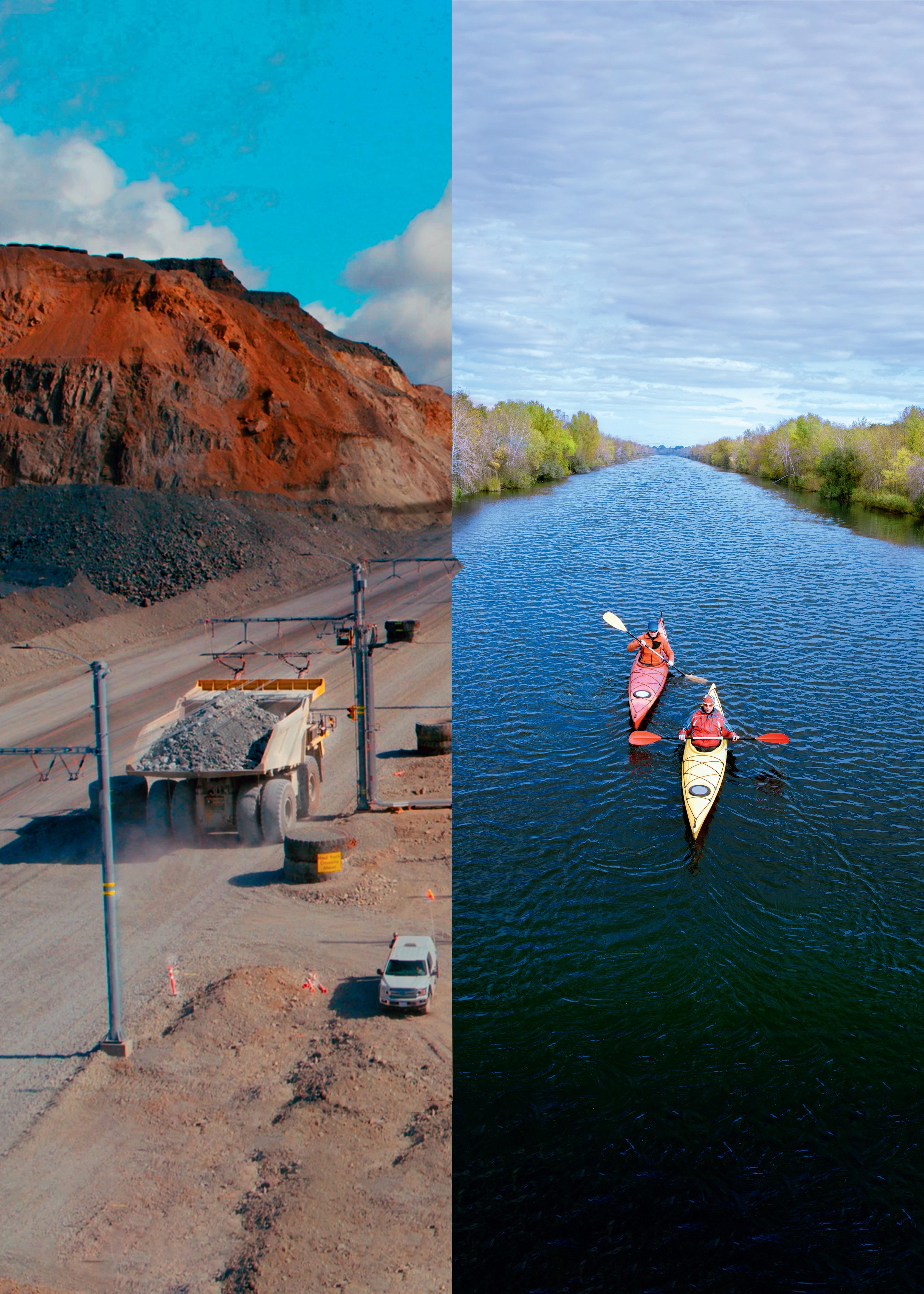
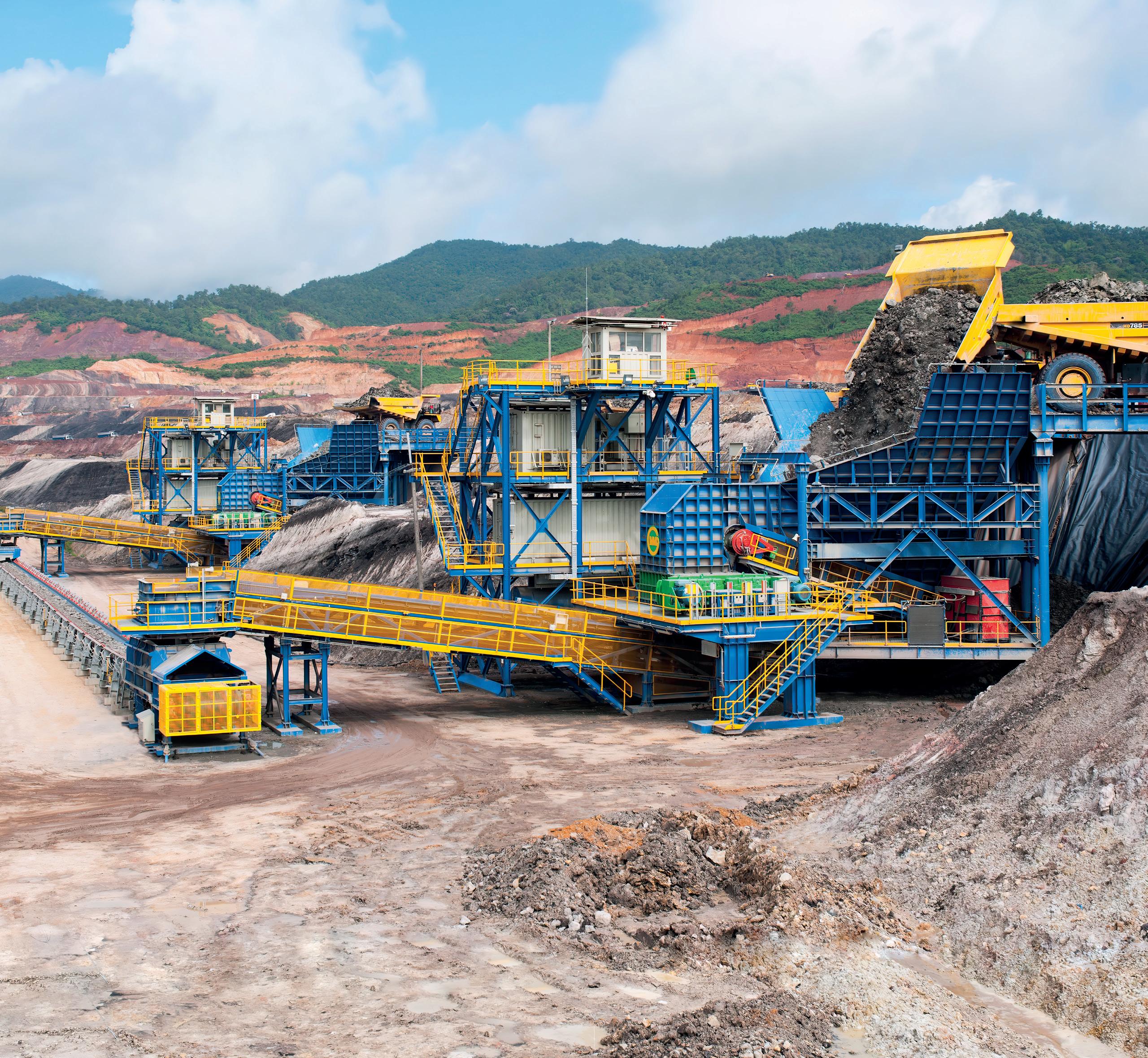
REDUCE COSTS AND IMPROVE PERFORMANCE WITH OUR
REDUCE COSTS AND IMPROVE PERFORMANCE WITH OUR
MMD remains at the forefront of In-Pit Sizing and Conveying (IPSC) technology, developing ground breaking sizing systems that optimize efficiency, improve safety, and delivers high productivity.
The Twin Shaft MINERAL SIZER™ sits at the heart of every IPSC system. To cater for today’s variety of modern mining methods, MMD has deployed successful modular Sizing stations and systems worldwide. High throughputs and short relocation times enable mines to achieve their efficiency and productivity goals.
MMD’s worldwide structure, technical expertise and service excellence will ensure your system always delivers optimum performance.
Discover our IPSC solutions +
03 Guest Comment
05 Industry News
08 Addressing The Battery Market’s Elephant In The Room
Priya Sreenivasan and Naphtal Haya, DNV, highlight the importance of clear regulations around transparency in the cobalt supply chain amidst the energy transition.
11 Supporting The Evolution Of Electrification
Mika Kinnunen, Normet, Finland, discusses why supporting new adopters of electrification and battery technology in the mining industry throughout the lifecycle is vital.
13 Mining’s Electric Revolution
Marc Melkonian, Aramine, France, considers the many benefits of adopting battery-powered vehicles for the mining industry’s future.
18 Technology At The Heart Of Real Progress
Max Luedtke, ABB, Switzerland, explains how connected engineering innovations such as truck electrification, gearless conveyor drives, and ventilation on demand are helping mine operators balance productivity with sustainability as they transition to the all-electric mines of the future.
22 Taking Control With Artificial Intelligence
Jürgen Kern, Mario Gerards, and Michael Panholzer, ANDRITZ, examine how adopting AI-based control systems in the filtration process can result in higher reliability and lower operating costs.
27 Innovation Unveiled
Daniel Greune, TAKRAF Group, Germany, provides an overview of the company’s recent projects and activities involving its crushing and material handling equipment.
31 Thinking Safety
Jerad Heitzler and Dan Marshall, Martin Engineering, USA, outline how implementing practical safety improvements around conveyor belts can prevent avoidable injuries and lower operating costs.
35 Conveyor Reliability On A Roll
Thibaut Leconte, SKF, Sweden, addresses how advanced bearing solutions are helping the mining sector improve the productivity and reliability of conveyor systems.
41 Smart Sorting
Stefan Jürgensen, TOMRA Mining, Germany, explores how artificial intelligence can help overcome the challenges of improving quality in sensor-based ore sorting.
45 Under Control
Michael Holmes, K+S Potash Canada; Duane Lunde, Spartan Controls; and Nolan Vollstedt, Emerson, describe the ways to identify and overcome challenges caused by incorrectly specified valves.
Whether on the road or underground, it’s imperative to adapt to all possible situations for vehicle safety and operational efficiency. The PDS4.0 kit for Heavy Duty Trucks was developed because of visibility constraints due to the size of vehicles and the inability to see personnel on the ground.
MANAGING EDITOR
James Little james.little@globalminingreview.com
SENIOR EDITOR
Callum O’Reilly callum.oreilly@globalminingreview.com
EDITOR
Will Owen will.owen@globalminingreview.com
EDITORIAL ASSISTANT
Jane Bentham jane.bentham@globalminingreview.com
SALES DIRECTOR
Rod Hardy rod.hardy@globalminingreview.com
SALES MANAGER
Ryan Freeman ryan.freeman@globalminingreview.com
PRODUCTION MANAGER
Kyla Waller kyla.waller@globalminingreview.com
ADMINISTRATION MANAGER
Laura White laura.white@globalminingreview.com
DIGITAL ADMINISTRATOR
Nicole Harman-Smith nicole.harman-smith@globalminingreview.com
DIGITAL CONTENT ASSISTANT
Kristian Ilasko kristian.ilasko@globalminingreview.com
DIGITAL EVENTS COORDINATOR
Merili Jurivete merili.jurivete@globalminingreview.com
EVENTS MANAGER
Louise Cameron louise.cameron@globalminingreview.com
The mining industry is poised for change, from skyrocketing demand and exploration, to a rapidly dwindling workforce and the proliferation of autonomous and AI-powered technologies. As the industry grapples with these existing challenges and opportunities, a new one is bubbling to the surface: electrification.
The need for electrification arises out of an interesting problem. Like every other industry, mining is looking to reduce emissions substantially. However, the mining industry is also looking to exponentially grow its output to enable – of all things – the energy transition. For example, global refined copper demand is expected to nearly double from 2021 to 2035.1 I believe electrification will play a key role in the future of mining – not alone, but in combination with autonomy. There are powerful synergies between these technologies that have the potential to make the industry safer, more productive, and more sustainable. In my conversations with mining companies, they understand the need for autonomy, but many are struggling to implement electrification. Now is the time to begin strategising; here is what the industry needs to know.
