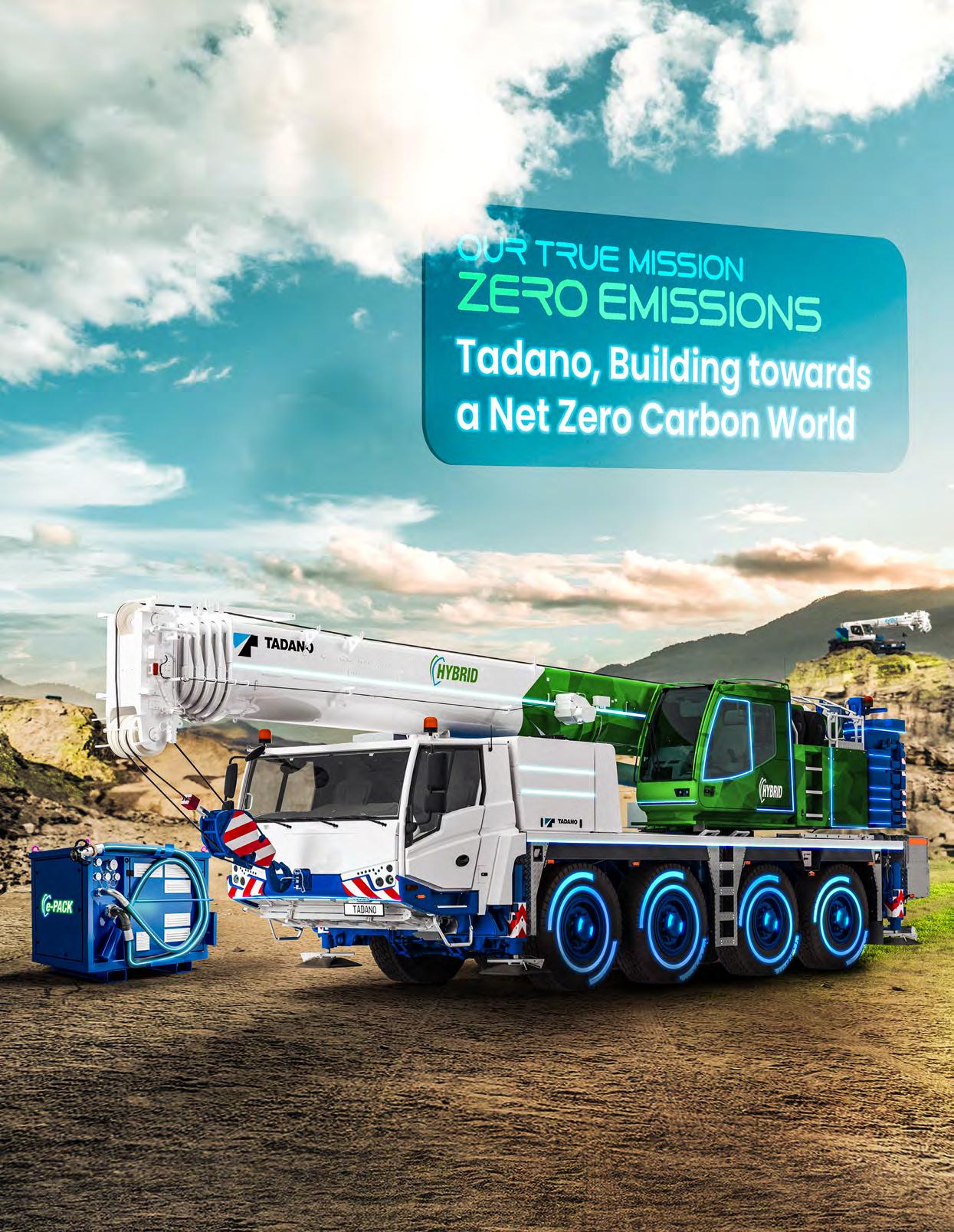

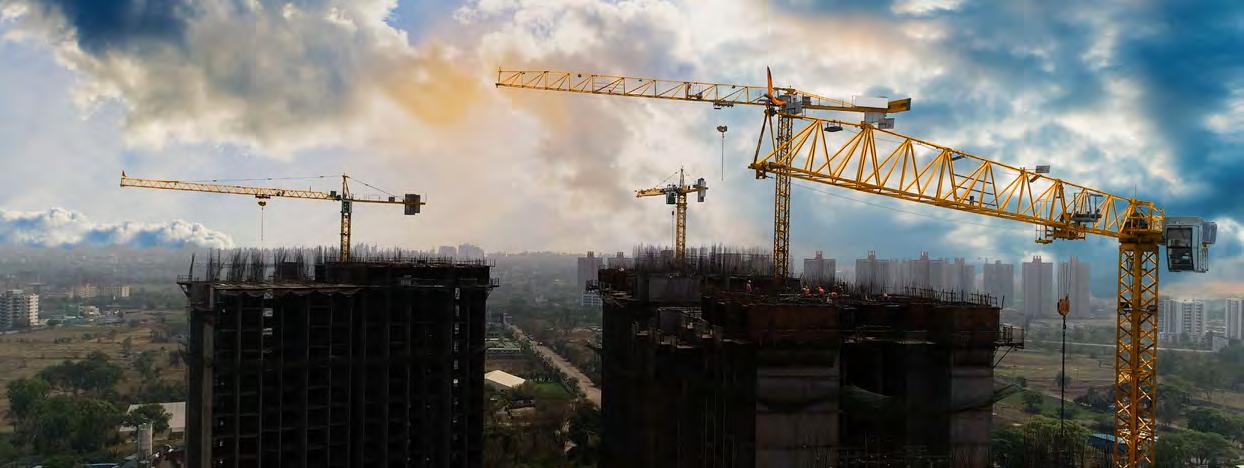

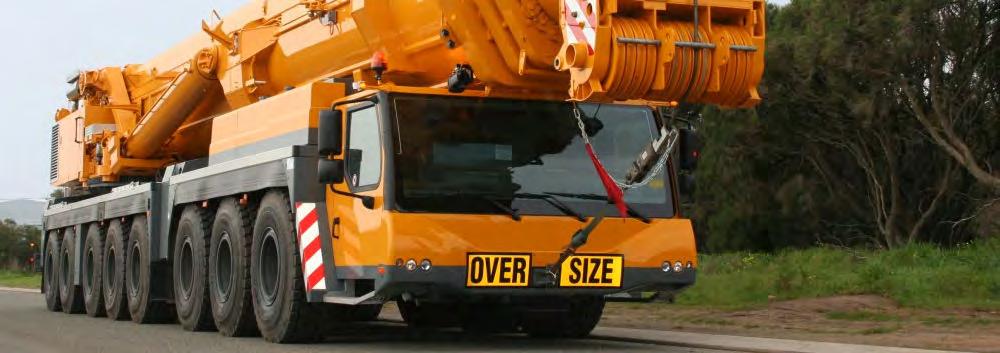
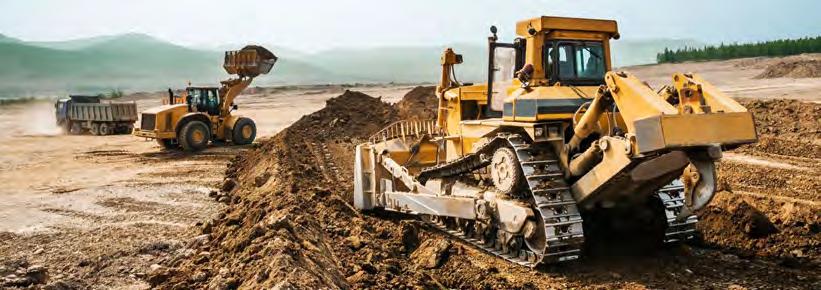
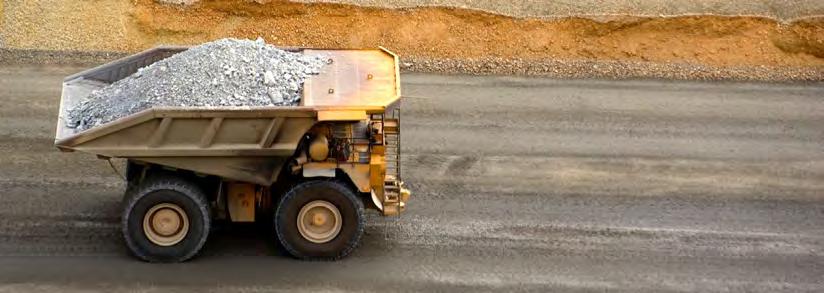
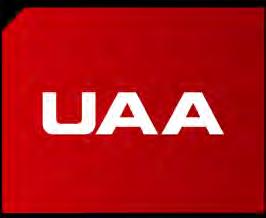

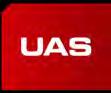
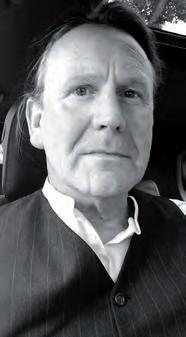
The Crane Industry Council of Australia’s (CICA’s) National Conference and Exhibition, we take a look at the South Australian crane sector in a special feature.
As the national economy continues to slow, the South Australian economy has continued to perform well, with unemployment reaching the lowest level in five decades. For the first time in its 14-year history, CommSec’s State of the States report ranked South Australia as the number one performing economy in the nation –twice in a row.
The state’s population has grown strongly (by 1.7 per cent in the year to September quarter 2023), particularly due to a strong recovery in net overseas migration and the return of international students. The labour market has performed even more strongly.
The pace of growth (in South Australia and nationally) has slowed, following rising interest rates, higher inflation and capacity constraints. Inflation has moderated but remains above target rates. Following two strong years of growth (3.4 per cent in 2022-23 and estimated growth of 2 per cent in 2023-24), employment growth is forecast to slow to 0.5 per cent in 2024-25, returning to longterm growth of 1 per cent per annum in 2026-27.
As always, this special issue of Cranes and Lifting coincides with CICA’s National Conference
and Exhibition and will be widely distributed and read during the event. We are delighted to bring you exclusive insights into new products that will be seen for the first time at the event, as well as updates on new models and the impact the ADRs are having on the industry.
The team at Cranes and Lifting has worked hard to bring you what we think is newsworthy and interesting content and we hope you enjoy the read.
Simon Gould Editor, Cranes and Lifting
Published by:
379 Docklands Drive, Docklands VIC 3008
T: 03 9690 8766
www.primecreativemedia.com.au
CEO
John Murphy
E: john.murphy@primecreative.com.au
Chief Operating Officer
Christine Clancy E: christine.clancy@primecreative.com.au
Managing Editor
Andrew Hobbs
E: andrew.hobbs@primecreative.com.au
Editor
Simon Gould
E: simon.gould@primecreative.com.au
T: 0404 865 109
Journalist
Jacob Lynch E: jacob.lynch@primecreative.com.au
Business Development Manager
Emily Schlegel
E: emily.schlegel@primecreative.com.au
T: 0466 317 555
Client Success Manager
Louisa Stocks
E: louisa.stocks@primecreative.com.au
Art Director
Bea Barthelson
Imaging Assistant
Paul Breen
Subscriptions
Frank Rapone
T: 03 9690 8766
E: frank.rapone@primecreative.com.au
The Publisher reserves the right to alter or omit any article or advertisement submitted and requires indemnity from the advertisers and contributors against damages or liabilities that may arise from material published.
© Copyright – No part of this publication may be reproduced, stored in a retrieval system or transmitted in any means electronic, mechanical, photocopying, recording or otherwise without the permission of the publisher.
1.5m
2.5m
ont with Tadano Tadano’s commitment to a zero emissions future.
A CEO report CICA Conference focused on a sustainable future.
A Member profile
Featuring Craig Davies and ANC Cranes.
Mobile Crane Industry Code of Practice.
A Training
An update on recent training courses.
ANZ report
Smith Cranes wins CANZ Lift of the Year Award.
Membrey’s Craig Membrey’s 60th was a celebration of Craig and the Membrey’s legacy.
27 Smithbridge Group celebrates 60th Smithbridge welcomes massive Liebherr crawler.
30 JYC
JYC’s exciting Liebherr delivery.
34 TRT and Freo Group
Freo Group purchases first TIDD PC28-3Gs.
38 Pace Cranes
Pace Cranes opens new Brisbane facility and welcomes CICA.
SA features
42 Urban Crane Hire
Authentically South Australian, the story of Urban Crane Hire.
45 Sany and McMahon Services
McMahon Services takes delivery of first Sany in the fleet.
49 Baden Davis Crane Connection and Max Services Crane Connection delivers new Kobelco crawler.
53 Lif tQuip LiftQuip paving the way for South Australia’s rigging industry.
CICA conference
55 Grove delivers new taxi crane Davo’s Crane Hire adds Grove ‘super taxi’ crane.
59 Tadano delivers for SureLift Crane Hire
Tadano delivers new 450t all terrain.
62 Future proofing Franna Terex Franna upgrades entire range.
64 Protective Engineered Safety
Working safely with overhead power lines.
67 UA A UAA continues investment in new systems and people.
70 Launch of The Buddie System New failsafe safety system for Dogmen.
73 New Liebherrs from Germany to Adelaide
Follow the journey of new Liebherrs.
78 New Grove rough terrains Grove launches new RTs
80 Senarc
The digital innovation behind Visual Dispatch.
82 Matusch
Matusch optimising your fleet management.
84 Crane Class
Upskilling your knowledge with Crane Class.
86 Potains in bridge build Potains about to set new world record.
89 XCMG
The remarkable story of an XCG crawler.
93 DR A and Humma Hummas mining for gold.
97 Zoomlion
A 200 tonne capacity crane arrives in Kununurra.
100 Andromeda
Great people making great slings at Andromeda.
103 Brighter economic outlook
Finlease bullish about the ecnonomy.
107 Fleet Cost and Care The American Freo connection.
110 TRT tour
Australian crane industry leaders tour TRT’s facility.
114 Resolution Rigging Services
RRS invests in new cranes including Australian first.
117 Tutt Bryant
A third HSC crawler tackling the North East Link Tunnel Project.
120 LEEA
Reflecting on a successful LiftEx Gold Coast.
122 PNOinsurance
Delivering far more than insurance policies.
127 Pickles
Pickles offers solutions to help uplift crane businesses.
131 Before You Dig Australia New app protecting Australians.
132 Modulif t
Slings lift cars at festival.
135 Sino Distribution
The team influencing the crane game on the East Coast.
138 Lif t of the Month
What our industry does best.
Tadano’s journey towards zero emissions starts with innovation and the AC 4.070HL-1 hybrid crane is a testament to this commitment.
Tadano’s commitment to sustainability is more than a statement; it’s a mission. Facing the global challenge of climate change, Tadano is taking decisive steps to reduce their carbon footprint, aiming for zero emissions by 2050. Tadano’s path to this ambitious goal is guided by Tadano Green Solutions (TGS), a comprehensive approach designed to make a significant impact on both its operations and the products it offers.
TADANO GREEN SOLUTIONS: LEADING THE CHARGE FOR A GREENER FUTURE
Product Developments: Hybrid Cranes
Tadano’s journey towards zero emissions starts with innovation. The AC 4.070HL1 hybrid crane is a testament to this commitment. The superstructure is capable of running a full workday on battery power alone, this crane matches diesel operation in performance, speed, and lifting capacity, all while maintaining optimal energy efficiency. With a quick charging system that reaches 80 per cent capacity within an hour and the ability to operate while charging, the AC 4.070HL-1 is a true pioneer in sustainable crane technology.
ELECTRIFYING TECHNOLOGY
The innovative AC 4.070HL-1 all terrain demonstrates that Tadano has already set the course so that customers can benefit from all the advantages of CO2-neutral crane operation in the future:
HIGH EFFICIENCY
• System efficiency of 85%, which is
considerably higher than the 40% obtained with diesel
• A significantly improved carbon footprint – on average 50% less CO2 emissions
• Working speed and lifting capacity correspond to those of the diesel drive
REDUCED MAINTENANCE REQUIREMENTS
• Maintenance-free battery
• Low-maintenance electric motor –compared to diesel a drive unit
• Lower servicing requirements for the electrified superstructure as a result
IMPROVED HEALTH AND ERGONOMIC FOR OPERATING PERSONNEL
• No pollutants affecting crane operators or the environment during crane operation
• Significantly lower noise emissions
• Perceptible reduction in vibrations inside the cab as a result of the electric motor running smoothly
• Lower total operating costs
Tadano is pushing the boundaries of electrification. At the CSPI-EXPO 2024 in Japan, the company unveiled the prototype of a fully electric aerial platform, EVOLT-Rough Terrain, which garnered significant attention. Alongside this, Tadano showcased other electrified aerial work platforms like the NUL07E-7, NUS21W-7, and the hybrid AT-100TTE, each demonstrating their drive to innovate in a range of work environments.
Tadano’s President & CEO, Mr. Toshiaki Ujiie, emphasises the importance of collaboration in advancing decarbonisation. He notes that while Tadano is developing groundbreaking electric products, the support of local governments, users, and service distributors is crucial in establishing the necessary infrastructure, such as charging stations, to maximise the impact of these innovations.
TadanoPro
The TadanoPro app is another step towards sustainability. By providing digital access to brochures and materials, we’re minimising paper usage, conserving trees, and reducing waste. This app not only makes information more accessible but also aligns with our eco-friendly practices.
SmaGo
In partnership with Force Technology, Tadano has installed “SmaGo” smart garbage bins in Takamatsu City, Japan. These bins, powered by solar energy, compress waste to maximise capacity and notify collection teams when they’re full. This initiative reflects our commitment to clean, liveable cities and underscores our role in building smart, sustainable communities.
Tadano’s solar panel installations at various plants are part of our strategy to harness renewable energy. Tadano’s Shido, Kozai, and Tadotsu plants now benefit from significant solar power generation, reducing the reliance on non-
In a significant move, Tadano has partnered with Vestas, a leader in wind power, to develop nacelle cranes for offshore wind turbines.
“Through innovation, collaboration, and a steadfast focus on sustainability, we are paving the way for a future where our operations and products are in harmony with the environment.”
renewable energy sources. Additionally, the modal shift to sea transportation further cuts CO2emissions, enhances logistics efficiency, and supports global sustainability.
Collaboration with Vestas for Offshore Wind Power
In a significant move, Tadano has partnered with Vestas, a leader in wind power, to develop nacelle cranes for offshore wind turbines. This collaboration marks Tadano’s entry into the renewable energy sector and strengthens its resolve to contribute to the global shift towards sustainable energy sources.
Power-Training Test Facility: Driving Innovation
Our Power-Training Test Facility, operational since 2022, is a hub for testing and developing new technologies aimed at carbon neutrality. This facility allows us to innovate with precision, ensuring that our future products meet the highest standards
of safety, quality, and environmental responsibility.
Small Operational Measures: Every Action Counts
From encouraging recycling practices across sites and facilities to organising beach cleanups and tree planting activities, Tadano recognises that every action, big or small, contributes to our sustainability goals. Tadano is also reducing its internal environmental impact by redesigning presentations to use less ink, encouraging the use of hybrid vehicles, and promoting virtual meetings to cut down on travelrelated emissions.
Tadano’s commitment to zero emissions by 2050 is a reflection of the belief that we can make a positive change in the world. Through innovation, collaboration, and a steadfast focus on sustainability, we are
paving the way for a future where our operations and products are in harmony with the environment. Together, we’re building a world that’s not just greener, but better for all.
The Tadano Group’s long-term environmental targets, in comparison to FY2019, are to reduce CO2 emissions from business activities by 25%, CO2 emissions from product use by 35%, and a 50% reduction in industrial waste emissions from business activities by 2030.
Overall, Tadano continues to work to conserve and contribute to the global environment.
In order to define important sustainability issues in management and manage policies, targets, and promotions, Tadano has established the Sustainability Committee, which is chaired by the President and consists of all Executive Officers.
The members of the committee, such as the Management Committee and the Board of Directors report and discuss sustainability issues and important matters in their divisions at regular management briefings and meetings.
In addition, Tadano has established the Sustainability Promotion Group as a department dedicated to supporting initiatives in each department. In addition, the Risk Committee is a subordinate organisation of the Sustainability Committee.
There are specialised committees consisting of the Compliance Committee, the Environment Committee, and the Human Resources Committee, which work on company-wide themes.
In addition, in 2021, Tadano established the CO2 and Energy Reduction Subcommittee and the Waste and Chemical Substance Reduction Subcommittee as subordinate organisations of the Environment Committee to consider specific measures, share information with each department, and achieve long-term targets.
Tadano is working on continuous improvements for this purpose.
Since 1977, PNOinsurance has delivered exceptional service and expertise, earning a reputation as one of Australia’s top insurance brokers.
The collective business experience of the PNO team, combined with leading technical industry knowledge across the crane industry, enables PNO to source and secure the right insurance solutions for all businesses.
Our areas of expertise include: à Mobile Cranes à Tower Cranes à Dry Hire
à Transport & Logistics
PNO Benefits
• Downtime cover
• Substantial portfolios of business with leading crane insurers
• Unsurpassed experience and knowledge of complex crane claims
• CICA member
• OHS investigation & defence costs cover
• Financial protection cover
• Specific policy benefits to PNO
• Tailoring of coverage to suit each individual business
• Servicing clients Australia wide
Additional Services include:
• Workers Compensation - Injury Management & Early Intervention
• Personal Insurance - Income Protection & Life Cover
• Buy-Sell & Key Man Cover - Life / TPD / Trauma Insurance
à Construction Dean Bassed - Director E: dbassed@pno.com.au P: (03) 9536 7317 M: 0409 979 346
Over the past year we’ve witnessed remarkable progress in our collective efforts to reduce environmental impacts, innovate with green technologies and support the renewable energy sector. This conference not only celebrates these achievements but also challenges us to continue leading the way in building a sustainable future for Australia.
AS WE LOOK TO MAINTAIN MOMENTUM within the lifting industry and its closely associated sectors—mining, transport and construction—our ability to regenerate and evolve is key. The needs of tomorrow’s markets are rapidly changing, driven by advances in technology and a global shift towards sustainability. One of the standout events this year was the CICA Cranes in Wind forum, held in Melbourne. We looked at the perspective of manufacturers, the struggles of finding a balance in engineering cranes tailored to wind farm construction and maintenance and the burdens of risk that weigh on crane owners and operators to meet the needs of an exploding industry.
But sustainability, to us, isn’t just industry contributions to renewable energy. It’s about fostering a culture of innovation and responsibility within the crane industry. A sustainable tomorrow is a greener one than today, but it’s also about building a future for our industry and the people within it. By supporting workforce development through programs like our traineeship initiative and continually pushing the boundaries of innovation, we are laying the groundwork for an industry that is resilient and ready to meet whatever comes in the future.
There’s been huge strides this year in industry resources - two Codes of Practice and the updated Dogging and Rigging Guide to name a few. These documents provide essential guidelines and best practices, ensuring that everyone involved in crane operations, from operators to rigging teams, is wellprepared to handle the risks associated with their work. By prioritising safety and continually updating these
of entries this year, showcasing the incredible skill, innovation and creativity within our industry. These awards celebrate the very best in
professionalism, expertise and passion that drive our industry forward. We can’t wait to kick off the festivities and acknowledge the extraordinary work
that has been done over the past year.
We can’t speak to building a sustainable tomorrow without acknowledging what’s driving us forward today - and for CICA, that’s our volunteers. Their dedication, passion and hard work make what we do with and for the industry possible. I want to take this opportunity to extend our deepest gratitude to each and every one of them for their unwavering commitment and for being an essential part of our own journey.
Through collaboration, knowledge sharing, and a commitment to continuous improvement, we can ensure that the crane industry remains a cornerstone of Australia’s infrastructure and economic growth. We are incredibly grateful to have Terex/Franna as our Platinum Sponsor for this year’s conference. The support of industry plays a crucial role in making this event possible, allowing us to bring together industry leaders, professionals and innovators under one roof.
Our annual conference has always been a platform for the exchange of ideas and best practices, uniting industry leaders and professionals in a shared mission to secure the future of the crane industry for generations to come. We’re excited to see you there.
Brandon Hitch Chief Executive Officer
“There’s been huge strides this year in industry resourcestwo Codes of Practice and the updated Dogging and Rigging Guide to name a few. These documents provide essential guidelines and best practices, ensuring that everyone involved in crane operations, from operators to rigging teams, is well-prepared to handle the risks associated with their work.”
CICA BOARD
Ben Pieyre – President
Marcus Ferrari – Vice President
Danny Adair – Director
Danny Black – Director
Andrew Esquilant – Director
David Solomon – Director
Karli Sutherland– Director
CICA OFFICE
Brandon Hitch Chief Executive Officer 03 8320 0444 0428 228 048 ceo@cica.com.au
Paul Arztenhofer
Membership Engagement/Business Development Specialist 04 9093 9274 paul@cica.com.au
Alice Edwards Road Technical Engineer 03 8320 0440 alice@cica.com.au
Patrick Cran CraneSafe and CrewSafe Technical Advisor 0488 004 274 pat@cranesafe.com.au
Damien Hense CICA Road Policy Advisor 03 8320 0460 0488 007 575 damien@cica.com.au
Julie Turner CICA Executive Assistant/ Board Secretariat 03 8320 0411 julie@cica.com.au
Kate Galloway Traineeship & Industry Engagement Coordinator 0491 047 118 Kate@cica.com.au
Shane Coupe CraneSafe & CrewSafe Administrative Assistant Officer
shane@cica.com.au 0491 047 134
Madeleine Flynn Senior Marketing Communications Officer madeleine@cica.com.au
Justina Blackman
Member Events and Engagement 0403 717 626 justina@cica.com.au
Ashleigh Gould Office Operations Coordinator, ashleigh@cica.com.au 03 8320 0466
Unit 10, 18–22 Lexia Place, Mulgrave Vic 3170
Phone: 03 9501 0078
Fax: 03 9501 0083
Email: admin@cica.com.au
Website: www.cica.com.au
For information, please visit our website or call the CICA office.
THE MOBILE CRANE INDUSTRY CODE OF PRACTICE
The recent endorsement of the Mobile Crane Industry Code of Practice by the National Heavy Vehicle Regulator (NHVR) marks a significant milestone in ensuring safety within the industry.
The consultation period for the code closed in May, and on the 12 of August it was officially endorsed and registered by the NHVR. The code concerns itself only with mobile cranes, which it defines as all terrain cranes, articulated steering cranes, hydraulic truck cranes and city cranes that are heavy vehicles. It does not include heavy vehicles with cranes mounted to them for loading or unloading
goods onto the vehicle.
WHAT DOES IT MEAN TO BE A REGISTERED INDUSTRY CODE OF PRACTICE (RICP)?
Industry Codes of Practice are a resource for members of industry to translate the requirements of the law into real-world, practical steps and procedures. To be registered the Industry Code must meet certain requirements - it must be high quality, applicable to the chosen sector, and adaptable for all participants in an industry; from an individual to a large corporation. It must also be grounded in and support risk management.
Registration does not mean that the Industry Code becomes a legally binding
document; those in industry do not have to use every control recommended by the Industry Code as written - but it can be used in legal proceedings as an accepted baseline – so parties to the the Chain of Responsibly (CoR) should reasonably know about risks, hazards and potential controls in their industry.
CHAIN OF RESPONSIBILITY PARTIES IN THE MOBILE CRANE CODE OF PRACTICE
• Employer The person or business that employs the driver of a mobile crane.
• Prime Contractor The person or business that engages the driver of a mobile crane under a contract for services.
• Operator The person or business responsible for directing or controlling the use of a mobile crane.
• Scheduler A person or business that schedules a mobile crane.
An important distinction to note about the terminology of The Mobile Crane Industry Code of Practice is that the term Operator in the context of CoR parties is not the driver of the crane, as seen above. Within the Risks, Hazards, and Controls section of the code you may see crane driver/operator - that is the operator of the crane, but if you see crane operator written it may actually be referring to the Operator as a party to the CoR.
The Mobile Crane Industry Code of Practice is an intensely detailed document, drafted over months of consultation with leaders in the industry and will be
an incredible resource for our industry going forward. It is important to note that for some crane companies it is not the only Industry Code to be aware ofThe Master Code, also registered by the NHVR, is applicable to all parties of a heavy vehicle in the CoR and addresses the risks associated with the four core responsibilities of that CoR regulated under the Heavy Vehicle National Law (HVNL).
The Load Restraint Guide, WHS law and relevant Australian Standards may also be relevant in considerations of whether a CoR party has done what is reasonably practicable to ensure safety and eliminate public risks.
Codes of practice are not exhaustive, there may be risks and hazards unique to businesses, projects, or areas of operation. Read the code and consider the hazards and controls, assess if they apply to your transport activities and if your activities contribute to risks affecting others. You do not have to use every, or any, control recommended by the code. You can use different controls altogether, provided you can prove that they eliminate or mitigate risk as effectively as those recommended. If you are an Executive (this term includes executive officers, managers, directors, or another person who takes part in the management of a business) overseeing a business relevant to the activities and hazards listed in the code you have a duty to familiarise yourself with the contents of the code.
