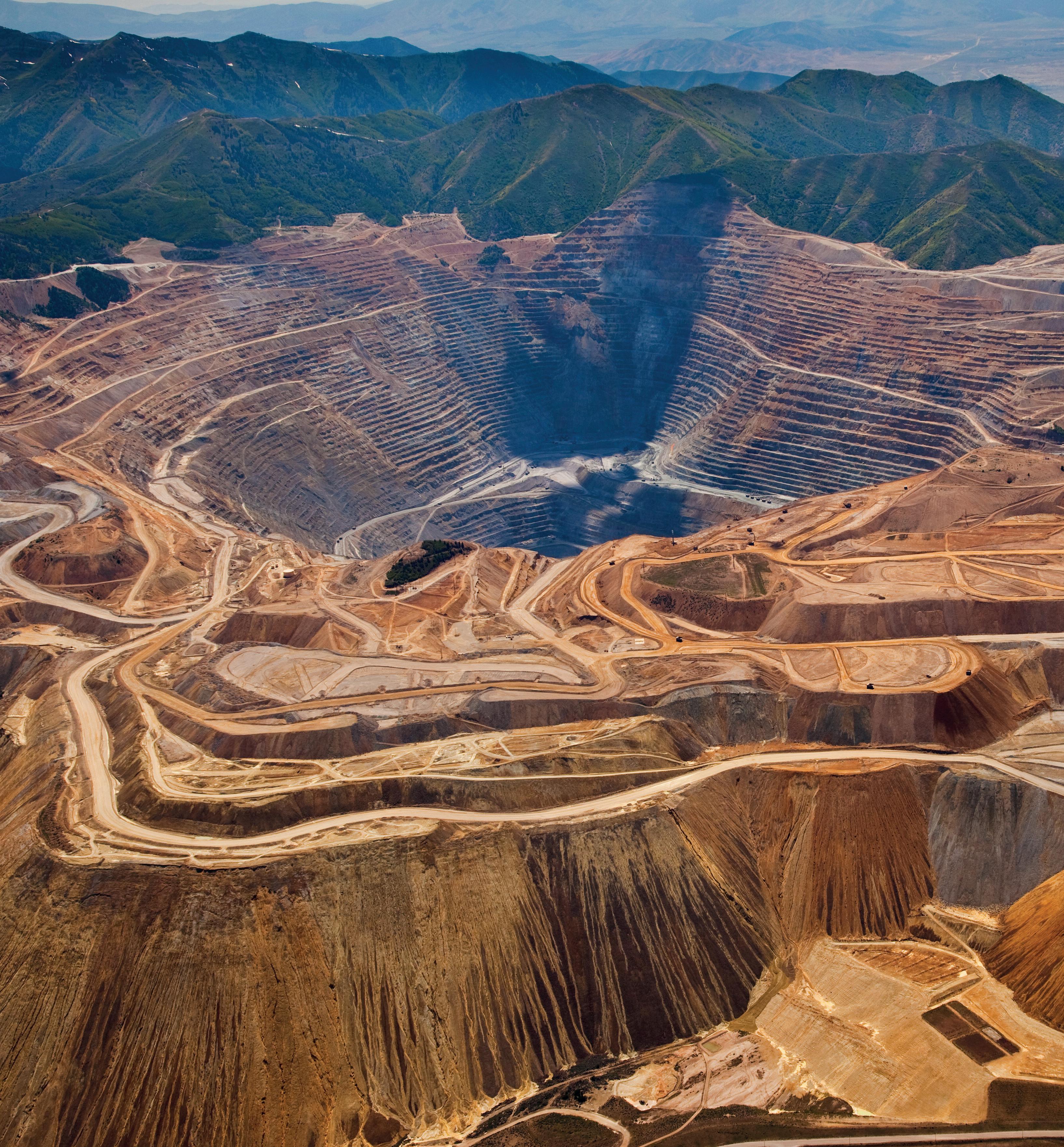
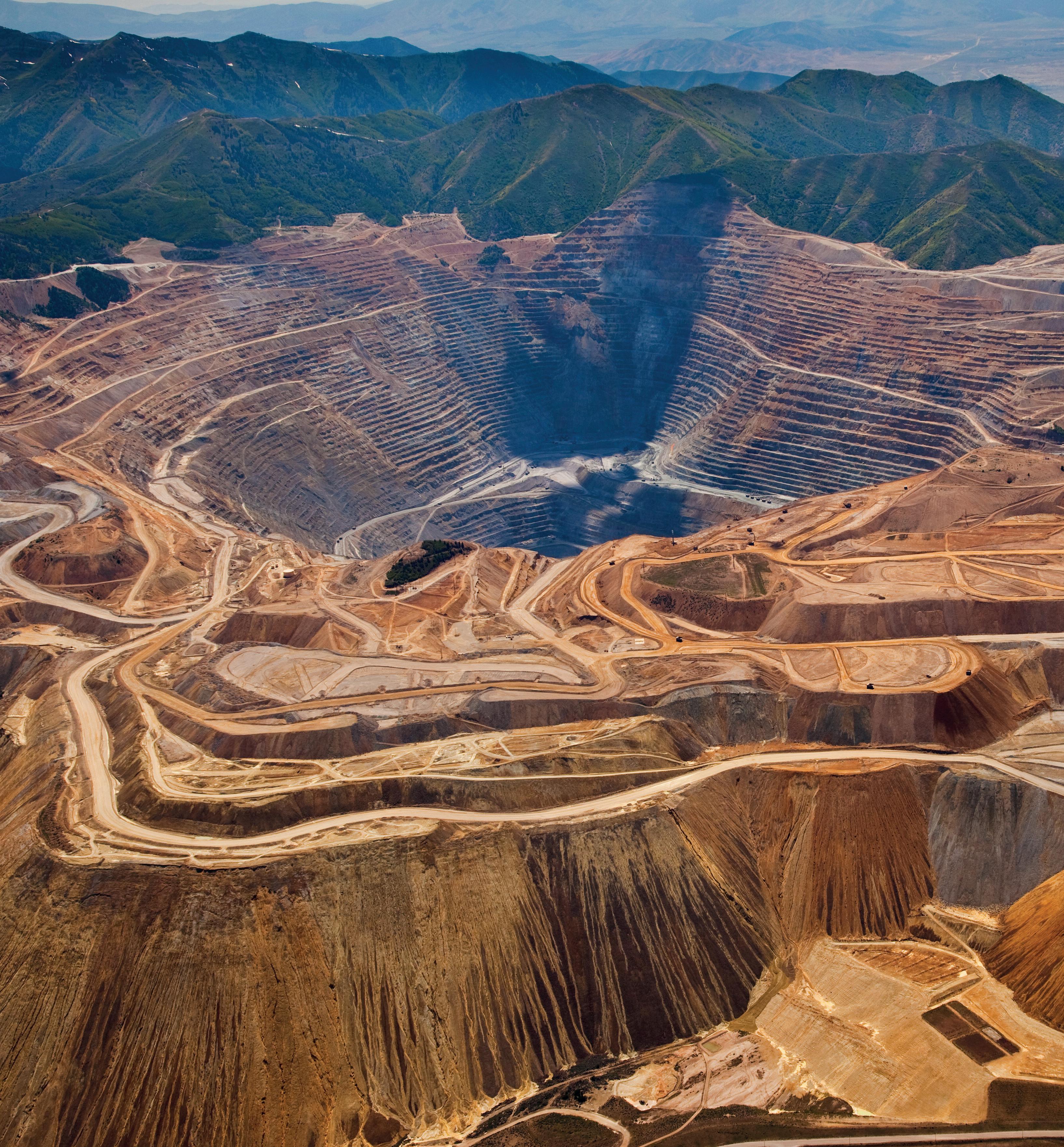
Super-efficient SmartROC CL
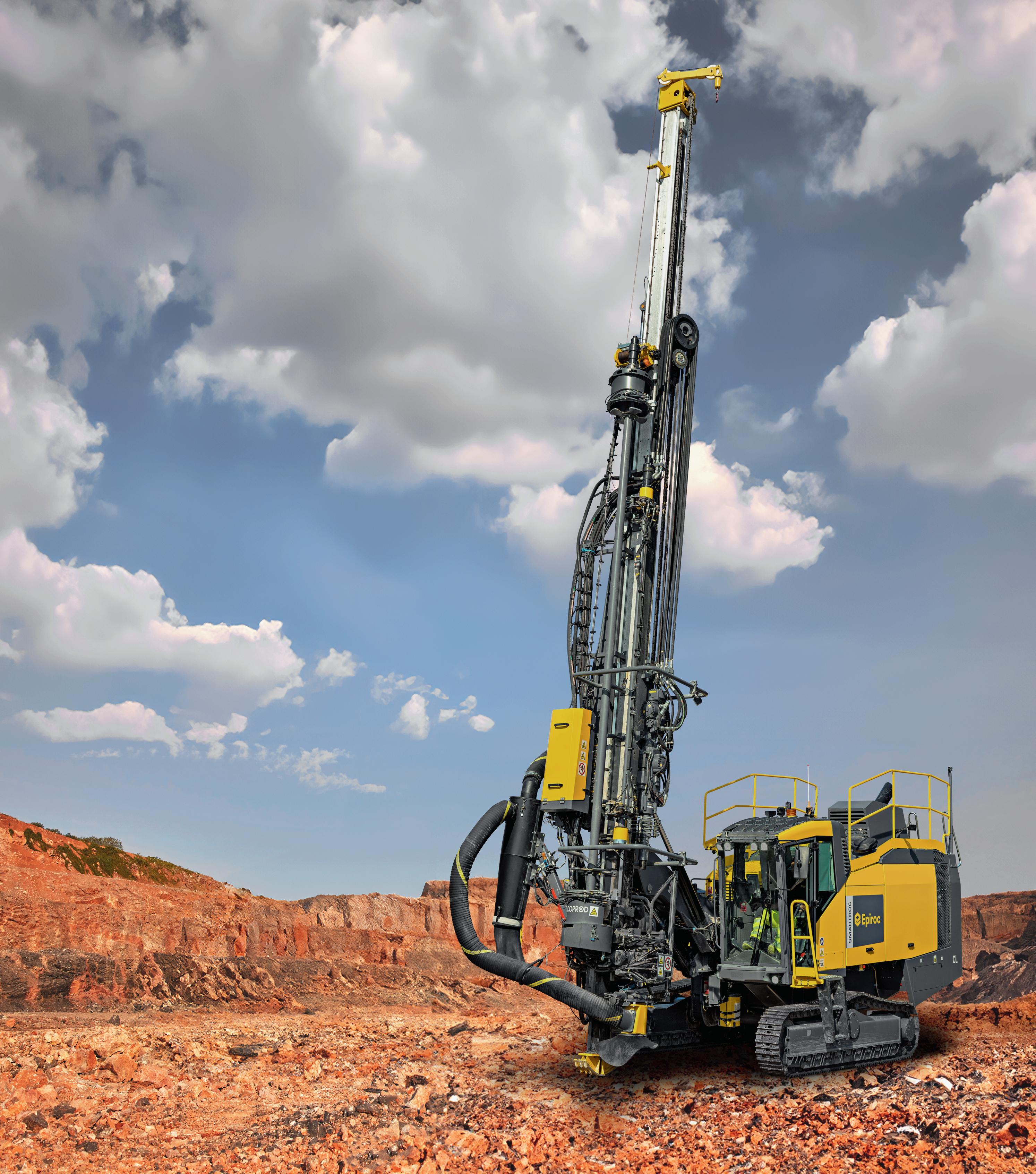
United. Inspired.
The new generation SmartROC CL
The new generation SmartROC CL is equipped with the new heavyduty COP QM50CR – next generation 50 kW rock drill specially designed for the COPROD drilling system. Higher efficiency, combined with an upgraded control system means the rig uses less energy. The new SmartROC CL offers up to 45% less fuel consumption compared to traditional DTH drilling

10 Bridging The Gap To Zero
John Essegbey, Cummins, evaluates the practical next step solutions that can help mining operators move forward in the energy transition.
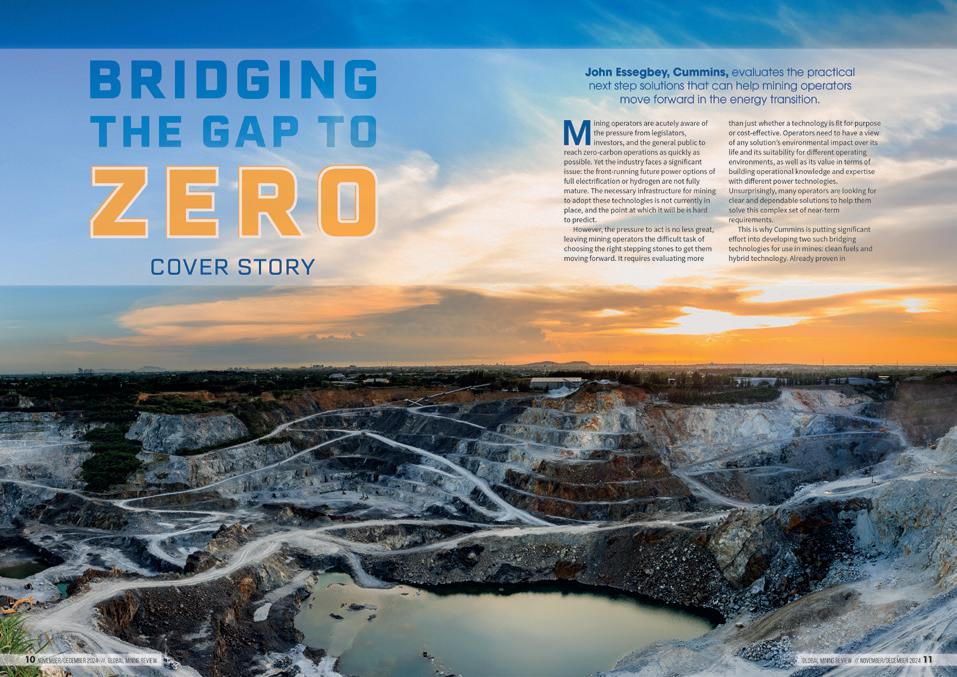
16 Roadmapping Sustainable Mine Optimisation
Brian Fox, Komatsu Mining Technologies, USA, discusses sustainable mine optimisation and its impact on customers in a Q&A with Will Owen, Global Mining Review.
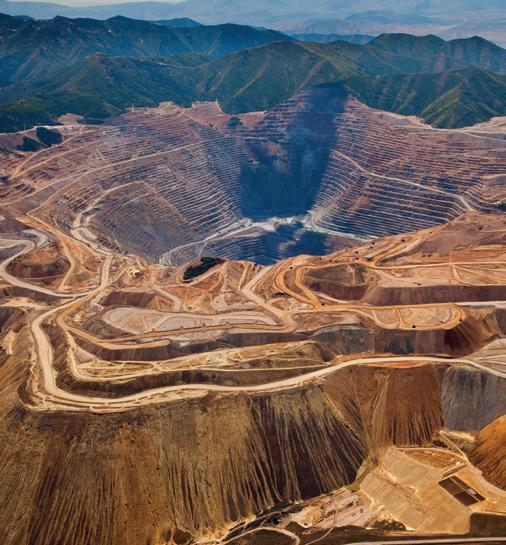


21 Dragline Engineering Innovation Meets Legacy
Jessica Moor, CR Powered by Epiroc, Australia, reviews the company’s history in dragline bucket and rigging technologies and highlights a recent significant industry milestone.
25 Unlocking Value In Mining
Gustavo Pilger, Dassault Systèmes, GEOVIA, assesses the critical role of centralised data management for efficiency, security, and innovation in mining operations in a Q&A with Will Owen, Editor of Global Mining Review.
29 Digitise The Mine To Optimise Operations
Mariana Sandin, Seeq, outlines how advanced analytics platforms are helping miners weather the global skilled labour shortage by providing automated data aggregation, predictive modelling, and deep insight generation.
33 Tackling Wear And Tear
Mark Doyle, Weir, examines how rubber wear solutions are making mining operations safer and more sustainable.
37 Under Control
Dellner Bubenzer describes how belt conveyor control systems can increase component life and improve performance and productivity.
42 Safer And Cleaner Conveying
R. Todd Swinderman, Martin Engineering, USA, addresses how preventing fugitive material around conveyors can improve safety and reduce the costs of operations.
49 Making Mining Cleanups Easier
William Nicholls, Movex Innovation, outlines how ultra-compact electric mini-loaders can provide a better alternative to manual material cleanups in the conveying and crushing processes.
53 Revolutionising Conveyor Technology
Simone Fiorini and Jessica Gamper, Aritec New Materials Group, Switzerland, explain how adopting aramid cord belts can improve the performance and sustainability of conveyor systems.
Can mining transition to cleaner energy in a landscape where full electrification or hydrogen technologies are not yet fully realised? The industry is used to tough challenges, but Cummins’ commitment to developing clean fuels and hybrid technology for use in mines means operators can approach the energy transition with confidence.

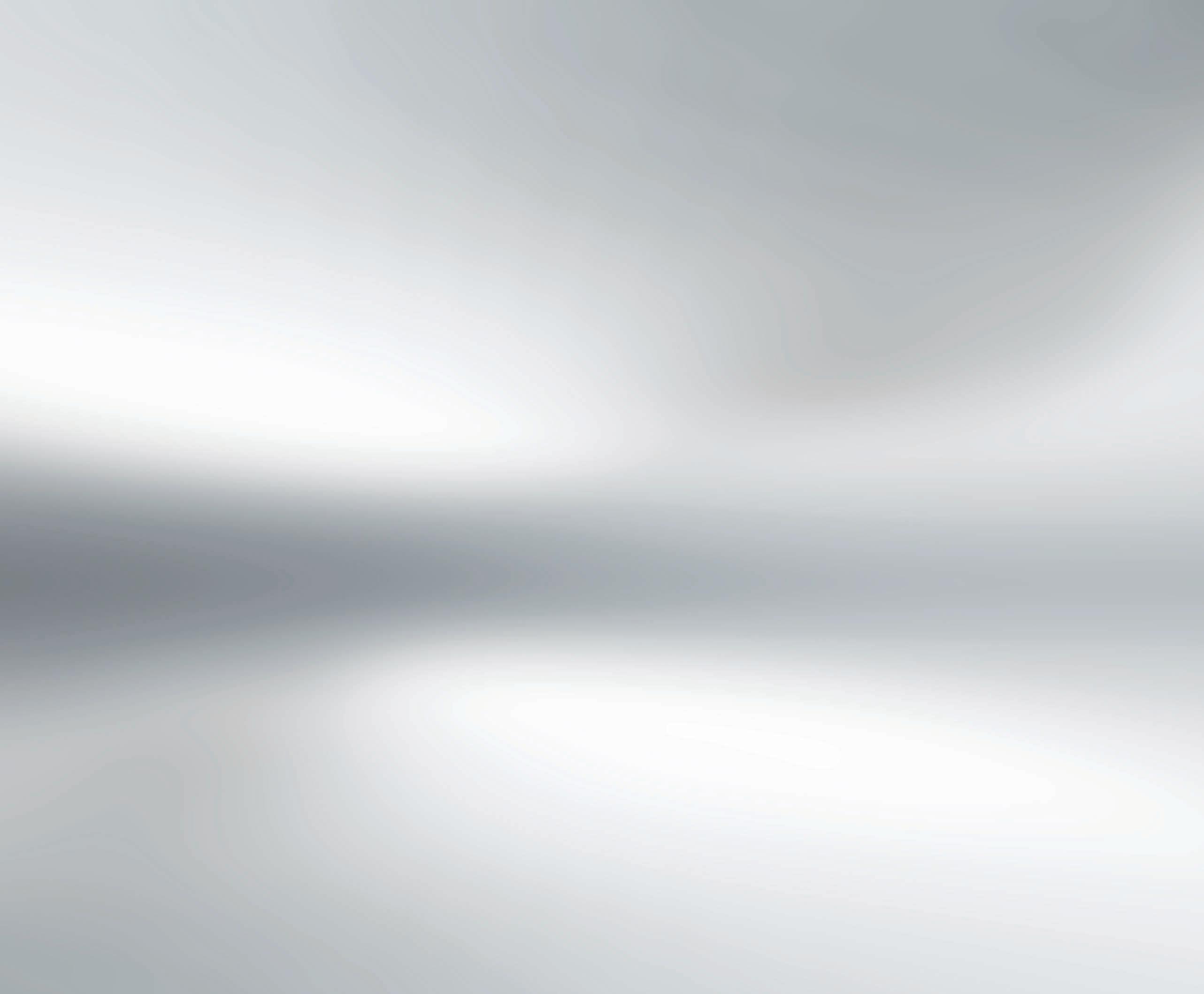
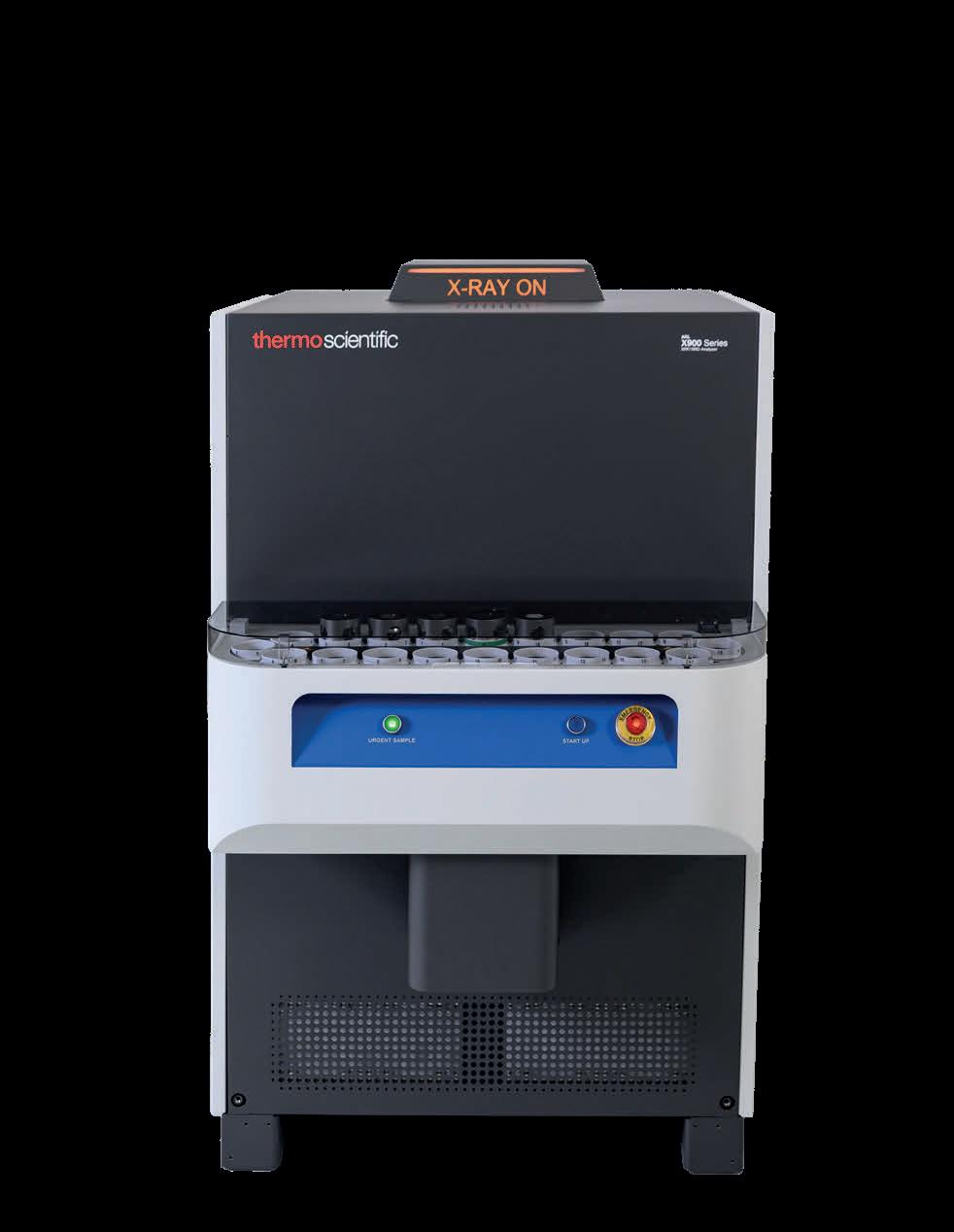


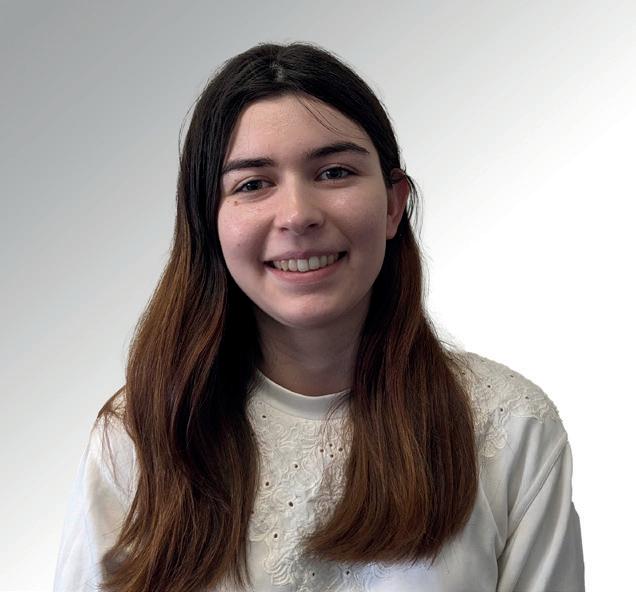
MANAGING EDITOR
James Little james.little@globalminingreview.com
SENIOR EDITOR
Callum O’Reilly callum.oreilly@globalminingreview.com
EDITOR
Will Owen will.owen@globalminingreview.com
ASSISTANT EDITOR
Jane Bentham jane.bentham@globalminingreview.com
SALES DIRECTOR
Rod Hardy rod.hardy@globalminingreview.com
SALES MANAGER
Ryan Freeman ryan.freeman@globalminingreview.com
PRODUCTION MANAGER
Kyla Waller kyla.waller@globalminingreview.com
ADMINISTRATION MANAGER
Laura White laura.white@globalminingreview.com
DIGITAL ADMINISTRATOR
Nicole Harman-Smith nicole.harman-smith@globalminingreview.com
DIGITAL CONTENT ASSISTANT
Kristian Ilasko kristian.ilasko@globalminingreview.com
JUNIOR VIDEO ASSISTANT
Amélie Meury-Cashman amelie.meury-cashman@globalminingreview.com
HEAD OF EVENTS
Louise Cameron louise.cameron@globalminingreview.com
DIGITAL EVENTS COORDINATOR
Merili Jurivete merili.jurivete@globalminingreview.com
EVENT COORDINATOR
Chloe Lelliott chloe.lelliott@globalminingreview.com
Global Mining Review (ISSN No: 2515-2777, USPS No: PENDING) is published 10 times per year by Palladian Publications Ltd., and distributed in the USA by Asendia USA, 701 Ashland Ave, Folcroft, PA. Application to Mail at Periodicals Postage Prices is pending at Philadelphia, PA, and additional mailing offices. POSTMASTER: send address changes to Global Mining Review, 701 Ashland Ave, Folcroft, PA. 19032.
Annual subscription (10 issues) £50 UK including postage, £60 overseas (airmail). Claims for non-receipt must be made within four months of publication of the issue or they will not honoured without charge.
EDITOR’S Comment
JANE BENTHAM ASSISTANT EDITOR, GLOBAL MINING REVIEW
As 2024 draws to a close, it is time to reflect on the highlights of the past year. And what a year it has been, for the mining industry and beyond. With significant political and economic changes across the world, and huge developments in technology and artificial intelligence, 2024 is one to be remembered.
The buzz and excitement leading up to MINExpo 2024 definitely paid off, as it proved to be a fantastic show highlighting the best the mining industry has to offer. MINExpo’s physical scale was undoubtedly impressive, featuring 2000 exhibitors and drawing in 45 000 attendees (more than double the previous show in 2021), as it expanded into Las Vegas Convention Centre’s West Hall for the first time. The myriad of innovations and technologies that were showcased, as well as the countless ideas and discussions about the green energy transition and digitalisation, were inspiring and demonstrate that mining’s future is truly a bright one.
However, it is important to note that the mining industry does not exist in a vacuum, and will be impacted by the widespread political developments that have occurred this year. More than 100 countries across the world have held elections, and many of these have a large presence in the mining sector, including India, Brazil, and the US. In an unprecedented victory, Donald Trump has been elected the 47th President of the US after the country’s recent Presidential Election at the beginning of November.
What impacts could this change have on the mining industry globally? After the passing of the Inflation Reduction Act under the Biden Administration, mining companies across the US have benefitted from loans and grants encouraging the exploration of critical minerals such as lithium. This legislation aimed to reduce the country’s dependence on Chinese imported materials that are key to the energy transition and manufacturing of electric vehicles. During his presidency, Donald Trump is likely to continue promoting domestic mining of critical minerals when highlighting the importance of American-produced goods. This could mean the introduction of harsher measures against China, as Trump has already promised to impose tariffs of 60% on Chinese goods. According to Reuters, China exports goods worth US$400 billion to the US,1 so these significant tariffs could have a large impact on China’s metals industry, and knock-on effects globally. The US coal mining sector could also be revitalised, as Trump has indicated his desire to reverse tax increases on oil and gas and coal producers and lower regulatory barriers.
Vast transformations of the global economic landscape are therefore on the way. Nevertheless, the mining industry has proved time again to be resilient in the face of uncertainty, and its growth and expanding innovation demonstrate that it will be able to adapt to whatever is to come next year.
After an exciting and eventful 2024, the Global Mining Review team would like to thank all of our readers, contributors, and advertisers for their continued support this year. We wish everyone well over the holiday period, and hope that you all have a joyful New Year!
References
1. CHEN, L., ‘China will work with US, government says, but more rivalry expected under Trump’, Reuters, (6 November 2024), www.reuters.com/world/china/taiwan-trade-china-braces-more-rivalry-closeus-presidential-race-ends-2024-11-05/
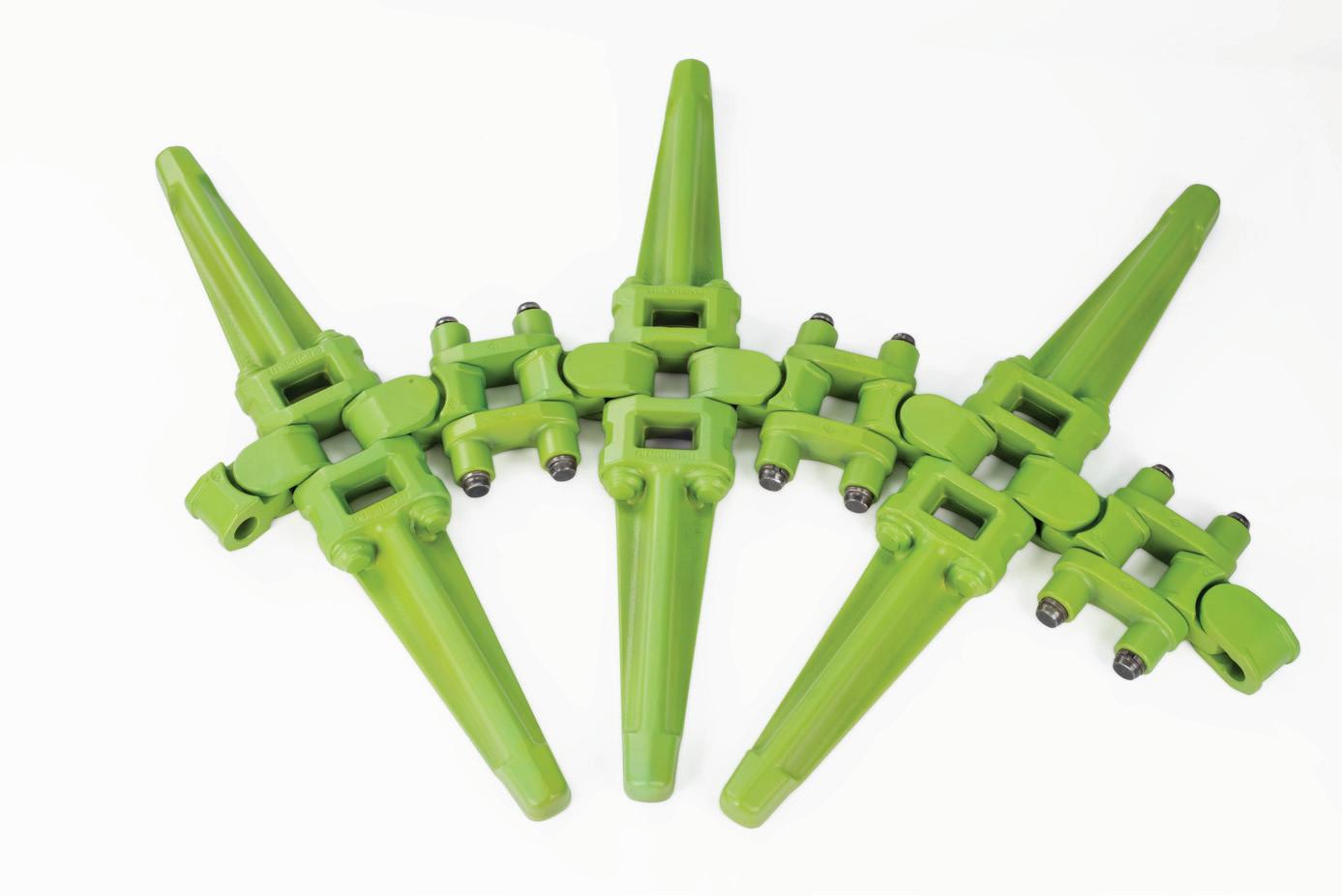

