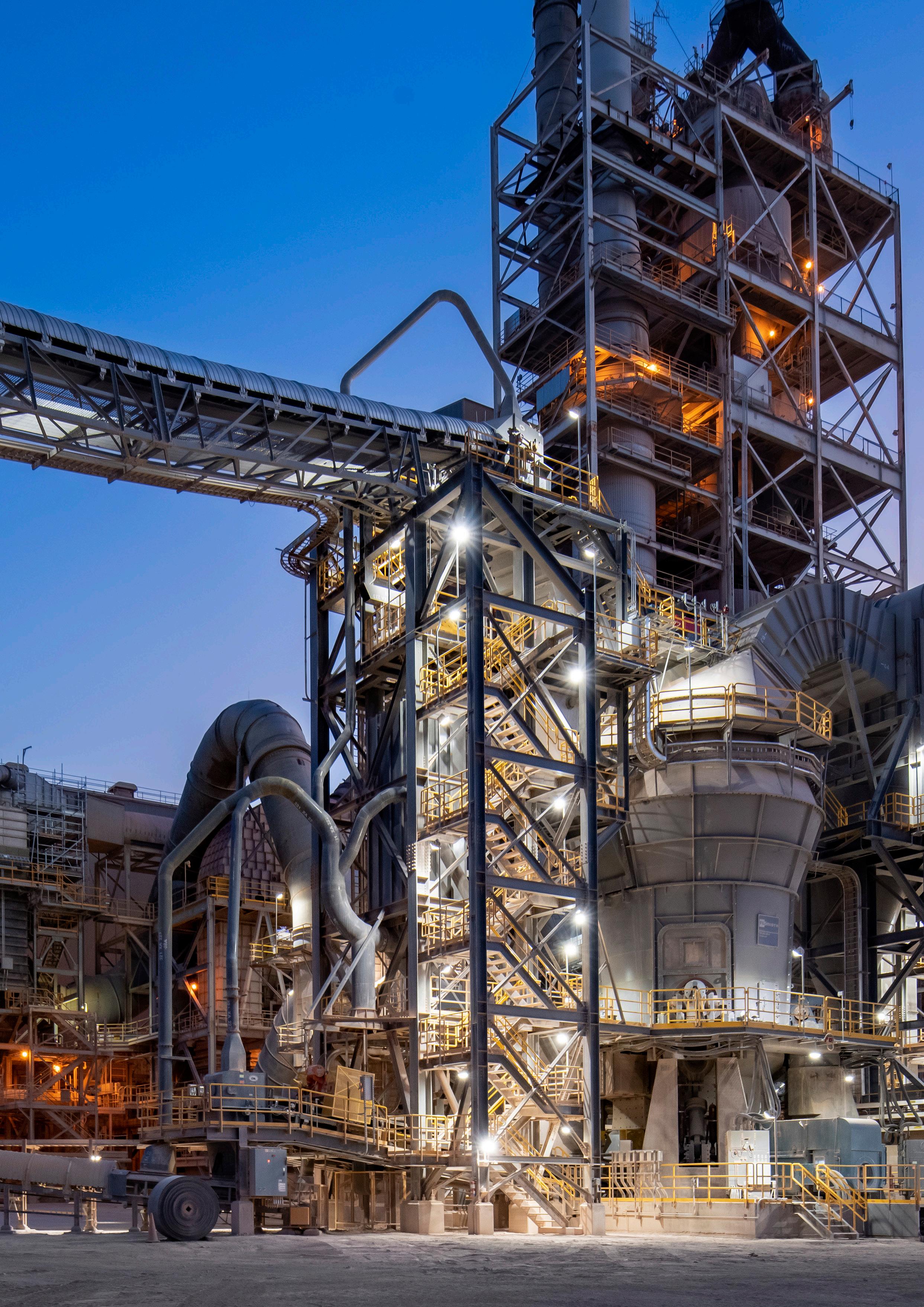
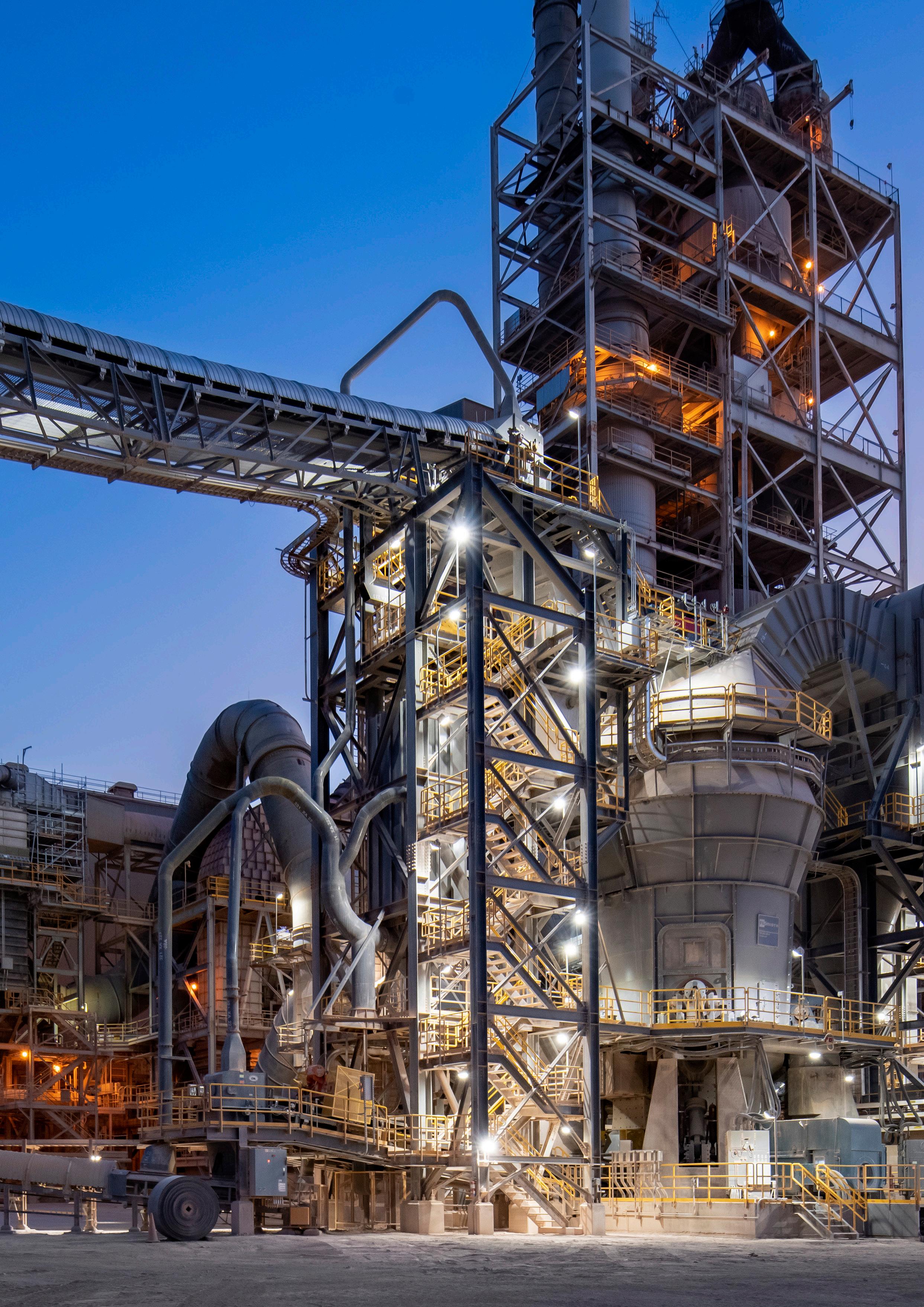
uptime starts
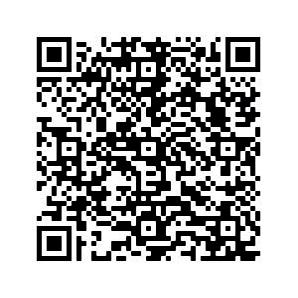
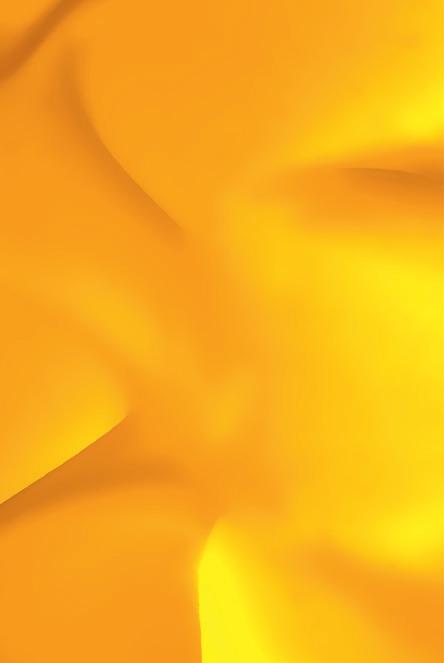
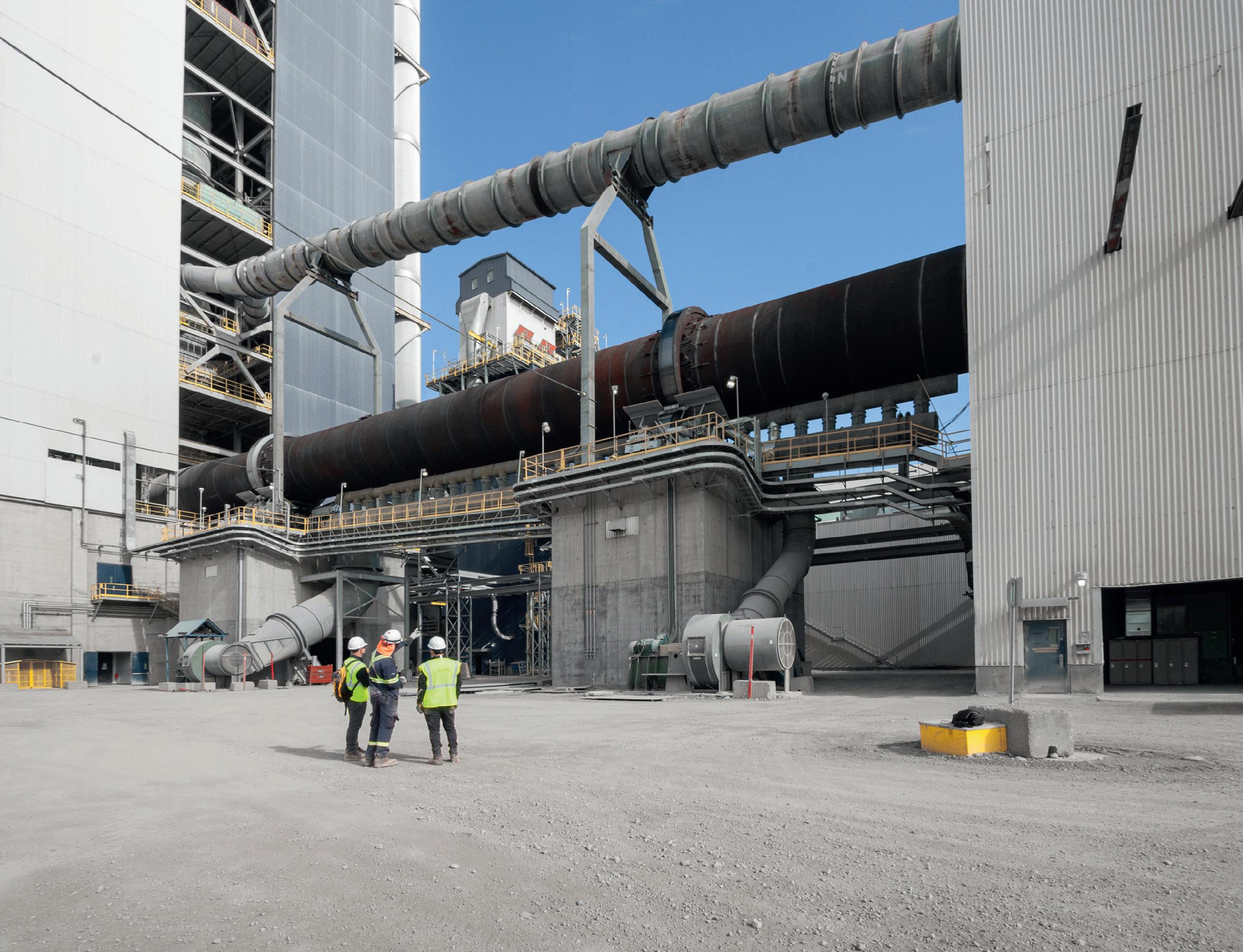
CONTENTS
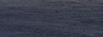
Comment
News
REGIONAL REPORT: MIDDLE EAST & NORTH AFRICA
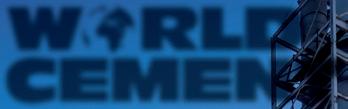
10 Weathering The Storm
Ahmad Al-Rousan, Secretary General of the Arab Union for Cement & Building Materials (AUCBM), highlights the key challenges faced by cement producers operating in the MENA region.
COVER STORY
16 New Raw Mill Increases Productivity At Mojave
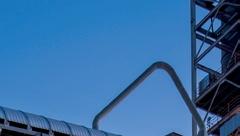
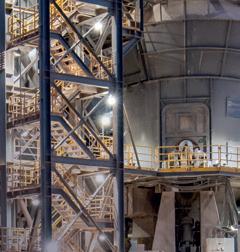

At CalPortland’s Mojave cement plant, kiln production and efficiency were adversely impacted by the reliability of the raw mill, which struggled with the increasing demands of a hot market. The decision was made to invest in a new mill. FLSmidth tells the story.
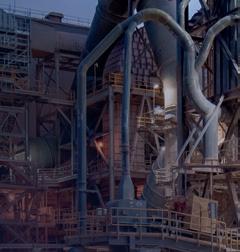
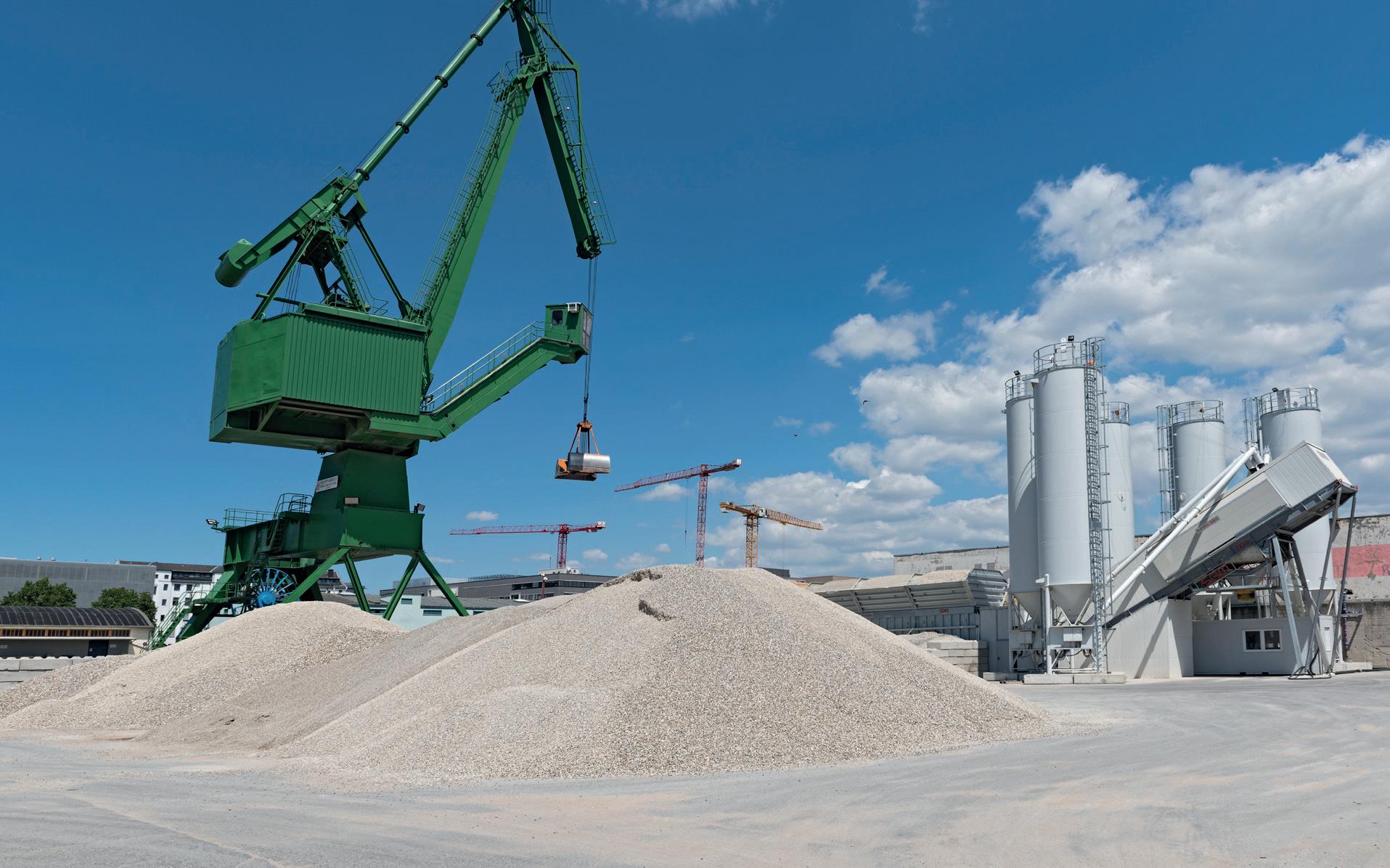
VRMs
22 Spellbinding Grinding Improvements
Dr. Caroline Woywadt, Gebr. Pfeiffer, discusses the state of VRM technology in the cement industry, with SCM integration and digitalisation becoming essential features of modern production.
LOADING & UNLOADING
31 A Proper Hopper Is A Dust Stopper
Intercem discusses a new clinker and raw material receiving hopper and reveals how it has transformed the materials handling capabilities of one Ivorian port operator.
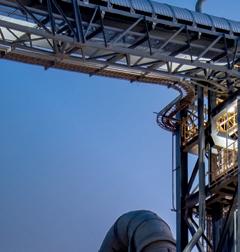
38 Plugging The Cement Industry’s Efficiency Gap
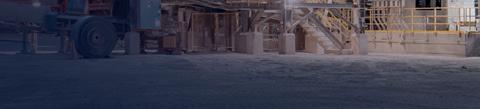
Per Hansson, Bruks Siwertell, explains how new levels of efficiency and environmental protection must be adopted if the increasing demand for cement is to be met.
DUST CONTROL
44 Save On Fuss, Collect The Dust
Steve Duncan, C&W DustTech, explains how effective dust collection can improve bottom-line performance, worker safety, and local air quality.
SILOS & STORAGE
49 Avoiding A Storage Ordeal With Bolted Steel
Wen Peng, Henan SRON Silo Engineering Co., offers an in-depth discussion of the features of a wide range of bolted steel silos and their applications in the cement industry.
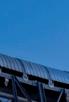
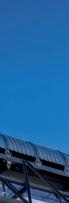
KILNS & PYROPROCESSING
53 Coming Full Circle
Heather Harding, Bricking Solutions, reviews a range of products that cement manufacturers can use to bolster worker safety and efficiency during refractory installations.
56 Placing Our Hopes In Hydrogen
Joel Maia, FCT Combustion, explores whether hydrogen is the right method for reducing CO2 emissions in clinker production.
64 Going Green
David Perkins, Lehigh Hanson, Inc., explains how a range of measures, including lower carbon cement and a new conveyor system at the Union Bridge plant will help it meet and exceed climate targets.
GREEN CEMENT
69 Turning Cement Green With XRD
Matteo Pernechele & Murielle Goubard, Malvern Panalytical, explain the pivotal role X-ray diffraction technology has to play in making green cement a reality.
75 A New Era For Low-Carbon Cement
Dr. Jose Casaban, MOF Technologies, presents a new system for carbon capture and explains why it represents a step-change for the production of low-carbon cement.
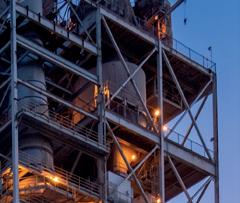
This month’s cover is brought to you by FLSmidth. At CalPortland’s Mojave cement plant, kiln production and efficiency were adversely impacted by the reliability of the raw mill, which struggled with the increasing demands of a hot market. The decision was made to invest in a new mill. Read the full article on page 16.
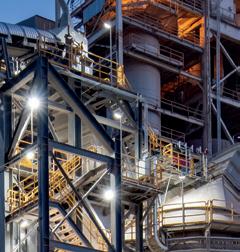
WE MOVE INDUSTRIES
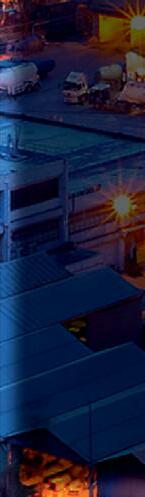

HEKO offers the whole range of chains, rollers, sprockets and scrapers for reclaimers. HEKO products are proven in thousands of bucket elevators and conveyors, worldwide.
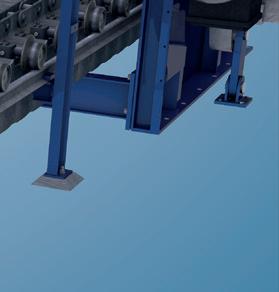
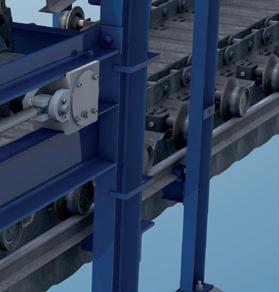
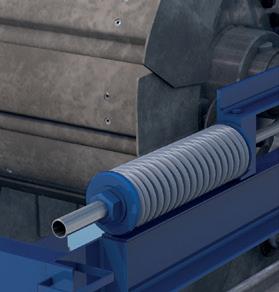
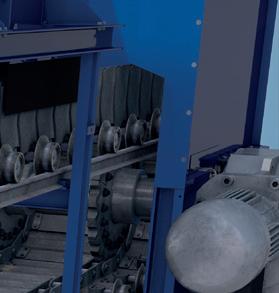
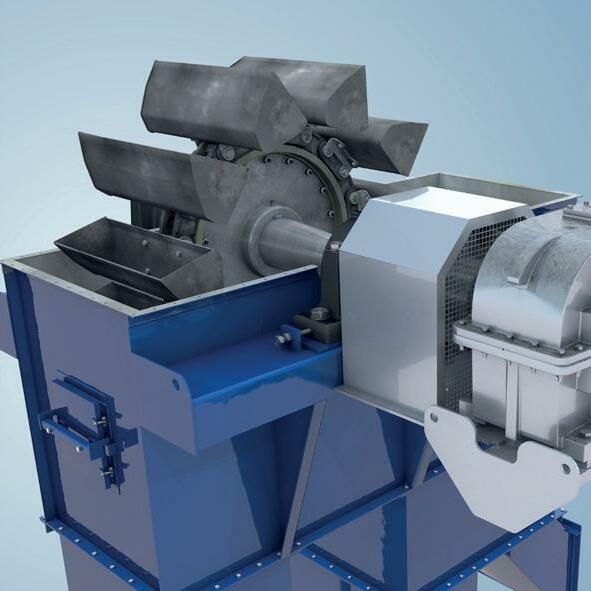
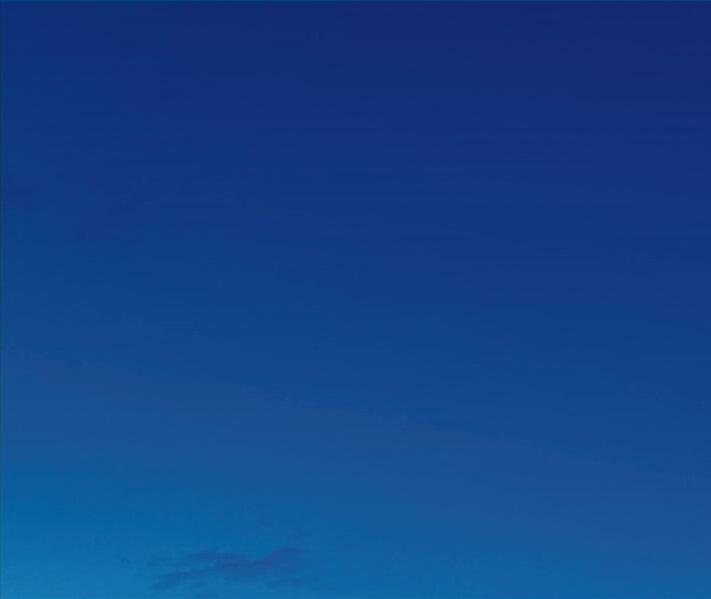
Our components for the cement industry: central chains, link chains, reclaimer chains, sprockets, bucket elevators and clinker conveyors.

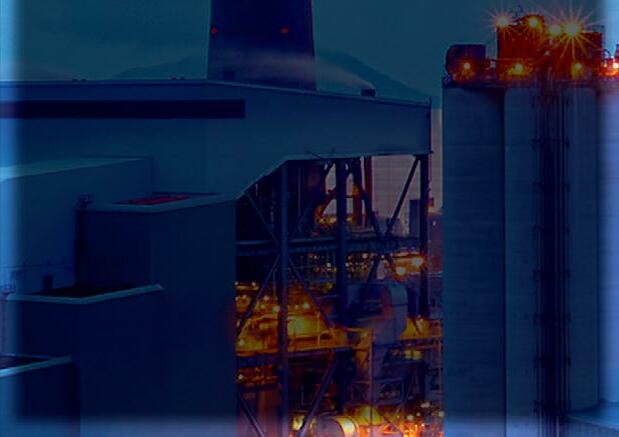
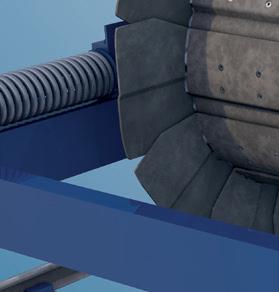
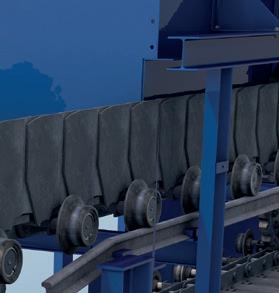
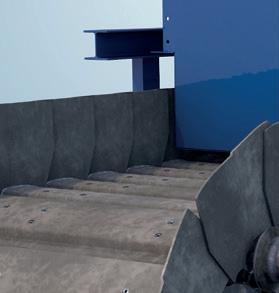
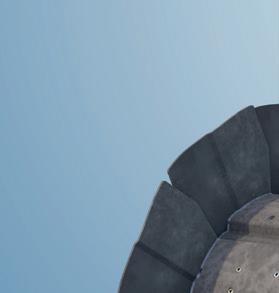
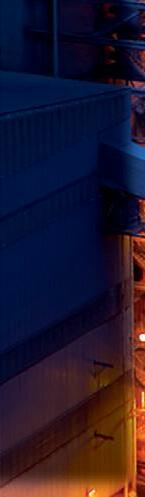
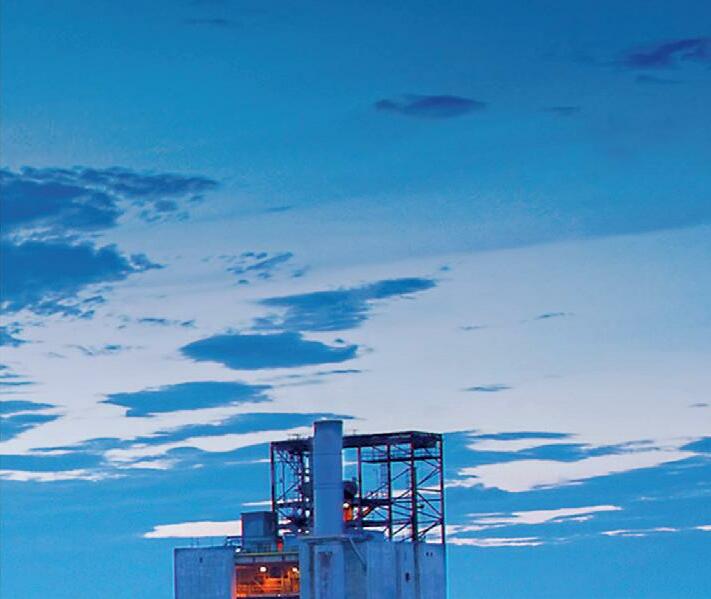
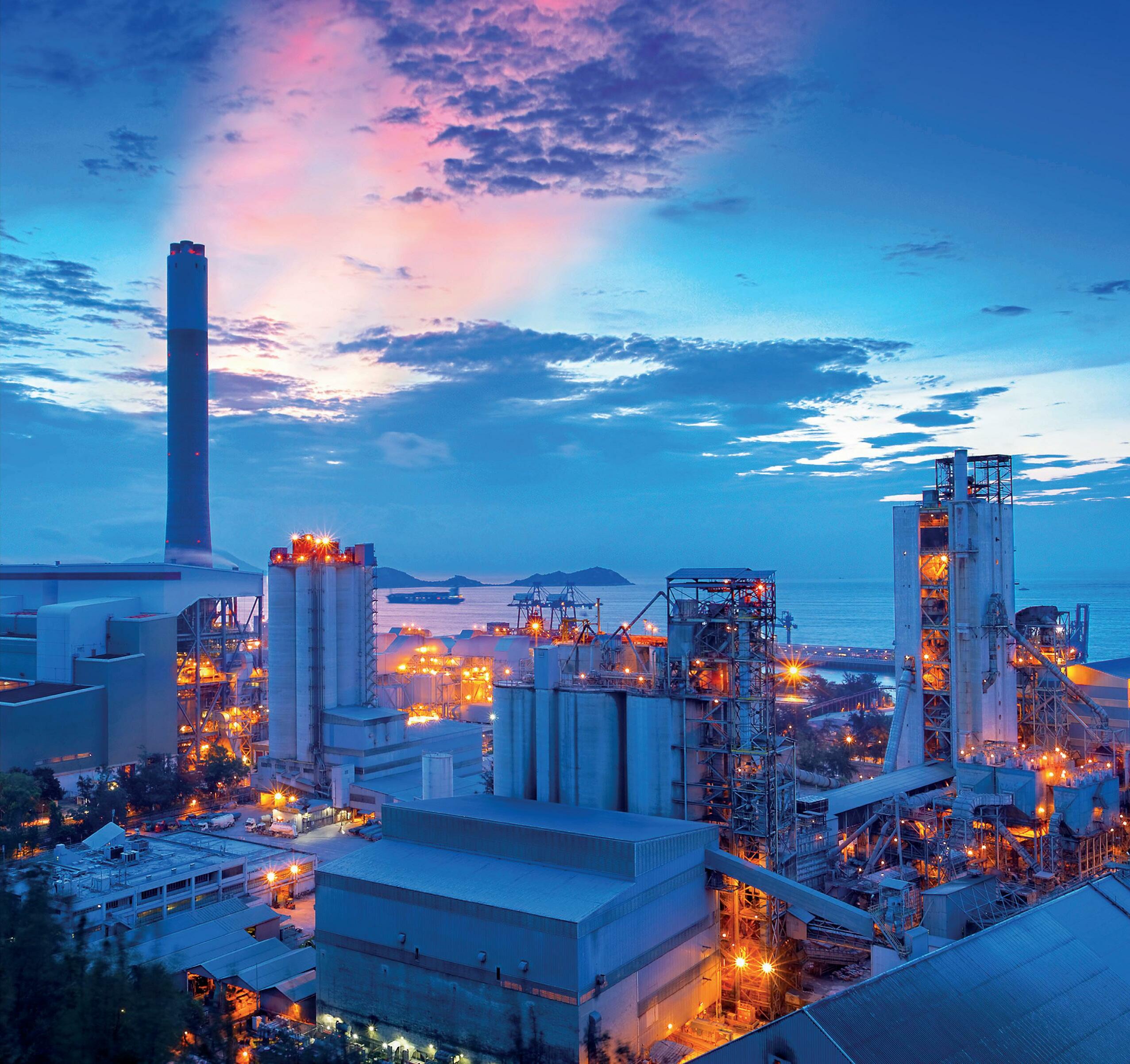
THAN
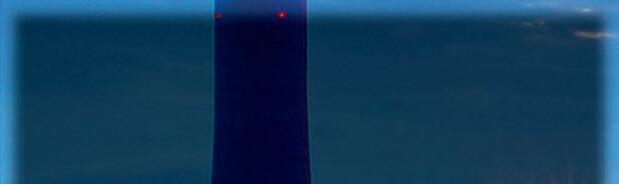


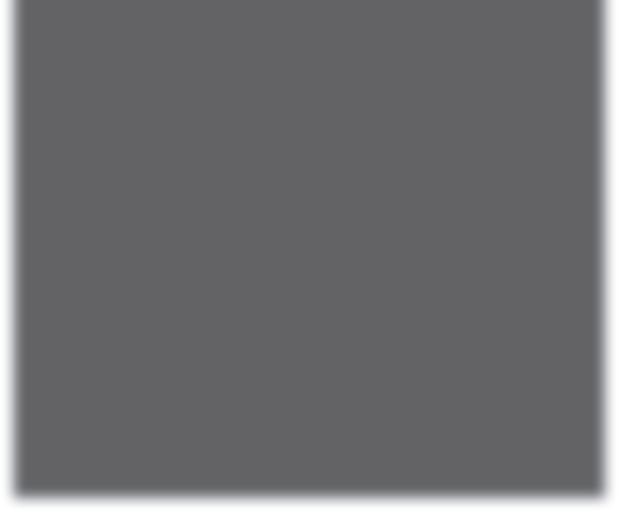

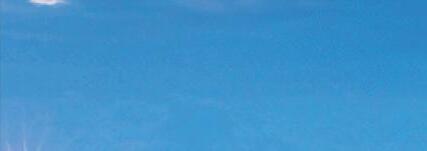
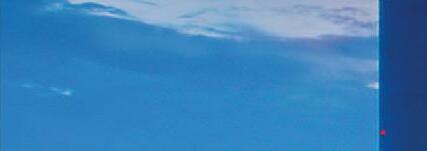

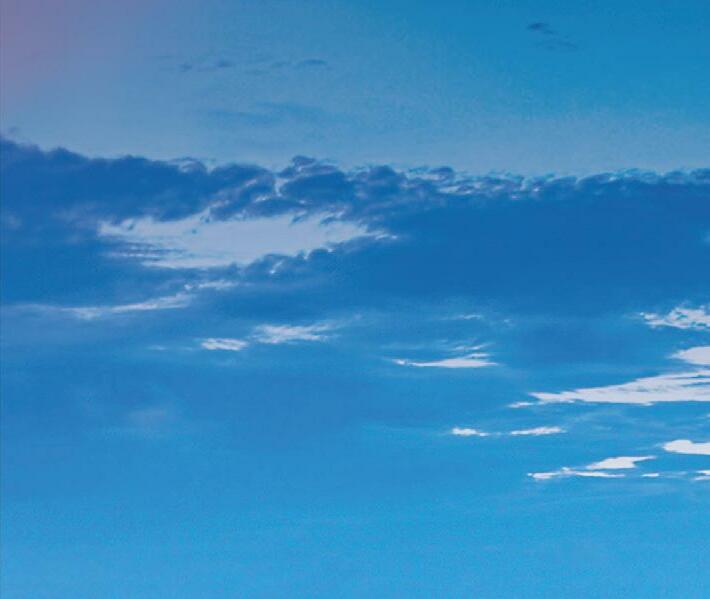
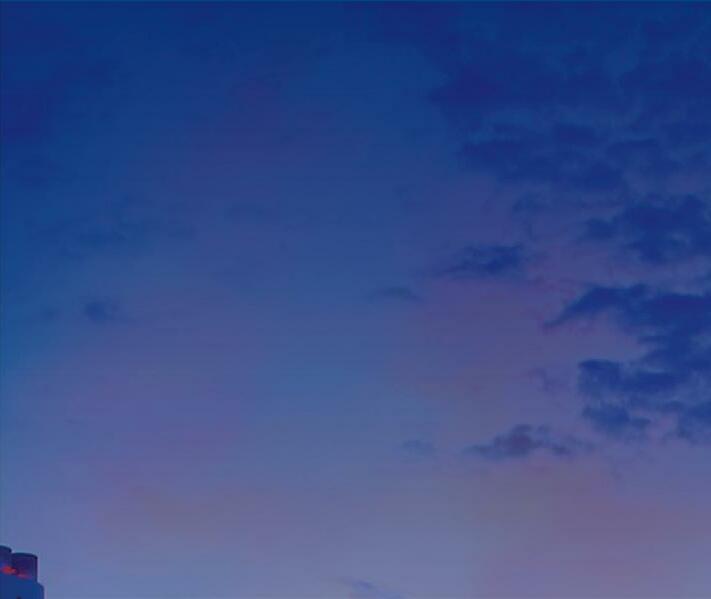
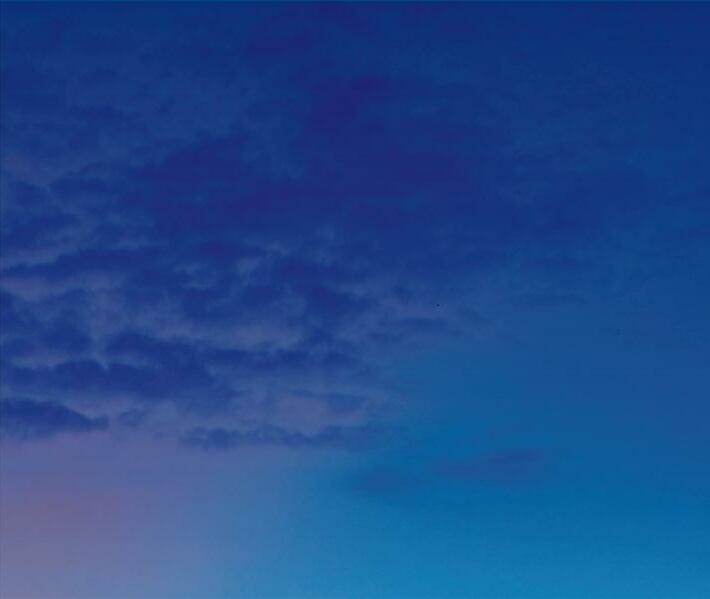
Sales Executive: Riccardo Saunders riccardo.saunders@palladianpublications.com
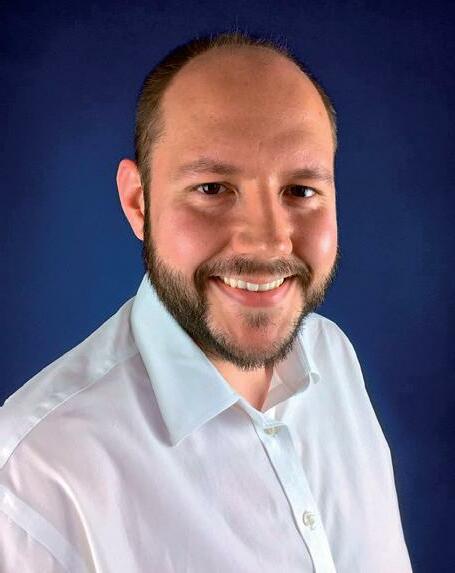
Events Manager: Louise Cameron louise.cameron@palladianpublications.com
Digital Events Coordinator: Stirling Viljoen stirling.viljoen@palladianpublications.com
Digital Administrator: Leah Jones leah.jones@palladianpublications.com
Carboncapture, utilisation, news once again as Holcim and TotalEnergies have announced a Memorandum of Understanding (MoU) to work together on the complete decarbonisation of a cement plant in Obourg, Belgium. These high-profile projects reviewing the deployment of industrial-scale CCUS in the cement sector have been popping up around the world in recent years, including: Lehigh Cement’s trial CCUS project at its Edmonton plant in Alberta, Canada (discussed in our October issue); the ongoing LEILAC 2 project in Germany; and the Norcem project in Norway, to name but a few.
The technologies being developed for the Holcim-TotalEnergies project include a new air-oxyfuel switchable kiln, designed to facilitate the capture and purification of CO2 in the flue gases, which will be provided as part of Holcim’s upgrade of the plant. And TotalEnergies will investigate options for the transportation and use of captured CO2 for an e-fuel production scheme and geological storage in the North Sea.
This particular project also touches on another hot-topic in the cement industry (and elsewhere): hydrogen. According to the MoU, TotalEnergies will assess the development of renewable projects to power an electrolyser, which would generate the green hydrogen needed to produce e-fuels. This new renewable energy production capacity would also power the oxyfuel kiln, thus further contributing to the decarbonisation of the cement plant. Finally, the oxygen emitted by the electrolyser would also be used to fuel the new kiln.
It is hoped that on completion, this project will enable the storage or utilisation of the 1.3 million tpy of CO2 emissions expected to be produced by the plant.
The urgent need to decarbonise has seen numerous start-ups with novel solutions make an appearance, with several promising to entirely electrify the calcination process and remove the need for a traditional cement kiln. Two such companies are Sublime Cement and Chement – both claim to have developed their own methods for creating cement with electricity at low temperatures. Sublime Systems refers to its process as ‘ambient temperature electrochemistry’, and Chement even claims to allow for the use of the standard OPC raw materials. Emissions reductions come from the removal of fossil fuels and the energy required to reach the high temperatures traditionally associated with cement production. A further bonus is that by removing the fossil fuels, it is far easier (and cheaper) to capture the pure CO2 that is produced.
Exciting though CCUS and other technologies may be, they are still very much in their infancy, and whilst they might ultimately be responsible for the lion’s share of emissions reduction in the cement sector, the industry needs to act today. Thankfully, the cement industry has shown innovation and a willingness to adapt to the challenge, with the adoption of alternative fuels, renewable energy, the use of SCMs, and the continued roll-out of digitalisation and optimisation programmes.
World Cement will be with you every step of the way as the industry works towards net zero.

The
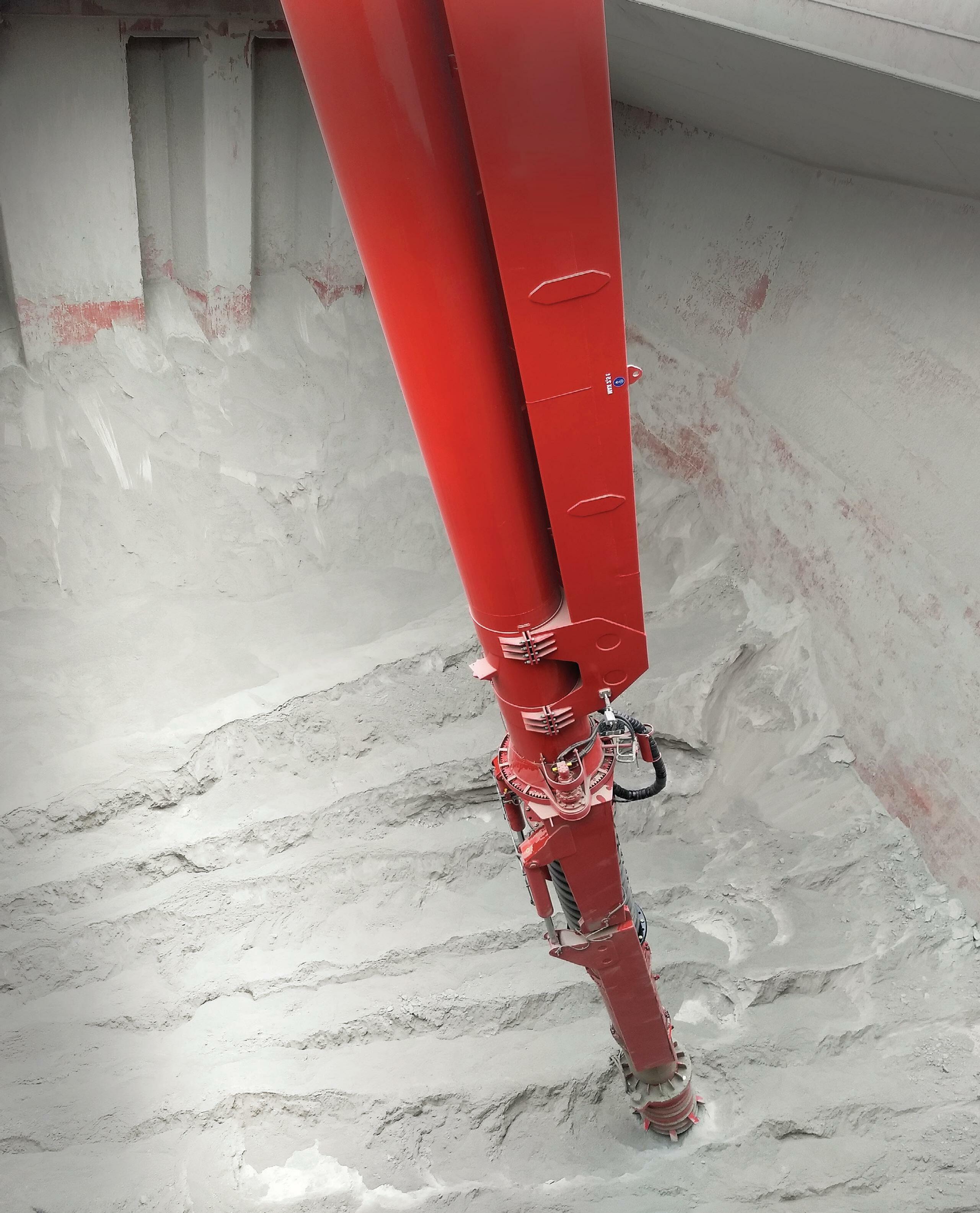
CEMEX has announced that it is working with the Science-Based Targets initiative (SBTi) to validate its 2050 net zero CO 2 roadmap and its 2030 decarbonisation goals to align with their recently announced 1.5˚C scenario.
f CEMEX commits to the most ambitious decarbonisation pathway in the building materials industry.
f CEMEX has submitted its Future in Action commitment to reach net-zero CO 2 by 2050 across its entire value chain and its 2030 decarbonisation roadmap to the SBTi for alignment with its 1.5˚C scenario.
The company’s previous goals were aligned to the well-below 2˚C scenario. After helping develop the new 1.5˚C framework as a member of the SBTi’s Expert Advisory Group, CEMEX has now aligned its Future in Action goals to the new standard and submitted them for review by the SBTi and encourages others within the industry to do the same. As part of this verification process, the company will also establish 2030 and 2050 targets for its main scope 3 emissions.
“Mitigating climate change and decarbonising the construction industry is our top priority,” says Fernando A. González, CEO of CEMEX. “The record-breaking CO 2 reduction we achieved through Future in Action in the past 18 months gives us confidence that a more accelerated pathway for 2030 is possible. We are keenly aware of the role that our industry must play in the race to zero and are committed to continue leading in this challenge.”
CEMEX has also submitted its long-term net zero roadmap to the SBTi for validation. The company’s intention to align its roadmap to SBTi’s Net Zero Standard reflects its confidence that it is on the right path to net zero and contribute meaningfully to the world’s 2050 goal. One of the key requirements to reach the SBTi’s Net Zero Standard is aggressive carbon reductions across a company’s entire value chain, including those produced by their own processes (scope 1), purchased electricity and heat (scope 2), and generated by a company’s suppliers and end-users (scope 3).
Dangote Cement shuts Nigerian plant after clash with state agents
Dangote Cement Plc, Africa’s largest cement producer, has provided an update for stakeholders and the public on the recent shutdown at its Obajana Cement plant in Kogi State.
The company reports that in early October 2022, people it described as “thugs and local vigilantes from the State Government” invaded and sealed the Obajana Cement plant over alleged claims of unpaid taxes and the Kogi State Government’s purported equity interest in Dangote Cement PLC. This development allegedly resulted in several Dangote staff being harmed.
The company has sought to reassure stakeholders and the public that it is taking firm action to address this situation, and has reiterated that Dangote Cement PLC continues to perform its obligations as a compliant corporate organisation.
The company stated that the welfare of its staff remains its key focus as it works hard to minimise the further impact on its people and operations.
Steel silo modernisations & new conveying systems for Aalborg Portland A/S
Claudius Peters Projects GmbH has won the contract to supply the basic and detailed engineering, mechanical equipment, erection, and supervision of new facilities at the Aalborg Portland A/S cement plant, Denmark.
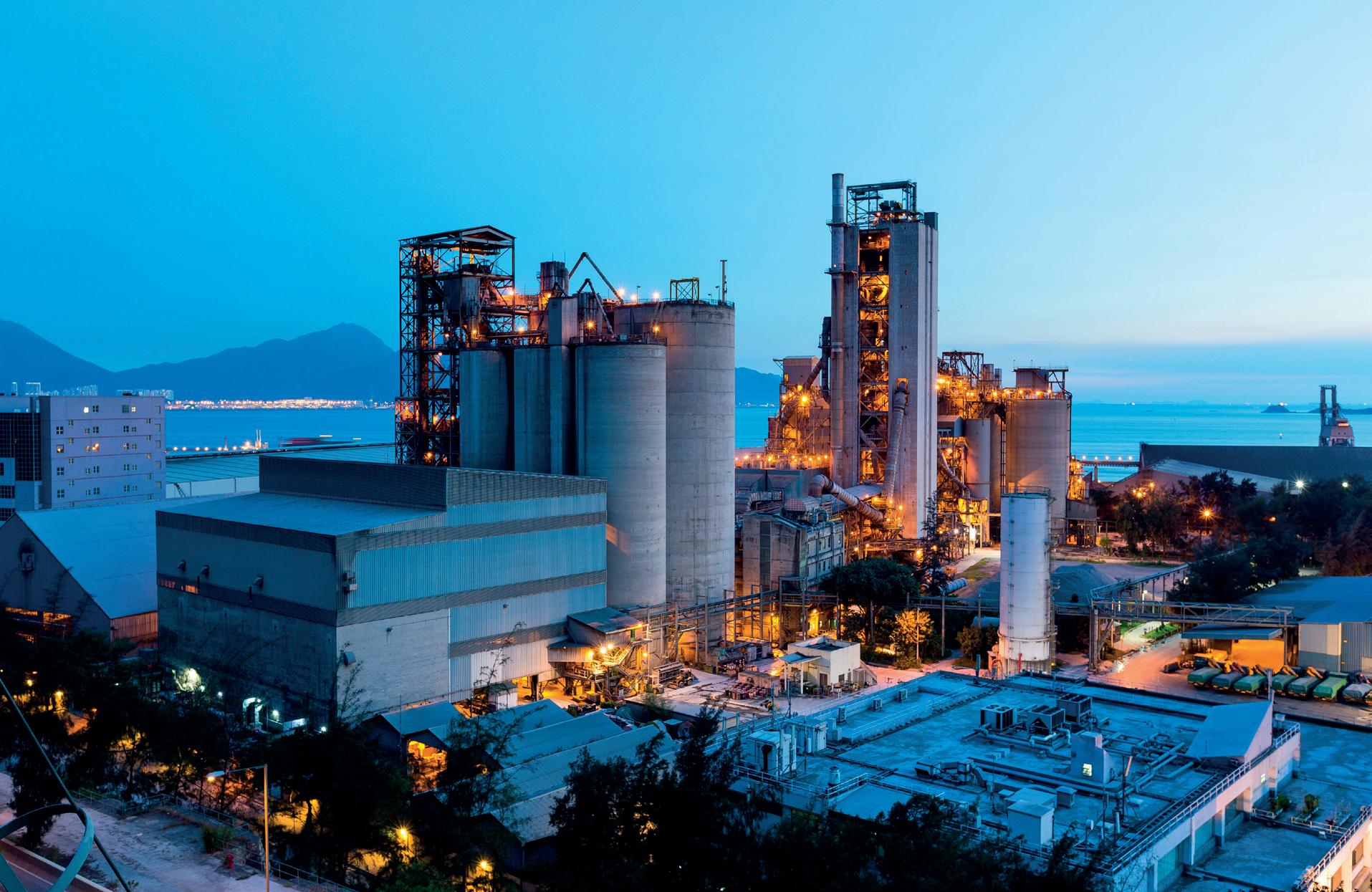
Chalk and grey kiln dust will together with calcined clay be used to substitute clinker for CO 2 reduction.
Planning in an existing building is always a special challenge. For this purpose, Claudius Peters Projects created a 3D scan on site. In addition, a material test was carried out at the technical centre, which led the customer to decide in favour of a C-Lever ® flow meter system. Another important requirement from the customer was the implementation of an existing pressure vessel system as well as ensure continuous operation of the cement mills during assembly. In addition to the modernization of the Chalk steel silo aeration, discharge & distribution system, Claudius Peters Projects GmbH will also supply: f 4 x Well proven CPP X-200 Pumps with two integrated hopper dedusting filter.
CEMEX to align decarbonisation goals with most ambitious 1.5˚C scenario
AUCBM: AICCE25
08 – 10 November, 2022
Amman, Jordan www.aucbm.net
NEWS
f 4 x Energy saving ‘Hybrid Rotary Blowers’ with piping.
f 1 x Set of Silo aeration panels with separate aeration blower.
f 3 x CPP Flow Control Gates PCD.
f 2 x Dosing rotary vales.
f 4 x Mass flow meters ‘C-Lever 50 direct (PSE)’.
f 4 x Conveying lines with pneumatic slide gates at end and complete supporting structure.
f 1 x Dedusting filter cyclone with rotary feeder & discharge chute.
The required electrical installation and integration into the plant control is carried out by the customer.
Hoffmann Green signs a three-year volume commitment contract with O.T.E.
INNOVATION IN CEMENT PRODUCTION09 November, 2022
ONLINE CONFERENCE www.worldcement.com/wct2022
Hoffmann Green will provide O.T.E with its carbon-free activated clay-based cement, H-EVA SOL, as part of the Greenpose process co-developed with the company TESMEC, a global and innovative solution of optical fibre installation with simultaneous treatment of spoil and backfill.
In practical terms, from this year until the end of 2024, H-EVA SOL will replace Portland cement in the burial of optical fibres, a rapidly growing market throughout France.
This contract with a volume commitment will allow Greenpose to reduce its carbon footprint by 95% compared to the traditional method of micro-driving with concrete backfill using Portland cement.
SOLIDS Dortmund
29 – 30 March, 2023 Dortmund, Germany www.solids-dortmund.de IEEE–IAS/PCA Cement Conference
23 – 27 April, 2023 Dallas, USA www.cementconference.org interpack 2023
4 – 10 May, 2023 Düsseldorf, Germany www.interpack.com
ACC Limited announces growth in cement volume and net sales
ACC Limited (ACC), the building materials arm of the diversified Adani Group, has announced the financial results for the quarter ended September 30, 2022.
ACC Limited records cement volume growth of 4% and an increase in net sales by 7% in the quarter ended in September 2022.
Operational highlights:
f During the quarter ended September 30, 2022, Cement Volume grew by 4% as compared to the same quarter last year. Ready Mix Concrete performed well with a volume growth of ~10% over the same quarter last year.
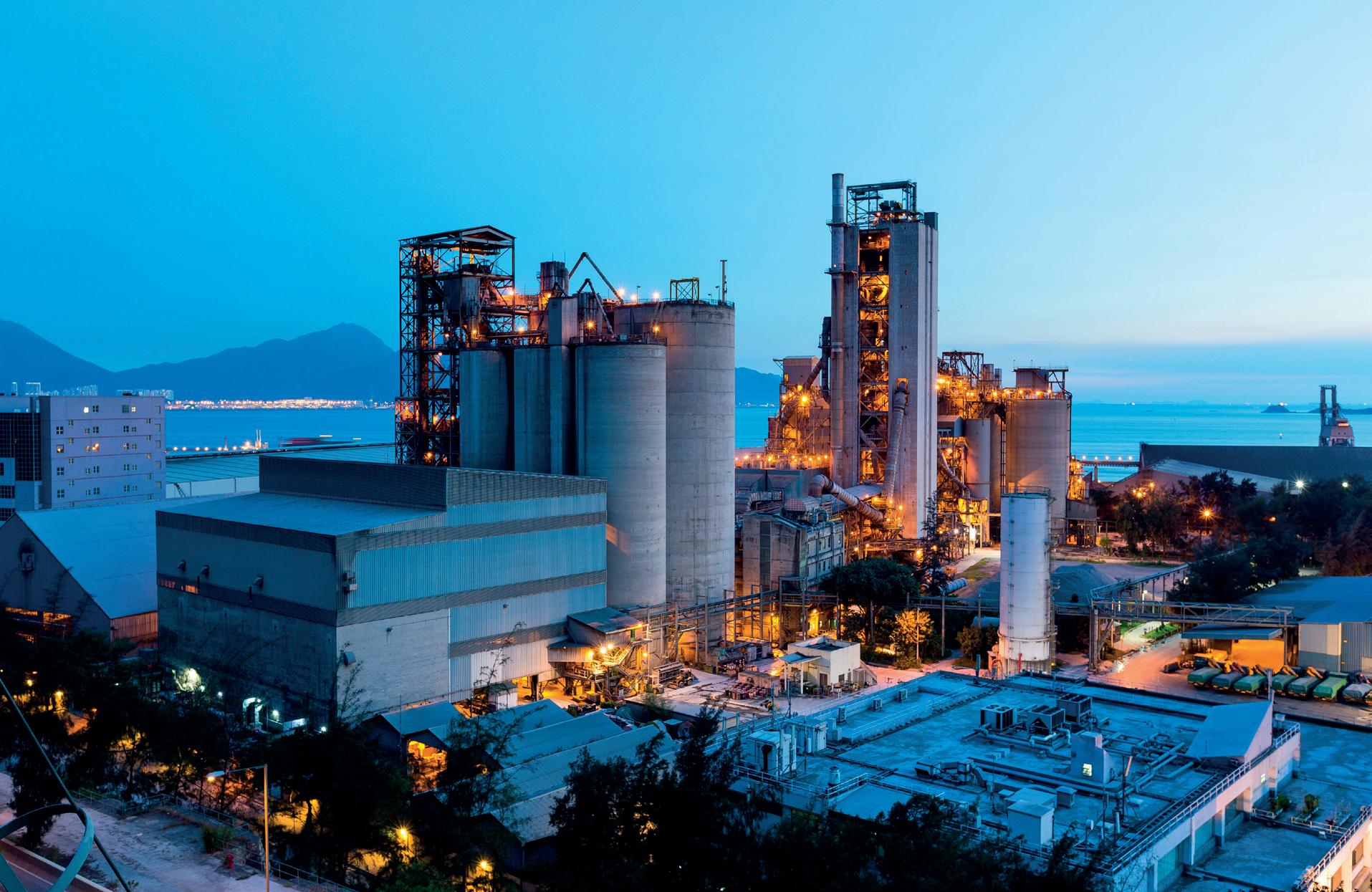
f With a focus on operational excellence & unlocking potential, ACC has accelerated de-bottlenecking of various plants & improvement in efficiencies. Alternative Fuels & Raw materials (AFR) platforms are being leveraged to maximise usage of wastes to reduce power and fuel cost.
Financial highlights:
f ACC recorded net sales of INR39.1 billion as compared to INR36.5 billion in the same quarter last year.
f EBITDA for the quarter ended September 30, 2022, stood at INR160 million largely due to steep rise in fuel cost.
Meet the new guy.