The Queensland Mobile Crane Code of Practice is a separate code, commencing on September 23 2024. It was developed by the Office of Industrial Relations Queensland (previously Work Health and Safety Queensland) and approved by the Minister for State Development and Infrastructure, Minister for Industrial Relations, and Minister for Racing. This code is an approved code of practice under the Work Health and Safety Act 2011 (the WHS act) opposed to the
registered Mobile Crane Industry Code of Practice. The scope of this code is to provide practical guidance to manage risks associated with mobile cranes, vehicle loading cranes and other mobile plant used as a crane to raise or lower freely suspended loads.
Both registered and approved codes of practice are admissible in court proceedings and may be used as evidence of what is known about a hazard, risk or control – and they reference the code when determining what is reasonably practicable in the circumstances. To decide what is reasonably practicable, you must consider the likelihood of the hazard or risk occurring, the harm that would result from the hazard or risk, what a person knows (or should know) about the hazard or risk and ways to eliminate or reduce it.
The Mobile Crane Code includes references to legal requirements under the WHS Act and WHS Regulationthese references are for reference only, not as a substitute for reading the texts. When the words ‘must’, ‘requires’, or ‘mandatory’ are used in the code, they indicate a legal requirement exists that must be complied with. ‘Should’ identifies the standard required in the code, and if a person conducting a business or undertaking relevant to the code wants to manage the hazard in a different way than standard that control must be of equivalent or higher standard of work health and safety. ‘May’ indicates optional courses of action.
Mobile cranes represent a huge proportion of the cranes currently in operation in Australia. These codes provide comprehensive, practical controls against risk – not only to property, but to our own workers and the public.
The Mobile Crane Industry Code of Practice and The Master Code can both be found online via the NHVR - https:// www.nhvr.gov.au/safety-accreditationcompliance/industry-codes-of-practice/ registered-industry-codes-of-practice , and the Mobile Crane Code of Practice can be found online via WorkSafe Queensland - https://www.worksafe.qld.gov.au/lawsand-compliance/codes-of-practice.
They say the fraternity of crane hire company owners accommodates some fairly big egos. If you have the privilege of knowing or meeting Craig Davies, Owner and Director of ANC Cranes, you know he isn’t one of them.
CRAIG STARTED WORK WITH HIS FATHER Arthur at Sydney’s Everwilling Cranes in the early 1990’s. They bought a crane and subcontracted to Everwilling. They called the business A and C Cranes, for Arthur and Craig, but the signwriter got it wrong and the crane came back saying “ANC Cranes”. The name stuck. A couple of years later they bought a second crane. Craig takes up the story.
“Until the mid ‘90s we had been happy to travel along subcontracting to Everwilling Cranes, but we could see other opportunities. When we bought our third crane, we knew we were getting too big to subcontract out of Everwilling’s yard.
cranes,” said Craig.
“On his retirement my father had some words of advice that went something along the lines of, “The worst you can do is go broke.” That was the challenge I needed, I rolled up my sleeves, found the yard in Marsden Park, Western Sydney, and managed to secure a few contracts and everything really started from there,” he said.
Craig has been hands on and dedicated to the business and still operates the cranes at all hours of the day. He has relied on his trusted and ‘tight team’ to manage the other areas of the business. In turn, this has attracted like-minded people to the
everyone working hard, being reliable and honest. We do not take on work that I don’t think we can deliver on and we always give our customers 120 per cent,” he said.
“We started out securing a number of steel erection projects because I could see that if we’re putting steel up, our cranes had a good opportunity of staying onsite – and so we took on some big projects. We managed the lifts for Laing O’Rourke at the Army base at Holsworthy and it really started to grow from there.
“Customers saw our approach and our abilities, and we generated a lot of general crane hire from those projects. A key fact for our businesses is that we haven’t needed a lot of advertising, we have worked hard, and customers have taken us onto their next projects and our reputation has spread through word of mouth,” said Craig.
He goes on to highlight the experience he has in the ANC Cranes team.
“At the moment, we probably employ about 20, 25 people and a lot of them have come up through the ranks – having good people attracts good people. I find if I advertise, the quality of people isn’t always there. But when people come to town from different regional areas looking for work, they come our way.
“Most our people have come up through the ranks. They have started as Dogmen and served their time Dogging cranes and then we’ll slowly introduce them to operating a crane. I won’t send cranes out unless I’ve got the right crew. One thing I can say with ANC Cranes, we come second to none with the people we employ,” said Craig.
With his team, Craig looks for loyalty, respect and dedication to the work.
“Our yard is like a family. Everyone puts in 100 per cent, and if one person starts to fall behind, we all rally and help them step up. I think the team sees how hard I work, and I know they also take a lot of pride in
their work and the contribution they make to the business and our customer’s projects.
“Jesse would be one of our longest serving employees and he’s been operating our City Crane for 15 years. There’s been a few others that have clocked up some time and have been here around the 10-year mark. Anyone that joins us agrees it’s a good place to work, the pay is right, and the opportunities are always there,” said Craig.
The Sydney market is very competitive with two or three big players. Craig explains how ANC Cranes competes in this market and what his point of difference is.
“Competing against the major players makes it hard to get government work. Although we are Tier One accredited and we have all the right paperwork, and we’re good, honest and skilled people, it is difficult to compete for this work and it has been for the past 10 years.
“I have had to diversify and look at work that is viable for our business model. I sat down and worked out that we needed to change our market, and move into general crane hire, managing smaller building projects, tree removals, pool installations as well as the smaller tower crane market,” said Craig.
“We lift a lot of construction equipment out of holes, it’s interesting work and no two days are the same. That said, because of the service we provide, we are starting to get back into some of the major builders but it is competitive,” he said.
Craig goes on to highlight his approach to projects.
“Most of the time I’ve conducted a pre-site inspection, and I relay what’s required to the crane crew. Everyone has been inducted and trained in their position so when they get to site, they analyse and set the crane up in the right spot and get the job done.
“As we are working on smaller projects, our teams understand the concepts of time management and working in a productive way. If the builder’s not getting productivity and the crane crew’s standing around, it is costing the builder a lot of money. Our teams have been trained to be profitable and an asset for the builder.
“We also have excellent backroom staff, and I’m very lucky to have Alyce on board.
She works in an organisational role and helps get everything done. It’s not a 9 to 5 job and Alyce knows it and she goes above and beyond to ensure we deliver on what we promise. Alyce works with Mel and together they manage allocations, payroll and work health and safety. In a short amount of time each day they get through everything. We couldn’t do what we do without them,” said Craig.
He goes on to discuss ANC’s fleet.
“The smallest crane we operate is a twotonne electric Galizia which we use for work in applications where there must be zero emissions. We then move into our fleet of 13 Maeda mini crawlers which ranges from
the 285 up to the four tonner. That fleet has grown on demand. The four tonner is diesel-electric so we can get that into food processing plants or inside buildings and run on zero emissions,” said Craig.
“We then move into the City Crane range. We’ve got a 13t capacity Tadano City Crane that’s only two metres wide which gets us into a lot of tight places that the 20 tonner can’t manage.
“We run two 20t capacity Tadano City Cranes and then move into our 40 tonner, two 65t all terrains and a 130 Tadano. All our cranes, from 13t upwards, are Tadanos. Operating one brand makes it a lot easier with familiarisation and the same computer
systems, and Tadano has been good to us and we have shown loyalty in return,” said Craig.
“We service all our cranes to comply with legislative requirements. Pace Cranes are great with the Maedas, we’ve had a long relationship with Anthony and his team. From the 13t upwards, everything goes back to OEM, back to Tadano. It’s easier that way to maintain the cranes and plan for future repairs.
“We operate prime movers and support counterweight trucks for the smaller cranes. Over the years I’ve bought five UD trucks. I find the reliability and fuel economy is great and the 24-hour service and support from UD doesn’t let us down,” he said.
Craig goes on to reflect on his 30 years in the industry.
“30 years ago the Sydney market was dominated by larger players with big yards for large crane fleets. Today, there are far more players in the market. The focus on safety is far more noticeable today and that is a good thing as we are operating in a high risk industry.
“The tower crane industry as changed as well. 30 years ago, you had Marrs putting big Favco Hammerheads up and now we are seeing much smaller cranes like Potains and now the Chinese brands. There are a lot more independent yards that have their seven-year hit and disappear,” he said.
“The cost of running cranes has increased dramatically. In the 1990s you
could get your paperwork passed with by a diesel mechanic, now everything’s virtually managed by the crane OEM.
“With the complexities of the computer systems today, you need to the OEM to sort out any issues have got all the support. The last couple of years have seen a few crane companies close their gates, sell their assets and finish up. Last year was probably a good time to get out, but it wasn’t my time,” Craig said..
Craig looks to the future and talks about his plans for ANC Cranes.
“I’ve never really had a plan or a goal for the business, but that has changed. I was lucky enough to have my father teach me how to drive a crane and also help me start the business with one crane.
“I’ve got a young bloke and he’s just turned 14 and I plan to hang around for at least another 10 years and pass on the opportunity to him. Where are we headed? We don’t want to get majorly big, but we can see there is room in the yard for a few more cranes,” said Craig.
“Basically, this job, the business and the people I work with keep me busy. I’m inspired to get out there with the team each day and do the best we can. It’s about being a ‘family’ and what we’ve got is good. I’d be happy with another five cranes in the fleet and to move premises,” he said.
Craig takes an active role in The Crane Industry Council of Australia (CICA) and attends as many meetings and functions as
he can throughout the year.
“It’s easy to sit on the fence and complain about the industry, but if you don’t attend the CICA meetings and you don’t put in, you only have yourself to blame when decisions are made that you don’t agree with.
“Being an independent company, I need to attend and understand the direction in which the industry is headed, mix with successful people and have my say. CICA is our industry body, it represents us at Federal and State Government levels and it is making decisions that are influencing how our businesses operate. In my opinion it is important that businesses like ANC Cranes have their say,’’ said Craig.
Craig attended the CICA NSW/ACT Regional Meeting in the Hunter Valley earlier in the year and generously donated to the chosen charity Touched by Olivia.
“The Regional Meeting was excellent and provided a great opportunity to meet colleagues in the industry and listen to important presentations during the seminars. The evening charity auction was special, and I noticed the room was full of good people, all had big and generous hearts.
“When you can see somebody’s passion and understand how much they have put into the charity and what the charity has delivered for so many, over many years, it doesn’t take much to donate a few dollars and be of support, and I was very happy to do so,” said Craig.
CICA provides valuable training that helps our industry grow and succeed. We have a responsibility to provide courses that reflect the real world we work in - not a theoretical one. Our content is designed in consultation with industry experts, specifically for our industry.
THIS YEAR HAS SEEN SOME FANTASTIC developments in participation and feedback for our programs, and now as we look to our annual conference and the shared learnings that always come from it, it’s the perfect time to reflect on how we’re tracking.
THE CICA LIFT SUPERVISOR COURSE
This time last year we published an article reflecting on the success of the initial pilot day of the CICA Lift Supervisor Course. Since then, we’ve seen a rapid, enthusiastic uptake - with over 150 graduated Lift Supervisors across four states and dates for 2025 already set in place.
The CICA Lift Supervisor Course is designed to make crane operations safer, smoother and more efficient on construction sites. The course introduces the role of a crane lift supervisor, who is in charge of overseeing all lifting activities involving cranes. This supervisor makes sure that everything is checked before lifting starts – including inspecting the equipment, checking load limits and ensuring all safety systems are working. The course covers everything you need to know about being a lift supervisor, from spotting risks to handling emergencies. Participants learn how to assess risks before any lift, plan carefully for things like weather, ground conditions and nearby structures. The course also stresses the importance of keeping in touch with crane operators during lifts to make realtime adjustments. Along with teaching technical skills, it helps develop leadership
qualities so supervisors can ensure safety rules are followed, and the work area stays secure.
We’re finishing up our training days for the year in October, but dates and locations for 2025 have already been confirmed and are available on our website.
The CICA On-Road Articulated Steering Mobile Crane Training Course is designed to address the specific needs of operating articulated or ‘Pick and Carry’ cranes on the road. These cranes are widely used in Australia due to their versatility and mobility, but their high usage increases their exposure to potential risks when transported on public roads. In response to a coronial recommendation and supported by a grant from the Federal Government through the NHVR, CICA developed this course to enhance safety and competence for operators of these cranes.
The course is divided into two parts. The first part is an online module available through the CrewSafe website, which uses Adaptive Learning to help operators understand the driving behaviour of articulated cranes. This online training ensures that operators have a solid theoretical foundation before moving on to practical assessment. The second part involves a hands-on evaluation of the operator’s skills in driving an articulated mobile crane, completed using the CrewSafe application.
The course is free of charge and accessible to anyone, anytime.
Designed to empower women in the Australian professional landscape, the Women’s Leadership Development Program creates a supportive environment where participants can develop essential leadership skills and gain the confidence needed for senior roles. By bringing together women from various backgrounds, the program provides valuable insights into leadership dynamics, personal branding and career progression strategies.
The course is structured to offer a comprehensive learning experience. It begins with an in-person kick-off event, followed by two 90-minute virtual sessions that dive into key topics such as communication, leadership and change management. The program concludes with another in-person event to reinforce learning and provide networking opportunities. Each session is tailored to the needs of the cohort, ensuring that the content remains relevant and impactful based on feedback from participants.
The inaugural cohort of the Women’s Leadership Development Program launched successfully on July 10-11, 2023, at the Amora Hotel Jamison Sydney. The feedback from participants has been overwhelmingly positive, and registrations of interest for the 2025 cohort are available on the CICA website.
We’re excited about the continued evolution of our training programs and the positive impact they will have on our industry. CICA remains committed to delivering practical, real-world training that equips members of industry with the expertise they need to excel.
Excellent Lifting Performance
· Max. lifting capacity of 88m main boom is 6.3T, max. lifting capacity of mainboom + optional 33.5m jib is 1.6T
Efficient Transit
· Counterweight can move via 0.55m, forward position suitable for narrow spaces,rear position for improved performance
· Can travel at low speed with on-board 27T counterweight and 4 outrigger pads
Energy-saving & Environmentally Friendly
· Equipped with an independent Cummins B5.9 engine, compliant with Euro non-road Stage IIIA emissions standards, eliminating the need for urea addition.
· Fuel consumption during operations is 35% lower compared to single-engine models of the same class
ZOOMLION All-terrain Cranes for Australia and New Zealand
ALL TERRAIN CRANE
ZAT1200V
ZAT600V
ZAT1600H ZAT2000V ZAT2500V ZAT3000V
Construction to assist with the installation of air conditioning units at the Manawa
2.7 tonnes and with hook and rigging included, the required lift was 3.15 tonnes.
The site is located less than one kilometre from the Auckland Airport
runway. Civil aviation imposed an obstacle limit surface of 45 metres above ground level at this location. This limits the heights at which a crane can operate.
If the obstacle limit surface has to be exceeded, there is a 90-day approval period, which did not meet the client’s program requirements.
Using a 400 tonne mobile crane with luffing jib was not possible, as it would significantly breach the obstacle limit surface during erection and still remain above it during the lift.
Smith Cranes proposed the use of a LR1280 Crawler Crane, with 25.7 metres of main boom, and 77 metre luffing jib. This allowed the crane to be assembled and operated entirely below the obstacle limit surface, before allowing an immediate start.
The 77 metre jib was used for the lifts at 95 metre radius. Due to the constraints of the site, the crane could only operate between approximately 93 and 95 metre radius, so it was tracked to allow the installation of the larger radius units.
The jib was then shortened to 53 metres to allow the remaining lifts to be undertaken. In this configuration, the crane could reach between 55 and 70 metre radius for the remaining installs.
Smith Cranes was able to plan and mobilise the site in under 10 days of a requests from the client, including moving the luffing jib from Christchurch.
As Craig Membrey celebrates his 60th birthday, the doyen of the Australian crane, transport and heavy haulage industry looks back on his own experiences, and what helped climb his business up the ranks.
CRAIG MEMBREY, MANAGING DIRECTOR
and Owner of Membrey’s Transport and Crane Hire, celebrated his 60th birthday in style in August this year.
Surrounded by his closest friends and family, Craig hosted about 300 guests from the crane and trucking industry at the Fox Classic Car Collection, in Melbourne’s Docklands, owned by Craig’s friend, the well-known Australian businessman Lindsay Fox.
There was a red carpet welcoming people in with Membrey’s Transport and Crane Hire merchandise everywhere.
Attendees were greeted with three Frannas, an AT22, a MAC25SL and an AT40 decked out in the limited 60th birthday colours that were sitting out the front of the venue – a birthday gift for Craig.
The party had it all; live music, a casino (with fake money), a free permanent tattoo parlour, an Elvis and Austin Powers impersonator, and not to mention all of Lindsay’s cars, everywhere you looked.
Craig’s party wasn’t short of glitz and glamour.
Bright outfits, sharp and sophisticated suits and fancy shoes were on show at the Docklands venue, as attendees enjoyed great food, views of trucks, cranes and the opportunity to inspect Craig’s brand-new Lamborghini – a birthday gift from him to himself, because, why not?
Membrey’s is a dynamic and leading transport business, based in Melbourne’s South-East, with the product range and technical expertise to service any
transportation or lifting requirement.
Operating across Australia, 24 hours a day, 7 days a week, Membrey’s has evolved into one of the most trusted haulage companies in Victoria and Australia-wide.
The business was founded in 1962 by Craig’s late father, Jack William Hadley Membrey. and was called J & N Membrey & Son. Craig took over the business in 1989, which saw the business name evolve to Membrey’s Transport and Crane Hire.
Despite the name change, the core values of the business remained: To foster strong customer relationships and provide exceptional service with an outstanding product range and technical excellence.
Today, Membrey’s offers an array of diverse and technical services.
Many customers turn to Membrey’s for solutions in areas such as crane hire, heavy haulage and oversize transportation, traffic management, crane lift plans, steel and timber bog mat rentals, forklift hire, crane trucks and extendable sideloader trailer services.
Craig says Membrey’s caters for many needs of those within the industry, with a fleet that includes a diverse range of Liebherr mobile cranes, including multiple LTMs and LTRs on offer.
Membrey’s recently took ownership of a Liebherr LTR 1220 telescopic crawler crane – further adding to its already
extensive fleet of over 300 pieces of some of the very best equipment.
“I think we’re most versatile transport crane hire company in Victoria – we’re a one stop shop for crane hire and transport services – you can get everything here,” Craig says.
With so many high-quality services on offer, Craig values service and safety as premiums, over everything else.
“In the crane game, you need to provide good service, the best equipment and incredibly high levels of safety. And off the back of good service, your business can foster strong relationships, which hold both parties in good stead moving forward.
“When the service is at a high standard, people in the industry just trust you. But it starts from the good service, the secret to a successful business is building friendships” Craig added.
The motto – Make it Happen – is a constant when talking to Craig. A motto friends and family of his constantly referred to during their speeches and positive remarks at Craig’s birthday.
“In our industry, sometimes you just need to find a way – you need to make it happen.”
A close friend and colleague of Craig’s made a touching video tribute in front
of Craig and the audience at the birthday party.
“You’re an incredible person and an amazing friend. This is all down to a couple of your quotes; ‘Hard work pays off’, ‘make it happen’, ‘never say no’.”
In his own speech, Craig spoke about how strong relationships taught him how to succeed in the heavy lifting, haulage and transport industry.
During his speech, Craig described a rougher period in his childhood – a threemonth period living on the streets after his parents separated when he was 14.
One day, Craig went to the local fish and chips shop with only two cents in his hand.
The shop, Meat Me, was owned by a Greek family known to Craig – a family that he knew from being around Melbourne’s South-East suburbs.
“I went to my mate’s father’s fish and chips shop and I put two cents on the table – it was all I had,” says Craig. “He then put a bag of fish and chips together for me and then he pushed the money back at me he said, “I like you son. I’m not charging you”. From that onwards, we’ve been family friends for 45 years.”
All these years on, sadly, the man at the centre of the story passed away at 90 yearsold, and Craig was there right by his side, right to the end.
“In his final moments, the family asked me to come and say goodbye. He was such
a good coach for me at that time of my life,” Craig remembered.
Craig then proceeded to interview people in the crowd, including his uncle, Bryan Membrey – the late Jack’s brother.
Bryan is 90 years-old and captivated the crowd with his wisdom and kind words to Craig. The bond between Craig and Bryan was palpable.
Cranes & Lifting paid Craig a visit at the company’s massive yard in Dandenong South, in Melbourne’s south-east – a place of work, but also of fun and colour.
At the yard, bedecked in Membrey’s famous green, red and black, there is a big shed decked out with custom plates covering both corrugated iron walls.
Inside, there is a loft which holds a projector for movies, cinema-style seating, a bar and a pool table with Membrey’s brand printed in the centre.
It is also home to a brand new truck and one of Craig’s favourite cars sitting under a tarpaulin – the reward for hard work well done.
Sadly for Craig, in some fields there will
always be work to be done.
His son, Rowan John Membrey, took his own life in March of 2011 – a dark time for Craig and the rest of his family.
Today Craig, an Ambassador for Beyond Blue, is a strong advocate for speaking up when something isn’t right.
“There is help out there,” he says. “When you’re in dark state in life and you need help don’t leave it too late, because if you leave it too late, it might be too late.”
“I’ve had depression myself, I’ve been in black spots, but once I sought help, things improved from there.” Craig added
More recently, Craig has suffered two heart attacks, the latest one, in October of 2023, where he had to be revived by medical professionals.
“They jump-started me,” he says.
“I was possibly dead for seven minutes, they revived me and thankfully I’m here to tell the tale.”
These life-altering moments have provided Craig with a new perspective on life.
“There is no rewind button, you can make mistakes, and everyone deserves second chances in life,” he says.
Craig exudes a vibrant zest for life, and that is obvious at his workplace – a place where he generates such pride and joy in what he does and the people he works with.
In between describing cranes and taking phone calls, Craig makes sure the employees he runs into know they need to go on their lunch break and offers to make them multiple coffees.
“If you hang around good people, life and work will become much easier.
“I’ve been lucky to have and still be surrounded by great people here at Membrey’s,” says Craig.
General Manager of Franna – A Terex Brand, Danny Black, attended the party.
A close friend of Craig’s, Danny says it was great to see a line of Frannas beside the red carpet at the party.
“I first met Craig when he started his love affair with Franna on 29/02/1996, a leap year day when Craig took a “leap of faith” and purchased his first Franna4WD16 S/N 3121.
“We (Franna) are very fortunate to have many, many passionate customers, but
The Membreys have a strong history of ‘Making it Happen’.
I’m sure others will agree Craig takes this to another level – just look at his specially customised “CM 60th Edition” AT22, MAC25 and AT40, surely no one is more passionate about his Frannas as Craig,” adds Danny.
Danny recognises the drive Craig possesses.
“Here are some words I would use to sum up Craig; next level, driven and passionate, wholehearted and genuine,” he says.
“For me personally, I feel blessed to know Craig is much more than trucks and cranes and his passion, care and dedication goes much deeper than his business.”
Jack Membrey’s motto, which he passed down to Craig, is “The World is your Stage.”
Craig says the motto symbolises the importance of every day; performing your role to the best of your ability all the time, always being kind to others and enjoying each day like it’s the last.
“Everyone who attended my party has meant so much to me and everyone there played a big role at some point in my life.
They helped me get to where I am now,” Craig says.
And if the world’s a stage, Membrey’s is one of the biggest shows in town –with daily performances ranging from hauling the largest of cranes along with all the accompanying accessories, servicing windfarms and, for over four decades, working as the trusted ally of the Melbourne Zoo.
In that role, Membrey’s has been responsible for orchestrating the seamless relocation of colossal animals – a testament to the enduring bonds forged through trust and reliability.
At the core of Membrey’s philosophy lies a faith in the symbiotic relationship between human connections and cuttingedge technology.
Craig Membrey’s journey to ongoing success underscores the value of modern equipment coupled with nurtured relationships.
Craig is proud of what Membrey’s is today and he is enjoying the ride.
Craig’s one wish in life is to pass Membrey’s Transport and Crane Hire down to his children Leah and Jack, just like his late father did to him.
shorter towers constructed on high, hilled exposed locations. When we started in the Australian wind industry, you needed a 600t capacity crane, typically a Liebherr LG 1550 truck crane or a Demag CC2800 narrow track crawler, to construct wind turbines that were typically 80 metres in height with efficient relocation between tower sites.
In 2015, the Australian wind turbines jumped to 120 metres in height and needed an 800t capacity crane to do the job, so the crane of choice became the Liebherr LG 1750,” said Albert.
“When the NZ market picked up in 2019, we purchased the Demag CC2800 narrow truck crawler crane - which was by then too small for the Australian wind farms - with the plan to transfer her to NZ to track between turbine platforms fully rigged,” said Albert.
Careful consideration of the site topography showed the CC2800 narrow truck, with its high centre of gravity in rigged travel mode, was a risky solution for the steep high New Zealand wind farm sites at Turitea Stage 2 and Harapaki.
17 were ever produced. Therefore, an LTR 11200 was purchased for the Smith Cranes & Construction Ltd New Zealand business in March 2022, ex-Germany, for deployment to the Turitea stage 2 wind farm in October 2022.
The LTR 11200, a 1,200-tonne capacity telescopic crawler crane, is the strongest telescopic crane on the market and has the longest telescopic boom in the world. Although designed for the wind industry due to its high lifting capacity, variable boom options and small footprint, the crane
is well suited to a wide range of jobs in the industrial, mining, infrastructure, wind and energy sectors.
The narrow-track crawler can travel on the 5 metre wide wind farm site roads and on infrastructure sites fully rigged with the boom telescoped in and luffed down so the centre of gravity is low, the transverse stability is good and the track-to-ground pressures are low and even along the track length. During crane operation, the LTR 11200 is supported on star-pattern outriggers with a square footprint of 13 metres by 13 metres on large low-ground pressure pads.
The LTR 11200 has strong lifting capacity charts and a small footprint compared to similar large-capacity mobile cranes. The 100m telescopic boom, Y-guy boom suspension, lattice fly jibs and much of the slewing platform are sourced from the LTM 11200-9.1 All-Terrain crane. Lift heights of more than 220 metres are possible with available boom attachments, including the Y-suspension system and fixed and luffing lattice fly jibs.
“We looked at what other crane companies were doing around the world. There was a need here for wind maintenance cranes and for big mobile cranes. But once we got to understand the capabilities of the LTR 11200 and looked at what other owners in the world were doing, a German company of similar style to ours – they were using it in the mobile crane business,” said Albert.
“When you take a very big hydraulic mobile crane, with the biggest on the East Coast a Liebherr LTM 1750 with a lifting capacity of 750t, you’ve got to pull it to pieces to move it using multiple truckloads, so the crane relocation logistics are like the LTR 11200 narrow track crawler.
“When you have a project lifting bridge beams in the middle of the night, you get to the site and lose the first four to five hours assembling the all-terrain crane in her exact working position. Then she needs a partial dismantle and re assemble each time you need to move her.
“The LTR11200 has the advantage that she can be assembled near the site and then very quickly be tracked into the lifting
position, or track between lifting positions fully rigged,” said Albert.
“With this crane, we intend to compete in the large capacity mobile crane space with a focus on the high, heavy, and long reach projects at confined or congested sites. Even though it’s a crawler crane, we see it as a taxi crane. That is a crane that goes to site sets up fast, really quick.”
Liebherr stopped making these cranes in 2015 due to lack of demand created by the increased height of turbines.
Smithbridge Group located its first LTR 11200 second hand in the German market, buying it for the New Zealand Smith Cranes business mid-2022 for deployment to the Turitea stage 2 Wind Farm in October 2022. Since then, the crane has completed two wind farms, plus bridge beams and precast building works, and is currently in a Hangar Project at Auckland Airport, where the telescopic boom is a significant advantage for air traffic safety. The second LTR 11200 was purchased from the Liebherr used crane team in late 2022, and is a trade machine ex-Mexico.
Main specifications include :
• 100m Main Boom
• M aximum Lifting Height: 189m
• M aximum radius: 124m
• C ounterweight: 202 tonnes
• C rawler Track Width: 4.80m
• S tar-pattern Outriggers 13mx13m
• F ly Jib up to 126m
“We love rebuilding machines ourselves, and the Universal Cranes business has excellent well trained crane technicians who thrive on these types of projects. We were therefore very motivated to bring the crane to Brisbane for the necessary in-house rebuild, 10-year major inspection and refurbish her,” Albert said.
“Liebherr then took me to their newly built refurbishment factory in Germany and convinced me to spend over a million Euros to have them rebuild her. Their labour costs are about the same as ours in dollars per man-hour. Still, their operation is an efficient re-manufacture process with the full support of the factory engineering and logistics and of nearby original component manufacturers. There was no comparison to what we might be able to do in Brisbane, as the Liebherr rebuild shop is run like a factory. All minor and wearing parts were replaced, and all major components, such as engines and winches, were returned to the original manufacturer supplier for reconditioning. The process took over a year, and she came out of the factory looking and working as a new crane.”
Albert looks to the future of the group, under the guidance of the third generation of Smiths, to identify industry sectors that will sustain the growth of the business.
