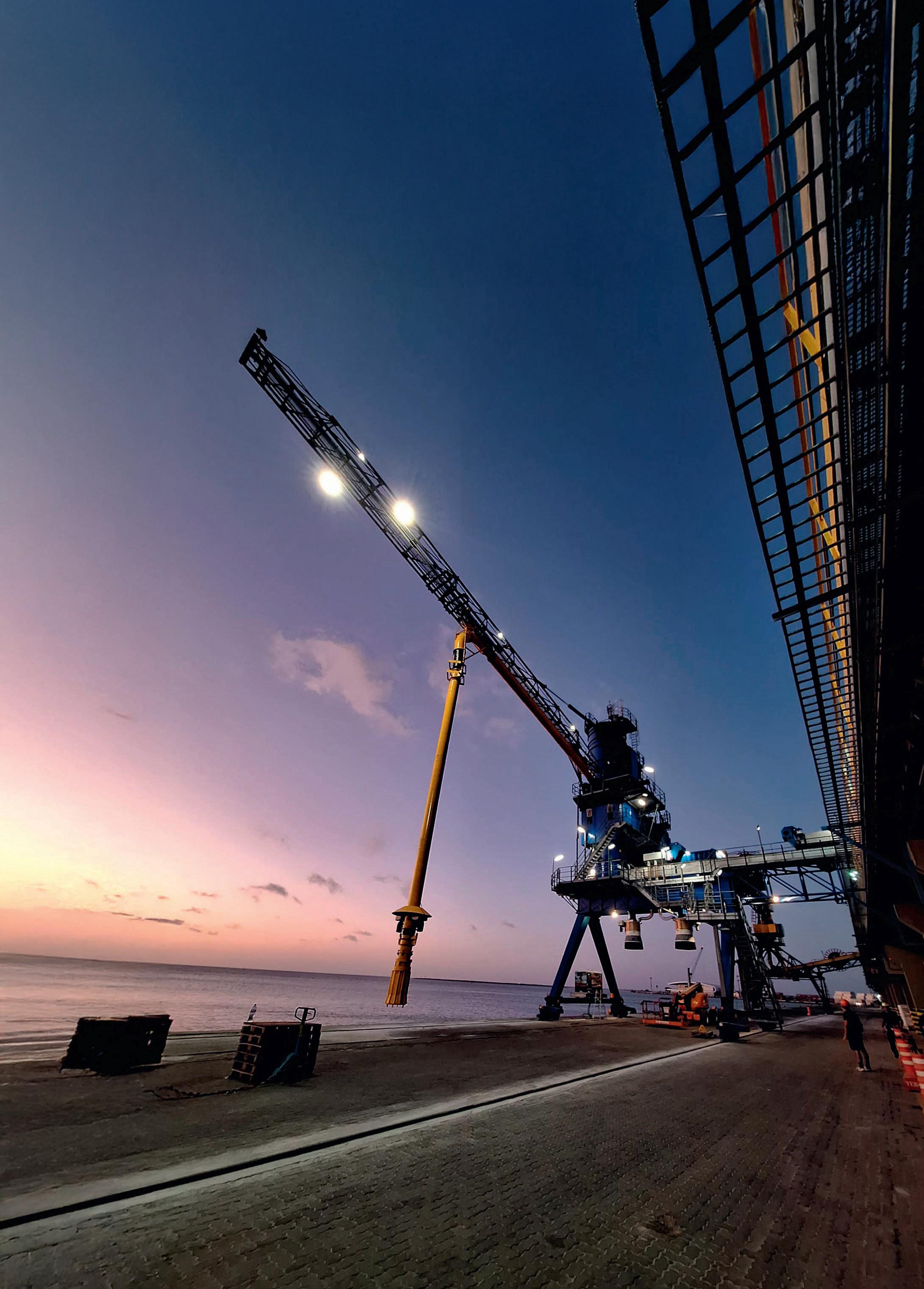
SPRING 2 025 - VOLUME 10 NUMBER 1
SPRING 2 025 - VOLUME 10 NUMBER 1
Crushing efficiency at the primary stage
Corey Poppe, Superior Industries, describes best practices for jaw crushers, such as identifying maximum feed size, determining desired product size, and defining tonnage goals.
Maria Bertzeletou, Signal Ocean, analyses the latest developments shaping the dry bulk freight industry, exploring the impacts of geopolitical tensions and examining the challenges and opportunities emerging during the new Trump era.
Paul Smith, Legacy Building Solutions, explains how modern fabric buildings can deliver strength and flexibility for the protection of loose bulk materials.
A world at multiple speeds
Dirk Janssens, VIGAN, outlines the new demands on machinery and infrastructure in the dry bulk logistics industry as global living standards change, and considers how operators can meet this challenge.
28 Uniting the future fuels supply chain
Julien Boulland, Bureau Veritas Marine & Offshore, describes how collaboration will help ensure the dry bulk sector’s decarbonisation transition.
33 Facing uncertainty with efficiency
Daniel Koch, Manta Marine Technologies (MMT), writes that even as uncertainty dominates international trade relations and geopolitics, fleet efficiency remains a wise investment regardless of which way the market moves.
37 The smarter way to simplify compliance
Tor Svanes and Jacob Clausen, NAVTOR, discuss how smart solutions can help shipping companies navigate compliance, unlock benefits and face the future with confidence.
40 Conveyors
Dry Bulk asked leading players in the conveyor sector for their insights on a range of topics covering everything from automation to reducing noise emissions and handling corrosive materials. A Vigan Pneumatic Unloader NIV 600 TPH on rails, recently assembled in Fortaleza, Brazil. This advanced machine is designed to efficiently handle wheat, which is directly transferred into a nearby mill on-site. With over 55 years of experience, Vigan offers reliable and customised solutions for agri-bulk handling. Our team is dedicated to creating optimally suited solutions for achieving profitable projects and installations. For more information, visit: www.vigan.com
MANAGING
James Little james.little@drybulkmagazine.com
SENIOR EDITOR
David Bizley david.bizley@drybulkmagazine.com
EDITORIAL ASSISTANT
Alf Hamer alfred.hamer@drybulkmagazine.com
SALES DIRECTOR
Rod Hardy rod.hardy@drybulkmagazine.com
SALES EXECUTIVE
Sophie Birss sophie.birss@drybulkmagazine.com
PRODUCTION MANAGER
Iona Macleod iona.macleod@drybulkmagazine.com
ADMINISTRATION MANAGER
Laura White laura.white@drybulkmagazine.com
EVENTS MANAGER
Louise Cameron louise.cameron@drybulkmagazine.com EVENTS COORDINATOR
Chloe Lelliott chloe.lelliott@drybulkmagazine.com
DIGITAL EVENTS COORDINATOR
Merili Jurivete merili.jurivete@drybulkmagazine.com
DIGITAL CONTENT ASSISTANT
Kristian Ilasko kristian.ilasko@drybulkmagazine.com
JUNIOR VIDEO ASSISTANT
Amélie Meury-Cashman amelie.meury-cashman@drybulkmagazine.com
Welcome to the Spring issue of Dry Bulk. Covering dry bulk news over the last few months and editing the articles you are about to read has shown me that this sector is one full of contrast. The rapidly advancing technology, regulatory environment, and consumer demand juxtapose with sometimes ageing and outdated infrastructure, which, as this issue’s cover story on pg. 19 from VIGAN points out, paints a picture of a “world at multiple speeds”. For material handling and port operators, meeting these new demands is of utmost importance.
By the end of 2024, the average age of the global dry bulk fleet had increased to 14.7 years, bringing with it a number of risks and prompting, for example, RightShip to update its vessel inspection threshold late last year from 14 to 10 years. But at the same time, dry bulk vessels are literally taking onboard new ideas. Innovations like onboard carbon capture and wind-assisted rotor sails are beginning to be adopted, in order to strategically meet the demand on the industry to decarbonise. Taking advantage of these new innovations is helping the dry bulk sector to, as the article on pg. 33 from Manta Marine Technologies puts it: “face uncertainty with efficiency”.
Yet more contrast is to be found in the dry bulk sector’s regulatory and geopolitical environment. On 1 January, FuelEU Maritime came into effect; an EU regulation that sets requirements on emissions from ships trading within the EU or EEA. As the article on pg. 37 from NAVTOR points out, there is mounting pressure on shipping companies to come up with smart solutions to simplify the enormous task of complying with these regulations.
The strategy that is perhaps highlighted most throughout this issue is collaboration, the focus of Bureau Veritas’ article on pg. 28. Strong partnerships and engagement between stakeholders, experts, and operators across the globe is vital to achieve the industry’s targets. And yet, the signs coming from the new administration in the US point to a potential heightening of geopolitical tensions, especially with China, but also even with long-term partners and historic allies.
Whatever happens, the actions and policies of the returning President and his government will be felt around the world. In this issue’s regional report on pg. 10, Maria Bertzeletou, Signal Ocean, analyses the impact that US activities will have on the dry bulk sector in the Americas and beyond.
These developments raise broader questions than anyone can fully answer right now. Fortunately, however, there is a topic for which we can provide some answers right now: conveyors. For this issue, we reached out to numerous experts to answer in-depth questions about conveyors – turn to pg. 40 to learn more about how conveyor systems are adapting to new technologies, addressing dust and noise emissions, and approaching sustainability.
Overall, this year is set to be one of the dry bulk sector’s most challenging and uncertain – but with collaboration and efficiency, it could also be one of its most transformative. I hope you enjoy this issue.
Convey units
Truck loading
Berge Bulk and BHP have joined forces to pioneer an iron ore voyage from Australia to China powered entirely by B100 biodiesel. The BergeLyngor , a 206 330 dwt Newcastlemax bulk carrier, is delivering iron ore from Australia to China. Last month, the vessel successfully bunkered B100 biodiesel. This pilot marks the first use of B100 biodiesel on the iron ore trade route between Australia and China.
“This collaboration with Berge Bulk represents an exciting step in BHP’s ambition to reduce greenhouse gas emissions from shipping of our products. Together, we are demonstrating that meaningful progress can be achieved through bold initiatives, innovation, and teamwork.” said Gerard Ang, Head of Maritime Iron Ore, BHP.
B100 biodiesel uses vegetable oil, animal fat, tallow and/or waste cooking oil from restaurants and industrial kitchens and translates to an almost 84% reduction in well-to-wake greenhouse gas (GHG) emissions compared to the equivalent quantity of conventional fossil fuel oil.
Converting to new fuels is a key part of Berge Bulk’s Maritime Marshall Plan for decarbonisation. The company has been proactively exploring various fuels with potential for lower GHG emissions voyages:
n Biodiesel: Berge Bulk has been gaining experience using biodiesel (B30, B50, and B100) on voyages from Europe and North America since 2021.
n Ammonia: in 2024, Berge Bulk announced plans to build two ammonia powered ships to be delivered by 2027.
n Methanol: in 2024, Berge Bulk also became a member of The Methanol Institute — the trade association for the global methanol industry, representing the world’s leading producers, distributors, shippers and technology companies.
This latest voyage of the Berge Lyngor represents the first time Berge Bulk will be using biodiesel on a voyage in the Pacific.
“Berge Bulk has committed to building and operating a zero Scope 1 emissions vessel by 2030 and achieving zero Scope 1 emissions fleetwide by 2050. This collaboration with BHP is a testament to what we can achieve together. By deploying B100 biodiesel on the Berge Lyngor, we are not only reducing carbon emissions for that voyage but also setting an example of how
partnerships and innovation can lead to a greener future for shipping.” said Duncan Bond, Chief Commercial Officer, Berge Bulk.
Rocktree Logistics Group, an infrastructure service provider through a network of offshore terminals, shuttle vessels, barges, and other turnkey solutions, has announced that it has agreed to acquire 100% of a group of companies known as ATRIA Soluciones Logísticas (Atria), a South American port services and river transportation group.
Through this transaction, Rocktree will expand its global footprint across the commodities and agriculture value chain, offering a broader range of services to new and existing customers. Rocktree will acquire Atria from Southern Cross Group, and the financial terms of the transaction were not disclosed.
Daniele Pratolongo, CEO of Rocktree, said, “We are thrilled to welcome Atria to Rocktree. This transaction represents an important step in our history, as we will significantly expand service offerings for our customers.
Atria’s assets, operations, and long-term customer relationships are unparalleled in our industry, and our combined company will be well-positioned for day-one scalability and long-term growth and value creation as we work together to expand our leadership in logistics solutions across the globe.”
