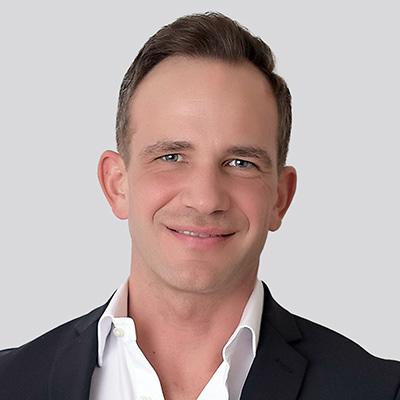
15 minute read
Emerald Textiles
LEADER
in Healthcare Linen
Andy Kratky, CEO
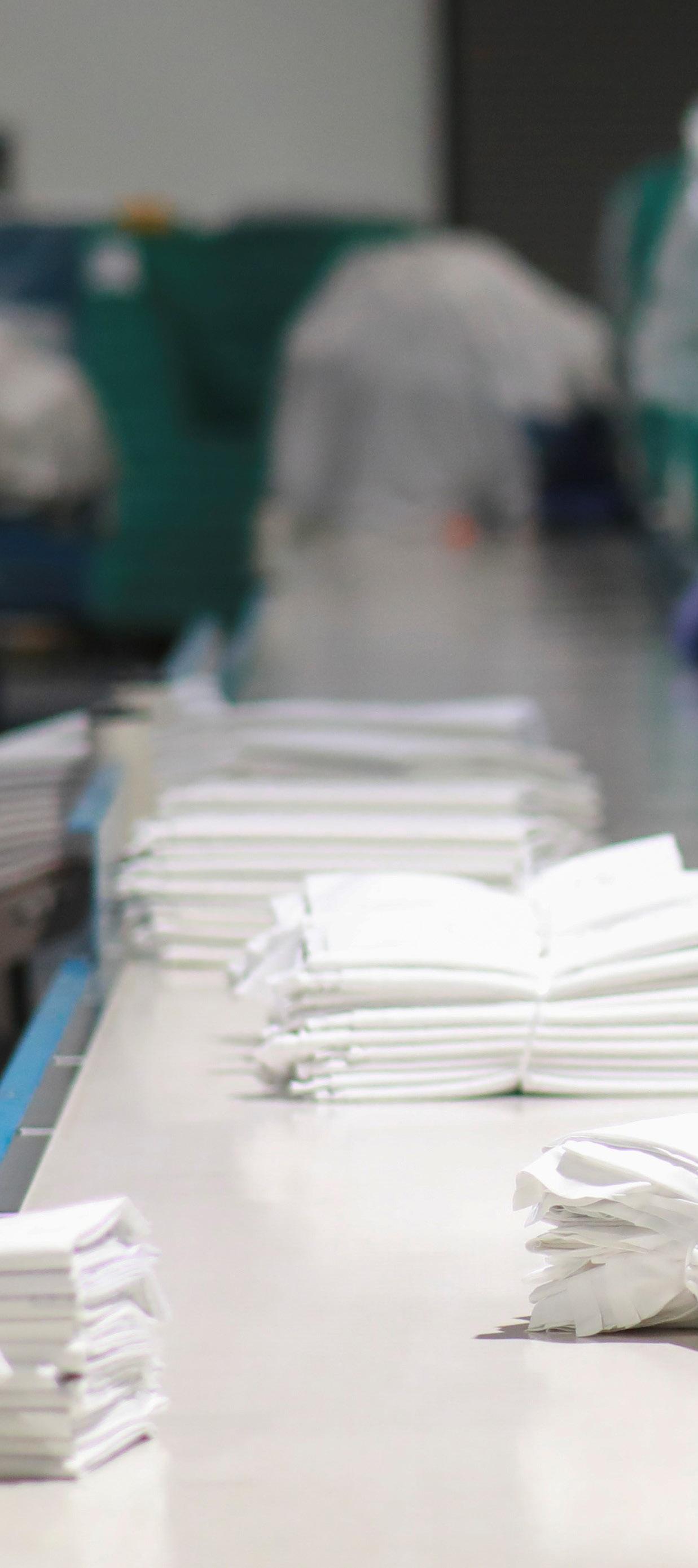
Emerald Textiles is the largest in linen and laundry commercial processing within acute care, servicing Hospitals, Medical Centers, and specialty clinics across four states in the Western US. CEO Andy Kratky discusses the company’s latest developments and its continual growth in the market
Writer: Marcus Kääpä | Project Manager: Felix Revell
Since the beginning of the COVID19 pandemic, we have been reminded that healthcare is one of the most critical sectors to the health and wellbeing of people around the globe, and the continued function of everyday life, from individuals to businesses and even governments.
Within the sector, there are key players who keep the wheels of the industry turning in one way or another, such as the suppliers of healthcare resources.
One such company is Emerald Textiles (Emerald), the largest healthcare linen service provider that specializes in servicing the healthcare industry, with 12 state-ofthe-art commercial linen processing facilities, three service centers, and industry leading operations across the Western US.
“We are the largest provider of healthcare linens in the region, and we have 12 different sites across four states,” introduces Andy Kratky, CEO of Emerald. “These are our processing facilities, and on top of this we have three service centers strategically located to serve a wide base of healthcare customers.