The business was started by Albert’s father, John Smith, in 1964 in Rangiora, just North of Christchurch. It was split in the early 1990s by the second generation into three groups, these being Daniel Smith Industries, which is still based at Rangiora, Smith Cranes and Construction Ltd, based in Christchurch, and the SmithbridgeUniversal Cranes operations are based in Brisbane. The combined full-time workforce of the three independent groups is more than 1,000 people and the combined fleet is over 500 cranes. Operations span the North Pacific Marianas region to Australia,
The Liebherr LTR 11200, 1,200 tonne capacity telescopic crawler is the strongest telescopic crane on the market and has the longest telescopic boom in the world.
“The transition to the third generation is well underway with the focus on the latest machinery technology, as well as devising innovative and alternative designs and methodologies and team management and advancement systems because that’s how the business has grown so successfully since its inception,” he said.
“Diversification and geographic expansion in the right places will stand us in good stead. We have a successful business model that combines size and capacity with a simple family-style, customer-first culture. The third-generation team plans to manage the combination of our capital, equipment, people, and systems to continue for many more years as a family business.”
Retaining family values and committing to providing engineering passion and adding value to its comprehensive operations are also key focuses.
Measures are being taken to ensure the third generation of Smiths—Ben, Dashelle and Joe—are well equipped to ensure success for the Australia based business for many more years, retaining the mindset that took Smithbridge Group from one Fordson Major backhoe to a multinational, multidisciplinary engineering and equipment company.
“The key to our long-term success is to make all our operations sustainable. This includes economic, environmental, cultural, technical, and social sustainability,” said Albert.
Another crane has donned the famous orange paint, as Johnson and Young Cranes takes delivery of a 750 tonne Liebherr LG1750 lattice boom mobile crane.
DIRECTOR OF JOHNSON AND YOUNG
Cranes (JYC) Brent Young says the LG is in great condition and is exactly what JYC needs.
“Reece and I had been considering adding a lattice boom mobile crane to our fleet for some time now to cater for major infrastructure works and windfarm construction and maintenance. This ex Mammoet Liebherr LG1750 was immediately available, it was in excellent condition with low hours which made the decision to acquire it an easy one,” says Brent.
750-tonne crawler crane combined with the mobility of a high-speed mobile crane. Combining the benefits of these two crane types in a single unit makes it the largest and strongest lattice boom mobile crane in the world and unrivalled in the market. Its high mobility and lift capacity were decisive factors for JYC before the purchase of the LG 1750, Brent said.
Having the chassis of an all-terrain crane, the bottom part of the 8-axle crane is roadgoing, providing JYC with a level of flexibility in getting to and from site. Its vehicle width of less than three
boom of a crawler crane makes the crane particularly powerful. The components can also be transported economically, thanks to the transport weight of less than 45 tonnes, which makes the compact lattice boom mobile crane ideal for fast erection work for wind power, industrial construction or infrastructure work.
There is a large selection of boom configurations for the LG 1750 which have been specially enhanced for deployment in the wind industry. The latest generation of wind turbines with hub heights of up to 170 metres can be erected using the SX system. For JYC the main area of application for the new 8-axle is in the wind segment.
Liebherr engineers have designed the LG 1750 so that the turntable and boom system works together with an eight-axle chassis of the very latest design, with speed-dependent rear-axle steering.
Brent says JYC has a very good relationship with Liebherr.
“Their support has been second
“Liebherr’s product stands up and, in my opinion, they are at the forefront of crane and lifting solutions technology. I feel like they are always a step ahead as they are constantly introducing new concepts and new crane technology.”
to none; whether it be from the sales process, from the beginning of the crane’s onboarding process right through to after the sales service and parts availability,” Brent says.
“Absolutely no complaints from us about Liebherr,” he added.
Brent adds he enjoys working with Liebherr and using Liebherr’s products to JYC’s advantage, completing projects in versatile and efficient ways.
“Liebherr’s product stands up and, in my opinion, they are at the forefront of crane and lifting solutions technology. I feel like they are always a step ahead as they are constantly introducing new
concepts and new crane technology,” Brent says.
JYC was founded in 2017 when Reece Johnson & Brent Young formed a partnership which saw the already established Brent Young Cranes transition into a new era as Johnson & Young Cranes.
JYC specialises in major infrastructure and renewable energy projects and Brent says the talented team at JYC is grateful for the opportunity to work on these large and important projects.
“Our clients involve us in these projects because we’re able to provide the right lifting solutions to deliver these often complex projects safely, on time and on
budget,” says Brent.
JYC’s engineering team is skilled in fast-advancing works such as renewable energy projects.
“We’ve got an engineering team that is eight strong, which is probably one of the largest in the state, there is a significant pipeline of work in the renewable energy space which is keeping us busy,” he says.
JYC has recently sent out its Liebherr LTR1100 (a 100t Telescopic Crawler) on long term hire for work in Melbourne’s north-east.
The Liebherr LTR1100 is a reliable and efficient crane that offers superior performance and safety for a variety of construction projects.
JYC’s telescopic crawler is responsible for undertaking a wide variety of general lifts contributing to the build of 6.5km traffic tunnel.
The crawler travel gear delivers outstanding off-road capabilities and can be driven with a load attached – even on constricted sites or at a lateral angle. The powerful boom has been taken from the telescopic crane and can be extended to almost any position.
The reliability of JYC cranes stands out, from the crane and transport crews to the back of house teams, the level of consistency is no different.
JYC employs about 200 people and each staff member plays a significant role in the day-to-day operation of the business.
“We’ve been fortunate as a business, as we’ve managed to attract and retain really good people,” Brent says.
“We have a number of ‘long term’ team members who have been with us for many years, they are all very professional. They know our business, they understand the capabilities of our cranes and what’s
expected of them and if there’s something that looks odd in regards to equipment or onsite environments, they will speak up immediately,” he says.
“Alongside them, JYC has around 30 people across both offices (Dandenong and Campbellfield) every department has experienced considerable growth over the last 2-3 years, and we are fortunate that we have teams of very capable and driven people.
“Our people are the cornerstone of our success.
“Our office staff and crane/transport crews are very customer focused and understand the importance of planning and preparation for every project. Our customers see this attention to detail and appreciate the levels of service we are able to provide, and with the addition of the LG1750 to our fleet, we are looking forward to taking this up to another level again,” he adds.
Freo Group, a leading provider of crane hire and logistics services in Australia, is renowned for its comprehensive lifting solutions that serve a variety of industries, including construction, mining, infrastructure and energy. Wit h an extensive fleet, Freo Group is well-equipped to manage projects of all sizes, from small-scale operations to large, complex undertakings.
to safety, quality and exceptional customer service has established the organisation as a trusted partner in the industry. The company places a strong emphasis on innovation, sustainability and building longterm client relationships to drive successful project outcomes.
Recently, Freo Group expanded its pick and carry fleet with the addition of two TIDD PC28-3G cranes. Procurement Manager Ray Martinez sheds light on the rationale behind these acquisitions and explains how the TIDD PC28-3Gs align with Freo Group’s roadmap towards a more sustainable future.
“Recently, the business was a little stretched in terms of pick and carry capacity and we were in urgent need of a number of cranes at short notice,” he said.
“The TIDDs performed really well. While there was initial hesitance from our operators regarding the change, they quickly adapted and came to appreciate the TIDDs’ performance and usability. Based on this positive experience, we recognised the need for additional pick and carry cranes. Consequently, we decided to invest in two TIDD PC28-3Gs, which are the first TIDDs we have owned,” he said.
Chris was given a survey with five questions to evaluate these key aspects. Chris reported that the TIDD Crane scored a perfect 10/10 in every category, stating, “The TIDD Crane is very comfortable with the latest technology advancements, all coupled with TRT’s team of great knowledge. The TIDD is a very well-refined crane, 10/10.”
Freo Group’s Principal Assessor, Chris Everleigh, was also invited to conduct a comprehensive product inspection of the TIDD Crane. This inspection included an intensive two-day test that assessed the crane’s drivability, manoeuvrability, comfort and operational lifting capability to ensure it was fit for purpose. After the test,
TRT has manufactured the TIDD PC283G using the highest quality components, prioritising safety and performance throughout its design and incorporating class-leading features including the Euro 6 Cummins Engine, the highest emission control diesel engine available with significantly more horsepower.
Neil Webb, General Manager at TRT
Australia, discusses the features and benefits of the new TIDD PC28-3G and what sets TRT apart from the competition.
“The new TIDD PC28-3G is equipped with the Cummins ISB6.7 Euro 6 on-road engine, a strategic choice as Euro 6 is set to become the new Australian Design Rule (ADR) standard by November 2025. We opted for the Cummins engine due to its extensive after-sales service and support network across Australia.”
“This upgrade from our previous standard Mercedes package to the Cummins engine brings an additional 34 units of horsepower, making a significant difference in operational performance.”
“Obviously Slew Safe is a key safety
TRT has manufactured the TIDD PC28-3G using the highest quality components, prioritising safety and performance throughout its design and class-leading features.
“The new TIDD PC28-3G is equipped with the Cummins ISB6.7 Euro 6 on-road engine, a strategic choice as Euro 6 is set to become the new Australian Design Rule (ADR) standard by November 2025.”
feature and has featured in our cranes from the beginning. The feature, developed and patented by TRT, serves as a significant standard for safety. It is specifically designed to assist operators in preventing rollovers. This preventative tool functions by alerting the operator when they are slewing in an unsafe direction, prompting them to slew back towards safety. This ensures a clear understanding of the operator’s role in maintaining safety standards. The feedback from our customers on the PC28-3G, especially from Tier One builders, has been fantastic,” said Neil.
The new TIDD PC28-3G also features the TRT patented Traction Air System.
“The Traction Air System is currently operating in approximately 10 countries around the world as a CTI system. It was initially designed for logging equipment, and we moved it into our TIDD pick and carry crane. It’s an option but we see more and more safety requirements from sites, and from customers which means it is almost a standard option that’s ticked by our customers.
“The Traction Air System provides a management system for tyre pressure. It allows the tyre pressure to increase or deflate to ensure optimal pressure of 130 PSI is maintained. It’s a great safety feature for the crane. Because the tyres are always at the correct pressure you also
While ABS has only recently become a requirement for ADR compliance, our commitment goes beyond meeting standards—we integrate these systems because ensuring the safety of our products is our highest priority.”
“When we began redesigning to comply with the new ADR emission standards, we assessed areas for improvement. We focused intensely on the exhaust brake system and decided to switch to a retarder. It is very similar to the technology used in a lot of heavy equipment, like large all terrains, and this Allison Transmission with Retarder really puts us ahead of our competition,” said Neil.
“It’s essentially an additional safety feature for our crane. Our customers recognise that TRT doesn’t just aim to meet standards; we consistently exceed them and continue to innovate. We are highly
customer-focused, incorporating their feedback into our product designs,” said Neil.
With improved engine performance, increased horsepower and better braking, the TIDD PC28-3G has been accepted into the marketplace really well. Another added safety feature involves neutralising the gearbox when the holding brake is on.
“This ensures the operator can’t take off down the road with the brake on, causing damage to the braking system. Also, during operation, it can be unsafe if the operator’s left the crane in drive and engaged the holding brake. The load can lurch when he applies the throttle,” Neil said.
“It’s just another complementary feature, along with our EN-13000 approved system, which allows us to have a 75 per cent static chart. We’re not just a pick and carry crane. We also have a static chart, which gives it a greater performance to 75 per cent instead of 66 per cent, which is a huge feature when you’re talking loads.”
“Innovation is crucial in a competitive market, and it’s deeply ingrained in our DNA. We’ve never stopped improving, consistently incorporating customer feedback to refine our products. TRT’s journey started in 1967 by tackling challenges head-on, and it’s this competitive ethos of solving the unsolvable that drives us to keep pushing boundaries and delivering the best solutions,” said Neil.
“TRT has consistently led the way in the pick and carry crane industry, designing a crane that has genuinely shifted the market. Previously the market was quite stagnated when it came to health and safety in this
The new TIDD PC28-3G features the TRT patented Traction Air System.
space. But TRT’s designs have helped set the standards where they need to be, and now there’s others out there that are having to play catch up as a result.”
TRT was the first crane manufacturer to introduce a fully compliant Stage 2 Australian Design Rules (ADR) pick-andcarry crane to the market. They also led the industry by launching a pick-and-carry crane equipped with a Euro 6 engine, surpassing the Stage 3 ADR emission standards.
these new cranes far outweigh any potential hesitations. As Ray mentioned, it’s only after operating and driving the TIDDs that users truly appreciate their value. This positive response is common, which is why we encourage people to either hire or test drive the cranes. Experiencing the TIDD PC28-3G firsthand confirms the high standards we promise.”
The resources sector and Tier One builders are increasingly focused on site safety, sustainability and reducing carbon footprints. Ray Martinez from Freo Group discusses how the TIDD PC28-3G fits into this evolving landscape.
“Freo Group is committed to meeting customer demands for reducing carbon footprints and offering sustainable lifting solutions. As the resources sector explores ways to lower emissions and adopt more sustainable mining practices, Freo Group is dedicated to advancing its own sustainability roadmap. We are actively engaging with crane manufacturers to incorporate emerging technologies and share these advancements with our customers.
“The new Australian Design Rules have prompted significant changes across the industry. Cranes now feature Tier Five engines and are capable of running on alternative fuels like biodiesel and HVO. The TIDD PC28-3Gs align perfectly with our sustainability strategy.”
TRT pioneered the design of a two-door pick-and-carry crane and was the first to invest in full ABS braking for this type of crane. Additionally, TRT is the only manufacturer to offer Slew Safe - Move Safe anti-rollover safety technology, making it Australia’s safest pick-and-carry crane. It also stands out as the only pick-and-carry crane in the market featuring an Allison Transmission with retarder.
“Freo Group’s decision to invest in two new TIDD PC28-3Gs is a significant endorsement of our product, especially given that major crane companies often have established fleets of other pickand-carry cranes. While switching can sometimes face resistance, Freo Group has clearly recognised that the benefits of
“The new Australian Design Rules have prompted significant changes across the industry. Cranes now feature Tier Five engines and are capable of running on alternative fuels like biodiesel and HVO. The TIDD PC28-3Gs align perfectly with our sustainability strategy.
Celebrating 50 years in business this year, Freo Group has had a long-standing partnership with TRT, having purchased bespoke TRT trailers for many years. Our relationship with the Carden family has been strong, and more recently, we’ve enjoyed collaborating with Neil Webb and Troy Hand from TRT Australia. We look forward to continuing to explore and benefit from TRT’s innovative products in the future,” Ray said.
Engine - CUMMINS QSB6.7 (Stage IIIA / Tier 3 or Stage IV / Tier 4f or EU Stage 5)
Capacity at Full Reach - 1.9t x 86m
Max Lift Capacity - 175t x 4.1m
Max Boom Length - 84m
The SCX1800A-3, a 175 t class crawler crane, is engineered for modern social infrastructure projects worldwide. It combines safety, energy efficiency, and user-friendliness with exceptional lifting capabilities in a compact design. With a reach of 75 m + 31 m, it excels in transportability and operational efficiency, and employs a clean-running Cummins engine, meeting EU Stage III and US Tier 3 emissions standards, with Stage IV and Tier 4 options available.
Pace Cranes recently opened a new facility in Brisbane’s West. The official opening was celebrated by hosting a Queensland branch meeting of The Crane Industry Council of Australia. David ‘Chalky’ White explains more.
“FOR SOME TIME, PACE CRANES HAS BEEN examining the possibilities of opening a branch in Brisbane. When I joined the team a couple of years ago, the requirement for a dedicated facility became a priority and, as with all things, it has taken us longer than expected to find the right premises that fits our requirements for now and into the future,” said Chalky.
The new facility is ideally situated on Boundary Road in Wacol, one of the original industrial areas in the West Brisbane corridor. Chalky explains why Pace Cranes chose this location.
“We looked at quite a number of places, most were in this general area and this one ticked all the boxes for us as a ‘startup’ branch. The fact that it happened to be situated close to my home was a valueadded bonus,” he said.
Chalky goes on to discuss the features
of the new facility.
“The building provides excellent floor space with a readymade showroom area, and we also have good exposure due the very high traffic area.
“The workshop certainly has service opportunities once we decide the time is right to increase our capabilities in Brisbane. In all likelihood, our short-term plan will be to start with a service van providing more on-site, mobile servicing for the growing population of cranes across greater Brisbane and the surrounds,” said Chalky.
The new branch premises is currently considered a sales office and showroom, whilst also carrying stock of certain popular machines, says Chalky.
Chalky discusses his interesting role in sales, being charged with increasing sales across Australia and also New Zealand.
“I receive amazing support from Michael Cawston and Anthony Heeks out of Sydney. We will continue to rely on Sydney to support the Brisbane office for
the time being. In terms of administration, we are very well supported by our Sydney Head Office.
brands which are manufacturing extremely reliable machines and very rarely breakdown.
“As I have mentioned, it is our intention to introduce mobile service capabilities in the Brisbane branch and this will come as we grow the Brisbane business. We are blessed to be working with recognised
“As the business grows, we will begin focusing more on the servicing side of machines. We will fill the missing local service support ‘hole’ as soon as is economically viable, and we are telling customers to watch this space,” said Chalky.
“I’ve been in the crane industry a long time and the opening of the Brisbane branch of Pace Cranes is an exciting highlight for me. It has been a long time coming but the timing is right. In my opinion, Brisbane is about to embark on a massive construction program in preparation for the 2032 Brisbane Olympics.
“We are experiencing rapid change in the way builders are approaching projects in terms of reducing carbon footprints, by reducing emissions and contributing to more sustainable construction processes. They continue to focus on safer work practices and look at products that eliminate manual handling, and this is why our Tracked Carrier range is gathering significant momentum,” said Chalky.
“Increasingly we are seeing the brands we represent working in applications we would not have considered a few years ago. We are now seeing Maedas working on tunnelling projects, for example, and Sennebogens continue to be recognised for their ability to thrive in extremely rugged conditions,” he said.
At the Annual Branch Meeting, Daniel Radaich from NMT Shipping presented a 2024 Shipping Update to CICA’s local members in both Queensland and New South Wales. The presentation drew upon global issues such as the surge of retail demand during COVID-19, Australian terminal congestion created due to delivery of record levels of new cars and how the 2023 draught in Panama that reduced the number of crossings through the Panama Canal caused significant delays to delivery times. Issues such as these demonstrate how global issues have a visible and real impact on the cost and flow of cargo such as cranes and other mobile machinery to and from Australia.
Jarrod Wilson and Vincent Wong from the NHVR provided an update on compliance and enforcement activities across Queensland following the transition earlier in 2024. Attendees were given some insights into the priorities of the NHVR and its focus on safe on road heavy vehicle operations across the country. NSW, Victoria, Tasmania and South Australia had already transitioned to the NHVR, with
Queensland being the last addition to the program. Members were presented with some data analysis on the compliance and safety performance of the crane industry compared to others, with a focus on preapproved road access either via notice or under permit. As part of the discussion, it was revealed that SPVs are currently high on the radar of the NHVR as part of a national heavy vehicle road safety blitz. Members are reminded to ensure that their use of the TMR road network is in line with the requirements of relevant notices / permits and that vehicles are properly maintained. Members also heard that many existing TMR staff have made the change to the NHVR, which should result in a smooth transition when it comes to roadside enforcement. That said, members were told not to hesitate to contact CICA directly if they experienced any issues related to NHVR compliance and enforcement activities.
As part of CICA’s ongoing road access updates Mandy Haldane and Matt Elischer from TMR provided a presentation and “live” system demonstration of the new Heavy
Vehicle Access Management System (HVAMS) which is planned for rollout for the Queensland crane industry in July 2025. The new system shifts the reliance from permits to access under notice and aims to create improved access across both state and local roads in Queensland. Building upon the success of the Tasmanian system, HVAMS offers a significant improvement in the road access application process, providing owners with greater flexibility when it comes to the on-road configuration of cranes. TMR also outlined the transition away from IAP to TMA which offers benefits to industry including lower costs, while providing state and local road managers with anonymised usage information of road assets including bridges. CICA will continue to support TMR in the rollout of HVAMS in Queensland and will facilitate the formation of the soon-to-be established working group to be made up of representatives of the industry from across the state. Keep your eyes out for further information and attend upcoming meetings for the latest updates on the HVAMS rollout.
When it comes to personability and product reliability, Urban Crane Hire is a brand those in the crane and heavy lifting industry can rely on.
SOUTH AUSTRALIA-BASED CRANE HIRE
company Urban Crane Hire recently took a deep dive into what makes its brand click with customers, and what it will take to go to the next level.
Urban Crane Hire General Manager, Jessica Atkinson says it’s the customers that come first.
“As a business, we want to make sure we keep our customer’s best interests at the forefront of what we do and we are excited to work with them on projects that are important to them,” says Jessica.
Urban Crane Hire is a versatile business, servicing the needs of many construction and residential clients in South Australia. Its focus on personability, matched with its five core values - Safety, Diversity, Integrity, Sustainability and Quality - hold it steadfast in remaining a dependable and trustworthy company in
the industry.
Using a fleet of smaller cranes, the company specialises in glass and steel frame installation, and has recently worked on major public art installation projects across Adelaide.
“We aim to service a niche market and we’re focusing on a few areas in the industry, which are glass installation and steel erection,” says Jessica.
“Predominantly, we do general crane hire, but we want to be good at what we do, and when we can focus on key areas of the market, such as delicate glass and steel jobs, alongside general crane services, that’s when we can deliver that promise of high standards, attention to detail and reliability to our clients.”
Jessica says the business aims to be the best in the SA market for specialised steel and glass jobs, whilst fostering close relationships with clients and maintaining those connections thereafter.
“We don’t want to take over the world… we want to be personable and be a South Australian brand that customers can trust, and I think we are well on our way in achieving that.”
Trained to the highest of standards, the skilled team of operators and riggers at Urban Crane Hire has extensive knowledge and experience in their field. “They are the backbone of the company and we aim not only to train them to the highest of standards, but also ensure they are cared for at the same level,” mentioned
Deeply committed to ‘Lifting The Standards’, the team at Urban Crane Hire can carry out planned lifts with ease and adapt quickly to provide solutions on safely completing even the most irregular lifts.
This depth of expertise allows Urban Crane Hire to provide a well-rounded labour hire division to complement its crane hire service for its client projects.
Urban Crane Hire holds a fleet of seven dynamic and versatile machines.
The GR-200EX crane, otherwise known as a “bubble crane”, makes up one of two of Urban Crane Hire’s fleet and is known for its efficiency, compact nature and safety.
The GR-200EX is made by Tadano and boasts several new safety features such as the Tadano View System and Human Alert System, as well as a radio control set-up and the tightest swing radius in its class.
“Our GR-130EX, also a Tadano City Crane, is compact but heavy duty, and has a total lifting capacity of 13 tonnes with an impressive 23.8m of boom. Great for long reach and tight spaces,” she says.
“Within the space of two years, our Director, Samuel Marshall, has hit the ground running and purchased a total of seven cranes to expand our fleet. Half of these are brand new, to ensure our customers are getting the best cranes as well as the best crew when we’re called to the job,” says Jessica.
As with all things small, it’s not the size that matters, it’s the way you use it! Urban’s remaining five cranes fit that motto perfectly. All being mini crawler cranes, they are highly versatile, easily transported and can be set up in minutes to get the job underway.
Comprising of two Unic URW295’s, one Unic URW547, one brand new Maeda MC405C and the baby of the fleet, a Maeda MK1033W 1t knuckle boom, the company has chosen a well rounded variety of smaller cranes to meet the demands of the current market.
Ranging from 4t lifting capacity, right down to the smallest 1t, each crane is easily transported via trailer or medium rigid truck. No one crane takes up more than 1.4m in width when fully stowed, and the largest footprint when outriggers are fully extended is a mere 6m x 6m.
Both Samuel and Jessica have played many roles in the crane industry over the years. Samuel having a more operational role, operating cranes and rigging, and Jessica providing background support in roles such as Crane Coordinator and Business Development Representative.
Over the years they have formed a working relationship and combined their experience to lead the team in good stead at Urban Crane Hire.
“I truly believe that all of our experiences before have led us to our individual roles and I’m grateful we’ve
Urban Crane Hire completes project work in SA to the highest of standards.
“Our GR-130EX, also a Tadano City Crane, is compact but heavy duty, and has a total lifting capacity of 13 tonnes with an impressive 23.8m of boom. Great for long reach and tight spaces.”
been able to fulfill them quite well,” explains Jessica.
“Samuel had a vision, and he went for it. It still surprises me to this day how far we’ve come in such a short time, but I’m proud to be part of such a great team and entrusted with the role of General Manager”
Both Samuel and Jessica recognise the importance of all those who helped build
Urban Crane Hire to what it is today.
“Without the support and trust from our very first clients who gave us a go in the beginning, we wouldn’t be where we are today. They trusted us with their projects, they backed us without any other reassurance other than our word that we would get the job done safely and efficiently. We are forever grateful,” says Jessica.
FOR ANY PROJECT
With over 15 years of experience in the crane industry, Urban Crane Hire aims to provide an exhaustive variety of crane hire and crane services in South Australia, including but not limited to:
- CRANES AND EQUIPMENT HIRE
- DUAL/MULTIPLE CRANE LIFTS
- GLASS INSTALLATION
- STEEL ERECTION
- RELOCATION AND TRANSPORTATION
- POOL INSTALLATION
McMahon Services recently took delivery of a Sany SCC2000A 200 tonne capacity lattice boom crawler, the first Sany in its fleet. Simon Laird-Barrington, Crane and Rigging Manager Demolition and Decommissioning for McMahon Services, explains more.
as well, particularly to accommodate the marine-type works we envisaged for the crane. The price was right, what Sany was offering was right so we made the purchase,” said Simon.
The Sany SCC2000A lattice boom
crawler has a 200t lifting capacity.
McMahon Services researched the market before deciding on the Sany.
“We priced a few brands. We had brands that were astronomically more expensive and others that were competitive, but they
Two key issues that put Sany over the line were price and delivery date.
“The key features that really sold Sany included the huge variety of counterweight reduction charts. Where some of their competitors only had a full counterweight chart or one reduction chart, Sany provided a huge variety of charts which gives you more options.”
couldn’t deliver in the same timeframe promised by Sany. Price, the quality of the product and delivery time frame were the key reasons we went with Sany.”
McMahon Services has a good relationship with Tutt Bryant and this was also a key reason for the purchase.
“We have a good relationship with Tutt Bryant and they have an excellent reputation in the market. We haven’t owned a Chinese brand before, but we
figured if Tutt Bryant are continually adding Sanys to their fleet and they are performing well, it can’t hurt to give them a go.
“We know they have a number of these in their dry hire fleet which was reassuring, and we also know that Sany is supported by the local Tutt Bryant branch in terms of service and parts availability,” said Simon.
He goes on to discuss the key features and benefits of the Sany SCC2000A.
Key features of the McMahon Services Sany include:
• 70m Boom
• 31m Fixed Jib
• Rooster sheave
• M ain & Aux winches with 26mm ropes and 13.5t line pull
• H ooks 150t, 80t, 35t & 13.5t ball hook
• 2 0 degree tilt cab
• F ull counterweight 74t Upper + 25t carbody Cwt
• Reduced counterweight charts
• B arge charts
• S elf assembly
• U pgrade C5 paint standard in McMahon Services colour
“The key features that really sold Sany included the huge variety of counterweight reduction charts. Where some of their competitors only had a full counterweight chart or one reduction chart, Sany provided a huge variety of charts which gives you more options.
“They also offered a thicker layer of high quality of paint which they wouldn’t normally supply with a crane and they also provided a number of barge charts. A barge chart for the full counterweight is normally provided, but Sany accommodated us and created some barge charts for their reduced counterweight options on the machine. They also provided us the ability to operate the crane from a barge,” said Simon Simon has been impressed with the service McMahon Services has received from Tutt Bryant.
“In the initial stages, we worked with Phil Chadwick who is extremely knowledgeable and helped make the sales process seamless in terms of his communication between us and Sany. During the delivery and commissioning stages we worked closely Daniel Waldhuter and his team from Tutt Bryant’s Mawson Lakes branch.
“During the commissioning of the crane when we had any questions or any niggling issues, Daniel jumped straight onto it and got his guys his guys down here. The Tutt Bryant team have been really supportive through the sales and commissioning process which augers well for our future with our new Sany,” said Simon.
MAX Services purchased the Kobelco CKS2500 due to its versatility and simplicity - which he said made it a great option for general construction works and also barge operations if required.
MAX Services recently took delivery of a Kobelco CKS2500, a 250t capacity hydraulic lattice boom crawler. MAX Services’ Chief Operating Officer Pete Koschel provides the background to the latest addition to the fleet.
“A FEW MONTHS AGO, WE WERE EXAMINING our fleet and we could see an opportunity to add another crawler. It wasn’t going to be a purchase for a specific project and, as timing would have it, Anthony Davis from The Crane Connection reached out, saying he had a couple of slots available with Kobelco for delivery later in the year and would we be interested in having a look at one? That conversation started the process,” said Pete.
“We looked at our pipeline of projects and we could see a whole range of opportunities coming up across the various different industry sectors
including oil and gas, mining and infrastructure. We have three crawlers in the business, a 75t, 150t and 350t and we thought a 250t class crawler would be a real workhorse. It’s easy to mobilise and de-mobilise and it provides us with a lot of opportunities across a broad range of work, both in wet hire and dry hire,” he said.
