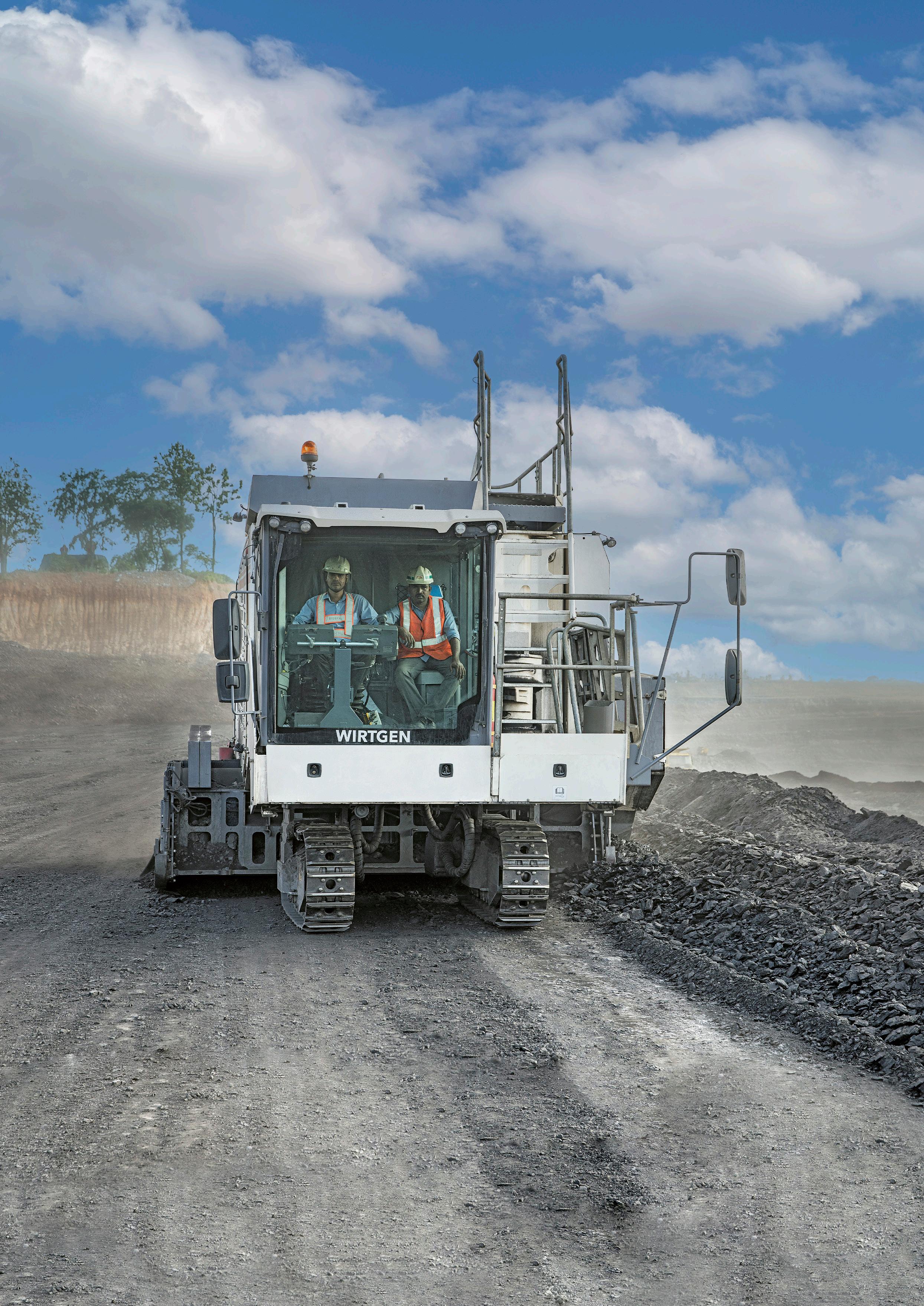
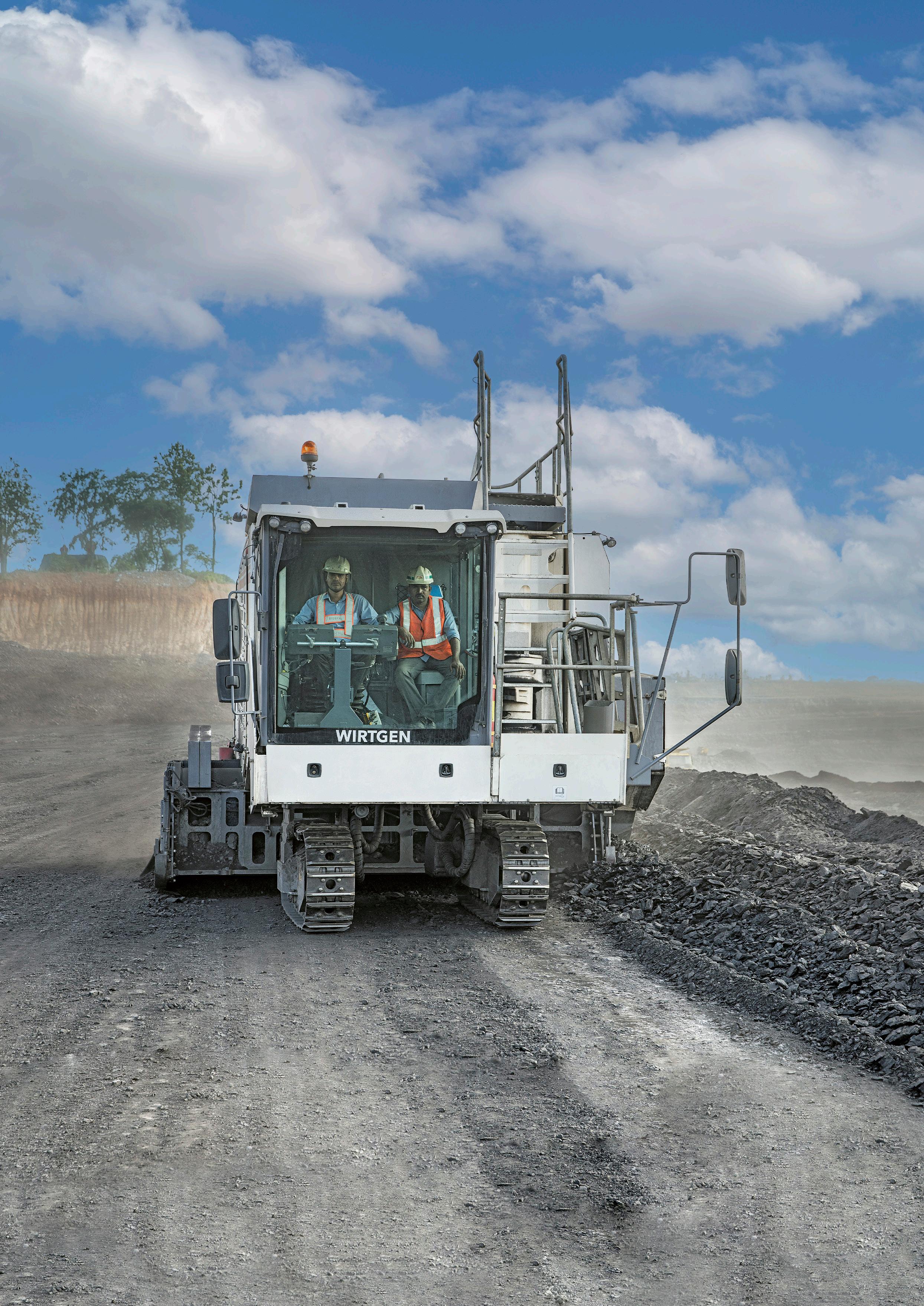
PROVEN IPSC SOLUTIONS
MMD remains at the forefront of In-Pit Sizing and Conveying (IPSC) technology, developing ground breaking sizing systems that optimize efficiency, improve safety, and delivers high productivity.
The Twin Shaft MINERAL SIZER™ sits at the heart of every IPSC system. To cater for today’s variety of modern mining methods, MMD has deployed successful modular Sizing stations and systems worldwide to take advantage of cost effective long haul by conveyor. High throughputs and short relocation times enable mines to achieve their efficiency and productivity goals.
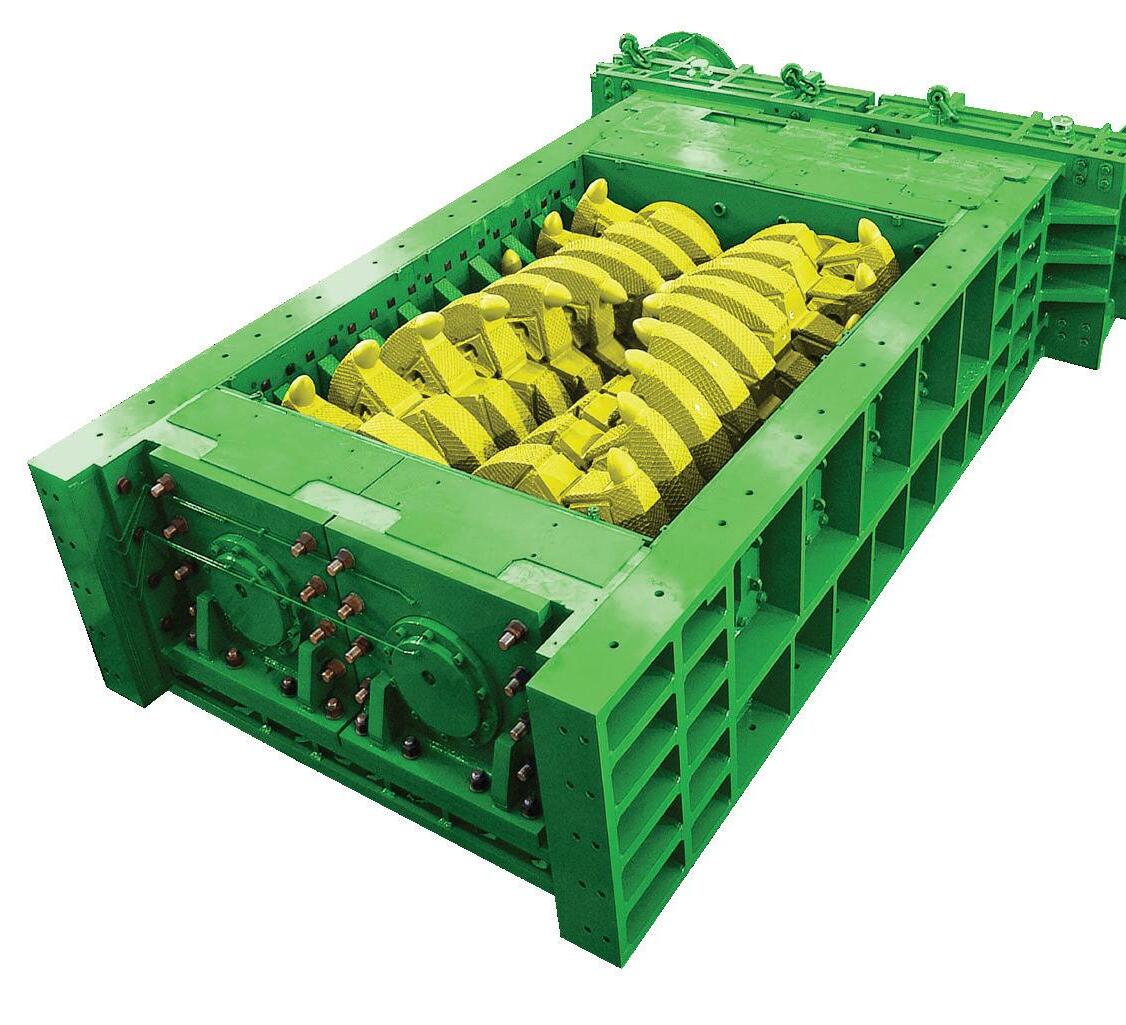
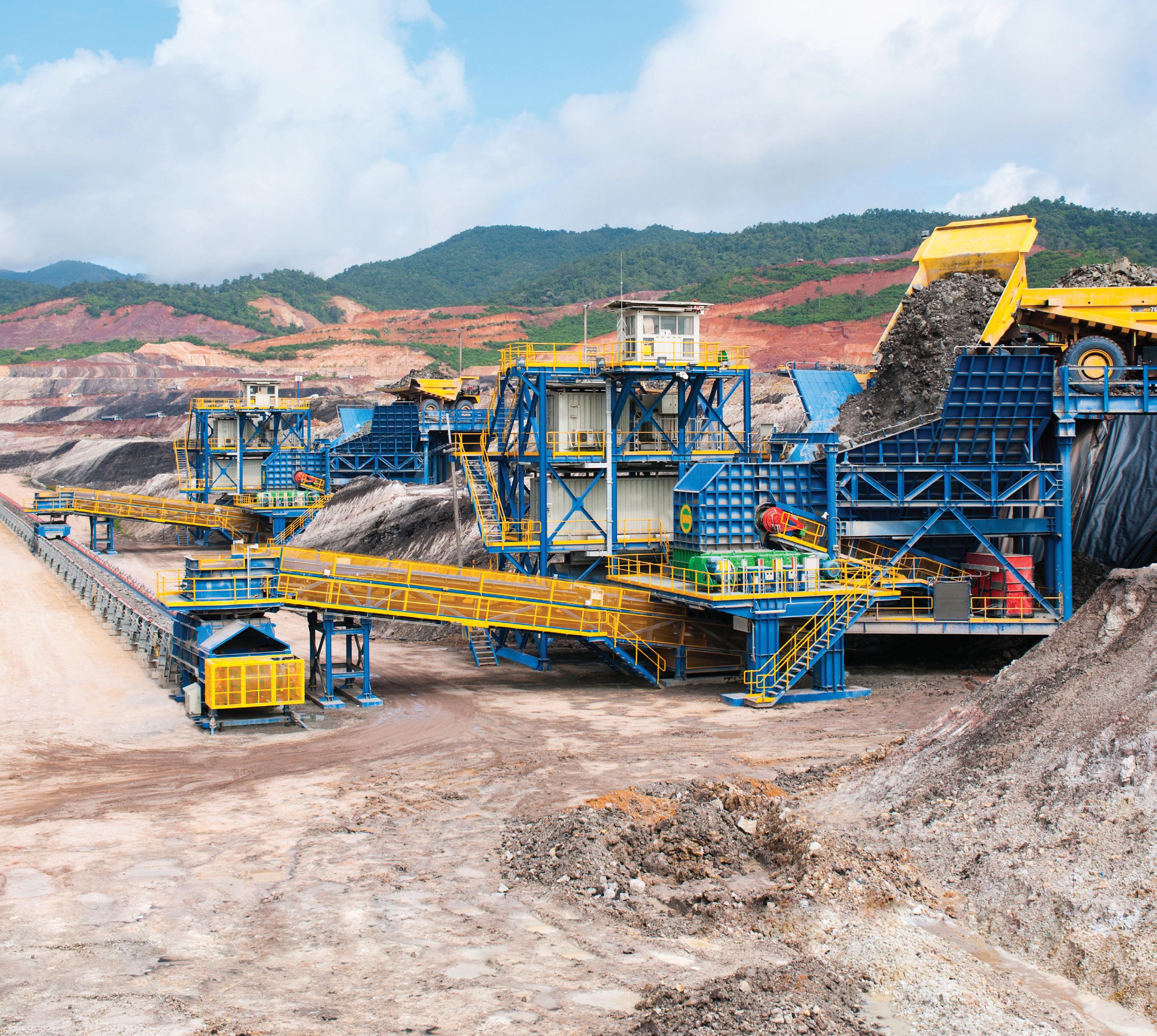
MMD’s worldwide structure, technical expertise and service excellence will ensure your system always delivers optimum performance. Discover how we can deliver the complete IPSC solution for your specific needs.
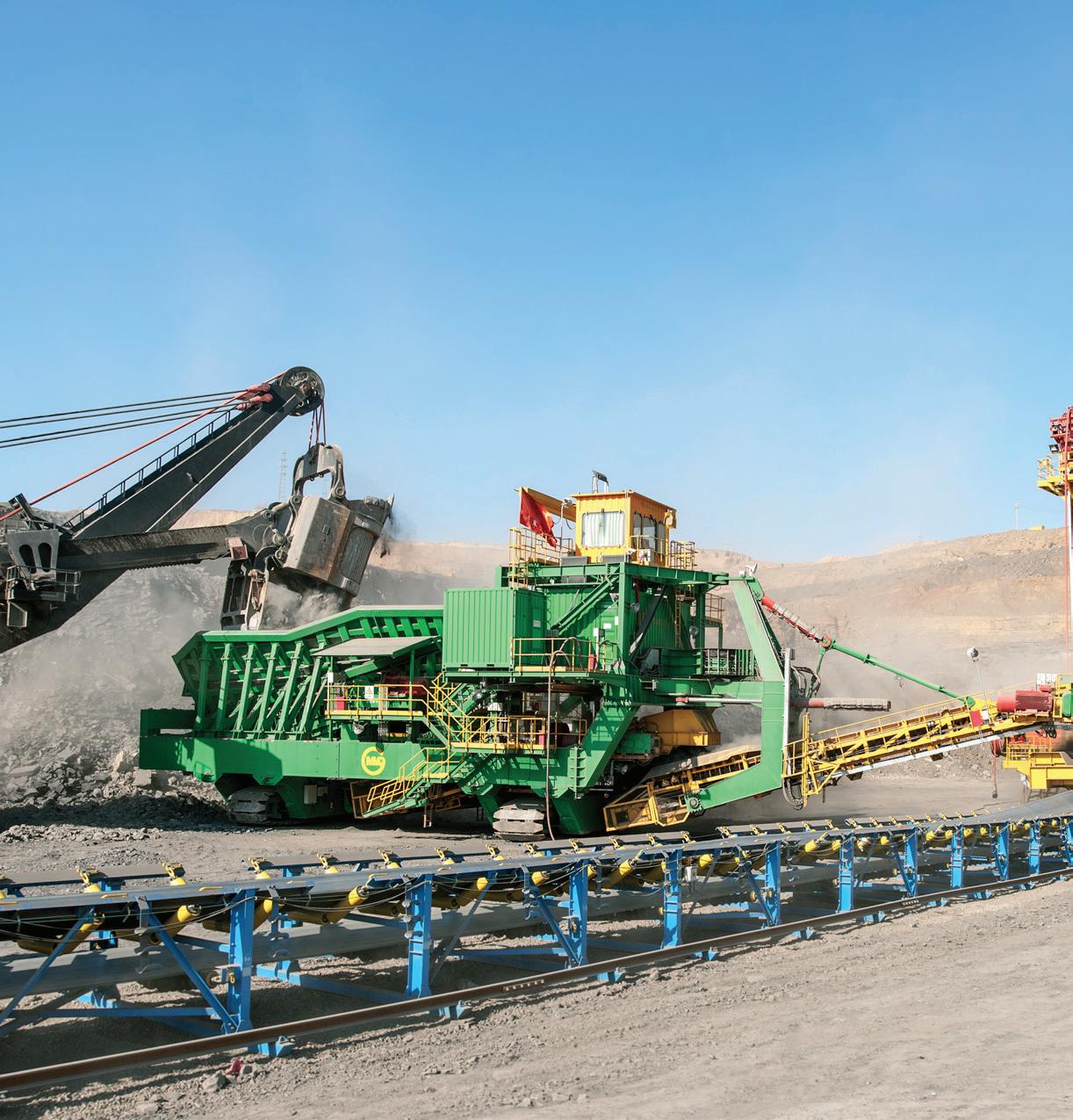
31 Revolutionising The ERS With Technology
Flor Rivas, Caterpillar, USA, discusses the importance of technology advancements in driving electric rope shovel efficiency and longevity.
35 The Right Connection
Paul Badeau, Applied Fiber, USA, examines the advantages of utilising fibre pendants as a connection point technology, and how they can be used as an effective alternative to steel wire.

38 Coal Processing With Screen Media

Serge Raymond, MAJOR, Canada, explains how it is possible to solve the three biggest coal screening challenges.
Productivity With Dust and Erosion Control
Lee Gailer, RST Solutions, Australia, considers how utilising advanced technologies for dust and erosion control is essential for keeping mines running during the wet season.
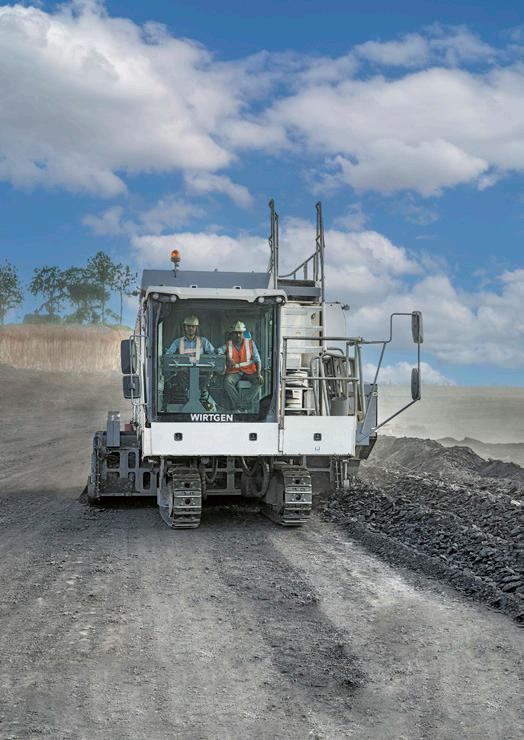

22 Going Back To Basics With Dust
Liam Sheeder, Belt Tech Industrial, USA, reflects on the problems associated with excess dust in coal mining operations and provides some solutions to mitigate this.
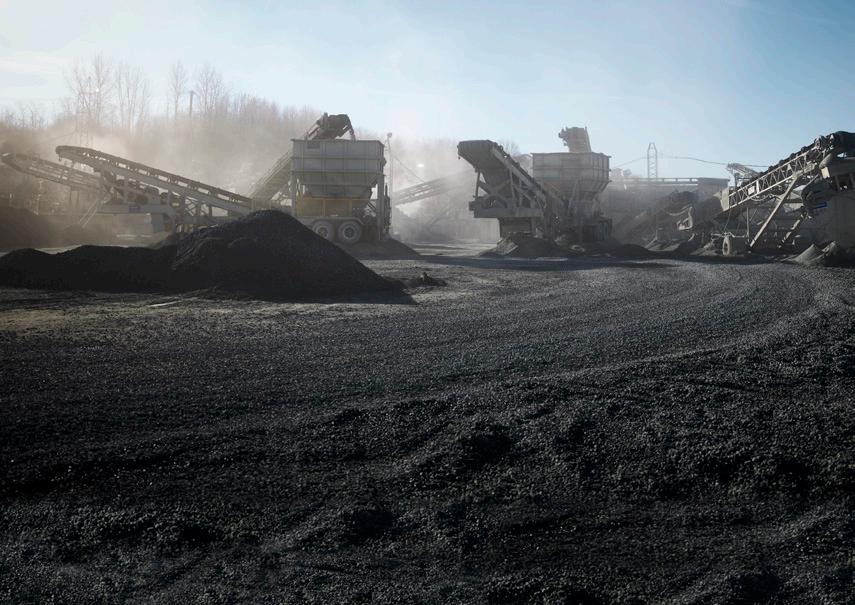

26
Cutting, Crushing, And Loading
Dr. Erik Zimmermann, Wirtgen, Germany, explores how cutting technologies can be used to optimise coal mining operations, and how they play an important role in reducing emissions.
43 Relying On Resin
Benjamin Mirabile, Jennmar, USA, reviews the critical role that resin plays in coal operations and how it is essential to all modern ground support systems.
46 The Importance Of Clean Coal Technologies
Nikhil Kaitwade, FMI, India, outlines how clean coal technologies can help reduce emissions within the industry.
Trust Your Separation Needs To Tabor Vibrating Screens
Trust Your Separation Needs To Tabor Vibrating Screens
Tabor Vibrating Screens
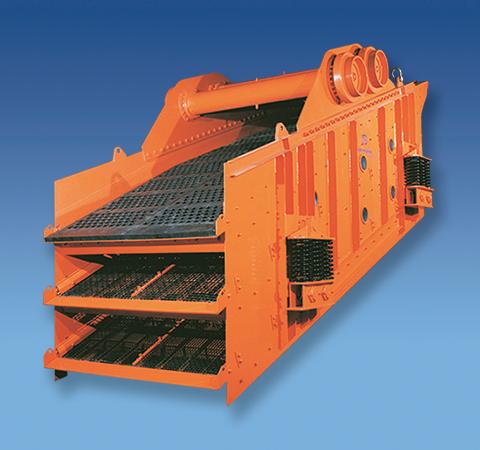
For over 60 years, Tabor vibrating screens have been the trusted choice in meeting industry’s most challenging separation needs. Our industry leading Tabor vibrating screens provide:
• Design Flexibility that provides rugged construction at a competitive price
• Dependable sizing for wet or dry applications
• Efficient screening of metallic/nonmetallic minerals, aggregate, sand, gravel, crushed stone, coal and recycled materials

• Wide selection of repair parts
• 24x7 emergency service
• Application assistance
Our full line of Tabor vibrating screens include Vibrating Incline, Multi-Slope, Horizontal and Fine Dewatering Screens to meet a wide range
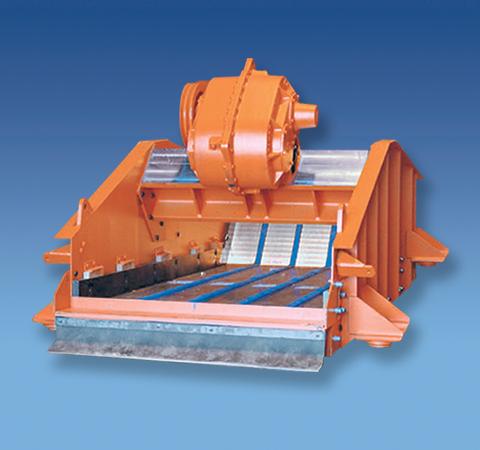
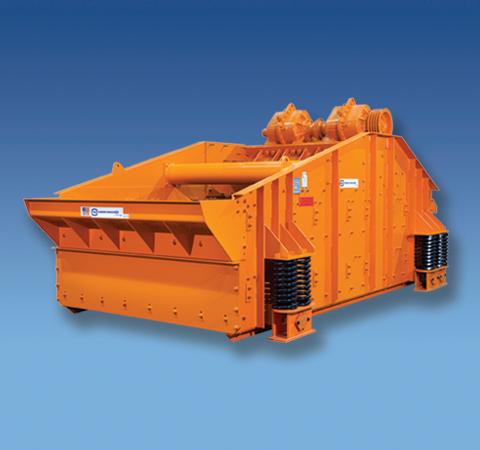
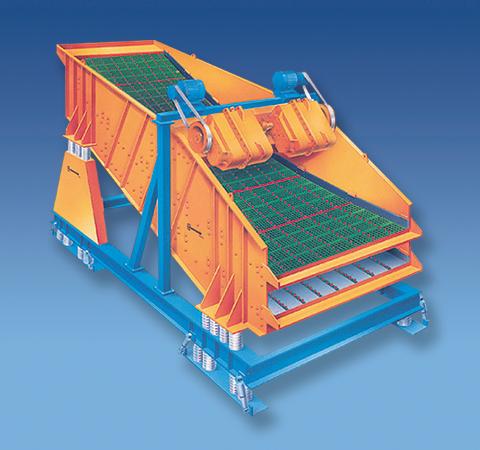
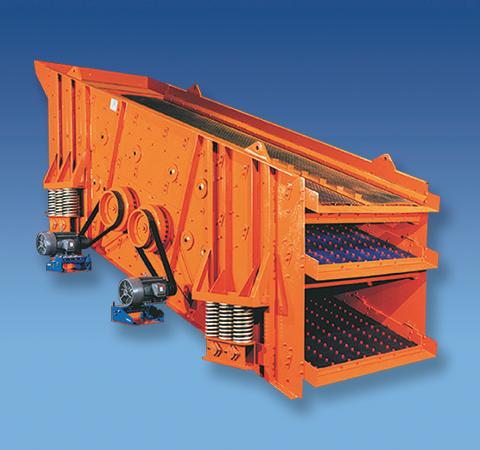
of demanding applications. Screens are available in single, double, triple or multi-slope decks in sizes ranging from 3’ to 12’ wide and 6’ to 28’ long.
Elgin Separation Solutions uses the latest technology and manufacturing techniques to provide service and repair parts to mining, chemical, industrial and recycling screening and separation facilities around the world. We are committed to delivering performance excellence and earning your trust in meeting your separation needs with Tabor vibrating screens.
Fine Dewatering Screen Incline Screen TMS Multiple Slope Horizontal ScreenMANAGING EDITOR
James Little james.little@worldcoal.com
SENIOR EDITOR
Callum O’Reilly callum.oreilly@worldcoal.com
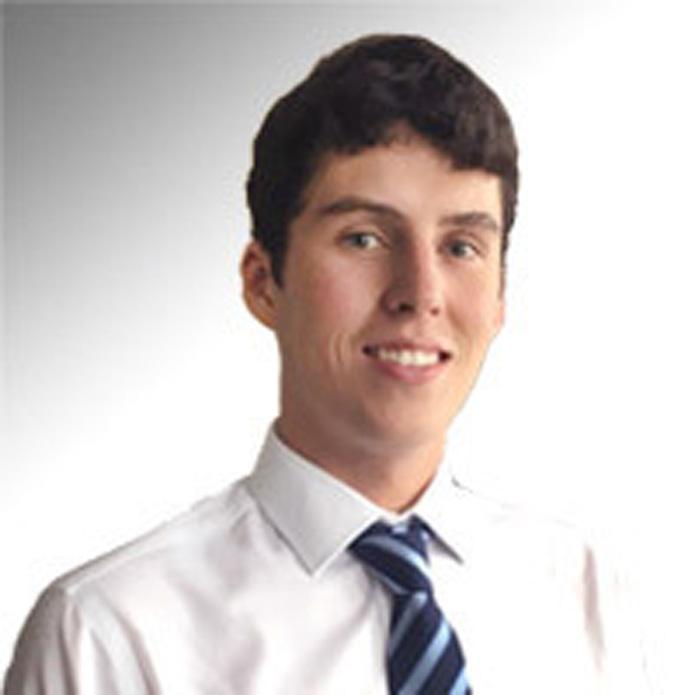
EDITOR
Will Owen will.owen@worldcoal.com
EDITORIAL ASSISTANT
Isabelle Keltie isabelle.keltie@worldcoal.com
SALES DIRECTOR
Rod Hardy rod.hardy@worldcoal.com
SALES MANAGER
Ryan Freeman ryan.freeman@worldcoal.com
PRODUCTION MANAGER
Kyla Waller kyla.waller@worldcoal.com
ADMINISTRATION MANAGER
Laura White laura.white@worldcoal.com
EVENTS MANAGER
Louise Cameron louise.cameron@worldcoal.com
EVENTS COORDINATOR
Stirling Viljoen stirling.viljoen@worldcoal.com
DIGITAL ADMINISTRATOR
Leah Jones leah.jones@worldcoal.com
DIGITAL CONTENT ASSISTANT
Merili Jurivete merili.jurivete@worldcoal.com
World Coal (ISSN No: 0968-3224, USPS No: 020-997) is published four times per year by Palladian Publications Ltd, GBR, and distributed in the USA by Asendia USA, 17B S Middlesex Ave, Monroe NJ 08831. Periodicals postage paid New Brunswick, NJ, and additional mailing offices.
POSTMASTER: send address changes to World Coal, 701C Ashland Ave, Folcroft PA 19032.
Annual subscription (quarterly) £110 UK including postage, £125 overseas (airmail). Two-year discounted rate (quarterly) £176 UK including postage, £200 overseas (airmail). Claims for non-receipt of issues must be made within four months of publication of the issue or they will not be honoured without charge.
Palladian Publications Ltd, 15 South Street, Farnham, Surrey, GU9 7QU, UK
t: +44 (0)1252 718999 w: www.worldcoal.com
As 1Q23 draws to a close, some might characterise the global coal industry as a poker player running low on chips. Despite its status as a veteran player, with much time and capital invested over the years, the feeling that coal’s ‘luck’ has turned for the worse has failed to dissipate with the dawn of the new year.
Indeed, large scale public opinion remains stoically opposed to the continued use of coal for power. This was apparent in January, as protests in Germany – backed and attended by climate activist Greta Thunberg – over the expansion of the RWE-operated Garzweiler coal mine made headlines across international mainstream media.
Furthermore, as illustrated by a recent presentation by Fitch Ratings, major financial institutions around the globe are continuing to withdraw from financing coal ventures. The writing on the wall seems particularly clear for Australia: “as part of the net-zero banking alliance, all of the big four banks in Australia have committed to stop financing new thermal coal mining projects, and to exit financing the thermal coal sector entirely, by 2030.”1 (For more information regarding the state of the Australian coal industry, make sure to read Fitch Solutions’ regional report on pp. 8 – 13).
This being said, coal has not been without its victories of late. For example, while UK environmental groups expressed dismay at the opening of a new coal mine in Cumbria – the first to be approved in over 30 years – in the town of Whitehaven, where the mine is being developed, the feeling is reportedly very different. According to The Guardian, the local community has shown strong support for the mine across the political spectrum, with a desire to see renewed economic growth and community spirit playing a key role in swaying opinions.2
Additionally, on the other side of the planet, China continues to ‘double down’ on coal. As reported by Reuters, in January-February the world’s largest coal miner and consumer increased its coal output to 734.23 million t, a 5.8% increase compared to the same period in 2022 (686.6 million t).3 Likewise, during this period the country also re-established trading relations with Australia, ending its unofficial ban on imports from Down Under, which has been in place since the end of 2020.4 With increases in global coal prices, as well as energy supply chain disruption resulting from Russia’s invasion of Ukraine, China has continued to favour coal as it prioritises its energy security.3
Moreover, ‘clean coal’ continues to gather momentum. As spoken to by many of the articles in this issue, technology is offering coal a viable way to ‘buy in’ into an extended period of viability. For example, FMI (pp. 46 – 48) discusses how as countries, such as the US, introduce new initiatives demanding lower emissions, clean coal technologies offer definitive ways to improve the efficiency of power plants. Likewise, this month’s cover advertiser, Wirtgen (pp. 26 – 30), outlines how cutting technologies can optimise coal mining operations and reduce emissions.
Fundamentally, coal is not out of the game yet. The UK switching to emergency backup coal plants to supply almost 5% of its energy during a cold snap this past winter, in addition to the positive trends mentioned above, is clear evidence of the critical role coal continues to play, in the absence of a truly fit-for-purpose alternative fuel source.5
The question of how many hands does coal still have left to play remains, however so does the industry’s consistent answer. As long as coal has chips left in its stack, it will not cede its seat at the table.
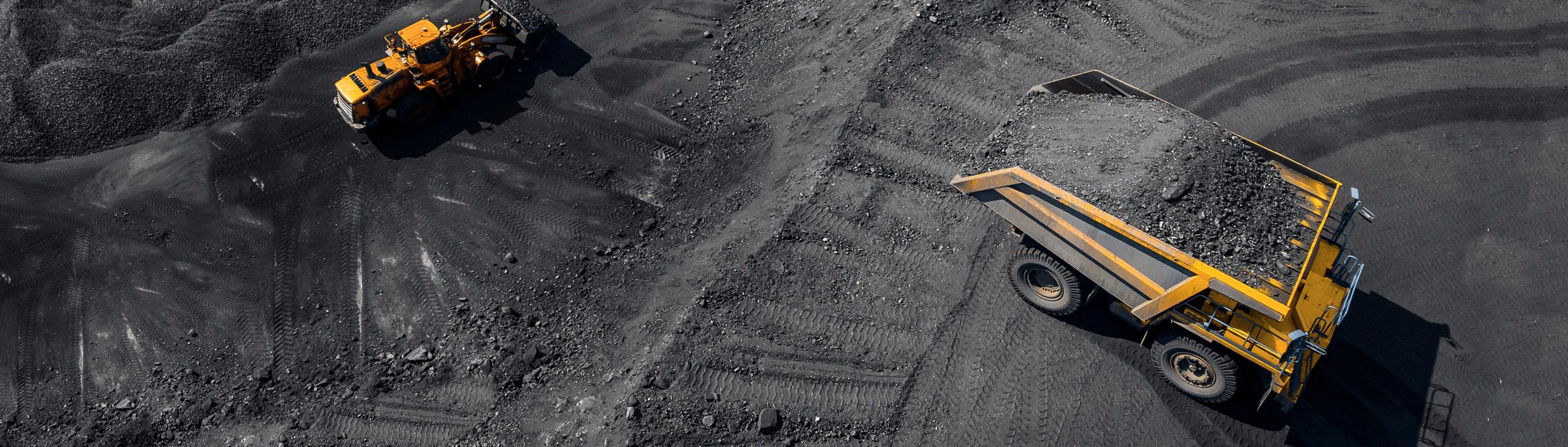
REFERENCES
1. ‘Insights On: APAC Coal Sector Outlook amidst the Green Transition’, Fitch Ratings, (16 February 2023)
2. ‘Why this town wants its coal mine back amidst the climate crisis’, The Guardian, (7 March 2023), www.theguardian.com/environment/ video/2023/mar/07/why-this-town-wants-its-coal-mine-back-amidst-the-climate-crisis-video
3. ‘China coal output up 5.8% in Jan-Feb as new capacity comes online’, Reuters, (15 March 2023), www.reuters.com/world/asia-pacific/chinacoal-output-up-58-jan-feb-new-capacity-comes-online-2023-03-15/
4. XU, M., and AIZHU, C., ‘China boosts Australian coal imports on hopes for more easing of curbs’, Reuters, (22 February 2023), www.reuters.com/markets/commodities/china-boosts-australian-coal-imports-hopes-more-easing-curbs-traders-data-2023-02-21/
5. ‘Britain fires up back-up coal plants for first time ever’, The Telegraph, (8 March 2023), www.telegraph.co.uk/business/2023/03/07/ftse-100markets-live-news-halifax-house-prices/

