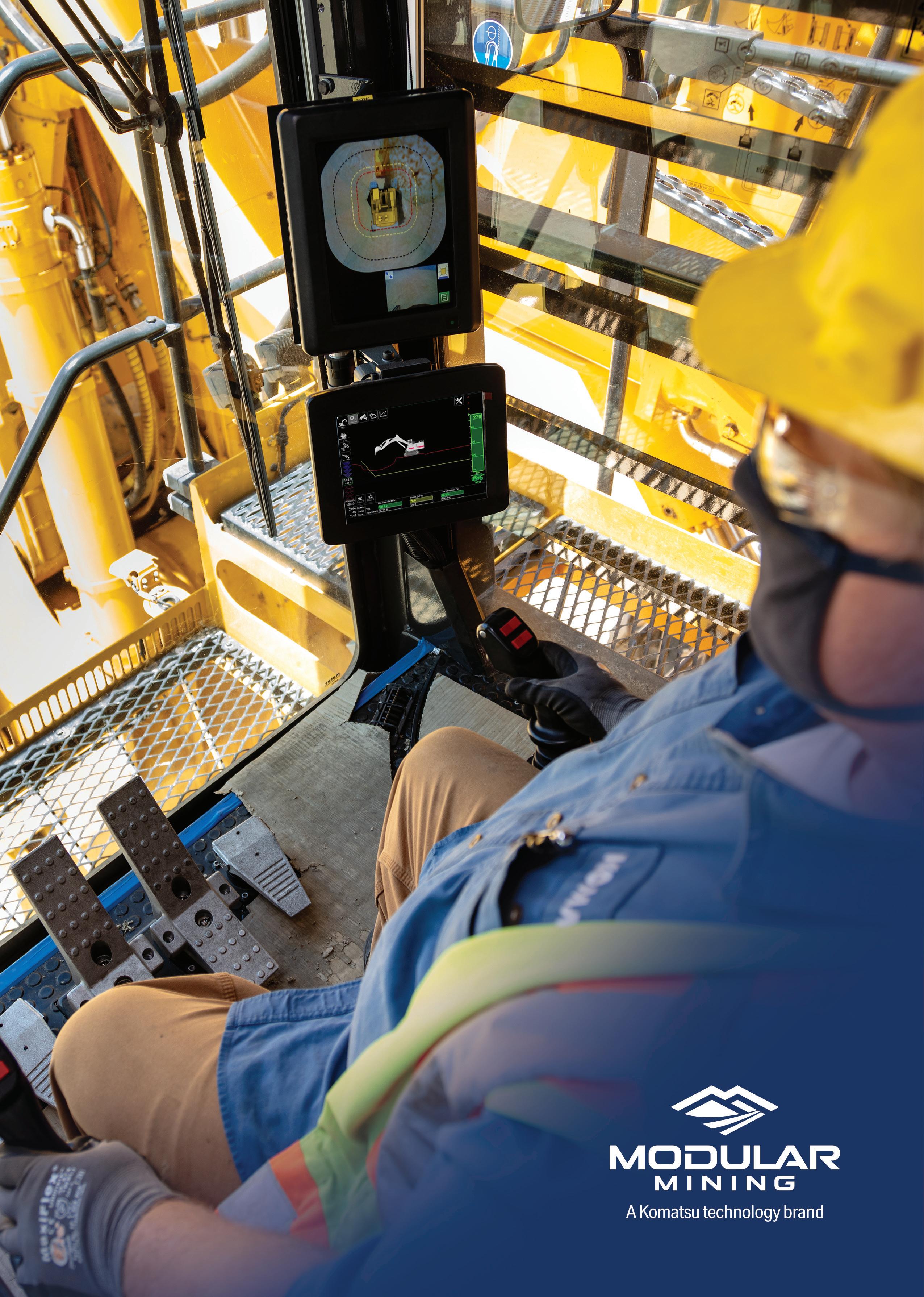

03 Guest Comment
05 World News
12 Optimisation: The Key To Successful Mining
Wesley Taylor, Komatsu, discusses the benefits and prospects of a new payload management solution in a Q&A with Will Owen, Editor of Global Mining Review
17 Operating Like A Well-Oiled Machine
Robert Dura, Jennifer Clark, and Gareth Fish, Lubrizol, USA, consider how choosing the right lubrication technology can prevent unnecessary downtime and component failure in open gear systems.
22 Invest In Uptime
Eric Matson, The Goodyear Tire & Rubber Company, USA, examines how a smart investment in tyres and tyre maintenance can be crucial in maximising uptime.
27 Brushing Up On Dust Control
Greg Bierie, Benetech Inc., USA, explores various technological and innovative solutions that can be used to improve dust control within conveying operations.
31 Overhauling Haul Road Maintenance
Josh Swank, Philippi-Hagenbuch Inc., USA, illustrates some new ways to increase efficiency and safety through haul truck customisations.
35 The Electric Path To Sustainable Mining
Atilson Neto, Vale, Brazil, analyses how the latest innovations in autonomous and electric truck fleets can help decrease emissions and increase efficiency and safety in mine operations.
40 Ensuring The Success Of Mining 4.0
Nathan Stenson, Nokia, UK, highlights the importance of leveraging partnerships - and private wireless - to ensure the success of the next generation of mining.
44 Crafting Clean Mining Technologies
Audrey Beurnier and Bryan Pons, Aramine, France, review the various keys to manufacturing a battery powered machine which prioritises energy efficiency, reliability, and safety.
49 NAA In Copper Mining
Gary Noble, Thermo Fisher Scientific, Australia, explains how neutron activation analysis can be used to revolutionise copper mining operations.
53 Sustainable Water Use
Eric Wasmund and Jose Concha, Eriez, Canada and Peru, weigh the growing importance of technologies in water management, and how it is crucial to achieving sustainable operations.
56 Mine Management From Above
Christopher Thomson, AgEagle, Switzerland, examines how fixed-wing drones can be used as a multi-purpose tool to optimise mine management and safety.
60 Establishing Exploration Excellence
American Pacific Mining Corp. profiles its recent experiences in becoming an established junior miner, and reviews some of the precious and base metals opportunities that are currently being explored in the Western US.
65 Driving The Green Transition With Chilean Copper
Sam Garrett, Great Southern Copper, Chile, provides an overview of Chile’s copper industry and how it is paving the way for a green energy future.
69
Eldur Olafsson and James Gilbertson, Amaroq Minerals, Greenland, evaluate the development of the Nalunaq gold project in south Greenland as it approaches production.
Lindsay Robertson, McCrometer, USA, outlines how choosing the correct flow meter can optimise slurry and tailings management.
dual 1675 hp Tier 4 engines, big 38 m³ shovel size and the Argus Payload Monitoring System, the Komatsu PC7000-11 surface mining excavator is a rare combination of power and precision. Operators can efficiently dig up and load 240 – 290 trucks with intelligent payload measuring technology, visible from the Argus display.
Amplified by COP27, the volume continues to increase on the importance of moving away from fossil fuels towards sustainable sources of energy. In turn, this movement fuels the need for critical minerals to support the burgeoning battery electric vehicles (EV) market.
Demand for these critical minerals is set to soar, with the International Energy Association forecasting that EV demand will require 50 new lithium projects, 60 new nickel mines, and 17 cobalt mines by 2030. The need for robust supply chains, highlighted by the COVID-19 pandemic, is coupled with the desire to unlock China’s grip on the sector, where 90% of rare earths and 60% of lithium are processed. China has been pursuing a critical minerals strategy for many years, but what are the governments of other countries actually doing to catch-up with China and support the requirements of the EV industry?
MANAGING EDITOR
James Little james.little@globalminingreview.com
SENIOR EDITOR
Callum O’Reilly callum.oreilly@globalminingreview.com
EDITOR
Will Owen will.owen@globalminingreview.com
EDITORIAL ASSISTANT
Isabelle Keltie isabelle.keltie@globalminingreview.com
SALES DIRECTOR
Rod Hardy rod.hardy@globalminingreview.com
SALES MANAGER
Ryan Freeman ryan.freeman@globalminingreview.com
PRODUCTION MANAGER
Kyla Waller kyla.waller@globalminingreview.com
ADMINISTRATION MANAGER
Laura White laura.white@globalminingreview.com
EVENTS MANAGER
Louise Cameron louise.cameron@globalminingreview.com
EVENTS COORDINATOR
Stirling Viljoen stirling.viljoen@globalminingreview.com
DIGITAL ADMINISTRATOR
Leah Jones leah.jones@globalminingreview.com
DIGITAL
The loudly trumpeted US Inflation Reduction Act in 2022 has seen the US Government pledge to provide US$7.5 billion in tax credits for EV buyers if their battery uses raw material extracted or processed from the US, from trade partner countries, or through recycling. This has caused a virtual stampede to relocate supply chains to the US, with companies committing over US$13.5 billion worth of investment since it was enacted (more than double the investment in the previous three months).1 This Act also promises to accelerate the long-awaited streamlining of the ‘permitting’ of new US mines.
In Canada, the Government has now launched its critical minerals strategy, which aims to boost the extraction, processing, manufacturing, and recycling of critical minerals.2 The Canadian strategy again recognises the need to streamline the regulatory approval process for new mines and fast-track environmental approvals, combined with investment in new infrastructure (i.e. roads, rail, and ports) to unlock new mineral projects. This boost to the domestic sector has been coupled with an announcement that the federal government would prevent foreign state-owned enterprises from owning and participating in Canada’s critical mineral sector, which was quickly followed by ordering three Chinese groups to divest their stakes in Canadian critical minerals companies, on the basis that these investments posed a threat to national security.
Australia, likewise, updated its critical minerals strategy in 2022, which includes substantial subsidies.3 The strategy also recognises the need to strengthen international partnerships and proposes various initiative in this regard.
The UK Government is not in a position to pledge much to the sector, but instead the UK’s critical minerals strategy focuses on relieving the bottle necks in the supply chain by accelerating what the UK can produce domestically, as well as collaborating with its allies in order to diversify supply.4
Most recently, the European Commission has proposed the European Critical Raw Material Act, which aims to help boost supplies of minerals such as lithium and rare earths – by identifying potential projects along the supply chain, from extraction to refining and processing to recycling – as well as build up reserves.5
The various governments seem to have adopted a common approach: to focus on supporting their own domestic sectors, but also to collaborate with ‘friendly’ jurisdictions to develop and strengthen the much needed critical minerals supply chain. However, given the significant head start that China have gained in the race to secure critical minerals, time will tell whether the profusion of strategies from western governments is too little too late.
1. Reported by Benchmark Mineral Intelligence.
2. ‘The Canadian Critical Minerals Strategy’, Natural Resources Canada, (2022).
3. ‘Critical Minerals Strategy’, Australian Government: Department of Industry, Science & Resources, (16 March 2022).
4. ‘Resilience for the Future: The UK’s critical minerals strategy’, UK Government: Department for Business, Energy & Industrial Strategy, (22 July 2022).
5. ‘Critical Raw Materials Act: securing the new gas & oil at the heart of our economy I Blog of Commissioner Thierry Breton’, European Commission, (14 September 2022).
15 South Street, Farnham, Surrey, GU9 7QU, UK t: +44 (0)1252 718999 // w: www.globalminingreview.com
To support growing demand, Komatsu has begun producing the company’s HM400-5 articulated haul trucks at its factory in Chattanooga, Tennessee. While the trucks were produced in Chattanooga in the mid-2000s, in 2009 production shifted to the company’s plant in Ibaraki, Japan, where it has remained until now.
Used primarily in construction, quarry and mining applications, the 473-HP HM400-5 is designed to move material across challenging terrain while delivering productive, consistent performance for operators of all experience levels.
To celebrate the new production line, Komatsu and the Association of Equipment Manufacturers (AEM) hosted US Represetative, Chuck Fleischmann, along with other local and state officials for a launch event at the company’s Chattanooga plant.
Fleischmann sated: “For years, Komatsu has been a proud member of our Chattanooga-area community, providing hundreds of good-paying jobs and generating a massive economic impact for Chattanooga and Tennessee. Bringing back production of Komatsu’s HM400-5 trucks is another sign of
our strong local workforce, and shows the confidence business leaders have in Chattanooga’s economy and our values of hard work, low taxes, and free enterprise. I am excited that Komatsu is expanding their operations here in Chattanooga and investing in our community.”
Production of the truck has already driven an increase in Komatsu’s spend with local and regional suppliers. Additionally, the new line will offer more opportunities for area students to gain experience in manufacturing. Komatsu’s Chattanooga plant currently has a pre-apprenticeship programme that employs high school seniors part-time, allowing them to earn credits toward a full apprenticeship certification through Chattanooga State Community College.
Rod Schrader, Chairman and CEO, Komatsu North America, said: “We have seen the demand for our HM400-5 trucks grow significantly in both the US and Canada, which is why we began producing the trucks here in the US. The domestic production of this popular truck supports Komatsu’s commitment to jobs and manufacturing in the US, and also enables us to contribute far more to the local Chattanooga economy.”
Barrick Gold Corporation grew attributable proven and probable gold mineral reserves by 6.7 million oz net of depletion in 2022, while maintaining grade despite an increase in the reserve price assumption. Reported at US$1300/oz, attributable proven and probable mineral reserves now stand at 76 million oz at 1.67 g/t, increasing from 69 million oz at 1.71 g/t reported at US$1200/oz in 2021.
Led by Pueblo Viejo and the Africa & Middle East region, Barrick has now delivered a second consecutive year of gold reserve growth over and above annual depletion, with nearly 12 million oz of attributable proven and probable reserve gains in 2022 before depletion.
Successful exploration at both the Lumwana and Jabal Sayid mines has driven the growth of attributable proven and probable copper reserves by 640 million lb, notwithstanding an increase in the annual reserve price assumption to US$3.00/lb. As a result, Barrick replaced 103% of annual global depletion at consistent quality, effectively maintaining attributable proven
and probable copper mineral reserves of 12 billion lb at 0.38% in 2022.
Total attributable gold mineral resources grew by nearly 10% relative to 2021, and total attributable copper mineral resources more than doubled, growing by 124% y/y, both net of annual depletion. This growth was driven by the successful completion of a preliminary economic assessment supporting the Lumwana Super Pit expansion, and the incorporation of Reko Diq following the reconstitution of the project in December 2022.
Attributable measured and indicated gold resources for 2022 stand at 180 million oz at 1.07 g/t, with a further 42 million oz at 0.8 g/t of inferred resources. Attributable measured and indicated copper resources for 2022 stand at 44 billion lb at 0.39%, with a further 15 billion lb at 0.4% of inferred resources.
Mineral resources are reported inclusive of reserves and for 2022, are based on a gold price of US$1700/oz and a copper price of US$3.75/lb.
PDAC 2023
05 – 08 March 2023
Toronto, Canada
www.pdac.ca/convention
CONEXPO-CON/AGG 2023
14 – 18 March 2023
Las Vegas, USA
www.conexpoconagg.com/conexpo-conagg-construction-trade-show
Expomin
24 – 27 April 2023
Santiago, Chile www.expomin.cl
Mines and Money Connect: London 2023
25 – 26 April 2023
London, UK
https://minesandmoney.com/connect
CIMTL23 Convention and EXPO
30 April – 03 May 2023
Montreal, Canada
https://convention.cim.org
Discoveries 2023 Mining Conference
30 May – 01 June 2023
Mazatlán, Mexico
www.discoveriesconference.com
China Coal & Mining Expo 2023
25 – 28 October 2023
Beijing, China www.chinaminingcoal.com
To stay informed about upcoming industry events, visit Global Mining Review’s events page: www.globalminingreview.com/events
Mine Vision Systems (MVS) has entered into a multi-year agreement with Hecla Mining Co. to introduce the FaceCaptureTM mapping system into two of its mines in North America.
As the largest silver producer in the US, Hecla’s rich history includes a consistent focus on applying innovative new practices. FaceCapture will enable Hecla to map and georeference the mine face in real-time, reduce production downtime, and bring higher quality information to its geologists at the moment they need it most.
“Our production, productivity, and safety objectives are directly affected by multiple decisions we make at the mine face every day,” said Matt Blattman, Corporate Director of Technical Services, Hecla Mining. “FaceCapture will allow us to process high quality 3D mine face data in real time, permitting our team to make critical production decisions and with reduced exposure at the mine face.”
“Hecla has over 130 years of experience driving and embracing new and innovative methods to achieve company objectives,” said Mike Smocer, MVS CEO. “We are proud to support Hecla’s culture of innovation and desire to provide better data to key employees when they need it.”
Rana Gruber has selected Sandvik Mining and Rock Solutions to supply a fleet of 19 battery-electric vehicles (BEVs), including trucks, loaders and drills, for its iron ore operations in Storforshei in northern Norway. The agreement underpins Rana Gruber’s aim to operate the world’s first carbon-free iron ore mine by the end of 2025.
Sandvik’s second-largest battery-electric mining fleet to date will include six Sandvik TH550B trucks, five Sandvik LH518B loaders, four Sandvik DL422iE longhole drills, two Sandvik DS412iE mechanical bolters and two Sandvik DD422iE jumbos. Delivery of the equipment will begin during 1Q23 and is planned to continue through 2024. Sandvik will also provide on-site service support and batteries.
Gunnar Moe, CEO of Rana Gruber, said: “We’re proud that our mining operations already have among the industry’s lowest CO2 footprints, but we have even higher ambitions to completely eliminate our carbon emissions. We have a crystal-clear decarbonisation strategy. When we announced our 2025 goal in 2020, many did not believe it would be possible, but we’re taking another major step forward partnering with Sandvik to implement a battery-electric fleet that will improve our work environment and reduce our operational costs. Most importantly, BEVs will help us achieve our ambitious goals for carbon-free mining.”
Moe said Sandvik’s philosophy around batteries and approach to battery safety was an important factor in Rana Gruber’s selection process.
“This is a new world for us but Sandvik has extensive battery-electrification expertise,” he said. “We are already very pleased with our cooperation with Sandvik and their commitment to support our BEV transition, not as a supplier but as a true partner wanting to take the journey with us.”