The decision to purchase of the Kobelco came down to the strength of the relationship MAX Services has with The Crane Connection. said Pete.
relationship with him and Ben and his father Gerhard. Mark Kuhn, Managing Director at MAX Cranes, has been mates with Anthony and I’ve known him for many years. Anthony is super respected throughout the industry and when all of this came together, it felt as though we were buying the crane from family,” said Pete.
“In my opinion, integrity in business is earned over many years, and Anthony, Ben and the team at The Crane Connection have it in spades.
MAX Services has really strong values around working safely with our customers and our employees, having IN FOCUS / CRANE CONNECTION,
“We were only considering a couple of brands, but Anthony was on the front foot, and we have a long-standing
the right attitude at all times - integrity and respect. Anthony aligns with all of these values almost unconsciously,” he said.
“We purchased the Kobelco CKS2500 due to its versatility and simplicity making it a great option for general construction works and also barge operations if required. Also, its breakdown and component sizes and weights make it very cost-effective and simple for transport from site to site,” said Pete.
The CKS2500 has a maximum lifting capacity of 250 tonnes and a maximum boom length of 91.4m plus 30.5 metres of fly. This model is part of the S series from Kobelco, which consists of crawler cranes with lifting capacities ranging from 80t to 550t. The S series is designed, upgraded and improved from the customer’s point of view with safety, reliability and efficient operations in mind.
The design of the CKS2500 is based on end-user feedback and real job site experiences. The design makes the model “transportation friendly,”
“assembly friendly” and “operator friendly.” Each are essential to fulfill the satisfaction of owners and operators.
The features of Kobelco’s S Series are consistent with these key concepts.
The S Series comes with a variety of optional safety support devices, including a counterweight amount detection device that always tells the correct amount of the counterweight. A swing angle detection device prevents over-swinging, while ground-level sensors prevent operations on uneven ground. Machine status is displayed on a new wide monitor in a luxurious operator cabin designed to enhance comfortable operation.
The models have an improved counterweight self-installation mechanism. Counterweights can be stacked up on the ground and installed
on the machine by vertical cylinders. Safety and work efficiency have been greatly improved. (*Counterweights of 80t and 90t are optional specifications.)
The models can also be adapted for both bucket and lifting applications. The hydraulic circuit can be set to dualpump flow or single-pump flow so that the circuit can be perfectly adequate for both applications. The newly designed circuit can be switched to choose the best circuit for the job application.
MAX Services already operates a fleet of support vehicles to manage the mobilisation and de-mobilisation of the new Kobelco, says Pete.
“We don’t need to add anything to our fleet to manage the transportation of the Kobelco. We already have the low loaders in our fleet to move the car body and then the rest comes down to
“The new crane will be a great addition to our crawler fleet and improve our overall capacity and ability to deliver a comprehensive lifting solution to our customer.”
The CKS2500 has a maximum lifting capacity of 250t and a maximum boom length of 91.4m plus 30.5 metres of fly.
just trailer fleet. The Kobelco CKS2500 is set up and ready for some other mods if we need it, but for MAX Services, at this stage it is a ‘toe in the water’ into that mid-class crawler range.
“The new crane will be a great addition to our crawler fleet and improve our overall capacity and ability to deliver a comprehensive lifting solution to our customer”, said Pete.
“The new Kobelco slots nicely into the fleet and fills a gap in our capabilities. The Kobelco features traditional Japanese engineering and manufacturing qualities which leads to a robust machine capable of managing the harsh environments it is likely to be working in.
“We also purchased the crane with the confidence of the support we will receive from The Crane Connection and also TRT in terms of service and spare parts availability. The Kobelco CKS2500 is going to be a good fit for MAX Services,” said Pete.
Crane
LiftQuip’s blend of industry experience and quality people holds the reliable South Australian company in good stead for its most recent Darwin expansion, Managing Director Mark Eberhard says.
MARK SAYS HAVING AN EXPERIENCED team with a clear understanding of crane and heavy lifting customer needs is essential for success - and LiftQuip embodies those aspects every day, he says.
“We have a really good team of people who understand customer requirements in the lifting industry, and I think that’s
very important,” says Mark.
The company, founded in South Australia, specialises in the manufacture and supply of Lifting, Materials Handling, Height Safety and Load Restraint equipment, drawing from experience to help customers with their lifting needs.
LiftQuip has grown exponentially
over the past seven years, today respected and recognised as being both technically capable and a valuable supply partner to the lifting and materials handling industry.
Mark says LiftQuip’s focus on customer service is key to delivering positive outcomes for both the business and the customer.
“Everything we do here at LiftQuip is quality-focused but equally as important to us is customer focus and having that real, personalised customer service,” Mark explains.
Mark says LiftQuip takes the “long game” approach with its customers to foster strong relationships within the industry.
“We’re in it for the long game; we like to foster relationships with the customers and really understand what they’re looking for in a supply partner.
Managing Director of LiftQuip, Mark Eberhard, is proud of the strong reputation the team has created for the business
for years to come,” Mark explains.
Mark also has a lot of trust in the 16 LiftQuip staff members across its Adelaide, Whyalla and Darwin branches to solve technical problems that the customer may present.
“It helps when you’ve got industry professionals that know what the customer requirements are. We get a lot of referrals from our customers who have had great experiences with us, which is a fantastic feeling and great recognition for the work that the team do”
“We work with you to solve your problem. We work through what products or services you need, and take
Experience, Quality and Service, LiftQuip offers technical support in areas such as product specification, design, asset management, repairs, maintenance and testing.
LiftQuip personnel have been involved in the crane and lifting industry for a combined total of over 100 years, offering customers peace of mind through quality products, experience and personalised service.
The company provides a full-service offering, including On-site Inspection and Testing, Overhead Crane Servicing and Repairs and Height Safety System Installations.
Another form of testing
1998 to 2004, I met my wife in Darwin and have family up there, so there is a pretty strong connection with the NT.
“I am looking forward to the opportunities across the whole of the Territory” he says.
In the meantime, Mark is also excited for the future of the South Australian market and the role LiftQuip will play in that.
“I believe that the future is bright for South Australian industry,” he says.
“There are some really exciting projects coming up and I think that we will see a good platform be laid out for South Australia over the next couple of decades.”
Davo’s Crane Hire will soon take delivery of the first Grove Super Taxi to arrive in the country, the Grove GMK 4080L. The Grove GMK 4080L is an extremely versatile crane that will be a true game changer. Davo’s Crane Hire’s Matt Davis introduces the business and the reasons for purchasing the new Grove.
WITH OPERATIONS IN BRISBANE AND the Gold Coast, Davo’s Crane Hire was originally founded by Paul Davis and his late wife Robyn in 2001. They started the business with the purchase of their first crane, an eight tonne capacity bubble crane which set the platform for where the company is today. Davo’s Crane Hire has always maintained a great family and professional culture with its ever-growing crew, ensuring no employee is treated as a number within the company.
growing at a sustainable and manageable rate that will ensure a long-foreseen future in the industry for both them and their team.
Matt discusses Davo’s Crane Hire fleet and his experience with the Grove brand.
Above:
Proud to work in a family-owned and operated business, Paul’s son Matt has taken over the running of the business for some time and they are constantly advising each other and making decisions daily as a father and son team. The company has been
“We currently are running a mixed fleet of brands which includes our Grove GMK 3060L and the new GMK 4080L. We currently operate 13 cranes which are constantly working daily, and at times 24/7 when night works are required. Our capacities range from 13t through to the new Grove GMK 4080L with a capacity of 80t. We also operate a fleet of support vehicles,” he said.
Davo’s Crane Hire purchased the 60t capacity Grove GMK 3060L-1 a couple of
years ago and everyone has been pleased with its performance, says Matt.
“The Grove GMK 3060L has proved to be a valuable asset in our fleet. The crane has lived up to all expectations that were outlined at the time it was purchased. The GMK 3060L has been averaging 2,0002,500 hours per year which has exceeded our expectations. The ability to utilise the MAXbase feature has reduced running costs negating the need for counterweight trucks, while still being able to complete the work,” he said.
“We are extremely pleased with the crane and as a result of its performance, the return on investment has been excellent. Our operators like the crane because the CCS system in these later model Groves is extremely user friendly and very simple to navigate. The performance and utilisation of the GMK 3060L has most definitely been the motivating factor in the purchase of the GMK4080L,” said Matt.
The 80t capacity GMK 4080L offers the strongest load charts and the longest boom in its class at 60m. At its full 60m length, the crane is able to lift an impressive 4.4 tonnes, while at 49m it will be capable of picking loads of up to 8.3t. When working at its maximum radius of 46m, the GMK4080L will lift 1t.
Up to 78m of maximum tip height is available when the 60m main boom is paired with its 15m swingaway jib option. These are capabilities more commonly associated with 100t cranes and allow the new model to take on jobs that would typically require larger cranes.
Offering unmatched versatility, the Grove GMK 4080L will give owners a host of options for travel. In situations requiring 12t per axle, it will carry up to 13.3t of counterweight, while at 45.8t for NSW Level 4 GVM, it will be able to travel with 11t of counterweight and for 10t per axle configurations it will be able to travel with 5.3t of counterweight.
The new high-visibility carrier cab offers the best levels of protection in line with European ECE R29-3 regulations, ensuring exceptional security in frontal impact, roof and rear wall strength. Power for both the carrier and the superstructure
will come from a single 320 kW (430 hp) Mercedes Benz OM470LA 6-cylinder diesel engine. Compliant with Euromot 5/Tier 4 Final requirements, this clean, efficient engine is approved for use with HVO Diesel, for customers looking to further reduce their CO2 emissions or meet tight environmental jobsite requirements. The engine’s ECO mode can be used in conjunction with the transmission’s Fuel Saver mode, for unbeatable fuel efficiency.
The Grove GMK 4080L offers the exciting Grove CONNECT digital platform that provides owners with real-time access to fleet data. Through Grove CONNECT, fleet managers can get instant insights into the crane’s performance with just a couple of taps on a screen. Service technicians are supported with remote, optimised troubleshooting, reducing the frequency of
onsite trips and strengthening preventative maintenance programs.
The digital platform enables remote monitoring through an app-based system providing owners and operators with the ability to view real-time crane information.
The versatile platform advances fleet management, boosts sustainability, streamlines service and maintenance for users and improves connectivity to cranes with the easy-to-use platform working across smartphones, tablets, and laptops.
The MAXbase feature helps users reduce setup time at the jobsite and give them a wider choice of outrigger positions. With this option, the crane becomes an ideal choice for confined spaces or projects where obstacles are preventing setup in the preferred location. The productivity enhancing MAXbase allows the crane’s outriggers to be easily extended to a range of symmetric and asymmetric positions. This maximises flexibility and enables
“The Grove GMK 3060L has proved to be a valuable asset in our fleet. The crane has lived up to all expectations that were outlined at the time it was purchased. The GMK 3060L has been averaging 20002500 hours per year which has exceeded our expectations.”
lifting work to continue in less-than-ideal environments.
Also making life easier for the operator is Manitowoc’s Crane Control System (CCS), which supports both setup and lifting. The CCS (Crane Control System) can be reached comfortably from a seated position and has been ergonomically integrated into the cab. The intuitive interface makes the operator’s job much easier as the most frequently used settings, such as chassis level and axle locking, can be selected via the CCS. Different drive modes can also be chosen via the CCS screen. As all CCS displays offer the same layout and navigation throughout the GMK model range, it is easy for operators to switch from one Grove all-terrain crane to another.
Using its Boom Configurator feature, the operator can select the optimal arrangement of the seven-section MEGAFORM boom with TWIN-LOCK dual-pinning system.
“We can see that the GMK4080L is an extremely versatile four axle machine with 60m of boom. It has the smallest outrigger spread of 6.6m x 6.2m in its class which will enable it to fit and lift on the tightest of sites. It carries 13t of counterweight on the crane which means we are only having to carry 6t on a support vehicle (12t per axle). It features the same CCS operating system as the 3060L making it a great for taxi crane for our type of work,” said Matt.
Under Matt’s guidance, the utilisation of family values within the business are most important and sons Bodhi (4yrs old) and Arlo (1.5 years old) visit the yard weekly, just to check on what Dad and Pop are doing and to lend a hand. These key family values are also applied daily to the crew within Davo’s Crane Hire.
“We provide crane, transport and traffic control solutions for all types of industries. From commercial high rise projects, infrastructure work, residential house builds, machinery moves, a dragline boom or through to simply lifting a lounge suite to a balcony, Davo’s Crane Hire will provide a solution for all lifting requirements within our capabilities,” he said.
“When lifts are outside our capabilities, Davo’s Crane Hire can call in back up. We are extremely grateful to have relationships
with other local crane companies who are always willing to help and work together to achieve a suitable solution for our customers,” said Matt.
“Our staff are our number one asset. Everyone in the industry knows how chaotic it is to navigate the daily allocations, servicing and accommodating 40+ staff. Adam has been our Operations Manager for the past eight years now. His consistent dedication and ability to problem-solve on the fly is a key contributor to the growth of Davo’s Crane Hire over the past years.
“We work hard to maintain a high retention of staff, and this has a lot to do
with the culture of the crew. The whole team at Davo’s Crane Hire is prepared to go ‘above and beyond’ on a daily basis for our customers. The smooth operations of Davo’s Crane Hire begin with our Operations Manager, Supervisors and office staff and this level of professionalism is filtered down the line to our remarkable crane crew,” he said.
“We have always built and maintained a consistent market for all our cranes, and I have no doubt that this new purchase will be the same. The Grove GMK4080L is a versatile crane that will complement and increase our company’s ability to undertake the most challenging of jobs,” said Matt.
SureLift Crane Hire recently took delivery of a Tadano AC 7.450-1 450t capacity all terrain. Owner and Director Mark ‘Chopper’ Read discusses the reasons for purchasing such a large capacity crane for work along Queensland’s Bowen Basin.
CHOPPER HAS BEEN IN THE CRANE industry for over 30 years.
“It all started for me 31 years ago when I entered the mining shut down industry. I began as a Trades Assistant and later acquired my dogman ticket, which opened up new opportunities for me working in the Bowen Basin and led to a gradual progression into the crane industry. It was during this time that I recognised a significant shortage of cranes in the area.
“This realisation prompted me to take action, and I purchased my first crane. This marked a pivotal moment in my career, as it not only began to address the immediate need for cranes in the Bowen Basin and surrounds, but also laid the foundation for my future ventures in the industry.
From there, I purchased several more new cranes helping to fill the demand in the area. Year by year the business has grown and the demand for our cranes continues
to increase,” said Chopper.
SureLift Crane Hire has been servicing the Bowen Basin region and surrounds since July 1st 2006, and today boasts an extensive array of cranes and a significant fleet of supporting vehicles. The fleet includes:
• 17 Cranes including Tadano Demags and Terex Frannas. Capacities range from 20t through to the new Tadano 450t capacity all terrain. The crane fleet also includes a crawler crane.
• 16 Light Vehicles
• 4 Body Trucks
• 3 Tilt Trays
• 13 Prime Movers
• 37 Trailers
Chopper discusses the reasons for purchasing the 450t capacity Tadano AC 7.450-1.
“The need for this size crane was evident in the coal industry and also other
industry sectors that we service in the surrounding areas. I made the decision to expand the fleet in terms of capacity which will make a huge difference to our capabilities,” he said.
“The brand spanking new 450t crane rolled out of the Tadano yard and headed straight to its first job for a gas plant in Wandoan QLD. We installed and utilised the SSL for the construction of the new hospital in its hometown of Moranbah where we placed 100 buildings from one set up.
“It is currently assisting with a major bridge build which also requires several of our other cranes to assist. It has been back to Wandoan for several more lifts, and has returned to the Bowen Basin where it is booked to assist with major Shut Downs for our local coal mines. We are currently looking at securing its first job utilising the luffer on the east coast of QLD.
“The capabilities of this crane opens us up for a wide range of work not only in mining but in gas, sugar mills, bridge works and the construction industry.
“It is the largest capacity crane in the area and as you can see there has been an ongoing need for a crane this size with 450t capacity,” said Chopper.
The Tadano AC 7.450-1 features a whole series of technical advantages that put it at the very top of its capacity class. The AC 7.450-1 is a significantly more powerful option than all six-axle units that are currently available on the market, claims Tadano.
Despite its additional axle, it still fits in the six-axle class in terms of its dimensions, having a carrier length of only 15.99 metres, an outrigger base of 8.49 metres, and a total length of 17.62 metres. On top of this, it offers significantly better
“It is the largest capacity crane in the area and as you can see there has been an ongoing need for a crane this size with 450t capacity.”
its capacity class.
Despite its additional axle, the AC 7.450-1 still fits in the six-axle class in terms of its dimensions, having a carrier length of only 15.99m, an outrigger base of 8.49m, and a total length of 17.62m.
performance, matching that of eight-axle cranes in many areas. Additional highlights include a powerful 80-metre boom; a patented luffing jib rigging system for particularly easy, fast, and safe setup; and a new SSL (Sideways Superlift) in which the Superlift arms are mounted right at the front of the head, meaning that they are ultimately longer and provide larger lifting capacities. And while on the subject of lifting capacities, this means that the AC 7.450-1 is considerably superior to other seven-axle cranes – in fact, it even leaves some eight-axle units behind in a number of boom positions.
The fully telescoped 80m main boom (without SSL) can lift a max capacity of 23.7t, adding SSL (Superlift) the AC7.4501 can lift a maximum capacity of 37.3t with a fully telescoped main boom. Maximum system length is 133.8m which
includes the 81m luffer + 2m runner which can be added to extend any lattice boom combination. Light fixed fly extensions 8m - 59m and Fixed offset extensions 11m - 56m are also available.
Tadano is using its new engineering design for the Sideways Superlift system for the first time ever on the AC 7.450-1. This new design is a decisive enhancement to the well-known Tadano SSL solution. The Superlift arms are now mounted all the way in the front, on the head of the base section, meaning that they are ultimately longer and accordingly well-suited to larger lifting capacities.
The functionality and handling have been improved as well. The new design only requires one single wire rope line for the connection between the main boom head and the SSL arm. In addition, the SSL arms are pinned hydraulically on the main
boom, which reduces manual work for securing the arms and the associated work at height.
The AC 7.450-1 features six cameras that keep everything in view. With the help of a computer-assisted diagram, this makes it possible to graphically show the possible extension lengths for the outriggers and the counterweight tail swing radius on the display in the carrier cab. This makes it significantly easier to position the crane at job sites. Surround View also helps on the way to the site by making it easier.
Chopper details the amount of equipment required to support the AC7.450-1 and how impressed he is with the team at Tadano.
“Purchasing a crane of this size required the purchase of three prime movers and nine trailers which accompany it to jobs transporting the counterweights. Tadano has always been an excellent partner to deal with, they have exceptional customer service and support,” he said.
SureLift provides lifting services for all lifting needs, catering to both local projects in its hometown of Moranbah, as well as well as major mining operations in the Bowen Basin and broader Queensland.
Chopper goes on to confirm the experience he has in his crane crews, his operations teams and how they approach complex projects.
“We have a vast amount of experience across our crane crews including our crane operators. The culture of the business is based on giving anyone a go in the industry and helping them reach their goals and ambitions,” said Chopper.
“Performing complex lifts in the crane industry requires careful planning, adherence to safety regulations and the skill of our crane operators and the crew. Risk assessments, site preparation, crane selection and open communication between the team and the client is important for a complex lift to be conducted safely and effectively. Some projects require engineering plans and 3D lift plans which we also manage,” he said.
With the new Australian Design Rules (ADR) compliance regulations now in effect, Terex Franna has taken the opportunity to incorporate new technology across the entire Franna range including the AT22-2, MAC25-5 and AT40-2. Each model in the line-up has received significant upgrades designed to minimise environmental impact and improve operational efficiency.
THE UPGRADES START WITH THE NEW Mercedes-Benz OM936 Engine Stage V and Tier 4 Final compliant engine for cleaner emissions, ensuring seamless compliance with evolving environmental regulations.
Although this is new technology for Franna, it is technology that has been powering European all terrains and other special purpose vehicles for many years. Whilst the technology has been implemented as a result of regulatory compliance requirements, Franna has taken opportunity to improve performance, the OM936 is a proven 7.7 litre engine versus the outgoing OM906’s 6.4 litre displacement, power and torque are up across the range, up to 230kW and 1300Nm respectively. The OM936 boasts a well-established track record, having undergone over a decade of refinements to achieve exceptional reliability.
Franna’s dedicated engineering team collaborated directly with the German manufacturer, MTU, in conjunction with Penske Power Systems, the authorised distributor of Mercedes-
Above: Terex Franna has implemented a series of additional enhancements across all models, designed to streamline customers’ lifting operations enhancing useability, productivity and safety.
Benz engines in Australia, to ensure seamless integration of the OM936 into the range. This collaboration included extensive emission reduction technologies, a power increase and fine tuning of the gearbox providing optimal performance within the demanding environment of pick and carry cranes.
A highly efficient and low-emission off-highway product, the OM936 meets specific mobile crane requirements for the stringent Australian Design Rule (ADR) regulation in addition to the EPA Tier 4f requirements, the stringent US engine emission regulation. The OM936 provides Franna with a significant advantage aligning with their export strategy. By the time this article is read, Franna will be shipping the AT24-2 US (the AT22-2 being 24USt) to the USA.
The OM936 engine is also fully compatible with HVO diesel fuels,
enabling a reduction in carbon emissions by up to 85%.
In addition, the OM936 is fitted with a ‘Jacobs’ style exhaust brake, giving effectively double the retardation over the existing OM906 engine. Franna selected the engine exhaust brake option rather than a transmission retarder as it has the advantage of providing additional retardation through every gear of the transmission selection.
“The innovative design of the OM936 engine cooling system has been engineered to achieve a Limiting Ambient Temperature close to 50 degrees Celsius. This optimisation was accomplished by incorporating an additional extraction fan into the cooling pack, ensuring the engine maintains optimal performance even in the most demanding environmental conditions.
Limiting Ambient Temperature refers to the highest ambient temperature at which the vehicle’s cooling system can effectively manage the engine’s
The rigorous testing process validated the cooling system’s capability, ensuring that the OM936 engine can deliver consistent performance under full load, even in ambient temperatures nearing 50 degrees Celsius. This breakthrough not only enhances the engine’s durability and reliability but also positions it as a leading choice for operators working in challenging environments where high temperatures are a critical factor.”
The Series upgrade goes beyond just the new OM936 engine. Franna has implemented a series of additional enhancements across all models, designed to streamline customers’ lifting operations enhancing useability, productivity and safety.
All Franna models have been upgraded to ensure they are compliant with current ADR compliance
During the design phase, extensive cooling performance testing was carried out using a dyno cart to simulate realworld conditions.
“Safety remains an unwavering priority for Franna. The Series upgrade elevates safety standards by incorporating Franna’s patented Safety Radar as a standard feature.”
heat output while allowing the engine to continuously operate at full power. Achieving a high Limiting Ambient Temperature is crucial for ensuring the reliability and efficiency of the engine, particularly in regions with extreme heat.
During the design phase, extensive cooling performance testing was carried out using a dyno cart to simulate real-world conditions. The dyno cart, equipped with a water brake dynamometer capable of a maximum retardation of 450 kW, was towed behind the cranes. This setup allowed the testing team to impose a variable load on the engine, enabling it to operate at full power even on flat terrain.
standards, including headlights, visibility, noise levels, ABS and emission standards, along with a suite of safety features.
Safety remains an unwavering priority for Franna. The Series upgrade elevates safety standards by incorporating Franna’s patent pending Safety Radar as a standard feature. The Safety Radar system adds an additional layer of protection and awareness over our patented Dynamic LMI system enabling the operator to plan their next move by viewing a colour contoured visual representation of the rated capacity for the entire working area of the crane. The operator can see the rated capacity of the crane before they move the load, hence well before any traditional rated capacity alarms or motion cuts.
Franna’s online Lift Planner (https:// www.frannaliftplanner.com.au) has also been upgraded to include all current models – AT22, MAC25 and AT40. This allows precise rated capacity and front axle load calculations to be performed for various crane configurations and
unlevel ground conditions.
The rear body of all the models has been reworked to improve serviceability of the cranes. ABS brakes, additional access features, battery isolators and larger capacity batteries have been upgraded as standard.
Franna’s Engineering team is working on a number of developments designed to further enhance the safety and sustainability of the range
In collaboration with the mining industry, Franna is committed to meeting all safety and operational requirements. To enhance safety features, it is exploring the integration of wet brake systems as an optional addition to our cranes. Wet brakes, composed of multiple discs enclosed in an oil-filled housing, provide effective, emissions-free emergency braking, offering an additional layer of safety in critical working environments such as underground mining.
Simultaneously, Franna is actively investigating the feasibility of developing
a zero-emissions mobile crane. This initiative is driven by the need to support the stringent legislative requirements, such as the 5% annual emission reduction mandate imposed on mines, refineries, and other industrial operations.
To ensure that our zero-emissions mobile crane meets the practical demands of these industries, Franna is working closely with fleet owners to define a comprehensive set of functional and performance requirements. As part of this process, we have equipped a fleet of mobile cranes with advanced data acquisition systems to collect real-world utilisation data across various vocational applications. This extensive dataset, which includes over 30 parameters such as power demand, fuel consumption, and lifting performance, is being analysed.
The insights gained from this data are instrumental in the development of a zero-emissions mobile crane that is not only compliant with regulatory standards but also robust enough to operate in the demanding environments of mining and beyond.
Protective Engineered Safety is the brainchild of Karl Rosewarne who has over 30 years experience working with overhead powerlines. Protective’s GoUpSafely system features design and detection capabilities creating an industry-leading high voltage sensing system. Karl explains more.
PROTECTIVE’S PATENTED GO UP SAFELY™ (GUS™) system, is a comprised of one or more wireless electrical field (E-Field) sensors coupled to a Base Controller. The system is designed to detect the proximity of energised overhead AC 50Hz or 60Hz electrical transmission lines in order to prevent inadvertent contact with hazardous and potentially lethal voltages. GUS™ was created to prevent machinery from contacting energised overhead highvoltage transmission lines (ie. power lines) when a hazardous situation is detected. This is achieved by stopping the machine in the current direction of movement, and only allowing movement away from the hazard until it is cleared.
Karl grew up on a large sheep station in New South Wales and growing up in the middle of nowhere provides a mentality that if an issue surfaces, you have to think outside the box to provide a solution.
“If there is a problem, you have to make something to fix it. You have to think differently to city dwellers because there isn’t a Bunnings on every corner. My journey in the electrical industry has seen me spend two and a half years working in Tanzania in East Africa, where life is genuinely cheap, meaning safety isn’t highly regarded nor heavily invested in. I’ve also worked in the Occupational Health and Safety side of the industry where I chaired the safety committee for Western Power for a number of years.
“Dealing with the incidents and accidents on a weekly basis you tend to hear the same feedback ‘we’ll just create another rule,” or “we’ll just tell them they
can’t do that,’ or ‘we’ll put another line in the switching program to remind them to do their job correctly.’ This attitude was frustrating to say the least. I could see the problem was the human interaction with power lines. Removing the hazard was totally impossible of course, but the very next step should be to create an engineered solution to remove the issues associated with the hazard,” said Karl.
In 2012, Karl sat at home thinking about how to prevent machines coming into contact with power lines.
“I concluded ‘the engineered solution is the only solution’ but what are the
and then to warn the operator that contact with the power line could be imminent. The solution needed to take control of the machine out of the operator’s hands by physically preventing the machine’s control system from hitting the power line. It took me nearly five years to develop the product. The company Protective Engineered Safety was created in 2017,” said Karl.
By 2018 Protective had a commercial product ready and attended the first Occupational Health and Safety Show in Melbourne, where it was extremely wellreceived.
“At that point we were one of only three companies in the entire venue exhibiting a real product that could help save somebody’s life. For me, it was a proud moment to take the vision I created five years earlier, have it physically in my hand and demonstrate to somebody that it really does work, and it will save lives.
“We embarked on the patenting exercise at the beginning, and we released 37 claims for the design of the GoUpSafely system, and in 57 countries, all 37 claims went through unchallenged, which our patent attorney said it was like winning the lotto and extremely hard to do but we Protective’s GoUpSafely system features design and detection
“With GoUpSafely version 1 we basically took it to industry saying, ‘all right, what else would you like it to do?’ We are now at Version 3 which is incredibly intelligent. We’ve been able to incorporate a secondary sensor into the system which prevents the end of machinery booms from hitting surfaces. That development occurred about two weeks ago, and I believe the system is currently being fitted to two cranes working on a major infrastructure project in Melbourne, Australia” said Karl.
The global statistics for powerline fatalities are worrying. In 2012, just under 1,800 people were killed globally from hitting power lines. In the last 12 months 4,732 people globally didn’t go home as a result of hitting power lines.
“These stats alone tell me that the paperwork solutions are not working. We need to get the word out there, we need to help people understand that there is a practicable and viable solution available and it’s not expensive, it will literally cost less than the replacement of a couple of tyres on the machine,” said Karl.
