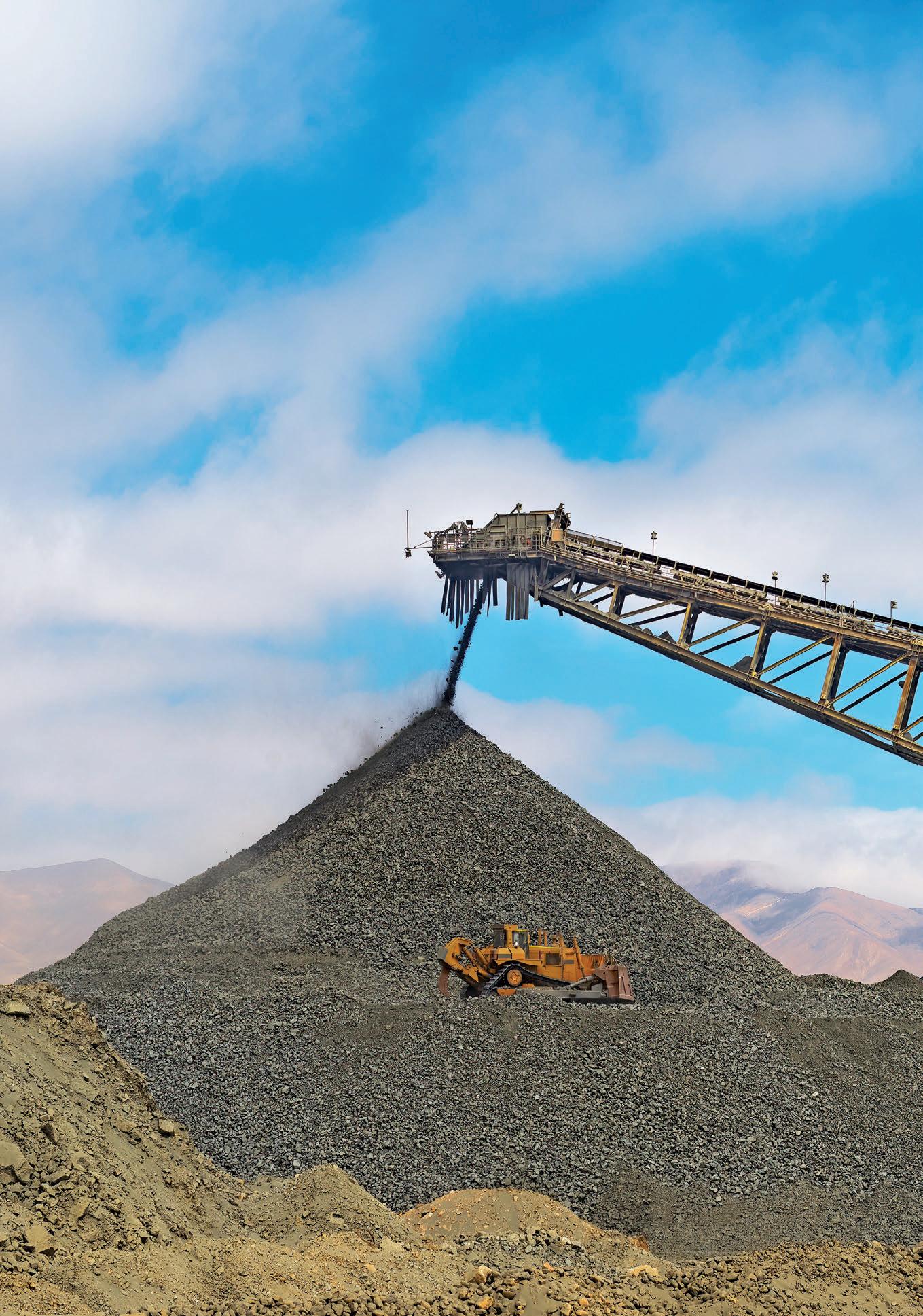
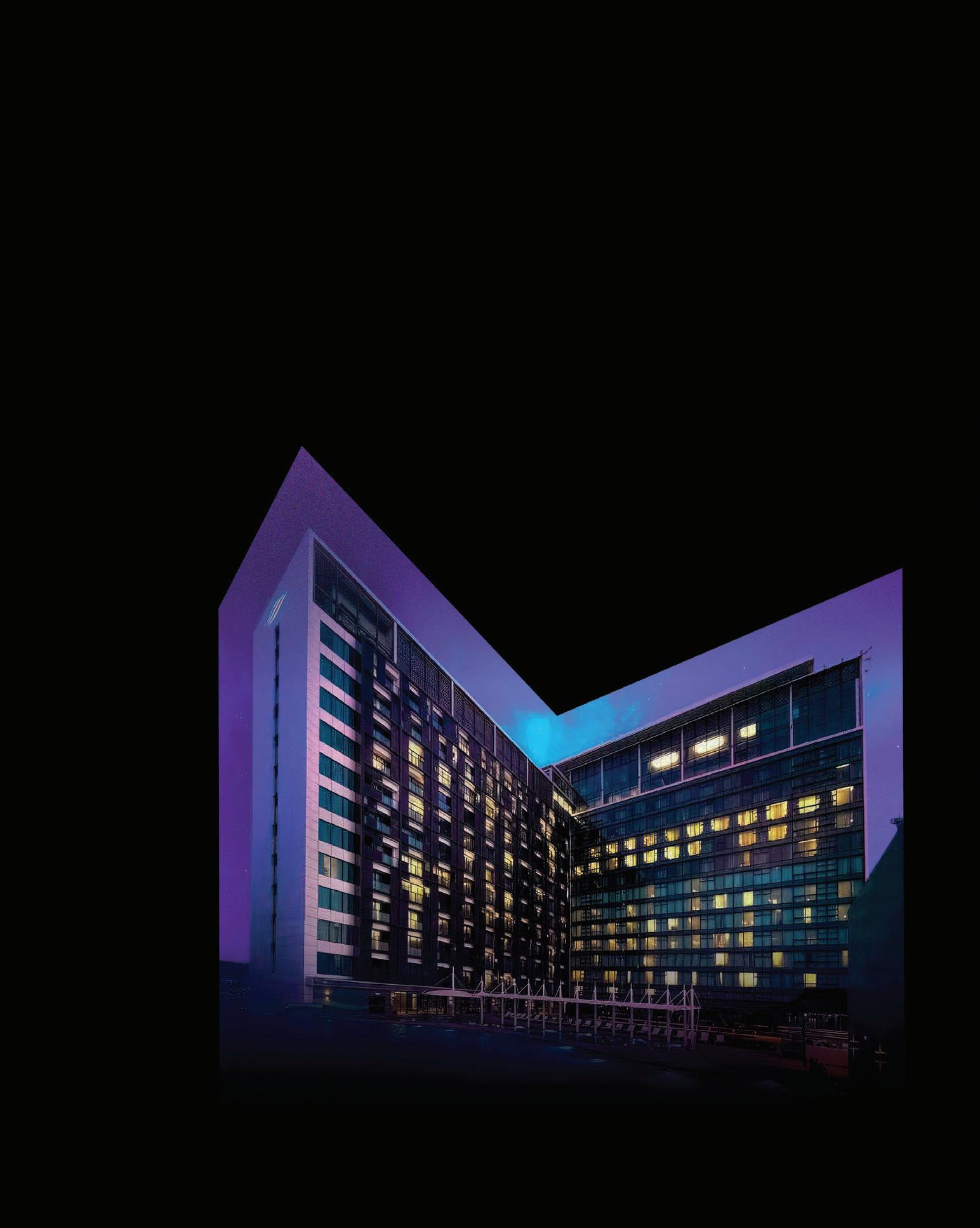
Setting the global standard for
For conveyor belts that deliver the lowest cost per tonne of material conveyed, you need more than just durability—you need synergy between the cover compound and the carcass, tailored to your specific needs.
Using the highest quality materials and state-of-the-art manufacturing processes, we consistently produce the toughest and longest lasting conveyor belts in the industry.
Bulk material handling and heavy mining operations that fit their conveyors with Fenner Dunlop Conveyor Belting benefit from maximum uptime, less belt maintenance, higher productivity, and lower total costof-ownership.
Flexco cushioning conveyors
BULKtalk: Rail-mounted mobile
Stockpile live capacity estimation
Revising AS 4324.1 for materials handling structures
ASBSH Member Profile: Daniel Grasser
Australia’s only publication 100%-focused on bulk solids handling. Australian Bulk Handling Review covers conveyors, silos, engineering, dust control, powder handling, weighing, pneumatics and much more, in industries such as mining and metals, ports and terminals, grain, fertiliser, sugar, salt, foods, milling, resins, cement and woodchips.
CRUSHING
The Agnew gold mine has a long history of gold production dating back to the late 1970s. Around 2018, with the mine expanding into a third underground source, there was a need to increase plant throughput. The 21-year-old tertiary crushing circuit, which was su ering from poor reliability, was unable to meet the demand. A er considering a bespoke solution, the Gold Fields team chose to go with a Sandvik modular plant.
Read more on page 12
Published by:
379 Docklands Drive
Docklands VIC 3008
T: 03 9690 8766
www.primecreativemedia.com.au
COO
Christine Clancy
E: christine.clancy@primecreative.com.au
Editor William Arnott
E: william.arnott@primecreative.com.au
Assistant Editor: Adam Daunt
E: adam.daunt@primecreative.com.au
Business Development Manager
Rob O’Bryan
E: rob.obryan@primecreative.com.au
Client Success Manager
Janine Clements
E: janine.clements@primecreative.com.au
Head of Design
Blake Storey
Design
Laura Drinkwater
Subscriptions
T: 03 9690 8766
E: subscriptions@primecreative.com.au
www.bulkhandlingreview.com
The Publisher reserves the right to alter or omit any article or advertisement submitted and requires indemnity from the advertisers and contributors against damages or liabilities that may arise from material published.
© Copyright – No part of this publication may be reproduced, stored in a retrieval system or transmitted in any means electronic, mechanical, photocopying, recording or otherwise without the permission of the publisher.
While they may not be as impressive as a mighty stacker or an overland conveyor, measuring systems play a vital part of the bulk handling process.
The most obvious benefit is monetary – knowing exactly how much material can be sold to a customer. Without knowing exactly how much material you are selling, you run the risk of not providing the right costs. Over time, this can quickly mount up to millions of dollars of lost profits.
In addition, having an accurate understanding of how much material is being conveyed is helpful for maintenance and diagnostic reasons. You can use this data to find faults, trouble shoot with greater effectiveness, or even spot problems before they emerge.
However, just as there is an incredibly vast range of bulk materials, so too are the ways to measure them.
Weight, volume, density, flow, level, and more are all important variables that should be taken into account in the process. Depending on the site and material, some may be more important than others.
There are also plenty points where this measurement can occur. Tracking how full a silo is, or how much material is flowing across a belt, for example.
One particularly important thing to measure are stockpiles. While a stockpile is just a mound of grain or rocks to the untrained eye, they are a vital asset to most bulk handling businesses.
Unfortunately, they are also difficult to accurately assess, with most methods relying on volumes and average bulk densities to determine tonnage.
This edition of Australian Bulk Handling Review shines a particular spotlight on the latest technologies to help bulk handlers accurately assess their operations. We highlight the organisations and individuals that are working on developing new products and procedures, and what the future of measurement might look like.
INTRODUCING AN EASY WAY TO PROTECT YOUR WORKERS AS WELL AS PROTECT YOUR INVESTMENT INTO YOUR EQUIPMENT. THE CONVEYOR SAFETY SYSTEM™ IS AN EASY, COST EFFICIENT WAY TO GET PEACE OF MIND AND PROTECTION FOR CONVEYOR EQUIPMENT. BY BUNDLING OUR MODEL RS SAFETY STOP SWITCH WITH OUR MODEL TA BELT ALIGNMENT SWITCH, MODEL DB DAMAGED BELT DETECTOR WE HAVE YOUR WORKERS AND EQUIPMENT COVERED. COUPLE THAT WITH ADDING ONE OF OUR MOTION SWITCHES (MAG-NEAT-O™ MODEL CMS
The RKM International Roller Company has embraced local and global manufacturing to support clients looking for custom-made rollers with fast turnarounds.
THE YEAR WAS 2020, AND THE world had recently been plunged into chaos. COVID-19 causes countries to completely shut down. International trade became a quagmire for Australian manufacturers to navigate.
It became clear to RKM International Roller Company director Brett Maiden that things needed to change. The company began working on a Perthbased manufacturing and warehouse facility, which would provide an opportunity to provide better support for customers who needed a quick turnaround.
“It has helped immensely especially in being able to offer short turnarounds and quick deliveries,” Maiden said.
“We have outgrown the current facility in Maddington and are moving into a new bigger premises in Welshpool. The interest in our new heavy duty composite roller has been the key driver in this move. I never would have thought that we would be exporting the composite tube back to our China facility to assist in the manufacture of the HD composite rollers,” he said.
The heavy-duty composite roller was created in collaboration with Wagners.
Together, they developed a heavy-duty, lightweight composite tube suitable for handling some of the highestduty cycles.
It weighs around half as much as a traditional steel roller but maintains the strength and durability to handle heavyduty applications like iron ore mining.
The roller uses the company’s RS seal package and is also equipped with a primary heavy-duty nylon protective outer dual labyrinth shield. The shield provides additional protection against contaminant ingress and eliminates rock jamming.
Dynamic balancing machines are used by RKM to ensure the rollers meet AS3709 G16 and achieve the best possible total indicated rollout.
“We now have the ability to manufacture the HD composite Roller in our Perth facility and the China factory,” Maiden said.
“The China factory being more automated still outperforms the Perth factory when it comes to faster production and lower overall production costs.
“Another new product we have been rolling out to solve heavy duty impact
failures is our Impact Absorption Frames coupled with our heavy-duty hot cast poly impacts, which has proven to be very successful to help with high impact loads and product spillage. These come with fixed slider bars that can be easily removed and replaced.”
A new precision combination laser and milling machine allow RKM to accurately profile the parts with very little clean up. This machine maintains its competitiveness in underground structure and conveyor frames, streamlining the whole fabrication and welding making it easier to program robots when welding together.
“The factory is fully equipped to make anything from scratch,” Maiden said.
“Customers can provide a basic sketch or drawing and then our drafting team will provide a detailed drawing. We can also do a full design review on the roller, structure and frames. With Navisworks we can then help with a new impact frame layout and match up with existing stringer holes.”
RKM stocks a wide range of conveyor components at its Perth warehouse, including off-the-shelf rollers and stock for its supply contracts. The company stocks from 600 belt widths up to 1500 belt widths for stock standard roller solutions but also stocks an array of shafts, tubing, seal kits, bearings, and housings to make applicationspecific solutions.
ust and fines escaping at material transfer point locations impact safety, efficiency, and profitability. Martin's comprehensive containment solutions include the versatile ApronSeal™dual-seal skirting system, self-adjusting skirts for space-restricted areas, and engineered wear liner options to protect those sealing components from the impact and abrasion of tumbling material. These smart, field-proven, belt sealing systems deliver extended service life with minimal maintenance — reducing fugitive material cleanup and maximizing operation production.
Martin Engineering global air cannon product manager Brad Pronschinske explains how flow aids can help avoid expensive delays when working with silos.
HUMIDITY, MATERIAL TYPE, or settling can cause serious material fl ow issues like clogging and expensive delays.
Once material adheres, the buildup is generally fast and dense, introducing a workplace hazard to remove from a silo.
When operators notice material is no longer flowing, spilling over the edge of the vessel or backing up on conveyors, they know a clog has formed.
Seeking ways to address it quickly without the proper tools or training can also be the moment when workplace safety degrades.
Flow aids are engineered to safely clear and prevent clogging, promote material flow and avoid costly downtime.
To know what technology will work best for a specific application, the first step is understanding how, where, when and why clogs happen in any given vessel or transfer point. The second step is removing any worker involvement in clearing the clog, aside from pushing a button to activate the flow aid if it isn’t automated or controlled by logistical software.
Discharge point geometries
Discharge channels come in varying shapes, depending on the vessel and the material flow characteristics.
Spouts that are narrow, such as those found on conical or pyramidal shapes, direct flow in a vertical column either into a chute or specific loading area. Slotted spouts, like those found on the wedge or transition shapes, distribute material in a narrowly defined line for loading onto conveyors or into containers (trains, trucks, etc.)
