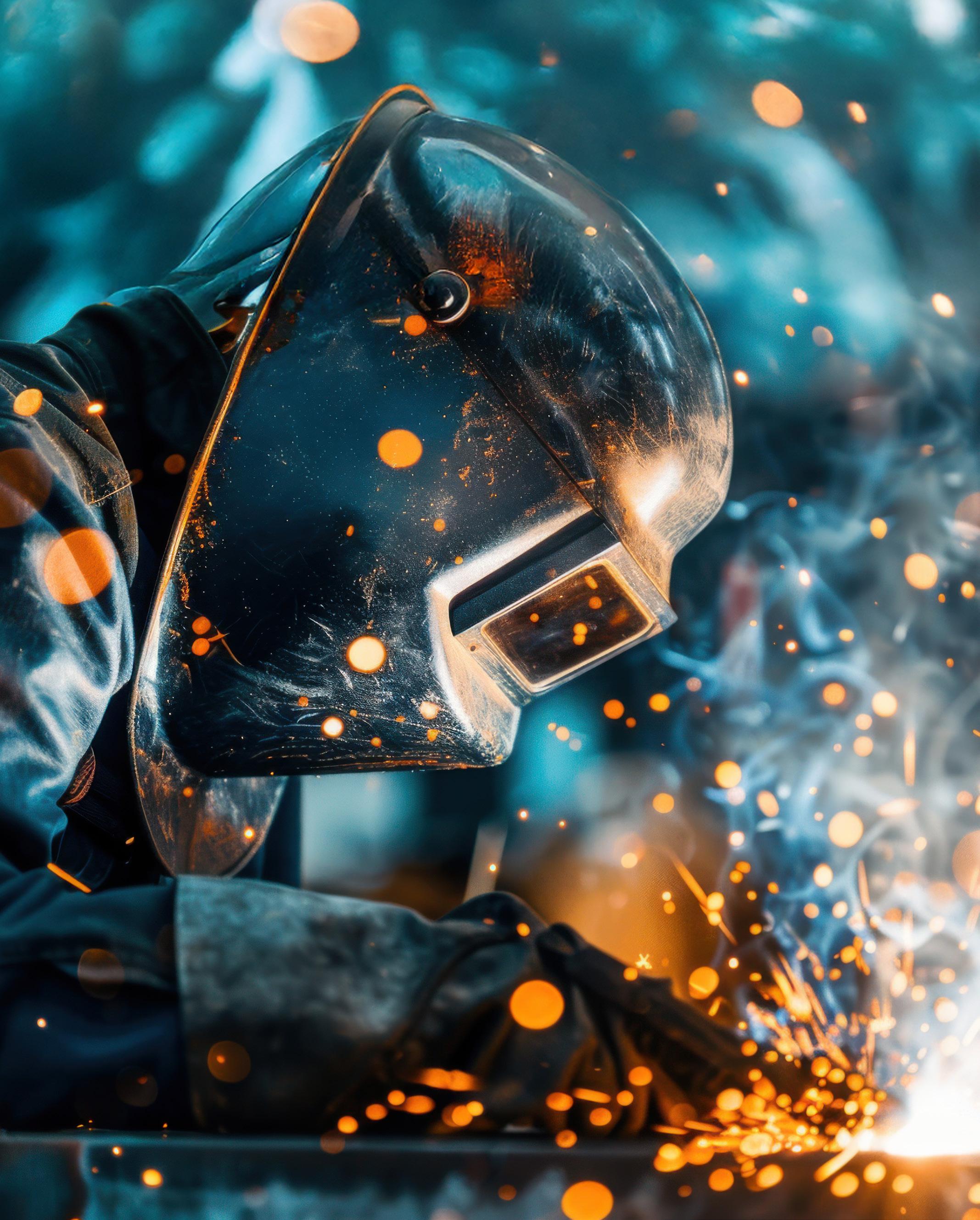
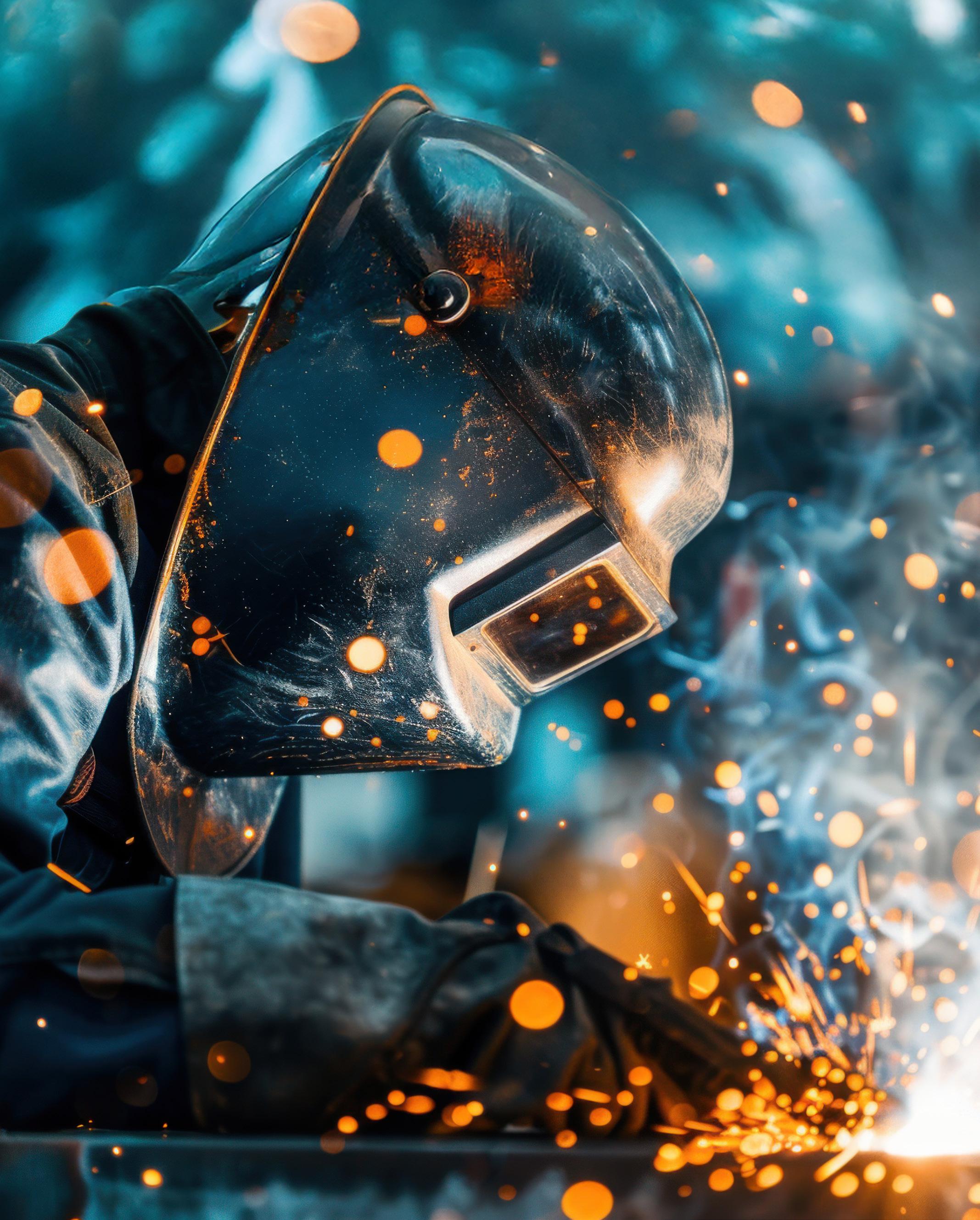
PROPAK SYSTEMS
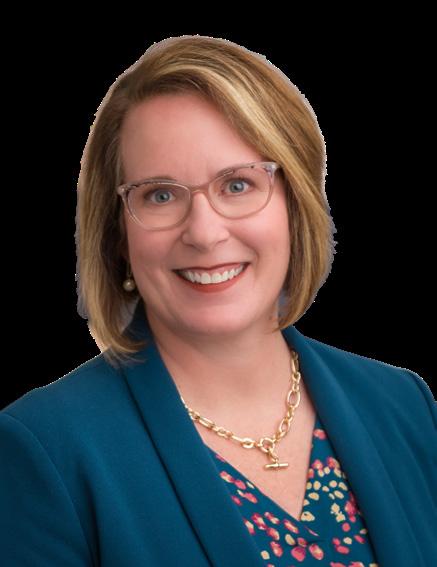
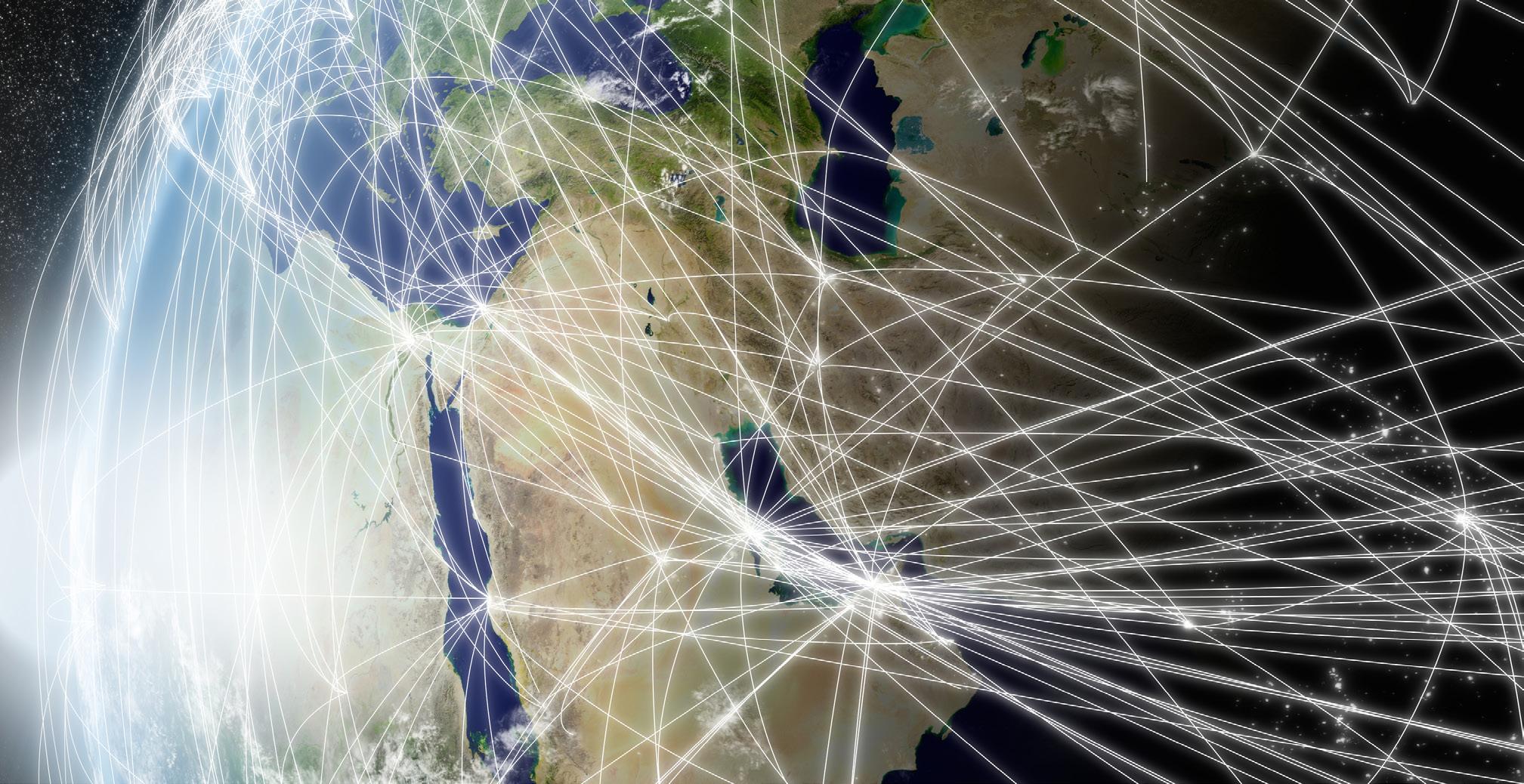
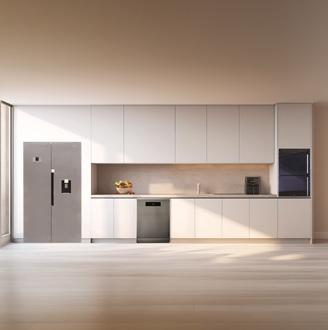

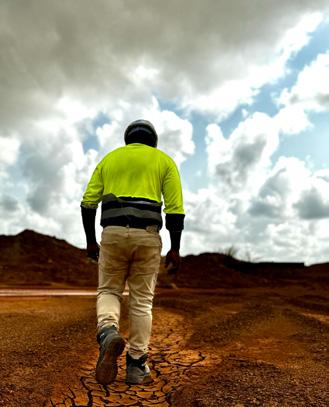


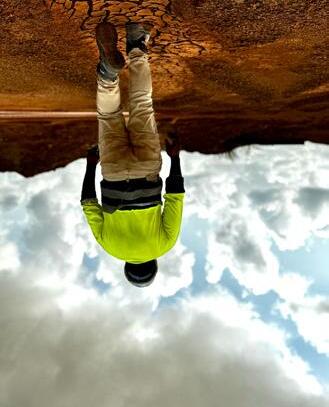
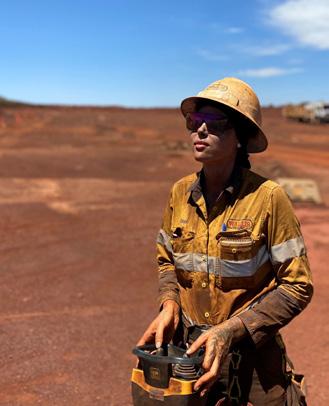

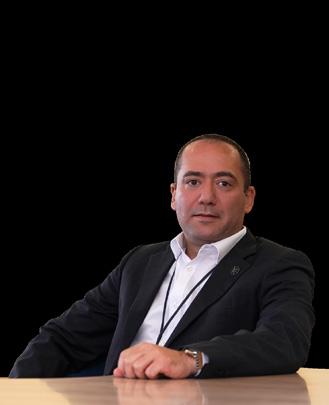

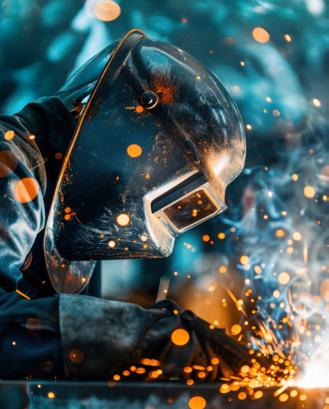

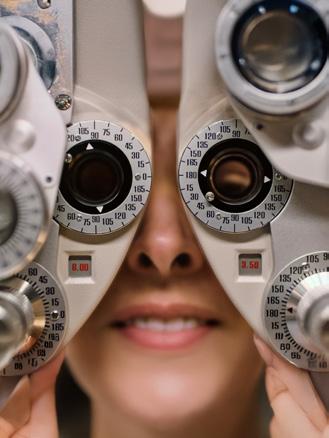

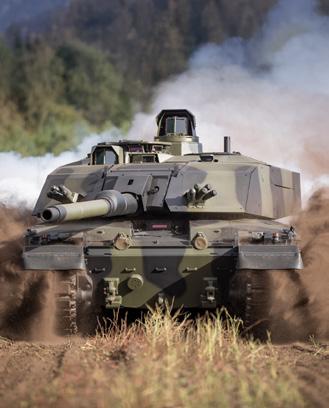




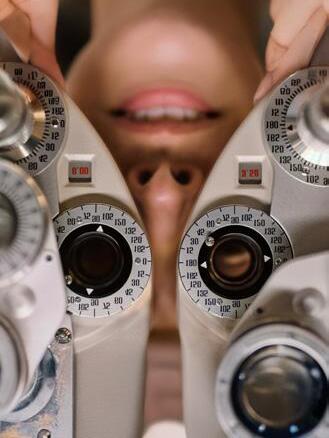


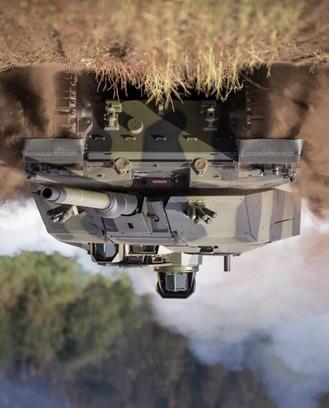

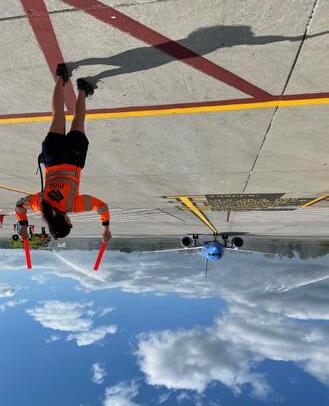

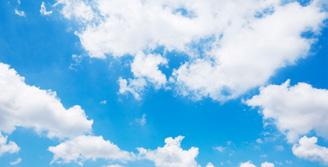

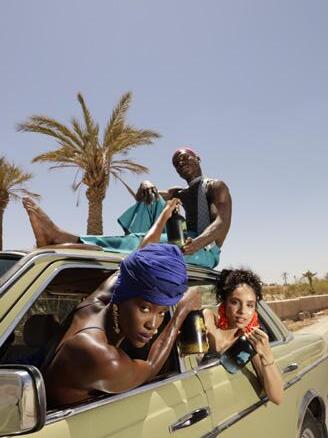
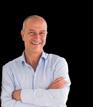
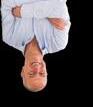
Africa Outlook, APAC Outlook, EME Outlook, North America Outlook, Mining Outlook, Healthcare Outlook, Manufacturing Outlook, Supply Chain Outlook, and Food & Beverage Outlook are digital publications aimed at boardroom and hands-on decision-makers, reaching an audience of more than 800,000 people around the world.

