THE JOURNAL OF THE BIOFOREST PRODUCTS SECTOR VOLUME 63, NUMBER 3 AUTUMN 2022 FEATURING: ABB; BRITEST; CASTOLIN EUTECTIC; GBC; PILZ; SCHILL & SEILACHER TECHNOLOGY: BARRIER COATINGS; CHEMICALS FROM PAPER SLUDGE; MES & DIGITAL TRANSFORMATION SAFETY: CPI SAFETY CONFERENCE; SENSORS FOR SHEET FEEDERS; WEAR PROTECTION SOLUTIONS COLUMNS: EXHIBITIONS; GOLD MEDAL ESSAY; LETTER FROM INDIA; NEWS; ORDERS; PEOPLE; STANDARDS PROMOTING SAFETY IN THE PAPER SECTOR



The European edition of Tissue World is the only dedicated event for tissue manufacturers and suppliers in central Europe. In 2023, the 昀agship show will make its stop in Düsseldorf for the very 昀rst time! A mature tissue market with high private label shares, Germany is home to some of the sector’s largest private label manufacturers. Tissue World is setting up there, ready to welcome back thousands of industry professionals for three days of trading, learning, and networking. Don’t miss your chance to unite with the global tissue industry at our inaugural event in Düsseldorf from 28-30 March 2023! info@tissueworld.comwww.tissueworld.com/dusseldorf
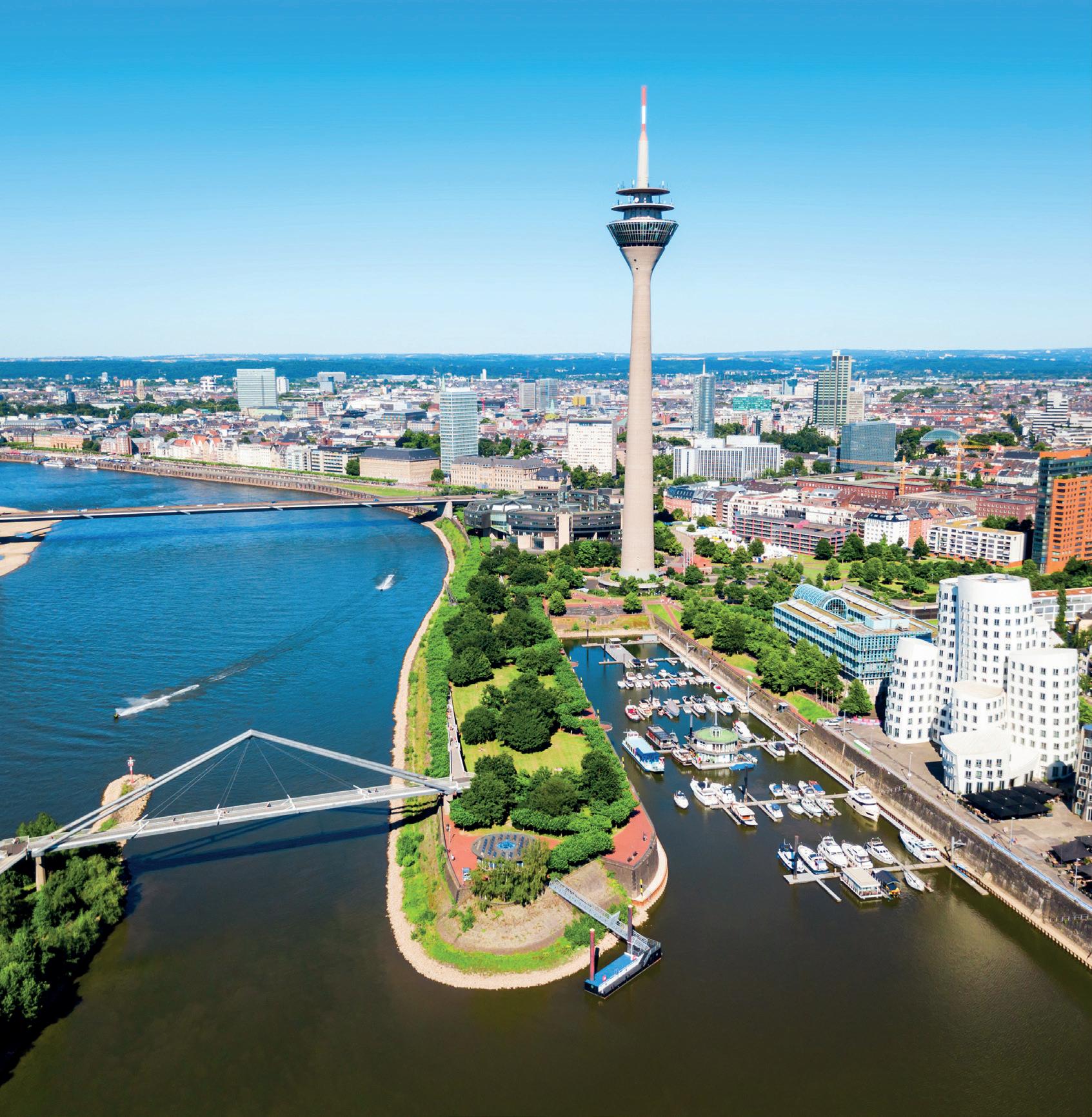
THE WORLD’S LARGEST DEDICATED TISSUE INDUSTRY TRADE SHOW
28 - 30 MARCH 2023 Messe Düsseldorf, Germany Portfolio Of昀cial MagazineOrganised By
LOCATIONNEW

email:Tel:BerksCookhamLaneDeanSL69PN03003020159editor@pita.co.uk UK Advertising Sales Contact the PITA Office Tel: 0300 3020 150 Email: info@pita.co.uk
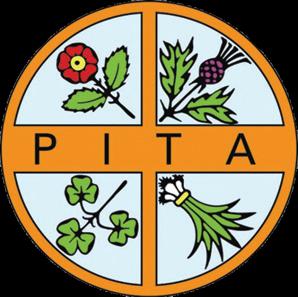

for
permission. Registered Number*2928961 England Limited Liability. ISSN
PROMOTING SAFETY IN THE PAPER
ISSN
Editor Daven Chamberlain St Johns House Spring
FRONT COVER PICTURE 2 Comment 4 Industry News 6 News Bytes 27 A Letter from India 34 People in the News 35 ........ Standards Update 36 ........ Compendium of Recent Orders 38 Conference, Exhibitions and Webinar Reports A.Celli 36 ABB 5, 6, 8, 9, 22-24, 36 AFRY 36 AFT Global 36 Andritz 8, 9, 36, 37 Aquapak Polymers ...............................9 Archroma 5, 9 Ardant 27 Arup 4, 19, 36 Avanti Conveyors 27 Babcock & Wilcox 36 Bellmer 9 BHS Group 36 BID Group .........................................36 BMH Technology 36 Bobst 4 Bonetti Group .......................................9 BTG 9 Cellwood 37 De Iuliis C&A (DJM) 37 Dieffenbacher 37 Euchner 26, 27 FrontWay ..............................................9 GBC 14-15 IPA 9 Kadant 34 KPA Unicon 37 Martor 27 Nipman 9 Otorio 9 Pasaban 7, 37 Pilz 26, 27, 28-29 Projet 37 Reifenhäuser Reicofil 37 Runtech ...............................................37 Runtech 4, 37 SAEL 37 Saur 9 Schill & Seilacher 14-15 Sema Systemtechnik 28, 29 Siempelkamp .....................................37 SKF 9 Solenis 9 SOSA 37 SPM 37 Sulzer 9 Tietoevry 37 Toscotec 6, 9, 37 Valmet 4, 5, 6, 7, 9, 34, 36, 37 Veolia 5, 9, 36 Voith 9, 37 ZoneSafe 27 Supplier Index Advertising List ABB 3 Axchem 7 CPI (career op.) IBC Paper One Show OBC Parason 2 PITA Training Programme 35 Romiley Board (career op.) 24 Tissue World Europe IFC
TechnicalJournal.papers
© PITA reserves all copyrights the contents of this may also carry first-authors’ jointly with the Association. None of the may be or re-published without (Print) 0 306-252X (Online) 2632-5799
Features 10 Sustainable Wear Protection (Castolin Eutectic) 14 ........ Water-based Barrier Coatings (Schill & Seilacher) 16 ........ Methodology for Setting Objectives for an Innovation Project (Britest) 22 MES – a Stepping Stone for Digital Transformation (ABB) 25 Health and Safety Conference (CPI) 28 Safety Solution for Sheet Infeed System (Pilz) 30 Paper Gold Medal Essay 1 Volume 63 Number 3 Autumn 2022 Contents Published by PITA PO Box 721, Bury, BL8 9UZ, United Kingdom Tel: 0300 3020 150 Tel: +44 161 746 5858 (from outside the UK) Fax: 0300 3020 160 email: website:info@pita.co.ukwww.pita.co.uk
RepresentativeEuropean Nicolas Pelletier 16RNPRue Bannier – 45000 Orleans, France Tel: +33 6 82 25 12 06 Fax: +33 2 38 42 29 10 email: europe@pita.co.uk
copyrights
SECTORInJune,after a break of three years, the CPI Health and Safety Event returned and was a triumphant success. Around 200 participants enjoyed the sumptuous surroundings of The Belfry in Royal Sutton Coldfield, and participated in numerous lectures, plenty of networking breaks and even a motivational magic show. The main theme, hammered home time and again, starting with Berry Wiersum who is pictured on the front cover during his keynote address, is that successful Health and Safety policies require strong backing from top management and open engagement with employees at all levels. The conference is summarised on pages 2527, and all presentation slides can be downloaded from the CPI website.
extracted, circulated,
Designed and typeset by Upstream Ltd, Deepcar, South Yorkshire Printed by Mixam Watford,UKHerts
contents
In conclusion, the current energy crisis is going to stimulate changes to the way we dry paper; but these are all going to take effect in the medium-to-long term. In the next year or two, noth ing apart from Governmental support will be available to any in tensive energy user sectors. So in the short term mills will have to struggle on, and some are already taking extended downtime in the hope that things will change sometime soon.
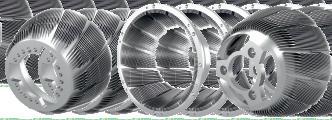
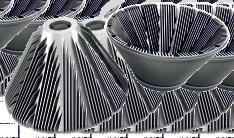

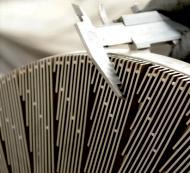
Although steam can be produced by electrical heating, it tends to be far too expensive and so commercial users prefer direct heat produced by burning fuel. Not so long ago coal was com mon, but this has been displaced by cleaner fuels: natural gas (though this is subject to the current price hikes because Russia is a major supplier); biomass (our industry is one of the biggest users in Europe); and more recently, energy-from-waste or refuse-derived fuel. All of these fuels have a similar drawback; they all contain carboniferous materials so release carbon dioxide upon combus tion, and since going forwards we need to reduce absolute levels of CO2 in the atmosphere, continuing combustion of carbonif erous material will require use of Carbon Capture and Stor age (CCS). This is why Drax, by far the biggest burner of biomass in the UK, has re cently undertaken studies on CCS at its huge plant hear Selby.What is done on the largest of plants will eventually have to filter down and be em braced by smaller power plants. To this end, Andritz has recently sold a carbon capture plant, based on amine technology, to a German ce ment manufacturer based in Rohrdorf. But remember: CCS is itself energy intensive, and tends to reduce energy ef ficiency of power plants by aroundHydrogen15%. is mooted as a possible fuel of the future for those requiring combustion pro cesses, and unlike all fuels covered to date, it does not give off CO2 when burnt – just water. However, you never get anything for nothing! Production of hydrogen is itself energy intensive; hydrogen has a nasty habit of causing embrittlement of metals, so the pipelines through which it is pumped will need lining; and while it has twice the energy density of natural gas, boilers will need to be modified to run with this fuel. CEPI ran an interesting webinar on this subject recently, but it is still over decade in the future before it will be usable commercially.
Daven Chamberlain
When Shakespeare wrote this line he was not thinking about our current economic climate, but there is no doubt that it is apt. Not since 1978/9 have we approached a winter period in such dire circumstances: rising inflation alongside industrial unrest –only in 2022 we have the added frisson of war in Europe. Being an energy intensive sector, paper manufacturing is bearing the brunt of the current swing in international energy markets. Unfortunately for UK industry, there is no price cap, so companies have experienced rises of several hundred percent, with no sign in the short term of any stability. With such volatility in the market, short term it will be up to Government to provide aid, and we wait to see how this will be apportioned between in dividuals and industry. But thinking longer term, our industry has to consider how in particular it can cover its heat requirements. Steam has been the preferred method of drying since 1821, when T.B. Crompton patented his steam-heated cylinders. To date we have over two centuries accumulated knowledge about steam: its properties, control, pressurisation etc. are all well-defined. As such, the in dustry as a whole will want to continue its use while ever we produce paper by dispersing fibres in water. (Other fluids, in cluding air and foam, have been tried, but water remains favourite, and is certain to for decades to come.)
Comment
Ammonia is another possible fuel, although here the CO2 emissions would be replaced by water and NOx – so a capture and disposal system would still be needed.
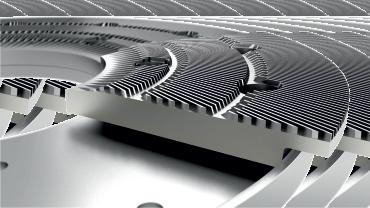
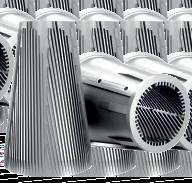
Now is the winter of our discontent
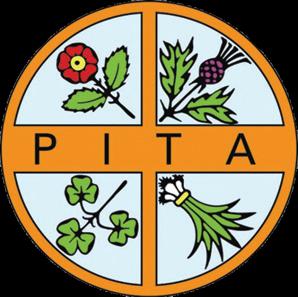
Small modular nuclear reactors provide an interesting option, because they would offer the condensing thermal load required for low pressure steam production. But currently these plants are still on the drawing board, and at a predicted cost of £Bn, are not a cheapFinally,option.although I have focussed mainly upon combustion processes for heat production, it is worth noting the recent de velopment from Toscotec of TT Induction STD where the steam / condensate removal systems are entirely replaced by an induc tion system composed of static coils installed inside the steel Yankee shell. Electricity can then be supplied from renewable sources to dry tissue. This development was only announced in June, and we still await the first report of an installation.
2
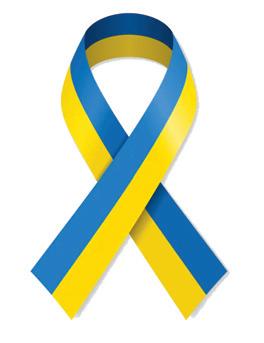
ABB— Ability™ Manufacturing Execution System for Pulp and Paper Real-time transparency for easier decision-making
Evolving market demands require agility and efficiency for mills to deliver products on spec and on time. Trust ABB and our MES specifically designed for pulp and paper to help you deliver the best operational results. Our comprehensive and modular solution covers all the core MES functionalities across the value chain, helping you achieve new levels of operational efficiency. Learn more: abb.com/pulpandpaper