Anglo American has agreed to acquire a 9.9% minority interest in Canada Nickel Company Inc., which owns the Crawford nickel project in Ontario, Canada.
Anglo American will also provide technology expertise to the Crawford project and has the exclusive right to purchase up to 10% of recoveries of nickel concentrate, iron and chromium contained in the magnetite concentrates and any corresponding carbon credits from the Crawford project. Anglo American’s equity funding will support Canada Nickel’s work to complete the necessary permitting requirements to proceed with development of the project.
The investment is part of Anglo American’s approach to expand its nickel product offering with additional battery-grade nickel for use in electric vehicles, complementing nickel production from Anglo American’s PGMs mines in South Africa, as well as ferronickel from its nickel assets in Brazil, which is mostly destined for the global stainless-steel industry.
Peter Whitcutt, CEO of Anglo American’s Marketing business, said: “As a responsible provider of future-enabling metals and minerals to our customers, we are committed to supporting our
industry in increasing the availability of critical materials that will underpin the success of the energy transition, and to do so sustainably.”
Anglo American will apply its FutureSmart MiningTM technologies to ore samples from Canada Nickel, with the aim of assessing opportunities to improve processing recoveries and reduce the project’s overall energy, emissions and water footprint.
“Our in-depth product knowledge and portfolio of innovative technologies has the potential to provide a value-enhancing contribution to the development of the Crawford project, with the objective of unlocking additional supply of nickel to meet the world’s growing demand for battery technology for electric transport,” Whitcutt added.
Located in a tier-one mining jurisdiction in Ontario, Canada, with optimal support infrastructure, the Crawford project is one of the largest undeveloped, bulk tonnage nickel sulfide resources in the world. If brought into production, the project is expected to play an important role in expanding the available supply of battery-grade nickel.
Hexagon’s Mining division has been awarded an eight-year fleet management project by PT Bukit Makmur Mandiri Utama (BUMA). As part of this project, Hexagon successfully deployed 150 units of HxGN MineOperate OP Pro to BUMA’s IPR site operation in Indonesia with the system optimally running within three months.
The phased deployment covers Hexagon’s fleet management, asset health and enterprise analytics solutions implemented by the Hexagon team on-site from June to September 2022. BUMA was established in 1998 as a family business and is currently the second largest independent coal mining contractor in Indonesia.
Delta Dunia Makmur acquired BUMA in 2009 and has been overhauling it into a more streamlined corporation since. It holds approximately 20% of the market share and provides coal mining services to many of Indonesia’s largest and longest-running names in the coal industry.
Simon Stone, Vice President of APAC, Hexagon’s Mining division, said: “We are looking forward to strengthening
our relationship with BUMA and accelerating their digital transformation journey. Like BUMA, Hexagon firmly believes in safety and efficiency, which makes this partnership and collaboration highly valuable to both parties.”
HxGN MineOperate OP Pro offers opencast mines high-precision guidance for dozers, drills, and loading equipment. The solution improves bench elevations, reduces dilution and decreases rework to improve site safety, efficiency, and profitability. Hexagon’s enterprise integration enables BUMA a single source for reporting and support across their fleet.
BUMA President Director, Pak Sorimuda Pulungan said: “In following management’s Technology Transformation project outline, Hexagon’s suite of integrated products and industry proven technology solutions played a major role in the decision-making process. Hexagon has set the new standard of being a reliable technology partner supported by an expert local team.”
Reducing the number of on-site accidents in a mine is crucial; ensuring that personnel remain safe in both in underground and surface settings is necessary. Becker Mining Systems developed both the PDS4.0 and the smartdetect system with safety and proximity awareness in mind.
Level 9 compliant, and with a full range of attachments, PDS4.0 and smartdetect
have been designed to offer V2V, V2P, and V2X detection solution in one comprehensive and robust package, allowing for upgrades, and simple system modifications, based on the needs of the customer.
With smartdetect and PDS4.0 enabled vehicles; you will never again have to wonder “how close is too close”
Freeport-McMoRan has achieved the Copper Mark at all 12 of its copper producing operations globally. Freeport’s most recent copper operation to receive the copper mark is PT Freeport Indonesia (PT-FI) Grasberg – one of the world’s largest copper and gold mines. In addition, Freeport’s two primary molybdenum sites, the Climax and Henderson operations, were awarded the Molybdenum Mark.
The Copper Mark is the assurance framework to promote responsible production practices for copper, built on the vision of improving practices across the whole industry over time. Its participants commit to fully meet the Copper Mark’s standards within two years of signing up to the assurance process and to continuously strengthen practices as these standards continue to be updated to align with increasing stakeholder expectations on ESG. The Copper Mark seeks to promote transparency and accountability of its participants in general and especially in the case where a participating site manages complex issues that have significant environmental or social impacts. PT-FI Grasberg operates a riverine tailings management system which the Copper Mark recognises as one such issue.
As a matter of principle, the Copper Mark expects participants to manage tailings with the goal of causing zero harm to people and the environment. It requires all participants to review all possible tailings systems alternatives and to implement the
system that is the most aligned with the overall objective to cause zero harm.
In addition, following extensive consultation in 2021, the Copper Mark adopted its interim guidance for tailings management. The interim tailings guidance requires all participants to implement the global industry standard for tailings management, where applicable, and also specifies the expectations for riverine, ocean and lake tailings systems.
The extensive, independent onsite assessment of PT-FI Grasberg confirmed the site’s conformance with the current Copper Mark expectations and standards, including the interim tailings guidance.
The Copper Mark is also developing additional guidance for any participating sites that are identified as having significant long term environmental or social impact issues. Once finalised, PT-FI Grasberg will be required to demonstrate conformance with these additional requirements through on-site third-party assurance.
Executive Director of the Copper Mark, Michèle Brülhart said: “We congratulate Freeport-McMoRan for achieving the Copper Mark at all of its copper operations globally and we are thrilled to see the company continue its commitment to demonstrating its responsible production practices with its two primary molybdenum sites to receiving the Molybdenum Mark.
TrajectorE Engineering has announced the commencement of a new project with Saskatchewan Copper developer, Foran Mining Corp., to support the development of Canada’s first carbon-neutral copper mine located in McIlvenna Bay, Saskatchewan.
McIlvenna Bay is a copper-zinc-gold-silver rich deposit intended to be the centre of a new mining camp and is part of the prolific Flin Flon Greenstone Belt that extends from Snow Lake, Manitoba, through Flin Flon to Foran’s ground in eastern Saskatchewan, over a distance of 225 km. McIlvenna Bay is the largest undeveloped VHMS deposit in the region and has a goal to become a fully carbon-neutral mining producer,
by utilising renewable power sources, battery electric vehicle fleet, and other first-in-kind initiatives.
trajectorE will be leveraging their history of hands-on experience in the mining and mineral processing sector to support Foran in the areas of Operational Readiness and Commissioning.
“We’re very excited to be partnering with the Foran Mining team to help develop what will be a leading example of what sustainable mining looks like in Canada. This project is perfectly aligned with our mission of partnering with Operators to realise sustainable productions,” says trajectorE CEO, Andrew Sinclair.
TotalEnergies Lubrifiants is a leading global manufacturer and marketer of lubricants, with 42 production sites around the world and direct presence 160 countries, delivering more than 600 mines per day. TotalEnergies’ Lubricants division offers innovative, high-performance and environmentally friendly products and services to help mining customers reduce carbon footprint and ensure lowest TCO.
In mining operations today, several buzzwords are frequently mentioned – electrification, sustainability, and decarbonisation – and yet the central theme that ties these factors together is optimisation. The fact is, every facet of mining operations is driven by optimisation, which ultimately affects sustainability and profitability.
Automating everyday operations, such as payload management, can play a big role in advancing optimisation at mine sites. Getting instantaneous, real-time visibility into the amount of material being loaded and moved can help increase operational efficiency, productivity, and utilisation. Miners can gain even more value from payload technology if they are able to integrate it with disparate systems.
The Argus Payload Management system by Modular Mining – a Komatsu technology brand – is a solution that can help optimise efficiency through automation. To learn more, Will Owen (WO), Editor of Global Mining Review, sat down with Wesley Taylor (WT), Automation and Surface Mining Product Manager at Komatsu.
Modular Mining and its suite of mining technology products, such as Argus, have been around since 1979. Aside from its notable track record, what differentiates Argus from other technologies in payload management?
One of the most notable things that Argus does is use a common strategy for all types of loading equipment. We talk about the importance of capability, user interfaces, features, etc. – with Argus these all can be shared across different loading tools. This allows operators to transition from one piece of equipment to another while retaining a very comfortable, easy-to-use interface with the same amount of information and knowledge.
Being a Komatsu brand and company, Modular Mining works with the factory teams that design some of our loading equipment – such as our electric wheel loaders and electric rope shovels. This collaboration enhances Argus’ accuracy and features when used with Komatsu equipment. It combines the feel of working with a third party with the strength of a true OEM backing.
Additionally, a software package is available with the Argus suite called mRoc. mRoc can add an immense amount of value, even outside of the operator in the chair. mRoc enables production and maintenance managers to evaluate the efficiency and operation of the loading equipment in action.
Thus, mRoc provides two significant capabilities, both in the operating chair and in the back office, all from one Argus product.
What are the unique ways in which Argus offers solutions to some of the day-to-day challenges of payload management at mine sites?
Load and haul optimisation is a pretty big buzzword in the industry right now, and this remains true for Komatsu’s big mining customers. One of the biggest challenges is also an opportunity: the wealth of data that can be generated from loading equipment haulage, especially in mixed-fleet operations.
Taylor, Komatsu, discusses the benefits and prospects of a new payload management solution in a Q&A with Will Owen, Editor of Global Mining Review.
It can take a great deal of workforce effort to consolidate, analyse, understand and verify this data, prior to implementing optimisation or process changes.
The exercise of checks and data analysis could require the attention of an entire team or department. However, this is one of the exceptional things that the mRoc software can handle. mRoc takes all of the rich loading and cycle data, organises it, analyses it and saves it all in one place in micro and macro level data sets, making it easy for the customer to evaluate the operational efficiency of their machine now and in the past.
Again, it is worth noting that it does not matter if it is a Komatsu loading tool or CAT – the same metrics and KPIs are generated by Argus. This results in a streamlined process and a large portion of the legwork being completed automatically for the customer, without the need for a large data-management infrastructure.
What are the current trends in payload compliance? How is it changing? How does the Argus solution enhance payload compliance?
Payload compliance can be split into two critical factors. One is loading optimisation – i.e. making sure that the maximum possible number of tonnes are being moved –and the other is ensuring that equipment safety and reliability thresholds are not exceeded.
Overloading a loading or haulage tool can lead to repair costs and other factors that could affect a customer’s profitability. You want to load as much as possible without loading too much. On the other hand, you do not want to underload either. Efficiency and optimisation are key when it comes to payload compliance, and this is what that the Argus solution does very well.
Argus’ ease of use really helps in this situation. Again, the commonality of the user interface, in addition to the alert operators receive when they are close to overloading, helps operations run as close to the optimal efficiency and capacity of their machines as possible.
Are there technologies available that can benchmark and help make continuous improvements in productivity? How does Argus promote payload performance for each operator?
Argus is a foundational technology that benchmarks what a customer could do when it comes to optimising their load and haul processes. It tracks all the relevant data – from the equipment loading a truck to the truck being loaded – and consolidates it into the mRoc platform, which then contextualises it for the operator in the chair.
When customers begin to integrate automation into their operations, they will not always know exactly how many tonnes per hour a machine is moving or how efficiently their fleet is being loaded. Adding technology, such as adaptive controls, can increase customers’ operational awareness and help them understand the level of productivity that could be achieved.
How flexible and scalable is Argus to meet the needs of operations of different sizes?
If you have aging equipment or trucks and new trucks coming in, the Argus’ truck-tracking modules can fit onto both without issue. The module (through mRoc) is also flexible through the use of its truck grouping function. Grouping is via make/model/tray size. Each truck KPI can be individually set if required – i.e. two haul trucks of the same make and model, but with different tray capacities, can be set. This is left in the capable hands of Modular Mining’s customer support team, allowing customers to flex the system out as far as they want it.
Argus’ easy installation is another big factor when it comes to utilising it on equipment and maintaining it. Modular Mining has ability to do remote maintenance. From that standpoint, we work with our customers to make sure that no matter how big their fleet, how large their potential market or where they are located, we can provide global installation support and knowledge. With this in mind, I do not really see a limit.
Can you outline some specific examples of where Argus has optimised overall payload management?
MDG finds the best technological solutions for Customers specific needs, proposing itself as “one source solution”, while offering Engineering, high-quality Manufacturing and mechanical handling Services
We have a couple of case studies available on our website, most notably an oil sands mine in Canada.
In this case, the mine sought to move more material while increasing payload compliance on its fleet of three CAT 495 electric shovels. The payload system it previously used relied on truck onboard scales to relay information to their fleet management system. These scales were often inaccurate – due to re-weighing the truck after it had left the pit (resulting in unexpected payload increases or decreases post load), difficult scale maintenance schedules, etc. – or often did not function at all.
In addition, the majority of the mine’s fleet of CAT 797 trucks are leased. As part of the leasing agreement, the mine is fined any time a truck weighs in over 120% of payload capacity. Given the inaccuracies mentioned above, the mine was experiencing > 120% payload events on a regular basis. It was threatened with millions of dollars in fines, as there were no other payload measurements to refute the scales.
Within a few weeks of Argus being implemented, operators became more aware of how their load distribution looked in terms of the shovel productivity and haulage. One of the biggest improvements to result was a 6% increase in productivity. Argus helped tighten payload distribution and minimise excessive overloads. Within this, some of the tails, the underloads, became more efficient as well. These performance improvements are a clear example of greater optimisation bringing about improved efficiency.
There is also a safety and a sustainability aspect to this case. Fewer overloads lead to less equipment damage. This leads to fewer repairs which, importantly, reduces the time people spend carrying out maintenance and repairs. Fuel and emissions savings can also be achieved when loading is completed with greater accuracy. When operators are better at hitting optimal loading targets, trucks can be sent on their way more quickly without needing to make additional, unnecessary passes.
Are there any other examples you can cite where Argus has improved payload management?
We have another case study from a coal mine in North America. One of the most unique aspects of this mine was its mixed fleet of four P&H4100 overburden shovels and a mixed haulage fleet of Liebherr T282s, Komatsu 960s, and Komatsu 930s. The mine sought to optimise the load and haul operations of its fleet of shovels after payload performance plummeted, with only 40% of loads falling within the acceptable payload range. Operator performance issues, ineffective payload management tools, and costly delays in payload feedback to operators contributed to this result. The mine wanted to optimise its load and haul operations by improving operator performance, truck compliance, and production – all while reducing costs.
The Argus kit’s mixed fleet tracking capabilities were essential in this scenario. Not only can Argus work with mixed fleets in terms of loading tools, but it can track mixed truck fleets as well. The benefits of Argus in this case became apparent quickly. Shovel operator performance improved after four weeks by 6.5%, delivering impressive advantages in productivity and haul fleet efficiency. The site increased its average truck loads per hour and moved more tonnes per day, resulting in a production increase equivalent to gaining two entire trucks. In other words, if the site removed two of its existing trucks it would maintain current production output while saving approximately US$3 million/yr based on current commodity pricing.
What does the future hold for Argus?
WT
Argus is a foundational technology for future-generation optimisation: increasing productivity, safety, sustainability, automation, etc. With the growing ease of collecting data from equipment, we are seeing increased opportunity for Modular Mining to help analyse data and produce reports that our customers can use at an enterprise level. Machine data will continue to help workers on the ground understand how their equipment is performing, but with Argus, management in local or global offices can see it as well.
Implementing Argus helps the full command of mining operations to better use and leverage site data to improve the wider enterprise. To me, that is the exciting thing, seeing what customers can do when they have access to this level of detail from their equipment. This insight can quickly lead to the promotion of better optimisation and efficiency across operations. I am excited to see what the future holds for Argus and what technology it will help benchmark next.
Robert Dura, Jennifer Clark, and Gareth Fish, Lubrizol, USA, consider how choosing the right lubrication technology can prevent unnecessary downtime and component failure in open gear systems.
Mining operations around the world depend on complex systems working in harmony to deliver maximum efficiency and profitability. Within the mining industry, many applications depend on open gear configurations due to the significant stress and harsh working conditions they experience. Mining draglines, rope shovels, and grinding mills are just a few examples that rely on properly maintained and safely operating open gear systems to ensure effectiveness.
As important as the open gear system is itself, the lubrication used is equally critical to the system. Open gear systems must contend with a wide variety of harsh operating and environmental conditions, necessitating high-performing lubrication that enables long-term reliability and performance. Open gear systems vary in size and can be up to 90 ft (27 m) in diameter. Gear systems this large typically take up to 12 months to manufacture, and, due to the increased cost of most metals today, can easily cost over
US$1 million to produce. Thus, extending the life of and reducing the damage done to these gears is extremely important for the continued function and life of the system.
Insufficient or improper lubrication can result in machine downtime, requiring costly maintenance and lost production. For example, replacing the swing rack on a mining rope shovel and returning it to full production after gear failure takes between 100 – 150 hr on average. And, since lost production time has the potential to cost a mining operation as much as US$175 000/hr, using the wrong lubricant simply is not worth the risk.
Given the cost associated with equipment failure, it is imperative that mining professionals make the right choice when selecting a lubricant for open gear systems. Recent advances in open gear lubricants (OGLs) help ensure even higher performance for increasingly reliable, long-term operations. To provide high-performing lubricants, new unique performance polymers (UPP) have been developed to solve many of the challenges inherent in today’s open gear systems, which directly translates to benefits in the field.
UPPs comprise a versatile class of compounds with unique architectures that offer thickening efficiencies, low-traction
coefficients, and high shear stability. UPPs can be used to optimise the lubricant depending on what types of performance attributes are required in the end-use application. They also exhibit excellent temperature and thermal stability — ideally suiting them for the rigorous demands of the mining industry.