It is still very early for electric heavy vehicles, but the interest is there; the off-road electrification market is expected to hit US$2.23 billion by 2028.2 Several factors make electric vehicles appealing to mining companies.
n Reduced emissions: First and foremost, electrification will play a critical role in shrinking mining’s carbon footprint. Climate change is ranked a top concern for mining companies,3 and McKinsey estimates that fully renewable power sources could reduce a mine’s carbon footprint by 60 – 80%.4 This enables companies to meet ESG or carbon neutrality goals and, in some countries, avoid regulatory wrist slaps for excessive emissions.
n Lower costs: Electric vehicles are 40 – 60% less expensive to operate than internal combustion vehicles,5 and operators can save in other ways too. For example, ventilation systems for underground mines can comprise as much as 30 – 40% of operating costs,6 while electric vehicles can reduce or eliminate the need for them.
n Operational improvements: Electric vehicles operate more efficiently, with a 70 – 75% higher tank-to-wheel energy efficiency to reduce fuel consumption.7
Of course, this transition will not happen overnight. The size of these vehicles alone presents a significant challenge; it is easier to create a battery large enough to power an electric car than a 400 t electric haul truck. There are also steep upfront costs, partly because companies need to establish charging infrastructure. Retrofitting vehicles – which, on its own, is a way to upcycle assets – can address some of these challenges by leveraging existing vehicles to reduce upfront costs. At SafeAI, we have started experimenting with this solution, combining it with autonomy; our first vehicle was for a construction use case and our next will be for mining, with a 90 – 100 t haul truck.
The transition will take time, but we will see more electrification pilots – in many cases, combined with autonomy. These projects will answer critical questions and establish a blueprint for how the industry can establish more innovative, sustainable, and productive operations.
Available upon request.
Nothing should stand in the way of your productivity – least of all the materials you move. With our compact Hägglunds direct drive systems, you can adapt easily to the job at hand, taking advantage of full torque at an infinite range of speeds. And should an overload try to stop you, the drives’ low moment of inertia and quick response will keep your machines protected. We’ll support you too, with an agile global network and smart connectivity to bring you peace of mind. Driven to the core.
Hägglunds is a brand of Rexroth. www.hagglunds.com
Canada Nickel Company (CNC) has selected Stantec, a global leader in sustainable design and engineering, to provide professional environmental consulting services for the Crawford Nickel Project, located north of Timmins, Ontario.
This critical minerals project, expected to be one of the largest nickel sulfide operations in the world, will help deliver the nickel and cobalt required to power the energy transition by supplying the rapidly growing electric vehicle market.
Stantec will prepare an Impact Statement, class environmental assessments (Class EAs) and the supporting technical studies to assess project impacts, identify mitigation measures, and confirm follow-up programmes for the project.
CNC has proposed to construct, operate, and eventually decommission the opencast nickel-cobalt
mine, located in Ontario’s Timmins Nickel District. In addition to nickel, other metals such as cobalt, chromium, palladium, and platinum are expected to be recovered from concentrate streams. The project is expected to produce nearly 50 000 t of nickel annually and operate for over 40 years. Once in production, the mine is also anticipated to become one of Canada’s largest carbon-storage facilities through sequestration of carbon dioxide over the project life. Canada Nickel has developed ‘In-Process Tailings Carbonation’, which is expected to enable over 1 million t of carbon storage annually.
The project has entered the Impact Statement Phase, under the Canadian government’s Impact Assessment Act. This phase concludes with the submission of an Impact Statement, a document that identifies and assesses the potential impacts of a project and the measures proposed to mitigate those effects.
Eurasian Resources Group (ERG) has signed a Memorandum of Understanding (MOU) with Mechema Chemicals International Corp, a battery raw material producer headquartered in Taiwan, and Marubeni Corporation, a major integrated trading and investment business conglomerate headquartered in Japan.
The agreement will explore a potential transaction involving the supply and refining of cobalt hydroxide, and the sale, distribution, and marketing of cobalt sulfate.
Under the MOU, ERG, Mechema, and Marubeni will explore potential cooperation opportunities to develop an alternative cobalt supply chain for the Japanese market. Specifically, Mechema will conduct a feasibility study into the construction of a new cobalt refining plant, supplied by cobalt hydroxide produced by ERG, while Marubeni will study the ability to place produced cobalt sulfate in the Japanese market.
Under the auspices of the parties’ agreement, ERG desires to supply cobalt hydroxide from its
flagship operation, Metalkol, in the Democratic Republic of the Congo (DRC), to potential customers in the Japanese market. Cobalt produced at Metalkol is quality assured by the Clean Cobalt & Copper Framework, underwritten by independent auditors PwC. In October 2023, Metalkol achieved ISO 9001:2015 certification for copper cathode and cobalt hydroxide production – globally recognised as the most comprehensive quality management system (QMS).
Benedikt Sobotka, CEO of ERG and Co-Chair of the Global Battery Alliance, said: “The signing of this MOU underscores ERG’s role as a global cobalt player, and our willingness to have a strategic presence in all key battery materials supply chains. Japan is one of the leaders in the production of battery materials and clean energy technologies, and the supply of cobalt to its market by ERG will support the green energy transition and the global agenda to reach net zero by 2050. We look forward to working with Marubeni and Mechema on this new opportunity.”
CIM Connect Convention & Expo
12 – 15 May 2024
Vancouver, Canada www.cim.org/events
Discoveries Mining Conference
21 – 23 May 2024
Mazatlán, Mexico www.discoveriesconference.com
Euro Mine Expo
28 – 30 May 2024
Skellefteå, Sweden www.euromineexpo.com
Exponor Chile
03 – 06 June 2024
Antofagasta, Chile www.exponor.cl
Elko Mining Expo
06 – 07 June 2024
Elko, USA
www.exploreelko.com/top-events/ elko-mining-expo
Tailings 2024
12 – 14 June 2024
Santiago, Chile www.gecamin.com/tailings
Hillhead 2024
25 – 27 June 2024
Buxton, UK www.hillhead.com
International Fairs EXPO KATOWICE
04 – 06 September 2024
Katowice, Poland www.expo-katowice.com
MINExpo INTERNATIONAL®
24 – 26 September 2024
Las Vegas, USA www.minexpo.com
To stay informed about upcoming industry events, visit Global Mining Review’s events page: www.globalminingreview.com/events
CSI Mining Services (CSI) has been awarded a crushing contract for Atlas Iron’s McPhee Creek project in the Pilbara, Australia.
The five-year contract is for the supply and operation of a 10 million tpy primary crushing plant, fed by Atlas Iron via dump trucks or front-end loaders, with product to be stockpiled for reclaim and haulage by Atlas Iron.
Chief Executive Mining Services, Mike Grey, said the contract adds to the strong pipeline of upcoming work for CSI.
“It’s fantastic to strengthen our partnership with Atlas Iron, with CSI also currently providing crushing services for their Sanjiv Ridge mining operations and crushing and haulage operations for Roy Hill,” Grey commented.
“This is an exciting period of growth for our business, with CSI recently awarded three new crushing contracts. The variety of projects we support ensures our people have opportunities to work on different mine sites with diverse clients, gaining experience across a range of crushing plants.”
The McPhee Creek iron ore mine site is located in the northeast Pilbara region, 30 km north of Nullagine.
CSI is scheduled to mobilise to site in late 2024 to commence construction activities ahead of crushing commencing in 2Q25.
Intramotev, the technology company building autonomous zero-emissions rail solutions, has announced that it has successfully deployed the world’s first self-propelled battery-electric railcar in a traditional freight train.
In a major step forward for sustainable freight transportation, Intramotev has deployed its railcar retrofit, known as the ReVolt, at Iron Senergy’s Cumberland Mine in Waynesburg, Pennsylvania. The car has run for over 1000 miles between the Cumberland Mine and its Alicia Harbor facility.
“We’re excited to deliver the fuel savings and environmental benefits of the ReVolt to our customer Iron Senergy,” said Tim Luchini, Intramotev’s CEO, “Today’s news marks an important milestone in our work to decarbonise mining and freight transportation, and we’re just getting started.”
Iron Senergy CEO and owner, Justin Thompson, added, “We’re thrilled to have partnered with Intramotev to deploy their forward-thinking technology. We’re always searching for ways to double down on our commitment to innovation and sustainability, and this partnership helps accomplish that in a big way.”
the world’s most compact and safe lhd
Pioneer in designing and manufacturing innovative machines for underground mining, Aramine unveils its new L440B machine, the only battery-powered LHD in its class. Its loading power of 13T offers maximum productivity, while guaranteeing comfort, reliability and safety.
Priya Sreenivasan and Naphtal Haya, DNV, highlight the importance of clear regulations around transparency in the cobalt supply chain amidst the energy transition.
As it stands, the market for battery energy and storage systems (BESS) is valued at around US$5 billion; a not insignificant amount, but a drop in the ocean considering what is to come. The pressure to decarbonise power networks means that market value will grow many times over in the coming years and, according to research from McKinsey, could hit US$150 billion before the end of the decade.1 Driving this rapid expansion are major policy plays designed to boost the deployment of renewable energy projects, such as the US Government’s Inflation Reduction Act.
If intermittent renewable energy sources are to be successfully deployed and integrated, without risking the reliability of supply that is now expected, then power grids will need to adopt BESS technology en masse. To put it in context, the International Energy Agency (IEA) expects that 10 000 GWh of BESS technology will be required worldwide by 2040 – roughly 50 times the size of the current market. However, there is a big risk for utilities that are building out large-scale energy storage projects and for the financiers directly investing in such initiatives, a risk that is often swept under the carpet. The mining of cobalt, the main element in lithium-ion batteries, is shrouded in controversy and the BESS supply chain remains murky. Even a perceived link to environmental damage or workforce exploitation is enough to erode social licence to operate, a project’s value, and shareholder confidence.
In early November 2023, the Congressional-Executive Commission on China (CECC), a US bipartisan congressional committee, held a hearing on the dominance of Chinese
companies in the cobalt supply chain. The hearing is the most recent of the discourse on cobalt supply chains in recent years, which is dominated by two key facts and one claim.
n Fact 1: The Democratic Republic of the Congo (DRC) produces around 70% of the global cobalt supply and possesses the world’s highest-grade cobalt (as high as 20%).
n Fact 2: Cobalt extraction in the DRC promotes abhorrent practices such as child labour, sub-human working conditions, unfair wages, and environmental pollution that bear maiming, birth defects, and deaths. Additionally, the mining sites have documented instances of sexual violence and little to no safety for the population engaged in or living around the sites.
n Claim: The cobalt supply chain is too complex to render itself to full traceability. Traceability is the ability to track a mineral from cradle to grave or cradle to cradle (in the case of recycling).
In short, this means that almost every cobalt mining and refining company, cobalt commodity trader, battery manufacturer, and consumer electronics manufacturer is enabling, promoting, or contributing to the irresponsible sourcing of cobalt in the DRC. This shadowy and complex supply chain, combined with increased consumer demand, offers a convenient shield to abdicate accountability and hide complicity.
The problems rampant in the supply chain have long been recognised as a pressing issue, but they are far from
being resolved. This is why the Organisation for Economic Co-operation and Development (OECD) established its ‘Due Diligence Guidance for Responsible Supply Chains of Minerals from Conflict-Affected and High-Risk Areas’. 2
The OECD guidelines operate on a five-point structure:
1. Establish a strong company management structure that includes a company policy for minerals coming from conflict regions, which is communicated to suppliers and other stakeholders.
2. Risk assessment.
3. Design a strategy in response to the risks identified and chart out an implementation plan.
4. Have a third party audit the supply chain due diligence system.
5. Publicly report on it.
Similarly, the Responsible Minerals Initiative (RMI) has developed assurance processes focused on supply chain ‘pinch points’, such as tools for validating midstream smelters’ compliance with OECD guidelines.
As the importance of cobalt in the global economy grows, the requirement for companies to demonstrate supply chain due diligence is progressing into a regulatory requirement. More than a decade ago, the US Securities and Exchange Commission (SEC) adopted a new disclosure form as part of the Dodd Frank Wall Street Reform and Consumer Protection Act, requiring companies to disclose their use of ‘conflict minerals’, though currently this just applies to the ‘3TGs’ – tin, tantalum, tungsten, and gold.