Austrian cartonboard and folding cartons giant MayrMelnhof has acquired Essentra Packaging, a speciality packag ing manufacturer focussed mainly on the pharmaceutical and beauty sectors. Essentra Packaging has over 20 manufacturing sites in 10 countries in Europe and North America, including Ban gor (Co. Down), Bradford, Newmarket and Newport in the UK, and Dublin, Cork and Glasnevin in Ireland. The company was founded in 1911 and is headquartered in Nottingham, UK. After over a year of transformative investment, the upgrade of the Medite Smartply OSB factory in County Waterford has been completed. The company has been supplying OSB to the con struction industry for more than 25 years and the most recent in vestment has been targeted at upgrading the drying, energy and screening facility. In particular, the construction of the biomass energy plant ensures that Smartply will operate on 100% renew able biomass material for process drying and heating. In late July Portals announced plans to close their historic Overton Mill in Hampshire. Despite completing a £20M upgrade of PM1 just two years’ ago, the company blame this decision on events following the global pandemic and other recent world events, all of which had an adverse impact on their banknote paper business. However, the company remain upbeat about the prospects for both their security paper business at Bathford, Som erset and those of their security features business in Milan, Italy, who are not facing the same challenges.
Kendal based papermaker, James Cropper, has launched The James Cropper Colour Academy. The two-year educational pro gramme has been designed by in-house specialists to develop colour technicians with unrivalled colour knowledge and exper tise. Blending technical and colour skill within the business, the Academy aims to build on the prestige paper innovator’s reputa tion for world-renowned colour expertise. Addressing the issue of succession planning, the Academy will ensure cross pollination of skills and resources between the papermaker’s colour lab and its colour blending team. Its on-site colour lab holds around 2,000 live shades with some 200,000 colours stored electronically.
The year 2022 marks Saica’s 10 year partnership with Valmet Global, who have supported the company in establishing their PM11 site in Manchester by using technology to enhance effi ciency & reduce the amount of water & electricity used. PM11, winder and main automation system (DCS) were supplied as part of the project by Metso Paper (now Valmet). The mill started up in January 2012 and exceeded all start up curve expectations. Since then, Valmet has remained supportive in several areas: speed development, efficiency development, electricity and water reduc tion, training and giving Saica paper making experts that have been working on similar type of machines all around the world.
UK & EIRE NEWS Built environment consultancy Arup has been selected to lead the transformation of the Shotton Paper Mill in Deeside, North Wales, by the site’s owner Eren Holdings. Arup announced that the converted facility will produce ‘up to 750,000 tonnes of card board each year’, as well as holding the capacity to recycle ‘all waste paper generated in Wales’. The redevelopment, also involv ing architects AHR, is expected to bring in £600 million to the local area, creating 660 new jobs. The site is expected to be fully operational by 2024, with the Arup-led team providing project management, design and engineering expertise for its final phase.
Encore Packaging Solutions, part of the Encore Group, has invested in a fourth Bobst machine as it aims to accelerate growth in the market. The company took delivery of a new Expertfold 110 A2; the new folder-gluer complements other Bobst equipment at the company’s Peterlee site in County Durham, which includes two die-cutters, Novacut 106 ER and Novacut 106 E, plus another folder-gluer, Visionfold 110 A2 and Handypick GT. The company produces cartons for the food, retail, medical and healthcare, and e-commerceNorthumberlandsectors.toilet roll manufacturer Essity has unveiled plans for a new multimillion-pound paper recycling plant. The Essity base at Prudhoe Mill is keen to reduce its dependence on virgin wood fibre, having seen supplies of waste paper drop dra matically in recent years in the wake of technology advancements and offices switching to hybrid or homeworking. Now the com pany is planning to replace its 50-year-old recycling plant with a new building believed to represent an investment of more than £30M. It will house the latest in recycling technology that will reduce energy costs and increase the company’s ability to make new products from recycled fibre. A planning application for the multimillion-pound investment has been submitted to Northum berland County Council – with a decision expected this year.
Danish Technological Institute has collaborated with Scot tish-based CelluComp to develop a fibre-based material made sugar beet. The new development consists of microfibrilated cel lulose from sugar beet and a newly developed coating that is said to block oxygen, water, and fat. Christian Kemp-Griffin, chief ex ecutive of CelluComp added: “We have developed a method for extracting micron-sized platelets from the sugar beet pulp (a coproduct stream from sugar production), which we call Curran. After this process, we produce a product that is in granular form – similar to grated cheese. Curran is particularly suitable for paper-based packaging because it makes the packaging signifi cantly stronger and closes the porosity of the sheet, enabling the application of water-based barrier coatings.”
4 PAPER TECHNOLOGY SPRING 2016 MONOTIER®: THE MILLION-TONNE DRYER FABRIC Industry News
Runtech Systems has received a repeat order from DS Smith Paper Ltd, Kemsley Mill, for a RunEco vacuum system rebuild on PM4. In the rebuild, existing liquid ring pumps will be re placed by four EP600 Turbo Blowers. Delivery also includes de tailed engineering, EcoDrop and EcoSep water separators. With the rebuild, PM4 targets significant energy savings and reduction in CO2 emissions. Ben Jennings, Mill Manager at DS Smith said: “We’ve had a successful collaboration with Runtech Systems in improving the energy efficiency of our PM6 and PM3, and we are looking forward to now achieving great results with PM4.”
Corrugated packaging manufacturer BoxWay Packaging Group has laid out its upcoming plans, including a strategic re structuring exercise that could see one of its sites close as well as investment in new kit. The business was established just over a year ago after Saica Group sold its sheet plants in Peterlee, Telford, and Exeter. But in a new statement the firm said it has concluded that the Telford plant “does not have the right cost structure, asset base or infrastructure”; as a result, the business has commenced a 30-day consultation with 18 employees at the Telford plant, which could lead to a proposed closure of the fa cility at the end of September 2022.
The Smurfit Kappa mill in Birmingham was affected by a fire on 12 June that saw several thousand tonnes of OCC col
Valmet launched the Valmet Mobile Maintenance (VMM) application to make maintenance data available at any time and to create smoother workflows in mill maintenance operations.
VMM is a mobile application for both iOS and Android devices. The application is designed to streamline the maintenance per sonnel’s and production operators’ work. They can save time and improve work efficiency by creating fault notifications and re viewing work orders on the go. The application is part of Val met’s maintenance development and outsourcing services allowing customers to focus on their core business.
PITA CORPORATE SUPPLIER NEWS
Archroma launched two innovations: Cartaseal® VWAF, a PFC-free and ammonia-free barrier coating for odourless paperbased food packaging applications – the resulting barrier offers class-leading performance against the penetration of oils, fats, water and vapour; and a new grade in its Appretan® NTR range of waterbased polymeric binders based on renewable natural ingredients.
Stora Enso and Tetra Pak are jointly examining a shared beverage carton recycling solution to meet the growing recycling need in Benelux, responding to the demand for circular paperbased packaging solutions. The joint feasibility study includes a plan for a comprehensive beverage carton recycling facility at Stora Enso’s Langerbrugge site in Belgium. Processing of the fi bres would take place at the Langerbrugge site, while the poly mer and aluminium barrier materials would be recycled by a ded icated partner. Approximately 75,000 tonnes of beverage cartons are put on the Benelux market annually, a growing volume of which more than 70% is already collected for recycling. Cur rently, there is no existing beverage carton recycling infrastruc ture in Benelux. The joint study with Tetra Pak will follow the same timeline as the study to convert the newsprint machine to packaging. The proposed recycling line in Langerbrugge will ini tially process an estimated 50,000 tonnes of recycled cartons per year with the potential to increase.
BENELUX NEWS Mayer Group closed the De Vroede Enveloppen envelope production and printing plant in Nijlen, Belgium, on 30 June, as part of its realignment and consolidation strategy. The company was founded in 1996, and became part of the Mayer Group in 2012; it was profitable up to 2016, after which it has shown yearon-year losses ever since. FOLBB stopped production at the FBB mill in Eerbeek in mid-September to carry out upgrades to the machine. The com pany announced in May that it would replace the shoe press on the folding boxboard (FBB) machine in September; more re cently it announced the upgrade of the infrared installation used to dry the cartonboard, which is planned to yield approximately 5% saving on the use of natural gas. Dutch solid board manufacturer Solidus Solutions is reacting to high costs and reduced demand for its products. The company announced it would curb its solid board output by 10% from Au gust until further notice. The company has a total capacity of 350,000tpy of solid board at its five plants. Stora Enso has started a feasibility study at its paper produc tion site in Langerbrugge, Belgium, for the conversion of a paper line into a high-volume recycled containerboard line. The mill currently has two paper lines in production, one for newsprint and one for supercalendared (SC) magazine paper. The feasibil ity study will focus on the conversion of the site’s newsprint paper line and is expected to be finalised in the first half of 2023. Depending on an investment decision, the converted line is ex pected to be in production during 2025. The annual capacity would be 700,000 tonnes of testliner and recycled fluting grades.
ABB has updated its KPM KC7 Microwave Consistency Transmitter portfolio with a larger flow-through sensor to fit pro cess pipes with a diameter of up to 16”, giving more customers the choice to measure the total consistency of mixed pulps with a flow-through sensor. The technology leader has also launched a redesigned insertion type with a new dual-plate sensor. Both of the device options will be used in the stock preparation area of mills, which feeds the wet end of the paper machine. The ap plication usage extends across paper, tissue, board and pulp pro ducers, from recycled pulping to end of machine stock preparation, and can even be used for municipal and industrial wastewater. KPM KC7 is particularly good for users of recycled raw material and pulp and paper mill teams that prefer to mea sure and control total consistency with microwave technology.
Valmet launched a new polyurethane roll cover, Valmet Press Roll Cover PL, for tissue machines. The roll cover’s wear-resis tant material and adaptive structure are developed to cope with the harsh operating conditions in tissue production, thus leading to longer lifetime of roll cover and energy savings. Compared to other cover products, Valmet Press Roll Cover PL is available with wider hardness range together with improved mechanical properties, from 5P&J to 50P&J. The adaptive roll cover struc ture of Valmet Press Roll Cover PL helps to achieve more uni form nip profiles and bulk savings.
5 PAPER TECHNOLOGY AUTUMN 2022 INDUSTRY NEWS lected for reuse destroyed. Subsequent work by the West Mid lands Fire Service has revealed that the huge blaze which was declared a major incident in Birmingham was started by coals from a disposable barbecue. WMFS fire investigators have li aised closely with West Midlands Police and said they are satis fied that the fire was started unintentionally. The person who dumped the foil barbecue tray in a skip marked ‘No Fires’ be lieved the charcoal in it had cooled enough not to be a fire risk; unfortunately the contents of the skip caught fire, and the flames spread quickly to the Smurfit Kappa site a few metres away. In May, the UK’s Competition and Markets Authority reported that the proposed merger of Veolia and Suez in the UK would “lead to a loss of competition”, and, subject to further discussion, it recommended that Veolia should either sell off Suez UK or even sell Veolia UK to ensure there is sufficient competition in the UK’s waste and recycling marketplace. More recently Veolia announced an agreement whereby Macquarie Asset Management irrevoca bly undertakes to acquire 100% of the share capital of Suez Re cycling and Recovery UK Group, effectively regrouping Suez waste activities in the UK. Zeus, the Irish-owned global packaging solutions company, has announced the acquisition of two UK packaging companies, Swan line Group and its sister company BoxMart. Established in 2001, Swanline Group is headquartered in Stone, Staffordshire, and has four purpose-built sites housing large format infrastructure, screen and digital printing and converting operations, as well as extensive warehousing and distribution capabilities. BoxMart is an awardwinning packaging supplier based in Shenstone, Staffordshire, of fering UK-made gift, retail and ecommerce packaging.
As part of services offering for tissue producers, Valmet has developed a service agreement to improve the performance and safety of the Yankee cylinder, hood, and air system. The new agreement offers a systematic approach to improve the perfor mance of the dryer section – its safety, reliability, availability, and energy consumption. Every agreement starts with a complete condition check and energy study; the rest can be tailored to the customer’s needs by adding the right combination of services, such as Valmet Industrial Internet solutions, remote support through Valmet Performance Center, improvement plans and maintenance guidance.
Smurfit Kappa has completed a large-scale sustainability project at its Zülpich paper mill in Germany. The in vestment included a major redesign of the plant’s multi-fuel boiler to provide a more sustainable fuel source (biogas, natural gas and rejects from the recycling plant)
HEALTH & SAFETY EUROPE - EASTERN EUROPE - WESTERN Bytes
Papierfabrik Adolf Jass Schwarza has successfully integrated ABB’s latest L&W Autoline automatic testing solution into its production process, largely replac ing manual laboratory measurements.
Fires occurred at: DS Smith Lucca Mill, Italy, in the recovered paper yard; Georgia-Pacific Corporation Zachary, Louisiana, USA; Greif Packaging Ser vices, LLC, Riverville Mill; Interna tional Paper, Newport Containerboard Mill in Vermillion County, USA; Louisiana- Pacific OSB plant, Thomasville, Alabama, USA, in a pile of wood chips; McKinley Paper Company, Combined Locks Mill, in baled paper; Mercer International, Stendal pulp mill, Germany, in the wood chip storage area; Nine Dragons Paper Mill in Old Town, Maine; Ox Industries Paperboard Mill in Harper’s Ferry in West Virginia, USA; Smurfit Kappa, Neschells Mill, UK, in the raw materials yard; Twin Rivers, Mo hawk Valley Paper Mill in Little Falls, USA; Twin Rivers, Madawaska ME, on PM7; WestRock, Cedar Rapids Mill, Iowa, in machinery; WestRock, West Point Paper Mill, Virginia, USA, on a conveyor system carrying wood chips; Weyerhaeuser, lumber processing plant in Kenora, Ontario, Canada, in a dust col Globallector. supplier of carton packaging and filing systems Elopak has announced the sale of its Russian activities to a local management consortium, in a move sim ilar to that announced by Tetra Pak at end of PolishJuly.cardboard packaging maker Janmar Centrum has opened a new pro duction facility in Stryków, covering 7300 sq.m. Mondi is considering plans to strengthen its position with a new kraft paper machine at the Štětí mill in the Czech Republic, capacity 200ktpy. A final decision is expected in late 2022. Mondi plans to sell its Syktyvkar Mill in Russia to billionaire Viktor Kharitonin; the deal is conditional on approval by the Russian government and Mondi share holders, and would see Mondi exit the Russian market. Vajda-Papír has started a doublewidth tissue machine (capacity 80ktpy), supplied by Toscotec, at is Dunaföldvár facility in Hungary. Circa and Valmet have signed a Heads of Agreement to industrialise the production of sustainable bio-based solvents at Circa’s small-scale ReSolute plant in France, and in future large-scale produc tion plants. The bio-based solvents will replace harmful petroleum-based solvents used in a wide variety of industries. Bain Capital Private Equity has signed definitive documents with interna tional investment firm BC Partners to enter into a joint ownership agreement for Fedrigoni. The partnership, a combina tion of reinvestment by Bain Capital and investment from BC Partners, will result in a change of control of Fedrigoni to joint control between Bain Capital and BC Partners.Dutch manufacturer De Jong Packag ing Group has acquired a controlling stake in German corrugated manufacturer Wellpappenfabrik Grünstadt-Sausen heimDelkeskamp is to close Nortrup Mill in Germany due to high energy costs; the site produced around 135ktpy of con tainerboard. Drewsen Spezialpapiere has with drawn from envelope paper production, due to the expansion of the sustainable paper portfolio and the ongoing develop ment of technical speciality papers.
6 Mercer International Inc. announced that an independent contractor’s em ployee suffered a fatal workplace accident at their Peace River mill in Peace River, Alberta, while working during a mainte nanceThereshut.has been a fatal incident at the Kemi bioproduct mill site in Finland, op erated by Metsä Fibre; the accident took place at the installation site of the recov eryAboilerworker was killed at the Packaging Corporation of America site in Harmar Township, Pennsylvania; the third-party contractor died after being pinned be tween a trailer and a loading dock. Emergency services were called to the Pixelle Specialty Solutions mill in Stevens Point, Wisconsin, to deal with a spillage of sulphuric acid.
Kronospan is investing in a new man ufacturing facility of wood-based panels for the furniture industry in Tortosa, Cat alonia, Spain. The new factory will work with up to 100% recycled wood sourced from discarded end-of-life domestic fur niture. Mondi has agreed to acquire the Duino mill near Trieste, Italy, from the Burgo Group. Mondi plans to convert the single machine from LWC to recycled containerboard (420ktpy).
Two workers were injured at Weyer haeuser Kenora mill in Canada, while in specting a piece of equipment. The two workers later received medical treatment at the local hospital for minor injuries.
News
GD board manufacturer Reno de Medici has announced plans to expand its GD board production capacity by up to 200kt over the next 3 years. European de mand for GD board has been growing over the last 18 months, while production capacity for the grade has reduced in Eu rope, creating major tensions and an ob vious business opportunity. The company plans to expand capacity in their existing mills, including Blendecques in France, which is scheduled to restart early 2023.
Drewsen Spezialpapiere is investing in three wind turbines close to the plant in Lachendorf, Germany. With approxi mately 2,400MWh per year generated by the three turbines, the turbines will cover about one quarter of the mill’s external electricityGermandemand.speciality paper producer Feldmuehle announced that it will be switching fuel for steam generation from natural gas to light heating oil during Q4 of 2022. In the medium to long term, Feldmuehle will continue to pursue plans to make the mill CO2-neutral, including the use of wind energy, solar energy and geothermal energy playing key roles.
Sappi is planning to abandon the use of coal at its German site in Stockstadt, and will decommission the current coalfired Boiler 9, so the mill will be operated using only renewable biomass and natural gas.
Stora Enso is leasing the former paper machinery hall at its Veitsiluoto site in Finland to the textile technology company Infinited Fiber Company, which plans to build a commercial-scale factory to produce regenerated textile fibre from textile waste.
Suominen has strengthened its posi tion as a frontrunner in sustainable non wovens by launching Hydraspun Circula, the market’s first ever nonwoven made with recycled paper. Following the successful completion NORDIC
The groundwood line (capacity 64ktpy) in Rottneros Mill to be closed down by the end of the year, while capac ity is to be increased on the CTMP pro duction line, from today’s value of 120ktpy to at least 150ktpy.
The demo plant produces finished 3D fibre packaging products directly from wet pulp without intermediate phases; the moulded fibre-based packaging can replace plastic for example in food packaging.
7 PAPER TECHNOLOGY AUTUMN 2022 NEWS BYTES for the generation of steam and electricity. Sofidel has produced around 30kt of tissue using clean energy from the Al camo II onshore wind farm in Sicily, Italy, one year after signing a partnership agree ment with RWE Renewables, thanks to the four installed turbines with a total gen erating capacity of 13.6MW. Sonae Arauco has officially inaugu rated a state-of-the-art particleboard line at the Beeskow plant in Germany. Al though the particleboard line was already commissioned in July 2020, it was only possible to formally open the new produc tion facility recently due to the COVID19 pandemic. The start-up of the first plant in Beeskow dates back to 1966 and today the site produces a wide range of wood-based materials (PB, MDF and MFC – melamine faced chipboards). Sumapel in Toledo, Spain, has taken delivery of a sheeter to cut coated card board, supplied by Pasaban. UPM has signed an agreement to sell 100% of the shares of its Austrian sub sidiary UPM Kymmene-Austria GmbH to the Heinzel Group. The transaction in cludes the UPM Steyrermühl site, includ ing a newsprint paper machine with an annual capacity of 320ktpy and the Steyr ermühl sawmill operations with an annual timber capacity of 370,000 cubic metres. The purchaser is planning to convert the newsprint machine, along with a second machine UPM idled in 2017, to packag ing grades. Ahlstrom-Munksjö plans to change its business name to BillerudKorsnäsAhlstrom and the Norwegian forest owner group Viken Skog plan to establish production of bleached chemithermomechanical pulp (BCTMP) in Norway at Viken Skog’s Follum mill in Hønefoss. Viken Skog bought the mill after Norske Skog ceased paper produc tion in 2012. The site already has much of the infrastructure needed to establish a pulp production line and is in an area with competitive and sustainable wood supply and good transport to BillerudKorsnäs’ board mills. Mayr-Melnhof is to invest in two cross cutters at the Kotkamills site in Fin land.Operations at the 3D fibre product demo plant run by Metsä Group and Val met in Äänekoski, Finland, have begun.
Stora Enso and wood technology company Modvion are partnering to es tablish wood as the material of choice for wind turbine towers. Modvion builds wind turbine towers with laminated ve neer lumber (LVL), which proportionate to its weight is stronger than steel.
REGION +44 (0)845 301 info@axchem.co.uk6710 Axchem House 1 Red Hall Crescent Wakefield West Yorkshire WF1 2DF
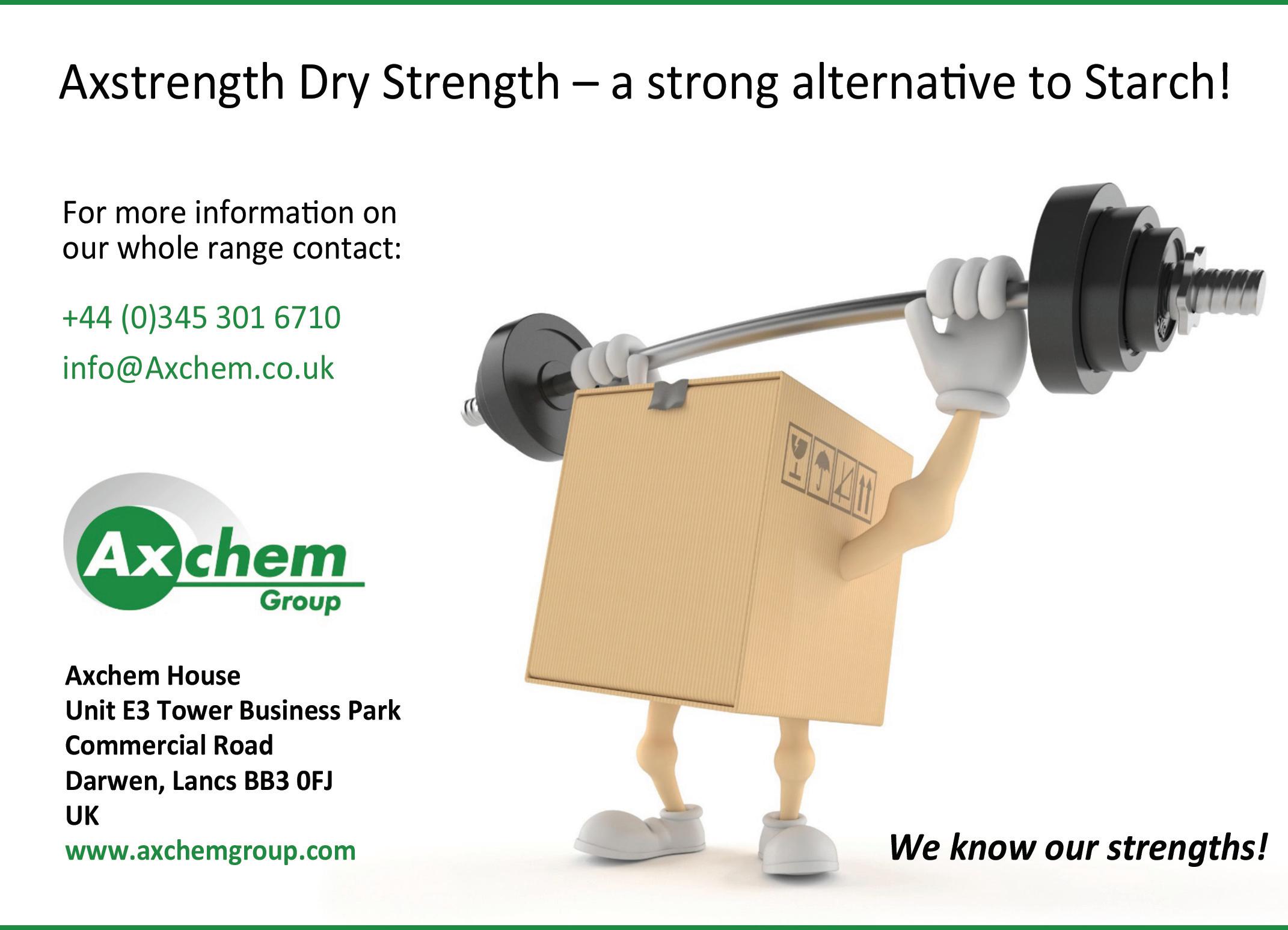
Total Fiber Recovery will construct an $80 million recycled pulp production facility in the city of Chesapeake, Vir ginia. The new facility and company is a joint venture between CellMark and Bulk Handling Systems, an affiliate of Total Fiber Recovery, and the ones who are furnishing the equipment for the facil ity.
The plant will be able to generate 50MW of electricity. Georgia-Pacific is expanding its Broadway mill in the state of Wisconsin. The investments will include building a new TAD tissue machine and adding as sociated converting equipment and infras tructure. Start-up is anticipated in 2024.
West Rock Company will acquire the remaining interest in Grupo Gondi, ex panding its geographical footprint in the NORTH / SOUTH
UPM is the first Finnish company, act ing as a shipper and charterer, to dis charge its ship-generated wastewater on land and utilise various circular economy solutions in wastewater treatment. The new model will be implemented in the ports of Rauma, Hamina, Kotka and Pietarsaari.
Ara Partners has acquired Genera Energy Inc, a manufacturer of non-wood agricultural pulp and moulded fibre prod ucts. Genera’s Vonore, Tennessee, pro duction facility is the largest vertically integrated non-wood agricultural pulp and moulded fibre manufacturing facility op erating in North America today. Chilean pulp and wood panel manu facturer Arauco is reported to have signed an agreement to build a new pulp mill in Brazil. The industrial plant, called the Sucuriu Project, will be constructed in the central-western state of Mato Grosso do Sul, and will have a capacity to process 2.5Mtpy of hardwood pulp. It is sched uled to start operating in early 2028. The conversion of PM9 at Cascades Bear Island paper mill in Ashland, Vir ginia, is progressing well. The idled newsprint machine is expected to be in production during Q1 2023, making con tainerboard (capacity 465ktpy).
AMERICA PAPER TECHNOLOGY AUTUMN 2022 NEWS BYTES
Walki, the innovative fibre-based packaging producer, has made a signifi cant investment in its Pietarsaari plant by purchasing a 10-colour flexographic printing press. The new press enables bet ter and more accurate printing, which is important particularly in the highly com petitive food industry.
N Ahlstrom-Munksjö is investing in new technology and converting its existing boilers at its Mosinee and Rhinelander plants in Wisconsin, United States, to re duce its carbon emissions and landfill waste.
8 of a 15-month commercial technology validation of a polymer-based barrier re placing the aluminium layer, Tetra Pak is now moving to the next level of devel opment – testing a fibre-based barrier that is a first within food carton packages dis tributed under ambient conditions. The aluminium layer currently used in food carton packages plays a critical role in en suring food safety; and even though it is thinner than a human hair, it contributes to a third of the green-house gas emis sions linked to base materials used by Tetra Pak. The trial with a plastic barrier commenced in Japan in 2020, and con firmed adequate oxygen protection for vegetable juice, while enabling increased recycling rates in a country where recy clers favour aluminium-free cartons.
The Dynos Group has acquired the major assets of the US manufacturer Ch eney Pulp and Paper, an important player for the processing of plant fibres on the international market. As part of this deal, the production of rags and linters in Bad Duerkheim in Germany has been ceased. Cheney has been active in the pulp and specialty paper market for over 75 years, and their site in the US state of Ohio will assume a central function in the supply of raw materials for the Dynos Group. Essity has acquired 80% of the Cana dian company Knix Wear Inc., a leading provider of leakproof apparel for periods and incontinence. Knix was founded in 2013 by CEO Joanna Griffiths with the mission to redefine intimates.
Vafos Pulp, a Norwegian producer of unbleached pulp for cardboard manufac turing, will switch its energy-intensive drying process from oil to electricity at the Kragerø pulp plant, capacity 80ktpy. The company will replace a 9MW oilfired boiler with electric heaters, con trolled by ABB technology.
Heinzel Holding GmbH and Paracel S.A. jointly announced that Heinzel has entered into an investment agreement to become the strategic equity investor in Paracel, an afforestation and pulp mill project in Paraguay, South America. Hood Container Corporation has ac quired the corrugated packaging business of Walker, MI based Kentwood Packag ing Inc. The transaction includes all of Kentwood’s design, manufacturing, as sembly, and fulfilment operations in Walker, including its membership in Great Lakes Wax Coatings, LLC Huhtamaki has broken ground on its expanded moulded fibre manufacturing capacity in the city of Hammond, Indiana, USA. North America. Kimberly-Clark is reported to be planning to sell tissue paper assets in Brazil and Latin America. Interested par ties are said to include Suzano SA, Nine Dragons Paper, Oji Holdings Corp, RGE and J&F Investimentos. Ontex group, Belgium’s leading inter national supplier of personal care prod ucts, is to sell its Mexican business activities to Softys, a personal hygiene company with operations across Latin America.British Columbia’s Paper Excellence Group is to buy Resolute Forest Prod ucts, which will continue to operate as a standalone entity. Resolute operates roughly 40 facilities in North America and will become a subsidiary of Domtar (Paper Excellence also purchased Domtar and its facilities in May of 2021.) In the wake of this deal, Domtar plans to sell their mills in both Dryden and Espanola to a third-party company due to antici pated regulatory requirements related to theThedeal. merger between SchweitzerMauduit International, Inc. and Neenah, Inc., which occurred earlier this year, has resulted in formation of a new company, named Mativ. Smurfit Kappa has upgraded its Nuevo Laredo sheet plant in Mexico to become a fully integrated corrugated plant. Suzano has announced plans to build a tissue mill with converting operations in the municipality of Aracruz, state of Es pírito Santo, Brazil, capacity 60ktpy.
Eldorado has issued a Final Accep tance Certificate to Andritz who supplied a biomass handling plant to the Onça Pin tada site in Três Lagoas, Mato Grosso do Sul, Brazil. This plant is part of the first thermoelectric power plant in Brazil to consume eucalyptus stumps and roots.
Georgia-Pacific plans to expand oper ations at its OSB mill in Clarendon County, South Carolina; the expansion is expected to be complete in 2023. GP Cellulose is investing to add fluff capacity at its Alabama River mill near Monroeville, Alabama. The Alabama River mill operates two lines, one cur rently producing only paper pulp bales. This investment upgrades production by adding the ability for this line to also pro duce fluff pulp rolls. Greif, a global leader in industrial packaging products and services, plans to expand existing operations in Greenville County, South Carolina. The mill utilises recycled paperboard for the production of spiral tubes and cores.
Solenis has closed on the acquisition of Neu Kimya Anonim Şirketi. Located in Istanbul, Turkey, Neu Kimya serves the heavy/light water treatment and oil and gas markets in Turkey, Southeast Europe and the Middle East.
The former Hindustan Newsprint mill in the south of India has been closed for more than three years; now, stateowned company Kerala Paper Products has restarted production.
Saur is to acquire MWS Europe (Mo bile Water Services division) from Veolia SKF and ABB have entered into a Memorandum of Understanding (MoU) to explore the possibilities for collabora tion in the automation of manufacturing processes.
ABB has signed a Memorandum of Understanding (MoU) agreement with ATS Global to extend the reach of the ABB AbilityTM Data Center Automation (DCA) business. Andritz has agreed to acquire the Bonetti Group, headquartered in Milan, Italy. Established in 1923, Bonetti is a global manufacturer and supplier of doc tor, creping and coater blades, as well as blade holders, and also provides services for paper machines.
Daio Paper has acquired all shares of Daiki Co. Ltd., a company manufacturing pet care products. Founded in 1984, Daiki is an OEM manufacturer and distributor of paper pellets cat litter, and already has 40% market share in Japan. It manufac tures high-quality paper pellet cat litter by recycling out-of-specification products such as diapers, wallpaper and pulp-based nonwoven fabrics. It has two production facilities in Japan, with products supplied promptly to eastern Japan from the Mooka production site in Tochigi Prefecture and to western Japan from the Shikoku pro duction site in Kagawa Prefecture. Essity has acquired the Australian company Modibodi, a leading leakproof apparel company in Australia, New Zealand and UK. Modibodi, founded in 2013, provides leakproof items for periods and incontinence including underwear, swimwear, activewear and maternity wear.
Toscotec has launched TT Induction SYD, a carbon-reduction breakthrough that uses electrical induction instead of steam energy to dry the paper web, thereby cutting direct greenhouse gas emissions to zero. Valmet launched a new polyurethane roll cover, Valmet Press Roll Cover PL, for tissue machines.
APP Guangxi Jingui Pulp and Paper, Guangxi Province, China, has released the final acceptance certificate to Andritz for their upgrade of two P-RC APMP (PreConditioning Refiner Chemical Alkaline Peroxide Mechanical Pulp) fibrelines.
Andritz has established a new inline Wetlace CP pilot line with an original de sign at its centre of competence in Mont bonnot, France. The Montbonnot pilot line has been rebuilt to integrate the new headbox inside the spunlace line. Andritz has successfully implemented new processes and tools for equipping all of its automation solutions with a high level of cyber security, thanks to its part nership with leading OT provider Otorio Archroma launched Cartaseal® VWAF, a barrier coating for food packag ing applications, and a new grade in its Appretan® NTR range of water-based polymericMachinebinders.maker Bellmer is investing to expand its Works 3 site in Enzberg, Germany, by some 2100 sq.m. Set up in 1842, the company employs a workforce of more than 750 people at 16 facilities.
Sun Paper (Guangxi Sun Paper) in Beihai, China, has successfully started up key pulping process equipment supplied by Andritz at their new pulp mill. In ad dition, Sun Paper has implemented the ABB AbilityTM DCS at the Beihai site.
Sulzer has decided to initiate the pro cess of exiting the Russian market and the closing of the Polish businesses, and the company has decided to write off most of its assets in both countries.
Toscotec has launched INGENIA, its new concept machine for a more sustain able premium quality structured tissue; INGENIA’s concept is based on consoli dated technologies for premium tissue, building on vast internal know-how of Toscotec’s and Voith’s R&D, and field data validation on TAD and structured paper systems.
Shanxi Qiangwei Paper in Jinzhong, in the central Chinese province of Shanxi, has started PM6, a 7m machine producing containerboard and plasterboard liner supplied by Voith Smurfit Kappa is to construct a new packaging plant in Rabat, Morocco, its first corrugated plant in the country.
REST OF WORLD SUPPLIERS PAPER TECHNOLOGY AUTUMN 2022 NEWS BYTES
Nippon Paper Industries Co., Ltd has established a new local subsidiary in Australia to further strengthen the liquid packaging carton business and facilitate global business expansion. Nippon Paper signed a license agreement covering the Oceania region with Elopak ASA, a global supplier of liquid packaging. Rengo Co., Ltd. has established a new plant in the Kanazu mill in Japan, to in crease production of “Viscopearl,” a spherical cellulose microbead manufac tured from wood pulp. This will be of fered as an alternative to microplastic beads used in a wide range of fields, such as additives for resins and inks and as abrasives, and in cosmetics.
9 attractive Latin American market. Grupo Gondi operates four paper mills, nine cor rugated packaging plants and six high graphic plants throughout Mexico.
BTG announced that all sensors are now supplied with the bCONNECT™ module, permitting them to be virtually connected and attaining all the benefits of IndustrySwedish4.0.software company FrontWay and Finnish Company Nipman have signed an agreement allowing Nipman to sell the FrontWay simulation software concept for the pulp and paper industry. Previously, FrontWay has built models and developed solutions for chemical pulping, TMP, Waste Paper, Board Ma chines, Paper Machine and Tissue. IPA and Aquapak Polymers have an nounced a collaboration to create new material packaging solutions ‘fit for the circular economy’. The two companies are working on research-led material where there are currently no workable al ternatives – the newest solution coming up is a high barrier and PVDC-free com postable film for packaging.
Valmet launched their new Dryer Sec tion Performance Agreement for tissue machines. Valmet is to invest in a new preneedling line and a new needling line at its press felt manufacturing facilities in Tampere, Finland. Voith and its wholly owned subsidiary BTG are merging their product portfolios. The two established data platforms, Voith’s OnCumulus and BTG’s data PARC, will be merged into an integrated, hybrid system solution. OnCumulus will henceforth be offered under the name dat aPARC cloud, while BTG’s MACS ad vanced process control solutions will join the OnEfficiency product family.
Valmet launched Valmet Mobile Maintenance (VMM) application to make maintenance data available at any time and to create smoother workflows in mill maintenance operations.
ABB has updated its KPM KC7 Mi crowave Consistency Transmitter portfo lio, giving more customers the choice to measure the total consistency of mixed pulps with a flow-through sensor.
Woodyard conveyor system
The arms of the ring debarker suffer severe abrasive wear under high pressure. Previous solutions to improve wear life used carbide-brazed segments but proved unreliable, with lifetimes as short as only three days. A high resistance to cutting under pres sure was achieved by applying two layers of protective Castolin Eutectic welding with a final hard coating. A reliable service life of three months is now possible.
Martin Kirchgassner, Vice President and Chief Technology Officer of Castolin Eutectic 1. Drum debarker.
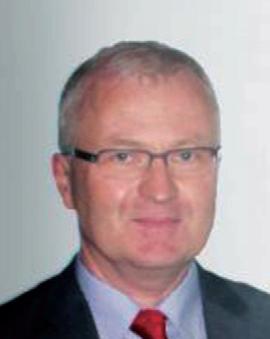
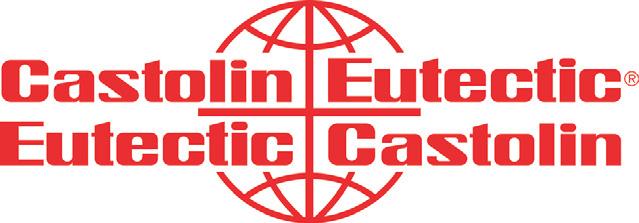
Sustainable wear protection solutions cut downtime for pulp and paper plant
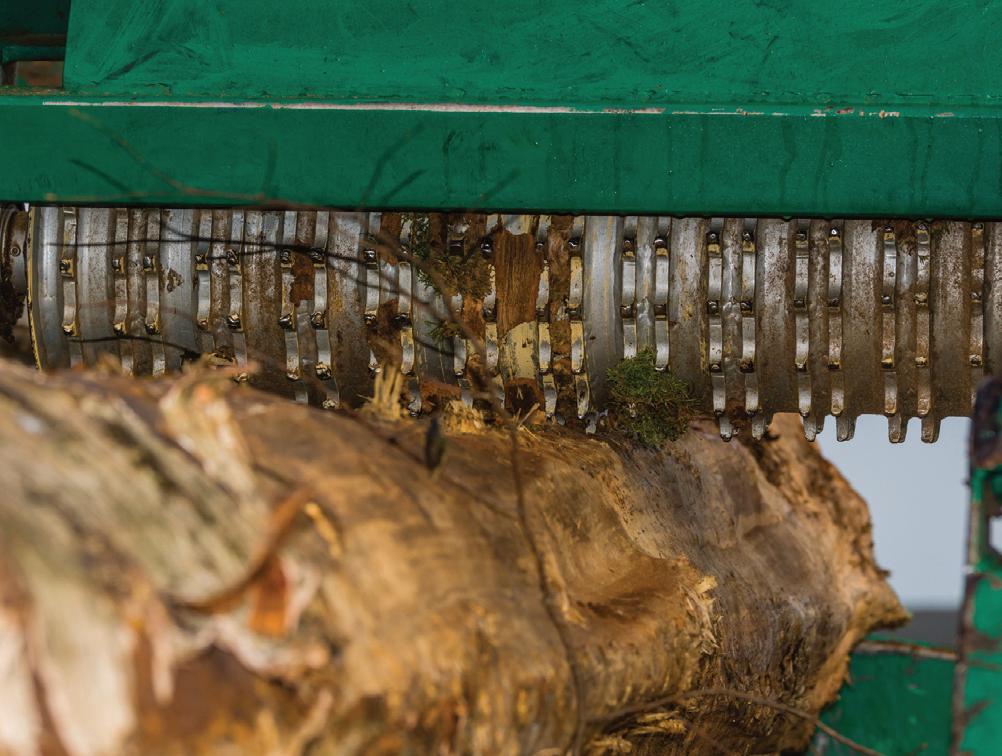
Figure
Pulp and paper machinery is subject to various different types of wear such as abrasion, impact, erosion, fatigue, corrosion, heat and combinations of these. Since 1906, Castolin Eutectic has been developing and applying innovative wear solutions for all aspects of the process from the woodyard through to mill ser vices. This approach is integral to its philosophy of Pioneering Industrial Sustainability, since when critical equipment functions optimally, it consumes less energy. Therefore, wear protection can not only help pulp and paper operators to boost productivity, it can also help improve energy efficiency and reduce their CO2 footprint.Thisarticle outlines the practical advantages of wear protec tion in key processes throughout the pulp and paper production process.
The links of the chain itself wear smooth on top from abrasion which causes log slippage on the conveyor. It is much worse in the winter when there is frost and ice on the logs. This can be addressed by coating each link with a fusible alloy that blends coarsely-sized tungsten carbide and nickel-base alloy powder. The result is a hard, wear-resistant coating that is ideal when a gripping, non-skid surface is required. This solution is known to last for over five years with no sign of wear or lack of traction.
Chipping After debarking the logs are reduced to chips suitable for the subsequent pulping operations. Several designs of chippers are used, the most common being the flywheel-type disc with a se ries of blades mounted radially along the face. Chippers operate at high duty cycles and are subject to high abrasive wear from theThelogs.primary disc chipper in the woodyard requires a very thorough and efficient maintenance program because of the ex tended operating cycles. Major wear is experienced on the chip per knives and the area immediately behind them. Sliding friction and abrasion from the logs wears down the bed knife face. This results in a larger wood chip size which requires rechipping and therefore higher energy consumption. Most mills use rebuilt chipper parts from the chipper manufacturer or an in dependent workshop. At one site, issues were encountered with the chipper log10
Debarking Log debarking is necessary to ensure that the wood chips will be free of bark and dirt. Several types of mechanical debarkers are used as well as hydraulic debarkers. The ring debarker is used on individual logs, usually in the woodyard, as it is portable. The drum debarker (Figure 1) is the most common type of mechan ical debarker and is available in a number of design variations.
Mulching
The conveyor chain sprocket is a key element in the wood yard conveyor system. The teeth on the sprocket are subjected to high levels of wear from loose bark, dirt, and sand. Conveyor downtime is very costly as chip production is stopped. Building up the teeth with two different layers of welding wire, a base layer selected for impact resistance while top layer provides abrasion resistance, will reduce wear significantly. However, it is important to ensure that the overlay is softer than the chain to avoid wear on the chain. This solution can extend the wear life of the chain sprocket by 200%.
The lumber and paper industries use the bark and wood waste from debarking in several ways. Lumber mills will utilise the ma terial as a fuel to produce steam for operating kilns to dry green lumber. Others set up bark mulching plants to process and package the waste to be used for horticulture as well as a filler in building board. The paper mills process the bark and use it in bark-burning boilers for mill steam. Bark preparation uses hammermills, con veyors, feed screws, and fans. All of this equipment is subject to wear from the abrasive action of the bark and wood waste. Some sites use hog shredders, where the hammer tips take most of the wear from shredding bark and wood. Foreign mate rial like nails, wire etc. cause additional wear. Rebuilding the tips with welding and coating with powder can increase tip life by over Other100%.installations with bark crushing machines experience rapid wear on the ejection strip installed at the exit. It wears quickly due to the high abrasion and erosion. In one case, replac ing the original plate manufactured from wear-resistant steel with a CDP® (CastoDur Diamond Plate) solution based on composite bi-metallic materials has increased the service life by 200%.
feeding spout that both guides and holds the logs during the cutting operation. The original had been factory-coated with cobalt alloy but had to be scrapped after one year of operation. Now with a preventive weld overlay coating, the service life has increased to three years. A “softer” alloy was selected because the opera tor was concerned that a hard brittle coating could break off and enter the chipper.
11 PAPER TECHNOLOGY AUTUMN 2022 SUSTAINABLE WEAR PROTECTION SOLUTIONS
Fan rotors also suffer from severe erosive wear due to the mixture of wood, sand and dust in the air stream (Figure 4). This results in costly down-time for each repair, as it has to be taken apart with a crane. For one repair, where the wear was found to be very localised, tailor-made CDP wearplate strips were cut and formed to suit. These were then quickly and easily welded to the fan. The joints were overlaid with protec tive welding. After two years, no signs of wear had occurred, confirming a very significant in crease in the fan’s working life.
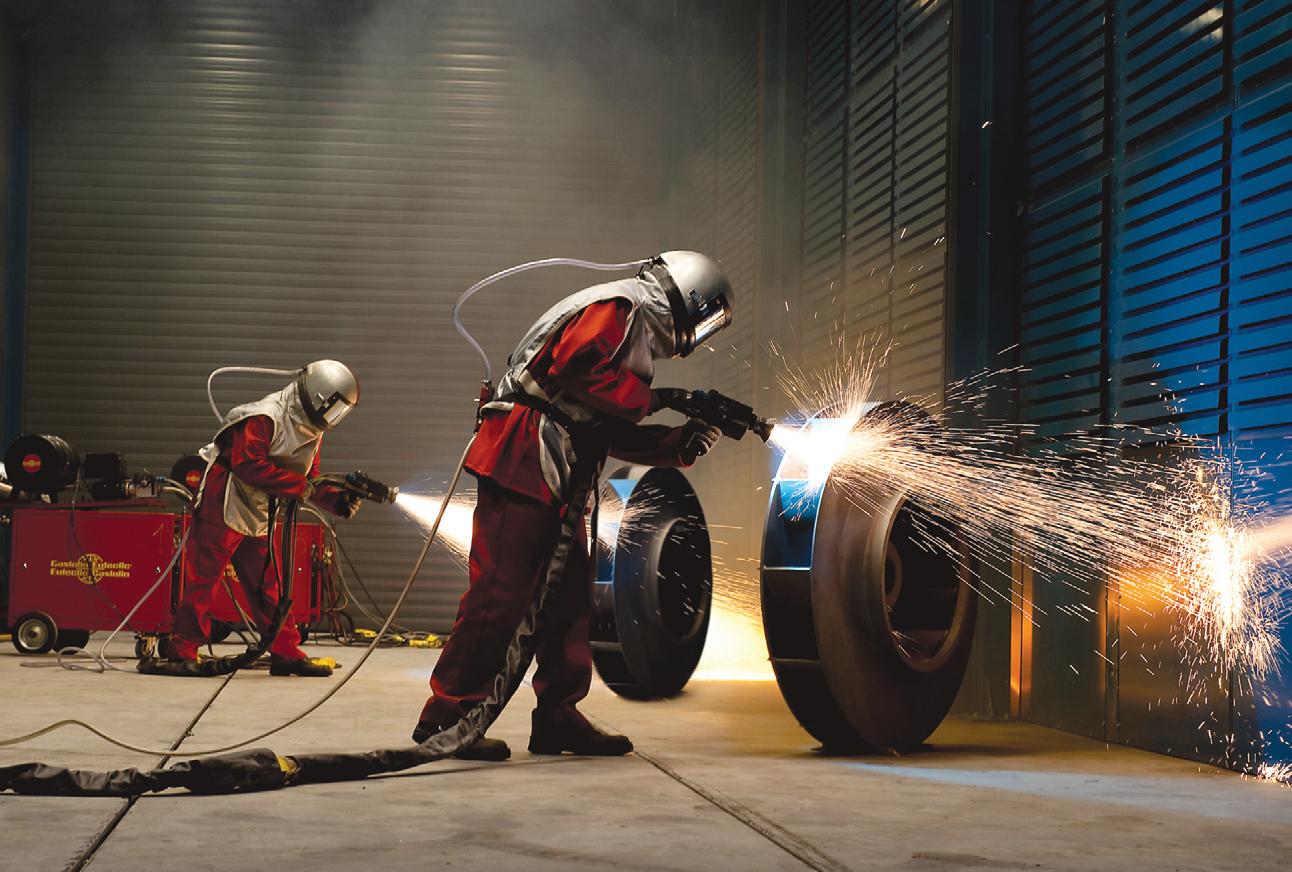
Chip transfer and cyclones Within mills, chips are commonly trans ported either pneumatically within pipes or on conveyor belts. Other systems such as chain and screw conveyors (Figure 2) are also used to move chips, but usually for relatively short distances.Inone case, strong erosion was found on a lifting tube situated on the exit of the chipper to the cyclone. Although wear-resistant steel had been used, a customer had found the unit failed prematurely. A replacement was manu factured from new using CDP wear plate (Fig ure 3). The outer side edges were reinforced with an iron profile and welded with a spe cially selected wire. The internal weld seams were also hard surfaced with welding wire. The result was a 400% increase in service life.
Figure 3. Screw reinforced with CDP wearplate. Figure 4. Fans refurbished by arc spray. Figure 2. Repairing a screw conveyor.
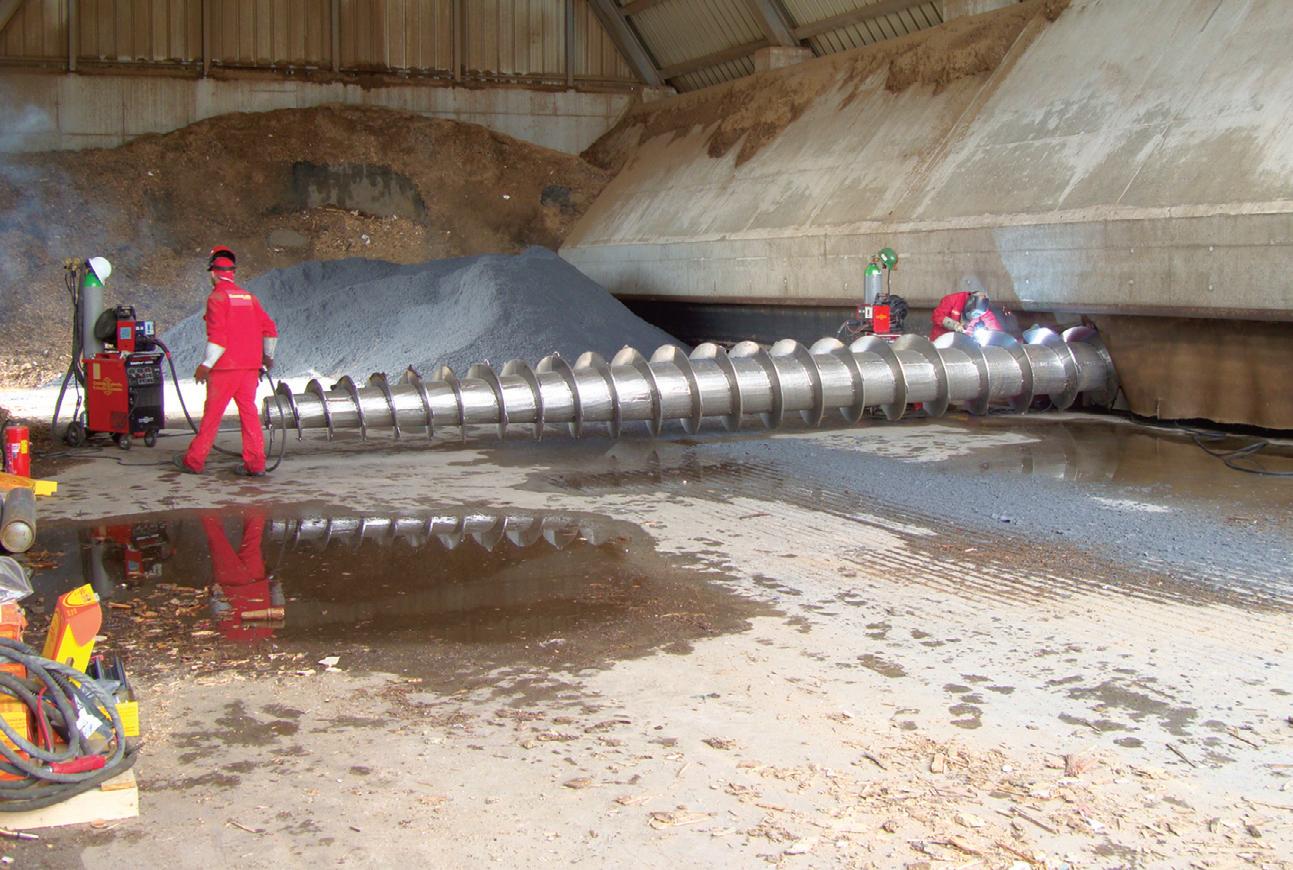
Considerable erosion wear also occurs in cyclones which separate air from the wood and sawdust. To address this at one site, a complete cyclone was manufactured from CDP wear plate with parts plasma-cut and formed to the small diameter. The joints were welded with specially-selected electrodes and the weld seam protected with a welded overlay coating. The result was a service life increased by five times over the original manufactured in wearresistant steel. Screening and storage Chips of acceptable size must be isolated from undersized (fines) and oversized pieces by passing the chips over a series of screens. The oversized chips are rejected to a conveyor, which carries them to some type of rechipper for reduction to a smaller size. In recent years, chip thickness has come to be recognised as an important pulping variable and modern disctype or roll-type screens, which segregate ac cording to thickness, are now widely accepted as the industry standard. This means that wear must be minimised in order to maintain the ac
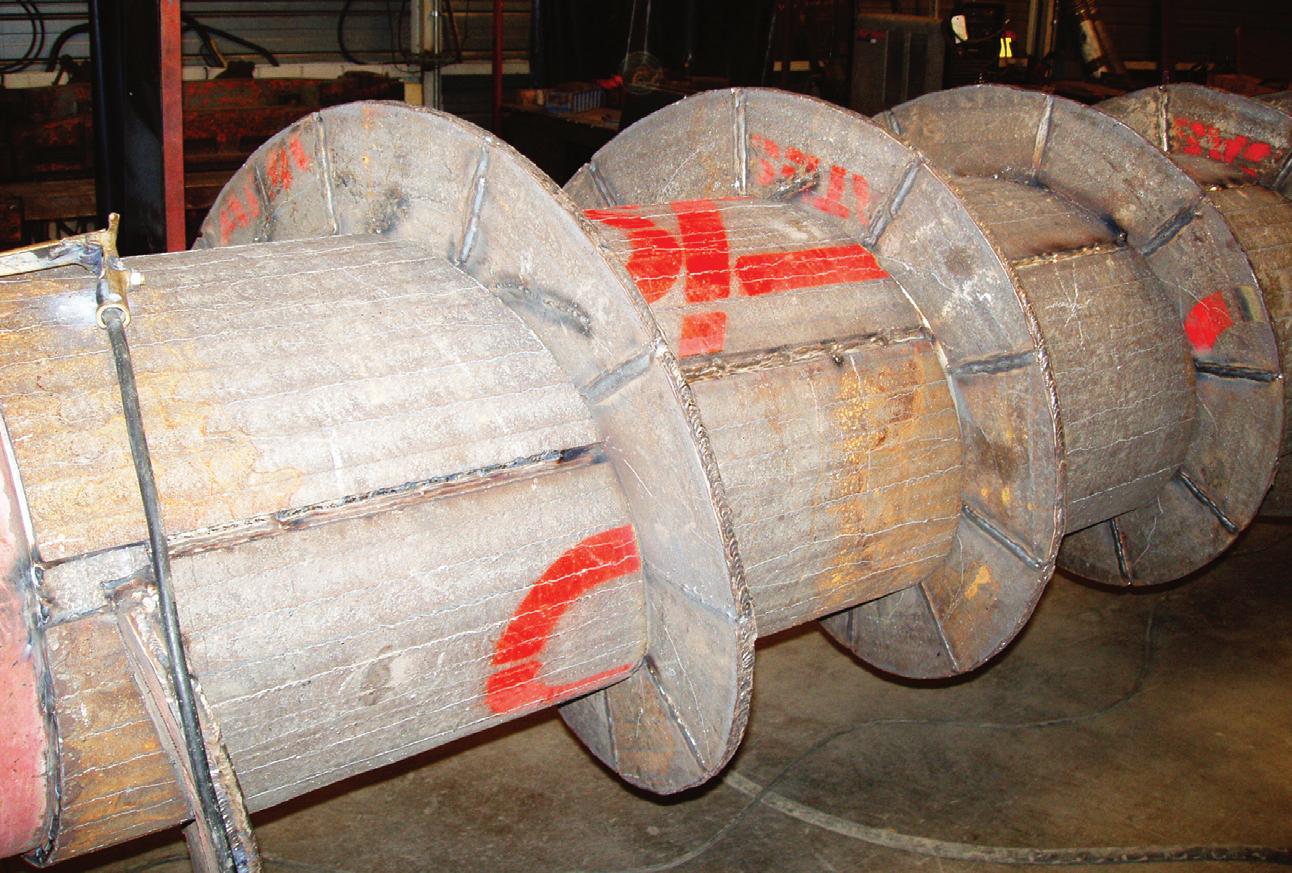
Corrosion and metal fatigue cause the washer screens to break and crack. Previously, this component would have to be scrapped, with the associated dismantling and replacement costs.
Bleaching Modern bleaching is achieved through a continuous sequence of process stages utilising different chemicals and conditions in each stage, usually with washing between stages. Washers and pumps in the bleaching operation must be made from high-alloy stainless steels, nickel alloys and titanium. Controlling chemical corrosion in the bleaching equipment is an ongoing problem.
Processing In most pulp and paper processes, some type of stock screen ing operation is required to remove oversized, troublesome and unwanted particles from good papermaking fibres. The major types of stock screens are vibratory, gravity centrifugal, and pres sure (centrifugal or centripetal). They all depend on some form of perforated barrier to pass acceptable fibres and reject the un wanted material. Further preparation of the pulp stock is refining of the fibres. Two major types of continuous refiners are used for stock preparation: disc refiners and conical refiners. In ad dition, efficient movement of stock through the various process ing steps is at the heart of a pulp and paper mill operation. No mill can operate successfully without reliable pumping units.
Scrap paper and cardboard
Figure 5. Wear on an impeller.
Many pulp and paper mills use recycled paper and cardboard as another source for papermaking pulp. Some mills operate with only recycled materials. The scrap is fed into a hydrapulper, which is a vertical tub with a revolving rotor in the bottom. Paper and cardboard with water are shredded by the rotor into pulp and a perforated extraction plate under the rotor pulls the fibres out of the vessel. Further cleaning and de-flaking of the pulp pre pares it for papermaking. The rotor in the hydrapulper is sub jected to high wear from the wastepaper as well as foreign materials such as stones and scrap metal. In one case repair was required on the impeller at the bottom of the tank. The production capacity decreases dramatically when the impeller is worn out (Figure 5). For the repair, critical areas were protected by welding with electrodes developed to offer combined protection against abrasion, pressure and mod erate impact. In addition to increasing the lifetime from 2 weeks to 5 months, the welding can be carried out three times to further reduce costs. Paper mill In the paper-making process the flowspreader takes the in coming pipeline stock flow and distributes it evenly across the machine. The pressurised headbox discharges a uniform jet onto 12
In another case, a pump housing suffered from numerous sur face cracks and cavities from the erosion and corrosion environ ment. A cold repair with a composite polymer gave a quick, simple repair and a smooth, corrosion and wear resistant coating with no modifications to the base metal. This had the advantages of speed, low coating thickness and smoothness and requires less skill to apply than the previous brazing rod solution.
A particular challenge is the refiner disk that suffers from stress corrosion cracking and wear at the transition area between the disk and cylinder. This can be repaired by sandblasting and then arc-spraying with a coating based on the nickel-chromium alloy 625. The coating can be machined and ground to the re quired dimensions and surface finish. The treatment is fast to apply and reduces the dangers of further stress corrosion crack ing, without causing distortion to the disk.
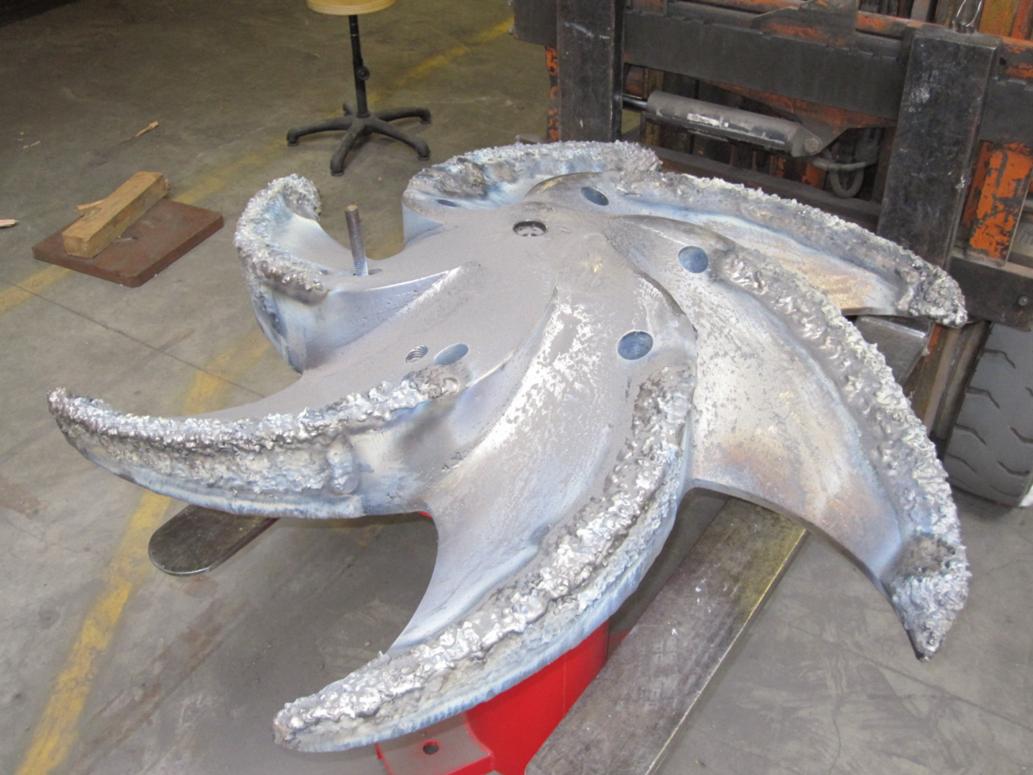
As an alternative, using a brazing rod with high silver content gives a quick and strong repair with its high tensile strength and low bonding temperature.
The cooked pulp from the digesters must be washed to re move residual liquor that would contaminate the pulp during subsequent processing steps and recover the maximum amount of spent chemicals with minimum dilution.
Pulping Pulping refers to any process by which wood is reduced to a fibrous mass. It can be accomplished mechanically, thermally, chemically, or by combinations of these treatments. The discharge elbow of batch digesters is subjected to severe corrosion, erosion, abrasion and thermal shock from cooking liquor, pulp and steam. In one example, worn areas in the elbow and piping were built up with welding electrodes developed for critically stressed areas. The faces of flanges were also overlaid in a similar way and machined to finish. This enabled wear life to be extended three times over that of the original elbow. The top screw transports wood chips through the liquor, mov ing within a sieve with a clearance of 0.5mm. Abrasion causes wear of the working edge of the screw. This can be repaired by rebuilding the base metal with a specially selected welding wire and machining it to the correct dimensions. A final protective powder coating is applied by the spray fusing process. The sub stantial increase in operating lifetime has resulted in this ap proach being adopted as the recommended repair procedure by the OEM.
PAPER TECHNOLOGY AUTUMN 2022 SUSTAINABLE WEAR PROTECTION SOLUTIONS
Washing
curacy of the screening operation. A chip screen separator has disks with points that wear from chip abrasion. Excessive wear would allow large chips to pass through to the digester. To rectify one worn unit, the surfaces of the points were ground and powder applied by a spray fusing process. This solution allowed an in-situ repair to be carried out, with no need to take the unit apart, remove the screen disk and replace it. Major costs savings resulted since downtime was re duced and there was no need to purchase a replacement part.
One challenge is found on the refiner shaft, where the stain less steel sleeve is worn by fretting from the collar bush that holds it in place; this wear is accelerated by corrosion. This can be solved by spraying the shaft with a torch-fused powder de veloped to prevent corrosion and reduce friction. The lifetime can be increased by 300% due to the superior hardness, corrosion resistance and sliding properties of the coating.
On one vacuum pump rotor, wear was found on the im peller, shaft sleeves and bearings, combined with erosion and cavitation wear to the cast iron body. The overhaul in volved a combination of welding electrodes to repair the cracked cast iron body, followed by the application of a composite poly mer coating to the exposed corrosion surfaces. The bronze im peller diameters were reclaimed using bronze welding wire. Finally, the soft packing sleeves and bearings were thermal sprayed with an alloy powder. This in-house solution was a lowcost alternative to replacement or external refurbishment.
On a kiln tyre, high pressures and contact stresses caused sur face cracking and the detachment of a large splinter. The exces sive cost of a replacement tyre and a lengthy downtime period resulted in the need for the splinter to be welded back on to the tyre. The traditional pre-heating was impractical due to the mass. A successful repair was made possible using low-heat welding electrodes and a tightly controlled procedure. Significant cost savings were achieved as no new part was required and the downtime was cut from 10 weeks to 2 weeks. Because the kiln rollers support the weight of the kiln they are subjected to large and cyclic compressive stresses. Over time, this can give rise to loss of material from the rolling surface in the form of “pitting” or splinters. Welding repair is difficult to perform in place due to the high stresses from the kiln weight and the need to maintain the roller’s exact circular dimensions. Welding with low-heat electrodes enables a successful repair to be performed in-situ, with the associated substantial saving in downtime costs. Repair and refurbishment often achieves better results than replacement The first instinct of maintenance teams in the pulp and paper industry is often to replace worn parts with brand new items. However, in this industry, continuity of operation is usually the primary concern. Therefore, repair and refurbishment can prove superior in many cases. As well as ensuring a faster return to ac tion, using the latest wearfacing technology can also significantly improve operational life, often several times over. The result is greater reliability, improved sustainability and the best possible total cost of ownership. For more information: https://www.castolin.com/pulp-and-paper
an endless moving fabric that forms the fibres into a con tinuous matted web while the table drains the water by suction force. (A properly designed and installed vacuum system is a vital component in a successful paper machine system.) The sheet is then conveyed through a series of roll presses where additional water is removed and the web structure is consolidated. Most of the remaining water is evaporated and fibre to fibre bonds are developed as the paper contacts a series of steam-heated cylinders in the dryer section. Finally, the sheet is calendered through a series of roll nips to reduce thickness and smooth the sur face. The dried, calendered sheet is wound onto a reel. An important area for repair is the rewinder roll that must have a gripping surface. Once wear occurs on the sur face, it becomes smooth and the paper starts to slip. This affects the paper quality and accuracy. The worn, polished surface can be restored with thermal powder spraying. As well as producing a very good gripping surface, this coat ing increases the wear life by over 200%.
In one case, a year after five cracks in a kiln shell had been repaired using a non-Castolin Eutectic procedure, a crack of 4.7m occurred, emanating from the heat affected zone (HAZ) of the previous weld. After determining the exact geometry and full extent of the crack, the repair was made with a low-heat input, high nickel-based alloy electrode, following a well-defined pro cedure. This repair held for six years before the shell was even tually replaced.
13 PAPER TECHNOLOGY AUTUMN 2022 SUSTAINABLE WEAR PROTECTION SOLUTIONS
Mill services
Figure 6. Lime kiln in a pulp mill.
Lime kilns
Mill services provide the support processes for the pulp and paper mill. The major areas are chemical recovery, lime kiln, power generation, and water and waste treatment. Each area is essential to the mill operation and requires a very active mainte nance program. The chemical recovery boiler and lime kiln are high maintenance areas and require joining and wear protection solutions. Thermal cycle-induced cracking in the lime kiln and corrosion of tubes in the chemical recovery boiler are typical problems.Reliable electrical power requires maintenance of steam and water turbines as well as the generators. Process control valves and pumps in power generation are constantly being rebuilt. Water and waste processing involves large centrifugal pumps, intake screens, vacuum filters, aeration pumps and piping. All must be maintained for continuous operation 24 hours a day.
One of the major challenges in the manufacturing of pulp has always been the maintenance and operating efficiency of the lime kilns (Figure 6) in the causticizing plant. These are large, round, fabricated steel tubes, of 4-6m in diameter, and between 45150m long. Since they are lined with fire-resistant refractory brick, constantly rotating on rollers (spaced approximately every 5m), and heated internally to 1450°C, they are susceptible to se rious operating and maintenance problems. The longer the kiln, the greater these problems can be, especially with respect to cracking and misalignment of the rollers. The kiln shell, however, does not run directly on the rollers. Around the kiln at each set of rollers, there is a large cast-steel tyre mounted around the kiln shell. The tyre is not actually at tached to the kiln shell; it is mounted on pads that are located around the shell and fixed in position by steel blocks, which are welded to the kiln shell. The tyre rotates with the kiln on the rollers. The kiln is rotated by a drive pinion that drives the kiln girth wheel. The lime mud, as it travels slowly down the kiln, is converted to pellets in the hot zone and continues to travel to the end of the kiln, where it eventually falls out over the nose casting into the lime coolers.
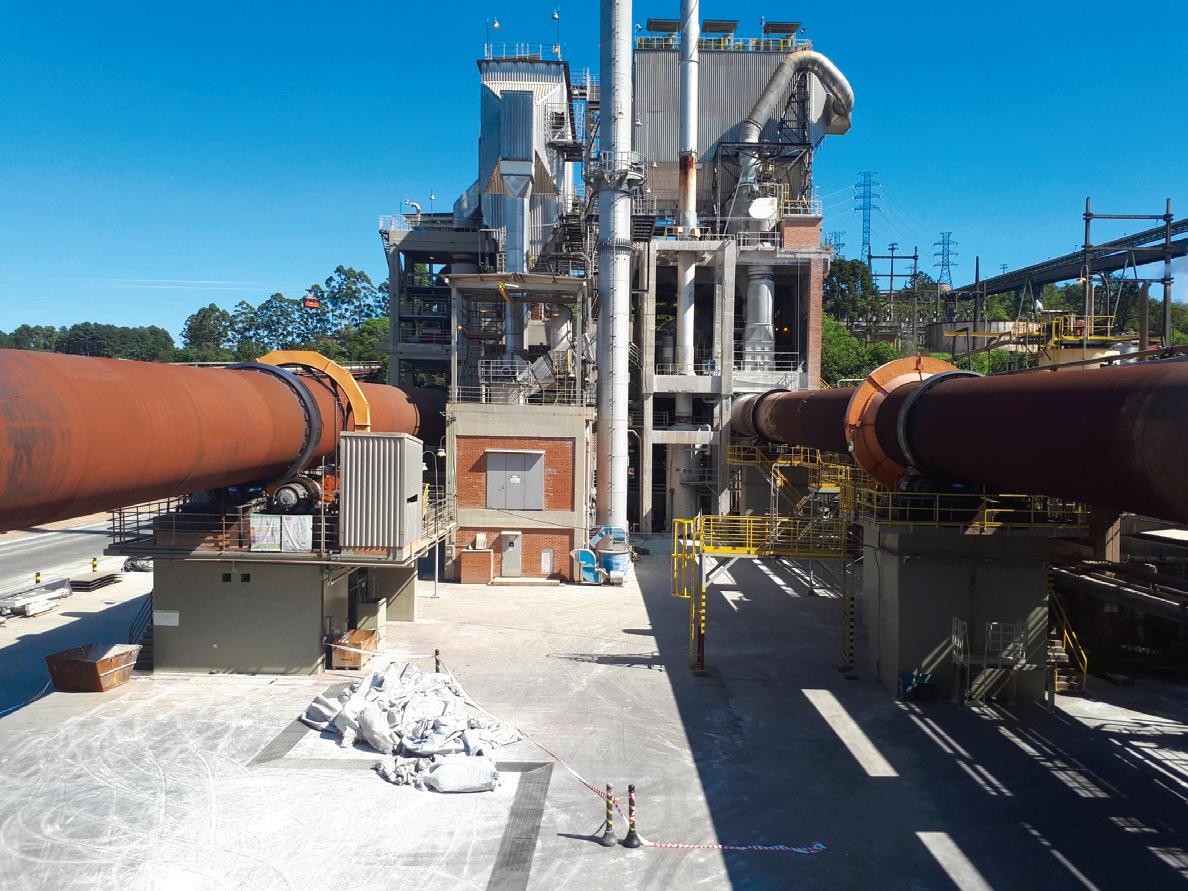
The group of substances, which is still mainly used for grease proof papers, is described under the generic term “perfluorinated compounds”. Germany and other northern European countries are already actively taking action against this group of sub stances, with the aim of banning the manufacture, marketing, im port and use of perfluorohexanoic acid (PFHxA) and all other perfluorinated compounds in Europe, if not already in force.

