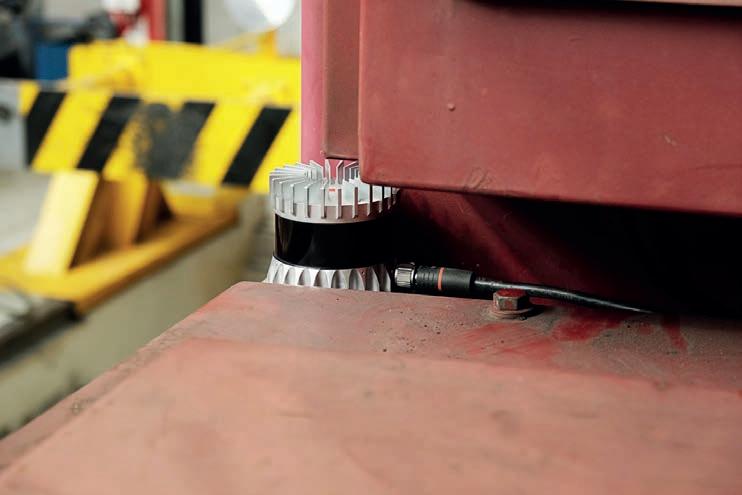
The solution can be used for all types of maintenance, from corrective to predictive, with remote access to data about the condition of the equipment. Users can get an instant view of incidents on the network, allowing them to co-ordinate action from operations and maintenance teams. They can also define and optimise their alerts, identifying potential new alert rules and removing alerts that are no longer relevant. By facilitating more efficient performance management and improved equipment reliability and availability, Maint’Up contributes to optimise energy consumption, save time and money and offer a better service to customers. In
Angers, France, where RATP Dev operates and maintains the tramway network, the deployment of Maint’Up led to a 20 per cent reduction in the tram network’s energy consumption per 100 kilometres, as well as a 40 per cent reduction in heat-related energy consumption.
Maint’Up was also used to carry out an analysis of 2.7 million passages of trams at traffic lights, to improve the traffic light priority system for trams. The RATP Dev team is currently developing an analysis of the tram doors’ opening and closing times to detect signs of incoming faults, applying predictive maintenance, thanks to Maint’Up.

RATP Group is striving to innovate for solutions such as underground geolocation using a LiDAR.
To maintain a high level of skill in its workforce and facilitate the operation of its network, RATP turned to LUNAAR, an expert in augmented collaboration.
Images: RATP
Passenger Rail

in Angers, RATP Dev is considering the deployment of this solution to other subsidiaries in France and Singapore.
As the company operates networks all around the world, from the United States of America to Australia, RATP Dev aims to create solutions that will take into account specificities of the local market and answer local needs.
To keep evolving with the technical progress of its time, and by leaning on the strength of collaboration with actors from the rail industry as well as the digital sector, RATP Group is investing in open innovation initiatives to keep experimenting and discovering what digitalisation can offer to improve its activities.
INNOVATION AT THE SERVICE OF THE RAILWAY INDUSTRY
RATP Group is also encouraging innovation for the railway industry through Labs such as Rail Open Lab (ROL).
Rail Open Lab is an open innovation accelerator for sustainable and efficient rail infrastructure, supporting collaboration between key actors of the industry to develop solutions since 2018. It brings together French infrastructure managers Société nationale des chemins de fer français (SNCF Reseau) and RATP Infrastructure, as well as professional unions from the railway and digital transition industries and about 30 industrial organisations.
The lab’s approach is based on reallife operations conditions experiments, taking place over short cycles (four months), to allow for agility, engagement and openness. Projects cover various fields, from sustainability to predictive maintenance and workplace safety. At the moment, they are testing a solution for
reduces the time to market of the innovation approach while supporting the development of the French rail industry expertise based on operational issues of industry actors.
The ROL has worked on seven case studies, five of which are being industrialised. Below are three case studies being tested and under consideration for large-scale deployment by RATP Group.
ANALYSIS OF INFRASTRUCTURE WITH LIDAR 3D DATA
RATP Group and The Cross Product (TCP) have developed an advanced solution for the analysis and management of railway infrastructures using 3D LiDAR data.
Optimising railway maintenance requires precise 3D analysis of infrastructures. 3D LiDAR data can identify defects (rail
deformations, gauge checks, collision risk detection) and improve predictive maintenance for safer and more efficient infrastructures.
The solution proposed by RATP Group is an approach combining 3D LiDAR data processing with digital twins and artificial intelligence (AI). Fast and accurate defect analysis is available directly, with detailed reports, complete with 3D measurements and simulations. Other key features include a simulation of a train gauge that can identify optimal locations for equipment and track layout analysis and generation of 2D and 3D cross sections.
A PRECISE GEOLOCATION SYSTEM UNDERGROUND
To accurately locate and track the usage data such as distance travelled, average speed of its Infrastructure Maintenance Vehicles (IMVs), RATP Infrastructures sought to develop a new tool. Dotflow, an expert in image processing and geolocation, committed to a four-month trial to address this requirement.
The solution proposed by Dotflow is a device comprising a camera, a LiDAR, an inertial measurement unit, and a data recorder powered by batteries. The device’s geopositioning system uses pre-existing cartographic data from RATP Infrastructures and real-time on-board data from sensors. When an IMV passes through a tunnel, Dotflow’s device can transmit the vehicle’s position to agents remotely, with a tolerance of five metres. The device can be installed or removed in one day, without the need for any special work or modifications to the IMV.

LUNAAR’s technology can be used for real-time learning, with a course broadcast through the headset.
LUNAAR’s connected headset can be used for remote assistance during troubleshooting.
RATP Group’s objectives are to ease the assembly of convoys in storage sites, improve the monitoring of IMVs and detect and localise certain defects, to move from preventive to predictive vehicle maintenance.
The solution was experimented at night on RATP’s metro network, in three successive phases:
1. Installation of the systems and calibration of the sensors.
2. Data collection during night work.
3. Data analysis and execution of Dotflow’s algorithms.
The experiment relied on existing 2D and 3D maps of the underground network. To address challenges related to the use of a camera, the data collected during the operations was anonymised and encrypted before being recorded, and awarenessraising actions were carried out for the parties involved.
Dotflow’s device showed impressive results, with 100 per cent availability of the device during the tests underground on more than 44,000 kilometres of travelled tracks, and 100 per cent track accuracy. The device proved robust to external disturbances and transitioned smoothly from tunnels to an outdoor environment.
Following the experiment, the teams made several observations:
• T here are few constraints in integrating the device into existing infrastructure, though some points still need to be clarified for vehicle integration.
• T he proposed geolocation solution meets the operational needs.
• Raising awareness about GDPR issues with employees at the early stages of the experiment helped facilitate the process.
• Ensuring the quality of the available mapping data is a key and significant step.
CONNECTED GLASSES FOR TRAINING AND REMOTE ASSISTANCE
To maintain a high level of skill in its workforce and facilitate the operation of its network, RATP Infrastructures sought to modernise its training system and strengthen the support provided to its agents during troubleshooting missions.
RATP Infrastructures was looking for a hands-free tool to help maintain the knowledge of its teams on specific and uncommon techniques. The goal was also to modernise training for PHT (High Voltage) lockout procedures and improve the comfort of agents during troubleshooting.
LUNAAR, an expert in augmented collaboration, aimed to meet this need by committing to a four-month sprint. The
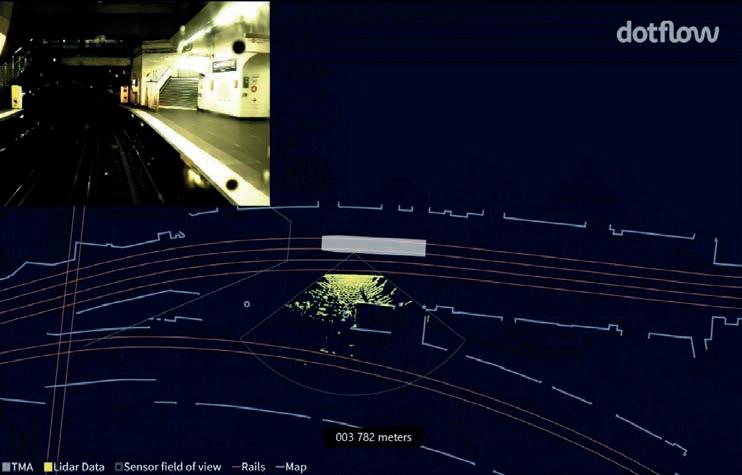
solution proposed by LUNAAR consists of a connected headset with glasses, a digital platform dedicated to RATP agent training, and remote troubleshooting software.
In the context of training, this solution allows for real-time learning with a course broadcasted through the headset, illustrating the trainer’s actions with images.
During a troubleshooting operation, the agent can request technical assistance or advice from a remote colleague, while sharing their field of vision. The aim is to improve the performance of maintenance tasks as colleagues can share information such as pictures, processes and schematics with the on-field agent, keeping their hands free.
RATP experimented the solution in highvoltage substations that supply power to the RATP network lines.
In the case of remote troubleshooting assistance, an agent was sent to perform maintenance, and the remote consultation with a technical expert allowed the issue to be resolved more quickly and calmly. Eight teams tested the connected glasses for remote troubleshooting assistance.
In the case of training, the agent followed a module on an RATP procedure via a pre-recorded training program displayed in their headset. The actions to be performed were detailed and illustrated with photos showing the trainer’s actions, allowing for effective immersion for the trainee.
Thanks to these experiments, the teams were able to get hands-on with this new system and enhance the digitalisation of training processes.
RATP Group was able to test the value of this type of solution with its teams. Real-time assistance, in particular, is a
significant asset for optimising operations. For the company, this innovative solution strengthens its pedagogical methods for better memory retention, sharing the practical activities of one trainee with the entire group and sustaining key technical skills. It also enables instant sharing of situations and information exchanges (diagrams, photos, procedures) to optimise problem-solving time and improve the quality of service.
This innovation was successfully tested during the Paris Olympic and Paralympic Games in 2024.
With further experimentation, this solution could open the door to the group’s experts sharing their knowledge or intervening in real time more broadly.
Denis Masure, Managing Director of RATP Dev Australia said: “We could imagine an expert in Singapore leveraging these innovations to help out a team in Australia.
“For Australian teams, it could mean accessing and sharing knowledge from the group with other experts in the APAC zone.”
BETTER SOLUTIONS
RATP Group is striving to innovate for better solutions that are more efficient, sustainable, and adaptable to each local context.
With RATP Dev and international subsidiaries such as RATP Dev Australia, there are testing grounds and collaboration opportunities for many different case studies and feedback.
Denis Masure said: “Our experts from all around the globe work together to improve urban transport solutions and respond to our clients’ needs and overall enhance our passengers’ lives.”

3D LiDAR data can identify defects and improve predictive maintenance for safer and more efficient infrastructures.
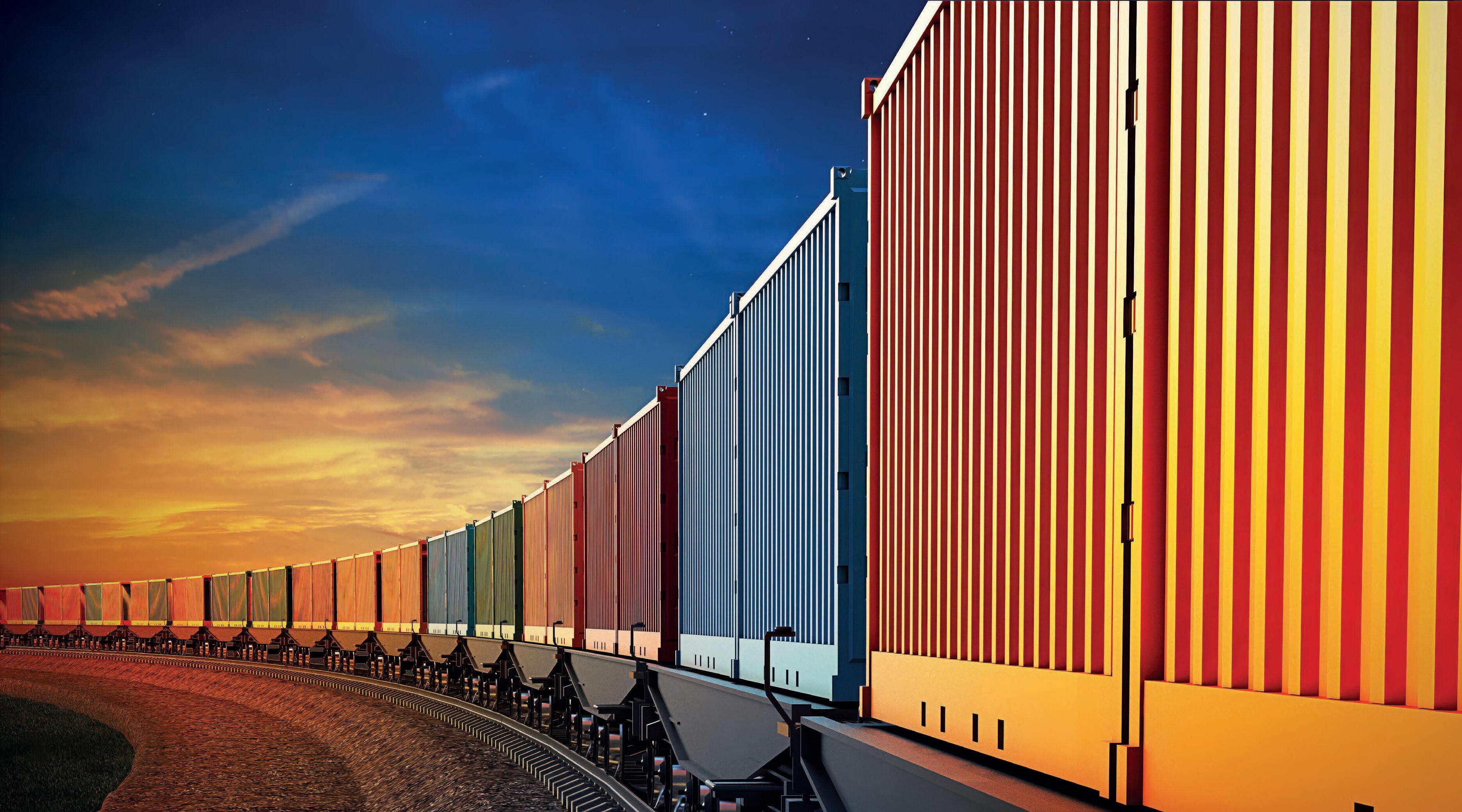
Pioneering the future of freight rail Technology
With its real-time, Cloud-based rail monitoring system, Transdiagnostics is ready to bring freight rail into the 21st century.
The transportation sector, including aviation, automotive, mining and shipping, has long embraced digital transformation, integrating real-time monitoring, Artificial Intelligence (AI), and the Internet of Things (IoT) to enhance safety and operational efficiency.
Aviation, though a much younger industry than rail, has used real-time diagnostics for years, enabling airlines to track aircraft systems and predict failures before they occur.
Automotive has incorporated advanced telematics to improve safety and performance, while mining and shipping operations rely on real-time condition monitoring to maintain missioncritical equipment. Freight rail, however, has not responded similarly.
Peter Hogg, Managing Director of rail company Transdiagnostics, said the industry remains entrenched in outdated practices and technology pioneered in the 1980s, which are directly linked to catastrophic derailments.
“Globally, the rail industry is lagging in adopting modern safety and efficiency technologies,” Hogg said. “Despite freight rail being the backbone of logistics and supply chains, operators continue to rely on fragmented and reactive safety measures that belong to the past.”
A DATA-DRIVEN FUTURE
With over 60 years of combined rail industry expertise, Transdiagnostics is driving the shift towards a more advanced, data-driven future. Its flagship product, Transend®,
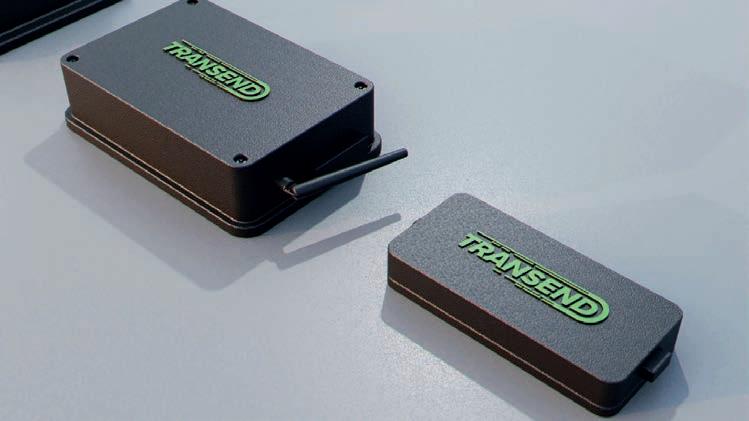
delivers 24/7 real-time monitoring, eliminating the need for unreliable wayside detectors and antiquated detection systems.
Standard derailment detection methods require each rail car to be fitted with an identification (ID) tag. As the train passes a wayside detector site, one module reads the rail car’s ID tag, another module measures the temperature, and both pieces of data are transmitted to a central server, where the two readings must be matched to identify the rail car with the problem.
“This process is inefficient and often inaccurate,” Hogg said. “By the time data is processed, it only relates to one location and does not show how the data is trending – if an ID reading is even recorded at all.”
Additionally, with freight trains growing longer, existing wayside detectors struggle to communicate alerts effectively.
“Ideally, if a train bearing is overheating, a radio signal should notify the train crew immediately,” Hogg said. “However, in more and more cases, the signal fails to reach the locomotive due to the surrounding terrain and sheer length of the train.”
Transend, by contrast, collects track temperature, force, and noise data every ten seconds, delivering contextualised insights directly to train crews, train control, and maintenance personnel. With Cloud-based connectivity, instant alerts, and predictive diagnostics, the system enhances both safety and operational efficiency.
“Our technology separates critical safety alarms from routine maintenance data,” Hogg said. “Maintenance teams receive track-related performance information,
Transend’s advanced sensors are easily attached to each wagon of a train via magnets.
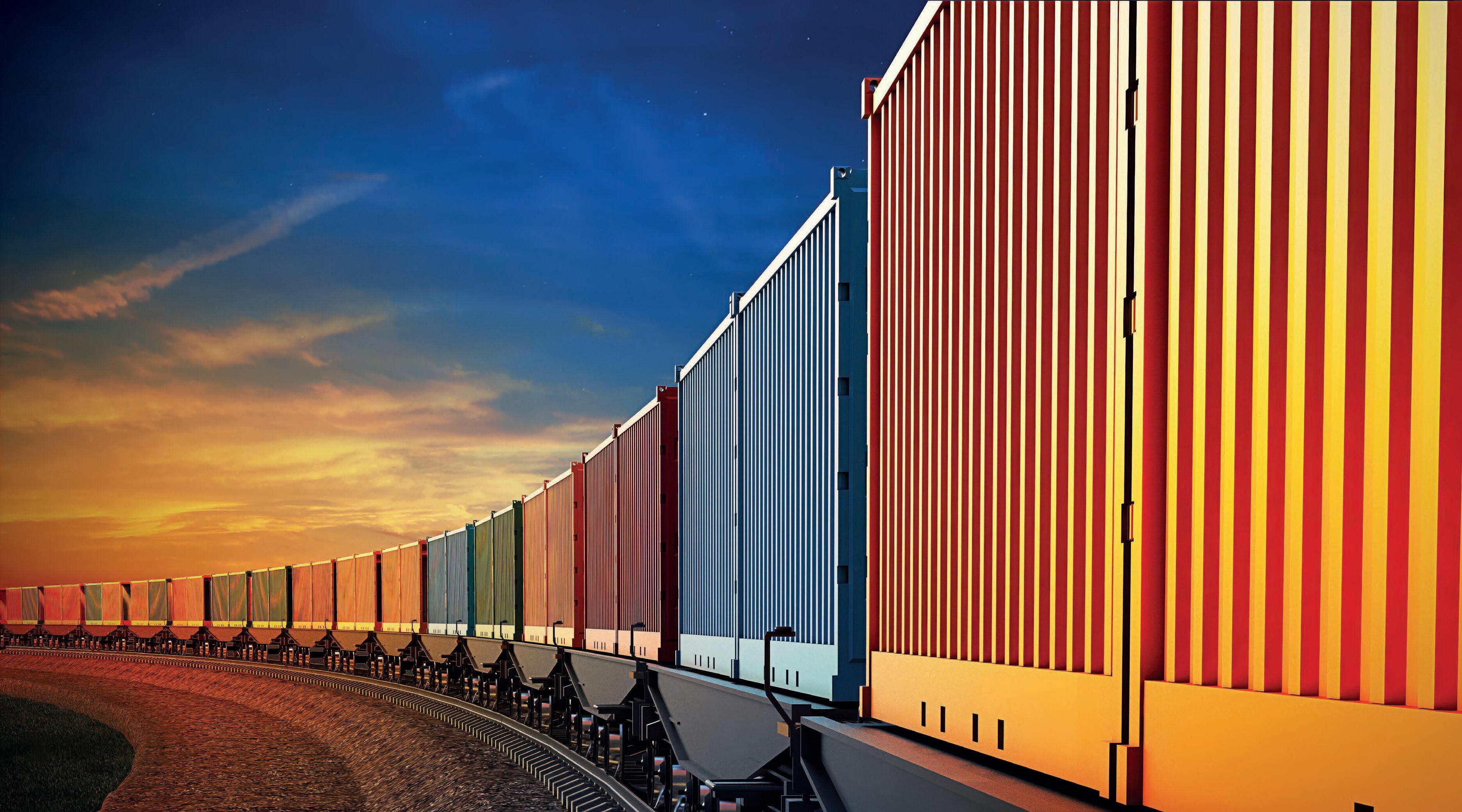
while train control is notified only of urgent safety alerts. If an operator prefers, the system can also be configured so that only high-priority warnings are sent to the train crew.”
TRIED AND TESTED
Transend has undergone extensive field testing over four years on the Mary Valley Rattler, a heritage railway in Gympie, Queensland.
Hogg said the patented technology, designed and manufactured in Brisbane, has transformed the Rattler’s aging infrastructure into a fully connected system, providing a real-world proving ground for its capabilities.
“One of the key challenges was maintaining the track, and previously, the general manager would ride at the back of the train, visually inspecting undulations and taking location details to share with maintenance crews,” he said.
“Transdiagnostics revolutionised this process by installing a camera under the train.
“Now, the system generates a digital map that pinpoints track irregularities in real time. If an issue is detected, a maintenance manager can click on the flagged location and instantly access a recorded video, eliminating the need for manual inspections.”
With readings taken every ten seconds across all wagons simultaneously, any anomalies are identified almost immediately, allowing for swift intervention.
DERAILMENTS AREN’T INEVITABLE
Freight rail derailments are disruptive, costly, and hazardous – but Hogg argues they are not an inevitable reality of the industry.
One high profile example is the East Palestine train derailment in Ohio in February 2023, where a train carrying hazardous materials derailed after the hot railcar bearing sparked a fire. The resulting derailment of 38 cars led to the release of toxic chemicals into the air, forcing residents within a 1.6 kilometre radius to evacuate.
The environmental and economic effects are still being felt more than two years after the crash, with Vice President JD Vance recently visiting the site and advocating for stricter monitoring, corporate accountability, and stronger federal oversight of railway operators.
Hogg said the United States National Transportation Safety Board’s final report hearing confirmed that real-time monitoring could have prevented the disaster. The train had passed three wayside defect detectors, each recording rising temperatures – yet no action was taken until it was too late.
“These outdated detectors generated an alert that was emailed to someone, but by the time action was taken, the train had already derailed,” Hogg said.
“Transend’s real-time monitoring would have made a crucial difference. The derailment report identified various forensic data, all of which our product is designed to detect.
“Notably, the bearing made so much noise that residents living nearby could hear it from their homes – six separate times. Our system would have flagged the issue early, allowing the train crew to stop the train 30 miles before disaster struck.”
THE TIME FOR CHANGE IS NOW
Australia has also experienced its share of derailments, including a 2022 incident in Inverleigh, Victoria, which disrupted both interstate and intrastate rail transport.
Hogg said the solution lies in onboard sensor-driven, continuous digital monitoring – technology that detects failures before they escalate, enabling proactive intervention.
“Derailments don’t have to be accepted as a fact of life,” he said.
“The technology to prevent them exists today, but it requires the industry to embrace innovation and move beyond outdated safety measures.”
The rail sector stands at a turning point, with increasing regulatory pressure and mounting operational risks demanding a shift away from legacy systems.
Proposed legislation in the United States, including the Railroad Safety Enhancement Act of 2024, is pushing for enhanced monitoring, improved safety protocols, and real-time data reporting.
“Companies that embrace digital transformation will not only improve safety but also increase efficiency, profitability, and stakeholder value,” Hogg said.
“Regulatory momentum, industry challenges, and technological advancements are converging –presenting an opportunity for rail operators to lead the way in proactive safety measures.”