“The post-monsoon quarter will see the traditional rebound for the cement sector, including for ACC. We have had significant cost pressures in the recent past due to steep fuel price rise. However, recent cooling off in energy costs will impact us positively in the coming quarters.” said Mr. B. Sridhar, the company’s Director & CEO. “During the quarter, ACC recorded strong growth in RMX volume of 10% and RMX business remains a huge growth engine for future. We have aggressive growth plans and our capacity expansion initiative through our new green field projects at Ametha is progressing well and is expected to be commissioned by March 2023.”
ESG highlights:
Targeting ESG leadership, ACC’s Sustainability strategy is led by its Sustainable Development 2030 plan.
In September 2022, WHRS projects at Jamul and Kymore have been partially commissioned. Next wave of WHRS projects at Chanda and Wadi plants are progressing well. Scaling up of renewable power-solar, wind and hydro is underway.
ACC continues its focus to build low-carbon portfolio through higher proportion of blended cement and accelerating green products & solutions through increasing usage of AFR. The company also continues to place a strong focus on water governance, sustainable livelihood and social inclusion for the community, with 400 000 new beneficiaries being added during the quarter.
TotalEnergies and Holcim sign MoU to join forces in developing carbon-free cement plant in Belgium
TotalEnergies and Holcim in Belgium have signed a Memorandum of Understanding (MoU) to work together on the full decarbonisation of a cement production facility being upgraded by Holcim in Obourg, Belgium.
Various energy sources and novel technologies will be assessed for the efficient capture, utilisation, and sequestration (CCUS) of around 1.3 million t of CO 2 emitted by the facility every year.
Each partner will contribute its best-in-class technologies and its know-how to explore and develop the project, including:
f An innovative new air-oxyfuel switchable kiln, to facilitate the capture and purification of CO 2 in the flue gases, as part of Holcim’s upgrade of the current cement plant.
f The transportation and use of the captured CO 2 by TotalEnergies for an innovative e-fuel producing scheme and/or deposit in geological storage in the North Sea.
TotalEnergies will assess the development of renewable projects to power a new electrolyser, which would generate the green hydrogen needed to produce e-fuels. This new renewable energy production capacity would also power Holcim’s new oxyfuel kiln, thus contributing to the decarbonisation of the cement plant. Finally, the oxygen emitted by the electrolyser would be used to fuel the new kiln.
“The unique, integrated and sustainable solution that we are looking to provide to Holcim for the full decarbonisation of its cement plant emissions – with its range of technologies and new decarbonised molecules – is a first, marking a milestone in the decarbonisation of heavy industry and its hard-to-abate emissions. We are pleased to partner with Holcim to work on the development of sustainable and carbon neutral industries in Europe, in partnership with our clients and in line with their decarbonisation strategy,” said Christophe Sassolas, Senior Vice President, OneB2B Solutions at TotalEnergies. “TotalEnergies is looking forward to deploying other integrated solutions like this one elsewhere, as we move toward reducing our scope 3 emissions, in line with our Climate Ambition to get to Net Zero emissions by 2050, together with society.”
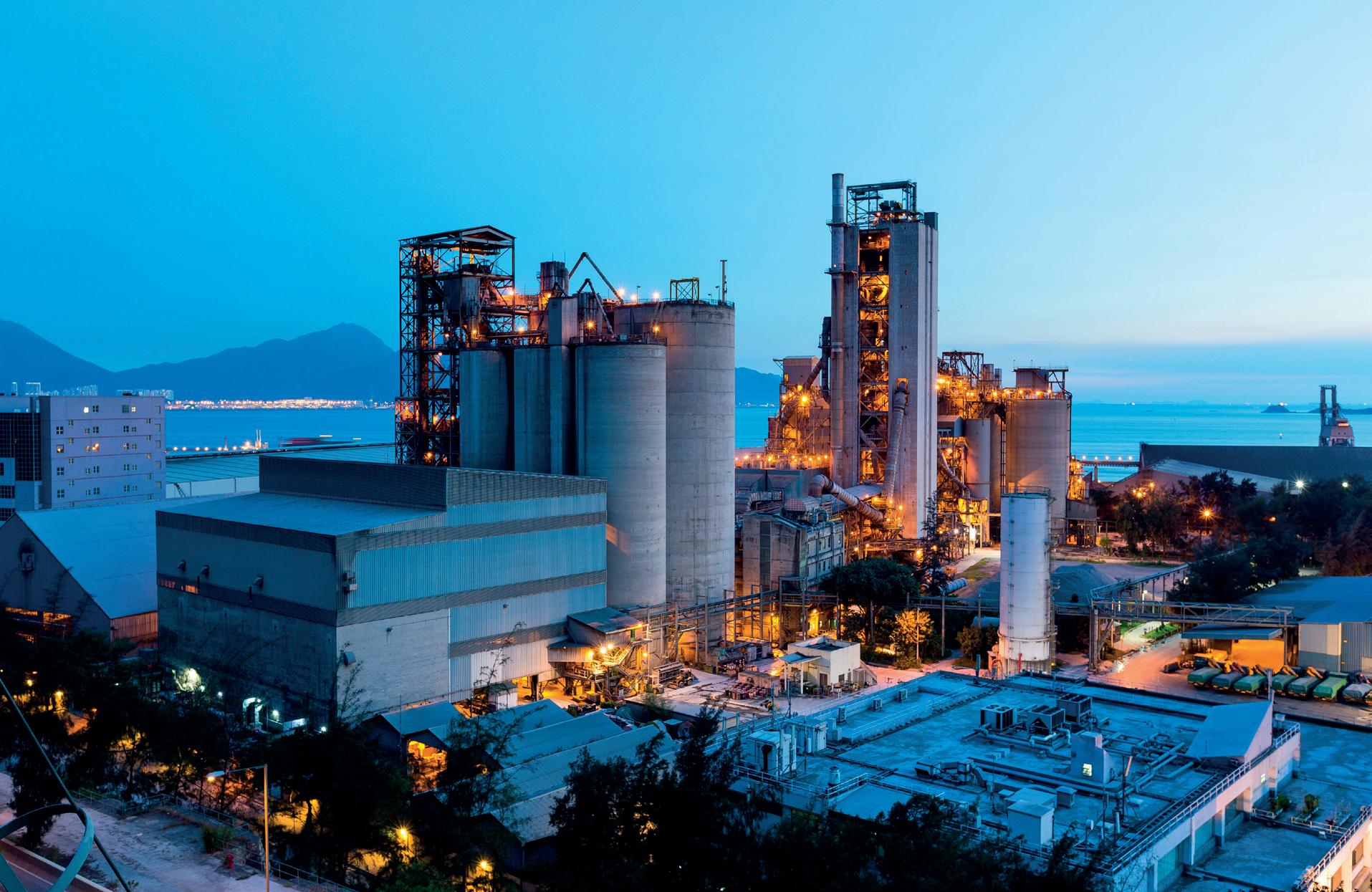
“Cement industry decarbonisation is extremely challenging because of the process’s inevitable CO 2 emissions, which put us firmly in the hard-to-abate sector. CCUS is vital for Obourg to become the first net carbon neutral clinker plant in northwest Europe. We are very happy to work with TotalEnergies to accelerate the development of these CCUS solutions for GO4ZERO.
By joining the first movers, we want to set the standards for future clinker manufacturing plants,” said Bart Daneels, CEO of Holcim Belgium.
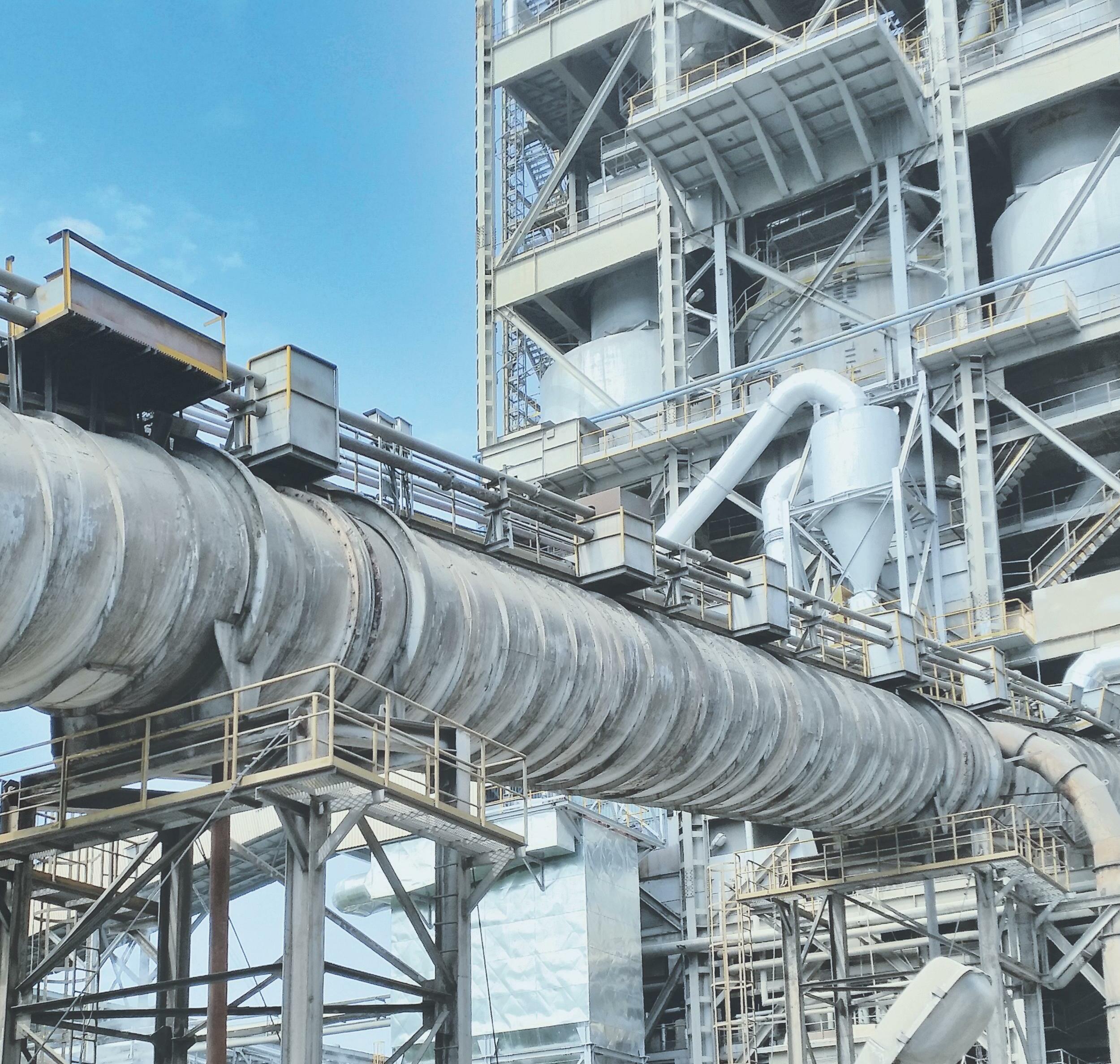
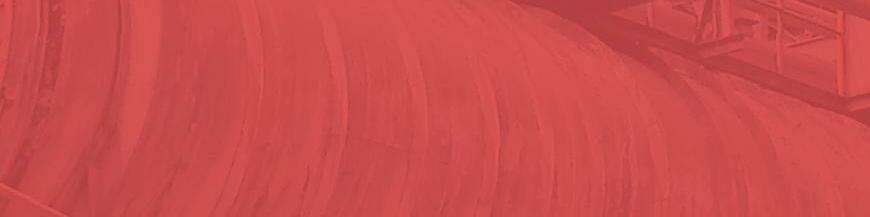
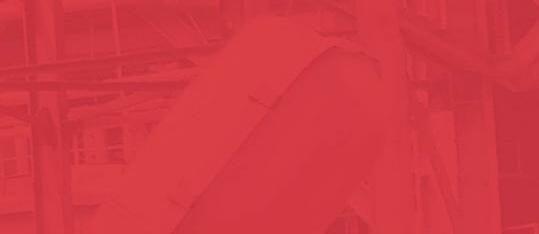
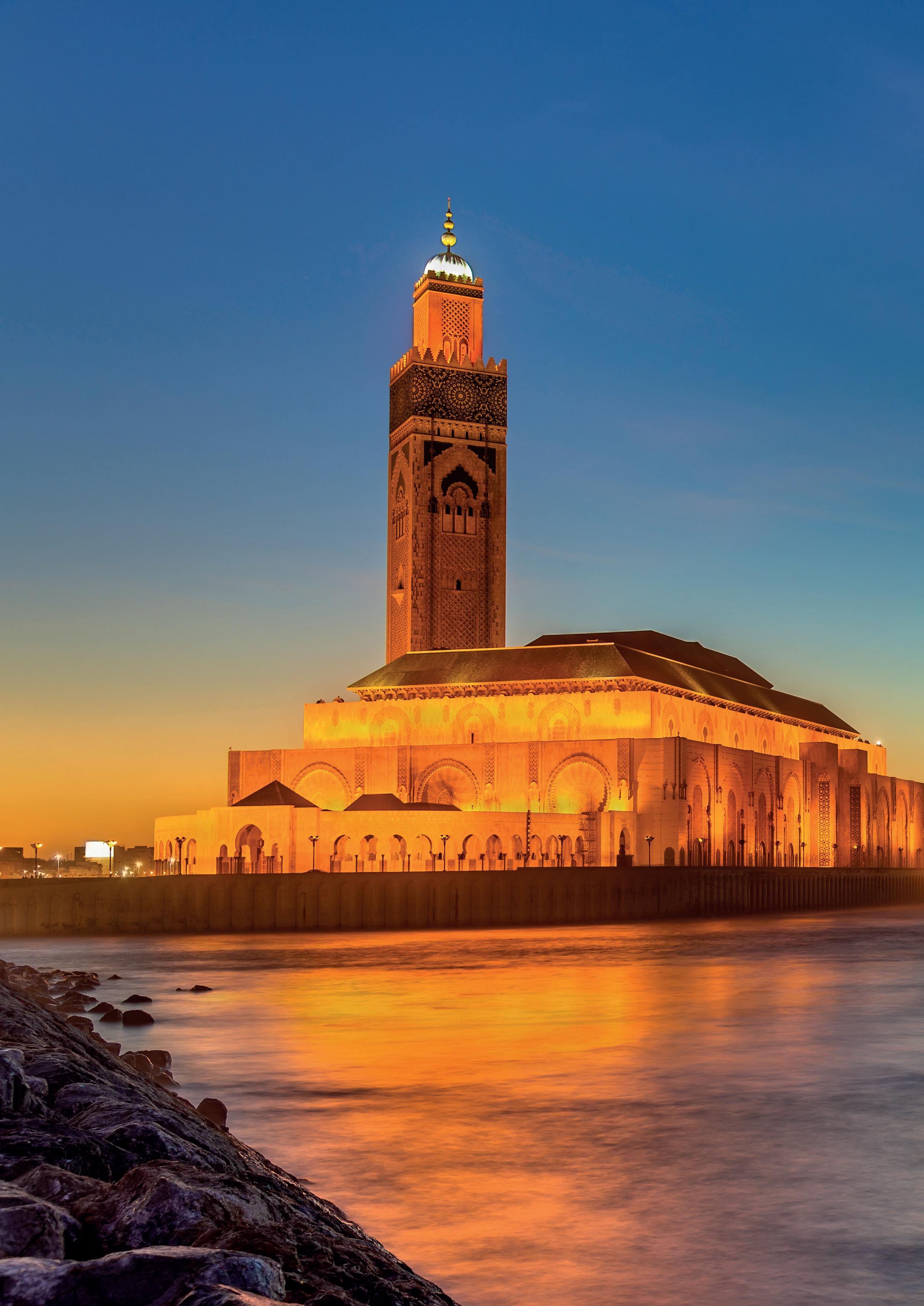
weathering the storm
During the years preceding the COVID-19 pandemic, the Arab cement industry witnessed a significant growth in terms of expansions and raising production capacity, especially in some countries of the Arab Gulf, most notably in Saudi Arabia, Egypt, and Iraq. This was accompanied by an expansion of the industry in Arab North African countries, namely: Algeria and Morocco.
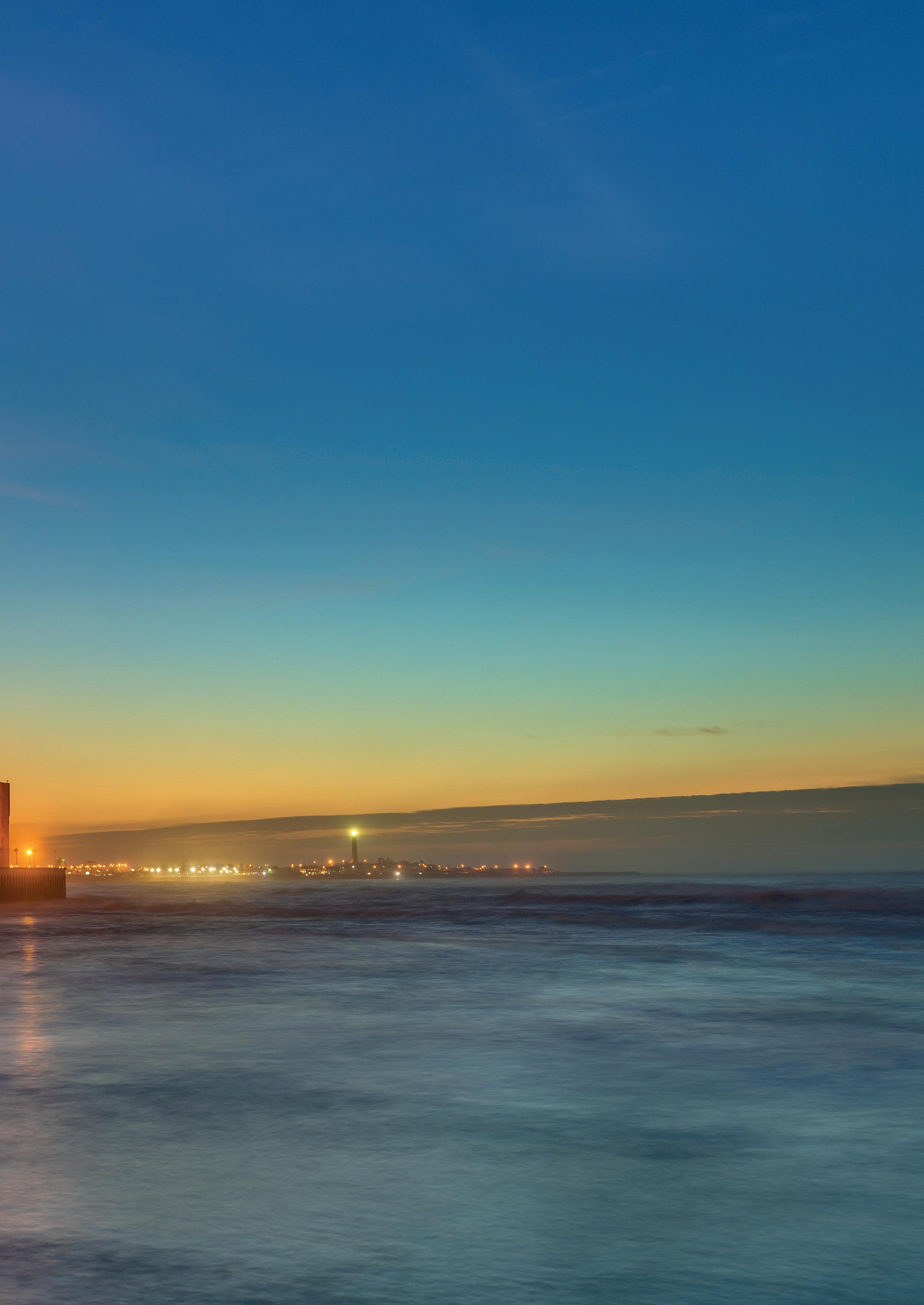
At this time, the cement production capacity of the Arab world amounted to 350 million tpy. Whilst growth had been seen in some countries, others – Libya, Syria, and Yemen – suffered from conflict, instability, and insecurity during the same period, which led to the destruction and closure of some of their cement plants.
By 2020, the COVID-19 pandemic had swept the world, and the Arab cement industry was greatly affected due to the preventative measures taken by governments, leading to closures, declines in production and consumption as well as the suspension of planned projects.
Despite the difficulties arising from pandemic measures and the accompanying economic conditions, some Arab countries (Saudi Arabia, Iraq, and Jordan, for example) recorded limited increases in consumption at fluctuating rates in 2020 and early 2021. This growth has since continued at varying rates.
The Arab cement industry is currently facing several difficulties, the most important of which are:
f The difficult economic conditions facing countries in the region, which are especially profound in the non-oil states. Adding to this is the inability to finance construction projects, for either infrastructure or housing, despite the need for them.
f Higher global oil and gas prices, as well as coal, which will affect the cost of production and prices in general.
f Restrictions and sanctions imposed on some countries and consequently on companies, whether cement or contracting companies, which will hinder them from contributing to the reconstruction of countries damaged by wars.
f The Ukrainian-Russian war, which has hampered logistics.
f Countries in economic difficulty are now having to give priority to securing food over other matters.
Regional highlights Egypt
Like many nations around the world, Egypt’s economy has felt the impact of rising prices and other adverse financial conditions that initially stemmed from the pandemic recovery, but have only been worsened by Russia’s invasion of Ukraine.
Prior to these external shocks that triggered a range of policy measures, including a significant depreciation of the currency, The World Bank reports that economic activity had been experiencing a strong recovery, despite rising inflation and building pressures on external accounts.
Focus Economics reports that while rising food prices are impacting consumer purchasing
power and raising social tensions, support from neighbouring countries and healthy revenues from the Suez Canal should help lessen the impact somewhat. However, growth is expected to further decelerate in 2023, a 0.1% decrease to 4.6%, as the country continues to face economic headwinds.
One positive sign from the Egyptian economy appears to come from the continued resiliency of the country’s construction sector, with GlobalData forecasting growth of 9.7% for 2022. Much of this growth is expected to be driven by the government’s focus on promoting and investing in domestic manufacturing and export industries. To date, the government has announced plans for 45 major national and strategic infrastructure project, including: 10 transverse axes on the Nile, 18 overpasses, the expansion of railway signal electrification, an expanded metro network and 47 train stations.
Dhananjay Sharma, Practice Head at GlobalData, commented: “Egypt is suffering severe economic challenges and in late March 2022, the monetary authorities devalued the Egyptian pound by around 14%, following a period of intense pressure on the currency that stemmed from a withdrawal of foreign capital. Egypt’s central bank also increased interest rates amid rising inflationary pressures, with the country facing soaring food prices given its heavy reliance of wheat imports from Russia and Ukraine. Notwithstanding the worsening economic environment and upward pressure on energy and materials prices, the construction industry is poised for relatively strong growth, supported by large infrastructure projects, such as the New Administrative Capital (NAC), New Alamein and New Galala.”
With the government so heavily focused on infrastructure development, with plans to invest tens of billions of dollars into various projects around the country, Egypt’s construction sector looks set to be a major pillar of the country’s economic growth over the coming years.
Saudi Arabia
According to the International Monetary Fund (IMF), The Kingdom of Saudi Arabia is likely to be one of the world’s fastest growing economies this year as sweeping pro-business reforms and rising oil prices drive a recovery from a pandemic-induced recession in 2020. GDP growth is expected to hit 7.6%, marking the fastest growth in almost a decade.
Despite this positive news, there are concerns that this current rally in oil prices might be the last and that the country will have to look to other sources of income as much of the world continues to gradually shift away from fossil fuels. Focus Economics therefore predicts that much of this
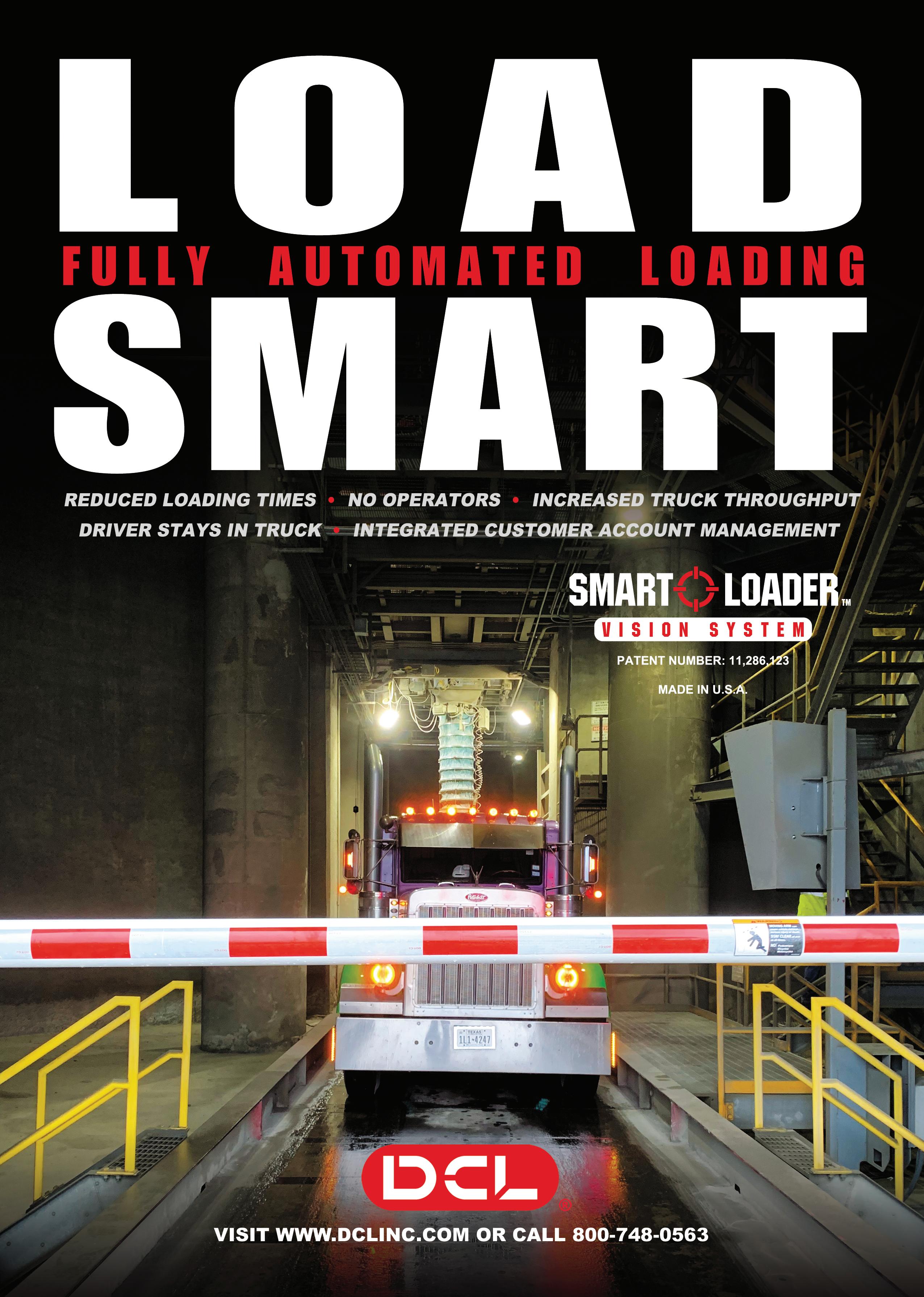
recent windfall will be directed towards the country’s US$600 billion sovereign wealth fund to help promote diversification of the economy, with the rest likely directed towards rebuilding foreign exchange reserves and reducing public debt.
While rising prices on expensive imported commodities are likely to add some pressure, The Economist Intelligence Unit (EIU) predicts that price inflation will be kept mostly in check by price caps and subsidies. Consumer price inflation is expected to end up in the 2.5% area – one of the lowest rates (along with China and Japan) amongst the world’s 20 largest economies. A wide range of reforms designed to help improve the business environment, attract foreign investment, boost private-sector participation in the economy, and support the labour market are also expected to bear fruit over the coming years.
However, the recent decision by the Saudi-led OPEC+ group to reduce oil production and maintain high prices has drawn the ire of the United States and prompted President Biden to state that “there will be consequences” for the apparent decision to side with Vladimir Putin’s Russia. In response, US lawmakers have made calls to end weapons sales and limit military cooperation with Saudi Arabia, which is heavily dependent on US weapons and support for its security against regional rivals, such as Iran.
At the time of writing, it is too early to tell exactly what impact this downturn in relations, or indeed the production cuts themselves, will have.
In terms of construction and cement news, the Saudi cement industry struggled with rising production costs and low demand in the first half of the year, partially exacerbated by the month of Ramadan falling in April. Arab News reports that data collected by Al-Yamama Cement showed that sales of 17 Saudi cement plants fell by 39% to 3 million t in April, down from 4.97 million t in March.
Despite this gloomy news, hope for the Saudi cement sector remains in the form of the multiple construction megaprojects that have been planned across the country, such as the Red Sea Development Co., AMAALA, NEOM, Qiddiya, and others. Omar Hatoum, General Manager of SACEP, was quoted by Arab News as saying: “The industry will be positively affected by renewed construction in the north, with The Red Sea Project, and residential developments. The effect won’t be immediate but will reflect on the long haul, until 2030.”
Morocco
Morocco experienced a strong economic rebound in 2021 (recording growth of 7.4%), which allowed the country to recover much of the output and job-losses caused by the
COVID-19 pandemic. However, the World Bank reports that “real GDP is still 6.4% below the pre-pandemic trend; potential growth has been declining since the early 2010s; volatile precipitations are increasingly affecting the economy; and the combined effect of the drought, rising international food and energy prices due to the war in Ukraine and the lasting impact of the COVID pandemic may leave socio-economic scars if not treated well.”
A further decline in growth, down to 1.1% is expected for 2022 as the country struggles with an ongoing drought that has reduced agricultural output by more than 17%. The Intergovernmental Panel on Climate Change (IPCC) has previously recognised Morocco as being particularly vulnerable to the impacts of climate change due to its economic dependence on sectors which are highly sensitive to environmental factors (agriculture, fisheries, tourism).
There are some upsides to the economic forecast, however. These come in the form of a rapid recovery in the tourist sector and ongoing reforms which are expected to increase potential growth over the medium-term.
Examples of the reforms include policies aimed at further developing the private sector through the promotion of small- and medium-sized enterprises to enhance growth and its inclusiveness.
Ciment du Maroc, a subsidiary of Heidelberg Materials reported a 5% increase in quarterly turnover at the end of the second quarter of this year, reaching US$170.7 million at the end of June, up from US$161.2 million a year ago. The company was also able to increase investment by 195% (US$15.1 million) compared to the previous year. Much of this investment was related to the construction of a new grinding unit, located in Nador in the north of the country. With a total investment budget of US$31.3 million, the Nador plant will have a production capacity of 700 000 tpy.
Earlier in the year, Holcim announced the opening of a cement plant in Agadir, in Southern Morocco, boasting a production capacity of 1.2 million tpy for an investment of US$299 million.
The plant, which is equipped with the latest technology, including an automated laboratory, and is modelled around the company’s plans for a ‘plant of tomorrow’, relying heavily on automation and AI technology to optimise the production process
Note
The ‘Regional highlights’ section of this article was compiled by World Cement staff. Sources include company press releases, quarterly statements, news agencies, Focus Economics, The World Bank, The International Monetary Fund, and others.
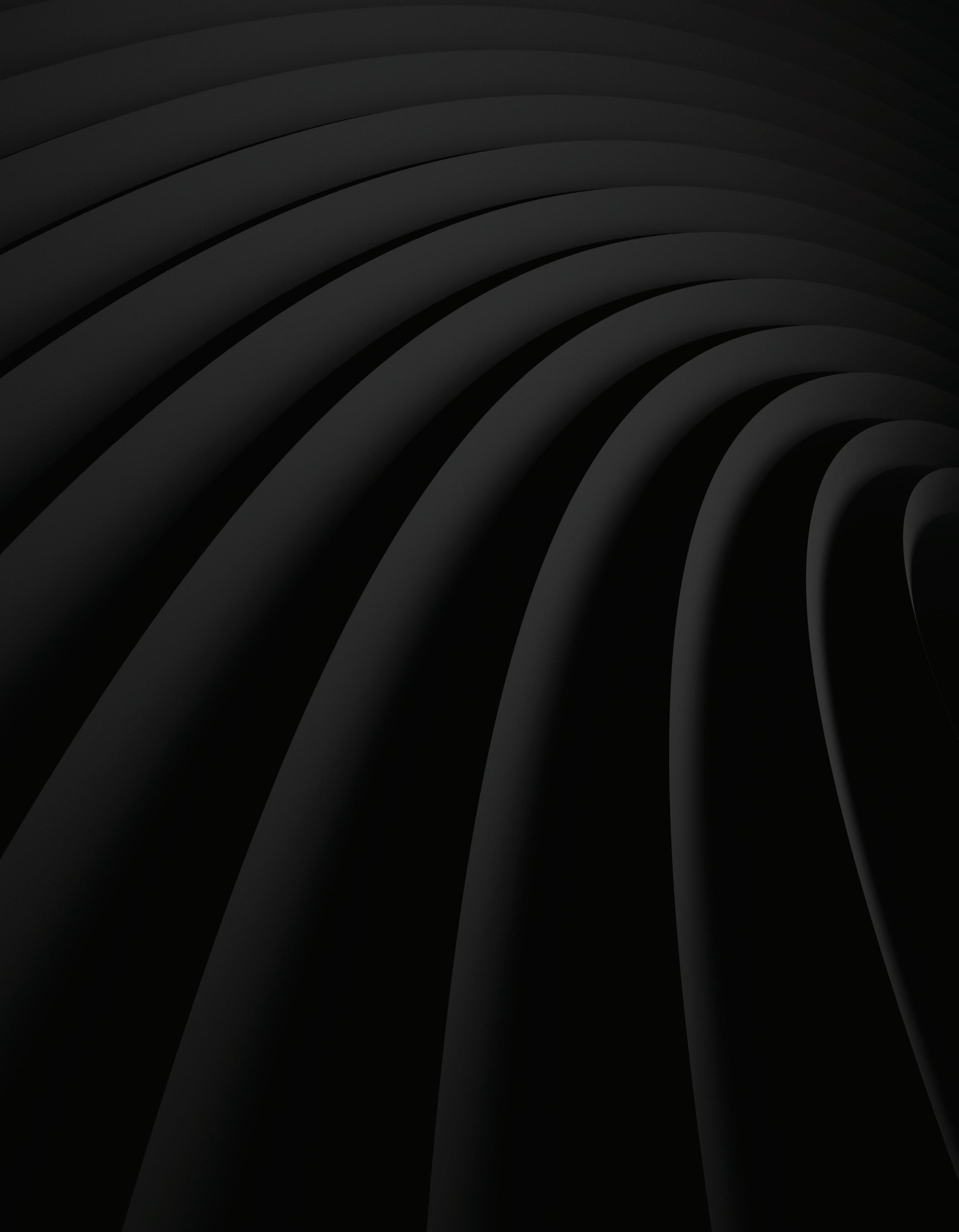
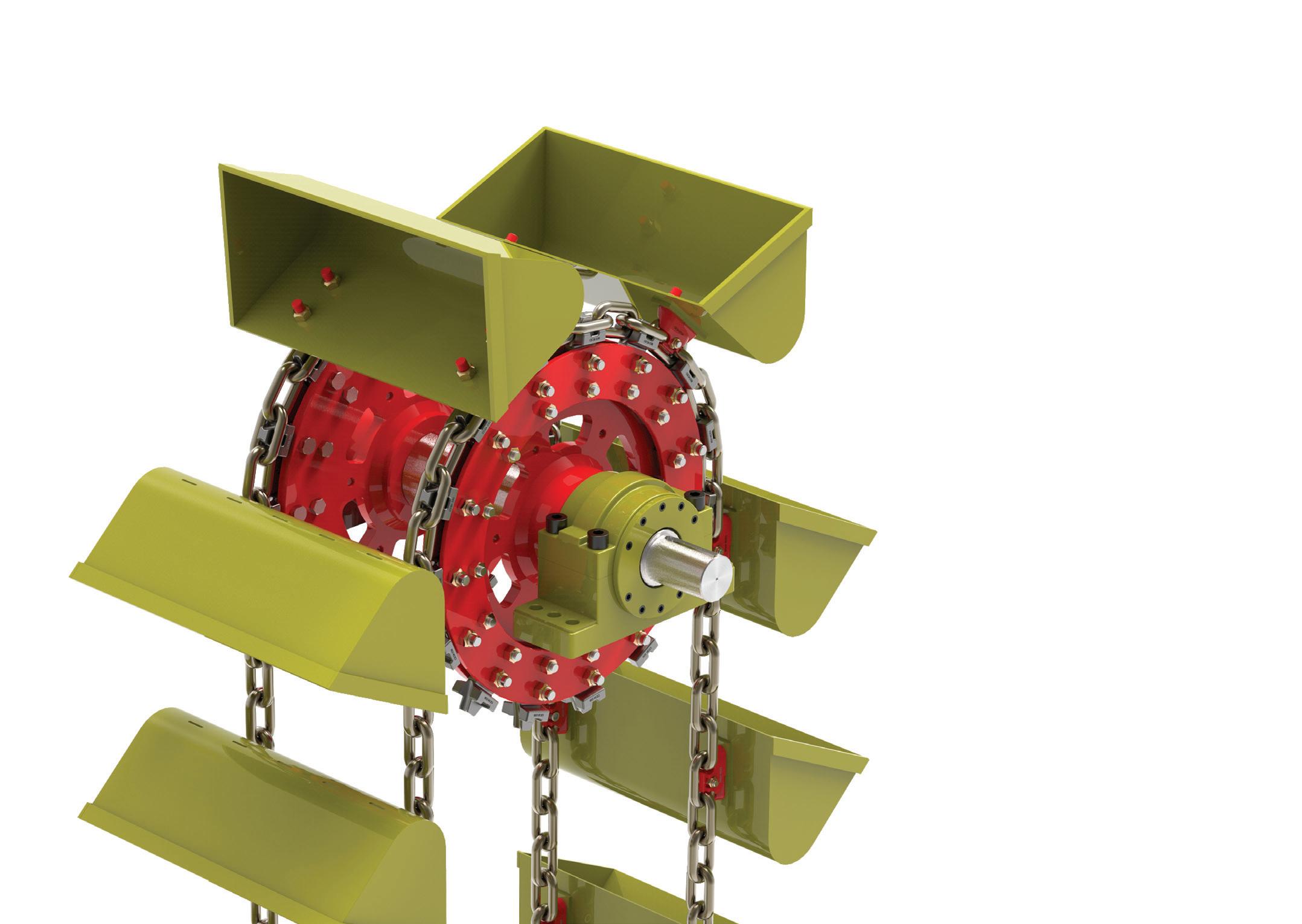