There is always the question first to the end user: “Do you really need a 100% barrier?” The reality is that most plastic packaging creates too great a barrier and consequently the food contents of the package decompose faster as a result. On the other hand, most effective alternative fully sustainable formulations will struggle to provide the desired functionality necessary to achieve a homogeneous and effective barrier to grease, oil and moisture. It is therefore necessary to understand that in many cases a fully sustainable solution cannot yet provide sufficient barrier prop erties. Schill & Seilacher Paper Division are the experts in this field and always search for the ‘most sustainable option’ when it comes to developing coatings for food packaging. They are confident that very soon they will be able to offer to the market a fully sustainable solution with excellent recyclability and pro viding the desired comprehensive barrier performance.
14 PAPER TECHNOLOGY AUTUMN 2022 SUSTAINABLE WEAR PROTECTION SOLUTIONS
The reason for this action is that this group of substances con sists of non-degradable organic compounds which do not occur in nature, and yet are to be found everywhere as “environmental toxins” due to their diverse industrial use. They may be detected in many environmental media and organisms and accumulate in living organisms which is of serious concern. They have already reached the human organism via the natural food chain.
Laboratory Size Press application
Water-based barrier coatings – the key to the future of sustainable packaging
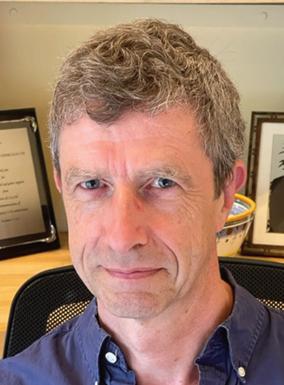
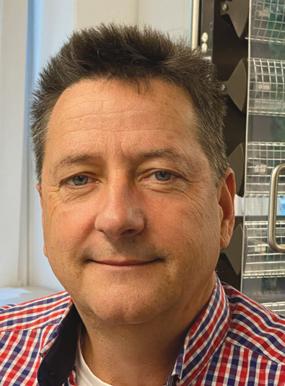
Reiner Joos, Adrian Iley, Commercial Director, Managing Director, G.B.C. (Speciality Chemicals) Limited Schill & Seilacher (www.gbcspecs.co.uk) GmbH., Paper (www.schillseilacher.de)Division.
Case Study : To achieve medium OGR without fluoro chemicals in a flooded nip size press Objectives :
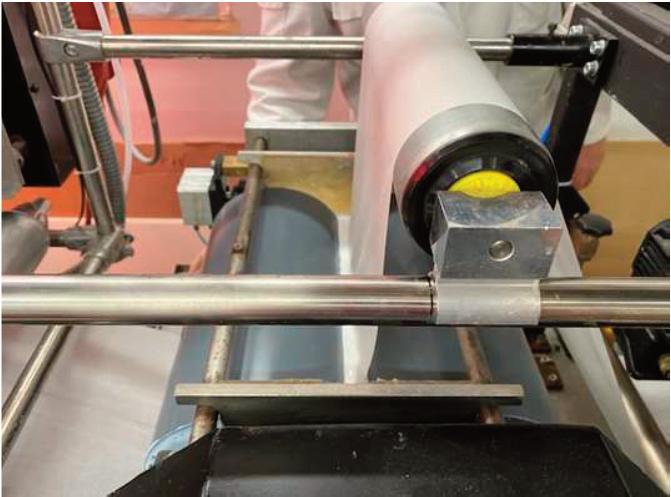
Schill & Seilacher has developed a PFHxA-free treatment of the paper surface in cooperation with several European paper manufacturers. This can be applied both by coating units or in size presses directly during paper production. These surface treatments give paper and board both oleophobic and hydropho bic properties. As a result, the appropriately treated papers and board may be used for the packaging of foodstuffs such as fast food, French fries and fresh cheese and sausage products in com pliance with the food contact recommendations of BfR XIV and XXXVI.Inaddition, and in contrast to Fluorocarbon-treated papers, these treated papers can be composted in accordance with DIN 13432. Due to their excellent recyclability, the treated papers can be fed back into the waste paper material flow and rejects can be processed thus giving a truly sustainable alternative solution.
It would be easy to forget when you consider that we are cur rently experiencing war in Europe, the continued effects of COVID 19 on supply chains and the escalating cost of living, that still the most serious and imminent threat to mankind is that of Climate Change. The focus of development efforts over the past 2 years has in evitably been to ensure that the mills keep running and despite the best efforts of pioneers in sustainable food packaging, progress to replace plastic in packaging has been slow. Today the use of oil and gas supply as weapons in the new ‘Hot war’ by Russia only serves to highlight the necessity for strategic and more sustainable alternatives now. These sustainable alternatives, however, often cannot achieve the same barrier properties in packaging compared to plastics.
Solutions are finally within reach for the replacement of flu orocarbon-containing packaging papers (POFA / POFS / PFHxA-free) with medium fat density, which are suitable for use in food packaging and have sufficient barrier properties.
1. Medium oil and grease resistance without fluorochemicals (POFA, POFS, PFHxA-free).
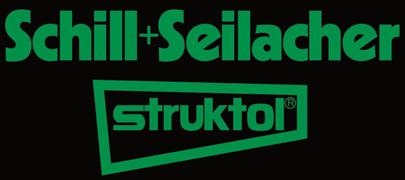
2. Barrier values suitable for e.g. fast food packaging such as burger wraps. 3. Low Cobb60 and Cobb1800 values for humid filling con tents. 4. Food contact approved (BfR XXXVI, FDA 21 FCR 176.170 and 176.180).
5. Realistic pick-up volumes for flooded-nip size presses. Substrate: 37gsm base paper, virgin pulp, unsized, porosity ca 90ml/minute.
HOT AIR CHANNEL
IR DRYERS
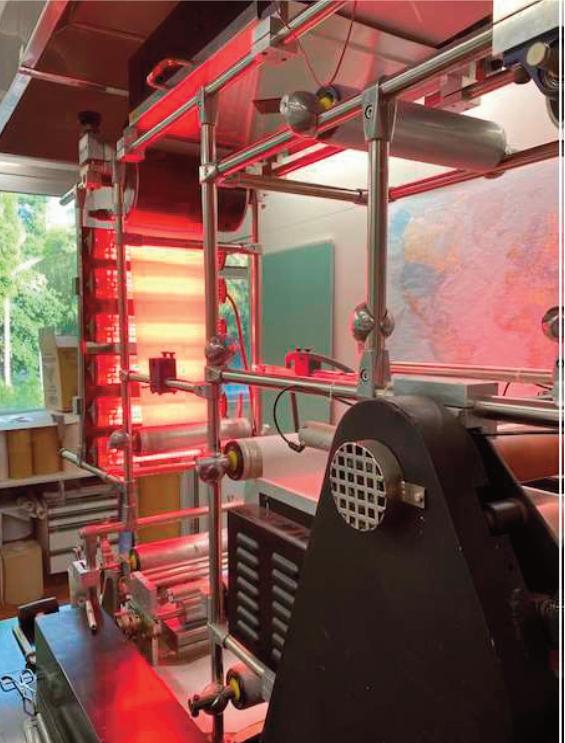
Formulation and Conditions: 5% solution of a modified potato starch (70%) UKAPHOB HR530 (30%) Target viscosity at 50oC = < 50 mPas. Temperature of the size press bath ca 45-50oC at the nip. Treatment both sides. Target pick-up ca 2.0-2.5gsm (dry)
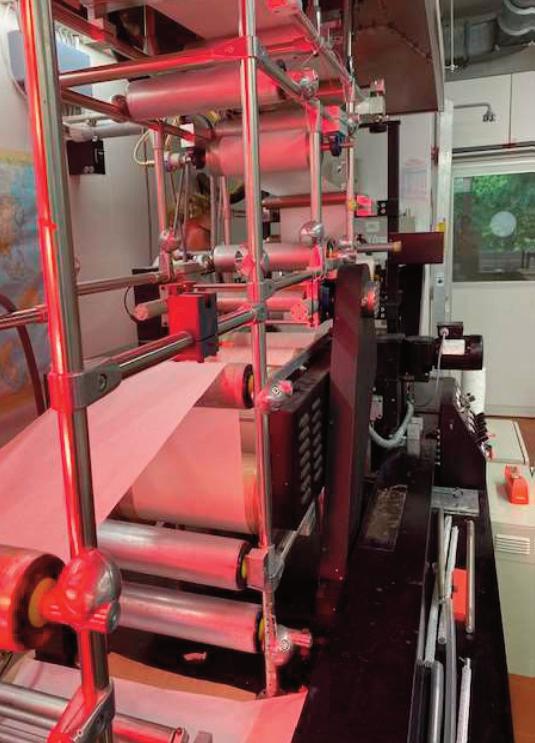
CONCLUSION:RESULTS
15 PAPER TECHNOLOGY AUTUMN 2022 WATER-BASED BARRIER COATINGS
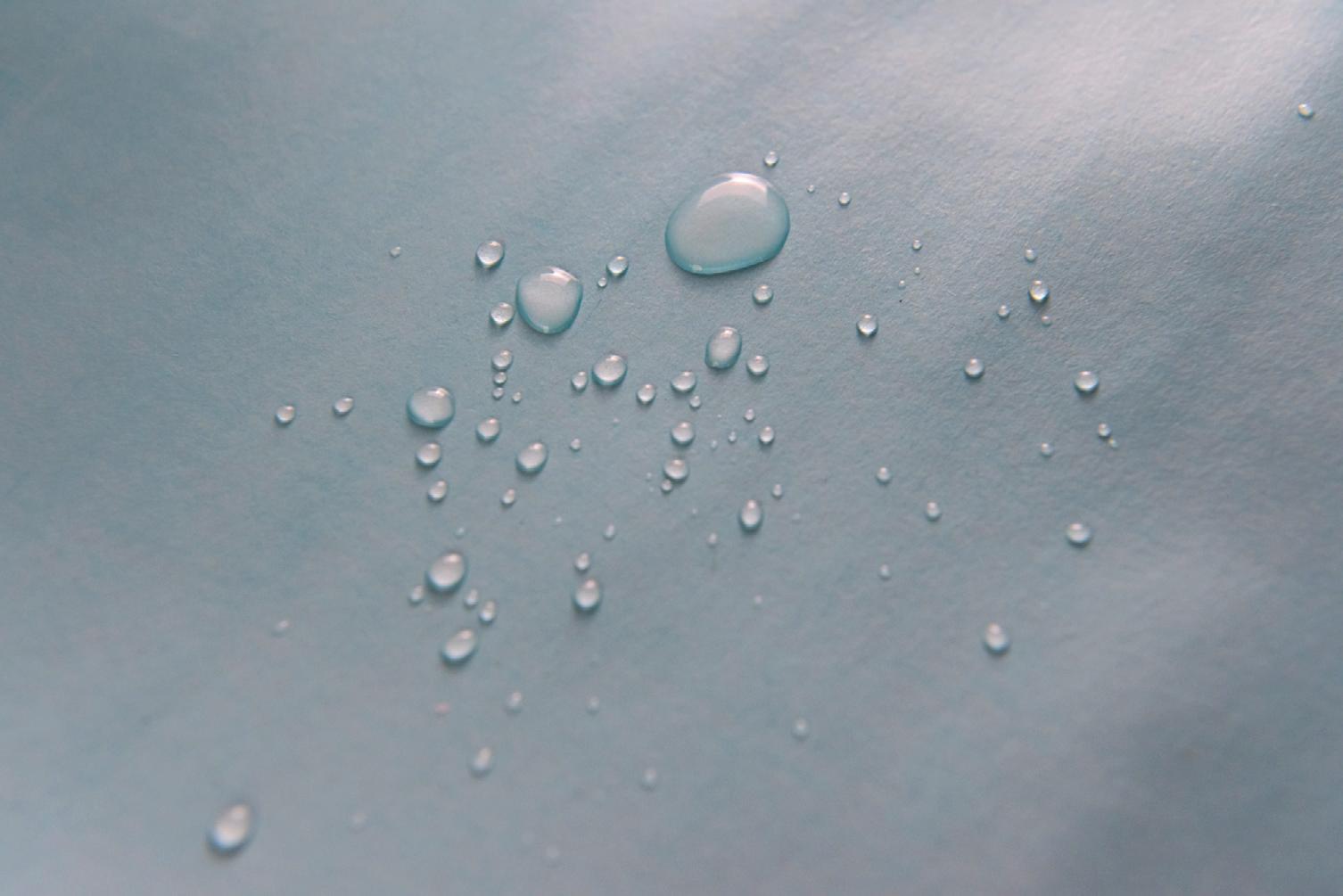
The application proposed by Schill & Seilacher has been proven in full scale production. It provides sufficient barrier properties to make treated papers perfectly suitable for fast food packaging. It provides a modern, recyclable and compostable al ternative solution to fluorocarbons in food packaging. About Schill & Seilacher GmbH., Schill & Seilacher GmbH., was founded 140 years ago and today employs 1000 people in 6 independent production sites supplying speciality chemicals on all five continents. The Group is owned by a foundation and is well prepared for the future with a very high level of Research & Development activ ities and an orientation to the market and satisfying customer G.B.C.needs. (Speciality Chemicals) Ltd., has represented Schill & Seilacher GmbH., Paper Divi sion in the U.K. and Ireland for more than 25 years. Sample Application (g/m2) Cobb60 (g/m2) Cobb1800 (g/m2) KIT Slip Angle MVTR 23/85 (g/m2) Base Paper <1 31o 1500 HR530UKAPHOB 2 13 26 6-7 14o 396 Treated paper showing Water repellency and Oil holdout
CONTACT DRYING
16 PAPER TECHNOLOGY AUTUMN 2022 NEW INSIGHTS ON APPLICATION OF HIGH-YIELD PULP
Rob Peeling, Technical Services Director, Britest Ltd.
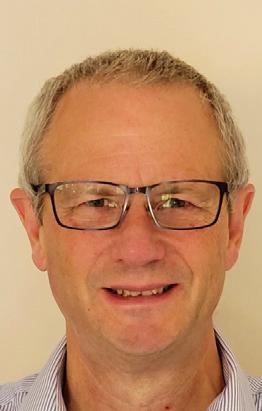