The geometry of a vessel must match that of the discharge point or it will be prone to clogging. These discharge points can feature gates
or grates that stop or separate the material. Grates can be used to slow or direct the flow of material when loading onto a conveyor or filling of transport bins on a train or truck.
Either way, operators find that they can exacerbate clogging by stopping or slowing material at a structural choke point.
Once a clog has been detected, there are several unsafe practices that at the time may seem harmless, but frequently cause serious worker injuries or fatalities year after year. The two main causes of injury are sudden discharge of adhered material and entrapment.
One unsafe method is beating the vessel walls with mallets or other objects to loosen adhered material. Over time, the more the walls are pounded, the worse the situation becomes, as the bumps and ridges left in the wall from the hammer strikes will form ledges that provide a place for additional material accumulations to start.
Another hazardous practice is poking or lancing underneath the clog at the discharge point. This can result in a sudden surge of falling material, burying or crushing the workers below.
Perhaps the most prevalent cause of worker injuries and fatalities is confined space entry of the vessel. Along with potentially sinking into the material in the centre, the material could be bridging and suddenly release. If a worker enters the vessel and stands on the volatile bridge, a sudden discharge could pull the worker into the cavity. Another serious hazard of confined space entry is material buildup on the sides of the vessel, reaching higher than the worker. This buildup could fall from above, causing serious injury or burial.
Air lancing the clog from the mouth of the vessel at the top is an option many operations have chosen, but guardrails are highly recommended. The reach of the lance and the pressurised air stream must match the size of the vessel. Workers can fall in trying to reach the lance down to the clog, even if guardrails are present. All these hazards can be avoided by introducing flow aids to the vessel to mitigate clogs, promote material flow and reduce downtime.
As the term implies, flow aids are components or systems installed to promote the transport of materials.
Flow aids come in a variety of forms, including rotary and linear vibrators, high- and low-pressure air cannons and aeration devices, as well as low-friction linings and special chute designs, to promote the efficient flow of bulk materials.
These modular systems can be combined in any number of ways to complement one another and improve performance.
The components can be used for virtually any bulk material or environment, including hazardous duty and extreme temperatures.
One of their primary advantages is that an operation can obtain a level of control over the material flow that is not possible any other way.
When employing flow aids, it’s critical that the chute and support components are sound and the flow aid be properly sized and mounted, because the operation of these devices can create potentially damaging stress on the structure. A properly designed and maintained vessel will not be damaged by the addition of correctly sized and mounted flow aids.
It’s also important that any flow aid device be used only when discharges are open and material can flow as intended. The best practice is to use flow aids as a preventive solution to be controlled by timers or sensors to avoid material buildup, rather than waiting until material accumulates and restricts the flow.
Using flow aid devices in a preventive mode improves safety and saves energy, since flow aids can be programmed to run only as needed to control buildup and clogging.
The age-old solution for breaking loose blockages and removing accumulations from chutes and storage vessels was to pound the outside of the walls with a hammer or other heavy object.
A better solution is the use of engineered vibration, which supplies energy precisely where needed to reduce friction and break up a bulk material to keep it moving to the discharge opening, without damaging the chute or vessel.
The technology is often found on conveyor loading and discharge chutes but can also be applied to other process and storage vessels, including silos, bins, hoppers, railroad cars, screens, feeders, cyclones and heat exchangers.
One solution for managing material accumulation in chutes and vessels is the low-pressure air cannon. It uses a plant’s compressed air to deliver a powerful discharge to dislodge the buildup.
Cannons can be mounted on metallic, concrete or wood surfaces. The basic components include an air reservoir, fast-acting valve with a trigger mechanism and a nozzle to distribute the air in the desired pattern to clear the accumulation most effectively.
The device performs work when compressed air (or some other inert gas) in the tank is suddenly released by the valve and directed through an engineered nozzle, which is strategically positioned in the chute.
Often installed in a series and precisely sequenced for maximum effect, the network can be timed to best suit
individual process conditions or material characteristics. The air blasts help break down material accumulations and clear blocked pathways, allowing solids and/or gases to resume normal flow.
To customise the air cannon installation to the service environment, specific air blast characteristics can be achieved by manipulating the operating pressure, tank volume, valve design and nozzle shape.
In the past, when material accumulation problems became a recurring issue, operators would have to either limp along until the next scheduled shutdown or endure expensive downtime to install an air cannon network. That could cost a business hundreds of thousands of dollars per day in lost production.
Many designers now proactively include the mountings in new designs so that a future retrofit can be done without hot work permits or extended downtime.
Over time, the valve in an air cannon will wear and it is common practice to refurbish them rather than replace with new ones.
Because clearances and fits are critical to proper operation, it is recommended that flow aid devices be rebuilt and repaired by the manufacturer, or that the manufacturer specifically train plant maintenance personnel to properly refurbish the equipment.
To simplify the process and avoid system downtime, one manufacturer has created a program to supply factoryrebuilt air cannon valves that carry the same warranty as new valves. Customers can receive a standard pallet-sized container with six refurbished valves, so there’s no need for users to rebuild worn-out components. The changeout can be accomplished in just ten minutes, at less than half the cost of new valves. The used valves are shipped back to the company, where the units are rebuilt to as-new condition by factorytrained technicians.
Customers save time and money, with no need to stock repair parts or provide the training to rebuild.
The number of bulk handling operations with centralised automated systems that monitor and support production is growing and becoming more sophisticated.
Flow aids can be added to the central control logistical system to be fired remotely. They are also accompanied by a separate solenoid box mounted a safe distance away that can be fired manually if need be.
Having these redundancies available allows operators full control over bulk material flow and produce a safer workplace with less downtime from clogging resulting in a lower cost of operation.
Reliable So ware Solutions, a so ware development company, has created the RSS Auto Scan volumetric scanning system, which is being used across the bulk material handling industries.
ineffi cient, it can hamper output and aff ect the site’s overall productivity and profi tability.
This was the dilemma facing a mine, which was not meeting the target payload for each train wagon.
“The site used a track scale to determine that the loaded trains, consisting of over 200 wagons each, were consistently falling short of the desired payload. This shortfall directly impacted the mine’s overall output,” Reliable Software Solutions managing director Andrew Sheppard said.
“The team knew that understanding the volume of material in each wagon might reveal the underlying issues. By calculating the material density using weight and volume, they aimed to identify inefficiencies and determine a path forward.”
The initial objective was clear: measure the volume of material loaded into each wagon to gain actionable insights into loading processes and identify areas for improvement. The development of the RSS Auto Scan
volumetric scanning system emerged as a solution.
The transition from a semi-automated to a fully automated system posed technological challenges. Initially, the site employed older LIDAR sensors to collect raw data. This data, in its rudimentary form, required extensive processing to extract meaningful insights.
“The data we received was essentially a cloud of points,” Sheppard said. “We needed to interpret, clean, and develop algorithms to convert that raw data into actionable metrics, such as train speed and material volume.”
Early trials relied on manual processes, with data being collected and processed post-collection. However, the system’s limitations necessitated a shift to newer LIDAR sensors and a more sophisticated data engine.
This upgrade enabled near real-time feedback, delivering results within five to 10 seconds after a wagon passed through the scanner.
Ensuring the accuracy and repeatability of the measurement
system was another critical hurdle. External validation and rigorous accuracy testing were conducted to ensure the system could reliably deliver precise measurements.
“Once we confirmed the data engine’s accuracy, we integrated modern sensors and linked the outputs to the site’s programmable logic controller system for seamless operation,” Sheppard said.
The integration of LIDAR technology and a live Modbus interface changed real-time decision-making for loadout operators.
“Operators could finally see exactly what was happening during the loading process,” Sheppard said.
Metrics such as the amount of remaining space in each wagon, both front-to-rear and side-to-side, provided invaluable guidance.
With this information, operators could fine-tune loading processes to achieve optimal wagon fill.
By leveraging the feedback from the volumetric scanner, operators adjusted loading techniques to maximise the
payload while staying within design limitations for axle and bearing loads.
“Previously, the site struggled with low-density material, which made it impossible to meet target payloads,” Sheppard said.
“The system revealed unused capacity, enabling the site to adjust and consistently hit target payloads, adding significant value without interfering with existing processes.”
The success of the auto scan system for train wagons paved the way for its adaptation to mining haul trucks.
“Many of the fundamentals apply to both trains and trucks,” Sheppard said. “The ability to scan in motion and provide near-instant feedback is crucial.”
For haul trucks, the system offers unique benefits, such as facilitating tray studies. Customised trays are often designed for specific materials, and the volumetric scanner helps validate their
performance by providing density and volume data.
Sheppard said a notable carry-back study where four different tray designs were tested for their effectiveness in reducing material sticking.
“We scanned each tray before and after use to quantify the amount of material left behind. The results were instrumental in identifying the bestperforming tray and monitoring carryback over time.”
In addition to point-in-time studies, the system is also capable of 24–7 operation, making it suitable for continuous monitoring near crushers or dumps.
This flexibility allows mining operations to adapt the technology to their specific needs.
Despite the proven benefits of the RSS Auto Scan system, Sheppard said that its adoption has been limited to a few sites.
“We’ve primarily worked on a project-by-project basis. While the system has been implemented successfully at multiple sites, we aim to broaden our exposure and reach other potential users who may face similar challenges.”
The system’s ability to deliver actionable insights, improve efficiency, and maximise payloads makes it a valuable asset.
“We believe there are many operators out there who could benefit from this technology but aren’t aware of its capabilities,” Sheppard said.
As mining operations face increasing pressure to optimise performance and reduce costs, innovations like the RSS Auto Scan system play a crucial role in achieving these goals.
By providing accurate, real-time data and enabling informed decision-making, the system not only addresses existing inefficiencies but also opens the door to new opportunities for improvement.
Gold Fields’ Agnew mine in WA has seen improved e iciency, throughput and safety since installing a new crushing and screening plant from Sandvik.
THE AGNEW GOLD MINE HAS A LONG history of gold production dating back to the late 1970s.
Situated around 375km north of Kalgoorlie and operated by international giant Gold Fields Limited, the mine is best known for its underground operations, primarily targeting the Agnew and Lawler gold deposits. The ore is extracted using a combination of underground and surface mining and is then processed on-site.
Around 2018, with the mine expanding into a third underground source, there was a need to increase plant throughput. The 21-year-old tertiary crushing circuit, which was suffering from poor reliability, was unable to meet the demand.
Gold Fields metallurgy manager Reg Radford is the company’s technical expert in the field of processing metallurgy. He works with process managers across all Gold Fields sites in Australia to assist in optimising the operations.
Radford could see that the crushing and screening circuit was not in keeping with the broader standards of the company.
“It was working to its limits, and if you compared it to other Gold Fields sites, it was not to the standard that would be accepted elsewhere,” he said. “It didn’t meet our criterion for a well-organised, safe, professional gold processing operation.
“The equipment was old, and there was little or no spare parts availability. From a metallurgical perspective, it was being pushed to its limits to deliver the tonnage required. At best it was giving us an 8–10mm output, which was putting pressure on the downstream grinding circuit.”
The age and complexity of the existing plant also meant that access for operation and maintenance was difficult, presenting potential safety concerns.
The existing crushers were reaching end-of-life, and rather than just replacing them, it was decided to build an entirely new crushing and screening circuit.
To do this, and address various other concerns regarding the existing plant, a comprehensive upgrade project,
known as the Agnew Stage 1 upgrade, was conceived.
The initiative examined bespoke and modular designs that could replace the existing plant. The project aimed to improve site water drainage and dust management (by installing a fine ore bin) while minimising disruptions during construction and commissioning.
Gold Fields manager – processing Tristan Freemantle was appointed as project director for the upgrade at Agnew. A veteran of the gold and copper industry, Freemantle originally worked for Barrick Gold and then transferred to Gold Fields around 12 years ago.
Since then, he has worked across several of Gold Fields’ Australian sites and is currently based at Gruyere, a joint venture project with Gold Road Resources located in the Yilgarn area of Western Australia.
“Agnew’s mine life had been extended for a further eight years, so upgrading the crushing and screening circuit was important to increase our processing capabilities: we needed to be in a position to process more ore from the new third mine coming online,” Freemantle said.
Gold Fields has enjoyed a longstanding relationship with Sandvik, with the company having Sandvik crushers installed at both their St Ives and Granny Smith operations.
After considering a bespoke solution, the Gold Fields team chose to go with a Sandvik modular plant.
“We needed a circuit that was simple, low maintenance and reliable, but also wanted the best crushers and screens that we could get,” Freemantle said.
“Sandvik showed a willingness to work with us within our parameters. Initially, it was just the crushers and screens, but in the end, they presented a complete plant design, which was modular and comparable with the bespoke designs that we were considering.
“Sandvik was also able to accommodate our desire to manage our own electrical and process control design.”
Key to the successful implementation was Sandvik’s expertise in crushing and modular plant design combined with the screening know-how of Schenck Process.
The scope of supply included a Sandvik reciprocating plate feeder, grizzly screen, jaw crusher, and two cone crushers, as well as a Schenck Process double-deck banana screen fitted with Screenex screening media. Sandvik also provided bins, chute work, associated wear protection, and conveyors.
The innovative plant design eliminated the need for two screening stations and associated conveyors when compared with other proposed designs.
“Having a single vendor was an advantage,” Radford said. “Sandvik’s initial designs and 3D models were quite detailed and comprehensive, which was encouraging. It gave us confidence in the circuit because we knew exactly how the proposed layout would interact with the existing plant.”
A significant challenge for the project team was that Gold Fields needed the new plant to be installed in parallel with the old one so that, ideally, there would be zero downtime.
“Agnew can’t afford to be down for two or three weeks,” Radford said. “The mill is pushed to its limits, so it has little ability to catch up.
“Solving this problem – where we could build the new circuit and how to tie it in – was a good part of the success story. Commissioning on-time and within budget, with limited downtime, was a very important part of the brief.”
To accommodate this requirement, the team decided to move the run-ofmine (ROM) pad and build the new circuit on the site of the old ROM pad. While this achieved the brief of zero downtime, it introduced a new challenge.
The geology of the ROM pad was untested, and some contractors argued that a substantial concrete foundation
RKM Impact Absorption Frames coupled with our HD Hot Cast Poly Impact rollers has proven to be very successful to help with high impact loads and product spillage.
Manufactured right here in Perth for shorter lead times and quick deliveries for all non-standard and special orders.
would be required to support the crushing and screening plant, greatly increasing both the build time and cost.
In the end, working with Gold Fields geotech consultants, Sandvik’s design team resolved this problem by delivering a support structure for the new circuit that was strong and rigid enough to reduce the concrete foundations required.
The new crushing and screening plant has been running for more than 12 months, and the Gold Fields team is very happy with its performance.
“It is going very well,” Freemantle said. “The Schenck screen is performing well, and the Sandvik crushers have an intuitive automation system that was easy to integrate with our process control.
“The new plant was designed for a two-million-tonne-per-annum (Mtpa) throughput, which is oversized for the current throughput of 1.3Mtpa.
“This means the crushers can be run tighter, producing smaller product. During the design stage, the crusher output was set at 8mm, but it is now regularly producing less than 6.5mm.
“The finer feed has improved downstream mill performance, increasing the maximum throughput rate from 155 to 170 tonnes per hour.”
A comminution crushing and grinding survey completed in October 2023 indicates that the new circuit is around 18 per cent more energy efficient than the previous one.
“Also, we were able to centralise the control room duties, where we now have one operator in one control room, and the crushers run pretty much automatically with extensive CCTV around the circuit,” Freemantle said.
“Previously, the crushers had their own control room, and the operator relied heavily on visual line of site monitoring.”
Safety has improved considerably with the simpler design, modern instrumentation, and improved automation. The new circuit addressed concerns associated with the old plant, exemplifying Gold Fields’ commitment to providing a safe workplace.
“Access to the new circuit is much easier and safer, with better, wider walkways, chutes that are accessible, and more room for cranes,” Radford said.
According to Radford, the design of the new circuit has reduced dust generation and improved water drainage around the plant.
“The new circuit has fewer conveyors and transfer chutes, and improved water sprays and belt scrapers,” he said. “We aimed to improve housekeeping and access to make things easier for our maintenance and operations staff. Comparing the two plants is like comparing chalk and cheese.”