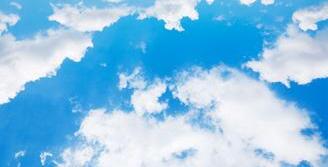
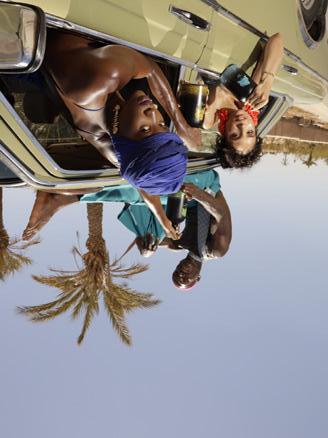
With original and exclusive content compiled by our experienced editorial team, we look to promote the latest in engaging news, industry trends, and success stories from across the globe.
Your company can join the leading industry heavyweights enjoying the free exposure we provide across our platforms with a free marketing brochure, extensive social media saturation, enhanced B2B networking opportunities, and a readymade forum to attract new investment and help you grow your business.
Visit www.outpb.com/work-with-us for details on how your company can feature for free in one of our upcoming editions.
EDITORIAL
Head of Editorial: Jack Salter jack.salter@outpb.com
Deputy Head of Editorial: Lucy Pilgrim lucy.pilgrim@outpb.com
Senior Editor: Lily Sawyer lily.sawyer@outpb.com
Editor: Ed Budds ed.budds@outpb.com
Editor: Rachel Carr rachel.carr@outpb.com
Editor: Lauren Kania lauren.kania@outpb.com
PRODUCTION
Art Director: Stephen Giles steve.giles@outpb.com
Senior Designer: Devon Collins devon.collins@outpb.com
Designer: Louisa Martin louisa.martin@outpb.com
Production Manager: Alex James alex.james@outpb.com
Digital Marketing Director: Fox Tucker fox.tucker@outpb.com
Website Content Manager: Oliver Shrouder oliver.shrouder@outpb.com
Social Media Executive: Jake Crickmore jake.crickmore@outpb.com
BUSINESS
CEO: Ben Weaver ben.weaver@outpb.com
Managing Director: James Mitchell james.mitchell@outpb.com
Chief Technology Officer: Nick Norris nick.norris@outpb.com
ADMINISTRATION
Finance Director: Suzanne Welsh suzanne.welsh@outpb.com
Finance Assistant: Victoria McAllister victoria.mcallister@outpb.com
CONTACT
North America Outlook
Norvic House, 29-33 Chapelfield Road
Norwich, NR2 1RP, United Kingdom
Sales: +44 (0) 1603 804 445
Editorial: +44 (0) 1603 804 431
SUBSCRIPTIONS
Tel: +44 (0) 1603 804 431 jack.salter@outpb.com
www.northamericaoutlookmag.com
Follow us on LinkedIn
Follow us on X: @OutlookPublish
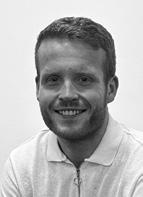
TRUST THE PROCESS
Welcome to our 30th edition of North America Outlook.
Canada’s midstream oil and gas sector plays a crucial role in transporting and processing hydrocarbons for upstream production and downstream distribution processes.
Propak Systems Ltd. (Propak) excels in offering products and services tailored to the needs of the energy processing sector.
This issue’s Canadian-owned cover star specializes in the design, engineering, fabrication, and construction of energy processing facilities and equipment.
The company supports projects from initial conception through detailed engineering and design to construction, commissioning, and start-up activities.
“Canada’s energy sector is known around the world for its efficiency, innovation, and high safety standards. At Propak, we’re proud to be part of that story, and we bring the innovation and quality that we’ve learned here at home to the products and services we deliver to customers globally,” states Jim Hanson, Managing Director of Technical Sales.
Innovation has also been the beating heart of Lockheed Martin since its humble inception over 100 years ago in 1912.
We revisit the global security and aerospace company proudly working to make the world a better place through technology.
Lockheed Martin is digitally transforming its operations throughout the design and production process, ensuring the greatest efficiency without sacrificing quality.
“It’s imperative that we maintain the safety and security of our nation, and that’s more than just military strength – it’s the industrial base that backs it up,” affirms Rick Cordaro, Vice President of Radar and Sensor Systems.
Premium open steel trailer manufacturer, Diamond C Trailers, builds highperformance equipment, including dump, auto, utility, and gooseneck trailers engineered to deliver lasting value.
From loading brush and dirt to hauling heavy machinery and equipment, there’s a Diamond C trailer for every customer.
“We don’t just build trailers – we build solutions that solve real problems for people who depend on their equipment day in, day out,” prides Jacob Crabb, Chief Customer Officer.
There’s plenty more to process in this issue, including corporate stories from Chart Industries, KNAPP, and Pinellas Suncoast Transit Authority, among others.
We hope that you enjoy your read.
Jack Salter Head of Editorial, Outlook Publishing
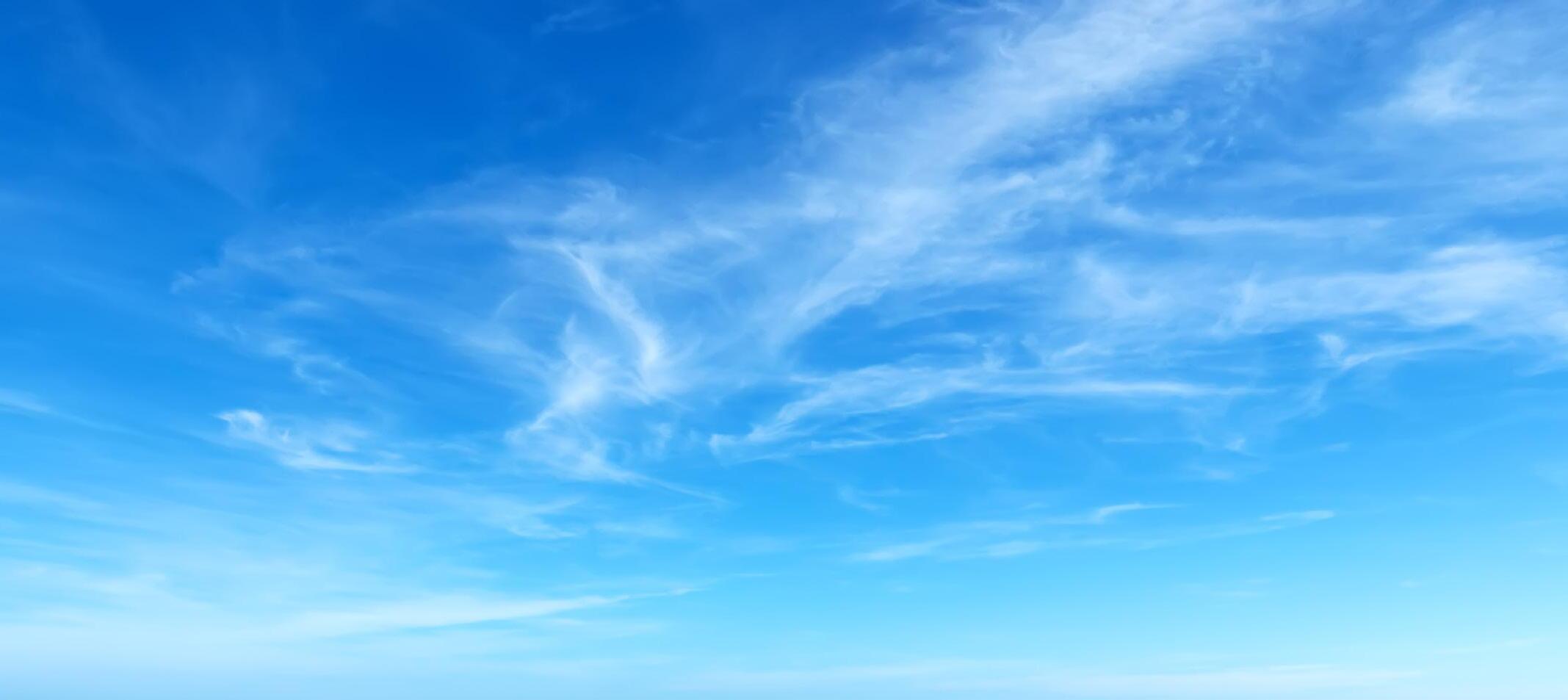
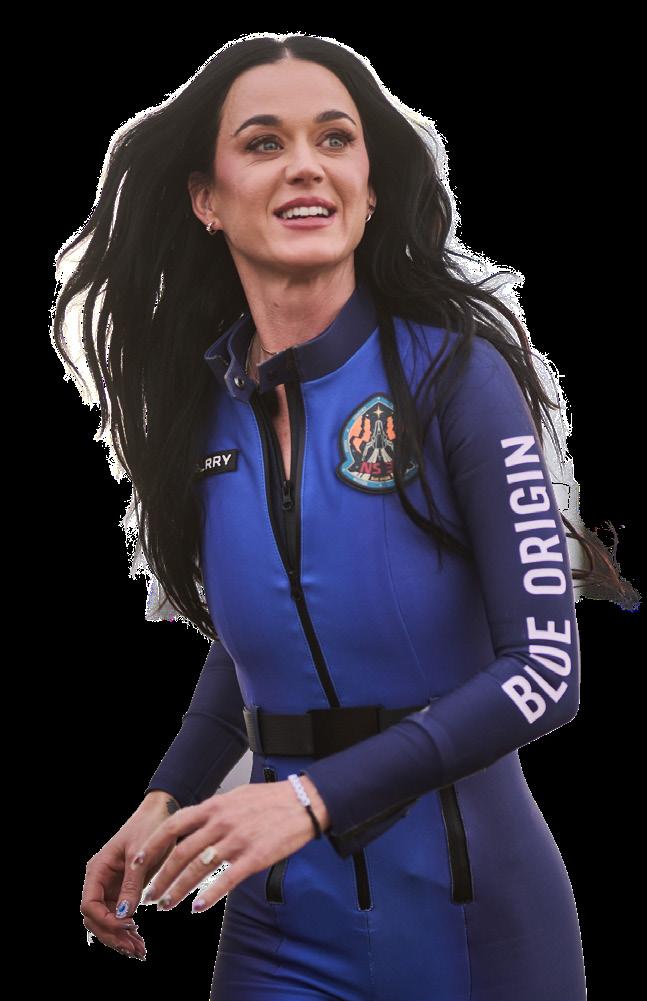
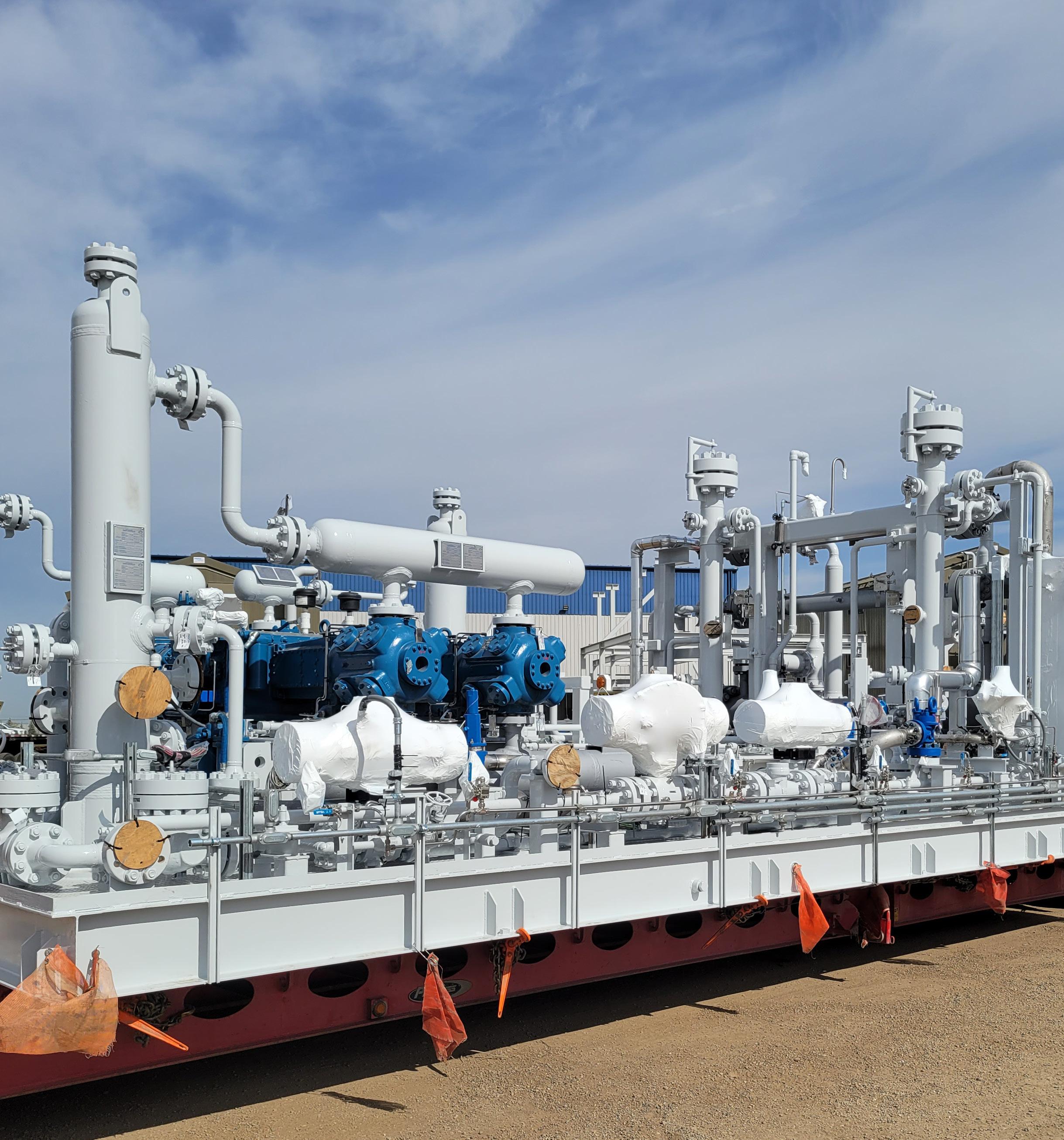
FEATURES
OIL & GAS
44 Propak Systems Ltd.
Canada’s Go-To Energy Processing Integrator
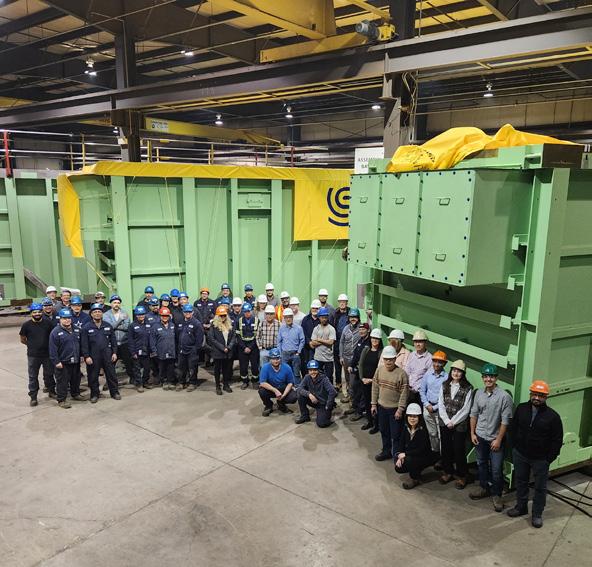
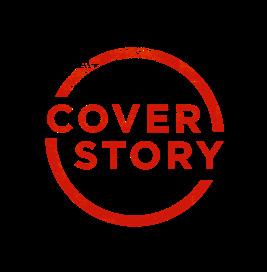
156 Pinellas Suncoast
Transit Authority
Connecting Pinellas County
Trusted public transport in the Sunshine State
164 GPA Logistics Group
Specialists in Consumer Goods
Logistics
Utilizing advanced technology
Turnkey energy processing solutions MINING
172 Arcadia Cold
The New Age of Cold Chain
High-quality, consumer-centric cold chain solutions
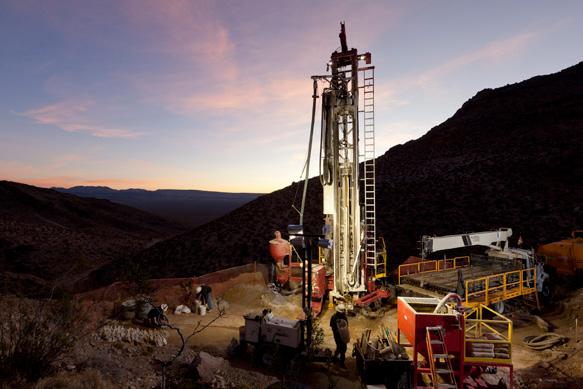
192 National EWP
Vanguards of Drilling
At the forefront of the Western US drilling sector
64 Endurance Lift Solutions
Run Longer, Produce More State-of-the-art artificial lift solutions
MANUFACTURING
72 Chart Industries
Cooler By Design
Charting a bright future
116 Lockheed Martin
Building the Next-Generation Missile Defense Shield
Deterrence begins with detection
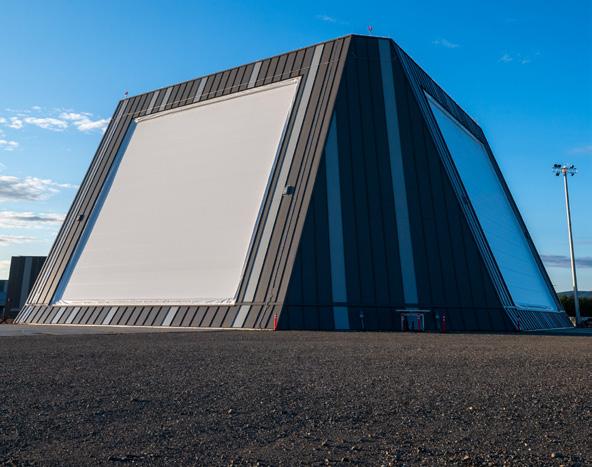
132 Diamond C Trailers
The Jewel of Premium Trailers
Fueling growth and success since 1985 SUPPLY CHAIN
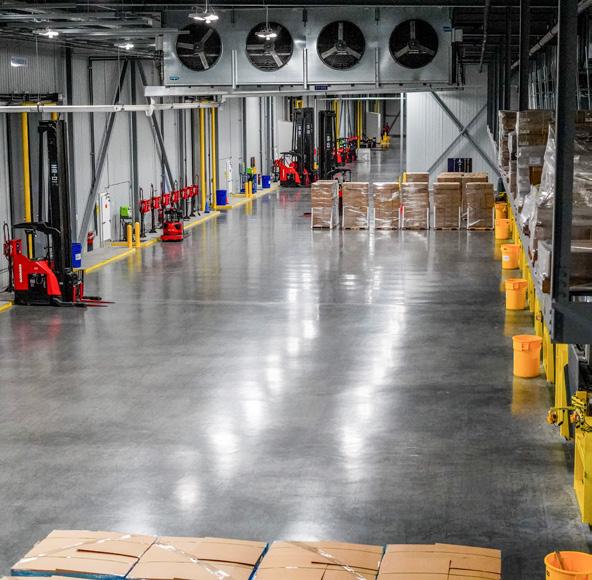
178 Radial
Fulfilling Promises from Click to Delivery
Scalable fulfillment for modern brands
184 Rio Metro Regional Transit District
Triumph on the Tracks
Rural and intercity public transportation
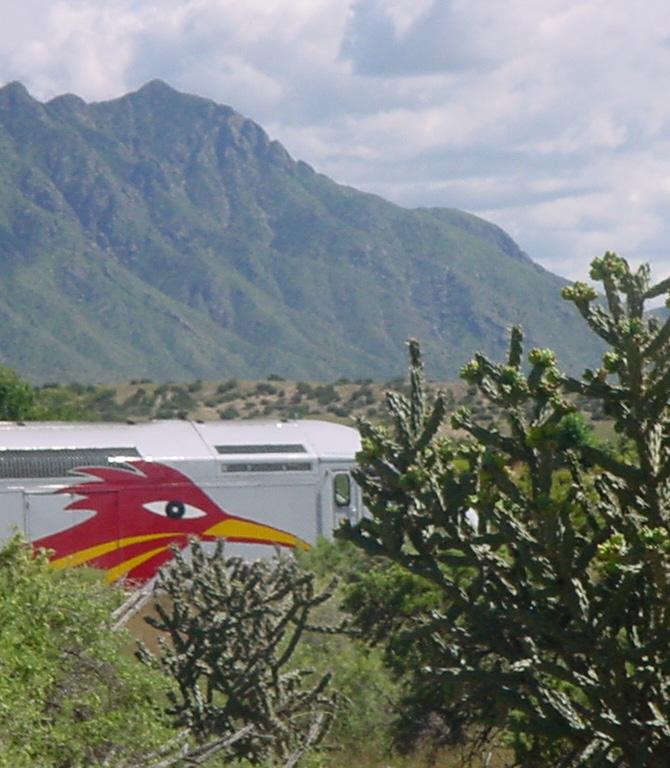
200 BM Group of Companies
Built on Synergies
British Columbia’s most diverse and versatile construction family
208 Kelso-Burnett
Illustriously Illuminating Illinois Radiating tradition and success
214 American Structural Concrete
Building the Future Together
Bringing construction visions to life
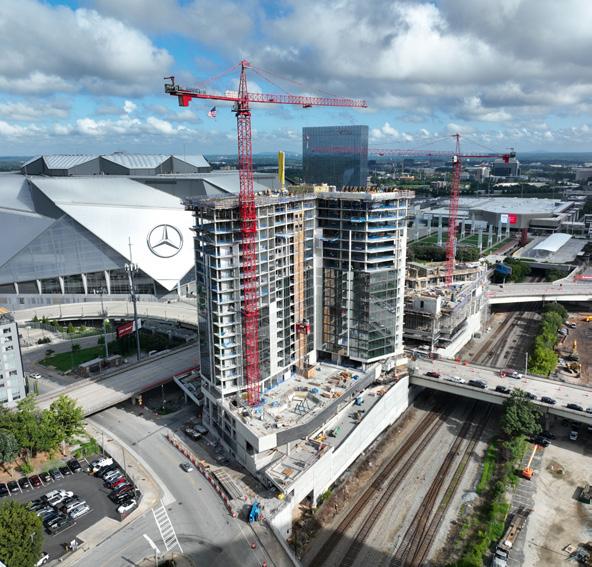
222 Uprite Construction
A Partnership Built on Trust
Delivering exceptional construction results nationwide
& BEVERAGE 232 Columbia Grain International
Harvesting Quality
Connecting local farmers to global markets
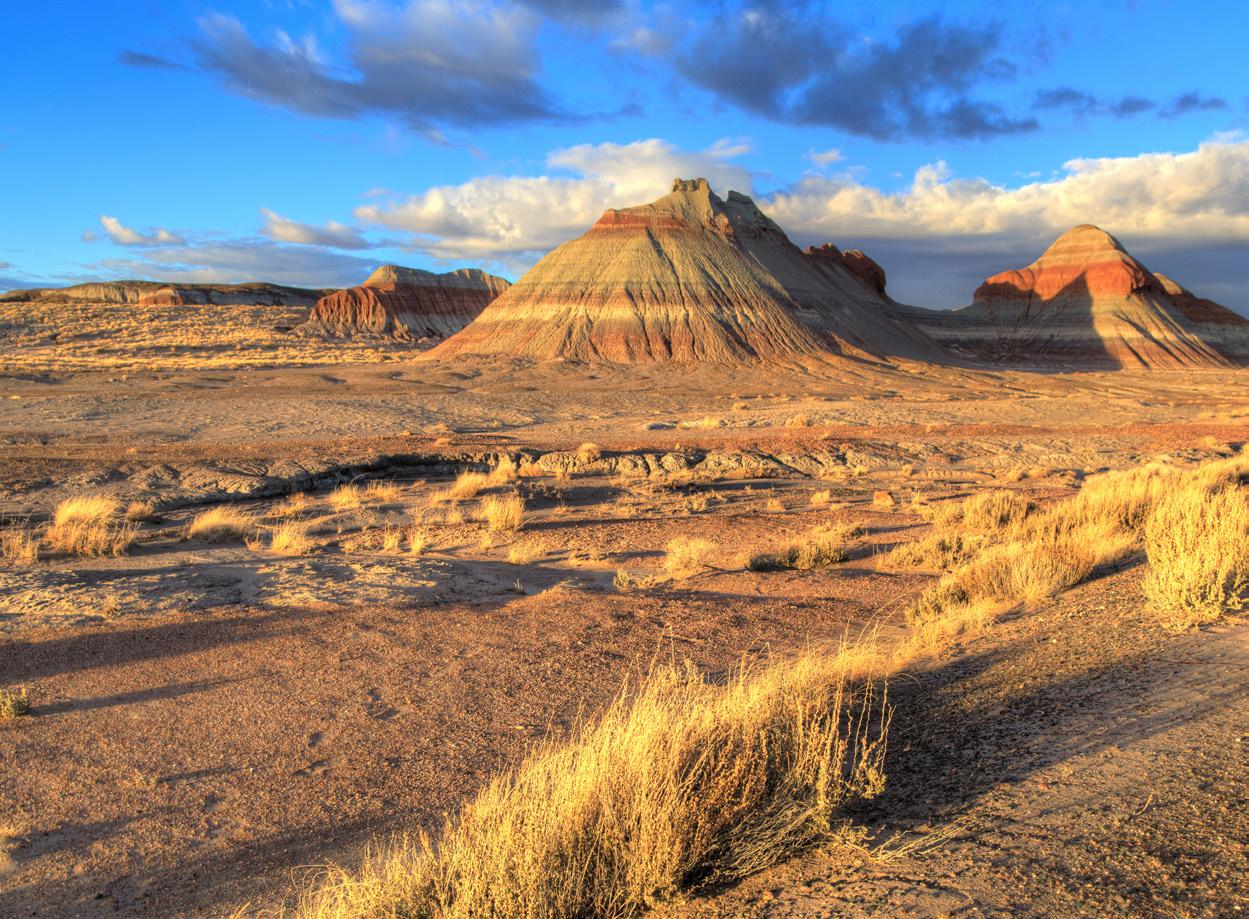
NEW DINOSAURS ROARING BACK TO LIFE
RECENTLY UNEARTHED
IN Petrified Forest National Park, Arizona, scientists have discovered over 200 million-year-old fossils from previously unknown species, including the likes of pterosaurs, primitive frogs, one of the earliestknown turtles, and lizard-like reptiles.
The national park is a well-known hotspot for plant and animal fossils,
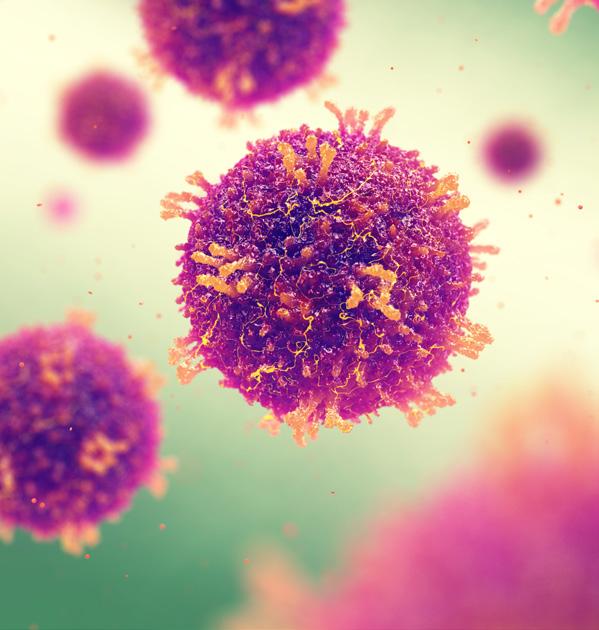
in addition to tree trunks dating all the way back to the Triassic Period. Discovered encased in rock rich with volcanic ash, these fossils provide a unique snapshot of a once-thriving tropical ecosystem, interlaid with rivers and complex lifeforms. The discovery is credited to former Smithsonian fossil preparator, Suzanne McIntire.
MEASLES WEASELS ITS WAY BACK INTO THE US
AS ANTI-VACCINE SENTIMENT in the US and abroad grows, the number of reported measles cases in the country has reached a 33-year high, with approximately 1,300 confirmed infections as of July this year.
AUTOMOTIVE
JAGUAR LAND ROVER SALES HIT BRAKES
JAGUAR LAND ROVER saw its sales decline sharply over the past three months due to a temporary pause on its exports to the US.
The break was in response to US President Donald Trump’s administration introducing new tariffs, which consisted of a 25 percent tax on car imports, in an effort to encourage production within the country.
This is in addition to the planned wind-down of the distribution of older Jaguar models, with quarterly retail sales decreasing by 15.1 percent from May to June, and wholesale sales dropping by 10.7 percent compared to the previous year.
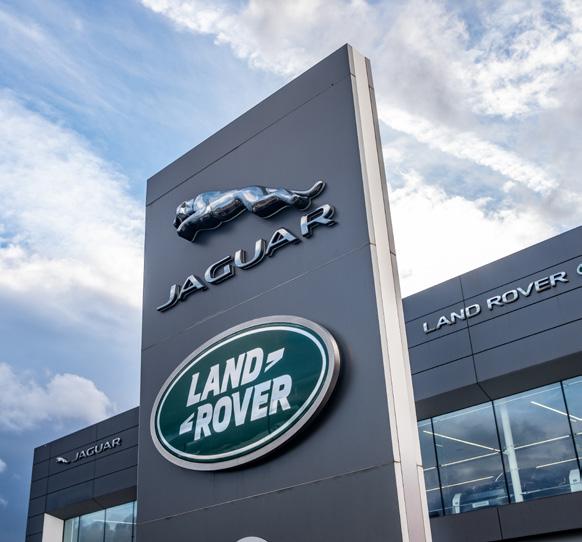
The information, released by Johns Hopkins University and the Centers for Disease Control (CDC), shows 92 percent of cases occurred in those who were unvaccinated or whose vaccination status was unknown.
The highly contagious yet preventable disease was once thought to have been eliminated in the US. However, states such as Texas, Kansas, and New Mexico have confirmed increasing cases, with the number of those infected continuing to rise.
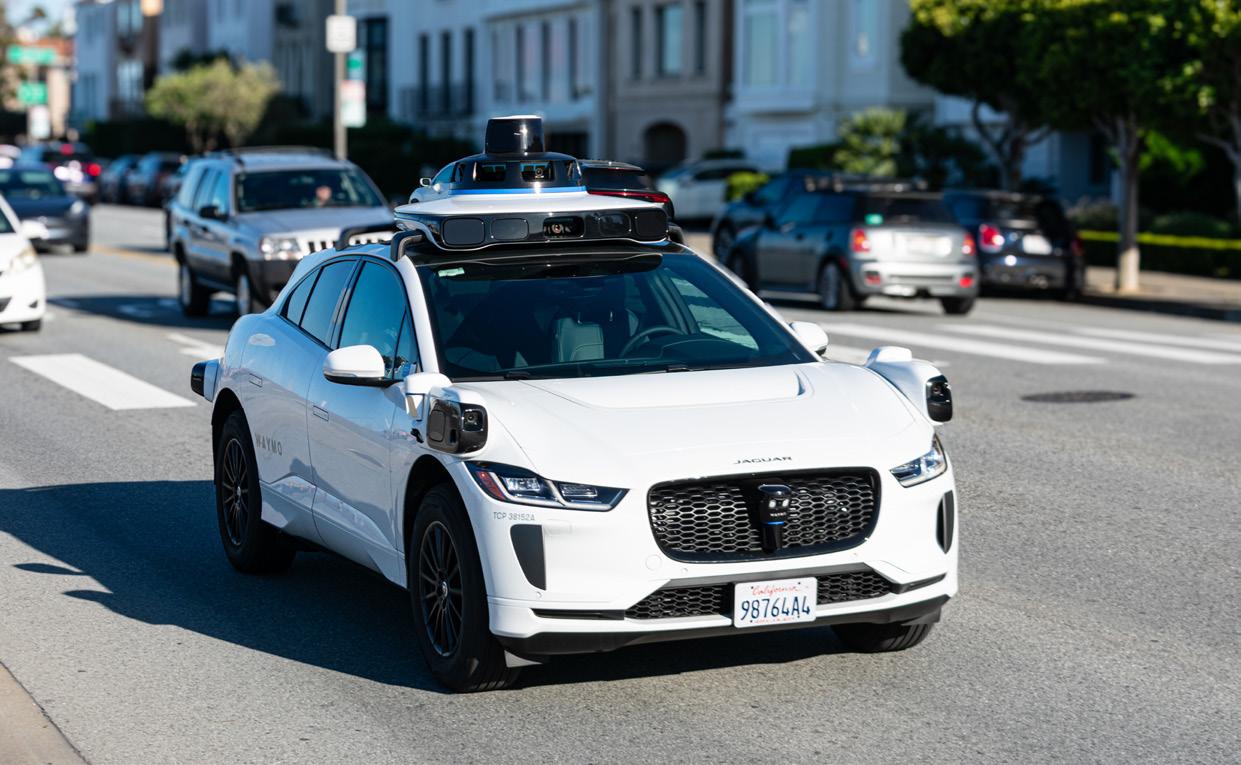
SERVICE TO CATER TO TEENS
WAYMO, THE WORLD’S first autonomous ride-hailing service, has announced it is offering teenagers between the ages of 14 and 17 the opportunity to create accounts and order their own rides.
With the first rollout to begin in Phoenix, Arizona, the company is providing specially trained rider
DEVASTATING
TRAGIC FLASH FLOODS that occurred in Texas over the Fourth of July weekend, which consisted of several months’ worth of rainfall over the course of only a few hours, resulted in heartbreaking consequences.
The incident has placed renewed focus on the US government’s ability to warn and protect its citizens from weather catastrophes.
Since February, mass staff cuts have occurred at two key
support agents who will communicate with parents if need be. Teenage riders are also able to share their trip status with parents for real-time updates, alongside all journey receipts.
This customer expansion allows Waymo to increase its ridership as it seeks to enter new market territories, such as New York City.
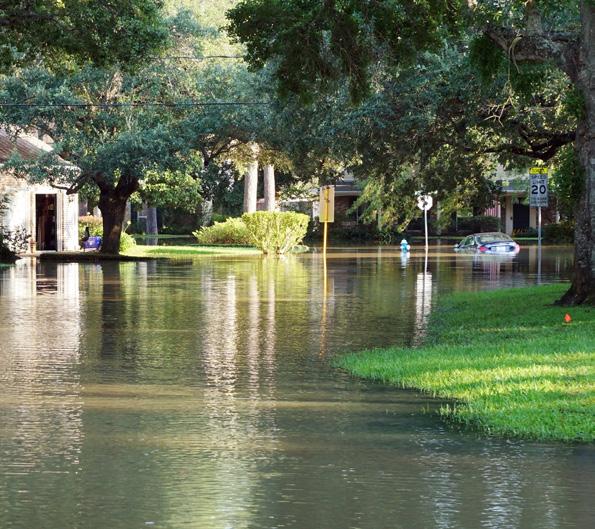
weather and climate agencies – the National Oceanic and Atmospheric Administration (NOAA) and the National Weather Service (NWS).
Many experts worry that calamitous incidents and an inability to sufficiently prepare residents will only grow if the NOAA and NWS are not properly staffed and funded.
MANUFACTURING
TARIFFS ON COPPER TO SKYROCKET
IT HAS BEEN announced that copper entering the US will face a new tax of 50 percent – a decision in line with President Trump’s declaration of tariff threats in early 2025.
Copper prices across the nation rose to a record high after news of the import tax, as the US imported approximately 810,000 metric tons of the refined metal last year. It is used as a key component in military equipment, electric vehicles (EVs), and the construction sector.
The anticipated tariff would match a recently imposed levy on steel and aluminium, yet is still significantly higher than many expected.
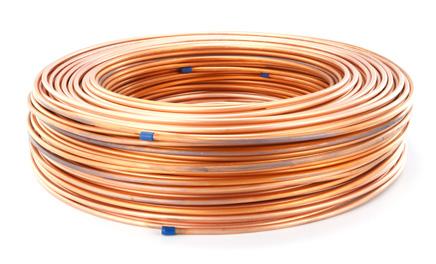
MARCO FRAUD-IO – AI IMPERSONATES US POLITICIAN TECHNOLOGY
HAVING USED ARTIFICIAL intelligence (AI) to mimic the voice of US Secretary of State Marco Rubio, an unknown imposter was able to pose as the politician, leaving voicemails for three foreign ministers, a US governor, and a member of Congress.
The US Department of State has confirmed it is aware of the incident and is currently investigating the individual who committed the offences while taking steps to improve its cybersecurity to prevent future incidents.
The identity of the impersonator has not yet been revealed, but the US authorities believe their goal was to gain access to sensitive information.
DOUX COMMERCE
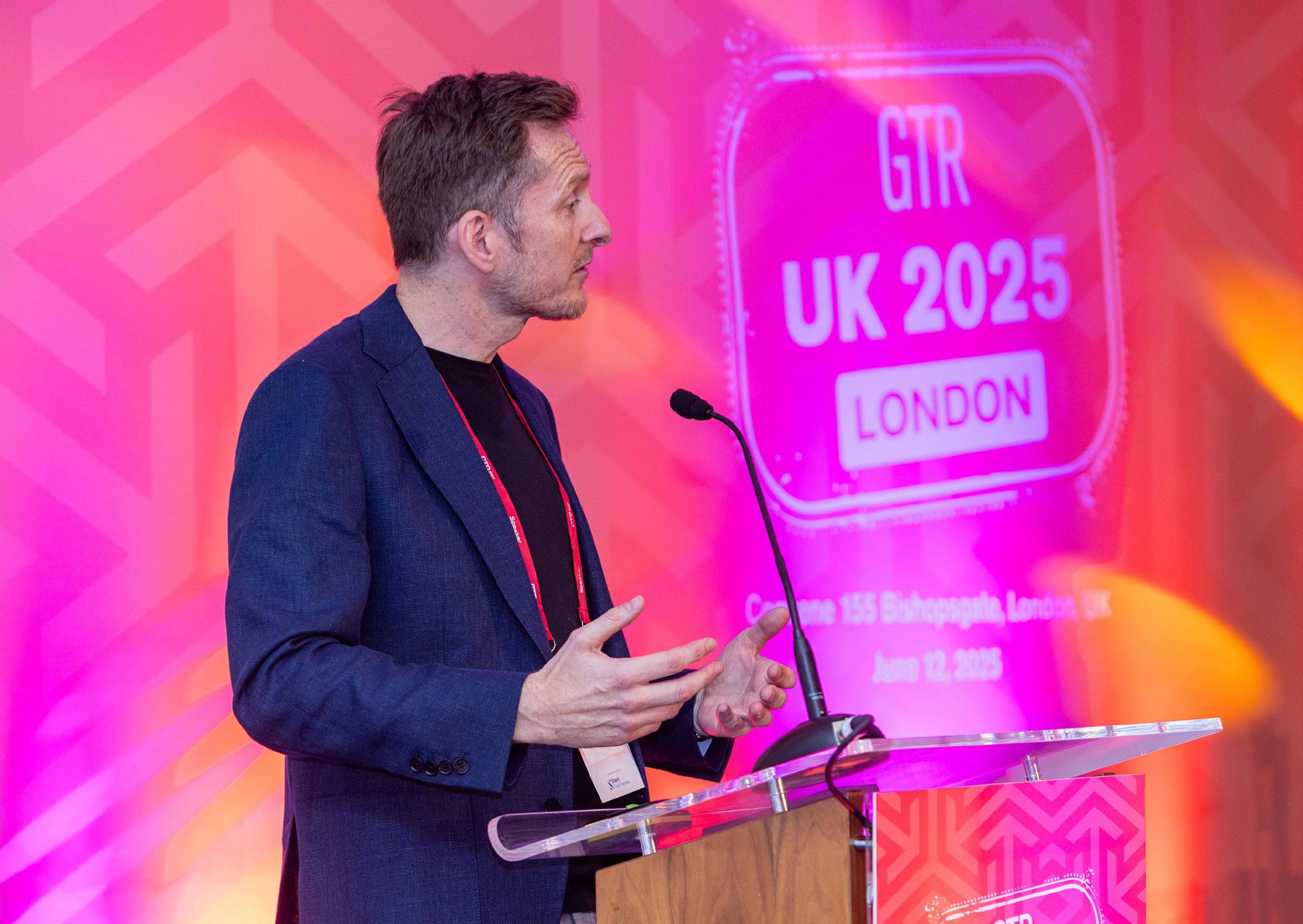
Matthew Ware, CEO of e-commerce trade and cross-border logistics company, Mark 3 International, discusses best practices for shipping products into and out of North America in the context of navigating emerging tariffs
Written by: Matthew Ware, CEO, Mark 3 International
The idea that mutual benefits arising from trade encourage peaceful relations between nations is often attributed to 18th-century Enlightenment thinkers from both sides of the Channel.
But nearly 2,000 years ago, Plutarch wrote that sea trade allowed states to “redress defects” in their relationships through mutual exchange.
‘Doux commerce’ – meaning sweet or gentle commerce – encapsulates this idea and posits further benefits that include fostering trust, integrity, tolerance, and fairness.
It’s a lot with which to burden a theory and, under its modern guise as globalization, there are detractors which point out how it can create increased inequality and exploitation. However, globalization is not new. From the ancient silk roads through to the industrial revolution, trade has expanded by creating shorter, faster routes and ever-better technologies by which to transport goods.
Today, shipping products around the world has never been more competitive which, for businesses that rely on it, means better service, lower costs, and more options.
Powered by a plethora of inventions, innovations, and ideas, today’s global trading ecosystem is vast, complex, and highly competitive.
Yet, it is driven by seeking to meet a single, simple need – someone, somewhere, wants to buy something from someone else, somewhere else.
Making that happen quickly, costeffectively, and securely is what drives the global ecosystem and is behind the explosive growth in e-commerce and supply chains underpinning virtually all the world’s manufacturing operations today.
So, when trade is disrupted through man-made interventions such as war or tariff manipulation, there are serious consequences.
For example, the US accounted for 13 percent of the UK’s total exports in April 2025, down from 21 percent the previous month.
Further to this, exports to the US fell by a staggering 47 percent compared
to March 2025 according to UK government figures.
The Office for National Statistics suggested this was likely linked to the implementation of tariffs on goods imported to the US.
Perhaps not a hugely surprising conclusion, but clearly one of major importance.
WHERE THERE’S A WILL
Companies can mitigate the impact of tariffs in several ways – perhaps the most obvious of which is simply to source products and components from other unaffected countries.
A more radical move would be to shift production to countries where the tariffs don’t apply.
For example, Apple is currently shifting some of its manufacturing from China to India and Vietnam.
Let’s just think about that for a moment. For an earlier generation, peaceful relations between the US and Vietnam seemed impossible – yet today the two countries are deeply involved in mutually beneficial commerce.
As much as these options are superficially attractive, they come with significant challenges, not least cost and delay.
Alternatively, companies can adjust their prices – seeking to recover profits from their customers. Again, a difficult choice as demand could easily fall.
Several other options, including entering into cost-sharing agreements with suppliers either temporarily or via discounts, could alleviate some of the pressure.
Other possibilities include the use of Free Trade Zones, whereby goods can be imported into the US but kept in bonded warehouses where no tariffs are due as long as they remain there.
For e-commerce traders, there are opportunities to structure shipments so they fall within the destination country’s tariff thresholds, including
the ‘de minimis’ threshold.
This can streamline logistics and improve delivery times, critical considerations for the global e-commerce trader.
A practical approach is to work with a logistics company that understands all these options so it can advise on the best way to cope.
They will typically have the ability to choose optimal routes that minimize costs and delivery times, made possible by having strong relationships with major carriers and local delivery partners.
Working with such a partner can also help with onerous paperwork associated with international shipments.
MAXIMISING DE MINIMIS
The UK is the third-largest e-commerce market in the world after China and the US according to the US government’s International Trade Administration.
De minimis thresholds are set by each country and imported goods below those values do not attract tax or duties, working to support global e-commerce that typically consists of small, relatively low-value packages.
In the US, de minimis is set at $800, whilst in the EU, de minimis is set at €150, and in the UK it is £135.
A report from Reuters notes that the number of de minimis packages entering the US approached 1.4 billion in 2024, largely due to the growth of online shopping.
This would soon overrun customs operations and major parcel carriers, if they were to process taxes and duties on each individual package.
The report adds that more than 90 percent of all packages coming into the US now enter via de minimis.
As such, it is clear to see how entirely removing de minimis exemptions could cripple e-commerce shipments across the world – but perhaps there is a case for lowering the threshold.
RECIPROCAL TRADE REALATIONS
Evidently, peace is necessary for trade to be conducted freely.
But the relationship is reciprocal – trade can be the foundation for peaceful relations, while commerce breeds trust.
The impacts of man-made disruptions to trade can be mitigated in a number of ways, but perhaps the best approach is to seek expert help.
Ultimately, if asked what to do when faced with challenges to the global trading order, the answer is – doux commerce.
ABOUT THE EXPERT
Matthew Ware was CEO of air shipment company, CFL, from 2017 until April 2025, before joining Mark 3 International (Mark 3) as CEO.
Founded in 1990, Mark 3 is a privately-owned company that specializes in e-commerce trade between the US and Europe and is an expert in cross-border logistics and e-commerce parcel management.
Ware is also the Chairman of Aviation Services UK – the trade body for the ground handling industry – and a member of the executive committee at AICES, the UK trade body for international express services.
Prior to his time at CFL, Ware held various senior roles over 16 years with FedEx.
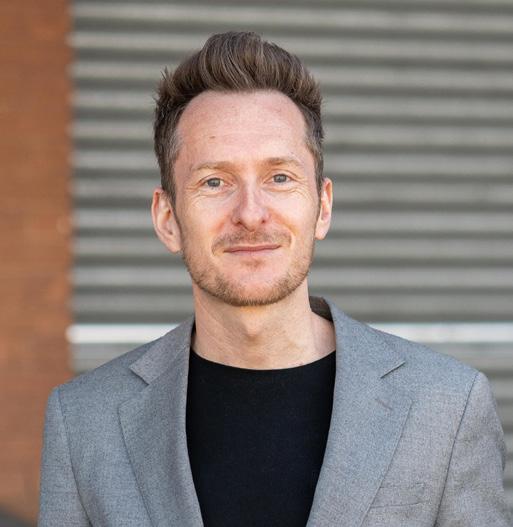
THE HEART OF NORTH AMERICA’S ELECTRICAL SUPPLY
Delivering on the region’s electrical supply and demand, the Midwest Reliability Organization expertly maintains the reliability, security, and resilience of the North American bulk power system. Sara Patrick, President and CEO, highlights how it navigates regulatory and industry challenges
Writer: Lucy Pilgrim
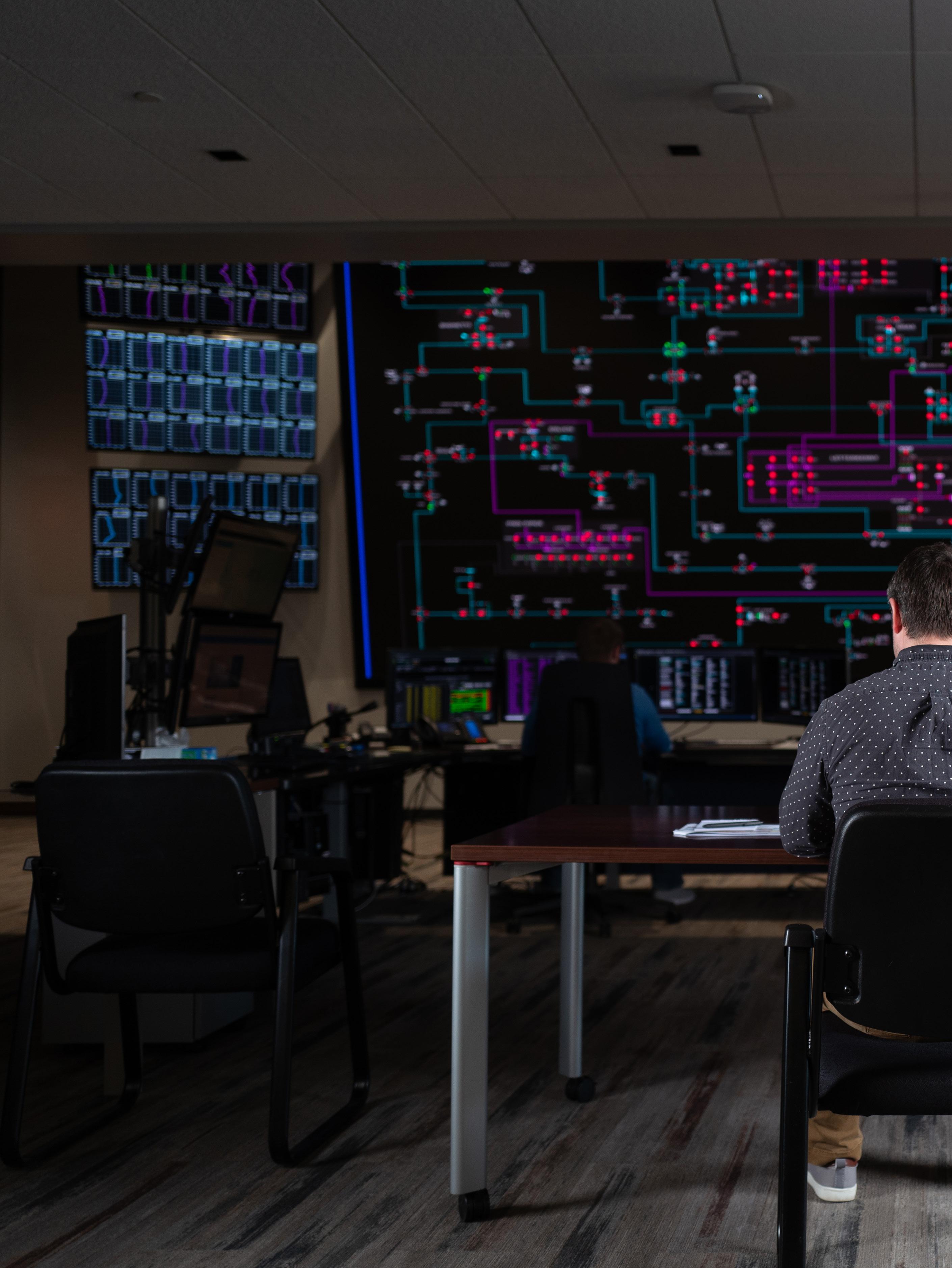
North America Outlook (NA): Firstly, could you introduce us to the bulk power system and explain how it works?
Sara Patrick, President and CEO (SP): The bulk power system is a network of power plants and high-voltage power lines that work together to produce and move electricity over long distances.
It is an incredibly complex and interconnected network of systems, where power grid operators are challenged to maintain a perfect balance between electricity generation (supply) and consumption (demand).
The system must maintain a steady frequency of 60 hertz in North
America. If the system significantly deviates from this level, the power grid is at risk of collapse.
A simple analogy of this is a playground seesaw. Imagine you are on one side, and I am on the other – it would take constant effort on both our parts to keep the seesaw perfectly level. If either one of us hits the ground, the fun would be over.
NA: What is your take on bulk power system use in the region at the moment?
SP: Like many other areas around the world, the electricity industry in North America is seeing significant changes in both supply and demand. These changes come on the heels of relatively flat
growth for more than four decades.
The bulk power system was built with traditional power plants – which use readily available fuel like coal, nuclear, and natural gas – in mind.
The energy stored in the large, spinning masses of these machines can accommodate fluctuations in generation and demand, such as a sudden outage or spike in electricity use. These units have the capacity to temporarily speed up or slow down, adjusting to grid conditions in real time.
Renewable energy sources, meanwhile, including wind and solar, have little to no spinning mass or readily available fuel supply. Therefore, their introduction makes the grid more dynamic.
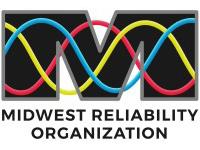
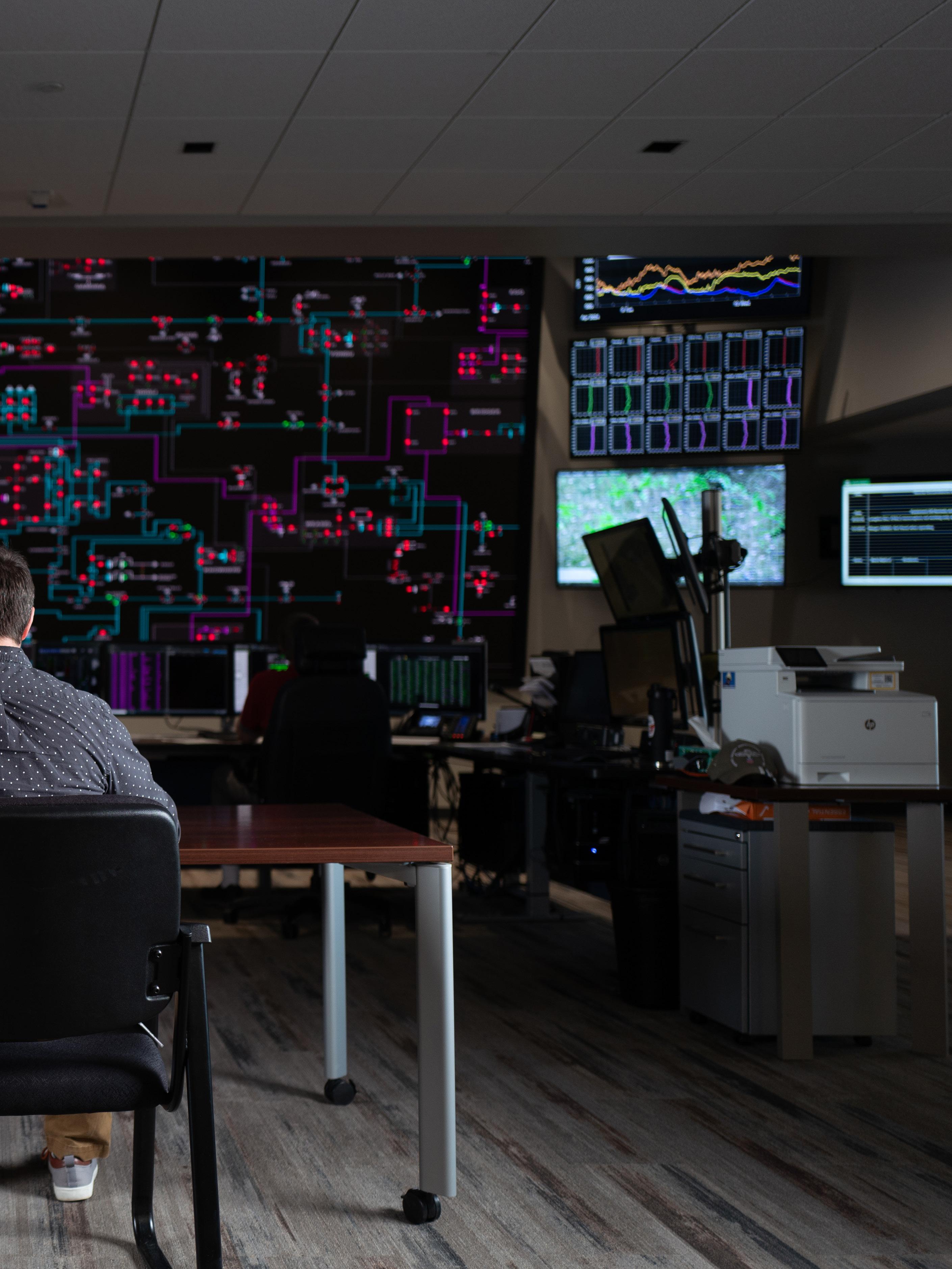
This is why, as the industry transitions to lower carbon energy sources, new technologies like advanced control systems and battery storage, along with demandside management programs that promote electricity conservation and encourage electricity use when it is most abundant, are so important to maintaining grid stability.
At the same time, we are seeing sharp increases in electricity consumption. This is primarily due to the introduction of large data centers that power new technologies like crypto mining and artificial intelligence (AI), and the electrification of other industries aiming to reduce carbon footprints, such as manufacturing, home heating, and transportation.
Photo ©: Minnkota Power Cooperative
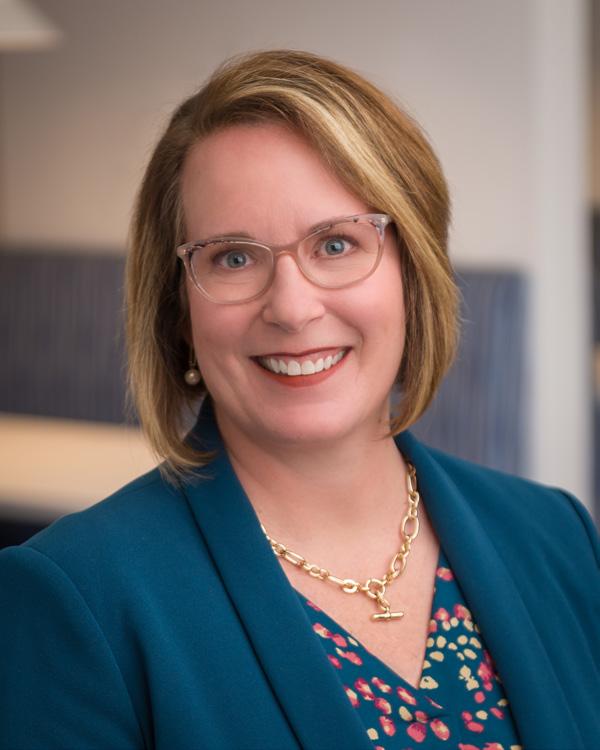
When and how we use electricity is also changing. Peak electricity hours – or periods when demand is the highest – are expected to shift due to changes in consumer behavior and the expanded use of electric vehicles (EVs) and appliances. More frequent and longer-duration severe weather systems are also impacting electricity use.
“MRO’S MISSION IS TO IDENTIFY, PRIORITIZE, AND ASSURE EFFECTIVE AND EFFICIENT MITIGATION OF RISKS TO ENSURE THE RELIABILITY AND SECURITY OF THE GRID BY PROMOTING HEROS®”
– SARA PATRICK, PRESIDENT AND CEO, MIDWEST RELIABILITY ORGANIZATION
All of this makes it much harder to balance the system and match energy generation with demand in real time, as well as predict how much supply is going to be needed in the future, which is referred to as resource adequacy.
Alongside these reliability challenges, securing the grid has become increasingly complex due to the rapid adoption of new technologies and the current geopolitical climate. As threat actors become more sophisticated and evolve their tactics, our defenses must also evolve to effectively mitigate cyber and physical security risks.
NA: Could you tell us about the history and founding principles of the Midwest Reliability Organization?
SP: The history of the Midwest Reliability Organization (MRO) is rooted in
the US government’s Energy Policy Act of 2005, which was created as a direct result of the massive Northeast Blackout of 2003.
This historic event left an estimated 55 million people across eight US states and the Canadian province of Ontario without power, some for days. The economic cost was in the billions.
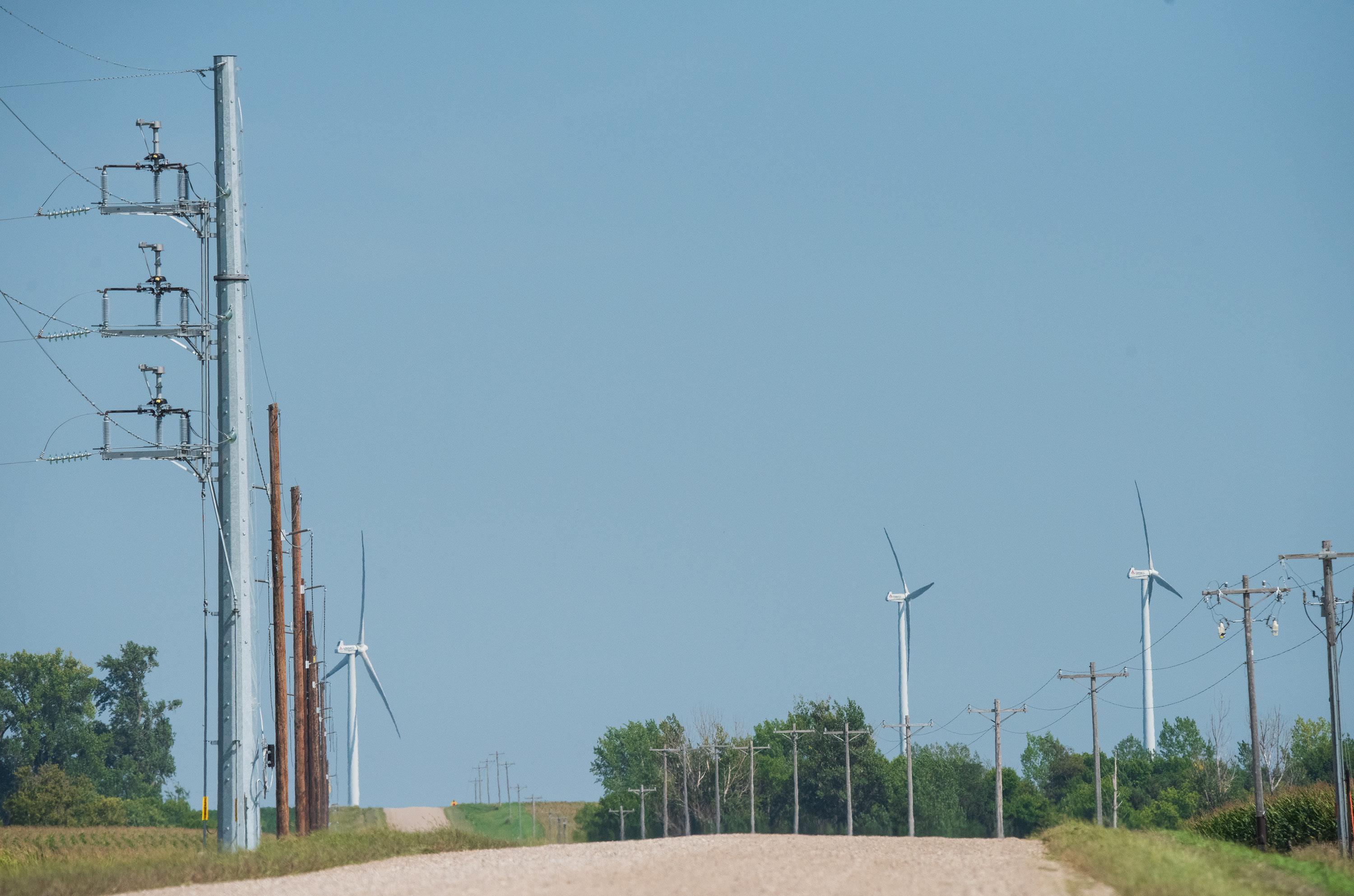
In response, Congress mandated the creation of the Electric Reliability Organization (ERO) to develop, monitor, and enforce mandatory reliability standards for those who use, own, and operate the bulk power system in the US.
ERO was named the North American Electric Reliability Corporation (NERC) by the Federal Energy Regulatory Commission (FERC) in 2006. NERC delegates its authority to six regional entities, including MRO. Together, NERC and the regional entities are known as the
Sara Patrick, President and CEO
Photo used by permission from Great River Energy.
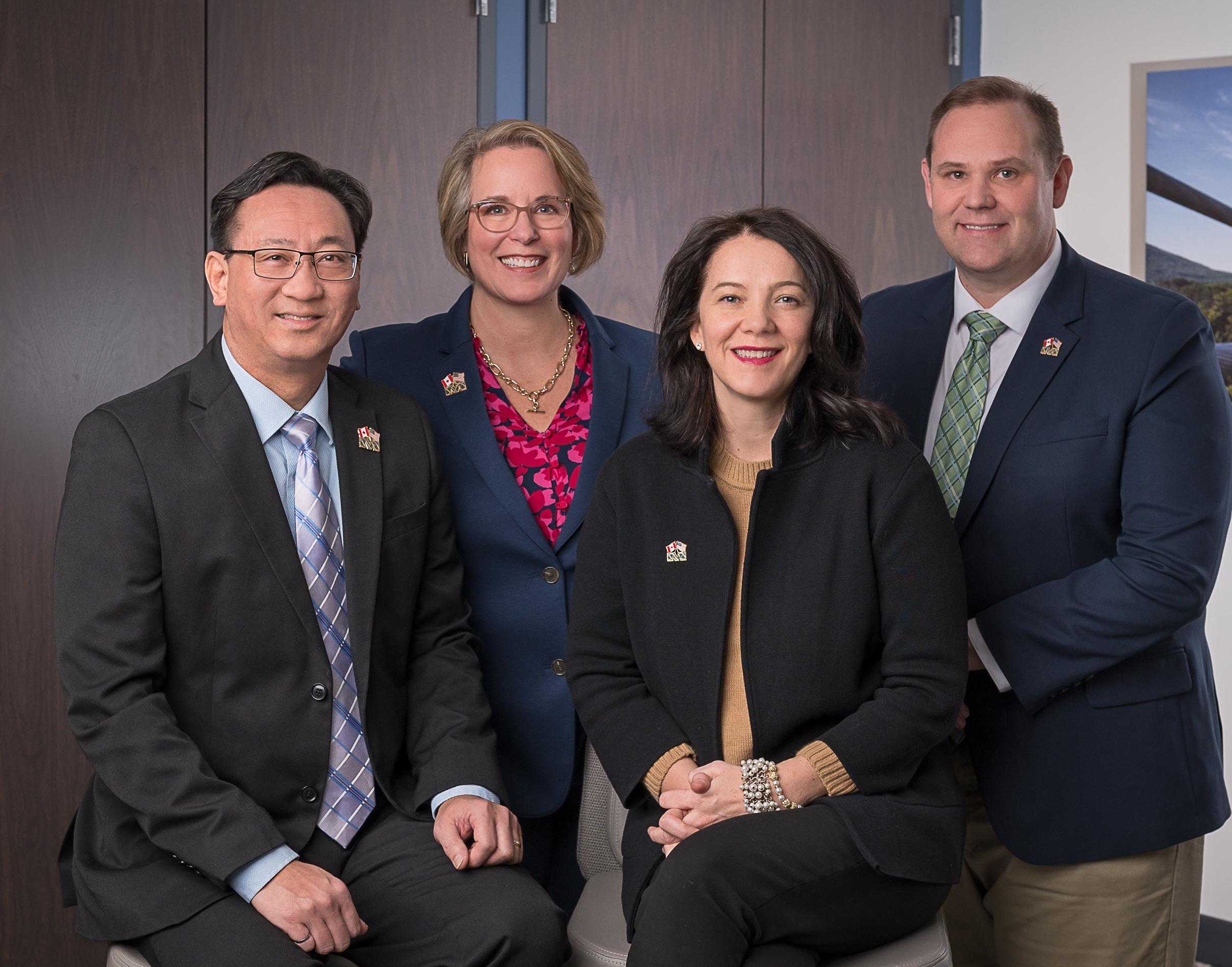
ERO Enterprise.
Due to the interconnected nature of the North American bulk power system, four of the six regional entities have oversight authority in both the US and Canada under different operating agreements with individual provinces, who are each unique and have their own governing authority.
The ERO Enterprise regulatory model is unique in that it combines mandatory standards and requirements with a collaborative structure that brings key stakeholders together to assess and mitigate risk. We share an important vision with the industry of a highly reliable and secure North American bulk power system.
MRO’s mission is to identify, prioritize, and assure effective and efficient mitigation of risks to ensure the reliability and security of the grid by promoting Highly Effective
NA: What about MRO’s primary responsibilities and geographical reach?
SP: MRO’s regional territory spans the Canadian provinces of Saskatchewan and Manitoba through to all or parts of 16 US states, all the way down to Texas.
The region includes approximately 245 organizations that participate in the production and delivery of electric power, including Canadian utilities, cooperative and municipal utilities, investor-owned utilities, federal power marketing agencies, generator power marketers, and transmission system operators.
Our primary responsibilities within our geographic territory are to:
• Register and certify entities that are users, owners, and operators of the bulk power system.
• Monitor and enforce compliance
with mandatory reliability standards by these registered entities.
• Conduct assessments of the grid’s performance and ability to meet electric power demand.
• Analyze system disturbances to determine root causes and share lessons learned with industry players.
• Identify, assess, and help reduce bulk power system risk.
Additionally, we provide an open forum for the region’s stakeholder experts to discuss important topics related to improving reliable and secure operations of the power grid. MRO therefore serves as a vital link between grid owners, users, operators, and other key stakeholders who share common reliability interests in the region.
Based in Saint Paul, Minnesota with just over 80 employees currently, one of MRO’s most unique attributes is that we lie at the intersection of three out
Reliability Organizations® (HEROs®).
MRO executive team from left to right: Lam Chung, Vice President and Engineer for Strategy, Innovation, and Finance; Sara Patrick, President and CEO; Julie Peterson, Vice President and General Counsel; and Richard Burt, Senior Vice President and COO
“EVEN THOUGH THE CHALLENGES BEFORE US ARE DAUNTING, I BELIEVE THAT BECAUSE OF THE WORK OF MRO AND OUR COUNTERPARTS ACROSS THE ERO ENTERPRISE, OUR FUTURE IS BRIGHT”
– SARA PATRICK, PRESIDENT AND CEO, MIDWEST RELIABILITY ORGANIZATION
of four North American bulk power system interconnections.
We represent the ‘man in the middle’ that brings together the policies and activities that connect the Western, Texas, and Eastern interconnections. As such, we play an important role in raising awareness of and mitigating bulk power system risks.
We are a foundational component of the reliability and security of the North American bulk power system, and we take this role very seriously.
Even though the challenges before us are daunting, I believe that because of the work of MRO and our counterparts across the ERO
Enterprise, our future is bright.
NA: In what ways does MRO help ensure the reliability and security of the bulk power system across its regional territory?
SP: While penalties for non-compliance with mandatory standards can deter certain behavior, most of our efforts focus on proactively addressing risk through data analysis, information sharing, and collaborative outreach. We dedicate significant time to working with stakeholders in the region to identify, assess, and mitigate the greatest threats to the reliable and
secure operation of the power grid.
These activities range from oneon-one discussions with individual entities and webinars and industry roundtables to larger workshops and conferences on specific risk topics.
The reliability assessments we publish help to raise awareness of current challenges facing grid operators and planners, as well as alarming trends we see through our data collection and analysis efforts.
Our premier product is a Regional Risk Assessment (RRA), which we conduct annually to identify the biggest risks to the regional power grid and develop and to prioritize mitigation strategies for the electricity industry.
This assessment is a collaborative effort between MRO staff and industry experts to evaluate continent-wide risks and determine their likelihood and potential impact on the regional grid.
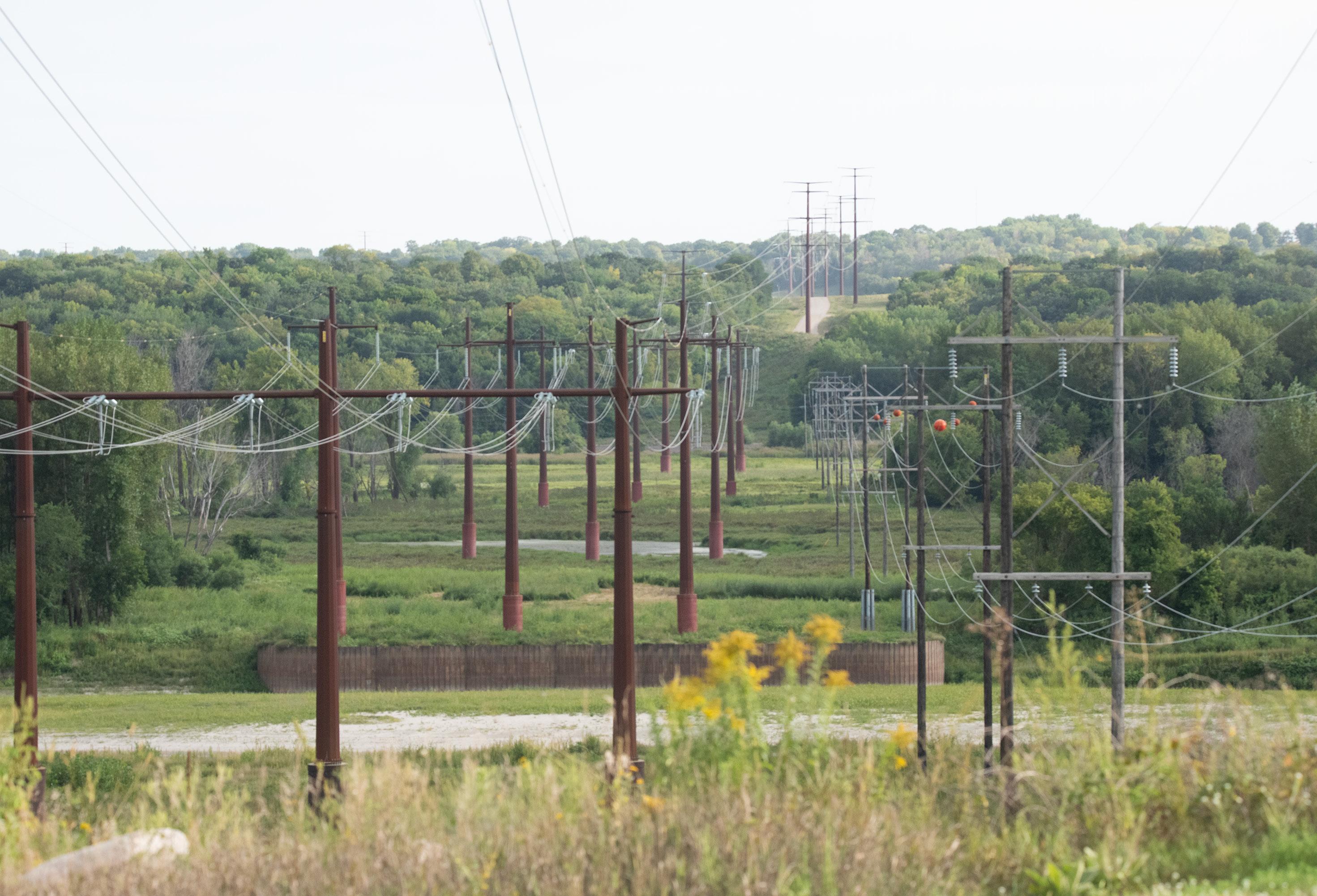
The RRA covers topics such as energy availability, extreme weather preparedness, cyber and physical security, and renewable resource
Photo
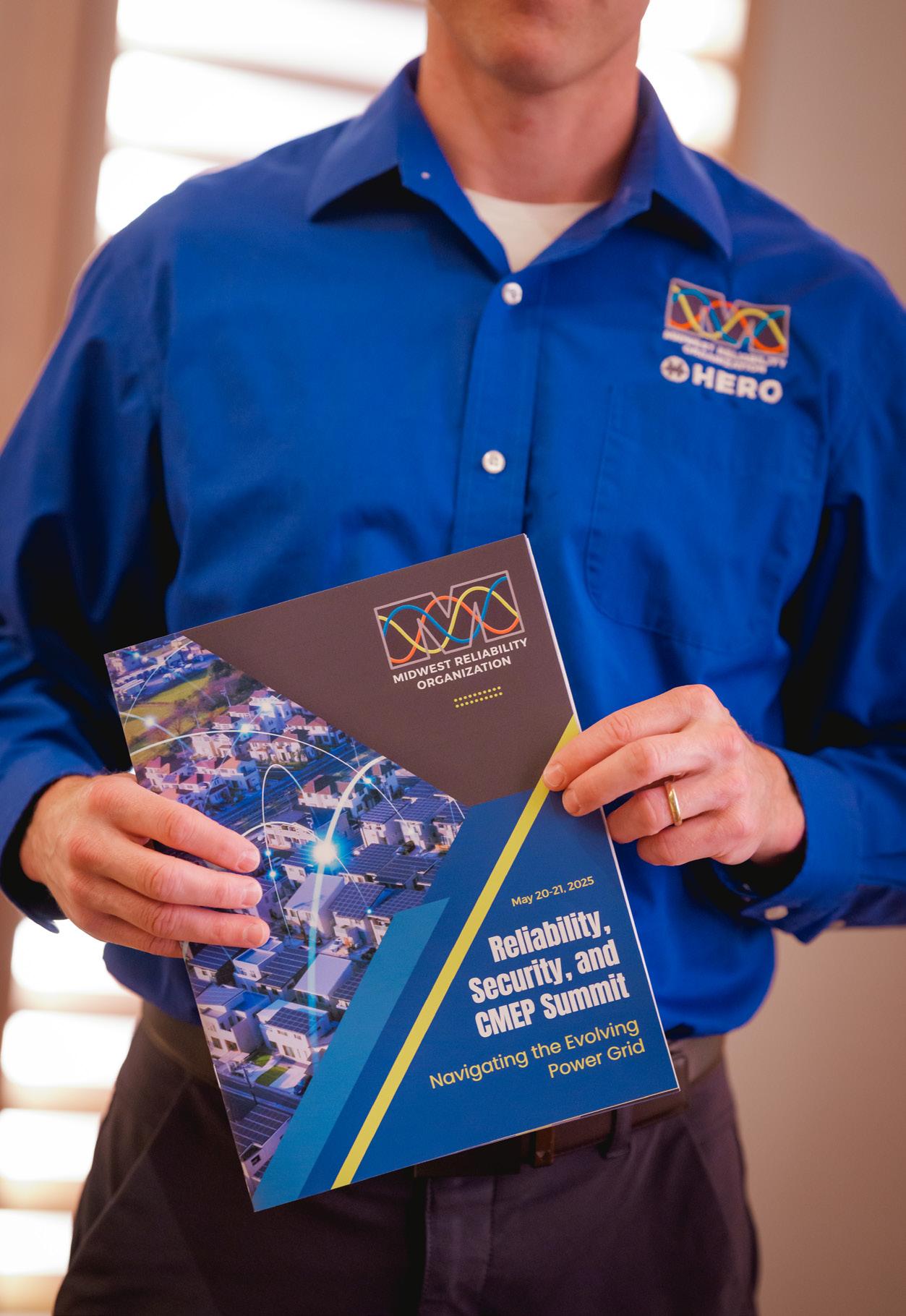
integration, among others.
MRO’s outreach initiatives are directly shaped by the RRA’s key findings, allowing us to prioritize communication around the most pressing risks identified in the report. Throughout the year, we deliver this information through a variety of channels, including numerous webinars, workshops, and news articles, all designed to keep our
stakeholders informed. As of June 1st 2025, we have successfully engaged over 2,200 individuals across North America through six webinars and two major conferences. Additionally, we have been working to strengthen relationships and increase dialogue with state, provincial, and federal regulators and policymakers.
Our goal is to inform these agencies
about the increasing demands on the bulk power system and how local energy decisions can impact the broader grid’s reliability.
These engagements also allow us to understand the unique energy challenges facing individual states and provinces.
NA: How does each of MRO’s organizational groups help identify risks to the security of the bulk power system?
SP: The work MRO undertakes to address risk leverages the experience and knowledge of industry experts who serve in our organizational groups.
These experts contribute their insights and technical skills to help identify current and emerging risks, develop mitigation strategies, address planning and resource adequacy issues, focus on critical cyber and physical security threats, and share information and best practices with industry participants across the region.
MRO has three advisory councils – the Compliance Monitoring and Enforcement Program Advisory Council (CMEPAC), the Reliability Advisory Council (RAC), and the Security Advisory Council (SAC), who each have subgroups reporting to it.
Collectively, the councils and their subgroups are focused on helping industry stakeholders in the region become aware of and reduce the risks in their individual systems, thereby improving the entire network.
CMEPAC and its subgroup, the NERC Standards Review Forum (NSRF), focus on communicating compliance monitoring and enforcement topics, as well as the development, application, and retirement of NERC reliability standards.
RAC and its subgroup, the Protective Relay Subgroup, focus on addressing operational challenges
2025 Reliability, Security, and CMEP Summit: Navigating the Evolving Power Grid
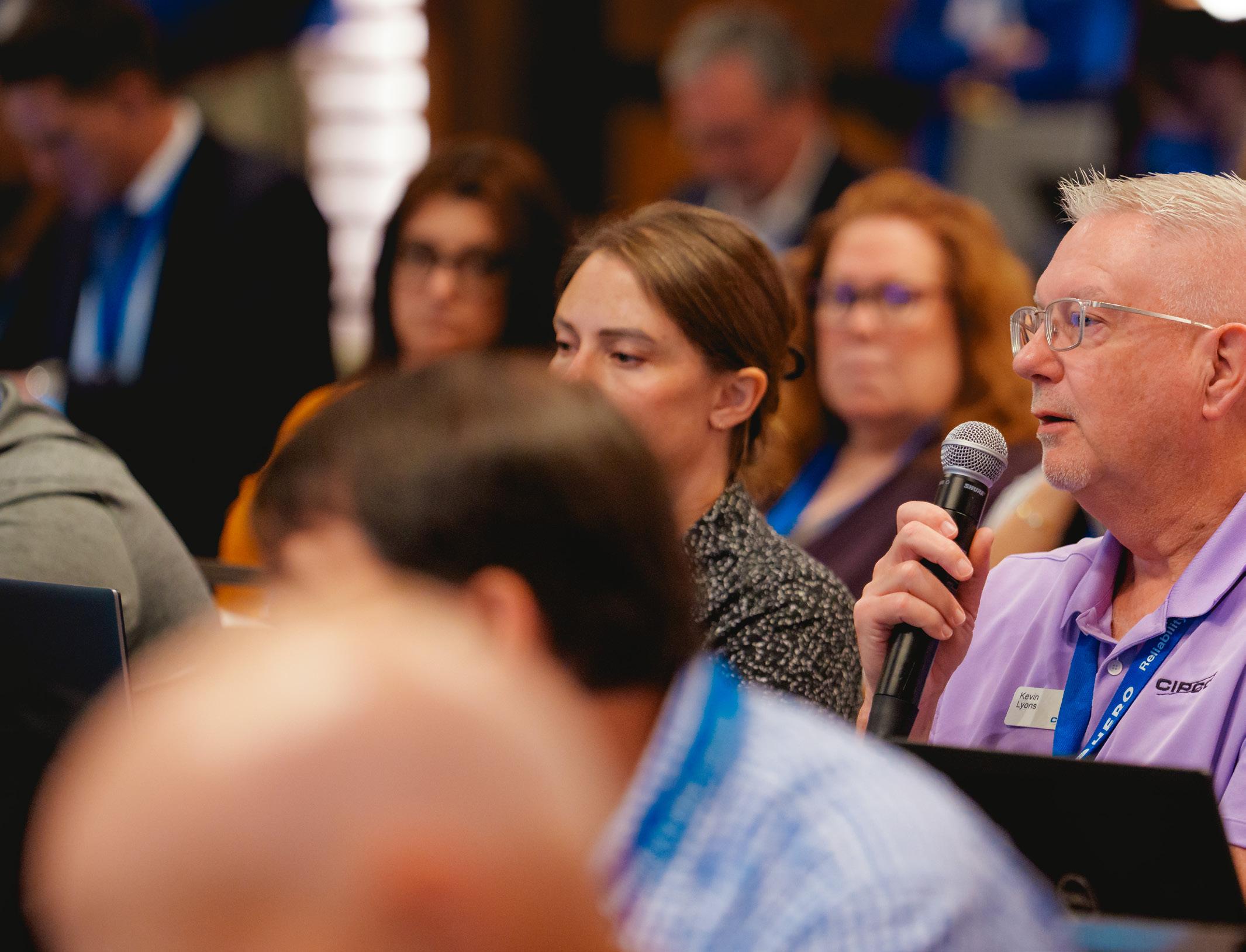
related to transmission adequacy and availability, resource adequacy, the integration of renewables, and essential reliability services. These groups also assist with reviewing power system events, reliability assessments, and related outreach.
SAC and its subgroup, the SAC Threat Forum, focus on raising awareness of emerging security threats and vulnerabilities to power grid operations, specifically sharing information related to cyber, physical, and operational security – including substation and generation control systems.
Collectively, these advisory councils contribute to much of MRO’s outreach and engagement efforts. For example, MRO held a Reliability, Security, and CMEPAC Summit between May 20th and 21st this year in Oklahoma City,
where there were plenary sessions each morning for all attendees with specific breakout tracks in the afternoon focused on information shared by each advisory council.
These councils collected information on topics of interest from MRO stakeholders before developing the content for the breakout tracks.
NA: How does MRO create a vital link between the grid’s stakeholders and an open forum of discussion for its member organizations?
SP: MRO, the ERO Enterprise, and the electricity industry sit squarely in the middle of a profound and rapid transformation toward a decarbonized future. Risks associated with this transition are interdependent, spanning multiple companies, sectors,
regions, and industries.
Extensive discussions are underway across various local, regional, national, and international stakeholder groups regarding the key drivers and associated challenges of this change. Our unique regulatory model enables us to facilitate these discussions with numerous stakeholders in the region.
For instance, the NSRF holds a weekly call to discuss new, pending, or revised reliability standards and requirements with regional constituents. Regional feedback is collected and provided to the NERC teams who draft new standards, offering a regional perspective during the continent-wide standards development process.
Another instance is the SAC Threat Forum, which convenes security experts from across the region to
2025 Reliability, Security, and CMEP Summit: Navigating the Evolving Power Grid
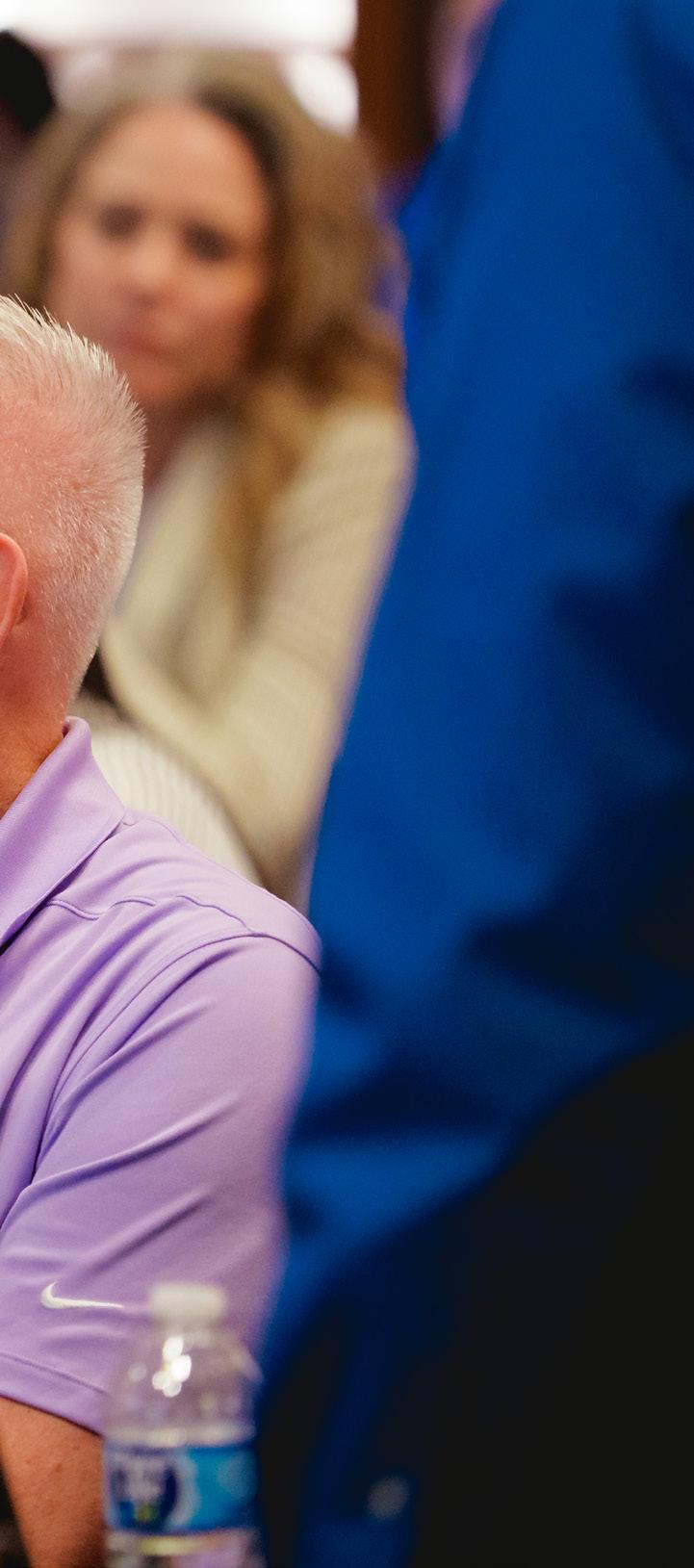
discuss new and emerging cyber and physical security threats to the grid. This activity occurs outside of MRO’s compliance program and in a closed forum to ensure the free exchange of information.
The events we host also offer an opportunity for regional stakeholders to connect and engage, sharing information and best practices to enhance the reliability, security, and resilience of the bulk power system.
There is no registration fee to attend these sessions for our members and industry stakeholders.
NA: What about your HEROs®? How do they help reduce risks to the grid?
SP: HEROs® are companies that work diligently to ensure we don’t experience uncontrolled cascading outages on the power grid, such as another 2003 blackout.
MRO uses the theory and principles of high reliability organizations (HROs) as a framework for promoting the reliable operations of the power grid in the states and provinces within our purview.
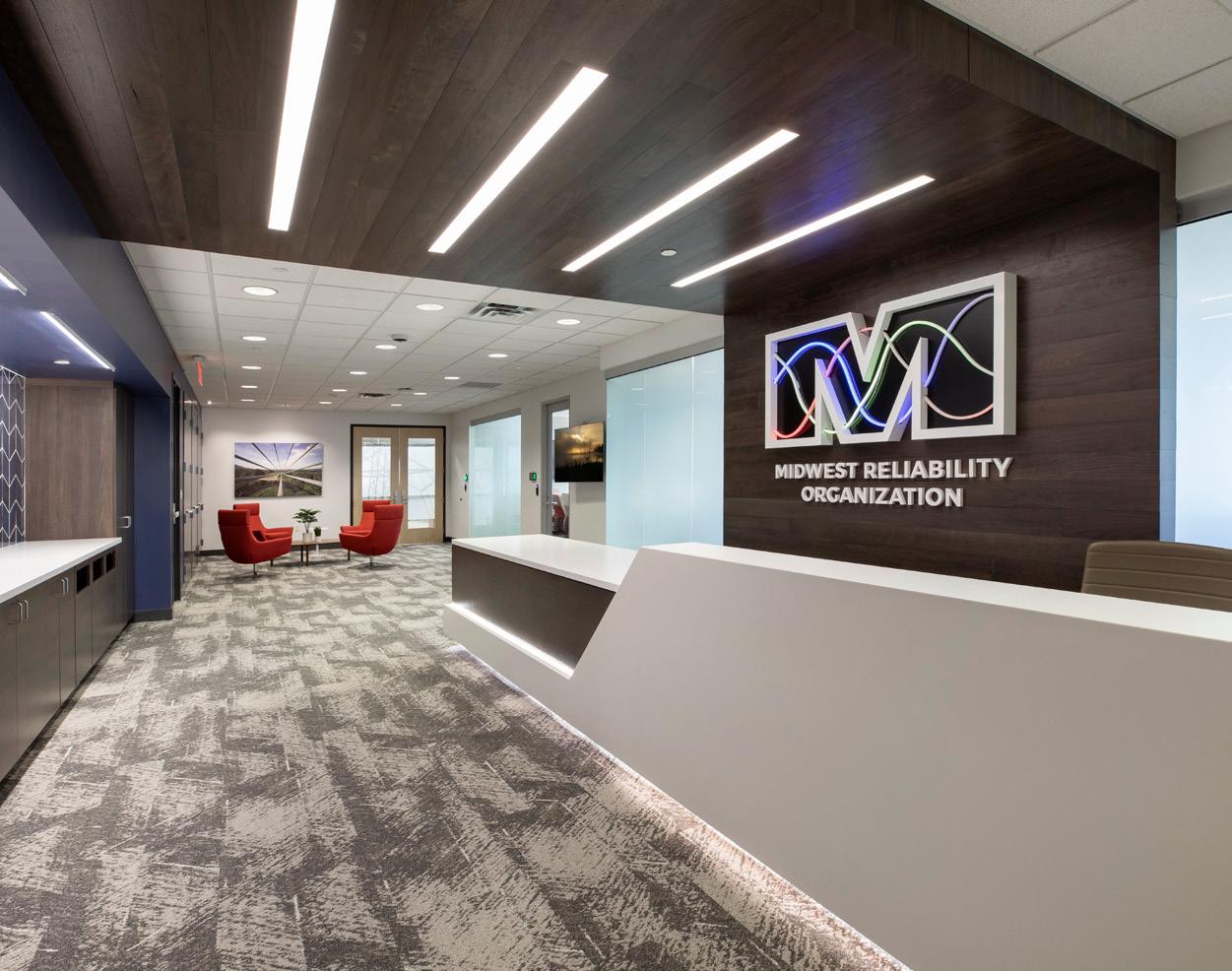
The concept of HROs emerged from observing organizations like air traffic control, nuclear power plants, and aircraft carriers, which operate in environments where errors could lead to catastrophic consequences. Yet, they consistently achieve high levels of safety and reliability.
Over time, HRO theories and principles have evolved to provide guidance for modern safety program design and are foundational to many industries seeking high reliability in critical functions.
The five HRO principles are:
• Preoccupation with failure –Attention to close calls and near misses; focus on learning from failure.
• Reluctance to simplify interpretations – Solid root cause analysis.
• Sensitivity to operations – Carefully designed change management processes.
• Commitment to resilience –Resources continually devoted to corrective action plans and training.
• Deference to expertise – Listen to your experts on the front lines; authority follows expertise.
We encourage utility companies in the region to be HEROs® by practicing these five principles and striving for operational excellence.
NA: Are there any recent projects that you feel are important to highlight?
SP: As more intermittent renewable resources, such as wind and solar, are added to the North American power grid, the ability to transfer power across different regions has become a vital component of system reliability.
In 2024, MRO partnered with the ERO Enterprise, the industry, and other key stakeholders to complete a congressionally mandated interregional transfer capability study. The purpose of the study was to determine the maximum amount of
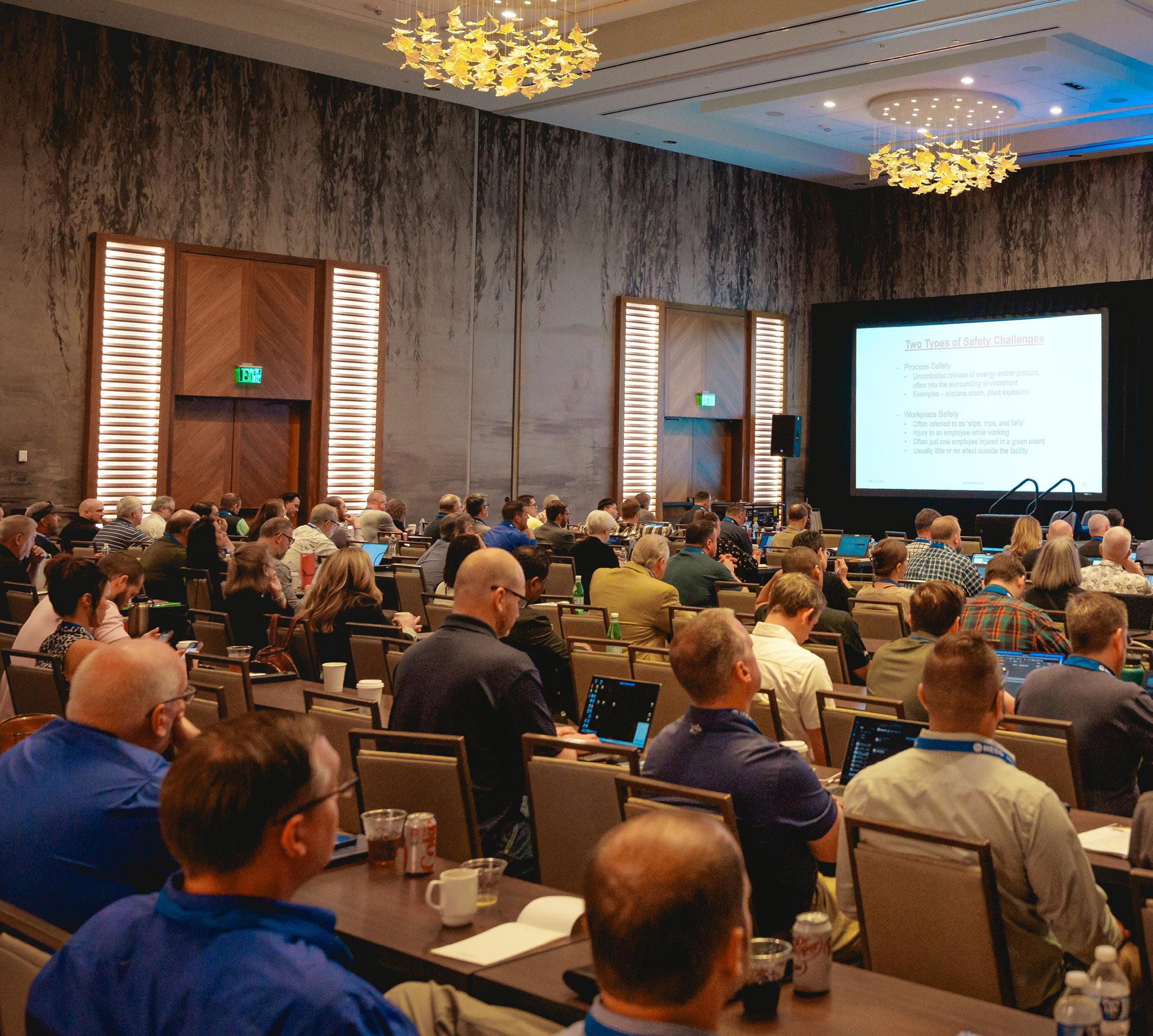
electric power that can be reliably transferred between different regions in the US and offer recommendations for increasing capacity to strengthen grid reliability.
The study’s second phase, which assessed transfer capability between the US and Canadian provinces, was completed in April this year. Analyzing transmission capacity will become part of the ERO Enterprise reliability assessments moving forward.
The ERO Enterprise also raised concerns about the need for cold weather standards after two extreme events – Winter Storm Uri in 2021 and Winter Storm Elliott in 2022 – severely stressed the grid.
Joint reports from FERC and the ERO Enterprise, issued after these storms, offered recommendations to the industry to protect utility infrastructure and improve resilience to cold weather.
The ERO Enterprise then implemented a focused strategy to improve cold weather preparedness among North American generator owners and operators. This effort led to the implementation of mandatory cold weather standards and improved coordination between the electric and natural gas sectors.
For our MRO region specifically, we developed a Generator Winterization Program that actively promotes cold
weather reliability by sharing best practices and offering actionable recommendations to minimize weather-related risks.
A challenge we are actively addressing with the industry is the rapidly increasing integration of inverter-based resources (IBRs) like solar, wind, and battery storage into the bulk power system.
These resources behave very differently from traditional power plants, and recent system outages have shown that if IBRs aren’t modelled, configured, or operated correctly, they can significantly impact grid stability. Solving this problem is a collaborative effort
2025 Reliability, Security, and CMEP Summit: Navigating the Evolving Power Grid
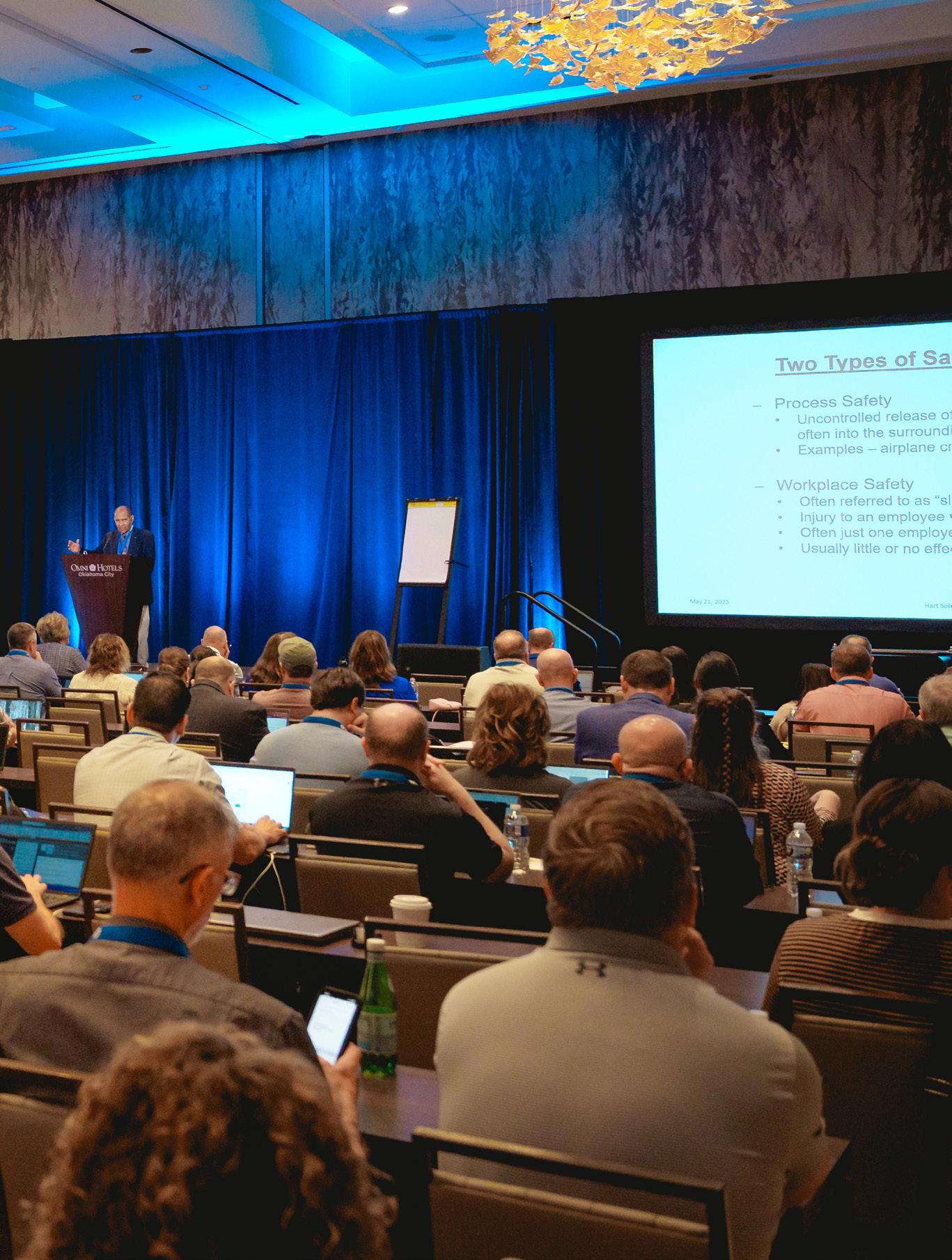
involving FERC, NERC, regional entities, and the industry.
We’re conducting extensive outreach to raise awareness, revising and adding new mandatory standards to provide a baseline of protection against IBR risks, and registering new IBR generator owners and operators who previously weren’t required to follow mandatory standards.
NA: In your opinion, what role does sustainability and tackling the climate crisis play in the operational success of North America’s bulk power system?
SP: Extreme weather remains one
of the most significant threats to the reliability of North America’s bulk power system. Not only does it impact the performance and availability of electricity resources, but its increasing prevalence demands enhanced grid resilience. The need to address the climate crisis is both urgent and complex.
Across the MRO footprint, more than 28 million individuals depend on a reliable electric grid, which underpins our economy and way of life. As such, it is essential that we prioritize grid reliability in tandem with efforts to transition towards low and zero-carbon energy sources.
This urgency is heightened by
the swift rise in electricity demand; therefore, a comprehensive, ‘all-in’ resource strategy is required for North America to appropriately tackle this challenge.
We are confident that the decarbonization of the energy sector can happen reliably and securely through collaborative stakeholder engagement and the thoughtful consideration of all resource options.
We must work together to ensure the pace of change does not overtake the reliability needs of the system.
NA: How does MRO work to reduce its environmental footprint?
SP: Despite being a small company of 80+ employees, MRO actively works to reduce its environmental footprint through a dedicated employee Sustainability Committee.
This committee has implemented various improvements including reducing paper, ink, and plastic bottle use, increasing recycling and compost awareness, switching to compostable dinnerware within the office, and promoting battery and office equipment recycling, alongside other community-focused sustainability efforts.
We have also maintained a hybrid work environment as part of MRO’s People-First Philosophy, which was implemented during the COVID-19 pandemic.
Working part-time in the office not only provides flexibility for our staff but reduces commuting trips to the office.
NA: Could you describe MRO corporate social responsibility practices and how they contribute to the company’s success?
SP: One of MRO’s greatest strengths lies in its remarkable diversity, which is essential for confronting the many challenges facing the electric sector.
Our expansive footprint spans the colder northern climates of Canada
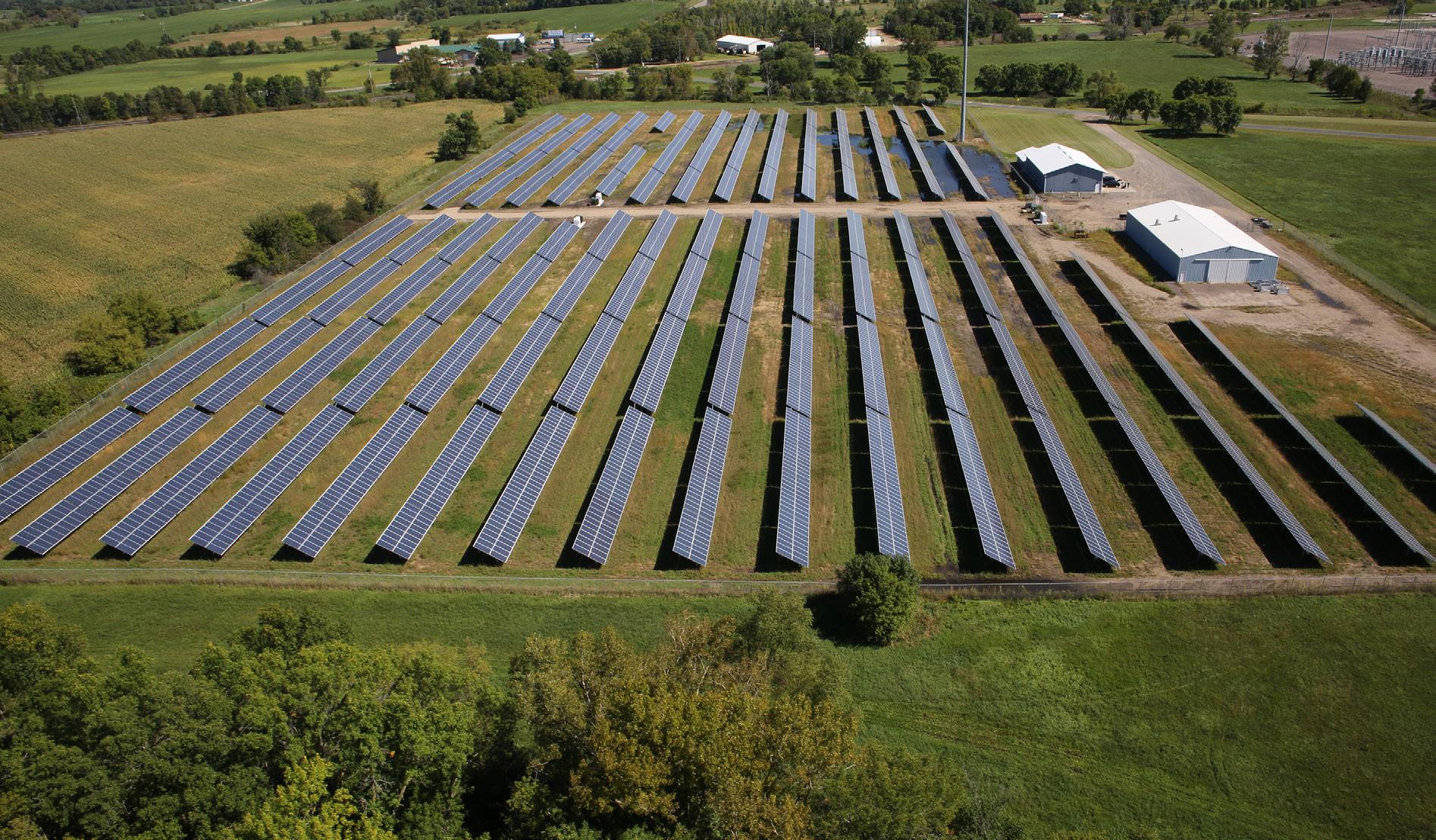
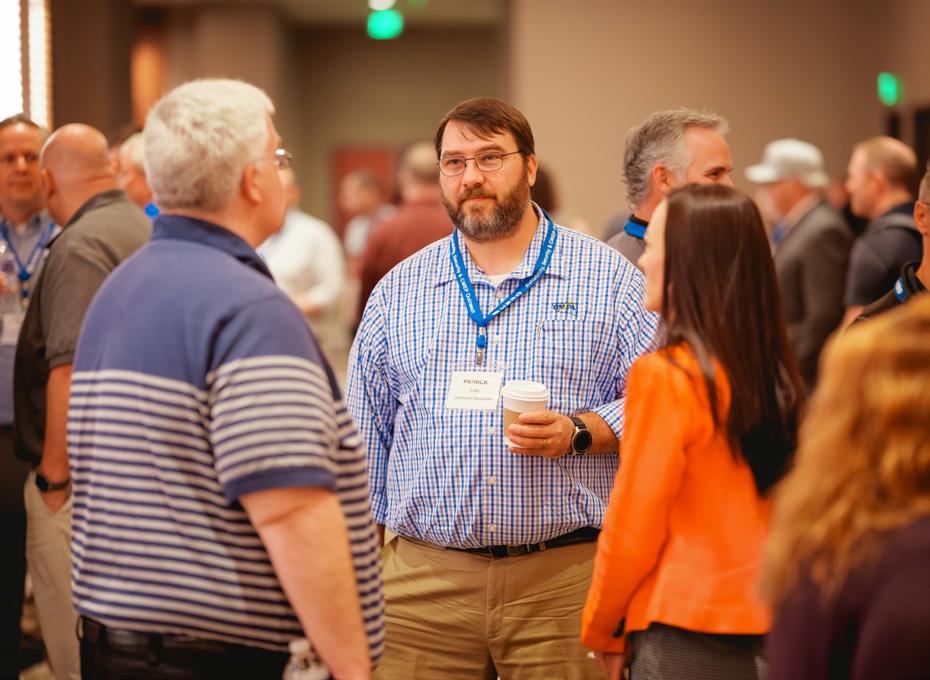
down to the hotter, more temperate regions of the US, including parts of Texas.
This geographic diversity is mirrored in our energy resources and infrastructure, encompassing a broad mix of electrical generation and transmission profiles.
We also work with a wide array of stakeholders, including municipalities, cooperatives, investor-owned utilities, and generator power marketers, all contributing to a reliable and secure regional power grid.
This strategy embraces diverse resources, perspectives, and operational models and is crucial for
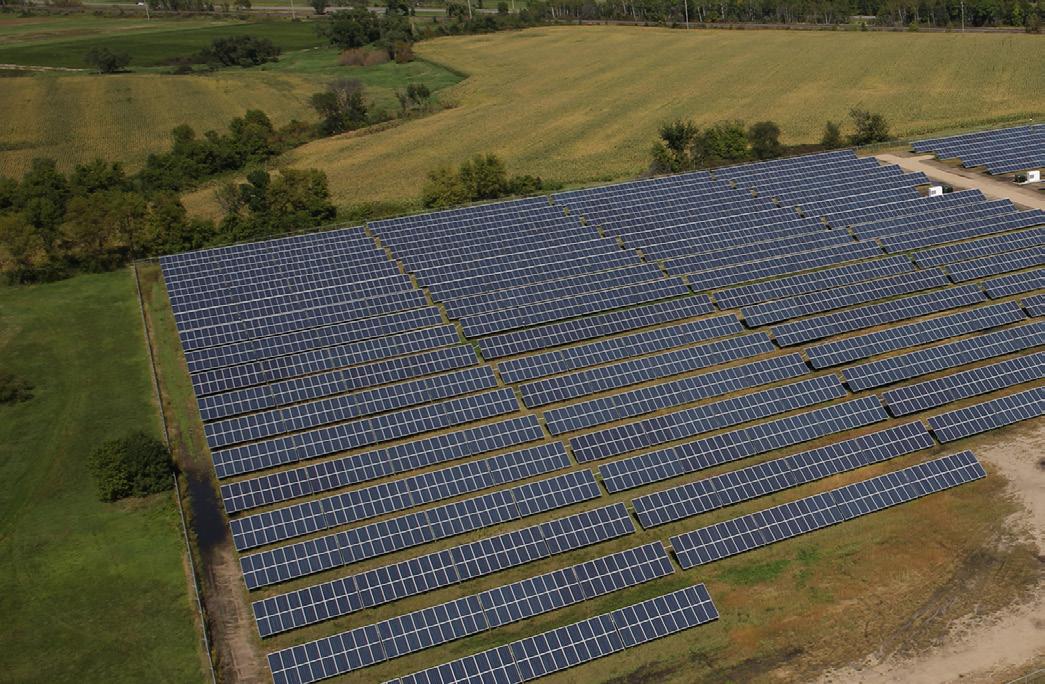
advancing our mission.
Diversity further extends to our team. We are fortunate to draw from the exceptional talent in Minneapolis and Saint Paul, home to numerous colleges and universities specializing in electrical engineering and bulk power system technologies, alongside innovative companies serving our industry.
MRO actively embraces this diversity in our hiring and operational practices, recognizing that a wide range of perspectives and expertise is vital for navigating the complex and evolving energy landscape.
During the pandemic, we put our People-First Philosophy into action by significantly expanding our employee benefits. It was a strategic move that proved crucial for attracting and retaining a knowledgeable and engaged workforce, serving us exceptionally well through a time of immense change.
This approach also earned us a top Minneapolis and Saint Paul workplace award two years running. Beyond benefits, we empower our staff through employee-led committees to actively drive societal initiatives that positively impact the
2025 Reliability, Security, and CMEP Summit: Navigating the Evolving Power Grid
Photo used by permission from Great River Energy
Photo used by permission from Great River Energy
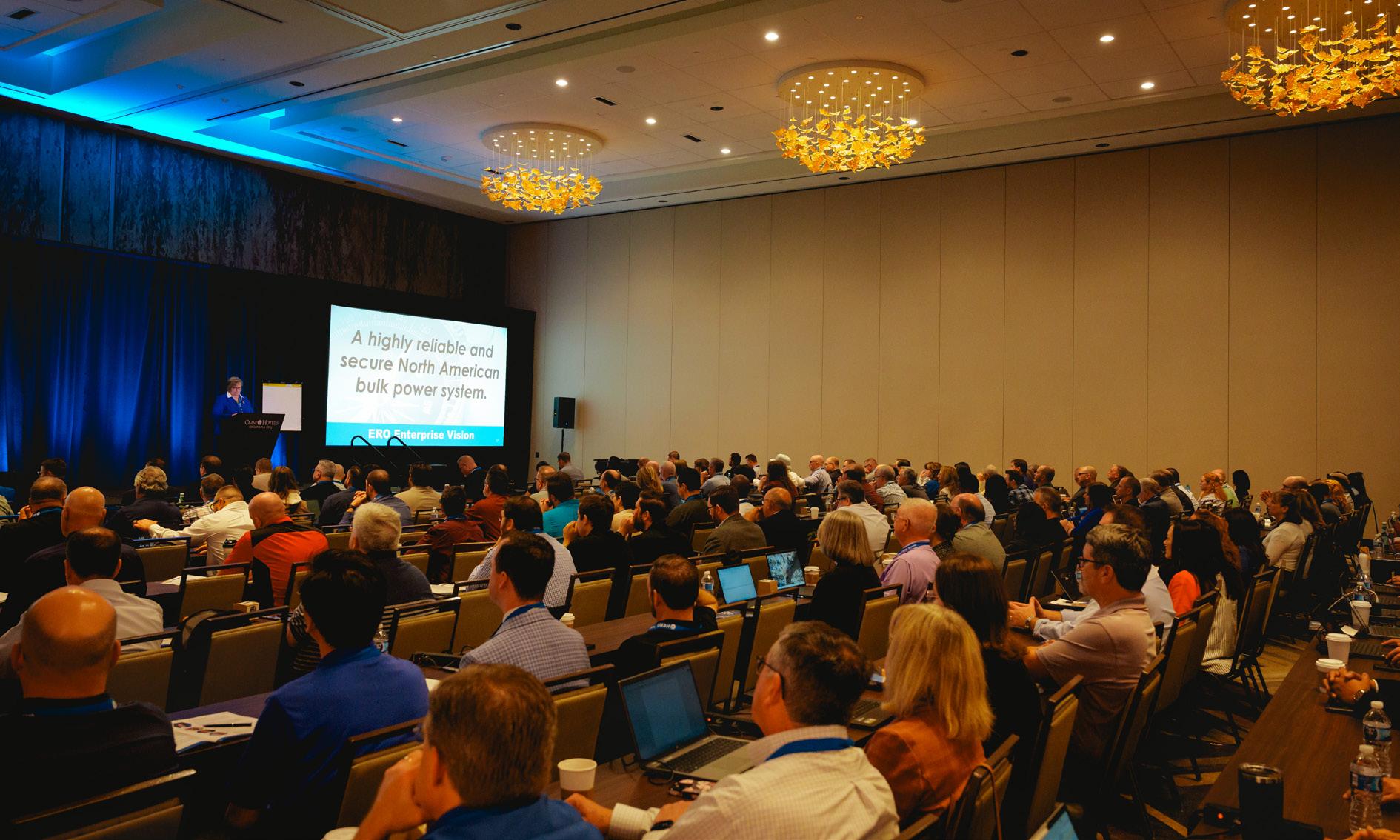
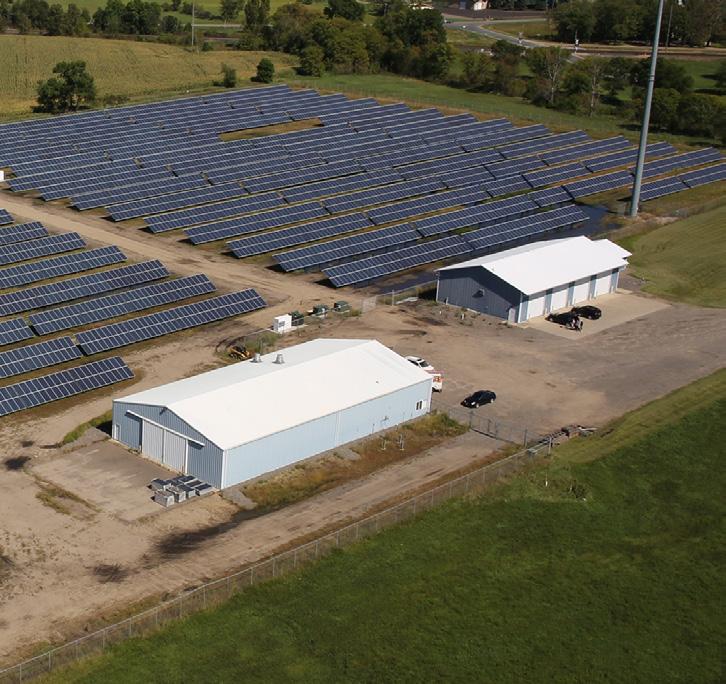
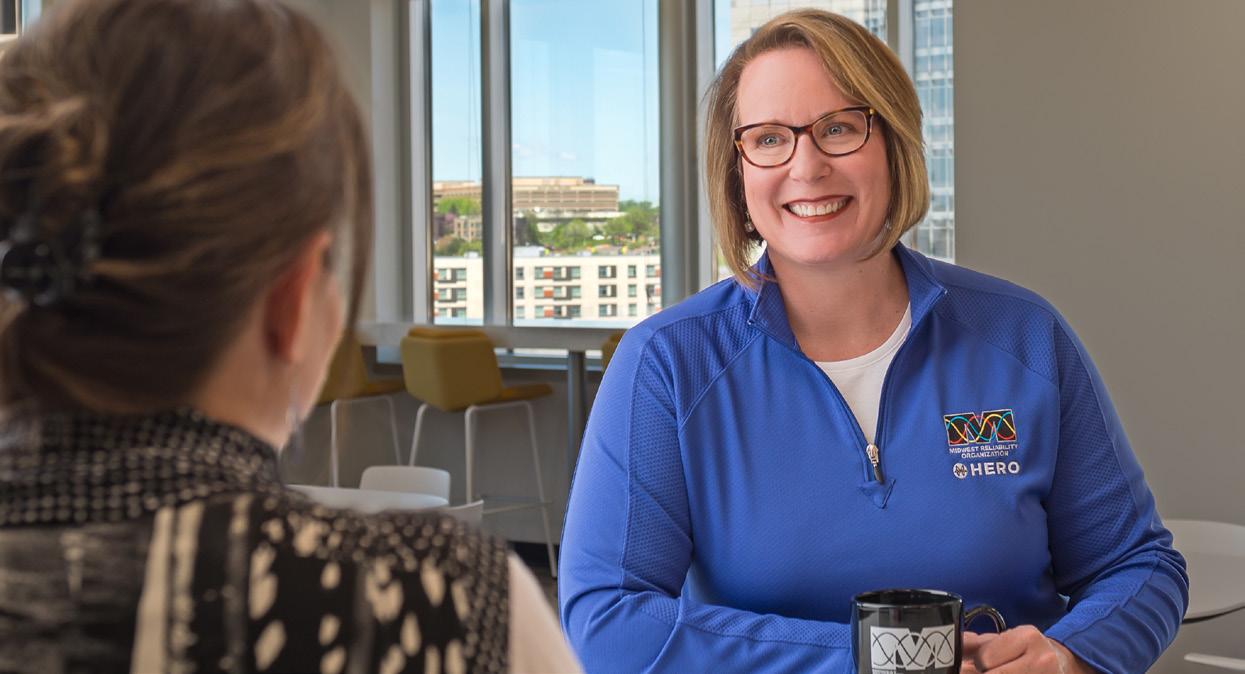
NA: Lastly, what are your key priorities for the coming year?
SP: The MRO Board of Directors recently approved our new strategic plan for 2025 to 2028. This plan highlights three core strategic priorities:
• People – Ensure MRO remains an innovative, resilient, and highperforming organization with requisite expertise and leadership to navigate the challenges and opportunities of a rapidly transforming grid.
standards of operational excellence in everything we do, emphasizing effectiveness and efficiency to deliver utmost value to our stakeholders.
• Partnerships – Foster an agile, adaptive, and collaborative relationship with internal and external stakeholders to effectively coordinate efforts to reduce risk and enhance reliability and security of the North American bulk power system
www.mro.net communities we work and live in.
security, engagement and agility and sustainability.
To help us execute our strategic plan, MRO launched new core values this year – connection, curiosity, commitment, and competency, which will guide our daily actions and organizational culture. Our future is bright.
• Processes – Implement high
Our strategic plan closely aligns with the broader ERO Enterprise Long-Term Strategy, which focuses on the critical risk areas of energy,
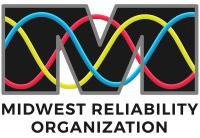
Tel: 651-855-1760
jessie.mitchell@mro.net
2025 Reliability, Security, and CMEP Summit: Navigating the Evolving Power Grid
Sara Patrick, President and CEO
RACING FOR ALL
F1 Arcade is the world’s first official Formula 1 racing experience venue, blending the energy of social gaming with the speed, style, and spectacle of the sport. We discover how it’s making Formula 1 more accessible, social, and fun than ever before with Jon Gardner, US President
Writer: Jack Salter
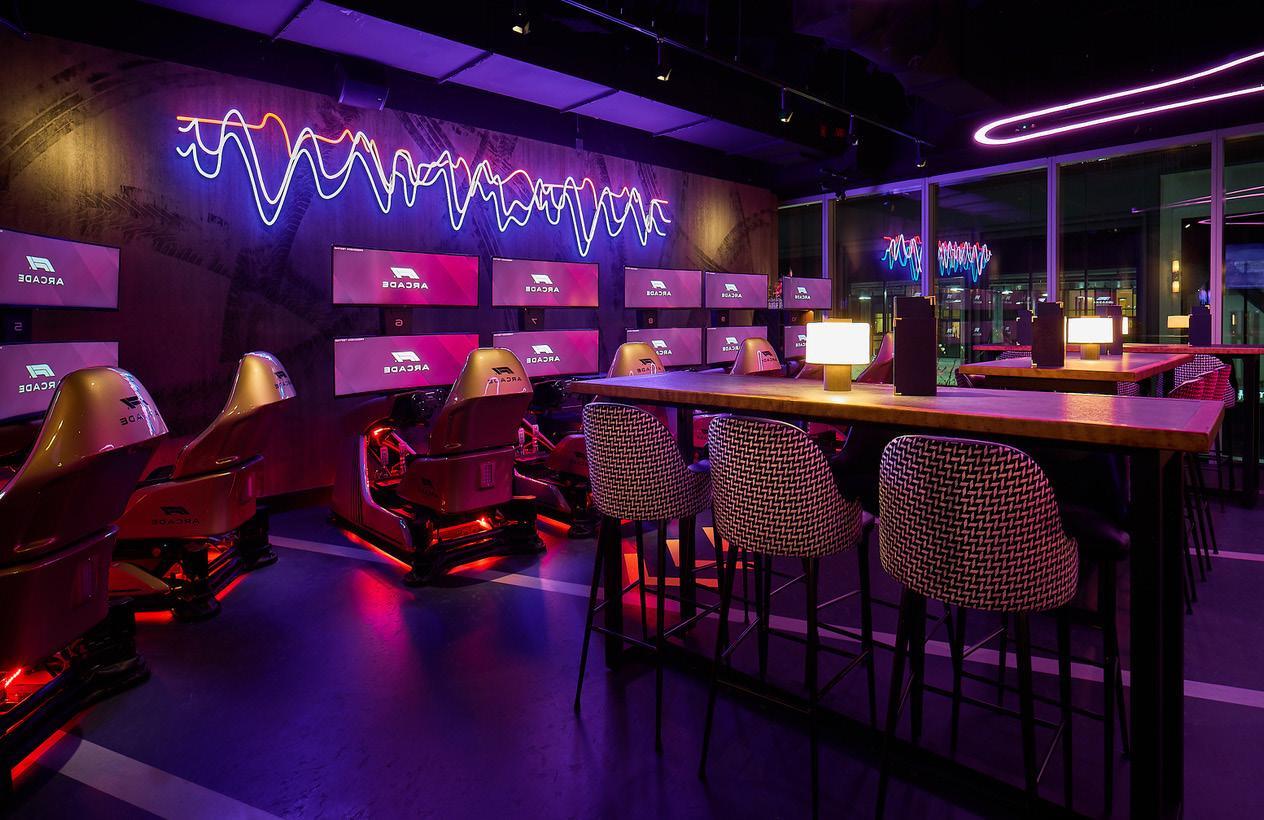
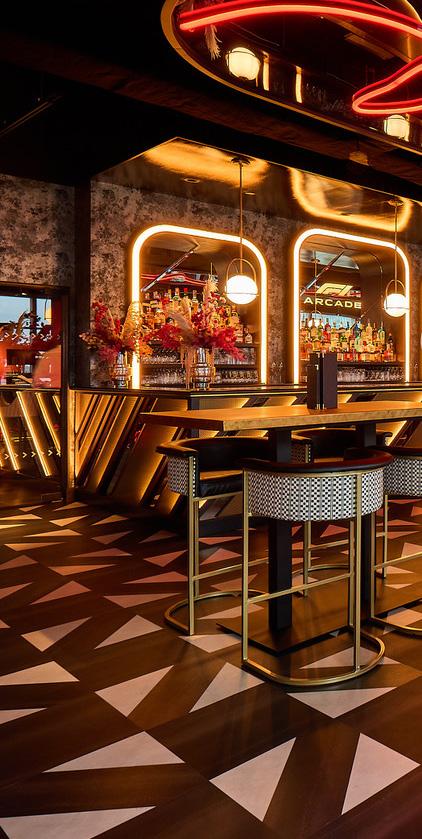
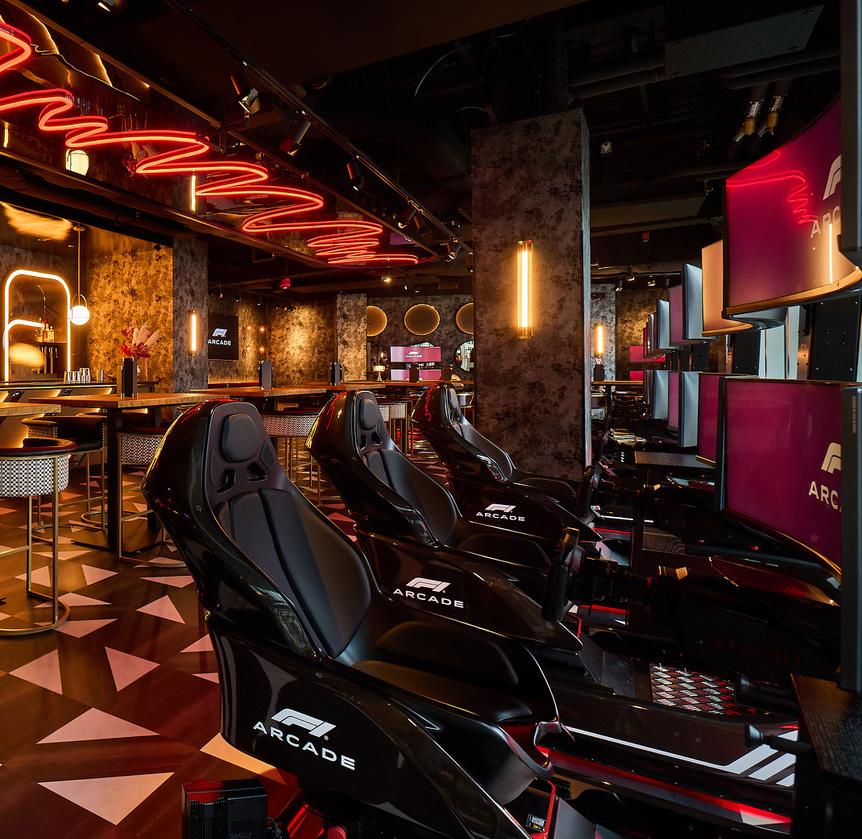
Formula 1 has experienced explosive growth in the US, and interest continues to grow in the country.
With the recent release of F1: The Movie, starring Brad Pitt and Damson Idris, the sport is becoming even more embedded in pop culture and fans are increasingly craving real-life experiences that bring the thrill of
Formula 1 to life.
That’s exactly what F1 Arcade delivers.
“Less than one percent of people in the world get to experience the Formula 1 paddock first-hand, but F1 Arcade brings that exclusive energy and excitement to everyone,” opens Jon Gardner, US President.
“From the moment you step inside, you’re immersed in the adrenaline and atmosphere of race day.”
F1 Arcade’s venues feature stateof-the-art full-motion simulators, including the debut of exclusive AXSIM simulators in Philadelphia, offering 180-degree visuals and realistic handling to authentically replicate the Formula 1 driving experience.
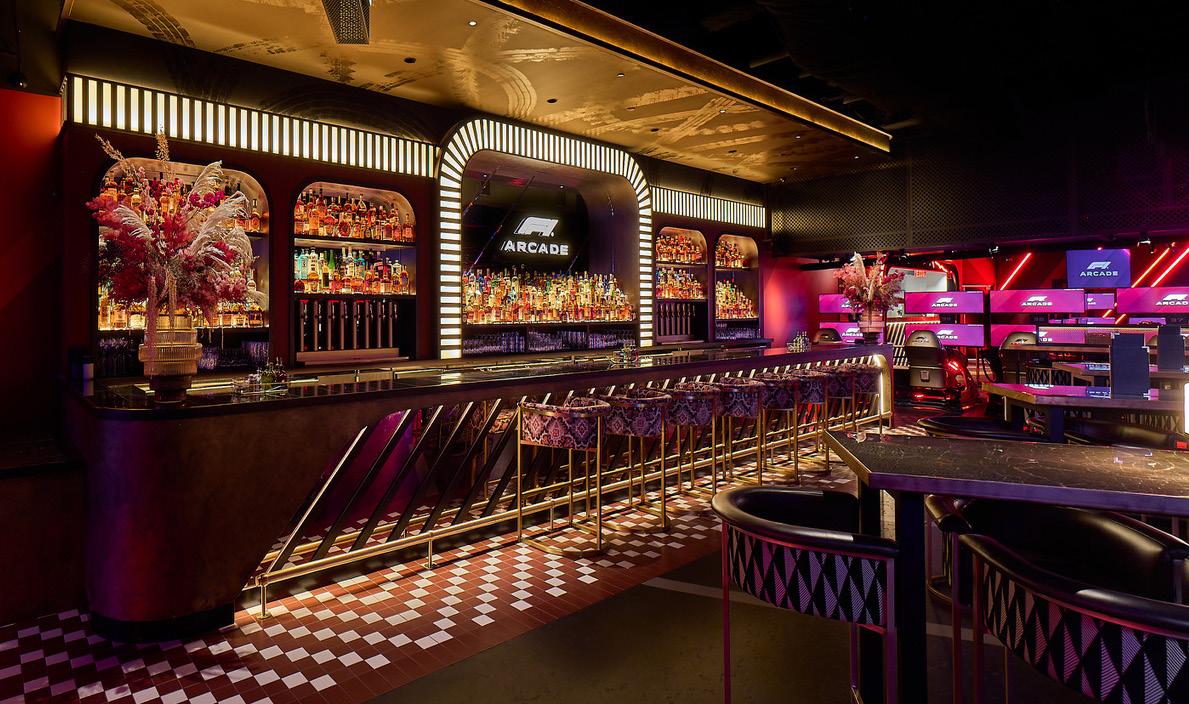
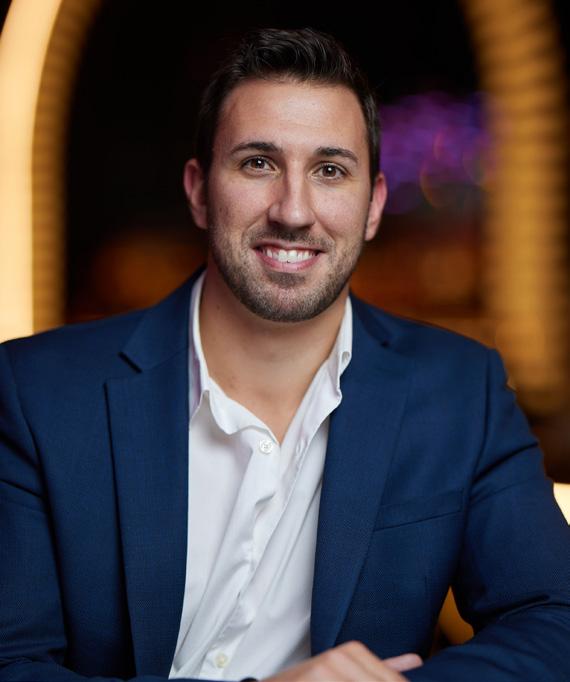
It’s not just about racing, however, as F1 Arcade is a destination that fuses immersive entertainment and premium hospitality, with dramatic lighting, high-energy social spaces, and a globally inspired menu.
“We’ve reimagined the arcade for a
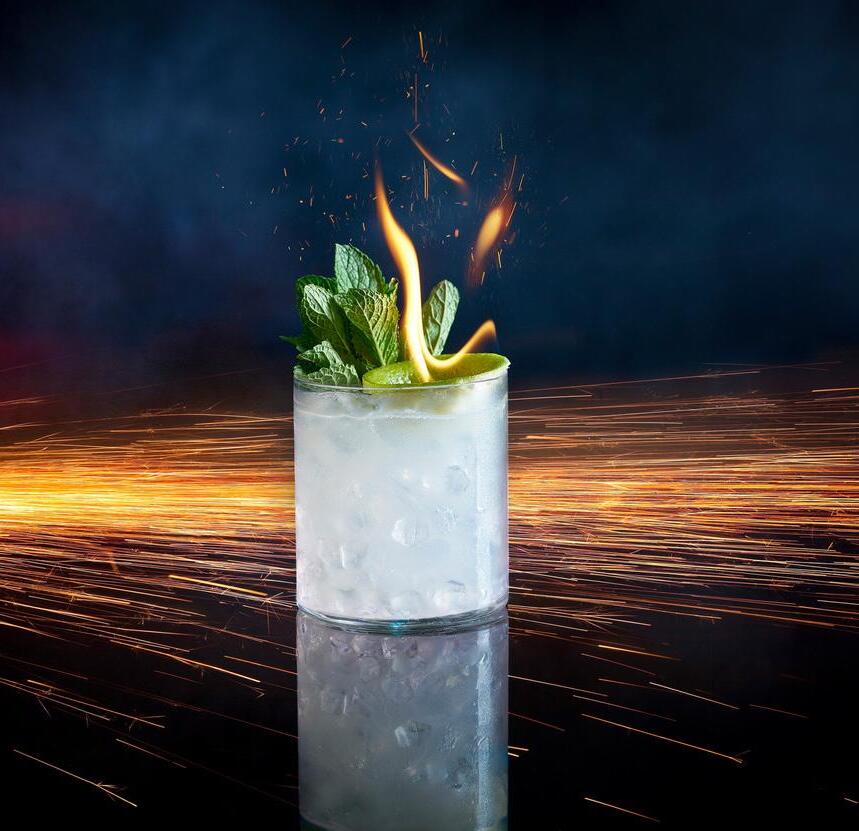
“WE’RE TARGETING CITIES THAT MIRROR THE PULSE OF FORMULA 1 – ENERGETIC, FAST-PACED, AND CULTURALLY RICH”
– JON GARDNER, US PRESIDENT, F1 ARCADE
new generation, combining cuttingedge full-motion simulators, a vibrant design, and an elevated food and beverage program led by awardwinning mixologist LP O’Brien,” Gardner tells us.
“Whether you’re a lifelong Formula 1 fan, avid gamer, or just looking for an unforgettable night out with friends, F1 Arcade is high-octane fun and offers something for everyone.”
US OPENINGS
The opening of F1 Arcade’s first US venue in the Seaport District of Boston in April 2024 was the perfect launchpad as the city has a vibrant sports culture and strong appetite for experiential entertainment.
It quickly became a go-to destination for locals and visitors alike, and F1 Arcade has seen tremendous engagement from both hardcore
Formula 1 fans as well as people who come to eat, drink, and enjoy a lively social atmosphere.
Moreover, it was the first US location to host official Formula 1 watch parties, giving fans an exciting new way to connect with the sport.
“The positive reception confirmed what we already believed – the F1 Arcade concept resonates across audiences,” affirms Gardner.
In October last year, another F1 Arcade opened in the Union Market District of Washington, DC. Known for its creativity and culture, the neighborhood is a natural fit for the F1 Arcade experience.
It is the most expansive venue yet, with 17,300 square feet (sqft) of immersive racing, vibrant dining, and dynamic social spaces, as well as an additional 1,500 sqft of outdoor space.
HOW IS F1 ARCADE REVITALIZING RETAIL SPACES AND CREATING HUBS FOR COMMUNITY INTERACTION?
JON GARDNER, US PRESIDENT:
“We see F1 Arcade as part of a new wave of experiential concepts that are reactivating urban spaces and transforming how people engage with retail and hospitality.
“By taking over large-format, often underused real estate, we’re creating high-energy venues that encourage social connection, competition, and celebration.
“Our spaces become community magnets, whether you’re racing, dining, or just watching a Grand Prix with friends. It’s a new kind of ‘third place’, rooted in shared experience and immersive design.”
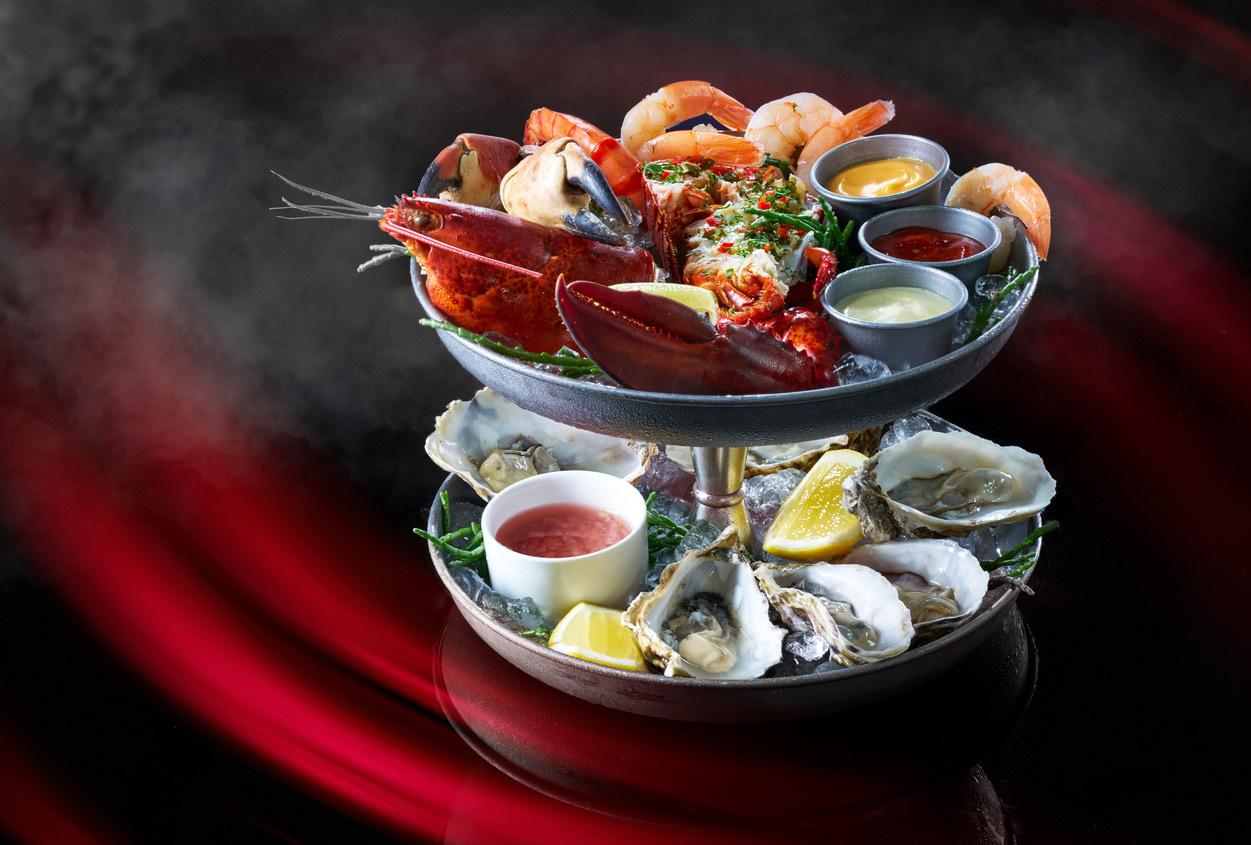
“We’ve designed the space to offer flexibility, with private rooms that feature dedicated bars and up to 16 simulators, ideal for large groups and corporate events,” Gardner informs.
“The response has been fantastic, and we’re proud to be part of such a thriving community.”
FUTURE EXPANSION PLANS
Most recently, F1 Arcade opened its
third US location in Philadelphia in May 2025 and is on track to launch 30 locations globally by the end of 2027.
The Philadelphia venue sets a new standard for what a flagship F1 Arcade venue can be as it includes 80 simulators, a 43-foot illuminated bar, and a private event space known as The Briefing Room with its own bar and 13 exclusive simulators.
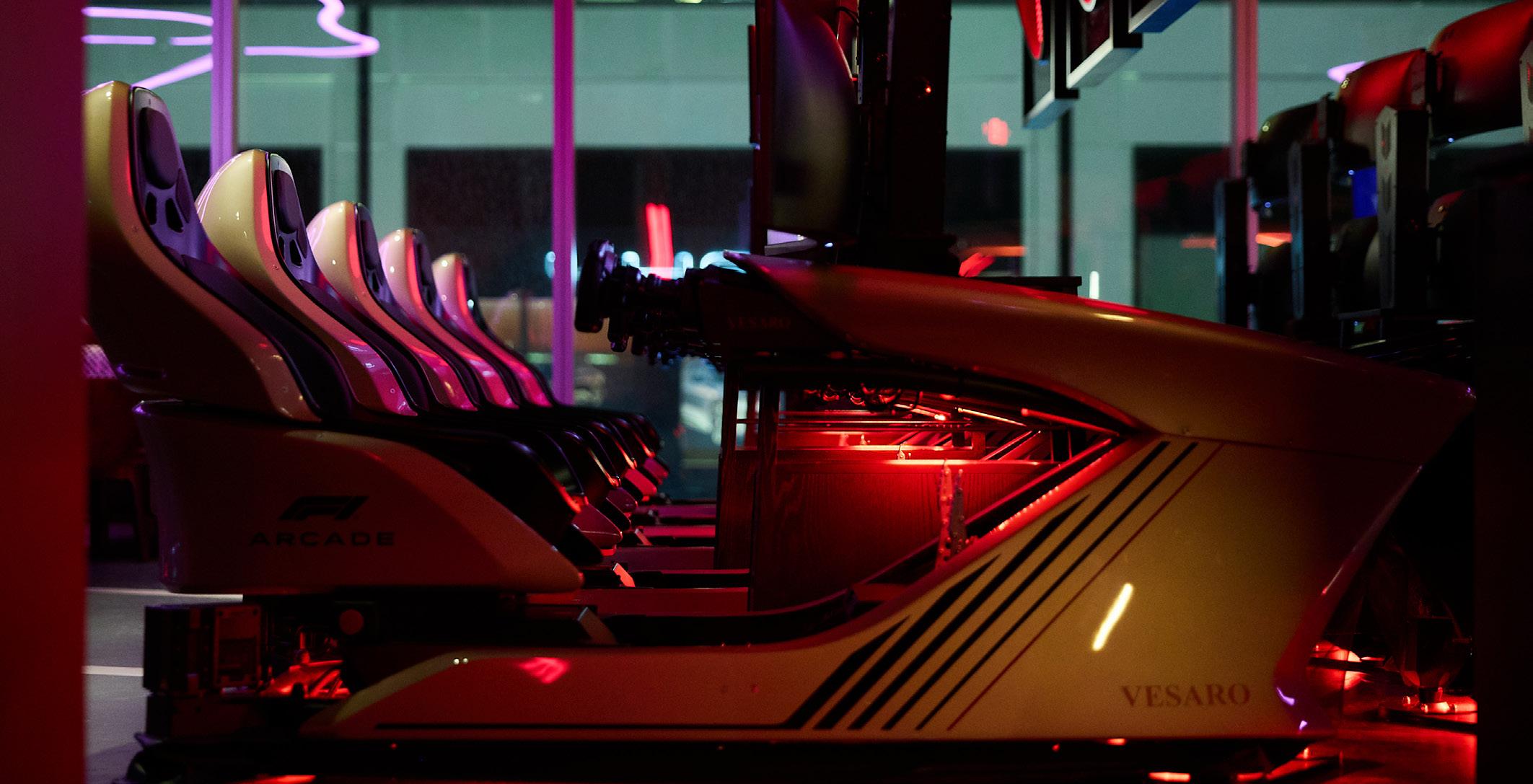
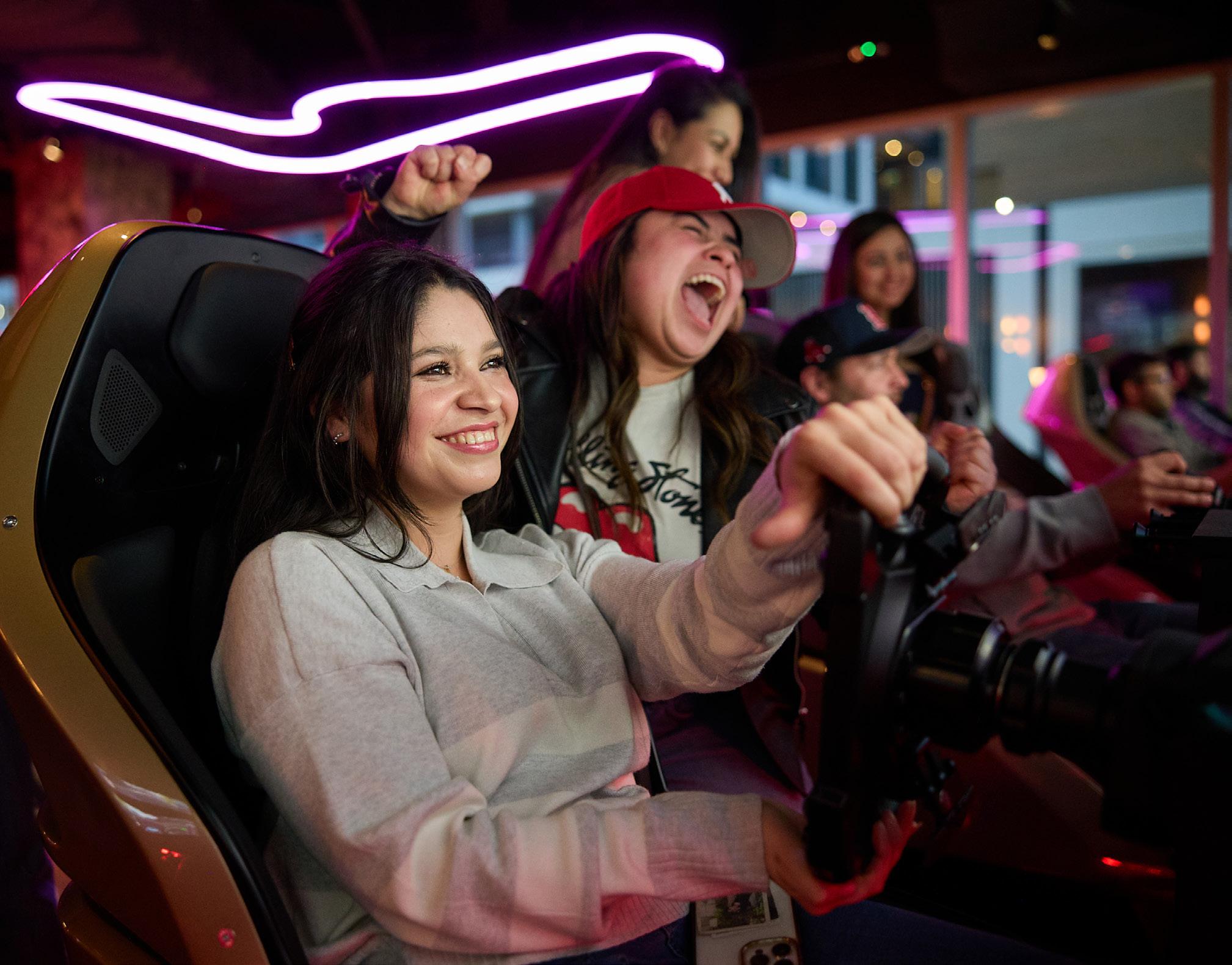
“WE’VE REIMAGINED THE ARCADE FOR A NEW GENERATION, COMBINING CUTTINGEDGE FULL-MOTION SIMULATORS, A VIBRANT DESIGN, AND AN ELEVATED FOOD AND BEVERAGE PROGRAM LED BY AWARD-WINNING MIXOLOGIST LP O’BRIEN”
– JON GARDNER, US PRESIDENT, F1 ARCADE
Next up are Denver, Las Vegas, and Atlanta, all launching later this year and doubling F1 Arcade’s current US footprint.
“We’re targeting cities that mirror the pulse of Formula 1 – they are energetic, fast-paced, and culturally rich,” outlines Gardner.
“Each venue is tailored to its local
market while maintaining the core elements of the F1 Arcade brand. The goal is to become a global network of racing destinations, accessible to fans and fun-seekers everywhere.”
Aside from these expansion plans, F1 Arcade is laser-focused on enhancing the guest experience. That means rolling out new game
modes and competition formats and continuing to evolve its food and beverage offering with seasonal updates and local partnerships.
“We’re also investing in corporate and group events, which have become a huge growth area for us,” Gardner reveals.
“Behind the scenes, we’re innovating constantly, reengineering our simulators for smarter design and scalability, and working on exciting new tech-driven features to keep guests coming back.”
F1 Arcade is just getting started and can’t wait to bring this experience to more cities across the US and the world.
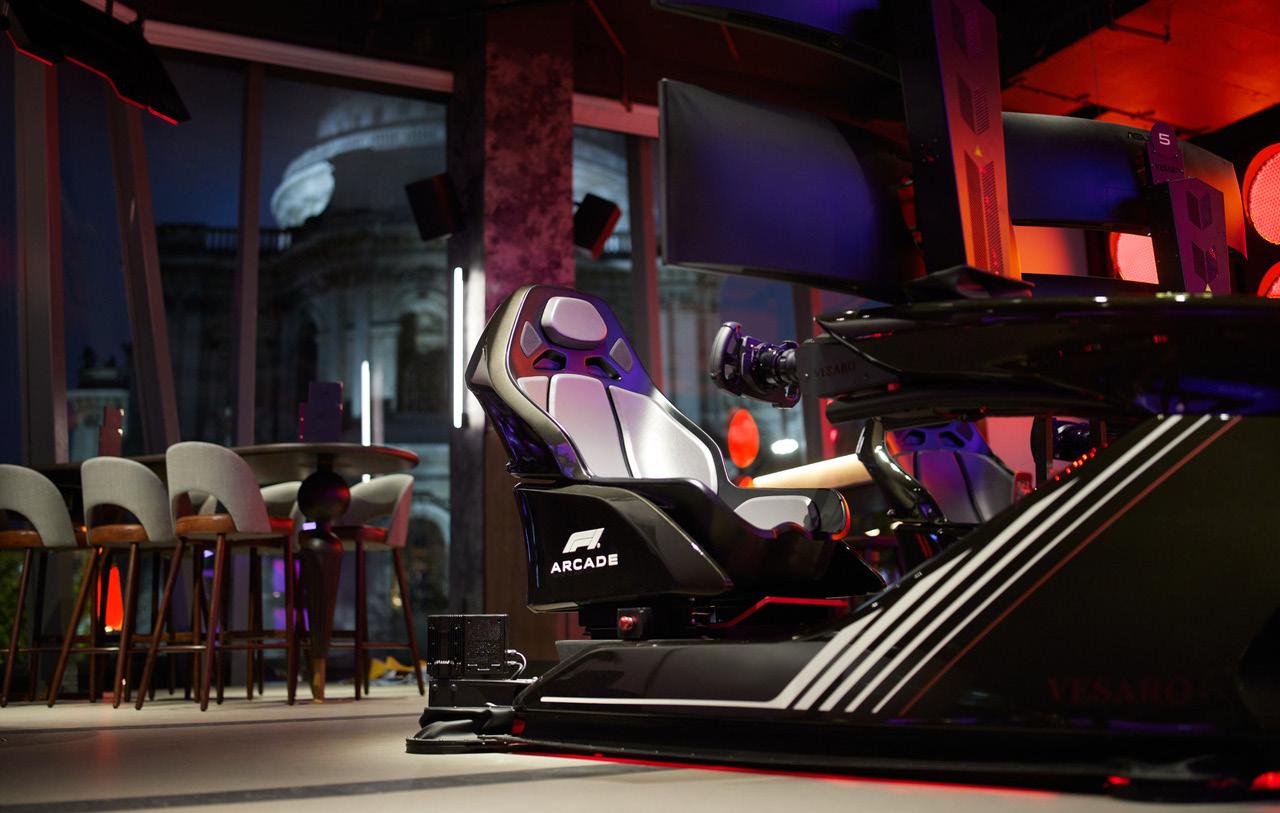
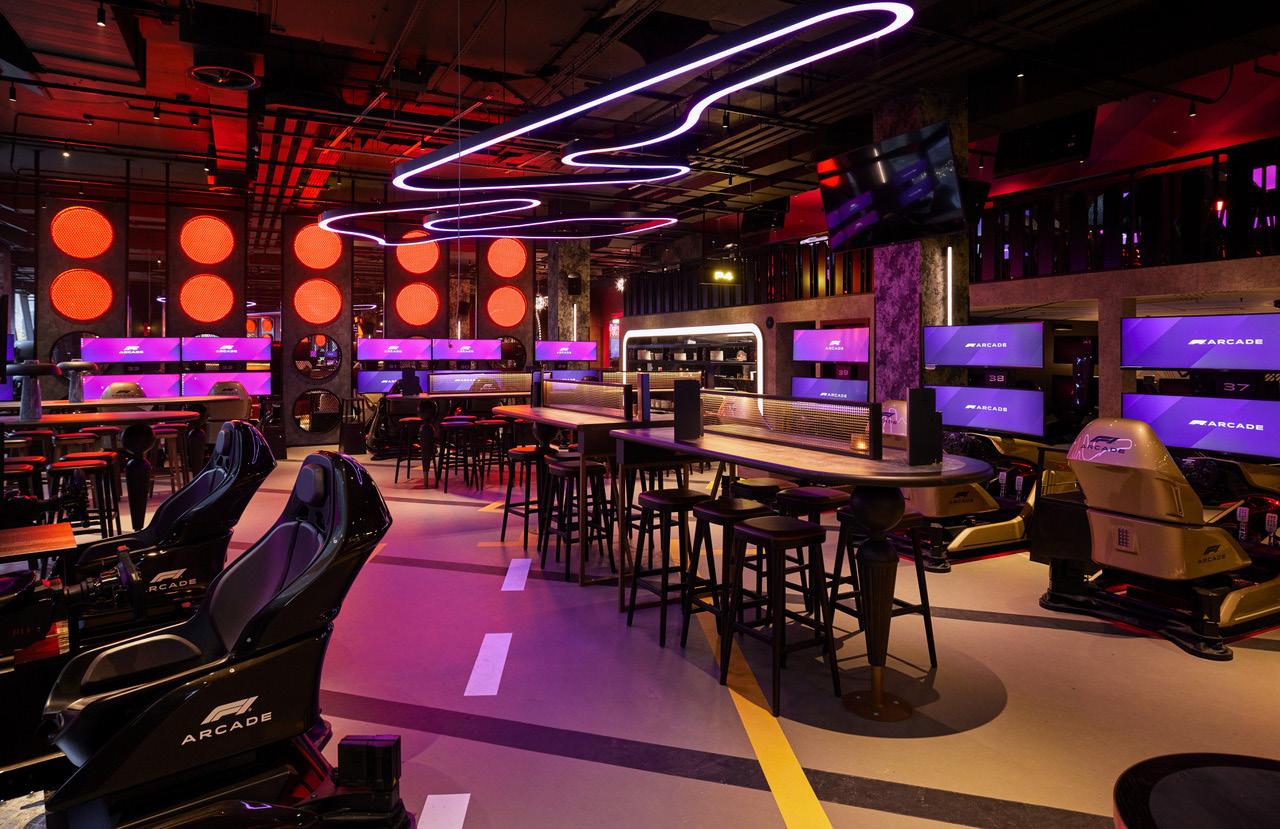
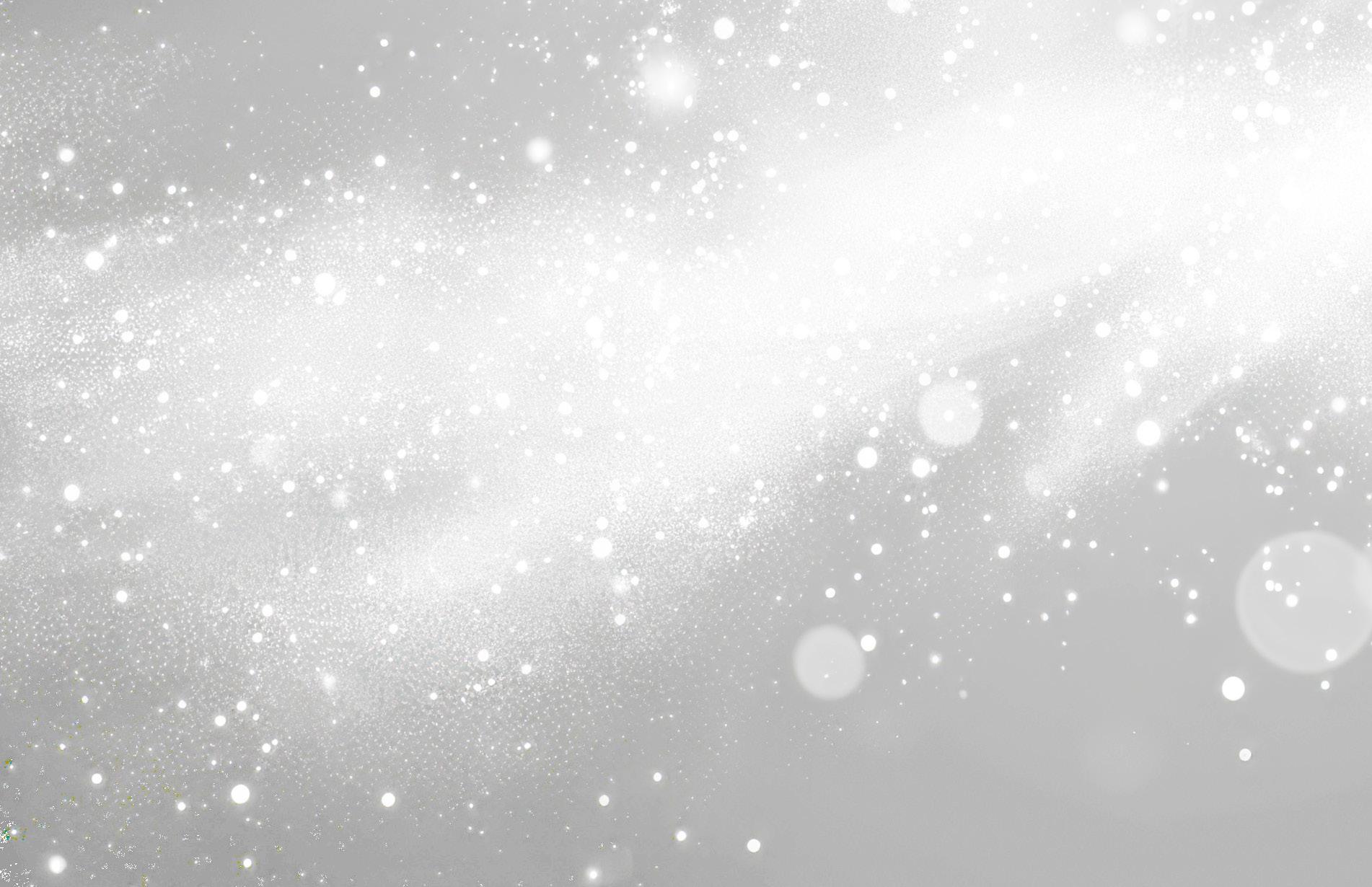
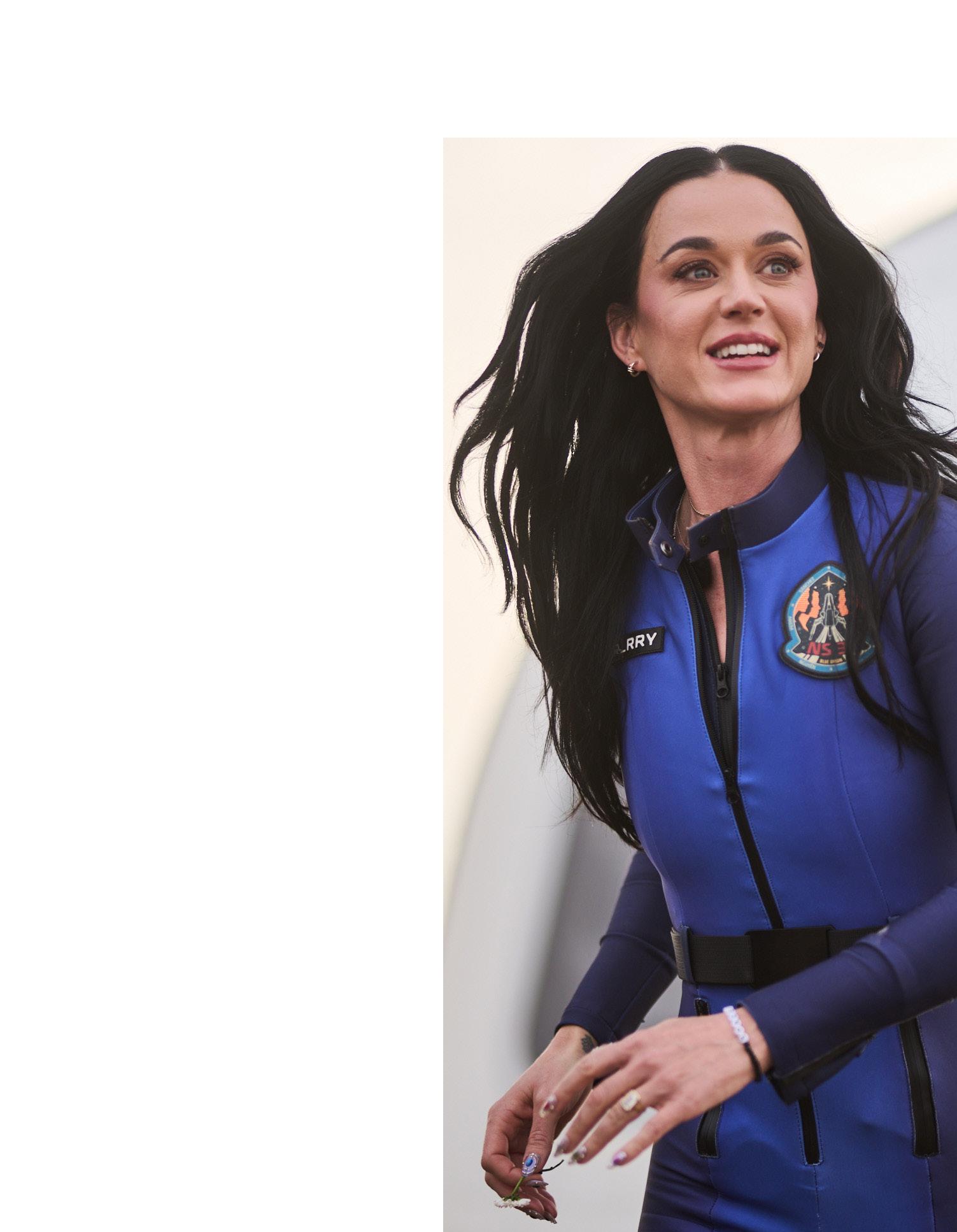
SPACE SPACE
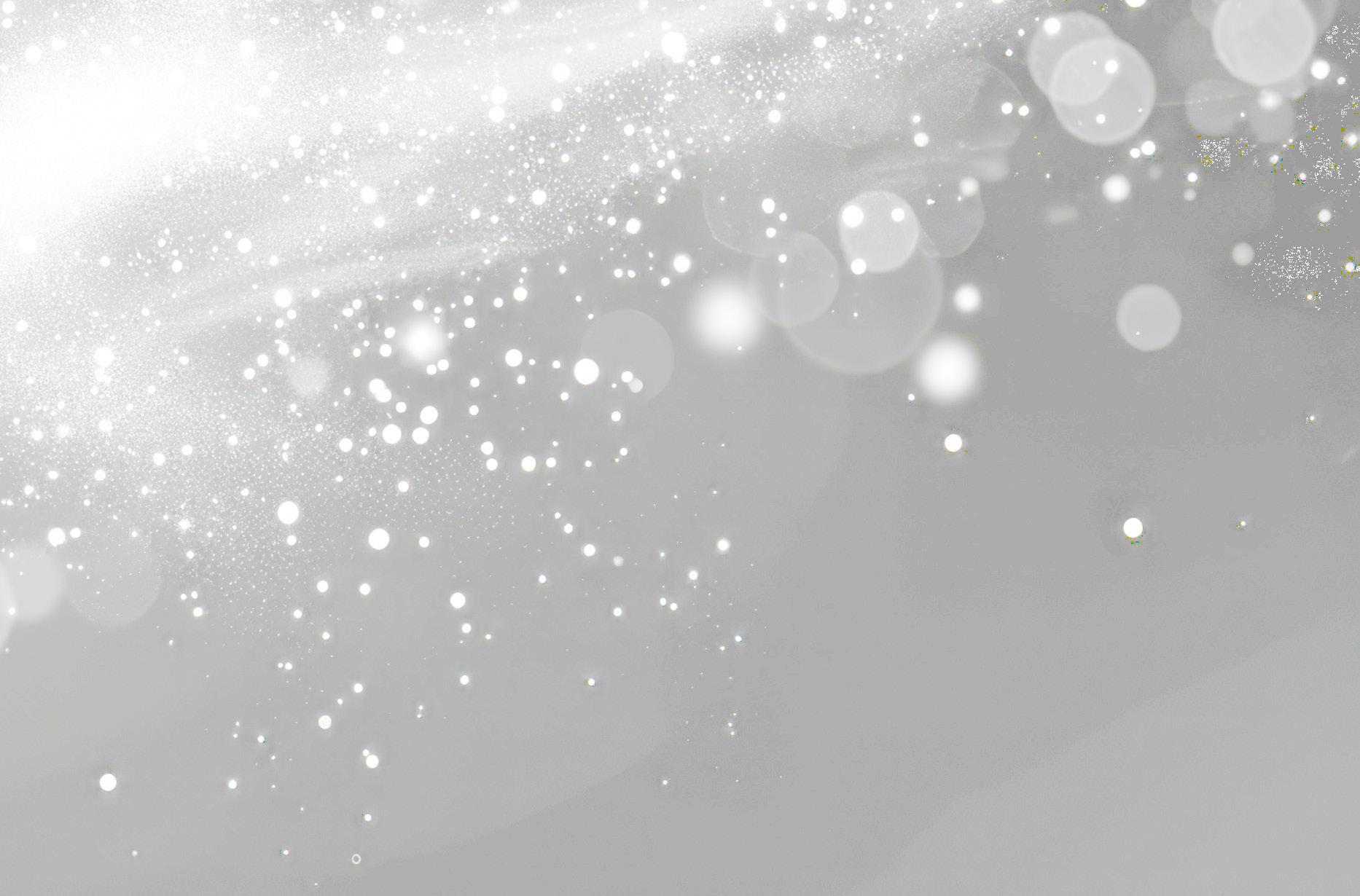
GIRLS GIRLS
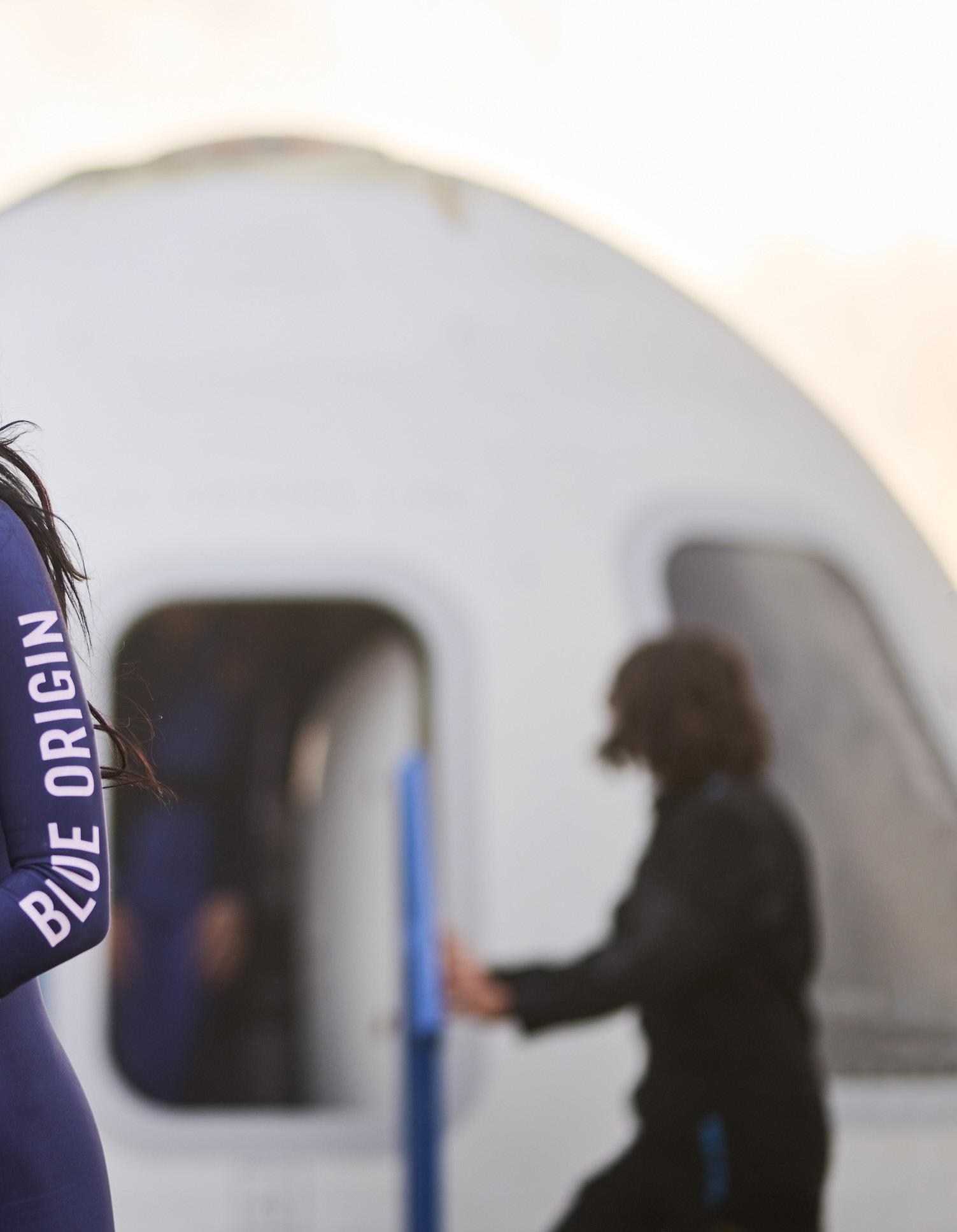
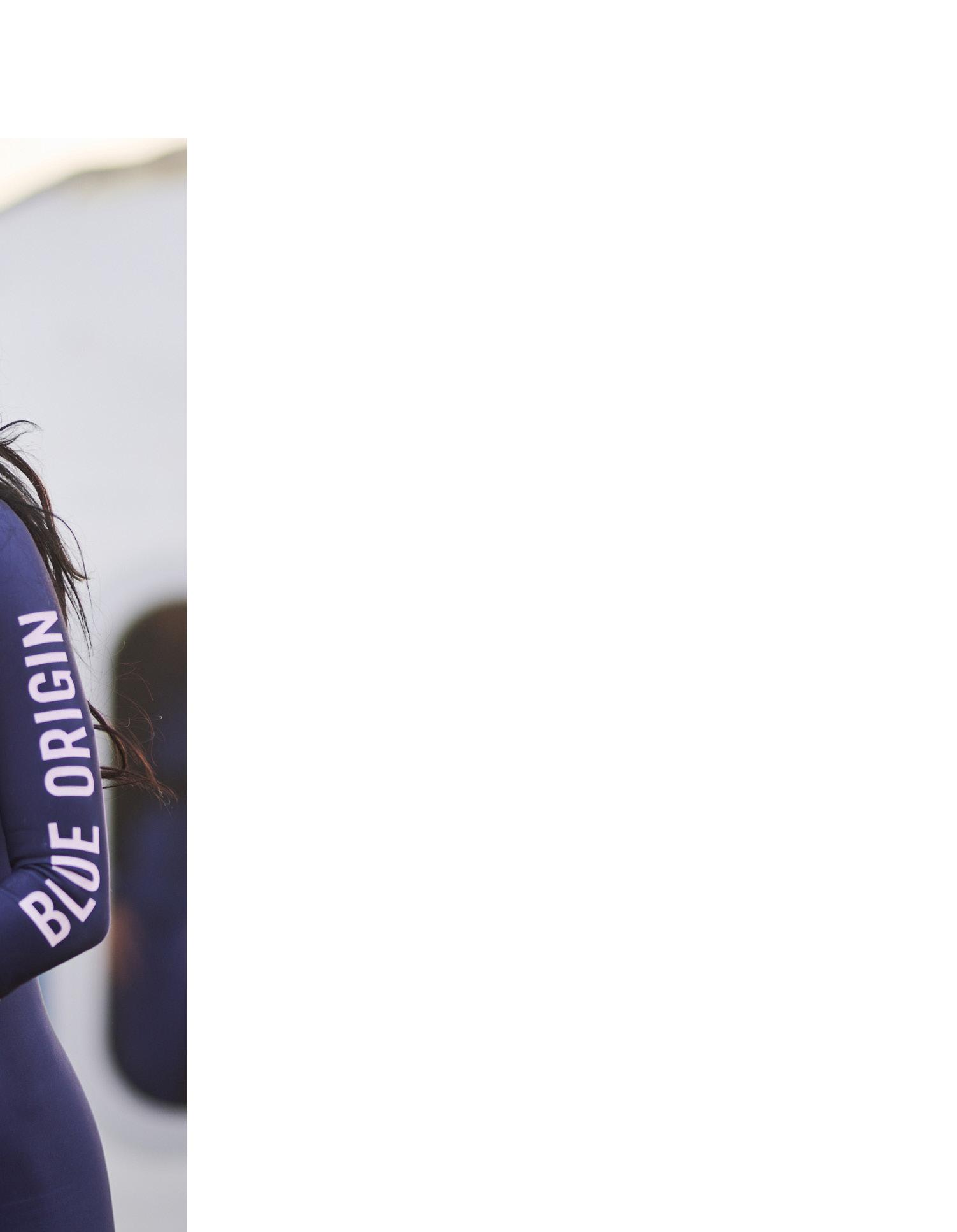
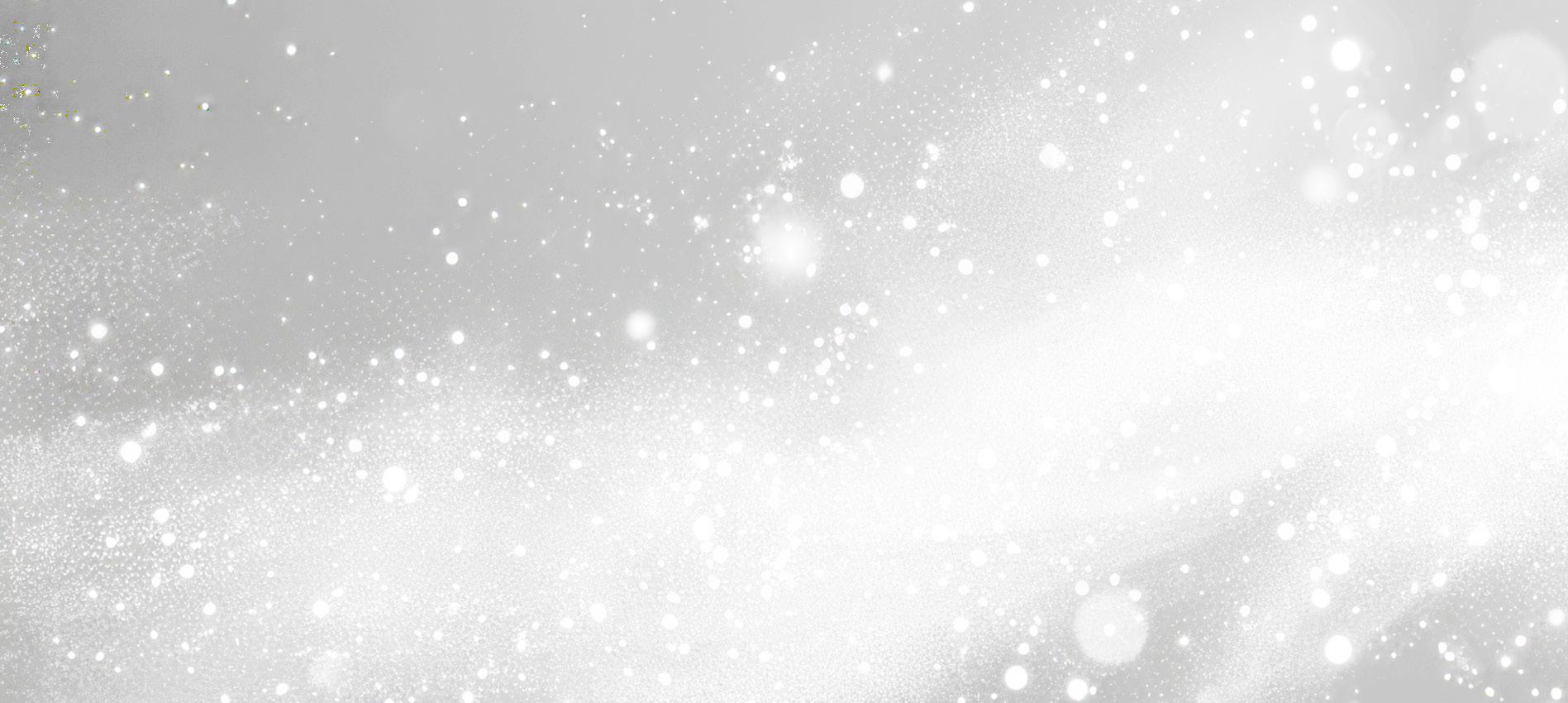
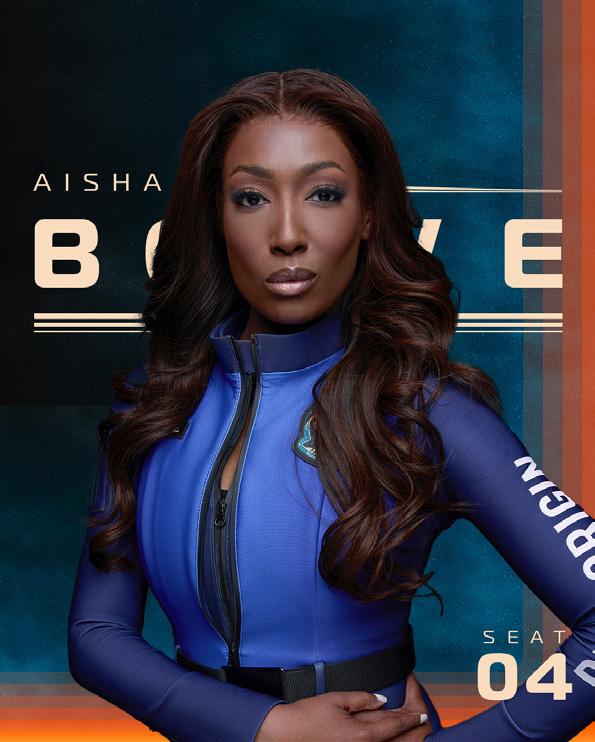
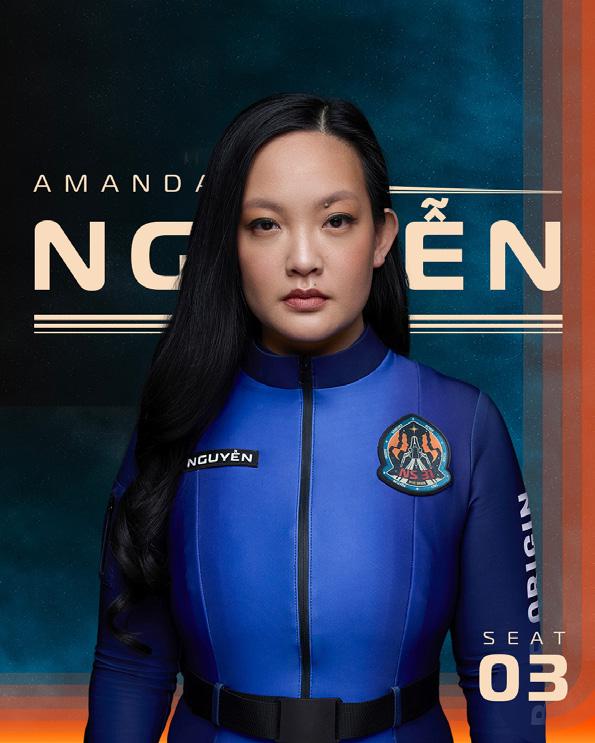
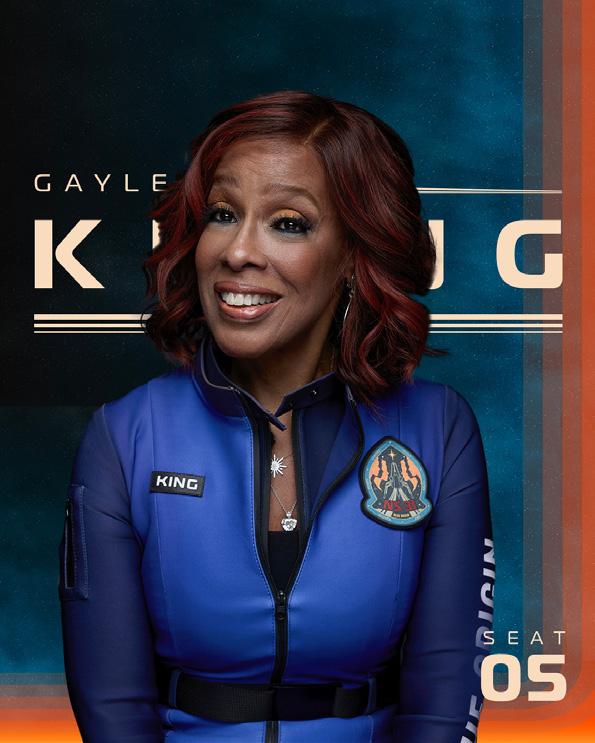
MEET THE NS-31 MISSION CREW
Aisha Bowe – A former NASA rocket scientist, entrepreneur, and global STEM advocate, Aisha Bowe is the CEO of engineering firm STEMBoard and Founder of EdTech company, LINGO. She became the first person of Bahamian descent to visit space as part of the mission.
Amanda Nguyễn – Bioastronautics research scientiest Amanda Nguyễn graduated from Harvard University in 2013. As the first Vietnamese and Southeast Asian woman astronaut, her flight was a symbol of reconciliation between the US and Vietnam and highlighted science as a tool for peace.
Gayle King – Award-winning journalist Gayle King is recognized as a gifted, compassionate interviewer capable of breaking through the noise and creating meaningful conversations. She is a co-host of CBS Mornings, editor-at-large of Oprah Daily, and host of Gayle King in the House on SiriusXM radio.
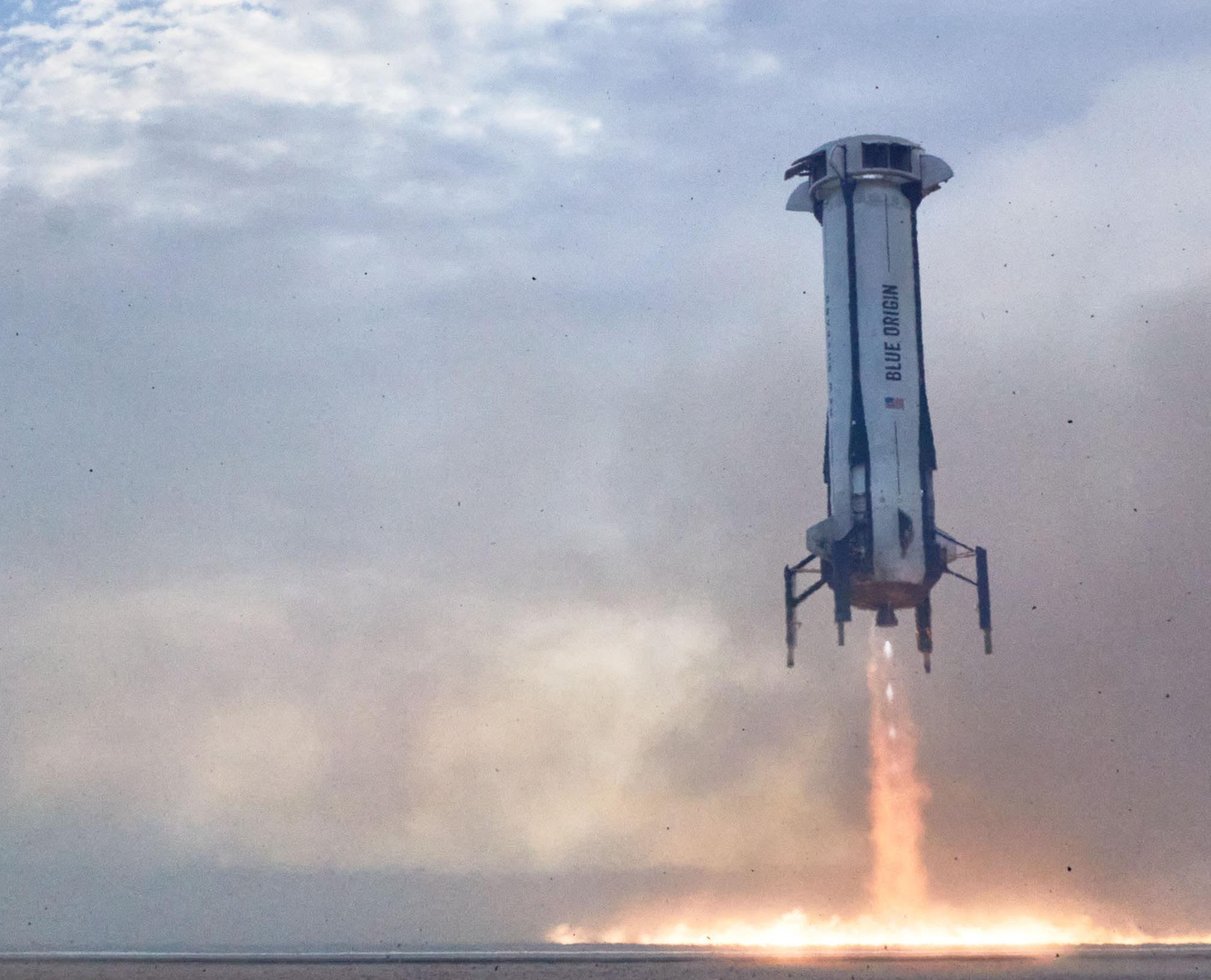
Katy Perry – The biggest-selling female artist in Capitol Records’ history and one of the best-selling music artists of all time with over 115 billion streams, Katy Perry is a global pop superstar.
Kerianne Flynn – Following a successful fashion and HR career, Kerianne Flynn has spent the last decade channeling her energy into community-building. She is passionate about the transformative power of storytelling and has produced thoughtprovoking films such as This Changes Everything and Lilly.
Lauren Sánchez – Emmy award-winning journalist Lauren Sánchez founded Black Ops Aviation, the first female-owned and operated aerial film and production company, in 2016.
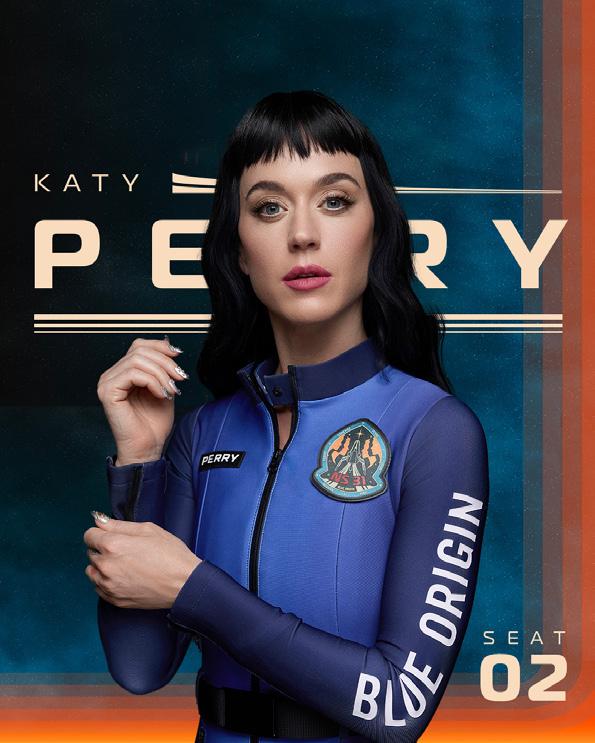
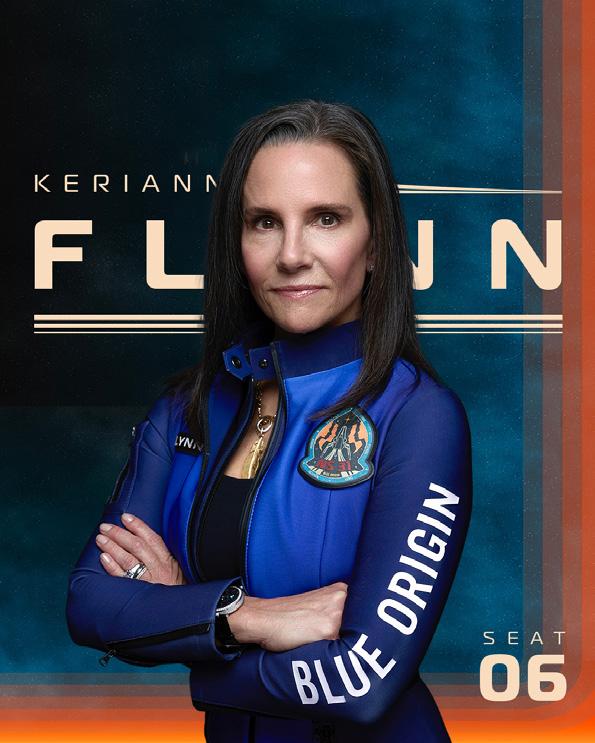
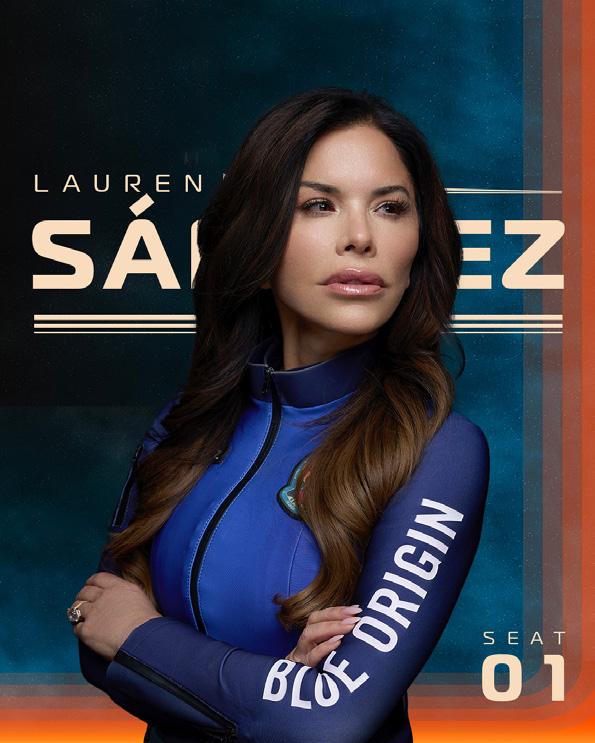
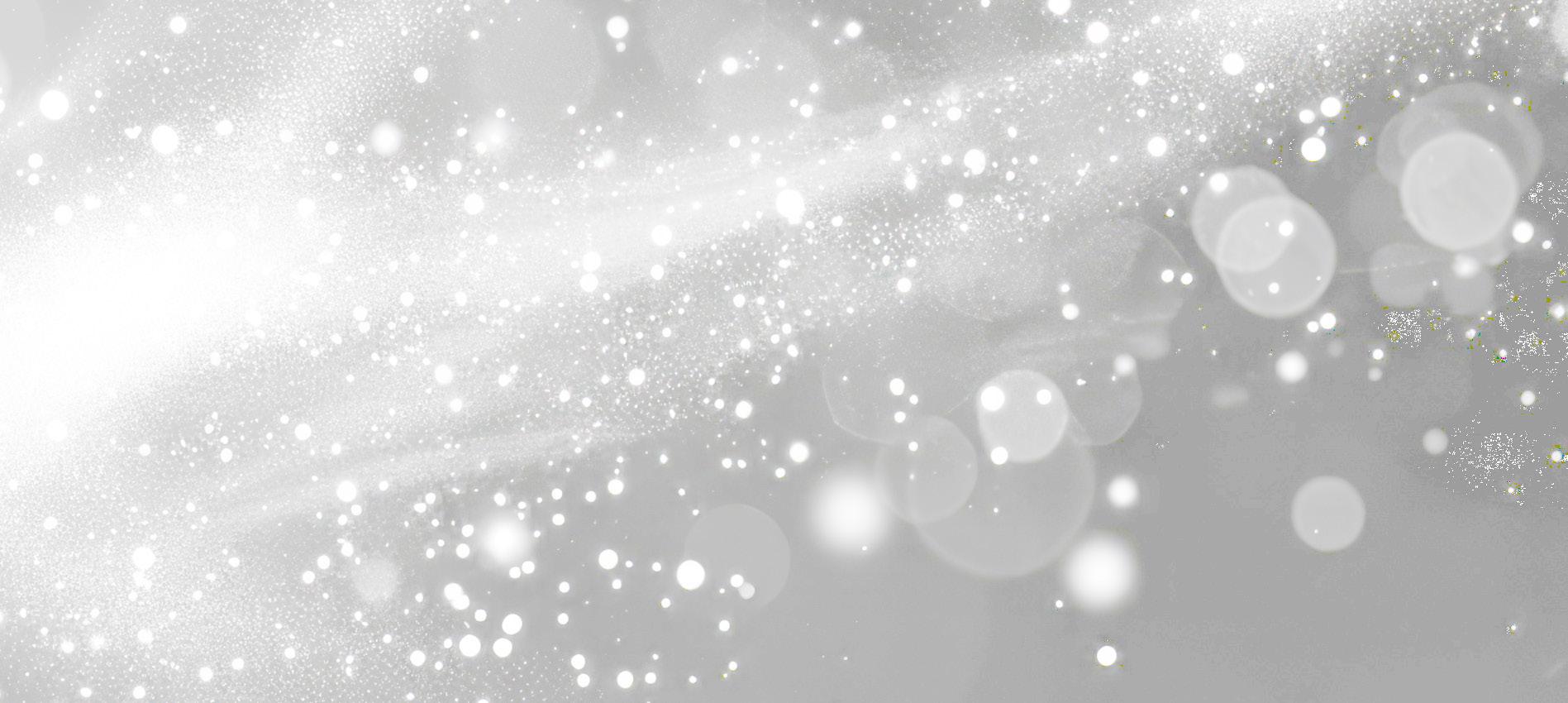
The vehicle features a vertical takeoff and landing architecture, enabling booster reuse up to 25 times with minimal refurbishment.
Its reusable, throttleable, and liquidpropellant BE-3PM engine, meanwhile, is fueled by highly efficient liquid oxygen and hydrogen.
During flight, the only byproduct of New Shepard’s engine combustion is water vapor, with no carbon emissions emitted.
The rocket system has also been designed to ensure minimal maintenance between flights, lowering the cost of access to space and reducing waste.
LADIES HAVE LIFT-OFF
On the 11-minute journey, New Shepard astronauts ascend towards space from Launch Site One, nestled in the Guadalupe Mountains near Van Horn, Texas.
At more than three times the speed of sound, they soar past the Kármán line – the internationally-recognized boundary of space – before unbuckling to experience several minutes of weightlessness and enjoy breathtaking views of Earth.
Though the vehicle is fully
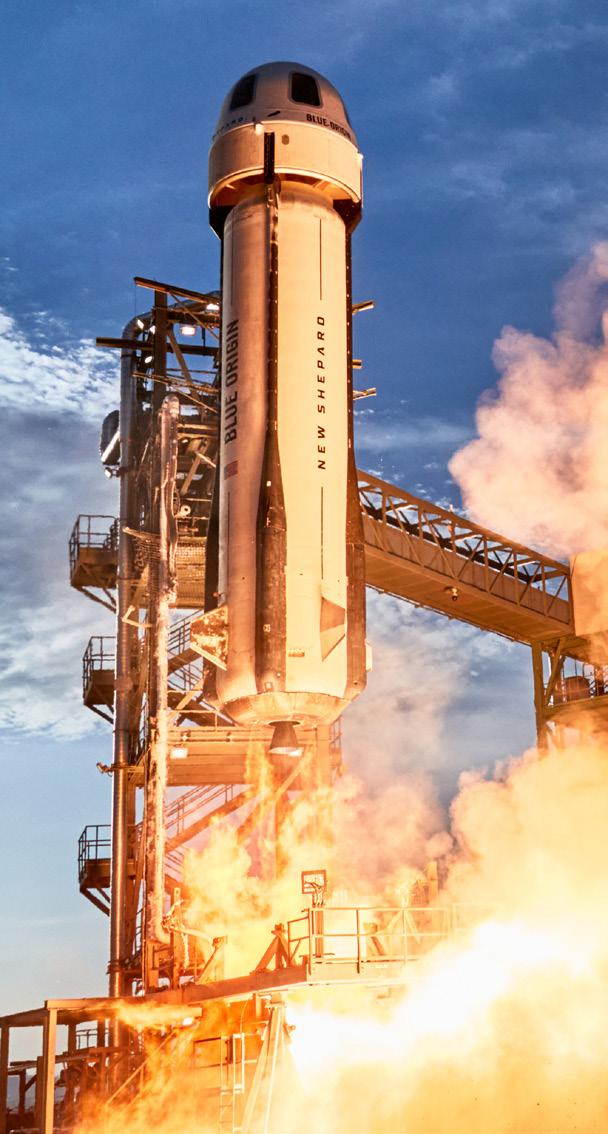
autonomous, meaning there are no pilots, New Shepard’s pressurized crew capsule has enough room for six people and is environmentally controlled for comfort.
In this spacious capsule, each
astronaut gazes upon the planet from their own giant windows, among the largest to have ever flown in space, which comprise one third of the capsule’s surface area.
Uniquely, on the NS-31 mission, the six astronauts – Aisha Bowe, Amanda Nguyễn, Gayle King, Katy Perry, Kerianne Flynn, and Lauren Sánchez – were all women, heralding the first all-female spaceflight since Valentina Tereshkova became the first woman in space in 1963.
The mission challenged their perspectives of Earth, empowered them to share their own stories, and created lasting impact that will inspire generations to come.
PRIORITIZING SAFETY
New Shepard began flying humans in 2021 following the conclusion of a rigorous flight test program.
This included several successful flight and capsule escape tests, demonstrating that the crew escape system, which separates the capsule from the booster in the unlikely event an issue is detected, can safely activate during any phase of the flight – whether from the launch pad, midflight, or in the vacuum of space.
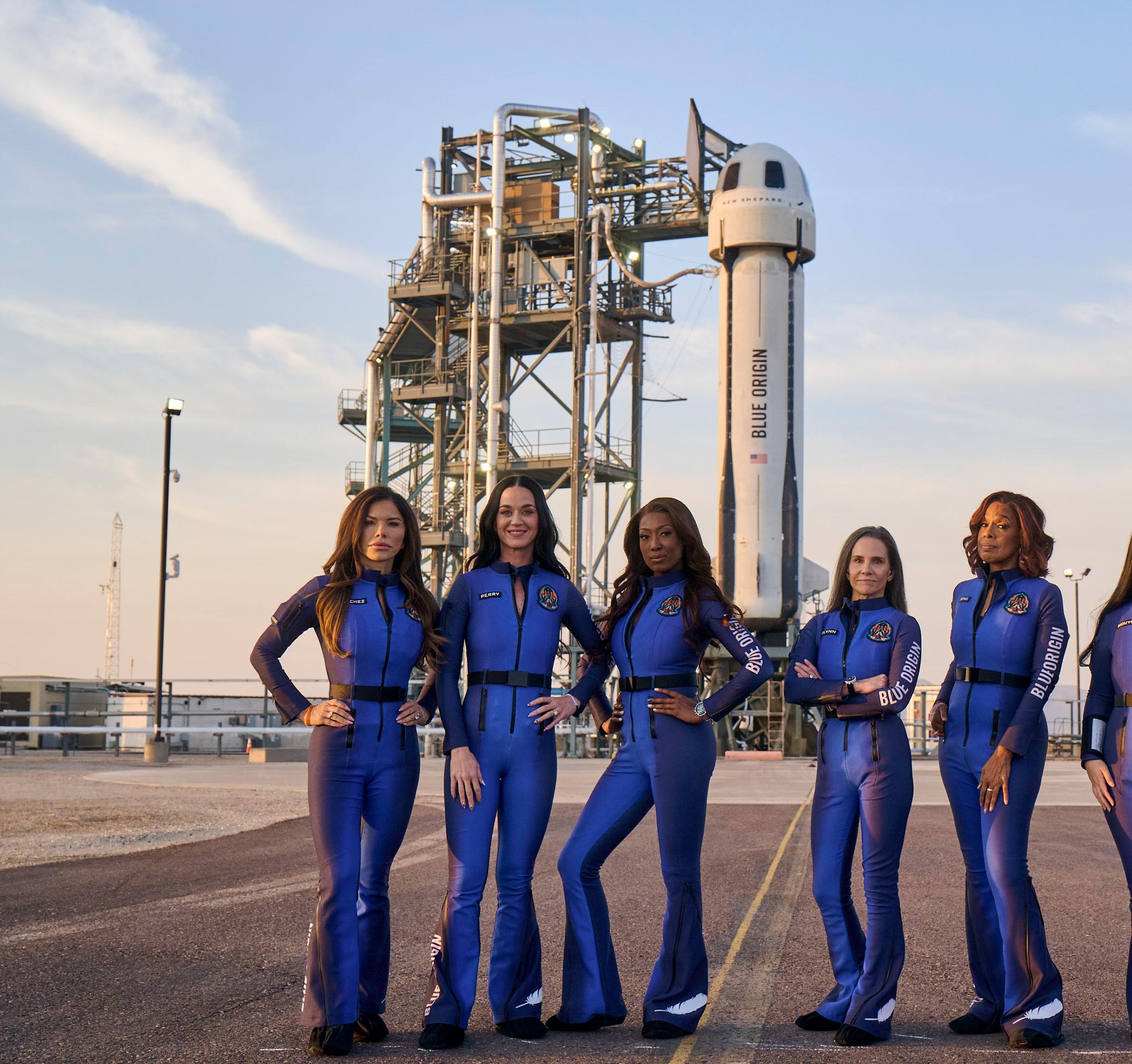
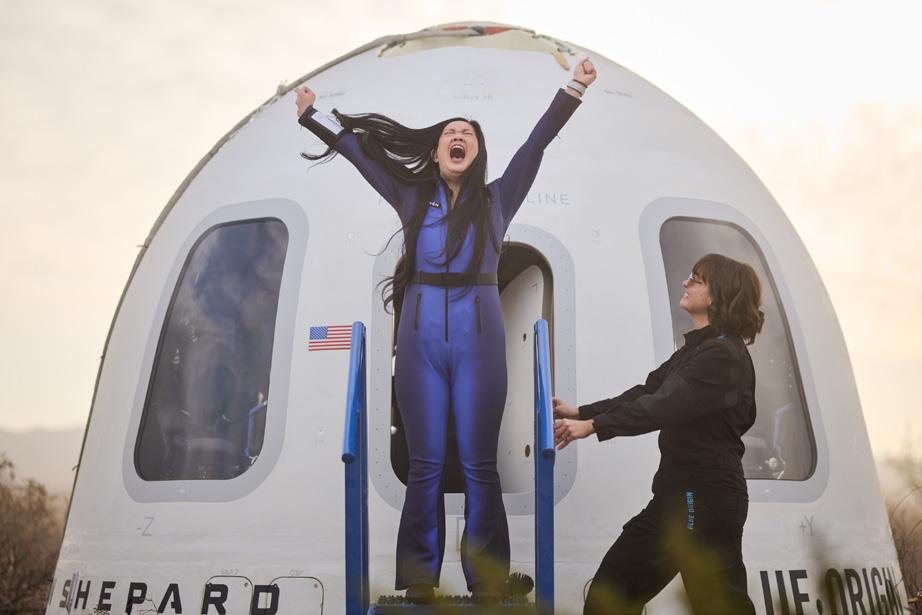
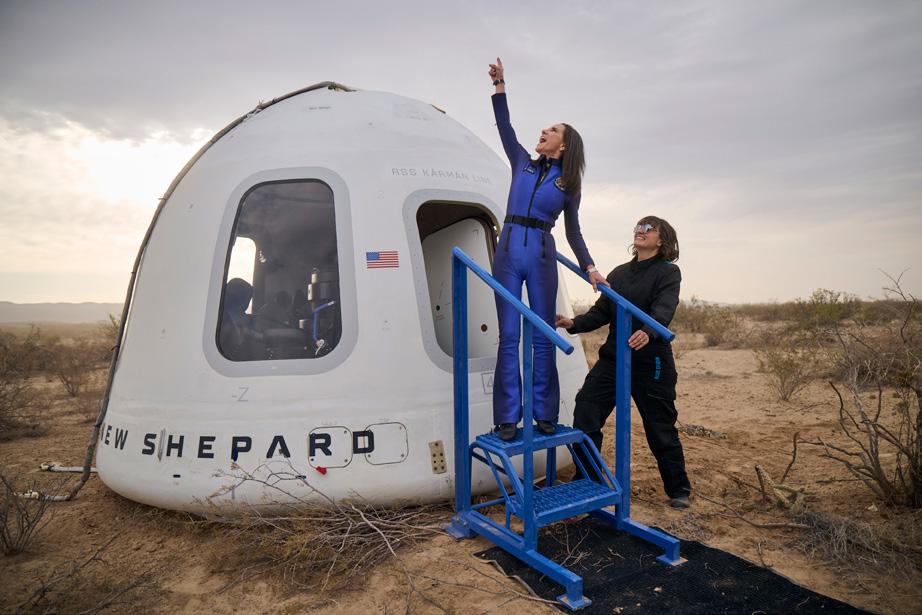
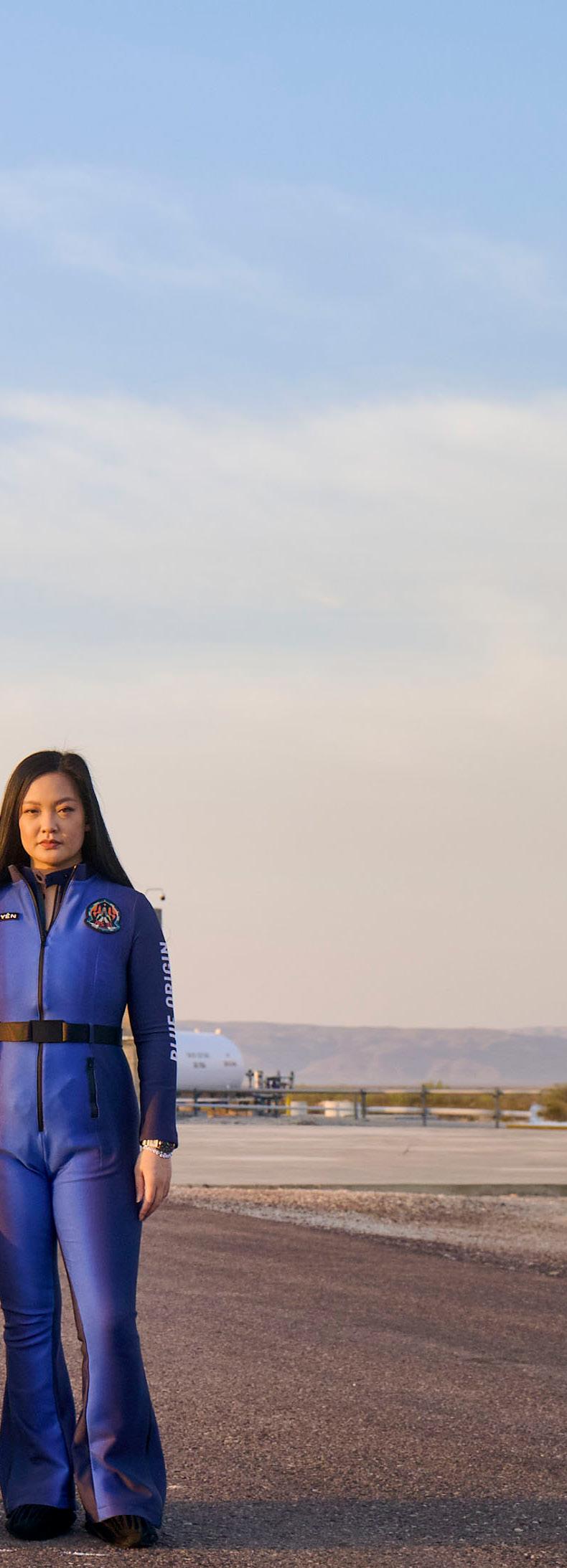
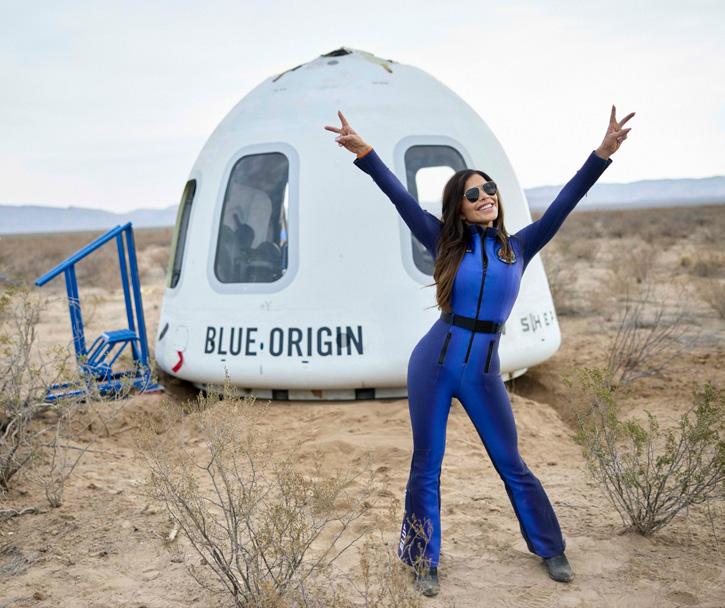
NS-31 MISSION PATCH – KEY SYMBOLS
• Target star – Aisha Bowe’s ambition for setting big goals, passion for STEM, and commitment to inspiring future generations.
• Scales of justice – Amanda Nguyễn’s efforts to advocate for civil rights, break barriers, and empower everyday people to create change.
• Shooting star microphone – Gayle King’s commitment to sharing important stories with the world.
• Firework – Katy Perry’s global influence across music, pop culture, and philanthropy.
• Film reel – Kerianne Flynn’s passion for filmmaking, storytelling, and crafting beautiful narratives.
• Flynn the Fly – The main character in Lauren Sánchez’s best-selling children’s book, The Fly Who Flew to Space.
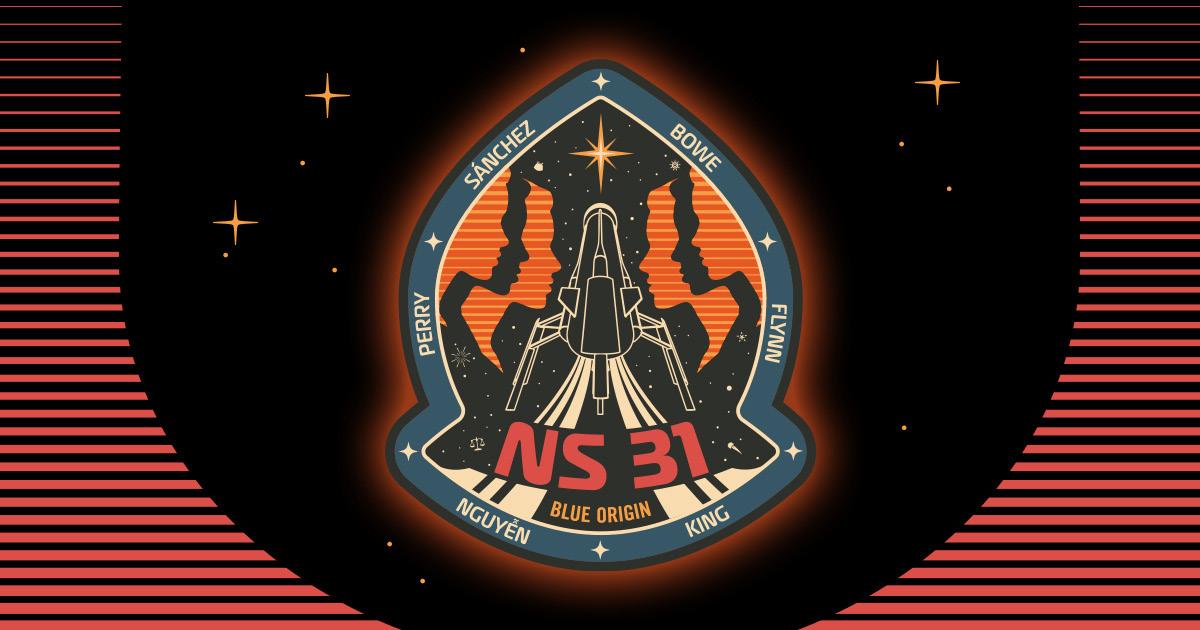
The crew capsule also has numerous redundant safety systems, including a retro-thrust system that expels a burst of nitrogen gas to slow the landing to around two miles per hour.
Additionally, the capsule can land with only one of its three parachutes deployed, while the seats and a crushable ring on the bottom of the capsule are designed to absorb g-forces.
Blue Origin’s on-site training program is also meticulously designed to teach astronauts everything they need to know for a safe spaceflight onboard New Shepard, from the mission profile
and safety systems to zero-gravity protocols.
These measures ensured the historic NS-31 mission was safely executed and created history with the first all-female spaceflight in over six decades.
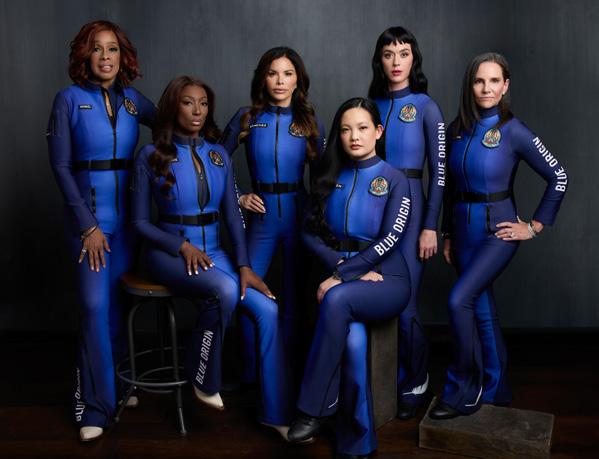
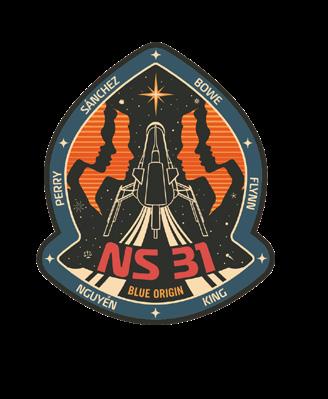