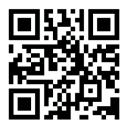
At CalPortland’s Mojave cement plant, kiln production and efficiency were adversely impacted by the reliability of the raw mill, which struggled with the increasing demands of a hot market. The decision was made to invest in a new mill. FLSmidth tells the story.
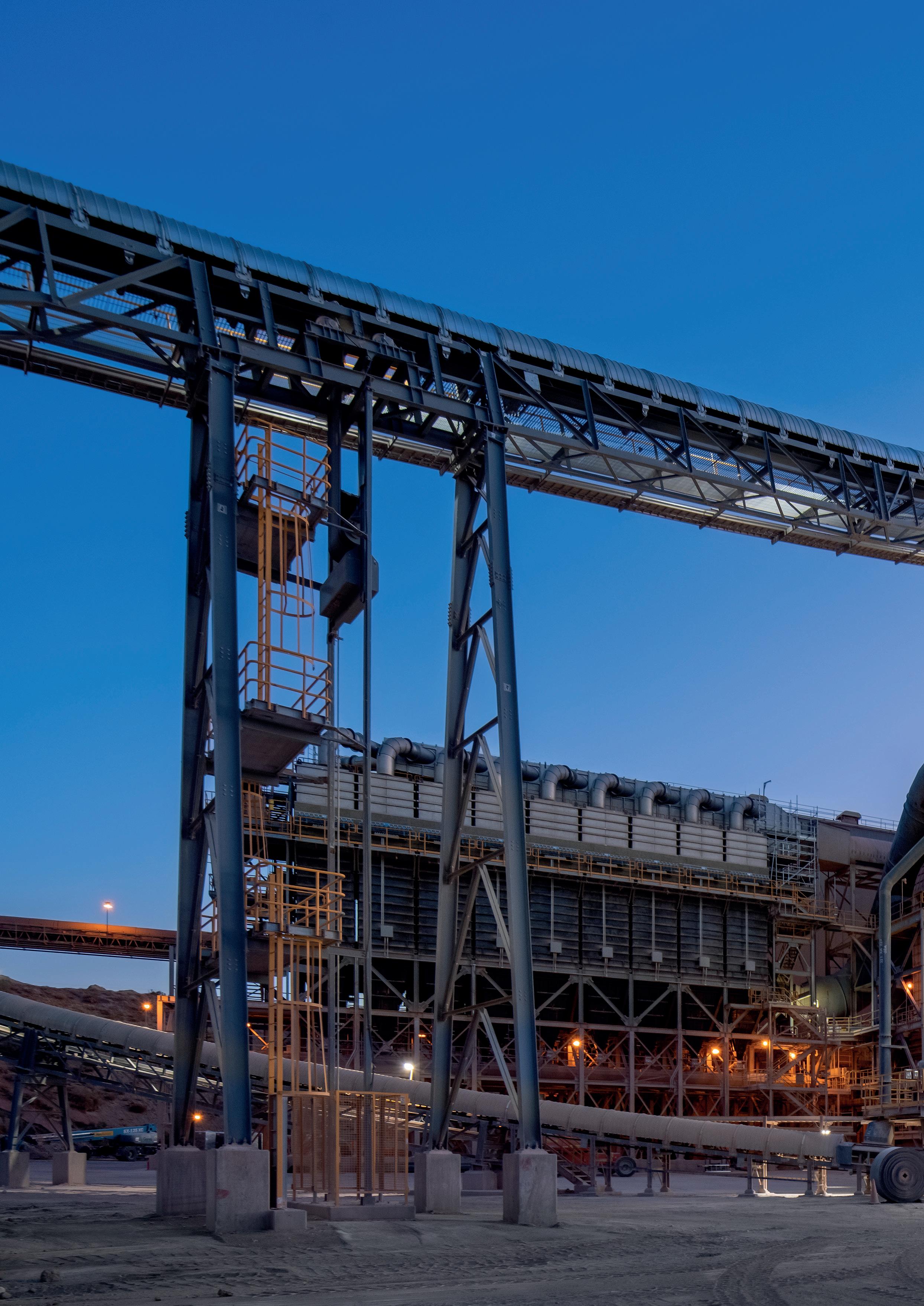
NEW RAW MILL INCREASES PRODUCTIVITY AT MOJAVE
TheMojave plant’s K6 line, operated by CalPortland Company (CPC), was built in the early 1980s and has been upgraded a number of times since then, but the plant was still operating the original raw mill – a non-FLSmidth brand VRM rated for about 250 stph. With cement demand running high in California, the plant was pushing the mill beyond its limits, but still not achieving the desired throughput – and experiencing reliability and quality issues as a result. CPC was ready to make the change.
Choosing the right supplier
When it came to choosing which raw mill would be the right fit for the plant, CPC went out to competitive bid for an EPC contract to supply and install a new grinding circuit.
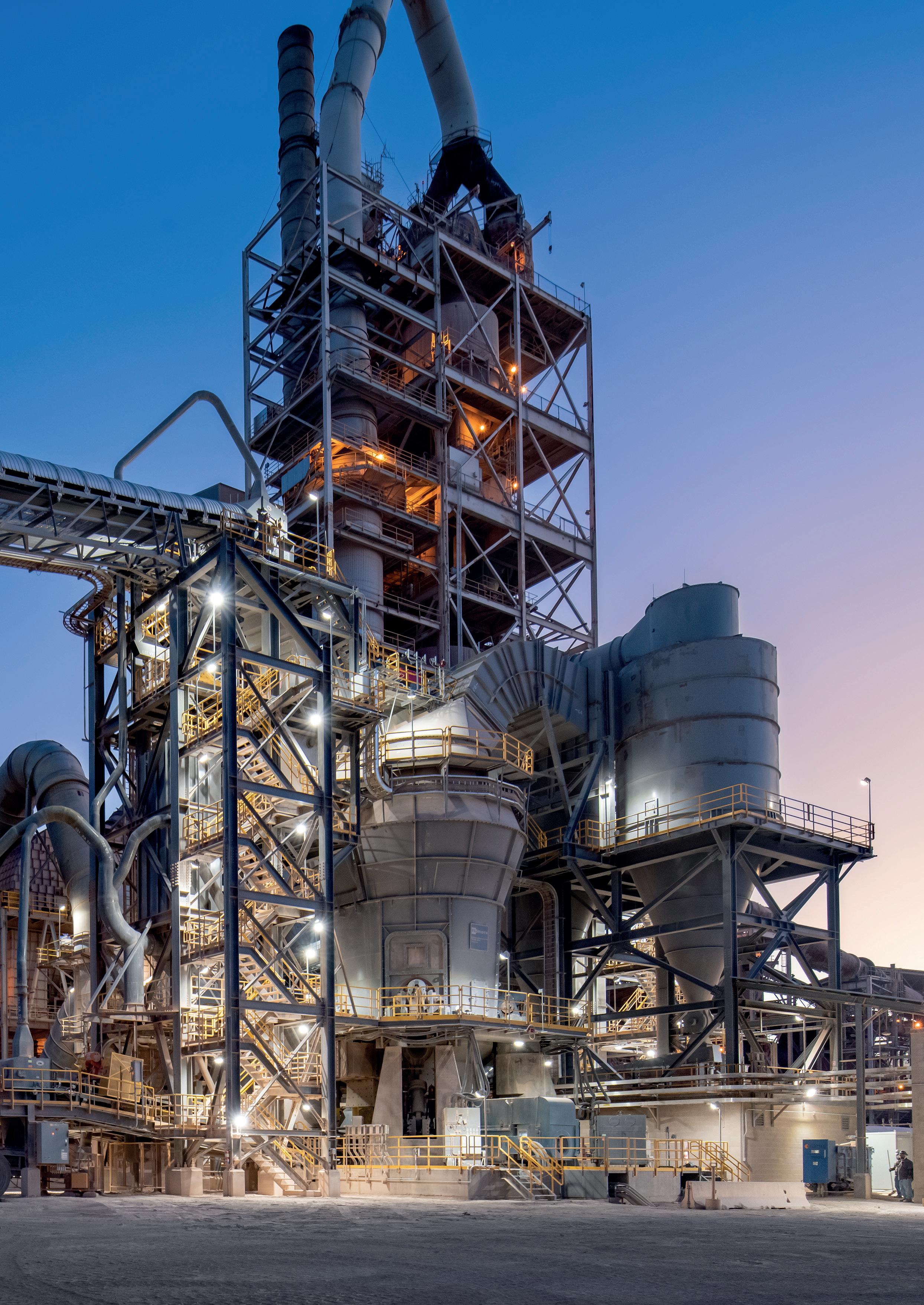
“We gave a basic design,” explains Alan Simmons, Director Electrical and Control Engineering, CPC. “It included some slightly novel concepts, based on our preferences and experiences. We found that some suppliers were more willing to accommodate our requests than others, and FLSmidth was one
of those that was willing to work with us on the engineering. We narrowed it down to several suppliers, but in the end FLSmidth came out on top. It was a question of the technical ability, the financial offering, and the fact that we were already operating an OK mill, which was a real advantage. For one thing, it gave us the economic benefits of common spare parts, but it also meant we were familiar with the workings of the mill and its control system.”
Commonality of spare parts is a major benefit for cement producers because it cuts their investment in half. In this case, the new mill was actually with an over-sized gearbox, just to ensure that commonality and provide CPC with these benefits.
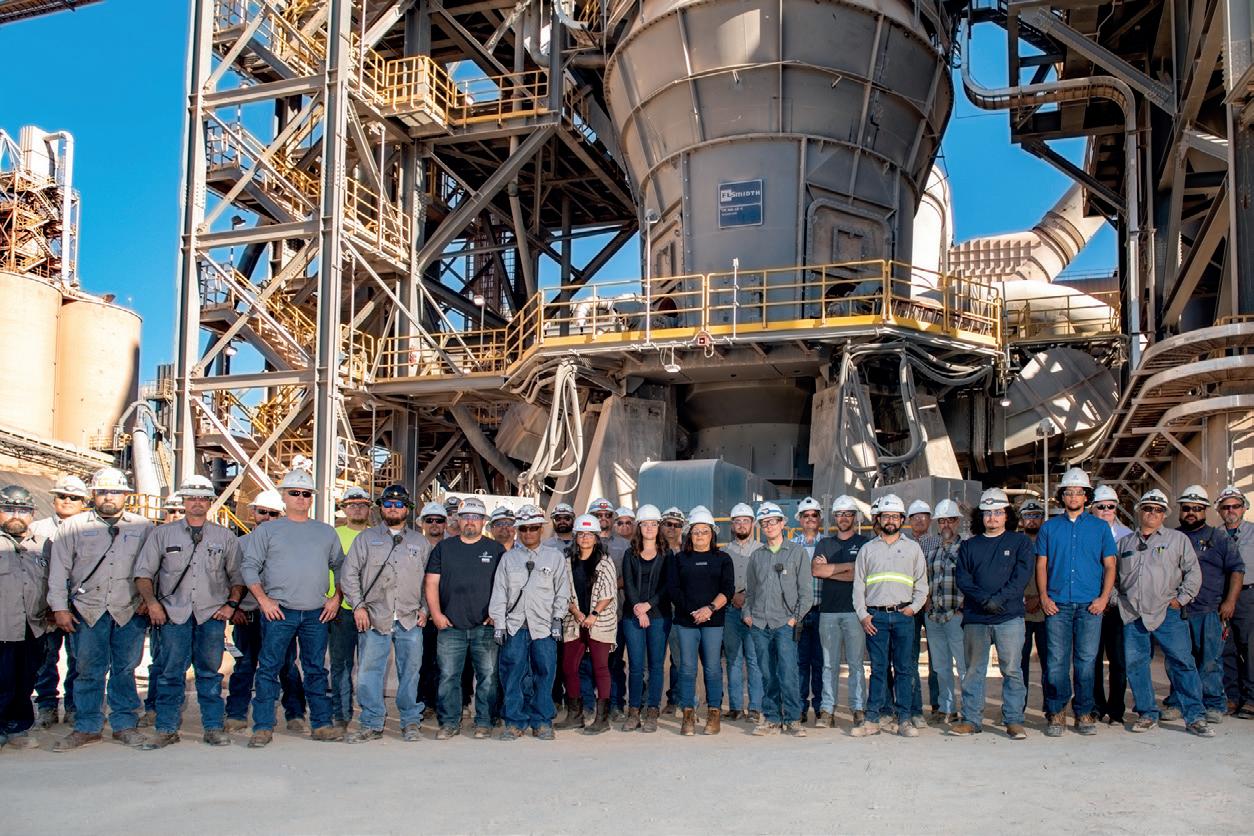
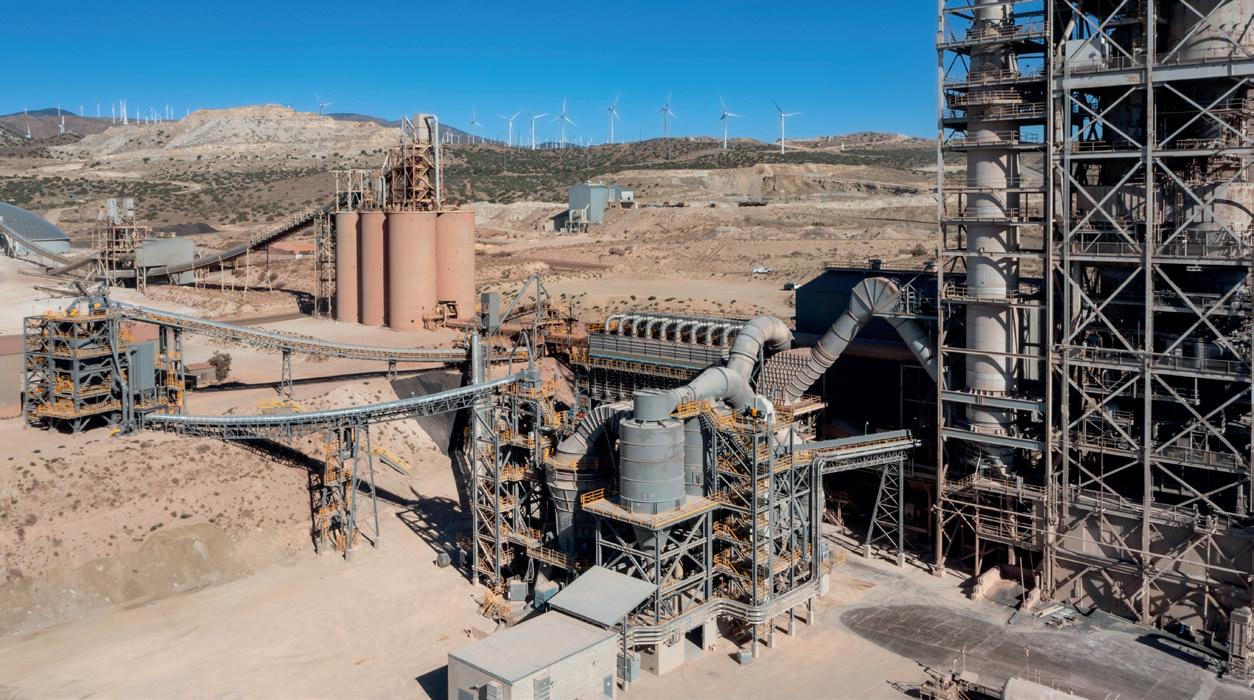
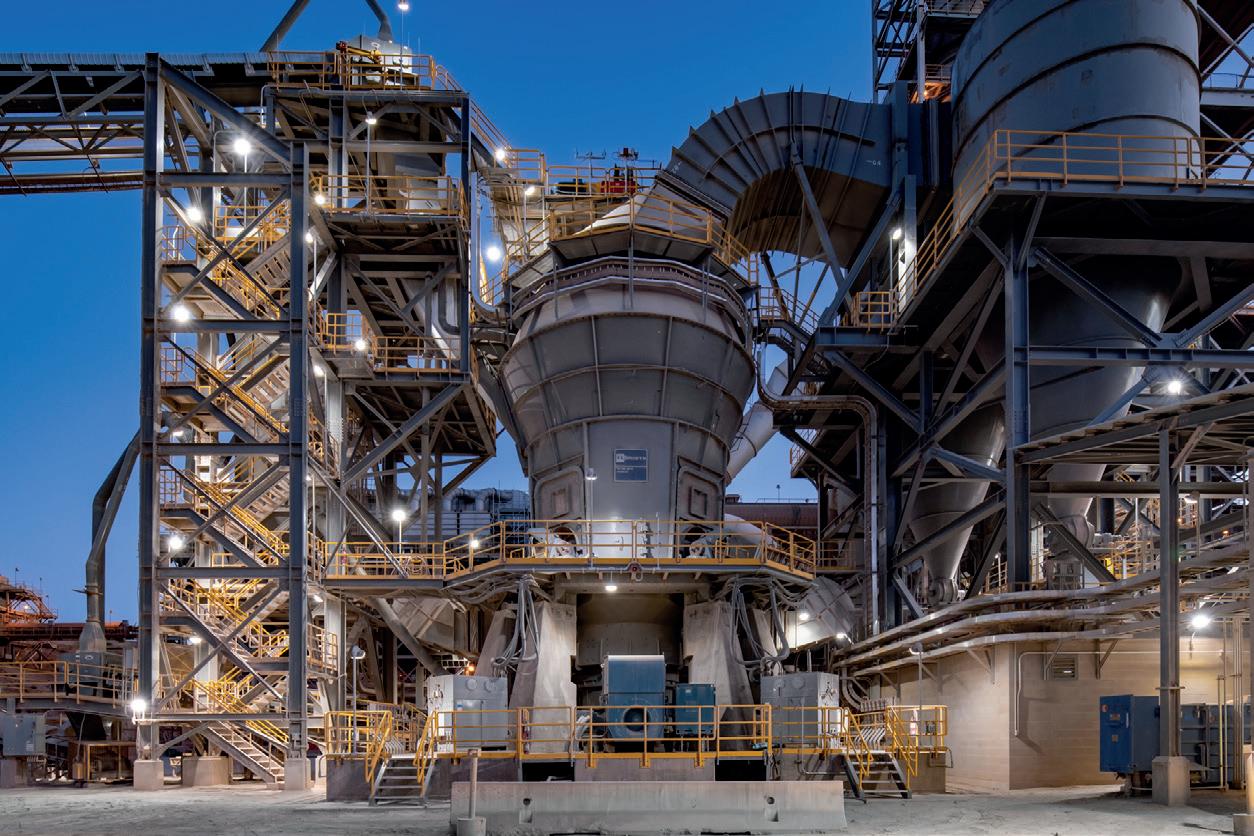
Optimising efficiency
“The old mill wasn’t just curtailing throughput,” says Alan, “it was also impeding our process efficiency. We wanted the new mill to enable us to overcome those challenges.
For example, because the old mill was running so hard, we couldn’t control the product fineness as much as we would have liked. Moreover, running the kiln below optimal feed rates was preventing us from achieving optimal fuel efficiency. The OK mill enables us to target product fineness to optimise efficiency. And by increasing capacity, we’re getting a better burn and less emissions per tonne.”
Another consideration that factored into CPC’s decision was the U.S. EPA’s NESHAP guidelines, which hold cement producers to extremely stringent emissions limits. The emphasis is on managing and measuring pollutants at the kiln stack, but 40-year-old kilns are not necessarily designed to operate in the manner required to control the emissions within the NESHAP limits. The new mill, however, can accommodate all the kiln gases through the mill system,
With cement demand running high in California, CPC was ready to upgrade to a new mill. The new mill started up in May 2022, delivering as promised.giving the plant more flexibility in managing emissions.
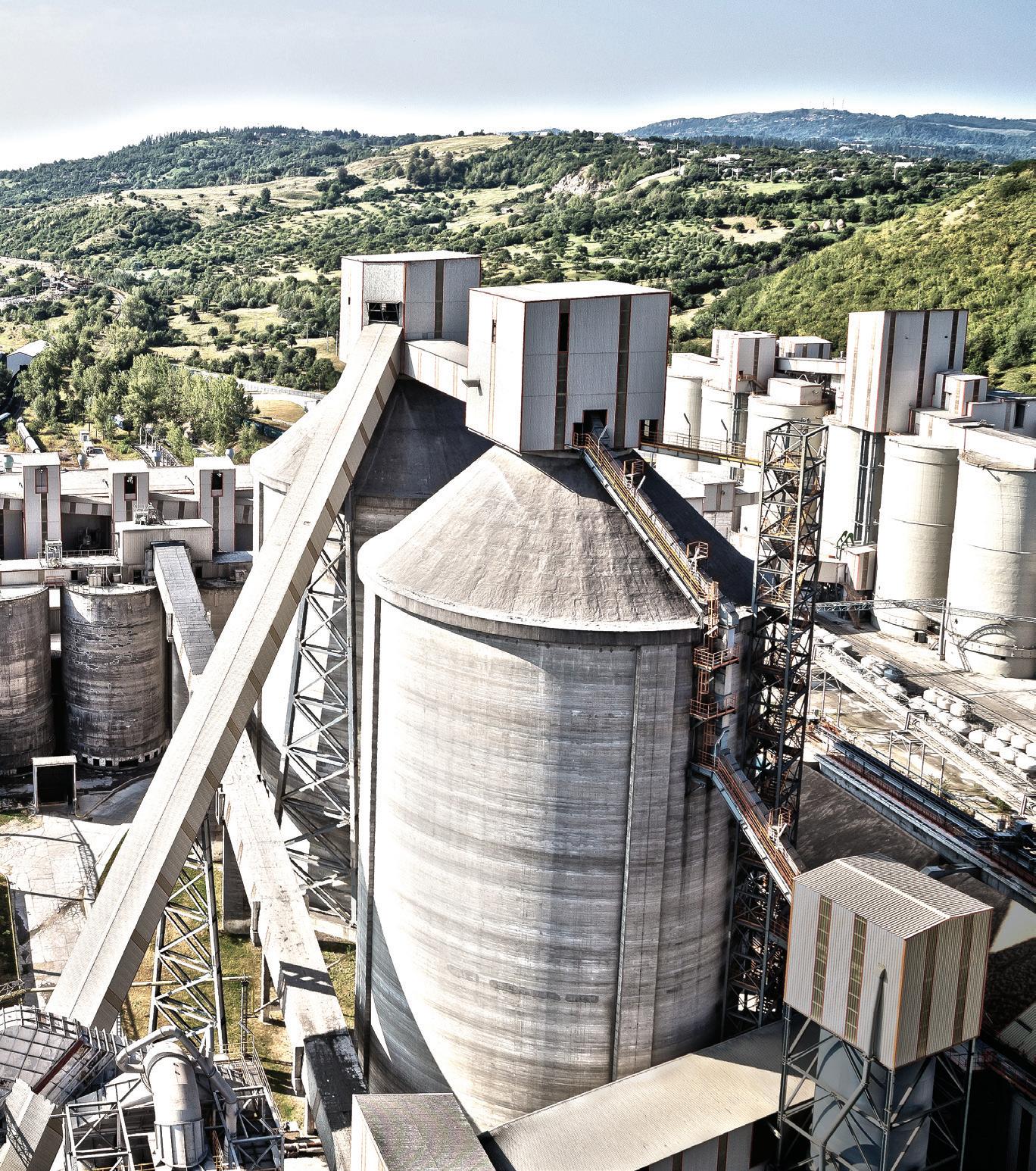
Commonality of experience
The existing OK mill was put in about 20 years ago and upgraded in 2018 with a new separator and ECS/ProcessExpert control system.
“The fact we were familiar with OK mill operations was a huge factor,” says Alan. “This knowledge doesn’t have a dollar value, but it is incredibly valuable – particularly as the two mills are on the same site. The OK mill has been updated in the last two decades and the raw mill operates a little differently to the cement mill, but having the existing expertise made the whole thing much easier. Our maintenance department is also very confident about what to look out for, what to expect, and how to manage it.
“The same goes for the control system. These systems can take a while to learn, so staying with the same technical solution was another advantage for the plant. We’ve seen a lot of benefits from implementing ECS/ProcessExpert on the original OK mill. It’s an important part of how we maintain and increase our process efficiency.”
Project planning versus COVID-19
The negotiations for the new raw grinding circuit concluded with the signing of the contract in May 2020.
“The world was in a state of uncertainty,” says Srinivasan Seshadri, Project Manager at FLSmidth. “But we were still thinking in terms of months of disruption, not years. We certainly didn’t expect COVID-19 to still be a problem when it came time to start work on site.”
Nevertheless, FLSmidth and CPC made the decision to get a head start ordering project supplies – a decision that paid dividends. By the time it came to shipping parts, the supply chain crisis had truly kicked in.
“There were logistical challenges from day one,” explains Srini. “Contract negotiations were carried out on Teams. We had to share huge files so that we could look over the 3D models together. It was a whole new way to collaborate, and it took a while for everyone to adjust, but we made it work. When it came to practical logistics – getting parts in from China, for example – we were faced with unprecedented demand, an almost total lack of shipping containers, port congestion, trucker shortages, etc. The logistics side of things was like a project all on its own.”
“On site, things were different too,” adds Alan. “The contractor had people working in bubbles. We worked to limit contact between the construction team and the CPC operations team. We also had to manage people’s time so
EXPERIENCE THAT TOWERS ABOVE THE REST
Experience
More than 35 years of tackling the most difficult silo cleanout projects in 30+ countries worldwide.
Safety
Professional service technicians are MSHA and OSHA-certified and adhere to a rigorous continuing education program.
Capability
We conquer the most difficult cleanout projects in the world with our proprietary silo cleaning technology.
that everyone was getting enough rest, and so that we coordinated people’s rest days so that the right people were on site at the right time. It was tough, but it was worth it.”
Everyone also had to adjust to the ‘new normal’ of extended lead times. Supplies that could previously be obtained within 24 hours were suddenly taking days or weeks to arrive.
“It was a mindset shift,” says Alan. “We did have a few long journeys to pick up supplies that FLSmidth or their sub-contractor hadn’t ordered in time, but for the most part we made it work.”
Fitting right in
Fitting an oversized gearbox underneath the new OK mill was a challenge. The mill rests on concrete piers, which had to be redesigned to accommodate the size of the gear box. Knowing that the gearbox would need to slide out for maintenance, FLSmidth decided that the gearbox should be slid into position to ensure it could be done.
“We’re talking about more than 100 metric tonnes of gearbox and a very tight fit, with just half an inch either side,” says Srini. “It would have been easier to drop the reducer in with a crane, but we needed to know it could be done. We didn’t want to hear in a few years’ time that the gearbox was stuck in place.”
Successful commissioning
Commissioning during Covid-19 could have been a catastrophe, but both FLSmidth and CPC teams are proud to say that the commissioning process went smoothly.
“For CPC, commissioning is a learning opportunity,” says Alan. “We set up a commissioning team to participate in the process, add value and learn from FLSmidth to ensure the mill not only got off to a great start, but would continue that way. It was a highly structured team, made up of a Commissioning Manager,
A more sustainable grinding circuit
discipline leads, and people under them. FLSmidth had the same structure and we collaborated very closely throughout.”
“We allocated more manpower for commissioning this mill because we were falling behind on electrical wiring and we saw efficient commissioning as a way to make up for lost time,” says Srini. “We had our commissioning people literally following behind the contractor, pushing them forward and checking everything as soon as we could. This gave us the edge when it came to commissioning.”
In fact, both teams began their commissioning checks before the outage. CPC’s commissioning team was initially assigned to go out and touch every single piece of equipment, ensuring not only that they knew where to find everything, but also that they would spot anything that might be incorrect or cause a delay.
“Because we had a large team on both sides, a number of the little issues that you often come up with – such as sensors not working – were addressed immediately,” says Alan. “By the time we got to wet commissioning, we knew everything was working, so the mill came up very smoothly.”
Within 7 or 8 days, the mill was running close to its guaranteed capacity of 400 stph. Having expected to wait several weeks before being able to increase kiln capacity, CPC soon found themselves with a full raw meal silo and were able to raise the kiln feed rate to optimise plant throughput.
“This was one of the most successful and trouble-free start-ups I’ve been involved with,” says Alan. “It went exactly as I’d hoped it would, which is a testament to how well the CalPortland and FLSmidth commissioning teams performed.”
Ready to face the future
CPC is pleased with the performance of the new mill, which started up in May 2022.
Increasing energy efficiency is one of CPC’s core goals, as it seek to reduce their environmental footprint. The OK mill uses 5 – 10% less power than other vertical roller mills, giving the plant an instant saving in energy consumption. Furthermore, the mill’s high run factor – typically 90 – 95% availability – means there are less starts and stops, therefore reducing the overall power demand. Greater stability in the mill benefits the rest of CPC’s process, enabling the whole line to be run at greater efficiency levels than previously.
In addition to the reduction in energy use, the other major environmental benefit of the new raw mill is its ability to have greater flexibility in the management of emissions and compliance with environmental standards.
“The mill is doing what it was promised to do, and we anticipate it will continue to serve us well into the future. We’ll be leaning on FLSmidth to help us get the most from the mill, I’m sure. They already give us a lot of support, and we value that partnership,” says Alan.
“CPC is at the cutting edge of cement production,” says Srini. “They’re really pushing the boundaries of what is possible in terms of energy efficiency. We’re happy to support them in their quest for optimisation, which aligns with FLSmidth’s own Mission Zero targets.”
of
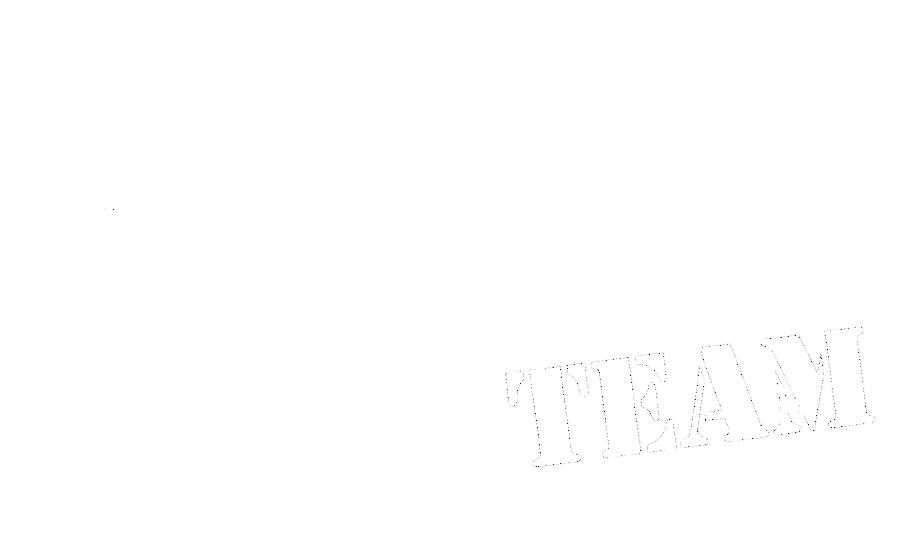
Seth »The
If you need a strong partner, simply hire “The Service Team”.
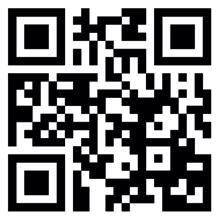
One of us is Seth Afari-Boateng. His super power is telepathy. That’s why he can understand even the slightest signals from his customers and interpret them correctly. This means he can identify all challenges in the shortest possible time and does everything to fix them. That makes him one of the most outstanding experts in our Service Team.
Are you responsible for cement plants and machinery? And do you place the highest demands on products and services? Then you should rely on a partner with more than 160 years of experience who always has a helping hand. This is exactly where we come in: The Service Team offers state-of-the-art technical solutions – from inspection and maintenance to the supply of innovative OEM spare parts. Meet us all: www.the-service-team.com
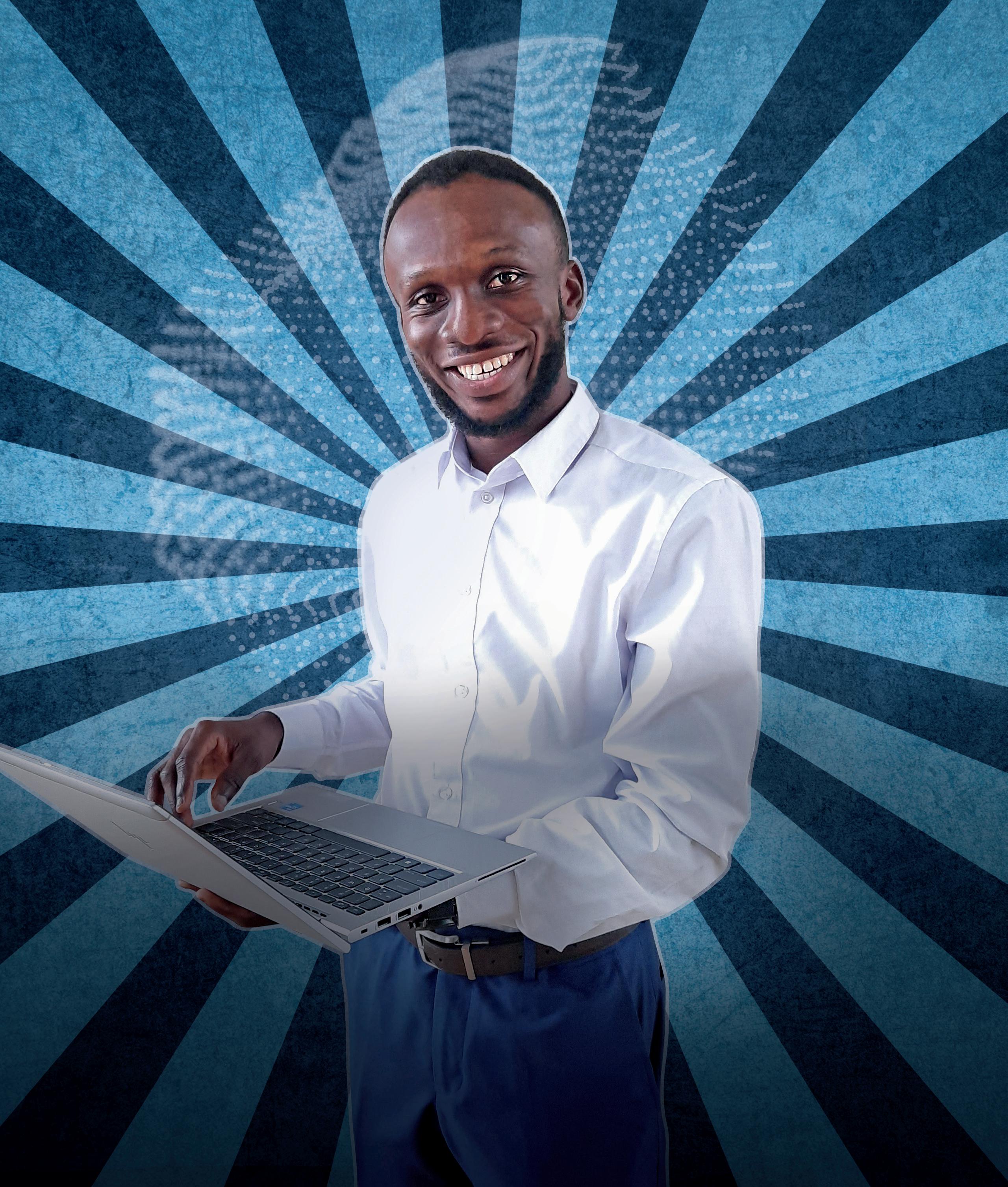
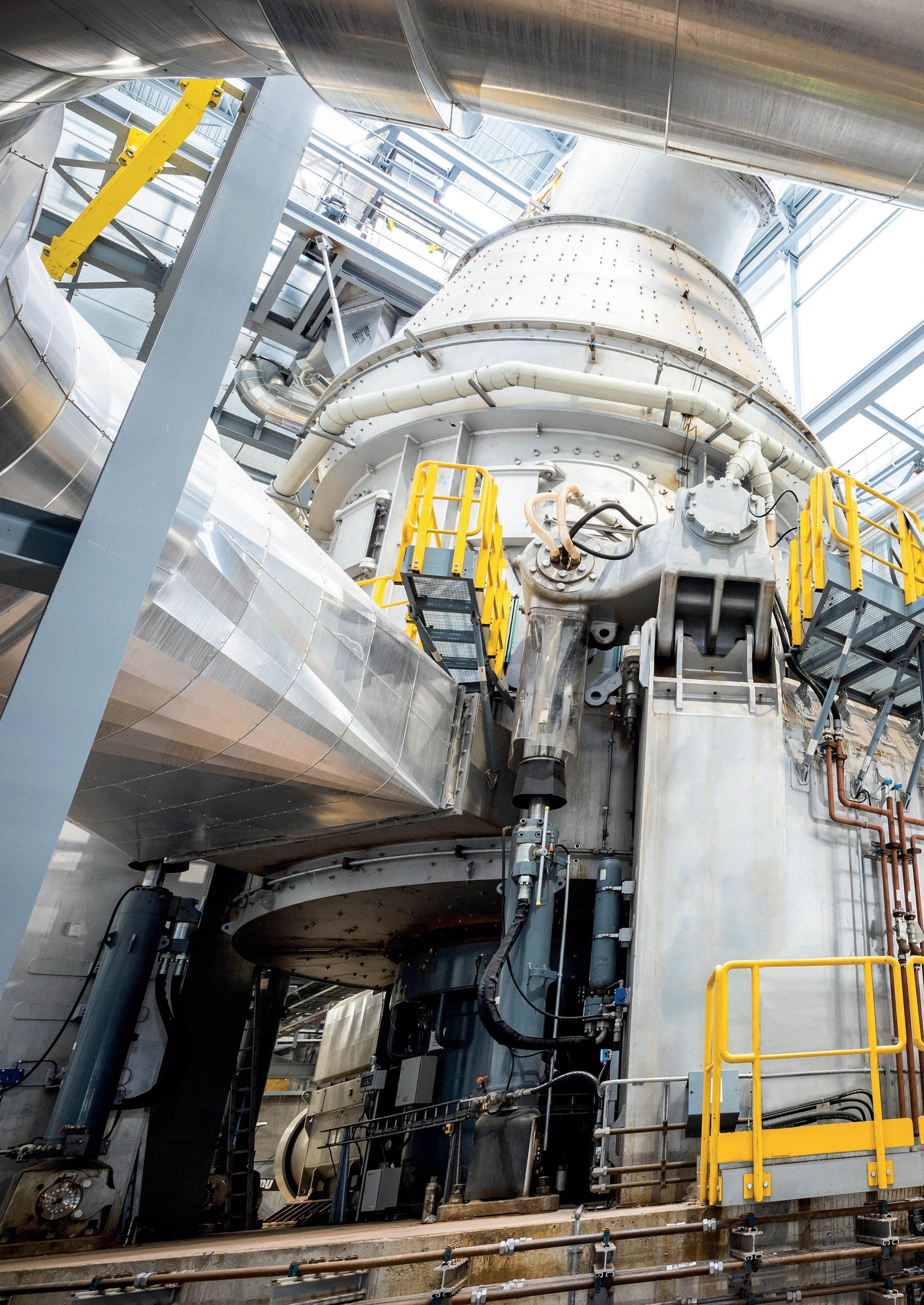
Spellbinding grinding improvements
Dr. Caroline Woywadt, Gebr. Pfeiffer, discusses the state of VRM technology in the cement industry, with SCM integration and digitalisation becoming essential features of modern production.
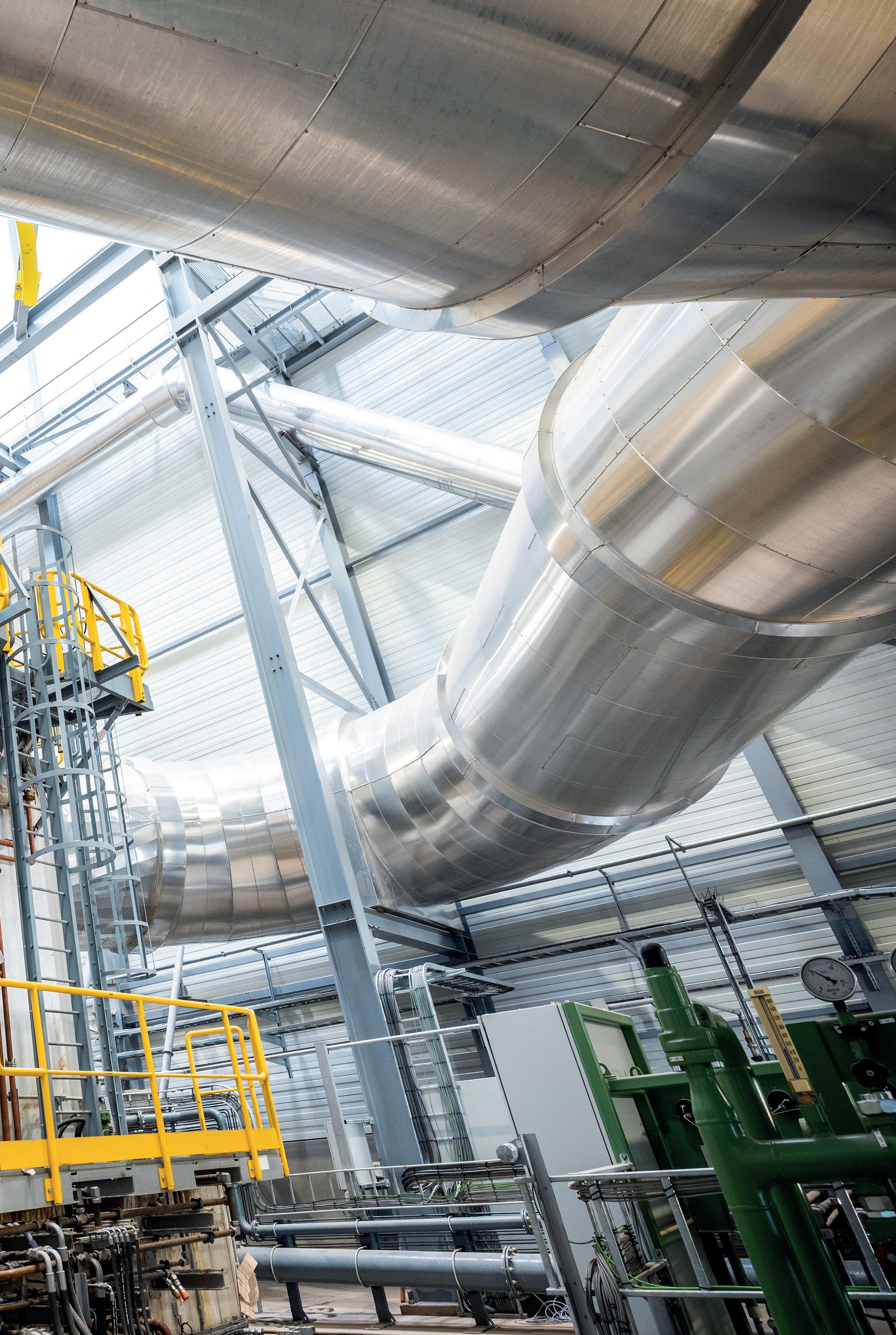
The cement industry is, like every other industry, driven by the best solutions providing efficiency, sustainability, and digitalisation. For the grinding of raw materials, solid fuels, and cements the vertical roller mill (VRM) system is one of the most energy efficient systems available. The combination of three process steps in one system – drying, grinding, separating – makes it very versatile in regard to handling dry and moist feed materials, and grinding these to very high fineness, creating the product properties required by the different market areas.
With the introduction of the MVR mill to the market in 2010 a new concept was available for very high throughput rates. By using a larger diameter, a larger contact area resulting from roller size and/or number of rollers, a faster rotational speed, and higher hydraulic force, the mill capacity can be increased.
Whereas the MPS mills for cement grinding and raw material grinding have been equipped with a power range between 500 kW up to 5400 kW resp. 6400 kW, the MVR mill covers a range of installed power between 60 kW and up to 11 700 kW.
With the MultiDrive ® there is sufficient scope to go up to 18 000 kW.
Performance
The performance of a vertical roller mill is defined by a required throughput at a required fineness paired with a low specific thermal and electric energy consumption. For cement grinding, the required product quality is the most important target together with the above-mentioned points. Some areas in general need special attention: feed uniformity, metal detection and extraction, and preventive maintenance to name just a few. The levers to pull for a well performing vertical roller mill are operational parameters such as table speed, gas flow, working pressure, and mechanical adjustments such as dam ring height and covering the nozzle ring.
The success of the VRM in cement grinding was determined by its production of the same or better cement quality. This can be traced back to not only adjusting to the same or similar Particle Size Distribution, but also to the adjustment of feed material properties (clinker C 3A) and especially sulfate agent proportioning.
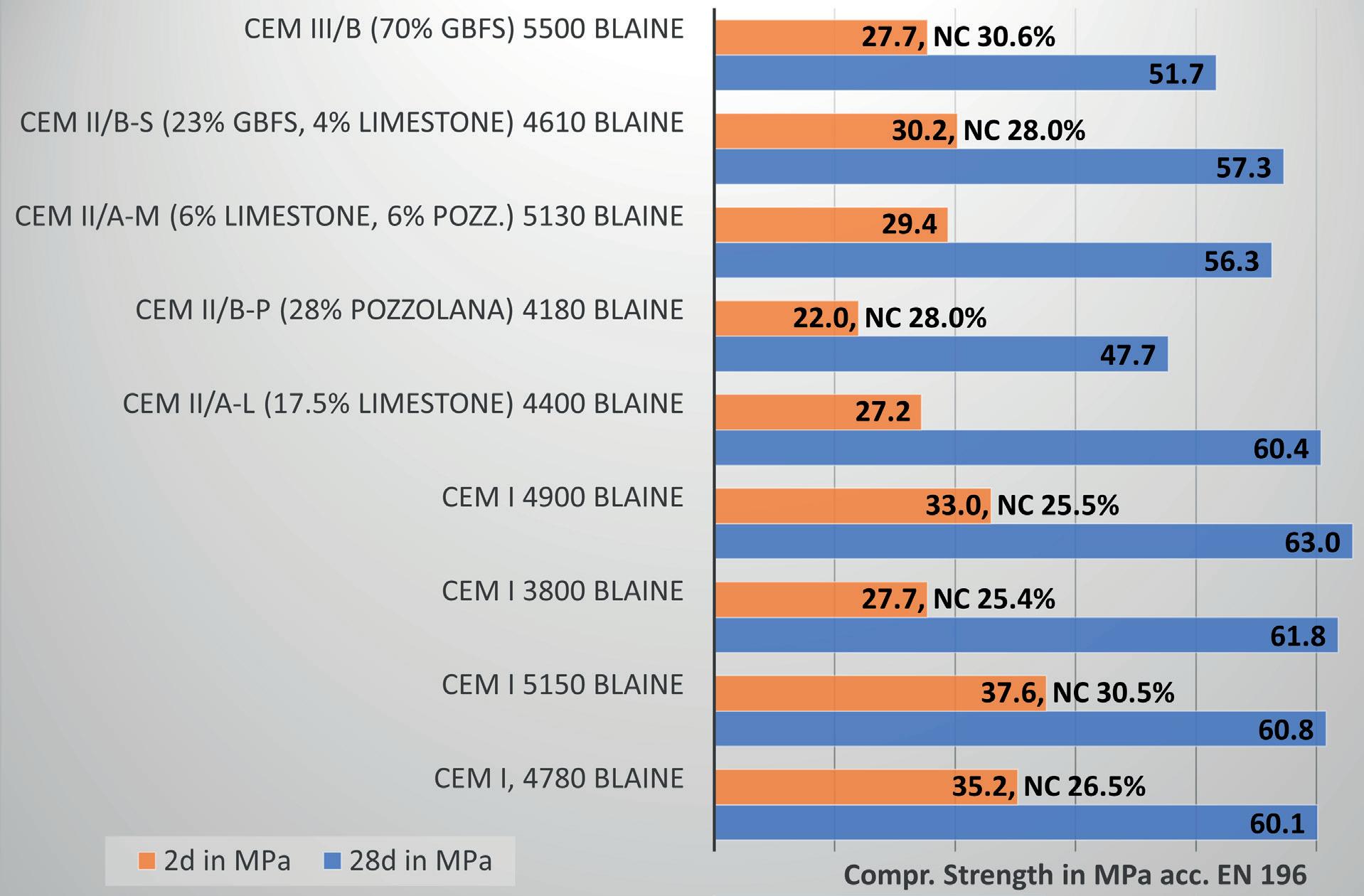
The sulfate agent needs a balanced proportion of di-hydrate, hemi-hydrate and anhydrite. As a VRM has a significantly higher energy efficiency than a ball mill, much less heat is put into the grinding process. As a result, the dehydration degree of the sulfate agent is lower. The lower hemi-hydrate or
plaster content can be compensated for by the addition of more gypsum (within the limit according to relevant standards), by the addition of a more reactive form of gypsum, or by the addition of more heat to the system. By installing the G4C ® system with a separate mill and hot gas generator to partially calcine the gypsum, the hemi-hydrate content can be controlled exactly for each clinker that is used. This is made possible by setting the outlet temperature of the mill to adjust the proportion of hemi-hydrate. This system is installed with an MVR 6000 C-6 in Australia and supports a tailor-made sulfate agent for the finished product.
An important factor in the characterisation of cement properties is strength development in combination with setting times. National standards define the procedure for testing. Due to differences in those standards, the results of compressive strength development are not comparable to each other.
Gebr. Pfeiffer has its own mortar laboratory and collects samples from the operation of MPS and MVR mills to characterise cement product properties. To ensure the reliability of results, the laboratory participates in annual round robin tests (ATIHL and BE CERT). Concerning the procedure for sample preparation, the proportions of cement, sand, and water are in accordance with EN 196-1. The properties of several cements produced in MPS and MVR mills are listed
Figure 1. Properties of cements produced in MVR mills.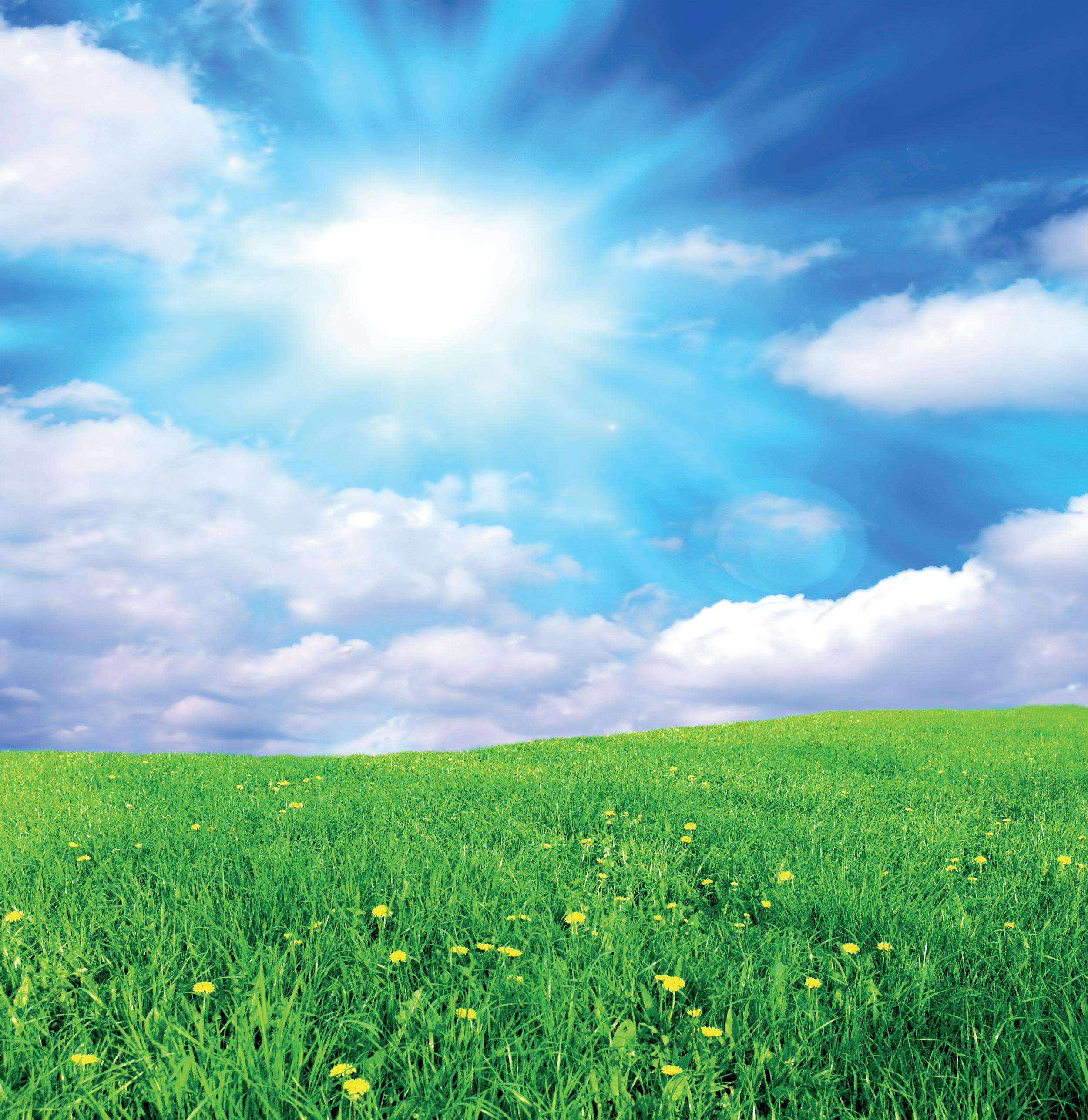
in Figure 1. Nearly all OPC/CEM I products have developed a 28-day strength of 60 MPa or higher. High 28-day strength figures are achieved as well with a product fineness less than 4000 cm 2 /g. Early strength after two days is clearly impacted by clinker quality and, for composite cements, the type of composite is an additional factor.
The composite cements achieve high 28-day strengths. Products need to be ground fine enough to enable composites to reach the required strength level. The given normal consistency (NC) figures have been determined in accordance with EN 196-3 and demonstrate that the workability of products from MVR mills meets the demands of industry. Custom adjustments have been made in many cases during the commissioning of MVR mills, for example: PSD adaptation, sulfate agent selection, or the use of the G4C system to get precise plaster-content. These results show that cements that are ground in vertical roller mills are clearly on the same level as cements ground in ball mills.
Supplementary cementitious materials (SCMs)
Supplementary cementitious materials (SCMs) or clinker replacement materials (CRMs) influence grindability, operational behaviour, and reactivity. SCMs have been used in the industry for many decades, and the amount of composite cements is still increasing considerably. SCMs can be artificial or natural. Artificial SCMs include, for example: fly ash, granulated blast furnace slag (GBFS), and silica fume. Examples of natural SCMs include: limestone, pozzolana, clay, etc. In many countries, limestone is the most easily available supplemental material. Limestone dilutes the clinker content of the cement and impacts its strength development. The hydraulic properties of natural pozzolana are advantageous for cement products, and so they are preferred if available. The definition of pozzolana includes any volcanic material, but it should be noted that it does not describe the specific origin of the material. 1 Therefore, the term ‘pozzolan’ also includes artificial supplementary materials, such as flyash, bottom ash, etc. The great majority of natural pozzolans is of volcanic origin. The global distribution of volcanic rocks can be compared with the occurrences of natural pozzolan deposits. But not all volcanic rocks are suitable as pozzolanic material. More siliceous magma produces more explosive volcanism with better pozzolanic properties. 2 The activity of some pozzolanas, for example phonolith, can be increased by thermal treatment.
By heating the material up to 300 – 500˚C, the crystal lattice expands and the surface area increases. Thereby supporting the formation of hydrate-phases. 3 The grindability of natural pozzolana varies widely. For achieving 5000 Blaine, for example, the time of exposure in the laboratory ball mill is between 30 – 80 min. (average 45 min.). This behaviour has to be taken into consideration for rating the industrial mill. Additionally, the reactivity of pozzolanas is very different and has a tremendous impact, in combination with the clinker, on the produced cement. Therefore, a fine adjustment of the feed material properties and the target fineness of the finished product needs to be done.
When it comes to composite cements, the versatility of MVR mills is impressive. These mills are very flexible for the grinding of different materials, such as: clinker, limestone, GBFS, pozzolana, fly ash, bottom ash, calcined clay, etc., with a wide range of properties. When moist materials are included in the feed mix, a heated rotary lock will be installed. When dry and already quite fine materials are included, an additional feeding point is provided at the classifier housing.
When producing composite cements the decision between inter- or separate-grinding is often under discussion. The MVR mill is able to switch from inter-grinding to separate grinding depending on the client’s needs without any changes to the mill’s internals.
Properties of, for example, GBFS and fly ash vary widely. In line with the required product properties it has to be taken into consideration that inter-grinding can result in finer fractions containing either very little or no GBFS or fly ash.
Depending on the reactivity of the GBFS, the mode of production can be achieved with inter-grinding as well with separate grinding of the single components. Operational experiences show that plants tend to grind clinker and GBFS together if GBFS is available with a good reactivity. One advantage of inter-grinding is the formation of a stable grinding bed due to clinker and GBFS granulometries which interact positively. If the GBFS needs to be ground to a high fineness due to lower reactivity the separate grinding might be a better way to achieve the overall required properties of slag cements. MVR mills are operated in both ways.
As cement is the most widely consumed building product in the world, a huge volume is produced. Cement production is responsible for about 8% of man-made CO 2 -emissions. 4 The International Energy Agency (IEA) has highlighted four principle
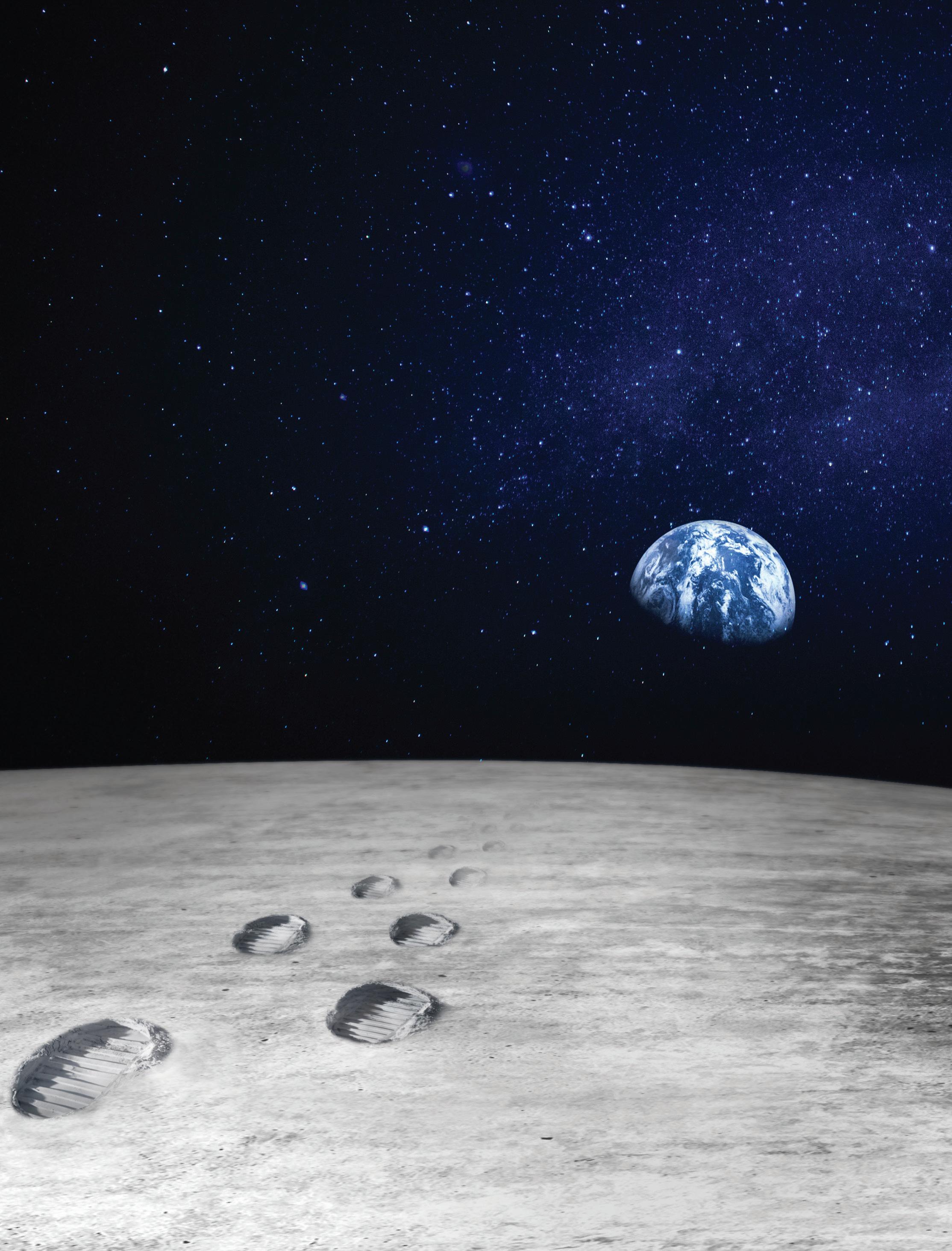
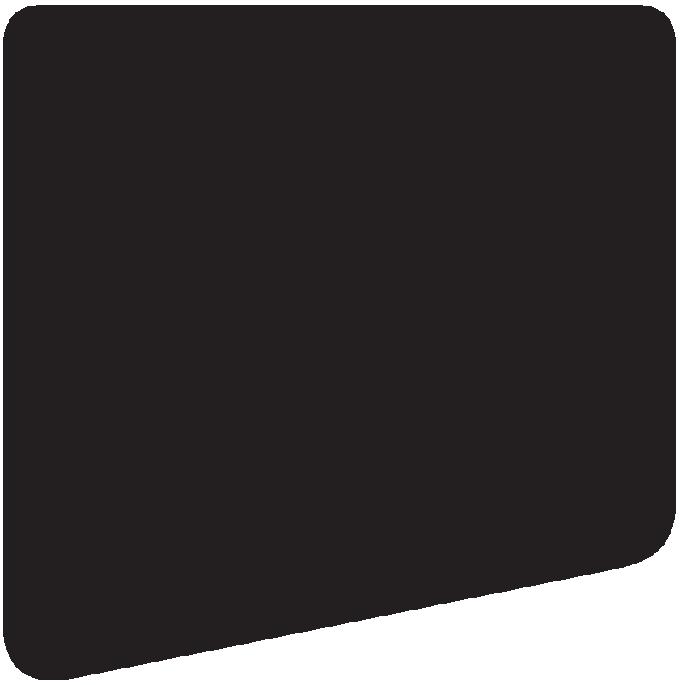
CO 2 reduction levers. Key strategies to cut carbon emissions in cement production include improving energy efficiency, switching to lower-carbon fuels, promoting material efficiency (to reduce the clinker-to-cement ratio and total demand) and advancing process and technology innovations such as CCS. 5 Reducing the clinker proportion in cement is said to be by far the most effective measure.
The use of SCMs to replace clinker in cement is only part of the picture but gives a good indication in order to evaluate the effectiveness of composite cements regarding their carbon footprint.
For the evaluation of energy use and CO 2 emissions, the proportion of SCMs has to be considered, but also likewise does the product fineness of the composite cement, as it is impacted by the reactivity of the SCM in use. As not all SCMs give a sufficient reactivity at lower Blaine, the product fineness overall has to be increased under certain conditions.
Calcined clays are one promising material for future applications as SCMs. The number of industrial production sites is increasing, but information available on the impact of grinding on its properties is currently limited. The process of grinding has significant effect on the reactivity and performance of SCMs, 6, 7 but specific procedures for the grinding of calcined clays have not yet been established. 8 Several influences originating from the grinding of calcined clays are known based on laboratory tests. Mineralogical composition especially of common clays (e.g. content of clays and quartz) will impact the particle size distribution and may lead to an enrichment of calcined clay particles in the finer fraction, but the quartz will also promote a deagglomeration effect. 9, 10 The fineness of calcined clays can significantly affect compressive strength of concretes made with blended cements. 11, 12
Table 1 shows a comparison of specific energy consumption and wear characteristics for CEM I, ground granulated blast furnace
slag (GGBFS) and different calcined clays. The results of the calcined clays are based on grinding tests conducted in the pilot plant in the test centre of Gebr. Pfeiffer. 13
The reactivity (determined by R3-Test and solubility of Si and Al ions) depends on product fineness and grinding parameters. Increasing the fineness of the material from 7600 – 12 500 cm 2 /g results in 15% better reactivity.
The activity index, determined as compressive strength according to DIN EN 196, reaches up to 90% for mixtures with a replacement level of 40 wt.-% calcined clay after 28 days. 13
Digitalisation
Industry 4.0 is also a driver for clients to cover operational support. This feature is offered as digital ‘modules’ where Gebr. Pfeiffer focuses on the maintenance and enhancement of operations at the moment. One of these digital modules is GPlink which stores sensor data for data analysis and enables 24/7 access to data from mobile devices. When transmitted to the company’s service team a solid basis for support and rapid and targeted assistance is given.
GPpro facilitates the Advanced Maintenance System with scheduled maintenance and is adapted for actual needs. This system includes a wider range of sensors as well as data analysis tools and reports partly with the help of artificial intelligence. Reacting on the changing requirements this product is developed further. The modular structure offers functions in the areas of e.g. preventative maintenance, protection of the mill, reduction of water consumption. The module ‘dynamic water injection’ enables the control of the injected water depending on vibrations in combination with working pressure and resulting bed height.
Outlook
The
of a vertical
by
throughput
EFFICIENT SIZING SOLUTIONS
For over 40 years MMD technology has been heavily involved in processing a wide range of raw materials used in cement production.
The MMD Twin Shaft Mineral Sizer™ ensures minimal fines generation and a well-shaped product, enabling your downstream processes operate more efficiently. Whether it’s primary, secondary or tertiary crushing, we have a range of machines, tooth designs and options to suit almost any material – from wet and sticky clays to soft chalks, hard dry limestone and everything in between.
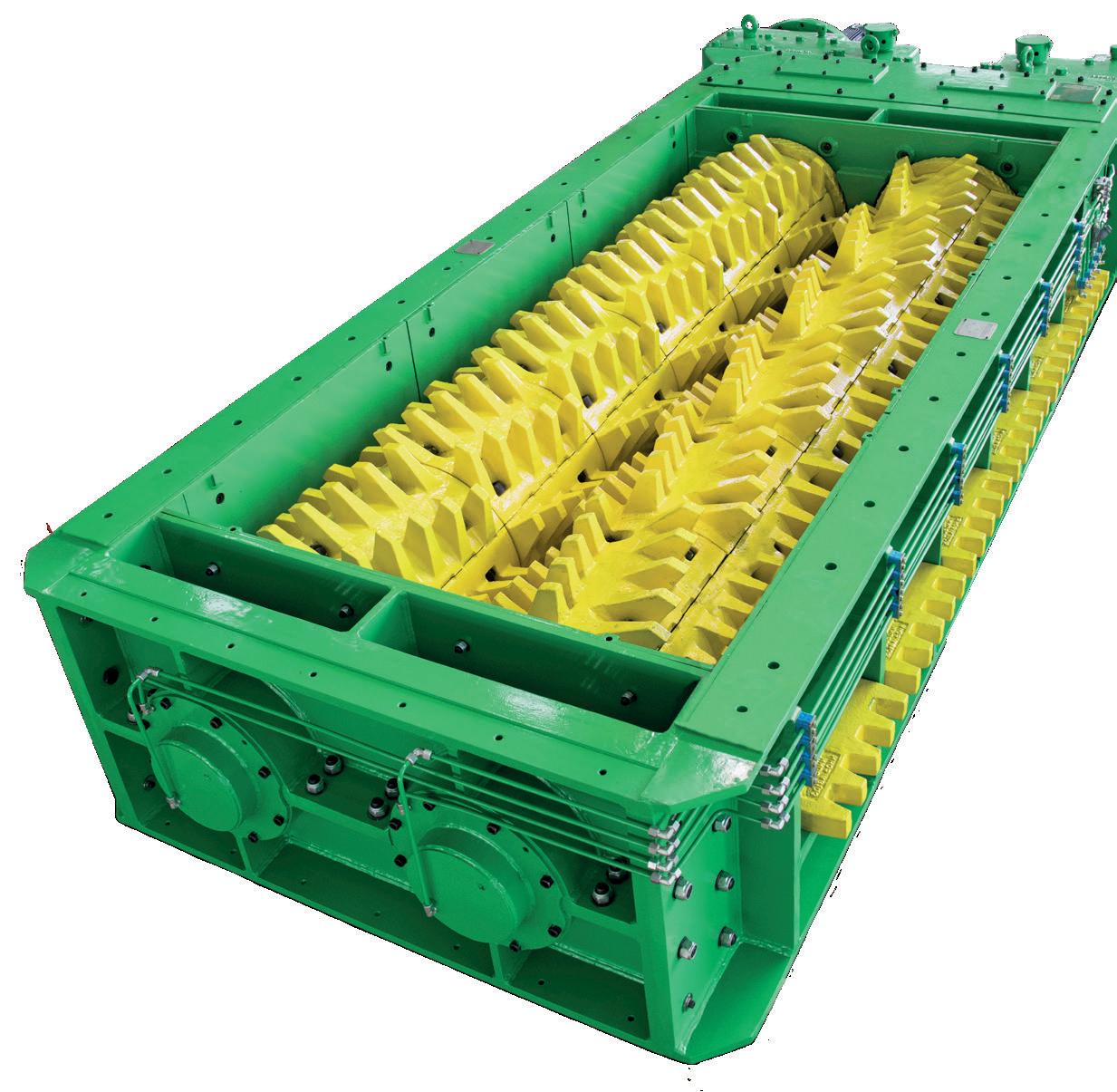
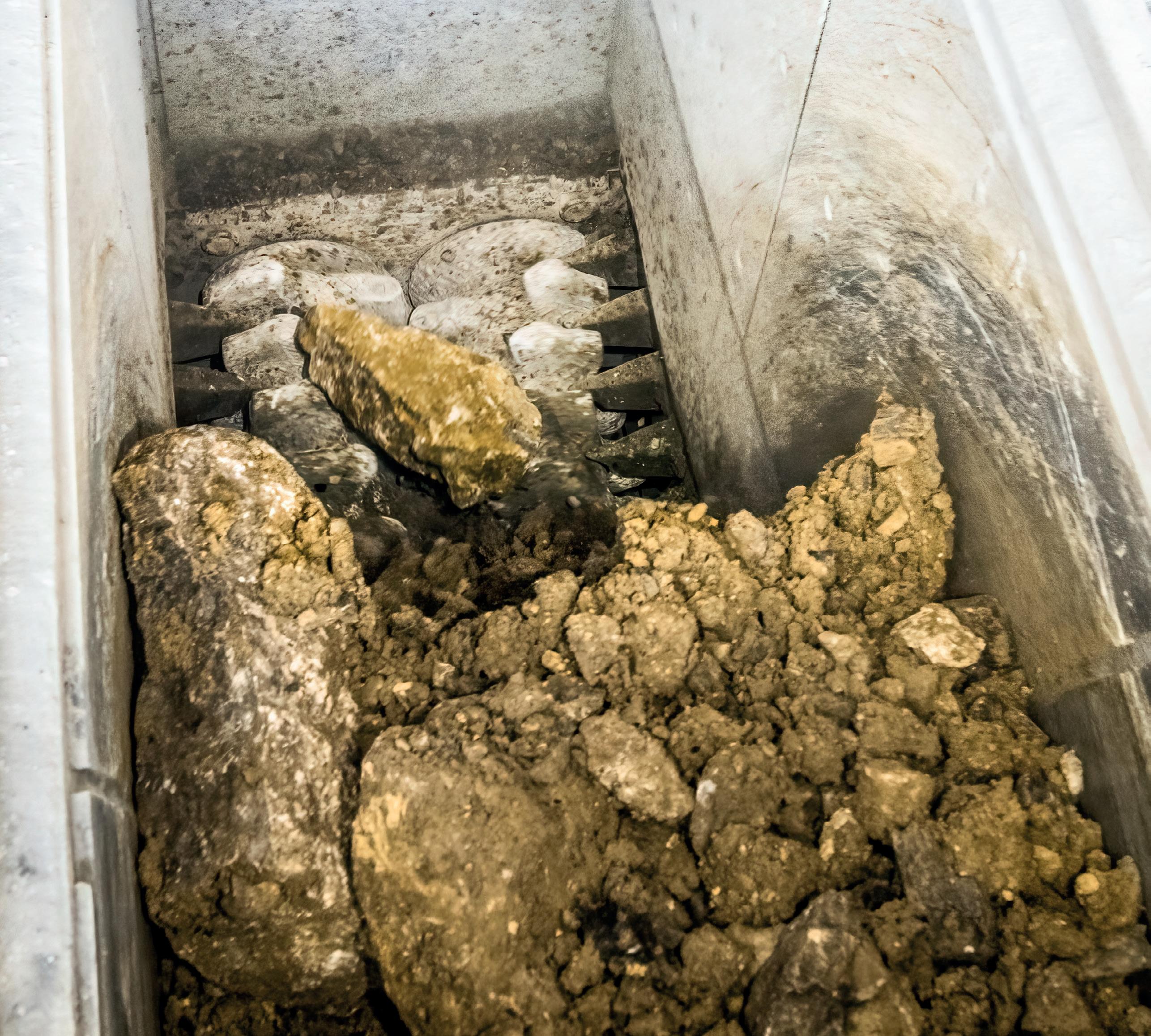
Working closely with our customers we have engineered numerous sizing solutions, enabling operations to maximise production, improve safety and reduce environmental impact.
Our worldwide support, technical expertise and service excellence will ensure your system continues to deliver optimum performance.
Lower costs and increase energy efficiency with our tailored Sizer solutions
fineness paired with a low specific thermal and electric energy consumption. Some areas in general need special attention: feed uniformity, metal detection and extraction, and preventive maintenance, to name just a few. Operational parameters such as table speed, gas flow, working pressure, and mechanical adjustments as dam ring height and covering the nozzle ring are the levers to adjust for a well performing vertical roller mill that is efficient in terms of electric and thermal energy. Support during commissioning in regard to the setting of operational parameters, reduction of stoppages and stable and smooth operation is very important. In addition to setting the operational parameters and the GPpro or GPlink system, supplementary features as ‘feed material detection’ and ‘optimisation by AI’ can help to achieve a well performing mill where energy efficiency is ensured. First trials with both features have shown very promising results and will be implemented in the future.
Not only is the use of SCMs an effective measure to reduce the carbon footprint, improving energy efficiency is also a key factor for grinding plants.
In cement production more than 60% of electricity is used for the grinding of raw materials and cement. With this huge amount it seems mandatory that energy efficient technologies should be used.
State-of-the-art grinding technologies such as vertical roller mills can provide up to 70% electricity savings compared to ball mill systems. Other electricity saving strategies include cross-cutting measures such as upgraded cement process controls and the use of variable speed drives to run mechanical equipment across the site.
This applies in particular for the main drive of the vertical roller mill and the main fan. The use of efficient grinding and milling technologies decreases the global electricity intensity of cement by 14% by 2050 compared to 2014 in the 2DS.14
The GPpro system has helped during the pandemic to bring plants into operation, where commissioning was assisted from a distance with online meetings. By providing additional images and footage from the plant sites the support could be targeted to specific topics.
All of the features described, such as the design and the wide range of duties of the MVR mill, the flexibility when using clinker replacement materials, the performance for cement grinding, and the overall innovative approach provide a very flexible system for the industry that is reliable to support decreasing the carbon footprint of plants.
References
1. CLARK, M., “Pozzolana is the key”, ICR (November 2017), pp. 48 – 49.
2. SNELLINGS, R., MERTENS, G., & ELSEN, J., ‘Supplementary Cementitious Materials’, Reviews in Mineralogy and Geochemistry, 74 (2012), pp. 211 – 278.
3. KASSAUTZKI, M., ‘Phonolith als puzzolanischer Zumahlstoff in der Zementindustrie’, ZKG (1983), pp. 688 – 692.
4. SCRIVENER, K., DEKEUKELARE, A., et al., ‘Financial Attractiveness of LC3’ – https://lc3.ch/financialattractiveness-of-lc3
5. IEA, Tracking Report Cement, November 2021 –https://www.iea.org/reports/cement
6. RAMANATHAN, S., et al., ‘Mechanically activated mine tailings for use as supplementary cementitious materials’, RILEM Technical Letters, 2021. 6: pp. 61 – 69.
7. GMÜR, R., K.-C. THIENEL, and N. BEUNTNER, ‘Influence of aging conditions upon the properties of calcined clay and its performance as supplementary cementitious material’, Cement and Concrete Composites, 2016. 72: p. 114 – 124.
8. HANEIN, T., et al., ‘Clay calcination technology: stateof-the-art review by the RILEM TC 282-CCL’, Materials and Structures, 2022. 55(3): p. 15.
9. SPOSITO, R., et al., ‘Physical and mineralogical properties of calcined common clays as SCM and their impact on flow resistance and demand for superplasticizer’, Cement and Concrete Research, 2022. 154(106743).
10. IRASSAR, E.F., et al., ‘Calcined illite-chlorite shale as supplementary cementing material: Thermal treatment, grinding, color and pozzolanic activity’, Applied Clay Science, 2019. 179: p. 105-143.
11. FERREIRO, S., HERFORT, D., and DAMTOFT J.S., ‘Effect of raw clay type, fineness, water-to-cement ratio and fly ash addition on workability and strength performance of calcined clay – Limestone Portland cements’, Cement and Concrete Research, 2017. 101: pp. 1 – 12.
12. VIZCAÍNO ANDRÉS, L.M., et al., ‘Effect of fineness in clinker-calcined clays-limestone cements’, Advances in Cement Research, 2015. 27(9): pp. 546 – 556.
13. WOYWADT, C., BEUNTNER, N., WAIBL, P., THIENEL, K.-C., GILLES, J., ‘Grinding of calcined clay in vertical roller mills – impact on reactivity’, Proceedings CCSC 2022 Lausanne: pp. 76 – 77.
14. ‘WBCSD, Technology Roadmap: Low-Carbon Transition in the Cement Industry 2018’ – https://www. wbcsd.org/Sector-Projects/Cement-SustainabilityInitiative/Resources/Technology-Roadmap-Low-CarbonTransition-in-the-Cement-Industry
About the author
Dr. Caroline Woywadt has been Director of Process Technology at Gebr. Pfeiffer since 2011.
After graduating from RWTH Aachen having studied Mineral Processing and obtaining her PhD in the field of grinding, she has worked as process and quality control manager at cement grinding plants in Germany and Poland and as the product manager for grinding products.
She is responsible for process technology and process development, pilot plants, and material characterisation. She is involved in projects and sales and plant optimisation.
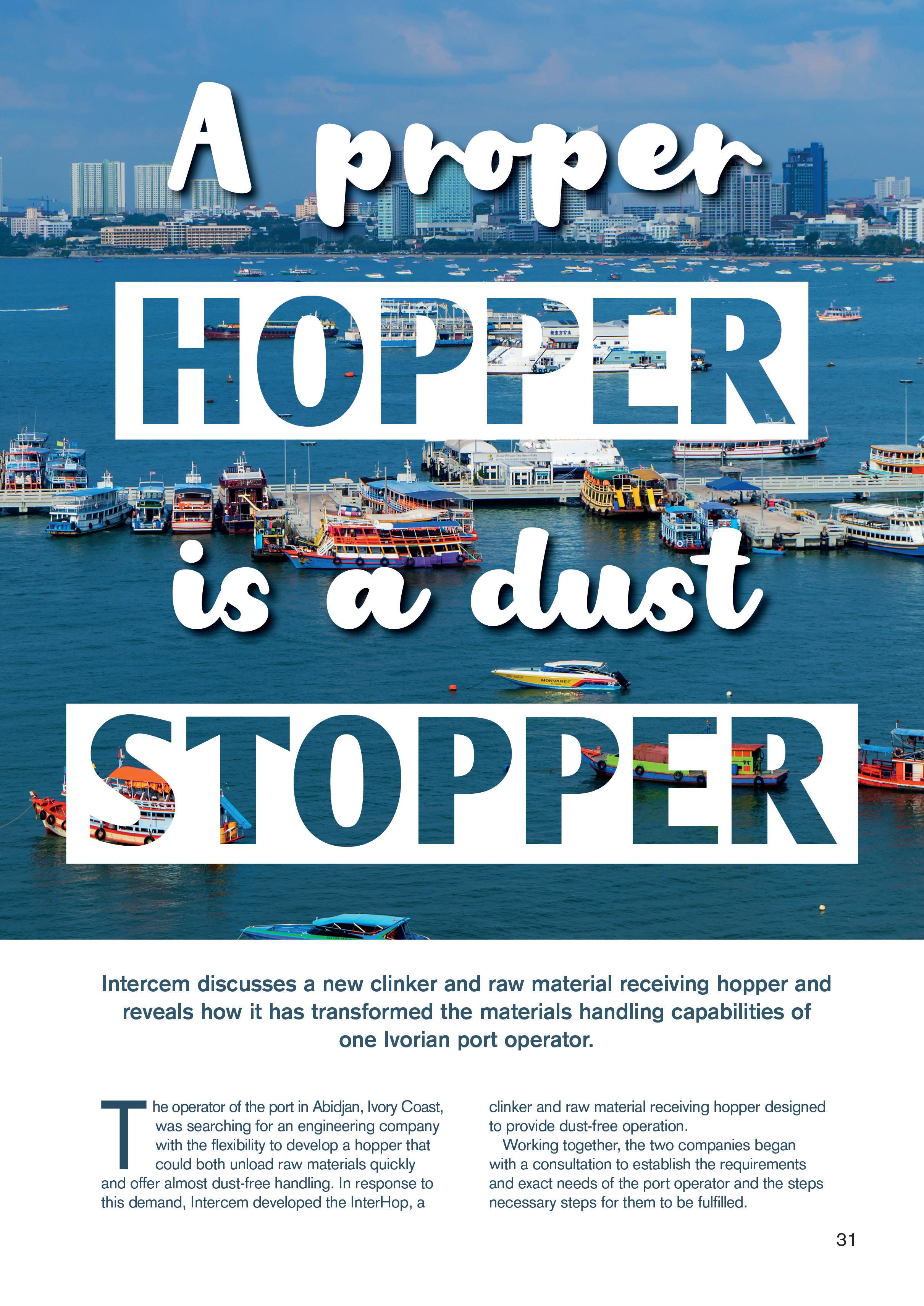
Without such a development, the import of clinker and raw materials for cement production might have been slowed down, and the further industrialisation of the country could have been severely inhibited or even stopped altogether.
The dust on the roofs of the warehouses in the port of Abidjan, combined with moisture and rain, had accumulated to such an extent that the permissible load-bearing capacity of the roofs was exceeded. This led to the collapse of a warehouse roof, which resulted in it being out of action for several months, as well as posing a hazard to the staff who were present. In order to avoid such dangers in the future, it was important to develop a hopper that enabled dust-free operation.
Construction of the hopper was undertaken in the UAE under the supervision of Intercem staff.
When finished, the hopper was loaded onto a heavy-duty transport truck and driven from the construction yard to the jetty in the port, after successful trial runs were executed at the point of manufacture.
Loaded onto a special heavy load transport vessel, the hopper was transported from the UAE to the port of Abidjan, Ivory Coast.
After commissioning the InterHop, the expected results were immediately achieved and the port operator has already ordered a second InterHop clinker and raw material receiving hopper.
Technical data
The InterHop is designed to allow for 40 t of material to be unloaded in 10 sec. Truck loading is possible as well as direct feed via belt conveyor to a clinker and raw material silo. With a flexible design, the Interhop is a tailor-made solution developed according to the client’s requirements.
f Low dust emissions during the bulk ship unloading progress with a gantry crane/shovel.
f Low dust emissions during truck loading or transfer with a belt conveyor.
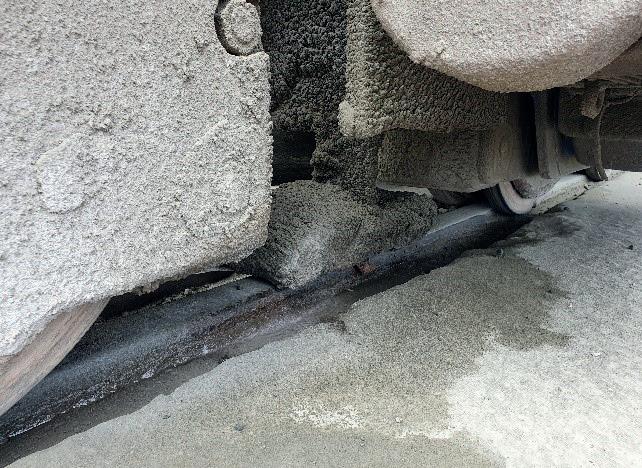
f Rapid loading process for trucks.
f High speed belt conveyor loading.
f Strong and long-life hopper design.
f Flexible hopper height in case of a new hopper position.
The grab intake has a diameter of 9.00 m and an intake opening at the top. The inlet (grate size) is 6.50 x 6.50 m and the height of the inlet (grate size) is 15 m. The overall dimensions (with walkways) are
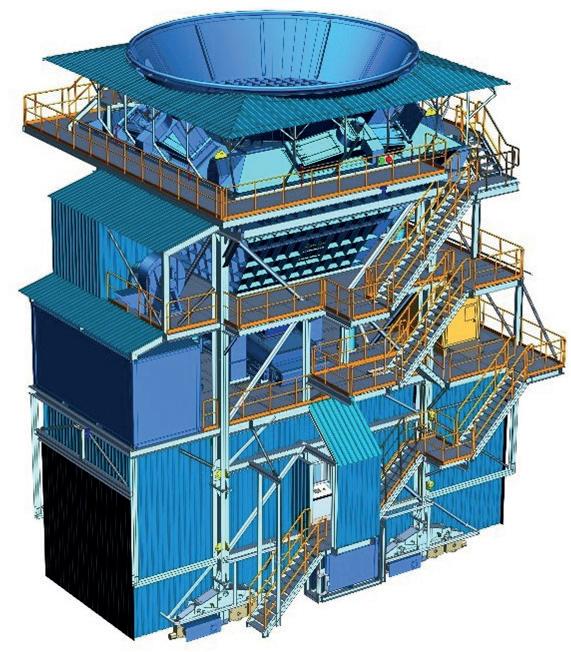
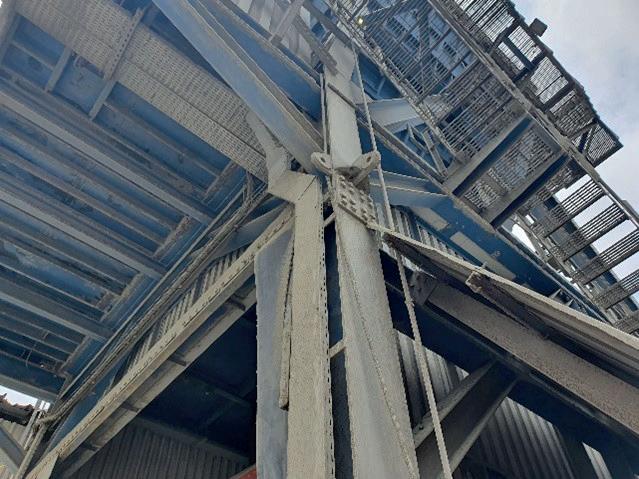
10.00 x 17.80 m. The hopper has a capacity of 65 m 3 with a density of 1.2 – 1.4 kg/dm 3 and its weight is approximately 205 000 kg.
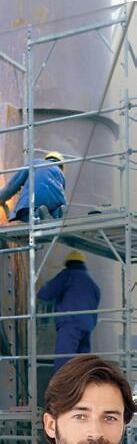

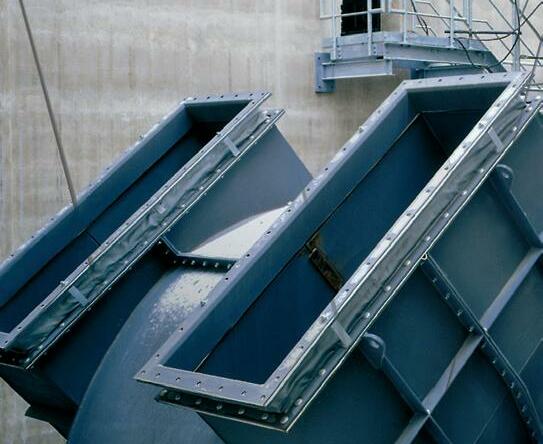

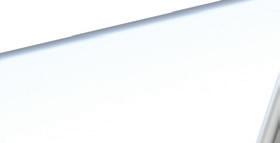
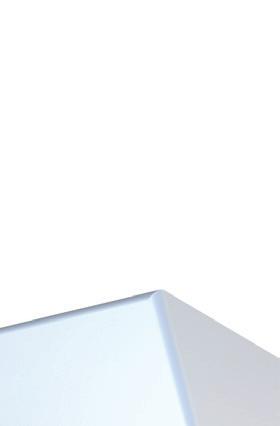
Serving the market
Intercem’s main market is Africa, which often lacks infrastructure in many areas. Environmental protection is not yet a top priority and is severely neglected in the ports. Due to the high demand for clinker and raw materials for cement production, the entire port is covered with dust. In order to advance industrialisation whilst limiting the pollution of the environment, environmental protection measures were necessary.
The clinker and raw material receiving hoppers used up to this point did not meet the requirements. This resulted in such a high level of dust in the port of Abidjan that the environmental authorities there and the port administration pressed for measures to reduce dust. The port operator, a client of Intercem, operates more than 25 ports in Africa alone. As Intercem was already known from previous projects (including the San-Pedro dust-free ship unloading station), it was approached to take on this problem.
The company’s experienced and trained specialist engineers took on the project and developed a solution that enabled the dust-free handling of raw materials – here the focus is on clinker with a very high fines content (unloading capacity in Abidjan approximately 8 million tpy).
Due to the high level of dust, which made other traffic almost impossible, the port authorities even decided to temporarily stop and interrupt port handling with raw materials for cement production (clinker). This was a disaster, of course, because the port of Abidjan is the country’s main traffic vein. All bulk raw materials arrive here. Cement is a key indicator of the health of the economy. Without cement there is no development or industrialisation. Therefore, it was of fundamental importance for the customer to find a solution to the dust problem as quickly as possible. The fact that the customer has already ordered a second hopper shows that the development of the InterHop has been successful.
Previously, clinker and raw material receiving hoppers had the disadvantage that large amounts of dust were released during filling, covering the entire port. As such, the goal was to develop a hopper that can be loaded dust-free and that can also be used to load trucks or conveyor belts without releasing dust.
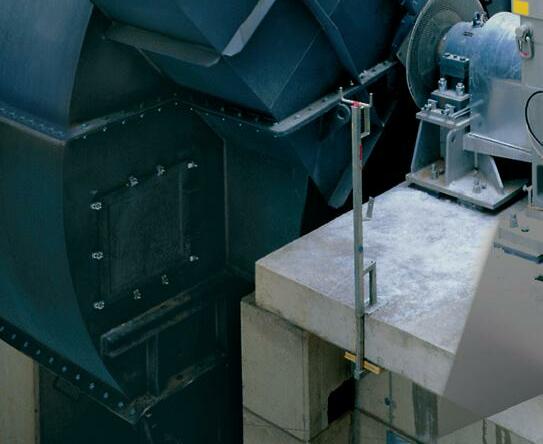
To achieve this, Intercem brought together different technologies and used only the latest available technologies (LTA). Only European products with the highest quality standards
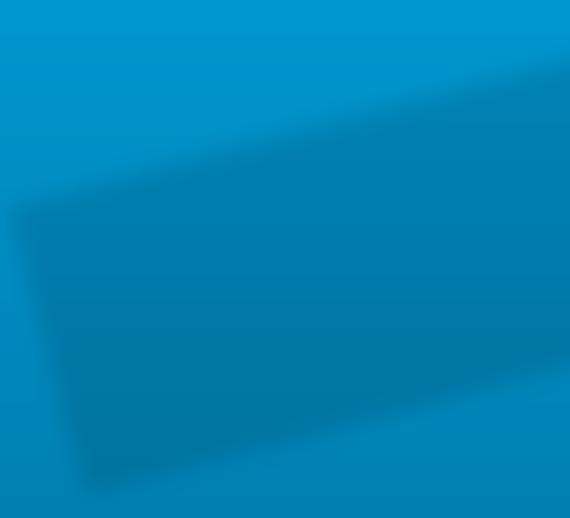


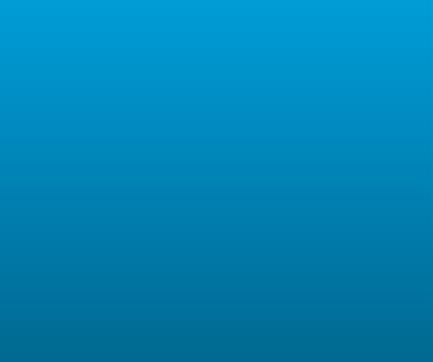

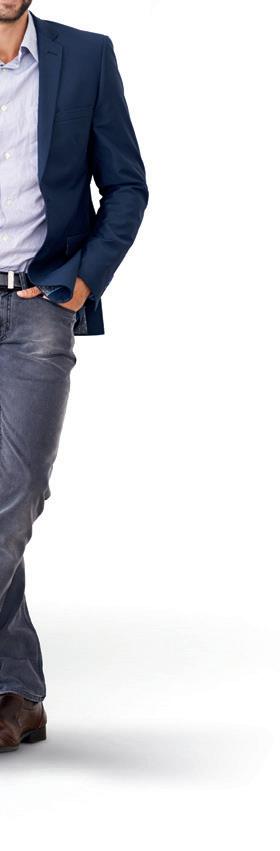
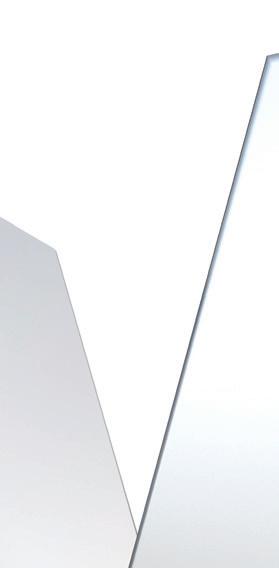
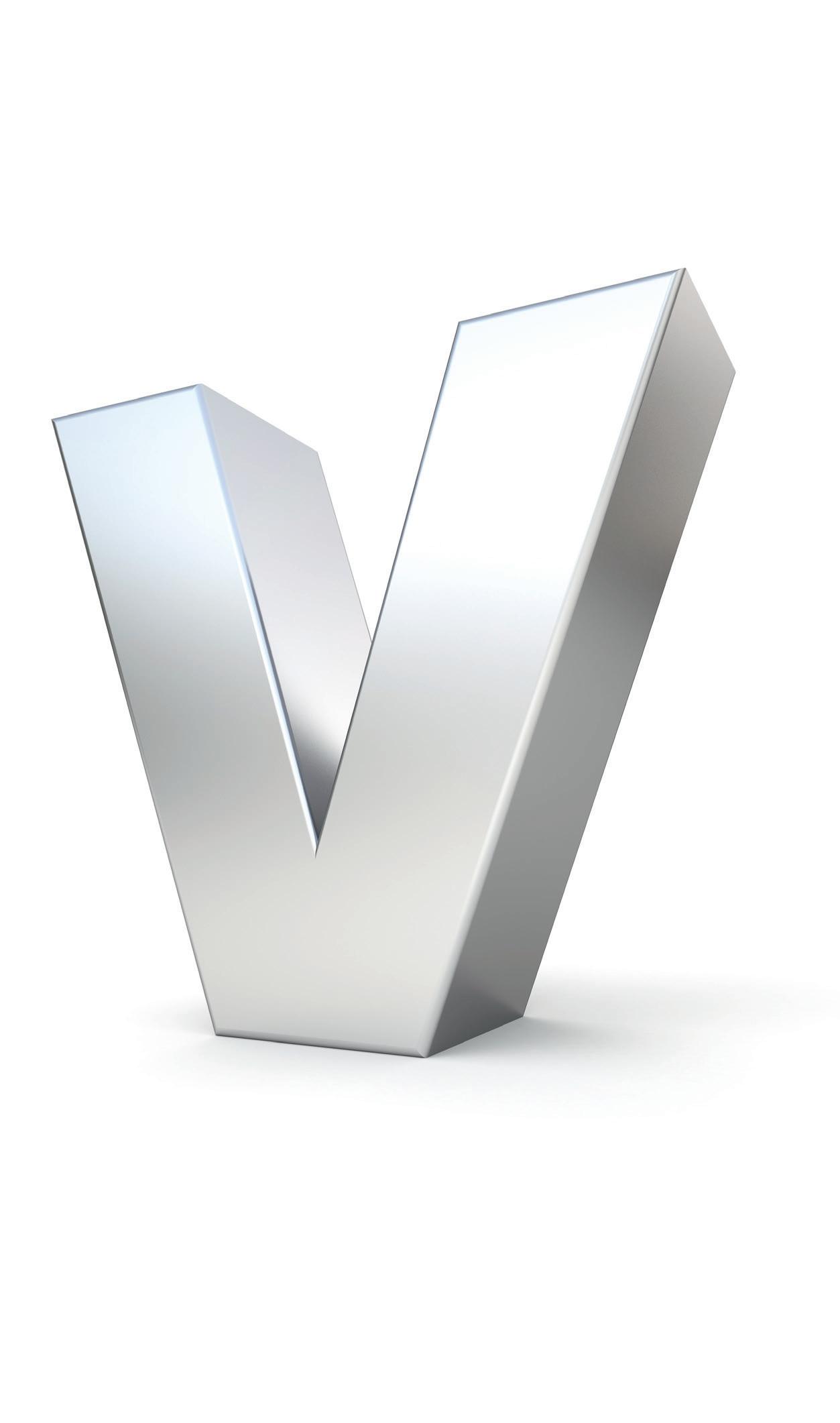
We save energy and improve efficiency.





