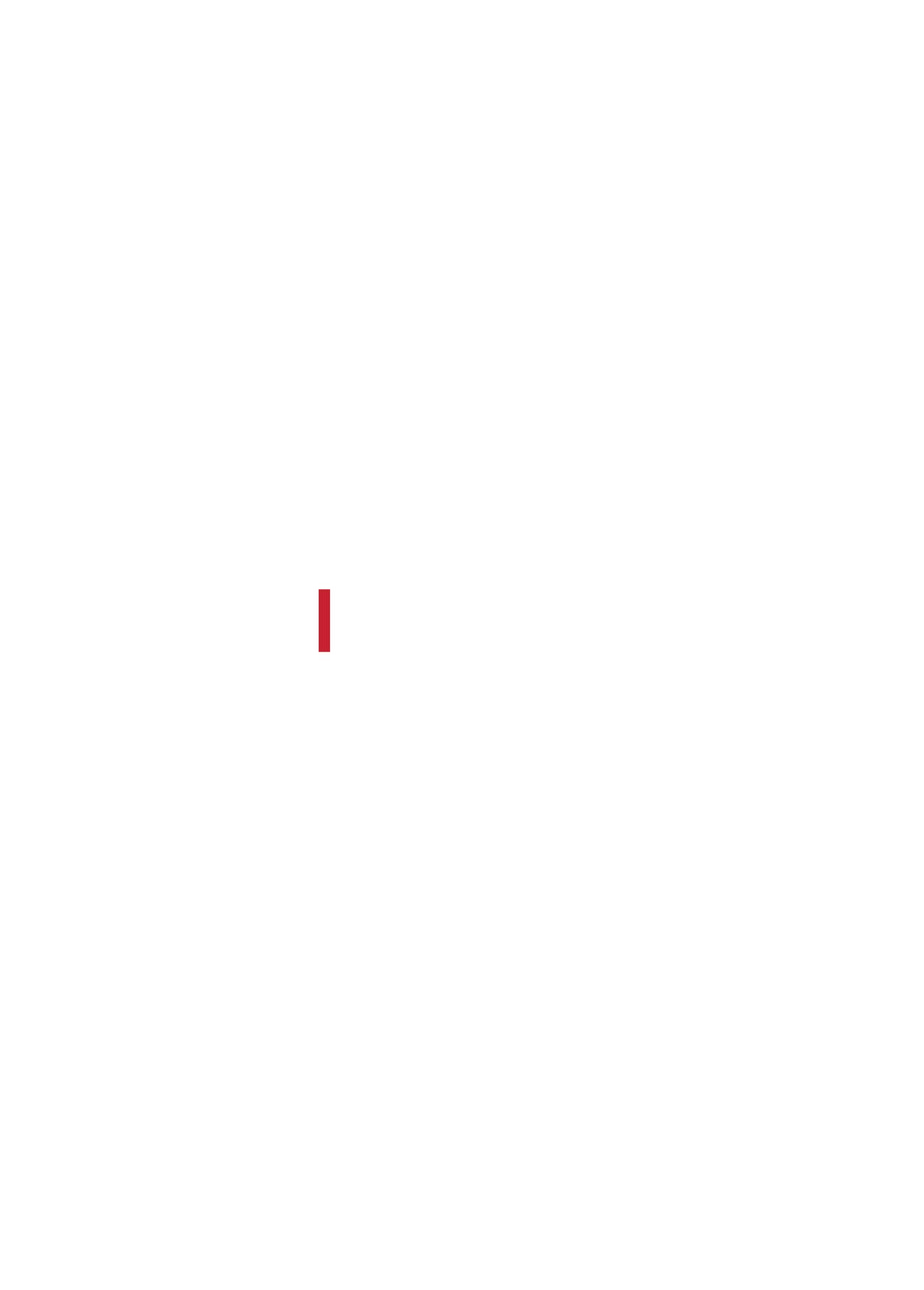
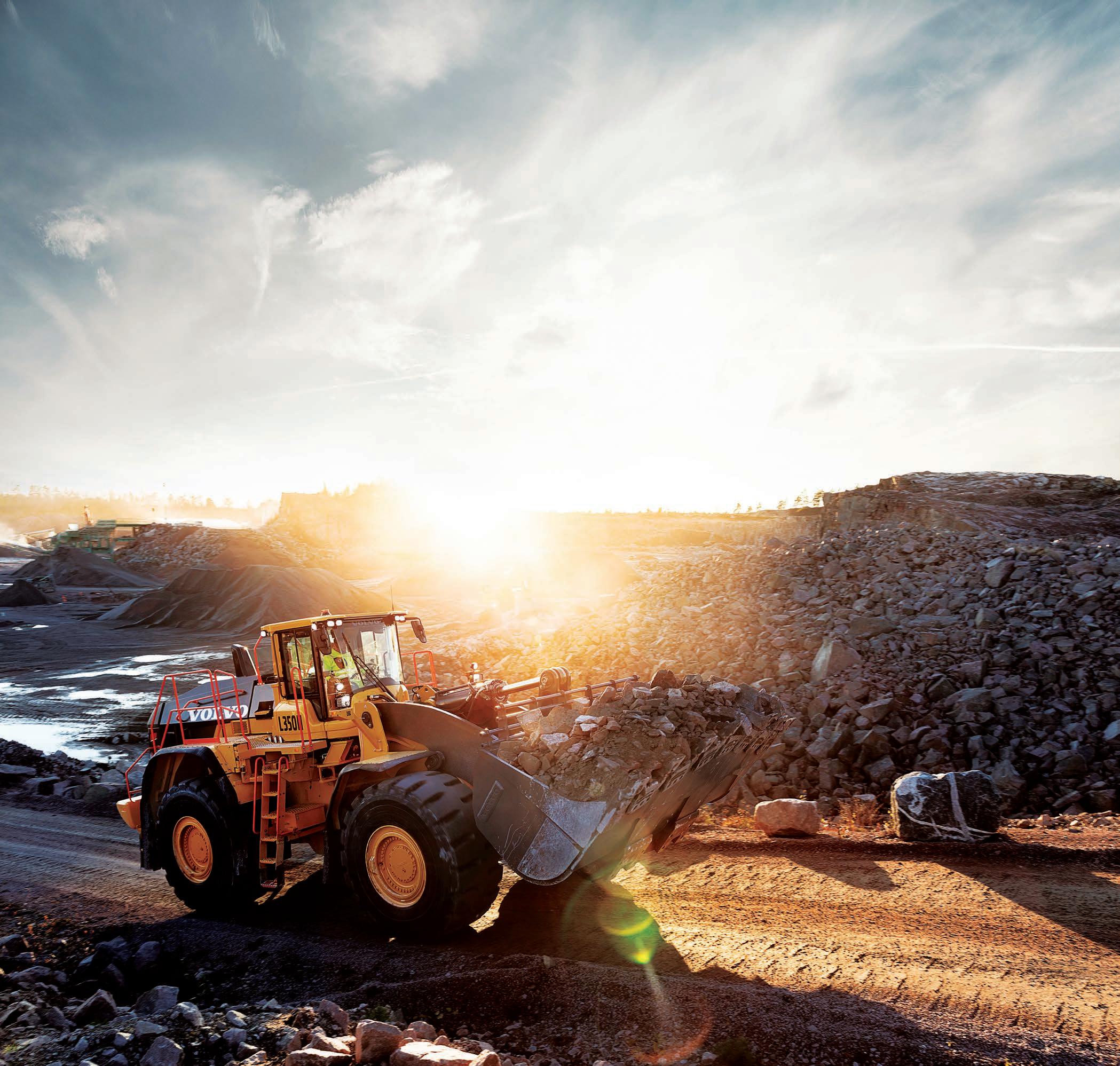
STEPS FOR SUSTAINABILITY
Looking at changes to the sustainable and recycled materials sector that could impact the industry.
STEPS FOR SUSTAINABILITY
Looking at changes to the sustainable and recycled materials sector that could impact the industry.
The newly designed WA475-10 features next-generation technology developed with input from customers like you to deliver improved productivity and lower fuel costs. quarry applications, this gentle giant is a unique solution for tomorrow’s challenges.
Up to 30% more fuel efficient
8% more breakout force* 20% more boom lift force*
The
How
How
Kleemann’s next step forward
Taking a look at Kleemann’s latest crusher, the Mobirex MR 130 PRO.
Practical parts
talks to Precisionscreen about how spare and wear parts can be key to a high-performing quarry.
No more heavy metal
Conveyors are built tough, but they’re far from indestructible – foreign metals in material flow can shred through belts.
28 Sandvik completes SP Mining integration
Sandvik has been working hard behind the scenes following its acquisition.
32 Jaw liner selection
Why
Quarry
Superior Industries looks at the key tips for matching a jaw liner to crushing applications.
36 The forefront of innovation
Quarry examines the recent IQA member event at Lynwood Quarry.
38 New wheel loader hits the mark
Komatsu’s new WA475-10 wheel loader is set to tackle a common pain point by delivering greater fuel efficiency.
40 Rebuilt vs reman
Emma Ford writes about John Deere’s commitment to remanufacturing and its environmental benefits.
46 Impactful legacy
Exploring the history and current role of Hazemag’s impact crushers.
Waste is an unfortunate side effect of most industrial processes, but what if it didn’t need to be?
That’s the question that governments around Australia are looking to answer in the form of a circular economy.
Our current economy is a linear one – resources are gathered, processed, sold, and disposed of, generating waste at almost every stage of the process.
A circular economy is an alternative where waste isn’t rubbish – it’s a resource.
Waste creates plenty of headaches for governments on all levels. Not only does it need to be collected, administrated, and processed properly – it can also pollute local environments and endanger people.
It’s a big issue, and it’s not one that has a simple solution. In fact, there’s an entire hierarchy that ranks ways of handling waste from most to least preferable. Just burying it in the ground is the least preferable.
Instead, recovering the lost resources (either through recycling, energy recovery, or reprocessing the waste) helps a lot more. The quarrying industry has a key part to play in this step.
Construction and demolition waste is one of Australia’s biggest waste streams, with millions of tonnes of concrete, steel, and more needing to be processed every year. Sending these resources to languish in landfill is a waste of potential.
Crushers and screening machinery can be used to transform construction waste into reusable products, incorporated into new construction projects entirely. It also means fewer natural resources are needed to supply major construction projects and helps keep councils looking for more renewable methods happy. Ultimately though, the best way to deal with waste to reduce how much of it is generated. This is something that original equipment manufacturers know and incorporate into their machinery’s designs.
If a machine creates less waste, that means more of the product can be sold. That means more profit for the quarry and less time spent cleaning up unsellable product. If the machines can also reduce emissions and boost sustainability, even better.
William Arnott Editor
Published by:
379 Docklands Drive
Melbourne VIC 3008
T: 03 9690 8766
www.primecreativemedia.com.au
Chief Executive Officer
John Murphy john.murphy@primecreative.com.au
Managing Editor
Paul Hayes paul.hayes@primecreative.com.au
Editor
William Arnott william.arnott@primecreative.com.au
Journalist
Adam Daunt adam.daunt@primecreative.com.au
Business Development Manager Les Ilyefalvy les.ilyefalvy@primecreative.com.au
Client Success Co-ordinator
Janine Clements janine.clements@primecreative.com.au
Art Director
Michelle Weston
Subscriptions
T: 03 9690 8766
subscriptions@primecreative.com.au
The Publisher reserves the right to alter or omit any article or advertisement submitted and requires indemnity from the advertisers and contributors against damages or liabilities that may arise from material published. © Copyright – No part of this publication may be reproduced, stored in a retrieval system or transmitted in any means electronic, mechanical, photocopying, recording or otherwise without the permission of the publisher.