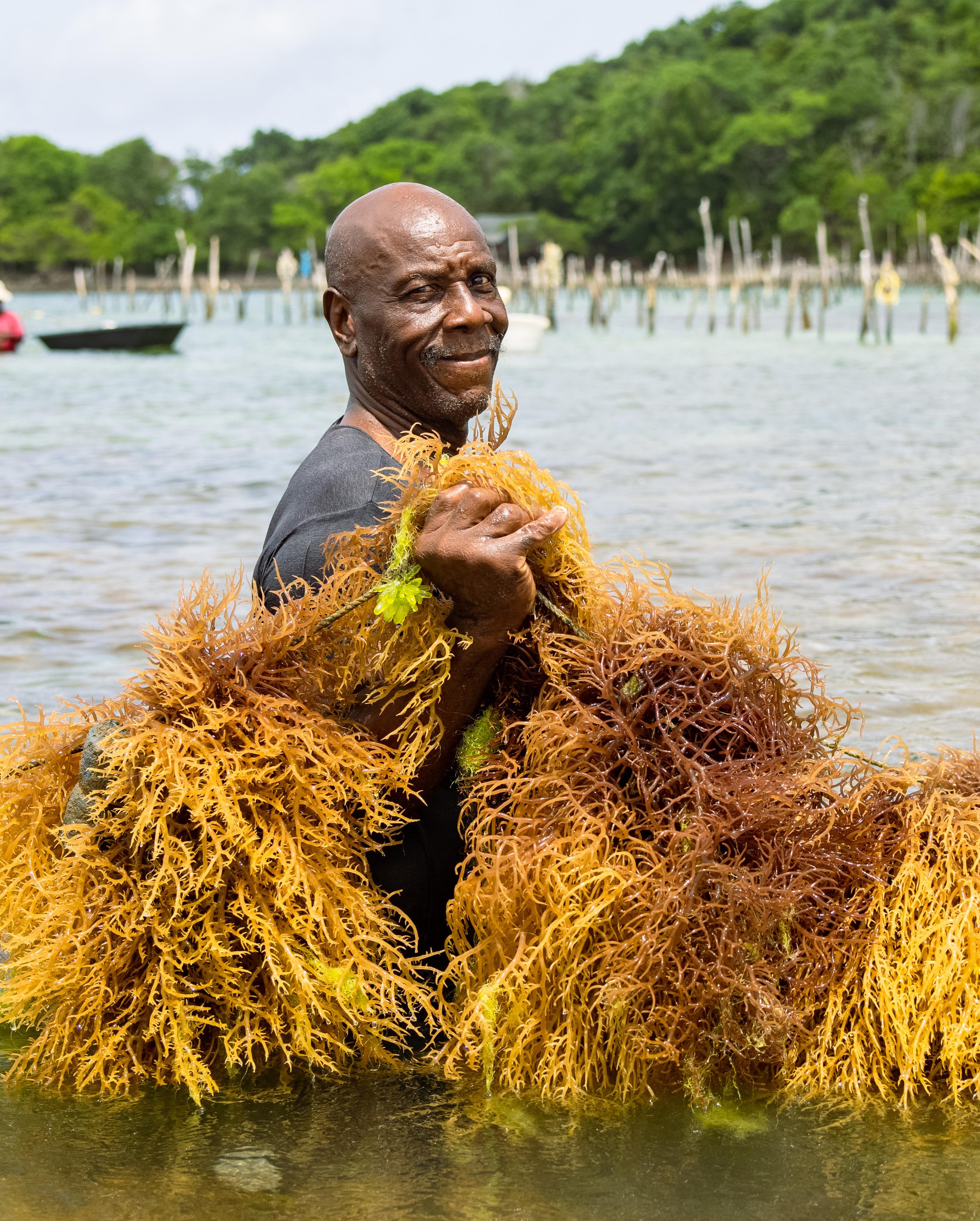
SPOTLIGHT ON SAINT LUCIA EXPORTS
Saint Lucia, once a leading exporter of bananas, is now diversifying its economy by focusing on highquality cacao, rum production, and a growing manufacturing sector. Additionally, the country is capitalizing on the rising popularity of sea moss while navigating challenges and seeking new opportunities in the global market
Writer: Rachel Carr | Project Manager: Krisha Canlas
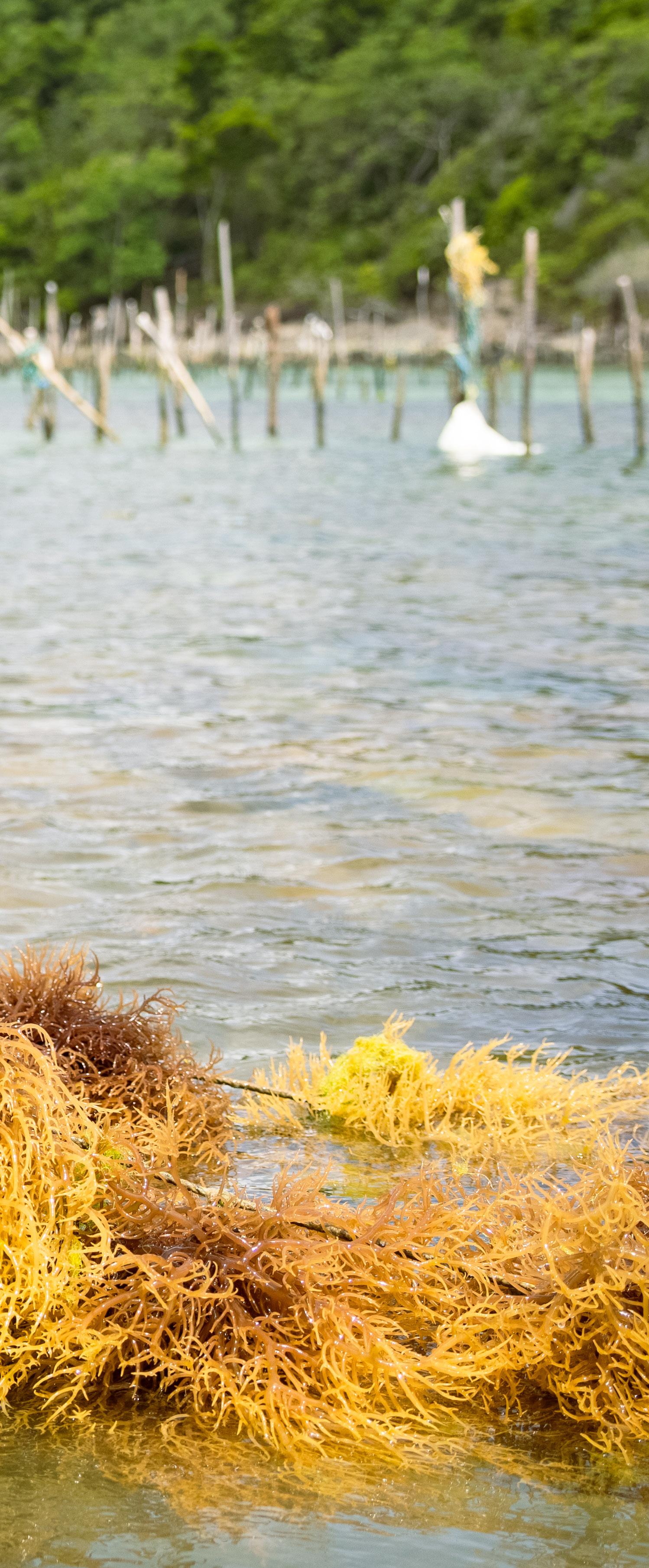
The tropical island of Saint Lucia is an emerald jewel in the Caribbean Sea, where history, culture, and quiet charm converge to present a diverse export market, primarily driven by agriculture, manufacturing, and tourism-related products.
These industries play a pivotal role in bolstering the country’s economy, making substantial contributions to its national income. Among the most prominent export destinations are Guyana, the US, Barbados, Dominica, and Jamaica, each offering unique opportunities and fostering international trade relations.
Although not as dominant as agriculture, the manufacturing sector includes the production of clothing and textiles, which are primarily exported to the US and other Caribbean nations.
The island is also renowned for producing highquality cacao, used in chocolate, as well as nutmeg and other spices, which are exported to various markets, particularly Europe. Additionally, it has a strong reputation for rum production, with several distilleries exporting different varieties of the popular spirit.
Tourism is a vital engine of economic growth, with its influence extending beyond local communities. This thriving industry fosters the creation of unique products often crafted by skilled artisans. As a result, these culturally rich items find their way into the export market, showcasing the region’s artistry.
Moreover, the festival industry not only highlights Saint Lucia’s rich cultural heritage but also, with a diverse line-up of events throughout the year, the vibrant scene plays a crucial role in promoting the island’s identity and attracting visitors from around the globe.
As the industry continues to grow, ongoing efforts are being made to enhance marketing and outreach, further tapping into international markets and making Saint Lucia a premier festival destination.
In recent years, the government has been working to diversify the economy and expand export opportunities beyond traditional sectors by promoting new industries and encouraging foreign investment. Furthermore, trade agreements with Caribbean partners and international markets are crucially shaping Saint Lucia’s export landscape. However, the island faces challenges, including vulnerability to natural disasters and reliance on a limited range of export products. Ongoing efforts to enhance production quality and explore new markets are hoped to strengthen its export capabilities in the future.
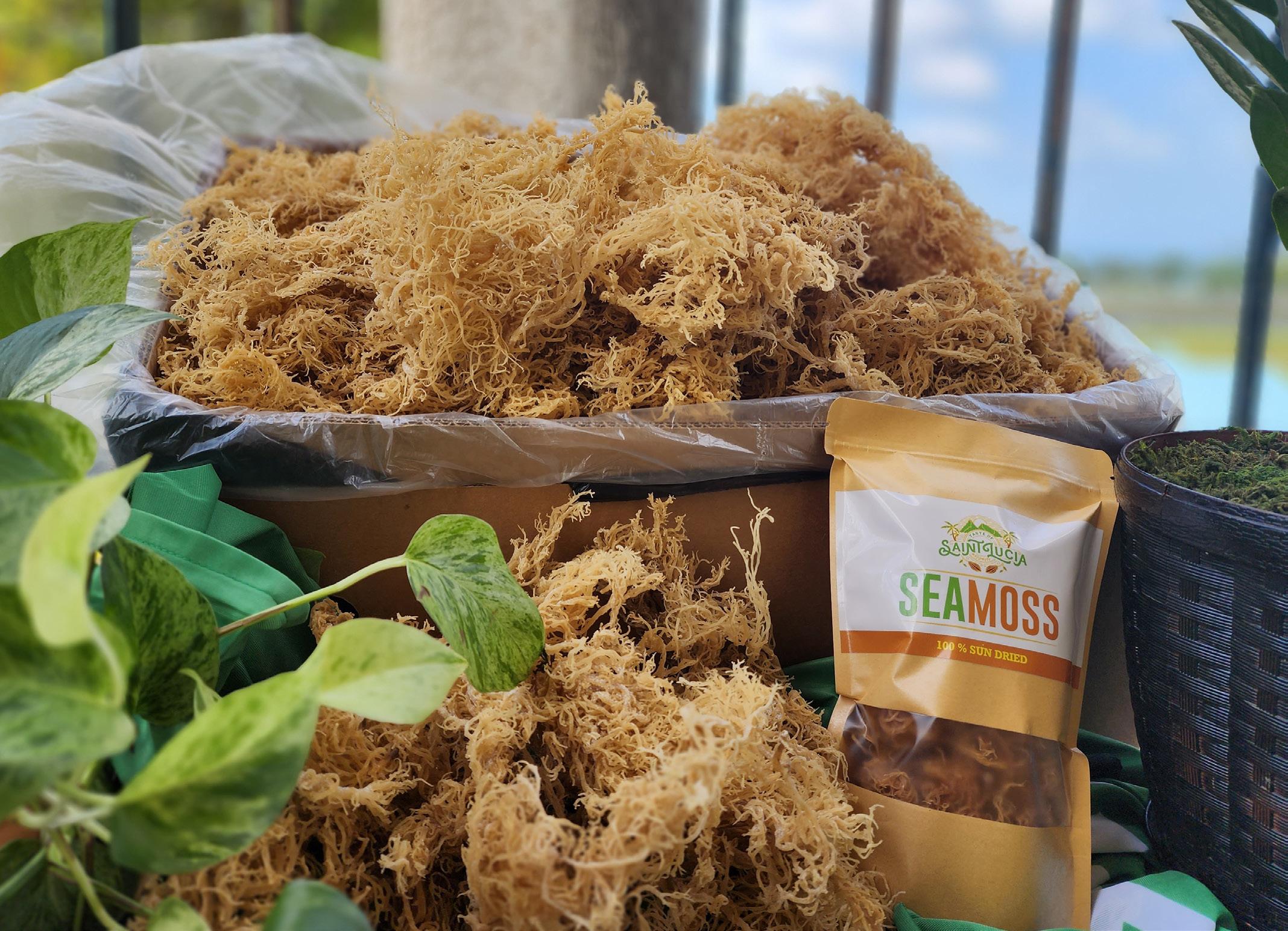
EXPORT SAINT LUCIA INTERVIEW:
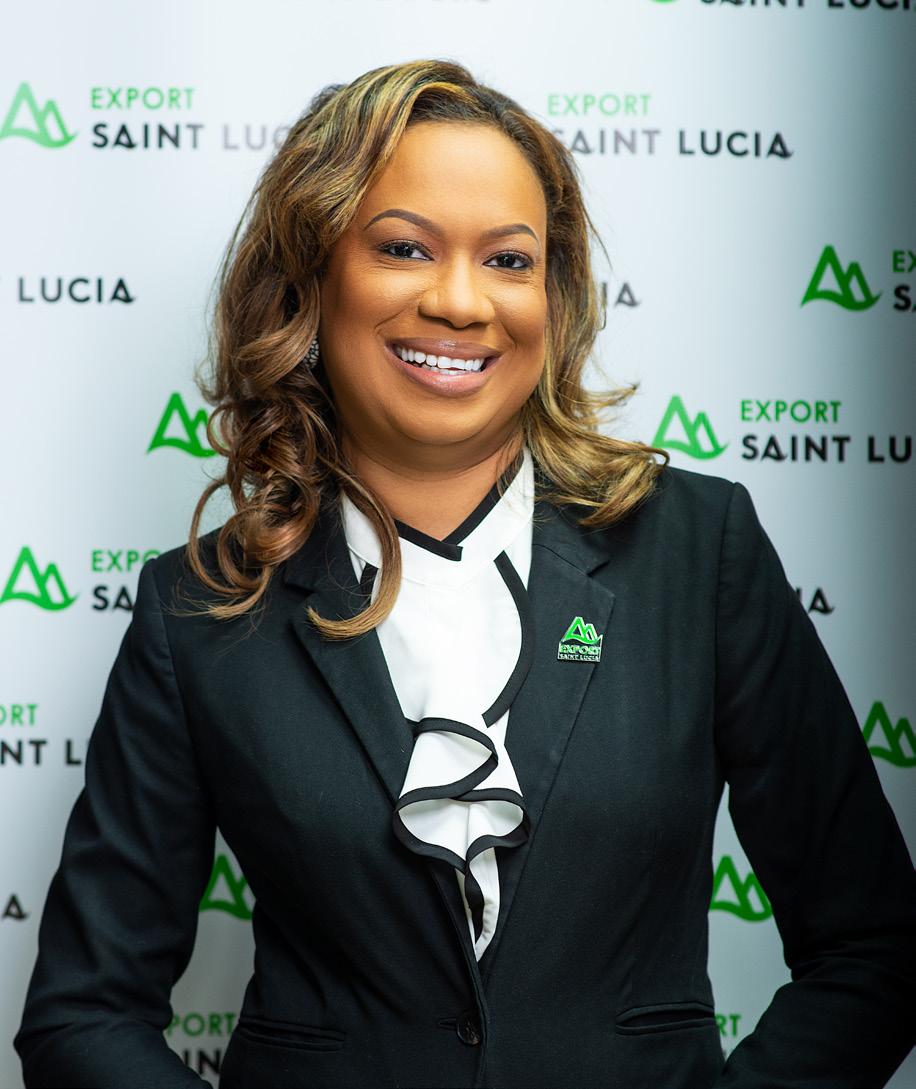
Sunita Daniel, CEO of Export Saint Lucia, outlines the strategic initiatives in place to enhance export capabilities and foster entrepreneurial growth, aimed at diversifying the island’s economy, supporting local businesses in global markets, and promoting high-quality Saint Lucian products
North America Outlook (NA): Firstly, could you talk us through the origins of Export Saint Lucia, its establishment, and the initial mission and vision?
Sunita Daniel, CEO (SD): Export Saint Lucia was created as the government’s dedicated export-promotion agency, operating as a statutory body under the Ministry of Commerce, Manufacturing, Business Development, Cooperatives, and Consumer Affairs. From the outset, the goal was clear – to diversify Saint Lucia’s economy beyond its traditional pillars, such as tourism and financial services,
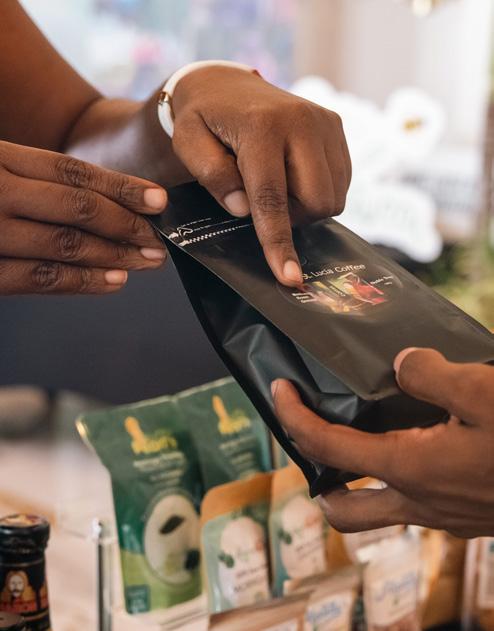
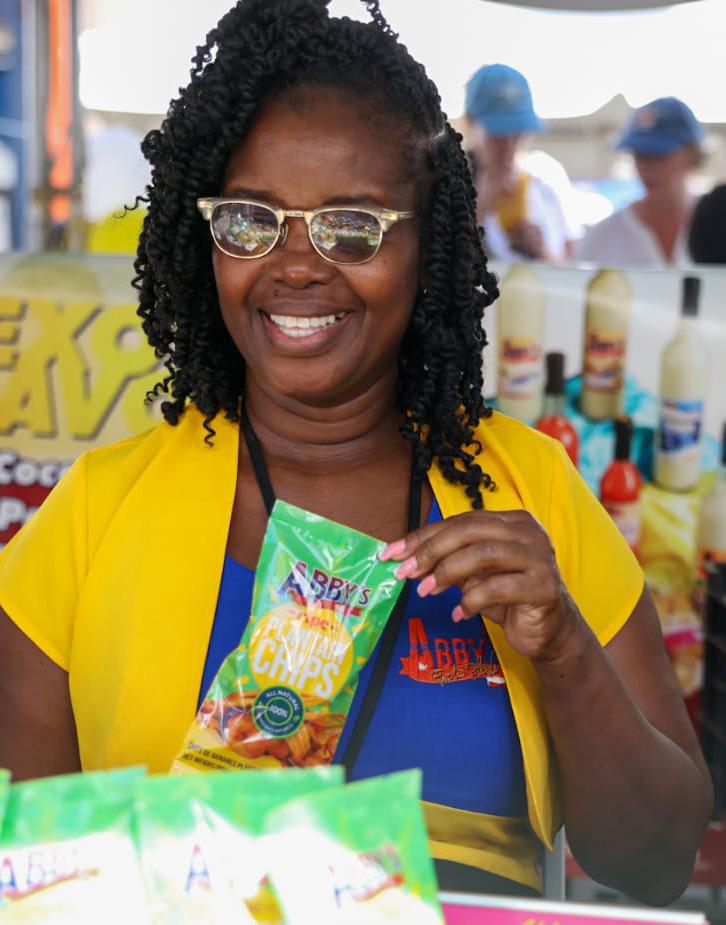
and to help local businesses compete and succeed on the global stage.
Our mission is to facilitate the growth of sustainable exports from Saint Lucia by providing targeted business support, reliable market intelligence, and strong promotional platforms. That mission has guided everything we do from preparing producers for export to connecting them with buyers overseas.
Our vision is to see Saint Lucia globally recognized as a source of high-quality, authentic, and sustainable products. We want our exports, whether it’s agroprocessed goods, wellness items, or creative products, to reflect the richness of our island’s culture and values. We also want to create an environment where Saint Lucian entrepreneurs not only reach international markets but grow within them by embracing global standards in production, packaging, and ethical practices.
In practical terms, this means offering hands-on support, which includes capacity-building workshops, certification assistance, mentorship programs, and international exposure. We’ve taken local businesses to key trade shows across North America and Europe, introducing the Taste of Saint Lucia brand to help buyers immediately identify the quality and origin of our goods.
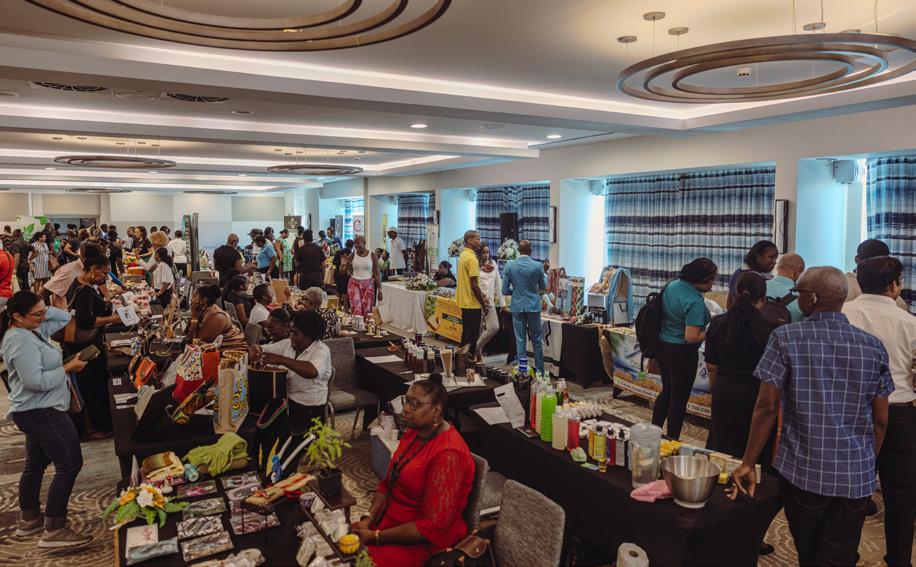
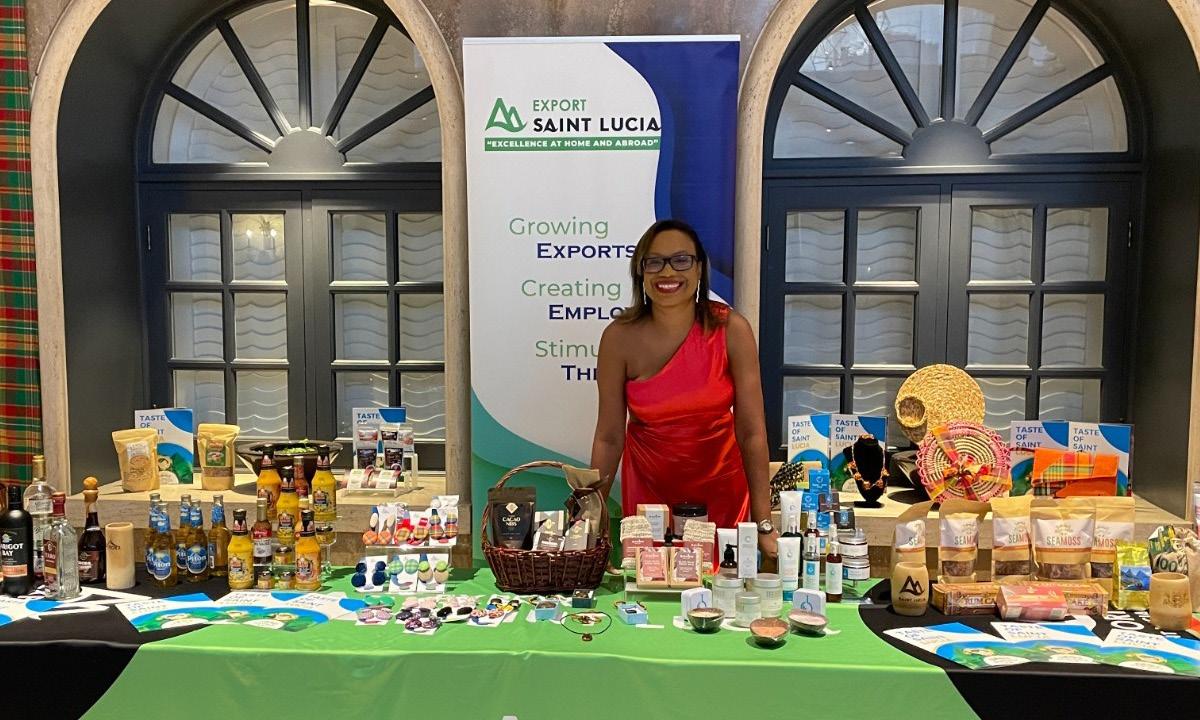
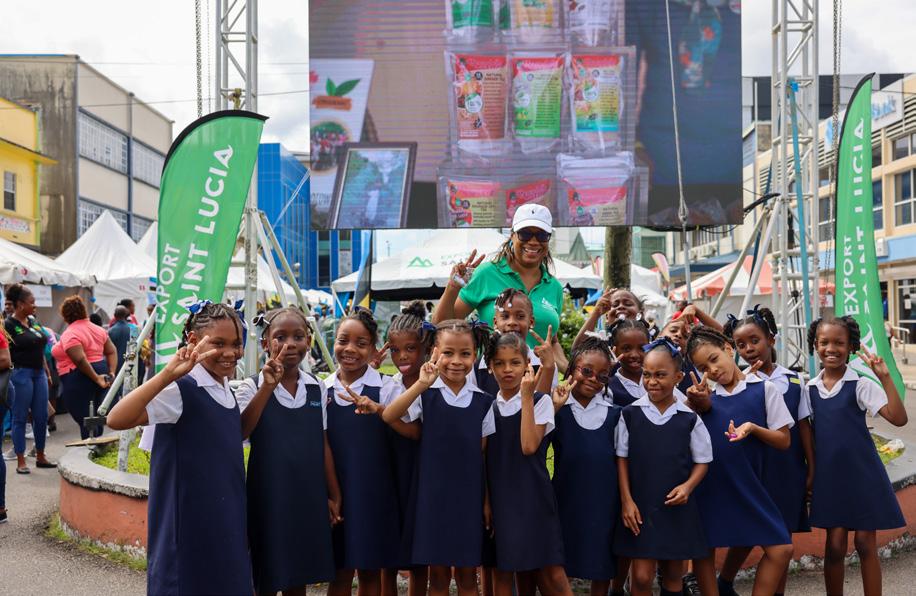
Since our inception, Export Saint Lucia has supported hundreds of small and medium-sized enterprises (SMEs), assisting them in entering markets in Miami, Toronto, New York, and London, among others, thereby opening new doors and expanding the country’s footprint in the global economy.
NA: How has Export Saint Lucia developed and progressed? What objectives has it achieved since its inception?
SD: Export Saint Lucia has undergone a significant evolution. When we first started, our main goal was to lay the groundwork by building awareness, educate local businesses on export standards, and create the support systems necessary for them to access international markets. Over time, we’ve grown from a facilitator to a strategic driver of Saint Lucia’s export growth.
One of our proudest accomplishments is the rollout of the Taste of Saint Lucia brand. This initiative has provided a strong, recognizable identity for Saint Lucian products, making them more appealing and marketable to international audiences.
Another significant milestone has been our Packaging for Exports project, implemented in partnership with the International Trade Centre (ITC). Through this program, we delivered 21 innovative packaging and labeling solutions
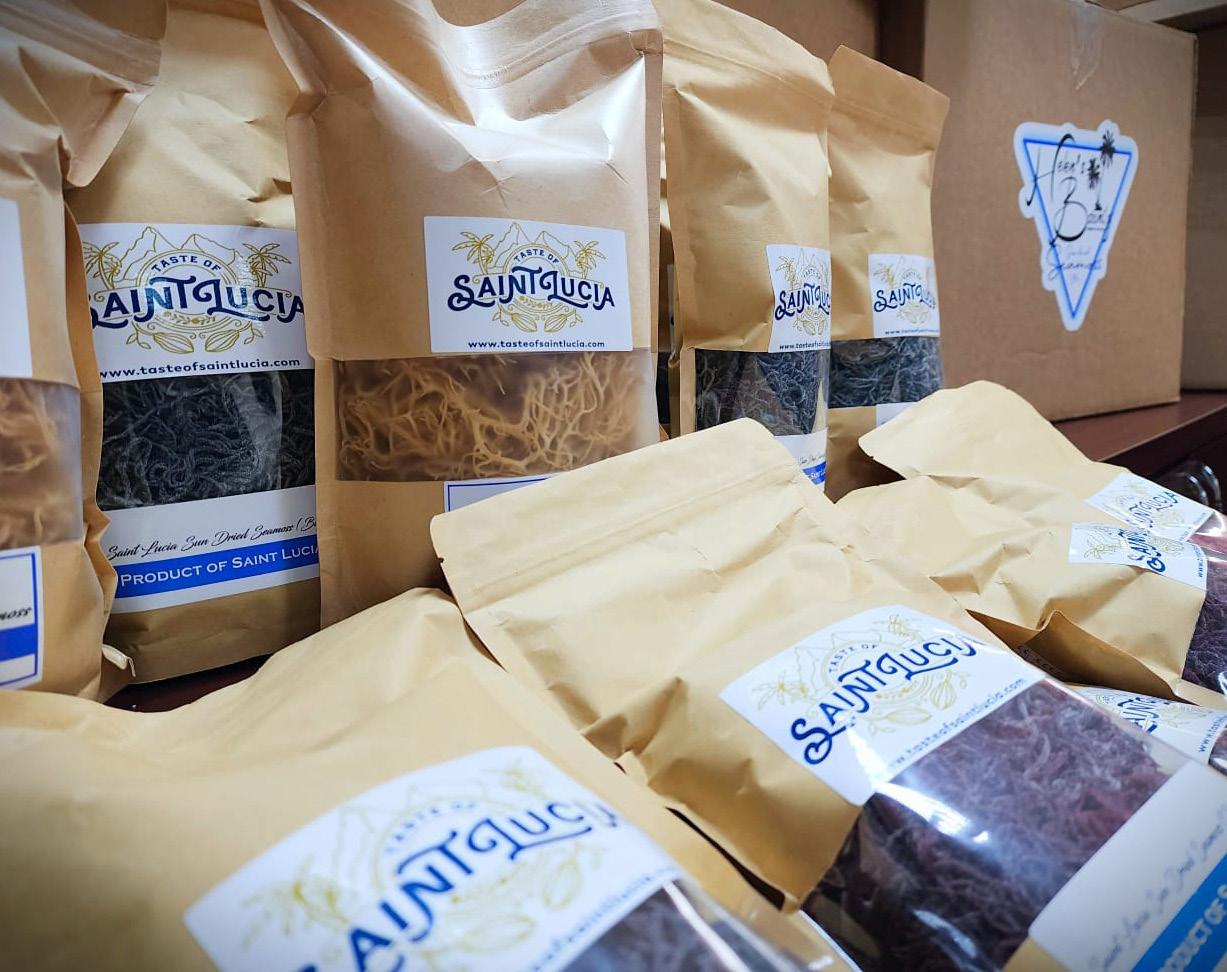
to micro, small, and medium-sized enterprises (MSMEs) across the island. This directly addressed one of the biggest barriers to export – presentation and compliance with market packaging standards, giving our producers a competitive edge.
The sea moss industry, however, is perhaps our most striking success story. Back in 2018, it generated only tens of thousands of dollars in export revenue. Today, it generates millions of dollars annually. That growth is no accident – it’s the result of direct intervention through our Sea Moss Development Programme. The socioeconomic impact of our intervention with the sea moss industry is far greater than the dollar value of the exports. Hundreds of jobs have been created in rural communities, with women being the group most widely impacted. We also did a program with at-risk youth, training young men at a juvenile facility in the practical and theoretical aspects of the industry.
Saint Lucia sea moss has garnered global recognition, and our consumers regard it as the best in the world. We are in the early stages of acquiring a Geographical Indication (GI) to protect it and reassure consumers that any product bearing the Saint Lucia sea moss mark is of the highest quality, standard, and is authentically Saint Lucian. If successful with our bid, it will become our second GI.
Saint Lucia is renowned for its high-quality products, and our rums have won numerous international awards.
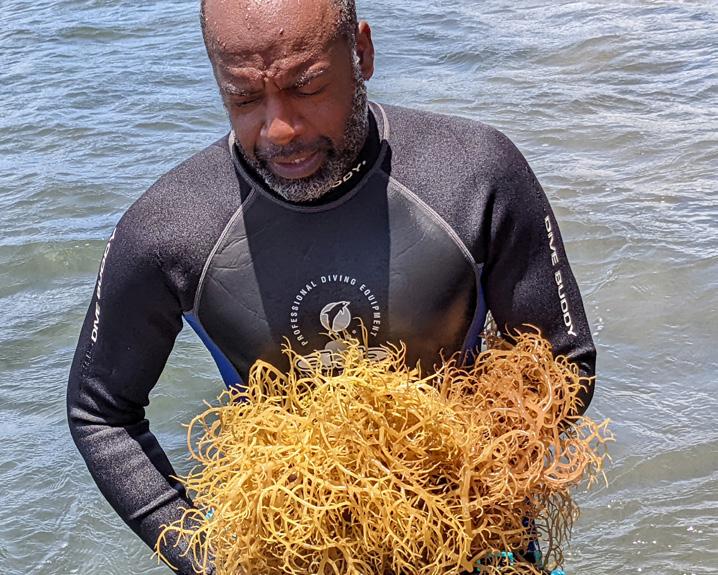
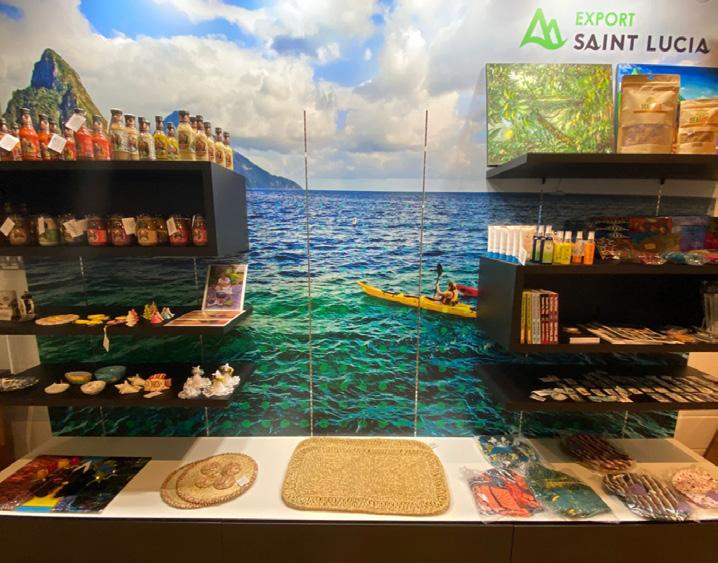
In 2023, Saint Lucia Distillers was awarded a GI for Saint Lucian Rum. The attributes of the spirit were considered unique enough, coupled with the distillation and production process, and, of course, its quality, to secure the prestigious mark.
“WE WANT OUR EXPORTS, WHETHER IT’S AGRO-PROCESSED GOODS, WELLNESS ITEMS, OR CREATIVE PRODUCTS, TO REFLECT THE RICHNESS OF OUR ISLAND’S CULTURE AND VALUES”
– SUNITA DANIEL, CEO, EXPORT SAINT LUCIA
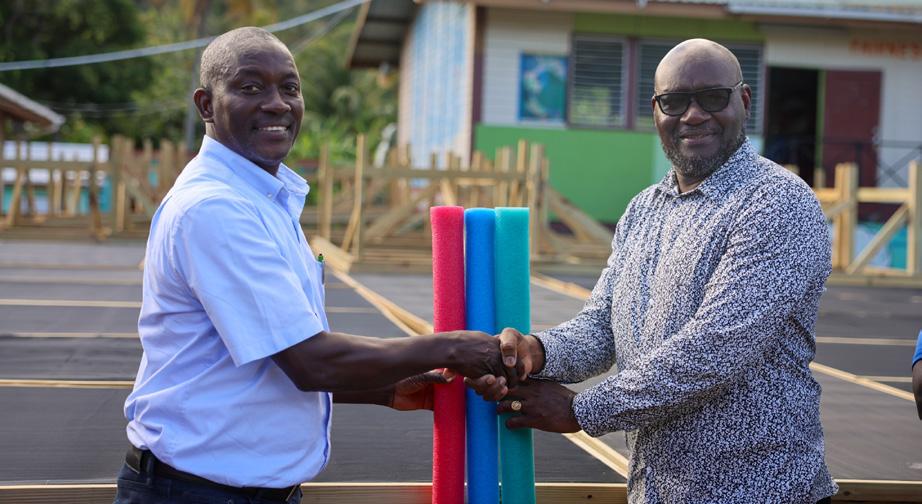
At the same time, Saint Lucia breadfruit has also been regarded as one of the best and is fiercely sought after by consumers in the US and UK. To ensure our consumers are purchasing authentic fruit from Saint Lucia, we have created a Lucian Breadfruit brand and trademark, which holds enormous potential as a climate-resilient, nutrientdense export. By giving it a distinct Saint Lucian identity and pursuing legal protection, we are building a foundation for long-term value in both raw and processed forms of the product.
NA: Could you discuss the cultural aspect of the island and how Export Saint Lucia enables musicians to penetrate international markets?
SD: Saint Lucia’s culture resonates with people. Nowhere is that more evident than with Lucian Carnival. Saint Lucia Carnival is an electrifying celebration of culture, color, and creativity, where pulsating soca rhythms, dazzling costumes, and contagious energy transform the island into a non-stop festival of freedom and expression. Held in July, it blends traditional Caribbean pageantry with a uniquely Saint Lucian flair, drawing revelers from across the globe to jump, wave, and dance in the heart of paradise. A critical element is the music, the heartbeat of the celebration, and it has become one of our strongest cultural exports.
On trade missions, we’re often struck by how far our music has traveled. Whether it’s hearing a Dennery Segment or one of our soca tunes pulsating through the airwaves at international events or meeting people who recognize Saint Lucia purely through our sound, it confirms that our culture has a global reach.
It was essential for us to ensure that our music maintained the same quality, standard, and global appeal as our products. As such, in 2024, we developed and introduced the Most Exportable Song award for Saint Lucia Carnival that recognizes a piece released during the season with the most international appeal, a song that resonates with carnival and music lovers globally – one that any reveler could sing at the top of their lungs and not compromise their sovereignty.
Imran Nerdy was our inaugural winner with his hit song ‘Start D Party’, which I encourage everyone to listen to. The winnings included a cash prize and additional marketing support for the artist. It’s part of our broader strategy to turn musical talent into international success stories. We are committed to continually growing this award to ensure that its legacy holistically builds the artist, song, sector, and, most importantly, the Saint Lucia Carnival.
In 2019, Export Saint Lucia launched the Business of Music developmental workshops, specifically for local artists. This focused on developing participants’ musical and business acumen, covering topics such as branding
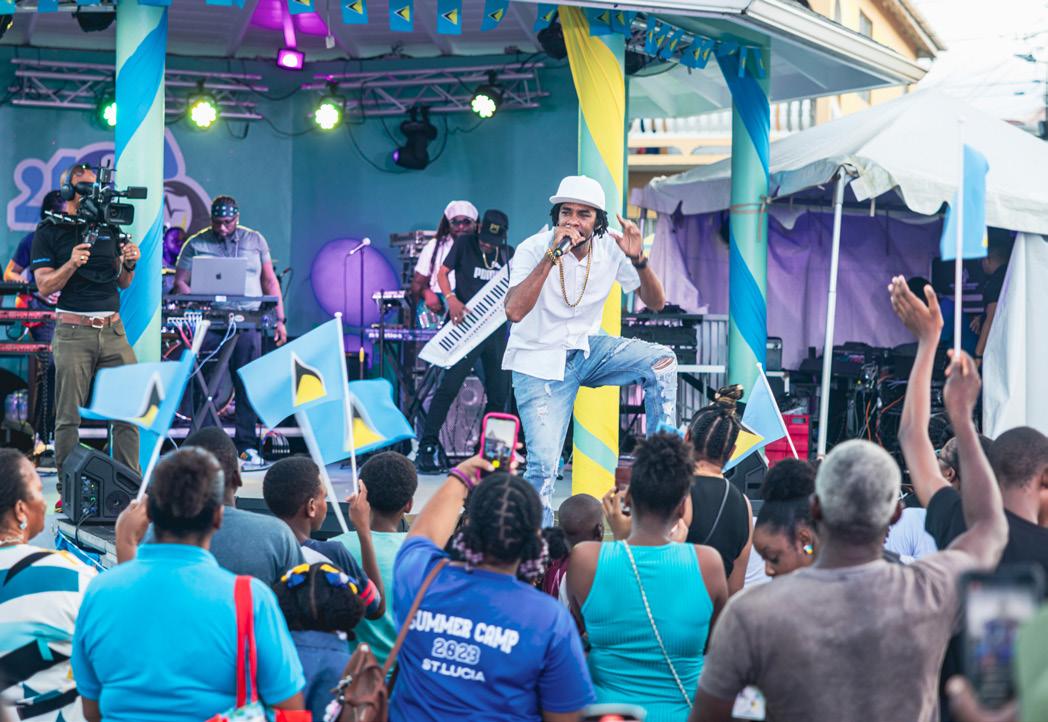
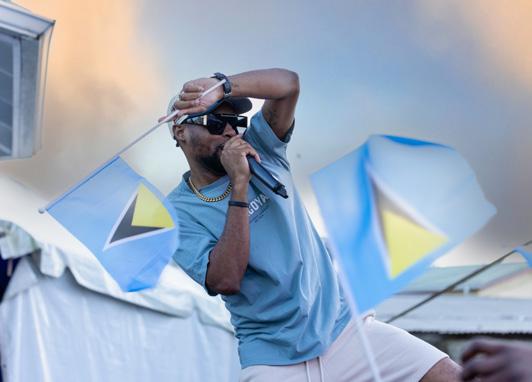
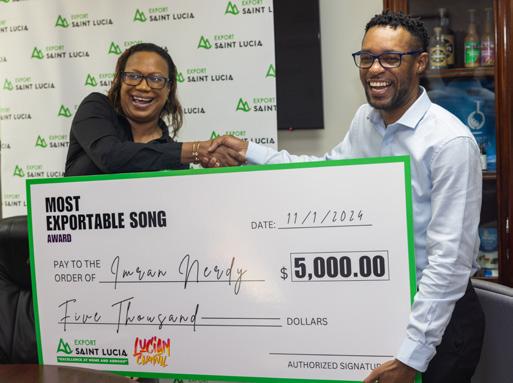
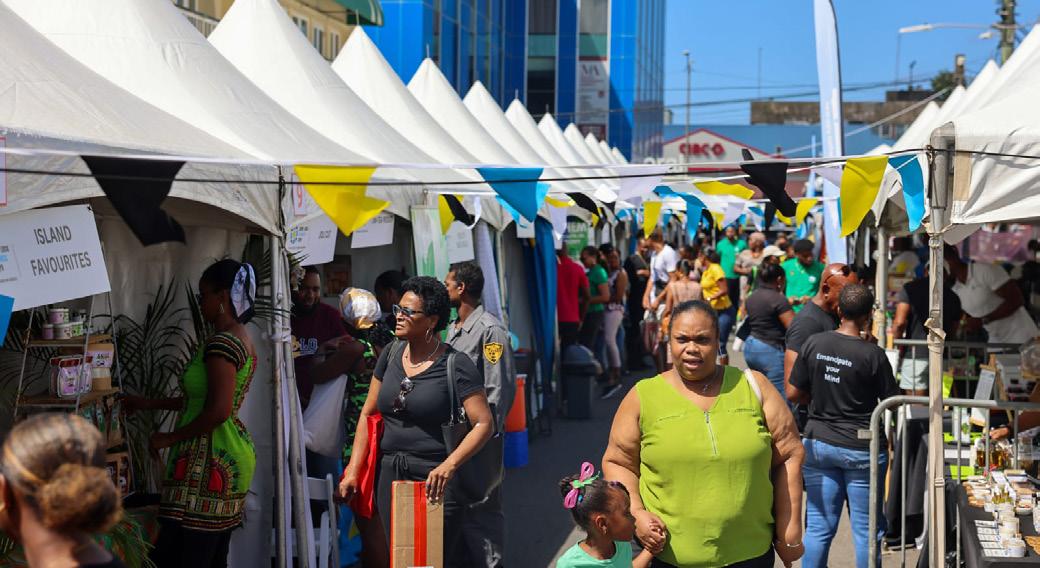
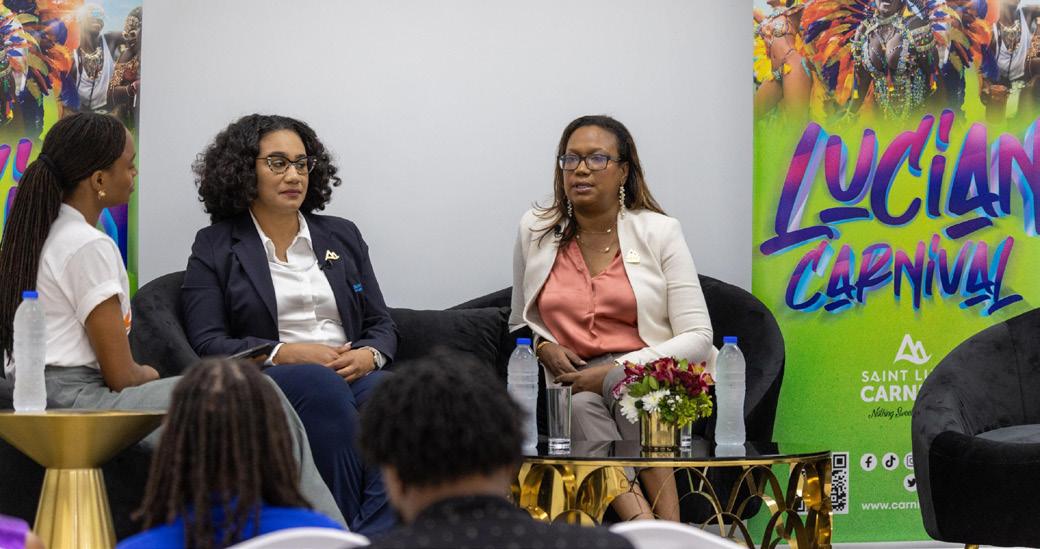
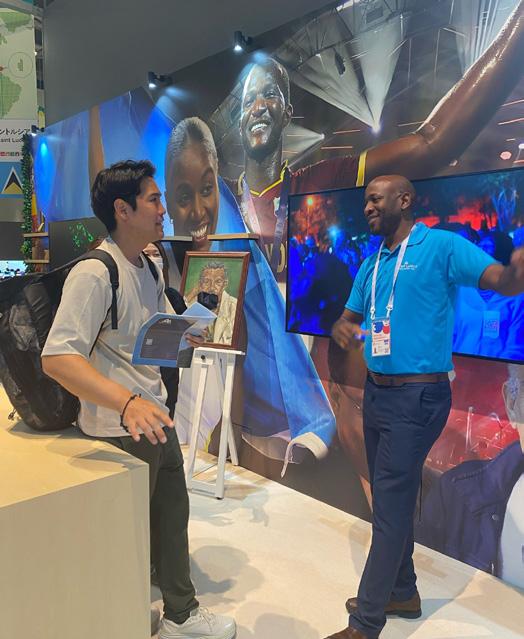
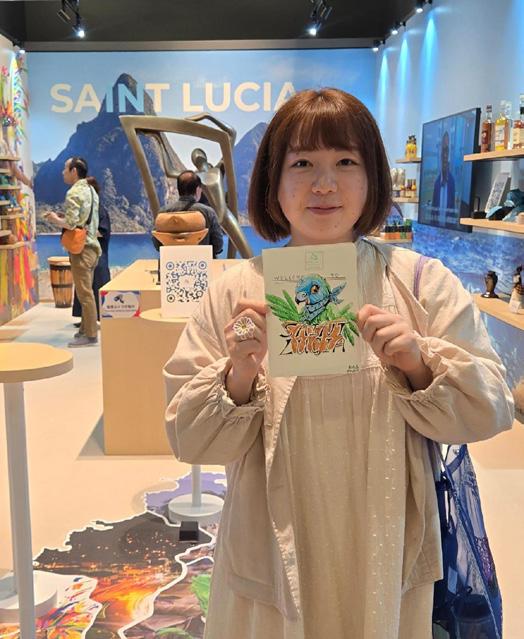
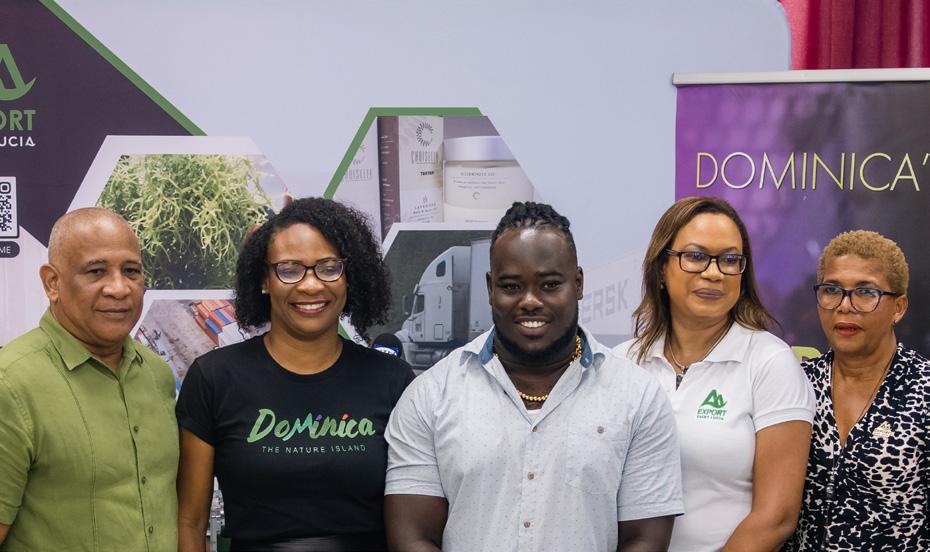
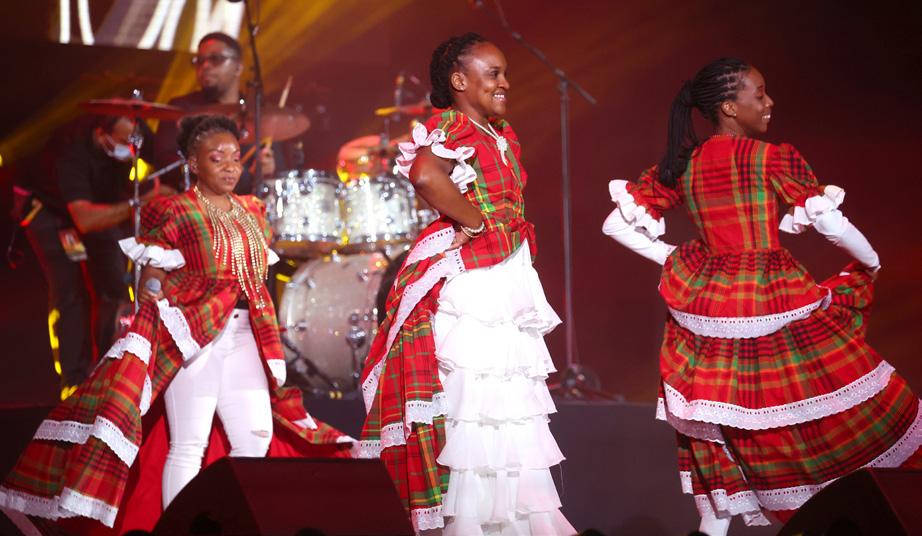
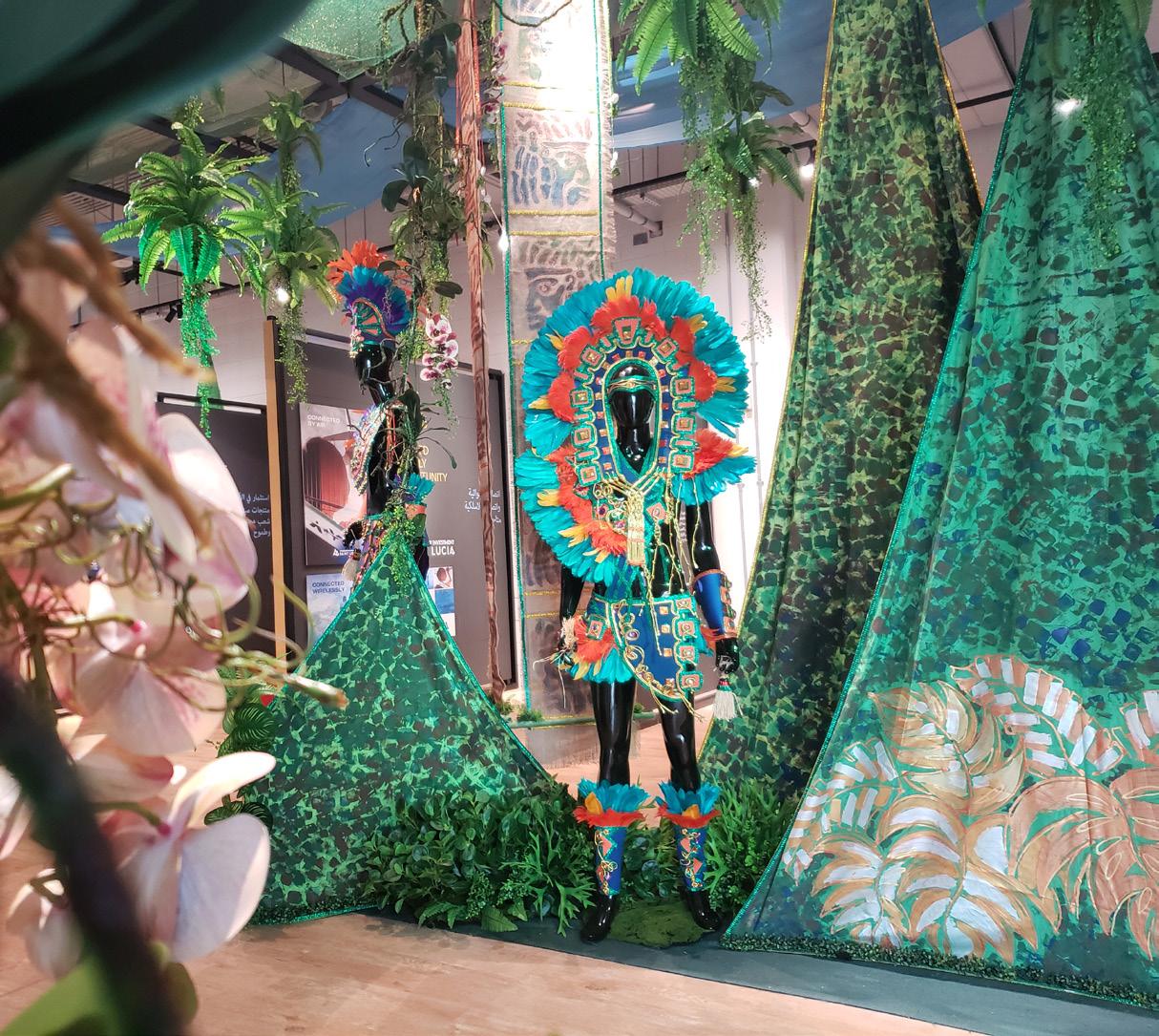
and marketing, performance preparation, and contract management. Our goal was to position them not just as performers, but as export-ready creative entrepreneurs. We have also provided direct support for artists performing internationally. Saint Lucian music was a standout feature at the World Expo in Dubai and will be part of our cultural presentation at Expo Osaka 2025 in Japan, where our artists will headline National Day celebrations, introducing Saint Lucian culture and sound to patrons and viewers from all over the world.
In 2023, Export Saint Lucia facilitated the debut of our Dennery Segment genre at the Dominica World Creole Music Festival with two of our local talents, Umpa and Subance. Dennery Segment is a fast-paced, percussiondriven style of music that originated in Dennery, Saint Lucia. It is a fusion of soca, dancehall, and Afro-Caribbean rhythms featuring raw Creole lyrics and infectious beats, designed for high-energy dancing. Known for its bold, unfiltered sound, Dennery Segment has become a vibrant expression of Saint Lucian culture, gaining international attention while staying true to its grassroots origins. It is a favorite among our Caribbean Francophonie neighbours, with whom we share a bond through the Creole language and culture.
NA: Additionally, how does Export Saint Lucia enhance the capacity of stakeholders in the agricultural sector? Following on, could you discuss the marketability of sea moss and its growth as an industry?
SD: That’s a timely question because over the past two years, we’ve been actively working on a project titled Enhancing the Capacity of Stakeholders in the Agriculture
Sector. It’s more widely known as the CDB Packhouse Project, and it’s funded through the CARIFORUM-EU Economic Partnership Agreement (EPA), with support from the Caribbean Development Bank.
Under this initiative, we’ve delivered targeted training to farmers across the island in Good Agricultural Practices (GAP), as well as to packhouse operators and exporters in Good Manufacturing Practices (GMP) and Hazard Analysis and Critical Control Points (HACCP). They’re internationally recognized standards that help our producers meet the requirements of major export markets.
One of the project’s most significant milestones was the procurement and delivery of a refrigerated truck to our farmers in March 2025, facilitated by the Saint Lucia Marketing Board. That vehicle has been instrumental in maintaining cold-chain logistics, which is critical for preserving product quality during transport, mainly when exporting perishable produce to North American and European markets. Since its procurement, it has played an integral role in exports of agricultural produce to regional markets as well.
Looking ahead, still part of the project, we’re focused on upgrading three communal packhouses around the island. The goal is to ensure that they meet the highest standards for hygiene, food safety, and packaging so our agricultural exports remain competitive and respected abroad.
As for sea moss, there’s no doubt it’s become our agricultural powerhouse. It’s currently the most lucrative agricultural export from Saint Lucia, and demand continues to grow globally, especially in the health and wellness sector. However, with success comes responsibility – we must protect the integrity and identity of Saint Lucian sea moss.
Tel: 1758-456-5900 | Email: info@ibsstlucia.com
Website: www.Ibsstlucia.com
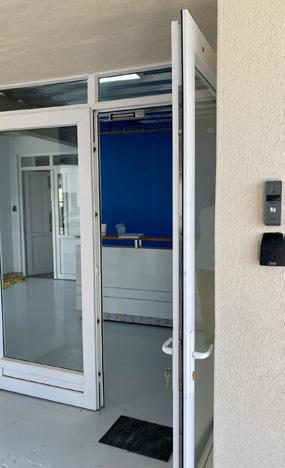
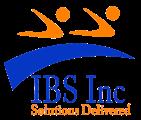
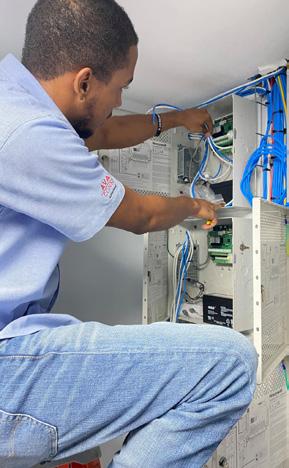
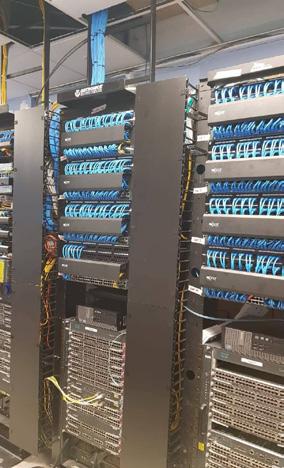
IBS Inc. – Pioneering Business Solutions Across the Caribbean
For over 17 years, Innovative Business Solutions Inc. (IBS Inc.) has been a trusted leader in delivering advanced business technologies that enhance efficiency, security, and connectivity.
From Managed IT Services and Cybersecurity to Structured Cabling, Phone Systems, Physical Security, and Fire & Life Safety, IBS Inc. provides tailored solutions that enable businesses to thrive in today’s fast-paced digital landscape.
With a strong foundation in Saint Lucia and proven success throughout the Caribbean
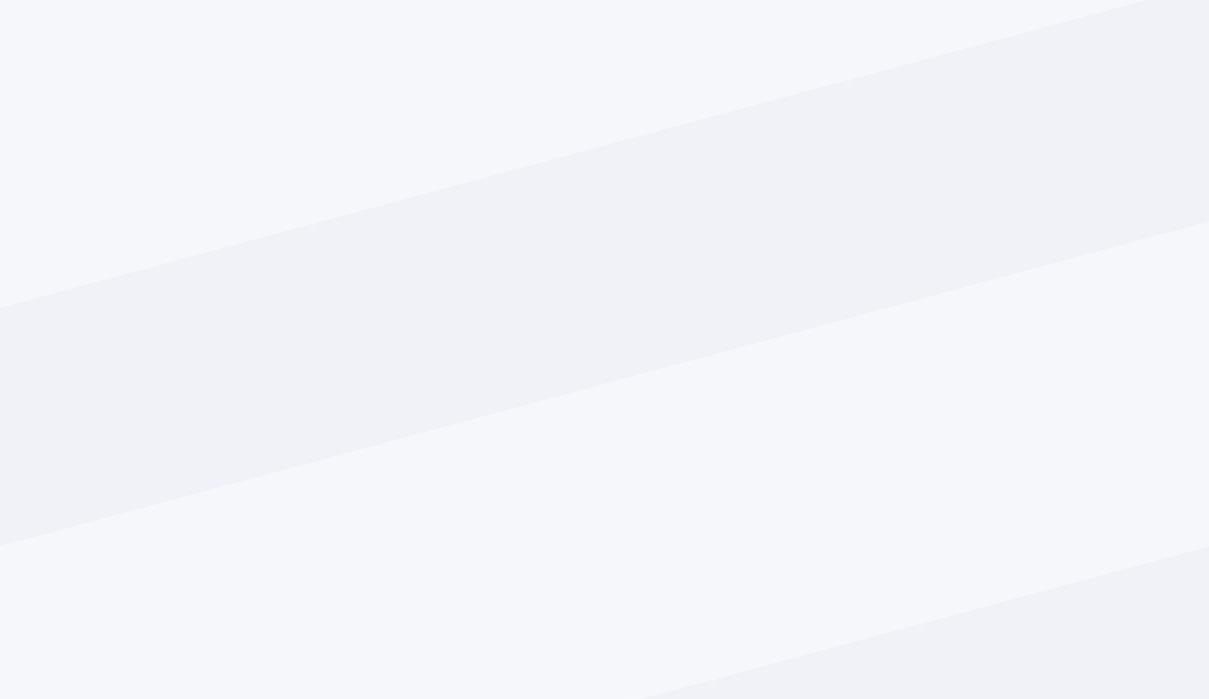
region, IBS Inc. is proud to announce the expansion of its footprint with a new office in Grenada. This strategic move reinforces the company’s commitment to regional innovation and growth, backed by a dedicated team of certified professionals.
Driven by integrity, expertise, and a forward-thinking mindset, IBS Inc. continues to empower organizations with reliable solutions that meet the demands of tomorrow—today.
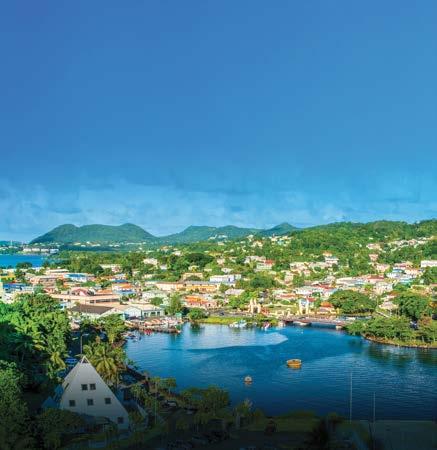
INTERESTING INDUSTRY INSIGHTS
• The first profitable commodity from Saint Lucia was sugarcane; however, after the industry declined, prosperity improved with the increase of banana and cacao cultivation, among other goods.
• Bananas became an essential part of the island’s economy in the 1950s and quickly became one of the main exports, along with other agricultural produce. However, with the end of preferential treatment for the fruit from European markets, tourism is now Saint Lucia’s primary source of income.
• Saint Lucia’s sea moss industry is growing rapidly due to the global demand for the superfood, which contains 92 of the 102 essential minerals. Not just used for culinary purposes, it also works its magic as a skincare product.
• As a key component of the island’s national identity, music exports are vital for the island. They not only celebrate culture but also provide artists opportunities to showcase their talent on the international stage. Notably, in 2016, Ronald ‘Boo’ Hinkson became the first individual from Saint Lucia to serve as a judge at the Grammy Awards.