The goal in capturing the current state of process understand ing is to explore and define the underlying science of the phe nomena being exploited by a process, and to identify the gaps in that knowledge. A critical aspect is thinking about the whole process, to understand the impacts of what is happening in one process task on preceding and following steps. Whole-process thinking also requires linking directly process understanding to the business objectives. The original ‘BRITEST’ (Best Route Innovative Technology Evaluation and Selection Techniques) collaborative project1 developed a collection of process under standing tools initially aimed at improving communication be tween chemists and chemical engineers, but broadening in utility to a much wider range of disciplines with time. The tools have become a proven, effective means of interrogating chemical, physical and biotechnological processes. Several of the tools are used in the methodology now described.
Figure 1: Original Process Definition Diagram (PDD) for LevWave.
At the very early stages of a project seeking to bring an innova tive process and its associated product into the market, it is usu ally true that there is limited available data coupled with plentiful sources of uncertainty. The project team and business face two problems: how to decide whether to commit valuable resources to continued development; and how to set objectives for a continued development programme that will drive towards commercial viability. The available data at the early stage considered here will typ ically take the form of lab-scale demonstrations using the pro posed route and technology to generate the desired product. This is also generally common for a wider range of new product in troductions (NPI), where the process route and technology are not necessarily seen as ‘innovative’ but nonetheless present chal lenges in the transition to commercial production. This paper explores the role of improving process understand ing in identifying and mitigating the risks encountered in scaleup and commercialisation. A methodology for systematic capture and development of process understanding to set objectives for continuing project development is described using the Industrial Strategy Challenge Fund supported LevWave project as a case study.
An understanding-based methodology for setting commercialisation objectives for an innovation project - a case study for platform chemicals from paper sludge
Capturing Process Understanding

From the whole process description developed it will be nec essary to identify what are considered to be the critical tasks within the state-task network. Subsequent stages of the method ology will describe how visual annotations can help identify ‘hot-spots’ in terms of (for example) sustainability, safety, oper ability and scale-up; however, an initial prioritisation can be made using the information currently at hand. The project team can then ‘home-in’ on the task, exploring the relationships be tween the physical and chemical aspects of processing, and con sidering the effects of spatial and temporal variability upon how the task will be performed.
Figure 2: Rich Cartoon for the original experimentsmicrowavelab at MMU.
Methodology
Develop the Whole Process Concept
Develop Qualitative Mechanistic Models
The LevWave project2 considered the feasibility of producing the platform chemical, levulinic acid, from a paper recycling byproduct stream3 using a solid-state catalyst and microwave heat ing. The process is envisaged as continuous, with the paper sludge passing through a reactor within which it is heated by mi crowave radiation. A solid-state catalyst promotes the reactions that convert cellulose into levulinic acid through the intermedi ates glucose and 5-hydroxymethylfurfural.
The starting point is to develop and describe the whole pro cess concept. The aim should be to describe the desired experi ences that all process materials, molecules, or particles need to undergo to obtain the required product. One way of doing this is to create a Process Definition Diagram (PDD), a form of State Task Network.4 A well-constructed PDD is independent of scale, equipment, and mode of operation (i.e., batch or continuous). This is possible because it considers the required new state of an entity after each task or experience, and the chain of these expe riences required to transform the feed materials into desired products. Conducting several tasks in the same equipment be comes a design decision which inevitably involves some com promise in the desired experience which needs to be tested against the business drivers. It is this focus that differentiates a PDD from a classic equipment related Process Flow Diagram (PFD).5Theoriginal PDD for LevWave is shown in Figure 1. The ex perimental programmes at Manchester Metropolitan University (MMU) and Drochaid Research Services (DRS) were focussed on understanding tasks 30 and 40. The PDD shown provides a qualitative description of the required processing experience for all the process materials in a complete LevWave process, in terms of material and energy balances, and phases present, in cluding whether they are dispersed or continuous. The visually rich presentation highlights the salient features of the process in a form that can be easily assimilated by someone not involved in the project.

Rich Pictures, and Rich Cartoons when the passage of time is considered, are very useful for exploring these questions to help build a deeper level of process understanding for individual tasks in the PDD. Figure 2 describes as a Rich Cartoon the mix ing, heat and mass transfer phenomena occurring in the original lab microwave experiments for LevWave at MMU. The limited mixing of the solids in the reaction tubes is clear. The design in tent for scale-up is to use a tubular microwave plug flow reactor and the very different conditions for the same three phenomena are apparent in the corresponding Rich Picture, Figure 3. Com parison of such figures can generally guide a project team’s thinking towards key challenges in moving from the lab to pilot and commercial scale operations. In this case it is evident that reaction kinetic and performance data from the lab experimental set-up is not directly related to the scaled up situation. Careful interpretation of the existing results, and attention to experimen tal design, will be required in any follow-up work intended to support scaling-up the process. This leads to the need for a wider 17
Case Study
PAPER TECHNOLOGY AUTUMN 2022 A CASE STUDY FOR PLATFORM CHEMICALS FROM PAPER SLUDGE
Preliminary Techno-economic Assessment
A tool such as Britest Limited’s Process Information Sum mary Map (PrISM) can be useful to capture the outline process and possible costs6 as a starting point for a preliminary TEA. PrISM captures a simple, semi-quantitative model of the pro posed process and is easily extended in both directions along the supply chain. By applying basic process engineering skills, with some ad ditional data (mostly physical properties), simple heat and mass balances for the main process steps can be compiled. These pro vide the basis for rough sizing and costing calculations for the main equipment items and variable costs for the process materi als. This is sufficient to give an outline of the cashflows and hence profitability (or otherwise) of the proposed process. Doing this with unoptimised lab-scale results would be expected to de pict a very pessimistic picture for commercial viability. Analysis of the results will readily reveal how the more significant costs arise in the model.
The task therefore is to use the simple TEA model with some ‘what-if’ scenarios for reducing the costs and moving the pro posal towards profitability. Successful scenarios become objec tives to be achieved by the development team, guiding the development programme forwards. For LevWave, six development objectives were identified in this way:Reduce catalyst to solids ratio (decreases cost of catalyst). Efficiently recover and re-use catalyst (decreases cost of Significantlycatalyst). increase slurry concentration (reduces equipment size, energy costs, and improves technical fea Significantlysibility).
improved yield of levulinic acid from cellu lose (increases revenue). Use recovered water from LA separation for slurrying (en hances Recoverysustainability).ofheatfrom the slurry leaving the reactor to heat the slurry entering the reactor (reduces energy costs, improves sustainability and technical feasibility).
18 PAPER TECHNOLOGY AUTUMN 2022 A CASE STUDY FOR PLATFORM CHEMICALS FROM PAPER SLUDGEP
Figure 3 Rich Picture for microwave plug flow/tubular reactor proposed for scaling-up LevWave.
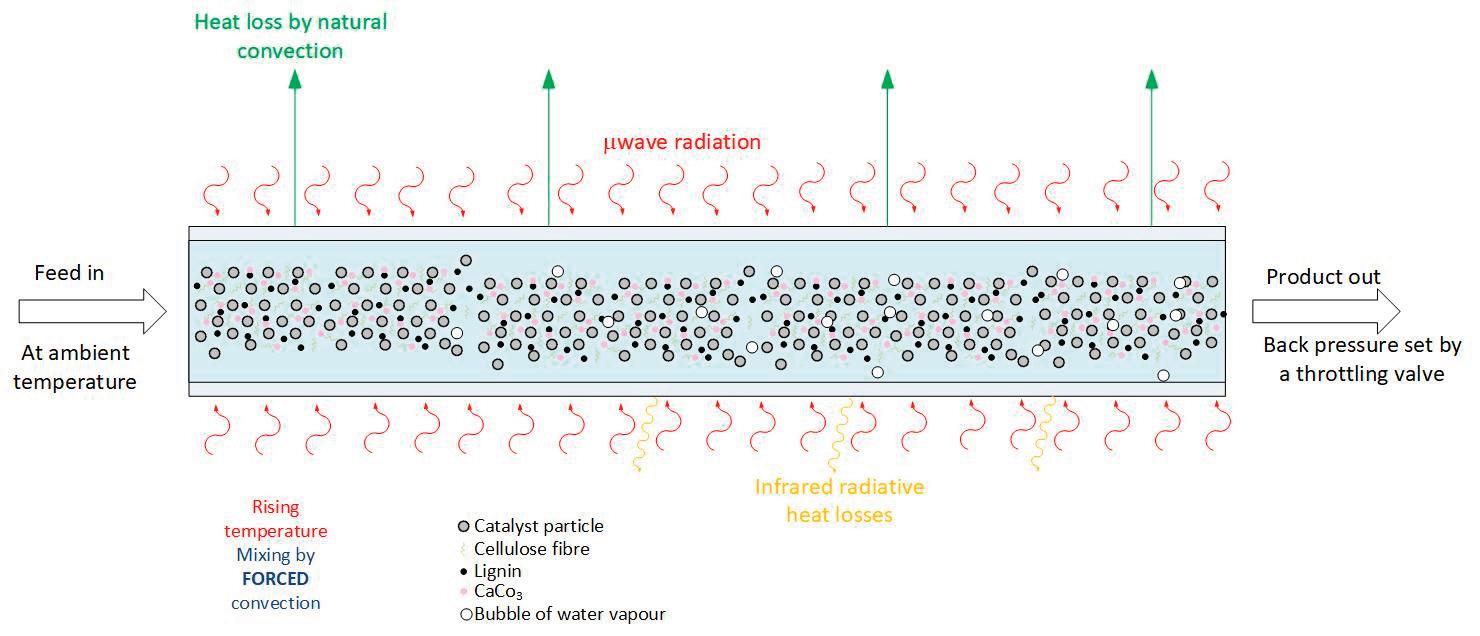
Table 1: Sustainability prompts used for LevWave.
Prompt impactTolerable impactReview/check impactSignificant Cost of goods Water MaterialsPollutionEnergyusageusageusage efficiency Time to process Quality C C C W W W E E E P P P M M M T T T Q Q Q
consideration of scale-up risk. Formal analysis, such as FMEA, could be used to identify scale-up risks and define mitigation strategies. This and related approaches can be and are used by some organisations to assess the technological risks associated with a project but are exhaus tive and time-consuming. At the very early stages of develop ment, a ‘short-cut’ method is compatible with the limited extent of process knowledge the associated high uncertainty and may be more suitable and sufficient. Such a method is now proposed.
Valuable guidance for project management and for stage gate decisions can thus be obtained at the earliest stages of a project because relative comparisons are being employed. This approach should not be extended into later stages of when significant cap ital expenditure decisions are required, and a more absolute model result is essential.
The impact of these scenarios on the TEA model for LevWave is illustrated in Figure 4.
Techno-economic assessment (TEA) is a standard tool for as sessing commercial feasibility. It usually accompanies detailed process design and market research and be used as a key data source for making the decision whether to commit significant capital investment. The Levwave project has explored the po tential advantages of carrying out a preliminary TEA at a very early stage of a project when uncertainty is high and detailed quantified information is unavailable.
Figure 5: LevWave PDD after applying sustainability prompts.
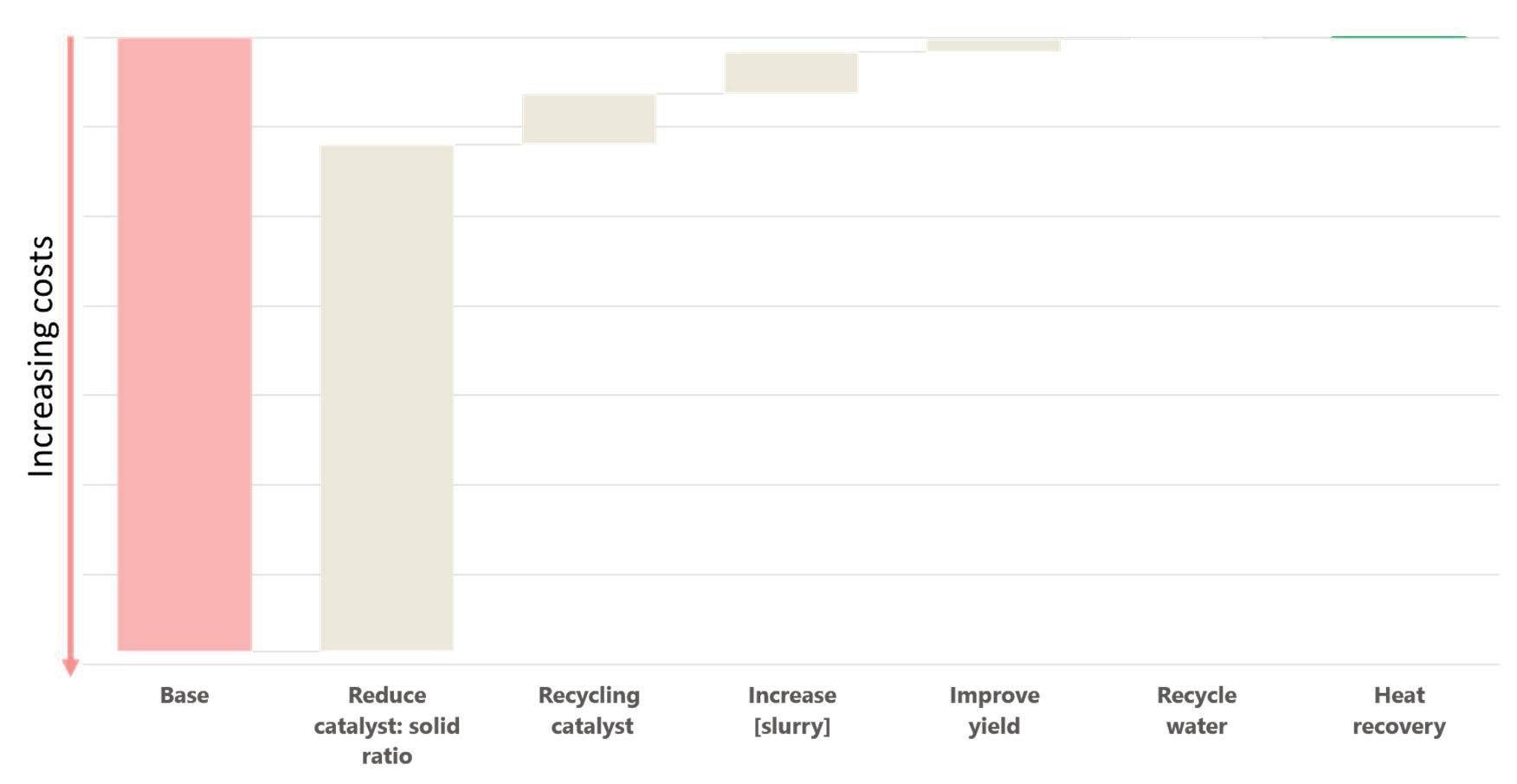
PAPER TECHNOLOGY AUTUMN 2022 A CASE STUDY FOR PLATFORM CHEMICALS FROM PAPER SLUDGE
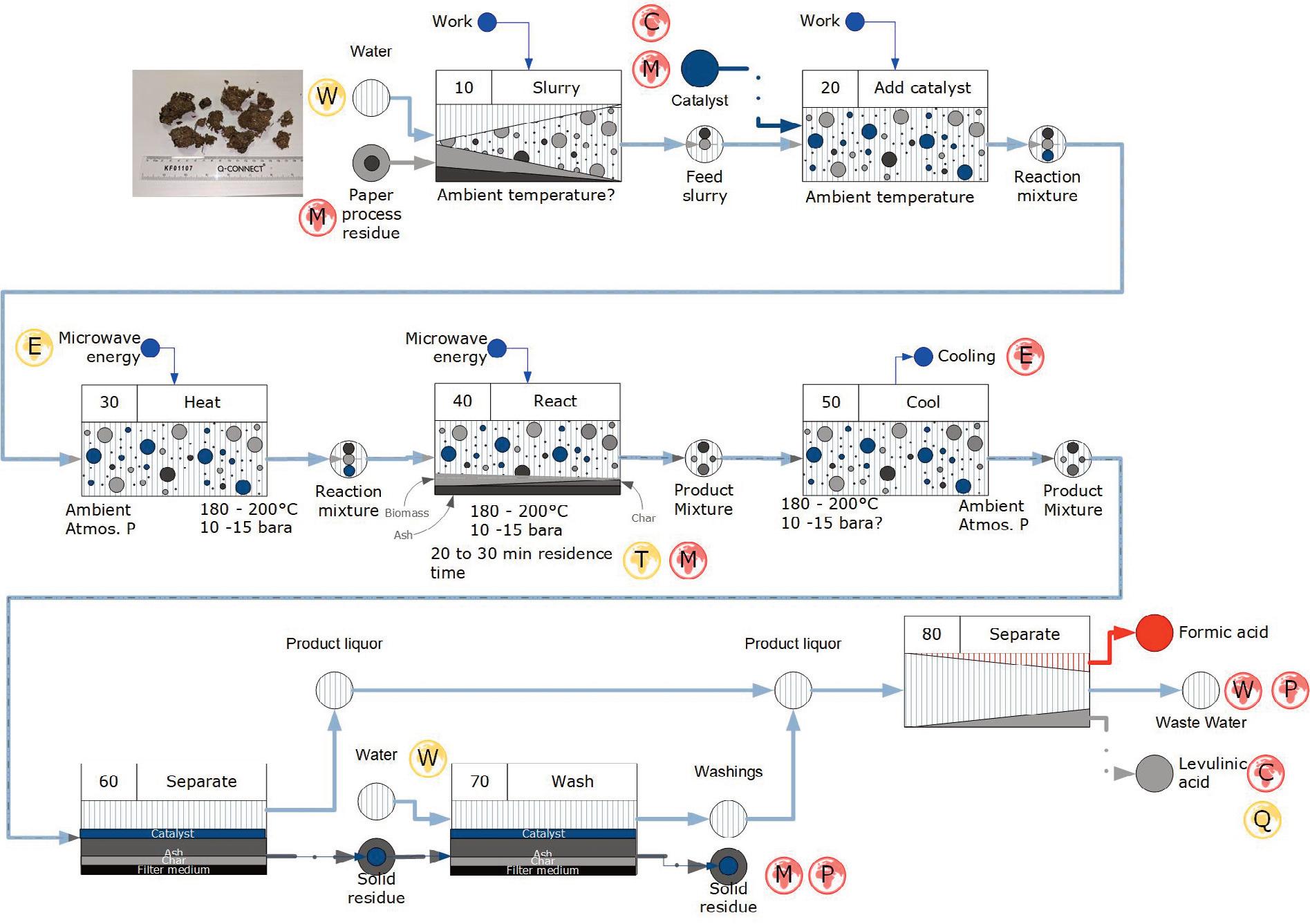
Sustainability Assessment So-called “sustainability prompts” may be used to highlight potential process re-design for sustainability opportunities sim ply and visually. This adapts and extends a similar approach that was developed in-house with one of Britest’s members in 2013. This in turn was inspired by the Fundación Entorno’s Eco-Com pass tool7 and Arup’s Drivers of Change cards8. The original Eco-Compass defined six key sustainability indicators. The cur rent sustainability prompts (Table 1) are a modified set based originally on an internal case study developed with Britest mem bers.9 Colour coding has been added signifying the sustainabil ity impact of each prompt: tolerable (green), review/check (amber), and significant (red). This was found helpful in en abling a rapid assessment and comparison of different process sustainability improvement options. The list only covers the two: environmental and economic ‘Pillars of Sustainability’. The social pillar is not included because it is more relevant at the whole enterprise level rather than when considering tasks in 19
Figure 4: Waterfall diagram showing the impact of development options on the preliminary TEA model for Levwave.
Figure 6: Eco-compass before and after respond ing to prompts.sustainability
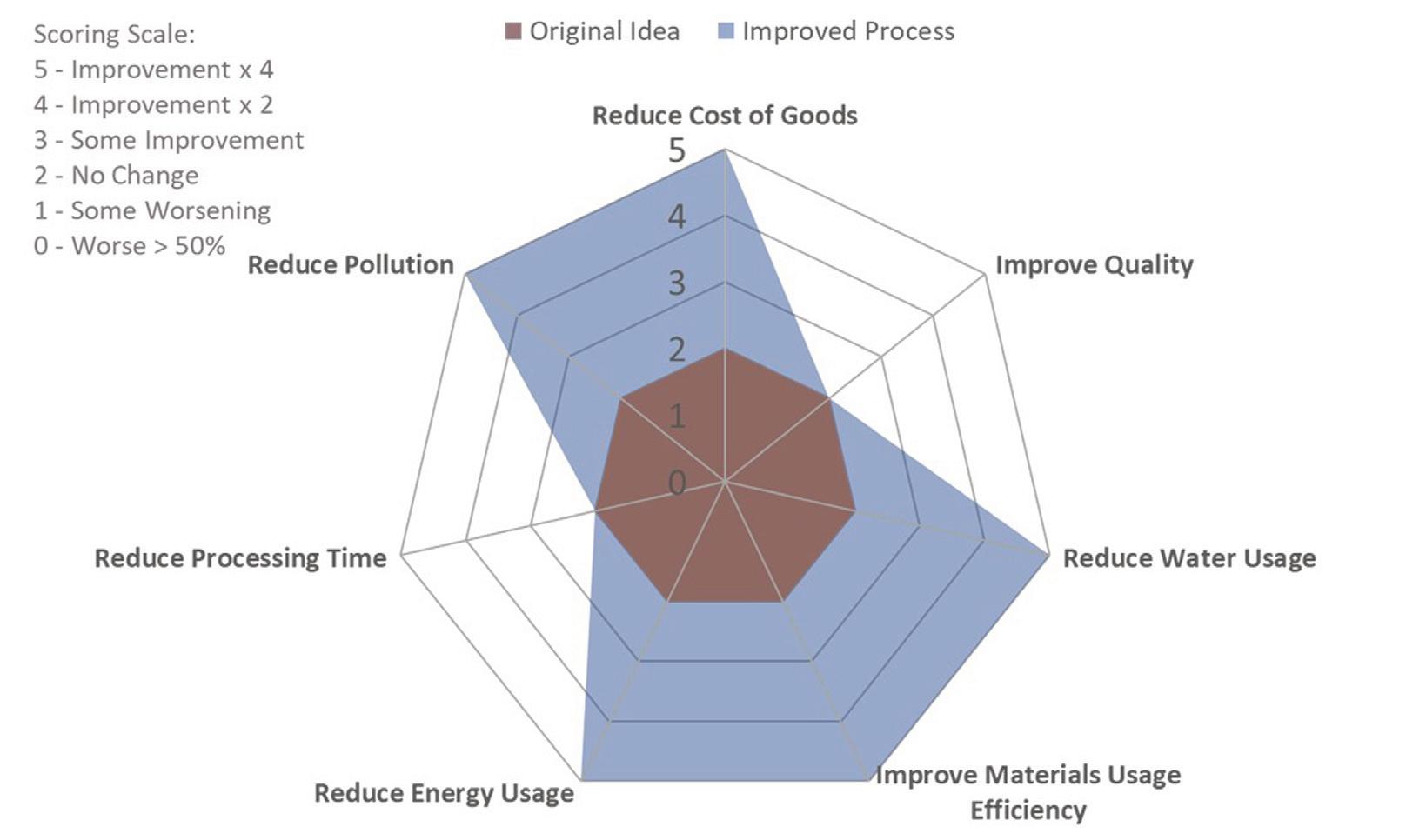
Task 20: Add catalyst
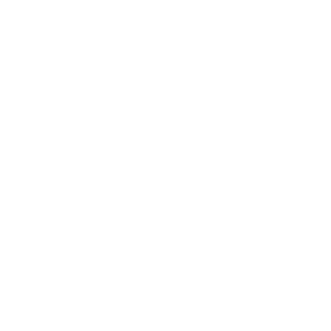
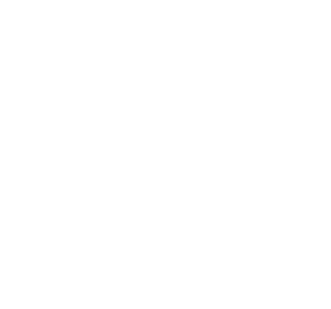
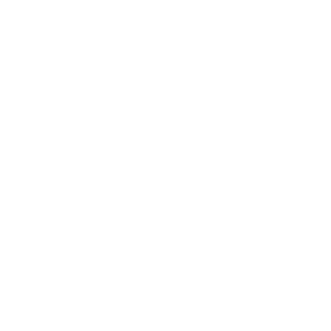
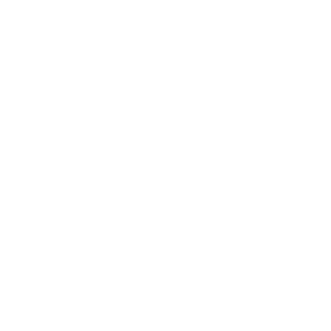
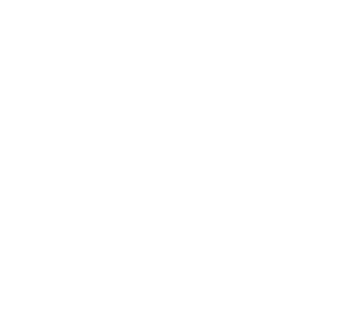
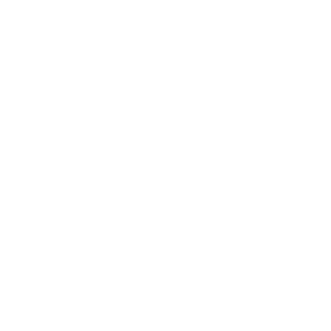
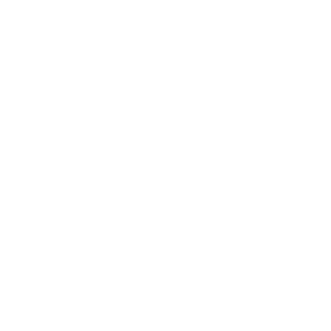
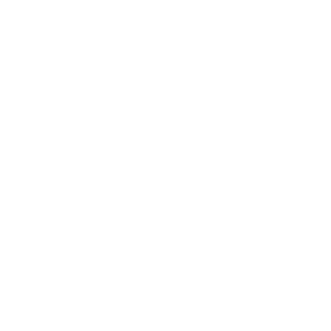
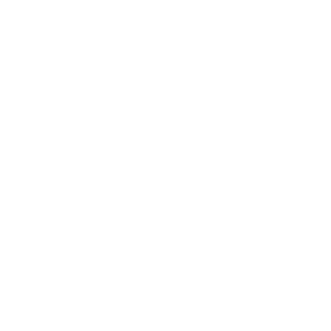
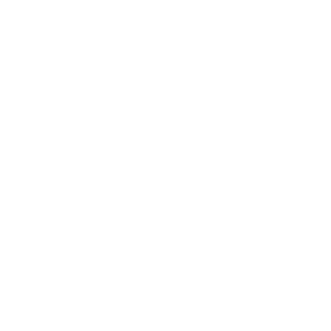
Recovery and recycling of the catalyst and substantial reduction in catalyst loading give significant mitigation to both these factors and justify reduction to a tolerable impact.
There is substantial temperature change from ambient to 180°C at this point. The energy demand for this change is fixed thermodynamically but there is scope to consider where the energy required comes from.
jectives identified from the TEA can be suc cessfully applied, the PDD can be revised and the sustainability prompts re-applied to assess the improvement achieved. In the case of LevWave all significant impacts were reduced to either tolerable or review/check level and some of the review/check impacts were re duced to tolerable. An Eco-Compass approach (Figure 6) may be used to indicate the progress made towards process sustainability through the improvements identified using a semi-quantitative metric for scaling scores de rived from the changes reported in the Key Process Indicators (KPIs) in the TEA.
Water is introduced into the process to slurry the paper sludge. In the original lab work for LevWave the slurry concentration is quite dilute at 2.5 % w/w. Can the process be operated at a high slurry concentration to reduce the water demand?
Both tags reflect different aspects of a single factor. In the lab work the catalyst loading is very high with more catalyst (w/w basis) used than paper sludge. This is a concern in terms of mass intensity and even more so in terms of cost of goods since in the lab trials to date, there has been no re‐use of catalyst (single use).
Task 30: Heat
Most of the heating required can be achieved by cross‐exchange with the slurry exiting the reactor. This reduces the impact to tolerable.
Task 10: Slurry
The paper sludge has a low cellulose content. A large proportion of the feed material will pass through the process unchanged and well need a suitable disposal route once recovered at the end of the process. Could other feedstock give better mass intensity?
To use the prompts the PDD in Figure 1 was simply marked up with appropriately coloured symbols to obtain Figure 5. Ac companying notes to record the thinking underlying the place ment of each prompt are valuable (Table 2). The sustainability assessment can then be responded to with suitable changes to the process. Assuming the development ob
a manufacturing process.10
From the annotations tagged on the PDD in Table 4: Risk reg ister for LevWave process scale-up (portion), a scale-up risk reg ister can be compiled (see Table 4). Each identified risk is given 20 2022 A CASE STUDY FOR PLATFORM CHEMICALS FROM PAPER SLUDGE
PAPER TECHNOLOGY AUTUMN
W M C M E E W M C M
A ‘short-cut’ technological risk assessment can be quickly and easily carried out (in a pro cedurally similar fashion to the sustainability prompts above) by tagging the tasks in the whole process PDD with scale-up risk factors and impacts taken from Table 3. At an early stage of process development, firm decisions on equipment selection will not have been made (and the PDD itself is focused on the ex perience of the process materials, independent of scale and equipment). The risk factors are experientially derived but have proven to be ro bust over a range of different and unrelated pro cesses, including the LevWave case study. The current operating scale for LevWave has been limited to ≈10g scale as small batches at MMU and as slightly larger batches at DRS. Scale-up risks have been assessed for continuous pro cessing of 30Ktpa of paper sludge. The scale up concept considered was a microwave-heated, tubular plug flow reactor processing the paper sludge slurry/catalyst mixture.
Scale-Up Risk Assessment
Initial Design After Re‐Design
The entire water demand for slurrying the paper sludge can be met by recycling the water separated in task 80. High purity water is not required here so no additional treatment before re‐use should be necessary. After making this change the impact can be considered as tolerable.
Table 2: Sustainability prompts for LevWave (portion).
Scale-Up Risk Register
Improving the yield at reaction mitigates the mass intensity with respect to the paper sludge. However, there will still be a large proportion of the feed material which will pass through the process unchanged and well need a suitable disposal route once recovered at the end of the process. Could other feedstocks give better mass intensity?
Conclusion A methodology has been proposed and exemplified using an ISCF fast start project, LevWave, as a case study. Whilst the methodology has been demonstrated in the context of an inno vation project, similar concerns face any NPI project team, and there is every reason to believe the approach will have equivalent value in other situations.
The methodology provides project managers with a system atic tool for planning development objectives in the ongoing pro gramme, together with support for decision making at stage gates based on the state of the project team’s process understanding at the time of assessment. It guides objective setting to address three key aspects of commercial viability: techno-economics, sustainability, and scale-up risk. Based around the Britest process understand tools, the methodology is designed to be simple, easily communicated and as non-onerous in time and effort as possible. The last point is particularly important for an early-stage project, perhaps with as-yet undemonstrated business value. Other techniques for cap turing process understanding can be substituted but compromise in terms of simplicity and efficiency may result.
We would like to thank Innovate UK for funding 50057 LevWave through the Industrial Strategy Challenge Fund (ISCF) call for transforming foundation industries: fast start projects and Britest’s co-investigators on the project, Drochaid Research Services, Croda Eu rope Limited, Manchester Metropolitan University, and Saica Paper UK Limited.
References 1. Checkedhttps://www.britest.co.uk/about_us/history/July2022
21 PAPER TECHNOLOGY AUTUMN 2022 A CASE STUDY FOR PLATFORM CHEMICALS FROM PAPER SLUDGE Tag Risk factor Rationale 1 Moving solids Solids handling can always cause challenges when changing scale 2 Multiple interacting phases Rule of thumb: complexity increases in proportion to [no. interacting phases]^1.6 (J. Atherton)Some physical forms are particularly challenging, especially solids (e.g. sticky or large particles) 3 Human engagement Any task requiring operator or other human engagement could introduce variability 4 Heat/energy removal/changeintroduction/ Potential challenges will depend on the magnitude and rate required 5 Sensitive chemistry Are any transformations operating in a tight window with respect to driving forces? 6 Chemical unintendedincompatibility/reactions Impact of unintended chemistry can increase on scale-up 7 Extremes of specification Is the process sensitive to the grade/source of materials used? Tag Type Impact Prompt Q Product Quality Y Yield O Process Operability S Safety & Environment Table 3: Risk factor and Impact prompts for scale-up risk assessment. NumberRisk NumberTask Task Description Risk / andopportunitytriggers Impact Priority / Risk Reasoning 4 20 - 40 Slurry transport Slurry pumping risk of blockages O 2 Fibrous slurry handling 5 20 Catalyst addition catalystrequirementFeeding/Dosingfor O 2 Little information on physical form and properties, handled wet. 6 20 Catalyst addition Mixing & catalystrequirementdispersalfor O, Q, Y 2 Gaps in data requirementson 7 20 Catalyst addition Variation in catalyst quality if recycled Q, Y 4 Re-use of catalyst has not been attempted in work to date. 8 20 Catalyst addition Additional provesadditionalcomplexityprocessifcatalysistoberequired O, Q, Y 2 Lab work suggests possible advantages from a catalysttwo-componentsystem 9 30 Heating Excessive power demand technologymicrowavefor O 3 Heat recovery from Cooling step is a valid mitigation 10 30 Reaction Complex, multiphase, reactionmulti-step Y, Q 4 Significant gaps in knowledge, especially around chemistryphysical Table 4: Risk register for LevWave process scale-up (portion).
3. Confederation of Paper Industries, Process Wastes from the Paper Industry, March 2021 4. Wall K., Sharratt P.N., Sadr-Kazemi, N, Borland J.N., Org Proc Res & Dev, 5(4) (2001).
7. Links to websites for Eco-Compass tool and Fundación Entorno seem to be no longer ac tive. Eco-Compass is not the same as the Horizon 2020 project of the same name. A description can be found in Tambovceva, Assessment model of environmental man agement: a case study of construction enter prises in Latvia, Economics and Management: 2010. 15 pp.799-806. 8. changelications/research/section/https://www.arup.com/perspectives/pubdrivers-of-
5. Ibid. 6. McLachlan et al., J Bioprocess Biotech 7(2), (2017).
a unique number. The risk is described, and the impact or im pacts noted. Each described risk is then scored to assign a pri ority or importance to mitigating the risk for scale-up to proceed successfully. As a project progresses, the risk register can be used to record the decreasing risk as understanding increases and mitigation strategies are implemented. Again, plotting the evolv ing priority scores in a compass plot can provide a valuable and highly visual reporting tool.
9. Internal Britest document: Driver Prompts Methodology — Case Study, 2015 10. 2022porate-sustainability.aspcles/investing/100515/three-pillars-corhttps://www.investopedia.com/artiCheckedJuly
2. G. Hurst, I. Brangeli, M. Peeters, S. SolidTedesco,residue and by-product yields from acid-catalysed conversion of poplar wood to levulinic acid, Chemical Papers, 3https://doi.org/10.1007/s11696-019-01013-(2019)
Acknowledgements
In addition, global disasters such as Covid-19 and the Ukraine war are impacting economies, energy costs and supplies – alter ing how industry views digital transformation. It has also under scored the need for leaders to accelerate the adoption of agile ways of working, as well as future-proof business against more volatility. As digitalisation progresses, it brings a free flow of data from both information technology (IT) and operational tech nology (OT) applications across the value chain, making inter operability a priority.
MES in pulp and paper operations
Bringing structure and standardisation to data that is under utilised is therefore a vital step towards creating an integrated digital infrastructure that allows asset and operational data to be accessed, visualised, and analysed for better performance.
However, data is nothing without context. IBM Research es timates that up to 88% of IIoT data goes unused, while the Economist suggests that 99% of the value of manufacturing data is lost, with only 3% tagged and analysed.8 Other hurdles include inaccessible legacy systems; a lack of real-time data; not la belling data logically; and the failure to effectively communicate data-derived conclusions.
Timo Nivalainen, ABB, Product Manager, MES
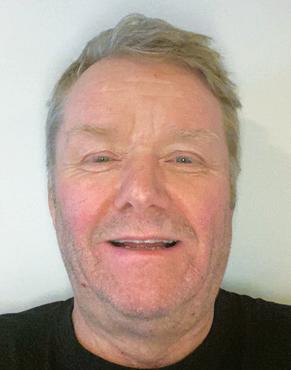
A layered approach to data: the lifeblood of modern pulp and paper manufacturing A report published by McKinsey in 2019 estimates that digital technologies could offer pulp and paper producers a 15% reduc tion in total cost and a 5% improvement in overall equipment ef fectiveness.7 A further report by McKinsey15 in 2021 reinforces that those digital technologies enable new levels of productivity in pulp and paper operations by leveraging large quantities of data to deliver better insights and outcomes. Successful digital innovators are seeing throughput gains of 5 to 10%, yield gains of up to five percentage points, and significant savings on mate rials, chemicals, and energy. For the industry, this represents a $4 to $6 billion opportunity, a realistic achievement here and now given there are already over 25 unique use cases generating value across the full pulp and paper value chain.
An effective Manufacturing Execution System (MES) is a key step on a pulp and paper manufacturer’s digital journey; optimising production efficiency, enabling visualisation of the entire value chain and helping reduce energy use as part of an integrated ap proach to data management, writes Timo Nivalainen of ABB.
ABB does this by using a layered approach,9 which starts with defining a strategy and the required data, mapping current net work architecture, its bottlenecks, possible limitations and cyber security needs, and then determining and configuring data sources and interfaces.
All too often digital innovations are not designed with the ev eryday user in mind, which can limit their effectiveness and up
An MES is, put simply, a system that connects and automates processes, providing visibility across the value chain from shop floor to enterprise.1 This enables better oversight for planning and scheduling to continuously improve efficiency and reduce waste.
The second layer examines physical distance and determines how best to collect data using Edge computing tools before map ping local applications within automation systems for later use. Finally, the third layer determines which data from the mill or facility, and which local applications and data, should be used and which of those applications should be transferred to the cloud.Retrieving and harmonising historical data from control sys tems and other sources in this way, using an integrated data man agement approach simultaneously with their MES, offers pulp and paper mill owners multiple benefits in terms of costs and ef ficiency. High-volume production data is organised hierarchi cally based on standardised models and structures, and data streaming between layers, to and from the cloud, is controlled and secured, and available in real-time at an optimised cost.
The latest modular solutions cover all the core MES function alities across the pulp and paper value chain, from order han dling, production, warehousing and shipping to customer service management, as well as the acquisition and storage of resulting data and reporting.2 The modules work seamlessly together and can be enhanced with additional digital applications to improve operational efficiency. MES is a long-term investment that supports different grades, production types and easy scaling of a company’s manufacturing footprint from numerous production lines to multiple mills. In this way, it can be used to future-proof manufacturing operations.
Against this backdrop, focusing on the entire pulp and paper op eration – from mill floor to enterprise level planning – is the best approach to convert digital data into world-class business results.
In the context of pulp and paper, MES can be specifically de signed to help producers achieve operational excellence and maximum performance across multiple lines, optimising storage, energy and raw material usage, and ensuring the delivery of products of the right quality at the right time.
22 PAPER TECHNOLOGY AUTUMN 2022 NEW INSIGHTS ON APPLICATION OF HIGH-YIELD PULP
An MES retrieves valuable process data seamlessly from fragmented control systems, interfaced with other data sources, ready to communicate with the Cloud and shop floor in real time. Using the industrial internet of things (IIoT), the MES is fed with data on the real-time status and working condition of ma chinery and processes, which can be used to help the operator identify inefficiencies and make informed, data-driven decisions that optimise performance and add value.
In today’s competitive, globalised marketplace, pulp and paper operators are facing the conflicting challenges of optimis ing production processes to improve efficiency and quality con trol to gain an advantage, while at the same time reducing raw material use, energy consumption and waste.
Flexibility and ease-of-use
This type of bespoke MES differs from a more ‘agnostic’ system in that it can be customised to solve production challenges specific to pulp and paper mills, driving the best operational results.
Why MES is a critical stepping stone in your transformationdigitaljourney
Digital and automation technologies, such as manufacturing exe cution systems (MES), offer a critical competitive advantage by providing unprecedented, real-time visualisation and control of the entire production chain, from raw materials to finished product.
An MES enables the real-time planning and optimisation of production blocks, runs and orders, covering all the production steps, including the paper machine, winder, rewinder and sheeters. Flexibility is key; production schedules can be reopti mised after change orders or process disruptions and the MES can be easily configured to cover restrictions set by orders – e.g., the maximum number of rolls per set or edge roll restrictions –helping keep production costs to a minimum while ensuring ontimeAndelivery.MEScan add value by optimising an everyday function. For example, ABB’s MES for pulp and paper incorporates a trim ming tool that prioritises customer-specific quality requirements to maximise the value of the produced paper and the yield. It does this by using the jumbo reel cut plan to apply quality data to individual roll positions before it is cut at the winder, comparing roll quality to set standards, and detecting if any roll position does not meet requirements. Roll positions are then swapped to maximise yield and meet quality standards. The re sulting optimised trim pattern is sent to the winder and can be applied automatically if the winder cutting is fully automated. At a fine paper mill producing 480,000 tons per year, deploying the ABB MES resulted in a reduction in trim losses of 2.9–4.8 MUSD per year.4
23 PAPER TECHNOLOGY AUTUMN 2022 WHY MES IS A CRITICAL STEPPING STONE
Production planning and trim optimisation
MES: a key step towards autonomous operations
At the beginning of this article, I mentioned the need to use digitalisation to adopt agile ways of working and value chain transformation, including the importance of free data flows and interoperability.Takingthisa step further, I would argue that installing an MES can help papermakers transition to fully autonomous op erations. In this scenario, the hundreds of different applications, processes and work silos that are typically present in a pulp and paper enterprise are integrated into a single digital ecosystem, where a single modular software platform integrates all IT and OTThisdata.holistic digital platform uses IIoT applications to monitor and optimise all facets of the manufacturing process in real time, from the integration of renewable energy from the smart grid to external partner solutions for end-to-end flexibility and speed. What does this look like in a real-life industrial setting, and what are the tangible benefits in terms of business value? In Abu Dhabi, ABB’s MES is helping IPM eliminate human error from production and shipment processes, enabling the company to achieve a high level of delivery accuracy with only two planners. IPM estimates that to achieve the same accuracy outside the sys tem they would need seven staff.5 ABB’s MES connects to the paper machine’s automation, quality control and web inspection systems to provide online moisture, grammage and caliper profiles in the form of colour maps. Samples of each jumbo reel are then sent to ABB’s auto mated paper testing solution,6 L&W Autoline – which is also di rectly connected to the MES – where additional quality measurements are performed and recorded as quality certifica tion records for each order are produced. In addition, the MES solution enables end-to-end product traceability from the head box through to final customer delivery.
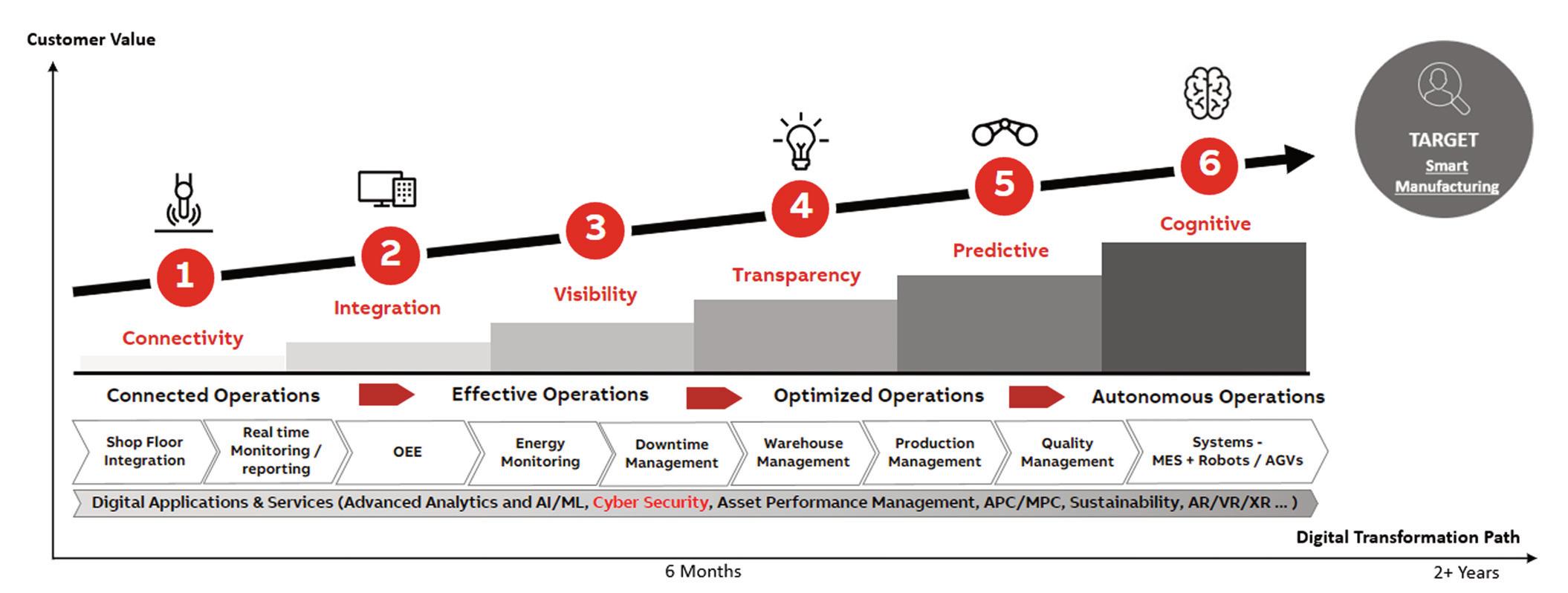
In fact, MES can be used for all order entry and invoicing functions for end-customer products to streamline the flow, per forming multiple checks to ensure the orders can be delivered in time, and providing the status of ordered, planned, produced, de livered and invoiced orders.12,13 This frees up sales or mill per sonnel to perform other important tasks since they only need enter the minimum information (pricing and production reserva tions are handled by the system).
take, as well as result in additional training and application costs. For this reason, MES user interfaces and navigation should be co-created with pulp and paper operators, offering intuitive dis plays – the majority web-based – for better mill-to-shop floor visibility.Let’stake the example of Ittihad Paper Mill (IPM) in Abu Dhabi, UAE, which annually produces 320,000 tons of uncoated, wood-free paper.3 IPM was the first pulp and paper site in the area, with many employees new to the operations and having lit tle experience of the systems, including the MES. ABB provided training on how to use the MES’s algorithms and functionality and soon the mill team was confident and able to optimise pro duction through the paper machine and beyond, right through to the fleet of sheeters.
The MES helps to plan production over the winders and sheeters, taking the full width of the paper web into use, helping to minimise waste at every stage of production, in turn saving money for the site. With easily configurable dashboards for different grades, MES users can generally make changes on the fly directly from the management environment. For instance, paper mills may find value in being able to email everyday delivery notes, packing lists, invoices and more from the system itself.
Digital energy management systems can be used for single mill energy reporting or as a company-wide system serving hun dreds of users that proactively manage energy planning and pro curement. Let’s take the example of a European Cartonboard mill that invested in ABB’s MES. By optimising refined mechanical pulp operation according to the electricity spot price and coming up with an accurate power consumption forecast for the electric ity purchasing, the mill saved 14.5% in electricity costs.11
This also offers seamless integration of manufacturing and business information with enterprise resource planning systems, enabling a single point interface, shortening implementation times and helping maximise the customer’s existing investments, while also saving on staff costs.