HOW TRANSEND SOLVES FREIGHT RAIL’S BIGGEST CHALLENGES:
• Real-time condition monitoring detects failures before they escalate.
• Transend ensures compliance with emerging regulations through seamless data integration.
• Data-driven decision-making reduces downtime, improves efficiency, and boosts network reliability.
For more information, contact Transdiagnostics at: info@transdiagnostics.com
Image: artegorov3@gmail/stock.adobe.com
TransDiagnostics plans to bring freight rail into the 21st century.

Battling the elements
We
take a look at how Queensland Rail got itself back on track after recent severe weather – and the role technology and equipment plays in flood recovery.
Operating a state’s rail network is no easy task – especially when you add severe weather into the mix.
When major floods hit North Queensland in January and February, the rail lines suffered serious damage.
The Mount Isa and North Coast line got the brunt of it, with services suspended while Queensland Rail employees and contractors mobilised to repair 164 sites in total.
The Mount Isa line was particularly bad between Charters Towers and Cloncurry, as the high-pressure water flow had displaced rocks and soil, resulting in some sections of track being suspended in the air.
More than 1.3 kilometres of washouts, requiring 5000 tonnes of ballast, had to be fixed before trains could resume. The line reopened on February 21.
Queensland Rail Head of Regional, Scott Cornish, explained that crews had to wait for flood waters to recede to gain full visibility and safe access to the track.
The North Coast Line was reopened as far as Townsville less than three weeks after the floods, but the section between Townsville and Cairns was closed for a month.
In total, the line suffered damage to nearly seven kilometres of track, with major washouts and scouring requiring
culvert repairs, bridge rebuilds, resurfacing works and new formation poured in several locations.
Recovery works were hampered by ground conditions and wet weather, as rain continued to lash the region.
“The North Coast Line runs the length of coastal Queensland and spans 1600 track kilometres, so inspecting and repairing
mammoth job,” Cornish said. “We are so pleased that containerised freight, sugar, grain and livestock, as well as our Spirit of Queensland services, can run again from Brisbane to Cairns.
“Queensland Rail continues to invest heavily in our rail lines and when we undertake renewal and maintenance works, we are always focused on increasing the
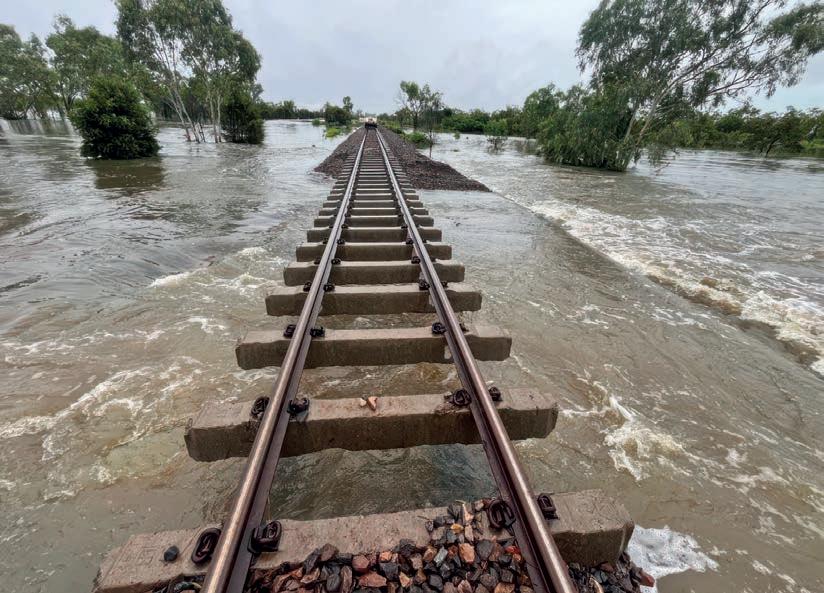
Debris had to be cleared from the tracks at Cattle Creek.
The Mount Isa line had to be closed during the flooding.
Images: Queensland Rail

important this vital link is in connecting our communities and I want to thank our hard-working crews who have done an incredible job.”
IMPROVING RESPONSE TIMES
Cornish said Queensland Rail is always looking at ways to improve response times to major weather events which impact the rail network, including investing in recovery equipment and new technologies to assist with track inspections.
“Before the onset of the wet season, we undertake a series of assurance activities to ensure network readiness,” he said.
Key tasks include:
• Ballast management: Identifying and positioning ballast at critical points across the network.
• Flood rock identification: Marking known flood-prone areas and plotting them for quick access.
• M apping key infrastructure: Plotting ballast trains, sleeper locations, culvert materials, and machinery positions on maps to ensure readiness.
• Strategic machine positioning: When an incident is imminent, resurfacing machines, trucks and loaders will be strategically deployed to facilitate quick recovery and ensure no equipment becomes isolated.
• Weather monitoring: All weather stations are checked. These stations provide live CCTV feeds of low-lying bridges and other problematic areas, as well as real-time water height data for predictive flood management.
• FloodMon System: A computer-based modelling system that aggregates data from public and Queensland Rail weather stations to predict river heights. This tool helps operators make proactive decisions about train stabling and network closures based on current rainfall and the effect smaller tributaries might have on the monitored river.
In addition to the above, Queensland Rail continuously assesses past incidents to identify opportunities for flood mitigation, such as strengthening bridge piers, culverts, and other critical infrastructure.
“Understanding the required culvert sizes in relation to changing weather patterns is vital for long-term network protection,” said Cornish.
“Given the scale of the regional network, it’s important to recognise that not every asset can be fully protected. Therefore, reducing recovery times becomes a costeffective strategy to quickly restore full network functionality.”
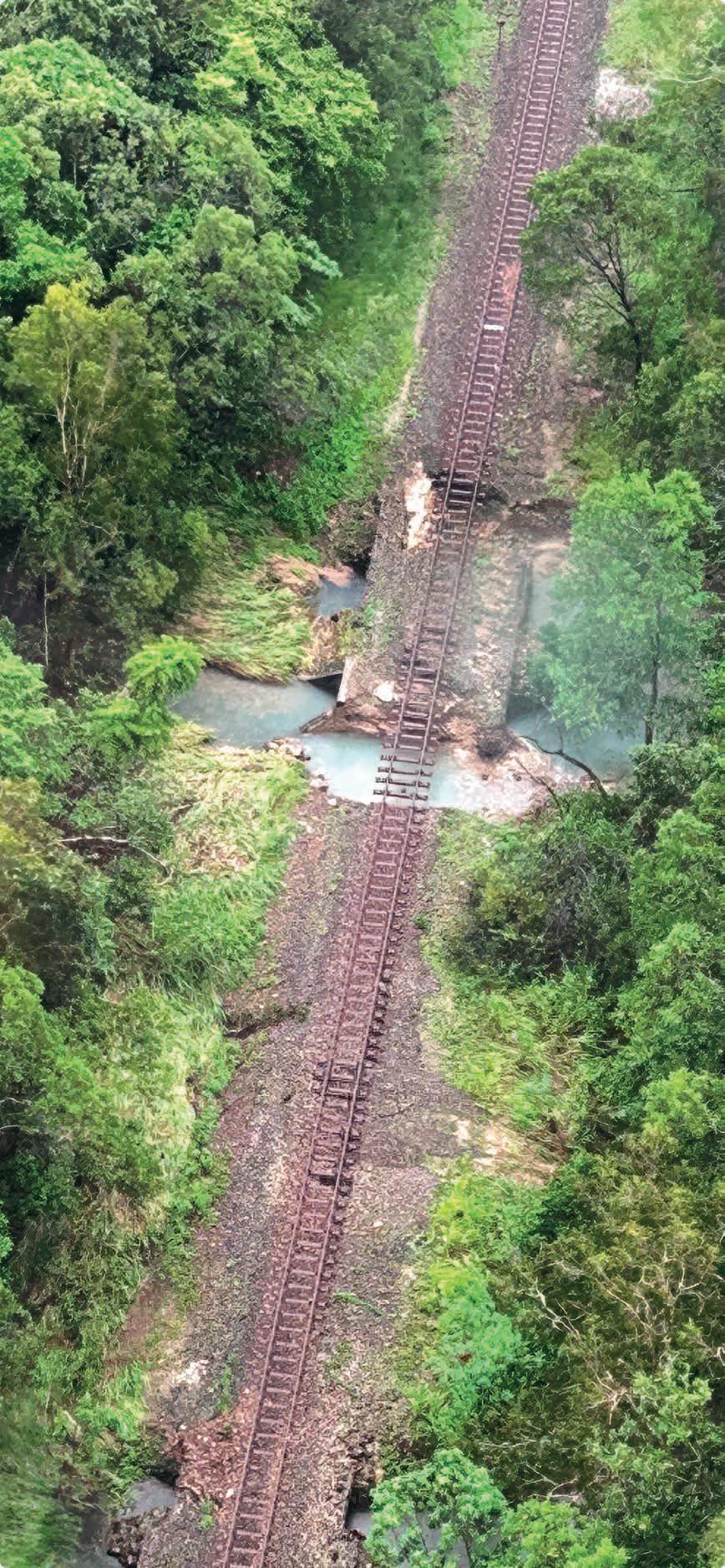
A drone image shows flood damage on the North Coast line at Conn, near Ingham.
Passenger Rail
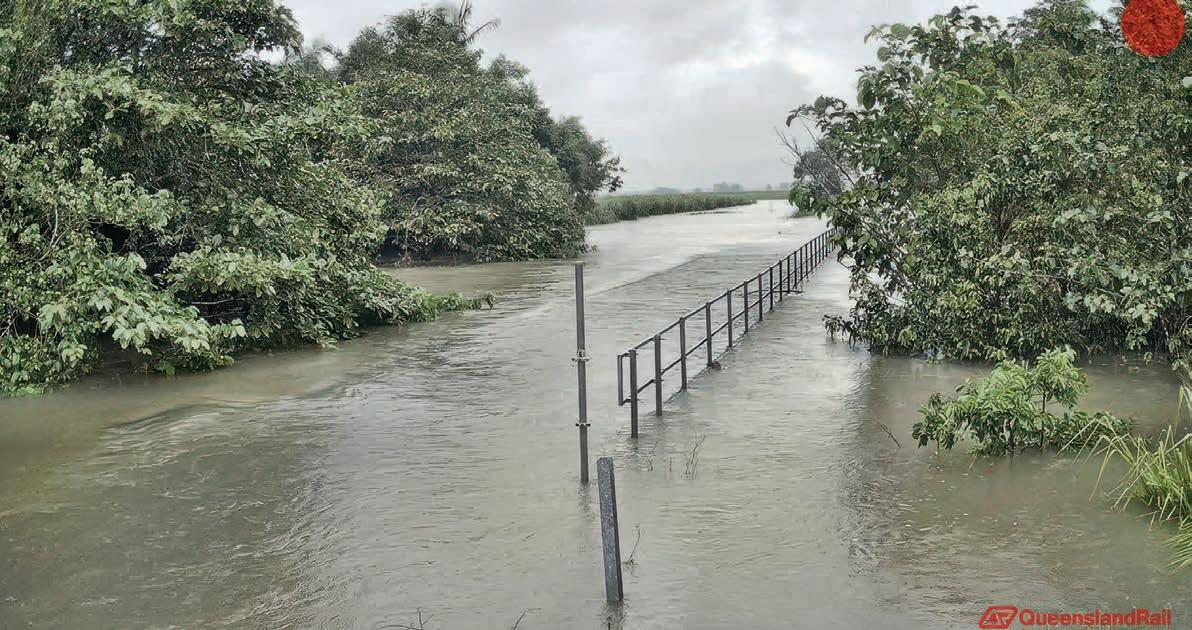
BOGGED DOWN
Cornish said bog mats – high quality and heavy-duty ground protection that form a temporary roadway for heavy vehicles –allowed Queensland Rail to get onsite during wet conditions and progress works safely and quickly.
“During the recent floods, bog mats provided essential access to otherwise inaccessible sites, which would typically require the construction of full formation roads due to the challenging soil types and heavy machinery needs,’ he said.
“Without them, the reopening of the Mount Isa line would have been delayed at least another week while waiting for the ground to dry out.”
OLLY TO THE RESCUE
One piece of equipment that was valuable in the cleanup was a special on-track recovery machine or hi-rail bus, nicknamed ‘Olly’.
Olly transported more than 3500 people, including emergency services and local residents, across Ollera Creek and between Ayr and Home Hill, while the track was closed to rail traffic during the floods.
The hi-rail bus entered service at Queensland Rail in January 2015. Originally built by Varley Specialised Vehicles in Brisbane, it was fitted with its rail guidance system by Harsco Rail Brisbane, which enabled it to travel on track.
Olly is an Isuzu FRR 600, medium truck fitted with a four-cylinder diesel engine. It can carry up to 12 passengers including the driver and is usually used by Queensland Rail to undertake track inspections and
give train controllers a visual experience of rail conditions and locations they are responsible for.
To date, it has travelled more than 152,000 kilometres on both road and rail. This includes more than 1,300 kilometres during the North Queensland floods alone, reconnecting isolated communities and delivering essential supplies and groceries.
TAPPING INTO TECHNOLOGY
In Brisbane and other urban areas of Queensland, the rail network is currently using Instrumented Revenue Vehicle (IRV) technology.
The brainchild of the Institute of Rail Technology at Monash University in Melbourne, an IRV is an intelligent automated condition monitoring tool which is retrofitted to standard rollingstock and integrated into normal railway operations.
The system was developed for heavy haul freight networks and has since been expanded to passenger applications.
IRVs automatically collect dynamic vehicle performance data and identify high risk track-related defects, and the precise locations of the defects. They can send remote data that can be analysed in real time.
This information is used for condition monitoring and targeted economical track maintenance planning, identifying maintenance effectiveness as well as assessing rollingstock performance.
Professor Ravi Ravitharan, Director of the Institute of Railway Technology, said that Queensland Rail has only recently acquired
Instrumented Vehicle Technology, but is already using it on the Redcliffe Peninsula and Springfield lines, Ferny Grove and Beenleigh lines, Shorncliffe and Cleveland lines, Caboolture and Rosewood lines.
He thinks the technology could be implemented to great effect in northern Queensland, to help crews locate faults and carry out repairs faster and easier.
“This technology can play a key role in assessing track conditions and system performance for floodwaters and rain-
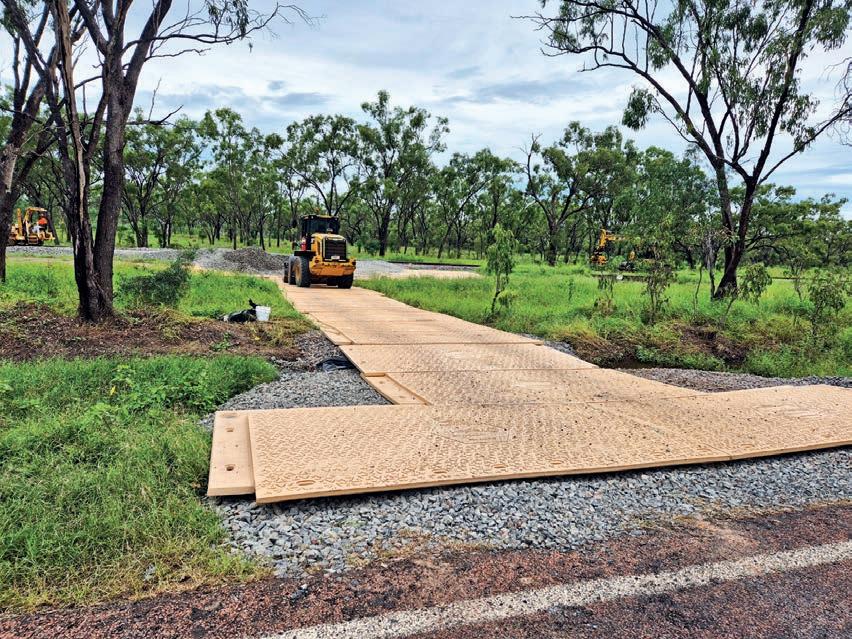
Crews had to wait for water to recede at Murray River before carrying out repairs.
In total, crews have carried out repairs to 164 sites.
operations,” he said. “Flooding can weaken railway infrastructure, causing track washouts and structural damage that aren’t always visible.
“Monash’s IRV continuously collects data on track alignment, vibrations and stability, helping to quickly identify issues and make data-driven operational and safety decisions.”
Professor Ravitharan added that the IRV also helps keep crews out of harm’s way.
“You don’t have to have people endangering themselves walking in flooded areas,” he said. “Also, even if you have someone on foot inspecting a track, you are not going to know what sort of loads are going to go through unless you have instrumentation.
“The instrumentation gives you an understanding of what kind of load carrying capacity it has got. You can run the IRV at a slower speed than you would usually, to assess the damage.”

Professor Ravitharan said modern railways need to look to the future when it comes to flood recovery.
“We have to start thinking what technologies are available, and how do we actually use the technology in the best way to improve our operations?
“MTR in Hong Kong is thinking ahead and using technology to tell them what is going to happen in the future. They are using it in the Pilbara as well, for heavy haul. But Australia hasn’t really invested on those type of capabilities yet, even though they are available.”
Dr Sabrina Sayers, a research scientist at Monash specialising in drone technology, said Queensland Rail is already making use of drones.
“What they normally do is use a drone to fly over an area after flooding, to see the extent of the damage,” she said.
“They use drones for that immediate overview, but you could be using the data to see how a ballast has moved, for example. You could also create a point cloud or an elevation or temperature model, to see how deep the flooding is.”
Dr Sayers said data from drones could also help with post-flood recovery when it comes to vegetation.
“If you put in ballast or some kind of grading, and you model it over time, you can see how the elevation changes,” she said.
“You could also use radiometric data to tell you how much a slope might move.
“That tells you the moisture content of the soil so you can say, OK, we need to vegetate the area or put in some geotextiles or whatever it is, to help bind it.”