“As far as retro fitting, it takes less than an hour to install. It’s predominantly wireless, making it very simple and the operational lifespan is in excess of 10 years. It’s been tested thoroughly by Cargotec in Sweden for HIAB Cranes. They have put it through their full military spec testing regime, which they weren’t expecting GUS to pass, but it did. We’ve been working with Cargotec since 2018, and although they are a slow moving wheel, they are methodical in their process and will not accept anything short of excellence, which is why we believe it’s been a worthwhile endeavour.
“In October of last year, we were pleased to see the European Union (EU) has given notice via the EU Machinery Regulation that as of 2026 you are no longer allowed to have a machine operating near power lines on any work site in EU countries without power line detection, so it’s starting to happen at the legislative level as well,” said Karl.
“Our system has just been approved for Freeport Mining Ventures in Indonesia. They recently completed an eight-month
Protective’s patented Go Up Safely™ (GUS™) system, is designed to detect the proximity of energised overhead AC 50Hz or 60Hz electrical transmission lines in order to prevent inadvertent contact with hazardous and potentially lethal voltages.
trial on a group of systems that we had on their large capacity all-terrain cranes, and they’ve just approved a purchase for another 28 systems. They also plan to fit the system to their large container handling forklifts,” he said.
A key feature of the GoUpSafely system is that it can be fitted to any machine that can reach a power line, from farm machinery through to construction equipment including telehandlers.
Karl recently showcased the GoUpSafely systems at the Crane Association of New Zealand’s (CANZ) Conference and Exhibition. This exhibition was a significant opportunity to demonstrate the system’s capabilities to a specialised audience in the industry.
“We exhibited at the CANZ show in Rotorua and a gentleman walked onto our stand and said he’d actually hit a high voltage power line two weeks earlier. He owns and operates a multitude of construction equipment, including a drill rig.
“During the discussion he said he’d come into contact with a power line with the drill rig and the only reason nobody was injured was because he actually managed to pull the entire power line down, which inadvertently shut it down.
“In a momentary lapse of concentration, he glanced at one of his operators as it looked like they were about to tip the excavator over. He was talking on the radio, not concentrating on his
machine and lifting the drill rig as he was setting up and didn’t take his hand off the lever and hit the power line. He was grateful that he survived, and no one was hurt.
“He asked, ‘How much is the two sensor system?’ and I said, ‘around $4,500’. He said, ‘that mistake cost nearly $30,000,” said Karl.
Karl goes on to discuss the system specifically designed for cranes and in particular pick and carry cranes.
“Our solution for cranes runs the standard high-voltage detection sensors but we have also now included an optional second product called Protective Shield. We originally designed this for the Elevated Work Platform industry as secondary guarding against crush injuries when operating scissor lifts and boom lifts.” said Karl.
“We were approached by a Tier One builder that was finding pick and carry operators were banging the booms into tunnel roofs and poking them through buildings. I consulted with our engineering team about the potential to use Shield’s ability to detect proximity to physical object with GUS and within two weeks I shipped them the finished product.
“This is exciting because there are a significant number of cranes working closely to existing infrastructure like mini crawlers in the industry. It’s a brand new development which we see being a genuine ‘game changer’” said Karl.
A wireless instant safety alert device designed for crane operators and dogmen enabling rapid alarm activation in emergencies.
The TBS device overcomes the shortfalls of two-way radio failure and often inaudible backup whistles. The TBS lanyard allows a dogman to instantly transmit an alarm signal to a crane operator to stop.
A quick snap on the TBS lanyard activates the alarm.
It’s that simple!
The Australian economy staggered into 2024, edging close to recession growing by a meagre 0.1 per cent over the first quarter of 2024 and just 1.1 per cent over the previous 12 months. George Grasso, UAA Group’s EGM – Claims & Procurement discusses the economic slowdown and makes suggestions on how crane business should be preparing for the upturn.
underwriting capabilities as well.
“The last 12 to 18 months have seen a significant increase in claims and we have heavily invested in people and systems to help manage claims. We understand we need greater efficiencies and more resources to ensure that we provide the
deliver on our promise and what we are offering and uphold our reputation. We’ve done the same in the underwriting space. Over the years we have seen an increase in machinery assets coming onto schedules which has required an increase in underwriting capabilities to ensure we are
’Smart’ businesses are focused on increasing efficiencies by implementing technology, particularly in the administration space and that includes the implementation of Artificial Intelligence
providing the best coverage in the tailored packages we are offering our customers.
don’t require human intervention.
“We are heavily invested in our people and clearly understanding the roles and responsibilities of each of our roles is a priority. But more important is the ever-growing need and requirement of compliance and regulatory expectations, particularly in the insurance and financial sectors.
“We have realised a growing headcount would not be sustainable into the future and more recently have embarked on implementing various technologies that will help with the data entry and administration side of the business as well making a contribution to compliance and regulatory expectations,” said George.
UAA is investing in a new computer operating system which will provide more efficient methods of underwriting and managing claims.
“We are investing AI for some of the menial, non-technical tasks that can create extraordinary amounts of bottlenecks in our processes in our systems. Utilising technology assists in ensuring we are compliant and assist with the tasks that
“UAA has also been investing in changing the way we operate and work within our offices. We recently underwent an upgrade in our office refurbishments and we’ve introduced a modern office environment featuring standup desks. We’ve done away with handheld telephones and our telecommunications are electronic through VoIP and the internet,” said George.
Over the last six months UAA has been restructuring its Executive Team, he adds.
“We have sound foundations but it has been timely to redesign the architecture, employing key professionals to ensure a sustainable and growing future in our ever changing industry of construction and insurance, an opportunity to work on the business now for the future needs of our customers and making it easier and efficient to work with each other.”
“Following the acquisition and merger with Mecon Insurance, we have been redefining roles and responsibilities and resetting our purpose, our vision and our values. Our strategy between now and 2030 will be to ensure sustainable growth
and strength, but most importantly, as an insurance organisation, we want to help our customers achieve the same objectives by managing the ever-increasing costs. We are examining and implementing strategies to reduce our own increasing costs, so that way we can ensure a sustainable future for us and our customers and technology is going to play a big part in that,” said George.
UAA is examining overseas opportunities and planning to revamp its policy wordings for greater ease of understanding, said George.
“We have been investigating opportunities with overseas market and we are in the process of launching into North America and Canada during the later part of next year. Another key project is a complete revamp of our policy wordings where we will bring the policy wording into the current era of language and a much easier flow, as opposed to the old English language that often exists in many insurance policies. This will make the intention of our policies a lot clearer and more concise, and detail what the coverage entails,” he said.
Faster Construction: Modular building techniques reduce construction time by up to 50%, and our cranes handle increasingly large and heavy modules efficiently.
Cost Efficiency: Larger cranes with extended booms can replace multiple smaller cranes, offering significant cost savings.
Reliability and Innovation: With advanced technology and robust support, RRS ensures high performance and minimal downtime for your projects. Why Choose Resolution Rigging Services?
Discover how Resolution Rigging Services can enhance your construction projects
The Buddie System is designed to be even more attentiongrabbing than a whistle, but with the convenience of the lanyard on which the whistle is so often attached.
In the case of an emergency, the Lanyard Device is designed to separate.
The Buddie System is a wireless, instant safety alert device designed for Dogmen by Dogmen – allowing a Dogman to set off a rapid alarm that alerts a crane operator to an emergency. The Buddie System has been designed by experienced Dogmen, Jade Harris and Gary Panagiotidis.
In so many cases, whistles are outdated, impractical and on large scale projects, often inaudible.
while providing Dogmen with another form
flat battery, frequency drop out, dropped radio or accidental channel change, or if the Dogman is unable to access his or her two-way radio – often the only way to communicate with the crane operator is through a whistle.
The Buddie System is designed to be even more attention-grabbing than a whistle, but with the conveniene of the lanyard on which the whistle is so often attached.
With an official launch planned for The Crane Industry Council of Australia (CICA) National Conference and Exhibition in Adelaide, October 17th to 19th, the Buddie System is designed to be “A redundancy safety system in case communication via the two-way radio fails,” says Gary.
“We’ve all experienced interference on two ways and on occasions there can be delays in the transmission. Batteries can start beeping and go flat halfway through a lift, which can delay the signal, that’s if the
signal gets through at all,” he said.
“You might have told the crane operator to bring the load down and then you’ve dropped your hand mic and you can’t get to it. Or you could be slinging a load and your handset gets caught somewhere in the load, which has probably happened to most of us. You then have to try to get back to that mic as quickly as you can to say stop.
“With The Buddie System, you have the device around your neck, you just pull it, the alarm goes off in the cab and the operator immediately stops the crane,” said Gary.
With The Buddie System, the Dogman wears a lanyard around their neck, fitted with an alarm mechanism called the ‘Lanyard Device’.
The Lanyard Device is paired with a Crane Device which sits with the tower crane or mobile crane operator and the two communicate via long range (LoRa) radio frequency.
In the case of an emergency, the Lanyard Device is designed to separate and when it does, it triggers an audible alarm and flashing lights in the cabin, immediately alerting the operator to the problem.
“That’s the signal for crane operator to stop all motions and he’ll get on his twoway to check if everything is OK,” Jade said.
“It could be that the Dogman’s lanyard had accidently been caught on something and it separated that way setting off the alarm or it could be that something has gone wrong.”
The Buddie System is available to be purchased individually or in sets.
Pairing is simple. The ‘Lanyard Device’ is paired with a Crane Device via long range (LoRa) radio frequency by pressing the pair function button on both devices or by plugging the Lanyard Device into the Crane
operators can pair up to 10 lanyards with the Crane Device.
The user-friendly system also allows Dogmen to unpair their lanyard from one crane and take it to another, if they are going to work with either another crane or to another job.
Gary can see plenty of interest from Tier One builders and crane hire companies.
“There already has been interest from crane hire companies because of the safety aspect of The Buddie System,” he said.
“Although there is a little initial outlay to purchase the system, this could be a large saving when The Buddie System prevents an accident.”
Device. Once paired the lanyard device’s unique ID is displayed on the Crane Device letting the crane operator know who he is paired with. . Once paired, the lanyard device’s unique ID is displayed on the Crane Device letting the crane operator know who he is paired with.
Confident everyone is paired, the crane operator can climb up into the crane and plug the Crane Device into the main power source. As with a radio check, there will be a lanyard check – with each Dogman pulling the lanyard and setting off The Buddie System’s alarm. One simple check that it’s all working and the day begins.
If there is a morning and afternoon shift,
“Although there is a little initial outlay to purchase the system, this could be a large saving when The Buddie System prevents an accident.
“We are thinking the construction, infrastructure, mining, wind energy and oil and gas industries will embrace The Buddie System and implement its use in their standard operating procedures,” Gary said.
“The conversations we are having with people high up in these type of organisations have been very positive with comments like ‘If the Buddie System was ready now we’d take it right away.’”
For further information visit www.thebuddiesystem.com
Liebherr-Werk Ehingen GmBH develops and manufactures highly modern telescopic and lattice boom cranes on mobile and crawler chasses. In this article, we follow the journey of two Liebherr all terrains, a Liebherr LTM 1110-5.2 and LTM 1100-5.3, the new flagships of the newest Liccon 3 mobile crane technology, which have been specifically selected for The Crane Industry Council of Australia (CICA) National Conference and Exhibition held in Adelaide, October 17th to 19th.
LIEBHERR-WERK EHINGEN GMBH IS A global leader in mobile cranes. The key to this success is its innovative products, high quality and a committed workforce. Since the company attaches a great deal of value to high technological standards, LiebherrWerk Ehingen GmbH invests heavily in research and development.
The cranes destined for the CICA event start their production run in the form of a raw pre-fabricated undercarriage and upper carriage components which are built in fabrication stages involving cutting steel plates and other materials into precise shapes and sizes using state-of-the-art techniques like laser cutting and plasma cutting. These pieces are then welded together to form the main structural
The crane is fueled with Hydrogenated vegetable oil (HVO), fuel derived from food waste and agricultural sources which is approved for use in all current Liebherr cranes and engines.
components of the crane, such as the boom, chassis, and outriggers.
Next, the components undergo precision machining. Each machined part is subjected to rigorous quality checks to ensure it meets the required standards.
Assembly begins with the creation of sub-assemblies, including carrier, boom assembly and control systems. The installation of hydraulic and electrical systems follows. Hydraulic lines, pumps, and cylinders are fitted to enable the crane’s lifting and movement capabilities. Electrical wiring, control panels and sensors are installed to ensure proper operation and safety features.
These sub-assemblies are then integrated into the main structure of the crane, with the fit out of the axles onto the chassis and the eventual joining of the upper and lower carriages with the fitting of the boom and crane operating cab to the undercarriage.
Before the crane is ready for delivery, it undergoes surface preparation and painting. The components are cleaned and treated to prevent corrosion and a highquality paint job is applied to protect the crane from environmental factors and give
prepared for final dispatch.
As a last factory-based step, the crane is then fuelled with HVO (Hydrogenated vegetable oil) fuel derived from food waste and agricultural sources to reduce carbon emissions. HVO is approved for use in all current Liebherr cranes and engines.
The journey of the cranes then continues from the factory gates to one of the largest ports in Europe, Bremerhaven in Germany.
Here the crane is prepared for shipment. To adhere to the stringent Australian Biosecurity requirements the complete cargo is cleaned and treated for the Brown Marmorated Stink Bug (BMSB) which is a seasonal requirement if shipping takes place from the months of September through to May. Cargo is separated between the self-propelled main machine and the bulk stored auxiliary equipment which is loaded onto standardised trailers and then loaded onto special Roll on / Roll Off vehicle carrier vessels. The crane then has an 8-12 week journey going from
“Before the crane is ready for delivery, it undergoes surface preparation and painting. The components are cleaned and treated to
prevent
corrosion, and a high-quality paint job is applied to protect the crane from environmental factors and give it a professional finish.”
it a professional finish.
The final stages of production involve extensive testing and quality assurance. The crane is subjected to functional testing, including load testing, stability testing and operational checks, to ensure all systems are working correctly. Final inspections are conducted to confirm that the crane meets all safety and performance standards.
This comprehensive process ensures that each Liebherr mobile crane is built to the highest standards of quality, safety and performance, ready to tackle the most demanding tasks with precision and reliability.
Once the cranes pass all tests, they are moved to the dispatch area where they are weighed and measured to pass the German roadworthiness certification. Once they pass, the cranes and all equipment are
Bremerhaven to its final destination in Australia.
Due to the deadline to have both cranes in time for the show, it meant the cranes had to be shipped to different ports and at different times. The earlier crane had a longer journey from Bremerhaven to Adelaide, however the logistical challenges of not having a direct route from Bremerhaven to Adelaide required the crane to be transhipped via Singapore. The coordination of this is a testament to the joint efforts of local and international partners in shipping and logistics.
The second, more time sensitive, crane was then loaded onto a vessel that embarked to a direct voyage to Port Kembla.
Upon arrival at their respective ports, both cranes were then collected by one of
Once the cranes pass all tests, they are moved to the dispatch area where they are weighed and measured.
Liebherr’s trusted local freight companies, which is experienced with the complex process of loading the crane on a flat top trailer and ensuring the cargo has arrived complete and without damage. This process also requires a high level of ability, knowledge and planning; with the booking of pick up spots at the wharf, permits for transport to Liebherr facilities and successful unloading of the cargo.
From the time the cranes leave the factory to when they arrive at the local Liebherr branch, a massive 16,500 km
The coordination of shipping the cranes this is testament to the joint efforts of Liebherr’s local and international partners in shipping and logistics.
journey has been completed. Given the complexity of global and local logistics, coordination of shipping and customs clearance at destination, Liebherr is extremely fortunate to have partners that acknowledge the importance of a quick and efficient delivery supply chain which enables Liebherr to service its customers.
Once the crane arrives at the respective branch the full pre-delivery process takes place to prepare the cranes for delivery to the customer.
The complete value chain that enables
Liebherr to produce a crane in the south of Germany which suits the needs and requirements of customers around the world and is delivered accordingly, requires a network of trusted suppliers and local customer support. This is a commitment that Liebherr has proven time and again, delivering a record 2,000 cranes in 2023 to customers across the world.
Liebherr looks forward to welcoming visitors to their stand at this years’ CICA conference and see the subject LTM 11005.3 and LTM 1110-5.2 on display.
The MCR 305A is a workhorse luffing jib construction crane with strong capacities and a remarkable 9.5m out of service radius.
Potain’s innovation is not going unnoticed with recent sales in large heavy lift Flat Top cranes and a full range of Luffers competing in the local market says Billy Rumble, Sales Manager – Tower Cranes Manitowoc Cranes Australia.
“BOTH THE MCT565 AND THE MCT1105 models have now landed in Australia and continue to turn heads and spark people’s interest,” said Billy.
Since its launch three years ago, Potain’s MCT 565 topless crane has surpassed expectations on jobsites
worldwide. Available in two capacities (25 tonnes and 32 tonnes), the MCT 565’s performance characteristics have helped contractors in their drive to lift ever-larger precast concrete sections and other heavy items as the construction process becomes more modular.
“The new 80t MCT2205 is due for shipment at the end of the year and, with it having a lifting capacity of 23.5t at 80m, this puts Potain into a new heavy lift category. The factory has already received orders from the Middle East and South Korea,” said Billy.
According to Billy, Potain’s innovation in the luffing market is second to none, with the MCH hydraulic luffing cranes dominating the smaller end of the market.
With erection times of just four hours, unmatched reliability and with an Out of Service radius of 10m, the luffing range has the ability to service most smaller construction sites.
“The new 25t MCR305A is proving to be equally popular and as a result of its unmatched specifications - which include a 9.5m Out of Service radius and 50m Freestanding with a 60m jib on 2m masts - we’ve already received 10 orders. It’s proving to be the ‘Real Deal’,” said Billy.
But Potain doesn’t just want to be the market leader for medium to smaller sized luffing cranes - with Billy saying the company now has a new range of large luffing cranes as well.
“The MCR625 arrived earlier this year and is due to be erected on the Snowy Hydro project in the coming months,” he said.
The MCR 625 combines the robustness of a heavy-duty luffing jib crane with a remarkably compact footprint to deliver exceptional performance in urban environments.
This enables contractors to take on major projects in densely populated areas with unprecedented efficiency and precision.
“We are excited about the opportunities the MCR 625 presents. It’s a crane that offers the perfect balance in power, precision and compactness. By leveraging the proven design of the MR 618 and adding design elements for fast-emerging global markets, we are empowering contractors to tackle ambitious projects in urban environments with unprecedented efficiency and reliability,” says Billy.
Additionally, the MCR 625 can work with one or two-fall reeving for faster hoist speeds and better productivity.
There’s a maximum capacity of 32 t when configured for two-fall operation, while with one-fall it’s 17.5t.
The maximum jib length is 65m, and a maximum tip load of 6.4t at 65m is available, enabling the crane to meet even the most demanding of high-rise project requirements.
Mounted on 2.45 by 2.45m mast sections, the Potain MCR 625 can be configured with multiple jib lengths – either 30 or 40m, and then in 5 m intervals up to the maximum of 65m, providing contractors with the versatility to adapt set-up to project specifications.
Even with its full 65 m jib, the crane travels in just 11 truckloads, minimising transportation costs and logistical challenges.
The MCR 625 offers a choice of three hoists for further flexibility, all equipped with 603 m of wire rope.
“Potain Engineering is keeping the innovation coming and with state-of-
We have the capability to heavy lift and shift loads from 30 tonnes through to 3,000 tonnes, enabling us to efficiently support our clients.
•Heavy Lift
•Project Hire
•Quality Endorsed
•Specialised Engineering
•Heavy & Oversized Transport
the-art design technology. There will be two additional luffing cranes coming to Australia in 2025! Potain will announce these two new cranes before the end of 2024,” Billy concluded.
The new Grove GRT765 and GRT780 rough terrains were presented to customers at the recent Manitowoc Crane Days event. Deliveries are set for later this year. Better reach and strength are combined with the latest productivity innovations and design for the ultimate jobsite performance.
MANITOWOC HAS LAUNCHED TWO NEW Grove rough-terrain cranes that offer best-in-class boom length and strength to set new standards for the 65t and 80t classes. The GRT765 and GRT780 also deliver improved operator comfort and easier servicing inside a compact design package. Deliveries of the first units will begin in the second half of 2024, and the new models were presented in the iron for the first time to dealers and
Overall width of both is less than 3m. Set-up is compact, and owners have greater flexibility with the MAXbase variable outrigger system, which gives increased lift capacity and asymmetric configurations to easily fit on congested sites.
customers at Manitowoc’s Crane Days event in Shady Grove, Pennsylvania, USA, this past May.
John Bair, product manager for rough-terrain cranes at Manitowoc, had this to say.
“Customers will immediately notice the significant improvements in reach and strength, but we’ve also packed a lot of other benefits into these new models. The operators will love the
comfort of our new, wider cab as well as the expanded CCS display. We’ve also added the latest productivity and fleet management technology with our MAXbase variable outrigger positioning system and the Grove CONNECT telematics platform. Not to mention we packed all of this into a very compact and lightweight package, which makes this crane very easy to transport, as well as manoeuvre around busy jobsites.”
The Grove GRT765 replaces the RT765E-2 in the current rough-terrain crane lineup. It offers a 65t maximum capacity and a 38.5m four-section full power boom. The Grove GRT780 will replace both the RT770E and the GRT880 in the current roughterrain crane lineup and offers an 80t maximum capacity with a 47.3m five-section full-power boom.
Both models feature a 10.117.1m bi-fold swingaway jib which can be manually offset up to 45˚. For the GRT765 there is 6.9t of counterweight, while the GRT780 comes with 7.9t, although customers can boost this to 9.3t for even greater strength. Both can add a hydraulic counterweight removal system as an option and powerful line pull is guaranteed, with both models
43t. For the GRT780, GVW is 46t. Overall width of both is less than 3m. Set-up is compact, and owners have greater flexibility with the MAXbase variable outrigger system, which gives increased lift capacity and asymmetric configurations to easily fit
terrains to offer the Grove CONNECT telematics and fleet management system launched in 2022. For the operator, there’s a wider, full-vision cab that tilts to 20˚ and comes with a three-camera system for better visibility. Operations can be managed via the new, bigger
common across the Manitowoc product line. For service technicians, the cranes include oCSI (on Crane Service Interface) for enhanced diagnostics and service, while centrally located service points on the superstructure and carrier make routine maintenance easier.
Going completely paperless means significant change, but it has been a welcome one at Metcalf Crane Services, as it has helped one of the market-leading lifting solutions companies take the next step.
of Visual Dispatch as the software has played an integral part in revamping the company’s entire quoting, scheduling and reporting system.
Chief Financial Officer at Metcalf Crane Services Dominic Cannata says in comparison to other offerings, the Visual Dispatch software had all the attributes his team and wider staff members were seeking. It integrates information from sales, operations, compliance and accounting departments into a powerful central depository.
“As far as a software tool is concerned, the Visual Dispatch system is the backbone of the organisation – due to the fact Visual Dispatch has taken ownership of our quoting processes and it all begins there,” he says.
“If you win the job, you can send it straight through to scheduling without having to double entry, reducing the risk of miscommunication between sales and operations. Once it’s scheduled, the tickets are issued electronically to the crew’s phone.
“Visual Dispatch contains crew attributes such as inductions and tickets, so it’s an efficient process in the staff selection process– eliminating the need for many phone calls and the keeping of separate lists and spreadsheets. The customer signs on the glass and the job information is transformed into an invoice format. The job is done. Essentially, it’s approved by the customer because you’ve got an approved docket which is automatically attached to your invoice and sent electronically within Visual Dispatch.” says Dominic.
Visual Dispatch is a streamlined approach to enable crane and heavy lift companies to optimise workflows, increase productivity, reduce costs and improve customer service.
Fundamentally a computer software
package, Visual Dispatch helps users say goodbye to manual filing, old papers and stacks of manila folders.
The software is designed to simplify the intricate operations of the crane hire and rigging industry. It has since become a desired industry product for management of employees, equipment and entire fleets of machinery.
“When I first started with the business there were piles of manila folders full of invoices and dockets with mark-ups and cross outs on my desk. Paper dockets were gathered from various parts of Melbourne as a result of staff driving to various job sites to collect sign dockets. Now there’s no paper, so we don’t need to worry about that anymore,” says Dominic.
Before Visual Dispatch, businesses relied on complex paper filing systems and hard-tounderstand spreadsheets to stay organised, Dominic added. But today, the job of filing is all but eliminated, as too are spreadsheets with errors.
Rather than email around reports, you can virtually report on it online through the dashboard.” Dominic says.
And with a fleet of approximately 40 cranes, Metcalf’s digital advantage, via Visual Dispatch, gives it an edge within the industry.
Nowadays, crane and lifting solutions companies that have purchased Visual Dispatch, such as Metcalf, rely on the system to do most of the computer-based heavy lifting.
“Importantly, Visual Dispatch interfaces seamlessly with our accounting system and, with the use of an integrated reporting tool, allows the organisation to move away from Excel spreadsheet reporting to an automated, very comprehensive business intelligence dashboard. So it becomes a tool rather than just information, with the ability to drill down into it, right to the lowest granular level of information which is timely and accurate.
“It’s transformational, and the business can review and manage results in an easier fashion, with all information at the tip of their fingers. It can be done in the boardroom or anywhere for that matter at any time and by anyone (permission-based of course).”
Visual Dispatch allows companies to measure performance on any type of dimension desired within business, whether it’s the performance of the business and its individual projects, customers and markets, tonnage and individual cranes, departments and crew and yards and individual profit centres.
“We’ve just implemented the Visual Dispatch timesheet system, and can now get weekly and daily utilisation of our labour. The software gives us a complete picture of our business,” Dominic added.
The remote-ability of the software also allows staff members to use the system away
from site, thereby not further compromising day-to-day operations when a team member is off work sick, for example.
“Being cloud based, it is easy to use the software remotely; whether you want to review quotes or reports from overseas or prepare and review invoices from home, managers have wide scope when it comes to looking after our employees,” says Dominic.
Staff can write notes in real time, through the Visual Dispatch app, which maintains current and live data regarding equipment and workflow.
“The software has certainty made us a more efficient organisation,” says Dominic.
“If someone is off sick, off-site or not at work, for whatever reason, the business operations can still run smoothly. Access is widespread.”
Dominic praises the culture at Metcalf Cranes and says the innovative idea to onboard the Visual Dispatch system is one of alignment to the company’s vision – not to necessarily to be the biggest, but to be the best in the lifting solutions industry.
Metcalf Cranes provides mobile crane hire services Australia wide, with a fleet ranging in size from 4 tonne mini-crawler cranes to 800t mobile cranes. The company’s stated aim is to be first choice for clients seeking lifting solutions in the rail network, building bridges, maintaining windfarms and more – while retaining a reputation for unparalleled service.
Tim Metcalf founded the company 28 years ago from humble beginnings with a solitary crane; “I think we all admire that and appreciate his journey,” Dominic explains.
Dominic says finding and keeping quality people is what makes the business culturally strong, and it starts from the top. “Tim’s focus is on doing a great job for the customer in a manner that safe for our employees. Speaking up and speaking plainly is encouraged – tell me what you can do and what you can’t do in a succinct manner. Everyone should know their job, and everyone knows where they stand.”
Dominic says the constant positive interactions Metcalf has with customers and industry decision makers helps improve the business through relationships.
“We always strive to have honest and positive interactions with our customers, employees and stakeholders. Without quality people, you can’t have quality organisation.
“At Metcalf, we have a dynamic and hard-working culture, which is vibrant and positive,” says Dominic.
And in-turn, the perks of the Visual Dispatch software has made those aforementioned relationships with internal and external stakeholders a lot better, but moreso has created strong support fundamentals for the business.
“We are striving to look after our employees and customers to the best of our ability, which in turn, underpins a strong business model,” says Dominic.
The course instructors are seasoned professionals who will mentor course participants through real-life scenarios, preparing them for the challenges and responsibilities of a Crane Lift Supervisor.
Crane Lift Supervisors are in high demand globally. Completing this course enhances employability and opens doors to a wide array of job opportunities and career growth.
The curriculum covers a wide range of topics, including lift planning, load calculations, safety protocols, communication strategies, and legal compliance.
Scan the QR code to book in now
Melbourne 5-6 February 2025
Sydney 19-20 February 2025
Brisbane 5-6 March 2025
Perth 19-20 March 2025
Melbourne 4-5 June 2025
Brisbane 10-11 July 2025
Perth 16-17 July 2025
Sydney 17-18 September 2025
Matusch GmbH brings yE.P.O.S. (Equipment Planning and Organisation Software) back to CICA this year, with the offer of On-Site Training during the event
Matusch’s E.P.O.S. system provides efficiency and clarity for industry professionals.
MATUSCH GMBH, BASED IN COBURG, Germany, is one of the leading companies specialising in the development of yE.P.O.S., a software solution designed to help businesses efficiently manage their equipment planning and organisation.
Founded over 30 years ago by Christian Matusch, the company has grown to now employ more than 15 committed professionals, with a client base of over 300 companies worldwide.
Having had a strong presence in Australia for more than 15 years, Matusch GmbH works closely with its customers to develop bespoke solutions that meet their specific needs.