7,8 successcles/data-management-the-formula-for-pulp-paper-analytics-https://new.abb.com/pulp-paper/abb-in-pulp-and-paper/arti 9 data-managementtems/collaborative-production-management-products/process-https://new.abb.com/pulp-paper/abb-in-pulp-and-paper/sys
2 ABB MES brochure: mentPartId=&Action=Launchaspx?DocumentID=3BFI200014&LanguageCode=en&Docuhttps://search.abb.com/library/Download.
3 cles/previous/ittihad-paper-mill-mes-case-historyhttps://new.abb.com/pulp-paper/abb-in-pulp-and-paper/arti
Using MES to future-proof mill operations
4 ABB MES brochure: mentPartId=&Action=Launchaspx?DocumentID=3BFI200014&LanguageCode=en&Docuhttps://search.abb.com/library/Download.
Sources 1 ufacturing-execution-system/https://www.epicor.com/en-uk/resources/articles/what-is-a-man
MANAGER Responsible for all the engineering func琀ons in the Paperboard Mill. Understanding and commitment to the relevant statutory requirements is a key requirement. Developing a planned maintenance system will be an early task.
ENGINEERING DEPARTMENT SUPERVISOR Responsible for the organiza琀on of a team of skill enhanced cra昀smen, and the quality of the mill maintenance. A working knowledge of the various engineering disciplines is required, ideally some electrical and control.
5 tId=&Action=LaunchID=9AKK107991A9411&LanguageCode=en&DocumentParhttps://search.abb.com/library/Download.aspx?Document 6 for-quality-management-at-wisconsins-newest-milllatest/automated-paper-testing-enables-data-driven-innovation-https://new.abb.com/pulp-paper/abb-in-pulp-and-paper/articles/
Opportunity to develop any skill gaps would be provided for the right candidates. You would be joining a dynamic Management Team, and there are clear promo琀onal opportuni琀es for the successful candidates. ROMILEY BOARD is a progressive employer, and an encouraging salary and bene昀ts package is available, including reloca琀on package if appropriate. If you feel you meet our requirements then send your CV to the Opera琀ons Director, johnjohnson@romileyboard.co.uk.
Limiting energy use and waste In the pulp and paper industry, energy consumption consti tutes up to 15% of total operating costs, so investing in energy efficiency and waste reduction solutions can make a significant difference to a company’s bottom line, as well as limit water and associated chemical use to improve energy and water se curity.10Applications can be integrated with an MES to manage en ergy consumption by leveraging real-time data from process monitoring, automation and production planning systems – as well as energy providers – to help manage and optimise mill op erations. For instance, many modern MES feature applications compare actual consumption against targets and identify areas for Energyimprovement.loadforecasting tools help operators plan supply or get the best price for energy. Energy monitoring and reporting calculates efficiencies and helps to visually analyse the use of both energy and utilities, while energy demand and supply tools determine the optimum use of supply resources to meet the con sumption schedules with user applied objectives.
Modular and flexible MES applications are designed specif ically for the requirements of the pulp and paper process,14 and in collaboration with the companies themselves, allowing them to be efficiently adapted to changing production environments, business rules and industry standards.
PAPER TECHNOLOGY AUTUMN 2022
MES
MES can be used to make pulp and paper manufacturing op erations robust enough to weather fluctuations in the market, and the economic impacts of unexpected global events.
ENGINEERING
Pulp and paper companies that develop meaningful partner ships with an experienced and trusted technology provider can look forward to an ongoing return on investment in software de velopment to future-proof their investment and operations. Easy configurability, updates and continuous services ensure that re sults and utilisation are preserved, and total cost of ownership is reduced.Inthis way, MES solutions equate not only to efficiency, cost and energy savings for papermakers in the here and now; they also make them more resilient in the future, paving the way for success.
10 https://www.pulpandpaper-technology.com/articles/energyreduction 11 Costs were saved over two sample periods - ABB MES 200014&LanguageCode=en&DocumentPartId=&Action=Launchhttps://search.abb.com/library/Download.aspx?DocumentID=3BFIbrochure: 12 newsprint-producer-selects-abb-for-mill-digitalizationhttps://new.abb.com/news/detail/71685/norways-largest13 across-its-entire-production-fleettive-mes-agreement-supporting-sappis-digital-transformation-https://new.abb.com/news/detail/78928/abb-awarded-collabora 14 ABB MES brochure: mentPartId=&Action=Launchaspx?DocumentID=3BFI200014&LanguageCode=en&Docuhttps://search.abb.com/library/Download. 15 and-paper-process-optimizationpackaging/our-insights/tapping-digitals-full-potential-in-pulp-https://www.mckinsey.com/industries/paper-forest-products-and24 WHY IS A CRITICAL STEPPING STONE Romiley Board is a successful recycled paperboard mill based near STOCKPORT. There are vacancies for the following:
Samantha Peace (Director of Field Operations, HSE) then gave a fascinating presentation on an investigation following the death of an amateur re-enactment enthusiast during a recreation of a mediaeval joust for the TV series Time Team – probably the first death in such an event for many centuries. Ultimately the incident was put down to poor planning and risk assessment by the team who organised the event; the right sort of engagement and questions were not undertaken by the team, and no one seemed aware of the potential consequences of an accident. If the correct questions had been asked by the leaders, there is every chance that the fatality could have been averted – something that transfers to any industry and industrial situation.
Session 1: Health and Safety Leadership Ed Corbett, HSE, “Health & Safety Performance: a Race to the Bottom, of a Journey to the Top?”. Organisations are not themselves necessarily perverse, but they are made up of human individuals, a fact which which tends to increase the complexity of said organisations. Furthermore, there are competing issues in organisations, such as profit and maximising shareholder value, individuals who are addicted to risk taking, management addicted to change (“the next silver bullet”), and the need for in dividuals to feel appreciated and achieve ‘success’. In amongst all of this, the need for health and safety is to be found.
Session 4: Implementing Management of Change in Practice
Session 3: Workplace Transport Load Security Nina Day, HSE, “Workplace Transport Load Security: the Past, Present and Future”. What has driven progress to where we are today (particularly since a series of pallets containing paper fell onto the A1(M) several years’ ago – and a 2 tonne reel fell onto the M27 in July 2018)? There has been significant in novation in trailer and equipment design, increased efficiency through more effective working practices, increased awareness of why incidents occur and how they can be prevented, and ef fective risk control through systems, training, and provision of equipment – but still incidents occur. The only way we can lower risk is to take active steps to reduce it. Effective, up to date risk assessment and control measures should be in place, the right equipment for the job can make a big difference, clear and straightforward information and training should be provided so everyone knows what they need to do, there must be clear com munication between different employers, and ultimately some one must manage and review the systems put in place.
Mike Reddish, Kimberly-Clark, “Safety Management of Change”. sMOC is the Kimberley-Clark ‘Safety Management of Change’ process. Introduced in the late 1990s in America, it has gradually been rolled out across the rest of the company, reaching EMEA in 2009. It is a collection of processes used to give guidance in the consideration of the possible EHS (Envi ronmental, Health and Safety) impacts of a change (such as to 25
Daven Chamberlain, PITA Publications Editor
In conclusion, people are complex: we are not necessarily log ical, rational, and evidence-based facts do not necessarily change minds; we are hard wired to bring bias and emotion into play, and individual goals may be totally different from those imag ined by management. The organisation is not simply the ‘sum of its parts’ but is made up of a huge number of individuals, all with complex needs and personal goals, therefore imposition of a sim plistic H&S policy that is not backed up or supported from above is never likely to work.
This was the first such event since 2019: the decision to skip a year was mainly due to COVID, but in doing so it fell in nicely with the CPI’s 150th anniversary. To celebrate, the foyer of the main conference event held a number of boards featuring histor ical photos, supplied thanks to the Apsley Paper Trail and Frog more Mill, along with modern images from sites operated by DS Smith, Essity, James Cropper and VPK. After initial opening remarks by Andy Braund, Berry Wier sum (ex CEO Sappi Europe) opened proceedings with his keynote address. He described some of the accidents (some fatal) that occurred during his time with Sappi, and how the company adopted the Sappi Performance Engine in 2013 to improve the situation. In enacting this system, management was engaged in producing a chronology of issues needed to be addressed at each site, to which they were tasked with finding solutions. Where there were teams engaged in safety improvement performance, it was found that absenteeism reduced; the secret for safety per formance was found to be engagement and collaboration. Giving operators more autonomy and therefore job enrichment was found key to the success of the process. But ultimately it is still necessary for this to be driven from the top, continually, with the message that safety trumps all, including production targets.
OVERVIEW OF SESSIONS
PAPER TECHNOLOGY AUTUMN 2022 NEW INSIGHTS ON APPLICATION OF HIGH-YIELD PULP CPI Health and Safety Conference 2022