The disclosure requires US-listed companies to determine and report on their mineral supply chain, as well as to disclose the due diligence systems they have in place to help determine the source of the minerals in question. Today, this means information on the location of smelters, and whether those smelters conform to RMI standards, is publicly available. Notably, cobalt is not on this list of critical minerals.
Similarly, the European Union’s regulation for conflict minerals only addresses the 3TGs and does not obligate companies to report their due diligence systems in place for cobalt. Excluding cobalt from these regulations massively contributes to the murkiness of the supply chain and the risk factors facing the industry.
While it is already a crucial component of the modern electric grid, the importance of BESS is only going to grow as the energy transition progresses. As society’s reliance on renewable sources, such as solar and wind, increases, providing a solution to intermittency will be the foundation on which future energy systems are built.
DNV’s North America Energy Transition Outlook 2023 estimates that the deployment of lithium-ion BESS in both solar plus storage and standalone storage configurations will soar leading up to 2050. Long duration energy storage capacity is also expected to experience massive growth.
The companies that make BESS (by designing and assembling key components – such as batteries, thermal management system, and controls) are called integrators. This market is dominated by just five companies: Sungrow, Fluence, Tesla, Huawei, and BYD. The battery cell manufacturing market, which directly sources the minerals required, is also largely dominated by a handful of companies, namely CATL, BYD, LG Energy Solutions, Panasonic, and SK On.
These companies are not uniform in their adherence to OECD guidelines, use of due diligence systems, or disclosure on supplier certification. What they do have in common is that none of them provide detailed disclosure on their cobalt supply chain. A lack of stringent regulations around transparency has led to inconsistent levels of disclosure about efforts to manage environmental and human rights risks in their cobalt supply chain.
It is the same story further up the battery manufacturing chain, where the patchwork method of disclosure highlights the inconsistency in transparency, which further exacerbates the problems, especially human rights violations on the ground at the mines.
As the demand for EVs and utility-scale BESS reliant on lithium-ion batteries grows, there will naturally be more capital investment and M&A activity in the market. With this growth will come more scrutiny and an increased likelihood of companies getting caught up in the human rights violations that are rampant in mines across much of the DRC.
Already, not-for-profit organisations are increasing their support for survivors of human rights and environmental violations associated with cobalt extraction. Public awareness campaigns and legal efforts are being deployed by the groups to hold companies, as well as corporate directors and senior management, to account.
History offers up a good example of what can be lost when a company fails to meet the standards of the consumer. In the 1990s, the reputation of a leading sportswear company was damaged almost beyond repair after reports emerged that its global supply chain included the use of child labour. It led to a huge decline in sales and an erosion of shareholder value – in a world where people are arguably now more conscious of such issues, it is a stark warning of what is at stake.
For companies to thrive from the battery storage boom, they will need to go above and beyond to show that cobalt sourced in the DRC does not come with a tragic environmental or human cost attached to it.
1. ‘Enabling renewable energy with battery energy storage systems’ McKinsey, (2 August 2023), www.mckinsey.com/industries/ automotive-and-assembly/our-insights/enabling-renewableenergy-with-battery-energy-storage-systems
2. ‘OECD Due Diligence Guidance for Responsible Supply Chains of Minerals from Conflict-Affected and High-Risk Areas’, OECD Publishing, (2016), p. 50.
Mika Kinnunen, Normet, Finland, discusses why supporting new adopters of electrification and battery technology in the mining industry throughout the lifecycle is vital.
Electrification and the adoption of battery technology in mining is a huge topic, cutting through all kinds of processes and applications. This technology transformation is not only an engineering challenge. Support for adopters is needed throughout the lifecycle, from planning to end of life, while stringent yet flexible concepts and plans need to be in place, even if the needs they address will only present themselves years in the future. Taking advantage of the breadth of experience offered by Normet and other OEMs makes the implementation of this lifecycle support process easier than one might think.
In terms of the electrification of mining spaces, there are multiple phases in the transformation and adoption story. The first step has been to answer basic questions about electrification and battery power – is it reliable, is it safe, and is it productive? Overall, the adoption of electrification and battery power in mining has become more accepted as similar pathways have been pursued in other well-known industries, such as the automobile industry. For companies, this might mean that they become less hesitant in pursuing the technology, even if they do not yet have dedicated personnel in this field. In mining also, to an extent, these issues have been resolved, and early adopters of the technology are generally in a position to answer the questions listed earlier in the affirmative.
From Normet’s point of view, it is essential to support every step of the transformation cycle. Mining operators need to perform comprehensive assessments and benefit from planning support at the infrastructure level that helps ensure productive strategies. Then, when the technology is known to be safe and efficient, and is suitable for a given project, there is the need for more detailed calculations concerning payback times and returns on investment. In the business environment in which mining operates, investment cycles tend to run over longer periods. Because new technology also takes time to research and develop, how these criteria can be met is only evident now, after electrification projects have already been implemented successfully in mines.
Finally, when the decision has been made to invest in electrification, then practical operations and their management must be implemented. Aspects such as safe operation, safety procedures, and maintenance are large topics in their own right. As more companies take these steps, the overall process becomes easier and mass adoption more likely.
From a customer’s point of view, the importance of securing quality of services can be even more crucial. OEMs face challenges to ensure that there is support available globally in an environment of fast-scaling mining technology. One of the most valuable things that can be done is to share information about best practices worldwide and coordinate that information for use in other projects. Everyone faces the same needs, and so it is a win-win situation. The mining industry’s global footprint makes this both a challenge and an opportunity.
For example, there are clearly global differences in the ability of certain mining sites to introduce electrification based on external factors such as available energy infrastructure and supply. Even if a site would like to electrify, the possibility might not be there immediately. Regional or country-specific regulations and standards also exert an influence on the potential for electrification. In many cases, governments want to accelerate their uptake to help meet sustainability and environmental goals. For mining companies that operate in more than one country, this often means that they learn good practice in one continent, adopt those learnings internally, and can then export them to other regions as a form of knowledge-sharing. OEMs with a global footprint can learn lessons the same way, cross-referencing knowledge from different locations and solutions.
Moreover, the creation of systematic training curriculums, to ensure personnel have the right knowledge in place for every service task, is vital. It should be remembered that it is not a simple thing to switch to a completely new kind of technology and be able to provide effective technical support and maintenance, even for experienced engineers and mechanics, and nor does it happen overnight. There is no well-populated pool of experts available at any time. Instead, educational paths and training programmes should be scaled up to improve customer capabilities, and the aforementioned global exchange utilised to accelerate regional learning.
Further, as an OEM, Normet is particularly concerned with the lifecycle management capabilities that are available for end-users. Building new partner ecosystems for different areas to ensure these capabilities and related service offerings is one aspect of this. End-of-life and recycling challenges, for example, are topics that are becoming ever more relevant since electrification and battery power have existed in the mining sector. Making it possible to recycle and utilise old mining batteries in other applications requires a lot of collaboration, new business models, and forward-thinking ecosystems, especially considering global differences and challenges.
Essentially, the mining electrification ecosystem is still developing. The technology has found itself, as examples from many companies attest. The mining environment has proven to be a frontrunner in the adoption of electrification technology, which means that companies in the industry can also be the ones who really push for wider use. Ensuring that the collaboration needed to further develop electrification can flourish has required the construction of a completely new ecosystem. This evolution is not something that will happen automatically, but it needs to be envisioned.
Electrification also lends itself very well to the use of other new technologies, such as connectivity enabled analytics and remote monitoring tools, to ensure optimal machine performance and safety. Keeping equipment connected and data flowing from the operations and analysing the data that comes in is extremely helpful. As a new technology without decades of accumulated experience behind it, using data and analytics to understand what is normal and predict the abnormal helps ensure everything is running safely and as it should be.
This knowledge from data and analytics can be used to encourage new adopters as well. The availability and utilisation of data accelerate the learning process on both sides. For Normet, having multiple physical environments using the same technology informs and enables the implementation of virtual environments for research and development. Real-life learning supports and justifies further adoption, especially when it can be aided by realistic and effective training, as mentioned earlier. Providing support for mining in any environmental and geological conditions likewise reduces limitations on introducing electrification in certain locations.
The need to expand electrification in the mining industry, and the benefits of doing so, are clear. On one hand, the technology will continue to develop, improving the functionality of electrified mining systems thanks to cooperation and collaboration between companies and other organisations. On the other, as usage increases, successful use cases and data collection provide powerful arguments for the technology’s adoption. However, this evolution and acceptance is not enough. Ultimately, the customer’s electrification journey must be supported by Normet and other OEMs throughout the rather long lifecycles of their mining projects, from commissioning and planning to installation and training.
Marc Melkonian, Aramine, France, considers the many benefits of adopting battery-powered vehicles for the mining industry’s future.
Anumber of trends have shaken up the mining sector in recent years, with the dilemma of how to maintain or even increase productivity while adapting to stringent environmental requirements. As mining companies look for ways to limit their environmental impact, it is necessary to look at one of the main sources of CO2 emissions: the use of diesel to power machinery engines.
For a long time, underground mines were able to operate solely on diesel vehicles, a reliable energy that provided unrivalled autonomy. Over the last few years, however, environmental and worker health concerns, among other factors, have changed the situation. Is it possible to use another form of energy to power the machines?
The use of diesel requires constant attention to air quality for workers, a particularly difficult challenge in a confined environment such as underground mines. Several exhaust air filtration solutions have been developed, including catalytic converters, particle filters, fuel thinners, and more. They have improved working conditions, but have also increased maintenance requirements and machine costs.
It is in narrow vein mines, which use smaller than average machines, that technological innovations have made it possible to offer unprecedented machines. The first step was taken some 30 years ago with the introduction of the first electric machines with a cable reel.
All that is needed is connecting the machine to the power grid to run it continuously, and thus maintain high productivity without any pollution. However, this cable, which is sometimes hundreds of metres long and permanently in the space between the machine and the electrical socket, is not the most practical to handle. Not to mention that it is occasionally immersed in water, which can be dangerous as these machines need a lot of electrical power to operate. However, the savings in ventilation costs and the reduction in exhaust gases in the galleries justify these limits.
How do you offer an alternative to diesel, while making the machine autonomous by removing the cable that connects it to the electricity grid? 10 years ago, the market opened up to a new innovation: battery-powered electric mining machines.
French manufacturer Aramine launched its L140B mini loader, based on a simple principle: the rear of the machine can be detached, thanks to an innovative system, and houses the battery packs, the battery charger, and the necessary electronics. This assembly, called the ‘battery energy module’, can be replaced in less than five minutes using a hoist, and then charged outside the machine.
Mining operators are looking favourably on the arrival of these innovative products on the market, as they present numerous advantages. In particular, they offer mine workers more comfortable working conditions: the machines are less noisy, they lower ambient temperature by 80% by removing the engine and hydrostatic transmission, and they avoid CO2 emissions, thus reducing ventilation costs. Above all, they provide unlimited autonomy, as the machine can run on a second battery while the first is recharging.
Although the initial costs of battery-powered mining vehicles may be higher than those of diesel machines, the long-term operational savings offer a compelling argument. Electric motors generally require less maintenance than their diesel counterparts, reducing downtime and increasing equipment availability.
Additionally, the cost of purchasing fuel, a major expense in mining operations, is eliminated. Mines can thus make substantial savings on their operating budgets, helping to offset the higher initial costs of electric equipment.
The development of the technology has had to go hand in hand with a change in mentality, as concerns have been expressed about the reliability of these new machines. Today, each machine manufacturer has developed its own battery-powered machine with its own technology.
Some have opted for fast recharging. However, this technology requires the installation of a large cooling system and a powerful electrical network to recharge the battery, which implies high costs and maintenance. Others have chosen to offer a battery replacement system with a powerful external charger. However, this solution requires dedicated recharging points. Aramine has opted for an on-board charger, with the rear of the machine completely detachable, allowing the battery to be recharged close to any electrical outlet.
Now, 10 years after the first battery-powered machines were introduced, reliability has been proven, and mining companies are making increasing use of these tried and tested technologies.
However, the transition to battery-powered vehicles is not without its challenges. Mines are often located in difficult environments, characterised by extreme temperatures, dusty conditions, and rugged terrain. These conditions can put pressure on battery performance. Low temperatures can reduce battery efficiency, affecting vehicle range and power. Engineers therefore need to design battery systems capable of operating reliably in hostile environments, ensuring their resistance to temperature variations and mechanical stress.
Initially proposed for small vehicles, rather than for narrow vein mines, battery-powered machine technology is now being developed for larger and larger machines, thanks to batteries that are increasingly powerful while remaining compact. In 2015, for example, Aramine launched its first electric mini loader, the L140B, with a tractive effort of 3.5 t.