“We measure ourselves on the pounds of linen produced each year. This number sits at around 330 million clean pounds provided to our
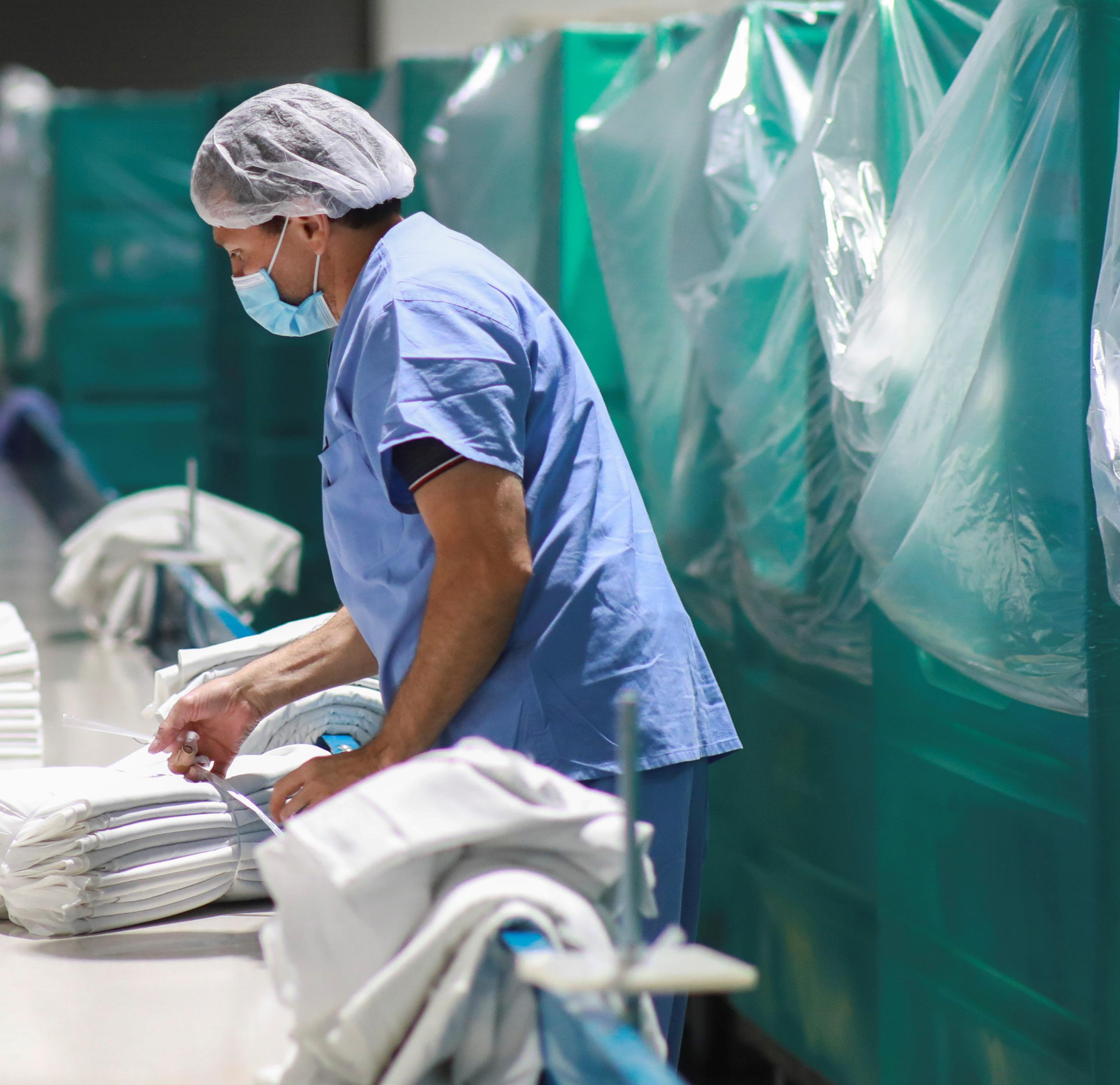
customers annually, which is sizable compared to others in the field.”
QUALITY AT THE FORE
Emerald’s 2,200 employees serve around 2,500 customer sites in the country, delivering the highest quality products to the sector across the western region.
“Emerald is 99 percent in the healthcare space, with one facility in Reno (Nevada) that additionally produces linen for the hospitality sector,” Kratky says. “Our standard items focus on any linen that you would find in a hospital room, such as bed sheets, bath blankets, pillowcases, and many other items. Another key part of our business is non-standard items such as reusable isolation (ISO) gowns, scrubs, and microfibers, for example.