Its software caters to businesses involved in renting, planning and selling equipment—including mobile cranes, tower cranes, construction machinery rentals, access equipment hire, heavy haulage, construction companies, traffic monitoring and more.
yE.P.O.S. is a versatile tool suitable for businesses of all sizes, from small enterprises with just two users to large clients with more than 100 users. Its diverse customer base includes
crane hire companies with fleets ranging from 5 to 500 cranes, access equipment hire companies with 50 to 3,000 platforms, businesses with hundreds of tower cranes, as well as wind turbine manufacturers, trailer manufacturers and providers of portable roadways.
With data security a top priority for Matusch GmbH, the yE.P.O.S. system is built to deliberately avoid the use of cloud services.
with major companies such as Shell, Visa, Dell and even NATO, ensuring the highest standards of security,” Matusch GmbH adds.
With Matusch GmbH currently working on a redesign of both yE.P.O.S. and its mobile app, the company says it is excited to engage with users to share the latest development at the CICA National Conference and Exhibition in Adelaide this year.
“We look forward to welcoming
“Our partner in this field works with major companies such as Shell, Visa, Dell and even NATO, ensuring the highest standards of security.”
“We are convinced that real data security is only guaranteed when you can decide where your servers are located,” the company says.
“Nevertheless, we do offer the possibility of securely accessing your systems from external locations through security-certified services.
“Our partner in this field works
you to our stand and showcasing the latest updates in yE.P.O.S. (Equipment Planning and Organisation Software),” the company says.
“After the event, we will also be offering on-site training sessions for our clients. If you haven’t booked your session yet, there’s still time—so be sure to get in touch with us soon!”
Liam Edwards’ journey through the crane and heavy lifting industry has led him to create a program that is set to take the crane world by storm.
IT
THE ‘CRANE game’, Liam Edwards has solved a problem that many in the industry face, bringing his diverse expertise to Crane Class.
Liam is the founder of Crane Class, a digital platform providing construction professionals with knowledge and expertise on cranes and heavy lifting.
Many forms of training and development across the building and engineering sector require students to attend in person, away from the workplace, taking valuable time away from projects - something that many companies cannot afford.
That isn’t the case with Crane Class, which is designed to give industry professionals crane and heavy lift knowledge through its online platform, without requiring them to leave the jobsite.
As the driving force behind Crane Class, Liam films and produces his own content, providing students with his knowledge from over 10 years in the game.
“I don’t want to be pulling people out of work, because neither crane companies nor tier one construction companies can afford for workers to disappear off-site and put strain on the industry,” said Liam.
“Essentially, this product is a culmination of my learnings and experiences as a heavy lift engineer, compiled into a structured, easy to digest format, to provide others with a pathway that was not there when I entered the industry.”
Crane Class aims to take minimal time out of the week for its students, whilst instilling them with significant knowledge, previously unavailable in this format.
The main course on offer from Crane Class, the Lift Operation Specialist course, contains six weeks of content with 12-to-14 hours of learning, rounding out to 2-to-3 hours per week.
The course casts a wide net, bringing students up to speed on crane basics in
the first week and guiding them through to interpreting and executing complex lift plans by the end of the course.
Students progress through the program in cohorts, tackling a new topic each week, with an optional weekly live Q & A session bringing the cohort together to answer any questions that have arisen.
The course is designed to train students with real-world skills and provide construction professionals with the expertise and knowledge they need to procure and execute heavy lifts of all sizes.
Crane Class’s Heavy Lift Designer course is for those working with cranes day in and day out who want the support of an experienced person to help them become an expert in the art of heavy lift design. It is due to be released as an add-on to the Lift Operations Specialist course in early 2025.
Ultimately, Liam says Crane Class is for any construction professional who wants to gain the confidence to safely and effectively deal with cranes in their role.
The beauty of Crane Class, he adds, is that it caters not only for those in the crane industry, but people who want to develop their learning and knowledge about cranes.
“We have people undertaking our course who were like me ten years ago, beginning their lift planning journey. In general, our participants are diverse – we have Site Supervisors, Temporary Works Engineers, Health and Safety Personnel, as well as some who work in the back end behind the scenes, such as in the Operations Team, Commercial and Finance Team,” Liam says.
“We also have some highly experienced operators and riggers in the current cohort and the feedback has been overwhelmingly positive. I’ve always had a great relationship with crews on the ground and helping them see it from the engineer’s perspective and understand the tools we have available when planning a job has been a real highlight so far.
“I really enjoy seeing people who are almost ancillary to the industry, who are
not directly dealing with cranes every day, come out of this course having developed knowledge of what a crane is, what different cranes are and how we can best use them to achieve certain lifts.”
Crane Class provides a deep understanding of Australian Standards, Codes of Practice and Guidelines, but also offers practical insights into crane operation and lift planning, gleaned by Liam’s extensive experience in the heavy lift industry.
Liam initially got a foot in the door of the industry at Advanced Cranes and Rigging, where an engineering office needed to be set up from scratch.
He then worked as a Site Engineer and Lift Operations Coordinator for CPB Contractors before he began his role as a Lead Project Engineer for BMS Heavy Cranes APAC.
“I’ve been incredibly fortunate to work
alongside some foremost experts in the crane industry in all my roles. Through Crane Class I can have a greater impact in extending the spread of this knowledge and experience to the greater industry.”
Crane Class is not just for individuals, but it is aimed toward teams developing and growing their crane knowledge together.
“Whilst our core program has been carefully curated with a broad spectrum of participants in mind, we are working with tier-one builders to customise bonus modules to fit the needs of their specific business and industry,” he said.
POTAIN MCT565
• Fast and easy erection
• Variable speeds and operator profile for smooth operating
• 90.9m max Free-standing on 2.45m Mast
• New display: Visu + data logging and built-in zone protection as standard
“Essentially, this product is a culmination of my learnings and experiences as a heavy lift engineer, compiled into a structured, easy to digest format, to provide others with a pathway that was not there when I entered the industry.”
“Whether it is a comprehensive introduction to cranes on wind farms or a lesson on their internal policies with regard to cranes and heavy lifting, we do it all.”
Liam is grateful for the outcome of his hard work developing Crane Class.
“It has been 12-to-18 months of mapping it out and solid weekends and nights filming all the content.”
“I’ve had the pleasure of training up my first cohort of students. It feels nice that I have had an impact on a lot more people by putting all my knowledge into Crane Class courses,” Liam says.
With a vertical distance of 625m between the bridge deck and the river, the Huajiang Canyon Bridge in Guizhou province, in southwestern China, is soon to set a new world record in bridge construction. The new bridge will surpass the Beipan River Bridge to become the tallest bridge in the world. Both were built over the same river with Potain cranes - and two Potain MCT385 topless tower cranes are currently helping build the new, nearly 3km, suspension bridge.
THE HUAJIANG CANYON BRIDGE CROSSES the 80km long Huajiang Canyon through which the Beipan River flows. The bridge traverses a rift valley which dates back to the Triassic Period. Each side of the valley has different geologic ages, separated by 45 million years.
The Chinese Province of Guizhou is known for having the greatest collection of high level bridges in the world but even for this mountainous province, the Huajiang Canyon Bridge is in a league of its own.
The main structure of the bridge is expected to be completed by the end 2024 and open for traffic in early 2025. Its completion will finish the Guizhou LiuzhiAnlong Expressway that began construction
in 2021 and will reduce the travel time across the valley from 70 minutes to one minute as it crosses the Beipan River, which has become synonymous with high level bridge crossings.
The Beipan, or North Winding River, is the only waterway in the world to have not one, not two, but now three successive world’s highest bridge records.
The first was in 2003 when the Beipanjiang Guanxing Bridge became the first suspension bridge in the world to surpass the 305m height barrier. Then in 2016 the Beipanjiang Duge Bridge blew past the 500m height barrier with a cable stayed span that was built with an innovative truss traveller.
Now, almost 10 years later, the deepest part of the Beipan River will been crossed with the longest high level bridge in history while also shattering the 610m height barrier for the first time.
The dimensions of Huajiang Canyon Bridge are incredible. The road deck bridge will be 625m above the river and will span 2.98km. The main span is 1.42km and the piers will be 262m high. The base of the tower cranes is 776m from the river.
Working on top of the bridge is the Potain MCT 385, which was designed jointly by Manitowoc engineers in Europe and Asia to serve several types of markets. It offers a 20m mast with a maximum free standing height of 64.9 m.
This compact mast along with a compact jib design and a streamlined counter jib make the MCT 385 easy to assemble and transport — an ideal solution for crowded urban projects.
The MCT 385 also has frequencycontrolled mechanisms for hoisting trolleying and slewing that provide smooth movement and precise positioning. Servicing the mechanisms is straightforward too as they are conveniently located and easily accessible.
With the Huajiang deck level needing to be at an elevation of at least 1,100m, bridge engineers had no choice but to go across the 625m deep gap with a suspension span of epic proportions.
The decision was made to use a stiffened steel truss with a main span of 1,420m10m longer than the Humber Bridge, a suspension span in the UK that held the record as the world’s longest suspension bridge for 17 years.
The steep slope on the north side of the Huajiang Canyon also required the construction of a concrete tower 262m tall with the south tower being 205m tall. The total length of the bridge is 2890m with more than two dozen approach spans of 40m.
As common as steel truss stiffened suspension bridges are, the designers of the Huajiang Bridge wanted to give the span a classic look that would be timeless. Nowhere is this more evident than in the tower connections which harken back to the Art Deco-era with a layered tower top connection that has dramatic setbacks that will remind many of the Golden Gate Bridge in San Francisco.
With only one small road winding through the remote canyon location, the crossing has an untouched natural beauty that is simply stunning.
With the project having so many “Grand” superlatives, the leaders of Zhenfeng County decided to turn the bridge into a full on tourist attraction, the likes of which we have never seen before on a suspension bridge. These new attractions would add enough weight and wind resistance to the original design that the planned 7.5 metre deep truss needed to be extended to a depth of 8m.
First up will be a glass elevator that will rise to the very top of the south tower where guests can enjoy the Stargazing Bar and Café that will be located directly between the two main cable saddles, more than 183m above the road deck.
The second adventure will begin at a lower level just below the road deck where the elevator will drop guests off inside the truss where an 800m long walkway will lead through several tourist rooms with glass floors that will allow guests to seemingly “float” 224m and 404m above the ground.
The third and final thrill awaits guests at the very last platform where the truss walkway reaches a maximum height of 670m above the Beipan River. Here the World’s Highest Bungy Jump will allow those who dare to leap into the Huajiang Canyon. For those who are not so fearless, the last platform will have glass panels to walk across and a café to eat at and enjoy views of Guizhou’s deepest river canyon.
Today the Province of Guizhou is home to more high bridges then every other country on earth combined. By 2030 Guizhou will have more than 1,000 bridges over 100m high as measured from the road or rail deck to the water.
Compare that with Italy which has the world’s second greatest number of high bridges, with only 60 spans exceeding 100m in height. Of the world’s 50 superhigh spans that exceed 300m from deck to water, all but three are in China.
After 13,500 hours of work in 3.5 years, an XCMG crawler presents remarkable durability upon major inspection.
IN WHAT IS A ROUTINE REQUEST for WA-based Ronco Construction, Equipment and Engineering, the company was recently approached to disassemble a few cranes, transport them down to its Maddington facility and store them for asset management services company Karridale Group. The cranes were delivered by XCMG three and a half years ago into the harsh environment at Citic Pacific’s Sino Iron project in the Pilbara region WA.
The environment in this area is one of extremes, with machines working in high temperatures, high humidity and close to the Indian Ocean.
Upon stripping the cranes and recording all the data and service history the team at Ronco noticed that one of the XGC300-I crawler cranes –fleet number KGPL017 - had performed approximately 13,500 hours of running time.
It is a known fact that many cranes
clock up hours on the air conditioning system. Ronco compared KGPL017 against its sister XCMG XGC300-I crane – fleet number KGPL016 – that was also on site, which only had 2,769 hours on the hour meter.
Ronco’s Mark Turner contacted Karridale Operations Manager Simon Cox; responsible for the operation, care and maintenance of the machines, and asked the million-dollar question. “Why would there be such a large discrepancy between machines?”
The answer from Cox was that fleet number KGPL017 had been assigned to continuous crusher maintenance for the plant.
This involved round the clock work lifting large crusher heads out and back into place. It involved a great deal of tracking and many other duties. But the main duties were the heavy lifts of the
crushers by Karridale Group.
Discussions were entered into with Karridale Group, XCMG and Ronco Group. Ronco sought advice from their consulting engineer, Beyond3D’s Greg Mitchell, on behalf of the customer, to complete an assessment as to whether the crane needed a Major Inspection (MI) or not.
Very quickly, Karridale Group was able to present lift studies from day one, maintenance records and a very short list of unscheduled stoppages over the working life of KGPL017, due to their impeccable record keeping.
It was agreed by all that despite the short working life of the crane it had worked incredibly hard. It was concluded that in case of any incident in the future, it would be prudent to complete a full Major Inspection.
The XCMG factory supplied a scope of works and Mark Turner of Ronco quoted up the MI. The scope was agreed and the work commenced.
“The small list of repairs required to meet the engineer’s scope, and the requirement of the final inspection was minimal.”
The crane components were stripped and measured against OEM specifications. They were found to have sustained very little wear, given the crane’s extensive utilisation records and the extreme conditions under which it had performed.
The crane has the usual three winches, all of which had no signs of wear or fatigue. The same was true of the slew motors.
The slew ring was checked in multiple positions and the dial tension indicator (DTI) read that there was minimal wear from the OEM specifications.
The tracks had some wear from the harsh baked ground of the Pilbara, but nothing that would not last another 10,000 hours.
The boom section’s paint had lost its shine from being in such a harsh
environment but had remained steadfast in protecting the steel that lay below. As such, MJ Engineering of Perth was able to use Eddy Current on each section. This reduced the overall MI cost and the need to remove the protective coating.
The small list of repairs required to meet the engineer’s scope, and the requirement of the final inspection was minimal. All parts were available on the ground in Australia at one of XCMG’s parts warehouses located at Hallam in Victoria, Welshpool and Karratha WA.
Upon completing the works, Training and Inspection Services was brought in to complete the final partthe CraneSafe inspection.
The final report was drafted and signed off by a chartered professional engineer for a further 10,000hrs or 10 years working.
That is, with the conditions that the crane is annually inspected by a competent person; is maintained in line with the XCMG guidelines supplied with the crane; and as always, operated as per the OEM operator’s manual.
The whole MI – including load in, assembly and testing – was less than 5% of the price of a new XGC300-I crawler crane.
Bill Wang, the owner of Karridale Group, insists that the gamble he took buying XCMG has made his company stronger, and his investment has given him a great return over those three and a half years – without the need to invest in a crane with a bigger name or better known brand.
Today the three XCMG crawlers –2 x 300t and 1 x 180t – are assembled at Ronco’s facility and are available for dry hire through Empire Equipment Hire.
The staff at Ronco is happy for anyone who is considering their next purchase to make an appointment. Come down, have a look and operate with a test weight.
The Simberi gold mine is located on Simberi Island in Papua New Guinea’s New Ireland province. The mine recently took delivery of two 35t capacity Humma pick and carry cranes. Matthew McGlaughlin, St Barbara’s Mobile Maintenance Superintendent explains why, and what is next.
The fixed plant requires ongoing maintenance and the Maintenance Team uses the Hummas for installing components.
“I AM RESPONSIBLE FOR BOTH THE Ancillary Workshop and the Mobile Maintenance Workshop. The Ancillary Workshop completes maintenance on our fleet of Cranes, Elevated Work Platforms, Generators, Pumps and the Mobile Maintenance workshop, maintains our fleet of articulated trucks, Hitachi excavators, dozers, graders and loaders,” said Matthew.
The Simberi mine used to operate three Frannas, but because of Matthew’s experience with the brand they recently purchased two Humma UV35-25.
“We moved to the Hummas because they offer much heavier lifting capacities and I have had plenty of exposure to the brand when I was working in both Western Australia and South Australia. We’ll be using the Hummas on the
maintenance of the fixed plant as well as the mobile equipment and for general work and lifting around the mine site.
“The fixed plant requires ongoing maintenance and the Maintenance Team uses the Hummas for installing components. We also use the Hummas for our field lifting requirements on the mobile fleet, which includes work on the Hitachi excavators and other heavy machinery we use in the open cut mining process,” said Matthew.
The Humma UV35-25 35t capacity crane is a highly versatile, highcapacity pick and carry crane. The design emphasis has been placed on the operator, with safety and comfort key features, while retaining the toughness of a mine quality machine.
The removable counterweight
makes the crane at home either on an infrastructure project, operating at high capacity, or on the road travelling between jobs.
Airbag suspension provides the operator with an extremely stable, safe and smooth ride while at the same time reducing maintenance costs, as there is no articulation and boom pivot wear. The automotive spec Cummins 8.3L engine is highly fuel efficient, with up to 25 per cent fuel savings over comparable machines.
As standard, the engine is fitted with a Jacobs exhaust brake, which supplies greater stopping power and greatly reduces wear in the standard braking system. All these features combine to produce a very low maintenance machine.
Humma UV35-25 has an advanced Load Moment Indicator comprising Dynamic Load Charts. This system calculates the SWL for the operator for the exact boom angle and articulation angle, which gives the operator their maximum capacity for each position. Stationary load charts are also available as standard. This provides the operator with a boost in SWL when the crane is stationary.
A fully automatic side slope deration system is included into the software when required. The system includes digital rope compensation. The winch rope is compensated for boom extension digitally, which allows the operator to turn it on or off. This also allows the winch rope to be reeved easily over the top of the booms rather than internally, which greatly improves ease of rope replacement and maintenance.
Matthew said he has always been impressed with the quality of the design, engineering and manufacturing of the Humma pick and carry in his experience of working with them.
“I have spent many hours operating the 25t Humma crane at Prominent Hill for about four years, and then I was operating a 35t capacity Humma
“The Humma is well designed, engineered and manufactured using quality components.”
in Western Australia, I was there for about a year and a half,” he said.
“I moved to a company in South Australia, and we completed a hirebuy plan for another 35t Humma pick and carry crane and that was used to manage maintenance on a mobile fleet and a mobile crusher as well.”
“We definitely needed the additional capacity for some of the lifts required on the mobile crusher,” he said.
Nonetheless, it’s the capacity of the Humma that has kept Matthew coming back.
“The Humma is well designed, engineered and manufactured using quality components,” he said.
“We are also impressed with the layout of the machine. The size of the cab was an important also a contributing factor in our decisionmaking process, and being a 35t capacity pick and carry crane provides us with a much higher lifting capacity
for our lifts, but the crane is still lifting well within its capabilities.”
Matthew adds that the company has also received significant support from Australian manufacturer, Perth-based DRA Engineering.
“Due to our remote location, we have worked closely with the directors of DRA Engineering, Peter Dalla Riva and Peter ‘Junior’ to ensure we have the right levels of spare parts and components in stock for servicing the cranes,” he said.
“The Dalla Rivas are passionate about their products and everything they do, and I’ve always found them to be helpful, easy to deal with and I’ve never had any issues.”
“I’ve been associated with the Humma pick and carry since 2006, so I’ve seen the development of the product for an extended period of time. The new series of cranes have improved to the next level which is great,” said Matthew.
Flexible on the construction site
• Short set up time
• Easy to transport
• Travel under 100 % load
Sennebogen 6133E
Telescopic Crawler Crane
130 Tonne Capacity
52m Main Boom 15m Fly Jib
Engineered to secureafeguard both personnel and machinery from high voltage dangers, GoUpSafely™ offers unparalleled protection with its patented High Voltage Detection System.
With its advanced detection capabilities, GoUpSafely assists in preventing contact with HV sources, ensuring uninterrupted productivity. Elevate your safety standards today with GoUpSafely™, the trusted solution for safe operations near power lines.
A 200 tonne capacity Zoomlion ZAT2000V553 has made its way to Kununurra, the first of its kind to hit Australian shores
WHEN KIMBERLEY CRANES MADE THE decision to buy a larger crane for its work across Western Australia’s Kimberley region, a 200 tonne capacity Zoomlion ZAT2000V553 through Gleason Cranes Sales and Rentals Group was the choice – a big crane to do work across a big country.
The scope of work done by Matthew Hopkins and the team at Kimberley Cranes is varied and vast as the region that gives his company its name.
Based in Kununurra, Western Australia, the company services the East Kimberley and through to the Northern Territory – though with cranes based across Western Australia.
First established in 2009 as Hopkins Hire, today Kimberley Cranes carries out some mining work and significant construction and civil contracts, including a large volume of work with utilities such as Horizon Power and Main Roads WA.
to try something new.
“We’ve had to cross hire in larger cranes quite a bit in the last few years, so it just made sense to finally buy a bigger unit and go ahead and buy a Zoomlion.”
alternatives – noting that Zoomlion has been highly consistent in its place among the top five heavy equipment manufacturers ranked by sales in the world over the past few years.
For much of that time, Matthew has worked with the team at Gleason’s, with
“We’ve got enough work for it! No massive projects for it but it’s going to
The 200-tonne capacity Zoomlion ZAT2000V553 all terrain will have the greatest lifting capacity in the
water-cooled diesel engine and equipped with a 12-speed gearbox, the crane was ordered in custom paint colours to match Kimberley Cranes company colours of red and white.
The all terrain features an all-wheel variable steering system with six steering programs, and all axles have hydro-pneumatic suspension and an automatic leveling system with load equalisation between the axle pairs.
The 4.0 series spacious panoramic cab can be tilted for 0-20° to improve operator’s field of vision and has a sliding door, outward pushing windshield, front foot pedal and safeguard rail around the roof of the cab, as well as heating and air conditioning.
On this occasion the 200t all terrain was imported directly from Zoomlion’s state-of-the-art factory in Changsha, in China’s Hunan province, to Fremantle before being taken to the yard of RJ Coleman Transport, owned by Matthew’s father-in-law Robert Coleman, for the official handover and delivery process.
Gary Robertson, Zoomlion’s sales manager based in Western Australia, attended the handover, saying the company will stock parts needed for the crane’s ongoing support and maintenance.
“If it’s an uncommon part, we can simply order it from the factory very easily - there’s everything you could dream of there, and it’s nothing to fly them in.”
“I think in a lot of cases, the likes of Gleason’s and others will do that – we’ll suggest what we think they will need, and they will have the parts ready to go,” he said.
The sale of the crane, pre-delivery to ensure the crane met registration and CraneSafe requirements and on-theground transfer was facilitated by the team at Gleason’s and West Australian Crane Services, with Matthew saying he was grateful for the support of Gleason’s Director Chris Logan.
“Gleason’s have been really good to deal with – they’ve crossed every T and
Able to reach a top height of 56.7m, the Zoomlion ZAT2000V553 will be the largest unit in Kimberley Cranes’ fleet.
dotted every I and done everything that we could have asked for,” he says.
“Natalie and Chris have both been magnificent – Chris sold a crane for us when we first started about 10 years ago now – for when we first sold a crane overseas – and we know they’re going to be there and provide an in-depth service for us going forward.”
Chris, working with the company’s Western Australian Sales Manager Wayne Reilly, is dedicated to working with Zoomlion and helping make life easier for customers through their extensive back up and service network Australia-wide, both through themselves and a highly valued extended
support network of subcontractors.
Wayne is keen to point out that customers are not just seeing significant savings when purchasing a Zoomlion, they are also receiving a high quality and high-performance piece of equipment which provides great earning potential.
“We are very positive about the new range of all terrains manufactured by Zoomlion, as well as the lighter truck mount cranes, telescopic boom and lattice boom crawlers as well as the rough terrain models,” he says.
“They are priced extremely competitively, providing great value as well as a fast return on investment.”
Andromeda Industries is a people first company that works tirelessly behind the scenes to create its leading supply of steel lifting slings.
MUCH LIKE A CLOSE-KNIT SPORTING team, connection and communication gets converted into results and the team at Andromeda Industries feels that bond from the top down.
Andromeda Industries’ Plaited and Woven division manufactures Superflex and Flat Woven steel lifting slings, which are commonly used to solve lifting problems in areas such as infrastructure, construction, liquefied natural gas, mining and offshore projects.
When transformed into various products, the specialised Superflex cable provides a robust, long-lasting and flexible option when compared to synthetic and chain products available in the market.
Founded by Raymond McLaren and located in Moonbi, NSW, north-west of Sydney, Andromeda is a family-oriented business. Recently acquired by long- time employee Annette Williams and her husband Brett, the Andromeda team is dedicated to consistently delivering topquality steel lifting slings daily.
The Superflex is one of the high-quality slings Andromeda produces
Today, the company uses a 4200-tonne Talurit Swagging Press to create its large slings and stropsincluding the Twenty Four-0 Superflex cable with a 96mm nominal diameter. This cable is the largest of Andromeda’s Superflex cable range and can lift up to 168.6 tonnes in a straight pull when made into its Double Ended Strop configuration.
Andromeda’s goal is to maximise the use of this press to consistently fulfill its customers’ lifting requirements, regardless of size.
HARRISON
“It’s great to work here; great work environment, strong camaraderie with all
the staff here, you can go to anyone and ask for help” says Steven Harrison, Sling Maker at Andromeda.
The roll of a Sling Maker isn’t without it challenges, presented both physically and mentally.
“he role requires you to do a lot of mathematics with working out your specific lengths of slings and cables, and so on and so forth. When getting into the bigger loads, you’re working with a lot of large, heavy cable products that weigh over a tonne” Steven explains.
But Steven says he feels supported by his colleagues and in particular, Annette Williams, Company Director and Owner of Andromeda Industries.
“I can go to Annette for solutions, and she and the team will put together forms and sheets to make the mathematics
requirements that help produce the slings easier to work out. Obviously, with the heavier loads, I can go to Annette and management with suggestions on how to make the job a bit easier on the body” says Steven.
Considering the critical and sometimes stressful environment of the lifting and rigging industry, Steven values Annette’s approach of treating her staff with respect rather than only as machine operators.
“I know if I’ve got an issue, whether it be personal or work related, you can go to Annette and talk to her about it” Steven explains.
“It’s very rare to find this day and age. Not often you can go to a boss and sit down and have a chat with them. In the past I’ve spoken to her about things, and
she has always helped me out” he added.
Andromeda is widely known in the world of heavy lifting for its production of the Superflex Plaited steel cables.
The Superflex is a specalised wire rope made up of 912 individual wires, ultimately forming a complete wire rope. By point of comparison, a standard 6 x 36 wire rope contains 216 individual wires.
What sets Superflex apart from the crowd is that unlike conventional laid or twisted designs of wire rope, Andromeda’s are plaited - ultimately giving the ropes extra flexibility, akin to that seen with a synthetic sling.
Michaels’ role is to produce the plaited wire rope and flat woven strap, using the specialty machines for this operation and he explains that he loves working for Andromeda. “I like new challenges that my role presents as well as learning new ways to produce the slings and operate the machines - that’s what I love doing”, Michael says.
After 18 years of experience with another manufacturing company, Michael found his new home at Andromeda - starting in the Rubber Division before making his way to the wire rope division.
As a plaited wire producer, Michael says he’s able to let his mind go to work to produce some of the best slings going around.
But while he is focused on the task at hand, he also enjoys being able to support his employees with their endeavours.
“We have a bit of a joke in the workshop, but we ensure we get our job done, so it’s a really happy culture here” he says.
“I love sitting there and figuring out how things work and bits and pieces. That’s why I really like the weaving machine, as I try and make new and wonderful things.”
Michael expressed his excitement about helping Andromeda become bigger by using his creativity to produce larger slings in the future. “I am keen
to use my creative skills to help develop the products here at Andromeda.” he explained.
As Andromeda’s Customer Relationship Manager, Geoff Bower is passionate about Andromeda’s steel cable slings and rubber products.
Geoff attributes Andromeda’s success to its local knowledge as the company continues to produce a premium product.
“People stay in the industry for a while, and Andromeda’s Superflex has benefited from that knowledge generated withing the lifting industry,” he says.
“Therefore, there is a lot of longevity as you’ve got a lot of older staff imparting their wisdom on those on the ground
producing the product.”
After starting out producing the Superflex product in an operations role, today Geoff’s role is to promote Andromeda’s trusted products across Australia. “I am constantly going out into the industry, speaking to people about Superflex and educating them about Andromeda’s products and how they can help these businesses,” Geoff explains.
With that local know-how leading to Andromeda becoming a reputable brand in Australia, Geoff adds that he’s still impressed by Andromeda’s work culture,
“The culture is fantastic here; I enjoy getting up in the morning and going to work, I really enjoy working with the team and in my opinion, the culture as Andromeda is second to none.” Geoff states.
Borger Cranes is a family owned and operated crane hire and rigging business servicing New South Wales and Queensland.
Borger cranes maintain a modern fleet of cranes and equipment and our fleet boasts some of the largest cranes on the east coast
2 x LG1750,1 X LTM 750, 2 X LTM 650 2 X LTM 500 2 X GMK 400 4 X GMK 300
With every job, our experienced and industry trained team delivers high quality performance and nothing but excellence. Borger Cranes getting the job done for you.