In connection with the transaction and other expansion plans, Rocktree has secured private credit financing of up to US$350 million from the Blue Ocean maritime investment platform managed by EnTrust Global, a leading global alternative asset management firm. Pratolongo continued, “Equally important to this acquisition is the firm that has helped to finance it. We would like to extend our thanks to the entire team at EnTrust Global. As we look to continue to expand Rocktree’s offerings with Atria under our wing, this financing will help fuel Rocktree’s next phase of growth, which may include a combination of organic growth initiatives coupled with other strategic M&A opportunities.”
GEAPS Exchange
22 - 25 February 2025
Kansas City, USA www.geaps.com/exchange
EnviroTech - The Gateway to Green Cement 09 - 12 March 2025 Athens, Greece worldcement.com/envirotech
bauma
07 - 13 April 2025 Munich, Germany bauma.de
TOC Europe
17 - 19 June 2025
Rotterdam, the Netherlands www.tocevents-europe.com
POWTECH TECHNOPHARM
23 - 25 September 2025
Nuremberg, Germany www.powtech-technopharm.com
Antwerp XL 04 - 06 November 2025
Antwerp, Belgium www.antwerpxl.com
Global Grain Geneva
11 - 13 November 2025
Geneva, Switzerland
www.fastmarkets.com/events/ global-grain-geneva-2025/
To stay informed about industry events, visit Dry Bulk Magazine’s events page: www.drybulkmagazine.com/events
UK Anemoi completes installation of Rotor Sails onboard VLOC in largest wind-propulsion project to date
Anemoi Marine Technologies completed the installation of five Rotor Sails onboard the 400 000 dwt very large ore carrier (VLOC), Sohar Max, making it the largest vessel to receive wind propulsion technology to date. Sohar Max is a first generation Valemax, built in 2012 in China’s Rongsheng shipyard.
The project showcased global collaboration between Brazilian mining giant Vale S.A., Omani shipowner Asyad and UK-based Rotor Sail provider Anemoi.
The five 35 m tall, 5 m diameter Rotor Sails were retrofitted onboard Sohar Max at the COSCO Zhoushan shipyard in China, in October 2024. In addition, Anemoi has installed its bespoke folding deployment system, which will enable to sails to be folded from vertical to mitigate any impacts on the vessel’s cargo handling operations.
With the installation of the Rotor Sails, it is expected that Sohar Max will now be able to reduce its fuel consumption by up to 6% and cut carbon emissions by up to 3000 tpy. Sohar Max has just completed a voyage to Tubarao, during which the rotor sail test period began and testing will continue on future voyages.
“Since 2010, Vale has been operating with highly efficient ships and, in recent years, has fostered initiatives for the adoption of wind energy, which will play a central role in the decarbonisation of maritime transport of iron ore,” says Vale’s Director of Shipping, Rodrigo Bermelho. “This project reinforces this tradition of Vale’s shipping area of investing in innovation and stimulating the modernisation of the fleet to reduce emissions, in partnership with shipowners.”
“This is an exciting landmark project for Anemoi, and wind propulsion in general, as it demonstrates the significant impact wind energy has on even the largest vessels. Installing our Rotor Sails on this scale is a proud moment, showcasing our award-winning technology on another ore carrier,” said Nick Contopoulos, Chief Production & Partnerships Officer of Anemoi Marine Technologies. “We are thrilled to be a part of Vale and Asyad’s ongoing sustainability plans and to support their efforts in driving decarbonisation across the maritime industry.”
“We extend our deepest thanks to all our partners who made this retrofit possible. Together, we’re advancing meaningful change and driving the industry towards a greener future.” he added.
In October 2024, Vale announced it is also set to install Anemoi’s Rotor Sails onboard the 400 000 dwt VLOC NSU Tubarao, which is owned by NS United Kaiun Kaisha. The project, which is due for completion in September 2025, is expected to achieve significant reduction of fuel consumption and carbon emissions.
These projects with Vale are the latest in a series of ongoing installation projects Anemoi has with some of the world’s biggest shipowners and operators, which are looking to harness wind energy to increase the efficiency of their vessels by reducing fuel consumption and carbon emissions.
DNV has released a competence standard (ST) for methanol and a recommended practice (RP) for ammonia, to enable crew and shipowners to tackle the safety risks and challenges posed by the introduction of new alternative fuels and technologies through shipping’s decarbonisation.
According to DNV’s Alternative Fuels Insights platform, the number of vessels ordered with alternative-fuelled capability is growing with 27 ammonia and 322 methanol-fuelled vessels currently on the orderbooks. To ensure safe operations as these vessels enter service, it is essential that shipboard crew has the right knowledge and skills and adhere to updated processes and procedures.
Knut Ørbeck-Nilssen, CEO DNV Maritime said: “Embracing new fuels and technologies is essential to achieving our decarbonisation goals, but these advancements introduce new risks, adding complexity to an already challenging operating environment. To obtain a safe, timely, and impactful maritime transformation, we need to ensure safe opecrations by supporting both our seafarers and onshore personnel. Competence development is crucial for managing the transition safely and avoiding a safety gap that could put crew, assets, the environment, and our decarbonisation efforts at risk.”
The DNV-ST-0687 “Competence related to the use of methanol as fuel” published in October, and the DNV-RP-0699 “Competence related to the use of ammonia as fuel,” published in December, apply to shipboard crew on vessels using methanol or ammonia as fuel. They clearly outline the expected competencies for using these fuels onboard, enabling the assessment and verification of an individual’s knowledge and skills to ensure they can operate and maintain systems and equipment safely.
Kirsten Birgitte Strømsnes, Business Development Leader in DNV Maritime Advisory said: “Introducing methanol or ammonia as fuel onboard vessels will impact personnel ashore, the shipboard crew and the shipowner’s organisation. It is critical that the crew can recognise risks and operate systems safely and the organisation needs to accommodate
for this through i.e. safety management system and other organisational means.
“DNV’s Methanol ST and Ammonia RP can provide the shipowner with an overview of competence needs for the shipboard crew, and assist in defining training needs, crew planning and input to manuals. The purpose of these documents is to be used by shipowners for onboard familiarisation and competence management, by maritime academies and training institutions to develop curricula and courses and by third parties, as a reference document, for certification or verification of learning programmes and competence assessments in examinations.”
The International Association of Dry Cargo Shipowners (INTERCARGO) marked a transformative year in its 2023 – 2024 Annual Review, launching major initiatives while reaching record membership levels amid growing industry challenges.
Outgoing Chairman Dimitri Fafalios reflected on key developments during 2024, including the August launch of the Dry Bulk Centre of Excellence (DBCE) and its DryBMS portal, demonstrating the sector’s dedication to operational excellence. The Association marked another milestone with its first-ever report communicating its messaging via ESG and showcasing progress in environmental stewardship, social responsibility and governance.
Safety maintained its position as the foremost priority, with the latest Bulk Carrier Casualty Report revealing positive trends in ship loss reduction despite fleet growth. However, the organisation emphasised that continued vigilance remains essential, particularly regarding cargo liquefaction risks.
The Review addresses critical challenges, including the implementation of the International Maritime Organization’s net-zero emissions target, maritime security concerns in the Red Sea region, and the implementation of the Ballast Water Management Convention’s.
YOUR PARTNER TOWARDS SUSTAINABILITY
Choosing the right crushing plant is vital for project success. For 45 years, MMD has led the way in Mineral Sizing and In-Pit Sizing & Conveying (IPSC) technology, offering solutions that enhance production, safety, and efficiency.
The Twin Shaft MINERAL SIZER™ uniquely defines product size in all dimensions while minimizing dust and fine material. It achieves some of the lowest power consumption per tonne compared to traditional crushers, efficiently handling various materials—from wet and sticky to hard and abrasive—while ensuring consistent delivery to stockpiles or ships.
MMD designs Fixed, Semi-Mobile, and Static sizing stations tailored for diverse operations around the globe. The compact design of the Sizer allows for easy retrofitting into existing setups.
Enhance your productivity today with MMD’s low-cost, environmentally focused Sizer technology.
Maria Bertzeletou, Signal Ocean, analyses the latest developments shaping the dry bulk freight industry, exploring the impacts of geopolitical tensions and examining the challenges and opportunities emerging during the new Trump era.
The grain dry bulk freight industry faces a complex landscape of opportunities and challenges in the new Trump era. Key dynamics include drought conditions affecting crop yields at major export hubs, ongoing geopolitical tensions in the agricultural sector, and evolving market conditions in major grain-producing nations like Russia and Brazil.
Russia’s agricultural sector is grappling with significant difficulties, exacerbated by one of the worst Winter grain harvests in 23 years. In 2025, 38% of Russian
crops are classified as poor, a substantial increase from the previous year’s 31%, while only 31% are deemed in good condition, compared to 74% last year.
Severe weather events, including an extended Summer-Autumn drought and damaging May frosts, have played a significant role in these challenges. However, experts point to more profound issues, such as a marked technological decline within the sector.
The Russian Grain Union has highlighted the need for modernisation and systemic reforms to reverse the ongoing downward trend in productivity and competitiveness.
Russia's invasion of Ukraine further complicates the scenario, impacting agricultural trade and the stability of the region’s grain markets. Exporters and freight operators will need to navigate these uncertainties carefully, as Russia’s diminished grain output could influence global supply chains and freight pricing.
On the other hand, Brazil is expected to deliver record-breaking harvests of soybeans and corn in early 2025, offering significant opportunities for the freight industry. According to Itaú BBA Consulting, Brazil is projected to produce 170 million t of soybeans and 125 million t of corn during the 2024/25 growing season. Total exports of soybeans, corn, sugar, and soybean meal are anticipated to exceed 205 million t in 2025, up 10 million t from the previous year.
However, this growth comes with logistical challenges. The soybean harvest, concentrated in February due to delayed planting, risks exacerbating bottlenecks at Brazilian ports, particularly if wet weather persists during this critical period. Freight rates, which saw a decline in 2024 due to lower diesel prices, are expected to rise again with the record harvest. Truck freight from Sorriso, Mato Grosso to the Port of Paranaguá dropped from R$473/t (July) to R$386/t (December) but will likely increase as harvest activities intensify. While Brazil has invested heavily in port infrastructure, the rapid growth in soybean and corn production has outpaced these efforts, potentially leading to congestion and delays. The surge in export volumes will demand careful planning and optimisation from freight operators to ensure timely deliveries and maintain competitive rates.
The combination of these factors creates a nuanced outlook for the grain dry bulk freight sector. Challenges in Russia may limit global grain supply, potentially increasing demand for exports from other major producers like Brazil. However, logistical hurdles in Brazil could constrain its ability to fully capitalise on this demand. Freight operators will need to
monitor these developments closely, adapt to fluctuating rates, and invest in technology and infrastructure to address systemic inefficiencies and ensure resilient supply chains.
The new Trump administration’s policies on international trade and infrastructure development may further shape the industry. Increased focus on US grain exports could heighten competition, while any changes to fuel prices or environmental regulations could impact freight costs globally. As the industry adapts to these shifting dynamics, strategic foresight and operational flexibility will be key to navigating these developments.
The US grain market is navigating a complex environment marked by uncertainty, with numerous factors influencing prices and trade dynamics. Global weather patterns, geopolitical tensions, biofuel demand, and critical USDA reports are key variables shaping the market. For producers and traders, this volatile landscape necessitates a proactive approach to seize opportunities and mitigate risks. January stands out as a critical month, with close attention on South American weather, the USDA’s WASDE report, and potential policy shifts under the new US presidential administration.
A strengthening US dollar since late 2024 has added another layer of complexity, as it makes American grain exports more expensive, potentially dampening demand. However, any weakening of the dollar in 2025 could enhance competitiveness. On the supply side, global grain production has been abundant, keeping prices under pressure. The upcoming WASDE report is expected to clarify US crop sizes and Brazil’s soybean output, with surprises in these estimates likely to impact market sentiment significantly.
Demand for grains such as corn, soybeans, and wheat remains robust, with ethanol production, soybean crushing, and Chinese soybean consumption being critical areas to watch. Additionally, weather conditions in South America, Europe, Russia, and North America remain vital to supply forecasts, with South American harvest outcomes likely to influence global price trends.
Geopolitical tensions continue to be a wildcard in 2025, as conflicts and trade disputes could disrupt markets unexpectedly. Seasonal price trends offer some guidance, with grain prices historically weaker during harvest and stronger during uncertain periods, aiding producers in strategic pricing.