WORLD NEWS
USA American Resources expands Carnegie 2 production
American Resources Corp., through its subsidiary, American Carbon Corp., a leading producer of high quality metallurgical and specialty carbon, has announced that it has expanded production at its Carnegie 2 metallurgical carbon mine in Pike County, Kentucky, by adding a second operating section. It is expected that the production from this section will initially ramp up to approximately 9000 – 12 000 additional tpm.
Mark Jensen, CEO of American Resources, comments: “Our McCoy Elkhorn complex is a showcase operation that possesses a significant opportunity for growth from our internal portfolio of assets. We applaud the hard work that the men and women onsite have put forth and the effort to achieve this growth safely and efficiently and to capitalise on the strength of the metallurgical carbon market. Adding a second operating section at this already producing mine is one of the highest margin growth opportunities we can execute upon as a company, given no additional fixed costs and minimal additional variable costs are needed to achieve
the incremental growth of production. Now that this has been achieved, we look forward to focusing on additional growth expansion at the McCoy Elkhorn complex, while we continue to minimise capex costs and maximise speed to market.”
Over the years, American Resources Corp. has acquired a significant fleet of underground and surface equipment that it can utilise to expand production. This new expansion at Carnegie 2 is utilising almost entirely owned equipment that the company has been able to acquire over the years. The company is still in possession of over three additional full operating sections of equipment that it intends to use for Carnegie 1 expansion, the company’s upcoming Mine #15A expansion, as well as its Wyoming County Coal LLC complex that it is currently developing. In the current market, owning quality assets and equipment for efficient growth offers a significant competitive advantage, given the current tightness in the equipment and infrastructure marketplace.
ZIMBABWE Contango completes pilot coke plant construction at its Lubu Project
Contango Holdings Plc has advised that the construction of a small-scale coke battery has been completed at the Lubu Coal Project in Zimbabwe. The pilot coke plant has been constructed to provide onsite capability to manufacture coke from washed coking coal produced at Lubu for testing by future offtake partners, and for the company’s internal studies and quality control. The ultimate coke batteries to be installed at Lubu for future production and sales will be considerably larger and a different specification.
To date the manufacture of coke and subsequent studies from washed coking coal from Lubu has taken place remotely, with highly encouraging results. The ability to now manufacture coke onsite is a significant step, providing accurate in the field results, a crucial step in securing partners in the company’s coke manufacturing strategy.
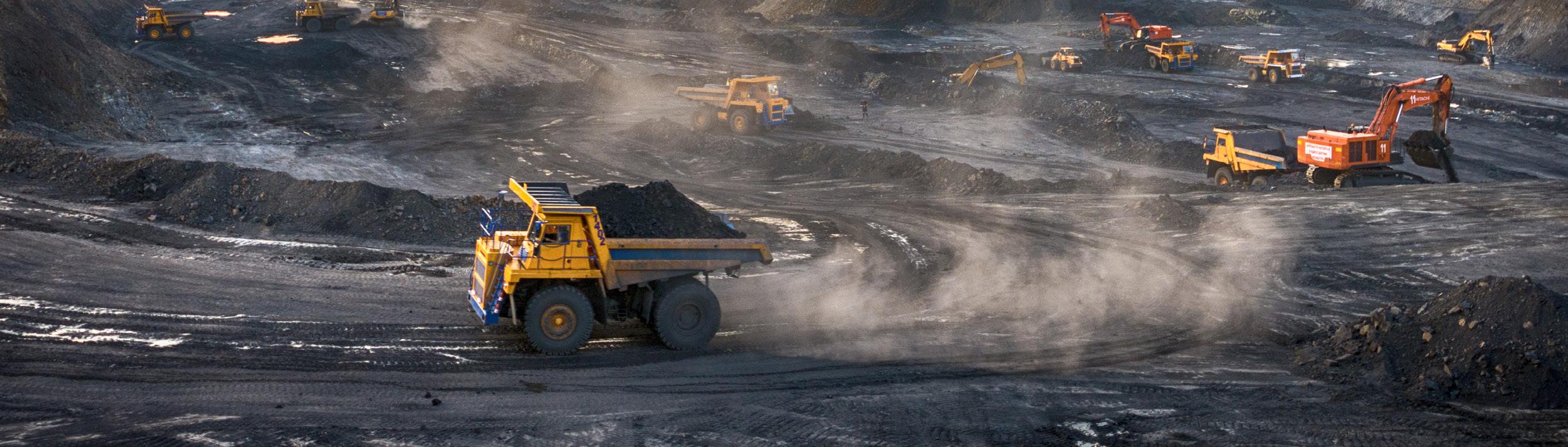
Following completion of the pilot plant, the company has subsequently produced approximately 4 t of coke, from a sample of washed coking coal from Lubu. A significant portion of this production will be delivered to the
multinational company that entered into a memorandum of understanding with Contango in December 2022. This is part of the ongoing due diligence process to confirm suitability for their requirements ahead of a potential transaction.
Carl Esprey, CEO of Contango, comments: “Whilst the expected margins on our coking coal production are very attractive, we have always maintained the highest margin business stems from the manufacture of coke at Lubu. Accordingly, we have already completed numerous small-scale tests remotely to assess the coke characteristics from Lubu, with highly encouraging results.
“The completion of the pilot coke plant will now enable us to generate larger coke production for testing, something required to enable us to conclude discussions under our MOU and, as required, provide additional samples to other parties who have expressed interest in coke produced from Lubu.
“This is a notable step in the evolution of the Lubu Project and I look forward to providing further updates with respect to the planned manufacture of coke in due course.”
DIARY DATES
Expomin
24 – 27 April 2023
Santiago, Chile
www.expomin.cl/registro-expomin
Mines & Money Connect
25 – 26 April 2023
London, UK
https://minesandmoney.com/connect
China Coal & Mining Expo 2023
25 – 28 October 2023
Beijing, China
www.chinaminingcoal.com
International Mining, Equipment, & Minerals Exhibition (IME 2023)
06 – 09 November 2023
Kolkata, India
https://miningexpoindia.com
To stay informed about the status of industry events and any potential postponements or cancellations of events, visit World Coal’s website: www.worldcoal.com/events
WORLD NEWS
CANADA Teck Resources to spin off steelmaking coal business
Teck Resources Ltd. has announced the reorganisation of its business to separate Teck into two independent, publicly-listed companies: Teck Metals Corp. and Elk Valley Resources Ltd (EVR). The separation will create two world-class resource companies and provide investors with choice for allocating investment between two businesses with different commodity fundamentals and value propositions. Teck Metals will be growth-oriented, with premier, low-cost base metals production, a top-tier copper development portfolio, and a disciplined capital returns policy. EVR will be a high-margin Canadian steelmaking coal producer, focused on long-term cash generation and providing cash returns to shareholders, with significant equity value accretion potential. Both companies will remain committed to strong environmental and social performance.
Jonathan Price, Teck CEO, commented: “This transformative transaction creates two strong, sustainable, world-class mining companies committed to responsibly providing essential resources the world needs.”
SOUTH AFRICA Canyon Coal develops new mine in Mpumalanga
Canyon Coal, a subsidiary of private investment company Menar, is constructing a new coal mine in Hendrina, Mpumalanga, South Africa, with production expected to start in 2H23.
The first phase of the Gugulethu project, on track to be completed in 8 – 10 months, is expected to produce 1.2 million tpy of 5500 kc NAR coal.
Jarmi Steyn, Gugulethu Colliery GM, commented: “We are in the development phase and have already done the tenders for the civils and the processing plant. Our mining equipment has started to arrive.”
Formerly known as De Wittekrans, Gugulethu is a greenfield project located southeast of Hendrina that Canyon bought out of business rescue. Phase 1 of the project holds an economically mineable reserve of 14.3 million t of run-of-mine (RoM) coal. It is comprised of three pits, one of which has been specifically designed to gain access to the underground reserve, as part of Phase 2.
This fully licensed project has a life of mine of over 20 years based on a RoM production of approximately 2.4 million tpy from the opencast section. The underground sections, which will commence operations in 2028 after the completion of the open cast reserve, will sustain production of 2.4 million tpy.
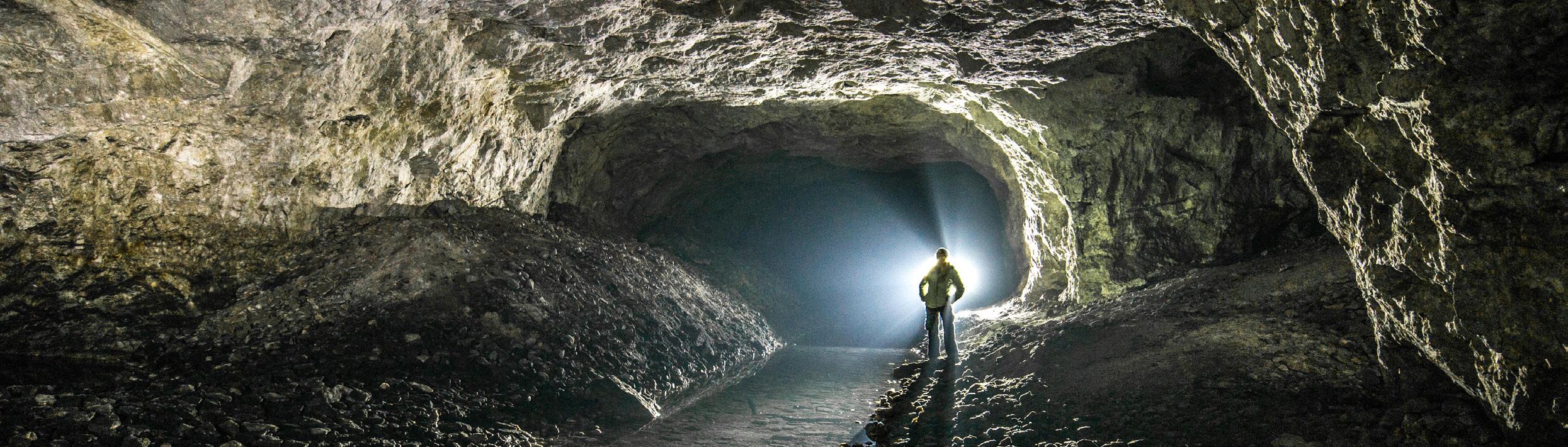
The commissioning of the processing plant is scheduled towards the end of 2023. The transfer of the plant from the depleted Hakhano mine – Canyon’s first opencast colliery – for reassembly at Gugulethu has begun.
Total investment earmarked to develop the mine is over R1.4 billion. Canyon Coal will invest R600 million in Phase 1 of the project. The development of the underground mining section will require a further R890 million.
Gugulethu’s product will be trucked some 43 km to the Rietkuil siding for transportation to the Richards Bay Coal Terminal in KwaZulu-Natal.
WORLD NEWS
TANZANIA Edenville Energy releases Rukwa Coal update
Edenville Energy Plc has provided an update on its Rukwa Coal Project in Tanzania.
The company has been focused on stockpiling run of mine coal to mitigate, as far as practicable, impact from the Tanzanian rainy season. A substantial stockpile of run of mine (ROM) coal was accumulated, but this stockpiled ROM coal has proven difficult to wash due to its moisture content. The production of washed coal is therefore expected to be reduced for as long as the rains continue, which could be for several more months.
The company continues to explore further opportunities in the Tanzanian coal market as they are presented, with efforts being increased given the robustness of the global coal markets and opportunities currently available within Tanzania.

Edenville is in discussions with the Mining Commission in Tanzania in relation to its Rukwa mining licence, having been advised by the Commission that the company had historically failed to perform certain tasks required under its licence and that the licence could
technically be in default of these requirements.
Edenville’s senior management have held constructive discussions in Tanzania with the Commission and both parties have agreed to work on resolving any outstanding issues, whilst also ensuring the company is in full compliance with local regulations.
The company is continuing to run the day to day operations at Rukwa, while continuing discussions with the Commission, and looks forward to remedying the outstanding matters concerning the licence in consultation with the Commission on a timely basis.
For the period from 1 January to 27 March 2023, the company has sold 948 t of washed coal, generating revenue of approximately £34 500.
Noel Lyons, CEO of Edenville, comments: “We remain focused on resolving any legacy issues at Rukwa and remain confident that the challenges can be overcome. However, in conjunction with this, we are also focused on securing potential new and exciting coal opportunities.”
CHINA Siwertell shipunloaders commissioned at new Chinese power station
Bruks Siwertell has completed the commissioning of two large scale Siwertell ST 790-D-type shipunloaders for a newly developed ultra-supercritical power station in southern China, ensuring clean and efficient coal handling for their new owners.
“The COVID pandemic presented a number of challenges for the commissioning process as it was impossible to send personnel from Sweden,” explained Björn Ohlsson, Contract Manager, Bruks Siwertell. “We had to get creative, developing a unique set-up that saw our local personnel carry out the commissioning and performance tests with remote support from Sweden.
“The whole process required us to be very flexible, not only with our approach, but also with our working hours. The result is two shipunloaders that are meeting their new owner’s expectations,” Ohlsson added.
The new unloaders secure the delivery of fuel to a two-unit 1000 MW power plant development.
Siwertell screw-type shipunloaders are designed to handle coal and other dry bulk materials in the most environmentally-friendly way possible, with totally enclosed conveying lines from start to finish, providing an operation free from spillage, and reducing dust emissions to a minimum.
“The proven performance of Siwertell unloaders was an important element in them being selected for this new development,” commented Ohlsson. “Our technology is also much lower in weight than any equivalent capacity equipment, which minimised the load on the jetty, delivering significant cost savings in jetty construction.”
In addition to their low weight, the Siwertell shipunloaders deliver market-leading through-ship capacities, which minimise berth occupancy. These new units are rail-mounted and offer a continuous rated coal handling capacity of 1800 tph, with a peak capacity of 2000 tph, discharging vessels of up to 100 000 DWT.
The Australian coking coal market is expected to receive some upside from China’s reopening, but weak global steel production will restrict coking coal’s demand outlook in 2023. Australian thermal coal will also experience limited growth in 2023 following milder winters, easing LNG prices, and increased domestic production from major importers. On the whole, Australia’s coal mining activity will continue to face domestic environmental opposition, while the
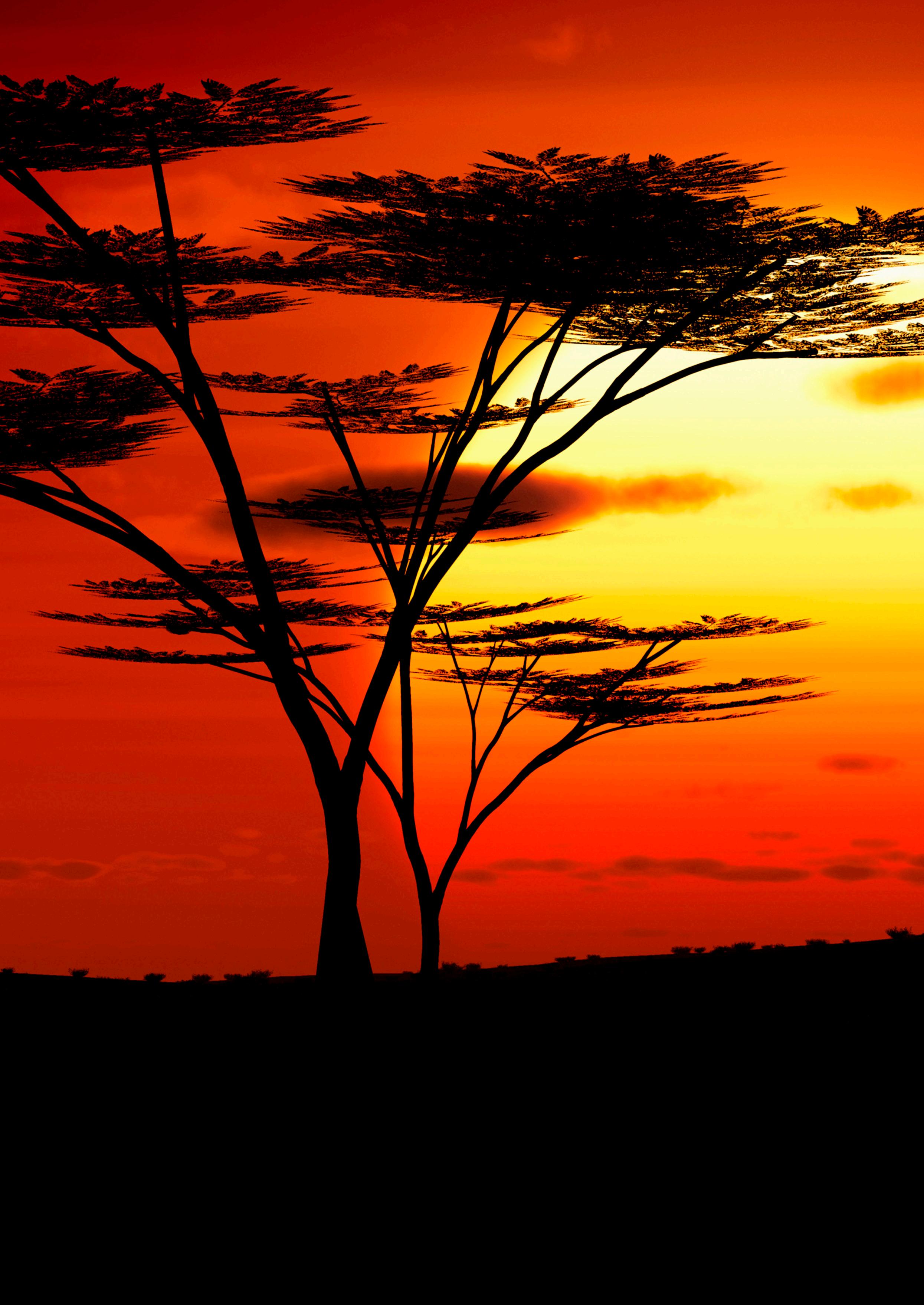
global focus on renewable power will edge out coal mining in the longer term.
Coking coal supply and demand
Fitch Solutions expects a modest 0.5% y/y growth for coking coal production in Australia this year, reaching 196 million t. After a two-year ban, mainland China has finally eased its stance towards Australian coal imports. China sourced a sizable portion of its coking coal
needs from Australia prior to the ban, due to its high quality. A reintroduction of Australian exports to China would mean a tighter supply in the market, translating to higher prices. However, weak global growth and poor steel consumption from importing countries will place a cap on Australian coking coal prices and, consequently, its production outlook. Prior to the ban, China imported 72.27 million t of coking coal in 2020, with 34.97 million t sourced from Australia.
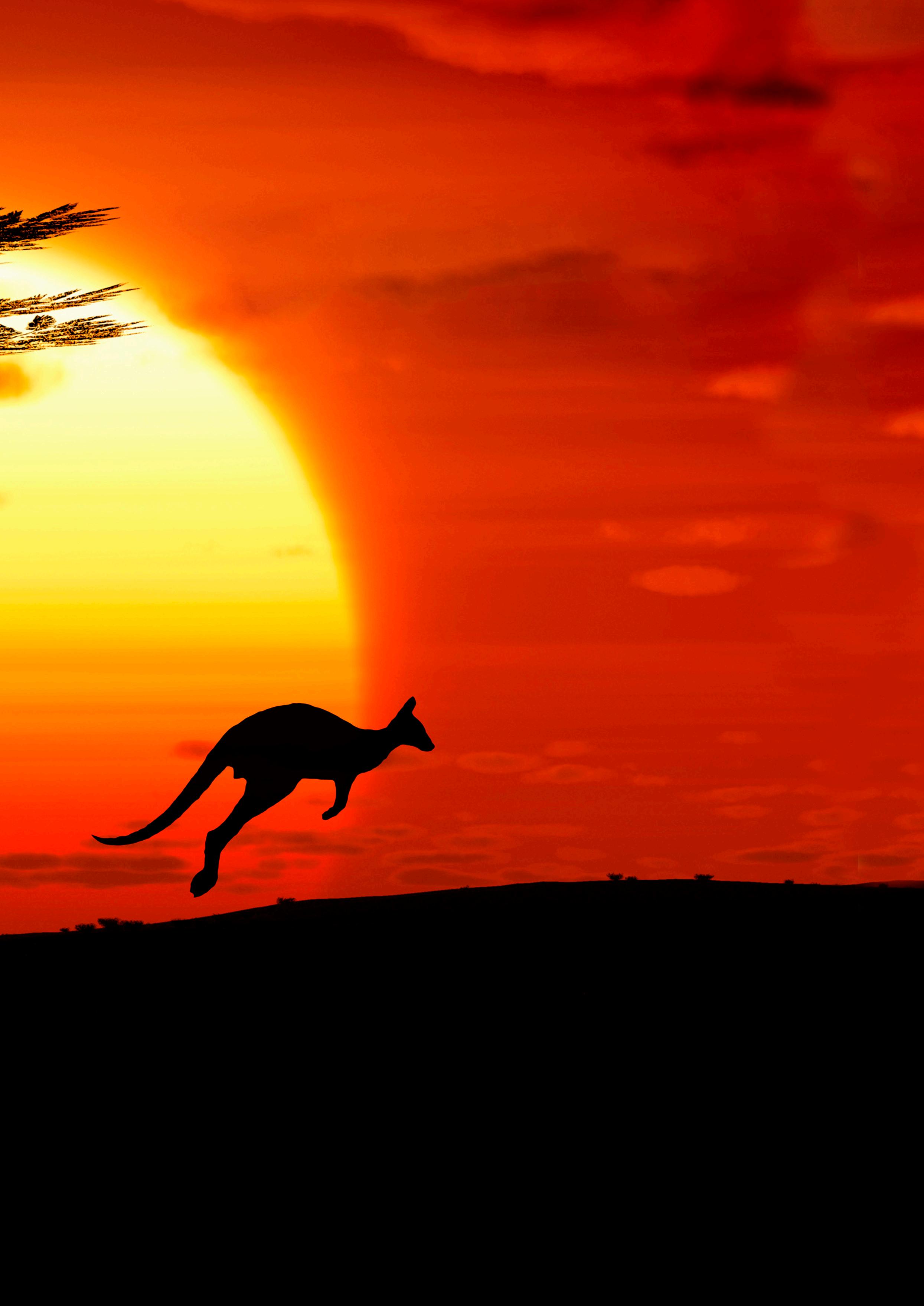
Johann Tan, Fitch Solutions, Singapore, presents some of the latest analysis of the Australian coal market.
China’s 2019 imports followed a similar trend, with imports reaching 74.49 million t and 30.77 million t imported from Australia, according to Chinese customs data. After the ban, coking coal from cheaper countries – such as Russia, Indonesia, and Mongolia – gained significant Chinese market share. Mongolia replaced Australia and supplied 40% of the China’s total imported 63 million t of coking coal in 2022. Russia was a close second at 33% of 2022 imports. As for Australia,
it turned to other countries to diversify the gap left by China. Exports went to markets such as India, Korea, Japan, and the EU.
Australian prime hard coking coal is still highly sought after in China due to its high quality. With increased efforts being made to reduce carbon emissions, higher quality coal produces less carbon and is more efficient in the steelmaking process.
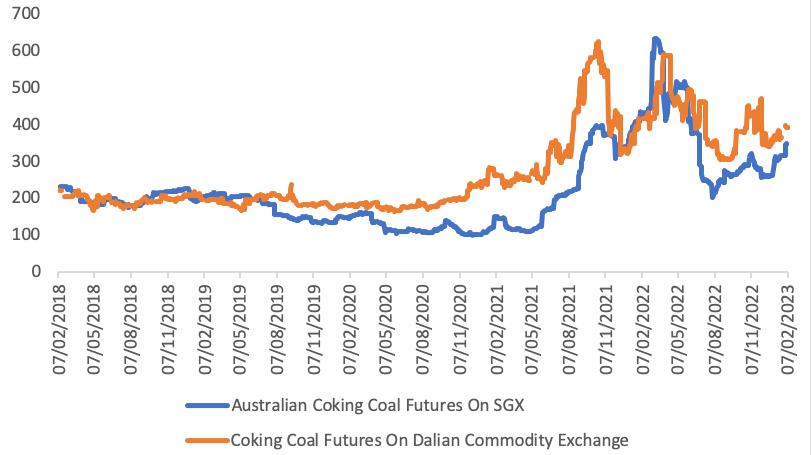
That said, competing coking coal exporters will still be strong competition for Australia’s exports in China’s market, limiting sharp demand spikes from Australia and consequently production as well. Hence, it is likely that the reintroduction of Australian exports will see modest demand from China. The diversified markets will also continue importing Australian coking coal together with China in 2023. As such, Fitch Solutions forecasts that the Australia origin coking coal price will average US$350/t in 2023. Prices will remain elevated around current levels throughout 2023, in response to Chinese demand and increased market tightness.
On the production front, better mining conditions from drier weather and revitalised Chinese demand will incentivise production for miners. Wet weather conditions have plagued Australian miners for most of 2022 –floods and rain reduced operational outputs and disrupted mining operations. However, in 2023, the La Niña event is expected to ease earliest by March 2023, based off forecasts from Australia’s Bureau of Meteorology. Drier mining conditions will support miners in their production outlook.
Moreover, coking coal mining will see some growth as it is expected to experience greater export volumes to China. Orders have already started coming in for deliveries in February 2023; two vessels carrying both coking and thermal coal arrived in China on 9 February. Three state owned utility firms and Baowu Steel were granted permission for coal imports and Fitch Solutions expects China to allow more companies to follow suit.
Lastly, weak global steel production will put a ceiling on coking coal prices, preventing them from hitting 2022 highs. Steel import nations are expected to pose weak economic growth due to global conditions, while China’s share of infrastructure growth is not expected to recover as quickly. Fitch Solutions’ macro teams forecast a mild global growth of just 2.13% in 2023. Weaker economic conditions will slow industrial activity and steel demand. According to Fitch Solutions’ estimates, steel production in coking coal import nations were weak throughout most of 2022. Likewise, the World Steel Association forecasts a flat global production outlook for 2023, at 1% y/y growth to 1.814 billion t.
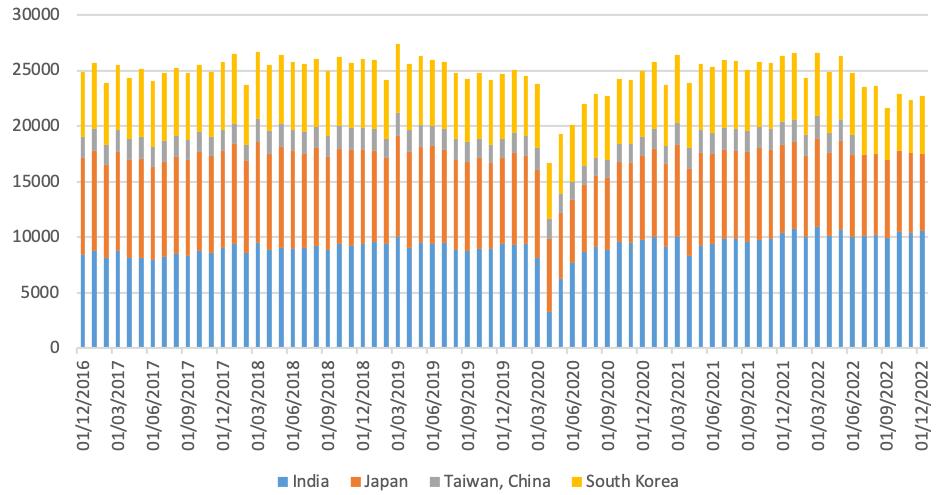
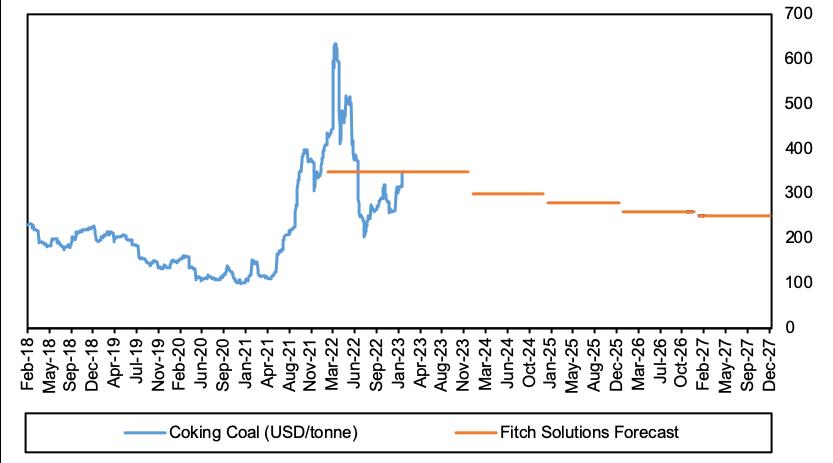
Infrastructure activity is vital to steel production and coking coal demand too, making up more than 50% of the world’s steel demand, according to World Steel Association. Market signals for China’s infrastructure activity still remain downbeat, new floor sales are down 31.5% y/y, while floor space of new housing starts slid 43.7% y/y in December 2022. The sector’s contribution to GDP fell to 6.1% in 2022, down from 6.8% in 2021. China’s real estate sector is not poised for a sharp recovery since real estate cycles are lengthier in nature. Stimulus measures and liquidity provided by the government will take time before it addresses issues of struggling developers. A recovery in the Chinese market will still come this year, but it is very unlikely to drive a sharp rebound in steel and coking coal needs.
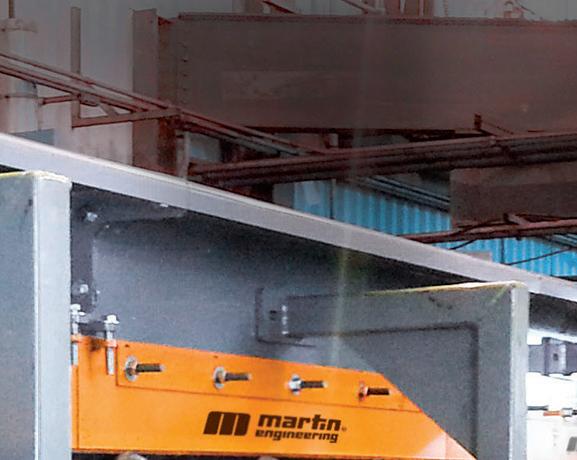
Thermal coal supply and demand
Australian thermal coal will face similar conditions to coking coal, with limited production growth in 2023, even as countries renew their perspectives on coal as an energy source. Drier mining conditions and reduced flooding at mine pits will alleviate production woes. However, higher levels of domestic coal production in importing countries and waning natural gas prices will reduce the need for coal imports, and, consequently, place a limit on production growth. Fitch Solutions’ expects thermal coal production in Australia to grow by 1% y/y this year, reaching 303 million t. Global need for thermal coal spiked after Russia’s invasion of Ukraine. Many countries in the EU turned to thermal coal for energy in view of intermittent natural gas supplies from Russia. Outright coal power generation in the EU increased by 7% y/y to 28 TWh in 2022, according to reports by Reuters. However, exports from Australia still fell in 2022 to a 10-year low, at 178 million t, a 10.3% y/y drop from 199 million t in 2021, according to reports from SXCoal. Persistent wet weather affected thermal coal supply chains, flooded mine pits, and disrupted freight rails reduced overall production in Australia throughout 2022, subsequently reducing exports.
As mentioned earlier, an easing of the La Niña cycle is expected in 2023, prompting better mining conditions for the smoother output of coal.
On the other hand, factors that created the price surge in the mid-2022s have begun to unwind and demand pressure is expected to ease this year, thereby reducing the need for coal. A warmer winter has translated to reduced demand from European countries, while a rise in coal inventories from higher domestic production in importing countries will help alleviate supply build up for next winter. Moreover, a fall in natural gas prices would relieve some demand from coal as an energy source. In 1Q23, natural gas prices in Europe dropped significantly compared to its
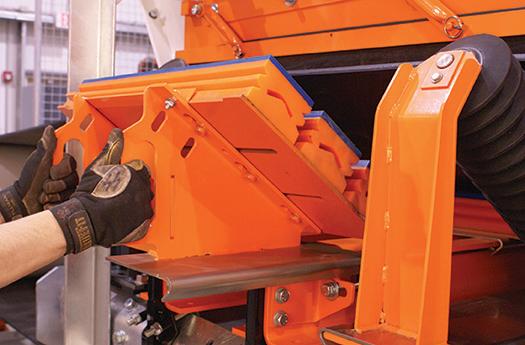