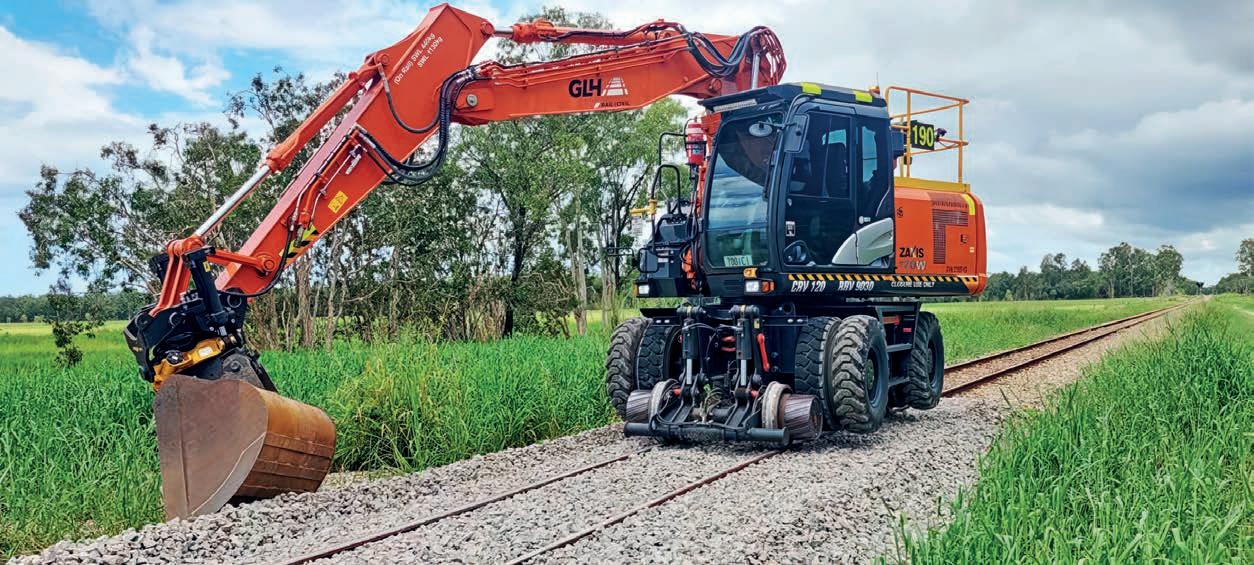
Dr Sabrina Sayers from Monash University said drone technology has a wide range of applications when it comes to flood recovery.
Queensland Rail employees and contractors were mobilised at Mundic Creek. Image:
Decarbonisation
The Byford Rail Extension project is exploring new ways to decarbonise – with great success so far.
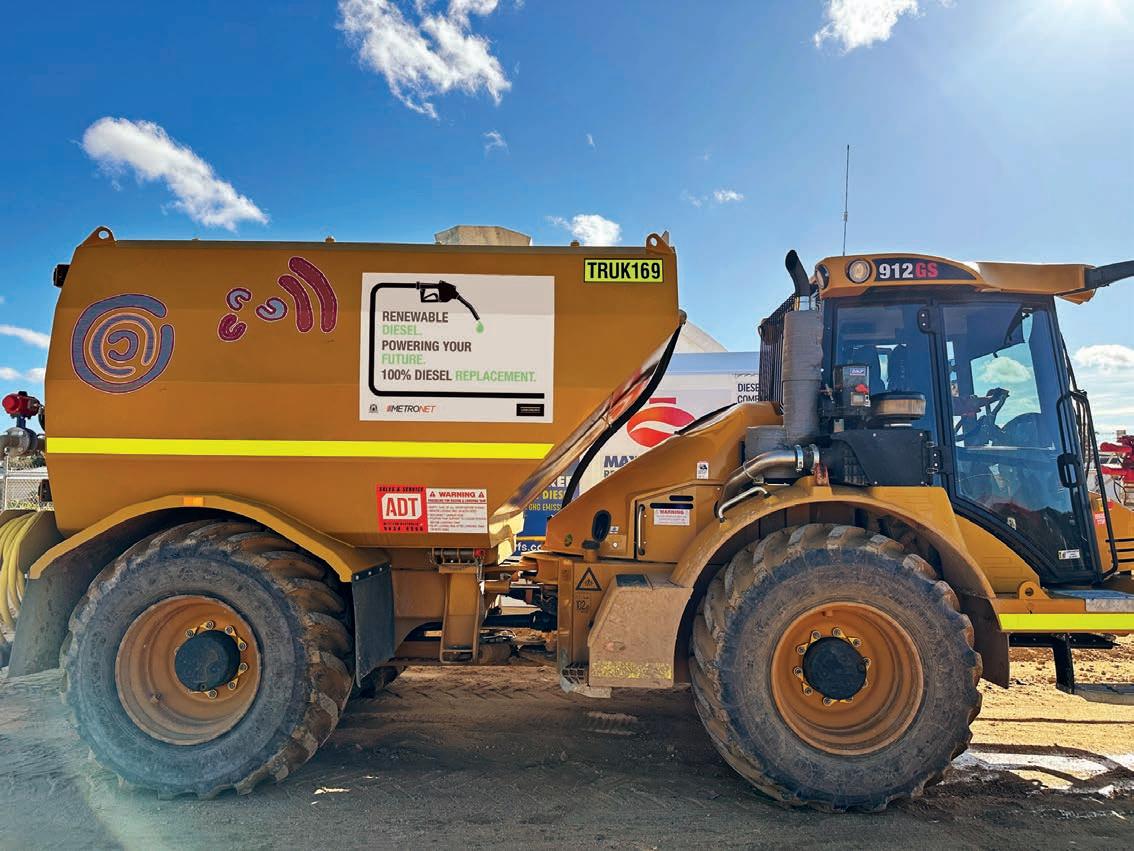
Rail travel is one of the most energyefficient forms of transport – with only 2.6 per cent of Australia’s transport greenhouse gas emissions attributable to passenger and freight rail.
Greenhouse gas emissions per passenger kilometre for rail transport is up to five times less than that of car transport, according to the Australasian Railway Association (ARA), and moving freight on rail produces 16 times less carbon pollution compared to trucks.
With Australia striving towards the lofty goal of net zero emissions by 2050, the rail industry is thinking outside the box for ways to do better. This often starts before a railway is even built, as is the case with Western Australia’s METRONET Byford Rail Extension project.
PAVING THE WAY
Western Australia’s METRONET Byford Rail Extension project is stretching the Armadale Line approximately eight kilometres south to a new ground-level station in Byford and supporting one of the fastest-growing areas in the country.
In line with the State Government’s net zero goals, METRONET has set a 20 per cent emissions reduction target for the project
do so.
In 2024, in a first for Western Australia, MetCONNX (the alliance name for the Bedford Rail Extension Project) began trialling the use of Hydrotreated Vegetable Oil (HVO) as fuel.
Made from fats, vegetable oils and waste products from the food industry and restaurants, HVO was used to replace regular diesel in a range of equipment including utes, watercarts, telehandlers, generators and excavators.
About 30,000 litres of traditional diesel were replaced with HVO, abating 7.98 tonnes of CO₂ emissions.
The trial, which has now come to an end, was run in collaboration with Perth’s Curtin University, which undertook studies to understand implications for fuel efficiency, emission reduction and impacts to engines.
The data captured will be provided to the Department of Transport to show the viability of HVO fuel for current and future infrastructure projects, and to help build the case for wider industry use once HVO is available in Western Australia in 2025-26.
Emma Kindness, MetCONNX’s Senior Sustainability Advisor, said that there were no issues reported with the operation,
HVO was used in. “Feedback from the operators has been overwhelmingly positive, noting there has been no detectable difference between the plant running on HVO and fossil diesel,” she said.
“MetCONNX will be writing a case study to share with industry as part of our annual report to METRONET.”
According to METRONET, reducing reliance on fossil fuels can have other benefits too, as lowering exposure to diesel fumes can reduce the risk of asthma, headaches, and lung irritation for workers and nearby communities.
Kindness said the health and safety of crews working on the Byford Rail Extension is a top priority, and that no symptoms such as headaches were reported during the trial.
“However, please note that our outdoor worksites naturally disperse emissions, minimising exposure risks,” she added.
“The trial was conducted alongside standard diesel-powered equipment, making it challenging to attribute any noticeable changes to the use of renewable diesel alone.
“The trial focused on renewable diesel’s environmental benefits, such as reduced CO₂e- emissions.”
The Byford Rail Extension project trialled the use of HVO instead of diesel last year, with great success.
Images: METRONET
THE NEXT TEST
The project is now undertaking a new trial, testing a HYDI unit that can be retrofitted to existing diesel equipment to produce hydrogen on demand for engines, with a lifecycle of about 20 years.
Developed by South Australian hydrogen technology company HYDI, the compact, self-contained unit uses proton exchange membrane cells to produce hydrogen from distilled water without needing any additional chemicals.
So far, the HYDI has been tested on a CAT 150 grader and both the CAT 962 and CAT 950 loaders (20T), which have been used for bulk earthworks along the expanded rail alignment.
As hydrogen produces three times more energy than diesel and creates less pollution when burned, it’s a win for sustainability –and the trial is going well, with a 19 per cent increase in fuel efficiency recorded.
“We are very pleased with the trial of the HYDI unit,” said Kindness.
“The unit has operated without issues and provided a clear reduction in diesel burn, contributing to our carbon reduction targets.
“There have been no discernible operational changes with the introduction of HYDI on various pieces of plant that it has been installed on, and early data from the CAT loader showed that after the install there was an improved efficiency to approximately 6.56 litres per hour from 8.18 litres per hour.”
Although hydrogen is highly flammable, the MetCONNX team has had no problems.
“The only input required for the HYDI unit to operate is distilled water,” Kindness said. “There is then a catalytic conversion within the unit which produces hydrogen to supplement the diesel.
“The conversion and combustion processes are well-contained, with no issues
Over 130 hours, the HYDI unit saved about 210.6 litres of diesel and used only 3.5 litres of distilled water.
Kindness said that in an industry such as construction, which is difficult to electrify, there is a need to explore other options.
“While electrification is the ultimate goal, its adoption faces challenges due to limited availability and high costs of electric equipment, as well as charging limitations, particularly for long, linear infrastructure projects and for the type of machinery required on large construction projects,” she said.
“The HYDI units are a novel solution, which work to immediately reduce carbon emissions by attaching the kit to a preexisting combustion engine. Alternative fuels like HVO provide a practical interim solution as well by serving as a direct (like for like) drop-in fuel substitute for diesel – however we still face the challenge of cost (double the price, currently, of fossil fuel diesel).”
The use of HYDI and HVO allows businesses to achieve emissions reductions without incurring the substantial costs of replacing internal combustion engines that may already have locked in investment decisions, ensuring a smoother transition to decarbonised operations.
“A combination of technologies will be required to meet our net zero goals,” Kindness said.
In addition to these two trials, the Byford Rail Extension project has also implemented a number of initiatives including solar panels on construction offices, solar lighting towers, and a portable power station for hand tools.
The project has also endeavoured to reuse pre-existing materials within the project, avoiding transportation of new materials to site. Examples include re-use of rail sleepers and ballast from the original rail alignment, as well as furniture items from
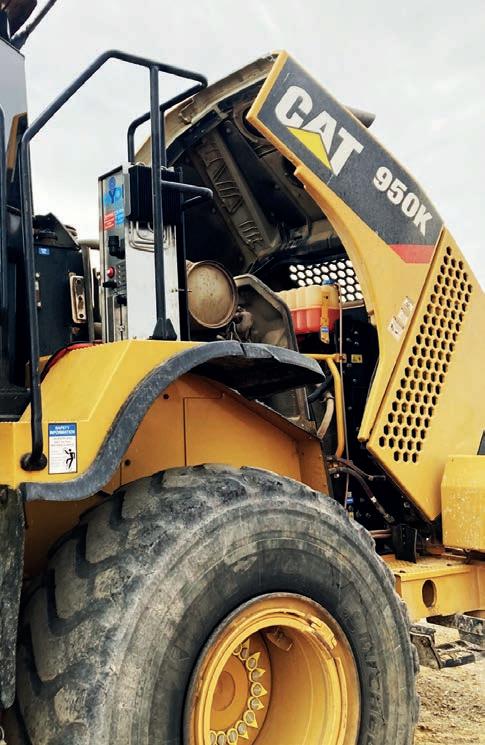
In a major sustainability milestone, Byford Station recently became Western Australia’s first train station to achieve a 6 Star Green Star Design Review. This is the highest rating under the Green Building Council of Australia’s Railways V1.1 Rating tool and represents world leadership in sustainability.
Key sustainability features of the station include the installation of solar photovoltaic (PV) systems capable of generating 100 kilowatts of electricity with future provisions for battery storage.
The station also boasts “quality indoor environments”, windbreaks, shading and rain protection and maximum natural light used to create “bright, inviting spaces”.
In a statement, METRONET said: “The 6 Star Green Design Review is a result of comprehensive, independent verification across multiple sustainability criteria including management practices, indoor environmental quality, energy efficiency, transport, water use, materials, land use and ecology, emissions reduction and innovation.
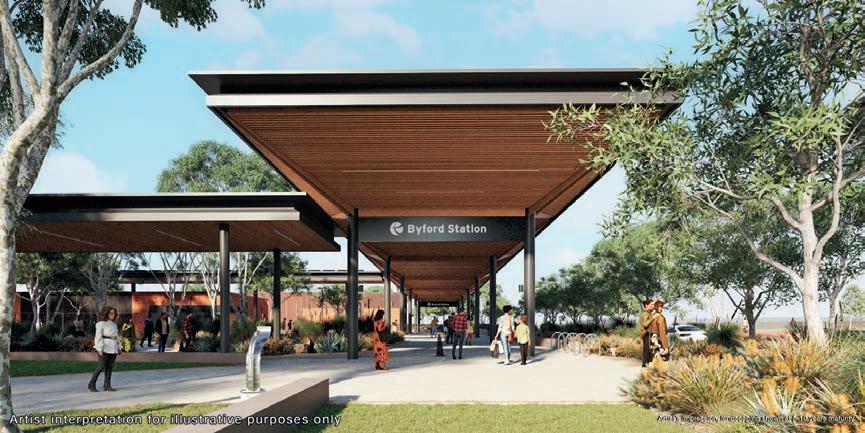
“The project is also exceeding recycled content targets for concrete used, further demonstrating a commitment to sustainable practices.”
METRONET’s official Sustainability Strategy states that it strives to create a sustainable legacy for Perth through the planning, design, procurement, and construction of transport infrastructure, stations and precincts.
It reads: “For METRONET, sustainability is the alignment of environmental, social and economic principles, to ensure ‘development that meets the needs of the present without compromising the ability of future generations to meet their own needs’.”

The HYDI unit has been tested on various CAT loaders.
An artist’s impression of the new Byford Station.
Passenger Rail
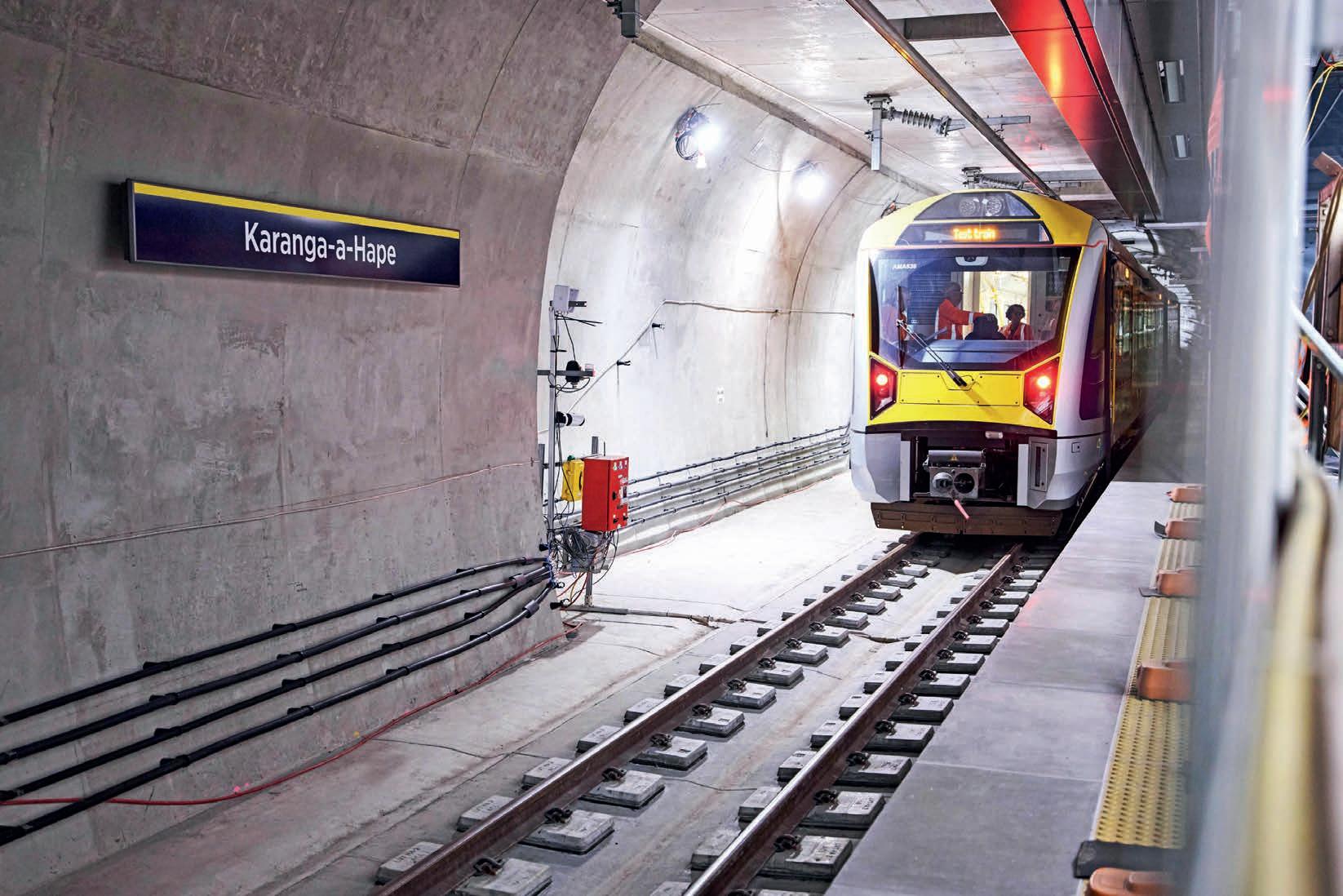
Major milestone
The Auckland City Rail Link has moved into its next phase with the first test trains travelling through the tunnels.
New Zealand’s biggest city recently celebrated a momentous milestone as the first test train travelled through the full length of Auckland’s City Rail Link (CRL) tunnels.
The 3.45-kilometre-long inaugural test journey, which took place late on February 12, ran south from Waitematā Station (Britomart) under central Auckland past the new underground stations at Te Waihorotiu and Karanga-a-Hape to Maungawhau Station on the Western/North Auckland Line.
The three-carriage train left on time at 9pm, and was in no rush to arrive at its destination – taking a leisurely two-and-ahalf hours to complete the journey.
The deliberately low speed allowed technicians to complete their first round of underground checks and balances around tunnel clearance, power supply and signalling.
As CRL is one of the steepest sections of railway in New Zealand, a focus of the testing is on braking, signalling and power.
Just one or two test trips had been planned, but the train successfully completed five trips during the night.
CRL, New Zealand’s largest transport infrastructure project, is a new rail connection at the heart of Auckland’s public transport network. It is also the country’s first underground railway.
It turns dead-end Waitematā into a through line station to better connect the central city and the wider rail network, with two brand-new stations being constructed, and will enable more frequent trains to run across all of Auckland’s rail network.
Getting the green light to test trains came after a lengthy planning process and numerous safety checks, with the tunnels’ overhead lines being energised the week beforehand to provide electricity to the trains. Hard work on the project dates back years, with the first spades hitting the ground at Britomart back in 2016.
City Rail Link Ltd’s Chief Executive Patrick Brockie described the first test trips as a “colossal milestone” in New Zealand’s biggest transport infrastructure project, and a “game changer” for Auckland.
“The test run is a major step in our transition from a construction site into a railway,” he said.
The next step for CRL is running a comprehensive testing schedule ahead of the first passengers boarding the trains in 2026, to confirm that trains can seamlessly transition between CRL and the wider network. Testing has been gradually ramping up, with the safety of everyone involved always remaining a priority – with crews working with about 25,000 volts of electricity in the overhead lines.
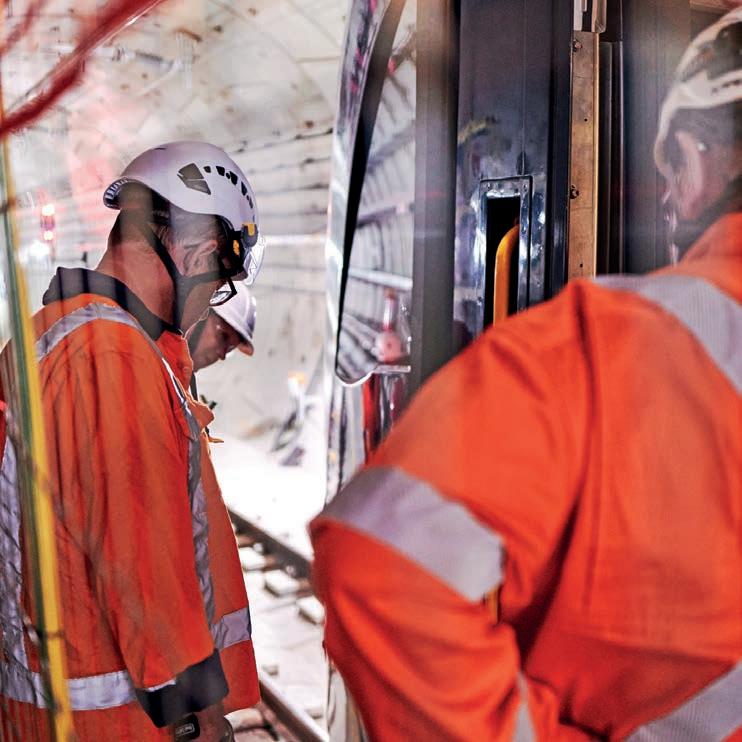
Trains started running at just 5km/h, with the speed increased in controlled steps.
By the end of 2025, the City Rail Link will have completed more than 8300 tests to be Auckland-ready by 2026.
Images: City Rail Link
Trains started running at just five kilometres an hour, with the speed increased in controlled steps.
In the early days of testing, polystyrene strips were temporarily fitted to increase the test train’s width, simulating full speed travel to ensure there were no issues with tunnel clearance.