“Since the COVID-19 pandemic, reusable ISO gowns have been a very important part of supporting the healthcare workers in hospitals. At the beginning of the pandemic, many experienced supply chain disruptions and we did a great job ramping up our inventories such as reusable ISO gowns. Being proactive in our inventory ramp up ensured our healthcare partners had enough supply and got what they needed. This was especially important when disposables became difficult to find,
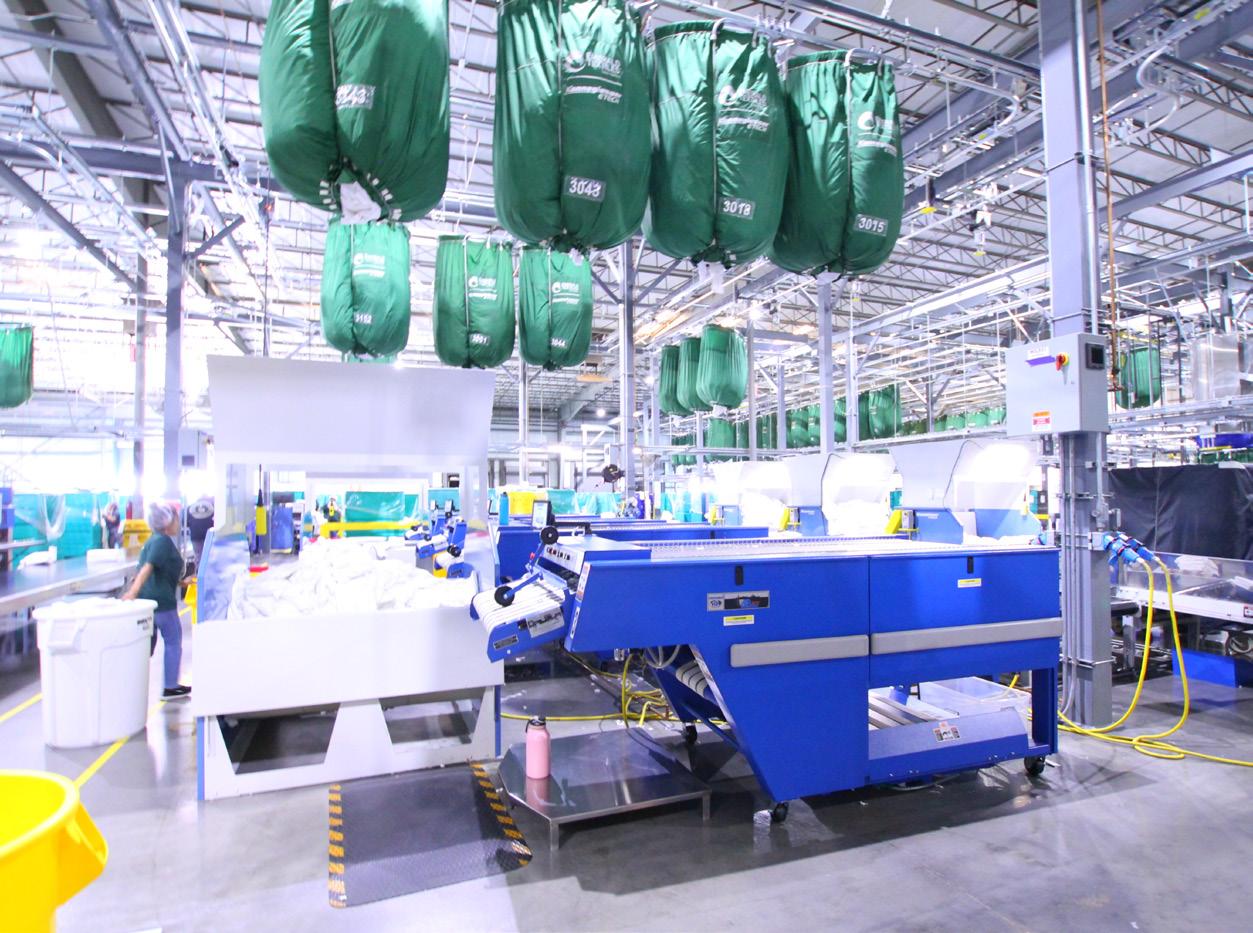
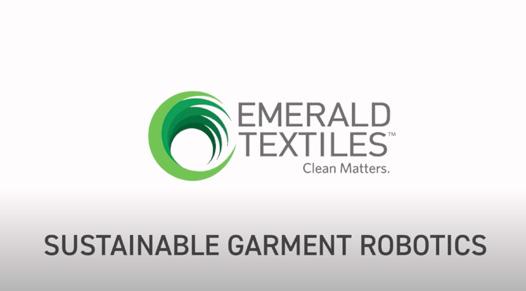
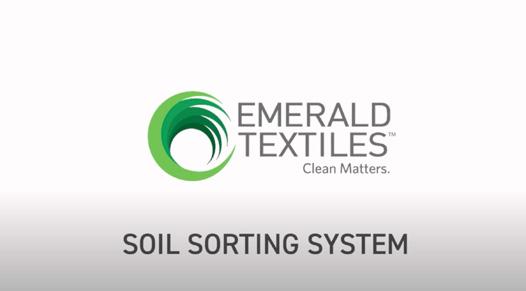
to ensure that the workers were as safe as they could be during work hours, all while providing sustainable, reusable, hygienically clean products.”
What truly sets Emerald apart from the competition in the industry is not just its scale of service across the Western US, but also the quality of specifications the company follows when it comes to its products.
“We provide a higher quality, higher spec product to service our customers and make sure that they have the best quality products within their hospitals,” Kratky continues. “The lack of issues when it comes to our quality, mixed with our dedication to making sure that our customers have the best products and enough supply on time, is critical to Emerald, and is what really differentiates us.”
GROWTH IN THE INDUSTRY
While quality remains key to serving customers, growth and a focus on consolidation are also instrumental in establishing a lasting foothold in the industry. Across the US healthcare space, players are competing to incorporate additional institutions and grow to best service regions and states in their specialized areas.
“Traditionally speaking, there are larger healthcare systems that branch out across the US, and then there are systems that have been more regionally focused, or super-regionally focused with market density based in large cities,” Kratky elaborates. “Then there are a lot of smaller independent healthcare facilities that support different local areas but do not really branch out throughout their state,
Norchem
PROVIDING EMERALD TEXTILES THE COMPETITIVE EDGE
Norchem began its partnership with Emerald Textiles in 2010 at their first plant located in San Diego, California. The ongoing goal of the partnership has been to increase textile cleaning efficiency through our green detergent programs, reduce utility consumption through our water recycling and heat reclamation systems, and consult on production process improvements by leveraging our plant automation expertise.