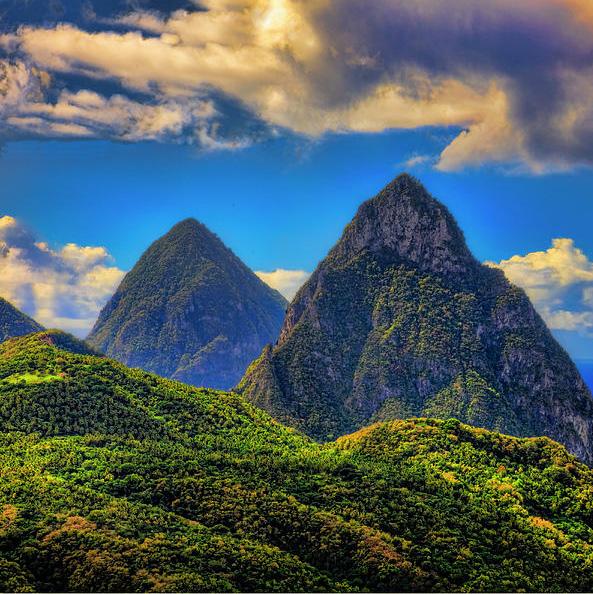
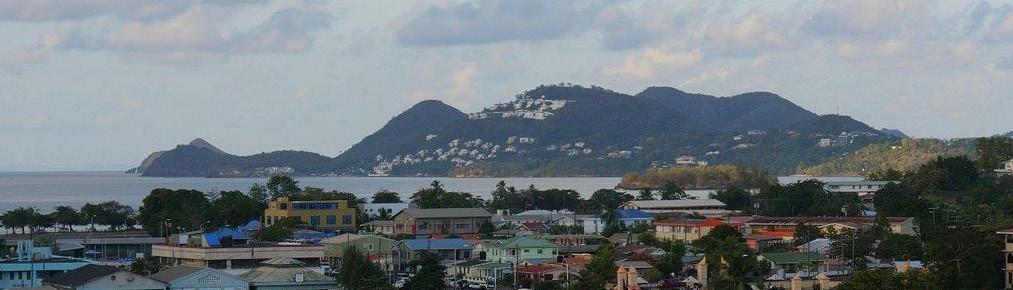
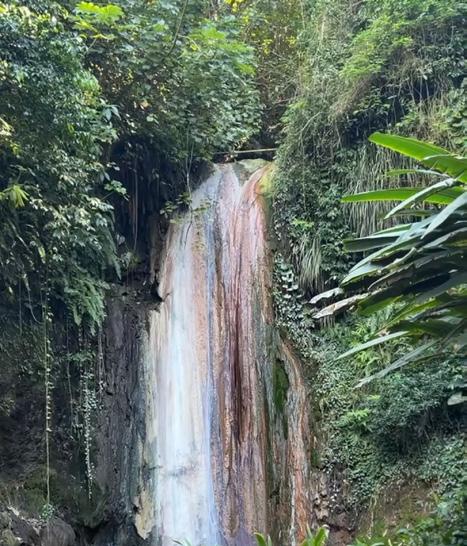
To that end, the Government of Saint Lucia has invested heavily in the sector. We want to ensure that all our facilities and processes meet the international standards of our consumer markets. Saint Lucia has also rolled out a Sea Moss Export Certificate to ensure that only highquality, traceable sea moss leaves our shores. Acquiring a GI would be another feather in the cap of high quality and authenticity.
NA: What do you find most exciting and challenging about the export industries in Saint Lucia?
SD: What excites me most about the export industry in Saint Lucia is the incredible potential of our homegrown products and the steady, inspiring growth we’ve seen among our MSMEs. There’s nothing more rewarding than watching a local entrepreneur who started at a village market evolve into a structured business, meet export standards, and then, with our support, facilitate their very first international shipment. That transformation – from local to global – is why we do what we do.
Another major highlight is the rise of Saint Lucian sea moss. It has quickly become our leading agricultural export, but what excites us even more is the opportunity for value-added products – everything from wellness gels to cosmetics and beverages. We’re actively working to ensure that the Saint Lucian sea moss brand is protected, standardized, and recognized globally for its premium quality.
There has also been an emergence of Saint Lucian coffee and chocolate, particularly from producers such as Noble Tree and rural women’s groups on the island, which have formed the Saint Lucia Network of Rural Women Producers (SLNRWP). They have begun carving out a name for themselves in specialty markets, and the potential for premium positioning is promising.
With that excitement comes a fair share of challenges. Infrastructure, logistics, and market access remain significant hurdles, particularly when handling perishable goods or maintaining the cold chain for agricultural exports.
There’s also the task of balancing rapid growth with sustainability. As demand increases, especially in sectors like sea moss, we have to ensure that our exports maintain high quality and that the Saint Lucian brand remains strong and trusted.
Ultimately, these challenges drive us; they force us to be strategic, collaborative, and forward-thinking.
NA: Does Export Saint Lucia have any projects, events, or key initiatives you would like to highlight?
SD: Right now, we’re gearing up for Export the Runway 3, and we’re genuinely excited about what it represents.
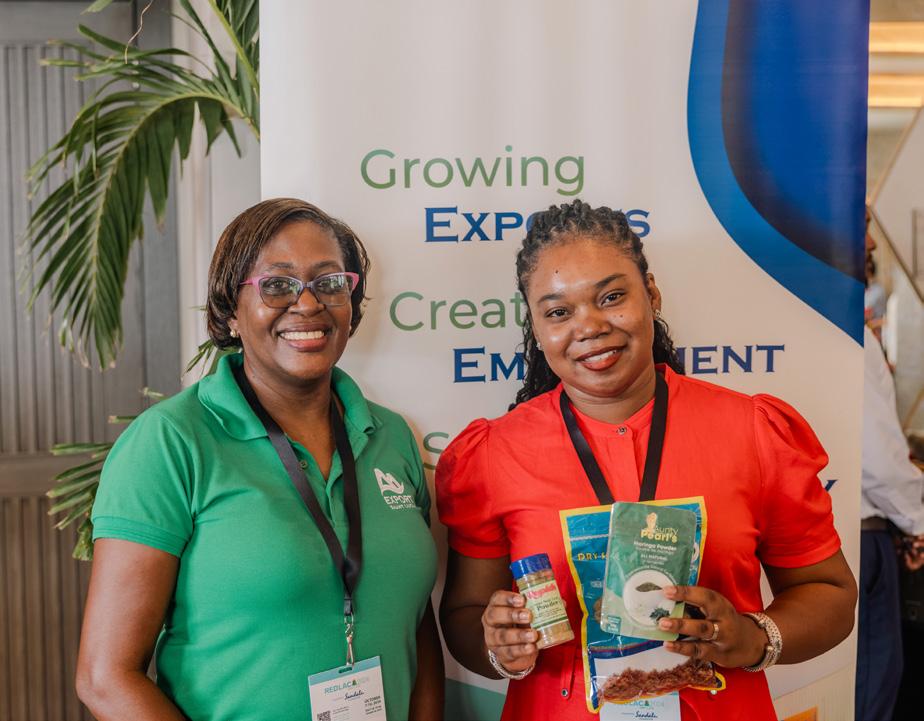
It’s our national stage for fashion – fusing design, music, and storytelling to showcase Saint Lucian talent with global potential. Every year, it gets bigger, bolder, and more refined. We’re creating space for our creatives to move from concept to commerce, where collections are positioned for real business opportunities.
We’re also proud to be representing Saint Lucia on the world stage through our participation at the World Expos. We’re leading Saint Lucia’s participation at Expo Osaka 2025, which is currently underway, and we’re already laying the groundwork for Expo 2027 in Belgrade.
These expos are massive opportunities. They provide us with a platform to promote not just tourism but also our full national identity – our culture, products, business ecosystem, and investment potential. We’re showcasing to the world that Saint Lucia has a great deal to offer.
Another key focus for us is the continued growth of the Taste of Saint Lucia brand. We’ve already opened our first international retail nook in London, which allows consumers to experience the best of Saint Lucian-made goods. We’re currently exploring similar expansions in North America to strengthen our footprint in that region.
Overall, we continually strive to discover innovative ways to help our businesses establish a presence in export markets – whether through cultural platforms, product development, or strategic international partnerships.
NA: How do you see the export industry developing over the next five years? Are you optimistic about its future?
SD: I’m genuinely excited about where Saint Lucia’s export industry is headed. The past few years have shown us what’s possible when we give our businesses the right tools, guidance, and opportunities – and I think we’re only scratching the surface. Over the next five years, I see even more local products and services reaching international
“OUR VISION IS TO SEE SAINT LUCIA GLOBALLY RECOGNIZED AS A SOURCE OF HIGHQUALITY, AUTHENTIC, AND SUSTAINABLE PRODUCTS”
–
SUNITA DANIEL, CEO, EXPORT SAINT LUCIA
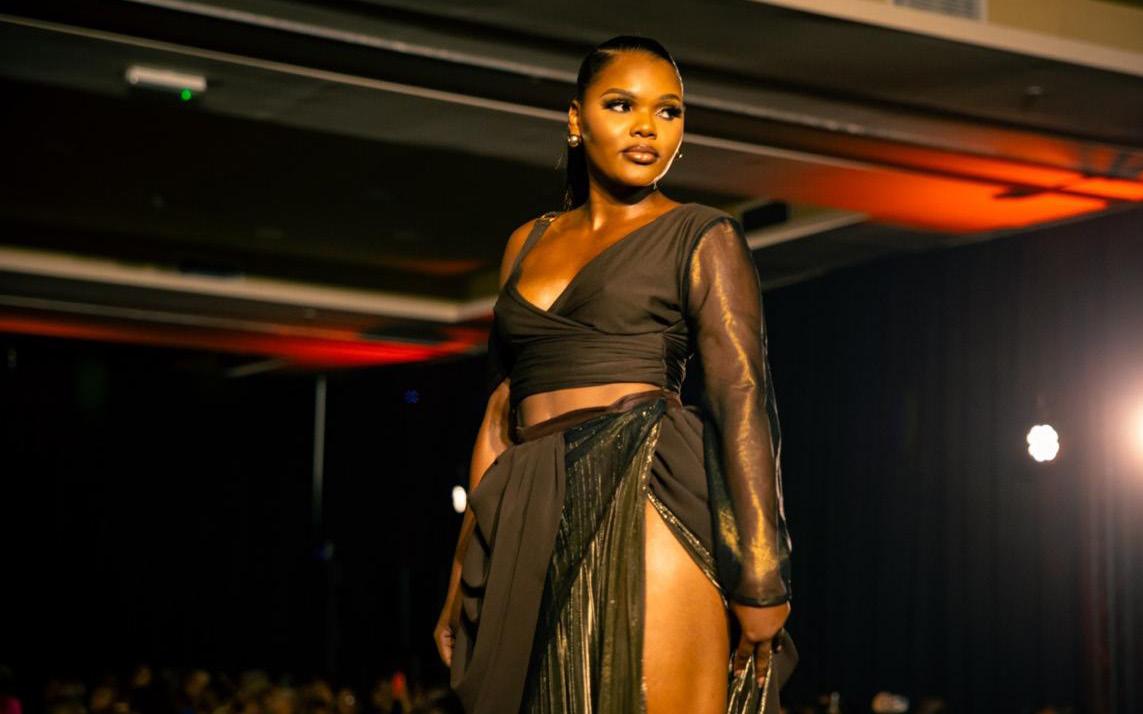
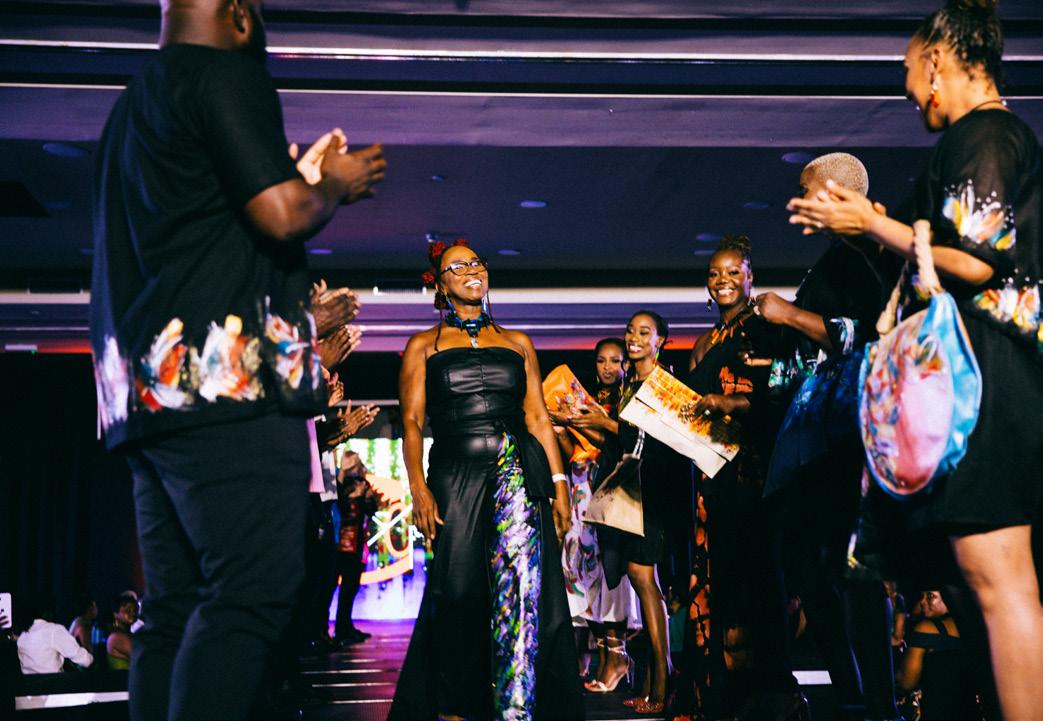
markets, especially as we continue to strengthen our support systems.
The strides we have made with sea moss and our hopes to diversify into more value-added products should bear fruit, so to speak. The addition of the GI, upgrading the processing facilities, and continued capacity building of farmers and exporters will make the sector more lucrative and resilient.
We’re seeing more MSMEs take themselves seriously as global brands. That’s a significant shift – not just in creating great products but also focusing on aspects like
packaging, certification, and market fit. I think we’ll see a lot more value-added products emerging from Saint Lucia, particularly in agro-processing, wellness, and the creative sectors.
E-commerce is going to be a game changer. We’ve already seen how powerful digital tools can be in expanding reach and reducing costs. That’s why we’re in the process of developing a service export registry, so that Saint Lucian professionals, creatives, and service providers can be discovered and hired by clients worldwide. Whether it’s a graphic designer, a videographer, or a wellness coach, they’ll be able to offer their services globally through a structured platform, opening up a whole new layer of export potential.
Of course, challenges remain – especially around logistics and shipping – but we’re making real progress there too. What gives me confidence is the mindset shift. Our producers are more informed, ambitious, and readier than ever to take their business beyond our shores. So yes, I’m optimistic because the talent is here, the products are here, and the world is starting to take notice.

