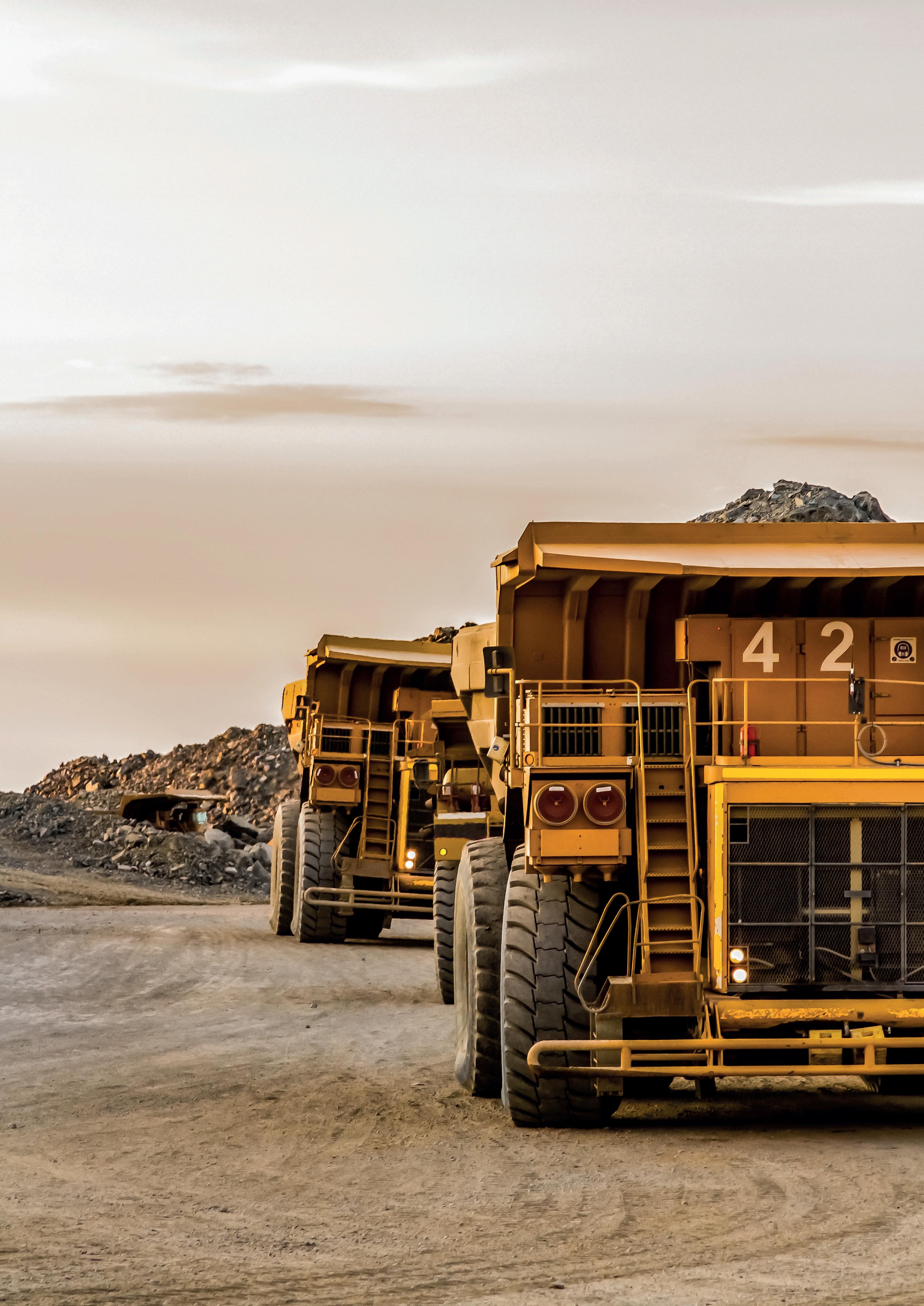
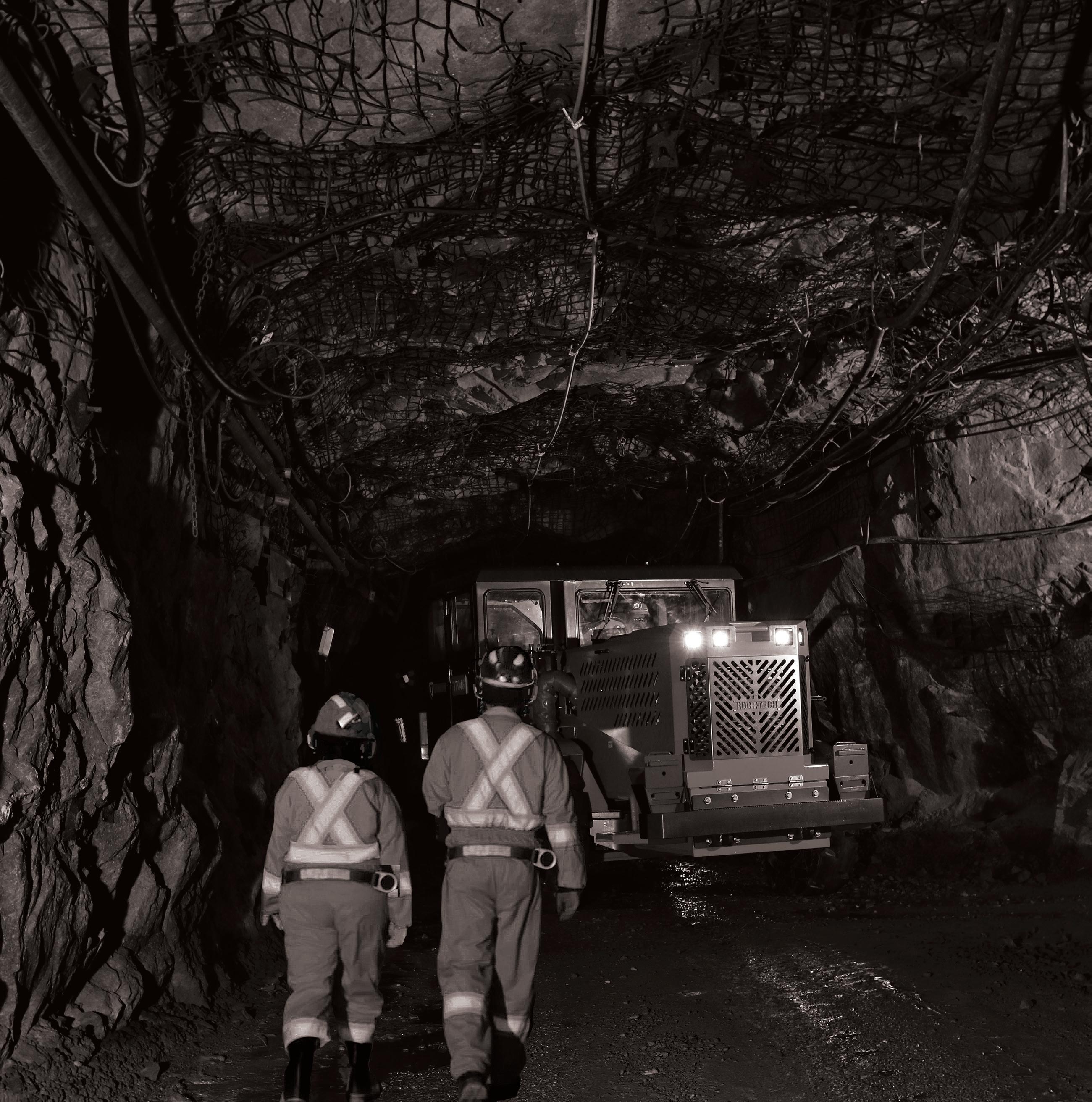
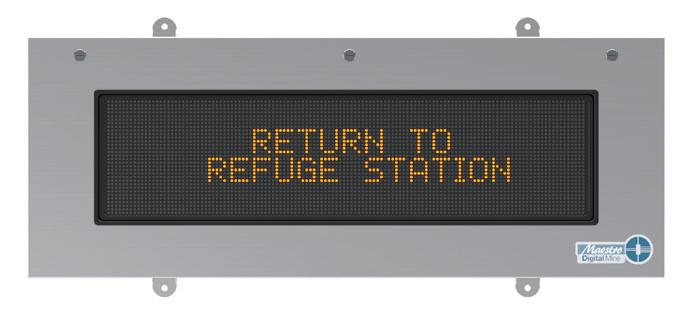
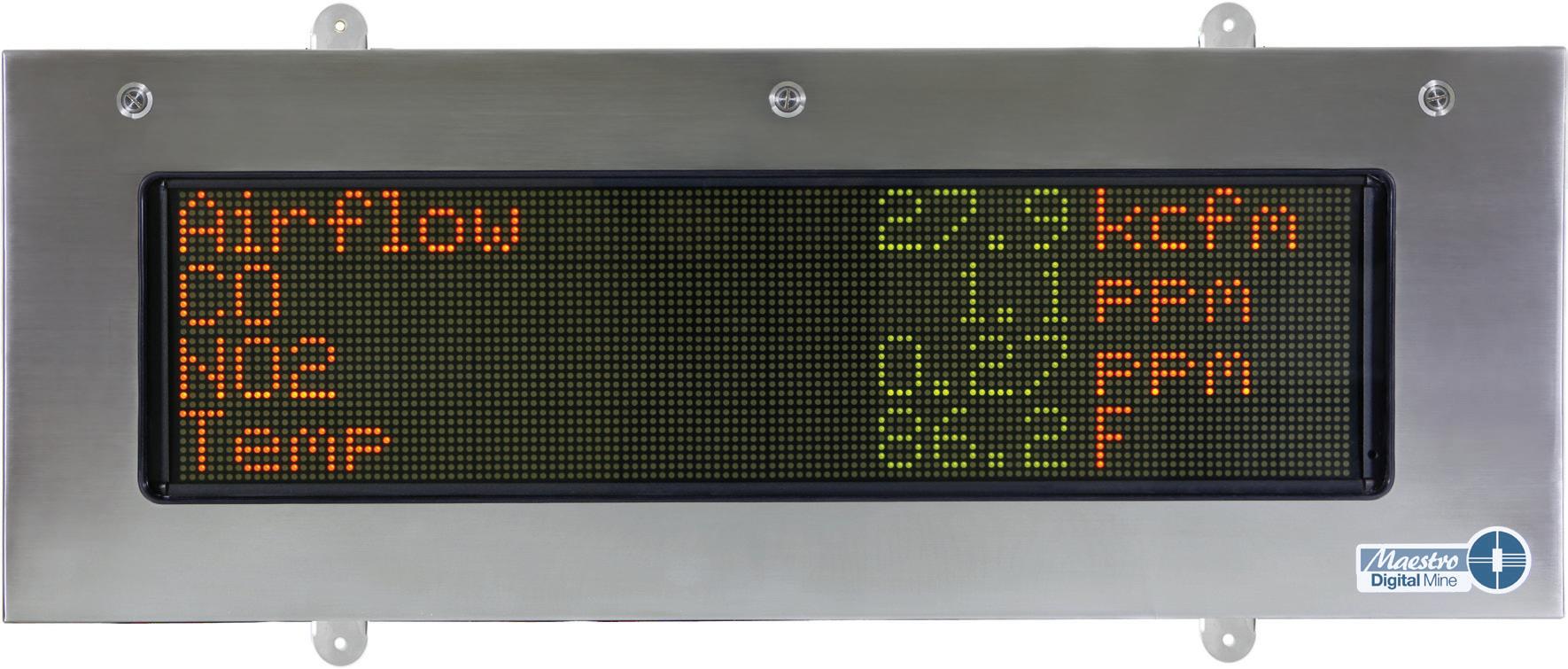
03 Guest Comment
04 Industry News
08 Enhancing Mining Operations Through Digital Twins
Tibor Nemes, Nokia, Hungary, explores the concept of the digital twin and its applications in the mining industry, with a focus on the profound benefits it brings in terms of safety improvements, operational efficiency, and predictive maintenance.
12 Covering A Lot Of Ground
Mario Molina, Emerson, Chile, outlines how a gold mining site uses wireless flow meters and pressure transmitters to gather data from multiple well sites scattered across a huge facility.
17 AUgmenting Operations With AUtonomy
Sagar Chandra, Rajant Corporation, USA, considers why reliable wireless network connectivity is imperative in making mining operations autonomous.
20 Do Away With Dusty Discharge
Todd Swinderman and Dan Marshall, Martin Engineering, USA, discuss how proper belt cleaning can mitigate emissions from carryback and control spillage, improving efficiency and compliance.
