Volume 25 Number 1 - January 2025
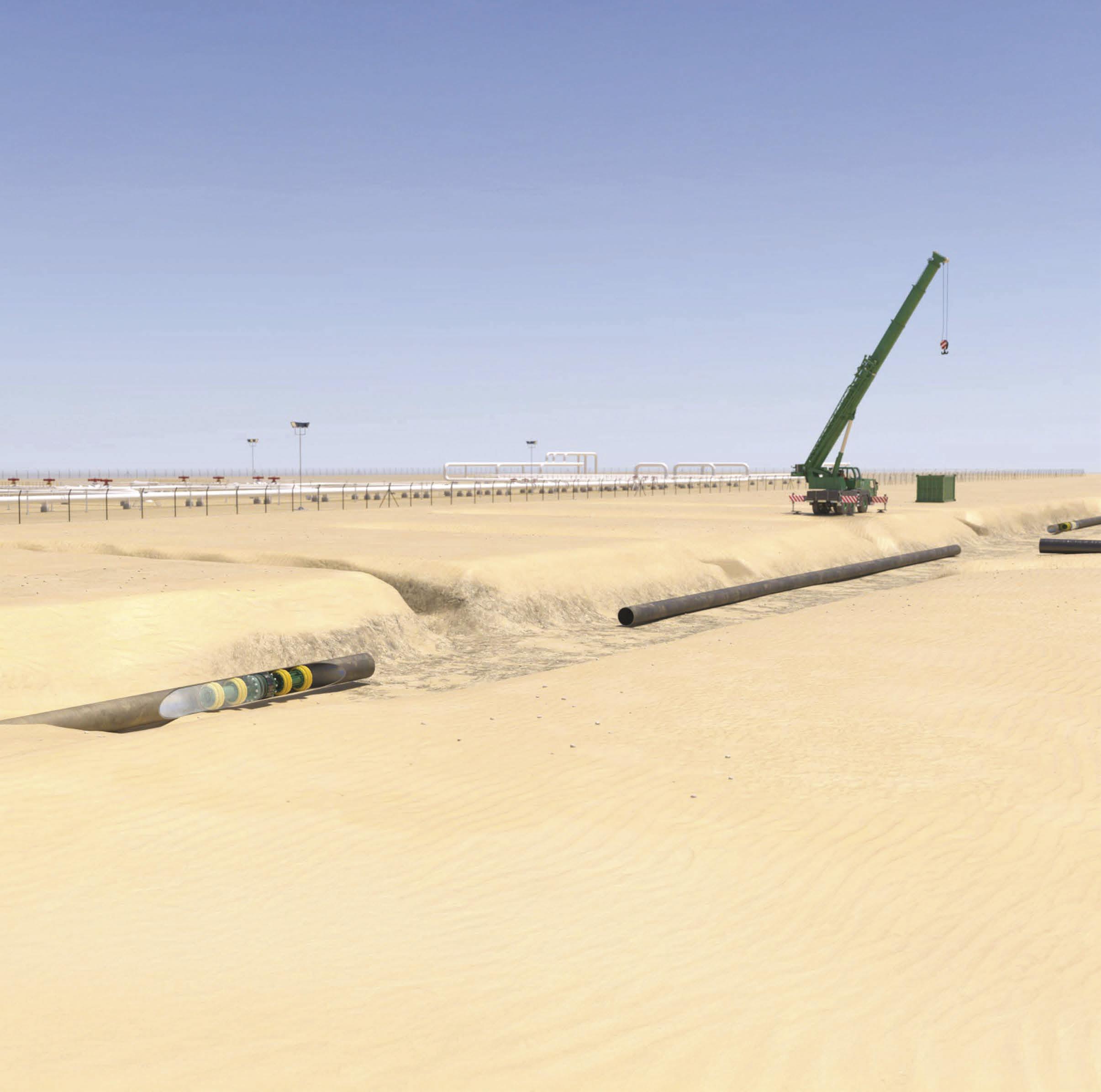
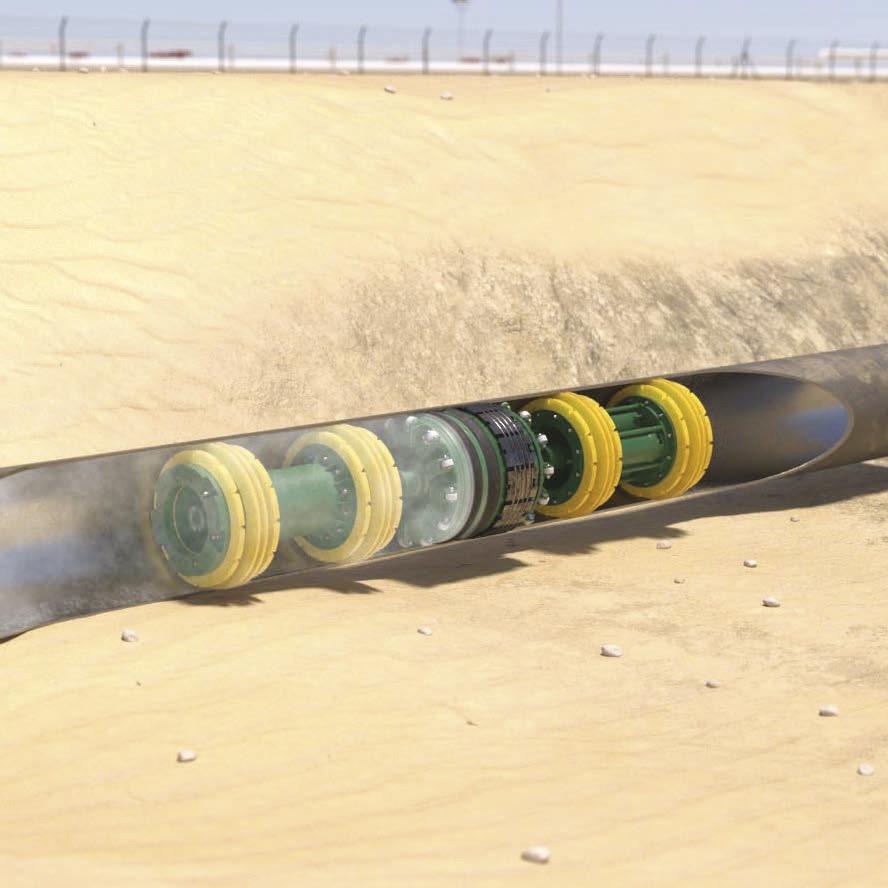
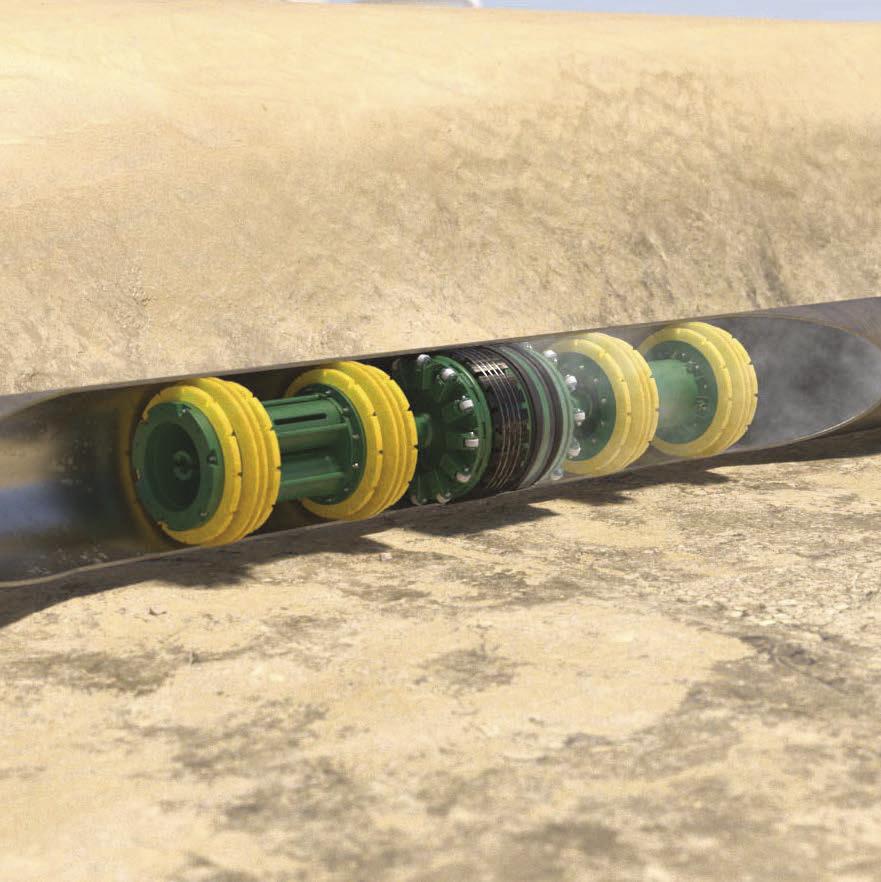
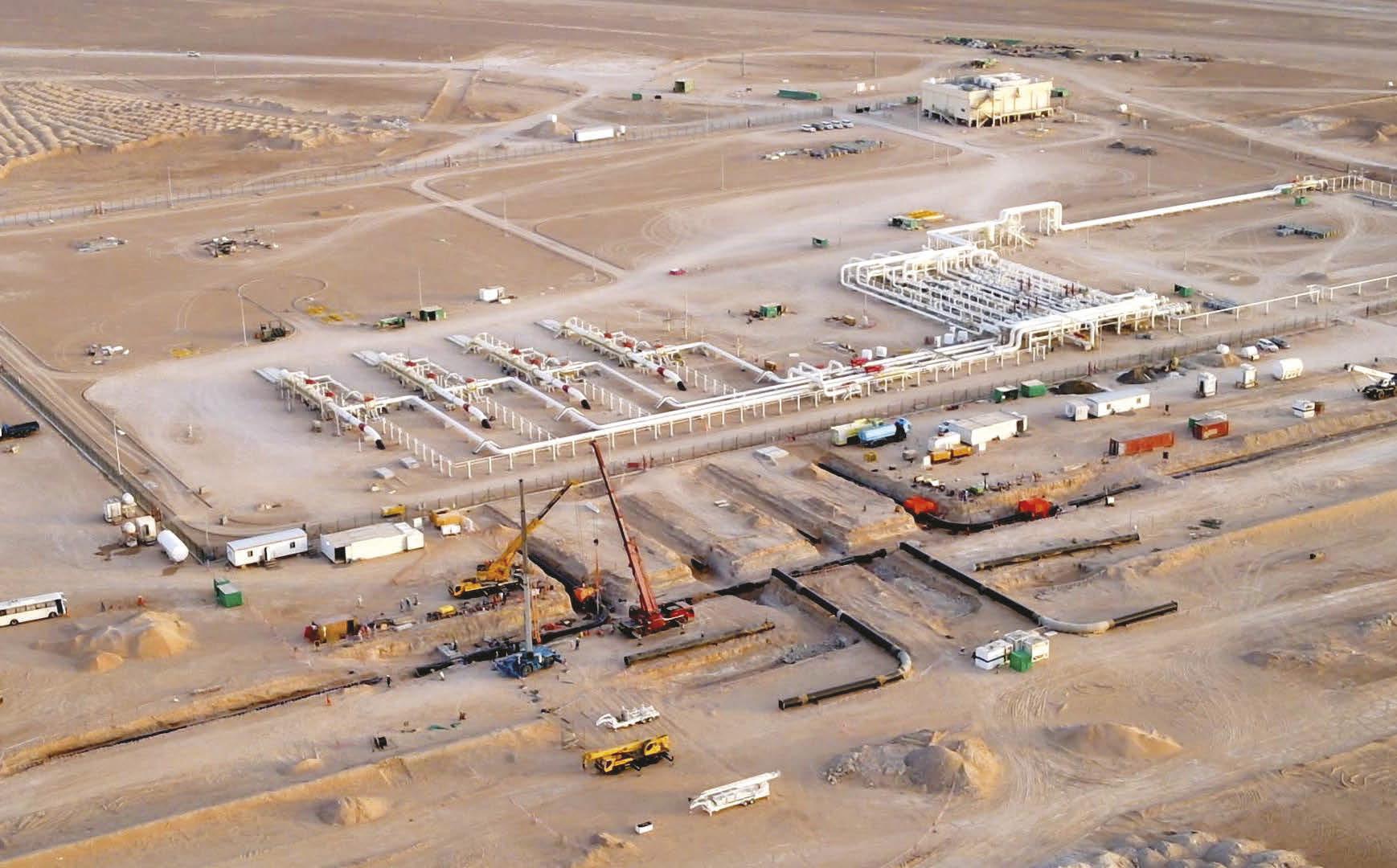
Oman, Middle East
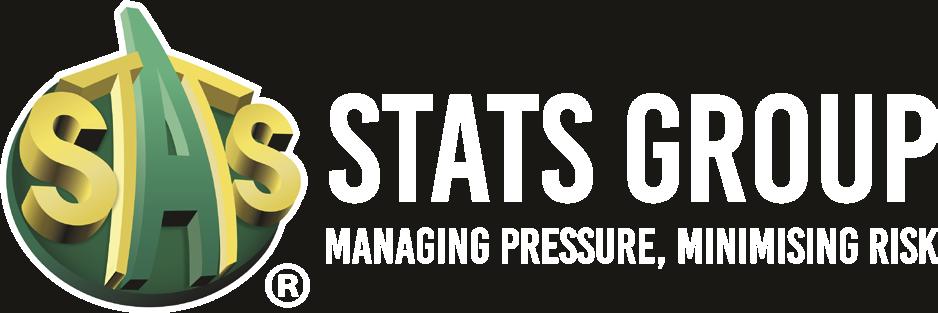
Volume 25 Number 1 - January 2025
Oman, Middle East
Elevate your asset integrity with unmatched data accuracy and unparalleled expertise
Our unique synergy of advanced inspection systems, cutting-edge analytics and human expertise allows us to transform data into knowledge. Knowledge enables smarter decision-making and delivers a comprehensive understanding of asset safety, lifetime, and performance.
03. Editor's comment
05. Pipeline news
Contract news and updates from ONEOK, Kinder Morgan, APA and more.
KEYNOTE: REGULATIONS AND COMPLIANCE
10. Litigation nation
Tom Sharp, Director of Permitting Intelligence, Arbo, details how legal battles are shaping pipeline infrastructure in the USA.
15. Picking up the momentum on methane
Mark Naples, Managing Director, Umicore Coating Services, illustrates how addressing methane emissions, through efforts like the Global Methane Pledge, is fuelling advancements in leak detection technology.
OPERATOR TECHNOLOGY
20. From laggard to leader Lars Larsson, Project Management Director, AspenTech, USA.
25. Pipelines in the digital age Philippe Willems, Global Engineering Manager, Ovarro.
PIPELINE FLOW
29. Staying grounded Essam Arfaj, Bader Jarallah, and Mohanned Tarabzouni, Aramco, Saudi Arabia.
COATINGS Q&A
33. Coatings Q&A With answers from Seal For Life.
PIPELINE WELDING AND MATERIALS
41. Innovation under pressure Niels Pörtzgen and Gerard van der Steen, Applus+, Netherlands.
MAINTENANCE AND SERVICES
47. Supporting software implementation from the ground up Jason Smith, ABS Consulting.
51. Simplifying soil remediation Eric Sigvaldason, Vande Consulting Services.
55. Better safe, than sorry Eric Farmer, Vice President of Clinical Operations, RMI.
SUBSEA PIPELINE MAINTENANCE
59. How deep is your ROV? Chad Gillen, Deep Trekker, Canada.
Drone footage captures a recent temporary pipeline isolation project on a 48 in. gas transmission line in central Sultanate of Oman. STATS Group deployed dual Remote Tecno Plugs® into the line 130 m apart to safely isolate a section of pipeline allowing the tie-in of two gas processing plants. This critical operation was successfully conducted while the line remained pressurised at 90 bar and significantly reduced GHG emissions compared to venting the entire pipeline. www.statsgroup.com
MANAGING EDITOR
James Little
james.little@palladianpublications.com
ASSISTANT EDITOR
Isabel Stagg isabel.stagg@palladianpublications.com
EDITORIAL ASSISTANT
Alfred Hamer alfred.hamer@palladianpublications.com
SALES DIRECTOR
Rod Hardy rod.hardy@palladianpublications.com
SALES MANAGER
Chris Lethbridge chris.lethbridge@palladianpublications.com
SALES EXECUTIVE
Daniel Farr daniel.farr@palladianpublications.com
PRODUCTION DESIGNER
Amy Babington amy.babington@palladianpublications.com
HEAD OF EVENTS
Louise Cameron louise.cameron@palladianpublications.com
DIGITAL EVENTS COORDINATOR
Merili Jurivete merili.jurivete@palladianpublications.com
EVENTS COORDINATOR
Chloe Lelliott chloe.lelliott@palladianpublications.com
DIGITAL CONTENT COORDINATOR
Kristian Ilasko kristian.ilasko@palladianpublications.com
JUNIOR VIDEO ASSISTANT
Amélie Meury-Cashman amelie.meury-cashman@palladianpublications.com
DIGITAL ADMINISTRATOR
Nicole Harman-Smith nicole.harman-smith@palladianpublications.com
ADMINISTRATION MANAGER
Laura White laura.white@palladianpublications.com
Palladian Publications Ltd, 15 South Street, Farnham, Surrey, GU9 7QU, UK
Tel: +44 (0) 1252 718 999
Website: www.worldpipelines.com Email: enquiries@worldpipelines.com
Annual subscription £60 UK including postage/£75 overseas (postage airmail). Special two year discounted rate: £96 UK including postage/£120 overseas (postage airmail). Claims for non receipt of issues must be made within three months of publication of the issue or they will not be honoured without charge.