Tel: +1 (758) 468 - 2145
info@exportsaintlucia.org exportsaintlucia.org

CANADA’S GO-TO ENERGY PROCESSING INTEGRATOR
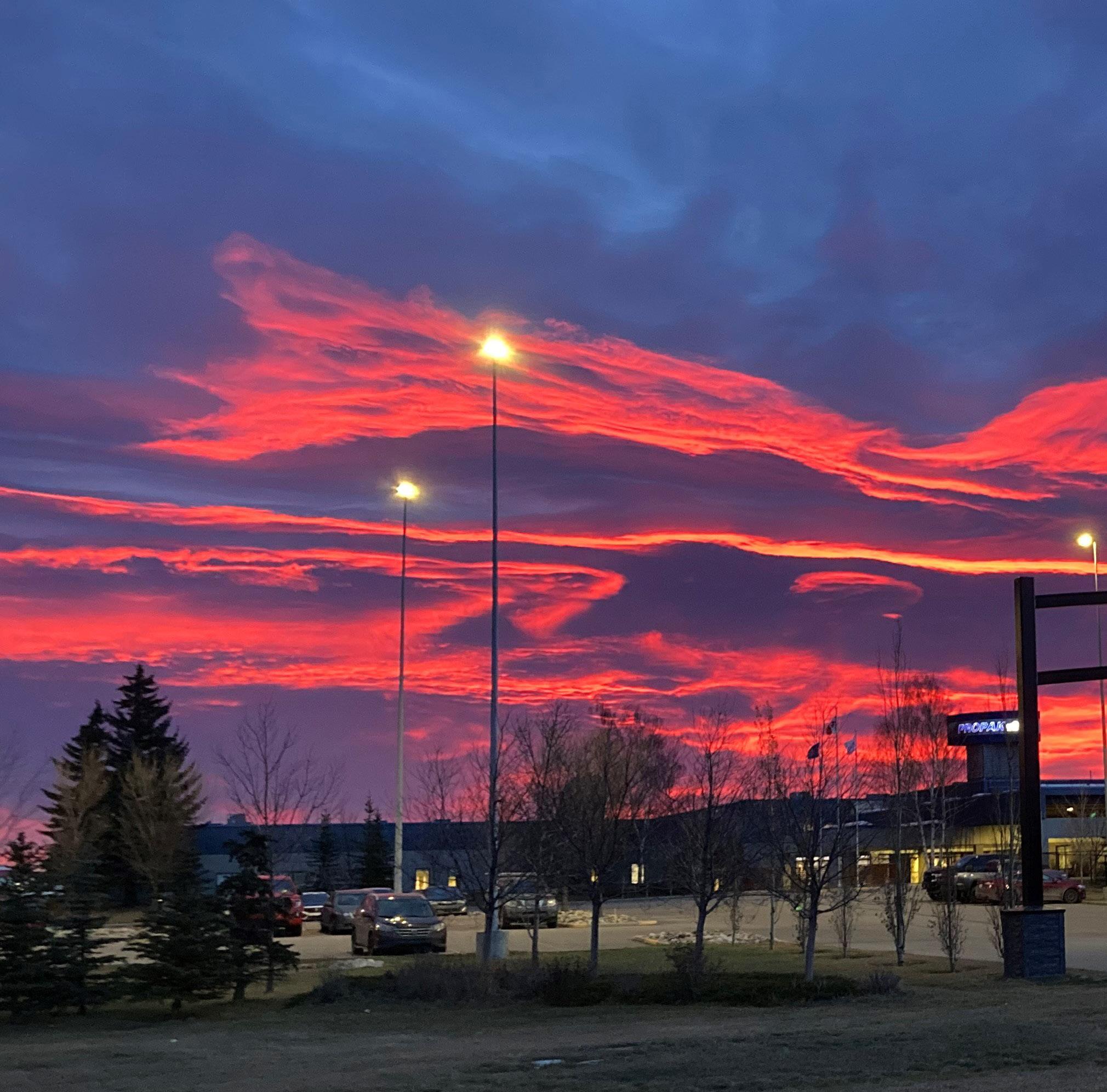
Canada’s current midstream oil and gas sector presents an equally challenging and dynamic environment, playing a crucial role in transporting and processing hydrocarbons for upstream production and downstream distribution processes. Although the industry has faced numerous challenges including evolving regulatory frameworks,
environmental considerations, and the need for technological innovation, these also present opportunities for market players to offer innovative solutions that enhance efficiency and sustainability in energy processing. This is particularly the case for Propak Systems Ltd. (Propak), a Canadian-owned company specializing in the design, engineering, fabrication, and
construction of energy processing facilities and equipment.
The company excels in offering products and services tailored to the needs of the energy processing sector, supporting projects from initial conception through detailed engineering and design to construction, commissioning, and start-up activities.
“Canada’s energy sector is known
Over the last 50 years, Propak Systems Ltd. has grown to become a leading engineering and fabrication services provider. Jim Hanson, Managing Director of Technical Sales, talks us through the company’s vast range of state-of-the-art facilities and turnkey solutions
Writer: Lucy Pilgrim | Project Manager: Ben Weaver
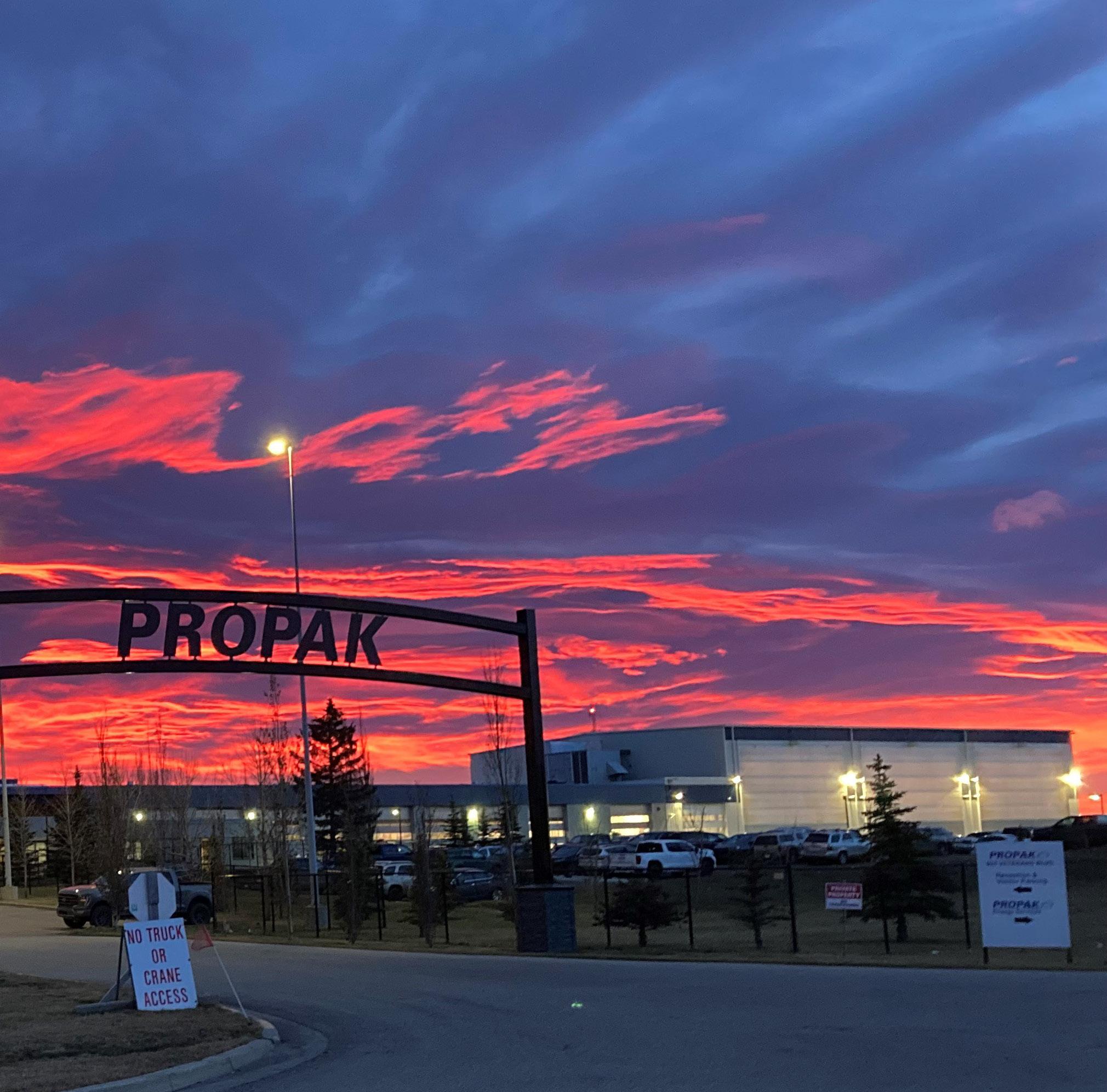
around the world for its efficiency, innovation, and high safety standards. At Propak, we’re proud to be part of that story, and we bring the innovation and quality that we’ve learned here at home to the products and services we deliver to customers globally,” opens Jim Hanson, Managing Director of Technical Sales.
The company’s expertise spans gas processing, gas compression,
enhanced oil recovery – including extensive experience in delivering thermal oil central processing facilities and associated well pads – heat recovery, and steam generation and power systems, including systems designed to minimize carbon dioxide (CO2) emissions.
Moreover, maintaining a high degree of quality is an imperative component of Propak’s activities
across the full life cycle of a project.
“We are creating a culture of quality to instill value into all aspects of our operations.”
Propak currently employs 1,500 staff across major manufacturing facilities in Airdrie, Alberta and Cambridge, Ontario, alongside a range of service facilities further across Canada and the US.
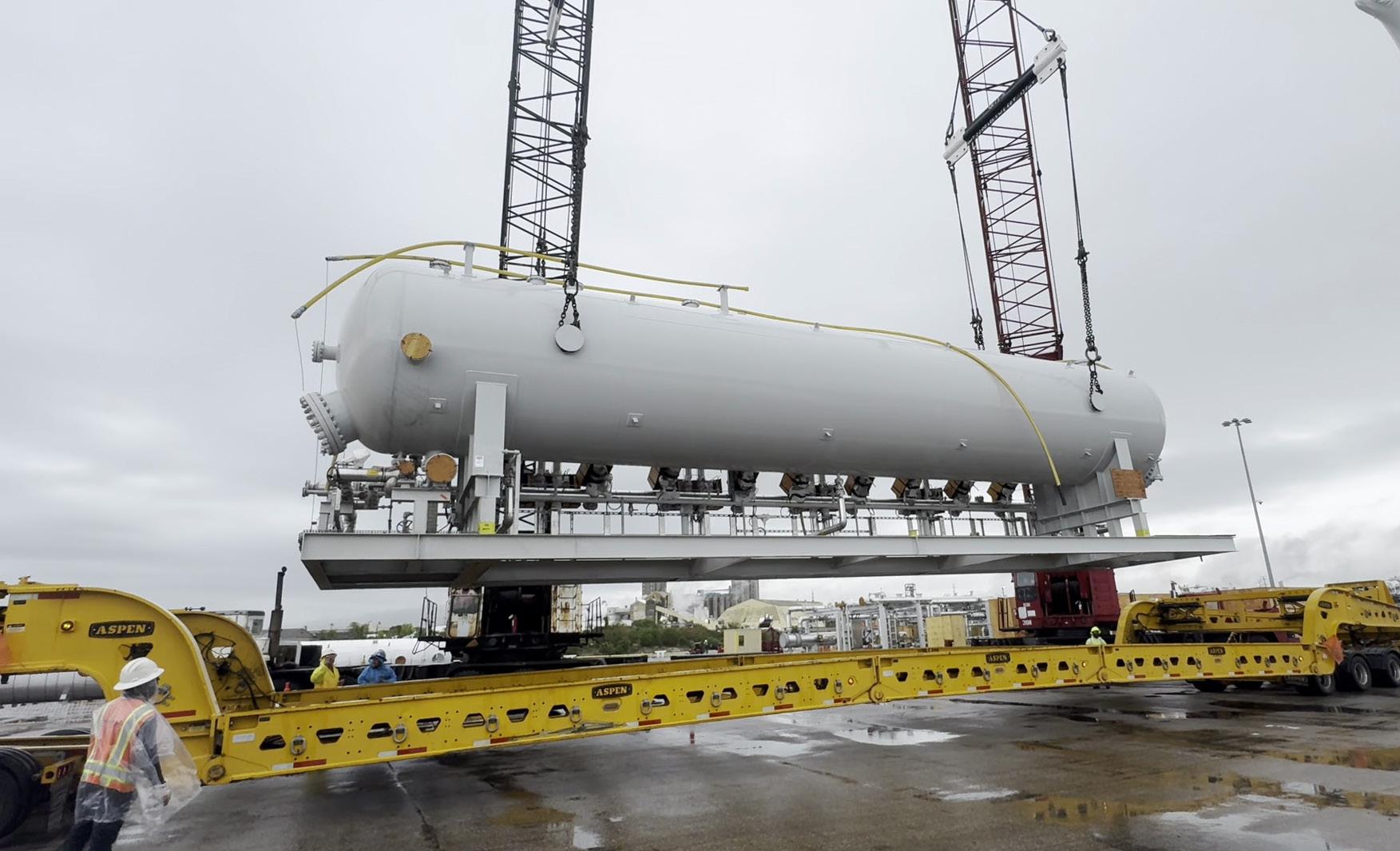
THE PROPAK ADVANTAGE
Since its inception in 1976, Propak has built a reputation for outstanding client service, integrity, and reliability.
In the last half a century, the company has cultivated a signature ability to design and construct both large turnkey processing facilities and individual processing units on modular, shippable skid-mounted packages, distinguishing the company from its competitors.
“Our unique integration of engineering and fabrication capabilities combine to create maximum customer value through bespoke design solutions, reduced capital costs, reliable project execution, and industry-leading product performance,” Hanson prides.
In addition, Propak’s modular expertise, standardized designs, and integrated engineering, fabrication, and construction capacities grant it the ability to accelerate its schedules to completion on a fast-track basis.
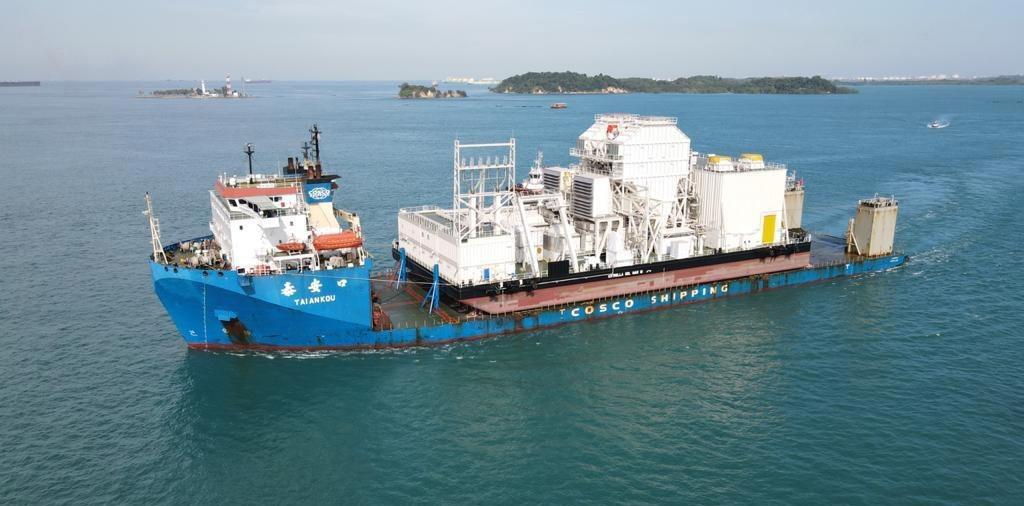
Such unparalleled expertise unlocks an international operational network for the company, which supplies energy processing facilities to businesses in more than 40 countries, working in every continent except Antarctica.
Propak’s exceptional experience and focus on the modularization of facilities has also allowed it to minimize field labor requirements, thereby enabling customers to deploy
modern, high-quality equipment to meet their processing needs in areas of the world where specialized labor is constrained.
“We are experts in designing equipment to be transportable from our facilities to anywhere a truck can go. We’ve even shipped facilities via barges to sites where no roads existed,” Hanson reveals.
Such success wouldn’t be realized without Propak’s extensive worldwide
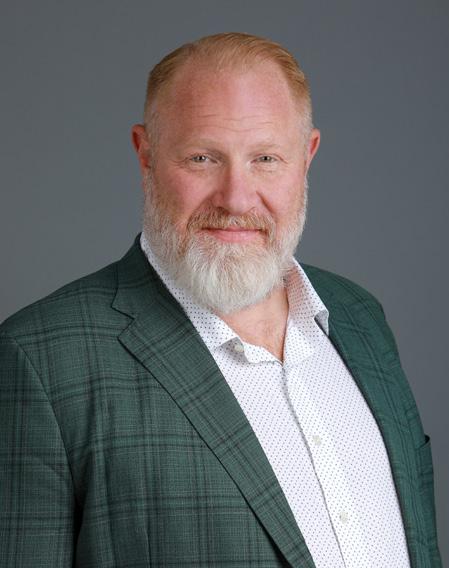
“OUR UNIQUE INTEGRATION OF ENGINEERING AND FABRICATION CAPABILITIES COMBINE TO CREATE MAXIMUM CUSTOMER VALUE THROUGH BESPOKE DESIGN SOLUTIONS, REDUCED CAPITAL COSTS, RELIABLE PROJECT EXECUTION, AND INDUSTRY-LEADING PRODUCT PERFORMANCE”
– JIM HANSON, MANAGING DIRECTOR OF TECHNICAL SALES, PROPAK SYSTEMS LTD.
network of partners and suppliers that support its operations and are foundational to its success.
“We rely heavily on the relationships we have with our suppliers to ensure we can provide the high-quality, cost competitive, and timely delivery of products to customers. Our company is made stronger by leveraging the strengths of our suppliers and partners.”
A noteworthy example of this is Propak’s role as the authorized distributor for Ariel Corporation (Ariel) gas compressors, which allows the company to benefit from Ariel’s market-leading expertise while bringing its own strengths to the market.
UNPARALLELED PROJECT EXECUTION
Propak boasts a vast range of projects across the US, Canada, and internationally that establish its track
record of engineering achievements and outstanding product performance.
The company has built hundreds of gas processing and compressor facilities around the world, including multiple Modularized Gas Compressor Stations in North Dakota.
One notable example, situated on the Bakken Formation, saw Propak supply eight modular compressor packages to pressurize and transport raw gas via a downstream pipeline.
The specifications of the modular compressors included 2,200 horsepower (hp), electric drive, fourstage reciprocating compressors, designed to efficiently compress gas. The station was supplied complete with all interconnecting piping, piperacks, and necessary auxiliary and utility systems.
The packages were purposefully designed for easy transportation within tight shipping constraints and
simple on-site reassembly. Moreover, thanks to a standard packaged design, the gas compressors were developed in a staged approach, granting the company the ability to fit additional compressor units as the station’s capacity increased.
Propak expertly engineered and designed the compressor modules to the client’s requirements and provided reassembly, start-up, and commissioning support on-site.
The compressor package design has subsequently been duplicated and installed at multiple different locations, emphasizing its repeatable modularity.
Elsewhere, the company boasts the provision of world-class cryogenic turbo-expander plants. An exemplary facility was constructed in Northeast British Columbia, where Propak provided detailed engineering and design, procurement, and fabrication services.
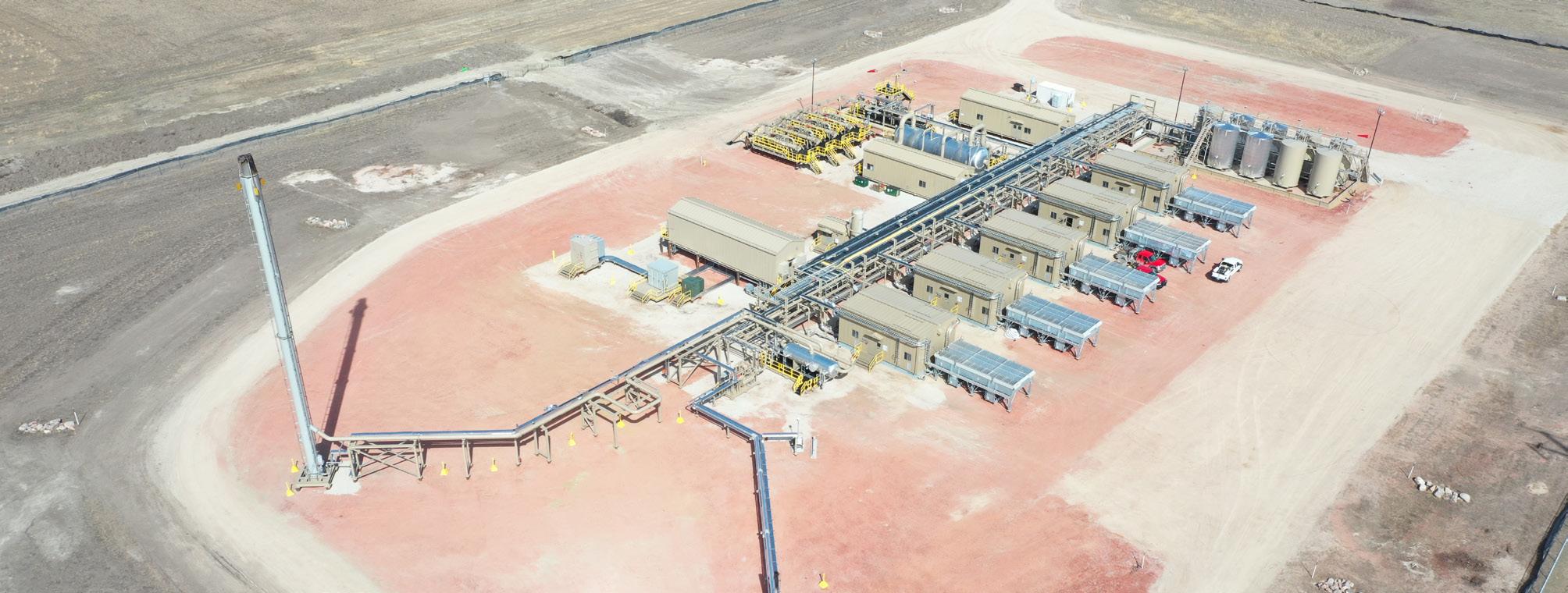
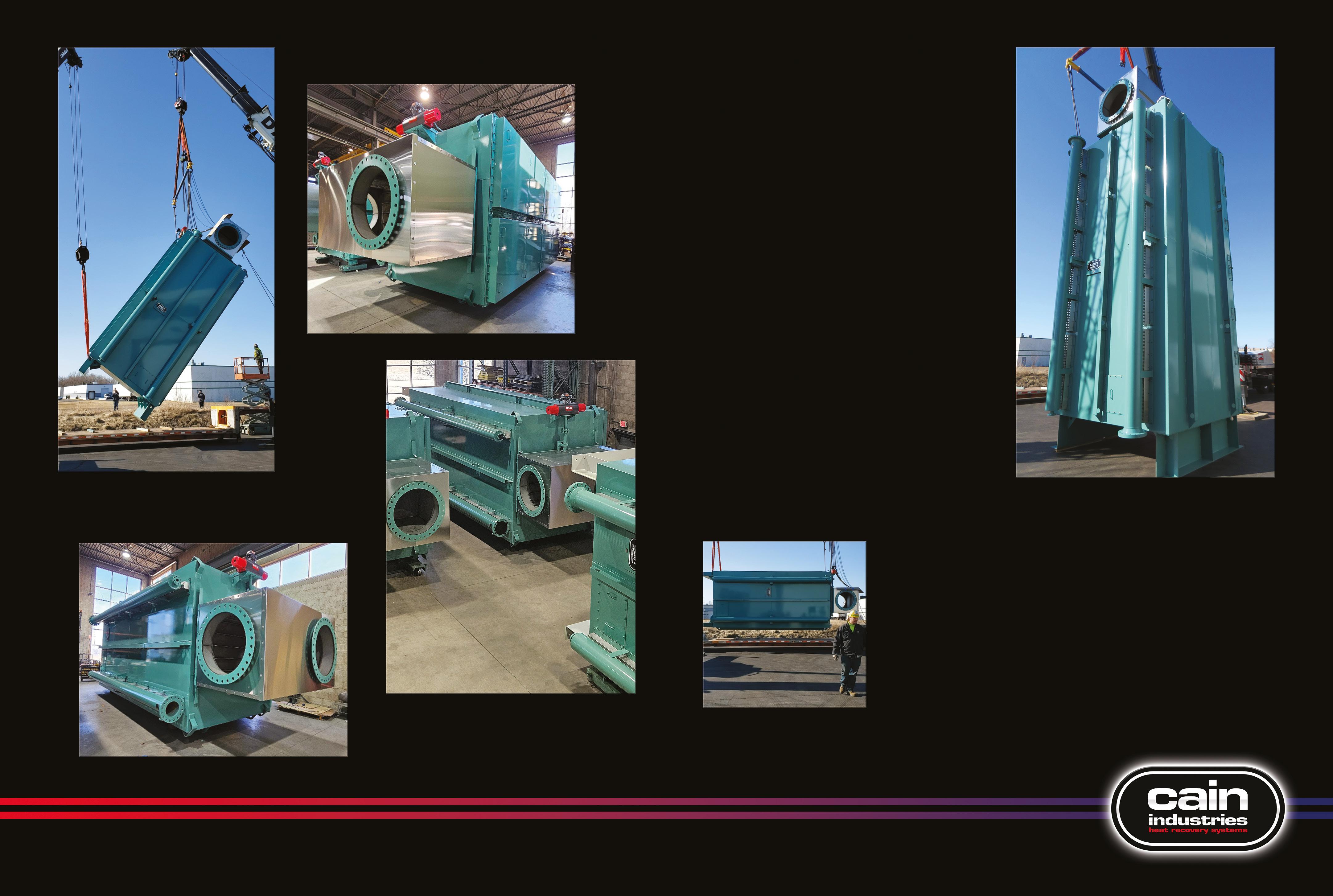
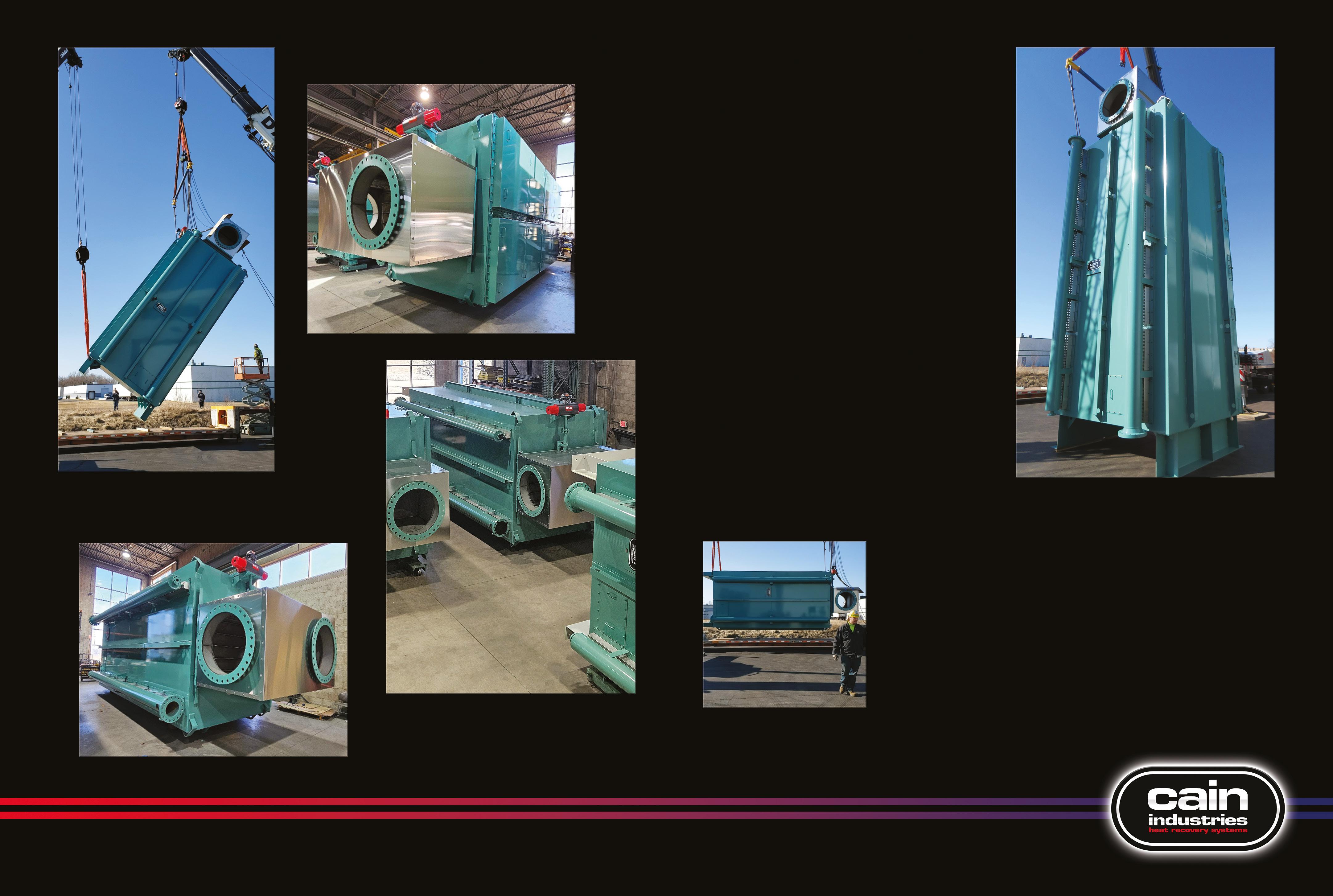
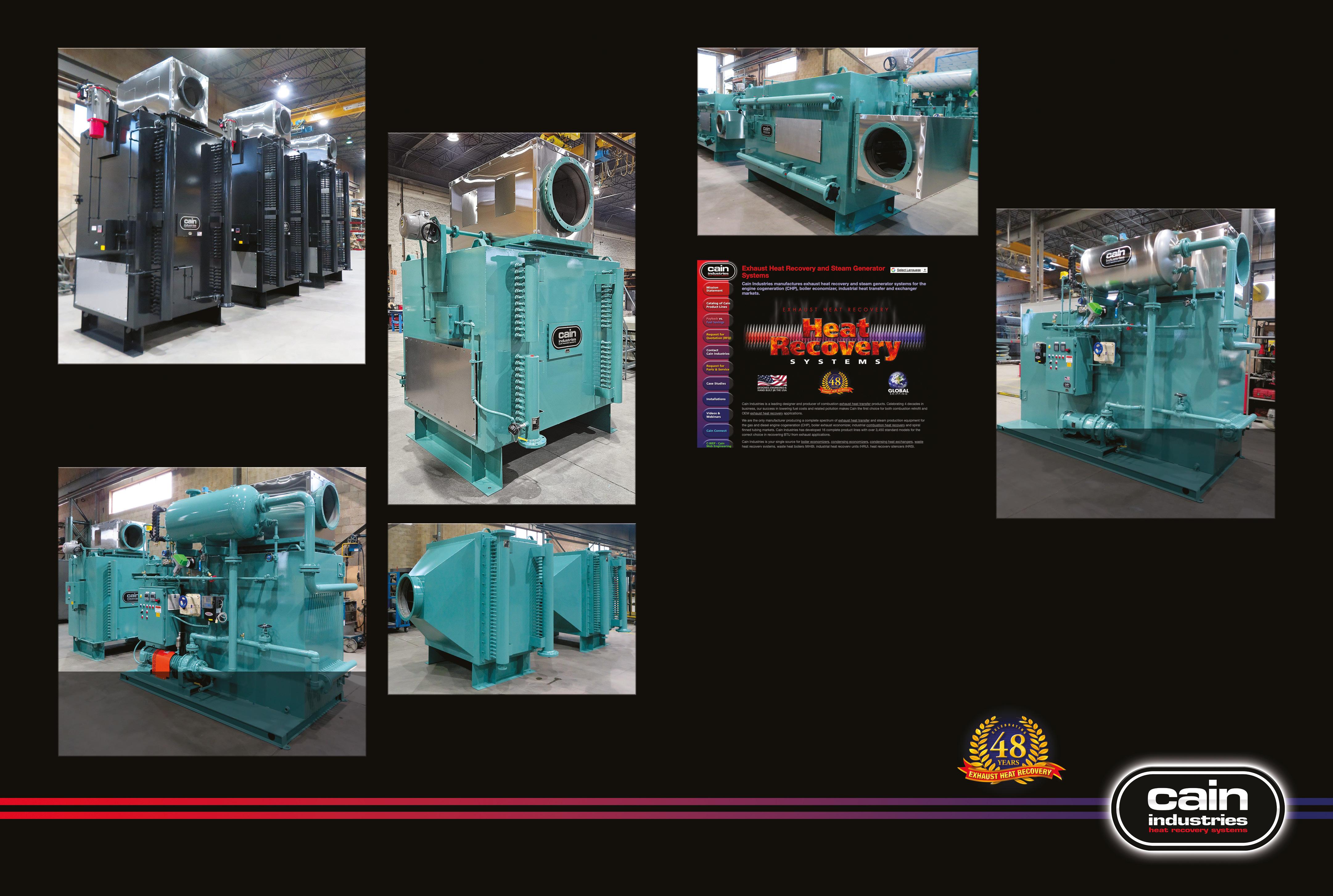
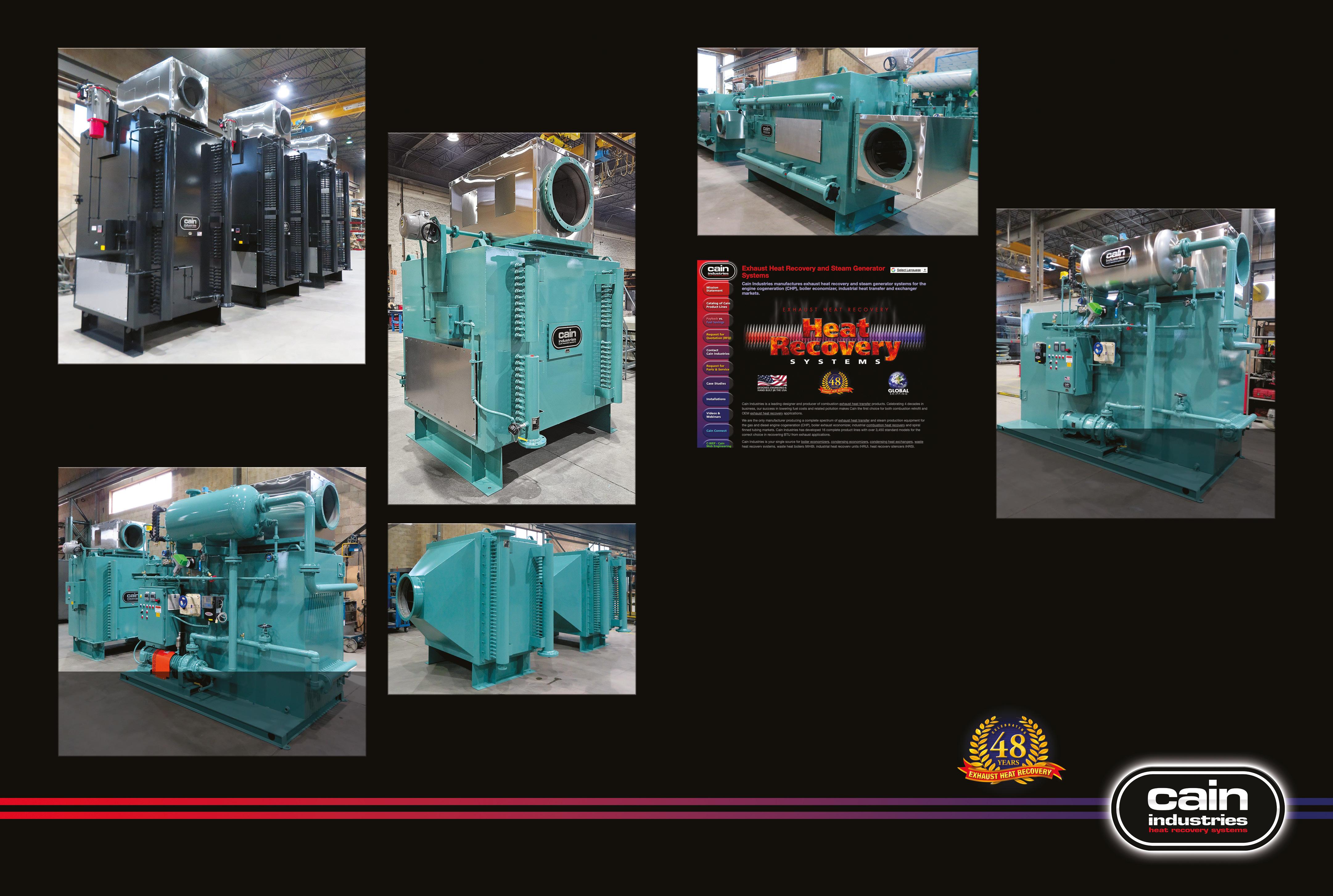
The facility was designed to process 200 million standard cubic feet per day (MMSCFD) of raw natural gas in order to meet pipeline specifications and efficiently extract and fractionate ethane, propane, and butane, alongside other natural gas liquids.
The plant involved the employment of Propak’s design strategy for facility modularization, which allowed for the trial fitting of modules prior to shipping. The modules were then staged and shipped in close coordination with field construction operations, thus providing efficient execution and improvements to the project schedule.
The project scope called for engineering, design, procurement,
and fabrication services, as well as start-up support, which were all provided on a lump-sum basis.
Based on the successful completion of the project, the client returned to Propak for a second, pre-planned identical facility.
VAST OPERATIONAL EXPANSE
Propak’s journey is marked by the strategic expansion of its manufacturing facilities across Canada, first sparked by the
company’s expansion to Airdrie in 1978, having outgrown its initial smallscale fabrication workshop.
This expansion facilitated the establishment of the company’s second building at a time when the city’s population was approximately 1,000 people.
“The Airdrie facility, which once housed the entire company, now operates as our primary pressure vessel manufacturing facility,” Hanson highlights.
“THROUGH THE DELIVERY OF PRODUCTS THAT IMPROVE EFFICIENCY AND REDUCE EMISSIONS, WE ARE ABLE TO SUPPORT OUR CLIENTS IN THEIR SUSTAINABILITY
INITIATIVES”
– JIM HANSON, MANAGING DIRECTOR OF TECHNICAL SALES, PROPAK SYSTEMS LTD.
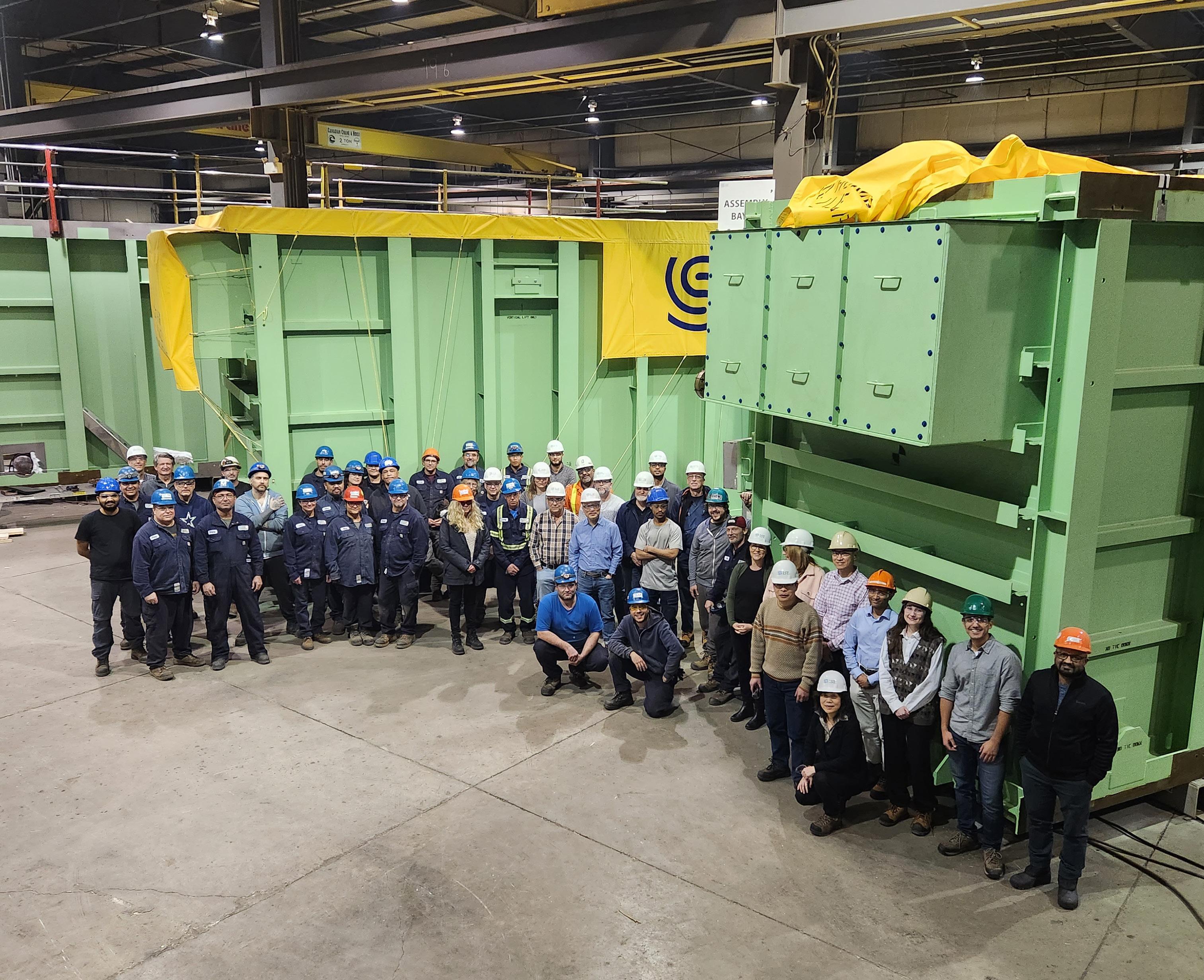
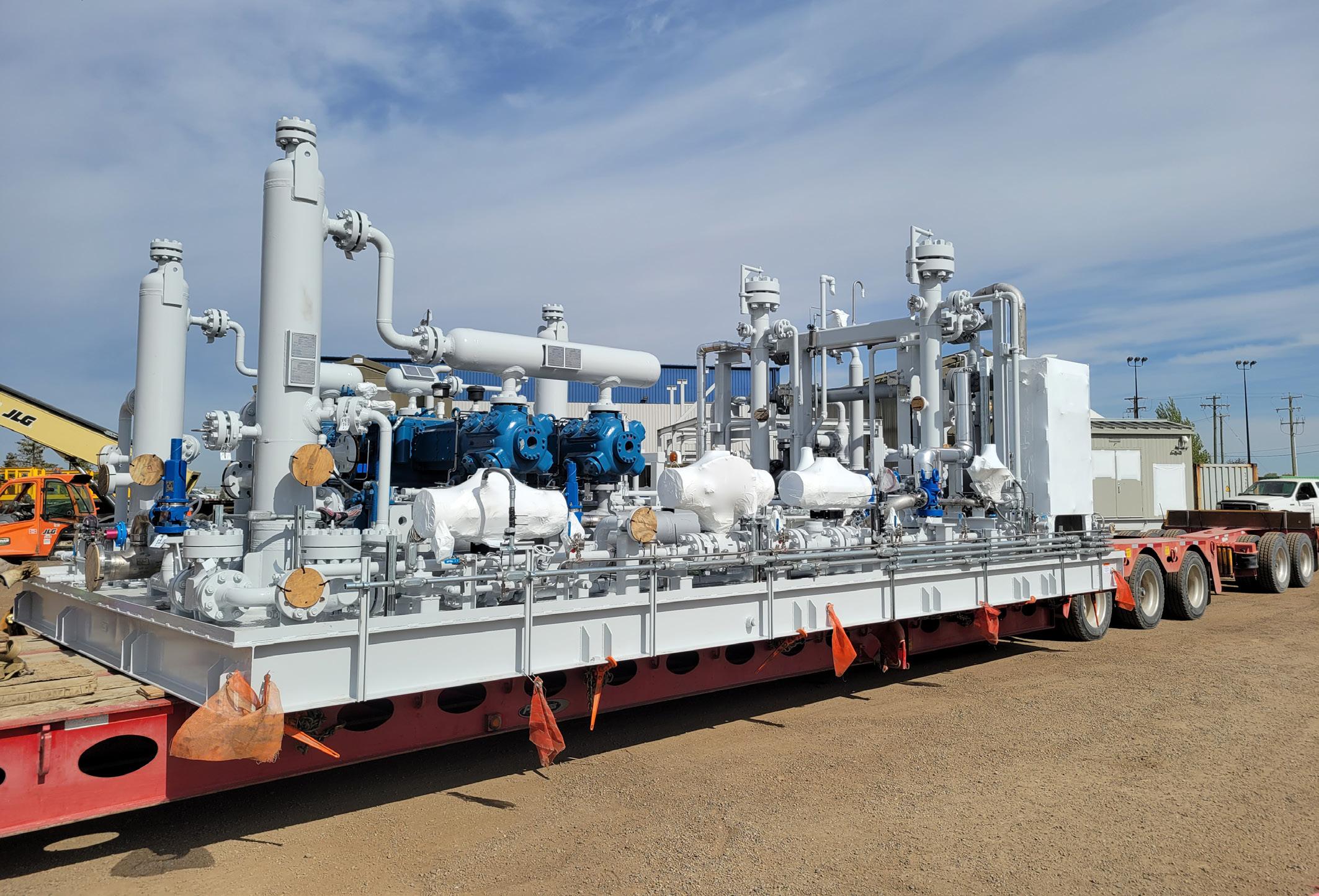
PROPAK’S MAIN PRODUCTS AND SERVICES
• Gas processing – Complete turnkey facilities and modular units used for natural gas processing. These include:
• Modular cryogenic processing facilities
• Amine-based gas sweetening facilities
• Turnkey gas compression stations for gathering Propak’s pipeline applications
• Mechanical refrigeration facilities
• Triethylene glycol gas dehydrators
• Molecular sieves
• Helium recovery facilities
• Enhanced oil recovery and heavy oil processing
– Modular thermal heavy oil central processing facilities, processing up to 20,000 barrels per day, per train. This is conducted in standardized modular well pad facilities for all types of lift mechanisms.
• Gas compression and power – Modular gas compressors and power generation units designed to reduce project schedules and installation costs. The company packages compressors and power generation units from 200 to 10,000 hp.
• Heat recovery and steam generation – Propak IST markets HRSGs for power generation and
cogeneration industries as well as gas-fired OTSGs for enhanced oil recovery applications.
• Energy systems – Propak’s Energy Systems business unit supports clientele in the execution of projects related to emerging technologies and sustainability initiatives.
Its products and services include the design, evaluation, and provision of carbon capture utilization and storage facilities and hydrogen production facilities, alongside novel technology and sustainable energy scale-up feasibility studies.
• Construction services – Domestic and international field construction and construction management services are provided through Propak’s whollyowned subsidiary, Process Plant Constructors Ltd. (PPCL).
The subsidiary’s expertise includes civil and earthworks, foundation installations, equipment setting and installation, full mechanical construction services, electrical and instrumentation services, and insulation installation.
PPCL’s projects include gas compressor stations, heavy oil treatment facilities, and gas processing and treatment facilities.
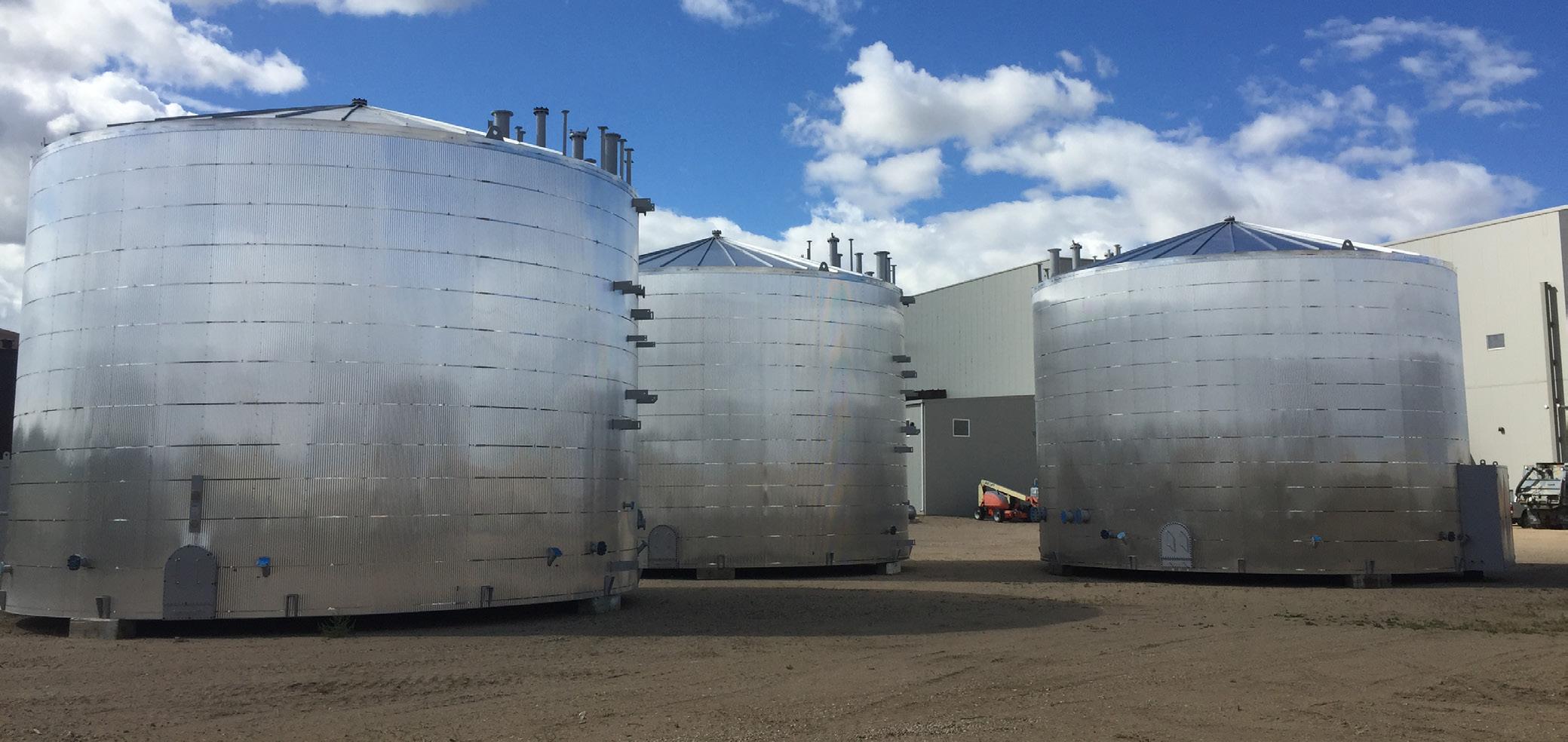
PREMIUM CUSTOM STEEL MANUFACTURING
Proudly serving the energy industry since 2010, Leading Manufacturing Group (LMG) is your premier choice for steel manufacturing services. With hundreds of years of combined experience in manufacturing, coating, painting, insulation, and quality control, we bring unmatched expertise to every project.
Founded by Lee Gottschlich in 2010, LMG has an extensive history in the industry. Our fabrication facilities are designed to optimize the fabrication process.
Whether it’s Steel Storage Tanks, Pressure Vessels, Pressure Piping, or Tank Accessories look no further than LMG.
We offer a wide range of steel storage tanks, designed to meet the diverse needs of various
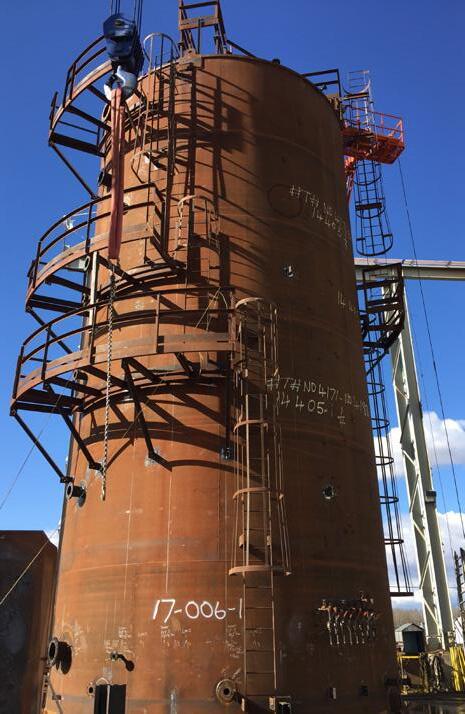
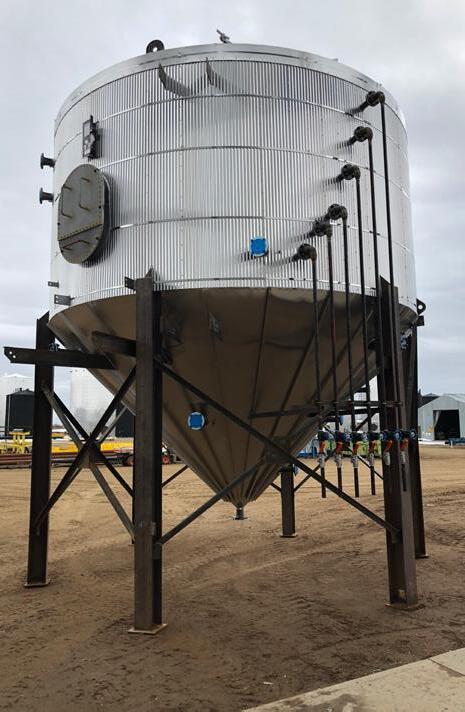
applications. Our tanks, made from stainless, duplex, and carbon steel, are engineered for durability and reliability, ensuring optimal performance in even the most demanding environments.
Our Quality Management System (QMS), controlled indoor environment and rigorous inspection processes ensure that every tank meets the highest standards. Our certifications include API, ASME, and CSA, with in-house API-653 and NACE inspectors overseeing quality control.
In addition to shop fabricated work, we also offer field tank fabrication and a full spectrum of field modification services. Our services include detailed inspections by our in-house API-653 and NACE certified inspectors.
Working with LMG offers numerous advantages designed to ensure the highest quality and efficiency. Our experienced team brings expertise and dedication to every project, guaranteeing exceptional results. We utilize advanced technologies and industry best practices to deliver precise and reliable services.
Our commitment to safety and environmental responsibility means that all our work adheres to the strictest standards, minimizing risks and protecting your investment. Partnering with LMG means benefiting from our unparalleled customer service, swift response times, and a track record of excellence.
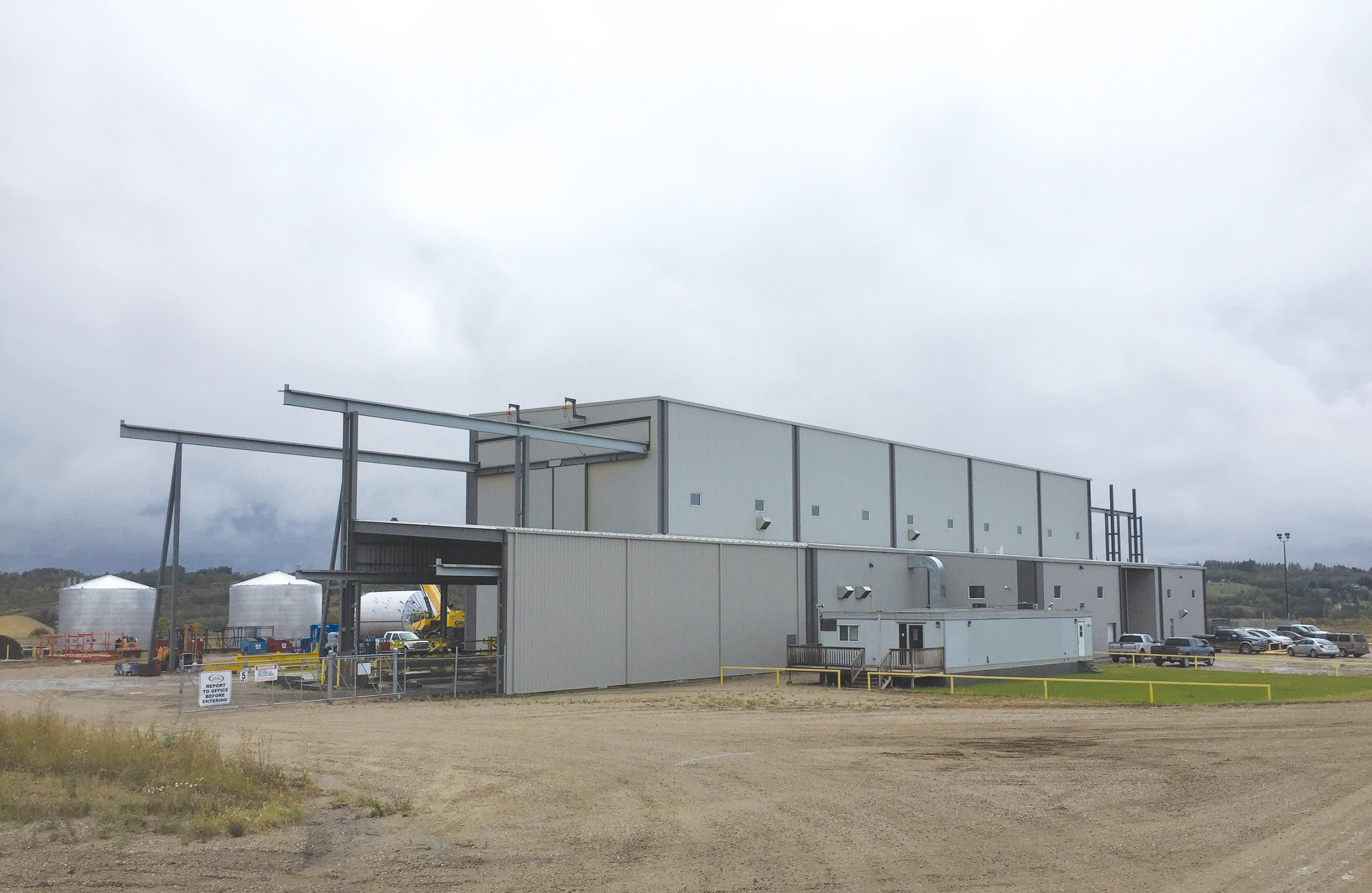
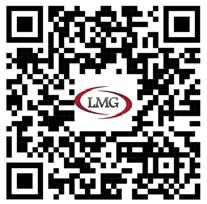
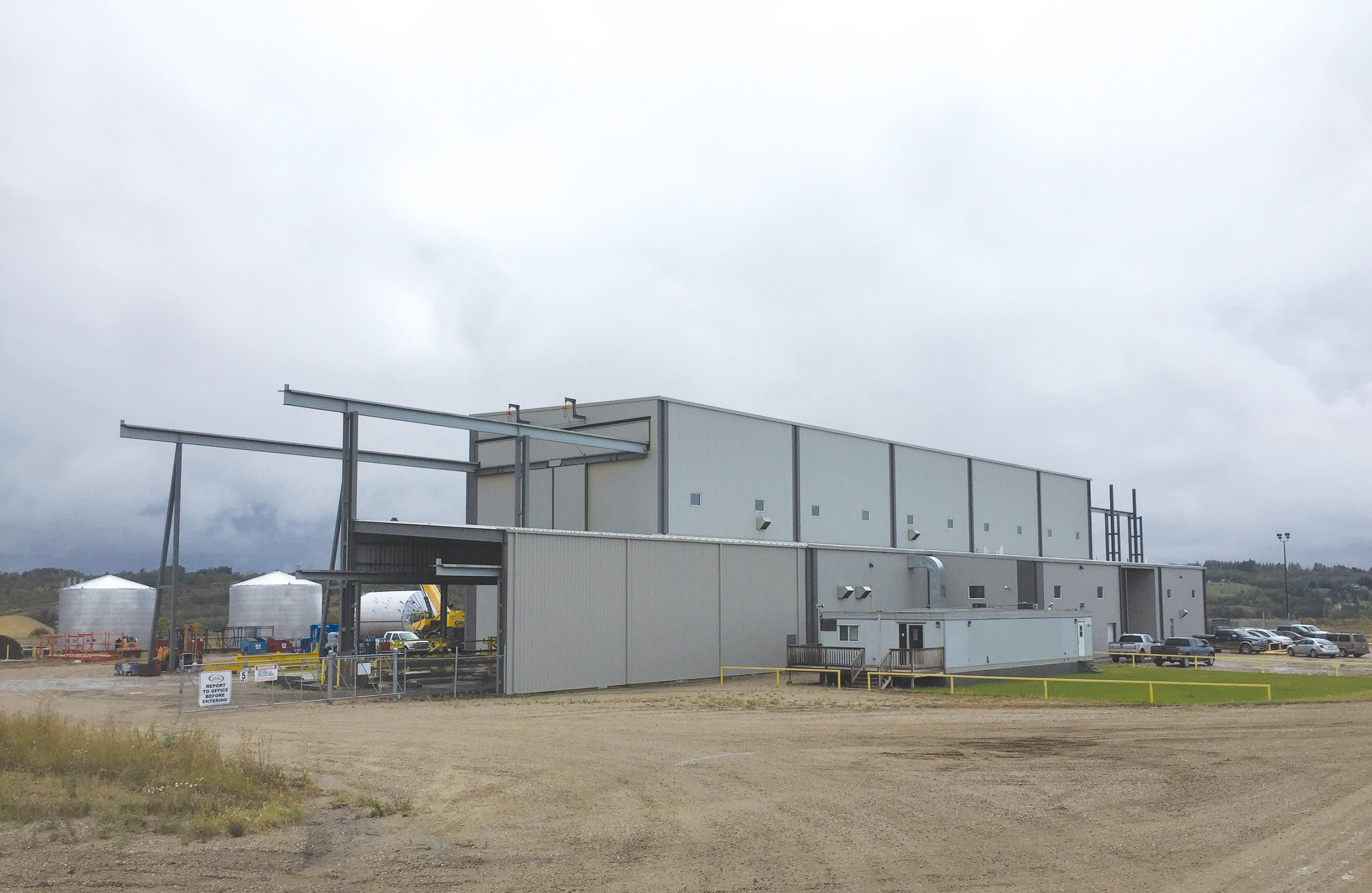
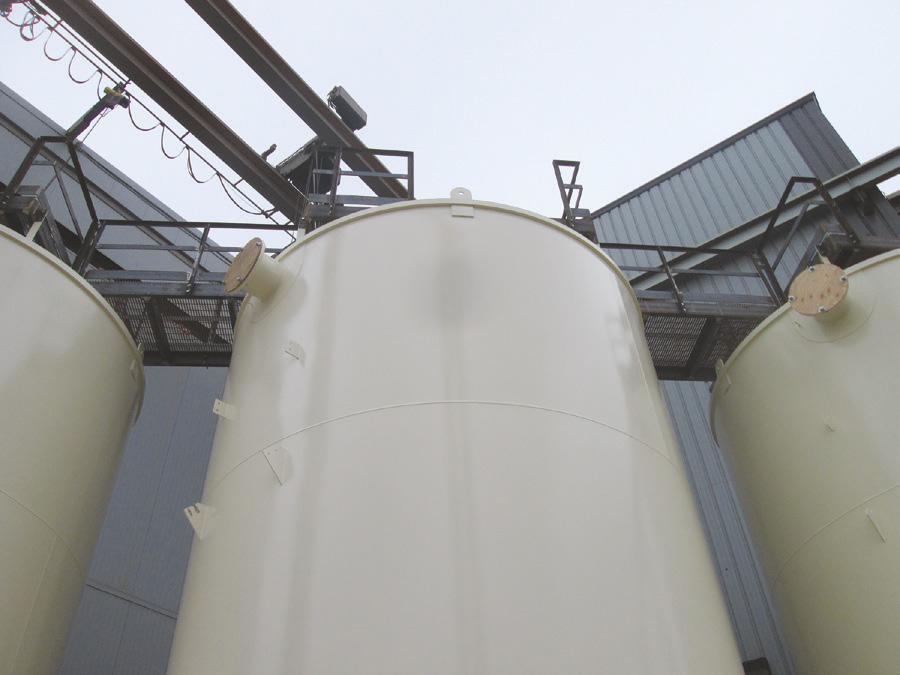
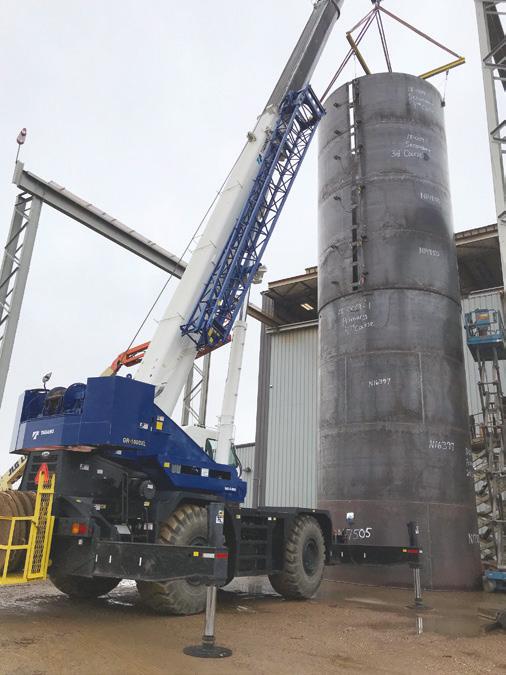
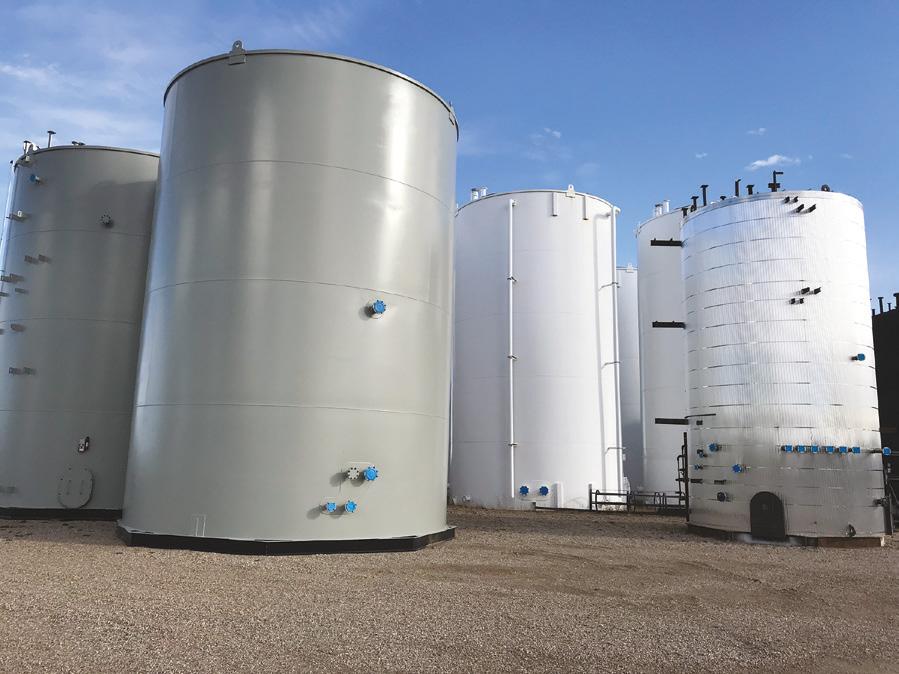
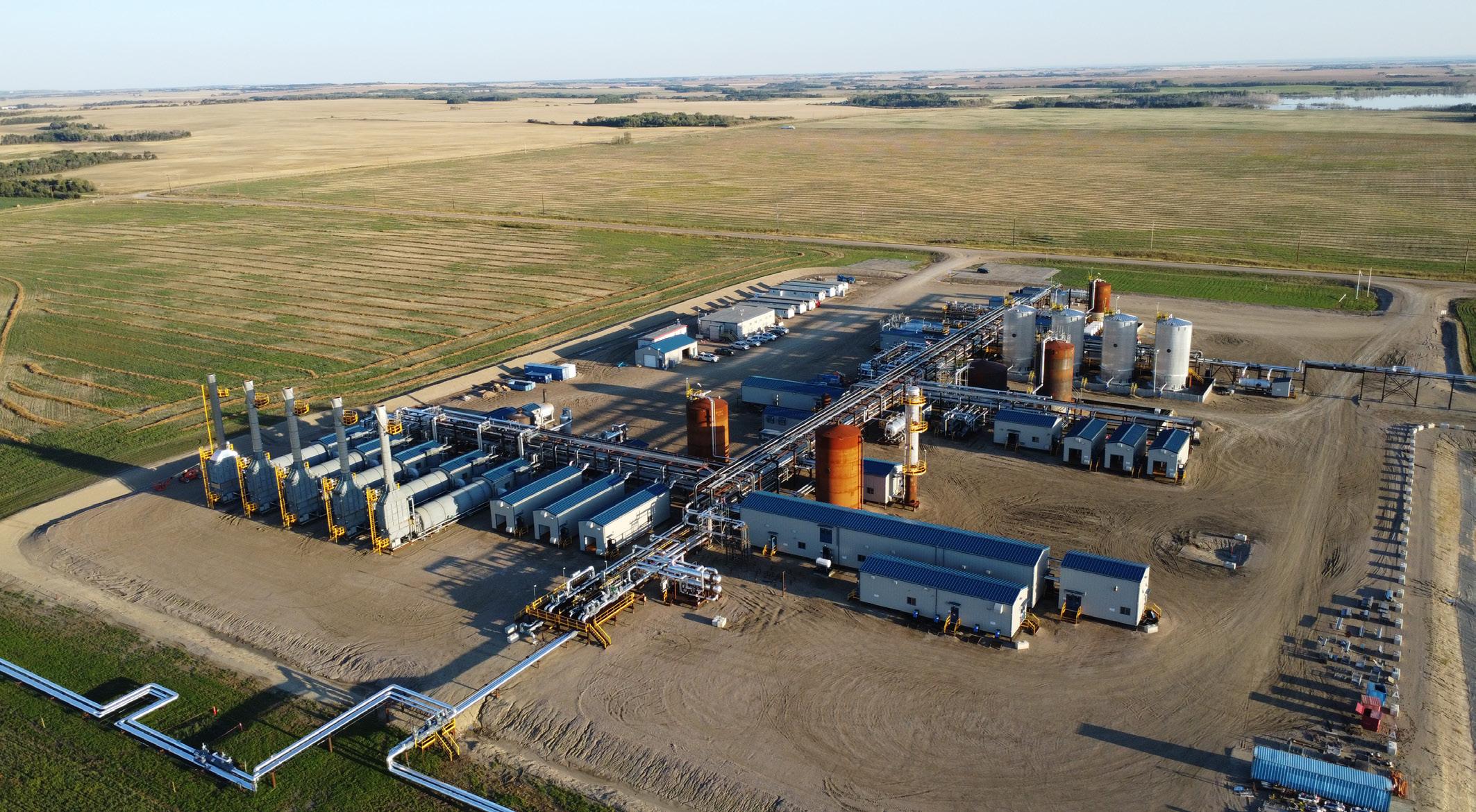
Located at 505 East Lake Boulevard, the facility houses specialized equipment to produce pressure vessels including a plasma cutting table, large steel profiler capable of cutting and beveling steel up to six inches in thickness, and numerous submerged arc welding machines.
The pressure vessel shop also regularly fabricates vessels in excess of three inches thick and up to 500,000 pounds.
Typical pressure vessels produced by the facility include:
• Two and three-phase separators
• Knockout drums
• Distillation columns, including demethanizers, de-ethanizers, depropanizers, debutanizers, stabilizers, amine contractors, and regenerators
• Filter housings
• Molecular sieves
• Mercury removal units
• Water treatment vessels
• Well test separators
“PROPAK REFLECTS THE COMBINED TALENT, EXPERIENCE, DEDICATION, AND DILIGENCE OF OUR STAFF.
INNOVATION IS ENCOURAGED AND NO IDEA IS DISMISSED WITHOUT CAREFUL CONSIDERATION”
– JIM HANSON, MANAGING DIRECTOR OF TECHNICAL SALES, PROPAK SYSTEMS LTD.
The facility’s heat exchanger shop, meanwhile, manufactures and assembles shell and tube heat exchangers built to meet Tubular Exchanger Manufacturers Association (TEMA) Class C and R standards and includes milling equipment used to fabricate heat exchanger tube sheets.
CUTTING-EDGE FACILITIES
Propak additionally has a number of locations in Airdrie, including the structural shop where the company fabricates structural steel skids, modular pipe racks, and miscellaneous steel structures.
Elsewhere, in the panel shop, Propak manufactures electrical and control panels. Here, the company can complete many types of explosion-proof and general-purpose custom panels that are certified to international standards. These panel types include programmable logic controllers (PLCs), remote input/output (I/O), distributed control system (DCS), DCS marshalling, compressor, communication, supervisory control and data acquisition (SCADA), lighting contactor, heat trace control, amongst others.
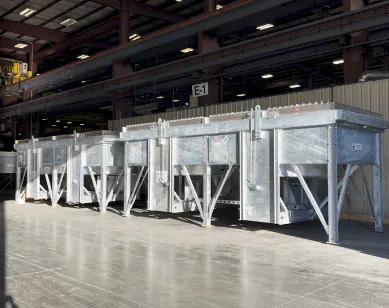
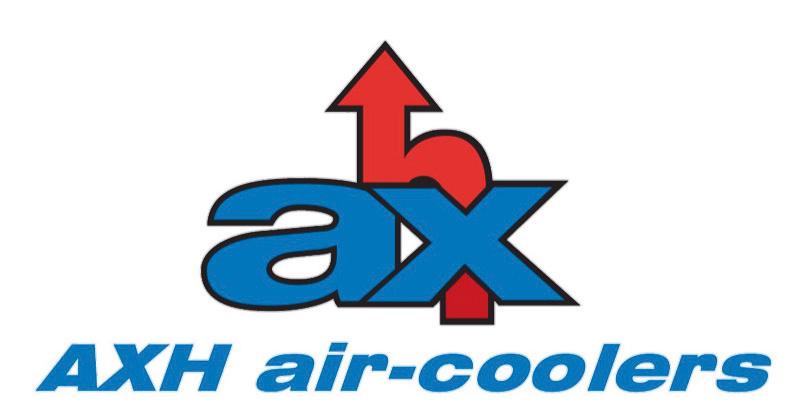
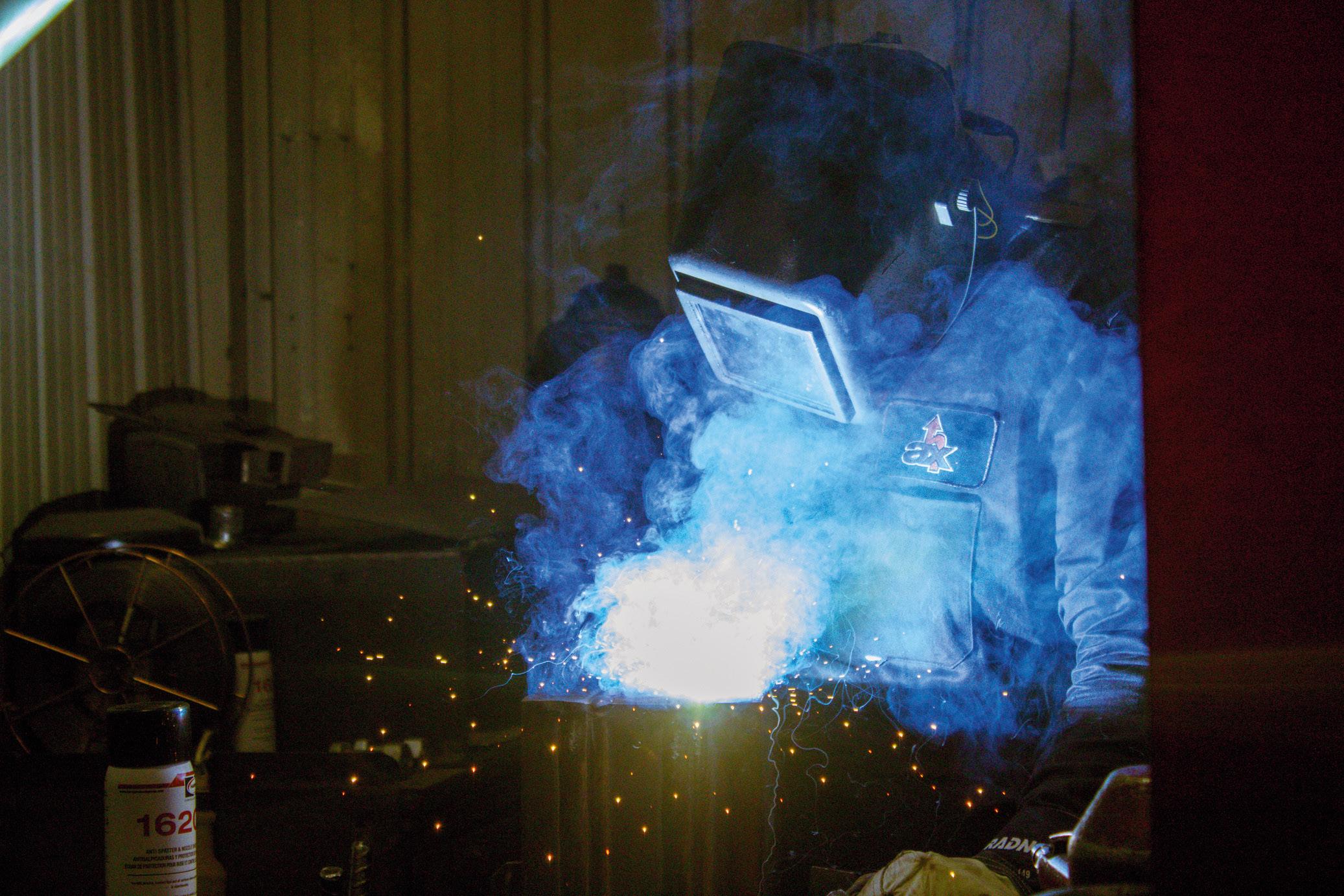
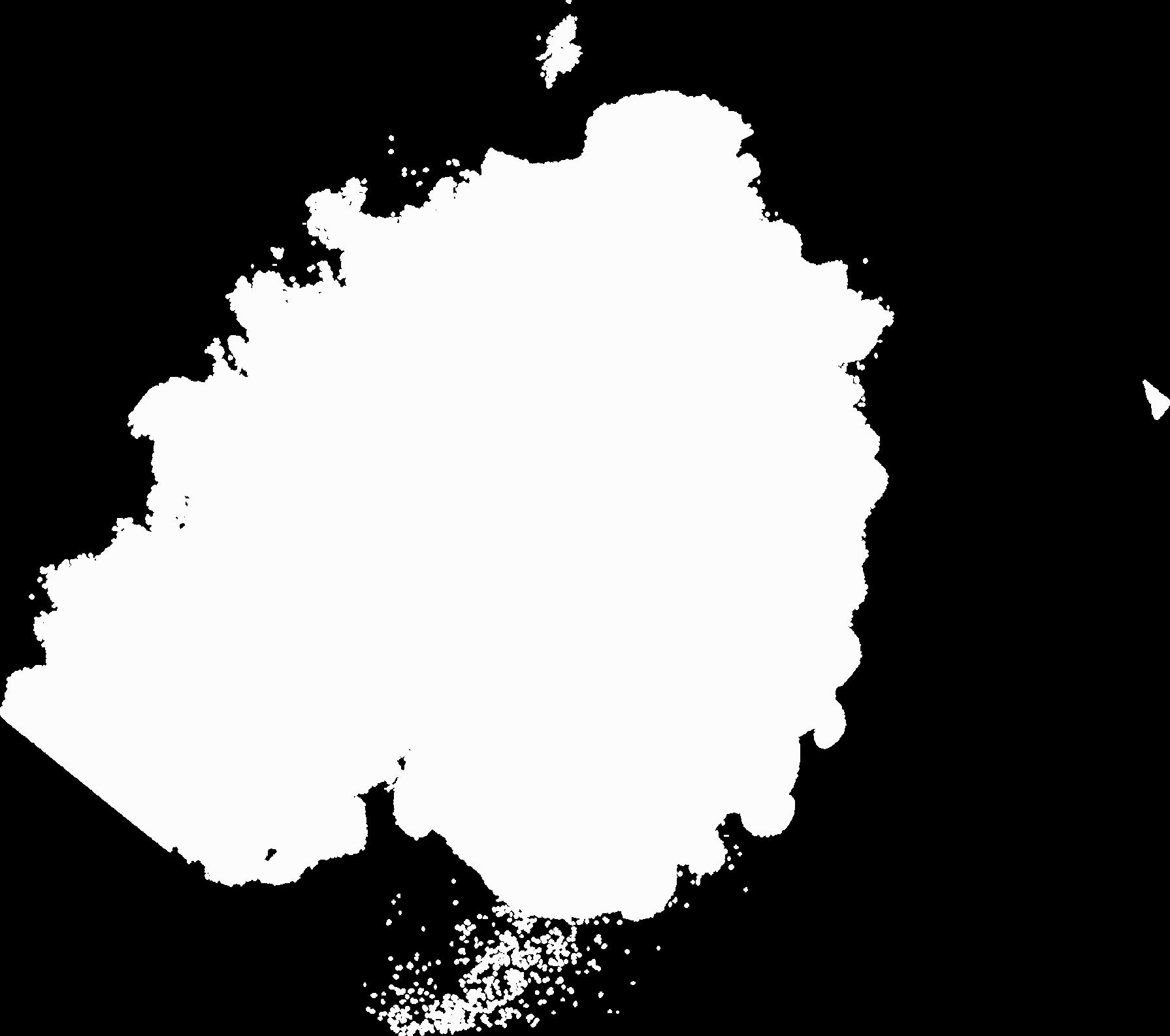
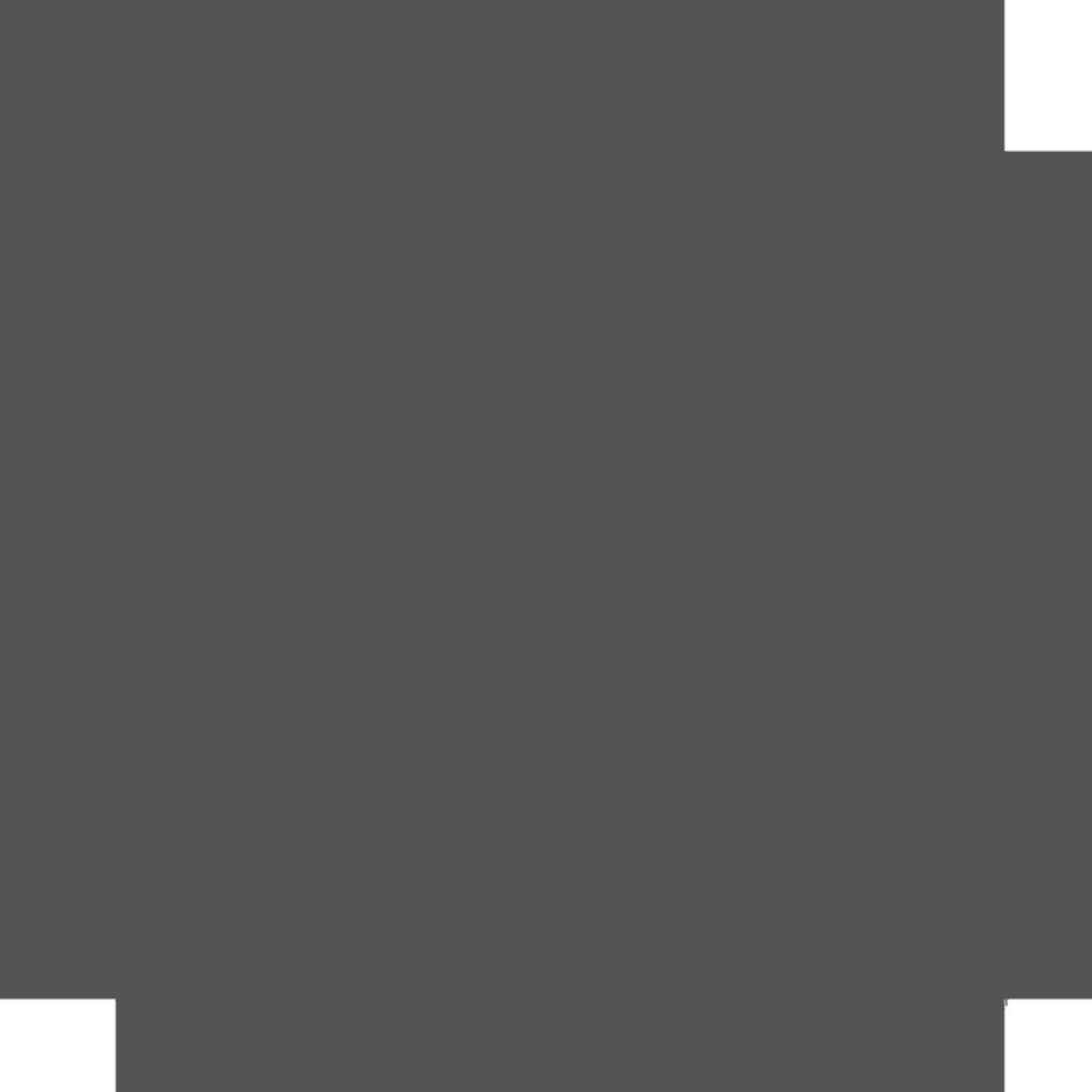
AXH air-coolers unparalleled level of experience and technical expertise throughout the entire organization, coupled with the largest manufacturing facility in the industry, enables us to offer a complete range of air-cooler models and types to fit any standard or custom application. We have the capacity to design, supply and duplicate virtually any replacement section or cooler and can respond to fully support the reapplication of existing coolers.
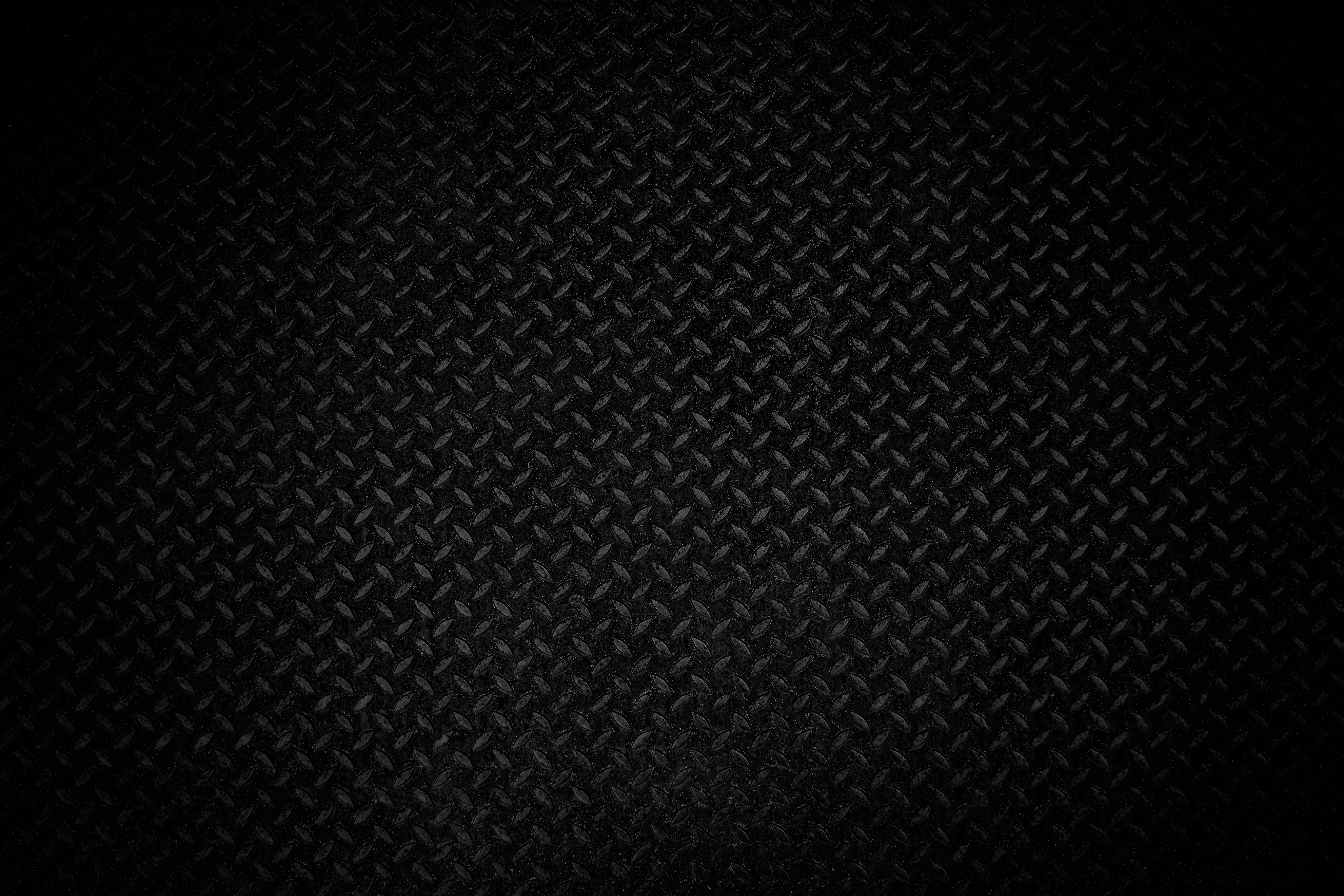
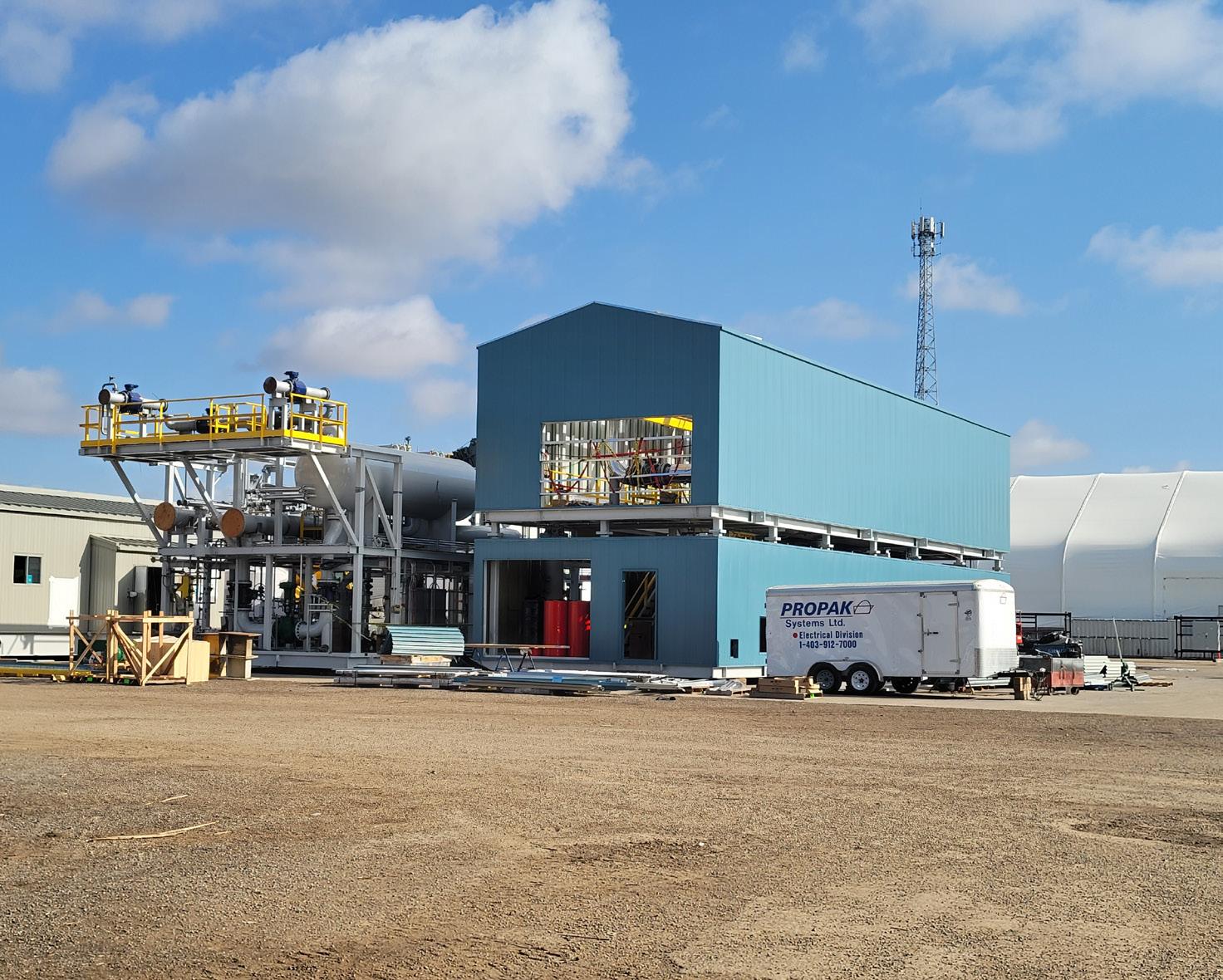
Most notable, however, is the 404 shop, Propak’s largest fabrication and assembly facility which is fully equipped to assemble large process and compression modules.
The facility includes numerous overhead cranes, semi-automatic welding machines, a profiler used to cut and bevel pipes, a large carbon steel pipe spooling shop, a stainless steel pipe fabrication shop, a hydrostatic testing facility, an enclosed sand blasting bay, and two paint shops.
“In addition to the painting capacity, we are also able to apply internal pipe coatings in this facility. Most impressive is its main shop, which has large work areas that enable the assembly of our process and compression modules,” Hanson adds.
Elsewhere, on Veterans Boulevard, Propak’s 925 facility houses the company’s Enhanced Oil Recovery, Energy Systems, and Power and
Steam Systems engineering teams. Its attached shop is equipped for pressure vessel manufacturing, OnceThrough Steam Generator (OTSG) fabrication and process module assembly.
The facility contains a fullyequipped engine cylinder head remanufacturing shop and spare parts warehouse which maintains approximately $10 million worth of inventory.
“It also contains our controls simulation room, which allows for full software acceptance testing activities to be completed prior to automation systems being deployed to the field.” he informs us.
DELIVERING SPECIALIST VALUE
In 2018, Propak acquired the assets of Innovative Steam Technologies (IST), including its intellectual property and facility in Cambridge, Ontario becoming a key division of the
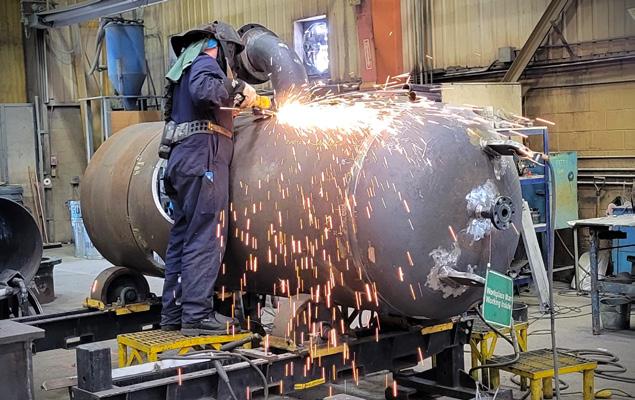
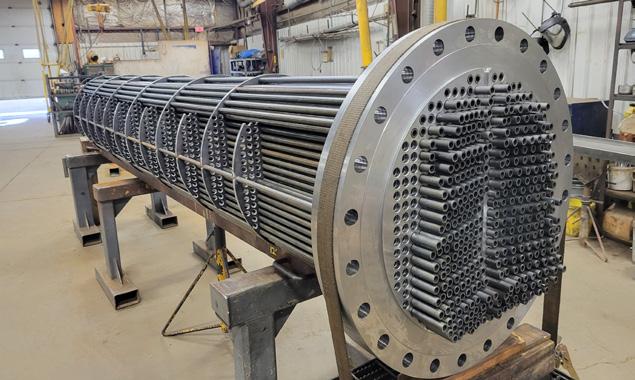
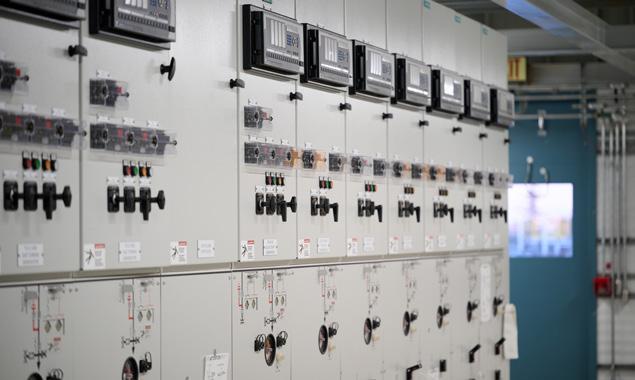
company.
Located at 549 Conestoga Road, the Propak IST facility includes office areas for engineering operations and a 100,000-square-foot manufacturing space for OTSGs used in heat recovery applications. The Cambridge facility also houses two tube-finning lines utilizing a proprietary brazing process.
“This process increases the quality of bonding between the fins and tubes, enabling higher performance than more traditional finning methods,” Hanson insights.
Propak IST adds significant value to the power generation and energy industries as a unique provider of Heat Recovery Steam Generators (HRSGs).
The division is therefore strategically positioned to provide improved energy efficient solutions to support the ongoing global energy transition.
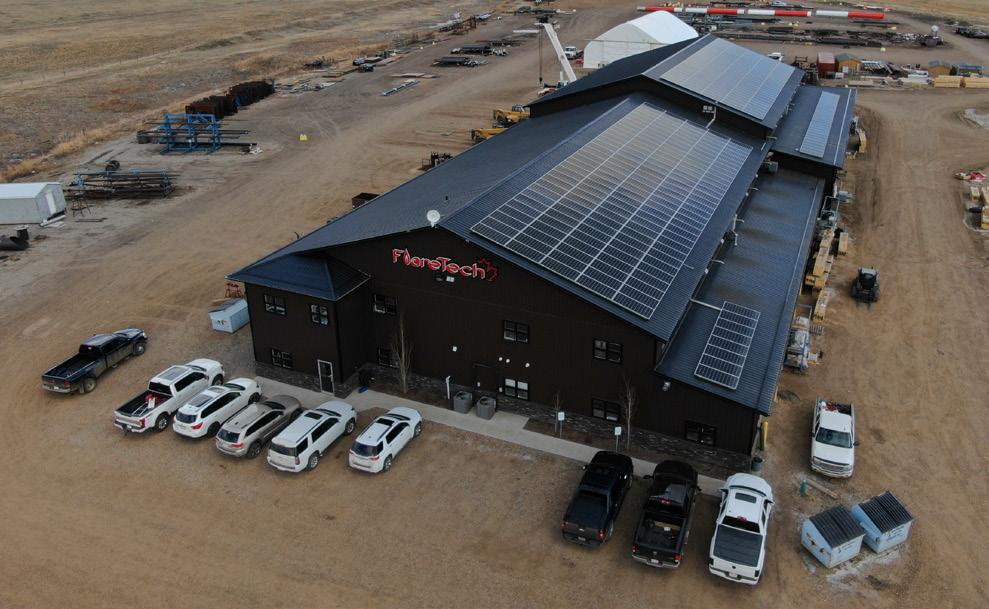
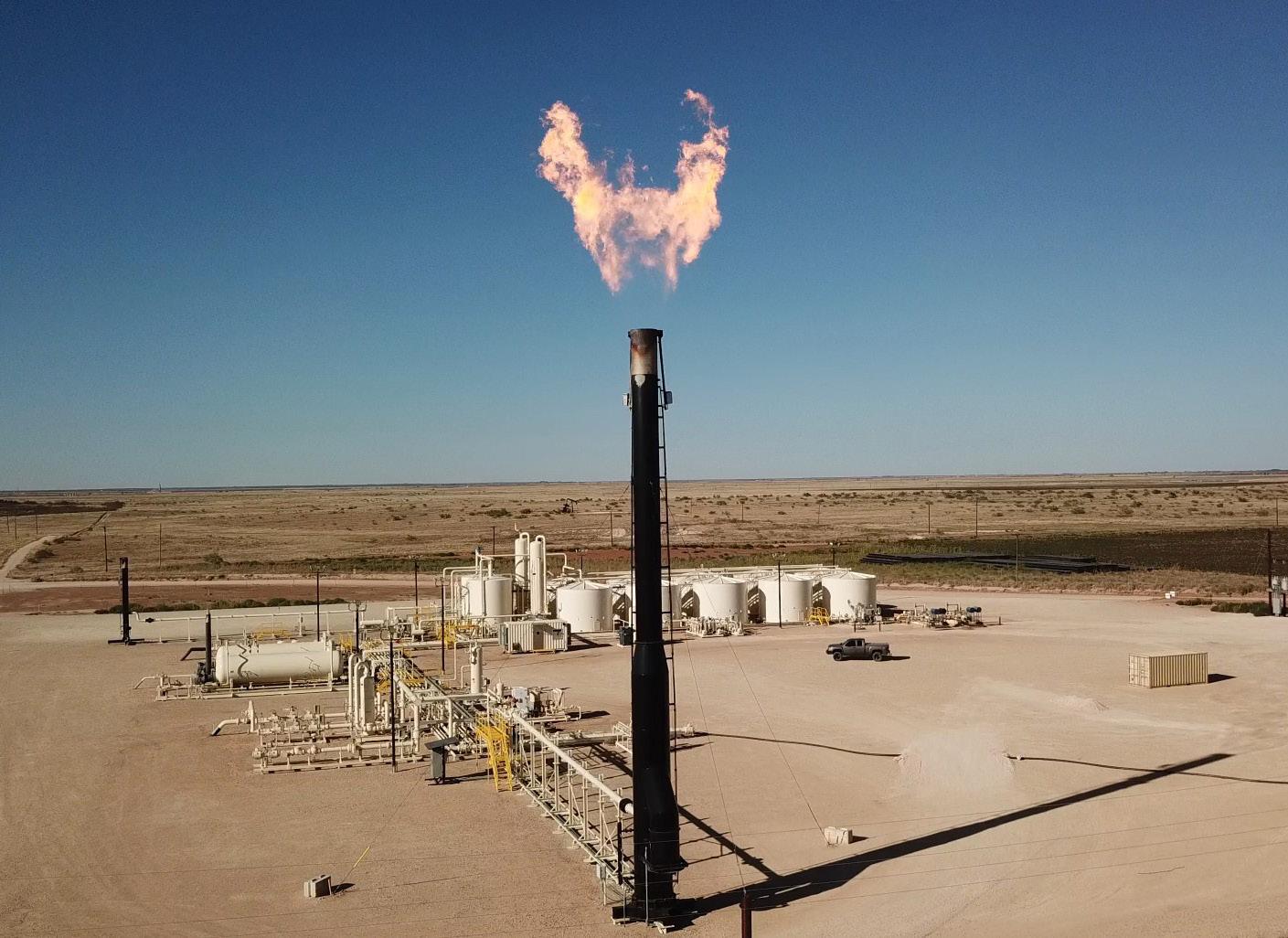
Canada’s Premier Flare System Manufacturer
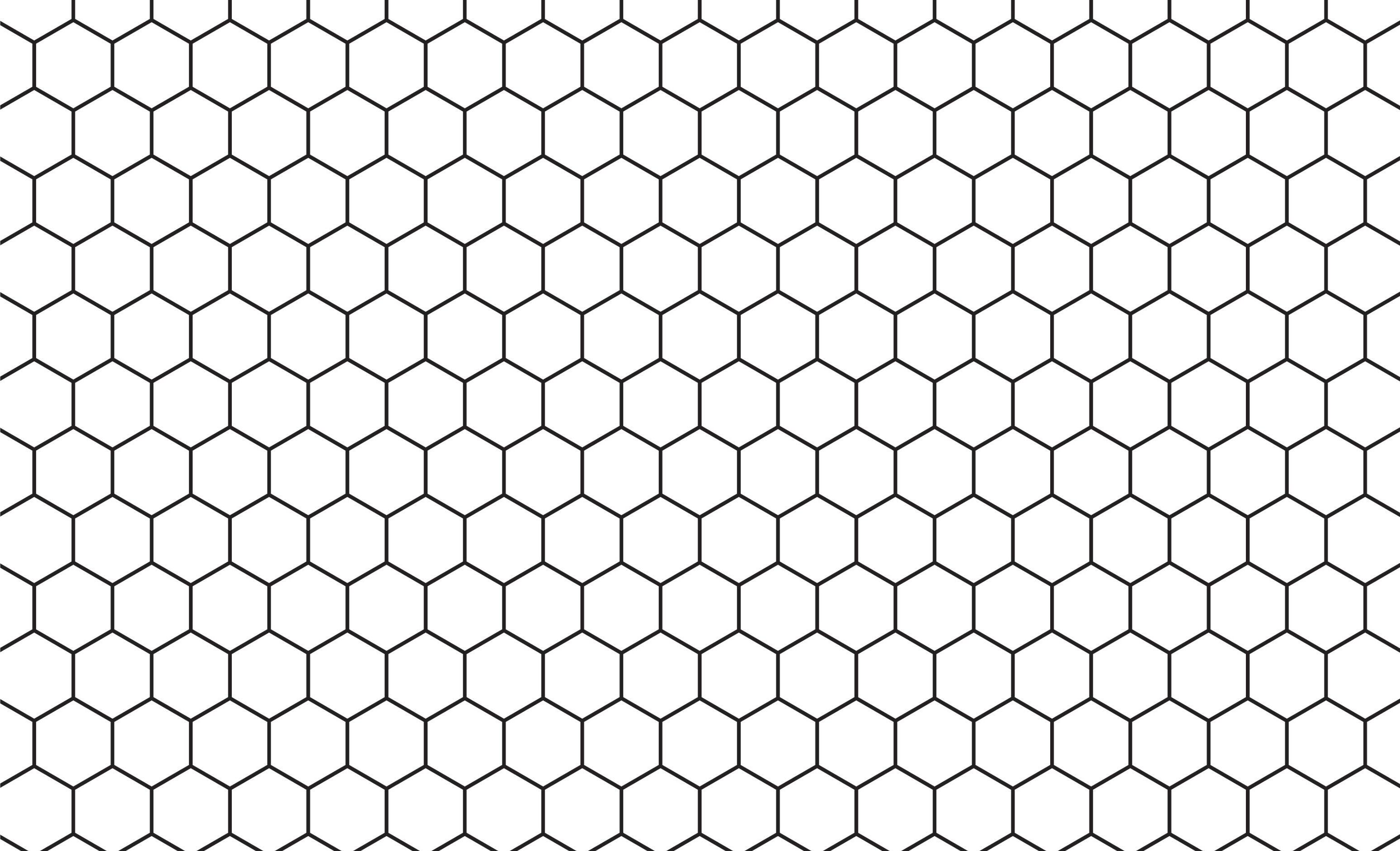
FlareTech Overview:
FlareTech is a family-run business based in Stettler, Alberta, established in 2009, with over 40 years of experience. The company operates a 25,000 sqft manufacturing facility, fully equipped with welding bays, overhead cranes, CNC automation, and plasma cutting capabilities. Their 20-acre storage yard supports operations and laydown.
Turn-Key Services:
FlareTech offers end-to-end solutions including flare system sizing and design, fabrication, installation, commissioning, inspections (UAV & hands-on), routine maintenance, shop repairs, stock flare availability, and rental units.
Flare Systems and Structural Design:
Their systems include utility, assisted (air, gas, low-pressure), sonic, Variable Slot Sonic, combination flares, Mobile flare trailers, Vent, Flue Gas, and Exhaust Stacks. They specialize in guy-wire-supported and self-supported flare stacks.
Ignition Systems and Monitoring:
FlareTech provides retractable pilot systems, fuel gas manifolds, and electronic spark ignitors (ESI). Their monitoring and ignition systems feature PLC-based control panels, duplex thermocouples, HMI displays, solar backup, and Modbus communication for seamless operations.
Enclosed Combustion Solutions:
They offer vapor combustion units, enclosed ground flares, and Thermal Oxidizers designed for temperature-controlled combustion, natural/forced draft systems, and refractory lining to maintain combustion efficiency.
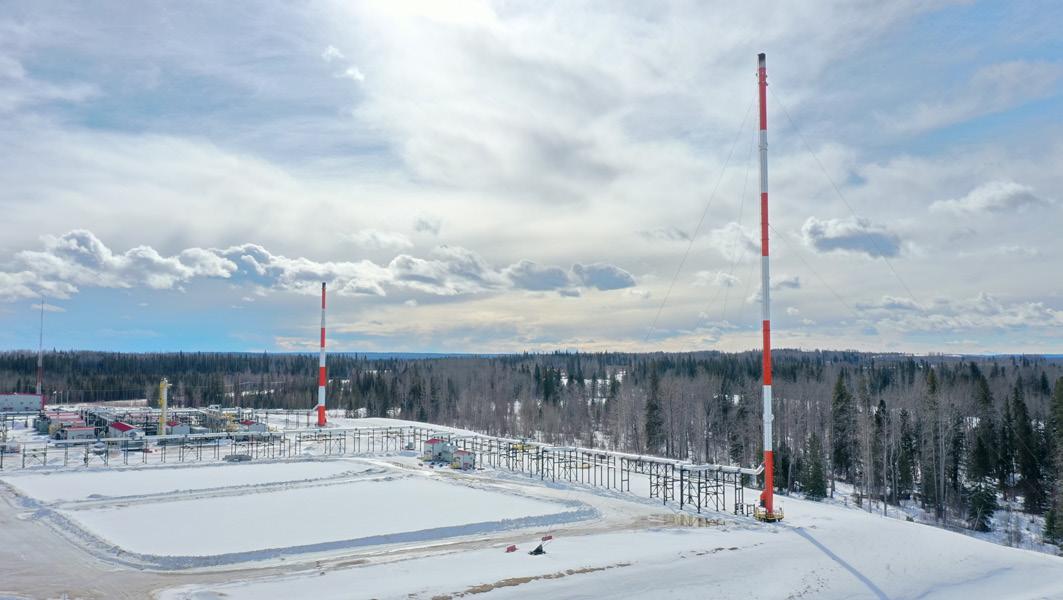
Retrofits and Maintenance:
FlareTech provides 24/7 service for retrofit projects, bolt-up & torquing, erection, guy wire tensioning, and flare tip replacements. Their teams include B-Pressure welders, High Angle Technicians, and they use UAV drones for inspections on Flare Tips and Internals, along with cleaning, including new drone pressure washing technology.
Additional Components and Engineering:
The company integrates knock-out drums, flame arrestors, detonation arrestors, variable frequency drive (VFD) blower systems, aircraft warning lights, beacons, obstruction lights, and flow meters into designs. They conduct Flare & Knockout Sizing, dispersion modeling, wind load analysis, skid and pile design, FEA, proximity planning. We are also designing and building enclosed combustion units.
In summary, FlareTech is an industry leader in flare system design, manufacturing, installation, and maintenance, delivering comprehensive solutions for oil, gas, and energy operations with a commitment to efficiency and safety.
Detonation and Deflagration Arrestors:
The FlareTech Detonation Arrestor is a revolutionary design in detonation safety technology. FlareTech has created a Detonation Arrestor that is lighter in weight, has a lower pressure drop, high continuous endurance burn rating, and a lower cost than competitors’. The design of the FlareTech Detonation Arrestor stops the sonic flame front, defusing the initial forces before it reaches the flame quenching element.
Guy Cassidy - Cell: (403) 742-2212 | guy@flaretechinc.com
Scott Phillips - Cell: (403) 510-9898 | Scottp@flaretechinc.com www.flaretechinc.com

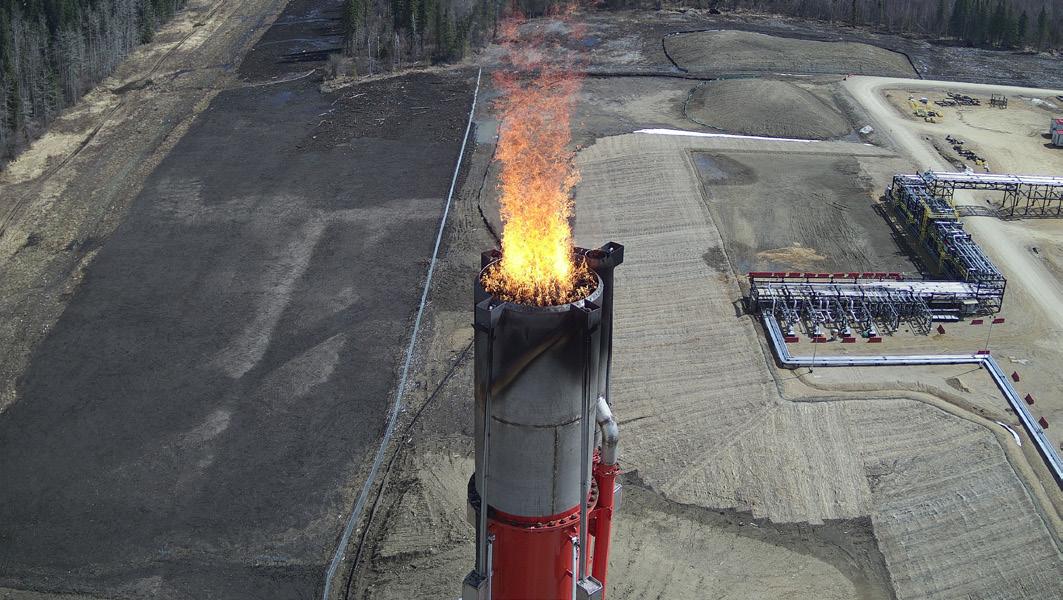
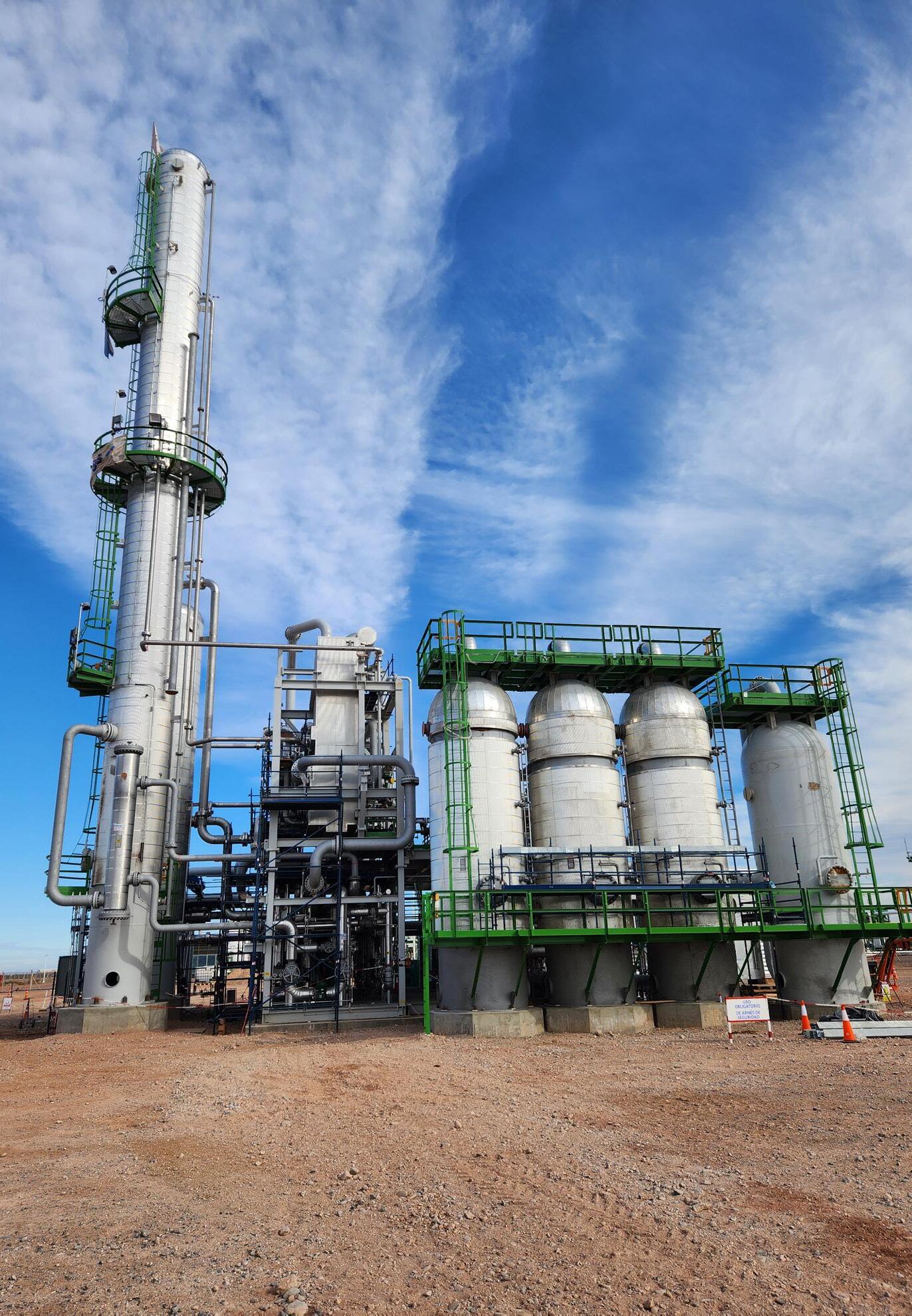
“Propak’s IST division has the expertise to provide the most efficient heat recovery and utilization solutions for our clients’ power needs.”
Additionally, its patented SQ-90 rifled tube technology provides an industry-leading solution for steam generation and enhanced oil recovery applications, delivering the highestquality steam for enhanced oil recovery applications.
“Propak IST is your solution for heat recovery and steam generation, done a better way,” Hanson excites.
The company also provides parts and maintenance services through Propak Energy Services, which equally addresses customers’ needs in an expert and highly efficient manner.
The division operates product support, service, and parts facilities throughout Western Canada and the US with locations in Airdrie, Grande Prairie, Medicine Hat, Lloydminster, and Red Deer (Alberta); Fort St John (British Columbia); and Kindersley, Weyburn, and Swift Current (Saskatchewan).
The company similarly has facilities in the US, including Williston, North Dakota and Casper, Wyoming.
“Propak Energy Services’ personnel are supported by our engineering and automation capabilities and staff, which differentiate us from other service companies,” he points out.
MAINTAINING HIGH STANDARDS OF QUALITY
Propak’s staff are the core of the company’s success, as its team members are empowered to employ their professional and technical skills to continuously improve product offerings.
“Propak reflects the combined talent, experience, dedication, and diligence of our staff. Innovation is encouraged and no idea is dismissed without careful consideration,” urges Hanson.
Staff are recognized through a variety of means, including annual service awards. The company’s manufacturing personnel specifically are rewarded with numerous safety accolades and afforded the opportunity for career development by gaining skills through in-house training programs.
Propak similarly supports the development of new tradespeople by setting up apprenticeships in cooperation with local technical education institutions.
Moreover, the company values its staff by continuously exploring how it can foster a better culture where its employees are passionate about engineering and manufacturing quality rather than simply obeying the rules of a project.
In order to deeply embed quality within its culture, Propak adheres to four key pillars – leadership emphasis, message and communication clarity, encouragement of peer involvement, and employee ownership of quality improvement.
Regarding the former, the company’s management team
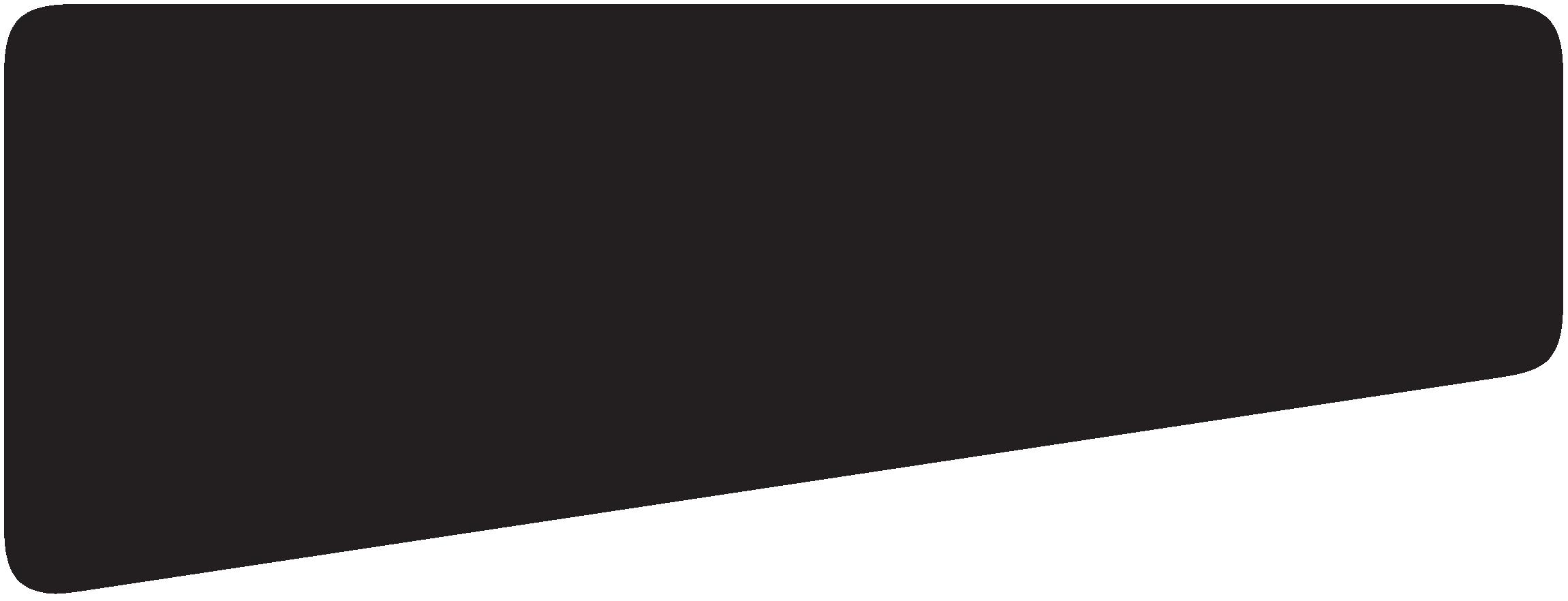
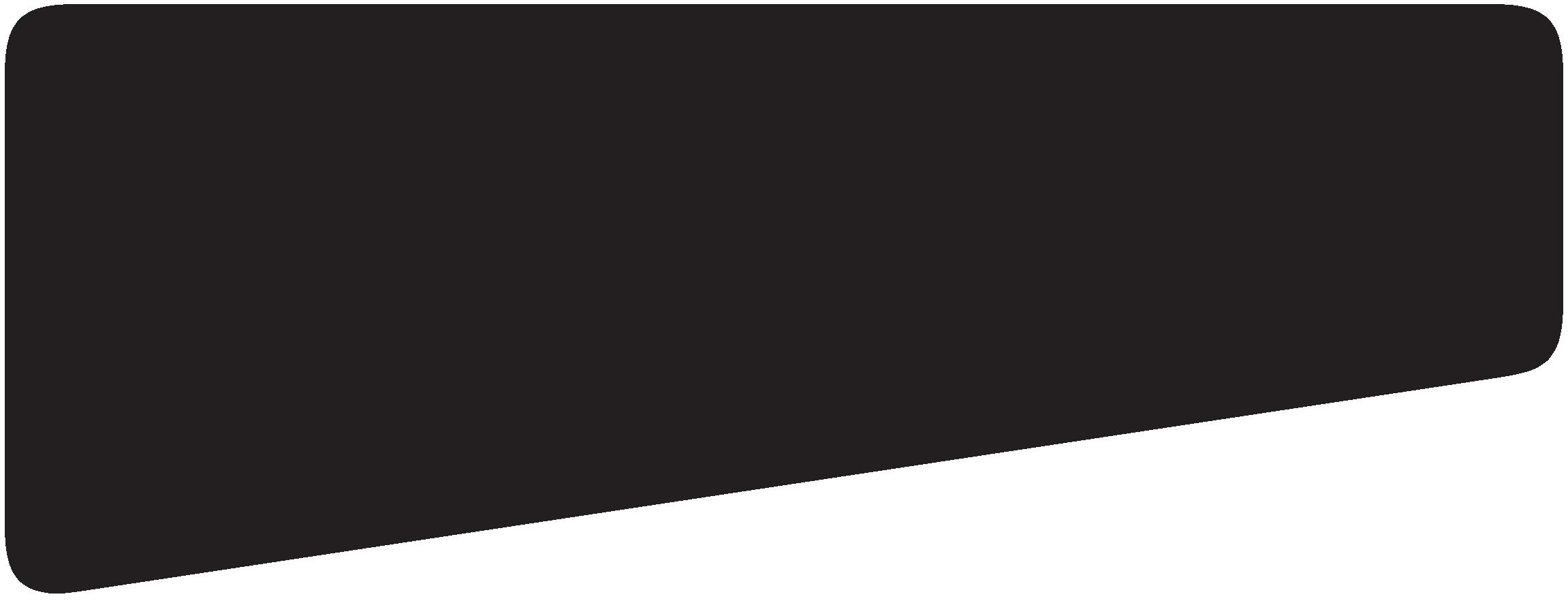
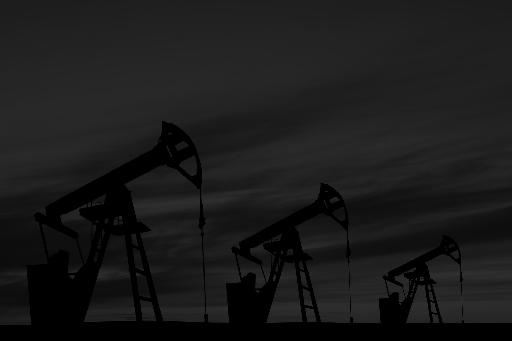
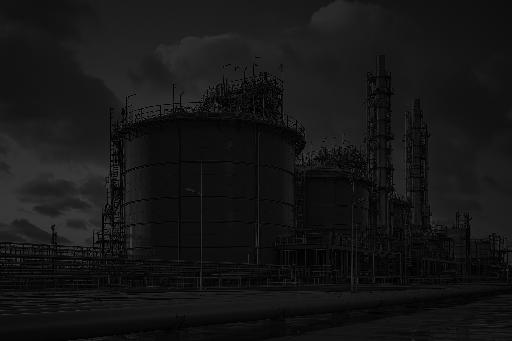
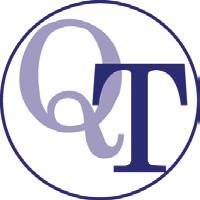
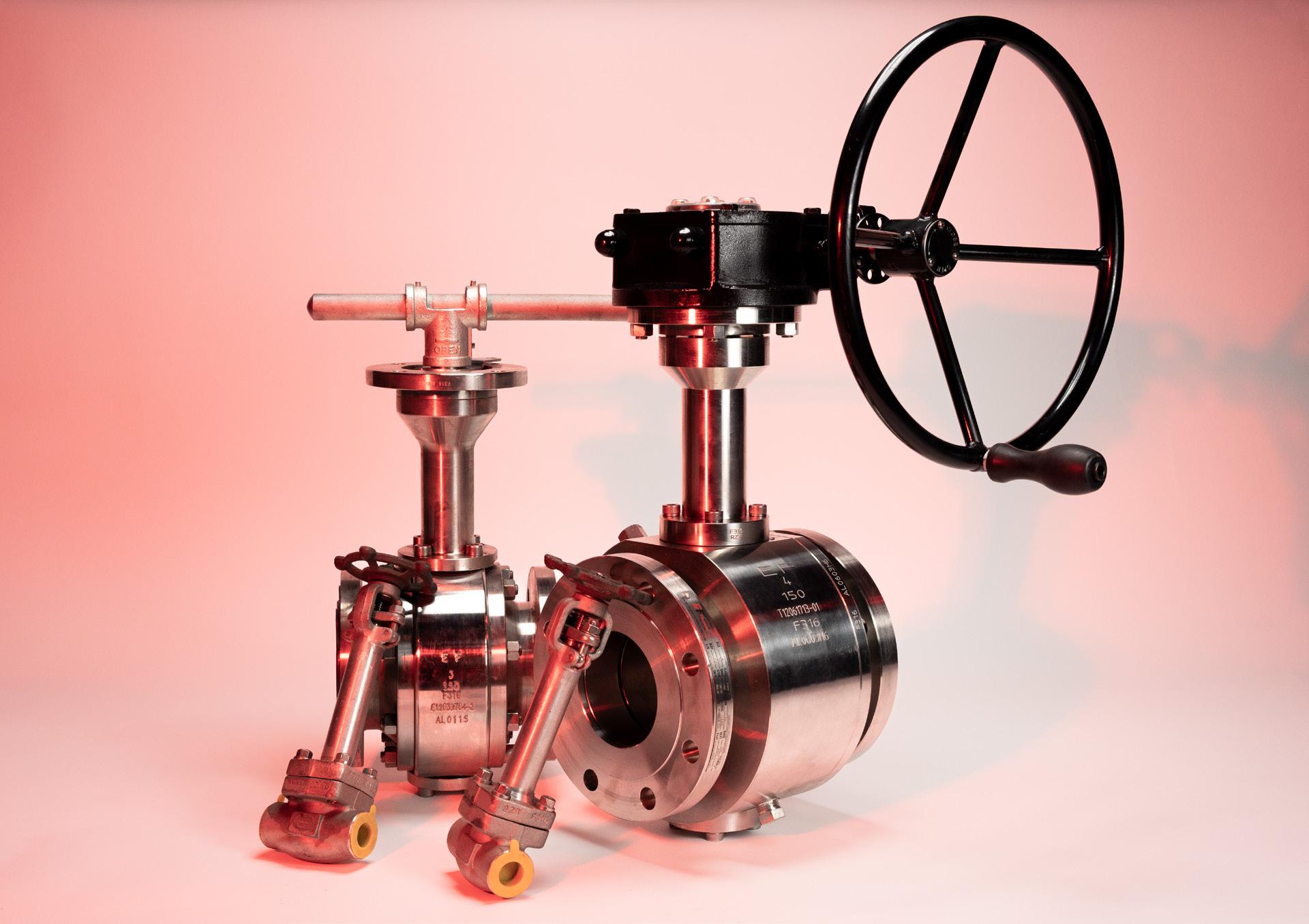
www.qualitytube.com
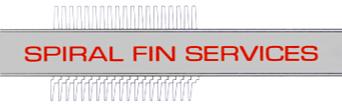
CONGRATULATIONS TO PROPAK ON 50 YEARS!