China and India remain central to global grain markets due to their growing middle classes and increasing demand for protein-rich foods. Monitoring economic and agricultural developments in these nations will be key to understanding future shifts in global demand. Together, these factors underline the importance of staying vigilant in a market defined by both challenges and opportunities.
The implications of the new 2024 US election and the resulting presidential administration on the freight industry are substantial. If tariffs on US grain exports to
In mining and materials handling, the Hägglunds Quantum Power motor reshapes reality with shared DNA. Adding a slim new connection block to the proven Hägglunds Quantum, it opens up an unthinkable space – stretching to 170 rpm while retaining full torque capacity at high efficiency. For belt conveyors, crushers, sizers, surface miners and more, it’s time to enter the Quantum domain: www.hagglunds.com/quantum
Hägglunds is a brand of Rexroth. www.hagglunds.com
China are increased, American grain exports could face further decline, shifting demand toward alternative suppliers like Brazil and affecting the traditional US – China grain shipping routes. Continued tariffs on US grain exports to China are likely to drive China toward sourcing more agricultural products from Brazil and other South American producers.
Using data from Signal Ocean (Figure 1), monthly grain shipments to China have been increasing since late 2022, as the US works to recover lost market share. In October, just before the 2024 US election, American grain exports surged, with shipments to China reaching 60% of Brazil’s total grain shipments – a significant jump from September’s 25% and August’s 10%, showing a notable rebound in US exports.
The Trump administration may consider renegotiating trade terms with China to regain ground in agricultural exports. However, if tariffs persist, the US agricultural sector may continue to seek new markets in Southeast Asia or Africa, while China strengthens its ties with Brazilian producers. This shift could lead to increased competition in the global grain market, impacting prices and the profitability of American farmers.
If US grain exports shift toward new markets in Southeast Asia and Africa, dry bulk demand along these trade routes could rise, potentially driving up freight rates for vessels transporting bulk grain. Signal Ocean data on
Supramax vessel movements (Figure 2) shows occasional spikes in activity, particularly in the months leading up to the end of 2Q23 and a similar period in 2024. However, these short-term increases have not been enough to offset the overall decline in the market. These fluctuations likely reflect temporary market adjustments or responses to seasonal demand changes in China. Notably, a rebound in September and October of 2024 was observed, but the growth in tonne days slowed as US grain flows to China tapered following the determination of the US election results.
The growth in tonne days – an indicator of how far and how much cargo is shipped over time – closely follows grain flow patterns, which underscores the link between trade volume and vessel demand. Despite recent spikes, the longer-term downtrend in tonne days for US grain shipments to China suggests a broader shift. As China increasingly sources grain from alternative markets, such as Brazil and Argentina, tonne days are likely to increase on Brazil-China and Argentina-China routes, favouring vessels operating between Latin America and Asia. This could lead to a reallocation of Panamax and Supramax fleets from US Gulf routes to South American routes, impacting freight rates along these corridors.
The competitive pressures faced by US grain exporters, largely due to tariffs and other trade barriers, are expected to exert downward pressure on demand for Panamax and Supramax vessels handling US-China grain flows. In contrast, as Brazil’s grain exports to China continue to grow, the demand for these vessel types on Brazil-Asia routes is likely to increase, which could drive up charter rates along these trade lanes. However, in 1Q24, the US saw a rebound in its monthly grain shipments to China, contrary to market expectations for a strong finish to the year for Brazilian market share (Figure 3). Despite this, Brazil’s grain flows to China experienced a downward correction in 4Q24, which ultimately failed to trigger a spike in Supramax tonne days. This resulted in a new low for Supramax tonne days growth, marking a significant decline not seen earlier in the year.
Looking ahead, if the US imposes additional tariffs on grain exports or if political relations with China further deteriorate, the dry bulk freight market may see a continued decline in US-China grain flows. A shift in demand towards South American exporters would not only reshape global grain trade patterns but could also increase volatility in vessel availability and rates across different routes.
Vessel operators may face increased pressure to adapt fleet strategies, deploying ships on longer Brazil-Asia voyages, impacting operational costs and logistics planning.
Paul Smith, Legacy Building Solutions, explains how modern fabric buildings can deliver strength and flexibility for the protection of loose bulk materials.
Selecting the ideal storage solution for dry bulk commodities involves evaluating multiple factors. Considerations include the type and quantity of material to be stored, the operational processes required on-site, and the influence of environmental conditions specific to the storage location.
Many operations have identified tension fabric buildings as the most practical and economical solution for storage applications. These structures are not only designed to protect stockpiles of loose materials such as frac sand, fertilizer, coal and
more, but they can also be designed to support comprehensive operational needs. From flat storage to loading and other material handling processes, today’s fabric buildings are engineered to enhance efficiency and adaptability.
For decades, fabric structures used for dry bulk storage relied on hollow-tube, web-truss framing that got the basic job done; however, the engineering of these buildings posed challenges in consistency and reliability. The hollow metal tubes often lacked the strength and longevity needed for demanding applications.
A significant breakthrough for the industry came about 14 years ago when Legacy Building Solutions introduced the combination of fabric cladding and structural steel I-beam framing. The adoption of rigid-frame structural design, universally accepted within the engineering community, immediately gave fabric buildings a higher level of credibility.
The introduction of I-beam framing also transformed the design process for fabric structures. Previously, users were limited to selecting from among a manufacturer’s pre-engineered size offerings. With the rigid-frame approach, buildings are instead designed with a clean sheet from the
start, with the dimensions and layout customised to a user’s exact needs.
This development has cemented tension fabric buildings as an optimal solution for the dry bulk industry, particularly for facilities that require long clear spans. The use of I-beam frames allows for larger, more economical designs, creating wide-open spaces for storage, loading, driving and other essential operations.
Optimisation of a facility goes far beyond specifying its dimensions. Items such as overhead conveyors or other collateral loads can also be accounted for in the original design. Using finite element analysis software, engineers can precisely calculate the optimal I-beam strength to support hanging loads, rather than over-engineering the entire structure and adding unnecessary construction costs.
By suspending equipment from above, the floor space below is left entirely open, allowing for maximum flexibility in layout and operations. Manufacturers often provide additional guidance on optimising interior floor layouts, offering recommendations on equipment placement and material pile arrangement to streamline load-in and load-out processes.
For material distribution applications like fertilizer storage, cast-in-place concrete retaining walls remain a traditional solution on the floor.
However, precast wall systems are becoming increasingly popular, as they can always be reconfigured as storage needs change. Some fabric structure suppliers will handle the sourcing, transporting, and installing of precast walls as part of their overall contract, ensuring the entire system integrates seamlessly with the building design.
The versatility of structural steel beams has also enabled fabric building manufacturers to develop more creative and efficient designs. For example, if land constraints prevent a user from having a typical rectangular footprint, a multi-section design can be employed, allowing for distinct operational zones while still maintaining a cohesive structure.
In such a design, the overall floor plan could remain free-flowing and unobstructed by posts or walls, but the amount of square footage dedicated to any given function can be plotted out more logically. For instance, in a three-tiered building design, the most spacious section could hold storage bins; a narrow outer section could have overhead doors and function as a drive-through lane for trucks; and finally, a centre section could hold hoppers and loading equipment for loading in and out of the other sections.
In effect, tension fabric buildings with I-beam design enable businesses to bring all their operations together under one roof, with everything precisely arranged to fit their unique requirements and enhance functional efficiency.
One of the obvious reasons that fabric originally became a popular cladding material for buildings is its inherent resistance to corrosion – a critical advantage over metal-sheeted buildings when needing to store salt, fertilizer, or other corrosive bulk materials. While the fabric itself is immune to rust, the same cannot always be said for the
Reduced handling costs, shorter turnaround times, reliability and flexibility: Nemag grabs give dry bulk terminals throughout the world that competitive edge they need in today’s demanding market.
Driven to achieve the best performance, we closely listen to our clients’ needs. For almost a hundred years, Nemag’s innovative grabs make it possible to realize the highest productivity at the lowest costs.
Explore our comprehensive range of high-quality grabs and discover the power of great bulk handling.
From coal and iron ore to wheat, scrap metals, minerals and clinker: Nemag has the optimal solution for every dry bulk flow!
Contact us find out how we can take your bulk handling to the next level.
framing system supporting it, which requires careful protection.
With traditional web truss fabric structures, while the cladding resisted corrosion, the hollow tube framing was prone to rusting from the inside out over time, creating long-term durability concerns. The transition to solid steel I-beams eliminated this weakness from the equation, but potential corrosion on the I-beam surface still needed to be addressed.
Most manufacturers initially relied on hot-dip galvanising, which provides a 3 mil zinc coating for protection. While effective in many dry bulk applications, galvanising truly only delays rust rather than preventing it entirely, making it susceptible to failing over time in highly corrosive environments.
To provide more reliable and long-term protection, manufacturers like Legacy have adopted advanced coating processes as a standard feature. This involves sandblasting the steel and applying a triple-layer coating – a 3 mil base layer of zinc followed by two 5 mil coats of epoxy paint. This combination creates a durable barrier that outright prevents corrosive dust and moisture from ever reaching the surface of each steel I-beam.
Epoxy coatings have become a popular solution among building operators looking to combat corrosion more
effectively. Many material distribution facilities have extended this approach to other metal equipment, such as conveyors, ensuring that all aspects of the operation remain resistant to harsh environmental conditions and potential corrosive damage.
Rigid-frame fabric structures can be ventilated easily, another useful advantage for dry bulk storage applications.
A standard fabric structure can address ventilation with a low-cost passive system that uses ridge and soffit vents. Passive systems like this rely on nothing more than the natural movement of warm air. Allowing for that air flow is typically all that is necessary to manage moisture and humidity inside the building. For situations where the user wants additional ventilation, the I-beam frame can be designed to support fans and other mechanical components.
The fabric membrane itself also plays a significant role in creating a better interior environment. Fabric roofs offer a high degree of translucency, which allows sunlight to permeate the inside of the building and provide ample illumination during daytime hours. The natural thermal characteristics of fabric also tend to keep the interior temperature more comfortable at all times – cooler during the summer and warmer in the winter months.
There has also been a shift in the type of fabric used. For decades, polyethylene (PE) was the most commonly used fabric for these structures, with polyvinyl chloride (PVC) fabric typically only utilised for more costly projects. Legacy Building Solutions recognised that the industry evolution to rigid-frame engineering could be further enhanced with an upgrade to the fabric cladding offered as well.
The company introduced a new higher-quality PVC to provide greater longevity, while also maintaining a price point similar to PE fabric. This PVC features a high-strength woven fabric with additional primer and lacquer layers. Through independent testing, the material has been found to retain more twice the tensile strength of standard PE, thereby providing several more years of life expectancy to the roof and sidewalls of a fabric structure.
Combined with advancements in structural steel frame engineering and fabric attachment methods, modern fabric material enables buildings to withstand harsh environmental forces, such as heavy snow loads or hurricane-level winds. The ability to customise structures based on regional climate conditions helps ensure they will provide reliable protection for storage operations in any location.
Modern tension fabric structures have transformed the landscape of dry bulk storage, offering the right balance of adaptability and durability. With rigid-frame I-beam designs, these buildings provide the engineering flexibility needed to customise layouts, integrate equipment, and optimise operations – all while addressing corrosion concerns with advanced epoxy coatings and durable PVC fabric. Combining faster delivery schedules, lower costs, and the ability to withstand extreme environments, tension fabric buildings deliver unmatched value for dry bulk facilities.
Dirk Janssens, VIGAN, outlines the new demands on machinery and infrastructure in the dry bulk logistics industry as global living standards change, and considers how operators can meet this challenge.
Feeding the world’s growing population is an ever-increasing challenge due to changing family patterns, eating habits, climate change, and geopolitical factors. The world population is continuously rising and people are changing their eating habits, leaving their homes to find a better future, migrating to vast cities, and are less willing to spend time to prepare their daily dishes.
In many industrialised countries there is also an increasing awareness of quality of life. People want to work less and closer to their homes, spend more time with their families, and live better.
What seems contradictory at first sight is logical upon reflection. In those countries where people have built a good standard of living, the next generation is ready to capitalise on the benefits of that. In other countries, people are living through their industrial revolution or are at its beginning. They are prepared to work harder for less, to drive further for good jobs, to travel when needed in often sub-optimal conditions.