WHEN THINGS GET REALLY TOUGH, YOU NEED A RESILIENT TEAM PLAYER. The mobile MCO 110 PRO cone crusher is distinguished by an extremely sturdy design, very high performance and favourable consumption figures. As a downstream crusher linked to a mobile jaw crusher, it proves its worth as a true workhorse and impresses in tough stone quarrying operations. Efficient and strong – the perfect team player.
www.kleemann.info
The quarrying industry is fast paced, continuously evolving with new technologies, practices, and legislation. Education remains the cornerstone of our industry’s growth and adaptation.
It is for this reason that the IQA is launching the IQA Education Hub - a comprehensive, user-friendly platform designed to centralise all our educational offerings.
In the past year, the Institute of Quarrying Australia (IQA) has successfully run over courses and workshops reflecting our commitment to enhancing the skills and knowledge of our members.
Our training programs encompass workforce development workshops, both face-to-face and virtual, ensuring accessibility and convenience.
The Education Hub will serve as a onestop-shop for all training needs, featuring a full catalogue of courses, tailored recommendations, and instant access to online and facilitator-led programs. A personalised user dashboard will allow members to track their training progress and access certificates immediately upon course completion, making it easier to maintain and update logbooks. Understanding the challenges of releasing staff for travel, many of our courses are now available virtually. This format facilitates live interaction, enabling participants to ask questions and learn from their peers without the time and expense associated with travel. Additionally, our modular course design allows for flexible learning schedules,
enabling participants to complete courses at their own pace.
Our webinars, led by experienced IQA facilitators, provide concise overviews of key topics, each lasting approximately one hour. These webinars are part of our education calendar and can be customised for specific organisations or teams upon request.
We have also partnered with registered training organisations to ensure our programs meet national and state standards, offering a holistic approach that includes both technical and soft skills.
Education is central to our mission as we address industry challenges such as workforce shortages and the need for greater diversity and awareness.
Our vision, “Thriving communities supported by a sustainable industry,” and our purpose, “Educating and connecting people engaged with the extractive and associated industries,” guide our efforts.
Under the leadership of CEO Jane Schmitt, the IQA will continue to prioritise education and connection, ensuring that our members are well-equipped to navigate the ever-changing landscape of the quarrying industry.
For more information, visit the IQA website and explore the new Education Hub. Together, we can build a stronger, more knowledgeable quarrying community.
Duncan Harris President Institute of Quarrying Australia
“OUR TRAINING PROGRAMS ENCOMPASS WORKFORCE DEVELOPMENT WORKSHOPS, BOTH FACE-TO-FACE AND VIRTUAL, ENSURING ACCESSIBILITY AND CONVENIENCE”
and
www.quarry.com.au
The IQA’s Strategic Plan 2023 to 2026 embodies the following vision, values and strategic priorities:
Thriving communities supported by a sustainable industry
Operational Priorities:
• Deepen industry participation
• Sustainable revenue streams
• Highly capable team
• Technological innovation
• Effective engagement
• Great governance
Strategic Priorities:
• Support industry participants with compliance and regulation
• Build a diverse and skilled industry workforce
• Foster strong industry connectivity
IQA Contacts:
Phone: 02 9484 0577
Email: admin@quarry.com.au
Chief Executive Officer
Jane Schmitt
Deputy Chair
Michael Close
Company Secretary
David Cowie
For all education, member and branch enquires please email: admin@quarry.com.au.
The Queensland Government’s new funding for South East Queensland councils has been welcomed by an aggregates advocacy body.
The SEQ councils will be able to receive funding from a $100 million pool to fund critical infrastructure, future housing, disaster resilience and community projects.
Under the new round, some councils will be able to use part of their allocated funding to plan for key infrastructure and train council staff to operate essential assets.
Under the arrangement, Brisbane
The new facility, located in Obourg, Belgium, has a planned investment of over €500 million.
City Council, Gold Coast City Council, Ipswich City Council, Lockyer Valley Regional Council, Logan City Council, Moreton Bay Regional Council, Noosa Shire Council, Redland City Council, Scenic Rim Regional Council, Somerset Regional Council, Sunshine Coast Regional Council and Toowoomba Regional Council are eligible for funding according to the state government.
“We’re backing SEQ councils to deliver essential infrastructure and services,” Local Government Minister Meaghan Scanlon said.
“WE’RE BACKING SEQ COUNCILS TO DELIVER ESSENTIAL INFRASTRUCTURE AND SERVICES.”
MEAGHAN SCANLON
“Queensland needs more houses, and I am pulling every lever to deliver them.
“We’re investing not only in critical infrastructure but also in the sustainability of our councils, with the option to strengthen their workforces and plan for key infrastructure needs.”
Cement Concrete & Aggregate Australia (CCAA) welcomed the announcement of the extra funding.
“CCAA welcomes the Qld Govt unlocking $100m to SEQ councils for critical infrastructure,” they posted.
“Highlighting the importance of planning & approval reforms to support supply of affordable critical construction materials needed to deliver the infrastructure.”
According to the state government, all councils can allocate up to 20 per cent of their SEQCSP allocation towards planning projects and up to five per cent towards capability development projects.
“We’ve already seen the benefits the SEQ Community Stimulus Program is delivering for local economies, tradies and families right across this region,” Assistant Local Government Minister Ali King said.
“We will work with local councils to ensure the best local projects are funded through this new round to support more jobs and liveable communities.”•
BODY: Holcim has revealed its new state-of-the-art GO4ZERO plant, which is engineered to produce two million tons of net-zero cement per annum by 2029.
The new facility, located in Obourg, Belgium, has a planned investment of over $500 million EUR which is in partnership with Air Liquide. The plant’s groundbreaking is being held in the presence of Alexander De Croo, Prime Minister of Belgium, and Wopke Hoekstra, European Commissioner for Climate Action.
“Belgium can take great pride in the foundation of Holcim’s new plant in Obourg. This investment symbolizes exactly the vision that our country has been pursuing for the past four years: build a future for industry in Europe, with the highest standards in terms of innovation and CO2 objectives. And here, in a crucial field like construction,” De Croo said.
Chief executive of the Holcim Group Miljan Gutovic, Holcim is on course to make net-zero cement and concrete a reality at scale this decade.
“GO4ZERO is one of our six large-scale, European Union-supported carbon
capture, utilization and storage projects. These aim to capture a total of over 5 million tons of CO₂ per annum, enabling us to offer over 8 million tons of fully decarbonized cement each year across Europe by 2030,” he said
The GO4ZERO project transforms cement manufacturing at every stage of the process. Accelerating decarbonized energy use, more than 95 per cent of its energy will be sourced from alternative fuels, while over 30 per cent of its raw mix will come from partly decarbonized alternative raw materials – predominantly waste generated by other industries, thereby advancing circularity.•
Australian Drilling Attachments (ADA), the proud exclusive distributor of TEI rockdrills in Australia, has taken steps to follow the American “Drill School Program” initiative.
TEI runs a Hollow Bar Installation Drill School each June at its facility in Montrose, Colorado. ADA’s technical staff enjoys product improvement and innovation opportunities at this exciting seminarstyle school with the TEI team and their customers. Stakeholders come from far and wide to attend the highly regarded and sold-out convention.
This year, ADA will run Drill School for its local and national customers at its facility in the Hunter Valley. The format is delivered in a classroom-style approach and includes a practical demonstration of the units and the hollow bar installation. If ADA’s clients prefer, the Drill School seminars can also be provided exclusively in a customised setting.
For more information, visit drillplus.com.au
To submit new product and equipment releases, email: les.ilyefalvy@primecreative.com.au
The ProStack Telson Telescopic Conveyor range has been designed for any job quarry operators may face.
The Telson range offers a diverse array of system options, providing operators with the flexibility they need.
With a radial movement capability of 270° and a working angle of up to 19.5°, the Telson range is a versatile solution for any job.
Telson conveyors range from 42 to 58 metres in length with a production capacity of 0 to 2000tph.
As a brand of Terex, ProStack customers receive the full benefit of an experienced team who can advise on the best options for their application. These options can allow operators to adjust the mobility and conveyor belt as well as add a radio remote control, roller and pulley lagging and dust containment arrangement to their system.
The ProStack Telson Telescopic Conveyor range is a tried and tested option to handle the needs of modern quarries.
For more information, visit terex.com/prostack.
- $710,000 +GST • 3685 - 6000 hours
3D GNSS Machine Control
Sigma Blade • Multi-Shank Rippers • Battery / Starter Isolators • Full Paint Respray
Komtrax • Serviced
Quarry learns how Volvo Construction Equipment is integrating cutting-edge technology into this product design to minimise accidents and improve the wellbeing of employees.
Volvo Construction Equipment’s (Volvo CE) wants to provide more to its customers than just machinery. The company strives to enhance site health and safety, creating an environment that promotes WorkSafe practices across all operations.
Its services and solutions are geared towards complying with and exceeding the Australian workplace safety standards. In addition, the company aims to improve the sustainability of its machinery, advancing towards zero-emission electric machines.
To deliver on its goal of enhanced efficiency and sustainability, Volvo CE has developed a sophisticated positioning service called Connected Map. It provides real-time visual overviews of all machines, vehicles, and personnel, maximising material handling efficiency, and allowing immediate communication of site changes to all users, which helps prevent accidents and ensure the welfare of all personnel.
It visualises critical job site features such as roads, load zones, dump zones, speed zones, restricted areas, and points of interest like offices, workshops, and fuel stations. This detailed mapping allows for better planning and execution of site operations, ensuring all resources are utilised efficiently and safely.
This service is accessible through the Volvo Co-Pilot, any Android/iOS device for on-site personnel, and the Office Portal web platform for office-based staff, ensuring
comprehensive accessibility and versatility.
The Connected Map is not limited to Volvo equipment but is compatible with Volvo and non-Volvo machinery. This compatibility makes it a versatile tool for all construction site needs, enhancing its utility across various job site operations. Integrating Connected Maps with Volvo Site Solutions creates a synergy that boosts site efficiency and significantly improves productivity and safety.
The Office Portal function of Connected Maps enables site managers to oversee multiple locations simultaneously and streamline the management of larger sites. Safety measures such as implementing one-way traffic and speed restrictions can be introduced and communicated instantly to all CoPilot software users, further enhancing the safety and efficiency of job site operations.
Volvo Connected Loadout, an online interface, complements the Connected Maps by simplifying various aspects of transport operations. It provides a digital home for profitable transport operations, offering data and insights accessible through a userfriendly interface with role-based access.
The Volvo CE Connected Load Out App integrates data from Volvo Co-Pilot, external mobile devices, adapting to individual customer needs and preferences.
By leveraging these advanced technologies, Volvo Construction Equipment
continues to lead in providing solutions in Australia that enhance the efficiency and safety of construction sites and contribute to environmental sustainability within the industry.
Volvo CE’s commitment to legal and ethical conduct is embedded in every aspect of its business, ensuring it adheres strictly to the laws and regulations of each country where we operate. This dedication extends to our business practices, promoting responsible actions in all policies and decisions.
Volvo Construction Equipment recognises the critical role that skilled operators play in enhancing jobsite health and safety. Its comprehensive Operator Training Programs are meticulously designed to ensure that Australian operators are well-versed in the features of their Volvo machines, which significantly boosts productivity and ensures safer operation.
