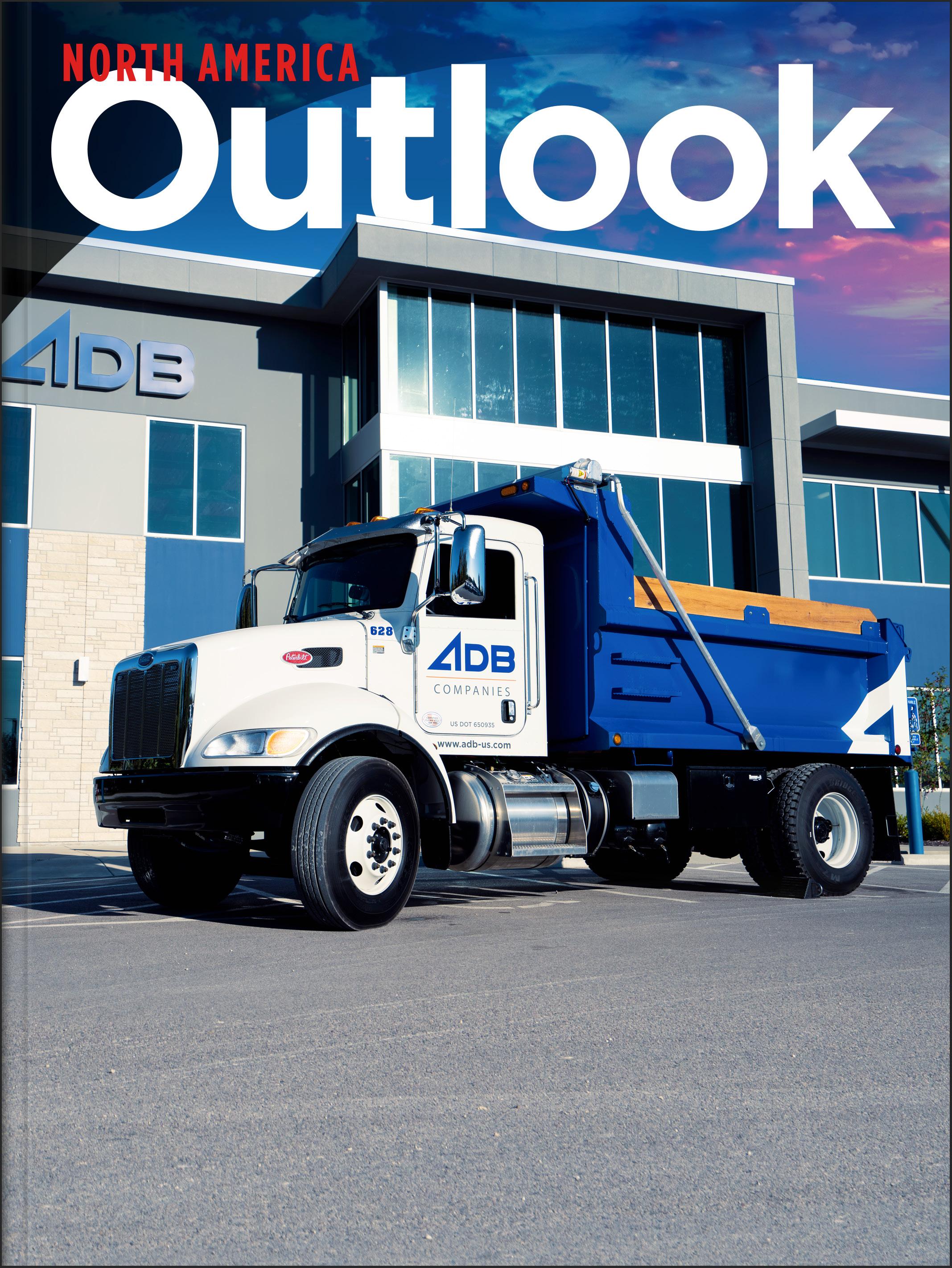
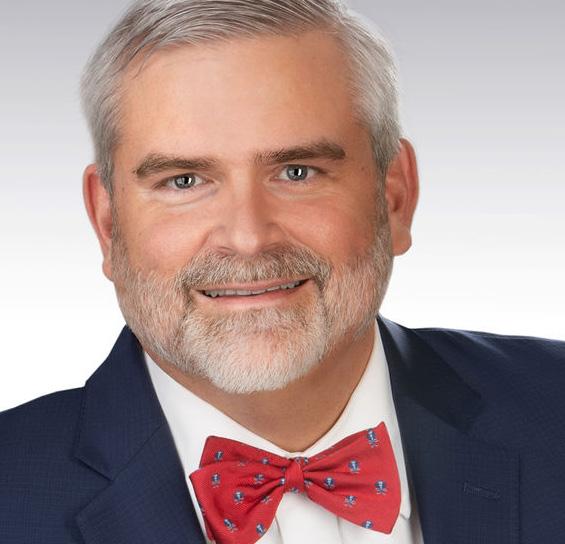
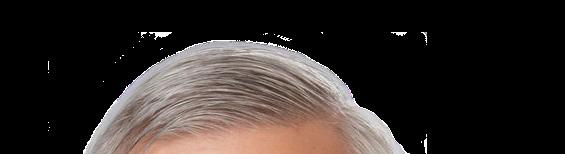
For over a decade, our portfolio of in-house magazines has been lovingly produced, printed, and distributed to our esteemed subscribers across the globe from our headquarters in the UK.
But now we are moving with the times, adopting a digital-first approach by producing online-only publications. A major factor in this decision is to minimize our environmental footprint, reducing the carbon emissions involved in the logistics of print magazine distribution and the resources required therein.
in-line with the requests
& expo
EDITORIAL
Head of Editorial: Phoebe Harper phoebe.harper@outlookpublishing.com
Senior Editor: Marcus Kääpä marcus.kaapa@outlookpublishing.com
Editor: Jack Salter jack.salter@outlookpublishing.com
Junior Editor: Ed Budds ed.budds@outlookpublishing.com
PRODUCTION
Production Director: Stephen Giles steve.giles@outlookpublishing.com
Senior Designer: Devon Collins devon.collins@outlookpublishing.com
Designer: Matt Loudwell matt.loudwell@outlookpublishing.com
Production Assistant: Talia Smits talia.smits@outlookpublishing.com
Digital Marketing Manager: Fox Tucker fox.tucker@outlookpublishing.com
CEO: Ben Weaver ben.weaver@outlookpublishing.com
Managing Director: James Mitchell james.mitchell@outlookpublishing.com
Sales Director: Nick Norris nick.norris@outlookpublishing.com
Commercial Director: Joshua Mann joshua.mann@outlookpublishing.com
Tom Cullum tom.cullum@outlookpublishing.com
Felix Revell felix.revell@outlookpublishing.com
Tom McConnell tom.mcconnell@outlookpublishing.com
Callam Waller callam.waller@outlookpublishing.com
David Knott david.knott@outlookpublishing.com
Eddie Clinton eddie.clinton@outlookpublishing.com
Matt Cole-Wilkin matt.cole-wilkin@outlookpublishing.com
Ryan Gray ryan.gray@outlookpublishing.com
Thomas Arnold thomas.arnold@outlookpublishing.com
Vivek Valmiki vivek.valmiki@outlookpublishing.com
Marvin Iseghehi marvin.Iseghehi@outlookpublishing.com
Donovan Smith donovan.smith@outlookpublishing.com
Alfie Wilson alfie.wilson@outlookpublishing.com
Deane Anderton deane.anderton@outlookpublishing.com
Josh Hyland josh.hyland@outlookpublishing.com
Krisha Canlas krisha.canlas@outlookpublishing.com
Finance Director: Suzanne Welsh suzanne.welsh@outlookpublishing.com
Finance Assistant: Suzie Kittle suzie.kittle@outlookpublishing.com
Office Manager: Daniel George daniel.george@outlookpublishing.com
Just one week prior to this magazine’s launch, President Joe Biden officially signed the Inflation Reduction Act into law.
A key area of emphasis in this seminal legislation is the role of mining across North America. Offering funding opportunities and expanded tax credits to encourage domestic mineral production, the new bill heralds the industry’s essential role in driving the energy transition by providing the resources to support the manufacturing of electric vehicles and other fundamental products such as solar panels.
It is in exciting times such as these, that we at Outlook Publishing are proud to publish a sneak peek at our forthcoming global brand and online publication – Mining Outlook. A multi-channel platform dedicated to showcasing industry news and the major players within these defining times, keep your eyes peeled for our online launch in October 2022.
Meanwhile, our front runner for this issue is ADB Companies, the end-to-end solutions provider connecting the utility, communication, and technology industries.
“ADB is a truly turnkey partner to our customers, providing infrastructure solutions from beginning to end,” says Chad Johnson, President and CEO of ADB. “With more than 1,500 members of the ‘A-Team’ across the US, we have completed projects in nearly every state.”
Elsewhere, we speak with major players in the North American healthcare sector, including Emerald Textiles - the largest healthcare linen service provider specializing in acute care, with 12 state-of-the-art commercial linen processing facilities, three service depots, and industry-leading operations across the Western US. In nearby Colorado, Sky Ridge Medical Center is the destination hospital priding itself on providing a healing environment based on clinical excellence and world-class services for both patients and colleagues.
Discover other exclusive corporate stories from Canadian aerospace manufacturing experts Avcorp, and Expediter Services – the driver-centric company at the forefront of the US trucking industry.
We hope that you enjoy your read.
NEXT MONTH, NASA will send a new crew into space, and for the first time ever there will be a Native American woman aboard.
Astronaut Nicole Aunapu Mann, from the Wailacki of the Round Valley Indian Tribes, will be responsible for all phases of flight in her role as mission commander.
The crew aims to reach the International Space Station on 29 September.
Additionally, in 2020 Mann was selected to be in a pool of astronauts eligible for Nasa’s Artemis program that will send humans to the Moon.
TOM CRUISE AND his beloved Top Gun Maverick, the long awaited and excellent sequel to the 1986 classic, has saved movie theaters across the US this summer.
The high-octane thriller has accounted for a staggering 23 percent of the domestic summer box office.
The hugely unexpected overper
ICONIC AMERICAN CAR manufacturer Dodge, has unveiled a new concept car called the Charger Daytona SRT. It is set to be its first all-electric muscle car and expected sometime in 2024.
This new supercar will replace Dodge’s current gas-powered Challenger and Charger muscle cars.
formance of Maverick has swooped in to save the day from an extremely product-starved, bleak, catastrophe of a summer for US cinemas. The commercial reception of Tom Cruise’s legacy sequel is the summer movie miracle theaters needed to stay afloat.
Its jaw-dropping performance has seen it become the seventh highest grossing film of all time in the US, and the biggest ever for Paramount as a studio.
It also features several new technologies meant to make it feel and drive like a traditional muscle car.
The concept vehicle resembles a futuristic, yet retro, version of the current Dodge Challenger with a more aerodynamic, but muscular, design.
THIS MONTH, MICROSOFT cele brated the official opening of its new Canadian headquarters. The new HQ reflects the significant investments the company has made over the past four years across Canada.
Microsoft chose Toronto for its new Canadian headquarters because of its strong technology ecosystem, depth of multicultural talent and extensive network of globally recognized universities. The 132,000 square foot state-of-the-art office has been
MEXICO’S PRESIDENT HAS proposed a ban on beer brewing as the nation’s drought intensifies.
The president has declared that beer in northern parts of the country will cease to be produced as the
designed to both engage with the community and support Microsoft’s inclusive hybrid culture.
UBER HAS DECLARED that the autonomous trucking future is almost upon us, to directly counter the ongoing truck driver shortage across the US.
Uber’s trucking logistics and supply chain management strand believes that autonomous trucking is the key to solving the driver shortage crisis.
“We’re getting ready for the future with drivers that will be available on both sides of the autonomous freight, available to pick up and drop off the freight that is being hauled by the autonomous truck, by providing a network of drop trails on both ends,” said Lior Ron, the head of Uber Freight.
region faces intense water shortages.
Much of northern Mexico is under severe drought warnings, which has left major cities such as Monterrey rationing water. Mexico is currently the world’s largest exporter of beer, shipping over USD five billion of beer in 2021. As a result, the ban may bring catastrophic ramifications for the country’s economy.
RETAIL SPORTS BRAND BEHEMOTHSNike and Adidas have finally settled a series of US patent disputes over sports trainer technology.
The conflict between the two companies started last year when Nike filed a suit in Oregon claiming that Adidas was infringing on several of its footwear patents, namely its knitted shoe technology.
Adidas then filed its own countersuit in June, claiming that Nike intentionally infringed on nine patents related to athletic technology, such as Nike’s Run Club app.
All the court filings say the dispute has now been settled, while details of the settlement have not yet been revealed.
Recent global events have ushered in a new consumer culture of online shopping across the US and whilst the logistics industry has mostly adapted to accommodate the boom in online retail and demand for e-commerce, it has also experienced multiple roadblocks in adjusting for the future. However, with new technologies becoming more freely available, smart warehousing is a viable option for logistics to keep pace with demand from the e-commerce industry.
The U.S. Census Bureau of the Department of Commerce set the estimate of US e-commerce sales for the second quarter of 2022, adjusted for seasonal variation, but not for price changes, at USD 257.3 billion - an increase of 2.7 percent from the first quarter of 2022. However, despite the industry’s exponential growththe warehouse sector is quite late to automation and is now looking at a rapid transition to modern processes - in a bid to ensure the smooth flow of operations across logistics for e-commerce. If transformation in logistics is not taken seriously, the growth of e-commerce could result in a host of ongoing challenges for logistics to manage capacity and demand.
As reported by Notified, “...the global Warehouse Automation Market
accounted for USD 18,937 million in 2021 and is estimated to reach USD 64,639 million by 2030, with a significant CAGR of 14.8 percent from 2022 to 2030.” These statistics indicate that transformation is greatly needed since the efficiency of piece picking in warehouses plays a key role in creating a frictionless course for the logistics to follow.
The surge in demand for e-commerce warehouse and distribution services also raised the question of to which extent the persisting labor shortage in logistics would impact effective supply chain management. Whilst keeping up with consumer demand became a greater priority than ever before, the influx of online shoppers led to serious pain points of transformation within warehouse automation.
Parcel sorting and distribution plays an integral role in efficient service delivery. In preparation for a future where e-commerce reigns supreme, logistics has to reshuffle existing processing and delivery systems to get goods out on time and deliver on the increasingly high expectations of consumers.
Smart warehousing is taking root. Smart warehousing refers to the instalment of robots, cobots and computerized systems in warehouses to complete common warehouse
operations which were previously performed by people. Not only does smart warehousing allow for greater capacity and efficiency in the warehouse, the labor shortage is largely mitigated.
We’ve experienced a surging adoption of automated processes across the warehousing sector. One driver hereof is the inability of human capacity to keep up with small batch order sorting. The vast number of parcels entering and exiting warehouses each day, let alone the ever-growing e-commerce sales, makes relying on human performance impractical in terms of system efficiency. This has had its share of influence in the shift towards smart warehousing.
A “cobot” is a smaller, safe to be around, robot. The term “cobot” is short for “collaborative robot”. In warehouses, cobots don’t need to be fenced off, or isolated from human contact - as with traditional industrial machinery, people can directly interact with the cobot. Cobots are designed with the intention to engage in a shared space, integrating with environments where robots and people operate in close proximity. In
a bid to increase efficiency, optimize speed and to reduce errors, cobots were developed to fulfil activities such as picking, packing, and palletizing.
Automated picking and sorting designs can commonly be seen in the shape of robotic arms that can handle parcels with the same motions as people, but in greater capacity and with more accuracy. The human labor element is removed from item sorting and stacking, leading to less injuries and faster processing. Robotised help also enables faster return on investment, since processing rates are much greater than what human performance allows for.
Take note, if e-commerce wants to increase productivity and harness the full potential of automation in the warehouse - a clear end-to-end strategy is needed. This will ensure a frictionless experience across the multiple activities involved in the logistics process.
Warehouses no longer exist to process bulk orders. With the shift to automation and robotics, orders can now be processed in small batches more easily. Single item processing is also made more economical. Small
batch order sorting can partially be credited to e-commerce promising a convenient shopping experience to their customers.
Picking, sorting and shipping items in small volumes from warehouses to their next destination requires meticulous planning to get right - due to the sheer volume of packages entering and leaving the warehouse. Warehouse solutions, such as automated item pick and place, is therefore a valuable investment to make in ensuring warehouse inventory and mobility can manage the volumes and frequencies against which small batch sorting is conducted.
Despite the roadblocks, automation in warehouses has a positive spillover effect. A combination of just a few pieces of smart technology can greatly improve productivity, resource usage and eliminate human error. Yet, a certain level of human oversight is needed to ensure that smart systems operate as they should.
The benefit of automation is that it could allow warehouse employees to focus their attention towards higherpriority tasks, instead of spending energy on physically straining and
repetitive tasks, such as parcel picking. However, with intelligent designs in robotics becoming more sophisticated, the future of robotics in the warehouse could very possibly be autonomous.
In conclusion, America’s reliance on e-commerce to deliver frictionless order and delivery experiences has created the fast-growing demand for greater capacity and faster responses in warehouses.
In due diligence, the warehousing sector needs to optimize to meet the standards of smarter warehouses - to keep up with an ever-growing industry.
Smart Robotics
Founder and CTO, Heico Sandee, holds a PhD degree and previously acted as program manager for robotics at Eindhoven University of Technology. With more than 15 years of experience in robotics development, Heico now leads Smart Robotics in developing intelligent, robot-independent software for flexible deployment of automated solutions.