—
Real Progress is leading the mining industry through the energy transition.
Our holistic framework eMine™ is empowering the conversion of fossil fuel mines to all-electric. Combined with energy efficient technologies for deep vertical ore haulage and grinding, we are optimizing the use of power while reducing greennhouse gas emissions in real time. solutions.abb/realprogress
Be part of Real Progress.
In 2024, the manufacturer is due to launch its L440B loader, this time with a tractive effort of 13 t.
Mining operators, seeing the efficiency and many advantages of battery-powered machines, are tempted to gradually renew their entire range of machines, including the largest trucks. At the moment, however, manufacturers are obliged to wait for the emergence of more efficient batteries before introducing battery-powered trucks.
Batteries, despite their compact size, can be heavy, which can affect the payload capacity of mining vehicles. Mines often operate vehicles with high load capacities, and the additional weight of batteries can limit this capacity. Designers need to strike a balance between payload
capacity and battery size to ensure optimum operational efficiency.
Battery autonomy must be significant to ensure mine productivity, and it is currently insufficient for these types of large, powerful vehicles that operate over long distances. For larger machines, it is important to ask the question of profitability, i.e. cost versus productivity.
In this case, as with private cars, it is tempting to opt for something in between: a hybrid solution, such as a truck using both batteries and a diesel engine. Unfortunately, the use of these two energy sources means that it is not possible to build a vehicle that is both powerful and compact enough to meet the requirements of mining companies.
Another solution would be to use both a trolley for long distances and a battery-powered machine for short distances, but this would require an expensive fixed installation.
Although the mining industry is embracing the transition to battery-powered vehicles, it is important to note that this evolution is generally taking place gradually. Mines are opting for a hybrid approach, integrating battery-electric vehicles into their existing fleets while retaining some diesel equipment. This strategy enables a smooth transition, minimising risks and disruption to operations.
The adoption of battery-powered vehicles in the mining industry also has positive social implications. Reducing its carbon footprint helps to improve the image of the mining industry, often criticised for its negative environmental impacts. This can strengthen relations with local communities and stakeholders, fostering wider acceptance of mining activity.
In addition, the transition to cleaner technologies is creating new employment opportunities in the renewable energy and battery technology sectors. Workers in the mining sector can benefit from training programmes to acquire the skills needed to maintain and operate the new equipment.
For now, therefore, diesel-powered machines are still essential for certain activities, particularly the most energy-intensive operations, such as moving machinery over long distances. As they wait for high-performance batteries suitable for large trucks, manufacturers are innovating with diesel engines that pollute much less than their predecessors.
By embracing this electric revolution, the mining industry can not only improve its own profitability, but also make a significant contribution to the global transition to a more sustainable economy. Battery-powered vehicles are reshaping the face of the mining industry, offering a promising glimpse into a future where natural resources are extracted in a more environmentally-friendly way. The future of the mining industry looks set to be innovative and increasingly carbon-free.
Global coverage on technology and market trends in the mining and minerals processing industries
Subscribe online at: www.globalminingreview.com/subscribe
Global coverage on technology and market trends in the mining and minerals processing industries
Global coverage on technology and market trends in the mining and minerals processing industries
15 South Street, Farnham, Surrey, GU9 7QU, UK
T: +44 (0)1252 718999 F: +44 (0)1252 821115
Subscribe online at: www.globalminingreview.com/subscribe
Subscribe online at: www.globalminingreview.com/subscribe
E: info@palladian-publications.com
15 South Street, Farnham, Surrey, GU9 7QU, UK
T: +44 (0)1252 718999 F: +44 (0)1252 821115
15 South Street, Farnham, Surrey, GU9 7QU, UK
E: info@palladian-publications.com
T: +44 (0)1252 718999 F: +44 (0)1252 821115
E: info@palladian-publications.com
Max Luedtke, ABB, Switzerland, explains how connected engineering innovations such as truck electrification, gearless conveyor drives, and ventilation on demand are helping mine operators balance productivity with sustainability as they transition to the all-electric mines of the future.
Can mine operators optimise both productivity and sustainability? This is the question on everyone’s lips in the industry right now. The answer lies in automation, electrification, and digital technologies that drive production efficiencies, while simultaneously reducing energy consumption and emissions.
In one way or another, the whole world is a mining customer. The industry not only provides the metals and minerals that help build and power 21st century society –everything from smartphones to houses and hospitals – but also vital commodities for electric vehicle (EV) batteries, wind turbines, and solar photovoltaic (PV) panels, without which the clean energy transition cannot take place.
Manufacturing a single EV, for example, requires five times more copper than a combustion-engine model (plus the infrastructure to power them needs much more copper and other critical minerals), while an onshore wind plant consumes nine times more mineral resources than a gas-fired facility.1
Moreover, as intermittent sources of energy such as solar PV and wind continue to grow their share in the overall energy mix, so the need to supply mines with continuous clean electricity using innovations like power microgrids and battery energy storage systems (BESS) becomes ever more important.
As a provider of digital solutions to the mining sector, ABB is committed to providing solutions to these challenges, empowering its customers as they convert from fossil fuel mines to all-electric.
The ABB eMine™ portfolio – part of the company’s Real Progress initiative aimed at embedding sustainable practices in every process – comprises fully integrated automation and electrification systems, from mine to port, in addition to its established range of motor, drive, generator, and power control technologies. By engaging with stakeholders early in the mine project life cycle, ABB is able to deploy these technologies to optimise all mine processes and equipment, reducing power use and greenhouse gas (GHG) emissions in real time.
eMine includes FastCharge, a fully automated charging system for trucks. Ramping up the speed and efficiency of the power supply keeps fleet downtime during charging to a minimum. FastCharge is vendor-agnostic, ensuring that current and future electrification technologies are compatible with existing OEM equipment.
eMine is built around five pillars, beginning with a broad portfolio of technologies designed specifically for the mining industry, delivered by a partner with deep domain expertise. The second pillar is about working together with mining companies, original equipment manufacturers (OEMs), retrofitters, mine designers, and the EPC/EPCM communities to co-create to meet customer demands that have been understood through meaningful conversations. Thirdly comes mine design, increasingly important because modern projects are energy-intensive and require 24/7-365 access to
a constant, reliable supply of renewable electricity – directly from the grid or on site. This benefits from partners and technologists working together as early as possible.
Moving forward in the development phase, innovative and bespoke monitoring and control solutions for both underground and opencast operations are key to ensure that power is integrated with power management and storage systems. Lastly, the pillar of lifecycle services for equipment over the long term is also important to maximise availability and confirm that all processes address environmental challenges, from installation to decommissioning.
Mining is responsible for a significant proportion of global GHG emissions, much of them from diesel haul trucks operating in opencast mines. Replacing fossil-fuel fleets with battery electric vehicles constitutes a step change as OEMs continue to work to solve the mass electrification of heavy vehicles.
In the meantime, ABB has solutions for this transition. For example, Swedish miner Boliden and Canada’s Copper Mountain Mine have implemented ABB’s eMine trolley-assist system, which can decrease the diesel usage on trucks by up to 90%, or even higher. At Copper Mountain Mine specifically, ABB’s eMine Trolley System has delivered a significant reduction in truck carbon emissions,
plus trucks that run twice as fast. This is a win-win for the mine, the surrounding environment, and the planet.
At Boliden’s Aitik copper mine, the flagship ABB Ability™ System 800xA distributed control system (DCS) acts as an operational technology (OT) platform connecting multiple aspects of the operation. By expanding System 800xA from the processing plant to the mine itself – and integrating both into a single platform – ABB can connect haul truck trolley systems to the same automated platform that runs the enterprise, so it can handle all of the on-site power generation, including renewables integration and off-grid storage.
The greenest energy of all is the energy that is not used. In large underground mines, air is pumped 24/7, accounting for around 50% of energy use across the enterprise. Using ABB’s VoD technology, the system becomes intelligent, improving air quality and saving up to 50% a year in energy costs.
It does this by automating and optimising ventilation so that air of the right quality and quantity is provided wherever people and machines are working. The smart tracking-and-tagging system, in combination with environmental and flow sensors, geolocates vehicles and workers underground.
ABB’s VoD solution, ABB Ability Ventilation Optimizer, uses this data – plus gas, flow, and temperature information – to operate the fans according to demands calculated from production schedules, as well as equipment status and location. The ability to dynamically adjust mine ventilation can reduce system energy use by 40 – 50% a year, which equates to as much as US$2 – 3 million in savings.
For example, since ABB Ventilation Optimizer was commissioned at Boliden’s Kankberg gold mine in 2015, the operator has seen ventilation energy savings of 54%. Air is also heated for the 500 m deep mine, resulting in savings of 21% in heating energy costs, too. Investing in VoD pays off very quickly.
Another way mines achieve Real Progress in energy efficiency and a longer life for equipment is by investing in gearless conveyor drives (GCDs) for the aforementioned energy-intensive 24/7 systems. The conveyor system is one of the major workhorses in a modern mine, often covering distances of several kilometres up steep gradients as it transports material to the surface or to the site crusher.
The gearbox is an integral part of the drive system; GCDs are increasingly selected for mining projects –particularly those that require high drive power – helping to boost the efficiency of high-capacity belt systems, while reducing energy usage, downtime, and maintenance.
GCDs are powered by permanent magnet motors rather than gearboxes, meaning they repay the initial CAPEX through their energy efficiency, lower maintenance costs and reduced downtime.
ABB has put GCDs to the test in extreme conditions at the Chuquicamata copper mine, 2850 m above sea level in the high desert of the Antofagasta region in Chile. In late 2020, ABB and TAKRAF collaborated to commission what is reputed to be the world’s most powerful belt-conveyor system. At almost 13 km long and operating across a 1200 m altitude difference, the GCD solution is replacing the equivalent of 120 large haul diesel trucks, and therefore 130 million l of gasoline consumption per year.
Conveyor systems are responsible for almost 80% of the energy consumption in mines, equating to many tonnes of CO2 emissions over the project lifetime. At Chuquicamata, emissions are reduced by 70% compared with diesel truck engines for the same copper production volume. The conveyor has also extended the mine life by 40 years, through allowing it to shift its operational focus underground.
As global demand for copper intensifies to drive more electrification, the deployment of GCDs at the Chuquicamata project constitutes Real Progress, not just around sustainability and decarbonisation, but also extending the life of critical mine assets, operational efficiency, and, ultimately, profitability.
The mining industry is under increasing pressure to improve its green credentials, being responsible for up to 7% of global GHG emissions. To reduce their carbon footprint,
mining companies are turning to the key enablers of decarbonisation – automation, electrification, and digitalisation.
Mining is also looking to new technologies to optimise safety and efficiency. It is time to not only adopt innovation, but also put to rest old methods in favour of technologies that drive down both energy consumption and emissions. Solutions such as ABB eMine cover the entire mining process, from pit to port, in order to help convert existing operations from fossil fuel to all-electric energy.
These electrification solutions can be integrated with digital and automation systems to gather critical data – energy consumption, available power, etc. – and allow for real-time scheduling and tracking of operations. By analysing this data, mine operators can monitor and optimise energy usage in real time, helping them make genuine, quantifiable progress towards their sustainability goals.
ABB’s saying, ‘Great Minds, Great Mines’ reflects the belief that together, everyone is laying the foundations for a mining industry that meets all of society’s needs – economic and environmental. Therefore, it is imperative to drive Real Progress towards the all-electric and automated mines of the future.
1. ‘The Role of Critical Minerals in Clean Energy Transitions’, IEA, (2021), https://www.iea.org/reports/the-role-of-critical-minerals-in-cleanenergy-transitions
Jürgen Kern, Mario Gerards, and Michael Panholzer, ANDRITZ, examine how adopting AI-based control systems in the filtration process can result in higher reliability and lower operating costs.
One of the most common technologies used for filtration and/or dewatering in the mining industry is the filter press. These robust machines are particularly useful in the management of mine tailings, where they represent an attractive alternative to tailings ponds and their associated dams and embankments. However, while the benefits of deploying filtration systems are considerable, tailings management is a demanding role for filter press equipment. Not only are there very high volumes of slurry to consider, but the abrasive nature of mining slurries is particularly hard on elements of the filter press, such as the filter cloths and plates. This leaves operators with complex decisions based on a host of parameters – especially when handling a complete filter press park.