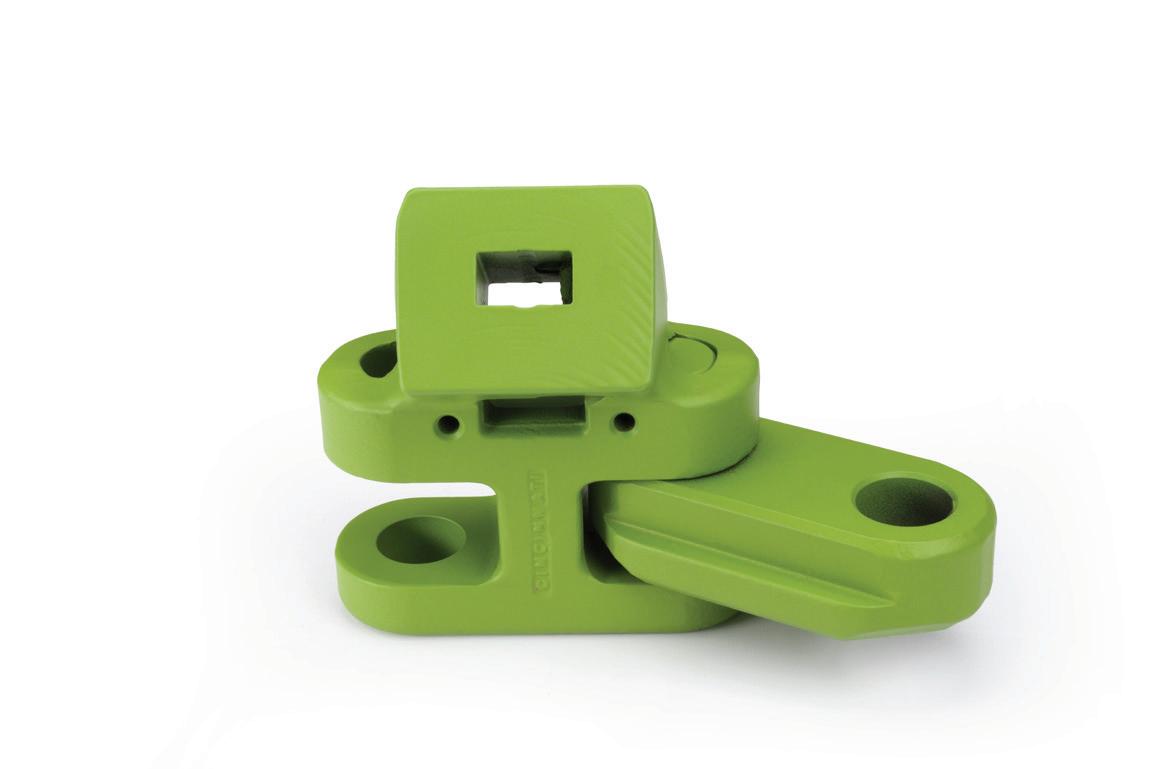

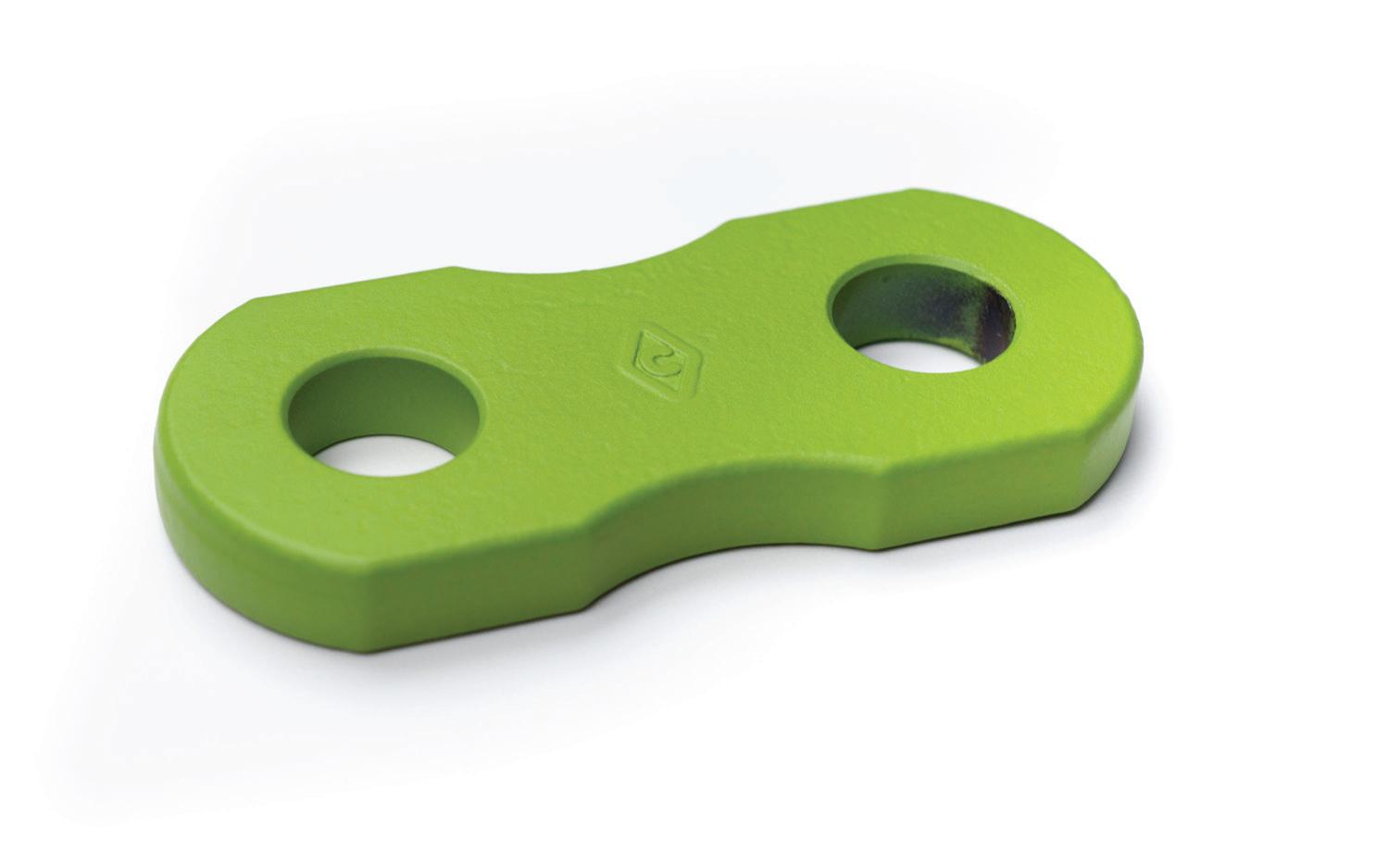
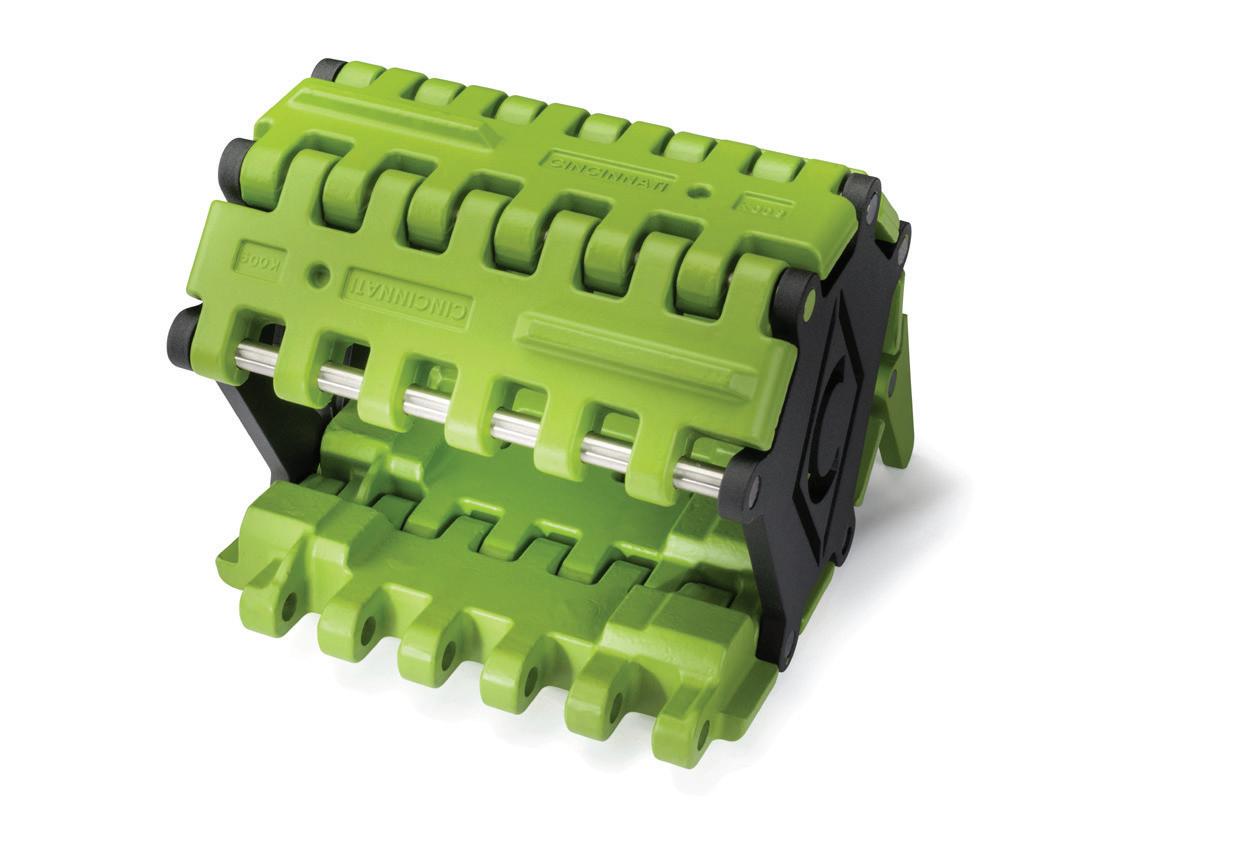
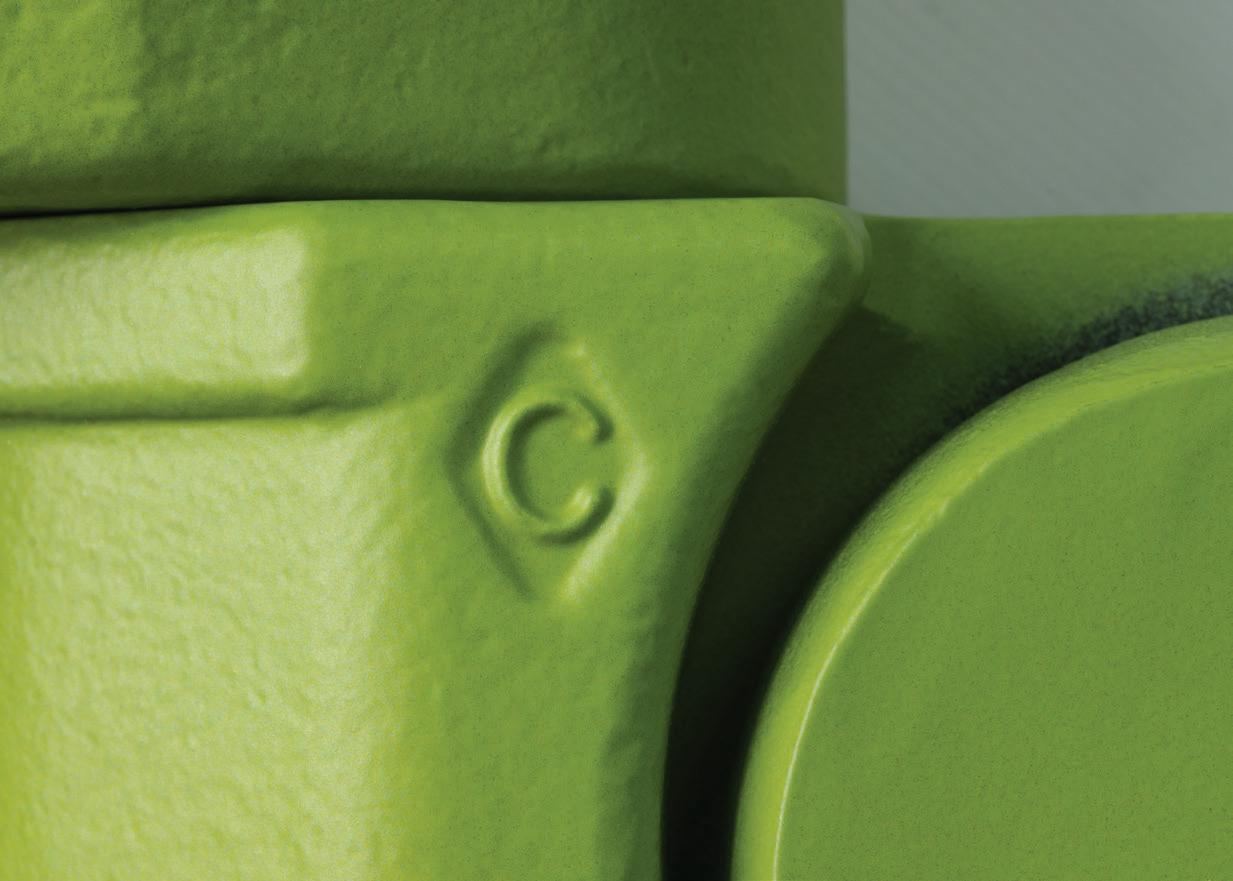
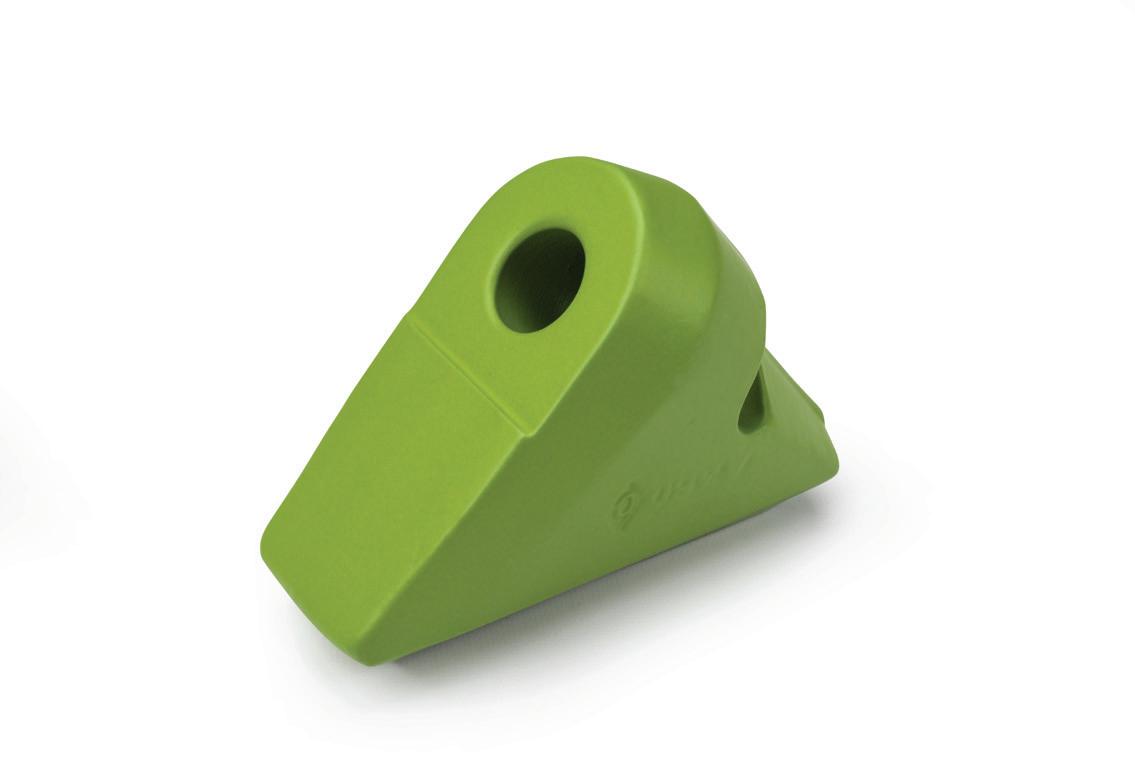
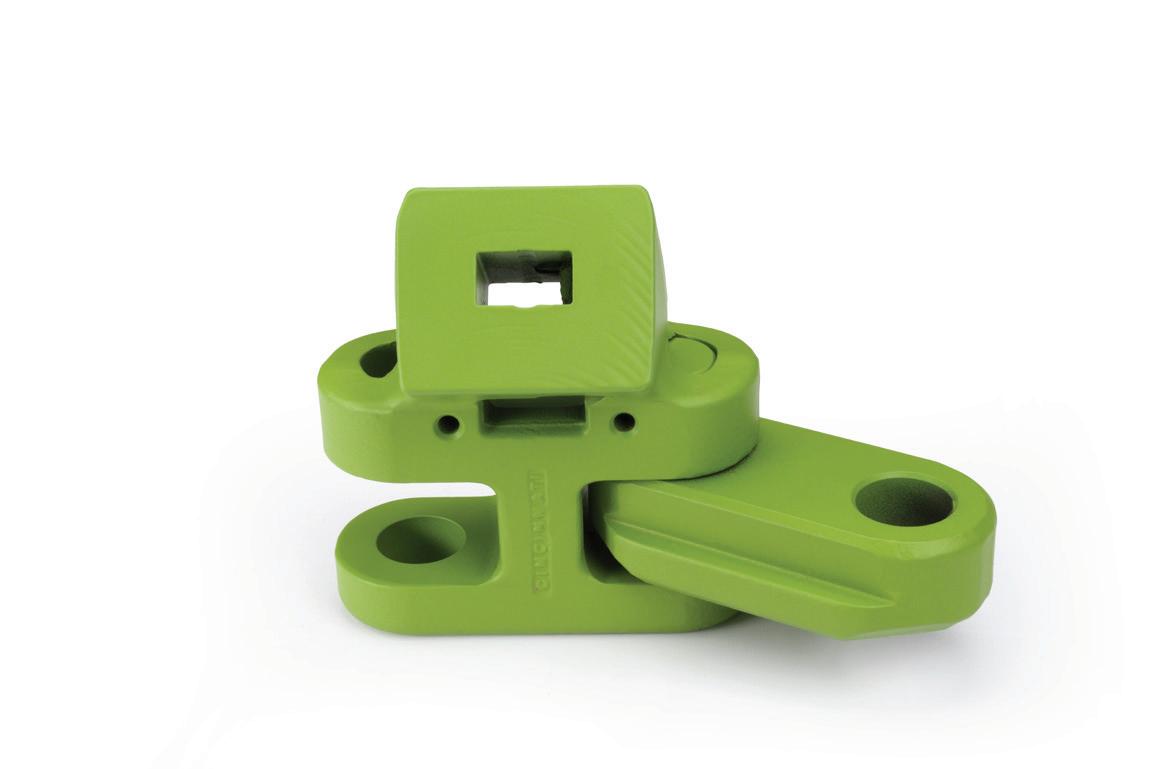
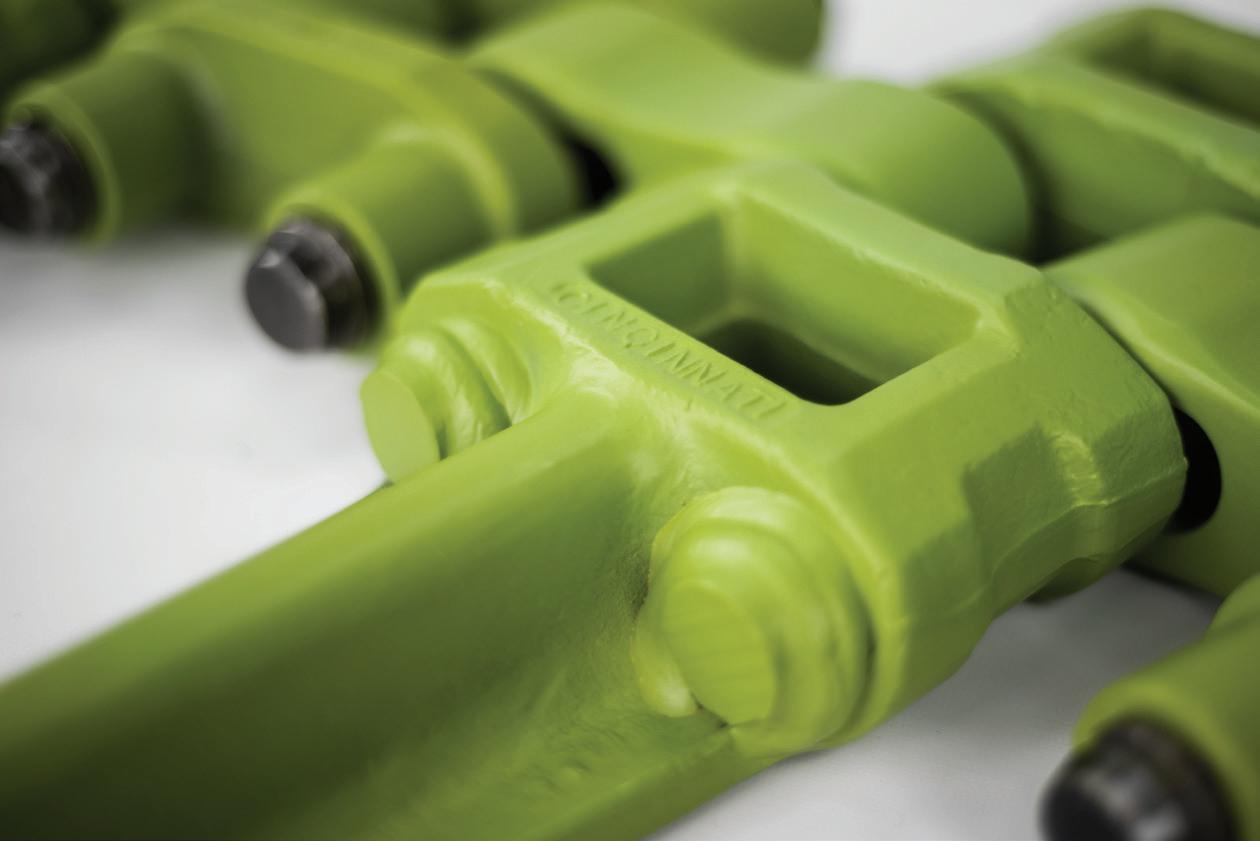
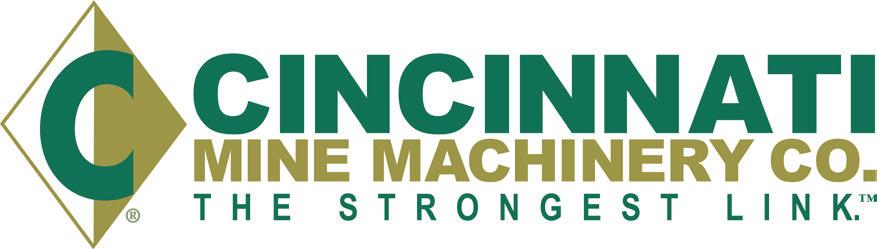
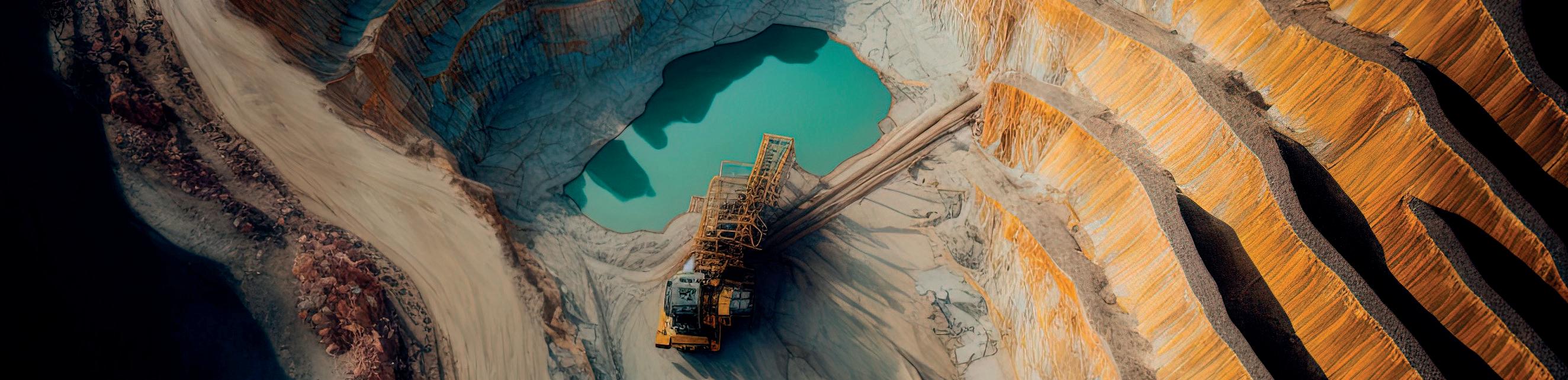
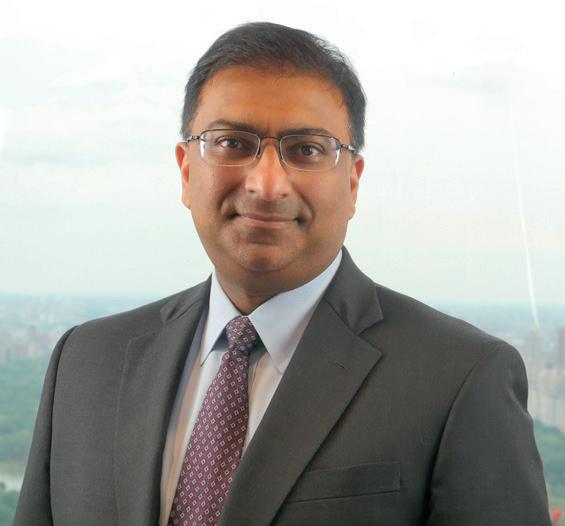
TGuest Comment
SUNIL BISWAS CEO, ION CORPORATES
oday’s metals and mining operators are navigating an increasingly complex landscape. The energy transition is driving unprecedented demand for metals, with renewable energy systems over 30 times more copper-intensive than conventional energy, and electric vehicles increasing the need for critical minerals – including lithium, nickel, and cobalt.
Although traditional supply chains are evolving to meet increased demand, they are frequently hampered by logistics disruptions, variable demand, and commodity price volatility. At the same time, the metals and mining industry faces mounting pressure to meet stringent ESG targets, minimise costs, and extract more value from their supply chains.
To make the most of mining assets and respond quickly to shifting conditions, the metals and mining industry –across geographies – is increasingly looking to automation to optimise mining, processing, logistics, trading, and risk management processes. While many metals and mining organisations are already highly automated, others recognise they are behind in integrating the technology they need to remain profitable and ensure they are maximising the value of their mineral resources.
In today’s challenging market, operators need to respond quickly to take advantage of opportunities, while managing price volatility and risk. Automation, when implemented correctly, enables timely and clear decision-making. With the capability to rapidly analyse large volumes of data, operators can quickly understand their current position, investigate plans by evaluating more options, forecast further into the future, and better understand the potential impact of decisions.
Across mining and logistics, the ability to understand physical inventory in terms of location, quantity, and grade is critical to enable effective blending, ensure logistics capacity is utilised, and avoid costs such as quality penalties or demurrage.
Within processing and refining, managing a plant requires measurement of metals flows and inventories. The measurements need to be both timely and precise for
plant optimisation. Adopting an automated metallurgical accounting system that is AMIRA 754 compliant enables accurate mass balances and more regular reconciliation of metal flows and inventories, resulting in the highest precision and protection from measurement error and bias.
To capitalise on market conditions and prevent losses from unmonitored trades, traders require automated, real-time monitoring of their positions, profit and loss (P&L), and cashflows. Automation and reliable sources of market and supply chain data are essential to enable optimisation and manage risk on a timely basis.
The vast amount of data in mining supply chains offers great opportunities for automation, but also poses challenges. Operators need a cohesive data framework that spans from control systems and networks to enterprise-level systems across various business domains like sales, logistics, and risk.
To fully benefit from automation, operators must have the capability to collect and validate the right data, with the ability to process it quickly and ensure accuracy. The pressure to meet ESG compliance is driving businesses to automate emissions data capture and use it effectively, to reduce both emissions and costs.
Smaller businesses often struggle with manual processes that are prone to errors and slow to update, while larger businesses face issues with siloed information that is often a result of mergers and acquisitions. Improved coordination and governance are needed to further automate data processing and maximise efficiency.
Across the metals and mining industry, the adoption of automation remains uneven. What is clear, however, is that the vast amount of data generated by complex and multilayered supply chains presents nearly limitless opportunities for optimisation. Those who invest in integrated software connecting the front, middle, and back office, and have developed an architecture for data management and processing, will be in the strongest position to identify emerging risks and capitalise on opportunities in the years to come.

UNLOCK PEACE OF MIND

Safeguard Tailings with Remote Monitoring
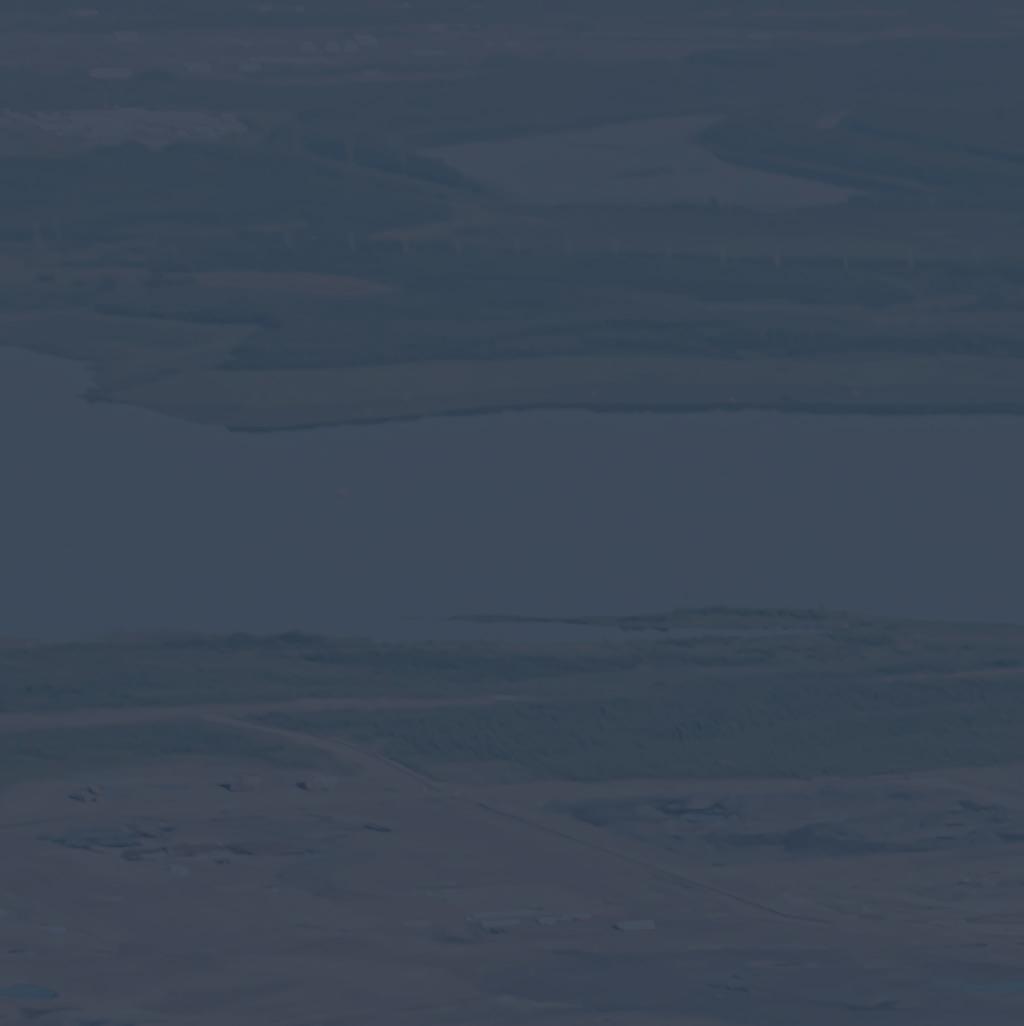
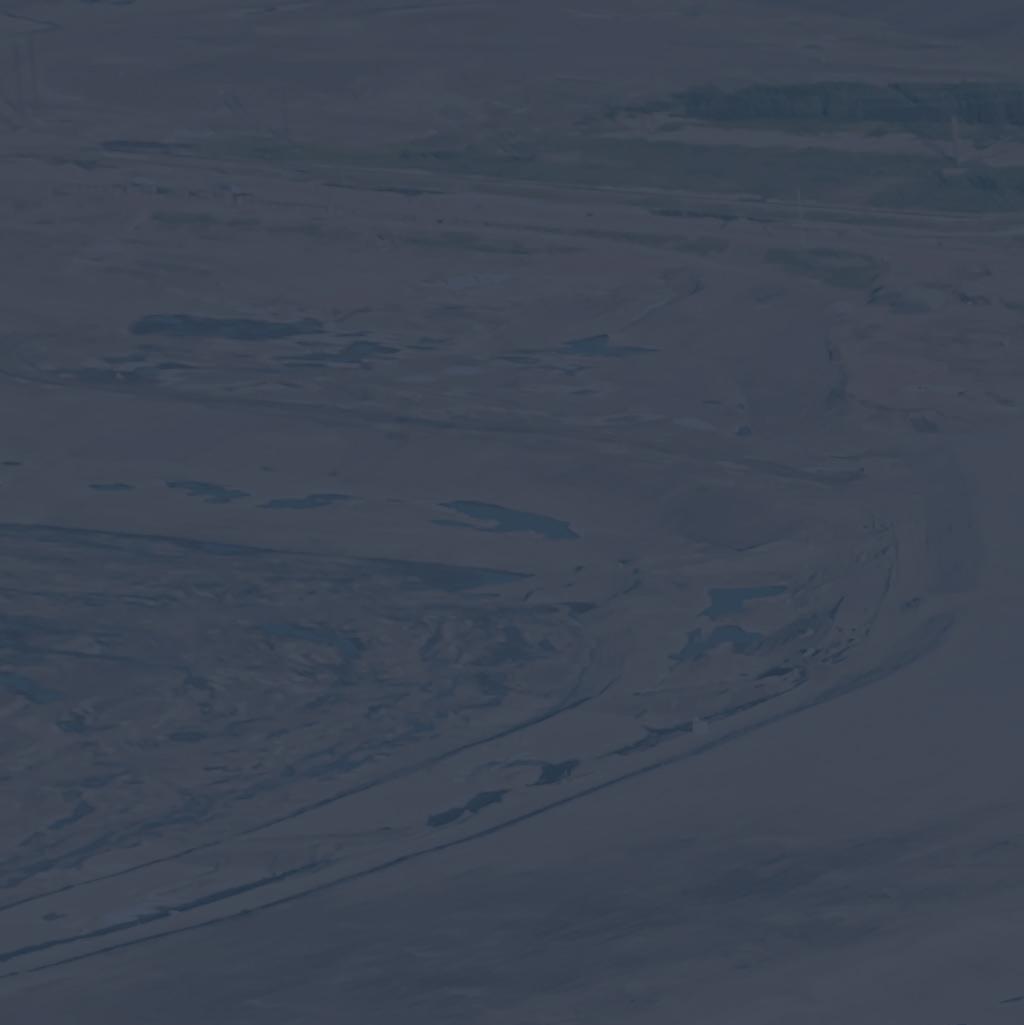
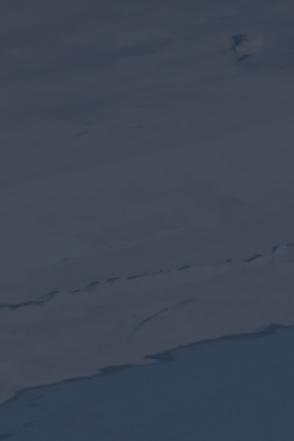

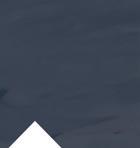
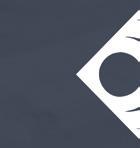

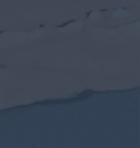
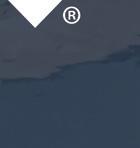

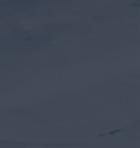
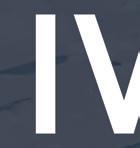
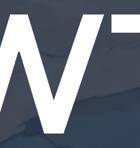
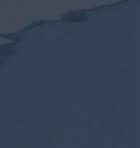
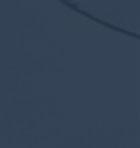
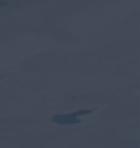
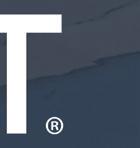
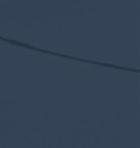


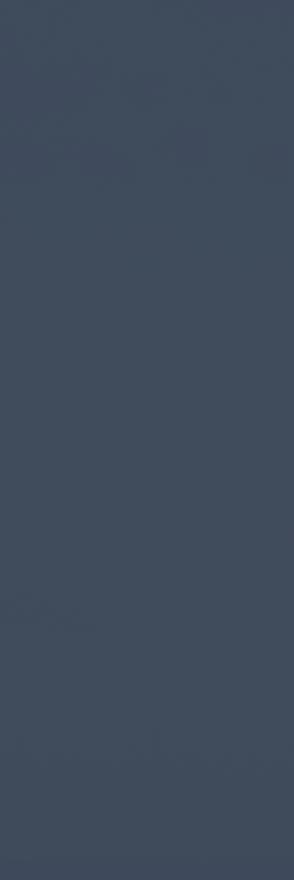
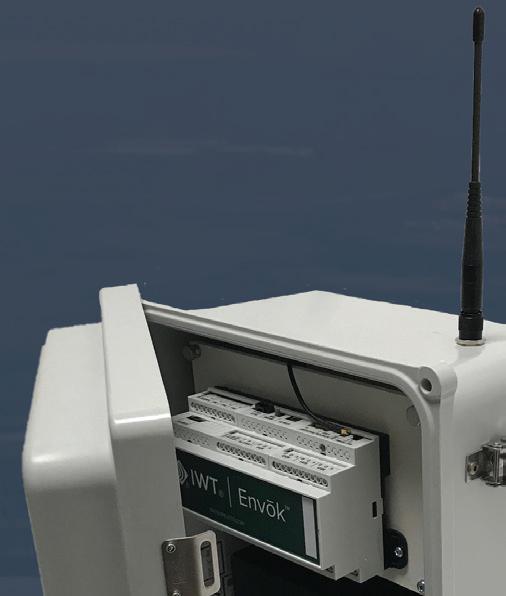
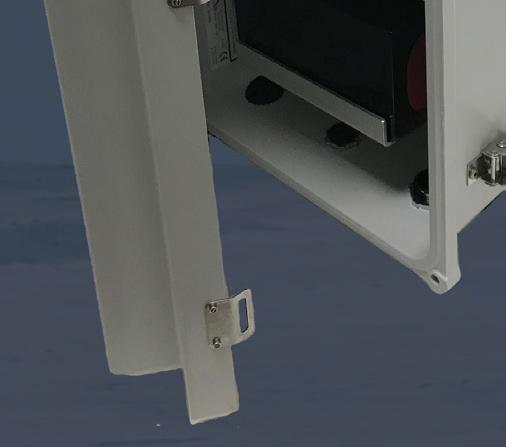
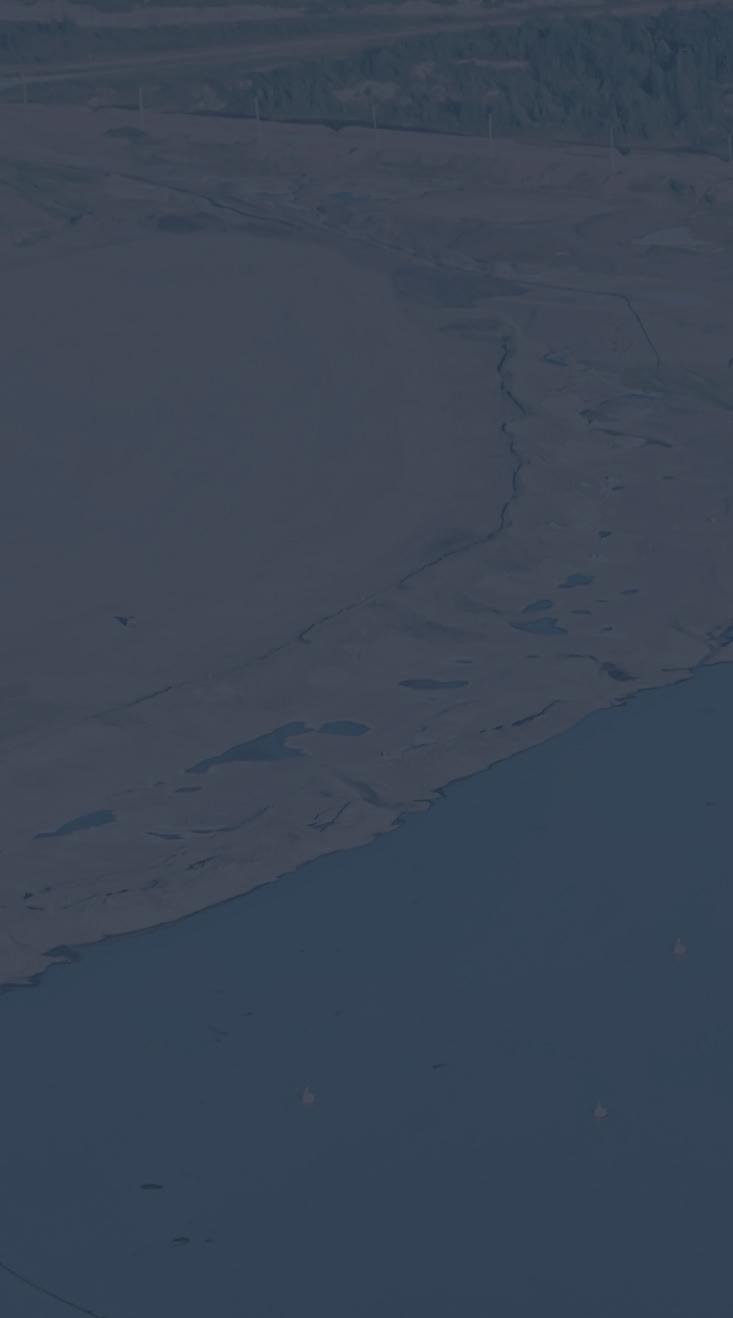
IWT’s Tailings Management Remote Monitoring Solution provides mine operators with peace of mind by o ering increased safety, risk mitigation, informed decision-making, compliance assurance, and cost-e ective operations.
Empowering operators to proactively manage their tailings facilities and ensure the long-term sustainability of their mining operations.
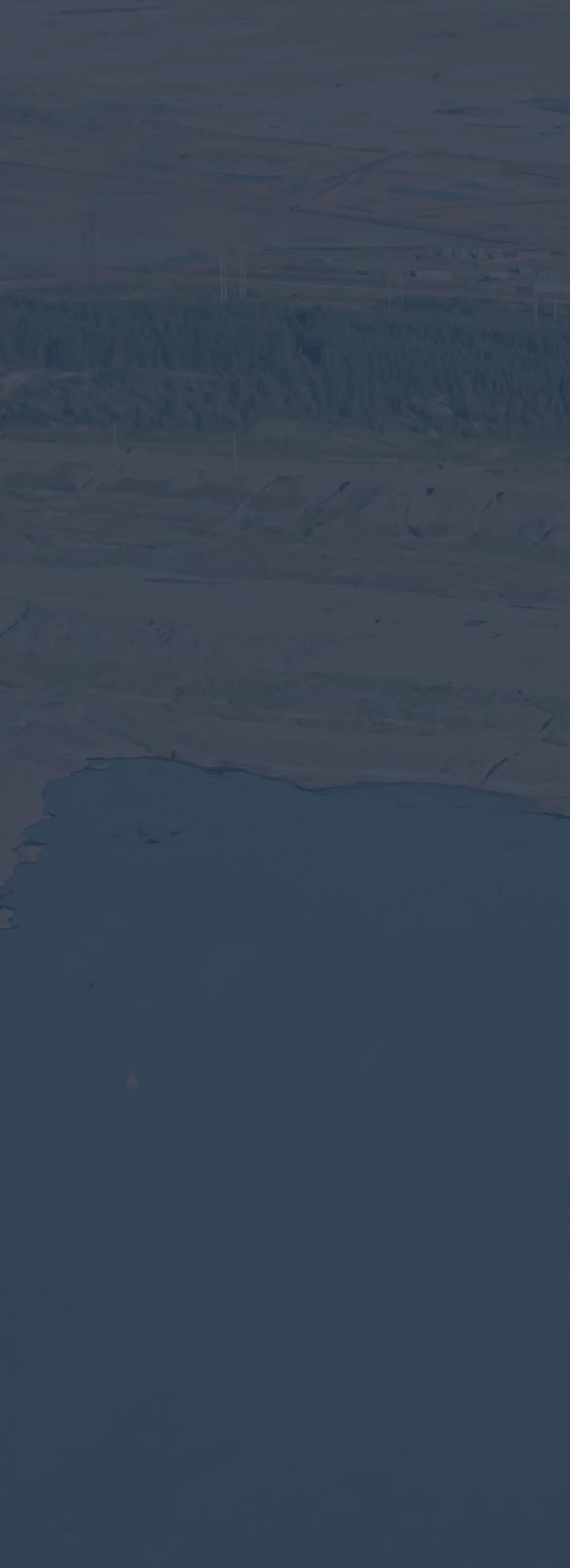
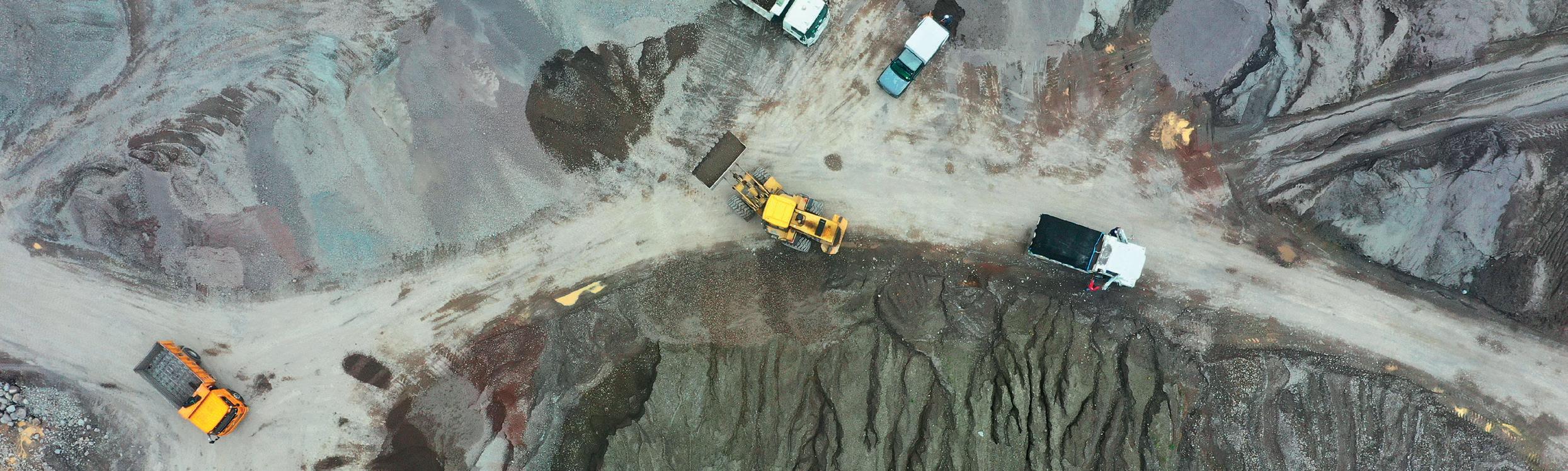
World NEWS
MONGOLIA Rio Tinto and China’s State Power Investment Corp. partner to trial battery swap truck technology
Rio Tinto will partner with China’s State Power Investment Corp. (SPIC) to demonstrate battery swap electric haul truck technology at the Oyu Tolgoi copper mine in Mongolia.
Battery swapping technology allows a battery electric vehicle to quickly exchange a discharged battery pack for a fully charged one, instead of recharging the vehicle at a static charging station.
The technology is already applied on haul trucks in mining operations across China, and this collaboration will enable Rio Tinto to demonstrate a complete battery electric truck and charging ecosystem at one of its operations.
The two-year project will demonstrate eight mining haul trucks (91 t payload), 13 batteries (800 kWh), and a robotic battery swap and charging station in non-production activities in the aboveground operations at Oyu Tolgoi.
Rio Tinto operates about 700 haul trucks across its global operations, of which 100 are classified as small or medium class (100 – 200 t payload).
Rio Tinto’s Chief Decarbonisation Officer, Jonathon McCarthy, said: “By partnering with the State Power Investment Corp., we will be demonstrating the latest technology and innovation available in China and assessing its potential to help decarbonise our operations quickly and cost effectively.
“This demonstration will allow us to explore applications for battery swap technology that deliver more flexibility and less downtime than current static charging technologies. This work will complement the electrification pilots of ultra-class mining haul trucks planned for the Pilbara.
“We look forward to partnering on more opportunities in the future to apply China’s innovations to the global resources sector and contribute to the world’s low-carbon transition.”
USA Caterpillar launches autonomous off-highway truck at Luck Stone Quarry
Caterpillar Inc. has announced it has successfully demonstrated the fully autonomous operation of its Cat® 777 off-highway truck.
The debut of this latest model of Cat MineStar™ Command for hauling at Luck Stone’s Bull Run plant in Chantilly, Virginia, USA, marks a significant milestone in Caterpillar’s objective to deliver an autonomous hauling solution for the quarry and aggregates sector.
This successful deployment of machinery and technology highlights the progress being made between Caterpillar and Luck Stone, the largest family-owned and operated producer of crushed stone, sand, and gravel in the US. In December 2022, Luck Stone and Caterpillar announced an agreement to accelerate the development of Caterpillar’s autonomous solutions for quarry and aggregate applications. This marks Caterpillar’s first deployment of autonomous technology in the aggregates
industry and will expand the company’s autonomous truck fleet to include the 100-t-class Cat 777.
Caterpillar has long been recognised as an industry leader in autonomy, with autonomous trucks on three continents having travelled more than 325 million km and autonomously moving more than 8.62 billion t. The current fleet of Caterpillar’s autonomous trucks with Command for hauling moves more tonnes per year worldwide than the total annual US crushed stone production. Some of the world’s largest mines are using Cat Command technology to achieve performance improvements. For two years, Caterpillar has been embedded with Luck Stone to build expertise in quarry operations, aiming to develop a system that is scalable and economically viable for customers across the quarry industry while also helping them to achieve a step change in safety and productivity.
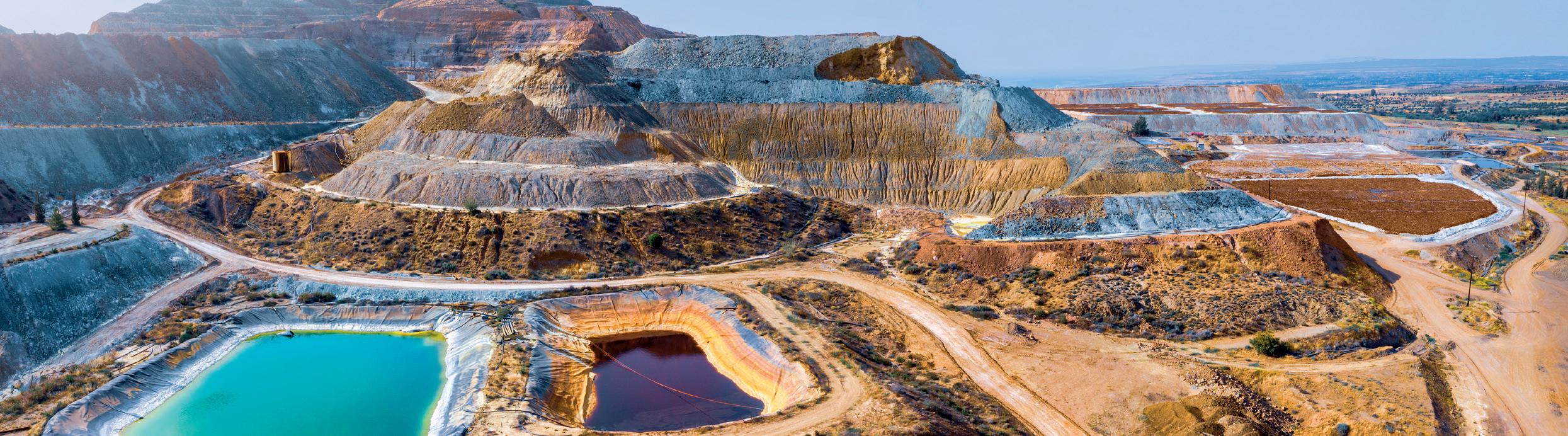
WORLD NEWS
Diary Dates
The Mining Show
26 – 27 November 2024
Dubai, UAE www.terrapinn.com/exhibition/ mining-show
ABMEC Conference & Exhibition
27 – 28 November 2025
Oxford, UK
www.abmec.org.uk/abmec_events/ abmec-conference-exhibition-2024
Resourcing Tomorrow
03 – 05 December 2024
London, UK www.resourcingtomorrow.com
Investing In Africa Mining Indaba
03 – 06 February 2025
Cape Town, South Africa www.miningindaba.com
SME MINEXCHANGE
23 – 26 February 2025
Denver, USA www.smeannualconference.org
PDAC
02 – 05 March 2025
Toronto, Canada www.pdac.ca/convention
GRX25
20 – 22 May 2025
Brisbane, Australia www.grx.au
UK Mining Conference in Cornwall
11 – 12 June 2025
Falmouth, UK www.ukminingconference.co.uk
China Coal & Mining Expo
28 – 31 October 2025
Beijing, China www.chinaminingcoal.com
To stay informed about upcoming industry events, visit Global Mining Review’s events page: www.globalminingreview.com/events
AUSTRALIA MMS acquires Western Australia gold project
Mineral Mining Services (MMS) has announced a significant expansion of its gold mining operations with the acquisition of the East Sampson Gold Project in Western Australia.
This strategic move strengthens the company’s position in the gold sector and reinforces its commitment to delivering exceptional results for its stakeholders.
“This is a major step forward for MMS”, said CEO Rob Ryan. “East Sampson aligns perfectly with our focus on high-potential open-cut gold projects with near term production potential. We’re bringing our proven expertise and track record of success to unlock the full value of this asset.”
The East Sampson Gold Project boasts a high-grade JORC Mineral Resource of 264 000 t @ 2.5 g/t for 21 000 oz with substantial exploration upside. MMS is confident in its ability to optimise production and maximise returns.
This acquisition comes on the heels of MMS’ recent successes at the Kal East Gold Project. The company has declared its intention to replicate this success at East Sampson and strengthen its standing as a leader in the gold mining industry.
CANADA Avalon enters into strategic collaboration with Qualcomm
Consistent with its strategy to become a leading North American vertically integrated lithium producer, Avalon Advanced Materials Inc., has announced it has signed a memorandum of understanding with Qualcomm Technologies Inc. on a strategic collaboration focused on Avalon’s Thunder Bay lithium processing facility, advancing cutting-edge digital solutions that enhance operational efficiency and optimise data management.
Under the MOU, Avalon intends to leverage Qualcomm Technologies’ Industrial & Edge technologies to create a robust digital infrastructure to support mining activities across Avalon’s operations. The collaboration will involve developing a strategic roadmap for Internet-of-Things (IoT) enabled solutions, with an emphasis on commercialisation over the next few years.
Additionally, this collaboration will solidify the province’s position as a hub for technological advancement in mining by fostering an ecosystem of Ontario-based technology small and medium enterprises (SMEs) to support the digital transition in Canada’s critical minerals sector.