Volvo Construction Equipment’s Volvo Site Solutions are designed to address operational challenges comprehensively, focusing on reducing waste, fuel consumption, and CO2 emissions. This strategic approach is pivotal in promoting sustainability while maintaining operational efficiency on construction sites. Its fuel and energy efficiency services are specifically tailored to minimise fuel
consumption, cut operational costs, and reduce the environmental footprint. The fuel and environment service integrated into Volvo Connect allows meticulous fuel consumption monitoring. This system provides insights that help identify areas where fuel consumption can be optimised, leading to significant cost savings and environmental benefits.
Volvo is at the forefront of electric construction, offering equipment that reduces emissions and noise levels, enhancing job site safety. Its range of fully electric solutions further demonstrates the Volvo Group’s commitment to sustainability. These include compact excavators, city buses, and heavy-duty trucks, all designed to operate with zero greenhouse gas tailpipe emissions. This diverse portfolio ensures that clients have access to sustainable solutions across a broad spectrum of applications.
This data-driven approach allows us to refine our strategies and enhance the overall effectiveness of our solutions.
operational efficiency and sustainability. Our commitment extends through innovative developments such as the Volvo Co- Pilot.
The Volvo Co-Pilot is engineered to reduce the need for operator interaction with its user- friendly interface, which minimises onscreen menu navigation and sets predefined operational limits, thus significantly enhancing focus and safety on the job site.
Volvo’s growth trajectory continues with the establishment of a new manufacturing plant in Slovakia and an advanced battery plant in Sweden. Additionally, the company is opening a new software testing centre in Gothenburg and Tech Hubs in Krakow and Singapore.
Volvo’s emphasis on regulatory compliance, ethical business practices, and the forward-thinking development of electrified machinery underscore a holistic approach to modernising quarry sites.
Volvo CE’s strategic focus on innovation, sustainability, and operational excellence positions it as a leading force in pushing the boundaries of what is possible in the
It’s efforts in embracing Industry 4.0, investing in sustainable solutions, and fostering collaborative initiatives provides a glimpse into a future where construction sites exceed in efficiency and productivity. In this journey towards a more sustainable and productive future, Volvo’s comprehensive suite of services and technologies lays the blueprint for the next generation of construction practices. •
For more information, visit cjd.com.au
Exploreing the history and current role of Hazemag’s impact crushers in the quarrying industry.
Hazemag’s impact crushers are more than just tools. They are a homage to the company’s history and have come to define it as an industry leader.
“Every crusher manufacturer has their legacy machine … with Hazemag, it is the impact crusher, we are the go-to company for impact crushing,” Hazemag SEA business development manager Marcus Benn told Quarry.
“It is our legacy machine, it is what our company was formed around, and we were the ones who designed it from scratch, and we’ve developed it over time.”
Hazemag has built its impact crusher based on the philosophy that the operator should be able to crush rock in a manner that provides consistency across all facets.
The company estimates that in the last 80 years since its impact crusher was created, more than 75,000 of its impact crushers have been sold worldwide. Some of the company’s impact crushers from as far back as 1950 are still in operation today.
Hazemag developed its impact crusher out of the embers of World War II.
The Andreas Crusher was designed in response to Germany’s need to process large
to reuse in other ways and remove it from central areas.
Over time, the impact crusher has been modified and adapted to keep it at the forefront of the industry.
The impact crusher’s role has remained largely the same at a core level: to help operators create a material in the correct size and shape to suit the required specification.
“It is all about getting a pile of rock at the end of the day that you can sell to help operators create a material in the correct size and shape to suit the required specification, and the higher the quality, the higher the price,” Benn said.
Hazemag impact crushers are used across several sectors in Australia, ranging from quarrying to recycled materials and waste.
A traditional crushing set-up, which uses gyratories and jaw crushers as primaries and cone crushers as secondary and tertiary, delivers a two-to-four reduction ratio in each stage of crushing. According to the company, the Hazemag impact crusher can achieve 10 to 1 reduction.
“You can actually get away with two (Hazemag) impact crushers instead of the three or four jaw and cone crushers used in
“Your footprint is smaller, and it means you are a much greener site, which is important, especially in Australia.
“By going to two crushing stations instead of three or four, you don’t have the capital outlay of the steelwork, conveyors and infrastructure. It is a lot cheaper to get to the end result.”
Hazemag has always focused on the rotor of its impact crushers, and for good reason. No part is more tested during a crusher’s lifespan than the rotor.
This is especially true in primary crushing, which requires heavy-duty rotors with high inertia to break down the material.
“It is the heart of the crusher. It is like our heart that is pumping blood through the body. That is what the rotor is to the crusher,” Hazemag and allmineral managing director of Australia Teddy Craies said.
“You’ve got the blowbars and all the different vessels that fit into the crusher, but the rotor is doing all the work.”
The GSK Rotor is one of Hazemag’s innovative patented designs, designed for the rigours of impact crushing.
The GSK Rotor is constructed using cast and welded steel where the individual cast discs are welded to the rotor body. This enables the rotor to accommodate the proprietary blowbars as primary crushing is initiated.
The blowbars are locked into position via wedges and a massive backing bar, which can be easily removed to accommodate changing the blow bars when required.
Hazemag has also designed a blow bar lifting device, hydraulic clamping device, and wedge extraction tool to help change the blowbars when required.
“It makes the removal of the blowbar easier and creates a safe work environment,” Craies said.
By designing the rotor body this way, the blowbars are fully secured and offer a 50 per cent utilisation factor.
The high utilisation factor results from the forward design profile, which enables the blowbars to deliver consistent gradation.
“A lot of design has gone into the blowbar itself to get maximum throughput and life out of those blowbars,” Benn said.
“For different types of materials, we have different types of blowbars and different types of options we can use there.”
An example of Hazemag’s rotor innovation is its dual-rotor system, which is showcased in its HPC primary crusher.
Because the dual rotor delivers a high level of reduction, it has become a popular choice in the cement industry.
“(The HPC) is two stages in one, it can give you almost 20-to-1 reduction ratio, and it is ideal for cement,” Benn said.
“(The HPC allows you to) go from a primary feed all the way to a ball-mill feed through one machine, which is practically unheard of.”
One of the most significant design changes to Hazemag’s primary impact crushers is the use of technology to streamline operations seamlessly.
Hazemag launched its HAZconnect system as a fully integrated software solution. The platform enables operators to control their Hazemag equipment from the software platform.
Hazemag’s updated HAZconnect system enables site managers and operators to access data on all Hazemag machines.
This data can generate tailored reports with production data to enable site
managers to make informed decisions that maximise crushing performance. The digital maintenance platform allows operators to perform preventative maintenance using detailed data insights from the dashboard on HAZconnect.
Recently, Craies and Benn took a customer from Southeast Asia to see the HAZconnect system work in real-time with Hazemag equipment.
The customer, who needed 28-32 people to run their quarry, was shocked to turn up onsite and see just two people operating it. The other six were focused on using the loaders, while the duo used the HAZconnect platform to run the quarry.
“(The customer) turned around to us, and they saw the HAZconnect and said we were far ahead of the opposition,” Benn said.
“They said they were amazed at what the HAZconnect system can actually do.”
“It enables them to have the adjustability and get the product size, and you can control the process as well as the safety features,” Craies said.
All of this comes with full support from Hazemag via its Australian facilities. It manufactures, delivers commissioning and installation support from its Western Australia base, and maintains spare stock across all of its crushing equipment. The company also has a warehouse in Brisbane for spare parts and a warehouse in Canning Vale.
“The infrastructure is here, the people are here. The service is here, and it is ongoing,” Craies said. •
For more information, visit hazemag.com
Taking a look at Kleemann’s latest crusher, the Mobirex MR 130 PRO.
Ocrushing equipment for more than a century.
Its machines are a common sight in quarries across the country, thanks to their high quality and accessibility.
To ensure it stays in touch with the industry, the company has listened closely to its customers to develop the Mobirex MR 130 PRO impact crusher, a new entry into the mobile crushing market.
The new machine brings innovations and flexibility to improve performance, safety and simple handling. It advances and improves upon the existing Mobirex impactor line, which is designed to provide maximum performance and high quality of end products while keeping operating costs low.
The MR 130 PRO mobile impact crusher has an inlet width of 1300mm and is stacked full of advanced developments normally associated with much larger crushing plants. It provides simple handling, meets high safety standards for the operators, and has
Kleemann said these features make the MR 130 PRO a total standout in a diverse range of applications in both quarrying and recycling applications.
It has a generously dimensioned feed hopper followed by an independent double deck vibrating pre-screen. The option of a 1550mm x 5500mm (8.4m2) double deck post screening unit adds to its versatility, allowing the machine to produce up to three graded end products.
In addition, the crusher has a fully hydraulic gap adjustment and overload system, along with an optional, all-electric, E Drive diesel electric drive concept as an external power supply, which is extremely efficient and can be operated with zero local emissions.
This is just one factor contributing factor to both running costs and environmental awareness. Kleemann have also continued to work on the improved power and performance of the unit to ensure more productivity and more efficient running costs.
to improve its machines sustainability.
The company aims to constantly evolve its offerings to keep up with its customers’ expectations and demands in this world where sustainable technology is highly regarded.
The operation of this machine is made simple and intuitive thanks to its operating concept Spective. The system allows the crusher to be operated via a 30cm touch panel, with all components and functions accessible from the ground.
Spective guides the operator step by step through the starting procedure, providing a graphical view of the plant with all adjustable functions. When the designed function is selected, clear instructions guide users through all the operating steps. If a fault occurs, a fault diagnosis appears on the display. The touch panel is resistant to dust and always easy to read, thanks to the light intensity and high contrast.•
For more information, visit wirtgen-group.com
It takes a different kind of brain behind the brawn. Fired up like a turbo diesel. Gears constantly churning. Hardwired beneath hard hats to solve problems, or avoid them altogether. With you and your crew at the helm, and Deere at your back. The workarounds, ideas and innovations that move earth, and your business, forward. Because that’s what it takes to win in the dirt. And that’s what it means to be Never Idle.
Quarry talks to Precisionscreen about how spare and wear parts can be key to a high-performing quarry.
Spare and wear parts can often be overlooked, until operators need them to get equipment up and running again.
In an ideal world, everyone wants machine and plant equipment to run for as long as possible, delivering less downtime, more production, and greater efficiency.
The reality, especially in a harsh operating environment like Australia, is that parts will need to be replaced. Time and efficiency are critical factors for any operator in this position.
This has become increasingly important as as older workers retire.
According to Precisionscreen chief operating officer Jonny McMurtry, original equipment manufacturers like the Brisbanebased company have had to adjust to this issue.
“There is this big gap, where we’ve had a high degree of technological advancement on our own machines and imported machines. So, there is that potential loss of knowledge within the industry,” he told Quarry.
“We want to make sure we cover all aspects of it; we want customers to feel like they can contact us.
“We don’t want to go solely down one avenue. That’s why we’re trying to develop multiple options for (the parts) they might want or need.”
This is why Brisbane-based Precisionscreen has invested heavily in to ensure its spare and wear parts department and technology offering. The investment means the company can offer standard solutions or tailored options depending on the customer’s needs.
“We stock, carry and sell standard wear parts but we have the ability to complete our technical site visits and understand the customer needs to advise on tailored options depending on what their needs are,” McMurtry said.
“We’ve got the company attributes and different departments required that enable us to do that.