Although tailings are a waste product that does not typically generate any profit, separating the solids can still offer considerable value to mining operators. For example, the extracted water may be reused in the mining process. This is a particularly valuable function in arid areas, or where there are limits on the available fresh water supply, representing a substantial cost saving. Separation also significantly enhances safety by enabling tailings to be stabilised as a relatively dry medium, saving space and largely eliminating the risk of contaminated water leaking into open or ground water sources.
This article will dive into an artificial intelligence (AI) specially developed to ease the operator’s work in filter press parks and will examine its impacts on filter press performance, as well as wash water recovery.
Due to the often-large volumes of tailings, multiple filter press units are usually installed in banks, known as filter press parks. If one of the units requires a wash cycle, a cloth change, or some other type of servicing or maintenance, one of the other units will step in to execute the separation process by switching out of idle mode or increasing the throughput rate, thus ensuring a continuous process with no gap in mining operations.
Given the importance of the continuous separation process to mining operations in many applications, filter press parks are already being designed to reduce the need for operational staff. However, operations and maintenance requirements for filter presses still demand regular inspection. During these inspections, operators have to make complex decisions based on a host of parameters, such as the optimal timing for executing a wash down cycle or for changing a filter cloth and thus switching to an alternative filter press unit for handling the process slurry. The decision obviously affects critical aspects of the overall mine production process, as well as other factors such as water consumption. The kinds of operational conditions found in mining applications can
also lead to higher operational expenditure, due to excessive filter cloth consumption. Operators therefore need to consider the efficiency of filtration operations as a whole, including any potential bottlenecks in throughput, the availability of water, and the operating status of both upstream and downstream equipment. Needless to say, the decision-making challenge becomes far more complex when multiple filter press units are in service at a single location.
In response to this testing task, international technology group ANDRITZ has coupled its filter press machines to its proprietary Metris addIQ control systems (addIQ control systems are part of Metris, the ANDRITZ brand for digital solutions) to create its Advanced Control Expert (ACE) platform, which combines the optimisation functions of Metris addIQ with AI-enabled functionality.
Key to effective decision-making is data – and the Metris addIQ ACE system gathers a comprehensive spread of data sets from an operating filter press park. Among the range of parameters required, Metris addIQ ACE uses parameters such as:
n The thickener underflow rate or the level in filter press feed tank.
n Inflation pressure for membrane plates.
n The filter press status (idle, cloth change, wash cycle, filtration cycle).
n Levels in the process water supply tank.
n Cycle times.
n The mass of solids discharged per cycle per press.
n Valve positions.
It couples these data sets with operational parameters, for example with information on wash down cycles, water availability, equipment status, and all of the other elements a human operator would consider. However, rather than a fallible human operator, Metris addIQ ACE uses a theory from the
Cutting edge innovations & the latest methods in mining
Register today!
Secure tickets and hotel rooms on our website for the best availability. euromineexpo.com
Explore our full conference program, now available on our website.
ALSO: EXHIBITOR LIST | SOCIAL EVENTS | FIELD TRIPS
gaming community, Utility AI, and automates the entire decision-making process. Taking important independent variables from each filter press and overall strategic imperatives, Metris addIQ ACE optimises the filter press operation, selecting the ideal point to run, wash, change filter cloths, or idle mode any of the filter press units in a press farm of perhaps four or more units.
By taking a holistic view of the whole system while prioritising the overall objective of maximum production, the system not only takes the efficiency of each filter press into account, but rather looks at the complete filter press system as well as the auxiliary equipment. By absorbing data from components like feed pumps, Metris addIQ ACE is able to hone its decision-making, while also identifying and preventing conditions such as excess power consumption, where pump units are in need of maintenance.
Adopting this system is expected to result in multiple operational benefits. For example, by optimising the overall system, the core objective of maximum production and stability is assured. This is especially the case, given a diligent and tireless operator is expertly assessing the situation and making decisions second by second, day or night, and making intelligent trade-offs between availability, filtration efficiency, and throughput.
Along with maximising production, there are other direct economic advantages too, for example energy use is reduced as the system becomes more efficient. Similarly, water consumption is cut too.
Water can be particularly challenging for mines located in remote locations, where this resource can be a scarce commodity. While separation of the tailings can mitigate this by recovering process water, filter presses require a regular washing cycle for optimal operation, which can be a significant source of water consumption if done at non-optimal times. This can easily become excessive within the pinpoint accuracy that AI delivers. For example, the filter press cycle is a batch process and the machine operating has to stop processing to execute a washing cycle. If poorly timed, this could lead to delays in starting a new cycle. Conversely, washing the filter press too rarely can lead to a higher moisture, resulting in lower quality filtrate and wasting of resources.
Metris addIQ ACE constantly monitors the filtration cycles of each filter press machine and quickly identifies any deviations from optimal parameters, such as a typical process throughput of a nominal 100 m³/cy that is reduced to 80 m³/cy in a later cycle. A big increase in the rate of pressure during filling is also indicative. Where it might normally take, for example, 240 sec. to reach 8 bar, if this is occurring in 150 sec. over several cycles, this suggests a wash cycle is needed. In either case, Metris addIQ ACE would notify the operator (for example, by a notification in the app) of the drop in process efficiency and advise commencing a wash cycle. In the case of a filter press farm, an idle unit could be switched into play while the wash cycle takes place. The overall benefit is an optimised number of cloth washing cycles, which increases the general filter press availability.
AI-based control systems clearly offer cutting-edge machine and process control for solid-liquid separation equipment and systems in challenging mining applications. Fundamentally, such an approach offers a shortcut to reducing the risk of operating errors that can lead to excessive consumption of energy and water, as well as higher than necessary maintenance costs. The AI system not only results in higher reliability and lower operating costs, but also optimises the overall process, ensuring maximum throughput for optimised mining operations.
Recognising these substantial benefits, the industry is already adopting this technology, with a pilot project using Metris addIQ ACE set to be deployed in the US. Maintaining an overview of the entire operation is unquestionably a complex task, but there is a simple solution.
Daniel Greune, TAKRAF Group, Germany, provides an overview of the company’s recent projects and activities involving its crushing and material handling equipment.
In today’s dynamic mining landscape, there are significant opportunities for cutting-edge technologies and solutions that promote safer and more environmentally responsible operations. This article dives into a comprehensive portfolio of projects and explores some of the latest advancements that are redefining industry standards.
As the mining industry faces an increasingly complex environment in which it strives to satisfy demand for raw materials while accounting for the challenges of depleting resources and the need for environmentally sustainable operations, TAKRAF Group’s technical expertise is attracting a record order intake. Projects underway, globally, range from the supply of various TAKRAF crushing and material handling equipment in Africa to a significant iron ore processing plant contract for DELKOR with India’s largest producer of iron ore.
TAKRAF is seeing an upsurge in work from West Africa, with the award, at the end of 2023, of a major contract in Mauritania.
The project was awarded by Société Nationale Industrielle et Minière (SNIM), with whom TAKRAF has a working relationship that dates back to the early 2000s. The contract covers the supply of a complete crushing, screening, and material handling system, along with a train loading station, for the F’Derick project, which aims to increase iron ore production from approximately 12 million tpy to 18 million tpy. TAKRAF’s scope of supply includes a primary crushing plant with apron feeder; secondary crushing plant with pre-screening; train loading (loadout) station, with the capacity to load 100 wagons
per hour; and associated belt conveyors, transfer tower, and auxiliary systems and accessories.
Delivery of the equipment to the port of Nouadhibou in Mauritania is expected to be completed in approximately two years, with the project drawing on TAKRAF’s global strength in delivering complex bulk handling systems.
In an earlier project award, TAKRAF is delivering an integrated In Pit Crushing & Conveying (IPCC) and material handling system for the Simandou iron ore complex in Guinea, one of the world’s largest unexploited high-grade iron ore deposits. The 13 200 tph system comprises two primary IPCC systems, incorporating two TAKRAF X-TREME class sizers to crush extracted ore received by truck; and an In Pit Secondary Crushing & Conveying (IPSCC) system, incorporating four TAKRAF Sizers for further ore processing. All stockyard equipment, which includes rail-mounted stackers, rail-mounted reclaimers, and wagon loading stations with buffer silos, was designed with scalability for future expansion.
These projects build on a track record in West Africa, which includes the successfully completed EPC contract for Phase 1 of Compagnie des Bauxites de Guinée (CBG) bauxite expansion project in Guinea. The contract included delivery of a greenfield wagon unloading and primary crushing station, as well as a secondary crushing station and a complex brownfields conveyor system. An order for a further two conveyors was subsequently brought forward and fast-tracked from Phase 2.
In South Africa, TAKRAF delivered, in another fast-track contract, a custom-designed solution for stockpiling crushed platinum ore. Awarded by Ivanplats (Pty.) Ltd. as an EPS project, the radial stacker was completed in under eight months from contract award to delivery of the equipment to Phase 1 of the two-phase Platreef Project, a greenfields platinum mine. The radial stacker, which has a capacity of 1993 tph and features a 44.6 m long fixed boom with dual walkway, was engineered with a modular approach for ease of transport and site installation.
Other recent projects across the globe include the replacement, in south Mexico, of a 6000 tph rail-mounted stacker within the client’s tight deadline. Disassembly of the existing stacker took just 2.5 days. Since the operation was in production 24/7, the new machine, designed to operate in the hot, humid, and corrosive environment, as well as in high-velocity winds, was constructed on an operating conveyor, feeding into an operating plant. In a previous project for the same client, TAKRAF replaced a ship loader within the same very tight time period.
In South America, a 13 200 tph conveying system is due for completion mid-2024 for a copper miner. An overland conveyor that is part of the system features a negative lift of 150 m and several horizontal and vertical belt curves. Earlier, completed work in South America includes the supply of a 7200 tph bucket-wheel reclaimer for iron ore.
In Australia, TAKRAF supplied a rail-mounted stacker for a bulk terminal, which is one of the largest ever delivered and one of the most technically advanced, with its 62 m long curved boom. Four portal scraper reclaimers supplied to a new multi-commodity power plant in Japan are also some of the largest of their type built. As two reclaimers are
The biggest heavy industry trade fair in Europe! 40 years of experience!
Join us! Showcase your machinery, equipment, and cutting-edge technologies to an international audience.
Enter our prestigious competition! Showcase your products and innovations!
Shape the Future of Industry at EXPO KATOWICE: Embark on a journey of innovation with Dynamic Networking, Growth Opportunities, and the Enlightening Conference “Industry 5.0 - Transformational challenges of industrial sector” - All Under One Roof!
Mark your calendars for September 4-6, 2024, and let EXPO KATOWICE be your gateway to global success.
Reserve your spot by the end of June and unlock your potential with EXPO KATOWICE
required to work on the same rail in the same warehouse, a dedicated safety and anti-collision system was implemented.
TAKRAF adopts a holistic approach to maintenance, from engineering technologies that incorporate intelligent solutions for optimal safety and efficiency of maintenance activities, to supporting its clients worldwide with highly experienced service and maintenance teams. These teams provide customised solutions, ranging from the fitting of crushers and high-pressure grinding rolls with improved wear protection, to refurbishments and upgrades of bulk material handling equipment, such as stackers and reclaimers. Such solutions are provided for TAKRAF’s own equipment, as well as for other equipment no longer supported by the original OEM.
TAKRAF is committed to the principle that any improved maintenance solution must have a safety upside to it, and that there is no need for increased safety to be at the expense of maintenance efficiency.
Intelligent solutions developed by TAKRAF to maximise safety and efficiency include rotable chutes and external chute access for the replacement of chute liners. The sizer hot change method for crushing plants enables a hot swap
between an operational machine and spare sizer on the platform.
The replacement of worn or damaged conveyor idlers, a global conveyor problem, is facilitated by TAKRAF’s maintenance cart to access any location along a conveyor belt – be it a tunnel, steep slope, or elevated structure – in the shortest possible time and in the safest manner. A TAKRAF maintenance cart services the steep, 26% decline, 1250 m section of an overland conveyor, which boasts more than 3700 idlers, at a major copper mine in North America.
Harnessing the power of Industry 4.0 for more efficient and safer maintenance, TAKRAF is making the benefits of data, connectivity, and automation available to its customers. TAKRAF’s Automatic Belt Training System (ABTS) provides a solution to belt twisting (rotation), a critical failure mode of tube conveyors. Already fitted to a variety of global TAKRAF tube conveyor installations, the ABTS automatically determines the belt overlap position via ultrasonic sensors. If the overlap exceeds the tolerance limit, servomotors are activated that rotate the tube profile through individual idlers into the desired position via targeted tilting adjustments.