Through testing, it has been found that UPPs can enhance the performance of finished fluids by lowering the traction coefficient and operating temperature, while increasing overall efficiency. These advantages have been demonstrated in extensive laboratory testing, and translated well to studies in the field.
The cooler industrial gears are when they operate, the longer their life spans will be. OGLs formulated with select UPPs can effectively reduce operational temperatures of the open gear systems, which contributes to longer-term reliability in the field.
Higher operating temperatures are known to cause issues for lubricants formulated with lower-quality oils, as it subjects them to oxidative degradation, which often leads to film durability issues. Since a lubricant’s primary objective is
Make sure your next mining body delivers extraordinary productivity and service life. Hardox ® 500 Tuf combines the hardness of Hardox ® 500 with the toughness of Hardox ® 450. This wear resistant steel is also tough enough to perform as a structural steel, allowing for stronger and lighter mining dump bodies.
15%
LONGER WEAR LIFE
Hardox ® 500 Tuf wear steel delivers a 30% longer service life than an ordinary AR450 steel or…
30% LIGHTER …save 15% or more weight in a mining dump body to reduce fuel consumption and CO2 emissions.
100%
GUARANTEED
Guaranteed flatness, thickness, and bending performance, making fabrication more reliable and minimizing waste in production.
Learn why Hardox ® 500 Tuf makes extraordinary mining equipment.
www.hardox.com
to provide protection, and elevated temperatures typically compromise that ability, the right chemistry must be carefully selected. With the appropriate chemical formulation, the lubricant is better able to resist heat-related breakdown, ultimately preserving its protective capabilities over extended run intervals.
As mentioned previously, a lubricant that runs cool lasts longer. Testing performed by Lubrizol (as detailed later in this article) has shown that if an OGL can reduce an open gear system’s working temperature by just 10˚F (6˚C), it can help reduce total lubricant consumption by approximately 30%, helping operators not only protect their equipment, but also reduce their environmental impact through reduced water consumption for cooling.
Remember, gear failure resulting from a degraded lubricant can cost significant time, money, and labour to rectify before the machine can be made fully operational again. Enhanced temperature control can help extend equipment life beyond ordinary expectations in harsh mining environments.
With a keen understanding of the threat that high heat can pose to open gear systems, Lubrizol set forth to design and validate a lubricant formulated with a UPP, in order to reduce operating temperatures and better protect bearings, while also improving overall operational performance.
In a controlled laboratory setting, a series of different OGL formulations were tested to compare performance and draw conclusions about the capabilities of UPPs. In both grease and fluid formulations, conventional mineral-based oils, synthetic oils using polyalphaolefin (PAO)-based formulations, and formulations enhanced with a specifically designed UPP were compared.
The results were as follows:
To simulate gear performance, an FZG test machine was used. Specially designed gears were loaded against each other under a series of stages and run for 21 700 revolutions or until scuffing occurred. In this study, the following were used:
n Conditions: FZG A/2.8/50.
n Gear type: FZG A = A.
n Pitch line velocity: 2.8 m/s (550 ft/min.).
n Starting temperature: 120˚F (49˚C).
Initially, the primary objective was to evaluate through FZG testing to see if there was an operational temperature difference among the product types and identify which sample consumed the least amount of energy. The conventional mineral-oil-based sample was used as a baseline.
After FZG evaluation, solid evidence was found that OGLs formulated with UPPs achieved the goal of reducing operational temperatures:
n UPP OGL ran 38˚F (21˚C) cooler than the baseline mineral OGL.
n UPP OGL ran 27˚F (15˚C) cooler than the PAO OGL.
n PAO OGL ran 10˚F (6˚C) cooler than the baseline mineral OGL.
The testing protocols for fluid formulations were very similar to the grease tests. An FZG A/8.3/90 study (8.3 m/s [1630 ft/min.]) pitch line velocity and 194˚F (90˚C) starting temperature was executed to examine a mineral OGL, a PAO OGL, and a UPP OGL over 12 load stages using the same samples. Once again, the objective of this testing was to evaluate if there was an operational temperature difference among products, and which sample consumed the least amount of energy. The mineral OGL was used as a baseline material.
Again, evidence was found that the UPP OGL offered significant temperature reductions. Here, the PAO-based OGL offered good temperature reduction versus the mineral-oil-based OGL. However, the UPP OGL ran 27˚F (15˚C) cooler than both the mineral and PAO OGLs. In addition to the temperature reduction, employing a UPP has also been shown to provide significant energy savings compared to PAO and mineral-oil-based formulations (Figure 3).
Research has shown that OGLs formulated with specifically designed UPPs can offer reduced operating temperatures and efficiency gains. These attributes make lubricants formulated with UPPs ideal for the demanding nature of open gear systems that major mining operations around the world depend on.
In order to achieve new operational benefits, operators should work with lubricant suppliers to investigate modern OGL formulations with UPP technology. In critical mining applications, it can mean the difference between success and failure.
Mines generate loads of digital information, and smart miners are using it to make better sense of their operations. It all starts with connectivity provided by IWT’s SENTINELTM System, an integrated communications solution that improves miner safety, enhances e ciencies and transforms job site data into actionable intelligence.
The search for uptime inevitably leads to a focus on tyres, because nothing rolls in business without them. As such, the investment in tyres is substantial enough that long-gone are the days of just ‘letting it ride.’ Today, companies are investing in technology that makes tyres perform better and building the service and support structure to help maintain their tyre investment. The opportunity to increase uptime can maximise benefits for a business, but means it needs the right partners to keep up with industry improvements and future developments. The mining industry has been an early adopter of impactful, innovative technology, and it continues to be the workshop for further development in key trend areas that will improve the longevity and impact of the mining industry for years to come.
For many in the mining industry, tyres are essential to the operation of the vehicles used on the job. Tyres also represent a substantial investment, in both up-front capital and ongoing maintenance. Evolving technology is improving performance of today’s OTR mining tyres in meaningful ways.
Today’s modern mining tyres are made of components that use advanced technology. The combination of components are selected to achieve the desired performance at a particular site. A tyre fit-for-purpose will use the right components, working as a holistic system to deliver what Goodyear calls ‘performance power’. The blending of technology in the tyre components is what makes today’s mining tyres unique. At Goodyear, the most important components of a tyre are broken down into three main areas: tread design, compounding, and sidewall construction. Here is brief look at each component:
To the untrained eye, most tread designs look similar, and many might assume they all perform in similar fashion. The truth, however, is far more complex and current tyre technology plays a big role in the performance of a selected tyre, especially in the mining industry. To understand the impact of a modern
Eric Matson, The Goodyear Tire & Rubber Company, USA, examines how a smart investment in tyres and tyre maintenance can be crucial in maximising uptime.
tread design, a fleet manager should first take a close look at what will be underneath the tyre.
A tyre’s underfoot condition will help determine the tread design that should be used. If the underfoot condition is soft, a tyre with a shallow tread depth might be in order. If the underfoot condition is rocky, a tyre that has deeper tread depth might be preferable. When evaluating underfoot conditions, the job site should be searched. Are other areas free of debris that can cut into tyres? How are surfaces manicured? Are there things that can be done to boost traction? Are machines required to navigate curves or steep inclines and declines? If in doubt about any of these factors, a qualified tyre technician should be consulted.
Although not visible to the naked eye, rubber compounds are a foundation of good tyre performance. Compounds comprise various formulary ingredients that can be adjusted to provide
certain performance benefits. Many compounds are found in a standard mining tyre, from the crown of the tread to its casing, and they interact with one another while the tyre is in operation. Like tread designs, rubber compounds – and their unique technology – can help meet performance requirements presented by different underfoot conditions. For example, machines that operate in severe service conditions can benefit from tyres that offer enhanced cut resistance. To achieve the desired feature, certain additives can enhance tread compounds, thus increasing a tyre’s ability to defend against cuts and improve scrub resistance.
Sidewalls are where the tyre gets its strength and today’s tyres use a mix of technologies to ensure a tyre can deliver performance when on the job. The sidewalls help support the tyre so it can carry the vehicle’s load and can play an important role in maintaining equipment stability. However, heavy loads
can cause sidewalls to bend. This can expose more of a sidewall’s surface area to rocks and other debris. Sidewalls that feature increased thickness, special compound technology, and/or added reinforcements can help reduce sidewall bending or deflection, which can cut down on a tyre’s exposure to potentially damaging objects on the ground. As electric vehicles begin to play an important role in the mining industry, sidewalls play an important role in managing the extra weight of batteries and absorbing the stress of additional torque. Sidewalls are also an important part of the tyre’s casing and should be built with longevity in mind, so retreading is an option to maximise the investment in a tyre and lengthen its overall service life.
The benefits provided by tread designs, compounding, and sidewall construction can be quickly negated by poor
tyre maintenance. Because tyres are a significant investment, it makes sense to take steps to optimise their performance and longevity. Since needs vary from customer to customer and site to site, Goodyear recommends a tailored tyre maintenance programme to help maximise tyre investment. A balanced maintenance program should include tyre inspection, performance tracking, and data analysis for actionable insights and reporting.
Daily inspection of tyre inflation and wear should be cornerstone of any maintenance programme. Maintaining proper inflation levels is one of the most effective practices that a mining operation can employ to help achieve enhanced tyre performance and longer service life. Correct, consistent inflation can positively impact tyre wear rates and help reduce the amount of fuel mining machines consume. Inflation checks are recommended as part of every pre-shift inspection, or typically, at least once a day. Goodyear offers a solution for mining applications that delivers up-to-the-minute information regarding key metrics on a fleet’s tyres. Goodyear TPMS Heavy Duty (HD) is designed for both fleet managers and operators ensuring that service needs can be addressed in near real time to keep business running. The TPMS HD predictive algorithm allows for fleets to be proactive and plan for upkeep and replacement. Regular monitoring and data collection can help avoid common over and under-inflation of a fleet’s tyres. Over-inflation can lead to premature and/or uneven wear. Under-inflation can cause tyres to flex more and forces engines to work harder. Overloading is another condition that can have a detrimental impact on sidewall durability and impact tyre performance.
In addition, a tyre maintenance programme should ensure tyres are not mismatched around the vehicle. For improved performance, it is best to stick with very similar diameters, tread patterns, tread depth, and tyre construction – whether radial or bias, but never mixed – regardless of application or axle. This practice can help reduce the incidence and rate of tyre wear.
It is also recommended that mining operations work closely with a qualified tyre dealer to implement a comprehensive OTR tyre management programme. A qualified dealer can evaluate existing maintenance programmes and offer suggestions for improvement, including the deployment of specific tyre management solutions, such as Goodyear’s EMTrack OTR tyre performance monitoring programme. The Goodyear EMTrack system enables faster, more accurate data collection of critical tyre data, including tread depth and inflation levels, via a special scanning tool; automatic uploading of captured tyre information to a secure, cloud-based storage platform; as well as downloading into customisable reports for real-time, on-site viewing.
Information captured through a tyre performance management system can enable better decisions to be made about the tyres currently being used and help predict future tyre requirements more accurately. By tracking performance and other indicators over time, it enables the ability to be able to predict when tyres
JENNMAR has been the innovative leader in ground control for the mining industry for more than forty years. Over the past decade, our growth has led us to structural support in tunneling and civil construction projects, implementing the same vigor and detailed processes. Because we understand the ever changing and demanding conditions above and below ground we have built the richest portfolio of diverse and complementary brands.
JENNMAR sets the bar in every industry we serve and as we continue to grow, our focus will always be on the customer. Our products are made in the U.S.A. and backed by experienced engineers and technicians who are with you every step of the way, from initial consultation to qualified instruction and on-going technical support. We support and are dedicated to rebuilding America’s infrastructure.
will need to be replaced. In today’s budget-conscious operating environment, efficient tyre forecasting and ordering can help with more effective tyre inventory management.
Once out of service, a post-mortem analysis of the tyres can yield valuable information about how the tyre was maintained while it was running. An out-of-service tyre that exhibits unusual wear patterns could, for example, have been operated in an under-inflated state for an extended period. Findings of this nature can prompt mining operations to re-examine their tyre maintenance practices and programmes. Information gleaned from scrap tyre analysis can help mining operations make better-informed decisions about their tyre assets.
Choosing proper tyres from the best available options and maintaining them with fleet solutions will help increase uptime, but there are industry changes and important trends that should be considered when planning long-term tyre needs. Goodyear’s forward-looking approach to market trends and innovations is called FACES, and it stands for fleets, autonomous, connected, electric, and sustainability. The FACES approach highlights where the company is investing today to be an impactful partner for its customers in the future. Many of these trends already have root in the mining industry, but Goodyear believes they will continue to shape the products and services that support the OTR industry for many years.
The importance of OTR fleets only continues to grow in importance. Industry consolidation and greater world demand
are making large fleets of heavy-haul trucks or dozens of port vehicles an important part of growth in the industry. As fleets grow in size and technological complexity, there is even more need to focus on maintenance and inventory to protect the investment in the collected or even individual assets.
The OTR industry has been in the autonomous vehicle space for many years with some of the largest mining and port customers having been in the space for more than five years. It is possible to observe fleets of 80 – 100 large earthmoving vehicles all operating without drivers. Those drivers used to be frontline defense to check inflation and defend against tyre wear. Now, with more autonomous vehicles, the need for complementary automated solutions for tyre maintenance is becoming a big focus. Finding partners to manage those automated solutions will keep fleets moving into the future.
With larger fleets running more complex tyre solutions, there is an opportunity to connect all of a fleet’s vehicles and collect data – often in real-time – and use it to make decisions about assets like tyres. Services and features available today mean mining companies have access to real-time data and can understand fleet and vehicle needs at any given moment. They can also plan ahead for just-in-time service or replacement to maximise investment.
As in other industries, there is a big movement toward electric vehicles in the mining space. OEMs are developing and rolling out large earth movers that run on electricity with more new advancements just around the corner. Electric vehicles have new needs and require new tyres. The added weight and increased torque on the tyres mean the tyres are under different types of stress and need new technology to ensure they can keep fleets moving.
More than just a buzz word, sustainability in the mining industry is changing how Goodyear thinks about tyres and solutions. Using tools and services today to make sure that tyres are properly inflated is a sustainable step almost all companies can take. A properly inflated tyre has less rolling resistance and needs less fuel to move, so it has a positive impact toward many company sustainability goals. From sourcing to technological advancements, sustainability is coming to life in many ways across the industry.
With the average time to change an OTR tyre around four hours, that means a very valuable asset is out of commission and that can have a big impact on efficiency and growth. Eliminating that stoppage through the right mix of products and services means increases in uptime, resulting in more OTR partners delivering on their promises to customers and stakeholders. As the industry continues to grow, innovative products and tailored solutions should be implemented to maintain a fleet’s tyre investment today, and maximise uptime in the future.
Greg Bierie, Benetech Inc., USA, explores various technological and innovative solutions that can be used to improve dust control within conveying operations.
Although the importance of a well maintained and fully operational conveyor system is critical, the belt is often viewed as nominal and insignificant when it comes to perceived importance and its contribution to the bottom line. There are, however, innovative technologies which now make it considerably easier to maintain conveyors, and eliminate many problems at the source.
Part of the problem with conveyor belts is that there are multiple moving parts and various transfer operations that require attention. Fugitive dust is one of the primary problems that results from bulk material cargo moving from initial loading points to final discharge points throughout the system (Figure 1). It is estimated that approximately 85% of the fugitive dust and spillage issues occur at the transfer points between conveyors.
When material leaves the head pulley of the feed conveyor, it is not uncommon for the material stream to spread out, and launch with seemingly a ‘mind of its own’. As the material spreads out and gains surface area, it also induces air into the material stream. As a result, multiple problems are caused further down the material handling system.
In addition to induced air, the velocity of the material stream itself generates an air velocity which further captures the dust released by the turbulent material. Dust generation at the transfer point is increased even further when the material is allowed to impact the receiving conveyor, and is not properly contained.
These issues can become quite severe over time if the problems are not resolved quickly and effectively.
Today, however, plant managers and operators have a variety of innovative options to choose from, and can implement newer, highly effective technological solutions that actually eliminate the source of the problem, not just try to clean up the mess.
A properly-engineered transfer chute is one solution that can eradicate problems at the source, by forming a homogenous material stream as it transfers onto the receiving belt (Figure 2). Proper design incorporates both centre-loading of material onto the receiving conveyor, while soft-loading the material at approximately the same speed as the receiving belt. These systems are most common in retrofit applications and utilise laser point cloud scanning, as well as DEM modelling, to analyse flow through the existing geometry. That information is incorporated into the design of the new chute and containment structure. In many cases, properly-engineered designs operate without the need for additional dust control measures.
A lower cost, more budget-friendly solution involves simply correcting material loading at the point where it is deposited onto the receiving belt (Figure 3). This method combines containment areas with internal parts that can be maintained externally, in order to eliminate confined space issues and drastically reduce downtime when service or inspection is required. This technology uses a fully-adjustable loading spoon, as well as adjustable loading plates, to ensure centre-loading and soft-loading of the material onto the receiving belt. Due to the modular construction of the components, the need for hot work during installation, service, or repair is practically eliminated.
Another highly effective method is the use of modular components, particularly externally-adjustable wear liners. Modular components make replacement less difficult, and also enhance safety by reducing the need for housekeeping around and near rolling components. In most cases, maintenance can be performed by fewer people, due to ergonomic design and simplicity in repair and replacement requirements – without the need for confined space entry permitting. The wear liners can be replaced as needed from the outside of the containment zone in minutes, instead of hours, when full production is critical and downtime comes at a premium.
As mentioned previously, approximately 85% of the dust and spillage is created at transfer points; however, the remaining 15% can also be reduced by looking at another
potential problem: improper belt cleaning. Belt cleaning and the elimination of carryback on the bottom (dirty) side of the conveyor belt becomes a common culprit in this area. To simplify maintenance and service for proper tensioning of belt cleaners, an air tensioning system can be utilised. Secondary overlapping cleaning blades, made of tungsten carbide or ceramic, utilise dual tension relief for better pressure distribution, and can also be used to clean belts requiring belt clips or fasteners without damage to the cleaner blades (Figure 4).