Applicable only to USA & Canada: World Pipelines (ISSN No: 1472-7390, USPS No: 020-988) is published monthly by Palladian Publications Ltd, GBR and distributed in the USA by Asendia USA, 701C Ashland Avenue, Folcroft, PA 19032. Periodicals postage paid at Philadelphia, PA & additional mailing offices. POSTMASTER: send address changes to World Pipelines, 701C Ashland Avenue, Folcroft, PA 19032.
Aston Martin’s Head of Race and Trackside Logistics, Franco Massaro, recently revealed how logistics preparations for the 2025 Formula One season started months in advance of the first race, which is scheduled in March 2025. The team faces a 24 race schedule this season, for which personnel and cars travel by air, but much of the equipment is transported by sea, and is already in transit.1
In order to meet the demands of overseas events, the UK-based team manages six identical sets of equipment, valued at around £2 million each (these consist mainly of garage and hospitality infrastructure rather than car components). Each set includes five 40 ft containers of garage materials and two of hospitality items, weighing a total of 50 – 52 t. Sea freight is a cost-effective solution compared to air freight, particularly for bulky items. By shifting equipment via sea freight, the team saves nearly £250 000 annually. Although this approach requires additional sets of equipment, the costs are recouped within one to two years, as equipment typically lasts five to ten years.
Transporting equipment globally presents several challenges, of course, not least the security risks inherent in using routes such as the Red Sea and the Suez Canal. Weather plays its part in the timing of deliveries, and extra time has to be factored in to mitigate any changes in scheduling, including port closures or reroutes.
These issues resonate with the challenges faced by other maritime industries, such as undersea pipelines, which are also vulnerable to deliberate damage and environmental factors. While the Aston Martin team entrusts their equipment to the high seas, the pipeline industry becomes more wary of maritime incidents that threaten subsea assets. Recent incidents have highlighted the vulnerability of undersea infrastructure, including pipelines and cables, to sabotage. The Nord Stream 1 and 2 pipelines were put out of action by explosions in September 2022. The Balticconnector gas pipeline between Finland and Estonia was damaged in October 2023, with investigations pointing to the involvement of a Chinese vessel. More recently, two telecommunications cables were severed in Swedish waters in the Baltic sea, and on Christmas Day an underwater power cable between Finland and Estonia was cut. Finnish authorities have seized a ship, believed to be part of Russia’s ‘shadow fleet’, and have found evidence that it had been deliberately dragging its anchor for over 60 miles.
These events demonstrate the increasing risks to subsea infrastructure from deliberate acts, often involving vessels operating covertly. The presence of ‘dark ships’ – vessels that turn off their tracking systems to conceal their movements – has been associated with such activities.
Nations and organisations are enhancing surveillance and monitoring of critical undersea installations: NATO has initiated efforts to oversee these infrastructures, emphasising the need for vigilance.
The safety of the sea as a domain for laying pipelines and other critical infrastructure is increasingly compromised. Ensuring the security of maritime operations now requires not only adherence to safety protocols but also proactive measures to detect and prevent malicious actions by vessels at sea.
1. https://www.linkedin.com/pulse/setting-sail-sea-freight-operation-supporting-our-2025-season-qx7se/
Kinder Morgan forecasted higher earnings for 2025 as the US pipeline operator bets on growth in its natural gas pipelines and energy transition ventures amid rising demand for the fuel, reports Reuters.
Shares of the Houston, Texas-based company were up 1.7% after the market close.
Pipeline operators such as Kinder Morgan are also banking on electric generation associated with artificial intelligence operations, cryptocurrency mining and data centres.
Net income attributable to the company is expected to be US$1.27 per share in 2025, in line with analysts’ average estimate, according to data compiled by LSEG.
Kinder Morgan had forecast a profit of US$1.17 per share for end-2024. The company’s Q3 profit fell short of Wall Street estimates earlier last year. It had also lowered its annual profit
forecast as the US pipeline operator contended with lower crude volumes.
However, the company now expects to generate US$8.3 billion of adjusted earnings before interest, taxes, depreciation, and amortisation (EBITDA) in 2025, up nearly 4% from the 2024 forecast of US$8 billion.
Kinder Morgan, one of the largest energy infrastructure companies in North America, operates about 79 000 miles of pipelines.
A lower net debt-to-adjusted EBITDA ratio would provide the company with good capacity for “additional opportunistic investment,” said CEO Kim Dang in the statement.
Kinder Morgan added it expects to invest US$2.3 billion in discretionary capital expenditures, including expansion projects and contributions to joint ventures.
ONEOK announces close of sale of wholly owned interstate natural gas pipelines
ONEOK, Inc., has announced that it has closed the sale of its three wholly owned interstate natural gas pipeline systems to DT Midstream, Inc, effective as of 11:59 p.m. Central on 31 December 2024, for a total cash consideration of US$1.2 billion, subject to customary adjustments.
“The closing of this transaction represents another milestone in the strategic optimisation of our integrated asset portfolio and advances our capital allocation priorities,” said Pierce H. Norton II, ONEOK President and Chief Executive Officer. “As the
new owner of these pipelines, DT Midstream brings a shared commitment to safety, reliability and excellence that will serve all stakeholders well”.
The three interstate natural gas pipeline systems included in the sale are Guardian Pipeline, Midwestern Gas Transmission and Viking Gas Transmission.
The net proceeds from the sale are expected to enhance ONEOK’s financial flexibility as it progresses toward its previously announced leverage target of 3.5 times during 2026.
Argentina’s YPF announces participation in Vaca Muerta Sur pipeline project
YPF S.A. has announced that it is participating in the Vaca Muerta Sur Project, in its capacity as a shareholder in VMOS S.A., together with Vista Energy Argentina S.A.U., Pampa Energía S.A., and Pan American Sur S.A.
In this regard, it is reported that at the VMOS board meeting held on 13 December 2024, the construction of the Vaca Muerta crude oil export pipeline was unanimously approved. The project will have an extension of 437 km, will have a loading and unloading terminal with interconnected monobuoys and a tank and storage yard.
Construction of the project will commence immediately with the objective of achieving mechanical completion during the 4Q26 and commencement of commercial operations on
Morocco to begin Nigeria gas pipeline tenders in 2025
Morocco plans to launch tenders in 2025 as part of the initial phases of the Nigeria-Morocco gas pipeline.
This development is part of the 2025 Action Plan by the National Office of Hydrocarbons and Mines (ONHYM), with the tenders focusing on the sections of the pipeline within Morocco.
The project’s first phase will include Morocco, Mauritania, and Senegal, and additional agreements for gas transport will be signed next year.
31 July 2027. The Shareholders have committed approximately 275 000 bpd of capacity and in turn VMOS has granted options to Chevron Argentina S.R.L., Pluspetrol S.A. and Shell Argentina S.A., among others, which may commit an additional capacity of at least 230 000 bpd of firm transportation.
The project’s design capacity will allow the transportation of up to 550 000 bpd during commercial operation, which can be increased to 700 000 bpd if necessary. The Project represents the largest hydrocarbon export infrastructure in Argentina and will require an investment of approximately US$3 billion, which will be financed by Shareholders’ contributions and local and/or foreign financing to be granted to VMOS during 2025.
The 5600 km pipeline is expected to cover 16 countries –most of which are along the Atlantic coast.
It will also be connected to the Morocco-Europe gas pipeline and the European gas network, the news outlet said, adding that the pipeline will not only benefit Africa but also Europe.
The project is being regarded as a milestone initiative, reflecting Morocco’s commitment to supporting economic integration and development across Africa.
USA
Boardwalk Pipelines, LP has made a final investment decision approving Gulf South Pipeline Company, LLC’s (Gulf South) 1.16 billion ft3/d Kosciusko Junction pipeline project.
Tenaris and IGI Poseidon, a joint venture between Greece’s DEPA International Projects and Italy’s Edison S.p.A., have joined forces to advance the hydrogen transportation via ultra-deep offshore pipelines.
SPIE is installing a new highpressure gas pipeline in Hagen, North Rhine-Westphalia. Westnetz GmbH, the largest distribution network operator for electricity and gas in western Germany, commissioned the project.
Northern Endurance Partnership (NEP) has announced financial close for the UK’s first CCS project. TotalEnergies, holding a 10% share in NEP, will contribute to storing up to 4 million tpa of CO2. The infrastructure will serve three projects in Teesside, featuring a CO2 network and offshore pipeline.
STATS Group has opened a new 2500 m2 base in Dammam in the country’s Eastern province. The newly created Saudi operating company STATS Limited Co. for Oil Services has been awarded Approved Vendor status by one of the Kingdom’s leading energy operators.
Ebara Elliott Energy (EEE) has announced a major electrical upgrade at its Jeannette, Pa., manufacturing facility. The upgrade will enable EEE to test compressors and electrical equipment up to 100 MW, or approximately 134 102 HP.
Reuters reports that China has built and connected the 5111 km (3175 mile) Power-ofSiberia pipeline to deliver gas from Russia’s Siberian fields to users as far as the financial hub of Shanghai, Chinese state media reported on Monday 2 December 2024.
The completion will allow the project to reach its full annual designed capacity of 38 billion m3 in 2025, roughly 9% of China’s consumption this year.
Chinese builders added the last section, a 167 km line from Nantong to Luzhi in the eastern province of Jiangsu, around midNovember, completing the massive project seven months ahead of schedule.
The pipeline has a diameter of 1.422 m, allowable pressure of 12 MPa and the largest transport capacity for a single pipeline, state television said.
The Power-of-Siberia pipeline began pumping gas in late 2019, and Russia has been ramping up supplies since. It is slated to deliver 38 billion m3 in 2025, state media said, a level 26% higher than the 30 billion m3 estimated by analysts for 2024.
Citing an official with state-run PipeChina, the report said Power-of-Siberia is currently sending 110 million m3/d of gas, versus 15 million m3 when the project first came on stream five years ago.
India to dominate oil and gas transmission pipeline length additions in Asia by 2028
India is expected to be at the forefront in terms of the trunk/transmission oil and gas pipeline network additions in Asia, accounting for more than 40% of the region’s total pipeline length additions by 2028, says GlobalData.
GlobalData’s latest report reveals that India is likely to witness the start of operation of more than 50 planned and announced pipelines by 2028, adding a total transmission pipeline length of over 26 000 km. Of this, around 24 000 km length additions would be from the planned pipelines that have received necessary approvals for development.
Bhargavi Gandham, Oil and Gas Analyst at GlobalData, comments: “Natural gas and product pipelines account for more than 80% of the upcoming transmission pipeline length additions in India by 2028. The upcoming Kandla–Gorakhpur product pipeline is likely to be the longest among all the upcoming pipelines with a length of 2809 km. The IHB Pvt Ltd-operated pipeline is expected to become operational in 2025 and will help to meet the growing LPG demand in the western part of the states of Gujarat, Madhya Pradesh, and Uttar Pradesh.”
The Alaska Gasline Development Corporation (AGDC) has released a statement regarding the AIDEA resolution supporting the development of Alaska LNG Phase 1, the in-state pipeline portion of Alaska LNG designed to bring North Slope natural gas to Interior and Southcentral Alaska:
“Today’s resolution authorises AIDEA to negotiate and sign a letter of credit to backstop front-end engineering and design (FEED) for the Alaska LNG pipeline, bringing Alaska a critical step closer toward a privately funded in-state natural gas pipeline. The letter of credit will allow AGDC to unlock up to US$50 million in private investment needed to move the Alaska LNG pipeline through FEED, the remaining development stage that must be completed before a final investment decision can be made. AGDC is in advanced
discussions with potential project partners to privately fund and complete FEED and will announce updates when new developments occur. The letter of credit for FEED will only be utilised if a final investment decision is not reached, at which time AGDC will own the completed pipeline engineering and design work.
“The State of Alaska is facing a looming energy crisis and Alaska LNG represents the best long-term energy solution for our state. The Alaska LNG pipeline will deliver reliable, affordable, low-emissions energy and uniquely provide billions of dollars in economic benefits for Alaskans. Building the Alaska LNG pipeline also strategically positions Alaska to increase the energy security of our Pacific allies by de-risking construction of the other Alaska LNG components that will generate and commercially export LNG.”
PROTECTIVE OUTERWRAPS
27 - 31 January 2025
Pipeline Pigging & Integrity Management Conference (PPIM) 2025 Houston, USA
https://ppimconference.com/
5 - 9 February 2025
77th Annual PLCA Convention 2025 Florida, USA
https://www.plca.org/annual-convention-events
11 - 13 February 2025
AMI Pipeline Coating 2025 Vienna, Austria
https://www.ami-events.com/event/c52c6186cbe4-4db1-b7bf-35e6f2e28614
6 - 10 April 2025
AMPP 2025 Nashville, USA
https://ace.ampp.org/home
5 - 8 May 2025
20th Pipeline Technology Conference Berlin, Germany
https://www.pipeline-conference.com/
5 - 8 May 2025
Offshore Technology Conference 2025 Houston, USA
https://2025.otcnet.org/
19 - 23 May 2025
29th World Gas Conference (WGC2025) Beijing, China
https://www.wgc2025.com/eng/home
25 - 29 May 2025
Annual Pipe Line Contractors
Association of Canada (PLCAC) Convention Banff, Canada
https://pipeline.ca/
Corinth Pipeworks secures landmark offshore contracts in the North Sea Corinth Pipeworks has been awarded two significant offshore contracts in the North Sea from Subsea7.
The Bestla project, operated by OKEA is located in the Norwegian Continental Shelf, approximately 13 km south of the Brage Field. The scope of the contract includes the supply of 12.5 km of 14 in., high frequency welded (HFW) steel pipes. The development plan for Bestla involves a two well subsea tieback to the Brage platform, which will serve as the host facility for production, processing, and export of gas and liquid fuels (NGL) from
the Upper Jurassic Sognefjord Formation. In the UK Central North Sea, the Bittern project entails the manufacture and supply of approximately 22 km of HFW steel pipes for a 12 in. water injection pipeline, scheduled for installation in 2025. Located approximately 190 km east of Aberdeen, this pipeline will replace the existing line to maintain reservoir pressure support for the life of the Bittern field. Subsea7, the main contractor, will manage the installation of the lined pipeline, subsea structures and tie-ins at the Triton FPSO vessel and the Bittern field.
Fugro extends contract for subsea inspection in Brazil for Petrobras Petrobras has signed a 175 day addendum to Fugro’s current inspection, repair and maintenance services contract, performed by the Fugro Aquarius, to include fully remote subsea inspection surveys of shallow-water infrastructure in Brazil.
Work will begin in January 2025, leveraging Fugro’s advanced Blue Essence® uncrewed surface vessel (USV) and Blue Volta® electric remotely operated vehicle (eROV) technology to enhance inspection safety, efficiency, and
APA signs project agreements for Stuart Plateau Pipeline
APA Group has announced the execution of a Development Agreement, long-term Gas Transportation Agreement (GTA) and Connection Agreement with Tamboran Resources Corporation and Daly Waters Energy, LP for the Sturt Plateau Pipeline (SPP) connection in the Northern Territory.
Under the agreements, APA will build, own and operate the SPP to connect the Tamboran Resources’ operated Shenandoah South Pilot Project to the Amadeus Gas Pipeline (AGP) in the Northern Territory (Australia).
The pipeline will be approximately 37 km in length, with construction targeted for completion in early 2026. APA’s total construction costs for the project are currently estimated to be around AUS$66.5 million.
The SPP is the first of a number of pipeline projects that APA is assessing to transport gas out of the Beetaloo Basin, provided ongoing exploration activities by upstream proponents achieve commercial success.
sustainability.
The contract marks Fugro’s first use of these innovations in the Americas, following successful applications in Australia, the UK, and the Middle East. By eliminating the need for on-site personnel, the uncrewed solution reduces carbon emissions by 95% and significantly lowers the risks associated with traditional offshore operations. It also provides clients with near real-time access to project data, enabling faster decision-making.