25 Dust Control In Coal Mines And Plants
Alwin Nienaber, Weba Chute Systems, South Africa, details how transfer chutes are now key in controlling dust, degradation, and segregation.
29 Conquering Contaminants
Johnny Sajland, SurfCleaner, Sweden, charts the recent progress and overseas growth potential of a new ‘wonder weapon’ that is taking aim at the mining sector’s carbon footprint.
Dr. Benjamin Miller, Pronto, overviews how to overcome the challenges associated with adopting automated mining technologies.
36 Reap The Benefits Of An Integrated System
Mehrzad Ashnagaran and Marcos Hillal, ABB, explain how by connecting electrification and automation solutions in a single, integrated system, companies can extract full value from digitalisation in terms of process efficiency, safety, and sustainability across the entire mine value chain – from pit to port.
Alan Stewart, Rubix, UK, examines how businesses need to ensure maximum bearing life in order to minimise costly downtime and maximise energy usage.
Machinery in mining can suffer extreme wear and tear. This is particularly the case with large industrial fans, whose assets are battered by airborne particles travelling at high-speed. Hans Bengtsson and Daniel Hoekfors, Castolin Eutectic, Sweden, review the impact of such abrasion and explain how to extend the life of components in the line of fire, potentially by years.
Fernando Pinto, UWT, Germany, evaluates a new contact-free radar solution for hot temperatures.
Experience the power of SaberEdgeTM, the ultimate solution for rope shovel lips that redefine excellence.
With unmatched durability and exceptional wear resistance, SaberEdge’s machined adapters result in a precise fit that you can install and forget, eliminating the need for re-tightening—you will only need to touch it again when it is time to remove it.
SaberEdge’s installation and removal require no welding or special tools—thanks to its simplified GET locking systems—enhancing onfield safety, saving time and extending machine availability.
Experience a new era of Whisler-style lips with SaberEdge. Let’s start the conversation.
crmining.com
MANAGING EDITOR
James Little james.little@globalminingreview.com
SENIOR EDITOR
Callum O’Reilly callum.oreilly@globalminingreview.com
EDITOR
Will Owen will.owen@globalminingreview.com
SALES DIRECTOR
Rod Hardy rod.hardy@globalminingreview.com
SALES MANAGER
Ryan Freeman ryan.freeman@globalminingreview.com
PRODUCTION MANAGER
Kyla Waller kyla.waller@globalminingreview.com
ADMINISTRATION MANAGER
Laura White laura.white@globalminingreview.com
DIGITAL ADMINISTRATOR
Leah Jones leah.jones@globalminingreview.com
DIGITAL EVENTS COORDINATOR
Merili Jurivete merili.jurivete@globalminingreview.com
EVENTS MANAGER
Louise Cameron louise.cameron@globalminingreview.com
We are undoubtedly living in a time of increasing complexity, in which the challenges in raw materials and energy supply are becoming ever more multifaceted. Mining plays a crucial role in realising the energy transition, which would be unthinkable without the availability of raw materials. In order to fulfill this important role, and at the same time operate in a more environmentally conscious way, new technological innovations in the areas of automation, digitalisation, and electrification are imperative for the mining industry.
The spectrum of opportunities for technological innovation are manifold, but, in the end, I am convinced that breakthrough effects rather can be expected how meaningful and successfully the full suite of technologies will be developed, implemented, and integrated across entire mining operations; moving towards digitally connected, autonomous systems.
Even though technological innovations are indispensable, we should not forget that people must always remain at the centre of our considerations. Technological advances are crucial, but we need to ensure that mining becomes more sustainable without losing sight of the fact that it is people who will shape the current transformation, and contribute the necessary skillsets and competencies to make this transformation succeed. This is what we have defined as the human-centred climate smart mine.
Aside from the challenge of educating and training the next generation of miners that can adapt to the transformation the sector is undergoing and enabling them to shape the mining of the future, promoting collaboration and partnerships between companies, but also between industry and research, is, I believe, a critical factor for a truly sustainable future for the mining sector. Thus, to drive innovation, we need to create spaces where industry, research, and other stakeholders can meet, interact, collaborate, and learn from and with each other.
The importance of science and research for the development of new solutions should not be underestimated. Close cooperation with research makes it possible to respond effectively to the challenges of mining and to develop tailored innovative solutions. Trust between all parties involved is of great importance in this process.
To promote this kind of hands-on and industry-oriented exchange and the building of trust as well as to foster new partnerships, the Institute for Advanced Mining Technologies organises an international non-profit conference every two years. The High-Performance Mining Conference is characterised by a high level of participation and attendance from industry, including mining companies, OEMs, and technology provider from within and outside of Europe, along with representatives from academia, industry associations and public institutions. This year, the conference will take place on 7 – 8 September in Aachen, Germany, and will bring together approximately 200 participants from the international mining industry.
Events, such as the High-Performance Mining Conference, we believe make a valuable contribution to making mining more sustainable and future-oriented. By working together to harness the opportunities of technology and foster collaboration, we can positively shape the future of mining.
Integrated Wireless Innovations Inc. (IWI), a Canadian-based innovation firm, has introduced its latest innovation and development for mining and tunneling operations: NeuraCOM, the first AI-based network infrastructure in mining. This technology promises to revolutionise the way mining companies operate, offering improved safety, efficiency, and productivity.
“Current mining communication networks are facing major challenges in supporting advanced mining applications such as autonomous mining, autonomous vehicles, systems automation, and control. Mining networks are required to be UNIFIED and intelligent to support multiple communication protocols (MCP), while maintaining high network capacity, low latency, scalability, and resiliency requirements for the advanced mining applications”, explains Dr. Wisam Farjow, Ph.D., President of IWI.
This patented innovation utilises AI-based processes and algorithms to introduce novel communication networks infrastructure. “Our self-organised network (SON) and neural networks were designed specifically for mining operations to provide the needed unified communication networks (UCN) platform and ensure reliable digital transformation and transitioning to Mining 4.0 applications”, Dr. Farjow elaborates.
At the physical layer, NeuraCOM features intelligent hybrid network architecture (I-HNA Architecture), where dynamic and integrated adaptations for number of networking technologies – such as leaky cable, fibre networks, and wireless mesh – are all integrated in adaptive and on-demand fashion under one network, in order to provide physical network unifications architecture.
At the application layer, IWI’s novel service oriented algorithms (SOA) unify number of communication protocols under one network infrastructure. Communication protocols for data and voice communications based on VHF/UHF, broadband, LTE, and Wi-Fi are all integrated in one network infrastructure to allow applications and users to adaptively access the requested services when required.
NeuraCOM is powered by NeuraVu, a complete graphical unit interface (GUI) application that enables network monitoring and access control to all network elements locally and remotely, via the cloud platform. The NeuraVu features advanced data analytics modules to provide state of the art network diagnostics and health monitoring systems. NeuraVu monitors all network elements, including: neura line amplifiers (NLA), neura fibre amplifiers (NFA), underground neura power supplies (N-UPS), leaky cable for damages, and fibre networks.
Rio Tinto has awarded Metso a detailed design and engineering contract for its continuous pilot plant (CPP) for the BioIron™ process.
The contract is an extension of the work that Rio Tinto and Metso have been doing together on the development of the BioIron process, the effectiveness of which was successfully proven through small-scale pilot tests conducted at Metso’s research centre in Frankfurt, Germany.
Rio Tinto aims to move further towards full-scale implementation of the BioIron technology through operation of a CPP. Metso has been entrusted with the detailed design of the CPP’s reduction furnace and certain other equipment for the BioIron process.
Hexagon AB has announced an agreement with Mineral Resources (MinRes) to provide an autonomous haulage solution for a fleet of 120 fully autonomous road trains in Western Australia’s Pilbara region.
The world-first, fully autonomous road trains are a full-site, truck-agnostic solution. The addition of unmanned and autonomous systems will form an essential part of the supply chain for the MinRes Onslow Iron project.
The centre of the autonomous platooning system is Hexagon’s autonomous solutions stack, integrating drive-by-wire technology with an autonomous management system to orchestrate vehicle movement in road train haulage.
AIMEX
05 – 07 September 2023
Sydney, Australia
www.aimex.com.au
High-Performance Mining Conference
07 – 08 September 2023
Aachen, Germany
www.hpm.academy-rwth.de
Mining Indonesia
13 – 16 September 2023
Jakarta, Indonesia
www.mining-indonesia.com
Iron Ore Conference
18 – 20 September 2023
Perth, Australia
www.ausimm.com/ conferences-and-events/iron-ore
China Coal & Mining Expo
25 – 28 October 2023
Beijing, China
www.chinaminingcoal.com
International Mining and Resources Conference (IMARC)
31 October – 02 November 2023
Sydney, Australia
www.imarcglobal.com
Resourcing Tomorrow
28 – 30 November 2023
London, UK www.resourcingtomorrow.com
To stay informed about upcoming industry events, visit Global Mining Review’s events page: www.globalminingreview.com/events
FLSmidth has been chosen to supply the key technologies and services for Ma’aden’s phosphate 3 phase 1 mine site in the Northern Province of Saudi Arabia.
The order is valued at approximately DKK 530 million and was booked in 3Q23. The equipment is expected to be fully integrated during 2025.
FLSmidth has partnered with Ma’aden from the onset of the new phosphate mine operations – starting with initial laboratory testing of samples retrieved from the ore body in 2019, through to the development of the flowsheet and pilot scale testing. The focus of the collaboration has all along been to ensure that the integrity of the flowsheet is maintained, while ensuring that the technology is well integrated into the overall plant design, in order to deliver best possible performance from the process plant operations.
With this new order, FLSmidth will supply all the key equipment associated with the phosphate beneficiation plant, as well as technical support services through the design, construction, commissioning, and ramp-up phases. The order includes both primary and secondary sizers, apron and HAB feeders, cone crushers, screens, cyclone clusters, ball mills, paste and high-rate thickeners, horizontal belt filter, slurry pumps, knife-gate valves, and flotation columns.
Murray & Roberts Cementation achieved a significant milestone at the end of July 2023, when it successfully reached the 1000 m mark on its contract to sink the 1200 m ventilation shaft at Palabora Mining Co. (PMC)’s Lift II expansion. This significant feat stands as a testament to the company’s capabilities and dedication to safety.
The PMC Lift II expansion project is a crucial endeavour for PMC, aimed at enhancing the efficiency and capacity of their operations. The 8.5 m diameter ventilation shaft will serve the Lift II block cave and plays a pivotal role in the overall mining infrastructure. Reaching a depth of 1000 m in the ventilation shaft is a major accomplishment, highlighting the expertise and commitment of Murray & Roberts Cementation in tackling complex mining projects.
Fred Durand, Murray & Roberts Cementation’s Senior Project Manager, says one of the most remarkable aspects of this project is the unwavering focus on safety:
“Despite the immense challenges involved in underground mining and especially blind sinking, we have maintained an impeccable safety record throughout the Lift II expansion project. The team’s relentless dedication to safety protocols and best practices resulted in an impressive milestone earlier this year of 574 consecutive days without a lost time injury (LTI).
“As the ventilation shaft project enters its final stages, the excitement and anticipation among all stakeholders, including PMC and Murray & Roberts Cementation, are palpable. The successful completion of this project will not only mark a significant engineering feat, but will also have a profound impact on PMC’s mining capabilities.”
ASI Mining, in conjunction with its distributor Epiroc, has received an order from Roy Hill Iron Ore to automate 18 Hitachi EH4000 haul trucks to be integrated with its current autonomous haulage fleet in Western Australia.
The additional trucks will increase Roy Hill’s fleet to a total of 96 haul trucks which, once converted to autonomous operation, will make Roy Hill the largest single autonomous haulage system (AHS) site in the world.
Once the entire fleet of 96 haul trucks is autonomous, it will boast not only being the largest AHS fleet at a single site, but also the first site operating four different model variants from two different truck OEMs.
The EH4000 fleet is being added to expand production capacity at Roy Hill’s mining operations. These new trucks will
join an existing fleet of Caterpillar 793F (models SSP and CMD) and Hitachi EH5000 haul trucks, in the process of being converted to autonomous trucks at the site.
The AHS project at Roy Hill commenced its fleet expansion phase in January 2023, following completion of a two year validation period. It is anticipated all 96 of Roy Hill’s trucks will be fitted out by the end of 2024.
ASI Mining’s Mobius AHS has been operating successfully 24/7 in a dedicated autonomous operating zone (AOZ) since July 2021, with Roy Hill achieving performance targets with a smaller fleet of 793Fs and EH5000 haul trucks.