A clean belt is much more likely to track properly and eliminate buildup from carryback materials which can build up on idlers, pulleys, and adjacent structures. Improper belt tracking also contributes to dust and spillage issues, as well as damage to the single most expensive item on a conveyor system; the conveyor belt. It is estimated that the conveyor belt can amount to
35% of the cost of the entire system, so it is important to avoid issues such as delamination from rubbing against structure, impact damage, and impingement issues arising from improper material loading.
It should also be noted that the belt has very little chance of containment for fugitive dust and materials at the load point if it is not centred under the load point at the load zone. Along with this, proper belt support is also very important for material containment and the elimination of dust and spillage in that area.
Another technology which introduces belt support with rolling components – as well as ease of service in areas where structural interference are common place – is a ‘drop and slide-in’ idler. Due to a narrower foot pattern, these idlers can be placed very close together in the impact zone, in order to provide under belt support to eliminate belt sag between rolls, and does so without friction due to the use of rolling components.
A benefit to this technology is that there is no friction and horsepower loss, which is common with alternative slider beds. This can be important to users that have the desire or need to reduce horsepower consumption without sacrificing sealing and performance. Slider beds are also subject to uneven wear and sealing difficulties after prolonged use, which contributes to fugitive dust and materials escaping at the load point. The service aspect and sealing advantage of a slide-in idler is enhanced by the ability to service and replace the idlers from one side of the conveyor. The idler allows tight spacing and removal of a single idler at a time. This also minimises difficulties in areas where structural interferences are present.
Last but not least, a recent particularly serious dust control issue is respirable crystalline silica. Both MSHA and OSHA are currently tightening compliance regulations and enforcement efforts. Preliminary testing of new technologies are achieving very positive results that can bring mining quarry operation into compliance. The system utilises a combination of dust collection and dust suppression. The dust collection filtration system – which purges on 20-minute cycles – is combined with a chemical binder for 20 sec. upon each purge cycle. The chemical binder agglomerates fine particulates into the material stream, and prevents re-release due to idler turbulence or subsequent transfer points.
This approach is used in respirable crystalline silica applications, where the very fine (1 – 5 µm) dust particles have caused serious concerns for personnel safety. To reduce exposure and health risks in areas where crushing and conveying creates respirable crystalline silica dust issues, those issues can be mitigated using this new development in engineering controls, for the reduction of respirable crystalline silica dust concerns in mining conveyor operations.
An apple a day keeps the doctor away. This phrase, while overused, offers an interesting point. There is something to be said about a person who looks at their current situation and makes choices that decrease future risk or increase the potential for prospective payoff. Now of course, this article is not about eating enough fruits and vegetables, but the true sentiment of the advice applies to a broad range of topics – including haul road maintenance.
Haul road maintenance can easily be categorised as just an unavoidable expense. While it is a fact that haul roads must be maintained, there are ways to decrease ongoing costs with preventative maintenance and boost efficiency in
the process – kind of like a person who eats an apple occasionally or lives a generally healthy lifestyle to lower their medical bills. Through preventative maintenance, operations can address areas that may seem small in the present moment, but reduce risk of more significant downtime and headaches in the future. The key is to incorporate equipment that helps operations realise the long-term benefits.
Every minute an operation spends on active haul road maintenance, such as clearing debris or bringing in additional material to repair the effects of wash boarding,
Josh Swank, Philippi-Hagenbuch Inc., USA, illustrates some new ways to increase efficiency and safety through haul truck customisations.
takes a minute away from producing and generating revenue. This expense significantly compounds over time. Consider also the cost of damaged tyres, and the financial benefit of proper haul road maintenance quickly adds up.
Mining operations can shell out over US$25 000 to replace just one tyre on a haul truck – not a cheap endeavour. Poorly maintained roads are harder on tyres, which causes them to wear out faster. Not only does this force more frequent replacement, which subsequently increases costs, but damaged tyres also impact operator safety, since a haul truck operating on even one problematic tyre can easily go out of control without warning.
Adopting preventative haul road maintenance practices that keep roads in good condition significantly reduces these costly risks. Additionally, it offers greater capacity for operations to focus on production and profit, rather than diverting resources to repairing roads and replacing tyres. Tailgates and custom truck bodies are two custom haul truck solutions that offer a significant benefit to tyre life, while addressing numerous other avoidable risks.
Good haul road health starts with prevention. Many haul roads contain an incline, so naturally gravity pushes the material to the back of the truck beds. When operations use standard off-the-shelf truck bodies, whether driving on the steep part of the haul road or not, material spillage is common because the truck body is not optimised for the material it is hauling and the open back allows gravity and bumps to slide material off the back onto the haul road. Haul truck customisations can address this issue and significantly reduce spillage.
Tailgates added to a standard haul truck allow operations to maximise capacity without risking material spillage. Without a tailgate, operators tend to adjust their loading strategy to decrease the amount of material they place in the truck, while also moving the loading target to the front of the body to prevent spillage. Because of this, trucks often carry 10 – 20% less than their rated capacity, and the additional weight in front leads to faster front tyre wear. This is simply not affordable. For example, consider a haul truck rated for 70 t that carries an average of three loads per hour. If that truck is hauling 12% less than its rated capacity, it can haul more than 200 t of additional sellable material over the course of an eight-hour day with the simple addition of a tailgate. While tailgates provide an excellent option to address spillage, mines can fully maximise hauling capabilities by replacing the OEM’s standard haul truck body with a custom-engineered body designed to fit the specific needs of the operation. Standard haul trucks are built with the premise of all materials possessing the same material density, resulting in a ‘one-size-fits-all’ approach. Alternatively, custom truck bodies take all aspects of the operation into account, recognising that properties of iron ore differ from those of overburden, coal, or fly ash. Custom bodies, optimised specifically for the properties of the material to be hauled, ensure maximum payload capacity. In mining, density varies significantly depending on the material being extracted. Custom truck bodies prevent hauling below capacity level, simply because space in a standard design is too limited to reach the gross vehicle weight with lightweight material.
Custom truck bodies are also designed to address spillage and ensure that the material stays in the truck and does not spill out the back or sides onto the haul road. They are engineered to match the body shape to the mine’s material, loading equipment and haul road inclines, in order to ensure the truck body is optimal for all aspects of the operation. Some manufacturers also add a liner to protect against abrasive or sticky materials that could cause extreme wear or carryback. Custom haul truck solutions – although more of an initial investment than generic, off-the-shelf options – benefit productivity by maximising the payload, decreasing costs related to haul road maintenance and reducing the carryback with each haul.
For smaller haul trucks, such as those used in quarries, gold mines and environments that use haul trucks in areas with
low overhead clearances, operations should consider a custom rear eject truck body. Like their counterparts, rear eject bodies are fully customised for the operation and designed to keep material in the truck and off the haul road. Rear ejects offer additional benefits for efficiency and operator safety. Rear eject bodies provide an ideal solution for constructing haul roads because they operate by pushing the material out the back of the truck body in a controlled fashion. This prevents the need to stop and raise the truck bed to dump material, and allows for a more even spread of the material along the haul road’s path. Additionally, rear ejects provide greater stability and the option to operate safely in low-clearance areas.
Once the initial phase of building the haul road is complete, operations can pair their rear eject with a material spreader attachment for finishing touches and ongoing maintenance. Material spreader attachments round out the haul road building process, as they fine-tune and place any additional material needed for a smooth surface. Later, material spreaders fill in maintenance gaps – both literally and figuratively – to maintain a good base layer of material, effectively addressing the washboard effects common on gravel roads. Some material spreaders handle aggregate material from very fine up to 2 in., with a spread width adjustable between approximately 5 – 60 ft or more (1.2 – 18.2 m).
The spreader attachment also increases haul road maintenance efficiency when dealing with the effects of winter weather. When snow and ice lead to dangerous haul road conditions, the traditional action is to dedicate crews of up to four people to spend a whole day spreading sand for safety. This reallocation of labour and resources negatively affects the mine’s overall efficiency. With a rear eject body and material spreader, a single operator can effectively distribute sand, grit or other crushed aggregate from the comfort of the vehicle’s cab, resulting in better workforce utilisation and increased productivity for the mining operation.
Another integral product for haul road maintenance is a water tank. Often overlooked in importance, the water truck serves as an important tool for meeting EPA dust restrictions and extending the life of the haul road. However, in order to maximise safety and efficiency, a customised solution offers the best option. By incorporating a custom water tank design, mines can convert an older haul truck into a water truck, extending the life of the truck and maximising its equipment investment. Properly spraying down haul roads prevents dust from migrating from the haul roads, thereby reducing the need to add more material as time goes on.
When looking for a water tank, the shape of the tank should not be overlooked. While it may seem insignificant, square tanks haul approximately 20% more water than round tanks with the same basic exterior dimensions. They also improve safety by creating a lower centre of gravity. The tank’s baffling system should also be designed to prevent water from churning and surging to improve stability and overall safety.
Additionally, it is important to look for a water tank that provides drivers with precise control of the tank’s water output. Individually controlled spray heads make it easier for drivers to optimise water use, while reducing the risk of oversaturating haul roads. With some systems, operators can turn on the individual spray heads and programme a spraying interval. By boosting precision in water output, operations can increase safety and efficiency.
When a mining operation sends a maintenance person or crew to clean and maintain a haul road, they give up the time that would otherwise be spent maintaining equipment. This impacts both productivity and the bottom line – 10 hr of haul road maintenance could equate to US$500 in labour expense – not to mention the additional expense in downtime and equipment utilisation.
It is a simple fact that risks such as these are a part of business. However, just as an apple may help decrease the risks that lead to a doctor appointment, certain preventative maintenance practices in mines offer the potential to decrease the risk of future challenges. Haul road maintenance is one of those practices that offers operations a way to minimise future risks simply by planning ahead.
Atilson Neto, Vale, Brazil, analyses how the latest innovations in autonomous and electric truck fleets can help decrease emissions and increase efficiency and safety in mine operations.
In the mining industry, the impact of climate change and how the industry can respond to it has increasingly been a topic of discussion over the past decade. While all business sectors feel the effect of climate change, mining companies often operate in inhospitable conditions and feel the immediate effect of heavy precipitation, drought, and other physical or climatic challenges to mining operations. However, many mining operations, such as Vale, also see the bigger picture, and are alligning with the
2015 Paris Agreement to limit global warming to 1.5˚C above pre-industrial levels.
Mining is a material contributor to global carbon emissions. The global metals and mining industry contributes to approximately 8% of the global carbon footprint. However, when focusing on one key industry – steel making – the climate impacts become very evident. 70% of steel production uses coal and coke. 1
If steel was a country, it would be the third largest emitter of CO 2 after China and the US. 2 The amount of CO 2 emissions from steel manufacturing is almost double the amount of steel created: 1.85 t of carbon for every 1 t of steel. 3
That is one reason many players in the mining sector have ambitious goals to reduce their emissions. Vale, for instance, intends to meet zero net emissions by 2050 (Scopes 1 and 2), and to reduce Scope 3 emissions by 15% by 2035. It intends to do this by investing between US$4 billion and US$6 billion to meet the targets.
As mining companies address the decarbonisation agenda aggressively, many are looking in detail at operations to see where emissions are coming from, and how innovation can be used to reduce them and optimise efficiencies.
According to a McKinsey report, emissions within mining can be broken down into three broad types: Scope 1 (emissions from diesel), Scope 2 (emissions from electricity generation), and Scope 3 (emissions from the supply chain and transport).
Today, 40 – 50% of CO 2 emissions come from diesel used in mobile equipment, and, within this, some 25% can be accounted for by emissions from diesel trucks – which is why one of the ‘pillars’ of Vale’s strategy to cut emission is by applying innovation to its truck fleet strategy:
electrification and use of autonomous trucks are two examples of this.
Vale, for example, in Sudbury, Canada, has been bringing an increasing number of battery electric vehicles (BEVs) into its fleet. Vale currently has approximately 40 electric vehicles operating underground in Canada, which is 5% of the Canadian fleet. Operations at the Creighton mine in Sudbury have also been incorporating the vehicles, and Vale has 33 electric vehicles on-site at the 8460 ft-deep mine. The Creighton mine, because it operates in a confined area and only uses BEVs, allows Vale to better understand the synergies obtained when increasing the number of EVs in the fleet. There are various key performance indicators (KPIs) to determine whether their usage is successful: operational feedback, vehicle data/telemetry, workplace environmental monitoring, and vehicle performance. Air quality is also a key factor in older and deeper mines that require more energy to access and extract the same amount of ore. In a survey of our operators, 71% reported feeling better after a shift when operating an EV compared to when operating the diesel equivalent.
Vale also, some months ago, became the first mining company to test 100% electric 72 t trucks. It received two battery-powered 72 t off-highway trucks, which will undergo tests in the mines of Água Limpa, in Minas Gerais, and Sorowako, in Indonesia.
The vehicles do not emit CO 2 as they replace diesel with electricity from renewable sources, which also results in reduce noise, minimising the impacts on the communities that live around the operations. The equipment, which was produced by XCMG Mining Machinery Co. Ltd., a subsidiary of Xuzhou Construction Machinery Group Co. Ltd (XCMG), the largest machine manufacturer in China, represent another step in the electrification of Vale’s assets.
The 72 t electric off-highway trucks – model XDR80TE – use batteries which are able to store 525 KWh. This could allow them to operate for up to 36 cycles along the established route in which they are being tested in, just over a day of operations, without the need to stop and recharge. They also have the abitily to regenerate energy during descents, reducing the use of mechanical brakes, maintenance work and vibration, in addition to providing more operational comfort to drivers. The machine has a multiple temperature control technology, allowing it to adapt to high temperatures, humidity and rainy working conditions, and to have excellent performance even in extremely cold, high altitude, and harsh weather conditions.
The trial is currently going very well on both sites. Currently the trucks are achieving more than 12 hrs of operation with a single charge. This number should increase as the process of learning and optimising the operation of the equipment accelerates.
Currently, emissions from off-highway trucks running on diesel represent approximately 9% of Vale’s total
Scope 1 and 2 emissions. The company are hoping to reduce this substantially. It is clear that each truck can reduce up to 82 t of CO 2 -e per month, when compared to the trucks currently being operated.
The trial is part of the Powershift programme, which was created by Vale with the aim of replacing fossil fuels with clean sources in its operations. The programme is promoting innovative solutions to reduce mine and railroad emissions. In addition to the 100% electric truck, Vale’s strategy for the electrification of assets also includes the operation of battery-powered locomotives in the yards of the ports of Tubarão, in Vitória, and Ponta da Madeira, in São Luís. In Canada, the Powershift programme has also led to tests with electrical equipment in underground mines – there are about 40 that are currently operational.
Vale's operational equipment electrification strategy also includes a partnership with its peers BHP and Rio Tinto. Last year, the three companies, along with 17 other mining companies, launched the ‘Charge On Innovation Challenge’, a global open innovation challenge with the goal of finding innovative solutions to accelerate the safe charging of batteries for future electric off-highway trucks.
The Charge On Innovation Challenge asks vendors to present interoperable solutions that can safely deliver electricity to large battery-electric off-road haul trucks in a way that maintains or improves current productivity levels. Specifically, mechanisms capable of delivering in the order of 400 KWh of electricity to each truck within a haul cycle (i.e. load, travel, dump, return, queue) are wanted. The delivered electricity is then used to charge a battery, and if applicable, directly propel the truck.
In addition to providing for a zero-carbon fuel source, conversion of mobile mining equipment to battery electric can potentially unlock value. However, mine electrification
requires considerable integration of infrastructure into mine planning and operations. It is essential to develop faster charging infrastructure in parallel to the development of battery-electric trucks, in order to ensure a complete electric haulage system. Due to this constraint, Vale is also looking to develop other types of solutions for a faster implementation, such as alternative fuels, hybrids and retrofits for the current fleet, among others things.
The founding patrons aim to identify charging solutions with broad industry appeal and applicability to mining. Developing solutions that enable decarbonisation via electrification, and that maintain or improve productivity are key. By multiple mining companies acting together, the aim is to demonstrate to adjacent sectors that there is an attractive market worth pursuing. Additionally, by bringing an industry perspective to bear on the applicability of different concepts across a range of operating environments, it adds value.
It is expected that some solutions identified in the challenge to provide propulsion to existing diesel-electric trucks may present a pathway to early implementation for dynamic charging solutions. However, to truly drive widespread take up of electrification in the industry, interoperability standards for the electrification of truck fleets is needed. In September 2022, Vale announced a collaboration that would advance this quest for greater interoperability.
Alongside BHP and Rio Tinto, Vale set up a mining taskforce within CharIN, supported by the International Council on Mining and Metals (ICMM). With the interoperability framework now developed through a co-design process led by professional service company GHD, the new task force is an exciting opportunity for the mining industry to lead, solving interoperability barriers and working towards standardisation. This task force builds on the success of the Charge On Innovation Challenge, with founding patrons, manufacturers, and GHD maintaining momentum to establish the interoperability of haul truck electrification solutions.
By driving interoperability standards, it will reduce the potential for unnecessary duplication in charging infrastructure and the total cost of ownership, along with safety considerations. Developing interoperability standards is also critical to continuous innovation that will enable increased efficiency, reduce costs, improve safety, and make a meaningful contribution towards the mining industry meeting its decarbonisation goals.
The electrification of truck fleets, especially for trucks under 100 t payload capacity, is important to Vale’s aims,
to lower the carbon footprint of its operations, but the company is also looking at the use of other solutions, such as low carbon fuels to achieve its emissions goals. Autonomous vehicles, which have added advantages of increasing employees safety and increasing operational efficiency, are also being implemented.
The company started a trial last year using six new autonomous haul trucks at the Carajás iron ore complex, the world’s largest iron ore mine, located in the state of Pará, Brazil. The autonomous haul trucks can carry 320 t at a go, and if the trial is successful, the trucks will be rolled out at more sites.
The implementation includes a human resources training plan for employees who work with new digital technologies, as the trucks do not require an operator in the cabin. The introduction of digital technology drives the evolution of employees’ professional skills and makes them more prepared for the industry’s digital transformation trend.