Including a fine ore bin seamlessly tied into the main mill feed conveyor reduced dust emissions, reduced freshwater consumption from sprinklers, and improved site drainage through an improved plant layout.
Replacing the crushing and screening circuit has also led to immediate financial improvements for the company.
The new modular crushing and screening circuit has delivered minimum annual savings of $1.5 million by increasing throughput at a reduced crushed product size,
improving downstream efficiencies, and introducing a fully centralised control room. This has eliminated the need for a permanent second crusher control process technician.
Combined with capital savings, this led to an impressive three-year payback period.
The Agnew gold mine’s transformative upgrade not only eliminated long-standing challenges but also ensured a more efficient, costeffective, and profitable operation.
The Gold Fields team feels that the teamwork between all those involved has greatly contributed to the success of the project.
“Overall, working with Sandvik has been quite stress-free,” Radford said.
“There have been challenges on both sides, but we were always able to meet in the middle and find solutions. Once the concrete civil issues were solved, the whole thing came together very quickly.
“Sandvik’s ability to work with multiple teams was a highlight, delivering a project to spec, and always listening.
“The Sandvik team really pushed themselves to deliver the project and helped us achieve what we needed despite the challenges – many of which were out of their control.”
An Australasian-based company plans to help mining companies prepare for the battery boom with robotic bagging systems.
positioned to benefi t from the battery boom, with easy access to minerals like lithium, nickel, and cobalt, and access to a mature mining industry.
With the Australian Trade and Investment Commission expecting global demand for batteries expected to quadruple by 2030, the Federal Government began funding a National Battery Strategy.
The strategy outlines four opportunities: build stationary energy storage to transition Australia’s grid to renewables, upgrade Australia’s battery minerals into active materials for electric vehicle manufacturing, produce batteries for heavy vehicles and equipment in Australia, and ensure safe and secure operations for batteries with enabling technology.
With millions of dollars of funding flowing through the industry, Aurora Process Solutions sales and marketing manager Braden Goddin has seen shifts in the market.
“We’ve noticed there has been a marked increase in the use of bulk bags for minerals, powders, and other granular materials like lithium and rare earth metals,” he told ABHR
“It’s likely due to the increased demand for batteries and similar technology, and it’s great to see the Australian economy has taken account of that.
“It’s also seen a spike in semi- and full-automated bulk bagging systems, something we are well positioned to help with.”
Aurora Process Solutions specialises in helping businesses in regional and remote areas improve their operations. It does this through supplying robots and packaging systems to support bagfilling, closing, conveying, palletising, and wrapping applications.
In particular, the company has primarily worked with industries that deal with heavy bags, such as the grain,
stockfeed, fertiliser, landscape products, sand, and cement industries.
Goddin said the company is well placed to support the mining industry automate its packaging operations.
“We’ve been working with bulk system for more than 20 years and have supported a diverse range of enterprises with very different materials and needs.”
With the incredible amount of different materials that are packaged across the world, few companies can claim they have worked with every product available.
Aurora Process Solutions uses its network of specialists, engineers, health and safety experts, and more to find the right specifications and technologies. It then develops a turnkey solution for customers looking to automate operations, taking staff out of dull, dirty, or dangerous situations.
Mining is no stranger to automation in Australia. The industry has embraced
the technology, using automated trucks, trains, and more to improve productivity and safety.
Goddin said the industry is also looking for ways to minimise the manual handling aspects.
“In a lot of cases, due to the remote locations of these mining and processing sites, there’s a desire to automate processes where possible,” he said.
“Often when minerals used in battery manufacturing are shifted, it’s in container trucks, so bulk bags make things much easier – especially if there is a long or complex logistic chain involved.”
Aurora Process Solutions can provide highly modular systems that can grow alongside the business, capable of packaging one bulk bag per hour, to up to 80.
It also has access to a variety of different bags, which often have specialised linings to better handle sensitive or dusty products.
The company has also seen an improvement in the technology that is uses for the labelling, barcoding, and tracking of bulk bags, which are further tasks that can now be automated.
Goddin said Aurora Process Solutions puts a lot of its effort on understanding its clients and what they want to achieve.
“We will work with all departments, from engineering, to maintenance, to project management, to find a solution that is fit-for-purpose,” he said.
“That makes all the difference. There’s a lot of drawing, testing, simulations, animated integrative graphics and modelling to ensure we get it right.
“A lot of the problem solving is done upfront, before the problems even eventuate.”
Remote locations aren’t an issue for the Australasian-based company. While it isn’t always possible to get a technician to site immediately, Aurora provides the next best thing through the use of
augmented reality glasses. Customers are provided with a Hololens headset, which allows technicians from Australia, New Zealand, and Europe to provide support as if they were standing there with the client.
The system was originally designed for military applications, providing soldiers in the field with easy access to support when needing to repair highly technical equipment, such as generators, GPS, or vehicles.
In addition, the company is always available to answer questions over the phone or through a video call.
Goddin said the team is excited to be branching into the mining industry and growing the business in Australia.
“We have recently onboarded two extra Australian personnel and are looking to increase that soon,” he said.
“Bulk bagging is diverse – one week it could be fish food, the next week it could be neodymium. There’s such a difference in products that it’s a science in itself.
“We make sure we have the fundamentals of bulk material handling sorted, and we have a robust system to make sure every aspect of a project is considered when we design a system. We’re excited to see what the future holds for us.”
DYNA Engineering has introduced new HDPE rollers to meet the growing demand for sustainable, long-lasting rollers.
DYNA ENGINEERING IS NO stranger to high density polyethylene (HDPE). The company has been using the relatively lightweight and durable material for several key products, including conveyor guards and protective guarding on underground shotcreting plant.
Mine sites across Australia have also seen the benefits of swapping from steel to HDPE. Not only are HDPE rollers significantly lighter than their traditional steel counterparts resulting in energy savings and improved productivity, but they also require no surface treatment, are quieter, and require less downtime.
DYNA Engineering general manager Thomas Greaves said this makes them an appealing package for any mining company or contractor interested in greater productivity, reducing downtime and minimising safety risks for maintenance and operational people.
To meet the growing demand for more sustainable, quieter-running, longer lasting rollers, DYNA Engineering has developed composite rollers that make use of glass fibre reinforced highdensity polythylene (GRHDPE)
Greaves said these rollers are better able to handle the harsh conditions commonly experienced by mining companies struggling to keep up with today’s increasing requirements for more sustainable and effective conveying of ore over longer distances.
He added that it was a “quiet and important success” for DYNA’s GRHDPE rollers when a valued customer in the far north of WA’s Pilbara rolled them out on site.
“We have complete confidence in the performance of our GRHDPE rollers. The Pilbara is a harsh and testing region of the world, but due to our extensive quality systems and experience in design manufacturing conveyor equipment, we know they are built to last in such trying conditions,” he said.
“We’re now in full production as the news gets out and the orders are coming in” he added.
Shell materials offered in DYNA’s roller range now include steel, stainless steel, aluminium and the new HDPE and GRHDPE Composite. They can be customised to suit almost any requirement including bearing brand, bearing size or series, and project standards and specifications.”
The company continues to offer many other types of rollers such as impact, rubber, coated rubber, screw, steel screw, and rubber disc. HDPE options are only available on plain rollers at this point.
One of the benefits HDPE rollers provide is significantly quieter running. This can be very important when
conveyors operating near built up areas continuously through day and night can cause discomfort to nearby residents.
Up to 10dB less operational noise than steel rollers could even mean the difference between a new land traversing conveyor being built and put into operation or not even getting approval to proceed in some cases.
“This latest addition using HDPE to further widen our range of conveyor componentry is concrete evidence that our decision to significantly invest in the design, development and manufacture of more HDPE products back in 2018 was definitely the right way to go” Greaves said.
“We have every intention of continuing to go down this path. All of us here at DYNA are genuinely pleased to see such progress and innovation in the conveyor space” he said.
As Australia’s longest running mining show, Asia-Pacific’s International Mining Exhibition (AIMEX) has a long, established history of showcasing and supporting the latest trends and developments in the industry.
SEPTEMBER 2025 23-25
AIMEX is relocating and will call South Australia home for the next 10 years, following market feedback and strong support from the local government and key mining players.
The move marks an exciting new chapter for the event and the region’s resource sector, with the state leading the way in future-focused mining.
AIMEX offers unparalleled opportunities to connect with Australia’s largest community of mining suppliers and professionals in an environment that stimulates innovation and collaboration.
Tom Stahura from ESS Engineering explains how carryback can be minimised with the right conveyor belt cleaners.
CONVEYOR SYSTEMS
are the backbone of bulk material handling across industries such as mining, construction, and cement production. However, one of the most persistent challenges operators face is carryback – the material that remains on the belt after discharge. Despite advances in conveyor technology, there is no magic bullet to completely eliminate carryback, making eff ective maintenance and cleaning solutions critical.
“Whatever hardware you select, it has to be maintained and kept up to speed. The more automatic that is, the easier it is to do,” ESS Engineering accounts development manager Tom Stahura said.
Safety and operational e iciency Carryback poses a dual threat: it compromises operational efficiency and worker safety.
“If there’s dirt on the ground, you slip and fall – your people get hurt,” Stahura said. “If there’s spillage, you’re losing part of your dollar input – whether it’s iron ore, gold, or any other bulk material. Sometimes you can recover it, but in cases like alumina, it’s so light and airy that it just blows away, wasting both material and energy.”
The accumulation of fugitive material – spillage, dust, and carryback – can also lead to equipment malfunctions, increasing maintenance costs, and unplanned downtime. In the worst cases, excessive build-up can cause belt misalignment or even catastrophic belt failures, requiring costly repairs.
ESS Engineering’s approach to belt cleaning utilises a system of primary, secondary, and return belt cleaners, which work together to minimise carryback and improve conveyor efficiency.
“The primary cleaner sits at the head pulley and removes the bulk of material that adheres to the belt. Secondary cleaners, positioned underneath, tackle the remaining fines. If additional cleaning is needed, multiple secondary cleaners can be installed,” Stahura said.
“Return belt cleaners then work on the underside of the belt to prevent material from falling onto the return strand, which can cause excessive wear or create hazards such as fire risks.”
By integrating features such as automatic tensioners, cameras, and spray systems, ESS Engineering aims to
reduce the need for manual intervention and inspection, enhancing both safety and reliability.
“With automation, we can tweak pressures, activate spray systems, and ultimately keep workers off the ground in dangerous conditions,” Stahura said.
A well-designed and well-maintained belt cleaning system offers significant long-term cost benefits compared to frequent cleanups and component replacements.
“What does it cost you to clean up? What does it cost you in lost material?” Stahura said. “If you’re losing processed material, you’re throwing away money spent on refining that product.”
Failing to maintain belt cleaning systems can lead to major equipment damage.
“Belt misalignment and spillage can cause major issues, like roof collapses due to excessive debris build-up or belts derailing due to large rock entrapment,” Stahura said. “These incidents create emergency situations that are physically dangerous and potentially financially devastating.”
ESS Engineering’s belt cleaners deliver significant impact across multiple industries.
“We work with everything from uranium to iron ore, salt and food products,” Stahura said. “Mining, construction, cement works – these industries deal with massive material volumes, and effective belt cleaning is essential for keeping operations running smoothly. Take Perth’s cement operations, for example. Keeping these facilities clean prevents dust from spreading into residential areas.
“Our belt cleaning systems ensure minimal material loss and environmental impact.”
Moisture content significantly affects how materials behave on a conveyor belt.
“I watched a demonstration where drops of water were added to a material in a loop conveyor system, and the changes were dramatic,” Stahura said. “Moisture can make material stickier or, if high enough, wash it away. But it all depends on the application – what works for a run-of-mine conveyor may not work for a final product conveyor.”
To address moisture-related challenges, ESS Engineering uses a combination of belt cleaners, vibration mechanisms, and cleaning systems.
“Just like independent suspension on a car, belt cleaning relies on the right pressure,” Stahura said. “Too much pressure generates heat, which can damage the belt. The goal is to use the minimum pressure required for effective cleaning while tracking wear rates and efficiencies.”
Engineering versus accounting
A major issue in conveyor design is the push and pull between engineers and accountants.
“Engineers would design a system to completely contain carryback, but accountants might not allocate the budget for that,” Stahura said. “Often, companies take a two-step approach –building a simpler system initially and upgrading later.”
At the heart of belt cleaning is workplace safety.
“A well-maintained system keeps material off the ground, reducing manual handling risks,” Stahura said.
“Conveyors don’t look fast, but they are. It takes very little to get caught, and getting sucked into a conveyor belt can be fatal.”
Investing in reliable, well-designed belt cleaning systemsnot only improves efficiency but protects workers.
“Think of your belt cleaners like a razor – you check it every morning before
Book a free on-site review and analysis of your current pallet wrapping performance
NZ 0800 55 77 33
AU 1800 318 019
hello@aurora-process.com
shaving, and you should do the same with belt cleaners,” Stahura said.
“Keeping them in top condition ensures smooth operations and prevents costly accidents.”
In an industry where every tonne of material counts, minimising carryback isn’t just a maintenance issue – it’s a business imperative.
Our breakthrough new range of pallet wrappers deliver real cost reduction per pallet and an extra level of performance.
Intelligent technology to get the best load containment whilst reducing your wrap usage.
Unusually shaped loads, unstable or light loads, sharp edges, and loads in cold or hygiene zones – we’ve got it covered.
Full range of performance wrap and pallet consumables - specified by process technicians not stationary suppliers.
Fully installed and serviced.
Ask us about paper wrapping options too.
Conveyor Components Company plans to expand in Australia through clear, concise communication.
AUSTIN SCHEID NEVER EXPECTED
to be selling conveyor components. When he left his hometown of Croswell, Michigan, he had ambitions of working in real estate. After graduating from college and seeing what was out there, he felt drawn back to where he grew up.
He told ABHR that even though he would drive past Conveyor Components Company facility most days, he had never thought much about it until a mutual connection invited him to tour the facility.
“I never knew that the company shipped equipment to more than 100 different countries, right here in Croswell,” he said.
“I was curious about the whole industry, and after some time they told me about a job opportunity that was available right now.
“That’s how I got my start as a customer service representative, and how I progressed into a business development specialist.”
When he started, he had no background in the industry itself. Instead, he brought with him transferrable skills that would prove to be vital. Clear,
effective communication is vital in Scheid’s role, especially when working with the bulk handling industry.
At Conveyor Components Company, it is even more critical. The business is based on learning what kinds of problems its clients are facing and finding the right solution for the job.
As part of his role, Scheid learns the needs and requirements of complex bulk handling sites located around the world. Importantly, he also attempts to understand their vision and what drives their business.
“That’s key,” he said. “Whether it’s a big customer looking for dozens of components for a big project or a smaller reseller looking for one unit, we need to understand what the client’s vision is to best help them reach their goals.”
Conveyor Components Company has a 60-year history and prides itself on manufacturing rugged equipment that monitors and protects conveyor systems. It specialises in producing conveyor controls, motion controls, level controls and bin aerators.
All of its manufacturing is done under one roof, with each unit undergoing physical tests and inspections to ensure
it will meet the client’s expectations. In addition, its units are made from cast aluminium, allowing them to withstand the test of time in some of the harshest environments.
Customer feedback is a vital part of this process as well. Conveyor Components Company listens to as much customer feedback as it can, following up with clients when possible.
This process is what led to one of the company’s latest developments, the Conveyor Safety System, a combined package including an emergency pull stop switch, a belt misalignment control, a damaged belt detector, and a motion control.
Traditionally, the company offered each of these systems individually but saw the benefits of combining them into one package. Each component works in tandem to ensure the belt is being protected and alerts the site if a problem arises.
Scheid said communication is even more important when working with Australian companies.
“We’re just getting into the Australian market and are looking to establish relationships there,” he said.
“That means being available for them, whenever they need. We know the communication windows and have to ensure we’re organised and ready to go so they’re not waiting on us.
“Any unplanned downtime costs money. When a client is asking for a unit, they need it as quick as possible. We have the ability to receive an order and ship it out in the same day.”
As the company grows internationally, it also aims to reinvest. It recently purchased a new computer numerical control machine that will allow its team to double its manufacturing capacity for cast units. This is expected to slash the turnaround times for companies in immediate need of switches and other products.
Conveyor Components Company also aims to invest in its people to build on the experienced team it already has.