• Intero - The Sniffers merges with TP Europe
• DeepOcean takes 100% ownership of Equinor pipeline repair contract
• Energy Transfer announces FID for Permian Basin pipeline project
• CRC Evans provides a dedicated fabrication division from its Texas facility
• EIA: Argentina’s crude oil and natural gas production near record highs
• Shell and Equinor combination creates a new UK superpower, says Wood Mackenzie
Follow us on LinkedIn to read more about the articles linkedin.com/showcase/worldpipelines
Versatile
High Strength
Convenient
Corrosion Resistant
Excellent Cost-to-Strength Ratio
Conformable
AQUAWRAP:
Low Cost
Simple and Easy-to-Use – Just “Rip & Wrap”
Cures in Wet Conditions and Underwater
Excellent Toughness – Resists Cracking
Heat Resistant to 250°F.
Non-Hazardous
30-Minute Working Time,
Perfect for Long Installations
High Strength
Tom Sharp, Director of Permitting Intelligence, Arbo, details how legal battles are shaping pipeline infrastructure in the USA.
eeting the rising demand for energy at home and abroad requires the US gas pipeline industry to navigate a legal and regulatory environment marked by increasing complexity and frequent challenges.
This dynamic landscape demands a proactive approach from stakeholders, as the judicial resolution of challenges to agency authority, heightened scrutiny of agency decisions, and congressional action on permitting reform are poised to significantly shape the future of American infrastructure development.
To succeed, developers must create robust, data-driven project plans that anticipate legal challenges and extended timelines. This requires keen attention to judicial trends and evolving policy frameworks with the potential to reshape the regulatory environment. The Federal Energy Regulatory Commission (FERC) remains central to this process, as its authority and decision-making frameworks continue to be tested in court.
FERC’s authority under judicial scrutiny
FERC reviews applications for the construction and operation of interstate natural gas pipelines; its staff responds to developers’ project applications with a series of assessments and analytics reflecting the requirements of relevant statutes and FERC’s regulations and policies. The issuance of a FERC Certificate hinges on whether a project demonstrates market need and whether its public benefits outweigh its adverse impacts. Established frameworks have guided this decision-making for decades, but
recent court cases have introduced new levels of scrutiny and additional tools for project opposition.
Market need
A recent court ruling in the Regional Energy Access case criticised FERC’s dismissal of third-party studies indicating New Jersey’s future demand could be met by off-peaking natural gas supplies. The court found that FERC failed to substantiate its claims about supply uncertainty and misinterpreted the enforceability of New Jersey’s legal mandates to reduce natural gas use. Because Local Distribution Companies (LDCs) can pass on costs to captive ratepayers, the court scrutinised FERC’s reliance on the project’s precedent agreements with LDCs. This case is one of several recent examples underscoring increasing uncertainty about what constitutes sufficient evidence of market need.
Another unsettled issue is the relationship between greenhouse gas (GHG) analysis and FERC’s public interest determinations. The same court recently remanded Commonwealth LNG’s FERC Certificate, in part because the Commission did not adequately explain why it could not determine the “significance” of the project’s GHG emissions in its environmental analysis. As this issue has evolved, the Commission was recently driven to overturn its own analysis from a prior case, where it found certain GHG impacts of Northern Natural to be “de minimis” because the court was pressuring the Commission to explain why it could not apply the same approach to find a significance threshold at the upper bound.
In other related litigation, the court has questioned FERC’s explanation as to why it does not use the Social Cost of Carbon tool to make “significance” determinations for GHG emissions. Most recently, in the Rio Grande LNG litigation, the court narrowly upheld the Commission’s explanation for why it was not required to do so, but left open the question of whether the tool could be used for that purpose more generally.
Environmental justice (EJ) considerations in federal decisionmaking are undergoing significant changes, with new regulations and tools shaping how agencies identify and address impacts on disadvantaged communities. In the Rio Grande LNG case, determining the appropriate radius for EJ analysis as it related to potential impacts of emissions on air quality proved contentious, highlighting the need for developers to closely monitor how FERC sets these boundaries for future projects, and whether the courts accept them.
The litigation landscape extends to other agencies and across all jurisdictions, as most projects require multiple permits from various federal and state authorities. Legal challenges can arise under multiple permitting laws and at different levels of federal and state court, compounding risks and extending timelines.
The poster child for this fractured landscape is the 300 mile Mountain Valley Pipeline (MVP) which entered service this year after nearly a decade of contentious legal battles over water quality certifications, land rights, and regulatory jurisdictional authority. MVP’s project footprint required permits from various federal and state authorities including the US Army Corps of Engineers, Bureau of Land Management, National Park Service, US Fish and Wildlife Service, US Forest Service, and more. Most of these were challenged by environmental NGOs like The Sierra Club. This litigation delayed the project significantly and drove up costs to more than double the project’s estimate. Other pipeline projects in the Northeast that faced similar challenges wound up being cancelled.
As a result, major interstate pipeline development has slowed to a crawl, but even much smaller projects face similar battles, like the Cumberland gas pipeline project – a 32 mile lateral expansion designed to provide feed gas to a new power plant which will replace two of the Tennessee Valley Authority’s coal-fired power plants. Despite the positive impacts of coal to gas switching, the pipeline component of the project faces opposition from environmental groups in the Sixth Circuit regarding Clean Water Act (CWA) permits and in the D.C. Circuit concerning its FERC Certificate. The generation facility faces NEPA challenges in the Tennessee Middle District Court.
To account for risks like these, developers must craft project plans with built-in flexibility that is informed by benchmarking similarly situated projects. Structured and normalised historic federal and state data is crucial to building permitting profiles that can reduce uncertainty. Furthermore, the choice of venue – what court could hear a potential challenge – has become increasingly important, as different jurisdictions have varied approaches to energy infrastructure challenges. For example, the D.C. Circuit has recently shown a preference for vacatur as a remedy for procedural violations, while the Fifth Circuit offers a potentially more favorable environment for certain projects.
Addressing the chronic re-litigation of permits is crucial for all infrastructure growth. That MVP required an act of Congress and Supreme Court intervention underscores the urgent need for such reforms, but it is just one example in one industry. Similar challenges have also delayed renewable energy projects and transmission infrastructure. Bipartisan support for permitting reform exists, but Congressional action remains uncertain in the immediate term. Absent meaningful reform, developers must anticipate litigation and balance the pressures from rapid development timelines with the need for thorough analysis to create durable permits. Proactively providing agencies with the data and analysis needed to craft stronger, more defensible permitting decisions can also assist in their timely issuance. Strategic decisions about permit timing and project location should account for regional opposition, court precedent, and regulatory overlap.
Presidential power is limited
While the executive branch can wield some influence over energy infrastructure through executive orders and regulatory priorities, it is constrained by Congressional support and judicial interpretation. The Supreme Court’s rejection of Chevron deference has fundamentally altered the regulatory landscape by weakening agencies’ ability to implement White House priorities through novel interpretations of their statutory authority, and instead emphasising agencies’ adherence to clear statutory mandates while empowering the courts to fill vague gaps in the law. This shift is evident in ongoing legal challenges to major EPA rulemakings and may further limit the ability of any administration to implement sweeping changes without Congressional backing.
NEPA’s regulatory foundation may be fracturing
Two major developments in NEPA litigation could fundamentally alter how agencies conduct environmental reviews. The D.C. Circuit’s ruling in Marin Audubon Society v. FAA has questioned the very foundation of NEPA implementation by finding that the Council on Environmental Quality (CEQ) lacks authority to issue regulations that bind agencies. This decision could transform how all federal agencies approach environmental review. However, chances for rehearing en banc are higher than usual given that the argument leading to this holding was not raised by the litigants, but by the court itself, and because all parties to the case oppose the outcome.
The second comes from the Supreme Court case, Seven County Infrastructure Coalition v. Eagle County which could significantly impact how far agencies must go in analysing environmental effects. If the Court adopts a more conservative view, it could narrow the scope of environmental analysis that agencies have to conduct and provide the incoming administration with justification to roll back Biden-era NEPA regulations in another rewrite if Marin is reversed on rehearing. CEQ’s rulemaking authority wasn’t directly at issue here, but it was briefed for the Court by other interested stakeholders, as was the Marin decision. Especially in light of the Chevron decision, industry is rightly watching to see if the Court narrows the scope of agency environmental review.
Growth in US infrastructure requires a balanced regulatory approach that aligns public interest, environmental considerations, and market needs. But with evolving judicial precedents, competing policy initiatives, and shifting demand fundamentals, success will continue to depend on strategic planning and flexibility.
Analysis of robust and relevant data points from regulatory and legal realms enhances the entire project lifecycle – helping to identify risks, manage stakeholder expectations, and streamline regulatory processes – ultimately reducing timelines and strengthening the durability of permits in what continues to be a challenging environment for development.
Tom Sharp is the Director of Permitting Intelligence for Arbo, an energy regulatory analytics, data, research and services provider to pipelines, producers, and commodities teams. His unique perspective is informed by 12 years of federal experience, most recently as Director at The Permitting Council, and by positions at the White House Council on Environmental Quality. Tom is an environmental attorney and former FERC staff; a specialist in NEPA and natural gas pipeline Certificates.
the Pipe Line Contractors Association has supported the union contractors that build and maintain the energy infrastructure in the United States.
PLCA members provide superior construction services with an industry-leading focus on safety, quality, training, environmental compliance, and community support.
The PLCA hosts two exciting and popular member events each year: its Annual Convention, held in January/February, and the National Pipe Line Conference in the fall. Both of these major industry events are highly educational and allow members to network with industry colleagues and reconnect with old friends.
Mark Naples, Managing Director, Umicore Coating Services, illustrates how addressing methane emissions, through efforts like the Global Methane Pledge, is fuelling advancements in leak detection technology.
aced with one of the most pressing environmental challenges in history, the oil and gas pipeline industry finds itself at a critical juncture. Methane emissions, one of the most potent greenhouse gases, continues to rise at unprecedented rates. According to the latest
Global Methane Budget, atmospheric methane levels have surged by 20% in the last two decades, now reaching 1931 parts per billion. 1 As the world casts its gaze on the urgent need to reduce emissions from the fossil fuel sector, operators are coming under increasing pressure to innovate and implement more effective methane detection and reduction strategies.
In part, this pressure is due to the ambitious targets set in 2021’s Global Methane Pledge (GMP). This commitment, launched at the COP26 climate summit, outlined goals of reducing methane in the atmosphere by at least 30% over the next six years. Achieving these goals will be instrumental to limiting global warming within proscribed levels, but with emissions continuing to rise, they are appearing increasingly out of reach.
The growing sense of urgency on emissions reduction has been met with a surge of innovation. Since the GMP, the oil and gas industry has presided over unprecedented momentum in mitigation technologies, with some truly impressive advancements enabling operators to replace traditional periodic inspections with something more effective. These technologies are helping fossil fuel operators to more accurately track and register their emissions, facilitating preventative maintenance strategies and providing a stronger backing for anti-methane policies.
The industry’s responsibility
The lack of progress against the GMP’s targets highlighted in the Global Methane Budget demonstrates that time is fast running out for the oil and gas pipeline industry to get its act together on methane emissions. Methane is a particularly potent greenhouse gas that has contributed to approximately one-third of net global warming since the Industrial Revolution. 2 Its impact on climate change is particularly significant in the short term, as it has a much higher warming potential than carbon dioxide over a 20 year period. This means that preventing methane emissions today could have more immediate results than any other greenhouse gas.
The oil and gas industry has a particular duty to act due to its outsized contribution to methane emissions. Fossil fuel energy production is the second largest source of human-caused emissions after agriculture, accounting for more than a third of total estimated anthropogenic emissions. 3 However, the sector is also uniquely well positioned to do something – according to the International Energy Agency (IEA), around 40% of all methane emissions from fossil fuels could be avoided at no net cost as the required spend on abatement would be less than the market value of the additional gas captured. 3
Addressing methane emissions in the fossil fuel industry would have the added benefits of improving safety and reputation. For the oil and gas operators, methane emissions pose not only an environmental challenge but also represent a significant health and safety risk due to the chance of combustion at sufficiently high concentrations. Such incidents threaten employees and infrastructure alike and require significant costly downtime to avoid through
scheduled maintenance. By reducing leak occurrence, the sector can protect its people and reduce spend on equipment.
The GMP was humanity’s first major concerted effort to tackle global methane emissions. This voluntary framework supports its 158 signatories to reduce anthropogenic methane emissions and commits them to a 30% reduction target by 2030. The countries that have signed it now represent more than half of all human-caused emissions, and if its targets are achieved, total global warming could reduce by at least 0.2°C by 2050. 4
Industry monitoring agencies broadly recognise that meeting the GMP’s goals will require the oil and gas industry to transform its emissions monitoring capability. The IEA identifies accurate data on methane emissions as an essential requirement for abatement activity, as it will improve understanding of emissions sources, production, and rates that are currently compromised by ad-hoc collection attempts. 3Accurate, timely, and comprehensive information on infrastructure condition can help to pinpoint the location and magnitude of methane leaks, enabling targeted mitigation efforts. Such measurements also facilitate tracking of emissions reductions over time, helping to improve accountability in the sector, and can support evidence-based policymaking to set more appropriate standards and targets.
As a result, detection and monitoring innovations have formed a large part of the momentum on emissions since the GMP was signed. One of the most significant developments has been the full launch of the Methane Alert and Response System (MARS). This satellite-based system, developed by the UN Environment Programme’s International Methane Emissions Observatory (IMEO), detected over 1000 energy sector methane plumes globally during its pilot phase in 2023, linking 400 of these plumes to specific energy sector facilities. This system demonstrates the power of combining satellite technology with data analytics to provide actionable information on methane emissions.
However, innovations have not been limited to multinational programmes alone. Ongoing commitments have catalysed developments in gas detection capability, leading to a suite of technologies that are revolutionising prevention efforts.
One of the biggest challenges in gas detection in the energy sector is the scale of land that must be surveyed. Many operators oversee vast networks of pipelines and storage equipment, which must be regularly inspected to prevent leaks. Doing so manually is time-consuming and inefficient, and as a result, technology that can provide a comprehensive view of existing infrastructure should be a vital tool in emission reduction efforts.
Aerial measurements from aircraft and drones are playing an increasingly important role in solving this challenge. Equipped with the right sensors, this technology
Once a pipeline is in production, debris within the system can be more extreme, with sand or scale or wax deposits. This can require more specialist pigs to be used, where designs are more focused and offer the ability to be adjusted as part of a progressive cleaning programme.
Propipe pigs are designed specifically for each pipeline and offer optimum performance to maintain maximum production pressures and flow.
Standard Pigs - No Bypass
Propipe Pigs with Bypass
Full testing facilities and the Trident pig tracking range are available.
can cover vast distances, providing detailed data on specific locations.
Drones offer an unmatched degree of manoeuvrability and flexibility. Their long range makes them well-suited for detection in the fossil fuel sector, where key infrastructure can often be spread across large, remote locations. However, this technology is not without its challenges. Any sensors mounted to the drone need to be light enough to not significantly impact flight times and must be capable of accurately measuring very low concentrations of methane from a long distance. The movement of a drone may also affect sensor readings, especially in wind or other weather conditions that can affect flight stability and data accuracy. These restrictions must be carefully considered when planning to use drone technology for emissions monitoring purposes.
As a result, drone technology is ideal for use as a complement to fixed-position sensors and mobile groundbased technologies. These devices can be deployed in a network that enables real-time data on emissions across a company’s infrastructure, with enhanced detection and quantification capabilities compared with traditional periodic inspections. Alongside advanced algorithms, this technology is enabling operators to combine data from multiple sources, including gas concentration measurements, wind speed, and location data, facilitating precision localisation and quantification of methane leaks. Further advances have been seen in the semiconductor and filter technology that enables infrared (IR) gas detection, with laser absorption spectroscopy (LAS) standing out as a prime example. LAS systems offer multiple advantages over other traditional detection methods, including high sensitivity and specificity that enable detection at very low concentrations and help to eliminate false positives. Deployable as fixed or portable detectors, this technology is ideal for continuous, realtime monitoring of methane levels across a large area, facilitating rapid responses to methane leaks.
At the heart of LAS technology are infrared filters such as those produced by Umicore Coating Services. Designed to meet the exacting requirements of high-performance infrared detection applications, these filters are engineered to isolate specific wavelengths of light absorbed by methane, enhancing detection accuracy. Modern filters are built to withstand the harsh environmental conditions often encountered in oil and gas operations, ensuring they are suitable for deployment across a company’s infrastructure network, and the advanced technologies used in their creation ensure uniform performance across large production batches. As a result, LAS systems incorporating this technology represent a powerful gas detection tool that closely aligns with the goals of the GMP and supports the oil and gas industry’s efforts to reduce emissions.