prices last year. Benchmark Dutch 3-month gas futures dropped to just €53/MWh as of 8 February, compared to €150/MWh two months earlier in December. In view of such trends, Fitch Solutions forecasts Newcastle thermal coal (6000 kcal/kg) to average US$280/t in 2023. This implies that prices are likely to get an increment from current levels in the coming months, as seasonal energy needs increase later on in the year, but remain significantly below the highs reached in 2022.

Compared to coking coal, many major importers have local production of thermal coal on top of imports. Hence, robust domestic production growth in countries like China and India, to ensure energy security needs, will restrict demand and production growth of Australian thermal coal. China and India accelerated thermal coal production after gas and thermal coal prices reached unprecedented highs last year. Imports are still essential, but are not expected to rise sharply given their higher domestic output. Specifically, India mandated power plants to import at least 10% of its coal needs to build coal inventories. However, most buyers sourced their imports from heavily discounted Russian coal.
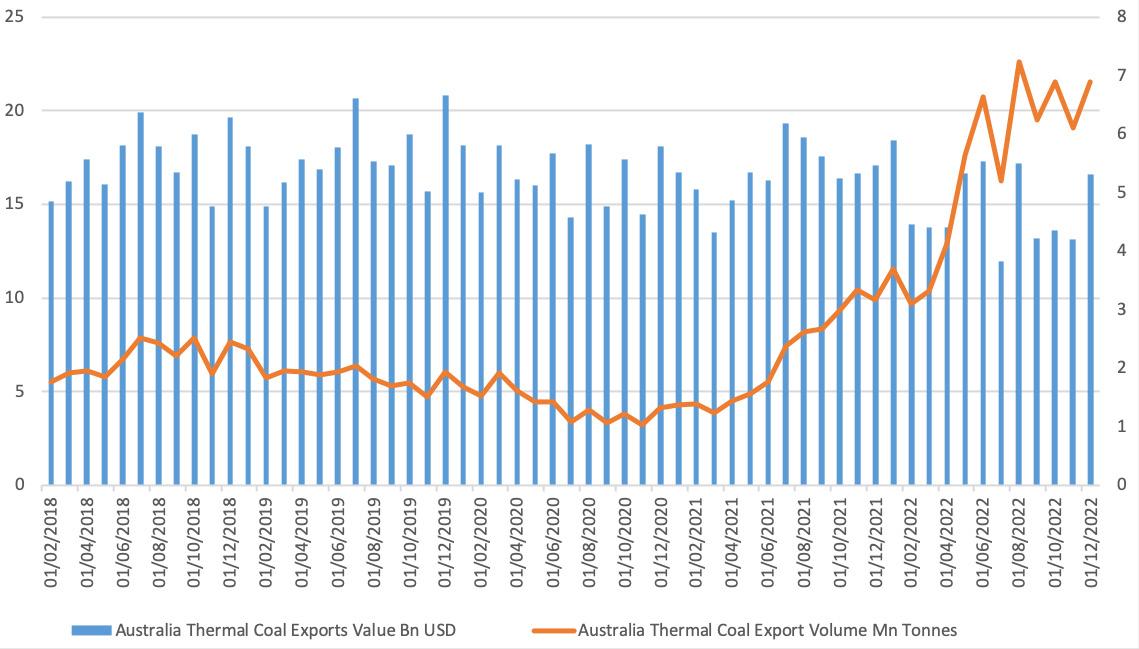
For 2023, China and India will lead global production growth, with authorities driving such initiatives through planned increases in coal plant permits and directly advising state-owned miners to ramp up production. Already, coal production in China is estimated to have surged by 9% y/y in 2022, reaching 4.45 billion t, while India’s production from April 2022 to January 2023 has risen 16% y/y to 693 million t. India’s Ministry of Coal has requested the Ministry of Environment, Forest, and Climate Change to allow coal mines to increase production, as of February 2023. Furthermore, India’s state-run Coal India, accounting for 80% of coal production, is expected to supply 620 million t to its power sector across FY23/24, as compared to a projected 580 million t in FY22/23. Meanwhile in China, Reuters reported that an additional 260 million t of coal mining capacity was approved in 2022, bringing total capacity to 5.05 billion t. Additionally, China’s National Development and Reform Commission advised electric utility firms to extend term contracts with local miners in 2023, translating to a definite rise in coal production. The increased self-sufficiency in markets from domestic sources and imports from cheaper sources creates headwinds for Australian thermal coal exports, restricting growth. Australian production will therefore likely suffer from a similar effect.
Other considerations
Besides supply and demand factors impacting Australia’s coal outlook, Fitch Solutions believes domestic environmental regulations will continue creating headwinds for coal production. Moreover, the overall global shift in the green transition to green steel and renewable power will inevitably drive miners away from coal in the long term. Global thermal coal use will remain robust in the short term, as a direct result of the Russia-Ukraine war and the pivot away from Russian energy. Energy issues will continue to make coal a priority for energy generation, but this also brings about an accelerated shift to alternative power, such as the EU’s REPowerEU plan to increase renewable energy targets from 40 to 45% by 2030. Elsewhere in Asia, India’s latest budget pledged INR350 billion to fund energy security and energy transition. India’s target is to reach 500 GW of clean energy by 2030. Meanwhile, China has committed itself to maintaining coal use for energy generation, however it insists that it is still on target with strict coal controls, pledging to start cutting its use by 2026 and peaking emissions before 2030.
As for coking coal, Fitch Solutions expects demand to decrease in tandem with global blast furnace steel production’s decline. As the global economy makes its shift to a greener future, the shift away from fossil fuels and highly polluting methods of production will see steel producers slowly transition to cleaner steelmaking processes. These include a greater adoption of electric arc furnaces, as well as the use of green hydrogen in steelmaking. Green steel’s rising adoption across EU steelmakers is underway, with pilots and plants currently under construction. That said, it will take some time before such steelmaking plants reach industrial scale, hence the continued need for coking coal in the near term. These trends mark an inevitable decline for coal, not just in Australia, but globally in the longer term.
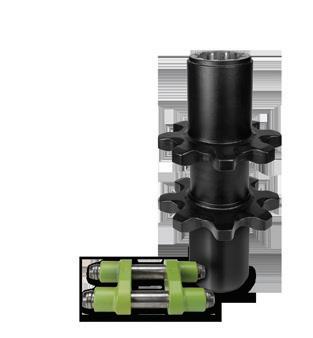

Australia’s growing emphasis on environmental issues will also play a part in reducing Australia’s coal production. Carbon emissions from coal are the most pollutive form of emissions relative to other forms of fossil fuels. Across a historical period of 1850 – 2021, coal contributed to 46% of total fossil fuel emissions according to data from Global Carbon Project’s 2022 report. Environmental regulatory developments are creating headwinds for Australian coal. New projects and coal developments are increasingly being scrutinised and scrapped due to environmental concerns. Most recently on 8 February, a thermal coal project by Central Queensland Coal was rejected by Australia’s environment minister, citing potential adverse environmental impacts. Glencore also announced several downturns to its coal assets in Australia. In December 2022, Glencore scrapped a new application of its Valeria Coal project, with a capacity of 16 million t of metallurgical and thermal coal. It adds that it would progress brownfield extensions
at existing mines, however its Liddell, Newlands, and Integra mines in Australia will close and undergo rehabilitation within the next four years.
For miners, as investors become wary of climate change issues and global energy consumption patterns shifting away from coal in the long term, established players will increasingly leave the high cost Australian coal market.
Anglo American, Peabody Energy, and Vale have all started liquidating their Australian coal portfolios, with Rio Tinto having completely exited the coal market and BHP exiting thermal coal production. These headwinds will only increase over time, hampering mine development and project pipelines for Australian coal. Fitch Solutions expects an increasing trend of blocks and scrutiny to hinder coal outlook in the country as long as environmental concerns continue, slowly enveloping the decline of coal mining activity.
There is no question that coal dust is more highly scrutinised and regulated compared to other bulk handling operations, due to the health of workers and a high risk of explosions. Ask any coal family and they would agree that the safety and longevity of workers should be a top priority. Controlling dust also makes sense from an operational aspect, as it can foul rolling components, machinery, and equipment air intakes – requiring extra parts and labour for cleaning and maintenance. All of these factors unnecessarily raise the cost of operations when there are methods
and technologies designed to control and suppress dust emissions before they become airborne and create these risks.
While obvious that one way to reduce coal dust emissions is to reduce the amount of dust created in processing, it is not always practical or easy to accomplish. There are many dust sources that have to be managed depending on the extraction, haulage, and storage methods. Most of the dust contained in bulk materials is from crushing or grinding, in order to reduce particle size, and from transfers from one step in the production
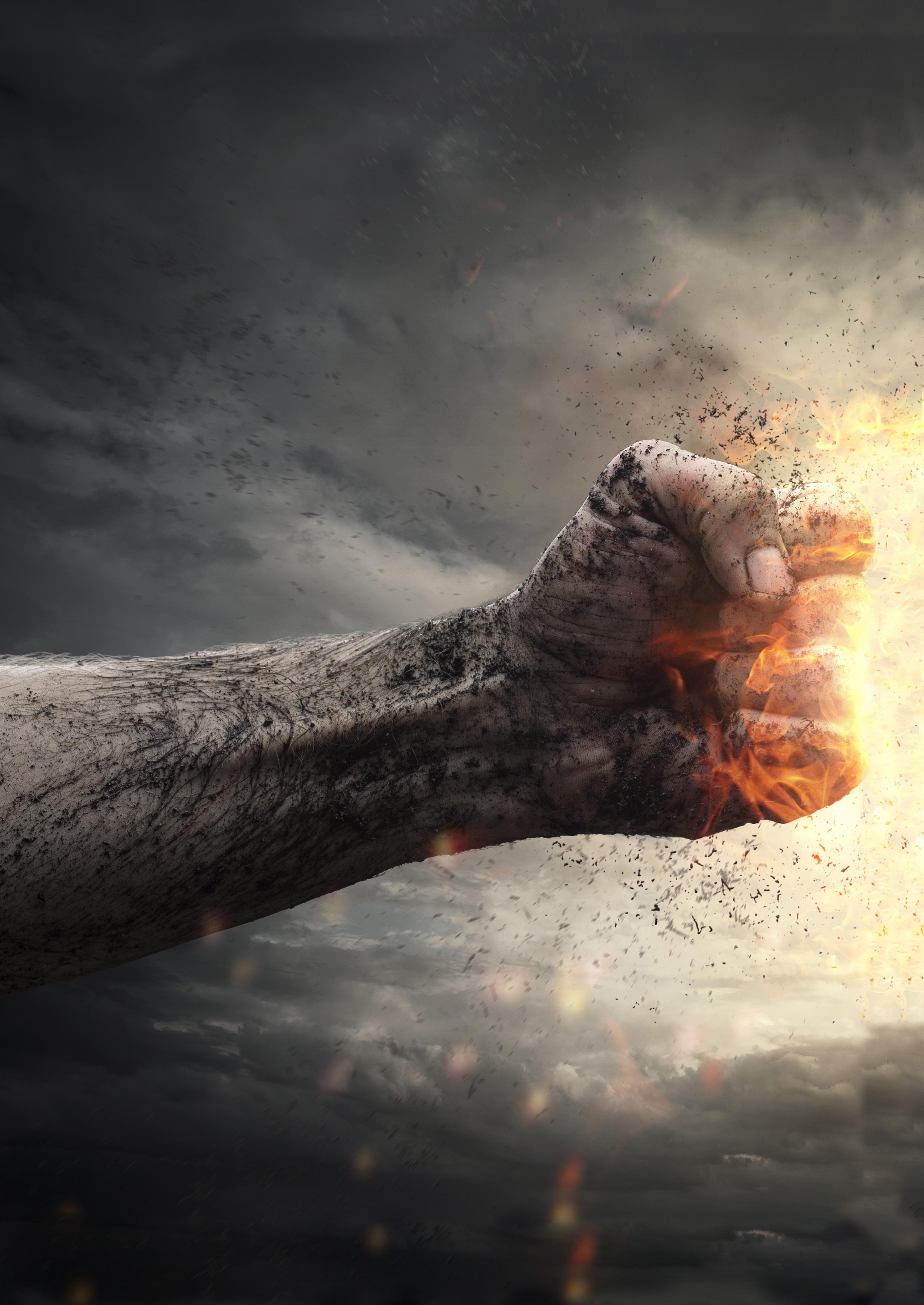
R. Todd Swinderman, Martin Engineering, USA, highlights the importance of controlling dust emissions in coal operations.
process to another, such as at conveyor transfer points or discharge onto a stockpile. The hydrophobic properties of coal also make it harder to control dust emissions using water without the addition of expensive surfactant additives.
Surface vs underground operations
In surface operations, control of dust is difficult because it happens in the open air, and the fracturing of the in-situ material creates dust. Typically, the bulk material is loaded into haul trucks at the point of extraction and taken either

to a conveyor transfer point or a crusher. As the material is dumped and crushed, the most effective dust control is the use of water, or if water addition to the material is a problem, foam is used. Water is not as effective as foam, but is often preferred due to the cost of foaming chemicals. There are some residual effects of water, but they are usually short-lived.
In underground extraction, water is often used at the face and conveyor transfer points to control dust. When water cannot be used, methods such as in mining salts, ventilation, and modular dust collection are options.
Conveyors
Conveyors are a major source of dust emissions, but they can also aid in reducing fugitive dust. For example, in pit crushing and overland conveying in a surface coal mine, there is reduced total site dust generation compared to truck haulage. Coal is easily windswept and, in some cases, may require an enclosed conveyor belt system, such as a fold belt, pipe conveyor, or air-supported conveyor.
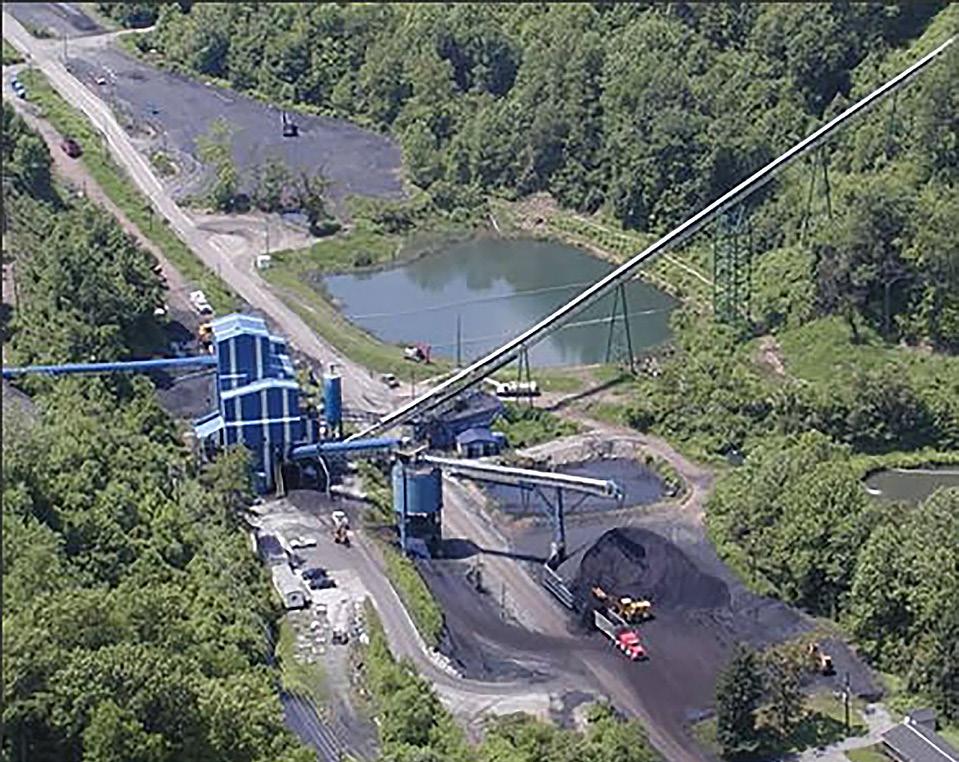
When the haulage involves a conveyor belt, dust generation is a function of the loading and discharge, as well as how it is managed. Closed conveyors are very useful for preventing contamination and protecting the cargo from the elements, but they still have to be opened and closed for loading and discharge. Passive dust reduction strategies include:
Shorter or directed drops: Transfer chutes (Figure 1) over loading zones that decrease the impact of cargo on the belt below reduce the amount of turbulence within the loading zone, lowering the amount of dust released.
Managing the flow: Although rock boxes can work, they can also be prone to clogging, so experienced engineers recommend a sloping system that slows material to minimise impact and induced air, as well as loads in the centre of the belt for less shifting and improved belt training.
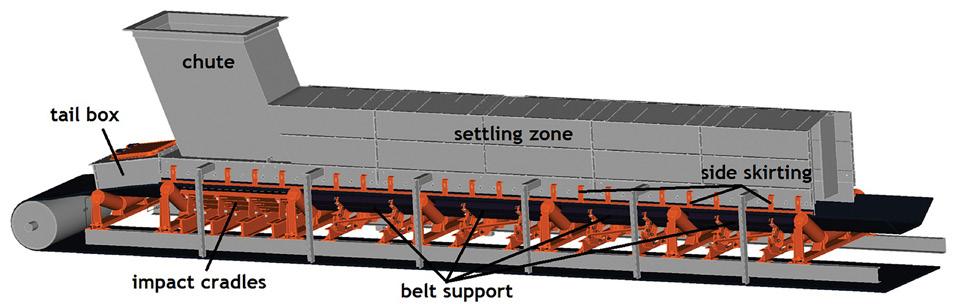
Preventing belt sag between idlers: The belt can dip slightly between idlers, creating gaps between the belt and skirting, causing the release of dust and
fines in the loading zone. Using an impact cradle with shock-absorbent polyurethane bars reduces impact strain on the belt, and creates an even belt plane with no gaps between the skirting and belt. Cradles can extend along the entire length of the stilling zone.
Fully enclosed transfers: By completely enclosing the loading and settling zone, dust is contained. Items such as dust curtains and dust bags can then be added to control airflow and capture dust.
Lower belt speeds
There are many suggestions for belt speeds based on the properties of the bulk material. The ANSI/CEMA 550-2003 Classification and Definitions of Bulk Materials lists miscellaneous properties of bulk materials that would contribute to a decision to use a lower belt speed and may be windswept as part of its classification code system, and includes:
B-1 Aeration-Fluidity.
B-6 Degradable-Size Breakdown.
B-8 Dusty.
B-20 Very Light and Fluffy.
With lower belt speeds, the belt width has to increase to convey the same tph, creating a capital cost vs operating cost dilemma. Many sources suggest belt speeds of 2 m/s (394 fpm) or less for reducing dust generation.
If a conveyor is being designed for an extended lifetime, then it is worth the effort to closely compare the capital savings from a higher-speed belt to the long-term costs of maintenance, cleanup, and safety. There are clear relationships between increased cleanliness, fewer safety incidents and more reliable production, so the tradeoffs should be examined closely. Foundations™ for Conveyor Safety – a comprehensive textbook for safe conveyor operation written by Martin Engineering – provides a detailed methodology and data sources for including direct and indirect costs in the financial analysis in section six.
Coal dust and belt tension
Similarly, at a critical speed, the bulk material loses contact with the belt at the idler and is launched into the air, falling back onto the belt at a slightly lower speed than the belt. This splashing action opens the profile, creating induced air flows that can release dust, creating turbulence, impact, and degradation as the material lands and returns back up to belt speed. Keeping the belt sag to 1% between idlers is a frequent specification. Usually, the concerns in conveyor design from these belt sag phenomena are the added belt tensions required to overcome the frictional losses.
Often overlooked in a dust reduction strategy are design choices that can minimise dust creation from the undulations of the bulk material on the belt as it is transported. Managing belt tension so the sag between idlers is minimised reduces the effects of material trampling and splash. Material trampling is the
Worldwide
Subscribe online at: www.globalminingreview.com/subscribe
15 South Street, Farnham, Surrey, GU9 7QU, UK
Subscribe online at: www.globalminingreview.com/subscribe
Subscribe online at: www.globalminingreview.com/subscribe
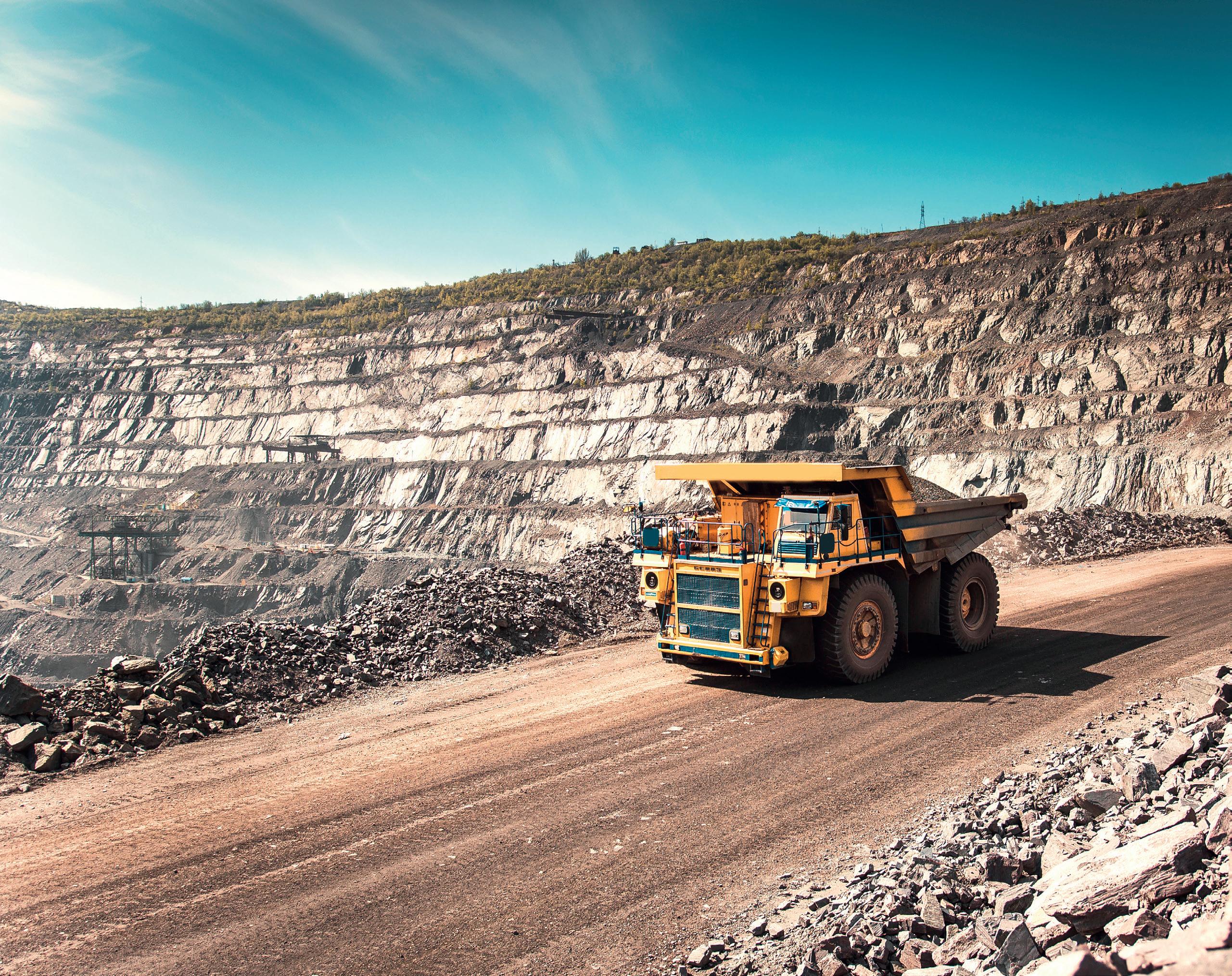
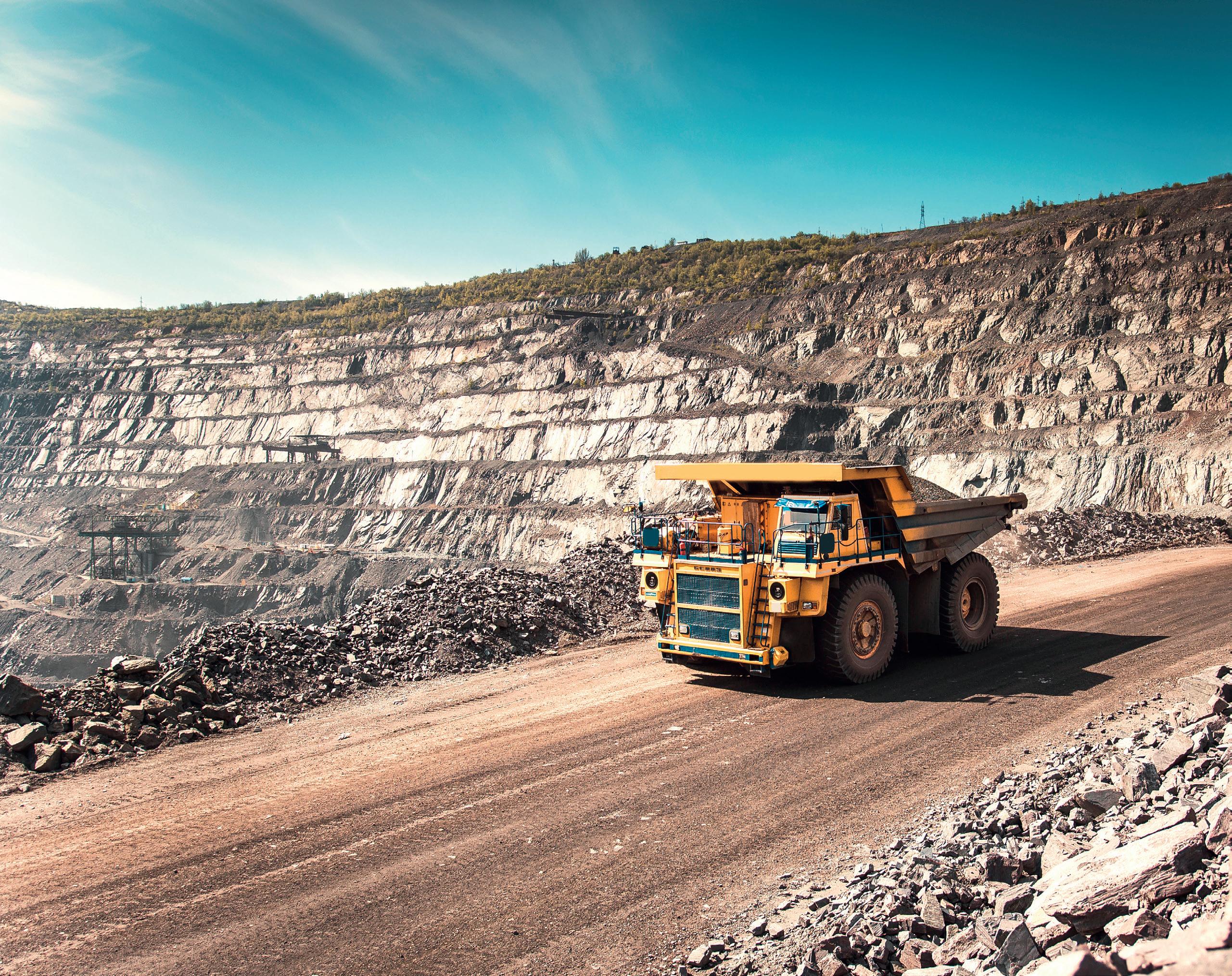
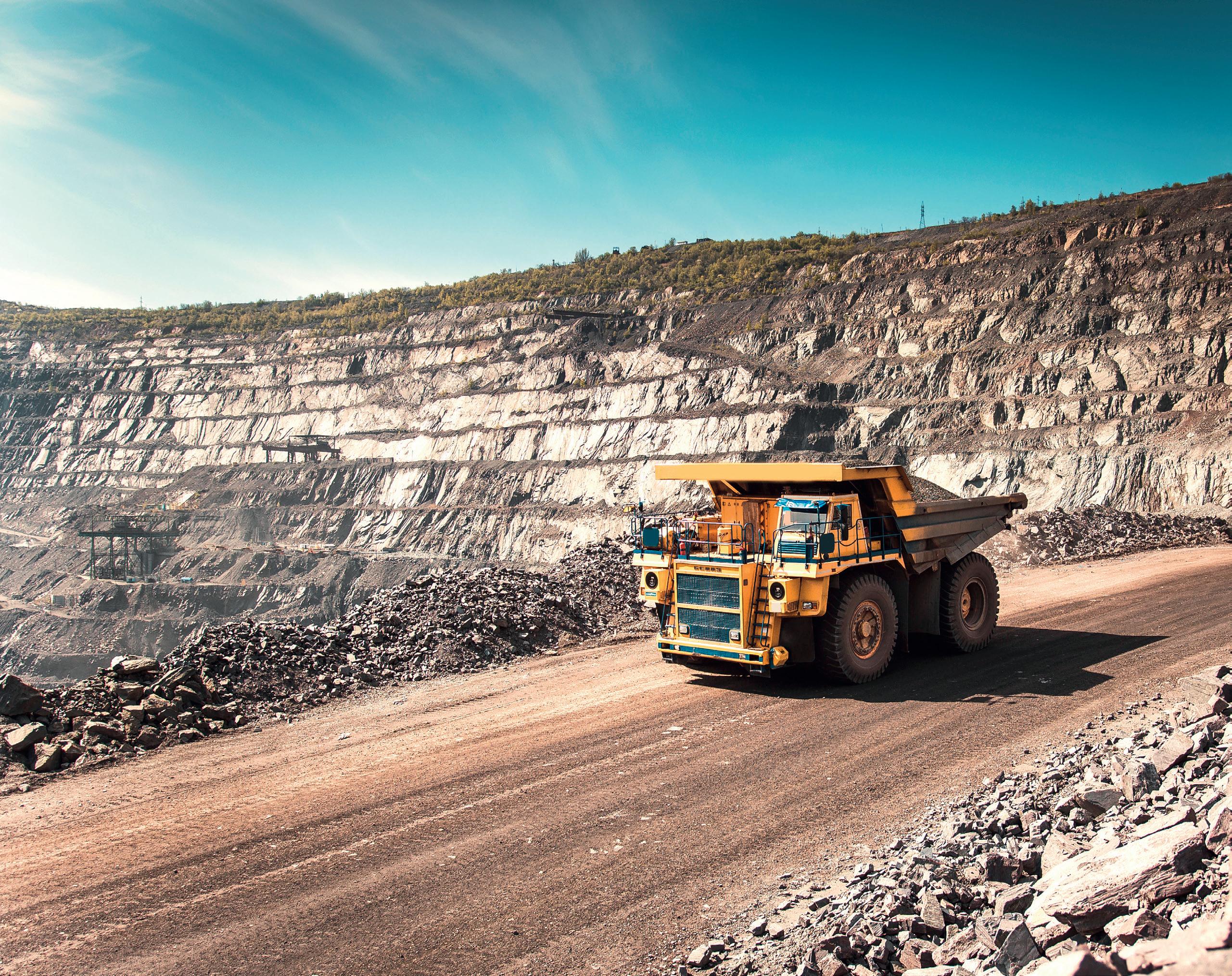
T: +44 (0)1252 718999 F: +44 (0)1252 821115
E: info@palladian-publications.com
15 South Street, Farnham, Surrey, GU9 7QU, UK
T: +44 (0)1252 718999 F: +44 (0)1252 821115
15 South Street, Farnham, Surrey, GU9 7QU, UK
E: info@palladian-publications.com
T: +44 (0)1252 718999 F: +44 (0)1252 821115
E: info@palladian-publications.com
particle-to-particle movement created by the change in the bulk material profile as it goes over the idlers. Trampling and splash can be a source of dust generation, given the large number of times the cargo passes over idlers every hour. The higher the belt tension, the lower the trampling loss.
Coal storage