So, the world is running at two or even more speeds. The bulk logistics industry might not be aware of the details of eating patterns or living standards, but it faces the consequences. More grains and oil seeds must be grown, harvested and transported. These needs transcend world politics. The vast agricultural areas where crops are grown most efficiently are generally less populated. Infrastructure must be implemented 'from farm to fork,' as they say.
In many important ports, the unloading and loading equipment is old and not adapted to the new demands in terms of capacity and vessel size. Countries like Brazil and Russia play an extremely important role in feeding the masses. New agricultural space has been created, sometimes at the detriment of the environment. The infrastructure in those areas is often new and adapted to the latest standards.
VIGAN sees this world at two speeds clearly. It has the chance to transform, improve, and adapt unloading and loading equipment in the old world. It is very challenging to transform equipment in an environment that was not foreseen for the existing quality standards, capacity requests and vessel size. VIGAN brings the equipment in line with the latest standards in terms of energy consumption, dust and noise emission levels as well as easiness to operate. People want to follow up on their unloading and loading equipment from their office chair and observe what is happening. VIGAN meets these requests, and still tries to provide machines with the level of sophistication necessary to function well but avoiding too much overkill, which would result in machines with a lack of availability.
When designing shiploading and unloading systems, several critical factors are considered to ensure efficiency and reliability. These include compatibility with different ship types and sizes, the characteristics of the cargo, desired capacity and throughput, environmental conditions, terminal layout, safety, energy efficiency, and maintenance requirements. VIGAN Engineering prioritises these elements to create systems that meet the specific needs of its clients.
There are very few complete white paper projects where VIGAN can start from scratch and create the best possible configurations. In most countries, existing ports are congested. They unload containers, cars and bulk in almost the same space. So, the
machines, being very vast, must still be moved to make place for other activities.
The company provides a variety of equipment tailored to meet these specific demands and needs:
n Mobile grain pumps: up to 250 tph.
n Pneumatic and mechanical ship unloaders: Available in both fixed and mobile versions, these unloaders are powered by diesel generators or cable reels, with pneumatic unloaders handling up to 800 tph and mechanical unloaders up to 1500 tph.
n Loaders: VIGAN’s loaders are versatile, suitable for various vessels including large and small barges, with mechanical loading capacities up to 2000 tph.
One of VIGAN’s features is its ability to also deliver complete turnkey projects. This includes not only the supply of machines but also the management of entire port terminal projects. From ship unloading and loading to storage facilities and bagging operations, VIGAN ensures a seamless integration of all components.
This adaptability and commitment to innovation and customer satisfaction are among the reasons why VIGAN Engineering, founded in the heart of Europe, has grown from a local company to a leader in the design and production of agribulk product handling equipment.
The company’s headquarters in Nivelles is also strategically positioned about 30 km south of Brussels, allowing it to serve a global market efficiently. Indeed, VIGAN exports 99% of its equipment, with emerging markets primarily in rapidly growing regions.
These are not the only ingredients for a successful recipe. The company’s vertical integration approach allows complete control over every aspect of operations, from initial design and calculation to manufacturing and shipping. In contrast to competitors heavily relying on subcontractors, VIGAN maintains a hands-on process.
VIGAN’s commitment to delivering top-notch machinery is shown through its practice of pre-assembling and testing each machine in its factory in Belgium. This care, from the initial design phase to commissioning, has been a cornerstone of the company's success.
While embracing new technologies, VIGAN remains cautious about the potential interference of sophisticated electronics in machine availability. The company prioritises durability and availability to prevent the machine’s unavailability when needed the most. VIGAN stays vigilant, implementing new technologies only when proven durable and easy to use.
A demonstration of this dedication lies in the establishment of a specialised department solely focused on the design and production of electronic
and electrical components. Since its inception, this department has experienced continuous growth. Fully integrated within the company, this department ensures in-depth expertise in the design and manufacturing of high-quality electrical and electronic components, thereby ensuring the reliability and performance of
VIGAN Engineering’s agricultural bulk material equipment.
As VIGAN introduces a new generation of CSUs with increased capacity, the company emphasises the importance of maintaining durability and availability.
Upscaling machine size involves addressing multiple parameters, including turbine size, piping diameters, air-lock sizes. The company has successfully solved these challenges in the near past, showcasing its ability to adapt to evolving industry needs.
VIGAN Engineering is designed to offer a comprehensive approach that combines proactive maintenance, long-term support, technological updates, and meticulous planning.
A strong is placed on emphasis on proactive maintenance, conducting regular inspections and providing precise maintenance recommendations to keep the machines in optimal condition. This proactive approach helps prevent potential issues before they become significant problems, ensuring the reliability and longevity of its equipment.
In addition to proactive maintenance, high-quality materials and robust designs are used in its machines. These elements contribute to the durability and dependability of its equipment, which in turn reduced the frequency and cost of repairs.
VIGAN also offers long-term support for its machines and maintains detailed records of all its machines, including exact drawings and photographs of the original configurations. This record-keeping allows for the provision accurate and timely support when customers need it. Spare parts for machines that are up to 40 years old will be provided, demonstrating its commitment to supporting the customers over the long haul.
Furthermore, the company offer technical assistance that includes detailed inspections of machines, comprehensive reports on their condition, and recommendations for maintenance or adjustments. This level of support ensures that customers can keep their machines running smoothly for many years.
To keep up with technological advancements, VIGAN modernises older machines with new technologies. For example, new electrical engines and frequency steering systems have been installed to improve energy efficiency. These updates can reduce energy consumption by up to 25%, which is particularly important in the context of rising energy costs. By integrating new technologies into older machines, customers are able to stay competitive and reduce their operational costs.
Finally, VIGAN ensures that any interventions are well-planned to minimise downtime and costs. It works closely with customers to plan updates or changes, providing dimensions of new configurations and supporting the preparation of the machines. This careful planning helps ensure that interventions are completed quickly and efficiently, with minimal disruption to operations. In many cases, the investment in these updates can be recouped within 1 to 2 years through savings in energy costs and improved operational efficiency.
By combining these strategies, VIGAN Engineering maintains high standards for its machines and ensures that its customers remain satisfied and supported throughout the lifespan of its equipment.
Pneumatic and mechanical ship (un)loaders
Up to 2500 tph for loaders and up to 1200 tph for unloaders.
Low noise & no dust emission
Turnkey solutions for cereals, soy flour, fertilizer, pellets and more...
Corey Poppe, Superior Industries, describes best practices for jaw crushers, such as identifying maximum feed size, determining desired product size, and defining tonnage goals.
Selecting the right crusher for an application depends on material characteristics, processing requirements, and desired output. Jaw crushers excel as primary crushers due to their ability to handle large feed sizes and high throughput.
They are particularly effective for:
n Hard and abrasive materials: jaw crushers are designed to crush hard, abrasive rocks efficiently, making them ideal for mining and quarrying applications.
n Simplicity and reliability: their straightforward design ensures reliable operation with minimal maintenance, a key consideration for producers seeking consistent performance.
n Cost-effective reduction: with high reduction ratios, jaw crushers efficiently reduce material size in a single pass, minimising the need for multiple crushing stages.
In contrast, cone crushers are often preferred for secondary or tertiary stages, where precise gradation control is critical. Impact crushers, on the other hand, are ideal for softer materials or applications requiring high-quality, cubical products. By offering a variety of crusher types, Superior Industries enables producers to tailor their crushing circuits to specific needs, optimising performance and cost-efficiency.
The crusher opening determines the maximum size of material that can enter the machine. For example, a 30 in. gape jaw crusher can handle material up to 24 in., adhering to the industry standard of limiting feed size to 80% of the opening. Oversized material can lead to production interruptions, excessive wear, and costly damage.
The closed-side setting (CSS) dictates the crusher’s output size. For instance, a 40 x 51 in. jaw crusher might have a CSS range of 4 – 8 in., producing material within that range. A reduction ratio of 6:1 is typical for jaw crushers, meaning the feed size is reduced to one-sixth in a single pass. Properly matching the CSS to the material flow ensures consistent downstream processing.
Production capacity depends on the width of the jaw and the CSS. For instance, a 42 in.-wide crusher might process 165 – 550 tph, while a 55 in.-wide unit can handle 265 – 855 tph. Material hardness and fine content also influence capacity.
Accurate data on feed size, product size, and production goals allows manufacturers to recommend the best-fit crusher for the application, ensuring efficiency and cost savings.
Maintaining the proper CSS is crucial for efficient crushing. Incorrect settings can disrupt material flow
throughout the plant, reducing productivity. Regular CSS checks and adjustments prevent issues such as oversized material overwhelming secondary crushers or inefficient downstream circuits. Modern crushers simplify CSS adjustments with hydraulic systems, such as:
n Hydraulic wedge adjustments: opposing wedges adjust CSS with the push of a button.
n Hydraulic toggle plates: these systems retract CSS during tramp events, avoiding damage and resetting quickly for continuous operation.
Frequent monitoring of CSS and jaw liners ensures consistent output, optimum plant performance, and reduced downtime.
Choosing the correct jaw liner profile is another critical factor in optimising crusher performance. Jaw liners, typically made from manganese steel, protect the crushing chamber while enhancing wear life. Key considerations include:
Liner effectiveness depends on matching manganese percentage to material hardness. While higher manganese levels can extend wear life, softer materials may not benefit and could waste costs.
Superior offers liners tailored to specific materials:
n Anti-slab liners: well suited for concrete recycling, breaking flat slabs more efficiently.
n Sharp tooth liners: suitable for slippery, rounded rock.
n Corrugated liners: versatile for general-purpose applications like gravel and shot rock.
Using the correct liner configuration ensures proper material flow and reduces maintenance costs.
Producers should replace liners when wear reduces effectiveness, typically when tooth height decreases to 3 / 8 in. Delayed replacement risks damage to components like toggle plates and bearings, increasing downtime and repair costs.
Properly specifying, maintaining, and operating jaw crushers significantly enhances efficiency, productivity, and profitability. Incorporating additional tools, such as grizzly feeders to remove fines before crushing, further optimises performance. Superior Industries’ comprehensive approach – from equipment design to aftermarket support – ensures producers achieve their operational goals.
Rope-, Motor- and Hydraulic Grabs
Our experience - Your advantage
Greifer GmbH
Talweg 15 - 17 - 74921 Helmstadt - Germany Tel.: +49 7263- 9129 0 - Fax.: +49 7263- 912912 export@mrs-greifer.de - www.mrs-greifer.de
Julien Boulland, Bureau Veritas Marine & Offshore, describes how collaboration will help ensure the dry bulk sector's decarbonisation transition.
The path to decarbonisation is complex, with regulatory pressures and technical challenges creating significant obstacles. Yet, collaboration and innovation hold the key to progress. Adopting low-carbon fuels, supported by strong partnerships and clear standards, will be critical in driving the industry’s energy transition.
For sectors such as dry bulk shipping, achieving sustainability will require integrating more sophisticated technological systems, reimagining operational practices, and deeper engagement with the entire supply chain. From port operators to commodity producers, every stakeholder has a role in reducing emissions and building a sustainable future.
The introduction of FuelEU Maritime is set to promote the uptake of renewable fuels and facilitate the gradual transition away from the industry’s reliance on traditional fossil fuels. Since January this year, vessels are required to decrease the average greenhouse gas intensity of their fuel use by 2% relative to the industry average, gradually reaching an 80% decrease by 2050.
Deploying low-carbon fuels, like hydrogen and ammonia, is a promising means of achieving these targets. However, robust supply chains and adequate infrastructure must be in place to support future fuel development, whilst more immediate actions must be taken to reduce vessels' energy consumption. Better operational efficiency, cleaner technology, and more sustainable operating systems can also be leveraged to support the industry’s emissions reduction targets.
The shipping industry faces significant obstacles in its transition to low-carbon fuel adoption. The high cost of implementing new low-carbon technologies, the need to retrofit existing vessels, and a fragmented supply chain make decarbonising maritime operations a complex challenge. The feasibility of alternative fuels depends on several factors, such as sustainable feedstocks and new production facilities, including reliable transport networks to deliver fuels globally.