The momentum on methane is not limited to technological innovations alone. In August, the EU introduced regulations
mandating improvements to measurement, reporting, and verification. This law requires the industry to monitor and report on their emissions for the first time, and will also apply to imported fossil fuels, encouraging international exporters to introduce the same stringent standards. In the USA, companies are now required to conduct more frequent surveys of their equipment to detect leaks, with regulations mandating immediate repairs, and a SuperEmitters programme has been established to identify particularly polluting facilities.
Further momentum is being seen in the suite of industry initiatives being formed. Since the GMP, the Oil and Gas Methane partnership has expanded to include over 120 companies, covering 35% of the world’s oil and gas production. The Oil and Gas Climate Initiative (OGCI) is also expanding its Satellite Monitoring Campaign to provide actionable data for reducing emissions from largemagnitude methane plumes and flares, and as the GMP continues driving action on methane, these programmes will help the oil and gas industry keep up. Upholding the GMP’s commitment represents an environmental and business imperative – better understanding of emissions supports mitigation efforts that can support the planet and help businesses maintain competitiveness in an increasingly eco-conscious landscape.
Achieving the ambitious targets set out in the GMP will require a continued push for innovation. As the oil and gas industry rises to the ambitious targets set by the GMP, it has the opportunity to not just contribute to climate change goals, but to position itself as a leader on the environment. In this regard, the advanced sensors supported by high-performance infrared filters that have developed since the GMP will be instrumental to success. Such technologies, backed up by high performance infrared filters, provide the detection capability needed for meeting compliance requirements, enhancing efficiency, and helping companies demonstrate true environmental stewardship.
References
1. https://www.globalcarbonproject.org/methanebudget/
2. https://www.globalmethanepledge.org/news/highlights-2023-globalmethane-pledge-ministerial.
3. https://www.iea.org/reports/global-methane-tracker-2024/key-findings.
4. https://www.globalmethanepledge.org/resources/global-methane-pledge.
For more on methane emissions from the pipeline sector, and the path towards ne t-zer o, visit www.worldpipelines.com/news
Since 1948, Tinker & Rasor has been a trusted name in holiday detection, relied upon by pipeline professionals worldwide. For over 76 years, our holiday detectors have set the benchmark for performance and reliability, ensuring the integrity of protective coatings by detecting coating flaws with precision. With a legacy of innovation and toughness, Tinker & Rasor continues to lead the industry, delivering cutting-edge solutions to safeguard pipeline coatings and maintain quality standards across the globe.
Lars Larsson, Project Management Director, AspenTech, USA, discusses how gas pipeline companies can fasttrack digital transformation in order to leapfrog ahead of the competition.
n the rapidly evolving landscape of energy, gas pipeline operators, particularly in Europe and North America, are facing unprecedented pressure to modernise their operations through digital technology. The energy sector is undergoing a significant transformation, driven by the global call for more sustainable energy production and the imperative to reduce carbon emissions. While some operators have made remarkable strides in their digital transformation journeys, integrating advanced technologies to enhance their operations, many others find themselves lagging behind.
These companies are grappling with legacy systems, outdated processes, and an ageing infrastructure that hinders their ability to adapt to the changing demands of the industry. For these organisations, the challenge is not merely to catch up with industry leaders but to leapfrog ahead. The opportunity lies in leveraging digital technology to enhance safety, efficiency, and reliability, thereby positioning themselves at the forefront of the industry’s digital revolution.
Gas pipeline executives are acutely aware of the risks associated with outdated systems. Negative publicity from incidents such as leaks, explosions, or cyber-attacks can severely damage a company’s reputation and financial standing. High-profile events like cyber-attacks on critical infrastructure, such as the attack on Colonial Pipeline in the US, have highlighted vulnerabilities that can no longer be ignored.
The industry is also facing increased regulatory scrutiny and a global call for more sustainable operations. In December 2020, the US Congress passed the “Protecting our Infrastructure of Pipelines and Enhancing Safety” (PIPES) Act of 2020, for example, while in October 2020 as part of the European Green Deal, the EU Methane Strategy came into force to reduce methane emissions across the energy sector. Operators must adapt to transporting alternative fuels like hydrogen and carbon dioxide, requiring more flexible and sophisticated systems. Additionally, the workforce is changing; experienced personnel are retiring, and new talent is scarce, since the oil and gas pipeline industry is not popular work among the younger generation.
McKinsey partner Christopher Handscomb, and his co-author, reveal that over a quarter of employees at US oil and gas companies are nearing retirement age, and many of these workers are frontline employees.
This situation exacerbates the risks associated with outdated systems and processes. Operators need solutions that are intuitive, user-friendly, and capable of capturing institutional knowledge before it is lost, and they need the same to attract the younger generation.
Digital transformation offers a pathway to address these challenges. By embracing advanced technologies, pipeline operators can enhance operational safety, improve efficiency, and ensure compliance with regulatory standards. Digital tools can provide real-time monitoring, predictive maintenance, and advanced analytics that empower operators to make informed decisions quickly.
Supervisory Control and Data Acquisition (SCADA) systems are the key foundation of this transformation. They have long been the backbone of gas operations, offering realtime data and control over critical infrastructure, and they continue to demonstrate growth across this sector today. In line with this, Grand View Research estimates that global oil and gas SCADA market size was US$3.73 billion in 2023 and projected to grow at a CAGR of 5.7% from 2024 to 2030.
However, to truly unlock the potential of digital transformation, these systems must evolve. They need to be integrated with advanced pipeline applications that enable predictive analytics, machine learning, and automation. Such integration not only enhances operational efficiency but also delivers insights that can drive strategic business decisions, optimise asset performance, and improve overall organisational agility.
Integrating advanced technologies into the energy sector is revolutionising operations, making them more efficient and cost-effective. Predictive analytics can analyse data trends to forecast equipment failures before they occur, allowing for proactive maintenance and reducing downtime. Machine learning algorithms optimise operational parameters, enhancing efficiency and lowering operational costs. Automation streamlines routine tasks, freeing up personnel to focus on higher-value activities.
However, as pipelines and systems become more interconnected, they also become more vulnerable to cyber threats. According to research by DNV, nearly half (48%) of energy professionals now worry that their sector is more susceptible to cyber-attacks than ever before. Moreover, a majority (56%) indicate that their organisations will invest more in cybersecurity in 2024 compared to the previous year.
Critically, thoughtful integration of technology can also enhance cybersecurity. Integrated systems with built-in security features protect against unauthorised access and data breaches, safeguarding critical infrastructure. While securing central systems is essential, it’s equally important to extend security measures to field operations. To achieve this, many leading companies are implementing DNP3 secure authentication. This enhances the secure transmission of critical data from remote terminal units (RTUs) to the SCADA system in the control room. The DNP3 protocol requires authentication between SCADA and RTUs during critical pipeline transactions – such as adjusting valve outputs or shutting down devices – to prevent external tampering.
By adopting these advanced security measures alongside technological innovations, the energy industry can mitigate risks while reaping the benefits of increased efficiency and productivity.
Despite the clear benefits, many operators hesitate to embark on digital transformation due to perceived barriers. These include the high cost of upgrading infrastructure, the complexity of integrating new technologies with legacy systems, and the potential disruption to operations during the transition. However, these challenges can be mitigated with a strategic approach.
Firstly, assessing digital maturity is crucial. Operators need to evaluate their current capabilities, identify gaps, and understand the specific needs of their organisation. This assessment provides a roadmap for transformation, highlighting priority areas that will deliver the most significant benefits.
Bleed area: 216mm x 303mm
• Extend your background to fill the full ‘bleed area’ - it’ll make sure you don’t end up with white edges round your advert when it is printed.
Trim area: 210mm x 297mm
• This is the size your advert appear
Safe area: 190mm x 277mm
• Keep all important bits of your design - text, logo, icons - inside this area. (Not your background - that still needs to run to the edges of the bleed.)
Art work specifications / our preferred form
• PDF-x/1a.
• PDFs generated using Press Settings. In addition, please note the following:
• PDFs should be compatible with Acrobat 4 0 or highe
• Please ensure all fonts are embedded.
• All original graphics must be saved as CMYK at 300 dpi they are to be used.
• Please ensure all PDFs are higher than 144 resolution
• Images should not be tagged with any ICC profiles.
We operate a preflight system prior to printing to check that all advertisement material complies with the above specifications. Any advertisement that does not comply with these specifications may need to be resupplied.
Prioritising integration is the next step. Focusing on integrating SCADA systems with advanced applications ensures that data flows seamlessly across the organisation. This integration enables a unified platform that supports real-time data analysis and decision making.
Investing in advanced analytics is essential. Technologies such as predictive analytics and machine learning turn raw data into valuable insights. These tools can optimise asset performance, reduce operational costs, and enhance reliability.
Adopting a phased approach minimises risks. Starting with pilot projects allows operators to demonstrate value and refine processes before scaling initiatives across the organisation. This method ensures that each step adds measurable value and reduces the potential for disruption.
Fostering a culture of innovation is vital for sustained success. Encouraging teams to embrace new technologies and providing training ensures that the workforce is equipped to operate in a digitally transformed environment.
Operators who have been slow to adopt digital technologies have a unique opportunity. Instead of playing catch-up, they can leapfrog ahead by adopting the latest advancements. Modern digital solutions are more accessible and user-friendly than ever before. They are designed to integrate with existing systems, reducing the complexity of implementation.
For example, many operators still rely on custom-built applications developed decades ago, often by personnel who have since left the organisation. These applications are not only outdated but also pose significant risks due to a lack of support and maintenance. By transitioning to modern, integrated solutions, operators can eliminate these risks and benefit from applications that are continuously updated and supported.
Furthermore, modern systems are designed with scalability in mind. Operators can start with essential functionalities and add more advanced features over time. This modular approach allows organisations to manage costs effectively and adapt to changing needs without significant overhauls.
This leapfrogging strategy enables laggard operators to not only catch up but surpass industry leaders. By adopting state-of-the-art technologies, they can implement best practices from the outset, avoid the pitfalls encountered by early adopters, and position themselves competitively in the market.
As operators consider leapfrogging into advanced digital solutions, the role of sustainability and regulatory compliance becomes increasingly significant. Sustainability is no longer a mere corporate social responsibility checkbox but a critical aspect of operational strategy. There is a growing demand for transparency in emissions reporting and a need to demonstrate tangible progress toward netzero goals.
Digital technologies enable operators to monitor emissions in real time, perform complex calculations for accurate reporting, and ensure compliance with diverse regulatory requirements across jurisdictions. For example, transporting hydrogen and carbon dioxide (CO2) through pipelines adds operational complexity. Teams need constant access to accurate, real-time data presented with full contextual understanding to navigate these challenges effectively. This ensures that critical information is not only received promptly but also interpreted correctly, making it actionable.
Regulators are also tightening cybersecurity requirements. Operators must ensure that their systems are secure and can respond quickly to emerging threats. Digital solutions with embedded cybersecurity features provide the necessary protection, ensuring that operators can safeguard their assets and maintain public trust.
Control Room Management (CRM) is still a focus for regulators since it protects both the public along the pipelines and the pipeline companies themselves. These applications integrate the functionalities operators need to create the evidence necessary to prove compliance with existing CRM regulations, and by extension helping to make operational safety second nature. CRM applications have become an integral part of control room operations, and it is now difficult to distinguish in modern SCADA technology where the SCADA applications end and the CRM applications start.
Furthermore, as financial auditors begin to include carbon emissions in their audits due to new regulations, the ability to provide transparent and auditable data becomes essential. Digitalisation facilitates this by automating data collection and reporting, reducing the risk of errors associated with manual processes like spreadsheet tracking. This not only ensures compliance but also builds investor confidence.
The gas pipeline industry stands at a crossroads. Operators who continue to rely on legacy systems risk falling further behind, facing increased operational risks, regulatory penalties, and loss of market competitiveness. Conversely, those who embrace digital transformation position themselves as industry leaders, equipped to navigate the complexities of the modern energy landscape.
By integrating advanced pipeline applications with SCADA systems, investing in predictive analytics and machine learning, and fostering a culture of innovation, operators can transform their organisations. They can enhance safety, improve efficiency, reduce costs, and meet the challenges of sustainability and cybersecurity head-on.
The journey from laggard to leader is not without challenges, but the benefits far outweigh the risks. Digital transformation is not just an operational imperative; it is a strategic necessity that will define the future success of gas pipeline operators. By taking decisive action now, organisations can secure their place at the forefront of the industry’s digital revolution, ready to meet the demands of the future with confidence.
Figure 1. As global energy demand surges, pipeline operators are turning to advanced remote telemetry systems to ensure the safe, efficient and uninterrupted flow of oil and gas across vast and challenging terrains.
he International Energy Agency (IEA) predicts that global energy demand will rise by 25% by 2040, driven by population growth and economic development in emerging markets. As demand grows, oil and gas pipelines are under increasing pressure to deliver uninterrupted service while ensuring safety and efficiency. The IEA’s World Energy Outlook 2024 forecasts a 50% rise in natural gas demand by 2040, highlighting the need for pipeline operators to manage larger volumes across expansive networks. Pipelines span vast distances, often through challenging terrain, making them vulnerable to risks such as corrosion, leaks and structural damage.
Philippe Willems, Global Engineering Manager, Ovarro, explains how remote telemetry units (RTUs) are emerging as key technologies to optimise performance and reduce failures in pipeline systems.
In fact, the US Pipeline and Hazardous Materials Safety Administration (PHMSA) reports over 800 significant pipeline incidents annually, emphasising the need for effective monitoring systems that provide real-time visibility into network conditions. While the demand for oil and gas remains robust, environmental concerns are prompting a gradual transition to renewable energy sources. Despite this shift, the IEA projects that fossil fuels will still account for nearly 75% of the global energy supply in 2030, reinforcing the importance of safe and efficient pipeline operations.
The rising global energy demand has far-reaching implications that extend well beyond the operation of pipelines. This surge in energy consumption not only affects energy prices, leading to increased volatility and potential geopolitical tensions among nations vying for energy resources, but it also accelerates the push for renewable energy solutions as countries strive to meet their energy needs sustainably.
Fortunately, advanced monitoring systems such as remote telemetry units (RTUs) and supervisory control and data acquisition (SCADA) systems are transforming pipeline management by enabling proactive oversight and control. By integrating these technologies, operators can manage potential risks more effectively, safeguarding pipeline infrastructure while meeting rising global energy demands.
The oil and gas industry faces several barriers to efficient and safe pipeline management, particularly with ageing infrastructure. Many pipeline systems were installed decades ago and show signs of wear, making them prone to leaks and cracks. As pipelines age, the risk of environmental and safety hazards increases, particularly in remote areas where regular inspections are challenging.
Extreme environments also complicate pipeline management. Pipelines operate in harsh conditions, from arctic temperatures to desert heat, which can strain materials and accelerate degradation. These conditions make maintaining pipeline integrity more difficult.
Additionally, many pipelines are located in remote areas where manual inspections are infrequent and communications unreliable, making real-time data collection difficult. Increasing regulatory scrutiny adds further pressure, requiring operators to comply with strict safety and environmental regulations. Precise and continuous monitoring of pipeline performance is needed to ensure compliance and avoid costly fines.
To address these barriers, the oil and gas industry has adopted modern technologies and methods to improve pipeline oversight and safety. One solution has been the digitalisation of pipeline networks. SCADA systems, combined with RTUs, allow operators to centralise control over large networks, providing real-time insights to address potential issues before they escalate into critical failures. With predictive maintenance as a key strategy, the focus shifts to how specific technologies are delivering measurable results in pipeline management. Pipeline operators are also shifting towards predictive maintenance strategies. Rather than relying on traditional, time-based maintenance schedules, data from RTUs can predict when equipment or pipeline sections are likely to fail. This enables timely interventions, preventing downtime and reducing the risk of costly repairs.
Automation of data collection and control processes has been another key approach. Advanced RTUs can operate autonomously, collecting data on pipeline performance and controlling processes even when communications with the central system are interrupted. This is especially useful for pipelines in remote areas where connectivity is unreliable.
Advanced monitoring with proven results
Remote monitoring solutions like those from Ovarro are helping operators overcome the challenges of managing large-scale pipeline networks. Ovarro’s TBox RTUs enable operators to control and monitor assets remotely, providing real-time data on flow rates, pressure and temperature. These units continue to collect and process data even if communication with the central system is lost, which is essential for pipelines in remote areas where on-site intervention can be difficult.
One example of Ovarro’s impact is its work with Distrigas of Belgium, a major supplier of natural gas across Europe. Distrigas has played a strategic role in Europe’s gas networks since the 1960s and has consistently adopted the latest technologies to ensure precise gas volume measurements. To improve efficiency, Distrigas launched a project to automate meter reading and transmit data to a central system. After evaluating several options, Distrigas chose Ovarro’s TBox telemetry system.