The autonomous vehicles are designed to be controlled by computer systems, GPS, radar and artificial intelligence, in order to cover the route between the mining front and the unloading area. They have safety system sensors capable of detecting large rocks and other trucks, along with human beings in the vicinity of the road. In the event of detection of any risks, the vehicle stops operation until the path is cleared, eliminating risky situations such as tipping and collision.
The autonomous operation will contribute to significant environmental benefits. Vale is already seeing reduced fuel consumption (by up to 10%), an anticipated increase in the life of equipment by approximately 15%, reduced waste generation, and enhanced performance. By 2024, 37 autonomous trucks will be operating in Carajás, which represents approximately 40% of the current fleet.
Innovation is one of Vale’s main pillars for achieving
its purpose. The trucking fleet is a key part of this and is becoming increasingly automated and electrified, reducing carbon emissions and people’s exposure to risks, whilst increasing the agility and productivity of operations.
1. ‘Coal Facts’, World Coal Association, www.worldcoal.org/coal-facts/
2. PEPLOW, M., ‘Can industry decarbonize steelmaking?’, c&en, (13 June 2021), https://cen.acs.org/articles/99/i22/steel-hydrogenlow-co2-startups.html
3. HALL, J., ‘Cleaning Up The Steel Industry: Reducing CO2 Emissions with CCUS’, Carbon Clean, (28 January 2021), www.carbonclean.com/ blog/steel-co2-emissions#:~:text=The%20amount%20of%20 CO2,per%201%20tonne%20of%20steel.
Nathan Stenson, Nokia, UK, highlights the importance of leveraging partnerships – and private wireless – to ensure the success of the next generation of mining.
If there were any doubts that Mining 4.0 has arrived, the IDC FutureScape: Worldwide Mining 2023 Predictions put them to rest in October 2022. Among other things, the report predicted that by 2027, 75% of organisations will have retrofitted critical major equipment with smart sensors, in order to improve the capture and analysis of asset performance.
The report also forecasted that more IT-enabled innovations would be adopted over the next three years, including greater levels of remote control, the use of digital twins, and the deployment of cloud-based
platforms for improved management and insight generation.
The acceleration of these trends may be surprising, but the reasons for them are not. As a 2021 industry survey conducted by IDC made clear, the mining industry believes that digital innovation is essential to furthering its top priorities: sustainability, expanded production, talent acquisition, exploration, and health and safety.
Clearly, Mining 4.0 is no longer a futuristic vision; it is a working, and proven, reality. Scores of mines around the world are undergoing a digital transformation, with many
already reaping the benefits of increased yield, greater productivity, improved safety and reduced environmental impact. Together, a broad spectrum of partners –
including network and automation solution providers, systems integrators, and mining machinery original equipment manufacturers (OEMs) – are supporting mining companies in bringing their Mining 4.0 visions to life.
As the mining industry is quite conservative in technology adoption, not all operators are transforming at the same speed. Some of them are likely taking a wait-and-see attitude; preferring to observe how early adopters are faring first, and hoping to learn from their experiences.
In fact, there are many lessons to be learned from other companies’ Mining 4.0 initiatives. Here are five of the most noteworthy:
The most critical decision regarding Mining 4.0 comes early in the process – choosing who to work with. Many commercial deployments of digital mining have been launched within the past three years. For this reason, rather than going it alone or assembling an implementation team piecemeal, mining companies would do well to seek vendors that have a proven record of working successfully as partners on other mining deployments.
There is no substitute for expertise and experience, particularly in an industry as unique and demanding as mining. Prospective partners that have worked together with other mining customers will know how best to avoid problems, address issues, and maximise efficiencies with digital transformation. In the IDC survey, 55% of mining sites identified systems integrators as the primary providers of their Internet of Things (IoT) platform strategies. Combining their expertise with those of mining technology solutions providers and wireless technology providers can ensure a faster, smoother deployment.
There are many use cases to choose from in mining –from autonomous haulage to health and safety improvements, and from predictive asset maintenance to 360˚ situational awareness. Companies should explore thoroughly which use cases will best serve their needs, support the corporate strategy, and deliver significant quantitative and qualitative ROI. The following are significant use cases for digital transformation in the mining sector:
n Enhanced safety: Keeping operators away from hazardous environments by bettering mine operations’ communications and providing real-time insights.
n Improved productivity: Solutions increasing effective production hours, eliminating bottlenecks, streamlining operations, and offering the fastest automation systems.
n Increased efficiency and profitability: Solutions reduce the total cost of ownership (TCO) of mining equipment, thanks to less downtime and
remote operations, increased transparency, and descriptive and predictive insights.
n More sustainable operations: Greener operations through electrification, improved energy efficiency, and less greenhouse gas emissions.
A thorough evaluation of each use case should include feasibility and availability of solutions, what it will take (and cost) to implement them, and which use cases should be rolled out first. Mining-experienced systems integrators, software and network solution providers, and mining machinery manufacturers are invaluable resources to consult in the planning and evaluation process. When this process has concluded, organisations should have a strong business case for funding the project, as well as a yardstick to measure its success later.
The upfront investment required for an ongoing digital transformation provides a strong incentive to achieve results quickly. Data collection for analytics and autonomous haulage are two use cases that can make an immediate, positive impact. As they prove their worth, they will help build confidence and lay the groundwork to pursue more ambitious, long-term use cases.
Resource extraction is the number one job of any mine, but it is not the only area that can benefit from innovation. There are significant savings to be found in non-pit use cases – also known as pit-to-port operations. For example, one mine operator recently noted that a private wireless digital solution that they implemented has reduced train loading time and maximised throughput, leading to expectations of US$150 million in annual benefits. That same operator is realising US$300 million/yr from other digitally driven process improvements.
Stockpile optimisation is another application that can deliver millions of dollars of value. By providing real-time visibility into stockpile contents and properties, a stockpile monitoring solution can reduce costly errors, eliminate variance in the feed to the mineral processing plant, and optimise throughput for greater productivity.
With mines often located in remote areas, thereby necessitating the use of multiple modes of transport, shipping is yet another application ripe for efficiency improvements with the use of digital logistics. With the entire mining supply chain connected via IP networks, mining companies can leverage artificial intelligence (AI) and machine learning (ML) to tighten gaps and speed delivery to meet rising demand.
Mines are among the most unforgiving environments in which to deploy a communications network.
Locations are often far from wired networking access. Operations may be conducted underground with natural barriers that inhibit Wi-Fi signals and require more antennas to ensure coverage. Network configurations may need to change frequently as work in the pit progresses and the mine expands. Radio signal interference and reflection can be a problem, as well as vibrations caused by explosives.
Above all, Mining 4.0 use cases are often mission-critical, demanding the highest levels of connectivity with extremely low latency. Anything less can stall operations and imperil safety.
When you consider all the factors that can affect network performance in mining, the network technology choice very quickly narrows down to private wireless. A 4.9G/LTE or 5G private wireless network is the only infrastructure option that offers the capacity and bandwidth to handle all Mining 4.0 use cases, while ensuring the prioritisation of health and safety. This is why in the IDC survey 86% of respondents planned to invest in wireless infrastructure, with the majority identifying 5G as the network of choice.
There is ample proof that these five recommendations can help deliver Mining 4.0 success. For example:
n At a mine in Finland – 150 km north of the Arctic Circle and the largest primary gold producer in Europe – a group of partners deployed a 5G private wireless network that supports operations above ground and in tunnels as far as 1 km below ground. Real-time data processing at the network edge is successfully supporting use cases, such as autonomous vehicles, high-precision positioning systems and group communications, further enhancing operational reliability, safety, and quality.
n A large Peruvian copper mine sought to centralise communications on a single network and incorporate IoT devices to reduce accidents, measure the use of resources and better control traffic to ensure continuous operation. They turned to a group of partners who installed a 5G/LTE network this year as the first step on the path to digital transformation.
n In a mine in Chile, a team of partners deployed a private LTE/4.9G network that connects 150 sensors for operational processes, monitoring and accident prevention in addition to 72 connected vehicles and machines.
n At the world’s largest iron ore mine in Brazil, massive driverless trucks – capable of holding 320 t of ore –are increasing productivity and safety thanks to the reliability of an LTE private wireless network.
What do these examples have in common? They all include a coordinated team of dedicated, highly skilled, and experienced partners working as one to support mining companies pursuing digital transformation. In each case, they utilised state-of-the-art private wireless solutions and customised those solutions to suit each mining customer’s unique location, operating environment, use cases, business needs, and budget. This is the key to Mining 4.0 success.
Audrey Beurnier and Bryan Pons, Aramine, France, review the various keys to manufacturing a battery powered machine which prioritises energy efficiency, reliability, and safety.
The mining industry plays a vital role in the global economy, providing the raw materials that are essential for various industries. However, traditional mining processes are known to have a significant impact on the environment and public health, making it imperative to adopt clean and sustainable methods. Clean mining technologies aim to reduce the environmental footprint of mining operations, while increasing their efficiency and profitability.
Aramine is already participating in this transformation with the creation of a full small section machine range, including various loaders, drillers, and mining trucks. These narrow machines help to reduce the dilution in a mine by increasing precision and reducing waste in the extraction process. Initially, the range was to be fully diesel powered, but Aramine quickly created an electric with cable version. With the need for a cleaner and more sustainable future, the adoption of a new, efficient, safe, and clean product became increasingly important.
In 2015, Aramine designed a battery-powered loader for use in underground narrow gallery mines. Now, there are currently several dozen machines successfully operating in narrow drift mines with zero CO2 emissions and minimal maintenance.
By identifying the key success factors mastered when designing this technology, the reasons for this growing success are clear.
First and foremost, when conceiving its battery-powered machine, Aramine considered the energy efficiency/performance ratio and did not ‘simply’ design a battery-powered machine by substituting the machine’s combustion engine with an electric motor (and installing batteries); a mistake that is most often made by machine manufacturers on the market.
The innovative aspect of Aramine’s design is that it contrasts with other manufacturers who, even today, use 2, 3, or 4-speed gearboxes, with or without a hydraulic torque converter. On the Aramine machine, in order to reduce energy losses, there is no gearbox or hydraulic torque converter, just a reduction gear. The motor is thus in direct connection with the wheels, and the wheel speed is proportional to the speed of the electric motor. This hydraulic and electrically controlled architecture innovation facilitates high energy efficiency, while ensuring good reliability, reduced costs, and lower mass.
Furthermore, as part of its innovative efforts, Aramine has designed the narrowest battery machine in the world: currently there is no competitor for its 1.1 m wide battery machine. The design of such a narrow machine required an important study on how to position all the internal
components in such a way that guarantees safety, stability, durability, and easy maintenance.
Aramine’s expertise has been built on more than 25 years of experience serving underground mines with electric and diesel-powered equipment, providing a solid foundation for new technologies implemented across the mining world.
As there are now more than 200 Aramine narrow vein machines operating around the world – utilised by large mining companies, such as Hoschild or Buenaventura in Peru, but also in Bolivia, Morocco, Mexico, Bulgaria, Serbia, and the Philippines – the technology had to be adapted to all the different altitude and temperature. In order to achieve this, Aramine has used a wide range of components that allow its machine to be operated in an optimal way, according to altitude and temperature: altitudes of up to 5000 m and in ambient temperatures between 0 – 35˚C in a mine. The system can withstand extreme, non-operating temperatures (from -40˚C up to 50˚C), so that it can be transported and stored on site. The hydraulic and cooling designs of the electrical/electronic components are likewise intended to meet these requirements.
In terms of reliability, Aramine has accounted for all constraints related to the use in underground mines and their harsh environment: high hygrometry, extreme heat or cold, mud, poor air quality, etc. For example, no water is used to cool the components (e.g. electric motor, frequency converters, etc.), but instead the hydraulic oil is used as a cooling fluid. This is made possible by the precise design and calibration of all the components and parameters of the machine, in order to avoid overheating due to friction or breaking points usually found on this type of mining machine. Operators are often tempted to use
mine water to level up their cooling circuit, however this is not a suitable solution, as this water can be corrosive, charged with minerals, etc. By eliminating water, a major risk of machine failure can be removed from consideration.
In addition, the electrical components (battery system, relays, frequency converters, etc.) are installed on a silent block to avoid vibrations when the machine hits gallery walls; the reducer has an automatic belt tensioning system (when the belt is installed or replaced) to ensure safe bearing stresses and, in turn, a longer operating life.
With regard to the batteries, Aramine has focused on easy battery recharging, introducing a battery charging system inside the packs. Therefore, users can charge the battery packs with two conventional power outlets. This enables full autonomy of each energy module, and relieves the owner of additional constraints and expenses related to specific infrastructures. Instead, the system works on the standard mine power grid.
In order to ensure machine safety, a procedure is used to check the brake status at machine start-up before moving the unit. To improve hydraulic efficiency (reduce pressure losses), the engineering department has increased hydraulic pressures (and therefore reduced flow rates). However, in order to maintain and improve hydraulic system reliability (filtration), it was decided to use a ‘return suction filter’ on the hydraulic system.
This filter makes it possible to always have clean oil for the hydraulic pumps that can be under pressure, as well as the use of this filter in the machine. In addition, the filter allows the pumps’ intake to be under pressure, so the system can operate at high altitudes (low atmospheric pressure).
Aramine analysed many parameters to achieve expected performance in terms of oil filter sensor pressure thresholds (depending on oil characteristics and temperature), in order to inform on filter replacement. The filter selection is determined in such a way that the filter by-pass is never enabled if the mine temperature is higher than 10˚C (which is usually the case). This way the hydraulic system always provides perfect filtration regardless of the machine’s operation, thus achieving the highest reliability and longevity of the hydraulic system.
From a kinematic perspective, the drive motor is directly connected on the wheels, so in the event of a ‘shock’ (entering the pile at full speed, hitting gallery walls, etc.), an accurate analysis of the machine’s deceleration distance has been calculated to match the torque limiter release limit on the drive train (protection of all the mechanical parts).
When setting up the hydraulic cylinders (steering, bucket, and boom stops), the hydraulic force is dissipated by the distributor’s pressure limiter. In order to prevent this energy loss and to avoid heating up the oil (and consequently having to cool it down again via the hydraulic cooler), pressure sensors indicate the cylinder pressure.
Regarding the technology of the electric motors, it has been designed by Aramine in close partnership with a French motor manufacturer, who aided the development of the motor cooling system through the machine’s hydraulic oil circuit. The Aramine
engineering department was able to establish the minimum oil flow rate required, whilst taking into account the thermal mass capacity of the fluid. This is made possible by the hydraulic circuit temperature control inherent to the kinematic chain, which does not produce any heat.
The technological evolution of the L140B has rapidly allowed its evolution towards a customised configuration, adapting according to the user’s application. All settings are developed at the factory before being transferred to a simple USB key, which allows the machine to be configured in the mine.
The programme enables the use of a ‘Start&Go’ system that saves battery energy throughout the operating cycle, coupled with a specific ‘loading’ mode that improves wheel torque while limiting speed to prevent loading skids.
Today, both the reliability and efficiency of the L140B have increased, as a result of being able to almost double the battery power, but while retaining a battery of the same size (from 24 – 42 kWh), therefore extending the working time of an energy module during a cycle to +60% of its initial working time – i.e. from 2 – 4 hours of use with the 24 kWh version, to 3 – 5 hours of use with the 42 kWh version.
Aramine has successfully designed a battery-powered loader for use in underground narrow gallery mines. The key success factors behind this growing success include the company’s focus on energy efficiency, reliability, and performance. Aramine carefully considered the energy efficiency/performance ratio and eliminated gearboxes and hydraulic torque converters to reduce energy losses.
In terms of design, the machine has a narrow width and a hydraulic and electrically controlled architecture to ensure high energy efficiency, reliability, and low costs. It has been designed to withstand extreme temperatures, and its hydraulic and cooling designs are intended to meet the harsh environment of underground mines. The battery system has been designed for easy recharging and operates on the standard mine power grid. In order to ensure machine safety and hydraulic efficiency, various parameters have been accounted for, such as: brake status, oil filter sensor pressure thresholds, and deceleration distance.
Clean machines in mines are essential to maintaining the overall health and safety of workers. They help achieve this by reducing worker exposure to harmful pollutants and dust, as well as the environmental impact of mining operations as a whole – by limiting the release of harmful chemicals and pollutants into the atmosphere. The adoption of clean machines in the mining industry is a crucial step towards ensuring a safer, more sustainable and more efficient future for the industry. That is why, Aramine will continue to innovate cleaner products.
In 2023, battery technology will still be in the spotlight, as a new Aramine machine (named L440B) is being released for production this year, featuring an important innovation in performance: 4.4 t haulage with only a 1.5 m width, as well as a similar system to the L140B for energy module replacement.
Copper ore was first extracted by humans over 10 000 years ago, and the demand has been steadily increasing ever since. Today, it is used in everything from telecommunications and transportation to renewable energy technologies. However, the number of accessible, high grade ore bodies is starting to dwindle, and mine operators are having to make do with ever-decreasing copper grades. In-line determination of the elemental constituents of the ore feed will be essential to ensure efficient base metal extraction, and neutron activation analysis (NAA) technologies – either prompt gamma neutron activation analysis (PGNAA) or pulsed fast thermal neutron activation (PFTNA) – are emerging as the forerunners for this application. This article discusses how PGNAA can be used to achieve real-time optimisation of grade control, stockpile blending, downstream grinding and flotation, and waste bulk sorting, taking copper mining and processing efficiency to the next level.
Today’s ever-growing focus on sustainability has profound implications for the copper mining industry worldwide. The ongoing transition to green energy is expected to significantly increase the demand for copper, because of its many uses in expanding electricity networks and manufacturing cleaner technologies, such as electric vehicles. At the same time, the global decrease in the availability of high-grade copper deposits –along with heightened scrutiny on the consumption of both energy and water – is impacting operating costs, presenting an increasingly complex challenge to the industry.
With a worldwide copper shortfall of 15 million tpy predicted by 2034,1 a major and sustained increase in mine output is required to meet growing demand in the next few years. Adopting greener processes and technologies will therefore be essential to improving efficiency and reducing the operating cost of mining, processing, and producing copper.