In addition, recovery procedures were tested for a train that has broken down in the tunnels, rescued by another train either by pushing or pulling it out.
In week two, validation started of CRL’s advanced European Train Control System (ETCS).
ETCS continuously monitors speeds, braking distances and safe stopping locations, ensuring trains do not exceed speed limits.
This allows trains to run closer together safely, enabling higher-frequency services.
When ETCS was approved, train speeds increased to more than 40 kilometres an hour to check tunnel clearance at full line speed.
Multiple trains were then tested in the system at full speed (up to 70 kilometres an hour), with hands-on driver training underway in the tunnel.
Noise and vibration monitoring was conducted with multiple trains operating.
Other work on the agenda includes checking complex ventilation systems, mechanics, electrics, security, fire, communications and hydraulic systems for the tunnels and stations.
By the end of 2025, more than 8,300 individual tests will have been completed on the various systems needed to run CRL safely.
To make the most of this extended network, Auckland Transport is expanding its fleet of three-carriage passenger trains by 23, bringing the total to 95.
Together with Auckland One Rail, which is contracted to operate the city’s train services, Auckland Transport is preparing the new trains and staff. They are training all existing drivers and train managers to operate on the City Rail Link.
Extra staff are also being recruited to support the increase in services, with the number of train drivers expected to rise from about 237 to 260.
Train managers will increase from 168 to approximately 190, while the number of station staff is still being confirmed, but is projected to increase by around 25 per cent to service the new and redeveloped stations.
The first successful test trip in the tunnels was welcomed by Auckland Council which is funding the NZ$5.5 billion project alongside the government.
“This is momentous for Auckland and the CRL program, which has had its fair share of challenges,” said Mayor Wayne Brown.
“It’s good to see progress being made because Auckland deserves a public transport system that will deliver benefits for Aucklanders and visitors alike.
“I’ve always said I was determined to get the project finished and over the line, and we can finally see the light at the end of the tunnel.”
Stacey van der Putten, Auckland Transport Director of Public Transport and Active Modes, said that when the CRL opens in 2026, it will better connect Aucklanders to the people and places they want to visit.
“For the first time the rail network is joined up for trains at the heart of our public transport system,” she said. “The test train has made the first direct, easier journey that tens of thousands of people will be making every day. But before that happens, we’ve still got a lot of work to do to make sure journeys on Auckland’s new railway are safe, reliable and seamless from day one.”
Brockie acknowledged the work of his CRL Ltd team, the project’s main Link Alliance contractors, KiwiRail, Auckland Transport (AT) and Auckland One Rail.
“Everyone involved in being ready for the first train has the right to be proud – a great achievement that demonstrated the very best in innovation and co-operation to deliver an outstanding outcome for Auckland and its more accessible future.”
Practical completion of the project is forecast for the end of 2025 when CRL Ltd will hand the newly built CRL over to KiwiRail and Auckland Transport – the transport arm of Auckland Council.
KiwiRail will look after CRL’s maintenance while AT will own the stations and be responsible for CRL’s operation, as well as the opening day activities.
Stacey van der Putten said AT’s work to be ready to open the City Rail Link and provide a great customer experience has started well in advance of CRL completing its work.
“For example, driver training, developing and implementing new timetables and updating a number of systems are also underway to ensure they’re completed as soon as possible after CRL Ltd hand over to AT and KiwiRail,” she said.
Van der Putten said the CRL will open to the public in 2026, but an exact date cannot yet be confirmed.
“These final phases of a complex new railway project are known, from international experience, to be the most challenging, with several potential scenarios to plan for,” they continued.
“AT and KiwiRail also have a range of work to do before CRL can open. This work has started now but will continue after CRL Ltd completes construction.
This work includes completing upgrade work on the wider rail network, carrying out final safety assurances, training
The first test train took 2.5 hours to complete its journey from Waitematā Station (Britomart) to Maungawhau Station.
Passenger Rail
staff, and carrying out practice and readiness exercises.
One of the most important things that must happen before opening are large numbers of practice runs across the entire rail network. There will be new, more frequent services on lines that operate completely differently to the way the Eastern, Western and Southern lines do today.
“Opening City Rail Link is like putting on a big new show, rehearsals are essential so that passengers have reliable journeys and a great experience from day one.”
“This will confirm we can provide a safe, reliable service and a great experience for Aucklanders in 2026.
“We’ll know more about opening dates as the testing and commissioning phase progresses, and we’ll continue to keep the public informed about our progress.”
The launch of testing in the tunnels closely follows another major milestone, as KiwiRail successfully completed the latest stage of its network upgrade program over the summer holidays.
An extended four-week rail closure – with buses replacing trains on all lines – allowed crews to blitz the network, with more than 1350 workers descending on more than 110 sites.
This was the first in a series of closures for a final push to get the network ready for CRL and the faster, more frequent services it will bring.
Working 24 hours a day, seven days a week whenever possible, KiwiRail achieved more progress than had been planned in many areas.
WHAT WAS ACHIEVED DURING THE WORKS:
• Stage 4 of the Rail Network Rebuild (between Papakura to Pukekohe) completed.
• A total of 7.4km of rail reinstatement and 11.4km of drainage works completed for the Rail Network Rebuild in some of the network’s most difficultto-access priority areas.
• Full track laid with overhead line and signalling system testing completed for the Third Main Line between Puhinui and Ōtāhuhu.
• New safer pedestrian access at Homai Station to replace two level crossings.
• A total of 14.3km of rail de-stressed to minimise potential speed restrictions caused by temperature changes.
• 13 turnouts replaced.
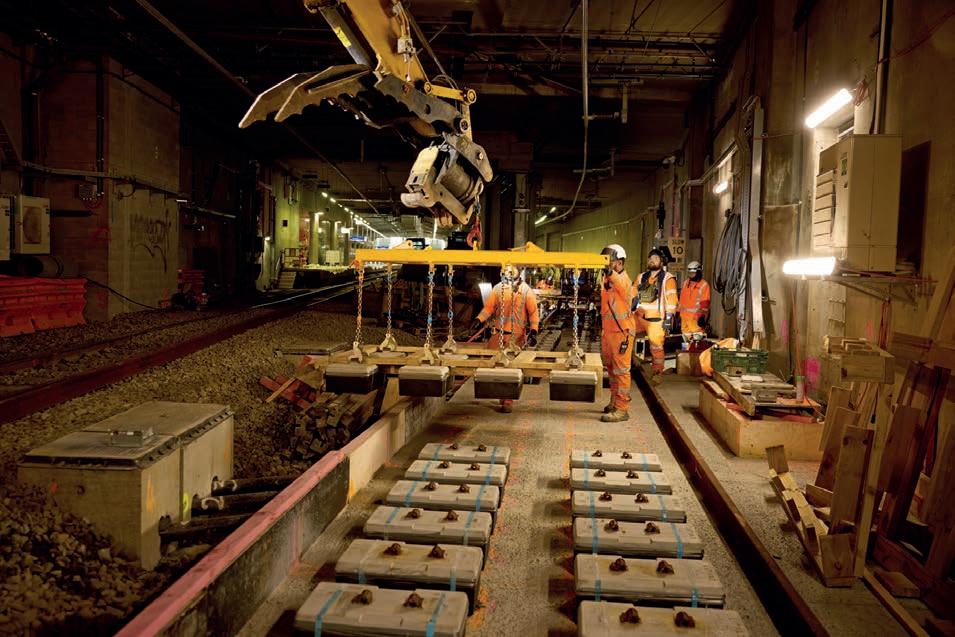
passenger trains are now running all the way to the city centre with no need to change from diesel trains at Papakura.
“Having a full four weeks with no passenger trains and therefore no energised powerlines meant we were able to deliver a massive amount of work without having to fit around trains,” said André Lovatt, Chief Infrastructure Officer at KiwiRail. “We know it’s a big ask for passengers.”
Lovatt said that the team is operating in a complex environment as it upgrades the network, integrating new systems with old.
• 3200 sleepers replaced across the network.
• 19km of tamping.
• 17.5kms of rail stabilised.
• Completion of a new pedestrian overbridge at Middlemore Station.
• 22 storm recovery sites repaired across the network using 6500 tonnes of rock.
• O verhead line modifications and continued civil and electrification installation activities for new western power feed at Glen Eden. Regular service suspensions during major holidays will be extended to deliver the majority of the final stages of the Rail Network Rebuild. This allows teams to safely work on the tracks and inside tunnels. The next extended closure will be for 16 days over the Easter and ANZAC long weekends – a school holiday period
provide some confidence that it’s worth the inconvenience when so much progress has been made,” he added.
Van der Putten thanked Aucklanders for their patience while the upgrade work took place and trains were replaced by buses to keep people moving.
“All of the upgrades happening during closures will maximise the benefits of the City Rail Link when it opens in 2026, with faster journeys, trains up to every four-to-five minutes, better connections across Auckland and improved reliability,” she said.
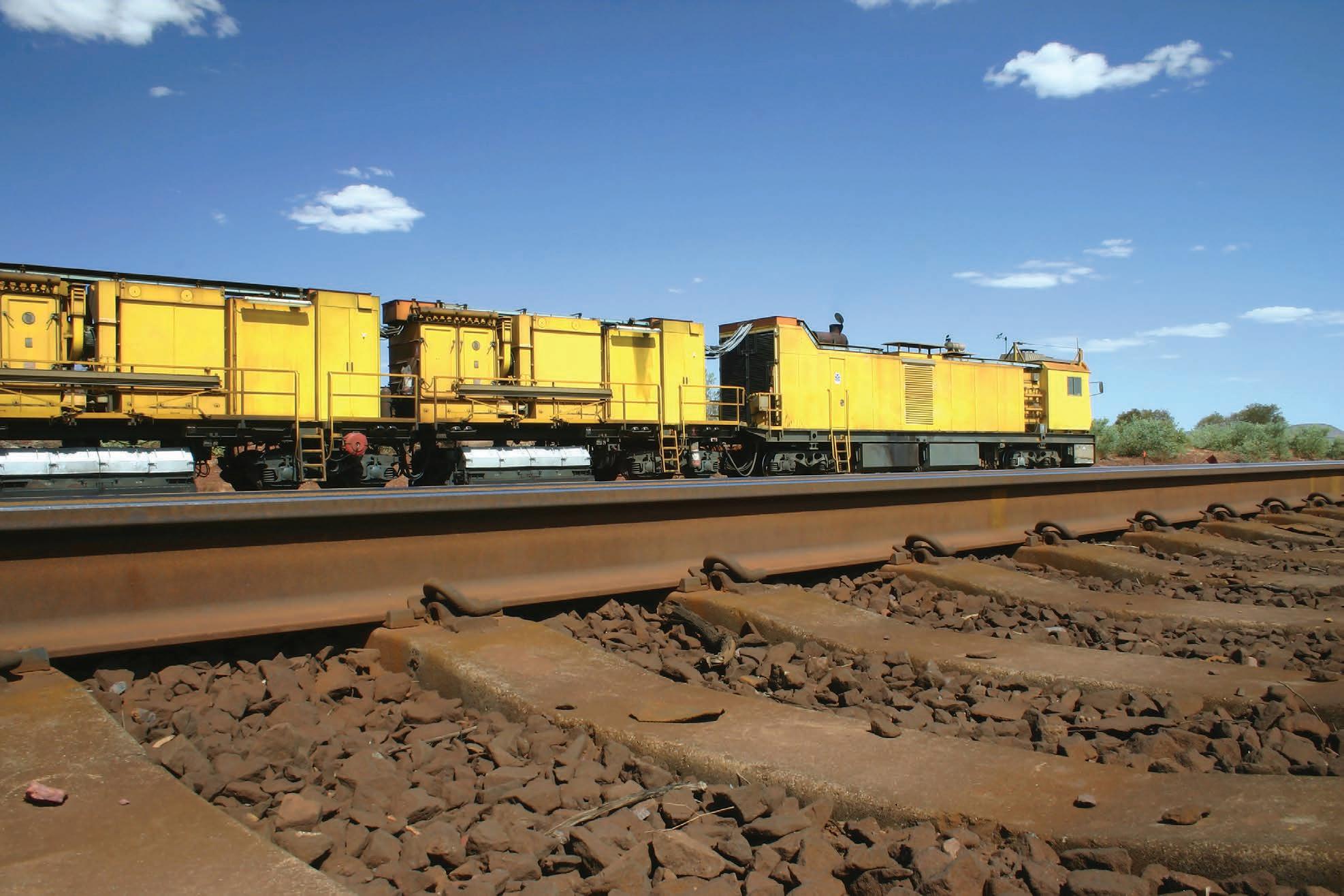