After implementing Norchem’s green chemistry for healthcare with consistent positive results in San Diego, the plant was under pressure from the city to manage TDS to sewer. As water costs and sewer costs increased, Norchem stepped in to design a complete turnkey UltraPure® Water Filtration system for wastewater reclamation and an RO system for incoming water TDS reduction. After installation, the plant was able to successfully reduce the TDS of the incoming water to stay below the discharge limit of 1,000 ppm TDS and recycle up to 70 percent of total plant wastewater.
Norchem now services eight Emerald Textile plant locations in the SouthWest with our Alkapon™ Detergent program. Their first location in San Diego after 11 years continues to benefit from the UltraPure® WasteWater Recycling System and the RO Pure® Reverse Osmosis System.
Since partnering with Norchem, Emerald Textiles has recycled 430+ MILLION gallons of water! Norchem’s application engineers and customer care technicians balance the injected chemistry with recycled water to maximize heat, water reclamation, and surfactant recovery. The result is BIG SAVINGS at the wash aisle and optimum utility conservation.
NorchemCorp.com
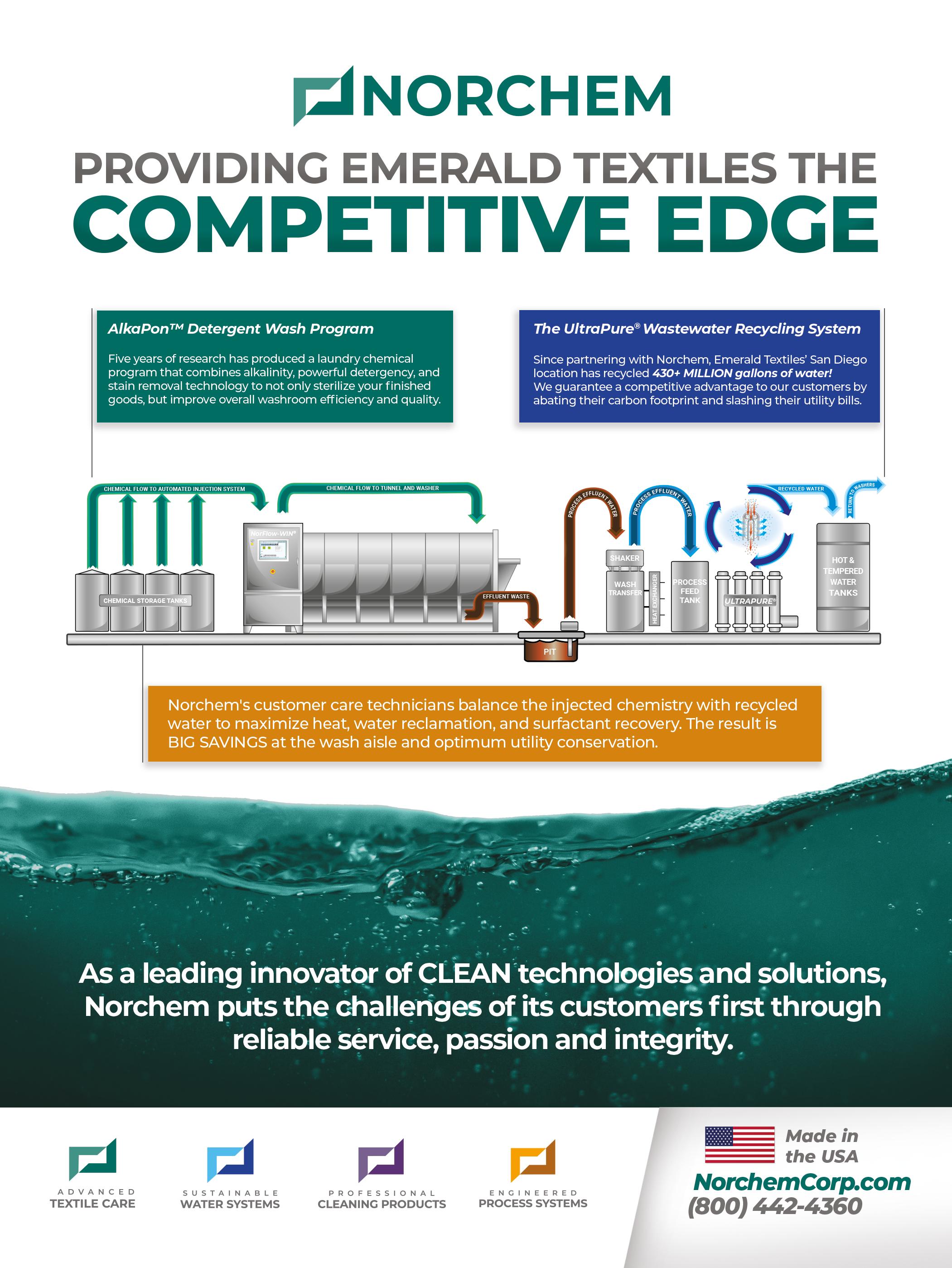
region, or the country.
“What we have seen over the past several years is a consolidation of the market. You have larger healthcare systems that are going out and acquiring smaller independent systems that are a good fit with their footprint, and they are also building new hospitals and medical office buildings to continue their outreach.”
Emerald has been able to achieve this trend in acquisition and growth, being able to implement additional facilities, whether they are greenfield developments or otherwise in order to successfully grow and expand with their customers.