The TBox system was integrated with existing gas meters across the Distrigas network. Connected to pressure and temperature transducers, the system ensures gas volume measurements are accurate and calibrated. Today, more than 550 TBox RTUs are deployed across the network, transmitting data to a central computer. This automation has reduced the need for manual meter readings and improved data collection accuracy and reliability. Distrigas now benefits from a streamlined monitoring process, enhancing operational efficiency and compliance with regulatory requirements.
Ovarro has introduced the extended TBox LT2 Family Series of RTUs to meet the growing demand for cost-effective monitoring solutions across various sectors, including oil and gas. The new models – LT2-500, LT2-510 and LT2-520 – offer enhanced scalability and ease of use, allowing operators to implement reliable monitoring capabilities without incurring significant costs.
These models retain the comprehensive functionalities of the TBox RTU and programmable logic controller (PLC) function set, supporting remote monitoring and control in industrial processes. With advanced communication protocols, the TBox LT2 models help streamline operations and improve energy efficiency, making them suitable for various applications within the oil and gas industry.
Pipeline management is being significantly shaped by emerging technologies such as artificial intelligence (AI), the Internet of Things (IoT) and big data analytics. AI and machine learning enhance predictive maintenance by analysing vast datasets to identify patterns and anomalies, enabling proactive interventions before issues escalate.
A recent report published in the Process Safety and Environmental Protection, ‘Future of process safety: Insights, approaches and potential developments’, predicts the use of, “advancements in modelling techniques, integration of real-time data, and consideration of dynamic factors to enhance the accuracy and reliability of risk assessments.”
The IoT facilitates real-time data collection from sensors embedded throughout pipeline infrastructure, providing operators with comprehensive visibility over their networks and allowing for agile responses to operational challenges. This underscores the vital importance of keeping pace with these innovations to ensure robust safety systems.
As these technologies advance, the imperative for effective and reliable pipeline management becomes increasingly critical in the face of global energy demands. Moreover, big data analytics unlocks valuable insights from the extensive information generated by the industry, driving continuous improvement in maintenance practices and operational strategies. As regulatory scrutiny and environmental responsibility intensify, advanced monitoring systems that ensure compliance while minimising ecological footprints will be crucial.
The advent of digital twins – virtual replicas of pipeline systems – further enhances risk management and planning capabilities. This forward-looking perspective emphasises the need for a shift from traditional reactive approaches to “more anticipatory models” that utilise advanced quantitative risk assessments. By embracing these innovations, pipeline operators can navigate the energy transition and maintain efficiency, safety and resilience in an evolving energy landscape.
As global energy demand rises, the oil and gas industry faces increasing pressure to manage pipeline networks more effectively. Given the complexities posed by ageing infrastructure, environmental extremes and remote locations make this a complex task, but advanced monitoring technologies like Ovarro’s RTU and SCADA systems equip operators to ensure safety, efficiency and regulatory compliance.
The transition to renewable energy will reshape the global energy landscape. As the IEA report highlights, states heavily reliant on fossil fuel exports must adapt to the energy transition or risk losing influence. In its report, ‘A New World: The Geopolitics Of The Energy Transformation’, the International Renewable Energy Agency (IRENA) also emphasises that “the energy transition will reshape relations between states and lead to fundamental structural changes in economies and society.”
Consequently, for the oil and gas industry, adopting technologies that improve efficiency, safety and resilience is essential to remain competitive during this transformation. Real-time monitoring will help ensure that oil and gas operations continue to be secure and efficient, even as the energy landscape evolves.
The IEA’s projected 25% rise in global energy demand by 2040 presents both challenges and opportunities for pipeline operators. In a world where energy demand is increasing and the need for safety and environmental stewardship is greater than ever, smart pipeline monitoring solutions are not just an advantage – they are essential.
Essam Arfaj, Bader Jarallah, and Mohanned Tarabzouni, Aramco, Saudi Arabia, weigh in on the debate between installing pipeline valves above-ground, underground, or in a valve box.
ith the advancements in pipeline construction methods and inline inspection tools, end users have found themselves in a debate around optimising pipeline installation methods – such as buried (underground) or above-ground installation. This has also expanded to the selection of valve installation methods, which include the aforementioned buried and above-ground installation, in addition to the boxed installation option. Several factors determine the most appropriate method, such as environmental protection and damage prevention, routing, population density, and safety hazards. While buried pipelines have become the preferred method for most end users, valve installation methods are still a point of debate. This article will shed light on the pros and cons for each, as well as a thorough review of key factors involved in the final decision-making process.
Pipeline installation methods
Installing pipelines is essential for safely transporting fluids and gases in various industries, especially the hydrocarbon industry. For underground pipelines, it is crucial to analyse soil conditions to prevent corrosion and ensure stability. Minimising environmental impact and following local regulations are also important steps, including obtaining
the necessary permits. For above-ground pipelines, structural support is key to preventing sagging and maintaining alignment. Pipes need protection from environmental factors like weather and temperature changes and accessibility is crucial for maintenance and inspections.
Overall, understanding the specific challenges and requirements of both underground and above-ground installations is vital for a successful, compliant, and efficient pipeline system. Regular inspections and maintenance protocols are essential to catch potential issues early and ensure long-term operation. Implementing safety measures protects both workers and the environment during the installation and throughout the pipeline’s operation.
The US, for example, houses one of the largest pipeline networks in the world with more than 3 million miles of pipes transporting hydrocarbon products across the country. The majority of these pipelines are buried below ground to safely carry and deliver products to end users.
In Saudi Arabia, this is also the case, as the majority of the over 25 000 km pipeline system is buried below ground, spread across the Kingdom and passing through multiple elevation changes, natural habitats and harsh desert environment.
While pipeline methods are generally clear to assess and select, installing valves in pipeline systems is a critical process that ensures the safe and efficient control of fluid flow. Proper installation is crucial, regardless of whether the valves are installed underground, above ground, or within a valve box. This article provides an overview of the considerations and steps involved in each type of installation. Typical methods of valves installation include the following:
Underground installation of valves entails completely burying the valve alongside the welded pipeline with extensions of auxiliaries above ground. In most cases, the depth of the valve and extended auxiliaries vary in length and design to accommodate and ensure the operability of the valve. Several design factors must be considered for underground installation, including, but not limited to, the following: ) Soil conditions: ensuring the soil can support the valve without causing corrosion or damage.
) Accessibility: allowing future access to the valve for maintenance, inspection or emergency responses.
) Protection: applying the required protective coatings or wrapping system to safeguard against corrosion.
) Environmental impact: minimising disruptions and protecting the environment.
On the other hand, above-ground installation in a fenced or designated location for valves is another potential option. This is a commonly used option among end users, due to the accessibility of the valve and associated components. This option depends on multiple considerations in design and construction, including the following:
) Environmental exposure: protecting the valve from environmental factors such as harsh weather and temperature fluctuations.
) Accessibility: ensuring that the valve is easily accessible for operation and maintenance.
) Security: protecting against vandalism and third-party damage.
) Civil structure: supporting the design to ensure the valve withstands and is aligned with all loads.
) Preparation: flanged connections with potential leak paths, requiring proper torqueing and commissioning.
The third installation option is installing the valve in a solid box, mainly made of concrete. The box is typically a concrete structure (or pit) equipped with a manhole or other access point that allows easy access to the equipment located within the vault. Access to the box is usually through a ladder, allowing inspection or maintenance on the pipe, valves, meters, or other equipment. The valve body itself is directly buried in the ground or soil.
This means the valve will be in a confined space, which increases the risks of operational hazards and unsafe work conditions when inspecting and maintaining the valve. Several factors must also be considered, such as:
) Material: choosing a durable material for the valve box to withstand environmental conditions.
) Size and fit: ensuring the valve box is appropriately sized to allow easy access to the valve.
) Site preparation: clearing and levelling the area where the valve box will be installed.
) Position: positioning the valve box over the valve to ensure that the valve is easily accessible.
) Security: securing the valve box to prevent movement and protect the valve from external damage.
) Labelling: clearly labelling the valve box for easy identification.
Additionally, CAPEX for valves may be higher with this option compared to the previous two, as it includes requirements similar to both above- and below-ground installation, such as the casing design, associated coating system, confined space restrictions, extended valve operator, and the internal layout of the box.
Regardless of the installation type, regular maintenance and inspection are vital to ensure the longevity and proper functioning of the valves. Depending on the maintenance and inspection strategies, these valves will require proactive approaches to ensure their integrity and readiness during normal and emergency operations.
Of the above-mentioned methods, above-ground installation typically requires less manpower and fewer
materials compared to underground installation. The underground option requires more construction-related work such as excavation, welding and back filling. On the other hand, above ground installation requires extensive design review for the required fencing, structural support, stress and load analysis, and civil foundations. Furthermore, manned or unmanned station requirements typically contribute to additional costs for utilities and operational continuity processes. Table 1 highlights major pros and cons for each installation option.
Regardless of the end user’s selection, codes will specify additional requirements that ensure the selected option
Detects holidays, pinholes, and other discontinuities using continuous DC
n Lightweight, one-piece ergonomic design provides comfortable all-day use
n One wand covers the entire voltage range from 0.5 to 30 kV
n Up to 16 hours of battery life—powerful Li-ion batteries fit neatly within the compact wand handle eliminating the need for a separate battery box
n Built-in Certified Voltmeter and Voltage Calculator feature
n Industry standard connectors and adaptors provide compatibility with nearly all existing electrodes
Above-ground
Accessibility and maintenance, quicker installation, and ease of access for quick repairs.
Underground Protection from the elements and third-party damage, space optimisation, and cost-efficiency.
Ease of maintenance and inspection, valve is not completely buried, and benefits of both aboveand underground installation.
Additional costs for fenced valve stations and higher possibility of leaking due to higher number of joints.
Full covering of the valve body and high cost of maintenance and inspection.
Risk associated with confined space and additional costs for box and accessibility.
covers the minimum safety, risk mitigation and design needs to guarantee safe operation and sustainable production. These include the following:
) The valves must be protected from external environments and impacts with a proper coating system such as fusionbonded epoxy coating.
) The number of joints on the pressure-containing parts must be minimised. In some cases, fully welded valve design is preferred over flanged connection.
) Any operational dead leg such as buried or inaccessible valves must be equipped with drain, vent, and sealant injection connections extended above ground.
) Where specified, these must contain a robust design with proper corrosion resistant material.
) Additional protection systems must also be specified to aid the overall system protection, which includes cathodic protection.
In summary, the choice of where to install valves involves trade-offs. Underground installation offers protection from the elements, longevity, and tangible benefits, while above-ground installation emphasises accessibility, ease of maintenance, and cost-efficiency. Though underground pipeline installation is typically the preferred option by end users, the final decision depends on factors like budget, intended use, and preferences for maintenance and aesthetics. Cost analyses must be thoroughly reviewed to identify any hidden or unplanned costs along the way associated with each installation method. Wrapping up, ensuring the integrity and reliability of valve auxiliaries is as essential as the main valve itself. Any risk imposed on any component will typically lead to unplanned outages and shutdowns. Proper design, material selection, specification, and inspection practices will ensure their readiness and prolong their design life to sustain operations and production.
Essam Arfaj is an Engineering Consultant at Aramco with 25 years of experience in the oil and gas industry. His expertise spans over technical leadership, management, professional engineering and human resources.
Bader Al-Jarallah is a Valve Engineering Consultant at Aramco Central Engineering. He served as the Chairman of the Valve Engineering Standards Committee and is a member of several engineering standards committees. Since joining Aramco in 2000, he has dealt with various aspects of design, commissioning, operations, troubleshooting and maintenance.
Mohanned Tarabzouni is a Piping and Valves Engineer in Downstream Technical Support at Aramco with a wide range of experience in valves and pipelines for more than 10 years, covering operations and maintenance.
In 2024, Seal For Life Industries was acquired by Henkel, joining brands such as Loctite and CSNRI. To understand more about Seal For Life and the growing demands for integrity management, World Pipelines spoke with three members of the business for their perspectives on today’s pipeline challenges.
Can you outline how Seal For Life’s oil and gas pipeline coating technologies address the challenges of corrosion and environmental exposure?
Mario Moreno: Seal For Life (SFL) offers a comprehensive pipeline coating portfolio addressing a wide range of applications critical to oil and gas infrastructure. From buried pipelines to offshore immersion service, hightemperature insulated pipelines, and horizontal directional drilling (HDD), SFL’s technologies are designed to meet the industry’s most demanding needs. Pipelines are vital infrastructure, enabling the transportation of energy and essential supplies that sustain industries and modern life. Given their critical role, these assets require long design lives with built-in redundancies. A single failure can result in significant environmental, economic, and societal consequences. Our approach to corrosion protection is rooted in a deep understanding of the challenges pipelines face throughout their lifecycle – from installation to decades of service. Our solutions are engineered to ensure maximum service life, offering superior protection against corrosion and environmental stressors.
Our product range includes proven technologies such as:
) Liquid epoxies for durable, high-performance coatings.
) Dual-layer and triple-layer heat shrink sleeves for robust mechanical protection.
) Viscoelastic solutions for self-healing corrosion prevention.
) Tapes and composites for versatile application in diverse environments.
) Polyurethanes for enhanced resistance to wear and abrasion.
The selection of the appropriate coating is critical to ensure optimal performance, ease of application, and compatibility with mainline coatings and cathodic protection systems (ICCP). Key factors to consider include economics, installation conditions, and compatibility with existing systems. A qualified coating expert must carefully evaluate these parameters to ensure the solution meets the pipeline owner’s performance and longevity expectations.
We are fortunate to have an extensive amount of experience across the group, from point of sale through to research and product development. Our focus is on delivering solutions that extend the service life of critical infrastructure protecting both investments and the environment.
What advancements have you recently introduced in coatings for pipeline protection, particularly for extreme conditions, or for complex installations?
Mario Silvestro: Our wide range of solutions address multiple markets and applications, ranging from thermal protection to deep sea high temperatures, to splashzone areas with exposure to extreme temperature variance, UV exposure and marine life/ growth. To expand further on splashzone applications, it is extremely challenging to rehabilitate a coating due to various factors. These factors include the surface preparation limitations, restrictions on available equipment for both surface preparation and application, application space and labour specialty, product cure times and asset time to commission.
Bonding to the substrate with high levels of moisture on the substrate often presents long term performance issues,
and raises questions on liability; product vs application. Seal For Life’s visco-elastic product line, STOPAQ, provides a fully amorphous polyisobutene based wrap coating system which can eliminate the need for stringent surface preparation, reduce complex equipment, does not require specialised labour, and can commission the asset as soon as the system is finished being applied. This surface tolerant coating system, Wrappingband WSH product, can be applied by hand and only requires a surface preparation of water jetting and minimum ST.2 hand wire brush equivalent. This technology is able to be applied in areas of high moisture on the substrate, including being able to be applied fully submerged underwater due to special additives and fillers which displace the water from the substrate allowing the polyisobutene based compound to adhere directly to the substrate. This provides a high level of bonding to the substrate and creates a long-term barrier of water and oxygen on the substrate.
How does Seal For Life ensure compatibility with newer pipeline materials, or specialised coatings required by regulatory standards?
Dirk Totte: Seal For Life has a robust and forward-thinking approach to research and development. Our dedicated in-house R&D teams remain at the forefront of technological advancements, actively engaging with regulatory bodies and continuously pushing the boundaries of our solutions to meet and exceed the most stringent standards.
For instance, we employ advanced accelerated long-term testing protocols to validate the performance and reliability of our products. One such test involves 100 days of hot-water immersion at TMax + 95°C, followed by rigorous adhesion testing on the pipe material. This process simulates approximately 20 years of service life under maximum temperature conditions, ensuring our solutions are not only compliant but also exceptionally durable in real-world applications.
What trends are you observing in the pipeline coatings market, especially with the energy transition towards renewables?
Dirk Totte: Developments towards energy transition bring with it a number of challenges along with the expectation in renewables that the assets have a longer design life. We are seeing more extreme operating temperatures, low as well as high, exposure to more extreme environmental conditions such as high UV index, salt spray, frequent temperature fluctuations together with thermal expansion and contraction. We also see the need for protective coatings that can be applied with minimal surface preparation, in confined areas with minimal footprint, without the need for shutdown. The sector requires coatings that can ensure asset life is reached and even exceeded.
How is Seal For Life working towards sustainability in its product lines, particularly concerning waste reduction or recyclable materials?
Mario Silvestro: We have very strong relationships with both asset owners and contractors/applicators by being involved in a project from conception to after commissioning inspection and life-time support of the coated asset. In more recent years, there has been a focus on reducing emissions, waste and hazards
for both people and the environment. Seal For Life specialises in field applied coatings. Often these coatings do not have the same number of efficiencies that plant applied coating systems have since they are able to control their application conditions and environments within a narrow window. By offering friendly field applied coatings, we are able to reduce emissions and waste by not having to produce these vary narrow and specific application conditions in the field which other mainline/plant coatings often require.