“The receipt of this expansion order from Roy Hill signals their continued commitment to OEM agnostic autonomy and their continued trust in ASI Mining and Epiroc”, said Diederik Lugtigheid, President of ASI Mining.
ABB is collaborating with Norge Mining to conduct a front-end engineering and design (FEED) study for a future Norwegian upstream mine, which has the potential to supply minerals used in electric vehicles and solar panels needed for the clean energy revolution, and fertilizer demand, for at least 50 years.
The deposit contains large resources of phosphate, titanium, vanadium, and phosphorus – four key EU-designated critical raw minerals that are essential for the clean energy transition and global food security.
Phosphate is processed and used to produce lithium-ion phosphate (LFP) batteries, as well as fertilizer for the agriculture industry, and is in high demand, with a recent US Geological Survey indicating phosphate reserves prior at 71 billion t globally. Norge Mining recently announced that it has discovered up to 70 billion t of a mineralised igneous phosphate rock at the new mine site in southern Norway, known as the Bjerkreim-Sokndal Layered Intrusion site.
“Norge Mining’s transformative partnership with ABB marks a new era for more sustainable, resource-efficient mining,” said Michael Wurmser, Founder at Norge Mining. “Together, we’re aiming to power progress through next-generation mining. With Norge Mining’s portfolio of significant, critical and strategic raw minerals, it will make significant global impacts on enabling food production and supplying the European battery manufacturing industry.”
“ABB is excited to begin this important project with Norge Mining, one that is anticipated to have a positive impact on European supply chains for the energy transition”, said Alex Kaufmann, Business Line Manager Mining for Process Industries Switzerland at ABB. “Through our early involvement, as well as our expertise in design and solutions for mining, we will support Norge Mining to optimise costs; both during the construction phase, as well as during the operation of the mine. Furthermore, our eMine™ approach for electrification and automation, which makes mines all-electric and includes integrated solutions that help eliminate CO2 emissions, will help to increase the mine’s efficiency and ensure energy efficient and seamlessly integrated systems across the entire plant.”
ABB and Norge Mining will explore the entire electrification of the future mining and downstream operations including control system options to provide a complete overview of the mine and seamlessly integrate advanced operations. The ABB study will address electrification, automation, and digitalisation to ensure maximum sustainability, cost-efficiency, and productivity at the mine from the outset and for the long term. ABB’s recommendations will also focus on low energy consumption within mine operations, as well as optimising CAPEX and lowering OPEX with solutions for lower maintenance and higher efficiency.
Tibor Nemes, Nokia, Hungary, explores the concept of the digital twin and its applications in the mining industry, with a focus on the profound benefits it brings in terms of safety improvements, operational efficiency, and predictive maintenance.
In recent years, the mining industry has been facing unprecedented challenges, such as: increasing demand for minerals, declining ore grades, rising costs, environmental and social pressures, and rapid technological changes. In order to overcome these challenges, mining companies need to embrace digital transformation and leverage the power of data and analytics.
The industry has also witnessed remarkable advancements in technology, leading to substantial improvements in safety, operational efficiency, and maintenance procedures. One transformative concept that has gained significant traction toward digital transformation centres around simulation and digital twins.
There are many different interpretations of the digital twin. Nokia’s approach is to provide a digital twin to monitor customer’s network operations in real time, and thus predict maintenance needs and potential downtime in the operational environment.1
The digital twin is a relatively new technology that is proving to be a game-changer in the mining industry. The idea of the digital twin entails making a virtual twin of a real-world system, process, or object. It creates a digital replica of the physical object using real-time data from sensors, Internet of Things (IoT) devices, and other sources. It provides a holistic view of assets and processes, enabling mining professionals to combine real-time data and advanced analytics to make insights-driven decisions, enhance safety protocols, improve operational efficiency, and implement proactive maintenance strategies.
A digital twin is not an application that provides a result to a user; instead, it serves as a platform for other applications, such as situational awareness via dashboards. It can be used by applications to derive insights or trigger actions implemented via the asset administration shell in the Industry 4.0 context, or send commands to actuators in a broader IoT context. This concept is in line with the definition given by the Digital Twin Consortium: “A digital twin is a virtual representation of real-world entities and processes, synchronised at a specified frequency and fidelity.”2
The concept of the digital twin has gained popularity, spawning three other significant applications or
evolution paths: simulation, geospatial digital twins, and network digital twins. All three are required for the metaverse to function. Simulation is an application that uses data from a digital twin to predict the outcome of a change or scenario prior to its physical deployment. Such a result would be used to make informed decisions before investing. The geospatial digital twin is the concept of incorporating geospatial data into a digital twin. Geospatial data is more precise data that describes the world. It could be about 3D models, precise location data, and attributes – such as the characteristics of the object, event, or phenomenon in question and/or temporal data. The value proposition of the geospatial digital twin is to enable immersive user experiences and simulations that are very close to reality. The network digital twin is a digital replica of a network. Network digital twins can be used to create a variety of networking applications. A network digital twin, for example, enables a network operator to perform online network optimisation, what-if analysis, troubleshooting, and network upgrade planning. Network automation and (re-)programmability are central to network digital twin value propositions.
There are also advantages to federating network and geospatial digital twins, so that simulations can study the end-to-end benefit of an operational change – including its effects on network configurations. The concept of (any digital twin) federation can also be applied more broadly, supporting users’ needs to use any data set (subject to access rights) and paving the way for a universal metaverse.
Digital twins offer a range of advantages to the mining sector, revolutionising traditional practices and enabling more efficient and sustainable operations.
n Real-time monitoring and predictive maintenance: Digital twins provide real-time monitoring of mining equipment by leveraging sensor data and IoT connectivity, allowing operators to assess performance, detect anomalies, and prevent breakdowns. Predictive maintenance algorithms examine data patterns and send alerts when maintenance is needed, reducing unplanned downtime and increasing asset utilisation.
n Safety and risk mitigation: Digital twins make it possible to create virtual environments for training and simulating dangerous mining scenarios. This improves safety training, lowers on-site risks, and increases emergency response readiness. Miners can also operate equipment remotely from safe locations, reducing their exposure to hazardous conditions.
n Process optimisation and efficiency: Mining processes – such as drilling, blasting, and ore extraction – can be optimised using digital twins and simulations. Mining companies can identify the most efficient and cost-effective approaches by virtually testing various parameters; improving productivity and reducing waste.
n Environmental impact reduction: Digital twins support sustainability initiatives in the mining sector. By integrating real-time environmental data – such as air quality, water consumption, and energy usage –
digital twins help optimise resource utilisation, reduce emissions, and mitigate the environmental footprint of mining operations.
n Reducing supply chain complexity: By projecting market circumstances, client preferences and price variations, digital twins can aid in synchronising supply and demand, tracking inventories and shipments, and managing logistics and transportation.
Implementing digital twins in mining is not a one-size-fits-all solution and not a simple task. It requires a cultural change, a clear vision, a strong commitment, and a collaborative approach. It requires a customised approach that takes into account the unique demands and objectives of the mining company and a collaborative effort among different stakeholders, such as: operators, engineers, managers, suppliers, regulators, and customers. Last, but certainly not least, it requires a robust digital infrastructure that can support the data collection, transmission, storage, analysis, and visualisation of digital twins.
To implement digital twins successfully, mining companies need to follow some best practices, such as:
n Clear understanding of the business requirements and the way these are implemented into the digital twin solution.
n A lean, agile cross-functional project team combining a deep know-how of the supply chain and an excellent development team.
n Advanced data management for accessing, retrieving, validating, and correcting of all needed data points.
n Engaging and empowering end users of digital twins – such as operators, engineers, and managers – by providing them with user-friendly interfaces and tools, training and support, and feedback mechanisms.
Digital twins certainly are a new frontier for innovation and efficiency in mining. They can help mining companies gain a competitive edge, improve performance, reduce costs, enhance safety, and minimise environmental impact. However, implementing digital twins in mining is not a trivial endeavour. It requires a strategic vision, a cultural shift, a collaborative effort, and a continuous improvement mindset. Mining companies that can master these aspects will be able to reap the full benefits of digital twins in mining.
Nokia can provide the first step of the digitalisation process by deploying a pervasive wireless coverage for critical operations at a mine site. The company can then provide the network digital twin to identify performance or coverage gaps before the introduction of the new automated process, as well as gain valuable insights of the network performance.
1. ‘Nokia Network Digital Twin’, Nokia, www.dac.nokia.com/nokianetwork-digital-twin/
2. ‘Glossary of Digital Twins’, Digital Twin Consortium, www.digitaltwinconsortium.org/glossary/glossary/#digital-twin
With demand for raw materials increasing and ore grades declining, it’s more important than ever to optimise process plant efficiency.
Our proven mobile sizing and ore diverting solutions, alongside new ore sensor technologies, can make this happen –separating ore from waste in the pit whilst uplifting ore grades through fines recovery. Introducing an automated ore sorting solution into your existing system ensures only the pay material is hauled to the process plant – meaning your mine can improve production whilst reducing energy usage and water consumption.
Whether you have an underground or open pit operation, our network of technical experts can help develop a tailor-made in-pit sorting solution to boost productivity and deliver a leaner, greener mine.
While the grizzled prospector with a pan and burro are long gone, a lot of gold is still pulled out of the ground worldwide. Today, the technologies are much different and the work is done by corporations, but the objective of finding this precious metal remains the same.
Mining for gold, silver, and copper are similar operations – each uses a combination of opencast and underground mines to dig out ore, which is refined using heap-leaching and other methods. This article will look at specific problems and solutions implemented at one site that operates a mix of opencast and underground mines in Nevada (Figure 1).
A mine is, ultimately, a hole in the ground, and water will inevitably find its way in. Depending on the location and depth, it can be surface water runoff or groundwater that gets
into deep excavations and shafts. Too much water destabilses the ground, creating conditions for accidents.
Since mining sites normally have both opencast and underground mines, there are many wells drilled at strategic points to control the local water profile and keep the mines dry. Some water is pumped into storage ponds on the site or used for process needs, and some suitable water is pumped off site – primarily for irrigation in the surrounding communities, since there are often few other water sources.
Individual wells are normally instrumented, most with flow meters, and some also with pressure transmitters (Figure 2). However, these instruments are rarely networked to send data to any automation system, but rather depend on manual rounds by operators to keep an eye on individual performance. At one point, the company investigated the possibility of implementing a supervisory control and data acquisition (SCADA) system, but the plan was rejected as too
costly and elaborate for the amount of data involved and its potential value.
Company engineers concluded that what they really needed was a historian capable of recording real-time data from the instruments in a way that operators could track and compare output from each well, but there was no need for real-time control functions. However, even this simplified approach proved too costly due to the amount of cabling necessary, since the wells to be monitored can be hundreds and even thousands of feet apart.
The full site covers more than 30 square miles, so distance enters into every technology discussion. While a wireless solution seemed like the only practical approach, the first question was always, “Can it handle the range?”
When Emerson’s local application engineer consulted with the mine’s design team, WirelessHART® was presented as the best protocol for the application. His answer to the key question was, “Range is not a problem if we configure the network correctly.” A small demonstration network with two wireless instruments reporting to a single gateway was installed as a result.
While this project was underway, the engineering team and the IT department studied how WirelessHART uses its 2.4 GHz radio to send data, how signals propagate, and how the network automatically organises itself to create a mesh capable of routing communication around obstacles and over long distances.
When it was clear that WirelessHART could handle communications over long distances, it was time to deploy
Mario Molina, Emerson, Chile, outlines how a gold mining site uses wireless flow meters and pressure transmitters to gather data from multiple well sites scattered across a huge facility.
the first full scale network. The part of the site selected was a series of dewatering wells deployed around the southern and eastern perimeter of the largest pit, along with a smaller number of wells around an adjacent pit. In the context of the site, these are considered small installations since the half-circle of wells around the larger pit is a little more than three miles from end to end, although the access point is located close to the centre.
There are 24 dewatering wells serving the large pit, all but one of which are equipped with magnetic flow meters, and 10 of which also have pressure transmitters. These flow meters and pressure transmitters have all been equipped with Emerson Wireless 775 THUM Adapters (Figure 3) to add WirelessHART connectivity to these existing field instruments. This adapter can be added to any HART-enabled instrument from any manufacturer, transforming it into a WirelessHART instrument.
All the instruments associated with the dewatering wells are powered via cables, but there are no data-carrying cables, hence the need for the WirelessHART adapters. The THUM requires very little power, so it can be supplied via the instrument’s power feed.