“If they’re looking to adapt their application or adapt their machine to suit their application, we can jump in the boat with them and give certain ideas a go.”
Precisionscreen has a fully outfitted manufacturing facility at its Wacol headquarters, where the Australianowned company can design, fabricate, and manufacture solutions in-house. The machine shop, featuring an in-house plasma cutter, is used to create Precisionscreen’s own equipment range and spare and wear parts range.
Using these facilities, Precisionscreen has recently been able to manufacture punch plates for scalping screens, pugmill parts, crusher wear parts, fabricated parts for imported machines, drum scrapers, and conveyor parts.
Recently, the company has seen a rise in requests to manufacture nonstandard drums or drums to be retrofitted onto imported machinery.
McMurtry said it showed the versatility of the company’s manufacturing facility that these could all be produced locally in Australia.
“Within reason, we can do different sizes of drums and different lengths of drums to fit all mobile or some standard conveyors in the industry,” he said.
“We can also do different sizes and applications of screens, different wires and apertures as well to suit the customer application.”
The company still maintains a stock of spare and wear parts for older machines, machines that were part of its hire fleet, or machines for which it was a previous reseller. Its dedicated team manages its stocked wear and spare parts range.
Graham Marks and Andrew Hines lead Precisionscreen’s spare and wear parts department. Together, they possess more than 20 years of industry experience and can advise customers on the best system solutions for their business.
The team recently travelled to their regional New South Wales and the ACT customer base as part of their commitment to technical site visits. During these visits, Precisionscreen was able to help its customers with any urgent needs and advise them on the best after-sales solutions.
McMurtry told Quarry it came down to how the Brisbane-based company valued its relationship with new and existing customers.
“(Andrew and Graham) have that point of reference within the industry so that if a customer phones looking for certain parts or has a certain application, they can offer their point of view,” he said.
“They can draw upon their experience to deliver a more tailored and educated assessment and solutions.
“We look at it as a long-term relationship with the customers that we service, so we want to make sure that we stock those high turnover parts and we can keep them running for as long as possible.”
Precisionscreen will expand its spare and wear part offering via technology in the coming months.
The company plans to roll out an online portal showcasing the standard “high turnover” parts. The Brisbane-based operation has invested in the service to give customers access to parts when and where they need them.
“If it is an owner-operator quarry and they don’t have time during the day as they are producing, they can jump online and order these frequently used parts at a time that suits them,” he said.
“We want to open up those avenues so that if a customer is time-poor or knows exactly what they want, they can access that online store as well.
“We’re trying to tailor our services based on the customer’s and the industry’s needs and requirements.” •
Looking at the latest changes to the sustainable and recycled materials sector which could impact the aggregates industry.
Advocacy groups have lauded the solutions detailed in the Federal Government’s interim sustainability report and a new procurement policy.
The Federal Government has released the interim report from its Circular Economy Ministerial Advisory Group, which identified roads and construction as a key contributor to Australia’s circular economy.
The group, established in February 2023, has focused on how Australia can improve its domestic manufacturing capabilities through reuse, repair and recycling which are the key parts of circular economy.
It comes after a CSIRO report from March 2024, Australian material flow analysis to progress to a circular economy, which showed Australia lagged behind the world in regard to circularity rate.
The circularity rate helps quantify the number of total materials used in a country’s economy that are recycled or recovered and fed back into the economy.
Australia’s rate, according to the report, had increased to 3.7 per cent from the 3.5 per cent reported in 2015. Despite the increase, the global average in this measure is 7.2 per cent, led by the Netherlands’ 24.5 per cent.
Among the 2024 report’s key findings, the researchers believed Australia had scope to achieve 32.5 per cent when accounting for the country’s “economic structure”.
Given Australia has lagged in this measure since 2015, the Federal Government’s announcement of the taskforce, chaired by former Victorian deputy premier Professor John Thwaites, was welcomed.
Industry and Science Minister Ed Husic, in 2022, suggested a circular economy was key to achieving net-zero by 2050.
“A circular economy will ensure that we are on track to make these changes and support the energy transformation,” he said.
“It’s a great opportunity to create manufacturing systems that are optimised to be less resource intensive, produce less waste, and have less impact on the environment.”
While the group’s advice will be consolidated at the end of the year when its term ends, the interim report has several relevant outtakes for the industry.
Professor Thwaites said the report will offer several suggestions.
“The report shows how essential circular economy actions are for reducing waste, pollution and carbon emissions. Our recommendations will incentivise innovation and shape new markets for circular economy products,” he said.
“Industry has told us that they want clear regulation that supports recycling and the circular economy and gives business the confidence to invest.
“The circular economy can help drive productivity and economic growth in Australia by using materials and resources more efficiently.”
The report spelled out that industries involved in and around the construction industries, working on the “built environment”, were “primed” to play a key role in boost the circular economy.
According to the Department of Climate Change, Energy, the Environment and Water’s data, the built environment accounts for a third of resource consumption globally and produces about 40 per cent of Australia’s solid waste.
The group believed it was important to use construction and demolition waste in new builds, which would also reduce emissions. It highlighted the impact recycled materials could have on road infrastructure, estimating that recycled materials could replace 27 per cent of virgin materials in the sector.
The report’s findings have been largely welcomed by key stakeholders in the sector.
AfPA’s chief executive officer, Tony Aloisio, supported the recommendations made in the interim report.
“Road sustainability is a critical aspect of the circular economy, and we are pleased to see it being prioritised by the Circular Economy Ministerial Advisory Group,” he said.
“By incorporating reused and recycled materials and promoting maintenance measures, we can significantly reduce waste and create more sustainable road infrastructure.”
Engineers Australia chief executive officer Romilly Madew AO, who was part of the CMEG group, believed the recommendations would be beneficial.
“These initiatives aim to create tangible benefits for everyday Australians,” she said.
“By transitioning to a circular economy and environmentally sustainable procurement, we are safeguarding our planet for future generations while driving economic prosperity for everyone.”•
Alex Fraser is a leader in infrastructure sustainability. Quarry learns how innovation and investment are shaping its operations.
Recycled materials may be a hot topic within the construction sector, but they define Alex Fraser’s past, present, and future.
From humble beginnings as metal traders in the 1800s, Alex Fraser has evolved to become recognised as one of Australia’s leading providers of sustainable construction materials. The company recycles millions of tonnes of material every year and supplies major projects around the country with a greener way to build Australia’s cities.
The company produces more than three million tonnes per annum of recycled roadbase, asphalt, aggregates, and sand derived from materials recovered through its Victorian and Queensland recycling facilities.
Quarry spoke to Alex Fraser’s managing director, Peter Murphy, about the company’s network of recycling and asphalt facilities and its impact on the broader policy changes driving the demand for recycled materials.
In the past few years, significant improvements have been made to the way major asset owners in Australian cities plan for infrastructure sustainability on major projects, as governments at all levels recognise recycled materials as a viable alternative.
Alex Fraser’s reputation for quality products, alongside broader policy changes, has been a key driver in the wider adoption of recycled materials.
Victoria’s Big Build, responsible for more than 100 major road and rail projects, led to the development of the revolutionary Recycled First Policy. Announced in 2020, Recycled First was designed to increase the use of recycled materials in the Victorian Government’s transport infrastructure projects. The policy strongly encourages and incentivises the use of circular materials on government infrastructure projects.
Companies wanting to be part of the Big Build had to detail how they would implement recycled materials in their works while maintaining specifications in their bids.
EcologiQ has supported the initiative through ongoing education and industry engagement, resulting in a significant shift towards prioritising the use of circular materials.
“Recycled First will boost the demand for reused materials right across our construction sector,” said Premier Jacinta Allan, Victorian Transport Minister at the time. Through the implementation of the policy, Alex Fraser, with its Green Roads Construction Materials, was well-positioned to supply quality, recycled construction materials and support Victoria’s Big Build.
As a result of the Recycled First policy, the company supplied more than 465,000 tonnes of its Green Roads Construction Materials to Victoria’s Big Build in 2023 alone.
The company has supplied recycled construction materials to an expansive list of projects including the Level Crossing Removal Projects and Victoria’s Big Build, including the Sunbury and Epping Road redevelopments.
For the recently completed Sunbury Road upgrade, Green Roads Asphalt, containing up to 40 per cent recycled materials, was supplied from Alex Fraser’s Northern Sustainable Supply Hub.
The company estimates the resurfacing project used more than 20 million recycled glass bottles, and more than 12,000 tonnes of reclaimed asphalt pavement (RAP) that has reduced carbon emissions by 585,000 kilograms.
“The Sunbury Road Upgrade is the latest example of how Victoria is finding practical ways to use recycled products in volume to build quality, greener infrastructure,” Murphy said.
Specifications that clearly and simply support the use of recycled materials have
proven to be critical to standardising the industry’s uptake of circular construction products. In the 1990s, VicRoads developed a specification acknowledging the use of recycled alternatives to quarried roadbase and virgin asphalt. As a result, proactive governments, councils and contractors were motivated to explore and innovate on their projects with recycled construction materials that would deliver further sustainability outcomes.
Similar updates to the Queensland Transport and Main Roads Specifications have recently been enacted, resulting in immediate impact on the major projects space with the state’s biggest infrastructure project – Cross River Rail – opting to use Green Roads recycled aggregates and roadbase in the project.
Few companies have invested as many resources into innovating recycled materials
as Alex Fraser. The company recently bolstered its recycling network around Melbourne with a new high-volume crushing plant in Epping, which will provide recycled material for the neighbouring asphalt facility and infrastructure projects in Melbourne.
The new plant represents a $13 million investment in the company’s Northern Sustainable Supply Hub. It will process one million tonnes of recycled material per annum, ranging from paddock rock to RAP. Those materials will be used to produce high-recycled sustainable asphalt, containing up to 70 per cent recycled materials at the company’s co-located asphalt plant.
“We continue to focus on maximising our recycling capability to ensure the construction market can rely on us to deliver a consistent and reliable supply of quality recycled materials to their projects, from municipal works to subdivisional developments and major infrastructure projects,” Murphy said.
“The Northern Sustainable Supply Hub in Epping is situated in close proximity to the northern suburbs growth corridor providing developers with an ideal solution to responsibly dispose of paddock rock, and to buy sustainable construction materials needed to complete their projects.”
The three-stage crushing plant combines a robust primary impact crusher, a secondary crusher and a tertiary crusher to achieve product specifications. The new facility is fitted with the latest automation, monitoring systems and advanced controls to ensure operational safety and efficiency.
“Stage two of the project will bring in advanced processing methods to recycle concrete and brick. The introduction of artificial intelligence and robotics will enhance material identification and sorting accuracy, while reducing risk exposure for our people,” Murphy said.
It follows the launch of the company’s newest asphalt plant, commissioned in early 2023 and designed as a fully integrated solution to operate in partnership with the company’s pre-existing construction and demolition recycling plant.
The $15 million Benninghoven asphalt
facility in Clarinda, and asphalt plant in Dandenong play a leading role in Victoria’s circular economy.
Up north, Alex Fraser has long established recycling facilities top and tailing the Brisbane CBD. The Archerfield and Nudgee Recycling Facilities are ideally placed to support the sustainable growth and transformation of the city’s infrastructure landscape ahead of the 2032 Olympic Games.
Alex Fraser’s sites have garnered awardwinning recognition from several key industry and stakeholder groups.
In 2020, the Victorian Government recognised Alex Fraser’s significant contribution to the state with a Premier’s Sustainability Award.