Seal For Life’s Polyisobutene based coating portfolio, STOPAQ, has the ability to be applied with minimal surface preparation of ST.2 (hand wire brush) requirements which eliminate abrasive blasting requirements, does not need heat for bonding or curing, and can be applied on operating lines which reduce shutdown times to mitigate start-up/shut-down inefficiencies. With these designed engineering benefits built into the coating system itself, the total applied lifecycle of the system is able to reduce physical waste by ≥95%, reduce carbon emissions by ≥91%, reduce PPE requirements due to no VOC, no hot work, no chemical exposure, no containment requirements, and do not require hazardous waste considerations. Seal For Life and STOPAQ also provides recyclable packaging for its products, and its packaging and product components contain a percentage of recyclable material within them.
Could you share insights into how your coatings support the longevity and integrity of pipelines installed by trenchless methodologies?
Mario Moreno: HDD has become a widely adopted methodology for pipeline installation, particularly as urban expansion and environmental concerns demand less intrusive construction methods. HDD is now considered standard practice for projects where minimising surface disruption is critical.
The most important factor in ensuring the long-term integrity and design life of pipelines installed via HDD is selecting the right mechanical and corrosion protection system. Robust abrasionresistant overlays (AROs), such as liquid epoxy polymer coatings, have been industry staples for over 30 years.
Seal For Life offers a comprehensive portfolio of solutions for HDD applications, including SCARGUARD Composite ARO Coating. With over a decade of proven performance,
SCARGUARD has established itself as the premier choice for protecting pipelines in demanding trenchless installations.
SCARGUARD is a moisture-cured polyurethane composite designed to deliver superior mechanical protection, outperforming traditional ARO solutions in critical areas such as: ) Fracture toughness: exceptional resistance to cracking under stress.
) Gouge resistance: high resilience against damage from sharp objects or rough surfaces.
) Abrasion and wear resistance: outstanding durability in abrasive environments.
SCARGUARD excels in the most challenging conditions, offering reliable protection even in extreme HDD operations. Its ease of application further enhances its appeal, allowing for efficient installation without compromising the mechanical protection necessary for pipeline integrity.
The product provides unparalleled protection for pipelines installed through trenchless methodologies. By combining advanced engineering, superior materials, and a proven track record, SFL ensures that pipelines remain resilient, corrosion-free, and operational for decades, even in the harshest environments.
With so many specialised brands and technologies under Seal For Life, how do you help customers determine the best coating system for their unique requirements?
Mario Moreno: We are working together with asset owners and engineers as early as possible in the process to understand the challenges of their project, we understand that no two projects are the same.
Each pipeline, whether buried, submerged, or operating under extreme temperatures, requires a coating solution that aligns with its specific operational, environmental, and economic needs. Our process begins with a detailed consultation, where our technical experts work closely with clients to understand the project’s requirements, including:
) Environmental conditions: environmental conditions, atmospheric, buried of submerged, exposure to temperature extremes, moisture, UV radiation, or chemical agents.
) Application methods including size of the project; installation conditions, such as HDD, offshore, or hightemperature operations, automated application or requirements for ease of application This also includes field applied or plant applied as both have their own challenges.
) Compatibility needs: integration with existing mainline coatings and cathodic protection systems (ICCP).
) Economic considerations: balancing performance with cost-effectiveness.
) Our technical team has experience across multiple industries, enabling them to recommend optimal solutions
Double Block & Bleed Line St op System
Double Block and Bleed Safety / Single Stop Simplicity
The new Dually TM Double Block & Bleed (DBB) Line Stop System combines the sealing security of DBB technology with the simplicity of a single seal line stop and avoids the downtime and rework problems DBB equipment with coupled heads or complicated hydraulics can create.
Dually’s compact design features a single, patent-pending dual seal, pivot-style plugging head with all its movement contained within the line stop fitting. The new design ensures more effective chip sweeping functionality by removing more debris that can interfere with a tight seal.
That means Dually is more maneuverable into and out of the pipeline than other DBB systems, and more reliable when it comes to first-time sealing success.
from a broad product range, including liquid epoxies, heat shrink sleeves, polyurethanes, viscoelastic coatings, and abrasion-resistant overlays (ARO). This expertise ensures that clients receive the best combination of performance, durability, and ease of application.
SFL’s sales and technical teams are backed by a global network of engineers, applicators, and field service specialists who have successfully delivered solutions for projects ranging from critical gas pipelines and aqueducts to high-risk offshore installations. Our teams stay at the forefront of industry advancements, continually refining our offerings to meet evolving standards and client expectations.
Beyond product selection, SFL provides comprehensive support throughout the project lifecycle – from design and application to inspection and maintenance. This end-to-end service ensures that the selected coating system delivers optimal performance, extending asset longevity and safeguarding investments.
Every coating technology has it merits and constraints. No company in the world can offer more solutions for the unique requirements of each project. The best coating system is very often a combination of multiple different technologies.
What key factors set Seal For Life’s portfolio apart in terms of performance, application ease, or lifecycle cost savings?
Mario Silvestro: Seal For Life’s vast portfolio allows its experts to designed tailored solutions for field applied applications depending on the performance requirements, application conditions, and operating conditions. Due to the extensive technological options, Seal For Life is able to pair products to projects for the most cost effective, easy to apply, and asset lifetime extending solution. This includes solutions with ease of application benefits of:
) No VOC primers requirements.
) No heat requirements.
) No abrasive blasting requirements, with minimum ST.2 (hand wire brush) only, which includes reduction of containment and waste handling.
) No complex equipment for application.
) No specialty labour personnel.
) Can be applied on operational lines between -45 to +120°C (-49 to +248°F).
) Can immediately bury or submerge with no or very limited cure times.
These application benefits reduce the total applied cost and combine with proven and tested product performance to reduce lifecycle costs by eliminating shutdown requirements during rehabilitation projects, reduce maintenance internals, and extend the operational lifetime of assets.
Are there any recent case studies or projects you could highlight that demonstrate the impact of your coatings on pipeline integrity?
Mario Moreno: Seal For Life (SFL) participates in hundreds of projects annually around the world, consistently providing top-tier professional advice and cutting-edge product technology. Our approach is centered on collaboration – working closely with clients from project inception to execution to ensure successful outcomes. Here are three notable projects that highlight our expertise and commitment:
A 433 km gas pipeline transporting natural gas from offshore fields to the new Pluto LNG processing complex. The field joint coating was completed using CANUSA CPS’s high-temperature three-layer heat shrink sleeve (HSS) system. This ambitious project, executed by SAIPEM, was completed in record time, demonstrating the reliability and efficiency of SFL’s coating solutions.
This 93 km, 84 in. diameter pipeline project, completed in 2023, was designed to alleviate the impact of a prolonged drought in northeastern Mexico. The pipeline was internally lined and externally coated with structural polyurethane from SFL’s LIFELAST division. The use of advanced coatings enabled the project to be completed ahead of schedule, ensuring critical water supply was delivered swiftly.
As part of the largest interstate gas pipeline owned by Williams, the Transco Pipeline System, this HDD project presented unique challenges in protecting pipeline integrity. POWERCRETE DD 410, a high-performance abrasion-resistant overlay (ARO) coating from SFL, was selected to safeguard the pipeline during installation. The successful execution of this complex project underscores SFL’s expertise in protecting critical infrastructure under demanding conditions.
These case studies illustrate SFL’s dedication to innovation, collaboration, and delivering reliable solutions that meet the complex needs of the oil, gas, and water industries worldwide.
Niels Pörtzgen and Gerard van der Steen, Applus+, Netherlands, outline the evolution of pipeline girth weld inspection.
n the dynamic world of oil and gas, where operational efficiency and safety must go hand in hand, the integrity of pipeline infrastructure is critical. As pipelines serve as the arteries of energy distribution across vast distances and terrains, their constant exposure to extreme environments makes maintenance and repairs a top priority. Over time, pipelines naturally degrade, sometimes under the pressure of water for pipelines installed on the seabed. When damage to such pipelines is observed, a repair system is required that can be used under
submerged conditions. Likewise, an inspection strategy under the same conditions is needed to ascertain the adequate repair of the pipeline.
A hallmark of technological advancement in the energy sector is the Pipeline Repair System (PRS), developed by Equinor and Applus+, which is designed specifically for subsea pipeline welding for repairs but also for tie-ins of pipeline extensions. The PRS consists of several pieces of equipment that can be deployed on the seabed for operations like cutting, bevel preparation, and positioning of pipe ends, as well as welding and weld inspection. As part of the PRS system, a novel technology for ultrasonic inspection, the IWEX system, has recently been validated and used to verify the integrity of the girth weld with high reliability and precision.
This article will explore the challenges of pipeline repair and tie-in operations under deep submerged conditions on the ocean or sea floor. Furthermore, requirements resulting from these challenges, as well as from client specifications and industrial standards, will be discussed. We will present and illustrate how the IWEX system has met these requirements.
When pipelines installed on the seafloor are damaged and require a repair, in principle, the damaged section must be removed, and a new section must be installed. Economically, the operation is usually more attractive than installing a new pipeline. However, since the line has already been installed on the seafloor, it is typically not practical to lift the pipe for repair operations. Consequently, this must be done on the seafloor. The same scenario applies to existing pipelines that require an extension, whereby a tie-in weld connects the existing line with a new section.
Pipeline operations under submerged conditions are obviously more challenging than on land. Any technology applied should be water-resistant, or alternatively, a water-free room must be created, such as a diver’s bell, i.e. a habitat, in which the technology can be used.
Not only does the water itself introduce a challenge, but at deep depths, the pressure due to the water will also be very high. Therefore, the technology should be able to perform under high pressure, i.e. hyperbaric conditions.
Typically, technology requires a power supply and communication lines. Such lines should be long and robust enough to secure reliable performance and avoid data loss. Moreover, the technology may require separate parts or tools, which must be supplied to the location below (Figure 1).
In cases where the technology can only be controlled by humans, a diver is required to wear a special suit and breathing gear, which may consist out of a mixture of
breathing gases. A diver will have a limited time window to perform activities, which will also introduce a challenge. Furthermore, due to the bulky divers’ suit, the technology should be easy to handle without the need for refined manipulations.
One of the components of the PRS system is the habitat, which enables welding and weld inspection under hyperbaric conditions. The habitat is a special chamber that allows divers to work under pressures up to 25 bar, the equivalent of being submerged 240 m below sea level. The habitat can be lowered on top of the two pipe ends, which are to be welded together (Figure 2). Then, the chamber will be dewatered (Figure 3) by creating an overpressure, and the chamber will become accessible for welding and inspection activities.
The welding and inspection equipment will be supplied to the habitat in separate containers (Figure 4), which are separately lowered into the water and attached to the habitat. The diver-technician will first descend towards the habitat in a diver’s bell. From there, the diver-technician will swim towards the habitat, which he can access through a water lock. Once inside, the diver-technician can retrieve the required equipment for welding and the IWEX system for weld inspection.
One of the unique aspects of hyperbaric work is the alteration in communication. As divers breathe the oxygen-helium mix, their voices become helium-altered, making clear communication more challenging. However, through rigorous training and coordination, these challenges are effectively managed, allowing the team to achieve their goal with precision.
Welding inside the habitat is performed with an automated welding system specifically designed to be used in the confined space (Figure 5). All activities will be monitored and recorded through multiple cameras, which are viewed in real time on board of the vessel. Right after the welding is completed, the inspection of the weld is done with the Applus+ IWEX habitat system.
The Applus+ IWEX habitat system is specifically designed to perform under the hyperbaric conditions in the habitat. Like the welding equipment, the IWEX system is an automated system that uses
a scanner that is mounted on a guiding band. The guiding band must be placed around the pipe by the divertechnician in the habitat. The scanner is designed for robust handling without the need for refined movements. Once the guiding band is positioned around the pipe and the scanner of the IWEX system is placed, the inspection can start.
The IWEX system is connected through a special umbilical to the vessel, and it can be controlled on board. As such, the diver-technician in the habitat is only must mount the guiding band and position the scanner at the start position, and he is not concerned with the data collection and interpretation.
Before the inspection, the IWEX system requires a system check or calibration. This is also performed in the habitat. The calibration requires a separate block, which is positioned on top of the pipe in the habitat (Figure 6).
For reliable detection and accurate sizing, the IWEX system is based on one of the latest methods for ultrasonic inspection based on full matrix capture (FMC) ultrasonic imaging. With this method, comprehensive 2D and 3D images from the interior of the weld can be constructed, revealing possible defects and geometrical features such as the front and back wall and the cap and root reinforcement (Figures 7 and 8). In addition, traditional ultrasonic channels for Time of Flight Diffraction (ToFD) and other inspection strategies can be added.
The IWEX system has been qualified according to the DNV ST-F101 standard, and in addition, for every project, a project-specific validation is performed. The projectspecific validation involves the scanning and interpretation of a weld that is manufactured with the same welding procedure and with intentional representative seeded defects. In the case of repair welds, the left and right pipe ends may not always have the same material properties (e.g. sound velocity, anisotropy, wall thickness, inner diameter chambering, etc.), which may impact the IWEX inspection procedure. Therefore, the IWEX application software has unique built-in modules to accommodate for such challenges. During the project-specific validation, the
results of the IWEX system are compared with destructive macro-sectioning of the seeded defects. The sizing and detection performance are derived from statistical analyses, and the results are documented.
A notable example of a successful effort with the habitat and the IWEX inspection occurred during the recent projects in 2023 - 2024, where a team successfully scanned a range of tie-ins between 18 in. and 36 in. welds.
For example, the 30 in. tie-in scanned in September 2024 had the following conditions:
) Wall thickness 22.2 mm - 24.2 mm.
) Material sound velocity: 3100 m/s - 3175 m/s.
) High and low on the OD side and on the ID side.
) ID tape on either side of the bevel.
The result is a clear view of the weld, as illustrated in Figure 9.
In addition, Applus+ and its client have set up training programmes to prepare all personnel involved with the high-quality demand during the project operation. In this programme, for example, operators and divers are trained repeatedly together before each campaign to maximise the best outcome as a team. Regardless of the background company or profession, all activities are executed smoothly and safely during each stage of the campaign’s onshore training and testing, followed by offshore testing and operation. Applus+ is proud of its team for working together to achieve this quality performance.
The inspection with the IWEX system was perceived as valuable by the client. The accuracy and comprehensive data display make the interpretation of the scans reliable and unambiguous. Where traditional inspection methods may lead to discussions about results, the IWEX method provides the right information for fitness for purpose, thereby reducing conservatism in weld acceptance.
Jason Smith, ABS Consulting, discusses the benefits of taking a holistic approach to pipeline management, beginning with the evaluation of operations and strategy development, all the way through to process and system implementations.
aintenance and reliability have shifted drastically in recent years, led by the digital transformation of Industry 4.0. This shift is evolving the global pipeline industry as more
operators embrace digitalisation to leverage better ways to ensure operational uptime and safety.
Pipeline operators are increasingly building robust processes that support improved safety and operational integrity
programmes by using real time data, predictive models, data-driven tools and approaches that can assess asset life expectancy as well as enhance their safety protocols and environmental performance – contributing to a more sustainable and efficient pipeline operation.
With the IBM Maximo Application Suite (MAS) being a critical piece in this transformation process, organisations trying to undertake MAS implementation or upgrades without considering what the full reliability journey will look like, or what they may need to do to prepare for its implementation, can create more confusion than progress.
Taking a more considered approach can solidify an organisations’ preparedness to successfully integrate MAS into its operations, thus reaping the associated benefits that the new system offers.
More pipeline companies are turning to enterprise asset management applications to gain better visibility into their critical assets, delivering more effective maintenance and management decision making, helping to maximise pipeline reliability and minimise maintenance costs.
Predicting issues before they occur is at the heart of Reliability Based Maintenance (RBM). And through a data and analytics-driven approach an organisation can typically help reduce unplanned pipeline outages by up to
50%, whilst reducing scheduled repairs through predictive maintenance by up to 12%, helping to save valuable time and resources.
Taking a more holistic approach to pipeline maintenance can help to identify any ‘bad actors’ within a business. And by identifying critical problems, an organisation can focus where they place their time and effort rather than trying to deal with every problem.
Good maintenance is about effective resource management, and central to this is computerised maintenance and management systems (CMMS) – typified by the latest version of MAS. Much of the information required to make better-informed decisions is already available to pipeline organisations, but experience shows that whilst they may have the information, the vast majority are not using it to their greatest benefit or to support an increase along the reliability continuum.
So, the question is: where to start? And the answer to that is numbers speak volumes. We should start by setting metrics – establishing a base-line picture so that you can see a much more comprehensive process moving up the maturity continuum.
Everything revolves around a continual improvement wheel. The goal is to relate what you do with maintenance and reliability at the heart of an organisation –ideally through identifying critical Key Performance Indicators (KPIs).
KPIs can help present a better business case. Examples could include:
) Total maintenance cost: as a Percentage of Replacement Asset Value (RAV).