Boosting the efficiency of mining and processing operations has never been more important, and smarter technologies are undoubtedly the pathway to achieving this. NAA is one such technology, and is proving beneficial for ore sorting and routing, offering high frequency online elemental analysis of an entire raw material process stream. This non-contact, non-destructive technique is used in cross-belt analysers and other online analysis systems to deliver accurate real-time visibility of material quality, to enable improved process efficiency and minimise production costs in copper mining and processing operations.
Until comparatively recently, online analysis was largely limited to measuring mineral slurry streams after the mill. However, today, with declining grades, measuring and controlling what material is sent to the mill is essential for process control and operational efficiency.
High accuracy, real-time cross-belt copper analysis is now readily available, allowing rapid waste or ore classification based on a selected cut-off grade, or based on gangue chemistry or impurities, enabling improved downstream process efficiency and metal recovery.
Gary Noble, Thermo Fisher Scientific, Australia, explains how neutron activation analysis can be used to revolutionise copper mining operations.
NAA works by bombarding materials with neutrons, which interact with elements in the samples and emit secondary, prompt gamma rays. Each element emits a characteristic energy signature as it returns to a stable state, which acts as a unique fingerprint. As gamma rays are a form of electromagnetic radiation, they can be measured using scintillation detectors. These detectors are composed of a high purity crystalline structure which, when exposed to gamma rays, produces photons proportional in energy to that of the gamma rays entering the crystal. The crystal is coupled to a photomultiplier tube that converts the pulses of light into electrical signals proportional in energy to the photon. These electrical pulses are amplified and combined in order to yield a composite energy spectrum that is analysed to determine the elemental composition of the material. The small wavelength and high energy of gamma rays allows them to penetrate and interact with even dense materials, including rock. For mining operations, this offers an advantage over surface analysis techniques – such as X-ray fluorescence (XRF) and X-ray diffraction (XRD) – as it ensures that all the material is analysed equally and accurately, allowing measurement of the entire material volume and not just the surface.2,3,4 PGNAA can be incorporated into various stages of copper processing, discussed below, providing valuable mine-to-mill data to enable informed decisions based on real-time elemental analysis.5
Preconcentration is used to maintain head grade for existing concentrators by rejecting waste or subeconomic material prior to the stockpile and mill. It may also reduce the size of the processing plant required for a low-grade ore body when establishing a new mine. Efficient bulk sorting can be achieved using elemental analysis to detect variations in grade and differentiate between ore and waste. A PGNAA analyser – such as the Thermo Scientific™ CB Omni™ Agile Online Elemental Analyzer – can be implemented on a conveyor feeding ore to the processing plant, enabling the rejection of waste-in-ore, in order to enhance the feed grade to the plant. Ore-in-waste can also potentially be recovered by bulk ore sorting.
As well as bulk ore sorting, PGNAA analysers provide an effective means of monitoring the plant feed to a coarse ore stockpile or, potentially, multiple stockpiles. Employing real-time analysis of the feed provides an overview of the composition and grade of material being fed to the plant. Operators can then make informed decisions and feedback to the mine, enabling optimisation of stockpile blending and composition prior to the mill. In addition to measuring the copper grade of the ore, PGNAA can also be used to provide representative analysis of many elements associated with the gangue that can impact downstream process performance.
Minerals such as talc and clay can negatively affect the flotation performance of processing plants. Talc is commonly associated with valuable sulfide minerals, such as chalcopyrite, and is naturally hydrophobic. Its natural floatability makes it challenging to separate out the valuable mineral from the gangue. Talc is also a problem for downstream processing, such as in smelters, where high levels of magnesium oxide in the concentrate stream can impact the primary slag properties and, ultimately, reduce the campaign life of the furnace. Depressants are often used to try and inhibit the floatability of talc, although these can be more costly than some of the other reagents used in flotation. Alternatively, a pre-flotation circuit removing hydrophobic impurities can be employed at the start of the process, to avoid contamination of the concentrate.
Clay in the ore feed can present a major challenge to maintaining froth stability, lowering the performance of the flotation circuit. Other issues associated with processing high clay content ores include slime coating the mineral surfaces and air bubbles, leading to over consumption of reagents and a reduction in recovery. Clay binders are often used as a slime depressant, causing the clay particles to agglomerate, increasing the size, and lowering the surface area of the particles. Depressants are also commonly used, which can act as dispersants to prevent the aggregation of fine and slime coating particles.
It is vital to optimise the dosage of costly reagents used during the flotation process to ensure the economic viability of lower grade feeds. Real-time PGNAA of the mill feed prior to the pre-flotation circuit can provide processing plants with the necessary information to control and optimise the rate of addition of these expensive reagents in flotation plants,
enabling optimal operation, reducing costs, and improving the recovery of the valuable minerals.
Over-sized SAG discharge material is commonly passed through the pebble circuit. This can have a significant impact on the milling capacity of the SAG mill circuit if it is recirculated directly back into the feed stream; the recirculating load can represent up to 25 % of the feed, depending on the ore characteristics. Typically, ore with a higher bond work index is disproportionately represented in the pebble circuit, and is usually lower grade material with a higher gangue content. PGNAA allows measurement of the grade and gangue elements in the pebble circuit, providing processing plants with the necessary information to make decisions on the economics of recirculating this material through the SAG mill. Subeconomic material can then, potentially, be removed from the pebble circuit, reducing the recirculating load to the SAG mill. A further advantage is that this could also increase the overall grade of the flotation feed, with associated processing benefits.
PGNAA has the potential to address many of the challenges facing the copper industry, offering significant benefits for real-time analysis on the mine-to-mill feed and pebble circuit. Equally importantly, elemental analysis throughout the flotation circuit provides essential information to help meet
grade targets, optimise recovery and implement process control strategies to reduce the use of – and therefore expenditure on – expensive reagents. The data provided by PGNAA can make a substantial contribution to copper mining and processing efficiency by eliminating waste and optimising stockpile management, plant feed quality and reagent consumption, enabling operators to maximise the value per tonne of ore.
1. DA SILVER, O, ‘Rio Tinto Copper CEO: Copper Market to See Deficit by 2020s’, Investing News Network, (10/04/2018), https://investingnews. com/daily/resource-investing/base-metals-investing/copperinvesting/rio-tinto-ceo-copper-market-deficit/
2. CESTARI, A, ‘Why Are PGNAA and PFTNA Technologies Used in Mining?’, Thermo Fisher Scientific, (20/05/2021), www.thermofisher. com/blog/mining/why-are-pgnaa-and-pftna-technologies-used-inmining/
3. ‘A guide to PGNAA and PFTNA technology for non-scientists’, Thermo Fisher Scientific, www.thermofisher.com/uk/en/home/ global/forms/industrial/pgnaa-pftna-technology-ebook-registrationform.html?icid=CAD_MM_PA_CementCoalMineralsLC_PGNAA_ PFTNATech?icid=CAD_blog_mining_2021May
4. ‘PGNAA and PFTNA Technology’, Thermo Fisher Scientific, www.thermofisher.com/uk/en/home/industrial/cement-coalminerals/cement-coal-minerals-learning-center/cement-analysisproduction-information/pgnaa-pftna-technology.html?icid=CAD_ blog_mining_2019Feb
5. NOBLE, G., THOMSON, E. and SANHUEZA, I., ‘Cross-belt elemental analysis, stockpile blending optimization & waste bulk sorting in copper using PGNAA’, Copper 2022, (presented on 16 November 2022 at Copper International Conference), https://copper2022.cl
TSi Sonic Drill Rigs feature a proprietary Sonic Drill Head that incorporates a revolutionary oscillator for precise and powerful performance. It’s innovation that outperforms.
The world is facing an existential global climate crisis; and miners and their technology partners have an essential role to play. In Canada, it is being recognised that climate change is changing many aspects of society. Warmer weather has led to major changes in patterns of rainfall, leading to flooding and water shortages, as well as unforeseen consequences such as the proliferation of pests. The pine beetle, for instance, although native to the Canadian boreal forest ecosystem, had been kept in check for thousands of years by occasional cold snaps that are now happening less frequently, which has led to forest and habitat damage, and combining with drier conditions to create forest fires. In other parts of the world, the consequences are much worse. The solution to climate change that is being accepted is the massive adoption of new scalable renewable energy generation systems (predominantly wind and solar farms), upgraded electrical transmission infrastructure, and large format energy storage systems such as lithium-ion batteries.
Eric Wasmund, and Jose Concha, Eriez, Canada and Peru, weigh the growing importance of technologies in water management, and how they are crucial in achieving sustainable operations.
All of this new infrastructure requires significant increases in mined materials, including the base metals nickel, cobalt and copper, as well as lithium, graphite, and rare earth metals. Recent forecasts from credible industry players suggest that global production of both copper and nickel will have to increase by 40 – 50% between now and 2030, in order to meet the green-demand. In the long-term, there will be a focus on sourcing these materials by a combination of improvements in the efficiency of metallurgical extraction and recycling. But in the short-term, the demand will be mainly satisfied by opening and expanding world-scale mines on an unprecedented level. Miners have been very responsive to the sustainability concerns of institutional investors and companies, such as Teck and Anglo American, which have made laudable announcements that they are sourcing electrical energy for some of their mines and concentrators from renewable sources.
Besides energy, the other major mining input is water. Unlike an energy source, which is easier to re-locate and interchange, water cannot be easily moved or diverted, and supply is finite. One of the consequences of global climate change is not just a change in the amount of available water in a particular region, but higher temperatures also encourage higher evaporation rates. The precise locations and seasons at which the rains fall is changing significantly
and becoming less dependable. This has a significant impact on water storage and harvesting, and it does not help that many of the largest mining districts are in very dry regions with local populations and farming activity that compete for a limited supply. A recent article in the Economist explained that part of the negotiation and development of the social license for the US$5.5 billion Quellaveco project in Peru came from the construction of a water reservoir, where more than 90% of the output is allotted to local farmers.
The key to mining developments in many crucial parts of the world will depend on how the proponents plan to use and share water, and this trend will increase greatly as demand and climate trends change. The companies that are successful will be those who can agree and demonstrate that they are water-conservationists. Others will simply not be allowed to operate, since permitting and regulation – rather than a true price of water – will likely control new mine development in many countries with a scarce supply of water.
At this point, some explanation is warranted to define what is meant by water-conservationists. Water inside the envelope of a concentrator plant is a key part of the mass transport, flow-sheets, and mass balances of the operations. Metallurgists are nowhere near being able to eliminate water use in this sense. The key is how much water leaves the envelope of an operation, and therefore the rate of new water that is required to run the operation. A plant that can recycle 100% of the water that it needs could be a ‘net-zero’ water user, and that should be the ultimate target that the industry is aiming for. ‘Net-zero’ water implicitly puts a price on water, since it requires cleaning up used water so it can be recycled, rather than discharging contaminated water into the environment and making up the difference with fresh water. Right now, many mining operations are not focused on water efficiency. Organisations such as the Coalition for Minerals Efficiency (CEEC), which years ago developed mining energy curves as a way for miners to benchmark energy efficiency, now have a comparable initiative to develop water curves. Measuring, benchmarking and comparing water use and best practises is the first step in moving towards the target of net-zero water. To show that the continuous improvement via technology is possible, the commercial aviation business can be used as an example. In 1960, the carbon intensity of a passenger km was approximately 1.4 kg of carbon dioxide. By 2018, mainly due to technological innovation, that metric has been reduced to 0.1 kg. Similar breakthrough improvements in water consumption are now underway.
This is where Eriez fits in. Eriez is a world leader in developing and commercialising innovative flotation technologies. Froth flotation using water is the major unit operation in most base metal concentrators. With existing concentrators, the technology responsible for more than 90% of flotation is the stirred tank mechanical flotation cell. Stirred tank mechanical cells only work with
high efficiency in a narrow size range of particles. As a result, mine output is over-ground to compensate for this weakness. Eriez has developed and introduced into the market the HydroFloat® CPF, the first commercial coarse particle flotation machine. This device is a fluidised-bed coarse particle flotation machine that overcomes buoyancy and froth recovery restrictions, through up current water velocity and plug flow conditions.
Anglo American recently published results from its“HydroFloat Coarse Particle Recovery” Demonstration plant at El Soldado, showing that this technology could be implemented on a commercial plant-scale, reducing the amount of grinding, and producing a substantially non-metals tail with an average particle size of 2 – 3 times conventional tailings.
How does this process support ‘net-zero’ water?
Substantially coarser particles will de-water much more quickly, with less energy and capital than current practice. It also helps that the coarse particle flotation (CPF) process also produces a tail that is closer to being monodisperse, since finer size fractions of the tail have been removed by pre-treatment, as well as classification that is inherent in a fluidised bed. A number of companies, including Weir Minerals and Anglo American, are developing unique and novel engineered systems to combine conventional and HydroFloat coarse tails, in order to create safe longterm impoundments that can return water back to the operation, rather than getting lost through evaporation.
Anglo American has recently published information about its technology, called Hydraulic Dry Stacking (HDS). This system uses interleaved layers of coarse and conventional tailings, with the coarse layers ‘wicking away’ water from the fine layers. HDS has also been piloted at El Soldado with a 250 000 m3 impoundment, taking advantage of feed from Eriez’ HydroFloat tail. Using a 3D network of alternating coarse and fine deposits with drainage channels, early results have already achieved 80% water recovery, and the target is to reach 85%.
Not only do these systems have the ability to efficiently recover water from the most significant concentrator out-flow, they also have the potential to create safer, waterless tailing impoundments that can be reclaimed much more safely, economically, and quickly than conventional water impoundments. In the same manner as water, tailings management is another major topic that miners must address, especially with the movement towards the green-economy and demand for metals increasing.
Water stewardship is a key topic for miners and the world. Adoption of new technologies and paradigms will be a key success factor in making necessary improvements.
The Eriez HydroFloat has made a key contribution in this arena, and now mining companies and other technology providers are combining their talents and expertise to transform water use and the sustainability of mining.
RIEGL VZ-i Series for highest accuracy and optimal performance
• ranges up to 2500 m, accuracy 5 mm
• customized apps written in Python programming language
• cloud connectivity for remote operation and data transfer via LAN, Wi-Fi, and 3G/4G LTE
RIEGL Mining Apps for highest efficiency in the field
• flexible scan data acquisition scheduling
• flexible threshold value setting
• no extra software required – webserver on scanner for browser-based data and result publication
Monitoring App data comparison and visualization of differences to the reference data set
Design Compare App
data comparison to a given 3D design model, visualization of undercut and overcut
Slope Angle App
calculation and visualization of local slope angles and the areas above the critical slope angle
Christopher Thomson, AgEagle, Switzerland, examines how fixed-wing drones can be used as a multi-purpose tool to optimise mine management and safety.
Ensuring the safety of people, profits and the planet has always been a crucial concern in mining. With the World Economic Forum citing a ‘trust deficit’ as one of the biggest challenges facing the mining industry today, the focus is now being placed on how organisations can improve their operations, and ultimately regain and maintain employee, community, and investor confidence.
Unmanned aerial vehicles (UAVs), or drones, are multi-purpose tools that can help optimise mine management and operations. Drones are established tools for surveying, monitoring, and managing mine sites. Global survey data shows that 65% of mining sites have invested in drone technology – an increase of over 20% since 2018.
Despite their broad acceptance by companies as an asset to operations, the on-site use of drones remains highly varied. Over 80% of mining operators said they use drones in their surveying and mapping activities, with only half of these respondents using drones to improve safety, and only a third to support tailings dam monitoring.
Contractors and managers could benefit a lot more from exploring the true potential of full-stack UAV technology to optimise operations, from inspecting
inaccessible areas to improving water management strategies.
Regular survey programmes are essential for successful mine management. Perimeter security, soil conditions, land usage, traffic conditions, as well as many other operations rely on a steady stream of monitoring data. In the past, acquiring this information required manpower, and lots of it; having staff manually scan and survey vast sites was a time and labour-intensive process that could potentially end with incomplete or inaccurate data. This method also required engineers to be physically present in remote or inhospitable locations, subjecting them to a wide range of hazards, including falling rocks, humid conditions, gas leaks, dust explosions, and floods.
It is, therefore, not surprising that many companies have transitioned to using drones equipped with highly accurate cameras, specialised sensors, and 3D mapping technology to conduct surveying and mapping operations. Fixed-wing drones, supported by flight management software, allow for the capture of on-site data up to 20 times faster than traditional ground-based
methods. Drones became an obvious choice for their improved accuracy, efficiency, repeatability, and safety.
The success of any mining relies on the effective management of stockpiled materials. Gaining an accurate measure of stockpile volumes can be
challenging due to factors including a site’s size, area of stockpile coverage, material type and safety, since traditional measurement methods required staff to be stationed near to large and sometimes unstable piles of heavy mining products. By supplementing or replacing terrestrial stockpile monitoring with aerial mapping, operators can eliminate the risk to personnel and improve stockpile management. Flight management software such as eMotion make it possible to create pre-set flight paths for fixed-wing drones, in order to consistently capture and accurately calculate complex stockpile volumes from the air. Precise and up-to-date information on the status of product stockpiles means mining companies can remain agile and address the impact of shortages or surplus. Regular survey data also allows operators to spot trends over time, and put in place realistic goals that reflect the reality of conditions on the ground.
Mines and quarries have many partially or completely inaccessible areas where manual inspection is either impossible or extremely dangerous, not to mention time consuming and expensive. Drone surveys combine the advantages of highly accurate manual inspections with the speed and safety of modern aerial mapping.
Some fixed-wing drones, like AgEagle’s eBee X, support up to 90 minutes uninterrupted flight time, offering the potential to cover up to 220 ha. (550 acres) at a time. RTK and post processing ensure high accuracy surveys that are reliable and more cost-effective than other available methods.