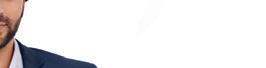
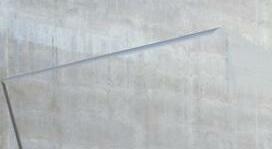


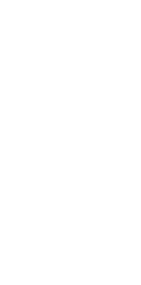
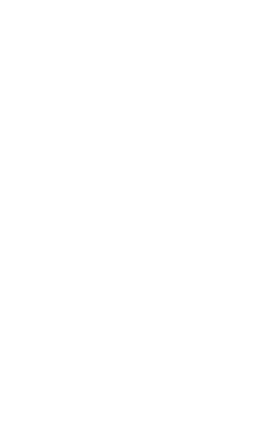



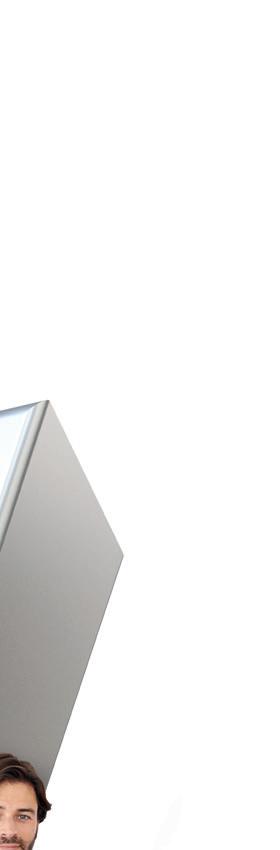
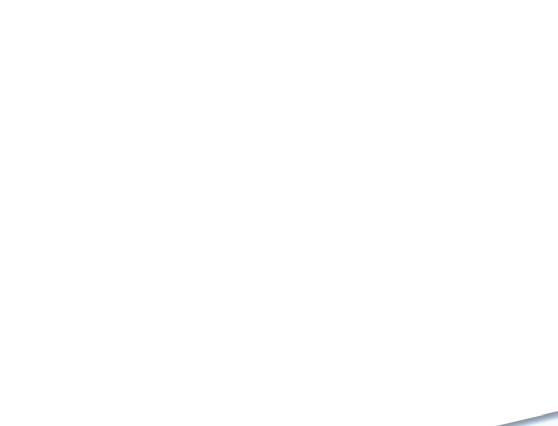
system check
cost effectiveness
were used. These included filter technology, automation technology and compressors, through the use of which Intercem was able to achieve the goal of dust- and trouble-free operation and low maintenance. Besides being dust-free, the last two points are particularly important in order to cope with the harsh conditions in bulk handling. In addition to this, a generator is installed to allow independent operation without a grid connection. The grid
connection was installed for temporary operation between the moves inside the harbour.
The company’s engineers stay informed on the latest available technologies and, in cooperation with the component suppliers, put together the most modern technologies and carried out a fluidic investigation of the overall concept with special consideration of the filter technology. The collaboration brought together R&D from all parties and achieved the desired result.
Annual bulk volume flows (cement, clinker, limestone, gypsum) worldwide amounted to 261 million t in 2019 and increased by 6 million t in 2020 (Figure 7).
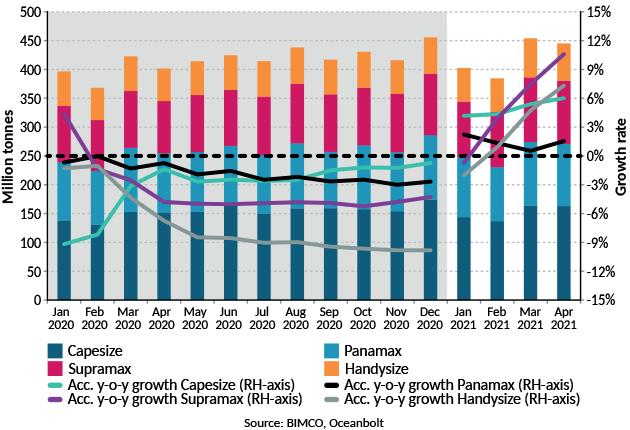
The advantages of dust-free hoppers are obvious. On the one hand, they are environmentally friendly and, on the other hand, they contribute to saving energy, as the use of the latest filter technologies reduces the drive power of the ventilators and thus lowers the specific energy requirement.
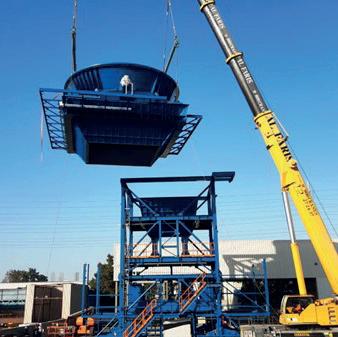
Additional application possibilities
In addition to ports, the InterHop Hopper can also be used for train and truck unloading stations. Such unloading stations are primarily integrated into Intercem’s overall projects (cement plants), but separate use is also possible.
Figure 3. Construction in UAE. Figure 4. Global Dry Bulk demand 2020 – 2021.1made possible by the

Combustion Device
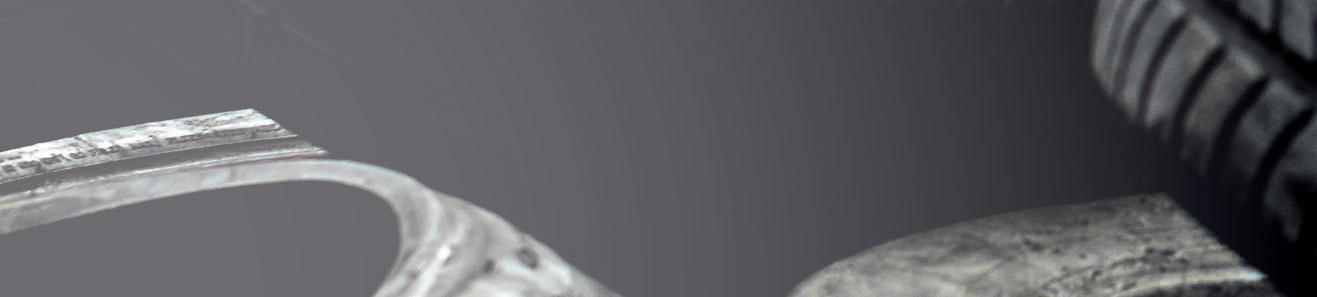
MissionZero it our pledge to enable you on your journey towards zero environmental impact from cement production. The HOTDISC® Combustion Device is the best way to substitute calciner fuel with a wide range of coarse alternative fuels – letting you use everything from sludge to whole truck tyres.
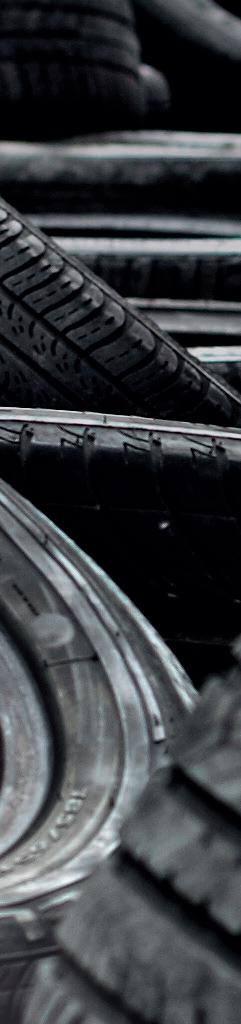
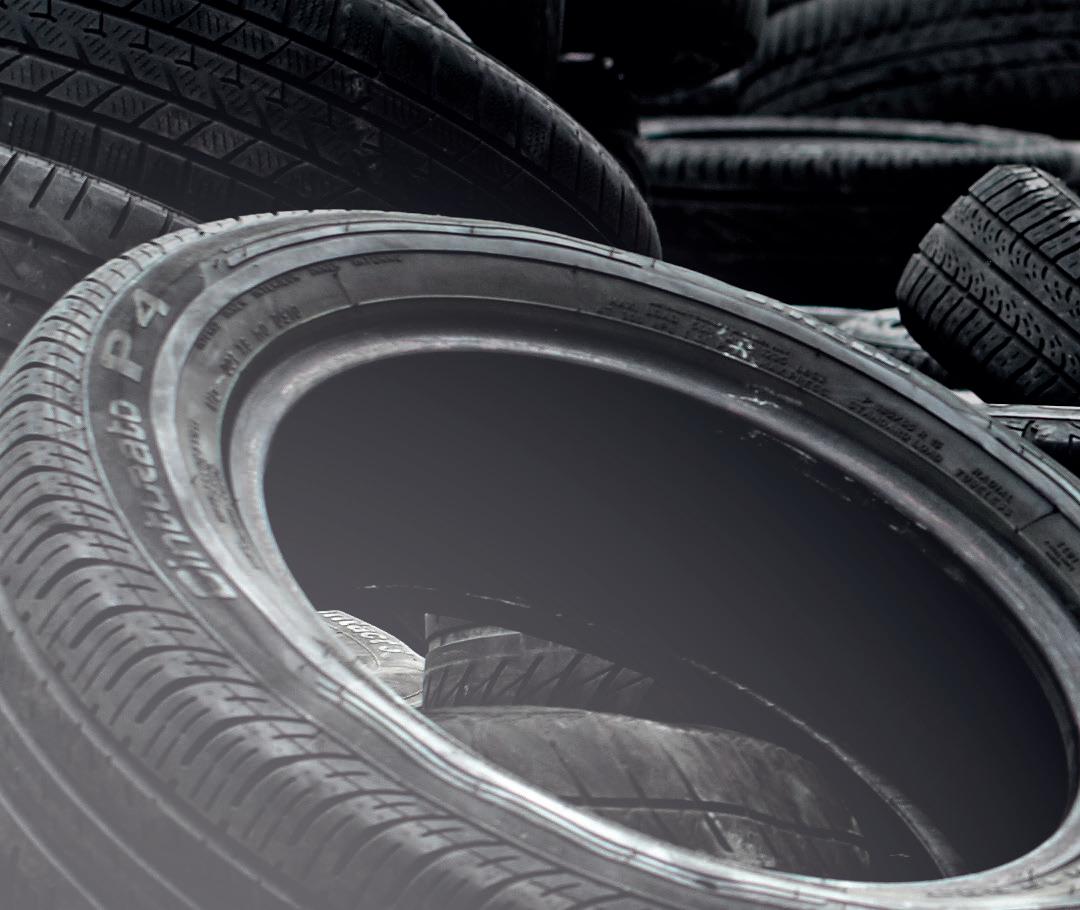
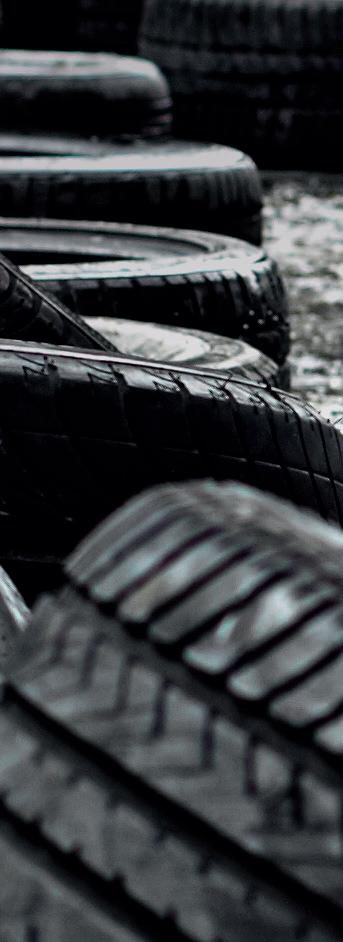
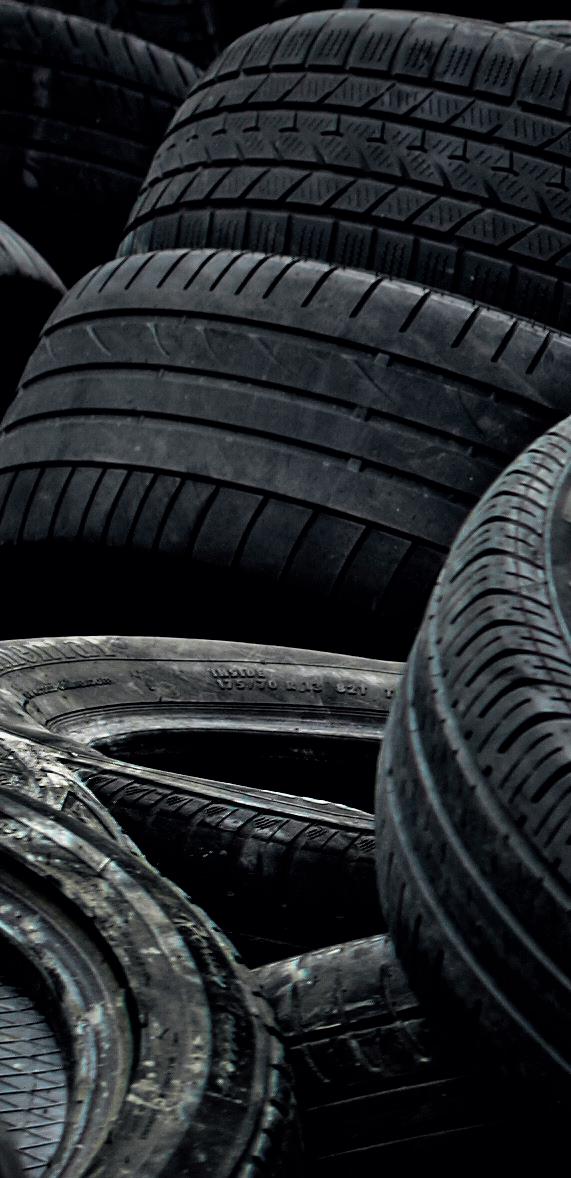
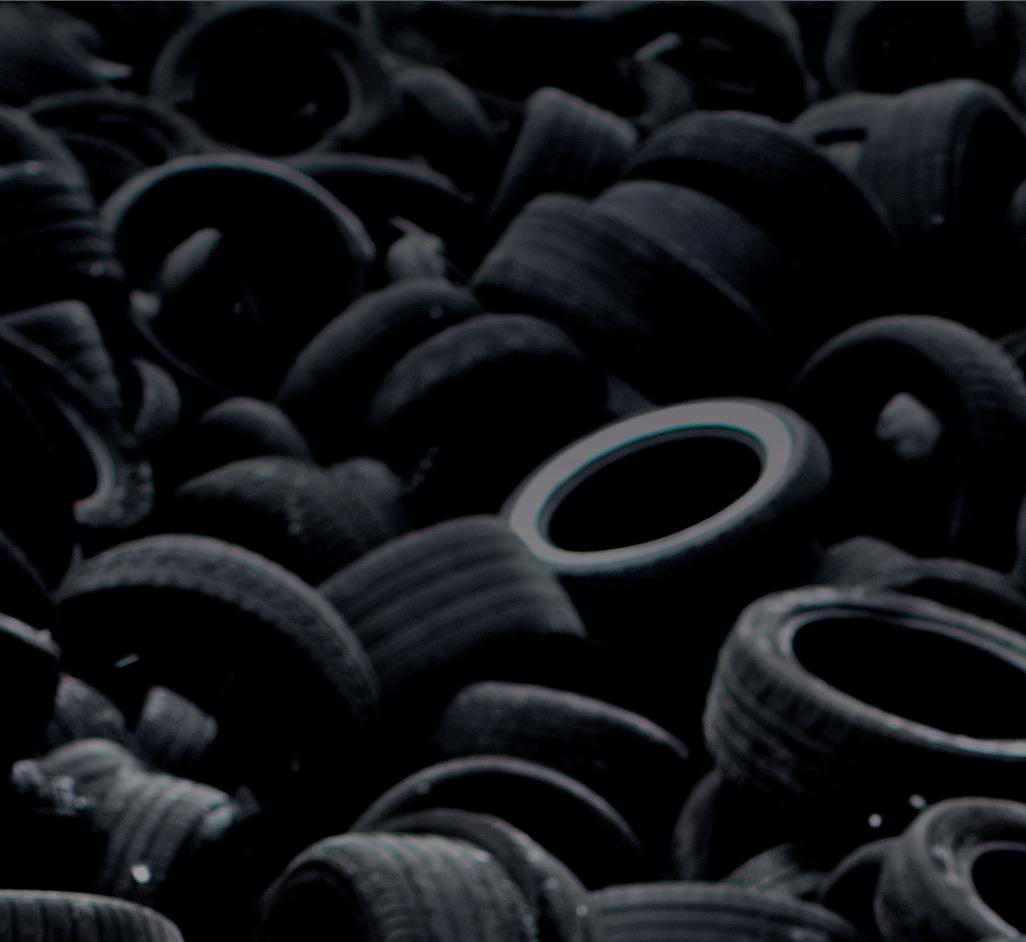
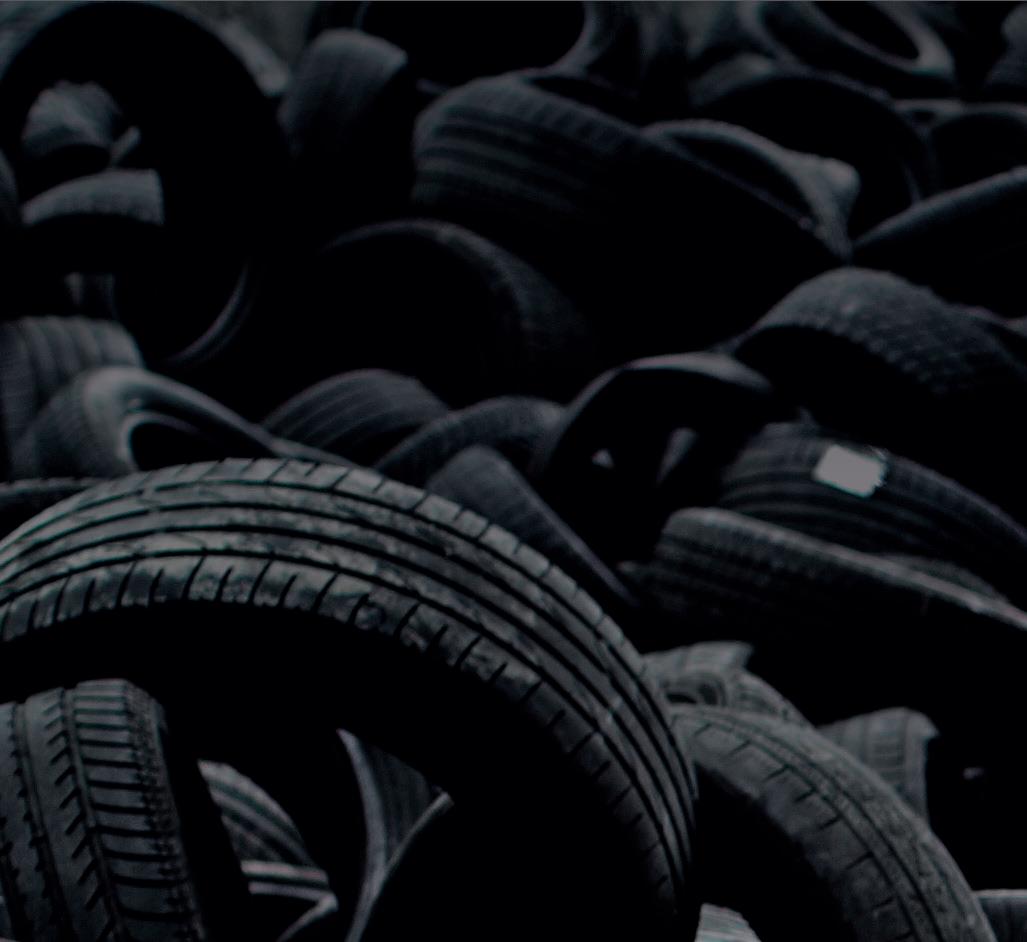

Intercem’s cooperation partners were the suppliers of the necessary technologies –filter technology, automation technology and compressors.
Their detailed knowledge and know-how of the respective technologies were combined with the experience of Intercem’s engineers to drive the development of the InterHop.
Conclusion
The InterHop’s primary objective is to sustainably support and improve the environment around it. Due to its high efficiency, the ship unloading process requires significantly less energy to carry out.
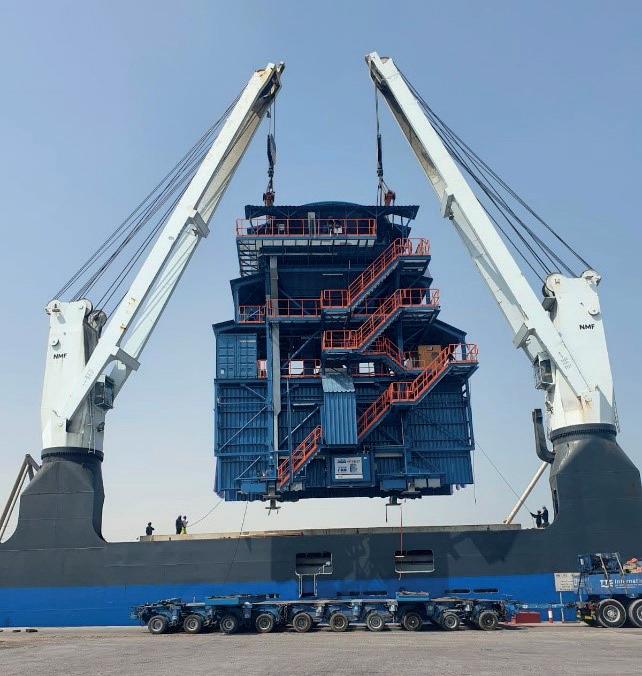
Similarly, the fast unloading also means that the docking fees of the ships are reduced considerably, which is another major optimisation goal in addition to the very low OPEX costs. From engineering and production, to commissioning, at Intercem everything originates from a single source.
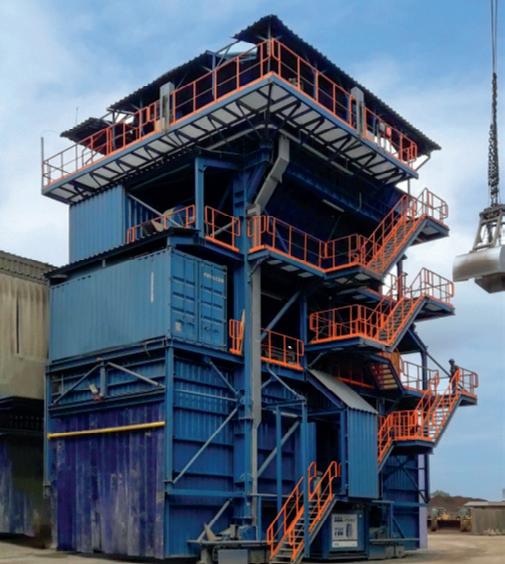
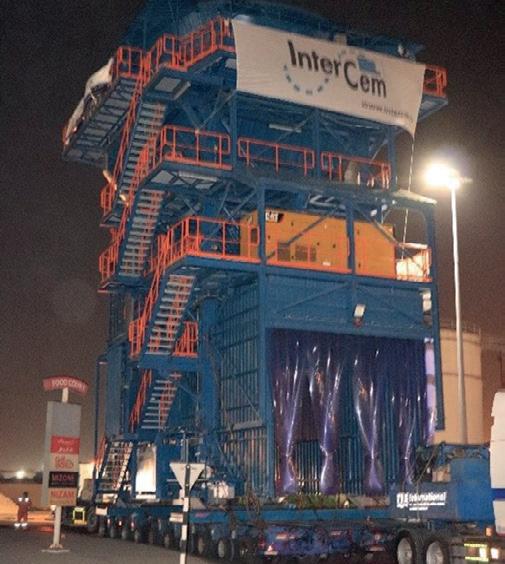
References
1. ‘Dry bulk shipping: record-breaking start to year drives earnings to decade highs’, Baltic and International Maritime Council, (2021) – https://www.bimco.org/news/market_ analysis/2021/20210601_dry_bulk_shipping
2. ‘2021 Dry Bulk Outlook – Minor Bulks’, Hellenic Shipping News, (2020) – https://www. hellenicshippingnews.com/2021-dry-bulk-outlookminor-bulks/
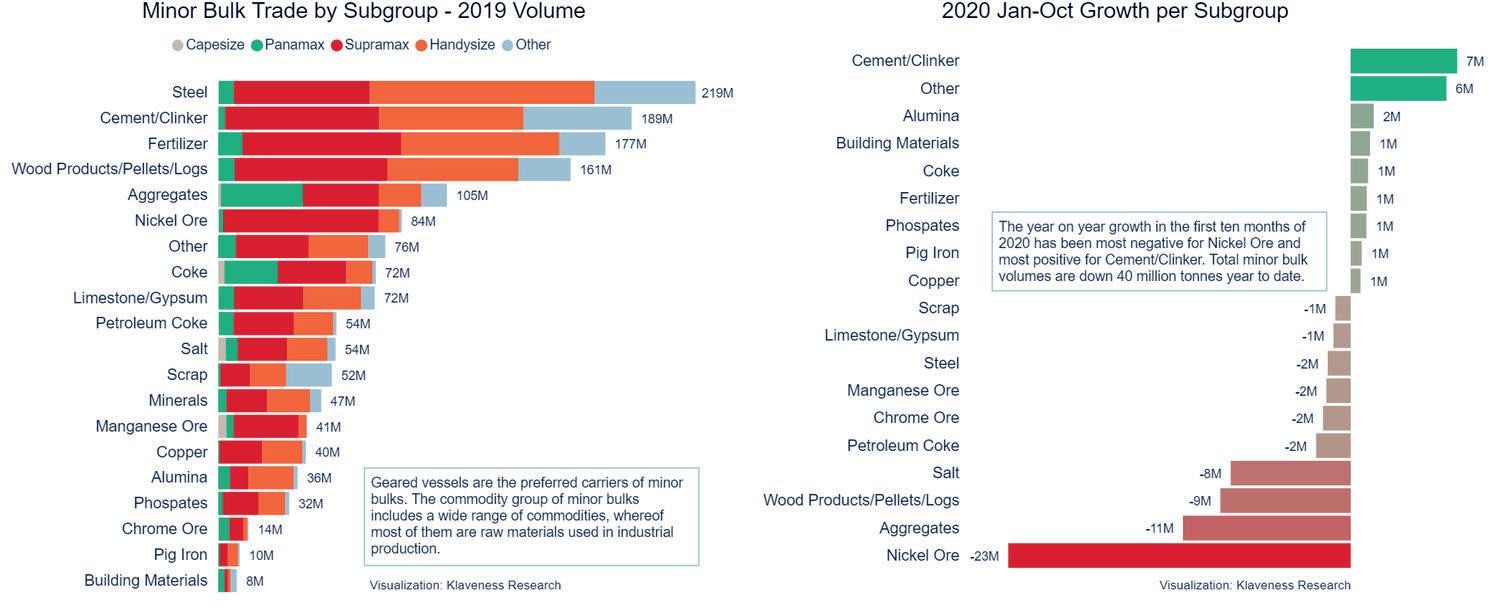
About the author
Olaf Michelswirth studied mechanical engineering in Paderborn and obtained a degree as a Graduate Engineer.
After years of experience in the cement industry, he became General Manager of Intercem Engineering in 2005, applying his expertise in many projects all over the world.
Figure 6. Transport to the port (left) and InterHop in operation in Abidjan (right). Figure 5. Loading onto a heavy load transport vessel. Figure 7. Minor bulk trade by subgroup – 2019 volume (left), January 2020 – October growth per subgroup (right).2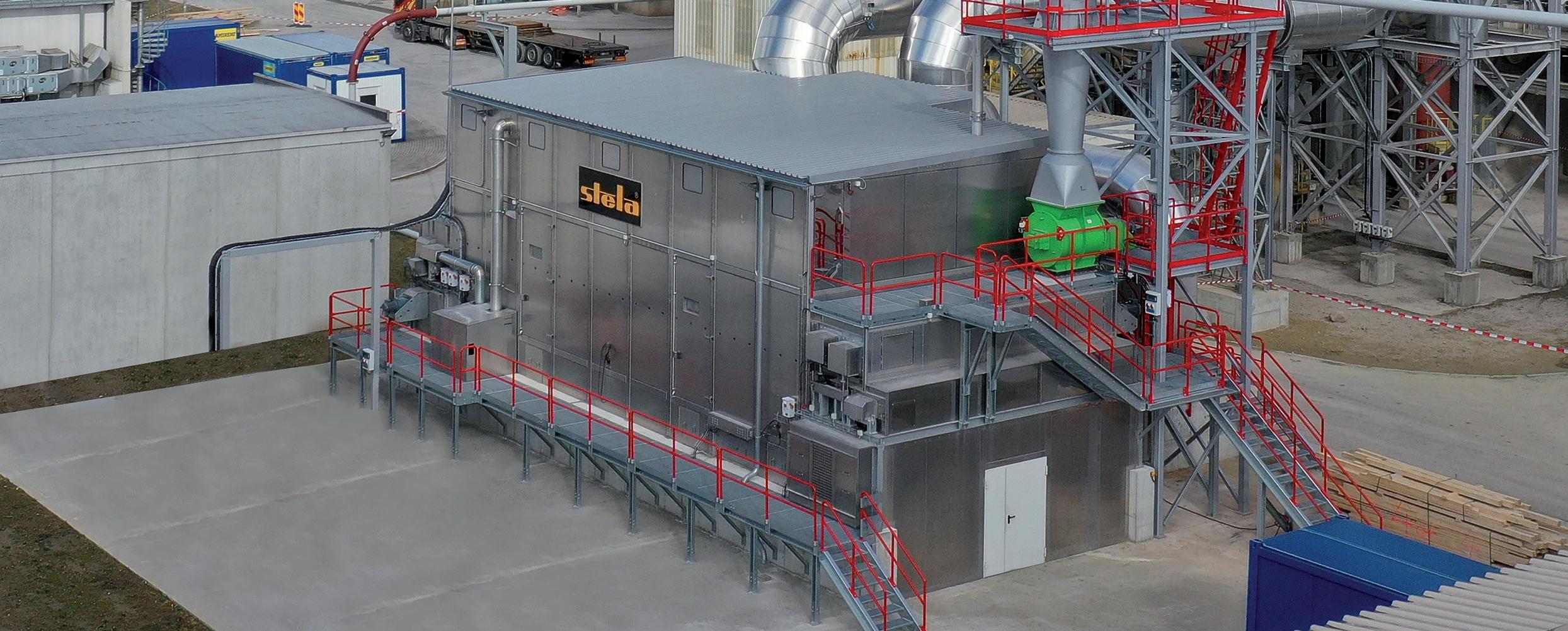
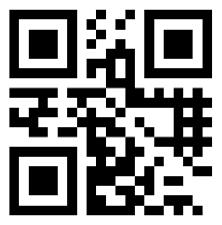
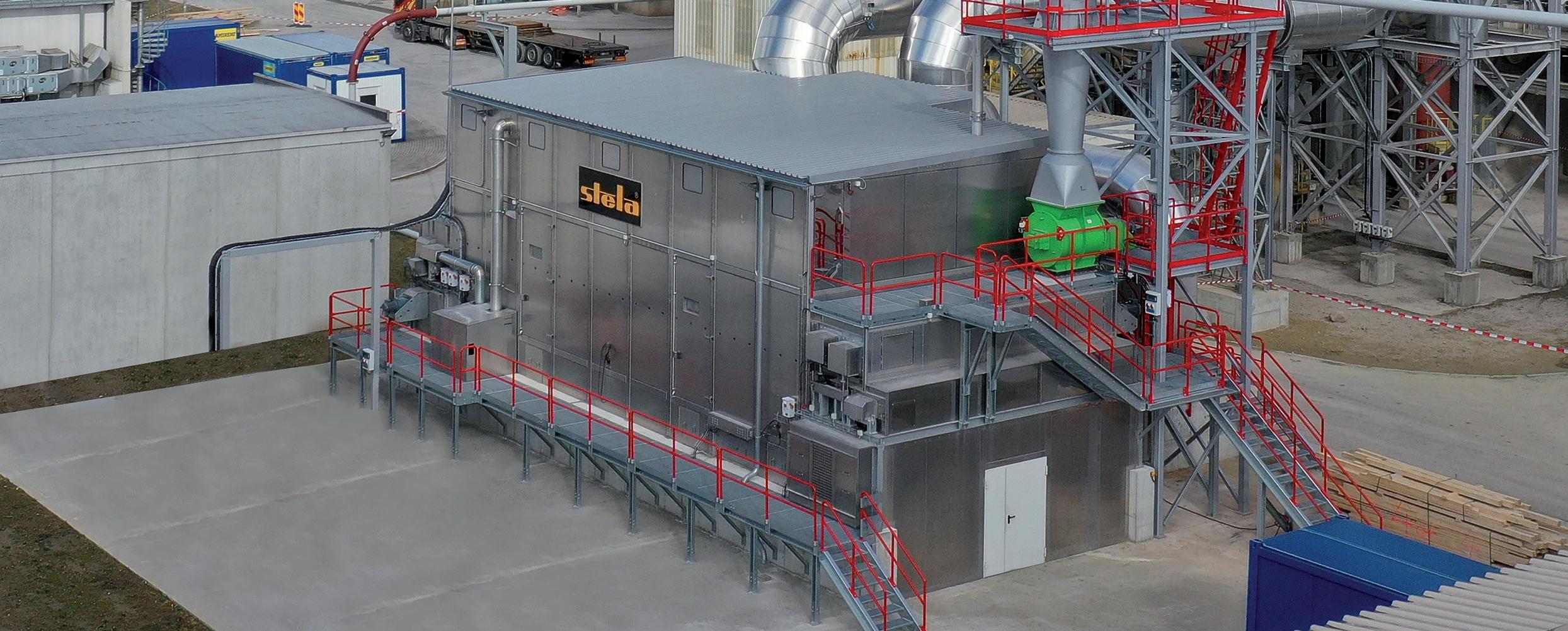
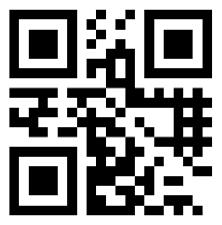

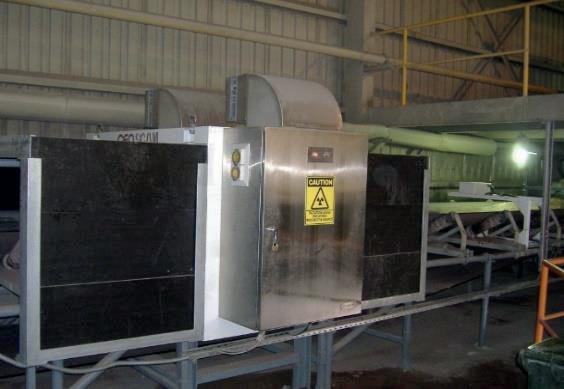
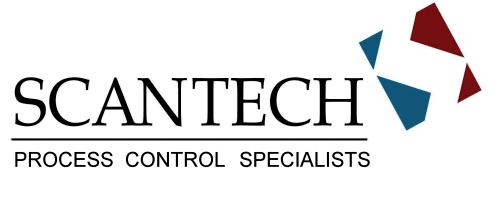
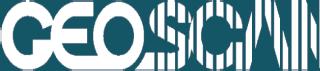
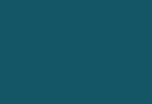
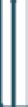
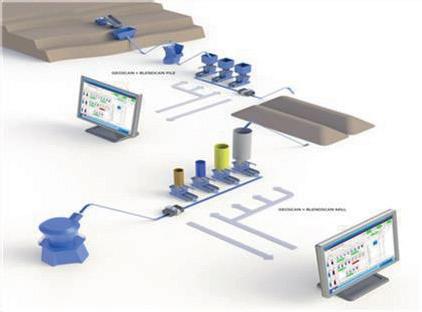

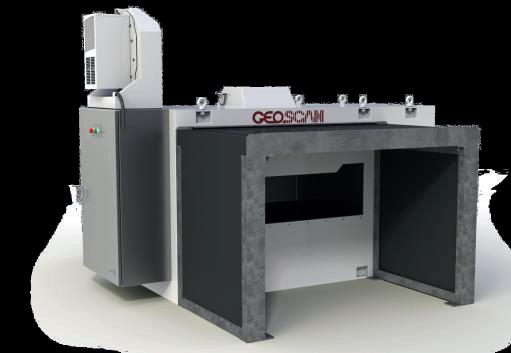
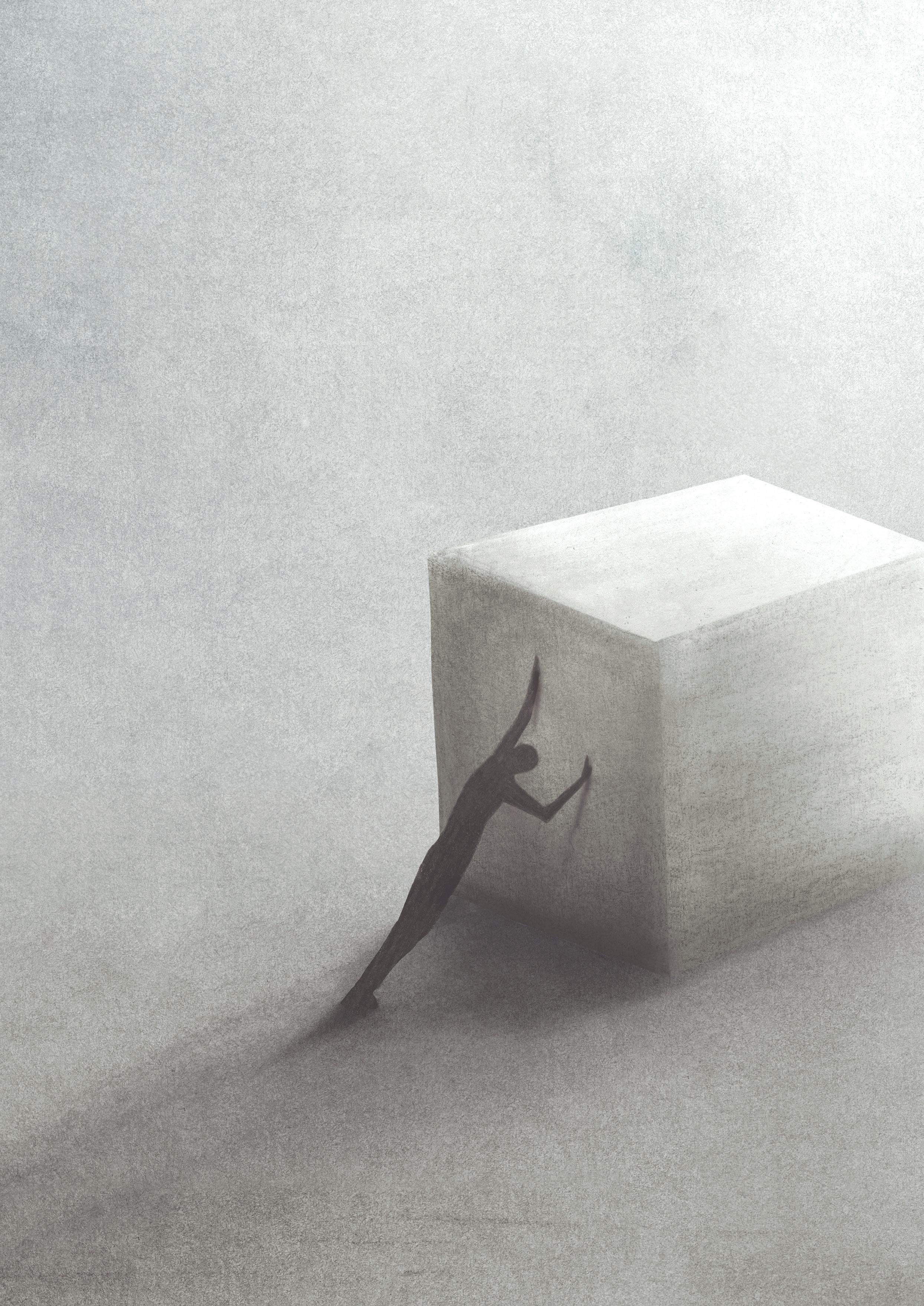
Second only to water, cement is the world’s most widely consumed commodity, and with the global pandemic only stalling its rising consumption, eyes are turning to increases in port handling efficiencies to help meet global demand.
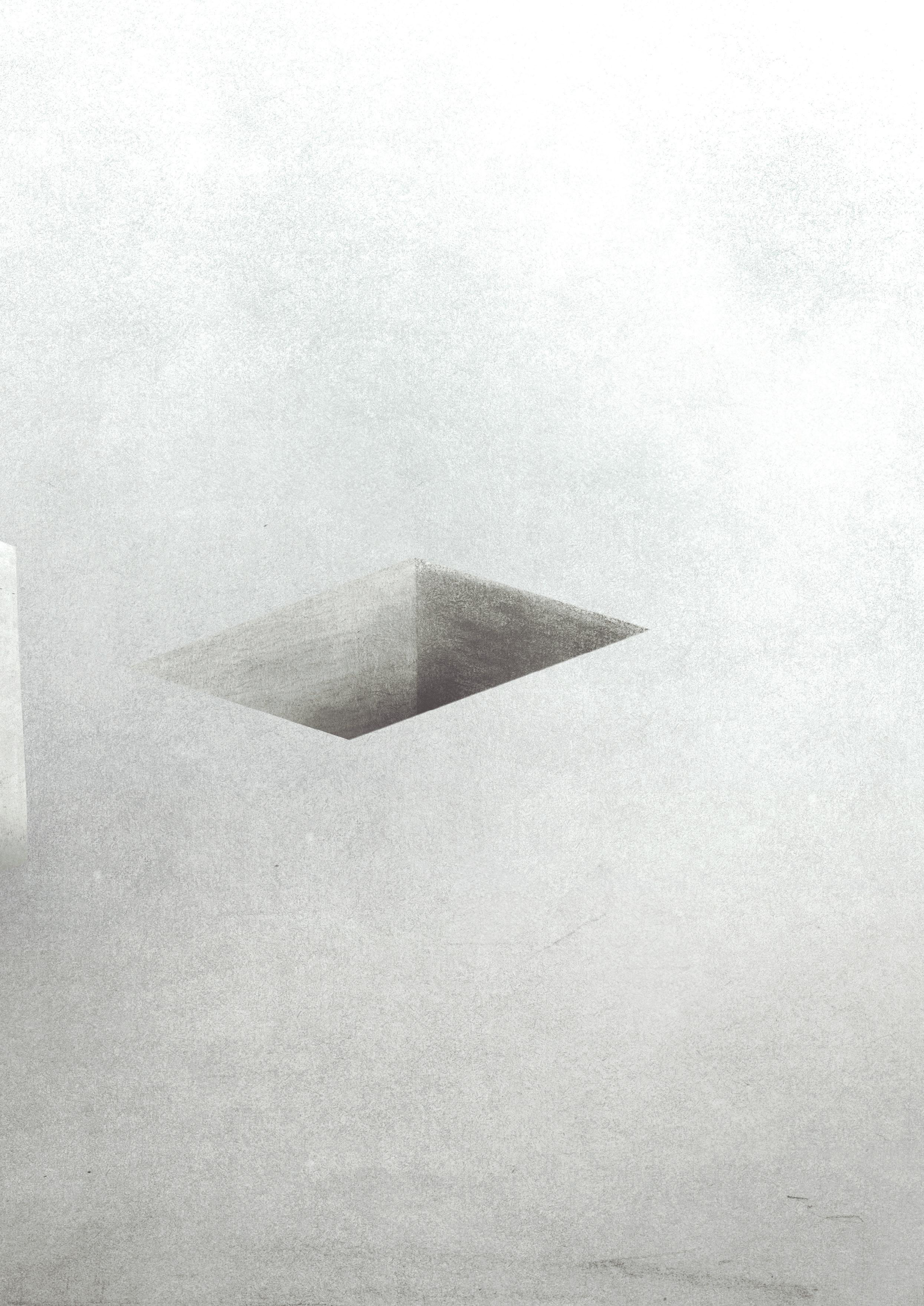
Demand predominantly comes from growing populations and their inherent need for food, energy and infrastructure; the United Nations (UN) predicts that by 2100 the world’s population will be about 11 billion, an increase of 4 billion from today’s levels.
Port terminals are at the face of meeting this challenging rise in dry bulk volumes and it is imperative that handlers adopt equipment that will not just accommodate today’s capacity requirements, but also meet a long-term
Per Hansson, Bruks Siwertell, explains how new levels of efficiency and environmental protection must be adopted if the increasing demand for cement is to be met.
vision of substantial increases and very strict environmental protection regulations. Equipment should also maximise a terminal’s profitability.
The most cost-efficient way to meet rising bulk demands is to design an optimised terminal. This could be installed from the outset, or through the replacement of out-dated equipment as part of a modernisation programme.
Three main options
Cement handlers have three main technical solutions at their disposal: mechanical, pneumatic, and grab unloaders. Each has their own benefits and limitations, all of which need to be carefully considered when making a choice about long-term efficiency and sustainability.
Pollution is one of the most significant environmental issues in ports, and grab unloaders are under increasing scrutiny. They can lose up to two percent of a shipment through spillage, and are one of the largest culprits for dust emissions in dry bulk handling operations. Material degradation is also a problem. Given the exorbitant imbued carbon costs in cement production, and the imperative for the world to curb its environmental impact, it is likely that replacing these machines will be regarded as a quick-win, and their presence in ports will be greatly reduced.
So, can pneumatics plug the capacity gap? Pneumatic unloaders are restricted to a capacity of about 600 – 800 tph with one pipe when handling cement, for example. To achieve higher capacities, they either need to have two nozzles or two unloaders. In both cases this comes with increased investment costs as well as higher operational costs. These systems work well in ports with low annual intakes, however if an existing or new port terminal needs to expand it is unlikely that they can step up, without considerable cost.
The other element to consider when analysing dry bulk unloading efficiency is hold reach.

A pneumatic unloader is very limited in this capacity and the vertical arm can only be operated within the area of the hold opening. There are pneumatic unloaders which have some pendulum movement, but all pneumatics have limitations relating to having very low or no digging force capability. This makes them unsuitable for any compacted bulk. The ability to move within a hold also impacts the necessity for payloader assistance; this can be as high as 18% for some operations.
In comparable conditions, a Siwertell screw-type ship unloader uses less than 5% payloader assistance, andSiwertell ship unloader handling cement with a capacity of 1500 tph.
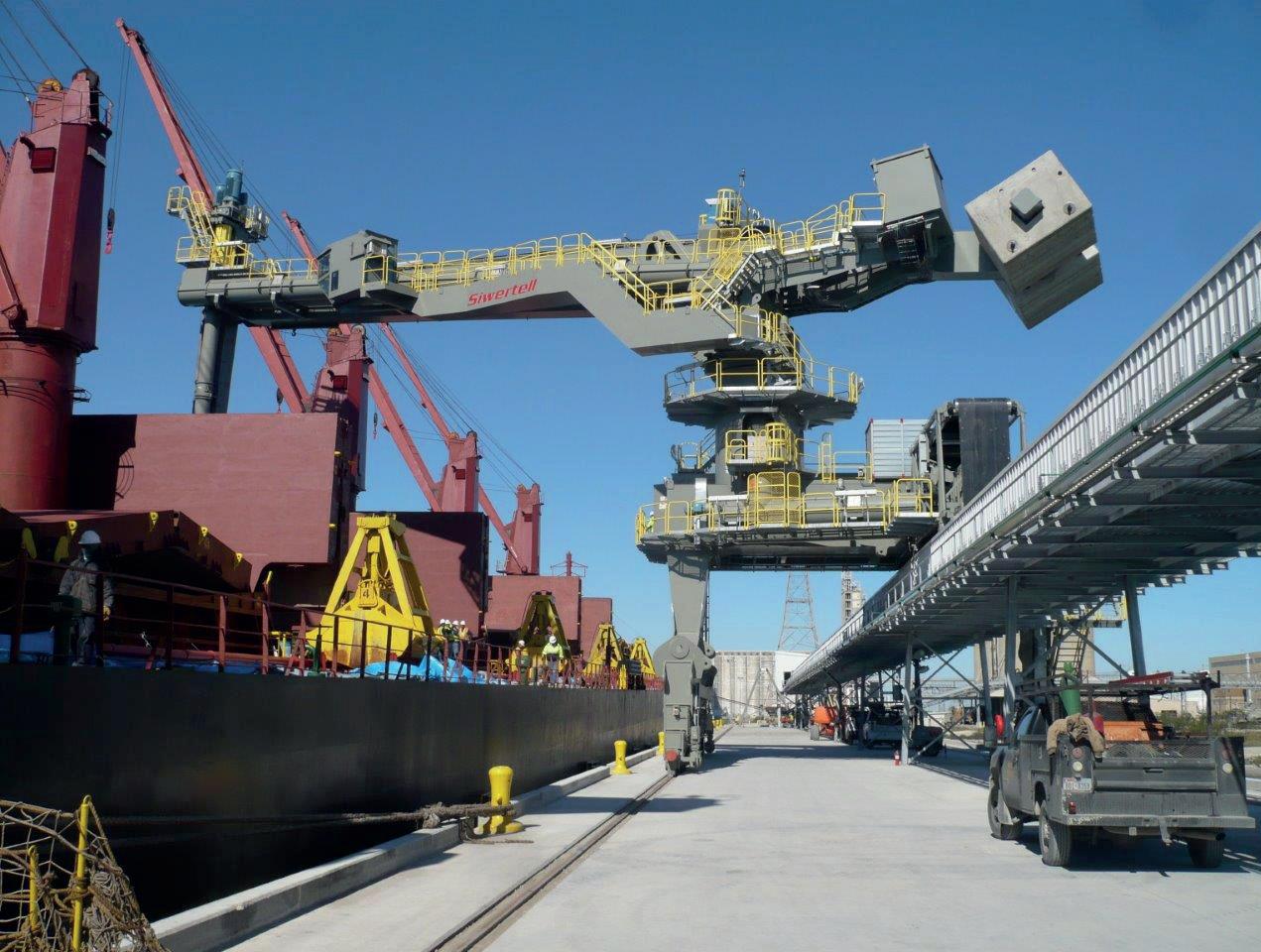
in barges with horizontal walls, the need for a payloader will be below 2%. This is because a Siwertell screw-type unloader can move its vertical arm +/- 30˚ and reach all areas of the cargo hold, including underneath the hatches, where material can build up.
Getting into the corners
Why is hold reach so important? Because it significantly impacts unloading efficiency, and positively contributes to minimising dust emissions, as there are fewer material avalanches in the hold.
Siwertell ship unloaders can have their hold reach potential further enhanced through a side-tilt adaptation on the upper turret. This adds to dust mitigation and further minimises material left for the clean-up phase.
A cement handler keen to put this to use is Kuwait Portland Cement Co. It has a ST 490-M Siwertell ship unloader, equipped with a side-tilt motion, on order, which is due for delivery next year. The new unit will work alongside another cement handling Siwertell ship unloader in Shuaiba Port, Kuwait City, Kuwait. It has been in service for over two decades and its operational performance is the main reason why the operator returned to Siwertell technology.
Both unloaders are designed to operate in Kuwait’s extreme heat, and to accommodate predicted temperature rises in the region, the latest unit can withstand ambient summertime temperatures of up to 55˚C.
Growing capacity potential
Siwertell screw-type ship unloaders offer some of the highest rated capacities in the world. The first Siwertell screw-type ship unloader was delivered in 1975 and within five years, the company set a new standard for cement handling by introducing the 800 tph Siwertell unloader to the market. Since then, potential capacity has grown considerably with today’s operators benefitting from continuous rated capacities in excess of 2000 tph.
One of the world’s largest consumers of cement is the United States (US), and around half of US cement imports are handled by Siwertell ship unloaders. Texas is its biggest net importer and home to a significant cement handling milestone for Bruks Siwertell. In 2006, the Houston Cement Company, received the delivery of a rail-mounted Siwertell ST 640-D unloader.
Designed to offer cement unloading rates of up to 1500 tph, it set a new world record at the time and still offers one of the market’s highest cement unloading rates. To give an example of the efficiency gains it delivered to the Houston Cement Company, ship unloading days were reduced by 50%, translating into a 50% reduction
APPGRADE YOUR INSPECTION!
We have digitized over a century of expertise and experience and combined them in an app with which you can now carry out your inspection.
Learn more on our Website or download on the App Store and Google PlayStore
PASSIONATE ABOUT THE FLOW.
EFFICIENT SEPARATION
Good mills are key to good grinding results. But with good separators you achieve even better results – in product quality, speci c energy needs and overall process ow.
Go for greater ef ciency – with separators from Christian Pfeiffer.