Controlling dust at the storage location is another challenge. Large stockpiles are impractical to enclose in buildings and are often stacked out and reclaimed by machinery that generates additional fines.
Open stockpiles are subject to the weather, where some bulk materials degrade upon exposure to the atmosphere, and some materials will revert to a solid state when exposed to humidity or rain. Those materials that can be wetted often use water sprays to reduce windblown dust. Other strategies include wind fences and compacting the pile.
Discharge onto the pile is a source of dust release as the material flows from the delivery equipment, often a conveyor, onto the pile. Cascading or telescoping chutes can be used to reduce the release of dust in these cases. If the material is easily broken, the drop height from discharge to the pile, or between cascade shelves, can create additional dust from impact degradation. One unexpected source of dust emissions can be the site layout. For example, if a slope conveyor going from the stockpile into a storage bin or building is orientated in line with the prevailing winds in a high wind locale, the wind flowing up the conveyor will overwhelm dust control strategies by creating positive pressure throughout the conveyor enclosures.
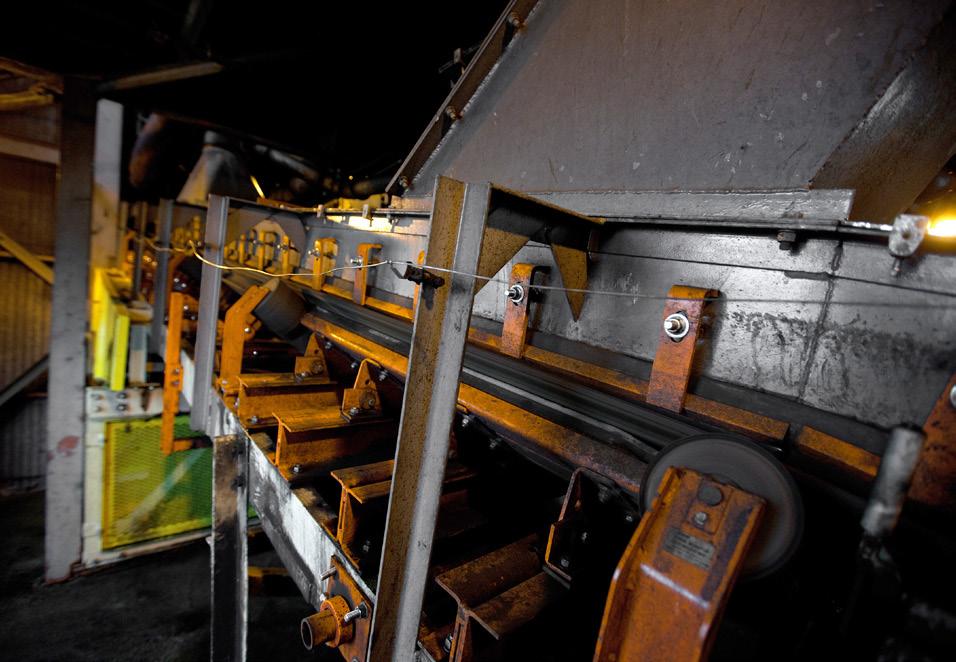
Best practices: Enclose the system
If the material stream can be constrained so that it does not open up when discharged, the amount of air induced into the transfer point is reduced. As the material particles spread out, it creates a low-pressure area in the spaces which induces airflow into the transfer point.
The amount of dust that can become airborne is directly proportional to the volume and speed of the airflow through the transfer point. If the openings in the chute work are restricted to the practical minimum, the inward airflow is restricted. A useful dust control strategy is to capture the material shortly after discharge and keep the stream coalesced as tightly as possible to reduce induced air.
There are a number of discrete element modelling (DEM) software programmes specifically designed for the design of material flow through chutes, and there are specialty chute manufacturers that specialise in these techniques. These chutes work best with materials of consistent size and adhesive and cohesive properties, such as coal. Wear on the chute surfaces may be accelerated, but this can be offset with a maintenance-friendly design for quick and easy change-out of wear surfaces.
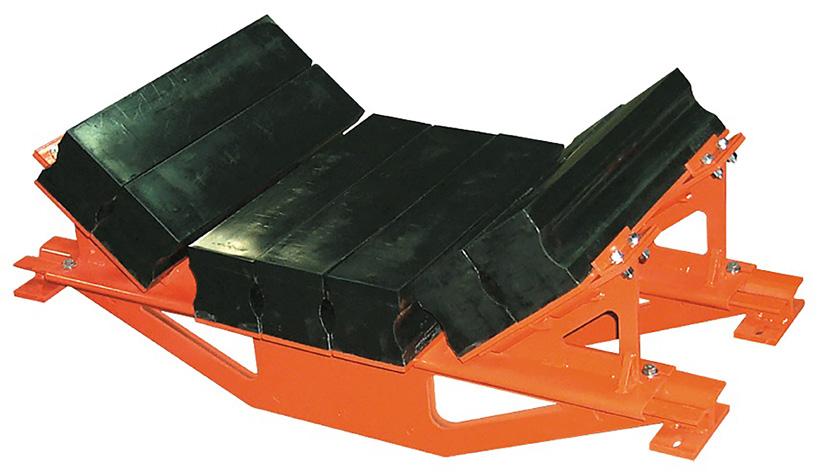
Conclusion
Much emphasis is placed on planning the mine to maximise profitability, but little attention is placed during the initial feasibility studies on how the layout can affect dust creation and emissions. Conveyor transfer points have a history of being drafted rather than designed. Design tools are now readily available to address these critical details. How the conveyor is operated and maintained also has a significant effect on dust generation and release.
Lee Gailer, RST Solutions, Australia, considers how utilising advanced technologies for dust and erosion control is essential for keeping mines running during the wet season.
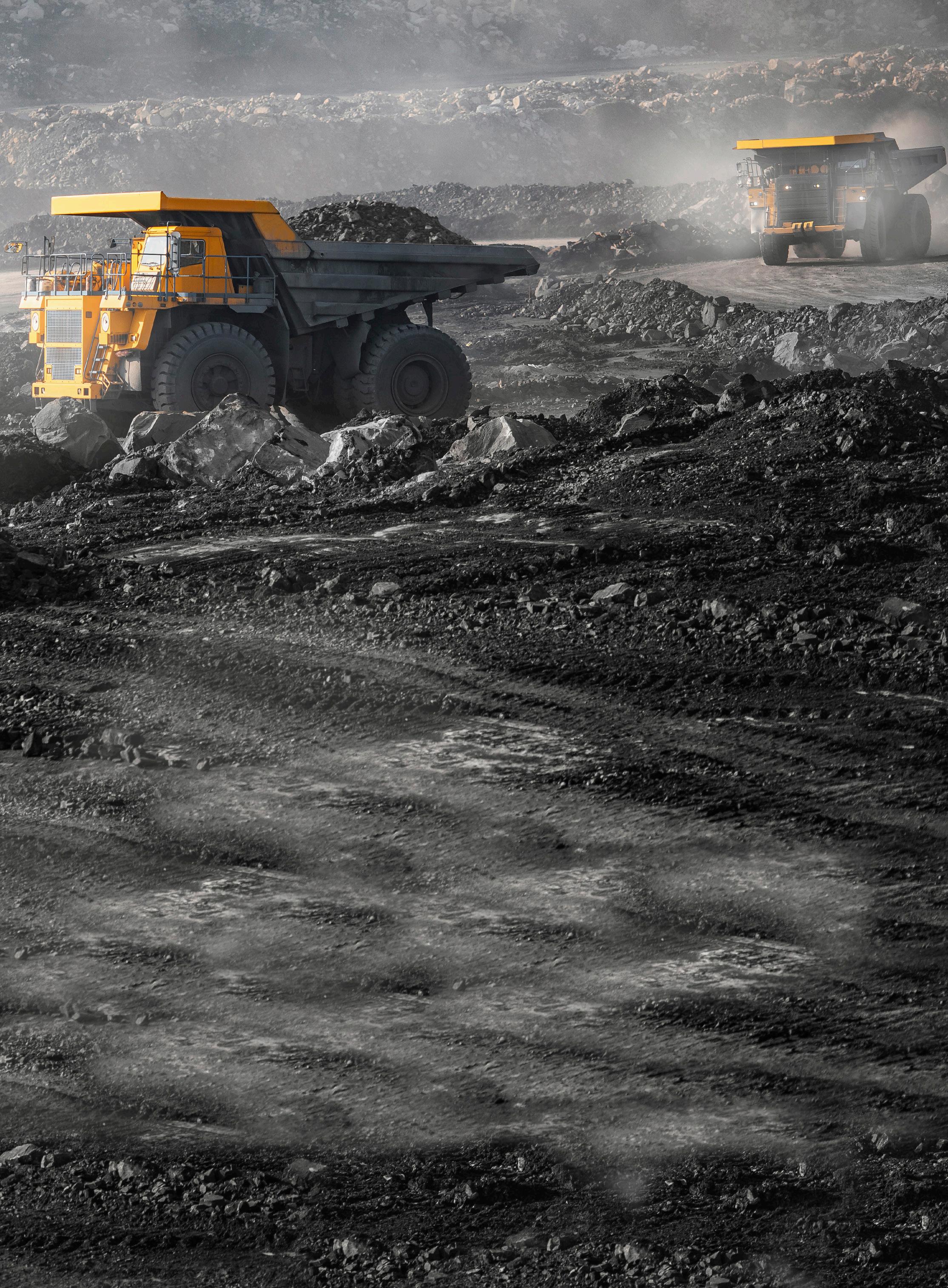
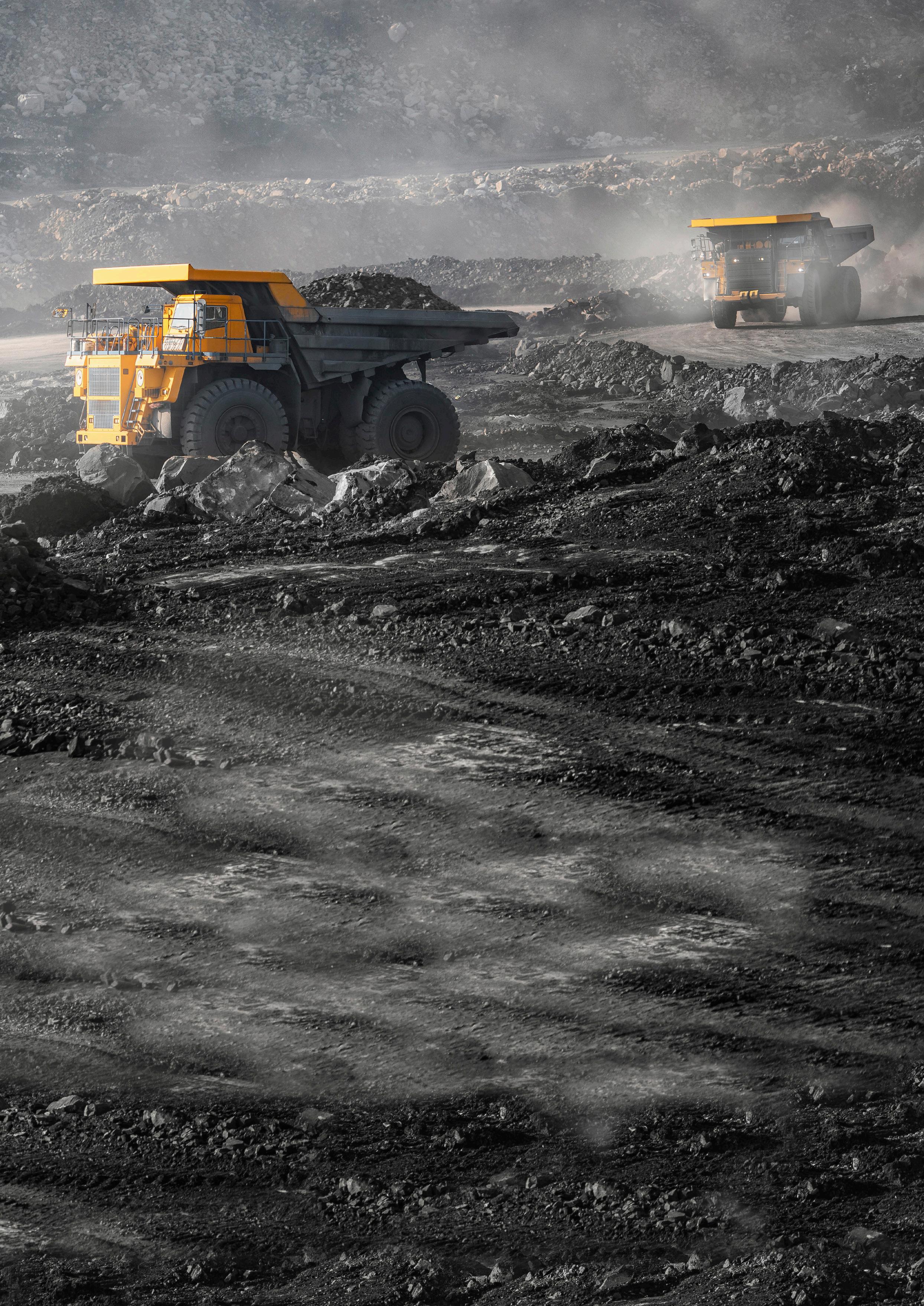
Australian mines have been stepping up their mitigation strategies to reduce the potential for large infrastructure and production losses during a ‘wetter than usual’ wet season, following the country’s ninth wettest year on record.
Fine particle management specialist Reynolds Soil Technologies (RST Solutions) has been assisting mine site operators with advanced technologies to help keep roads open and operations
running during wet seasons.
Many mining operations globally that use RST Solutions’ technologically advanced dust suppressants are unaware that the team started out 30 years ago as a chemical soil stabilisation company, and is now well known throughout Asia as a leading supplier of chemical soil stabilistion products, which treat the region’s highly reactive road construction materials in an extremely wet environment.
Advancing Australia’s road network
RST Solutions’ chemical soil stabilisers are used to improve and maintain the structural integrity of road materials, regardless of the change in moisture content, by modifying the unfavourable interactions between water and soil that cause road and material failure.
These high-performance road stabilising chemicals assist in managing the challenges and risks presented by extreme wet weather conditions around the globe, so it has been easy for RST Solutions to step up and offer Australian mining companies advanced solutions for wet weather operational strategies.
At the beginning of 2023, just a third of the way through Australia’s wet season, Western Australia and Northern Territory experienced a one-in-100-year flooding event, while severe flooding inundated parts of Queensland.
Curtin University transport and logistics expert, Liz Jackson, spoke to ABC News about Australia’s road network being the veins that held the country’s
cultural and financial economy together.
Associate Professor of Supply Chain Management and Logistics, Ms Jackson, called for desperate attention to upgrading the nation’s roads, in order to better withstand more extreme weather events, as well as heavier freight, pointing out that cut roads impacted the ability for major mining sites to ship their goods.

Solutions for unsealed roads
RST Solutions says high quality, rain resistant roads can be achieved without the need for bitumen or cement, through using advanced treatments that permanently change the unfavourable interactions between water and the reactive soil particles in the road materials.
By treating the road materials with advanced stabilising solutions, the road maintains its design strength when saturated during heavy rain events, with only minimal delays, as haul truck drivers must still drive to the conditions.
Further compaction happens as the road is being used, with the huge haulage tyres acting like massive filters, compressing the water out of the mud and removing void spaces.
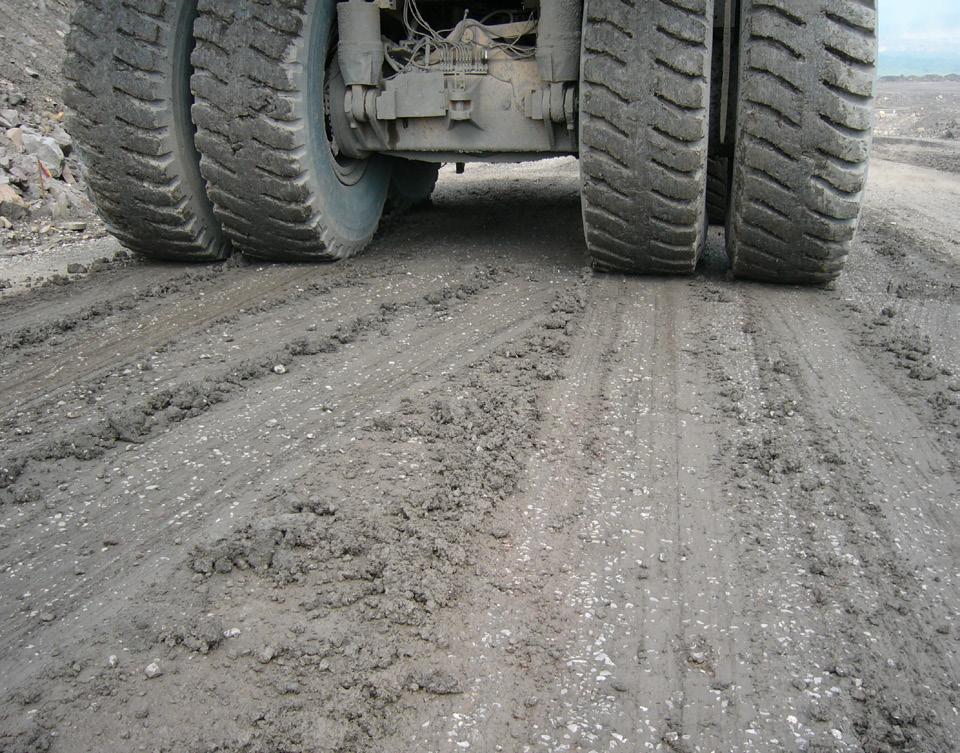
As part of an ongoing management plan of unsealed, stabilised haul roads, RST Solutions strongly recommends the implementation of a haul road management system (HRMS), incorporating a compatible advanced dust control product continually through the watercarts at ultra-low dosage rates.
This provides a continued stabilising and tightening effect of the haul roads wearing surface, delivering many benefits including reduced roll resistance and road maintenance, faster road recovery after rain and significantly reduced haul road watering requirements, in order to achieve the desired dust control efficiency (DCE).
The combined implementation of soil stabilisation and dust suppression in an HRMS offers autonomous mining operations enormous benefits, as it minimises the interaction time between autonomous vehicles and secondary equipment (water carts and graders) operated by people.
Road quality improves in both the short and long term, reducing the requirements for road maintenance activities to treat both dust and erosion. The use of water carts will also decrease by up to 50%, and haul road grading requirements can drop by as much as 30%.
Targeting onsite materials
RST Solutions has developed a range of high-performance products that target a variety of issues associated with the construction of high-quality, unsealed roads and hardstand areas to withstand wind and rain erosion.
Advanced dust suppressants, Avenger and Guardian, were developed as both long-term and instant solutions, that continue to add value over time by improving haul road structure after rain and with heavy vehicle traffic compression.
Haul roads built from quality road base materials with this type of treatment have proven over time to demonstrate a cumulative effect, as the material compacts more after each wetting and drying event, reducing permeability and increasing in strength.
By adjusting the chemistry to target the specific materials being used onsite – which could be anything from high plastic clays to very low plastic silt – the whole road construction process is significantly improved, resulting in more durable, weather resistant haul roads that help keep productivity at an optimum level.

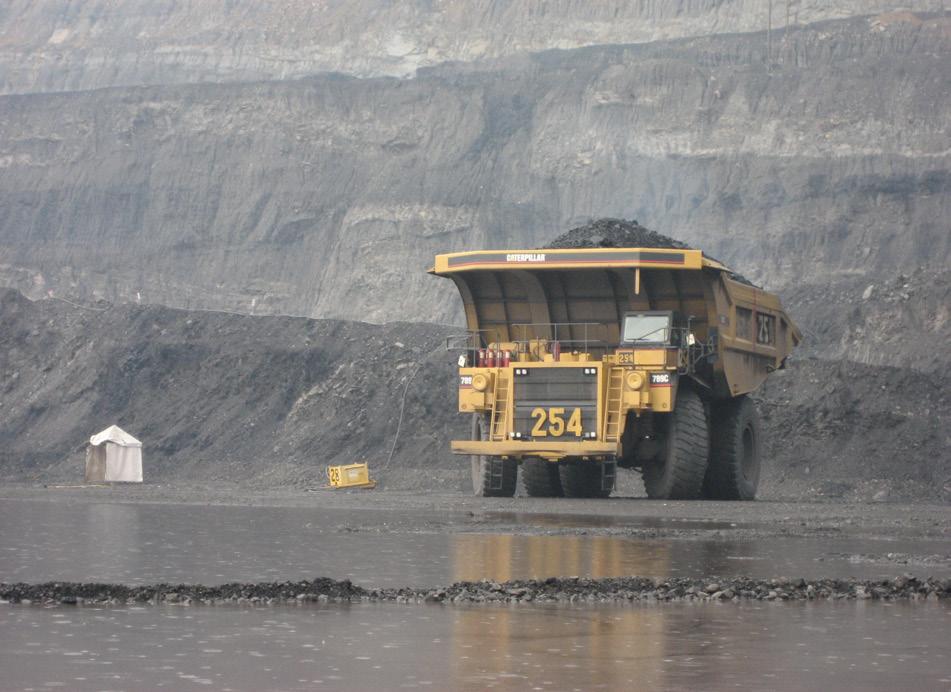
Red soils and other challenges
RST Solutions has recently developed advanced soil binding and stabilising chemistry specifically for Pindan and red soils to improve the quality of bulk material being used. The results include increased moisture control throughout the road construction process, resulting in material being more friable and less likely to clump, speeding up compaction rates to improve pavement strength and densities.
‘Titan’ is a new chemical road stabiliser designed for the construction and reconstruction of strong, durable unsealed roads using pindan and red soils that will withstand extreme wet weather and support high volumes of heavy vehicle traffic.
Immediate results have been reported as “remarkable”, with Titan’s strengths including the unique ability to form mechanically high-resistant road pavements that remain flexible and in good condition during wet weather.
By adding a high-quality chemical soil stabiliser to the structural layers during road construction works, as well as in water cart applications for ongoing surface maintenance, the road quality is greatly improved, helping to keep them safe, with minimal dust, and open to traffic during extreme wet weather.
Compaction aids
High quality compaction aids also increase the stabilisation capacity of all material types in earthworks, in order to achieve higher levels of compaction with much higher densities and strengths than the usual substandard, natural surface-building materials.
When the material is ripped or laid out, it contains an open framework of particles with the pore or void space usually filled with air and water. Advanced compaction aids such as RST Solutions’ CompaK, keeps working long after application to reduce void spaces between
individual soil particles.
This occurs primarily through a lubricating and dispersive action, which results in a more efficient packing of the particles to deepen the effect of the mechanical compaction.
Conclusion
RST Solutions develops advanced technology in response to mines seeking more project optimisation strategies, particularly for the construction of unsealed roads and infrastructure, in order to achieve higher levels of dust control and strengthening against rain and wind erosion.
By selecting the most appropriate solutions and adjusting for compatibility with site-specific material types, infrastructure forms, and seasonal changes, RST Solutions assists mine sites to manage unexpected shifts in construction and weather patterns.
Liam Sheeder, Belt Tech Industrial, USA, reflects on the problems associated with excess dust in coal mining operations and provides some solutions to mitigate this.
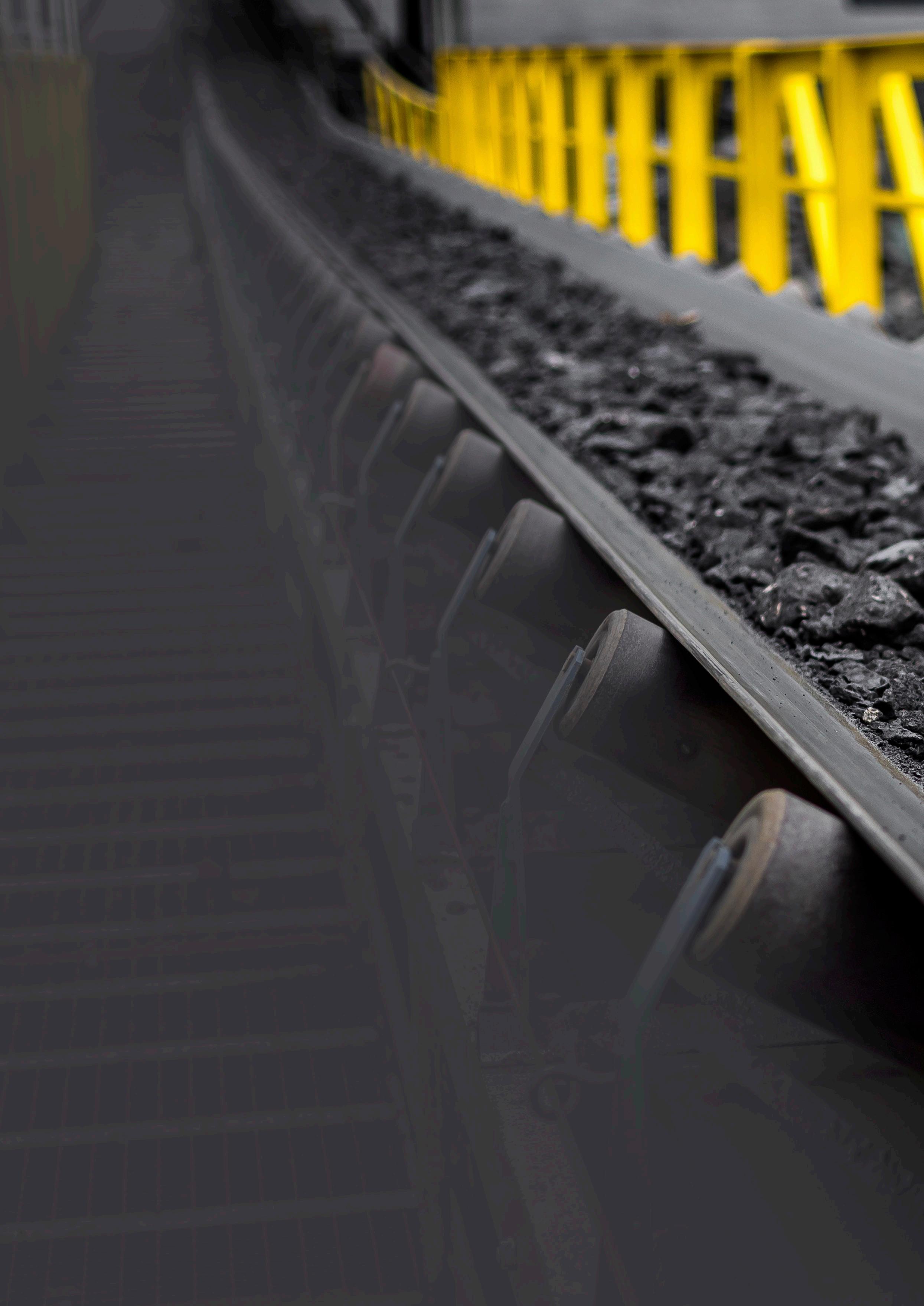
Dust is a fact of life. If homes can indicate anything, it is that dust will make an appearance anywhere and everywhere. It is a war that will never be won – but one that needs to be fought nonetheless.
Obviously, the dust issue facing a coal mine or material handling operation in general is not just average everyday dust. According to the Mine Safety and Health Administration, dust is defined as: “finely divided solids that may become airborne from the original state without any chemical or physical change other than fracture.”
Put another way, dust is the material that becomes airborne when disturbed and lands on surfaces when it is at rest. It becomes a problem when it flies or lands where it is not wanted.
Effects of dust
It is easy to get used to things over time and develop ‘blind spots’. This happens gradually in the same way that dust accumulates over time. The daily demands of an operation can cause a rush from one issue to the next, while other problems quietly go about their business of making life harder.
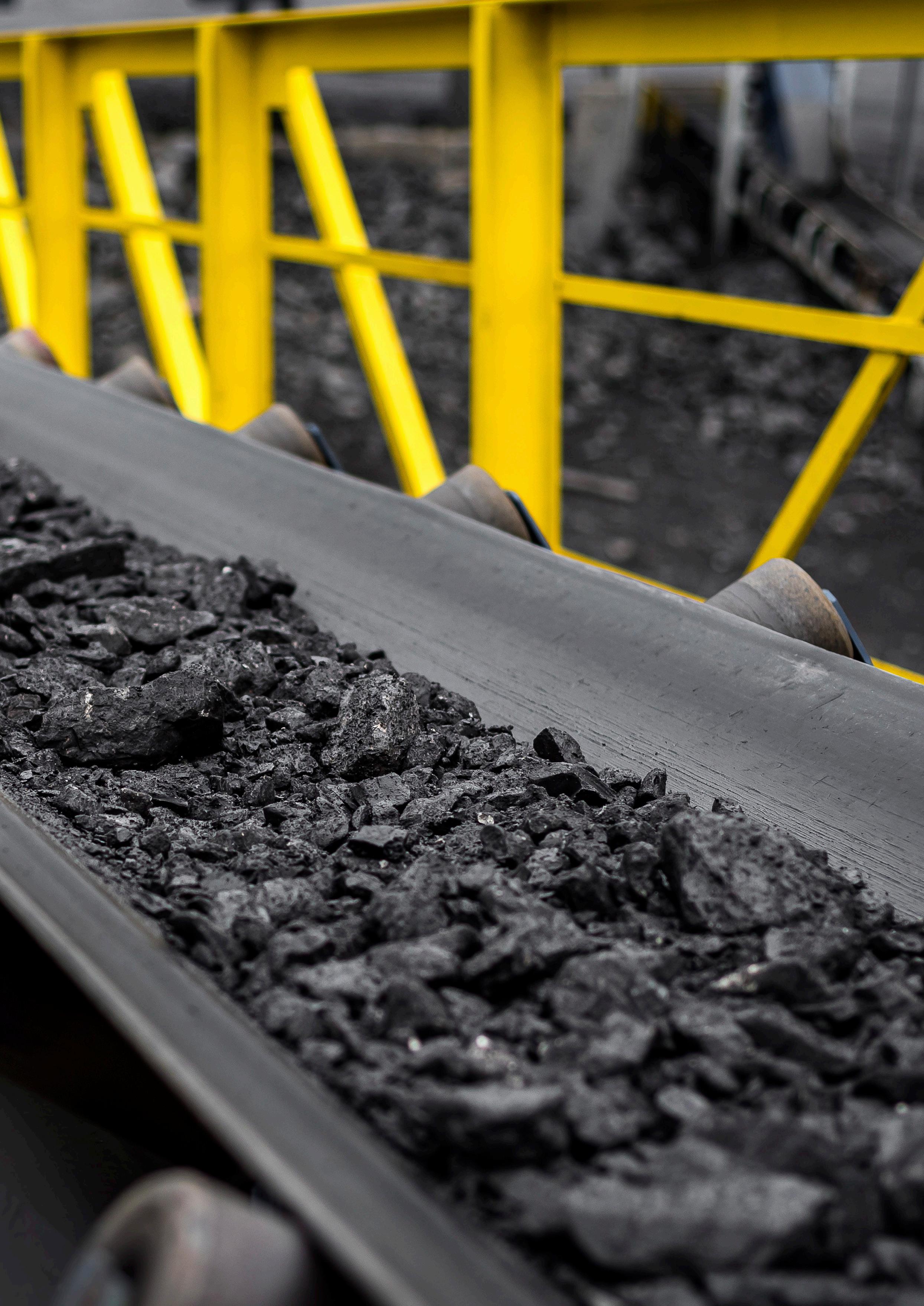
For this reason, it is a good idea to reflect on the ill effects of excess dust and look for ways to manage it at the source.
Failure to do so effectively can have very real legal and financial consequences, not to mention the impacts on the health and safety of workers. Dust inhalation can lead to potential respiratory and other problems, such as: pneumoconiosis (black lung disease), silicosis, and eye and skin irritation. Long-term exposure to dust can also increase the risk of lung cancer and other disease variants.
As evidenced by silo explosions in the grain-handling industry, dust explosions are very powerful and a very real risk. Consequently, extreme care must be taken to minimise this risk. For many dusts, a settled layer as thin as the thickness of a paper clip – only 1 mm (1/32 in.) – is enough to create an explosion hazard. A 6 mm (1/4 in.) layer is a bigger problem – it is big enough to destroy a plant.
That being said, the following outlines the problems and solutions.
Determining if there is a problem
A certain amount of dust is to be expected, so taking some measurements can go a long way towards determining if the dust is perfectly usual, or a sign of something else.
Personal dust sampling with a small vacuum pump that is worn by a worker is one method. The dust captured at the end of the shift is weighed, and that number is divided by the total amount of air the pump has pulled in for the duration of the shift. This can help to determine the amount of dust in the air.
Basic location-specific dust sampling involves placing many containers in a dusty area for a designated amount of time. The amount of dust collected is then weighed.
More sophisticated methods exist, such as a microwave opacity tester, but the main point is that having raw data can help to put a number on something that could seem very abstract.
If these tests determine that there is in fact a problem, then the actual work of tracking it down and fixing it starts. Thankfully, controlling dust is not rocket science when the focus is on doing the basics well, and that means finding the source.
Transfer points
Transfer points are a usual suspect when it comes to the generation of dust, and for good reason. They have all the ingredients for creating dusty conditions.
Material separates as it falls, exposing smaller particles to greater airflow. In turn, the falling material itself creates vortices which convince the now free particles to make a home elsewhere.
Taking a closer look at both the drop and the landing zone can help. Shortening the drop between conveyors can reduce the velocity of the material. Directing the material onto the receiving belt in the
same direction that the belt is moving avoids drastic changes in material trajectory.
All of this is a lot easier to consider in the initial design stage, but much can also be accomplished by retrofitting existing systems. For instance, installing custom chutes, hood and spoon systems, settling zones, and even using old belting as a curtain for the entry and exits of transfer points.
These are all methods of controlling air movement which is a primary ingredient for controlling “finely divided solids that may become airborne from the original state.”
Belt support in the load zone
While a ‘soft landing’ may be nice for a plane touching down on a runway, too soft is not the ideal situation for a load zone.
Belt sag places unnecessary stress on the belt, adds resistance to the entire system, and – more to the point of this article – breaks the seal between the skirted area and the belt. This lets air in, which should be avoided, and lets dust out, which is the exact opposite of what is trying to be achieved.
And it does not take much. A small amount of sag, which may not even be apparent to the naked eye, is enough to let fines out.
Increasing the number of idlers in the load zone is one option. Another is to dispense with idlers altogether and install a belt support cradle. These impact cradles are composed of a steel framework with a set of impact-absorbing bars.
Using low-friction bars instead of rollers means belt sag is minimised, while belt seal is maximised. Providing good support for the entire length of the loading zone provides the best results.
Hybrid designs are also available which employ rollers under the centre of the belt and bars, in order to maintain a continuous seal at the belt edge.
In any case, having a solid foundation will keep the material flowing, protect the belt, and reduce the amount of escaped dust.
Belt scrapers
When material clings to the belt after being discharged at the head pulley, it dries out on the return, releases from the underside of the belt, and can become airborne.
Belt scrapers play a key role in reducing the levels of dust in an operation. When properly installed and maintained, they effectively reduce the amount of carryback.
Carryback is often a more cumbersome and costly problem than transfer-point spillage. It can drop off at any point all along the conveyor return, which requires cleaning crews to work along the full length of the conveyor.
Depending on the consistency of the material being conveyed, a primary, secondary, or even tertiary scraper may be necessary.
Belt washers