Scheid said the company is growing tremendously and is
OPTIMISE YOUR ENTIRE PACKING
looking forward to working with the Australian bulk handling sector.
“It takes a lot of people to make things work,” he said. “Teamwork is everything for us.”
“We have a lot of experienced people here at Conveyor Components Company. Everyone shares the one goal – helping customers wherever we can,” he said.
The partnership for Australian manufacturing has been renewed with a new five-year contract.
Rio Tinto representatives at its conveyor belt manufacturing facility in Kwinana, Western Australia, to formally mark a renewed partnership for Australian-made manufacturing and local economic growth.
The contract will see Fenner Conveyors supplying conveyor belts and splice kits for Rio Tinto’s iron ore operations across Australia for the next five years.
Through quality, Australian-made conveyor belting, Fenner Conveyors and Rio Tinto are dedicated to fostering supply chain security and sustainable manufacturing operations that benefit local communities and industries.
During the last contract period alone spanning five years, Fenner Conveyors supported Rio Tinto sites with over 473km of conveyor belt.
During the visit, Fenner Conveyors and Rio Tinto discussed safe and quality manufacturing processes, as well as recent efforts
to reduce environmental footprint during manufacturing.
Fenner Conveyors has a road map for achieving net zero at its Kwinana conveyor belt factory, which Rio Tinto has shown keen interest in supporting over the years.
Both companies are also aligned on a commitment to social responsibility. Recently Fenner Conveyors and Rio Tinto both participated in a community event in Karratha with the National Association of Women in Mining (NAWO).
Fenner Conveyors became a NAWO member in mid-2024 as part of its gender diversity strategy, which is currently being developed by Fenner Conveyors’ executive management committee, as it looks to champion a more inclusive future and rethink established systems of work within the industry.
Last year Fenner Conveyors was the official host for its first NAWO event in Karratha, collaborating closely with NAWO’s Western
Australia regional sub-committee, and various industry stakeholders and companies operating across the Pilbara.
“We are thrilled to be able to host these events which provide an avenue for local youth to learn about the diverse career opportunities across the field of operations,” Fenner Conveyors managing director Jen Green said.
This commitment to diversity and inclusion in the workplace is shared with Rio Tinto, who has launched a number of initiatives to build a culture of trust on its sites where its people feel safe, respected and empowered.
Alongside the supply of coveyor belting, Fenner Conveyors has been servicing conveyor systems on Rio Tinto sites across the Pilbara for decades. This experience and understanding of Rio operations helps Fenner Conveyors design solutions tailored to site needs.
“We have inland and coastal crews based on Rio Tinto mines, and ports who are established and recognised as valued members of Rio Tinto’s site
teams,” Fenner Conveyors area manager Ryan Giltinan said. “Each and every member of these crews are dedicated to helping Rio Tinto achieve optimal operating results.”
The renewed contract highlights Fenner Conveyors’ dedication to Australian manufacturing. With manufacturing facilities in Melbourne, Sydney and Perth, Fenner Conveyors is well-positioned to meet the demands of Rio Tinto’s extensive operations.
The partnership will enhance the efficiency and reliability of Rio Tinto’s conveyor systems, and support local jobs and economic development.
“We are thrilled to continue our strategic partnership with Rio Tinto,”Green said. “This contract is a testament to our commitment to delivering high-quality, Australian-made conveyor belting. We look forward to working closely with Rio Tinto to support their operations and contribute to the growth of the Australian economy.”
TUNRA Bulk Solids develops custom solutions to suit the individual needs of our clients.
Flow Properties and Materials Testing
Dust (environmental) Testing
Wear Testing (Impact, Abrasion and Erosion)
Conveyor Belt, Idler Roll and Pulley Testing
Discrete Element Method (DEM) Modelling
DEM Calibration Testing
Materials Handling Consultancy and Contracted Research Bin and Stockpile Design
Pneumatic and Hydraulic Conveying
Computational and Scale Modelling
Site Visits
Professional Development Courses
Kinder Australia’s primary belt cleaner is keeping belts free of meddlesome carryback.
WHEN MOISTURE IS PRESENT on a conveyor belt, it can lead to the maintenance team’s nightmare – carryback.
Carryback is an all-too-common occurrence in the bulk handling space, the result of material sticking to the underside of the return belt beyond the discharge point.
Over time, it begins to build up and often requires extensive manual labour to remove it, exposing staff to risks like higher likelihoods of slips and falls and proximity to heavy industrial machinery.
Carryback can also cause damage to the belt and surrounding conveyor structure, as more fugitive material builds up on idlers, conveyor components, and structural supports. This exacerbates the problem even further and can lead to expensive repairs and lengthy downtimes.
Kinder Australia field application specialist Peter Laskey said carryback also shortens the life of equipment.
“Carryback causes all sorts of problems for our clients, which is why we want to take away as much of the manual handling and cleanup by installing a primary cleaner,” he told ABHR
“Primary belt cleaners, like Kinder’s Micro Eraser primary belt cleaner can play a vital role in reducing carryback and keeping conveyor belts running smoothly and efficiently.”
Kinder’s Micro Eraser primary belt cleaning system is designed to be lightweight yet provide strength and durability with a 6 mm thick, 51 mm x 51 mm tube stock steel mainframe and corrosion-resistant, galvanised Schedule 80 pipe stub ends.
The compact mounting footprint makes it ideal for applications where
space is limited – it only protrudes 114mm from the mounting structure.
Laskey said what sets it apart is its central tensioning system, which is adjustable from 7–27Nm.
“This central system gives even tension across the entire belt,” he said. “That’s vital, because if a belt cleaner only has tension on one side, it may only clean one side effectively.”
It also features a single pin blade attachment, which makes change out quick and easy, with no springs, bolts, or hoses.
The Micro Eraser system is available in a vast array of different sizes to suit all belt widths. It has undergone a recent upgrade and now uses universal mounting plates that are designed to retrofit existing layouts, allowing easy mounting onto conveyors designed for use with other cleaners. It also features an improved spring-loaded bolt ratchet tensioning system.
Laskey said the Micro Eraser conveyor belt cleaner represents a significant advancement in the field of bulk material handling.
“Its innovative design and ease of use make it an ideal choice for any operation looking to enhance efficiency and reduce carryback,” he said.
“By choosing the Micro Eraser cleaner, you’re investing in a solution that offers superior performance and long-term reliability.”
Kinder Australia’s team of field application specialists work closely with bulk material handling sites around the country to find the right tool for the job.
One such site was a supplier of asphalt and road base aggregate materials.
For many years, the company’s production plant had used an old primary belt cleaning system. Normal wear and tear resulted in weakened tensioning and pressure on the conveyor belt. The uneven pressure significantly reduced the overall cleaning effectiveness of the belt cleaning system which required rectification.
Carryback and the buildup of material on the conveyor belt return side was also a major concern as it could cause excessive material spillage, production downtime and escalated safety hazards.
Kinder Australia’s team of field application specialists conducted a comprehensive review of the operations existing conveyor system. The review addressed key areas of belt cleaning and included the recommendation of a solution to improve operational
productivity and minimise safety hazards on site.
The small diameter of the head pulley was identified as a key factor in recommending Kinder Australia’s Micro Eraser primary belt cleaning solution. Lightweight, durable and high strength, this compact primary belt cleaning system delivers a highly powerful and proven cleaning performance. The single pin blade attachment means quick and simple blade change out with minimal production down time.
Laskey said this process of visiting clients to learn more about the issues they are facing means Kinder can provide the ideal solution.
“Our field application specialists will find out what belt scraper is best suited to the conditions of a specific site. They’ll consider things like belt speed, the material being conveyed, and pulley diameters to find the best scraper for that environment,” he said.
“Kinder’s engineers are looking to get out and about, servicing our customers and anyone who needs assistance with conveyors.
“We’re a solutions-based company and are excited to help solve any problem our customers are facing.”
Your Partner in Precision
Our Analytical Stockpile Assessment (ASA) solutions offer unparalleled accuracy in evaluating your stockpiles, providing you with critical data on volume, tonnage, and composition. Whether you are optimising resource consumption, improving financial reporting, or ensuring compliance with stringent regulations, our advanced technologies and proven methodologies empower you to make informed decisions with confidence. Our tailored services are designed to meet your unique business needs, supporting your operational and financial targets efficiently.
With a global network of experts and a reputation for confidentiality and quality, Intertek Caleb Brett is the partner of choice across diverse industries. Trust us to deliver precise, reliable, and actionable insights that drive your strategic planning and financial success.
TO LEARN MORE, SCAN THE CODE!
Thayer Scale’s regional sales manager southeast Bryan Martins speaks to ABHR about its accurate and versatile weighing solutions.
in the weighing industry is built on innovation and ruggedness, delivering durable equipment that can handle some of the most challenging industrial settings.
Bryan Martins, Regional Sales Manager Southeast, shared insights with ABHR on what he believes sets Thayer Scale’s technology apart, and why it’s favoured in sectors like cement, steel, and coal-fired power plants.
At the heart of Thayer Scale’s offering is a robust design philosophy. Martins said the company’s equipment is purpose-built to endure harsh conditions, utilising heavy-duty construction materials to ensure longevity and reliability.
“Our choice to utilise structural steel wherever possible is key,” he said. “We use components like I-beams and C-channel steel to create a product that’s incredibly durable.”
This isn’t just for aesthetics – it’s crucial for the practical realities of industries where equipment must perform under constant stress and exposure to abrasive materials.
“The largest weigh-belt feeders the company has delivered are larger than
a typical pickup truck and weigh up to 14 tonnes. We’ve had some units needing a 60-tonne crane just to be lifted onto a flatbed truck,” Martins said.
“This level of durability enables the company’s equipment to withstand years of continuous operation in demanding environments without significant wear.”
Thayer Scale’s patented FMSS force measurement suspension system is a key innovation that sets its weigh-belt feeders apart from its competitors.
“This system enhances the accuracy of measurements by allowing the use of smaller load cells, which offer finer resolution and greater sensitivity. You get a more sensitive product, able to measure small variances that can translate into dollars and cents,” Martins said.
Precision is critical in industries where measurement accuracy directly impacts profitability.
Thayer Scale’s technology allows operators to detect minute differences in material flow, which can be the difference between operational efficiency and waste.
“This feature not only improves accuracy but also contributes to
This flexibility is vital for clients seeking reliable and long-lasting solutions, no matter the industry.
Scale’s controls offer alarm tracking, calibration history, and programmable options that facilitate maintenance
This capability is vital in industries where a consistent material feed is crucial to maintaining operational
DHHI’s local After Sales team supports your operation and equipment throughout its entire lifecycle, providing reliable and cost effective solutions every step of the way.
Along with low cost sourcing, rotables and service exchange, DHHI’s key strength is manufacturing high-quality and low-cost spare parts for both DHHI and non-DHHI equipment.
offshore structural, mechanical, electrical, reliability engineering as well as ongoing
Intertek’s Nicholas Davies speaks to ABHR about how the company is providing accurate tonnage via its Analytical Stockpile Assessment method.
material stockpiles has long been a challenge for industries reliant on precise inventory management. From coal-fi red power stations to mineral concentrate processing facilities, the need for reliable stockpile assessments is paramount.
Traditional measurement techniques, however, often relied on radioactive methods, raising both efficiency concerns and environmental risks. Recognising these challenges, Intertek pioneered its patented Analytical Stockpile Assessment (ASA) method, providing a groundbreaking, nonnuclear solution with superior accuracy.
A game-changer for stockpile assessment
Intertek developed the ASA method in response to the growing demand for precise coal stockpile tonnage measurement, particularly within the energy sector. Nicholas Davies, commercial director at Intertek, said the company sought to address inefficiencies in existing technologies.
“Historic methods involved using nuclear-based density measurement techniques. While effective, these methods posed significant environmental and logistical concerns,” he said. “Transporting and handling nuclear devices around Australia was both complex and restrictive, making it difficult to implement those technologies widely.”
The ASA method emerged as a nonnuclear alternative, leveraging advanced analytical techniques to measure stockpile tonnages with an accuracy of ±1.8 per cent. This innovation not only improved safety and efficiency but also expanded applicability beyond coal, enabling accurate measurement
of mineral concentrates, fertilisers, and agricultural products.
The development and continual enhancement of the ASA method have been driven by a diverse team of experts. Led by Dr. Sergei Fedorenko and Nicholas Davies, the team combines expertise from land surveying, physics, and chemistry to ensure a robust and scientifically rigorous approach.
“We have land surveyors, physicists, and chemists, all contributing their technical expertise,” Davies said. “The front end of our method is landsurveying heavy, requiring precision in volume calculations, while the back end relies on laboratory-intensive processes. Having NATA-accredited scientists ensures the accuracy and repeatability of our results.”
In the past year, Intertek has integrated degree qualified land surveyors into its ASA team. These specialists employ advanced LiDAR surveying techniques to measure stockpiles with exceptional accuracy, ensuring compliance with industry best practices. The combination of scientific excellence and innovative measurement technology reinforces Intertek’s commitment to delivering high-quality solutions for bulk material assessment.
One of the most significant advancements in ASA has been the integration of LiDAR-equipped drones, which has substantially improved stockpile measurement accuracy. According to Davies, LiDAR technology achieves volumetric assessments within ±1 per cent accuracy, a
major improvement over traditional surveying techniques.
“LiDAR brings three key advantages to stockpile assessment,” he said. “Firstly, it enhances safety by eliminating the need for personnel to physically interact with stockpiles, reducing risk. Secondly, it significantly reduces time spent in the field, as volumetric calculations are now completed much faster. Thirdly, the technology captures millions of threedimensional data points, ensuring that every contour of the stockpile is accurately recorded.”
These high-resolution 3D models provide clients with detailed spatial insights, improving inventory management and operational planning. Additionally, drone-mounted LiDAR enhances accessibility in challenging environments, such as large-scale stockyards or hazardous locations.
Originally developed for coal stockpile assessment, Intertek’s ASA method has since been successfully applied across multiple industries, including mineral processing, agriculture, and fertiliser storage. Davies said the methodology consists of three main components:
1. 3D land surveying – Using UAV LiDAR to capture stockpile volumes with extreme precision.
2. Physical sampling – Collecting material samples for laboratory analysis.
3. Compression testing – Conducting laboratory tests to assess density and gravitational properties, ensuring accurate tonnage determination.
“Depending on the commodity, we adhere to ISO standards for sampling methods, whether for grain, iron ore, or
fertilisers,” Davies said. “Following these best-practice protocols ensures that our assessment process remains consistent and reliable across different industries.”
Intertek is committed to further refining its ASA methodology and expanding its capabilities through automation and remote monitoring solutions.
“We are exploring in-situ processes where we install systems for continuous monitoring and assessment,” Davies said.
“This includes automation in both sampling and volumetric surveys, integrating real-time LiDAR technology for instant volume calculations.”
Intertek is also planning collaborations with robotics and automation firms to streamline sample collection processes, further reducing manual intervention and enhancing safety.
Intertek’s role extends beyond stockpile tonnage assessment. The company also provides comprehensive quality assurance testing, ensuring stored materials meet industry standards.
“For example, in grain stockpiles, we don’t just measure tonnage – we also assess factors such as moisture content and infestation levels,” Davies said. “These quality parameters directly impact the monetary value of a stockpile, providing clients with a complete understanding of both quantity and quality.”
Intertek also engages with clients on stockpile management strategies, offering insights into storage capacity and optimal handling practices between shipments.
“We’re continuously learning alongside our clients. As new challenges arise, we adapt our methodologies to provide the most effective solutions,” Davies said.
Through its pioneering ASA method, Intertek has changed stockpile assessment, providing industries with a non-nuclear, highly accurate, and scientifically robust solution.
For 40 years Kinder Australia has been a leading independent supplier of engineered products that enhance the performance and efficiency of conveyor systems.
Our extensive range of products, including dust mitigation systems, are engineered to meet your conveyor’s needs.
Our engineers are innovation experts who can design bespoke solutions that increase efficiency and reduce downtime.
We specialise in:
› Belt Support
› Conveyor Skirting
› Belt Cleaning
› Conveyor Hardware
› Safety and Environmental
› Flow and Anti-Wear
› Process Equipment
Book a FREE conveyor inspection today. Kinder’s Field Application experts can pinpoint problem areas, recommend tailored solutions, and help improve efficiency.