MUSWELLBROOK
20 Strathmore Road, Muswellbrook NSW 2333 P: 02 5542 0077
BRISBANE
119 Brownlee Street, Pinkenba QLD 4008 P: 07 3333 5513
SUNSHINE COAST
CENTRAL COAST 8 Ainslie Close, Somersby NSW 2250 P: 02 4346 4262
HUNTER VALLEY
10 Rosedale Close McDougalls Hill NSW 2330 P: 02 5504 5525
65 Enterprise Drive
Kunda Parl QLD 4556 P: 07 5445 4900
GOLD COAST
52 City Link Drive
Carrara QLD 4211 P: 5588 5158
Although the 2023/24 financial year proved to be difficult for some, with a considerable slowdown experienced by many crane hire companies, Chris Burke, Senior Partner with Finlease, is anticipating more positive times are ahead.
“I’M GOING TO PAINT A POSITIVE PICTURE for the industry. All the data we are catching from the banks indicates that 2025 and 2026 are going to be positive years. We’ve just been though a tough year as an industry, and I think most people would nod in agreement when they read this article, this year has been tough,” said Chris.
There are number of identifiable reasons for the recent slowdown, says Chris.
“Over the last 12 months there has been a significant reduction in investment for infrastructure. The cost of labour has increased, the cost of cranes has increased and the cost of borrowing exploded. It takes time for businesses to adjust to these conditions.
“Also, the last quarter of 2024 was the slowest economic quarter Australia has seen since the Global Financial Crisis. We grew at 0.1%, which means we are teetering on the thought of a recession. We are very close, but I don’t think we will experience a recession. By definition a recession is back-toback quarters of negative growth. Expectations are that growth numbers will return to somewhere near normal by the middle of next year, which will be coupled with interest rate cuts at the start of next year,” said Chris.
“I am having conversations all the time with customers wanting to understand ‘the lay of the land’ asking me for direction on what is likely to happen. Businesses want to make decisions and continue to grow but to do this they want to know what the ‘runway’ is going to look like. Hopefully the team at Finlease have the
Chris Burke, Partner, Finlease
right answers,” said Chris.
“Working out borrowing costs is straightforward. You know the cost of your crane is $5 million, and the interest rate is 5 per cent. You can work out the financial package because
they’re all fixed costs.
“What’s been difficult is the volatility in this economic environment. Businesses don’t know where the work is, they don’t know where to find staff including experienced operators,
“We have noticed a move from crane companies towards the purchase of quality used cranes. The cranes are still usually relatively ‘new’ and I think this trend supports a broader cost saving exercise for businesses.”
Riggers and Dogmen. It is difficult to make investment decisions with volatility in the market
“I’m seeing that the ‘runway’ is starting to stabilise, and we are entering into a period of slow but modest economic growth. There has been a sharp upturn of skilled labour coming into the country, meaning labour costs will soften and the cost of borrowing is starting to come down. When we see reductions in the cost of borrowing, we will see the ‘runway’ level out and that’s what businesses need,” said Chris.
Having worked at NAB prior to Finlease, Chris always pays particular attention to the NAB Business Confidence Survey.
“It’s an interesting survey. Rather than using tangible economic data, NAB would sample 1,000 business customers and ask them questions that they would rank one to 10. Questions would include, ‘What is the likelihood of you bringing on extra staff in the next quarter?’ What is the likelihood of you purchasing a new piece of equipment in the next quarter?’ The answers are compiled and indexed to provide a score.
“The NAB Business Confidence Survey for the last quarter was the first one in 12 months that demonstrated a little a spike of confidence which couples with what we are seeing. The ‘runway’ into next year is starting to look more positive than where we currently sit. I think it is fair to say we’ve hit the bottom of the curve and we’re now heading back up into more positive times,” said Chris.
The Energy Sector will provide significant growth opportunities in the years to come says Chris.
“During my conversations with customers, I make reference to the ongoing investment in energy. We are
seeing significant investment in the energy sector, in wind, solar, hydrogen, gas, and potentially in the future, nuclear, if that gets off the ground.
“I recently attended a summit in Gladstone and there was a presentation by a group called the Gladstone Engineering Alliance (GEA). They were presenting about how they’ve essentially had to redesign the whole town because they are forecasting 7,000 wind farm turbines will be erected there between now and 2050. The presentation referenced close to 25 years worth of work,” he said.
“In August the Federal Government approved the first stage of the $30bn SunCable project, which environment minister Tanya Plibersek described as the ‘biggest renewable energy project ever’ saying the project will be ‘transformational’ for Northern Territory.
“We are going to see a shift from traditional infrastructure spends, like bridges, rail, roads and tunnels, although there will obviously be ongoing projects, but the investment will not be at the levels we have seen in recent years. The investment is going to be in the Energy Sector,” said Chris.
The 2032 Brisbane Olympics will also see a significant building program, says Chris.
“The ‘Olympic Build’ is going to be huge for the Brisbane construction sector, we’re even hearing it from the banks. It’s interesting, as states like Victoria slow down as projects are completed, Queensland comes on the boil. There is a lot of work coming in the construction and energy sectors in Queensland,” he said.
Chris is seeing a change in purchasing and he has advice for crane businesses when it comes to the borrowing process.
“We have noticed a move from crane companies towards the purchase of quality used cranes. The cranes are still usually relatively ‘new’ and I think this trend supports a broader cost saving exercise for businesses. Given everything has inflated so much over the last 12 months, crane businesses are being more rigorous with their budgeting and purchasing.
“The advice we are providing customers is to plan the investment. Obviously, we still need all the fundamental financial details but we are advising customers to plan their purchases up to 18 months in advance. Regardless of whether it’s a second hand or a brand new model, there needs to be strategy around the purchase. Not so long ago, customers would come to me saying ‘Chris, I’ve bought a crane, here’s the invoice, please sort the finance’.
“There’s far more to it now, especially for your larger machines. When I was at NAB, we could turn around a 60 tonne Liebherr in 24 hours, no problem. That’s not the case anymore, customers must be strategic and really plan the financing. Even for motor vehicles and smaller assets, it’s very much a thought out, planned process,” he said.
“A customer contacted us recently having noticed an upcoming auction. They wanted to secure a pre-approval so they could potentially successfully bid on some cranes. This is a safer and smarter way to transact. Pre-approvals unfortunately take time in the current lending environment, emphasising the importance of planning your purchases. It can put strain on a relationship when a supplier is requesting payment, but this is delayed because you haven’t been preemptive and taken the necessary steps for preapproval,” said Chris.
Precision Rigging and Logistics provides an end to end solution for any lifting job in Queensland.
Precision Rigging and Logistics can visit your site at any time to suit you, to conduct a comprehensive, cost free site evaluation and consult with you to provide you with a cost effective, efficient solution to all your logistical needs.
Providing an innovative solution for the impossible job.
• On Site Mechanical Rigging
• Relocation and final positioning of sensitive and heavy equipment
• Removal of redundant equipment/debris from site
• Comprehensive crane, transport and traffic control logistics packages
• Demolition and removal of mechanical equipment
• Commercial and residential equipment removal & relocations
Precision Rigging and Logistics service a range of industries including:
• Mechanical Air-Conditioning
• Electrical
• Medical
• Heavy Industrial factory equipment
• Telecommunication and I.T Equipment
• Universities and Hospitals
• Heavy Art
Fleet Cost & Care is a technology partner that is embedded within the crane industry. The Americanbased software management provider strives to bring companies along a path of digital transformation; a journey to a better way of enhanced crane system automation that improves efficiency, centralises systems, increases safety and compliance and generates greater profits for customers.
HAVING GROWN UP AROUND CRANES, JEFF
Curran is well and truly a part of the fabric of the crane, rigging and heavy lift industry in the United States.
His father, John, and mother, Jacquelyn, started the JJ Curran Crane Company in 1950 and the family’s commitment to each other and the broader crane industry is the reason JJ Curran Crane company has been a thriving business in Detroit for over 70 years.
In the early 1990s Jeff began thinking about crane systems technology and was curious to find ways of modernising the crane and fleet industry. Shortly after that in 1993, Fleet Cost & Care was born.
When he talks about the inception of the now deeply influential Fleet Cost & Care business, a venture in which he takes a lot of pride, Jeff allows himself a broad smile.
“I was a dreamer,” he says.
“We are really proud of what we’ve become as a fleet software management company and we can’t say enough about
our customers and how loyal they have been to us. They are deeply passionate about the industry, too, which aligns to what we are about as a brand in the crane industry,” says Jeff.
Jeff lauds the connection and work ethic of his tight-knit family, which helped him mature into a leader as a young man. However, a pep-talk with his father went a long way in helping Jeff choose his direction.
“I was born into a family that exposed me to good education, we played a lot of sports, we didn’t travel much; We were a family that enjoyed the Midwest US and occasional trips to Florida, but the family stayed close to the business,” says Jeff.
“My Dad had a tremendous work ethic, and he was a great role model for me in that aspect.”
Jeff graduated at age 22 with a bachelor’s in business administration from Bowling Green State University, Ohio. He then had a meaningful conversation with his father, John.
“At the time, I wasn’t sure I was going to go in the family business, but my dad gave me a little pep talk and asked me to join,” Jeff says.
“Once I knew Dad was right behind me and he backed me in, I gave it a lot of consideration and chose to join the JJ Curran Crane business.”
Fleet Cost & Care is already an incredibly strong player in the crane and heavy lift fleet management software field, as the company has helped hundreds of its customers in areas of standalone system elimination, process standardisation and profit generation for over 30 years.
“We have had quite a big head start, as I was keen to bring my IT knowledge and skills to the business and create something special,” says Jeff.
“We identified the challenges of paper and physical documentation and after speaking with customers for a long time about these industry hurdles, we’ve now
committed to digital transformation.”
Digital transformation is about utilising new technologies, new tools and new best practices to achieve greater outcomes. It applies to all levels of a company - from a high-level perspective (C-suite, managers) to the operations team – including dispatch, crane operators and service technicians.
Fleet Cost & Care has customers all over North America, the Caribbean, Australia and New Zealand.
Jeff says a part of Fleet Cost & Care’s vision is to move with, leverage off and therefore benefit from advanced systems such as application programming interface (API) technologies.
API can be understood as an automated system whereby different software entities are able to communicate with each other by defining a set of rules.
For example, Fleet Cost & Care’s API system allows customers to track crane GPS data, fuel card and digital work order information together simultaneously. Jeff wants Fleet Cost & Care to continue its exploration phase in this area.
“We want to grow our company with the help of all kinds of other logistical fleet management technologies that relate well to us,” he explains.
“The API ability within Fleet Cost & Care’s software is a very strong and powerful operational functionality. Our API informatics could be anti-fraud oriented, security-oriented or it could
enhance efficiency relating to logistics, GPS – anything and everything that fits into that digital world,” Jeff adds.
Interim Chief Operating Officer Tony Durey plays a major role in one of Australia’s biggest crane and heavy lifting service providers. Freo Group has 21 branches across Australia and has over 497 modern crane units, ranging from 3 tonnes to 800 tonnes in lifting capacity.
Freo Group and Fleet Cost & Care entered a partnership in 2019 which saw the Fleet Cost & Care product rolled out across all Freo branches.
The process included the inclusion of 2,000 tablets – one for each staff member.
Tony led the project and says the process first appeared to be an extremely large task. However, Freo’s relationship with Fleet Cost & Care ensured everything ran as smoothly as possible – despite a few teething problems in teaching staff how to use the tablets.
“There will always be challenges when making major change to systems and processes, but the entire FCC team provided us with a great software and effective roll-out measures to mitigate the stress and strain in the process,” explains Tony.
Tony says Fleet Cost & Care’s product was brought into Freo Group to enable staff to do their jobs more effectively,
saving them from the old-fashioned and arduous task of pen to paper timesheets and general reporting.
“At the time, FCC appeared as the only end-to-end paperless process providers, so I met with Jeff and his team and then we put a business case forward for a pilot fleet,” he says.
“We wanted to ensure we free our staff up from the traditional reporting methods, which honestly, takes time, so now with this new software, our staff have gained further efficiency and time spent performing their roles.”
Tony told the story of a staff member that was not as open-minded initially about the Fleet Cost & Care product. The staff member was not keen on the change, but soon realised the software would be a great help to herself and her team.
“She wasn’t a fan initially, but the next week she came back to us and had a brandnew perspective on the product; she said the product was awesome,” says Tony.
NexGen and Atom are the primary software solutions of Fleet Cost & Care featuring some of the latest fleet management technology. Both impressive systems are designed to enhance the customers’ reporting output, fleet database, field services, production line and revenue within the wider Fleet Cost & Care framework.
Jeff says the Atom and NexGen features
help maintain an “assembly line” to support efficiency.
“I call it an assembly line, which allows you to pay your employees, pay your vendors and buy goods and materials, service the equipment, all at the same time, while keeping the job going,” says Jeff.
NexGen is designed by fleet owners to help heavy equipment rental companies operate more efficiently.
In NexGen, customers can quote and schedule jobs, add or remove equipment, view daily, weekly, or monthly schedules, track service schedules, manage parts inventory and perform all of the back
“We identified the challenges of paper and physical documentation and after speaking with customers for a long time about these industry
office administrative tasks required by its businesses.
Overall, NexGen helps fleet and operations managers improve data accuracy, increases safety and bolsters revenue.
The Atom feature offers a variety of different features that help complement NextGen.
Atom is a comprehensive mobile fleet management app that allows fleet owners to manage operations from a tablet or smartphone. Dispatchers, sales managers, operators and service managers use Atom to create quotes and work orders, assign work to mechanics, enter labour,
capture signatures on a job site, perform safety checklists and check in on the status of jobs for any given time period.
Atom proves a point of difference in the automated fleet operations space, as the software increases sales per employee and profit margins, while reducing operating costs and expenses.
Both systems help create a versatile fleet management toolbox for all customers in a myriad of Fleet Cost & Care software options, says Jeff. “There’s a strong database in there (NexGen and Atom), in which security is air-tight and there is lots of functionality, this is the direction the industry will go in,” he says.
Prior to the Crane Association of New Zealand’s National Conference and Exhibition in Rotorua, a group representing the Australian crane industry enjoyed a factory tour of TRT’s manufacturing facility in Hamilton, New Zealand.
FOR BEN PIEYRE, CEO OF BOOM LOGISTICS
and President of The Crane Industry Council of Australia, this was his second visit to the TRT facility.
“I toured the facility two years ago and I was very pleased to see that Bruce Carden and his teams have implemented the developments they highlighted at that time. The quality of manufacturing is very high and includes ‘state of the art automation’ supported by skilled and experienced employees,” said Ben.
TRT’s site in Hamilton, New Zealand, is 33,000 square metres with 9,000 square metres under the roof line. In line with a recent board initiative to reduce the organisation’s carbon footprint, TRT has made significant strides in sustainability. Since Ben’s first visit, TRT has installed a comprehensive solar power system on two of its sheds, generating enough power to run all its machinery, plant, and equipment. Currently, TRT has 600 kW of solar panels in operation, and once the project is complete, this will increase to
nearly a megawatt at its head office and manufacturing facility. With the current 600 kW setup, TRT is already reducing CO2 emissions by 50 tonnes annually, cutting their overall CO2 footprint by 44%.
Stephan Becherand, General Manager of Sales for Preston Hire was also on the tour.
“The warm welcome from the staff was a clear indication of TRT’s commitment to fostering strong relationships. The friendly and professional attitude of the employees set the tone for the day, making the visit both pleasant and informative.
“The tour of the factory was a journey through a world of innovation. The sight of cranes being assembled with precision was inspiring. The company’s commitment to utilising cutting-edge technology was evident in every corner of the facility. From state-of-the-art machinery to advanced design software, TRT is clearly at the forefront of technological advancement in the crane and transport industry. The engineering department is working very
closely with their clients to ‘Make it Possible’,” said Stephan.
To continually improve its products, TRT’s management team has invested heavily in capital equipment and plant. These investments were made in brand new plasma cutting technology, enabling smarter cuts, cleaner cut lines and greater accuracy in their designs. There has also been significant investment in robot welding technology.
“When visiting the factory, you can follow the production and manufacturing process from the raw steel in the yard to the finished products – including the TIDD pick and carry crane, bespoke trailers and crane pads,” said Ben.
2023 saw significant improvements in manufacturing processes which are called ‘Drive Efficiency’. To drive greater efficiencies, TRT completely reorganised how it manufactures the TIDD pick and carry crane. This reorganisation has created a flow-on effect to the manufacturing processes, ensuring
The investment in modern manufacturing technology is certainly a contributing factor to the build quality and the reliability of the product.
parts are handled in a timely manner and maintaining a high standard of work through visual control and Quality Assurance checks.
The factory manufactures two and a half to three TIDDs a month. They are built on a 14-week cycle and if a customer provides nine weeks’ notice, TRT will paint the TIDD on site in any two colours the customer wants.
“The investment in modern manufacturing technology is certainly a contributing factor to the build quality and the reliability of the product. I was also impressed with the culture and the level of skills and knowledge of employees. I experienced this when I interacted with various employees on the factory floor during my visit. Many have been with the family business for decades,” said Ben.
From the moment the factory receives and cuts the high-grade steel to ‘waving the mudflaps’ goodbye in the case of the TIDD, TRT manages all processes inhouse. The steel is cut with new plasma technology and the factory has bending and press capabilities, where all the
“The company’s commitment to utilising cutting-edge technology was evident in every corner of the facility.”
booms, the chassis and everything else are manufactured. All the major components are built in-house before going through to the new final assembly manufacturing facility.
“The innovation included in the new TIDD PC28-3G is impressive and I really look forward to seeing this crane in action. The visit to TRT was a testament to the company’s dedication to innovation, and sustainability. It was a glimpse into a company that is not just manufacturing cranes but is also shaping the future of the industry. The positive impressions from the visit reflect on a company that is poised for continued success and growth,” said Stephan.
TRT currently has 234 staff overall with 28 in the Australian business. Of the 234, 114 work in manufacturing.
TRT talks with pride about its people
and its ‘Make it Possible’ culture. This attitude was apparent during the visit, said Ben.
“There was a positive attitude at all levels of the business, from Reception to the Research and Development team through to the factory floor. TRT organises a fortnightly meeting on innovation which no doubt drives the ‘can do’ attitude of the staff,” said Ben.
“It is clear there are also some exciting works in progress for the development of trailers and cranes. They use high quality design software and are able to tailor designs to accommodate and execute specific requirements for customers,” he said.
TRT manufactures several products in the facility, including the TIDD pick and carry crane, bespoke crane trailers and crane pads. Ben was impressed with the
recently installed a complete
new TIDD PC28-3G.
“The TIDD PC28-3G features a high level of technology with enhanced safety innovations and I was impressed with the high build quality of the product. Boom Logistics operates a fleet of TIDD pick and carry cranes as well as trailers designed and built by TRT. We are always focused on quality and innovation when choosing products for our fleet and for this reason, we would not dismiss consideration of any of the TRT products,” said Ben.
Crane and Lifting’s Emily Schlegel was also on the tour and had this to say.
“I wasn’t prepared for the enormity of the operation and the amount of innovative and ‘state of the art’ manufacturing technologies TRT has implemented to manufacture the TIDD pick and carry range, TRT bespoke trailers and TRT Crane Pads. It was fascinating to watch raw steel enter one door and a finished product roll out of another, out at the end of the manufacturing process,” she said.
“As a major manufacturer, TRT is focused on reducing its carbon footprint and has invested in a massive solar panel
“It is clear there are also some exciting works in progress for the development of trailers and cranes. They use high quality design software and are able to tailor designs to accommodate and execute specific requirements for customers.”
system that generates enough power for all manufacturing requirements. We were able to interact with personnel in the factory and everyone was extremely friendly and obviously passionate about what they do.
“The tour included a number of significantly influential individuals from the crane industry, and many had seen other Crane OEM manufacturing facilities around the world. The TRT facility compared favourably with anything they have seen. If you are given the opportunity to visit TRT, I strongly recommend you take it - you will not be disappointed,” said Emily.
Apart from manufacturing the TIDD, trailers and crane pads, TRT is proud to be the Kobelco Crawler Crane distributor
for all of Oceania, covering Australia, NZ and the Pacific region. TRT is also the New Zealand and Queensland distributors of Manitowoc which includes Grove all terrains.
“Having known of TRT’s capabilities for many years, this visit was an eye opener to the dedication and abilities of everyone in the factory. Thank you again to Bruce and the TRT team for making the tour so enjoyable. TRT stands as a shining example of what can be achieved when innovation, excellence and a commitment to stakeholders and the environment are at the heart of a company’s ethos. The visit was a powerful reminder of the exciting possibilities that lie ahead in the world of crane manufacturing,” said Stephan.
The New GMK5150XL is the latest sibling of the GMK5150L-1, with longest boom (69m) and most versatile road weights in class
• Reach further with 69m boom and 30m hydraulic luffing fly
• 50t GVM with outriggers in situ for reduced cost legal travel in all Australian states and territories
• 10.2t counterweight in situ at 12t per axle
• Increased safety and flexibility with MAXbase variable outrigger positioning
• Faster, intuitive set-up with CCS (Crane Control System)
• Grove Connect Telematics
• Capacity: 150t
• Main boom: 68.7m pinned*
• Maximum Jib: 30.2m (40O hyd luff)
• Maximum tip height: 99m
By investing in larger capacity cranes, Resolution Rigging Services (RRS) has been expanding its tower crane fleet to service growing momentum towards the adoption of Modular Construction processes in the construction industry. Tony Noronha, Director of RRS explains more.
in which a building is constructed off-site, under controlled plant conditions, using the same materials and being designed to the same codes and standards as conventionally built facilities – but in about half the time. Buildings are produced in “modules” that when put together on site, reflect the identical design intent and specifications of the most sophisticated site-built facility.
“We have been seeing a significant change in the construction sector and the move towards Modular Construction is gathering significant momentum and we are investing in larger capacity tower cranes to keep up with the demand,” said Tony.
“There are a number of reasons for this. Onsite construction has become extremely expensive due to labour costs, so builders are manufacturing modules in factory type environments and bringing them to site prefabricated or in forms of precast panels or precast columns or girder beams.
“The concept minimises labour costs on site and greatly reduces the amount of rubbish generated during the construction process and therefore reduces the costs of moving and disposing of rubbish from a construction site.
“With 60 – 90 per cent of the construction completed inside a factory, the risk of weather delays is also mitigated. Buildings are occupied sooner, creating a faster return on investment. We have been finding these modules are getting bigger and heavier and that’s the reason we have been investing in larger capacity cranes,” he said.
Tony goes on to discuss the additions RRS has made to its fleet.
The additions include a new Favelle Favco M220DX tower crane with a freestanding height of 48m. It features
a 61.5m boom length lifting 29t to 15m and 2.5t at 60.4m radius. It has just been recommissioned with a brand-new power pack to lift a 4t load at speeds of over 205m per minute.
“This is perfect tower crane for high rise projects when speed is required to elevate materials to 40 stories and above,” said Tony.
“Seeing the move towards Modular Construction, we also invested in a brand new Favelle Favco M630D with a freestanding height of 64m tower height and a 73.4m jib length lifting 50t to 20m and 5.1t to 71.7m radius was recently commissioned for work on a data centre,
where it worked for 15 months lifting precast columns and precast panels.
“We’ve gone a little bit further and made a significant capital investment in a brand new Favelle Favco M860DX MK II, which is an upgraded version of the current M860DX. With this model, Favelle Favco added an extra boom section, meaning it has 82.6m of boom and can lift 5.7t at 80.7m. In our opinion, Favelle Favco dominates in the bigger end of the market although there are obviously other brands of luffing cranes,” said Tony.
Another recent purchase is a brand new Favelle Favco M860DX with a freestanding tower height of 64m and an 82.6m jib
“We have been seeing a significant change in the construction sector and the move towards Modular Construction is gathering significant momentum and we are investing in larger capacity tower cranes to keep up with the demand.”
length lifting 96t to 13.5m and 5.7t to a 80.7m radius. This was also commissioned for a recent data centre project where it will be lifting precast columns and precast panels.
Resolution Rigging Services has also welcomed other new arrivals, including a Liebherr 340EC-B 16 flat top tower crane
with a freestanding tower height of 57m and with a 78m boom able to lift 16t to 21m and 2.1t to a 78m radius. Upon its arrival it was immediately commissioned to a project for a valued client.
Another arrival is the Liebherr 470EC-B 20 flat top tower crane, freestanding 80.1m and with an 83m boom lifting 20t to 24.4m and 2.2t at 83m radius. Resolution Rigging Services says it was the first to introduce this model into Australia.
“We were honoured to be the first to introduce the crane into the market, it’s the biggest flat-top manufactured by Liebherr and we look forward to having this crane alongside our other 4 Liebherr 280EC-H 12 model tower cranes,” said Tony.
Tony and the team at Resolution Rigging Services are busy with the construction of Data Centres as well as servicing other areas of the construction sector.
“We are working on a number of Data Centre projects and this type of work has
increased significantly over the last few years,” said Tony.
“With everyone using smartphones and other devices, and all of the data being stored in the cloud, we are going to see more centres to store the data. Big players like Microsoft, Airtrunk and Amazon are making considerable investments in the Australian data storage market.”
“The greater Sydney construction sector seems to be travelling reasonably well, although the residential market is very, very slow. We are seeing that smaller builders are finding it hard to finance and actually build units.
“We are fortunate in that for some time we have worked for one particular developer and builder which continues to supply the market with housing, which is an advantage to us. We’ve got quite a number of projects online with this particular developer.
“We are also seeing a lot of activity coming in commercial construction with schools, hospitals, shopping centres and
office space going up. We are also seeing more hospitals and infrastructure projects coming online which are obviously being backed with a lot of government funding,” said Tony.
There are significant benefits for the customer with larger capacity cranes, says Tony.
“These larger capacity cranes also feature significantly longer booms which means more coverage on site. One large luffer can replace two or three smaller cranes with significant cost savings for the customer,” he said.
The Resolution Rigging Services fleet is growing and so are the teams supporting the fleet, says Tony.
“We have 25 tower cranes in the fleet and there are more cranes arriving later in the year. We are employing more people, including more office staff, to cope with the demand. There are definite signs that despite some of the challenges
“These larger capacity cranes also feature significantly longer booms which means more coverage on site.”
the construction sector is currently experiencing, the demand doesn’t seem to be backing off,” said
Over the years, Tony and his team have worked on providing customers with turnkey solutions, starting with the cranes and including retractable loading platforms and the BlokCam wireless camera and audio system.
Resolution Rigging Systems operates over 100 Crane Deck retractable loading platforms.
“We’ve been offering our Crane Deck retractable loading platforms for a few years now. They come in two configurations, decks that are 2.2 metres and 3.2 metres in depth. They are Australian designed
and engineered and manufactured from Australian steel. We offer them as a package with our cranes and customers are happy to receive a quote for the crane and the platforms because it saves them having to go elsewhere,” he said Tony.
“We also continue to offer our Blockcam cameras that are fitting to the hook blocks of the crane and provide great images of the load suspended directly under the hook block. The cameras also provide audio directly to the driver should a two-way radio ever fail in transmission. You can even add a sim card to the monitor and have real time viewing of the crane’s lifting operations from your desktop in the office,” said Tony.
Back in July, Tutt Bryant delivered a first HSC SCX2800A-3 crawler crane to an intersection in Melbourne’s north-east, where the North East Link Tunnel Project is still underway.
A TOTAL OF THREE HSC SCX2800A-3 crawler cranes will assist with the project, which aims to take 15,000 trucks off local roads every day and reduce travel times by up to 35 minutes.
The overall project is a part of Victoria’s Big Build, which is costing around $90 billion and plans on delivering over 165 major road and rail projects across the state.
The team at Spark North East Link Tunnels D&C was eagerly awaiting the two remaining HSC SCX2800A-3 crawlers, with the first crawler holding the fort at the Yallambie site in Melbourne’s north eastern subburbs, as
Cranes & Lifting went to press.
The first HSC crawler had been holding the fort at the North East Link Tunnel construction project site in Yallambie, in Melbourne’s northeastern suburbs.
“Everybody onsite here at Spark saw the value of having the three crawlers from Tutt Bryant here on the job,” says Lift Supervisor Spark North–East Link Tunnels D&C Mick Nixon.
“The HSC crane provides us with a large radius, which allows us to excavate dirt and rock from a strong working position.
“The beauty of getting two more
of the HSC crawlers is that they are a carbon copy of the one we have right here, therefore we can easily shape the lift documents and consolidate lift plans a lot easier, compared to if we onboarded a new type of crane; the plans for the new two cranes will piggy back off the one we have right in front of us,” Mick added.
One of the main tasks of the HSC SCX2800A-3 crawlers at this project is to scoop up the dirt using an 8-tonne bin; the bin then drops its load from underneath into a pile, where an excavator transports all the dirt into a truck.
The overall project is a part of Victoria’s Big Build, which is costing around $90 billion and aims to deliver over 165 major road and rail projects across the state.
Each “bin” (process whereby dirt is collected by bin and dropped on pile) takes approximately six minutes and the team at Spark averages around 35 bins in one day.
To assist with the job, Spark contacted construction equipment supplier and heavy lift service provider, Tutt Bryant.
Tutt Bryant is a reputable Australian brand and Mick and his crane operations team knew exactly who to talk to.
“When we were looking for a crane for this box cut, we spoke to Tutt Bryant about what was available and they mentioned that this crane was on its way from Japan.