“Victoria continues to lead the way in recycling and reuse of valuable materials,” Murphy said.
“Alex Fraser’s Sustainable Supply Hubs and
The Lokotrack® LT220D™ combines a cone crusher and a screen into one highly efficient mobile unit, making it unique with its dual functionality on a single chassis. This model comes equipped with either an HP200 or GP220 cone crusher, alongside a precise ST4.8 screen (18’ x 5’), enhancing operational efficiency and simplifying transportation.
Designed for quick installation, the unit can be set up in less than 20 minutes. It prioritizes safety and easy maintenance with service points accessible at ground level, making it suitable for a variety of crushing tasks.
For more information on the extensive range of Metso mobile plants, email us today at metso@tuttbryant.com.au!
Conveyors are built tough, but they’re far from indestructible –foreign metals in material flow can shred through belts. Kinder Australia has designed a solution.
There are countless ways that metal can fall into material at a quarry. A tool could be dropped on the conveyor, or it could have been introduced upstream.
If left undetected, it poses a serious threat to the conveyor belt. When metal fragments become mixed with materials, they can wreak havoc as they travel at speed along the conveyor system. The sharp metal edges may tear into the conveyor belt resulting in expensive repairs and downtime.
David Zhungu, a design engineer at Kinder Australia, said metal is a common contaminant. The goal is to target certain areas of the conveyor with engineered solutions to prevent damage of the belt.
“One thing people often disregard when running metal detection systems is how impactful the reduced downtime and maintenance costs can be,” Zhungu said.
“The belt is one of the most expensive components of a conveyor system. Any small puncture and tear can rapidly rip the belt.
“Early warning systems save operators a lot of money, which is why we provide a solution that aids in the longevity of the belt.”
As part of its belt protection system, Kinder Australia supplies metal detectors, which
have a high level of accuracy and adaptability. When installed correctly, they can inform a site immediately if there is a foreign metal present in the conveyed material. Metal detectors are best installed before the transfer point to prevent metal from going through the crusher or piercing the conveyor belt after picking up speed in the conveyor transfer.
The sensitivity of the metal detector can be adjusted accordingly to prevent false alarm metal detections. When metal is detected, the relay output is deactivated, allowing for various actions to be triggered. The relay can be connected to activate an alarm, send a stop impulse to the conveyor belt, or signal a scraping device, among other possibilities.
Depending on the application and space limitations, Kinder Australia can recommend the ideal metal detector configuration.
Zhungu said Kinder works with engineers to assist in fine tuning the systems.
“The manufacturer also provides us with support and assistance for our customers through the provision of detailed installation, operation and maintenance manuals,” he said.
“Before we recommend a metal detector, we always ask the customer questions such as what materials they are conveying at the
quarry, the belt width and burden depth to ensure they have the right tool for the task. It’s vital to get the correct information here, as there are several things that can affect installation, such as electrical interference, vibration, and mounting limitations,” he said.
“Our field engineers go out to a customer’s site to provide technical advice on the mechanical installation of the metal detectors. I provide the electrical expertise in determining the size of search coil required and if any electrical interference is within the chosen installation location of the search coil. As well as the power requirements to run the electronic control unit of the metal detectors and provide trouble shooting tips if any problems arise. It is vital qualified electricians carry out the installation work,” Zhungu said.
If foreign metal manages to slip through undetected, Kinder Australia includes another line of defence in the form of its K-Flexal Elastic Belt Support System.
The system is made up of flexible polyurethane saddles that effectively allow the absorption of impact forces under the chute as product is dropped onto the belt. The UHMWPE pads on the surface of the saddles provide low friction contact with the belt. The drop height, belt speed and material’s abrasiveness are used in determining the K-Flexal’s effectiveness.
If the metal has embedded into the belt, the damage may already be done before any operator notices. The belt rip detector switch will alert to tears in the belt immediately. When a rip occurs in the belt, any material or ripped section of conveyor belt caught by the wire rope activates the switch, halting the conveyor operation. The belt rip detector switch gives operators peace of mind that no tear will pass by undetected. To monitor all sides of the belt, two belt rip detector switches and wire kits are needed.
Zhungu said organisations that take proactive measures to mitigate the risks associated with foreign metal contaminants benefit more than they would expect.
“When a belt rips, the downtime can be extensive. Not only do you need to replace or repair the belt, but you also lose days of vital productivity,” he said.
“Our quarry customers have provided great feedback, saying that the system keeps conveyors operational for much longer.” • For more information, visit kinder.com.au
Following its acquisition of the Schenck Process mining-related business, Sandvik has been working hard behind the scenes to bring its new offering and capabilities to market.
In October last year, Sandvik reached a key milestone in the integration of Schenck Process Mining into its Rock Processing Solutions Business area, when the company changed the names of the legal entities that came with the Schenck Process acquisition.
The newly acquired entities provide Sandvik Rock Processing with a much better global reach, particularly in geographies where it previously had little presence.
This is especially true in Australia, where Sandvik Rock Processing only had a small team, while SP Mining had most of its engineering and R&D teams as well as production and service facilities in Australia.
Schenck Process Australia, which employed over 400 people became Sandvik Rock Processing Australia, and is now a major hub for Sandvik’s global Screening Solutions Division.
unparalleled range of vibrating screens, feeders, screening media and train loaders.
In early May the company achieved another key integration milestone, shipping out the first Sandvik branded SP Mining screen from its Jandakot production facility in Western Australia. Pleased with the result, Sandvik’s global head of marketing – screening solutions, Peter Newfield, previously head of marketing APAC for SP Mining, said, “Apart from the change to the look, branding and Sandvik nomenclature, nothing else has changed. Our legendary reliability,
technology and aftermarket support remains as our customers have come to expect.”
We are now better equipped than ever to help our customers to optimise their comminution and material handling operations for maximum performance, safety, and efficiency,” he said.
Newfield said that combining the industry leading screening, feeding, and loading expertise of Schenck Process Mining and Kwatani with Sandvik’s mastery of crushing and wear protection allows the company to bring an unrivalled equipment lineup to market.
“This unique offering is underpinned by the expert process knowledge of our teams, a full range of digital tools, high quality OEM spare parts, consumables, and life-cycle services.”
But the integration wasn’t just limited to the equipment. Newfield said it has been a major project that involved every part of the business. In essence, the acquired Schenck Process entities had to become Sandvik Rock Processing entities and so SP Mining staff had to embrace the Sandvik culture and learn the company’s systems, and ways of working.
“Of course, a big part of the integration was making sure that our key stakeholders understood the benefits of us becoming a fully integrated part of Sandvik. It takes time for people to adjust to change, and they need to know what is happening throughout the process. We have worked hard to communicate the changes to all our key
stakeholders including our customers and employees,” he said.
The company has changed the branding of all its Australian facilities, motor vehicles, and the work clothes that its people wear on the job every day.
The Sandvik Rock Processing Solutions website and other marketing collateral have also changed to showcase its new product offerings and brand.
According to Newfield these were the final steps in the integration process.
“Our new offering along with the advances that our combined R&D teams are making, allow us to partner with our customers to address our industry’s biggest challenge - making mineral processing more ecoefficient,” he said.•
Selected to increase your efficiency and reduce downtimeIf it’s above, around or below the belt, we have the answer.
Lippmann 300c and 400c. These mobile cone crusher plants were specifically designed to take on the most abrasive and toughest materials in aggregates and mining — all with mobile capabilities. Heavy duty cone crushers with an innovative material flow that maximizes capacity and throughput while delivering a consistently high quality product.
• MC400 High Speed Cone Crusher
• CAT C18 Engine
• Direct Drive
• 250mm Feed Opening
T: 1300 859 885 E: sales@triconequipment.com.au www.triconequipment.com.au
Effective and efficient.
The MDS M515 Heavy Duty Trommel excels at crafting rip rap and reclaiming rocks entangled with clay and other adhesive materials. Comes complete with fold out stockpiling conveyors and has four hydraulic jacking legs to raise the machine to increase stockpile capacities and lower for transportation. See triconequipment.com.au or call 1300 859 885
Superior’s Telestacker® Conveyor is a material handler’s most effective weapon against costly stockpile segregation. Its variable height, length, and axle positions allow for layered stockpile construction, which is key to achieving partially and fully desegregated piles. The design has been carefully fine-tuned for hard work and dependability in numerous applications.
Call Tricon on 1300 859 885 or see triconequipment.com.au
It is critical to match a jaw liner to the right crushing application.
Superior Industries looks at the key tips for doing so successfully.
Matching a jaw liner to the crushing application is a crucial factor behind achieving maximum liner wear life.
Achieving a correct combination can allow quarries to increase the uptime on their crushing application, which bolsters productivity.
Superior Industries crushing product manager Jarrod Adcock assists aggregate producers with overall plant productivity in his role as a member of the company’s product management team. This process begins with well-designed primary circuits and ongoing assistance with aftermarket wear parts.
Adcock shares a few facts that Quarry readers need to know to select a liner with the ideal characteristics to suit their feed material and the product size they desire.
“Having the correct liner profile will boost cost-efficiency,” he said.
Constructed of manganese steel (or other alloys), jaw liners form a protective layer to the inside of the crushing chamber, preventing excessive wear to the crusher body caused by the material being processed. The given feed material type
will dictate the optimum percentages of manganese required.
Adcock said that some operations might equate higher manganese content with longer liner life.
“(However) if their material is not hard enough to ‘work harden’ the liners – they could simply be throwing money away,” he said.
“Superior’s application engineers help producers pinpoint the manganese percentage they need – as an operation may be able to access a lower manganese content and be far more cost-efficient.”
Adcock said that while a standard liner may cover many applications, it’s important to consider the variety of application-specific liners available.
“Superior offers five different liner configurations – from a standard flat tooth liner to a wavy sharp tooth liner, and also a corrugated, bellied-filled, or anti-slab liner,” he said.
Adcock explained that the anti-slab liner is engineered for concrete recycle or slabby laminated material applications for example. Its uneven tooth height generates less Superior offers five different liner configurations.
“slabby” product from the flat slab of material that enters the jaw.
The protruding teeth or ridges of the anti-slab liner help to initially break up the material. In comparison, a standard flat tooth liner that will chew up that material longer before reducing it to a size that passes the closed-side setting.
For rounded or slippery-type rock, a sharp tooth liner may be the best choice. It offers moderate spacing between each tooth to really grab the rock and help pull it down through the machine. Alternatively, the tooth height and spacing on the corrugated liner is designed for all-purpose applications such as shot rock and gravel.
For applications with varying feed gradations (like portable crushing), a bellied and filled-ends liner, helps to maintain a high position of crushing while providing maximum liner life in these variable feed applications.
An industry rule of thumb on proper liner usage is defined as wearing the jaw liner surface evenly along the length of the liner and utilising 50 per cent to 55 per cent of the original liner weight.
to change out a set of liners, one of them is the tooth height. During maintenance, measure the distance between the teeth’s peaks and valleys. If the distance is less than 10mm, the liners should be replaced.
Adcock said that if liner replacement is delayed, crushing operations lose the advantages of the liner design. Both tooth height and corrugation are required to properly crush the material as the configuration provides voids for material to fall into.
When that corrugation wears away, there is a lot more force that gets generated down
Quarry finds out how a local quarry was able to supply 170,000 tonnes of highly technical materials for the Newcastle Airport upgrade project.
Downer EDI Works had been tasked with upgrading the Newcastle Airport’s runway, a “game-changing” project that aims to directly connect the Hunter and northern NSW regions to the rest of the world.