ASIA-PACIFIC’S INTERNATIONAL Mining Exhibition (AIMEX) is a key event for professionals in the mining and engineering sectors, providing an unparalleled platform for showcasing current and new solutions, networking with industry leaders, and exploring advancements in sustainable mining practices.
For Martin Engineering Australia, AIMEX represents an opportunity to demonstrate its expertise in bulk material handling solutions and strengthen relationships with existing and potential customers.
Martin Engineering regional sales manager, Marcelo Silvestre, emphasises the importance of AIMEX in driving industry engagement.
“AIMEX is a key event for Martin Engineering Australia. It provides a
valuable platform to connect with mining professionals, showcase our advanced bulk material handling solutions, and strengthen relationships with existing and potential customers,” he said.
This year, the exhibition’s relocation to Adelaide presents a unique opportunity for Martin Engineering to enhance its reach in South Australia’s mining sector.
“We hope the move to Adelaide will generate inquiries from the region and help increase our recognition. South Australia has significant mining operations, and this relocation represents an opportunity to engage more directly with stakeholders in the area,” Marcelo said.
“At the same time, we hope to maintain or even surpass the attendance levels we had at the last event in Sydney. Sydney tends to attract more
international attention, but we’re optimistic about the potential in Adelaide as well.”
AIMEX places a strong emphasis on decarbonisation and the future of sustainable mining practices, a focus that aligns closely with Martin Engineering’s commitment to innovation in environmental efficiency.
“Martin Engineering’s expertise strongly aligns with AIMEX’s focus on decarbonisation by delivering innovative bulk material handling solutions that enhance operational efficiency, reduce waste, and minimise environmental impact,” Marcelo said.
“Our technologies optimise conveyor performance, control dust emissions, and prevent material spillage, directly contributing to improved energy efficiency and a lower carbon footprint. By reducing material loss and waste while minimising equipment wear, our solutions extend the lifespan of mining assets, decreasing the need for frequent replacements and conserving valuable resources.”
Beyond product innovation, Martin Engineering has embedded sustainability into its local manufacturing processes.
“We integrate responsible waste management systems, recycling programs, and renewable energy sources to reduce our environmental impact. For example, we reinforce our commitment to sustainable practices by equipping our facility with solar panels to reduce energy consumption. We also focus on minimizing waste generation across operations,” Marcelo said.
Additionally, Martin Engineering supports mining companies in achieving their decarbonisation goals while ensuring long-term operational and environmental benefits.
“We are dedicated to helping our customers meet sustainability targets through advanced material handling solutions that optimise efficiency and reduce energy consumption,” Marcelo said.
With AIMEX now set to remain in Adelaide for the next decade, Martin Engineering sees this as a strategic opportunity to strengthen its footprint in both the Australian and broader AsiaPacific mining sectors.
“South Australia is home to large mining operations, particularly in copper, gold, and uranium. This long-term move allows us to establish stronger relationships with key industry players in the region, increase brand recognition, and generate more enquiries from South Australian mining companies. It also provides a consistent platform for us to showcase our advanced bulk material handling solutions to a targeted audience over the coming years,” Marcelo said.
“Additionally, AIMEX attracts industry professionals from across the country and internationally, making it an excellent platform to expand our reach beyond Australia. We can engage with mining companies, suppliers, and decision-makers looking for solutions to improve operational efficiency, reduce downtime, and enhance sustainability.”
Martin Engineering is working towards renewable energy and sustainable mineral processing by offering solutions that improve efficiency, reduce waste, and enhance workplace safety.
“We have developed blade replacement technology for our scrapers that minimises waste generation by ensuring only the necessary material is replaced, reducing overall resource consumption,” Marcelo said.
“Additionally, our solutions optimise conveyor performance, lower energy use, and extend equipment lifespan, directly contributing to reduced waste and environmental impact.
“Through our stewardship program, we continuously develop and implement new technologies that improve both our customers’ operations and environmental outcomes.
“For example, our air cannons require smaller tanks that generate more force while using less air, significantly reducing compressed air energy consumption.”
With a larger booth at this year’s exhibition, Martin Engineering aims to make itself truly seen.
ABHR speaks to Tecweigh’s Barry Gamble about the weighing company’s TT20 gravimetric processor.
processor is designed to enhance volumetric screw feeders, bringing unparalleled accuracy and effi ciency.
“With the addition of the TT20, you’re using the weight signal from either a scale base or a series of load cells to improve accuracy throughout the process,” Tecweigh business development manager Barry Gamble said.
This integration effectively bridges the gap between traditional volumetric methods and the precision demanded in today’s industries. By continuously measuring weight, the TT20 eliminates inaccuracies associated with inconsistent material flow, ensuring the right amount of product is delivered every time.
Tecweigh’s continuous weighing solutions, particularly the TT20, have found their way into diverse industries.
“In the cement industry, for example, we’re filling 10 and 20-kilo bags of cement commonly seen in hardware stores,” Gamble said.
Snack food producers utilise the system to add precise amounts of flavourings like chilli and salt. Tecweigh even offers a specialised auger for salt, tailored for its low throughput and high bulk density. In agriculture, the TT20 addresses unique needs.
“For instance, it can dispense additives onto the middle of a conveyor belt carrying a product, ensuring even distribution,” Gamble said.
This adaptability underscores the processor’s versatility across varied operational demands.
One of the TT20’s standout features is its ability to operate in multiple modes, catering to different application needs.
“With continuous loss-in-weight mode, it dispenses at a specific rate until instructed to stop, making it ideal for processes like tumblers or dryers in the food industry,” Gamble said.
For applications requiring precise quantities, such as filling bags or drums, the batch gain-weight mode is invaluable.
“It dispenses material until the target weight is nearly reached, then slows to account for in-flight material, ensuring exact measurements,” he said.
The TT20’s Ethernet TCP/IP output enables seamless integration into modern plant control systems.
“While the TT20 can operate independently, it can also connect to a central control system,” Gamble said.
This capability allows real-time monitoring of load cell data, screw speed, and paddle movements, to help operators optimise processes dynamically.
Ease of use is another hallmark of the TT20. Its bright, intuitive interface and programmable logic controller protocols simplify operation.
“The interface reduces errors during setup and remembers programmed parameters, making it as simple as hitting the start button,” Gamble said.
The system’s automatic tare function further enhances efficiency, zeroing out the scale before each operation.
For customers, the TT20 promises return on investment.
“It saves money by preventing overfilling in gain-in-weight mode and ensures flavour consistency in snack foods, reducing the risk of customer returns,” Gamble said.
The processor also streamlines workflows by minimising operator intervention. Supervisors can set global parameters, leaving operators with straightforward controls to start or stop the process.
Proudly made in Australia, Tecweigh’s TT20 is a reliable solution. Constructed from food-grade stainless steel, the system is designed for durability. With a 12-month warranty and readily available spare parts in Melbourne, Tecweigh ensures minimal downtime.
“We’ve been manufacturing feeders for over 20 years, and they’re used worldwide,” Gamble said.
“The system is so robust that 99.9 per cent of our customers can handle maintenance themselves,” he said.
In an era of heightened environmental awareness, the TT20 contributes to sustainability by reducing material waste. Its precise dosing capabilities ensure that only the required amount of material is used, aligning with global efforts to minimise resource consumption.
With the TT20, Tecweigh continues provide useful weighing solutions, helping businesses accurately weigh materials, optimise their operations, and save on costs.
ROBUST ✓ LIGHTWEIGHT ✓ ECONOMICAL ✓
DYNA Engineering has developed a “chamfered mesh pattern”, designed to reduce washdown splash back and increase visibility through the guard panels.
This design feature is a major “point of difference” compared to standard HDPE mesh and will improve inspection and cleaning operations.
Washdown Mesh
• Up to 50% additional spray-through for washdown.
Increased Visibility
• Up to 25% additional viewing angle and see-through visability.
Industry, academia and government collaboration is required to drive breakthroughs in greening aluminium.
ALUMINIUM PLAYS A VITAL ROLE
in aerospace, transportation, construction, and renewable energy infrastructure. However, its production is highly energyintensive, making it one of the most challenging industries to decarbonise. Monash University’s Alcoa distinguished professor Christopher Hutchinson said the complexities of this transition must be overcome to ensure aluminium remains sustainable in a low-carbon future.
The multi-step challenge of aluminium production
“It is important to understand that the aluminium production process consists of multiple steps,” Hutchinson said.
“There is the mining of bauxite, its crushing and preparation, the refining of bauxite into alumina, and the smelting of alumina into aluminium. All three steps are important.”
Smelting consumes the largest amount of energy, but refining also requires significant power. Decarbonising aluminium production means addressing all these stages comprehensively. Recent media attention has focused on smelting, where alumina (Al2O3) undergoes electrolysis to extract aluminium. The smelting process demands an immense amount of electricity, highlighting one of the industry’s greatest decarbonisation challenges.
“The challenge of decarbonising that electricity is truly enormous,” he said.
“A typical aluminium smelter consumes so much power that South Australia’s big battery – one of the largest in the world – could only run it for a few minutes. The electricity must also be reliable and continuous. If the electrolysis cells solidify due to a power outage, they are effectively ruined.”
Aluminium smelting relies on consumable carbon electrodes to conduct electricity, which react with the oxygen released from the alumina (Al2O3) to form carbon dioxide.
“An aluminium smelter actually produces more carbon dioxide than aluminium,” Hutchinson said. “We either need effective carbon capture and storage or new smelter designs that do not use carbon electrodes. Many companies and research institutions are developing non-consumable electrodes, but none have reached full commercial scale yet.”
Beyond smelting, refineries rely on high-temperature heat for the Bayer process and calcination, which are mostly fuelled by fossil energy. Alternative heating methods must be developed to further reduce carbon emissions. Another critical issue is red mud, the by-product of the Bayer process. “At the moment, we just store it, and it remains an environmental liability,” he says. “We need better solutions for managing red mud.”
Australia is well-placed to become a leader in sustainable aluminium production, with good bauxite resources, refineries, and smelters.
“We also have a lot of renewable energy,” Hutchinson said. “But the challenge is using that energy efficiently and solving the problems of energy density and storage.”
Australia’s research institutions provide another advantage.
“We have world-class universities, CSIRO, and industry expertise that can contribute significantly,” Hutchinson said. “These challenges are so vast that we need a whole-of-nation effort to bring together research, industry, and government. Certainly there are already some activities addressing these problems but, considering the magnitude of the challenge, they need to be greatly expanded and magnified”
The push for green aluminium should be part of a broader national strategy for green metals.
“Aluminium is not the only important metal Australia produces,” he said. “We should be thinking about becoming a green metal powerhouse, adding value to iron ore, steel, copper, rare earths, and lithium while reducing carbon footprint.”
Strengthening industry–academia collaboration
Training the next generation of engineers and material scientists is critical to sustaining innovation in this field.
“Decarbonising aluminium production requires expertise across multiple disciplines – energy systems, chemical engineering, metallurgy, and materials science,” Hutchinson said. “We need to train more engineers and scientists and create incentives for them to enter the green metals industry.”
He notes that Australian industry struggles to attract enough engineering talent. “The national shortage of
engineers is well understood, but in metallurgy and materials science which are critical to green metals development, it’s especially pressing. Universities have a key role to play in addressing this gap.”
Driving innovation and policy support
Radical innovations are required to transform aluminium production. “These are not minor tweaks to existing processes,” he said.
“For example, if non-consumable electrodes can be developed and made durable enough, smelters would need a complete redesign. The technical, material, and process challenges are enormous.”
“Decarbonising electricity for smelting is a great first step, but we need much more support across the entire green metals sector. A national approach –perhaps a National Institute for Green Metals – could bring together industry, research, and policymakers to drive coordinated efforts.”
Australia’s natural mineral resources have historically been a key to Australia’s wealth and our current standard of living. They now present a unique opportunity to lead in green metals production. “We need to add as much value as possible to these resources sustainably,” he said. “That will determine whether we become global leaders in this space.”
The necessity of aluminium in a sustainable future
“It’s easy to look at the high electricity demands, CO2 emissions, and red mud and question whether aluminium is worth it. But the reality is, there is no substitute,” Hutchinson said.
Aluminium is the second-most used metal globally after steel and is indispensable for many industries.
“Without aluminium, modern aviation would not exist. You can’t build aircraft from steel – it’s too heavy. Electricity transmission would be far less efficient, as aluminium is the preferred material for power lines. It’s used in car radiators, solar panel frames, and increasingly in electric vehicles due to its lightweight properties.”
As demand for electric vehicles and renewable energy rises, aluminium consumption will increase.
“A future with widespread electric vehicles will require much more aluminium than today’s cars because of the weight constraints imposed by batteries,” Hutchinson said. “If we want to meet our climate targets while maintaining essential infrastructure, we must find a way to green aluminium production.”
Decarbonising aluminium is one of the toughest sustainability challenges in the metals industry, requiring technological breakthroughs, policy support, and workforce development. However, the urgency of the task is matched by its importance.
“This is a great challenge for Australia’s young scientists and engineers,” Hutchinson said.
Increased production demands have resulted in faster, wider, more heavily loaded conveyor belts and increased carry-back.
Carry-back leads to excessive wear on conveyor components, buildup on return idlers, misalignment of the belt, adverse effects on the conveyor operation and plant efficiency, and increased OH&S risks.
The ESS IPS Cleaners deliver superior belt cleaning performance and unparalleled serviceability for a variety of applications.
The IPS is an upgraded version of the ESS InLine 20-Ten Premium Cleaner & the original ESS InLine cleaner, which set the standard for cleaning performance, safety, and ease of service.
Design features of the new IPS Secondary Cleaner include;
• Improved encapsulated slide design – reduces jamming for easier service
• Stainless steel manufacture – to resist product wear and suitable for corrosive environments
• New tensioning bracket design – increases the cleaners sensitivity to belt movement to maintain optimal cleaning pressure and angle
• New Air and Spring Tensioner design – interchangeable to offer flexibility as the requirements of the client evolves
• Same footprint as the 20Ten Premium InLine cleaner - once an existing 20Ten InLine Premium cleaner comes to the end of its service life, a new IPS Cleaner can be retrofitted.
A Western Australian company has expanded its output using automation and bags from HAVER & BOECKER.
Medium, a manufacturer of DMI-65 fi ltration media, found its current facility and processes could no longer support its rapid growth.
Having expanded into more than 100 countries around the world, its manual packing process needed a major overhaul to keep up with its growing business.
After doing some research, the Quantum team decided the best solution for current needs and future expansion was a fully automated packing and palletising solution.
DMI-65 is a water filtration product made from crystalline quartz sand, chemically infused with manganese dioxide. Groundwater travels through filters with DMI-65 filtration media to pull out heavy metals like iron, manganese and arsenic.
DMI-65 filtration media requires six to nine times fewer chemicals than the traditional process, which uses regular sand and chemical treatments to purify water. This unique property of the DMI-65 material has led to increased
demand and a need for higher production – 10 times more than the production capacity of the original facility.
The only way to meet this heightened requirement was to switch from a mostly manual process to a fully automated approach.
After reaching production capacity at its original plant, Quantum’s team began planning a move to a new factory in Collie, Western Australia, where it could replace its manual processes with automated, sustainable packing methods.
The manual process of loading bags onto the packing machine, handstamping production dates, and manually palletising the bags required excessive time and labour.
Its research showed investing in and setting up automated technology requires extensive preparation, expertise and support. So, it started simple: find a manufacturer with a local service centre. This narrowed down the pool of manufacturers, and the team ultimately decided on HAVER & BOECKER.
The manufacturer’s service centre was located less than two hours away, in Perth. After looking into the company, it found it provided both industry knowledge and packing equipment.
“Our goal with the new factory was to jump forward, technologically, 50 years into the future,” Quantum general manager James Glaskin said.
“We went into our research with only a base understanding of the automated packing industry, so we needed a manufacturer with the knowledge to back up their equipment and the ability to adapt to our unique product composition. HAVER & BOECKER’s team kept consistent communication with us for more than two years to make sure they could meet our needs and that we were happy with the results.”
When HAVER & BOECKER heard the needs of its facility and the plans to update its processes, it recommended the Integra 1L packing machine, a fully
enclosed, automated unit with integrated SEAL Technology and a Newtec Terram 300 G Bag Palletiser.
The HAVER & BOECKER team introduced Quantum to the Integra 1L as a solution to its packing needs.