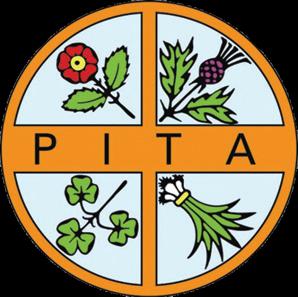
Session 2: Working Minds Peter Kelly, HSE, “In the Eye of the Storm: Mental Health Post-Pandemic”. Anyone can suffer with stress and poor mental health – it can affect people at different times and in different ways. Individuals typically show signs including mood swings, being withdrawn, showing increased emotional reactions, pos sibly being more titchy or nervous, and may take more time off work or start to arrive late. Meanwhile, stress in a team or busi ness will manifest as more complaints, arguments, more sickness absence and impacts on productivity and performance or higher staff turnover. If someone is experiencing stress or a mental health problem, they should be encouraged to talk, with regular opportunities taken to check-in on mental health and stress. To help with this HSE has published their Talking Toolkit: Prevent ing Work-Related Stress, which was developed to help engage ment with employees and developing solutions to stress-related problems.
In conclusion, an effective safety management system is a business enabler, helping to cut the costs of disruption and delays and avoid financial, reputational, and legal risks. Assessing the risks, putting effective risk control measures in place, and man aging and reviewing their ongoing operation, will significantly reduce the risk of something going wrong.
Dave Bromme, DJB Machinery Compliance Ltd; Jason Reed, Pilz Automation Technology UK; Matt Androsiuk, Cobots and Machinery Safety Ltd; and Mark Staples, Euchner (UK) Ltd, “Safety Design and Emerging Safety Technologies”. Every year the UK Paper Industry invests £millions on purchasing and in stalling new machinery, plant and equipment, or refurbishing and upgrading old machinery. In addition, every year employees working in the UK Paper Industry are injured, some seriously, as a result of a ‘contact with machinery’ incidents. However, use of collaborative robots and mobile robots is expected to grow 20-30% year on year through to 2028, so opportunities for ma chinery contact incidents will only increase. So, what was ac ceptable in the past is NOT acceptable NOW! To this end, BS EN ISO 13849-1.2. Safety of machinery. Safety-related parts of control systems -Part 1. General principles for design was pub lished in August 2021, and expect all Safety of Machinery stan dards to be updated in due course to take account of changes in how we use machinery.
Session 8: Implementing a Mental Health & Wellbeing Strategy
equipment, work processes or procedures, and operating guide lines). It is a ‘steps and gates’ style of process requiring checks and adjustments at key stages in the life of the change. Its power is in the requirement for discussion, collaboration and commu nication. It gives a systematic approach that removes reliance on individuals and places responsibility for the consequences of change onto a group. Overall the process is aimed at safer work ing, both in terms of health, and also business profitability.
The DS Smith strategy for wellbeing is ‘Vision Zero’ launched in late 2018. It was developed to raise the profile of health and wellbeing, and to embed this in ‘business as usual’. To start, the company asked for feedback from staff, and then they used ‘Mates in Mind’, which was developed in the construc tion industry, as a baseline to undertake a mental health audit. This led to development of a health and wellbeing policy with support at leadership level, and communication of a strategy across the company. Health and wellbeing has become a standard topic for discussion during leadership site tours, and sub-teams have been encouraged to form and develop local approaches –such as 5k runs, healthy eating initiatives, charity activities and picnics.ThePrinting Charity was established as a benevolent charity in 1827 to support printers and their dependents. The aim and objectives are to help make life better for people in our sector, help everyone in genuine need through practical, emotional and financial support, and champion workplace skills and opportu nities within our sector for young people. Their work is delivered through: Welfare & wellbeing, and Education & partnerships. In particular they have a free confidential helpline, manned 24/7/365 which can offer information, advice and counselling; also MyEva Financial support via a digital expert, management support and mental health first aid support.
Session 9: Fire Prevention Planning Debbie Stringer, CPI, Peter Buckley and Spence Seaman, EA, and Karen Gilbert, Saica Paper UK. Spence Seaman summarised findings from the Environment Agency fire prevention audits, then Peter Buckley identified important safety measures that should be in place – all of which can be found in the excellent publication Fire Prevention Plan: A Paper Sector Guide, pub lished by CPI and available free of charge on their website. Fi nally, Karen Gilbert gave a case study based upon SAICA Paper, Partington (PM11), which experienced two significant fires in the Paper for Recycling Yard during April and May 2019. This pre sentation outlined their experience in dealing with these fires, and the subsequent experience in generating a fire prevention plan.
26 PAPER TECHNOLOGY AUTUMN 2022 CPI HEALTH AND SAFETY CONFERENCE 2022
Kevin Stevens, FM Conway, Mark Ryan, Logson Group, Andy Gordon, Leadership Consultant, and Daniel Johnston, The Card board Box Company. What is Safety Differently? It is a safety news site (https://safetydifferently.com) crafted by professionals and enthusiasts from various industries around the globe. Tradi tional Safety Thinking revolves around ideas that: (1) Workers are the problem to be fixed, and more rules leads to safer work ers; (2) We must tell workers what to do and more importantly, what not to do; and (3) Safety is about the absence of negatives – accidents. By contract, Safety Differently Thinking considers: (a) Workers are the solution, being dynamic problem solvers in complex environments, needing fewer rules; (b) We should ask our workers what they need, not tell them what they can have; and (c) Safety is not the absence of accidents – it is the presence of capacity.Theapproach used at Logson has involved asking some chal lenging questions (“Are people placed at the centre of the solu tion or are they seen as the problem?”, “Do we measure safety as the presence of positives or the absence of negatives?”, “Has safety become a bureaucratic activity or an ethical responsibil ity?”), logging what their employees think, and using these re sponses to develop and implement their approach. Everything is centred around conversations with the employees, and is relevant to each specific site and business.
Heather Beach, The Healthy Work Company, “Building a Mental Health and Wellbeing Strategy”. Wellbeing is not just the absence of disease or illness. It is a complex combination of a person’s physical, mental, emotional and social health factors. Wellbeing is strongly linked to happiness and life satisfaction. In short, wellbeing could be described as how you feel about your self and your life. In designing a wellbeing strategy, H&S and HR must work together to create and implement the strategy. En gagement at senior team/group level is imperative, along with some wellbeing ambassadors at more junior level in the business? In particular, getting the senior team to speak out about life strug gles will help to get buy-in from lower ranks. Most importantly, a ‘wellbeing strategy’ is not a simple, single run through of a pro cess; it is iterative, and must be adaptive to change.
Session 6: Safety Design and Emerging Safety Technologies
Session 7: Looking at Safety Differently
Julie Stevens, DS Smith, Kemsley, and Nigel Elias, Smurfit Kappa, “Mental Health and Wellbeing”. Also Julie Way and Nicola Peacock, The Printing Charity, “Introducing the Printing Charity”. Smurfit Kappa instigated their ‘LifeWorks’ pro gramme about 10 years’ ago, but it was poorly communicated and not given sufficient leadership support. More recently they revisited the area of wellbeing, which has involved mandatory training for all in leadership roles within the company, in order to get top-down support. In turn they have trained almost 300 mental health first aiders – voluntary roles from all areas of the business. In particular, the role of MHFA involves active listen ing then signposting the person to those best placed to help –these people are not mental health professionals, and are not there to diagnose or offer practical assistance. Overall the process has been so well received that Smurfit Kappa recently won the Health & Safety Gold Award (see PTI, Summer 2022).
Slides from all of these sessions can be viewed on the CPI website.
Session 5: Building a Mental Health and Wellbeing Strategy
The conditions are that the importers need to submit advance information in an online system for imports and obtain an auto matic registration number. Information has to be submitted within 75 days and before five days of the arrival of the consignment.
While, this compulsory registration may appear an additional or cumbersome job, it will ease importing of required paper with out any fear of holding by the custom office and the exporters will feel ensured of their products reaching India without any problem and in timely fashion.
Avanti Conveyors Ltd. A supplier of palletisers to the cor rugated converting industry; the company has recently produced new electrified machinery which can be retrofitted onto existing lines and replaces machinery working using pneumatics.
To quote Monty Python, the plenary session was something “completely different”. John Hotowka, Director of Achievement Thinking gave a 45 minute motivational talk interspersed with conjuring tricks, some involving audience participation. To say the least, it was very different from anything we have had before. CPI President Stuart Begg (Ahlstrom) then gave the vote of thanks and other closing remarks, before we all left.
. Supplier of fire suppression systems for light and heavy mobile plant, including FLTs, that can be retrofitted onto older vehicles.
Euchner (UK) Ltd. Specialists in industrial safety engineer ing, they develop and manufacture products and solutions tai lored to the requirements of customers from a wide range of sectors. Free copies of their excellent Safetybook: an Introduc tion to Safety Engineering were distributed at the event. (Golf and BBQ sponsor and presenter.)
Apart from tackling dumping, Government wants to ascertain if the items can be manufactured indigenously. The decision to mandate compulsory registration for paper imports, is not only to address dumping concerns of the domestic industry but also to know the profile of paper coming into the country in the ‘oth ers’ category tariff lines. It may be because someone may try to avoid a specific code where duty could be high or may be just for the sake of conve nience. The idea is to have an import system where those who are importing will file what kind of products they are getting so that it could also be judged whether the domestic manufacturers have the capability to produce the same kind of paper.
EXHIBITORSArdantLtd
The Healthy Work Company. A company that offers cor porate wellbeing training and programmes. (Presenter.)
A letter from India
27 PAPER TECHNOLOGY AUTUMN 2022 CPI HEALTH AND SAFETY CONFERENCE 2022
The paper products were being dumped by way of under-in voicing, entry of prohibited goods by false declaration and rerouting of goods through third countries to take advantage of India’s trade agreements with certain trading partners. Based on the present Government policy of “Make-in India”, these manipulative elements have been eliminated, which will lead to more transparency and consolidate anti-dumping mea sures and it will serve in favour of the domestic paper industries.
Dr Mahendra Patel, industrypaper@yahoo.co.uk (www.industrypaper.net)
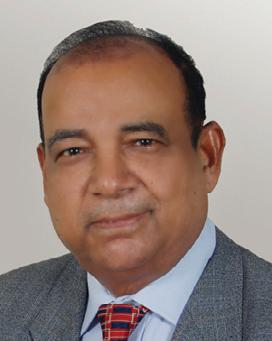
The Government of India (Directorate General of Foreign Trade) issued a notification on 25 May 2022, amending the pre sent import policy of paper from “free” to “free subject to com pulsory registration” under Paper Import Monitoring System, to be implemented from 1 October 2022.
ZoneSafe. A supplier of active safety devices to prevent peo ple/vehicle and vehicle/vehicle collisions. Uses 360° RFID sen sors on vehicles, assisted by active tags worn by personnel or fitted to assets, to identify hazards. (As used by Mondi.)
In fact it was the Indian paper manufacturers that initiated the move and requested the Government for an amendment, which resulted in formation of the new monitoring policy.
It is hoped that the problems of alleged dumping and re-rout ing will be checked through this monitoring system because it tracks all transaction details including type of product and price.
The hope is that this new import monitoring system will work effectively and that the fear of domestic paper manufacturers for dumping from abroad will not exist anymore and that the Gov ernment of India will be able to better meet its objectives in its policy of “Make-in India”.
Martor UK. A supplier of high quality safety knives with concealed blades. Pilz Automation Technology. A supplier that offers complete automation solutions based around its core skill of safety – from sensor technology to control and actuator technology. The main new product on show was RFID coded entry technology. (Main event sponsor and presenter.)
India is producing many grades of international quality, such as printings and writings, as well as other types of papers. How ever, there may be need for importing some specific types of pa pers, and it is here that the importers will have to follow strictly the new registration system.
It was being felt for the last many decades that the papers im ported to India from different countries lacked transparency and that even quality papers were getting imported at very cheap price. Such dumping was definitely not a healthy sign for the sustainence of domestic paper industries. The Government some time back imposed dumping duty, but that was not found to be working effectively. There were obviously elements which could be manipulated to play foul in the imported paper.
The amendment covers 201 tariff lines including items such as newsprint, handmade paper, wallpaper base, duplicating paper, coated paper, uncoated paper, litho and offset paper, tissue paper, parchment paper, carbon paper, wall paper, envelopes, toi let paper, cartons, account books, labels and bobbins.
New Paper Import Policy
The Healthy Employee. A company we have featured many times before, that offers corporate health and wellbeing pro grammes, covering both physical and mental health, and nutrition.
However, many paper items covered under monitoring system are also under the ‘others’ category which does not specify what the item exactly is and the government is keen to shed more light on such products.
The Printing Charity. A charity for people working in the print, paper, packaging and publishing sector. Support includes finance, helpline, counselling and sheltered accommodation. (Presenter.)
PAPER TECHNOLOGY AUTUMN 2022 NEW INSIGHTS ON APPLICATION OF HIGH-YIELD
The advantage of this solution is that the safety function is re alised with the devices of the PNOZmulti 2 family, which means it can also be implemented in existing applications. In addition, multiple cardboard feeds can be monitored with just one base unit. Only the necessary hardware inputs and outputs have to be considered in the configuration. The function blocks for the eval uation are included in the PNOZmulti Configurator V11.0, which does not require a licence fee, and its predecessor versions. Two diffuse sensors at the material feed permanently monitor PULP
Safety not left to the feed
28
Digitalisation, too, has long since arrived in the packaging sector: Powerful control systems have come to replace relaybased hardware, and modern safety concepts are being imple mented to provide the best possible protection while neither hindering flows nor encouraging operators to engage in manip ulation. Digitalised processes have made flows more efficient, handling easier and breakdowns rarer. Based in Hüllhorst, near Bad Oeynhausen, Sema Systemtechnik has been manufacturing plant and machinery for the semifinished goods and packaging industry for more than 35 years. It focuses on machines for the packaging, transportation, palletising, straight ening and re-packing of primary packaged products, especially for the dairy industry. With a workforce of around 100, the SME offers a comprehensive portfolio of services extending from design through manufacture to commissioning and line integration.
Safe with and without cardboard: Safe and flexible solution from Pilz protects operators at the tray former
In normal operation the cardboard blanks queued for processing act as a movable guard. If the material feed runs empty, though, the operator can reach unhindered right inside the tray former –which constitutes a significant hazard. That’s why two diffuse sensors from Pilz keep a permanent eye on the feed opening: If there are no blanks left in the feed, the safety function triggers an immediate stop to the hazardous movement (Figure 1). The TÜVSüd-certified solution, consisting of a configurable safe small controller PNOZmulti 2 and special diffuse sensors with back ground suppression, ensures that the tray formers of Sema Sys temtechnik meet the very highest safety requirements. The safe solution removes the need for “fixed” guards in the feed area. Outer packaging or cup trays made of cardboard carry a huge range of articles. Their design depends both on the form and size of the product and on the requirements made of the respective production and logistics processes. Since outer packaging is now also used for presenting merchandise, individual handling and design requests from the product manufacturers have to be fac tored in as well. That means modern tray formers need to offer extreme flexibility: Cassettes that can be exchanged quickly and easily enable format changes at ultra-fast speed.
Figure 1. Compact, fast, flexible: a tray former from Sema Systemtechnik. The Pilz solution for safe cardboard feeding here ensures that the feed opening does not constitute a risk if there are no longer any cardboard blanks there.
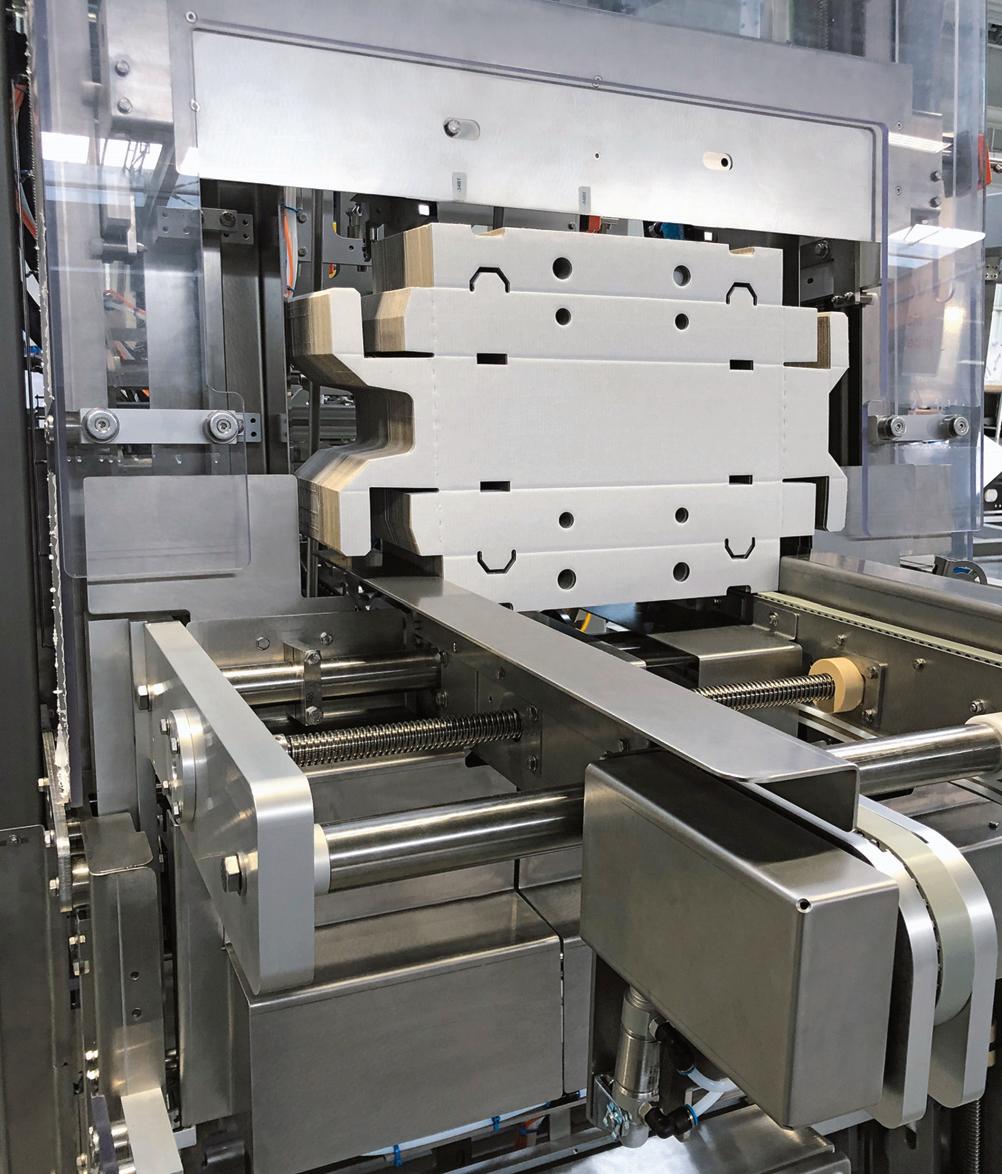
A tray former such as the 1200 s model from Sema Sys temtechnik, which has an overhead servo drive and large-surface panel cladding, outputs up to 60 trays per minute. The compact machine is a flexible-format system with short change-over times. “It’s essentially a standard product which we have adapted to meet the relevant customer requirements and offer as a standalone or fully integrated machine,” says Thomas Wehrhahn, who is responsible for hardware design at Sema. To demonstrate, Wehrhahn places prepunched blanks in the feed magazine: The machine starts when the stack has reached a depth of at least 80 millimetres. The vacuum-driven puller pulls the cardboard blanks in and presses them onto the carrier of a toothed belt. The blanks are then folded, glued and sealed in a number of steps at one-second intervals. Once formed, the trays are carried on a conveyor either directly to the filling station or for onward transport.
Flexible product adaptation
As long as multiple cardboard blanks cover the feed opening, the operator is unable to reach into the danger zone while the machine is running. Since many blanks are smaller than the opening of the tray former, the area not covered by the blank is sealed by a Plexiglas pane made to the precise contours. This is replaced without the use of tools and scanned by coded, manip ulation-proof RFID sensor safety switches PSENcode from Pilz.
It became clear from the risk analysis that an effective security solution restricting neither the operator nor the process had to be found for the case that there is “no cardboard in front of the feed opening.” Sema opted for an integrated, TÜV-Süd certified safety solution from Pilz. “We have been relying on the robust and reliable products from Pilz for more than ten years already. What’s more, many of our customers don’t want to see safety and security solutions from anyone other than Pilz in their ma chines,” emphasises Thomas Wehrhahn.
Sema recognised that the focus is increasingly being placed on efficient safety solutions for end customers. That, after all, is how process efficiency can be improved, standstill times reduced and, ultimately, a competitive edge achieved. It has long been clear to Thomas Wehrhahn that it’s not just a matter of reliable products – process and solution expertise and in-depth industry knowledge are also essential: “Another reason we’re happy to work with Pilz is that we always get detailed answers to our questions, are kept regularly informed of changes and new fea tures and, quite simply, get good advice,” he says in summary. 29
AUTUMN
Commissioned solution saves money and labour
The solution removes the need for rigid protective devices such as tunnels, while the blanks can also be reloaded from both sides, which makes sense from an ergonomic point of view. To prevent the machine moving needlessly to a “safe stop” and stop ping in the middle of the cycle, a light sensor installed at the feed magazine acts as a notification stage: This constantly verifies the level of cardboard and sends an alert if more blanks need to be supplied.Forcompact packaging machines such as the tray former, Pilz offers a TÜV-Süd certified solution for PL d and Cat. 3 of EN ISO 13849-1 or SIL CL 2 of EN IEC 62061 (Figure 2). If the sensors are operated in combination with PNOZmulti 2 or the new kind of modular safety relay myPNOZ (Figure 3), the users can be confident that this solution meets all safety requirements.
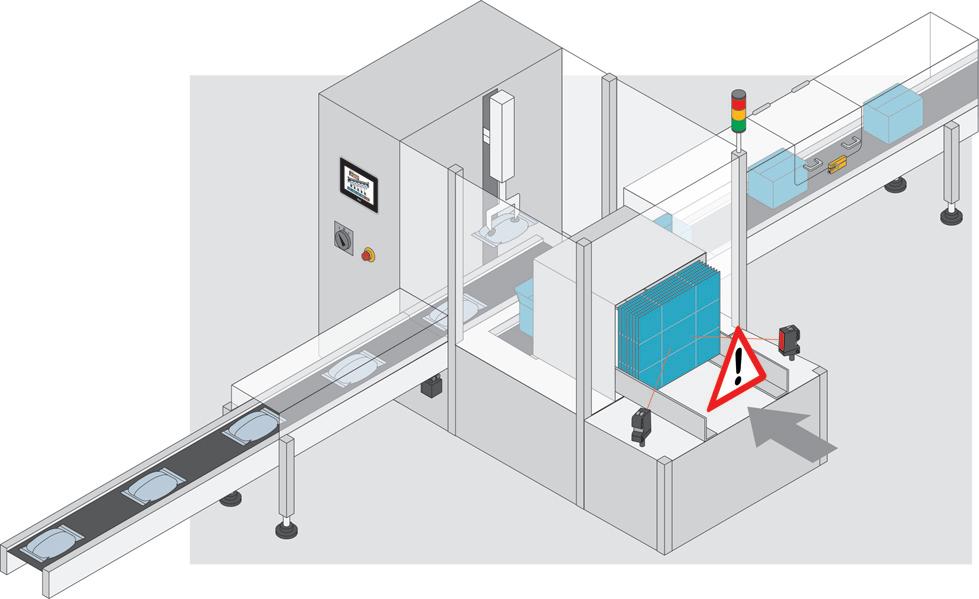
AND
Alongside monitoring protection of the feed magazine, PNOZ multi 2 also evaluates the signals of the safety gate systems PSENslock (Figure 4), which are installed as magnetic process guards on doors and hoods, as well as those of the installed ESTOP pushbuttons. The plain text messages from the PNOZmulti 2 primarily enable possible problems to be detected immediately and standstills to be rectified quickly. “We only use the config urable small controller PNOZmulti 2 from Pilz in our tray form ers. There it normally has to monitor at least ten or even more inputs and outputs. When combined with the feed protection, PNOZmulti 2 offers sufficient flexibility for adjustments and real added value for our customers,” explains Thomas Wehrhahn.
PAPER TECHNOLOGY 2022 WITH WITHOUT CARDBOARD
SAFE
Sema Systemtechnik is based in Hüllhorst near Bad Oeynhausen and has been manufacturing plant and machinery for the semi-finished goods and packaging industry for more than 35 years. Their focus is on machines for packaging, transportation, palletising, straight ening and re-packing, particularly of primary packaged dairy prod ucts. A medium-sized enterprise with around 100 employees, it offers a comprehensive service portfolio, from design and produc tion through to commissioning and line integration.
Figure 3. The TÜV-Süd certified solution for safe cardboard feeding from Pilz comprises the small controller PNOZmulti 2 and the safety relay myPNOZ as well as special sensors.
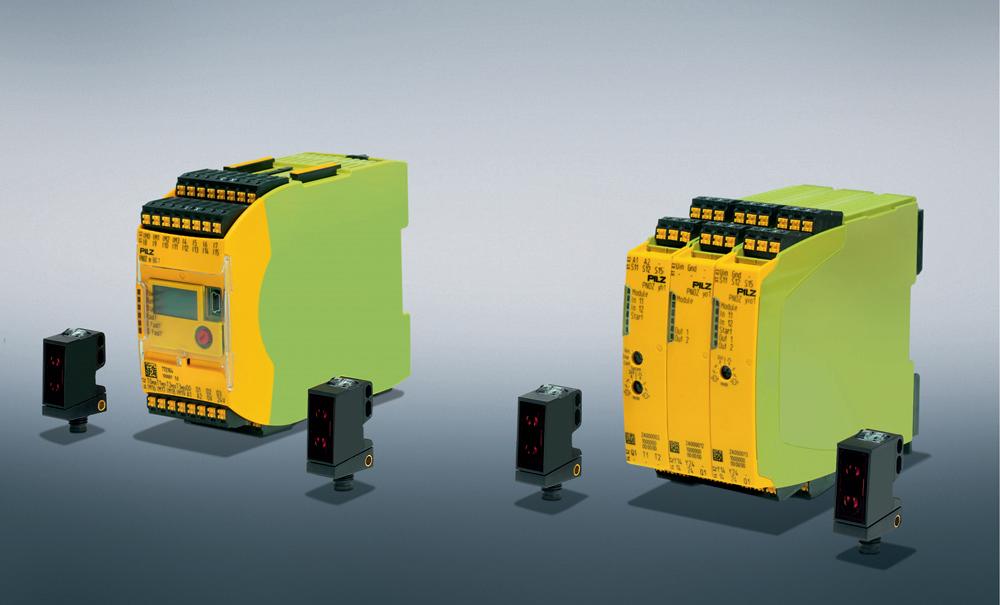
Figure 2. The safety solution for cardboard feeding is configured for PL d / Cat. 3 of EN ISO 13849-1 or SIL CL 2 of EN IEC 62061. The outputs of the safety controller – either PNOZmulti 2 or myPNOZ – switch the machine off and bring it to a stop, notably when the amount of cardboard in the magazine has gone down to below the defined minimum. Figure 4. The safety gate system PSENslock from Pilz performs safe, magnetic process guarding at the gates and hoods of the tray former. It prevents the safeguard being opened inadvertently and offers maximum safety thanks to the manipulation-proof actuator.
the presence of cardboard blanks. The sensors have to be located 30 mm to 100 mm away from the cardboard stack, which allows flexibility in positioning. They can be mounted on the side or, as in this case, on the top of the feed opening, a useful option en abling them to detect all formats processed on the machine and ensuring they do not obstruct the insertion process. If the sensors don’t scan anything, the safe small controller PNOZmulti 2 brings the hazardous movement of the machine to a safe stop. Once the cardboard has been replenished, the machine can be restarted after confirmation.
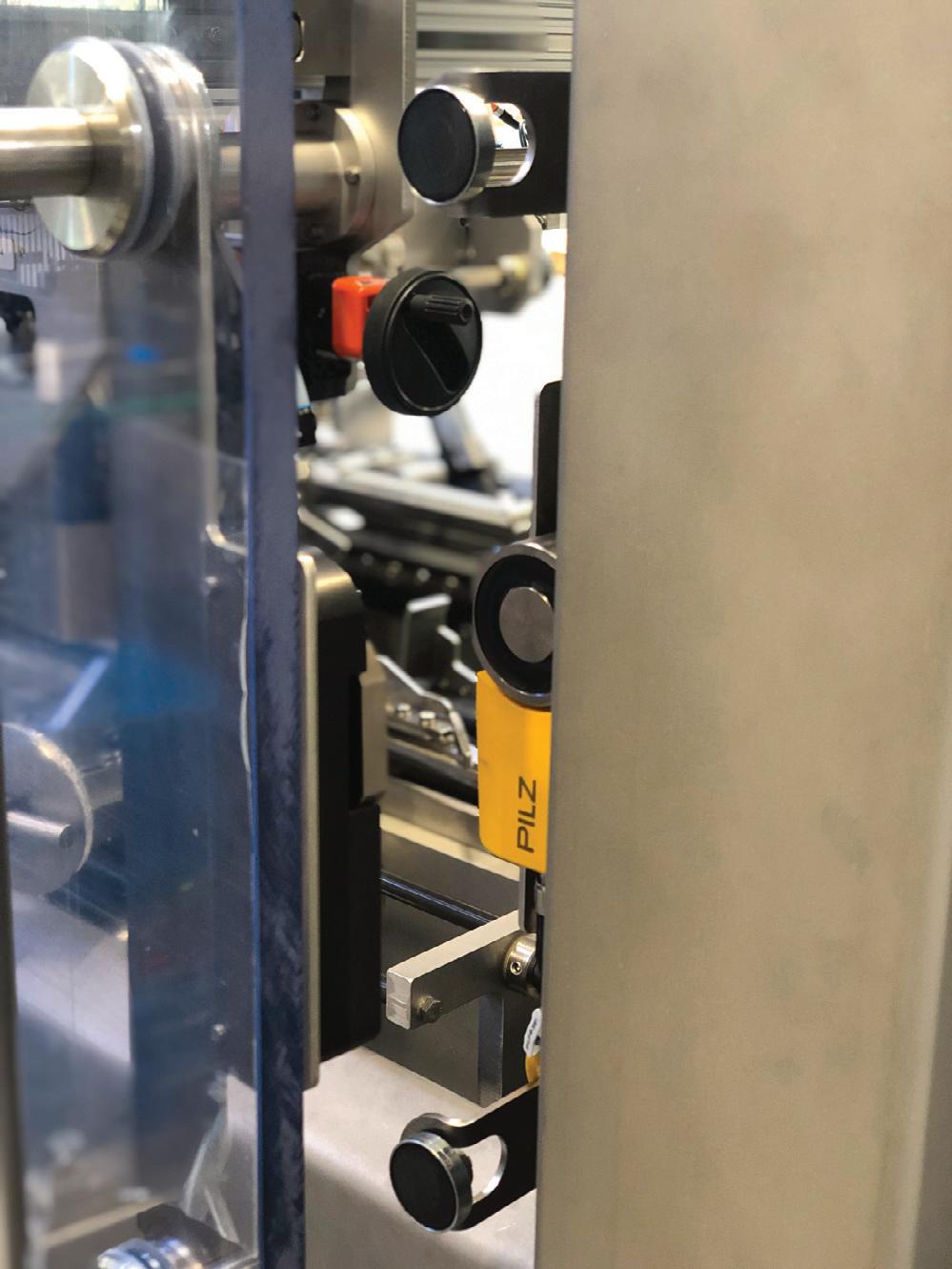
Some knowledge of quality assurance led me in 1976 into my first role in the paper, print and packaging industry with Norprint Limited in Boston, Lincolnshire, at the time the largest UK man ufacturer of self-adhesive labels, tags and tickets, as part of the newly formed quality assurance department. Quality assurance was to be the basis of my activities for the next fifteen years but at Norprint I also covered a technical service role and acquired a good basic knowledge of paper and board technology. I retain good memories of visits to Reed’s Lower Darwen Mill, John Dickinson’s Nash Mills and on one occasion James Cropper’s mill near Kendal, the subject of the 2011 Gold Medal paper.
I shall come back to these topics but I first need to conclude the story of my career progression. It can actually be summed up by pointing to a neat symmetry whereby I spent another 14 years working out of the Hinckley plant, followed by 14 years based in Brussels.
Progression (1990 – 2018)
“When
2022
Summer 1984 saw me move to Leicester to become Quality Assurance Manager with Bostik Limited but perhaps the paper industry already had its claws in me because in 1987 I made the short trip down the M69 to take up a QA role at the Hinckley plant of Bowater’s Corrugating Division. At last, a real paper making company although by the time I joined them the only paper Bowater made was tissue in Australia. I was soon however to be introduced to the mills supplying us. Seeing the production of kraft liner from SCA’s 8 metre wide machine in Obbola made an interesting comparison with the production of tag board I had seen in the Lower Darwen mill a few years earlier.
When I retired at the end of March 2018, some 4 months short of my 70th birthday, I calculated that I had spent 49 years 2 months in gainful employment. Someone asked me why I hadn’t gone on to complete 50 years. The truth was that I had run out of steam – it was time to finish. I had spent some time ensuring an effective transfer of all my responsibilities and resisted the urge to keep in touch with the progress on the issues in which I had been involved. I therefore entered a fairly deep and very enjoyable full retirement.
Engagement with Regulatory Affairs
When some four years later I received a ‘phone call to tell me that I had been awarded the Paper Gold Medal, it was with a mix of surprise and huge pride. I had been very happy that my efforts had already been recognised in various presentations be fore my departure, but this really was something special. Con tributing a meaningful paper as part of receiving the award is however challenging given that it’s not feasible to effectively reengage with any of the topics on which I had spent so much time. With apologies therefore that this might be a little lightweight, my response is to review as briefly as I can the issues and topics I was involved with and then to address the thorny issue which perhaps underlies the reason for the award. What follows is a paper that is partly history or at least my recollection of it, partly a plea/polemic and partly a hope for the future.
In 1995 Bowater changed its name to Rexam but the really big change came in 1999 when SCA Packaging acquired the Rexam Corrugated Division. Now I was with a totally integrated company with everything from forestry operations, paper mills, converting operations to finished goods in the field of tissue and hygiene products. Pretty well coincident with this acquisition SCA Packaging Division appointed a new Environment Director and because he didn’t know much about environmental issues I was the one chosen to provide a crash course in these. This led to me assisting him in setting up a brilliantly effective system for handling the issues in conjunction with the appropriate Eu ropean trade associations and with those responsible across the divisions of the company. The system was criticised by some in the company for us spending too much time with the trade asso
John Swift Paper Gold Medal Award A Career in the Paper and Board Industry
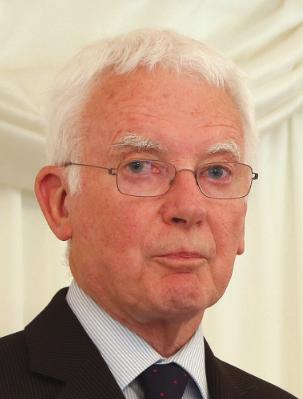
My first task in Hinckley was to take the lead in gaining ap proval for the quality management system to the relatively new BS 5750 standard (subsequently ISO 9002) and then to guide what subsequently became a very successful quality improve ment programme. A career progression however resulted in my also taking over the leadership of the Division’s Central Testing Laboratory, a group-wide role and also my first proper introduc tion to the world of trade associations. I’d been to a few meetings of the British Adhesives and Sealants Association whilst at Bostik but now I was the representative for technical matters in what was then the British Fibreboard Packaging Association (BFPA) which had its offices in Central London. After attending one of my first meetings of the Technical Committee, I was greeted the following day in the plant by one of the management team, with the words “oh, you’re back, when are you going to do some work for us”. This was how I learnt of the antipathy across companies to any activities which didn’t involve being on site and preferably either making or selling the product. This was to become a recurrent, although happily, not a dominant theme across the rest of my career. At that point in the early 1990s, I was still very much engaged with all the usual work of the laboratory dealing with issues in the corrugated plants together with customers and suppliers. Two linked issues were emerging which were about to have a pro found effect on my career: the European Union’s Packaging and Packaging Waste Directive and the decision by the European standards body to form a technical committee on packaging.
PAPER TECHNOLOGY AUTUMN 2022 NEW INSIGHTS ON APPLICATION OF HIGH-YIELD PULP
Background (1970 – 1990) I completed a degree course in industrial chemistry at Lon don’s City University in the summer of 1970, having already un dertaken three six month periods working in industry. I took up a job with one of those companies, the Ever Ready Company, in their R&D laboratories in North London, initially as a materials scientist but subsequently in the then newly emerging discipline of quality assurance.
30 are you going to do some work for us?”
CITPA (International Confederation of Paper and Board Con verters in Europe) – a long-standing association which continues to fulfil a vital function for the European paper converting sector chair of the CITPA Product Safety Group from 2005 until my retirement.
CEPI (Confederation of European Paper Industries) – only formed in 1992 but became quickly established. member of its PPCG (Paper Packaging Coordination Group) – a useful forum in the 1990s for issues relating to packaging waste legislation chair of CEPI’s Environment Committee, from 2013 to 2015 – one of the four standing committees and I think I was the first (and possibly only) person with a non-paper making background to become Chair chair of the Cross Industry Working Group – developed the Industry Guideline (see below), also chair of Food Contact Strategy Group chair of the Environmental Data Issue Group and subse quently the Environmental Footprint Issue Group.
CPI (UK) (Confederation of Paper Industries) – interestingly I was never an appointed chair of a CPI Committee, although I did on occasions chair the Issues Management Committee in other’s absence.
FEFCO (European Federation of Corrugated Board Manufac turers) chaired the Regulatory Affairs Committee for some years and as such attended the FEFCO Board and Executive Committee.
THE EnvironmentalISSUES
Topics Packaging and Packaging Waste
The Trade Associations
PAPER TECHNOLOGY AUTUMN 2022 PAPER GOLD MEDAL AWARD 2022
It’s necessary to identify the principal trade associations with whom I worked. They are listed alphabetically below as they were when I retired in early 2018. The committee structure within associations changed, sometimes significantly over time and ad-hoc groups formed and were disbanded. Being based in Brussels gave me the opportunity to attend quite a number of these groups, sometimes at short notice. I’ve indicated in the list below the most significant committees and groups, particularly where I had the responsibility for chairing them.
31 ciations and staff spending too much time in meetings but from my point of view it maximised our influence with the associa tions and was an effective use of people’s time. It had the total support of top management but not necessarily at all levels below that. It did mean however that I gradually spent more and more of my time on the Division’s activities. I was travelling exten sively, was in Brussels most weeks and eventually in 2004 I was appointed the Division’s Regulatory Affairs Director based in Brussels.From2004 through to 2012 I thus spent the majority of my time engaged with the issues I shall describe below, externally in conjunction with the European trade associations and inter nally through the structure which had been set up. In June 2012 DS Smith acquired SCA Packaging. This led to a whole new set of circumstances and, specifically for my position, a broad ques tioning of the engagement with external bodies and regulatory issues in general. In practice however I did continue to engage with all the same regulatory affairs topics, representing DS Smith. After some 18 months however we reached agreement that I would, from the start of 2014, represent DS Smith on a consultancy basis, an arrangement that turned out to suit both parties very satisfactorily. I was able to secure further consul tancy contracts principally with European trade associations but also from 2015 onwards with CPI to enable me through BSI (British Standards Institution) to continue being active in Euro pean and International standards activities. This brings us to March 2018 and a final handing over of representation in the raft of activities that had engaged me since the early 1990s.
EUROPEN (The European Organization for Packaging and the Environment) – an essential Brussels association bringing to gether the key elements of the packaging and branded goods sup ply chain.chairman of EUROPEN from 2009 to 2013, leading its Executive Committee and Council of Members meetings.
The European Union’s Packaging and Packaging Waste Di rective (PPWD) was published in 1994 and the UK’s regulations followed in 1997, although activity on the topic had started sev eral years before. Michael Clark’s Gold Medal paper of 2010 gives an overview of how the UK paper sector dealt with the leg islation on packaging waste, including through the formation of PIMO (Paper Industry Materials Organisation). Michael’s tren chant views on this topic and indeed how the sector handled en vironmental challenges in general certainly reflect my own. My particular niche speciality in the issue however was how to deal with the “Essential Requirements” for packaging in the PPWD. Without going into excessive detail, these required the drafting of a series of European Standards and a mandate had been issued by the European Commission to CEN (the European Committee for Standardization) to write these. I already had, through the BSI and its committee on Packaging some engagement with new CEN committee on Packaging and was soon heavily involved in the large amount of drafting needed. It turned out that a tradi tional grammar school education, with its serious grounding in the basics of English, aligned with scientific training, was the ideal background for European and International Standardization activities and on many occasions I was the one “holding the pen” in drafting groups. The development took an inordinately long time but the suite of CEN standards was eventually adopted in 2004. Already schemes had been drawn up by UK companies, including Bowa ter and SCA and by trade associations, including the then Cor rugated Packaging Association (previously the BFPA and subsequently merged into the CPI), for their use in demonstrating compliance.Underlying the engagement with packaging waste legislation was the need if not to secure advantages for the paper and board sector then at least achieve equitable status and ensure the merits of paper and board products were recognised. This, it turned out, was a long-term struggle and in a gap between revisions of the PPWD there was a revision of the EU’s Waste Framework Di rective (WFD). An on-going challenge for the corrugated box sector was the incursion of returnable plastic crates into areas of the market previously the domain of corrugated packaging and often based on the questionable assertion of the environmental superiority of reuse. Through EUROPEN we were able to pre vent the introduction of a “strict hierarchy” into the WFD placing reuse above recycling. By such small but important steps, often just maintaining the status quo, did we safeguard the position of ourTosector.conclude on packaging waste, there was actually a really good story to be told which showed that some things did change and which some of us did promote quite widely. A key objective of the PPWD was the reduction of waste. Using Eurostat data,
A very significant proportion of corrugated packaging is used by the food and drink sector, the large majority as what can be described as “secondary” packaging. Its presence in food man ufacturing operations does however lead to many of the same re quirements applicable to food contact materials being applied. This was already recognised when I joined the industry and through the early 1990s Bowater was involved in various initia tives to draft hygiene management standards for packaging in cluding those by Pira International and the Royal Society of Health. In 1999, citing concern over a diversity of standards and certification schemes, the British Retail Consortium (BRC) to gether with the Institute of Packaging (IoP) led an initiative for a unified standard together with a certification scheme. I partic ipated in this initiative on behalf of the corrugated industry and the outcome, published in October 2001, was the “Technical Standard and Protocol for Companies Manufacturing and Sup plying Packaging Materials for Retailer Branded Products”. Al though somewhat lengthy, this was a practical and workable standard which quite quickly became established as the pre-em inent UK standard. Attempts by the BRC to extend its use across continental Europe were not very successful and a diversity of standards started to appear, including a Good Manufacturing Practice document published by FEFCO for which I (naturally)
I was happy to receive at my last ISO plenary in 2017 ISO’s Excellence Award for an “outstanding contribution” to standards development and I also received BSI’s Distinguished Service Certificate.
32 PAPER TECHNOLOGY AUTUMN 2022 PAPER GOLD MEDAL AWARD 2022
Product Safety Issues Materials and Articles in food Contact
we were able to show that between 1998 and 2008 packaging placed on the market was decoupled from growth in GDP and the tonnage of packaging sent to landfill was reduced in absolute terms by some 40%.
Additional Standardization Activities
From the legislative point of view this concerns the Regula tion on Materials and Articles in Contact with Food (as it became in its 2004 version). The story however for paper and board is all about the lack of specific legislation. Since European food contact legislation was introduced in 1976 it had always been envisaged that there would be specific directives for material types but so far the legislative focus has been almost entirely on plastics. I think it’s fair to say that the paper and board sector didn’t have a particularly coherent position on food contact but at some point in the early 2000s a Cross Industry Working Group had been formed, comprising, as its name implied, representa tives from interested parties across the paper and board sector. This group had been meeting in virtual secrecy to discuss possi bilities for a specific measure for paper and board but from the beginning of 2006 when I was asked to take the Chair a more open approach was encouraged.
Hygiene management standards
Alongside the standardization activity was involvement in an extremely ambitious pilot project initiated by the European Com mission in 2013 to develop a series of Product Environmental Footprints (PEF) including one for “Intermediate Paper Prod ucts”. CEPI formed an Environmental Footprint Issue Group to engage with this initiative and decided I was the best candidate to chair it. This proved to be complex work on both the technical and political level and was not complete when I handed it on early in 2018.
Although of high strategic importance (and also for me providing a fascinating level of involvement) these will be summarised briefly as Packagingfollows:– in addition to the activities on the PPWD, I chaired the BSI committee on Packaging and the CEN sub-committee on general packaging for quite a number of Environmentalyears Labelling – I had significant involvement in the development of the International Standard on selfdeclared environmental claims, ISO 14021, and subse quently ISO 14025 on environmental product declarations. I chaired the BSI sub-committee on the topic for some Bio-basedyearsProducts – a strategic piece of work piece of work where we managed to achieve a sensible outcome for the sector.
The outcome was the Industry Guideline for the Compliance of Paper and Board Materials and Articles for Food Contact pub lished jointly by CEPI and CITPA in March 2010. Following the publication by CEPI of the document “Good Manufacturing Practice for the Manufacture of Paper and Board for Food Con tact” in September 2010 and further feedback, a second edition of the Industry Guideline was published in September 2012. The response to these documents might be described as “critical ac clamation” but in my view they did represent a very important step forward for the industry, for end users of paper and board packaging and for legislators. Further developments took place subsequently but I think that the principles established in the In dustry Guideline remained the basis of the approach.
If I had to identify the most significant piece of work I did at European level for the paper and board sector it would be this one. It was also the most challenging.
“Footprinting” The concept of environmental footprinting had been around since the 1990s but the profile of carbon footprinting was raised significantly when the UK retailer Tesco announced in January 2007 that it planned to put a carbon footprint label on all its prod ucts. The topic had the potential to raise all sorts of competitive issues across the paper sector but CEPI, principally through its Environmental Data Issue Group, managed a magnificent feat of coordination in pulling together an industry wide coordination and resulting in the famous “Ten Toes” document. FEFCO also needs much credit for having had the foresight to collect and publish Life Cycle Inventory data going back more than 20 years. The “Ten Toes” gave CEPI the ability to obtain a very favourable approach to paper and board in the first standard on the subject to emerge the following year, the British PAS 2050. The interest in the topic probably reached its zenith at around that time but by then the standards-making process was in pro cess and a number of us spent a lot of time with the development of the carbon footprint quantification standard ISO/TS 14067 and a subsequent standard on communication of footprint infor mation, ISO 14026. The topic of water footprinting never reached the same high profile but care was needed to ensure that the methodology used in the development of an ISO standard (ISO 14046) was appropriate for paper and board. I ended up as the lead UK ex pert in the development of the standard. There was also an in teresting diversion in CEPI where we attempted without success to persuade the environmental NGO, the Water Foot print Network, that rain falling naturally on non-irrigated forests should not count towards the water footprint of the paper subsequently produced.
All the activities I describe above were collaborative in na ture. The advances and progress we made could not have been achieved without the input, help and guidance of a very large number of colleagues, within the companies I worked for, across the industry and of course in the trade associations. I took the decision not to credit any individuals in the text of this paper but the Gold Medal is theirs as much as it is mine and they all have my sincere thanks.
The message has no doubt become clear – even if not very popular. Of course keep a focus on the efficiencies of trade as sociations and the level of representation but do support them and do give the right members of staff the opportunity to get in volved with the issues – and perhaps most importantly of all give them the opportunity to report back, even if their report is a page of text rather than just one sentence. Receiving the Paper Gold Medal Award was a huge honour and very much the icing on the cake at the end of a long career. Whilst I can’t pretend that every single day working in the sector was pure joy, I did have a great time and believe that I did also do some useful work with lasting benefit. Paper and board is still an excellent industry to work in and I do hope others are being given and will be given in the future the opportunity to have the same experience as I had.
PAPER TECHNOLOGY AUTUMN 2022 PAPER GOLD MEDAL AWARD 2022