– taking advantage of times when fewer people use the trains.
The work program has been designed to leave it fully operational at busier times. For example, the network will be fully operational for more weekends in 2025, compared to 2024, and there is a focus on keeping trains running for special events.
Lovatt said that through the Rail Network Rebuild, KiwiRail is achieving a decade’s worth of work over 14 months.
“We know it’s vital to get the most out of this time period,” said Lovatt. “That’s why we will continue to work 24-7 wherever possible.
“We thank commuters, passengers and freight customers for their patience with these disruptions as we safely deliver the huge amount of work.”
Crews at work in the Britomart tunnel over the summer holidays.
Image: KiwiRail
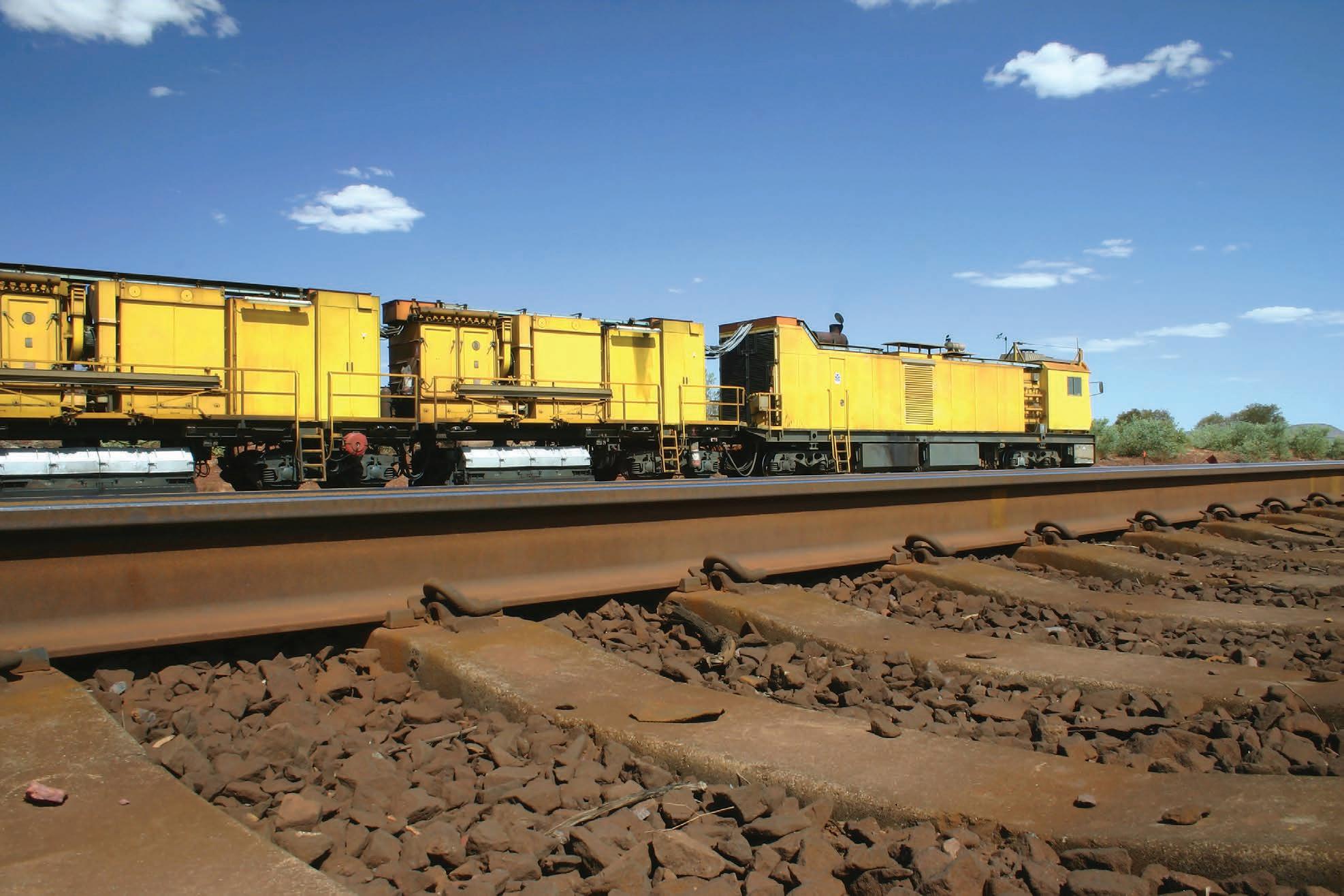
The Australasian Rail Directory is a comprehensive, all encompassing rail services directory, available both online and as a traditional hardcopy publication.
The Rail Directory is an industry driven project to provide a complete listing of all businesses involved in the Australasian, Oceanic and Asian rail industries.
This year’s rail directory will be revamped to become even simpler to use. Listings will be sorted into categories allowing users to easily find businesses working in each area of the rail industry.
With over 1000 listings from areas as manufacturing, signalling and maintenance, make your listing standout with a frame advertisement.
To ensure you are in prime position in this year’s rail directory contact Arron Reed today.
Free Listing
To ensure that the Australasian Rail Directory is comprehensive, we offer all businesses who operate or trade in the region one free listing in the directory.
Premium Category
Listing Available
From $600 (+gst)
Double page, full page, half page and quarter page advertisement space also available.
To discuss the advertising opportunities available, please contact: Arron Reed on 0466 923 194 or email: arron.reed@primecreative.com.au
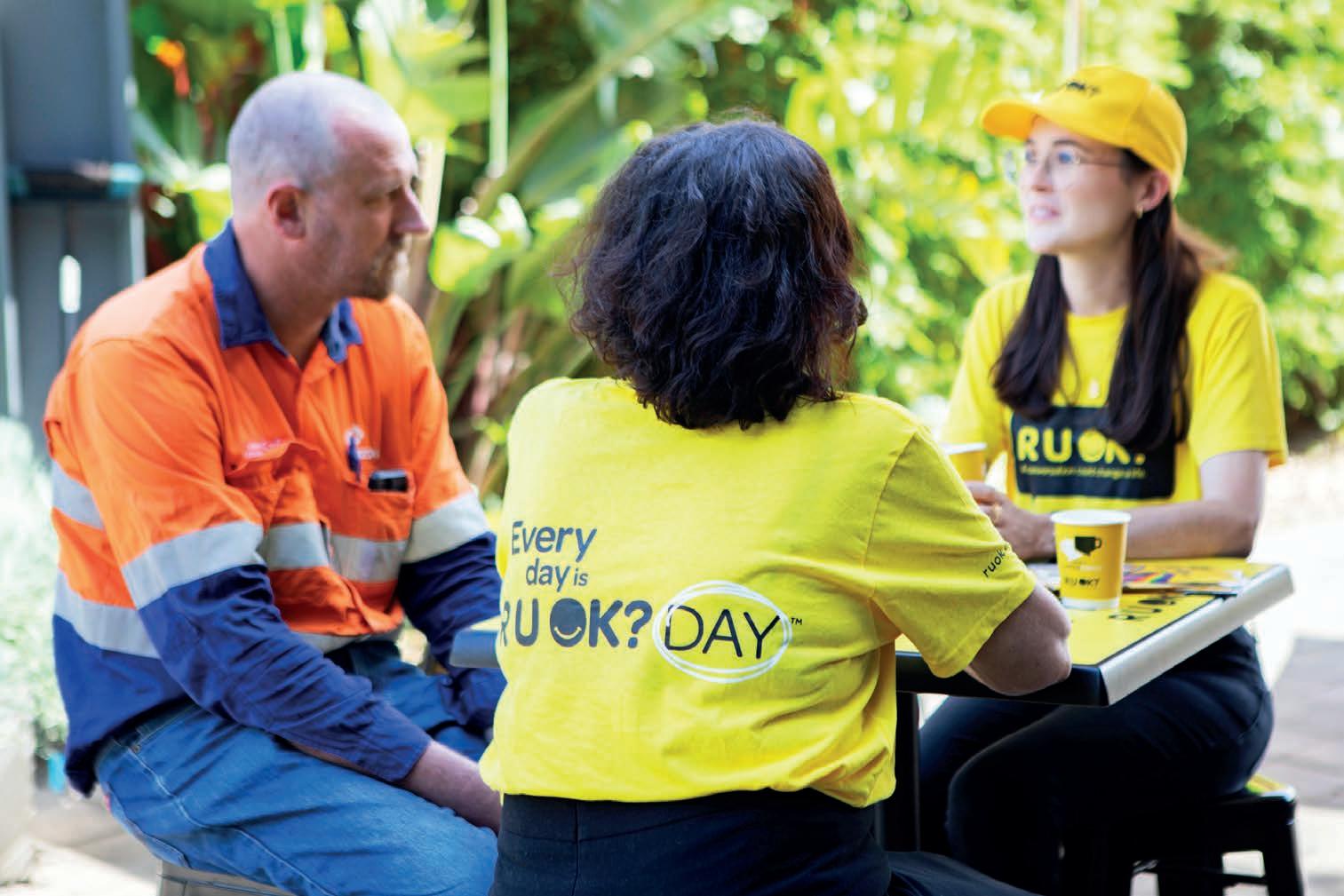
Time to check in Health and Safety
To mark this year’s Rail R U OK?, two rail industry employees share why a conversation with someone today could change their tomorrow.
Rail was the first sector in Australia to have its own dedicated R U OK? Day, a national day of action that encourages people in the industry to stay connected and have conversations that can help others through difficult times.
Since the first Rail R U OK? in 2015, participation has grown to over 120,000 people annually.
Rail staff from across Australia and New Zealand have come on board and are helping to transform workplaces into strong and resilient communities.
This year’s industry day of action will take place on Thursday 3 April, 2025, but Rail R U OK? is more than just a day, it’s a movement that aims to empower rail workers to identify the signs that someone might be struggling and lend a listening ear.
In 2014, suicide prevention charity R U OK? partnered with the TrackSAFE Foundation, a charity that aims to prevent
suicides and reduce accidents and injuries on the rail network, as well as improve the wellbeing of rail employees.
Together, R U OK? and TrackSAFE promote meaningful connection across the rail industry.
TrackSAFE’s Executive Director Heather Neil said Rail R U OK? has evolved over the past decade from a national day of industry-wide action into a year-round movement based on compassion and understanding among rail colleagues.
“Rail R U OK? is breaking down stigma and encouraging authentic and open conversations,” Neil said.
“As we join together on 3 April to connect, share experiences of when support has helped during tough times, and further build our conversation confidence, we want to reiterate the value of making space to really listen.
“Remember, an R U OK? conversation can happen any day. And it can save a life.”
TROY TAYLOR, CHANGE MANAGER FOR BULK ROLLINGSTOCK AT
AURIZON
For Troy Taylor, Change Manager for Bulk Rollingstock at Aurizon in Forrestfield, Western Australia, Rail R U OK? Day is an important reminder to check in on friends and colleagues.
“About three years ago, I lost a friend to suicide,” he said. “We worked together for a while and then we went our separate ways, and we only caught up now and again. But he always seemed happy, he always had something on the go and something to be proud of. I hadn’t had an opportunity to catch up with him for a while – and next thing I heard was that he had passed on.”
Taylor also had an upsetting experience recently as he was riding his bike along the rail line.
“I saw a lady on the wrong side of the fence, so I pulled my bike up and ran over. She was in her nightwear and had a little dog under her arm.
Members of Aurizon’s staff joining in the conversation.
Image: TrackSAFE
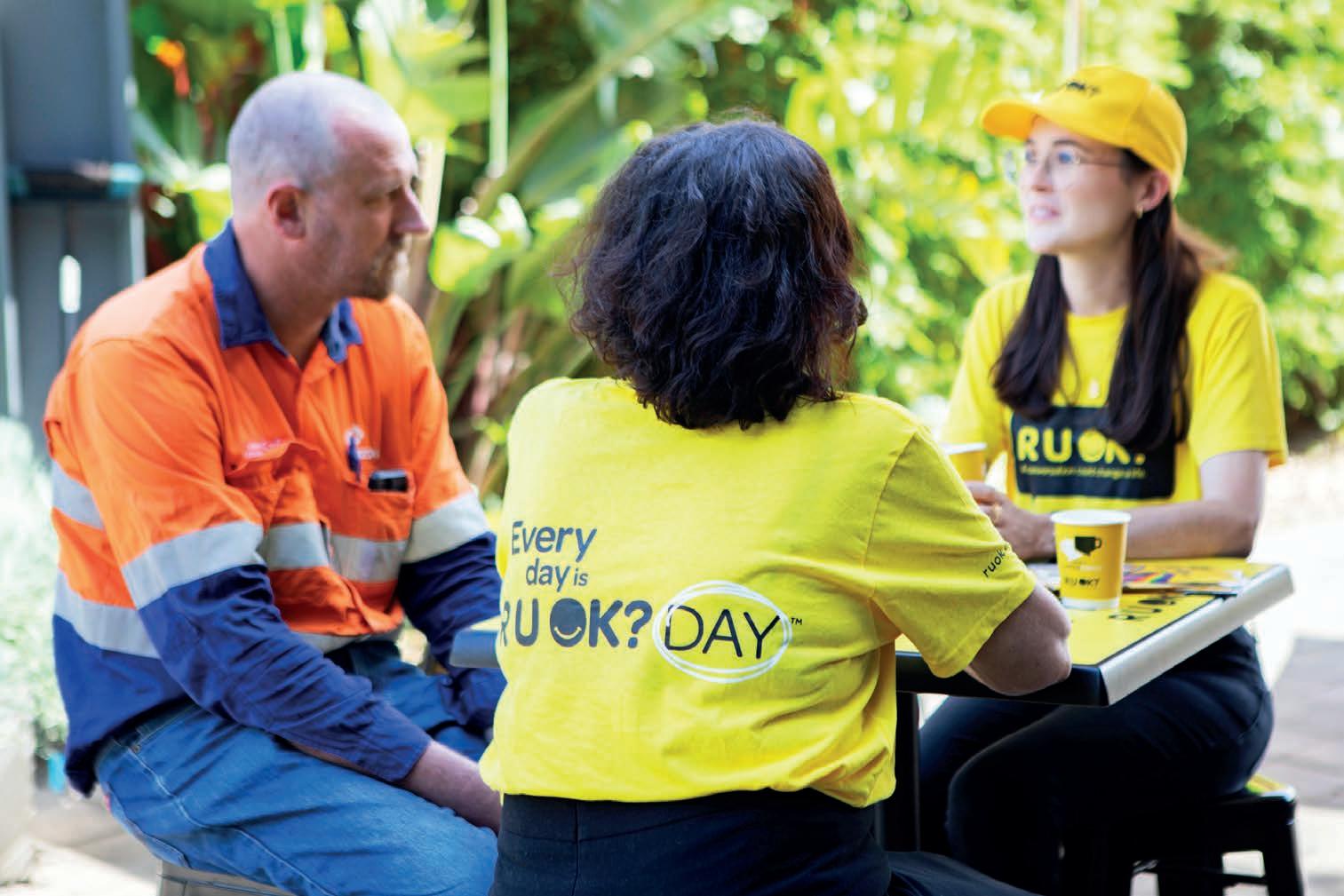
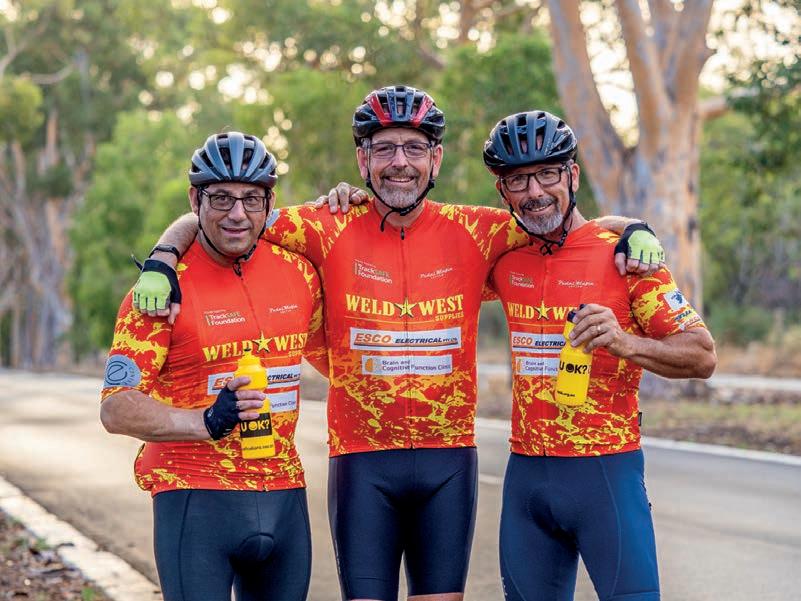
“I held her until someone else stopped and helped, and we kept her occupied while I called the ambulance and the police. That was scary.”
Taylor said R U OK? is spreading the critical message that social connections can make all the difference when it comes to mental health.
“I think R U OK? is about the importance of keeping in touch with people and having the ability to notice and understand if they aren’t quite themselves,” he said.
“It’s about checking in and asking friends and colleagues if they are OK, and making sure you are one of their useful connections.”
He has made a concerted effort to touch base with people if he sees they are going through a tough time.
“I make sure to check in with my colleagues and let them know that if they need to talk or just vent, they can always come and find me,” he said.
In support of Rail R U OK? this year, Taylor, his colleague Tony Dimovski and friend Neville Smith have organised a 300 kilometre bike ride from Bunbury to Perth.
“The three of us are calling ourselves ‘Wheels of Wellbeing’,” he said.
“We cycle around Perth quite regularly and we wanted to do something good with our hobby.
“So, we decided to do this cycle from Bunbury to Perth, which will probably be about 14 hours in the saddle.”
Taylor and his friends have previously done a 200 kilometre cycle in aid of Rail R U OK?, but this year they’re going bigger and better – and at the time of going to
print, they had raised $3300 in donations and sponsorship.
“We designed a jersey and are selling space on the jersey for donations,” he said.
“We have gained support and sponsorship from a number of our suppliers plus local health industry organisations.”
Taylor said it’s not just about the fundraising and awareness, though.
“We’ve managed to sign up nine riders and a support person, and it’s a group of
sharing an experience together. I’m hoping that by the end of this, we’ll be a group of mates.”
LIAM BRUCE, EMERGENCY RESPONSE MANAGEMENT AND RECOVERY LEAD AT QUEENSLAND RAIL
As someone who has worked in high-pressure emergency response roles throughout his career, Liam Bruce is passionate about the ethos behind Rail R U OK?
Bruce has been employed by Queensland Rail for 11 years and is currently on secondment within the Major Projects area.
“I’m looking at all the emergency response and recovery operations for Cross River Rail, and then my substantive position is with the Rail Operations response unit for surface level,” he said.
“I’ve always worked in challenging environments, worked with critical incidents, worked with systems and processes that don’t really fit the general day-to-day operation, because it’s all pretty much failed.
“R U OK is important to me because working at that level has, or could potentially have, an impact on not only me, but my colleagues and the people I care about in the workplace.”
The Brisbane native said engaging in genuine conversations with colleagues and asking how they are doing can really make a positive impact on their mental health.
“It’s not about leaving these conversations to one day a year, but having them any day.
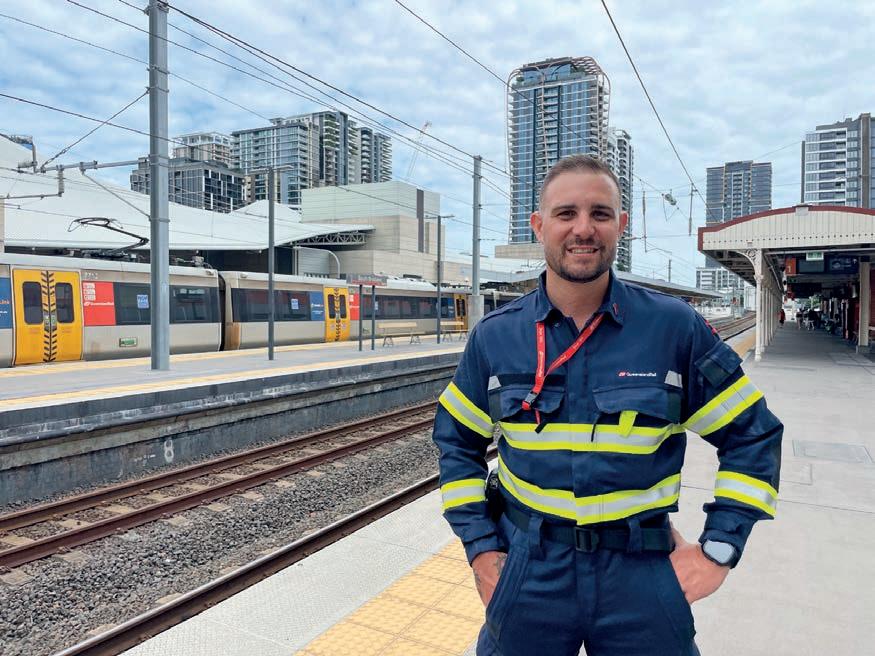
Neville Smith, Troy Taylor and Tony Dimovski (L-R) are organising a cycle in aid of Rail R U OK?
Liam Bruce is passionate about the ethos behind Rail R U OK?
Image: Nat Tan Photography
Image: Queensland Rail
Health and Safety
interests? What is their family up to? What are they watching on Netflix?
“If you get to know them, you’re more likely to be able to spot when something may not be right.”
Bruce said building a connection makes it easier to be open about how you’re feeling.
“Men, in particular, don’t always like to talk about their emotions,” he said.
“It helps to build up trust so you can have those more challenging conversations.
“You don’t have to be an expert either –you’re just being a resource for someone, so they feel like they’re being listened to. That’s essential to being able to manage workplace stresses and catching something before it eventuates or turns into a consequence.”
Working to resolve conditions affecting the network and other rail-based emergencies, Bruce often has to operate at a high-intensity level for a long period of time.
“You’re working at capacity, at times physically and then mentally as well, you’re problem solving, dealing with people, prioritising, trying to process what you’ve seen, potentially dealing with emergency services, and recording information,” he said. “It does take a toll.”
Bruce said he’s lucky to have a long-term work partner, Shane, with whom he can debrief after an incident.
“I get along really well with Shane, and we can talk about things openly.
“We ask each other – what did we do, what can we do better next time?
“It helps both of us to process what happened and decompress.”
He thinks the rail industry has come a long way when it comes to physical safety, and it’s heading in the right direction with mental health too.
“For such a long time, we’ve been so focused on physical injuries, with great initiatives like ‘Work safe, home safe’ and ‘No-one gets hurt’,” he said.
“Now we have an opportunity to shift the conversation to normalise mental health just as much as the safety elements that we can physically touch and see and feel.”
He is grateful to Queensland Rail, who appointed its first Chief Mental Health Officer (Teegan Modderman) in February 2023.
“I think we’re one of the only organisations that has a Chief Mental Health Officer,” he said. “Throughout my career, I’ve done thousands of risk assessments – but we’ve never done a mental health risk assessment.
“Teegan and the Healthy Minds crew have been providing support for mental health

to be introduced to risk assessments and helping us look at how we operationalise that. Queensland Rail is an industry leader in this space, and I’d really like to thank them for everything they are doing.”
As Emergency Response Management and Recovery Lead, Bruce hopes to be the kind of leader his team can depend on.
“I read a quote from [motivational speaker] Simon Sinek that said leadership is not about being in charge, it’s about taking care of those in your charge.
“There are so many ways we can do that, from noticing where someone might need extra support at work to catching up with them after a big day at work.
“A conversation with someone today could change their tomorrow.”
Queensland Rail plans to partially cover two of its trains in R U OK? branding to coincide with Rail R U OK Day? on 3 April, to ensure this important message is seen by a wide audience.
Queensland Rail will also host a range of networking events across the organisation to enable opportunities for these important conversations.