“We wanted a crawler crane that is versatile, from throwing packs of reo and shutters at a 50-plus metre radius for the FRP (Formwork, Reo, concrete pour) works to a spoil removal bin at about 40-tonne for excavation, this crane was able to tick all the boxes,” Mick explained.
Servicing multiple levels of the project across several disciplines takes a lot of coordination from all
teams onsite; Spark has relied on the experience of the crew that operates and maintains the HSC SCX2800A-3 crawlers to create solutions for the challenges of the varying work scopes and this crane.
Challenges have included high winds and other weather-related delays. However, Mick says the crew and their crane has stood up when it mattered.
“The crane crew here haven’t missed a beat and due to the strong progress being made, it has allowed us to buy two more exact carbon copies of the HSC to help develop the project even further,” says Mick.
At the site where the HSC cranes will be eventually situated, there project there is to build ramps that will connect the community to the M80 Ring Road, whereas new ramps in Yallambie will connect drivers to the Eastern Freeway.
The new tunnels are set to create simpler interchanges at Lower Plenty Road, Manningham Road and Eastern Freeway.
There will also be a twokilometre tree-lined boulevard along Greensborough Road and a two-hectare
Yarra Link green bridge over Bulleen Road.
New wetlands will be revealed along the Yarra River and Koonung Creek in Bulleen and Balwyn North.
Following years of community feedback, the longer tunnels to Watsonia from Bulleen will include an extra 1.9 kilometres built by tunnel boring machines (TBMs) to keep most of the civil construction work underground.
Mick says the bond between the crew on the Yallambie job site is strong, as this isn’t the first rodeo for the team behind the cranes.
“I have worked with these guys previously, so it was an easy one for us, in regards to asking some great people to join our team for this project,” Mick says.
Spark also has a Women in Construction program, where Alexandra Anchen, has impressed from day one on the job.
The program offers trainee placements for women in the industry to join the crane and heavy lift operations team, to improve skills and
bring their strengths to the team.
“Alex has been fantastic and there’s plenty of good feedback coming her way,” says Mick.
Alex says she’s enjoyed her time thus far onsite.
“The job has been fun and I’ve learnt a lot since I’ve been here. They’re a good team to learn off,” says Alex.
General Superintendent, Cranes & Lifting at Spark – North East Link – D&C, John Foster is excited by the arrival of the HSC cranes. “We did our due diligence and went through all the possible crane options for this particular job; we settled on the HSC Tutt Bryant has rented us, as it suited the frame for the work area and was the conducive to the location of where we are digging out of.”
“The success of this HSC SCX2800A-3 crawlers has been a great contribution to the program,” says John.
The North East Link Tunnel Project is expected to be open in 2028.
One of the main purposes of the HSC SCX2800A-3 crawlers is to scoop up dirt using an 8-tonne bin.
“The success of this HSC SCX2800A-3 crawlers has been a great contribution to the program.”
StartSafe is comprehensive tool designed to streamline your crane operations, enhance safety, and ensure accountability.
Machine specific checklists are in line with the CraneSafe program.
StartSafe streamlines the process for collecting pre-start information, with instant data retention to a central location for the crane owner to access.
Photos tell the story.
When a faulty item is recorded by the operator, the maintenance team is notified of the issue by email, which includes photo evidence of the fault. This also assists with gathering major inspection data.
LiftEx Gold Coast 2024 was nothing short of a resounding success.
THE SPECTACULAR VENUE AND THE beautiful surrounds of the Gold Coast brought together global manufacturers and distributors, LEEA members, industry leaders and professionals from across the region. The array of products on display reflected the industry’s commitment to new technology and ingenuity. The exhibition floor was a hive of activity, as suppliers and end-users from sectors as diverse as mining, construction and renewable energy mingled and discussed the latest and greatest pieces of equipment.
This year was LEEA’s first full exhibition outside the UK and set a high benchmark, as we look to grow and
learn for next expo in 2026. However, planning for this event began back in May 2023, when LEEAs Regional Council for Australia and New Zealand endorsed a vision to extend ourselves and decided the best mechanism to expose the wider market to LEEA was via our very own LiftEx. This event was testament to their vision for the Association and their desire to promote LEEA and their industry far and wide.
LiftEx attracted over 500 guest registrations, which for a specialist association, is a feat worth celebrating. Our event planner and media partner, L2 Events and Cranes & Lifting Magazine were spectacular (as usual), and we thank them for their ongoing support in making the event well known and highly attended.
Parallel to the exhibition, the conference component of LiftEx offered exceptional knowledge sharing opportunities, with a free training session on pre-use inspection delivered by our LEEA Training Partner – ATC Offshore, being a significant highlight.
The Queensland Government was also key stakeholder and supported LiftEx with a great speaker and a lean manufacturing workshop, ensuring we had a great content program. The Women in Manufacturing - Diversity, Equity and Inclusion Masterclass was a session critical for our industry. With few women involved directly in lifting equipment testing and inspection, Teagan Dowler presented a practical workshop on making the lifting equipment industry attractive to a broader range of workers.
Additionally, standards and regulatory discussions and their associated panel sessions sparked engaging dialogue on product development and best practice.
A heartfelt thanks to the event sponsors – TNC Cranes, Pacific Hoists and AusLift, whose support was pivotal to making LiftEx a landmark event. I’d also like to thank the exhibitors for their support
in ensuring the expo was the enormous success that it was. Given this was our first exhibition in Australia, they showed commitment to the industry’s growth and the Regional Council’s vision. I hope the event bought them exceptional returns.
And to the attendees, whose enthusiasm and eagerness to learn and connect turned LiftEx into the success that it was, the intent for it to become a community celebration came to fruition. Their participation not only contributed to the event’s success but also reinforced our collective pursuit of a safer, more effective and collaborative industry.
This year we again awarded members who’ve maintained their membership for 10 years. In the 14th year of LEEA being in Australia and New Zealand, our 2025 event will highlight those who’ve continued to contribute to LEEA’s success for 15 years and those “Legends” who’ve shaped our industry into what it is today.
For me, LiftEx was a brilliant opportunity to speak to our members, and their guests, to truly get a sense on how their businesses are performing and what additional products and services they need from LEEA as we evolve as an industry and association.
So, as we reflect on LiftEx 2024, we will look ahead to learning and growing from this event. The spirit of our industry, collaboration and innovation was on display over those two days and although LiftEx as concluded, plans for our next event are already in full swing. As announced at LiftEx 2024, we’re reconvening for our conference in 2025, but our next exhibition in 2026 will be bigger and better. LEEA’s journey towards a Lifting Industry with no accidents, injuries or fatalities continues and each participant at LiftEx will continue playing a crucial role in shaping that vision.
Here’s to LiftEx 2024—a giant step forward for our industry. Thank you, for making it an unforgettable event.
Since 1977, PNOinsurance has prided itself on delivering exceptional service and leveraging its deep expertise, earning a reputation as one of Australia’s top insurance brokers.
THE COLLECTIVE BUSINESS EXPERIENCE of the PNO team, combined with leading technical industry knowledge across the crane industry, enables it to source and secure the right insurance solutions for all businesses.
Being 100% independently owned, PNO offers the flexibility to find the most suitable insurance partner for each unique client, regardless of their complex needs.
Its extensive industry knowledge spans across various sectors, with some of those including:
• Mobile Cranes
• Tower Cranes
• Transport & Logistics
• Construction
• Dry Hire
PNO’s in-house claims team handles all claims, including the most complex
ones, ensuring customers receive the support they need when it matters most.
Benefits to the Crane industry: PNO works with substantial portfolios of business with leading crane insurers, backed by its unsurpassed experience and knowledge of complex crane claims.
As a member of CICA, PNO provides comprehensive coverage, including downtime cover, OHS investigation, defence costs and financial protection cover.
They offer specific policy benefits tailored to PNO and tailor extensions to suit each individual business, servicing clients across Australia.
In addition, PNO provide a range of other services including:
• Workers Compensation - Injury Management and Early Intervention
• Personal Insurance - Income Protection and Life Cover
• Buy-Sell & Key Man Cover - Life, TPD, and Trauma Insurance
PIONEERING PROJECTS ACROSS VICTORIA
Since 2017, PNOinsurance has been the trusted insurance broker for Johnson & Young Cranes, a company that has grown from humble beginnings into a powerhouse within the Australian crane industry.
Starting with two cranes, Johnson & Young Cranes now boasts a multi-milliondollar fleet and multiple depots across Victoria.
Johnson & Young Cranes is a market leader, supporting some of the largest and most significant infrastructure projects in Victoria. Its expertise spans major road, rail, bridge and tunnel projects, renewable
energy maintenance and construction projects and significant building and maintenance projects that are transforming the Victorian landscape.
Initially operating from a single location, the company identified the need for multiple depots to efficiently manage both its increasing fleet and its team. Today, the company operates from major depots in Campbellfield and Dandenong South, complemented by smaller satellite depots in Preston, Laverton and Geelong. This strategic distribution ensures the company can quickly and effectively respond to any job across Victoria.
Central to Johnson & Young Cranes’ success is its investment in a fit-forpurpose crane fleet. With a wide range of mobile and crawler crane capacities, the addition of two Liebherr LTM1750-9.1 cranes, each with an impressive 800-tonne capacity – and more recently, the addition of a Liebherr LG1750 SX machine, underscores the company’s commitment to handling complex and demanding projects.
To get to these projects, JYC is well supported by its extensive truck and trailer fleet moving counterweight and boom sections from site to site.
With comprehensive coverage provided by PNOinsurance, this cutting-edge equipment is efficiently insured, allowing Johnson & Young Cranes to confidently undertake vital infrastructure projects across Victoria without interruption.
As Johnson & Young Cranes has scaled new heights, PNOinsurance has been there every step of the way, providing crucial support through a range of services tailored to the unique needs of the crane industry.
PNOinsurance’s offerings include:
• Efficient and effective claims management to minimise downtime and ensure swift resolutions.
• Comprehensive strategies to identify, assess, and mitigate risks, ensuring the safety and continuity of operations.
• Rapid response times to meet industry demands and the fast-paced nature of the business, particularly when
insuring new units or vehicles, allowing Johnson & Young Cranes to maintain its competitive edge.
The partnership between PNOinsurance and Johnson & Young Cranes is a shining example of how collaborative efforts can drive remarkable growth and success. As JYC continues to expand and take on even more ambitious projects, PNOinsurance remains a steadfast ally, ensuring they are protected and primed for continued success.
In a dynamic industry where precision, reliability and innovation are paramount, Johnson & Young Cranes and PNOinsurance have set a benchmark for excellence. Together, they are not just building infrastructure; they are building a legacy of quality and trust.
Brent Young, Director at Johnson & Young Cranes (JYC) had this to say about Dean and his team at PNOinsurance.
“When I bought my first crane, it was insured through another insurer. I met Dean at a couple of CICA events and he was obviously knowledgeable about the industry and easy to get along with. Come policy renewal time I engaged Dean and he explained not only what I was insured for but what I wasn’t insured for.
“Dean made it very easy to understand what the minimum requirement was to
operate in our space, as well as making very clear the value of add-ons for other types of insurance we would need as the business grew. That was seven years ago,” said Brent.
PNOinsurance has always been super responsive to JYC’s requirements when it comes to incidents.
“When there have been incidents the response from Dean and his team has been immediate. They are very helpful with generating the claims but also in assisting with the repairers of choice. We had a significant claim that had to be dealt with through an OEM and it was managed seamlessly by both PNO and the loss adjusters, which made getting the crane back on site so much quicker and easier,” said Brent.
Today, JYC operates 50 cranes of varying capacities – which makes for a delicate process come renewal time.
“We understand that we’re getting value for money with Dean, and we receive no claims bonuses for not claiming. We rely on Dean’s industry knowledge and also his understanding of asset values. It’s not just the plant insurance we rely on from PNOinsurance, it’s the management liability products as well.
“With the larger capacity cranes, we receive ‘layup policies’ so if they’re out on site working, obviously fully insured, there is zero risk to our clients and ourselves.
When they’re in our yard there’s a reduced risk element and so we get a layup type insurance – there’s been significant savings there.
“But as you can appreciate, when you have seven plus cranes in the fleet each with significant values, there’s a fair bit of coverage required and how that coverage is applied when they’re working and not working is important. At the end of the day, Dean is very knowledgeable, he’s a good guy and a pleasure to deal with,” said Brent.
When it comes to the crane industry, PNOinsurance demonstrates a national footprint that spans across all states. While their main office is situated in Victoria, their influence and services extend all over Australia. This reach enables PNO to cater to a diverse range of clients, each with unique needs.
Dean Bassed, Director of PNO, says “We are committed to continuous growth at PNO, ensuring that we provide a top service to our crane clients across Australia. As we expand our reach, our dedication to supporting and elevating the industry remains firm.”
Shane Rouhan, Managing Director of Nationwide Crane Hire, first met Dean Bassed two years ago at a Crane Industry Council of Australia (CICA) Queensland Branch Meeting where Dean was presenting.
“We were having issues with our broker at the time, so I spoke to Dean and he was immediately very helpful. We bought Dean on board and he quickly gave us pointers and helped steer us in the right direction and actually saved us quite a bit of money.
“His approach to our business was more thorough than we had seen before and he explained to us where we were probably under covered and had left ourselves exposed to claims in the future,” said Shane.
“One of Dean’s strengths is his knowledge of the products, he understands our industry. His approach wasn’t to push us to make changes. He didn’t think that what was happening
with us at the time was right and he suggested ways of addressing this.
“We cover everything with PNO now. We cover our premises, the machines, we also cover for claims that may come about through HR, unfair dismissal or even harassment and workplace bullying. Before we engaged PNOinsurance we were probably behind with a lot of this coverage and it could have led to us having issues in the future,” he said.
Beyond claim management, PNO is dedicated to advancing industry knowledge through educational initiatives across Australia. Partnering with the Crane Industry Council of Australia (CICA), PNO leads numerous discussion sessions, providing insights into the Crane Industry and market trends. These efforts not only benefit established industry players but also focus on supporting newcomers entering the market.
PNOinsurance is dedicated to elevating support for clients in the crane industry, which has driven the recent launch of its newest expansion – PNO Workplace Risk.
Responding to client concerns about claims management and high premiums, they established this new venture to address these critical issues head-on.
Leading PNO Workplace Risk is Paul Marsh, an allied health professional with over 20 years of experience in the field. His expertise and commitment ensures that their clients receive the highest level of service and innovative solutions tailored to their needs.
Addressing issues such as workers’ compensation, injury management and early intervention, safety and training and development, the team helps create another level of support for clients in the crane industry, PNO says.
The team, a blend of broking, strategic claims management, and allied health qualified people, help ensure that clients get the best outcome.
Freo Group’s Principal Assessor, Chris Everleigh, conducted a comprehensive two-day inspection of the TIDD Crane, evaluating its drivability, manoeuvrability, comfort, and operational lifting capability. Chris rated the crane a perfect 10/10 across all categories, stating:
“The TIDD Crane is very comfortable with the latest technology advancements, all coupled with TRT’s team of great knowledge. The TIDD is a very well-refined crane, 10/10.”
Pickles offers solutions to help uplift crane businesses, whether it’s time to retire or to invest in the future.
SOME AUSTRALIAN BUSINESSES ARE feeling the pressure of tough economic conditions and have had to innovate and strategise to stay ahead in 2024. The crane industry has been one of the most fluctuating sectors, with a boom-andbust cycle that started during COVID-19 and is still ongoing and impacting operators. With a range of unavoidable economic and operations-based matters impacting the industry, Pickles has ramped up its crane-specific sales and solutions to service the Australian
businesses that need it most.
After 60 years in the business, Pickles is used to navigating transitional markets and how conditions can impact sales of industrial assets like cranes. The Australian crane industry fills a vital role in infrastructure and construction, making it a cornerstone of the industrial sector. And as one of Australia’s leading resellers of used industrial assets, Pickles is well positioned to offer crane-focused services to both buyers and sellers throughout the market. By monitoring data and trends, Pickles has been able to guide partners through the sales process during the last few years and is constantly improving these solutions to ensure that crane operators are supported in the years to come.
Over the last two financial years
combined, Pickles sold 201 crane industry assets across dozens of sales events. Its huge marketplace offers operators the most exposure for their assets and, within the niche sector of cranes, more views, more potential buyers and better chances of maximising the returns on an asset.
This extensive database ensures assets reach the right buyers quicklymaximising returns and minimising the time assets spend off the market.
It is this exposure to the market that has enabled Pickles to truly magnify the potential of each asset for each owner. These efforts were successful and well-
have started strategically planning the lifecycle of their assets to maximise business profits and returns.
One of the ways businesses can maximise returns on their asset is by offloading it in a timely and efficient manner. With the ever-growing cost of crane inspections and maintenance, considering when best to retire, offload or replace an asset has become a crucial aspect of business ownership. With a foot in every industrial sector, Pickles is hyper aware of the growing need to offer and cater to crane-specific sales in a way that benefited both buyers and sellers. That’s why Pickles revitalised its auction schedule, to implement consistent quarterly crane auctions and dedicated event sales for operators who wanted to offload their assets all at once.
These quarterly national crane sales have now been running for three years and have become a way for sellers of any size to access Pickles’ huge international buyer base.
As a business with a strong commitment to both customer and community, Pickles’ Vision, Purpose and Mission statement is centred around being the first choice for anyone buying and selling assets, to be a trusted marketplace and to earn lifelong partnerships.
These values are integral to structuring sales that directly benefit every customer. South Australian Sales
“Our aim is to take the pressure off the customers, particularly during times of heightened stress like shutting down a business after so many years.”
rewarded, as the sale of cranes at Pickles in the last two financial years totalled $54 million, with the sale price of an individual asset fetching $268,000 on average.
With the average asset fetching over a quarter of million dollars at a Pickles auction, businesses have become very aware of the value of their assets and
Manager Andy Sweetman notes the importance of these changes for the industry.
‘Because the crane industry has had so much movement in the last few years, Pickles jumped to the challenge of creating sales and services that really suited the niche needs of crane operators,” he says.
“Pickles has the resources to provide whatever our partners needmaintenance, transport, advisory and whatever else they’re looking for.’
For some Australian businesses, 2024 has proved the perfect time to close the final chapter on their business – and Pickles has become the first choice for retiring businesses, particularly those navigating business closure during difficult economic times.
For some operators, retiring has come earlier than expected and where this is the case, Pickles provides solutions to assist in the difficulty of closing a business.
For others, who are simply ready to shut up shop, Pickles is the most useful medium in which to get assets in front of Australia’s biggest pool of buyers.
For businesses amid the most acute
circumstances, Pickles’ dedicated team of Advisory executives can lighten the load of stress.
It’s this range of helping hands that guides Pickles partnerships, according to Pickles’ National Sales Manager of Trucks & Machinery, James Chauncy.
“Our aim is to take the pressure off the customers, particularly during times of heightened stress like shutting down a business after so many years,” James says.
“We know that when a client comes to us for a business closure sale, they already have their plates full of organising their final months of operation. So, we like to take the whole reins for the auction, including dedicating a full team to helping their closure.
“This can sometimes entail sending a project team to unpack up to 50 years’ worth of crane ancillary gear and
paperwork. We then manage everything from a chain to a crane - and we’ve got the experts that do it.”
Sometimes, Pickles is asked who the buyers are – if everyone is selling or retiring. Luckily for the retiring businesses, Pickles is always ahead of the curve. Being a digitally led business, Pickles can sell assets to businesses across the country, meaning there is always a large buyer pool to be tapped into.
And while most sales are national, Pickles also cultivates international buyers, usually from the United Arab Emirates, Egypt and Asia to access some of the cranes that go to market. Meaning that crane sales are consistent for vendors, irrespective of the movements of the Australian market.
Pickles is ready to do the heavy lifting for your business. Find out more at pickles.com.au
Are you in need of unparalleled performance for heavyduty lifting and high hook heights? Look no further than the Liebherr NC-LH 12-55 — the first hydraulic luffing jib crane by Liebherr. Experience the efficiency of a minimal slewing radius and outstanding out-of-service radius, thanks to its hydraulic concept. Optimized for assembly, this crane impresses with short set-up times and requires only four transport units for the whole slewing part. Don’t compromise on productivity and contact your dealer at www.liebherr.com
The Look Up and Live tool will build on Before You Dig Australia’s commitment to safety.
THE NEW LOOK UP AND LIVE APP IS a one-stop resource for Australians planning work near both above-ground and underground utility infrastructure, positioned alongside Before You Dig Australia (BYDA)’s underground plan service.
The app was originally developed by Ergon Energy Network and Energex in 2017 to promote safe work practices near Queensland’s electricity network.
But today, Look Up and Live has expanded to include overhead networks in New South Wales, South Australia and Victoria.
The app provides users with realtime access to powerline locations and imagery, free of charge, via an interactive geospatial map.
It allows for real-time location searches, map overlays with third-party
mapping programs and the option to print maps as needed.
The program aims to mitigate risks associated with overhead powerline work.
In the past 20 years, more than 135 people have died due to contact with overhead powerlines, with many more suffering life-altering injuries, including permanent disabilities.
BYDA Chief Executive Office Mell Greenall says the group is dedicated to making safe work near utilities as straightforward and practical as possible.
“By integrating Look Up and Live with Before You Dig, we are simplifying the process of accessing utility plans and essential safety information, empowering workers to operate safely around utility infrastructure,” she said.
“This further embeds BYDA as a trusted source for utility safety
Above: Over the past 20 years, more than 135 people have tragically lost their lives due to contact with overhead powerlines, with many more suffering lifealtering injuries, including permanent disabilities.
information and simplifies safety planning for the construction sector and broader community.”
Energy Queensland’s Community Safety Specialist, Glen ‘Cookie’ Cook, is excited to see the app be used out in the field.
“The lookupandlive.com app is an essential lifesaving planning tool, free for everyone to access; I am proud that the lookupandlive.com app is protecting people from harm and is reducing community power disruptions,” he said.
“I look forward to seeing the product continue to grow at its new home at Before You Dig Australia.”
A Modulift CMOD 24 has been used to lift iconic supercars at the prestigious Goodwood Festival of Speed in the United Kingdom.
AS AN INTERNATIONALLY RENOWNED motorsport event, Goodwood marks a significant date in the diary for car enthusiasts, attracting around 200,000 visitors each year to its location in the surrounds of Goodwood House, in West Sussex, England.
Celebrating the best of automotive culture, the festival features a mix of historic and contemporary vehicles, both on display and racing up the estate’s famous hill.
For the 2024 event, which wrapped up in July, a Modulift CMOD spreader frame was used to assist with both the build and breakdown of event
infrastructure – lifting vehicles such as the all-electric Rolls-Royce Spectre coupe that made its debut at Goodwood last year.
The lifts were carried out by West Sussex-based Southern Cranes & Access, using the versatile CMOD spreader frame as recommended for loads that have more than two lifting points.
Featuring a modular design, CMOD components are interchangeable with MOD struts and can easily be assembled on site for multiple lifts.
Modulift managing director Sarah Spivey says the CMOD is one of the company’s most popular products.
“Customers who already have MOD struts can simply add corner units to make the 4-point CMOD frame,” she said.
“The CMOD can also be combined with T-Pieces to make a 6- or 8-point CMOD Spreader Frame.”
Looking to maximise returns on your equipment? Pickles are remarketing experts and can help your business offload used assets to recoup capital or free up funds for new equipment. Why sell with Pickles?
As Australia’s leading used asset marketplace, we have the reach and resources needed to take craning equipment to a large and diverse range of competitive buyers. Our results for FY23 and FY24 National Crane Sale speak for themselves:
Mid-Coast Business Development Manager at Allied Crane Hire, Ivan Batista, is bullish about the company’s upward trajectory and the mechanical and sales support of its dealers.
BASED IN NEWCASTLE, NSW, ALLIED Crane Hire exudes a “family” culture and boasts a rapidly growing fleet of cranes to service Australia’s east coast.
With depots in Tomago, Mid Coast, Muswellbrook and Coffs Harbour, Allied boasts a comprehensive range of allterrain mobile cranes to suit almost every lifting requirement.
Mid-Coast Business Development Manager Ivan Batista said many of these have come from registered suppliers, adding that the relationship Allied has built with them ensures smooth delivery of positive outcomes.
Allied’s recent addition to its crawler crane fleet was an example of this, he added.
“We found an opportunity in the market for crawler cranes, especially wet hire. We looked at what the demand was, the available machines to fit that, how we could fit in that hole, and our suppliers came up big,” Ivan said.
Allied Cranes engaged Ganz based on its merits as a Zoomlion crawler distributor.
“We saw Zoomlion machine that was available for us, and it looked to suit our needs,” said Ivan.
“Our suppliers, such as Ganz are great to deal with; They supplied what we needed from them, and then backed us up
even more with their after sales service as well,” Ivan explained.
When discussing the Zoomlion crawler cranes – cranes that predominantly make up most of Allied’s mobile fleet, Ivan said the reliability is obvious with the machines.
“They are very reliable machines, but for whatever reason, they’ve really stepped their game up, and we haven’t had a mechanical issue with it since we’ve bought it,” Ivan said. “The machine turns on every day and does what we need it to do for our clients.”
And Ganz, amoung other registered suppliers have been there for Allied Crane Hire to provide some of the best cranes on the market, he adds.
“Ganz helped us a lot with the acquisition of the machine and thereafter, as they gave us a lot of support too. It helped that they were in Newcastle,
where our head office is,” Ivan said.
“It just a very logical decision for us to have a machine so close to us that’s going to fill our needs. Obviously, you got to factor in one hundred different things, like transport, compliance, availability, timelines, prices, all those really important components.”
Ivan spoke to the reliable and trusted service Ganz has provided Allied Crane Hire.
“Ganz has been fantastic; they’ve supplied everything perfectly every time and the staff there have honoured their word by assisting us when we’ve needed them. Fantastic,” Ivan said.
Ivan said Ganz has been “extremely quick”, able to assist the growing team at Allied Crane Hire in remarkable time.
“When you look into the logistics of actually getting somebody interstate
services for construction, infrastructure, industrial, residential and commercial projects.
As a trusted professional crane hire service, its certified equipment and expert team ensures every lift is performed safely and in line with all required certifications and registrations.
With a diverse range of meticulously maintained hire equipment, all available at competitive prices, Allied Crane Hire can provide a personalised and highperforming approach to almost any lift.
Allied Crane Hire offers flexibility across a range of industries, including construction, infrastructure and industrial projects.
The business’s range of all-terrain mobile cranes provides a comprehensive selection to suit every lifting requirement.
The seamlessly operated cranes, delivered by registered suppliers, are available at competitive rates, helping customers complete big or small projects.
Ivan said he can envisage the company growing at a rate of knots, by expanding its mobile crane fleet and developing the already incredibly high skill level of Allied Crane Hire staff.
“I see us growing and growing; I think we’re taking leaps and bounds, especially
“When you look into the logistics of actually getting somebody interstate to arrive at the drop of a hat, jump on a plane, fly to your destination from the airport get out to site with his spanners ready to go and ready to tackle anything in front of him, it’s pretty impressive.”
to arrive at the drop of a hat, jump on a plane, fly to your destination from the airport get out to site with his spanners ready to go and ready to tackle anything in front of him, it’s pretty impressive,” Ivan explains.
“They’re committed to supporting their customers. And that’s something that goes a long way in this industry.”
Allied Crane Hire provides all-terrain mobile, Franna and crawler crane hire, lifting logistics and transportation
the past sort of six to eight months, we’ve grown considerably as by now we operate out of four depots,” Ivan said.
Ivan rates Allied Crane Hire as a family-first crew. With many likeminded and most with young families, the team at the trusted crane provider has a special bond.
“We’re very family oriented, a lot of us have young kids and we understand that life is a balance, so we’re all built from the same cut of cloth,” said Ivan.
PLEASE SEND YOUR LIFT OF THE MONTH ENTRIES TO SIMON.GOULD@PRIMECREATIVE.COM.AU
WHO: Superior Crane Hire
WH ERE: Logan Hyperdome South East Queensland CR A NE: Liebherr LTM1230-5.1
WEI GHT: 1.1 tonne
COMP LEXITIES: Superior Crane Hire was engaged by a client to replace the shade sail that covers the Logan Hyperdome Shopping centre, radius 80 m SWL 1.3 tonnes
Longest powered boom to 20.9m with 5.5m telescopic fly extends to 26m
All Models (25T, 35T, 55T) rated @ 1.4m boom position, highest boom strength available, fully fabricated
Air-spring suspension with shock absorbers eliminating cabin noise and vibration
High Stability at all positions to 42 degrees
Low centre of gravity with rigid chassis design, safest crane available
Dynamic Load Chart and Digital Rope Compensation
Safe road speed 90-100kph with 180 degree unobstructed front vision with four cameras to sides and rear
Humma Heavy Lift Crane design, specification with proven componentry has set the new Industry standard for performance. ONE FOOTPRINT FOR ALL MODELS.
Crane owners require low operating and maintenance costs, highest level of safety in both driving and crane mode, achievable on all Humma Models.
Patented Auto-leveller on Humma 55, the largest and safest Pick and Carry available.
Highest level of safety at all articulation positions to 42 degrees using Humma low twist chassis design.
Cabin rated the safest and quietest available at 65 decibels.
Remove the removeable counterweight from 35T and 55T and you have a heavy duty 25T and 35T.