There are also 25 dewatering wells serving the smaller adjacent pit. These wells have not been as heavily instrumented as those around the larger pit, but five of the wells are outfitted with magnetic flow meters and pressure transmitters, all now equipped with WirelessHART adapters. For this initial project, 43 WirelessHART adapters were installed and connected to the network.
Previously, operators performing manual rounds read the data from each instrument’s local display and noted it as required. In addition to the current flow reading, the flow meters also acted as totalisers. Operators would record the total for whatever period of time and then reset the figure manually at the device.
WirelessHART is a communication protocol supported by the FieldCommGroup, and it is designed specifically for process field instruments measuring common variables such as pressure, flow, temperature, level, and more. It is an extension of the original HART protocol, which is virtually universal for wired, 4-20 mA analogue instruments. The underlying concept is that each instrument sends its variable at a prescribed interval, typically every 10 secs. for a fast-moving variable, to once per minute or even less frequently, for a variable that changes slowly.
Many instruments are now available as native WirelessHART transmitters, but any existing wired HART instrument can be outfitted with an add-on adapter, as with this project. The team did not add any new flow meters or pressure transmitters, but simply added THUM adapters to what was already installed.
The individual instruments form a self-organising mesh network (Figure 4),
Subscribe online at: www.globalminingreview.com/subscribe
15 South Street, Farnham, Surrey, GU9 7QU, UK
Subscribe online at: www.globalminingreview.com/subscribe
Subscribe online at: www.globalminingreview.com/subscribe
T: +44 (0)1252 718999 F: +44 (0)1252 821115
E: info@palladian-publications.com
15 South Street, Farnham, Surrey, GU9 7QU, UK
T: +44 (0)1252 718999 F: +44 (0)1252 821115
15 South Street, Farnham, Surrey, GU9 7QU, UK
E: info@palladian-publications.com
T: +44 (0)1252 718999 F: +44 (0)1252 821115
E: info@palladian-publications.com
meaning that each instrument functions both as a receiver and transmitter. All the instruments in the network eventually send data to a gateway, which is used to join the wired network and connect to a host system, in this case, a process historian.
The 2.4 GHz radios in each wireless device normally have a relatively short distance range, but this can be greatly increased because the network passes data packets from device to device in hops, relaying it from the most distant instrument to the access point and gateway. This functionality provides the performance needed for a site where devices are spread over a large area, such as a mine. Its self-organising capability allows the network to adjust itself as needed if there is interference, or if individual devices go offline.
In areas where the device distribution is especially thin, adding a repeater (a transmitter without an associated instrument) strengthens the network by adding additional paths. For this project, four repeaters were added to improve network density and add more communication paths. Reliability of the network since startup has exceeded 98%.
As mentioned earlier, data from the field instruments is captured and recorded by a process historian running on
servers in the site’s operating building. Here, operators can see what is happening in the field and reset totalisers, although opening and closing valves or turning individual pumps on or off is still a manual operation.
Eliminating manual rounds allowed site managers to deploy personnel on higher-level tasks to improve and optimise production. Operators, engineers, and environmental department personnel can compare what is happening at multiple points as needed – they can scroll through historical data quickly and easily, rather than sifting between manually-recorded reports. In addition, ready availability of this operational data informs all stakeholders of key performance indicators related to environmental, sustainability, and safety objectives.
When first deployed, operators often compared their manual readings from the local instrument displays against data collected on the network, but quickly found this was not necessary as the data always matched.
The company is already looking at areas where WirelessHART can support more effective data collection over even longer distances. Many instrumented application points are spread across the site that need to be monitored more closely, calling for WirelessHART networks.
These additional projects will require communication with remote field instruments installed six miles or more from an access point. Since new instrumentation will be involved, facility personnel are looking at using Rosemount transmitters with native WirelessHART connectivity, rather than adapters. Parabolic and other directional antennas (Figure 5) able to increase range will be part of this deployment, so additional testing is underway to verify the capability, but the success so far bodes well for the next step.
This WirelessHART deployment has saved the company thousands of hours previously spent by staff making manual rounds to gather data from instruments. Safety has improved because personnel now spend less time in the field. Finally, collecting data more often and with greater reliability has improved operations through performance optimisation.
Most mining sites are spread out over large areas, making wired communication between instruments and host systems impractical. As shown in this application example, this challenge can be overcome by installing a wireless network, for a fraction of the cost of hard wiring. With WirelessHART, instruments can be purchased with this protocol natively built in, and existing instruments can be joined to the network by adding an adapter, which converts the instrument’s 4-20mA output to a wireless signal. The result is a network that can cover very large areas reliably, supplying the data needed to improve operations and safety.
Sagar Chandra, Rajant Corporation, USA, considers why reliable wireless network connectivity is imperative in making mining operations autonomous.
The net profit margin of the mining industry has slipped recently, decreasing 10% from 2015 to 2021.1 This has placed mounting pressure on mining operators to produce and process ore at a lower cost per tonne. To remain profitable in an increasingly competitive landscape, all while operating in some of the most complex and ever-changing industrial environments, mining companies must leverage new technologies to optimise their productivity. Constant mobility is critical in ensuring that opencast mine production never ceases to operate, as any
downtime experienced will mean that real-time applications will be affected, which can be costly.
Much of the world's annual output of copper, gold, and iron ore is delivered from opencast operations. Essential for central banks, investors and modern technology, gold has significant financial value. As of February 2023, the price of gold was more than US$1870/oz.2 In growing numbers, gold mining operators are realising the importance of intelligent automation to improve efficiency and reduce costs. This includes the integration of robotics with components from
different emerging technologies, such as artificial intelligence and the Industrial Internet of Things (IIoT). But this is just the first step.
The shape, depth, and configuration of a surface mine constantly change as extraction occurs. Equipment and infrastructure must be moved almost daily away from new blast zones, which means network coverage must frequently shift accordingly. This creates a problem for traditional wireless networks that operate from fixed infrastructure, such as Wi-Fi Mesh, Point-to-Multi-Point (P2MP), and LTE. Companies must implement a reliable network to overcome the connectivity issues posed by a challenging mining environment and achieve connected opencast operations.
The mining industry invests in various technologies – such as fleet management, machine guidance, remote machine health monitoring, and real-time video of working areas – to improve safety and efficiency.
The work zone environment transforms when machinery, equipment, and people are constantly interconnected. Onboard and fixed sensors can monitor temperature and air quality in underground operations to ensure adequate ventilation, while cameras can stream dynamic video to central command. Wearable devices, in combination with sensors, can alert workers when they are entering an unsafe area and track their progression. Real-time data captured from these sensors and cameras can also transmit to numerous screens residing in control rooms to alert operators with warnings – for example, regarding worker safety.
As more and more devices interconnect, the volume of data transmitted grows exponentially; providing management teams with greater insights into the conditions and operations of the mine. In addition, real-time telemetry enables them to monitor and control autonomous and remote-controlled vehicles, machinery and processes, leading to more efficient use of resources and better adherence to safety standards. As risks are mitigated, workers are moved out of harm’s way, and fatigue is reduced, leading to fewer accidents.
To unleash and fulfil sitewide autonomy, new technology requires reliable wireless network connectivity. Networking keeps operations running smoothly ensuring staff, equipment, and applications remain functioning 24/7, 365 days a year. A solution that allows opencast mines to quickly interconnect existing infrastructure, introduce new technology, and relocate or remove network infrastructure all without causing network downtime is needed.
At opencast mines, the wireless network faces propagation issues primarily due to changing topography and the constant movement of the fleet. Therefore, the network needs to be capable of extending over many miles and being easily redeployed as the mine moves. Traditional wireless networks rely on fixed transmission points, so they cannot be easily reconfigured and expanded.
Decentralised wireless mesh networks, free of infrastructure constraints, are the answer to these problems. In a wireless mesh network, there is no single point of failure, as each node acts independently, forming connections to other nodes. If one node becomes temporarily unavailable or goes down, it should have no impact on the network. The type of mesh required for mining should be self-healing, so that if one node becomes unavailable, the next node self-optimises to find another efficient path to transmit data.
Mesh networks with such capabilities have radio nodes that can be installed on machinery, vehicles, wearables, and drones/robots, as well as fixed locations. This means that the network is
incredibly flexible and mobility enabled. As equipment, vehicles, and people move around, so does the network. This is because each moving equipment functions as a repeater for the rest of the fleet. As operations expand, involving more people and equipment, the network seamlessly scales with more nodes added, so the network grows in sync with operations. Similarly, if the mining operation relocates, so too can the network. With few or no fixed nodes, the network is essentially portable.
Wireless mesh networks are far easier to set up than traditional fixed networks, and they are inherently more versatile, reliable, and flexible than traditional wireless and fixed networks. Up and operational in minutes, no downtime is experienced.
Located in a remote area in the mountains of Northern Chile, a gold mining company selected Wenco as the provider of fleet management system (FMS) to help increase productivity.
A vital facet of the Chilean economy, the mining sector accounted for more than 14% gross domestic product (GDP) of the country’s GDP in 2021 and also generated 200 thousand jobs.3 Chile is known for being the top producer of copper in the world, and its production also ranks amongst the highest globally for production of a series of metals and minerals, including gold.
The mine is nearly 4500 m above sea level, with adverse weather conditions where winds can reach speeds of up to 100 km/h and temperatures close to -30°C. In addition to the constantly changing operations, there was an added pressure to deliver a turn-key solution at a time when global supply chain issues were going to create a 10-month delay in the project due to the initial choice of the wireless network. Faced with such a risk to the project, there was a strategic change to the strategy, and the FMS was implemented using Rajant Kinetic Mesh® industrial wireless networking, which efficiently addressed the need for real-time connectivity to work in extreme conditions.
The ruggedised wireless and high bandwidth Rajant Kinetic Mesh was easy to deploy in a short space of time to meet the mining operators ‘go live’ milestone.
For ever-moving and changing conditions typical of a mining operation, the right wireless network can ensure that operational productivity never fades. Networking unleashes comprehensive sitewide autonomy to allow mining operators to reap the transformative benefits that future-proofed technologies promise.
1. ‘Mining industry worldwide – statistics & facts’, Statista, www.statista.com/topics/1143/mining/#topicOverview
2. FOLGER, J., ‘What Drives the Price of Gold?’, Investopedia, (15 April 2023), https://www.investopedia.com/financial-edge/0311/ what-drives-the-price-of-gold.aspx
3. ‘Mining in Chile – statistics & facts’, Statista, https://statista.com/ topics/6550/mining-in-chile/#topicOverview
Todd Swinderman and Dan Marshall, Martin Engineering, USA, discuss how proper belt cleaning can mitigate emissions from carryback and control spillage, improving efficiency and compliance.
The handling of raw and processed materials in mines and quarries introduces several opportunities for cargo to be exposed to the elements and emit dust. From the time the material is extracted, it does not sit still for long. From storage to train/truck transport, processing, and shipping; the material passes through several conveyor transfers, shedding dust at every step.
One of the most highly regulated particulate emissions of any bulk handling material is respirable crystalline silica (RCS), which is found in nearly every raw material on earth. The fact that particle sizes for the substance are tested in micrometres (1000 th of a millimetre) and volumes are monitored in micrograms (1 000 000 th of a gram) makes controlling the fugitive dust in mines and quarries a challenge.
Although there are many opportunities for dust emissions, this article covers fugitive dust at the discharge point of the conveyor transfer where cargo leaves the belt.
Large amounts of emissions at a discharge can cause piles of dust to settle on every surface, creating an unpleasant and possibly hazardous work environment. Working in a dusty atmosphere reduces worker productivity –
in some studies as much as 20% – if respirators must be worn. Respiratory illness from exposure to even nuisance dust often leads to workers being put on long-term disability, increasing worker compensation costs. A dirty operation also attracts the attention of regulators and neighbours. A reputation as a ‘dirty place to work’ reduces the pool of employees who are willing to work in such an environment, and those already employed often suffer from low morale.
Fugitive materials are often a root cause of catastrophic events. Many types of dust present fire and explosion risks in addition to health and safety concerns. The destructive power of dust explosions is well documented in the coal industry. Static discharge into a dusty atmosphere is a common cause of many of these fires and explosions. Dust can foul components that create hazards. Friction from a seized idler due to fouling is a common root cause of major incidents. In many cases, a frozen idler bearing is the heat source that ignites the grease which catches fire.