We are Canada’s leading stocking distributor and project partner specializing in tubing products for the heat exchanger, boiler, condenser, and air cooler markets. In addition to bare tubing, we bring a series of valueadded products and partnerships through our in-house facilities and extensive international supply chains. We focus on Canada only, with crane-serviced warehouses located in Calgary, Alberta and Ancaster, Ontario.
From day one, Propak Systems has been a valued partner. We cherish this relationship and look forward to building on our partnership and supporting them for years to come.
purchaseorders@qualitytube.com | cpotter@qualitytube.com
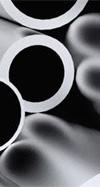
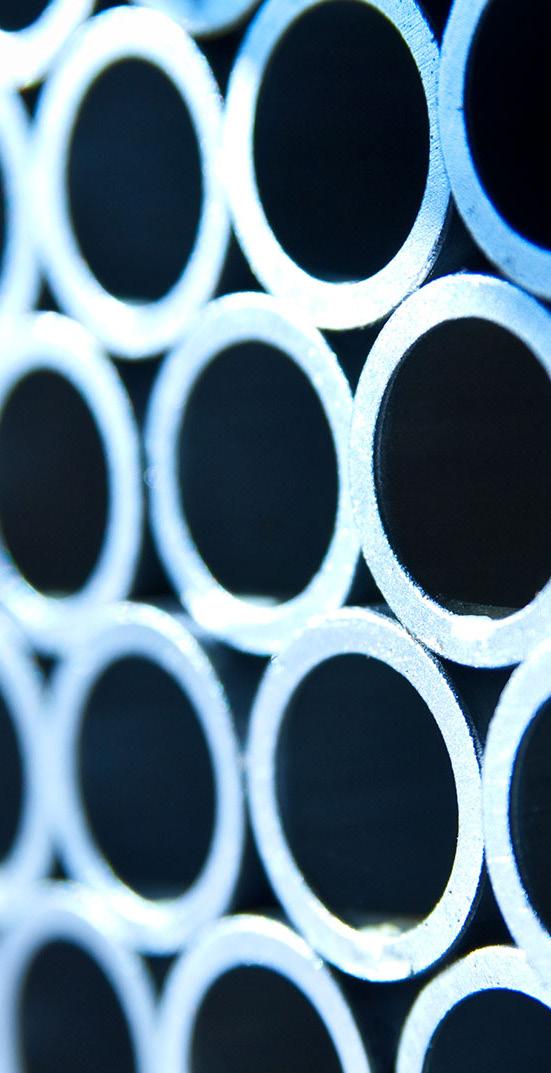
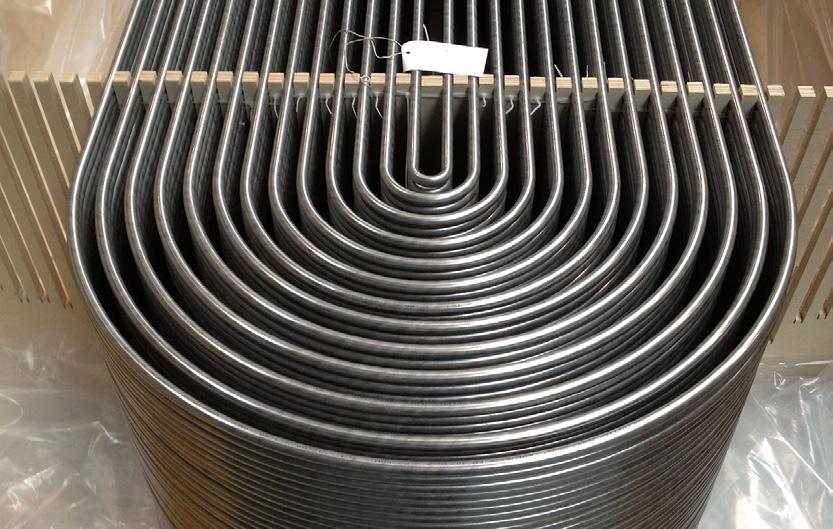
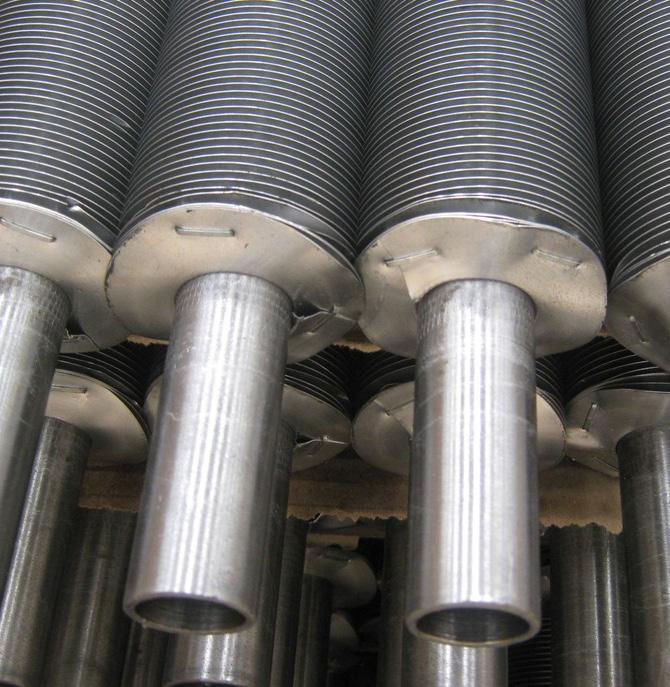
PROPAK’S KEY MILESTONES
• 1976 – Incorporated on 1st October.
• 1976 – Opened for business in Calgary with a staff base of 15.
• 1978 – A new workshop and office was constructed in Airdrie to handle growing business demand.
• 1979 – Awarded a major Canadian gas plant project.
• 1981 – Executed its first major gas processing plant construction project in the US near Vernal, Utah.
• 1984 – Opened a sales office in Denver, Colorado to enhance business growth in the country.
• 1986 – Awarded and executed its first turnkey project outside North America for the Barbados National Oil Company.
• 1990 – Awarded a contract to build the first liquefied petroleum gas (LPG) recovery plant for Petrobras, a Brazilian energy company, in the Amazon. Propak subsequently fabricated two major expansions at the plant location in 1996 and 2003/04.
• 1995 – Opened an office in Buenos Aires to enhance business growth in South America.
• 1995/96 – Awarded major projects in Argentina, Poland, and New Zealand, which were all successfully executed. The company also continued to expand its product lines, such as aerial coolers.
• 1997 – Commenced the design and manufacturing of directfired process heaters.
• 1999 – Opened a sales and service office in Beijing, China.
• 2004 – Completed and put into operation the first liquefied natural gas (LNG) plant equipped with a methane liquification unit.
• 2005 – Opened its PPCL subsidiary.
• 2006 – Number of staff across all divisions exceeded 750.
• 2009 – Created a fully modular steam-assisted gravity draining (SAGD) well pad design.
• 2013 – Developed the engineering for a fully modular SAGD central processing facility.
• 2016 – Worked in partnership with IST to design and modularize an OTSG for use in enhanced oil recovery projects.
• 2018 – Acquired the assets of IST.
• 2024 – Awarded the contract for the supply of HRSGs to power a large data center in Ireland.
instils a culture of quality by engaging with all disciplines throughout every stage of the project.
Moreover, Propak’s integrated organizational structure allows fabrication, construction, and field service personnel to be involved across all project stages, from initial reviews through to closeout sessions where teams reflect on the lessons learnt on a project, thereby fostering continuous improvement.
Quality is further interwoven into the business with message and communication clarity.
“Open, transparent, and clear communication is essential for spreading the message about quality. Propak utilizes a variety of channels to communicate the importance of quality to employees across all levels and departments of the organization,” Hanson emphasizes.
The company additionally greatly focuses on encouraging peer involvement as it relies heavily on the engagement of its workforce to advance many quality aspects.
From developing new internal process standards to delivering detailed questions to engineering teams and suggesting design improvements, employees across the company are encouraged to engage.
Finally, employee ownership of quality improvement resides as a key component in its mission to maintain quality throughout the organization.
“Propak’s culture of quality requires employees to apply their skills and make decisions to foster an environment of continuous quality improvement.”
SUPPORTING SUSTAINABILITY INITIATIVES
Propak considers sustainability, environmental impact, and quality in the development of all its projects and are key parts of its product design process.
“Through the delivery of products that improve efficiency and reduce

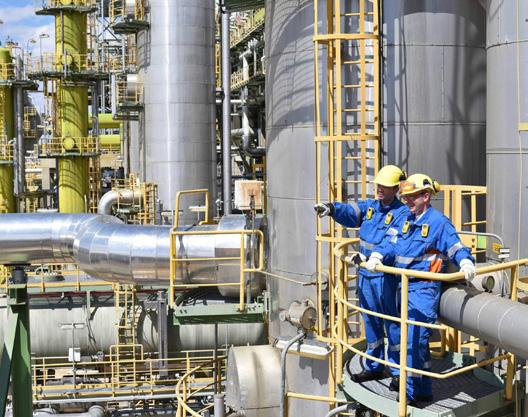
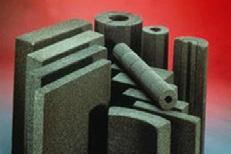
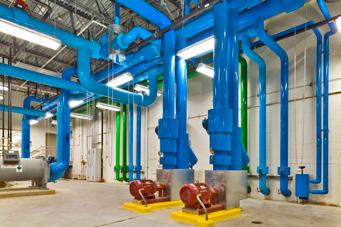
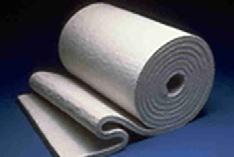
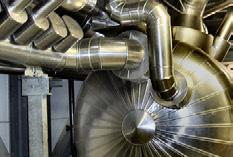
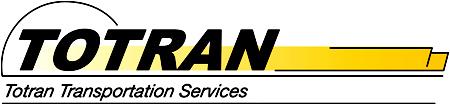
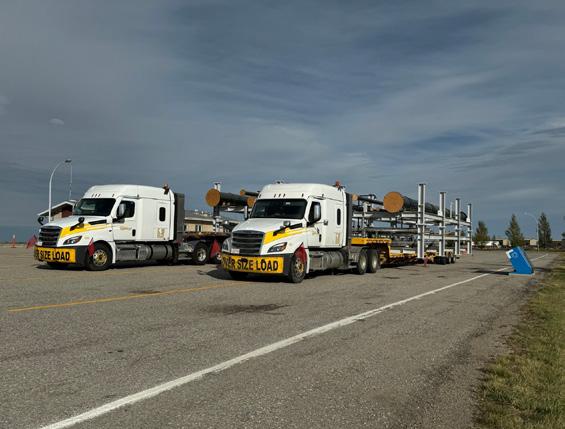
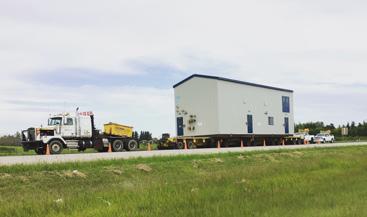
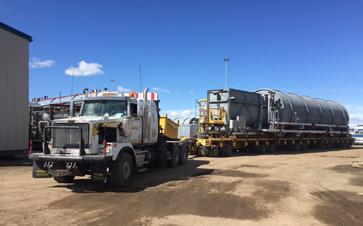
Congratulations on reaching this incredible milestone! For half a century, Propak Systems has demonstrated excellence, innovation, and a lasting commitment to quality, service, and community. Your journey is a testament to strong leadership, dedicated employees, and a vision that continues to
Totran values our long-term relationship with Propak and we are grateful for the partnership we have developed over the past 20 years. Everyone at Totran Transportation Services is wishing Propak Systems continued success and growth for many more years to come!
Head Office: 403-723-0025 | Conroe TX: 713-450-4700 info@totran.ca | totransales@totran.ca | www.totran.ca


emissions, we are able to support our clients in their sustainability initiatives,” Hanson insights.
More specifically, the company focuses on efficiency, modularization, emissions control, produced water recycling, process heat integration, noise control, and spill and leak prevention and control when developing products.
Propak’s Energy Systems business unit was specifically formed to provide sustainable solutions to clients seeking to reduce their emissions and minimize the environmental impact of their activities and business endeavors.
Propak IST likewise delivers on strong environmental commitments, particularly its patented SQ90™ OTSG technology. The equipment’s industry-leading design produces 90 percent quality steam which provides a number of key benefits when compared to typical industry standards.
For instance, the SQ90™ OTSG reduces fuel consumption and the blowdown rate while maintaining the same dry steam flow as competitors, resulting in less greenhouse gas emissions during operation.
Additionally, due to the lowered feedwater flow rate, the technology utilizes less pumping energy while also decreasing the amount of chemicals used in the process.
On the manufacturing front, Propak partners with a local metal recycling company to send carbon and stainless steel, aluminum, wire, and other materials to be recycled, processed, and returned to the market.
“Last year, we recycled just over three million pounds (lbs) of steel product, diverting it from landfills,” Hanson closes.
Propak also possesses an on-site cardboard baler that is used to compress the cardboard boxes its abundance of materials arrive in. As such, the company can collect,
bale, and palletize large amounts of cardboard before having it sent to a processing facility.
In 2024, Propak recycled approximately 60,000 lbs of cardboard, as well as recycling soft plastics – such as pallet wrap and bags – separately from its landfill waste facility.
As one of Canada’s largest manufacturers of energy processing equipment, the company will continue to create maximum customer value through fit-for-purpose design solutions, reduced capital costs, reliable project execution, and industry-leading product performance, cementing its enviable position.
Tel: 403-912-7000 sales@propaksystems.com www.propaksystems.com www.otsg.com
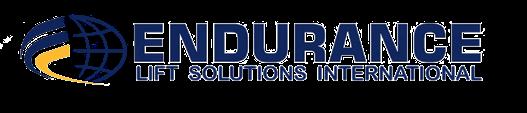
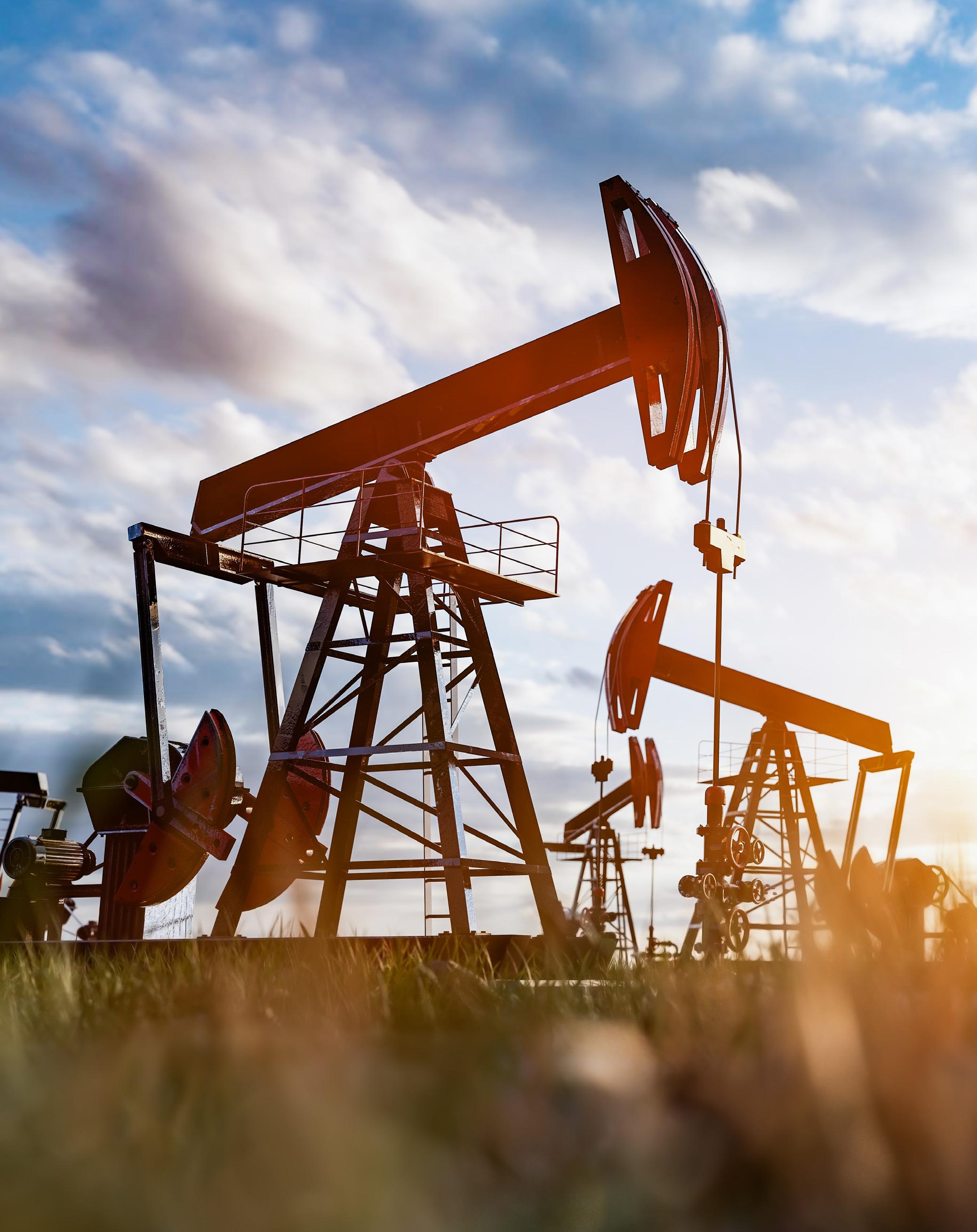
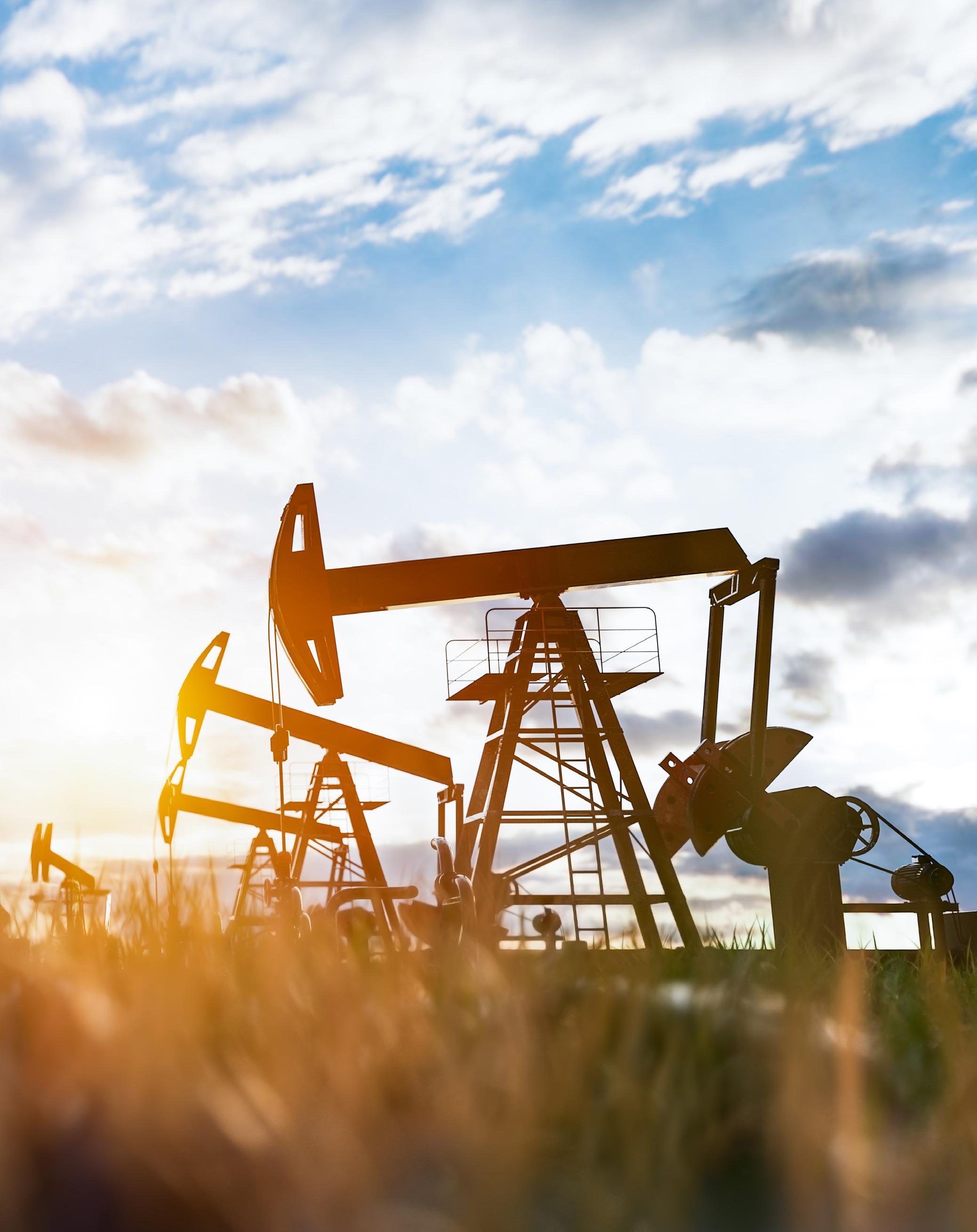
RUN LONGER, PRODUCE MORE
Driven by teamwork, technology, and transparency, Endurance Lift Solutions offers state-of-the-art artificial lifts alongside in-house application engineering, installation, and field services to extend the life of its clients’ oilfield wells
Writer: Lily Sawyer | Project Manager: Scarlett Burke
Helping its customers in the oil and gas sector to maximize production throughout the life of their wells, Endurance Lift Solutions (Endurance) provides technologyenabled artificial lift solutions, combining deep-rooted industry experience with leading-edge equipment to offer state-of-the-art products.
Founded in 2014, Endurance has expanded through strategic growth and acquisitions over the years, emerging today as one of the nation’s biggest independent artificial lift companies with service centers strategically located in key oil and gas producing regions.
Dedicated to responding rapidly to its customers, Endurance delivers high-quality support, ensuring it builds long-lasting client relationships.
The company’s basin-specific expertise also allows it to assist clients in overcoming the most difficult well challenges, in turn increasing flow rates and cash flow to reduce overall ownership costs.
On a mission to provide leadingedge lift technology alongside first-rate customer service, Endurance seeks to establish itself as a one-stop solution for artificial lift solutions in North America, empowering its team members, suppliers, and customers every step of the way.
STANDING OUT FROM THE CROWD
Proudly offering six unique product lines, Endurance’s growing portfolio of innovative artificial lift solutions is second to none.
The plunger lift system, for example, featuring Endurance’s own design, allows the company to respond quickly to customer requirements and provide system assistance with its own comprehensive range of spare parts.
Its gas lift, meanwhile, allows customers to reduce the total cost of ownership by ensuring clients’
field assets have the necessary infrastructure.
Moreover, Endurance’s rod lift maximizes production by offering a wide variety of operating environments, while downhole gauges enable artificial lift optimization, providing high-quality bottom-hole data which can be utilized by reservoir engineers.
The company’s capillary equipment and injection services enable operators to treat downhole conditions at the point of failure, improving the lifetime of artificial lift systems.
Finally, the electric submersible pump (ESP) offers a full suite of application-specific equipment.
The latest advancement in the
ENDURANCE’S ARTIFICIAL LIFT OPTIMIZATION SERVICES
Application engineering –
Offering deep knowledge of the application, design, and analysis of artificial lift systems, Endurance’s engineering and research laboratory delivers a broad range of testing, modeling, and analytical services.
Installation and field services – Thanks to its dedicated 24/7 technician service, an independent research firm ranked Endurance’s field services as the highest in the US in terms of customer satisfaction.
Rod inspection and reconditioning – Endurance is proud of its status as the industry’s most advanced steel sucker rod inspection and reconditioning service, having reimagined the entire process to deliver best-inclass rods.
company’s ESP system design is a robust, high-pressure bolt-on head, designed to provide exceptional durability and performance.
Whether targeting deeper horizontal drill work, managing highflow artificial lift systems, or ensuring peace of mind in high-stake well completions, the high-performance ESP bolt-on head sets the bar for reliability, installation flexibility, and mechanical durability.
Part of Endurance’s wider commitment to advancing ESP technologies, the new head simplifies operations, reduces failure rates, and maximizes production uptime.
A TRAILBLAZING SOLUTION
Enhancing the speed of artificial lift equipment by up to five times, Endurance’s BLAZE® surface technology is changing the face of oil and gas lift solutions by dramatically increasing the run life of pumps, plungers, valves, guides, couplings, trim kits, and downhole components. BLAZE® is not merely a coating or plating as with conventional market alternatives – it’s a thermal-chemical diffusion technology featuring an intermetallic boride layer that can’t peel or crack.
The abrasion and corrosionresistant surface is uniform and smooth, extending the life of artificial lift components.
Capable of remaining on the job longer, BLAZE®-treated artificial lift products lead to reduced downtime and equipment failure alongside lower maintenance and repair costs.
In addition, as a result of reduced downtime, BLAZE®-treated equipment has a positive effect on the user’s environmental, social, and governance (ESG) efforts by providing sustainable benefits.
For example, gas wells experience reduced methane emissions by using BLAZE® as the wellhead needs to be opened less frequently to change lift plungers.
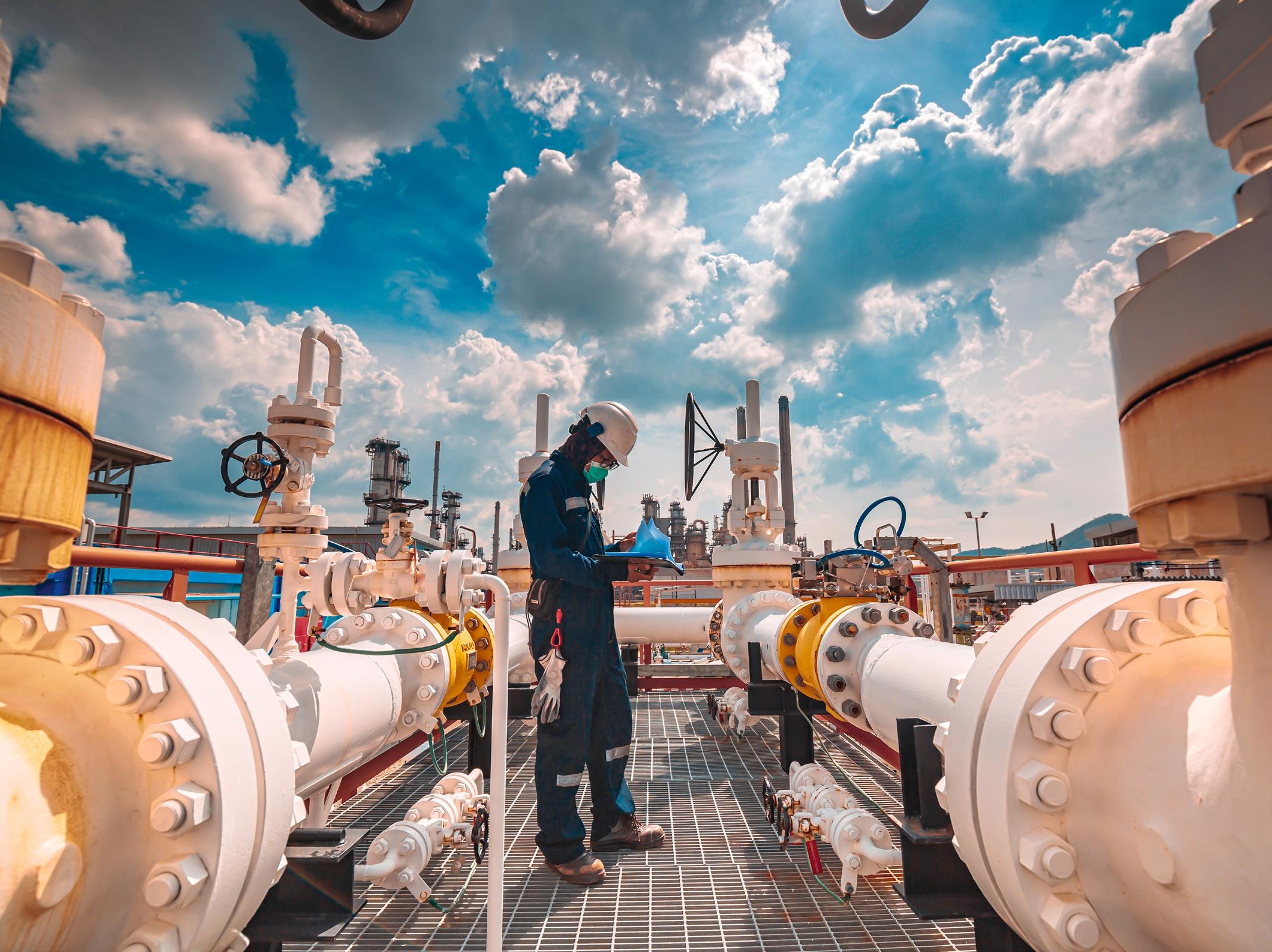
BLAZE® also leads to reduced fuel utilization, energy usage, and emissions by offering an environmentally friendly alternative, while its processes are safe and fully recyclable.
In addition to BLAZE®, Endurance has recently launched its industry-first Series 300 fiberglass sucker rods, which boast unmatched strength and durability.
Offering the industry’s highest loadhandling capacity, as well as superior performance in major corrosive environments, the rods enable users to increase production without scaling up their beam unit equipment, thereby reducing capital expenditure.
Elsewhere, Endurance’s proprietary predictive failure system for end fittings, which can be found on every fiberglass rod the company produces, practically eliminates rod body failure.
SMOOTH OPERATION
Having recently launched a new ESP facility in Oklahoma City offering a full suite of application-specific equipment, Endurance has earned an unmatched reputation for highquality service.
The strategically-located facility allows the company to respond rapidly to the service needs of its clients in Oklahoma, Kansas, and North Texas.
Featuring a cutting-edge pump test bench equipped with a state-of-theart Coriolis flow meter and dual choke system, the facility sets itself apart.
It also undertakes pump construction in-house, with highstrength shafts, stainless steel heads, and bases on hand to maximize durability and reliability.
High-voltage testing and advanced
full-service cable inspections are also available from the Oklahoma site, complete with in-house cable and capillary spoolers, completing Endurance’s portfolio of state-of-theart US-manufactured power cables.
Dismantle, Inspection, and Failure Analysis (DIFA) and pump tear-down services are also on hand to ensure timely performance and diagnose potential failure.
SAFEGUARDING THE FUTURE
Committed to enabling better stewardship of the Earth’s resources, Endurance recognizes its responsibility as a long-term contributor to the oil and gas industry to improve ESG performance.
Fostering a service-driven culture and pursuing industry-leading innovation has allowed it to achieve
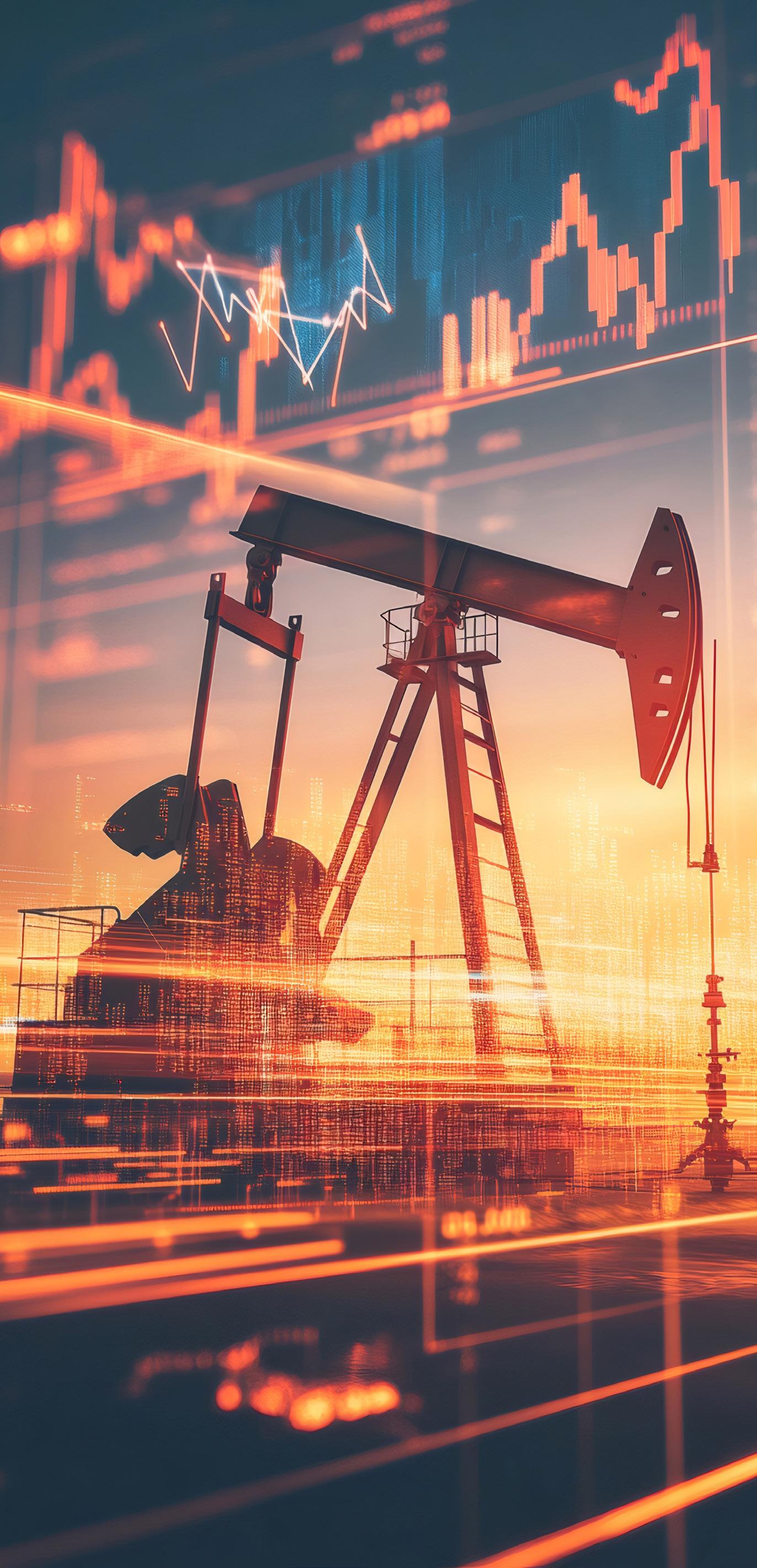
this, and the company remains dedicated to further enhancing the efficiency of its operations to reduce the collective carbon footprint across its value chain.
Developing and seeking innovative technologies has allowed Endurance to increase the automation of its equipment, utilizing predictive analysis alongside this to reduce the potential for workplace harm and operational waste.
The company’s leading products provide significant value to customers, while it continues to pursue improved stewardship of its resources around the globe by upholding its three core values – teamwork, technology, and transparency.
In terms of promoting teamwork, Endurance seeks to treat its customers as partners by collaborating closely on projects while equipping and empowering its workforce by supporting health and safety standards through a health, safety, and environment (HSE)-first mentality – providing opportunities for growth and development.
In addition, the company invests in industry-leading technology to create more enhanced and efficient product operation.
Applications such as BLAZE®, for example, extend run times and reduce energy output. Endurance also uses sensors to reduce waste and improve quality by better monitoring manufacturing efficiency.
Meanwhile, Endurance is also committed to honesty, integrity, and transparency, offering the most transparent equipment performance platform on the market – IntelliWell™ – which provides clear and measurable performance data. By ensuring its values are at the center of everything it does, Endurance takes a proactive approach to sustainability and delivering social impact.
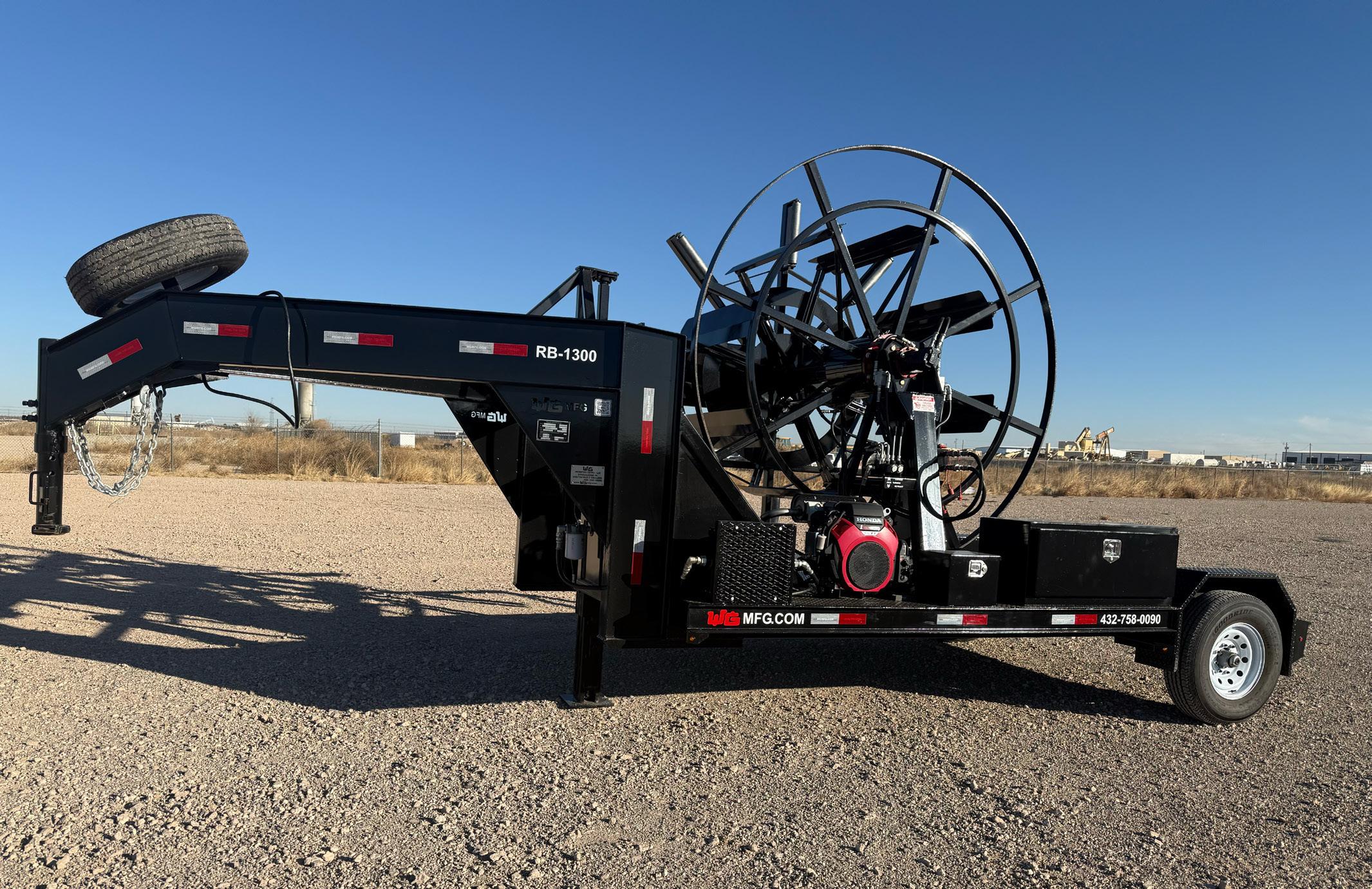
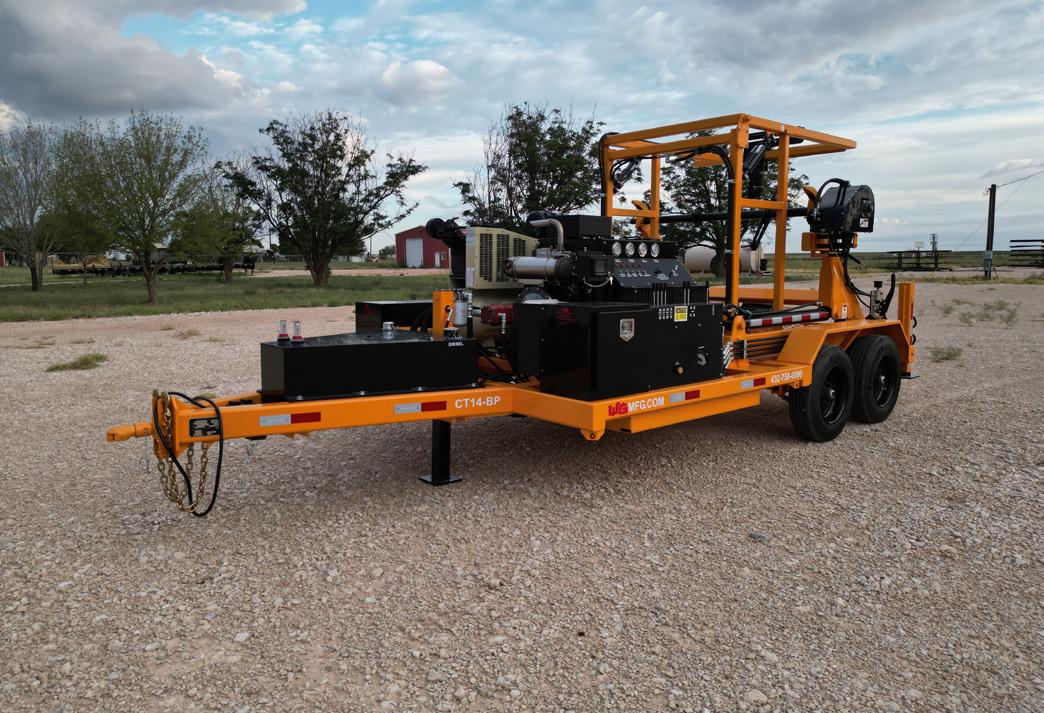
Website: www.WGMFG.com
• Roller Bed Trailers
• Fuel Tank Trailers
• Poly-pipe Rigs for Farm use
• Poly-pipe Rigs for Oilfield use
• ESP Spooling Trailers
• Capillary Tubing Trailers
• Rebanding Trailers
• And much more! WG Manufacturing LLC, 1378 US Hwy 180, W, Seminole, TX 79360
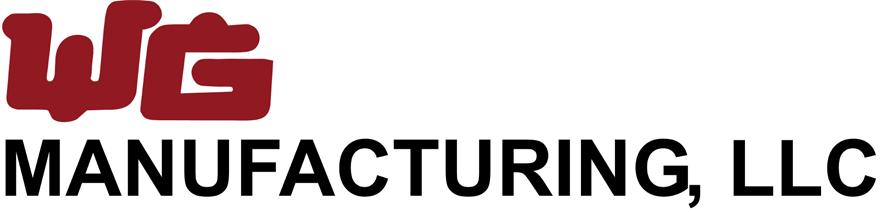
Emails: accounting@wgmfg.com eddie@wgmfg.com johan@wgmfg.com
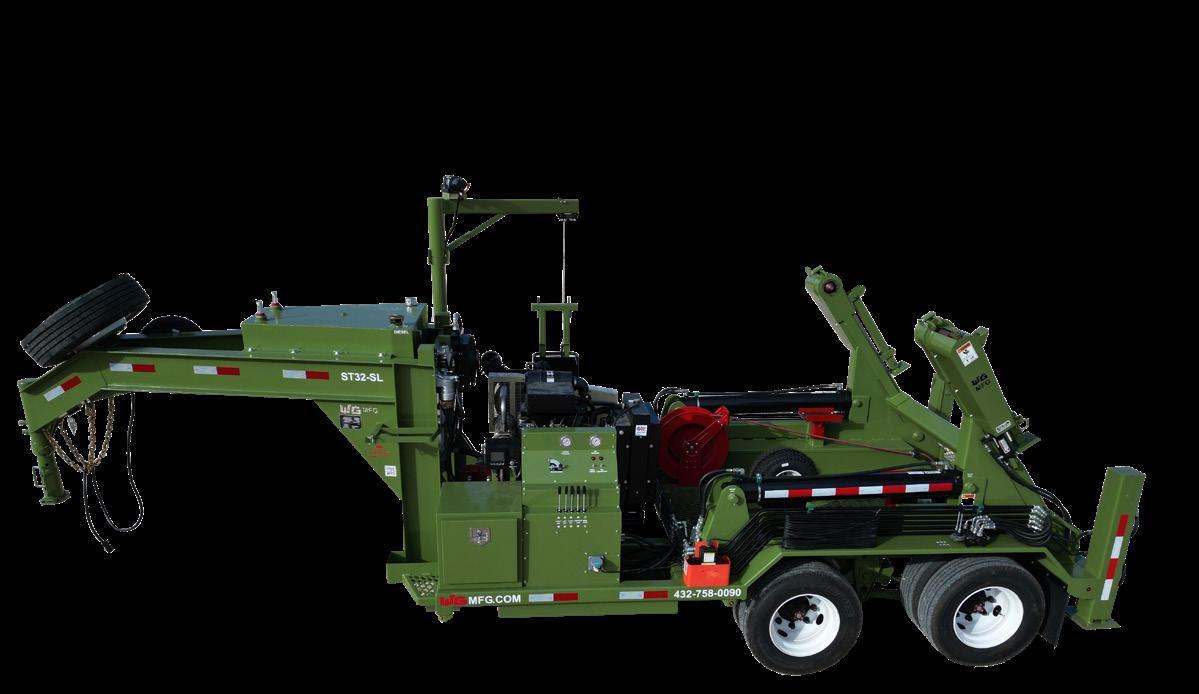
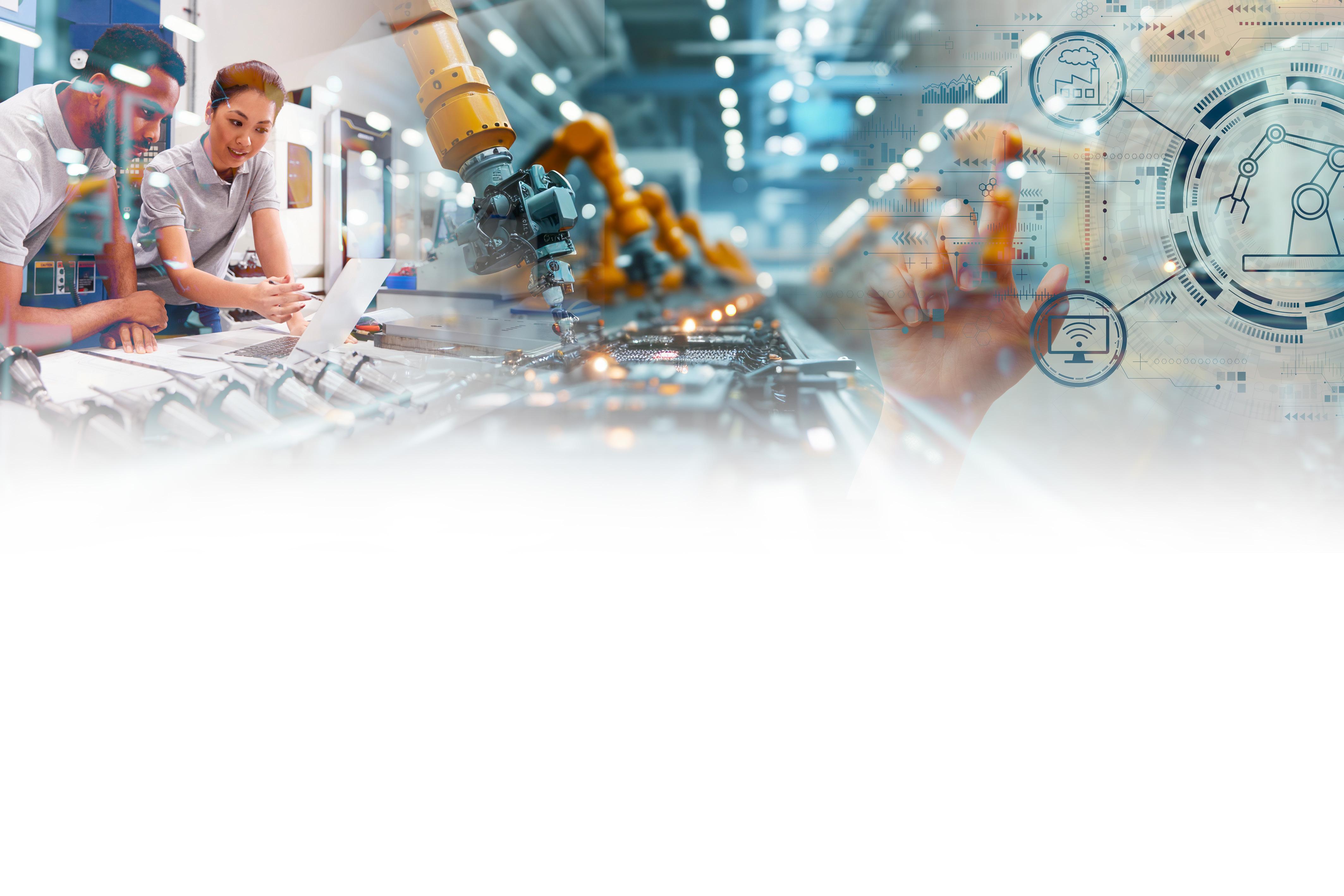
A production-line of exclusive content, delivered straight to your inbox
As manufacturing organizations worldwide confront unprecedented change, embracing technological innovations and incorporating critical environmental sustainability agendas, now more than ever is the time to showcase the strides being taken in this dynamic sector.
A multi-channel brand, Manufacturing Outlook brings you the positive developments driven by organizations across the global manufacturing industry through its various platforms.
Discover exclusive content distributed through its website, online magazine, social media campaigns and digital dispatches, delivered straight to your inbox with a bi-weekly newsletter.
Through these compelling media channels, Manufacturing Outlook will continue to foreground the movers and shakers of the industry.
To participate as a featured company and join us in this exciting endeavor, contact one of our Project Managers today.
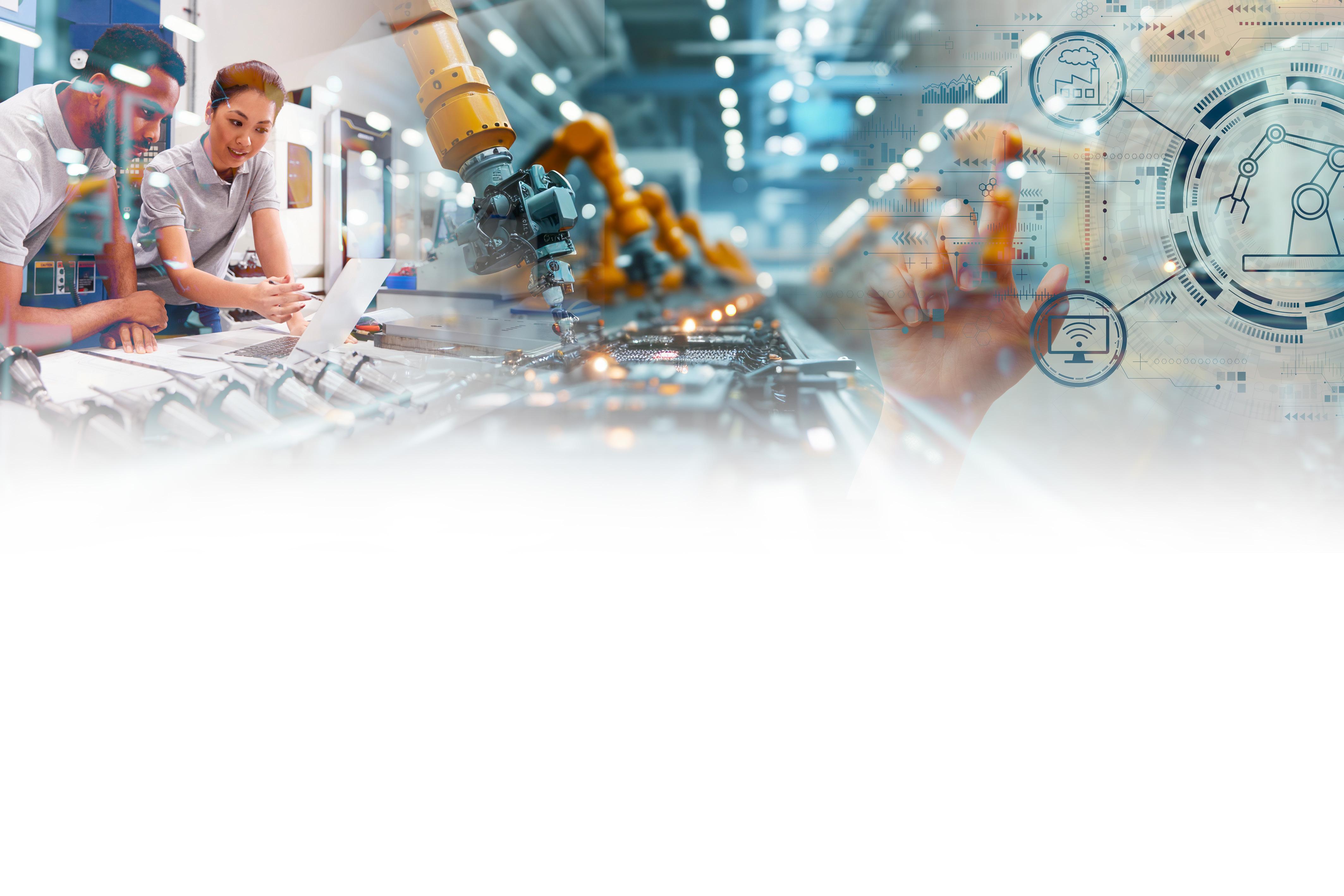
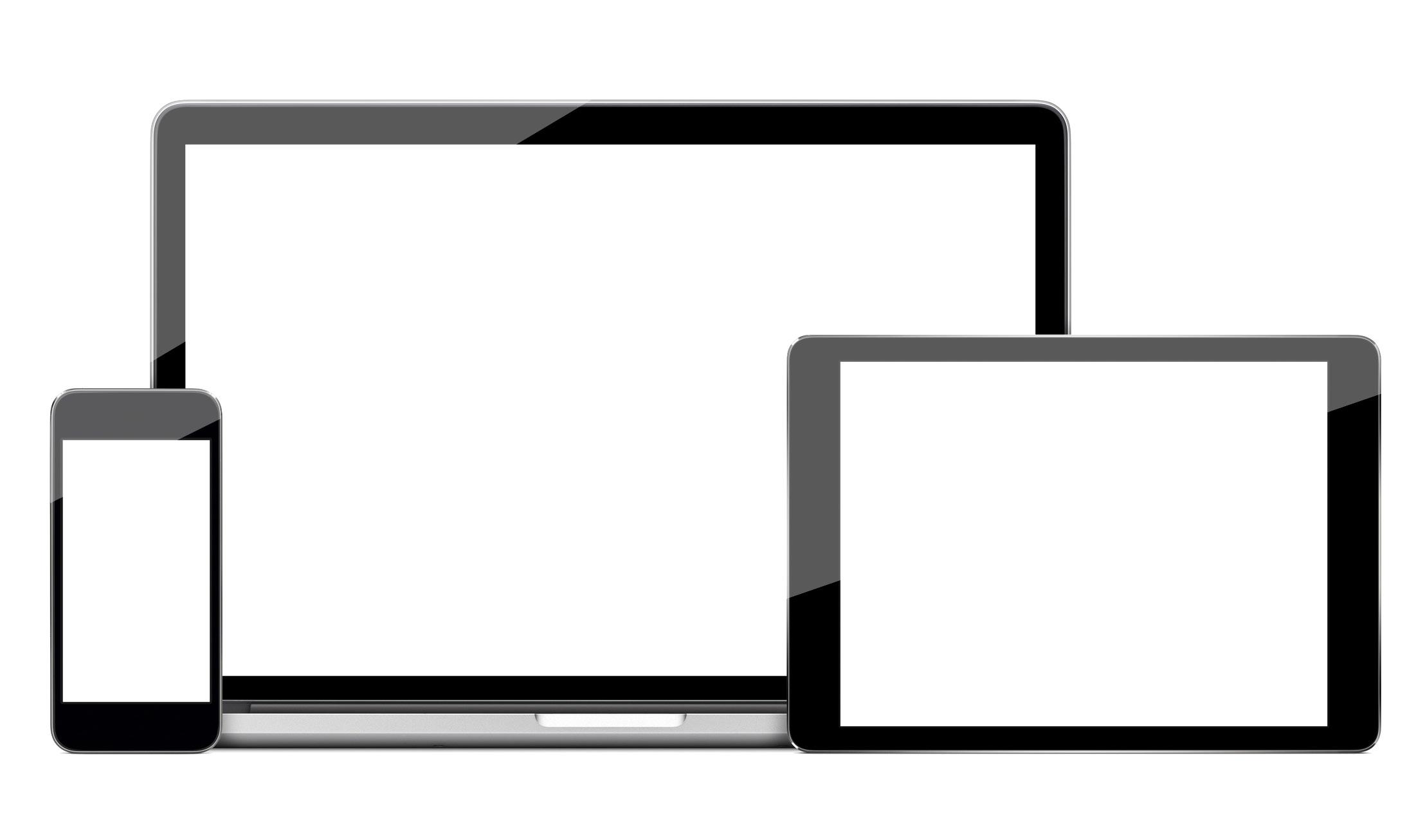
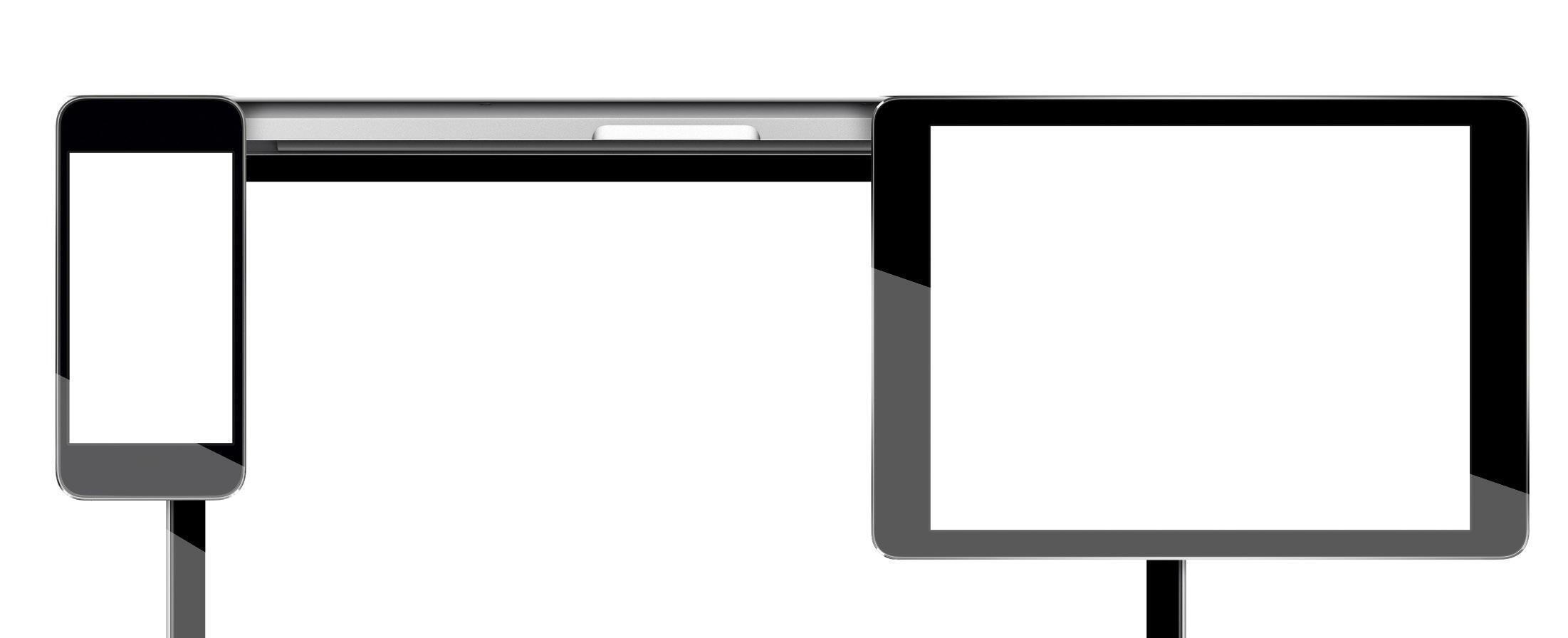
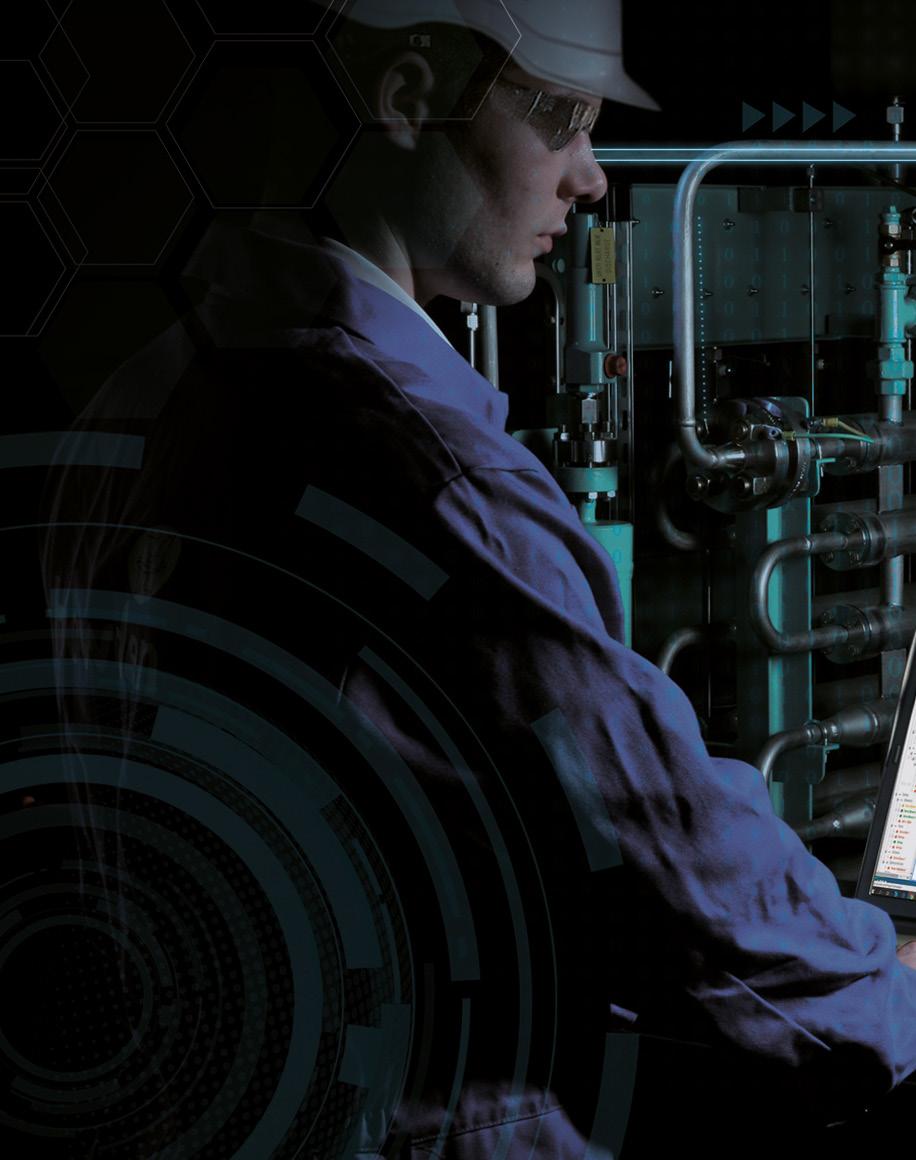
COOLER BY DESIGN
Chart Industries is a global leader in the design, engineering, and manufacturing of process technologies and equipment for gas and liquid molecule handling for the Nexus of Clean™ – clean power, clean water, clean food, and clean industrials, regardless of molecule. We take a deep dive into the company’s incredible story with CEO, Jillian Evanko
Writer: Ed Budds | Project Manager: Michael Sommerfield
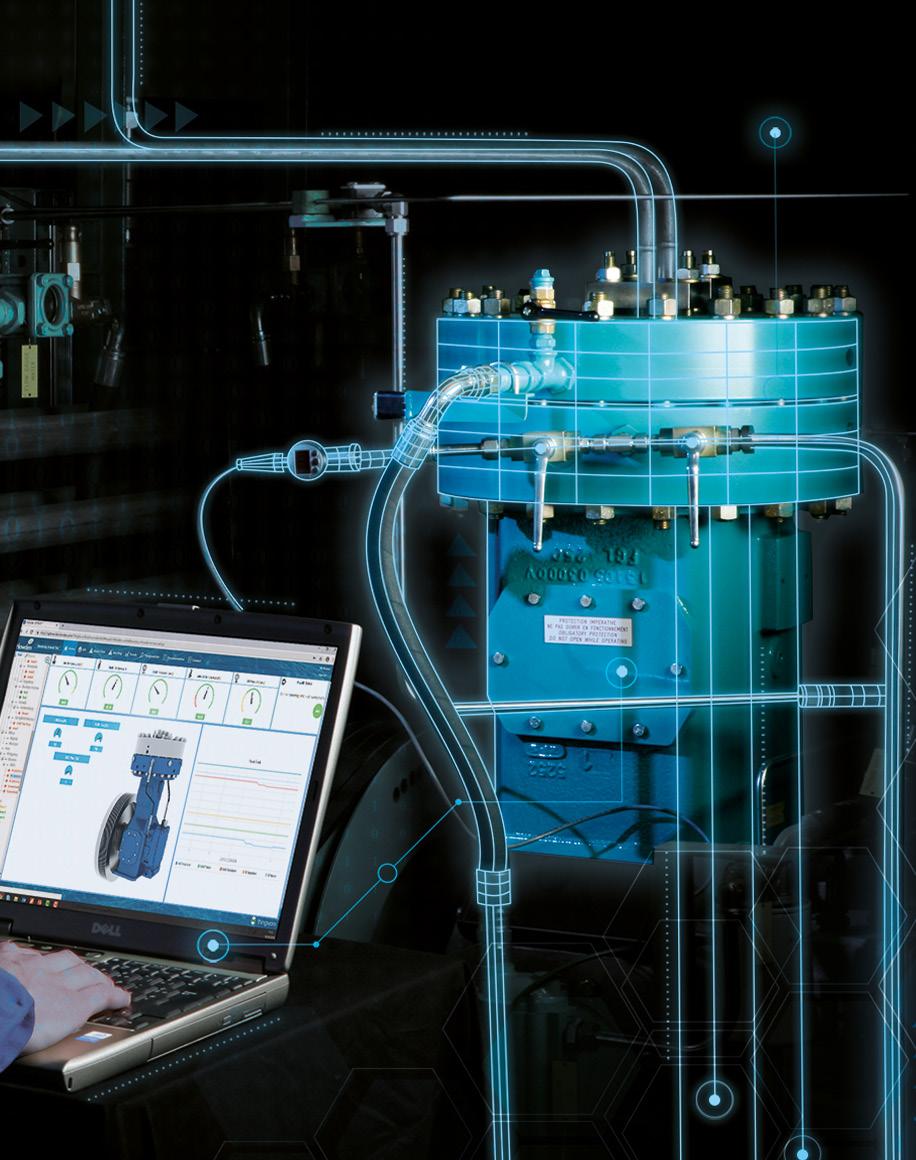
Molecules are the fundamental building blocks of countless substances and form the basis of chemistry as we know it.
These tiny groups of atoms are fundamental to understanding the world, from the smallest components of life to the immense vastness of the universe.
Helping a worldwide network of customers navigate the entire molecular value chain, Chart Industries (Chart) (NYSE: GTLS) is paving the way in the provision of equipment and solutions for the energy and industrial gas markets.
Chart has worked tirelessly to establish itself as a global leader in the design, engineering, and manufacturing of process technologies and equipment for gas and liquid molecule handling, for what it affectionately refers to as the ‘Nexus of Clean’ – a commitment to clean
power, water, food, and industrials.
The incredible work being pioneered by Chart includes enabling the complex production of a molecule itself.
A prime example is the process of creating liquefied natural gas (LNG), where customers use the company’s equipment such as brazed aluminum heat exchangers or its process technology – Integrated Pre-cooled Single Mixed Refrigerant® (IPSMR®) – in order to produce that specific molecule.
Chart then helps its clients to handle the safe transportation of the molecules across a variety of methods, each specific to the individual requirements of the product and the conditions in which they must be kept.
As such, the company’s unique portfolio of products and solutions across stationary and rotating
TO DATE, WHAT ELEMENT OF THE COMPANY ARE YOU MOST PROUD OF?
Jillian Evanko, CEO: “I’m most proud of our team – and how they’ve shown up through numerous stages of growth, transformation, and many different challenges.
“Over the past few years, we’ve more than doubled in size, expanded globally, and accelerated our role in the industry, all while staying grounded in our core values. That is because we have talented people who are adaptable, mission-driven, and willing to lead from every level of the organization.
“We view safety as our number one priority and it is a point of pride at Chart. As such, we’ve achieved some major milestones at several of our global sites, including multi-million-hour streaks without lost time incidents (LTIs) and a record total recordable incident rate (TRIR) of 0.40 at the end of 2024, but we won’t be satisfied until we have zero accidents.
“Each of our team members is authorized, empowered, and expected to stop work if they see a potentially unsafe situation.”
equipment is used in every phase of the liquid gas supply chain, including engineering and service and repair, as well as from installation to preventive maintenance and digital monitoring.
Now utilizing an impressive 64 manufacturing locations and over 50 service centers globally, along with approximately 11,700 dedicated team members, Chart provides industryleading technology, equipment, and services related to LNG, hydrogen, biogas, and carbon dioxide (CO2) capture, amongst other applications.
“Our unique product portfolio is used throughout the liquid gas supply chain in the production, storage, distribution and end-use of atmospheric, hydrocarbon, and industrial gases,” introduces CEO, Jillian Evanko.
“We now leverage domestic operations located across the US and enjoy an international presence
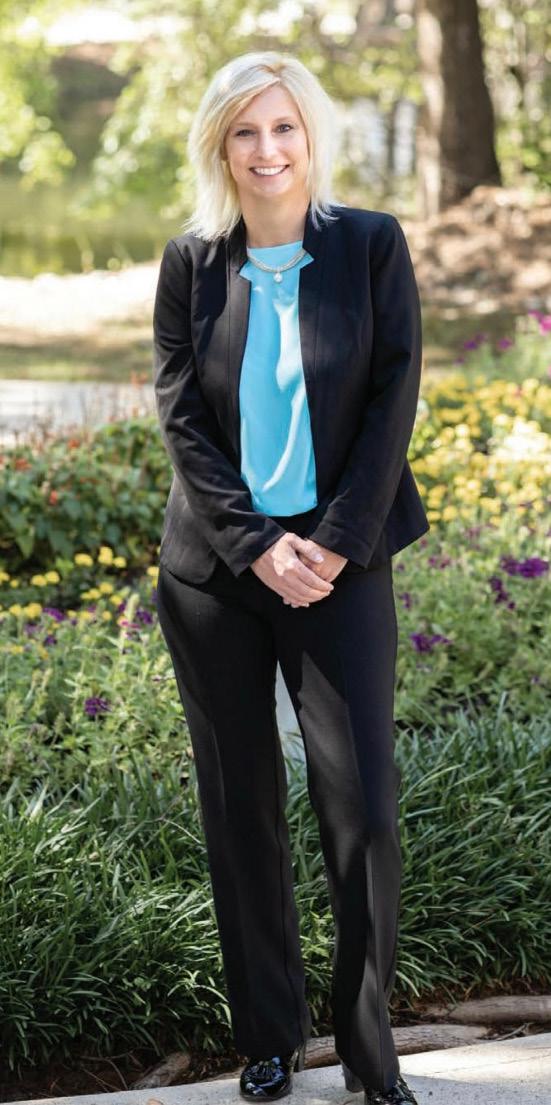
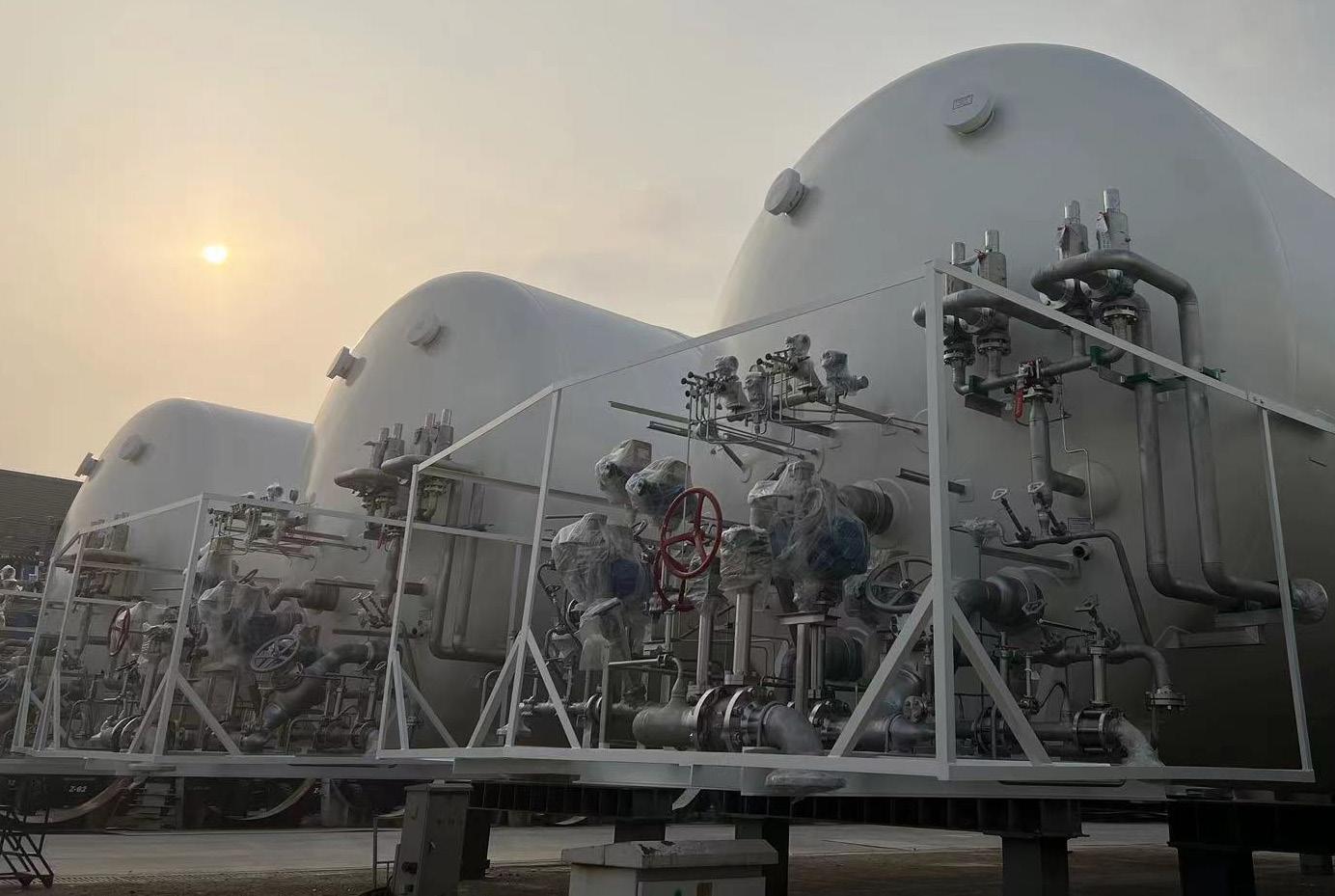
“I QUICKLY REALIZED HOW ENERGIZING IT WAS TO BE PART OF SOMETHING TANGIBLE – TO BUILD, SOLVE PROBLEMS, AND WORK WITH INCREDIBLY SMART, HANDS-ON TEAMS IN THE FIELD”
– JILLIAN EVANKO, CEO, CHART INDUSTRIES
in Asia, Australia, Europe, and Latin America,” she informs us.
The company’s impressive global scope and expanding geographical presence continues to level up and develop alongside the broader energy and industrial gas sector, positioning Chart at the forefront of this burgeoning industry.
A VAST AND VARIED CAREER
Evanko didn’t set out to build a career in industrial manufacturing, but once she got into the space, she never looked back.
“My formal education is in finance, and I started my career at accounting firm, Arthur Andersen – just before
the Enron scandal shifted the entire landscape. That unexpected turn pushed me to take a role at Honeywell, where I got my first exposure to industrial operations,” she recalls.
“I quickly realized how energizing it was to be part of something tangible – to build, solve problems, and work with incredibly smart, hands-on teams in the field.”
Since then, Evanko has held numerous leadership roles across finance, operations, and strategy.
“I’ve always been drawn to industries where you can see the real-world impact of your work. That’s what continues to motivate me every day,” she enthuses.
Serving as CEO since June 2018, Evanko initially joined Chart in February 2017 as Chief Financial Officer (CFO).
Prior to joining the company, she was CFO of Truck-Lite and held multiple operational and financial executive positions at Dover Corporation and its subsidiaries.
Before this, Evanko held financial and operational roles at both Honeywell and Sony Corporation. Now, in addition to her role at Chart, she also serves as an independent Director of the Board at Parker Hannifin Corporation.
EXCEPTIONAL LEADERSHIP
As recognition of her hard work and exceptional service throughout the industry, in both 2022 and 2023, Evanko was named as one of the Hydrogen Economist’s ‘Top 50 Women in Hydrogen’, as well as making it onto Hart Energy’s ‘25 Most Influential Women in Energy’ list for 2021.
Ingersoll Rand is a global leader in the manufacturing of mission-critical flow creation products and life science and industrial solutions, operating under 80+ brands. Our success is made possible by our 21,000+ employees (and counting!). Powered by an ownership mindset and more than 160 years of expertise, we’re driving differentiated performance with purpose.
Our Purpose
Lean on us to help you make life better is deeply embedded in all that we do. We wake up each and every day with the goal of Making Life Better for our employees, our customers, our shareholders, and our planet.
For our Employees For our Customers
For our Shareholders For our Planet
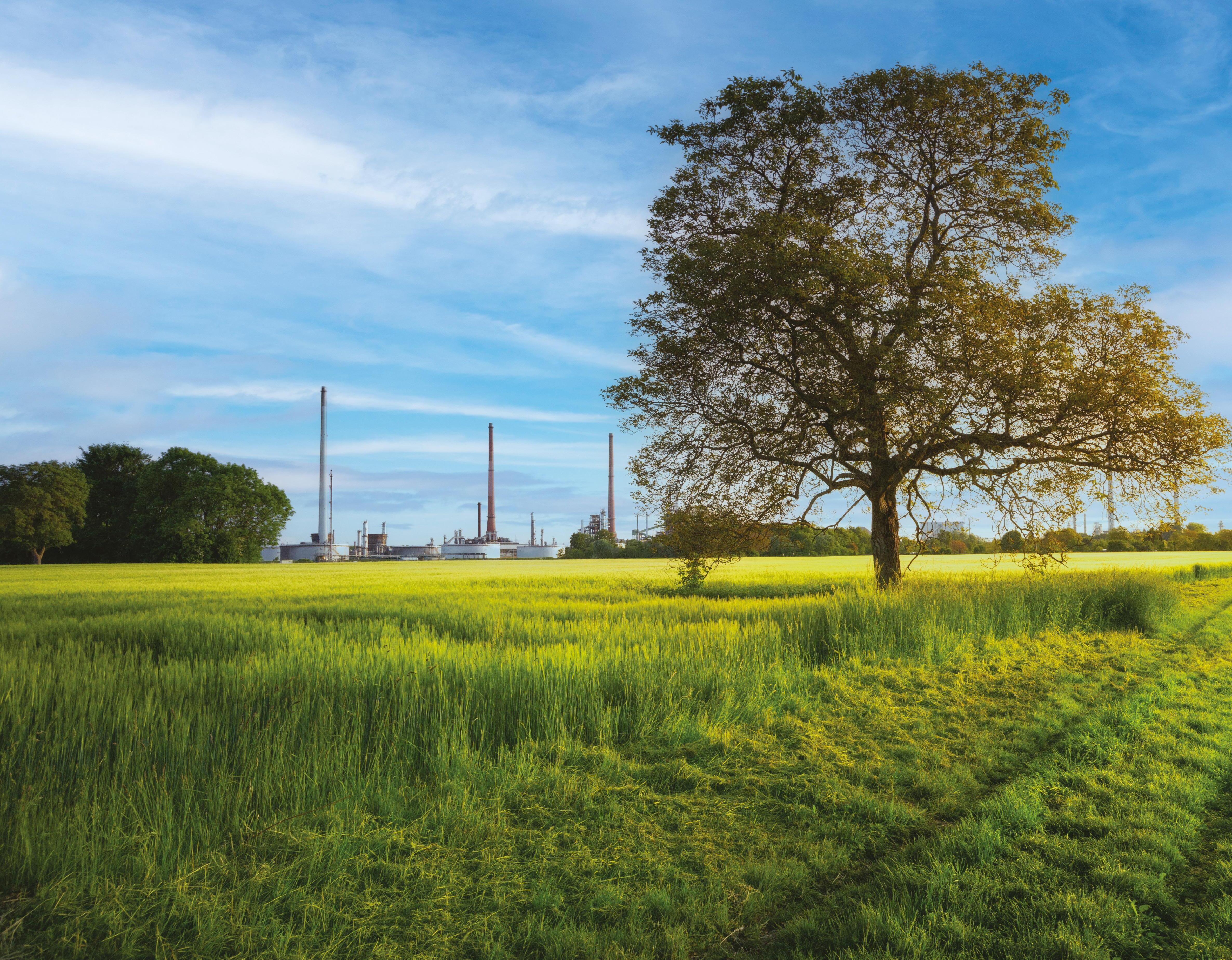
Awards won
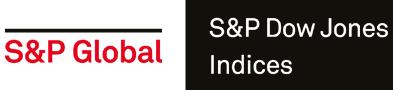
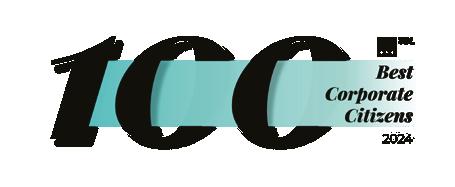
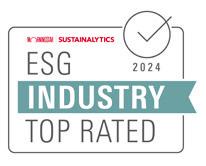
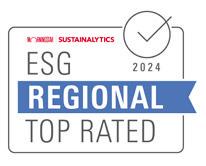
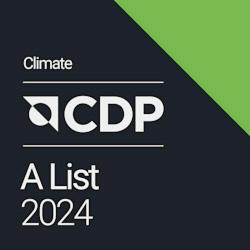
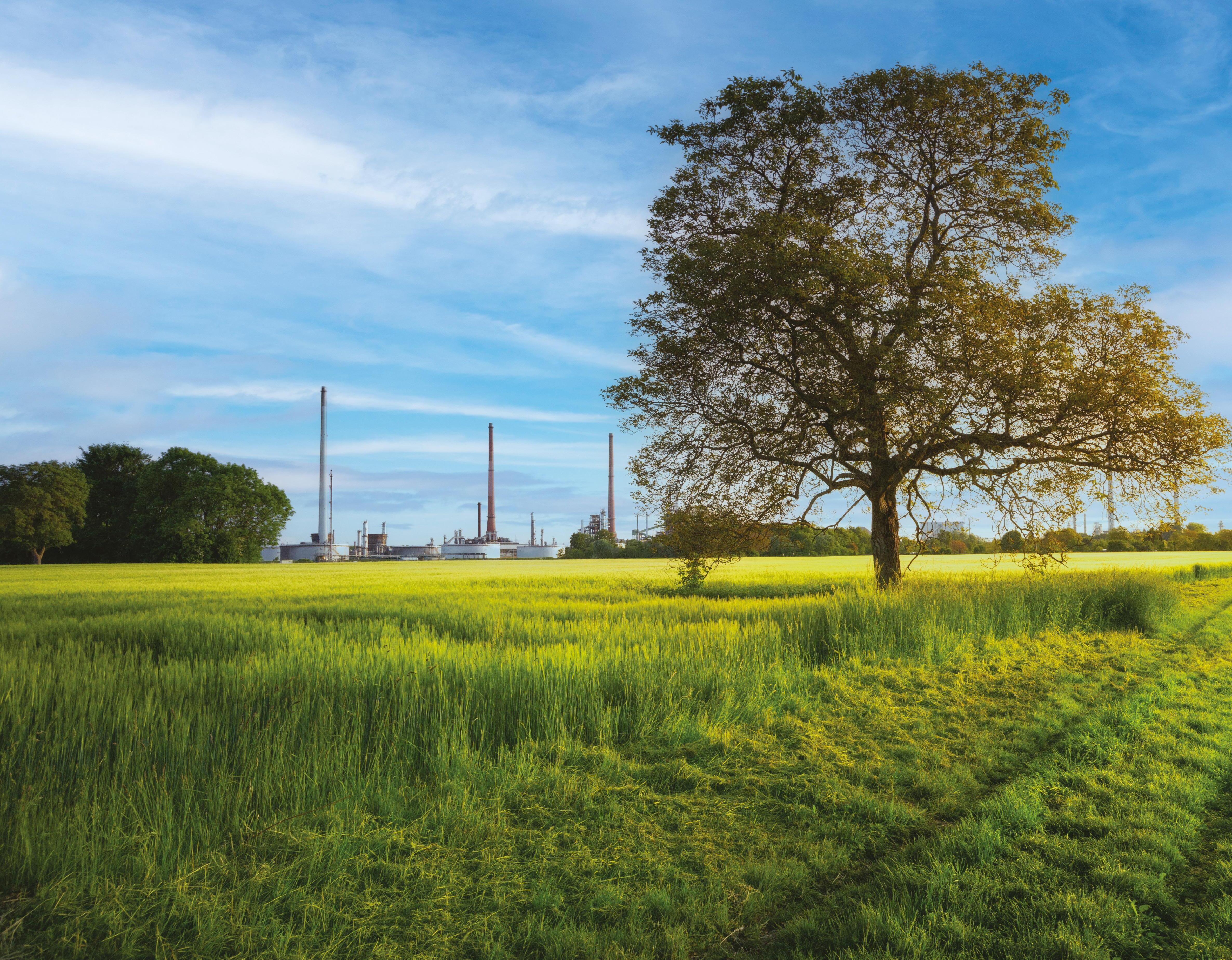
Leading Sustainably
We have a proven track record as an industry leader in sustainability.
Leading sustainably means both growing and operating sustainably. Growing sustainably refers to developing intrinsically sustainable products and services and supporting customers in high-growth, sustainable markets. With a focus on improving efficiency, circularity, and safety, we employ a Design for Sustainability (DfS) process for all new product development. More than 65% of our current product portfolio includes products with sustainable attributes.25 Additionally, we continue to expand our presence in the life sciences, clean energy, food, and water end markets.
As of December 2024, we have 59 green energy sites and 90 sites that have achieved zero waste to landfill since 2020. Operating sustainably also means taking care of our employees. We prioritize employee safety as an important aspect of our culture, holding our first annual company-wide Safety Day in 2024. Our Total Recordable Incident Rate is world class and 72% better than the industrial machinery manufacturing average.26
Our sustainability program has achieved remarkable success and acknowledgment by the top sustainability ratings providers. We were included on the Dow Jones Best-in-Class Indices (formerly the Dow Jones Sustainability Indices) for the third year in a row based on our score on the 2024 S&P Global Corporate Sustainability Assessment.27 For the second year in a row, we were named to CDP’s “A List” for our commitment to global environmental leadership. Additionally, we maintained our low-risk rating from Sustainalytics, with a top 1% performance in our industry and top 3% among all rated companies.28
25 Current management estimation for 2023 indicates that over 65% of our product portfolio incorporates sustainable attributes such as energy efficiency, waste minimization, water conservation, and extending the useful life of the product through remanufacturing.
26 Average Total Recordable Incident Rate (TRIR) for all Industrial Machinery Manufacturing companies in 2023 (most recent data available) was 1.9 according to the U.S. Bureau of Labor Statistics. World Class is defined as the top quartile of manufacturing companies with >1,000 employees per U.S. Bureau of Labor Statistics (2021). 27 Receipt of an S&P Global ESG Score does not represent a sponsorship, endorsement or recommendation on the part of S&P Global to buy, sell or hold any security, and a decision to invest in any subject company should not be made based on the receipt of any such note. S&P, S&P Global, and the S&P Global logo are trademarks of S&P Global Inc. or its subsidiaries, registered in many jurisdictions worldwide.
28 As of November 2024, Ingersoll Rand received an ESG Risk Rating of 10.2 from Morningstar Sustainalytics, ranking it first in the Machinery industry group, which places it in the 1st percentile for its industry. This risk rating also places Ingersoll Rand in the top 3% of all companies rated by Morningstar Sustainalytics. This risk rating is based on information and data developed by Sustainalytics and is proprietary to Sustainalytics and/or its third-party suppliers and is provided for informational purposes only. The risk rating does not constitute an endorsement of any product or project, nor an investment advice and the information upon which it is based is not warranted to be complete, timely, accurate or suitable for a particular purpose. The use of the risk rating is subject to conditions available at: https://sustainalytics.com/legal-disclaimers. In no
Advancing Clean Energy
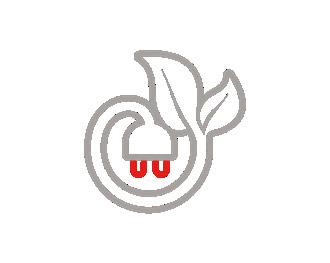
Enabling the transition to clean, low-carbon and zero-carbon energy.
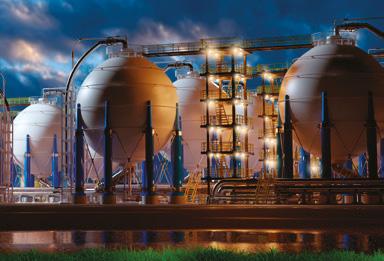
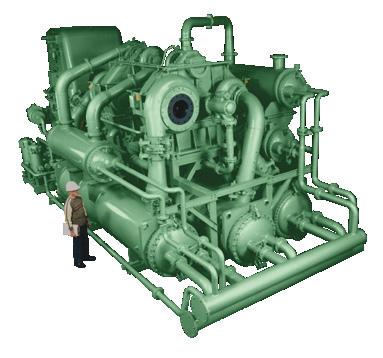
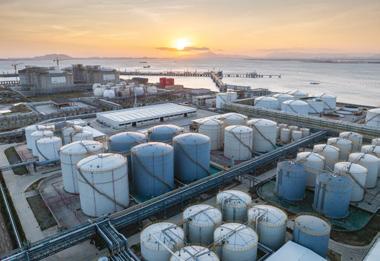
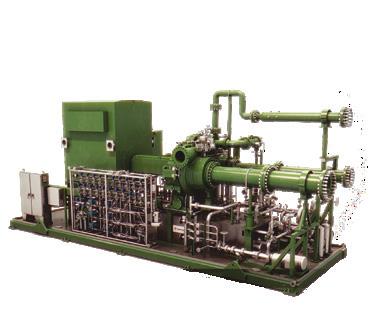
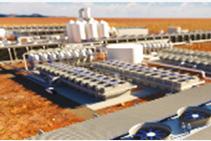
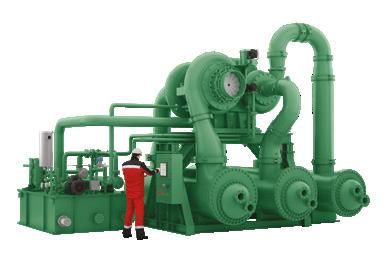
Ingersoll Rand Powers Progress in Green Hydrogen
Green hydrogen is gaining momentum as a cornerstone of the global energy transition. Ingersoll Rand is supporting this shift by providing four-stage centrifugal compressors that deliver 12 MW of nitrogen refrigeration for a major hydrogen liquefaction facility in the United States. Once complete, the site will be among the largest permitted green hydrogen production centers in the country, powered in part by solar energy. This milestone project reflects Ingersoll Rand’s continued commitment to enabling clean energy infrastructure and accelerating the path to net-zero emissions.
LNG Projects Powered by Reliable Ingersoll Rand Compression
As part of the shift toward cleaner, more resilient energy systems, a U.S. LNG peak shaving facility was developed to store and deliver natural gas during high-demand periods. Ingersoll Rand played a key role in this sustainable energy project by providing a custom-engineered MSG® integrally geared centrifugal (IGC) compressor package. Powered by a gas turbine and equipped with an advanced seal gas recovery system, the compressor enables efficient natural gas liquefaction in remote locations with limited electrical infrastructure. By supporting grid stability and enabling cleaner-burning fuel alternatives for power generation and transportation, Ingersoll Rand continues to deliver compressor solutions that help drive the energy transition forward.
Enabling Direct Air Carbon Capture with Ingersoll Rand Air and Gas Compressors
Ingersoll Rand compression equipment supports the world’s largest Direct Air Capture (DAC) plant, located in the Texas Permian Basin. This plant will advance large-scale carbon capture to reduce emissions and accelerate the path to net-zero. Ingersoll Rand provided four centrifugal compressors to a large-scale energy company building the DAC plant. The plant is expected to provide costeffective solutions that hard-to-decarbonize industries can use in conjunction with their own emissions reduction programs to help achieve net-zero. The captured carbon will be safely and securely sequestered in saline formations or used to produce low carbon products. Once operational, the plant is expected to capture up to 500,000 metric tons of CO2 per year with the capability to scale up to one million metric tons annually.
Reducing Energy Consumption
AI-Driven System Optimization
Ingersoll Rand delivers solutions to help drive the energy transition and decarbonization efforts. We have unique expertise in designing essential technologies needed to help on the journey to create a net-zero economy, including energy-efficient equipment and lower GWP refrigerants. Likewise, our services, including digital offerings, promote energy efficiency and improved air quality.
System Performance Manager powered by Ecoplant represents innovative technology which uses machine intelligence to improve compressed air systems offer approximately 15–20% in energy savings. Predictive algorithms assess a company’s daily, weekly, and seasonal energy use and then dynamically control systems via production profiles to lower energy waste, redundancy, and excess utility costs.
Up to 20% savings
Average annual savings for System Performance Manager customers
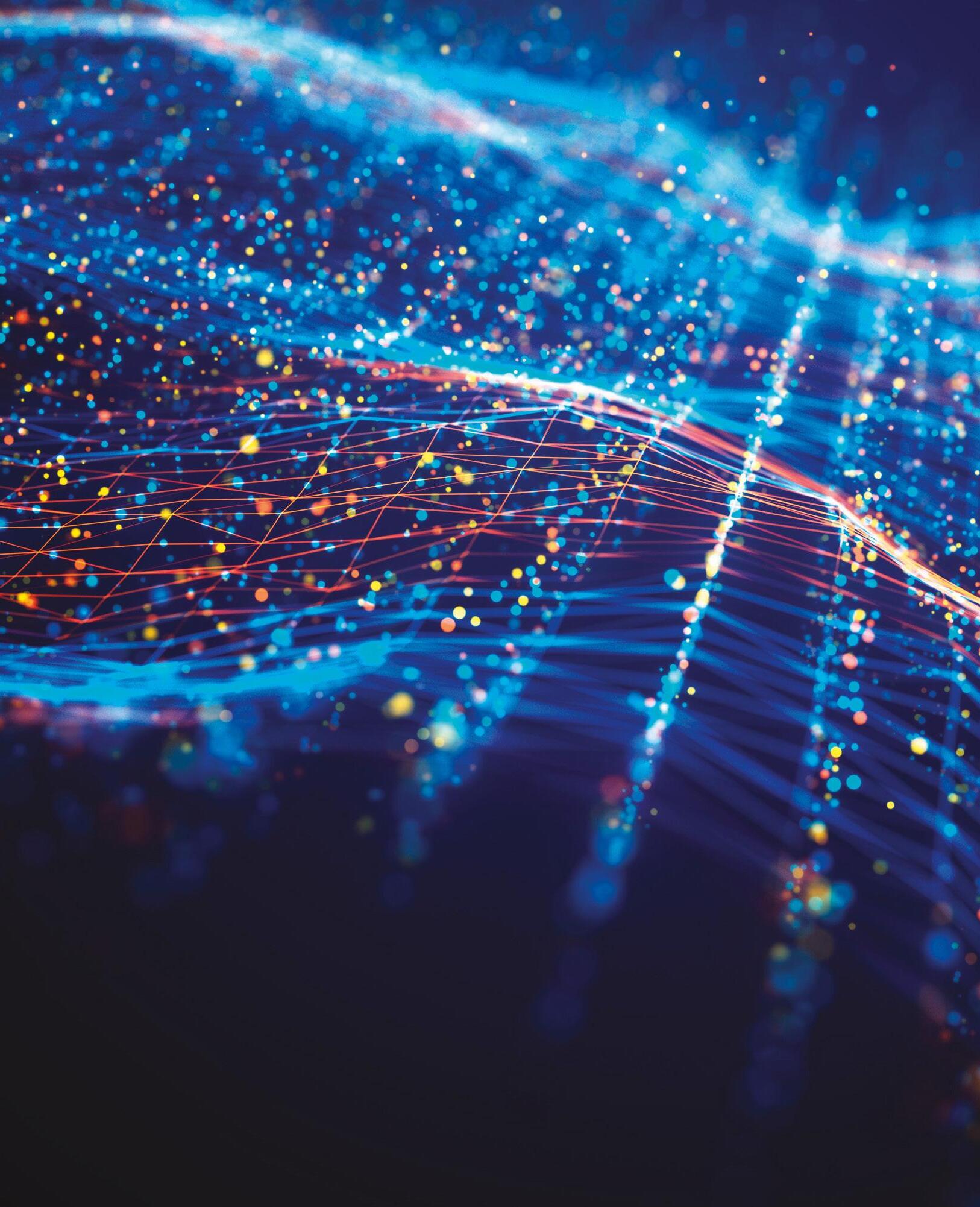
<1 year payback
For most applications
FEATURES
‣ Patented technology and proprietary algorithms in Al and machine learning (ML)
‣ Real-time, dynamic control of compressed air systems
‣ Brand and technology-agnostic
‣ Subscription-based
BENEFITS
‣ Predict maintenance, minimizing outages, and avoiding costly downtime
‣ Real-time visibility to energy savings, GHG reduction, system health, and alerts
‣ Monitor sites from anywhere in the world using a cloud-based platform
‣ Detection and isolation of leaks
‣ Smart decision enabler with historical data and personalized analytics
‣ Installation within two days
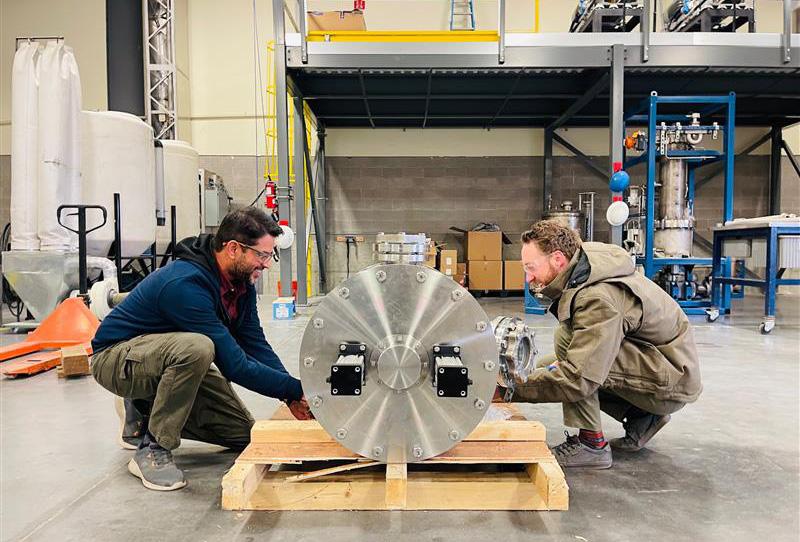
However, despite these numerous prestigious accolades, Evanko cites her proudest workplace accomplishment as being part of an exceptional team at Chart.
“Because of every dedicated member of staff that I’ve had the pleasure to work with across the entire spectrum of our operations, I’ve always enjoyed the immense privilege of leading an amazingly talented team and an awesome company that has more than doubled in size, entered new markets, and shifted its portfolio,” she prides.
Under Evanko’s exceptional leadership since 2018, Chart has worked toward clean energy and sustainability goals, joining the UN Global Compact, a voluntary initiative to implement sustainability principles, and initiating strategic acquisitions that has allowed the company to significantly expand its product offerings.
“I’VE ALWAYS BEEN DRAWN TO INDUSTRIES WHERE YOU CAN SEE THE REAL-WORLD IMPACT OF YOUR WORK. THAT’S WHAT CONTINUES TO MOTIVATE ME EVERY DAY”
– JILLIAN EVANKO, CEO, CHART INDUSTRIES
Additionally, in this time, Chart made the decision to take calculated risks that previously would’ve been viewed as too hazardous or something that no one else wanted to do.
However, she believes these types of decisions are critical to give businesses such as Chart an advantage in such a competitive environment.
Meanwhile, as a leading female executive navigating the twists and turns of a male-dominated industry, Evanko firmly believes her gender shouldn’t be seen as a defining issue.
“I just aim be the best CEO, not the best female CEO,” she affirms.
“I would say 100 percent of the accolades that I’ve been lucky enough to receive to date are the result of my incredible team. It’s really a credit to the people out there that are designing and building our products.”
Evanko also stresses the vital importance of being a responsible leader, which is why to this day she answers every message she gets, from a conversation on LinkedIn to a text or email.
“At the heart of the company, we want to profitably grow, and we
want to continue to deliver unique solutions, but I never want any one of our team members or customers to walk away and say that I wasn’t a kind leader who had no time for her staff,” she muses.
AN INDUSTRY FULL OF POTENTIAL
Across the globe, a multitude of trends across the industrial manufacturing and energy sectors are always fluctuating.
Evanko views both these industries as exciting and full of potential regarding both the domestic US market and on a more global basis.
“The US energy sector is currently balancing two key forces – rising demand and the need for greater flexibility,” she comments.
“Right now, we’re seeing a renewed focus on energy security and a strong role for LNG as a reliable,
lower-carbon option that can be deployed quickly and at scale. LNG continues to be a critical part of the equation.”
For Chart, what’s clear is that the path forward won’t be linear, and no single energy source will solve everything for everyone.
“That’s why our molecule-agnostic approach is so important. We’re not tied to one fuel or technology – we enable the infrastructure behind a broad range of solutions,” asserts Evanko.
This includes solutions across industries such as energy, industrial, power generation, LNG, nuclear, water, chemical, space, industrial gas, carbon capture, and hydrogen – to name a few.
“Our focus is on delivering flexible, scalable systems that help our customers adapt and lead – no matter where they are on their energy or sustainability journey,” she lays out.
Backed by its 158 years of experience in designing, engineering, and manufacturing hydrogenrelated equipment, Chart now provides customers with all process technologies and major equipment across the entire gaseous and liquid hydrogen value chain.
THE CORE STRENGTH OF THE COMPANY
The vast and fascinating field of cryogenics is at the foundation of what Chart does – and it continues to be a core strength across both established and emerging markets.
“Our cryogenic systems support industrial gas storage and distribution, LNG applications, and energy infrastructure around the world. These are long-standing areas of expertise where we continue to innovate, scale, and serve a global customer base,” Evanko declares.
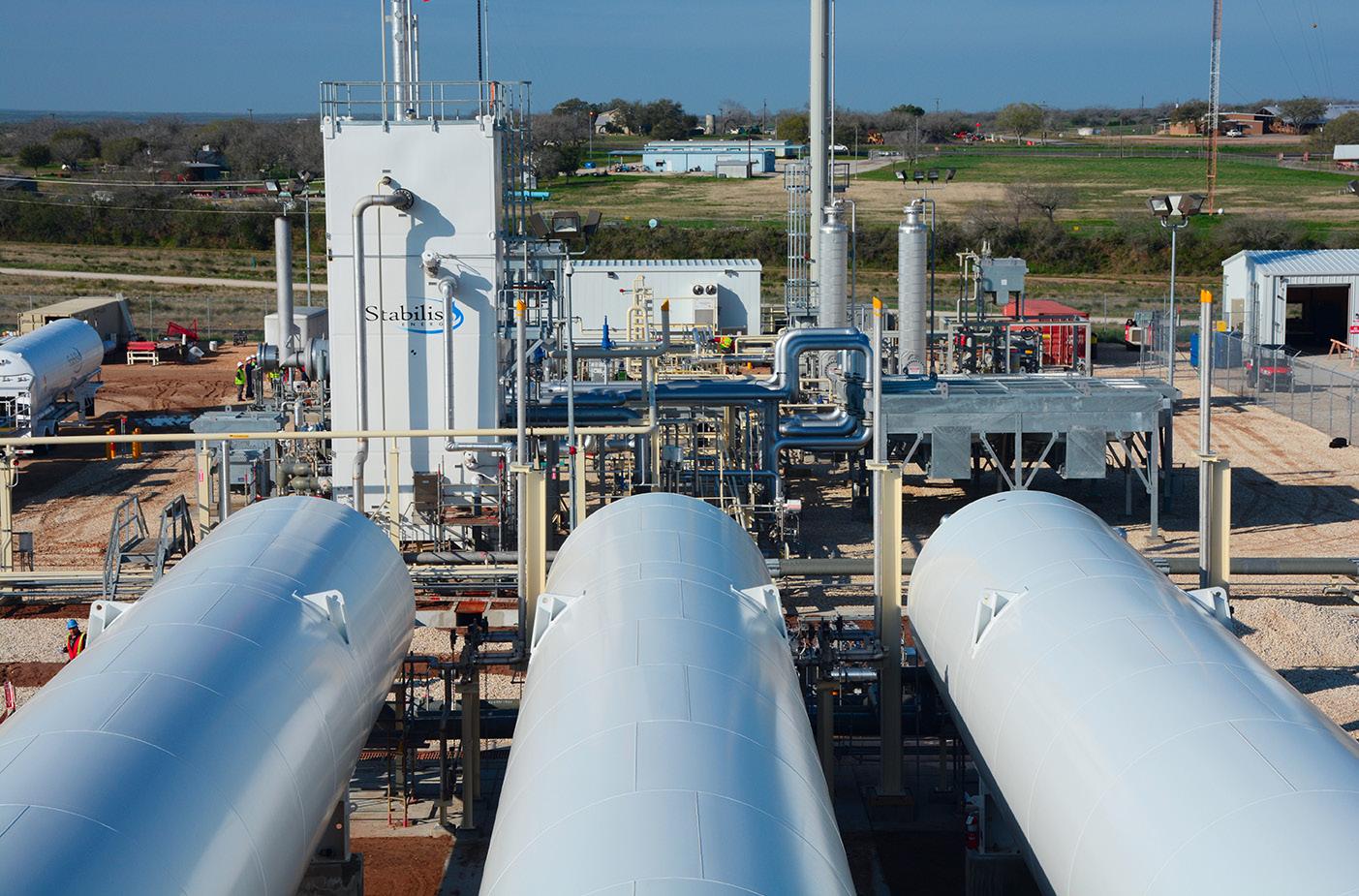
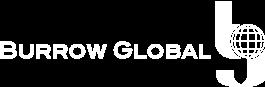
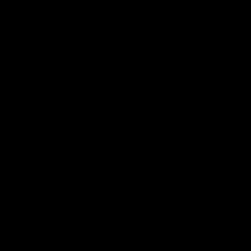
World-Class EPC Services, Built for Your Success
Burrow Global is a uniquely positioned, full-service Engineering, Procurement and Construction company. We offer the comprehensive EPC capabilities of a larger firm, but can adapt quickly to client-specific needs as a mid-sized organization.
Our Flexibility is just one of the reasons clients choose us. For more than 40 years, Burrow Global has provided general construction services for process industries throughout the United States and abroad with more than 20 years without a lost time incident.
Optimized Project Execution:
Our Quality Program documents and validates that the plant assets have been engineered properly, installed per design and regulatory requirements and commissioned and started up properly. To improve quality and value in project delivery, we have proven programs and processes, optimizing project execution with testing programs that combine mechanical completion and precommissioning requirements.
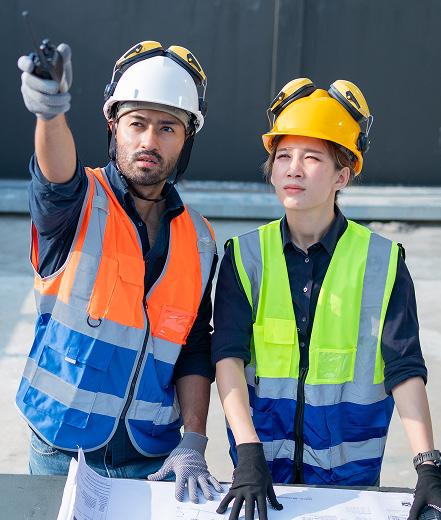
Multi-Discipline Design and Engineering Capabilities:
• Process
• Piping
• Buildings
• Civil/Structural
• Mechanical
• Instrument
• Electrical
• Architectural
• Automation
• Process Safety
9MM+
7MM+ 0.00
Service Profile:
• EPC Execution with Strategic Offices and Fab Shop Location
• Fabrication (ASME, U, R, S, PP Code Stamps)
• Commissioning, Startup, Planning and Execution
• Turnaround Management
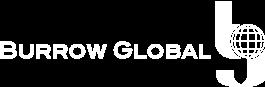
Mission Critical, Data Centers
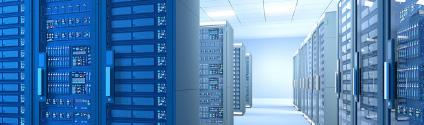
By working cohesively with the designer and owner to understand needs and objectives, our team led by Burrow Global with 51 years of experience to develop optimal solutions to seamlessly solve complex issues. Our integrated teams partner early to drive collaboration to accelerate project delivery.
Services:
Whether it’s a greenfield development, projects of all shapes and sizes, firstgeneration fit outs and retrofits of existing structures Burrow Global can provide efficiency to cover your project from planning, budgeting all the way through commissioning. Always considering customer objectives in mind.
Turnkey
Burrow Global offers Design, Construction Management, and HSE Services for building deployment. As the general contractor, we manage subcontractors, suppliers, and schedules across civil, electromechanical, and support systems.
Our Health, Safety, and Environmental team ensures the well-being of all personnel through established safety plans, protocols, and training. Additional disciplines include access control, fire detection and suppression, automation, control, and commissioning.
Full-Service Design
Burrow Global team which includes fabrication, consultants and partners
COMBINED PROJECT EXPERIENCE
of data center practitioners implement the latest digital innovation across the full engineering spectrum, life safety/fire protection, security, interior and landscape design and architecture planning to ensure a tailored design/build.
Construction Management
Burrow Global construction management team’s program management, project controls, vendor/contractor management, procurement, scheduling, commissioning, coupled by our safety record ensures your project’s longterm success.
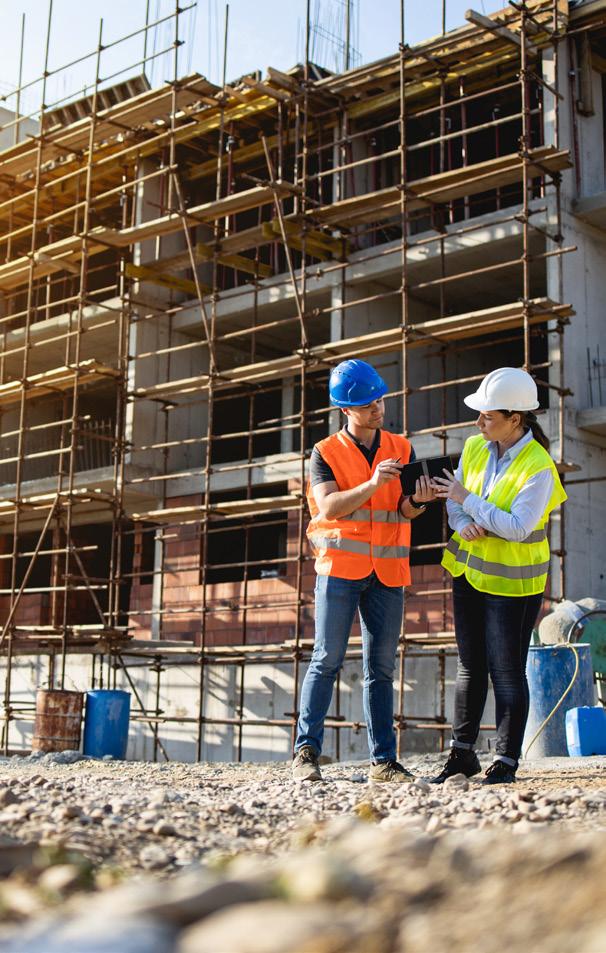
Managing Data Centers with Precision, Expertise,
and Scale
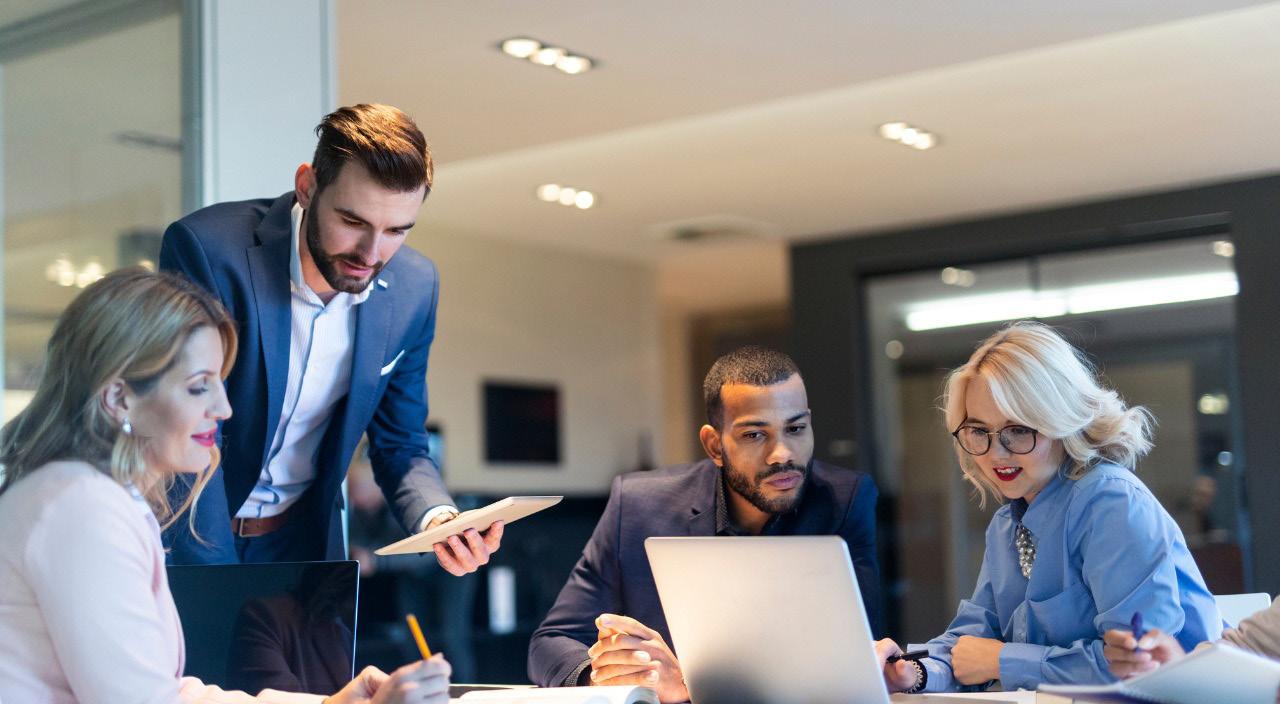
Building a data center is just the beginning. Keeping it running at peak performance - securely, efficiently, and without disruption - takes a partner with deep technical knowledge and a track record of global success.
That’s where Maintech comes in.
With over 50 years of IT support excellence, Maintech specializes in comprehensive data center management through its full Tower of Services. From legacy hardware to the latest hybrid infrastructure, we ensure missioncritical environments are maintained, monitored, and optimized around the clock, anywhere in the world.
Maintech’s outsourced support model is designed
to give businesses the confidence and control they need, without the overhead of managing complex systems in-house. We provide everything from rapid-response break/fix services and IMAC (Install, Move, Add, Change) work to full-scale hardware lifecycle management, asset tracking, secure disposal, and realtime monitoring. Our global command centers enable seamless oversight and coordination. Meanwhile,
Our goal is simple: To help you deliver uptime, resilience, and operational excellence from the inside out.
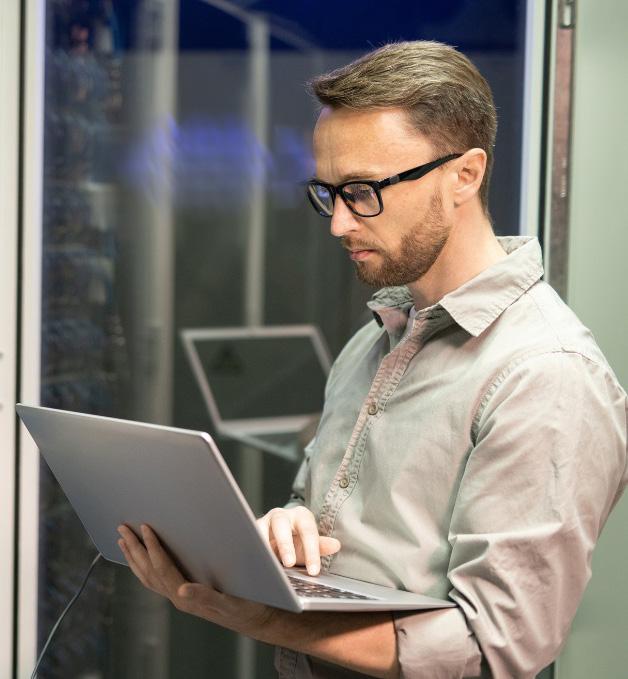
our certified field engineers deliver hands-on support when and where it’s needed. What sets Maintech apart is the depth of our third-party maintenance expertise. We’re vendor-agnostic and skilled across all major OEMs, ensuring consistent, expert-level support no matter the equipment mix. For businesses with multiple sites, global operations, or aging infrastructure, this approach delivers flexibility, cost savings, and performance gains without compromise.
Outsourcing data center maintenance to Maintech means you gain access to the right people, trained
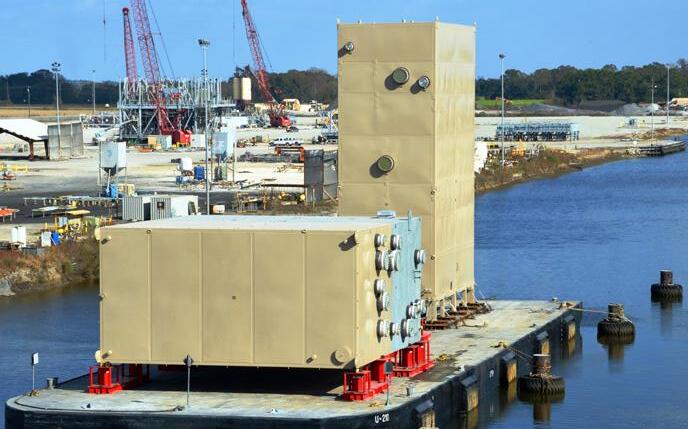
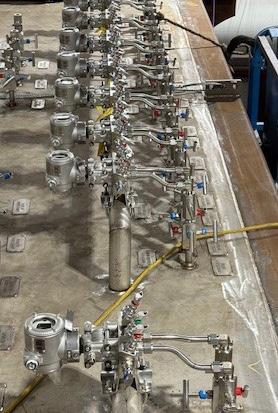
to the highest standards, ready to support the full range of your IT environment. Whether you’re consolidating hardware, expanding capacity, or simply need boots on the ground for regular upkeep, our teams integrate seamlessly with yours. This extends your capabilities and reinforces your reliability.
With decades of experience supporting Fortune 100 enterprises, financial institutions, government agencies, and fast-growth businesses, Maintech has become the trusted name in third-party IT services. Our goal is simple: to help you deliver uptime, resilience, and operational excellence from the inside out.
Data centers don’t just need to work. They need to work flawlessly, every hour of every day.
Let Maintech manage the maintenance so your team can focus on innovation.
Learn more about our full suite of IT infrastructure services at www.maintech.com
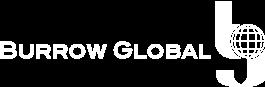
Burrow Global Delivers Precision Execution for CHART Industries
Houston, TX — Burrow Global, a leading full-service EPC and automation firm, continues to showcase executional excellence and industry leadership through its collaboration with CHART Industries at their New Iberia facility.
Through ECCO, A Burrow Global Company, Burrow Global has established itself as a vital service provider to CHART’s New Iberia Operations Team by developing and executing a comprehensive Instrument and Electrical (I&E) installation strategy for cold box assemblies.
To date, Burrow Global has safely, efficiently, and cost-effectively completed I&E installations on more than 100 cold boxes at the New Iberia site. From working alongside CHART Engineering to executing real-world installations, Burrow
Global’s scope of work includes:
• Comprehensive I&E routing and installation
• Extensive testing and data logging of all electrical and instrumentation components
• Long-term system maintenance and support
• Full collaboration with CHART’s Engineering team to ensure design-to-execution alignment
Burrow Global’s smart routing plans and rigorous testing protocols not only ensure system functionality and traceability, but also help CHART meet critical project timelines and reduce maintenance needs postinstallation. This collaborative approach underscores Burrow Global’s commitment to safety, quality, and schedule performance in highly technical environments.
At the same time, the engineering and manufacturing capabilities that serve traditional energy and industrial gas markets are also enabling newer technologies – from hydrogen mobility and aerospace to carbon capture and even clean fuels for marine and aviation.
“For example, we’ve supported rocket launches with liquid oxygen tanks, enabled liquid hydrogen systems for space and trucking, and delivered ultra-large tanks for highcapacity storage applications,” she adds.
“What sets our portfolio apart is the breadth of solutions we offer –from tanks, heat exchangers, fans, compressors, trailers, and vaporizers
COULD YOU TELL US ABOUT THE COMPANY’S SUPPLY CHAIN OPERATIONS AND HOW IMPORTANT PARTNER AND SUPPLIER RELATIONSHIPS ARE TO
YOUR SUCCESS?