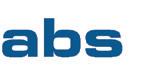
Some studies have shown that the oversized material is more easily removed through scraping, but the smaller respirable-sized particles tend to remain adhered to the conveyor. When this occurs, a belt wash can be installed.
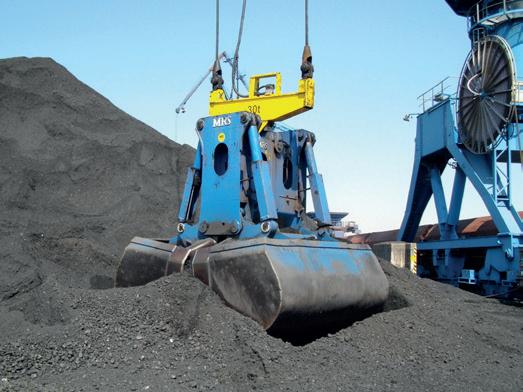

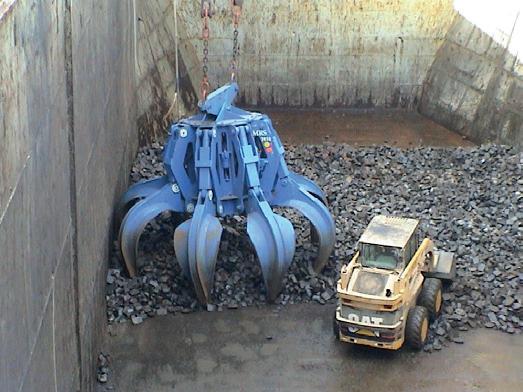
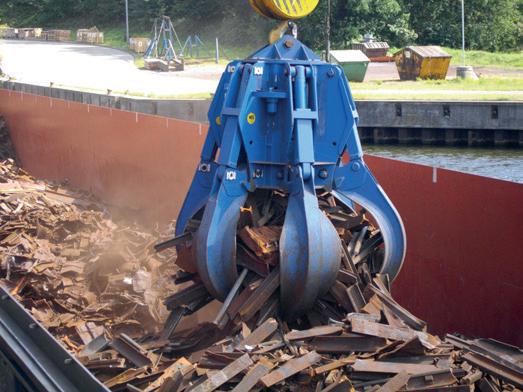
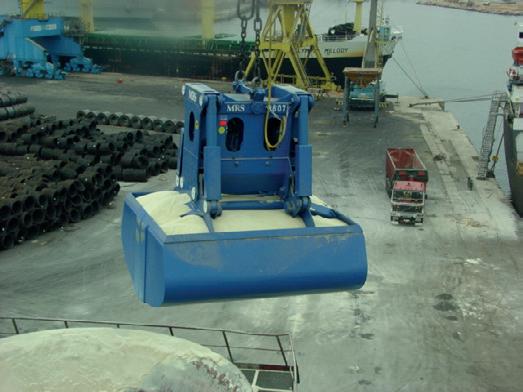
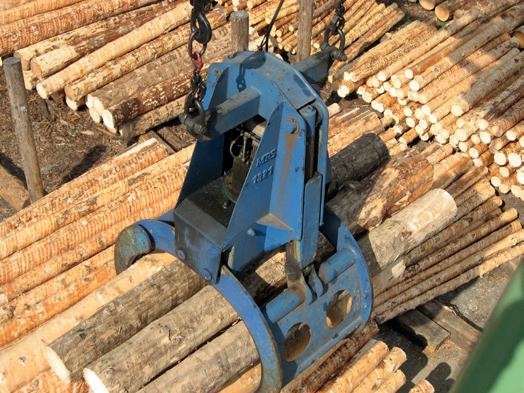
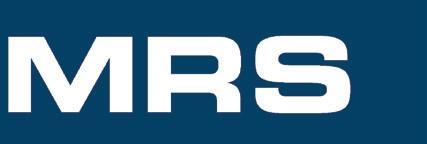


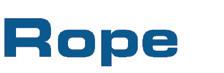
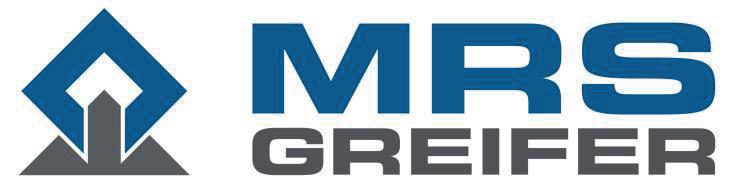
A belt wash sprays the conveyor belt with water, while simultaneously scraping it to remove the product. In a number of published studies in this area, this technique has been shown to increase the cleaning effectiveness by approximately 14%.
Belt maintenance
Proper maintenance should not be overlooked. Worn or cracked belt covers, seized rollers, belts miss-tracking, and inadequately or over-lubricated components all contribute to a poorly operating conveyor system. In turn, those deficiencies add to a dusty environment.
Properly maintaining the belts is one of many vital operating practices necessary to keep respirable dust levels low along the belt entry.
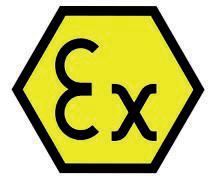
Conclusion

The war on dust should be fought with a multi-faceted approach. Further forms of dust control can involve collectors, water sprays, fog suppression, foams, and so on.
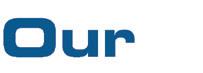
However, the hierarchy of control that applies to mitigating hazards and the use of PPE applies to managing dust. First, look to remove the source, manage what is left, and finally use additional equipment if needed.
Neglecting the small things may create large quantities of dust. However, the opposite is also true. Small consistent improvements produce a much cleaner system. And, a cleaner system is not just nicer to work around, or better for relationships with neighbours, it is more efficient. Dust may be a fact of life, but excessive, harmful levels can be controlled by recognising the problem and doing the basics well.
References
1. SWINDRMAN, T., MARTI, A., GOLDBECK, L., MARSHALL, D., and STREBEL, M., ‘Foundations™’, Martin Engineering, www.martin-eng.com/sites/default/files/Fo21undations/ Book%20Downloads/f4-2012.pdf















2. The National Institute for Occupational Safety and Health (NIOSH), ‘Best Practices for Dust Control in Metal/Nonmetal Mining’, Centers for Disease Control and Prevention, (18 November 2018), www.cdc.gov/niosh/engcontrols/ecd/ detail79.html




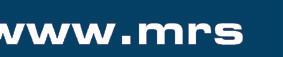




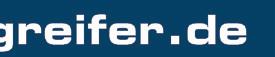


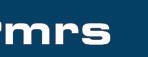
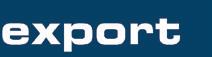
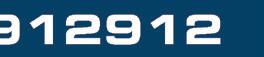





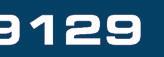








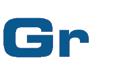




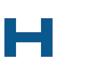




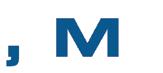
3. COLLINET, J., RIDER, J., LISTAK, J., and ORGANISCAK, J., ‘Best practices for dust control in coal mining’, Information Circular, (January 2010), www.researchgate.net/ publication/283924262_Best_practices_for_dust_control_in_ coal_mining
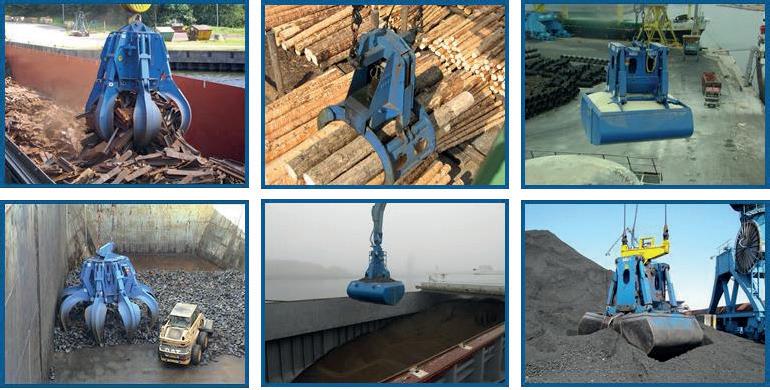
Dr. Erik Zimmermann, Wirtgen, Germany, explores how cutting technologies can be used to optimise coal mining operations, and how they play an important role in reducing emissions.
The drilling and blasting process is common practice and problem-free on many construction sites. However, there are opencast mines with conditions that make blasting operations very difficult, if not impossible. Problems include the vibrations caused by the blasting process, and the complicated storage and handling of the explosives.
Coal mining using the cutting technology of surface miners is an option that is attracting increasing interest. These miners achieve in one working pass what would otherwise require several operations; cutting, crushing, and loading – all in a single working pass.
Surface miners are cost-effective, environmentally friendly, and reliable in coal mining applications. At the beginning of a mining project, all key factors are taken into consideration. The most important of these include the required mining volume, the geological characteristics of the area, and the logistical conditions at the operating site, all of which determine the right choice of machine.
For decades, Wirtgen has been renowned as a manufacturer of machines for cutting rock in opencast mining. The company can look back on more than 30 years of experience in this particular field and can optimally incorporate its know-how
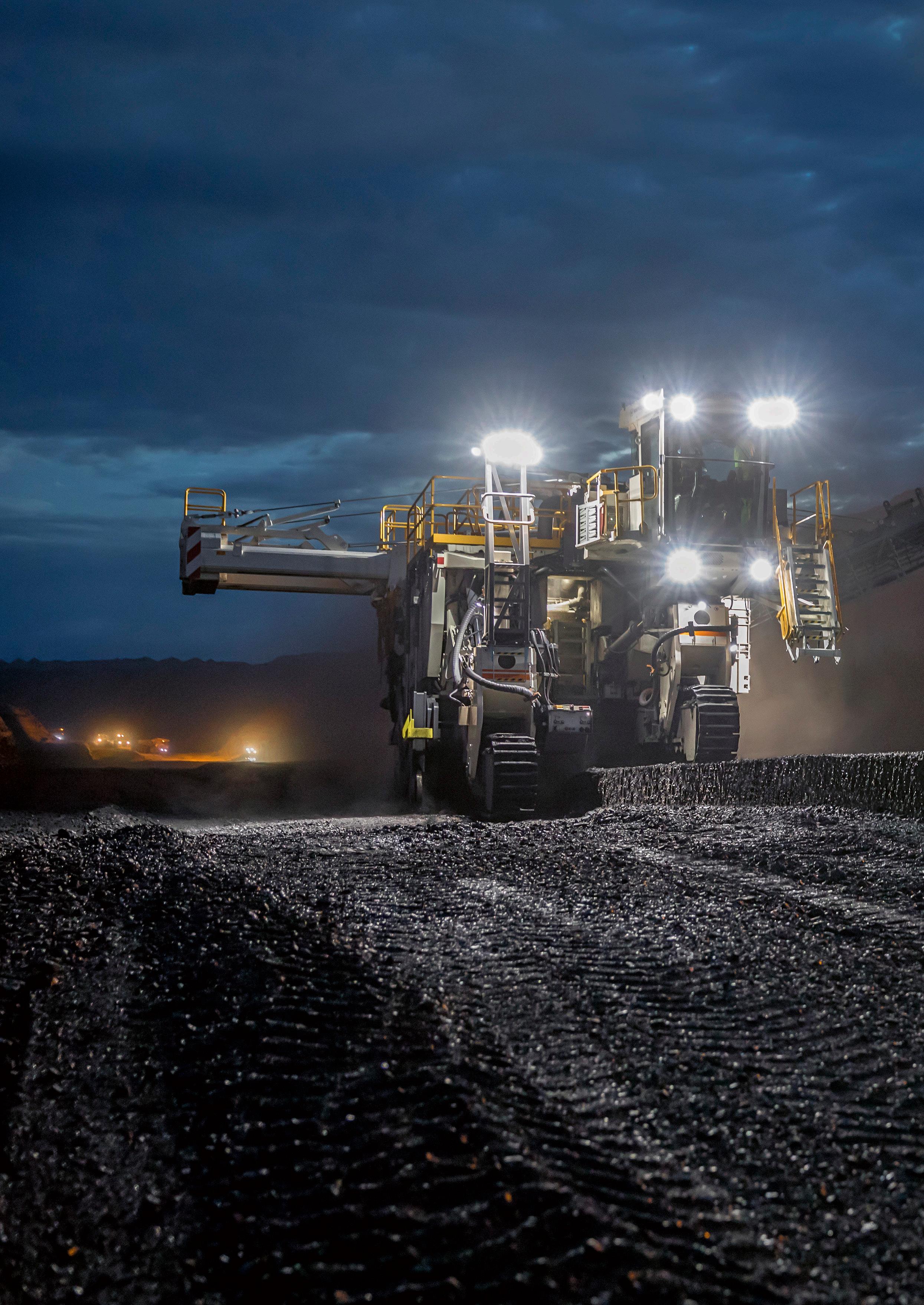
into the production of its machines. Wirtgen experts provide advice on selecting the right machine and the appropriate cutting tools for the given conditions, ultimately resulting in optimum implementation onsite. To cover the entire performance range in mining, earthworks and rock construction applications, machines are available in different weight and performance classes.
Continuous progress
Wirtgen gains a great deal of insight from discussions with customers and uses this in the further development of its machines, in order to offer them

optimal solutions. After all, surface miners are also continuously progressing.
Wirtgen sold the first machine of this type in 1983, successfully entering the market with what was then the Surface Miner 1900 SM. A mere six years later, Wirtgen presented the prototype of the 2600 SM, which was used specifically for mining coal and limestone. The machines have not only changed in appearance since then, new technology has also brought with it various advantages, progressively resulting in more efficient processes and an enhanced end product. This is confirmed by a study from 2014 involving various tests conducted by
Wirtgen in cooperation with RWTH Aachen University, Germany. The basis for this study was a coal mine in Queensland, Australia. The advantages of the Wirtgen surface mining technology include, in particular:
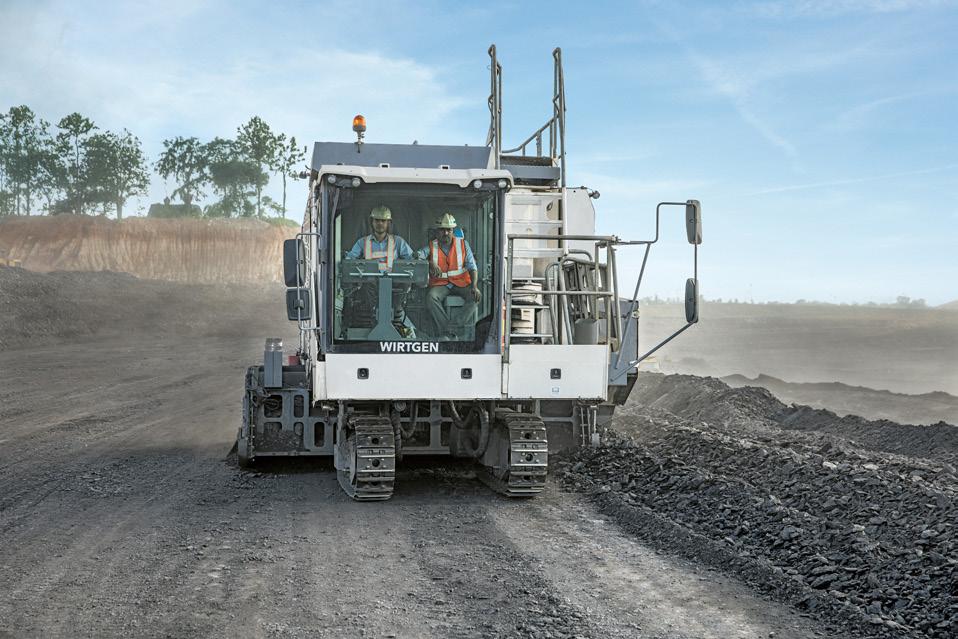
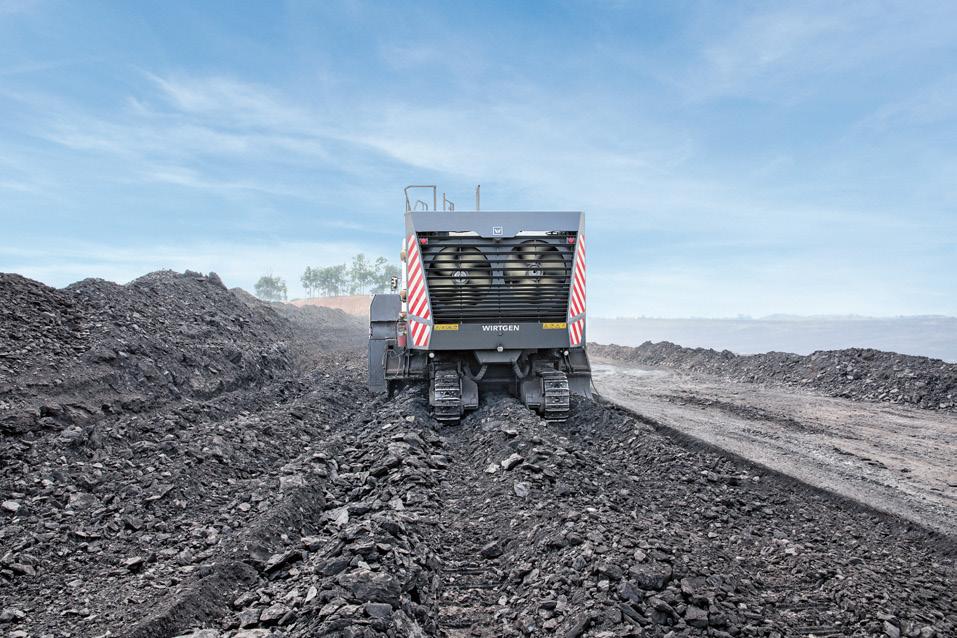
Selective mining.
Avoidance of blasting.
Cutting, crushing, and loading in a single working pass.
Maximum deposit exploitation.
Reduced transport costs.
The study focused on the use of the 4200 SM, performing particularly well due to the selective mining, increased process efficiency, and reduced dust emissions. This miner in the 200 t class has a cutting width of 4200 mm and a cutting depth of up to 830 mm. When mining with Wirtgen surface miners, the cutting depth can be individually adjusted to reach the desired layer and ensure the purity of the material. The continuous cutting operation increases process efficiency compared to conventional discontinuous methods that use rippers and wheel loaders. Unlike these machines, which produce considerable quantities of dust, the surface miner has very low dust emissions. The miner
collects what dust is produced in its cutting drum housing, before an integrated water system sprays water into this housing, thereby reducing the quantity of dust even further.
High environmental sustainability
Lowering dust emissions is just as important today as minimising CO2, noise, and vibrations. At the same time, of course, construction machines should continue delivering the same high mining performance and productivity. Conservation of resources and environmental awareness are the keywords in the development department at Wirtgen. Here, experts implement these principles with innovative technologies that can be found, for instance, in the Surface Miner 280 SM(i). This newcomer, among the miners, can be equipped with different cutting drum units. For coal mining, for example, there is a cutting drum unit that has been optimised for high material throughput in soft rock. The miner has a low specific fuel consumption, boasts an integrated water management system, and it minimises dust emissions during the cutting process.
Material removal in the cutting process, without drilling and blasting, results in an almost vibration-free operation and low dust generation. There is not as much noise as in a conventional opencast mine, where many other machines have to be used for mining in addition to the main extraction equipment. Alongside the low environmental impact, maximum exploitation of the deposit is also ensured. This is due to the highly selective mining process when using a surface miner, and the ability to produce steep slopes that are very stable.
Innovative machine technology for efficient extraction of primary resources
Wirtgen surface miners extract primary resources such as coal, gypsum, iron ore, salt, phosphate, bauxite, limestone or granite, achieving high degrees of purity in the process. The selective mining method reduces equipment, personnel, and time requirements in equal measure. Hundreds of machines are in use to date. The operating sites are spread all over the world and include the USA, India, China, and Australia. In addition to the widely used 220 SM(i) 3.8 and 4200 SM(i) models, the 280 SM(i) – launched in 2022 – also cuts a fine figure in coal mining applications. The machines are used both in newly developed opencast mining areas, as well as in extensions of existing mines. The 220 SM(i) 3.8, with its extra-wide drum, is particularly well represented in opencast coal mines. This model achieves its maximum mining performance in soft rock, such as coal, chalk, or gypsum.
The cutting drum, which is fitted with picks, rotates against the direction of travel, cutting layers of material from the rock formations. In the cutting
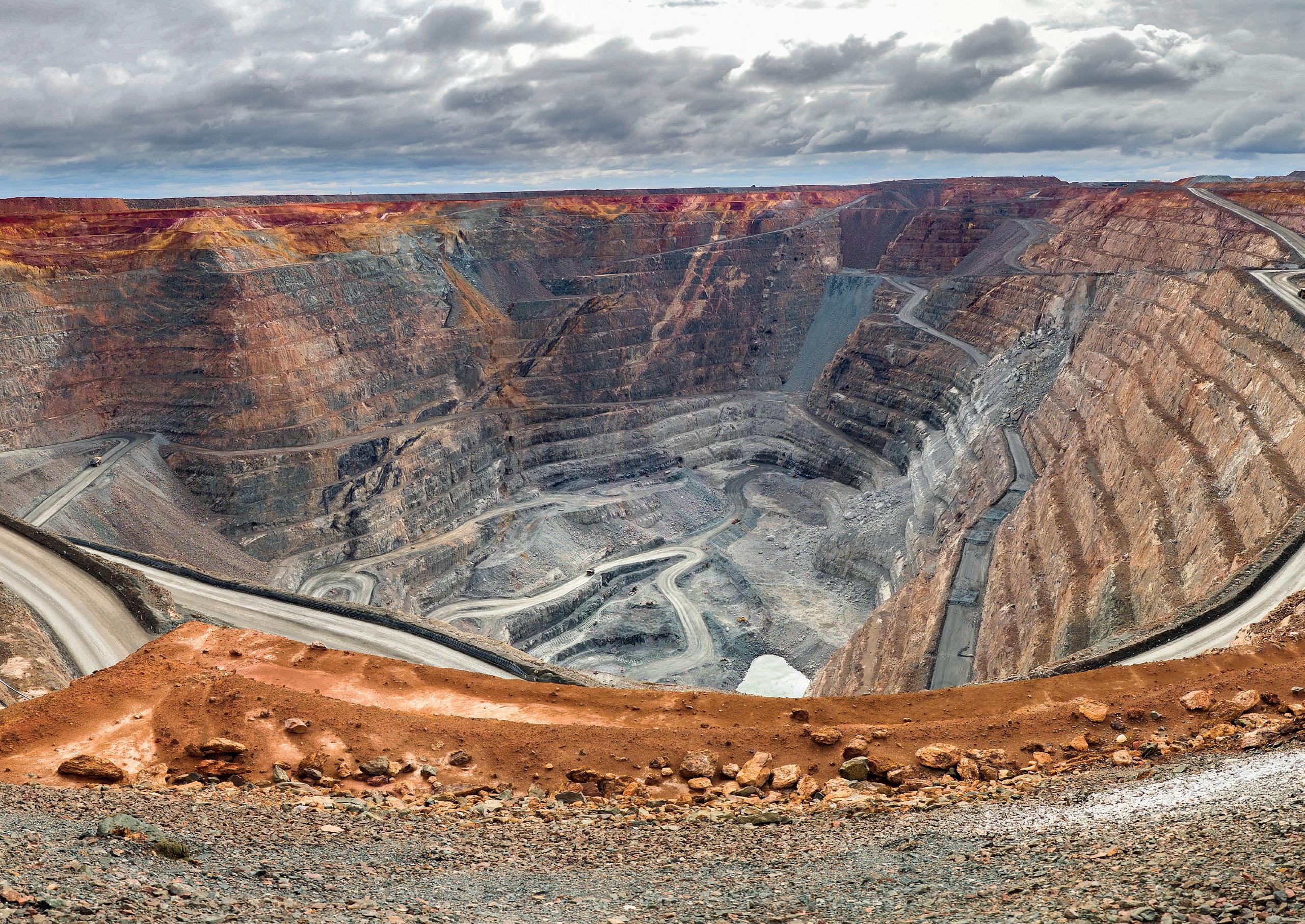
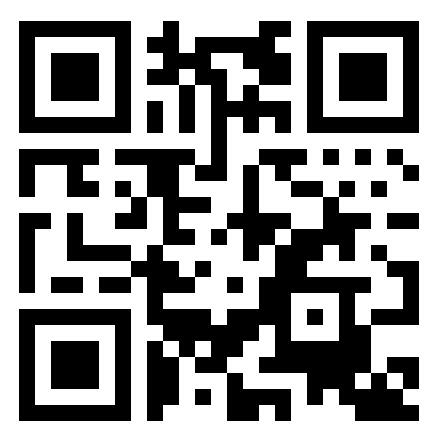
drum housing, this material is then crushed to the desired size. Depending on the machine and the requirements, the material can now either be discharged – cut-to-ground process – or loaded. For loading, the material is brought via the primary conveyor to the discharge conveyor. The discharge conveyor can be adjusted in height and slewed to either side to adapt to the discharge position. From there, the material is either discharged to the side of the machine – sidecast – or loaded onto lorries or dumpers. The customer can decide on this based on efficiency considerations and the prevailing conditions.
Four steerable and height-adjustable crawler units ensure reliable propulsion and accurate control of the surface miner. An automatic levelling system guarantees precise adherence to the cutting depth, thereby enabling even thin seams or layers to be mined selectively and with maximum accuracy.
Level surfaces suitable for direct use as roads
The precise and level surfaces produced are particularly valuable in mining, earthworks, and rock applications. This is because the processed surface behind the surface miner can be used directly as a road for other mining vehicles. Due to
the excellent evenness of the surface, it can also be used by road-legal trucks. This increases the transport capacity of the entire truck fleet, as the quality of the road surface is a decisive factor affecting the wear on the tyres, frame, and suspension of the transport vehicles. For mining companies, this is a compelling argument, as not only are transport costs reduced, but also the overall production costs per tonne of material used. The excellent evenness of the cut surfaces can also be used for other application scenarios. Tunnel floors, for example, can also be produced or lowered with the surface miner.
Maximum efficiency
Cutting, crushing, and loading – Wirtgen surface miners carry out these processes in a single working pass. Pre-crushing the rock, as is common in conventional mining, is also rendered unnecessary, making the surface mining method a cost-efficient option. At the same time, it is important to take the mined material itself into account.
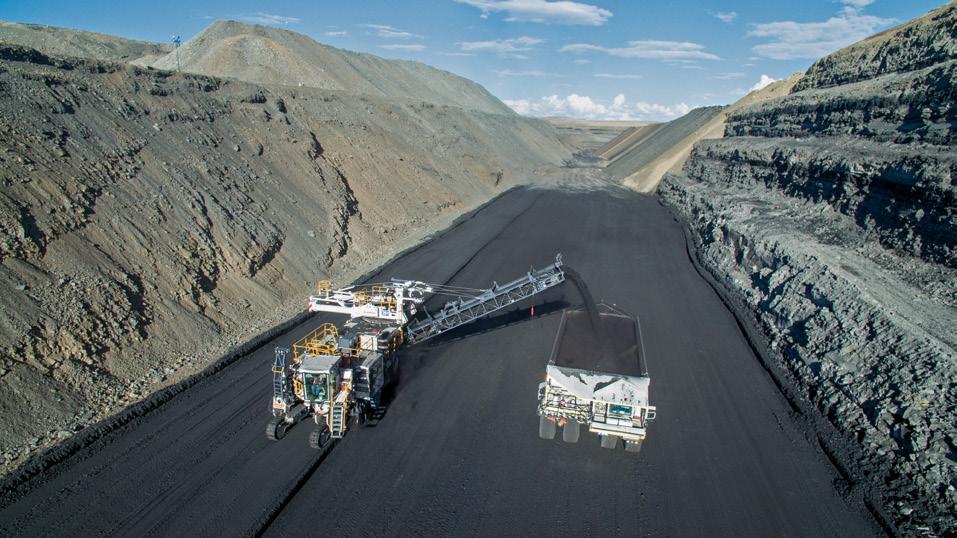
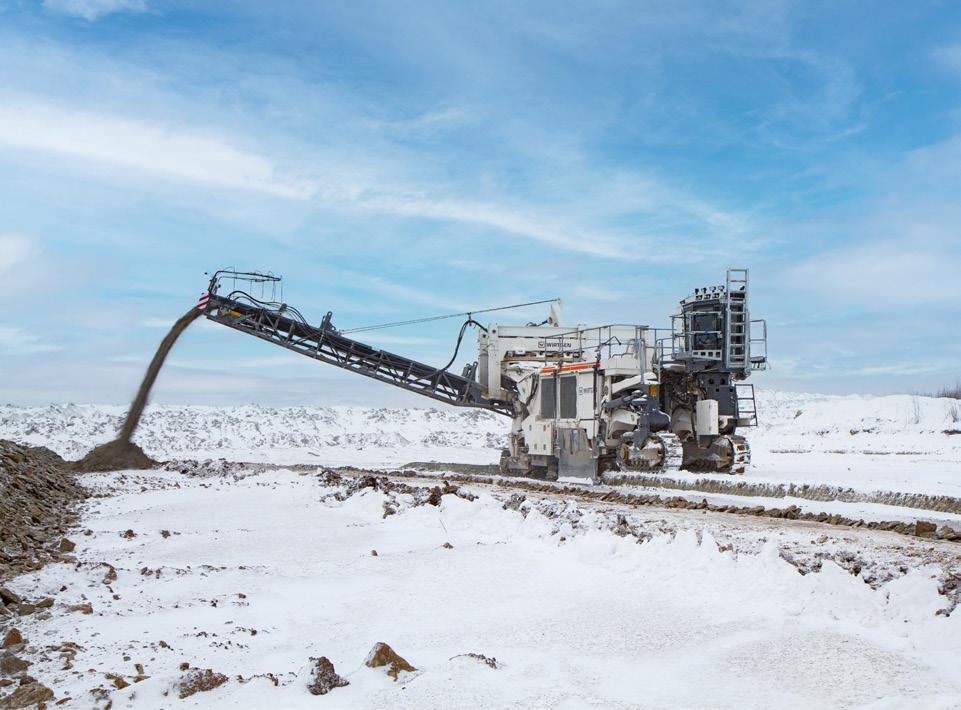
The use of surface miners, and the selective mining process made possible with them, enables the reduction of CO2 emissions during subsequent conversion of the coal into electricity at the power plant. The mined coal has fewer contaminants and therefore a higher purity, so that ‘better’ coal is converted into power.
Coal seams are generally of varying thickness and separated from each other by layers of interburden. The different materials have to be separated from each other. In conventional mining methods, this operation is associated with high processing costs. When using a surface miner, the coal can be mined more cost-effectively, thereby reducing the processing costs. Overall, Wirtgen surface miners reduce mining losses and the dilution of the extracted coal in the mine, leading to an increase in the quality and purity of the primary resource, and, ultimately, in the revenue generated. Exploitation of the deposit is maximised, and an improved overburden-to-coal ratio is achieved.
Greater onsite safety
The fact that extraction is carried out without the need for drilling and blasting leads to additional advantages in opencast mining. For example, by not having to store and handle explosives, employees benefit from increased safety. Furthermore, the slopes created are extremely stable and rockfall occurs less frequently than when conventional mining methods are used. Opencast mine operators not only benefit from enhanced safety, but their work is also made easier. This is because closures of the mine are no longer necessary, the relevant permits and documentation do not need to be obtained, and no certified blasting personnel are required.
Flor Rivas, Caterpillar, USA, discusses the importance of technology advancements in driving electric rope shovel efficiency and longevity.
The iconic electric rope shovel (ERS) is the stalwart overburden and ore material loader for the mining industry. From the Panama Canal shovels weighing 63 500 kg (140 000 lb) to today’s shovels weighing in at more than 1.36 million kg (3 million lb), these massive machines have loaded mining equipment with dipper capacities up to and in excess of 100 t for more than 140 years.
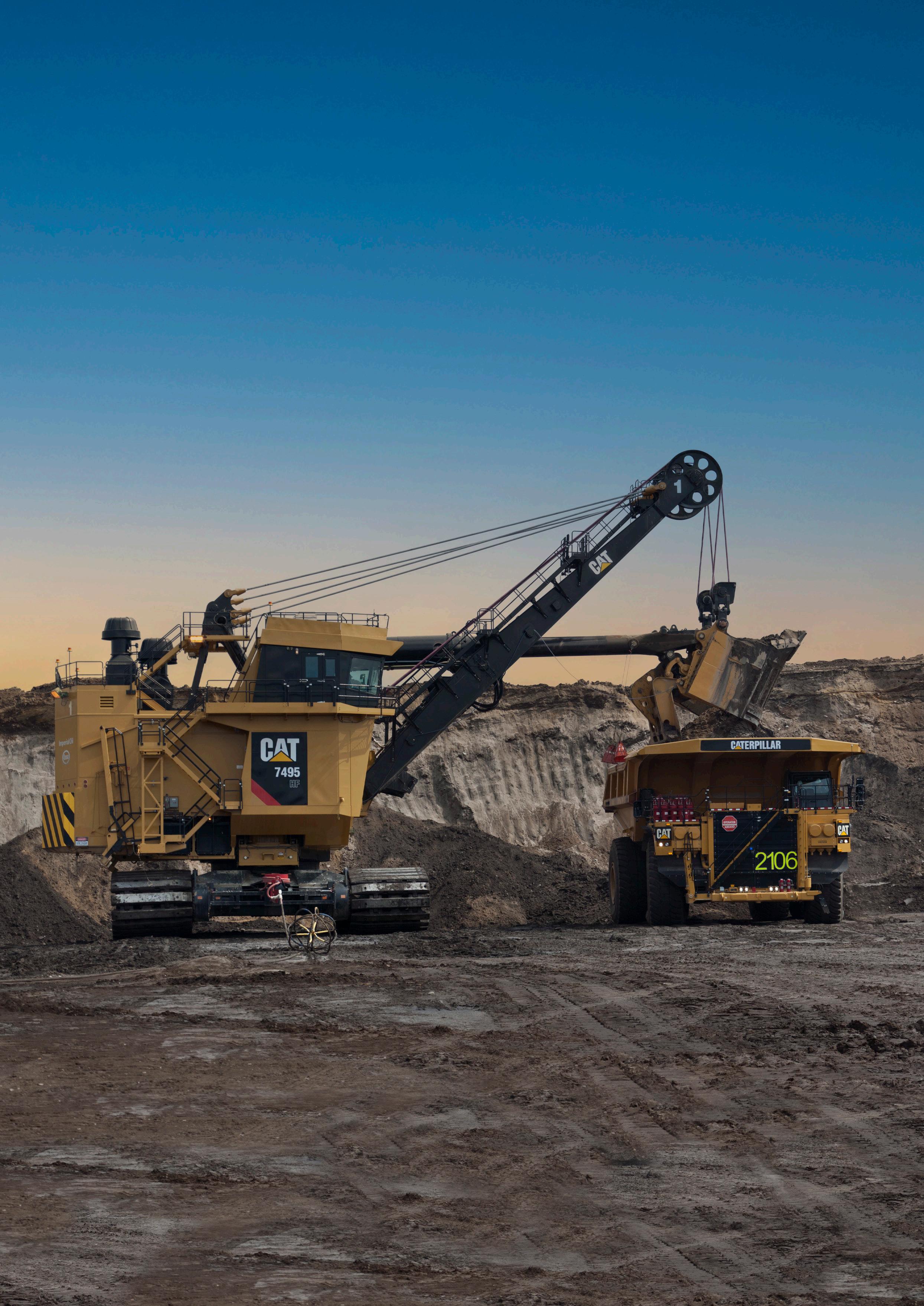
While some of today’s ERS models have distant relatable appearances to those of the 20th century, the shovels currently operating at mine sites are much more efficient. As a matter of fact, the quest to drive machine efficiency has never stopped over the decades. Steam power gave way to diesel engines and finally to electric power in the 1930s. DC motors evolved to much less complicated AC drives. Analogue systems evolved into digital gate turnoff (GTO) systems with the introduction of insulated gate bipolar transistor (IGBT) fuseless technology, pushing drive system availability upward to 99%. All along, OEMs have advanced the durability and reliability for structures and mechanical items to extend the target design life for these massive machines.
In the hands of a skilled and experienced operator, the ERS loads haul trucks smoothly and efficiently with some of the lowest costs per tonne of material moved. However, as operator experience wanes, loading efficiency can suffer – causing cost increases and decreases in uptime availability.
For years, the mining industry, like many others, has had difficulty replacing retiring highly skilled ERS operators, and mounting evidence is showing that even the most skilled operator can be more efficient when loading trucks.