Our world is rapidly growing, and the future is increasingly urban.
By 2050, the global population is expected to reach a staggering 10 billion people, of which 70 percent are expected to live in built-up cities.
Recent data from The World Bank, meanwhile, shows that the urban population of Canada reached a record high of 82 percent in 2021.
There is evidently a critical need for livable cities with adequate housing and infrastructure; with this in mind, building progress for people and the planet is Lafarge Canada, a leader in sustainable construction materials and member of the global group, Holcim.
Lafarge Canada, whose longstanding commitment to sustainable development dates all the way back to 1977, is always seeking ways to increase the environmental performance of its operations.
For example, the company works to develop innovative solutions such as ECOPlanet, an ultra-low carbon cement product, to help achieve sustainable construction.
Equally, innovative collaborations with the likes of Blue Planet are helping to scale technology that can sequester carbon emissions and provide circular economy benefits. By leveraging mineralization technology to produce carbon-neutral or carbonnegative sand and gravel products, Lafarge Canada is looking forward to advancing its Net Zero strategy.
Recycled aggregates are a key component of the company’s journey to Net Zero, directly associated with the global demand for sustainable building solutions to support better living standards.
With the ambitious goal of doubling recycled aggregate volumes in Eastern Canada by 2025, Lafarge
A leader in sustainable building materials and solutions, Lafarge Canada’s journey to Net Zero is rooted in innovative solutions and collaborationWriter: Jack Salter
“ECOPlanet is our low-carbon limestone cement product that allows us to extend our technology to reduce the carbon content in our own concrete. Lafarge combines other products to produce a blend that concrete mix designers can use in their product offerings.”
Canada has demonstrated its commitment to a circular economy.
Its efforts to make the world a better place don’t stop at technological innovation, however. As well as participating in volunteer opportunities to strengthen and better communities, understanding and supporting the company’s sustainability initiatives are essential for all roles within the organization.
The initiatives implemented by Lafarge Canada reduce expenses, help the company to expand into new markets and diversify its offering, and stimulate the industry to develop more innovative solutions.
Lafarge Canada is clearly changing to reflect the world around us, and for a deeper dive into the company’s environmental efforts, we catch up with Robert Cumming, Head of Environment and Public Affairs.
North America Outlook (NA): Could you expand on the role that sustainability plays within the company culture at Lafarge Canada?
Robert Cumming, Head of Environment and Public Affairs (RC): At Lafarge Canada, we have been on what we call “a journey to Net Zero”. It has been fascinating to see the rapid evolution of sustainability, and the reengineering of our management systems to put sustainability at the core of everything we do.
Currently, all of our internal report ing structures include sustainability reports, and our short- and long-term planning is sustainability focused. We understand it is essential to our busi ness strategy and growth.
NA: In terms of the company’s products, what are the sustainable advantages of ECOPlanet?
RC: First, it is good to differentiate between cement and concrete. Concrete is the final product you
see everywhere around you, and it is made of cement, sand, gravel, and water.
Our large, centrally located cement plants ship cement to our own concrete plants and to independent ones.
ECOPlanet is our low-carbon limestone cement product that allows us to extend our technology to reduce the carbon content in our own concrete, but also in our customers’ concrete. We do this by implementing known technologies at the plant, as well as combining other products to produce a blend that concrete mix designers can use for their customers.
Our own concrete mix designers have additional proprietary technical solutions that build on ECOPlanet to form a suite of low-carbon concrete products through our ECOPact product line.
NA: Could you tell us more about the company’s efforts in mineralization and how this will impact your Net Zero strategy?
RC: This is one of the next big things. We have shown we can chemically react carbon dioxide with calcium to form limestone.
If we can produce sands and gravels in part with this mineralization technology, our final ECOPact concrete will move closer and closer to zero carbon content, so it represents one of the core strategies towards our targets.
NA: How does Lafarge Canada embrace or incorporate the circular economy?
RC: We need to end the single-use pathway from cradle to grave. We are already one of Canada’s largest recycling companies with volumes of over two million metric tons being reused in Eastern Canada alone.
We have set a target to double this within five years. We replace fossil
fuels with low-carbon fuel derived from selected waste materials, use by-products from other industries in customer cement and concrete blends, and set the best possible example by taking our own final products (concrete rubble) from demolition sites and turning them into new building material products.
Lafarge Canada is a founding partner of Circular Economy Leadership Canada (CELC). CELC engages partners in cities, provinces, and other industry participants to increase the use of recycled aggregates, with two full-scale virtual conferences and hundreds of expert participants leading to formal reports for action.
NA: Finally, do you have any upcoming projects or investments with sustainability in mind that you would like to highlight?
RC: Our recent ownership stake in Blue Planet, involves an exciting new mineralization technology to produce negative carbon sands and gravels.
We see strategic partners such as Blue Planet as central to our own ambitions to reach Net Zero. We are also mid-way through an all-electric loader demonstration at a quarry in Ontario.
Mining may not be the most obvious industry to play such an integral role in a bill designed to tackle climate change and inflation. Yet in President Joe Biden’s recent climate law, the $69 billion Inflation Reduction Act (IRA), the sector seems set for a fruitful future.
After the bill’s signing on 16th August, the industrial landscape has become defined by celebration and expectation, poised to reap the benefits that the new legislation will offer.
This primarily entails major tax breaks for domestic mining companies producing minerals that play a pivotal role in driving the US decarbonization agenda. Lithium is a key example of one such critical mineral, as a vital
resource in the development of products for electric vehicles (EVs). This expanded EV tax credit is a key move in realigning the balance of the US’ reliance on China as the global leader of mineral supply chains.
Whilst it is proven that lithium can be successfully mined in the US, uncertainty prevails over other battery-producing minerals such as graphite, nickel, and cobalt. These minerals are the foundation for a host of energy transition solutions, be it EVs, wind turbines, or solar panels.
To encourage domestic production will only heighten national security in a world that has become defined by fraught geopolitical tensions and disrupted supply chains.
As reported by Greenwire, the Biden administration is also turning its attention to Canada in its pursuit of raw materials, with funding opportunities proposed for mining and metals companies. This will be available through the Defense Production Act – legislation that was originally passed in response to the Korean War as a means to strengthen US supply chains.
In addition, the IRA hints at Pentagon funding for other miningrelated projects taking place across the country. This will encompass certain mining activities, including processes to produce minerals as a by-product of other commodities, carrying out improvements on existing mine sites, and undertaking feasibility studies.
This new law effectively encourages the birth of a new industry within the wider mining sector, one that is defined by exclusively serving the e-mobility and energy space. Although the question of the law’s success and impact is yet to be realized, the next few decades represent a defining moment in the US’ journey to become a polestar for mineral production.
Building on the global success of our regional titles – North America Outlook, Africa Outlook, APAC Outlook, and EME Outlook – Outlook Publishing is proud to be launching a dedicated platform for the Mining & Resources sector.
As mining organizations worldwide confront unprecedented change, embracing technological innovations and incorporating critical environmental sustainability agendas, now more than ever is the time to showcase the strides being taken in this dynamic sector.
A multi-channel brand, Mining Outlook will bring you the positive developments driven by organizations across the global mining industry through our various platforms. Discover exclusive content distributed through our website, online magazine, social media channels, and dispatches delivered straight to your inbox with a bi-weekly newsletter.
Through this compelling new venture, we intend to foreground the movers and shakers of the industry. To participate as a featured company and join us in this exciting endeavour, contact one of our Project Managers today.
www.mining-outlook.com
In the latest major retail acquisition, Reebok owner Authentic Brands Group has taken over British fashion brand Ted Baker. A sink or swim move, we discuss the necessity of brand identity and a marketsavvy e-commerce strategy with UK Lead at Shopware, Justin Biddle
Writer: Phoebe HarperFormerly a common instalment on the Great British high street, the fashion brand Ted Baker is now relocating to American shores.
Earlier this month, the US retail giant Authentic Brands Group (ABG) announced the conclusion of a $254 million take over. ABG is the name behind iconic brands including Reebok, Juicy Couture, and holds the image rights to both Elvis Presley and Marilyn Monroe.
Ted Baker’s business began to suffer after having to close stores during the COVID-19 lockdowns. However, the question of brand
identity and e-commerce efforts also have a role to play in the brand’s demise.
Facing an uncertain fate, the news may generally be perceived as a welcome step in the next phase of Ted Baker’s journey. Indeed, according to the BBC, the brand’s share price increased by 17 percent after Ted Baker officially accepted
the offer from ABG. But how will the company fare in this new transition and does this fall into a larger pattern of US companies acquiring British brands?
Justin Biddle sits as UK Lead at Shopware - the highly customizable, future-oriented open commerce platform for brands and retailers. Through a unique ‘open commerce’ approach, Shopware allows clients to seize the collective force of its worldwide network of established developers, wider community, and partnerships. This gives them the flexibility to build their own e-commerce platform infrastructure according to their business needs, while also allowing them to continuously advance and update their platforms to meet the latest market developments. We seek his expert opinion on the move and what it means for the brand’s future.
North America Outlook (NA): What are your thoughts on ABG’s recent acquisition of British brand Ted Baker? Are you confident that this latest move will aid the brand’s recovery?
Justin Biddle, UK Lead, Shopware (JB): I think that this will be less of a recovery and more of a new era for Ted Baker. They face multiple challenges, from supply chain issues through to the future of the physi cal store and also need to adapt to changing consumer habits and re quirements. While ABG can free Ted Baker from its supply chain issues, the future success of this brand, in comparison to its former glory days, remains very uncertain.
NA: What role has e-commerce played in Ted Baker’s journey? Would you say that the brand’s
consumer habits post-pandemic have led to a decline in demand for this type of fashion, but its high pricepoint for its casual wear continues to make it less accessible for consumers.
NA: Do you foresee a difficult transition for a British brand entering the US retail landscape?
efforts in this area have been unsuccessful?
JB: E-commerce has played an important part in Ted Baker’s journey, as it has in all retailers. However, Ted Baker was a lot slower to adopt it and its investment felt half-hearted. There is huge competition in this field now, especially with pure players enter ing the market and excelling in their online capabilities.
Ted Baker’s current predicament is not, however, entirely to do with failures in e-commerce, but more to do with its vague positioning in the market. It’s neither luxury nor high-street and more of a mid-market brand, so it’s a victim of the squeezed middle. Ted Baker has also traditionally been popular for its formal or workwear. Changing
JB: British brands entering the US always face significant challenges and I don’t see Ted Baker as being particularly well equipped to succeed. The key to success is having a brand that has a strong – and differentiated – offering that means it can stand out from the local competition. But Ted Baker is not ostentatiously British, nor differentiated from other mid-mar ket brands. They do however have a footprint in the US, and if those stores, outlets and concessions have been well managed then they may provide a springboard (if they are retained at all by the new owners). Success will depend on the old fundamentals: know who your customer is (and what they want), engage and communicate with them in a timely and appropriate manner, and ensure the service offer ing is above expectations.
NA: Do you forecast that the brand’s e-commerce platform will be a major focus going forward under ABG?
JB: E-commerce will be a crucial part of the offering going forwards, both as a channel (and channel manage ment) platform, but also as a key way to engage and communicate with the target audience.
However, ABG is in the business of franchising brands – so it is a question of what the franchisee’s strengths are. It depends on whether this ends up being a manufacturing play or a concessions play. Certainly, digital commerce is growing for all merchants, but it remains to be seen whether Ted Baker has the will or the means to ‘own the customer’.
North America Outlook, Africa Outlook, APAC Outlook and EME Outlook are digital publications aimed at boardroom and hands-on decision-makers, reaching an audience of more than 800,000 people around the world; spanning the full range of industrial sectors.
With original and exclusive content compiled by our experienced editorial team, we look to promote the latest in engaging news, industry trends and success stories from across the globe.
Your company can join the leading industry heavyweights enjoying the free exposure we provide across our digital platforms with a free marketing brochure, extensive social media saturation, enhanced B2B networking opportunities, and a readymade forum to attract new investment and to help you grow your business.
Visit www.outlookpublishing.com/get-involved for details on how your company can feature for free in one of our upcoming editions.
www.outlookpublishing.com/get-involved
Welcome to our series of spotlights. These reports dive into specific segments of economies across the region, featuring exclusive insight from associations and organizations in the know.
Manufacturing is a lynchpin of the industrial economy in the state of Georgia. Indeed, the state’s sector has earned a reputation as a national leader for advanced manufacturing practices, outpacing the US in 10-year GDP growth in manufacturing products including machinery, electrical equipment and components, and fabricated metals.
The versatile strengths behind Georgia’s manufacturing prowess, serving a whole host of sectors, translates to an output of $59.5 billion
and a labor force of roughly 289,000 production workers. At the backbone of these operations is a robust shipping and logistics network that provides critical speed to market, effectively giving Georgia a competitive edge against other US states. A global gateway for connectivity, Georgia hosts the fastest growing and third-busiest container terminal in the US with the Port of Savannah, and the most extensive rail system in the southeast. In terms of air transport, Hartsfield Jackson Atlanta International Airport is the nexus of efficient aviation services, connecting
Specializing in advanced manufacturing and the automotive industries, we foreground Georgia as the southeast’s industrial capital for the manufacturing sector
Georgia with the rest of the US within a short flight.
Since 1909, Georgia has represented a dynamic hub for automotive manufacturing, hosting the innovation centers and headquarters of global industry leaders including Hitachi Automotive Systems America, Honda Precision Parts, and Panasonic Automotive to name just a few.
Continually building on its automotive strengths, today Georgia has become known for its electric vehicle (EV) manufacturing sector. A significant major development in the field, in December 2021, Georgia was selected by American EV automaker Rivian as the location for a new carbon-conscious EV manufacturing plant. The company cited Georgia’s robust infrastructure, environmental impact, renewable energy production, and availability and quality of talent as the defining reasons for the move. On May 20, 2022, Hyundai Motor Group entered an
agreement with State of Georgia to build full EV battery manufacturing facilities in Bryan County. This project represents an investment of approximately $5.54 billion.
This availability and quality of talent remains an overriding focus for all involved in Georgia’s manufacturing sector. The state boasts highly advanced training programs, leading universities and a state-wide technical college system designed to continually nurture new talent that will ensure the sector’s sustainability. However, despite Georgia ranking as the eighth most populous state in the US, with a labor force of 5.3 million, a lack of skilled workers represents the manufacturing industry’s greatest challenge.
We delve into the industry today with the trade alliance foregrounding a collaborative approach to spearhead the future of manufacturing, both in Georgia, and beyond.
North America Outlook (NA): Firstly, could you briefly introduce us to Demand Driven Technologies; what led to the company’s inception and what is your mission?
Erik Bush, CEO (EB): Demand Driven Technologies (DD Tech) provides a cloud-based suite of Integrated Business Planning (IBP) which support end-to-end supply chain planning, management, and execution capabilities. Our solutions are powered by innovative demand-driven methods and concepts which dramatically improve supply chain performance for our clients.
During my 30-year career at IBM, I was astounded by the fact that manufacturers had not improved their inventory turnover rates despite billions of dollars invested on ERP deployments. I asked myself how can it be that in an era when civilians can be sent to space on an automated journey, with minimal training, cool looking space suites and an iPad, companies
have not been able to improve the most basic metric of inventory performance? There is a tremendous need to challenge the status quo in supply chain management methods and solutions and to deliver tangible value to companies across the world. DD Tech was founded in 2011 and since then, we’ve helped over 130 companies such as Coca Cola Beverages Africa, Michelin, Caterpillar and Hutchinson build more responsive and reliable operations. And, we’re just getting started!
NA: What differentiates Demand Driven Technologies from market competitors as a supply chain solutions provider?
EB: The reality is that the world we live in today is drastically different from the world we lived in 50 years ago when conventional MRP techniques were developed. Today, companies face an increasing number of SKUs, longer lead times, global sourcing, more demanding customers, and less reliable forecasts. Trying to solve this complexity with more “sophisticated” technology, like many do, is futile. To build a resilient supply chain, a paradigm shift is key. Our software Intuiflow, (formerly known as Replenishment+), was the first supply chain solution to be compliant with the disruptive demand driven methodologies and continues to be the most widely deployed DDMRP solution in the market. Intuiflow enables planning material procurement and manufacturing based on the most accurate demand signal available –
the actual consumption in the market – instead of forecasts. This approach mitigates the damage of inaccurate forecasts and ensures constant material availability improving order fill rates and compressing planning lead times. Our revolutionary planning approach helps you ensure you’ve got the right products, in the right place, at the right time. We also reduce the level of effort required to achieve those improved results. Our proven, six–step process has delivered results for manufacturers and distributors of all sizes and in many industries. And we’ve designed Intuiflow to seamlessly integrate with all major ERPs so that no matter the environment your company is in, you can benefit from a demand-driven approach.
We also fully embrace our responsibility to keep our client data secure. We are certified SOC2 compliant and remain vigilant with our software and business processes to continually improve our security perimeter. We monitor our networks for threats, maintain detailed audit trails, and take swift action whenever we detect potentially malicious activity.
NA: Could you tell us more about Intuiflow and the impact this suite of solutions will have on supply chains?
EB: Connecting supply with real market consumption — it’s the hallmark of the demand driven method, and it’s what enables demand-driven organizations to quickly identify strategic inventory positions, analyze operational priorities, and respond to sudden changes in market requirements. On average companies that transition to a demand driven approach with Intuiflow see a 35 to 45% reduction in their inventory levels, an 80% compression of their lead times, and their service levels rise up to 99%. Additionally, clients report their environment becomes more operationally stable and agile through our solution. These performance improvements also reduce waste by reducing expedited freight, warehouse storage space requirements, and the manufacture of finished goods not needed in the market. This in turn enables companies to bring to life a greener supply chain.