) Availability: how often the pipeline is running or capable of running compared to its actual operational schedule.
) Unscheduled downtime: the amount of time the pipeline is unavailable due to repairs that are not on the weekly maintenance schedule (break-in work).
) Wrench time: the actual time maintenance crews are affecting repairs.
) Stockouts: the frequency at which parts are requested from the stock system but not available.
By establishing and measuring key metrics an organisation can start to identify what is causing the most loss. And any loss that can be prevented is positive – both in time and money. Through this approach an organisation can better position itself to measure
Overall Equipment Effectiveness (OEE) – looking at the full productive time of equipment.
Everything is related. If you want to run a business at a world class standard, all this should be considered. Furthermore, this approach is both achievable and affordable.
You should be aiming for 80 – 85% of planned maintenance work with not more than 15% unplanned via this method, not the 30 – 40 – 50% emergency work levels which are common when this approach is not utilised.
The more unplanned work you are forced to react to, the heavier the cost incurred. This can be the most inefficient and the least safe way of operating because the pipeline is dictating what is happening within the organisation, not the organisation planning what will be done, and when.
The goal should be to move from reactive (repair after failure), through to planned (repair before failure), predictive (measure and repair), reliability (not only repair, but improve) and ultimately an enterprise approach (improve and sustain).
Most businesses will have the capability of undertaking this process themselves, but just don’t know where to start or the processes to take. They know they want to be more efficient, but there are often cultural dynamics between pipeline maintenance, reliability and operations teams within the organisation.
It is very difficult to move up the maturity continuum if you are not planning and managing your maintenance and repair schedules. It’s about having a maintenance action before there is a functional failure. And MAS is a key tool that can help to achieve this.
MAS now leverages automation and smart data, providing customisable dashboards, live health statistics, advanced AR capabilities and more.
It allows an organisation to set a single metric or request specific equipment alerts by using both current and historical data trends, helping to move a business from reactive to proactive through data-driven decision-making.
MAS represents the next level of pipeline maintenance. Asset health scoring is available, allowing hidden risk conditions to be revealed before they impact business, and can accelerate ROI with the capability to start realising maintenance savings in weeks.
The IBM MAS can significantly enhance pipeline operation and maintenance through these key features:
) Real-time asset monitoring: MAS enables real-time health monitoring of pipeline assets, which helps in early detection of issues and reduces the risk of downtime.
) Predictive maintenance: by integrating IoT sensors and predictive analytics, MAS can forecast potential failures and schedule maintenance proactively, minimising unplanned outages.
) Regulatory compliance: MAS supports comprehensive reporting and compliance features, ensuring that pipeline operations adhere to industry regulations and environmental standards.
) Regulation records: MAS allows you to create and manage regulation records that apply to employee health, safety, and environmental standards. These records can be associated with assets, job plans, hazards, and work orders to ensure all activities comply with relevant regulations.
) Electronic signatures and audit records: MAS includes electronic signature verification and electronic audit records, which provide an additional layer of security and auditing capability. This helps in tracking changes, verifying user actions, and ensuring that all modifications are compliant with regulatory requirements.
Calibrations for more than 200 different gases
4 – 20mA, HART®, FoundationTM Fieldbus, PROFIBUS, Modbus
Temperature service to 850 °F [ 454 °C]
Pipe sizes from 1″ to 99″ [25 mm to 2500 mm]
100:1 up to 1000:1 turndown
4-function: flow rate, total flow, temperature and pressure
Best-in-class digital / graphical display
Global agency approvals for Ex locations
) Health, safety, and environment (HSE) integration: MAS integrates health, safety, and environmental data into its workflows. This integration helps in maintaining compliance with safety and environmental regulations by ensuring that all operational activities are monitored and managed according to regulatory standards.
) Compliance reporting: MAS supports comprehensive reporting features that help in documenting compliance with industry regulations. These reports can be used for internal audits and to demonstrate compliance to regulatory bodies.
) Maintenance planning and scheduling: MAS streamlines maintenance workflows, optimises resource allocation, and improves the efficiency of maintenance activities.
) Enhanced safety and environmental performance: the suite integrates health, safety, and environmental (HSE) data to improve operational safety and environmental performance.
) Integrated health, safety, and environment (HSE) processes: the suite includes applications that support integrated processes for improving safety, reliability, and environmental performance. This helps organisations comply with regulations and certifications.
) Predictive maintenance and AI: by leveraging AI and predictive maintenance, MAS helps in identifying potential issues before they occur, reducing unplanned downtime and extending the lifespan of asset. This not only enhances safety but also minimises environmental impact by reducing waste and optimising resource use.
) Emission tracking and management: MAS allows for efficient tracking and management of emissions, including data on leaks and spills captured by sensors and technicians. This helps in identifying and mitigating the worst offending assets, thus controlling, and reducing operational emissions.
) Data-driven decision making: the suite uses IoT data, analytics, and AI to provide insights that help in making informed decisions. This includes extending asset life, minimising carbon footprint, and optimising operations to support sustainability goals.
) Compliance management: MAS automates the capture of regulatory requirements tied to compliance activities and emissions events, ensuring that organisations can monitor and manage their environmental impact effectively.
One of the first steps in moving to MAS is to consider the existing position and knowledge within the business from a
MAS perspective, helping determine how ready it is to move to and utilise the benefits MAS delivers. One of the key success factors could be to bring in support to help make a successful transition.
MAS implementation starts with acknowledging the role that Change Management will play. Leadership engagement and a willingness to adopt the changes that MAS will necessitate are critical success factors and a foundation for a successful MAS journey.
Identifying the changes in approach to maintenance strategies that will be required is essential. Where are you today and where do you want to be tomorrow are fundamental questions to ask at the start of the process.
From there an organisation will need to consider its:
) Master pipeline/asset list.
) Pipeline criticality listing.
) Required reliability strategies.
Why is asset criticality important?
Identifying pipeline criticality is a key step in the process as it provides a detailed profile of the characteristics that make each asset critical, allowing you to better ensure that your reliability strategies and improvements are made based on calculated risk rather than perception.
This approach also supports the prioritisation of daily CMMS workflow processes such as planning, scheduling and material procurement, acting as a primary mechanism for prioritising improvement activities.
Reliability strategies
) Focus on critical pipeline assets.
) Simplify and shorten process to implement strategies.
) Deliver performance monitoring.
) Offer continuous improvement.
While previous updates were more straightforward, MAS has distinct differences from its previous incarnations, including a new interface, updated integration authentications as well as other technical changes.
Conclusion
Overall, IBM Maximo helps in extending asset lifecycles, reducing operational costs, and improving the reliability and safety of pipeline operations.
While the benefits of MAS are considerable, successfully transitioning to it is not always straightforward, and organisations should plan specifically for the move if they are to take advantage of the benefits MAS provides.
MAS specialists within organisations such as ABS Consulting can help to support the migration process, helping set the successful foundations to make MAS a fully integrated tool that can significantly increase pipeline maintenance and reliability programmes.
Eric Sigvaldason, Vande Consulting Services, thinks that soil remediation could be much simpler –by using non-toxic spray-on soil remediation treatments, contaminants can be broken down in situ, mitigating the need for expensive, disruptive excavation.
pray-on soil remediation treatments for hydrocarbons and salts offer a quick, effective way to clean contaminated soils by simply saturating the affected area. The treatment is non-toxic, non-hazardous, non-carcinogenic, with no forever chemicals. It breaks down contaminants more efficiently than traditional soil excavation methods with no excavation required and minimises disruption to the environment. No foreign microbes are introduced, such that no residue or by-products remain.
The high stakes of soil remediation
While consumers are flocking to dealerships to compare the latest gasoline, electric or hybrid vehicle options that align with financial, environmental and personal
values, the oil and gas industry is engaging in a cost-benefit analysis of its own. Understanding the science and efficacy behind various soil remediation systems is a moving target, subject to regulatory pressure, industry standards, and available services. What if you could take these decisions into your own hands and take care of your own soil remediation needs without the need for consulting or outsourcing?
While economies and governments debate the future of oil and gas, savvy companies can get a head-start on addressing the environmental impacts either way. At the crossroads of conventional and renewable energy, there exists a need to repair the mistakes of the past while mitigating harmful environmental effects for future generations. Despite the most stringent of safety precautions, oil spills will sometimes occur. Past global oil spills have been highly publicised, with many left untreated, drawing the ire of environmentalists and private citizens alike. Vibrant communities and sensitive ecosystems transform into contaminated wastelands, with media coverage shining a spotlight on the devastating effects on wildlife, agriculture, ways of life, and local economies.
Oil spills are often seen as preventable disasters. Many feel angry with corporations or governments, citing negligence and irresponsibility, with a lack of accountability compounding these frustrations. However, even the most altruistic site owners have found that remediation is not a straightforward process. Between the massive price tag, the
challenging coordination of environmental liabilities, and navigating available solutions, site owners have often fallen short of public demands. Polishing a tarnished reputation has proven difficult for oil industries.
Typical soil remediation commonly involves digging and trucking contaminated soil to a landfill. While still a common practice, this method disturbs the soil, releasing volatile organic compounds into the air, and further dispersing through the transportation process via unsealed trucks. Landfills, in addition to rapidly filling up, may produce leachate. Leachate is a toxic liquid that is formed when rainwater filters through waste. Leachate can seep into the soil and groundwater, contaminating water supplies with heavy metals, chemicals, and pathogens. EPA-established guidelines seek to minimise, but not eliminate leachates. A better solution exists through cleaning the soil right where it lies. In situ treatments have been commercially deployed for several years, and eliminate the need for transportation while lowering the risk for future leachate contamination.
Vande’s RemediMaker is a unique, proven, spray-on treatment for both oil and saltwater spills that addresses old contamination and new spills. Designed by a team with environmental engineering and PhD chemistry expertise, this novel improvement on existing processes combines cutting-edge technology with ease-of-use features: simply spray, saturate, allow to soak, and remediate in place, all through a process similar to watering a lawn. One treatment is all that is needed for most applications. RemediMaker differs from existing products by eliminating the need to introduce foreign microbes and by adding a soil conditioner. This pharmaceutical-grade blend prepares the soil to accept the treatment, while a high-grade catalyst introduces seven components to activate natural microbes existing in the soil. Additional degradation reactions are triggered and may be verified by odour reduction in as few as four hours. A nutrient boost is added to leave soil healthy and capable of sustaining vegetation after treatment.
Soil contaminated with salts has previously been categorised as untreatable. RemediMaker can reverse both salt and hydrocarbon damage without removing topsoil, meaning no excavation, heavy equipment or landfill costs are incurred. RemediMaker’s engineered treatment generates multiple reactions shortly after the fluid combines with soil. The reaction is hydrophilic, with rain or snowfall providing overall benefits. All ingredients are considered non-hazardous and pharmaceutical grade, with no harmful by-products or residues generated. Specially formulated to incorporate multiple chemical processes without the use of forever chemicals, hormone disruptors, or carcinogens, RemediMaker offers an economic, green solution. No foreign bacteria are added, by design. With up to 60 000 native species in a teaspoon of soil, this ratio is not disrupted. Furthermore, salt
Dairyland decouplers are critical to cathodic protection systems — keeping workers and valuable assets safe from AC faults, lightning, and induced AC voltage — all while optimizing your CP systems.
We were the first company to introduce solid-state decoupling products to the industry, replacing the unreliable and dangerous polarization cells that exposed workers to shock hazards and highly caustic chemicals. In the decades that have followed, our solution-focused team ha s continued to deliver innovative decoupling products, solving critical problems across numerous applications and industries.
For more than forty years, Dairyland has pioneered new technologies and set new standards in the market. And we’re not done yet. If a solution to your problem does not yet exist, we’ll work to find one.
Let us help you find the right solution to your problem.
remediation can be difficult to treat due to the tight sodiumto-soil bonds and particle disaggregation. Our chemistry harnesses the powerful, natural process of healing, digestion, molecular bonding, and soil vulnerability.
Benefits
It is difficult to quantify the benefits of RemediMaker without discussing cost savings. Costs for in situ treatment are a fraction of other options. Companies will find that remediating multiple sites is possible for the equivalent budget of one site using conventional excavation methods. Third-party lab tests confirm both oil and produced water-treated soil contamination improved by over 80% in about 2.5 months. Costs typically come in less than half of conventional methods.
RemediMaker is at the helm of mitigating environmental impacts in several arenas. With this treatment, overall emissions are reduced by about 90%. RemediMaker treatments have a significantly small carbon footprint. Common logistics of trucking soil contamination to a landfill contribute to climate change, especially since diesel trucks are major emitters of carbon dioxide, and dozens of truckloads are typically needed. In addition to the noise and emissions from trucking, the increased vehicle traffic is inconvenient for residents and can be harmful to wildlife. By contrast, one application of RemediMaker may be all that is needed, and this can be accomplished in as little as one truck. Treatment is available to scale, with options for pails, barrels, and truck loads.
Need a reprint?
A vision for the future Vande is a small organisation that is growing rapidly. Our product was designed for generations of today and tomorrow. We believe that oil and gas have an important role that needs to be continued, and RemediMaker was designed to assist our industry in both production and accountability. Stakeholders ranging from energy providers to energy users all deserve a fair, environmentally friendly, economical, and easy solution for contaminated soil. Offering a remediation solution for fractions of conventional remediation costs provides stakeholders an opportunity to reach environmental targets quickly and efficiently.
This is not a conceptual product. It is actively being used today by the construction, mining, equipment and energy industries. After over a decade of research and development, field testing and third-party verification, the product has seen a successful launch in Canada and the US. The ease of application and positive remediation results have been introduced to multiple government agencies as of this printing, though the acceptance of soil remediation treatments by government authorities is a multi-step process that can span many years. High levels of government approvals have been obtained for RemediMaker treatments. The West Virginia Department of Environmental Protection (DEP) endorses RemediMaker. The Legislative Energy Committee recommends RemediMaker. The Alberta Energy Regulator (AER), Ministry of Energy and Resources (MER), and Oil and Gas Commission (OGC) all allow RemediMaker treatments (provincial governments are unable to endorse or recommend any company or product at all). The US Federal Department of Energy encourages RemediMaker. Although semantics differ between countries and agencies, RemediMaker government support is apparent.
To summarise, this solution offers the following:
) Significant cost savings.
) Ease of use .
) Six to eight weeks to eliminate the hydrocarbon(s)/ salt(s).
) Non-toxic, non-hazardous.
) No microbials left behind.
In conclusion, spray-on soil remediation treatments offer a groundbreaking solution for soil remediation, delivering exceptional results with minimal disruption. Their ease of use, cost-effectiveness, and non-toxic composition make them a smart choice for anyone looking to address contamination without the environmental and financial burdens of traditional methods. For both large-scale industrial sites and smaller, localised spills, quick, efficient treatment is a step toward cleaner, healthier soils. With government endorsements and proven success across multiple industries, now is the time to embrace the future of remediation.
Eric Farmer, Vice President of Clinical Operations, RMI, offers guidance on increasing operational efficiency on pipeline sites with health and safety.
ipeline construction is accelerating. Globally, a total of 41 999 miles of pipeline is currently under construction while another 80 557 miles are in the planning stages. Europe continues to expand its gas pipeline networks as it seeks to reduce its reliance on Russia, and both China and India continue to build out their pipeline infrastructure.
Reducing operational downtime and improving efficiency is essential to ensure that these projects are delivered. Safety is a crucial determinant of operational efficiency in a highrisk industry such as oil and gas, and robust health, safety and environmental practices are paramount to protect workers and scale pipeline infrastructure.
The American Petroleum Institute (API) 2023 Performance Report shows improvements in pipeline safety across several key performance indicators over the past five years. Comprehensive safety management systems and robust safety programmes, including advanced inspection and leak detection technologies, contribute to safer working environments.
According to data from the U.S. Department of Transportation’s Pipeline and Hazardous Materials Safety Administration (PHMSA) between 2019 and 2023: ) Total pipeline incidents decreased 23% over the past five years.
) Operations and maintenance incidents impacting people or the environment declined 54%.
) Total equipment failure incidents impacting people or the environment decreased 50%.
The International Marine Contractors Association’s (IMCA) latest safety report indicates a similar trend towards safer operations in the oil and gas industry; its latest report indicates a 50% increase in safety hours. While it is positive to see incremental safety improvements, the recent offshore explosion in Louisiana highlights that there is still work to be done to protect workers and reduce avoidable incidents and deaths.
Trenching, excavation and controlled explosive operations on pipeline sites mean that workers are consistently exposed to an extremely hazardous working environment. A combination of harsh weather conditions, steep inclines, confined spaces, pipeline leaks, failed excavation attempts, and the use of heavy-duty machinery present a unique set of safety challenges that must be addressed to mitigate risk to human life and operational delays.
Without the proper foresight, site planning and a comprehensive approach from an experienced safety and medical provider, pipeline construction sites will continue to be extremely dangerous.