PROdUCT NEWS
If there is a sector where drive solutions have to be extremely powerful and robust, then it is in mining. All over the world, vertical and tube mills ensure that raw materials from surface and underground mines are crushed professionally. The power required for this is transmitted by top-class gear units, such as those developed, built, and installed by Flender.
There are thousands of extraction sites, mines, and surface and underground mining operations for the extraction of raw materials all over the world. The trick is to crush the overburden in such a way that it can be used as efficiently as possible by the process industry. In addition to the actual crushing and milling technology, drive technology plays a central role in the economical, efficient, and reliable crushing of raw materials.
Flender GmbH, headquartered in Bocholt, Germany, with its 125 years of company history and associated know-how, is one of the top addresses in the mining sector worldwide. There is no continent on which Flender does not provide reliable mill drives with its sustainable gear units and couplings. Users can also benefit from an almost nationwide service network, large delivery capacities, and short delivery times. Not least due to its high level of vertical integration, the gearbox manufacturer is a reliable system partner in the mining industry that can easily cater to individual requirements in addition to its large standard range.
Vertical mill gearboxes as a flexible option
The mining business is booming around the globe, and with it the demand for higher performance and stable process reliability. Flender is naturally responding to this trend and offers the KM2P series in its vertical mill gearbox portfolio. The designation refers to the fact that even higher drive powers can be realised with these double planetary gear units. In the power range from 1000 – 12 000 KW, the KM2P is therefore the measure of all things.
From the manufacturer’s point of view, this vertical mill gearbox series is the best solution for most mining applications. This assessment is due to its high-tech design, which is based on the mill requirements on the market and the standards established there. Consequently, the desired compatibility is provided with the KM2P, so that there is a corresponding vertical mill gearbox from the standard modular system for virtually every mill for raw meal, clinker, and slag grinding, as well as other applications.
Tube mill gearboxes for an efficient system
The premium segment in terms of performance is represented by tube mills, which often have a diameter of 15 m and are up to 20 m long. Turning them is one of the Herculean tasks to be mastered in the minerals, ores, and cement sectors. Flender has developed single pinion drives, central drives, and load sharing girth gear units for the power range up to 30 MW. Flender builds the complete drive system for all three variants, consisting of motor, gearbox, couplings, pinion, and girth gear, as well as auxiliary drive, safety devices, and diagnostic systems.
Overall, Flender gear units for both tube and vertical mills also have the advantage that they offer an optional measuring sensor system in addition to the optimum energy balance. For this purpose, Flender has developed the Condition Monitoring System, which gives users the assurance of high process stability. This includes maintenance recommendations, fault predictions, and diagnostics.
Where performance and process reliability are the most important basis for economic success, as in the mining sector, Flender supplies suitable gear unit solutions. From the KMP to the KMPS, the KM2P, the MultiDrive variants, and the DMG2, there is a suitable solution for every vertical and tube mill.
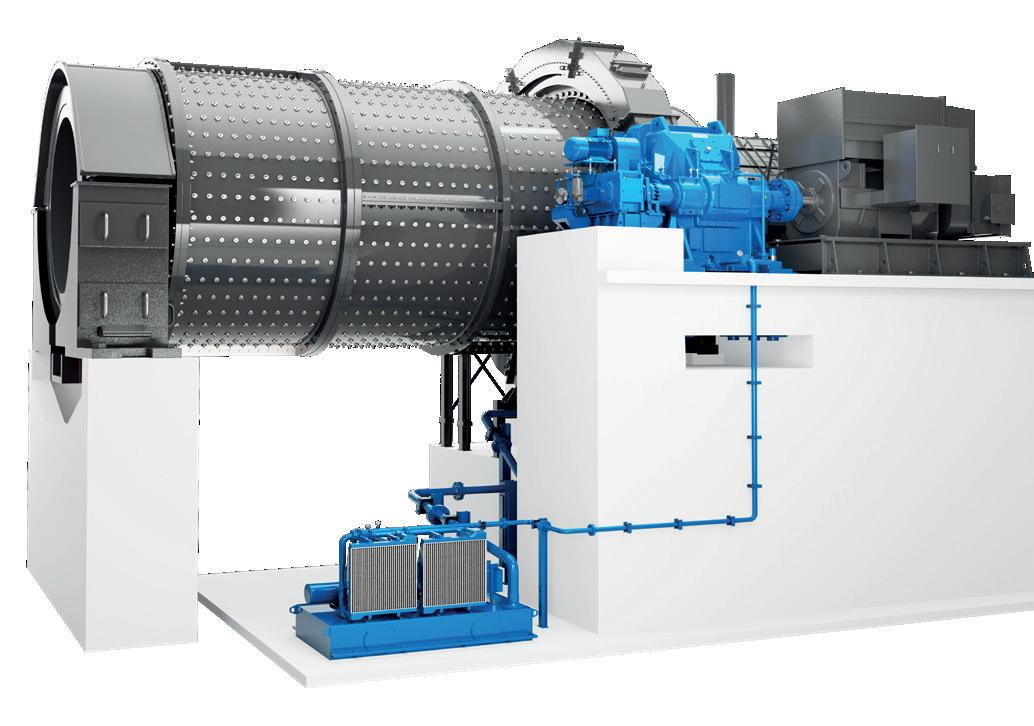
Figure 1. Flender, with its 125 years of company history, builds efficient and sustainable gearboxes and couplings for the highest outputs, as are commonplace in the mining sector.
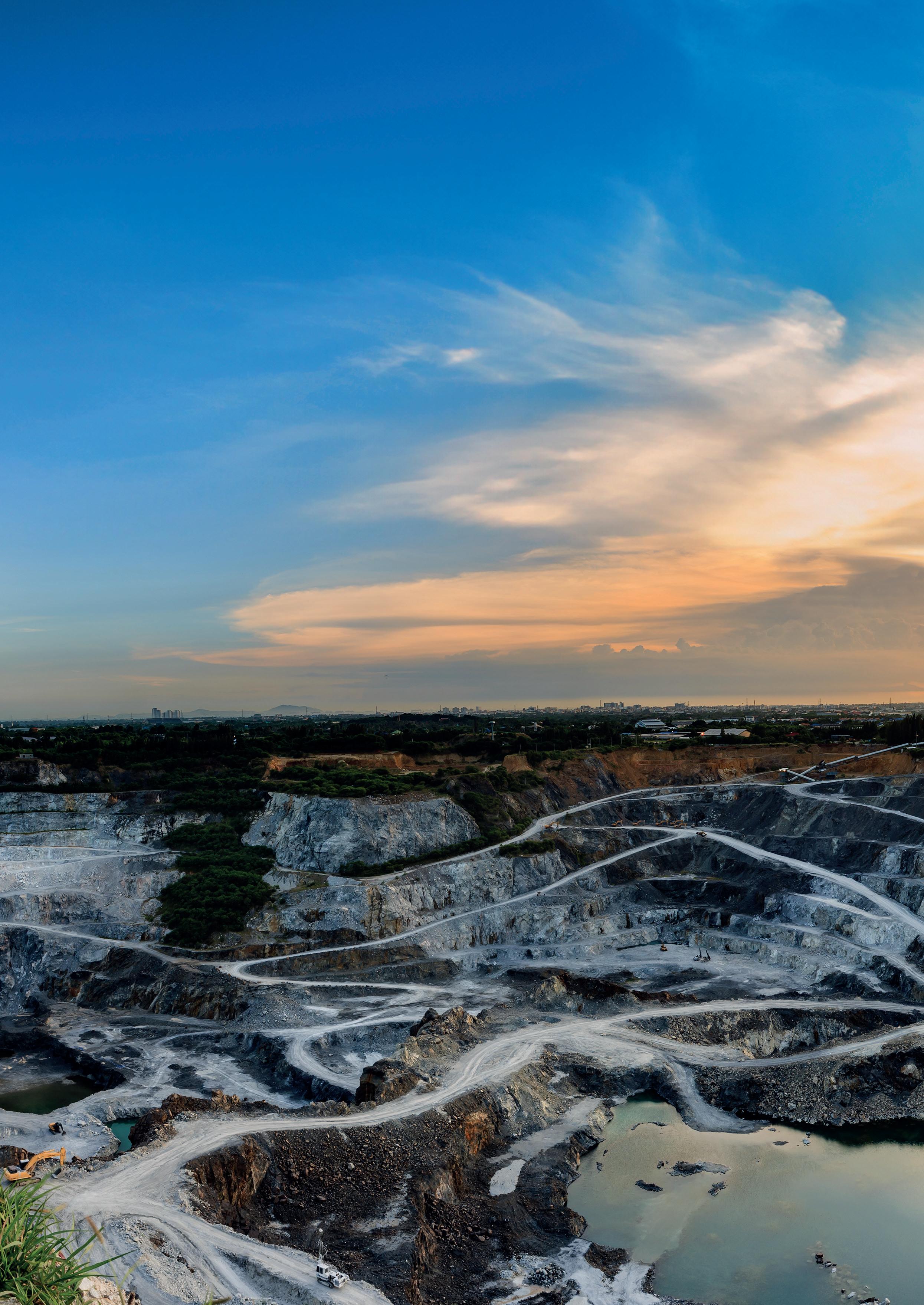
John Essegbey, Cummins, evaluates the practical next step solutions that can help mining operators move forward in the energy transition.
Mining operators are acutely aware of the pressure from legislators, investors, and the general public to reach zero-carbon operations as quickly as possible. Yet the industry faces a significant issue: the front-running future power options of full electrification or hydrogen are not fully mature. The necessary infrastructure for mining to adopt these technologies is not currently in place, and the point at which it will be is hard to predict.
However, the pressure to act is no less great, leaving mining operators the difficult task of choosing the right stepping stones to get them moving forward. It requires evaluating more
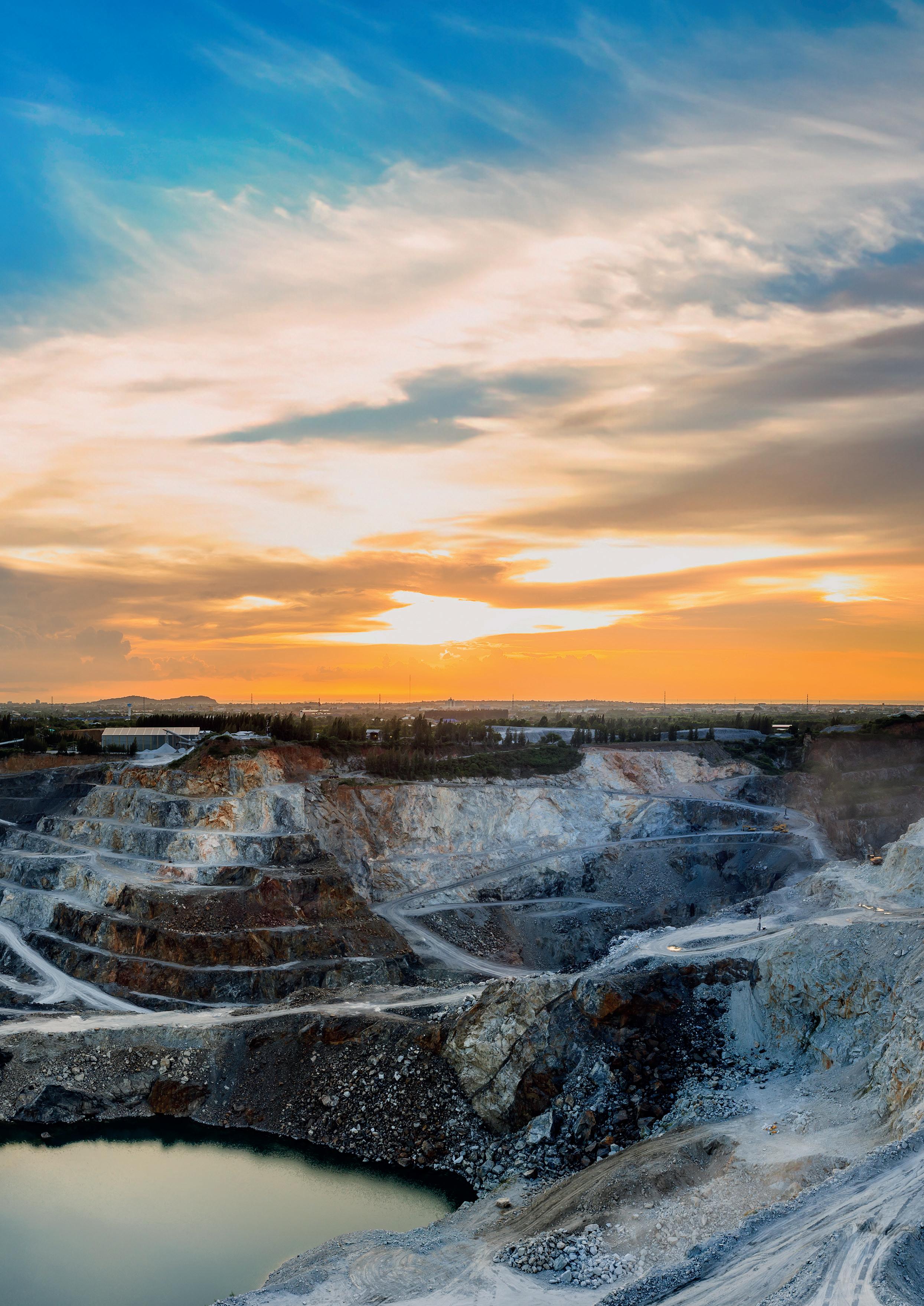
than just whether a technology is fit for purpose or cost-effective. Operators need to have a view of any solution’s environmental impact over its life and its suitability for different operating environments, as well as its value in terms of building operational knowledge and expertise with different power technologies. Unsurprisingly, many operators are looking for clear and dependable solutions to help them solve this complex set of near-term requirements.
This is why Cummins is putting significant effort into developing two such bridging technologies for use in mines: clean fuels and hybrid technology. Already proven in
other applications, these solutions are primed to give mining operators a sure-footed step towards zero emissions.
Cummins has taken big strides with both progressive decarbonisation pathways. Field tests and partnerships are already taking place with leading OEMs and mine operators to make sure industry needs are met.
Hybrid: Electrification now
Hybrid systems offer a small change in terms of operations, but a significant impact in carbon reduction. It is a clear path forward, offering incremental gains from a tried-and-tested technology that gives the flexibility and and reliable power mining needs.
Cummins has developed a core, modular architecture design that can be customised for first-fit or retrofit applications. Retrofitting, where appropriate, can be an excellent way to extend the service life of existing equipment, while meeting evolving regulations and carbon reduction commitments. Furthermore, it allows operators to build experience and understanding of electrical systems and how they operate in the conditions of their operations.
Key consideration points for adopting hybrid systems
Cost-effective decarbonisation
Compared to alternatives such as trolley assist, hybrid systems provide a more affordable way to reduce emissions. The possibility of retrofitting existing trucks also means companies can extend their assets’ lifespan and lower their overall costs.

Flexibility in operations
Hybrids do not require infrastructure changes to maintain peak power and transient load capabilities. This allows hybrid applications to adapt to hard-to-abate terrains and route changes, whilst maintaining performance levels.
Improved efficiency and total cost of ownership (TCO)
With the right battery technology and controls, hybrid systems can boost productivity and/or fuel efficiency. This not only cuts emissions, but also reduces the TCO for operators.
Key evaluation points for operations
Mine profile
Because of the effects of regenerative braking, the geography of mines can play a large part in carbon reduction with hybrids. Cummins modelling shows that mines with higher average gradients and more elevation could expect fuel reductions of up to 30%, while flatter operations might only save 6 – 10%. These percentages increase when the entire hybrid system is optimised, inclusive of the entire powertrain.
Optimisation
While hybrid systems are suitable for a wide variety of applications, not all hybrid systems will operate the same and achieve the same levels of fuel efficiency. Cummins understands the intricacies of the internal combustion engines working with battery systems and can optimise the powerplant controls, modulating power sources, and their integration with vehicle and traction controls for the specific application.
Progression
In the long term, full electrification via battery power is a potential end-state solution. As the industry innovates to accelerate technology readiness and supporting infrastructure to make full electric feasible for mining applications, hybridisation provides critical building blocks on the electrification pathway. This enables change management, learning high voltage skills, and infrastructure development without adversely impacting productivity.
Cummins hybrid in action
Cummins is performing field testing of a mining diesel-battery hybrid truck solution with North Hauler Joint Stock Co., Ltd. (NHL). In the hybrid NHL NTH260, a 220 t payload mining truck, the hybrid system allows the truck engine to be downsized from the previous 2500 HP QSK60 to the current 2000 HP two-stage QSK50. Early field test results show 15 – 20% average fuel savings compared to a non-hybrid system.
Clean fuels: Low carbon, simple implementation
There are many types of clean fuels that have the potential to offer low or zero-carbon power. Some of these are already commonly available and in use, some are seeing increases
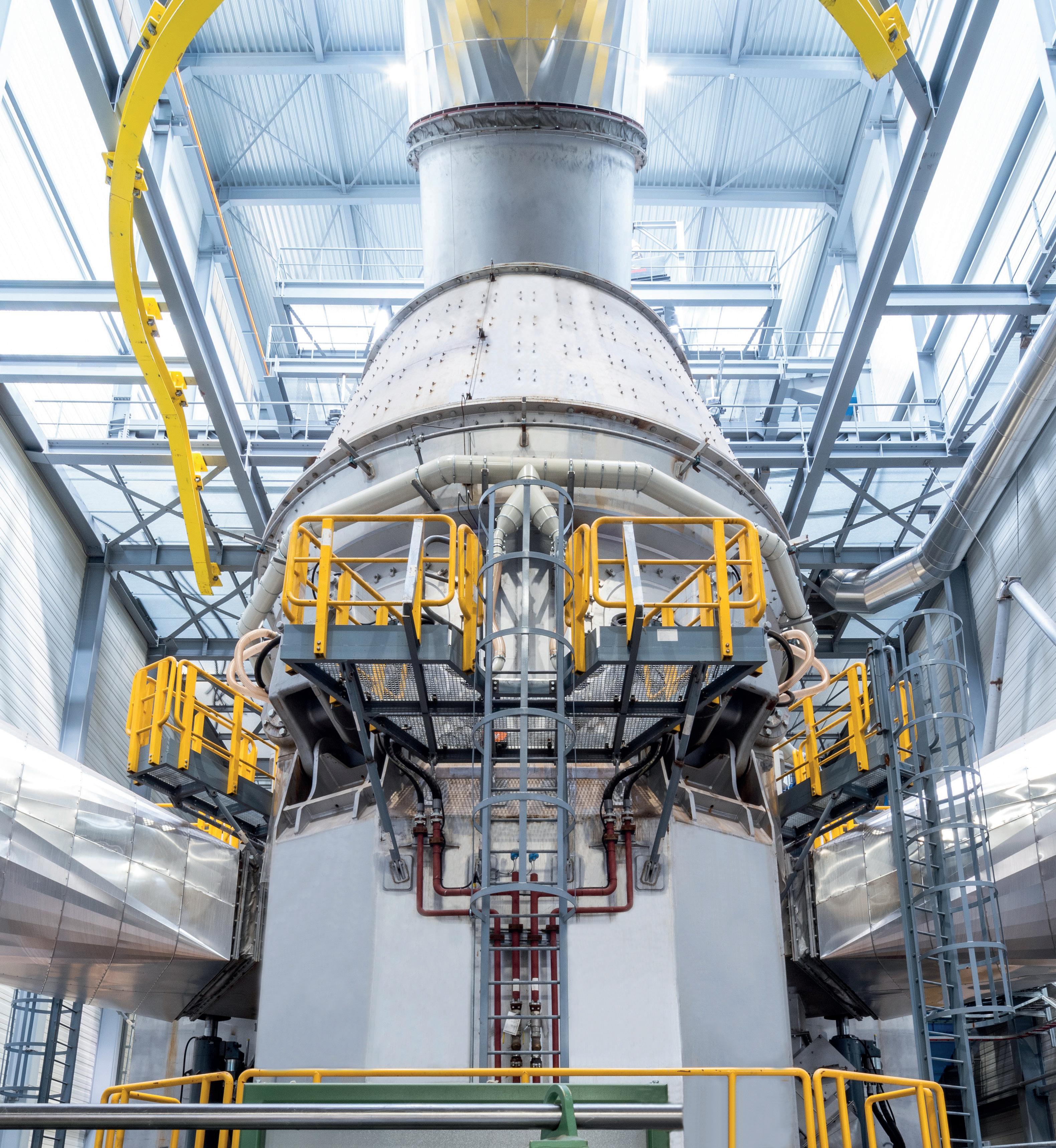

in adoption, and others are further away from being implementable options.
For miners looking to make small changes that deliver big impacts, the most promising options in alternative fuels look to be:
n Hydrotreated vegetable oil (HVO).
n Biodiesel.
n Ethanol.
n Methanol.
What mining operators really need is the ability to be able to take advantage of all these different fuels in accordance with their suitability and availability. Cummins’ entire line of high horsepower engines already accommodate varying blends of biodiesel and unblended HVO. Cummins is also developing additional solutions to
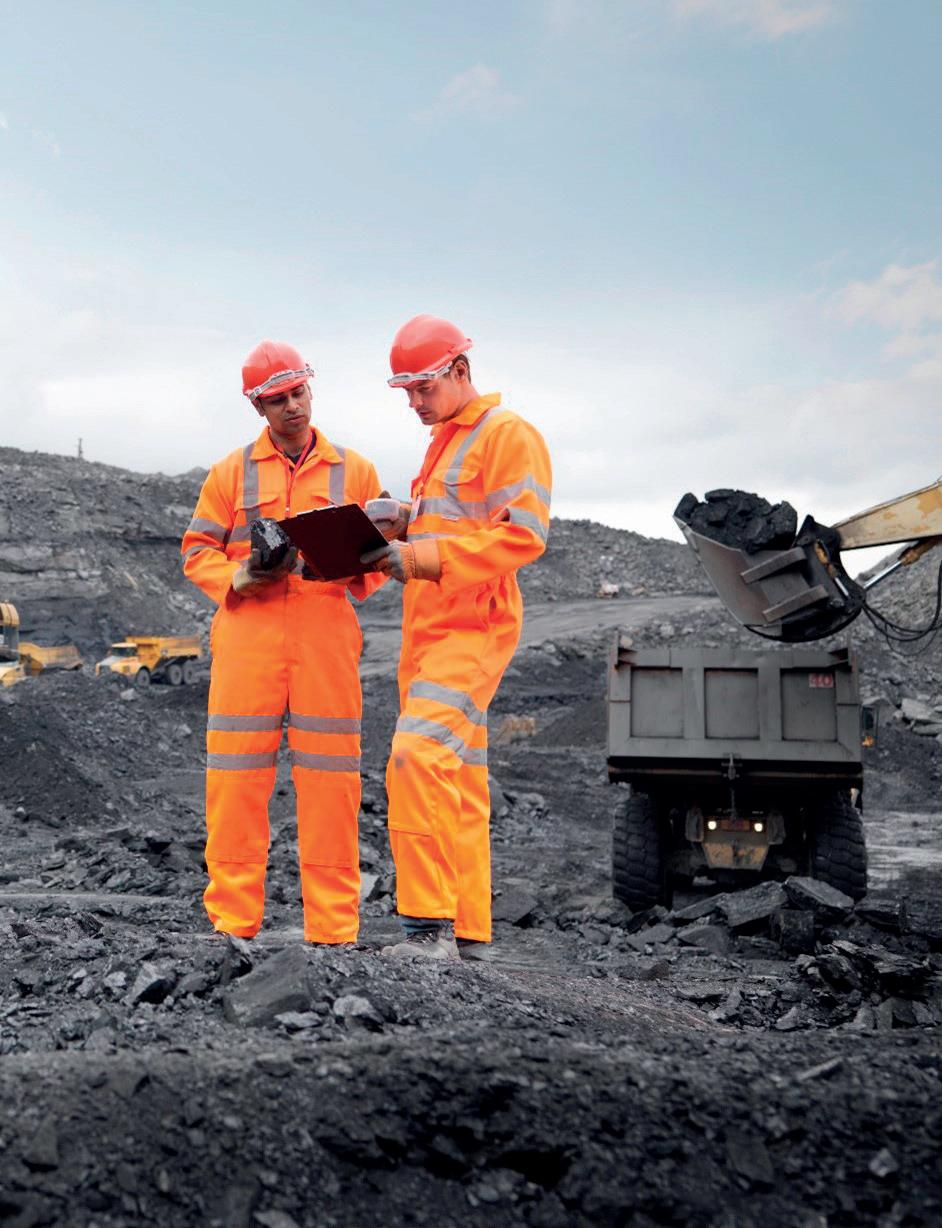
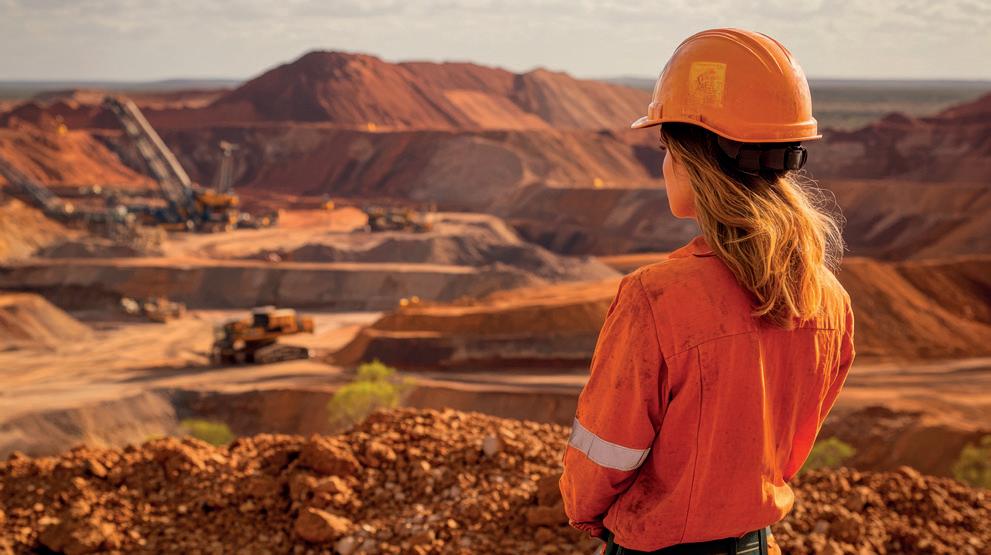
leverage ethanol and methanol. Specifically, dual-fuel systems provide flexibility for engines to run at varying diesel substitution rates based on fuel availability and performance needs.
Key consideration points for adopting clean fuels
Ease of implementation: Biodiesel and HVO
Biodiesel B20 and HVO are classed as drop-in fuels, requiring no adaptation of machinery. Higher biodiesel blends, such as B50, may require some machinery adaptation. They are liquids at room temperature and pressure, so the tank does not need to be cooled or pressurised (unlike hydrogen, natural gas, ammonia, and propane). This means less new training, procedures, and infrastructure are required.
Ease of implementation: Ethanol and methanol
Ethanol and methanol both require some vehicle level integration for dual fuel architectures. Both fuels are also liquids at room temperature and pressure, so the same advantages of a tank that does not need to be cooled or pressurised apply.
Vehicle space: Ethanol and methanol
The volume required, while more than conventional diesel (2.2x for methanol, 1.7x for ethanol), is still less than batteries and hydrogen, allowing mining trucks to operate normally without significantly more frequent refueling.
Immediacy
Many regions have biodiesel, HVO, ethanol, and methanol available and relatively affordable. The internal combustion engine technology is proven, and existing machinery can be used or modified, meaning this approach may be less dependent on procurement cycles and other factors.
Key evaluation points for operations
Maximising efficiency
Biodiesel and HVO perform very similarly to fossil fuels, while ethanol and methanol are less energy dense. The optimal outcome with these types of fuel is to maintain performance with no power loss, while achieving as high of a substitution rate as possible. This is why it is vital for operators to know that their power supplier has the experience and technical know-how to make the most of these fuels.
This comes down to the combustion process: Cummins has expertise in this area and is continuing tests and development to make sure that mine operators get the best performance, no matter what stage of the energy transition they are in.
Availability
Regional economies will play an important part in a decision process. Brazil, for example, has a strong ethanol economy using sugar cane. The infrastructure is in place and it is cost-effective with very good carbon intensity.
Carbon intensity
It is important to consider the entire lifecycle of a fuel, as focusing solely on tailpipe emissions is a mistake. Fuels like HVO, methanol, and ethanol have similar tailpipe emissions as conventional diesel, but the ‘well-to-work’ carbon intensity is reduced through fuel production using renewable resources. For example, depending on the fuel feedstock and pathway used, using renewable diesel like HVO can reduce well-to-work carbon emissions by as much as 90%.
Cummins’ methanol and ethanol solutions in action
In July 2024, Cummins, Vale, and Komatsu signed an agreement to develop and test dual-fuel haul trucks, powered by a mixture of ethanol and diesel. They will be the world’s first dual-fuel powered trucks of their size, with payloads of 250 – 320 t.
In 2023, Cummins was selected by the UK Department of Transport for its high-horsepower methanol vessel retrofit project. The project will see Cummins develop a methanol kit for its QSK60 engine.
You do not have to have all the answers now
One of the most difficult parts of finding the right path through the energy transition is the number of moving parts. Trying to keep pace with ever-advancing
technology, evaluating what is going to be the right choice, and matching this with procurement cycles, maintenance schedules, and economic turbulence can feel like an impossible task.
Cummins’ bridge technologies offer an excellent way out of this cycle. Customers can make progress, see results, and continue down the path of progressive decarbonisation, maximising the useful life of current fleets.
Work with a partner who helps you build bridges to the future
The best possible outcome from adopting bridge technologies is not just seeing immediate results, but creating the stepping stones to zero emissions. The way to achieve this is by working with partners who have sight of the bigger picture and the ability to provide the right solutions for you.
Cummins’ global scale and service network can help mine operators manage the complexity of multiple solutions, enabling a clean fuel approach in one location in the world, whilst implementing hybrid vehicles in others. These are just a few examples of how Cummins bridge technologies close the gap between what is practical and what is possible. This flexibility and adaptability are the key to achieving more gains quicker and setting yourself up for a smoother, more cost-effective path to zero.

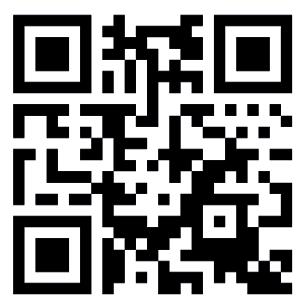
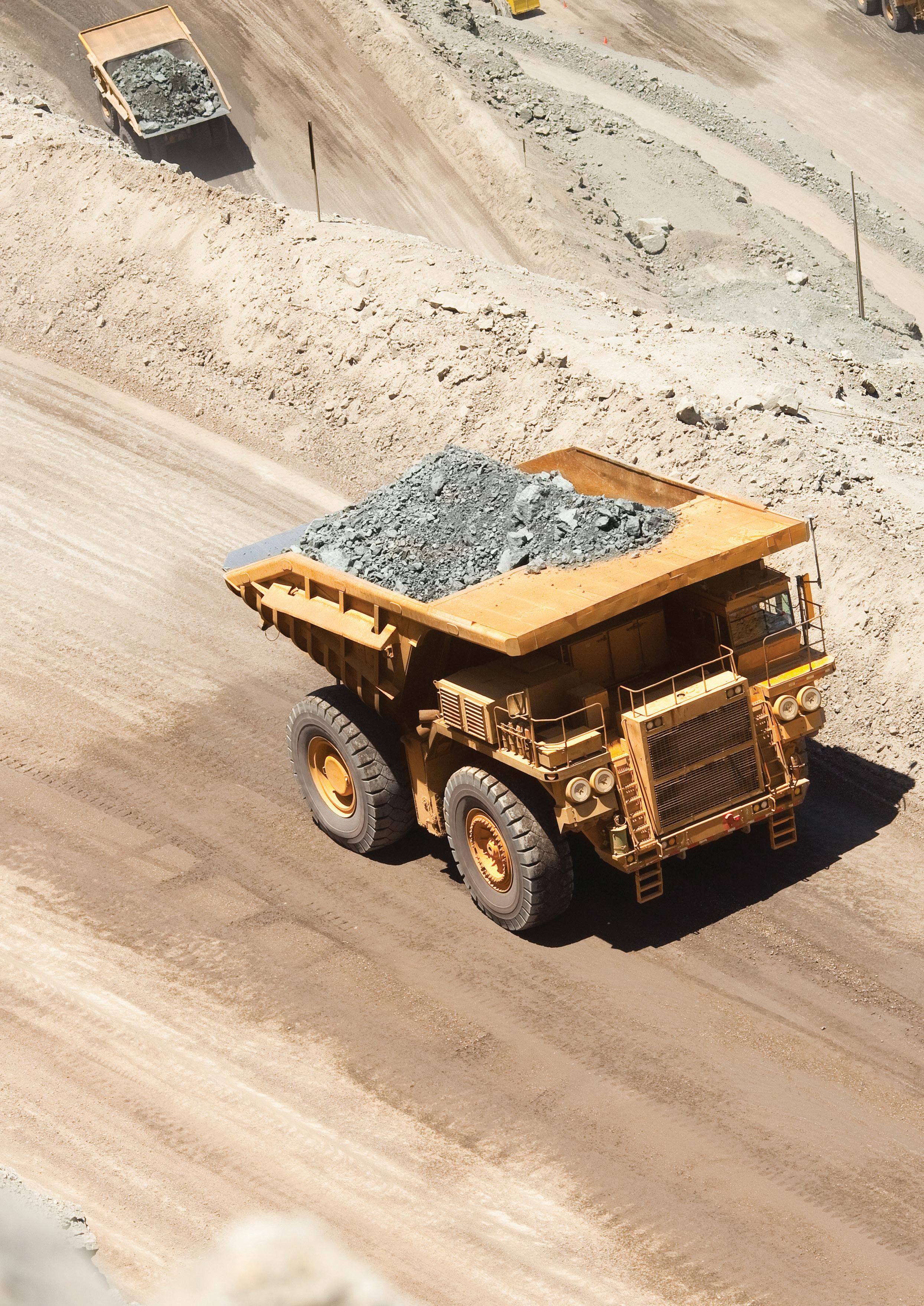
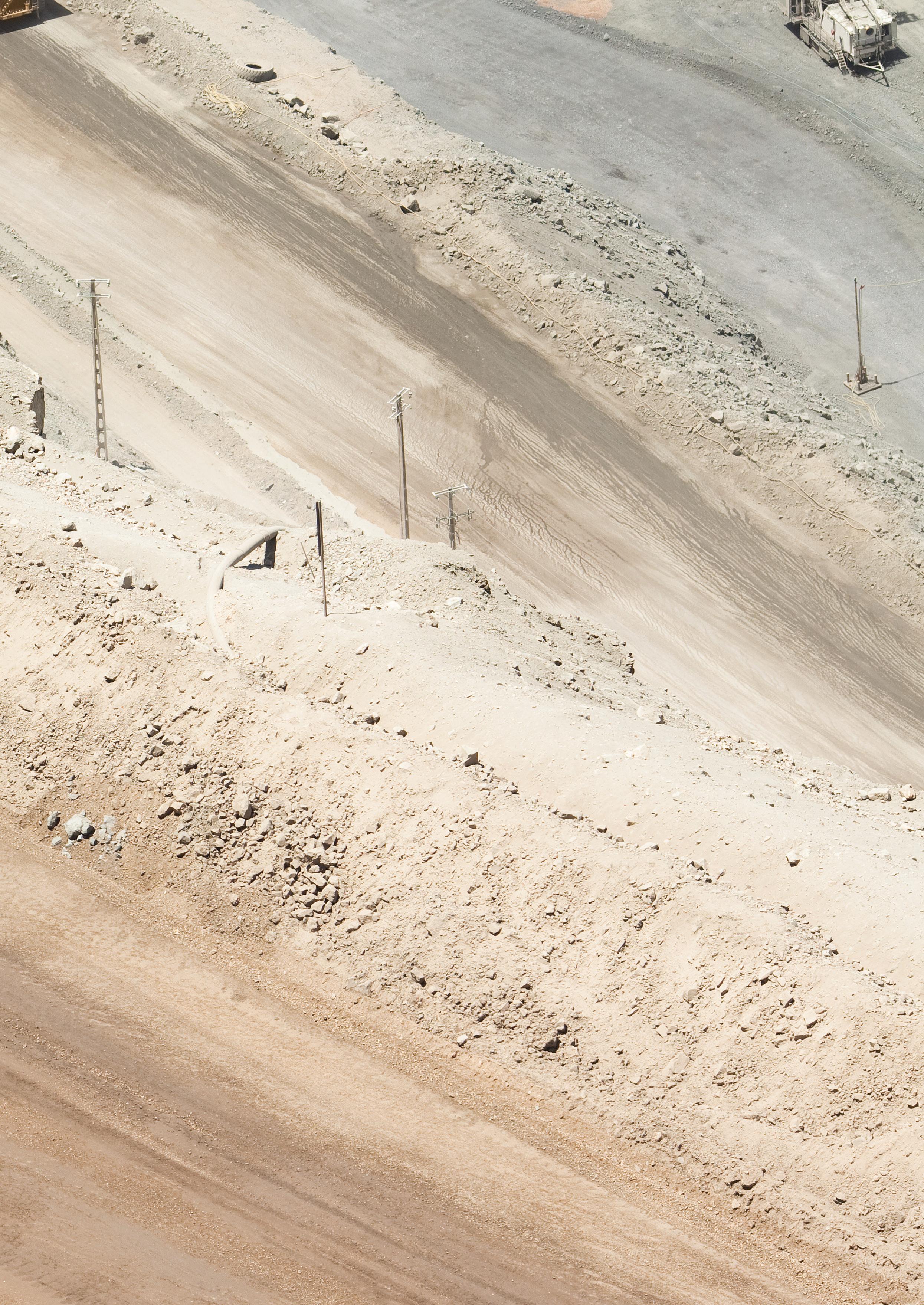
Brian Fox, Komatsu Mining Technologies, USA, discusses sustainable mine optimisation and its impact on customers in a Q&A with Will Owen, Global Mining Review.
Today’s mine operators need more than tools or equipment. They need solutions that are capable of implementing and integrating workloads at the task, process, and enterprise levels. They need cohesive and connected solutions that can take advantage of the latest technologies to help them mine more responsibly; meet and exceed production demands; sustain mining resources; and protect the environment. A tall order, but one in which the demand for mined material, in many cases, is outpacing the supply. More than equipping their needs, mine operators are seeking partners with plans and solutions that assist them in balancing these objectives.
WO
What is the strategy or thinking behind sustainable mine optimisation?
BF
Sustainable mine optimisation is a guiding principle and approach for helping mine operators meet the challenges of sustaining their resources, while still optimising their current operations. It is a commitment to partnering and collaborating with customers to unlock the full potential of commercially-available solutions and technologies, and working together to prioritise and balance safety, reliability, cost-effectiveness, and environmental impact.
From optimising existing fleets to providing alternative-fuelled equipment, sustainable mine optimisation helps customers find the right path forward for their operation. For example, there are now interoperable solutions available that are capable of uncovering next-level value and innovation via technology, such as our recently launched Modular ecosystem. Partnering with customers, we are collectively striving to:
n Operate with promoting safety as a priority.
n Assist in exceeding environmental regulations and standards.
n Leverage the latest technologies to aid in improving efficiencies, productivity, and total cost of ownership (TCO).
n Contribute to optimised fleet capabilities through digitalisation and automation.
WO
You explained the rationale behind sustainable mine optimisation. What is spurring the development of products that meet this definition?
BF
Komatsu is focused on helping customers sustain their own operations, with the additional goal of reducing the carbon footprint across their entire value chain. Komatsu, like many companies in the industry, have committed to a goal of net zero emissions, or carbon neutrality, by 2050. However, operators are still charged with sustaining, growing, and enhancing their operations and adopting a plan of reducing carbon emissions and those of our customers.
To accelerate our development, Komatsu formed the Greenhouse Gas (GHG) Alliance in 2021 with founding partners Rio Tinto, BHP, Codelco, and Boliden. The Alliance has now grown to 12 members. Working collaboratively, the Alliance is focused on developing reduced emission solutions, starting initially with electric drive haul trucks, through the implementation of a variety of power sources including diesel electric, trolley, batteries,