Dry bulk shipping – the backbone of global trade for commodities like coal, grain, steel and iron ore, faces challenges in this transition. Unlike container shipping, which benefits from fixed routes and regular schedules, bulk carriers’ variable trade patterns and charter requirements require the option of bunkering in
a large number of ports – often worldwide – limiting the opportunity to either arrange for the supply or even have the option to access lower carbon fuels. Furthermore, many dry bulk carriers operate older vessels, which are less energy-efficient and costly to retrofit for low-carbon fuel use. The varying resources within the sector exacerbates these issues, as smaller operators may lack the necessary CAPEX to invest in new technologies and infrastructure. Despite these challenges, the emergence of LNG as a viable transition fuel can significantly contribute to the sector’s efforts to decarbonise.
The global demand for LNG has led to considerable investment in its production, infrastructure, and distribution networks. Bureau Veritas (BV) has played a significant role in developing and integrating LNG into maritime operations. From as early as 2012, BV has been involved in awarding Approval in Principle (AiP) certification of ship designs dedicated to ship-to-ship bunkering of LNG and has led in developing rules and guidelines for LNG bunkering. Rules such as NR 620 LNG Bunkering Ship focus specifically on the transfer system of the vessels to prevent leads and boil-off gas handling systems for ships that are not sailing continuously but are waiting for fuel delivery.
BV has been leading the charge in classifying LNG bunkering vessels, which are integral to supplying the world’s fleet with LNG. To date, BV has classified 35% of the world’s bunkering ships in service and has around 50% of the world’s orderbook. Recently, BV's fleet has grown with several newbuilds, including two 18 000 m 3 LNG bunkering vessels for Peninsula at Hyundai Mipo Dockyard and one 18 600 m 3 vessel for Ibaizabal at Hudong-Zhonghua which will be ready for delivery in 2026.
Moving the needle on low-carbon fuel production requires pragmatic solutions that will unlock the necessary investments to reach the required scale. As such, the industry must engage with innovative methodologies designed specifically to accelerate the adoption of alternative fuels. Dry bulk carriers vary greatly and will require different solutions based on scale. Indeed, smaller vessels between 10 000 and 40 000 dwt are often owned by smaller operations with limited financial power. In comparison, owners of larger vessels have much greater financial freedom to invest and lead the charge on carbon reduction soultions. This has resulted in the sector largely adopting a 'wait-and-see' approach to clean technologies to see which solutions will become most widely implemented throughout the shipping industry. However, initiatives are currently
available that look to spread the significant cost of alternative fuels with supply chain partners.
Energy insetting represents such an initiative. It will stimulate the production of renewable and low-carbon fuels at scale, connecting fuel buyers and sellers across the value chain, whilst also addressing the cost disparity between conventional and very low-carbon fuels.
Carbon insetting refers to the creation of digital certificates, known as insets, which are issued based on the verified emissions reductions achieved through the use of renewable and low-carbon fuels, compared to conventional fossil fuels. These emissions savings are assessed through a proof of sustainability (PoS) provided by an independent, accredited body that validates the environmental credentials of the fuel. Once issued, these insets can be traded using a book-and-claim system – a framework that allows transactions to occur digitally through a secure, dedicated registry. This system enables organisations to track, verify, and exchange certificates without the need for physical fuel transfers, fostering transparency and efficiency in the process.
A broader engagement with carbon insetting methodologies across all transportation modalities could transform the industry. Carbon insetting can promote the necessary market signals to drive investments in renewable fuel production facilities and expand distribution networks. For dry bulk carriers, these investments could include onshore storage for hydrogen or ammonia and retrofitting vessels with dual-fuel engines capable of using future fuels. By providing a clear and credible market signal, carbon insetting could stimulate the large-scale adoption of renewable and low-carbon fuels, accelerating the transition to cleaner energy systems.
The successful adoption of low-carbon fuels hinges on close collaboration between fuel suppliers, shipping companies, and regulatory bodies.
If the industry is to achieve its ambitious GHG reduction targets by 2050, stakeholders must engage with a wide variety of experts – both upstream and
downstream – to utilise the breadth of knowledge and capability that wider industries can provide. Practically, that means immediate action to boost the efficiency of the existing fleet and, secondly, longer-term collaborative action to develop and scale up supply chains for green fuels.
To support this unprecedented level of collaboration, BV recently launched the Future Shipping Team (FST), a multidisciplinary initiative bringing together internal and external experts to tackle the complex and multifaceted issues that the modern maritime industry currently faces. With over 250 specialists across 12 key areas, the FST focuses on emerging fuels, advanced technologies, lifecycle analysis, and ESG (Environmental, Social, and Governance) progress. By driving research, building strategic partnerships, and developing new standards, the FST is helping the maritime sector transition to low-carbon fuels and supporting broader decarbonisation goals.
The team has been specifically selected to respond to the industry’s growing demand for expert insight on some of the technologies that are serious contenders for the energy transition, including alternative fuels, carbon capture, battery storage and nuclear energy. The team’s work includes actions on several fronts, including the development of classification rules, and training, as well as actively participating in innovative projects whilst developing large-scale partnerships. And because it is one of the world’s leading inspection and certification bodies, BV brings something unique to the table: independent expertise that will help build trust between stakeholders throughout the global supply chain. A good example of this is fuel certification, using BV’s independent expertise to validate fuel’s sustainability credentials and ensure that it is safe to use on board. In a multi-fuel landscape, the focus is on fuel quality and validity. This is where BV's Verifuel colleagues are playing a critical role in the FST.
Making net-zero shipping a reality will rely heavily on creating new supply chains to make alternative green fuels for shipping available at scale. This will require significant investment, which will only happen with better communication and collaboration between stakeholders, within and outside shipping.
BV and the FST are dedicated to leading the maritime industry’s transition by supporting the development of efficient systems for green fuel production and distribution. However, immediate and collective action is crucial. Only through a unified effort can the industry overcome current supply chain fragmentation, meet its environmental targets, and pave the way for a cleaner, more sustainable future.
Note
Front page image credit: Peninsula.
Daniel Koch, Manta Marine Technologies (MMT), writes that even as uncertainty dominates international trade relations and geopolitics, fleet efficiency remains a wise investment regardless of which way the market moves.
Looking back to 2024, the dry bulk market has plenty to reflect upon in after a year that rewrote trade routes across the maritime industry. There is little time for reflection, however, as the next market-moving changes are on the horizon, and their impacts are hard to predict.
The effective closure of the Red Sea for most of 2024 supported tonne-mile demand for dry commodity transport by increasing sailing distances as ships took the Cape of Good Hope instead of the Suez Canal. Broadly, underlying demand was supported by low
commodity prices in 2024, and the longer voyages soaked up vessel supply to support charter rates.
The result was longer voyages on new routes, burning the extra fuel to avoid potential dangers to crew, ship, and cargo. Owners with more efficient ships have had the opportunity to reap their operational cost savings over the thousands of extra nautical miles added to some common trade lanes.
The market forecast for 2025 and 2026 again depends on the situation in the Red Sea, but whether or not the route reopens, the picture is not as bright as in 2024. BIMCO puts 2024 seaborne dry bulk transport demand growth at 5.5%; for 2025, full commodity stockpiles help turn growth negative at -1.0%, and the 2026 forecast is a subdued 2.5%. These figures presume a return to the Red Sea in 2025, and if that return is delayed until 2026, BIMCO estimates demand growth of just 0.5% in 2026.
The outlook is uncertain, and vessel operators may face last minute voyage changes as global supply chain readjust to Suez routes. Lower earnings may also be on the horizon as the market loses support from Cape of Good Hope rerouting, estimated at an equivalent of around 2% in demand.
Planning ahead in an uncertain market can be challenging, but even in the toughest downturns, efficiency makes sense. Controlling costs and remaining adaptable to market changes are key to riding out the lows until the next cyclical upswing.
The lowest-hanging fruit in operational cost-cutting is reducing waste – eliminating completely unnecessary outgoings. Manta Marine Technologies’ mission is to help ship owners and operators across the maritime industry to stop burning excess fuel. After all, optimised fuel usage is the fastest and simplest way to cutting down on bunker bills and reducing carbon emissions.
Over 450 vessels are already benefiting from optimised fuel efficiency using the FuelOpt system,
which independent testing has shown to enable fuel savings of up to 3 – 4%. Completely fuel agnostic and installed without commercial downtime, the system is about as flexible as it gets, and will optimise fuel usage whether a vessel is in the Gulf of Aden or rounding South Africa’s coast.
As the dry bulk fleet continues to age and fleet growth slows, universal and adaptable technologies will be key to keeping pace with tightening regional and global environmental regulations.
The dry bulk fleet is expected to grow by around 3.0% in 2024, according to BIMCO and Clarksons Research, dropping steadily to 2.4% in 2026. Lacking confidence in the right long-term solution for decarbonising shipping, owners have proven hesitant to invest in new tonnage. Newbuild contracting activity for dry bulk ships was 10% lower in the first nine months of 2024 than the same period in 2023.
Despite slowing newbuild activity, investments are being made into improving the environmental performance of the dry bulk fleet as a lack of new ships necessitates making the most of existing assets for longer. Shipowners need easy-to-retrofit solutions compatible with their existing machinery and operations in order to meet growing regulatory pressure. With this in mind, FuelOpt is designed to be installed without the need to dry dock, allowing operators to avoid the impact of commercial downtime on their business while advancing their sustainability goals.
After all, the writing on the wall is clear: a ship’s environmental performance is increasingly a differentiator to charterers as global industries face their own pressures to slash supply chain emissions.
The dry bulk sector is rising to the challenge. Some of the most visible examples of investment in fuel saving and regulatory compliance are wind-assisted propulsion technologies, solutions with a growing install base and impressive orderbook. Driven by charterers and shipowners alike, wind propulsion installations and contracts in the dry bulk sector cover Handysizes up to Capesizes.
The open decks of bulk carriers are a prime location for mounting the multi-story rotors and sails necessary to harness the power of the wind, yet a wind power system would be completely non-viable were it to block hatches and crane movements, or even prevent a ship sailing into a covered berth. The range of tilting bases, telescopic systems and rail-mounted platforms developed by wind propulsion technology providers perfectly demonstrate the need for efficiency improvements and emissions reductions not to impede ship operations.
In a similar vein, FuelOpt is an independent system that is compatible with wind-assisted propulsion whether the additional propulsion
Grain Elevator and Processing Society (GEAPS) champions, connects and serves the global grain industry and its members.
GEAPS network of industry professionals includes more than 3,000 individual members from about 1,000 companies around the globe.
Membership Types
Individual Members:
$370 USD
Company/Facility
Up to six members: $1,000 USD
Seven + members: $2,500 USD
Student Members: Free
GEAPS members receive discounts for courses, trainings and credential programs held throughout the year.
Members have exclusive access to the online member directory to find other grain professionals who can share practical advice.
Prepare for leadership roles in your career through GEAPS volunteer leadership opportunities.
comes from a sail, rotor, or wing. The system will continue to optimise fuel use, accounting for changes in the environment including the irregular contribution from wind power.
Adjusting existing operations to account for a significant new technology like a rotor sail could pose an operational challenge to crews trying to make the most of their wind boost, adding to their administrative burden. FuelOpt works by making real-time, automated adjustments to a ship’s propulsion system, keeping the vessel within user-defined parameters. The system frees up crew from the task of repeatedly adjusting propulsion settings as conditions change, boosting efficiency by eliminating those minutes and hours where conditions have changed, but adjustments have yet to be made manually to variables like propeller pitch, engine power, or speed – maximising fuel and cost savings.
As the world bulker fleet gradually improves its environmental performance with new technologies like wind propulsion, energy saving devices, and alternative fuels, the broad compatibility of FuelOpt makes investment decisions easier by avoiding clashes where one upgrade blocks the installation or efficacy of another. As a fuel agnostic solution, owners can install FuelOpt to gain fuel savings safe in the knowledge that it will remain useful through any future technology retrofits or changes in fuel.
The regulations driving the shipping industry’s focus on reducing emissions and increasing efficiency have introduced an administrative burden that creates further opportunity to optimise operations. Compliance with emissions regulations such as the EU Emissions Trading System (EU ETS), the Carbon Intensity Indicator (CII), and the Monitoring, Reporting and Verification (MRV) for the UK and EU require the recording and processing of large volumes of data, a process ripe for digital intervention.
Simplifying emissions reporting is one of the benefits of the Fleet Analytics platform, using the system’s data gathering prowess to provide tailored reports aligned with EU-MRV, EU-ETS, FuelEU Maritime, IMO-DCS, and CII. By automatically recording operational data and enabling crew to easily enter their own inputs, repetitive admin workloads are reduced both onboard and in the office, freeing up time for staff on land and at sea. Furthermore, being on top of fleet data unlocks the transformative short- and long-term potential of data analysis.