Many pipeline construction projects operate on a tight schedule and may rely on short-service or independent workers to quickly fulfil roles and keep projects running on time. New personnel can expose the existing workforce to infectious diseases from the simple common cold to more serious viruses such as COVID19 and Mpox.
Due to the physical nature of the work, operators who invest in preventative measures against illness and injury can see a markable decrease in lost time. Facilitating a pre-screening process is one solution to reduce the operational disruption caused by workers with an existing illness or health condition which often delay operations due to sickness or injury.
Pre-screening serves to protect both the employee and the employer. For employees, working with a medical provider ensures access to support, care and any medication needed to manage conditions while on a long placement. For employers, having a clear understanding of pre-existing conditions of their workforce, and working with a trained provider to manage the requirements of the workforce, reduces the risk of disruption during a project. Having the constant presence of a medical and safety professional who builds trusted relationships with employees also helps them to feel comfortable when reporting medical conditions, which, in turn, can stop them from escalating into more urgent cases.
Galaxy Brushes is proud to unveil the Pit Hog, a cutting-edge innovation designed to take your pipeline cleaning to stellar heights, blasting through grime, one pipe at a time. With a powerful strip brush technique, this brush outshines traditional flat wire and pencil brushes, ensuring unparalleled cleaning efficiency.
Out-of-this-World Features:
Superior Cleaning Power: The Pit Hogʼs strip brush design maximizes wire contact with the pipe, delivering superior results in clearing out debris.
Custom Fit for Any Mission: Choose your wire diameter (ranging from 0.010" to 0.020") and tailor cleaning effectiveness to your needs.
Durable Materials for Any Terrain: Available in both carbon and stainless steel, the Pit Hog is built to withstand even the toughest pipelines.
Galaxy-Grade Quality: Backed by the legendary service and craftsmanship that make Galaxy Brushes the star of the industry.
Take your pipeline maintenance to the next level with the Pit Hog.
Short-service employees may also pose additional risks to themselves and their crew if their experience with heavy equipment is limited – equipment that can pose a serious safety threat when not properly manned. Combined with the remote and dangerous environments, short-service personnel are at higher risk of injuring themselves and potentially putting colleagues in harm’s way. Hand and eye injuries are common but, by educating workers on the importance of wearing the appropriate personal protective equipment (PPE), organisations can help prevent unnecessary injuries.
Any medical and safety service provider operating on mainline pipeline projects should have experience in providing high-quality onsite care in remote working conditions, such as the OSHA 500 qualification. This authorises them to conduct OSHA’s Outreach Training Programme on the recognition, avoidance, abatement, and prevention of safety and health hazards in workplaces. Designating an individual for reviewing the overarching safety strategy for projects through to delivery ensures that the highest standard of care is in place, especially in hazardous areas.
In mountainous regions, rapidly changing weather conditions can lead to slips and falls on uneven surfaces due to moisture while the cold weather presents its own challenges with the potential for frostbite to set in after as few as 30 min. without proper clothing. Since certain articles of clothing, such as hoods, are restricted on pipeline projects due to safety concerns, cold weather makes the work even more dangerous. Injury and illness are leading causes of medical evacuation. While they may be inevitable in every workplace, the negative impact on productivity can bring operators to a halt with serious implications for production time and costs.
In environments where weather conditions can change hour by hour and day by day on any given project, adequate planning and preparation can be a challenge for any team leader. With support from an onsite medic to provide training and education, incidents can be prevented, and teams can operate with greater efficiency and safety, avoiding potential delays to projects.
As well as training and education, regular briefings can help identify and manage any potential risks. RMI’s onsite experts hold team safety meetings each morning, known as ‘Toolbox Talks’, during which they review the projects for the day, who is involved and any evacuation or extraction plans, if necessary.
Despite the industry’s recognised workplace pressures, the stigma regarding mental health remains.
While varying degrees of mental health support for workers are already in place across the industry, there is still more that can be done. Workers endure prolonged periods away from family and friends, and long shift patterns can make it difficult to maintain healthy habits. This combination of factors can be challenging for employees’ mental health and can increase the likelihood for any pre-existing health problems to escalate.
Simple practices such as self-care, a varied and wholesome diet, regular exercise, and avoiding excessive phone use between shifts can positively impact employees’ mental health
and wellbeing. Operating heavy-duty equipment, working at elevated heights and handling hazardous materials means that it is essential for pipeline construction workers to be physically and mentally capable of the work and all health and safety professionals should ensure workers are getting enough rest to prevent avoidable injuries.
Beyond the wellbeing of the workforce, it’s equally as important for pipeline construction projects to continually review the environmental impact of their work. While the majority of materials in the industry are environmentally safe, it remains good practice to have someone who understands these challenges to help protect local biodiversity. Additionally, site safety assessments are crucial to identify potential hazards and mitigate the risks they pose to human life. Soil condition analysis, terrain, utility and other environmental factors inform the procedures for handling hazardous materials, confined spaces, evacuations and more.
How do safety and medical professionals benefit pipeline construction projects?
A large pipeline project in Texas has been working with RMI since 2009 to deliver medical support for its 2200-strong workforce. As the project is extensive, the highly experienced RMI team consists of occupational health physicians, onsite paramedics, and multiple emergency medical technicians. The team ensures the onsite workforce is healthy and immediately supported in any medical emergency.
As the location of the project moves, RMI medics are deployed to set up and outfit multiple onsite clinics for the workforce, including two Mobile Treatment Centres (MTC). These four-wheel drive clinics allow RMI’s medical staff to provide treatment in remote environments that standard emergency vehicles are unable to reach. In addition to a treatment area, storage and hand washing facilities, the MTC is equipped with first aid supplies and emergency response equipment, including an automated external defibrillator, trauma management equipment, and a backboard and litter for patient transport. This equipment ensures that the onsite medics are well prepared to respond to any type of medical emergency, no matter where the project is situated or how remote the location.
It is not just large projects that benefit from onsite medics. During one project supported by RMI, a worker received a minor head injury. Historically, the patient would have needed to be taken to a local clinic for assessment and treatment. However, since RMI’s remote paramedic was able to evaluate the patient onsite and suture the wound, the employee was able to return to work within 45 min. A rapid response from a highly-trained onsite medic means that workers can be back onsite as quickly and safely as possible, without the need for costly and timeconsuming transfers to offsite clinics or hospitals.
With the unique safety challenges present on pipeline sites, it is essential to have trustworthy, professional medical support onsite. Expertly trained onsite medics can provide immediate medical support to reduce operational disruption, treat common injuries and ailments as soon as they happen, and deliver health and hygiene education campaigns to improve crew health.
Chad Gillen, Deep Trekker, Canada, explores the role of ROVs in underwater pipeline inspection, offering real-world examples of improved efficiency, safety, and inspection standards.
he midstream sector of the oil and gas industry, encompassing the transportation, storage, and wholesale marketing of crude or refined petroleum products, plays a critical role in the global energy infrastructure. Ensuring the integrity of pipelines and other underwater infrastructure is vital for operational efficiency and environmental protection.
Deep Trekker’s remotely operated vehicles (ROVs) offer advanced solutions for underwater inspection. This article explores the role of Deep Trekker ROVs in underwater pipeline inspections, providing realworld examples of how these advanced technologies improve safety, reduce costs, and enhance the overall effectiveness of inspection operations.
Midstream pipelines, which transport oil and gas between production and refining or distribution, are subject to harsh underwater conditions that can lead to corrosion, damage, and other issues.
Regular inspections are crucial to ensure pipeline integrity and prevent environmental hazards. Traditionally, divers performed these inspections, facing significant risks due to underwater conditions, currents, and potential exposure to hazardous materials. The introduction of ROVs has revolutionised these inspections, offering a safer and more efficient solution.
Pipeline integrity is essential for preventing leaks, ruptures, and environmental hazards. Regular inspections are necessary to detect corrosion, cracks, and other potential issues. Traditional inspection methods, often involving divers, present serious dangers and limitations. ROVs offer a safer and more efficient alternative, capable of performing detailed underwater surveys and inspections.
ROVs, or remotely operated vehicles, are underwater robots designed to perform a variety of tasks, including detailed
inspections of underwater pipelines. These vehicles are equipped with high-resolution cameras, sonar systems, and other sensors, enabling them to conduct thorough surveys and inspections even in challenging environments. ROVs provide operators with real-time data and video feeds, allowing for precise assessments of pipeline conditions without the need for human divers.
ROVs are versatile tools used in various underwater operations, including:
) Pipeline inspections: detecting corrosion, biofouling, and structural damage.
) Valve and joint inspections: ensuring the integrity and functionality of critical components.
) Leak detection: identifying leaks through visual and sensor-based inspections.
) Environmental monitoring: Assessing the impact of pipelines on marine environments.
Key advantages of using ROVs for pipeline
ROVs eliminate the need for human divers in hazardous conditions, reducing the risk of accidents and injuries. They are capable of operating in challenging environments, including strong currents, low visibility, and confined spaces, ensuring thorough inspections without compromising safety.
Deploying ROVs for underwater inspections significantly reduces operational costs. ROVs can be deployed quickly and operated remotely, reducing the time and labour costs associated with traditional inspection methods. Rapid deployment and efficient data collection also minimises downtime and associated costs. ROVs also reduce the need for extensive support vessels and crew, further lowering expenses. Their ability to operate for extended periods without the logistical challenges associated with manned inspections leads to further cost savings, especially in remote or deepwater locations.
Equipped with high-resolution cameras and advanced sensors, Deep Trekker ROVs provide precise and reliable data. They can capture detailed images and videos, allowing for thorough analysis and accurate assessments. The integration of sonar technology enhances their capability to detect and measure defects in pipelines and other underwater structures.
ROVs enhance efficiency by quickly covering large areas and reaching depths that are challenging for divers, enabling comprehensive inspections in less time. Their ability to operate in challenging environments, such as strong currents or low visibility, ensures that inspections are completed efficiently without compromising on quality. They can also operate continuously and transmit real-time data to onshore teams further streamlining the inspection process, reducing downtime and improving overall productivity.
ROVs are designed to perform inspections with minimal disruption to the surrounding environment. Their precise maneuverability reduces the risk of damaging marine ecosystems, making them an environmentally friendly option for underwater pipeline inspections.
Advanced navigation and positioning
Deep Trekker ROVs are equipped with state-of-the-art navigation systems, including recent advancements in ROV GPS and Dead Reckoning technologies. These features ensure precise maneuverability and accurate positioning, essential for thorough and reliable underwater inspections.
Robust design and versatility
Designed for durability and adaptability, Deep Trekker ROVs can operate in diverse underwater environments. Their modular design allows for easy customisation with various attachments and sensors, enhancing their functionality for specific inspection tasks.
Deep Trekker’s intuitive control systems enable operators to conduct inspections with ease. The user-friendly interface facilitates real-time data collection and analysis, streamlining the inspection process and improving efficiency.
Orion Serviços Industriais operates in industrial maintenance and inspection services across various sectors, including oil and gas, mining, and energy. One of their critical areas of focus is pipeline inspection, a task that requires precision and reliability, especially in offshore environments. To meet these demands,
Orion has incorporated Deep Trekker ROVs into their operations, with impressive results.
These ROVs are equipped with ultra high-definition (UHD) cameras, multiple sensor integrations, and powerful thrusters, making them ideal for challenging underwater conditions. Orion’s team utilises the ROVs for external pipeline inspections, inspecting weld joints, detecting biofouling, and assessing the structural integrity of subsea pipelines.
Orion also conducts internal pipeline inspections, utilising Deep Trekker ROVs to navigate confined spaces within pipelines. The ROVs’ compact design and 360˚ manoeuvrability allow them to traverse bends and turns, providing clear visuals of internal surfaces. This is essential for
detecting corrosion, debris buildup, or potential blockages that could compromise pipeline performance.
Internal and external pipeline assessments, corrosion evaluations, and leak detection inspections are important for preventing environmental hazards and ensuring the safety and efficiency of oil and gas transportation. In offshore environments, where currents can be strong and visibility low, the use of reliable technology is crucial.
Felipe Oliveira, CEO of Orion, emphasises the advantages of Deep Trekker ROVs in these challenging conditions. “Deep Trekker really shines in comparison to other ROVs in strong currents. I’ve used several mini and observation
class ROVs, and it is hard to describe but the Deep Trekker is much easier to pilot and holds against strong currents automatically much better than others.” This capability is key when navigating long stretches of pipelines, where maintaining a steady position is necessary for capturing detailed visual data.
In addition to their performance in harsh conditions, the ROVs also offer innovative features that streamline operations. For example, Orion’s inspectors utilise the BRIDGE app for remote viewing, allowing real-time monitoring of inspections from a safe distance.
“The key capabilities that stand out for offshore inspections are the ability to view remotely through the BRIDGE app, easy repairs, great customer service, and easy operation,” Oliveira notes. The app allows Orion’s inspection teams to share live footage and data with engineers and decision-makers, facilitating immediate analysis and response.
Deep Trekker ROVs are also built with modular components, simplifying maintenance and repairs. This reduces downtime between missions, ensuring that Orion can maintain continuous operations. The ROVs are equipped with powerful LED lighting and sonar systems, enabling them to operate effectively in lowvisibility conditions – a frequent challenge in deepwater inspections.
With their ease of use, durability, and advanced capabilities, Deep Trekker ROVs have become an integral part of Orion’s pipeline inspection strategy, helping the company maintain high standards of safety and performance in demanding offshore environments.
Overcoming challenges in underwater inspections with ROVs
Underwater inspections in the midstream sector present many challenges, such as strong currents, limited visibility, and the complex geometry of some pipeline systems. Deep Trekker ROVs are specifically designed to address these challenges with a suite of advanced technologies and features.
One of the key advantages of Deep Trekker ROVs is their six-axis thruster propulsion system, which provides exceptional manoeuvrability in harsh underwater conditions. This system enables precise movement in all directions, allowing operators to maintain stability and control even in strong currents. This is crucial when navigating along long stretches of pipelines, where steady positioning is necessary for capturing accurate inspection data.
In addition to their propulsion capabilities, Deep Trekker ROVs are equipped with ultrahigh definition cameras and powerful LED
The forum for the corrosion protection community, exploring pipeline coatings, hydrogen transportation, new technology and markets
Highlights from the 2025 agenda
Panel discussion Evening Networking event Expert speakers
Martin van Agteren Principal Advisor Asset Management
Gasunie
10 sponsors and exhibitors
Industry-leading speakers include:
Hassan Al-Sagour Chairman, Paints & Coatings Standards Committee
Saudi Aramco
Talal Al Nabhani
Materials and Integrity Manager
Petroleum Development
Oman
Also sponsored by: Media Supporters:
Denis Melot
Expert Non-Metallic Materials & Coatings
TotalEnergies
lighting. These imaging systems are designed to operate effectively in low-visibility environments, such as deepwater or turbid waters where natural light is minimal. The ROVs can capture detailed visuals of pipeline surfaces, weld joints, and potential areas of corrosion, enabling thorough assessments despite challenging conditions.
For navigation and positioning, Deep Trekker ROVs utilise advanced Dead Reckoning systems combined with GPS capabilities. Dead Reckoning allows the ROV to calculate its position based on its previous location, speed, and heading, which is essential when GPS signals are unavailable, such as when operating in deep or confined environments. This feature ensures that the ROV can accurately track its path and return to specific points of interest during inspections.
Deep Trekker’s ROV GPS further enhances the accuracy of inspections by providing real-time location data when the ROV is near the surface or in shallow waters where GPS signals can be received. This integration of GPS and Dead Reckoning allows operators to precisely map the pipeline’s layout and monitor the ROV’s progress, ensuring comprehensive coverage of the inspection area.
The compact design of Deep Trekker ROVs also enables them to navigate confined spaces, such as the interiors of pipelines, which are often difficult or impossible to access with larger equipment. This makes them suitable for a wide range of inspection scenarios, including the inspection of small-diameter pipelines, bends, and complex geometries that are commonly encountered in the midstream sector.
By leveraging these technical features, Deep Trekker ROVs provide a robust solution for overcoming the challenges associated with underwater pipeline inspections, ensuring that operators like Orion can deliver precise and reliable results in even the most demanding environments.
As the midstream sector continues to evolve, the adoption of advanced technologies like ROVs will become increasingly important. By improving safety, reducing costs, and providing accurate data, these underwater robots are transforming how pipeline inspections are conducted.
As the technology continues to evolve, ROVs are set to play an increasingly vital role in ensuring the integrity and safety of underwater pipelines, ultimately benefiting the entire industry. Future developments may include enhanced automation, more sophisticated data analysis tools, and the integration of artificial intelligence for predictive maintenance.
These advancements stand to make ROVs an even more integral part of midstream pipeline inspections, offering greater efficiency and safety while further reducing operational costs, setting new standards for inspection practices in the oil and gas industry.