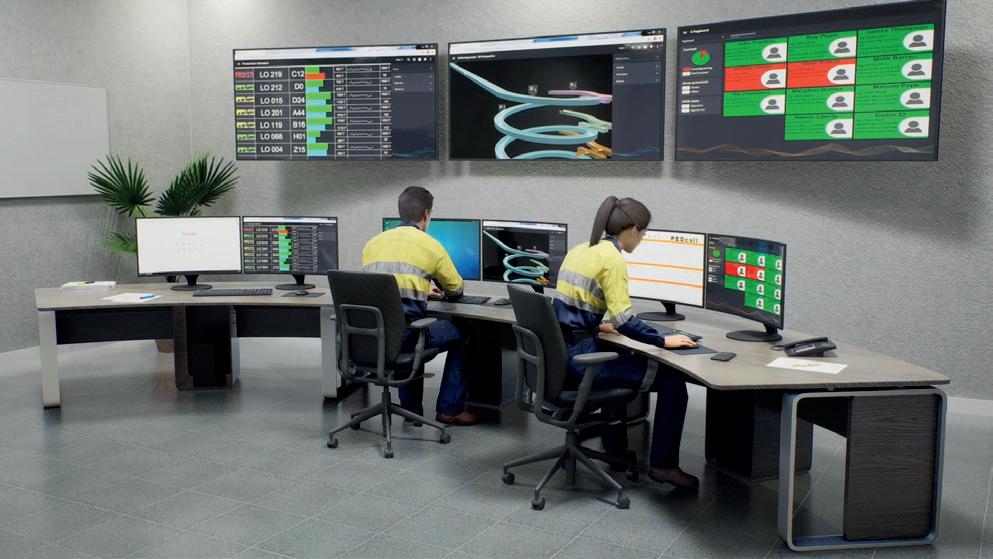
and hydrogen fuel cells. Komatsu has a legacy in the use of electric drives, which dates back nearly as long as the company itself.
As companies shift to alternative means to power their equipment, we are encouraging them to take a look at their own operations to find ways they can achieve peak efficiencies and reduce their current emissions. Tools, such as remote health monitoring, can help improve fleet efficiency, reduce idle times, and prevent shutdowns. Applications, that assist in improving payload and provide guided truck spotting, can help increase productivity. Innovative apps like Look Ahead, introduced at MINExpo, can execute multi-objective mine plans, taking optimisation to the next level.
WO
What are the principal benchmarks that ensure mine operators are getting the best available solutions to optimise and sustain their operations?
BF
Many of our products and solutions are built and measured against three foundational pillars: sustainability, interoperability, and automation. This helps to ensure that our products are aligned to help customers sustain and protect the environment; promote workplace safety; automate repetitive tasks; and leverage leading available technologies.
Drilling down to an operational standpoint, products at the mine task, process, and enterprise levels are evaluated against additional value drivers that include: safety, productivity, reliability, and digitisation.
WO
You outlined some goals and objectives that most mine operations need to accomplish to stay competitive. Can you point to some tangible offerings that are helping operators meet these challenges?
BF
We are proud of the fact that we are more than just an equipment company. We are well-positioned to offer companies a wide array of solutions – at the task, process, and enterprise levels – that can help them operate more sustainably and cost-effectively.
At MINExpo, we were excited to unveil the innovative Modular ecosystem, a connected, interoperable system that contributes to optimising surface mining operations, such as managing an autonomous haul truck fleet. The Modular ecosystem is being designed to seamlessly integrate solutions from other companies as well. Like an operating system for your mine, it will provide a data set that serves as a ‘single source of truth’ and feeds whatever vendor applications that mine operators choose to use. Modular has been engineered to be secure, easy-to-adopt, and we keep updating it and adding features to enable mine sites to perform at optimum levels.
Much like Modular, Mine Site Technologies (MST) is the backbone of the mine digital ecosystem for underground hard rock mines – specifically, communications and data.
Explore
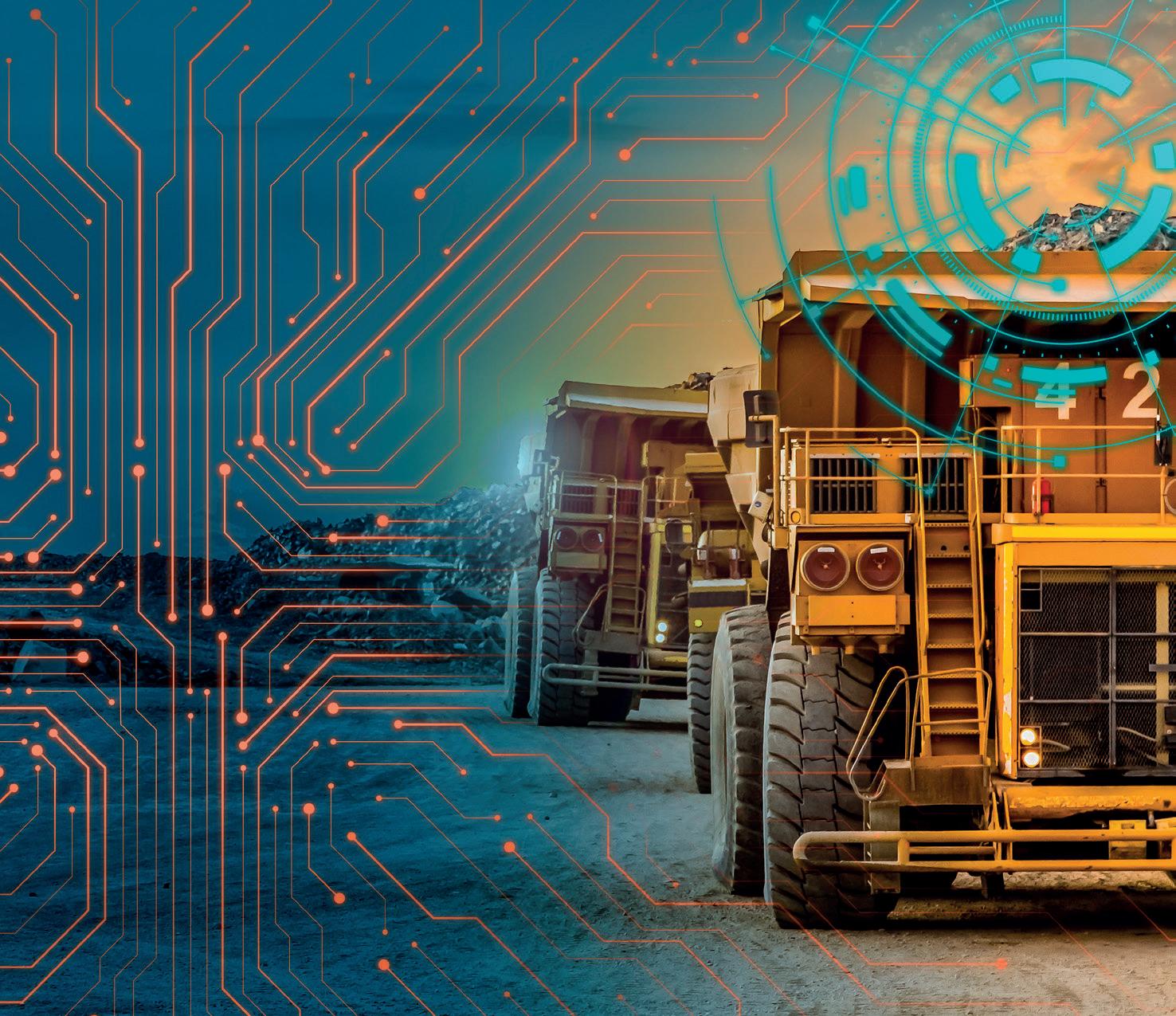
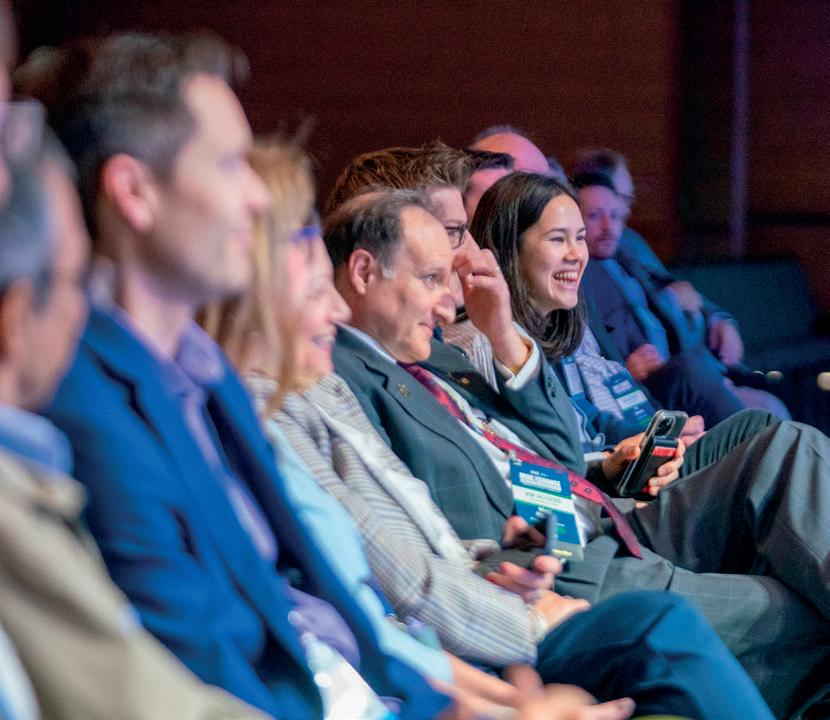
Like Modular, MST systems are OEM-agnostic and integrate easily with others. Also introduced from MST at MINExpo is Helix Dispatch, which is software designed to help optimise dispatch processes underground.
In addition, tele-operation and autonomous capability enables operators to run machines from remote operator stations. It removes operators from harm’s way for enhanced safety, but it also helps reduce the number of people at remote sites. Staff can manage these functions in an urban office thousands of miles away from the working machine.
WO
Can you point to an example where this approach has been successful?
BF
Earlier this year, published reports announced that the truck fleet at BHP’s Spence copper mine in Chile became fully autonomous. The Spence mine, which produced 249 000 t of copper last year, is the largest autonomous fleet operating in Latin America. Komatsu is proud to have provided the autonomous haulage system.
In making the announcement, BHP stated that it is possible to reduce worker risks associated with the mining industry by up to 90%. The company believes autonomous haulage has helped them become more competitive and has allowed them to help manage their resources more efficiently.
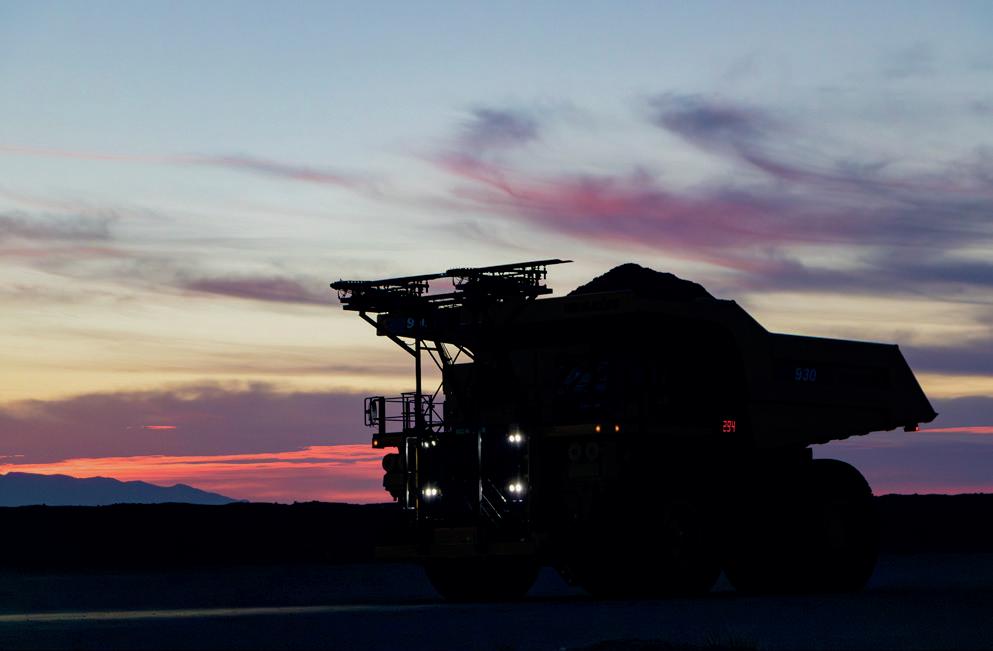
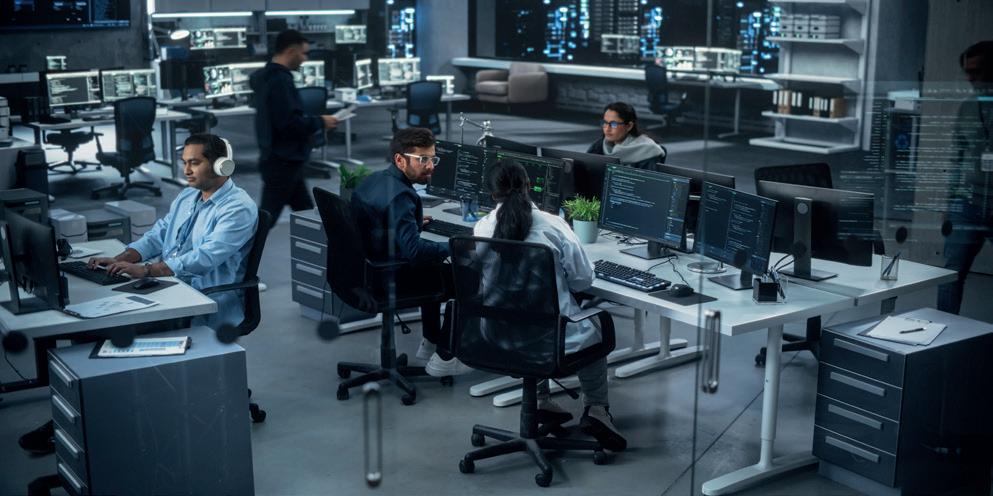
WO
You explained what Komatsu is doing to integrate, automate, and connect mining operations. Are there some component products that support the goal of sustainable mine optimisation?
BF
There are a growing number of power solutions being developed by the mining industry. One is hydrogen. Komatsu is working with General Motors to co-develop a hydrogen fuel cell module for ultra-class electric drive trucks. Battery development is also key. Komatsu acquired a battery company (American Battery Solutions) in 2023 for development and manufacturing capability. Finally, Komatsu and ABB recently announced a strategic collaboration initially focused on energy transfer solutions such as robotic and dynamic charging.
We have introduced a new wheel loader – the WE2350-4 – which uses hybrid technology to help boost performance, efficiency, and sustainability. When the machine decelerates, energy is fed into a kinetic energy storage system to be used later. With a 44 m3 bucket capacity, it is designed to centre-load ultra-class, 400 t haul trucks with ease.
Komatsu’s power-agnostic drive truck (PADT) equipment platform can help increase productivity and reduce costs over its life, while transitioning to promote zero emissions. By starting with diesel performance, the customer can aid in advancing the technology, as each step forward can drive these improvements and progress towards reduced emissions. PADT is adaptable to various power sources or energy systems to suit the demands of each operation, such as diesel/trolley, battery (with dynamic or static charging), battery/trolley, or even hydrogen fuel cells.
WO
Any final thoughts to share?
BF
It is no secret that the mining industry will soon be facing a significant labour shortage, as an older generation retires and cycles out of the industry without a cohort of workers to replace them. As a result, remote operations, automation, data analytics, and AI are becoming increasingly consequential. This concept of ‘the mine coming to the city’ is real and is driving the development of a host of product innovation that supports remote-operated command centres for the mining industry.
Automation and electrification will remain a focus, moving forward, as fewer and fewer employees are entering the mining industry, widening the gap between demand for mined material and the workforce to produce it.
In my almost 40 years of working in mining, there has never been this much excitement. The industry is changing for the better. I hope that the focus on safety, environment, and new technology – paired with the realisation that minerals are critical to our future – will draw the next generational talent to mining.
Jessica Moor, CR Powered by Epiroc, Australia, reviews the company’s history in dragline bucket and rigging technologies and highlights a recent significant industry milestone.
CR Powered by Epiroc, a leading engineering partner in productivity, safety, and sustainability for mining operations, recently marked a significant milestone by delivering its 300 th dragline bucket to the Stanmore South Walker Creek mine. This achievement is a testament to CR’s commitment to innovation and customer satisfaction, and underscores the
company’s dedication to giving back to the communities that support the mining industry.
The evolution of dragline bucket technology
Founded in Mackay in 1979, CR Powered by Epiroc –formerly known as CQMS Razer – has long been a trusted partner in the mining industry, both in Australia and globally. Over the years, CR has built a reputation for innovation, with product portfolios for both surface and underground operations that have consistently pushed the boundaries of what is possible in mining equipment and technology.
The journey towards the 300 th dragline bucket began with CR’s initial offerings of dragline teeth, adaptors, and rigging. However, recognising the evolving needs of the mining industry, CR expanded its product line in 1998 with the launch of the EarthEater dragline bucket. This early innovation laid the foundation for innovation in dragline bucket design.
By 2007, the development of the first-generation Hurricane™ bucket marked a turning point in the industry. This bucket – designed using advanced engineering capabilities, scale testing, and simulation tools – introduced a new geometry that significantly increased fill factors and overall productivity. The Hurricane bucket quickly became the industry standard, known for its fast-filling capabilities, reduced weight, and increased payload. These features improved operational efficiency and reduced downtime, making the Hurricane bucket a preferred choice for mining operations.
Introducing the Hurricane bucket represented a significant leap forward in dragline technology. By employing a range of critical geometric features, CR was able to offer industry-leading fill factors and energy savings of 19%, due to reduced drag energy. The performance gains, which exceeded 12% compared to traditional buckets, made the Hurricane bucket a game-changer in the mining sector.

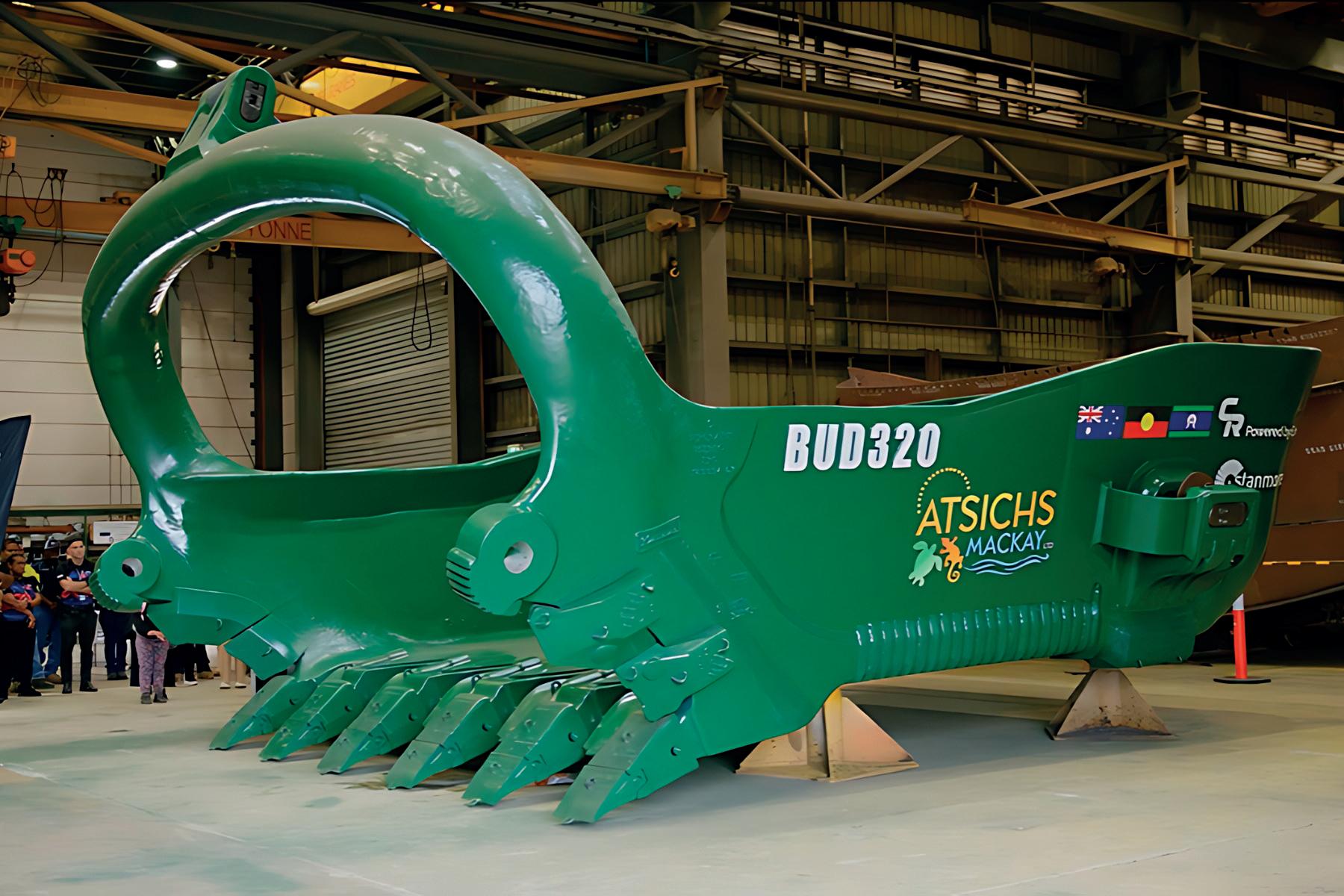
Advancing to the Hurricane 2.0
The success of the original Hurricane bucket set the stage for further innovation. By 2016, CR had developed the Hurricane 2.0, a bucket that pushed the limits of operational productivity even further. This next-generation design featured a lower profile and a wider front rig, which saw increased productivity results by 16% compared to traditional dragline buckets. The fill factor also improved, rising by up to 130%.
The Hurricane 2.0 was not just an evolution in design, but a response to the ever-changing demands of the mining industry. Through close collaboration with customer partners, CR was able to refine the bucket’s design to deliver even greater strength, durability, and performance. The result was a product that met and exceeded the industry’s expectations, solidifying CR’s position as a leader in dragline bucket technology. Today, nine out of ten draglines in Australia are fitted with a CR bucket, a testament to the impact of the Hurricane and Hurricane 2.0 buckets on the industry.
The 300 th dragline bucket: A milestone in mining
Fast forward to today, and CR is set to deliver its 300 th dragline bucket, the CQ300, to the Stanmore South Walker Creek mine. This milestone is particularly significant as South Walker Creek was the first mine site to purchase the


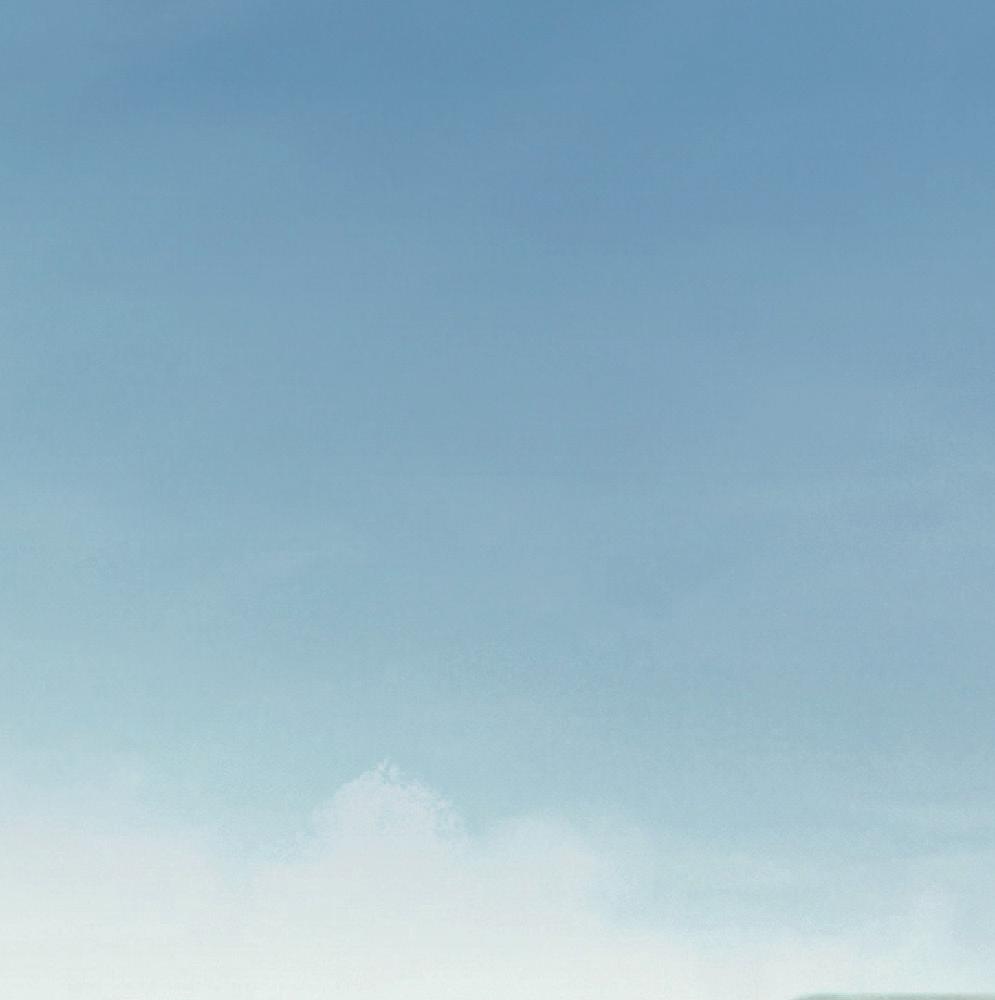
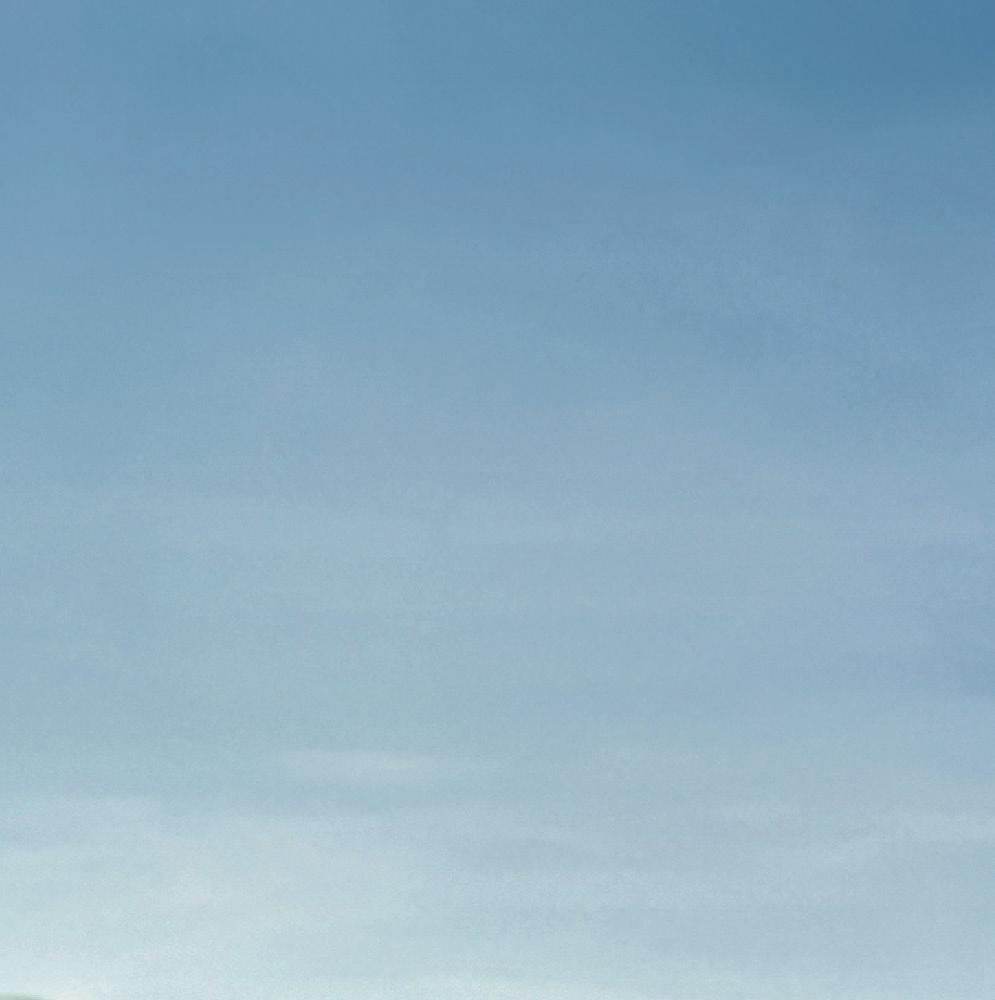
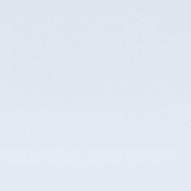
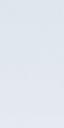

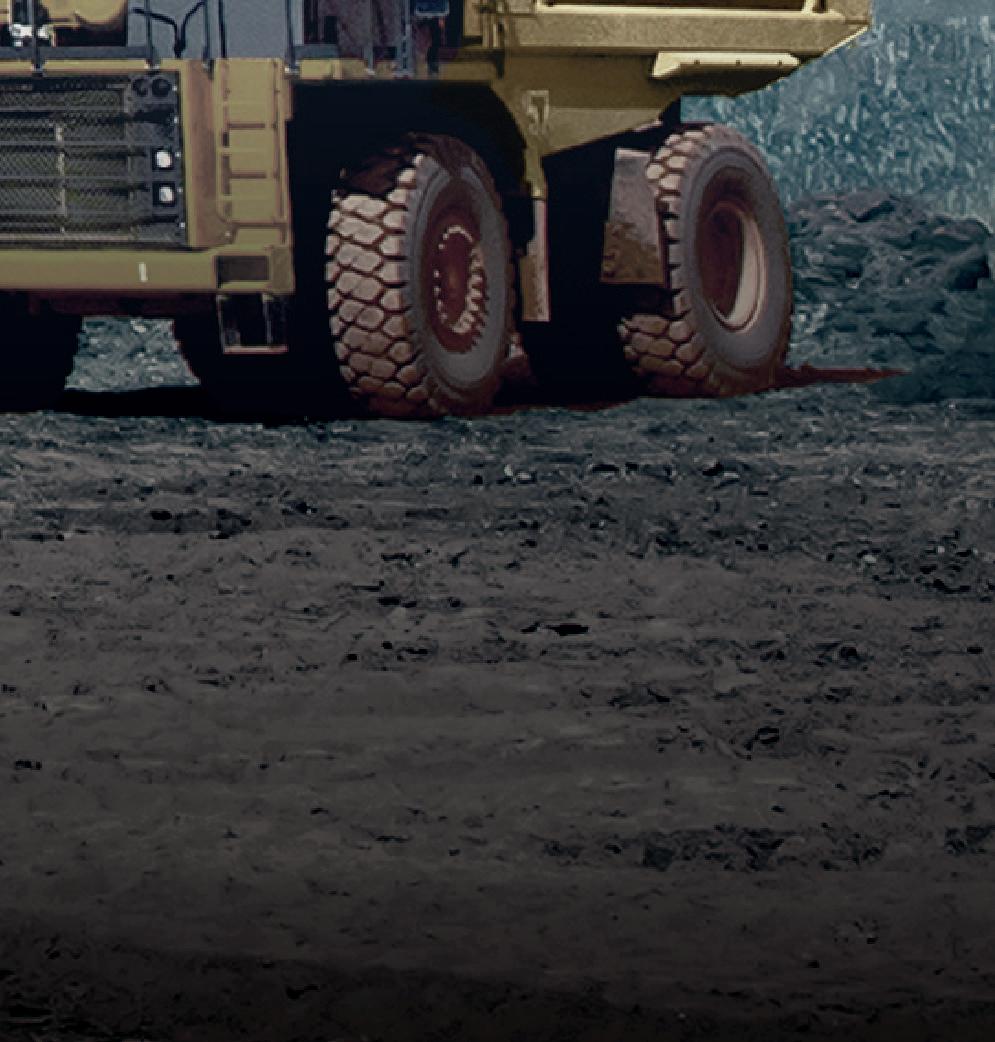



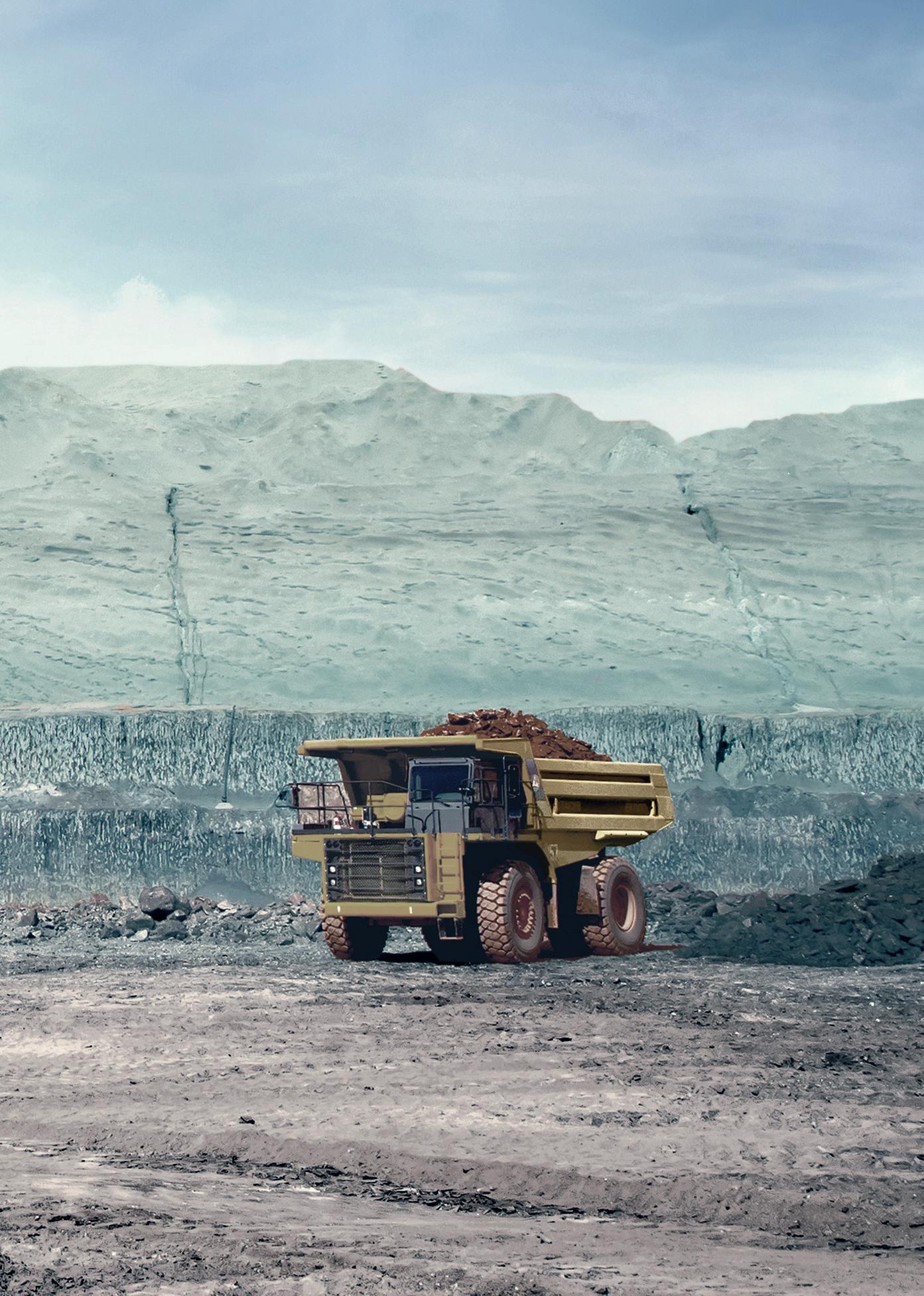
Hurricane-style bucket in 2007. The CQ300 represents not just a numerical achievement, but a continuation of a legacy that began over two decades ago.
The long-standing relationship between CR and Stanmore South Walker Creek has been built on a foundation of trust, collaboration, and mutual success. Over the years, the Hurricane-style buckets have consistently delivered productivity and efficiency results, helping to optimise operations. The CQ300 is the latest in a line of products that have been fine-tuned through years of real-world application and industry feedback.
The case studies documenting the impact of Hurricane buckets, such as those found on the CR website, highlight the significant gains in payload and productivity that customers have experienced. These case studies serve as a powerful testament to CR’s innovative bucket designs’ benefits to the mining industry.
Pioneering rigging and chain rope-to-rope solutions
In addition to their advancements in bucket design, CR has also been at the forefront of developing rigging solutions for dragline excavators. For over three decades, CR’s Australian-made rigging systems have set the standard for quality and wear life in the mining industry.
CR was the first to introduce hammerless rigging to the marketplace, a development that has had a profound impact on the safety and efficiency of mining operations. The Surelock™ rigging lock system, launched in 1999, was a pioneering product that provided a safer, more secure locking mechanism for draglines. Building on this success, CR continued to innovate by introducing the C-Lock, a hammerless retaining system with double locking mechanisms.
The C-Lock is engineered to ensure that locks last as long as the rigging and bucket, allowing mining operations to keep digging for longer without interruption.
These rigging solutions, like the dragline buckets, have been developed through a relentless pursuit of excellence and a commitment to meeting the industry’s needs. CR’s rigging systems are not just about improving efficiency – they are about setting new benchmarks for operational safety and reliability in the mining sector.
Community engagement: Giving back to Mackay
Marking the delivery of the 300 th Hurricane dragline bucket, CR collaborated with industry partners –including Stanmore, IMS, Bisalloy Steels, SunCity Signs, Centurion, iScope, INDT, and RPG Australia – to support local communities. Together, these partners raised AUS$60 000 for the Aboriginal and Torres Strait Islander Health Services (ATSICHS) in Mackay, a local not-for-profit organisation dedicated to providing holistic healthcare to Aboriginal and Torres Strait Islander people in the region.
This initiative is more than just a charitable donation, it reflects CR’s commitment to the communities integral to the mining industry. The funds raised will support various areas of ATSICHS’s work, including school programmes, community events, and health education initiatives to address the specific health risks First Nations people face.
The partnership with ATSICHS and the broader community engagement efforts align with CR’s ethos of giving back and positively impacting their communities wherever possible. This milestone, therefore, is not just about celebrating an industry achievement, but also about recognising the importance of community support and collaboration in driving meaningful change.
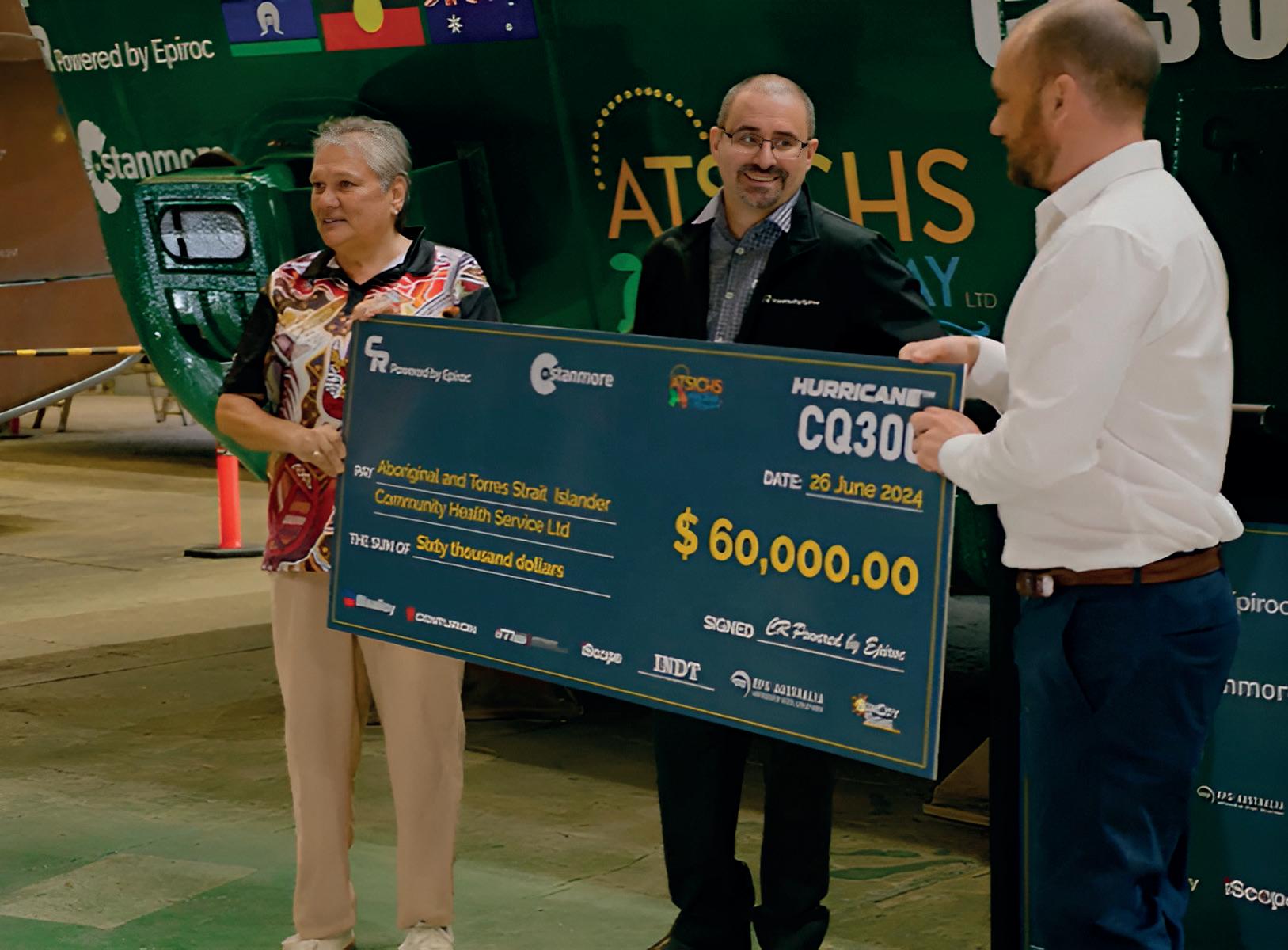
The future of dragline technology
The delivery of the 300 th dragline bucket, CQ300, underscores CR Powered by Epiroc’s commitment to innovation, customer satisfaction, and community involvement. As the company builds on its legacy of pioneering bucket designs and leading rigging solutions, it remains focused on advancing dragline technology and optimising rope-to-rope solutions. Future research and development will enhance safety, productivity, and efficiency while reducing downtime, wear rates, and maintenance costs. By incorporating cutting-edge materials and engineering techniques, CR seeks to exceed the rigorous demands of modern mining operations – ensuring safe, sustainable, and efficient mining practices for the future.
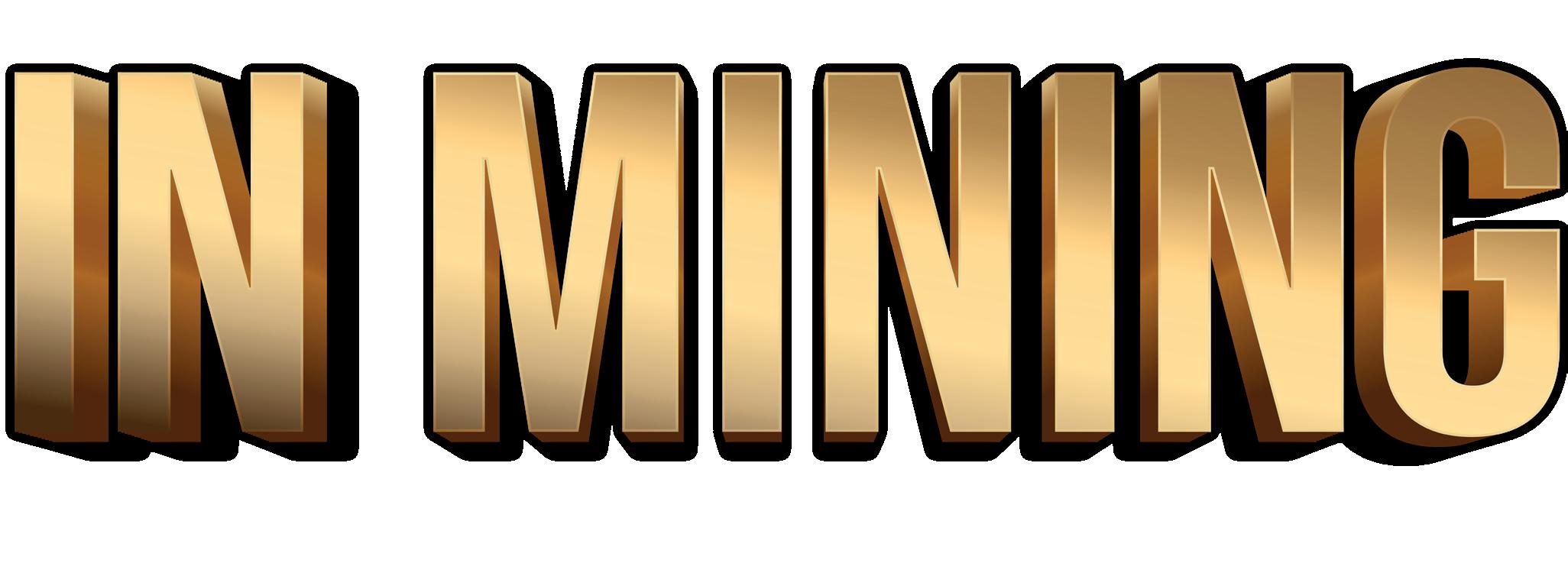

Gustavo Pilger, Dassault Systèmes, GEOVIA, assesses the critical role of centralised data management for efficiency, security, and innovation in mining operations in a Q&A with Will Owen, Editor of Global Mining Review.
The rapid growth of data, driven by technological advancements, presents both benefits and risks.
Consolidating and centralising data management are important to enhance efficiency, cybersecurity, and business intelligence. Will Owen (WO), Editor of GlobalMiningReview, recently sat down with Gustavo Pilger (GP), Worldwide GEOVIA R&D Strategy & Management Director at Dassault Systèmes, to discuss the critical challenges and opportunities in managing data within the mining industry. They also explore the role of Dassault Systèmes’ 3DEXPERIENCE platform in enabling mines to optimise processes, ensure data security, and improve disaster recovery capabilities.
WO
Please outline the key challenges that the mining industry faces in managing, protecting, and storing data.
GP
Data is part of the IP portfolio of a company (together with a range of assets). Therefore, it should be managed as any other valuable asset. Over the last two decades in particular, with technology advancements and the advent of a range of sensors, we have seen an ‘explosion of data’ across industries, including mining. This brings opportunities and challenges at the same time. The opportunities are mainly associated with the
potential to better understand processes, enabling people to improve them with productivity and efficiency gains that often lead to cost savings. To achieve this state, however, one needs to overcome a few challenges: from navigating through a plethora of data for extracting knowledge, to cybersecurity risks that could expose corporations to significant financial losses. The ability to count with a range of data to unlock or optimise mining processes is great. However, one of the first challenges is to consolidate the data that is often captured and stored in different systems. Not only is this data stored in decentralised (local) disparate repositories, but these systems are administered by different people – with different levels of responsibility and awareness when it comes to data integrity and related risks. So, it is important that data is properly stored and managed in a way that allows one to extract the most knowledge out of them, while preserving its integrity and exposure.
WO
How should mining companies approach consolidating and centralising their data management to enhance data security?
GP
The first step towards data consolidation is to compile a data inventory across the mine, including information about type, format, purpose, frequency of change, etc. This allows one to map out the data flow intra and inter-processes across the mine to then assess what matters the most and where potential bottlenecks are, in order to prioritise where to begin. Therefore, understanding the data ecosystem, together with the impact it has across KPIs, is key to drive change in this space.
All sorts of data are being collected from a range of equipment (including sensors) across the environment of a mine. Together with good, valuable data also comes noisy data – and lots of it. Therefore, ideally, the data collected across the mine not only needs to be federated (or consolidated), but also needs to be indexed, sanitised (filtering out the noise), and contextualised so that meaningful insights can start to be extracted for decision-making. This could be achieved with the adoption of a centralised system that allows for ingesting data collected by equipment across the mine, as well as managing it in a safe and secure environment. The Dassault Systèmes 3DEXPERIENCE platform offers this solution.
WO
What critical benefits do mines gain from centralising their data management?
GP
I think the ultimate benefit is about being in control of the data instead of data taking control. One can only improve what is measured and understood. A centralised platform that allows data federation, indexation, 3D contextualisation, analytics, and action management – all in a secure environment – puts users in control of their assets, enabling them to extract the most value.
Also, typically with decentralised systems, a great amount of time is dedicated to finding the right data or the latest version of data to work with. This translates to enormous inefficiencies, errors, re-work, and frustration, leading to employee
disengagement and creating a vicious cycle of inefficiency. On the other hand, a centralised system, with rigorous access control processes, eliminates these inefficiencies. Every employee has access to the right data, in terms of permissions and versioning for conducting their work. Every decision taken by employees is recorded and justified within the system, providing an inherent layer of traceability and auditability. Other benefits include de-risking data integrity and exposure.
WO
Tell me about the role of centralised data management in improving data analytics and business intelligence, and how this benefits mines and their personnel.
GP
GEOVIA, a Dassault Systèmes brand, provides software tools that allow our mining clients to model and simulate processes. They are able to interact with adjacent (connected) processes before anything is actually built, in early project development phases, or to correct the train of action on projects already in production, in order to keep chasing value during operation.
Since the underlying data is federated, indexed, standardised, and contextualised in a safe and secured single repository, and systems are connected with input and output associated through common data models, one can test multiple hypotheses or scenarios in the virtual world (virtual twin experience) to efficiently apply a given design or plan in the real world – eliminating unnecessary waste, reducing risk, and minimising material re-handling while maximising productivity. Data is not only safe and secured, but it is indexed (for quick retrieval), standardised through semantic dictionaries, and contextualised, enabling meaningful links and associativeness between processes and data. It is this data associativeness, combined with smart methods and algorithms, that allows one to constantly chase value while in operation, adjusting to (previous) uncertainty and unplanned events (being of technical, mechanic, or of market nature). It is this core data, industry knowledge, and know-how – supported by semantic dictionaries (ontologies) central to Dassault Systèmes’ business platform (3DEXPERIENCE) that is built on a multi-physics and multi-scale foundation – that facilitates progress beyond generative AI and large language models (LLMs). With this core set of characteristics, what Dassault Systèmes offers instead are industry language models (ILMs) that indeed leverage LLMs, but are combined with ontologies, industry knowledge, and know-how within a platform environment (3DEXPERIENCE) that inherently provides governance and traceability.
WO
Please explain the ways in which centralised data management enhances a mine’s disaster recovery capabilities, and why this is critically important?
GP
A decentralised data management system, with data fragmented and scattered across the corporation, would need to rely on systematic discipline by personnel in charge to regularly back up local stored data, which could be a challenge by itself. Therefore, it would make it really hard (if not impossible) to fully recover, should a disaster occur.
Instead, a centralised system can be restored in a matter of hours in case of disaster. Of course, this is assuming appropriate levels of redundancy, training, and protocols would be in place to allow minimum levels of disruption in case of disaster.
The bottom line is that a centralised system deployed either on premises or on the cloud would make the execution of the company’s disaster recovery plan way more straightforward compared with decentralised systems.
WO
Ultimately, how does centralising data management improve both a mine’s cybersecurity and the safety of its employees?
GP
Data centralisation enables the significant reduction of risks associated with data integrity and cybersecurity. Consolidating the data in a single repository reduces the risk of losing or corrupting data that otherwise would reside in local drives of desktop computers located across mine sites, or in laptops of those employees required to work on the data. Instead, on a centralised system, such as the 3DEXPERIENCE, the right version of the right data is available at any time to the right people. Since 3DEXPERIENCE counts with a rigorous access control process, this means that data is made available to employees according to their roles and needs. For example, a surveyor would not need access to sensitive data – such as gold grades from core logging – but a resource geologist would, as they must use this data to conduct their work. So, the risks associated with data integrity, exposure, and cybersecurity are mitigated quite significantly.
For those who choose to embrace the cloud to store and manage data via a cloud provider, be assured that the risks are well-managed. Risks are arguably better managed than in in-house data centres. This is because most cloud vendors, such as Dassault Systèmes, operate with heightened security practices tailored towards protecting their infrastructure, applications, and customer data. A good cloud provider will adhere to industry standards and best practices that include:
n IOS 2700x standards, and in particular implementation of Guide ISO 27002.
n NIST 800 series.
n Open web application security project (OWASP) methodologies.
n CobIT framework.
Also, good cloud providers employ multiple, independent, and redundant mechanisms at various levels to block attacks. These measures provide far better security than most organisations can provide for themselves. Therefore, in terms of risk management, it is a win-win proposition for all, including corporations, employees, contractors, and customers.