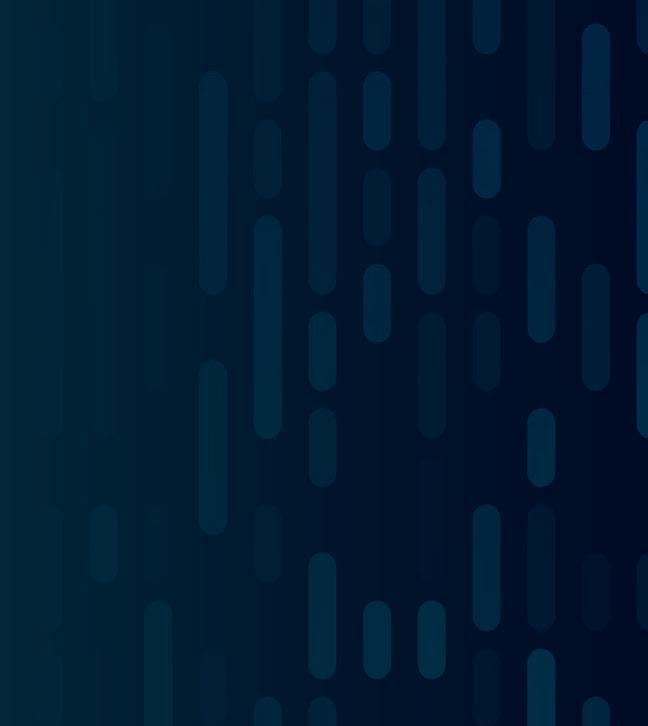
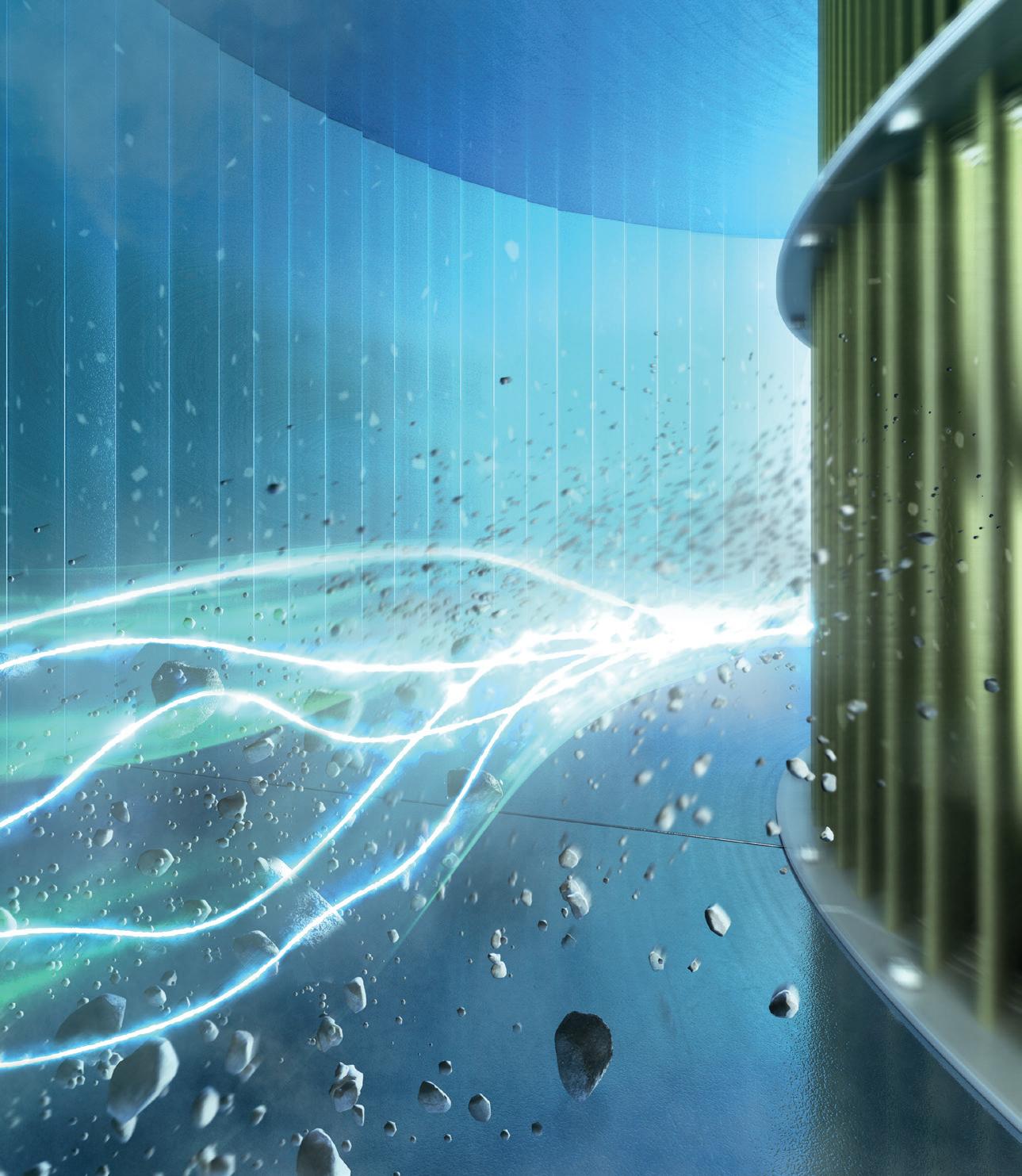
in berth occupancy and the possibility of higher annual intakes; return on investment was achieved in less than two years. It has now handled more than 10 million t of cement.
Other operators in Houston also benefit from Siwertell ship unloaders. This includes a Siwertell ST 640-M screw-type ship unloader that has been operational for almost two years. It offers continuous dust-free cement handling at a rated capacity of 1500 tph, with a peak capacity of 1650 tph, and discharges vessels carrying up to 80 000 DWT.
The ship unloader was part of a strategic growth plan, which has enabled its owners to switch from bagged to bulk deliveries of cement and building materials. These bulk deliveries vastly improve efficiency and cost-effectiveness, enhancing the operator’s ability to increase its cement intake and reach market potential.
Bruks Siwertell has also recently commissioned a high-capacity Siwertell 490 F-type ship unloader for Colonial Group’s Georgia Kaolin Terminals, in Savannah, Georgia. It was brought online to support the switch from bagged cement deliveries to bulk deliveries.
Early feedback has been positive; the unloader has increased the terminal’s unloading capacity, which in turn delivers faster vessel turnarounds on the jetty. It offers a rated cement handling capacity of 800 tph, discharging vessels up to 55 000 DWT.
Environmental considerations were a key factor in Colonial’s choice of Siwertell equipment. Like all Siwertell ship unloaders, this unit has an enclosed dry bulk material conveying line, ensuring no spillage and minimising dust emissions. Savannah is a historic port with strict environmental regulations; the Siwertell unloader comfortably meets these.
Keeping it flexible
As well as large-scale cement unloaders, Bruks Siwertell has received a number of orders for Siwertell road-mobile unloaders. These deliver the efficiency and environmental capabilities operators require, as well as flexibility. Demonstrating this capability, a pair of road-mobile units have recently been ordered to support two US cement import sites. The new 5000 S units will join other existing Siwertell technology owned by the operator, and will enable better access to barges and port facilities.
The first unloader, heading for the Midwest, will be commissioned this year, and the second unit, destined for the Southeast, will be commissioned early in 2023. Both of these new unloaders will have a rated cement handling capacity of 300 tph for vessels up to 5000 DWT, and as next-generation models, have technology for remote diagnostics and trouble-shooting. They will
also have electric as opposed to diesel-drives, further reducing environmental impact.
Another returning operator is in the Gulf of Mexico. It has recently brought online a new Siwertell 10 000 S-type road-mobile ship unloader. The unit was selected for its unloading capacity and ability to accommodate and discharge barges as well as vessels up to 10 000 DWT. It offers a continuous rated capacity of 300 tph for the totally enclosed, dust-free handling of cement, with low operating costs in comparison with other technologies.
The undisclosed operator also already owns several Siwertell road-mobile unloaders, at different locations in the US, as well as large-scale bulk terminal unloaders. This particular unit will ultimately be barge-mounted and move between locations within the Gulf of Mexico, but is initially planned to work along the Mississippi river in the state of Louisiana.
A recent contract, which was also partly driven by environmental and efficiency considerations, has been placed by Swedish operator, Swecem AB. It selected a Siwertell 10 000 S next-generation road-mobile unit, which will have a continuous cement unloading capacity of 300 tph and can accommodate vessels up to around 10 000 DWT. It will serve the operator’s import terminal in Helsingborg.
Reduce the dust
Globally, there is a legislative drive to reduce the environmental impact of the cement industry. Every country also has to balance maintaining capacity, and also having to exceed it to keep up with predicted future growth, and protecting the environment. If not met, a potential gap between supply and demand will arise.
Environmental protection from cement dust emissions should be addressed with urgency. The industry needs to enclose cement during transfers, eliminating the risk of fugitive dust, and also addressing wasteful spillage.
Siwertell screw-type unloaders, from large-scale units to road-mobile and port-mobile systems, all deliver totally enclosed material handling from the ship’s hold to the receiving system. They have a counter-rotating inlet device that picks up material below the cargo surface, offering a layer-by-layer unloading process, avoiding any avalanches, and therefore dust clouds, within the hold. They also maintain continuous unloading at a steady discharge rate, regardless of the level of cargo in the hold, right up to the hold clean up stage.
It is Bruks Siwertell’s aim to be part of the industry’s environmental shift, offering enclosed systems that protect the environment, whilst also delivering the necessary extremely high through-ship efficiencies that the market needs.
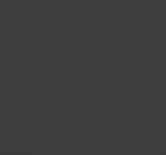


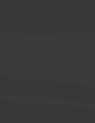


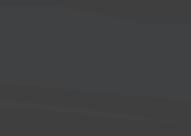




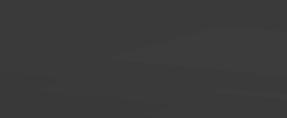
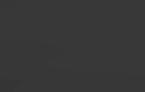
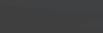






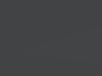



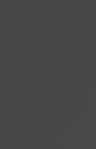


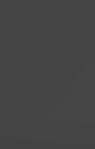


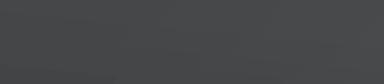
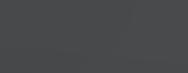

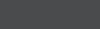
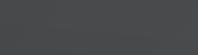




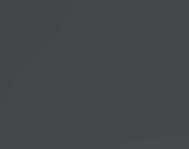
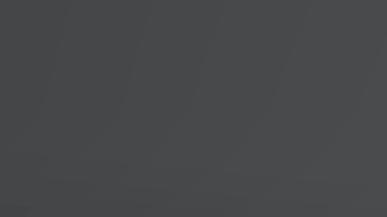
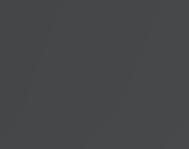
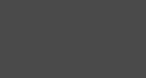
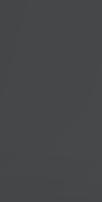
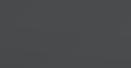
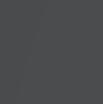

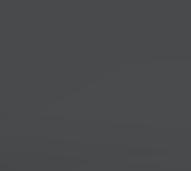
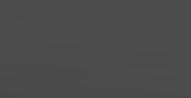
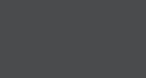
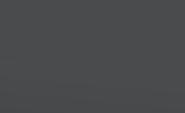
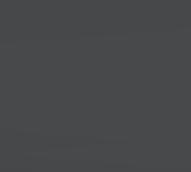
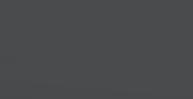
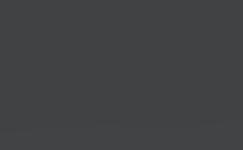


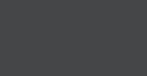
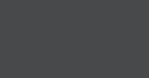
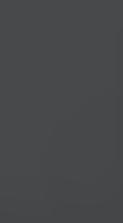
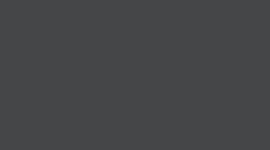
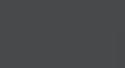













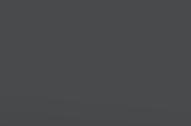
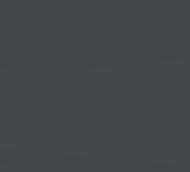

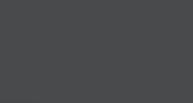
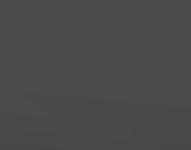
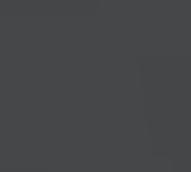

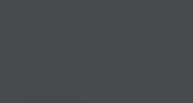





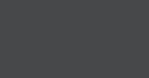







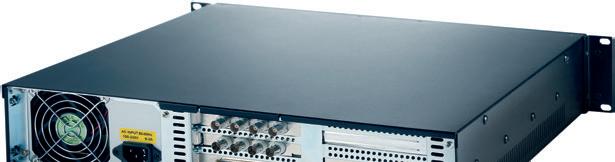
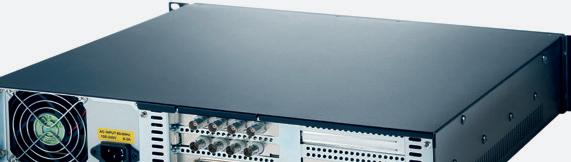
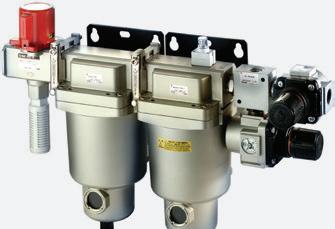
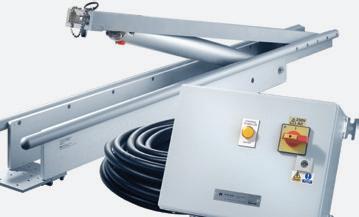
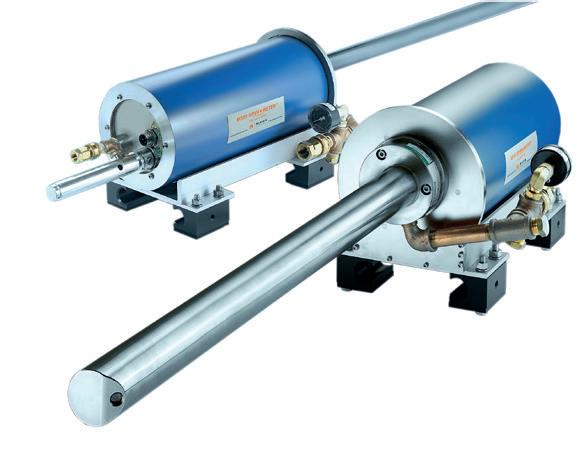

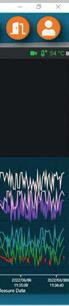
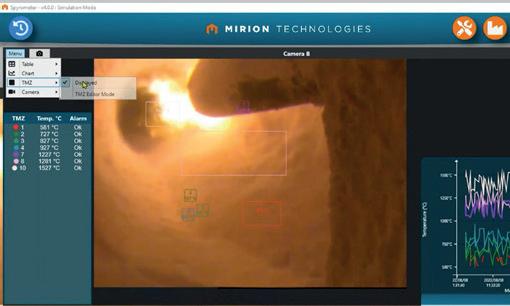
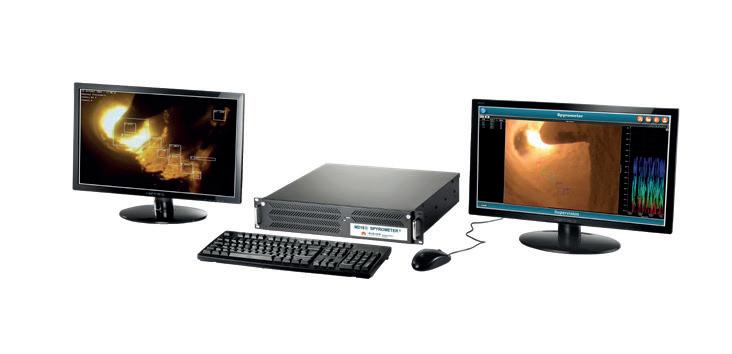



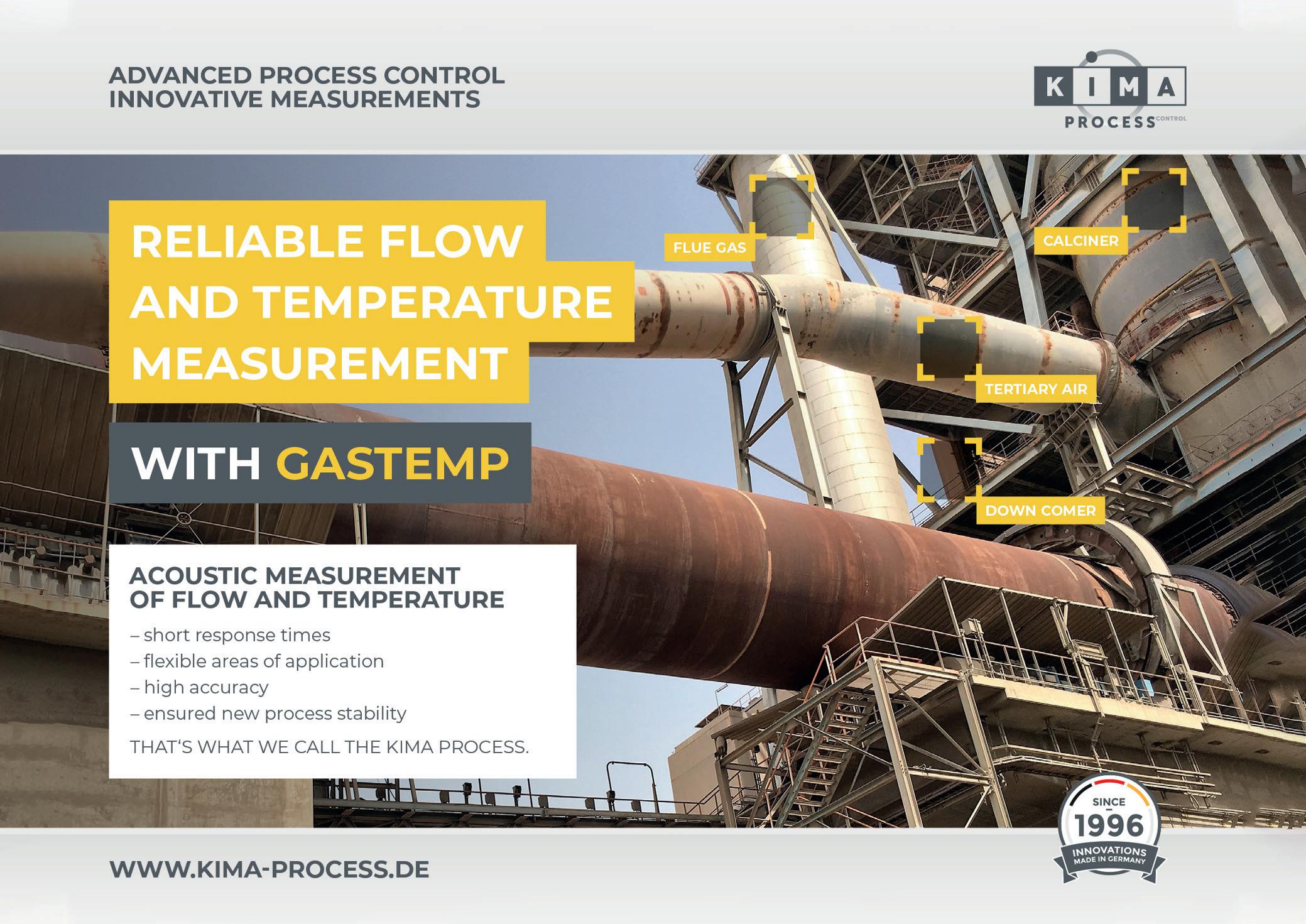
Thecement industry is experiencing a boom thanks to the United States’ US$1 trillion ‘Infrastructure Investment & Jobs Act’ passed by the Senate in 2021. But just like other essential materials, the cement industry faces the same challenges impacting the bottom line: price increases, supply chain disruptions, and labour shortages.
With the rising cost of cement, staying profitable in this environment requires that cement and concrete producers find every opportunity to maximise value. Though long perceived as a necessary expense in a production facility, a high-performing dust collection system can make a major impact on a cement producer’s bottom line. This is due to the fact that dust collection technologies play a pivotal role in helping cement producers reduce waste, increase efficiency and create cleaner operations that lead to a better, safer world. Whether looking for a new dust collector to upgrade a pre-existing mill or terminal to increase performance, or installing an
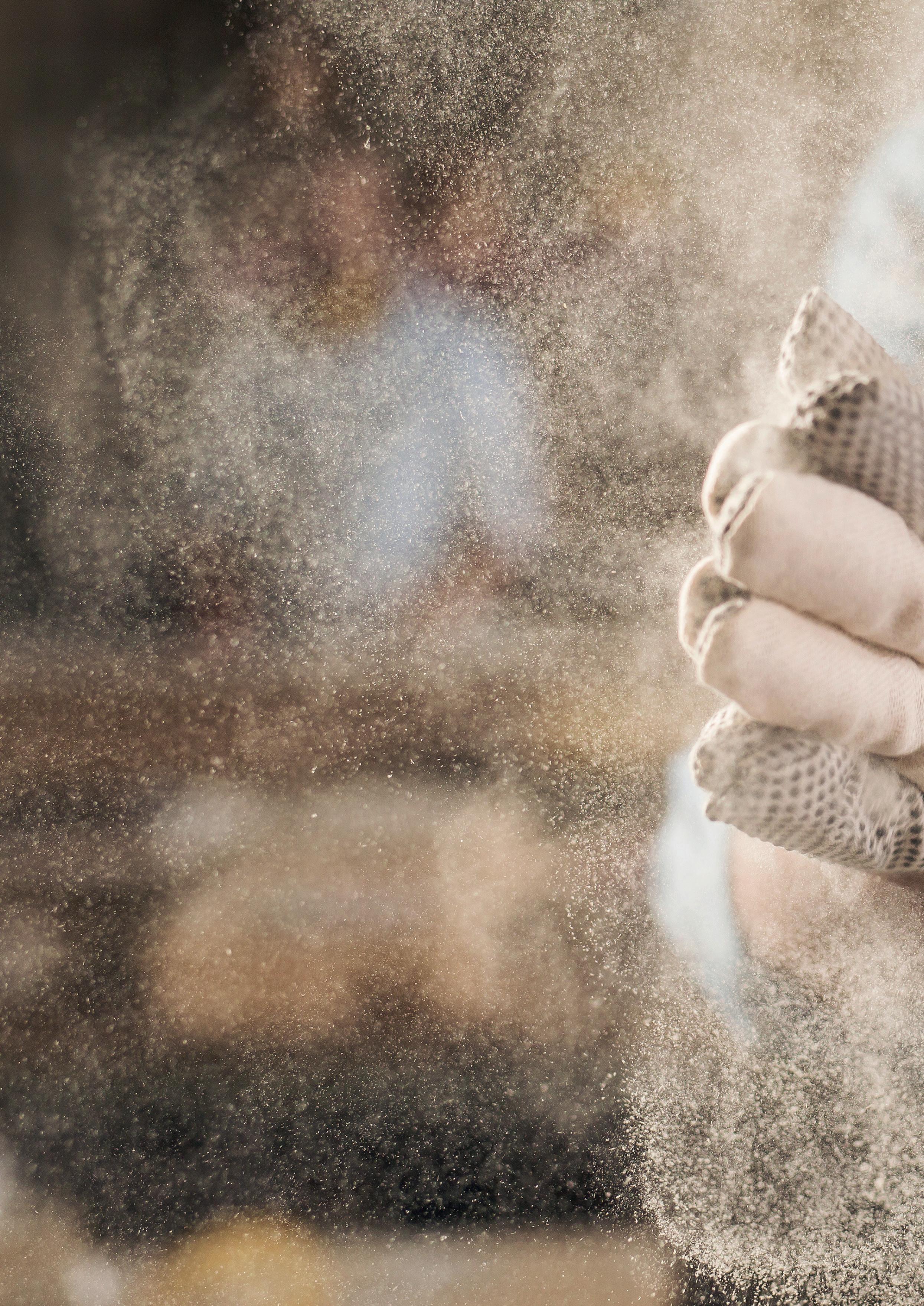
Steve Duncan, C&W DustTech, explains how effective dust collection can improve bottom-line performance, worker safety, and local air quality.
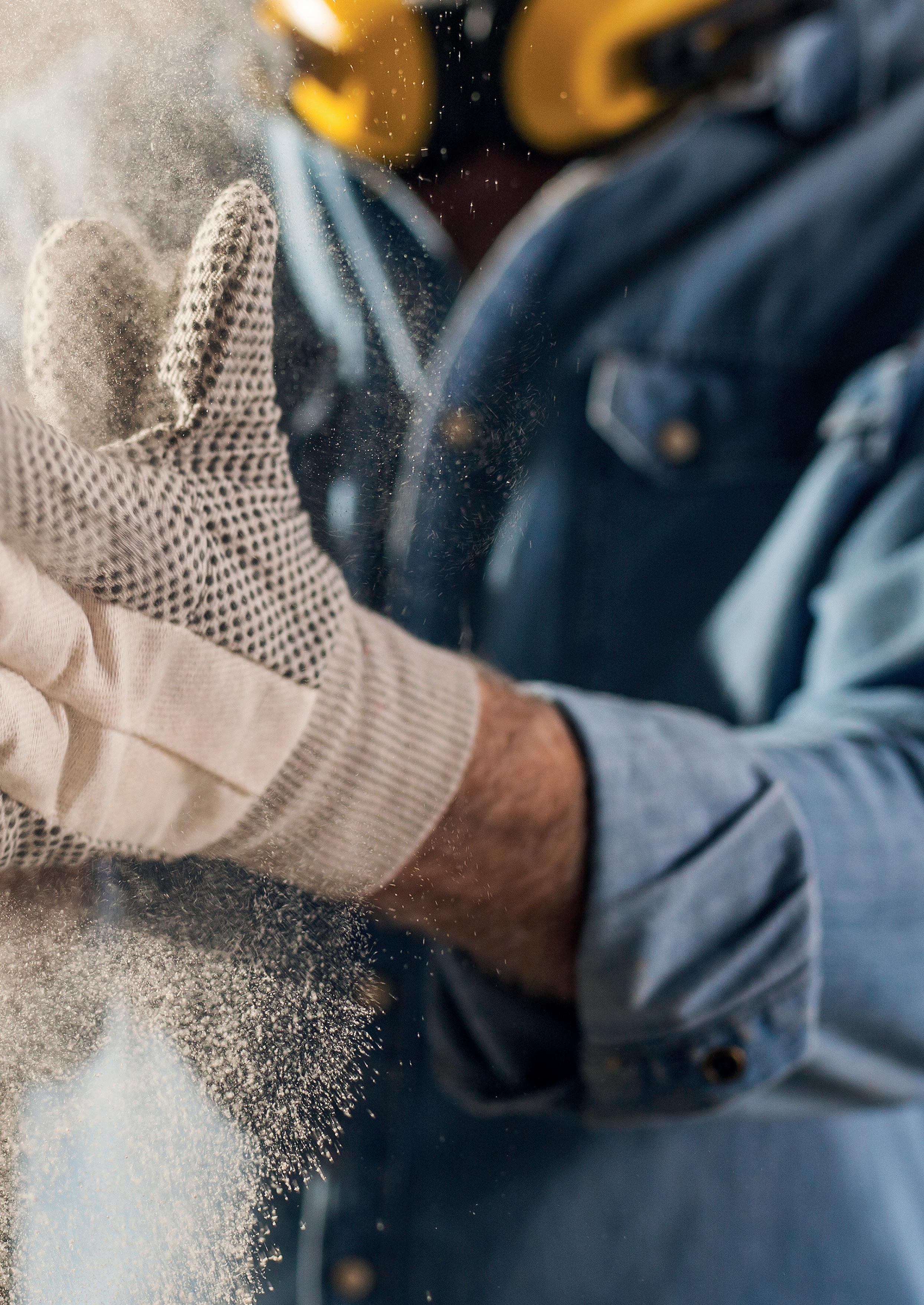
entirely new system to meet environmental requirements, this article explains how the right dust collection system can improve a plant’s bottom-line performance and drive meaningful change in its operation.
Understanding the risks of fugitive dust
Particularly in heavy industries, such as ready-mix, concrete, cement production, and mining, abrasive dust poses several inherent concerns that impact bottom-line performance.
These include:
f All dust presents the risk of inhalation that can impact a worker’s lungs, heart, respiratory system, and more.
f Not being compliant with the Environmental Protection Agency (EPA), Occupational Safety and Health Association (OSHA), and Mine Safety and Health Association (MSHA) standards and regulations can lead to fines and a potential shutdown.
f Dust settles onto floors, machinery, workspaces and more. This impacts machine performance, requires additional maintenance hours, increases the risk of falls, and limits visibility.
f Some dust can pose a combustion or explosion risk, putting both employees and operations in danger.
f Escaped dust emissions can potentially harm the surrounding community, negatively impacting a company’s relationships with neighbours and its reputation.
f Employee satisfaction will suffer, and turnover will increase, with employees not seeing a clear and visible commitment to their health and safety.
Bottom-line benefits of a customised dust collector
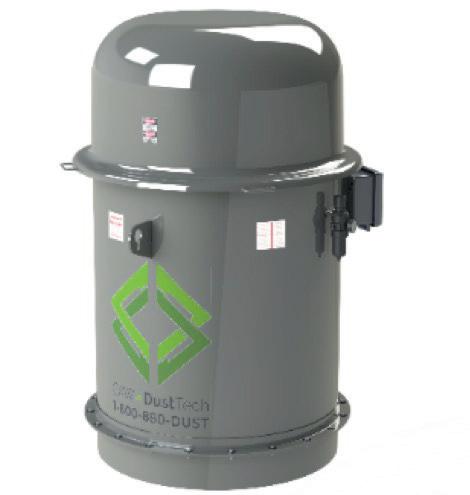
Taking the time to design a dust collection system that is customised to its application – including a properly sized unit, filter media, airflow, and setup – can have a positive impact on a producer’s bottom line. In an environment where companies are looking to preserve profits amongst rising labour and equipment costs, an investment in a dust collection system can lead to long-term benefits that can eliminate the risk of hidden costs, and often turn them into a cost advantage.
These benefits can include:
f Reduced operational and facility maintenance costs.
f Increased production efficiencies.
f Minimised employee safety risks – especially from harmful effects of silica dust.
f Healthier work environments.
f Preserved product integrity and company reputation.
f Maximised production uptime.
f Improved employee morale.
f Enhanced equipment performance and longevity.
f Eliminated monetary fines from regulatory bodies.
f Increased customer confidence in the company’s environmental and social focus.
Additionally, a properly engineered system can collect reusable materials to eliminate unnecessary scrap, decrease material costs and drive efficiencies throughout the production process.
Maximising dust collection investment over the long-term
A dust collection system is not just a one-time expense. It is an investment that should be evaluated with a long-term return on investment (ROI) in mind.
Regular proactive investments in maintenance and proper operation ensure that what matters most is protected and the desired bottom-line results are realised.
C&W DustTech’s clean air technologies help cement producers reduce waste, increase efficiency, and create cleaner operations. The Low-Profile Round (LPR) silo dust collectors offer pulse jet technology, with cartridge filters that provide a highly effective, efficient, and affordable solution for dust control.
Fugitive dust collected throughout the production process is often dirty, heavy, and abrasive. It takes a continuous toll on the equipment and the emotional and physical well-being of the employees. It also jeopardises any investment in the plant – and its surrounding community. The best way to safeguard any operation in this sector
is by ensuring there is an efficient, reliable dust collection system installed. This can only happen with continuous monitoring of a unit’s health and a commitment to ongoing maintenance to protect and preserve the investment.
Properly cleaning, maintaining, and replacing the collector, filters, ducting, and other components will help eliminate escaped emissions and production stoppages, while ensuring that your dust collection system continues to perform at its highest level. An improperly maintained collector can also entail an inability to keep the plant up and running due to EPA, OSHA, and MSHA regulations that regulate the amount of dust allowed in the air, and malfunctioning equipment due to dust build-up, or other easily addressed maintenance issues.
What is the maintenance plan?
Careful attention to the dust collection system’s routine maintenance needs can offer reliability while mitigating serious safety and reputational risks for the business. From the beginning, it is critical to identify the steps a maintenance team should take to ensure the plant stays up and running – and the team members stay safe. Here are key steps to follow for an effective maintenance plan.
Establish a baseline
Any maintenance programme should begin with a thorough understanding of a system’s ‘normal’ operation. Note readings where possible – i.e., the baseline magnehelic gauge reading – to set benchmarks and help make it easier to readily identify when the system is performing sub-optimally.
Determine a schedule
Regular visual inspections, level checks, filter cleaning, and timely replacement and other tasks help identify and fix emerging issues and avoid unplanned downtime.
Gain the team’s buy-in
Make sure the whole team understands the importance of the programme – including the risks of not understanding its importance – and commits to owning the tasks involved.
Ensure employee safety
For employees responsible for executing the maintenance plan, it should be ensured that they always follow OSHA and the company’s Safety Procedures and Lock Out/Tag Out procedures when maintaining the dust collector. With the presence of high air pressure, moving parts and high electrical
Cement plants all over the world rely on Alimak rack and pinion elevators to provide reliable, efficient vertical access for maintenance and inspection. Designed to operate in demanding industrial environments, outdoors and indoors, Alimak elevator s require no expensi ve shafts or machine rooms, and they can easily be installed on new and exist ing structures Standard capacities range from 30 0 k g to 7,0 0 0 kg, with up to 24 ton capacity available upon request
info@alimak
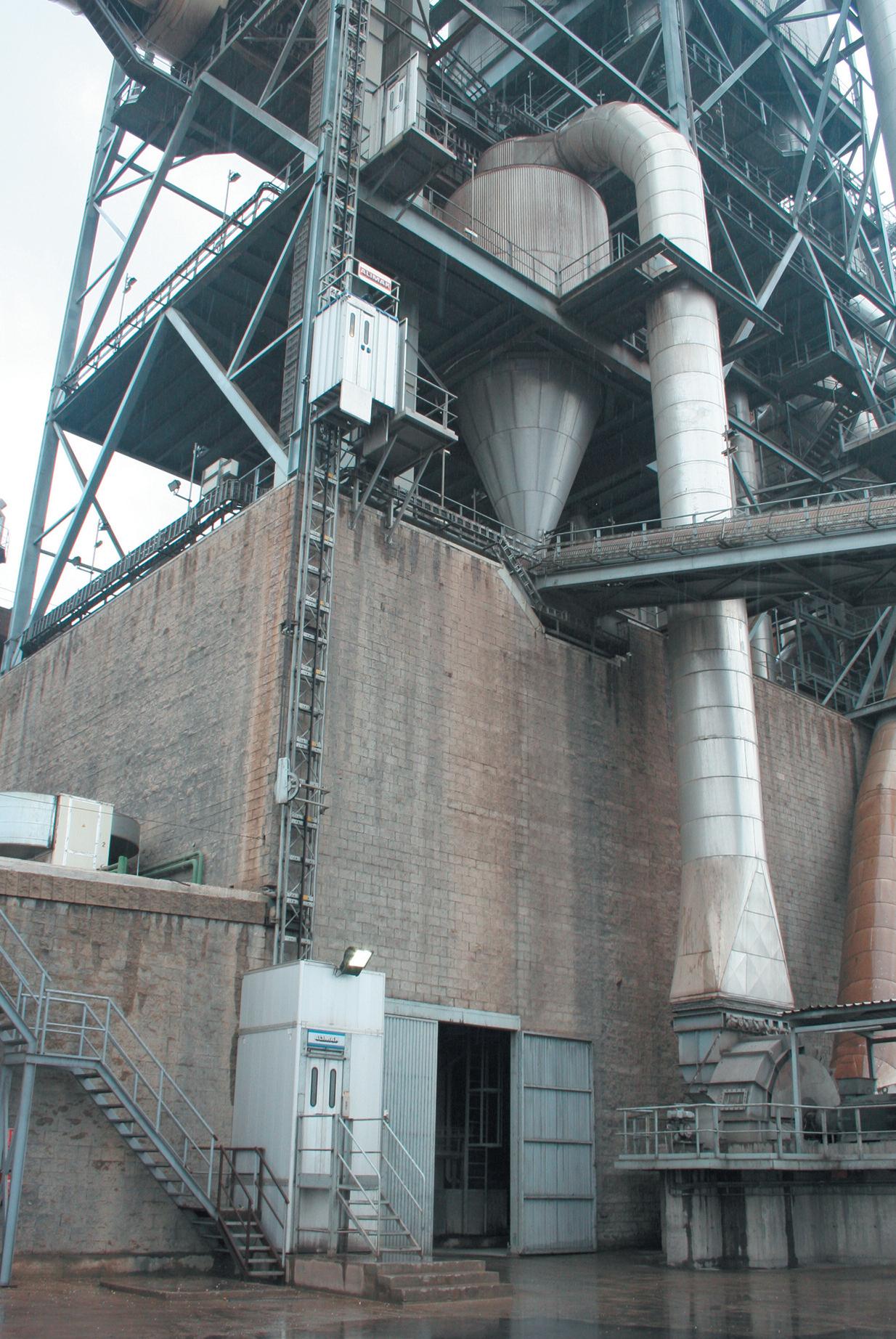
voltage, it is critical to be aware of how to keep all staff involved safe.
No matter the makeup of the system, making regular system maintenance a priority is the only way to safeguard a system’s efficiency, effectiveness, and reliability. Even dust collectors engineered to the highest performance standards are subject to dust build-up and excessive wear. Allocating resources to ongoing maintenance will ensure that long-term returns on essential system investment are maximised.
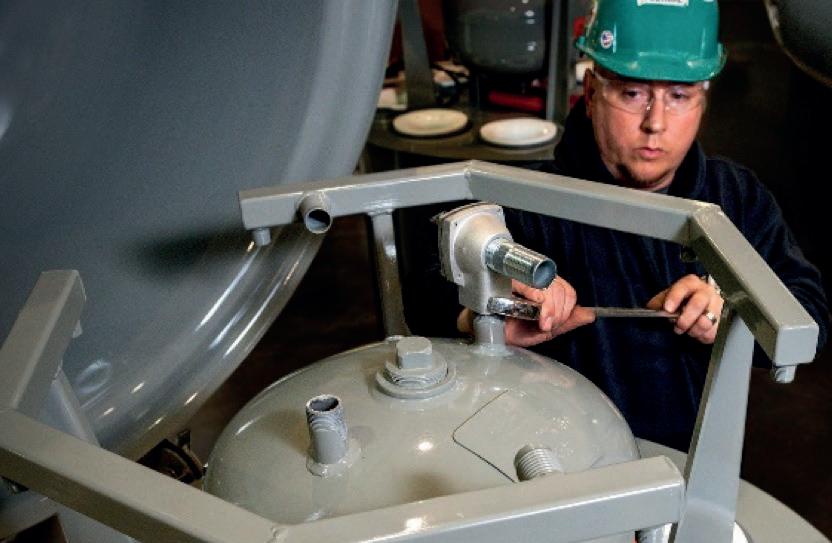
Put this learning into action
Do not just guess. To implement a dust collection solution that is best suited to an operation’s needs, it is essential that there is a consultation with dust collection experts that
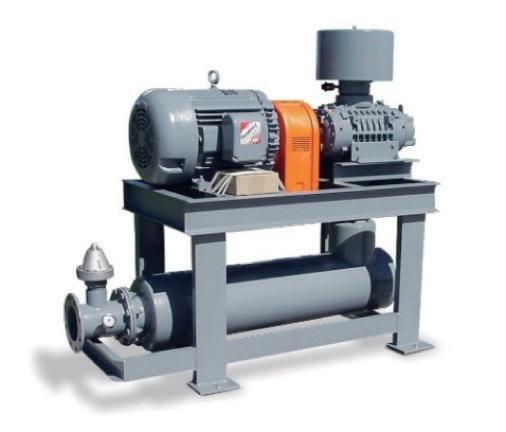
will walk through the following considerations and customise the right system for improved long-term, bottom-line results.
Know the dust
No matter how harmless an operation’s dust may seem, understanding the characteristics of this dust is vital to ensure operational safety. Many types of dust can be combustible or can cause health issues if not properly controlled. Because each type of dust is different, it has unique safety requirements, regulations and equipment specifications. It is important to analyse specific dust characteristics such as particle shape, gravity, size, abrasiveness, and moisture level. This will help to determine the best dust collector, filter media, and system accessories for a dust-free operation.
Specify the proper equipment
Properly sizing the dust collector is a critical step to ensure any system will perform at peak efficiency. Improperly sized dust collectors can cause serious inefficiencies that impact production and increase operating costs. The right dust collection partner will work with a cement producer to audit their operation, identify the plant’s precise needs, and design a system that is uniquely suited to accelerate success.
Invest in ongoing maintenance
When owning and operating a dust collection system, it is critical to establish an ongoing maintenance programme that keeps the system running at peak performance. Without a comprehensive maintenance plan, you may face serious fines, operational shut down and inefficiencies – that easily could have been prevented.
Drive operational changes today
Every operation is different and has unique requirements and regulations. But when it comes to improving the bottom line, do not underestimate the impact an effective dust collection system can have.
Cement producers should talk to expert partners that will work to create a customised solution that not only meets the company’s needs, but also complies with regulations governing air quality in their region. Following these steps will help start driving meaningful change throughout the organisation today.
C&W’s transfer systems enable producers to move cement and other materials to a silo or for transport, without the risk of product contamination or loss. Invest in a dust collection solution that ensures reduced emissions, maximum operational efficiencies, and delivers a long-term ROI.Avoiding a storage ordeal with bolted steel
The bolted steel silo offers an improvement on the application and promotion of steel silos in the cement industry. Hean SRON Silo Engineering Co. has been committed to researching bolted steel silo assembly technology. Compared with other types of steel silo, the primary characteristics of the bolted steel silo are: First, a modular construction, with high stability, which is convenient for
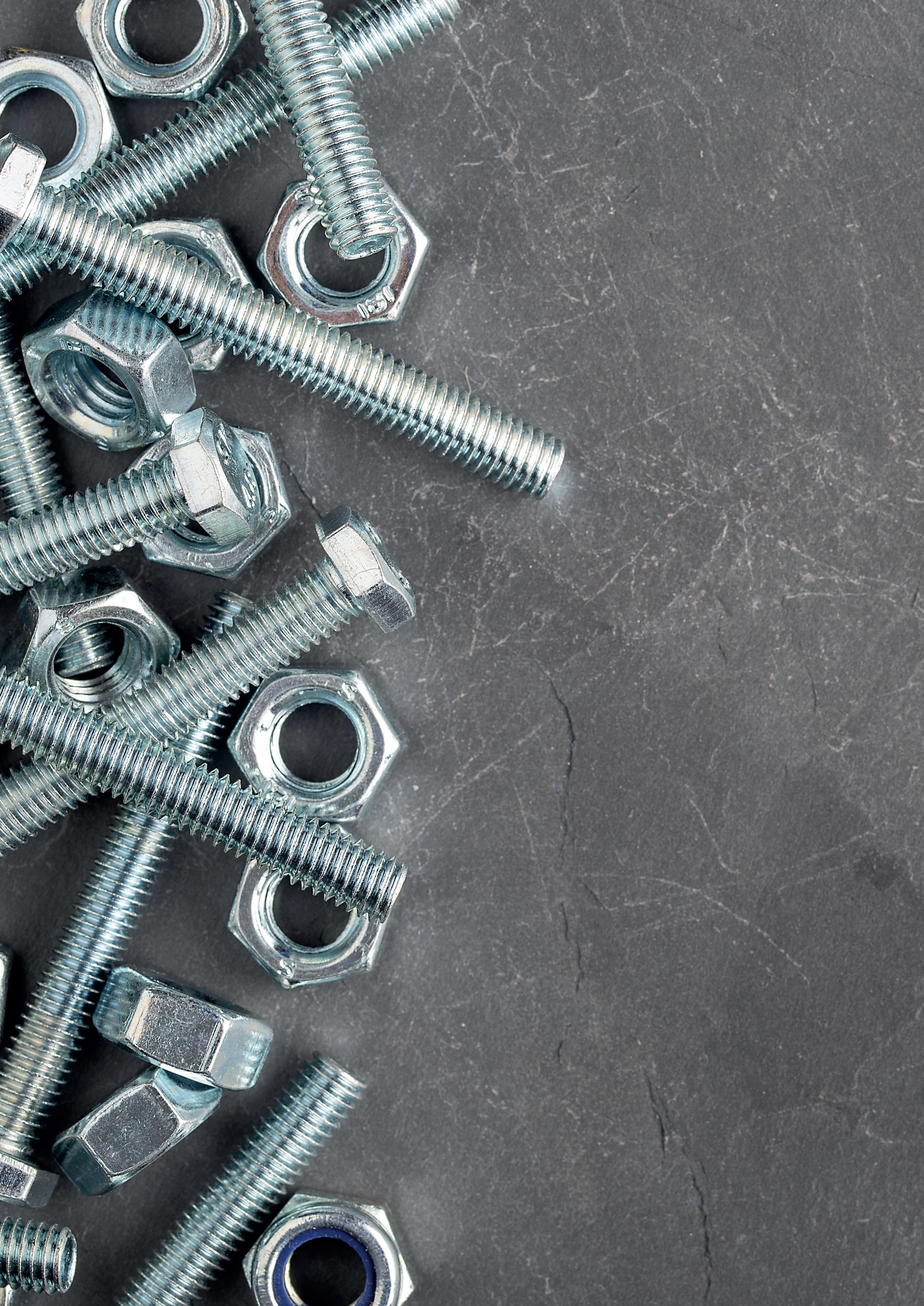
long-distance transportation. Secondly, after these pieces are transported to the site, they can be quickly installed with bolt connections, which is convenient for construction and has low technical requirements
for workers. At the same time, it can make significant labour savings, shorten the construction period, facilitate quality control, greatly improve power efficiency, and reduce construction costs. And thirdly, the more reasonable structural calculation also improves the safety of the bolted steel silo body.
Types of bolted steel silos
Henan SRON’s bolted steel silos are divided into three main categories. Using cement storage as an example, the characteristics of each type of silo are as follows:
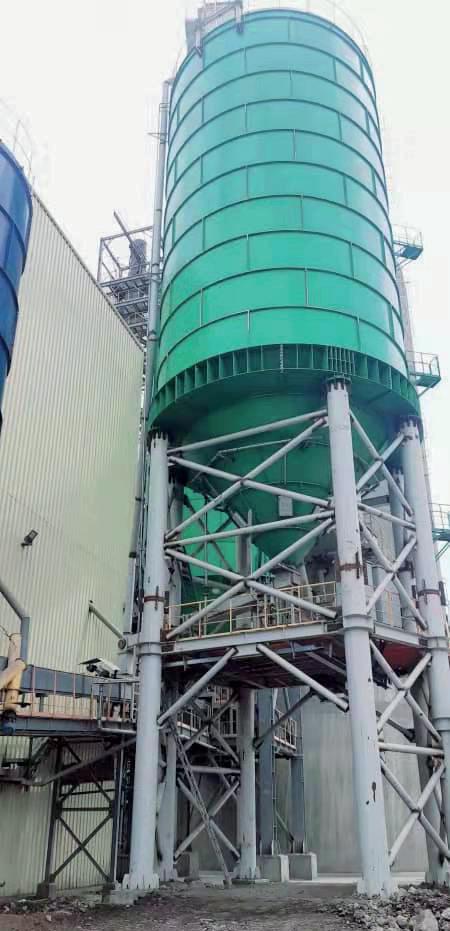
Flange-type bolted steel silo
All wall plates and roof plates of the flange-type of bolted steel silo are connected by flanges. There is no column support inside or outside the silo wall, but there is a cone, and the silo is supported by steel brackets.
When storing cement and the specific gravity is 1.3 t/m3, the reserve range is 50 – 1000 t.
Profiled-wall-plate-type bolted steel silo
The wall plates of the profiled-wall-plate-type bolted steel silo are pressed steel plates, the top plates are connected by flanges, the silo wall can be supported by columns. The silo also has cones and is supported by steel brackets.
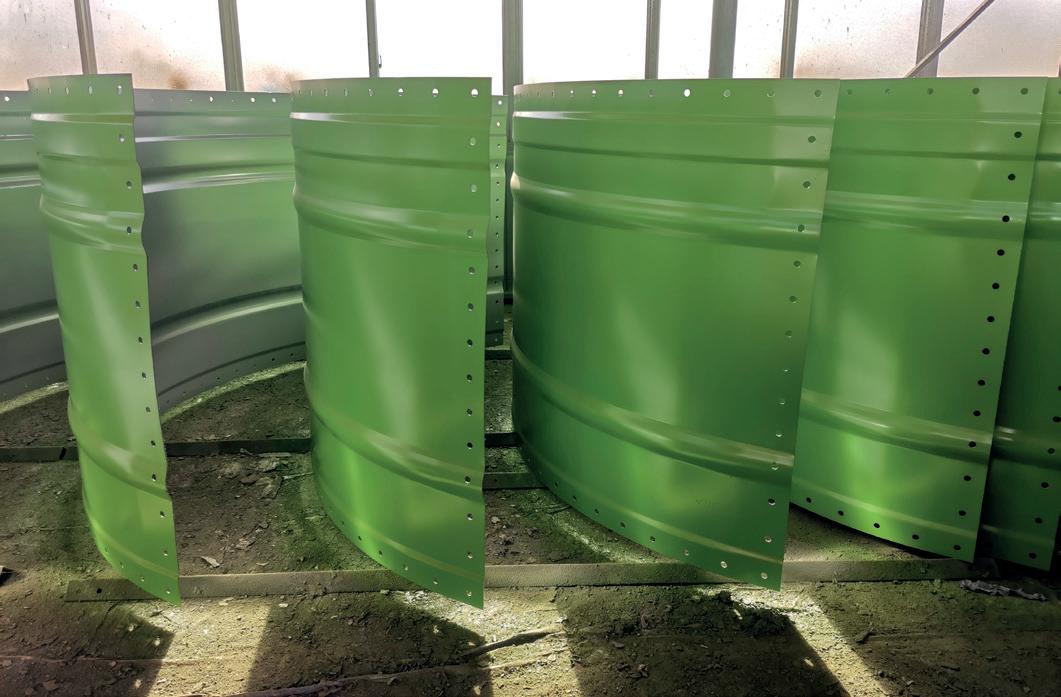
When storing cement and the specific gravity is 1.3 t/m3, the reserve range is 50 – 3000 t.
Large bolted steel silo
The large bolted steel silo wall plates are connected by flanges and double plywood, the top plates are connected by flanges, and the silo wall can be supported by columns without cones.
When the material is cement and the specific gravity is 1.3 t/m3, the reserve range is 1000 – 50 000 t.
Structural safety guarantee
Through market research, fully absorbing the advantages of similar products at home and abroad, through a comparison of the overall entity analysis and local entity analysis, and using ANSYS and STAAD structural calculation software for simulation analysis to calculate and optimise design, the structural safety of the steel silo can be fully guaranteed.
Take the design and calculation of 50 000 t cement steel silo example. The silo body conforms to Q355B. In accordance with the Chinese national standard, ‘Technical Specification for Steel Silos’ (GB 50884-2013), ‘Code for the Loading of Building Structures’ (GB50009-2012), ‘Code for the Seismic Design of Buildings’ (GB50011-2016), ‘Standards for the Design of Steel Structures’ (GB50017)-2017) and other regulations, SRON uses the general finite element software ANSYS to check the safety
1000 t flange-type bolted steel silo. Wall plates of the profiled-wall-plate-type bolted steel silo.LUBRICANTS
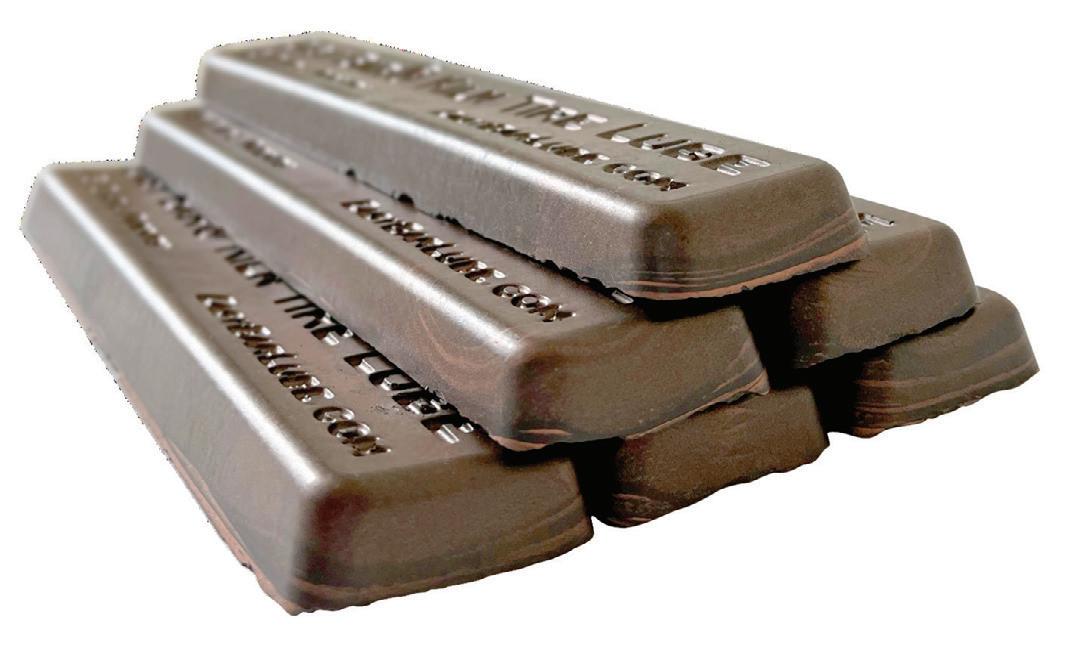
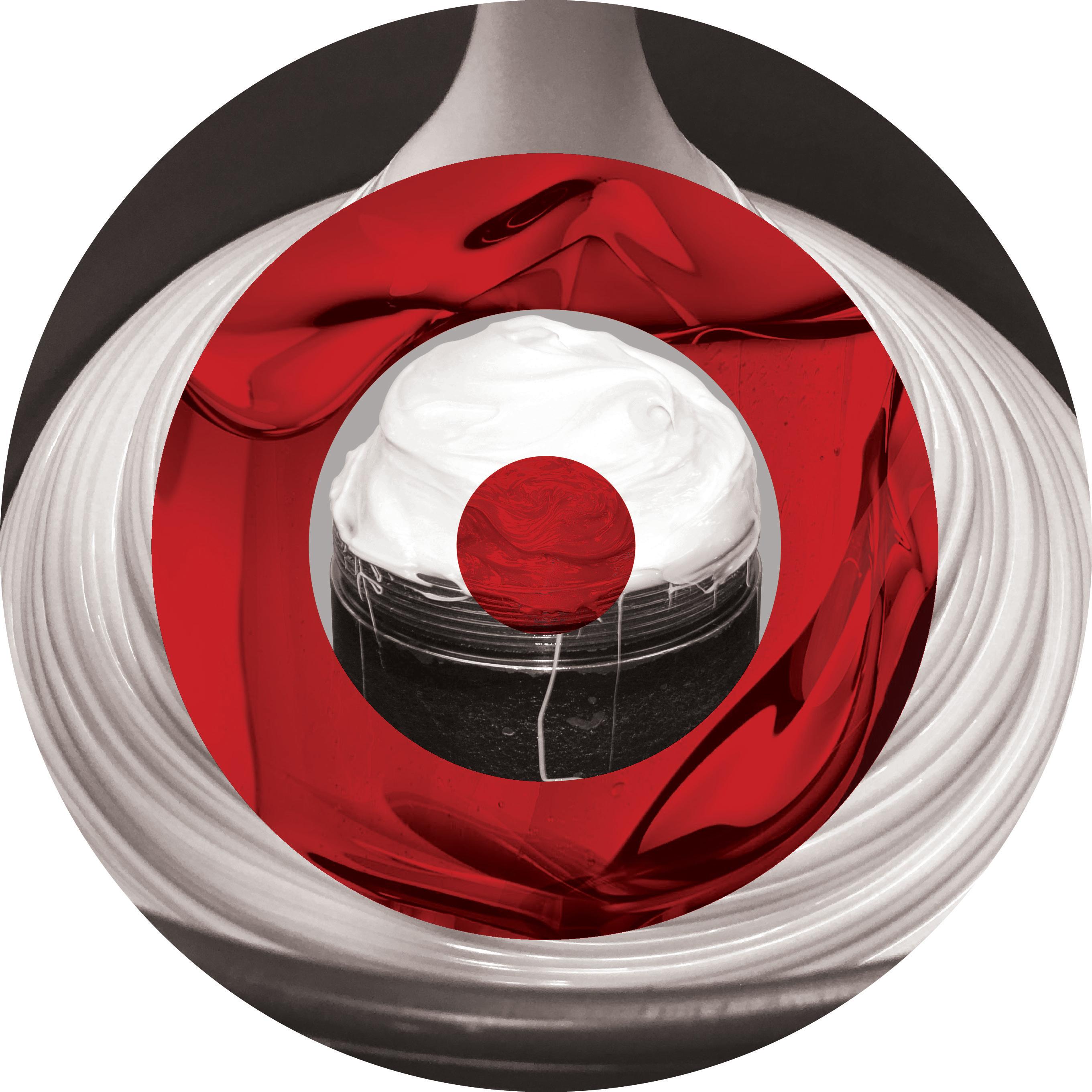
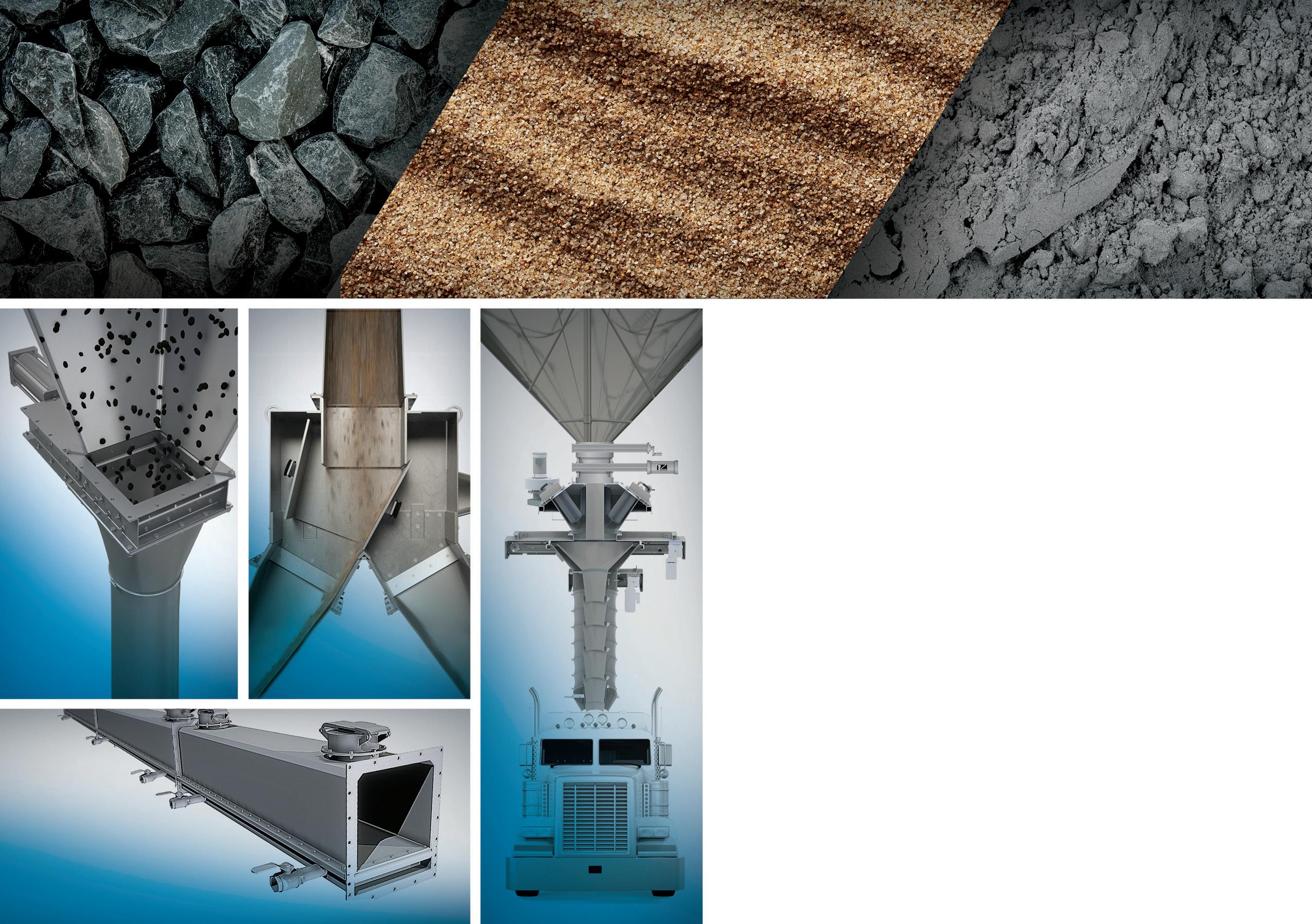
of the steel silo under a combination of different loads such as structural self-weight, storage loads (friction and horizontal pressure), silo roof constant loads, live loads, wind loads, and earthquakes.
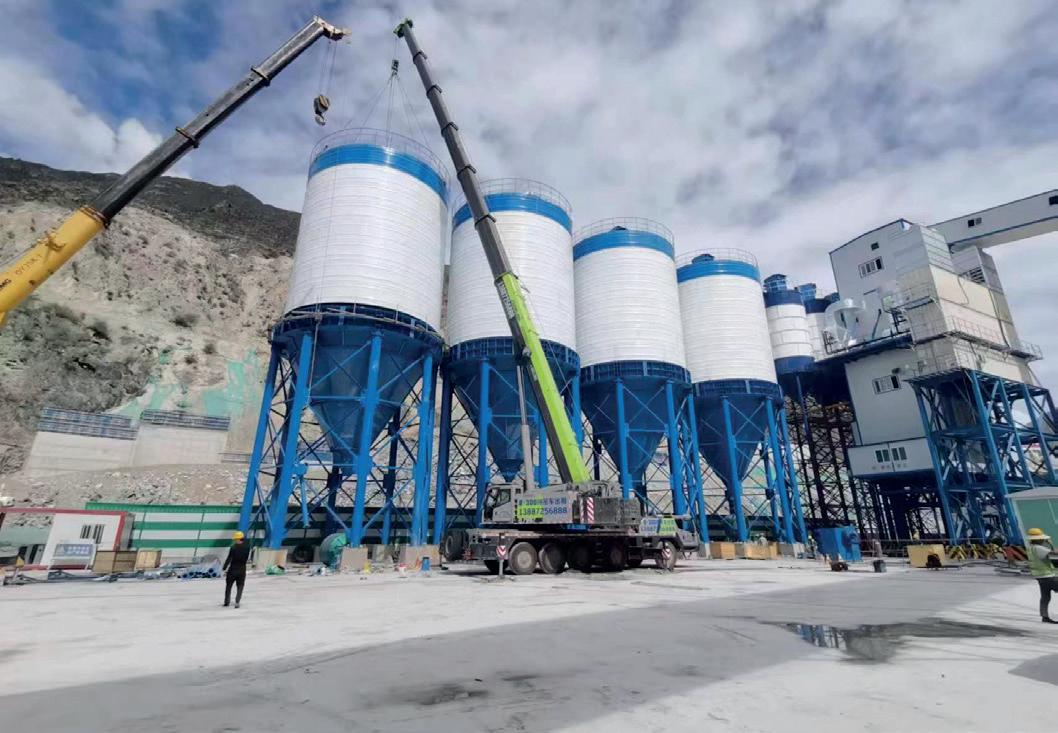
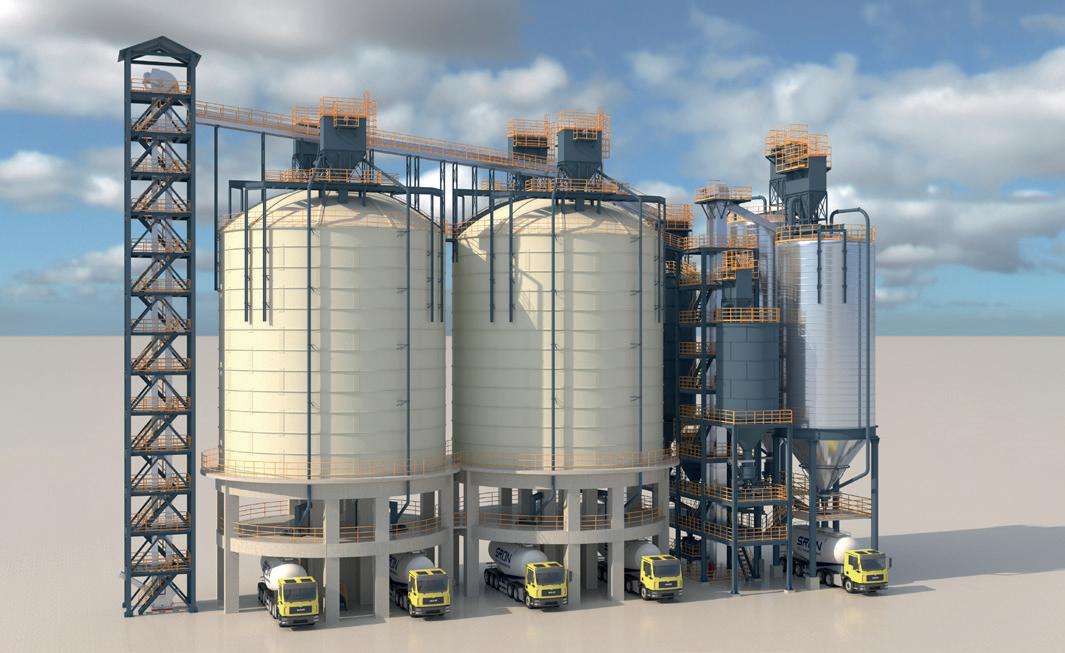
According to ‘Standards for the Design of Steel Structures’, the design value of tensile strength of the Q355 steel plate is f y = 310 MPa.
When wind load is involved in the combination:
The maximum equivalent stress is: f max = 265.3 MPa < f y = 310 MPa, meaning that the structure of the steel silo is safe.