NA: Looking ahead, what are your key plans and priorities for the future?
EB: At Demand Driven Technologies, we believe artificial intelligence and machine learning will play a substantial role in making sustainable results even easier and faster to achieve. The conventional solutions in the market are far too dependent on deep user skill and experience. This can overwhelm users and often leads to users relying on Excel formulas of their own design.
Our Ai/ML capabilities focus on helping the user understand recommended orders, settings and adjustments in a clear and visual way improving their confidence in the system recommendations. We believe their role is to focus on monitoring and intervening on an exception basis instead of constantly checking the math of their planning system.
From our inception, our mission has been to provide tangible and sustainable improvements to our clients. Moving forward that will remain our top priority and will guide the continued improvements we will deliver to the market via Intuiflow and the services we offer our clients.
info@demanddriventech.com | https://demanddriventech.com Erik Bush, CEO
GMA is the trade body fostering a spirit of connection amongst manufacturers in Georgia through the sharing of industry best practices. CEO Jason Moss tells us more
North America Outlook (NA): Could you talk us through the origins of the association, how it came about, and its initial vision?
Jason Moss, CEO (JM): The organization was founded back in 2008. At the time, I was working in sales, providing 3D CAD engineering software to the manufacturing community. I noticed that there wasn’t a place for manufacturers to network with each other across the industry, since all of the associations were extremely siloed. As there was nothing that covered all aspects of manufacturing across the board, I identified the need in the market for people to be able to get together and share best practices. This was what led to our foundation.
Jason Moss CEO, Georgia Manufacturing Alliance (GMA)GMA was set up as a for-profit association, which is quite unique in this industry since the majority of associations are not-for-profit because they provide education and certification, or they are political in nature and undertake lobbying activities.
We do neither, although we do focus heavily on education through the events that we offer. In terms of politics, we don’t do any lobbying because we find that it creates a much more effective space for people to come together if there is no political agenda attached.
The way I see it, is that if something is good for Georgia, and it’s good for manufacturing, then we’re all about it.
NA: What do you identify as the major trends shaping the industry in Georgia?
JM: The trends that are having the biggest impact in Georgia right now have been in the electric vehicle (EV) space. The EV world has been transformative for our economy and our manufacturing base. That’s a big area that we’re working on, especially as the Rivian plant is underway in Rutledge (East of Atlanta) and Hyundai has just announced Savannah as the location for its EV and battery manufacturing plant. We’ve got several additional new battery manufacturers in Georgia.
Solar is another major area for us. I work with
a company named Coastal Solar and they’re helping many of our member companies meet their requirements for greener initiatives. The cost of energy in manufacturing across the US and especially in Georgia, has gone up dramatically and that’s a major input cost for manufacturers. It’s skyrocketing, so companies are looking for ways they can quickly mitigate that challenge.
NA: What challenges does the manufacturing industry currently face and how does GMA seek to overcome them?
JM: The workforce is the number one challenge that any manufacturer across the country is currently facing. Trying to find qualified people to come in and work has been an ongoing challenge. Industry peers in Savannah estimate that over the next five years there will be an additional 20,000 production jobs in the coastal area, and they’re already shorthanded. So, trying to figure out how to manage, develop and grow the workforce in the manufacturing space is a priority.
NA: Has the association got any projects in the pipeline that you would like to highlight?
JM: Our organization was designed to help support and grow Georgia’s manufacturing community, and that’s the baseline of what we do. Pre-COVID-19, we were doing roughly 120 live events a year. That included plant tours, networking events and educational sessions. Back then, as soon as anything was put on the calendar, it would sell out and hit full capacity within a day or two. We’re still not back to those levels today because there’s been COVID-19 hesitancy, but on the other side, manufacturers are now so busy that they can’t afford time to go off-site to learn new best practices.
For GMA, we try to provide information to the general population about the benefits of manufacturing, which is why we do so many events including plant tours and networking, to help educate consumers about what’s being made in Georgia, while also encouraging them to consider the industry as a potential career path. This is particularly true for those who may be transitioning out of the hospitality industry or other areas that have recently been negatively impacted long-term due to market changes. As people move out of those areas, we want to ensure that we position the manufacturing space in a positive light so that they will be attracted to our industry.
The companies that are truly focused on developing their workforce, and staying on the cutting edge encourage their employees to get outside the factory walls. Most manufacturers have more business than they can handle, so turning anybody loose to go and learn new things is difficult. The companies who make the decision and dedicate the time, always let us know that the investment is worth it.
We have just rolled out GMA 2.0 announcing our plans going forward as an organization. As part of GMA 2.0, we’re committed to hosting one factory tour, two B2B networking events and one educational session each month. We now have our schedule laid out until the end of the year for the general manufacturing community.
In addition, last year, I launched the Manufacturing Mastermind, which is for top-level executives of successful manufacturing companies that are interested in personal and professional growth. This Mastermind is what I’m super excited about because through it, I’m able to have a bigger impact on the leadership of manufacturing companies across the state. We’ve been doing it since June last year and we are already seeing phenomenal results from executives having the opportunity to sit and talk with
each other in an unfiltered way to learn and share best practices.
We’re going to continue to run GMA but this next tier, the Manufacturing Mastermind, is the piece that we’re really spending some time on to make sure that we’re helping these leaders in the manufacturing community to build their network, grow their relationships, and then learn best practices from each other.
NA: Finally, what are the association’s key priorities for the near future?
JM: Manufacturing Mastermind remains a major focus, running parallel to continuing GMA 2.0 with a more robust and scheduled line up of events. We’re taking applications now and screening a handful of key leaders for the next group to participate in the Manufacturing Mastermind. Although the focus is on Georgia at present, ultimately, we’ll be rolling out this program nationwide. (770) 338-0051
www.georgiamanufacturingalliance.com
GMA 10th anniversary photoFacing the dilemma of unprecedented labor shortages combined with an unexploited energy opportunity of enormous potential, we take a deep dive into the modern quandary of Pennsylvania’s manufacturing sector
Writer: Phoebe Harper | Project Manager: Krisha Canlas
Since the early days of North America’s very inception, Pennsylvania (PA) has proven its nickname as ‘the Keystone state’ thanks to its fundamental role both geographically, economically, and politically, in the foundation of the United States. Within the dynamic nexus of the American manufacturing sector, this still rings true today as the state confronts major opportunities that could redefine PA as a polestar for industry investment and unlock economic security on a nationwide scale.
As geopolitical tensions abound on the global energy landscape, PA’s natural gas deposits hold the
key to attaining national energy security whilst also providing essential feedstock to local manufacturing facilities. Yet in the fraught context of a heightened environmental movement, this resource remains untapped in its full potential.
At the forefront of fighting for change, and strategically headquartered just a stone’s throw from the state capitol in Harrisburg, the Pennsylvania Manufacturer’s Association (PMA) is the trade organization at the forefront of championing a competitive industry that combines workforce development with economic prosperity.
President and CEO of the PMA, David N. Taylor, envisions a competitive and prosperous future for Pennsylvanian manufacturing
North America Outlook (NA): Could you talk us through the origins of the association, how it came about, and its initial vision?
David N. Taylor, President & CEO (DT): PMA is the state-wide, not-for-profit trade organization representing the manufacturing sector in Pennsylvania (PA) and our mission is competitiveness. We want to develop the kind of pro-growth environment where people will choose to invest, locate, operate and expand. That’s been the association’s mission from the very beginning. We were founded by a textile manufacturer from Bucks County, a highly influential figure named Joseph Grundy, who ended his career as US Senator for PA.
We interact with the state government to improve PA’s business climate, for example by encouraging spending restraint so that politicians don’t spend money faster than we can earn it which suffocates growth or fighting for pro-growth business tax relief. PA’s business tax structure is currently very poor and the burden is too high. We are also fighting for regulatory reform where such rules are based on sound science and are subject to systematic review to ensure they remain relevant and are working as they should.
Lawsuit abuse is another major challenge for PA, since the Commonwealth is an extremely litigious environment and Philadelphia may be America’s lawsuit abuse capital. A priority of ours is putting reasonable limits on the litigation industry, as is building out the workforce.
We are the official state partner for the National Association of Manufacturers. As allies, we have relationships with many peers throughout other states through the Conference of State Manufacturing Associations (COSMA). Through
my position on the COSMA Executive Committee, competitiveness becomes vivid to me, particularly as governmental leaders in other states are far more attuned to the concept that the economy of the productive sector is a garden to be tended to, rather than a beast of burden to be whipped.
NA: With regards to the energy sector, how is PA’s natural gas supply impacting the state’s manufacturing industry?
DT: It is a godsend, and we need to appreciate its full enormity. When the Marcellus Shale Natural Gas Play was discovered in 2005, PA was an importer of natural gas, and the energy that we harvested was only enough for 25 percent of our in-state needs. Since production ramped up in 2008, PA has become the second-largest producer of natural gas in America, behind Texas. These two states combined generate just over half of the US’ natural gas production, and PA’s contribution to that portfolio has helped make America a global energy leader.
However, this industry is still in development. In Texas, natural gas is a co-product of drilling for oil, and the state benefits from a mature energy sector with a stable legal and regulatory climate, and billions of dollars of state-of-the-art infrastructure. In PA, we are still putting the major arteries in the ground to connect the energy from where it’s harvested to the downstream industrial, commercial, and residential customers. There is enormous potential for this to become so much bigger than it currently is and it’s a major part of what we’re fighting for.
Firstly, all manufacturing processes consume enormous amounts of energy, and this tends to be the highest cost input for most manufacturers.
Therefore, to have abundant, available, and affordable energy is a huge competitive advantage. Depending on your location in the state, the natural gas either comes out of the ground as pure methane, which doesn’t require separating or processing (dry gas), or it contains an abundance of other chemicals such as ethane (wet gas). Whilst dry gas is ready to go straight to the pipe for use, the other chemicals found in wet gas are all feedstocks for manufacturing.
In Beaver County, Royal Dutch Shell has invested roughly eight billion dollars in an ethane processing
facility that will become operational in a few months. This operation will be able to convert the ethane and produce millions of tons of polyethylene every year.
Polyethylene is at the top of a spectrum of products from which you can derive every kind of plastic, rubber, Styrofoam, solvents, and adhesives – all of these inputs are used in everyday consumer goods.
It is estimated that this region could support seven plants the size of the Shell facility, and by enabling access to that feedstock, we are creating an economic reason for people to want to locate their manufacturing facilities in Western PA.
David N. Taylor, President & CEOHowever, the environmentalist movement means that we confront a lot of propaganda and agitation. On the New York state border in northeastern PA, you will find the number one gas-producing county in America – Susquehanna County - with close proximity to major New England states such as Massachusetts and Connecticut. But since the state of New York has prevented us from building the infrastructure we need, we can’t get a volume of energy to those states. If we could, it would displace significant amounts of home heating oil and wood-burning stoves that emit more carbon than natural gas, so it would effectively reduce carbon emissions. We are going to keep fighting for this until we win because it’s too important for our state,
for our sector, for general prosperity, but especially for American economic strength and the national security of being a major energy provider. This is the good that PA can do for America, and for the world.
NA: How does the association confront the challenge of workforce development?
DT: This is the most complex and multi-faceted challenge that we face, and it remains a grave concern to employers since it can be a cap on economic growth. There’s business to be had, but if manufacturers can’t find the qualified new hires to fully staff their work, then what’s the point in bidding on a new contract?
“WE WANT TO DEVELOP THE KIND OF PROGROWTH ENVIRONMENT WHERE PEOPLE WILL CHOOSE TO INVEST, LOCATE, OPERATE AND EXPAND”
– DAVID N. TAYLOR, PRESIDENT & CEO, PMA
PMA supports a strong workforce by working for educational reform. The US public school system is very expensive, and yet too often delivers very mediocre results for our young people. By supporting scholarships, charter schools, and the kinds of innovations that introduce accountability and market competition in the same way that FedEx, DHL, and UPS have improved the performance of the US postal service, we want to help public schools to improve.
PA is incredibly diverse, but we are one of the most rural states in America with the largest number of people living in small towns, villages, or farmsteads. Meanwhile, Philadelphia is a major metropolitan area and one of America’s largest cities, but it is also among the poorest. As with Pittsburgh, there are extremely wealthy suburban areas, but generally a very troubled urban core. The way that you are assigned to a school as a student entirely depends on your ZIP code, and the state is both the provider of the service you receive there and the guarantor of its quality. The only other case where this applies is the prison system.
In the virtual charter school where I serve on the school board, the one thing common to the diverse group of students and the places they come from is the need to find something different from what is offered at their local ZIP-based public school.
Aside from supporting educational reform by trying to improve public schools, we also try to make people understand the great career opportunities found within manufacturing and the skilled trades. We have a state-wide television program where we feature tours of places like the Penn College of Technology in Williamsport, the Thaddeus Stevens College in Lancaster, and other PA institutions.
We have a cultural problem that encourages enrolment into college education as the standard, but this shouldn’t be the answer for everyone. If a society doesn’t have the doers and makers –electricians, forklift drivers, plumbers, steelworkers and so on, we would be without our entire modern civilization.
To treat as “grease monkeys” the people who sustain that work is a terrible dereliction. This is part of what we try to convey with our messaging and our educational outreach - to help people understand that there are great careers waiting, with family-sustaining wages, benefits and pensions, and that any honest work is honorable and we need to appreciate one another much more.
NA: Finally, what are the association’s key priorities for the near future?
DT: We will continue to work with the goal of competitiveness. As with many states, part of our problem is that we’re terribly parochial and looking beyond our borders isn’t something that our leaders do often. We need to benchmark PA against nearby high-performing states including Indiana and North Carolina. We need the government to live within its means, and we need to prioritize business tax relief, limit lawsuit abuse, streamline the regulatory process and lift those burdens, and build out the workforce, especially with the energy opportunity. We want to maximize domestic energy production in the Commonwealth and build out the infrastructure to deliver it to customers. We need to harness this wealth and bring it to the surface so that it can benefit human beings and supercharge our economy.
717 232 0737
Taylor@pamanufacturers.org
www.pamanufacturers.org
NORTH AMERICA OUTLOOK is a digital and print product aimed at boardroom and hands-on decision-makers across a wide range of industries on the continent.
With content compiled by our experienced editorial team complemented by an in-house design team, the resultant Outlook Creative Services department ensures delivery to the highest standards in promoting the latest in engaging news, industry trends and success stories across the length and breadth of the US & Canada.
As a bi-monthly publication, North America Outlook constantly has its finger on the pulse of the latest trends, biggest developments and business successes from each corner of the region, epitomized by the diversity displayed across each magazine. It incorporates an annual calendar-tailored front-of-book section, a showcasing segment dedicated to the most fascinating success stories in North America, and an event focus assortment sure to fill executives’ diaries throughout the year. The aligning North America Outlook website is also honed and ready to serve as a host for these facets and much more.
To get involved, please contact Outlook Publishing’s Managing Director, James Mitchell, who can provide further details on how to feature your company, for FREE, in one of our upcoming editions.
We talk turnkey telecoms with Chad Johnson, President and CEO of ADB Companies, whose infrastructure solutions are safely and efficiently addressing demand in the sectorWriter: Jack Salter | Project Manager: Tom McConnell
There is an unprecedented demand for power and telecommunications infrastructure.
The rapid deployment of 5G wireless technologies, and a seemingly endless need for faster internet speeds, is driving telecommunications providers to invest billions of dollars into infrastructure in order to meet this demand.
Likewise, the US government is investing $65 billion to expand high-speed internet in the country, ensuring all Americans have access to important services such as telehealth, virtual education, and remote work.
Proudly building networks, connections and partnerships nationwide within the telecommunications sector, is ADB Companies (ADB). As businesses and communities search for ways to be more efficient and stay connected, ADB is upgrading technology infrastructure to support these needs.
“ADB is a truly turnkey partner to our customers, providing infrastruc ture solutions from beginning to end,” introduces Chad Johnson, President and CEO of ADB since 2014.
“With more than 1,500 members of the ‘A-Team’ across the US, we have completed projects in nearly every state. We are headquartered just outside of St. Louis, MO and have offices across the country.”
ADB, whose client base includes large telecommunications service providers (both wireless and wireline operations), cable TV operators,
power companies, regional internet service and telephone providers, government organizations, and data center operators among many others, has four primary lines of business that work seamlessly together in order to fulfil the needs of customers.
“Our Engineering group can design a range of solutions from basic concept to dig-ready, including permitting and project management,” Johnson outlines.
“We are also capable of installing nearly any type of wireline infrastructure both underground
– CHAD JOHNSON, PRESIDENT AND CEO, ADB“OUR STRONG REPUTATION FOR QUALITY WORK, EXCELLENT PROJECT MANAGEMENT CAPABILITIES, AND A STELLAR SAFETY RECORD WERE ALL VERY SIGNIFICANT CONSIDERATIONS IN AWARDING THE WORK TO ADB”
ADB Technology delivers white-glove, turnkey IT solutions across the rapidly evolving technology industry. With a focus on network architecture efficiency, ADB ensures seamless connectivity between people and devices to enhance the end-user experience.
ENGINEERING – Well-versed in the latest design technology to create comprehensive networks.
WIRELINE – Underground and aerial services for numerous industries nationwide.
WIRELESS – Building and maintaining towers for major carriers.