The era of technology
Over the last decade or so, the ERS design has undergone a technological revolution of sorts. Supplementing proper operator training and machine operation, OEMs and third-party suppliers have introduced a number of operator-assist software supplements to simplify machine operation and reduce occurrences of some of the most common operating miscues.
For Caterpillar, the first technology advancement came in the form of Operator Assist – Enhanced Motion Control (EMC) for the Cat® 7495 shovels, introduced in 2016 after studying the operating habits of numerous operators with varying skill levels. Protecting the machine from inadvertent misuse has led to significant benefits for ERS components, such as crowd and hoist ropes, brakes, gears, and the swing rack.
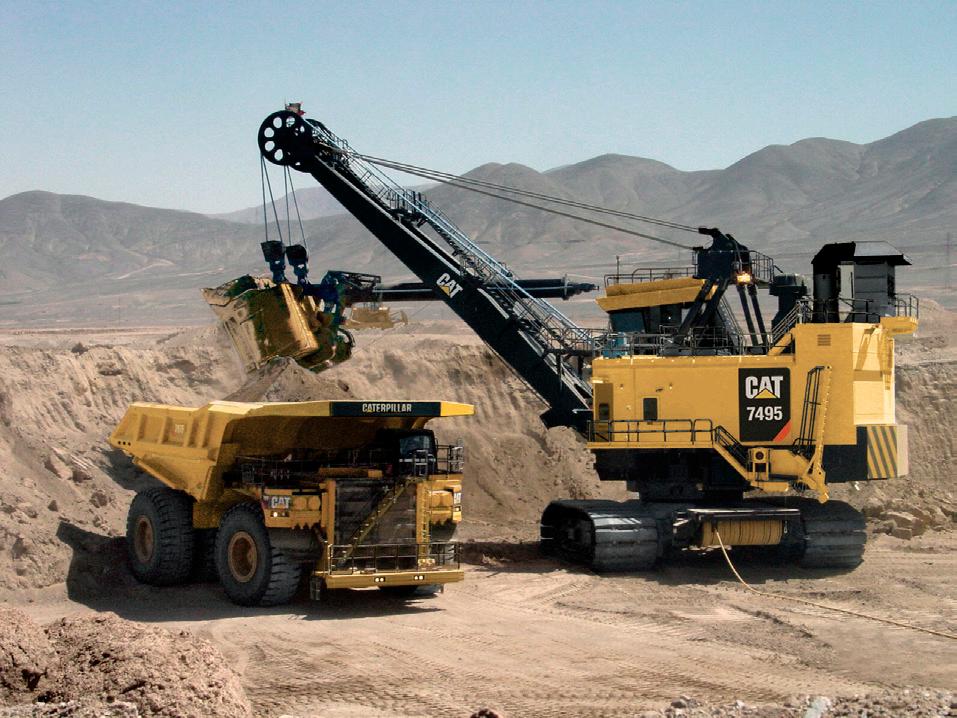
The new technology offered machine protection and simplified machine operation. Some of the best examples of the software’s powerful capabilities included detecting and automatically limiting swing forces when the operator attempted to swing the dipper through the bank. This prevented the added side-loading forces that can damage shovel components.
Machine protection software also helps to safeguard the crowd ropes and the brake. When the dipper hits the bank with high inertia, the resultant impact produces high crowd rope stresses and potential shock loads if the crowd motor continues to apply force. To avoid this, the software automatically adjusts motor output.
When the command speed is exceeded, a crowd overspeed occurrence takes place, which requires the brake to automatically apply. This interrupts the digging cycle and causes unnecessary wear on the crowd brake. Available software for ERS models provides more braking power to prevent over-speed situations, in order to improve crowd brake life.
Another common miscue with these shovels, boom jacking occurs when the ERS crowds against the bank floor and lifts the boom with the dipper handle, triggering faults that adversely affect cycle times and machine productivity. The technology exists to prevent this situation by automatically adjusting the hoist and crowd to maintain proper rope tension, so the operator experiences fewer digging interruptions.
The benefit of these technology features is evidenced in a copper mine in Chile, which installed the EMC technology on its electric rope shovels and analysed the data collected by the software. In one year, it detected an astonishing 779 309 anti-swing
in-bank events across the mine’s shovel fleet. Additionally, anti-boom jack year-over-year comparisons showed 60% fewer incidents when using the motion control technology. Crowd overspeed incidents were reduced by 80%.
The mine also experienced longer lasting crowd and hoist running ropes, which led to fewer rope changeouts that put maintenance people in harm’s way, reduced costs, increased reliability, and elevated production per set of ropes. The mine also realised hoist stall protection, crowd anti-impact, and hoist rope slack prevention. Ultimately, over the analysis period the site saw overall production increase by 25%.
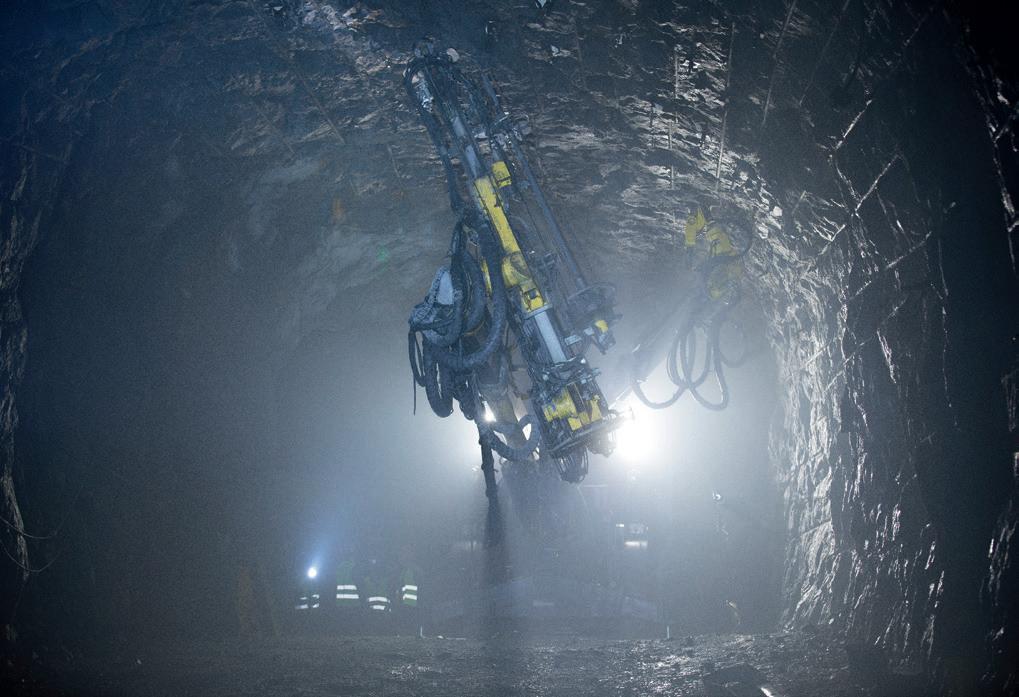
An easier tech installation
Mining operations now realise the significant benefits offered by the expanded use of technology with a range of equipment at mine sites, and they are requesting that ERS manufacturers expand technology offerings. This has led to third-party suppliers and OEMs expanding software capabilities to include anything from bearing temperature and vibration monitoring, to payload management and cycle segmentation.
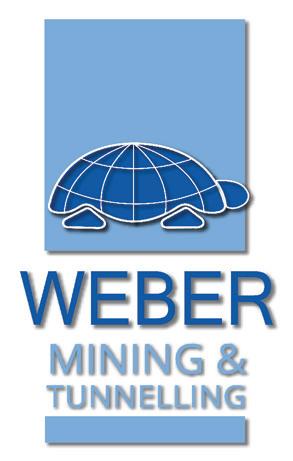
The catch, however, is these technologies often require customised hardware and software installation, demanding longer machine downtime which cuts into productivity. Additionally, the more



one-off technology solutions installed on the shovel increases the potential for these offerings to not work well together.
Manufacturers now offer technology bundles and updated ERS electronics packages that allow for future upgrades the mine may want on its journey towards automation. Caterpillar will offer two such new technology solutions – the Integrated Technology Package and the Operator Assist Technology Package – for the Cat 7495 and 7495 HF models, starting with the 2023 production year models, and retrofit kits for field machines will also be made available.
The Integrated Technology Package fully integrates Cat electronics into the machine’s design to provide the foundation for future technology expansion. The technology eliminates the need for additional in-cab displays from each one-off tech package, making it easier for the operator to get critical machine operating data without sensory overload. It also provides seamless integration and quicker installation of Cat® MineStar™ Solutions’ operational technologies that help track, monitor, and manage the shovel. The revamped Operator Assist Technology Package furthers machine self-protection and operating simplicity.
An item many mines are requesting is a way to further safeguard these massive shovels against accidental collisions between the dipper and machine. The upgraded Cat technology
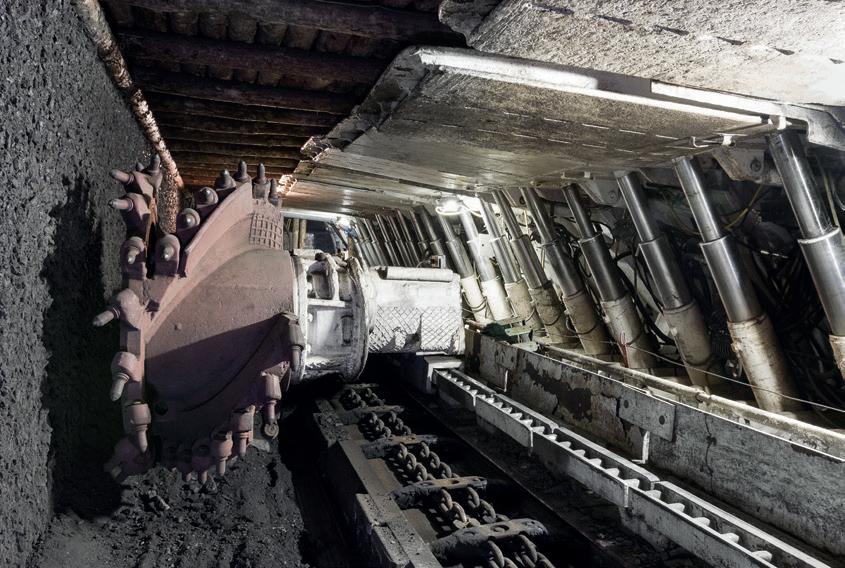
incorporates a LiDAR vision system – similar to the technology found on mining trucks with an autonomous haulage system (AHS) – to scan the area in front of the shovel.
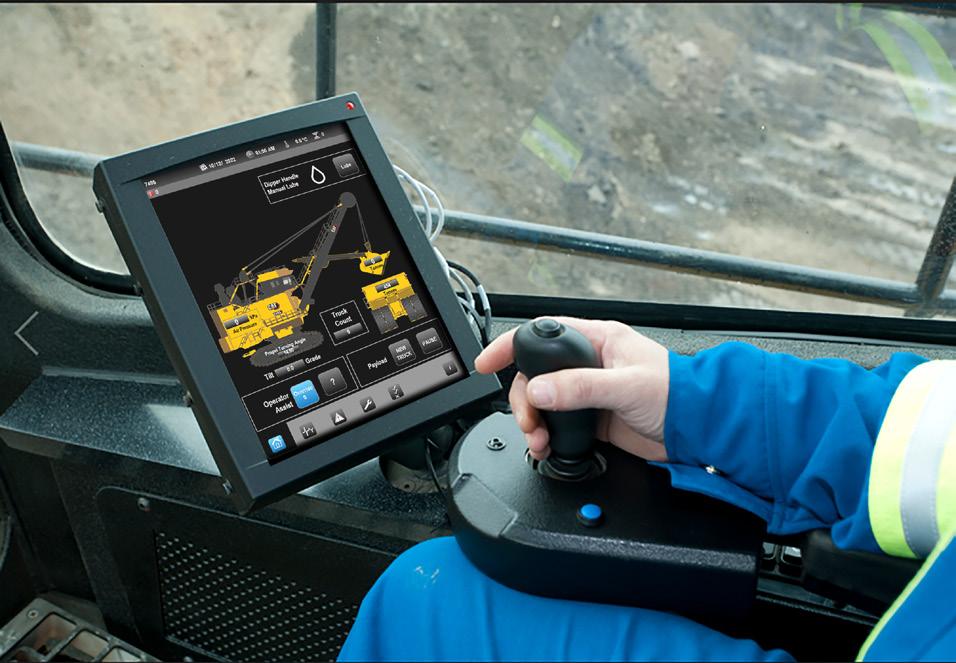
Sensors positioned at the hoist, crowd, and swing systems work together with LiDAR and software algorithms to help detect and avoid potential collisions. The algorithms integrate with operator commands to provide the least intrusive avoidance path. In the case of an unavoidable collision, the system will automatically arrest machine motion to mitigate the collision.
Proper technology implementation
While technology can help improve machine operating efficiency, extend component longevity, and lower overall operating costs, how a mine site implements new technology features is just as important as selecting the right technology provider. Technology can be perceived as a threat to the operator or an attempt to take away jobs. Therefore, change management with a people-centred process is key to achieving greater engagement of the workforce, adoption of the technology change,
commitment to the cause, and enhanced rope shovel performance.
Indeed, after introducing EMC, Caterpillar saw great interest from multiple mining organisations. Once installed on the machine, some operations reported strong results, while others reported mixed feedback. The Chilean copper mine reaped some of the strongest benefits after installing the technology.
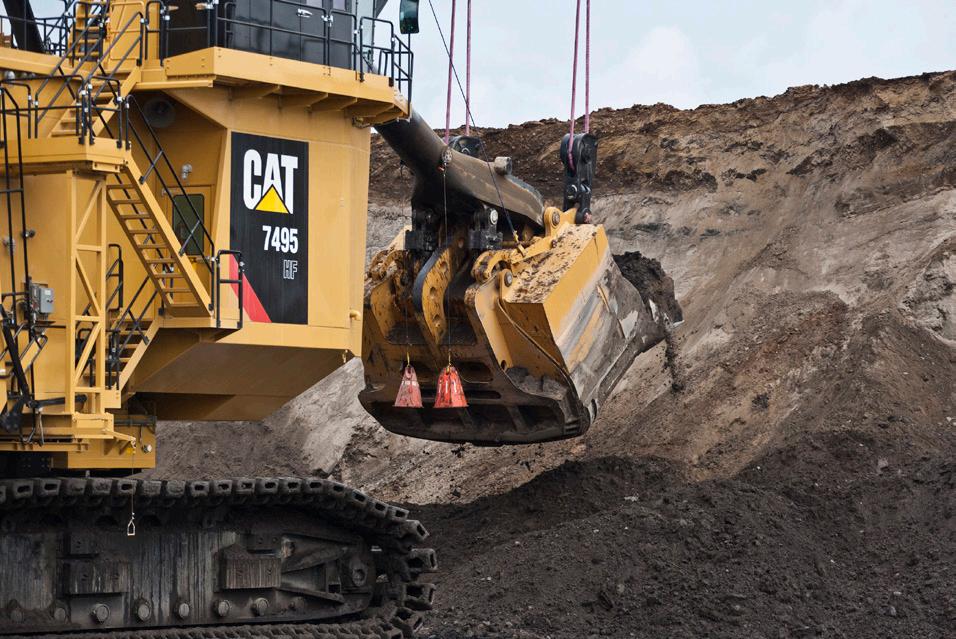
Upon analysis, individual mine site results showed where proper change management practices were put into place and where they were not. On sites where EMC was properly explained, key performance indicators (KPIs) were defined and measured, and operators were trained. The results outlined the value promised by the new technology. Where operators were not provided detailed information or timely training, there was frustration and negative feedback.
Caterpillar worked with the mine sites that were experiencing technology adoption issues to boost operator acceptance and machine efficiency. To start, instructors offered insight into how the system worked, covered the features, and showed operators what they would experience. Explaining the purpose of the technology – as a machine protection feature and not operator control – went a long way in achieving operator acceptance.
Virtually every situation in which mines experienced less-than-desirable results was rooted to a lack of communication and training. Proper training helped these sites to achieve the same levels of success experienced in other locations with successful implementation.
Conclusion
Available for more than a decade, ERS technology is ushering in a new era of production and efficiency gains. Beyond improving operating efficiencies, the software offers machine self-protection, as well as improved health and productivity data tracking, so mines can reduce the number of unplanned outages, create a more predictable maintenance schedule, and extend component life.
Initially, these technologies often required customised installation, which took more time to set up, and operation of the one-off features did not always integrate seamlessly with one another. However, updated electronic infrastructure being integrated into today’s rope shovel allows for faster integration of technology, reducing machine downtime for installation. These designs are future-proof –eliminating the need for additional in-cab displays, as well as allowing for easier integration of technology upgrades as the site moves on its journey toward automation. Yet, no matter how easy it is to install the new technology, how much it simplifies operations, or the longevity increases realised to lower costs; new machine software and features not properly implemented using a people-centred approach will not allow mines to reap its full benefits.
The connection point is critical to maintaining safety when using high performance steel cables. Shackles, masterlinks, hooks, and poured and wedge sockets have long been used on mine sites to make the tension connection for all kinds of applications, and work very well with steel wire ropes, rods, or chains.
Fibre rope has numerous benefits for utilisation, but is held back because the methods to terminate or connect have been limited to a knot or splice as the only options. While this works in many applications, the termination method is not suited for long term use and is not robust enough to handle the rough mining environment, as the connection is susceptible
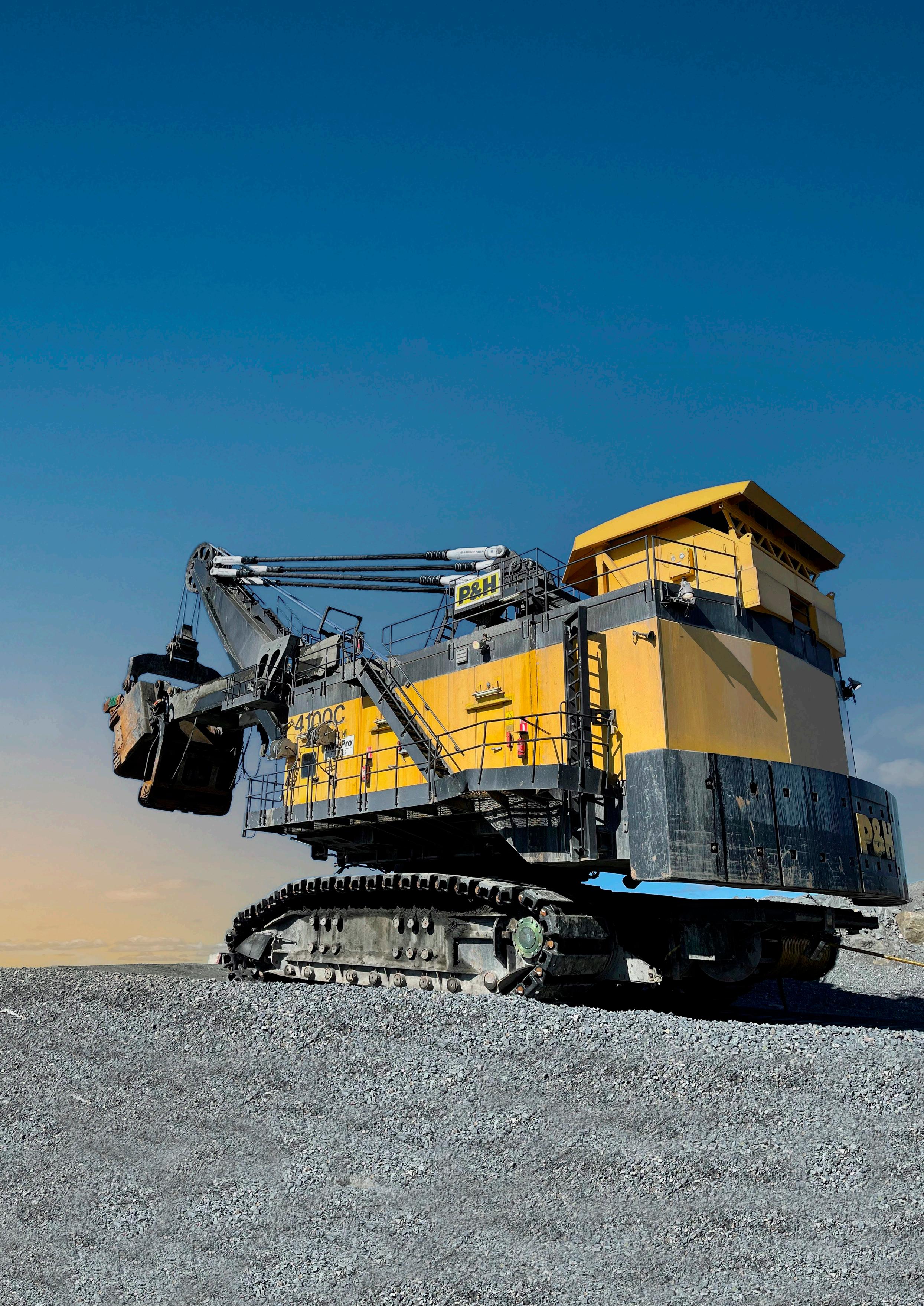
to early wear, outside contamination, and inspection and retirement issues are long standing.
Why change?
Performance fibres are used in large rope applications and have many advantages over steel. Examples include: reduced weight, non-corrosive, ultra-low-conductivity, easier and safer handling, higher efficiency in task-oriented jobs, no grease or lubrication needed, increased damping and reduction in impact loads, and a lower environmental footprint among others.
Gaining these advantages are substantial if the drawbacks on termination can be addressed –particularly for large ropes used in heavy industries.
Socketing fibre is a challenge, as unlike wire ropes that have thick wire strands for which sockets can be easily poured, fibre filaments are the thickness of a human hair. It takes millions of these filaments to make up a high strength rope. Pouring sockets in the traditional manner using fibre does not work, the fibres are loose and fall over, tangle and become misaligned, resulting in inconsistency and unreliability. Break strengths are greatly reduced and there is no assurance on outcome.
Assured socketing performance opening new fibre rope markets
Applied Fiber technologies address these issues relating to connection and allow utilisation of the performance benefits of fibre. Through integration of Applied Fiber’s proven fibre socketing technology with a robust termination, the final product is a highly efficient and repeatable performing rope assembly. This technology has opened up new applications for fibre rope adoption.
It is most widely known on coal mines that draglines are the work horse to remove overburden and are critical to its success. Dragline boom pendants require a robust termination and precise pendants lengths for proper long-term use,