As I’ve intimated, I encountered quite some resistance, not to say antagonism, at plant level but this was nothing new having spent some years implementing quality assurance procedures and subsequently environment systems and policies. Being told that I was damaging my career prospects could be disturbing but ba sically went with the territory. I do have concerns however that it has become increasingly difficult for people to engage effec tively in the type of cross-industry work that I did, vital though it still remains. The ever-increasing focus on shareholder value drives a short term view which disregards the longer term chal lenges particularly if they’re not immediately apparent and/or difficult to explain in one sentence. So, engagement with these issues unfortunately has indeed in many companies become a career threatening move with the result that the people who might well be very good at it don’t want to pursue it.
Conclusions What I realised in the course of my career was that I enjoyed dealing with issues as opposed to managing people, achieving production targets or selling products. I did at times however have a significant technical service role, enjoyed both customer and supplier interactions and contributed significant financial benefits, both direct and indirect to the companies I worked for.
The one person I will name is my wife Sue who has been my supporter, guide and friend for more than fifty years and she has my everlasting thanks.
Other Activities
Two other initiatives in which I had significant involvement will only get a brief mention here even though they absorbed much time:Packaging Ink Joint Industry Task Force (PIJITF) – a use ful initiative by the European Food Producers association FoodDrinkEurope, which I was asked to chair, starting in 2006 to bring together printing ink manufacturers, pack aging converters and food producers to review issues re lated to inks used for food packaging. It produced a very useful report on the issue in 2008. Interestingly for paper and board packaging this report identified the potential problematic use of mineral oils in inks but sadly this did not prevent mineral oils subsequently becoming a major issue for the sector.
33 took a leading role for the UK. In an attempt to halt this diversity of standards CEN formed a working group to prepare a European Standard and I, with other UK colleagues, joined this group. The outcome was EN 15593 published in 2008 and in my view a masterpiece in both clarity and brevity but sadly neither it nor the subsequent ISO document, ISO/TS 22002-4 could succeed in becoming a unifying document. Despite this, those of us work ing on the topic felt that we did succeed in having published doc uments which did provide stringent but workable and appropriate levels of control for the industry.
European Union project known as FACET (Flavours, ad ditives and food contact material exposure task) – this was another ambitious EU project in which I together with col leagues from CEPI and CITPA had much involvement. Suffice to say that we satisfactorily defended the interests of the paper and board packaging sector.
It’s no doubt clear that I enjoyed the interaction with trade asso ciations, enjoyed working on cross-industry issues which became a bigger and bigger part of my activities as my career progressed. To say that my enthusiasm for working with trade associations was not shared across the companies I worked for would be an understatement. Many, if not most, at plant management level regarded it as a waste of time and money. Happily, I generally had the support of senior management, although even here this was not without questions. I lost count of the number of times we had to add up how much trade associations cost the business and of course for a large company with diverse operations across numerous countries it adds up to a lot of money. In all of this I can’t remember us ever actually leaving a trade association. The bald fact is that industry can’t operate effectively without trade associations. In some circumstances, for instance with stan dardization bodies, the trade association is the only effective route to representation. In other cases, a common industry view is the best means of influencing government and working with other industry sectors. Achieving a common view can be labori ous and every now and then a CEO gets fed up with this and de cides to go off and lobby government or others as a single company. This can be effective for the very largest companies but in my experience, given the relative sizes of companies across the paper and board sector, it usually caused more prob lems than it solved.
Acknowledgements
the news OBITUARIES
, doyen of the UK paper industry for almost eight decades, passed away on 8 July after several months of declining health. Brian started work at the age of 14 as a junior in the St. Anne’s Board Mill records office in 1942. After conscription into the Royal Air Force as a radar techni cian he re-joined St Anne’s in the newly formed research depart ment. Work on the simulation of multi-cylinder drying led the company to build pilot plant, then research on new forming methods for multi-ply board led to development of the nowfamous Inverform process for which Brian’s name would for ever be synonymous. Brian stayed with St Anne’s until 1980, ending as Director for Process and Technology; he then be came a consultant and formed St. Anne’s Paper & Paperboard Dev. Ltd. He was active worldwide, and was a member of CPPA, EUCEPA, PI, RSC (Royal Society of Chemistry), TAPPI, and, of course, PITA – for which he was National Chairman (1982-1984). He received numerous awards includ ing: City and Guilds Insignia Award; Technical Section Jubilee Medal (1969); TAPPI Paper and Board Division Medal (1977); PITA Gold Medal (1987); TAPPI Fellowship (1987); the Paper Industry Gold Medal (1994); TAPPI Gunnar Nicholson Gold Medal (2000); and he was inducted into the Paper Industry Hall of Fame (2000). He held singularly or jointly over 30 patents, was a prolific writer and presenter, travelled widely and was unfailingly curious about everything and always courteous to all he met. A gregarious man by nature, he will be missed by his loving wife of 61 years, Janet, and by his wider family of Paper Industry colleagues.
EmiEmiStefaniStefani
34 BrianBrianAttwoodAttwood
The International Council of Forest and Paper Associations (ICFPA) has announced Jori Ringman as its new President. He is the Director General of the Confederation of European Paper Industries (Cepi). Mr. Ringman was elected at the ICFPA’s An nual Meeting, which was attended by representatives from 18 ICFPA member associations. He will take over the role from Derek Nighbor, who is the CEO of the Forest Products Associ ation of Canada (FPAC) and served as ICFPA President from 2019-2022. Ms. Heidi Brock, President and CEO of the Ameri can Forest & Paper Association (AF&PA), has been elected as ICFPA Vice President. Mr. Ringman and Ms. Brock will serve for a two-year mandate. Sustainability, forestry regulation and policies on carbon and climate are expected to occupy the top of the ICFPA’s agenda during their tenure.
Kadant UK David Moss has been promoted to Senior Sales Manager; he has worked for Kadant for over 20 years, and has particular expertise in forming, pressing and drying. Meanwhile, Dave Clarke, Re gional Sales Manager – Industrial, has retired after 18 years with the company.
CEPI / ICFPA
Kemira Antti Salminen (1971) has been ap pointed to lead Kemira’s Pulp & Paper segment as of mid-August. Previously he had several prior leadership posi tions in Kemira, most recently as Pres ident, Industry & Water segment, and has been a member of Kemira’s man agement board since 2011. He has a PhD in engineering. He replaces Kim Poulsen, President, Segment Pulp & Paper, who left the company in May. Valmet Katri Hokkanen (M.Sc. Econ) has been appointed CFO as of 1 August, after having held the appointment as interim CFO since May. in
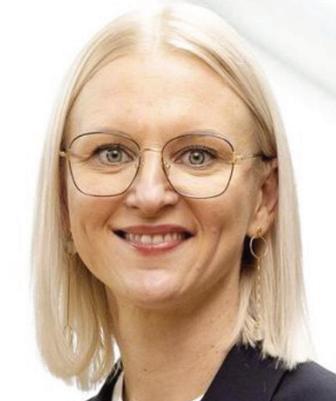
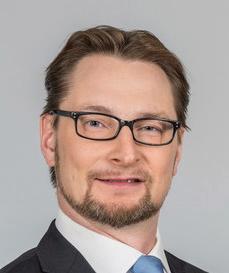
PAPER TECHNOLOGY AUTUMN 2022 NEW INSIGHTS ON APPLICATION OF HIGH-YIELD PULP People
, Co-founder of the Sofidel Group in 1966 and Chair man until March 2021, passed away suddenly at his home in Por cari, Lucca, on 28 June. Born on 9 October, 1930, in Villa Basilica (Lucca), Cavaliere del Lavoro (Order of Merit for Labor) Emi Stefani was one of the leading fig ures in the great history of the de velopment of the tissue paper industry (paper for hygienic and domestic use) and an industrialist with great vision, work ethic, courage, and a rare human sensitivity. “Emi Stefani has been like a second father to me. A figurehead who supported and sustained me when I joined the company. His passion for the company, his ability to face challenges, and his natural predis position for human relationships have made the entire Sofidel community richer and stronger. We unanimously embrace and thank him with enormous affection and gratitude for all that he was able to give.” These were the words of Sofidel Chief Executive Officer Luigi Lazzareschi upon learning the news.
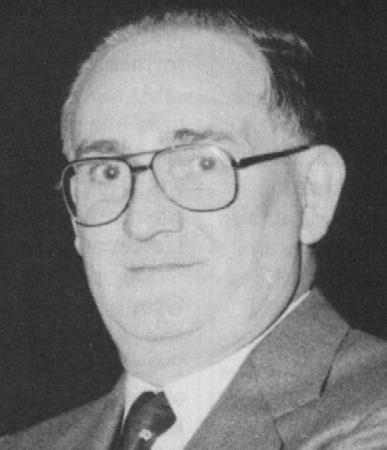
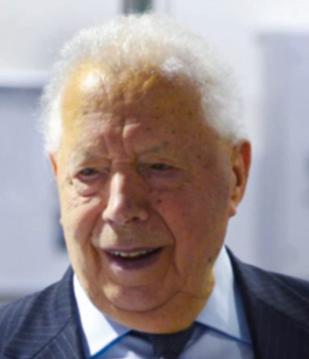
2. Chemical: ISO 11480:2017 Determination of total chlorine and organically bound chlorine; ISO 15320:2011 Determi nation of pentachlorophenol in an aqueous extract.
8. Surface: ISO 8791-3:2017 Determination of roughness/ smoothness (air leak methods) – Sheffield method. Anyone interested in any of the standards or work mentioned above should contact the PAI/11 Chairman (telephone 0300 3020 159 or email daven@pita.co.uk).
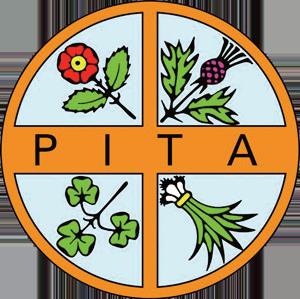
2. General: ISO 187 Standard atmosphere for conditioning and testing and procedure for monitoring the atmosphere and conditioning of sample.
6 Tissue: ISO 12625-12 Determination of tensile strength of perforated lines – calculation of perforation efficiency; ISO 12625-15 Determination of optical properties – Measure ment of brightness and colour with C/2° (indoor daylight) illuminant; ISO 12626-16 Determination of optical proper ties – Opacity (paper backing) – Diffuse reflectance method; ISO 12625-18 Determination of surface friction; NWIPISO 18671 Flushable products.
New or updated standards that have been issued recently:
5. Optical: ISO 2470-2:2008 Measurement of diffuse blue re flectance factor – Outdoor daylight conditions (D65 bright ness); ISO 2471:2008 Determination of opacity (paper backing) – Diffuse reflectance method; ISO 9416:2017 De termination of light scattering and absorption coefficients (using Kubelka-Munk theory); ISO 11475:2017 Determina tion of CIE whiteness, D65/10 degrees (outdoor daylight).
1. Food Contact: EN17600 Paper and board intended to come into contact with foodstuffs – Determination of the fastness of fluorescent whitened paper and board – Analysis by highperformance liquid chromatography with fluorescence de tection; ISO 8784-2 Microbiological examination –enumeration of bacteria, yeast and mould on surface.
Current Standards that have been submitted for Periodic Review: 1. Cores: ISO 11093-1:1994 Sampling; ISO 11093-2:1994 Conditioning of test samples; ISO 11093-3:1994 Determi nation of moisture content using the oven drying method; ISO 11093-8:2017 Determination of natural frequency and flexural modulus by experimental modal analysis.
3. Corrugated: ISO 3035:2011 Determination of flat crush re sistance; ISO 3038:1975 Determination of the water resis tance of the glue bond by immersion.
1. BS EN ISO 638-1:2022 Paper, board, pulps and cellulosic nanomaterials – Determination of dry matter content by oven-drying method: Materials in solid form 2. BS ISO 8784-3:2022 Pulp, paper and board – Microbiolog ical examination: Enumeration of yeast and mould based on disintegration Subject reports and other documents submitted for vote / comment have included:
4. Recycling: ISO 15755 Estimation of contraries; [unnum bered] Estimation of Stickies and Plastics – Part 3: Deter mination by applying near-infrared measurement.
5. Surface: ISO 24118-1 Stylus contact method: Determination of surface roughness.
7. Recycling: ISO 22754:2008 Determination of the effective residual ink concentration (ERIC number) by infrared re flectance measurement.
This column contains a summary of recent work performed under the auspices of PAI/11, the BSI committee that deals with Methods of Test for Paper, Boards and Pulps.
6. Pulps: ISO 9184-6:1994 Fibre furnish analysis – Determi nation of fibre coarseness.
Standards Update Daven Chamberlain Chairman PAI/11 PITA TRAINING COURSES PITA organises a wide range of courses in partnership with a host of top trainers, covering important managerial and technical subjects, including: • Control & Instrumentation • Modern Papermaking • Energy Optimisation • New Engineering Manager • Fundamentals of Papermaking • Pneumatics • Introduction to Wet End Chemistry • Pump E ciency • Maintenance Best Practice • Wastewater Treatment • Maintenance Planning & Scheduling For more information about any of these courses, see the PITA website (www.pita.org.uk ¦ E: info@pita.co.uk ¦ T: +44 0300 3020 150)
3. Lignins: ISO 6350 Determination of dry matter content –oven-drying and freeze-drying methods; ISO 9795 Deter mination of inorganics content in kraft lignin, soda lignin and hydrolysis lignin.
4. General: ISO 534:2011 Paper and board – Determination of thickness, density and specific volume.
AFRY 1. Metsä Board (Husum Mill, Sweden) Industry 4.0 digital so lution to act as the data information hub, directing the as signed logistics devices from the board machine to the planned destination
5. Kim Tin MDF Chon Thanh Corporation (Binh Phuoc province, Vietnam) pressurised refining system for MDF line 6. Nanning Sun Paper (Nanning Pulp & Paper Mill, Guangxi Province, China) pulp production technologies for the fibre line and lime kiln plant as well as energy-saving OCC lines and a complete reject treatment system for RDF (refuse-de rived fuel) production
BID GROUP 1. Canfor Corporation (Southern Alabama, USA) state-of-theart sawmill complex (in collaboration with strategic partner Rockwell)
A.CELLI 1. Reno de Medici (Blendecques Mill, France) paper rewinder
The list below contains a summary of orders reported by a host of major suppliers to the Paper Industry and related sectors be tween the Summer edition of Paper Technology International® and mid-August 2022. Further information on each entry can be found online. Supplier companies wishing to publicise their suc cess in gaining orders should send details to Daven Chamberlain via editor@pita.co.uk.
4. Guangxi Sun Paper (Beihai, Guangxi Province, China) four stock preparation systems to process NBKP (Needle Bleached Kraft Pulp) and LBKP (Leaf Bleached Kraft Pulp) for tissue production
2. Sichuan Huaqiao Fenghuang Paper (Guanghan City, Sichuan Province, China) two 8m width rewinders to pro cess fluting, testliner and kraftliner (PM6 line)
36
6. Saigon Paper (Vietnam) spare parts and maintenance program
8. Paracel S.A. (Concepción, Paraguay) all process equipment and energy-efficient and environmentally friendly pulp pro duction equipment for 1.8Mtpy pulp mill
7. Papelera Guipuzcoana de Zicuñaga (Hernani, Spain) lime kiln
1. Cellmark & Total Fiber Recovery (Chesapeake, Virginia, USA) recycled pulp production facility (capacity 300,000 tons of mixed paper and Old Corrugated Containers)
ABB 1. Andhra Paper Limited (Rajahmundry Mill, East Godavari district, Andhra Pradesh, India) advanced process control for optimised lime kiln production
3. Asia Symbol Group (China) software and service contract to provide the ABB Ability™ Manufacturing Execution System (MES) for a new production line 4. Cheng Loong Corporation (Vietnam) L&W Autoline auto mated paper testing solution 5. Klabin (“Puma II Project”, Brazil) power distribution sys tem, drives and motors (supplied to Valmet)
PAPER TECHNOLOGY AUTUMN 2022 COMPENDIUM OF RECENT ORDERS
9. Shandong Canfield Wood Industry (Chiping County, Liaocheng City, Shandong Province, China) pressurised re fining system 10. Shanying Paper (Jilin) Co. Ltd. (Fuyu City, Songyuan, Jilin Province, China) a complete OCC line, including fibre re covery and reject handling system
11. Sichuan Huaqiao Fenghuang Paper (Guanghan, Deyang City, Sichuan Province, China) patented combi-pulping sys tem combining drum pulping, LC (low consistency) pulp ing, and HD cleaning in one innovative system (2200tpd capacity PM2)
AFT 1. Papeles y Conversiones de Mexico (Monterrey, Nuevo Leon, Mexico) POM approach system for containerboard line (two POMp degassers, two POM Dynamix static mix ers, two POMlock seal tanks, two POM headers, and two POM head tanks for PCM’s two-ply PM2, along with ac companying spare parts and system engineering)
15. Wakayama Gobo Biomass Power Plant G.K. (Wakayama Prefecture, Japan) high-efficiency circulating fluidized bed 50MW boiler (from Toyo Engineering Corporation)
Compendium of Recent Orders
Daven Chamberlain
1. BillerudKorsnäs (Frövi/Rockhammar Pulp Mill, Örebro, Sweden) lime mud filter for the recausticizing plant
ARUP 1. Shotton Paper Mill (Eren Holdings, Deeside, North Wales) transformation of Shotton Mill site (also involving architects AHR)
1. Anon (Pulp Mill, South America) highly efficient cooling technology (18 cooling cells for three wet towers)
1. Visy Paper (Gibson Island, Brisbane, Australia) new fuel preparation plant to ensure efficient and sustainable opera tion of the upgraded Multi-Fuel Boiler (MFB)
3. Dongfang Smart Energy Co., Ltd. of Shaanxi Power Gen eration Group (Wugong County, Xianyang City, Shaanxi Province, China) two paper machine approach flow systems and LC (low consistency) refiners
12. Steinbeis Papier GmbH (Glückstadt, Germany) a complete stock preparation line for conventional wastepaper and spe cial grades (capacity from 78-200tpd)
BMH TECHNOLOGY OY
16. Zweckverband Müllverwertung Schwandorf (Schwandorf, Germany) retrofit of the flue gas cleaning system in a fur nace line at the municipal waste incineration facility
2. Vattenfall (Juktan, Sweden) feasibility study for restoring pumped storage power plant
ANDRITZ
2. BMC Moerdijk (Moerdijk, Netherlands) SMART service contract to power boiler using remote web platform
13. Suzano Aracruz (Espírito Santo, Brazil) modernisation of lime kiln B 14. Veolia Services Suomi (integrated into Metsä Fibre’s bio product mill in Äänekoski, Finland) a biomethanol purifi cation plant
BULK HANDLING SYSTEMS (BHS)
2. Arauco (five Pulp Mills, Chile) remote supervision to ensure greater reliability and monitoring across all processes
BABCOCK & WILCOX
4. ND Paper (USA) two dry end high pressure tail cutters (order to YueLi of Taiwan)
8. Natron-Hayat Pulp and Paper Mill (Maglaj, Bosnia-Herze govina) press technology upgrade including two refurbished Twin Roll Presses and additional equipment and services to secure the trouble-free operation of the presses
11. Vilnius Combined Heat and Power Plant (Lithuania) biomass boiler, flue gas cleaning and flue gas condensing system works
7. Suzano (Cerrado, Brazil) two new wet end Tail Cutters for the new pulp lines (supplied to Andritz)
TIETOEVRY 1. Reno de Medici (mills across Italy, France, the Netherlands and in the Iberian Peninsula) to modernise their core business processes and enable digitalisation across nine mill sites TOSCOTEC 1. Cartiere di Guarcino (Guarcino Paper Mill, near Frosinone Italy) rebuild of PM2 forming and press sections
5. Mayr-Melnhof Group (FollaCell Pulp Mill, Norway) new baling line and flash drying rebuild
10. Södra Cell (Mönsterås, Sweden) the world’s first electrical folding machine for pulp bales
VOITH 1. ITC Limited (PaperBoards & Specialty Papers Division, Chandrahati site, India) to rebuild PM1 including stock preparation (décor machine)
1. Anon (South America) vacuum system for tissue machine (supplied to Replus Tissue) 2. DS Smith (Dueñas Paper Mill, Spain) modify PM2 vacuum system 3. DS Smith Paper Ltd (Kemsley Mill, Kent, UK) rebuild of PM4 vacuum system
4. Liaoning Yusen Sanitary Products (Liaoning Yusen Mill, Tai’an, Liaoning province, China) two tissue machines
2. Vajda-Papír (Budapest, Hungary) digital documentation platform OnCare.eDoc for the comprehensive and userfriendly management of all the technical information of its new tissue line 37
PROJET
3. Kimberly Clark (Tlaxco Mill, Mexico) power cleaner sys tem (nonwoven line)
2. Greenpac Mill (Niagara Falls, New York, USA) additional three years of Performance Agreement
1. Cartularia SPA (Italy) two new sheeter machines for pre mium FBB cardboard (converter) 2. Sumapel (Toledo, Spain) sheeter for coated cardboard
4. Kipas Söke (Söke, Turkey) vacuum system for container board line (PM3)
1. Burgo Mosaico (Lugo plant, Italy) entire renovation of the Jagenberg sheeter drive and automation
DIEFFENBACHER
9. Siempelkamp Maschinen- und Anlagenbau GmbH (for two anonymous panelboard plant end customers, one in Europe and one in Asia) two chip washing and defibrator systems
6. Mercer Rosenthal (Lignin Center, Thuringia, Germany) Lig noBoost plant for extraction of kraft lignin from pulp mill black liquor
6. Smurfit Kappa (Wrexen Paper & Board GmbH, Germany) dryer section modification (including contactless web sta bilisers) of PM3 SAEL
7. Mufindi Paper Mills Ltd. (Mgololo, Tanzania) recovery boiler rebuild
1. Kastamonu Entegre (Kastamonu City, Türkiye) new parti cleboard line 2. Mekong Wood MDF (Vietnam) complete MDF plant
2. Versowood (Otava Sawmill, Finland) major modernisation of mill, particularly installation of bio-boiler PASABAN
1. Berneck SA (Curitibanos, Brazil) world’s largest drum dryer KPA UNICON
6. Siam Cement Group (SCG) (Thailand) high pressure show ers for press felts (PM1)
3. Hitachi Zosen Inova AG (Slough, Berkshire, UK) automa tion of energy-from-waste plant
1. Kuhmon Lämpö Oy (Kuhmo Sawmill, Finland) bio-bioler (to produce heat for the residents of the city of Kuhmo and the sawmill)
5. Metsä Group (all mills in Finland) eight Turbo Blowers in seven different tissue and board machines to upgrade vac uum systems
1. Domtar (Kingsport Mill, Tennessee, USA) fabric cleaners 2. Keryas Paper (Oman) dryer fabric cleaners (PM1)
RUNTECH
DE IULIIS (DJM) 1. Favini Group (Rossano Veneto plant, Italy) update drying section with new dryer cans
PAPER TECHNOLOGY AUTUMN 2022 COMPENDIUM OF RECENT ORDERS
1. Maruti Papers Limited (Uttar Pradesh, India) dispersing unit 2. Padmavati Paper & Pulp (Maharashtra, India) dispersing unit
SOSA 1. CMPC (various sites, Brazil) to utilise open innovation ca pabilities to implement cutting-edge tech solutions that will optimise the efficiency and sustainability of CMPC's forestry supply chain (in collaboration with Brazilian Na tional Confederation of Industry)
2. Saudi Paper Group (Dammam second industrial city, Saudi Arabia) new tissue line (capacity 60ktpy)
1. Sinaatec Spa (Algiers, Algeria) two nonwovens lines (3.2m single-beam meltblown line and a 3.2m composite bico line)
SPM 1. Ahlstrom-Munksjö (Aspa Bruk, Sweden) advanced online system Intellinova Parallel EN to monitor the mechanical and lubrication condition of the mill’s pulp dryer and wood chipper
SIEMPELKAMP
VALMET 1. Águas do Tejo Atlântico (Alcantara, Lisbon, Portugal) solids measurements and Valmet Sludge Dewatering Optimizer (water treatment plant)
2. Fedrigoni (Verona Mill, Italy) new sectional drive for PM3
REIFENHÄUSER REICOFIL
CELLWOOD MACHINERY
5. Port Townsend Paper (Pt. Townsend, Washington state, USA) three dryer fabric cleaners (PM1)
Daven Chamberlain, PITA Publications Editor
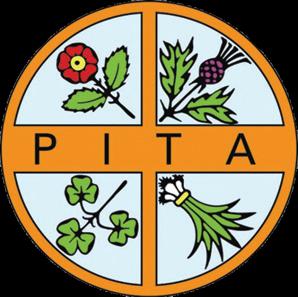