Efficient throughput is all about controlling the cargo stream and proper discharge is at the heart
of that control. The nature of fugitive material problems from any conveyor is indicated by the location and particle sizes of the accumulations. Fugitive materials at the discharge zone are generally categorised into spillage, dust, and carryback:
n Spillage is cargo that escapes the belt and accumulates on either side of the conveyor. Piles are formed rapidly and can occur from inadequately maintained transfer points.
n Dust is the fine particles, usually less than the diameter of a human hair in size, that are created as the bulk material moves through a conveyor system. Fine airborne dust is emitted at locations where the cargo is exposed or disrupted. Because dust particles are very small, when dry, they are easily dispersed.
n Carryback is fine material that sticks to the belt surface or becomes lodged in the cracks and crevices of the carrying side of the belt. Carryback material collects on components that the carrying side of the belt touches and eventually dries out, dropping beneath the system along the return path.
The design and function of belt cleaners have come a long way. In the past, belt cleaners were rigid, linear pieces of hardware made out of various materials from brick to plastic that earned the name ‘scrapers’ or ‘wipers’, because that is what they did. They had a low operational life, broke or cracked frequently, and contributed significantly to belt wear.
Modern primary cleaners are usually mounted at the head pulley and made from engineered polyurethane. This specially formulated material is forgiving to the belt and splice, but still highly effective for dislodging cargo. Typically supported by mechanical or pneumatic tensioners, the designs require significantly less monitoring and maintenance of blade tension.
One primary cleaner design requires no tensioning at all after initial installation. It features a matrix of tungsten carbide scrapers installed diagonally to form a 3D curve around the head pulley and typically delivers up to four times the service life of urethane cleaners without ever needing re-tensioning.
As conveyor speeds and cargo volumes increase to meet production demands, secondary belt scrapers are often installed immediately after the belt leaves the head pulley to address dust and fines that escape the primary cleaner. Generally equipped with spring or air tensioners that easily adjust to fluctuations in the belt, secondary cleaners are particularly efficient for applications that produce wet, tacky, or dusty carryback.
A carbon-tipped spring-loaded secondary cleaner takes a different approach from the standard secondary blade cleaner. It features independent 6 in. wide blades with
carbide tips set on a stainless steel assembly. Each tip is supported on spring-loaded arms at both ends with a wide range of motion that provides equal load pressure across each blade and requires less tensioning over its lifespan. This design absorbs obstructions, responds to belt fluctuations, and is able to arc safely in the event of a belt rollback.
A US rock quarry was experiencing carryback on one of its conveyors. The system transfers thousands of tonnes of 4 in. (101 mm) minus aggregate on a 30 in. wide (762 mm) belt travelling 420 ft (128 m) at 250 fpm (1.27 m/sec.) from one crusher to another. The crusher-to-conveyor process results in the aggregate being reduced to 0.5 in. minus sand. Leading from the quarry to the interior of the facility, the outdoor portion of the belt was exposed to extreme weather, even though it is covered. Material adhered to the return side of the belt, collected around the mainframe and gummed up rollers, requiring downtime for maintenance and raising the cost of operation.
Martin Engineering showed managers the latest innovation in belt cleaning technology, the CleanScrape® Cleaner. Technicians needed to drill just four small holes required for mounting. Installed diagonally across the head pulley, it forms a 3D curve that allows the matrix of tungsten carbide scrapers to exert a low contact pressure with the belt, but still offer excellent removal of stuck material. Suitable for belt speeds up to 1500 fpm (7.5 m/sec.) with vulcanised splices and 800 fpm (4 m/sec.) if mechanically spliced, the light touch of the cleaner glides safely over splices while still effectively dislodging material and reducing carryback.
Having installed the cleaner on the system with the most carryback and experiencing instant and measurable results, operators immediately had one installed on a second conveyor and ordered five more. Operators say that the cleaner has reduced the labour needed for cleanup and improved system efficiency, and they expect a longer service life than previous cleaners.
When fines are allowed to cling to the return side of the belt, suddenly dust can be detected along the entire length of the system. Spillage beneath the system is exposed to wind and adds to the dust. These fugitive emissions can cost mines and quarries in violations and potential lawsuits.
Innovations in both blade design and tensioner engineering have improved cleaning ability, increased equipment life, reduced the need for tensioning and blade changes, and decreased labour for maintenance and cleanup. Along with lowering the cost of operation, the most noticeable change is less dust along the belt path and in work areas. This improves employee morale and retention and results in better compliance.
Alwin Nienaber, Weba Chute Systems, South Africa, details how transfer chutes are now key in controlling dust, degradation, and segregation.
Design innovations in recent decades have meant that transfer chutes today make an important contribution to reducing coal dust at mines and in processing plants, while at the same time helping address the related challenges of coal degradation and segregation.
In the distant past, the mining and industrial sector had no such expectations of the simple chute at a transfer point. The construction was traditionally a modest ‘box’, which was intended only to channel coal or other commodities from one piece of equipment to another.
Today’s world is a different place, where modern design and manufacturing technology can ensure a smoother material flow with less impact and dust. Powerful software now supports not only the structural design, but the prediction and verification of material flow within that design, even before the manufacturing of the chute begins.
This trend has been driven not only by tightening occupational health and safety regulations and policies, but also the broader environmental, social, and governance (ESG) concerns that mines and industry have embraced. Where dust cannot be adequately controlled at a mine or plant, for instance, it can be blown across farmers’ fields or into neighbouring communities.
The way that dust and pollution can affect adjacent industries and settlements is increasingly in the spotlight – as stakeholders have become more vocal about the hazards that coal dust creates for them. Where dust starts to affect crops, for instance, it becomes not just a legal issue but a food security issue; similarly, where dust permeates communities, a health problem can develop into a serious human rights conflict.
For reasons like these, it is no surprise that companies have embraced various technologies within their supply chains to become more responsible corporate citizens –and to reduce their exposure to compliance risk and even reputational risk. It is clear that transfer points have long been ‘problem areas’ for dust creation. Where fast moving material must change direction, there is obviously the opportunity for impact and aeration in the material flow leading directly to raised levels of dust dispersal.
The real aim of an engineered transfer point solution is to avoid uncontrolled velocity and impact, as these are the key factors behind dust creation. Modern designs achieve this by controlling the material flow, and consolidating it as a more homogenous stream.
This demands the application of sound engineering principles, including the ‘supertube’ effect which helps to control the flow and velocity. This importantly also controls the transfer of material onto the conveyor belt – reducing wear on the belt.
The way that these custom designed chutes have improved dust control has been well documented over the years by mining sites at which the dust problem had become chronic. There were even conveyor inclines which mine personnel could not enter during operation, as there was little visibility due to the dust.
With the installation of specially engineered chutes at these sites, the improvement was significant
Figure 2. Engineering each aspect into the design means that dust at transfer points can be reduced through optimal flow of material.and immediate. Dust levels came down by between 46% and 77% across a number of conveyors, allowing personnel to stand next to transfer points while material was passing through. The greater access to the working area would also have had various benefits for operational efficiency.
Better control of material flow at transfer points also leads to less degradation. This is a factor that can have serious financial implications for producers who are contracted to supply certain size requirements, with limitations on the fines content. Indeed, this applies in a range of commodities, including iron ore and manganese, where penalties are levied if fines content exceeds a stipulated maximum.
The other side of the degradation coin is, of course, the creation of fines – which become naturally segregated from the larger material during its journey on the conveyor. The idler rollers create a vibration which exacerbates the movement of fine material to the bottom, leaving the more granular material on top.
This segregation is yet another contributing factor to dust, as the separated fines tend to aerate quickly in free fall and create clouds of dust at the transfer point if not carefully controlled. Dust suppression systems are often used to address this, specifically chemicals which cause
particles to coalesce and to drop out of suspension in the air.
A challenge with this is that – with a range of commodities including coal and manganese – these chemicals make the fines sticky, which can create other problems. If the chemical is not well managed within a chute, it can become a running liquid rather than an atomised spray; this causes the fines to clog chutes, and causes costly downtime while the chute has to be cleared.
This dust accumulates in areas of insufficient flow –also called low pressure areas – within the chute. It creates a negative angle of build-up on the front cover, hanging rather like a hornet’s nest and constricting the space for material to flow freely. As the wet dust accumulates, it dries and more dust collects, eventually taking up the chute’s internal space and causing a blockage.
While addressing the dust factor, the right chute design can also allay other negative impacts of segregation at a coal mine or plant. An important challenge often emerges at the storage silo, if the conveyor belt – feeding from the top – comes in at 90° to the line of chutes.
When the segregated material leaves the conveyor at the head pulley and falls into the silo, the fine material tends to almost run backward under the head pulley,
while the larger material is thrown slightly forward onto the other side of the apex. This creates a divide which affects the mix of the coal at different points along the base of the silo, where material is drawn off into chutes and onto vibrating screens.
Depending on the size of silo there will be a number of chutes and screens, but the segregation of the coal means that each chute and screen will perform differently, as it is receiving a different combination of fines and coarse particles. To solve this problem, the material needs to be homogenised, and the right anti-segregation chute can also accomplish this.
A rotary chute, located at the top of a silo, can effectively ensure that the fines and coarse are mixed so that the resulting material in the silo is more homogenous.
Returning to the benefits of effective dust control through chute design, it must be re-emphasised how critical conveyor operations are to a mine or plant – and how their efficiency and reliability can be compromised by excessive dust.
In many operations where Weba Chute has worked globally, the dust created at transfer points prevents safe access by technicians for vital inspections and maintenance. At these sites, it is often impossible for service staff to even check machinery while the conveyor is running. At best, this means that stoppages are necessary for this work to take place, and at worst certain problems might be missed that lead to costly and unexpected breakdowns.
In this sense, the significance of dust control goes well beyond the universal imperative of health and safety; it extends into the efficiency and productivity of operations. Insofar as chute technology can reduce dust creation at transfer points, it has also become a valuable contributor to cost reduction. Where conveyors are not accurately fed, for instance, spillage occurs that must be regularly cleaned – demanding time and equipment. Uncontrolled dust also coats and penetrates mechanical and electrical equipment, affecting its performance and longevity in ways that are difficult to measure, but which are nonetheless undeniable.
A final important insight into how chutes are effectively designed to reduce the hazard of coal dust in operations is simply that an effective solution must be based on the prevailing conditions and requirements. It is a truism to say that one size does not fit all applications. No two chutes can really be the same, as each must deal with material of different densities, abrasiveness and moisture content, and with specific operational conditions from conveyor speeds to heights and throughput volumes. Engineering each aspect into the design means that dust at transfer points can be reduced through optimal flow of material, while also using custom chutes to control degradation and segregation through the system.
Figure 4. A conveyor onto conveyor transfer chute at a power station in Wyoming. This transfer point handles 1000 tph.The 2015 Paris Climate Agreement resulted in 175 United Nations member states agreeing to pursue actions to limit global warming to below 2°C. However, implementation of the current pledges are only expected to reduce temperatures to around 2.6°C by the end of the century. The metals and mining industry alone contributes to approximately 8% of the global carbon footprint. While coal and gas extraction will decline in a low-carbon future, the opposite is forecasted for the wider mining market which is intrinsically linked to the energy transition. This is due to increasing demand for more than 20 ‘energy-transition’ enabling metals, including: iron, copper, aluminium, nickel, lithium, cobalt, platinum, and silver. As the world continues to navigate the climate crisis, it is clear that the actions of a number of key industries will play a central role in determining progress towards a low-carbon future.
With this backdrop, the topic of sustainability is becoming increasingly important for mining. There are a number of key themes directing the sustainability agenda for the sector. Firstly, a major shift away from fossil-fuel powered operations in favour of global electrification is
Johnny Sajland, SurfCleaner, Sweden, charts the recent progress and overseas growth potential of a new ‘wonder weapon’ that is taking aim at the mining sector’s carbon footprint.
being witnessed. Indeed, many forms of machinery and processes are now ‘going electric’, in order to increase energy efficiency and reduce pollution, while lowering costs to customers and society. This is all part of an integrated approach to deep decarbonisation.
Secondly, the global environmental, social, and governance (ESG) movement recommends taking core values into account when deciding which companies to invest in. As such, there is greater pressure than ever before for major industries to comply with fast-developing ESG standards, and plan for future legislation to ensure sustainable practices. In turn, investors have lower tolerance for companies which are not prioritising sustainability or displaying strong environmental credentials. This is well reflected in sustainability reports, which are frequently produced by leaders across the mining sector. The pressure from investors is huge.
One area where the mining sector can make rapid improvements to boost sustainability credentials involves better wastewater management. Mining uses vast quantities of water – primarily for mineral processing, dust suppression, slurry transport, and employees’ needs. More specifically, during the drilling and excavating process, underground engineering equipment releases grease and hydraulic oil into water sources. This water collects in pools, tanks and basins, together with wastewater from the underground workshops and cleaning facilities. It is then
pumped back to the surface and either released into nature or disposed of using vacuum trucks. In all scenarios the water must be treated carefully, in order to comply with stringent and ever-increasing environmental standards.