Visit tracksafe.org.au for free resources to help you have an R U OK? conversation and plan your Rail R U OK? activities.
If you or someone you know needs some extra support, you can find contact information for national support and services at: ruok.org.au/findhelp
For support at any time of day or night, Lifeline Australia provides free and confidential crisis support. Call 13 11 14, text 0477 13 11 14 or chat online at: lifeline.org.au
13YARN is a free 24/7 service offering crisis support for Aboriginal & Torres Strait Islander people. Call 13YARN (13 92 76).
MensLine Australia is a free 24/7 service offering support for Australian men. Call 1300 78 99 78 or chat online at: mensline.org.au
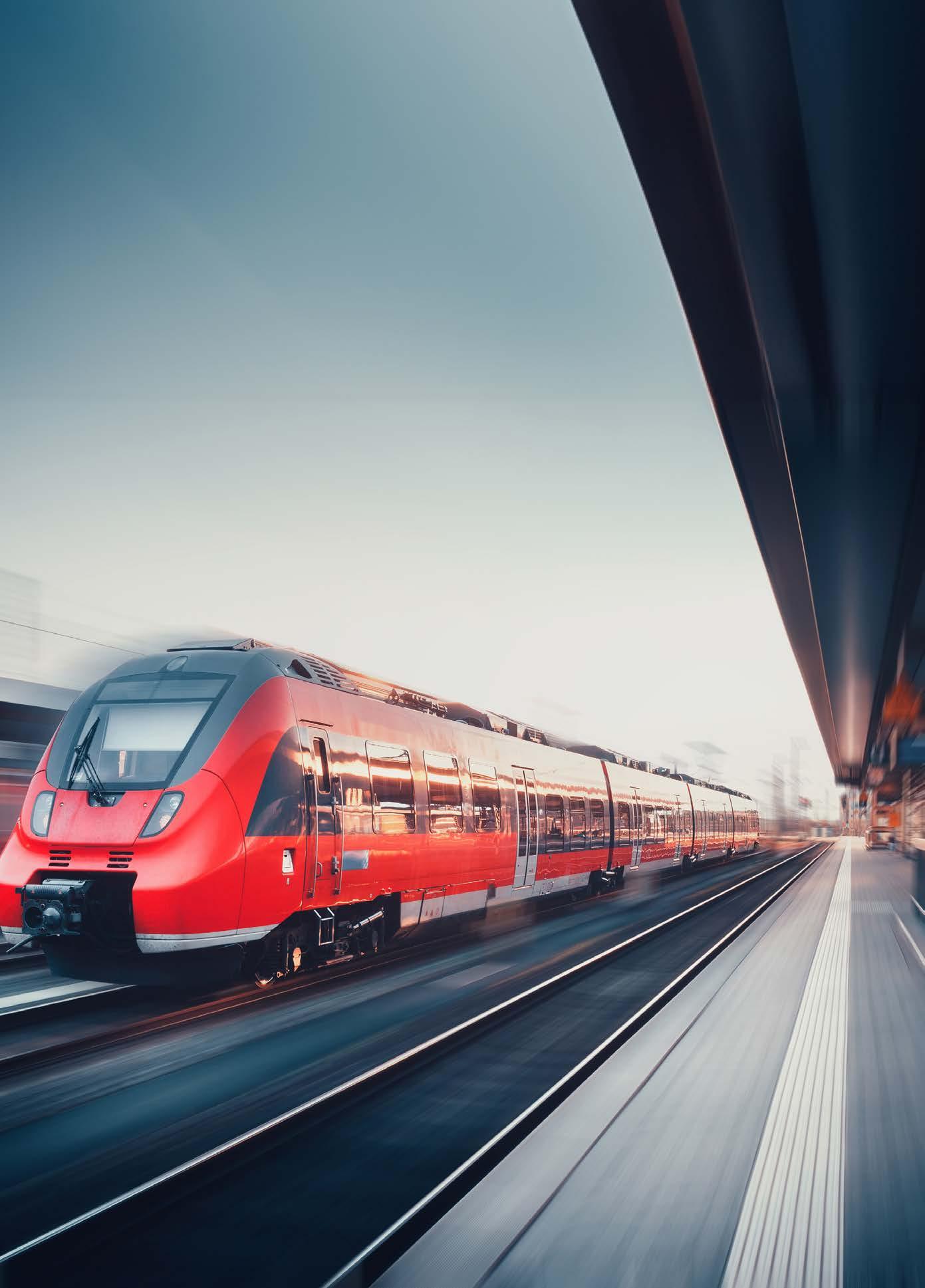
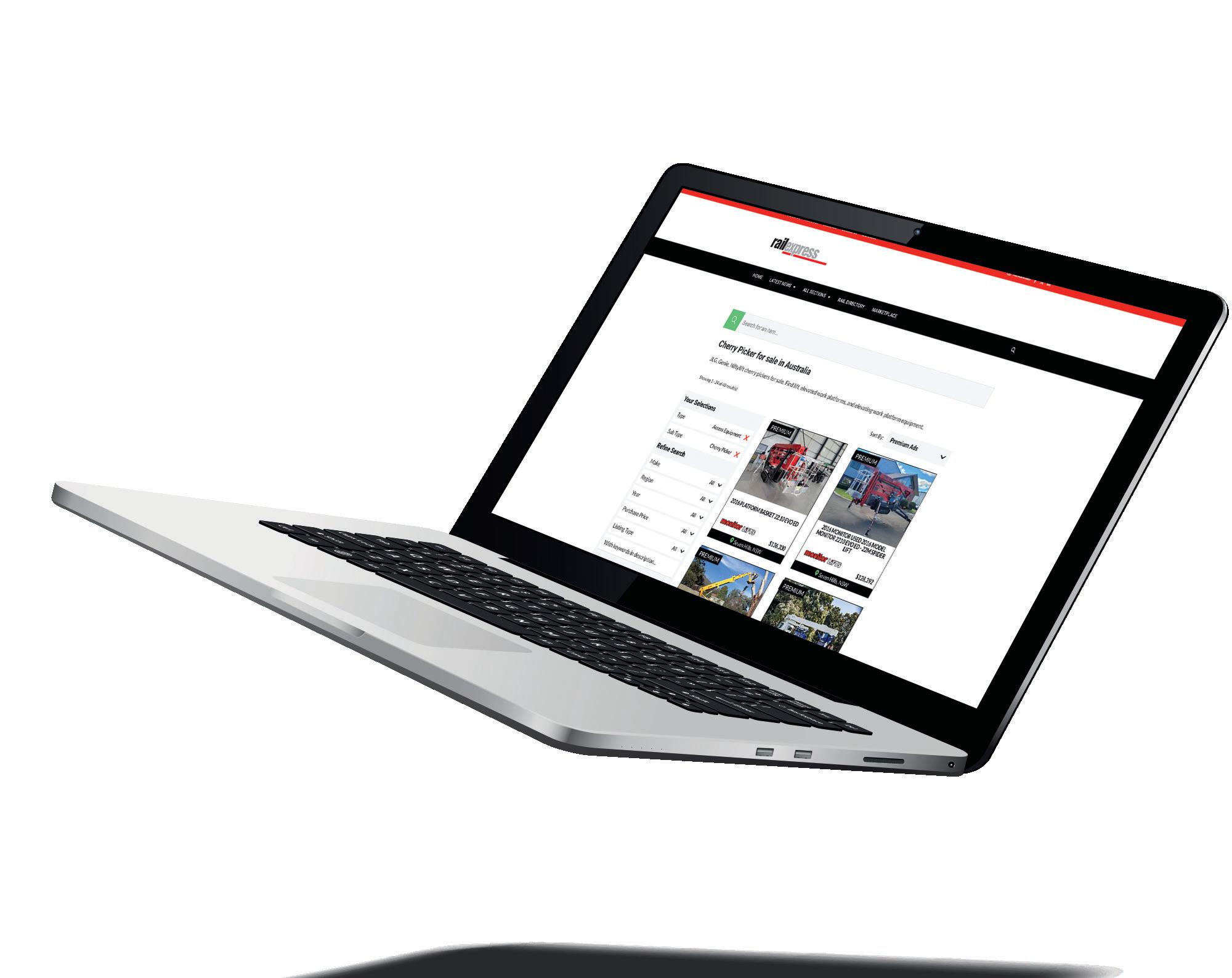
This year’s Rail R U OK? Day will take place on April 3.
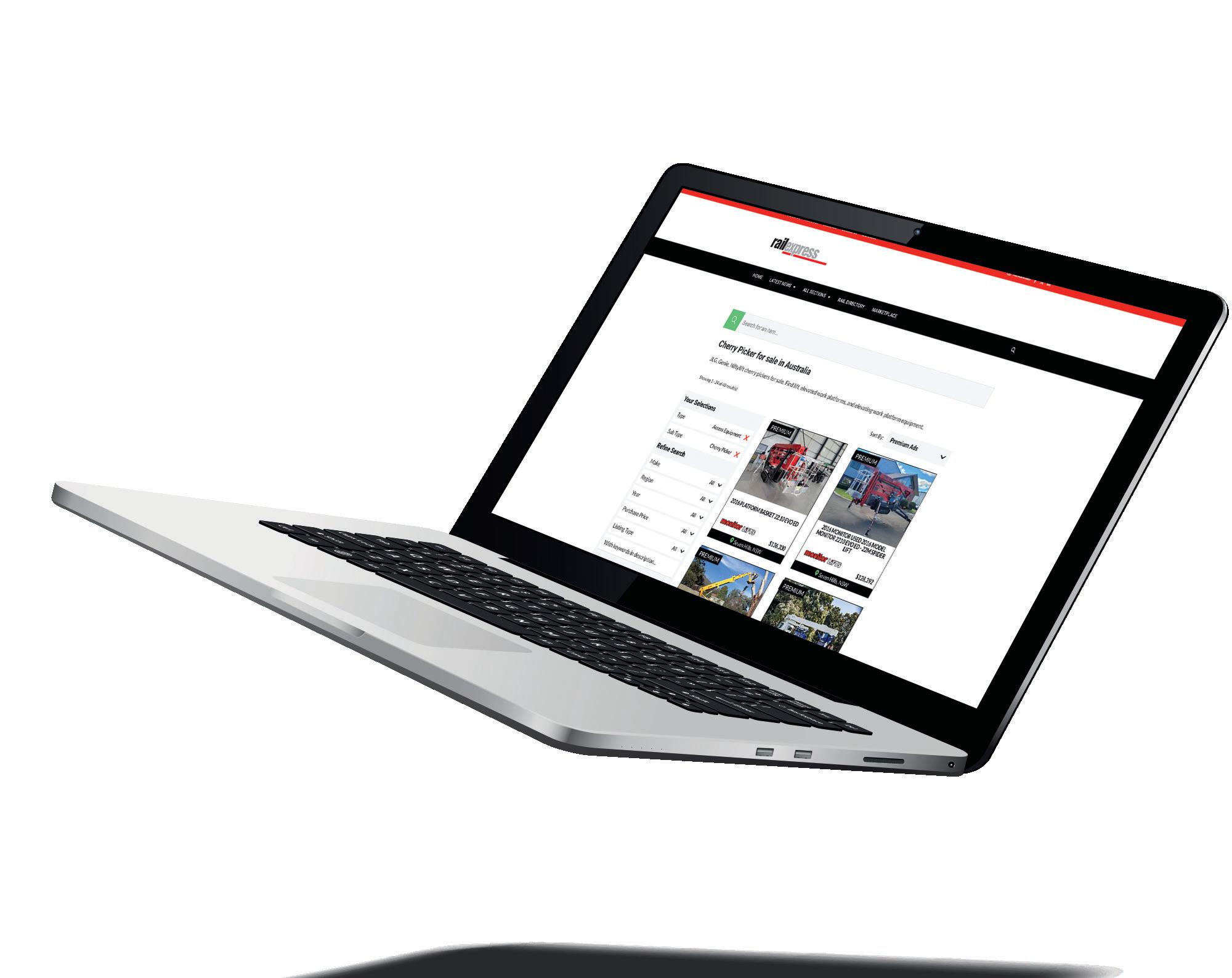
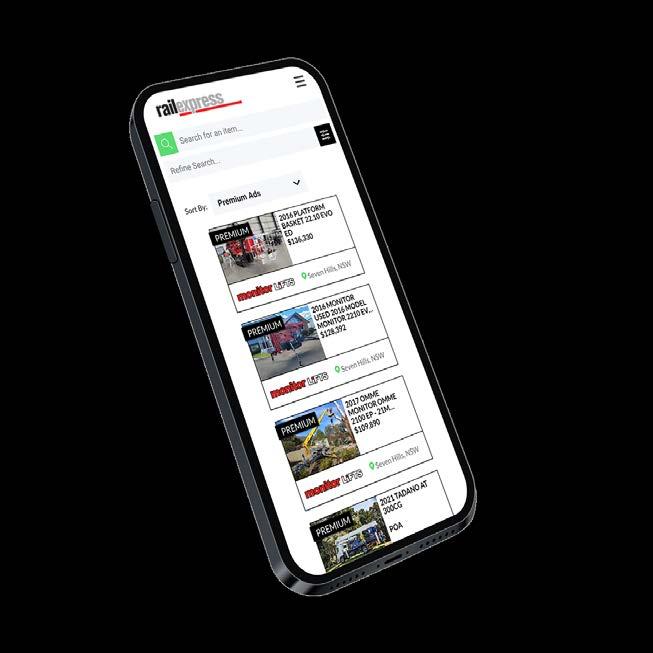
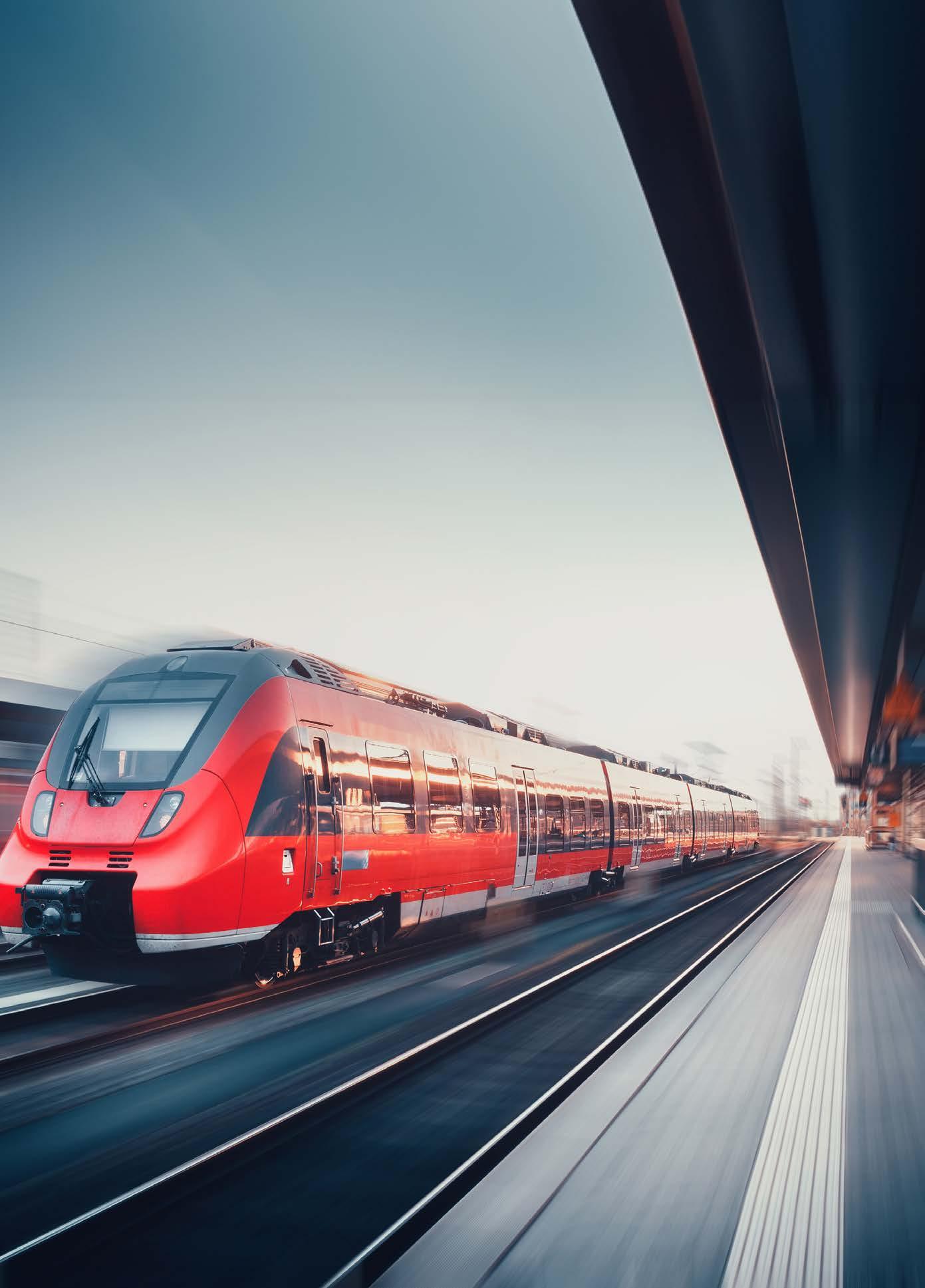
Celebrating excellence Industry Organisations
The annual Permanent Way Institution Awards celebrate outstanding achievements in the rail industry over the past year, recognising individuals and teams that tirelessly work to maintain, innovate, and enhance rail infrastructure.
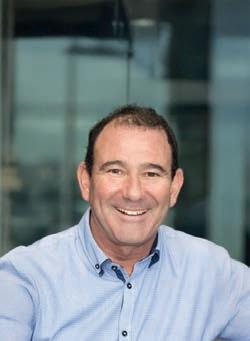
At the recent Permanent Way Institution Awards held at the Ivy Ballroom in Sydney, rail industry professionals, asset owners, and project teams gathered for an unforgettable night celebrating ongoing projects’ scope and depth.
The event provided a snapshot of the passion and dedication driving the industry, from large-scale infrastructure overhauls to detailed, smaller works.
The room buzzed with conversation about groundbreaking designs, collaborative efforts, and technological advancements reshaping rail across New South Wales.
From the energy in the room to the high calibre of entries, it was clear that these awards were not merely about handing out trophies; they were a testament to the pursuit of excellence and the shared mission of enhancing rail infrastructure for generations to come.
PWI AWARDS 2024 HIGHLIGHTS
The PWI Awards 2024 showcased the achievements of rail industry professionals, recognising individuals and teams that work to maintain, innovate, and enhance rail infrastructure.
The ceremony served as a powerful reminder of how collaboration, cutting-edge strategies, and unwavering commitment propel the sector’s growth. With winners across various categories, attendees experienced first-hand the importance of these projects in supporting asset owners and maintenance, providing safer and more efficient travel experiences for everyone.
PWI WELDERS AWARD
WINNER: Royce Hura, Independent Contractor with Multi Civil and Rail and Cat5 Rail Royce Hura was the recipient of the PWI Welders’ Award 2024. Over the past year, Royce completed an incredible 387 welds without a single defect.
His achievement highlights his dedication, craftsmanship, and attention to detail. More than merely a testament to his skill, it emphasises the crucial role welders play in maintaining the safety and longevity of rail tracks across New South Wales.
Attendees applauded Royce’s ability to establish a new benchmark for quality rail welding and motivate his peers to push the boundaries of technical excellence.
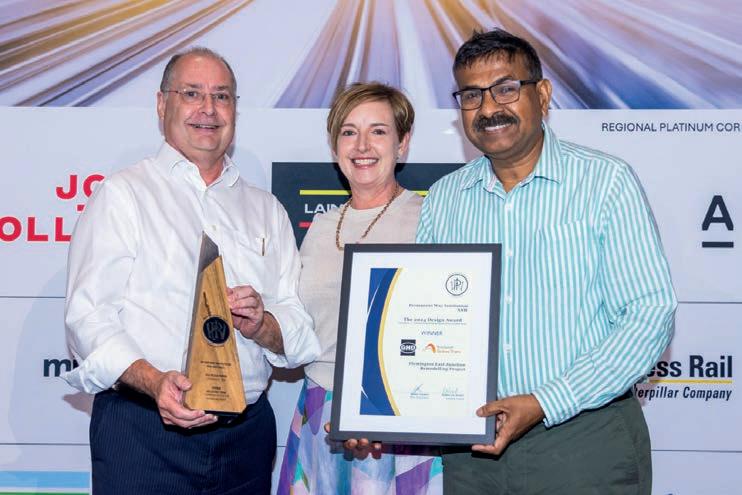
PWI STEVE MAXWELL PLATELAYING AWARD
WINNER: Rhomberg Sersa Australia (RSA) – 358 & 359 Crossover Resurfacing at Bankstown
Rhomberg Sersa Australia (RSA) took centre stage when it won the Steve Maxwell Platelaying Award.
The project focused on the 358 & 359 Crossover Resurfacing at Bankstown, exemplifying precision, ingenuity, and workmanship.
Attendees learned how even smallerscale projects can significantly impact rail networks, enhancing safety and operational efficiency for countless commuters. RSA’s commitment to innovation and quality was widely celebrated, serving as motivation for the rest of the industry to strive for similar achievements.
MINOR WORKS CATEGORY (<$5M)
WINNER: Marrickville Sewer Bridge Replacement Project – Delivered by a Joint Venture between John Holland and Laing O’Rourke
Taking the top honour in the Minor Works category, the Marrickville Sewer Bridge Replacement Project impressed the audience with its successful blend of traditional platelaying craftsmanship and modern construction methods.
The project underscored the importance of skill, precision, and careful planning in extending the life of vital rail infrastructure.
Team members from John Holland and Laing O’Rourke took the stage to accept the award, discussing how collaboration and a profound respect for the heritage of rail work contributed to their success.
HIGHLY COMMENDED: Rhomberg Sersa Rail –Cabramatta Loop Trackworks
In a proud moment for the Rhomberg Sersa team, its Cabramatta Loop Trackworks project was Highly Commended in the Minor Works category.
This accolade acknowledged the team’s dedication, innovation, and meticulous approach to overcoming challenges in an environment where precision and reliable outcomes are paramount.
GHD and Sydney Trains scooped the PWI Design Award in the minor category for work on the Flemington East Junction Remodelling Project. Images:

The evening’s celebrations highlighted how small but significant undertakings like this can enhance the overall rail network.
MAJOR WORKS CATEGORY (PROJECTS OVER $5M)
WINNER: Botany Rail Duplication Project –Executed by ARTC and John Holland Group
The Botany Rail Duplication Project won the Major Works category, recognised for its role in increasing freight capacity between Port Botany and metropolitan intermodal terminals.
Industry professionals praised the project’s scale – 2.9 kilometres of duplicated freight rail track – and its extensive benefits, from alleviating road freight congestion to optimising Australia’s logistics network.
The award demonstrated that large-scale rail initiatives enhance existing networks and lay the foundation for future economic growth and sustainability.
PWI DESIGN AWARD – MINOR CATEGORY
WINNER: GHD with Sydney Trains –Flemington East Junction Remodelling Project
A highlight of the night was the announcement that GHD Group, in collaboration with Sydney Trains, had secured the PWI Design Award 2024 in the Minor Category.
The Flemington East Junction Remodelling initiative demonstrated how innovative thinking and resourceful execution can achieve superior outcomes, even in the face of stringent budget constraints.
HIGHLY COMMENDED: Lycopodium –Southern Highlands Overtaking Project Receiving a Highly Commended nod for design excellence, Lycopodium garnered
praise for the Southern Highlands Overtaking Project.
The audience learned how the team’s inventive solutions and focus on sustainable practices facilitated more efficient train movements while enhancing the rail network’s overall functionality. This recognition affirmed Lycopodium’s growing influence as an industry leader dedicated to advancing railway design.
PWI DESIGN AWARD
– MAJOR CATEGORY
WINNER: NEXTRAIL – Airport Tunnel
NEXTRAIL was lauded for its cuttingedge work on the Airport Tunnel Upgrade Project. The project team detailed its successful strategies for tackling historically problematic flooding issues and preventing future disruptions within such a critical transport artery.
Its emphasis on robust and resilient infrastructure resonated with the crowd, highlighting the tangible benefits of fusing advanced technology with industry expertise.
PWI KEN ERICKSON INNOVATION AWARD
WINNER: Australian Rail Track Corporation (ARTC) – Harnessing Machine Learning and the Decision Support Platform (DSP) for Proactive GIJ Failure Management
ARTC received the highly coveted Ken Erickson Innovation Award, gaining recognition for its use of machine learning alongside a Decision Support Platform (DSP) to proactively tackle GIJ failures.
Attendees discovered how this datadriven approach is transforming predictive maintenance, enabling timely interventions before disruptions take place.
This pioneering effort not only reduces operational downtime but also represents the innovative spirit that Ken Erickson championed.
PWI ELECTRICAL SAFETY AND INNOVATION AWARD
WINNER: NEXTRAIL – Wolli Creek Junction and Mascot Substation Projects NEXTRAIL continued to receive accolades for its Electrical Safety and Innovation. The team’s forward-thinking approach to the Wolli Creek Junction and Mascot Substation projects introduced transformative safety protocols and operational enhancements, exemplifying how digitalisation and practical work method modifications can work together to future-proof essential urban railway substations.
The crowd was impressed by the team’s innovations, which have the potential to
set new safety benchmarks throughout the industry.
HIGHLY COMMENDED: Sydney Trains –The Remote Site Inspections
Completing the electrical category was Sydney Trains, which was Highly Commended for its Remote Site Inspections initiative.
The project captivated attendees with its innovative use of drones, laser scanning, and other advanced technologies to perform inspections in a safer and more efficient manner.
By minimising the need for personnel to be physically present on-site, Sydney Trains lowered operational risks while achieving greater accuracy in data collection.
PWI ALAN BARHAM MAINTENANCE AWARD
WINNER: ARTC – Port Waratah Provisioning Centre
The ARTC Port Waratah Provisioning Centre is a dedicated, stand-alone unit responsible for overseeing Sydney train assets, ensuring reliability and continuity at one of Australia’s busiest coal terminals.
With 39 staff – including signalling experts – this team maintains 248 kilometres of track and 338 turnouts around the clock, safeguarding the seamless movement of more than 100 million tonnes of coal annually through the Hunter Valley. Their tireless dedication and operational excellence earned them the prestigious PWI Alan Barham Maintenance Award for 2024, highlighting their crucial role in sustaining regional economic growth and supporting a key artery of Australia’s rail network.
A NIGHT TO REMEMBER
The PWI Awards 2024 showcased the passion, innovation, and teamwork thriving within Australia’s rail industry.
Every project, whether celebrated for design excellence, safety efforts, or maintenance achievements, highlighted the commitment of asset owners and professionals to provide more reliable and future-ready rail services.
Congratulations to all the winners and participants of the PWI Awards 2024. Your collective commitment to quality, sustainability, and technological advancement ensures that our rail infrastructure remains a world-class model for efficiency and resilience.
As these teams continue to exceed expectations, the industry will undoubtedly follow suit, reaching new heights in the future.