in order to balance the tensions on the boom and loads properly. If fibre could be utilised instead of steel wire between the sockets, a number of benefits could be realised. A practical and efficient termination or socket did not exist for synthetic ropes until Applied Fiber developed the technology to repeatedly process sockets with predictable performance criteria, delivering both pendants that are perfectly matched in length with an end fitting that can handle high fatigue loading cycles that a dragline endures over numbers of years.
The first synthetic pendants were reported on in World Coal seven years ago. The fibre pendants installed on a Marion 8200 are still going strong and have outlasted the normal life of steel.
The first dragline installed fibre main pendants were in 2016 in Wyoming, US. It was noted during its seventh annual inspection that the pendants have been performing even better than anticipated. Where some steel pendants are changed out as soon as every five or six years, the pendants on the Marion 8200 at Navajo Transitional Energy (NTEC) appear “just broken in”, and that they will also exceed double the life of the steel with numerous additional benefits. This additionally will allow for extension of the time between boom laydowns, as they will not have to be replaced as soon, which will result in both maintenance savings and a production boost.
The first-installed set of cables have seen over 1350 machine cycles daily, which equates to millions of fatigue cycles and over 200 million micro-bending and tension cycles in this time. The pendants provide the machine, operator, and production a number of benefits.
Pendants at NTEC
The Applied Fiber pendants are a big step for change in dragline technology. NTEC converted the Marion 8229 in 2016, the 8233 in 2017, and a BE1570 lot 12 in 2018 – all of which have significantly smoothed out the machine operation.
On the first 8200, key 29, the bucket capacity was effectively increased to 2 yd3 (due to increased soil density) and only limited operating issues have been reported in six years – a noteworthy change from prior years with steel pendants. The pendants have made a huge difference; the machine swings well and has noticeably less bouncing and vibration.
The second 8200 that the pendant was installed on was getting beat up, so the steel was replaced two years early and the payload was increased by 5 yd3 (from 82 to 87 yd3). Since installing the pendants on this machine four years ago, the machine now operates much more smoothly, due to the lack of pendant bouncing and overall system damping.
On the 1570, the machine is also running much smoother, with significantly less fatigue. Before, regular cracks would typically be seen in boom nodules 8, 10 and 14, creating one to two weeks of
downtime a year. Since installing fibre pendants years ago, there has only been minor cracking in this region. It is estimated that several weeks of production in the years of operation with the fiber pendants has been gained.
Visitors can see the difference from a distance and the operators appreciate how much it quietens the machine movement. One operator went from having numb hands at the end of a shift to having no issues, outlining that the difference both in the cab and outside the machine is very noticeable. So, putting a low-mass dampener into the boom can make all the difference.
More production, less wear and tear, less downtime, and much smoother operation – NTEC was pleased with what the pendants have done for its draglines. It was forecasted just under a two-year ROI and actual performance has met and in many cases exceeded predictions.
Since the first installment, several draglines in the US and in Australia have been upgraded to fibre pendants. All of these pendants are expected to surpass the life of steel and gain the additional benefits that NTEC achieved.
Conclusion
The product, now installed on draglines globally for both main and IBS pendants, is running on electric rope shovels. The product is providing benefits to both

production and maintenance, as the multiple benefits of fibre are delivering weight savings and lowering the burden on the equipment.
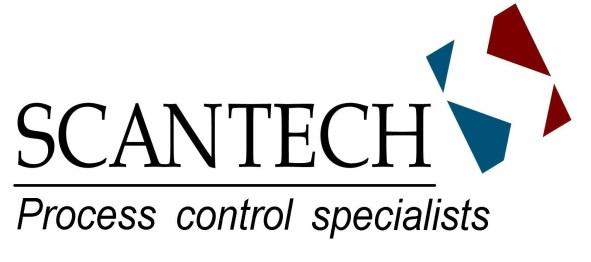
Electric rope shovels are benefiting from fibre in ways that were not previously expected. Reduced shock loads when the boom jacks and dampened vibration are in operation are proving to be a valuable maintenance benefit of fibre rope pendants on shovels, reducing welding. The 4100 Shovels are outfitted with fibre pendants, and are benefitting from these improvements during operation.
On-Belt Real Time Coal Analysers
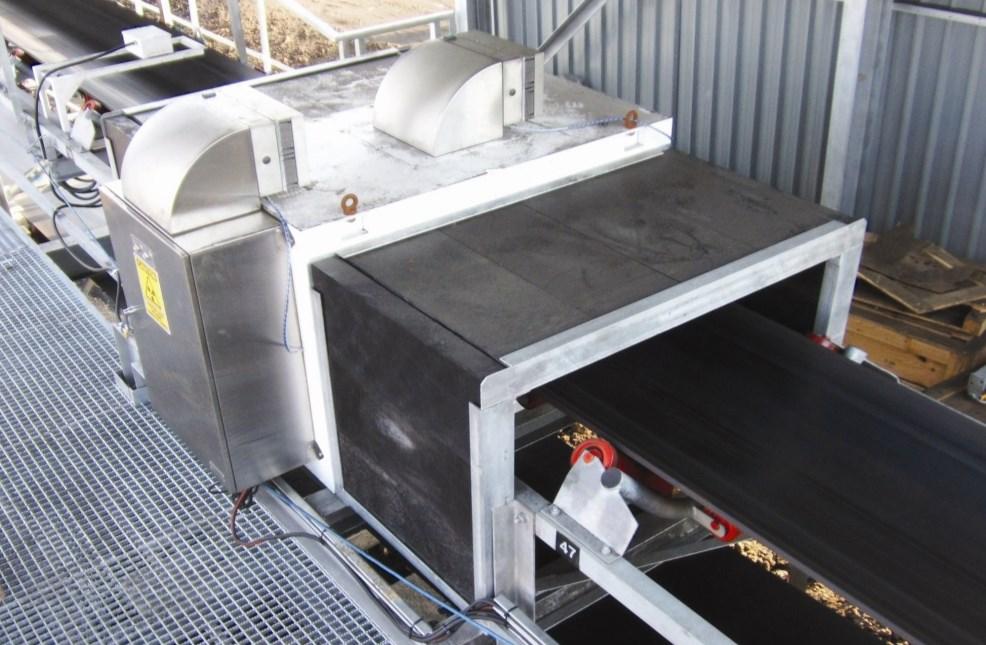

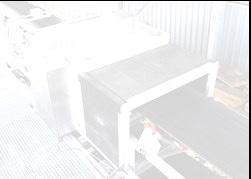
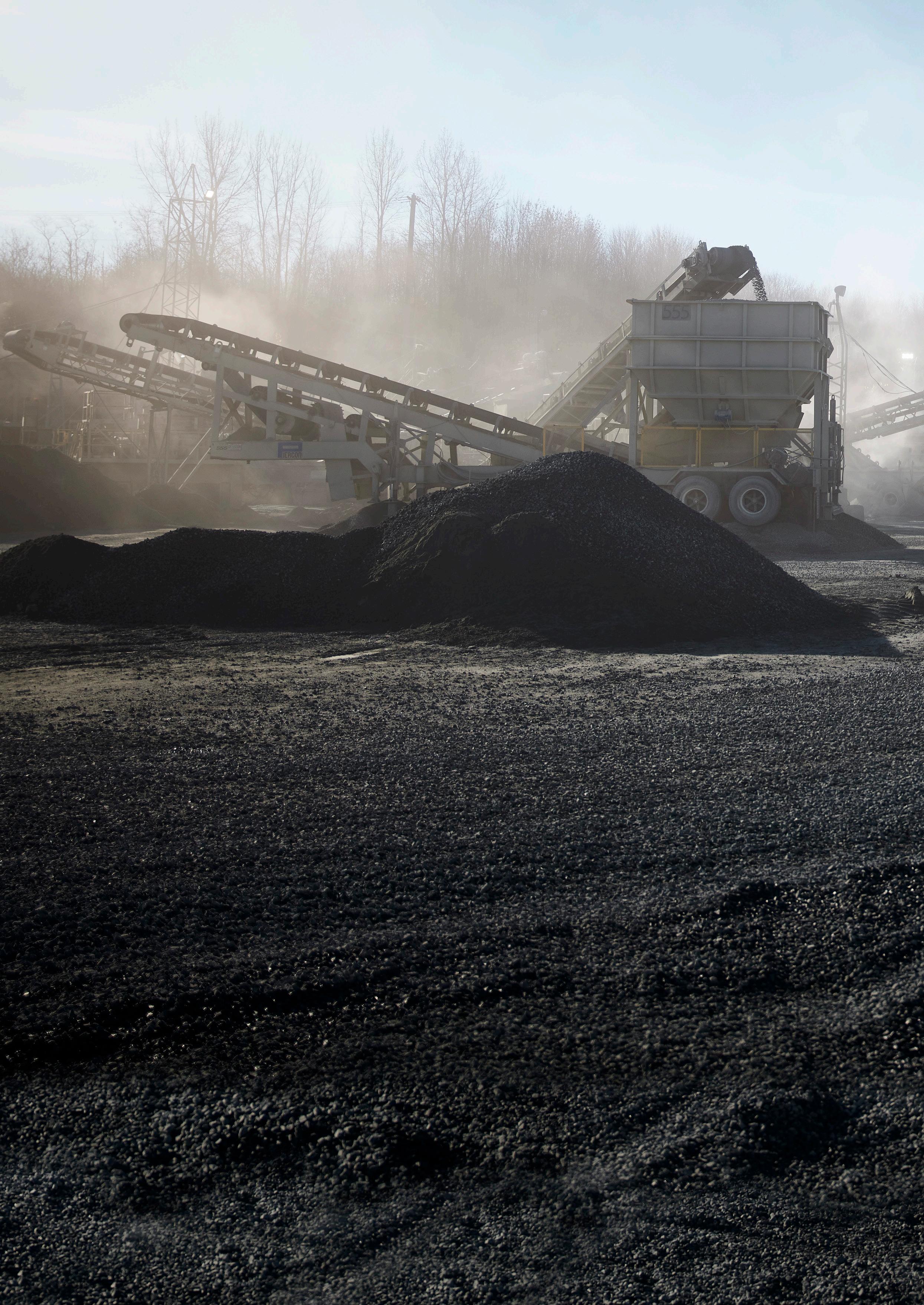
Serge Raymond, MAJOR, Canada, explains how it is possible to solve the three biggest coal screening challenges.
Energy is a hot topic in any country or socioeconomic circle these days. Though politicians will forever argue and debate the virtues and evils of one system of energy over another, the majority of the population – no matter what part of the globe they live in – simply want to make sure that when they need heat, light, or transportation it is readily and economically available. In 2022, the demand for coal, especially in the power generation industry, hit a record high.
At the same time, the specifications and requirements for coal production have become even tighter, and the pressure on mines to find more sustainable processes has never been more rigid. Coal operations must examine many facets of their business to ensure efficiency and sustainability, and one significant consideration is screening and classifying. When it comes to screening coal, most operations will agree that tighter specifications, issues with blinding and pegging, and a constant need to increase production are three of the most common
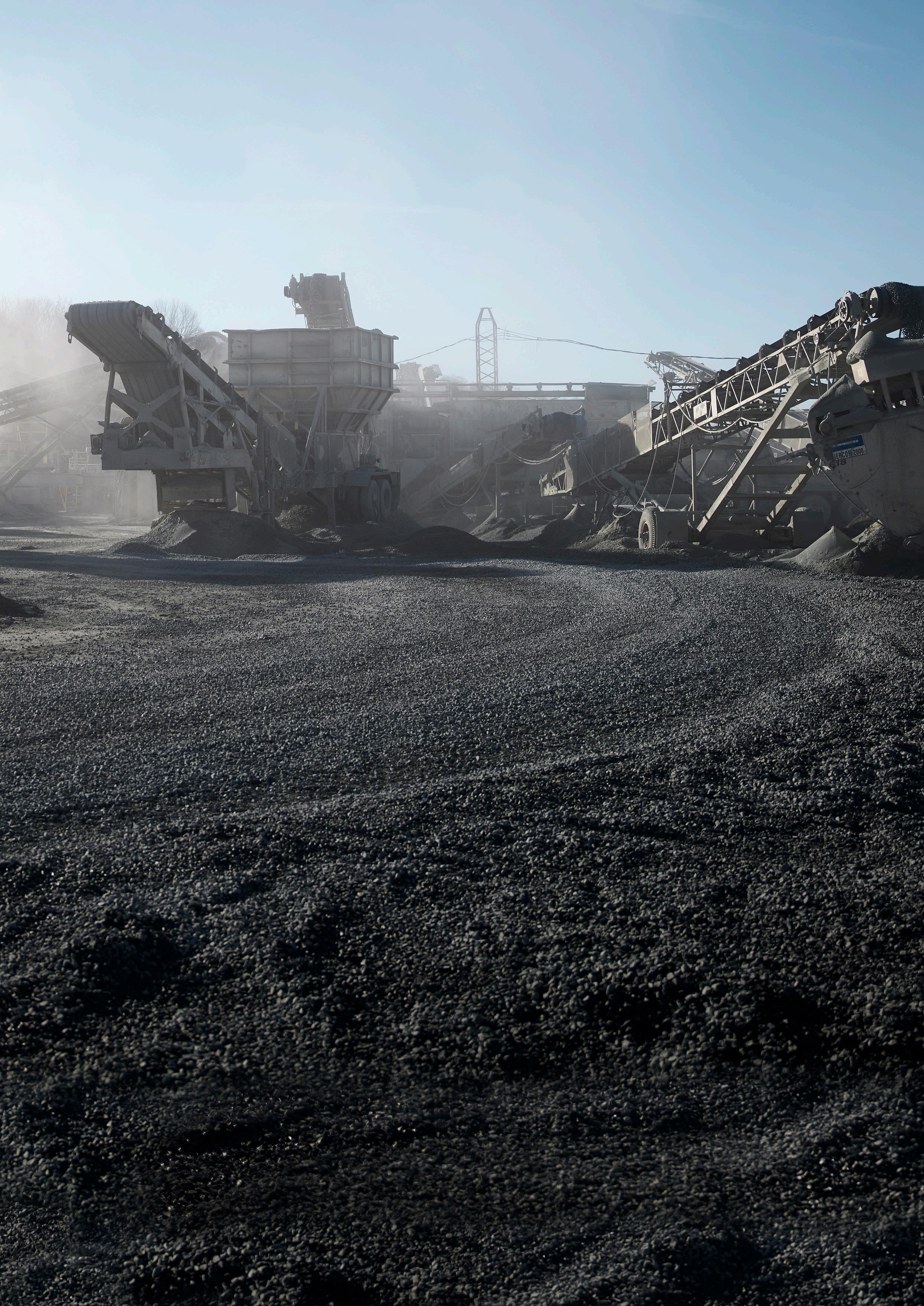
challenges they face. While it is second nature to immediately look at the screen box for solutions, the key may actually lie in screen media.
Tighter specifications = greater margins
Throughout the past 20 years, the material specifications for all industries have tightened –including coal. While the once standard increments of woven wire cloth openings used to adequately meet all specifications, today’s tighter specifications demand infinitely more size options to produce the requirements for various applications and uses. Often the premium products offering the most margin require the most difficult specifications to attain.
Because coal is light and non-abrasive, most coal screening operations use standard woven wire screens. These mass-produced screens are inexpensive and old school – seemingly an easy decision – but, when precision for a variety of materials is key, old-school media is often not the right path. Because of the design and weaving process
of traditional woven wire, only specific opening sizes in 1/16 in. increments are available. Innovative high vibration media styles eliminate the design limitations of weaving, allowing infinitely minute adjustments of wire spacing to accommodate a plethora of specification requirements. This provides coal mines with the capacity to meet specifications and capitalise on the products or specifications that provide the highest profit margins.
Blinding and pegging
The lightweight and relatively soft properties of coal lead to the production of many fines that stick to the surface of the screen, causing issues with blinding. Though running the coal through a wash plant before screening may reduce the fines, the added moisture – even 5% – leads to equally troubling issues with blinding. Whether from the sticky fines or the moisture laden slime, blinding
and pegging present a major problem to both the quality and quantity of the final screened product. Left unchecked, blinding and pegging lead to incomplete screening and contaminated product, or the need to stop the screen three to four times a day for a thorough cleaning. Each cleaning stops production completely from anywhere between 20 to 30 minutes. Depending on how severe the blinding or pegging issue, if a chain is needed to vibrate the material off, not only do producers need to figure in the cost of shut down, but also the cost of the added wear and potential damage to the screen media. If cleanings must occur four times a day, it results in upwards of two hours of lost production every week. With one tonne of coal priced at approximately US$30 and 250 t processed per hour, that translates to US$15 000 of lost production each week (or more than US$60 000 per month). Over the course of an average year, a coal mine is effectively leaving more than US$720 000 on the table.
Alternative screen media offers a more efficient solution to overcoming the blinding and pegging issue. While traditional woven wire cloth relies solely on the vibration of the screen box to create the frequency needed to stratify the material, high vibration screens are designed in a manner that allows each wire to vibrate independently, enhancing the overall effectiveness and allowing the screen to self-clean. The high frequency vibration produced by the screen wires, virtually eliminates blinding and pegging, erasing the need to pre-wash the coal or shutdown the machines for cleaning. In turn, eliminating that step can also reduce water use and costs, leading to a more sustainable overall process.
To further reduce the chance of material buildup, the high vibration screens offer customisation options using stainless steel wire. While the porous nature of standard wire might attract the coal powder, allowing it to build up and eventually close off the entire opening, the stainless-steel wire combined with high vibration effectively eliminates the chance of material buildup.
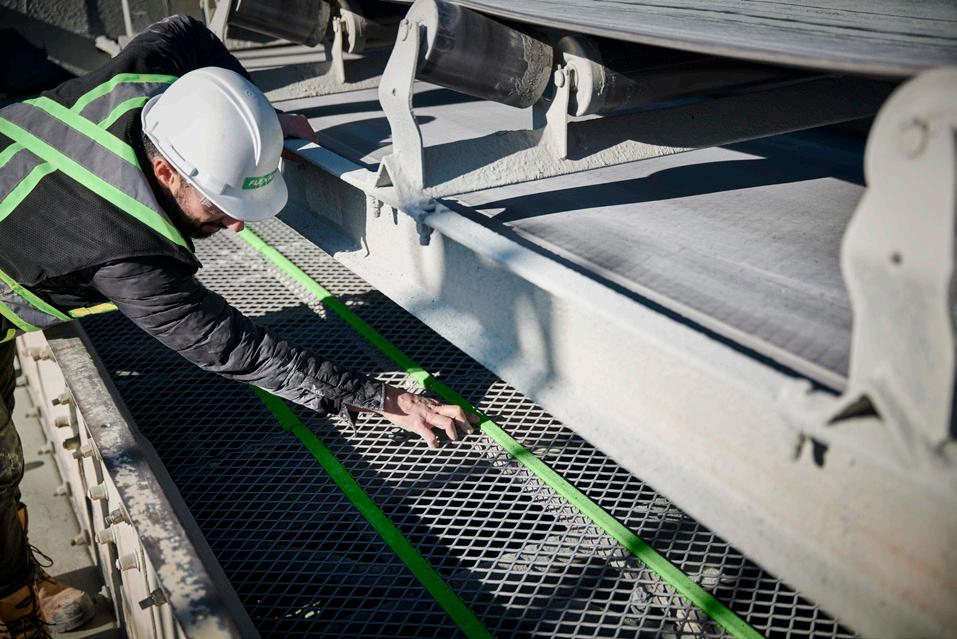
The proof is in production
Often in screening applications, mines focus heavily on reducing the frequency of screen change outs. While both the cost of new media and the time to change out the screen panels can result in significant costs, the significance is often misplaced. Rather than focusing on cutting costs, coal mines would be better served focusing on making money. Ultimately, in achieving higher production, most costs can be offset or completely negated. While traditional woven wire might last more than a year between change outs in coal applications, that should actually be a red flag to a coal mine, alerting them that they are significantly under producing. By switching to a high vibration screen, most coal mines will see an increase of
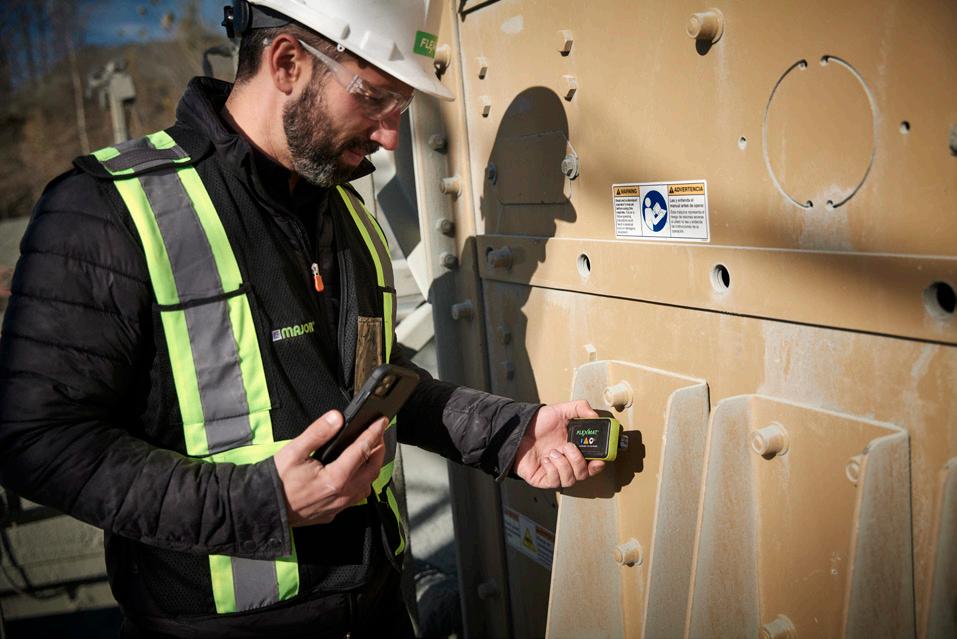
upwards of 40% in production. Though pushing more material across the screens may result in slightly more frequent screen change outs, the revenue generated by increased production and a better-quality product more than offsets the additional screen media costs.
Performance is of course only one aspect of productivity; the other is uptime. Any coal mine knows that the key to successful production is avoiding unscheduled downtime, and instead employing tools to optimise performance and predict maintenance, so it can be completed at scheduled times rather than unexpectedly. One tool some screen manufacturers offer to monitor the health of the screening system is predictive vibration analysis. Predictive vibration analysis, which includes vibration analysis tests, detects miniscule changes in baseline operation before the effects are seen in screening performance and output. Some vibration analysis systems even capture data while the machines are running material. This provides producers with up-to-date information on the machine and operational health, without making sacrifices in production time. Issues, such as improper tensioning or a broken wire, can be identified and remedied through scheduled downtime. The system also gives an indication of how the screening machine is working, allowing operations insight into adjustments or
maintenance on the machine that could help improve productivity.
Building on those benefits of automation and data collection, some screen media manufacturers also embed tracking chips into each screen panel. These chips can be easily scanned to get data on the machine placement, the specifications of the screen, and other relevant data for both reorder and flexibility in changing specs. Rather than worrying about putting screen panels in inventory to switch to a different specification, coal mines know that the data for the placement of the screen is housed in the chip, which can easily be scanned for precise placement when the specifications change again. The data contained in the chip also makes it simple and seamless to reorder screen media.
Making the switch
While the success of a coal mine’s processing is often placed on the screening machine itself, in reality the screen media likely plays a more important role. Progressive mines with a comprehensive and strong understanding of frequency and amplitude, as well as the overall effects of vibration and movement, recognise that the static screen panels of the past simply fail to meet the challenges they face today. As a result, customised high vibration screen media continues to grow as the solution for the myriad of challenges in the coal industry.
Even in severe environments, Richwood belt cleaners provide a real return on investment through increased belt uptime, decreased clean-up costs, low maintenance and longer component life.
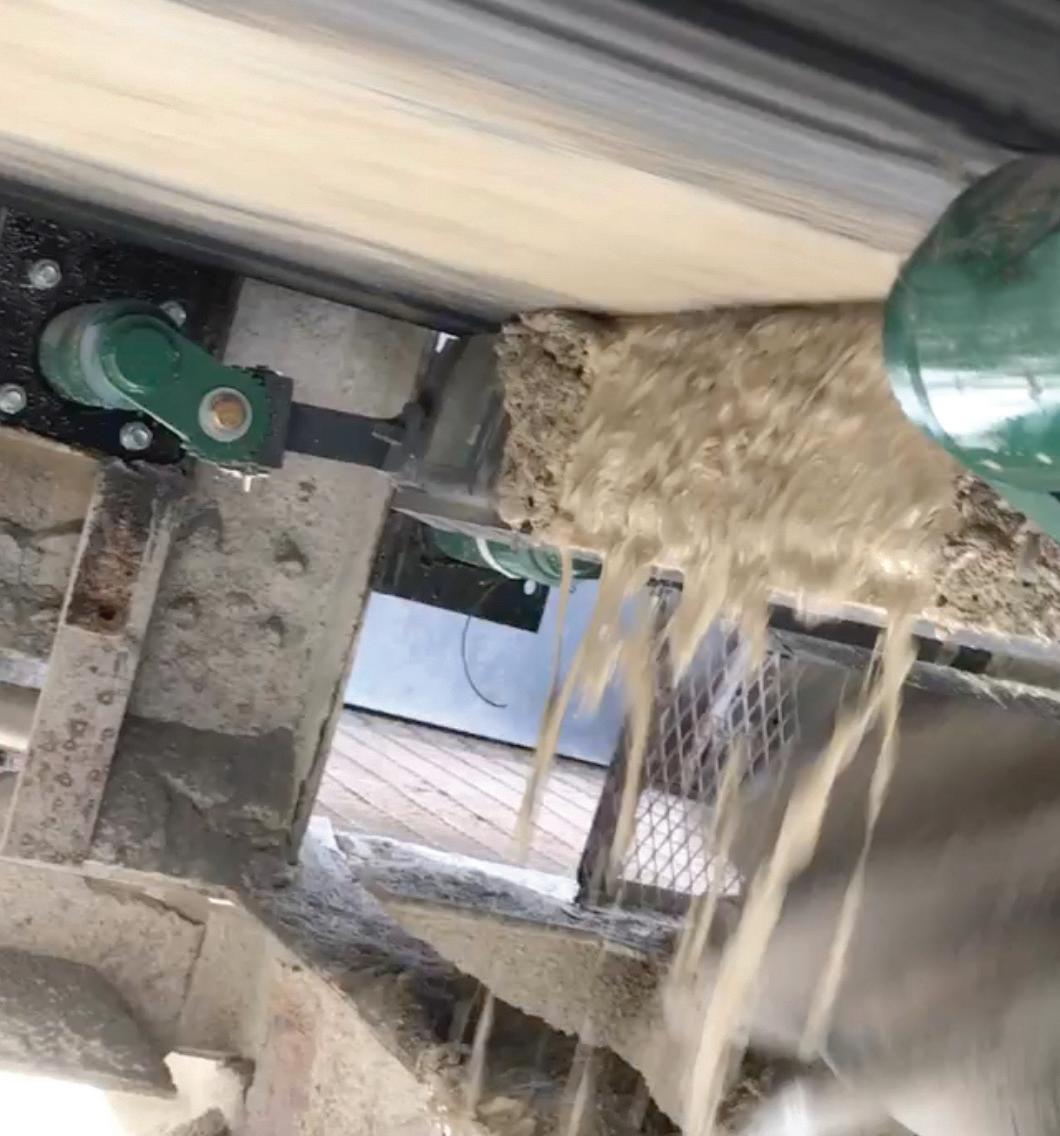
What would it mean for your productivity if carryback issues were eliminated?
Contact Richwood today for an on-site evaluation (304) 525-5436.
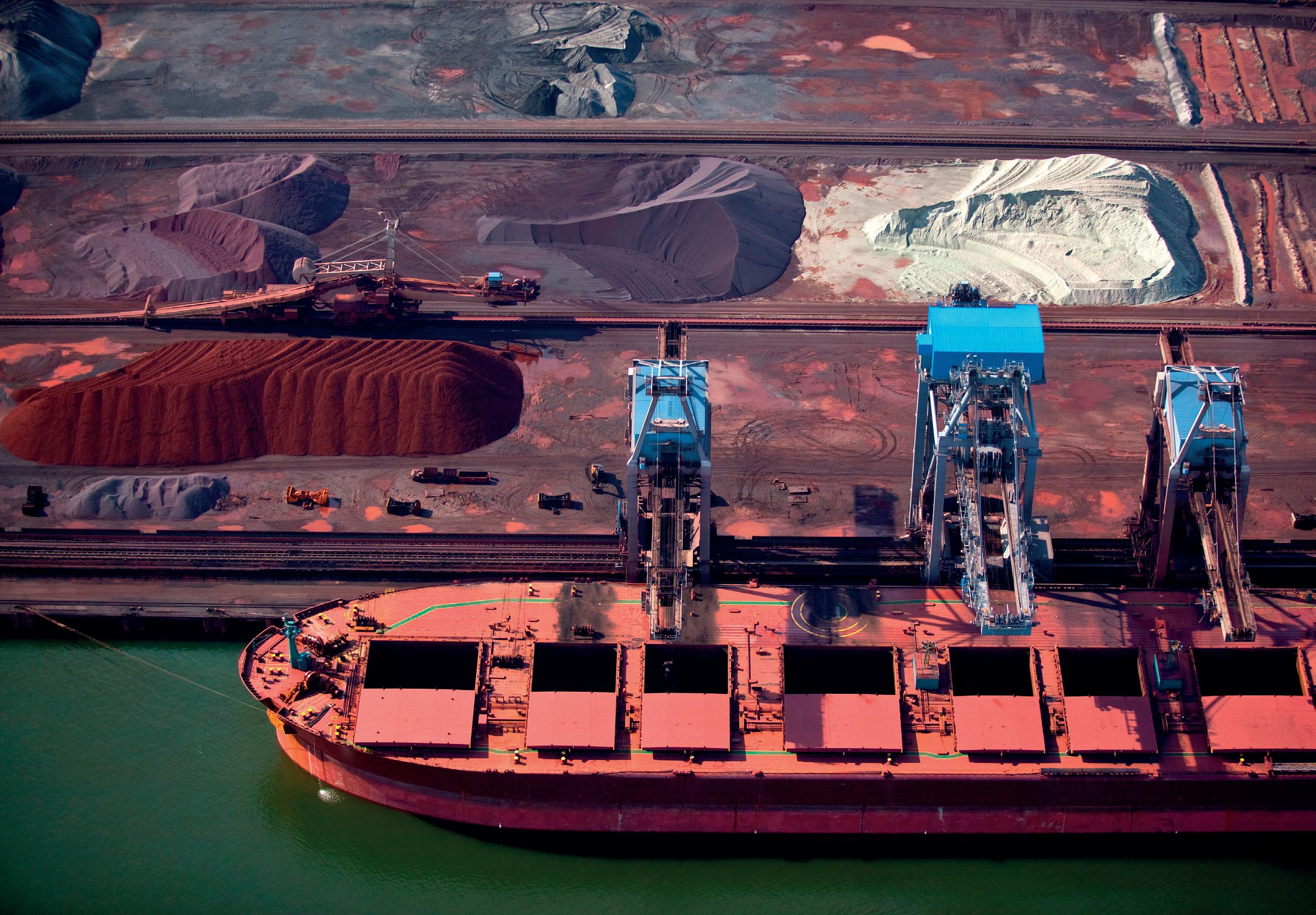
Benjamin Mirabile, Jennmar, USA, reviews the critical role that resin plays in coal operations and how it is essential to all modern ground support systems.
Polyester resin is used in conjunction with nearly all modern ground support systems. Over the past 45 years, the use of resin products in ground support has evolved from a specialised solution for difficult conditions to an everyday consumable in the mining cycle.
Resin was first trialled in European mines in the late 1950s and early 1960s. Coal mines in the US
began using resin anchored bolting systems in difficult ground conditions in the early 1970s. The 1980s saw widespread adoption of resin bolting systems, as the cost of resin became competitive with other ground support products, and bolting innovations, such as #5 rebar, were introduced (Blevins, 2006). While hardrock mining continues to use a substantial portion of friction-based rockbolts, nearly all ground
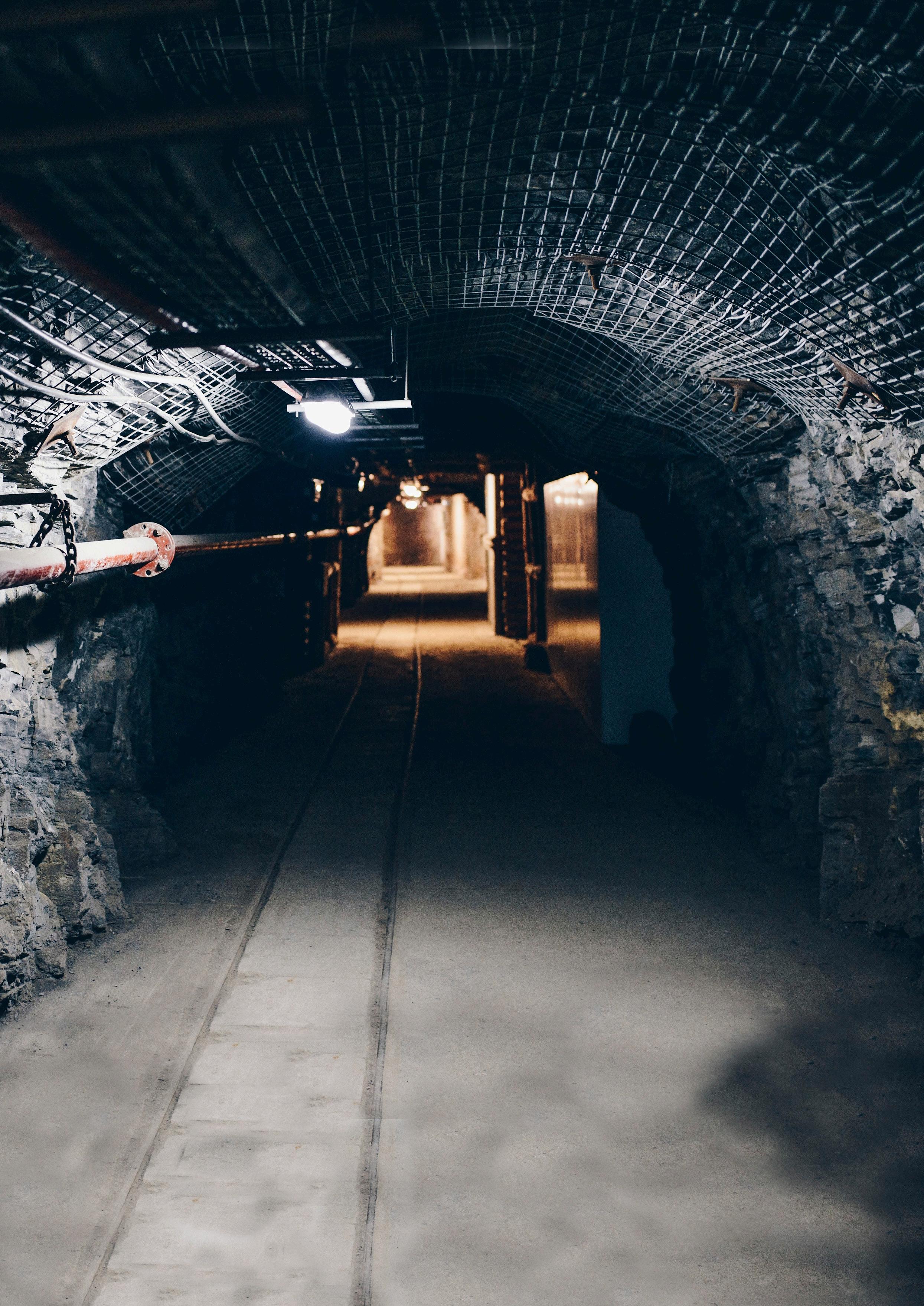
support in modern coal mines uses polystyrene resin for anchorage. Coal mine rib bolting is one of the few applications where bolt anchorage is achieved solely with mechanical anchors on a widespread basis. Successful application of polystyrene resin, like other ground control products, depends on several key factors. These factors include proper storage and handling, proper installation procedures, and utilising the appropriate size and type of resin for a specific application.
Resin overview
Modern polyester resins are supplied to the mining industry as a two-component cartridge system.
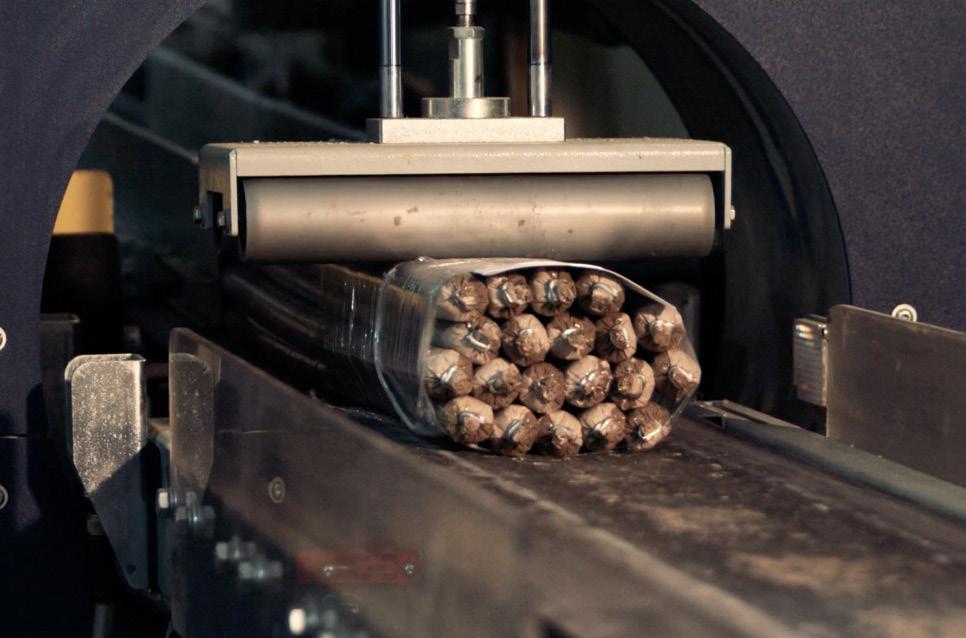
A mylar resin cartridge consists of a resin side and a catalyst side separated by an internal film, in order to prevent the premature reaction of the two components. The resin cartridge is sized to fit in various common borehole diameters, and to provide a specified equivalent grouted length for a given bolt diameter. In the US, resin cartridge size specifications are outlined in ASTM F432-19; in other countries, cartridge sizes are specified by agreement between the manufacturer and customer. In all cases, resin cartridge sizing is based on the volumetric relationship between the rock bolt diameter and the drill hole diameter. While many underground operators will refer to resin cartridges as ‘glue’, polyester resin is not an adhesive. Resin grout relies on friction and mechanical interlock to provide bolt anchorage. Consequently, most rock bolts used in conjunction with resin will have features designed to provide mechanical interlock between the bolt and resin. These features include: deformations on rebar bolts, expansion shells, and bulbs or birdcages on cable bolts.
Resin strength
J-Lok produces water-based polyester resin cartridges in the US. Typical resin/catalyst ratio sold in the US produce laboratory UCS values of up to 60 MPa (8700 psi). Other manufacturers also produce products with similar composition in the US. All of these products meet or exceed standards set forth in ASTM F432-19. Some countries in the EU and APAC regions utilised oil-based polyester resins with a higher resin to catalyst ratio. These higher resin/catalyst ratio resins can potentially produce cured resin UCS in excess of 80 MPa (11 600 psi) in a laboratory environment.
However, the actual in-situ UCS is highly sensitive to installation quality and environmental factors present at the installation site. The bond strength of a resin-grouted rock bolt system is a reliable, easily measurable metric of the effectiveness of a resin grout system. The bond strength can be readily tested at the installation location with short encapsulation pull tests (SEPT). Empirical evidence has shown that the performance of a lower resin/catalyst ratio resin is less sensitive to installation methods and site-specific conditions than traditionally manufactured higher resin/catalyst ratio resins. While lower ratio resins may not achieve laboratory test UCS values, their overall effectiveness as a structural element of a rock bolting system meets or exceeds that of a higher ratio resin system. Ultimately, onsite pull tests are the best methods to qualify a resin product for a specific application in a specific set of conditions. JENNMAR highly recommends that resin systems are designed based on their tested in-situ strength characteristics, rather than laboratory test results.