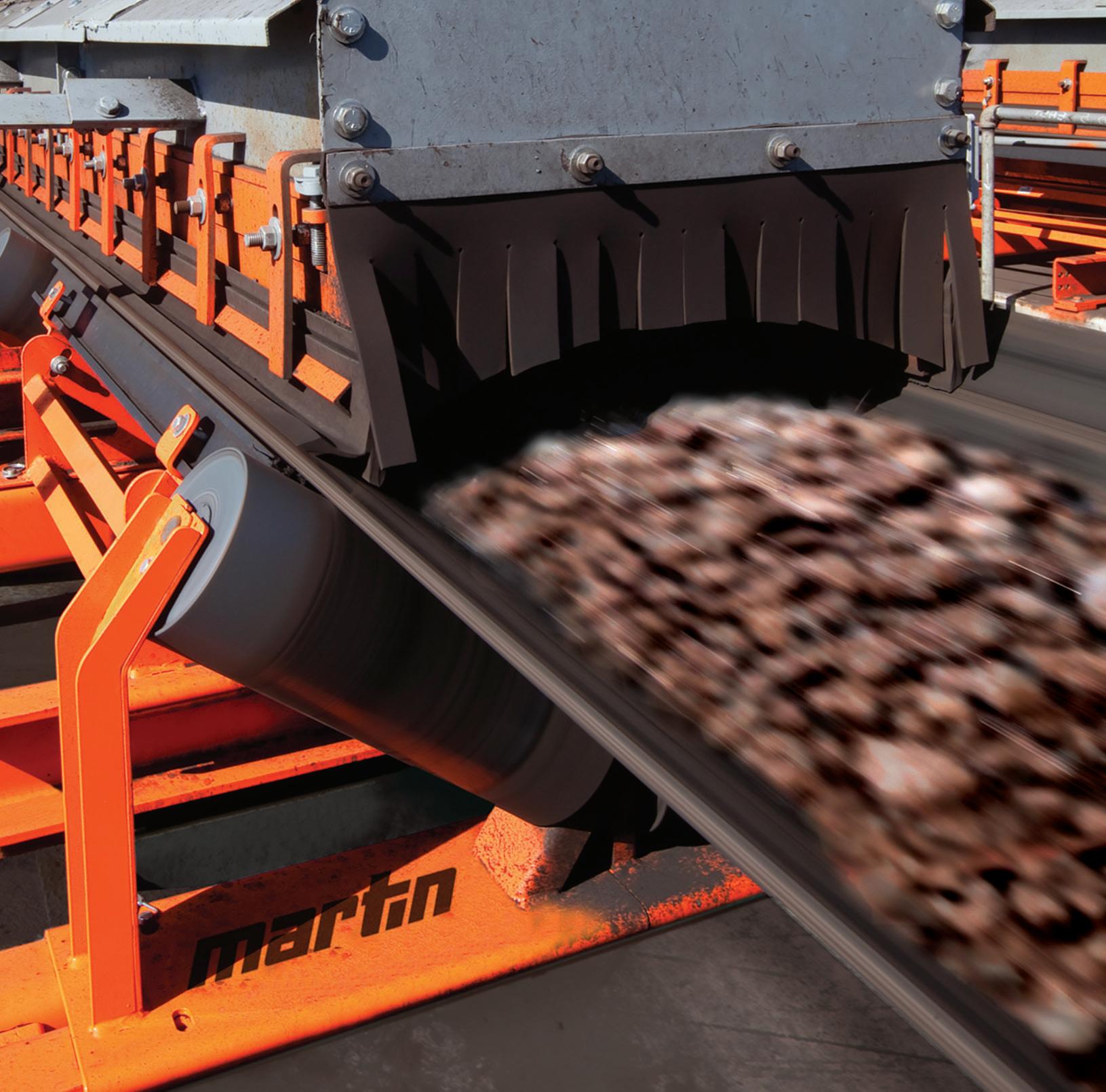

3-6 February 2025
CTICC, Cape Town

Mining Indaba: Creating opportunities for African miners and laying the groundwork for a greener, more inclusive future.
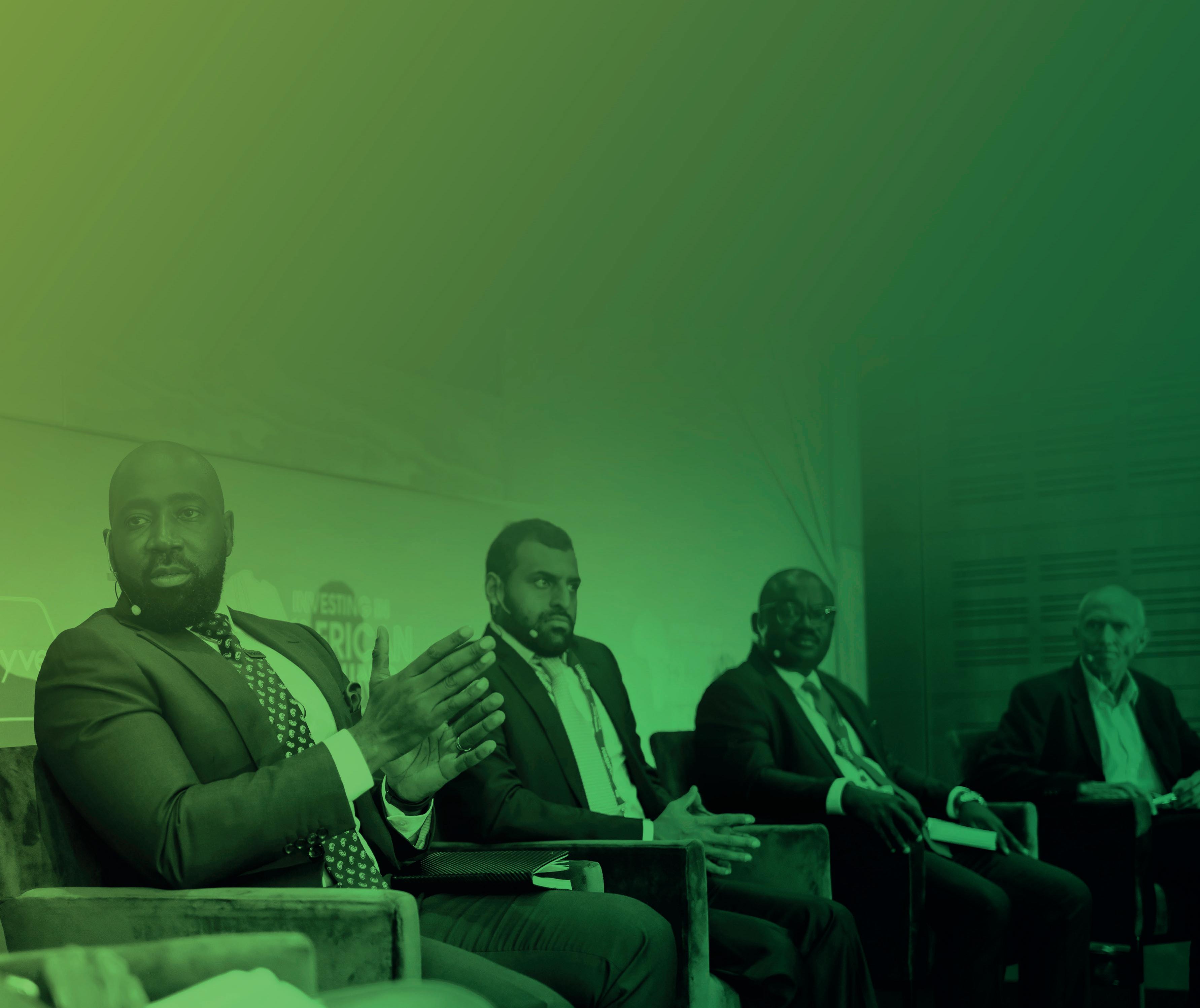
WHAT TO EXPECT AT MINING INDABA 2025
• Implementing innovative technological solutions for enhanced operational efficiency.
• Developing new standards for sustainable and innovative mining practices.
• Increasing resource efficiency and minimise waste.
• Contributing to productivity and health safety while reducing the environmental impact.
For more information contact: marketing@miningindaba.com
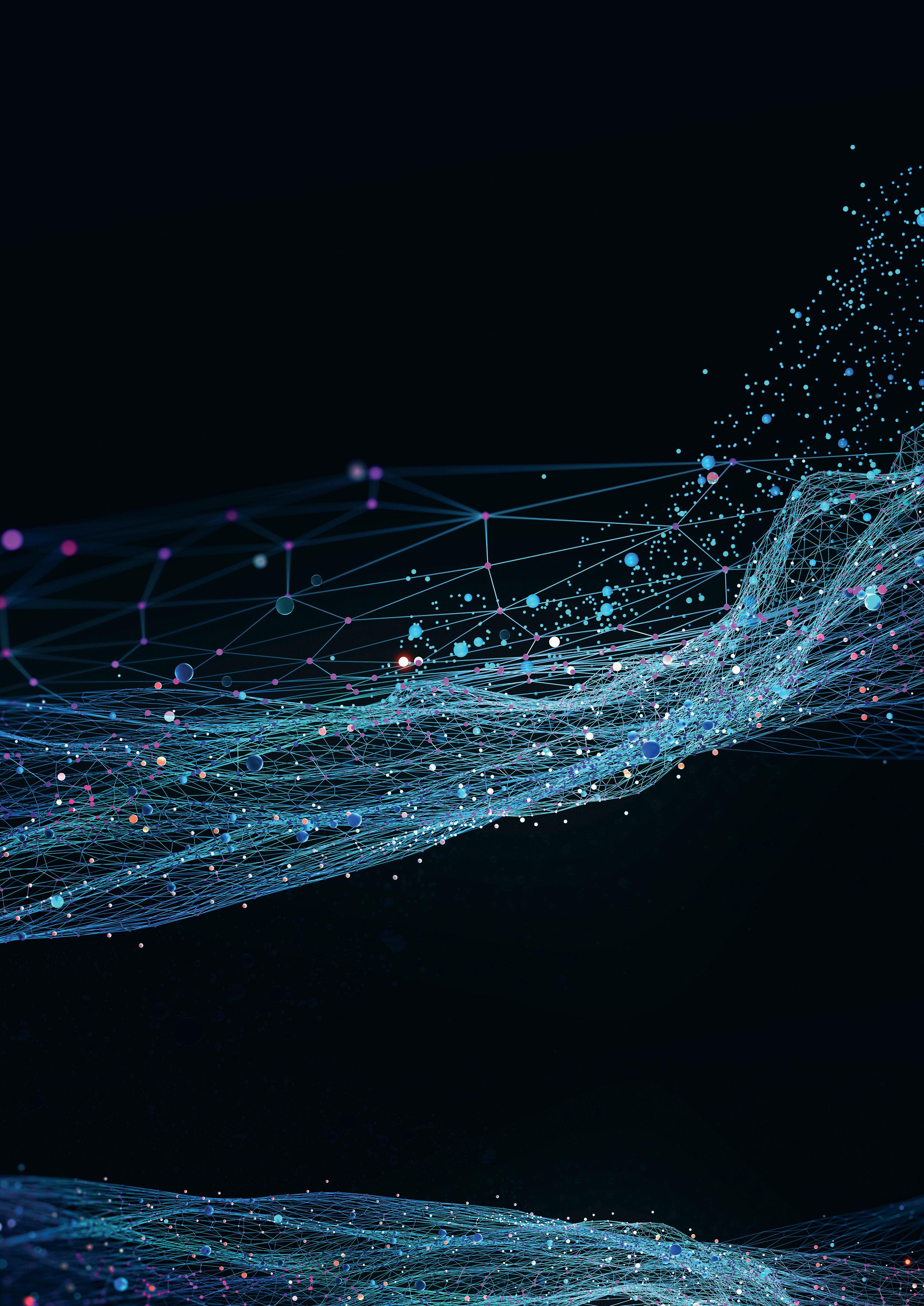
Mariana Sandin, Seeq, outlines how advanced analytics platforms are helping miners weather the global skilled labour shortage by providing automated data aggregation, predictive modelling, and deep insight generation.
There is an ongoing data revolution throughout the process industries, and the mining sector is no exception. Traditionally, mining operational decision-making relied on raw data amalgamated from various sources and sites, which required manually collecting, cleansing, and organising the information using spreadsheets. However, this method was labour-intensive and error-prone, and it often resulted in analyses that were difficult to validate for accuracy, putting multimillion-dollar decisions at risk.
Additionally, engineers and analysts with the expertise to handle these tasks are becoming increasingly rare as a large portion of the industrial workforce nears retirement. Because of the growing scarcity of subject matter experts (SMEs) and the complexity of manual data management, mining teams often avoid analyses like seasonal air quality, even though they are critical for effective asset upkeep and efficient operations.
To tackle resulting issues, the mining industry is turning to automated digital solutions that streamline the connection, cleansing, and analysis of time series data from disparate sources. Advanced analytics platforms now provide the ability to combine live data from process historians, data lakes, enterprise resource planning, manufacturing execution, and other systems in a central location, without the need to move or copy the data. This provides near-real-time process data access and empowers SMEs –
including engineers, operations managers, analysts, and data scientists – to quickly gain operational insights with comprehensive context.
By implementing these types of solutions across their organisations, mining companies are accelerating critical initiatives and achieving quicker business outcomes.
Overcoming challenges
Before the mining and metals industries can fully embrace a data-driven culture with advanced analytics, there are several challenges that must be tackled, the first being limited SME availability. Engineers in these sectors often find themselves engaged in reactive problem-solving, leaving little room for innovation and process improvement. In the rare cases when engineers do find time for these critical optimisation tasks, tool limitations – such as spreadsheets – often hinder progress and diminish morale.
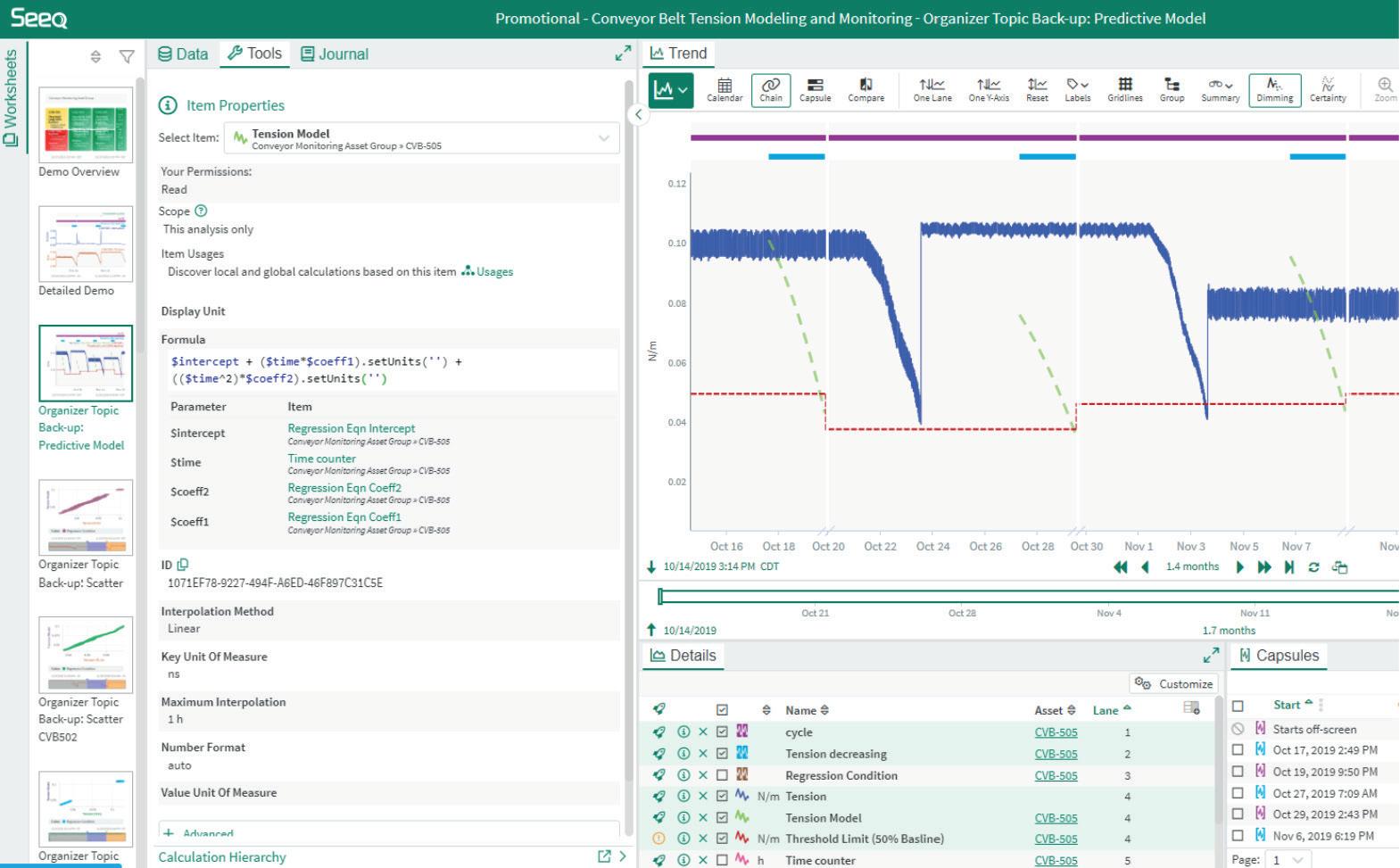
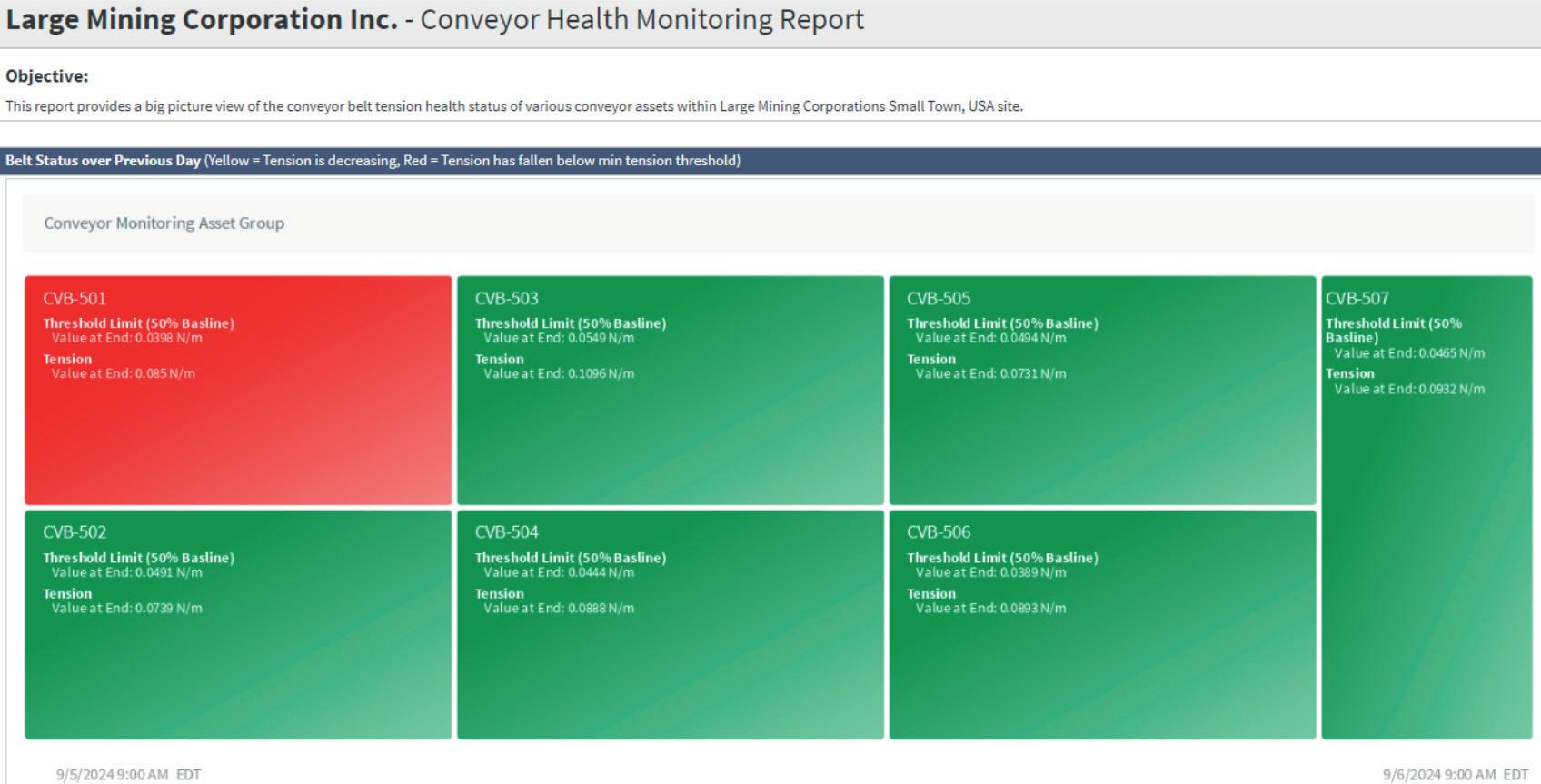
Additionally, the mass exodus of experienced employees to either retirement or other industries is intensifying the difficulty of retaining experts. The Society for Mining, Metallurgy & Exploration reports that 50% of skilled engineers in this industry are expected to retire within the next decade. This creates a demand for efficient knowledge transfer methods so organisations can sustain productivity, in addition to the growing need to recruit new talent. Mining companies are competing with tech companies and other sectors for graduates who possess the specialised data and analytics skills needed to drive digital transformation in process manufacturing. Furthermore, mining operations must run efficiently around the clock regardless of staffing or budget constraints. Particularly when facilities are short-staffed or personnel are consumed with constant figurative firefighting, scaling operations effectively poses significant difficulty. Fortunately, digital tools are becoming more widespread.
The mining industry is showing significant progress on the digital maturity index compared to other manufacturing sectors. A 2023 report scored mining between 62 and 67 out of 100, depending on the application, compared with an average score of 30 across other manufacturing segments. This digital adoption is helping transform the mining industry, with software capable of generating deep operational insights and automating progress towards process optimisation. Of the software toolsets being implemented, advanced analytics platforms are specially created to integrate raw data from various sources, then automatically cleanse and format it for productive analysis. These platforms provide numerous user-friendly features that save invaluable SME time.
Advanced solutions for connectivity and collaboration
Mining companies can leverage advanced analytics platforms to transform raw data into actionable insights, from basic to highly complex analyses. These tools combine automated functions with intuitive no-code and low-code interfaces for descriptive, diagnostic, predictive, and prescriptive analytics (Figure 1). This empowers users to easily assess the impact of their analyses, identify errors and successes, and innovate their operations.
Additionally, advanced analytics platforms enhance SME effectiveness, whether they are collocated at a site or distributed across the globe, such as between a remote monitoring centre and field operations on another continent.
With built-in reporting and insight-sharing functions, these tools facilitate collaboration and knowledge exchange among employees regardless of geographical boundaries.
Automated analyses help predict common failure modes, such as issues with conveyor belt tensioning. These sorts of insights can be shared across sites and used to train new personnel, helping prevent costly downtime and operational disruptions.
Case study: Predicting conveyor belt tensioning needs
Conveyor belts are a key asset for mining operations, used to transport solids collected from a mine through various pre-processing steps, and eventually to shipping vessels for transit to the final customer. Transfer on these conveyors is a critical process step, and a single conveyor belt failure can result in a partial or full line shutdown, resulting in hundreds of thousands of dollars in loss.
Conveyor belts lose their tension over time, requiring periodic tensioning to maintain optimal operations and prevent premature failures. One method for upkeep is scheduling maintenance on a predefined periodic basis. However, this approach results in excessive unnecessary maintenance, straining valuable mechanic time. Furthermore, this can increase the risk of inducing problems. Condition-based monitoring is a better approach, using sensors and software to detect when a belt is due for repairs. Leveraging historical data and common failure profile models, advanced analytics platforms can proactively
Are Your Conveyor Belts Carrying Their Weight in Energy Savings?


Belts with Aramid Cords are: E i eered for exceptional performance 15% more energy efficient ned to reduce CO₂ emissions o last longer in the toughest ions
*Compared to steel cord belts

identify impending belt failures and generate alerts. Predictive maintenance was difficult or near-impossible with historical software tools, but new technologies are prompting many mining companies to abandon traditional time-based maintenance approaches in favour of condition-based maintenance predicated on analytical models.
Engineers at one large mining company used Seeq, an advanced analytics platform, to create a generalised conveyor belt failure mode model. Leveraging the platform’s asset hierarchy integration, the team quickly and efficiently scaled their model across a vast network of conveyor belts within the operation. On each belt, the software forecasted the runtime remaining before failure, identifying the belts closest to failure and in need of

Figure 3. Prebuilt dashboards in Seeq make it easy to toggle among variables and correlate cause and effect.
prioritised tensioning. This empowered the team to remain productive with their time and avoid excess expenditures on unnecessary maintenance activities. The company rolled this information into treemap visuals, enabling it to effectively and affordably scale a condition-based preventive maintenance programme throughout the organisation (Figure 2).
Averting just one belt failure – which can result in line backups or lost production – can save mining companies upwards of US$10 000 in lost opportunity costs and break-in maintenance operational expenditures (OPEX). Over the course of a year, this can translate to US$1 million or more.
Case study: Truck fleet monitoring
Trucks are also critical assets for mining companies, regarded as the ‘work horses’ used to move minerals and earth under harsh conditions. As with conveyors, they must be maintained to ensure reliable operation, especially the engines.
Historically in the mining industry, truck engines were scheduled for maintenance on a fixed calendar frequency. Similarly to conveyor belts, modern telemetry and software tools can be used to preemptively identify engine failures and designate trucks for maintenance, but signal readings can vary from truck to truck, making it difficult to scale this approach across an entire fleet.
Addressing this and other issues, advanced analytics platforms enable dynamic analyses that consider multiple variables in evaluating truck health. For example, these factors evaluate drift from an operational baseline in the time required to traverse the mine, the gear selected by operators when ascending, engine load, payload, throttle position, and ground speed. Treemaps help identify trucks with significant deviations over time, providing personnel with a fleet-wide view to identify assets that require maintenance attention.
Using this approach, one mining operation simultaneously reduced annual truck engine failures and maintenance time dramatically, saving an estimated US$100 000 for each failure averted (Figure 3).
Equipping mines with digital advancements
With diminishing personnel, yet growing demands, sustaining process optimisation in the mining industry is increasingly reliant on modern software solutions to collect, cleanse, and analyse data, as well as generate insights. Traditional manual data wrangling depletes SMEs of the time for critical process improvements.
Modern advanced analytics platforms address these issues by providing not only tools to configure, review, and assess automated analyses, but also methods for sharing insights and managing assets across an entire enterprise. These practices can foster cross-disciplinary collaboration, minimise downtime, and reduce OPEX, enabling miners to remain competitive in the rapidly evolving digital era.
References
1. ‘Digital Maturity Report 2023’, Digitopia, (February 2024), https://6887774.fs1.hubspotusercontent-na1.net/hubfs/6887774/ Digital-Maturity-Report-2023-Manufacturing-Focus.pdf

Mark Doyle, Weir, examines how rubber wear solutions are making mining operations safer and more sustainable.
Wear parts are often overlooked or taken for granted when it comes to their role in ensuring the sustainability and safety of mining operations. They are the frontline defence against abrasion and corrosion and, if they fail, the consequences can be catastrophic from an environmental, safety, and financial perspective. Conversely, when wear parts perform well, they can provide
miners with the predictability and reliability that allow them to focus on improving throughput and increasing production.
For example, when Weir lines large, expensive capital equipment, like flotation cells and thickeners, with LINATEX® premium rubber, the customer typically gets between 10 – 15 years of service life out of that lining. If the life of mine (LOM) is, say, 50 years, then the miner might only have to replace that lining three or four times.
In addition to the operational benefits, a longer lasting product means less waste is generated. However, in order for a product to be truly environmentally-friendly, sustainability needs to be built into its lifecycle. Take LINATEX rubber as a case in point. It is 95% natural, high-quality latex, and the manufacturing process, which uses a unique liquid compounding phase, ensures that it remains as close as possible to how nature made it.
The unique compounding process retains the long molecular chains of natural rubber, ensuring unmatched abrasion resistance. While its formula and the proprietary process have remained unchanged for 100 years, continuous equipment modernisation and future-proofing have made LINATEX one of the leading sustainably manufactured rubbers on the market.
Weir uses microwave energy to dry its unique rubber, which is a more environmentally-friendly method. The manufacturing processes produce very little effluent with no waste and use less power compared to standard rubber production. The company has also implemented a number of sustainability initiatives at its Malaysian facility – the sole manufacturer of LINATEX rubber – including solar panels, rainwater harvesting, and a rubber recycling programme.
Wear part selection
In a typical mill circuit, LINATEX rubber can be used from the discharge of the ball and SAG mills, which then feed the
cyclone clusters. The cyclone underflow feeds back to the ball mills, while the overflow feeds the thickeners, tertiary grind areas, and flotation. This is the part of the processing plant that requires a product that can withstand wet sliding abrasion – and that is where LINATEX rubber excels.
The mill circuit is the heartbeat of the mine; it is where the mill pumps and cyclones are located and it is where the run-of-mine (ROM) is pushed through the pipes to the concentrator. In other words, maintaining the life of the equipment and pipes and ensuring they stay in service for the longest amount of time possible are vital, because failures and shutdowns can cost a significant amount of money.
When it comes to selecting the appropriate thickness of the LINATEX rubber for specific applications, Weir’s extensive installed base in mines all over the world, and in various areas within these mines, ensures that it can select the right product and guarantee its wear life with a high degree of certainty. Crucially, this provides operators with the predictability they need.
Conversely, it is important not to install a rubber that is too thick – this reduces the diameter of the pipe, which in turn reduces the throughput and efficiency of the system. It is about striking a balance between optimal efficiency without compromising the wear life.
Broadly speaking, in areas of the mine where wet sliding abrasion is the norm, like the cyclone feed area, LINATEX typically lasts twice as long as alternative rubbers. And, in the right application, compared to, for example, metal wear liners, the performance can be exponentially better.
Safety, maintenance, and monitoring
Better, reliable, and more predictable performance also directly correlates with improved on-site safety. If a pipe wears out unbeknownst to the operator, then slurry can leak, creating a line-of-fire hazard and potentially having an adverse effect on the environment. Moreover, there are also slipping hazards associated with having to clean up the site.

Figure 1. Conventional dry processing reduces the average molecular weight distribution and leads to a significant drop off in properties and performance of the rubber. The proprietary liquid compounding method of LINATEX rubber gently blends the latex, causing minimal damage to the microstructure of the rubber.
Additionally, every time a pipe or piece of equipment has to be removed from its service, the people carrying out the work are at risk.
Weir utilises its NEXT Intelligent Solutions to monitor wear on pipelines, providing operators with increased visibility over wear, enhanced control over performance, and greater predictability when scheduling maintenance. A sensor is integrated into the LINATEX hose or spool


Global coverage on technology and market trends in the mining and minerals processing industries Subscribe online at: www.globalminingreview.com/subscribe
Global coverage on technology and market trends in the mining and minerals processing industries Subscribe online at: www.globalminingreview.com/subscribe
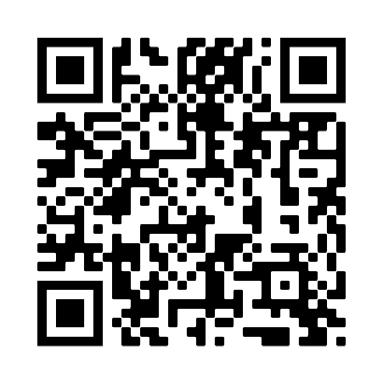
and a simple traffic light system enables quick visual identification of its condition. If the hose or spool is less than 50% worn through, then the light displayed is green; if the wear is between 50 – 70%, then it is yellow; and when it is greater than 75%, it flashes red, indicating that it is time to carry out preventative maintenance.
It was recently installed as part of a solution in Chile, helping the customer recover almost 60 000 tpy that was
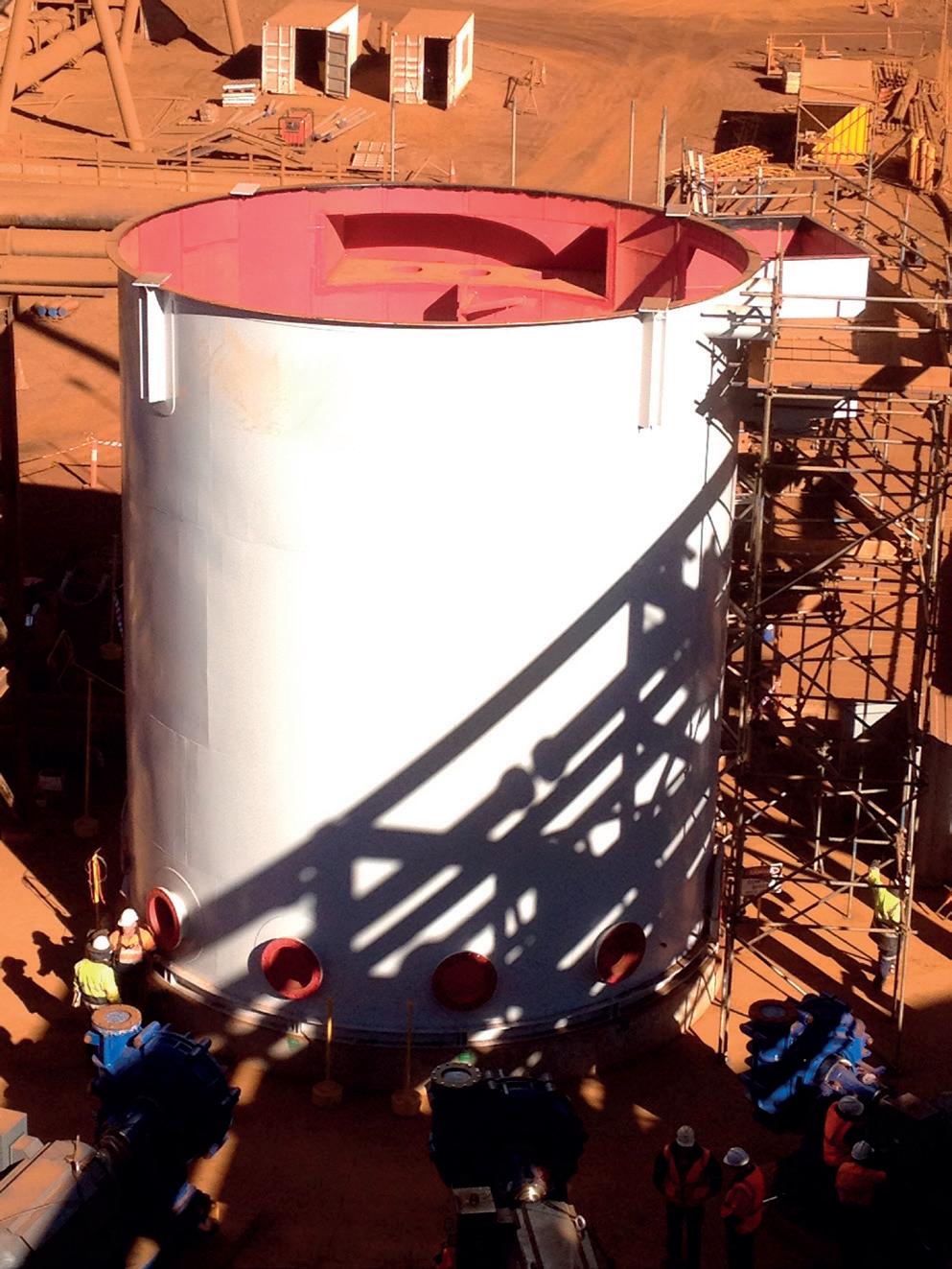

being lost because of unplanned downtime and increased maintenance requirements.
Enhanced efficiency, increased production
At a magnetite plant, the primary ball mill plays a crucial role in achieving target production levels. However, frequent stoppages due to seal-related issues hindered its availability. Every two to three weeks, the maintenance team had to halt the mill for intermediate repairs –adjusting stainless steel rings, water injection lines, or replacing rubber seals – to sustain a maximum campaign duration of three months.
This low availability posed challenges for the plant in achieving its objectives of extending seal lifespan; eliminating water injection; reducing spare parts consumption; enhancing safety during future interventions; and ensuring uninterrupted operations.
Weir identified an improvement opportunity and conducted a 3D scan of the mill seal. The proposed solution featured the LINATEX rubber mill sealing system, which includes premium rubber seals lasting two to three times longer than conventional ones.
Additionally, the plan addressed misalignment issues by recommending feed spool changes. A static ceramic to rubber seal and an adjustable base for field alignment were introduced to ensure correct concentricity with respect to the mill feed.
Furthermore, the incorporation of NEXT Intelligent Solutions enabled real-time wear monitoring of the interior lining of the ducts. This facilitated efficient job planning and spare parts forecasting and streamlined ordering for the customer’s maintenance team.
The customer aimed to extend campaign duration to over four months. After implementing the LINATEX mill sealing system, a post-campaign inspection revealed a dynamic seal lifespan of six months. The system’s components remained in excellent condition during preventative maintenance, resulting in increased equipment availability.
The seal-related issues were resulting in shortfall of over 57 000 tpy of material – the LINATEX solution helped the customer overcome this. Notably, the new solution completely eliminated water consumption associated with the previous seal, contributing to reduced environmental impact and lowering water costs by US$20 000. This pioneering Weir solution, incorporating the LINATEX mill seal, marked a commitment to efficiency, intelligence, and sustainability – the first of its kind in Latin America.
Taking an integrated, holistic approach
In many ways, LINATEX typifies Weir’s approach to sustainability. It is something that it builds into every part of the value chain – starting with responsible sourcing, environmentally-friendly manufacturing, and, eventually, delivering a product that helps its customers improve their efficiency and preserve the environment they operate in.
Dellner Bubenzer describes how belt conveyor control systems can increase component life and improve performance and productivity.
At the heart of production at Mongolian copper and gold mine, Oyu Tolgoi, is Dellner Bubenzer’s Belt Conveyor Control (BCC) 3000 system.
Last year, underground production began at Oyu Tolgoi, making it a high-performing surface and underground integrated copper business – and one of the most important copper producers in the world.