The Steve Maxwell Platelaying Award went to Rhomberg Sera.
RAIL EXPRESS is compulsory reading and a vital tool for all people working in and around the rail sector.
Rail Express is Australia’s authoritative business to business rail publication.
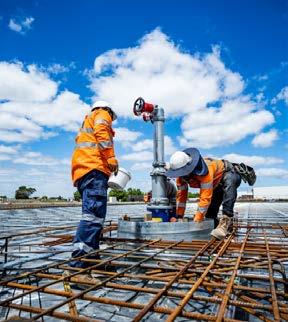
Combining the resources of our respected journalism team and our unparalleled industry contacts and affiliations, Rail Express provides extensive, comprehensive and balanced coverage of breaking news and trends in key areas like infrastructure, investment, government policy, regulatory issues and technical innovation.
Published both in print and digitally every month, Rail Express is the only publication to have both the official endorsement and active participation of the main railway associations in Australia and the broad support of the rail industry.
The only way to ensure you get every copy of Rail Express is to subscribe today. Visit railexpress.com.au/subscribe.
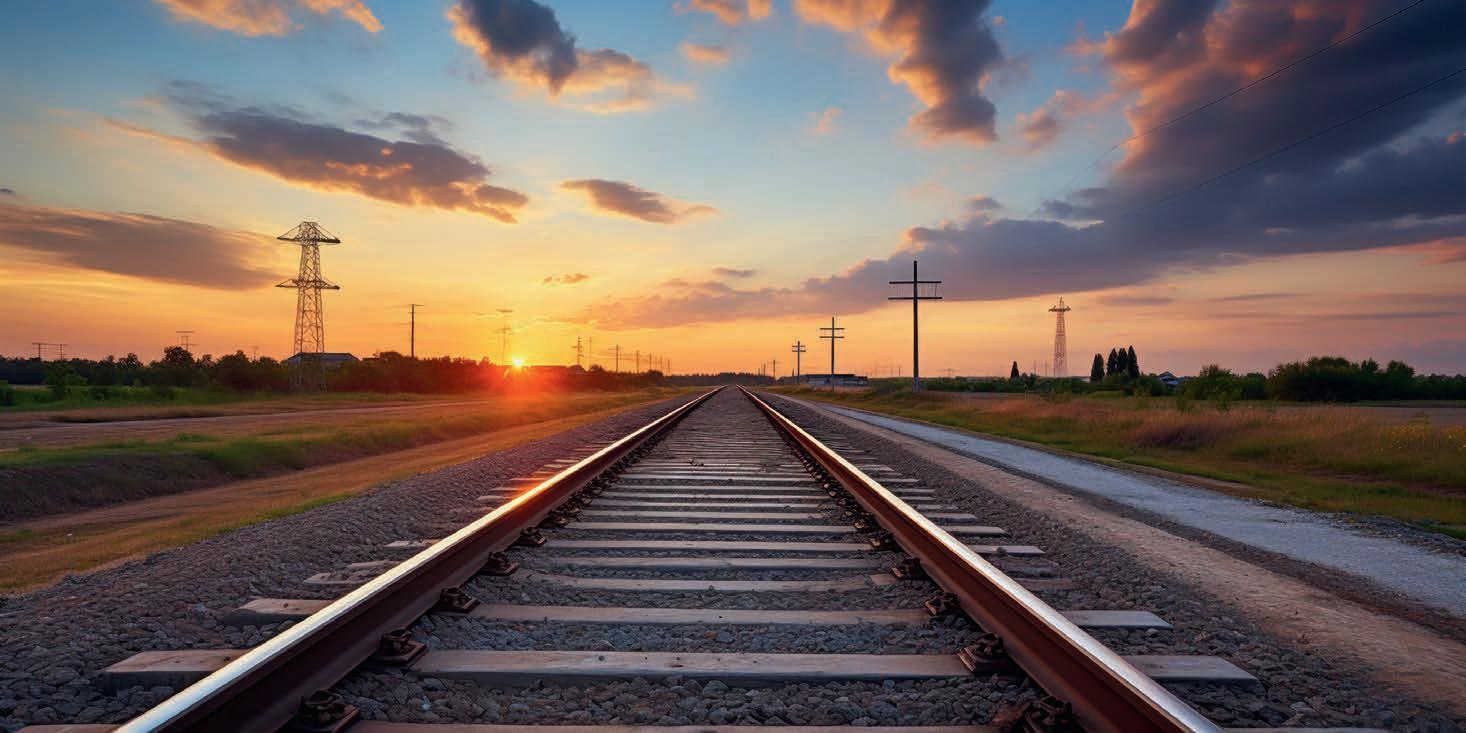
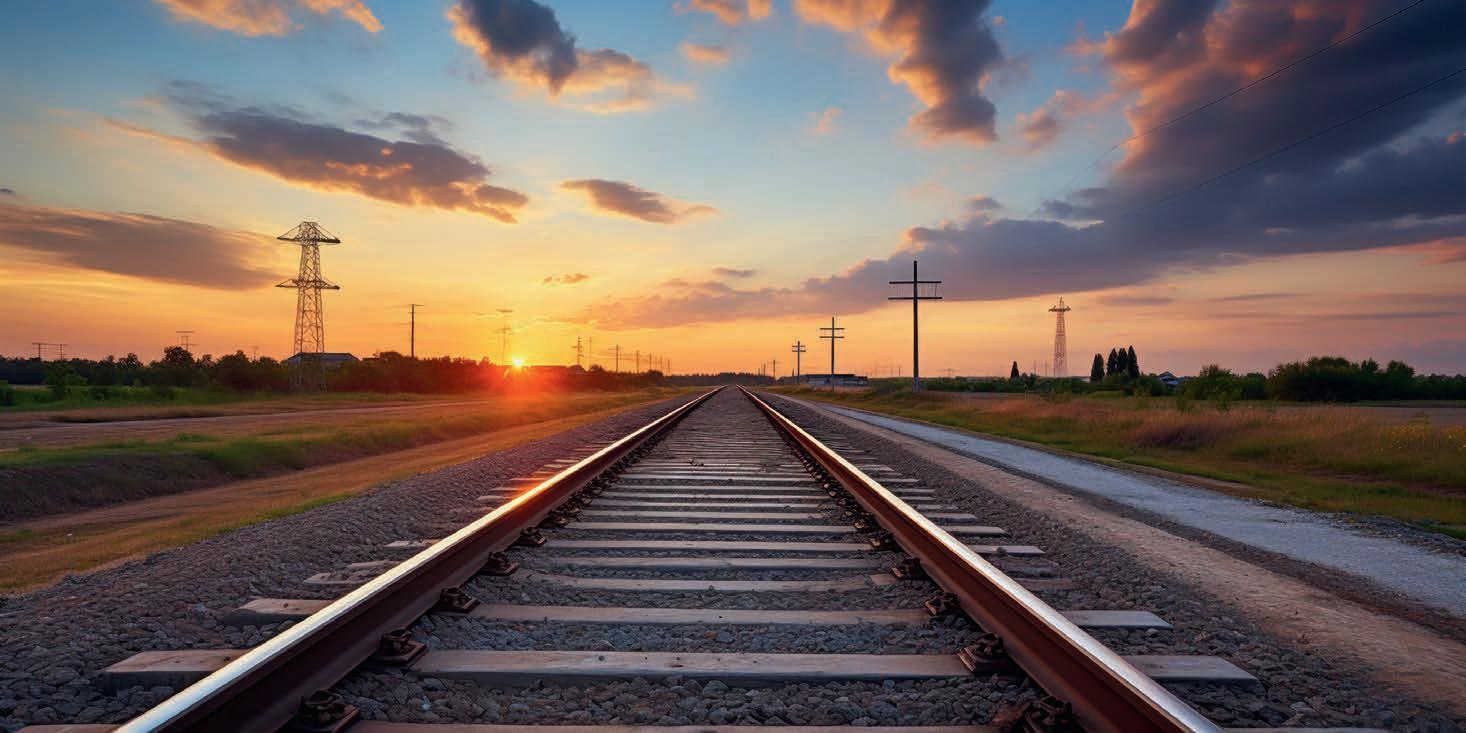
New faces at RISSB
The Rail Industry Safety and Standards Board has welcomed a number of changes to its lineup, with a new chair and two new directors.
The Rail Industry Safety and Standards Board (RISSB) has announced some changes to its Board of Directors.
At its Annual General Meeting on November 28, 2024, resolutions were passed providing continuation and rejuvenation of the board.
Dr Gillian Miles was endorsed as the Independent Chair, replacing Deborah Spring, who retired after serving her full term.
Dr Miles brings a “unique, experienced and strategic skillset” to the position, and has a clear passion for the industry.
She has more than three decades of experience across the public sector, holding senior roles in national, state and local government organisations.
Her other engagements include being Commissioner at Infrastructure Australia, Director on the board of the National Heavy Vehicle Regulator and the Chair of Chisholm TAFE Victoria.
Dr Miles formerly served as Chief Executive Officer (CEO) of the National Transport Commission, where she led work on designing the National Rail Action Plan.
This uniquely positions her to steer the board in delivering and elevating its role within the future rail landscape, with a clear vision of RISSB’s role in driving rail industry interoperability, efficiency and safety in this time of rail reform.
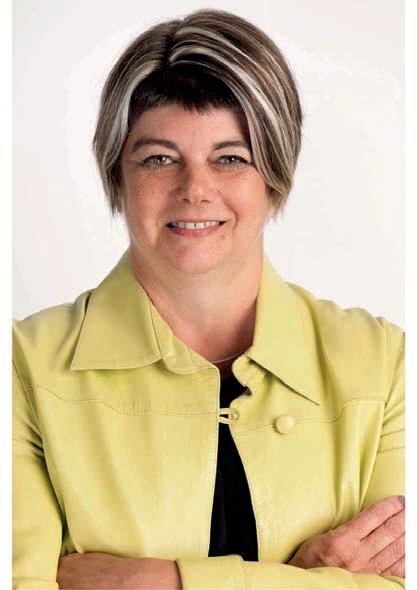
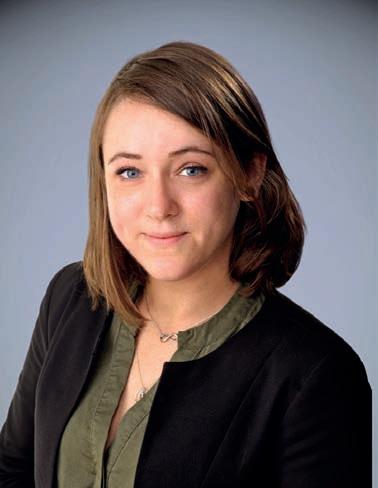
RISSB receives government funding through a Memorandum of Understanding (MoU) with the Infrastructure and Transport Senior Officials Committee (ITSOC) and recently signed a new MoU for a further two-year period.
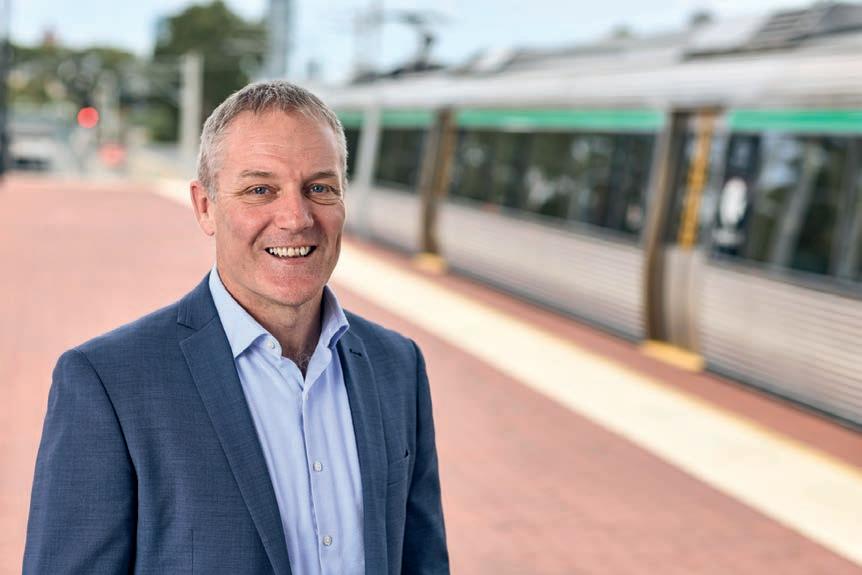
Management Systems. Now as the Executive Director for PTA Project Delivery, he is responsible for a portfolio of projects that includes the High-Capacity Signalling upgrade to the Perth rail network.
This includes an agreement to facilitate two new government-appointed directors on the RISSB board: Amy Lezala, Chief Engineer – Rail, at the Victoria Department of Transport and Planning, and Garry Taylor, Executive Director of Project Delivery for the Western Australian Public Transport Authority.
Lezala is a Registered Professional Engineer, holding EngExec and Fellow qualifications from Engineers Australia. She has worked in rail for 17 years across the globe, starting her career maintaining trains in the United Kingdom.
She joined the Department of Transport and Planning as the Victorian Chief Engineer – Rail in 2022, supporting the operators and major projects with practical engineering governance from the state.
Taylor is a career railwayman with 25 years of experience in the UK rail industry under his belt.
He joined the Public Transport Authority (PTA) in Perth as the head of rolling stock and led the PTA’s railcar project through the business case and procurement stages and into production.
He became a member of the PTA Executive in 2020 as the Executive
The appointment of the two new directors is an extremely positive step which will improve industry and government understanding at this critical time for the national rail reform program.
Dr Tim Kuypers was also re-appointed to the RISSB Board as an Independent Director for his third and final term.
Dr Kuypers has more than 30 years’ experience as a regulatory and safety professional in the United Kingdom, Europe and Australia and is currently a Special Advisor at HoustonKemp Economists and Principal of Walbrook Partners, a rail safety consulting firm.
These appointments will help position RISSB to be a part of the solution in the national rail reform agenda, supporting the organisation to continue to play a key role in driving rail industry interoperability, efficiency and safety.
Other members of the board include Tony Braxton-Smith (Independent Director), Scott Cornish (Industry Director, Passenger Operations), Kylie Gallasch (Industry Director, Network Managers/Owners), Mark Carling (Industry Director, Suppliers & Contractors) and Genevieve Nix (Industry Director, Freight Operations).