ACQUISITION AND EXPANSION
In recent years, Emerald has been driven by this growth focus across the Western US. According to Kratky, the initial vision of the company was to create a linen and laundry healthcare provider that could service larger healthcare systems, with the business starting up in Northern California catering to a small number of different facilities.
Emerald has grown significantly through organic growth, but also continues to grow through acquisition and expansion.
“The most recent acquisition was with Angelica Corporation (Angelica),
CONTINUAL INVESTMENTS IN EQUIPMENT AND INNOVATION
Emerald continually invests in the latest equipment, technology, and infrastructure systems that result in fewer manual processes, greater automation for uninterrupted laundry processing, and produce the highest quality linen for patient satisfaction and greater peace of mind. It’s the Emerald Difference. Investments include: • Computerized loading and transferring systems, automated conveyors, stainless steel surfaces, microbe resistance flooring.
• Award-winning and resource saving continuous batch washers, energy saving dryers, automated steam finishing processes, and folding robots. • Gravity-enabled overhead E-Tech rail systems that automate laundry bag transferring are all around better to preserve Emerald’s hygienically clean linen, maximize linen processing and efficiency, save more on natural resources, and better for employee satisfaction. • High tech automation and rail systems that move Emerald’s garments from steam to racks ready for customers.
SUPERIOR CLEANLINESS AND HYGIENICALLY CLEAN HEALTHCARE CERTIFIED
Emerald’s clean linen processing is Hygienically Clean Healthcare certified through its partnership with TRSA Association for Linen, Uniform, and Facility Services Industry. Emerald is dedicated to quality assurance and best management practices to ensure the highest quality and safety for customers, their patients, and employees. • Hygienically Clean Healthcare Certifications adhere to all healthcare standards and policies • Ongoing inspections and microbiological testing for the highest quality assurance • Full compliance with all State, Federal and OSHA regulations • Monitors complete textile processing cycle from handling and transporting to in-facility processing • Best Management practices and personnel training
American Textile Systems
With almost 30 years of history within the textile industry, American Textile Systems (ATS) is a key player specializing in supplying leading quality textile products to the linen supply, hospitality and governmental industries.
Based in Southern California, ATS has grown to become a medium-sized business with company success owed to an exceptional and dedicated team of employees, many of whom have been with the business for decades.
ATS’ supply chain has been carefully curated and nurtured to provide the company with industry leading quality products, sourcing from the very best mills in the industry, carrying complete lines of the following products:
• Bath linen, including wash cloths, hand towels, and bath towels. • Bed linen, including pillowcases, bed sheets, contour sheets, and knitted contour sheets. • Over the bed products, such as blankets, spread blankets, and comforters. • Patient wear, including patient gowns and iv gowns in poly/cotton blends and 100 percent polyester. • Ability to customize products including property marking, kaumographing, and continuous imprinting (cim). ATS can build products with any construction, dobby pattern, color, and shade of bleaching.
Today, ATS has distribution centers in Southern California, Texas, Georgia, and New Jersey, allowing the company to serve customers promptly, efficiently and just-in-time with same-day and next day deliveries via company operated delivery trucks and excellent logistics control.
When timings are extra tight, ATS can easily accommodate “emergency” shipments and deliver goods within hours of the purchase order being placed.
www.amtexsys.com
another provider of hospital linen and laundry, in which we acquired nine different facilities from them in the west of the US,” Kratky says. “The idea was to continue to scale up, and there were certain facilities that were very good, and we didn’t have to alter. Some other facilities we have had to deploy capital and invest in upgrading them.
“We have a strong market position because of our success in growing organically and through the investment in acquisitions such as Angelica. Because of our footprint and the deployment of our strategy, we are able to support larger healthcare system customers without compromising quality or customer experience. Recently, this has accelerated and put us in a good position from a customer standpoint as well as in terms of capacity. Angelica was a large integration due to the number of sites that we incorporated, but this was completed in around five months. I would call this a success from start to finish, because usually it takes far longer to fully integrate a company of that size. Our team was also able to support our customers and partners during this time and did a really great job.”
On top of the Angelica acquisition, Emerald has undergone several plant expansions, including at its Phoenix (Arizona) plant, to improve capacity, efficiency, and customer service.
“The Phoenix expansion has been a really nice success story for us since we acquired the business,” Kratky tells us. “We knew that it was one of
MIP
As a global supplier and manufacturer of healthcare textile solutions, MIP provides comfort and efficiency for the healthcare community and its people.
As a proud partner of Emerald Textiles, we hold people at the heart of all that we do. We provide innovative, as well as cost-effective, products, services, and solutions for the commercial laundry industry.