Traditionally, mining operations have used a range of water collection and separation tools to complete this task, including filters and band skimmers to aid this process. However, these methods have proved both inefficient and costly, leaving large volumes of contaminated water to be transported long distances away from mine sites to specialist locations, so as to ensure legal disposal.
SurfCleaner’s technology is addressing this challenge head on by maximising water collection efficiency rates. The core principle behind the technology was created by clinical physiologist, Dr Stig Lundbäck MD PhD, following his discovery of the human heart’s dynamic adaptive piston pump (DAPP) functionality.
Lundbäck built on DAPP to invent and develop the SurfCleaner, but he also applied other universal laws of physics from nature and the universe, such as: gravity, equilibrium, variation in rotation velocity in the centre and the periphery, different density, and more. This makes the SurfCleaner a truly natural machine, working in concert with the laws of nature, instead of trying to combat them. By enhancing gravity and setting the liquid in vertical and horizontal motion inside the body of the SurfCleaner, this creates a circular inflow at the top, and an outlet at the bottom. The rest is pure physics. The technology does not require a pump, powerpack, hydraulics or pneumatics, instead it offers a light, versatile, and flexible solution.
Today, SurfCleaner is led by the late inventor’s daughter, Christina Lundbäck, who relaunched the business in 2018, and now serves in the capacity of Chief Sustainability Officer & Head of Corporate Relations. Driven by a deep desire to solve environmental challenges and the looming climate crisis, Christina is upholding the Lundbäck legacy as an outspoken advocate for sustainable industry.
For environmentally conscious mining operations, there are multiple benefits. Firstly, through more efficient water separation, SurfCleaner vastly reduces the quantity of contaminated water requiring treatment and associated disposal, transport, and labour costs. There are also a host of environmental benefits from lowering VOC emissions on site, reducing shutdowns, and decreasing overall energy use to creating a cleaner, safer working environment. Furthermore, it enables mining operators to make meaningful contributions to the circular economy while generating new income streams, by neatly collecting by-products which can be reused and resold.
While boosting operational efficiency and slashing costs, SurfCleaner’s technology crucially helps to reduce the mining sector’s carbon footprint.
A recent case study actively demonstrating SurfCleaner’s benefits involves one of the largest underground iron ore mines in the world. Here, electric machines are used
extensively throughout the colossal mineral deposit – roughly 4 km long and 2 km deep. Due to a build-up of grease and hydraulic oil, these machines require consistent cleaning. This activity is performed in a washing hall deep underground, where used water is transported through pipes to an API separator in the mine’s water treatment plant.
One of SurfCleaner’s SCO 1000 devices is currently located in the API separator helping manage the first stage of the water treatment process. It collects, separates, and empties oil and grease into an IBC tank around the clock. Another SCO 1000 device is used in a second API separator, further along the process, collecting thin layers of remaining oil. The separated oil is then pumped into a container and later collected by an oil recycling company, while the purified water can be reused as process or wash water. The ability to reuse both oil and water is a major win-win for the circular economy.
SurfCleaner’s technology has essentially replaced the former oil filtration system and eliminated an entire stage of the water treatment process between the API separators. By comparison the oil filter solution was expensive, cumbersome, and hard to maintain. The first SCO 1000 device is currently separating around 1 m3 of oil per week, while the second device is deployed when required removing any remaining oil from the API separator within a single day. As such, the mine operator is able to avoid the 800 km round trip with vacuum trucks to transport oil-damaged water to third-party treatment facilities.
• Surface deposits exploration and resource valuation
• Heap leach resource valuation and process enhancement
• Waste rock pile resource valuation
• Tailings resource valuation
• Gold placer deposit large diameter continuous sampling
• Geo-technical and environmental drilling
• Pre-collars for diamond drilling in tough overburden geology
The project has also led to modifications to SurfCleaner’s technology, specifically geared towards use in underground mining environments, which experience high volumes of abrasive media like sand and gravel. This includes the development of protective screens, which collect and reduce inflow of unwanted debris.
Following this breakthrough, SurfCleaner now has half-a-dozen machines running in mining operations across Sweden. Due to the market response, it is building skills and resources to facilitate a major growth drive and expand its mining portfolio internationally. SurfCleaner is currently focusing its efforts on Europe and the Middle East, but it is also preparing to explore Africa, Western Australia, and South America later in 2023 and beyond.
This comes as the mining sector itself forecasts significant growth due to mega trends including urbanisation, connectivity, electrification and shifts in technology, which all demand higher material intensities. In addition, a rise in new technologies supporting the energy transition – including solar PV, wind power, electrolysers, battery energy storage systems (BESS), electric vehicles, and semi-conductors – also require a wider range of materials. In combination, these key drivers will dramatically increase demand for critical materials, such as: lithium, terbium, cobalt, neodymium, nickel, iridium, copper, and steel.
Autonomous haulage is not a novel concept in mining. Caterpillar commenced its autonomous mining truck programme in 1985 and deployed its first truck in 1995 at a Texas limestone quarry. Larger scale roll-out of an autonomous haulage system (AHS) took root more than 20 years ago. Sites utilising the system have deployed over 500 trucks and are pushing toward 2 billion tpy hauled with zero lost time injuries (LTIs). Komatsu has had a very similar journey, with its initial trials beginning in 1990 and over 20 years of commercial application. It, too, has an excess of 500 trucks and is pushing toward 2 billion tpy hauled with its system. ASI Mining recently made its debut into large
scale systems at Roy Hill iron ore, after working toward this goal with its first mining trial in 2006.
Globally, it is clear that major progress has been made for the mass adoption of autonomy in mines, and, today, a group of collaborators from the Society of Mining, Metallurgy, & Exploration (SME) are working on deployments in the US, supported by a NIOSH-sponsored project titled: ‘Eliminating Barriers for the Implementation of Automation in the Mining Industry’. The study initially was focused on US regulatory impacts to the adoption of autonomous systems, but was expanded to include broader barriers. The project includes hosting workshops at SME and other industry
Dr. Benjamin Miller, Pronto, overviews how to overcome the challenges associated with adopting automated mining technologies.
events to engage mining companies, equipment manufacturers, consultants, and academics. Consistently, mining organisations and leaders consider five barriers to adoption of AHS at their sites:
n Economics.
n Regulations.
n Technology readiness.
n Corporate willingness.
n Social license.
While the study is not yet complete, the order of those barriers matches the rank assigned at each of the completed workshops.
A few other principal drivers for adoption of AHS are safety, availability, and productivity. AHS delivers significant safety improvements through the reduction in exposure to hazards by removing people from the active mining operations. This can clearly be seen with no reported LTIs. Improved availability of the autonomous trucks by removing shift change, lunch breaks, and other standby interruptions can add over 20% to the annual working hours of a truck. AHS further improves the productivity of the base trucks by removing non-productive time from the haulage cycle. Both Caterpillar and Komatsu are reporting 30% improvements in productivity through AHS. 1
These drivers address the first three barriers from the NIOSH study.
The corporate willingness and social license barriers are primarily related to workforce impacts. One of the long-standing arguments against implementing technology, specifically autonomous and artificial intelligence (AI)-based tech, has been the contention that it will replace humans entirely and leave millions out of a job. This argument has been utilised since the Industrial Revolution in the 1760s, but it has failed to come true. Automation is a tool to improve the productivity of the workforce. It takes away many repetitive tasks and arduous and physically demanding labour, replacing them with new roles within the industry.
Numerous reports and studies over the last few years demonstrate that the mining industry faces demographic impacts within its workforce. Research from McKinsey 3 indicates that numerous factors are contributing to the pressure for mining employees to perform and deliver more, including uncertainty about global energy, price and demand volatility for commodities, 4 and heightened ESG expectations. There is more work to be done, but fewer workers to do the job.
Additionally, the mining workforce is an ageing one. Deloitte found that 50% of mining engineers will reach retirement age in the next decade. 5 In a similar vein, Mercer found that more than 50% of miners are over the age of 45, and one-fifth are over 60, closing in on retirement. 6 The McKinsey report also found 70% of people ages 15 – 30 definitely, or probably would not, consider a mining career. Embracing autonomy and other technological advances will allow the industry to not only increase the productivity of its workforce, but also better attract new talent and bring a younger generation into mining to offset the retirement of long-time employees.
The current large scale AHS deployments have only occurred at tier one mines on ultra-class haul trucks (>250 t capacity). When the current AHS deployments are compared to the worldwide ultra-class fleets, 10% or more of those fleets have been converted to autonomous operations. Geffrey A. Moore defined a technology adoption curve in his seminal work, ‘Crossing the Chasm’. This curve helps describe the rate of adoption of disruptive products into a market. The industry is currently crossing the chasm, or may have already crossed the chasm, for ultra-class adoption. Moore defines the transition from early adopters to early majority by the contrast of their tolerance of a new product.
Notably, Moore shares in his study, “By contrast, the early majority want to buy a productivity improvement for existing operations. They are looking to minimise the discontinuity with the old ways. They want evolution, not revolution. They want technology to enhance, not overthrow, the established ways of doing business. And above all, they do not want to debug somebody
else’s product. By the time they adopt it, they want it to work properly and to integrate appropriately with their existing technology base.”
The barriers to adoption within the ultra-class fleets may have been crossed, but what about within the larger mining industry for adoption of autonomous haulage? There are over 50 000 rigid frame trucks larger than 100 t capacity. Of that 50 000, roughly 20% are ultra-class trucks. When looking below the 100 t capacity, the number of trucks is at least an order of magnitude greater, if not two orders of magnitude greater, when including vocational trucks. Only a handful of deployments have occurred within the smaller truck classes.
Adoption of AHS within the greater mining market will still be driven by safety, availability and productivity, but will also have tighter margins and less access to CAPEX. Miners are looking for ways to invest in aftermarket AHS that extends their initial investment of their trucks, without purchasing ready-made autonomous equipment. So far, one of the issues with adopting autonomous technology has been cost; major industry players have the resources for integration, but smaller operations have often been left behind.
There is a famous quote from author and cyberpunk pioneer, William Gibson, that says, “The future is
already here. It is just not evenly distributed yet.” With automation and other smart technologies, the future can be more evenly distributed across the mining industry. AHS is not only for tier one miners – solutions exist that can be adapted to the needs of mines of all sizes. Smaller mines and quarries can finally access and adopt autonomous solutions thanks to modern technological advances, new autonomy kits, and lower price points. An increased deployment rate of AHS fleets worldwide is expected, driven by safety improvements and better financial outcomes. The time for autonomy is now.
References
Available on request.
Much has been written about mine industry digitalisation, electrification and automation, and how new technologies such as artificial intelligence (AI), machine learning, and the Internet of Things (IoT) can help operators maximise production and efficiency, while simultaneously reducing costs and emissions.
ABB’s eMineTM portfolio, for example, is designed to facilitate the transition to the all-electric mines of the future, with fully integrated electrification and automation systems from mine to port. Mine design will integrate these technologies to optimise all processes and equipment1 –from grinding to hoists, vehicles to conveyors – leading to more efficient, sustainable energy and resource consumption.
Until relatively recently, many mining companies were content to keep automation to a minimum, as long as they continued to hit their production key performance indicators (KPIs). Now, when talking to those working in the industry, the conversation inevitably turns to sustainability and digitalisation; specifically, how electrification and automation can best be deployed to reduce carbon footprint.
In the past, however, electrification and automation were treated as two different disciplines. Now, they are rightly
seen as a single entity that, when deployed in partnership with a trusted technology provider, connect the mine to the processing plant for better efficiency along the entire value chain.
This article will discuss this relationship between electrification and automation; how process and power control systems can be connected to manage intermittent power from renewables, for example; and how distributed control systems (DCS), such as ABB AbilityTM System 800xA, enable complete visibility and control of every electrical substation throughout the mine site for improved safety and maintenance operations.
The ‘2021 State of Play: Electrification’ report from the global management consultancy, VCI, revealed that 98% of survey respondents believe mine automation is the technology that will benefit the most from electrification. This is both true and encouraging, and a sign that mining is beginning to catch up with industries such as oil and gas and chemicals, both which were early adopters of digitalisation.
Oil and gas and chemical companies have become adept at dealing with challenges around networks, administrating generators, connections, and grid changes – and they have
Mehrzad Ashnagaran and Marcos Hillal, ABB, explain how by connecting electrification and automation solutions in a single, integrated system, companies can extract full value from digitalisation in terms of process efficiency, safety, and sustainability across the entire mine value chain – from pit to port.
done so by connecting electrical and automation systems and teams together to visualise operations in a broader way.