TECHNOLOGY – Turnkey IT solutions with a focus on network architecture efficiency, ensuring seamless connectivity between people and devices to enhance the end-to-end user experience.
and aerially, servicing a variety of end customers in the telecom and power space. Our team is highly experienced in all aspects of wireless communications infrastructure development and maintenance from the base of the tower to the top.
“ADB’s Technology group specializes in inside-plant networking and commercial audio-visual implementation. We can plan, design, and install a full communications network from the source right to the point where the end user interacts with it,” he continues.
ADB is seeing more activity in the market than ever before, as evidenced by its record-high project backlog.
With a number of exciting projects coming up, ADB is working closely with its customers to help them effi ciently build out their utility, electrical, and fiber optic infrastructure.
Johnson highlights a $275 million extensive fiber build-out, awarded following a highly competitive process in which ADB was chosen based on the outstanding value it can provide.
Ditch Witch Worx is an authorized dealer of Ditch Witch underground construction equipment. We have over 60 years under our hats, which includes selling, leasing, and servicing the world’s leading name in trenchless technology systems, trenchers, vibratory plows, and underground tools and accessories available in today’s market.
From humble beginnings to current technology, our top-of-the-line equipment constantly pushes boundaries in the underground construction industry.
Continuing in the family tradition of hard work and dedication, Ditch Witch Worx strives to be the most important asset for your business needs. With 10 locations to serve you, we believe that we can best continue our success by providing the finest equipment available, excellent service, and by rewarding our employees for their individual and team efforts, generation after generation.
Proud to be a preferred partner of ADB Companies for over 27 years. Congratulations to ADB Companies on your unprecedented growth in the underground construction industry.
ditchwitchworx.comSAFETY – ADB’s incredible safety program, ADB Safe, is focused on getting every team member home safely every single day. ZERO unsafe acts is the expectation and team members are empowered to do whatever it takes to ensure everyone goes home safe.
HEALTH AND WELLNESS – ADB Well is the company’s robust health and wellness program. ADB believes in the importance of balancing physical, mental, and financial health, and is committed to providing opportunities for team members to enhance their overall wellbeing.
An industry-leading learning and education platform, ADB Academy is vital to the company’s growth. Every member of the A-Team is given the opportunity to learn skills and achieve professional development goals through online courses, instructor-led sessions, and on-site roadshows.
DIVERSITY AND INCLUSION – ADB believes in creating a diverse and inclusive environment that empowers every member of the A-Team to thrive. ADB Together is focused on ensuring all team members have access to the same incredible opportunities to grow personally and professionally.
SOCIAL RESPONSIBILITY – ADB Community is possible because of a culture of giving. The company wholeheartedly believes in serving the communities where it lives and works to make a positive impact.
of products and services the company relies on to provide infrastructure solutions to customers.
Whilst ADB has the ability to perform any part of the job, fluctuations in capacity and equipment availability often require the company to engage with partners in order to meet customer expectations.
“We want to be an easy-button and provide full turnkey solutions in a way that ensures customers are satisfied, not just today, but well into the future,” says Johnson.
Having also invested heavily in acquisitions throughout the last 18 months, ADB is now positioned better than ever to serve customers.
“Five companies have been added to the ADB family since the beginning of 2021, giving us the ability to provide additional services and an expanded geographical reach.”
A customer-centric partner providing innovative solutions, the safety, wellbeing, and career growth of ADB’s team members are the benchmarks of its success.
– CHAD JOHNSON, PRESIDENT AND CEO, ADB
Exponential growth over the years hasn’t come at the expense of staff welfare, and has resulted in ADB having an industry-leading safety record.
“Our strong reputation for quality work, excellent project management capabilities, world-class culture, and a stellar safety record were all very significant considerations in awarding the work to ADB,” he notes.
“We have all the in-house capabili ties needed to support a project of this size. With an excellent network of part ners to complement the ADB team, we are well-equipped to excel in delivering a world-class project.”
ADB’s partner network has been absolutely critical to its rapid growth and success, given the unique breadth
“ADB’s differentiator is our people, who are driven by our culture and core values. Every single team member is ‘ALL IN’ for doing the right thing for our customers, and getting home safely to their families every day,” Johnson emphasizes.
“All our value is on our people – no question. We don’t make products that could be churned out by automated equipment; we provide critical infrastructure that people rely on every day.”
Safety (ADB Safe) is one of the company’s five cultural pillars, along with health and wellness (ADB Well), development and education
“FIVE COMPANIES HAVE BEEN ADDED TO THE ADB FAMILY SINCE THE BEGINNING OF 2021, GIVING US THE ABILITY TO PROVIDE ADDITIONAL SERVICES AND AN EXPANDED GEOGRAPHICAL REACH”Chad Johnson, President and CEO, ADB
We are located in Springfield, Missouri and we specialize in underground horizontal directional drilling for pipes, internet, cable fiber and other underground utilities.
We have decades of directional drilling experience and have worked with various large enterprise organizations and clients across many utility projects to install commercial underground utility pipelines.
Our service area includes greater Springfield Missouri area, along with St. Louis and Branson. We also service clients located in Little Rock Arkansas, Tulsa Oklahoma and even Kansas City Kansas.
Need professional directional drilling services? Our commitment is to successfully complete your next underground utility construction project on schedule, on time and on budget.
(ADB Academy), diversity and inclusion (ADB Together), and social responsibility (ADB Community).
“The pillars, along with our mission and values, define our culture and what it means to be ‘ALL IN’,” Johnson shares.
Through ADB Community, the company works very closely with a variety of local non-profit organizations and encourages all team members to support community involvement where they live.
ADB has several team members on advisory boards for community organizations, sponsors a significant number of events and activities, and sends out weekly newsletters that outline a variety of volunteer opportunities available for people to participate in.
“As we do with all parts of our business, we develop social responsibility goals through our strategic planning process and deploy these goals through a number of specific objectives that are managed through our balanced scorecard process,” Johnson informs us.
“Team and individual performances
are not only judged on business financial results, but also on how well we foster our culture and meet our social responsibilities.”
The environments in which ADB works are extremely complex and often very dangerous. As a result, team members are constantly solving problems and finding ways to deliver on customer specifications safely and efficiently.
From team members on the ground or in the air to project managers and team leaders, everyone at ADB needs to be “ALL IN” at all times when it comes to safety, taking care of partners, and embracing the company culture.
This approach is how ADB will continue to succeed, grow, and create amazing opportunities for team members to grow their careers.
“Because successful teamwork is so crucial, and each role extremely valuable, we focus heavily on team member development and strive to promote from within. A significant portion of our leadership team,
The Permit Getters® is a dedicated team of field research, design, CAD and permitting specialists working together in the common goal of customer satisfaction.
From identifying the scope to developing the most cost and time effective plan to determining permitting requirements to delivering the design and permits to you, we are focused on you, our customers.
The Permit Getters® are passionate about excellence and doing our work right the first time. You trust us to bring quality and hit the targeted timelines. We are there for you, all the way.
thepermitgetters.com
Vermeer Midwest values its relationship with ADB and strives to provide the best equipment, training, and service in the industry.
Vermeer Midwest has supported ADB on a variety of directional drill and plow projects.
The culture of both companies, built on family values, has allowed for a cohesive partnership that is dedicated to safely developing infrastructure and serving our communities.
At Vermeer Midwest, we believe that customer service is not just what we do, but it is who we are. Our culture inspires us to do whatever it takes to maximize the customer’s productivity and profit.
T 888-809-5640
www.vermeermidwest.com
Vermeer Midwestmyself included, started in entry-level field roles,” reveals Johnson, who now has over 30 years of experience in the telecommunications industry.
“This gives our leaders a fundamental understanding of our work and helps to encourage valuable communication throughout the organization. In addition, all team members know that they have the opportunity to move into different roles within the business, if they choose, and that the rest of the team will support them.”
Johnson’s love for the industry, one he is excited to be part of in the age of rapidly changing technology, is rooted in these relationships.
“I have a natural love for building and maintaining relationships, and truly care for people beyond what they simply offer our business,” he beams.
“Being part of creating and fostering the amazing culture at ADB has been an incredible journey. It extends beyond our team members, as our community, customers, and partners are all critical to our success and our ability to make a difference.”
On making a difference going
forwards, ADB has “extremely aggressive” goals for the coming year and beyond, according to Johnson.
“We have plans in place to grow our revenue by more than 25 percent in 2023, and double our business between now and 2025,” he says.
Increased geographical density and expanded service offerings, courtesy of ADB’s recent acquisitions, will enable the company to offer more of the turnkey solutions that customers need.
With such a fast growth trajectory, however, it would also be easy for ADB to neglect its focus on culture and people.
“We are keeping team members at the center of our strategic plan, and dedicating more resources to training, development, and to our cultural pillars to ensure we don’t lose sight of the most important aspects of our business – the people,” Johnson concludes.
“As we continue to take ADB to the next level, it’s exciting to think about the opportunities each person in our business has to grow their career and how we can help each other along our personal and professional path.”
314.426.5200 www.adbcompanies.com
Member-owned and not-for-profit, we explore expanding energy generation in Iowa with Bill Cherrier, Executive Vice President and CEO of Central Iowa Power Cooperative Writer: Jack Salter | Project Manager: Tom McConnell
From changing generation options to new technologies, the electric utility industry is evolving faster than ever before.
Utilities across North America understand the importance of diversity in generation and are working as quickly as possible to integrate renewables and other technologies, while using a balanced approach to ensure grid reliability.
Though the industry is changing, new energy projects can nevertheless take up to 10 years to plan, site, develop, and construct.
Careful planning is therefore essential, and nobody knows this better than Bill Cherrier, Executive Vice President and CEO of Central Iowa Power Cooperative (CIPCO) since October 2017.
A graduate in accounting from Loras College in Dubuque, Iowa, Cherrier joined the organization with a sizable 35 years of experience in the utility industry, most recently serving as Chief Planning and Finance Officer for Colorado Springs Utilities.
In his time at CIPCO, a generation and transmission electric cooperative, he has overseen the organization’s changing generation landscape.
“CIPCO’s generation expansion includes Heartland Divide Wind’s 104-megawatt (MW) purchase power agreement, the $85 million repowering of Summit Lake Generation Station to efficient natural gas-fired reciprocating engines, and the recently completed 100 MW Wapello Solar and 54 MW Independence Wind Energy longterm power purchase agreements (PPAs),” Cherrier tells us.
“In previous positions during my career, I have also led the acquisition of a 480 MW combined-cycle gas power plant and was an integral part of the executive team on a $1 billion water supply project,” he adds.
With approximately 100 employees,
CIPCO serves 13-member rural electric cooperatives and associations across 58 of Iowa’s 99 counties.
Electric cooperatives such as CIPCO are not-for-profit organizations that are owned by their distribution cooperative members. They first brought power to rural America when other utilities did not, and to this day, electric cooperatives are governed by an elected board of directors who come from the distribution cooperative members served by the cooperative.
An emphasis is therefore placed on people over profits, as cooperatives return patronage margins, above the cost of providing electricity each year to its member-owners.
“As a not-for-profit energy provider, CIPCO is committed to providing safe, reliable, and cost-effective power, and has returned an impressive $120 million in patronage to its memberowners since inception,” shares Cherrier. “The make-up of Iowa’s electric service boundaries allows cooperatives to focus on providing the best for those we directly service, not shareholders with a focus on profits.
“Our board is comprised of individuals who live on our
No matter who you are or what you do, it’s critical to get the power you need right when you need it.
This is something many take for granted. No one understands the U.S. energy market like ACES. We are an industry leader in helping our clients buy, sell, and manage energy more efficiently, with less risk—ultimately helping to deliver the reliable, affordable power that lights our homes, fuels businesses and industry, and connects our world.
member-owned service lines, so the decisions they make directly impact their neighbors. It’s this local focus that allows an electric cooperative like CIPCO to make decisions in the best interests of our member-owners and not based on profits,” he continues.
With a balanced portfolio of energy sources, CIPCO provides energy to its member-owners that is a diverse mix of wind, hydro, solar, landfill gas, natural gas, and coal energy resources.
CIPCO takes great pride in providing a diverse portfolio that includes multiple fuel sources to its member-owners. This focus on diversity allows CIPCO to maintain stable wholesale power rates, ensuring that member-owners continue to provide safe, reliable, and cost-effective power to memberconsumers down the line.
“Rural electric cooperatives electrified rural Iowa and are committed to providing energy for decades to come,” Cherrier affirms.
REPOWERING PROJECT CIPCO is headquartered in Cedar Rapids with offices in Des Moines, Wilton and Creston, the latter of which is also home to the wholly-owned
ACES’ clients include electric cooperatives, municipalities, independent power generators, and financial institutions. ACES is unique in that we never take ownership of the energy we help our clients buy, sell, and manage. Rather, we act as an agent on their behalf, as an extension of their organizations. We are impartial, always governed by the cooperative principles upon which we were founded, helping ensure we will never have a conflict of interest on any transaction.
Just as important, we help our clients understand and anticipate what is happening in the energy markets today and in the future. So, if you are looking for the experts—a team that understands the complicated intricacies of the energy markets and how crucial energy is to every facet of our daily lives—we are your team. We want to show you all the ways ACES can make you even better at what you do. Let’s get to work.
Summit Lake generation plant, complete with combustion turbines and natural gas reciprocating engines.
Each turbocharged engine generates 18.8 MW, and because they run at a very low and constant speed, the reciprocating engines can start and stop quickly and be tuned for efficiency.
Having met all environmental and performance goals after rigorous testing, the new generators reached commercial operation in 2021 and were part of a substantial $85 million repowering project at the site.
“With the new engines, Summit Lake produces 110 MW of power as a peaking facility. The project also included the demolition of the 70-year-old steam plant, construction of a new administration building and garage, and significant substation upgrades,” outlines Cherrier.
The expansion of Summit Lake, CIPCO’s largest generation construc tion project to date, provides CIPCO member-owners with a low-cost natural gas peaking option that will run when demand is high, particularly during the summer months.
It adds flexibility to the system, thereby maintaining the stable prices CIPCO has provided to member-owners for the last decade while allowing the organization to strategically purchase energy and capacity from new, cost-effective wind and solar resources.
“Repowering Summit Lake adds greater diversity to CIPCO’s portfolio and complements the continued build out of resources with dispatchable, quick-start natural gas capacity to run when the wind and sun aren’t produc ing electricity. Keeping the lights on for our members 24/7 is our top priority,” Cherrier says.
Elsewhere, CIPCO’s generation expansion includes the recently completed 100 MW Wapello Solar project developed by Clēnera LLC.
“AS A NOT-FOR-PROFIT ENERGY PROVIDER, CIPCO IS COMMITTED TO PROVIDING SAFE, RELIABLE, AND COST-EFFECTIVE POWER”
– BILL CHERRIER, EXECUTIVE VICE PRESIDENT AND CEO, CIPCO
CIPCO, which also owns six smallscale solar sites (totalling 6.4 MW) in six communities throughout southern and eastern Iowa, announced its intent to purchase 100 percent of the energy and capacity from Wapello Solar in December 2018, with the project reaching commercial operation in March 2021.
Despite beginning construction during the COVID-19 pandemic, Iowa’s largest solar project located in Louisa County progressed with little to no delay.
“Wapello Solar is located on nearly 800 acres of land and contains 318,000 bifacial solar panels on single-axis trackers, which are optimized for bifacial performance,” Cherrier informs us.
“As an intermittent energy source,
Wapello Solar provides energy during peak heat times in the summer, as well as peak heat times throughout the year.”
Hot on the heels of Wapello Solar,
CIPCO is once again working with Clēnera LLC to develop Coggon Solar, another 100 MW solar facility in northern Linn County.
Maintaining a similar footprint to
Wapello SolarWapello Solar, with the milestone project scheduled for completion in late 2023, Coggon Solar will bring significant economic benefits to the local area.
According to Clēnera LLC, the project will contribute several million dollars in property tax revenue to Linn County over the life of the generating facility. An estimated 350 construction jobs will also be created, many of which will be taken up by local labor.
Complementary to CIPCO’s solar endeavors is wind energy, with the new Independence Wind Farm reaching commercial operation in December 2021.
CIPCO currently has a PPA in
operational in December 2018.
HDWEC represents an investment in Iowa of more than $150 million and is expected to deliver millions of dollars in additional revenue to landowners and local communities as it generates power for CIPCO.
It has already created a great deal of enthusiasm and positive economic activity in the community, with the extra tax revenue generated going a long way to help the county enhance its schools, roads, and essential services.
CIPCO’s relationship with vendors is critical to the success of its energy generation activities, particularly during times of supply chain stress.
“It’s essential that we have access to the necessary supplies, poles, wires, transformers, etc. to maintain CIPCO’s reliability standards,” says Cherrier, who concludes by outlining CIPCO’s equally emphatic emphasis on community relations.
place to acquire 100 percent of the energy and capacity output from the generation site, owned by BHE Renewables.
“The 54 MW intermittent energy source provides cost-effective power for CIPCO members. Wind is a complement to solar, as its availability is excellent in cooler months or on windier days,” Cherrier states.
CIPCO’s largest wind energy project to date, meanwhile, is the Heartland Divide Wind Energy Center (HDWEC), whose 43 GE wind turbines are designed to pivot and capture the prevailing wind and convert it to electricity.
Through a 20-year, 104 MW PPA, CIPCO member-owners have been served with energy produced by HDWEC since the project became
“CIPCO and its member-owners are committed to the Seven Cooperative Principles. Principle number seven, concern for community, is important to us; we give back to the communities served through donations to non-profit organizations and by supporting economic growth with low- or zero-interest loan opportunities for businesses looking to grow and expand in rural Iowa.”