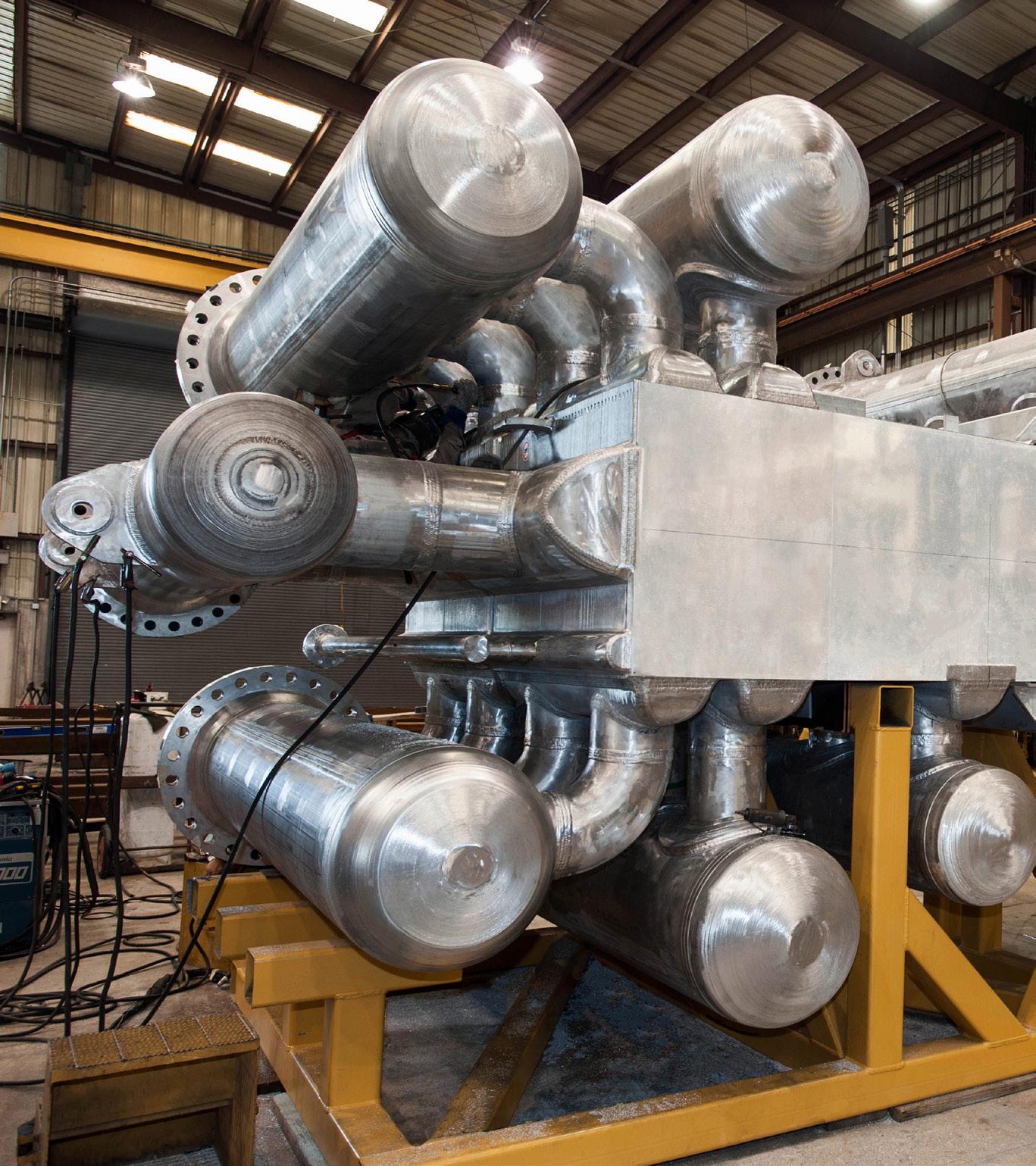
Jillian Evanko, CEO: “Our supply chain is critical to Chart’s operations and is a strategic asset to the business. We’ve worked hard to diversify sourcing, localize and globalize where it makes sense, and build strong relationships. In today’s environment, resilience really matters.
“We’ve also invested in digital tools to improve forecasting, transparency, and decision-making across the supply chain.
“Whether we’re serving a project in Texas, Germany, or Southeast Asia, we’re focused on delivering safely, on time, and with the flexibility our customers need.
“We are committed to the highest standards of ethics and business conduct. As stated in the Chart Code of Ethical Business Conduct, we seek to ensure that our product and service suppliers share our commitment to acting with integrity and to open and trusting relationships.
“We therefore require our suppliers to meet our expectations for ethics and compliance with all applicable laws. In addition, Chart understands and expects that our suppliers will have their own internal codes of ethics and conduct.”
to complete integrated systems – and our ability to tailor those solutions to each customer’s needs.”
BUILT TO LAST
Within its substantial and varied portfolio, Chart’s bulk cryogenic storage systems are customengineered to meet application specifications for its clients.
The company’s complete system solution package ensures quality liquid or gas, which is used to keep processes operating at peak efficiency. Built for long-term integrity and industry-leading efficiency, these systems give clients the highest performance at the lowest operating cost.
Each Chart tank is engineered with a high degree of standardization for cost-efficient production and to keep delivery times short.
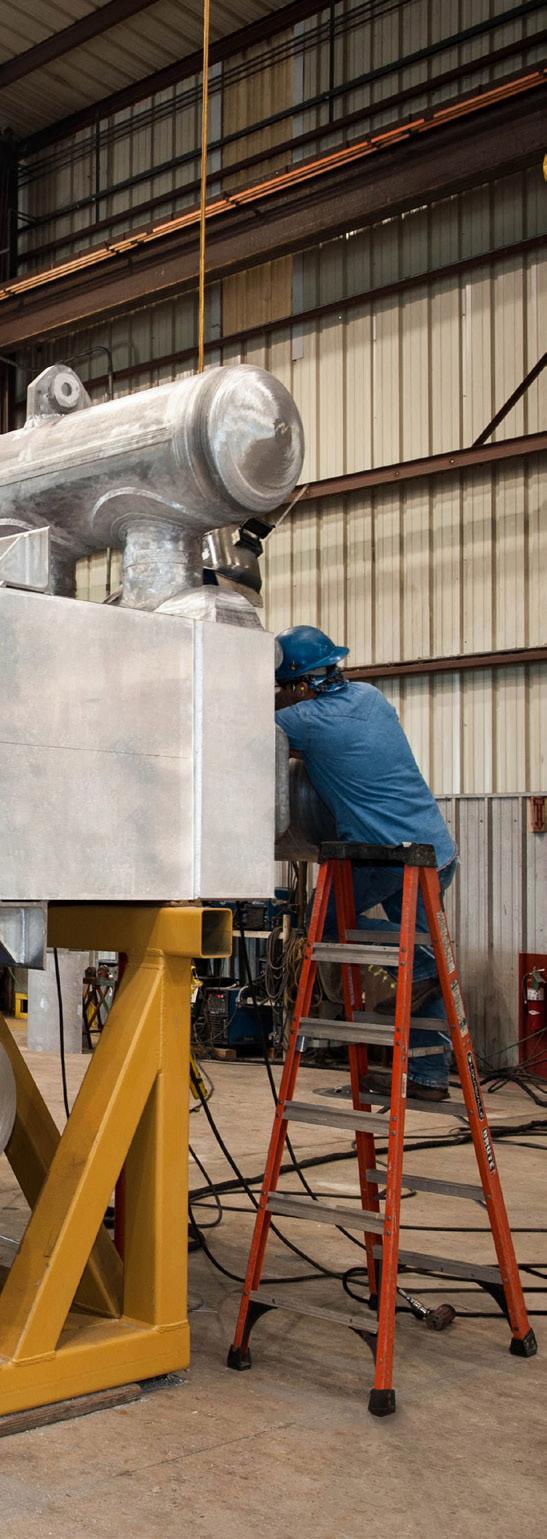
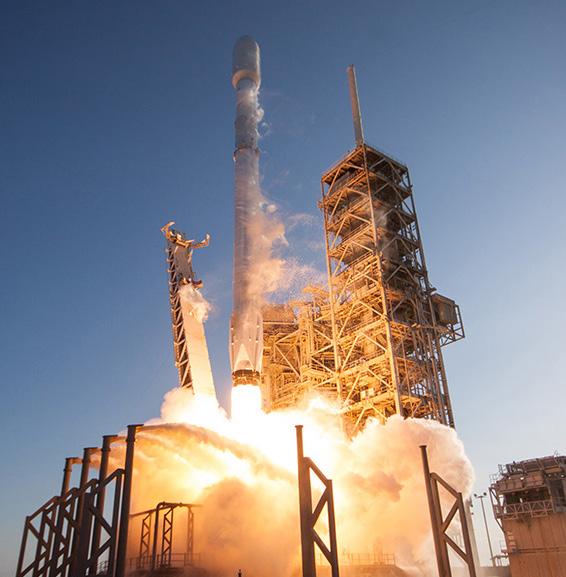
Parallel to this, a diverse range of bolt-on modular options ensure that its standard tanks cater to customer requirements, while further customization options are also available on request.
Boasting superior design and engineering prowess, Chart’s storage tanks feature state-of-the-art modular piping systems which combine high performance, durability, and low levels of required maintenance.
The key features of these tanks include a reduced number of joints which minimizes the risk of external leaks and facilitates simplified installation, as well as a comprehensive range of safety features to afford maximum protection for operators and the equipment itself. Additionally, they possess
easy access to control valves and instrumentation, meet seismic requirements, boast unrivalled engineering and manufacturing capacity, have world-class facilities strategically located in centers of demand, and Chart now leverages a dedicated range for the storage of CO2
Engineered, manufactured, and tested in accordance with all major international design codes and associated regional requirements, these impressive products are truly engineered to excel and built to last.
CRYOGENIC TRANSPORT TRAILERS
Cryogenic transport trailers are specialized vehicles designed for the safe and efficient transportation of materials at extremely low
temperatures, typically below -150 degrees Celsius (°C).
These state-of-the-art trailers are essential for industries such as healthcare, energy, and food production, where cryogenic liquids need to be transported safely and securely.
Different transport trailers are designed for specific gases and distances, with features such as a reinforced chassis for overcoming challenging road conditions and optimized designs for maximum payload.
Chart’s cryogenic trailers utilize multi-layer vacuum super insulation and other advanced technologies to maintain the necessary low temperatures and keep them at a constant and ideal level during the course of transit.
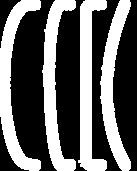
Shaping the World One Tank Head at a Time
Based in Fort Worth, Texas, on a 20-acre manufacturing facility fully equipped with state-of-theart machinery, Baker Tankhead’s legacy of leadership in the US metal fabrication industry sets them apart. We sat down with the company’s executive leadership team to find out more.
Founded in 1977, Baker Tankhead is an expert manufacturer of American Society of Mechanical Engineers (ASME) and noncode tank heads, rolled cylinders, and cones that are custom designed to meet the needs of a wide range of industries and customers.
Keeping pace with rapid changes in North America’s metal fabrication space, the company believes continuous adaptation and improvement is key to securing long-term success.
“As the industry evolves, so do we – whether that means investing in new equipment, streamlining our operations, or recognizing and promoting talent from within. We’re proud of the products we manufacture and the services we provide,” opens Aaron Baker,
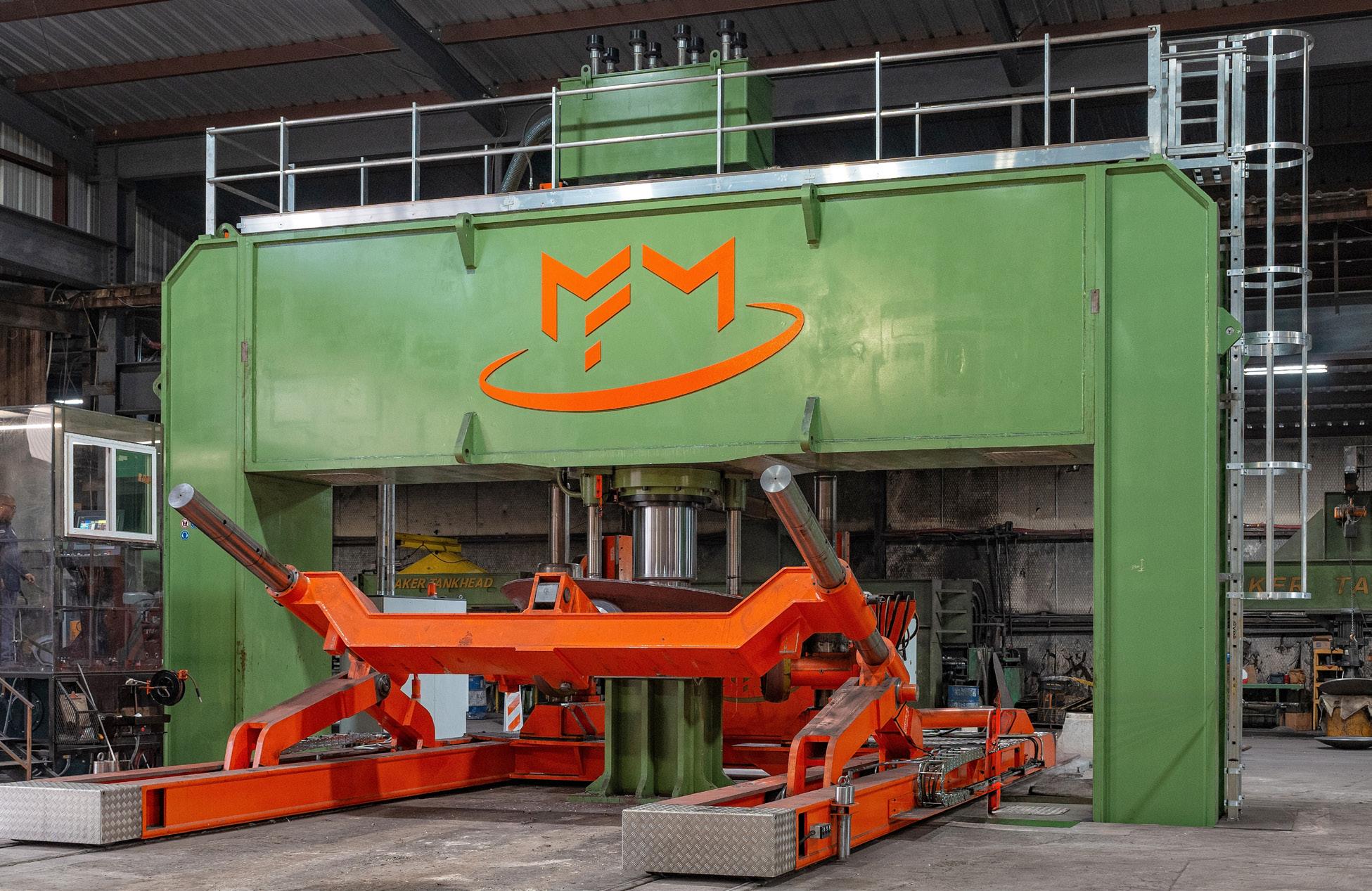
Vice President.
One of the most significant shifts shaping the industry today is the rise of automation, robotics, and smart technologies, enabling Baker Tankhead to deliver increasingly customized solutions to its clients. Yet, because dishing and flanging tank heads remain fundamentally handson processes, the company leverages innovation to complement rather than replace human skill.
“Our creative ability is very important to us, so we use technology to make our processes better and faster while still relying on hands-on skills that take years to master,” comments Jorge Sigala, Production Manager.
Recently, Baker Tankhead expanded its technological
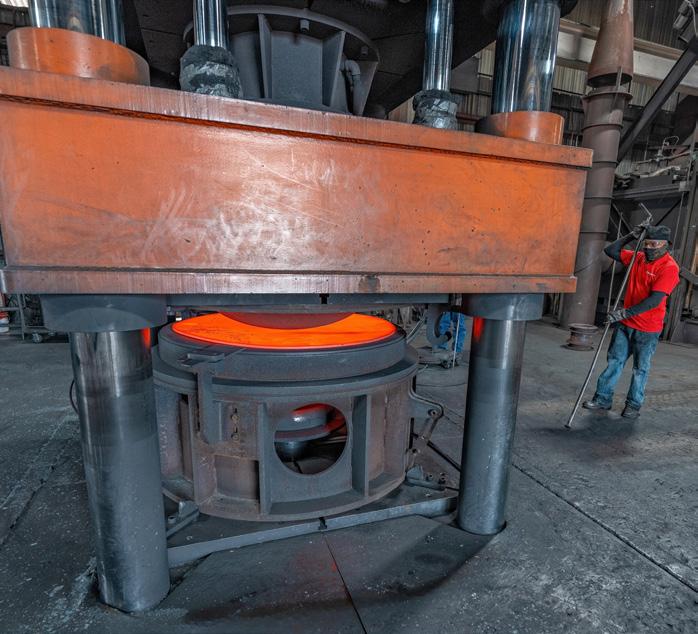
capabilities by adding an 800ton press to its equipment lineup. The company first manufactured their presses in-house before adopting earlier versions of this machine. Now operating with ten presses, Baker continues to acquire new models as advancements emerge.
“The European manufacturer of the press continues to make
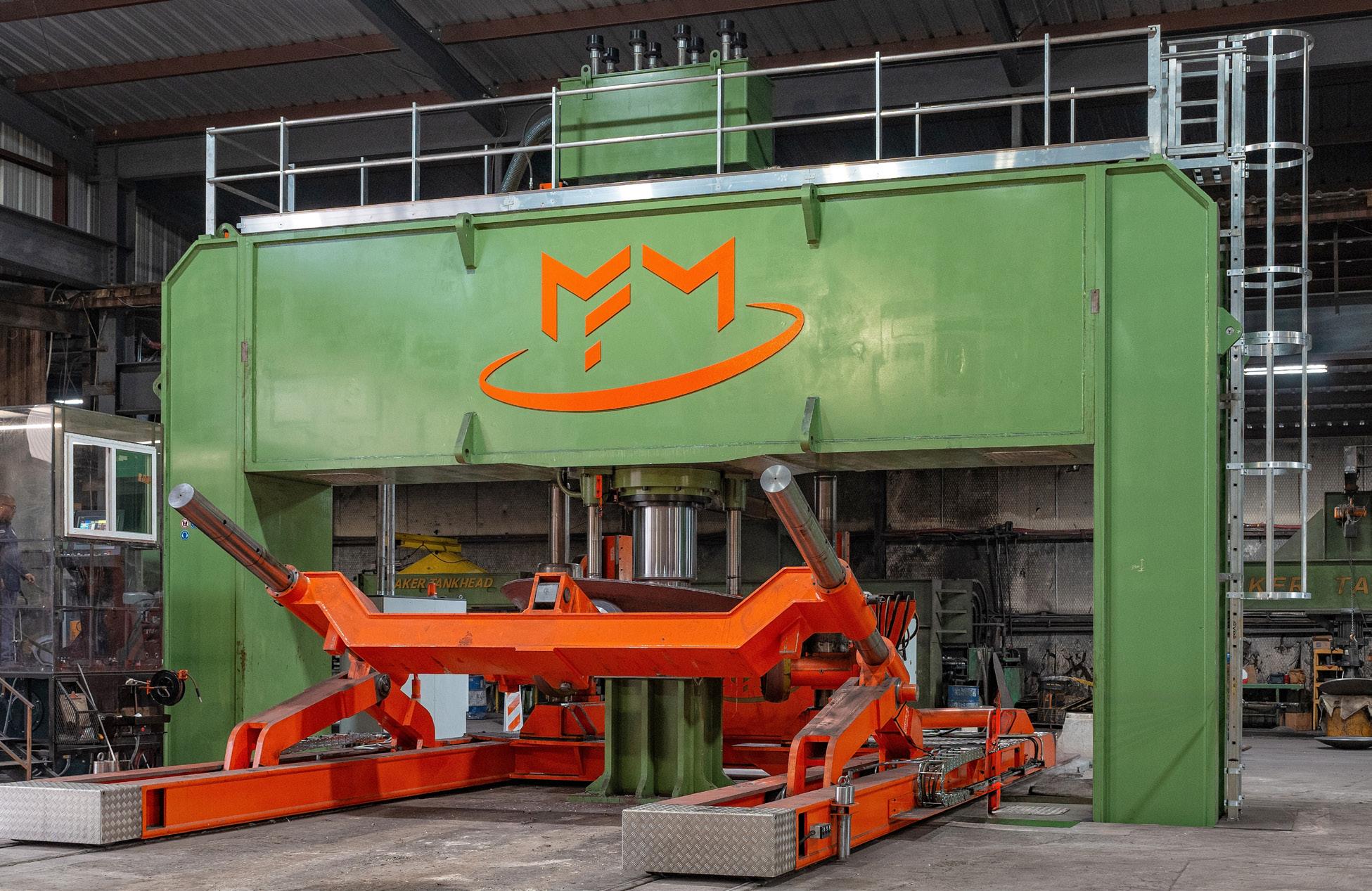
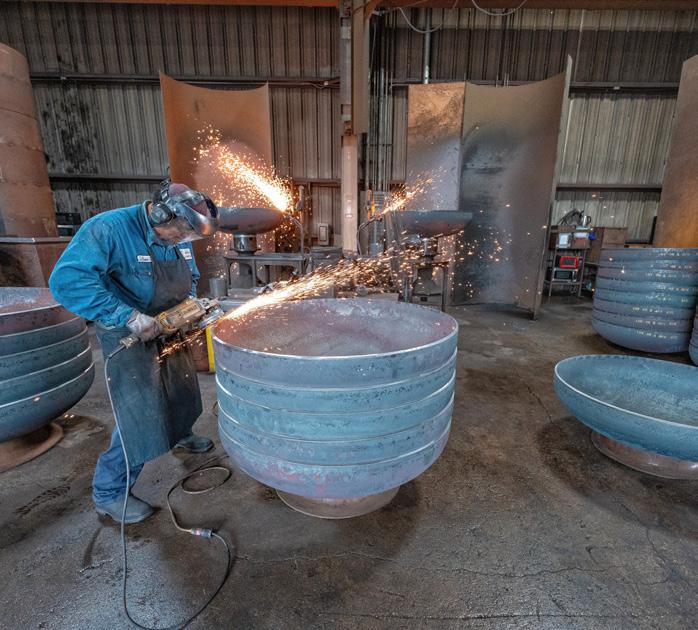