Other applications include provision of remote support through, for example, the use of smart glasses to connect TAKRAF Group experts in the office with the client’s maintenance staff on site, and the use of intelligent augmented reality (AR) based tools for maintenance support.
TAKRAF Group is increasing its presence in Australia in 2Q24, with the opening of another warehouse located in Perth, and the further expansion of its footprint in the services business by adding more specialists to its existing complement.
Currently, the Group provides services to the whole of Australia, supporting both the TAKRAF and DELKOR product lines. Going forward, the new Perth warehouse, in Western Australia, will provide additional support to the west coast, with all warehouses supporting TAKRAF Group’s portfolio of specialised mining systems and equipment and bulk material handling technologies, as well as the DELKOR range of liquid/solid separation and wet processing equipment and systems.
In addition to the warehouses, TAKRAF Group has three sales and execution offices in Australia, providing equipment and systems to the mining and associated industries.
With its longevity in the dynamic mining environment, combined with its commitment to the strategic development of advanced technologies, TAKRAF Group is well-positioned to take advantage of the current climate. Consequently, as it approaches its 300th anniversary in 2025, TAKRAF Group is focusing on providing clients worldwide with sustainable, low environmental impact solutions across the value chain, from overburden removal and raw material extraction through processing to ship loading.
The number of injuries and deaths from conveyor accidents has generally plateaued since 2015, compared to 20 or 30 years ago, where the annual number of worker fatalities was nearly 400 times what it is today.1 Safety experts attribute some of the decrease in injuries and fatalities in the past decade partly to stringent regulation and reporting by the Mine Safety and Health Administration (MSHA) and the Occupational Safety and Health Administration (OSHA). Contributing factors also include modern safety-conscious equipment designs and operators addressing the root causes of injuries in mining environments, rather than treating the symptoms.
According to industry expert R. Todd Swinderman, there are five root causes of conveyor injuries: a ‘production first’ culture, ‘low bid’ purchasing, overly complex designs, too many rules, and understaffed or undertrained personnel. He has stated that companies who truly focus on safety are more productive, operate cleaner and safer facilities than their competitors, and have a higher share price.2
Reduced workplace injuries and fatalities is a positive trend, but there are still predictable and preventable injuries happening. The goal of Martin Engineering’s ‘Production Done Safely’ philosophy is to help mine operators achieve the greatest amount of production at the lowest cost of operation, with the least number of injuries possible. This is accomplished through awareness, extensive training, and safety-conscious equipment design.
The following examples display common injuries that could have been prevented through several established safety methods. Beyond the tragic loss for the workers and their loved ones, the companies in which the fatalities occurred were heavily fined. Consequently, some are also enduring ongoing litigation, serious morale issues, and higher than normal turnover.
The first fatality is a common one. On a January morning in 2020, a 33-year-old worker was cleaning spillage around a running conveyor system at a facility in New Jersey. Listed as a temporary non-union worker, he got too close to the moving belt, and a piece of loose clothing came in contact with the belt, dragging him into a pinch point. He was strangled with the fabric before aid could be administered or the system shut down. This incident resulted in US$36 500 in fines from OSHA.3
There were several details left out of the public report. One is the presence of guarding around the belt, which prevents limbs and objects from ‘breaking the plane’ of the system. The ‘plane’ is the line (generally indicated by the outside of the stringer) that, once crossed, becomes a hazard for this type of incident. Guarding is designed with mesh that prevents incidental contact but allows for inspection. Often, there is a procedure required to remove guarding, and in some cases, removal triggers an automatic shutdown of the system.
It was not revealed in the report how much training the individual had received, but a trained worker would have been aware of the hazards around a moving belt with regards to loose-fitting clothing or long hair. Moreover, the presence of a buddy or supervisor is unknown, but the implementation of work teams might have allowed a faster response to shut off the system or free the worker before asphyxiation occurred.
On an August day in Southern California, a 21-year-old worker with just over a year of experience at a sand and gravel mine noticed a clog in the drop chute of the cone crusher. After entering the vessel to remove the obstruction, while he was inside, material that had built up on the sides fell inward, encasing him up to his chest. Fire crews were able to extract him, but the injury damage from the pressure and force of the material was too significant and he later died in the hospital. Citation and litigation data were not available for this case.4
What was not revealed in the report was whether the worker was certified for confined space entry. Knowledge of chute entry rules specifies safety procedures for these types of actions, including clearing all loose material, which would have likely prevented the worker from entering the hopper.
There are safe and economical accessories designed to mitigate obstructions in chutes, hoppers, bins, and silos. To prevent injuries and equipment damage associated with methods such as striking the sides of the vessel with mallets, stabbing at obstructions from below, or dangerous chute entry, equipment manufacturers offer vibration and air cannon technologies.
Vibration at specified points agitates dust and fines that adhere to surfaces, preventing buildup that leads to clogging. Going one step further, air cannons use a forceful shot of
pressurised air pointed towards the material flow to free buildup over wide areas of the vessel’s surface. Air cannons not only prevent clogs, but also promote the consistent flow of cargo through the process.
In April of 2020, a 49-year-old worker in Illinois was using a broom to clean dust and spillage around the conveyor feed pit leading to a moving conveyor transporting dried manure to a transfer point. The worker accidentally slipped and fell onto the belt. He was quickly conveyed 100 ft to the blade cleaner at the discharge point, where he suffered multiple life-threatening injuries and later died. According to the report, the employer was initially fined US$66 794, but was able to settle with OSHA for US$30 000. Any further pending litigation was unreported.5
Conveyors in full production mode often move so fast that they can exceed the reaction time of even a highly-trained Olympic athlete (see Figure 1). When faced with a situation where a worker suddenly contacts the cargo side of the belt, the only hope may be another worker making it to the shutoff switch in time.
The report cited the presence of a guardrail but did not specify the circumstances by which it was crossed. However, the best practice is to prevent as much dust and spillage discharging from the system as possible, then clean safely during scheduled downtime. Employers can mitigate excessive dust and spillage by installing equipment specifically designed for sealing the conveyor belt and controlling emissions.
The importance of protecting workers should be the top priority for any employer. The loss felt by family and coworkers after a workplace fatality can weigh heavily on a community and staff, not to mention the financial consequences. Thus, investing in equipment and training that protects workers from injury and illness is essentially investing in the community and the company culture.
In its 2002 white paper, the American Society of Safety
Engineers (ASSE) concluded a direct, positive correlation between investment in Safety, Health, and Environment (SH&E) and its subsequent return on investment (ROI).6 The organisation reported that of the American business executives polled, 95% believed workplace safety also has a positive impact on a company’s financial performance. The same poll revealed that 61% believed their companies received an ROI of US$3 or more for each US$1 they invested in workplace safety.
Calculating these costs is specific to each operation, but in general, they can be broken down into ‘direct costs’ and ‘indirect costs’.
Direct costs are explicitly associated with the accident or illness. In general, these include fines, medical bills, insurance premiums, indemnity payments, and temporary disability payments.
Indirect costs comprise a variety of other expenses resulting from the incident. They include: n Cleanup time and product loss.
Cincinnati Mine Machinery Company designed and installed the first Dual Sprocket Conveyor Chain. Our unique design utilizes superior metals and a proprietary heat treatment process for unparalleled strength. Our Dual Sprocket Conveyor Chain runs longer and stronger which means less downtime and lower cost per ton. So when it's time to choose, choose the strongest chain under the earth. For over 90 years, Cincinnati Mine Machinery continues to be THE STRONGEST L INK
n Equipment repair or replacement.
n Purchase or installation of safety components.
n Overtime to fill in for the missing worker.
n Cost of hiring, training, and equipping new employees.
n Legal fees and litigation costs.
n Increased insurance premiums.
n Production delays and missed shipment targets.
n Reduced employee morale, greater absenteeism.
n Negative publicity.
n Increased scrutiny by regulators.
Tallying the direct and indirect costs, the impact of an accident on a company’s bottom line can be devastating. Safety rules are not maliciously created to complicate operations or limit profit. When taken into account, they actually improve a company’s bottom line.
To demonstrate the benefit of safety to a company’s bottom line, OSHA created the online tool, ‘$afety Pays,’ which uses company-specific economic information to assess the potential economic impact of occupational injuries on that firm’s profitability. The programme estimates direct costs (claim cost estimates provided by the National Council on Compensation Insurance) and indirect costs (provided by the
Stanford University Department of Civil Engineering) and weighs them against financial details supplied by the company (see Figure 5).
The commonly used ROI model is calculated against a time frame in which the capital expenditure on new equipment is recaptured by the improvements. If a proposed project is within the budget expectations and has a payback period of less than one year, it is usually approved by mine management.
An issue with the ROI model is it requires someone to get hurt to provide a benchmark for calculating return, which is not a reasonable point of entry. Using the OSHA’s ‘$afety Pays’ tool to provide a cost model to calculate the ROP is a more practical approach.
Working with abstract numbers implicitly creates pushback, making it more difficult for safety-conscious managers to obtain approval for their proposals. However, the hard costs of worker injuries and fatalities are very real. The ROP model expresses the direction and strength of occupational safety and health programmes in helping to achieve company goals.
The death or injury of a worker in a conveyor accident is always tragic. Investigations usually reveal the incident could have been partially or entirely prevented with practical and cost-effective safety improvements. The ROP on durable, well-designed conveyor accessories and professional training not only makes good financial sense, but also produces a culture of safety that ripples throughout the company’s balance sheet.
1. ‘Commonly Used Statistics Portal’, OSHA, www.osha.gov/data/ commonstats
2. SWINDERMAN, R.T., et al, ‘Foundations for Conveyor Safety’, First Edition, MartinEngineering, Worzalla Publishing Company, (2009), p. xi, www. martin-eng.com/content/page/552/foundations-conveyor-systems-book
3. ‘Inspection: 1456761.015 - Safestway Labor Force Llc’, OSHA, (18 January 2020), www.osha.gov/pls/imis/establishment.inspection_ detail?id=1456761.015
4. HEBEL, G., ‘MSHA Preliminary Report of Accident: Event #6871921’, MSHA, (18 August 2020), www.msha.gov/datareports/fatality-reports/2020/ august-18-2020-fatality/ preliminary-report
5. ‘Inspection: 1472178.015Pearl Valley Farms, Inc.’, OSHA, (4 October 2020), www.osha. gov/pls/imis/establishment. inspection_detail?id=1472178.015
6. ‘Return on Investment (ROI) for Safety, Health, and Environmental (SH&E) Management Programs.’ American Society of Safety Engineers (ASSE), (8 June 2002), elcosh.org/document/1082/ d000047/asse-white-paperaddressing-the-return-oninvestment-for-safety,-healthand-environmental-(sh%26e)management-programs.html
Conveyors play a crucial role in the efficient, cost-effective, and environmentally-friendly transportation of materials in large-scale mining. Conveyor installations are used across mining operations wherever there is a requirement for the continuous transportation of bulk materials from place to place. They are found between the mine pit and processing facilities, within processing operations, and as downstream links to ports, railheads, and other logistics facilities.
This wide range of applications has led to significant diversity in size, capacity, and technology. The highest capacity conveyor systems in German lignite mines can transport 40 000 tph of material, or 240 000 m3 per day.1
Thibaut Leconte, SKF, Sweden, addresses how advanced bearing solutions are helping the mining sector improve the productivity and reliability of conveyor systems.Overland conveyor systems can span distances of tens of kilometres. The world’s longest conveyor carries phosphate 98 km from the Bou Craa mine in Western Sahara to the port at El Marsa. In the sparse desert landscape, this conveyor installation is large enough to be visible from space.2
Despite their ubiquity, conveyor systems can be troublesome for mine operators. Failure rates are among the highest of any asset type used in the industry. Problems with conveyor systems have the potential to influence the overall throughput of a site. In 1Q23, for example, the failure of a conveyor linking the mine to the concentrator at Rio Tinto’s Kennecott copper mine in Utah contributed to a 36% reduction in production.3
Working on conveyors can also be hazardous for mine personnel. Industry studies have found that 43% of accidents and 24% of all fatalities occur while maintenance is done on conveyors.4
Equipment manufacturers have invested significant resources to improve the safety and reliability of mining conveyors. Advances in the sector include embedded sensors in belts to detect wear and damage,
sophisticated control systems, and gearless drives that claim higher efficiency and greater long-term reliability.