It is these Iowan communities that will continue to benefit for years to come from the cost-effective, safe, and reliable energy that CIPCO provides for its member-owners.
Tel: 800-373-8011 cipco@cipco.net www.cipco.net
Emerald Textiles is the largest in linen and laundry commercial processing within acute care, servicing Hospitals, Medical Centers, and specialty clinics across four states in the Western US. CEO Andy Kratky discusses the company’s latest developments and its continual growth in the market
Since the beginning of the COVID19 pandemic, we have been reminded that healthcare is one of the most critical sectors to the health and wellbeing of people around the globe, and the continued function of everyday life, from individuals to businesses and even governments.
Within the sector, there are key players who keep the wheels of the industry turning in one way or
another, such as the suppliers of healthcare resources.
One such company is Emerald Textiles (Emerald), the largest healthcare linen service provider that specializes in servicing the healthcare industry, with 12 state-ofthe-art commercial linen processing facilities, three service centers, and industry leading operations across the Western US.
“We are the largest provider of
healthcare linens in the region, and we have 12 different sites across four states,” introduces Andy Kratky, CEO of Emerald. “These are our processing facilities, and on top of this we have three service centers strategically located to serve a wide base of healthcare customers.
“We measure ourselves on the pounds of linen produced each year. This number sits at around 330 million clean pounds provided to our
Andy Kratky, CEOcustomers annually, which is sizable compared to others in the field.”
Emerald’s 2,200 employees serve around 2,500 customer sites in the country, delivering the highest quality products to the sector across the western region.
“Emerald is 99 percent in the healthcare space, with one facility in Reno (Nevada) that additionally
produces linen for the hospitality sector,” Kratky says. “Our standard items focus on any linen that you would find in a hospital room, such as bed sheets, bath blankets, pillowcases, and many other items. Another key part of our business is non-standard items such as reusable isolation (ISO) gowns, scrubs, and microfibers, for example.
“Since the COVID-19 pandemic, reusable ISO gowns have been a
very important part of supporting the healthcare workers in hospitals. At the beginning of the pandemic, many experienced supply chain disruptions and we did a great job ramping up our inventories such as reusable ISO gowns. Being proactive in our inventory ramp up ensured our healthcare partners had enough supply and got what they needed. This was especially important when disposables became difficult to find,
to ensure that the workers were as safe as they could be during work hours, all while providing sustainable, reusable, hygienically clean products.”
What truly sets Emerald apart from the competition in the industry is not just its scale of service across the Western US, but also the quality of specifications the company follows when it comes to its products.
“We provide a higher quality, higher spec product to service our customers and make sure that they have the best quality products within their hospitals,” Kratky continues.
“The lack of issues when it comes to our quality, mixed with our dedication to making sure that our customers have the best products and enough supply on time, is critical to Emerald, and is what really differentiates us.”
While quality remains key to serving customers, growth and a focus on consolidation are also instrumental in establishing a lasting foothold in the industry. Across the US healthcare space, players are competing to incorporate additional institutions and grow to best service regions and states in their specialized areas.
“Traditionally speaking, there are larger healthcare systems that branch out across the US, and then there are systems that have been more regionally focused, or super-regionally focused with market density based in large cities,” Kratky elaborates. “Then there are a lot of smaller independent healthcare facilities that support different local areas but do not really branch out throughout their state,
Norchem began its partnership with Emerald Textiles in 2010 at their first plant located in San Diego, California. The ongoing goal of the partnership has been to increase textile cleaning efficiency through our green detergent programs, reduce utility consumption through our water recycling and heat reclamation systems, and consult on production process improvements by leveraging our plant automation expertise.
After implementing Norchem’s green chemistry for healthcare with consistent positive results in San Diego, the plant was under pressure from the city to manage TDS to sewer. As water costs and sewer costs increased, Norchem stepped in to design a complete turnkey UltraPure® Water Filtration system for wastewater reclamation and an RO system for incoming water TDS reduction. After installation, the plant was able to successfully reduce the TDS of the incoming water to stay below the discharge limit of 1,000 ppm TDS and recycle up to 70 percent of total plant wastewater.
Norchem now services eight Emerald Textile plant locations in the SouthWest with our Alkapon™ Detergent program. Their first location in San Diego after 11 years continues to benefit from the UltraPure® WasteWater Recycling System and the RO Pure® Reverse Osmosis System.
Since partnering with Norchem, Emerald Textiles has recycled 430+ MILLION gallons of water! Norchem’s application engineers and customer care technicians balance the injected chemistry with recycled water to maximize heat, water reclamation, and surfactant recovery. The result is BIG SAVINGS at the wash aisle and optimum utility conservation.
NorchemCorp.com
region, or the country.
“What we have seen over the past several years is a consolidation of the market. You have larger healthcare systems that are going out and acquiring smaller independent systems that are a good fit with their footprint, and they are also building new hospitals and medical office buildings to continue their outreach.”
Emerald has been able to achieve this trend in acquisition and growth, being able to implement additional facilities, whether they are greenfield developments or otherwise in order to successfully grow and expand with their customers.
In recent years, Emerald has been driven by this growth focus across the Western US. According to Kratky, the initial vision of the company was to create a linen and laundry healthcare provider that could service larger healthcare systems, with the business starting up in Northern California catering to a small number of different facilities.
Emerald has grown significantly through organic growth, but also continues to grow through acquisition and expansion.
“The most recent acquisition was with Angelica Corporation (Angelica),
Emerald continually invests in the latest equipment, technology, and infrastructure systems that result in fewer manual processes, greater automation for uninterrupted laundry processing, and produce the highest quality linen for patient satisfaction and greater peace of mind. It’s the Emerald Difference. Investments include:
• Computerized loading and transferring systems, automated conveyors, stainless steel surfaces, microbe resistance flooring.
• Award-winning and resource saving continuous batch washers, energy saving dryers, automated steam finishing processes, and folding robots.
• Gravity-enabled overhead E-Tech rail systems that automate laundry bag transferring are all around better to preserve Emerald’s hygienically clean linen, maximize linen processing and efficiency, save more on natural resources, and better for employee satisfaction.
• High tech automation and rail systems that move Emerald’s garments from steam to racks ready for customers.
Emerald’s clean linen processing is Hygienically Clean Healthcare certified through its partnership with TRSA Association for Linen, Uniform, and Facility Services Industry.
Emerald is dedicated to quality assurance and best management practices to ensure the highest quality and safety for customers, their patients, and employees.
• Hygienically Clean Healthcare Certifications adhere to all healthcare standards and policies
• Ongoing inspections and microbiological testing for the highest quality assurance
• Full compliance with all State, Federal and OSHA regulations
• Monitors complete textile processing cycle from handling and transporting to in-facility processing
• Best Management practices and personnel training
With almost 30 years of history within the textile industry, American Textile Systems (ATS) is a key player specializing in supplying leading quality textile products to the linen supply, hospitality and governmental industries.
Based in Southern California, ATS has grown to become a medium-sized business with company success owed to an exceptional and dedicated team of employees, many of whom have been with the business for decades.
ATS’ supply chain has been carefully curated and nurtured to provide the company with industry leading quality products, sourcing from the very best mills in the industry, carrying complete lines of the following products:
• Bath linen, including wash cloths, hand towels, and bath towels.
• Bed linen, including pillowcases, bed sheets, contour sheets, and knitted contour sheets.
• Over the bed products, such as blankets, spread blankets, and comforters.
• Patient wear, including patient gowns and iv gowns in poly/cotton blends and 100 percent polyester.
• Ability to customize products including property marking, kaumographing, and continuous imprinting (cim). ATS can build products with any construction, dobby pattern, color, and shade of bleaching.
Today, ATS has distribution centers in Southern California, Texas, Georgia, and New Jersey, allowing the company to serve customers promptly, efficiently and just-in-time with same-day and next day deliveries via company operated delivery trucks and excellent logistics control.
When timings are extra tight, ATS can easily accommodate “emergency” shipments and deliver goods within hours of the purchase order being placed.
www.amtexsys.com
Jennifer@amtexsys.com
Toll Free: 888-737-2689
T: 562 229 0036
C: 562 292 7727
Your one-stop textile supplier, offering in-house manufacturing and custom finishing.
Alan@amtexsys.com
Toll Free: 888-737-2689
T: 562 229 0036
C: 562 307 0464
10631 Hathaway Dr. Santa Fe Springs, CA 90670
www.amtexsys.com
another provider of hospital linen and laundry, in which we acquired nine different facilities from them in the west of the US,” Kratky says. “The idea was to continue to scale up, and there were certain facilities that were very good, and we didn’t have to alter. Some other facilities we have had to deploy capital and invest in upgrading them.
“We have a strong market position because of our success in growing organically and through the investment in acquisitions such as Angelica. Because of our footprint and the deployment of our strategy, we are able to support larger healthcare system customers without compromising quality or customer experience. Recently, this has accelerated and put us in a good
position from a customer standpoint as well as in terms of capacity. Angelica was a large integration due to the number of sites that we incorporated, but this was completed in around five months. I would call this a success from start to finish, because usually it takes far longer to fully integrate a company of that size. Our team was also able to support our customers and partners during this time and did a really great job.”
On top of the Angelica acquisition, Emerald has undergone several plant expansions, including at its Phoenix (Arizona) plant, to improve capacity, efficiency, and customer service.
“The Phoenix expansion has been a really nice success story for us since we acquired the business,” Kratky tells us. “We knew that it was one of
Our dedicated account management and service team partners with our customers to create a program that best fits the specific needs and goals of each of our healthcare facilities and departments.
• Providing dedicated, local customer experience teams for personalized care, assurance of stock, and monitoring usage
• Building solution-oriented, customizable programs that meet the specific needs of each department
• Generating goals and savings with improved linen utilization and linen management best practices
• On-site product and usage training education with a local team of experts
As a global supplier and manufacturer of healthcare textile solutions, MIP provides comfort and efficiency for the healthcare community and its people.
As a proud partner of Emerald Textiles, we hold people at the heart of all that we do. We provide innovative, as well as cost-effective, products, services, and solutions for the commercial laundry industry.
We know the value of our products because we see the impact that they have on the lives of laundry operators and staff. Find out how we can help you at mipinc.com
www.mipinc.com
the better running facilities that we acquired, and it has a great team of people working there. Earlier this year, we were able to secure a large new health system partner in Phoenix, and we had to expand our capacity to take on such a customer.
“We are currently deploying another of what we call a continuous batch washer (CBW) tunnel system, to make a total of three CBWs, along with five new industrial sized dryers to expand such capacity. This will also allow us to continue our growth efforts in that market. In addition to Phoenix, we have deployed $50M of capital over the past four years to upgrade several facilities and expand capacity to take on new customers, which results in better customer support and improved efficiencies in the facilities.”
Since Emerald’s acquisition of Angelica
and its additional facility investments, the company has undergone substantial growth in the market.
“Last year we grew 18 percent organically, and this year to date we have grown 12 percent; because of this, we have expanded capacity in certain facilities and continue to do so,” Kratky tells us. “We have also increased investment in our linen products, continue to invest in hightech automation through quality equipment, and internal investment of our people.”
For Kratky, Emerald’s workforce is the center of the company’s success, and reinvesting in employees has been, and continues to be, a primary focus on in-house development across Emerald’s many sites.
“We are firm believers in making sure that we have the best equipment used for production, and we continue to deploy capital across our sites for
our manufacturing capabilities as well as our staff,” he elaborates. “This is one of the reasons for our year-onyear organic revenue growth, but the second is the focus on our people.
“We have a lot of employees within our facilities, and we make sure that our employees have a good work environment and the support they need to thrive in the workplace. We need to make sure that we take care of our employees.”
Within this sphere, Emerald ensures to recognize and reward its employees’ efforts and performance, and celebrate such achievements.
“We have had employee recognition in the company for a number of years now, and we host events and other things to keep our teams motivated,” Kratky tells us. “We also have quarterly business meetings with all employees across our 15 locations with the intent on providing
Left/top: Automated slings and rail system. Above: A computerized control system tracks every sling that is transported within the facility. After the linen is processed and folded through automated machines, folded linen stacks are transported on conveyors to the final processing stage where its prepared for order fulfillment.all of our teams with a perspective of what is going on with the company and how we are moving forward.
“I am a believer in open communication to our team to ensure they have an understanding of what is going on in the entire business, not just their portion of it. This gives them the perspective of how they impact the company as well as how their co-workers impact the company. Maximized communication to our team is critical, and providing the team with the status of the company and performance goals, both internal and external, is extremely important, as is recognizing and celebrating individual performance.”
Environmental, social and governance (ESG) is at the core of the company’s mindset and defines the way in which Emerald operates across the western US.
“From an environmental standpoint, our ESG strategy helps Emerald reduce our use of natural gas, electricity, water and other resources used at our facilities to be good stewards of the environment,” Kratky explains. “Doing our part will help the planet that much more, and our ESG plan is very important to our overall strategy as a company as well as our healthcare partners.”
Emerald’s primary focus for the rest of 2022 and beyond is building on the organic growth experienced from the company’s multiple investments and facility developments. Despite holding a predominant share of the market, Emerald seeks to drive value for its customers and their businesses, while keeping its eyes peeled for opportunities for acquisition.
“We see an opportunity in independent outpatient facilities that we think are a very good fit for Emerald, and that we can align with from a product and service perspective,” Kratky says. “So, we are working on, and in the process of,
deploying a strategy to really hone in and focus on generating more outpatient and independent care facility business.
“Outside of this, despite our super-regional reach, we have had customers reach out to us and ask directly if we have the ability to serve them in other states across the country. Because of this, I believe that green field expansion is definitely going to be a part of our future, where we build a processing facility based off an anchored customer in a certain area. We did this with our Livingston CA facility, so we are well versed in creating a world class greenfield facility.”
Stemming from this customer demand, Emerald is prospecting expansion into adjacent markets as well.
“This is a pillar of our growth strategy,” Kratky reveals. “There are plenty of opportunities out there in the market, and we will always look towards expanding our product and service base to reach customers further afield.”
info@emeraldus.com www.emeraldus.com
Emerald Textiles Pomona facility with their high-tech, computerized automated garment system – also referenced in the article in what Emerald Livingston, CA (a greenfield expansion) will be installing at the end of the year. Left: Automated sheet folder Bottom: Industrial sized, energy efficient dryers, gentle on healthcare’s most critical textiles.Sky Ridge Medical Center, a member of HCA Healthcare, has established itself as a destination hospital offering a vast selection of services. Kirk McCarty, CEO, dissects the power of community and forging a healthier tomorrow for patients
Writer: Ed Budds | Project Manager: Felix Revell
Sky Ridge Medical Center (Sky Ridge) offers the latest in medical innovation, delivered in a calm, soothing and most vitally, a healing environment.
This, in combination with a worldclass array of services and a team of the area’s top healthcare professionals, places Sky Ridge as a model of care for the rest of the country. The impressive facility offers an array of patient-cen tered programs, including its compre hensive Cancer Center, Trauma and Stroke Centers, Center for Robotic Surgery, award-winning Birth Place and state-of-the-art Spine and Total Joint Center.
With the significant expansion of services over the last 19 years, Sky Ridge takes pride in its Level II Trauma Center, delivering exceptional care for stroke, heart attack and trauma
patients, as well as its impressive growth in oncology care with the addition of fellowship trained oncologists, gynecology, urologic oncology, breast and colorectal surgeons.
Since its opening on August 20, 2003, Sky Ridge has grown to a 284-bed hospital, located in Lone Tree, Colorado, boasting an evergrowing reputation for providing clinical excellence and world-class services to both its patients and colleagues. Complemented by the latest technology in women’s care, spine, neuro and orthopedic services, robotic surgery, and top-rated emergency care, Sky Ridge seeks to provide a healthier tomorrow for every patient and family, so they rarely need to leave the community for care.
“We are fortunate to be part of HCA Healthcare, which has provided us with the encouragement, resources and capital to expand and adapt to the changing healthcare needs in our community,” says Kirk McCarty, CEO of Sky Ridge.
Reflecting on his path to CEO, McCarty recalls a formative experience whilst attending an event held for children battling cancer. During this time at “Camp Quality”, he was paired with one of the young patients.
“It was this life-changing experience that helped me realize that I wanted to help people, and I immediately started formulating a plan to enrol in medical school,” he reflects.
Later, while visiting his hospitalized grandmother, McCarty saw the remarkable work of the nurses who patiently and compassionately cared for his beloved relative.
Soaking up this behind-the-scenes insight of hospital operations, getting a sense of the noble work that was being done in the ICU, and how those amazing nurses forged personal connections with patients, helped ignite the spark to become a nurse.
• A helipad for AirLife medical transports
• Board-certified emergency medicine doctors on-site 24 hours a day
• Direct access to two cardiac catheterization “cath” labs
• Experienced emergency nurses
• Intensivist coverage 24 hours a day
• Rapid access to specialists for orthopedic emergencies
• Spine surgery expertise
• State-of-the art diagnostic equipment
• Rapid response teams for trauma, cardiac, stroke and sepsis alerts
This led to 16 loyal years working at the same hospital, starting as a nurse and leaving as Vice President of Operations. Grasping an exciting opportunity to join Sky Ridge almost eight years ago, he believes that his extensive and varied accumulation of industry experience prepared him effectively to take on the complex nature of the Chief Operating Officer role that led him to become CEO.
In the hectic day-to-day operations of a complex medical facility like Sky
Ridge, no two days are the same. Caring for patients 24 hours a day, 365 days a year, the hard-working professionals of Sky Ridge encounter the very best days when a baby is born as well as the worst days when a patient loses his or her battle for health.