When seismic load is involved in the combination:
The maximum equivalent stress is: f max = 301.97 MPa < f y = 310 MPa, which again shows that the structure of the steel silo is safe.
In terms of load value, a sufficiently large safety factor has been considered. Therefore, after the above calculation is conducted, the safety of the steel silo is fully guaranteed.
Safety guarantee measures for transportation
In order to facilitate transportation, the silo body and silo roof of SRON’s bolted steel silo are disassembled in the design stage, and formed into pieces in the processing plant. The connection nodes, after forming pieces, mainly include vertical splicing nodes and horizontal splicing nodes. Each segmented steel silo is surrounded by assembly connection nodes, which can form and achieve at least equal strength after assembly.
The packaging of SRON’s goods meets the requirements of science, economy, firmness, appearance, and marketability. For multiple loading, unloading and handling needs during long-distance ocean and land transportation, and preventing goods from mechanical damage, corrosion, mould growth, reduced technical performance, and losses during transportation and storage, the packaging of each product has a product mark, a packaging storage and transportation indication mark, and a shipping mark.
Benefits of bolted steel silos
With the improvement of environmental protection requirements in various countries in the world, more and more steel silos will be used in cement industry projects in the future. The application of bolted steel silos, designed with structural safety and transport guarantees can not only save on labour, shorten the construction period, and enable rapid installation and construction, but they can also facilitate better quality control and improve the safety of the steel silo body while greatly improving the power efficiency. Due to the global impact of COVID-19, in order to facilitate construction, the probability of customers using bolted steel silos in engineering projects has increased significantly, and the number of general system contracts has also increased year on year.
Steel silos are very common in the electrical power, coal, chemical, Portland cement, and other industries. The demand for these systems in domestic and foreign projects is high. The application and promotion of bolted steel silos are wide because of their various advantages, and in the future, it will partially replace the current welded steel silo system. Its market prospects are very broad, and it will achieve good economic and social benefits.
Profiled-wall-plate-type bolted steel silo installation site. Pre-assembly of large bolted steel silo. Structural stress diagram when wind load is involved in the combinationHARDING, BRICKING SOLUTIONS,
reviews a range of products that cement manufacturers can use to bolster worker safety and efficiency during refractory installations.
W ith advancements in kiln technology, outdated refractory lining installation techniques – such as pogo sticks or jack and timber – have slowly been replaced in cement factories around the world. Bricking materials have not changed much, but the way in which contractors align, place, and secure them has become safer and more productive than ever.
Most people are familiar with bricking machines, but some original equipment manufacturers offer specialised tools for every stage of kiln maintenance. Equipment designed specifically for this purpose and that works together seamlessly can contribute to a new level of safety and efficiency.
Safety cages and personnel tunnels
Starting with the initial inspection, plants have come to rely on safety cages and personnel tunnels to protect workers from falling debris throughout the maintenance process. Not all regions allow workers to enter kilns before coating and clinker are removed, but in areas where this practice is used, facilities that employ cages and tunnels have been able to reduce injuries. Like many pieces of refractory inspection equipment, cages and tunnels appear deceptively simple. However, careful material selection and design are key to optimising safety. Models manufactured with 6061-T6 aircraft aluminium offer the best strength-to-weight ratio. The material is
mocni g f u l l circle
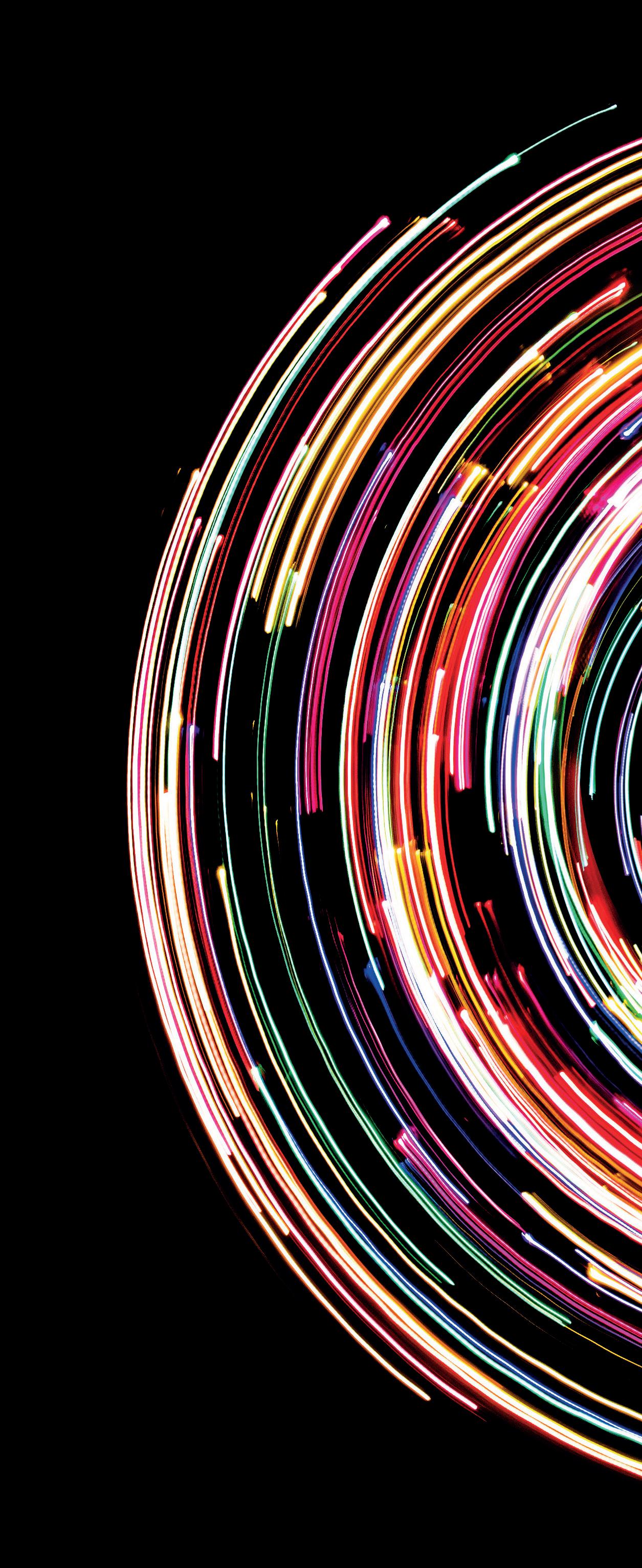
strong enough to protect workers from debris up to 112 kg (250 lb) falling from a height of up to 2.44 m (96 in.) and can be as much as 50% lighter than comparable steel models.
Industry-leading manufacturers incorporate additional safety features for even more protection. Crumple zones, for example, absorb the energy of a collapse, preventing serious injury or death. Stainless-steel netting protects workers from falling debris. To increase peace of mind, manufacturers perform a battery of destructive tests to ensure these features perform as intended in emergency situations.
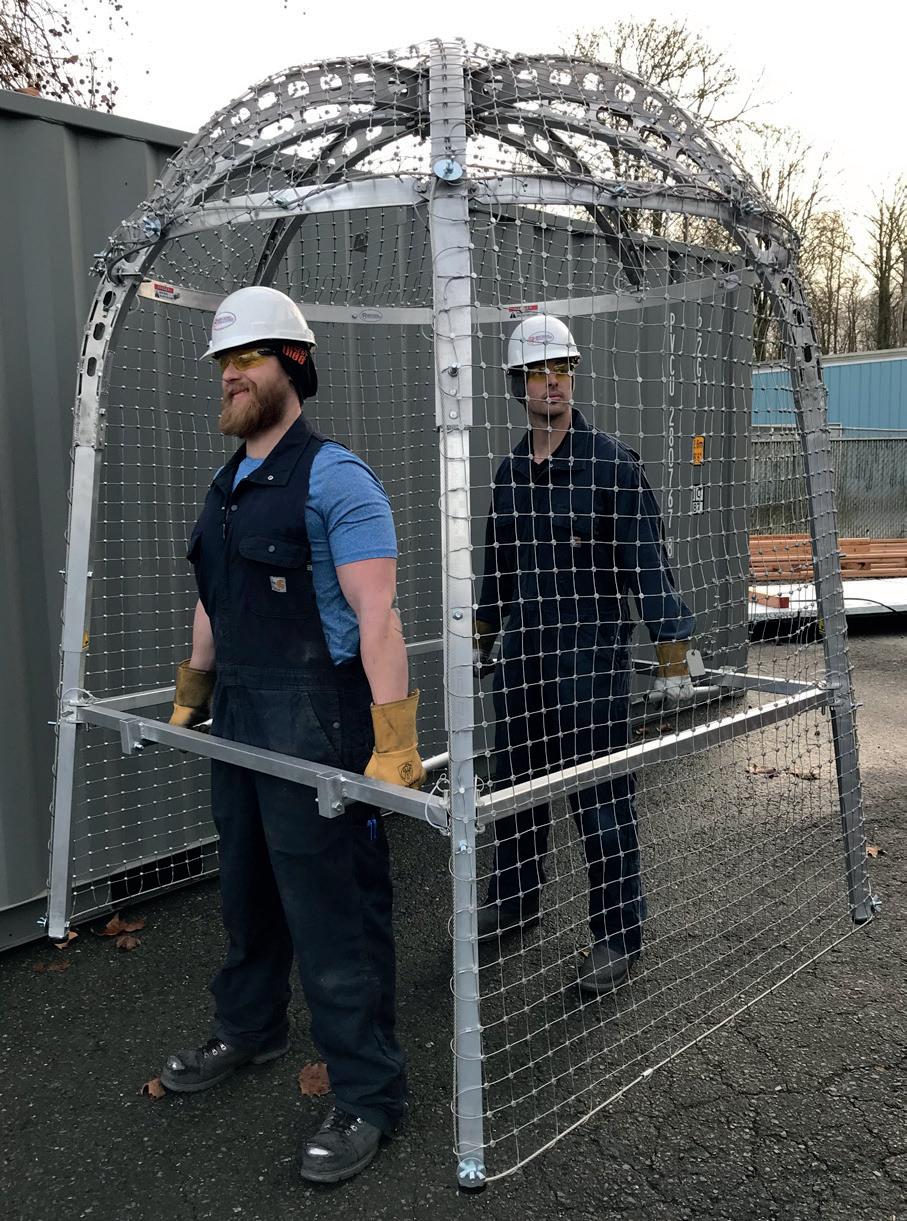
Kiln access ramps
Custom-engineered kiln access ramps also provide a significant safety benefit for refractory maintenance applications. While a simple plank bridge might have sufficed in the past, today’s refractory installation relies on heavy equipment, such as skid steers and tear-out machines, to expedite the process. To get people and tools safely across the cooler, metal access ramps have become standard in facilities worldwide.
Keeping in mind that every burn floor, cooler, and kiln is unique, partnering with a manufacturer that provides individualised products will help maximise safety benefits and efficiency for this vital installation component. Heavy-duty aluminium equipment provides durable, long-lasting results at half the weight of steel. An access ramp manufactured with this material can support as much as a 6804 kg (15 000 lb) live load. Custom-designed equipment can also incorporate features such as curbs and fall guards, when necessary, to protect workers as equipment moves across the ramp.
Conveyors
Incline and hydraulic conveyors are tools that refractory installers find increase efficiency as well as employee safety. Parts of the world with access to large labour pools might still find ‘bucket brigades’ a viable option for transferring refractory material up the kiln. However, this method results in excess brick handling, which could cause damage to refractory materials – not to mention unnecessary sprains, strains, and repetitive motion injuries. So, with safer options readily available, progressive facilities and contractors are embracing a more automated approach.
Using a conveyor, workers can easily move materials twice as fast as manual methods with significantly less physical strain. In addition, refractory equipment specialists provide lightweight,
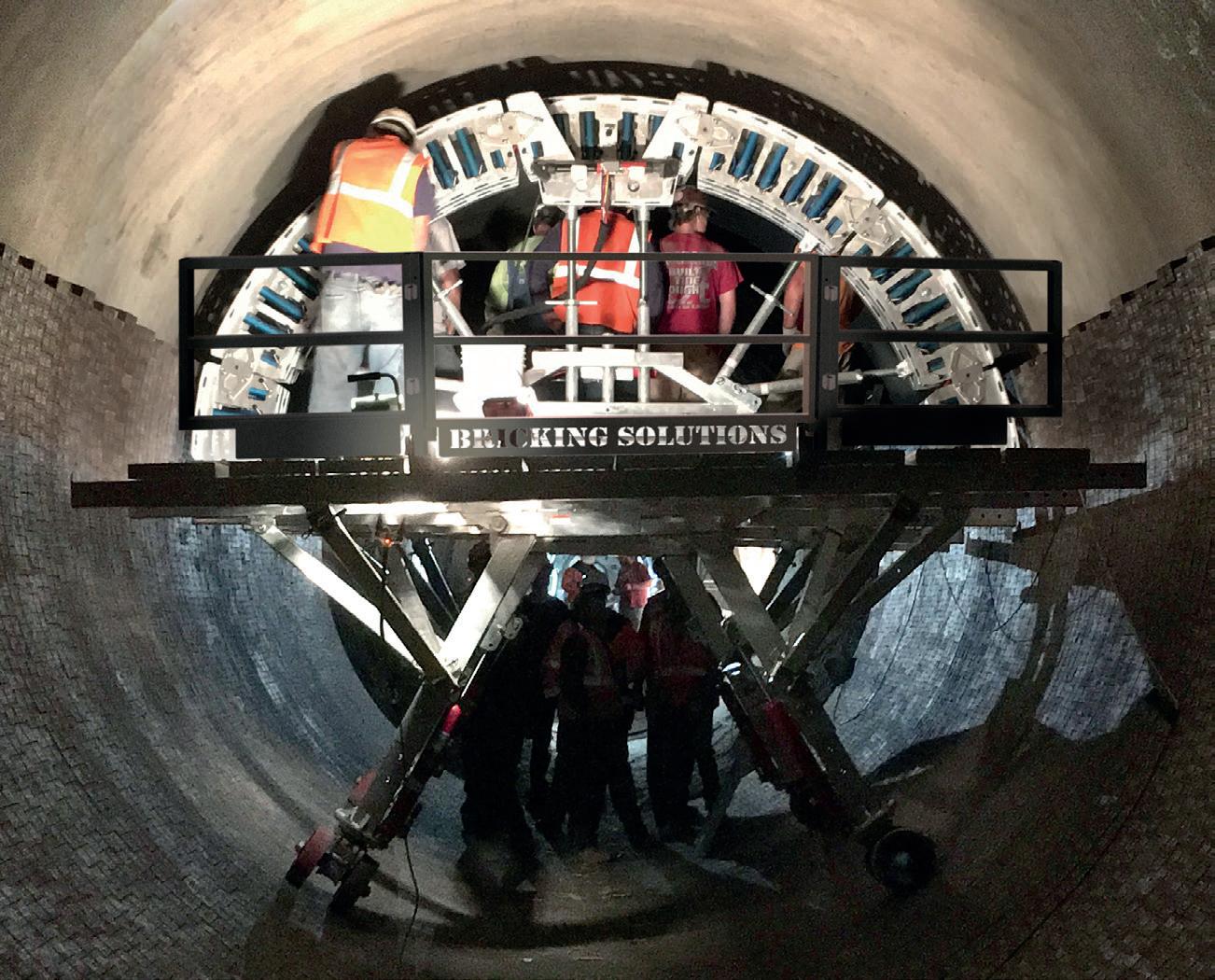
modular equipment that is easily adapted to fit a specific kiln, including kiln diameter, burn floor length and terrain adjustments. With sections weighing just 16 – 19 kg (35 – 42 lb), transportation and installation are easy for a small crew.
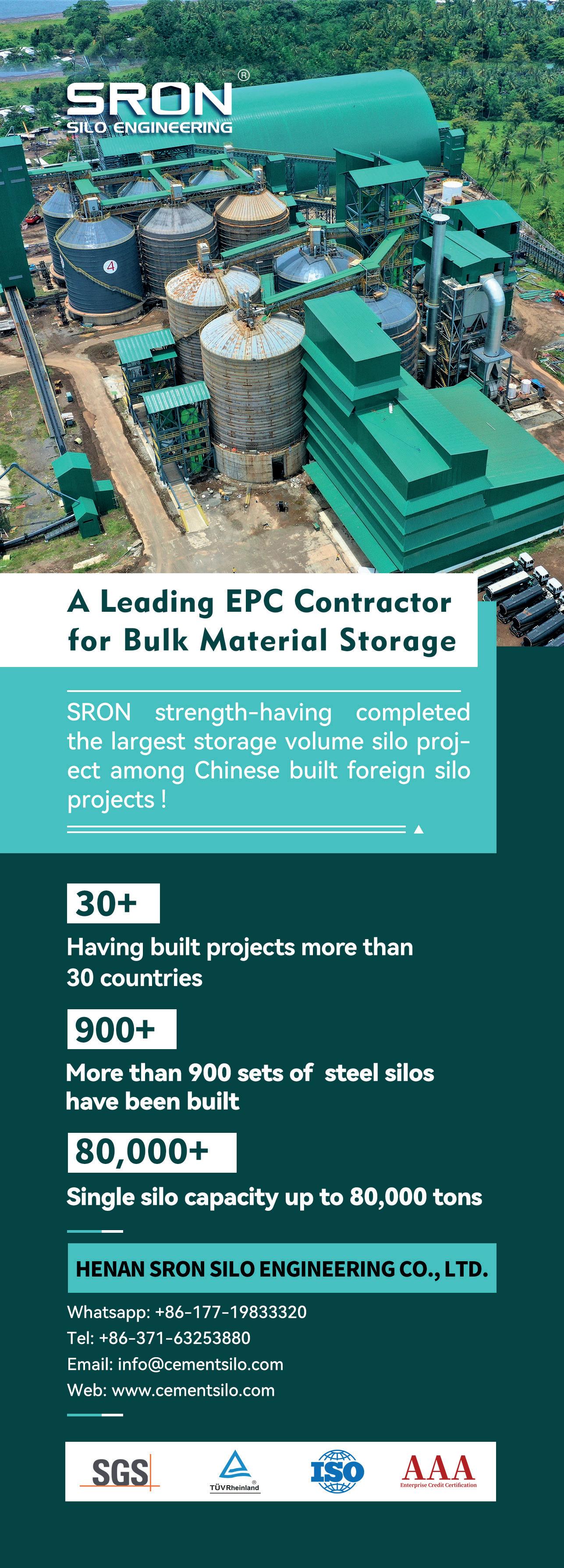
Bricking machines
While support equipment has played a major role in increasing safety during refractory installation, perhaps the most significant gains have been made in the bricking process itself. The widespread adoption of bricking machines in recent decades has revolutionised installation application speeds and overall safety. Pogo sticks, mechanical jack screws, gluing, and jack and timber techniques are still used by some contractors, but most installations worldwide employ a bricking machine.
Features and safety benefits vary among bricking machine models, but their overall contributions to installation efficiency are undeniable. Decades-old, first-generation machines can still reduce physical strain and safety risks compared to outdated installation methods – as long as they are well maintained. Newer models provide the most innovative and cutting-edge technology such as adjustable dual-arch systems with pneumatic cylinders to push bricks into place, greatly reducing the risk of injuries from unsupported overhead bricks. Machines featuring ergonomic design elements further increase worker comfort and safety. For example, models from innovative manufacturers offer a cut-away section for unobstructed keying access to increase ease and visibility for closing out a ring. Additional safety features are also available from specialised manufacturers including non-slip decks, dual braking systems and fall guards.
An experienced crew using a bricking machine can install 1 m (3.3 ft) of brick per hour, compared to roughly 0.6 m (2 ft) with other techniques. The end result is better refractory installation, which increases longevity and decreases downtime and repairs. The widespread use of bricking machines has also significantly decreased refractory installation-related injuries and fatalities.
And many more
From tear out to clean up, innovative manufacturers offer a full range of support equipment to make refractory installations faster, safer, and more efficient. A comprehensive range of refractory safety options ensures facilities can maximise uptime without risking injury.
About the author
Heather Harding is the managing director for Bricking Solutions, a leader in kiln refractory installation solutions. She has served in industry leadership positions for more than 14 years.
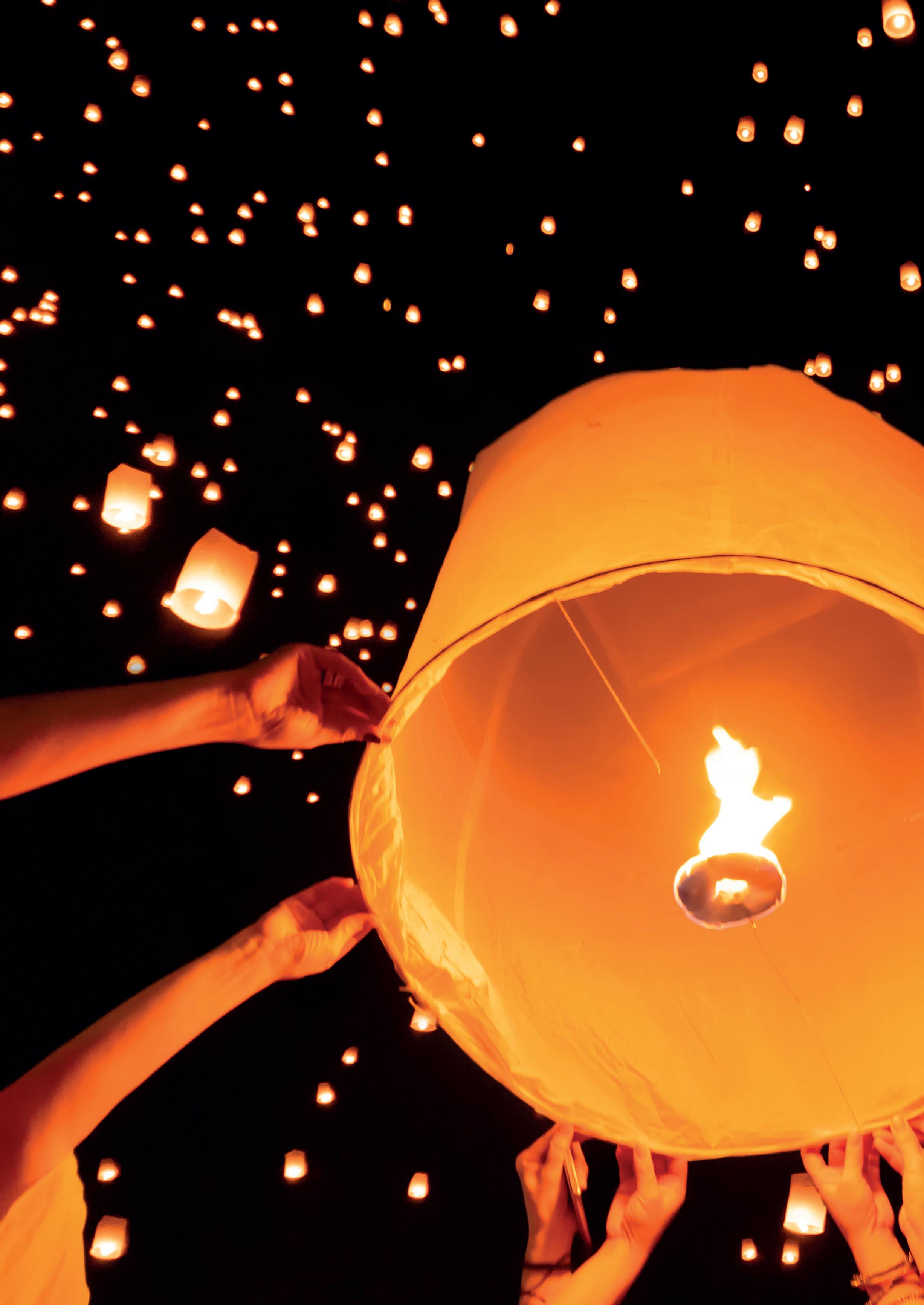
PLACING OUR hopes
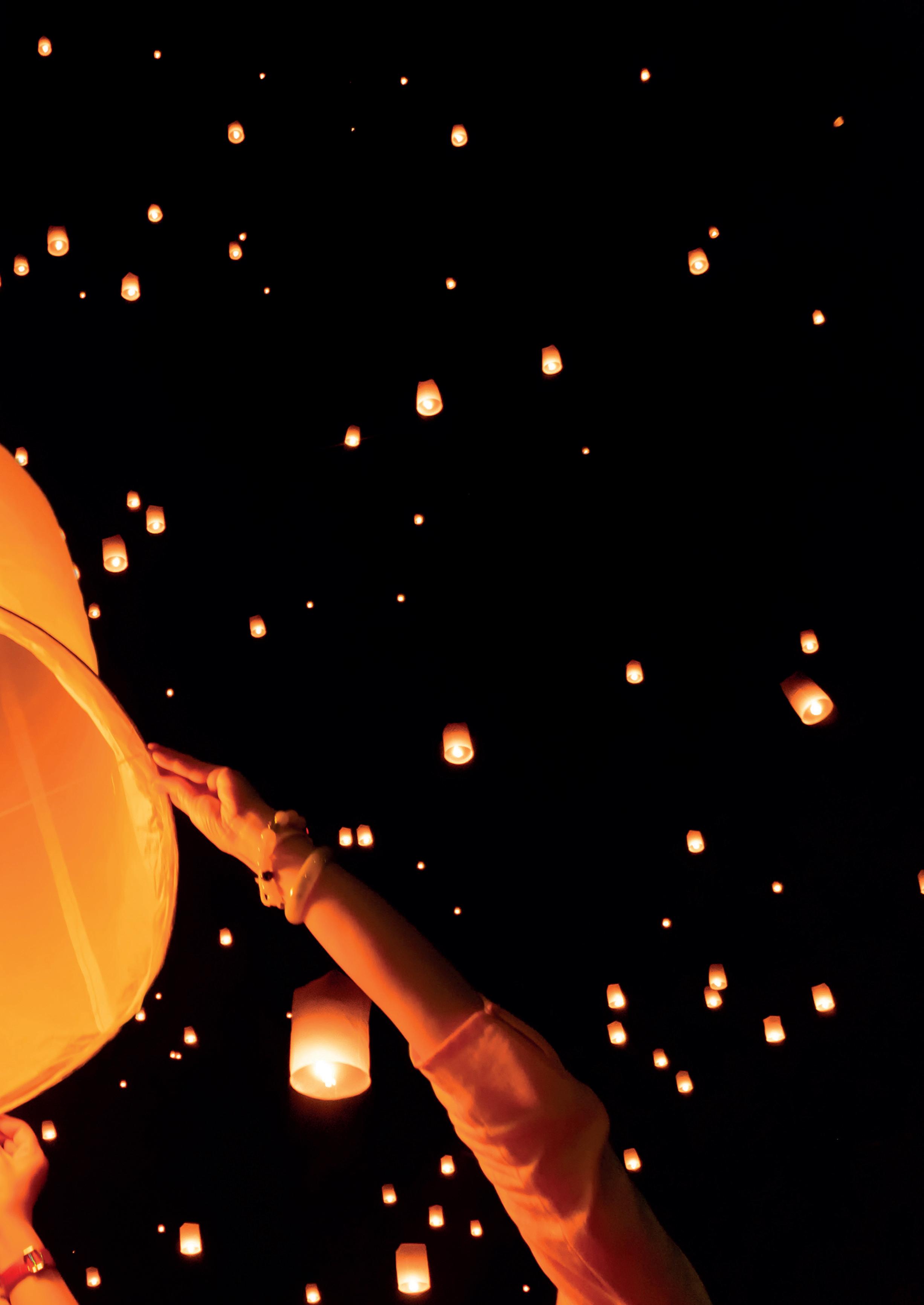
IN HYDROGEN
he factors involved in the rapidly-evolving hydrogen industry, seen by many as the ultimate silver bullet for mitigating CO2 emissions, create a very broad topic which needs to be discussed in more detail. Obviously, there is no carbon in the hydrogen. But, is it that simple? The necessity of transitioning to a ‘low-carbon’ economy is a widely accepted concept. Nonetheless, the decarbonisation of human economic activity is a complex matter that can only be responsibly assessed and executed by considering the myriad differences among social and economic conditions of differing nations, and where those are positioned in the hierarchy of needs.
In that context, the utilisation of hydrogen on a large industrial scale has been identified as one of the paths to reducing carbon dioxide emissions, but it is still ‘only one piece of the puzzle’, as highlighted
by the International Energy Agency (IEA) in its Global Hydrogen Review 2021 Report (Figure 1).
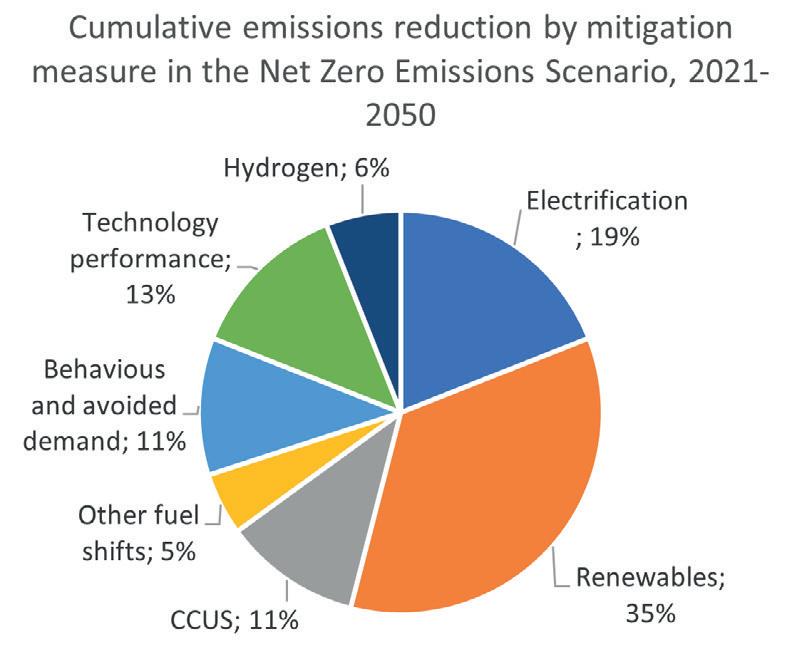

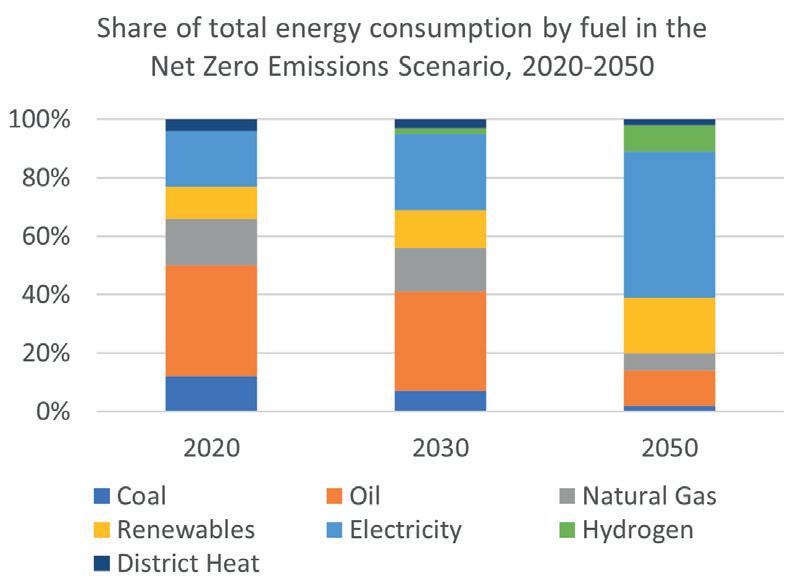
This article will try to shed some light on the potential role of hydrogen utilisation in the cement industry by breaking down the approach into three main categories: environmental footprint, economics, and specific challenges in clinker production.
Hydrogen’s environmental footprint
The first myth to be addressed is that hydrogen is a clean fuel. Although the straight combustion of hydrogen does not generate any carbon dioxide, most of the hydrogen produced in the world is responsible for a fair amount of greenhouse gas emissions. The IEA estimates that hydrogen production accounts for the formation of 830 million tpy of CO2 (with the current hydrogen production matrix (Figure 2), 1 kg of hydrogen produced generates around 10 kg CO2).
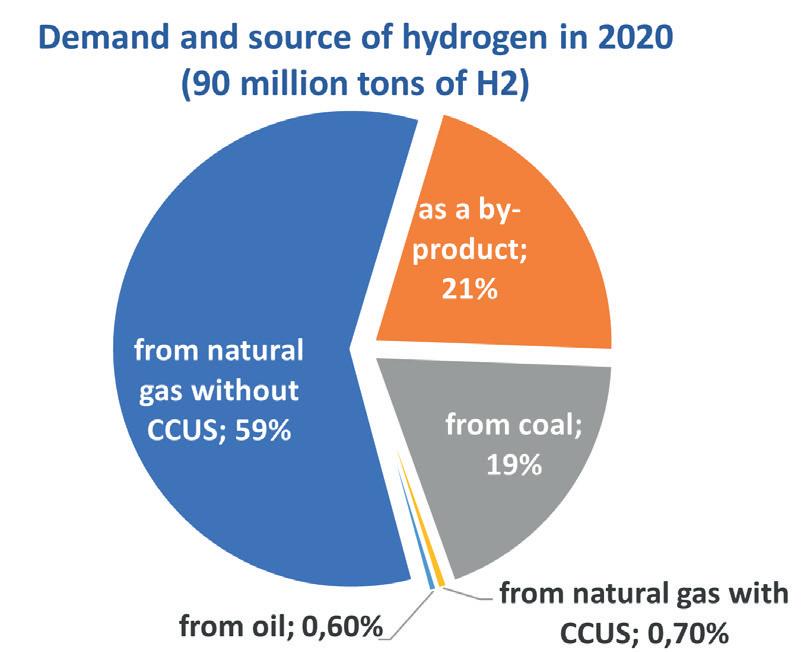
However, there is an important differentiation to be made depending on production processes. Colours are often used to indicate how ‘clean’ the hydrogen production is: ranging from grey (brown or black are also used), to blue, and green, from the least to the most environmental-friendly process.
f Grey (brown and black) hydrogen is produced from fossil hydrocarbon-based fuels, typically natural gas (grey hydrogen) or coal (brown or black hydrogen). The fossil fuel components are broken down into hydrogen and carbon dioxide, among other minor components.
This method, known as the ‘steam reforming process’ (SRP, or SMR for steam methane reforming, when the hydrocarbon used is methane), releases the same or larger amounts of CO2 per unit of energy when compared to the direct use of the originating fuel (natural gas or coal for example). The reason for this is that this process requires an additional energy source to break the fossil fuel into hydrogen and CO2 and this additional energy source usually comes from fossil fuels.
f Blue hydrogen: the production process is similar to grey hydrogen, with the difference being that the majority (80 – 90%) of the CO2 produced by the blue hydrogen process is captured and stored through a carbon capture, usage, and storage (CCUS) unit.
f Green hydrogen: the hydrogen is produced using water electrolysis powered by renewable energy such as solar or wind. As a consequence, oxygen is released to the atmosphere (or used for other processes) as a byproduct. From this list, it is clear that green hydrogen is the only truly carbon neutral source of hydrogen (not considering the CO2 generated to produce the solar or wind equipment).
There are other ‘colours’ of hydrogen, depending on the processes, or the power source used to
Figure 1. Hydrogen is an important part of the net zero emissions scenario ZNE, but it is only one piece of the puzzle (IEA).Figure 2. Demand and source of hydrogen in 2020 (IEA).
generate it. Up to now, these continue to represent a pretty minor percentage of the hydrogen production environment and therefore will not be discussed.
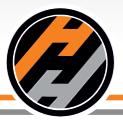
It means, in a broader context, that the combustion of grey hydrogen has a larger CO2 footprint per unit of energy released than natural gas and fuel oil (Figure 3) and a similar CO2 footprint to coal combustion. Therefore, the use of grey hydrogen as direct substitute for natural gas or fuel oil is actually environmentally detrimental, while even direct coal substitution is barely environmentally beneficial.
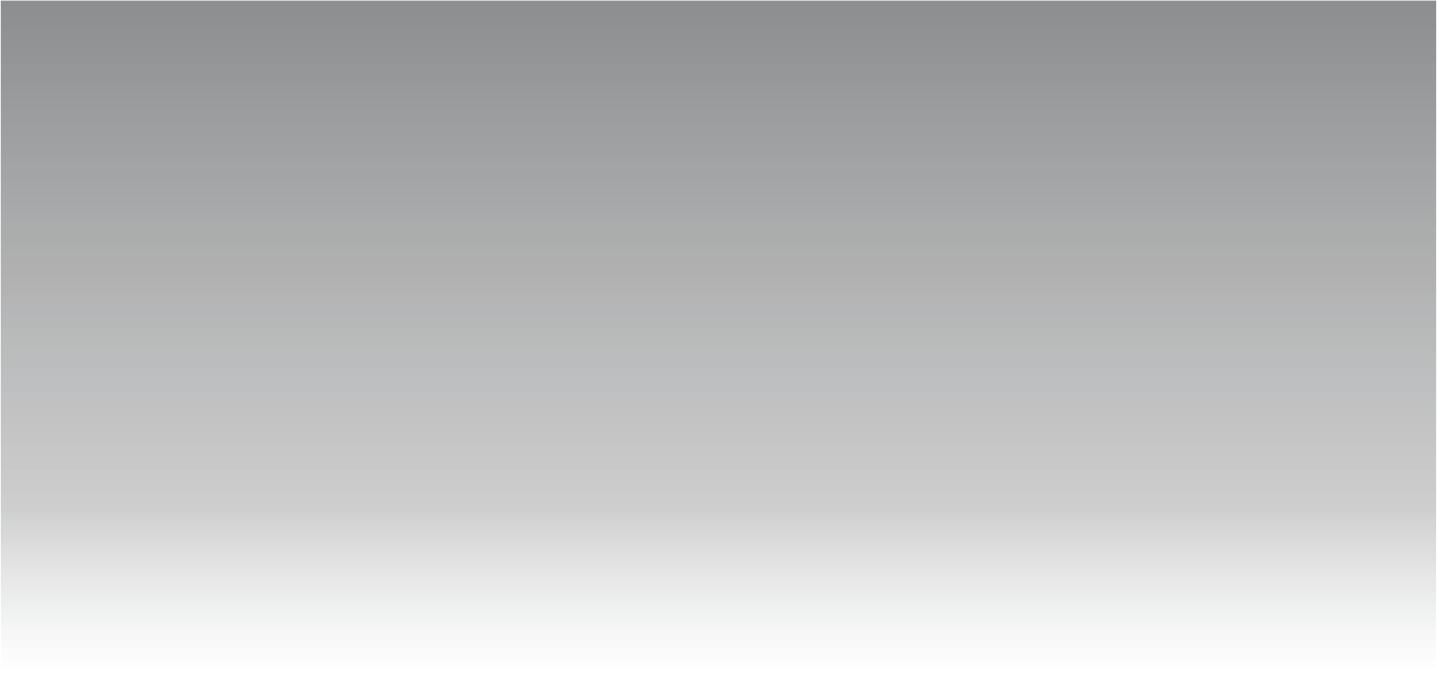
As a matter of fact, over 99% of the hydrogen produced in the world is still in the ‘grey’ category – blue/green hydrogen accounts for less than 1% of total production.
Economics
Production cost
Production of blue/green hydrogen is not cheap (Figure 4). There is still an important price gap between natural gas and hydrogen.
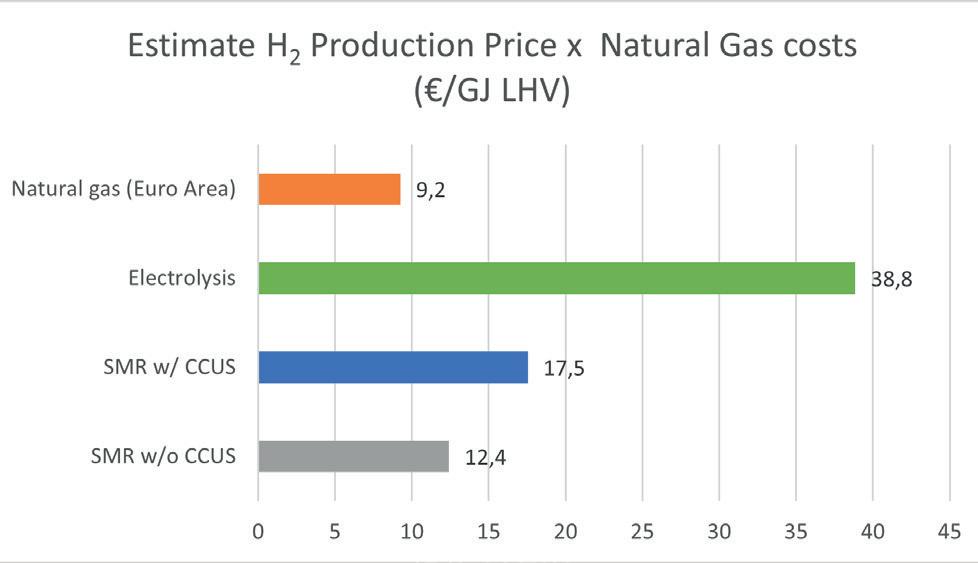
The electrical consumption and CAPEX of electrolytical units varies depending on the technology (proton exchange membrane, alkaline, anion exchange membrane or solid oxide), configuration of the unit and provider, however production of hydrogen using electrical power is still energy intensive (Figure 5).
From Figure 5, it is possible to conclude that the production process of green hydrogen is still pretty inefficient. For each kW of ‘chemical energy’ in hydrogen, it requires between 1.50 and 2.35 kW of electrical energy, meaning an efficiency of between 42 and 66%.
If compounded with the conversion efficiency of renewable energy sources (15 – 20% and 20 – 50% for solar panels and windmills, respectively), the result is a meagre 6 – 33% overall efficiency. This is something that is worth considering, although the renewable sources mentioned are virtually endless.
Scalability
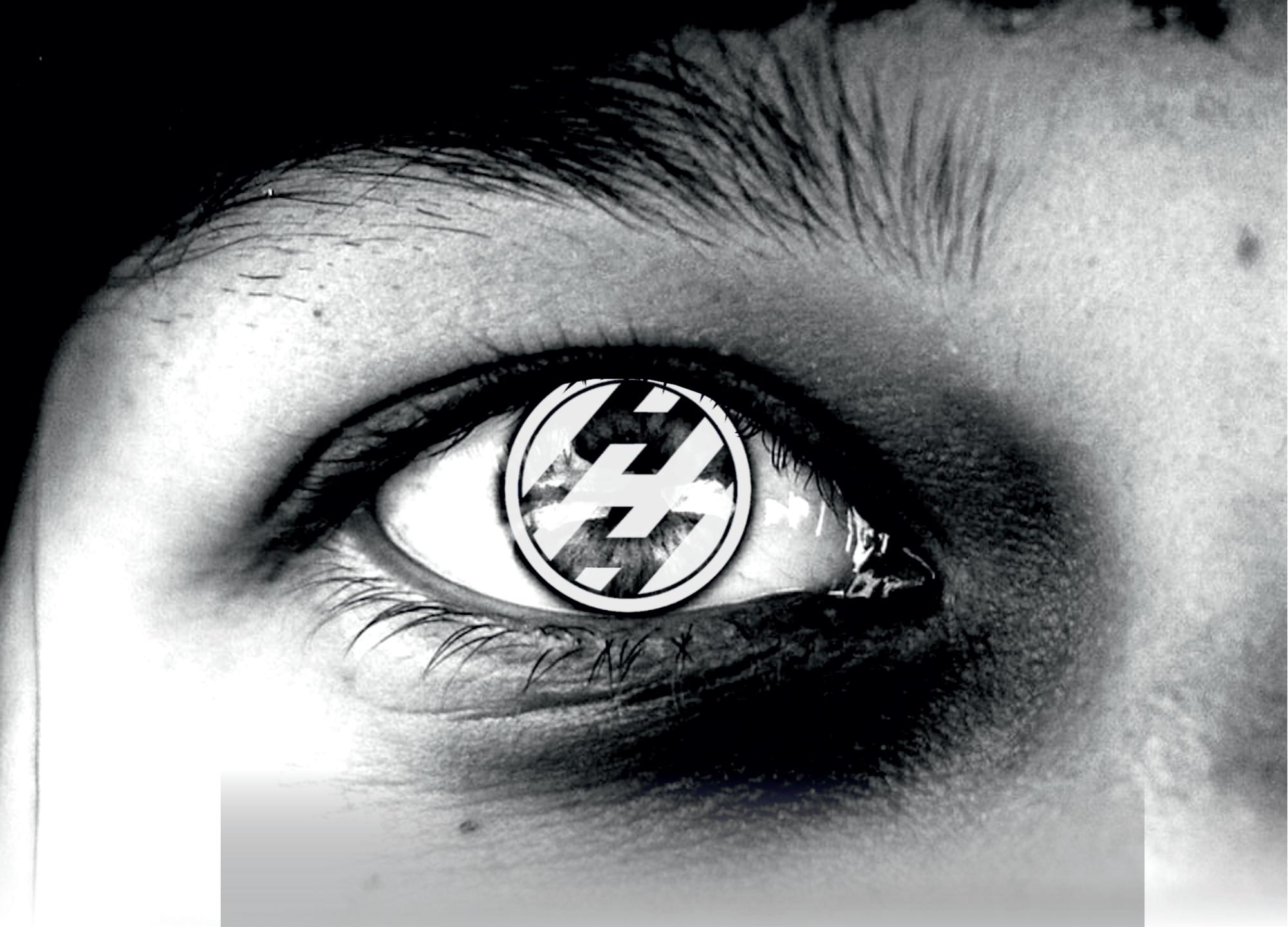
Green hydrogen production facilities are quite small. Although this is a fast-evolving field, it is believed that the largest green hydrogen plant in the world in 2020 had a hydrogen production of equivalent to 20 MW, and it was in reality an assembly of smaller units. More recent information indicates the development of newer plants, with larger capacity in 2022.
Likewise, the total production of green hydrogen in 2021 was around 300 MW. If all of this energy was used for clinker
Figure 3. CO2 emission (kg CO2/GJ LHV heat released).
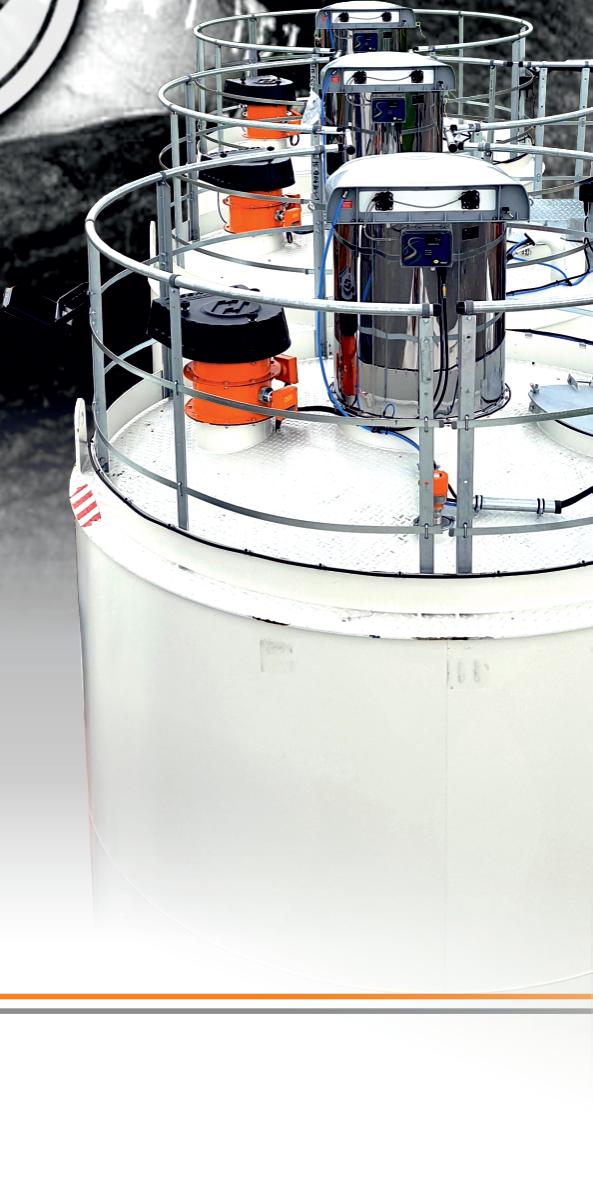

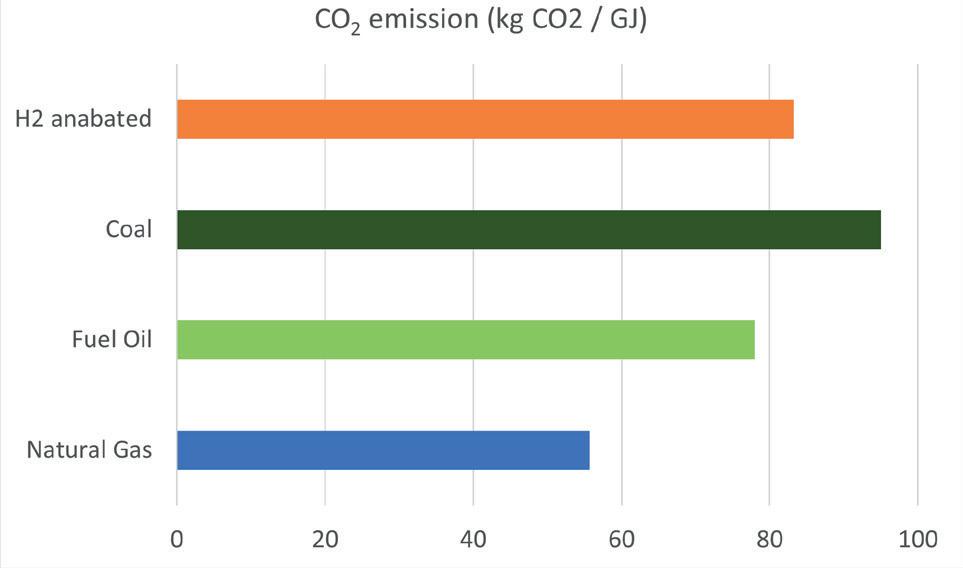
production, it would be possible to operate just two kilns at a production rate of 4000 tpd and 775 kcal/kg over the course of a year, considering 100% hydrogen as fuel.