By expanding System 800xA from the processing plant to the mine itself – and integrating both into a single platform – ABB is able to connect haul truck trolley systems to the same automated platform that runs the mine. At the same time, the DCS is designed to be an open-standard solution, meaning the mine electrification system can be connected and transfer data to non-ABB systems.
This vendor-agnostic approach also applies to ABB’s pilot eMine FastCharge, set to be the fastest and only fully automated charging system for mining haul trucks offering up to 600 kW of power.2
By following open automative/industrial standards and targeting a battery electric vehicle (BEV) original equipment manufacturer (OEM) agnostic approach that offers maximum flexibility when it comes to vehicle charging, eMine FastCharge allows underground and opencast projects to seamlessly integrate charging of haul trucks into their work order schedule, minimising infrastructure expenditure and maximising the return on investment for mine operators.
Connecting electrification and automation systems is no longer a ‘nice to have’. Without this type of integrated control system, operators cannot gather data on systems such as trolley lines for electric trucks effectively – what is the status of each vehicle, for example, or why is truck A consuming more power than truck B with the same payload? Using tools like System 800xA, connected to energy management systems (EMS) systems and mine operations systems,
production schedules and cycle times can be formulated in an optimal way so that mines extract full value from the technology.
As mentioned earlier, the mining sector is in a relatively early stage in its digitalisation journey, which means that many of the benefits to be had from connecting and integrating electrification and automation systems are yet to be realised. Knowledge and insights from data extracted from day-to-day operations can only come with time spent monitoring and running vehicle fleets, for example.
ABB’s involvement with the Copper Mountain project in British Columbia, Canada, is a case in point.3 Combining ABB’s electrification and automation expertise, the installation includes engineering, supply, and construction management for a DC substation and overhead catenary system (OCS).
The company reported that the haul truck trolley assist infrastructure has cut carbon emissions by 90% on the trolley segment, contributing to Copper Mountain's final target of zero emissions by 2035.
Customers say they want more data, more connectivity and integration of production planning, short interval control, and fleet management systems to enable them to make more informed decisions that improve throughput, reduce emissions, and add real business value.
Mines are becoming increasingly energy-intensive; 60 – 70 MW operations are now the norm rather than the exception – while at the same time being located far from infrastructure and grid systems.
The traditional centralised power generation model provides constant and reliable power matched to demand profiles that are well understood, balancing production and demand and stabilising the power grid to avoid frequency fluctuations.4 Renewables, such as wind and solar, disrupt this pattern, so identifying the supply needs of the project –ideally at the design stage – is of critical importance.
Questions mine operators should be asking include:
n Is the external grid robust enough to transfer sufficient quantities of continuous power – i.e. 24/7/365?
n Can the network cope with fluctuations caused by renewables?
n Has the mine’s internal power network been modelled with these specific operational demands – everything from hoisting and grinding to hauling and material handling – front of mind?
Electrification, automation, and digital solutions that integrate renewables with power management and storage systems to provide stable power distribution and decarbonise operations are important, of course, but so is power quality. That is why, in addition to trolley line and rapid-charging systems, ABB also provides solutions like active dynamic voltage reactors, power factor correction capacitors and static VAR compensators, combined with digital and automated control and monitoring applications.
Together, this portfolio of solutions helps mitigate the potential impact of intermittent power supply – costly production downtime from blackouts and short circuits, for instance – and maximise profit.4
So, to the future. It is feasible that one day mines will be run using AI. By deploying automation and electrification solutions now, companies such as ABB are paving the way for the next evolution in mining. The company would go even further and say that this future transition from more simple PLC/SCADA (island operated plants) systems to all-electric, fully automated mines cannot happen until existing automation and digital systems are fully integrated –supported by the transformation of mine processes and workforces.
Underpinning all this is the fact that decarbonising mines not only requires the latest power quality and digitalisation technologies, but also a fresh approach to the provision of power; one that relies on a holistic view of the entire mine energy ecosystem, and that is connected and fully integrated.4
Technology vendors, such as ABB, are evolving too. In greenfield projects in particular, the company now adopts more of a power management role, whereby it not only provides mining customers with reliable grid connection, but rather a total integrated electrification solution encompassing power behaviour modelling,
recessionary energy storage, and micro-grid concepts independent from the main grid.4
For many years, ABB has helped mining companies manage power usage using the company’s systems and services. This will continue, but now there is an evolution towards solutions such as ABB eMine, where complete power management is associated with automation and digital solutions, creating a complete ecosystem for the entire power generation at the mine, including the integration of renewables and off-grid storage.4
In conclusion, then, automation and electrification should not be viewed in isolation; instead, they should be linked and embedded together at mines, so that the vehicle fleet is connected with the process area. This allows for complete continuity from mine to port, facilitating innovations such as remote monitoring and predictive maintenance, and, eventually, the fully autonomous mine of the future.
1. ‘Electrifying innovations in decarbonization and sustainability’, ABB, (October 2022).
2. ‘Mining EV fast charging pilot solution: ABB AbilityTM eMine FastCharge’, ABB, https://new.abb.com/mining/emine/fastcharge
3. ‘ABB to deliver trolley assist solution to meet Copper Mountain Mining’s sustainable development goals in Canada’, ABB, (26 April 2021), https://new.abb.com/news/detail/77184/abb-to-deliver-trolley-assistsolution-to-meet-copper-mountain-minings-sustainable-developmentgoals-in-canada
4. ‘Integrated solutions give mines the power to succeed’, ABB, (November 2022).
Alan Stewart, Rubix, UK, examines how businesses need to ensure maximum bearing life in order to minimise costly downtime and maximise energy usage.
Bearings keep machinery moving. Wherever there is a machine or vehicle that has rotating parts, you will find bearing units. Across all industries, bearings are one of the most often replaced components, but in mining all the more so due to the exceptionally harsh operating conditions. Here, bearings face multiple challenges, from ingress of dirt and dust, through to very heavy loads and frequently working in extreme temperatures.
As with any component, you want your bearings to provide long, trouble free performance. To maximise lifetime expectancy, the bearing must be correctly installed, lubricated, and maintained. However, regular lubrication and maintenance is problematic when it comes to mines – they are often remote, downtime for maintenance is very expensive, and safety is a running concern with such heavy equipment at hand.
Selecting the correct bearing is therefore essential to ensure a reliable and long life. This article will look at the top three challenges faced in this sector and suitable bearing options to meet those challenges.
Mines are notoriously wet and dusty and are often impacted by extreme temperatures. Furthermore, the machinery and vehicles in operation are heavy duty, placing substantial loads on to the bearing units.
In this environment, open bearings quickly become damaged from ingress of dirt. Using proper sealing solutions such as sealed bearings and shaft seals is therefore essential. Sealed bearing units are initially lubricated and then sealed, preventing dirt for entering and mixing with the lubricant. Specialist sealing solutions have been developed for this sector, including SKF’s three-barrier solution which consists of a sealed spherical roller bearing, bearing housing with labyrinth S seals and a specially formulated lubricant to act as a contamination barrier.
These three barriers protect the bearing from contaminants, leading to an extended bearing service life on average three times longer than standard open bearings. It is particularly well suited to conveyor systems.
To function in applications where heavy loads are the norm, you want a bearing that is both hard and tough. In the past, hardened steel did not have all of the necessary properties to make it suitable for use, but new heat treatment processes have been developed to remedy this. Also, consider both axial and radial loads when choosing your bearings. Double row tapered roller bearings are a good option, as they accommodate combined loads and can locate a shaft axially in
both directions with a precise axial clearance or preload.
Remote locations are common when it comes to mining, making next day part delivery doubtful.
Businesses therefore need to ensure maximum bearing life to minimise costly downtime. This means using a product that is fit for purpose: a bearing that has been designed to cope with the strain of this specific environment and its heavy loads. This applies to the bearing itself, plus sleeves, housings, seals and transmission products. SKF’s Slewing bearings, for example, have been designed with a high carrying capacity and high resistance to overturning moments in excavators, bucket wheel excavators, and stacker/reclaimers. There are countless more examples of bearings that have been specifically designed for this demanding sector, but the point here is not to compromise on the choice of bearing based purely on price – this is a false economy leading to early bearing failure. Of course, the bearings must also be correctly mounted using the right tools and maintained.
When you are miles from anywhere, relubrication can also present a number of challenges. You need to have the appropriate lubrication on site at all times, as well as people who can reapply it regularly and correctly. Ineffective lubrication represents over half of all bearing failures. That is why we recommend having a lubrication strategy in place.
It may seem obvious, but as part of that strategy one should check that they have the right lubrication for each application. One lubricant will not work for all. If in doubt, refer back to the machine manufacturer to identify the correct lubricant. Lubricants should always be kept clearly labelled so mistakes can be avoided. It is also imperative to ensure that staff are trained in lubrication application, and therefore apply the right amount of lubricant when it is needed. Alternatively, consider the use of single point or multi-point automatic lubrication systems which will safely apply the correct amount of lubricant, regardless of where the site is located.
A further option is to simply avoid relubrication issues altogether by opting for sealed bearing units.
Health and safety concerns are key in mining. Working with heavy equipment in often remote and dangerous locations makes injuries more likely to be potentially life changing or threatening.
The main cause of casualties in the mining industry occurs during maintenance and repairs, with maintenance on conveyors being one of the
major culprits. Every time a piece of equipment fails, safety is compromised. Using optimised bearings, sleeves, housings, and seals can improve machine reliability and ease of assembly
and disassembly. SKF ConCentra Roller Bearing Units, which are ideal for conveyors, for example, come ‘shaft-ready’ – i.e. they simply slide onto the shaft and are locked into place by tightening the screws. It is fast – requiring far less time and skill to install than a split pillow block housing assembly – and helps provide proper alignment while reducing the risk of assembly-related mounting errors.
Lubrication is essential to keep moving parts in optimal condition, but lubricants can be a hazard in themselves. If dripped on to a floor during application or as a result of overapplication, they become a slip hazard. Lubricants can also be an accelerant, and thus a potential fire hazard. Use of an automatic lubrication system decreases the quantity of lubricant used, which reduces the probability of leakages and the need for workers to enter hazardous locations for relubrication. It is best to use suitable seals to reduce maintenance requirements and leakages. If possible, it is best to opt for sealed bearing units to remove the need for relubrication and potential spills altogether.
Extracting something out of the ground and processing it on an industrial scale is an energy intensive business. At a time when the world is looking to limit its energy usage and impact on the climate, pressure is mounting on the mining industry to reduce its overall environmental impact.
Poor bearing performance can directly affect energy usage. Although the amount of energy per bearing is relatively small, when you consider how many bearings are used in machinery on a given site, it starts to mount up. Choosing the right product – i.e. those that have lower operating temperatures and vibration levels – makes for a more energy efficient approach.
Ensuring that a product is correctly fitted also has a part to play. Misalignment can lead to friction and vibration which can significantly increase energy consumption, plus the risk of premature failures. Shaft and belt alignment tools are readily available that allow customers to increase their machine reliability through easy to use and accurate alignment. Other options include selecting products that do not require realignment or that do not require the drive coupling or the cantilevered drive to be dismounted to replace the bearing; these bearing types are easily and safely replaced in situ.
Bearings may not be the most expensive part of onsite machinery, yet they are in widespread use. One should always be looking to apply the three ‘R’s: reduce, reuse, recycle.
Reductions in the number of replacement bearings used can be achieved by using good quality bearings that have been designed to both do the job at hand and operate in the appropriate environment. Furthermore, the amount of lubrication used can be reduced through employing automated lubrication systems or sealed bearings.
When it comes to reusing, some manufacturers offer a remanufacture service which can significantly prolong bearing service life, as well as reduce costs and lead times. Bearing remanufacturing can significantly reduce carbon emissions, consuming around 10% of the energy of making a new one.
In terms of recycling, not every part of a bearing can be recycled and not every manufacturer can do this. Users will need to check to see if their supplier offers this service.
Figure 3. Use bearings that are fit for purpose. SKF’s slewing bearings, for example, have a high carrying capacity.Machinery in mining can suffer extreme wear and tear. This is particularly the case with large industrial fans, whose assets are battered by airborne particles travelling at high-speed. Hans Bengtsson and Daniel Hoekfors, Castolin Eutectic, Sweden, review the impact of such abrasion and explain how to extend the life of components in the line of fire, potentially by years.
Industrial mining fans face a major challenge: their components are exposed to abrasive airborne particles impacting at ultra high-velocity. Add to this that the particles can often be very hot (up to 400°C) and it is easy to understand why they are prone to heavy wear.