We know the value of our products because we see the impact that they have on the lives of laundry operators and staff. Find out how we can help you at mipinc.com
VALUE DRIVEN WITH CUSTOMIZATION, SAVINGS AND HIGHQUALITY CUSTOMER EXPERIENCE
Our dedicated account management and service team partners with our customers to create a program that best fits the specific needs and goals of each of our healthcare facilities and departments. • Providing dedicated, local customer experience teams for personalized care, assurance of stock, and monitoring usage • Building solution-oriented, customizable programs that meet the specific needs of each department
• Generating goals and savings with improved linen utilization and linen management best practices • On-site product and usage training education with a local team of experts
www.mipinc.com


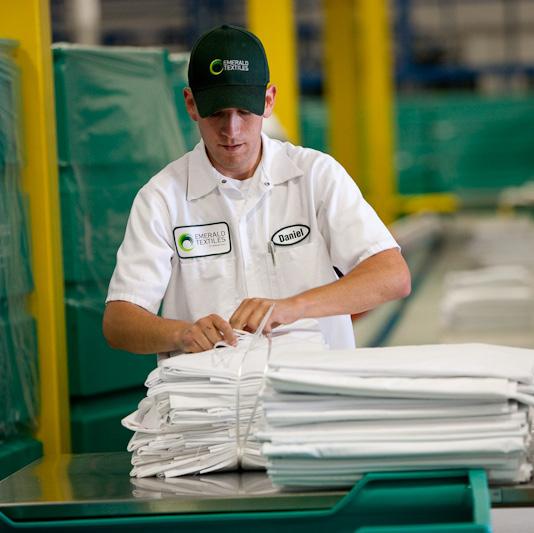
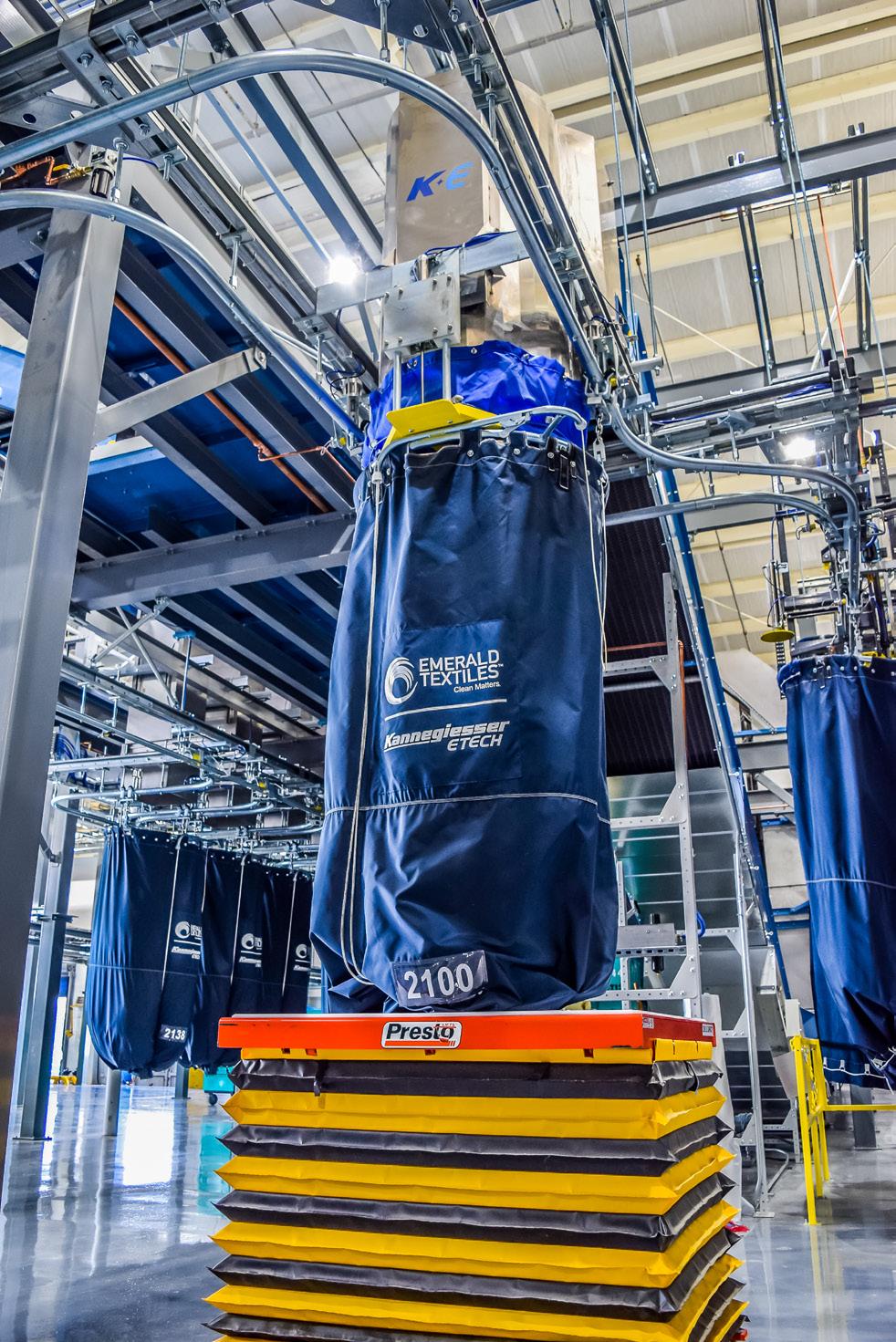
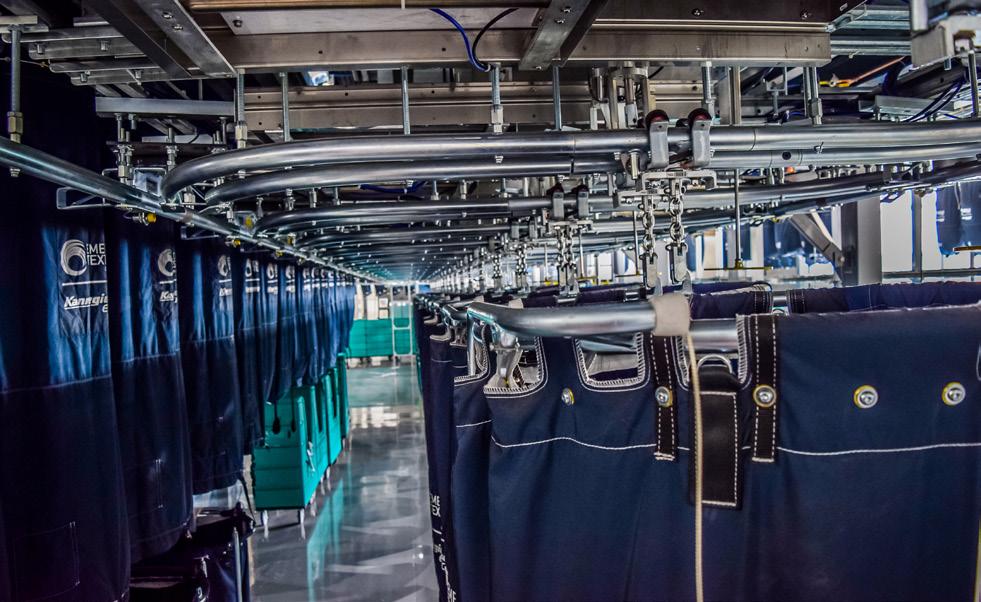

Left/top: Automated slings and rail system. Above: A computerized control system tracks every sling that is transported within the facility. After the linen is processed and folded through automated machines, folded linen stacks are transported on conveyors to the final processing stage where its prepared for order fulfillment.