Nevertheless, McCarty is keen to express how exhilarating the healthcare industry is and how daily activity in a hospital can provide both motivation and inspiration.
“It is honestly the most exciting thing that I can imagine doing.
Sky Ridge Medical Center and Skyler Design Build, LLC (“Skyler”) have been working together for over five years on a daily basis. Whether a small refresh project or large complex project there is one thing that never changes –quality, assurance, safety, and above all, dedication. Together, Sky Ridge Medical Center and Skyler have developed best in class interim life safety measures and infection control to accommodate and protect all guests, visitors and staff throughout the construction process.
As healthcare design and construction continues to evolve with advancing technology, medical breakthroughs, and stricter regulatory guidelines, Sky Ridge Medical Center and Skyler have worked together to navigate such changes. The Skyler team brings experience from across the country to meet Sky Ridge Medical Center’s ongoing construction projects.
At Skyler we understand that every healthcare facility and medical practice has different needs and priorities to meet their patients’ and business goals. In order to address these unique needs, Skyler’s team offers conceptual services to understand the business and end-user’s requirements to engage the right design team, construction process, and in some cases, technology partner.
Skyler’s goal each year is to allow Sky Ridge Medical Center to exceed their dedication to excellence with every project we complete together.
Congratulations to Sky Ridge Medical Center which continues to be the elite healthcare provider, caring for their patients and contributing to their community.
Working in a hospital is like working in a city. We encounter all the same challenges of hectic city life in our hospital daily.
“What makes this profession truly unique is that you’re caring for people at their most vulnerable moments, and they entrust you with their lives. This truly impacts me as a person and as a leader, since we always want to do the right thing for our patients and their families,” he explains.
“The biggest challenge we face here in the US is staffing, as is the case in many industries post-pandemic. Therefore, we need to rethink how we recruit and retain staff as well as how we provide care to ensure that we are always here to fulfil our patients’ needs,” McCarty adds.
“My number one job as CEO is to ensure that every member of our team feels supported, valued and appreciated.”
Sky Ridge now boasts a fully operational Robotics Center to support its hugely successful robotics program. With more robots than any other hospital in Colorado, this Center of Excellence has performed more than 8,000 robotic procedures.
“Before robotic techniques, open surgery was most frequently used, which involved major incisions, and this meant patients were in the hos pital for four or more days to recover after an operation. Robotic surgery gives surgeons greater precision, requires much smaller incisions and there is less blood loss. Patients are typically going home the same day, which has truly transformed care,” McCarty describes enthusiastically.
Sky Ridge performs more than 1,600 robotic surgeries a year. With the opening of its new, dedicated Center for Robotic Surgery, Sky Ridge has created a modern space that appeals to patients and their families as well as the surgeons who use these state-of-the-art surgical suites.
“With this new Center, our goal was to offer the feeling of being in a private physician’s office to help reduce anxiety and create a comfortable experience for the loved ones who are waiting,” he adds.
“When we opened, Sky Ridge was the first hospital in Douglas County – one of the fastest growing counties in the country - and we are proud that we have contributed to the robust growth in our area,” says McCarty.
It was this same spirit and pride in the community that saw people rally around Sky Ridge during the COVID-19 pandemic, writing supportive mes sages in chalk outside the building.
“COVID-19 really helped me realize how important community is to Sky Ridge, and likewise how important we
are to the community. Being nimble and adapting to what the local area needs has been vital for us,” says McCarty.
Determined to always strive for the best and create a winning attitude, McCarty relies on feedback from the Employee Advisory Group, compris ing colleagues from all areas of the hospital. Members report directly back to McCarty once a month, creating
process for new policy or procedures as well,” expands McCarty. “This is an important aspect of employee engagement and belonging.”
After navigating a major operational pivot post pandemic, Sky Ridge has proclaimed this year as ‘Year of the People’.
“COVID-19 was a challenging time for all of us and tested us in ways we had never experienced before. There
an effective feedback loop to enact meaningful change.
Through the ideas put forth by the Employee Advisory Group and the Colleague Engagement Committee, colleagues may take advantage of an on-site gym, a ‘Recharge Room’ with massage chairs, and a roving ‘Lavendar Cart’ with treats and uplifting messages.
“We lean on shared governance, and really try to engage with our staff to be part of the decision-making
were so many unknowns when the pandemic first hit and our team worried that they would make it home to their own families,” says McCarty. “My goal was to get us through that period better and stronger than ever.
“The hospital simply cannot run without people. Our staff drive everything, and it’s my job as CEO to ensure that the team is focused and has the optimum conditions in place to succeed,” he concludes.
SKY RIDGE MEDICAL CENTER
Ph. 720-225-1000 publicrelations@healthonecares.com www.skyridgemedcenter.com
Community members write supportive chalk messages around the building during the COVID-19 pandemic.Against the backdrop of COVID-19, John Chapman, President and CEO of San Antonio Regional Hospital, highlights clinical care for communities of the Inland Empire and the growing role of robotics
Writer: Jack Salter | Project Manager: Felix Revell
inequitable decimation of certain patient demographics from COVID-19.
“Dealing with COVID-19 has also interrupted or halted strategic plans, as leadership teams have spent the majority of their time handling the pandemic and its impact on our hospitals.”
SARH, a 363 not-for-profit acute care hospital located in Upland, California, treated more COVID-19 patients than any other hospital in San Bernardino County at the height of the pandemic and through to today.
Access was delivered by SARH to the latest medical treatments to best serve patients during the pandemic, and the hospital’s emergency department (ED) was even among the first in the area to provide monoclonal antibody infusions and treatments.
“We stayed on top of the most recent literature, allowing for immediate shifts in treatment as needed. Quick responses from our care team resulted in at least a 30 percent lower mortality rate compared to the state average,” Chapman acclaims.
“SARH was also one of the first in San Bernardino County to open its doors for mass vaccinations, typically vaccinating over 600 community members per day, and partnered with several school districts to vaccinate teachers and staff, recognising the need to get students back into classrooms and create a positive impact within our community.”
I
n the way we lead our day-to-day lives, the COVID-19 pandemic has turned our world upside down.
Healthcare in particular has been impacted in many significant ways. For example, the pandemic response has necessitated new and creative methods of patient care, such as remote telehealth services.
The industry has equally begun to understand the utmost importance of health equity in the community, having experienced first-hand the
Many employees in the industry, none more so than nurses, have also had to contend with a huge surge of patients without the assistance of additional staff in the industry, on top of their own personal and medical concerns.
“Most industry experts, and I, believe the recovery will take multiple years, and that we must actively market healthcare careers to students at every level of education,” opens John Chapman, President and CEO of San Antonio Regional Hospital (SARH).
With over 2,300 employees, SARH continues to grow and is proud to serve the largest share of the population in San Bernardino County, which at 2.1 million makes it the fifthmost populous county in The Golden State.
However, the region has a concern ing dearth of both primary care and behavioral health access. Indeed, latest assessments suggest that over 120 primary care physicians are needed in San Bernardino County.
In an effort to close this deficit, the San Antonio Regional Medical Group was created this year, with the goal of satelliting at least 10 new outpatient service centers, through the combination of primary care clinics and urgent care clinics in the community over the next three to five years.
“We currently have three satellite
facilities in the region: Eastvale San Antonio Medical Plaza, Rancho San Antonio Medical Plaza in Rancho Cucamonga, and Sierra San Antonio Medical Plaza in Fontana,” Chapman notes.
“We plan to staff our primary care clinics with behavioral care specialists. I look forward to continuing the mental health drive, partnering with
JOHN CHAPMAN, PRESIDENT AND CEO: “Similar to many new university graduates, I had to determine the path forward with my degree. I graduated with a BA in Microbiology and Immunology from the University of California at Berkeley.
“At that time, I was working as a Research Assistant for Dr. Lawrence Drew, an Infectious Disease Chief and world-renowned Clinical Virologist at Mount Zion Hospital in San Francisco. He convinced me I should consider becoming a licensed Clinical Microbiology Scientist.
“The only problem was there were no programs in northern California, so I convinced him to start one for me. One year later, I was the first ever graduate of his program, accredited by the California Department of Public Health. His mentorship was the primary reason for my passion for healthcare.
“Within six months, I was his Clinical Supervisor of Microbiology, and within five years, we merged with the University of California at San Francisco (UCSF) where I became the Director of Clinical Lab Services at UCSF Medical Center. I excelled at new program development and UCSF invested in me attaining my MBA and hiring me as their Executive Director of Clinical Services, responsible for leading their Service Lines.
“In 2011, I decided to work for Alameda Health Systems, running Highland Hospital in Oakland, California. Now I serve as the President and CEO at SARH in Upland, leading a beloved 363-bed acute care facility in IE.”
AMN Healthcare is proud to support San Antonio Regional Hospital with workforce solutions and vendor management services.
It is a privilege to provide solutions to leading organizations, but the opportunity to be a trusted partner is an honor that we do not take for granted.
With San Antonio Regional Hospital, we sit side by side, ever evaluating challenges and opportunities, providing the services and perspectives that help them make informed decisions for their staff and the community they serve.
In one instance, we partnered to implement adjustments to their overtime rules and rates that led to a savings of more than $125,000 in just over eight months.
During the COVID-19 pandemic, our ShiftWise vendor management system helped them achieve 95%+ fill rates for their contract needs, while helping cut costs, improve quality, and maintain compliance.
As we move forward with San Antonio Regional Hospital, we know that we are helping support an organization focused on its mission, committed to its vision, and rooted in its values. We are here for their continued success and for the health and wellbeing of their community.
our regional leaders in hospitals, city and county leadership, and the County Public Health Department.
“Maternal health is also a large part of our focus in the upcoming years, with plans to create a new birthing center with the latest technology and comfort in mind,” he continues.
It follows the recent completion of a $160 million expansion in 2017, one of the most important projects in the history of SARH. The expansion included the new 52-bed ED, which has since played a critical role during the pandemic, as well as the 92-bed Vineyard Tower.
Demand for emergency care in the Inland Empire (IE), comprising San Bernardino and Riverside Counties, has continued to grow as the population in the area increases.
“The new ED, which nearly tripled in size, has helped to ease the burden by adding much-needed capacity,” emphasises Chapman.
“Vineyard Tower provides the latest medical technology and advanced care delivery systems, along with the comfort of private rooms. We have also opened our third best-inclass interventional cardiology suite, focused on cutting-edge procedures such as TAVR, LVAD, and EP mapping and ablations.”
The vision of SARH is to be a leader in creating healthy futures for communities, and as such, patients are one of the hospital’s key priorities
and central to all decisions.
The Lewis-San Antonio Healthy Communities Institute (HCI) was established in 2016 to provide oppor tunities for partnered solutions that positively impact the region’s health.
HCI focuses on community outreach, offering health education classes to parents and students in surrounding school districts, community physician lectures in both English and Spanish, as well as health screenings to underprivileged communities.
The program also focuses on
building relationships within the community, to allow pathways for future workforce development.
“We seek to establish robust pipelines for all possible job types, and are investing in pipelines out of high school, community college, and universities to fill both clinical and non-clinical needs,” Chapman reveals.
“Developing and investing into that symbiotic relationship is a win-win for our community and our hospital.”
As the highest-scoring hospital in IE in terms of quality and patient satisfaction, according to Medicare,
SARH has dedicated performance improvement teams that prioritize the identification of opportunities to continuously improve quality and safety metrics.
“For example, we are proud of our cutting-edge ultraviolet (UV) robotic technology, used for sanitizing our clostridium difficile (C. diff) patient rooms and other isolation rooms, significantly reducing the risk of hospital-acquired infections,” Chapman outlines.
“We have introduced the use of coated chlorhexidine/silver sulfadiazine antimicrobial catheters for central line bloodstream infections, and invested in both da
Vinci and Mako orthopedic robotics in our operating rooms to improve the accuracy and outcomes of surgical interventions.”
SARH continues to invest in technology, such as robotics, that can help to diagnose and treat patients. For Chapman, robotic-assisted surgery is perhaps the most cuttingedge medical technology of modern times.
“Robotics are helping to transform the healthcare industry through the benefits it offers to patients, such as fewer complications, quicker recovery, less blood loss, and shorter hospital stays,” he says.
A third cardiac catheterization lab
has also been constructed by SARH in the past year, to handle the growing demand for traditional and interven tional cath lab procedures and to support the hospital’s expansion into electrophysiology (EP).
New state-of-the-art EP technology has been added to the cath lab to support this growing subspecialty within the field of cardiology.
“We will soon be launching a digital application which will allow patients and caregivers to review a personalized video of their own inpatient discharge instructions and care intervention techniques,” adds Chapman.
“We believe this will be a gamechanger in reducing return admissions to our ED or hospital.”
It’s clear that healthcare has become a highly specialized industry. As medicine evolves and best practices
“THE NEW ED, WHICH NEARLY TRIPLED IN SIZE, HAS HELPED TO EASE THE BURDEN BY ADDING MUCH-NEEDED CAPACITY”
– JOHN CHAPMAN, PRESIDENT AND CEO, SARHSierra San Antonio Medical Plaza The Scheu Family Building
emerge, SARH wants to bring that expertise and knowledge to patients in every service line.
Centers of excellence have therefore been developed by SARH in key service lines such as cardiac, stroke, emergency services, orthopedics, cancer, women’s services, and more.
“We take pride at SARH in our extensive service, expertise, and centers of excellence that rival larger academic medical centers,” Chapman lauds.
SARH’s Heart Institute, for instance, has earned numerous accolades in recent years, including one of Healthgrades America’s 50 Best Hospitals for Cardiac Surgery™,
the only hospital in IE to receive this honor. The hospital is also a destination cardiovascular center in the region.
Partnerships with Cedars Sinai for advanced heart failure and City of Hope for cancer care, meanwhile, provide patients with access to innovative research, clinical trials, and leading-edge treatment close to home.
While SARH’s teams specialize in their specific areas of expertise, it is still a collaborative team approach that can involve experts in many disciplines within the hospital.
“When expert care is hard to recruit, we partner with other worldrenowned institutions to bring their
care here to our front doors.”
SARH encourages open communication and a collaborative spirit, in which everyone’s contributions are important.
“We have an awards and recognition program that acknowledges the contributions of care team members who go above and beyond to exemplify our values of excellence, integrity, respect, compassion, safety, and patientcentric care,” shares Chapman.
Likewise, establishing honest, transparent partnerships with suppliers is key to ensuring supply chain sustainability.
With the current supply chain issues being encountered across
Building 901
the US, it is more important than ever for SARH to have strong, supportive partners that can ensure it has the necessary supplies to take care of all patients.
“As an independent hospital, it allows us to work with both national and local suppliers. We are able to decide who we purchase from without any of the concerns that a hospital in a corporate environment would have,” Chapman tells us.
Like most hospitals, SARH continues to remain profitable, despite the many additional costs inflicted on the industry related to the COVID-19 pandemic.
Retention and recruitment are the hospital’s biggest internal focus,
according to Chapman; externally, SARH is looking to grow primary care, find partners to tackle behavioral care throughout the County, and improve health equity.
“We look forward to the challenge!”
Ph. +1 909-985-2811 info@sarh.org www.sarh.org
“ROBOTICS ARE HELPING TO TRANSFORM THE HEALTHCARE INDUSTRY THROUGH THE BENEFITS IT OFFERS TO PATIENTS, SUCH AS FEWER COMPLICATIONS, QUICKER RECOVERY, LESS BLOOD LOSS, AND SHORTER HOSPITAL STAYS”
– JOHN CHAPMAN, PRESIDENT AND CEO, SARH
BAE Systems, Boeing, Bombardier, Lockheed Martin, and Space X – whether commercial aerospace or defense, major titans of aviation look to Canadian manufacturer Avcorp as one of North America’s primary suppliers for integrated metallic, composites and hybrid structural assemblies.
“We can take on any sort of complex challenges that our customers have. We bring the balance of cost competitiveness as well as the reliability,” opens Avcorp’s CEO Amandeep Kaler.
Primarily based out of Delta, British Columbia, since its inception over 65 years ago, Avcorp has grown to develop a global customer base and acquire two additional facilities that are strategically located within North America’s aerospace hubs.
“The Delta facility focuses on complex aerostructures and the integration side of the business, where we assemble all different types of materials and parts into large assemblies,” Kaler elaborates. “We’re a Design Approved Organization. Our Burlington facility is able to repair extensively damaged components well outside typical SRM limits,” he shares.
The company has a second Canadian facility in Burlington, Ontario, specializing in the design and manufacture of composite components whilst providing a host of additional services, including spares and repairs, which are available to all the airlines that Avcorp works with.
After 65 years in business, Avcorp is an established leader in aerospace manufacturing. We discuss an esteemed legacy in performance excellence with CEO, Amandeep Kaler
Writer: Phoebe Harper | Project Manager: David Knott
AMANDEEP KALER, CEO: “We try to take the collaborative approach of planning for any project, deliveries or end-to-end schedules where we work with our customers and bringing in the suppliers to keep very open communication. We also encourage our suppliers for their improvement ideas and what can we do to reduce the costs or lead times to remain competitive in that way.
“Given all of the challenges that we’re seeing across the world with COVID-19’s disruption of supply chains, we also support our supply chain on the technical side wherever we can.
“We feel that our team has been very transparent throughout this time, and we want our suppliers or any of our other partners to tell us at the earliest possible time if they see any risks. We always do a full assessment of the requirements to identify any risks and work together between us – our suppliers and customers - to ensure that the impact is minimal.”