Storage and handling best practices
A perfectly manufactured resin cartridge will produce unfavourable anchorage properties if it is not stored and installed properly. Most resins have a shelf life of approximately one year when stored under ideal conditions. Ideal storage conditions for resin are in a temperature controlled environment of approximately 16˚C (60˚F), and out of direct sunlight. Indoor storage is ideal to protect resin packaging from precipitation. Nearly all product performance exceptions are a result of improper handling or storage of resin cartridges. Excessive heat tends to separate liquid and solid components, leading to dry, hardened segments inside the resin cartridge. These segments will often prevent bolt insertion into the drill hole through the resin cartridge. Frozen resin can be used after it has thawed. However, the expansion resulting from freezing stretches the mylar cartridge film, making limp cartridges that are difficult to insert into a drill hole. Temperature extremes also affect the gel time of the resin, with higher temperatures shortening the gel time and lower temperatures extending the gel time. Packaged resin on a pallet will take 48 hours or more to stabilise to an ambient temperature.
Installation best practices
There are two major factors that most influence the installation quality of a resin bolting system. These factors are the appropriate volume of resin, appropriate resin annulus, and appropriate duration of resin mixing. ASTM F432-19 specifies the volume calculations for use with most bolting systems in US coal mines. In all applications, it is good engineering practice to provide excess resin volume in case of oversize drill holes or discontinuities in the mine roof. Resin cartridge volumes are often designed to grout boreholes 1 – 1.25 mm (0.040 – 0.050 in.) diameters over nominal size. Resin cartridge volumes also typically account for 25 – 40 mm (1 – 1.5 in.) overdrill.

A properly sized resin annulus is necessary for quality resin installation. This resin annulus is the space between a rock bolt and the drill hole into which it is inserted. With bolt rotation, the shearing action between the bolt and drill hole walls mixes resin and catalyst, shreds the mylar cartridge, and generates heat to promote resin curing. Modern resin formulations have increased the range of optimum bolt/resin annulus size. However, excessively small or large resin annuli can negatively affect the performance of a bolt/resin system. An annular radius of approximately 3 mm (0.125 in.) is ideal. Modern low insertion force resins have allowed
practical application of slightly smaller annular radii. However, excessively small annular radii require excessive bolt insertion pressures and may lead to bolt bending upon installation. Excessively large annular radii do not produce enough friction, shearing, and heat to mix cartridge resin. Further, there is a potential risk of resin glove fingering. Glove fingering occurs when an inserted roof bolt does not rupture or tear the outerwalls of the resin cartridge. The intact mylar cartridge material then introduces a plane of weakness between the grout column and the drill hole wall, negating any mechanical interlock or frictional resistance on the grout/rock interface. Onsite installation tests and short encapsulation pull tests are the best methods to confirm an appropriate resin annulus.
Most water-based resin cartridge systems require approximately 30 revolutions to sufficiently mix the resin and catalyst. Therefore, resin mix time should be based on the rotational speed of the equipment used to install the rock bolts. Overmixing of resin can be detrimental to the resin grout’s anchorage performance. Resin gel time is the time from the start of mixing until the resin begins to harden. This gel time is the sum of mixing time and hold time. The mixed components begin to form chemical bonds during the gel time. If overmixing is allowed to occur during the gel time, the rotation of the rock bolt damages these chemical bonds and reduces the final strength of the resin. Therefore, spin time should be solely based on the rotational speed of the installation equipment. Any adjustments to account for ambient conditions should be applied to the resin hold time. High heat conditions tend to shorten the hold times, while cooler conditions and moisture tend to extend hold times. If installation times are unsatisfactory, the manufacturer can often make adjustments to the product selection to meet most conditions.
Nikhil Kaitwade, FMI, India, outlines how clean coal technologies can help reduce emissions within the industry.
The most prevalent and frequently used fossil fuel in the world is coal, and it always will be. Nevertheless, burning coal causes pollution and releases CO2 – but technologies that use clean coal can resolve this issue. More recently, as a result of the need to reduce growing CO2 emissions to combat climate change, CO2 capture and storage technologies have been included in the category of clean coal technologies (CCT).
In order to increase the environmental acceptance and efficiency of coal mining, the implementation of clean coal technologies are the next phase of advanced coal utilisation techniques. By lowering greenhouse gas
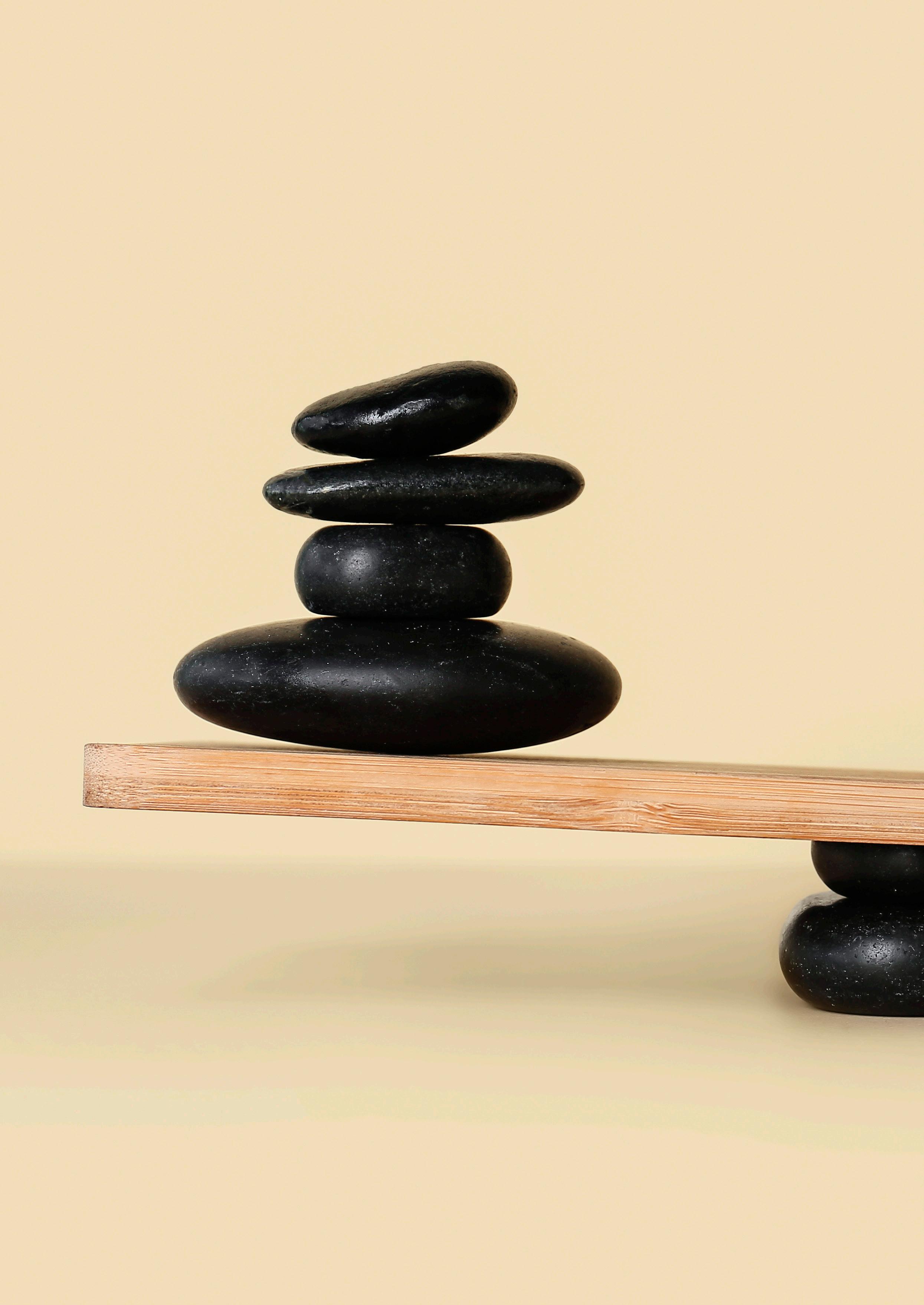
emissions, these technologies aim to diminish the damaging effects of coal energy production on the environment. This article will focus on some of these technologies’ beneficial effects across numerous sectors.
Pristine M technology: A clean coal technology to improve the efficiency of power plants
The gasification technique being developed by US-based CCT, Pristine-M, attempts to improve the effectiveness of coal-burning facilities by 33%, while lowering the environmental impacts. The three-step process used by CCT consists of the following steps: first, mined coal is depolarised,
which drives off volatile residues of nitrogen, oxygen, and hydrogen; second, the coal is left to dry at a temperature of approximately 250˚F to drive off extra liquid; and third, the volatile matter is reincorporated into the pore spaces of the coal in which the humidity was driven off. By doing this, the moisture content in the coal is eliminated without affecting its structural integrity and preventing it from burning effectively to produce energy.
After the coal has been mined, operators utilise the technology to process it, which removes a significant proportion of the water content from the coal. This percentage depends on how much moisture the final consumer wants
to keep in the hydrocarbons, but they can reduce the moisture levels from 30% to less than 5% if necessary, while at the same time reducing carbon emissions by 35%. The coal is cultivated with a heavy hydrocarbon to make it stable and hydrophobic, and to provide a byproduct that is dust-free. Thus, such factors will affect the usage of clean coal technologies in various power plants fired by coal.

Selective catalytic reduction: A technology used to reduce emissions in automobiles
In response to increasing carbon emissions and the rise in other greenhouse gases (GHG) emitted
from automobiles, clean coal technology has proven to be an efficient method to control operator emissions to a great extent. Selective catalytic reduction (SCR) is a state-of-the-art active emissions control innovation system that reduces nitrogen oxide and carbon dioxide emissions from diesel-powered machinery and automobiles to almost zero. The SCR system consists of several pieces that are assembled with other pollution control components within the system. The type and arrangement of various system components varies depending on the manufacturer.
SCR technology is mostly preferred for its cost-effectiveness and fuel-efficient solutions for practically eliminating diesel car emissions. To meet the most recent EPA emissions rules, all heavily loaded diesel truck engines have used SCR technology for a long time. These guidelines call for nitrogen oxides (NOX), as well as particulate matter (PM), to be reduced to almost zero.
SCR can cut NO emissions by up to 90%, while also cutting CO and HC emissions by 50 – 90%, and PM emission levels by 30 – 50%. This SCR system can also be used in conjunction with a particulate diesel filter to reduce PM emissions even further.
Capturing carbon from industrial activities
There are several ways to remove CO2 from industrial gas streams, but none of them have been scaled up to the level needed in coal-fired power plants. Previously, acquiring pure CO2 for industrial use has frequently taken precedence over lowering CO2 emissions from power plants. It is well established that CO2 and methane from wells containing natural gas can be separated in certain situations. There are several procedures employed, such as hot potassium carbonate, which consumes a lot of energy and
necessitates a big plant, a monoethanolamine process, which produces highly pure CO2 and membrane processes. For instance, the vacuum swing adsorption gas separation method is being used for carbon capture in a US hydrogen generation facility.
Solid adsorbents like zeolites, as well as activated carbon, can be used to extract CO2 from industrial gas mixtures as an additional method of carbon capture. In pressure swing adsorption (PSA), a gas mixture is passed over a packed column of adsorbent under high pressure until the proportion of the target gas reaches equilibrium. Lowering the pressure regenerates the mattress. As a result, these techniques collect and isolate the carbon, which may then be used for other industrial processes. As a result, the emissions decrease by approximately 35 – 40%.
Conclusion
Various federal governments aim to introduce new initiatives and programmes that would help different sectors lower their emissions. For instance, the US Clean Coal Power Initiative (CCPI), a new government programme, focuses on reducing pollutants emitted like particulates, as well as mercury, improving technologies that increase effectiveness and thereby cut carbon emissions and other GHG emissions, and also reducing carbon emissions via carbon capture and storage technology.
Other technologies, such as coal liquefaction and gasification, are being researched to develop low-cost, secure replacements for natural gas and oil for use in power production and transportation. With such innovations in the domain of clean coal technology, the world can expect to see some significant carbon emission reductions in the next 10 years globally.
SAFETY, SERVICE, AND INNOVATION
JENNMAR designs and manufactures a wide range of dependable ground control products, from bolts and beams to channels and trusses, resin, rebar, and more. We’re proud to make products that make the mining, tunneling, civil, and construction industries safer and more efficient.
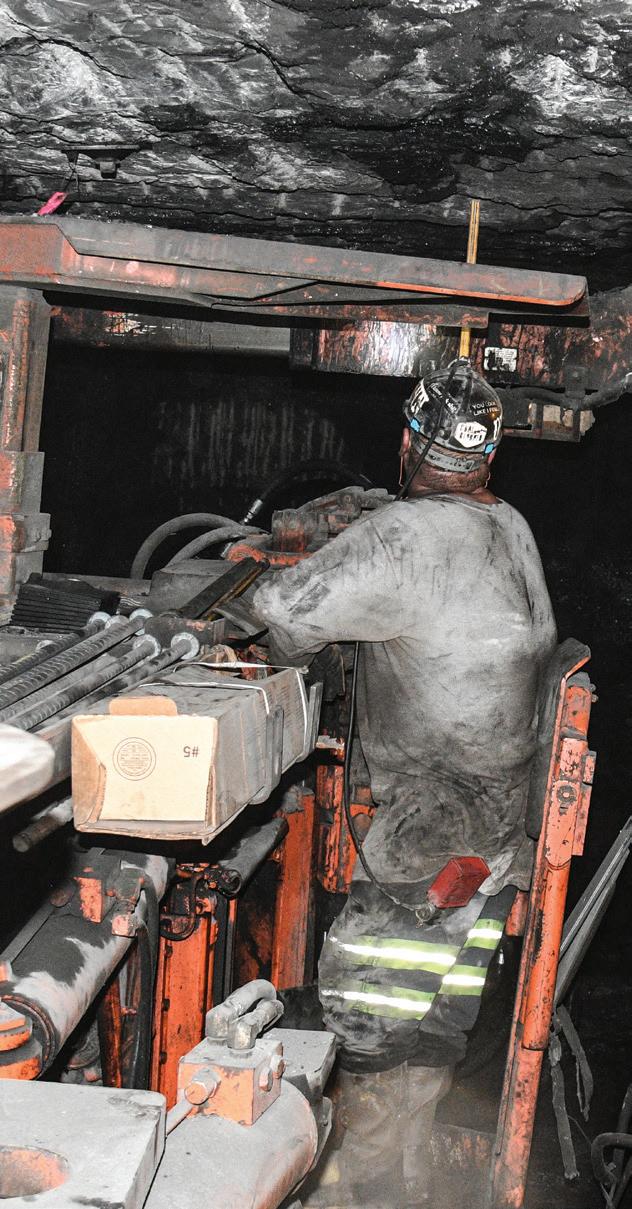
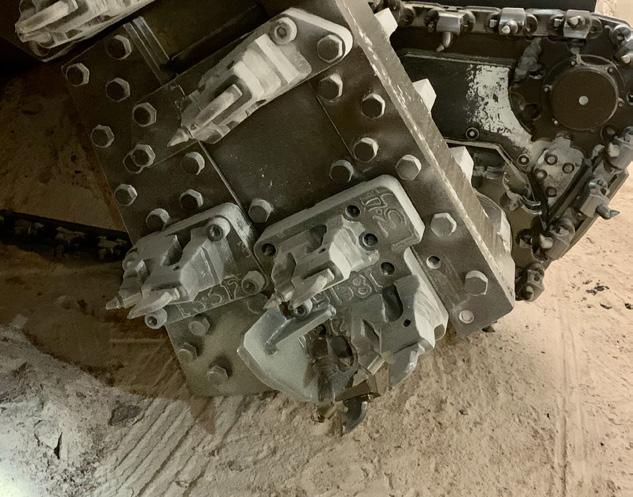
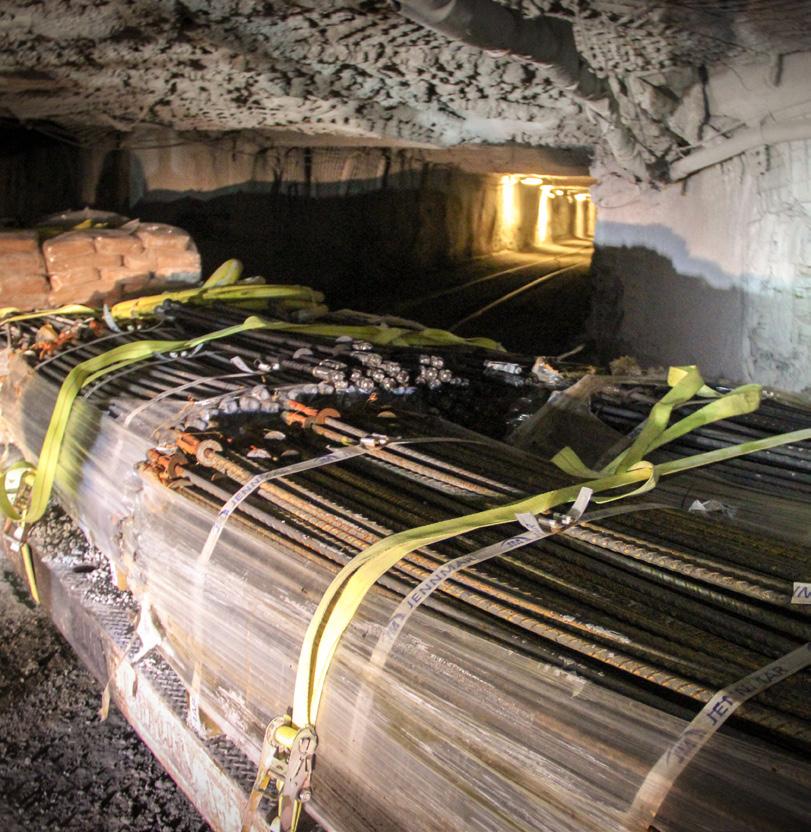
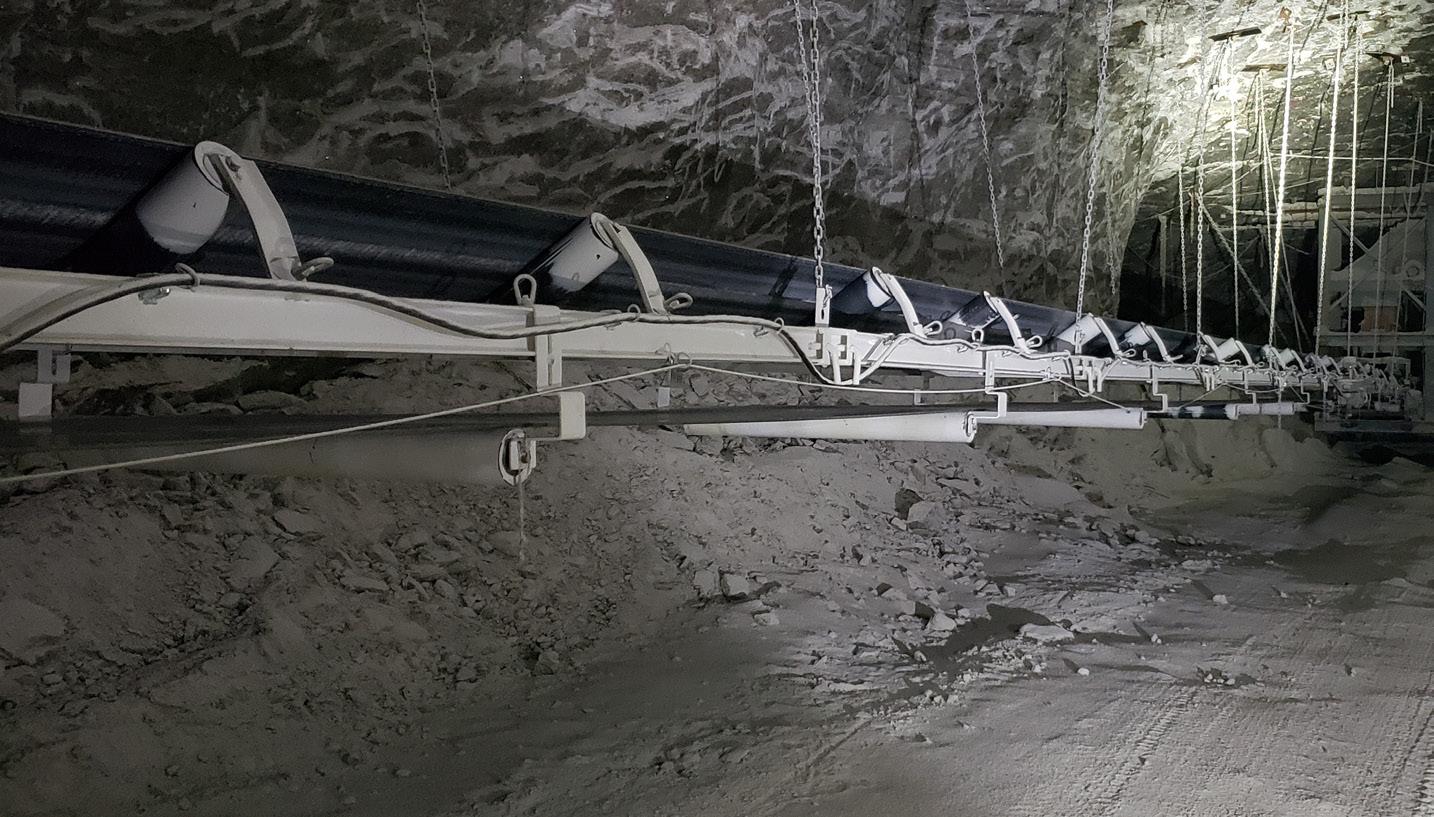
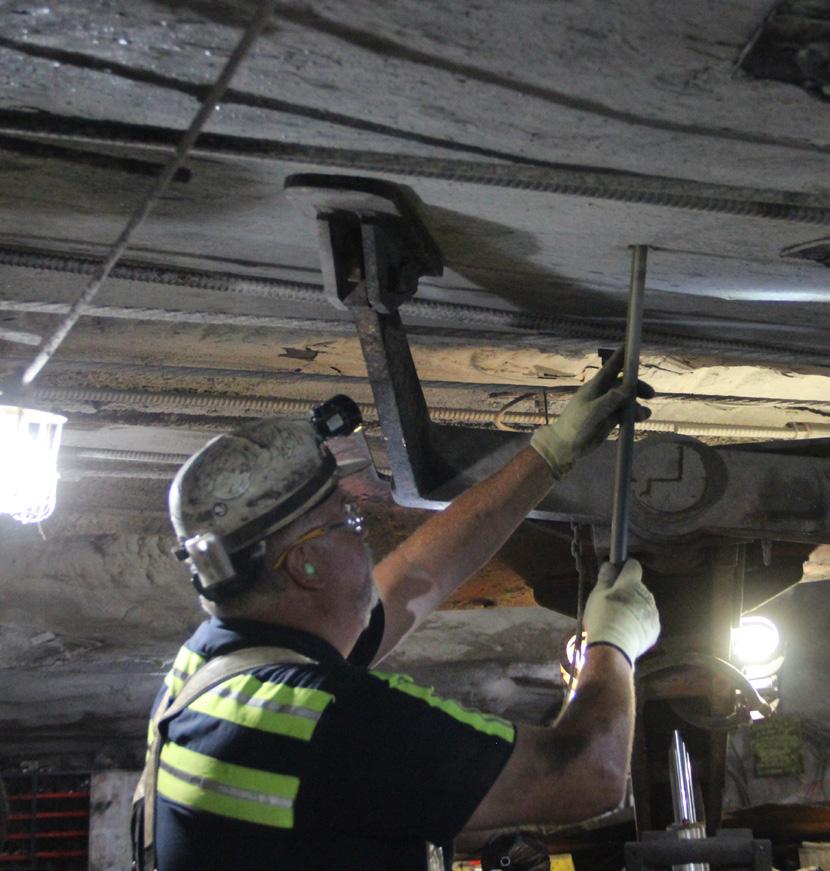
Because we understand the everchanging and demanding conditions above and below ground we have built the richest portfolio of diverse and complementary brands. JENNMAR sets the bar in every industry we serve and as we continue to grow, our focus will always be on the customer.
We feel it is essential to develop a close working relationship with every customer so we can understand their unique challenges and ensure superior customer service. Our commitment to the customer is guided by three words: SAFETY, SERVICE, and INNOVATION. It’s these words that form the foundation of our business.
It’s who we are.
85 YEARS OF SOLUTIONS.
Since 1937, Fletcher has been answering some of underground mining’s toughest questions. At Fletcher we provide more than solutions, we provide an atmosphere for an open dialogue with customers to ensure their operations are reaching maximum efficiency. Fletcher provides lifetime support through an experienced, knowledgable team of sales staff, engineers and field service technicans. Is your operation facing obstacles that mass produced equipment isn’t addressing? Get your custom solution started today. Learn more at www.jhfletcher.com