the better running facilities that we acquired, and it has a great team of people working there. Earlier this year, we were able to secure a large new health system partner in Phoenix, and we had to expand our capacity to take on such a customer.
“We are currently deploying another of what we call a continuous batch washer (CBW) tunnel system, to make a total of three CBWs, along with five new industrial sized dryers to expand such capacity. This will also allow us to continue our growth efforts in that market. In addition to Phoenix, we have deployed $50M of capital over the past four years to upgrade several facilities and expand capacity to take on new customers, which results in better customer support and improved efficiencies in the facilities.”
PEOPLE FIRST
and its additional facility investments, the company has undergone substantial growth in the market.
“Last year we grew 18 percent organically, and this year to date we have grown 12 percent; because of this, we have expanded capacity in certain facilities and continue to do so,” Kratky tells us. “We have also increased investment in our linen products, continue to invest in hightech automation through quality equipment, and internal investment of our people.”
For Kratky, Emerald’s workforce is the center of the company’s success, and reinvesting in employees has been, and continues to be, a primary focus on in-house development across Emerald’s many sites.
“We are firm believers in making sure that we have the best equipment used for production, and we continue to deploy capital across our sites for our manufacturing capabilities as well as our staff,” he elaborates. “This is one of the reasons for our year-onyear organic revenue growth, but the second is the focus on our people.
“We have a lot of employees within our facilities, and we make sure that our employees have a good work environment and the support they need to thrive in the workplace. We need to make sure that we take care of our employees.”
Within this sphere, Emerald ensures to recognize and reward its employees’ efforts and performance, and celebrate such achievements.
“We have had employee recognition in the company for a number of years now, and we host events and other things to keep our teams motivated,” Kratky tells us. “We also have quarterly business meetings with all employees across our 15 locations with the intent on providing
all of our teams with a perspective of what is going on with the company and how we are moving forward.
“I am a believer in open communication to our team to ensure they have an understanding of what is going on in the entire business, not just their portion of it. This gives them the perspective of how they impact the company as well as how their co-workers impact the company. Maximized communication to our team is critical, and providing the team with the status of the company and performance goals, both internal and external, is extremely important, as is recognizing and celebrating individual performance.”
Environmental, social and governance (ESG) is at the core of the company’s mindset and defines the way in which Emerald operates across the western US.
“From an environmental standpoint, our ESG strategy helps Emerald reduce our use of natural gas, electricity, water and other resources used at our facilities to be good stewards of the environment,” Kratky explains. “Doing our part will help the planet that much more, and our ESG plan is very important to our overall strategy as a company as well as our healthcare partners.”
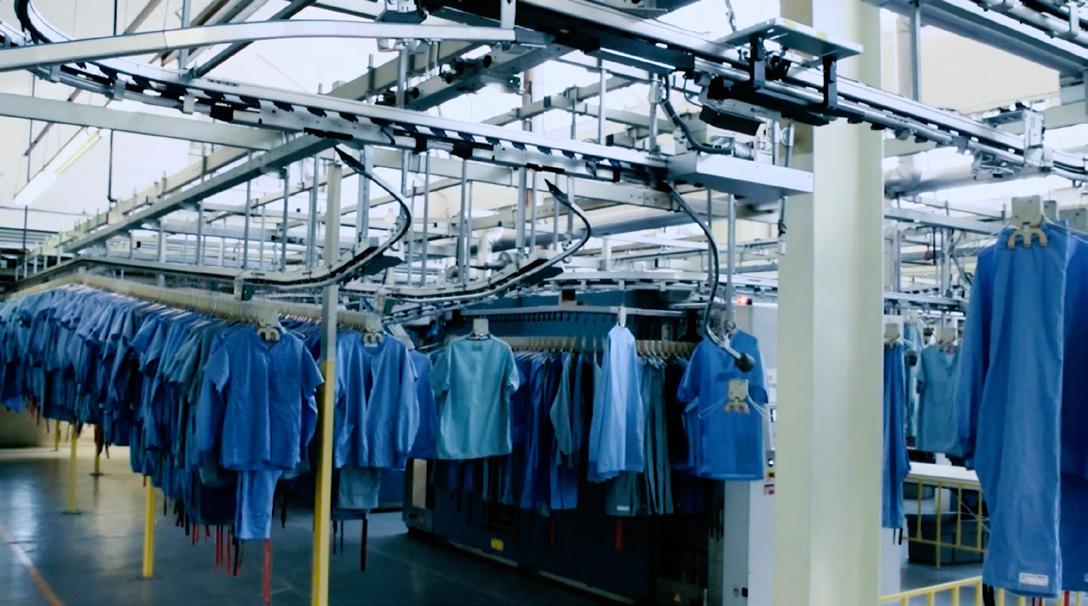
EXTENDING REACH
Emerald’s primary focus for the rest of 2022 and beyond is building on the organic growth experienced from the company’s multiple investments and facility developments. Despite holding a predominant share of the market, Emerald seeks to drive value for its customers and their businesses, while keeping its eyes peeled for opportunities for acquisition.