In almost all instances, using drones to perform tasks typically undertaken by staff is the safer option. That being said, drone technology varies widely. There are hundreds of different drone types on the market, ranging from multi-rotor ‘quadcopters’ to fixed-wings and VTOLs. To maximise safety on the mining site, operators should carefully consider the class, specifications, and regulatory status of their chosen drone, opting, where possible, for a model that is lightweight, robust, easy to use and approved for flight over ‘uninvolved personnel’ – such as AgEagle’s eBee X.
Securing an accurate aerial view of mine sites also helps streamline water and sediment management. In addition to the benefits of regular, reliable, and repeatable terrain surveys, fixed-wing drones give operators a bird’s eye view that reveals information that would not be visible during ground inspections. This has great potential for more effective water control, accumulation and extraction, balance, storage, condition monitoring, and better
management of adverse hydrological changes – all of which improves operational efficiency.
Underpinning these benefits is the ability to carry out detailed risk assessments and pre-plan flight routes before the drone leaves the ground. Flight mapping software such as AgEagle’s eMotion allows operators to chart flight paths, cross reference them against air traffic control data to minimise risk from other aircraft, and establish in-flight fail safes to assure the safety of ground crews.
Mines, quarries and aggregate sites, for all their diversity, typically have one thing in common –proximity to the natural environment. In a time of tightening regulations and fragile investor confidence, operators are under pressure to safeguard local wildlife through tighter waste management controls. Here again, drone technology provides an answer. Highly accurate, site-wide status updates allow companies to quickly identify potential environmental hazards, and take swift action to prevent catastrophic accidents. In the case of surface and ground water monitoring, for example, an archive of reliable digital surface model (DSM) imagery can help inspectors spot changes in the environment surrounding the mine site, and monitor the condition of wastewater to ensure it meets required standards for discharge.
Another pertinent aspect to the sustainability conversation is tailings dam management. In the wake of multiple high-profile tailings dam failures, their construction and maintenance has come under scrutiny from environmental and regulatory groups alike. Fixed-wing drone fleets are an invaluable asset to mine companies when it comes to securing tailings dams, enabling regular slope integrity monitoring that does not put personnel at risk. These comprehensive surveys also help planning, letting operators identify where tailings dams can be scaled up, down or retired completely.
Drones are an incredibly versatile asset to mining operators. The question is where will drone technology take the industry next?
Looking ahead, the nature of drone use in the mining industry is likely to change. More and more, mining and excavation companies are demonstrating their commitment to drone technology in the long term by investing in their own in-house UAV fleets. As drones become increasingly integrated into operators’ workflows, the challenge will be to find suppliers who go beyond hardware to provide full stack, advanced solutions designed to make the future of mining a safe bet for all.
In just three years, Vancouver-based junior miner American Pacific Mining Corp. has successfully leveraged its capital markets and field expertise to position itself in the Western US, building a portfolio of precious and base metals projects. With a proven track record of finding opportunities in Montana, Nevada and Alaska, the company has gained partnerships with industry majors Rio Tinto and Dowa Metals & Mining, grown its portfolio, and continually advanced its projects.
Building off this success, American Pacific has raised funds for further growth and garnered industry acclaim. This has included award nominations recognising the company, its projects, and its leadership team. Most notably, the company was named a finalist in five categories for the 2022 S&P Global Platts Metals Awards – an annual programme that recognises exemplary accomplishments in 17 performance categories.
American Pacific is a precious and base metals explorer and developer focussed on opportunities in the Western US. The company’s portfolio is headlined by two high-grade flagship assets; namely the Palmer Volcanic Massive Sulfide
American Pacific Mining Corp. profiles its recent experiences in becoming an established junior miner, and reviews some of the precious and base metals opportunities that are currently being explored in the Western US.
(VMS) Project in Alaska, and the Madison Copper-Gold Project in Montana.
The Palmer VMS Project is a 14 million t, high-grade, zinc-copper-gold-silver VMS project under a joint-venture partnership with Dowa, owner of Japan’s largest zinc smelter. Acquired by American Pacific in 2022, Palmer is an advanced project currently at the preliminary economic assessment (PEA) stage.
Madison is a high-grade, past-producing project under an option to joint venture with Kennecott Exploration Company, a division of the Rio Tinto Group. American Pacific acquired the project in 2020, and Rio Tinto may spend US$30 million to earn up to 70% of the project. For its Madison transaction, American Pacific was recently selected as a ‘Deal of the Year’ finalist nomination in the S&P Global Platts Metals Awards.
Also, in American Pacific’s asset portfolio are the Gooseberry Silver-Gold Project and the Tuscarora Gold-Silver Project. These two high-grade, precious metals projects are located in key mining districts of Nevada – known as one of the world's most prolific precious metals jurisdictions. The company’s Nevada portfolio also includes the Red Hill and South Lida gold projects.
At the Palmer VMS Project, American Pacific and Dowa are advancing the resource to feasibility under a five-year plan. Together, they are working to define a multi-deposit district with exceptional exploration upside. Total project expenditures of approximately US$68.7 million were allocated to the end of 2022.
The project hosts two NI 43-101 compliant resources – the Palmer Deposit and AG Zone Deposit (Table 1) – with a total consolidated mineral resource of
4.68 million t of 10.2% zinc equivalent in the indicated category, and 9.59 million t of 8.9% zinc equivalent in the inferred category.
In June 2019, a PEA was completed for Palmer (Table 2). The results of which showed it to be a low capital expenditure, low operating cost, and high-margin underground mining operation with attractive environmental attributes. The project includes numerous drill-ready high-grade prospects that define more than 15 km of favourable mineral trends, all hallmarks of a significant massive sulfide system and opportunity to discover multiple deposits.
American Pacific’s Madison Copper-Gold Project in Montana is highlighted by significant copper upside, a defining feature of the project’s history and regional heritage. The project is analogous to and just 48 km from Montana’s legendary Butte mine, which produced 21 billion lb of copper, 715 million oz of silver and 2.9 million oz of gold, in addition significant zinc, lead, and manganese when it was in production between 1955 and 1982.
Madison was last in production from 2008 to 2012. During those years, it produced 2.7 million lb of copper, with grades ranging from just under 20% to over 35%, and 7570 oz of gold at an average grade of 16.1 g/t. Since then, American Pacific has continued to achieve significant exploration results at Madison (see Table 3).
With its depth of expertise in evaluating opportunities in the Western US, American Pacific’s mission is to continue to acquire high-grade assets that would be desirable to major mining companies and support its growth trajectory.
American Pacific has a proven history of identifying and purchasing past-producing assets in its target
*CuEq = (25.3 x Zn% + 66 x Cu% + 22 x Pb% + 0.51 x Ag g/t + 40.19 x Au g/t)/66
See news release dated 18 December 2018. Net Smelter Return (NSR) equals (US$16.01 x Zn% + US$48.67 x Cu% + US$23.45 x Au g/t + US$0.32 x Ag g/t). NSR formula is based on estimated metallurgical recoveries, assumed metal prices, and assumed offsite costs that include transportation of concentrate, smelter treatment charges, and refining charges. ZnEq equals = (US$66 x Cu% + US$25.3 x Zn% + US$22 x Pb% + US$0.51 x Ag g/t + US$40.19 x Au g/t) / 25.3. Assumed metal prices are US$1.15/lb for zinc (Zn), US$3.00/lb for copper (Cu), US$1250/oz for gold (Au), US$16/oz for silver (Ag). Estimated metal recoveries for Palmer Deposit are 93.1% for zinc, 89.6% for copper, 90.9% for silver (70.8% to the Cu concentrate and 20.1% to the Zn concentrate) and 69.6% for gold (49.5% to the Cu concentrate and 20.1% to the Zn concentrate), as determined by 2018 metallurgical locked cycle flotation tests. No recovery data is available for AG Zone deposit. Barite (BaSO4) not included in the Cut-off determination or reported ZnEq and CuEq.
geographical market. The company has identified properties where little to no modern exploration work and/or data interpretation have been done. In turn, by applying modern techniques, American Pacific can advance a project to discover its full production potential. Modern techniques used by the company to aid in discovery include: 3D modelling and mapping, drone magnetic surveys, drone video survey footage to produce a ‘bird’s eye view’ perspective to strategise exploration, trenching, shallow percussion, reverse circulation and core drilling, GIS mapping, and more.
An example of these techniques being applied is when American Pacific’s regional acumen and technical expertise led to a comprehensive 3D geologic model at the Madison project, assisting the company and joint venture partner, Rio Tinto, in targeting porphyry and skarn systems. This approach was mirrored at American Pacific’s Nevada-based Tuscarora and Gooseberry projects, for modelling and targeting prospective gold and silver resources.
Wearpact is the premium continuous edge lip for LHDs, suitable for any material and loading conditions.
The consistent shroud profile protects the lip, offering unparalleled wear protection.
We can customize a configuration and profile combination for your site conditions to increase production and campaign life.
The result? Improved productivity through higher machine availability.
When the time comes for replacement, our patented Wedgenut integrated lock system keeps hands out of harms way.
Complementing data generated via modern techniques, historical records have been effectively integrated into the 3D models, enhancing analysis. American Pacific has successfully uncovered overlooked or scattered archival records, including ‘dusty, old banker boxes’ at the University of Nevada, Reno. The company has also created local ‘reward for data’
campaigns to incentivise industry peers to find past research.
Through modernisation and creative strategies, American Pacific has found innovation through integration – melding historical and modern data into a more comprehensive geologic model. This has proven invaluable in courting producers, achieving exploration results that have exceeded expectations, and building investor confidence.
Building upon its expertise in evaluating and implementing opportunities, outcomes have included a
strong relationship with Rio Tinto’s Kennecott Exploration to advance work at Madison. American Pacific is also working to build an equally strong relationship with Dowa at its Palmer VMS Project. Both Madison and Palmer are poised to contribute to the company’s growth, while creating value for shareholders.
Indeed, American Pacific has built trust with its shareholder base, including retail and institutional investors, delivering on expectations to create value and market visibility. The company’s market capitalisation has grown from CAN$11 million in 2020 to approximately CAN$79.5 million in mid-January 2023. In 2021, the company was consistently ranked the number one best-performing stock by the Wall Street Journal US Gold Index for a six-month period.
US$266 million at 7% discount rate
IRR
24% pre-tax and 21% post-tax
Life of Mine (LOM) 11 years after 24-months of pre-production
Mining and processing 3500 tpd (steady state)
Operating cost US$54.2/t (mining, processing, G&A)
Ops cost and sustaining capital US$65.4/t
Net ops income US$92.6/t (US$81.4/t including sustaining capital costs)
Zinc AISC cash cost US$0.11/lb net of by-product credits
Capital cost US$278 million (pre-production)
Sustaining cap and closure costs US$140 million; total LOM capital cost of US$418 million
Post-tax payback
Grade and tonnage
LOM recovered metal
3.3 years
12.48 million t mined at a diluted head grade of 4.24% zinc, 0.81% copper, 49.6 g/t silver, 0.33 g/t gold, and 22.6% barite
1068 million lb of zinc, 196 million lb of copper, 18 million oz of silver, 91 000 oz of gold, and 2.89 million t of BaSO4
The PEA is preliminary in nature and includes inferred mineral resources that are too speculative geologically to have economic considerations applied to them that would enable them to be categorized as mineral reserves. There is no certainty that PEA results will be realized. Mineral resources that are not mineral reserves do not have demonstrated economic viability.
*Assumptions: US$1.22/lb zinc, US$2.82/lb copper, US$16.26/oz silver, US$1296/oz gold are the average of three years past and projected two years forward based on London Metal Exchange futures, as of 16 April 2019. Barite price of US$220/t provided by third party barite industry experts. **PEA amended March 2022
Over CAN$11 million has been raised through private placements. American Pacific successfully courted and secured Michael Gentile, an active junior mining strategic investor, as a key shareholder. The company and its executives are also regularly interviewed by business and trade press for their financial, commodity, and exploration insights.
American Pacific is persisting in building upon the strength and reputability of its asset portfolio in the Western US, alongside the track record from its partnerships with Rio Tinto and Dowa. To this end, it plans to pursue new high-grade assets that complement its existing projects, further enhancing its overall results and value.
The company has outlined a number of near-term objectives for 2023. Among them, it plans to undertake surface construction, surface drilling, hydrogeology monitoring, and baseline environmental studies at the Palmer VMS Project. This work is to be funded by Dowa.
At Madison, the company is continuing its 2022 – 2023 exploration programme. This work is also partner-funded, with Rio Tinto’s Kennecott Exploration covering the expenditures.
In Nevada, American Pacific is moving forward with exploration initiatives on its Tuscarora, Gooseberry, South Lida, and Red Hill projects, with updates expected during the year.
Sam Garrett, Great Southern Copper, Chile, provides an overview of Chile's copper industry and how it is paving the way for a green energy future.
As the world struggles to deal with the escalating global energy crisis, the need to transition to renewable forms of energy has become more acute as governments look to become energy self-sufficient. Copper – the metal of electrification – is one of the key minerals that will underpin this clean energy transition.
In the past year, copper prices have faced considerable headwinds due to macro-economic pressures.
Goldman Sachs and Bank of America recently predicted that 2023 will see a resurgence in copper prices fuelled by supply constraints and the energy transition, with Goldman Sachs increasing its twelve-month forecast to US$11 000/t from US$9000/t.1
A Goldman Sachs report, 'Green Metals: Copper is the New Oil,' highlighted how reliant renewable energy systems are on copper. Electric vehicles have more than five times the copper of internal combustion engine vehicles, there are approximately 4.56 t/MW of copper in solar power systems and every wind turbine contains up to 4.7 t of copper.2 This global shift in focus to copper intensive energy systems contrasts an ever-widening supply gap. A report from S&P Global in July 2022, 'The Future of Copper: Will the looming supply gap short circuit the energy transition?,' stated the energy transition is expected to increase copper demand from 25 million t today to 50 million t by 2035.3
Unless supply is drastically increased, the goal of net-zero emissions by 2050 looks increasingly unattainable, and copper scarcity could become a real threat to geo-political security. A report in October 2022 from Wood Mackenzie said 9.7 million t of new mine supply will be required over the next 10 years from projects yet to be sanctioned, a shortfall that to date has not yet been overcome in a decade.4
Pre-2020, unattractive copper prices led to stagnant investment in the development of new projects, with new mines historically taking up to 10 years to come online due to challenging greenfield approval, especially in the face of ESG concerns; supply is therefore very inelastic. Industry stakeholders are attempting to expedite the time it takes to get mines up and running, in order to bring on new supply more rapidly.
Funding and sustaining new exploration projects has never been more important to fill an increasing forecast supply gap for copper. One country that is a global powerhouse for copper and hopes to be leading the charge
to new discoveries is Chile, the world’s largest producer and exporter of the red metal.
The level of commercial copper mineralisation in Chile is unparalleled in world terms and the highly sought-after mining regions have historically been home to some of the largest domestic and international copper mining companies, including Codelco, BHP, Rio Tinto and Freeport McMoRan.
Chile is home to six of the ten largest copper deposits in the world and produces nearly a third of the world’s supply of the metal. As demand for copper rises globally, spurred on by a shift to sustainable energy sources, Chile’s role in fuelling this transition cannot be overstated.
Recently, however, some of the largest mines in Chile have seen declining grades and production volumes for copper. Escondida for instance, BHP’s mega mine, has seen a reserve grade that is a third of what it was when the operation started, which is making mining efficiently even more difficult. This question of declining ore body grades can be seen in many of the major mines, and illustrates both a challenge facing the mining industry in Chile today, as well as an opportunity for smaller exploration companies to discover and begin to operate new greenfield projects that could help bridge this burgeoning future supply gap.5
Mining in Chile has been adapting quickly to changing environments and new challenges. Companies have found an imperative, both social and economic, to invest in the sustainability and efficiency of their mines. New projects are incorporating desalination and renewable energy systems to reduce the carbon footprint of their operations, as well as deploying automation and remote operational technologies to improve efficiency and safety.6
There has been significant debate in Chile on key issues impacting the mining industry, including questions around government involvement in the sector, Chile’s mining royalty bill, and matters surrounding environmental impact and sustainability. The issue of potential nationalisation of the copper industry was raised in a constitutional referendum on 4 September 2022, which, if introduced, would represent a fundamental transformation of the mining sector in Chile. Ultimately, this amendment was rejected by the voters who instead opted to keep the status quo intact.
In October 2022, an amended mining royalty bill was proposed, which, if passed, would introduce an ad valorem tax with a flat rate of 1% on large scale copper miners that are profitably producing over 50 000 tpy. In early January, a Chilean congressional committee approved the bill, moving it a step closer to final approval, and it will next be reviewed by the Treasury commission. The bill has drawn criticism from some mining majors and the wider industry for potentially harming the country’s competitiveness and risking future investment. The argument being that the current system has worked well for decades and that the focus should be on protecting the
mining sector, which has been a vital economic sector for Chile, reinforcing jobs, inward investment and ultimately generating valuable foreign currency earnings.
Chile's overall tax-to-GDP ratio and income levels remain among the lowest in the OECD. A report, 'OECD Tax Policy Reviews: Chile 2022,' states Chile's current tax burden is among the lowest found in OECD countries, and has been consistently lower than the OECD average for the past 30 years. In 2019, Chile's tax burden was 20.7%, compared to 33.8% in the OECD.7
In central-northern Chile, modern-era copper exploration is primarily located in the high-altitude Palaeocene metallogenic belt, which contains giant deposits such as Escondida, Chuquicamata, and El Salvador. The Early Cretaceous-age metallogenic belt that dominates the coastal region of northern Chile also hosts large scale porphyry copper deposits, such as Teck’s Carmen de Andacollo mine and, in addition, also hosts IOCG and manto type copper deposits, such as Candelaria and Manto Verde. For junior explorers the coastal region provides a significantly less challenging environment in which to explore and operate with better access to road, power, and port infrastructure. The coastal belt exhibits significant evidence of historical artisanal and small scale mining and processing activity; however, it has not attracted the same level of modern exploration interest or investment as the corresponding high-altitude belts.
It is in regions such as these where junior explorers can help source new discoveries to fuel the global transition to sustainable energy. One example of this is Great Southern Copper plc, which listed on the London Stock Exchange in December 2021, and is focusing its exploration efforts on the under-explored coastal belt. It has identified two early-stage projects in Chile, the Especularita and San Lorenzo projects.