Like many regulations in shipping, FuelEU Maritime will not carve an acceptable baseline for performance in stone.
Instead, the greenhouse gas intensity of the fleet will need to improve over time compared to 2020 levels. In 2025, FuelEU Maritime will require a 2% reduction in intensity, by 2030 it will rise to 6%, increasing every five years until reaching 80% in 2050.
Improving environmental and operational results year-on-year requires more than maintaining records for each individual ship and filing reports on time, it takes fleet-wide understanding of each vessel’s characteristics and performance, along with transparent analysis that presents clear actions to reach fleet goals.
A fleet-wide view makes it easier to identify any outliers in need of attention, and any issues can be seen at-a-glance with real-time performance monitoring in Fleet Analytics. The fleet view also amplifies the impact of operational changes and technology trials in pursuit of efficiency, using other vessels as a yardstick to present clear feedback on what is working, and what is not having the desired effect.
From 2025, FuelEU Maritime’s pooling mechanism will make understanding individual and fleet insights more important than ever. Pooling will allow shipowners to reach compliance by grouping ships together, allowing the greenest ships to offset compliance deficits from those falling short of targets.
The mechanism aims to allow shipowners to spread the benefits of high-capital investments in new ships and retrofits across the fleet, de-risking the most expensive investments to encourage the uptake of newer, greener ships ready to face decades of rising performance expectations.
The mechanism will allow pooling of vessels from different owners. Understanding each ship’s emissions and operations will be essential to striking pooling deals, reaping the commercial benefits of beating performance targets, or giving early warning where a ship may not be on the track to compliance. In a time of slow fleet renewal, owners of the most efficient newbuilds will look to maximise financial returns, and owners of older tonnage will be seeking partnerships to minimise financial penalties. Reliable and up-to-date fleet performance data will be at the heart of managing compliance costs for vessels travelling to, from, and within the European Union.
Over time, the MMT online data collection platform, Fleet Analytics, will allow its users to build a valuable repository of historical ship data, developing a deeper understanding of how each ship in the fleet responds to operational changes and allowing crews to squeeze every percentage point of performance to minimise fuel consumption and contribute to regulatory compliance.
The dry bulk sector faces an array of challenges in the coming months, years, and decades, and both their market impacts and ideal solutions are not necessarily clear today. The right commercial solutions today are the key to unlocking NetZero by 2050. Embracing compliance, staying competitive, utilising futureproof technologies, and maximising fleet efficiency are vital next steps toward a shared sustainable future.
Tor Svanes and Jacob Clausen, NAVTOR, discuss how smart solutions can help shipping companies navigate compliance, unlock benefits and face the future with confidence.
The ripple effect from FuelEU Maritime’s arrival is likely to grow into a wave of change, redefining future regulations and business strategies as the industry voyages towards sustainability. Readers currently reeling from the challenge, complexity and potential costs of future compliance need to take a deep breath, right about now.
“FuelEU Maritime is just the start,” cautions Tor Svanes.
The CEO and Founder of NAVTOR, which has e-Navigation, monitoring and performance products and services on over 18 000 vessels in the world fleet, says that the regulation “sets a standard others will follow.”
He firmly believes that, once the EU measure has demonstrated its efficacy, organisations such as IMO will emulate the move in an effort to work towards ambitious climate goals.
“It’s highly likely we’ll see a ‘FuelGlobal Maritime’ within the next five years,” he opines, “so owners and operators need to prepare now – not just for Europe, but globally.”
Performance Director Jacob Clausen agrees, underscoring how FuelEU Maritime’s framework exemplifies a new breed of
regulations that are accelerating in speed and impact: “It introduces a whole new approach to measuring and reducing emissions. The key challenge for the industry is its ‘well-to-wake’ requirements, which demand comprehensive tracking of fuel consumption and emissions throughout the entire fuel lifecycle. This level of detail is unprecedented.” As is the cost of non-compliance.
Svanes points out that many shipping companies may look at potential penalty costs and believe them to be 'manageable'. But, he argues, they could quickly spiral out of control if shipping companies fail to take proactive steps.
“Take a Supramax bulk carrier sailing from New York to Rotterdam. In 2025, FuelEU non-compliance penalties could cost around US$5000 for a single voyage. By 2030, that figure jumps to nearly US$18 000, and by 2050, if no changes are made to fuel and energy use, it could exceed US$250 000. These penalties will double for vessels sailing exclusively within Europe.
“The financial implications are huge, making informed preparation absolutely essential.”
Both NAVTOR executives stress that the complexity of compliance, with FuelEU and other 'sophisticated' environmental regulations (such as EU ETS and CII), calls for a paradigm shift in how data is collected, managed, and utilised.
As Clausen emphasises: “spreadsheets have had their day!” Tor Svanes notes: “The foundations for confident, cost-effective compliance are, without a doubt, digital.”
Clausen, expands on the point: “The scale of data and calculations required opens up huge possibilities for missteps, omissions and human error, with each wrong move potentially setting off a domino effect of FuelEU pain.
“So integrated, intelligent solutions capable of automating data collection and calculation – from a multitude of different sources, without human intervention – deliver real benefits, enabling operators to accurately track fuel sources, calculate GHG intensity, and evaluate compliance options in real-time.”
Svanes says the best smart shipping technology is tailored to make such tricky tasks simple, using the automated data collection and reporting functionality of NavFleet as an example.
He goes further, noting: “Leading solutions should also offer added value functions such as in-system validation, secondary validation from domain experts for optimal quality control, automatic dispatch to designated verifiers, and integration with, for example, digital logbooks and performance monitoring tools.
“The more you can work towards a single ‘point of truth’ for data, the more transparency and control you can unlock across your fleets. This is essential for regulatory reporting, but also strategic decision-making.”
Which puts the focus changing mindsets – or how to approach FuelEU as a mandated 'carrot' rather than a 'stick'.
The experts say that the new approach to data has the power to give shipowners a far greater understanding of both the business and environmental efficiency of their fleets, providing a solid platform for optimising performance and costs.
“You can unlock insights that go far beyond compliance,” states Tor Svanes. “You gain the ability to continually benchmark current performance and then drive fuel efficiency, reduce emissions and enhance operations.
“In a competitive industry, these are game changers.”
The incentive to reduce GHG intensity can also accelerate adoption of green technology, such as wind assisted propulsion systems, and greater use of shore power. Clausen says these are “meaningful steps on the pathway to sustainability” delivering immediate reward, with less energy consumption, emissions and cost, while reducing reliance on less readily available, and more expensive, alternative fuels.
“An in-depth, data driven understanding of how your fleet performs in relation to the FuelEU GHG intensity baseline can be a powerful catalyst for smarter strategic decisions,” he says.
Clausen explains: “Our latest update introduces advanced visualisations and interactive dashboards, clearly showing fleet overviews, individual vessels, fuel consumption (both within and outside the EU), GHG intensity KPIs, emissions in relation to EU voyage statements, penalty costs, and much more, in addition to EU ETS information. Reports can be produced at the touch of a button, with detailed evidence to create understanding of GHG Intensity balance and penalty costs at the end of the voyage. This is helpful for passing on penalty costs to charterers, when necessary, as well as enabling effective management of allowance banking, pooling, and borrowing mechanisms. All essential factors in achieving both cost-effective compliance and commercial advantage.”
Each expert is keen to finish with some ‘top tips’ to help readers navigate FuelEU Maritime.
Clausen begins by stating “you can only plan your voyage when you know where you’re starting from,” adding: “So understanding where your fleet currently stands in relation to the 91.16 gCO2e/MJ regulation baseline is absolutely essential.
“An advanced smart shipping solution, as we’ve been discussing, will give you that foundation […] and allow you to keep building your environmental performance into the future.”
He adds that all shipping businesses should “begin to assess compliance options now to maximise options”, taking into consideration everything from changing fuel mixes (to adopt more low carbon fuels), to adding wind and shore power, or, when necessary paying non-compliance penalties as a stopgap when alternative options to reduce GHG intensity are too costly or unavailable. Making use of the regulation’s pooling, banking and borrowing abilities are also
highlighted as also a key factor by Clausen, who emphasises this can be much more cost-efficient than paying penalties.
“Every vessel, fleet and owner faces their own individual considerations, so there’s no one size fits all solution here. The key thing is understanding the best options for you.”
And as Tor Svanes reiterates, that needs to start now.
“The submission date for compliance with FuelEU Maritime comes into force on 30 April 2026 when 2025’s figures are digested,” he explains. “That may create the illusion that there’s plenty of time. There’s not. Delaying decisions to the last minute will leave operators vulnerable to higher costs and fewer options, while planning ahead creates insight and opportunity.
“Those with surplus emissions reductions can consider banking or pooling their allowances, while those anticipating compliance challenges must plan ahead for alternatives such as biofuels and shore power. They can also borrow, as well as take advantage of pooled, allowances. A proactive strategy not only reduces risk, but positions your fleet for long-term sustainability – both commercially and environmentally.”
Svanes and Clausen agree that shipping companies may be able to achieve compliance without using cutting-edge digital solutions, but that the amount of work, resources and time to do so raises the simple question of ‘why would they bother?’
“NAVTOR, and other leading companies in the field, are working very hard to make compliance as easy as possible for our customers,” Tor Svanes says.
While Clausen goes back to the ‘added value argument’, stating: “The most forward-thinking owners and operators will realise that, although challenging, regulations like FuelEU can be a launchpad for knowing, and running, their businesses better than ever before.”
He continues: “Understanding where efficiencies can be made, emissions cut, performance optimised, and costs managed can edge companies ahead of their competitors, while also building trust and reputation with stakeholders. It’s impossible to fight these regulations, but you can embrace them and, with smarter shipping solutions, really take advantage. Getting off to the best start now, in 2025, will put you in pole position for future success.”
Tor A. Svanes, Founder and CEO of NAVTOR, is a maritime technology pioneer with nearly six decades of experience. After leading C-Map Norway, he founded NAVTOR in 2011 to simplify and enhance shipping. Today, NAVTOR is a global leader in e-Navigation and performance, with Svanes driving innovation, sustainability, and smart shipping solutions.
Jacob Clausen is the Performance Director and Managing Director of NAVTOR Denmark. For the past 15 years, he has been working on optimising the design and operation of ships to enhance efficiency and reduce GHGs. He has also worked on projects covering topics such as performance optimisation, innovation management, big data, and decisionsupport models.
sales@samson-mh.com aumund.com
sales@schade-lagertechnik.com aumund.com
DryBulk asked leading players in the conveyor sector for their insights on a range of conveyor-related topics covering everything from automation to reducing noise emissions and handling corrosive materials.
Rob Van Oijen – Application Engineering Manager
Rob van Oijen is Manager Application Engineering for Fenner Dunlop Conveyor Belting in The Netherlands. Rob has specialised in conveyors for over 17 years, supporting businesses throughout Europe, Africa, the Middle East and South America and has become one of the most respected application engineers in the conveyor belt industry.
Davide Gambarotta – CEO
The new establishment of the Gambarotta Group, led by the current CEO, Davide Gambarotta, took place between 2019 and 2020 and is made up of five leading companies in the sector and about 130 people specialised in 44 different fields. The companies involved are: Gambarotta Gschwendt SRL, Gambarotta Australia, MDG Handling Solutions SRL, MDG America Inc. and Ossitaglio SRL.
Martin Engineering
Jerad Heitzler – Training Manager
Jerad Heitzler is a leader in helping the industry learn how to make the handling of bulk materials cleaner, safer, and more productive. He started with Martin Engineering as a Customer Development Representative in 2006. He soon realised his love for teaching about conveyor systems, and so in 2010 took over management and development of the company’s FOUNDATIONSTM Workshop programme. Under his leadership the programme has expanded to offer several levels of conveyor improvement workshops around the world.
Scott Gulan – Director of Business Development
Scott Gulan has been with Superior Industries for 18 years, including 10 years as National Sales Manager. He has been in his current role as Director of Business Development for 3 years.
Vortex Global
Kyle Langley – Content & Campaign Manager & Adam Schrage – Technical Sales Manager
Kyle Langley has been with Vortex for eight years with six of those years spent as a Sales Application Specialist before transitioning to Marketing. Adam Schrage who has an esteemed engineering background in Loading Systems also contributed to this article and has been the Technical Sales Manager for Vortex Loading Solutions for the past 13 years.