The fully automated packing line increased their production output by more than 10 times.
The machine features an automatic filling spout, weight scale and discard chute alongside the ability to print batch codes on the packaging.
Bags are transported into the machine, filled, ultrasonically sealed and transported out before being conveyed to the Terram 300 G Bag Palletiser, where its positioned strategically on the pallet for maximum efficiency.
Quantum’s team agreed the packing machine and palletiser made sense, but then it came across another challenge. What bag should be used?
“We found that a lot of bag manufacturers wanted us to go with the type of bag they were most comfortable producing instead of the best bag for our product,” Glaskin said.
“In many cases, the bags changed hands half a dozen times before coming to our facility, creating rips, tears and unusable batches. After contacting three different bag manufacturers, we spoke with HAVER & BOECKER’s team about the problem.”
Through its Bespoke program, HAVER & BOECKER helps research and provide custom bagging solutions to customers.
Bespoke typically starts with a bag optimisation plan (BOP) or testing completed at the HAVER & BOECKER Institute.
The BOP includes a bag volume test, bag valve check, visual pallet check, and a bag specification check to see how the current bags are performing and what type of bag is best suited to the material being packed.
HAVER & BOECKER experts help customers identify the ideal bag for their product, packing line, and brand.
In this case, the manufacturer helped Quantum find the best valve bags compatible with both the DMI-65 filtration media and the packing machine. The bags not only look good, but they are 100 per cent sealed with ultrasonic sealing technology, meaning they ’re safeguarded against contaminants while also protecting the environment from spills of the corrosive material.
A long-term partnership
Quantum invested in the full array of suggested materials, including the Integra 1L packing machine, the Newtec Terram 300 G Bag Palletiser and custom valve bags provided through Bespoke by HAVER & BOECKER.
The company found working with HAVER & BOECKER just makes sense.
“HAVER & BOECKER offers fully customisable maintenance contracts.
We’re currently in talks to plan out a maintenance and parts ordering schedule that works with our equipment,” Glaskin said.
“Because our product is so niche, they want to continually
monitor the packing unit for a few months to see what wear parts are needed and how they can best support our process. Their help has been invaluable, and we look forward to this continued partnership.”
MANAGING UNPREDICTABLE weather conditions during harvest has always been a challenge for Australian farmers.
Rain, humidity, and sudden temperature changes can lead to signifi cant grain losses, quality deterioration, and storage issues.
Agridry, an Australian manufacturer of grain drying technology, is providing innovative solutions that allow farmers to take control of their harvests, reduce weather-related risks, and improve profitability.
One of the key advantages of using Agridry’s grain drying technology is the ability to harvest earlier, without being at the mercy of ideal weather conditions.
“Farmers no longer have to wait for the perfect conditions,” Agridry managing director Steven Morrison said. “They can harvest at higher moisture levels and use our dryers to bring the grain down to the required standard.”
By drying grain in a controlled environment rather than leaving it in the paddock to dry naturally, farmers can reduce weather-related losses.
“Unexpected rains, high humidity, and storms can cause sprouting and grain quality deterioration,” he said. “Our technology minimises these risks by ensuring farmers have a reliable method to dry their crops, protecting their yield and profitability.”
Additionally, drying grain before storage prevents spoilage and other quality issues.
“High-moisture grain stored in silos can lead to mould growth, self-heating, and increased risk of spoilage,” Agridry general manager Joshua Morrison said. “By drying the grain before storage, we ensure safe long-term storage and prevent financial losses.”
The Australian-made advantage
Agridry’s dryers are specifically designed for Australian conditions, making them well-suited for local businesses.
“Our dryers are built to withstand hot, dry summers, humid coastal climates, and unpredictable inland weather patterns,” Steven said. “Australian farmers face unique challenges, and our technology is tailored to meet their needs.”
Durability and reliability are also key advantages of Agridry’s products. “We have dryers that are 30 to 40 years old and still running,” Steven said. “Australian manufacturing standards are high, ensuring long-term performance. Plus, because we manufacture locally, we have parts readily available – unlike imported alternatives, where farmers may face long delays waiting for shipments.”
Another benefit is energy efficiency. “Our machines are designed to work with Australian power supplies and fuel options,” Joshua said.
“Diesel is often the most viable fuel for Australian farmers, whereas alternatives like LPG can be costly. We also continue to explore hybrid energy solutions, such as solar and hydrogen, to reduce operational costs.”
Agridry’s Predator mobile grain dryer also enhances flexibility and efficiency during harvest.
“The Predator series is fully mobile, allowing farmers to move the dryer directly to where it’s needed,” Joshua said. “This reduces transport costs and delays, enabling farmers to dry their grain on-site as soon as it’s harvested.”
The Predator’s batch drying system ensures quick and efficient drying, allowing continuous harvesting without bottlenecks.
“Unlike silo-based drying, our system provides fast results, so farmers can keep moving through their harvest efficiently,” Joshua said. “It’s also easy to operate, designed for single-user functionality, making it practical for farmers managing multiple machines.”
Additionally, the Predator is versatile across various crops, including wheat, barley, corn, canola, and pulses.
“This makes it a multi-season investment, providing value beyond a single harvest,” Joshua said. “It’s also a cost-effective alternative for farmers who don’t want to invest in permanent drying infrastructure.”
Agridry is actively collaborating with research institutions such as CSIRO and universities to develop grain drying technology.
“We’re exploring renewable energy solutions, including hydrogen-powered drying systems, to reduce reliance on traditional fuels,” Steven said. “While hydrogen technology is still emerging, we are investing in research to ensure our dryers are more energy efficient.”
The company is also implementing AI-driven moisture sensing and smart drying automation.
“By integrating advanced sensors and remote monitoring, we optimise the drying process to maintain grain quality with minimal manual input,” Joshua said. “These innovations are based on real-world testing with farmers, ensuring they meet practical on-farm needs.”
Agridry is working to reposition grain dryers from being seen as a reactive solution to a proactive tool in harvest management.
“Grain dryers aren’t just for rescuing wet grain,” Steven said. “They’re a strategic investment that allows farmers to harvest earlier, secure better pricing, and maintain grain quality.”
Education is a key focus for Agridry. “We’re encouraging farmers to integrate drying into their harvest planning,” Joshua said.
“By planning ahead, they can optimise their yields, reduce losses, and improve storage outcomes.”
Return on investment is another crucial aspect.
“We work with customers to demonstrate how grain drying can increase profitability,” Steven said. “By reducing spoilage, improving grain quality, and enabling more efficient storage, farmers see tangible financial benefits.”
Additionally, Agridry is developing user-friendly, automated drying solutions.
“Through sensor-driven technology, remote monitoring, and AI-powered controls, we’re making grain drying easier and more accessible,” Joshua said.
Agridry is committed to supporting Australian manufacturing.
“It’s all about promoting Australian industry,” Steven said.
“There aren’t many manufacturers left, and we believe in producing high-quality, locally made products that support Australian farmers and businesses.”
The mechanisation of loading logs onto ships is coming to Australasia. Page Macrae Engineering breaks it down for ABHR
AFTER MORE THAN 30 YEARS of loading logs with wire ropebased touch release spreaders, the log industry is moving to implement grapple loading systems to remove staff from the active log marshalling area.
This is a huge challenge for the industry in terms of both the equipment needed and the changes it brings to staff processes and procedures. The support needed for the new mechanical equipment differs greatly from what a wire rope-based system requires.
Page Macrae Engineering is proud to be selected by key industry providers to play a role in this important industry change. In supplying design, manufacturing, and supporting expertise for the different grapple systems utilised, the company has provided a complete end-to-end service to its clients.
Each design-build project starts with a conversation about these essential deliverables to get clarity on what’s important and the order of importance.
Working closely with the client to understand their safety, commercial, and technical objectives means Page Macrae’s engineers have a level of clarity that saves a lot of time and effort.
In the design process, the company works closely with clients to lean on their operational knowledge and technical expertise to get to the finished design. This is the fastest and most efficient way to deliver a solution that has minimal requirements for design iteration.
A significant challenge in changing from wire ropes to a grapple operation is ensuring clients can maintain or improve their load rate productivity.
With the weight of a grapple system coming in at approximately 12 times that of a wire rope unit, capacity and cycle times from load pick up to delivery to the hold become very important.
Page Macrae Engineering has designed an innovative grapple tine system that is light and has the weight and volume capacity that our clients need to keep up the productivity they require. The company worked closely with its clients to identify where it could improve the important operator experience and functionality of its designs and controls to optimise the operations.
The story of one of the grapple solutions, the Smart Log Vessel Grapple (LVG) illustrates this collaborative approach.
“We knew we had to eliminate the need for workers to manually sling
logs, but we couldn’t compromise on productivity,” Page Macrae Engineering product development manager Bruce Ennis said.
The result was the Smart LVG, an innovation that has now handled over 10 million Japanese agricultural standard (JAS) of logs through more than 552,243 lifts across 34 operational units.
The success of the LVG, which won the 2022 Chartered Institute of Logistics and Transport (NZ) Safety Made Simple Award, demonstrates how innovative thinking can transform port operations. By replacing manual slinging with automatic hydraulic
tensioning straps and adding features like radar-controlled safety lockouts, the system has dramatically improved worker safety while maintaining operational efficiency.
One of the challenges in supporting Page Macrae Engineering equipment across Australasian Ports and is accessing the data already gathered by the machine.
Recognising the growing importance of data in port operations, Page Macrae Engineering is now integrating advanced telematics across its equipment range. This technology provides real-time insights into equipment performance, maintenance needs, and operational efficiency.
“It’s not just about collecting data,” Page Macrae Australian business development manager Charles Hennessy said.
“It’s about turning that data into actionable insights that help our customers optimise their operations.”
It provides real-time tracking of vessel discharge operations, monitors grab cycles and performance, and even helps schedule preventive maintenance.
Page Macrae Engineering is firmly focused on supporting its clients in their
aspirations for cost control, growth, and industry innovation. Automation and products that maximise the productivity of customers’ port staff are areas the business is focusing on.
It has new products coming to market that the company believes will support this approach.
An Australian manufacturer is helping replace obsolete impact weighers with a simple bolt-in replacement.
REPLACING MOST INDUSTRIAL equipment causes headaches. Often production needs to be paused, and the overall design of the plant might need to be changed – an expensive proposition.
When it comes to impact weighers, things can be even more complicated, as often these important parts of the process are connected to important equipment.
Glenn Jobling, managing director at Flowforce Technologies, said companies around Australia are having a dilemma when Thermo Fisher Ramsey announced it would no longer support the DE 10/20 model impact weigher.
“With support ending, that meant there were only so many years’ worth of spare parts available,” he told ABHR.
“Some businesses decided to make a change, changing to different brands. Others didn’t. Cut and shut works in a plant isn’t quick – it involved a lot of engineering and work.
“At the time, there just wasn’t
enough demand to manufacture a replacement. That was until we had an enquiry from a customer with 36 impact weighers that needed replacing.”
FlowForce knew if this South Africanbased client was in trouble, others in the market would be too. The team soon realised there would be a big market looking for quick replacements when the supply of spare parts ran out.
The company’s engineering and design team got to work to find a solution. The impact weigher had to conform to the footprint of the Ramsey DE 10/20 weighers, while also being easy to install. The solution was the Series 5 impact weigher.
FlowForce’s Series 5 is designed to continuously measure mass flow in mechanical conveying systems, ensuring a smooth material flow without disruption. It is particularly effective in vertical flow streams where traditional weigh feeders or conveyor scales may not be practical.
The system is compatible with a variety of pre-feed devices, including screw or vibratory feeders, belt conveyors, drag conveyors, air slides, or rotary valves. It can handle a diverse range of materials, including fertiliser, fly ash, charcoal, mineral sands, potato chips, and confectionary materials.
Jobling said the unique tool can measure the mass flow rate and total mass of freely flowing particulate materials.
“The Series 5 offers a costeffective yet highly accurate method for gauging the mass flow of dry solids and powders, making it valuable for inventory process control,” he said.
“We also made sure to include important features that FlowForce had developed. For example, most impact weighers mount the impact plate with the sensing equipment. That leads them into the path of the flow, and if there is any moisture or heat, it can impact the electronics and cause them to fail.
“Around 15 years ago we invented the Magnaflow, which magnetically couples the force impact plate to the force sensing electronics. This magnetic coupling technology improves sensing reliability and removes the sensor from the process path, allowing for high temperature applications and significant impacts.”
Additionally, certain industries need to control the quality and purity of the material being measured. One feature FlowForce has included in the Series 5 is the ability to take real time samples from the flow path for laboratory testing and sampling.
The Series 5 was designed and prototyped just before COVID-19 caused global chaos. When the borders reopened, FlowForce was able to install the first of two test units at different sites in South Africa.
Several months later, the customer had replaced all of the DE 10/20 model impact weighers across both sites.
Jobling said the Series 5 had performed so well it grew rapidly in popularity.
“One of the key features is the ability to bolt the Series 5 into the same bolt holes and connections of the DE 10/20,” he said.
“Instead of cutting, welding, and rebuilding connections, you can spend about four hours unbolting the obsolete unit and replacing it.”
Based in South Australia, FlowForce Technologies can support its customers with technical support in person and over the phone.
Spare parts are stored locally at its Adelaide warehouse, with international representatives also maintaining their own supply.
Jobling said the FlowForce team is looking forward to helping customers with the Series 5.
“We really want to let people know there’s an easy solution when it comes to replacing their impact weighers,” he said. “Using the Series 5 minimises
downtime and allows plants to be more efficiently run.
“We are also looking overseas to help international clients, too.”
Flexco engineering manager Shaun Santana explains how the newly developed Flextreme PXT cushion is being used with conveyors for mining operations.
demand unparalleled effi ciency and durability from high-speed conveyor systems.
Increasing volume and speed of materials transported is posing new challenges, necessitating innovative solutions that ensures operational reliability and worker safety.
Addressing these issues head-on is Flexco’s Flextreme PXT cushion, a product that Flexco engineering manager Shaun Santana calls a game-changer for conveyor belt cleaning and maintenance.
The shift toward faster conveyor belts carrying greater tonnage has introduced significant challenges.
“The increased speed results in greater loads, which exponentially heightens the forces acting on belt
cleaners. The materials being conveyed also play a crucial role, as modern belts are thicker and experience higher stress levels,” said Santana.
Traditional cushioning systems often struggle to withstand these conditions, leading to delamination between plates and reduced cleaning efficiency.
Flexco recognised the limitations of existing systems and sought to develop a next-generation solution.
“The traditional P-type cushions have been a staple in the industry for years, but it was clear we needed a more robust design to handle modern demands. That’s how the Flextreme PXT Cushion was conceived,” Santana said.
The PXT Cushion eliminates the delamination issue by replacing the rubber core with a polyurethane core and adopting a single-piece steel construction in a ‘J’ design.
“The new design removes the failure points associated with older systems and provides a future-proof solution. Polyurethane offers greater flexibility, allowing us to adapt to industry-specific needs, such as higher temperature resistance,” Santana said.
The PXT Cushion has been rigorously tested to ensure its reliability.
“We’ve tested and rated the cushion up to 7.5m per second to provide a proven solution for the industry,” Santana said.
Extensive internal testing, complemented by trials in mining sites across Australia and internationally, validated its performance.
“The feedback from customers was instrumental. We needed to confirm that the cushion-maintained cleaning efficiency and longevity under realworld conditions. The results exceeded expectations,” Santana said.
Another critical improvement in the PXT Cushion is its 15 per cent lighter weight compared to its predecessor.
“On smaller belts, this weight reduction may seem negligible, but for wider belts, it’s a game-changer. It’s easier to install, transport, and maintain,
reducing the risk of strain and injury for workers,” Santana said.
This weight reduction does not compromise strength.
“The cushion is almost three times stiffer than previous models, enabling it to handle higher loads without sacrificing durability.
“This balance of reduced weight and increased stiffness enhances both worker safety and operational efficiency,” he said.
The PXT Cushion is designed to seamlessly integrate with Flexco’s existing P-type setups, minimising downtime by simplifying maintenance.
“By ensuring compatibility, we’ve eliminated the need for retraining or reconfiguration. Operators can easily swap out old cushions during their regular maintenance cycles without any additional adjustments,” Santana said.
Flexco’s focus on extending maintenance intervals also sets the PXT Cushion apart.