The integration of the underground project, part of a long-term programme, marked the dawn of a new era at Oyu Tolgoi, located in the Umnugovi province of Mongolia.
Dellner Bubenzer – a manufacturer of high-performance disc and drum brakes, hydraulic power units, couplings, clutch, and monitoring and
control systems for mining, cranes, and other severe duty applications – has installed a Belt Conveyor Control BCC3000 system at the mine, which is designed for the controlled braking of mining machines and applications. It is especially suited to installation on belt conveyors, where smooth braking is vital to prevent undue belt tensions leading to reduced component life. In addition to protecting the machine from excessive stresses during braking, the BCC3000 also offers system monitoring and diagnostics functions.
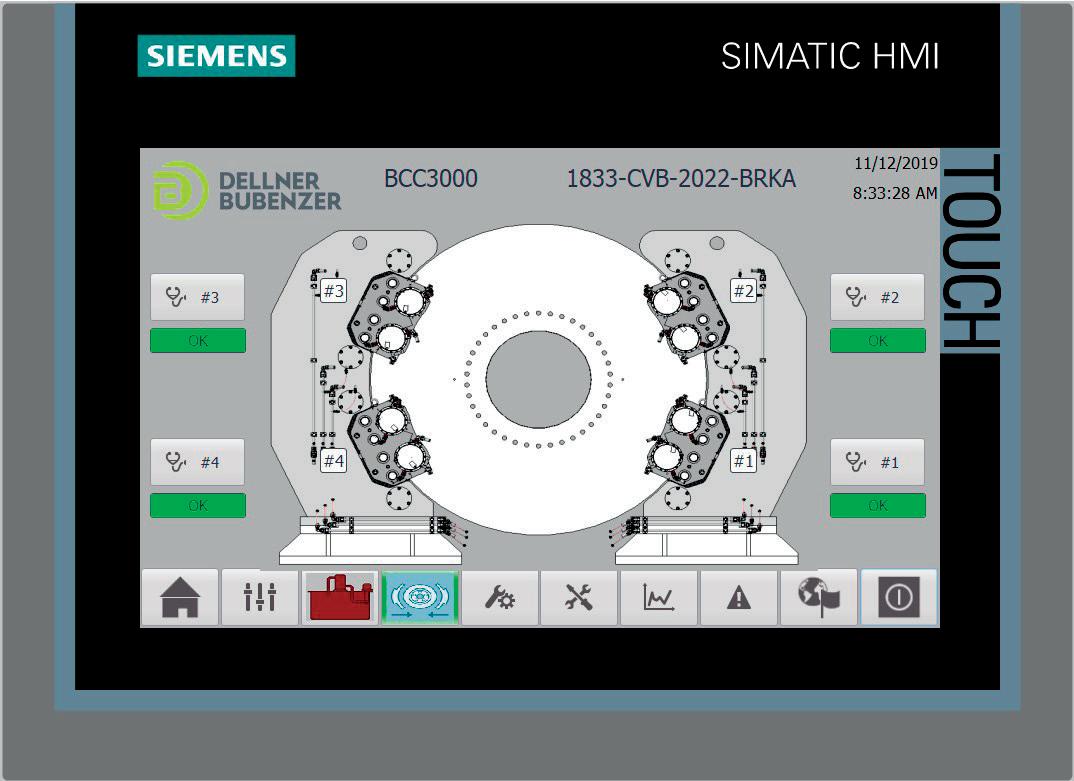
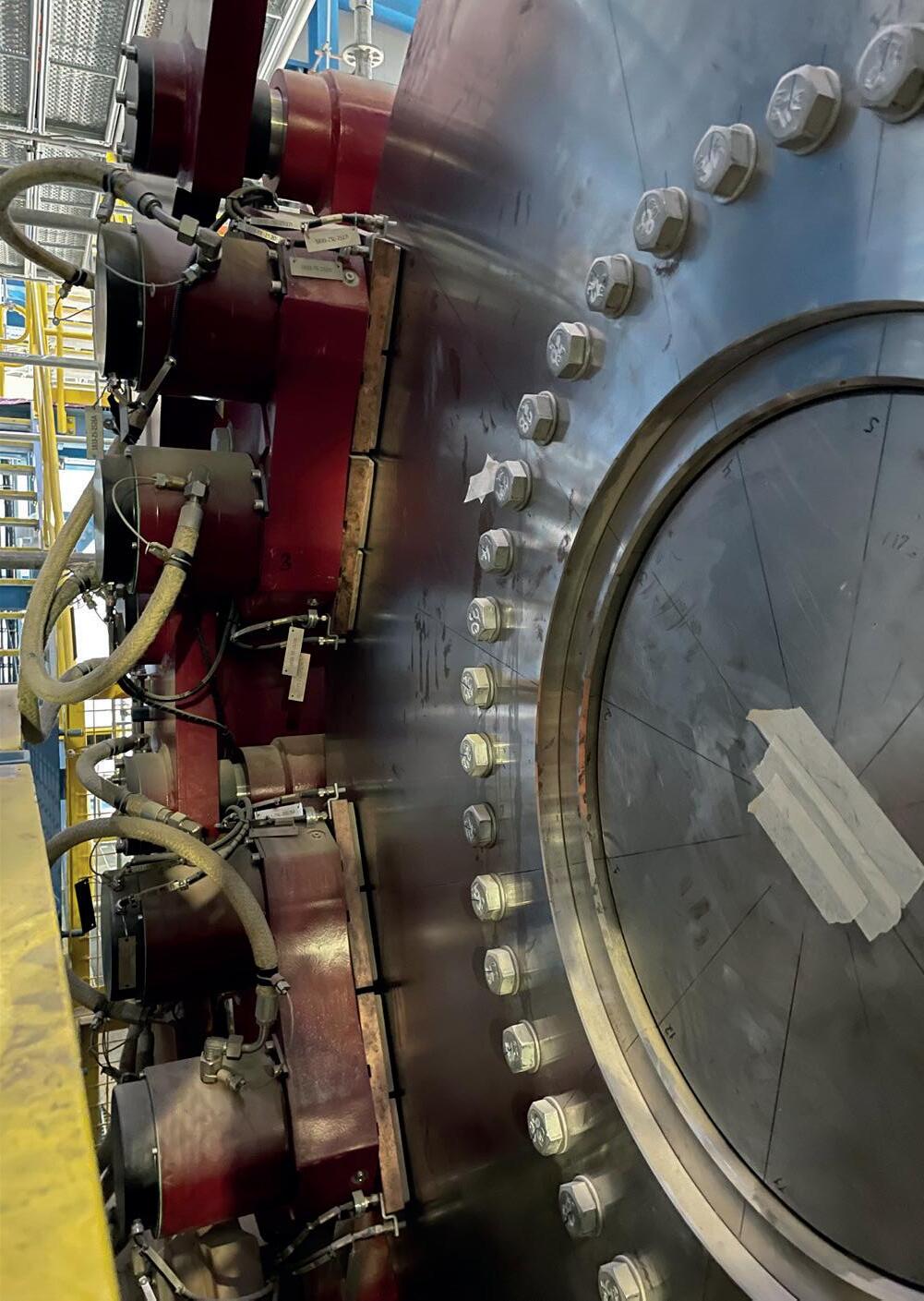
Around the clock
Oyu Tolgoi originally issued a scope of work to deliver a belt conveyor control system that offered premature fault detection; precise diagnostics; planned preventive maintenance; reduction of down times; minimised costs; and improved performance and productivity. These non-negotiables were agreed upon, despite the fact that the machines are located outdoors, are running 24-hours-a-day, seven-days-a-week – and cover long distances.
Oyu Tolgoi is harnessing several benefits of the resulting installation, including a fully integrated closed loop control system and stopping time that is constant and independent of the load. Synchronous braking times are achieved for the flight of conveyors, while automatic compensation is reached for small variations of friction coefficient.
Dellner Bubenzer also supplied a battery back-up for all control functions, and a hydraulic accumulator back-up for full control in the event of total power fail. Profibus and Profinet connection was installed for control and monitoring functions.
Four cornerstones
The Oyu Tolgoi BCC3000 system consists of four main elements:
1. Redundant encoders, to measure and control the speed.
2. An electronic unit, which fully controls and monitors the system.
3. Hydraulic power pack, incorporating the proportional control valve.
4. Brake caliper.
Encoders
The shaft speed is measured using an encoder mounted to the shaft that is to be controlled. In the case of this conveyor, the driven pulley, with the brake disc and encoder fitted to the shaft accordingly, was selected as the control. Typically, an encoder would have 2048 pulses per revolution, but this depends on the application; in this instance, the encoders have 1024 pulses and are mounted on a not driven (bend) pulley.
It was recommended that a second encoder is used for safety critical applications such that, in the event of an encoder failure, the system will be fully functional throughout, using the second encoder signal. Both encoders are fitted to the same shaft. Any failure of the encoder is detected by the electronics and a signal sent via Profibus to warn of the condition – not just when the brakes are operated.
Electronic control unit
The electronic BCC3000 control unit is the heartbeat of the Oyu Tolgoi unit, as it controls all of the logic and operating functions of the braking system. Its primary function at this mine is to control the deceleration (stopping time) of the machine or conveyor.
The unit is based on a Siemens programmable logic controller (PLC) with a graphics interface to view and
PRECISION ENGINEERED BRAKING SYSTEMS FOR THE TOUGHEST MINING OPERATIONS
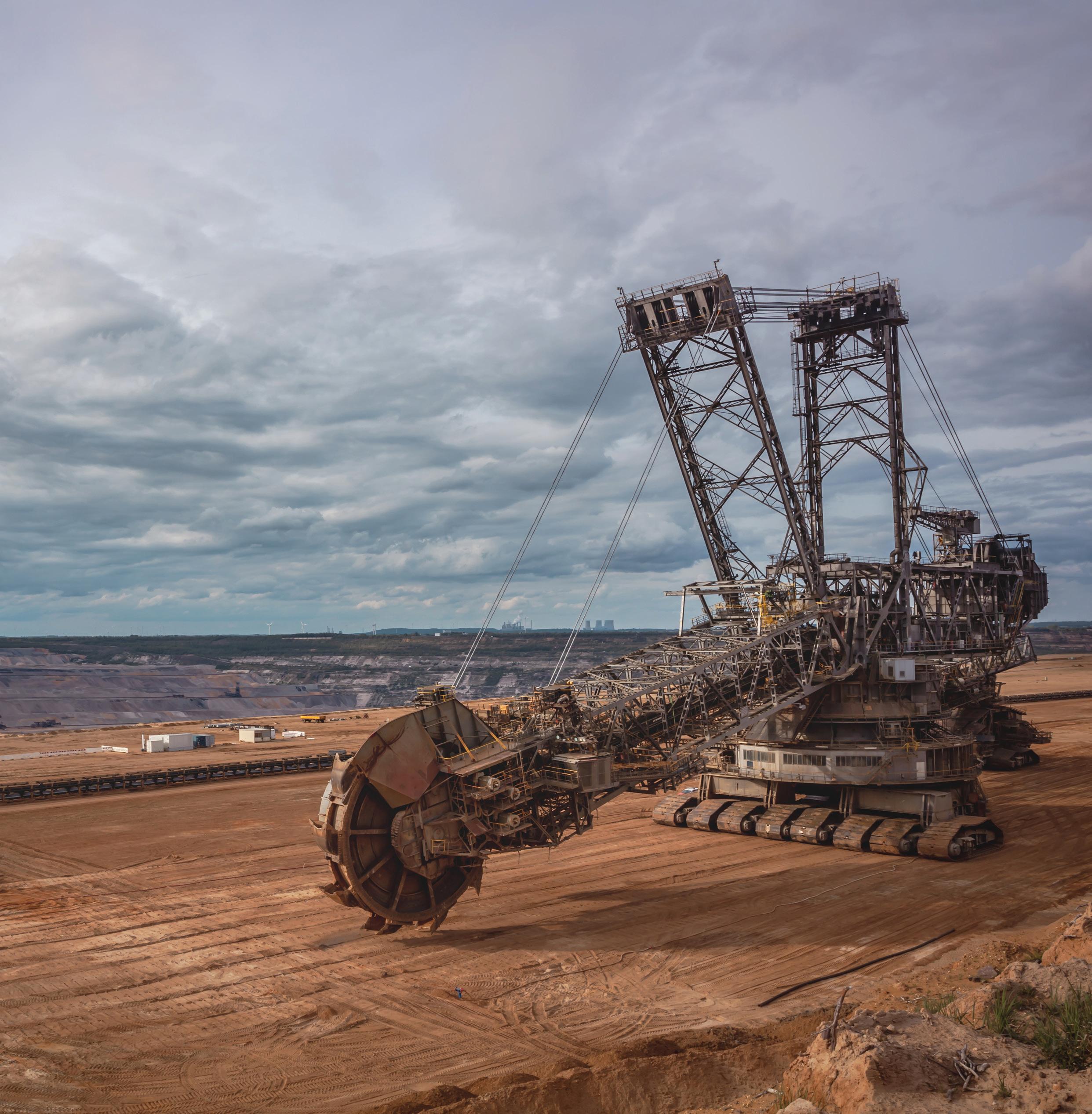
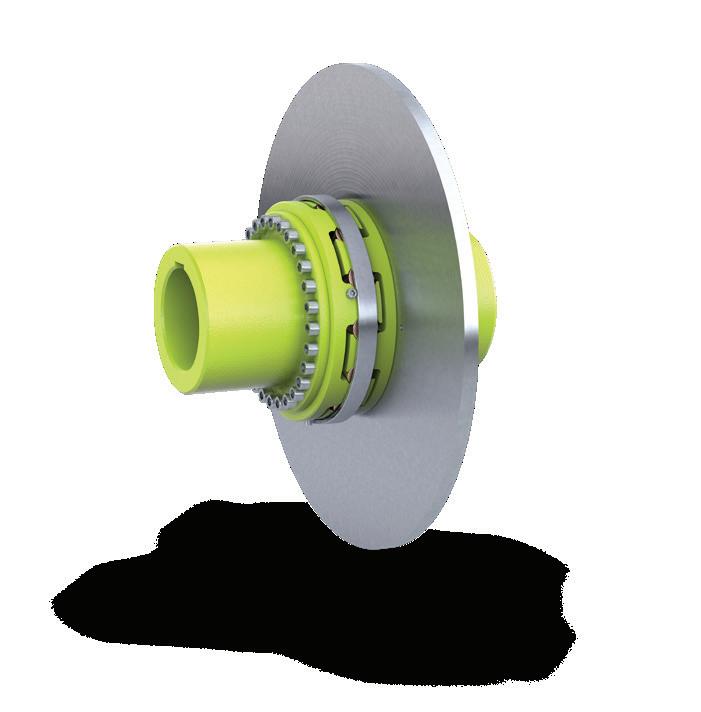
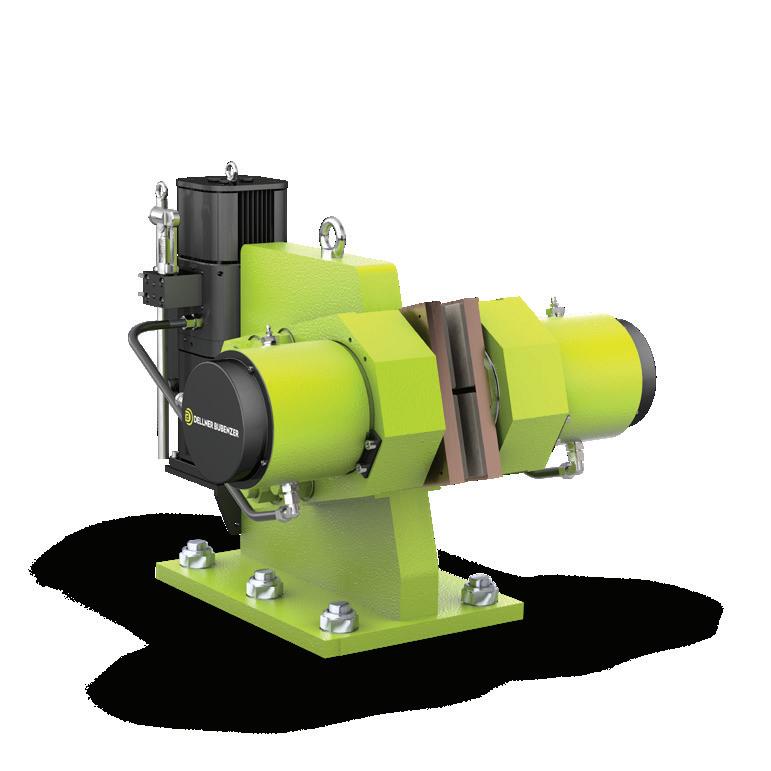
SYSTEM DESIGN & MANUFACTURING KHD HIGH-DYNAMIC LOAD COUPLINGS
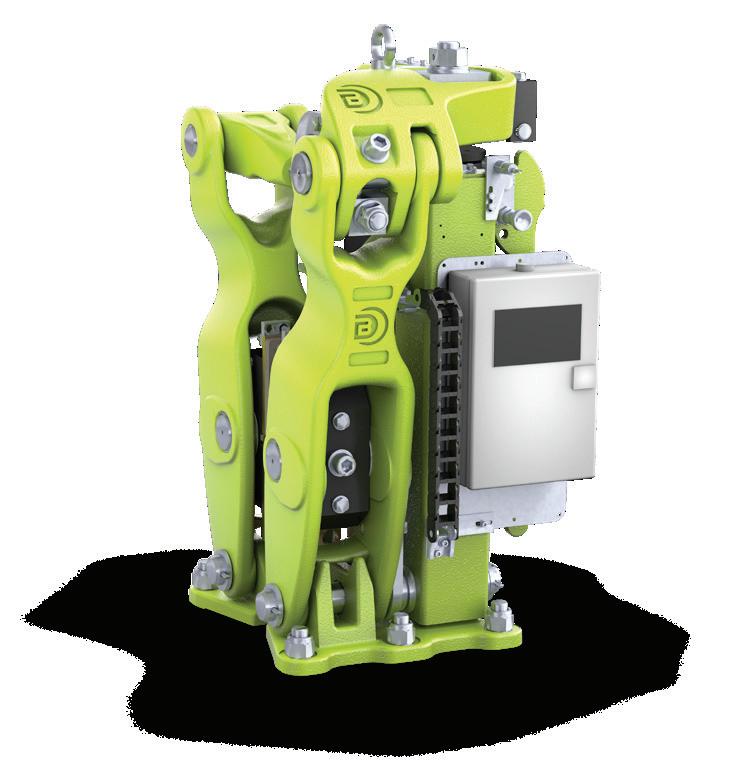
VSR-3 FOR SB BRAKES ELECTRONIC STATUS INDICATION SYSTEM
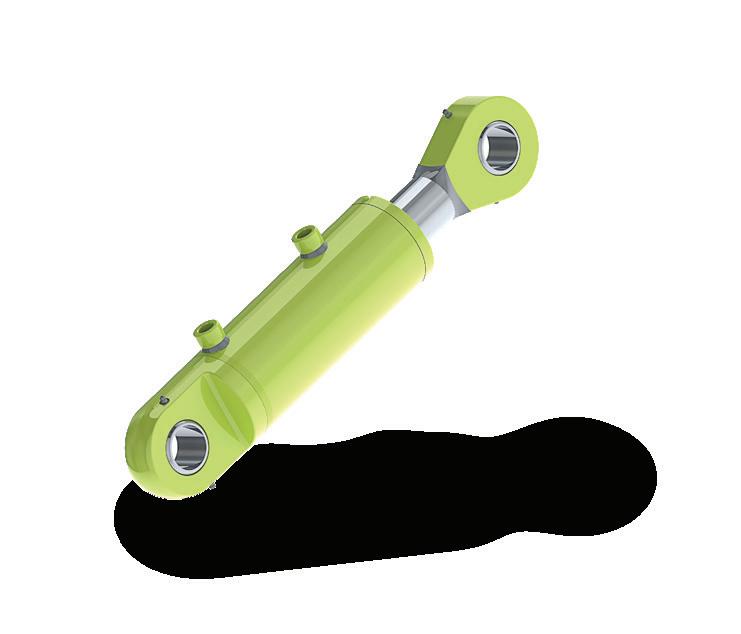
LEADING THE WORLD IN BRAKING
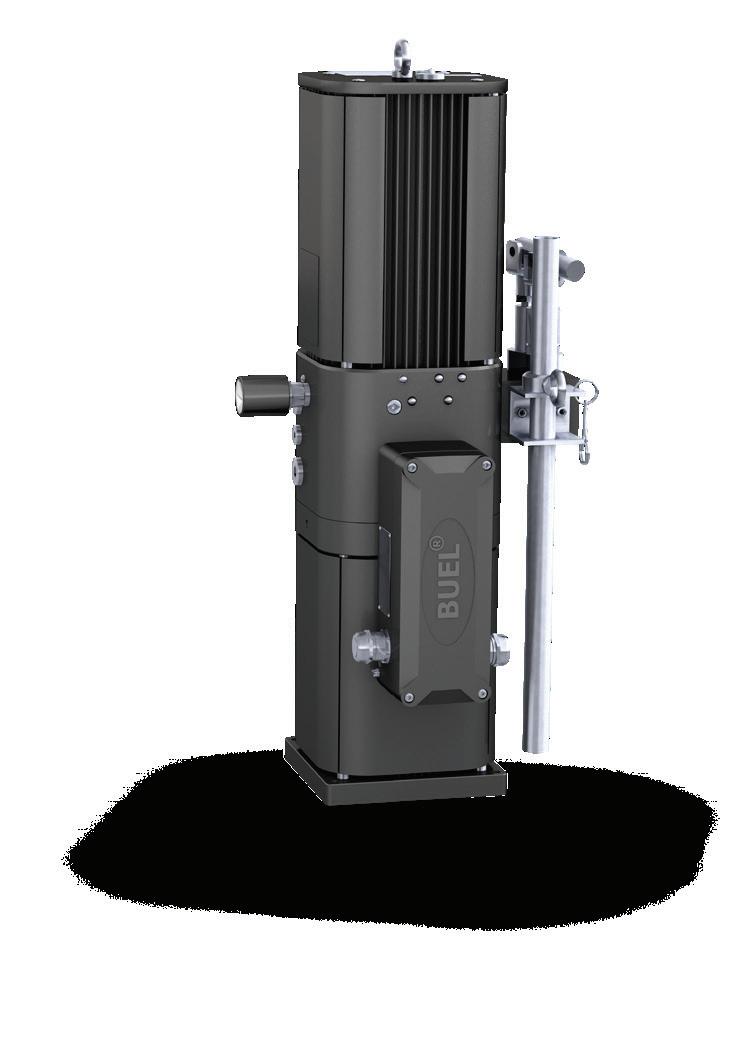
BUEL G® SUSTAINABLE, HIGH PERFORMANCE THRUSTERS
check programme data. During commissioning, a speed ramp was entered into the system.
The value of the stopping time and the two intermediate states (percentage speed/time) can be entered and adjusted until the desired profile is achieved. When the conveyor is commanded to stop (either by a hard-wire or Profibus external command, or both), the speed of the machine is determined from the encoder and this is then compared to the desired speed profile.
If the actual speed is high, then the pressure to the brake caliper is reduced. This increases the clamping force of the unit, thus increasing the braking torque
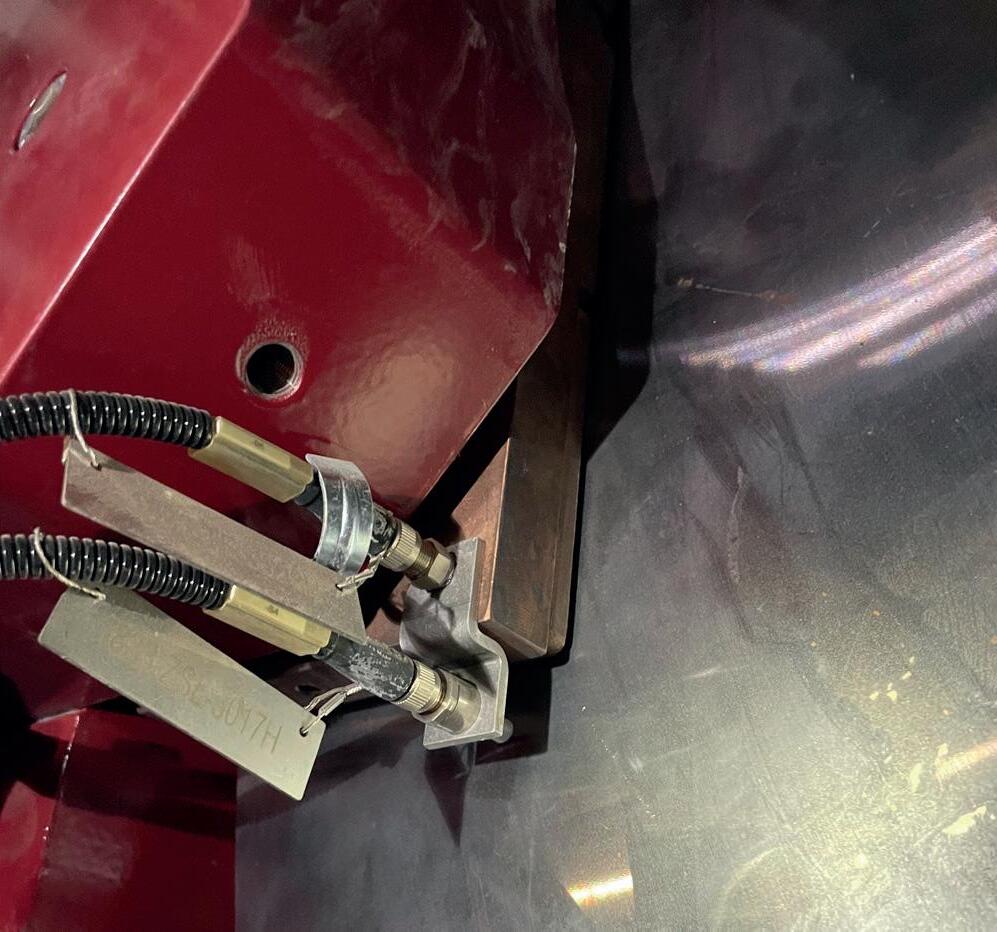

until the desired speed ramp is reached. If the actual speed is too low, then the pressure to the caliper is increased, reducing the amount of braking torque, until the desired profile is reached.
These adjustments are carried out on a continual basis throughout the stop, using a proportional/integral control algorithm to adjust pressure via the proportional valve on the hydraulic unit. Once the conveyor is at rest, then the system removes all hydraulic pressure to set maximum braking torque for parking the machine.
The system is built into a stainless-steel cabinet, and includes all interface and control relays to be able to operate and monitor the braking system.
Features
n Siemens outdoor PLC with additional internal graphics display.
n Motor starter with thermal protection.
n Profibus connection to main plant PLC.
n Battery back-up to give controlled power – available for 30 minutes in the event of external power failure.
n Optional local operation with external e-stop and override.
n All control relays for each valve on the hydraulic power pack.
n Drive amplifier for the proportional valve (pressure).
n Two-speed inputs with failure warning.
n Central interface between customer PLC and brake monitoring systems.
Hydraulic power pack: Main features
n Motor-driven radial piston pump.
n In-line filter with clogging indicator.
n Pressure relief valve, pressure switch to control operation.
n Proportional valve for a controlled stop.
n Dual 3/2 directional valves for ‘soft’ e-stop (safety feature).
n Hand-pump for manual release (switch to indicate position).
n Analogue oil level sensor.
n Analogue oil temperature sensor.
n Pressure transducers for monitoring and control.
n Can operate up to four linked calipers (depending on spacing).
n Pre-wired terminal box (stainless steel).
Operation
When power is first applied, the pump is started to charge the main system accumulator. This accumulator is used in the event of a stop; needed when no electricity from the grid is available. Oil discharges through the proportional valve to give full pressure control.
Normally the pump will be used to provide control; when the brake is released, all parts of the circuit are fully closed with seated low leakage valves. This means that the pump operation does not cycle frequently.
All functions of the hydraulic unit are controlled through the electronics. Functional switch positions are added to the Profibus connection. This enables detailed monitoring to assess service and maintainability requirements.
Brake calipers
Brake calipers are connected to a single hydraulic power pack and control system if they all brake the same shaft in the machine. These can be on the high speed (gearbox input shaft) or on the low speed (gearbox output shaft). In this conveyor system, there is only a low-speed application.
The brakes used on the high-speed shaft can be based on the standard calipers from Dellner Bubenzer that have many years of reliable service in a multitude of applications.
In this solution, the standard electro-hydraulic thruster is replaced by a simple low friction hydraulic cylinder. On the low-speed side of the conveyor system, one or more SF brake calipers from Dellner can be used. Such brakes can be fitted with instrumentation that connects via Profibus, Profinet, or linked through the BCC controller to the main plant PLC using the CMB monitoring systems from Dellner.
Such systems, together with the monitoring of the hydraulic power pack using the BCC3000, offer complete system feedback on the operational parameter through the service life of the brake system.

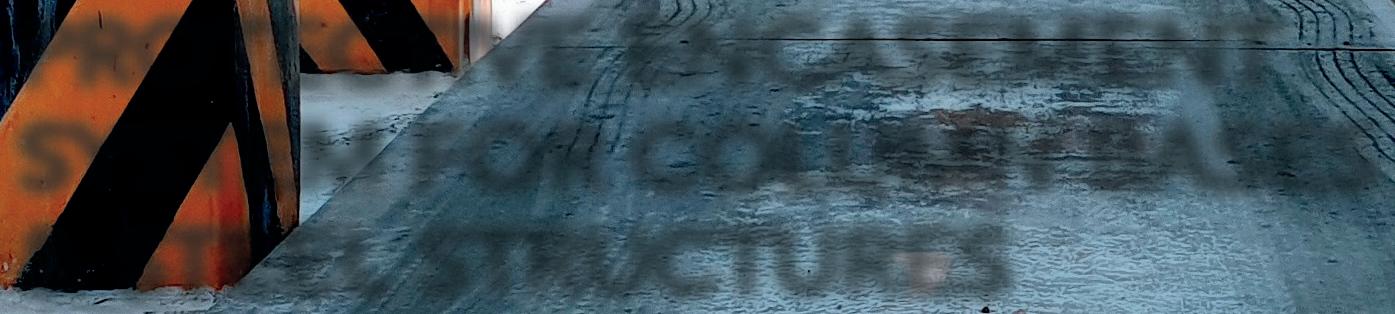
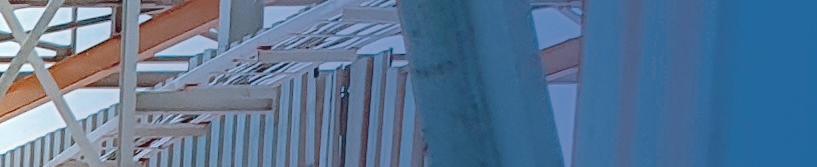

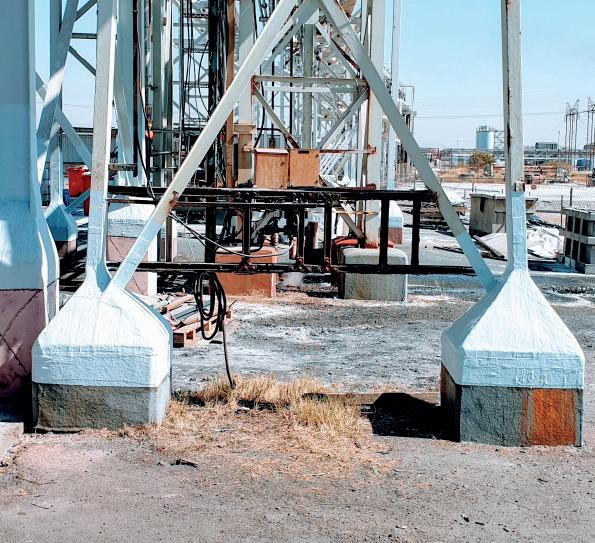
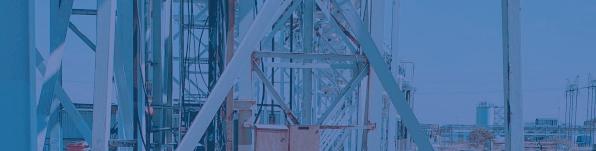



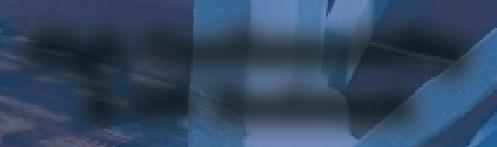
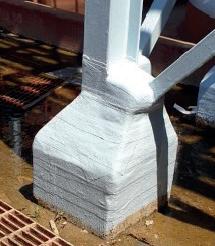