The project was designed to make the airport’s runway eligible for Code E status, which allows it to accommodate long-range, wide-bodied aircraft.
To support these larger planes landing and taking off all day, every day, Downer required 170,000 tonnes of highly specific asphalt aggregates.
Hunter Quarries, a local quarry that specialises in road base and asphalt aggregates, was tasked with supplying it.
Hunter Quarries general manager, Dylan Nagle told Quarry the asphalt aggregates needed to meet GHD airport runway specifications. The materials supplied included Barmac Manufactured Sand (BMS) as well as premium asphalt aggregates in 7mm, 10mm, 14mm, and 20mm sizing to fulfill the project’s AC14 and AC20 mix design requirements.
To deliver this material, the company needed to mobilise a previously moth-balled plant within just one month.
“We operate two quarries that are side by side,” he said. “One of these quarries was operational on an as-needed basis if the main quarry didn’t have the capacity.”
“That quarry’s lifespan was coming to an end, and we were focusing on the newer quarry for day-to-day operations.
“Because of the amount of aggregate required for the airport project, and due to how specific the technical requirements were, we felt the best way to support the client was to dedicate the entire quarry to that project.”
Significant electrical and structural enhancements were made to increase plant capacity, ensuring efficiency in production and delivery. Despite the short lead time, Hunter Quarries managed to mobilise its workforce
promptly to guarantee the on-time delivery of all products meeting project specifications.
The technical team set an extensive testing regime in a short period of time, to ensure adherence to the site specifications.
“Our technical team were very busy running tests on the material. Changing the screens on a plant, takes a good two to three hours per change, but it’s important to make sure you’re providing the right material.
“Leveraging the synergies within the Hunter Construction Group, our materials underwent
“Our technical team also learned about new testing methods and the benefits of ongoing communications with the client.”
Hunter Quarries and Downer scheduled weekly meetings to ensure that any issues were quickly identified and relayed. The enhanced communication helped build a strong connection between the two businesses and allowed all stakeholders to plan around any delays.
The previous runway measured 3500m by 45m, and Downer’s team integrated 7.5m
2/6
limited, and are often the ideal solution for processing difficult materials such as clays. Due to its design and open passage system, which allows all fines to pass very quickly, sizers can be very compact but still achieve very high capacities.
• Low specific energy demand
• High to very high throughput rate
• Intelligent design
• Simple maintenance
• Wide range of crushing tools
• Cubicle product with minimal fines
• Trouble-free operation with sticky and moist materials
• Also applicable for adhesive feed material
Examining the recent IQA member event at Lynwood Quarry and the demonstrations that took place.
When Craig ‘Shine’ Summerfield organised the latest event for the IQA’s Southern NSW Region SubBranch, he wanted to showcase new insights and an innovative product.
The answer was the XMOR Bucket from Australian-owned and operated manufacturer ONTRAC Group, which he heard was drawing some strong reviews from Holcim’s Lynwood Quarry and other quarries abroad.
Some of the industry’s best and brightest gathered at Holcim’s Lynwood Quarry to witness an exclusive demonstration of the XMOR Bucket from ONTRAC Group. One
XMOR Bucket was live for observation from the pit viewing platform and another XMOR Bucket was on display on a flatbed truck.
In the evening, the IQA members gathered for a dinner and presentation from ONTRAC product specialist Nick Espie about the history, unique design and potential savings the XMOR Bucket could deliver to their quarries.
Quarry spoke to Summerfield, the IQA Southern NSW Region Sub-Branch chairperson, about the event, which saw 50plus industry figures in attendance.
The event took place just prior to Australian Made Week, which celebrates local manufacturers. Summerfield told Quarry the connection with ONTRAC was a “no-brainer”.
“It’d be so cool to do everything domestically if you could, and it is just a bit of a no-brainer if you can see these locals innovate for our own industries and export it,” he said.
The XMOR Bucket is one of ONTRAC’s best-selling products. The licensed design is manufactured in Australia and features Hardox 500 Tuf wear plates and Strenx 700 structural steel to make it bigger yet lighter than standard attachments. Unlike traditionally made buckets, some of the XMOR Bucket’s wear parts are bolted on rather than welded, which enables maintenance to be performed in hours rather than days.
The unique keel design further reduces weight and enables more structural stability. The inverted shape of the keel helps minimise ground contact and wear on the
bottom of the bucket, which saves customers time on maintenance and repairs.
Summerfield said the XMOR Bucket was one of the more innovative products he’d seen in his time in the industry.
“With buckets, in the quarry industry, for example, there hasn’t been a lot of change for a lot of years. You might get double radius curves on the back of buckets to avoid drag or you might get different wear packages or steel wear components.
“This XMOR Bucket has been quite a large shift in design, like it is totally out there. The XMOR is totally at the forefront of innovation.
“It looks totally different, we refer to it as the ‘bum bucket’ with how it looks from behind.”
The attraction of the XMOR Bucket saw the event attended by quarry operators and civil construction workers, given its versatility across different sectors.
“To draw them to the event, if you’ve got something different, innovative and practical that they are going to use in the industry, that is a sweetener on the hook,” Summerfield said.
“The bucket was able to bring in civil construction people as well, not just quarry people, because that bucket is multidimensional across different groups.
“Networking is important in any industry, (at) the IQA, we seem to enjoy that. It is about saying ‘this works really good’, from an industry perspective, we’re here to help each other along as well.”
The XMOR Bucket’s bigger size, combined with its unique design, has led some quarry operators to report they shaved one to two, sometimes three passes, off their truck
loading. Other operators have reported to ONTRAC that the XMOR Bucket is wearing very well despite being used daily in a hard rock environment.
ONTRAC Group manufactures a wide range of bucket variations for 45-tonneclass excavators and above. Each bucket is carefully suited to the application.
Nearby Lynwood Quarry is Hy-Tec’s Penrose sand quarry, which purchased a premium bucket from the ONTRAC Group. Summerfield, who works as an application engineer for Komatsu, said the premium bucket from ONTRAC had performed well attached to the site’s Komatsu PC450.
“It’s the wear factor and the wear components because the (ONTRAC premium bucket) is a similar size in volume, but you’re saving money in downtime because of the wear in that application,” he said.
“ONTRAC has other solutions (for quarries), and the XMOR is probably one of their more innovative solutions. (Whereas) the premium standard bucket looks like a normal bucket, but it has that nice steel in it.”
ONTRAC’s warehouse stocks a full range of wear and spare parts for all its buckets. The company can conduct a complete excavator loadout productivity study for interested quarries that considers production levels, machinery, environment, and similar sites’ achievements. •
For more information, visit ontracgroup.com.au
Komatsu’s new WA475-10 wheel loader is set to tackle a common pain point by delivering greater fuel efficiency for Australian quarry operators.
Komatsu has introduced the WA475-10, 26-tonne wheel loader to Australian shores with the aim of addressing a common pain point for quarry operators.
Fuel costs are one of the largest cost drivers for quarry operators and their machinery, especially in the Australian market.
The WA475-10 is up to 30 per cent more fuel efficient than the previous model and is designed for any hauling or loading jobs. It possesses a combination of fuel efficiency, productivity and ease of handling for operators.
The company says the versatile machine combines power with Komatsu’s cuttingedge loader technology to provide an efficient and productive model for quarry sites.
Komatsu Australia’s national business manager Nick Vrontas said the WA47510’s overall upgrades make it an appealing addition to quarry fleets.
“The WA475-10 features Komatsu’s Hydraulic Mechanical Transmission (KHMT), which is a newly developed and innovative solution that makes the loader more powerful and more fuel-efficient,” he told Quarry.
“Variable speed control allows operators to adjust the machine’s top speed to meet specific site requirements, and the adjustable variable traction control also limits wheel spin on unstable and slippery ground conditions often found on quarry sites.
“We’ve also completely innovated the power control on this latest model. It’s never been easier for an operator to find the right balance between traction and lifting power, with the
hydraulic speed independently controlled from the accelerator pedal, and the boom speed controlled by the hydraulic lever.”
Due to the optimised Z-bar linkage system on the WA475-10, operators can achieve a higher lift force and higher tonnes-perhour production rate compared to previous models. The hydraulics’ response time and the dumping or lifting can be set to specific quarry site requirements.
Komatsu has developed a reputation as a leading manufacturer of technologies, equipment, and services for the construction, mining, and heavy industries including quarrying.
Frontline industries in Australia and worldwide use Komatsu solutions to develop modern infrastructure, extract fundamental minerals, maintain forests, and create
customer operations, focusing on enhancing safety and productivity while boosting worksite performance.
Dirt & Turf Expo at Sydney Dragway earlier this year. At one of Australia’s largest construction exhibitions, attendees were able
to cast their eyes over the newest addition to Komatsu’s wheel loader line-up. After the event, the new wheel loader received plenty of positive reviews from attendees about its shovel and design.
Vrontas said the WA475-10 wheel loader would be a flagship model in the Komatsu line-up for the Australian market.
“The WA475-10 engine is Tier 4 compliant, and at even low engine speeds, the engine puts out high power and delivers more engine torque and performance,” he said.
“The engine’s advanced electronic control system manages the airflow rate and the fuel injection, combustion parameters and after-treatment functions, which provide optimised performance, reduced emissions, and advanced diagnostic capabilities, making it a powerful, yet environmentally friendly machine.
“The loader can also be tailored for specific applications, whether that is the demanding nature of a waste site, or the abrasive environments of quarries. The Komatsu team will work with customers to provide a solution that is tailored the loader’s application, from enquiry to post-delivery, maintaining service checks and requirements.
“We’re beyond excited to have the loader on our shores, and we’re looking forward to introducing it to many quarry sites across the country.”•
For more information, see komatsu.com.au
Emma Ford, John Deere director of aftermarket and customer support for Australia and New Zealand, writes about the company’s commitment to remanufacturing and its environmental benefits.
By 2030, there will be nine billion people on earth who will need to be fed, clothed and housed.
John Deere believes it has a critical role to play in helping achieve this in the most sustainable way.
Global Reman Day is an initiative of the Remanufacturing Industries Council to help advance the remanufacturing industry. It’s an opportunity to reflect on how remanufacturing creates positive environmental impacts across various industries from agriculture to aviation to medical equipment.
The company is focused on supporting its customers to do ‘more with less’ by providing solutions like remanufactured parts that reduce environmental impacts and input expenses – both of which are important markers of a sustainable industry that can rise to meet the needs of the future.
For example, not needing to make a new engine or axle from scratch means natural resources are preserved, melting furnaces aren’t fired up, and carbon footprints are smaller.
Nearly 12.5 million kilograms of material was recycled through John Deere Reman in 2022, and its remanufacturing is on track to grow 50 per cent by 2030 in line with the company’s Sustainability Strategy, outlined in the 2022 Sustainability Report.
As input costs and the global population continue to rise, Reman is about much more than just replacing an engine.
But how does ‘remanufacturing’ relate to other terms like refurbishing, reconditioning and rebuilding?
The definition of ‘Reman’ can be unclear, so John Deere is using this Reman Day to clarify exactly what it means, how it works, and how it benefits customers and the environment.
‘Remanufactured’ is not the same as ‘rebuilt’ or ‘repaired’. A rebuilt part is disassembled only to the point of failure, and rebuilt using the same, new or aftermarket part. When a component is repaired, only the defective parts are examined and replaced.
The remanufacturing process is much more involved. It’s not just about restoring functionality, but returning previously used, worn, or damaged parts back to likenew condition.