“As maintenance schedules in the industry are pushed further apart, these cushions are designed to maintain performance across extended cycles. In some cases, they’ve lasted beyond two cycles, reducing downtime and enhancing overall productivity,” Santana said.
Flexco’s development process prioritised customer feedback to ensure the PXT Cushion addressed real-world needs.
“We engaged with customers early in the development process to understand their challenges and integrate their insights into the design. This collaborative approach ensures the product meets industry demands effectively,” Santana said.
Flexco’s PXT Cushion resolves existing challenges and anticipates future
requirements. Its design, durability, and adaptability make it ideal in high-speed conveyor operations.
“Our goal was to create a product that improves performance, enhances safety, and simplifies maintenance. The PXT cushion delivers on all fronts, setting a new standard for the industry,” Santana said.
STEVE DAVIS
Steve Davis discusses Australia’s bulk handling sector, highlighting the advancements the industry has made and the organisations that are providing local innovations and expertise. Steve has worked in bulk handling for 30 years, for both resource companies and professional engineering firms, in Australia, South Africa, the Middle East and Canada. His experience encompasses such commodities as iron ore, coal, potash, phosphates, petcoke, sulphur, sands and grain.
Steve Davis explains the ins and outs of the various types of rail-mounted or balanced machines and how they must be considered in project implementation and design stages.
categories of machine that are considered as rail-mounted or balance machines: stackers, reclaimers, shiploaders and shipunloaders.
These machines are typified by having the structure wheel mounted and running on rails, and either being fed by, or receiving material from, or delivering material to a conveyor system. Most travel on parallel rails, however some like radial stackers and quadrant shiploaders run on arc rails.
Typically, these machines are the longest lead items in a
bulk materials handling plant. Rail-mounted machines are expensive. Most are custom built for a specific project due to many possible variations in design parameters and requirements.
Early in project development, regulations applicable to manufacture of one of these machines should be defined. In Australia, AS4324-2017 applies due to Acts and Regulations and our duty of care to obtain the safest outcomes. AS4324 applies to all balance machines, small or large. AS4324 is an incomplete Standard, when acquired, as parts of the document must be
defined to suit the project and regional requirements. AS4324 requires that machine design is audited and approved before any manufacture can take place. I have found that the best practice is to engage a knowledgeable auditor and complete the Standard prior to engaging suppliers in procurement discussions. Engaging the auditor during the procurement process allows a sensible assessment of any bid deviations and a smooth transition into design and audit phases of implementation. From experience, it is critical that materials used in the
manufacture are the same as those used in the audited design, and of acceptable quality. The auditor may also certify the final weight and balance of a machine. Materials and weights can be surprisingly different from expectations in some machines.
The audit must be compiled and agreed before any manufacture takes place. Any post audit changes to the machine will almost certainly delay manufacture. Changing requirements, even in seemingly minor ways, adding guards to a boom for example, can result in the need to reaudit the design. Once the audit is complete and fabrication is under way, change will be expensive and likely to change delivery schedule. Changing design and not reauditing can result in a non-compliant machine. I have seen machines that have a significant weight and/or balance issue when completed, with no communicated change from supplier or auditor review of the structure.
Outside of Australia FEM rules or ISO5049 may be required. These rules are less stringent than AS4324, but still comprehensive. FEM II and ISO 5049 documents also require buyer input for completion.
Each mobile machine: stacker, reclaimer, ship loader and unloader, should be supplied to the user with a complete data book which has all
details of the design basis, design changes, audits, material tracing, manufacturing check lists and any required artisan qualifications, shipping, erection and commissioning records. This should be accessible and changeable electronically. This data book should be updated every time a machine changes from initial award through its lifetime.
All build, inspection and repair audit reports should be included in the machine data book and should have been remitted during the process.
Delivery times for a large machine typically vary from two to four years from start of bidding to commissioning on site. It will generally take two to three months to appoint the auditor, three to six months to compile procurement documentation, three to six months to bid and award the order for machines, 12 to 30 months to build machines. (Slew bearings can have extended lead time), three to six months to erect machines on site.
Several months, even years, may be needed to prove operation and availability of the machine and systems. Extended warrantees and Defect Liability Periods are worthwhile.
Balance machine delivery is often the longest duration for an entire project, and the schedule must accommodate this from the start of the project. It is common to initiate
the order process for rail -mounted machines in feasibility, or earlier, to allow sufficient time to meet the overall schedule.
Transport routes to site and available site cranage must be evaluated, as it is often possible to have machines delivered in very large pieces to minimise erection time and effort. Water side installations can allow rail-mounted machines to be delivered fully assembled. Evaluation should be completed early in the project as it will define when and how to bid to meet schedule.
All stacking and reclaiming machines should be automatically controlled. Many machines are supplied without any control cabin. Control systems should be able to automatically stack and reclaim, and accurately map all aspects of stockpiles in real time.
Automated technology is currently immature for wharf machines but could be considered. Potential collision with ships, and resulting costly damage to machine and ship, is the main reason given for not automating shiploaders and shipunloaders. However, with manual control and anti-collision protection we often see these collisions.
If provided, the location of the operator’s cabin, and its configuration, is critical to the safe operation of machines and to the health and safety of the operators.
Machines must be provided with anti-collision systems to prevent collision with other machines, with stockpiles, with ships, with fixed structures such as conveyors, with mobile vehicles, and with people. Typically, systems installed include:
• Duplicate absolute encoders for all movements; long travel, luffing and slewing. These instruments advise the control system exactly where the machine is within or outside of its operating parameters and are linked to an off board anti-collision system that should be programmed to prevent collision with known fixed objects.
• Multiple redundant end travel switching, including sensors and a mechanical or ‘dead man’ switch at each end of travel to prevent running outside travel limits.
• Each machine should have a positive stop system in the event of control failure, usually oleo leg buffers into a stop block or another machine.
• GPS in various locations as a back-up for encoders and in the control logic for defining stockpile locations. For example, GPS is used on automated machines to track the exact movement of grabs on grab crane unloaders.
• Various trip wires, ultrasonic, radar, lasers, tilt switches that are connected to the on-board anticollision system to stop the machine when it makes contact with defined objects or mobile objects. The latest technology allows the operation to slow as a potential collision point is reached, so that the machine can work close to the limits of operation.
• Tilt switches and sensors on booms to measure the height of the stockpile.
• Digging systems should have overload systems and algorithms to immediately remove the overload. When on and off board control systems are programmed correctly, machines safely stack, reclaim, load and unload without contacting each other or other things. Collision damage can include fatalities but will cause downtime and repair costs. Machines must always know location through encoders in the track and GPS and should determine whether one side of the machine is skewed in respect to the other. The control system must know where all machines are in respect to others, stockpiles or ships. The control system must be able to stop any unsafe movement and should
be able to recalibrate the system to continue operating if it should go out of alignment.
It is often possible to minimise component differences across several machines to benefit maintenance. Issues to consider are:
• Long travel drives, including brake motors and rail wheels, should be identical on all machines on a site and of identical handing. There are often 20 to 40 of these per machine, and some suppliers will have four different variants per machine. Following on from this is that similar rail should be used for all machines on a site, if possible.
• Slew drives can be standardised across machines on a site.
• Where there are multiple machines, it may be possible to standardise slew bearings.
• Hydraulic systems components can be standardised on all machines.
• Instrumentation and control can be standardised on all machines.
• All machines will have trailing electric/control cables, which can be standardised. All machines will need support for trailing cables, which is often a full-length cable tray. Define the interface between machine and cable early as this defines reeler on the machine and the site layout. Many machines will have a trailing hose for water feed. It is convenient to have this hose sit on the same cable tray. Cable trays can give rise to a moving pinch point between the machine superstructure and the tray. Make this safe.
Machines are normally lightning exposed and require earthing consideration via grounding shoes onto rail systems to avoid damaging equipment. Earthing should be separate to bogie wheels to avoid bearing damage.
It is critical that earth straps are fitted across any flexing joint on the sub structure to avoid damaging currents on bearings. Rails must be adequately grounded to prevent damaging potentials on the machine. Lightning rods must adequately shield radio masts and equipment.
It is preferable to keep rails clean by installing cleaner blocks on bogies. These are often square wooden blocks that plough spillage off rails. Shaped ploughs can be added for dirtier installations.
Cable and hose reelers are made by few companies. They can be a cause of ongoing maintenance issues if wrongly specified or installed. Use a supplier that is well known and has service facilities in the project area.
All machines should have maintenance bays with tie down equipment for wind conditions. There are few machines that do not require automatic locking rail clamps as a safety measure when winds preclude moving to the tie down area. If you chose not to have rail clamps, there should be a reason for this. They will be an expensive addition if this decision is reversed after the machine contract has been awarded. Rail clamps can be standardised across a site.
All machines should have fire prevention systems for electrical houses and transformers and for hydraulic power packs or belts. Dry transformers are normally used to avoid potential environmental containment issues. Some machines will need fire water (possibly doubling as dust sprays) on board, which can be from a tank or from a trailing hose reel.
Consider carefully how maintenance of all items might be completed in the field, especially centre chutes, boom conveyor, shuttle and bucketwheel drives, and conveyor components.
Machine rail loading limits are critical to design, so ground conditions and drainage need to be understood early in project development. Ground settlement must be limited as machines have little tolerance for misalignment.
All luffing booms should have duplicate redundant failsafe operating systems and maintenance locks or blocks in addition to maintenance tie
down structure. Consider any other aspect of the machine where it would be possible for uncontrolled movement from actuation failure. Slew and long travel for example, where it is common to have redundant capacity, eg, four drives where three are adequate. It must be possible to remove all potential energy in the system for safe maintenance.
All machines should be designed to shed spillage, as material build up can significantly increase weight, change machine balance and rail loading, and seriously damage electrical and mechanical components.
All operators’ cabins should consider a separate means of emergency egress to ground if the main access is compromised. This can take many forms; permanent walkways, drop down walkways, rope ladders, rappelling equipment. Engage operator guidance in the location and design of the cabin.
Jenike and Johanson’s Jie Guo, Aleef Rahman, and Corin Holmes provide an overview of gravity reclaim fundamentals, and how to estimate the live capacity from gravity reclaim stockpiles.
STOCKPILES PROVIDE AN economical means of storing large volumes of bulk solids in all types of industries. Stockpiles vary in shape (conical or prismatic), and size, and can be covered or open to the environment, and they may be built by varying types of mobile equipment such as scrapers or front-end loaders, or by belt conveyors with various confi gurations for stacking. Once built, reclaiming from the stockpile is required and this can be by forced extraction, such as with scrapers, bucket wheels or front-end loaders, or by gravity, which employs diff erent types of feeders or gates contained in tunnels beneath the stockpile.
A common method for gravity reclaim from large stockpiles is to use a series of hoppers and belt or apron feeders discharging onto a single belt conveyor. The primary hoppers/feeders can be arranged parallel or perpendicular to the belt conveyor. The number, size and location of the hoppers/feeders depend on key factors including the size of the pile, the reclaim rate required, and whether the material is free-flowing or cohesive. In some cases, with highly cohesive
bulk solids, it may not be economically feasible to use a gravity reclaim system. This decision can be arrived at quite readily through the evaluation of representative flow characteristics of the stockpiled material.
General flow patterns in a silo
There are two primary flow patterns that can develop in a silo during discharge: funnel flow and mass flow. It is important to understand them before conducting the analysis. Both patterns are shown in Figure 1.
In funnel flow, an active flow channel forms above the hopper outlet, with stagnant material at the periphery. As the level of material in the hopper decreases, material from stagnant regions may or may not slide into the flowing channel, depending on the bulk solid’s cohesive strength. When the bulk solid has sufficient cohesive strength, the stagnant material does not slide into the flow channel, which results in the formation of a stable rathole. In addition to flow stoppages that occur as a consequence of ratholing, funnel flow can cause material degradation, results in a first-in-last-out flow sequence,
and increases the extent to which sifting segregation impacts the uniformity of the discharging material.
In mass flow, all of the material is in motion whenever any is withdrawn from the hopper. Material from the centre as well as the periphery moves toward the outlet. Mass flow hoppers provide a first-in-first-out flow sequence, eliminate stagnant material, reduce sifting segregation, and provide a steady discharge with a consistent bulk density and a flow that is uniform and well controlled. Requirements for achieving mass flow include sizing the outlet large enough to prevent arching and ensuring the hopper walls have sufficiently low wall (material/surface boundary) friction and are steep enough to achieve flow at the walls.
A third type of flow pattern, called expanded flow, can develop when a mass flow hopper (or hoppers) is placed beneath a funnel flow hopper, as shown in Figure 2. The mass flow hopper is designed to activate a flow channel in the funnel flow hopper, which is sized to prevent the formation of a stable rathole. Particularly for large diameter silos, the major advantage of an
expanded flow discharge pattern is the savings in headroom, as compared to an all mass flow design. This approach not only reduces the capital cost, but also facilitates retrofitting existing silos by minimising the additional headroom requirement. The mass flow hopper beneath the funnel flow hopper still has the benefit of discharging material reliably with a consistent bulk density. Note that segregation and material degradation problems are not necessarily minimised with an expanded flow pattern.
For cohesive materials, as shown in Figure 3, they flow within a gravity reclaim stockpile (if designed properly) by following the same expanded flow pattern as they will in an expanded flow silo. In the case of the stockpile, the flow channel is established above the base of the pile. The combine effect from the reclaim hoppers and feeders results in the funnel flow component of the expanded flow design. Similarly, the discharge hoppers below the base of the pile should act as the mass flow portion of the expanded flow design; the active area resulting from the hoppers and feeders is ideally sized to prevent the formation of a stable rathole, although this is rarely achieved with cohesive materials.
Even though stagnant material will remain within the pile, eliminating or minimising the formation of a stable rathole will allow for a greater percentage of the pile volume to be reclaimed by gravity alone. This design approach ensures an even feed rate and a low feeder load, and therefore low feeder power requirements. A non-mass flow discharge hopper design, regardless of the occurrence of ratholing above, will result in high feeder / power loads.
H = stockpile height
Hd = critical height at which rathole becomes stable and enlarged crater forms above
Df = flow channel diameter
D = drawdown angle
ӨR= angle of repose
X = offset of pile center to center of reclaim hopper
If free flow materials, such as dry sand, are stored in a pile, the flow pattern is simple as shown below in Figure 4. The drawn angle, D, and angle of repose, ӨR, are very similar.
The methodology to determine the stockpile live capacity can be defined as follows. When material is withdrawn through the mass flow hoppers at the base of the stockpile, a flow channel forms within the stationary mass, and the material flows within that channel
toward the openings. The flow channel above an individual hopper will relatively quickly expand to a round area, above which it will tend to be a steep sided circular cone, with a bottom diameter close to the largest dimension of the hopper inlet. The level of material in the channel falls as discharge proceeds, and the top surface of this cone sloughs off and slides into the channel at a drawdown angle, D (see Figure 3), which is governed by the internal friction of the material. For free-flowing materials, this angle is approximately equal to the angle of repose, ӨR, which describes the
outer surface of the pile (and hence, its total capacity).
For cohesive materials, the angle is steeper than the angle of repose, and can be attributed more to the internal friction angle of the material.
Discharge within the gravity reclaim pile continues until the height, Hd, is reached where the stress in the rathole, of diameter Df, equals the strength of the material. A plot to demonstrate where the rathole collapses is shown in Figure 5.
Below this point, the flow channel angle will be very steep (generally on the order of 3-5° from vertical, again based on internal friction of the material), and the surrounding material will remain stagnant once the material above has emptied to the drawdown angle.
An example of the stockpile live capacity analysis is shown in Figure 6. As flow channels from adjacent feeders intersect (assuming there are multiple), then their combined effect will govern the potential for stable ratholes to remain, or if a larger reclaim area (described by the drawdown angle) will form above.
As discussed above, the live capacity of the stockpile highly depends on the flow property of the material. A good understanding of the material properties is essential for estimating the live capacity of the stockpile under gravity reclaim. The typical flow property tests required are listed below.
• Particle size distribution
• Full-size bulk density test, which assists in estimating the bulk density on the surface of the stockpile.
• Compressibility test, which provides the bulk density change with the increase of the consolidation pressure within the stockpile.
• Cohesive strength test, which informs the internal friction of the bulk material and critical
outlet dimensions to avoid arching and ratholing.