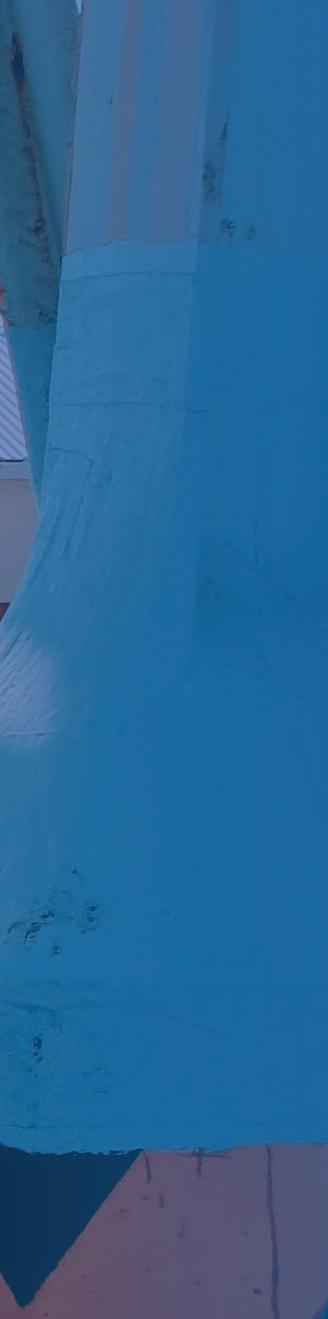
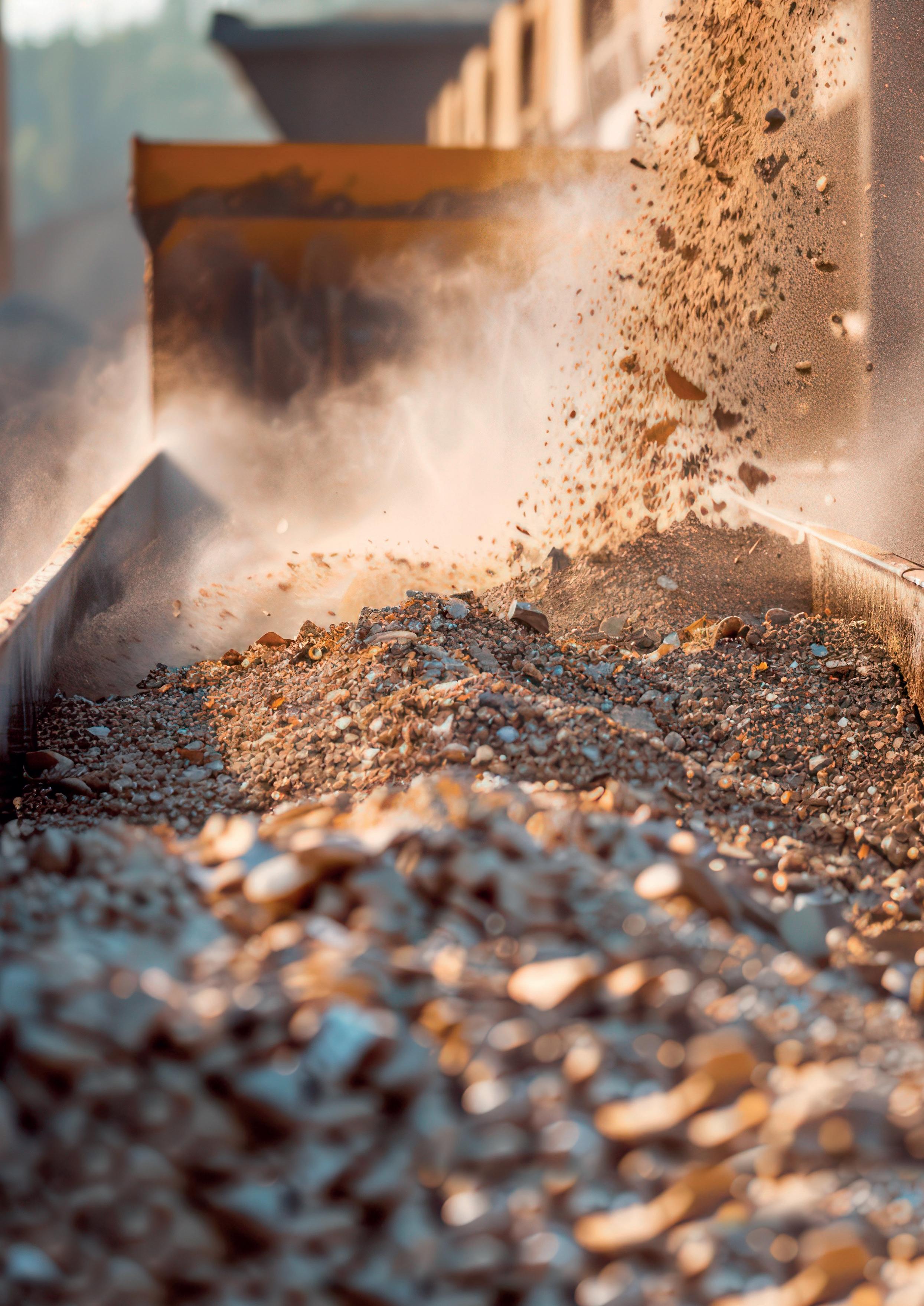
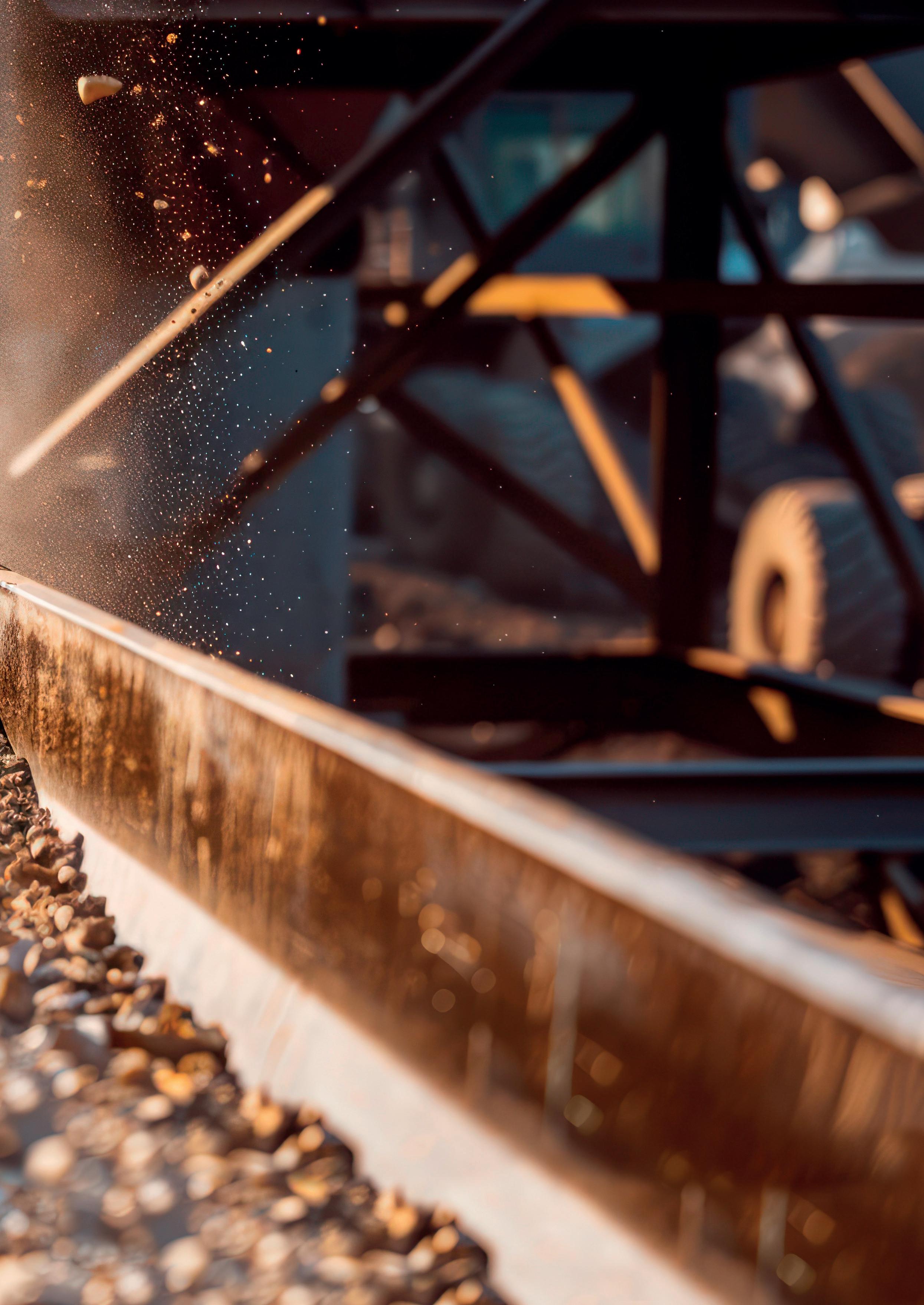
Conveying Cleaner Safer and
R. Todd Swinderman, Martin Engineering, USA, addresses how preventing fugitive material around conveyors can improve safety and reduce the costs of operations.
Most conveyors have some amount of material loss from spillage, leakage, dust, and carryback emissions, collectively called fugitive materials. The loss can range from 3% of the cargo for poorly operated and maintained systems, to less than 0.1% for world-class operations. The result is degraded component life, workers exposed to hazards, and reduced product quality. While fugitive materials cannot be totally eliminated from bulk material handling conveyors, the problem can be managed.
The root causes are often obvious, but rarely addressed. Rather, the standard approach is to treat the symptoms. The symptoms of a failure to control fugitive materials include unplanned downtime,
excessive cleaning costs, regulatory actions, poor public relations, and safety incidents. Addressing these symptoms with workable long-term root cause solutions will improve availability, housekeeping, safety, and improve the company cash flow.
Types of fugitive material
The nature of fugitive material problems from any conveyor is indicated by the location and particle sizes of the accumulations. Fugitive materials are generally categorised into spillage, leakage, dust, and carryback.
Spillage is cargo that escapes the belt, accumulating on either side of the conveyor and characterised by a range of particle sizes similar to the cargo. Piles of spillage can accumulate quite rapidly and can occur intermittently from plugged chutes, overloaded belts, and mistracking, or continuously from poorly designed or inadequately maintained transfer points. Inclined loading zones can also have material roll backward, causing spillage out of the back of the transfer point.
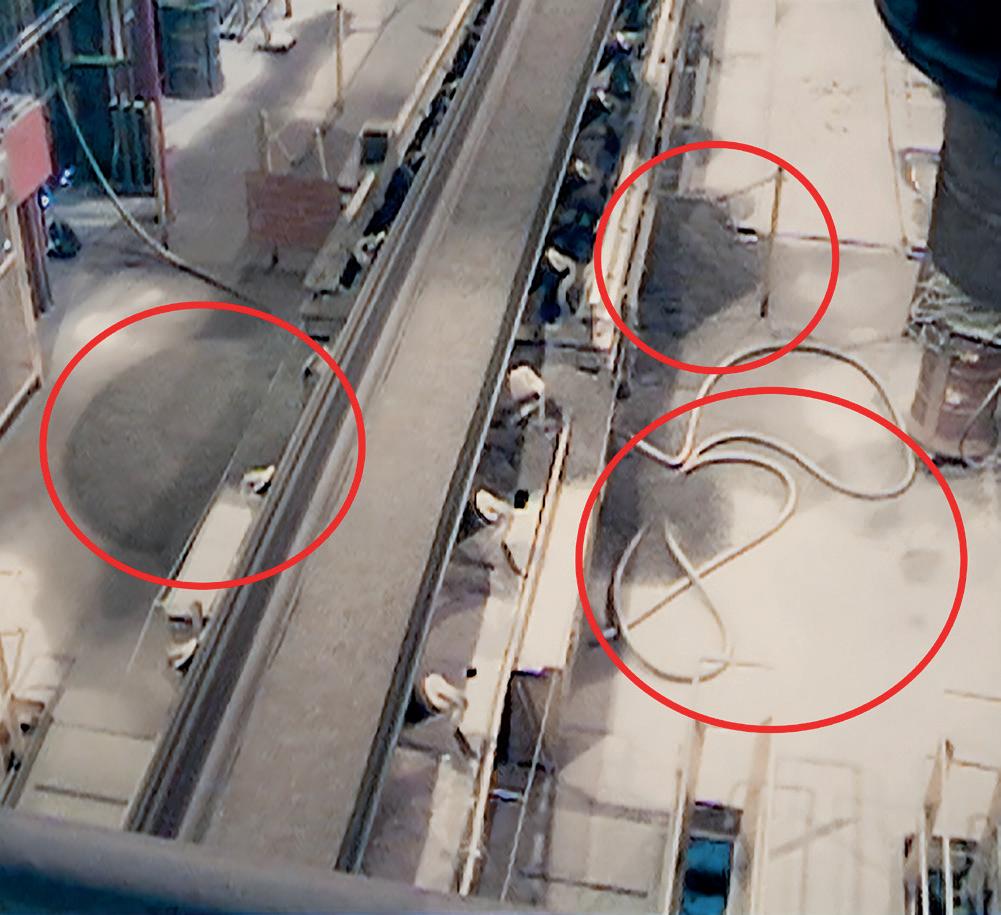
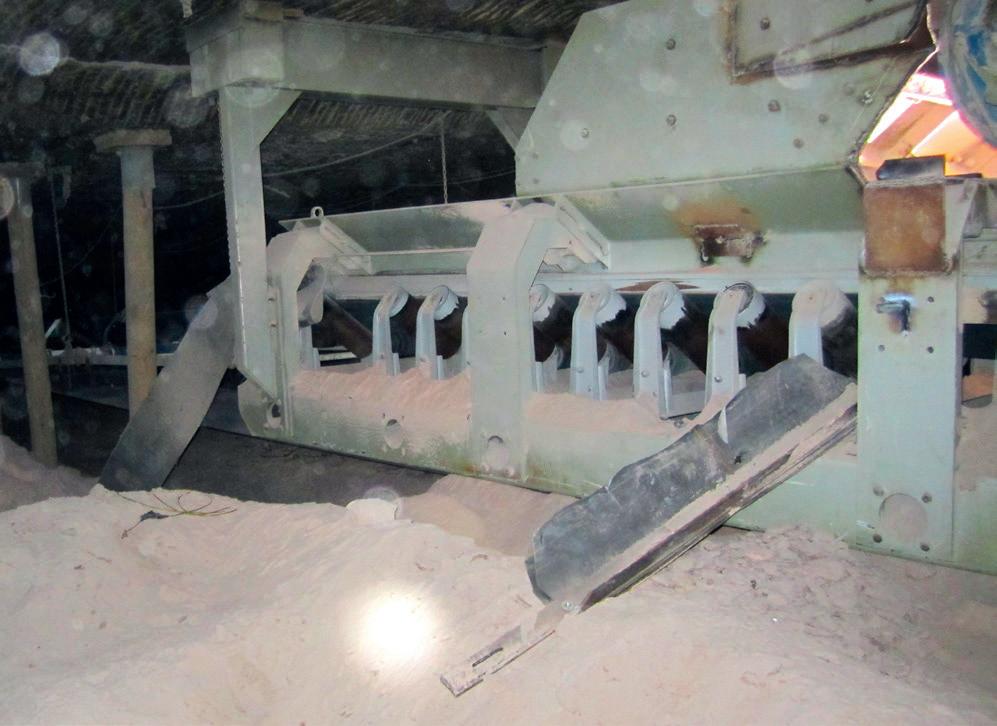
Dust is the fine particles, usually less than the diameter of a human hair, that are created during processing and the degrading action as the bulk material moves through a conveyor system. Fine airborne dust is emitted at locations where the cargo becomes airborne and is emitted from open inspection doors, missing covers, worn skirtboard seals, and the exit of transfers. Because dust particles are very small, when dry they are easily dispersed by wind, blanketing wide areas, but the sources are often visually obvious. In processing involving hot materials, the fumes given off often saturate dust particles and cause them to build up inside chutes and on equipment.
Carryback is fine material that sticks to the belt surface or becomes lodged in the cracks and crevices of the carrying side of the belt. Carryback material collects on components that the carrying side of the belt touches and eventually dries out, dropping beneath the system along the return path. Carryback accumulations tend to range from pyramid shaped piles of dry dust particles to puddles of muck. In severe cases, large chips of material form thick layers of buildup on return rollers and are thrown off of return rollers as they dry and break up.
Issues created by design
Bulk material handling investments are often capital projects because of the significant cost and the expected life of the equipment. Control of fugitive material requires attention to detail in the design stage that is often not considered because of the additional design time (capital cost) required, and the perception that fugitive material control costs are hard to quantify and it is therefore difficult to justify design improvements. Belt Conveyors for Bulk Materials and FOUNDATIONS are excellent resources for design. 1,2
In new projects, careful thought must be given to capacity calculations, angle of incline, transfer point design, and access for cleaning and maintenance. To improve fugitive material control, it is advisable to derate the capacity to 80 – 90% of the theoretical capacity and use slower belt speeds. A common spillage problem is created during rainy periods, when the angle of incline is appropriate for dry cargo but not for wet material. Loading at less than a 5° angle and reducing the angle of incline will decrease flooding and material rollback at the tail.
Designing a skirtboard enclosure that is longer and taller, with the proper number and placement of dust curtains, will help control dust emissions. Designing access for cleaning and maintenance can shorten downtime for these activities by 33% and significantly reduce exposure to hazards that can result in safety incidents. If future capacity increases are likely, they should be planned for in the initial design. In most cases, adding 10% to the design time of a project will allow for these details to be designed into the project, with little impact on the overall equipment cost but a huge return on the investment over time.
Don’t miss the world’s premier mineral exploration and mining convention
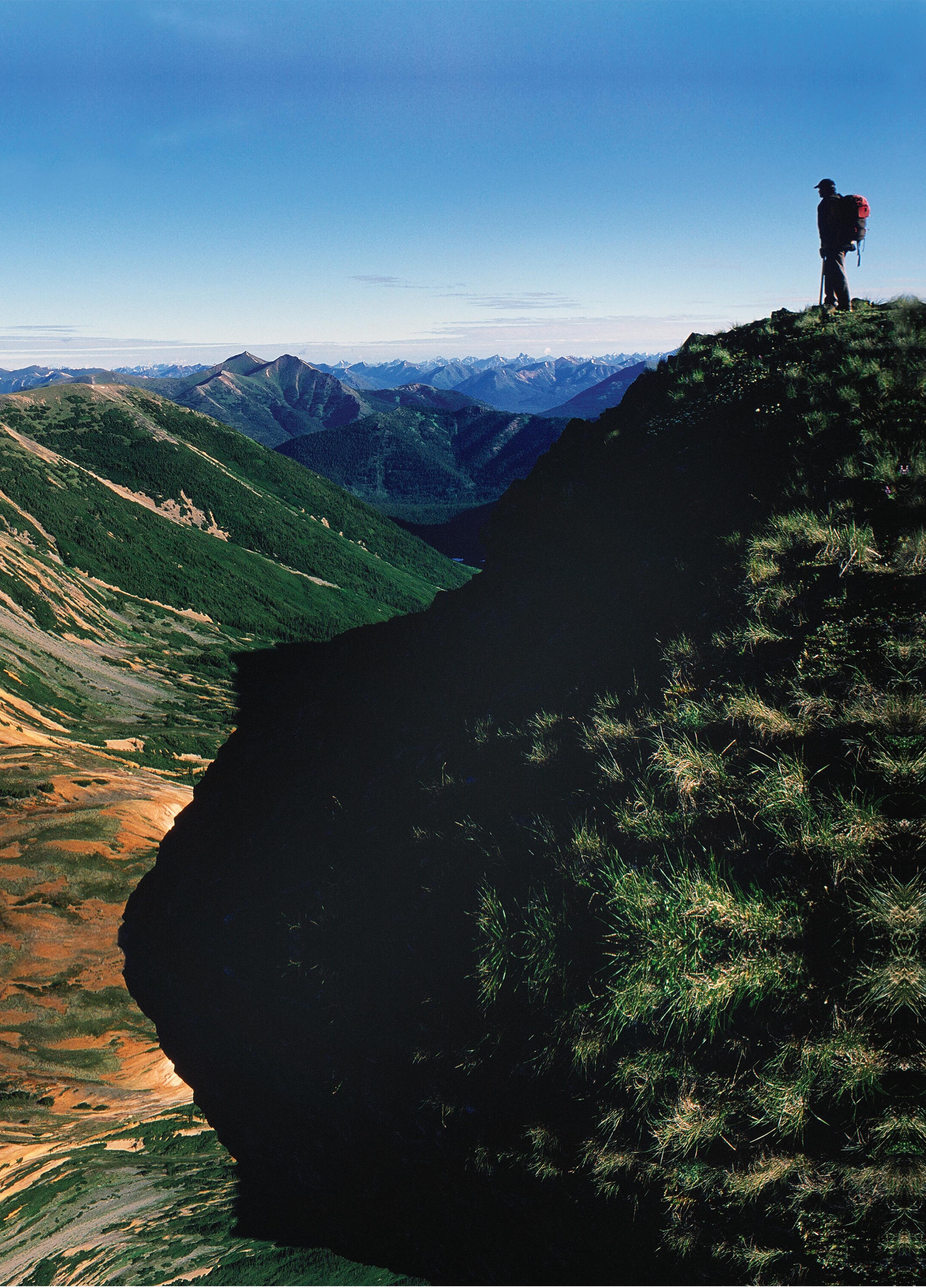
2-5 5
PROSPECTORS & DEVELOPERS ASSOCIATION OF CANADA
Up to 30,0 00 attendees 700+ hours of programming
1,100+ exhibitors Delegates from 130+ countries
Meet investors & senior executives Unrivaled networking pdac.ca/convention | Toronto, Canada
Quite often, existing conveyor systems are ‘upgraded’ to increase capacity or handle alternate bulk materials. An upgrade is often actually a downgrade, because control of increased fugitive emissions was not considered in the upgrade plans and shortcuts taken in the original design have left minimal space for changes. A common ‘upgrade’ is to increase the speed of the belt. Fugitive material problems are roughly proportional to the speed of the conveyor (or tonnage). Therefore, if the belt speed is doubled, the fugitive material problem and costs may also double. Quite often, an upgrade results in less capacity rather than more, because of changed material trajectories resulting in chute plugging and increased wear, both requiring increased downtime or reduced throughput to keep running. The old adage that you cannot put 5 kg in a 1 kg bag holds true, but many a conveyor operator lives to regret trying it.
Issues created by fugitive material
Because of the large number of variables in handling bulk materials – both in the bulk materials themselves and in the condition of the conveyors – it is physically, financially, and statistically impossible to reduce fugitive emissions to zero over a long period of time. Accumulations of fugitive materials are often an
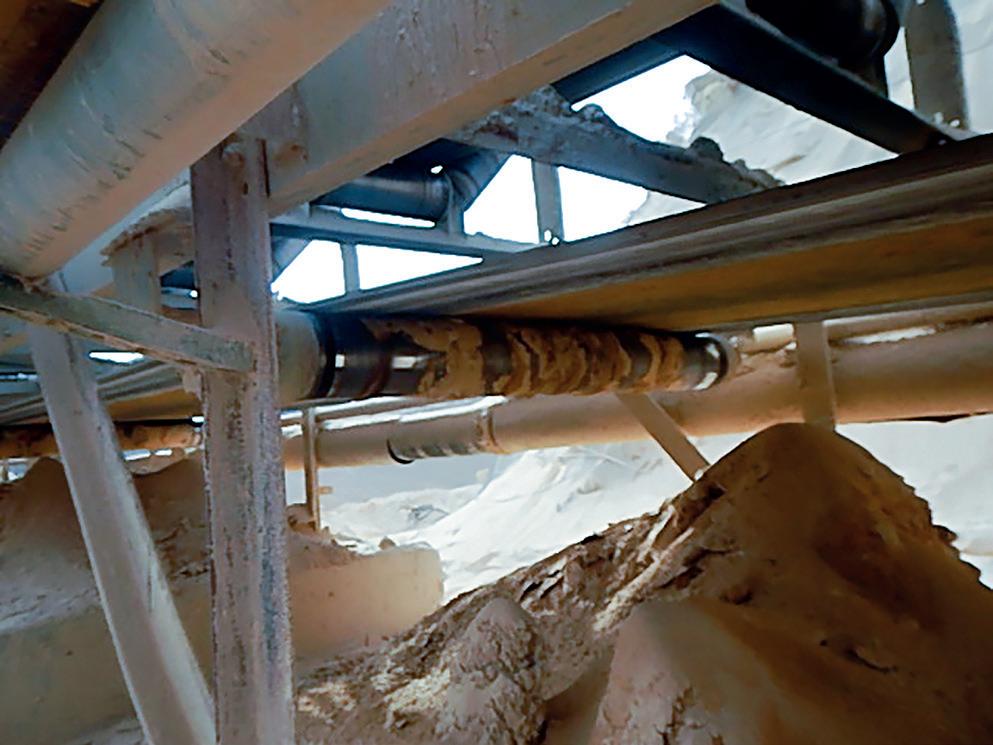
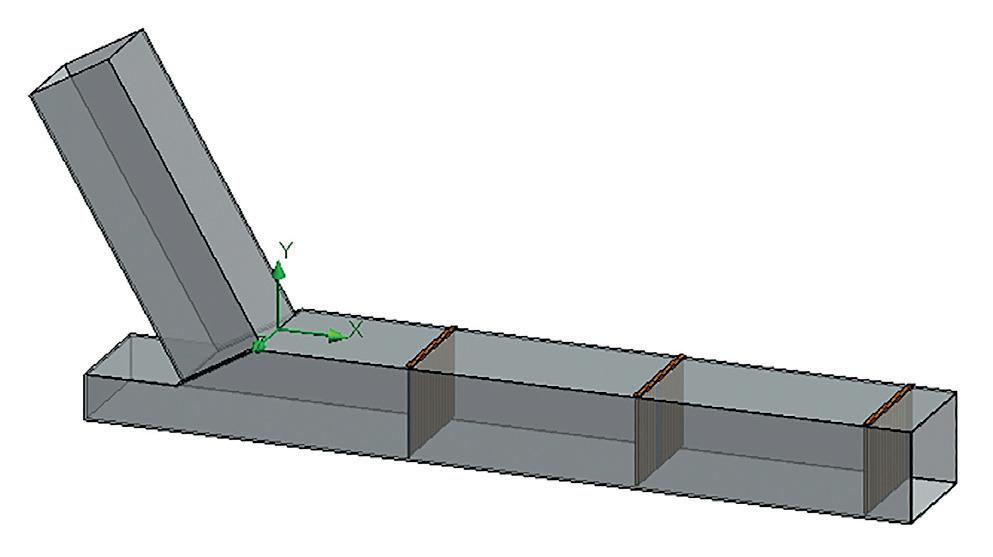
indication of an underlying culture of ‘production first’. In this environment, frequent cleaning is an accepted necessity to keep production running.
Many safety incidents happen during cleaning, and many fatalities have occurred trying to clean with the conveyor operating. Piles of spillage on waking surfaces present slip, trip, and fall hazards. Accumulations of carryback and buildup that falls when cleaning a chute or spillage of cargo from overhead conveyors can increase the risk of blunt trauma or crushing hazards. Safety incidents range from minor first aid to lost-time cases. A common lost-time event is a muscular skeletal injury manifested as a back or shoulder injury. These sprains and strains are often hard to diagnose, and on average result in a multiweek recovery. Control of fugitive materials to the point where cleaning is seen as a periodic housekeeping task rather than a daily production-enabling strategy should be the goal.
The need to clean to keep running is one obvious cause of unplanned downtime. Another less obvious productivity thief is the large role fugitive materials play in reducing equipment life, which leads to more frequent outages for maintenance than necessary. Idler bearings are particularly susceptible to contamination from dust. Material escaping under the wear liners and skirtboard seals leads to shorter belt life, due to belt grooving under the seals. The belt (because of its total mass) and idlers (because of their numbers) are expensive and time consuming to replace.
There are additional hidden costs that are often overlooked when justifying improvements to control fugitive materials. Working in a dusty atmosphere reduces worker productivity – in some studies as much as 20%, if respirators must be worn. The leading cause of death in industry is from disease, not accident. Respiratory illness from exposure to even nuisance dust often leads to workers being put on long-term disability, increasing worker compensation costs. A dirty operation also attracts the attention of regulators and neighbours. A reputation as a dirty place to work reduces the pool of employees who are willing to work in such an environment, and those already employed often suffer from low morale.
Fugitive materials are often a root cause of catastrophic events. Many types of dust present fire and explosion risks, in addition to health and safety concerns. The destructive power of dust explosions is well-documented in industries such as coal mining, grain processing, and sugar production. Static discharge into a dusty atmosphere is a common cause of many of these fires and explosions. What is often harder to detect is the chain of events that led up to a conveyor belt fire. In many cases, a frozen idler bearing is the heat source that ignites the grease and in turn causes the belt to catch fire. In other cases, mistracking belts, caused by spillage or carryback built up on pulleys, creates friction between the belt and structure that can actually cut steel beams in two, or create enough heat to become an ignition source. Friction is another common root cause of major incidents.

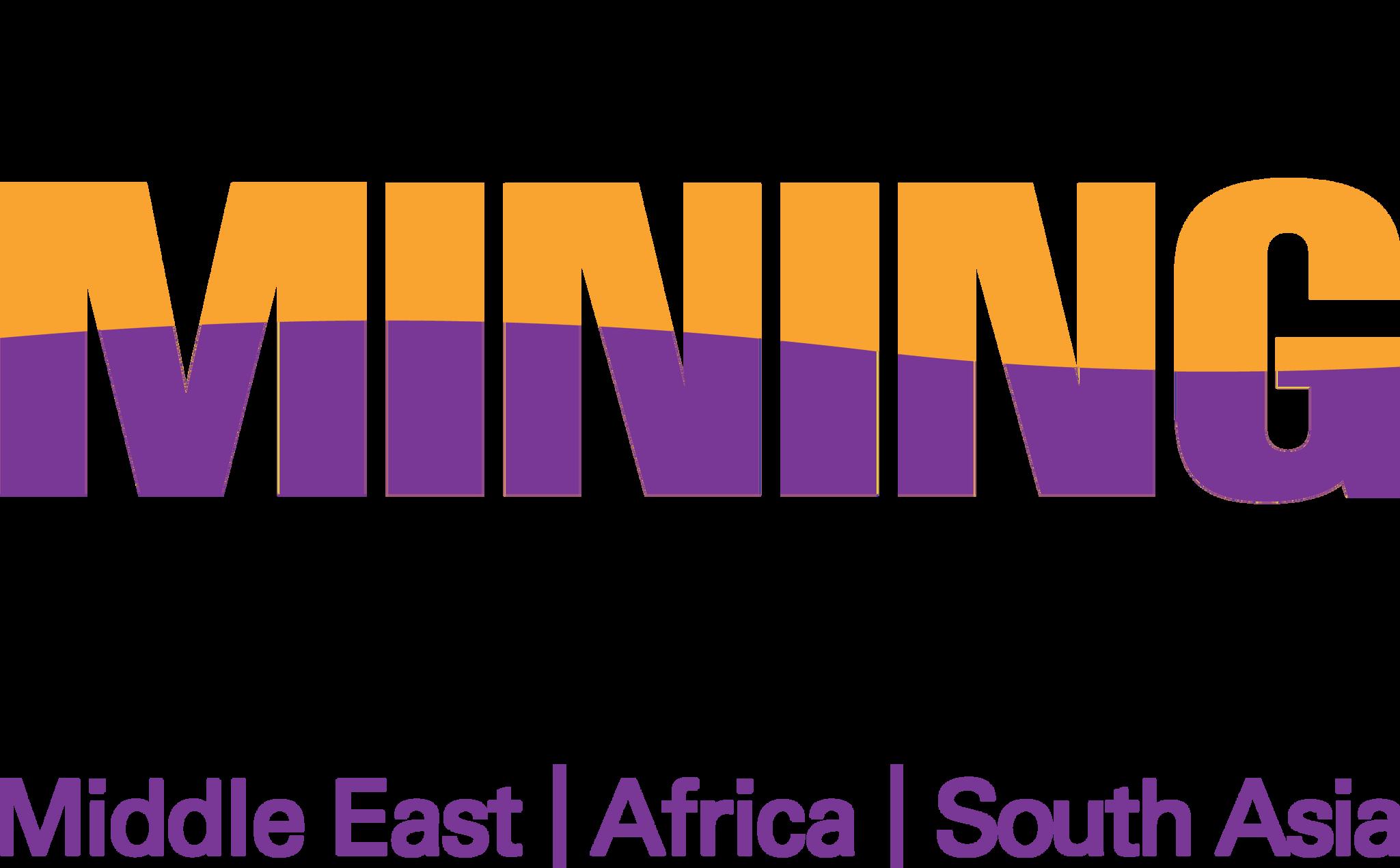
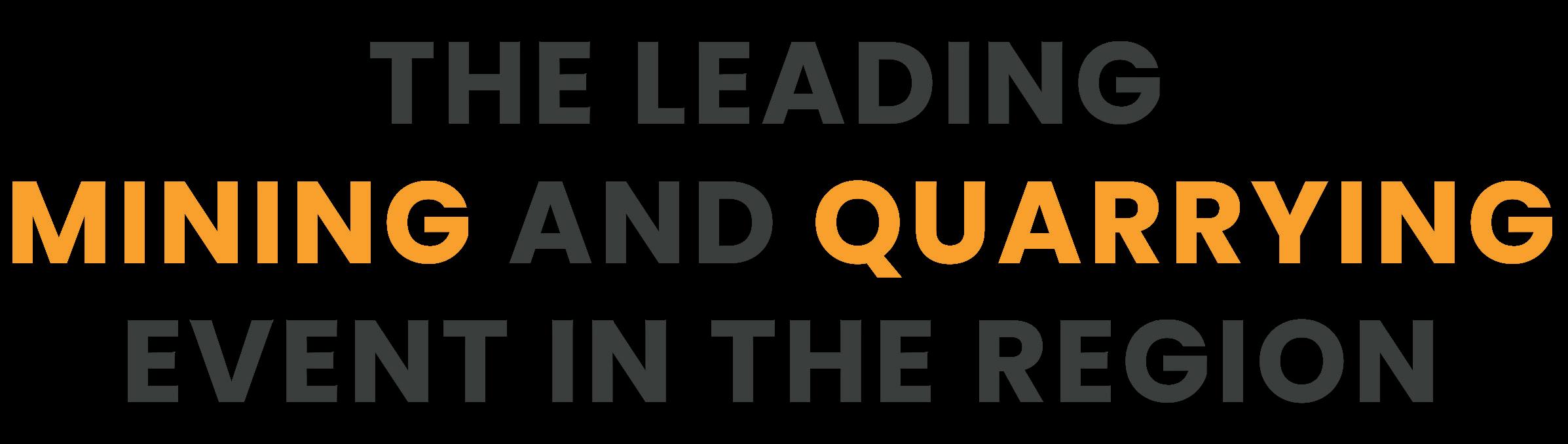

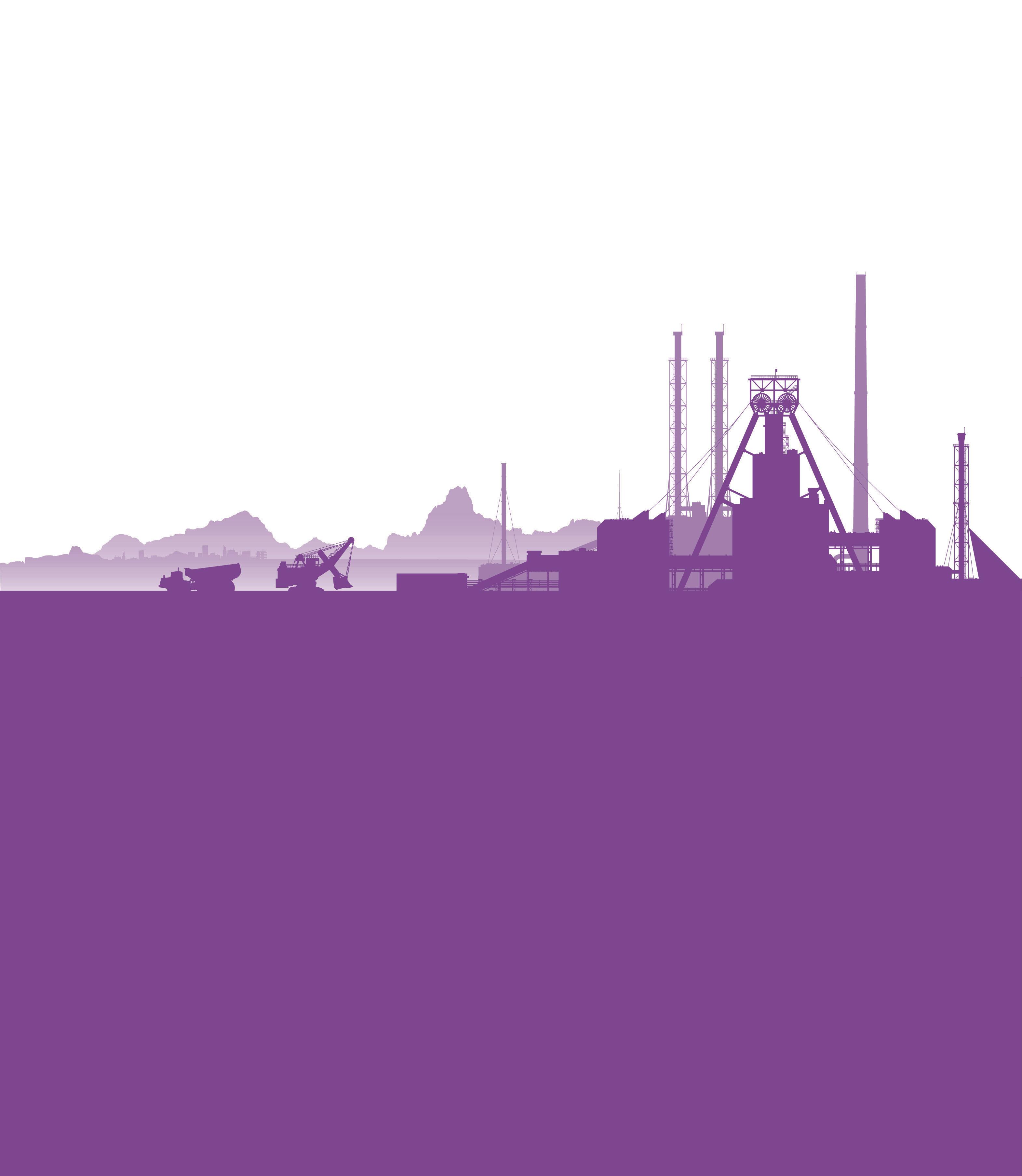

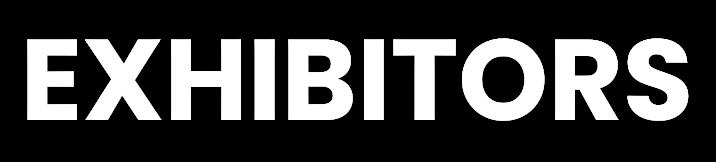
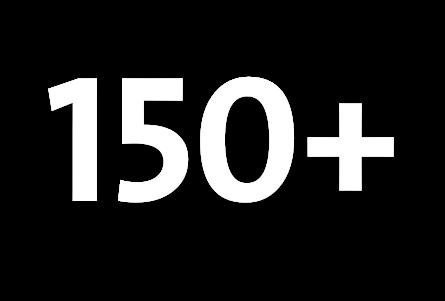
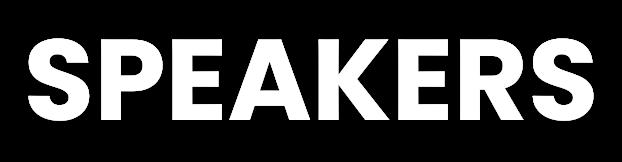
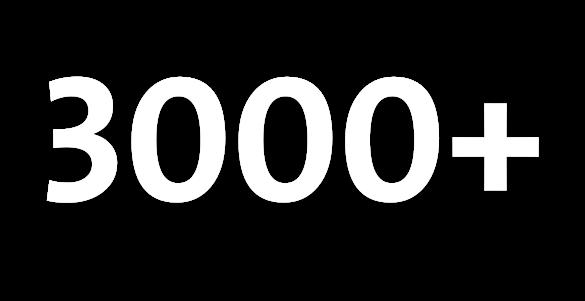
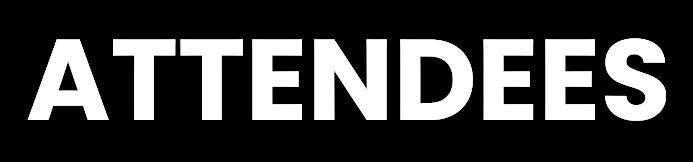
Detecting and measuring fugitive materials
Indirectly, safety switches and conveyor parameter sensors create data outputs from problems created by fugitive materials, and thus can provide some measurement or indication of problems to come. In many operations, acceptable fugitive material control performance means keeping the emissions to a level that allows cleaning or maintenance during scheduled routine production outages or maintenance time. Through good design techniques, well-trained operators, and predictive maintenance practices, most conveyor systems can go weeks without a need to shut down just for cleaning without causing a safety problem or significant production loss.
The application of indicators such as belt wander switches, zero speed switches, and plugged chute detectors has been practiced for as long as there have been conveyors. These devices are often purposely defeated due to false trips or other signals that interrupt production. The bulk material handling industry is starting to adapt sensor technology to the rigours of bulk material handling to better monitor
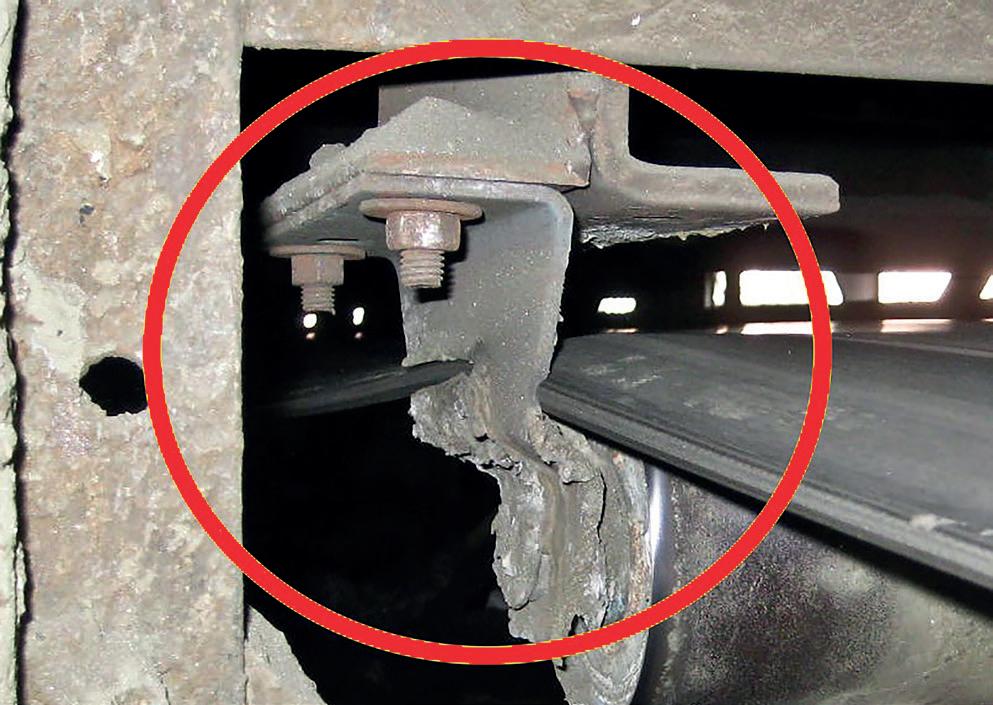

conveyor performance and provide proactive warnings of problems that are developing. For example, wireless technology can gather data from numerous sensors without the need for hard wiring. Fibre optics are being used to detect heat rise in idler bearings. Many conveyor components that were simply considered ‘dumb’ brute force devices, such as belt cleaners, are now being remotely monitored and controlled to improve cleaning effectiveness and provide indications of malfunction.
In new designs, case study data can be used to estimate the potential size of the fugitive material problem and costs associated with not addressing the issues. With existing operations, the information needed to justify improvements may at first seem difficult to quantify. In reality, as few as five independent observations of the problem can provide facts that represent the problem with a reliability of over 90%. 3 While some company data or information may not be kept or readily available, there are many resources completing the picture of the costs of fugitive materials and the benefits to be derived from implementing controls. 4
Measuring the amount of fugitive materials can be as easy as laying a tarp under the transfer point or conveyor return run and weighing the accumulations over a period of days. The same observation and measurement techniques can be used to judge the success or failure of mitigation efforts. There are even ways to empirically judge the extent of the problems and determine whether or not the changes are having the desired effects. 5
Conclusion
Because the problem of fugitive material has been around since conveyors first came into use, in the minds of many operators, fugitive material is merely a sign that the plant is producing. They may believe that as money is being made, dust and spillage are inevitable. However, fugitive material leads to major issues that can and should be addressed.
Managing fugitive material is a more economically and operationally sound choice than merely chalking it up as ‘the cost of doing business’. The effect that spillage, dust, and carryback have on an operation is a tangible reminder of unnecessary inefficiency. By working with experts, installing modern solutions to age-old conveyor problems, and practicing state of the art maintenance, operators can significantly improve safety in the workplace and dramatically reduce the cost of operation.
References
1. ‘Belt Conveyors for Bulk Materials’, Conveyor Equipment Manufacturers Association, 7th Edition, www.cemanet.org
2. SWINDERMAN, R. T., et al.: ‘Foundations™: The Practical Resource For Cleaner, Safer, More Productive Dust & Material Control’, 4th Edition, Martin Engineering, Worzalla Publishing Company, (2009), p. 552.
3. HUBBARD, D.W., ‘How to Measure Anything, Finding the Value of Intangibles in Business’, John Wiley & Sons, (2010).
4. ‘Foundations’, pp. 492 – 504.
5. ‘Swinderman Scale of Fugitive Material Measurement’, COSCIONE, M., ‘Measurement of Fugitive Material for Belt Cleaning Assessment’, ENCOM, www.encommz.com

William Nicholls, Movex Innovation, outlines how ultra-compact electric mini-loaders can provide a better alternative to manual material cleanups in the conveying and crushing processes.
Efficient material cleanup during the crushing and conveyor processes in the mining sector can significantly impact a mine’s productivity, the frequency of downtimes, resource management, worker safety, and overall operational costs. The task of removing waste material under conveyors has been a longstanding challenge for mining supervisors and workers.
The ongoing challenges in material cleanups in mines
Material cleanups in mines are notoriously difficult because of constant spillage and blockages. Conveyor systems frequently experience material overflows, particularly at transfer points, requiring regular cleanups. Conveyor carryback – when material particles stick to a conveyor belt and gradually accumulate under the system, or on key parts – also intensifies the number of times crews need to remove debris.
Traditionally, this task meant assigning multiple workers to manually remove dust, rocks, and debris using shovels, a process that could take hours or even days. During this time, conveyors had to be stopped to ensure worker safety, leading to significant downtimes and losses in productivity – sometimes costing tens of thousands of dollars per hour.
Under time pressure, some maintenance teams delay spillage removal until it accumulates to the point of causing material blockages, mechanical breakdowns, and downtimes that can last several days or even weeks.
For example, in Global Mining Review’s April 2024 article, ‘Conveyor Reliability on a Roll’, in 1Q23 alone, a conveyor failure at Rio Tinto’s Kennecott copper mine in Utah resulted in a 36% drop in production. The article points to the fact that replacing conveyor belt parts can result in over US$2.5 million in production – not to mention a day-long outage.
Moreover, manual material handling in these conditions poses substantial safety risks. Workers are exposed to hazardous environments, often under extreme temperatures. Repetitive motions, slips and falls, musculoskeletal injuries, and other health issues increase employee absenteeism. Even when conveyors are turned off, the system’s residual energy and the risk of accidental start-ups make working near these machines extremely dangerous.
In the same Global Mining Review article, studies reveal that conveyor maintenance accounts for 43% of all injuries and 24% of worker fatalities. The aftermath of these incidents greatly affects long-term worker health and their families. In addition, accidents can lead to regulatory penalties, higher insurance premiums, and damage to a company’s reputation in a sector increasingly susceptible to occupational health and safety inspections.
Cleanup risk mitigation is a must
Given the ramifications associated with conveyor cleanups, risk mitigation strategies are essential. Apart from regular maintenance and employee training, investing in conveyor belt cleaning systems with scrapers, belt ploughs, impact beds, and belt skirts can minimise carryback. Real-time condition monitoring solutions can assist in preventing critical blockages and equipment damage from occurring and optimising conveyor performance.
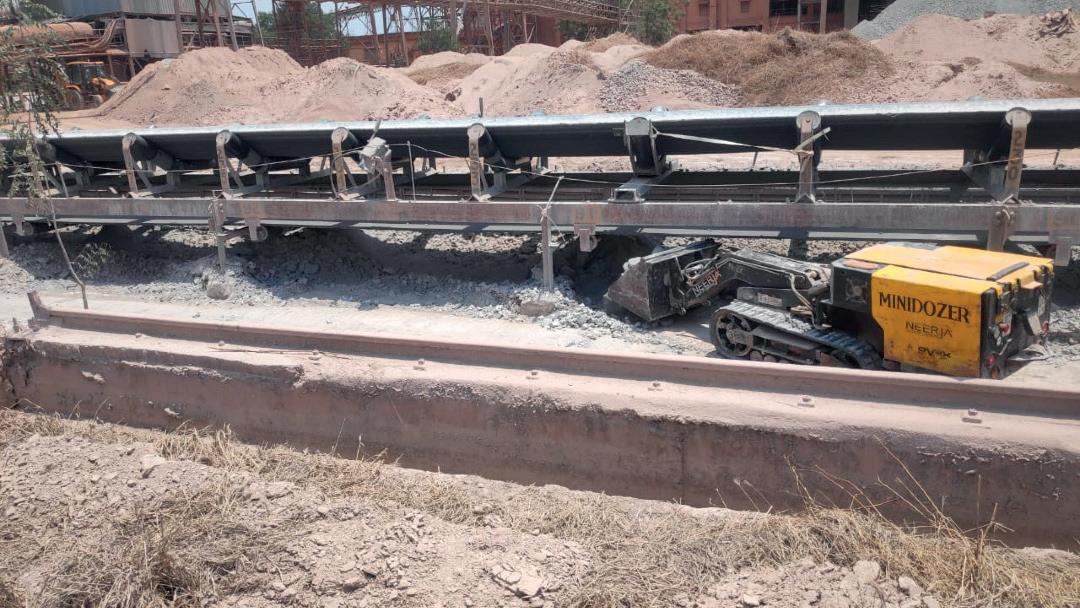
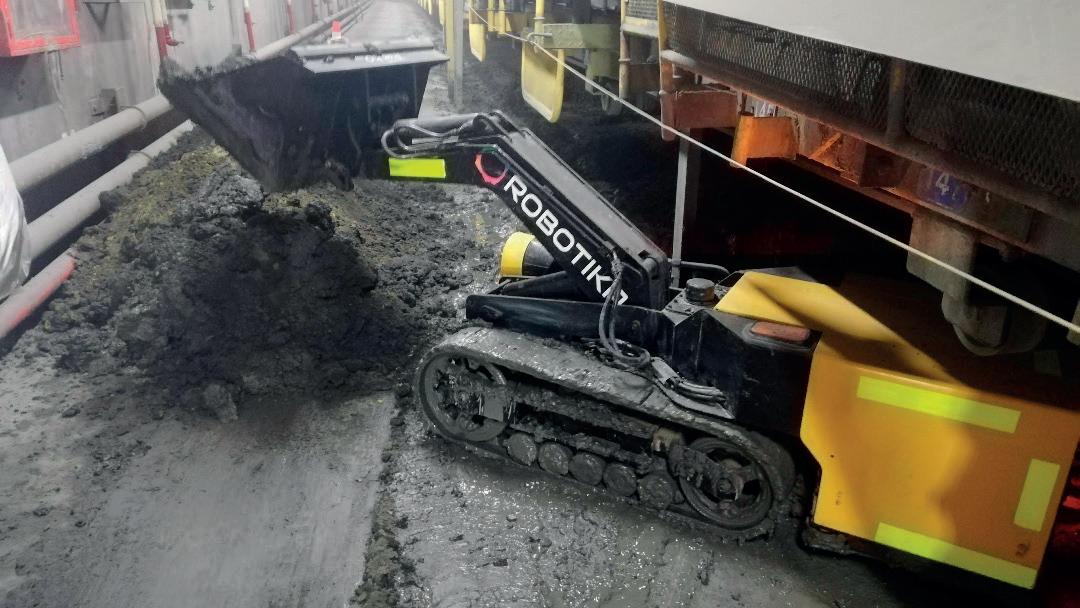
Nevertheless, spillage and material build-up will continue to happen. With the limitations of traditional shovelling in mind, the industry has turned to material handling equipment to make cleanups efficient and safer.
Limitations of conventional material cleanup equipment
Skid-steer loaders have emerged as one potential alternative to shovelling. These machines can help reduce the reliance on manual labour, yet they come with their own set of problems. Many models are still gas-powered. This exposes employees to noise and greenhouse gas emissions, and drives up fuel costs.
Some vendors have introduced electric and remote-controlled versions of skid-steers, which address some of these issues. However, the bulky design of many of these machines makes manoeuvring under conveyor systems difficult. The challenge is particularly acute in tight spaces, where turning can be problematic, and on rough terrains, where traction is difficult due to their wheels or caterpillar wheels.
New ultra-compact and electric mini-loaders make cleanups hassle-free
To overcome the difficulties in material cleanups, some companies have developed ultra-compact, remotely operated mini-loaders
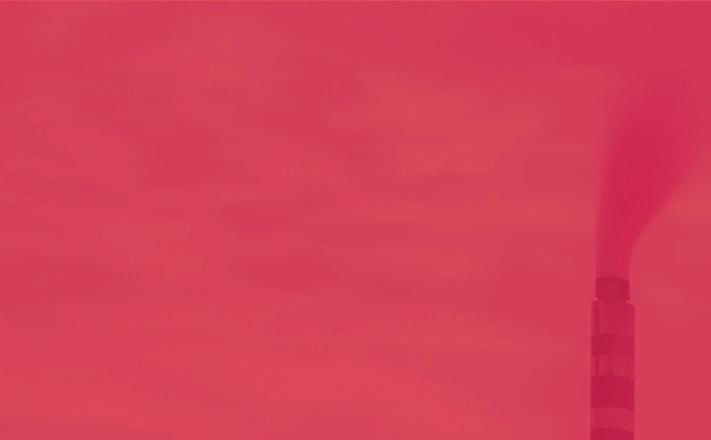
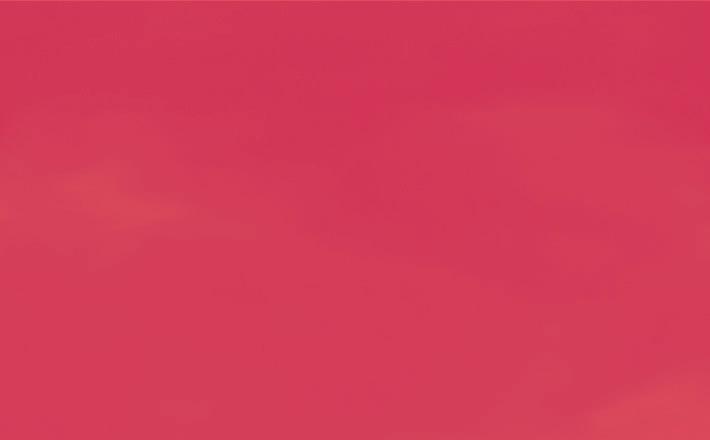
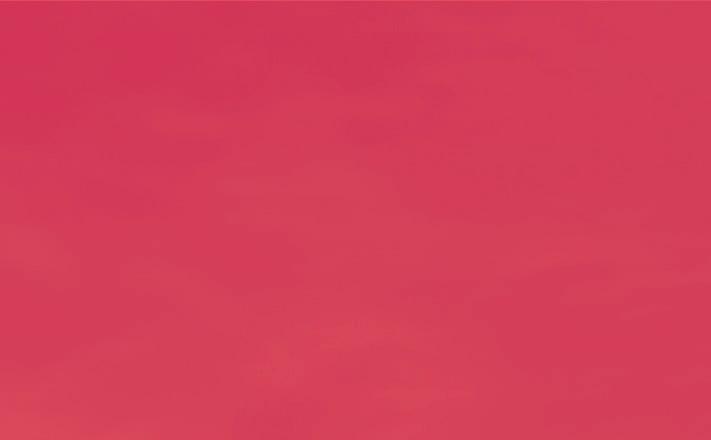