Meanwhile, in Gardena, California, the Avcorp Composite Fabrication (ACF) plant focuses on medium to large sized, complex shape composite aerostructures for the world’s leading aircraft OEMs and their suppliers. With advanced layup, autoclave and machining technologies, ACF can produce composite structures at scales far beyond the capabilities of most of the company’s competitors.
With its breadth of facilities and services, Avcorp offers a comprehensive range of services that support aircraft programs at any stage from conception to end-oflife, with advanced manufacturing, integration and in-service support through spares and component repairs.
The company boasts an esteemed roster of major clients, including BAE Systems, and the production of commercial aircraft including the 737, 777X, and 787 for Boeing. On the defense side, Avcorp undertakes assembly work on the Boeing KC-46 and works closely with Lockheed Martin on the F-35 program.
“Another of our main customers is Bombardier, where we produce the horizontal stabilizers for business jets. Many business jet programs will have Avcorp-produced floor panels, so it’s a wide range of products and services
DGI Supply has been a proud partner with Avcorp Industries for over 20 years.
Our Automated Procurement Solutions program has evolved during our partnership while adapting to Avcorp’s growing needs.
We look forward to the continued partnership and many years of continued success for Avcorp Industries.
www.dgisupply.ca
that we provide,” adds Kaler.
From the shop floor to CEO, Kaler has climbed the ranks of Avcorp, joining the company as an assembly mechanic then taking on a supervisory role and progressing to a General Manager position overseeing one of the three Avcorp units.
“As an immigrant, I came to Canada looking to further my studies with my engineering degree,” he recalls.
“Through Avcorp, I had a lot of opportunities to move into other areas and slowly moved through the different roles in the organization, until in 2018, I took over as CEO.”
Much like Kaler’s own career path, Avcorp itself has evolved significantly from its origins in undertaking repair work for the float planes servicing Vancouver and Canada’s west coast.
With over 65 years in operation, the longevity of Avcorp’s history attests
to its commitment and reliability in a sector where wait times can be long, and patience is key.
“It’s an advantage that our customers know we have such long relationships, particularly in our industry where the cycle times for any new product can be very long. It takes multiple years to develop a new product or supplier, and the costs are high,” Kaler observes.
“We have a very good performance history through our delivery and quality, and our customers appreciate that. That’s what gives us the advantage to continue these longterm relationships.”
As one of Avcorp’s major customers, the company has maintained a strong relationship with Boeing for over 25 years.
Fueling these undertakings is a spirit of continual innovation and a commitment to excellence that truly makes Avcorp a supplier of choice.
Indeed, for Kaler, it is the potent
mixture of innovative ideas with strong technical solutions that truly differentiates Avcorp from other market competitors and is a key factor in attracting customers.
“You have to continue to innovate and find new ways of doing thingsthat’s the culture of the business.
“We live our tagline - that we provide ‘Better Solutions’,” he states.
The recipe behind Avcorp’s prowess in the aerospace manufacturing field relies on a combination of advanced technical capabilities with its ability to react and adapt.
As Kaler attests, “we are a very strong technical organization but also extremely agile and nimble.”
All three of Avcorp’s facilities boast a location in strategic proximity to major North American aerospace hubs. The Delta head office is just 25 minutes from Vancouver International Airport, whilst the Gardena site sits just 20 minutes from Los Angeles International Airport (LAX).
In addition, the Avcorp Gardena facility effectively positions the company to be able to service and rapidly fulfil the needs of some of its major customers including both Boeing, and
“WE ARE A VERY STRONG TECHNICAL ORGANIZATION BUT ALSO EXTREMELY AGILE AND NIMBLE”
– AMANDEEP KALER, CEO, AVCORP
“Whether in North American commercial aerospace or around the globe, Boeing is one of the two main competitors.
“We are literally two and a half to three hours away depending on which facility we need to be in, and we provide daily delivery services of the product, right to the assembly line. We provide just-in-time services and deliveries to the Boeing line. That’s a huge plus for us, and we think a huge plus for the customer as well.
“It’s the proximity, the capability and the know-how which really helps us with these customers,” surmises Kaler.
Leading with its unwavering commitment to providing customers with better solutions, Avcorp has its hands full for the immediate future.
“Currently, many of our production rates are increasing in line with the demand. After COVID-19, and the Boeing 737 MAX groundings, our Boeing 737 rate is starting to ramp up,” Kaler explains.
“Boeing has also started the delivery of the 787 program which is welcome news for us, so our focus really is going to be on ramping up the 787 line as that rate increases while also continuing to support the 737 rate increase as Boeing has planned.”
To support this increase, Avcorp will be investing in more resources, including a major recruitment drive to hire more staff, so that customers don’t feel the impact.
“That’s really our focus for the rest of the year - to make sure that we have enough products, materials and resources available to support the customer ramp ups that we know are coming.”
AVCORP Ph. 604 582 6677
www.avcorp.com
“WE’RE ONE OF NORTH AMERICA’S PRIMARY SUPPLIERS FOR INTEGRATED METALLIC COMPOSITES AND HYBRID STRUCTURAL ASSEMBLIES”
– AMANDEEP KALER, CEO, AVCORP
Expediter Services stands today as a leader in capacity solutions and ownership opportunities within the vast trucking industry. We explore the growth of Women In Trucking and nurturing sustainable profitability with CEO, Jason Williams
Writer: Ed Budds | Project Manager: Tom Cullum
I didn’t so much choose to get into transportation and the trucking business, as much as I was forced into it. We had a family-owned business in another industry that we were forced to close, and my father asked me to stick around to see if we could do something together. He was the first to see an opportunity in trucking and we jumped in with both feet.”
The opening recollections of Jason Williams, CEO of Expediter Services
(ES) encapsulate a resoundingly innovative spirit and determination, as well as an entrepreneurial hunger that lies at the core of this industry leader in trucking capacity solutions and ownership opportunities.
According to Williams, the entire US transportation industry is in a state of flux right now, from the complicated nature of labor laws, to what used to be the relative simplicity of new truck deliveries. Today, it’s becoming increasingly common to see smaller fleets of trucks and owner operators struggling with the current increases in expenses, whilst trying to maintain profitability. Technology and payment methods within the industry are also changing quickly
which create their own challenges, even though the long-term effects are expected to be good.
Springing from humble initial intentions of operating as a corporate provider of capacity to non-assetbased motor carriers, ES as a company was never meant to be a motor carrier, and consequentially an industry niche was identified for becoming a stable capacity provider.
“We started from the very beginning, focusing on what the driver needed. It didn’t take us long to realize that what they needed most was opportunity. This caused a major shift in our company towards helping contract drivers open and grow their own business,” explains Williams.
With this change of focus, ES began in earnest to develop the items these small businesses would need to operate safely and profitably. Today, this includes financing, leasing, renting, insurance, fuel, safety training, shop and tire platforms. Anything that a large carrier requires, ES now has the capacity to offer, to either a single truck owner or the owner of an entire fleet.
“We have proven that by creating profitable small businesses within our community, that we can address most of the issues that the industry has experienced when owner-operators are forced to function without the impressive array of support services we bring to the table,” he adds.
Currently, ES is participating in a five-year project with the Women In Trucking Association, a non-profit organization with the mission to
encourage the employment of women in the trucking industry, promote their accomplishments and minimize obstacles faced in the sector. The project aims to create 150 womenowned businesses, which is close to a highly successful completion.
Gender diversity brings new per spectives, fuels greater idea genera tion, problem solving and innovation, increasing business performance and overall revenue generation.
“This accomplishment won’t mean an end to the ongoing effort, as it’s
Ellen Voie, Founder & CEO, Women in Trucking Associationwhat we do every day, and we will continue to do into the future, but it does showcase who we are within the industry,” states Williams proudly.
ES also endeavors to invest heavily in technology that will allow the company to help its community members achieve better access to ES’s services through a newly developed mobile app.
“We have built our company around the idea that we want I.T. to move and crunch data, but we want people to service people. While we’re not changing that approach, we do want to be nimbler in presenting data that can allow our members to take advantage of information and services when needed.”
ES cut its teeth in the expediting sector of the trucking industry, providing a safe place to develop the company model with some highly efficient carrier partners.
“My father, Paul Williams, was always wanting to move into the Truck Load (TL) and Less Than Truckload (LTL) sectors of the industry, and we leveraged our existing partner carrier relationships to do so,” offers Williams.
ES has now been operating in the expediting, TL and LTL sectors for many years and has a proven model that provides opportunities and services that can support contract drivers, owner-operators and fleet owners across the industry.
This diversity in freight provides ES and drivers that make up the ES Community with stability and certainty even in unpredictable environments.
Williams believes that the value of the company is truly highlighted in times of uncertainty. “While we don’t look forward to the industry going through hard times, we know that truck owners tend to take better notice of us when times are tough. Our ability to drive profits up for these small businesses really promotes stability throughout our entire community, and this is where the larger brands we service also see the overall value of the capacity we generate really pay off,” he acclaims.
East Brooks Road, Memphis, TN 38116 | (901) 332-4000 Committed to delivering the #DobbsValue experience to our customers.“WE COULD NOT DO WHAT WE DO WITHOUT GREAT PARTNERSHIPS WITH OUR VENDORS AND MOTOR CARRIERS”
– JASON WILLIAMS, CEO, EXPEDITER SERVICES
In trucking, so many elements and technicalities are always changing and regenerating, but by keeping a focus on the stability of the truck owner and their profitability, ES maintains an ability to take advantage of times where others may struggle, placing them in an advantageous position in the marketplace for these vital services.
“Anyone who is aware of us knows that we’re constantly talking about the stability of our community and how to make it better. We could not do what we do without great partnerships with our vendors and motor carriers.”
If it were not for Stoops Freightliner and Dobbs Peterbilt, the new businesses ES has created this year
would not have emerged successfully. Despite an unprecedented time for the trucking industry, in the hazardous post-COVID-19 landscape, these partner dealerships have fought alongside ES and helped the company to get through this challenging period.
Elsewhere, Panther Premium Logistics, a service of ArcBest, and Forward Air, has continued to support the ES community with favorable
freight and contracted rates, which has allowed ES to finance a wealth of new and growing truck owners. ES partners are supporting the ES Community at every level. TVC Pro-Driver gives access to legal representation that helps protect drivers’ CDLs and save money while they’re on the road while other partners like Infinit-I Workforce Solutions play an important role in
“WE HAVE A WELL-ROUNDED HOST OF SERVICES AND MOVING INTO THE FUTURE, WE WILL FOCUS ON EVOLVING AND EXPANDING THOSE OFFERINGS TO WHAT BEST FITS DRIVERS’ NEEDS”
– JASON WILLIAMS, CEO, EXPEDITER SERVICES
keeping safety top of mind as they’ve worked with ES to offer DOT training online designed to simplify training, reduce accidents and violations, and save time and money.
“We are only able to be aggressive in supporting truck ownership and fleet growth because of our partners. When you look at what our other vendors such as TA/Petro have done to fight rising fuel costs and what Midwestern Insurance Alliance has done with keeping insurance premiums in check, you quickly realize that it truly is a dynamic community of support at multiple levels,” adds Williams.
ES looks to accelerate towards a position of industry dominance over the next year and a half, whilst additionally encouraging and promoting general growth at all levels within the sector. ES utilizes Baker
Donelson, one of the largest law firms in the US, allowing them to focus on the growth and success of ES and all the members of the ES Community with the confidence they’re making sound decisions handled by an attentive, responsive legal team.
“Our goal for the next 12 to 18 months is really to just get in front of these small businesses and help them thrive. We also want to help drivers who make the jump into starting their own business for the first time,” Williams divulges.
Constantly searching for the next new motor carrier to partner with, ES knows that it must be the perfect, most compatible fit possible before entering a fresh collaboration. As the company continues to develop this capacity, its current partner carriers are guaranteed to be delivered all that they want and need first, as they’ve
been so instrumental in the overall development of ES.
“Our contract drivers, owneroperators and fleet owners count on us to only put them in a position to operate safely, stably, and profitably. I believe we’ve now reached a point where we have a well-rounded host of services and moving into the future, we will focus on evolving and expanding those offerings to what best fits drivers’ needs,” finishes Williams.
Tel: (877) 349-9303 info@expediterservices.com www.essuccessintrucking.com
BOE Exploration & Production LLC is laser-focused on oil and gas operations in the Deepwater Gulf of Mexico. We speak to Joseph Leimkuhler, COO of the company, about the latest technology and the future of exploration and production
Oil and gas - and their importance to the global economy - cannot be understated.
From transportation and heating build ings to producing electricity and raw materials (everything from plastics to pharmaceuticals), oil provides a reliable and affordable foundation for many comforts of daily life.
The US is the world’s leading producer of oil, and collectively with natural gas and coal, provides approximately 80 percent of the country’s energy needs.
While renewable energy is increasing in scale based on global climate concerns, oil and gas are fundamental to the global energy solution for the foreseeable future. According to the U.S. Energy Information Administration’s (EIA) Annual Energy Outlook 2022, in their base case, petroleum and natural gas will remain the mostconsumed sources of energy, and is actually increasing in the country through to 2050. This highlights the importance of domestic oil and gas development and production in areas with the
Writer: Marcus Kääpä | Project Manager: David Knottlow emissions footprint, such as the Deepwater Gulf of Mexico.
In Texas alone, the oil and gas industry accounts for over three million jobs, and together with Louisiana, the two states make up over half of the oil and gas-related jobs in the entire country. These states border the Gulf of Mexico and offer abundant access to oil and gas reserves both inland and offshore.
“It has had its share of ups and downs during the past 35 years, but the geology and significant existing infrastructure of the Deepwater Gulf of Mexico is the gift that keeps on giving,” says Joseph Leimkuhler, Chief Operating Officer (COO) of BOE Exploration & Production LLC (BOE).
BOE Exploration & Production LLC is an operator in the deepwater Gulf of Mexico.
To responsibly deliver high value, low carbon energy to the US market from the Deepwater Gulf of Mexico.
BOE has assembled a cohesive team of experts who share a large-scale vision for the company as a partner of choice in the Gulf of Mexico.
The barrels of oil and gas produced by companies like BOE, in the Deepwater Gulf of Mexico - renowned as the lowest in carbon intensity - make up 15 percent of the US production, according to the EIA.
As COO for BOE, Leimkuhler is responsible for all offshore engineering and operations. During the last 38 years, he has worked in a variety of offshore engineering capacities: Vice President of Drilling for LLOG Exploration; various
positions for Shell International E&P Co, and Shell E&P-Americas, including Well Delivery Manager for Gulf of Mexico well operations, Subsea Development Manager, Deepwater Drilling Superintendent, and teaching Shell’s drilling engineering classes; and positions with M-I Drilling Fluids and ARCO.
Leimkuhler was one of several significant operational experts who joined BOE in 2019, a time of significant expansion.
“THE GEOLOGY AND SIGNIFICANT EXISTING INFRASTRUCTURE OF THE DEEPWATER GULF OF MEXICO IS THE GIFT THAT KEEPS ON GIVING”
– JOSEPH LEIMKUHLER, COO, BOE EXPLORATION & PRODUCTION LLC
The Gulf of Mexico is well-known for its deepwater oil and natural gas reserves.
1938 saw the first offshore well drilled in Texas, with the first discovery of oil made a few years later in 1941. Today, the Gulf remains the primary offshore source of these resources for the entire US, generating approximately 97 percent of all the country’s OCS (outer continental shelf) oil and gas production.
“Deepwater offshore operations require substantial offshore experience,” Leimkuhler says. “The collective experience of the BOE team - coming from a diverse group of offshore operators - includes many successful discoveries and developments over the years, across a range of offshore projects. The overall breadth and capability of the team is impressive, and BOE’s team is energized by new opportunities in the Gulf of Mexico.”
With the geological, engineering, development, construction, finance, accounting, land, and legal functions in its Houston office, BOE opened a
second office in Covington, Louisiana in 2019.
“Over the years, a substantial portion of the offshore oil and gas industry moved from Louisiana to Texas,” Leimkuhler tells us. “BOE saw an opportunity to attract talent with Louisiana roots, and Covington was a great choice - providing the ability for our employees to work in an industry they love at home in Louisiana.”
By the summer of 2019, BOE assumed operation of several subsea producing fields, and continued to grow. In late 2019, BOE signed its first deepwater rig contract for the Deepwater Asgard, a deepwater,
“WE SEE A BRIGHT FUTURE FOR BOE IN BEING A SIGNIFICANT CONTRIBUTOR TO ENERGY SECURITY, AS WELL AS SMART SOLUTIONS, THROUGH THE ENERGY TRANSITION”
– JOSEPH LEIMKUHLER, COO, BOE EXPLORATION & PRODUCTION LLC
Founded in 1960, Edison Chouest Offshore (ECO) is recognized today as the most diverse and dynamic marine transportation solution provider in the world. ECO operates a growing fleet of almost 300 vessels and serves an expanding global customer base. ECO has the largest base of shipyards in the U.S., owns and manages world-class port terminal facilities and operates worldwide in all oceans. Staying on the forefront of new technologies is an integral part of the ECO vision, as evidenced by recent advances in the areas of emissions reductions, subsea support services, integrated bridge systems, remote monitoring systems and global communications. The ability to design, build, own and operate diverse, high-capacity and technologically superior vessels has made ECO an unrivaled leader in the maritime industry.
ECO affiliate C-Innovation is a global, integrated marine services company specializing in advanced subsea solutions including ROVs, AUVs, subsea construction, fleet services, survey and positioning, and tooling services. C-I provides innovative solutions to complex challenges in engineering, project management and subsea field development.