Infrastructure
There is no large-scale infrastructure or distribution network supplying hydrogen to industrial facilities. The existing natural gas pipelines, compressors, accessories are not fully adapted to transport 100% hydrogen for several reasons, including among others:
f Hydrogen carries about 67% less energy per cubic meter (distribution equipment and
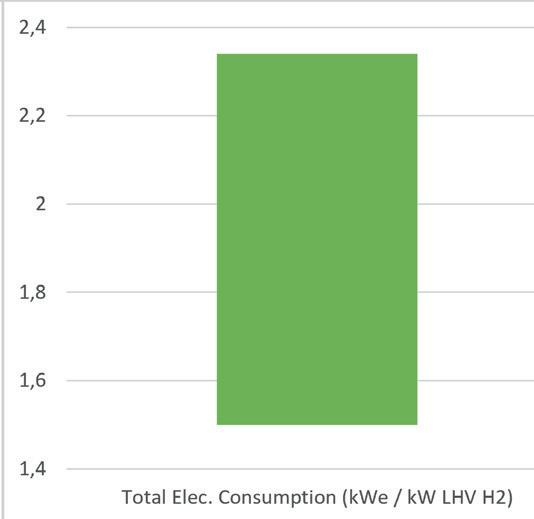
pipelines depend mostly on volumetric flow rather than mass flow) when compared to natural gas.
f Hydrogen at high pressures may penetrate the steel structure and cause embrittlement of the metal.
Therefore, the implementation of distribution networks will require substantial CAPEX.
At this point, it is clear that the only environmentally viable type of hydrogen is green hydrogen. Extensive research is being conducted and large incentives are being granted, in order to reduce the price gap between the green hydrogen production and other types of fuels, to improve the efficiency of its production process as well as making it available to ‘heavy consumers’. Although there is still a long way to go, there is a general optimism that these gaps will be reduced or eliminated in the future.
Cement production
Assuming that all the other aspects are addressed, i.e. green hydrogen is readily available at the kiln platform at a reasonable cost, next the cement process itself must then be tackled. Firing hydrogen in clinker kilns requires special attention to few points:
Heat transfer
Pure hydrogen flames are non-luminous and poorly radiative because, unlike solid fuel flames, they do not generate soot or contain particles.
FCT foresees co-firing as a feasible solution to improve radiative properties of the flame. Although none of them have been tried in large scale combustion units, FCT is confident there is sufficient evidence to back those alternatives.
Recent studies suggest that a mixture of up to 25% hydrogen/75% natural gas (volume basis) has no significant impact in the overall emissivity of the flame, when compared to 100% natural gas.
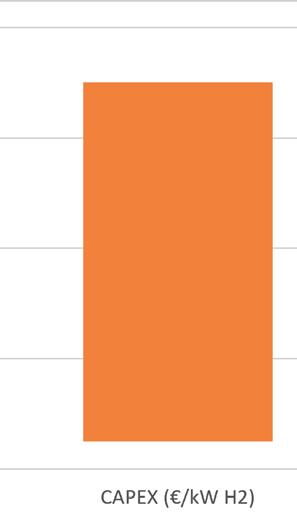
Other experiments with propane/hydrogen mixtures have shown that heat transfer by radiation sharply drops, but only when the blend is over 60% hydrogen (Figure 6).
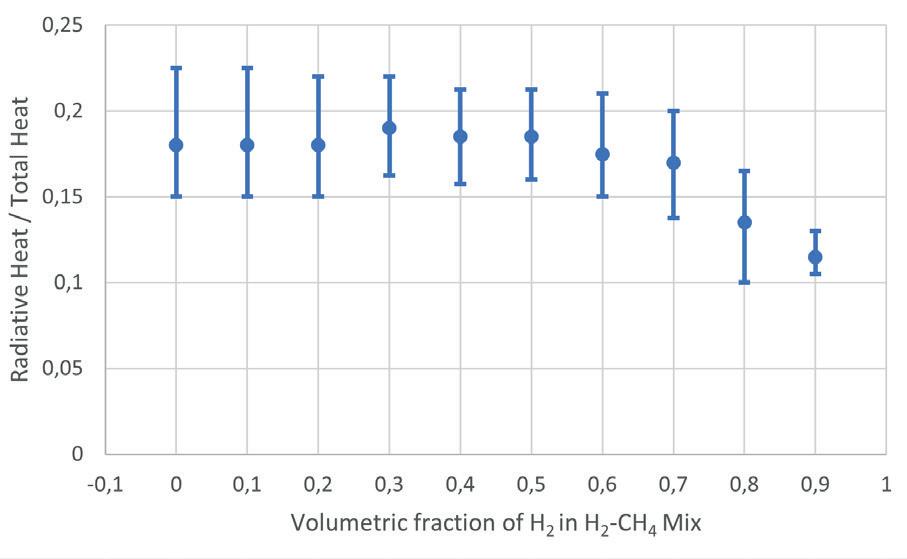
The injection of pulverised fuel is another alternative to address the emissivity and heat transfer issue. It significantly increases the emissivity and therefore the heat transfer properties of a gaseous fuel flame (Figure 7).
Figure 6. Decrease in emissivity over 60% of H2 in H2/propane mix (top). Decrease of turbulent flame length with the increase of H2 in H2/propane mix (bottom).2
Obviously, the addition of materials without any calorific value increases the fuel consumption as part of the energy will be used to heat such particles, however, it is believed that the benefits of the higher emissivity and improved heat transfer properties of the flame overcome the increased fuel usage in a typical clinker kiln. An easier way, that is already available today, to avoid the reduced emissivity of hydrogen
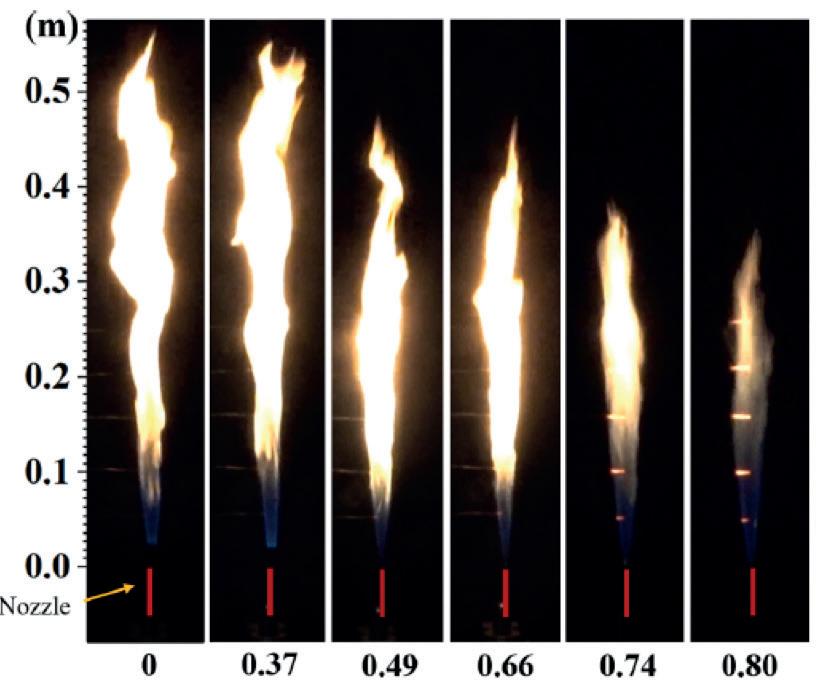
InterSep enables you to separate a wide variety of raw materials in a highly energy-efficient manner, while remaining flexible and compact. With the upgrade of the new high-performance separator of the latest generation, InterCem has the right product for every specific application. A low bypass rate ensures the highest possible separation efficiency. Whether as a single component or in a complete plant.
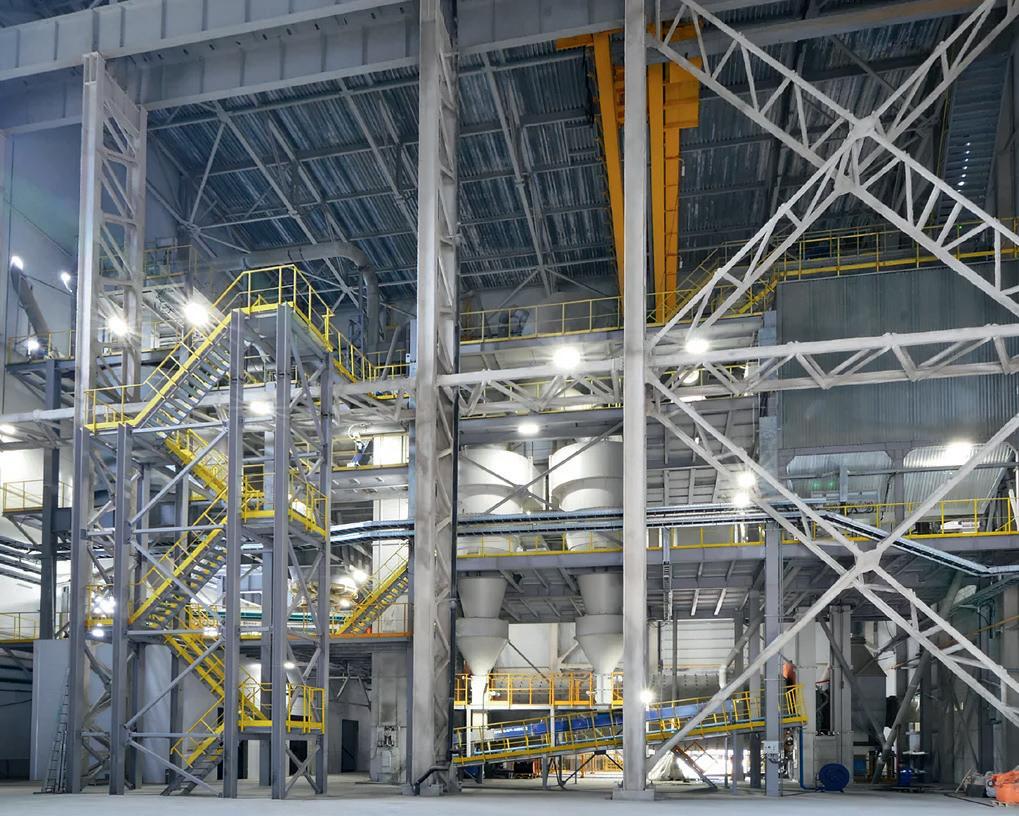
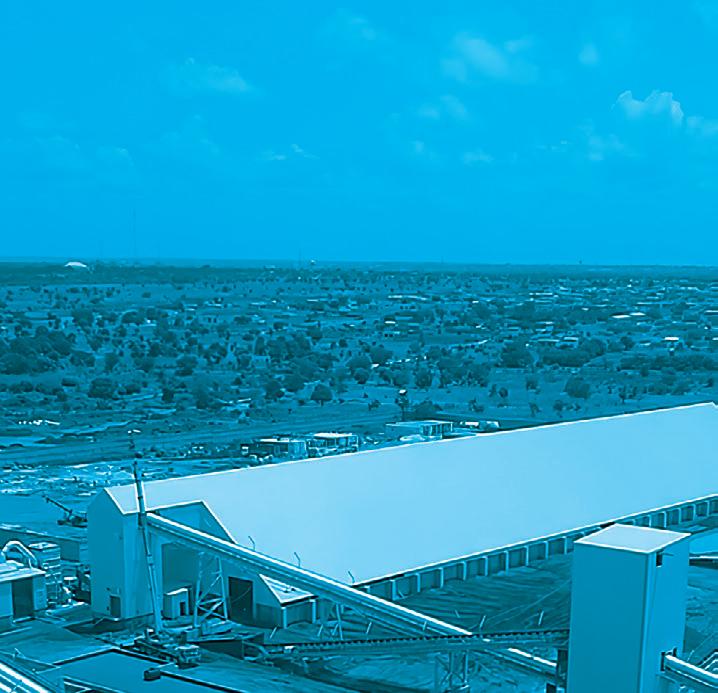
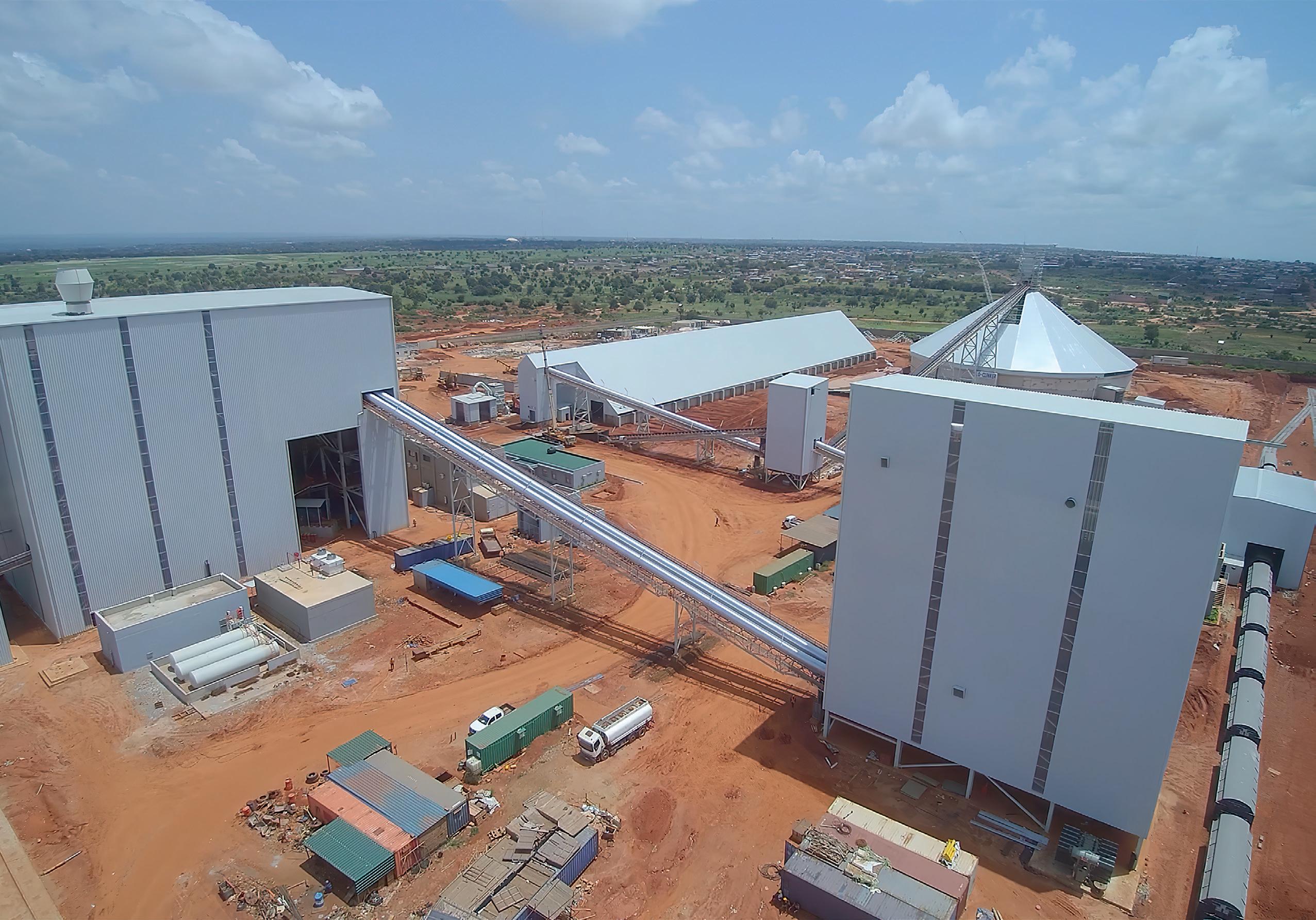
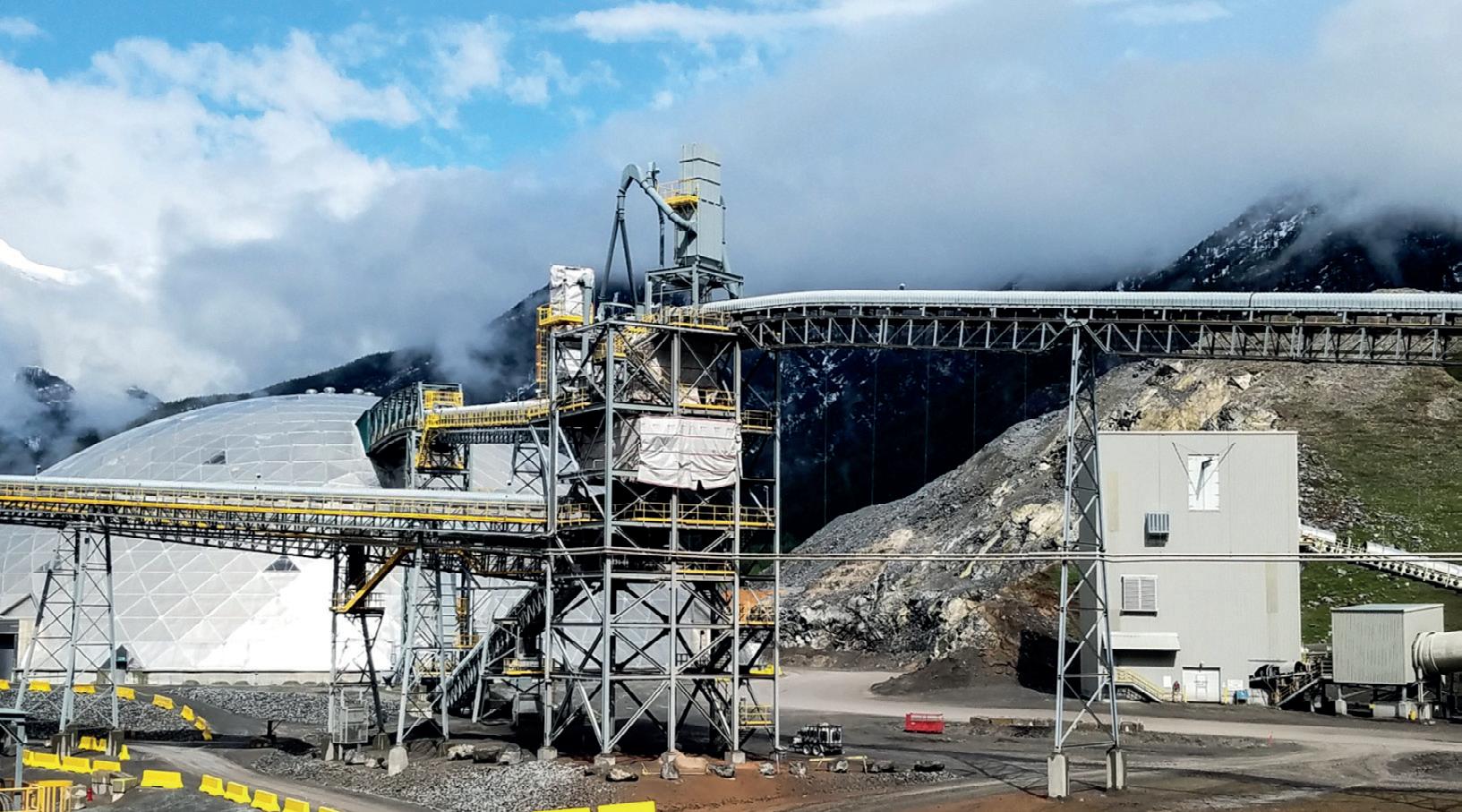
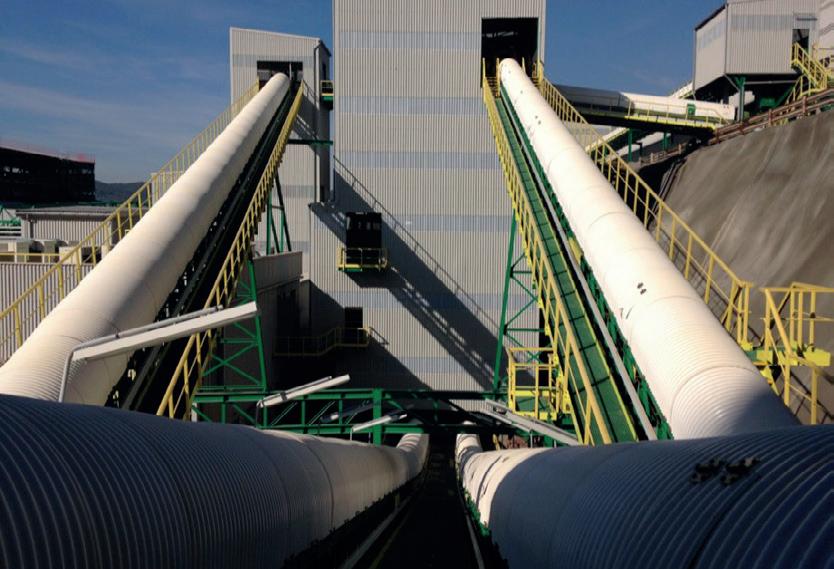
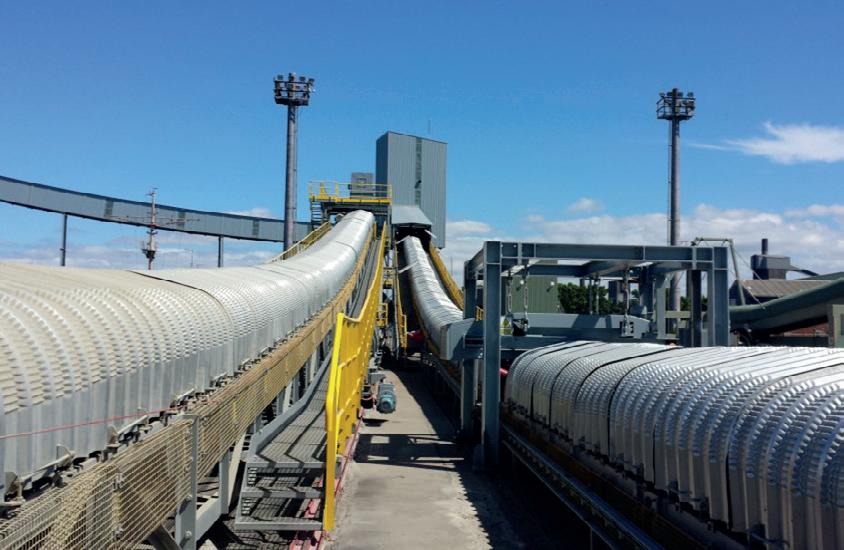
Contact us: InterCem professionals will also find the right solution for your requirement.
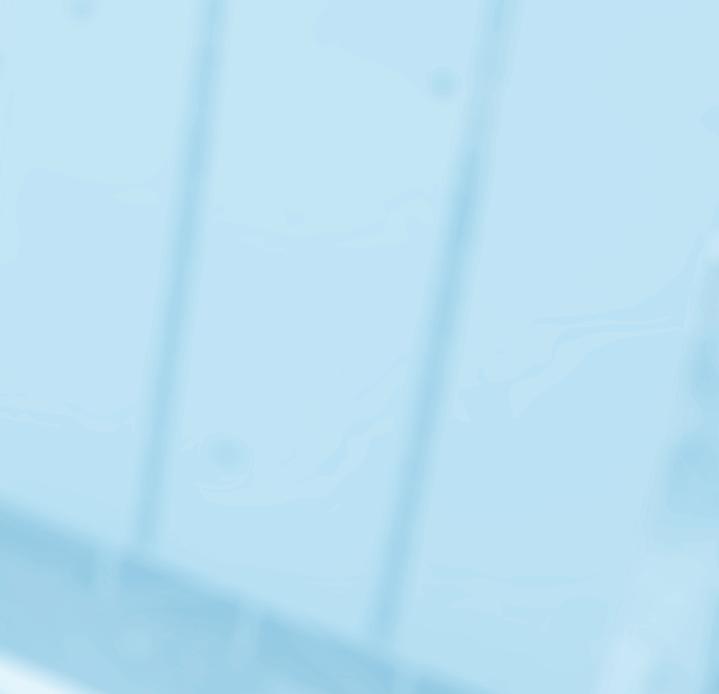
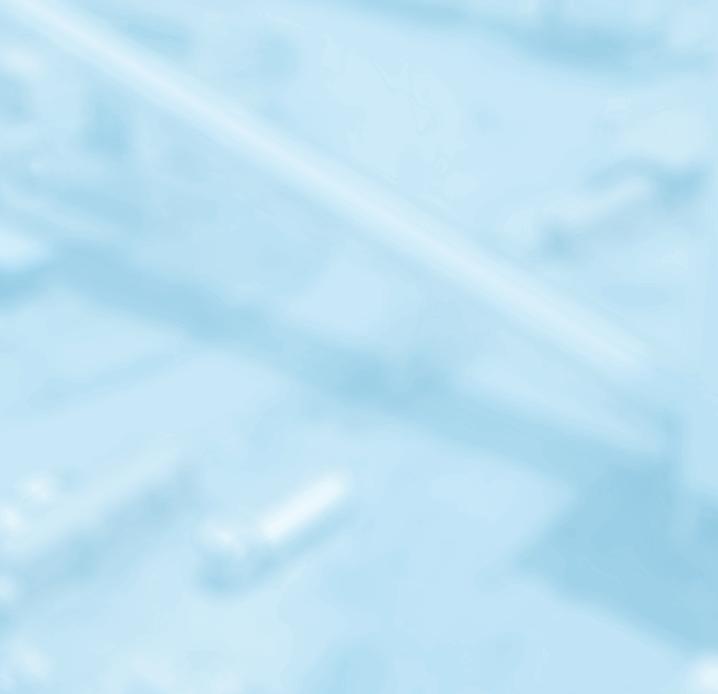
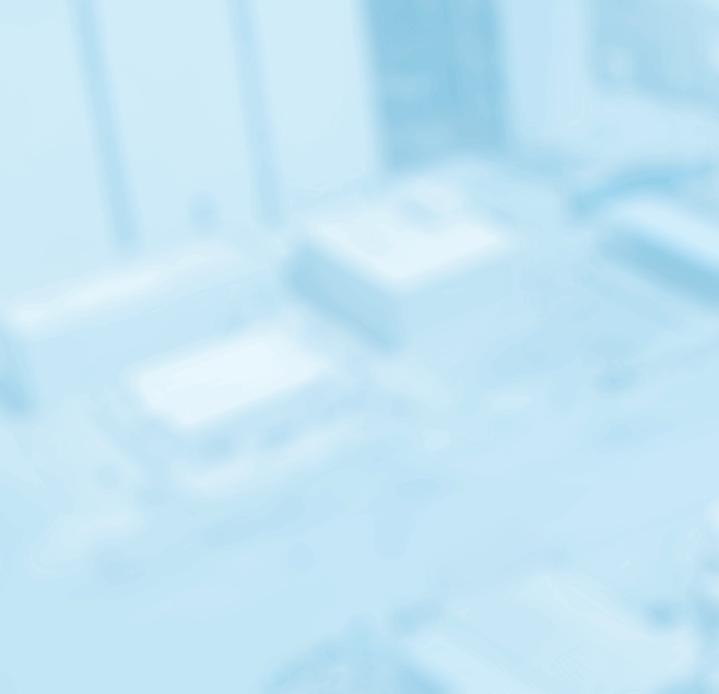
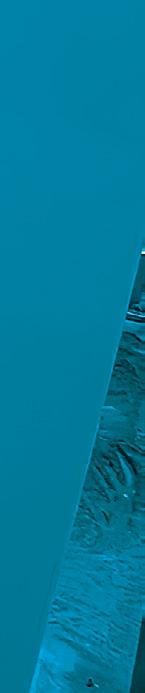
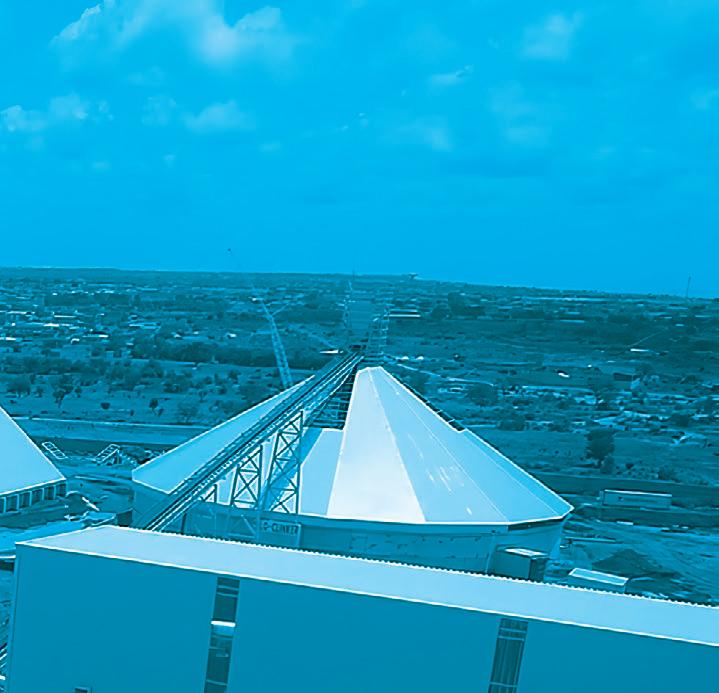
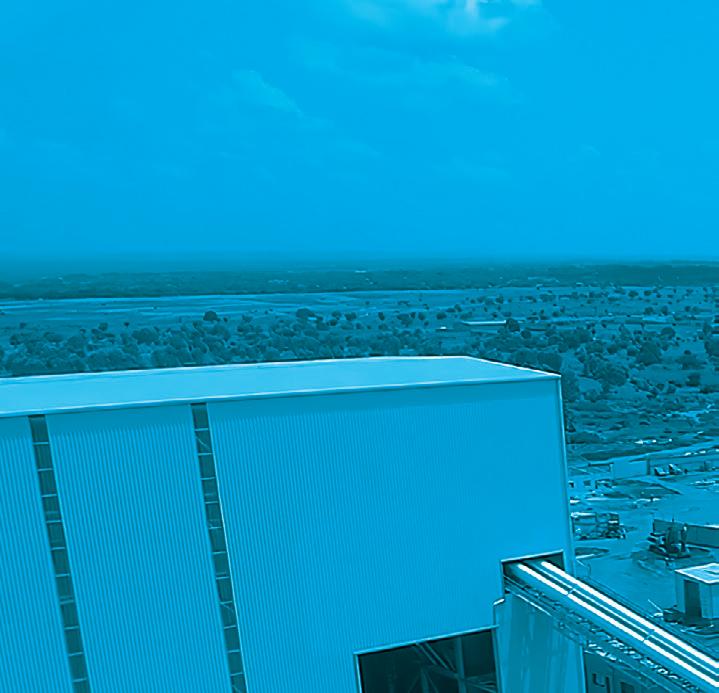
combustion would be to use it in calciners, where the flame’s radiation is not the main energy transfer mechanism.
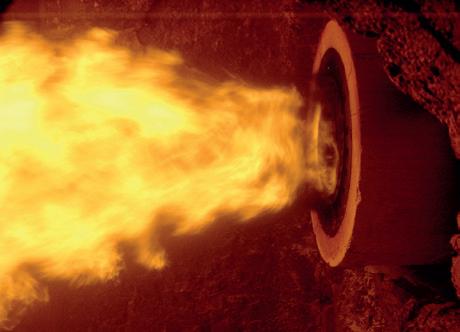
NOx
Hydrogen generates a higher flame temperature, and therefore increased NOx emissions. Some research points out that up to 10% blending of hydrogen in natural gas (in volume) is manageable in terms of NOx emissions, with no significant
impact detected; however, a 25% hydrogen mixture causes a significant increase in NOx formation (Figure 9).
Laboratory-scale research leads to the same conclusion: the higher the hydrogen concentration, the higher the NOx formation. The industry must bear in mind that the aggregate effect of lower radiative heat transfer and higher flame peak temperatures potentialise the kinetics of NOx generation reactions.
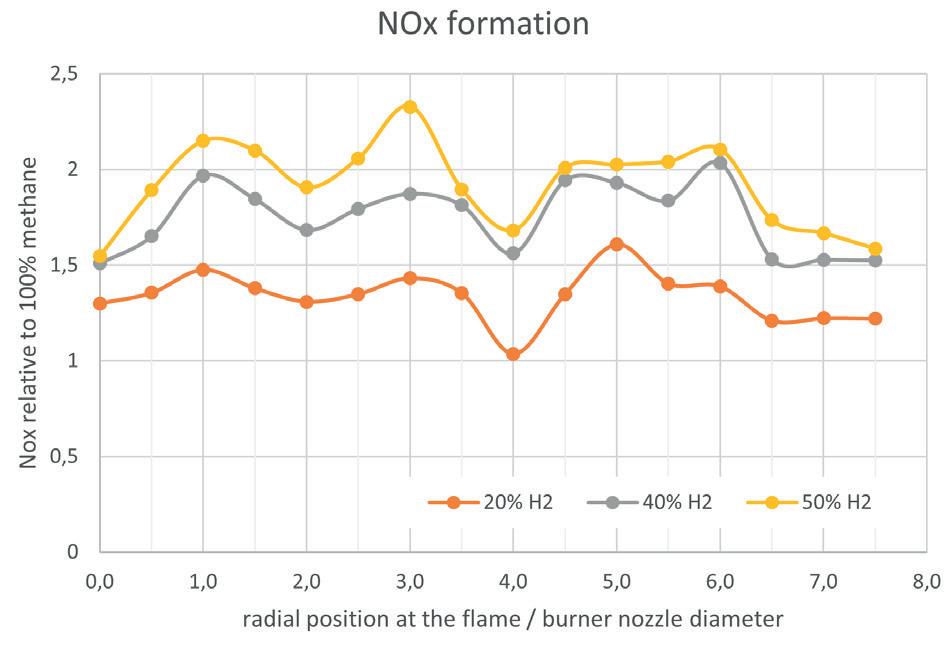
Conclusion
Despite cement production being an energy intensive process, combustion accounts for around 35% of the total CO2 emissions of the cement production chain (from quarry to final consumer).4
Any potential reduction in CO2 emissions in this area will only impact around one third of the total CO2 generated. The vast majority of CO2 emissions come from the calcination of the limestone, a field in which advances are also being made for reducing the CO2 emissions, but this is a topic for another article.
For the time being, hydrogen as a fuel is still a widely unavailable, expensive to be produced on a large and sustainable scale, with challenges that inhibit it being used efficiently in rotary kilns for clinker production, even though fewer challenges are present for its use in the calciner. However, these challenges are being intensively investigated by both industry and academia, leading some to believe that breakthroughs are about to happen in the short- to medium-term.
References
1. Natural gas price reference of €33/MWh LHV delivered at consumption point in 2020 used to avoid effect of recent volatility in the energy market. Natural gas price for large non-household consumers, including VAT, taxes and levies. Electrolysis assuming renewable power price at €70/MWh
2. SCOTT, R., RANGANATHAN, S., PETROW, D., ZALOSH, R., RANGWALA, ALI., ‘Radiative fraction of dust entrained turbulent premixed flames’, Journal of Loss Prevention in the Process Industries, Volume 51, 2018
3. GAO, Y., YU, Z., HUA, Y., LIU, Y., TAO, C., and GOA, W., ‘Experimental study on the flame radiation fraction of hydrogen and propane gas mixture’, School of Automotive and Transportation Engineering, Hefei University of Technology, Hefei, Anhui 230009, China & School of Chemical Engineering, Dalian University of Technology, Dalian 116024, China
4. CZIGLER, T., REITER, S., SCHULZE, P., & SOMERS, K., ‘Laying the foundation for zero-carbon cement’, McKinsey & Copmany – https://www.mckinsey.com/ industries/chemicals/our-insights/laying-the-foundation-forzero-carbon-cement
5. EL-GHAFOUR, S., A., A., EL-DEIN, A., H., E., & AREF, A., A., R., ‘Combustion characteristics of natural
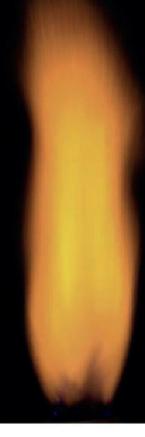

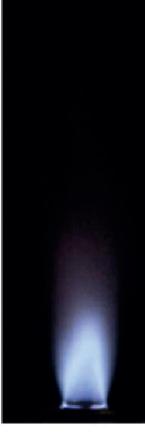
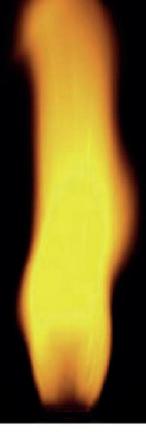
fuel turbulent diffusion flame’, Mechanical Power Engineering Department, Faculty of Engineering, Suez Canal University, Port-Said, Egypt
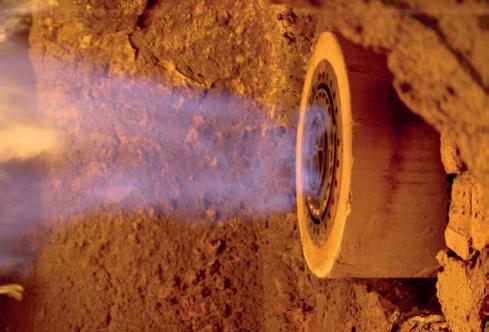
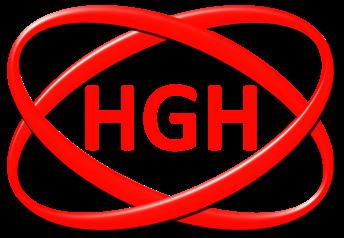
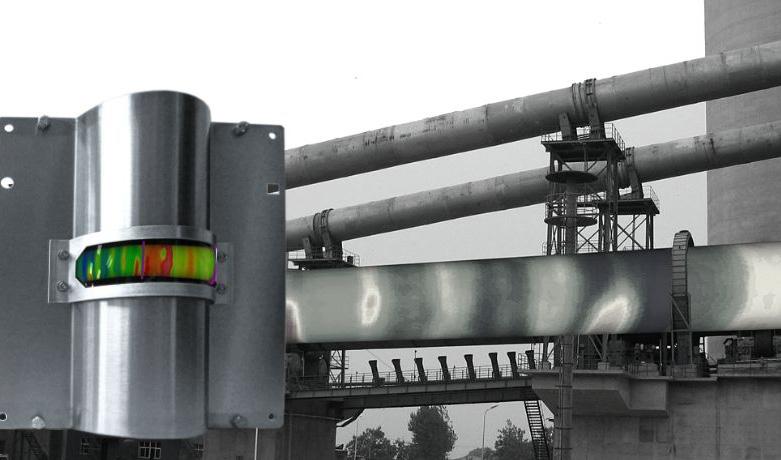
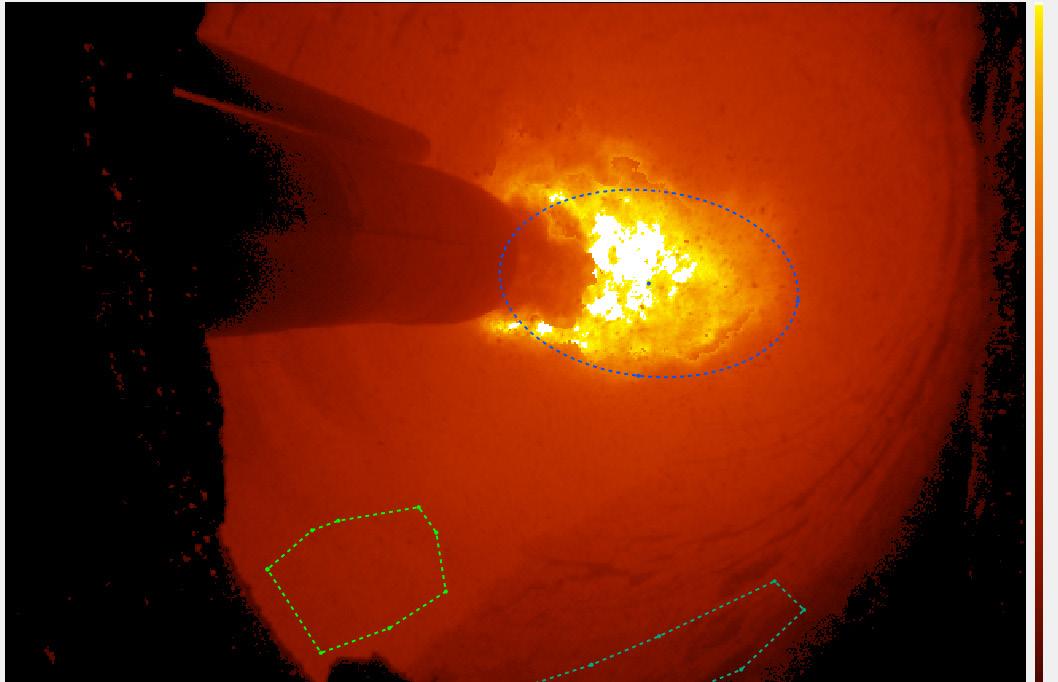
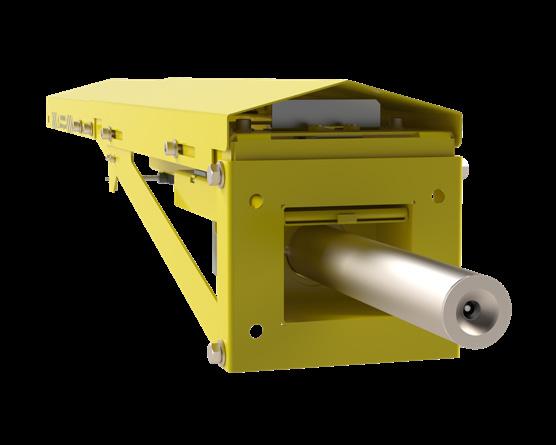
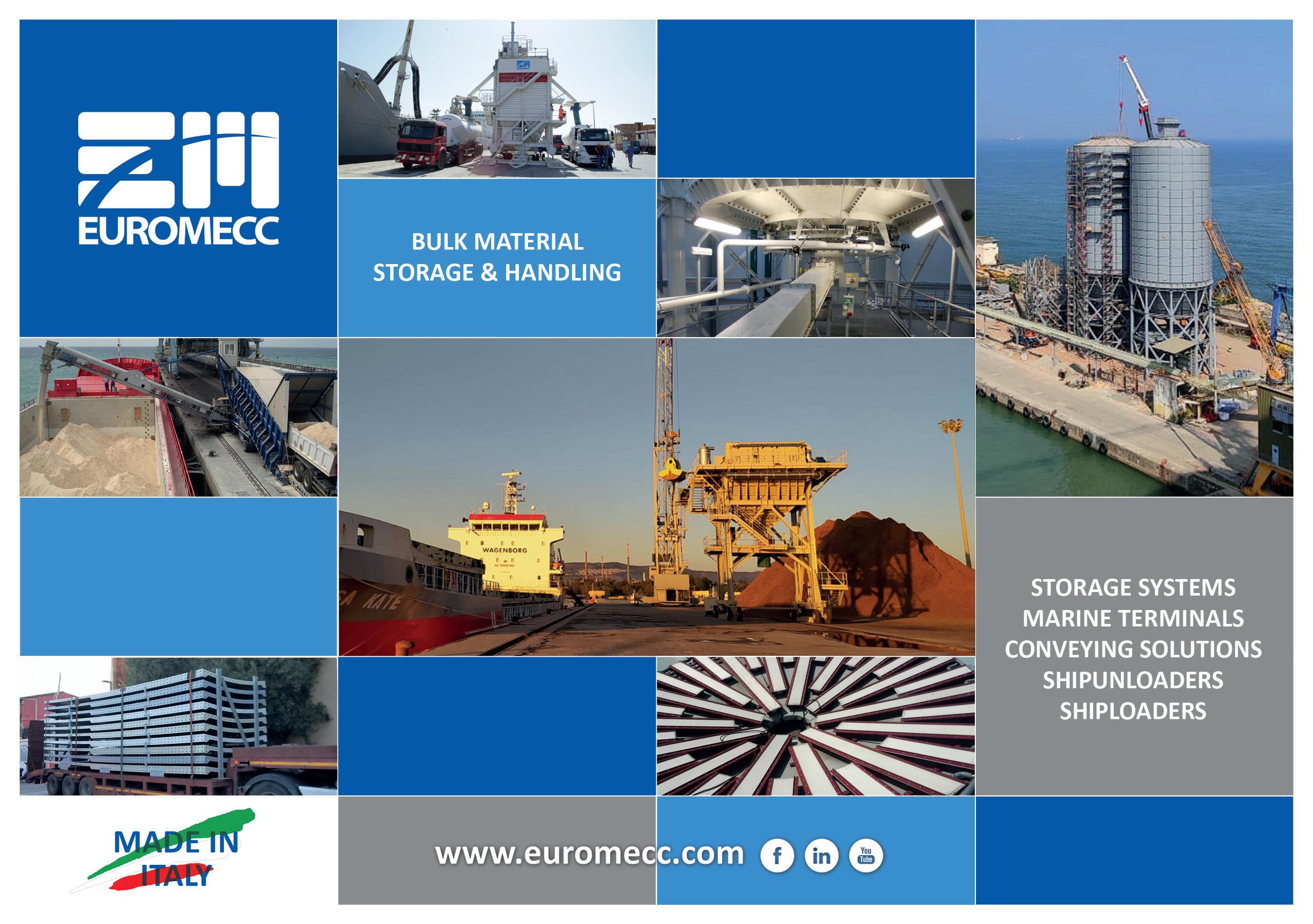
GOING GREEN
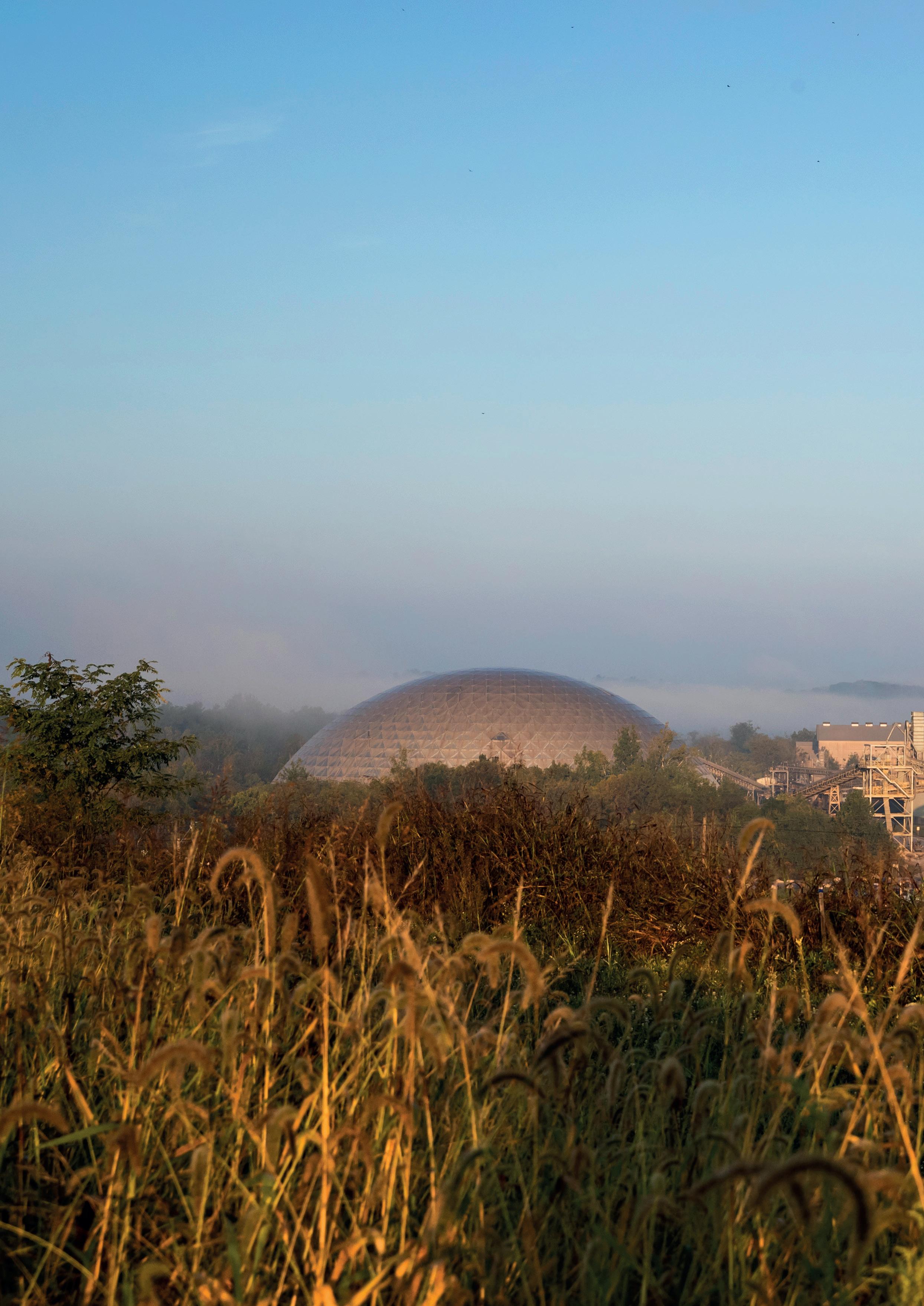
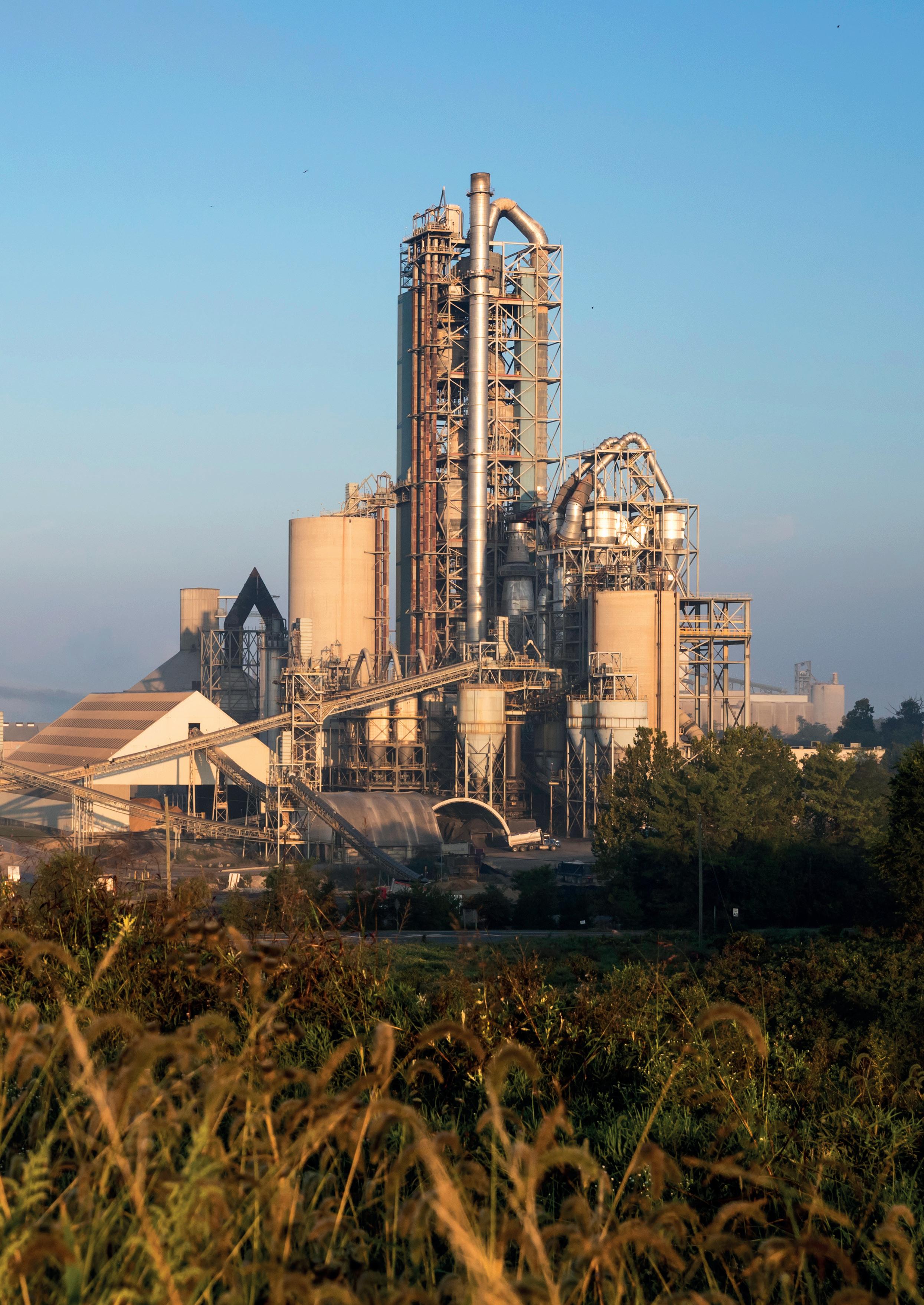
The Lehigh Cement plant in Union Bridge produces 2 – 2.5 million tpy of cement – and, within the next year, its primary product will be a lower carbon cement. With this transition, the cement plant will avoid approximately 126 000 tpy of CO2 – the equivalent of removing about 27 000 cars from the road. The framework for this transition, and subsequent carbon reduction, requires a clear plan, hyper focus on logistics, and creative thinking that included a high efficiency overland conveyor system.
Roadmap to neutrality
The Union Bridge plant represents an important step in achieving the company’s industry-leading goal to reduce carbon emissions as a result of cement production.
The primary product is EcoCemPLCTM, a lower carbon Portland limestone cement (PLC) that uses higher amounts of limestone and lower amounts of clinker. It is a combination that reduces both the energy required for production and the associated emissions. The resulting carbon footprint can be as much as 10% lower than ordinary Portland cement.
Transitioning to the lower carbon solution has been a logistical challenge for the plant management team. Kent Martin, plant manager for the Union Bridge facility, explained, “Currently we have two primary general use cements –ordinary Portland cement and EcoCemPLC. To meet our existing demand, we have to balance production on our mills and silo inventory between both products.”
Jeff Hook, Regional Quality Control Director, added, “During the changeover, it’s all about mill time and mill allocations. Once the transition is fully complete, we’ll go back to normal operations with just one product.”
Key in the overall transition and future production of the Union Bridge plant to
EcoCemPLC is the connection to the nearby limestone quarry – a link that opened up another window of opportunity for the Lehigh Cement team to further its sustainability goals.
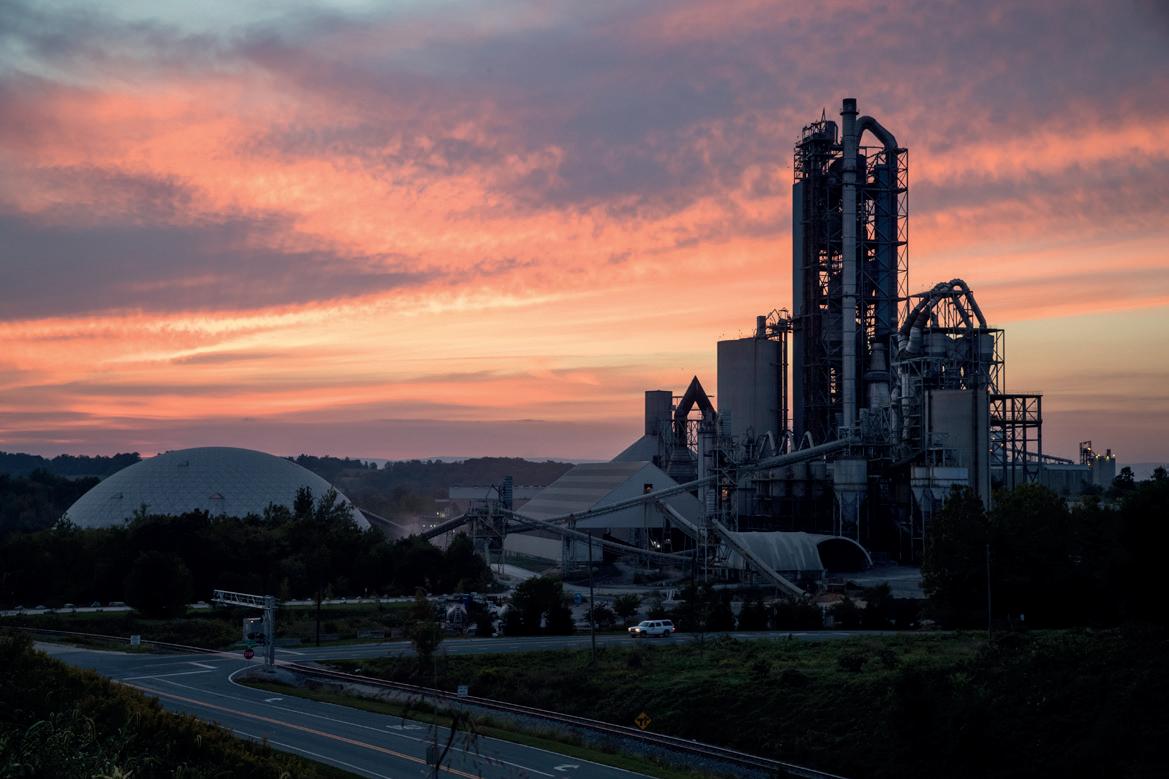
Quarry connections
The approximately 900-acre New Windsor limestone quarry, about 4.5 miles away from the plant, is a critical source of raw material for the long-term future of the Union Bridge plant. Conventional material transport methods simply did not fit the needs of the business, environmental, or community.
“We had three options to transport stone from New Windsor to Union Bridge – trucking, a rail line, or a more automated connection. The trucking option would have been detrimental for the environment and the surrounding community, as it would require almost 600 trucks a day moving between the quarry and the plant. The rail line would have to incorporate some 120 rail cars on a newly constructed rail line, which would create considerable noise,” recounts Martin.
Instead, the team imagined a third option – a conveyor system that would span agricultural preserve land, five county roads and the Lehigh property.
“From an environmental perspective, the conveyor project was by far the best solution, for the community and for the business,” added Martin. “It’s a win-win-win all the way around.”
The engineering team gained approval from regulatory agencies to tunnel the conveyor under the roads and worked closely with the local landowner to cross agricultural land, gaining all necessary permits along the way. The result is an above- and below-ground conveyor system. The section below ground is essentially a concrete culvert, wide enough to accommodate a utility vehicle for maintenance. The above ground portion is enclosed by a jumbo cover.
The team worked with the owner of the agricultural land to assure that the conveyor cover would blend with the surrounding rural community. Hook recalled, “We would paint and place pieces of plywood in the farm field to show the cover. The owner had final say on the colour that was selected.”
It took construction crews about two years to build the conveyor from the New Windsor quarry, and the final result pleased all parties. It was an effort that further reinforced Lehigh Hanson’s emphasis on community and communication.
Hook noted that during the near decade-long permitting and community discussion process,
By transitioning to EcoCemPLC, the Union Bridge plant will avoid 126 000 tpy of CO2 emissions.Wednesday 09 November
Wednesday 09 November
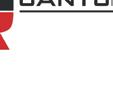
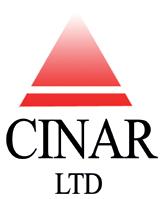

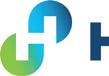
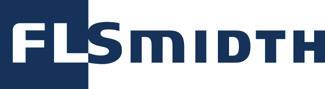
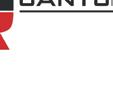
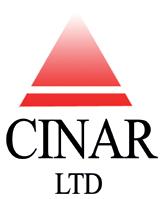

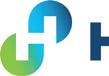
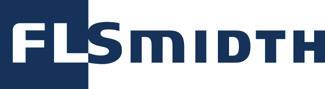
The flagship virtual conference from World Cement. WCT2022 focuses on innovation in cement production, and will feature technical presentations and live Q&A sessions with industry experts.
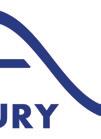
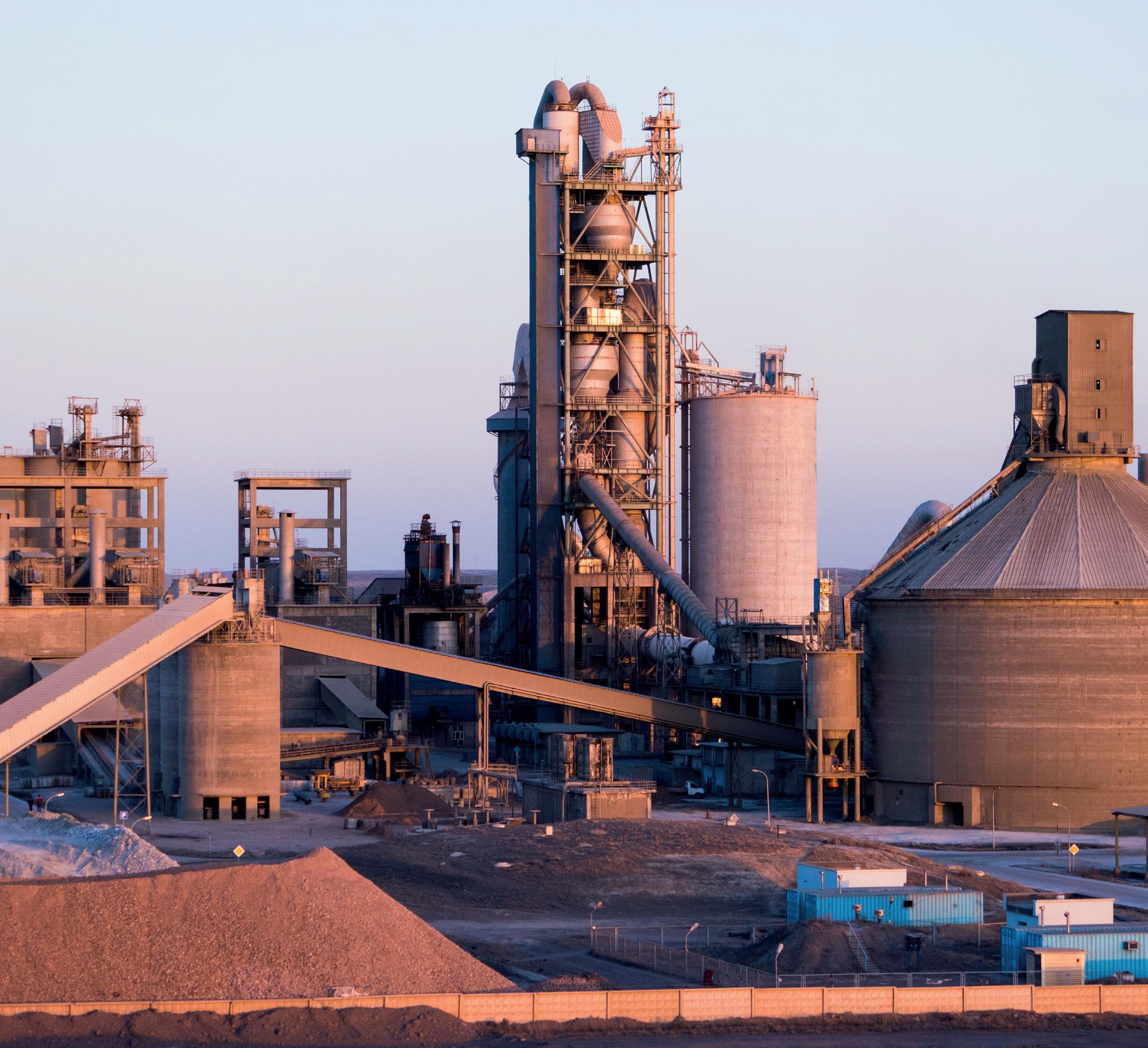
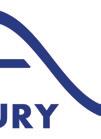
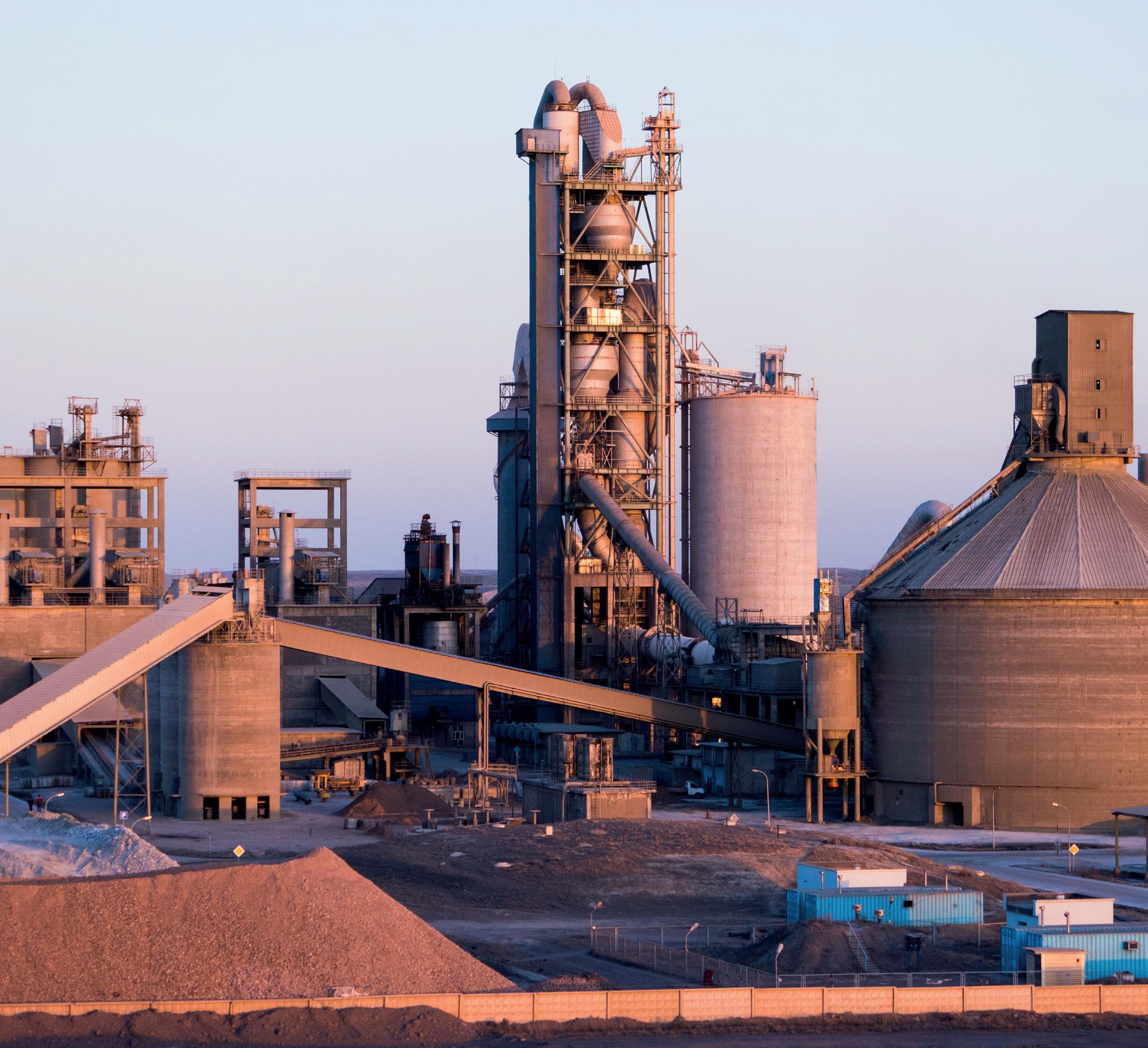
The flagship virtual conference from World Cement. WCT2022 focuses on innovation in cement production, and will feature technical presentations and live Q&A sessions with industry experts.
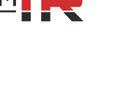
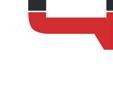
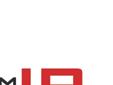
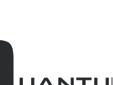
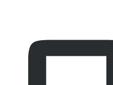




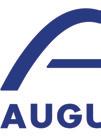
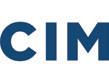
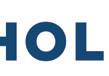
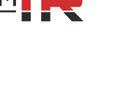
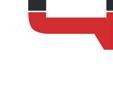
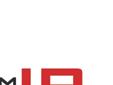
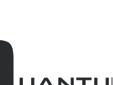
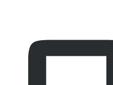