Subscribe online at: www.worldcoal.com/subscribe

designed specifically for the confined spaces and rugged conditions of mines.
These machines are engineered to operate under conveyor systems without stopping them, minimising downtime and maximising throughput. Their low-profile design allows for efficient spillage removal in areas where taller equipment simply cannot reach.
Mining operations that use electric mini-loaders save on fuel costs. Workers are also not at risk due to equipment noise and emissions.
One of the standout features of ultra-compact mini-loaders is their ease of use. Operators require minimal training to get started, as these machines often come equipped with intuitive controls, such as a simple joystick interface. This user-friendly design reduces onboarding time, allowing workers to start operating the equipment within a day, speeding up field deployment. For mining companies, this translates to less downtime for training and more immediate productivity.
One critical consideration for battery-powered mini-loaders in mining operations is performance in extreme temperatures. Depending on the vendor, many mini-loaders are equipped with batteries that can operate reliably in harsh conditions, from the freezing cold of
northern mines to the intense heat of operations in places like Australia.
While ultra-compact electric mini-loaders are perfect for material cleanups, they can also be used for a variety of other maintenance activities, such as removing other types of debris, transporting tools and mechanical parts, or moving smaller loads of materials across the site. Mini-loaders can transport conveyor belt rollers, motors, and other components across a processing plant.
Regarding a mini-loader’s return on investment (ROI), mining operations that switch to ultra-compact electric mini-loaders can expect a substantial payoff over time. The initial investment is offset by the savings in operational costs, reduced downtime, and faster cleanups without pausing the conveyors.
Key considerations when choosing a mini-loader supplier
When selecting a supplier for ultra-compact mini-loaders, it is crucial to consider more than just the machinery itself. Look for a partner who demonstrates a deep understanding of a mine’s operational challenges. Do they offer custom modifications based on the specific terrain or conditions of the mine in question? The ability to adapt the mini-loader’s design for an operation – whether it is extreme weather conditions, confined spaces, or specific safety concerns – can make all the difference in a material cleanup process.
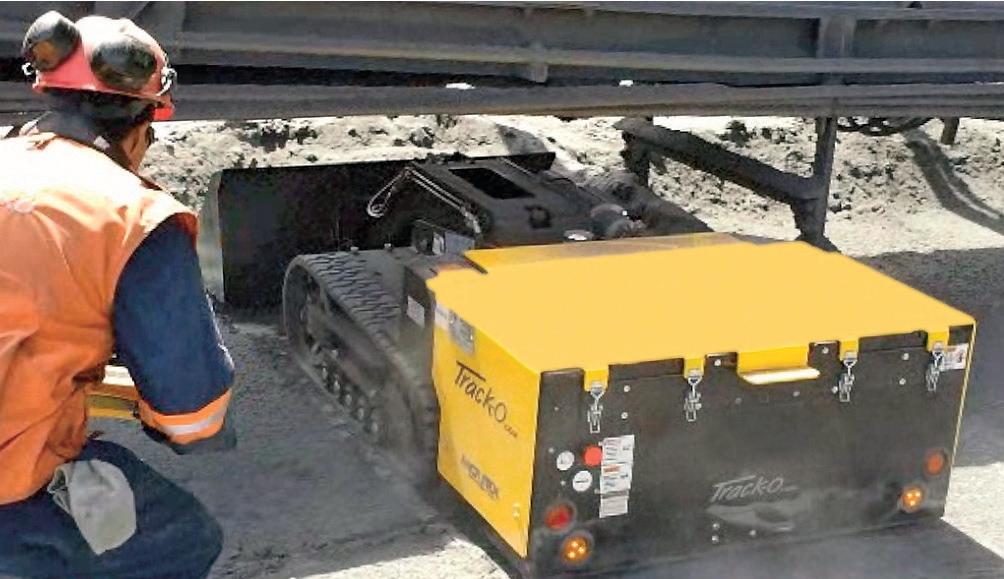
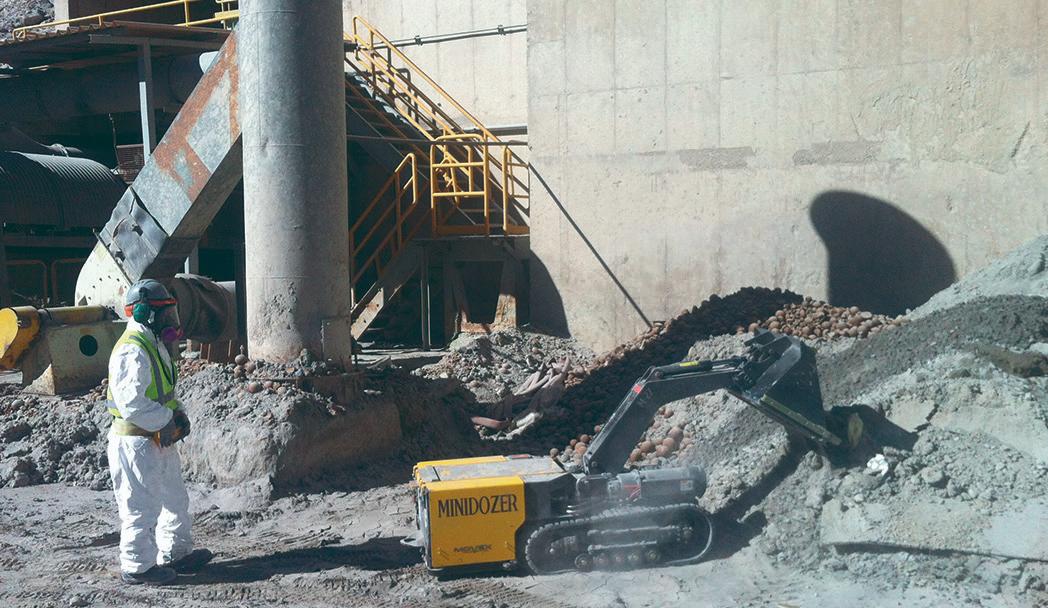
While many mini-loaders are simple to use, never underestimate the need for product and safety training. A vendor should provide comprehensive, hands-on, or online training to make the most out of material handling equipment. Again, while mini-loaders may initially be attributed to cleanups, you may quickly realise they can be used for other tasks.
Another often overlooked factor is the quality of post-purchase support. Does the vendor offer responsive technical assistance and fast turnarounds for spare parts? It is important to choose suppliers with a strong local presence and/or responsive remote support services.
Finally, when scouting out potential mini-loader manufacturers, inquire about their financing options and extended warranty protection. Do they have any leasing programmes? Reading the fine print will enable customers to better plan for future costs.
As innovations in material handling equipment continue to evolve, electric, ultra-compact mini-loaders are a compelling option to finally resolve the headaches caused by manual material cleanups.
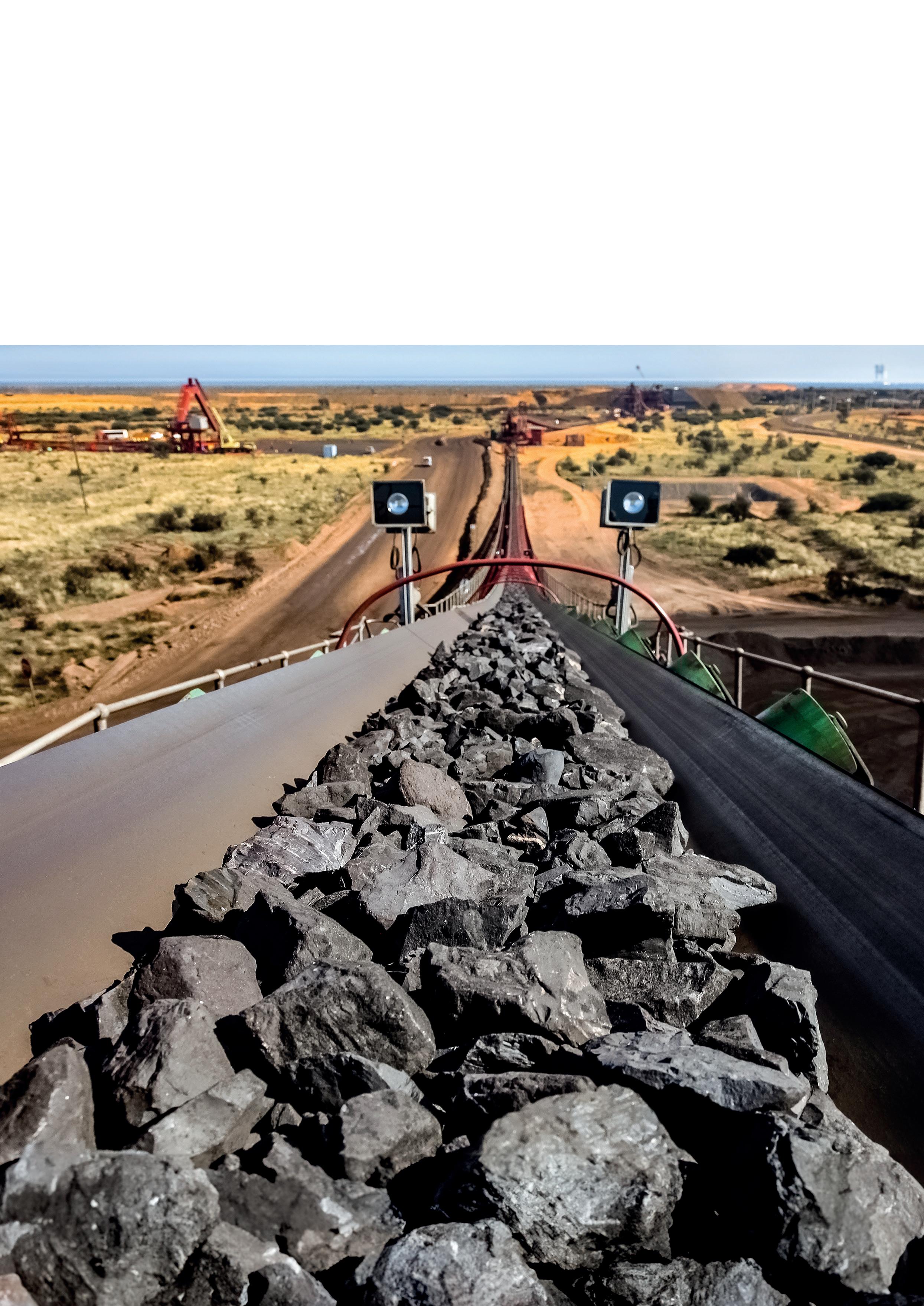
Simone Fiorini and Jessica Gamper, Aritec New Materials Group, Switzerland, explain how adopting aramid cord belts can improve the performance and sustainability of conveyor systems.
Conveyor belts are the lifeblood of mining operations, moving vast amounts of material in some of the most extreme conditions. While steel cord belts have long been the industry’s go-to solution for durability and strength, the growing emphasis on sustainability and operational efficiency is driving the search for alternatives. Aramid cord reinforced belts offer mining companies an opportunity to reduce energy consumption, cut down on carbon emissions, and streamline costs – all without compromising on performance.
This article explores the technical merits of aramid cord belts, examining their potential to reshape the future of mining by optimising energy use, extending belt life, and reducing the environmental footprint of conveyor systems.
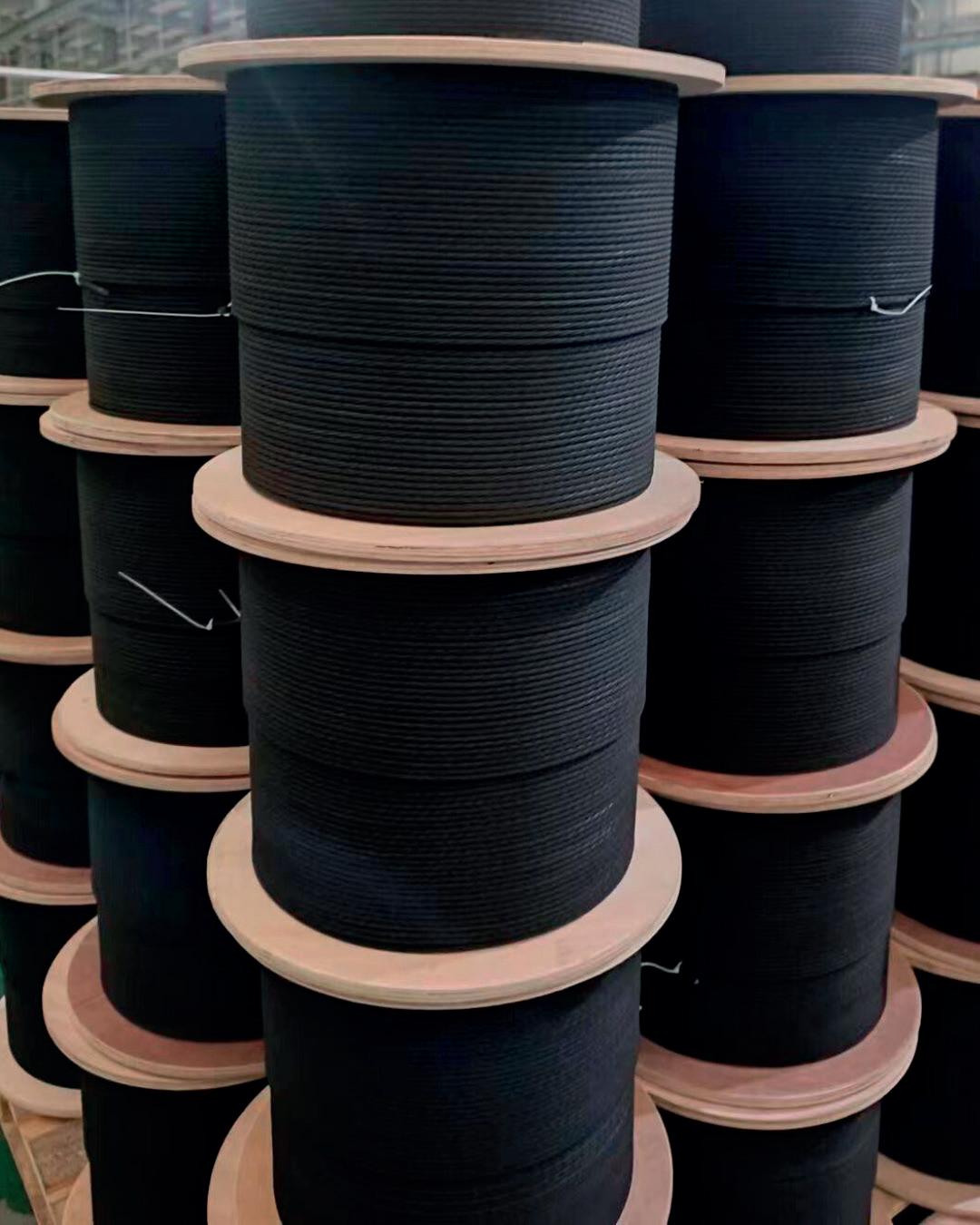
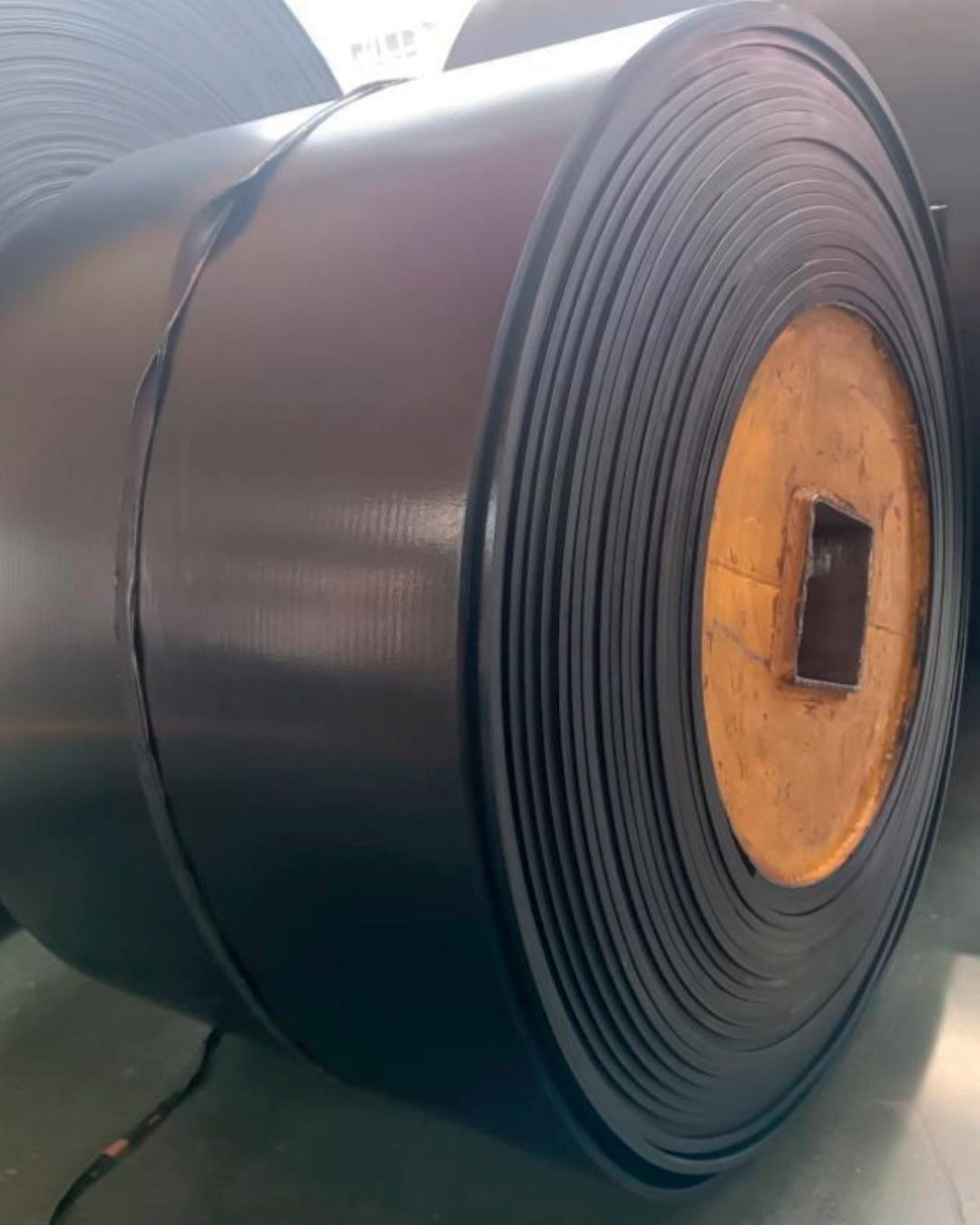
Reducing the total cost of ownership (TCO)
Aritec New Materials Group’s cost-benefit analysis of a 5000 m conveyor belt, 1 m wide and transporting 2000 tph of bauxite, highlights a major finding: aramid cord reinforced belts can reduce the total cost of ownership (TCO) by up to 10% compared to traditional steel-cord belts. This is mainly due to energy savings, as aramid belts are generally 25% lighter than steel-cord belts, resulting in lower rolling resistance and, consequently, reduced energy demands.
The lighter weight of aramid belts also leads to reduced transportation and installation costs. Since aramid belts are lighter, it is possible to transport up to 25% longer belts per reel, reducing logistics costs, especially in regions like Europe where there are transport weight limits. Moreover, the installation process is faster because fewer splices are required, and the belts are easier to handle. This reduces downtime, which is critical in industries where conveyor belt stoppages directly impact production.
Static and dynamic splice efficiency test results indicate that aramid cord technology is on par with steel cord, as per the relevant industry norm (DIN22110-3).
While the model assumes typical conditions – 7200 hours of use per year with a belt lifespan of six years, actual savings may vary depending on factors such as materials being transported, conveyor speed, and operating environment.
Energy efficiency: The key to long-term savings
One of the standout features of aramid cord reinforced belts is their energy efficiency. Traditional steel-cord belts are heavier, increasing rolling resistance and energy consumption required to operate the conveyor system. In contrast, aramid cord belts are significantly lighter and are less stiff, which enhances the belt’s flexibility and throughability and reduces indentation rolling resistance (IRR). Additionally, there is notably lower IRR during the return phase when the belt is empty.
This reduced rolling resistance translates to significant energy savings – ranging from 7% – 15%, depending on the configuration of the conveyor system. In mining operations, where conveyor systems are often running 24/7, these energy savings can result in substantial long-term cost reductions.
In mines that generate their own power from renewable sources like wind or solar, aramid belts further improve energy efficiency, allowing operations to maximise self-generated energy and reduce reliance on external sources.
Aritec’s data indicates that, depending on the specific conditions of the mining operation, these energy savings can add up to significant cost reductions over the life of the belt, helping mining companies maintain a competitive edge in an increasingly energy-conscious world.
Reducing CO2 emissions: A step towards sustainability
One of the most critical advantages of aramid cord belts lies in their potential to substantially reduce carbon emissions – an increasingly urgent goal for the mining sector. Over the lifespan of a typical conveyor system, Aritec estimates that
aramid cord belts can cut CO2 emissions by approximately 4600 t, primarily through improved energy efficiency. The lighter material reduces the energy to operate, making it a game changer for mining operations focused on sustainability.
These energy savings directly address scope 1 and scope 2 emissions, which stem from on-site energy use and purchased electricity. Additionally, the reduced transportation requirements for aramid belts contribute to lower scope 3 emissions, which account for the broader value chain’s environmental impact. While synthetic materials and optimised logistics play a role, the majority of the CO2 reductions come from operating the conveyor system more efficiently.
As the mining industry strives to lower its environmental footprint, aramid cord belts offer a practical solution for companies looking to balance operational performance with aggressive sustainability goals.
Strength and durability: Built for mining challenges
Beyond energy efficiency, aramid cord belts offer superior strength and durability. Aramid fibres provide tensile strength comparable to steel, while offering higher resistance to bending fatigue. This makes them ideal for conveyor systems with smaller pulley diameters or more complex layouts, where belts must navigate tight curves or steep inclines.
In harsh environments – such as wet, acidic, or abrasive conditions – steel cords are prone to corrosion, which shortens their lifespan and increases maintenance costs. Aramid cords, being non-corrosive, can last three to four times longer under these conditions, reducing the need for belt replacements. While Aritec’s models assume a standard six-year belt life, real-world applications often surpass this in corrosive settings. This extended lifespan not only enhances operational efficiency, but also contributes to substantial cost savings for mining companies.
Aritec’s proprietary rubber bonding technology also eliminates the need for toxic chemicals like resorcinol formaldehyde latex (RFL) in the manufacturing process. This shift away from harsh chemicals not only reduces the environmental impact, but also aligns with the industry’s movement towards safer and more sustainable manufacturing practices.
The lighter weight of aramid belts also enables longer belt sections to be installed with fewer splices, which are often weak points in conveyor systems. Fewer splices mean fewer opportunities for failure, reducing both installation time and long-term maintenance requirements. This enhances system reliability in continuous-use operations.
By combining strength, durability, and ease of maintenance, aramid belts are engineered to thrive in the most challenging mining conditions, where performance and reliability are paramount.
Installation and logistics: Faster, easier, and more cost-effective
One often-overlooked benefit of aramid cord belts is how much easier they are to transport and install. Their lighter
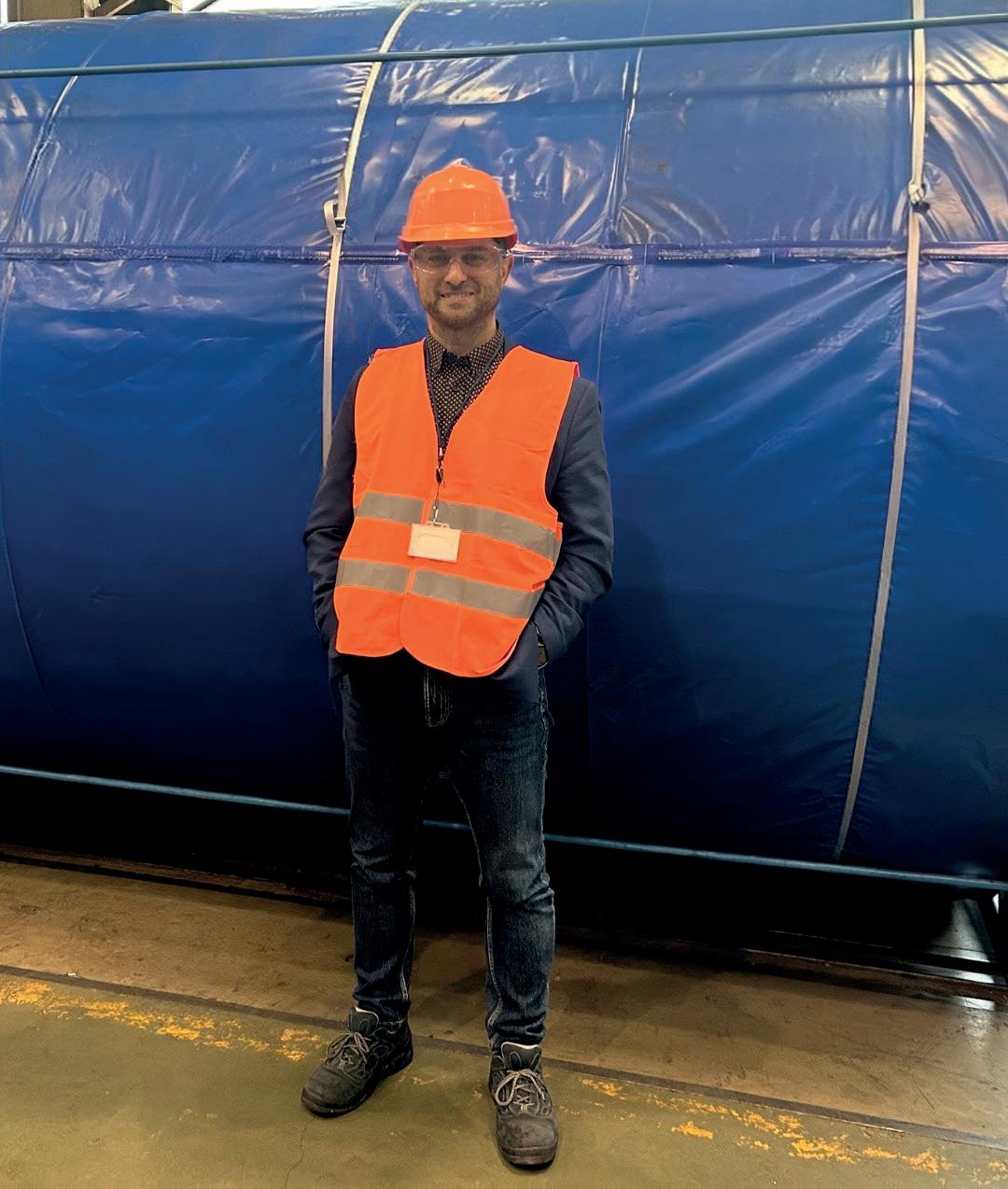

Figure 5. A bucket-wheel excavator in an opencast mine. Aramid cord reinforced belts offer a lighter alternative to steel, reducing the strain on mobile equipment, without requiring structural changes to the machinery.
weight allows for longer belt sections to be transported in a single shipment, reducing transportation costs and improving logistics efficiency. In areas with strict weight limits, such as Europe’s 50 t transport limit, the ability to ship more material in fewer trips can lead to measurable savings.
The lighter weight of aramid cords also proves advantageous in high-altitude applications. Transporting heavy steel belts to remote or elevated sites can be costly and logistically challenging, but aramid belts, with their lighter mass, make the process far simpler. Additionally, the reduced weight enables the construction of taller conveyors, crucial for vertical transport in certain mining operations.
The reduced weight also translates to faster and easier installation, which means less time is spent assembling the belt on-site, and the lighter material is easier to handle, reducing labour costs. By shortening installation times,
mining companies can get their operations up and running faster, minimising the costly downtime that often accompanies conveyor belt replacements.
Fewer splices also mean fewer points of weakness in the belt, reducing the likelihood of premature failure and minimising maintenance requirements over the belt’s operational life.
This combination of logistical ease, faster installation, and enhanced system reliability makes aramid cord belts an attractive option for mining companies aiming to improve operational efficiency.
Future-proofing mining operations with aramid technology
While Aritec continues to optimise the performance of aramid cord belts, the current technology is already fully developed and ready for implementation. The belts are compatible with existing monitoring technologies, such as sensors for predictive maintenance, which can detect wear or potential issues before they lead to failures. This integration mirorrs systems used with steel-cord belts, allowing mining companies to seamlessly incorporate aramid belts into their existing digitalised operations.
Smart technology that monitors motor life relative to conveyor load can be applied to aramid belts, just like steel cords, making them a flexible, future-proof solution for companies adopting more advanced, automated systems.
However, one of the most promising areas for aramid belts is in conveyors equipped with metal detection systems. Steel cord belts often interfere with metal detection, making it
challenging to identify unwanted metallic contaminants in transported materials. Aramid belts, free of steel components, eliminate this issue, allowing for improved detection accuracy and more reliable system performance. This unique advantage makes aramid belts particularly valuable in operations where material purity and contamination control are critical.
With the increasing focus on automation, digitalisation, and sustainability in mining, aramid cord belts are well-positioned to support the industry’s evolving needs.
Conclusion: A clear path forward
For mining companies committed to reducing operational costs, while pursuing sustainability targets, aramid cord belts represent an evolution for greener operations and moving down the path to net zero. With up to 15% energy savings, lower CO2 emissions, and faster, more efficient installations, aramid cord belts address some of the industry’s most pressing challenges. The superior strength, corrosion resistance, and extended lifespan of these belts offer long-term value, making them a smart investment for companies looking to stay competitive in a rapidly evolving landscape.
As the mining sector faces increasing pressure to operate more sustainably, adopting innovative solutions like aramid cord belts is no longer a matter of ‘if’, but ‘when’. The opportunity to future-proof operations, while meeting the demands of both economic performance and environmental responsibility, is here – and Aritec’s aramid cord belts are ready to meet that challenge today.

Advert Index
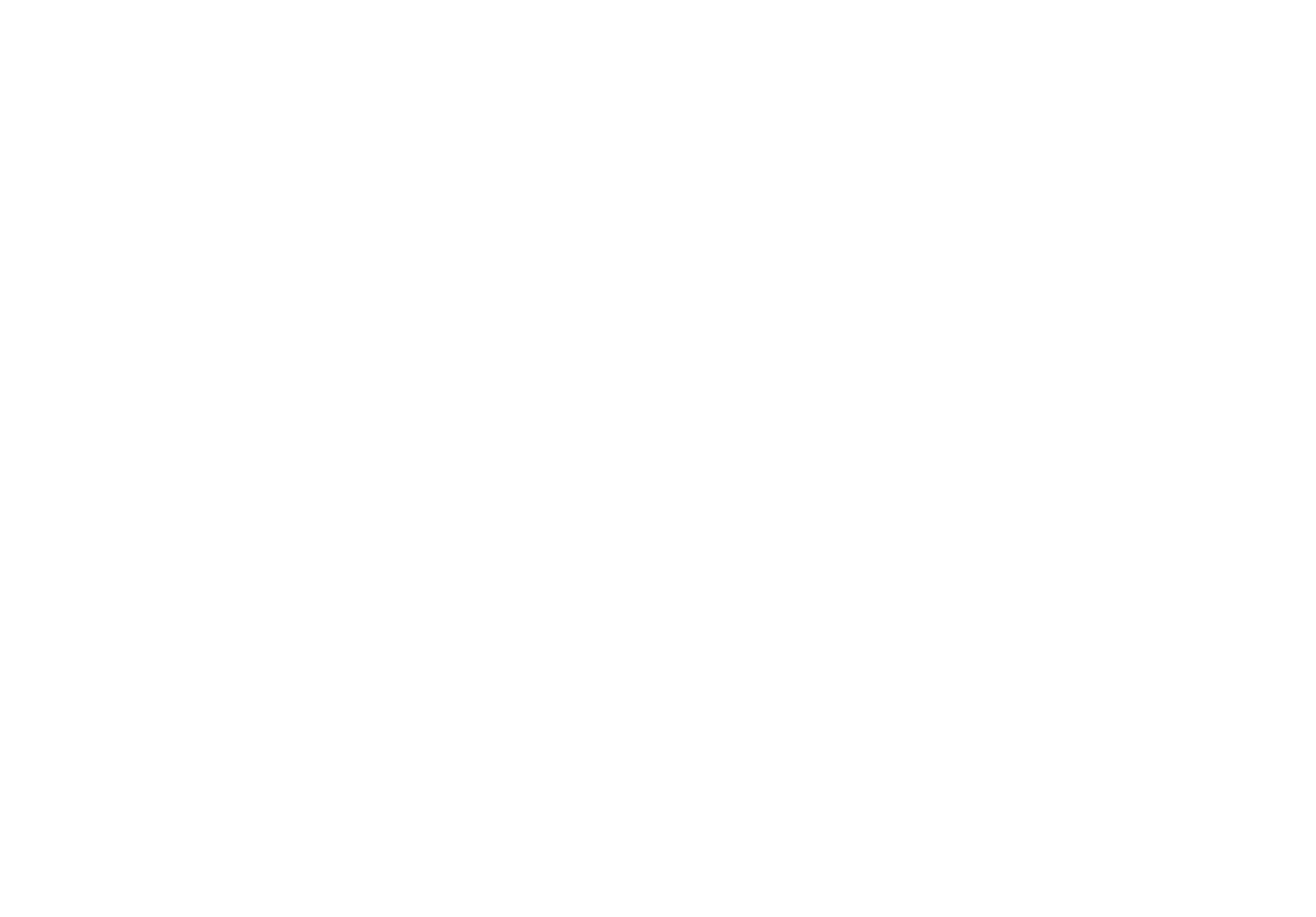
Trust MAAG for unmatched dependability and quality.
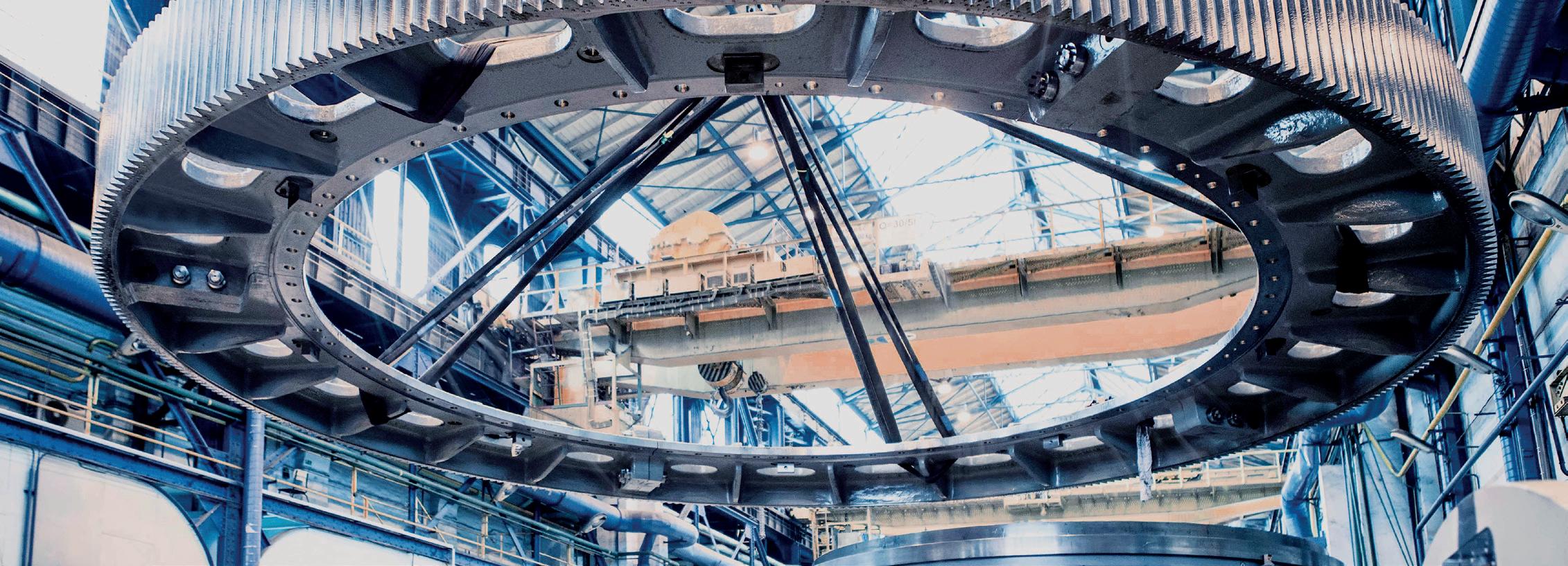
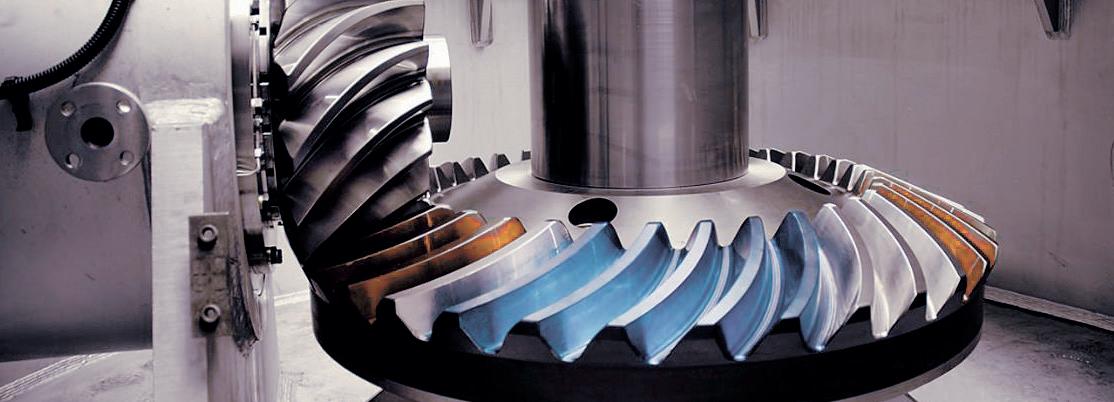
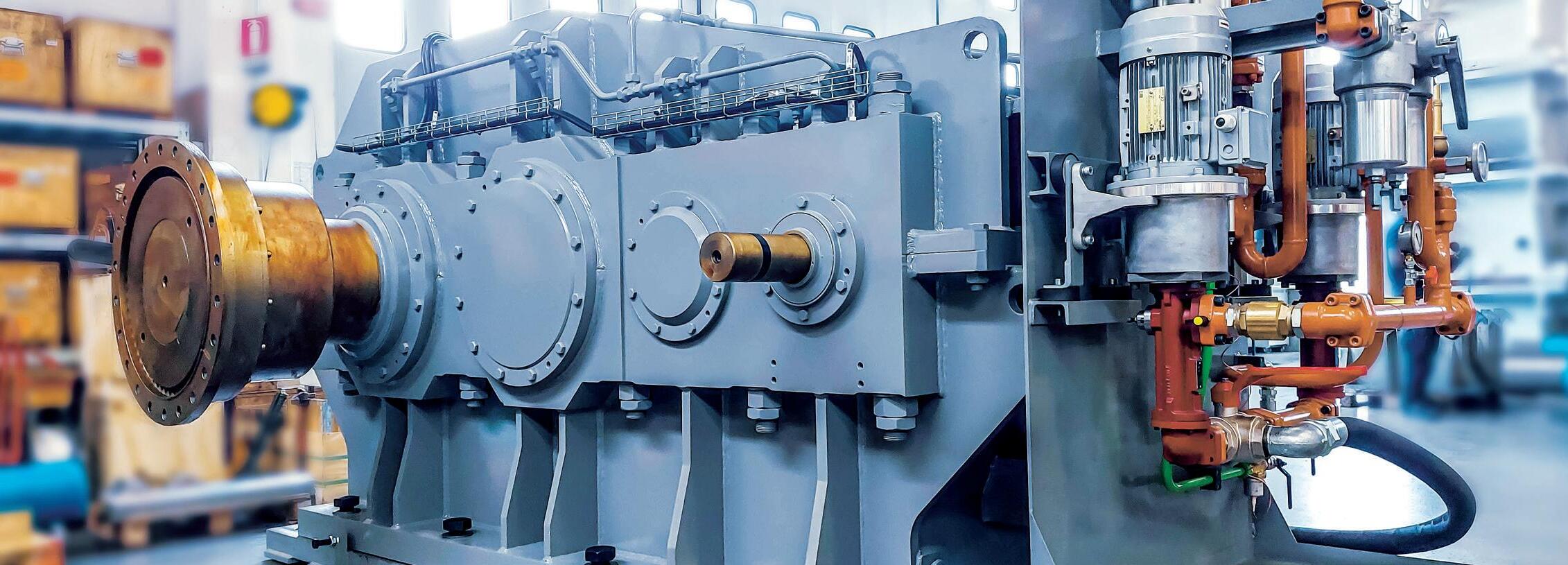
Don’t spend more on tailings than you have to.
Weir Minerals’ unmatched technology and expertise means you can find a solution that’s built to your operational and site requirements. We’ve reduced customer energy consumption by 51%, average water usage by 76% and lowered TCO all while safely improving the stability of tailings and reducing the tailings footprint. Plus, we can even help re-purpose waste into useful materials for dam wall construction and backfill that saves valuable resources and increases efficiency.
Now it’s your turn to re-think tailings with a Weir Minerals tailored solution. global.weir/rethink_tailings
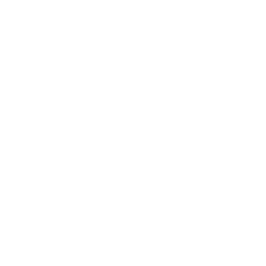
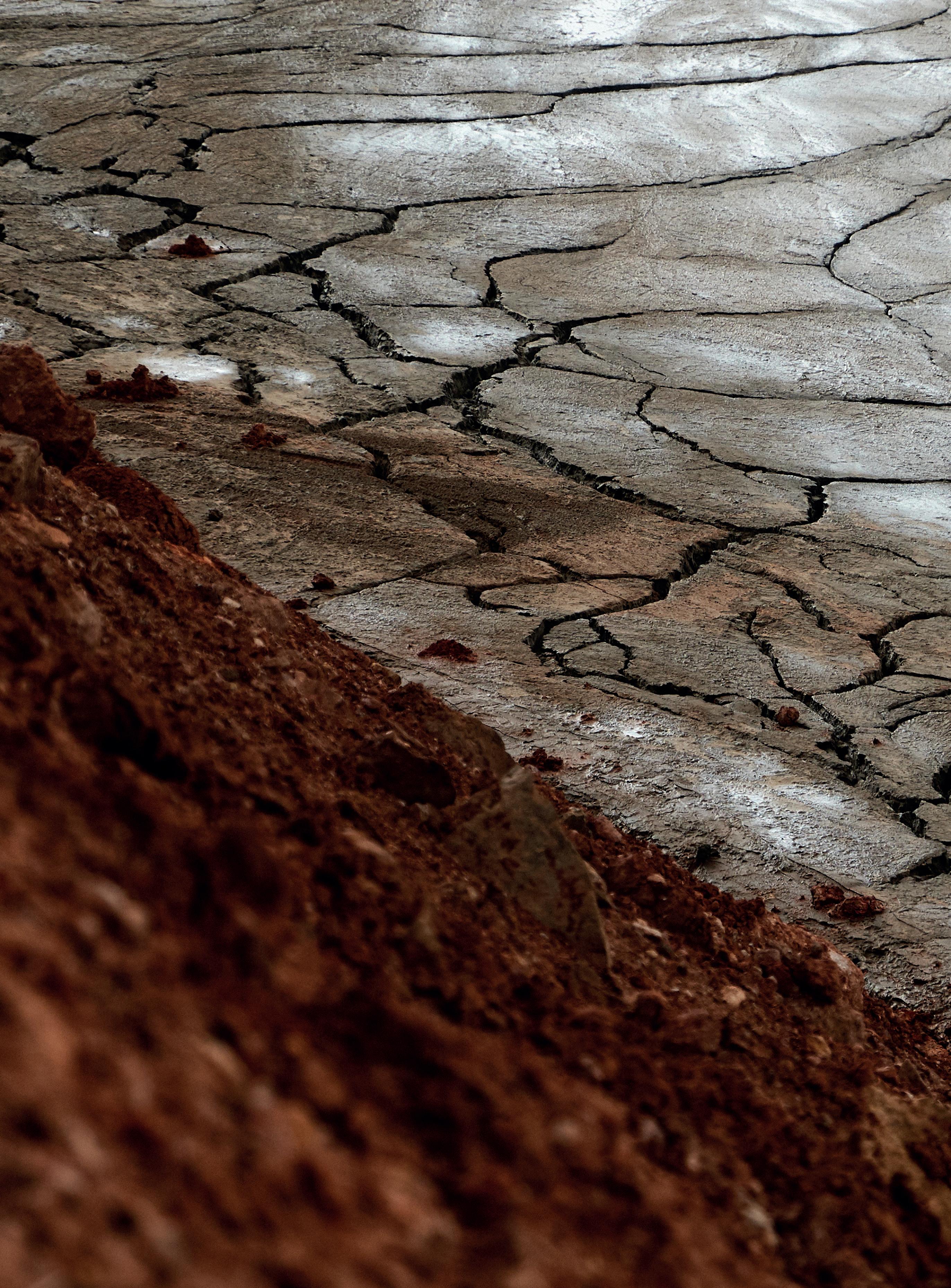