Ensuring the reliability and durability of core conveyor mechanical components remains a key challenge for mine operators.
In part, this is due to the high number of these units required in every conveyor. Carrying idlers, used under the loaded side of the belt, are installed every 0.6 m to 1.7 m along the length of the conveyor system, depending on the bulk density of the transported material. Typical spacings for return idlers, which support the unloaded side of the belt, are 2.4 m to 3.0 m.5 Long overland conveyors may use larger spacings to reduce costs.
Each idler frame may include multiple rollers to hold the belt in an appropriate shape, and each of those rollers is equipped with two bearings. Large conveyor installations require many thousands of bearings. One recent overland conveyor project in Australia used around 150 000 SKF bearings in its construction.
Conveyor idler bearings work in difficult conditions. These units operate under high loads at low or medium speeds, in widely varying temperatures and with exposure to significant contamination from water, dust, and debris. In addition, the bearing assembly must be able to tolerate misalignment due to the imposed loads, thermal expansion of conveyor components, and assembly tolerances.
Bearing system and component selection are key considerations in the design of conveyor systems. In demanding environments, the operating life of a pulley bearing can vary from as little as a few months for poorly specified units operating in demanding conditions, up to several years for the most advanced bearing systems.
Bearing systems also have significant implications for conveyor maintenance. Lubrication issues, including contamination or insufficient lubricant availability, are a primary cause of bearing failures. Maintaining appropriate lubricant conditions in open or poorly sealed bearings necessitates short relubrication intervals. Frequent manual lubrication means high-maintenance labour costs, high grease costs, challenges around the management and safe disposal of used lubricants, as well as regular exposure of personnel to physically demanding, risky work.
Frequent relubrication requirements also mean frequent opportunities for maintenance errors. Common issues in busy mines include forgotten bearings, the uses of inappropriate grease types or quantities, or the introduction of contaminants via dirty, unprotected grease nipples.
Reliable, energy-efficient conveyor bearings require careful consideration of the complete system, including bearings, seals, housings, lubricant section, monitoring, and maintenance regimes. That approach begins with the selection of high-quality bearings from a supplier with appropriate manufacturing, supply, and technical support capabilities.
Conveyor systems may use different types of bearings, including deep groove ball bearings, tapered roller bearings, or spherical roller bearings. Spherical roller bearings, such as
+130
Papers Received by Authors from 18 Countries
Technical Courses Given by the Co-Organizers Institutions
Geraldo Paes Tailing 2024 Chair Corporate Geotechnical Director, Vale, Brazil
Tamara Johndrow Director Tailings & Water, Freeport-McMoRan, USA
Silvana Dal Pozzo Tailings Principal, BHP, Chile
MAIN SPONSOR
ORGANIZED BY
SHERATON HOTEL
SANTIAGO, CHILE
Mining Operations Papers Received
Different Instances for Effective Networking +40
Edgar Quiroz Tailings and Water Manager, Minera Las Bambas, MMG, Peru
Jorge Troncoso Tailings Corporate Manager, Antofagasta Minerals, Chile
the SKF Explorer range, are commonly selected for modern conveyor applications, thanks to their high load capacity and tolerance for angular misalignment.
Manufacturers generally produce bearings of all these types in ‘open’ or ‘sealed’ designs. Open bearings are used in applications where a regular supply of lubricant is available, via frequent manual relubrication or using an automated lubrication system. The exception is deep groove ball bearings that are most often unsealed and lubricated for life. In highly contaminated environments, such as mines, bearing systems require additional ingress protection to increase lubrication intervals and prolong bearing life.
Sealed bearings are lubricated with a long-lasting grease at the factory. The seals serve to retain the grease within the bearing and provide protection from the ingress of external contaminants.
Contamination protection for open bearings can be provided using external seals installed in the bearing housing. SKF’s new TXL seals have been developed to provide effective additional protection to their versatile SNL range of bearing housings. Manufactured from ECOPUR polyurethane, the new seals are split for easy replacement in the field. A12 seals can be used for imperial dimension housings (SAF, SDAF).
The most advanced bearings systems for these applications offer multiple levels of protection. The SKF three-barrier solution, for example, uses a housing specifically developed for mining applications and equipped with external seals. The external seals may be contact seals or, for the ultimate protection in the most critical applications, SKF Taconite seals. The SKF Taconite seal consists of two rings (one stationary and one rotating), which form a narrow labyrinth between the two rings. The rotating labyrinth ring carries a V-ring seal that seals against the stationary labyrinth ring. The V-ring seal blocks contaminants from entering the bearing housing and aids the purging of contamination and old grease. The stationary ring includes grease nipples to purge contaminants from the seal.
The housing cavity is filled up to approximately 80% with grease to provide the second barrier. SKF recommends a biodegradable grease (SKF LGGB 2) in this application to simplify waste management and minimise environmental impact. A sealed SKF Explorer spherical roller bearing provides the final barrier. A cost-effective and environmentally-friendly option, the SKF three-barrier solution for conveyors can extend bearing service life and reduce grease consumption by about 90%.
A copper mine in Peru underwent a major expansion of its concentrator plant to 360 000 tpd in 2015. 14 conveyors with 72 pulleys are used to transport crushed mineral up to the mill’s high-pressure grinding roll. Due to extreme contamination and abrasive wear, pulley bearings had to be replaced every six months to avoid breakdowns and excessive unplanned production stops.
To minimise downtime and production losses, the mine owners wanted to extend the service life of their conveyor pulleys. All open bearings were replaced with contamination-resistant SKF three-barrier solutions. Today, the mine’s conveyor pulley bearing uptime is more than 26 months. In addition, the SKF three-barrier solution is virtually relubrication free.
Mine conveyors are long-lasting assets, with operating lives that can extend into decades. While the most durable bearing systems can operate reliably for years, replacement will eventually become necessary. Changing a conventional bearing incurs significant downtime, especially in trapped positions such as between the pulley and drive coupling or between the pulley and back-stop system. Replacing these bearings may require shafts to be dismounted, remounted, and realigned during the operation.
A time-saving alternative is the use of a split bearing design, where the rings and roller assembly are constructed in two halves. SKF Cooper split spherical roller bearings, for example, are designed to be easily replaced in situ, requiring very few changes to the shaft alignment or driveline. This approach can reduce mean time to repair (MTTR) by two-thirds compared to conventional bearings. Split spherical roller bearings can replace conventional spherical roller bearings installed on an adapter sleeve without any modification to the conveyor.
SKF Cooper bearings include several features designed to extend the life of the bearing. For example, the inner and outer rings are manufactured in one piece and wire cut,
ensuring good surface quality and consistent geometry. A sealed variant of the bearing is available for increased protection against contamination, lower grease consumption, and reduced maintenance.
Another ongoing development in mine conveyor operations is the wider use of automated condition monitoring systems. Continuous online monitoring of bearing temperature and vibration can provide users with early warning of problems, allowing them to intervene before failures occur and helping to optimise maintenance plans and schedules.
Conveyor systems have traditionally been considered difficult applications for condition monitoring due to their large size and high number of bearings involved, but advances in sensor and analytical technology are now addressing some of these challenges.
Since 2020, Boliden’s Aitik copper mine in northern Sweden has been running an advance condition monitoring system on its 7 km ore conveyor. Developed and operated in partnership with SKF, the system measures the performance of critical bearings, such as those in drive pulleys and drums. Vibration is analysed offsite by SKF specialists, who alert the mine maintenance team to any unusual behaviour and assist them in diagnosis and root cause problem solving.
Since its introduction, the condition monitoring approach has eliminated unscheduled downtime at the site, something that was previously a weekly occurrence. As a further benefit, the new system has allowed the mine to optimise replacement intervals, increasing the share of worn components that are suitable for remanufacturing. In 2022, 22 items, both bearings and bearing housings, were remanufactured, and by the end of March 2023, a further 10 items had been sent for remanufacture. In addition to realising savings of approximately SEK 6 million (US$1 million), remanufacturing drastically reduces carbon emissions compared with making new products.
Conveyor systems are a vital part of mining today, and their relevance is only set to increase as the sector tackles the challenges of rising demand, remote sites, and the imperative to improve efficiency and
reduce the environmental impact of their operations. The industry is on a roll, and advanced bearing solutions are helping it to stay that way.
1. ‘World Records: Highest Efficiency Conveyor Belts’, Phoenix Conveyor Belts, (2012), www.krk.com.br/wp-content/ uploads/2015/02/World-Records.pdf
2. CASSIDY, E., ‘World’s Longest Conveyor Belt System’, NASA Earth Observatory, (21 January 2023), www.earthobservatory. nasa.gov/images/150869/worlds-longest-conveyor-belt-system
3. ‘Rio Tinto releases first quarter production results’, Rio Tinto, (20 April 2023), www.riotinto.com/en/news/releases/2023/rio-tintoreleases-first-quarter-production-results
4. ‘A User’s Guide to Conveyor Belt Safety’, IRSST, (2003).
5. ‘Belt Conveyors for Bulk Materials, 7th Ed.’, CEMA, (August 2020).
The Martin® Manufactured Canoe Liner has the backbone to stand strong while absorbing the impact and abrasion of punishing bulk handling environments. This proprietary design features impact-resistant urethane molded directly around a supporting steel plate. This rugged construction prevents the bonding issues of urethane separation from the plate that can result in damage to belts and enclosures. Our canoe liners shield the sealing system and chute walls better, control more dust and spillage, and improve overall safety. All benefits contributing to reduced cost of operation. Steel plate embedded within
Sensor-based sorting in mineral processing has seen substantial advancements over the past century. It began in the 1920s with basic photocells and trap doors for copper ore sorting. Today, it is characterised by mature components, high levels of computerisation, and the use of sensors specifically chosen for their ability to measure relevant properties.
Continuous evaluations of modern technologies aim to further enhance this processing method, striving to provide the most robust yet sensitive sensors, the most energy-efficient and precise ejection systems, and the most advanced and reliable data processing technology.
Sensor-based sorting of particle streams involves three distinct stages, each executed individually for every detected particle. First, sensors measure the particles’ properties. These sensors are often developed specifically for use in sensor-based sorters, aiming for rapid and accurate property measurement. Next, computers assess the acquired data to make a sorting decision. The sorter generates a data set detailing the properties of each processed particle. Finally, this decision is physically carried out by directing the particle to the appropriate outlet of the sorting machine.
What sets sensor-based sorting apart from other separation technologies is its use of independent technologies for detecting particle properties and dividing the particle stream into different fractions. Unlike conventional gravity or density sorters that use a specific physical property for both discrimination and sorting, sensor-based sorters measure particle properties with specially selected sensors and handle ejection independently with physical separators. This separation allows for individual optimisation of detection and ejection, avoiding the compromises found in other physical sorting methods. Moreover, the data processing capabilities of sensor-based sorters are continuously improving, a significant advantage given recent advancements in computers and algorithms.
The separation process itself requires a high degree of precision in the ejection process. Thousands of particles of varying size, mass, and shape that are moving with high velocity through the sorting machine need to be hit exactly at the right spot and at the right time with the appropriate amount of force to ensure a stable trajectory to the required outlet of the sorting machine. Furthermore, the ejection process must be highly energy-efficient, as tonnes of material per hour are moved by air jets.
Extracting the necessary information from sensor data is complex. The subtle distinguishing characteristics separating valuable minerals from waste often require a
sophisticated combination of several attributes, considering the particle’s total mass, to make a satisfactory sorting decision.
The central element of sensor-based sorters, the data processing that couples the detection and ejection of particles, is especially benefitting from technological progress. In recent years, a wealth of new developments has led to astonishing results achieved by systems that implement artificial intelligence, a technology that mimics human intelligence.
Earlier generations of sorters relied on rule-based systems to reach sorting decisions. With the progression of machine learning, which involves computers evaluating enormous amounts of data to detect statistical patterns, the influence of human error is minimised.
Deep learning, a new field within machine learning, uses artificial neural networks for data processing. In these systems, the statistical analysis is adjusted within the neural network during a training phase. These networks have proven extremely capable of recognising patterns that are difficult to capture using other statistical methods. The unique features of the deep learning approach perfectly complement current sorting technology to enhance throughput without compromising sorting quality. This adds an extra layer of intelligence to the sensor-based sorting system.
Sorting methods can be categorised into bulk and particle sorting based on the sample size analysed in one batch. Bulk sorting involves analysing larger samples and moving the entire sample based on its average measurement values. On the other hand, particle sorting measures and analyses each particle individually, providing high detection accuracy but limiting the equipment’s capacity.