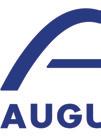
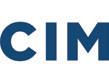
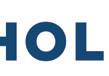
Register here:
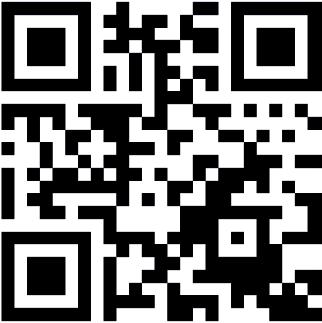
Register here:
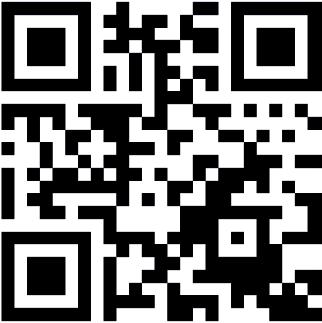
he developed a website to better disseminate information about the then-proposed project. “That website was so heavily used that we expanded the system to include things like blast alerts or potential road closures and slowdowns,” Hook said. “Through the subsequent alerts, emails and meetings, 90% of complaints common in construction projects such as this, went away. The community truly felt like their concerns were heard and acted on.”
Martin agreed and added, “For me, one of the greatest outcomes of the conveyor project is that the renditions matched reality. The actual system came out as good or better than planned. That’s exciting. We implemented the solution that was best for community, environment and the business.”
The sustainable continuum
The move to EcoCemPLC at Union Bridge follows similar changes at the company’s cement plants in Picton, Ontario; Delta, British Columbia; Mason City, Iowa; and its three cement plants
in Indiana – though Union Bridge is the largest. In 2021, the company produced more than two million t of EcoCemPLC and is well on its way to more than double that in 2022.
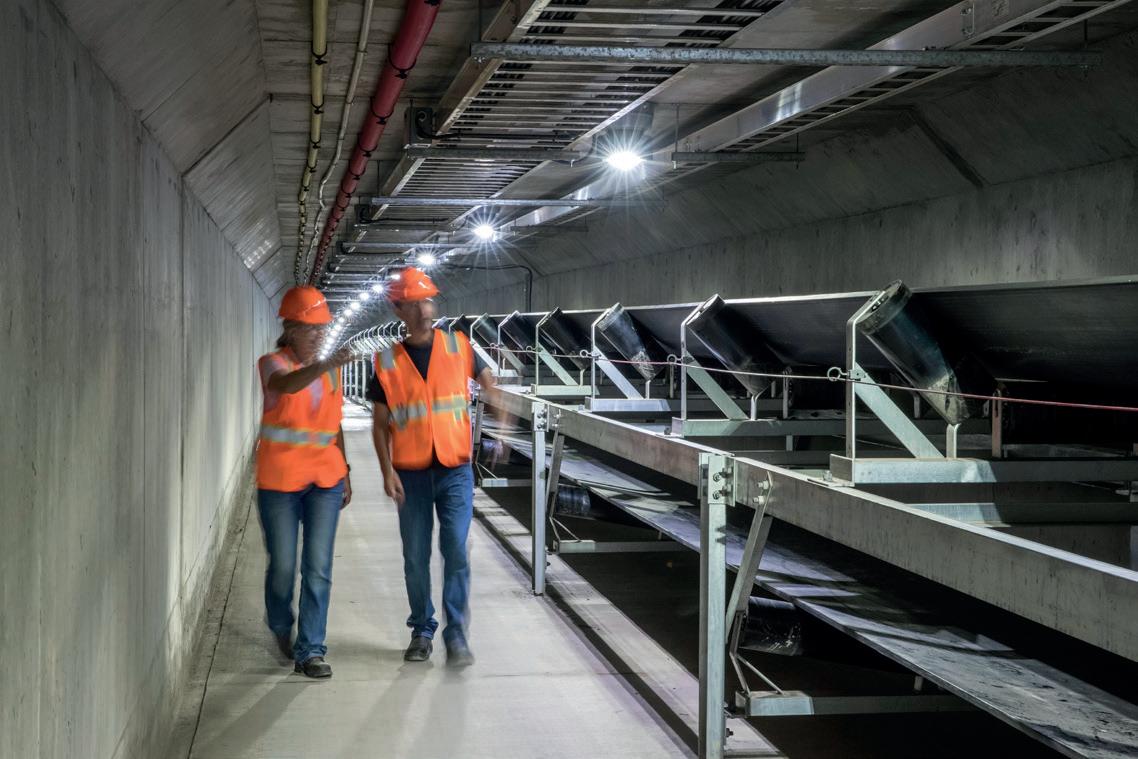
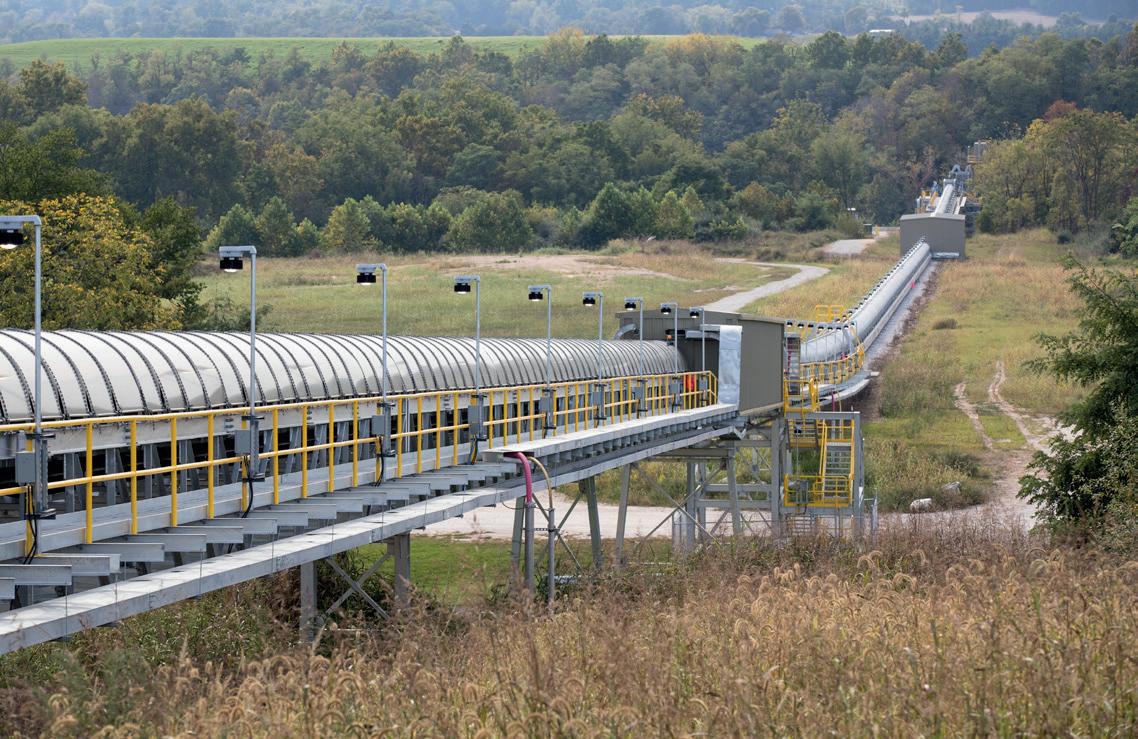
But the lower carbon PLC is not the only sustainable programme to reduce CO2 that is ongoing at the Union Bridge and other company facilities. For example, the team continues to evaluate the use of alternative fuels to further reduce its carbon footprint. The Union Bridge plant’s shift to EcoCemPLC reinforces their commitment to reducing their carbon footprint and reflects the ambition of its global parent company, Heidelberg Materials, to become the first to offer carbon neutral cement and concrete at scale.
Further, Heidelberg Materials and its operations across the globe are leading the way in scaling carbon capture, utilisation, and storage (CCUS) technologies. CCUS projects that have already been launched or are in process of being launched by the company are targeted to achieve a cumulative reduction of 10 million t of CO2 by 2030. Lehigh continues to work with customers and key stakeholders such as agencies, architects and engineers to further accelerate the transition to more sustainable solutions. One of the most significant company goals which was announced by Heidelberg Materials earlier this year during its Capital Markets Day in May is to cut emissions by almost half, to 400 kg CO2/t CEM (compared with 1990), which is a further decrease of 30% compared to 2021. In addition, half of the company’s revenue will be generated with sustainable products targeted for 2030.
Compared to 2021, the company aims to reduce CO2 emissions by a further 30%. Thus, in the next eight years, CO2 emissions are to decrease more strongly in percentage terms than in the last three decades. Dr. Nicola Kimm, Member of the Managing Board and Chief Sustainability Officer of Heidelberg Materials, recently noted: “We are significantly tightening our climate targets. We are focusing on the optimisation of products and processes, as well as in particular on the expansion of CO2 capture, utilisation, and storage (CCUS).”
Through efforts such as the Union Bridge plant’s transition in conjunction with a variety of other ambitious efforts across the company, the company is on track to achieve net zero emissions by 2050 at the latest.
The Union Bridge team worked closely with regulators, the community and landowners during the construction of the conveyor. The enclosed conveyer system eliminates about 600 trucks moving between the quarry and the plant each day.TURNING CEMENT GREEN WITH XRD
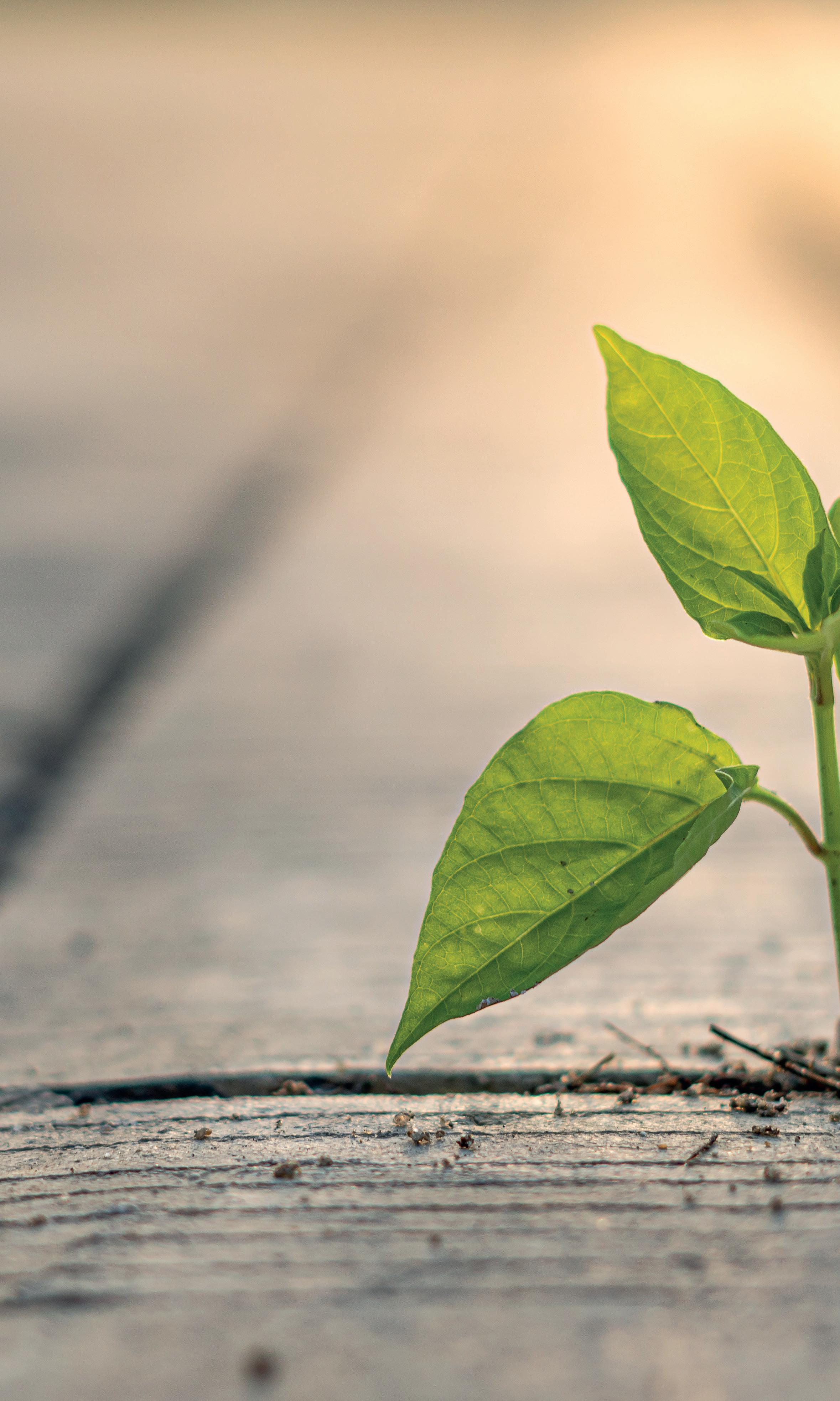
Sustainability is an increasingly important priority in the cement sector. Despite challenges such as higher fuel prices, the scarcity of supplementary cementitious materials (SCMs), and water and electricity regulations, there are encouraging opportunities. The European Union’s Emissions Trading System is helping to alleviate the shortage of resources and reduce carbon emissions. Moreover, an improved understanding of the

impact and performance of alternative fuels and alternative raw materials has opened doors for new processes and materials. Indeed, the solutions for producing green cements and decarbonising the cement industry in the short and medium term are co-processing alternative fuels and reducing the clinker in cement using new SCMs. For that to happen, mineralogical analysis with X-ray diffraction is essential for selecting the proper raw materials and SCMs, optimising pyroprocessing and its intermediate products, controlling blending, and maximising SCMs in the final green cements.
Cement manufacturing is a complex process. The manufacture of ordinary Portland cement starts by mining and then grinding raw materials that include limestone and clay into a fine powder called raw meal. It is then heated to a sintering temperature as high as 1450˚C in a cement kiln. The resulting clinker is ground to a fine powder in a cement mill and mixed with gypsum to create cement. The powdered cement is then mixed with water and aggregates to form the concrete that is used in construction.
Cement manufacture is an energy and resource-intensive process. If it were up to the quality managers, only raw meal made from the best part of the limestone quarry would enter the kiln, and only fossil fuels would be used. However, in recent years, sustainability has become an increasingly important priority in the cement sector. New SCMs are being used, such as calcined clays, as well as new alternative fuels (AFs) such as biomass, refuse-derived fuel, municipal solid waste, tyres, sawdust, and many other types of wastes and byproducts.
Mineralogical analysis is currently helping the cement industry to transition to a low-carbon and more circular economy. It is providing the sharp eyed analysis in order to identify solutions for producing greener cements. Fast and automatic full mineralogical analysis using X-ray diffraction (XRD) makes it easier to select the right raw
materials for blending. It helps to optimise and control the calcination and clinkerisation processes. It is the only reliable and proven industrial technology capable of quantifying the amorphous content of SCMs and verifying that composition of complex cement meets the required standards.
X-ray diffraction heightens mineralogical awareness
XRD has been around since the 1970s. Today, it is the go-to technique for identifying and quantifying minerals and crystalline phases in a completely automated fashion. In fact, it is the only industrial technique available for quantifying amorphous materials (including some SCMs), which are solids that do not possess order beyond a few nanometres. The lack of order makes these materials extremely reactive and therefore a good SCM that can reduce clinker in cement.
Modern industrial diffractometers tap into the full potential of XRD. Instead of focusing on a specific mineral, they can identify the full mineralogical composition of materials in just a few minutes. This heightened mineralogical awareness can be used to further improve clinker quality, produce new green cements and increase the know-how of entire processing plants. The current use of XRD systems in cement plants focuses on maintaining product quality and ensuring smooth operations while reducing the carbon footprint and overall environmental impact of cement production.
Alternative fuels
A clinker kiln is a particularly attractive destination for alternative fuels for several reasons. The emissions generated by the combustion of AFs are considered neutral and can help the industry to achieve carbon neutrality, while helping to remove municipal wastes and industrial byproducts. Inorganic ashes from the combustion of AFs are incorporated into the clinker, and small amounts of other solid waste such as cement kiln dust can be added to the cement.
Schematic representation of a X-ray diffractometer for cement analysis. From left to right: X-ray source, optical components, sample, optical components and X-ray linear detector.
AFs can be highly variable, however, and can have a negative impact on the preheater operation, the kiln operation, and clinker quality. AFs high in sulfur and chlorides can generate coatings in the cyclone preheater which can lead to a complete blockage. XRD systems can help detect
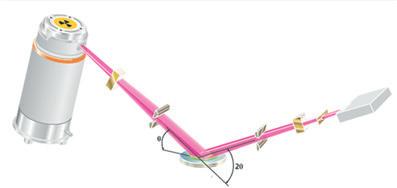

the onset of these coatings by analysing the mineralogical composition of the hotmeal.
The use of AFs can modify the temperature gradient of the kiln and affect clinker quality. High temperatures are essential to guarantee the reaction between belite and lime to produce alite. XRD systems can easily monitor the yield of this reaction and accurately measure the free lime with a repeatability of 0.1 Wt%. The amount of lime and periclase needs to be kept below certain limits, 2 Wt% and 5 Wt% respectively. The hydration of those minerals is associated with volume expansion that can compromise the dimensional stability of the cement.
The belite and alite in industrial clinker are not pure phases but contain impurities that –together with the proper quenching of the clinker – stabilise high temperature phases with superior hydration kinetics. For instance, improper quenching of the clinker can induce a phase transformation from belite beta to belite gamma, the latter having no cementitious properties. Alite can occur in industrial clinker in two different monoclinic forms or polytypes: alite M1 and alite M3. Most clinkers contain both forms, but it is possible to favour the alite M1 by increasing the sulfur trioxide/magnesium oxide ratio. The alite M1 displays higher compressive strength, and XRD systems can distinguish it from the alite M3.
Using XRD in grinding plants
As the amount of clinker produced in integrated plants increases, so does the number of grinding plants importing clinker. A full mineralogical analysis of the imported clinker is essential to guarantee its quality and avoid potential performance issues in the cement. Also, XRD is widely used to assess the quality and proper dosage of cement additives.
The mineralogy and amount of calcium sulfates must be adjusted in relation to the aluminates content and type to optimise the setting time, strength development, and dimensional stability. The XRD analysis results can be aligned with the sulfur trioxide content measured with X-ray fluorescence (XRF), with the added value of differentiating sulfates in gypsum, basanite, and anhydrite.
The most promising approach to lowering the carbon emissions of cement is to reduce the clinker factor: for instance, by replacing the clinker in cement with natural or synthetic pozzolana. What makes a material pozzolanic is its ability to react with portlandite generated by hydrating cement, increasing its strength and durability. The quality of pozzolanas is defined by their mineralogy as some phases are highly reactive, while others are detrimental or inert.
Volcanic materials rich in quartz, felspars, pyroxenes and magnetite are not a good natural pozzolan. Pozzolanas rich in smectite and kaolinite need to be thermally activated before being used as SCMs. Zeolitic minerals such as analcime, leucite, chabazite, phillipsite, and clinoptilolite have suitable pozzolanic properties.
The quality of ground granulated blast furnace slag (GGBS) and fly ash also strongly depends on their mineralogy and on their amorphous content, which have distinct and quantifiable XRD signals. Slag which has not been properly quenched can contain significant amounts of crystalline melilite and merwinite and therefore has lower reactivity. Fly ash generated at a high temperature can contain large amounts of mullite, a phase without pozzolanic properties. Amorphous determination of SCMs through XRD analysis provides a much faster indication of the suitability of the SCMs compared with other methods. In addition, it is also fully automatable. The amount of clinker which can be replaced by SCMs is strictly regulated by standards. For instance, standard EN-197-1 describes the 27 types of cement, each with well-defined ranges of clinker, limestone, slag, fly ash, pozzolana, burnt shale, silica fume and other additives. The most recent version of standard EN-197-5 is an update that now includes Portland-composite cement CEM II/C-M and a different type of composite cement CEM VI, neither of which are covered by EN 197-1, whose intended use is the preparation of concrete, mortar and grout in a more sustainable way.
The Aeris black-box solution is based on robust industrial X-ray diffraction (XRD), proven algorithms to quantify the mineralogy of complex materials and seamless integration with the local LIMS systems and fully automated laboratories.
XRD is widely used to verify the proper blending and homogeneity of the product. It is in the interest of grinding plants to stay as close as possible to the allowed upper limit of SCMs, therefore minimising the amount of clinker and the overall production cost of
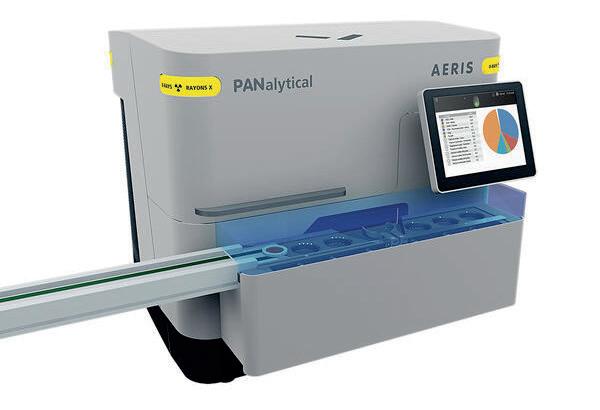
the cement. An imprecise SCMs quantification obliges the quality manager to take larger safety margins at the expenses of the product profitability. XRD systems can provide a precise quantification of the SCMs, and as a result, the return on investment for grinding plants producing blended cement is extremely attractive.
Calcined clay and new cements
The recently discovered synergy between calcined clay and limestone in cement has aroused the interest of regulators and cement producers. In Europe, the new EN 197-5 standard has increased the maximum clinker substitution from 35% in CEM II/B-M(Q-LL) to 50% in CEM II/C-M(Q-LL). These new cements, such as LC3, can potentially reduce carbon emissions by up to 40% without affecting the strength of the cement. Accurate mineralogical analysis is critical for identifying and exploiting suitable clay deposits, calcinating the raw clay, and ensuring the proper blending with clinker and other additives.
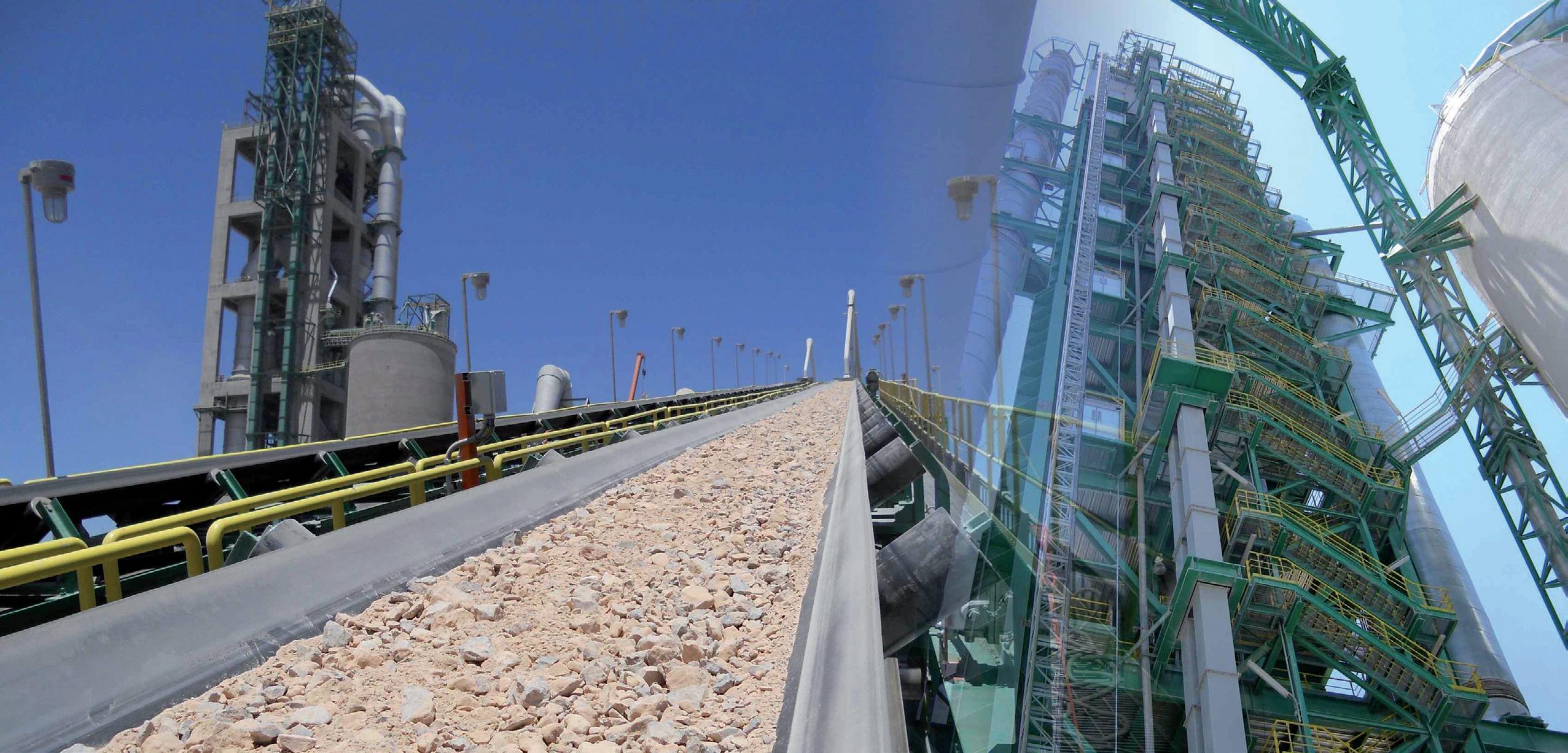
Using the wrong clay can severely compromise the performance of the cement. Kaolinite and smectite are the only common clay minerals displaying pozzolanic properties upon calcination. Their concentration should
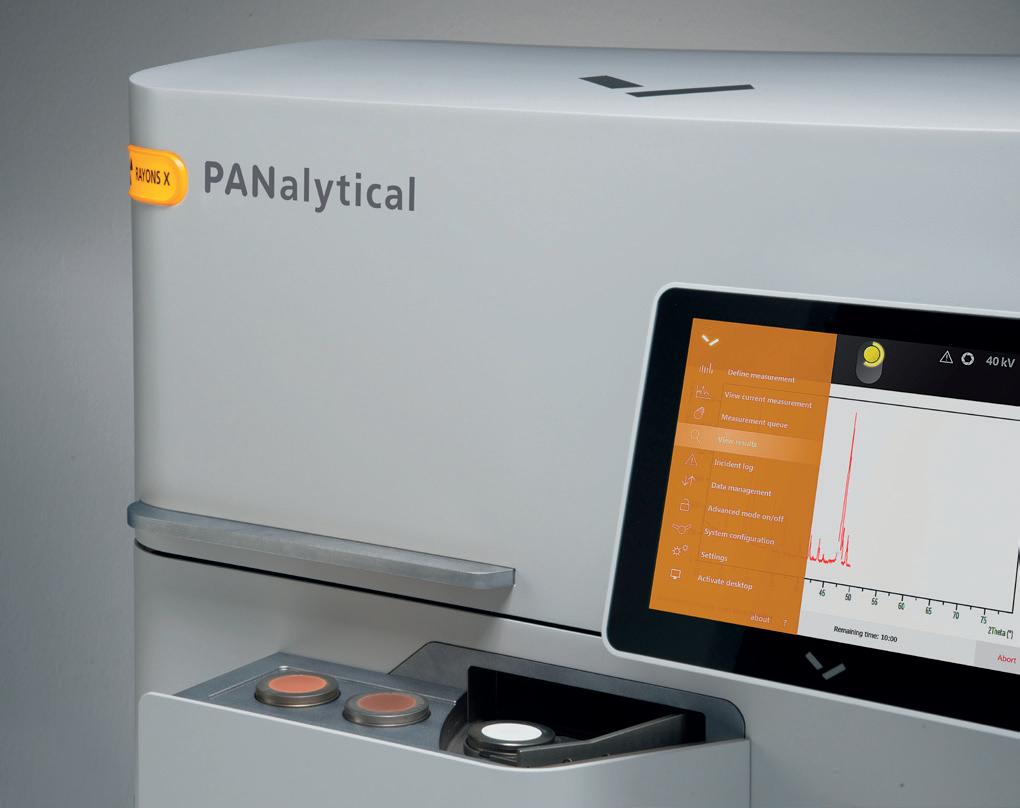
be above 30 – 40 Wt% for the clay to be suitable for calcination and blending with clinker. Other minerals, such as quartz, hematite, calcite, feldspar, and other clays such as micas and illites, act as filler.
XRD analysis has determined that the dehydroxilation reaction occurring during calcination can cause the collapse of the clay’s crystal structure and a loss of crystallinity. These changes are necessary to give the material
pozzolanic properties. Low temperatures or short residence times result in residual kaolinite or smectite that do not contribute to the cement’s strength and affect workability. The onset temperature of the dehydroxilation reactions is approximately 550˚C for kaolinite, and 700˚C for smectite.
Therefore, the optimum calcination conditions strongly depend on the clay’s mineralogy. High temperatures or long residence times can lead to the crystallisation of refractory phases, such as mullite, cristobalite, anorthite, wollastonite, diopside, and gehlenite. The optimum window is quite narrow, and XRD can provide the necessary data to produce calcined clay in the right way.
The absence or low concentration of calcite combined with the lower kiln temperature dramatically reduce carbon emissions compared to the production of clinker. The resulting calcined clays are then blended with clinker, gypsum, and limestone in the appropriate proportions. These proportions can be accurately quantified with XRD to comply with local standards.
The production of many other types of clinker and cement can benefit from XRD analysis. The list includes, but is not restricted to: geopolymers, calcium aluminate cements or ciment fondu, calcium sulfoaluminate cements, belite-ye’elimite-ferrite cements, carbonatable calcium silicate clinkers based on wollastonite, alkali-activated materials, supersulfated cements based on slag and gypsum, magnesia-based cement, and phosphate cements. The application of these cements varies from low-carbon cement, fast-setting cement, refractory cement, and cement for the encapsulation of radioactive and toxic materials.
XRD for a sustainable future
X-ray diffraction has become a key analytical method for controlling the quality of clinker and cements. It is especially important now, given the urgent need to align with net zero targets.
This has led to the manufacture of new green cements, based on the use of various alternative fuels, SCMs, and by adopting a circular approach when possible. XRD is the only technique that allows rapid, accurate, and automatic quantification of the mineralogy of all these different compounds, so manufacturers can retain full control over the cement process and make it as green and profitable as possible. Most importantly, it offers a way of making quality, sustainability, and profit compatible as the cement industry searches for new ways of manufacturing green cement.
About the authors
Dr Matteo Pernechele holds a PhD in Materials Engineering from the University of British Columbia, Canada and a Master’s degree in Materials Science from the University of Padua, Italy. His work spans from scientific research in the general field of solid-state chemistry to industrial projects, especially in the construction and mining sectors.
Matteo has 14 years of experience in X-ray diffraction and Rietveld refinement. He has been with Malvern Panalytical since 2018 as an XRD application specialist at the Application Competence Center in Almelo, The Netherlands.
Dr Murielle Goubard is the Global Segment Manager – Building Materials for Malvern Panalytical. She has extensive experience in materials chemistry and worked 15 years at Solvay Research Center. She has a deep interest in the cement making process and has been involved in developing applications and solutions for French plants and key European cement companies, while looking to improve efficiency and product quality. With 15 years working at Malvern Panalytical, she is now an expert in building materials and is very involved in solutions for green cement plants, circularity, and net zero.
More precise mineralogical quantification (95% confidence intervals in green) enables smaller safety margins. The maximum level of allowed limestone in CEM II/A-L is 20 Wt%. By improving the analysis precision from 0.5 Wt% to 0.2 Wt%, the plant can respectively increase limestone and decrease clinker by approximately 0.6 Wt%.
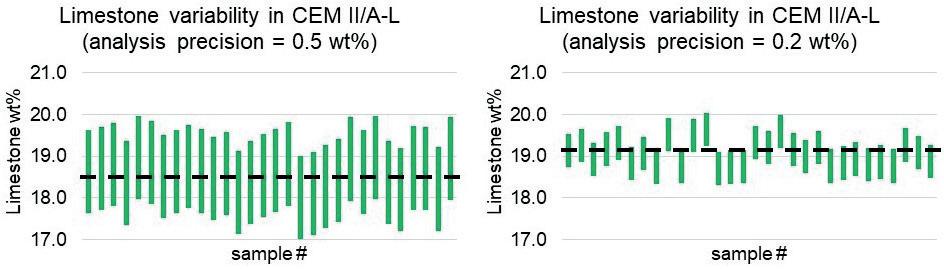
A NEW ERA FOR LOW-CARBON CEMENT
Dr. Jose Casaban, MOF Technologies, presents a new system for carbon capture and explains why it represents a step-change for the production of low-carbon cement.
The cement industry faces an intractable problem. It is well known that concrete accounts for 2.8 billion t of CO 2 emissions each year, equivalent to roughly 8% of the global total and more than any country other than China or the US. 1 But it is also one of the world’s most-consumed resources, second only to water, and essential for virtually every building project, not least key infrastructure. There is also no viable alternative, leaving economic stability and climate targets in the balance.
This is not another article imploring the industry to change its ways. Everyone reading this will be keenly aware that decisive action is needed to bring emissions in line with ambitious targets, especially when legislation and impending changes to the carbon tax credits scheme effectively force a new approach. 2 The focus of this piece is instead on solutions, and in particular a new system called Nuada that can be seen as in important development in carbon capture technology.
CCUS: huge opportunities and savings
CCUS – carbon capture, utilisation, and storage – is widely seen as one of the best methods for industry to cut emissions in ‘hard-to-abate’ – and yet essential – sectors like cement production. It is not without its challenges, but this technology currently offers the most viable and fastest route to a more sustainable state
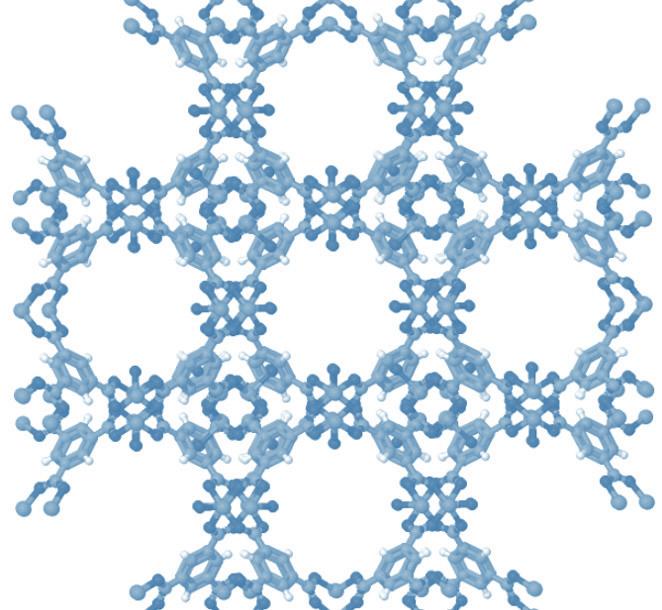
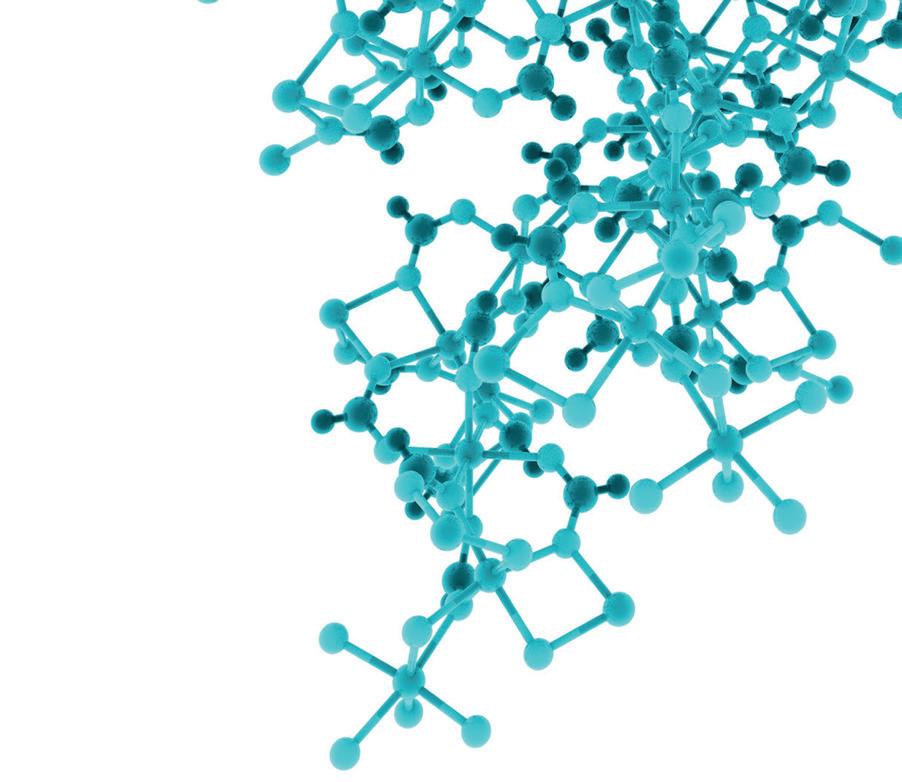
of play. Some of the most recognisable names in the heavy industries have started to take note of the technology. Mining giant Rio Tinto, for example, recently announced plans to deploy the technology at an aluminium smelt in Iceland, while the UK government signed off two multi-billion-pound schemes backed by several oil majors in the north of England. Cement production is also making moves, with a pledge to build 10 industrial-scale projects by 2030. 3
As the International Energy Association points out: “Key strategies to cut carbon emissions in cement production include improving energy efficiency, switching to lower-carbon fuels, promoting material efficiency (to reduce the clinker-to-cement ratio and total demand), and advancing process and technology innovations such as carbon capture (CC).” The latter two contribute the most to direct emissions reductions in the IEA’s net zero by 2050 scenario. 4
It is clear that current demand cannot be met without some continuation of current practices, not least because a drastic, unmanaged transition would be far too damaging. Indeed, the main draw for CC is its feasibility, providing a practical means to cut carbon while also maintaining a level of output needed for growth. The potential savings are also impressive. The International Energy Agency, for example, estimates that CC projects could help reduce global carbon emissions by almost a fifth and lower the cost of tackling the climate crisis by 70%. 5 Savings of that kind are often based on long-term projections but game-changing technologies.
Efficiency has been lacking CC is hardly a new concept for the industry and many are aware of the significant emission reductions it can deliver. The Global Cement and Concrete Association (GCCA), for example, recently laid out a carbon reduction roadmap

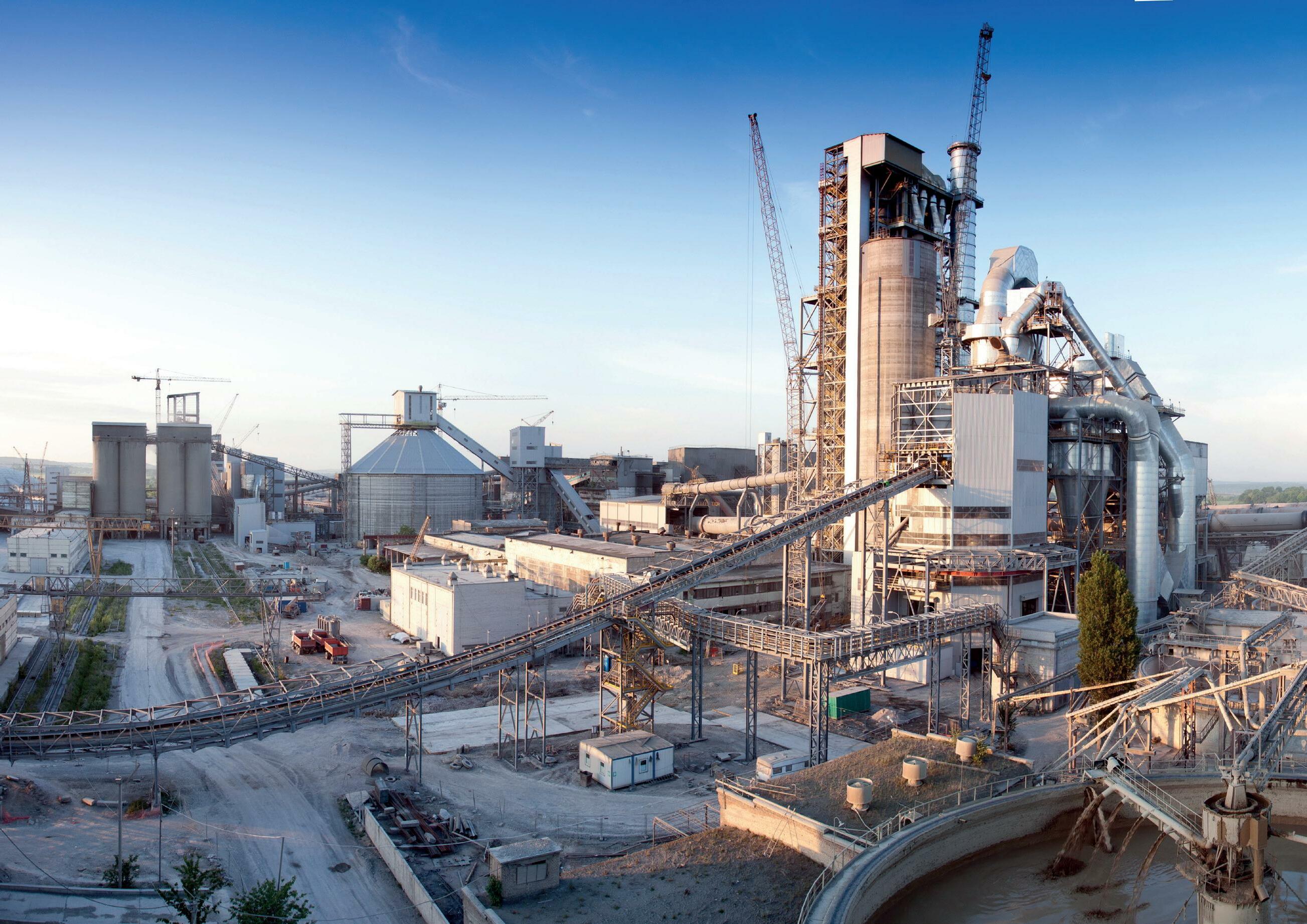
on behalf of 38 major producers across the world. CC has a central role in the plan, with its authors suggesting that 36% of the industry’s emissions can be addressed directly by CC technology – a huge saving when considering the 2.8 billion t emitted every year. 6 The GCCA concludes by emphasising the need to “bring forward the required breakthrough technologies to be ready for commercial-scale deployment” by the end of the decade. 7
The roadmap’s aims are commendable, though the idea of commercial-scale deployment has been an ongoing challenge that few businesses have been able to overcome. Some might suggest this is a convenient excuse for the cement industry to continue down the same path, but that argument belies the GCCA’s decision to make significant, lasting changes before 2030. Even the Global CCS Institute admits a current lack of convincing business incentives are among the biggest barriers to the technology becoming standard practice across heavy industry. 8
It is not surprising the CCS Institute has drawn this conclusion. There is a long list of carbon capture technologies that are, in theory at least, ready to help cement producers, such as oxyfuel combustion and chemical looping. Yet few have been tested at scale in the field. The only technology that has achieved this so far is amine gas treatment, sometimes called ‘carbon scrubbing’, which requires a series of separators at different processing stages.
Getting this infrastructure in place can be disruptive, not to mention expensive if it has not been costed-in when a facility is first designed.
But that is not the biggest problem. The commercial risk when using amine is only made worse by the high amounts of energy required when using it to strip CO 2 from a gas stream.
One 2020 study from the Carbon Science and Technology Institute found that regenerating solvent on its own contributes 50 – 80% of the total energy requirement – and that is before any other processes are factored in. 9 These solvents are also corrosive, can be chemically unstable, and lead to further environmental complications due to subsequent amine leakage. These issues not only hit a business’ bottom line but also further complicate CC, making it harder to convince decision-makers that it is actually worth pursuing in the first place.
Breakthrough
The difficulties around amines will soon prove negligible as newer methods of CC begin to replace them. Solid sorbent technologies, and in particular metal-organic frameworks (MOFs), hold the greatest potential for low-carbon cement production as they can deliver significant emissions savings without having to re-imagine the industry’s business model from the ground up.
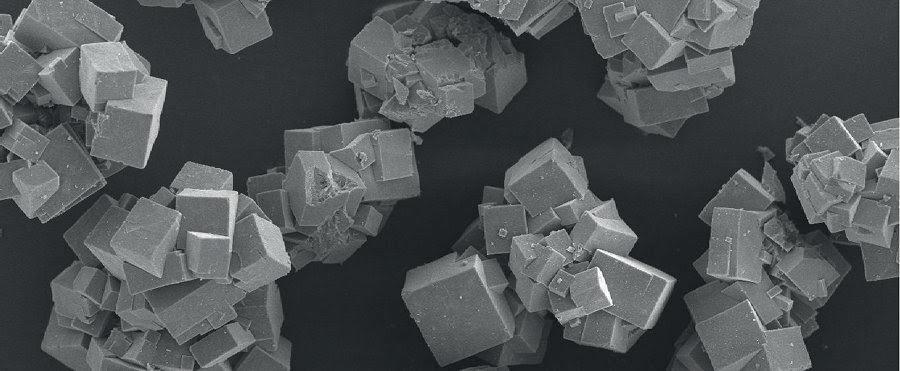
MOFs are highly engineered filters that use bespoke chemistry to target, capture and remove specific gases like CO 2 . It is this selectivity combined with an ability to release with minimal energy input that gives them such promise – not least for heavy industry where cost-effective CC is now sorely needed. Nuada, a system that has been developed by the team at MOF Technologies, has broken new ground in this area, with a new method for CC that is ideally matched to cement production.
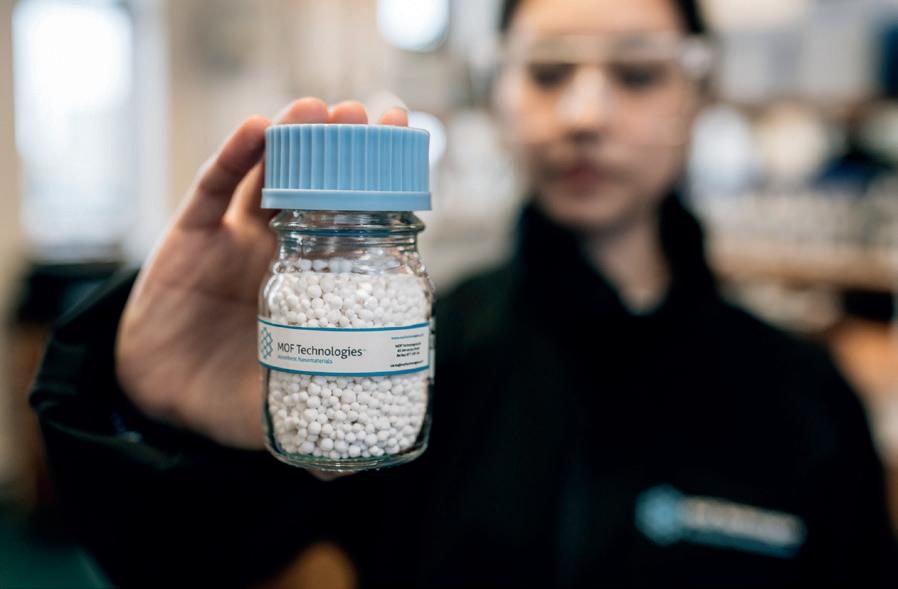
Nuada’s enhanced performance is driven by vacuum pressure swing adsorption technology coupled with an MOF-based filter that has been specifically designed to capture and remove CO 2 . With this system, existing plants do not need to be redesigned and the technology can work independently of, or be combined with, cement reformulation strategies.
The environmental hazards associated with amines are also avoided.
It sounds fanciful but, when deployed correctly, this technology can give manufacturers a credible
Shaped MOF product. MOF crystals.way to maintain current outputs while also meeting the obligations of business in a net zero era.
Beyond energy efficiency, Nuada has also addressed some of the practicalities that have troubled other methods of CC. Unlike traditional approaches using amines, this new system is modular, meaning it can be easily connected to a facility’s waste gas line without extensive redesign or installation work. The units can then be scaled according to demand, giving concrete production a non-invasive and far more cost-effective means by which to capture CO 2 at source. This is the kind of flexibility that has been sorely needed, particularly throughout the last three years where market demand has fluctuated. 10
The system is deceptively simple but the results speak for themselves. MOF Technologies has shown that users can reduce the amount of energy used for CC by an average of 80%, not to mention save money by adopting a ‘plug and play’ solution that bypasses the financial burden found with so many alternative technologies. MOF-based approaches also make the process of isolating CO 2 more straightforward, allowing it to be redirected back into the cement formation process.
Perhaps the biggest boon, however, is a capture cost as low as US$16 per t of CO 2 . This is virtually unmatched by current standards, providing the crucial first step for unlocking other parts of the CCUS value chain. Businesses could, for example, valorise their surplus CO 2 into high value chemicals and fuels and sell them on to secondary markets for a profit.
These are the kinds of opportunities that will convince investors and help CC become standard practice in a sector that recognises the need for change.
Nuada’s system cannot solve all of the challenges associated with CCUS, but it will ease some of the bottlenecks and, crucially,
offer businesses a credible route towards a more sustainable future.
References
1. RODGERS, L., ‘Climate change: The massive CO 2 emitter you may not know about’ – https://www.bbc. co.uk/news/science-environment-46455844
2. HODGSON, C., NOONAN, L., ‘Cost of neutralising carbon emissions soars as demand escalates’ –https://www.ft.com/content/29565f44-ba71-4a448e84-d1e421ddb958
3. BARRETT, E., ‘So you’ve captured carbon. Now what?’ – https://fortune.com/2021/12/12/carboncapture-usage-storage-technology-profitable-net-zeroemissions/
4. HODGSON, D., ‘Cement’, IEA – https://www.iea. org/reports/cement
5. AMBROSE, J., ‘What is carbon capture, usage and storage – and can it trap emissions?’ – https://www. theguardian.com/environment/2020/sep/24/what-iscarbon-capture-usage-and-storage-and-can-it-trapemissions
6. BROGAN, C., ‘Best ways to cut carbon emissions from the cement industry explored’ – https://www. imperial.ac.uk/news/221654/best-ways-carbonemissions-from-cement/
7. ‘Concrete commitment: Cement industry sets 2030 climate goals on road to net-zero by 2050’ – https:// www.edie.net/news/6/Concrete-commitment-Cement-industry-sets-2030-climate-goals-on-road-tonet-zero-by-2050
8. ‘Carbon capture and storage: Challenges, enablers and opportunities for deployment’, Global CCS Institute – https://www.globalccsinstitute.com/news-media/ insights/carbon-capture-and-storage-challengesenablers-and-opportunities-for-deployment/
9. PLAZA, M., MARTINEZ, S., RUBIERA, F., ‘CO 2 Capture, Use, and Storage in the Cement Industry: State of the Art and Expectations’ – https://www. mdpi.com/1996-1073/13/21/5692/pdf
10. ‘The Impact of COVID-19 on the Cement Industry’, IFC – https://www.ifc.org/wps/wcm/ connect/industry_ext_content/ifc_external_corporate_ site/manufacturing/resources/covid-19-impact-oncement-industry
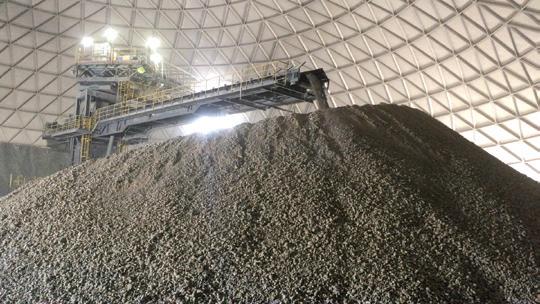
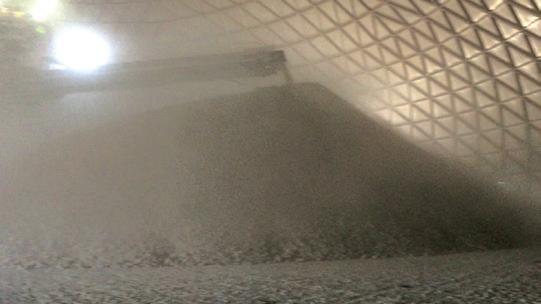
AD INDEX
ABC www.abc.org.uk
Alimak www.alimak.com
Christian Pfeiffer www.christianpfeiffer.com
Chryso S.a.S. www.chryso.com CICSA www.cicsa.com Cintasa www.cintasa.com DCL www.dclinc.com
Euromecc s.r.l. www.euromecc.com
FLSmidth A/S www.flsmidth.com
HEKO www.heko.com
HENAN Sron Silo Engineering Co., Ltd www.cementsilo.com
HGH-Infrared Systems www.hgh-infrared.com
Hycontrol www.siloprotection.com
IKN GmbH www.ikn.eu
Intercem Engineering GmbH www.intercem.de
KIMA Automatisierung GmbH www.kima-process.de
Klüber Lubrication www.klueber.com/cement
Lubrication Engineers www.lelubricants.com
Maerz Ofenbau AG www.maerz.com
Mirion Technologies www.mirion.com
MMD GPHC Ltd www.mmdsizers.com
Mole•Master Services Corporation www.molemaster.com
Promecon Process GmbH www.promecon.com/cement PSCL www.pscl.com
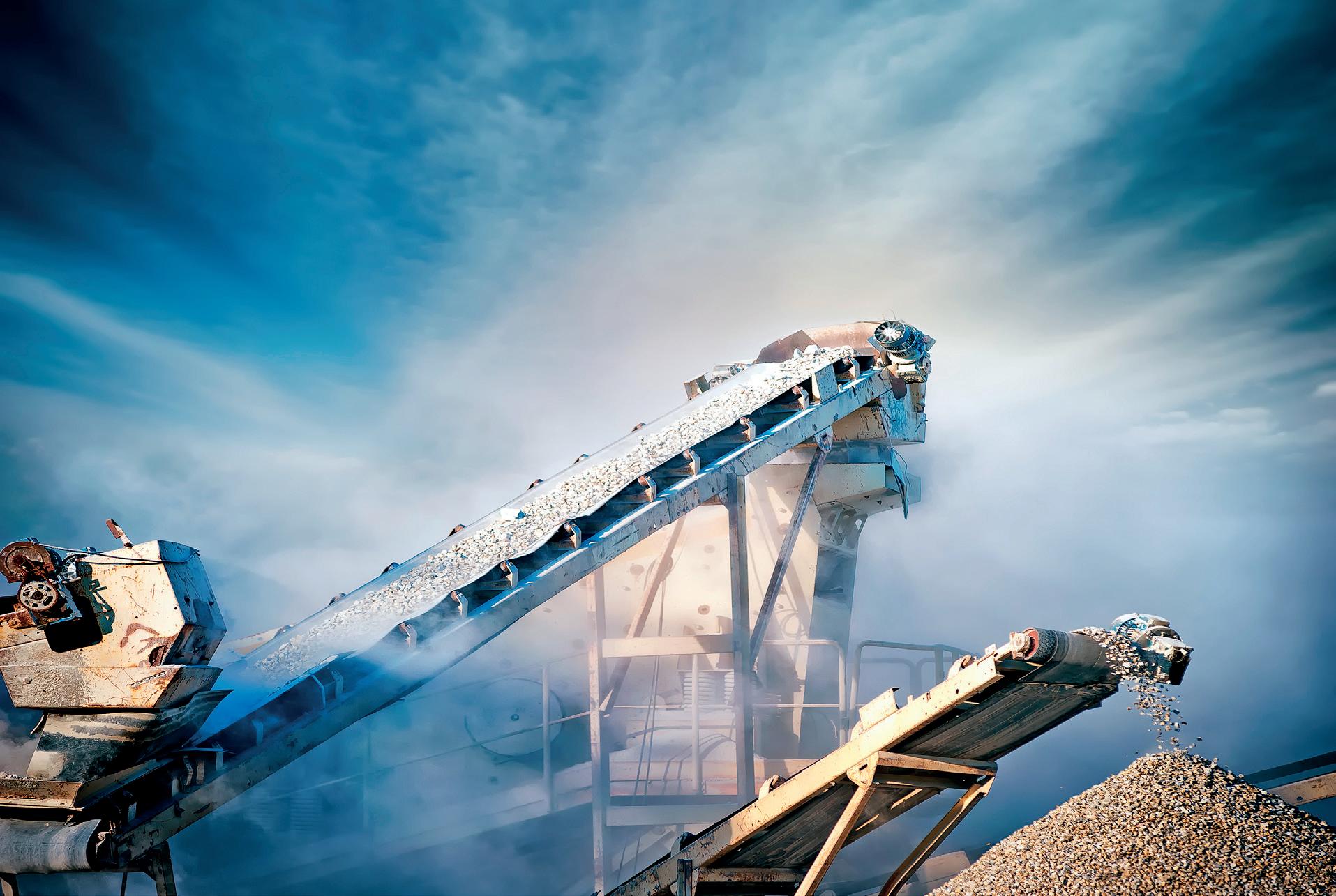
Redecam Group S.p.A www.redecam.com SIG www.sig.it Scantech www.scantech.com.au
Seaco Technologies www.seacotech.com
Stela Laxhuber GmbH www.stela.de
thyssenKrupp Industrial Solutions www.thyssenkrupp.com
Van Aalst Bulk Handling www.vanaalstbulkhandling.com
Ventilatorenfabrik Oelde GmbH www.venti-oelde.com
www.vortexglobal.com World Cement www.worldcement.com
NO PROBLEM.

Maerz lime kilns are extremely efficient in every climate. For decades. Is it a bit dry where you are? No problem: maerz.com
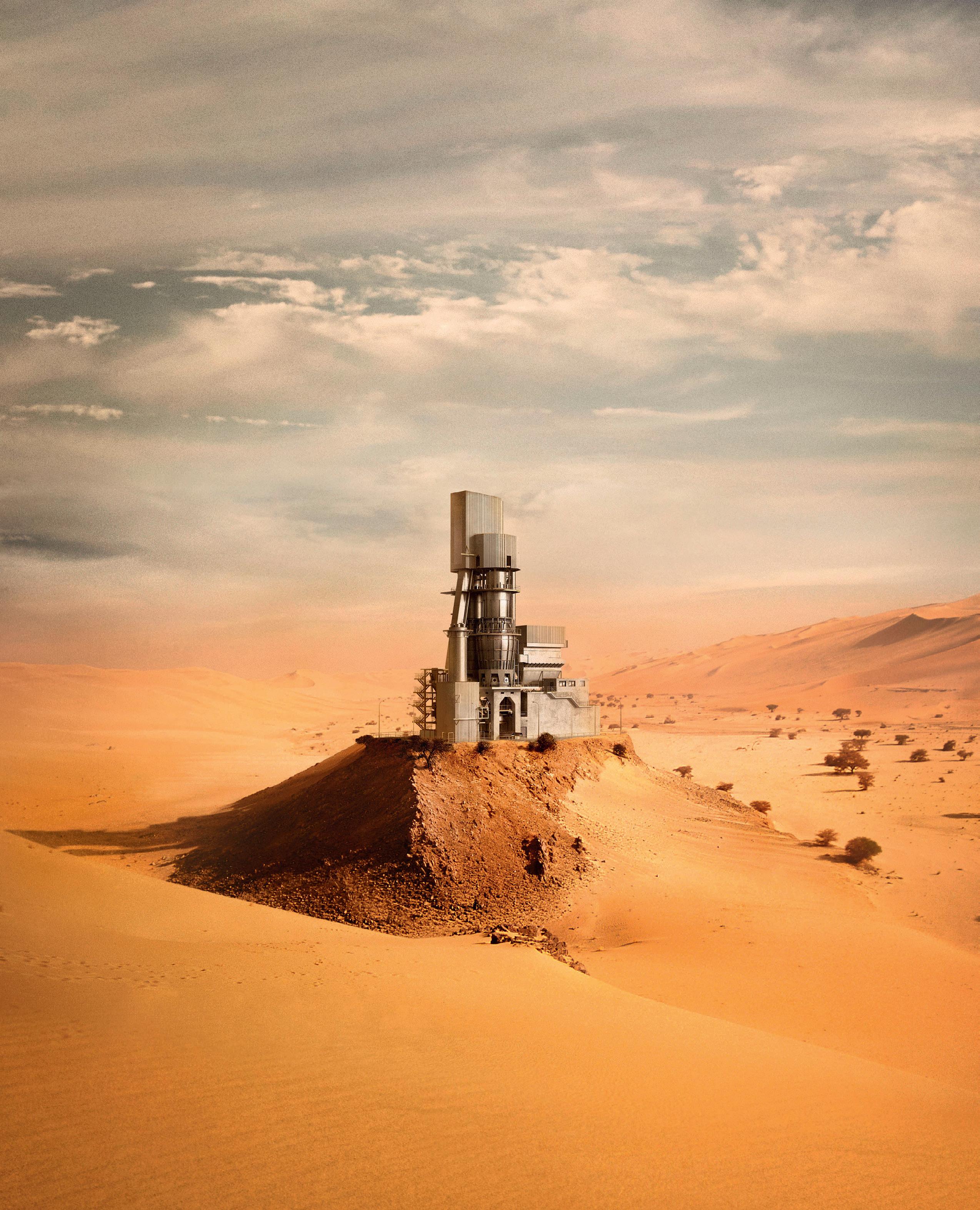
COLD AS ICE
IKN – Experts in clinker cooling
More about our clinker cooling passion on ikn.eu
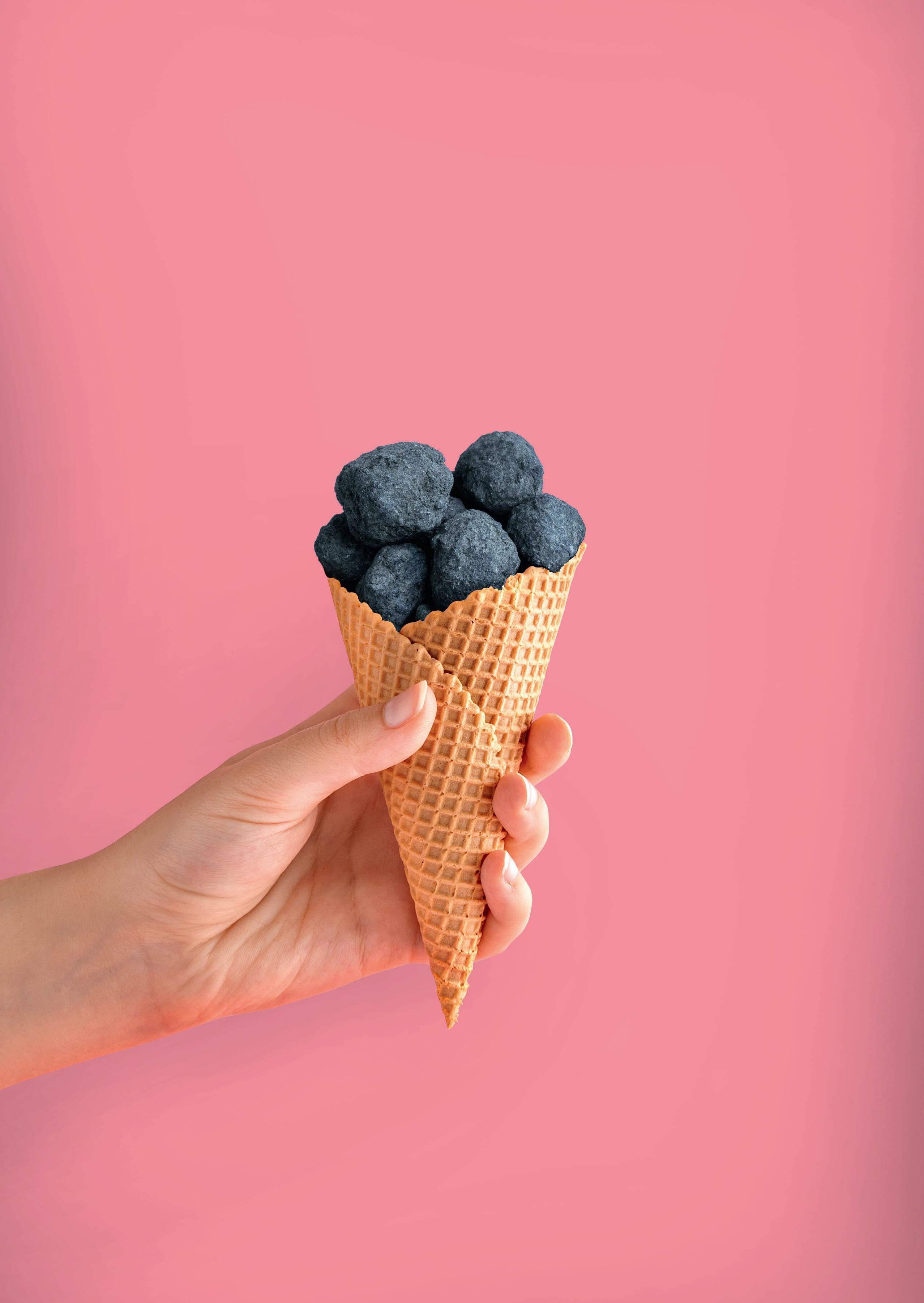