ECO’s expansive port facilities provide superior vessel support and unmatched efficiency. In an industry where the bottom line is controlled by efficiency in cargo movement, expediting vessel turnaround is a key factor in determining profit or loss. Chouest’s port services are second to none, reinforcing ECO’s role as the preeminent offshore supply source in the Gulf of Mexico, Brazil and Guyana.
Halliburton enhances offshore development with advanced products and services that include rotary steerable systems, downhole tools, and fluids. Through collaborative engineering, automation, and remote operations, we help plan, design, and execute the optimal well.
Whatever your drilling environment, our rotary steerable systems accurately place the well bore in the reservoir, preserve borehole quality, and maximize rate of penetration, to reach target depth.
The iCruise® intelligent rotary steerable system reduces well time through fast drilling, fast tripping time and quicker casing drill outs. The system accurately places the wells in the reservoir using precise steering capabilities, and reliably reaches total depth so you can drill longer wells, predictably, on time and on budget.
The iStar™ platform acquires highdefinition measurements closer to the bit and deeper into the formation for enhanced subsurface insight. It provides real-time visibility of the type and quantity of reservoir fluids and uses data science techniques to optimize reserves calculations and improve well placement.
dual-activity drillship owned and operated by Transocean, an offshore drilling contractor offering well construction services worldwide with a focus on deepwater rig operations. Drilling operations began in January 2020, and continued through the COVID-19 pandemic, with two discoveries made in the first campaign.
PASSIONATE ABOUT SAFETY BOE is passionate about the offshore industry and safety. Bestin-class performance in Health Safety & Environment (HSE) is a
core value, and the BOE staff are empowered to build programs that are fit-for-purpose. A robust and responsive Safety and Environmental Management System (SEMS) developed by its HSE team meets BOE’s high standards.
“The BOE SEMS is not just a binder on the shelf, we strive to make it the way we work,” Leimkuhler continues. “Offshore operations depend on every person, and every company, focusing on safe operations as a core value: “priorities change, but values don’t”. We work with our trusted contractors, ensuring alignment with
The BaraECD® solution helps manage risk, improve well site safety, and improve overall performance. It helps prevents barite sag and risky weight variations by maintaining stable gel strengths and low-shear viscosity at advanced temperatures and pressures.
And, during real-time operations, our automated drilling platform helps directional drillers make quicker, smarter decisions to stay on plan and achieve predictable results consistently.
www.halliburton.com
Using our advanced drilling technologies
Make quicker, smarter, real-time decisions to stay on plan and achieve predictable results consistently with our automated drilling platform.
Enhance performance with our performance-driven services, solutions, and advanced products that include rotary steerable systems (RSS), drilling mud motors, turbodrill turbines, downhole tools, and fluids.
Reduce well time and cost by digitally collaborating to plan, design, and model high-angle and complex well trajectories utilizing our software.
JOSEPH LEIMKUHLER, COO: “After graduating from the University of Montana in 1981 with a dual degree in Geology and Forestry, my career in the oil and gas industry started as a “Mud Engineer” for MI Drilling Fluids working in the Overthrust Belt play in Wyoming. This was a great fit with my interest in clay chemistry, geology and just digging big holes!
“By 1984, as a result of the volatility in the industry, I was ready to leave and go to law school. On my last hitch, a professor from the University of Wyoming brought his drilling class to the rig for a tour of the drilling fluid or mud system. That started a long relationship with Dr. Jack Evers, and he convinced me that I was an engineer and belonged in graduate school studying petroleum engineering.
“Thus, I went to the University of Wyoming in Laramie, earned a master’s degree in petroleum engineering in 1987 and then headed south to the Deepwater Gulf of Mexico. I’ve been in the Deepwater ever since, enjoying a 25-year career at Shell, seven years at LLOG Exploration Company, and now three years at BOE.”
our contractor’s SEMS to achieve safe, efficient operations. We work with excellent offshore service providers, those who can safely deliver the best technical solution, and who are committed to good corporate citizenship.
“There have been significant changes and tremendous improvements in safety and technology over the past few years, from well designs to the equipment used to drill and complete the wells. For example, improved well designs
allow deep sub-salt wells to be drilled faster, and more safely compared to years ago.”
According to Leimkuhler, state-ofthe-art deepwater rigs and fit-forpurpose production platforms enable safe and efficient production of oil and gas in the Gulf of Mexico, with the world’s lowest emissions and attractive overall lifecycle cost per barrel.
“Specialized equipment, such as MPD (managed pressure drilling), has become more effective, allowing
the potential to conduct drilling operations efficiently with a reduced risk profile,” he adds.
MPD is an adaptive drilling process that accurately and continuously monitors and controls the pressure in a wellbore. The ability to change operating parameters in real-time and with automated adjustments by the MPD system adds both safety and efficiency.
In addition, Leimkuhler is also enthusiastic about continued improvements in seismic imaging
NORTH AMERICA OUTLOOK: CAN YOU TELL US ABOUT YOUR ENTRANCE INTO THE OIL AND GAS INDUSTRY?
and data processing. He says those advancements allow the industry to “see” the geology below the seafloor better than ever, revealing new and exciting plays, such as the Norphlet and the Wilcox formations, often below massive sections of salt.
Leimkuhler’s passion for the industry translates to action. He serves on the HWCG Well
Sooner has unparalleled inventory availability, access to all major domestic and international manufacturers, and multiple wholly owned service and logistics centers.
Sooner delivers to any location servicing every major US Basin and offshore shelf and deep-water regions. Whether you are a small independent producer or a major multinational, Sooner provides multiple product options and the services to help your project succeed.
Sooner has been a strategic business partner to BOE Exploration & Production LLC since the beginning. Sooner remains diligent in providing the best service and products to our customers with safety as our top priority.
Sooner has a clear purpose: to connect the people who create the world’s energy with the supplies they need. For nearly a century, we’ve been serving and expanding on that purpose, growing into one of the world’s largest OCTG distributors and logistics service providers to the oil and gas industry.
Sooner’s growth has enabled us to reach further and deliver better service to our customers. Each of Sooner’s acquisitions has brought a distinguished history and strong customer base to the combined company.
In our latest moves to connect the world’s energy creators with the supplies they need, Sooner acquired CTAP, LLC in February of 2019. In 2020 Sooner announced the creation of TerraTech Services, offering a full suite of oilfield services and logistics.
Containment Group (Chairman of the Board of Directors); the National Ocean Industries Association (NOIA) (Board of Directors, Chair-HSE Committee); and the American Association of Drilling Engineers (ADDE) (National Board and National President from 2007 to 2009). A 35-year member of the Society of Petroleum Engineers, Leimkuhler
From here, the future is very promising, we look forward to continuing to provide the best products and logistics services to our loyal customers.
www.soonerpipe.com
Connecting the people who create the world’s energy with the supplies they need
Sooner offers more while providing better service for our customers. We are number one in the industry for a reason.
serves on various advisory boards focused on Petroleum Engineering. He is a recipient of Meritorious Service Awards from API and AADE (2011), the AADE Lifetime Outstanding Service award (2017), and the Distinguished Alumni Award (2022) and Eminent Engineer Award (2019) from the University of Wyoming.
Leimkuhler brings significant safety insight to the entire industry through his service to the well containment response issue, as the Chairman of the HWCG Well Containment organization. Fourteen companies
that are active in deepwater, including BOE, have pooled their resources to make sure state-of-the-art well containment response capability is immediately available across the US Gulf of Mexico.
CREATING VALUE FOR THE LONG TERM BOE is particularly proud to be a member of NOIA (National Ocean Industries Association), an organization that represents and advances the offshore energy industry, providing solutions
Long recognized for extraordinary performance, game-changing technology, superb safety and long-standing partnerships, and now incorporating Frank’s International, Expro is focused on enabling our customers to make timelier and better-informed decisions.
The combination of both companies has brought together decades of market leadership, best-in-class safety and service quality performance, and exceptional talent. With now global capabilities in well construction, well flow management, subsea well access, well intervention and production services, we are a visionary full-cycle energy services expert providing customers with cost-effective, innovative solutions across the entire well lifecycle.
As a recognized global well expert and one of the most trusted partners in the energy industry, Expro is well positioned to play a leading role in enabling our clients to achieve their carbon reduction goals in support of the energy transition.
We have committed to achieving our own Net Zero emissions by 2050 and, since 2020, have been on a clear path to invest in adopting and adapting our technology portfolio in line with new energy demands. By unleashing the power of data and digital transformation, together we can address the critical energy challenges.
Long recognized for extraordinary performance, game-changing technology, superb safety and long-standing partnerships, and now incorporating Frank’s International, Expro is focused on enabling our customers to make timelier and better-informed decisions.
Innovative, high value, low risk well construction solutions provider with a focus on operational efficiency and well integrity.
By unleashing the power of data and digital transformation, together we can address the critical energy challenges of today, jointly engineering the answers of tomorrow.
Proficiently gathering valuable well and reservoir data, with the utmost regard for well-site safety and environmental impact.
Fast-track cost-effective, early field production, optimization and enhancement systems.
Ensuring safe, efficient and cost effective subsea well access systems across the entire lifecycle of the well.
Deployment, insight and enhancement solutions to enable reservoir and well surveillance, production optimization and asset integrity assurance.
that support communities and protect workers, the public and our environment. BOE embraces the foundational ESG principles of NOIA. BOE’s desire to produce low carbon barrels as efficiently and safely as possible reflects those principles.
“The barrels coming from the Gulf of Mexico have a low carbon production footprint, as well as a low carbon transportation footprint, resulting in the lowest overall carbon footprint barrels on the planet, making offshore barrels especially attractive during the energy transition,” Leimkuhler explains.
“The U.S. Energy Information Agency’s (EIA) 2022 base case
DSDS’s association with Beacon comes through their relationship in well containment response preparation as well as with supporting ongoing production operations and maintenance activities.
DSDS is also supporting Beacon with the groundbreaking Shenandoah development as a key member of the small but focused BOE project team overseeing the work of their EPIC contractor Subsea 7.
In addition to the Shenandoah development, DSDS is involved in BOE’s efforts to identify and execute development opportunities that grow Beacon’s portfolio as a responsible operator and desirable technical partner.
DSDS’s role in this effort involves bringing our experience to the table to de-risk schedule acceleration and cost optimization.
estimate is that the country’s oil needs in 2050 will be greater than they are today, even with a substantial ramp up in renewable energy. In our industry’s efforts to achieve a greener future, the lowest carbon barrels will be the most valuable in the years to come and the Deepwater Gulf of Mexico will be a very important contributor while also providing efficient domestic energy supply.
“Cycle times for oil and gas developments has compressed through standardization, but nevertheless often require multi-year investment commitments prior to first production. In order to meet the projected demand for oil and gas in
TechnipFMC and Beacon Offshore have developed a strong relationship built on mutual trust. Through collaboration, both teams strive for the best technical solution to successfully and safely execute a subsea project.
For the Shenandoah project, TechnipFMC is responsible for the delivery and installation of industry-leading high-pressure, high-temperature (HPHT) Subsea Production System (SPS) equipment, including wellhead, trees, controls and chokes. Our 20K tree system is an industry-first, and these innovative technologies address the challenging conditions of the deepwater Gulf of Mexico field.
TechnipFMC looks forward to strengthening the relationship and supporting Beacon’s future developments.
Deep Sea Development Services, Inc. 19219 Katy Freeway, Suite 260, Houston, Texas 77094
Phone: (713) 725-4082
Andy Jefferies, President ajefferies@dsds-usa.com
Deep Sea Development Services Inc. (DSDS) is a Houston-based engineering consulting company focused on subsea and deep-water development projects in the Gulf of Mexico, Southeast Asia, West Africa, and Eastern Canada.
The company was formed in 1996 to meet the need for experienced subsea systems personnel and to support operators with their deep-water development activities from concept framing, through execution, operation, and eventual abandonment.
DSDS has been in continuous operation since its formation and continues to be involved with operators who are pushing the technology envelope to meet the worlds energy needs in an environmentally responsible way.
Weatherford consistently delivers a trusted approach to our customers’ wells, and we continue to innovate and push the industry forward.
We have redefined what our customers can do with managed pressure. By applying our field-proven technology to deliver higher quality, stable wellbores with fewer surprises, we help create comprehensive pressure management strategies that enhance safety, lower wellconstruction costs, reduce wellcontrol risks, and increase production.
Since 2018, Weatherford has used managed pressure wells solutions in the Gulf of Mexico on 40 deepwater wells for a total of more than 350,000 feet.
the next eight to 10 years, companies must invest now in offshore assets and exploration/development activities.”
For Leimkuhler, increased focus on renewable energy can present challenges to access capital for oil and gas projects. The offshore leasing environment for US federal waters has recently been delayed and questions regarding incremental regulation can impact the ability to proceed with near term developments on existing leases. On top of this, as with all industries, the offshore industry is challenged by shortages
of materials and experienced staff due to the lasting impact of the COVID-19 pandemic, fragile supply chains, and the subsequent economic implications.
“BOE has been focused, authentic and diligent in its ESG journey, embracing challenges head on,” Leimkuhler continues. “The unique culture, purposely cultivated by BOE’s leaders “empowering experience” results in engaged team members who collaborate to deliver results.
“It has been impressive to watch the team come together. From geology, engineering, construction, drilling,
www.weatherford.com
Exmar Offshore Company (EOC) is the designer of the OPTI® series of production semisubmersible hulls.
The OPTI® hull is a standard design that has been successfully used on three floating production systems in the Gulf of Mexico. Beacon Offshore Energy (BOE) contracted EOC to leverage its past and recent experience on previous projects to size the hull for the Shenandoah project resulting in the largest OPTI® design to date.
EOC’s OPTI® hull utilizes proprietary technology to optimize motions and connect risers with its FAST® system and process. EOC is honored to work on behalf of BOE and to bring its technology and experience to the benefit of the Shenandoah project, BOE and its partners.
Weatherford“BOE HAS BEEN FOCUSED, AUTHENTIC AND DILIGENT IN ITS ESG JOURNEY, EMBRACING CHALLENGES HEAD ON”
With the knowledge earned from more than 50 years of experience, thousands of jobs, and millions of operating hours, we are the pressure professionals. Our Managed Pressure Wells solutions enable you to combine your knowledge of your wells with our industry leading portfolio of products and services to manage pressure. Weatherford.com/ManagedPressureWells
• NOIA member companies provide the energy that is essential for everyday lives and raises the quality of life of communities, reducing poverty and hunger while promoting good heath and well-being.
• NOIA operates in coastal and ocean environments with safety, health, environmental protection and sustainability as core values.
• NOIA shares a commitment to a high standard of corporate citizenship and continuous improvement in ESG performance.
• NOIA recognizes the risks of climate change and the need for continued action. As innovators, NOIA is committed to contributing solutions and best practices to optimally balance societal and environmental needs.
Leimkuhler connected BOE with a research project on improving carbon capture efficiency, that if successful could have a lasting onshore and offshore impact. Hopeful for carbon solutions that can positively impact the industry, BOE elected to underwrite part of the study.
BOE is excited by the way that the offshore energy industry has embraced the energy transition. Working through organizations such as the NOIA, BOE is motivated to leave a positive legacy of change.
“We see a bright future for BOE in being a significant contributor to energy security, as well as smart solutions, through the energy transition,” Leimkuhler concludes.
completions, reservoir, land, finance and accounting, BOE professionals know how to put a plan in place, work with regulators to gain approval, and then execute with success.”
BOE views opportunity through an ESG lens and seeks opportunities for
carbon reduction, big or small. For example, BOE is working with its key vendors to reduce fuel consumption and improve efficiencies. Additionally, in conjunction with his service on the University of Wyoming, College of Engineering Advisory Board,
To round off each issue, we ask our contributing business leaders for their views on the same question THE FINAL WORD
“My greatest motivator at work is the team surrounding me. ADB is as much of a people business as it is anything else and being able to help people grow and flourish drives me to work hard and give everything I have every day. It sounds a bit cliché, but I truly view the ADB team (A-Team) as family. A lot of our leaders have been with the company for many years, and we’ve been through a lot together as we’ve grown this company from a handful of employees to more than 1,500 in a short time. I’ve had the opportunity to watch people grow from laborers to leaders and I’ve been able to help them get through rough patches and be successful in tough times.”
“It is the plans and strategies we create that encompass the major points of business, from supporting our customers to supporting our employees and partners, that remains one of the largest motivators for me. This envelops our company mission and all the people that we have an impact on, be they customers and the patients in healthcare facilities, or the families of our employees. This support and positive impact is our key motivation.”
“For me, the biggest motivator is seeing the complex products that we make and then delivering them to become a part of a large commercial or defense aircraft. When our employees see
those products performing anywhere, we feel really proud and that’s what motivates us to continue doing the work we’re doing. It is seeing how our customers are supporting us, or the recognition we receive when we deliver a good product, which is reflected by the performance awards we have received from our customers for the past six years in a row. All these things are a huge motivator.”
“The changing industry is a motivator. I’m constantly challenged to develop new ways to bring costeffective renewables into the energy portfolio. The opportunity to increase generation diversity while reducing costs is inspiring.”
Are you a CEO/Director with a company story to tell? Contact North America Outlook now!
What is your greatest motivator at work?
Complementing the production of North America Outlook, APAC Outlook, EME Outlook and Africa Outlook magazines, Outlook Publishing’s awardwinning in-house team is now utilizing these same specialist production skills to offer a full and bespoke range of editorial, design and marketing services via its new Outlook Creative Services division.
For more information on how we can work with you in providing a plethora of completely flexible and customizable production services, please visit: www.outlookpublishing.com/creative-services