To ensure accurate measurements, particles must be presented in a single layer with sufficient spacing. This level of separation is necessary to convert precise measurements into equally accurate ejection results. However, as the need for higher throughputs increases, so does belt occupancy, reducing the separation between individual particles and negatively affecting detection and ejection quality.
Previously, this issue was addressed by sorting coarser particle size fractions. However, this approach has its drawbacks. Coarser particles often contain a mix of valuable ore and gangue minerals, limiting the physical separation process to moving the entire particle to the machine’s outlets. This leads to a compromise in the purity of material streams if higher throughputs can only be achieved by sorting coarser material.
Breaking rocks into smaller particles enhances the liberation of the ore and allows for a purer sorting result. However, to optimise the performance and efficiency of detection and ejection systems, the entire particle size
distribution must remain within a specific range. Therefore, while breaking down rocks increases the liberation of the ore and optimises the sorter’s systems for that liberated ore fraction, it sacrifices the ability to handle significantly larger rocks.
Furthermore, as rocks are crushed down, the sorter must handle more individual particles, limiting its maximum throughput. Finer particles also increase the processing load due to the greater number of objects to track and evaluate. It also requires higher sensor resolution, more sensitive detectors, and a faster ejection system with finer ejector pitch.
The total volume of the feed stream remains constant after crushing, so reducing the material stream thickness increases its spread across the belt. As particle count increases, inter-particle distance decreases until no empty space remains.
In situations where particles touch, the ability to use the achieved ore liberation depends on determining the boundaries between touching particles. The liberation achieved by crushing is only a benefit if every individual particle in a heap can be detected.
If touching particles have different properties, with some being gangue minerals and others high in ore concentration, treating a particle cluster as one lump negates the benefit of the crushing process. TOMRA’s OBTAIN™ feature can determine each particle’s actual shape in a material cluster on the belt. By distinguishing every particle, the sorter can evaluate the liberated material regardless of belt occupancy, reducing the negative impact on the sorter’s throughput.
Processing low-grade ores is challenging due to their low value, requiring highly efficient processing for economic viability. Crushing, an energy-intensive step, can reduce the throughput of subsequent sorting stages. Thus, maintaining throughput, even with finer, better liberated material, is crucial.
Improving the overall sorting result requires not only detecting individual particle properties in clusters, but also leveraging recent advancements in physical separation technology. Modern ejection modules now control air jets
with unprecedented precision, using less air for significant energy savings. These modules are faster in adjusting particle trajectories through the sorter, and an increased density of ejector channels contributes to higher trajectory control accuracy.
However, these enhancements in particle handling are futile if the data processing system cannot process the high number of small particles necessary for good liberation and economically viable sorter operation. By applying deep learning to particle characteristics, OBTAIN enables the same analysis used for single particle sorting at throughputs of tens of thousands of particles per second, even when particles are clustered.
Sensor-based particle sorters inherently collect a detailed picture of the processed material stream, as each particle must be individually analysed for a sorting decision. This unparalleled level of detail and insight into the material stream’s properties is now available at much higher throughputs by using OBTAIN in dissecting particle clusters. The sorter reaches its sorting decision in the brief time it takes for a particle to travel from the detection area to the ejection module, often less than 0.1 seconds. It gathers information from tens of thousands of particles per second, with the resulting data immediately available as the material exits the sorter. This rapid feedback can enhance the control of processing plants for greater accuracy, speed, and efficiency.
Finally, developing technologies for sensor-based sorters requires knowledge and experience in many fields, from geology, sensor physics, data processing, and artificial intelligence, to mechanical and electrical design. Only if work in all of these fields is expertly done will the resulting sorting technology also be exceptional. TOMRA has not only been active in this field for more than 25 years, but also has acquired many providers of sensor-based sorting technology as part of its strategic management, and, today, it offers one of the most comprehensive portfolios of sensor-based sorting solutions in the world. Half of TOMRA’s 5000 employees are working on sensor-based sorters, with a substantial number of them in the research and development of innovative technologies for future sensor-based sorters. This enables the cost-efficient use of the most modern technology available for sorting today. Innovation is always a continuous journey. Each new generation of sorters builds upon the foundation of its predecessors, incorporating advancements in technology, efficiency, and accuracy. The introduction of modern technologies is continually pushing the boundary of what is possible in sensor-based sorting, maximising resource utilisation and promoting sustainability. By implementing OBTAIN, mining companies achieve consistent performance from sensor-based ore sorters across a wide range of throughput. This flexibility allows them to either process more material or improve sorting quality. Additionally, the statistical data collected from the sorted material streams becomes more accurate.
When actual operating conditions vary from those in the initial design specifications, problems can arise, requiring a coordinated and prompt response from plant personnel and partners.
In 2012, K+S Potash Canada embarked on a project to build a large potash plant near Moose Jaw, Saskatchewan. After just a few years of production, the plant began to encounter a series of control and automated valve challenges, which impacted production.
This article describes the issues, including initial design parameters that did not correspond to actual operation conditions. It then explains how those problems were successfully resolved through the efforts of K+S plant personnel, who worked with Emerson and its local Impact Partner Spartan Controls to leverage Emerson facilities and engineering support.
K+S has been mining and processing potash and salt for over 125 years. The company supplies mineral products and natural fertilizers for the agricultural, industrial, consumer, and community markets. In 2012 K+S broke
Michael Holmes, K+S Potash Canada; Duane Lunde, Spartan Controls; and Nolan Vollstedt, Emerson, describe the ways to identify and overcome challenges caused by incorrectly specified valves.ground on a US$4.1 billion solution mine north of Moose Jaw, Canada, and the plant began production in 2017.
Potash solution mining involves injecting water into bore holes, where it dissolves potash, salts, and minerals in mining caverns. The resulting brine is brought back to the surface, where it is processed to recover potash and other minerals.
The plant includes 320 control valves, with an additional 216 control valves in the wellfield. The process conditions are challenging, involving erosive slurries, significant chloride concentrations, and elevated temperatures. Control valve applications across the facility require careful consideration as flow
conditions can often create the risk of erosion, cavitation, and/or corrosion.
After just a few years of operation, the plant began encountering problems with several control valves, particularly the larger ones, as well as all sizes of valves in slurry service. When the valves were taken out of service for inspection, maintenance, review, and analysis, it was clear that many of the issues were related to process conditions that varied from those specified in the initial design.
The breadth of issues was evident to plant personnel, so they reached out to Spartan Controls to partner and find long-term solutions. Spartan Controls in turn contacted experts within Emerson for additional assistance. An initial review of the damaged valves revealed the following problems:
n Excessive cycling, resulting in actuator O-ring breakdown and failure, along with linkage damage.
n Damage to valve stems and bearings.
n Valve response issues due to unexpected process conditions.
n Erosion damage due to high solids slurry service.
n Undersized actuators.
n Corrosion due to elevated temperatures and an unanticipated concentration of specific chlorides and minerals.
A team consisting of K+S plant personnel, Spartan Controls, and Emerson joined forces to investigate each issue so they could further understand the problems and determine appropriate solutions.
The original plant design called for large Bettis™ G-series actuators to achieve the desired failsafe position, and to provide sufficient torque for controlling the larger (16 – 20 in.) Fisher™ Vee-Ball™ valves. These actuators were paired with Fisher FIELDVUE™ digital valve controllers to provide continuous loop control and maintain flows close to setpoint.
Unfortunately, some of the larger valve assemblies were cycling too frequently, impacting control. For example, one assembly cycled 116 931 times in a month (Figure 2), compared to a more typical assembly that only cycled 102 times in that same time period. Such continuous and unnecessary movement created significant wear spots in the actuator linkages, as well as damaged actuator O-rings, which caused air leaks –ultimately leading to poor flow control.
After some investigation, the troubleshooting team realised that the digital positioners were tuned incorrectly during the initial commissioning. After consulting with the Emerson team, site personnel adjusted the gain and deadband to factory-recommended settings, which allowed the valves to respond quickly, while eliminating the ‘hunting’ that created the cycling. The distributed control system was also de-tuned for these loops to
reduce cycling, while maintaining tight control of the process.
The actuator linkages were repaired as required, and the actuator O-rings were upgraded to a polymer better suited for high frequency modulating service. The standard O-rings that were initially specified were more appropriate for on/off service, rather than what turned out to be continuous, high cycling, analogue service.
These adjustments and modifications greatly reduced the valve cycling, eliminating the need for excessive actuator repairs.
Most control valves can be installed in any orientation and still operate as designed, but there are benefits to installing very large rotary valves with a horizontal (i.e. actuator beside the valve), rather than a vertical (i.e. actuator above the valve) shaft orientation. With these larger valve sizes, the ball weighs more, and it therefore exerts more downward force due to gravity. A horizontal orientation can act as a counterbalance to this force, resulting in less wear and tear on the assembly.
This was evident in several large valves, including those installed in 20 in. lines, which were exhibiting consistent seal and bearing failures, requiring frequent valve overhauls. An analysis of these failures determined that many of the valves were originally installed with the valve shaft in a vertical orientation (Figure 3).
The vertical shaft installation exerted excessive thrust force on the bearings and seals, causing premature failures. Simply rotating the valve assembly 90° eliminated these problems, as it greatly reduced the thrust forces that had been creating the damage.
A few valves operated sluggishly and were experiencing cavitation damage, with some struggling to maintain consistent flow under certain conditions. The team revisited the original sizing conditions and compared them to the current operating process pressures, flows, percentage open, and temperatures. In many cases, the team found the operating conditions to be significantly different than those utilised during initial valve selection and specification.
Revisiting the sizing calculations with the actual plant operating conditions allowed the team to determine a more appropriate valve and/or actuator type/size for each application. In some cases, an anti-cavitation trim was installed to better handle the damaging phase change phenomena. In other cases, larger actuators were required. These actions greatly improved the control and reliability of the previously troublesome valves.
The most difficult challenge was addressing the severe erosion and corrosion attack that bedeviled multiple valves across the plant (Figure 4). Many valves were
exhibiting serious damage when they were pulled for routine inspection and maintenance, with internal components nearly wasted away.
Valves with serious damage were sent to the materials labs in the Emerson Innovation Centre in Marshalltown, Iowa, for evaluation and testing to better understand the mechanism and pathway for the corrosion attack. Metallurgical testing showed that various damaged valve parts were inflicted with a particularly difficult combination of pitting corrosion, erosion, stress corrosion cracking, crevice corrosion, galvanic corrosion, and chloride attack (Figure 5), all of which are common for these types of facilities. This damage was accelerated by process temperatures and concentrations of potassium chloride that were much greater than anticipated in the original plant design.
Once the corrosion mechanisms were understood, the team was able to address the problems by changing the materials of construction to better suit the service conditions. S20910 valve stems were upgraded to Super Duplex to eliminate the galvanic corrosion problems. The 316SS and Alloy 6 valve trim components in high potash concentration service were respectively upgraded to Super Duplex and R31233 (a cobalt alloy), to prevent localised corrosion within the valve body itself. In addition, chrome carbide coatings were utilised in some instances to better withstand the erosive effects of the slurry (Figure 6).
These construction upgrades reduced valve wear and tear significantly. When modified valves were pulled for
inspection almost a year later, little, if any, damage was apparent.
Extensive collaboration and hard work allowed the team to achieve dramatic success. Before the valve improvements were implemented, the plant was spending US$40 000 – 50 000/yr for actuator repairs.
Once the actuator issues were identified and resolved, those repairs dropped to US$10 000 or less. The impact of the upgraded valve materials on construction saved another US$90 000/yr. More importantly, plant uptime and reliability have been improved due to the dramatic reduction in unplanned outages.
Such savings are not uncommon when a knowledgeable and talented team is focused on a common goal. If a new process facility is encountering unexpected valve problems, plant personnel would be wise to collaborate with their local partner and automation vendor to jointly investigate the problem. Often, actual design conditions do not match the original specifications, and these unexpected process conditions can cause control issues and inflict serious damage to valves.
By jointly addressing the problem, a cohesive team can bring the necessary knowledge and expertise to understand and alleviate these types of issues.
There is LINATEX® premium rubber – and there are other red rubbers.
Starting in 2024 we’re introducing branding on LINATEX® premium rubber sheet, so that when you order LINATEX® premium rubber, you can be sure that you’re getting LINATEX® premium rubber and its legendary performance.
LINATEX® premium rubber
Your first line of defence against abrasion.