Dr Gillian Miles brings a “unique, experienced and strategic skillset” to her new role.
Amy Lezala is Chief Engineer –Rail at the Victoria Department of Transport and Planning.
Garry Taylor joins the board as a government-appointed director.
Images: RISSB
Driving Rail Reform: The ARA’s 2025 Advocacy Priorities
The Australasian Railway Association sets out its current focus areas, from increasing rail’s freight mode share to addressing the workforce shortage.
The Australasian Railway Association (ARA) advocates for policy and regulatory reforms to enhance rail’s role in a sustainable transport future.
The ARA is actively working with industry and the National Transport Commission (NTC), Office of National Rail Industry Coordination (ONRIC), Office of the National Rail Safety Regulator (ONRSR), and state and federal governments to identify opportunities for reform in several key areas – harmonisation, interoperability, workforce development, sustainability, supporting local manufacturing, increasing freight mode share and resilience and improving gender diversity.
We are at an important juncture in the political landscape and must keep up the momentum to ensure rail is front and centre on both sides of the fence and at both levels of government.
The COVID pandemic highlighted the importance of strong supply chains and a sustainable workforce and there is also an increasing focus on the need to step up decarbonisation efforts now to meet future national net zero targets.
Harmonisation and poor interoperability remain huge challenges for rail. We need a national approach to increase productivity and reach our full potential.
The current boom-and-bust cycle of rail infrastructure projects hinders local suppliers, making it difficult for them to invest in workforce development and asset capability. Without a steady flow of projects, rail risks losing suppliers and skilled workers to other industries.
Our industry is also facing a 70,000-workforce shortage, exacerbated by a retirement cliff, and skills gaps are also growing, largely because of increasing digitalisation, with emerging technologies that require new skills in areas such as signalling. In the freight sector, there is a strong focus on increasing mode share in
Australia and New Zealand and the need for continued resilience investment due to disruptions from repeated severe climate events. This is also a priority area for the ARA.
Managing growth in both passenger and freight will be more important than ever with increasing urbanisation and congestion in our cities, aging populations and the freight task set to more than double by 2050.
We also need to see further improvements in level crossing safety at a national level, with too many distressing incidents still occurring on our networks despite extensive public campaigns.
A NATIONAL APPROACH
Australia operates across 29 separate rail networks, each with distinct standards, operating rules, and workforce requirements. This fragmentation creates inefficiencies and drives up costs.
The ARA strongly supports a national rail standards harmonisation strategy, ensuring a consistent regulatory environment to enhance interoperability and drive efficiency.
In 2024, we launched the Harmonisation of Rail Standards Research Report , which was jointly funded by the ARA, NTC, ONRIC and the Rail Industry Safety and Standards Board (RISSB). It is a watershed moment for the rail industry, providing an important body of evidence to progress this essential program of reform.
This report provides rigorous analysis to better inform ways to address current challenges in rail interoperability and prioritise the highest value areas of harmonisation.
It proposes practical recommendations and pathways for implementation.
We hope this work will give decisionmakers the justification, business case, and solutions needed to drive change,
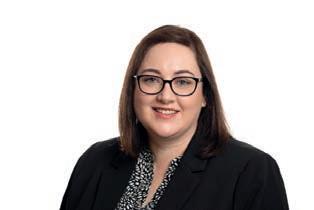
Caroline Wilkie, Chief Executive Officer of the Australasian Railway Association
particularly in supporting the National Standards Framework under the NTC’s National Rail Action Plan, ONRIC’s National Procurement and Manufacturing Plan, and RISSB’s critical role in developing standards.
The ARA fully supports the proposed approach and the development of a national rail standards harmonisation strategy to be developed by a national body.
An Australian-first framework to adopt a nationally standardised product type approval system for rail and road projects is also underway, following advocacy by the ARA.
A nationally consistent approach to local content policies would also reduce unnecessary capital investment and duplication of capability, deliver greater industry stability, job security, and support a more cost-effective, competitive rail manufacturing sector.
Rollingstock approvals is another important area for reform. Complicated and repetitive approval processes mean it can take longer to get a train approved to run across the country than it does to build it.
The ARA is working with industry to support ONRSR work to develop guidance on rollingstock safety assurance processes, pilot a single national application approach to register rollingstock operating on the national network of interoperability, and investigate ways to harmonise testing requirements and locations for rollingstock.
We are also working with the National Rail Manufacturing Advocate and the Rail Industry Innovation Council on supporting the development of the National Rail Procurement and Manufacturing Strategy.
The strategy is focused on a nationally coordinated approach to rollingstock procurement and manufacturing, growing manufacturing capability through harmonising standards, maximising public investment outcomes (including local content policies), and improving
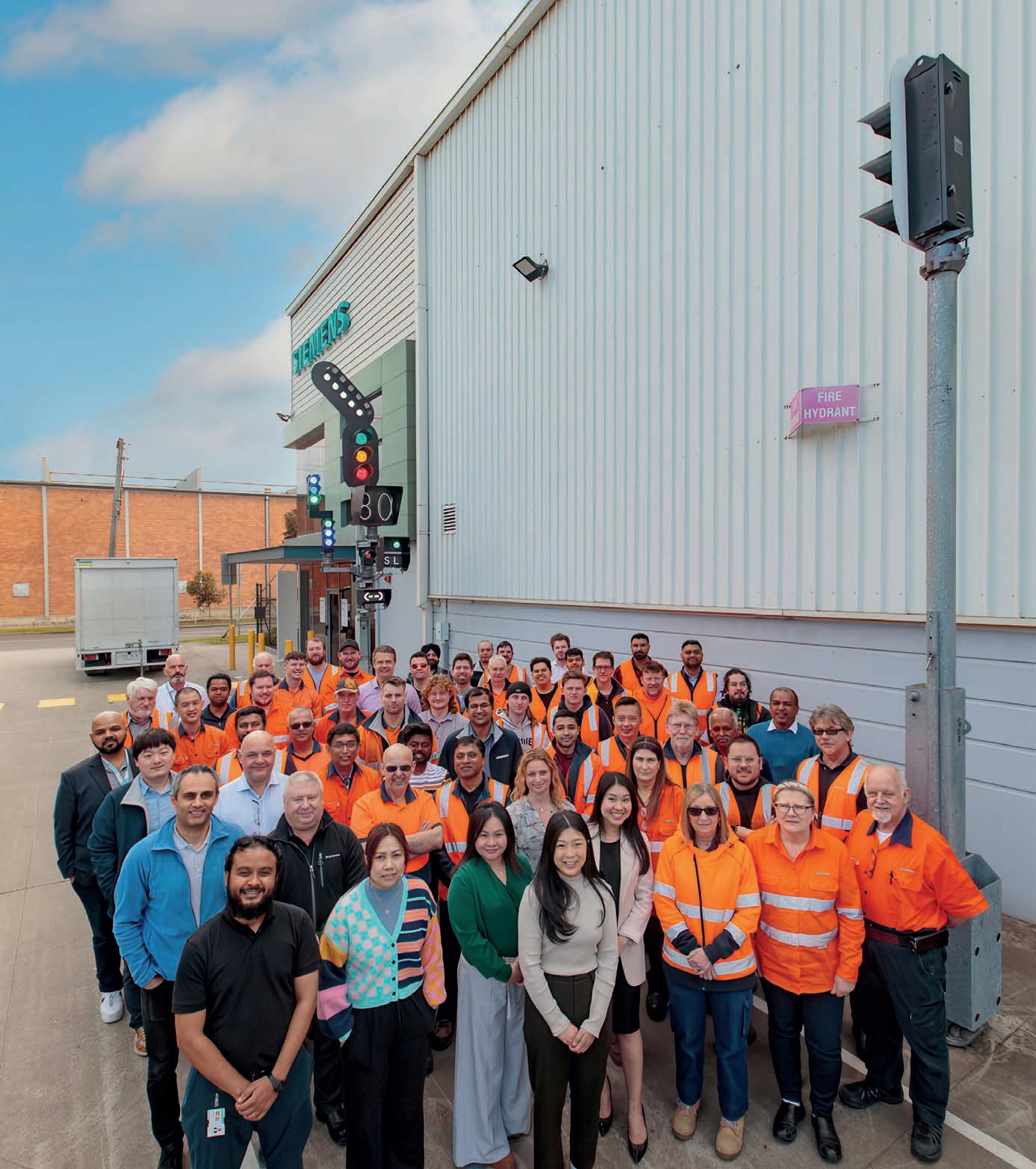
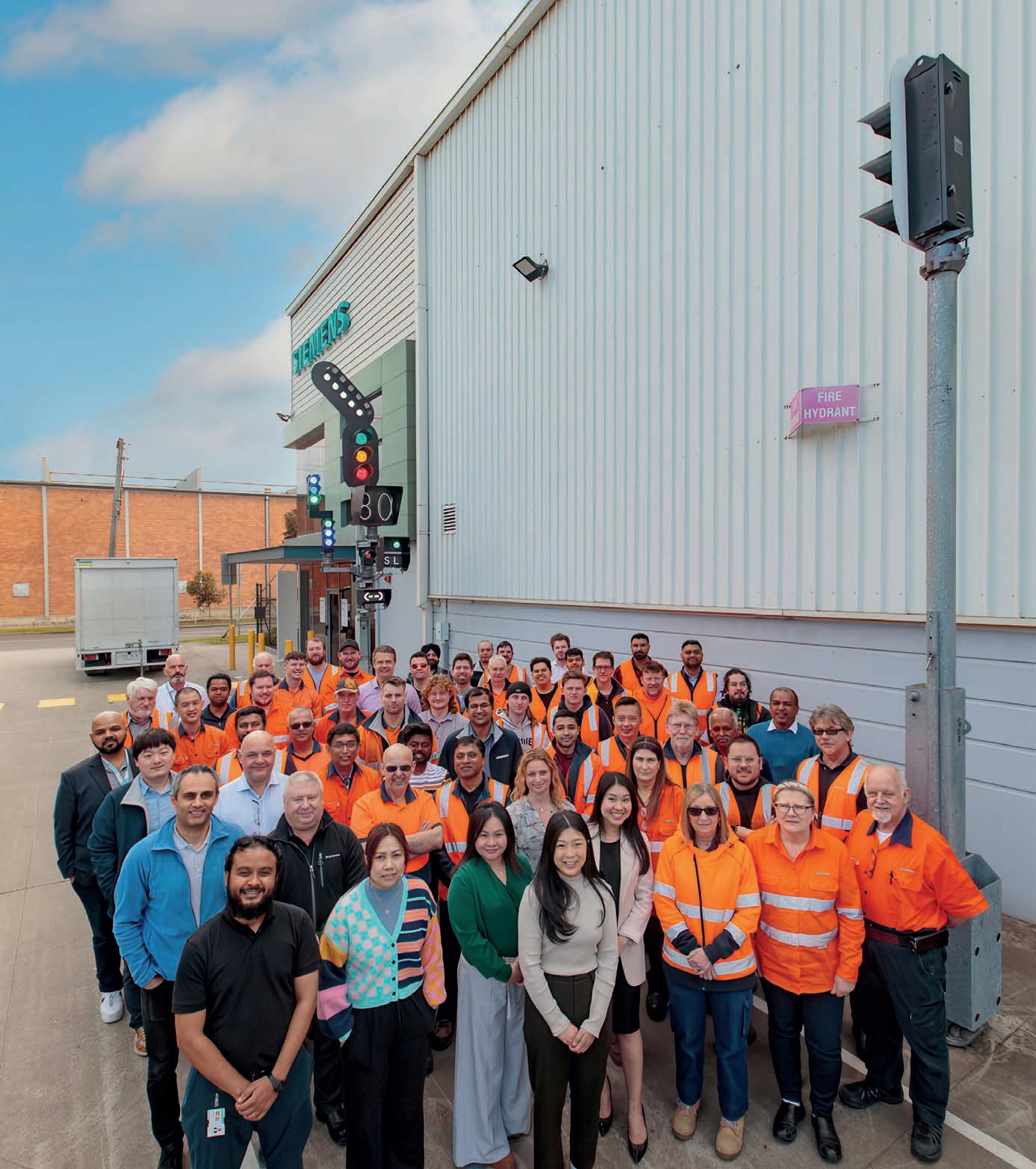
research and innovation collaboration between industry, customers, researchers and designers.
INCREASING FREIGHT MODE SHARE AND RESILIENCE
Since the release of the joint report Future of Freight by the ARA and the Freight on Rail Group just over a year ago, we have made several key submissions to government to support increased rail freight mode share and investment in rail freight.
The ARA welcomes the $1 billion allocated to enhancing rail resilience in last year’s Federal Budget, following extensive advocacy by the ARA and rail freight stakeholders for investment in the nation’s ageing rail infrastructure.
There will be an ongoing need to regularly review the state of infrastructure along key rail freight routes to ensure continued investment in upgrading and maintaining assets to withstand more frequent and severe weather events. In terms of heavy haul priorities, the Pilbara
Rail Collaboration Centre (RCC) was established last year with funding from the Western Australian Government and in partnership with the ARA and CORE Innovation Hub to identify common sector challenges and opportunities to mitigate the costs and complexity, as well as accelerate the pace of transformation.
It will support initiatives to localise supply chains, improve workforce mobility, and work towards net-zero goals.
WORKFORCE DEVELOPMENT
The ARA is actively working with governments and TAFE and universities to develop targeted courses and training programs, as well as developing our own professional development opportunities for industry. We recently launched our own industry-recognised Professional Certificate in Rail which took its first cohort of 65 people in March.
With female participation in the rail workforce at only 28 per cent, in 2024 the ARA commissioned significant research
to inform best practice initiatives and training that fosters an inclusive and diverse workforce.
The report, Progressing Gender Equality in the Australasian Rail Industry, builds on the ARA Gender Diversity Data Report released every two years. We hope to have implemented most of its recommendations by the end of 2025. We would like to see rail become an employer of choice for women in the very near future.
The ARA is also undertaking important First Nations research to better understand barriers to participation.
We also continue to develop our Rail Industry Worker (RIW) program, which is a national competency and safety management system that has streamlined qualifications tracking for over 100,000 rail workers.
With the increasing need for workforce mobility, the RIW system ensures workers can seamlessly transition across projects and networks, helping address skill shortages and improve safety outcomes.
The ARA is developing its own professional development opportunities for industry.
Image:
Industry Organisations
DECARBONISATION AND SUSTAINABILITY
The ARA’s Sustainability Strategy and the Critical Path to Decarbonise Australia’s Rail Rollingstock report provide a roadmap for transitioning to low and zero-emission technologies and we are actively working with government and industry to support the acceleration of decarbonisation in rail.
Inconsistent resilience strategies and outdated procurement practices remain challenging for the industry and the ARA is pushing for reforms that encourage sustainable infrastructure development and the adoption of low-carbon materials.
The critical path makes several recommendations to support the availability, uptake and implementation of low and zero emission technologies to address traction emissions related to dieselpowered locomotives.
The ARA is also working with Infrastructure Net Zero, including further research mapping net zero skills which
is nearing completion, and developing guidance on the circular economy.
DRIVING INCREASED PATRONAGE
The ARA is excited to see increasing patronage on rail and more focus on the significant urban renewal benefits that major rail projects deliver. Projects such as the Sydney Metro, Melbourne’s Suburban Rail Loop, and Brisbane’s Cross River Rail have the potential to completely transform their cities, while improving customer experience and accessibility.
The High Speed Rail Authority’s work on an east coast high-speed rail network also presents a transformational opportunity. With $500 million committed for SydneyNewcastle corridor planning, the ARA is advocating for a long-term vision that ensures this project delivers maximum benefits for connectivity, sustainability, and economic growth. The ARA is also supporting industry input into the Australian
Government’s review of the Disability Standards for Accessible Public Transport and working on initiatives to enhance security, accessibility, and passenger information services.
A PRODUCTIVE AND SUSTAINABLE FUTURE
As Australia’s transport sector continues to strive to improve productivity and transition towards a more sustainable future, the rail industry must be at the forefront of this transformation.
The ARA is committed to working with governments, regulators, and industry stakeholders to drive reforms that enhance efficiency, improve safety, strengthen workforce capability, and accelerate decarbonisation. With a national approach to investment, harmonisation, and innovation, rail can continue to play a pivotal role in Australia’s economic, environmental, and social future.
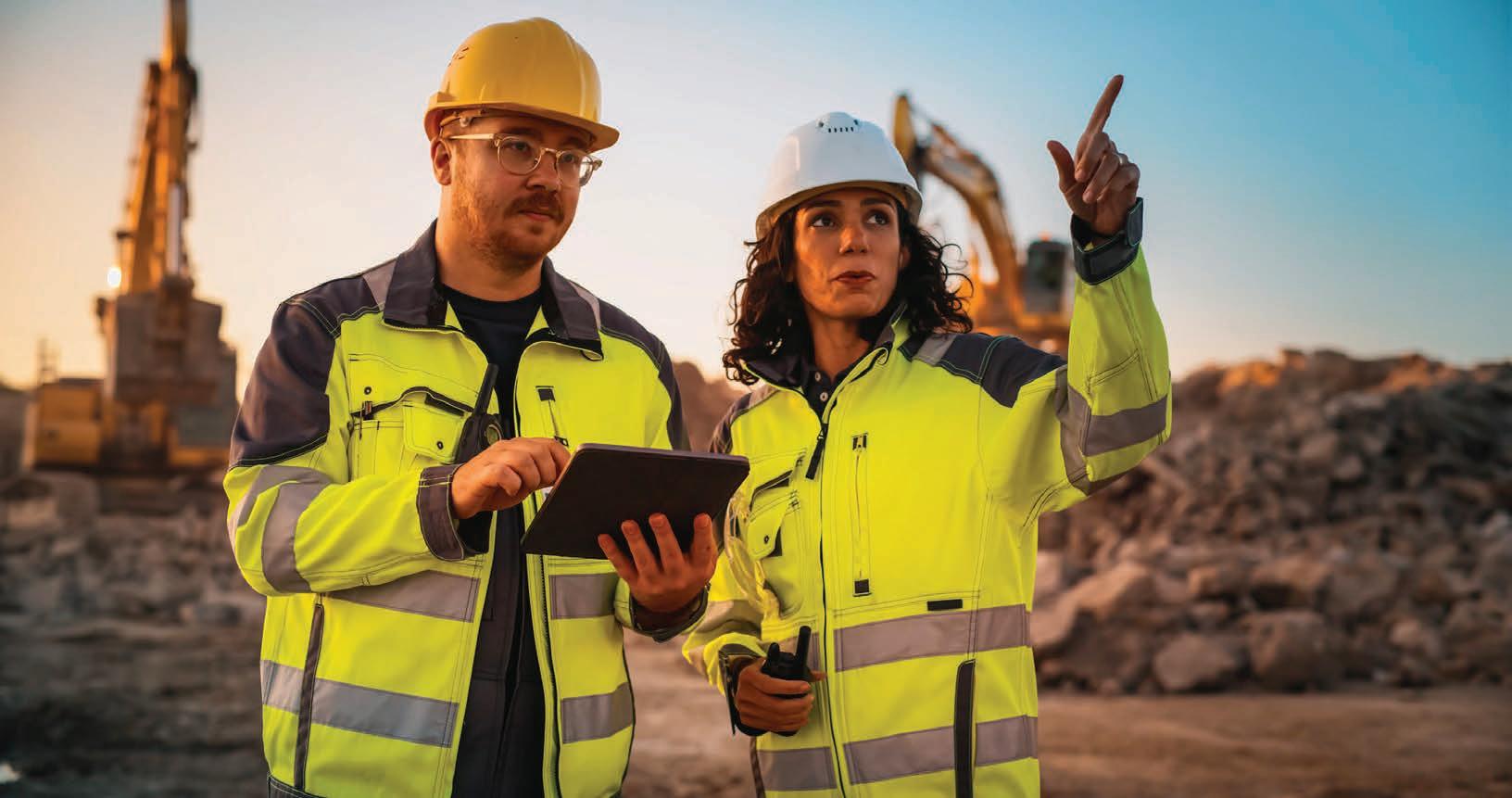
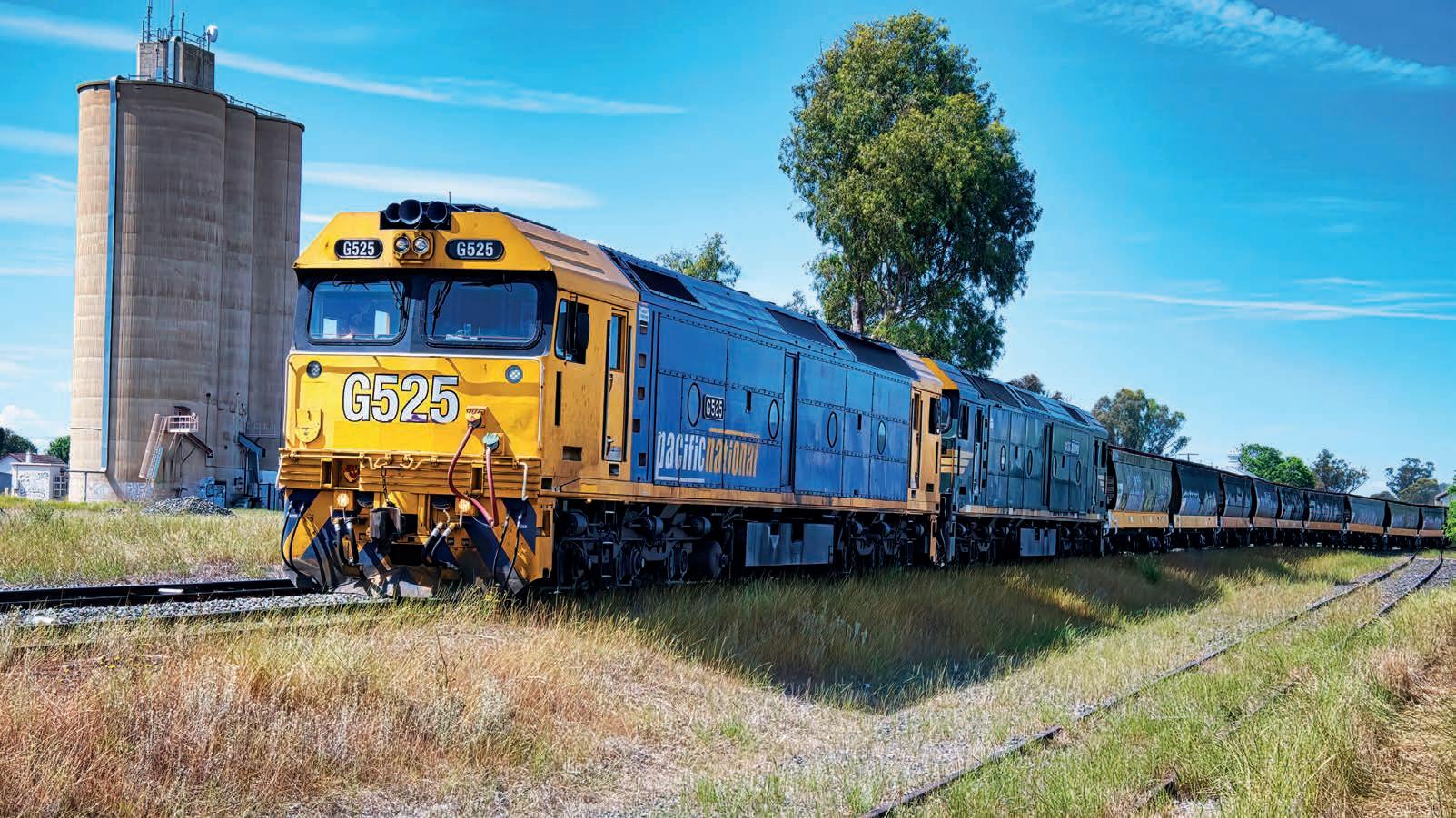
The freight task is set to more than double by 2050.
Building Australia’s Future – together.
Over
17–18 SEPTEMBER 2025
Melbourne Convention & Exhibition Centre
LEARN MORE
convergeexpo.com.au
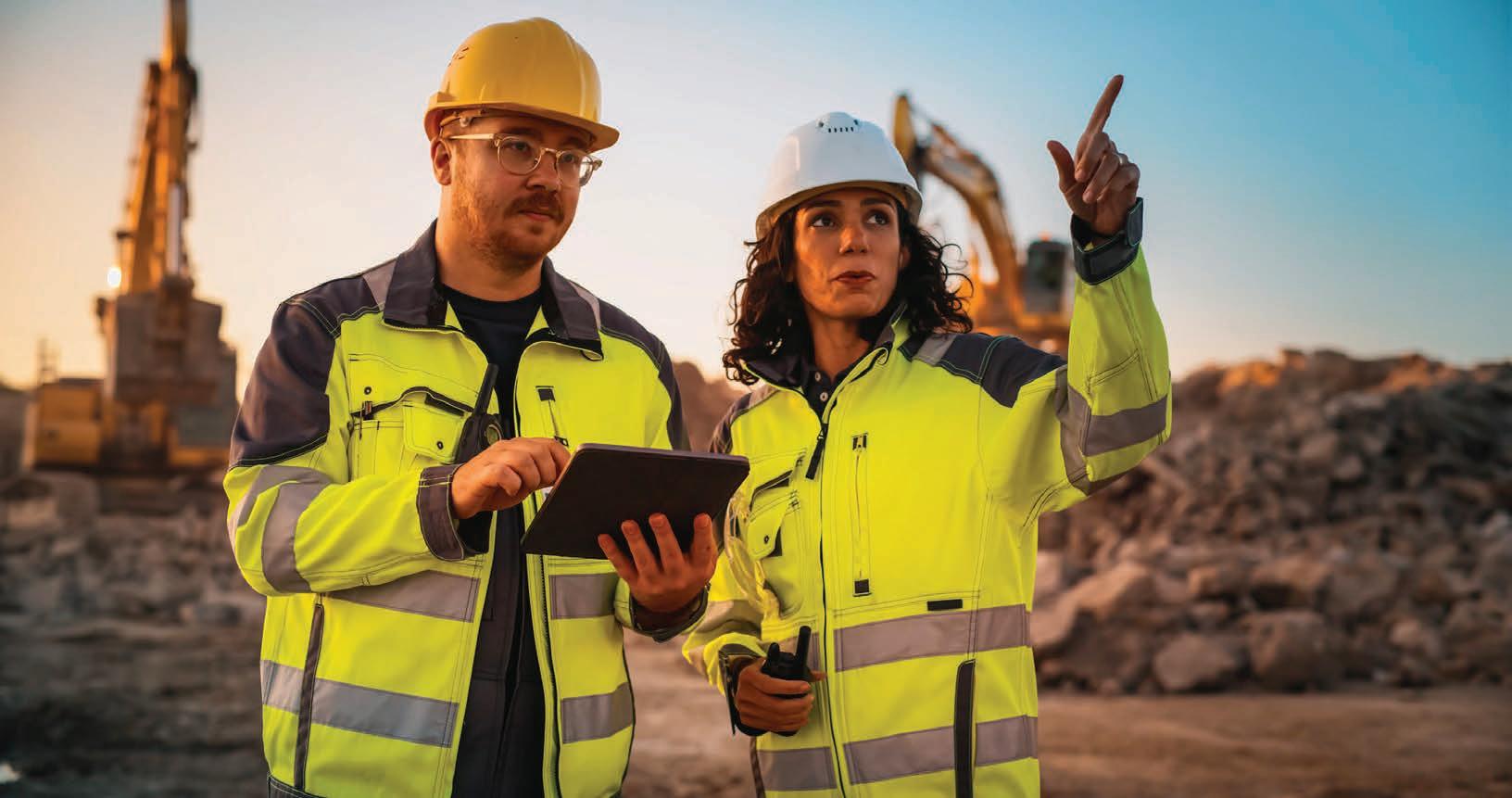



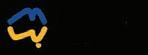


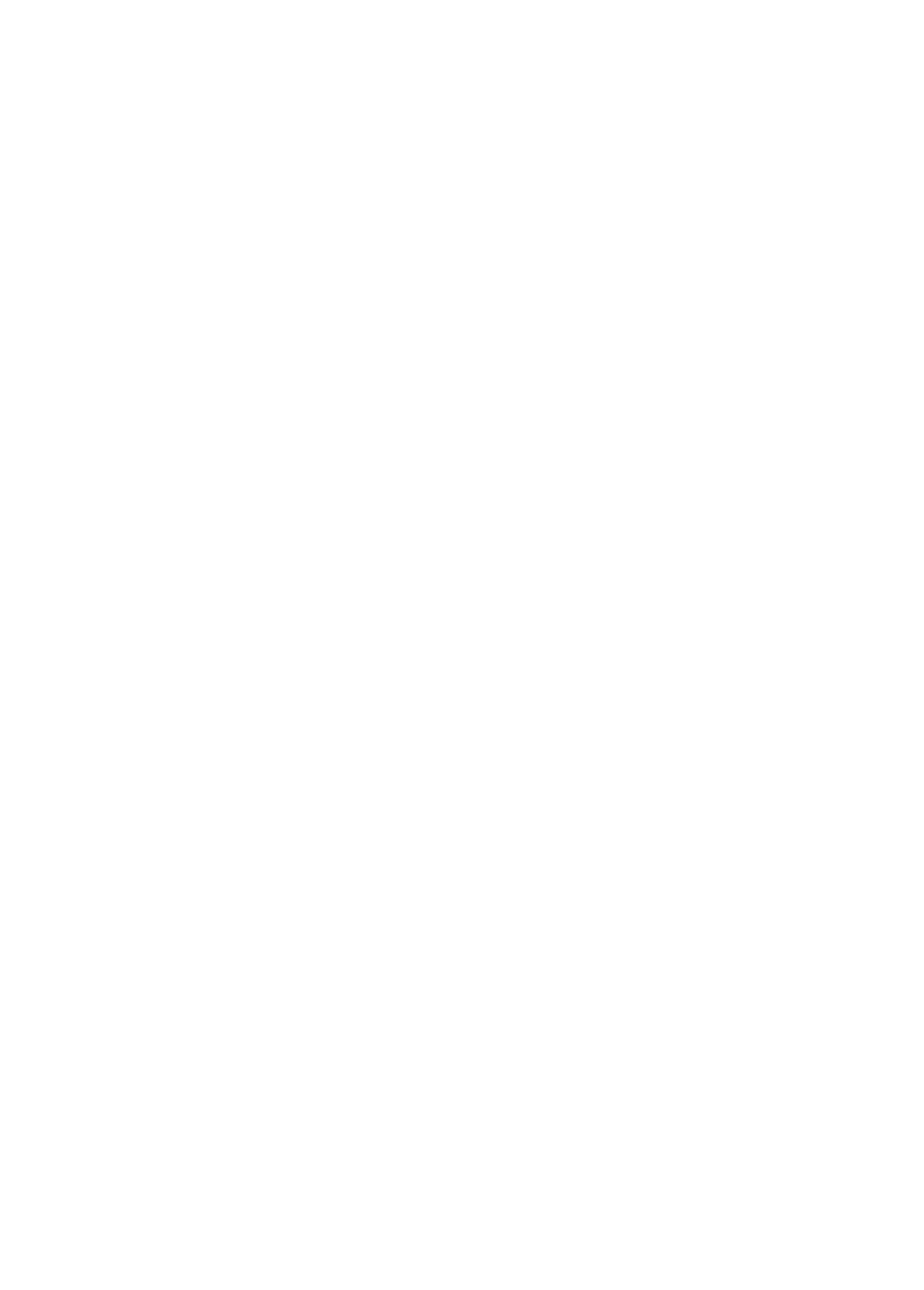
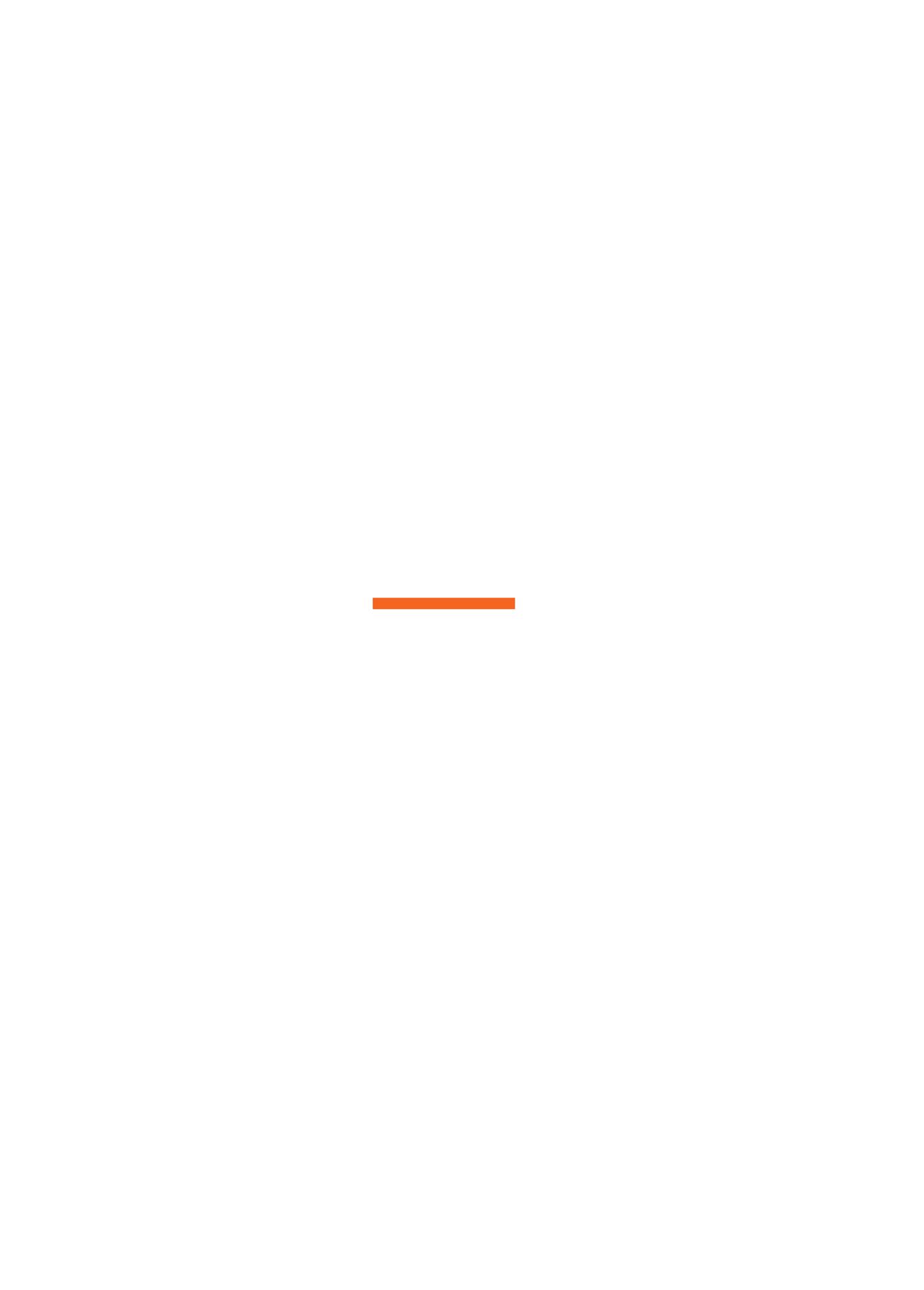