“We see an opportunity in independent outpatient facilities that we think are a very good fit for Emerald, and that we can align with from a product and service perspective,” Kratky says. “So, we are working on, and in the process of, deploying a strategy to really hone in and focus on generating more outpatient and independent care facility business.
“Outside of this, despite our super-regional reach, we have had customers reach out to us and ask directly if we have the ability to serve them in other states across the country. Because of this, I believe that greenfield expansion is definitely going to be a part of our future, where we build a processing facility based off an anchored customer in a certain area. We did this with our Livingston CA facility, so we are well versed in creating a world class greenfield facility.”
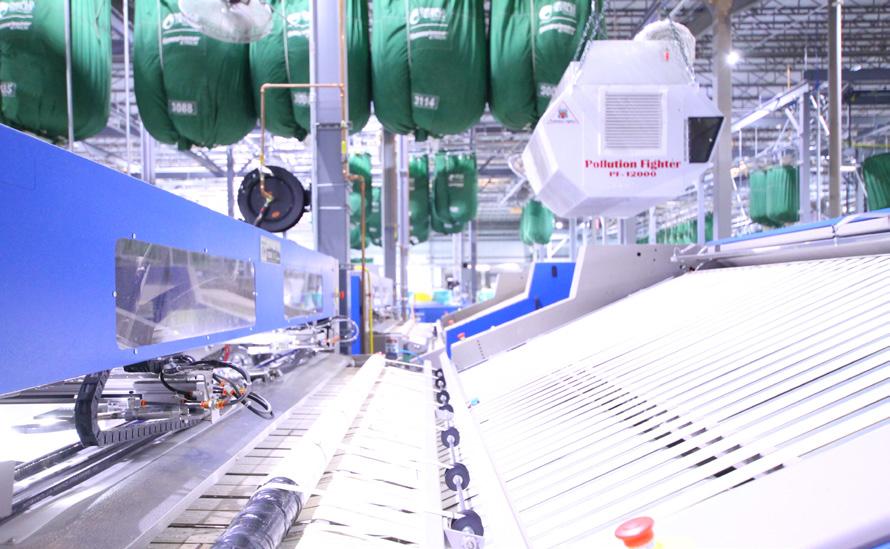
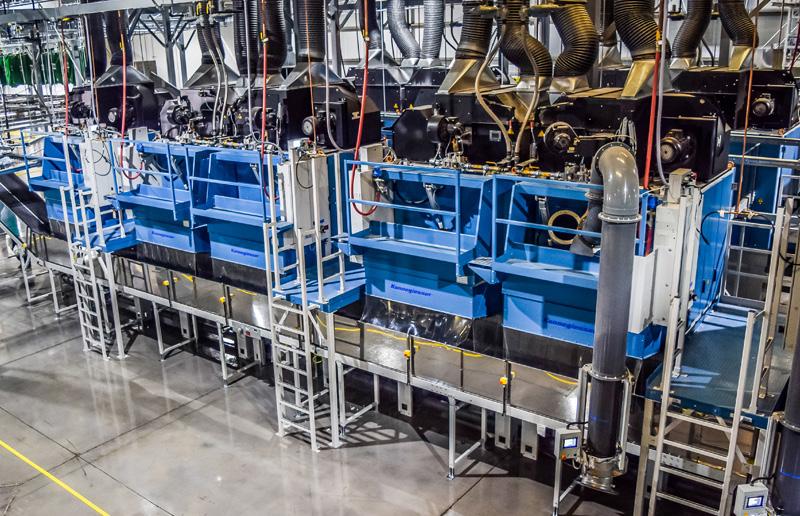
Emerald Textiles Pomona facility with their high-tech, computerized automated garment system – also referenced in the article in what Emerald Livingston, CA (a greenfield expansion) will be installing at the end of the year. Left: Automated sheet folder Bottom: Industrial sized, energy efficient dryers, gentle on healthcare’s most critical textiles.
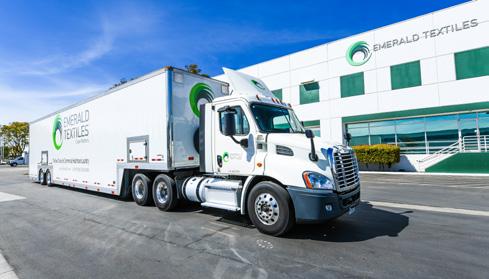
Stemming from this customer demand, Emerald is prospecting expansion into adjacent markets as well.
“This is a pillar of our growth strategy,” Kratky reveals. “There are plenty of opportunities out there in the market, and we will always look towards expanding our product and service base to reach customers further afield.”
info@emeraldus.com www.emeraldus.com