Conveyor systems can be customised to meet the individual needs of dry bulk operators by tailoring their design and components to specific operational requirements. Factors such as material type, capacity, environmental conditions, and space constraints are analysed to ensure the system is optimised for efficiency, reliability, and safety. Adjustable configurations, modular designs, and material-specific solutions (e.g., special liners for abrasive materials) allow conveyors to handle unique challenges.
As automated systems, belt conveyors carry tons of material at blazingly high speeds over short and long distances, making these systems the past, present and future of bulk handling. They’re also safer, cleaner, and require less maintenance than trucks, rail systems, etc. But many operators have treated conveyors like an afterthought, putting maintenance at the bottom of the list until they breakdown and cause excessive downtime. Martin realises that preventative maintenance and diligent monitoring of conveyor systems is the key to maximum productivity of most applications and has meticulously designed accessories and services that promote safety and efficiency.
This starts back at the design stage, making sure the OEM has a clear understanding of what the user is looking for. Conveyors have several different options that can be incorporated into their design. All of which can provide some benefit in the conveyor’s operation. With any conveyor application there can be several considerations that need to be properly designed for. These might include capacity, material specific, perhaps environmental, mobility or flexibility, added safety features and, of course, money.
Vortex Aero Slide Conveyors are custom designed for each project to meet specific operational demands. For example, they can handle lightweight, fluidisable dry bulk materials like cement, fly ash, and gypsum. Their flexibility allows for tailored configurations, such as varying slopes and lengths, ensuring optimal flow rates and efficient material transfer that cater to the unique needs of dry bulk operators.
Rob van Oijen – Fenner Dunlop Conveyor Belting
Thanks to the continual R&D work being carried out by a (very) small number of premier brand conveyor belt manufacturers, rubber technology is constantly evolving, especially ‘multi-task’ rubber compounds that can cope with a combination of demands such as oil, fire, abrasion and ozone & ultraviolet light. Fenner Dunlop is fortunate to be owned by Michelin, the biggest tyre manufacturer in the world. Like us, they believe in investing in such development and improvement which, as with most products, is in stark contrast with those targeting the ‘economy’ end of the market.
The basic construction of rubber conveyor belts has not changed significantly since 1905 when they were made from layered cotton and rubber. Since then, most rubber is now synthetic, and the cotton layers have been replaced by synthetic (usually polyester and polyamide) fabric ply material with a thin layer of rubber in between. By far the most common construction, this multi-layered carcass structure is known the world over as ‘multi-ply’ belts. However, this dominance is under threat. Since their introduction more than two decades ago, Fenner Dunlop in Europe and North America have very successfully developed single and dual-ply construction belts. Although thinner and lighter, they are much more robust and resistant to damage than their multiple ply counterparts.
In theory, a higher number of inner plies should result in a stronger belt. However, the greatest influence on the strength and other essential physical properties of a conveyor belt is the design and quality of the ply material used to create the carcass. The big advantage that we have is having our own fabric weaving facility in the USA. The result of R&D efforts has been the creation of a unique super-strength single-ply belt (Ultra X) and the longer established dual-ply UsFlex. Both carcasses possess a longitudinal rip resistance that is more than five times that of multi-ply belts of equivalent rating and up to three times greater impact resistance compared to conventional belting.
Recent advancements in conveyor technology include:
n Smart sensors and IoT integration: Enabling real-time monitoring of system performance.
n Energy-efficient drives: Reducing energy consumption through variable frequency drives (VFDs).
n Dust control systems: Advanced sealing, dust suppression, and containment methods.
n Predictive maintenance tools: Using AI and data analytics to prevent unexpected failures.
n Lightweight materials: Utilising materials like composites to reduce wear and improve longevity.
Martin has recently introduced technologies and equipment designs that can significantly enhance the bulk handling industries. The most impactful amongst them is the N2® belt cleaner remote monitoring system. This device has an embedded chip that senses the rotation of the mainframe, which indicates when a belt cleaner might need re-tensioning, replacement, or is no longer in contact with the belt.
Think about some of the incredibly complex and widespread conveyor systems you’ve seen. That simple data allows operators to eliminate the hours inspectors need to travel through the entire system, climb towers, stretch to examine hard to reach areas, or protect themselves from flying debris when they open inspection doors. Beyond the labour savings and the safety benefits, the data allows operators to better predict required maintenance and order the proper equipment before scheduled outages. This drastically reduces downtime, lowers the cost of operation and increases productivity and equipment life.
As it relates specifically to conveyor designs, we are seeing more implementation of overland conveyors over trucking. Conveyors that are longer and wider. Telescopic conveyors are getting longer and wider.
Marine terminals, both ocean port and river terminals, often require a custom design product because these sites just are not standard. So, lots of bespoke equipment is being developed to fit those needs. Some of those designs are being developed to become standard products. Making them more affordable.
The other area of development related to conveyors is the components that can be installed on conveyors. The development and incorporation of IoT Connectivity in components is becoming more of a reality. Some other developments include new options for conveyor load zones. These are mostly designed to keep the belt supported and sealed to prevent spillage. Dust control options are becoming more readily available and affordable to the market.
Recent advancements in conveyor technology include improved porous media materials, integration with automation systems like PLCs, and enhanced durability features. Vortex Aero Slides utilise a non-woven, polyester porous media that resists wear and tear better than traditional woven fabrics, which reduces downtime. Additionally, Vortex systems incorporate smart technology to enable unmanned 24/7 operations, further enhancing efficiency.
How can conveyor systems deal with particularly dusty, flaky, or powdery bulk materials?
Davide Gambarotta – Gambarotta Geschwendt Srl.
To manage such materials, conveyor systems incorporate:
n Dust suppression systems: Water sprays or foam to minimise airborne dust.
n Enclosures and sealing: Full or partial enclosures with robust sealing to prevent material escape.
n Air filtration units: Capture and recycle dust particles.
n Anti-adhesive liners: To avoid material build-up and clogging.
Without the proper components installed at a loading zone, dust and spillage is inevitable. Proper skirting systems installed along chute work are critical to sealing the loading zone. The belt must also be stabilised with support cradles or closely spaced idlers to eliminate belt sag between the idlers, which can cause gaps for dust emissions and fugitive material to escape. By ensuring the belt remains flat and stable, the skirting system has the proper surface to seal against.
Finally, attempts to slow air speed inside a skirted area should be done with dust curtains and dust bags. The impact of tonnes of heavy raw material creates incredible turbulence. Strategically installing dust curtains slows air velocities allowing dust to settle in the cargo stream. On shorter loading enclosures, dust bags at the end of the settling and stilling zones give excess air a place to escape, as the fine mesh collects the particulates. During shutdowns, the mass of collected dust is deposited back onto the conveyor.
This is a timely topic in view of the recent MSHA regulation concerning limiting airborne silica content. One area of quick improvement is for operators to set aside the time to keep up with maintenance on their conveyor systems. Often is the case that conveyor maintenance gets neglected over other priorities. This is especially true in the load zone area where much of the airborne dust is generated. Maintaining liners and skirting material is a good first start. Keeping the belt fully supported into and through the load zone is another good practice to stop material leaking out.
The addition of discharge hoods at the discharge of the feeding conveyor helps to contain the air flow and the fines suspended in it.
Striving to get the material loading on the new conveyor, in the direction of travel, helps to reduce the turbulence. As opposed to just dropping it straight down onto the new belt. This creates agitation and dust in suspension.
In the last six months, we have seen an increase in interest and requests for information on a passive dust containment system. This involves a fully sealed skirting system in combination with a larger volumetric capacity stilling box. This would also include hanging curtains on the inside of the stilling box. This larger capacity box greatly reduces the air speed of the material causing it to fall out of the air flow. The curtains create a bit of a tortuous path that also helps to knock out fine particles from the air flow.
Vortex Aerated Equipment is specifically designed for dusty and powdery materials. Aerated systems use downward gravity and low-pressure, dry air to fluidise materials, allowing them to flow seamlessly. Dust collection vents and inline compact filters ensure dust-tight operation, containing fine particles and reducing environmental hazards. This maintains safety and compliance while being cost-effective.
Davide Gambarotta – Gambarotta Geschwendt Srl.
AI and IoT are transforming conveyors by enabling:
n Real-time monitoring: IoT-enabled sensors provide live data on belt speed, tension, and material flow.
n Predictive maintenance: AI analyses wear patterns and schedules maintenance before failures occur.
n Automation integration: Systems can adjust operational parameters autonomously based on AI insights.
n Enhanced safety: IoT alerts operators to hazards or anomalies.
Operators and Maintenance staff can use AI to get interpretations of safety regulations and better define their internet search criteria. Many software packages on the market for business have built-in AI features that can make the software work better and anticipate a user’s needs. Bulk material handlers and conveyor users should be looking for software options and open AI platforms that can make their technology needs more efficient.
More focus is being placed on telematics in almost all processing systems for bulk handling. Specifically, as it relates to conveyors we have introduced idlers with a sensor inside each roll. These sensors monitor bearing and roll temperatures, vibration, roll thickness and other data points. While giving the user continuous monitoring and real time alerts via the web or a phone app.
Conveyor systems, including Vortex Aero Slides, are beginning to incorporate AI-driven monitoring and IoT-connected devices to provide real-time feedback. Systems like the Vortex VALS System integrate smart sensors, cameras, and PLCs to monitor operational flow, detect anomalies, and automate adjustments. These advancements not only improve material flow precision but also allow for predictive maintenance, reducing unplanned downtime.
Can you provide a case study of a recent conveyor project at a port, terminal or mine, listing any challenges that arose and how you faced them?
Davide Gambarotta – Gambarotta Geschwendt Srl
Case study: Port terminal conveyor upgrade
n Challenge: Handling corrosive materials in a saline environment.
n Solution: Installed stainless-steel components for corrosion resistance, used fully enclosed conveyors with dust containment systems, added IoT sensors for monitoring humidity and wear.
n Outcome: Increased system longevity, reduced downtime, and safer material handling.
A coal-fired power plant in Illinois run by Dynegy Inc. with a bulk transport volume of 1000 tph was experiencing spillage issues due to ageing equipment at two of its main bulk material transfer points. Located side by side, the transfer chutes suffered from belt tracking and belt sagging issues, which allowed material to escape the chute and build up around the work area. Moreover, the old wear liners were difficult to remove and replace, requiring torch work. Operators sought a solution to the excessive equipment maintenance, regular clean-up around a running belt and system downtime that increased the cost of operation.
After reviewing the most essential components needed to control material flow and improve working conditions, Martin Engineering technicians installed Martin Wear Liners and Martin Tracker TM systems. Designed to protect the chute wall from material impact while keeping a tight seal on the belt to stop fugitive material, the external wear liner is bolted on from the outside, making replacement of worn sections a oneperson job with no need for a torch. To mitigate spillage along the belt path, the Martin Tracker utilises extended arms with roller sensors and a troughed idler to detect slight variations in the belt path and train it quickly.
Nearly one year after the installation, operators have seen a vast improvement on the amount of spillage and fugitive dust around the transfer points. Labour costs for clean-up and maintenance have been reduced and the area around the loading zones and along the belt path is considerably safer. “We are very pleased with the results of the solution,” said a Fuels Supervisor close to the project. “We set a goal to create a cleaner, safer and more productive material handling process, and Martin helped us successfully achieve that.”
Recently, we completed a conveyor project for a large-scale salt mine. The main challenge was of course corrosion. Like saltwater port facilities, corrosive materials and environments can very quickly degrade equipment if it is not properly designed. The engineers carefully reviewed and adjusted the design accordingly. This includes using quality stainless steel components, special covers to prevent material build up, epoxy paint coatings and more. By taking these steps, the equipment is set up to perform for its full lifecycle.
n Scenario: Vortex installed Aero Slide systems at a cement terminal with four silos, each holding 2500 t, to transfer cement at 500 tph.
n Challenges:
§ Material compaction led to 'rat-holing' in the silos.
§ Dust and maintenance were concerns.
n Solutions:
§ Installed Aero-Troughs and Bin Bottoms to fluidise materials effectively, eliminating ratholing.
§ Implemented inline compact filters to manage dust and return it to the vessel.
§ Integrated a Positive Displacement Blower for consistent airflow.
n Outcome: The system operates 24/7 with automated control, loading multiple trucks daily without interruptions.