Sometimes components need to be repaired or replaced as often as every few weeks, and this is a huge setback for productivity, no matter how frequent. Unless spares are stored onsite, then waiting for deliveries can cause delays, on top of the downtime already required for technicians to repair or replace the part. It is an outage that no mine operator wants to face.
The good news is that it is possible to extend the useful life of parts, reduce maintenance costs, and increase industrial productivity with wear solutions that protect components for many more weeks, months, and potentially even years of wear.
With sustainability as a key objective for the mining industry, it is worth noting that, as well as increasing productivity and profitability, extending the service life of existing parts is much better for the environment than repeated replacements, which leave a heavy carbon footprint by comparison.
Centrifugal fans are typically used for airstreams that have a high particulate content in materials handling applications, and in systems at high temperatures. This makes them a perfect match for mining.
These centrifugal fans use rotating impellers that increase the speed of the airflow through the fan. Usually, wear appears on the part of the blade that is driving into the flow of particles. Also in centrifugal fans, the tangential speed of the blades’ trailing edge, or tip, is far higher than the blades’ leading edge. Therefore, the blades’ trailing edge will likely suffer higher erosion than areas that are close to the leading edge, particularly with straight radial and forward curved blades.
This being said, the airflow distribution throughout the fan is never homogeneous; some positions are exposed to higher flow depending on an individual fans construction. For instance, damage could be found close to the blade base in fans with a large impeller inner diameter and short blades. Other vulnerable points include areas on the impellers central disc and blades, and particularly the leading edge of the blades.
This depth of knowledge enables predictable maintenance: by identifying weak spots, components can be reinforced right where they need it most. A good solution for this is a wearplate, particularly for structural components, such as fan casings or elbows, in ductwork that direct air flow round corners.
Wearplates are made of hardened material that form an abrasion resistant barrier to reduce wear and tear on surfaces that are exposed to intense abrasion and erosion, just like the components inside of industrial mining fans or at key points in ductwork.
There is a wide range of wearplates on the market, which vary in terms of base materials, sizes, coating alloys, and welding processes adopted. Hardened steel wearplates are often used as structural material or lining for fan blades and also impeller discs. They can be a good option in various cases. For example, when no extreme wear resistance is required; there is little or low corrosion; weight is not critical; the reduced mechanical strength of the substrate is not considered vital (in other words, parts are not exposed to high mechanical stress); and flow particles are larger than 1 mm, so they will not get stuck in cracks. However, alternatives are available – made from various, ultra-hard materials – that are superior in that they not only resist extreme wear and abrasion, but they also can be cut and formed for the perfect fit.
Another way to protect industrial fan components from abrasion is to apply a protective coating. This technique is known as wearfacing, or hardfacing. The solution consists of the same materials as are used for wearplates, but applied as a coating from wires.
Coating is useful for protecting key areas, such as the leading edge of impeller blades. Supplying the coating in the form of a pattern can further enhance the wear-resistance, as the pattern disrupts the flow of air and abrasive material over the surface to reduce the level of wear. However, this should be done with care as some surfaces should be smooth and flat to avoid potential build-up of material.
It is also worth mentioning that welding can reduce yield strength, since it undoes the heat treatment that the
component had when it was first manufactured. Specifically, welding melts the steel, which then recrystalises and undoes the carefully controlled heating and cooling that locks in the particular type of crystal originally sought for its strength and durability.
Alternative coating techniques can also be used to apply hardfacing, such as: arc spray, powder thermal spraying, plasma transferred arc, or laser coating. The advantage of these is that they create a coating in a thinner layer than welding or wearplates.
The latest development is a new supersonic spraying technique called XupersoniClad, or high velocity air fuel (HVAF), which creates lightweight and energy-efficient protective coatings. This cutting-edge thermal spraying method is applied by a robot and can deliver significant benefits for the protection of components, vessels, and structures against abrasion. It creates a highly dense and consistent microstructure that better protects surfaces against corrosion. Moreover, it enables extremely fine coatings that will not significantly increase the weight of the impeller, or the energy required to drive the fan. The service can be delivered onsite or components can be sent to a purpose-built workshop, either as new components or as a retrofit solution.
Often a challenge will require an agile approach, utilising more than one method for success. It is a case of choosing the right combination of wearfacing materials and coating techniques to achieve a balance between strength, toughness, impact resistance, weight, and cost. A final step in the repair of large fans or the manufacture of fans up to 1 m in diameter is balancing to ensure safe and reliable operation.
In one such case, Castolin Eutectic helped a Nordic mine operator resolve several wear-related issues with a 2.8 m diameter industrial fan turning at 900 rpm to extract hot, dusty air from the pelleting plant, where small pellets are made in an oven at 200 – 400°C. The fan extracts hot, dusty air through a vent, with the fast rotation meaning that the impeller’s outer edges move at 600 – 800 km/h.
Initially, the operator found that they needed to replace the carbon steel impeller every few weeks due to extreme wear on the blades. Upgrading to hardened steel extended the service life to five months and the operator wanted to push this even further, to minimise outages.
To achieve this, Castolin Eutectic technicians applied wearfacing to the blades using a special technique, which allowed the fan to withstand the high-velocity impact of abrasive particles. It successfully extended the life of the blades significantly. However, after 11 months the operator identified excessive wear on the impeller’s centre wheel. The same technicians solved this by applying small wearplates to the entire centre wheel. The upgraded impeller now provides a service life of three years, rather than weeks.
High flow rates of abrasive materials will cause wear when impact forces are high, but it is possible to upgrade to
ultra-hard and tough materials for critical components to extend service intervals and gain a significantly longer life from assets.
Ultimately, with the right methods and expert technical support, operational efficiency can be improved, increasing plant productivity and reducing the risks associated with costly equipment failure. What is more, extending the service life of existing mining equipment is the best approach for the environment too, reducing an operation’s carbon footprint and making sustainability targets much more achievable.
Fernando Pinto, UWT, Germany, evaluates a new contact-free radar solution for hot temperatures.
Amining and steel company in the Dominican Republic recently equipped their factory with more modern level measurement tools. For the continuous content control of coal, as well as molten iron, a special solution was requested due to the high temperatures within the related processes of coking and iron smelting. A specific solution was found with a UWT radar sensor working with a non-contact measuring principle and equipped with a special heat dissipation adapter.
The mining operation in question mainly extracts nickel and coal. Due to its usually high iron content, ferronickel is of interest to steel producers and an increase in demand is expected in the stainless steel industry, but above all for battery production. A lot of the most common lateritic deposits are in the tropics and subtropics.
The facilities close to Santo Domingo – the capital of the Dominican Republic – include amongst others: open-pit mines, reduction furnaces, electric furnaces for the smelting and refining of metal, an ore preparation plant, and a power plant. One process used, which combines pyro and hydrometallurgy, consists of thermally reducing the ore in rotary kilns or deck furnaces before the actual leaching, and subsequently leaching with an ammonium carbonate solution at approximately 80°C (46.4°F). The reducing agent for the thermal pre-treatment can be process gas. Fuel oil or coal is regularly added to the pre-dried ore. The temperature required for the reduction process is 700 – 760°C (1292 – 1400°F). As a result, approximately 85% of the nickel is metallically finely distributed, and is therefore accessible for subsequent leaching.
At this point, a more extraordinary solution was needed to equip the coke dry quenching, in order to cope with the high prevailing temperatures of up to 1000°C (1832°F). Further the coal raw material related processes during coking are characterised by large dust, lumpy material, and serious scouring. The measuring range was 20 m and the coal material had a density of 1000 g/l with a DK value more than four.
The company in the Dominican Republic had also some difficulty during measuring the level of molten iron, with the appearance of magma. In some parts of the blast furnace process the maximum temperature reached 1600°C (2912°F). With the environment external to the process works reaching 210°C (410°F), the manual level measurement process became very difficult, due to the risk of workers suffering burn injuries to their skin.
For these applications the requested level measuring instruments needed to withstand the high
temperatures both from the environment and the process – many sensors had previously been damaged and rendered ineffective by the inhospitable environment.
Safety and efficiency were the most important factors for the plant operator. Level instruments needed to be equipped with all relevant international Ex certifications and offer flexible solutions for limited space and rough process environments.
Together with the local UWT partner, Naniki Automation Solutions SRL, several inspections were made to find the proper level measurement technology. A continuous level measurement should provide the user with information on the exact level of the medium in real time. The installation and process conditions, as well as the media type and its properties, had to be considered carefully.
The decision was made to select a non-contact measuring principle with the radar sensor NivoRadar® NR 3000 high temperature version with a heat dissipation adapter. Free-radiating radar sensors can determine the level of a medium without contact. The so-called frequency modulated continous wave (FMCW) radar measurement method is used for this purpose. The transmitted signal is modulated between two known frequency values (NivoRadar 78 and 79 GHz) and the difference between the transmitted signal and the echo signal is measured. This difference frequency is directly proportional to the transit time and thus to the distance. The level can then be calculated by adjusting the respective vessel height. Free-radiating radar sensors are used in both bulk solids and liquid applications. The 4° narrow beam, robust design with dust proof housing, and a measuring range of up to 100 m (328 ft) make the sensor a compatible solution for the plant.
Due to the process conditions with very high temperatures, the NR 3 with heat resistant standpipe was configured. This special solution could be installed for temperatures up to 2000°C (3632°F). The standpipe flange has the dimensions of 500 mm (19.68 in.) height and a diameter of 150.5 mm (5.91 in.). The flanges fit 80 mm (3 in.), as well as 100 mm (4 in.) universal radar flange. For the part of the high ambient temperature, a cold air chamber was built around the housing of the radar transmitter to guarantee a maximum ambient temperature of 70°C (158°F), thus creating conditions for accurate measurement of the level even at high temperatures. Due to the self-cooling function there was no need for external temperature regulation. The material is made of robust 316 stainless steel, and the ceramic insulated high temperature mounting socket was further fitted with a nitrogen cooling purge inlet, including a ball valve, and mounted at an angle.
Using the adjustable aiming flange, the radar was perfectly aligned since the probe could be fixed to the
desired point. The easy to operate display, the Quick Start Wizard, and displayed diagnostic data allowed the simple and quick installation on site. The radar sensors generate a fast response and reliable on time measuring results.
Primary nickel is formed from nickel that is mined. It goes through the processing process from the mine to a refinery. The output are different grades of primary nickel. In contrast, there is the secondary nickel, which is obtained from recycling, and which the mining company in the Dominican Republic wants to focus more on. Products made of nickel-containing stainless steels are designed for long-term use. However, after use, nickel and nickel-containing alloys can be restored to their original metallic state or transformed into another, but still valuable, product form. Approximately 68% of the nickel in used consumer goods is recycled and starts a new life cycle. However, around 17% of nickel still ends up in landfills, mainly contained in discarded metal-bearing goods and products, as well as in waste electrical equipment.
In the future, the company will invest more in the production of nickel used in the manufacture of electric vehicle batteries. The question of more sustainable solutions is playing an increasingly important role. The manufacturer’s ferronickel operation is already certified under the ISO 14001 environmental standard. The company does not use water or explosives in its extraction process, which prevents it from contaminating the tributaries. In addition, it uses a water management system that avoids indirect contamination, anticipates floods, and guarantees water supply for the communities. The goal is to exercise a new type of mining, which is environmentally responsible.
around the world with mining company management teams, Mines and Money will leverage off the scale of the International Mining and Resources Conference (IMARC) to bring its unrivalled network of investors to the ICC Sydney from 31 October - 2 November 2023.
Co-locating with Australia's largest mining event will not only put mining companies in front of hundreds of investors that are attending, but will also reach thousands of private investors, with the event expecting upwards of 8,500 attendees.
The Mining and Investment Hub will feature over 120 junior mining and energy companies, showcasing global projects from diversified producers and some of the most compelling exploration and development companies.
Mines and Money @IMARC provides an excellent opportunity for professional investors
development companies and cash generative producers to discuss their next big mining investment.
Gold, silver, copper and battery metals are just some of the commodities you can expect to hear about from some of the greatest leaders in mining, investment and finance, with more than 500 mining and resource experts providing the latest market commentary, project updates and insights into current commodity trends that can shape investment strategy.
Visit minesandmoney.com/imarc to find out how you can showcase your mining projects at Australia’s largest mining investment forum.
Mines and Money will take advantage of Australia's largest and most in-depth mining and energy event, the International Mining and Resources Conference (IMARC) to bring hundreds of investors in-person to Sydney from 31 October - 2 November.