John Deere completely disassemble the product, thoroughly cleans and inspects each part for wear or damage, replaces where necessary and reassembles the product using the same processes to produce new components.
A ‘core’ is a used or worn-out part that is returned to a John Deere core collection facility. There, it is completely disassembled and thoroughly cleaned by either a bake or chemical cleaning process.
All parts are dimensionally verified against the latest John Deere parts specifications, and any part not meeting original factory specifications is either recycled or brought back to specification.
All wear-type parts such as pistons, liners, bushings, bearings, gaskets and O-rings are
replaced 100 per cent of the time with new John Deere parts.
The product is assembled by highly-trained technicians to exact criteria. Finally, each product must pass a thorough inspection and testing process to ensure it meets or exceeds specifications, meaning it can be offered with a full warranty.
Unlike any other remanufactured products, John Deere Reman only uses parts that are completely aligned with John Deere design and dimensions. In other words, it doesn’t use any aftermarket or “might-fit” parts.
On top of engines and engine components, John Deere dealers offer Reman parts including transmissions, fuel injection systems, electrical components, hydraulics and generators.
As well as offering customers the option of like-new parts for 30 to 40 per cent less than the cost of brand new parts, remanufacturing is also an integral part of its mission to help farmers sustainably support and feed communities as the global population grows. • For more information, visit deere.com.au
Eltirus founder Steve Franklin examines why are smooth roads so important and, in many cases, so overlooked.
As a young shift supervisor in the mining industry, one of my most important functions was to ensure the loading tool operators were “digging to grade”. By this was meant that rather than “digging to hard” i.e. to the bottom of the blast, we used laser levels to ensure that the operators dug to “design floor” or “grade”.
This matter was not taken lightly. Many of the mining contracts that we worked to had extremely strict tolerances for floor levels and adherence to them was non-negotiable. At the time I used to think that this was “over the top” but with a few more years (and some more experience) under my belt I began to realise that it was a vital discipline and one that was needed not only to reduce the incidence of being yelled at (in the bad old days of “it’s my way or the highway”), but was in reality, just sound operational practice.
WHY IS IT IMPORTANT?
The simplicity is this: Smooth roads do make more loads. A smooth level floor enables higher truck travel speed across the floor and with it less wear and tear on both truck and operator.
It also makes it much easier to drill and blast the next shot, as a constant bench height can help ensure more even breakage of material towards the top of the bench because of consistent blast pattern geometry. Lastly, it also ensures that loading tool operators (particularly face loader operators) are not subjected to the stress and impact of digging “toe”. Unless you have been on a large wheel loader digging out of a face or on a dozer ripping rock, you really can’t comprehend just how uncomfortable it is to go from full throttle in first gear to a complete stop instantly – it is very hard on your body.
WHY
Firstly, let’s look at the blasting process. When a blast pattern is designed, one of the key parameters to consider is the sub-drill depth. That is, the depth below the design floor level. So, if for example the correct design level for the bench is 100mRL, the drill and blast designer will always design the holes to go deeper than this level to ensure that there is additional depth to cover any fall back of material into the hole and also to ensure that when the blast is fired, that
all the material below the design level is completely broken. Realise that the subdrill needs to be enough to ensure that consistent breakage, but not so much that it breaks too much material on the next bench which would be wasteful from a cost perspective but will also make it harder for the driller to get through next time.
My training as a drill and blast supervisor (in addition to shift supervisor) was such that we always worked to ensure good breakage in the subdrill zone through taking care to drill holes to the correct depth, dip them and correct them as needed. Likewise, as a shift supervisor, I was rigorous in ensuring that we didn’t dig below the design RL.
When I moved into the quarry industry, I was very surprised to find out that these concepts were not universally practiced. I famously remember working on a site where there was a tremendous moaning about “toe” and continual complaints about the blasting contractor. Out of curiosity, I went across the bench with a laser level and found that every single instance of “toe” was below the design RL. In essence, the drill and blast contractor had done their job and was falsely maligned.
In this instance, the blame fell entirely on the loading tool operator who consistently dug out the sub-drill zone. By way of example, take a look at the bench cross section shown in Figure 2. In this example you can see that while much of the material in the sub-drill zone has been broken (and indeed loaded out) there is an area of what many operators would call “toe” on this floor. The reality however is that in the example shown, the “toe” is actually below the design floor level and if the operator was digging to grade, it would not have been hit.
In most quarries, operators dig to level as best they can. This inevitably means that they either dig too deep (into the sub-drill zone) and experience “toe” or they leave anything from 0.5-1.5m of blasted material on the bench (which means you are paying your drill and blast contractor to shoot the same material twice). Where the sub-drill zone is dug out, the site generally compensates for the poor floor condition by bringing dust back into the quarry to level up the floor, resulting in a better running surface, but also in the drill and blast contractor being paid to blast the volume of the backfill on each bench. I did some rough back of envelope calculations on a quarry moving one mtpa and a bench height of 12 metres. Just leaving half a metre of material above design floor level means that you would be paying your
drill and blast contractor to shoot some fifteen thousand additional cubic meters of material a year – what does that cost your site?
The key to resolving this issue is two-fold. First, you must have an appropriate quarry design and your drill and blast contractor must be drilling to the design RL’s and with sufficient depth of sub-drill.
Take the time to make sure that you have a good quarry design that is realistic, takes into account the site geological and geotechnical structures and has been created by a competent, qualified, Chartered Professional mining engineer. Note that in Queensland, any engineering work must be conducted (or closely supervised) by a Registered Professional Engineer of Queensland (RPEQ) and that this also goes for work that a Queensland based company does for a quarry in another state. A draftsperson with a CAD licence might seem like a cost-effective way to create your pit design, but it should be realised that that person (in Queensland and increasingly other states) is committing an offence and is liable for prosecution. If there is any doubt about whether the person you have engaged to work for you (if Queensland based) is appropriately qualified, take the time to check the RPEQ directory online. In other states, at the very least, you should expect the person to be a Chartered Professional mining engineer.
Likewise, select a drill and blast contractor who can take the pit designs and create blast designs in accordance with them. It is of no use whatsoever having a good pit design if the drill and blast contractor cannot accurately blast to it. The days of just throwing a tape over the face or shooting to the level of the floor in front of the face are past. A reputable, competent drill and blast contractor can shoot to design, will run GPS equipped rigs and give you the confidence that they won’t inadvertently blow out berms and ramps in the process. This may appear to cost more in the short term but will save you a lot of heartache in the long run.
Secondly, you must have a way of indicating to the operator whether they are digging to grade or not.
There are several ways that this can be achieved, from the simple (using a laser level) to the more complicated (and expensive) which is to use 3D machine guidance systems. While 3D machine guidance is extremely common in the civil construction and mining industries, it is much less common in the construction materials space. Part of this is due to expense ($50-100k), part due to unfamiliarity on behalf of quarry operators and also as a result of a lack of understanding by the suppliers of what it takes to implement such a system in our industry.
Having been involved with the implementation of 3D machine guidance on face loaders, large excavators and dozers, I can tell you that it is worth the cost.
If you don’t think this is the case, do a quick exercise to determine what it costs to re-blast the material that is left on each bench blast to blast, but also more importantly, take the time to think through the impact (no pun intended) on your face loader operator who hits an unexpected piece of toe (through digging too deep) and damages their back.
Whether you go simple with a laser level, use a GPS rover for bench checks or go the whole hog and implement 3D machine guidance, there are solutions to this issue.
As a side note, we have seen some tremendous low-cost GPS rovers (approx. $4k) come on the market recently and trials have shown them to be an excellent fit in the quarry space. If 3D machine guidance is a bridge too far, take the time to explore the GPS rover route and regular supervisor checks of bench level.
You might be aware that to get high accuracy (± 2cm) you need not just a GPS receiver and a view of the sky, you also need a correction service, either by 4G/5G (NTRIP correction over the internet) or from a base station on site (via radio signal).
We generally favour NTRIP solutions and when combined with the free AUSCORS
NTRIP service, part of the National Positioning Infrastructure Capability (NPIC) network, these can supplement or replace commercial services costing thousands of dollars a year. In essence, if you have mobile data coverage, you can have a free correction service and achieve high GPS accuracy. If you would like to know more about this subject or have any questions, please feel free to reach out to me and I will be only too glad to give you a briefing on the concept and pass on some of our learnings to you.
As an aside, if Microsoft Copilot is to be believed, American journalist, Doug Larson is responsible for the quote “smooth roads make more loads’ and apparently was not originally intended for the extractive industries•
For more information, email steve.franklin@eltirus.com
Delta Rent operates one of the largest earthmoving equipment rental fleets of more than 450 high performance machines in Australia.
We understand that production is key for quarry owners and operators. In particular, the importance of high optimisation rates for the heavy plant and machines required to process raw materials and meet demand.
24/7 service Australia wide
Our late model, low hour and meticulously maintained fleet – combined with expert 24/7 advice and analysis from an experienced and professional sales team – ensures our clients maximise production output without compromising quality, safety or environmental performance standards. Expert advice and analysisPurpose built fleets tailored
The IQA’s national conference for the quarrying industry is set for Adelaide. Quarry sits down with James Rowe to see what’s in store.
The quarrying industry will descend upon Adelaide later this year as the City of Churches hosts the Institute of Quarrying Australia’s national conference.
The major industry event will take place from October 15-17 at the Adelaide Convention Centre with a jam-packed, threeday calendar prepared for attendees.
With a theme of “Create and Innovate”, the conference will celebrate the best achievements and quarrying’s role in contributing to sustainability and netzero goals.
Quarry sat down with the IQA’s National Conference chairperson, James Rowe, to discuss the conference and its importance for the sector.
HOW ARE YOU FEELING AHEAD OF THE IQA CONFERENCE IN ADELAIDE LATER THIS YEAR?
Excited! The IQA Conference, I feel is the best opportunity we get as an industry to come together. The IQA Conference Committee has pulled together an interesting program featuring technological advancements, regulatory insights, technical presentations, and a social program which I am sure will exceed all other conferences.
WHY ARE THESE EVENTS IMPORTANT FOR THE QUARRYING INDUSTRY?
The IQA Conference is a platform for all of us within the Essential Construction Materials Industry to meet, collaborate, learn and understand the latest advancements
and trends that are leading and challenging our sector.
Personally, I have been lucky enough to attend several IQA National Conferences over the years. They are a great way to catch up with old friends and meet new friends in the industry while staying on the cutting edge of technology and trends that affect our sector.
CAN YOU TALK TO US ABOUT THE THEME OF THIS YEAR’S EVENT, INNOVATE AND CREATE?
When we met as a National Conference Committee, a few different themes were discussed; however, Innovate and Create was a premier selection. ‘Innovate’ is based upon the sector’s continual learnings regarding advancements in operational applications such as crushing and screening, drill and blast, and the development of innovative and sustainable Heavy Mobile Equipment (HME) together with regulation, rehabilitation, and end-use innovations.
The above examples ‘Create’ opportunities for sharing knowledge as a sector, differing employment opportunities for our up-andcoming quarry people, and discussing challenges that our industry faces from a regulatory perspective.
WHAT CAN ATTENDEES EXPECT TO SEE AT THE CONFERENCE THIS YEAR?
This year, we kick off with a site tour of the historic Boral Stonyfell Quarry. The site hosts Private Mine (SA Tenement) 1, that being it was the first Private Mine to be granted within
the state. Most of you would fly into Adelaide overlooking the site. The quarry is iconic as a majority of the raw materials extracted from this quarry in the early days created what is the Adelaide CBD today.