Located 50 km northeast of the coastal city of La Serena, the project comprises of 25 680 ha. of exploitation and exploration concessions both granted and in the process of being granted. GSC owns rights to 100% of the projects via a US$2 million purchase option agreement payable over 6 – 8 years with no additional royalty payments or consideration to vendors.
Work to date by GSC has discovered outcropping evidence of intrusive-related Cu-Au style mineralisation, comprising sheeted fracture-vein systems hosted within a granodiorite intrusive. The granodiorite is invaded by clustered monzonitic stocks with associated high-level unidirectional solidification texture (UST) style alteration and Cu-Au mineralisation. The sheeted fracture-vein system is typically oxidised in surface outcrops and appears to define a broad zone of inner calc-potassic alteration that is coincident with medium-high grade copper-gold anomalism in rock chip samples. The relationship between the mineralised fracture-vein system
and invading monzonitic dykes is not fully understood at this stage, and GSC hopes that recent drilling at San Lorenzo will resolve questions such as this. Results from these programmes will be used to continue to target reconnaissance drilling programmes in 2023.
Located within the coastal metallogenic belt of northern Chile the Especularita project is dominated by a large, partially-eroded advanced argillic lithocap formed in volcanic rocks near the contact with a granodiorite batholith. Alteration and mineralisation related to the
system is observed over a 100 km2 area and includes skarn-type base-metal deposits, mesothermal Au-Cu veins, and Cu-Au breccia pipes. Near-surface porphyry-style Cu-Au style mineralisation may also exist beneath shallow cover and the lithocap and is a primary exploration target for GSC.
Reconnaissance geological mapping and sampling across the project commenced earlier this year and is designed to identify specific areas with potential to host economic Cu-Au mineralisation. Results to date confirm that multiple styles of mineralisation and alteration occur within the area, consistent with a large mineralising system with potential to host porphyry-related Cu-Au type deposits. The reconnaissance work is on-going, and the company expects to generate further exciting prospects in 2023.
Technology is increasingly making its mark on the industry and is being seen as a solution to help close the looming global supply gap for copper. An Equinix Mining Technology report, 'Mining Technology Report 2021-22,' noted that 93% of respondents plan to increase their overall spend on technology.8 Big industry players are turning to innovative solutions that range from using artificial intelligence to scan the earth’s surface for previously undiscovered deposits, to software companies helping mining firms more precisely and quickly measure ore in order to increase production and reduce waste.
Many of the technological innovations aimed at the industry also focus on improved sustainability, with advances in the reprocessing of tailings and the recovery and reuse of water, this is key to attracting new investments into the industry as companies increasingly look to projects with ESG metrics in mind. This push to increase copper supply by more innovative and sustainable means demonstrates just how key new exploration projects are to the industry, and this focus on technological advancements will undoubtedly aid the exploration industry.
Goldman Sachs has called copper "the New Oil." As a commodity, oil has dominated the last century, bending the arcs of technology, society, and geopolitics around its gravitational centre. It is not difficult to see how the same might apply to copper in the coming century. New technologies and business models are being defined by the ongoing green transition which in turn rests firmly on global copper production.
Now a new wave of exploration projects is needed to accelerate levels of supply to a place where they can support global electrification. Chile will continue to lead the charge, with new greenfield projects filling the gaps left by global majors, providing extremely exciting possibilities for copper exploration. The race is on to find the new mega-mines of this century, that can keep our turbines turning and our EVs on the roads.
References:
Available on request.
Eldur Olafsson and James Gilbertson, Amaroq Minerals, Greenland, evaluate the development of the Nalunaq gold project in south Greenland as it approaches production.
Amaroq Minerals is developing the Nalunaq gold project in South Greenland.
The Nalunaq deposit includes a past operating gold mine, first opened in the early 2000s, which produced 350 000 oz of gold before being partially decommissioned in 2014. Amaroq acquired the deposit in 2015 and has since
expanded the known orebody following further drilling, sampling and geological research. In September 2022, Nalunaq was confirmed as one of the world’s highest-grade gold projects, within the top 2% in terms of global reported gold resource grades, with a total inferred mineral resource of 320 000 oz gold.
Having completed a £48 million fundraise in 2022, Amaroq is now looking to proceed with a bulk sample phase ahead of full commissioning at Nalunaq, targeted in 2024. This operation will then underpin the future development of the group’s broader exploration portfolio in South Greenland.
This stage of the Nalunaq development will see the extraction of an approximately 10 000 – 15 000 t bulk sample from the deposit. This sample will provide further geological confidence towards the mineral reserve estimate as well as initial revenue generation potential.
Amaroq’s strategy is to pursue a low-risk redevelopment pathway for Nalunaq, which is known to be high-grade and has already demonstrated its potential through past production. The company will then use the proceeds from the Nalunaq development to fund further opportunities across its South Greenland portfolio. For now, the team is focusing on infrastructure development, such as the
processing plant at the Nalunaq site, so that Nalunaq can also act as a central ‘hub’ for Amaroq’s other assets.
In 2022, a near-10 000 m drilling programme across 46 drillholes resulted in the expansion of the Valley Block (a newly discovered zone of the deposit) on the Nalunaq licence, extending the high-grade core by around 300 m.
These exploration results provided the team with confidence in a second near-term development area within the Nalunaq deposit. Amaroq is expanding the orebody in all directions across multiple headings, as well as increasing its geological knowledge in preparation for a maiden mineral reserve estimate.
As a 21st century mining jurisdiction, Greenland is relatively immature. Mining legislation in Greenland was only established in 2009, and the region remains relatively underexplored, with just two producing mines currently in operation – the Greenland Ruby operation, producing ruby and pink sapphire at Aappaluttoq, and the White Mountain anorthosite mine.
However, in recent years, growing awareness of Greenland’s global strategic position as well as its mineral reserve potential has placed it firmly on the map. This is coupled with the country experiencing progressively increasing exploration expenditure over the last four years. Former US president, Donald Trump, made headlines in 2019 when he expressed an interest in purchasing Greenland from Denmark. The region has also attracted interest from billionaires including Jeff Bezos, Michael Bloomberg and Bill Gates, who are financial backers of mineral exploration startup Kobold Metals, which has partnered with Bluejay Mining in a joint venture to develop critical metals across the country. Amaroq also has an established joint venture with ACAM, backed by US billionaire Louis Bacon, to focus on strategic mineral opportunities.
Greenland, which has limited soil cover and sparse vegetation, resulting in high degrees of mineral exposure, is also home to the Kvanefjeld rare earth project operated by Australia’s Greenland Minerals Ltd, home to an identified over 1 billion t of mineral resources; around 1.5% of global reserves.
Mining the arctic does not come without its challenges. Greenland is sparsely populated with just 50 000 inhabitants overall, limiting local recruitment options. Mining services are underdeveloped, with no new operations constructed for some time, and the remote mining locations are chiefly accessible by helicopter.
In addition, the harsh climate and terrains make for difficult working conditions. These factors, create significant challenges for mineral development. At the height of the COVID-19 pandemic, a travel ban
prevented international workers from accessing the site, leading to the temporary halt of operations for Amaroq and others. One strategy to overcome these challenges involves becoming self-sufficient in terms of accommodation and logistics, something Amaroq has been investing in since the setup of an all-weather 50-person camp, enabling the continuation of exploration and development through winter.
In addition to the camp, Amaroq hopes to overcome both the remote access and staff shortage issues through automation. The group has enlisted ABD Solutions to investigate the potential for introducing vehicle autonomy systems for various mining vehicles at the Nalunaq site. ABD Solutions are currently assessing the site to determine its suitability. This is with a view to reducing human involvement in the operations by producing a fleet of autonomous mining vehicles, also holding potential to address industry-wide labour shortages and reduce costs longer term.
Labour shortages have also led to procurement risks and project delays for miners. The industry lead times for services at the moment are exceptionally long, at times up to a year. To counter this, one of the areas Amaroq is concentrating is its ‘operational readiness’, so the team can be ‘ready-to-go’. The all-weather camp goes a long way towards helping achieve this, but Amaroq also made sure to procure equipment ahead of time, which should keep costs lower longer term.
Building on Amaroq’s intention to develop a modern and responsible operation in Greenland, it is intended that Nalunaq will build and operate Greenland’s first dry stack tailings facility. Dry stack tailing management is widely accepted to be a more sustainable method, having a less hazardous effect on the environment.
Amaroq’s latest resource estimate for Nalunaq was guided by a new working geological model, known as the Dolerite Dyke model, which works to predict the location and extent of the project’s high-grade zones, something that has been particularly difficult historically.
The orogenic gold that Amaroq is targeting at Nalunaq is notoriously sporadic and hard to predict. Over the last two years, the team has built and tested the Dolerite Dyke model, in order to focus resource more effectively.
The 2022 results are now bearing fruit from this labour and Amaroq continues to develop numerous parallel high-grade zones as future mine headings.
With volatile commodities markets, miners globally are facing constrained energy supply with increasing input costs, bringing the renewable transition even further into the spotlight. Whilst Amaroq’s operations
E L E V A T E
O P E R A T I O N A L
The
elevator is the perfect solution for both underground and surface mining applications, such as pelletizing plants, smelter s, concentrator s, and other ore processing plants Alimak elevator s have been enhancing operational efficiency and safety for the global mining industry since 1957.
• Built to perform in the world’s harshest environments
• Enhances operational effi ciency, HSE performance and reduces maintenance costs
• Unparalleled track record in reliability and durability
Visit our website for further information.
E F F I C I E N C Y alimak.com
are currently powered by diesel generators, longer term, Amaroq hopes to introduce renewables to power its mines and other facilities.
Amaroq hopes to be in a position to produce green metals, powered by green energy. This will help to power the company’s sites more sustainably, but also to provide cleaner energy for local communities.
Greenland holds significant potential in this area and is ultimately, for the rollout of renewable energy throughout the country, modelled on the Icelandic system – in which Amaroq can play a role.
The company is now in dialogue with the Greenlandic government to assess potential for green energy production in Greenland. Amaroq hopes to establish whether green energy can be sourced to supply its sites and how to facilitate the development of green energy within Greenland.
Since the outbreak of war between Russia and Ukraine, it is now more crucial than ever to secure raw material supply. Greenland has the potential to become a strategic supplier of rare earths and critical minerals to the West, reducing dependency on Russia and China, who currently dominate supply.
Greenland’s resource potential goes beyond precious metals, holding a variety of raw materials used to develop new technologies.
In 2022, Amaroq agreed a joint venture with resource investor ACAM to fund exploration across its strategic mineral prospects. Amaroq holds a land package portfolio that spans across South Greenland’s emerging strategic metals belt, including copper, zinc, lead, titanium, vanadium, graphite and rare earth minerals. Cash flow from Nalunaq’s operations will be used to fund the future development of these assets.
This exciting development pathway is how Amaroq believes Greenland can become a frontier jurisdiction to supply the highly in-demand materials that are critical to the future.
Lindsay Robertson, McCrometer, USA, outlines how choosing the correct flow meter can optimise slurry and tailings management.
Efforts to improve productivity, decrease downtime, and increase the bottom line are ramping up now more than ever due to the current economic environment. Rising inflation and a severely impacted supply chain have caused many industries, mining included, to seek out methods of curtailing costs and improving manufacturing output. While production, personnel and spending might be the immediate low-hanging fruit that operations managers focus on, there is a way to spend money that helps mining operations increase revenue and improve operational efficiency.
Mining operations may already have flow measurement devices installed in various applications, such as pit dewatering, feed water and air and exhaust flow, but may not be utilising the right flow meter for these applications, or using the meters to their full potential.
For tailings operations and mining applications measuring slurries, companies are often required to report flow to local or federal regulatory bodies, as well as record flow for internal monitoring of efficient system performance. When flow data is critical to both compliance, as well as performance and output, effective flow measurement devices are crucial.
Taking the following factors into consideration when optimising flow measurement can improve overall management of slurry and tailings operations:
It must be said, not all flow meters are alike. There is an assortment of technologies available that suit various flow media, pipeline conditions, and application specifications.
Mining, metals, and mineral processing all vary in their flow measurement needs. For instance, in mineral processing, thickeners may be added to the flow media to increase particle size during water recovery and reuse. This type of application requires a flow meter that can tolerate a potentially caustic and viscous flow media, and can provide the communication outputs needed to send real time flow data to operators and technicians.
While traditional propeller meters, or other mechanical devices, might be suitable for initial feed water, more robust technologies are needed for flow media such as slurries and tailings. Slurries are extremely harsh, corrosive flows with large particles that can damage meters with moving parts or gum up devices, such as Venturis or Coriolis meters. Electromagnetic flow meters are a popular choice for slurries and tailings due to their tolerance for suspended solids, and their lack of in-line components that obstruct flow.
Many mining and mineral processing operations want to reduce water usage and increase output in a slurry and tailings pipeline. Electromagnetic flow meters tolerate slurries with 50 – 60% solids, a benefit to operators and engineers with substantial slurry flows. Additionally, some meter manufacturers offer mag meters with a variety of electrode materials, including stainless steel, hastelloy and tungsten, which can be specified into the project for added corrosion resistance.
In many cases, mag electronics, also referred to as a converter or transmitter, have a specific calibration for slurry flows that include a high amplitude, high frequency signal required for pipeline noise filtering to receive a steady state pulse signal. Some older-style mag meters will rely on analogue dampening to compensate for the pipeline noise created in these applications, which may cause the electrode
signals to take longer to produce a stable measurement. When choosing the right flow meter technology, it is also imperative to select a suitable meter offering the most advanced measurement methods.
A meter that reports accurate flow for years, or even decades, without fail is an incredibly valuable resource. Not only will it ensure precise reporting to environmental regulators, but it will provide operators and engineers with the data needed to make informed decisions about daily operations.
Metering at intake/feed water, effluent, and water treatment processes provide multiple data points to operators and engineers calculating resource efficiency and carbon footprint. For corporations with water savings initiatives, this is incredibly valuable data to have, especially in an industry with pressure to meet socially responsible standards.
In slurry applications, maintaining accuracy can be a challenge due to highly abrasive flow media eroding sensors, dulling orifice plates, or damaging the mechanics of a flow meter. For a high pressure, high velocity slurry, the best recommendation is a full-bore electromagnetic flow meter with a high accuracy. The electrodes will still dull over time (with a slurry, this is inevitable), but installing a ±0.2% mag meter with a durable liner or protective coating will be an effective defense against accuracy loss and erosion. When it comes to slurry processes, even minor improvements to the overall operation can make a positive impact on production and output. Additionally, ensuring that a slurry process does not exceed a velocity of 8 ft/sec. will help prolong the lifespan of the flow meter, as well as prevent premature valve degradation and quality issues.
For slurry and tailings applications, implementing reliable metering devices with repeatable measurements can also become an indicator of surrounding equipment performance. If slurry meter readings deviate from what is expected, it could indicate problems with pumps, pressure surges, valve malfunctions, or even pipeline leaks. Any of these issues can warrant costly maintenance, process shut downs, or environmental impacts. Multiple metering points in a slurry pipeline, especially one transporting from a remote mining site, can identify potential problems before they become damaging.
Tailings, the wastewater produced after mining refining processes, are stored in embankments and ponds protected by liners. These liners provide a barrier between the chemical-heavy tailings and the surrounding environment, preventing the waste material from seeping into the groundwater, affecting local flora and fauna, and endangering the greater community. Tailings storage facility failures pose a massive risk to the environment, and are highly regulated by the Environmental Protection Agency (EPA) and other supervisory bodies.
While tailings management challenges may vary based on the mining operation, location and size of project,
the consensus is that the industry needs better data reliability, insight, management, and integration. A tailings operation has many monitoring points and components, the flow measurement of the tailings effluent and the intake for water treatment and reuse are critical measurement points.
Choosing a meter that tolerates harsh flow media is imperative, but selecting a meter that integrates with the operation’s overall monitoring system is also essential. A flow meter that is battery-powered or solar-powered is an ideal choice for a remote tailings application, and output options such as 4-20mA, Modbus, Hart and others ensure that operators receive flow data as a part of the overall smart mining IoT process. Smart output options save operators and engineers time as well as miles/kilometers traveled, and increase safety measures and the productivity of the overall mine. For companies with tailings ponds in multiple areas, being managed by staff in various locations and time zones, having a fleet of flow measurement devices transmitting accurate, reliable flow data to one streamlined software management system is extremely valuable.
Many flow meter electronics offer datalogging as well, retaining up to five years of historical flow data within the converter or transmitter as a backup. The meter body itself is the conduit for flow measurement, but the signal converter is the reporting, input and output control device, which ultimately provides mining operators and engineers with the data they need to manage their processes.
Mining, metals and mineral processing operations have a multitude of measurement points transmitting data on various flow media. When choosing a flow meter, it is also helpful to consider continuity and standardisation across the entire operation. Many flow meters that are successful in slurry and tailings applications are also satisfactory meters for effluent measurement, water treatment and reuse, raw water intake, desalinisation, dewatering, and more. If the mag meter is exceptionally durable in slurry and tailings applications, they will require less routine maintenance, recalibration, and replacement. This contributes to more system uptime and increased overall process efficiency.
Additionally, streamlining flow meters across applications ensures operators and technicians can programme meter electronics and manage flow data easily from their integrated software. Flow meters are a useful component within the smart mining IoT, bringing efficiency to the next level.
Ultimately, there are a variety of meters on the market from numerous global and domestic flow measurement manufacturers to choose from. Flow meters allow companies to comply with regulations and fulfil data sharing requirements, but they also provide an extremely valuable insight into the health and safety of the overall operation. A truly beneficial flow meter contributes to a company’s overall resource conservation, sustainability objectives, and profitability.
Chances are, we have it. Our bearings, chain, gearing, belt drive, and IoT solutions provide protection against the toughest conditions, to maximize uptime and long-term reliability.
To learn more about our power transmission solutions, including gearing and condition monitoring, visit:
regalrexnord.com/conexpo-2023