38
When the learner driver is shown a situation they are supposed to wait until an explicit hazard comes into the video frame (like an oncoming vehicle on the wrong side of the road while over taking a parked car). However, an experienced driver may note the parked car as a potential hazard, way before the oncoming vehicle comes into view; but this early recognition of hazard is not rewarded – worse still, it actually fails the test!
HEALTH & SAFETY EVENT
Hands on the wheel and eyes on the road isn’t enough! This goes for hands-free and hand-held devices. To summarise, there is a lot of free interactive educational material available on OpenLearn (www.open.edu) such as “Are You a Focused Driver?” and “Are You Driven to Distraction?”. Try it – you might be surprised to discover exactly how distract ing external conversations can be!
Conference, Exhibition and Webinar Reports
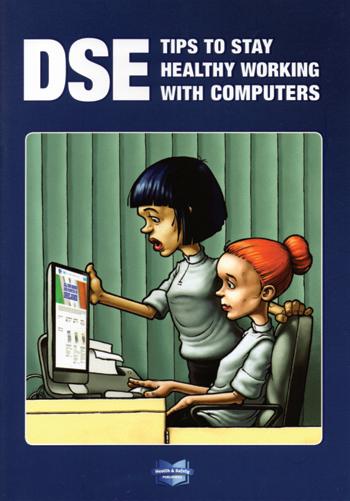
HEALTH & SAFETY EVENT April 2022 (NEC)
As always, I feel that if you attend the event and simply trawl the stalls, you are missing a major part of the learning experi ence, namely the free seminars. Due to time restrictions I con fined my visits to just two of the five lecture theatres: Driving Safety (an obvious choice for any driver) and Safer Logistics. Below are the highlights of the three lectures that I attended: Driver Safety Theatre Dr. Gemma Briggs, Open University, “Distracted Driving: What Employers and Drivers Need to Know.” Death and injury statistics on UK roads are frightening, the main being that on av erage five people die each day in road accidents. Many of these incidents are attributed to ‘driver error’, a significant number of which are likely to be down to ‘cognitive distraction’. Put simply, this means ‘looking without seeing’. If the brain is already engaged on a cognitively-demanding task, its processing capability is reduced with regards to other stimuli. For example, with hands-free phones the core distraction imposed on the user is not manual, but is the conversation taking place. Although drivers don’t necessarily feel distracted when they use hands-free, the problem is reduced awareness of their surroundings.Researchshows that using a phone while driving leads to a fourfold increased risk of crashing; and this effect last up to five minutes AFTER ending a call! This suggests that after stopping a phone conversation, the brain continues to process the discus sion, which acts as a distraction and affects driving performance.
April 2022 (NEC) I covered this event last September, and half a year later it reappeared again, as usual co-badged with The Security Event, The Fire Safety Event and The Workplace Event (the successor to The Facilities Event). Last time it was a surprise to see so many people gathered together for an indoor event; now it seems commonplace. Furthermore, the requirement for a COVID-pass had gone – effectively it was ‘business as usual’.The exhibitor list in the catalogue showed over 180 compa nies were represented, which again harks back to the numbers we saw pre-pandemic times. Alongside many old friends (such as Martor and The Safety Knife Company, both producers of bladed products) there were a very large number of new firms that I don’t remember seeing before, such as: MCR Safety (prescription safety glasses); Univet SRL (prescrip tion safety glasses); Casella (air sam pling equipment); and Health & Safety Publishers. This last company does A5 safety booklets, which can be cus tomised with a company logo, on a wide range of safety themes and is well-worth checking out if you want to upskill staff in a simple and inexpensive way (www.hspublishers.co.uk).
Indeed, there are problems with the hazard perception test methodology, which uses response time as its key measurement.
So to be of use for more experienced and professional drivers the tests need to be updated, they need better context (such as the view from an HGV cab rather than a car, or travelling at high speed for emergency vehicle crews) and they also need to reward early recognition of hazards. Part of the new training being de veloped adds a further aspect – hazard prediction – which has been shown to differentiate professional drivers that score well in hazard perception tests.
PAPER TECHNOLOGY SUMMER 2022 NEW INSIGHTS ON APPLICATION OF HIGH-YIELD PULP
New training video techniques have been developed for drivers operating HGVs, emergency vehicles, transit vans, etc, which use different configurations of mirrors and different graph
Dr. David Crundall, Nottingham Trent University “Hazard Perception and Beyond: Are These Tools Suitable for Commer cial Fleets?” This talk followed on from that outlined above, but dealt with training programmes looking at hazard perception and their application to different drivers. Evidence shows that younger drivers can be trained in this skill, which makes them safer; however, video training methods that were developed for learner drivers have been found less effective for more experi enced or professional drivers – in particular for HGV drivers.
So how is talking to a passenger different from talking on a device? Well, research shows quite conclusively that it is! In a vehicle, the passenger and driver are in a shared environment; both individuals see the same issues on the road, and so can reg ulate conversation to take account of differences in traffic flow. For example, conversation will probably stop if a potentially challenging situation becomes apparent; and the passenger may even help out the driver with observations. Compare this with talking to someone on a device, who cannot share the conditions on the road and so doesn’t regulate their conversation to suit the roadTalkingconditions.withsomeone external on a device creates mental im ages in the minds of both participants. This uses up cognitive re sources in some of the brain areas associated with assessing accurate visual perception and hazard detection. Distracted drivers are poorer at noticing hazards, especially in their periph eral field of view, and also their reactions times are increased.
Hutamaki: Only showed food trays, including microwave able versions using a think PE liner. No moulded fibre on show – which was surprising given the amount displayed elsewhere in this show.
Safer Logistics Theatre Alex Samson, RTITB Ltd, “Tackling Manual Handling in Lo gistics: Eliminating the Risk with Online Learning.” There’s one ‘machine’ that we take for granted: the human body. It’s adapt able and flexible, and can perform a wide array of tasks. If we operate within a set of parameters (that will vary person-to-per son) it functions well, but outside of these damage may occur.
Xiamen Basebetter: Chinese moulded pulp manufacturer with factory in China. Microwaveable products with oil / water barrier technology (almost certainly a dispersion coating as did not appear to be a laminate). Also they had the first example of moulded fibre cutlery that I have ever seen. Other paper-based exhibitors included Henry Moulded Products and Pulp-Tec – two manufacturers of moulded fibre products; Mondi who showed function barrier grades (though it is not obvious whether they are laminates or coated products); and PilloPak, part of the Palm Group who buy in virgin paper and make ovenable greaseproof products.
The Navigator Company: This well-known Portuguese company has expanded significantly in recent years outside of its original publication paper market, into tissue, and most re cently to kraft wrap. So far they have transformed their smallest fine machine to produce gKraft, their new packaging brand, and on the basis of their success are now transforming the second smallest machine. They are still using 100% virgin eucalypt –both unbleached and bleached – and are looking mainly at paper bags but also high end corrugated (for which they will produce liner, not fluting). Marketing is based upon high quality printing on smooth eucalyptus surface. Walki: This major packaging producer is on the compost vs. recycle road. They stated no particular preference. Mainly use PE laminate, but also have a biofilm laminate made from tall oil. Also investigating a biopolymer coating preparation from No vamont; meanwhile also use PE emulsion devised by Kotka.
Protega Global: A UK manufacturer of paper-based packag ing and void-filling materials, including the innovative Hexcel product which can best be described as ‘paper bubble wrap’ de signed to cushion 3D structures such as bottles.
The last time this Midlands iteration of the Packaging Innova tions franchise ran was two weeks before lockdown in 2020, so it was good to see it back, and on a reasonably large footprint as well (unlike for the London edition last December which was disap pointingly small). Exhibitors of significant interest were as follows:
Ankutsan Packaging: Turkish manufacturer of paper and corrugated board. Operates five converting factories, on one of which (Adana) there is also a paper mill producing 60,000ktpy of kraftliner, imitation kraftliner, HP fluting and testliner.
Cullen: Were keen to show off their fibre bottle which uses OCC as raw material and 10-12% natural wax to act as moisture barrier for use with dry contents only. They claim potential to hold liquids as well, and are trialling five patented plastic-free liners and soon hope to have a favourite. The company worked with Choose Packaging on development of bottle; CP was pur chased earlier this year by HP. Currently Cullen is working with Unilever, Holland & Barret, Boots and a leading supermarket to get the fibre bottle to market. Around the time of the exhibition they announced a major expansion of their site, to increase moulded fibre production capacity by 45%; currently they have 15 production lines but by 2023 will have added a further 5. Greenearth Food Packaging: This UK company is a distrib utor for the Italian firm Ecopack. Included in their range was cocoa paper liners and shaped cooking materials – these must be papers produced by Favini. HP: They were keen to talk both about their mould-producing tooling technology and about the future of fibre-based bottles containing a liner as a replacement for single-use plastic bottles. They have a prototype line in Edinburgh at the site of Choose Packaging, which they purchased earlier this year. They see dis placing plastic bottles as a major market to target. The company gave two presentations at the meeting, and it will be very inter esting to see how this technology develops, since it is backed by such a major player as HP.
Leipa: Packaging side of business on show. Had two lots of board covered with plastic (can also do biofilm, but mainly use fossil-based films). Deformable paper applications 80% paper 20% plastic; flat paper applications 90% paper 10% plastic. Looking mainly at food-contact applications so are buying in board as the company makes mainly recycled grades. More in terested in recycling rather than composting, as want to take the returned paper and reuse in their mill LXD UK: Showed ‘stone paper’ brand name Limex, a blend of calcium carbonate with a resin binder. (Most appears to be petrochemical-based resin, but they are claiming to have bioresins produced from sugar cane.) Applications include shopping bags. A major benefit is high tear strength.
Humidity Solutions: UK producer of humidity control solu tions. Had an excellent A4 booklet Humidity & Temperature Control for Print, as a free giveaway. (This company has already signed up for the 2023 event in February next.)
Neenah Coldhoven: Showed multiple-coated barrier papers involving latexes for water and grease resistance and heat-seal able layers applied to virgin base sheets. The products are claimed to be repulpable and recyclable.
Kipas Paper & Packaging: The company website shows they are mainly a producer of corrugated case materials, but at this event they had impressive swatches of white lined chipboard samples (200-400gsm).
PACKAGING INNOVATIONS May 2022 (NEC)
39 PAPER TECHNOLOGY AUTUMN 2022 CONFERENCE, EXHIBITION AND WEBINAR REPORTS ical representations of cabins. Also, new video tests to assess risk taking are also being developed, looking at situations such as traffic light changes, overtaking and tailgating.
Tessera: Greek distributor of food containers, cutlery and cups. Showed Chinese moulded fibre food product coated with acrylic emulsion on the smooth inner surface; also beverage cup tops made from moulded fibre.
According to HSE, logistics has 50% higher national average of Musculoskeletal Disorders (MSDs) which are generally related to manual handling issues. Typically they will relate to backs, joints, and sprains. If a lift truck develops a defect do we keep using it, or get it fixed? Yet with the human body, a twinge or ache is often over looked, which can lead to significant injury. So greater awareness about the human body and about techniques of lifting, pushing and pulling is needed. RTITB has developed a range of training applications that covers this important subject.
Wipak UK: This company develops and manufactures pack aging solutions for food products and medical instruments. At this show they highlighted a recyclable paper butter wrap that is both foil and plastic free. The product has a thin barrier coating that is oil and grease resistant and acts as an oxygen barrier.
Professor Ipsita Roy (University of Sheffield) opened pro ceedings with a talk entitled “Natural Polymers of Bacterial Origin and their Biomedical Applications”. Her research in volves using bacterial fermentation to produce polymers (such as novel Polyhydroxyalkanoates – PHAs) or most recently working on bacterial cellulose. Most of her work focusses upon medical applications, but she is slowly branching out to industrial applications, and has recently been in discussion with a huge Finnish packaging manufacturer about using biopolymers (PHAs) for coating applications. (Here it is of in terest to note that the EU has instigated their INGREEN pro ject to develop new chemical building blocks from paper mill wastewater, and extraction of PHAs is of particular interest –so Professor Roy’s work area is of interest to us! Dr. Helena McMahon from Munster University is principal investigator for the INGREEN project.)
General conferences such as these can be hit and miss affairs, but more often than not interesting connections are made, as here with University of Sheffield and SRUC. We have over 160 uni versities in the UK, each with numerous departments which could be working on materials or applications of interest to our industry. Events like this allow a brief look under the lid at what is going on.
PAPER TECHNOLOGY AUTUMN 2022 CONFERENCE, EXHIBITION AND WEBINAR REPORTS HP MOLDED FIBRE TOOLINGADVANCED July (Webinar) ECR MATERIALS CONFERENCEANNUAL July 2022 (SCI, London)

Following hard on the heels of their entry to the Packaging Innovations event, where they gave two short 30 minute presen tations on tooling and bottles, HP did an hour-long webinar on the subject of advanced tooling, taking an extended look at the benefits they perceive from their new system.What is particularly in teresting about their offer ing is that it uses 3D printing to form the mould, which is designed using CFD to model the flow characteristics of the shaped mesh. Using 3D printing allows the chan nels to be designed better than by compressing a flat mesh to form the drainage element. The re sult is claimed to be faster dewatering, and better formation, allowing for higher throughput of the moulding line. In addi tion, improved formation means better strength and potentially allows for lightweighting, which in turn would lead to faster drying and lower energy costs. This was a very interesting presentation, with some fascinat ing case study results, but has yet to be released (as was promised) for general viewing; hopefully HP will put it online soon.The
James Wickson (Croda) and Sara Papini (Synthomer) both gave talks on their respective company’s approaches to sustain ability, mainly on how they are trying to source more materials from renewable resources (and the inherent problems in doing so). Both are suppliers to the paper industry, and so it is impor tant to follow what steps they are taking to ensure sustainability going forwards. (In 2010/2011 I ran a short series on ‘Green Chemistry’ in this journal on exactly this subject, but it only ran a few issues because it was then ahead of its time, and very few chemical companies were (publically) investigating this subject – so it is fascinating to see the subject now receiving such in terest.)Maria Inam and Glenn Lamming (Centre for Process Inno vation – UK-CPI) discussed where they sit in the pantheon of non-profit R&D establishments set up by government to aid in dustrial research. CPI forms part of the High Value Manufac turing Catapult set up by Innovate UK in 2011. Both speakers were from the National Formulation Centre in Sedgefield, and discussed case studies around formulating new products using sustainable resources, or recovered resources from waste streams.Federico Trotta (Metalchemy) discussed “A Sustainable and Frugal Approach to Manufacturing Natural Bionanocomposite Materials with Silver Nanoparticles: Focus on Food Packaging Applications”. This is a relatively recent start-up working in the packaging arena, specifically on biofilms and also on green routes to producing nano-silver particles. Currently they are only working on films, but it is possible that in time may also look at coatings; even so, films can be laminated onto paper, so this is a company well worth watching.
The final keynote speech was given by Vijay Thakur (SRUC, Scotland’s Rural College, where he is Professor in New Products from Biomass, Agriculture & Business Management, Biorefining and Advanced Materials Research Centre) who covered a vast swathe of research areas in record time! Subjects included re placements for styrene derived from lignin sources, and a large body of work on cellulose (especially micro and nano) such as wood panel structures derived from fly ash and cellulose fibre, and insulating foams from wood or hemp cellulose.
Dr. David Fengwei Xie “University of Newcastle” was up next, discussing “Facile preparation of starch-based biodegrad able materials with ionic conductivity and strain-responsive ness”. Here starch films are combined with metal salts and other layers to give flexible sensor applications, where strain shows as a voltage response.
40 As a final thought, it would be fair to say that moulded fibre has never been given such high profile – not only in the number of exhibitors, but also in the presentation arena where there were three separate talks on the sector. Aside from this, barrier coat ings (and some laminates) were very much to the fore, and as yet there is no consensus as to whether compostability or recy clability is more preferable. Finally, a comment I have made sev eral times previously: why do so many foreign (especially Turkish) firms think it is worthwhile coming to this exhibition, yet their direct competitors from the UK stay away? This is an international event so come on UK manufacturers; this is an ideal marketplace which more of you should be attending!
Early Careers Researcher conference brings together aca demics (lecturers and postdocs) and PhD students in an informal forum to discuss ideas and make connections. This year the gen eral area of discussion was around Sustainability.
Contact: Alec Ze琀er (alec@ellwooda琀ield.com)
Energy Data Manager c.£50,000 + bene昀ts – Home based with travel
This is an exci琀ng opportunity with CPI to help drive the decarbonisa琀on e昀ort for the UK’s Paper‐based Industries. Work with members on CCA ma琀ers, co‐ordinate and deliver mill and sector obliga琀ons under CCA legisla琀on and act as required on other energy policy and technical energy issues. Candidates must be technically literate, numerate and comfortable dealing with process industry issues. CPI is recrui琀ng!
41
For more informa琀on and to apply, please visit the Ellwood A琀ield website via the QR code.
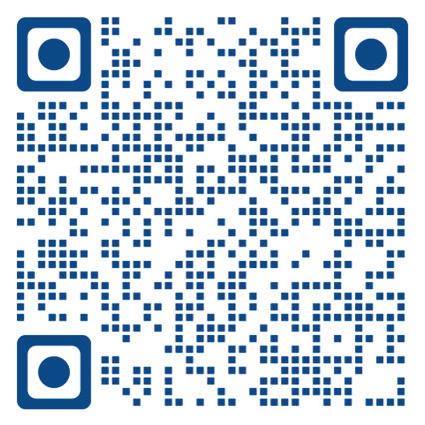
Ellwood & A琀ield Ltd, 26th Floor Millbank Tower, 21-24 Millbank, London SW1P 4QP
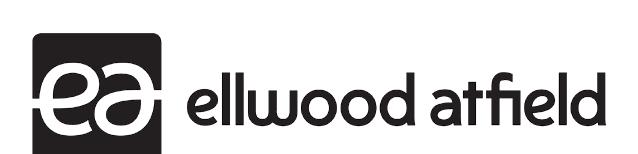
The Confedera琀on of Paper Industries (CPI) is the leading trade associa琀on represen琀ng the UK’s paper‐based Industries, comprising paper and board manufacturers, converters, corrugated packaging producers, makers of so昀 琀ssue papers, and collectors of paper for recycling.

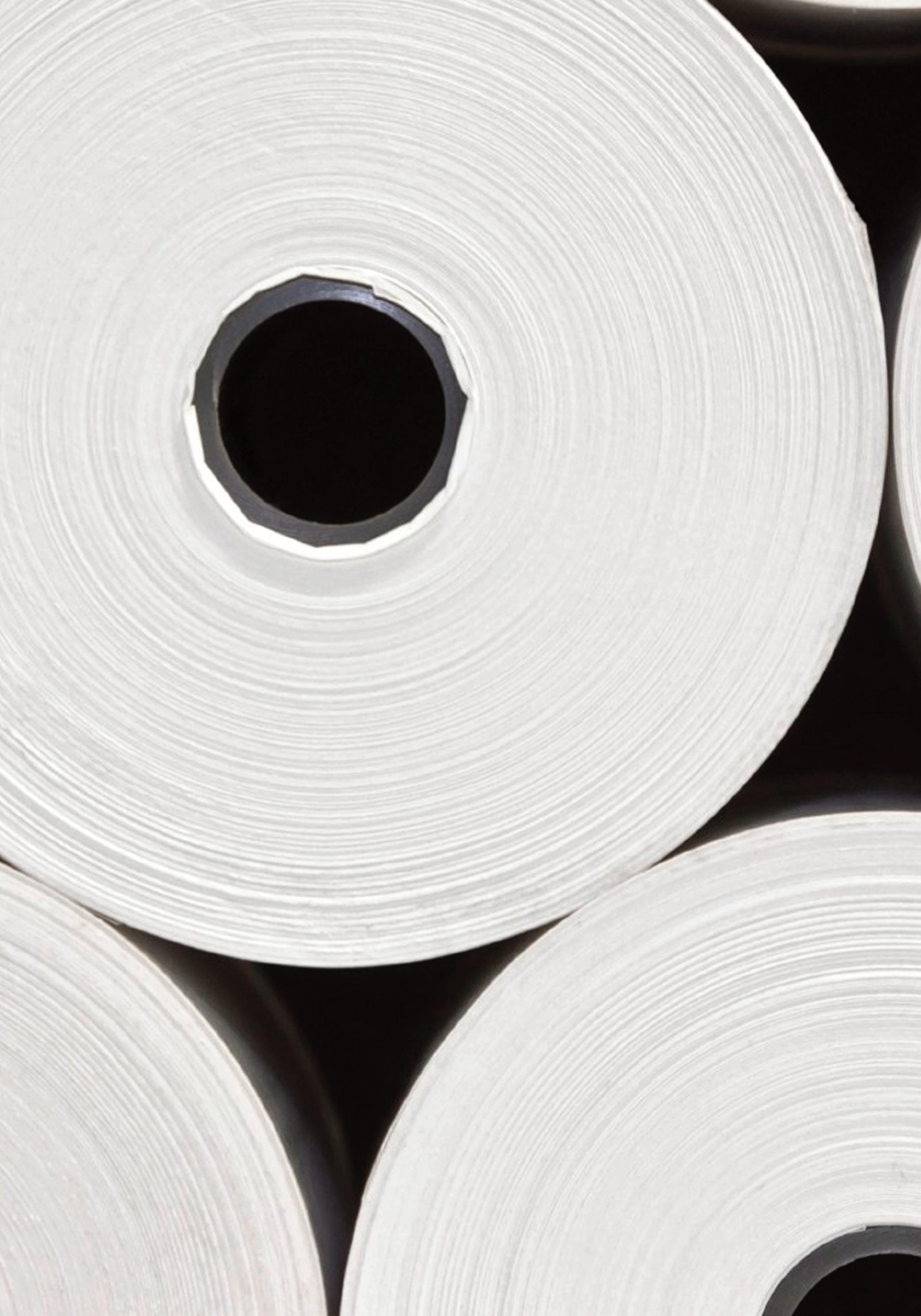
21-22-23 FEBRUARY 2023 SHARJAH, UNITED ARAB EMIRATES SAVE THE DATE! 100+ Exhibitors in 2022 Exhibiting Countries Qualified Visitors Amount of Countries Visitors Represented 21889798 BOOK YOUR SPACE or REGISTER NOW



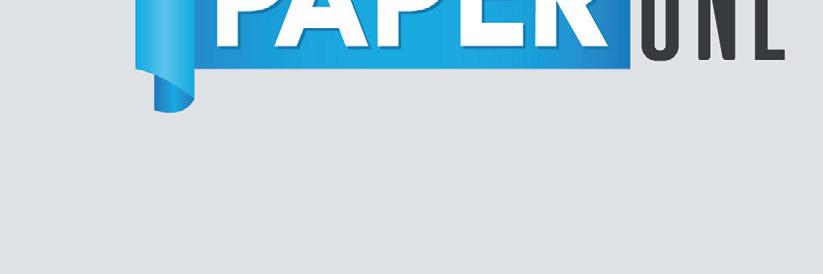



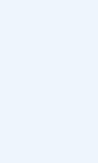

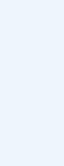

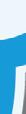
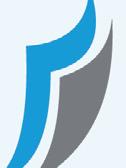
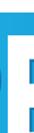



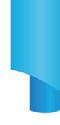
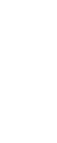

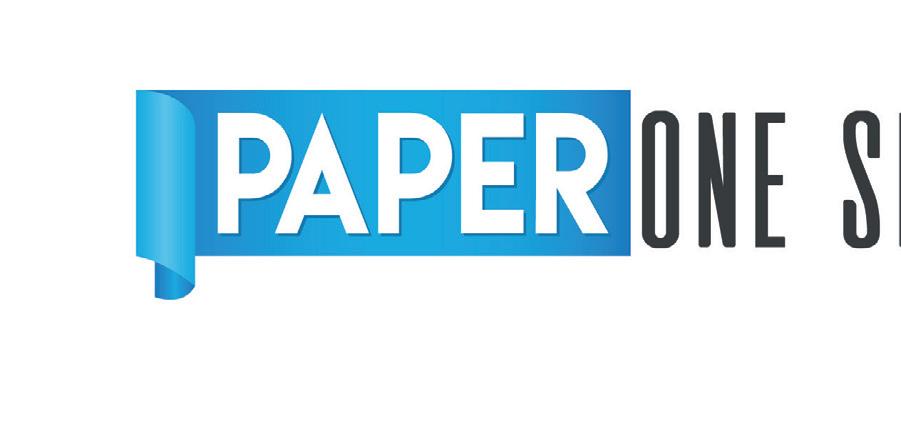

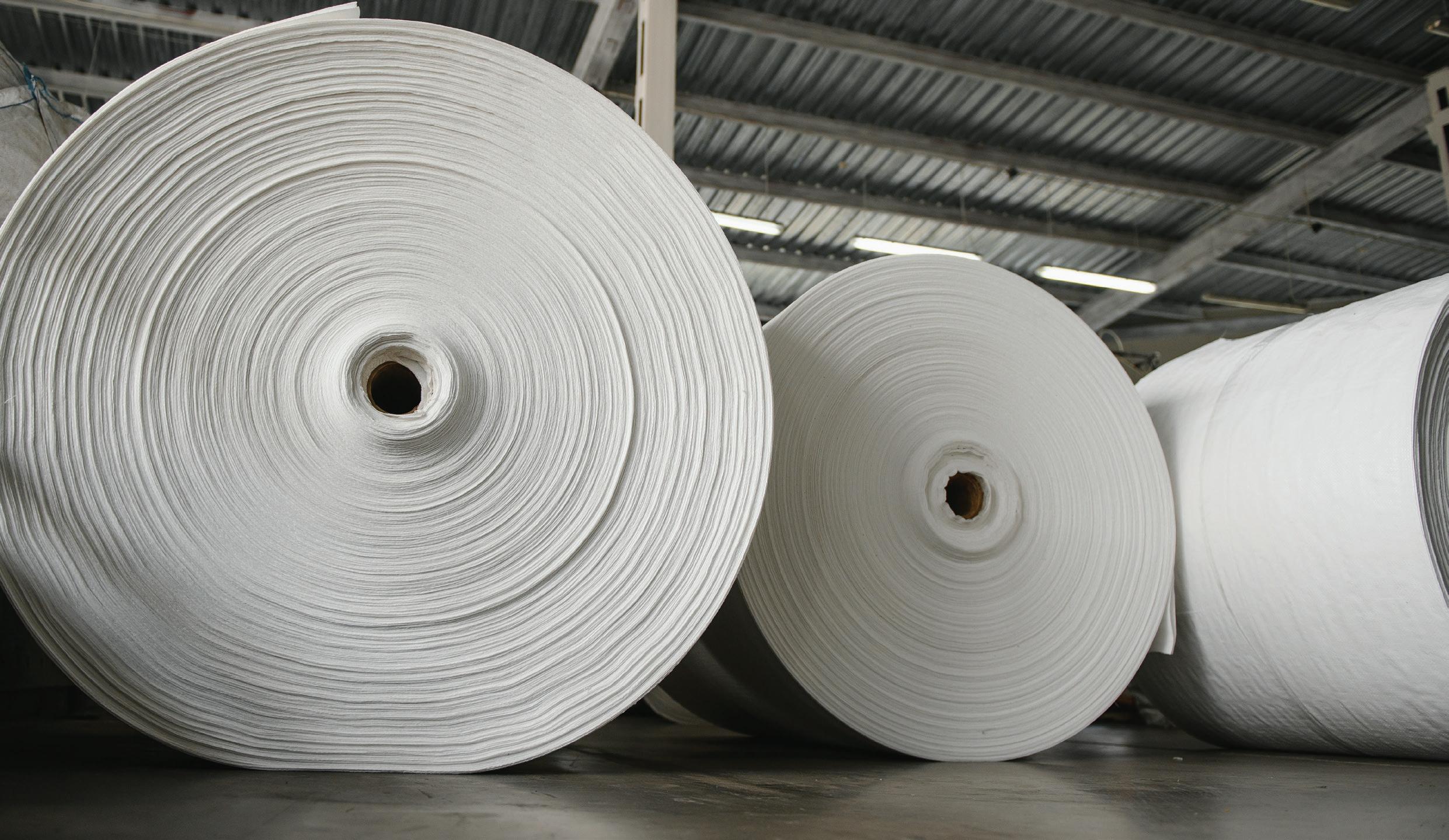






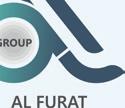