We will undertake a site tour, enjoy lunch, and overlook the awesome views over the CBD of Adelaide. The first evening, we will enjoy the first of three social events with Platinum Partner Hitachi, hosting us at the National Wine Centre. It is a great event and an opportunity to catch up with old friends in a relaxed atmosphere.
On day two, we are grateful to the South Australian Energy and Mining and Infrastructure and Transport Minister Tom Koutsantounis, for giving the Official Opening of the Conference speech together with an industry outlook.
This opening is followed by Claire Madden, one of our Keynote Speakers, delivering an informative presentation relating to the future of work and innovations for attracting people into the workforce. We have several awards to present prior to heading into a Technical Session later in the morning with a blend of presentations on drill and blast (Orica), digital transformation (Eltirus), Kayasand (Concrete Sand Supply) and CJD Equipment.
For the first time, we have a National Regulatory Panel. This is a great platform to hear from our regulators from Queensland, NT, SA, NSW, and Victoria about some of the challenges we face as an industry and the innovations they are taking to streamline our approval processes.
The discussion will also include the interface between extraction and recycling and how this is being managed in each jurisdiction. We then will have our Industry Leaders Panel, which will be well represented with CEOs, COOs, and GMs from the major and independent quarry business leaders collaborating on topics such as technology advancements, sustainability, supply chain optimisation, and addressing challenges as we see them today.
We will then hear from the Institute of Quarrying UK (IQUK)) on advancements within the IQUK before Scott Tipping provides us with insight into useful leadership steps.
The evening will flow into Platinum Partner Komatsu, showing their blue and white extravaganza at the renowned Adelaide Oval. Komatsu always goes ‘all out’ on social functions, and yet again, it will be a great networking opportunity.
On day three, we will kick off with Stefan Hajkowicz discussing global megatrends that may have an influence on our sector, followed by the International Presidents Panel. We are lucky to have representatives from the UK, South Africa, NZ, Hong Kong and South Africa in attendance, and this will be a great opportunity to learn what is driving quarrying in their given countries.
Late in the morning, we will have another round of technical sessions followed by innovative presentations by our Platinum Partners in Caterpillar, Komatsu, and Hitachi. We will have an industry legends panel followed by what is promised to be another great Caterpillar Gala Dinner. We know planning is well underway for this finale and are looking forward to seeing delegates’ reactions
to what is planned for this evening. After the CAT dinner, if you need more, we even have an after-party at the Strathmore Hotel.
Throughout the conference, there are a range of fantastic awards on offer, from operational awards to environmental excellence, safety, community engagement, and leadership. Our sponsors have been very generous with the awards provided, and we encourage any person within the industry to consider applying for the awards for themselves, a colleague, or for what they have achieved as a business at their site.
The last IQA National Conference was held in Adelaide in 2015. As a state and on behalf of the SA IQA Branch Committee and the National Conference Committee, we are really excited to showcase South Australia and what we have achieved as an industry over the past nine years since the last conference.
Our social program looks amazing and together with the conference program, we anticipate delegates will head home satisfied with increased technical knowledge and networking opportunities that will present. We also have insight into the Orica Partners Program, which sounds fantastic, so I encourage all delegates to bring their partners along and enjoy what we have on offer.
The quarrying industry is a special sector that largely depends on volunteers to run our branches and sub-branches. I would like to take the opportunity to thank all of our conference committee for your dedication in pulling together an awesome event, along with our IQA staff, who have been instrumental in delivering this conference. Again, to our sponsors, we thank you for your ongoing support of our industry and the provision of funds to make this conference realise its potential. Lastly, on behalf of the committee, to the companies that invest in their people to attend the IQA National Conference and grow their knowledge, thank you for investing in your people.•
For more information, visit iqa.eventsair. com/2024iqaconference
SNSWR sub-branch members were treated to presentations on two XMOR buckets.
SOUTHERN NSW REGION SUB-BRANCH SITE VISIT
The SNSWR sub-branch event of the year took attendees to the state’s Southern Highlands/Tablelands region, with Holcim
Lynwood quarry hosting IQA members and guests for a site visit. The event was sponsored by the ONTRAC Group. During the visit to Lynwood, attendees witnessed an XMOR BHC in action on a 976
excavator, loading HD785 dump trucks. A static XMOR BHB bucket was also on display at the pit-viewing platform, allowing all to examine this unique bucket design up close. ONTRAC Group’s Nick Espie explained key
Plant and equipment safety: Conveyors webinar Thursday July 11 12.00pm – 1.00pm (AEST) Online
North Queensland 2024 safety and health conference and networking sundowner Friday July 12 10.00am – 5.00pm (AEST) Mercure Townsville, 166–194 Woolcock Street, Currajong, Qld 4812
Queensland effective leadership for senior managers workshop Tuesday July 16 8.30am – 5.00pm (AEST) Wagners, 1511 Toowoomba Cecil Plains Road, Wellcamp, Qld 4350
Plant and equipment safety: Maintenance webinar Friday July 19 1.00pm – 2.00pm (AEST) Online
NSW southern region learning from disasters workshop Tuesday July 23 8.00am – 4.00pm (AEST)
Boral Peppertree Quarry, 843 Marulan South Road, Marulan, NSW 2579
NSW quarry materials production and quality management workshop Thursday July 25 8.30am – 4.00pm (AEST) Holcim Quarry Teven, 129 Stokers Lane, Teven, NSW 2478
Southern NSW sub-branch Christmas in July 2024 Saturday July 26
6.00pm (for 6.30pm start) – 9.30pm Mittagong RSL Club, corner Hume Highway and Bessemer Street, Mittagong, NSW 2575
Managing performance and behaviour Wednesday July 319.00am – 5.00pm Online
differences between the two models and shared practical findings since they have been on the market.
At the dinner meeting later that evening, Espie took the spotlight to delve deeper into these ground engagement attachments.
By comparing the older 976 bucket to the installed 6.6m3 XMOR, he highlighted significant improvements in production and loading times.
The ONTRAC Group’s offerings were thoroughly discussed, with a focus on the XMOR BHB and BHC buckets. Key points included their origin, history, science and design, to name a few, emphasising the use of high-quality, wear-resistant steel to increase payload without compromising the original equipment manufacturer (OEM) loading tool. Espie emphasised that contemplating an XMOR is not a one-size-fits-all rule; ONTRAC takes the time to understand the site and operational dynamics to get a suitable solution. The buckets are well worth a look.
Thank you to all members and guests in attendance, and to Holcim Lynwood and to the ONTRAC Group for their sponsorship and for showcasing innovative solutions.
VICTORIAN BRANCH YOUNG MEMBER NETWORK EVENT
The Victorian branch Young Member Network (YMN) event, held on Friday May 3, kicked
off at Lendlease, where senior development manager Samantha Wright presented the Aurora development.
Wright discussed the challenges faced by large infrastructure developments, including juggling multiple contractors on-site, environmental and community pressures, exporting excavation rock (excavation and cartage challenges), and importing construction materials (cartage and supply chain challenges).
Later in the day there was a lunch stop and networking opportunity at Republic Tavern, followed by a visit to Aurora Construction Materials, which was divided into two sections – the recycling fixed plant tour and the batching plant tour.
Attendees were guided around the recycling plant and presented with a discussion on general site challenges – staff, maintenance, weather, production, etc. This was followed by a walk-through of the large fixed plant before moving to the batching plant with information on how the operation works, as well as discussions regarding the challenges of using recycled materials in concrete batches and challenges around truck loading and water usage.
The event was a wonderful opportunity for education, networking, and professional development for all that attended.•
powered by
Quarry looks at how a Welsh quarry played a critical role in preserving Britian’s sprawling art collection from the National Gallery during World War 2.
If a Canaletto or Van Gogh and Rembrandt had walked into Wales’ New Manod Quarry, they would be horribly lost.
Yet, the slate quarry, also known as Bwlchy-Slaters Quarry, was key to preserving the National Gallery’s art collection during World War II, as Britain feared losing it to an invasion.
The National Gallery director at the time, Kenneth Clark, reportedly considered Canada as a safe haven only for the threat of German U-boat attacks to scuttle it. When he sought out Winston Churchill, the story goes, he was told in no uncertain terms that the National Gallery could “hide them in caves and cellars, but not one picture shall leave this island”.
Left with Churchill’s veto, everyone was scrambling for a safe place to harbour the National Gallery’s collection, albeit as safe as a place could be in wartime Britain in 1940.
New Manod Quarry, near the town of Blaenau Ffestiniog, was isolated and unused, which make for a terrible tourist attraction but a great place to hide art.Its 300-feet thick slate encasement was a bonus.
Paintings, including Canaletto’s The Stonemason’s Yard, were stored in New Manod Quarry. Recently, the National Library of Wales hosted an exhibition featuring The
Stonemason’s Yard which celebrated its time in the quarry.
“Working with the National Gallery on this exhibition to mark their 200th anniversary has been an incredible privilege. Being able to welcome Canaletto’s masterpiece back to Wales after having taken refuge here 80 years ago is tremendously exciting, and we cannot wait to share with the public this fascinating story,” National Library of Wales interpretation officer Mari Elin Jones said.
The National Gallery scientific adviser Francis Rawlins suggested the quarry, which had man-made chambers of 100 feet high due to its slate excavation, was suitable. Work began immediately to transform the quarry from a slate site to a pseudo-art house.
Squat brick “houses” were built inside the quarry to ensure the paintings were kept in air-conditioned and tempered conditions with room for conservation works. Entrances were widened and rail bridges altered to ensure the paintings, including Anthony van Dyck’s 11-foot-tall Equestrian Portrait of Charles I, could fit with work completed by 1941.
While the storage facility was a reaction to the immediate impact of war, it eventually had a major effect on art conservation.
Minna Moore-Ede, who curated the National Gallery exhibition Manod: The Nation’s Treasure Caves, explained the quarry’s set-up changed the National Gallery’s design to include air conditioning when it was remodelled following the war.
Martin Davies, the National Gallery’s chief curator, used the remoteness of Manod Quarry to produce new catalogues on the permanent collection.
“(Davies) did a lot of research because (the paintings) were so accessible,” she told the BBC. “He was a shy, quiet man who really relished the opportunity to have no public around.
“There was a small studio built outside the quarry where they did a lot of conservation work, it was actually a very formative time for the gallery.”
By 1945 the paintings were returned to the National Gallery in London. However, the quarry was maintained under government control until the 1980s.
Alfred McAlpine, the British construction company, eventually took it over after the government gave it up and began untopping the mountain to create a modern open-cut quarry which it operated until 2007. The operations from New Manod extended and combine with Old Manod Quarry so McAlpine renamed Cwt y Bugail Quarry.
Welsh Slate, part of the Breedon Group, took over the quarry which is still operating with the company lodging an application in 2022 to extend its life until 2048.
“Cwt y Bugail Quarry (also known as Graig Ddu or Manod Quarry) is a small quarry which produces high quality roofing slate and architectural slate products,” the company stated in 2022.
“The quarry produces a dark blue-grey with occasional white veins and unique riven texture.
“Whilst it is a small production unit, it is nonetheless an important supplier of Welsh slates to the market.”
Writer and explorer Will Millard, who was behind the BBC Wales series Hidden Wales, said attending the New Manod Quarry was left him in “awe”.
“I was in absolute awe of what had been achieved there in just six months, it is truly a testament to the ingenuity and determination Britain showed during the War,” he told the BBC.•