Reducing noise in conveyor roller systems is crucial for enhancing workplace comfort and efficiency. A quiet running conveyor is almost invariably more energy and load efficient. Noise can be caused by a number of factors, including misaligned belts, rollers, pulleys, or bearings that cause friction, vibration, and wear. Loose or damaged components can affect belt alignment while a loose belt can cause slippage, all of which can contribute to the volume of noise. Surprisingly, belts where the manufacturer has applied an embossed branding is another cause of noise, which is created as the indentations of the embossing pass over the rollers. This is why Fenner Dunlop we use a branding method that is entirely flush with the belt surface. Other causes of noise include debris or material build-up on the rollers and heavy or uneven loads that can put extra stress on the rollers. The various sources of noise not only accumulate but can be amplified if the conveyor frame itself is vibrating.
The solutions to nearly all the above fall within the realms of basic routine maintenance and good housekeeping. Aside from these, the key to noise control is the type and quality of the rollers and the conveyor belt itself. Good quality nylon rollers are much quieter than steel rollers. Although steel rollers are longer-lasting, correctly aligned, well-maintained nylon rollers can considerably reduce noise emissions. Fitting premier-brand belts rather than lower-priced Asian imported belting makes a big difference in noise levels because compared to low-grade ‘economy’ belting, high quality belts use rubber that contains much higher proportions of top-grade polymers such as carbon black. Rather than being rigid, the rubber is much more elastic, which helps to reduce its rolling resistance, together with the added advantages of fewer stoppages for repairs and much greater longevity.
Better still, fitting lighter, thinner, single-ply and dual-ply belt carcass construction belts can make even more of a difference. High quality rubber covers combined with some 10% reduced belt weight thanks to having fewer plies, means that less drive power is required, so the belt is therefore quieter as it passes over the rollers and drums. Another benefit of single-ply belts is that they use finger splice joints rather than step splice. These are generally smoother with the added benefit of greater splice joint reliability.
Davide Gambarotta – Gambarotta Geschwendt Srl
Noise can be mitigated by:
n Using low-noise rollers and idlers.
n Installing noise reduction liners inside hoppers.
n Encasing conveyors in acoustic panels.
n Ensuring proper alignment to reduce unnecessary friction and noise.
Industrial bulk handling environments are, by nature, loud. However, for conveyor systems, reducing noise is also improving efficiency. One method is eliminating dead drops at conveyor transfer points and replacing them with sloped transfer chutes ending in scooped feeders. This not only significantly reduces noise, it also lessens the impact on the belt for greater belt health, ensures centred loading for better belt tracking, and reduces splash and turbulence for less dust and spillage. An enclosed loading, settling, and stilling zone with a proper wearliner and skirting system should contribute to reducing noise.
The best approach here is to combine some of the advancements in conveyor componentry.
Chevron style wing pulleys run quieter than traditional straight wing pulleys, there are noise dampening materials, such as acoustic foam, that can help in specific areas, utilisation of anti-vibration isolators/pads for structure, enclosures around the conveyor including just adding covers to the conveyor, represent a few of the options.
However, even without any of the above, users can reduce noise with some practical steps that they can implement without much investment.
n Limiting the drop height to a conveyor and making sure the material gets up to speed fast will reduce noise.
n If possible slow the material down, this may require going to a wider belt to meet the capacity requirements.
n Vulcanised belt splices are a much quieter option than running steel mechanical fasteners on a conveyor belt.
n Maintain proper belt tension to avoid a belt that is loose and flops around.
n Just good preventative maintenance practices including looking and listening for components that are squeaking, growling and thumping. And then replacing them.
Vortex Aero Slide Conveyors are designed with low-pressure blowers, which are quieter compared to high-pressure alternatives. The placement of centrifugal blowers away from the conveyor system further reduces noise levels. Additionally, the absence of moving parts in the systems significantly minimises operational noise, making them ideal for environments where noise control is critical.
How do you adapt your services for abrasive or corrosive bulk materials?
If conveyor belts are being used to carry a variety of different dry bulk materials, then the type of rubber (cover grade) used on the belt needs to be able to ‘multi-task’. First and foremost, the abrasive wear properties of ALL conveyor belts should be at least DIN Y standard (ISO 4649 / DIN 53516 test maximum 150 mm 3 loss) to achieve reasonable economic longevity (whole life cost). If particularly sharp, abrasive materials are sometimes conveyed then higher-grade DIN X covers (maximum rubber loss under testing of 120 mm 3 ) may be more suitable because as well as abrasive wear, it is also more resistant to cutting and gouging.
Additionally, it is important to understand the nature of the material and the operational conditions throughout the conveyor system. The ISO 4649 abrasion index is an important starting point but much depends on the granulometry and shape of the materials, properties like the rubber strength, it is resistance to tear propagation and elasticity, which all play a crucial role in a belt’s ability to withstand the conditions of the application. These conditions include loading angle, loading height and speed difference to the belt movement. With varying ‘mixes’ of available polymers, we can create a range of rubber compounds with their specific strengths, and weaknesses. Obviously, choosing the correct one for the application is key!
In terms of their effect on the day-to-day operational reliability of conveyor belts, the wide variety of oils or corrosive materials that are contained within the different types of dry bulk cargo such as grains, fertilizers and biomass, pose the single biggest challenge. Oil absorption causes a dramatic decrease in the ability of the rubber to withstand abrasive wear. As the rubber softens it also steadily loses tensile strength while at the same time becoming prone to ripping and tearing. The next stage is that the rubber begins to swell and distort. There are two distinct sources of oils that damage rubber – mineral and vegetable/animal. Good quality oil resistant belts should have outer covers that are based on a combination of SBR (Styrene Butadiene Rubber) and NBR (Nitrile butadiene rubber). Because of the high cost of nitrile butadiene, manufacturers who engineer their belts based on the principle of price competitiveness rather than performance and longevity, not only use lower-grade nitrile but also use it in minimal quantities.
Mineral oil tends to be much more aggressive than most vegetable oils, so a full Nitrile butadiene rubber (NBR) based synthetic rubber is required. The greater the concentration of nitrile within the polymer, then the greater resistance there is, not only to oil but also to corrosives because nitrile provides protection against aggressive chemical elements such as sodium hydroxide and potassium hydroxide, nitric acid and ammonia and Urea Formaldehyde (UF), which is used as an anti-caking and de-dusting agent in fertilizers. Although premier brand quality belts come with a higher price tag, their vastly superior resistance to abrasive and corrosive materials will undoubtably result in higher productivity and a significantly lower whole life cost.
Davide Gambarotta – Gambarotta Geschwendt Srl
We adapt by:
n Using wear-resistant materials, such as ceramics or hardened steel, for high-wear areas.
n Coating components with anti-corrosive treatments like epoxy or galvanisation.
n Offering modular components for easy replacement and reduced downtime.
Abrasive material can be challenging, so Martin offers specialised belt cleaner blades to clear highly abrasive material from the belt at the discharge zone. When loading the belt, abrasion will erode a chute wall at a surprising speed. The typical wearliner and skirting systems used to protect the chute wall (aka, 'skirtboard') generally do not suffice in these punishing applications. We recommend installing a wearliner made from smooth abrasion-resistant steel with the grain pointing in the direction of the material flow as close to the
belt as possible without contact. Ensure that it is not so close that material can get trapped and cause friction damage and heat on the belt. A well-appointed wearliner should protect the softer rubber or polyurethane skirting enough to retain the proper seal and not erode too quickly.
Abrasion is a condition that is common to most bulk handling systems. Beyond promoting good conveyor hygiene there are other tips for users. Design systems that promote good inline transfer points by reducing the turbulence that can be created. This reduces wear on the belt covers and all the components in the load area.
Utilisation of specially engineered rubber compounds, application of wear coatings and different abrasion resistant steel for the various wear surfaces is a problem solver. The use of stainless steel or galvanised steel/epoxy coatings and HDPE and other corrosion and abrasion resistant polymers have been very beneficial to extend service life for conveyors.
For abrasive or corrosive materials, Vortex uses durable construction materials such as stainless steel and needled polyester porous media. Options like stainless steel media grates and protective coatings enhance resistance to wear and chemical damage. Custom modifications, including cleanout ports and reinforced structures, ensure that the equipment lasts longer in harsh conditions.
What is your approach to sustainability – both in terms of the environment and in terms of the longevity of your conveyor systems?
This is a great question because above all else, it is the longevity of conveyor belts that has the biggest positive influence on sustainability. Manufacturing conveyor belts uses an enormous amount of energy and materials. The most common type of conveyor belt is the rubber covered ‘multi-ply’ belt, which mostly have a carcass comprising of 2 – 4 layers of synthetic fabric, usually a combination of polyester and nylon. Because of its adaptability, most of the rubber is entirely synthetic. The raw materials used to create the rubber and fabrics are almost all directly or indirectly derived from crude oil. In fact, a typical conveyor belt is effectively 45% oil. Add to this a vast array of different chemical components such as anti-degradants, antiozonants and accelerators.
Some of those chemical components are potentially dangerous. Fortunately, in Europe, there are very strong regulatory controls in place that are designed to protect humans, wildlife and the environment. Unfortunately, and again in pursuit of a price-competitive edge, many European manufacturers have chosen to ignore the regulations. However, the biggest source of rubber belting is Southeast Asia, predominately China. They are not subject to such regulations so they are free to use much cheaper, unregulated raw materials even though they may be prohibited or have strict usage limitations within Europe.
The harsh reality is that recycling conveyor belts is both ecologically and economically problematic. Consequently, the amount of redundant conveyor belting being recycled is estimated to be less than 10%, resulting in countless thousands of tons of rubber, polyester, nylon and associated chemicals being disposed of each year, most of which goes to landfill. This is precisely the reason why producing and using conveyor belts that have the longest possible working life has the biggest positive influence on sustainability.
Good quality belts can quite easily achieve double or treble the lifetime of so-called ‘economy’ belts and up to five times greater longevity compared to low-grade imported belts. Fortunately, the price itself invariably reflects the difference in performance and sustainability that can be expected.
Environmentally, buying better quality, longer lasting belt, dramatically reduces the amount of belting that needs to be manufactured in the first place, along with an equally dramatic corresponding reduction in the amount of harmful chemicals used and non-biodegradable synthetic fabric. The added bonus is that it also reduces ‘whole life’ cost due to the substantial reduction in repairs, stoppages, replacement belts and lost production. Every way you look at conveyor sustainability, longevity is the key.
Davide Gambarotta – Gambarotta Geschwendt Srl
We prioritise:
n Energy efficiency: Incorporating energy-efficient drives and components.
n Durability: Designing systems with long-lasting materials to reduce replacements and waste.
n Recycling and reuse: Promoting the use of recyclable materials.
n Environmental impact: Implementing dust suppression and low-emission technologies to protect the surroundings.
There are several things facilities can do to improve their environmental footprint. Dust is not just a workplace safety issue, but seriously impacts the water, foliage, and animals around the site. Controlling dust emissions at a transfer point and dust from carry back at a head pulley should be well executed and an enclosed process. Dust can cause premature breakdowns of equipment and tons of spillage around a conveyor that is not added back into the process can overwhelm local landfills with waste product. Dust and spillage that are added back need to be re-processed cause inefficiencies in production, which raises energy usage, impacts on sustainability and raises the cost of operation.
We are often involved in onsite training for users to teach the recognition, cause and resolution of all the various issues that may develop on a conveyor system. Often, this is the result of just not being aware of how to address problems. The benefit of this approach is reduction in the frequency of replacement parts installs and longer lifecycle to conveyor systems.
Further, having in-house electrical engineering and automation departments gives us the ability to recommend and install the most energy efficient conveyor componentry. This includes the ability to develop automation programs that are best suited for the required run time for a given operation. Lastly, education on the benefits of conveyors versus trucking has been an ongoing conversation. The benefits go well beyond just a lower operating cost. They extend to environmental and operational benefits as well.
Kyle Langley & Adam Schrage – Vortex Global
Environmental sustainability at Vortex is achieved by designing conveyors that are dust-tight to the atmosphere, reducing environmental impact. Additionally, conveyors are energy-efficient, requiring only a single power source (e.g., centrifugal blowers). For product longevity, the systems feature durable materials, easy maintenance access, and design elements that minimise wear, ensuring a life cycle that outlasts traditional conveyor systems.
Domes provide reliable, year-round protection for your stockpiles, ensuring material safety and minimizing environmental impact.