• Wall friction test, which assists in assessing or designing mass flow reclaim hoppers underneath the stockpiles
• Angle of repose test, which is useful for estimating the angle of the stockpile around its circumference.
As illustrated in Figure 5, the pressure within the stockpile governs the critical rathole dimension Df required to collapse the rathole, i.e. where the draw-down occurs. It is vital to determine the pressure within the stockpile correctly.
One of the methods of calculating the pressure within the stockpile is to assume the pressure is hydrostatic and apply a relaxing factor, 0.7 for conical stockpiles and 0.8 for prismatic stockpiles, for the hydrostatic pressure.
In the mining industry, it is common to build two stockpiles adjacent to each other as shown in Figure 7. The pressure distribution within a stockpile can be influenced by the adjacent pile depending on the distance between the two piles.
For engineering design purposes, the following are recommended as a rule of thumb.
• L > 1.5*H, the influence from each other between the two stockpiles can be neglected.
• 0.5*H < L < 1.5*H, the two stockpiles can be considered as one prismatic pile with a flat top, joining the two peaks.
• L <0.5*H, the two piles can be deemed as one single stockpile with the peak on the center line of the two piles and
the height being the same as the two piles, as shown by the light blue pile in Figure 7.
Some simulations were performed to demonstrate the pressures at the base of two adjacent stockpiles with varying distances, as shown in Figure 8. The dimensions of the stockpiles are shown in the figure, and the material was calibrated to have the same angle of repose for all three simulations. Note that they are much smaller than the stockpiles in the mining industry. Only the pressures above 36 kPa were displayed (orange represents pressures above 36 kPa, and red represents pressures above 45 kPa). As Figure 8 shows, high pressures are observed between the peaks of two stockpiles, which suggests the overlapping zone of the two piles is experiencing the same high pressures as the two peaks. Hence, the two piles should be considered as one prismatic pile with a flat top, as suggested above.
There are various facets to consider when designing or reviewing a gravity reclaim stockpile, such as:
• Sizing the outlet of the mass flow hopper(s) large enough to prevent mechanical / cohesive arching, and so that the desired flow rate will be achieved.
• Selecting the slope of the mass flow hopper(s) such that the material will slide along the walls.
• Sizing the inlet of the mass flow hopper(s) such that a sufficient percent volume of material will be reclaimed from the total volume of the stockpile (i.e., “live capacity”).
• Selecting the number and size (and distance X, from the stockpile symmetry axis shown in Figure 3) of the reclaim hoppers, if multiple hoppers are used, to again ensure that a sufficient live capacity will result. The most cohesive material tested will provide the limiting design criteria for the pile being considered, both in terms of arching/ratholing potential and in designing the mass flow hoppers. Values of cohesive strength at lower consolidation pressures will have a greater influence on reclaim hopper outlet sizing to prevent arching, while cohesive strength at higher consolidation pressures will have a greater influence on ratholing and the resulting live capacity of the pile. Higher wall friction will, by design, require steeper hopper angles to ensure mass flow. Hence, a suitable liner or surface of construction is required not only from a flow perspective but must also be selected based on minimising abrasive wear.
Manufacturer of conveyer belt scales (weightometers), weigh belt feeders and volumetric and gravimetric auger feeders all manufactured in Australia
Conveyer Belt Scales and Weigh Belt Feeders to measure instantaneous and total throughput or control Blending, Dosing or Feeding.
Volumetric or Gravimetric Auger Feeders with TT20 Weight Controller.
The TT20 is a single unit gravimetric processor that offers four modes of operation: Loss-in-Weight, Loss-of-Weight,
Gain-in-Weight, and controlled-rate-batching for bag filling The controller accurately and consistently feeds material into a process at desired rates and batches.
The TT20 has a user friendly HMII allowing the operator to monitor critical process operations. In addition, PLC communication protocols enable the controllers to seamlessly interface with a plant’s control system with access to the Scales Parameters in Real Time.
ASPEC Engineering director Richard Morgan explains some of the significant changes in AS 4324.1 and how they will impact the future of materials handling safety.
AS 4324.1, THE AUSTRALIAN
Standard that underpins safety and performance for materials handling structures, is undergoing revisions.
Marking three decades since the standard’s initial release, the 2025 revision introduces advanced guidelines that reflect both industry advancements and lessons learned from past incidents.
The primary goal of the AS 4324.1 revision is to make these structures safer and more resilient. Some of the key changes include:
New load cases for wind: The AS 4324.1 revision introduces new load cases for wind due to thunderstorms. This is crucial for improving the stability and safety of materials handling structures in extreme weather conditions. Thunderstorms can produce sudden, intense wind gusts that can catch machines off
guard, leading to potential failures. By including these new load cases, the standard ensures that machines are designed to withstand such unexpected forces, thereby reducing the risk of accidents and improving overall safety.
Simplifications and clarifications:
The standard has been simplified and clarified for suspension elements and hydraulic cylinders. Additionally, the steel material requirements have been updated to ensure better compliance and understanding. These changes make the standard more user-friendly, reducing the complexity for engineers and designers. Clearer guidelines help prevent misinterpretations that could lead to design flaws or safety issues.
Materials requirements: The revised standard allows automatic acceptance of steel conforming to AS 4100 or
AS/NZS 5100.6, simplifying the materials requirements and ensuring consistency with other standards. This change streamlines the material selection process, ensuring that only high-quality, compliant materials are used in construction. It also reduces the need for additional testing, saving time and resources.
Safety factors for suspension members and hydraulic cylinders: The revision includes modifications to safety factors, allowing single suspension elements with a revised minimum factor of safety and specifying minimum safety factors for hydraulic cylinders in compression. This ensures that even if a single suspension element is used, it will have a high enough safety margin to prevent failure. For hydraulic cylinders, the specified safety factors ensure they can withstand the loads
and stresses they will encounter during operation and extreme overload situations.
New load case for loss of chutes: The inclusion of a new load case for the loss of chutes or telescopic chutes addresses potential risks and enhances the design’s robustness. Chutes are critical components in materials handling, and their sudden loss can destabilize the entire structure. By considering this scenario in the design phase, engineers can implement measures to mitigate the impact, such as reinforcing the structure or adding fail-safes.
The requirement for available drive force during driving against a relocation wind has been modified, maintaining a minimum factor of safety against drifting whilst allowing some over torque on the electric motors due to wind gusting effects. This change ensures that machines remain stable without oversizing the drive motors which would have flow on effects to other load cases such as buffer impact and travel device obstructed.
One of the critical aspects of the revision is learning from past failures. Machine structures have shown higher failure rates compared to static structures. A notable failure occurred in Western Australia in the early 1990s, where a bucketwheel reclaimer’s shaft fractured, causing the machine to collapse and resulting in a fatal accident. This incident led to a coronial inquiry and the publication of the original AS 4324.1 in 1995. In the preparation of the original AS4324.1- 1995 and in subsequent revisions, the committee has introduced load cases based on known causes of failures.
The current protocol for dealing with wind loads involves stopping operations at defined wind speeds (20-22 m/sec), relocating
to a storm tie-down location (30-33 m/sec), and resisting ultimate design wind in tie-down configuration (over 60 m/sec in cyclonic regions).
Many of wind failures have been due to thunderstorm events rather than tropical cyclones. A feature of these systems is that they occur as a localised cell or super cell and can approach and impact a machine with little warning. In recent cases, records show wind gusts have increased from less than 10 m/sec to over 45 m/sec within minutes. This is not enough time to stop loading and relocate to the storm tie down. If the site is susceptible to this type of event the machine needs to be able to anchor to the rails at any position along the track.
• Operational wind speed: Machines are designed to operate safely up to a certain wind speed, typically 2022 m/sec. Beyond this, operations are halted to prevent accidents.
• Relocation wind speed: When wind speeds exceed the operational limit, machines are moved to a storm tiedown location where they can be securely anchored. This relocation wind speed is usually higher, around 30-33 m/sec.
• Ultimate design wind speed: In the storm tie-down configuration, machines must be able to withstand the maximum wind speeds expected in the region, which can exceed 60 m/sec in
The inclusion of a new load case for the loss of chutes or telescopic chutes addresses potential risks and enhances the design’s robustness.
cyclonic areas. This ensures that even in the most extreme weather conditions, the machines remain stable and secure.
• Stranded from tiedown case: One of the significant additions in the revised standard is the load case for machines “stranded from tiedown.” This scenario addresses situations where a machine cannot be relocated to its storm tie-down location in time due to sudden, severe weather events like thunderstorms. In such cases, the machine must be able to anchor to the rails at any position along the track to withstand the wind forces. This ensures that even if a machine is caught in a storm without being properly tied down, it can still remain stable and secure, preventing potential catastrophic failures.
The revision to AS 4324.1 is a significant step towards improving the safety and reliability of materials handling structures. By addressing historical failures and adapting to evolving environmental conditions, we can ensure that these structures remain robust and efficient. I am excited about the positive impact these changes will have on the industry and look forward to the release of the revised standard in 2025.
The most valuable lesson I have learned is … it takes time to appreciate the complexity of bulk materials handling. My advice would be to getting a project started without overcomplicating it – the learning process will come along the way.
Setting the global standard for durability, reliability, and manufacturing excellence in conveyor belts, trusted by industries worldwide to deliver the longest-lasting solutions.
For conveyor belts that deliver the lowest cost per tonne of material conveyed, you need more than just durability—you need synergy between the cover compound and the carcass, tailored to your specific needs.
The ASBSH’s mission is to enhance the discipline of bulk solids handling through research, education and sound engineering practice. It aims to promote cooperation between universities, research establishments, consultants, equipment manufacturers & suppliers and industrial users.
Using the highest quality materials and state-of-the-art manufacturing processes, we consistently produce the toughest and longest lasting conveyor belts in the industry.
The Society also aims to encourage research and development, technology transfer and training. It holds national and international conferences at regular intervals.
I am currently researching … the wear behaviour of conveyor belts. Substantial costs occur during the wear of conveyor belts and, obviously, the goal is to increase the service life of these belts. New rubber compounds are being developed worldwide, however, adequate testing methods which can predict the wear performance of rubber compounds are still being improved. This research includes experimental testing under controlled conditions, numerical simulations and experimental analysis, such as micro-imaging of the worn surfaces.
My plans for the future are … continuing applying and widen my skills in the bulk materials sector.
Bulk material handling and heavy mining operations that fit their conveyors with Fenner Dunlop Conveyor Belting benefit from maximum uptime, less belt maintenance, higher productivity, and lower total costof-ownership.
I love my current work because... I appreciate the opportunity to apply a combination of fundamental scientifi c principles and the practical application of these principles, with
My motivation in solving problems related to the very complex topic of wear and wear reduction is still persisting. Beside my personal interest in this topic, more effi cient bulk materials applications are desirable for the mining sector and the future of our planet. I am looking forward to tackling this challenge both using an experimental approach and numerical simulations.
Early Bird Delegate Registration: $3,250+ GST (Before 20 April 2025)
Delegate Registration: $3,750 + GST 5 or more delegates receive a 10% discount.
All fees are in Australian dollars and must be paid prior to the event. Fees include electronic program notes, lunches and refreshments.
Hyatt Regency, Brisbane 33 Burnett Lane, Brisbane, Queensland Ph: 07 5647 1234
All face-to-face courses are subject to current COVID government regulations. If you are unable to attend the event a substitute delegate is welcomed at no extra charge. If notification of withdrawal is received no less than 14 days prior to the event, 80% of the fee will be refunded. No refunds will be made if notification of cancellation is received less than 13 days prior to the date of the event. The organisers reserve the right to alter or cancel the course due to unforeseen circumstances. In the event of cancellation, a full refund of fees will be made.
The storage, handling and transportation of bulk solid materials are major activities for a vast number and variety of industries throughout the world. These range from the gentle handling of very small quantities of material in the pharmaceutical and chemical industries to the large quantities handled and processed by the mining and mineral companies. This diversity is particularly evident in Australia where the wide-ranging nature and scale of operations is somewhat unique.
Considerable advances continue to be made in research, development, application and implementation of the technologies associated with various aspects of bulk solids handling. This course will be of particular interest to a wide range of industries including:
• Mining and mineral production and processing
• Power generation
• Energy and environment
• Chemical and petrochemical process industries
• Agriculture processing and production
• Manufacturing
• Pharmaceuticals
• Food industry
TUNRA Bulk Solids are world leaders in applied and fundamental bulk solids handling research and have been in business for 50 years. TUNRA has built a strong reputation in industry for its professional services and world class research in materials handling and flow properties. TUNRA have completed more than 4,000 projects for over 1,000 companies across Australia and more than 40 countries internationally.
Comprehensive laboratory test facilities which are ISO 9001, ISO45001 and ISO14001 certified, are available at TUNRA to aid research and consulting activities at the University of Newcastle. TUNRA is committed to forming long term partnerships with businesses to help them overcome existing handling problems and assist with planning projects to ensure trouble-free plant operation.
The Centre for Bulk Solids and Particulate Technologies (CBSPT) is actively involved in both fundamental and applied research on a range of problems associated with bulk solids and particulate technology. Research areas include storage, flow, processing and transportation of bulk solids.
It was established in 1995 and supported by the Australian Research Council (ARC) as one of a prestigious handful of national Key Centres of Teaching and Research between the University of Newcastle and the University of Wollongong. The Centre’s Newcastle Node is strongly linked with TUNRA Bulk Solids and the Faculty of Engineering & Built Environment at the University of Newcastle.
• Description of test equipment and procedure used to determine flow properties
• Influence of storage time and environmental factors such as moisture
• Test methods for the evaluation of hopper and chute lining materials for friction and wear
• Application specific testing (inc. Dust and TML)
• Analysis and application
• Mass-flow and funnel-flow design procedures
• Basic hopper geometry
• Interpretation of flow property reports in relation to bin design
• Case studies
• Influence of flow properties and geometry on drawdown and live capacity
• Selection and positioning of hoppers and feeders for optimising gravity reclaim
• Dynamic modelling of bulk solids systems
• Introduction to the Discrete Element Method
• Modelling approaches and limitations
• Overview of critical model parameters including particle size and shape
• Considerations and best practices for industrial application
• Application of AS3774 for static and flow load cases
• Gate Loads
• Symmetric versus Eccentric Discharge
• Silo Quaking and Shock Loads
• Loads on hoppers and feeders
• Case Studies
• Importance of hopper and feeder interfacing
• Review of basic feeder types
• Determination of optimum hopper and feeder interfacing for uniform draw-down
• Determination of feeder loads
• Controlling feeder loads and start-up torque
• Basic principles of chute design
• Application of flow properties in the design process
• Chute flow problems due to adhesion and wear
• Dynamic modelling of hood and spoon for optimum accelerated flow
• Optimising chute profiles for feeding and transfer
• Optimising chute geometry for controlled wear in the flow zone and at the belt feed point
• Dust control in transfer chutes
• Application of DEM and CFD in chute design and performance evaluation
• Overview of open and closed systems. Special belt conveyors and conveyor selection recommendations
• Review of static design procedures to International Standards.
• Technical considerations in optimising conveyor design
• Analysis of main resistances – idler indentation, idler spacing, bearings and seals, stress states in bulk solids and contribution to drag
• Current research priorities in belt conveying
• Troubleshooting of common issues and maintenance considerations
• Specialised testing facilities
• Diversify your expertise and further knowledge of materials handling concepts
• Professional Development (CPD hours)
• Increase awareness of material phenomena occurring on site
• Learn methods for troubleshooting, optimisation and best practice design
• Develop skills in fundamental and numerical analysis approaches
• Learn how to apply flow properties test results to benefit your operation or designs
• Stay up to date with the latest developments in industry and bulk solids research
Emeritus Professor
Solids in 1975 to facilitate research and consulting services in bulk materials handling. Following Alan’s long standing commitment to the bulk handling industry, he developed, guided and led a team of experts at TUNRA Bulk Solids who continue to be at the forefront of the materials handling industry. Following in Alan’s footsteps, TUNRA continues to offer professional training courses to industry as a part of our commitment to continuous improvement of the materials handling field. These training courses are run by a minimum of 3 experts from our engineering group who are specialists in their fields.
Should you require any further information regarding the course, please contact: TUNRA Bulk Solids
The University of Newcastle Callaghan NSW 2308, Australia
Tel: +61 2 4033 9039
Email: danielle.harris@newcastle.edu.au www.bulksolids.com.au