improvements, changing up the speed and efficiency, which is very exciting,” Austin Baker, Owner and President, explains.
The new press will enable the company to achieve thicker products, while the machine’s wide frame will allow it to manufacture tank heads up to 30 feet in diameter.
“It’s one of the largest cold forming presses in North America,” Sigala confirms.
“It’s fascinating not only to see what we can build from a flat plate of steel, but what our customer base does with it.”
– Robert Paine, Business Operations Manager, Baker Tankhead
OPENING DOORS
On a mission to provide unparalleled services with a family focused culture, Baker Tankhead sets itself apart from the competition.
Collaboration is central to achieving this ethos, as the company maintains close relationships with both customers and employees.
“When it comes to our clients, we seek to develop long-term relationships – partnerships that are an extension of our family as we listen to their needs and anticipate challenges,” observes Alan Button, COO.
For example, Baker Tankhead is proud to have collaborated with a client in the aerospace industry who had previously struggled to find a manufacturer.
“We opened our doors to this customer, working closely with their engineering department
to provide the quality service they were looking for,” Austin elaborates.
By adopting an open-door approach in this way, the company has since built a strong relationship with the customer as well as countless others.
“We’re always willing to welcome customers with open arms – having been in this business for almost 50 years, I can safely say that’s an advantage we’ve had from the others and how we’ve built the company from the ground-up,” he continues.
Also applying this mentality to its team and employees on the shop floor, consistent collaboration contributes to Baker Tankhead’s greater goal.
“We offer a supportive environment for our staff, ensuring employees feel heard, empowered, and motivated to grow and progress,” Button comments.
Meanwhile, attention to detail and a deep-rooted commitment to quality further contribute to the company’s leading status.
“When you work with us, it doesn’t take long to see why Baker Tankhead has been growing strong for nearly 50 years – and why we’re excited about what’s ahead for the next 50,” says Aaron.
ENDLESS POSSIBILITIES
As a company that collaborates with a wide range of clients, Baker Tankhead takes pride in discovering the various uses of its products across different industries.
“It’s fascinating not only to
see what we can build from a flat plate of steel, but what our customer base does with it,” reflects Robert Paine, Business Operations Manager.
Historically, the company’s collaborations have included customers in cryogenics, oil and gas, and water treatment, however it has recently witnessed a boom in data centers.
“We’re seeing increasing demand from companies focused on green energy initiatives and carbon capture technologies,” Paine notes. “In other sectors, our products are used to build boring equipment for horizontal drilling.”
Beyond these diverse
“As the so do means equipment, operations, and promoting within.”
– Aaron Baker
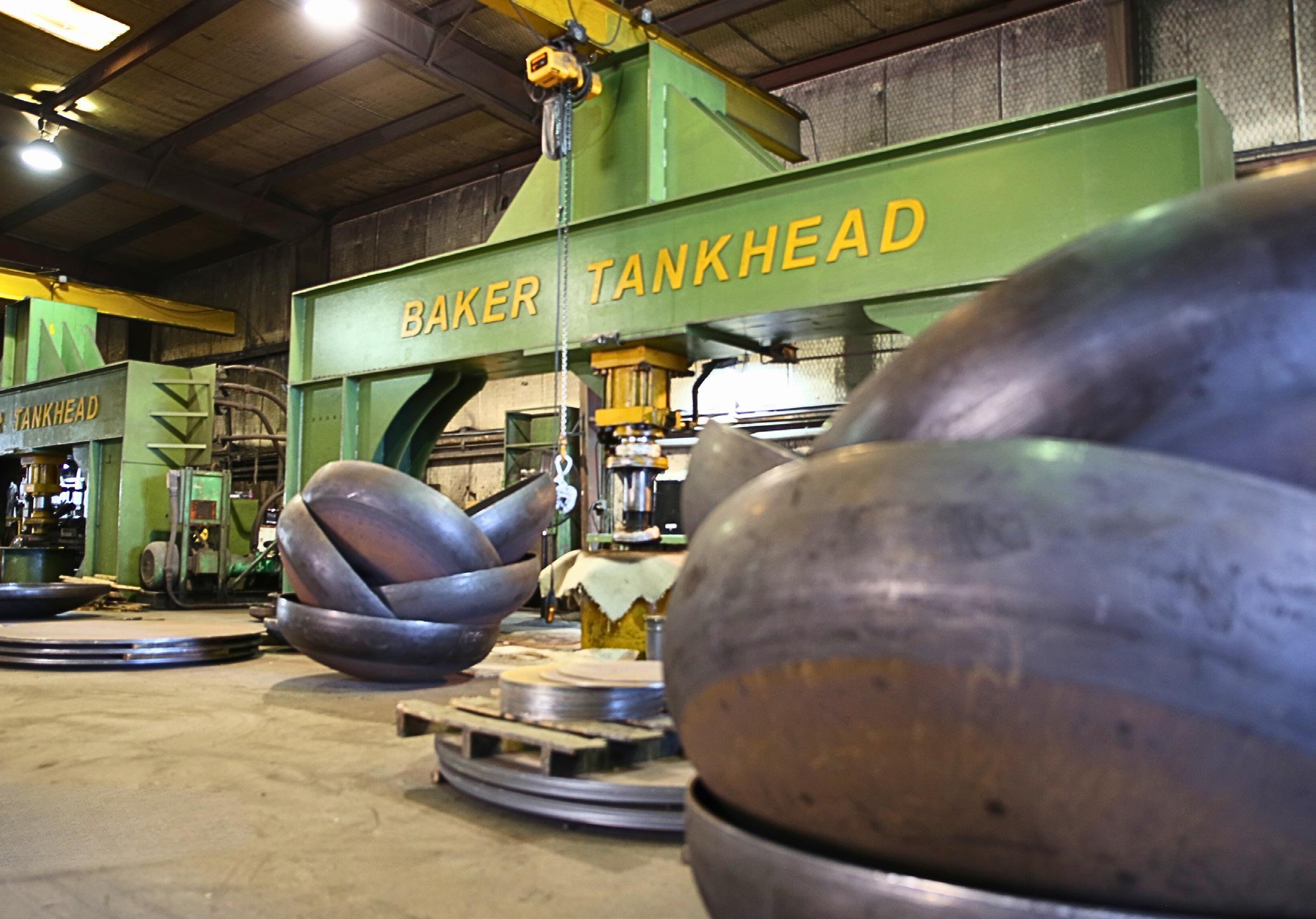
applications, Baker Tankhead’s components have journeyed into space and contributed to oceanographic exploration.
“Tank heads are everywhere – from the food industry to vacuum trucks, water heaters, and liquor distilleries. The list goes on.”
ONGOING EVOLUTION
As the diversification of Baker Tankheads’ products continue to evolve alongside its customers’ changing needs, the possibilities for growth are endless.
Having started as a small 1,200 square foot shop that has now expanded to 200,000 square feet across 20 acres, the
the industry evolves, do we – whether that means investing in new equipment, streamlining our operations, or recognizing promoting talent from within.”
Aaron Baker, Vice President, Baker Tankhead
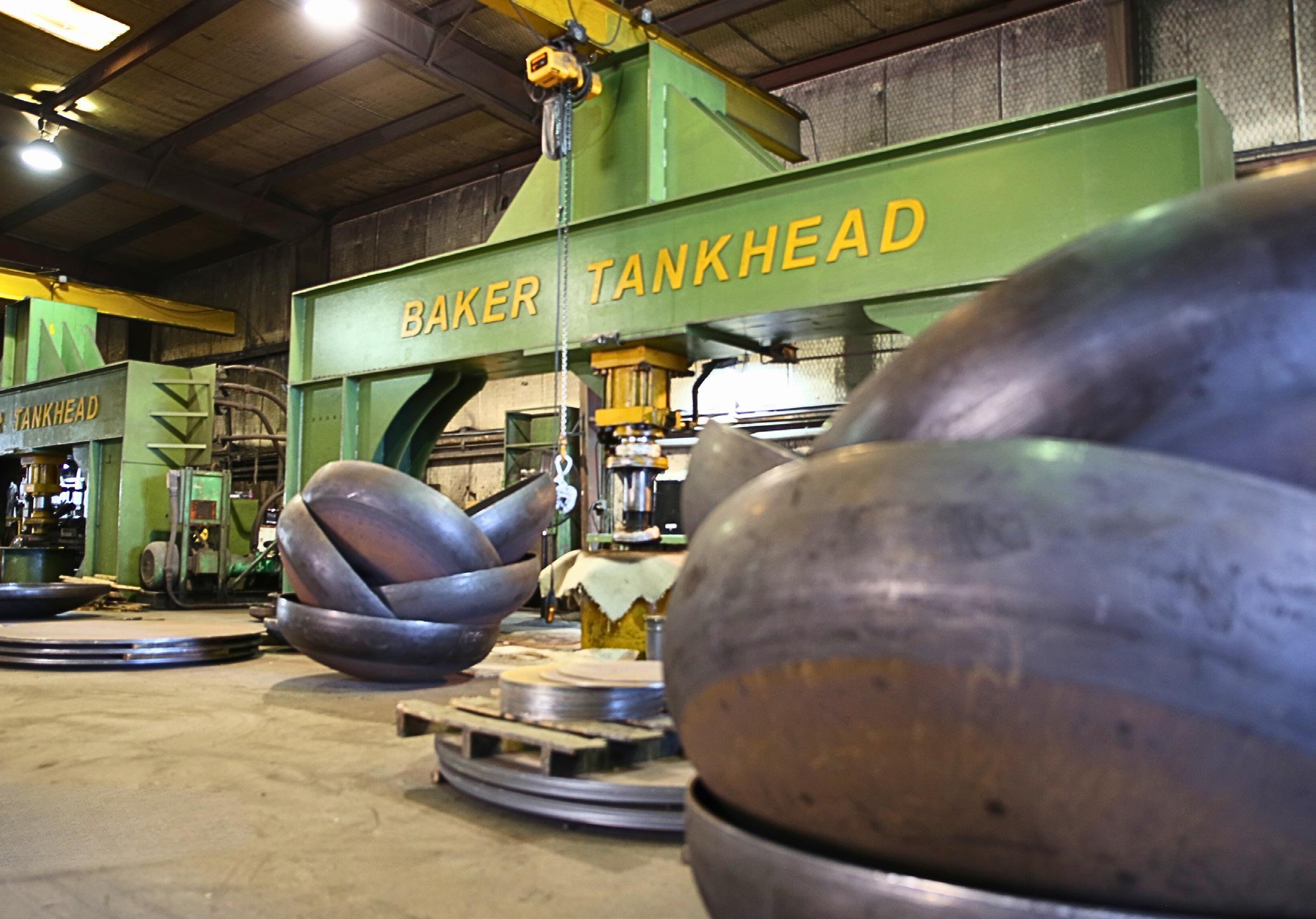
company’s historical growth is tangible.
It has implemented new on-site facilities and technologies over time and is always on the lookout for further opportunities to innovatively fulfil its customers’ requirements.
“We also boast various key differentiators such as maintaining the fastest lead time in the business, alongside our unparallelled service and high-quality products,” Paine prides.
“Once we’ve built a long-term relationship with a customer, I really think they begin to see what they were missing prior to working with us,” Austin adds.
Charting the course to continued collaboration
Having been a long-term partner of Chart Industries (Chart) for 20+ years, Baker Tankhead has established a solid partnership with the company.
“We’ve grown alongside Chart across multiple locations, maintaining a great relationship and a lot of repeat business,” Austin recalls.
Equipped with its new 800 ton press, Baker Tankhead is looking forward to manufacturing additional work for Chart, further elevating not only the caliber of products delivered, but their partnership as well.
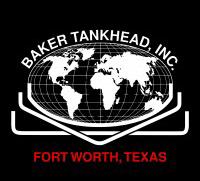
Meanwhile, Baker Tankhead has never shied away from investing in the business, recognizing financial support as the key to success in the face of constant change – not only in terms of technology but in order to meet customer requirements.
“Companies who are willing to invest in themselves are going to be the ones that continue to succeed, and that’s exactly what we plan to do” Austin confidently concludes.
LinkedIn: Baker Tankerhead inc
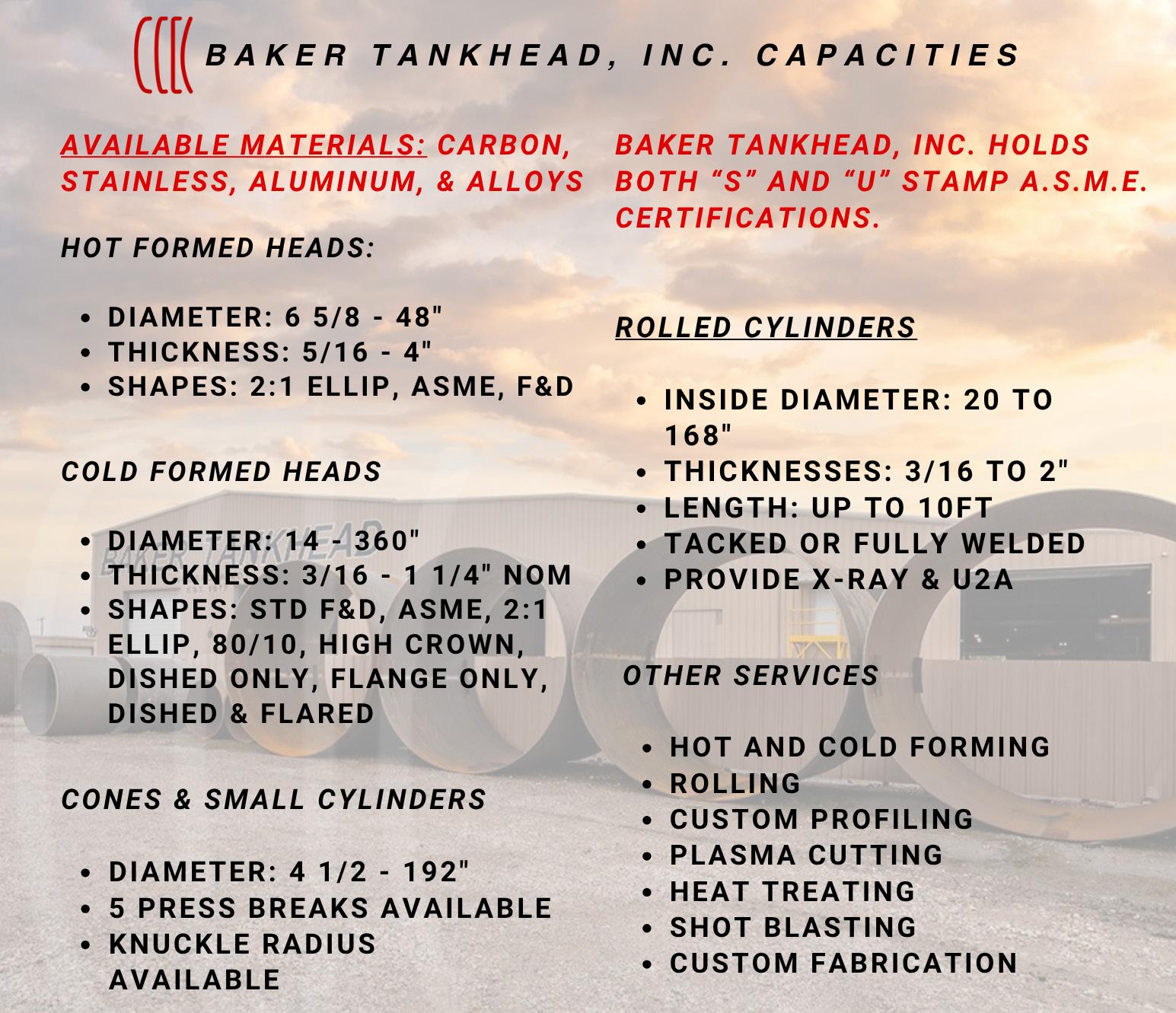
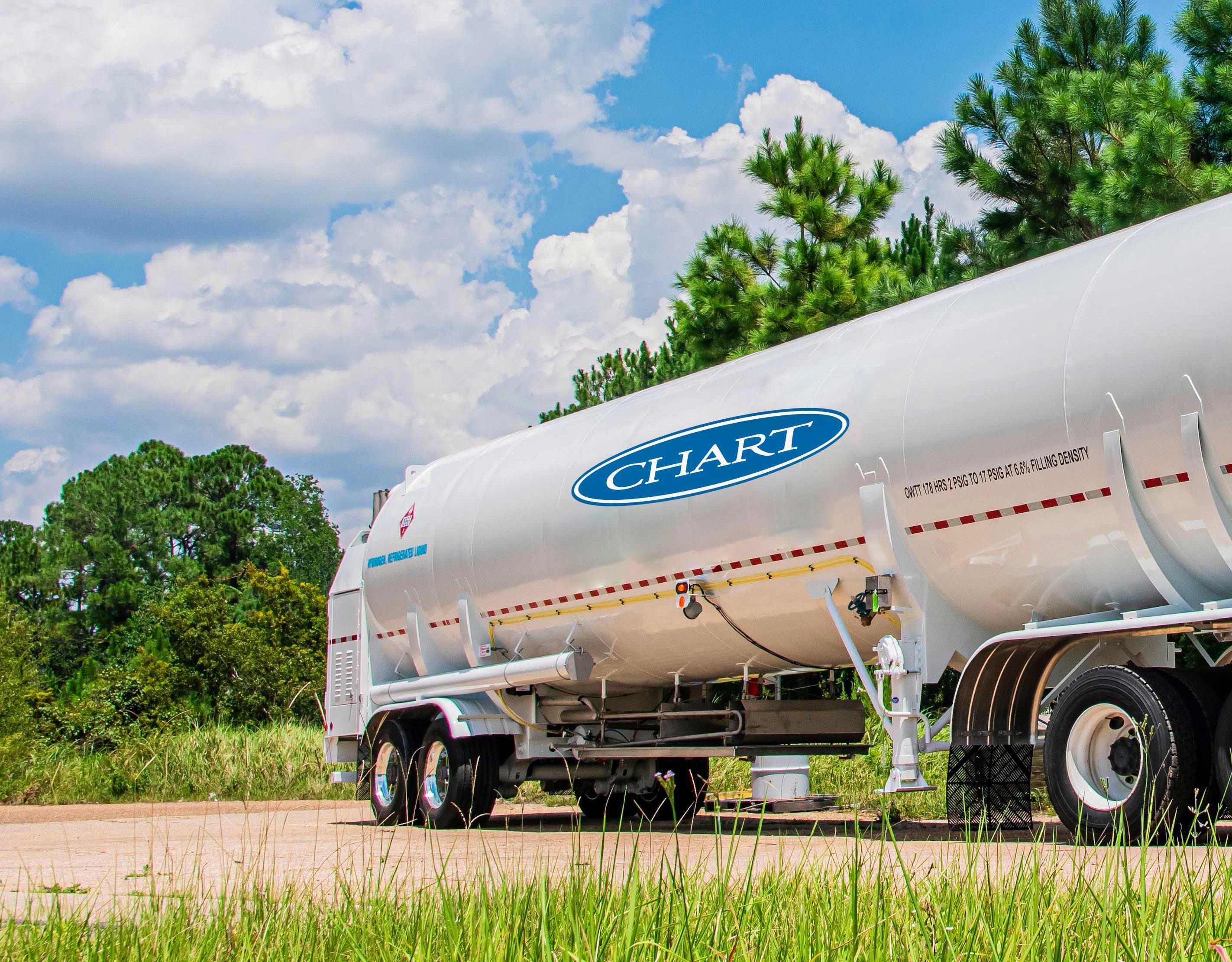
Crucially, these trailers are engineered to withstand the high pressures and extreme temperatures associated with cryogenic liquids, meaning Chart ensures safe and reliable transportation every time. With engineering and manufacturing capabilities now stretching across three continents, Chart offers trailers, semi-trailers, swap bodies, liquid tube trailers, and railcars for the safe and efficient distribution of liquid gases including nitrogen, oxygen, argon, CO2, hydrogen, natural gas, and more.
As well as these standard liquid gases, a range of transport solutions for liquid nitrous oxide, ethylene, propane, butane, butadiene, and ethylene oxide are available on request for Chart’s customers.
“WE COMBINE ROTATING AND STATIONARY EQUIPMENT WITH PROCESS EXPERTISE TO SOLVE COMPLEX ENERGY AND INDUSTRIAL CHALLENGES”
– JILLIAN EVANKO, CEO, CHART INDUSTRIES
Leveraging unrivaled expertise and exceptional pedigree in this enormous field, Chart manufactures its cryogenic trailers across the US, Europe, and China.
Furthermore, Chart’s engineers dedicate themselves to working with clients to determine the best configuration for their specific requirements.
Meanwhile, regardless of manufacturing location, all equipment
is built to the same high-quality standards and in accordance with all associated relevant pressure vessel and stringent transportation codes and regulations.
NITRO INNOVATION
In recent years, Chart’s growing plethora of products have found a way to penetrate countless new sectors and markets across the globe. If you’ve ever sat back and enjoyed
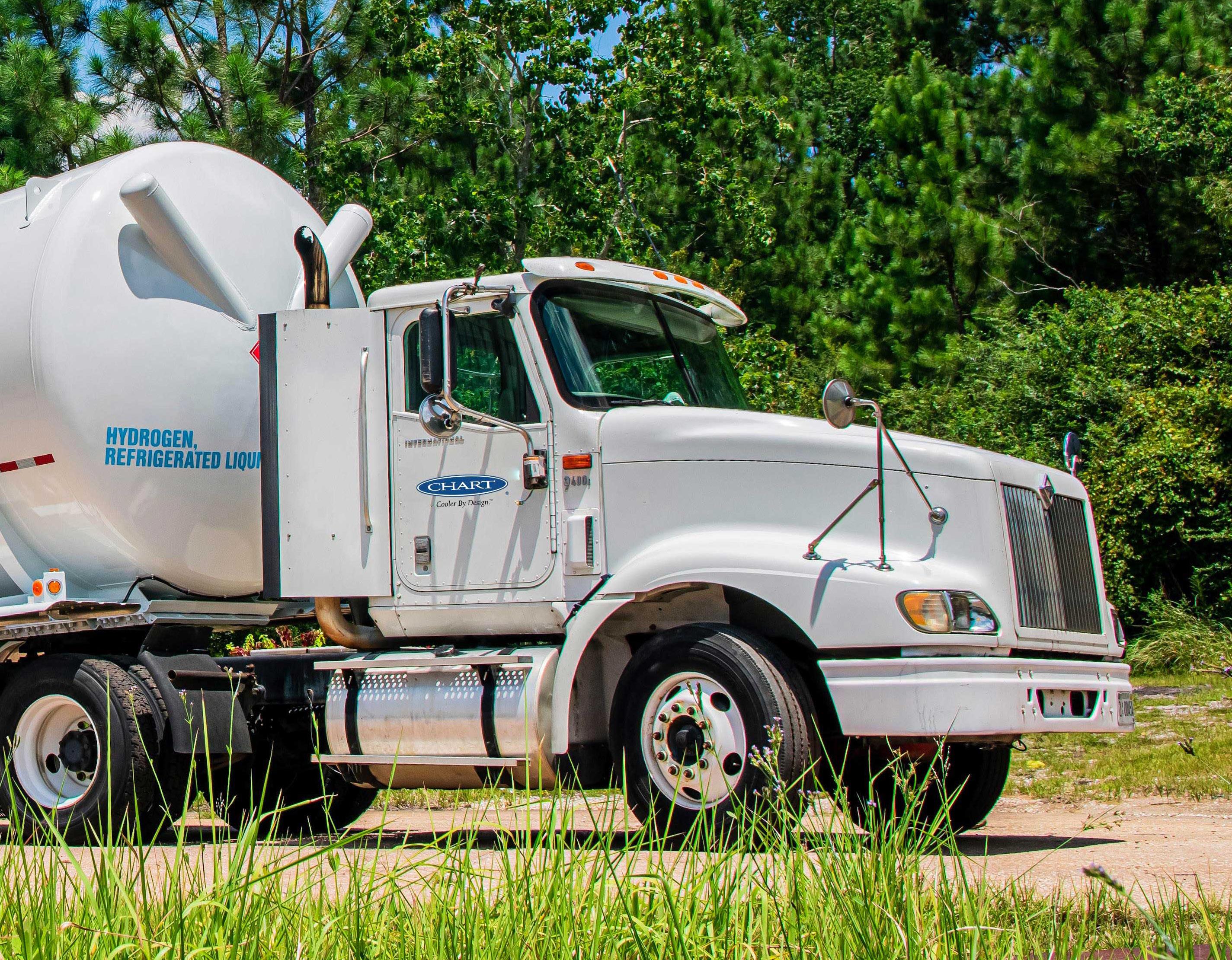
a refreshing nitro beer, you can thank Chart’s frost-free, vacuum-insulated liquid nitrogen equipment for making that possible.
A nitro beer is a recent innovation that is primarily carbonated with nitrogen gas instead of the more common CO2, resulting in a noticeably smoother taste and a dense, cascading head.
Nitrogen is less soluble in liquid than CO2, meaning it forms smaller, more numerous bubbles.
Popular examples of nitro beers within this market include Guinness, which has popularized the use of nitrogen in stout beers, and various other beers and porters that utilize this technique.
Furthermore, many of the Chart’s customers are global household
names – from Starbucks, which uses the company’s liquid nitrogen dosing technology for beverages like its Nitro Cold Brew, to Viking Cruise, which is exploring using hydrogen fuel cells with their ocean vessels, and ExxonMobil, which is using Chart’s state-of-the-art liquification technology in Northern Mozambique at the Rovuma LNG project.
“Our company has become particularly adept at taking oldschool designs and equipment and transferring these concepts into new and emerging markets,” Evanko explains.
This expertise undoubtedly stems from over 157 years of hydrogen design and equipment building.
“During the COVID-19 pandemic, many companies became more
focused on sustainability and the future of the world, so having this amount of hydrogen experience gave us a great jumping-off point to be able to serve these different end markets,” she continues.
SOCIAL SUSTAINABILITY
For Evanko, an element of the business which she sees as of vital importance is that of social sustainability, a concept that the company endeavors to uphold to the highest possible standards.
“We understand that the more variety we have in our perspectives and ideas, the more successful we are. As such, we are actively ensuring that all levels of the Chart family look like the societies we live in,” she tells us.
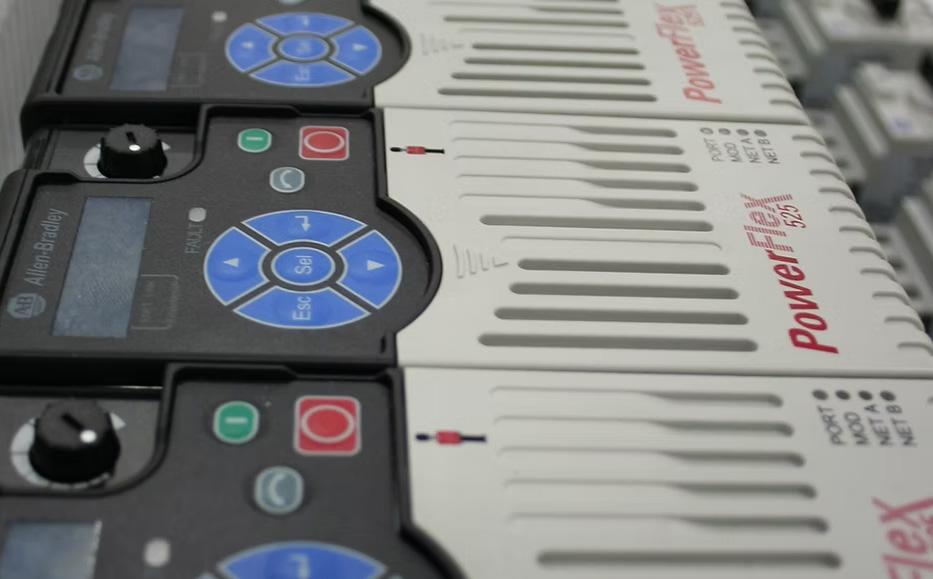
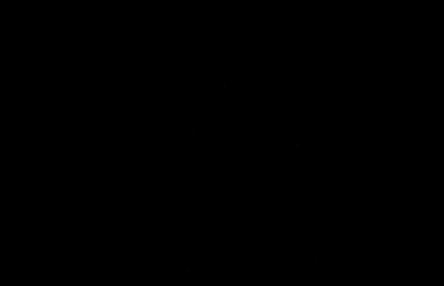
Complete Control System Solutions
Your full-service provider for control systems, automation, and panel fabrication.
BW Systems Inc. is more than a Control Systems Integrator and UL Panel Shop — we are a trusted partner committed to delivering reliable, high-quality control system solutions. With comprehensive in-house capabilities in design, engineering, and fabrication, we provide fully customized solutions tailored to your specific requirements.
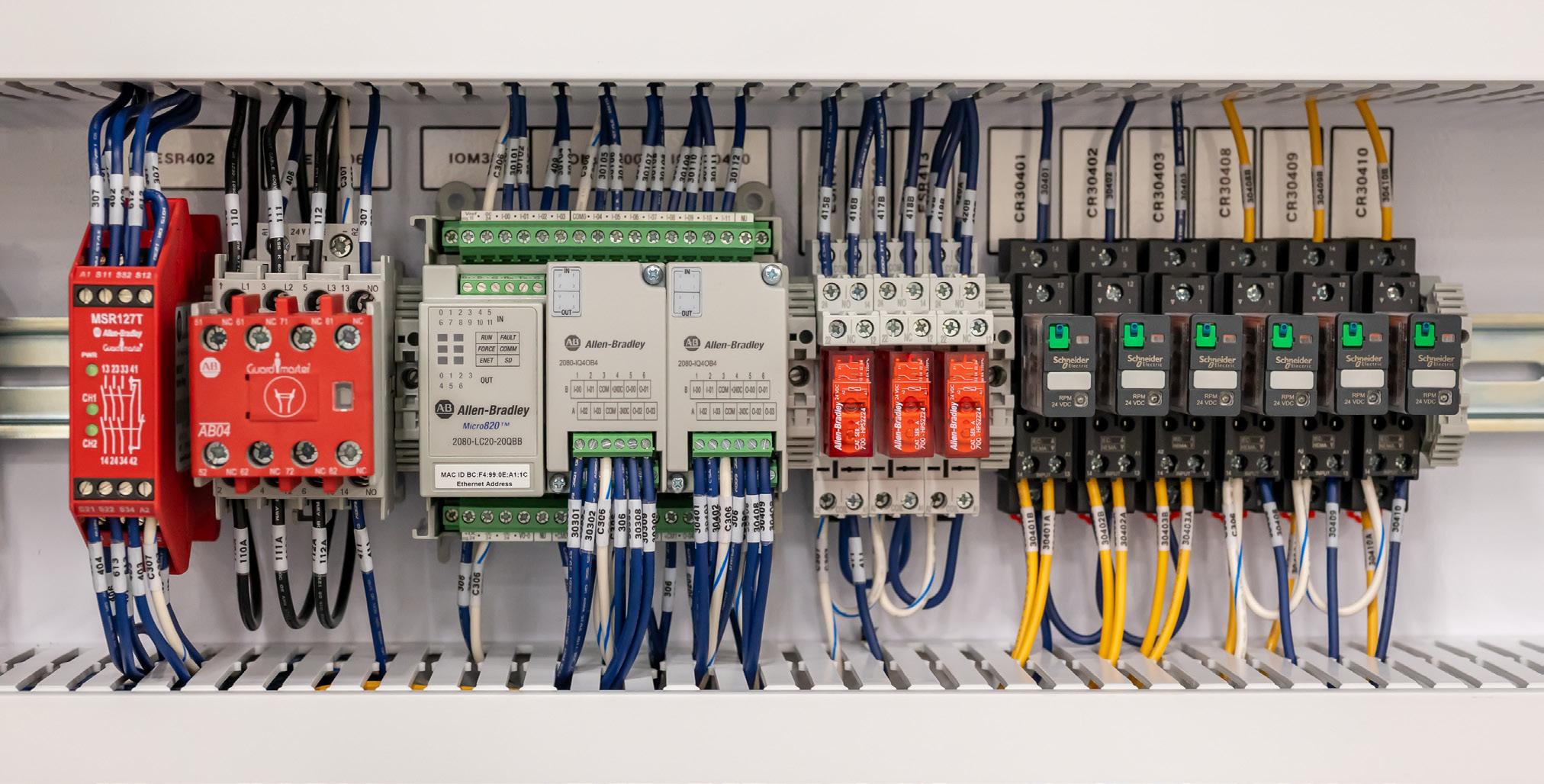
Your full-service provider for control systems, automation, and panel fabrication.
Our 55,000 sq. ft. manufacturing facility is equipped to handle a wide range of control system production needs, from unique, one-off builds, high-volume OEM production, as well as complete on-machine wiring.
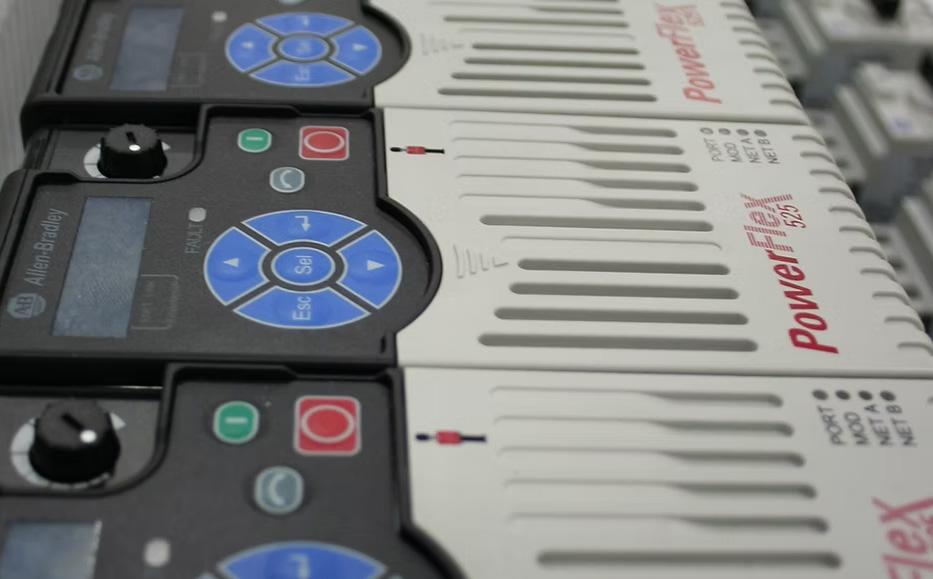
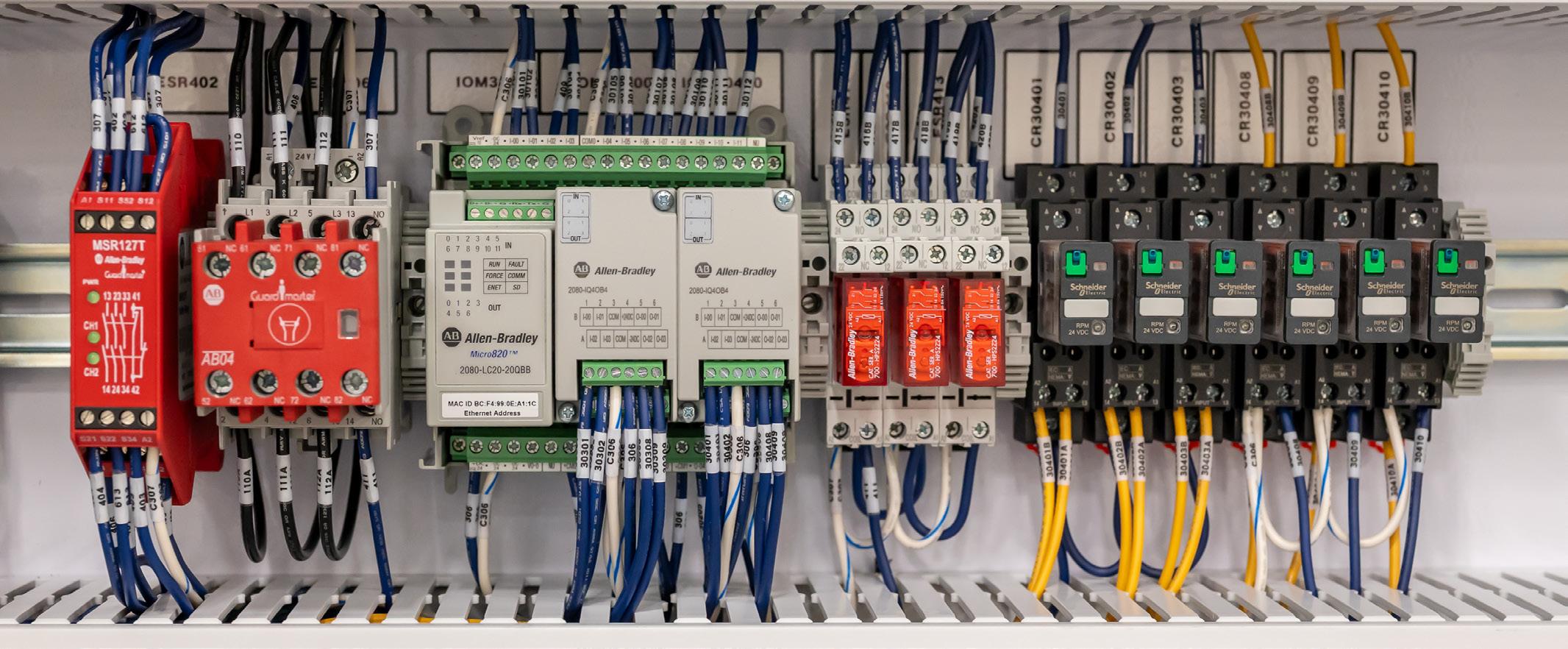
Engineering Expertise
• Web Transport Systems with Related Coating & Ovens including Div I and DIv II areas
• Batch & On-Demand Systems used in Food/Chemical/Adhesive Manufacturing
e Control
• Plastic Extrusion & Hot Melt Adhesive Systems
• LNG Transport Systems
olutions
• Pollution Control Systems
• High Performance Motion, Singleaxis, Multi-axis, Robotics, Assembly & Automation
Electrical Control Panels
Since opening its doors in 1997, BW Systems Inc. has been designing and building control systems for both general purpose (UL 508A) and hazardous locations (UL 698A/NNNY). Whether working from comprehensive assembly drawings or a basic set of schematics, our experienced team is fully equipped to fabricate industrial control panels that meet all applicable code and regulatory standards.
Checkout \ Quality Controls
Upon completion of construction, all panels and machines are routed to our segregated QA/Testing area for a comprehensive inspection and testing process. This area is equipped with various voltages and current capabilities which allow exhaustive testing for both domestic and foreign systems.
• Warehouse Conveyors, Sorting & Auto-picking
• Factory Floor/ERP Integration
• Machine and Process Safety
Manufacturing Services
• UL508A: Control Panel Fabrication
• UL698A: Extensions into Hazardous Locations NNNY: Hazardous Location Fabrication
ering Expertise
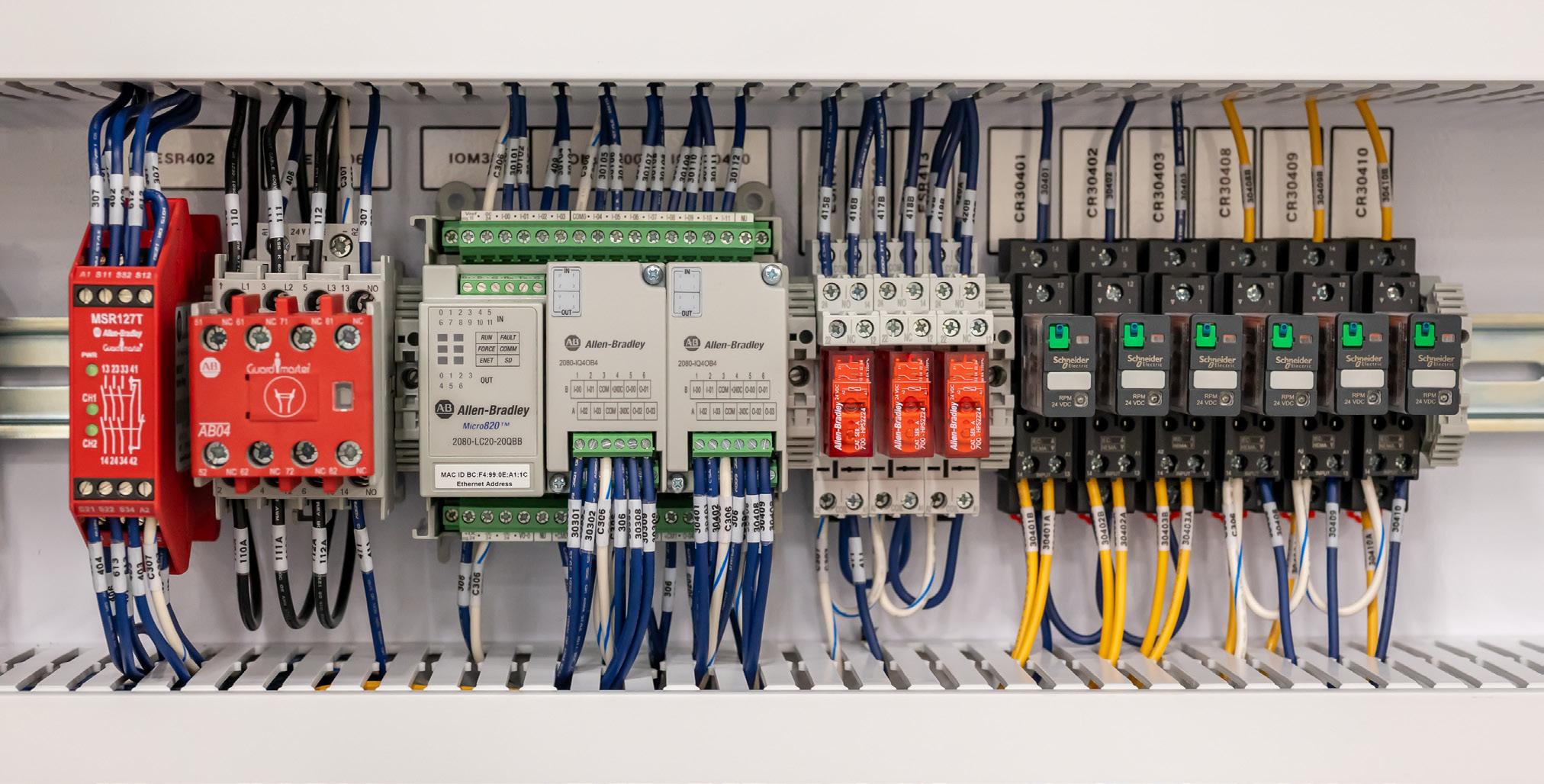
t Systems with Related Coating &
• Self-Certified Panel Listing with UL or ETL (Intertek)
ng Div I and DIv II areas
emand Systems used in al/Adhesive Manufacturing
on & Hot Melt Adhesive Systems
t & Pollution Control Systems
To ensure the highest level of safety and compliance, BW Systems Inc. has configured our QA/Testing area to meet Category 0 standards wherever applicable, aligning with customer requirements and industry’s best practices for safety.
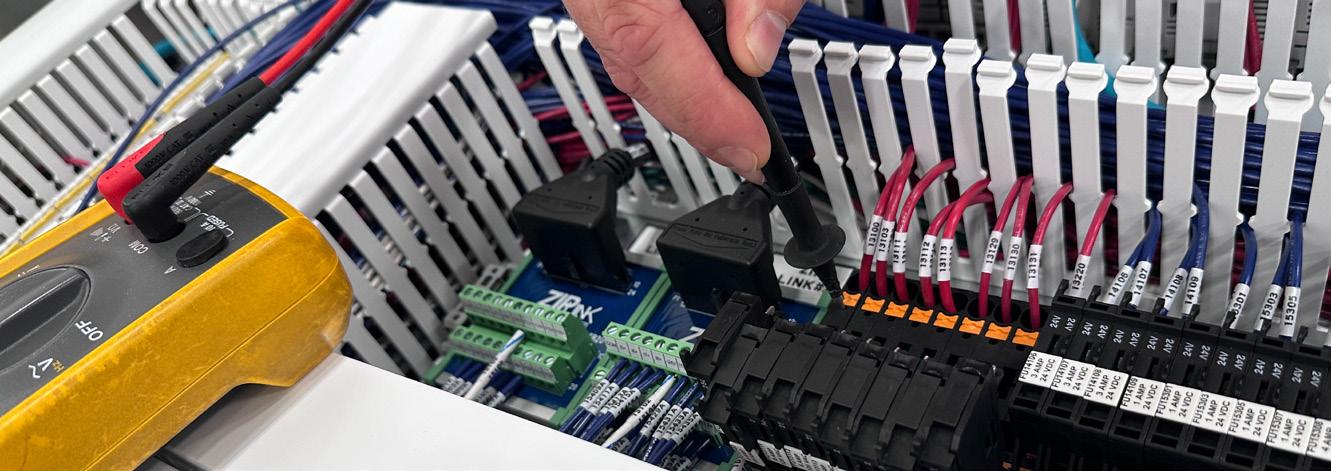
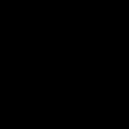
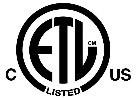
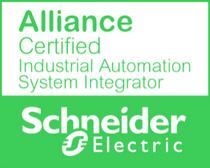
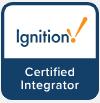
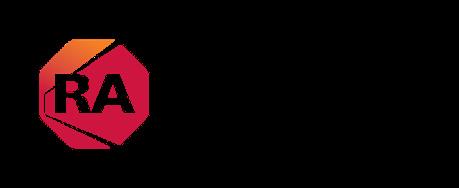
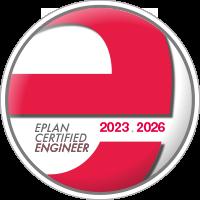
or need a quote?
The company’s commitment to equity is evidenced by its diverse board of directors, with 40 percent of its current directors being female.
People are at the heart of the company, and they must be taken care of. As such, Chart looks after its ‘cool communities’ – referring to cryogenics, where it operates in many interesting locations.
“Every seven days, I send a daily spotlight out to our whole organization highlighting a team member or a group of our team members that has done something exceptional, or even just something kind or related to our key themes,” she continues.
‘Cooler By Design’ is more than
just a tagline for the company. Whether it’s volunteering together through its Giving Back Program or team members competing in some friendly competition through the many fun activities on offer, Chart has perfected the art of enjoying each other’s company and having fun as it makes incredible results happen while ensuring that there is a healthy and enjoyable work culture.
“Some weeks, we host Motivational Mondays, which is put together by our teams and built around improving overall health, making sure our staff have a good work-life balance. We ensure they are taking care of their mental health and encourage them to spend more with their families.”
CHART’S VALUES – AT A GLANCE
SAFETY ABOVE ALL – Chart’s commitment to zero harm drives every decision it makes and every action that is taken. Everyone at the company is empowered to speak up and stop unsafe actions. Chart continually develops its environment, health, and safety (EHS) culture to prioritize safety and well-being and positively impact the environment.
HERE FOR CUSTOMERS – The company forges strong partnerships with its customers to understand their goals and aspirations. Chart is always responsive and uses its considerable expertise to deliver world-leading solutions and outstanding customer service to drive shared success.
PEOPLE MAKE THE DIFFERENCE – By recognizing the talent and different perspectives that each team member brings, Chart leads with honesty and integrity, fostering an environment where everyone can grow professionally, be themselves, and have fun. The company gives back to local communities, using its time and resources to positively make a difference.
PURSUIT OF EXCELLENCE – The company aims to be proactive and curious, always looking to do things better. Through Chart’s global engineering expertise and world-leading technology, it consistently pushes boundaries and takes on tough challenges to find the best and most innovative customer solutions.
PASSION FOR RESULTS – Chart remains dedicated to delivering profitable growth and takes full ownership of its range of commitments. The company aims to stay flexible, adapting to changing business needs, and continually focus on achieving stakeholder value.
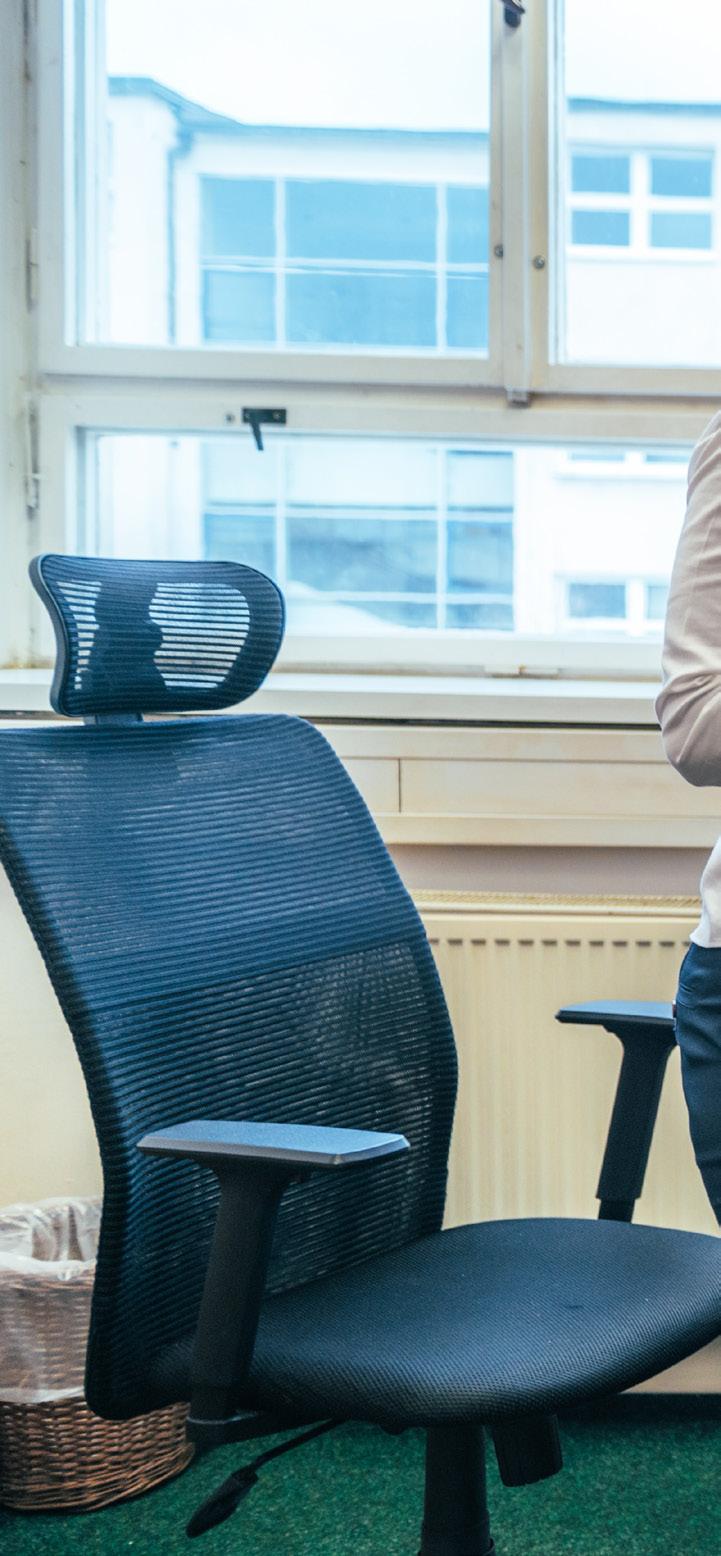
Chart also leverages a slate of geographically specific programs across all of its regions globally, as the company remains conscious of giving back to the communities it serves.
UNVEILING TEDDY 2
In the US, Chart’s new cryogenic facility in Theodore, Alabama (AL) was unveiled in March 2024.
The plant can manufacture the world’s largest shop-built cryogenic tanks with a capacity of up to 1,700 cubic meters (cbm).
These large tanks are used to store liquid gases including hydrogen, oxygen, and LNG for industries including aerospace, clean power, marine, gas-by-rail, and many others in the ever-expanding science and decarbonization sectors.
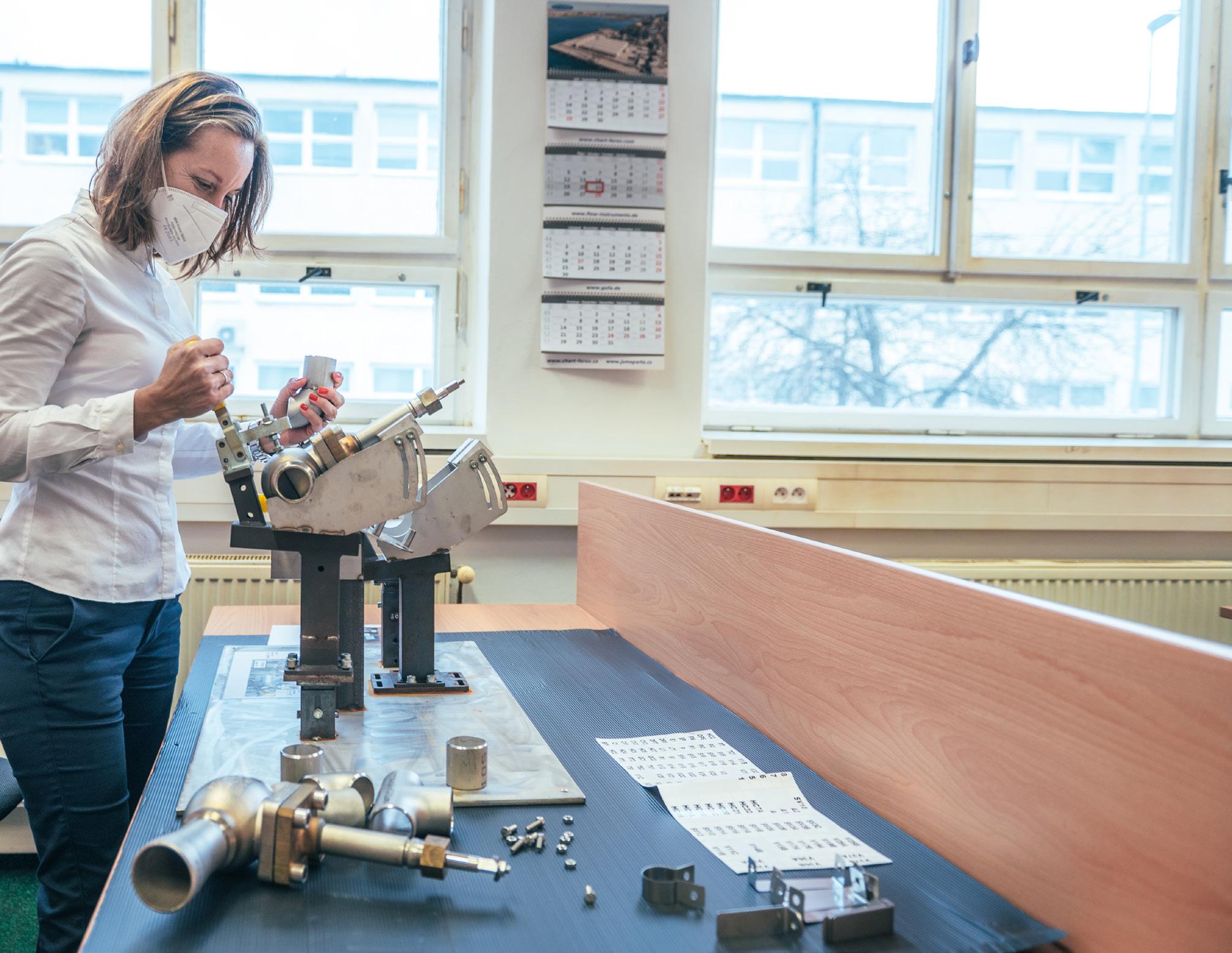
Known affectionately as “Teddy 2” because it’s the company’s second facility in Theodore, the facility has an optimal location, including direct access to waterways and railways which are key in providing customers with lower freight costs and faster transportation to site.
The expansion has also contributed significantly to local job creation and economic development efforts for the state of AL and its citizens.
“We were thrilled to officially expand our presence in Theodore with the ability to offer the world’s first shop-built cryogenic tanks of this scale,” Evanko recalls.
“This expansion further supports our customers through increased capacity and scale as well as lower freight costs and shorter lead times.
We look forward to continuing to hire from the strong, skilled workforce in AL,” she prides.
BREAKING RECORDS AT SEA
Chart was recently pleased to announce a major milestone for the company and indeed the broader industry with the successful shipment of the first two jumbo cryogenic tanks built at the Teddy 2 facility.
Each with an impressive capacity of 1,700 cbm, they are considered to be the largest shop-built cryogenic tanks ever produced.
Made to support next-generation space launch infrastructure, these tanks reflect the growing demand for large-scale liquid gas storage across a wide range of emerging applications in aerospace, clean energy, maritime
and carbon capture.
In addition to increased storage capacity, the process of shop building reduces on-site construction and facilitates modularization, thereby reducing overall project cost, schedule, and risk.
The expansion has also contributed to local job creation as well as significant economic development and is consistent with the region’s ambitions as an innovation hub for cleantech.
BUSINESS EXCELLENCE
What continues to set Chart apart is that the company is not just an equipment provider – it consistently delivers engineered solutions across a wide range of applications, tailored to the specific requirements of customer needs.
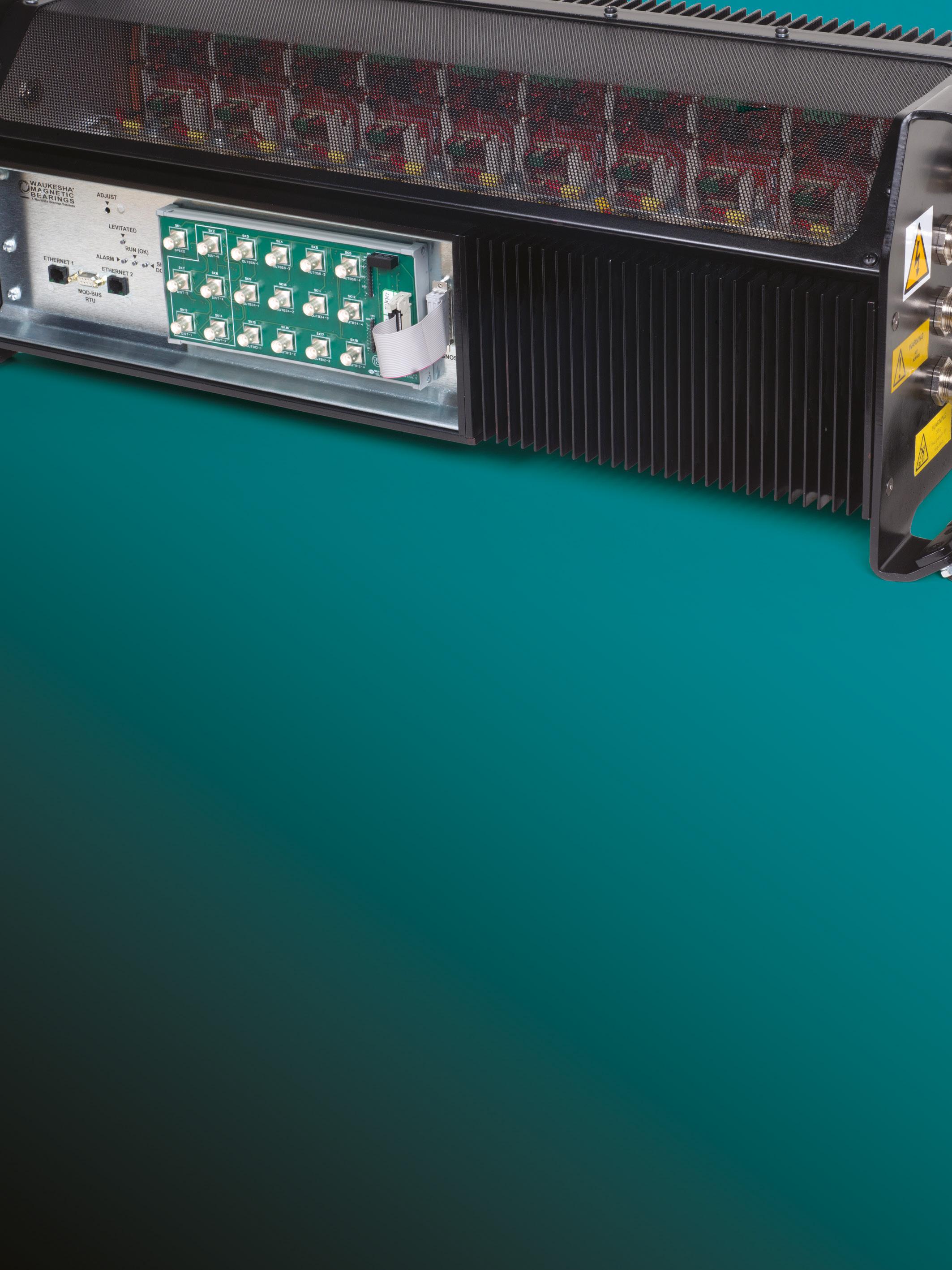
AMB CONTROLLER UPGRADE OPTIMIZES TURBOEXPANDER PERFORMANCE IN NGL RECOVERY
Turboexpanders are the beating heart of midstream natural gas liquid (NGL) operations, helping enable fast and efficient liquid recovery. Bearings are a crucial component of a turboexpander, supporting the weight of the turboexpander’s rotor to maintain correct relative positioning. Active magnetic bearings (AMBs) are an oil-free bearing system that uses electromagnetic forces to maintain the relative position of a rotating assembly (rotor) to a stationary component (stator). An advanced electronic control system adjusts these electromagnetic forces in response to forces generated from machine operation, and any issue that compromises the operation of an AMB controller can bring NGL processing to a halt.
So, when an NGL processing company approached L.A. Turbine (LAT), a Chart Industries company, looking for the best way to upgrade an outdated analog AMB controller, they understood the importance of finding a reliable and expedient solution.
Luckily, LAT had a history of successful collaboration with Waukesha Magnetic Bearings, a subsidiary of Waukesha Bearings, that has been providing complete solutions for AMBs and magnetic bearing controllers in a variety of specialized applications for nearly 40 years. This versatility and experience enable the company to design controllers that are effectively brand-agnostic, making them the perfect partner to help LAT promptly deliver a cost-effective application-specific solution.
Outdated Analog AMB Controller Stalls NGL Processing
The troublesome analog AMB controller and the cabinet in which it was housed were due for an update. Over several months, the company tried to troubleshoot its shortcomings, but the original manufacturer considered the controller obsolete and would no longer provide support. Instead, the OEM pushed its customers to upgrade to new AMBs, which would require significant investment and potential extended turboexpander downtime.
The company sought an alternative to upgrading to entirely new AMBs and controllers, but most companies proposed replacing the entire AMB system, including the controller, for easy compatibility. It seemed like
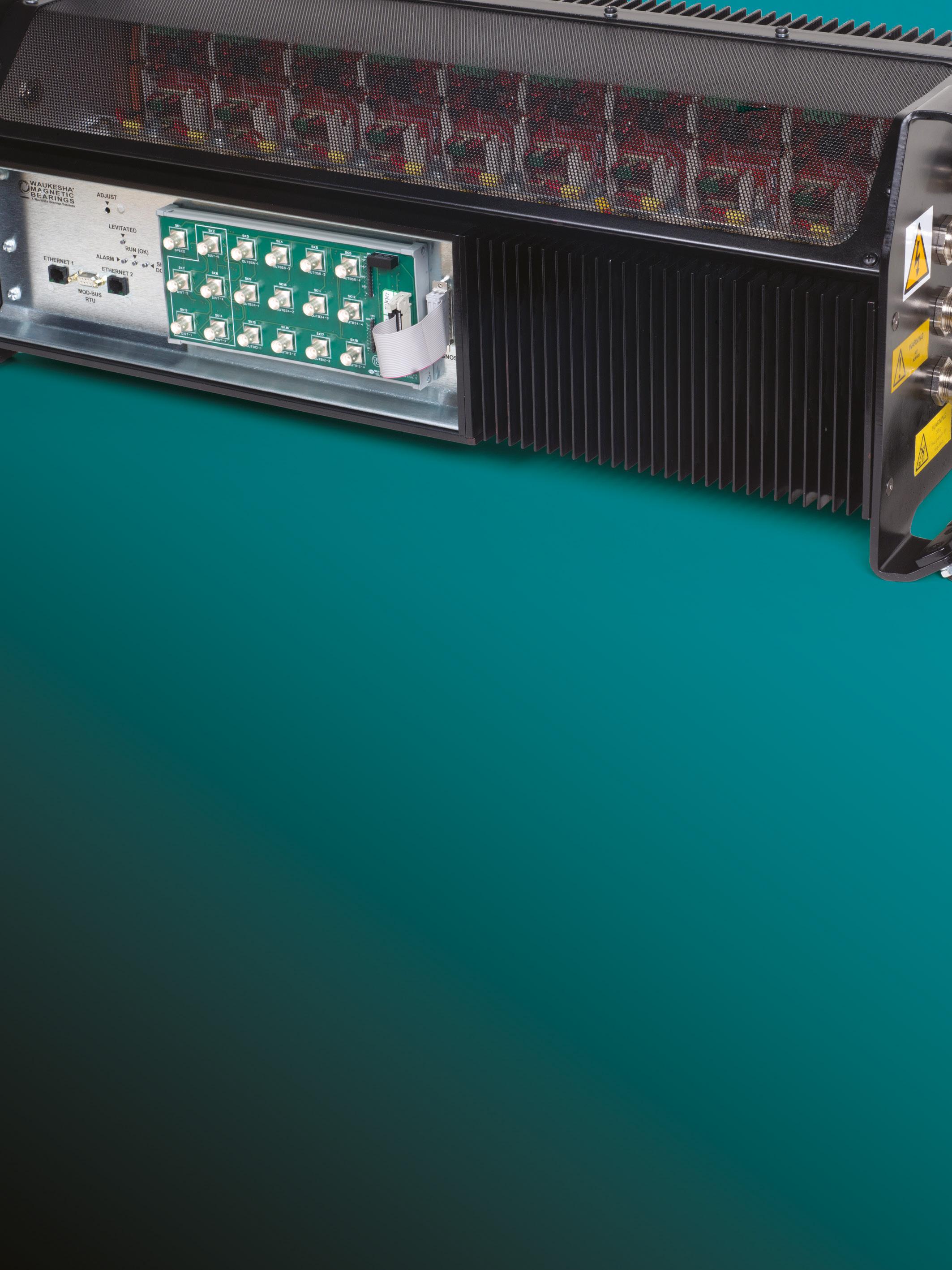
there was no choice but to purchase the expensive replacement AMB system until a service call with LAT yielded a different, more satisfying solution.
Controller Retrofit Beats Costly Replacement
Rather than replacing the entire system, LAT proposed working with Waukesha Magnetic Bearings to retrofit a new, more modern and feature-rich controller for the existing AMBs and turboexpander. Pairing a new controller with an existing AMB is not typical because most companies require using the same manufacturer for both pieces of equipment. However, LAT and Waukesha Magnetic Bearings had already collaborated on similar projects in the past with great success.
In fact, the two companies had a history of ambitious collaborations. When LAT set out to design the industry’s first and only skid-mounted turboexpander cabinet for hazardous-area applications, they reached out to Waukesha Magnetic Bearings to be a design partner. Together, the companies built the ARES AMB Turboexpander, featuring a skid-mounted Zephyr® controller.
The Zephyr controller also proved to be an ideal solution for retrofitting the midstream energy customer’s obsolete analog controller. The Zephyr controller is highly configurable, making it “bearingagnostic,” or able to integrate with many different sensors and magnets.
Beyond technical compatibility, Zephyr controllers are simple to operate, which was a key requirement for LAT’s customer. After relying on the outdated analog controller for so long, they were also seeking a more robust solution with modern features such as remote monitoring and adjustment capabilities. All in all, Zephyr fit the bill.
A Dedicated Service Team Makes Installation Seamless
While it was clear the new controller and cabinet would be an enormous upgrade, the engineers at LAT and Waukesha Magnetic Bearings most impressed the customer with their responsiveness and customer service.
Because the LAT and Waukesha Magnetic Bearings teams understood the impact downtime has on NGL-processing companies, they worked tirelessly to install the upgraded equipment as quickly as possible.
In this case, that meant constant communication – plus sharing lessons learned from previous retrofitting projects. As a result, the LAT and Waukesha Magnetic Bearings teams were able to install the controller and make it operational quickly.
Advanced New Controller Exceeds Expectations
The new controller has proven to be an optimal solution. Now, LAT’s customer can keep an eye on the AMB remotely and make adjustments if needed. Zephyr’s remote monitoring and adjustment functionality includes multi-coordinate control, runout compensation, an automatic balancing algorithm and an advanced amplifier algorithm for software flux feedback.
With inductive sensor support, Zephyr also boasts simple troubleshooting features – a stark contrast to the old analog controller. Its diagnostic capabilities include a web-server interface, event logging, automatic clearance check, and built-in tools that show compliance with ISO sensitivity performance criteria. It offered everything the customer wanted, and then some.
Backed by the LAT team’s exceptional customer service and field support, the upgraded controller gave the customer renewed peace of mind about the AMB’s long-term performance. In fact, Waukesha Magnetic Bearings’ devices are known to stay operational for decades, and Zephyr controllers have the same reputation for long-term reliability. With no moving parts, predictive maintenance and an extended warranty option, the AMB controller is expected to perform reliably in the field for many years to come.
www.waukeshabearings.com | info-wb@doverprecision.com
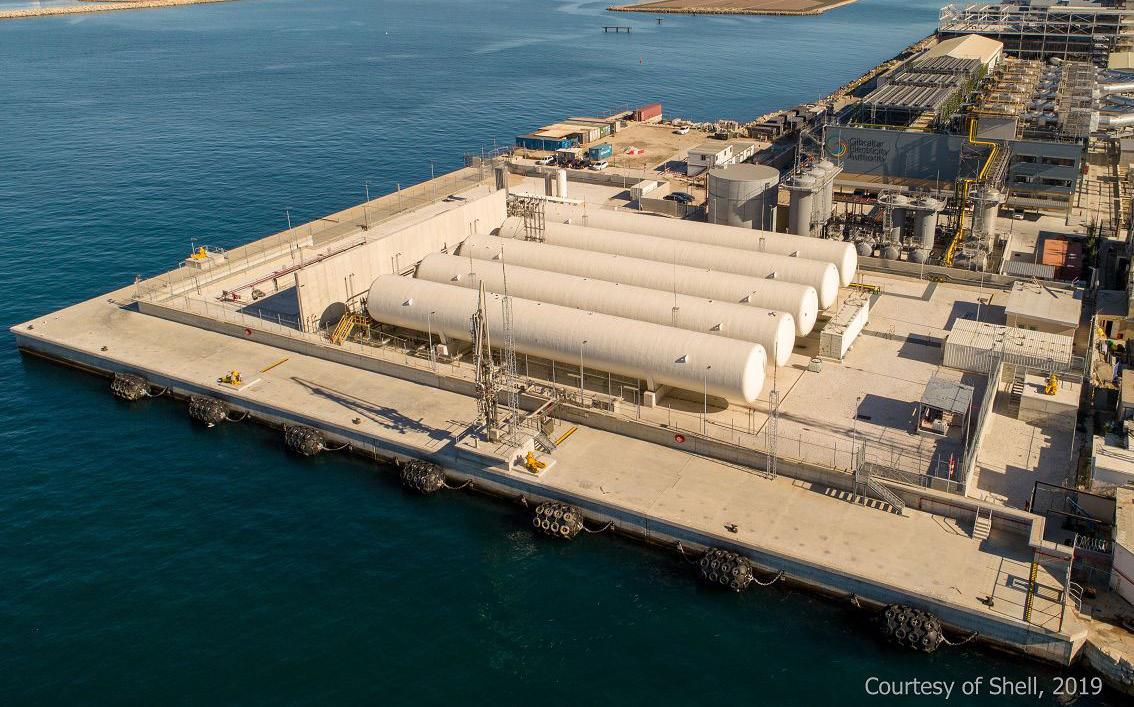
“We combine rotating and stationary equipment with process expertise to solve complex energy and industrial challenges,” Evanko explains.
As such, Chart’s moleculeagnostic approach to its operations is another key differentiator.
“We don’t compete with our customers in molecule production. Instead, we focus on enabling infrastructure across hydrogen, LNG, CO2 capture, water, biogas, and more, regardless of the molecule in play,” she adds.
The company also invests in R&D for cryogenic systems, carbon capture, and hydrogen technologies, amongst other areas.
This innovation, combined with a flexible manufacturing footprint and Chart Business Excellence – a unified approach to operations, pricing, and efficiency – allows it to move quickly without sacrificing
“OUR PRODUCTS AND NUMEROUS TECHNOLOGIES ACROSS OUR PORTFOLIO SUPPORT OUR CUSTOMERS’ EMISSIONS REDUCTION, ENERGY EFFICIENCY, AND DECARBONIZATION INITIATIVES”
– JILLIAN EVANKO, CEO, CHART INDUSTRIES
even a fraction of quality or performance.
“Finally, we maintain strong proximity to our customers globally, with facilities and service operations across the globe. That local presence, combined with more than 170 years of technical expertise and a culture that prioritizes people and safety, allows us to act as a true partner – not just a supplier.”
Like many companies, Chart has had to navigate supply chain
constraints, inflationary pressures, and global uncertainty.
“What helps us manage these challenges is our diversified footprint, strong supplier and customer relationships, and an innovative culture.
“We continue to localize manufacturing where needed, lean into flexible production models, and use our Chart Business Excellence approach to drive efficiencies across operations,” Evanko reveals.
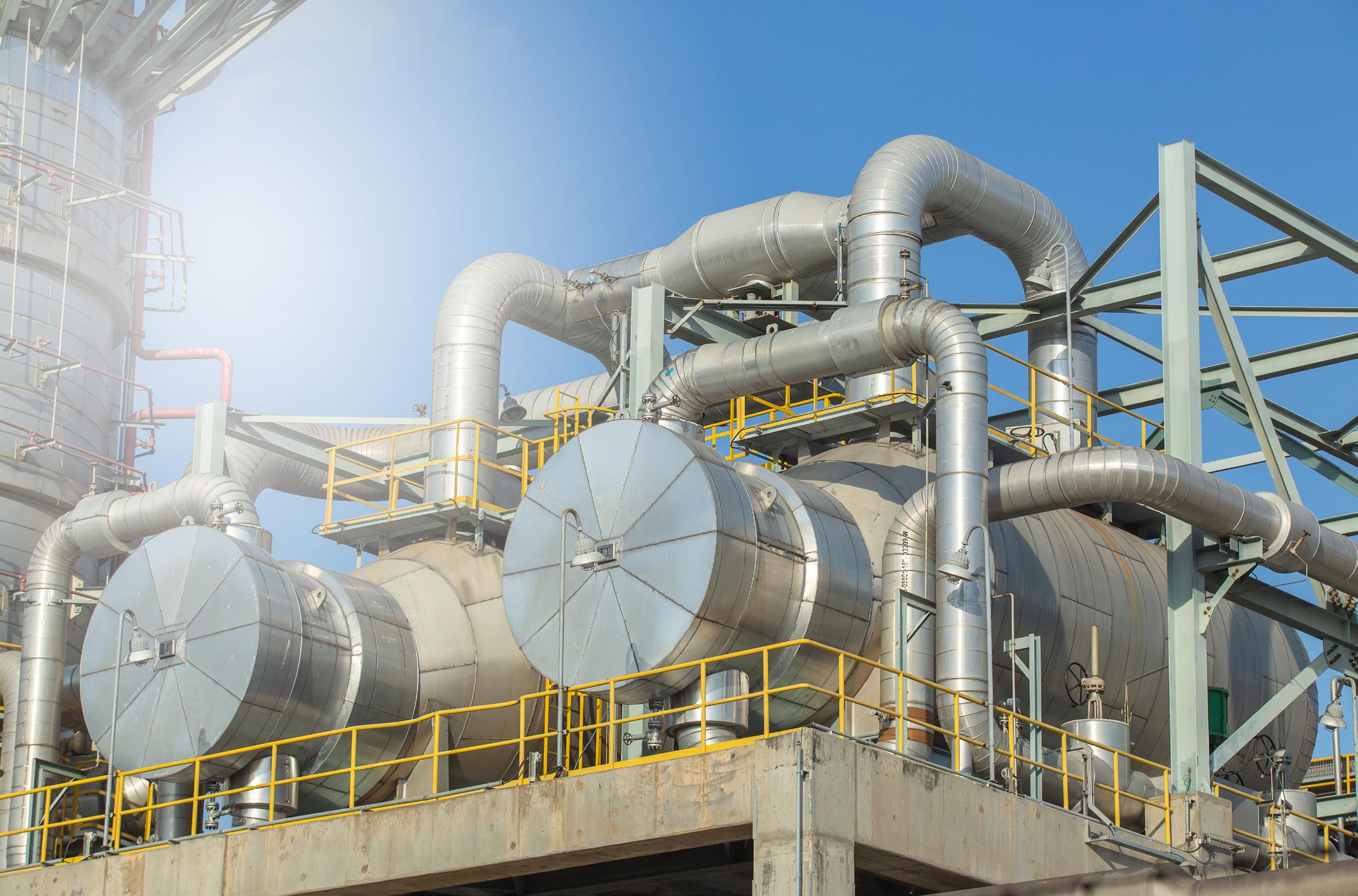
YOUR PARTNER IN PRECISION
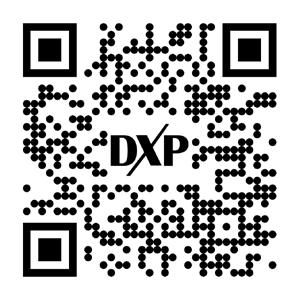
CHART’S ONGOING PROJECTS
One partnership Evanko is especially keen to highlight is Chart’s global master service agreement with ExxonMobil, including its ongoing work supporting the Rovuma LNG project in Mozambique.
“We are proud to expand our relationship with ExxonMobil through this enabling agreement. Chart’s industry-leading LNG technology, including our cold boxes and IPSMR® process, aligns with ExxonMobil’s commitment to efficient, scalable, and reliable LNG solutions,” she outlines.
“This agreement further strengthens our role as a trusted partner for ExxonMobil’s energy initiatives worldwide.”
In less than two decades, Chart has made a significant impact on the global LNG industry with its IPSMR® liquefaction technology.
Having curated a formidable reputation within the sector for its decades-long expertise with brazed aluminum heat exchangers, the company has quickly secured a leading position in the mid-scale segment.
With 29 million tons per annum of LNG liquefaction across operational and under-construction facilities, Chart has expertly established
CHART’S VISION AND MISSION
VISION:
Providing engineered solutions to enable a better tomorrow.
MISSION:
Chart connects its people, leading technologies, and global expertise to deliver innovative and sustainable solutions for its customers and the world around us.
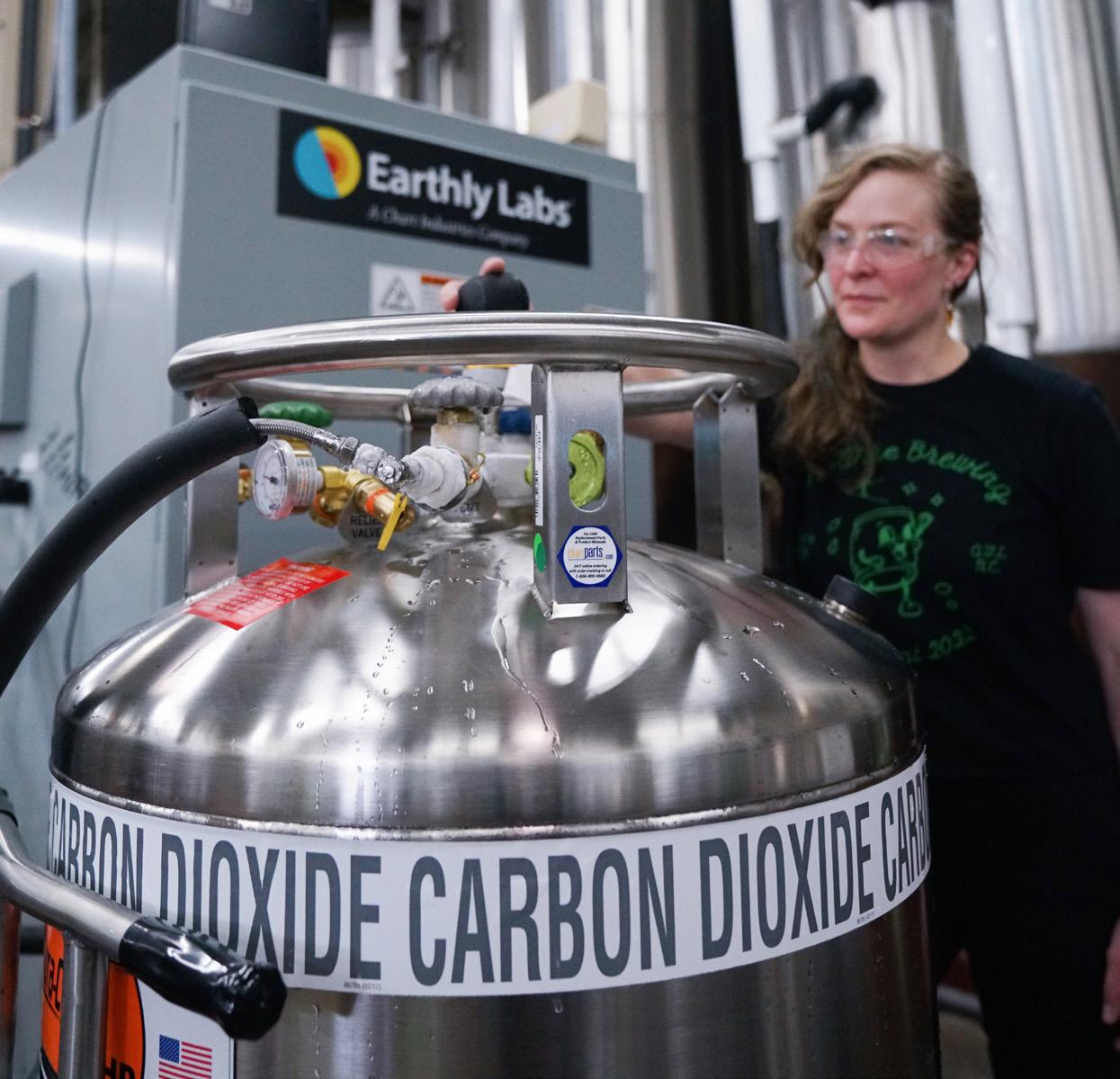
strategic partnerships with industry leaders like New Fortress Energy, Wison New Energies, Fluor Corporation, JGC, and various other international oil and gas and engineering, procurement, and construction (EPC) companies.
In the hydrogen market, Chart has delivered state-of-the-art equipment for the world’s largest hydrogen refueling station in China, supported the first green steel project in Sweden, and is enabling liquid hydrogen systems for marine and aviation markets.
“Our broad scope covers the full hydrogen value chain – from liquefaction and storage to transport, fueling, and end use – which allows us to serve a wide range of customers and end markets.”
Elsewhere, on the carbon capture front, Chart is advancing a number of initiatives across different industries and scales.
One example is its partnership with Bloom Energy (Bloom), in which the company is working together on an integrated solution that captures CO2 directly from Bloom’s high-efficiency fuel cells.
“What makes this partnership unique is how it combines commercially available technologies to make carbon capture more accessible and cost-effective. We’re also collaborating with Bloom on emerging opportunities in the data center space, where energy efficiency and emissions reduction are becoming critical priorities,” Evanko enlightens.
Parallel to this, across its portfolio of LNG projects, Chart is continuing to support a growing number of infrastructure projects globally – providing leading liquefaction, storage, and fueling systems that help meet near-term energy needs while enabling a lower-carbon future.
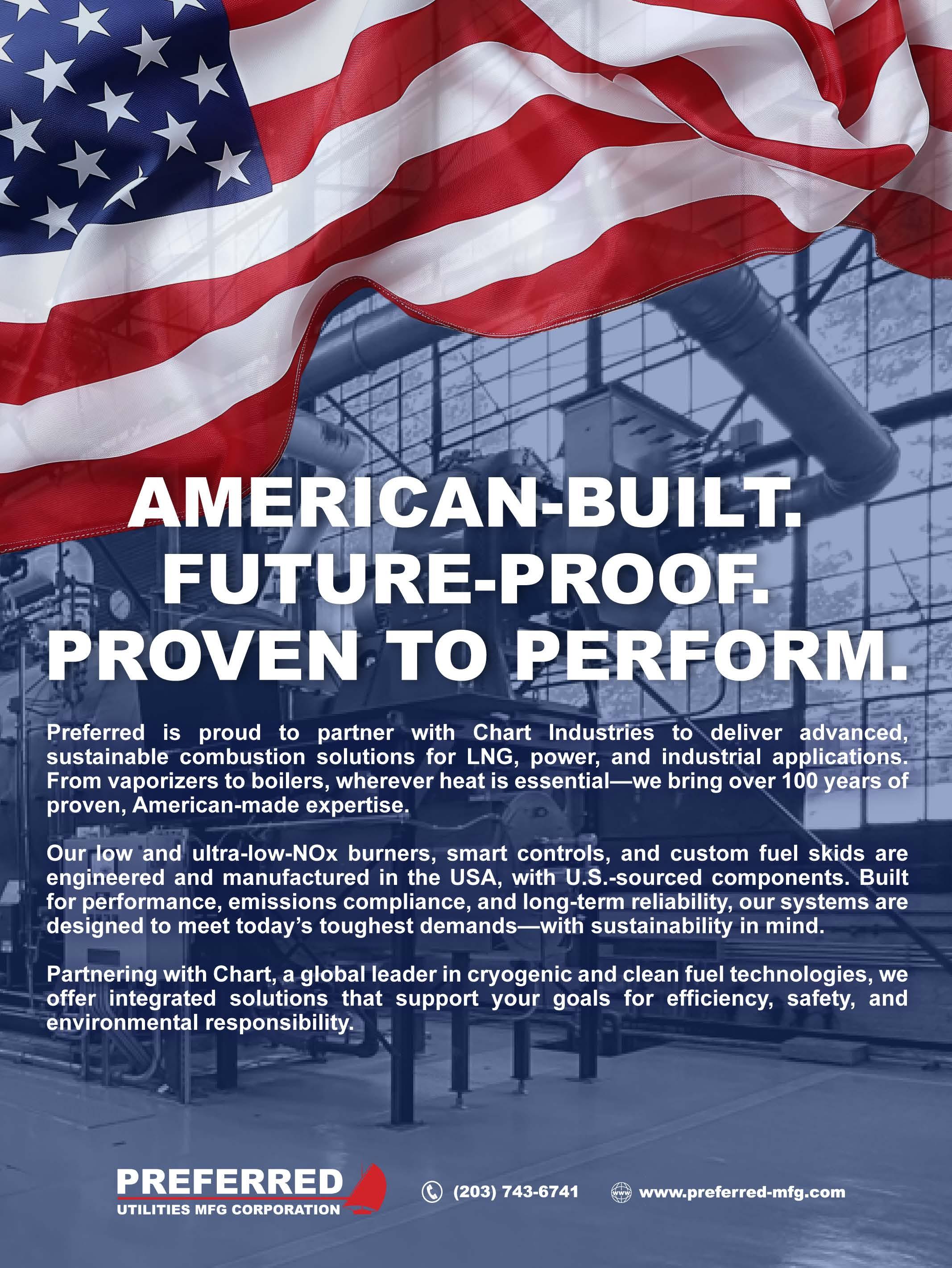
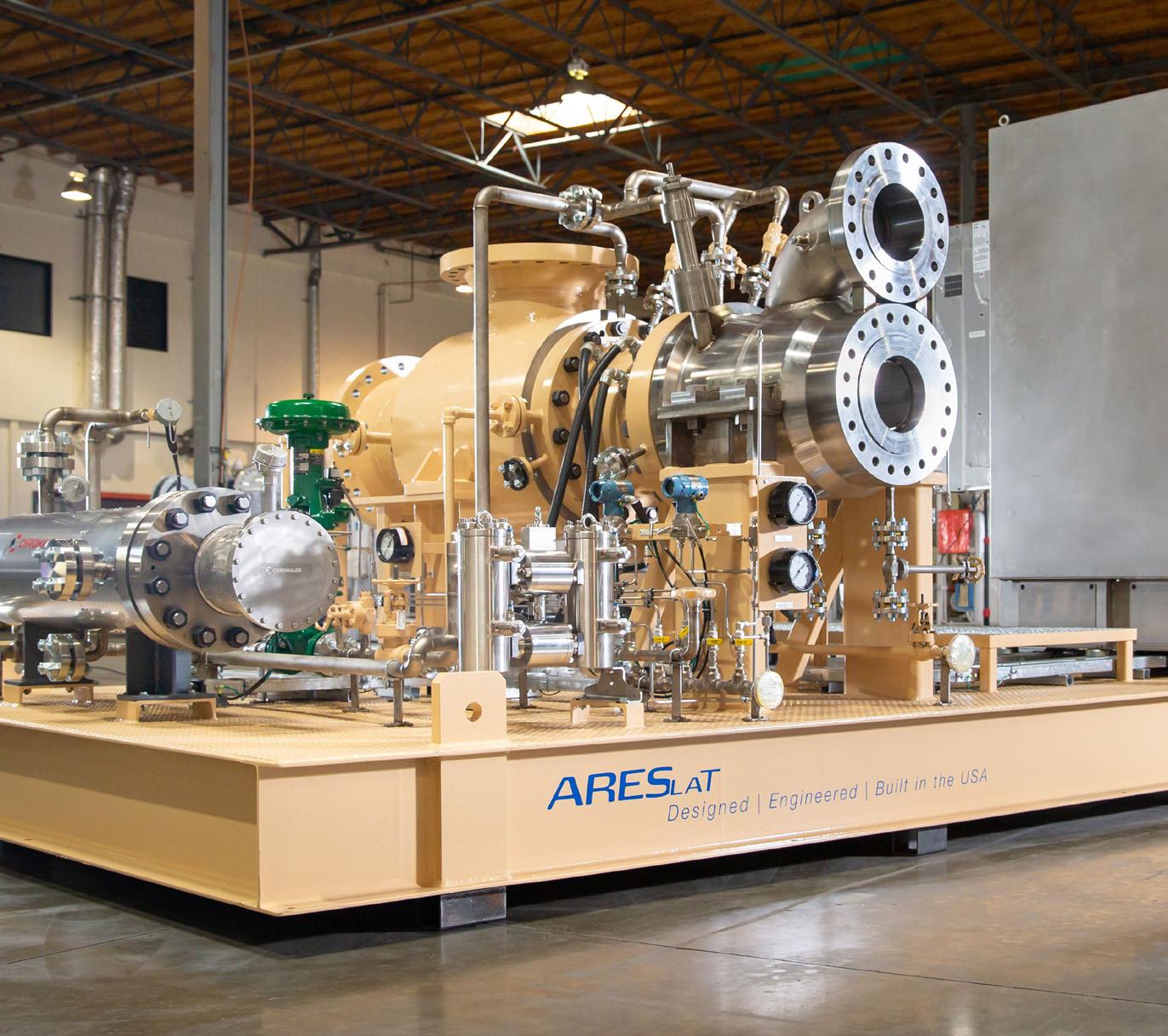
“SUSTAINABILITY DRIVES INNOVATION, STRENGTHENS OUR COMMERCIAL PIPELINE, AND INCREASINGLY, IT’S WHAT OUR CUSTOMERS AND INVESTORS EXPECT. WE DON’T VIEW IT AS A SEPARATE STRATEGY – IT’S FULLY EMBEDDED IN OUR CULTURE AND HOW WE OPERATE AND GROW AS A BUSINESS”
– JILLIAN EVANKO, CEO, CHART INDUSTRIES
“Our full lifecycle capabilities range from liquefaction start-up to service, spares, and retrofits.
“One thing we remain very proud of is that all of these efforts reflect the same core principle – enabling our customers to move forward with practical, scalable solutions that balance performance, cost, and sustainability.”
AEROSPACE HAS LIFT OFF
Chart is also trusted supplier of cryogenic equipment and engineered systems to the aerospace industry. Products and systems include cryogenic rocket propellant storage tanks, vacuum-insulated transfer piping, high-pressure pumping systems, knock-out drums, and deluge systems.
To date, the company has been integral in achieving operational success for its customers switching from RP-1 to LNG propellant, while it also provides on-pad storage of liquid oxidizers and upper-stage liquid propellant.
“We have been designing, building, and testing advanced cryogenic system equipment for more than half a century.
“Our team works closely with each customer to ensure that systems are designed in accordance with their requirements, function at their peak performance, and minimize risk to operators,” Evanko tells us.
“Built for long-term integrity, Chart system components and product designs provide the highest level of performance at optimal operating costs,” she asserts.
GOING WITH THE FLOW
In June 2025, Chart announced an all-stock merger of equals with Flowserve Corporation (Flowserve).
Flowserve is one of the world’s leading providers of fluid motion and control products and services. Operating in more than 50 countries, the company produces engineered and industrial pumps, seals, and valves, as well as a range of related flow management services.
“This combination takes our strategy to the next level – creating a differentiated leader in industrial process technologies with a broader portfolio, greater scale, and even more opportunity to serve customers across highgrowth markets,” Evanko passions.
“Flowserve brings deep expertise in flow control, and when combined with Chart’s leadership in thermal technologies, we’ll be able to offer fully integrated systems and solutions.
“That means our customers can benefit from project streamlining, shorter lead times, and more efficient process design – particularly in complex, multi-technology applications,” she says.
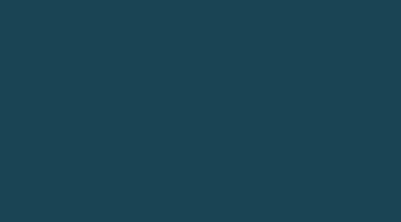
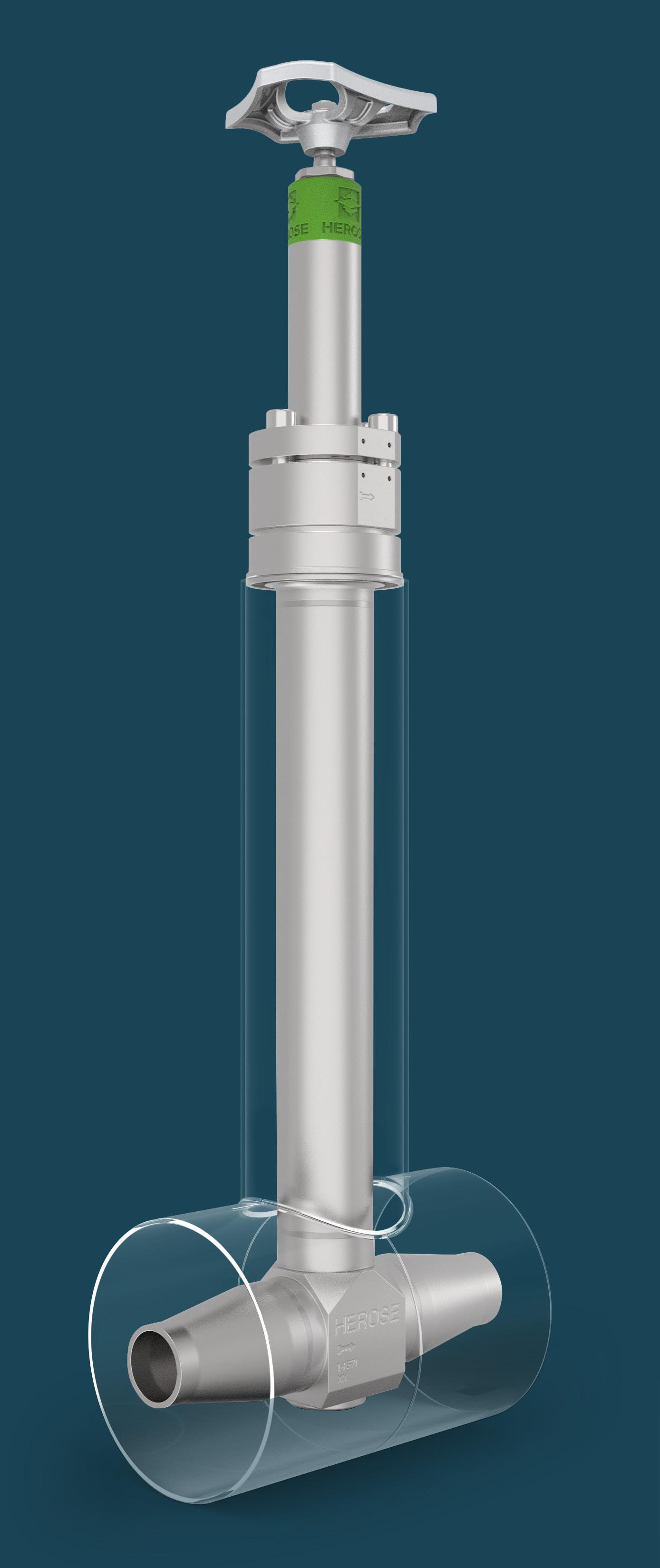
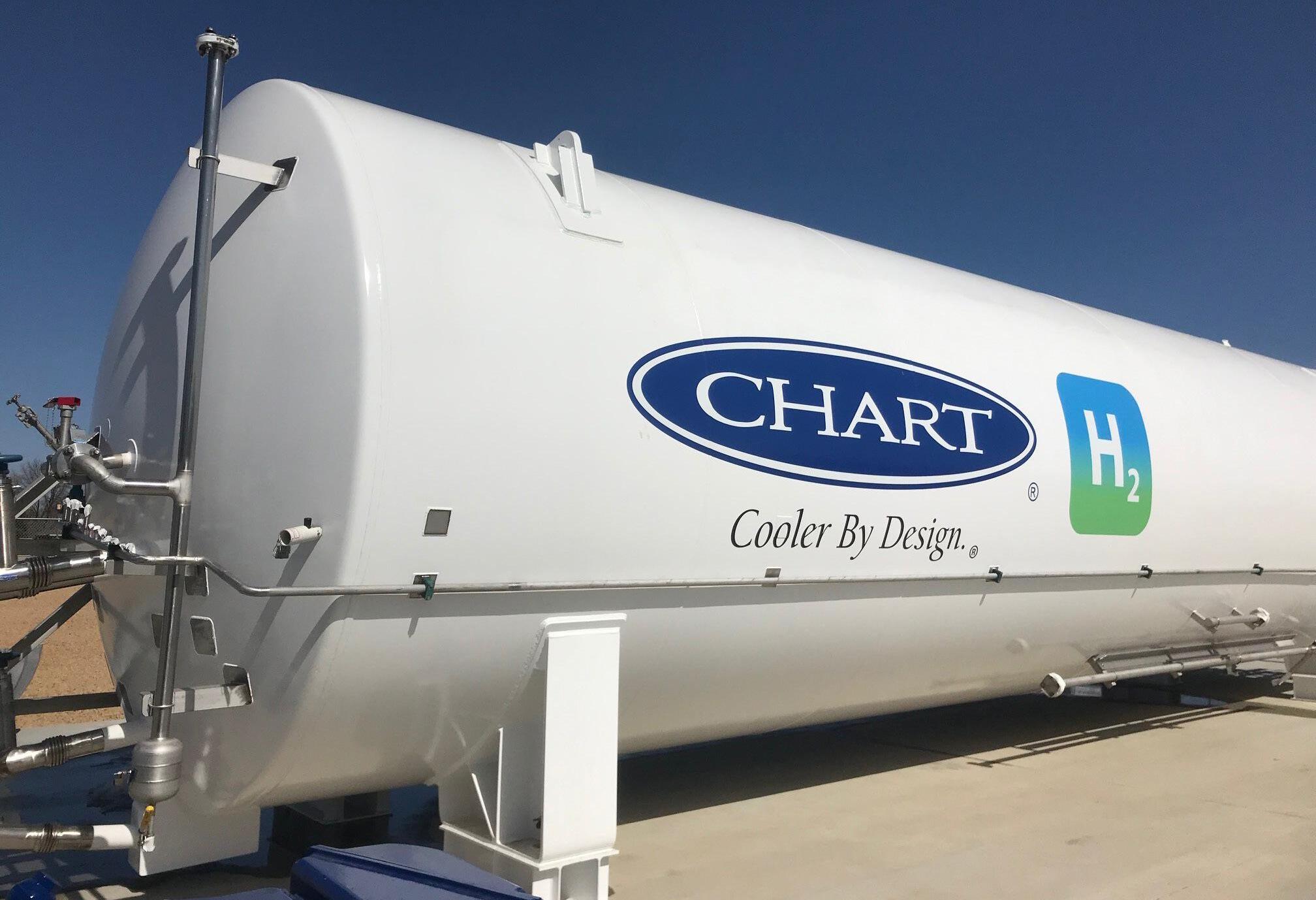
Furthermore, this merger of equals also aims to enhance Chart’s aftermarket, service, and repair capabilities, expanding the company’s geographic presence and strengthening its balance sheet by accelerating deleveraging.
“We see clear cost and commercial synergy opportunities with this merger of equals, and we’re excited about the long-term potential to return value to shareholders,” Evanko gushes.
Most importantly, the two sets of teams across both companies are energized about what this means for the future of each business.
“By bringing together our complementary technologies, commercial pipelines, and digital capabilities, we’re creating a platform that’s positioned to accelerate innovation, strengthen customer
partnerships, and drive long-term growth.”
Together, they are expected to have an enterprise value of approximately $19 billion based on the exchange ratio and the closing share prices for Chart and Flowserve as of 3rd June 2025.
With an installed base of more than 5.5 million assets in more than 50 countries, the combined company will expertly address the full customer lifecycle from process design through to aftermarket support.
STRATEGIC AND FINANCIAL BENEFITS
There are numerous strategic and financial upsides to the merger of equals for both Chart and Flowserve.
Firstly, with a comprehensive suite of world-class, differentiated solutions, it seamlessly brings
together Chart’s leading expertise in process technologies across compression, thermal, cryogenic, and specialty solutions alongside Flowserve’s leading capabilities in flow management.
Combining digital platforms that underpin this full suite of solutions will enable further opportunities to differentiate solutions, offering a comprehensive digital overlay, including monitoring and predictive capabilities.
Elsewhere, the combined company will boast leading capabilities across countless areas including industrial gases, data centers, space, transportation, carbon capture, energy, power generation, nuclear, chemical, LNG, water, mining, and minerals.
As such, with this wealth of capabilities, the combined company will be more predictable and resilient.
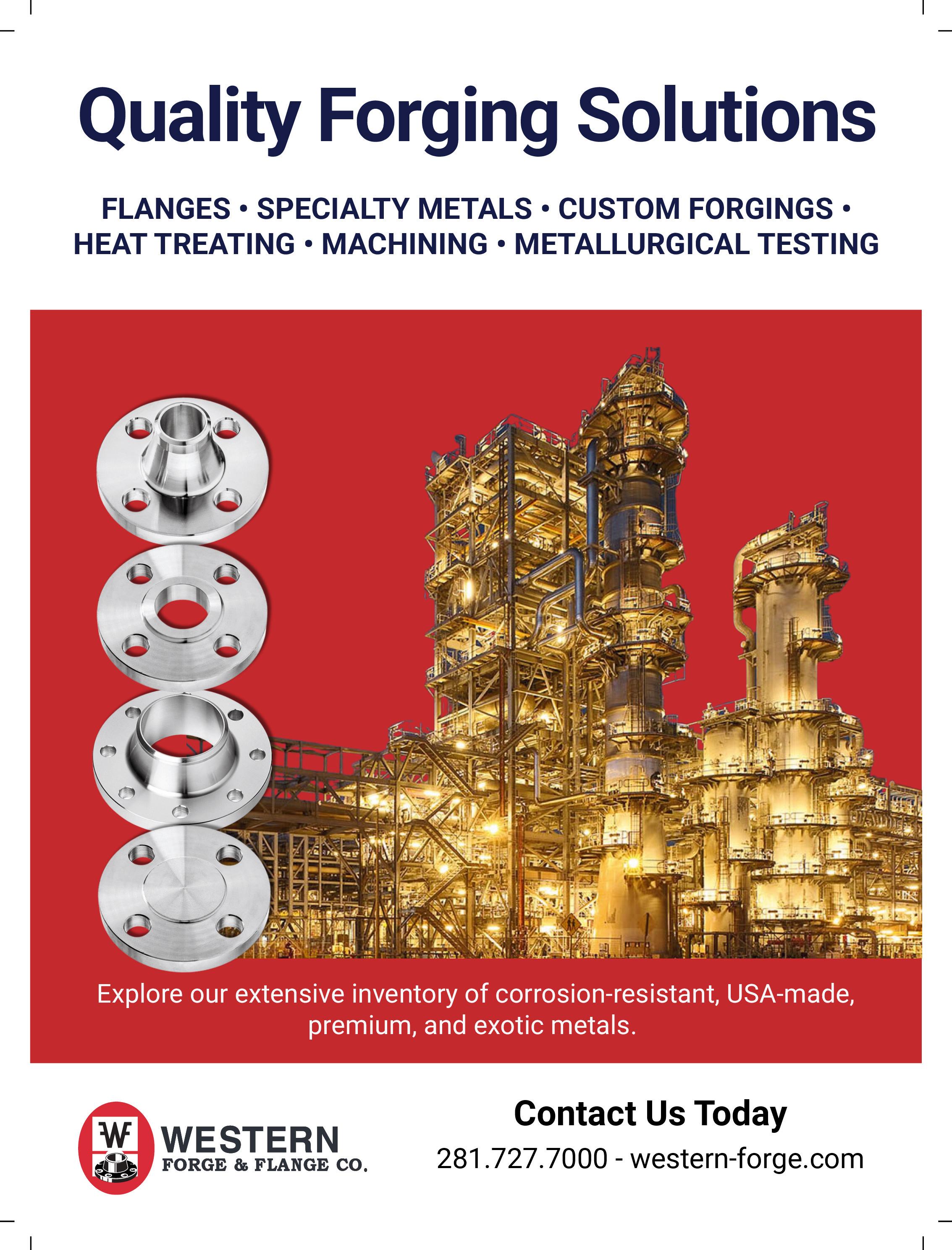
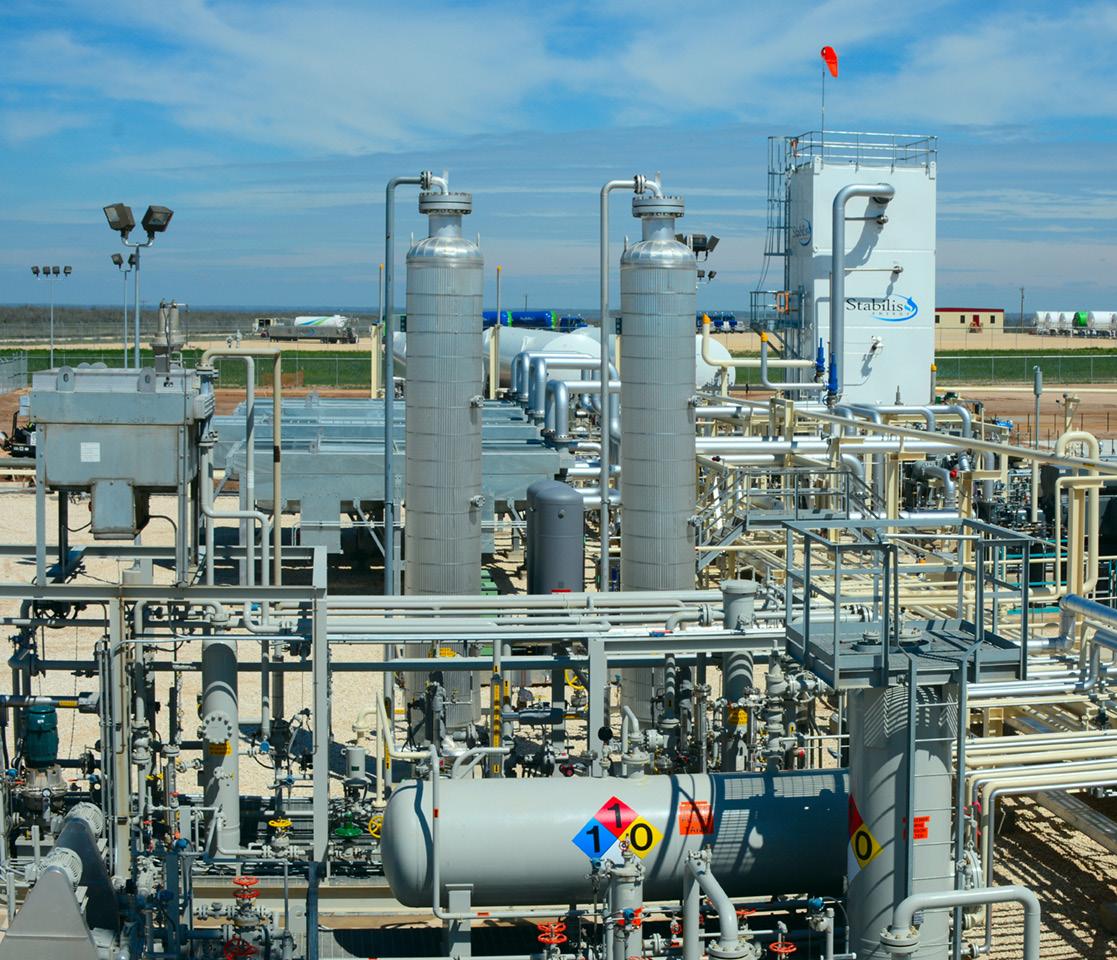
“THE US ENERGY SECTOR IS CURRENTLY BALANCING TWO KEY FORCES – RISING DEMAND AND THE NEED FOR GREATER FLEXIBILITY”
– JILLIAN EVANKO, CEO, CHART INDUSTRIES
A further benefit is that it will have significant recurring revenue streams, with a global installed base of more than 5.5 million assets and 42 percent of total combined revenue from aftermarket and service.
Chart and Flowserve expect to grow the aftermarket businesses by offering enhanced services and
solutions to customers through an expanded global installed base and broad geographic reach.
Upon closing, the combined company board of directors will comprise 12 members – six each from Chart and Flowserve – with Evanko proudly serving as Chair of the Board.
DEDICATED TO SUSTAINABILITY
Across each individual facet of the company, sustainability is central to who Chart is as a business and what it does.
“Our products and numerous technologies across our portfolio support our customers’ emissions reduction, energy efficiency, and decarbonization initiatives,” Evanko tells us.
“We provide the state-of-the-art infrastructure that enables lowercarbon fuels, scalable CO2 capture, water treatment, and cleaner industrial processes,” she follows up.
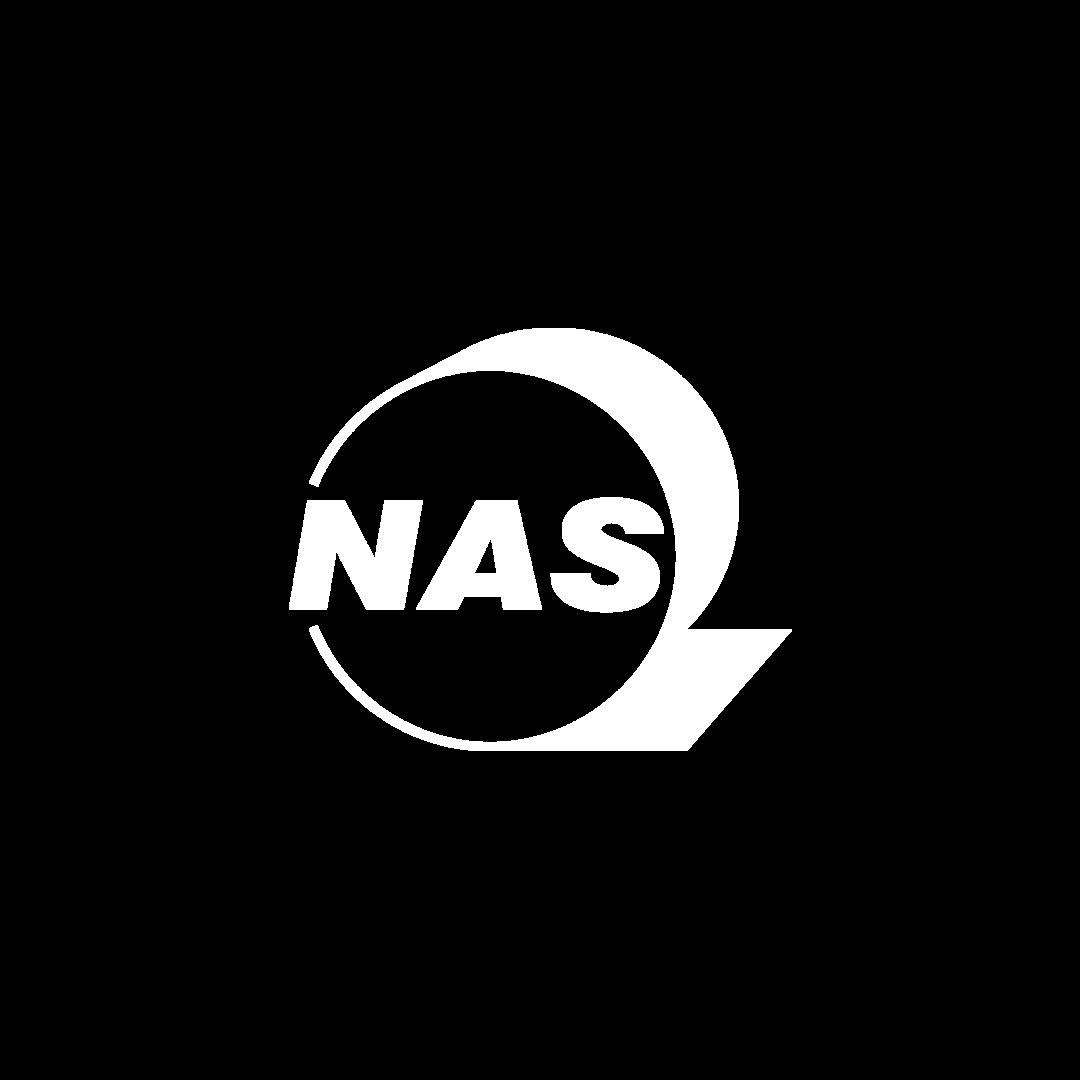
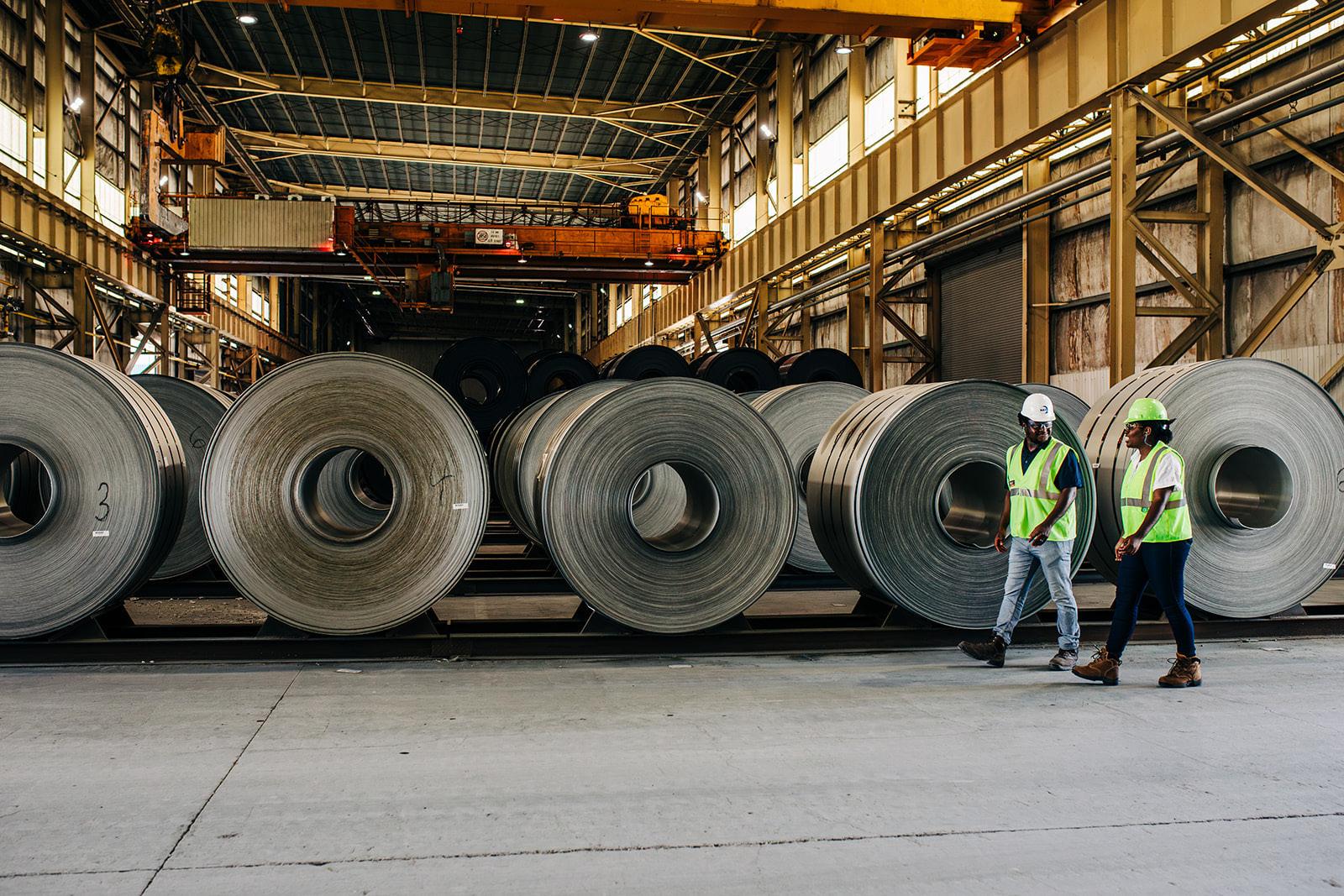
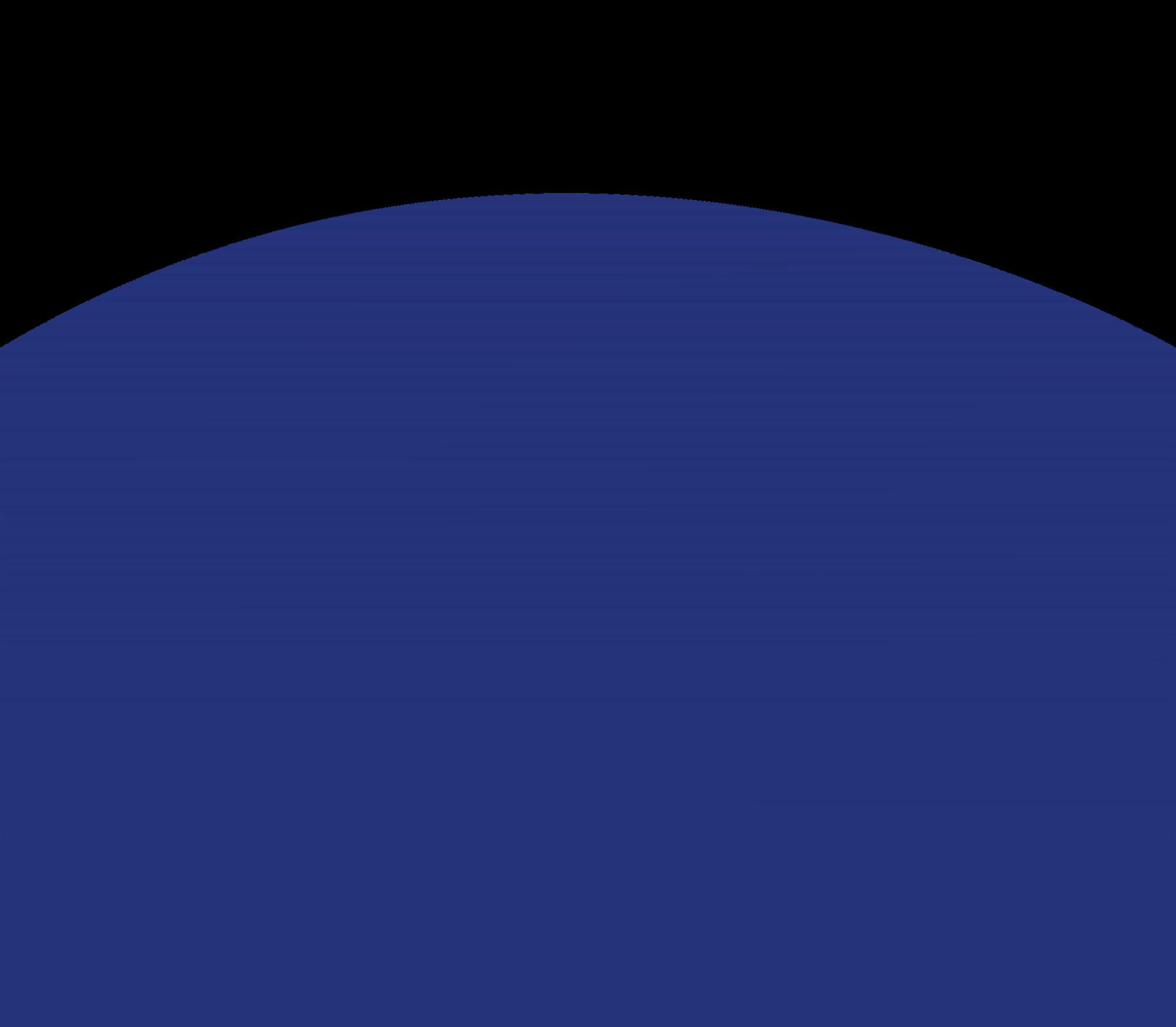
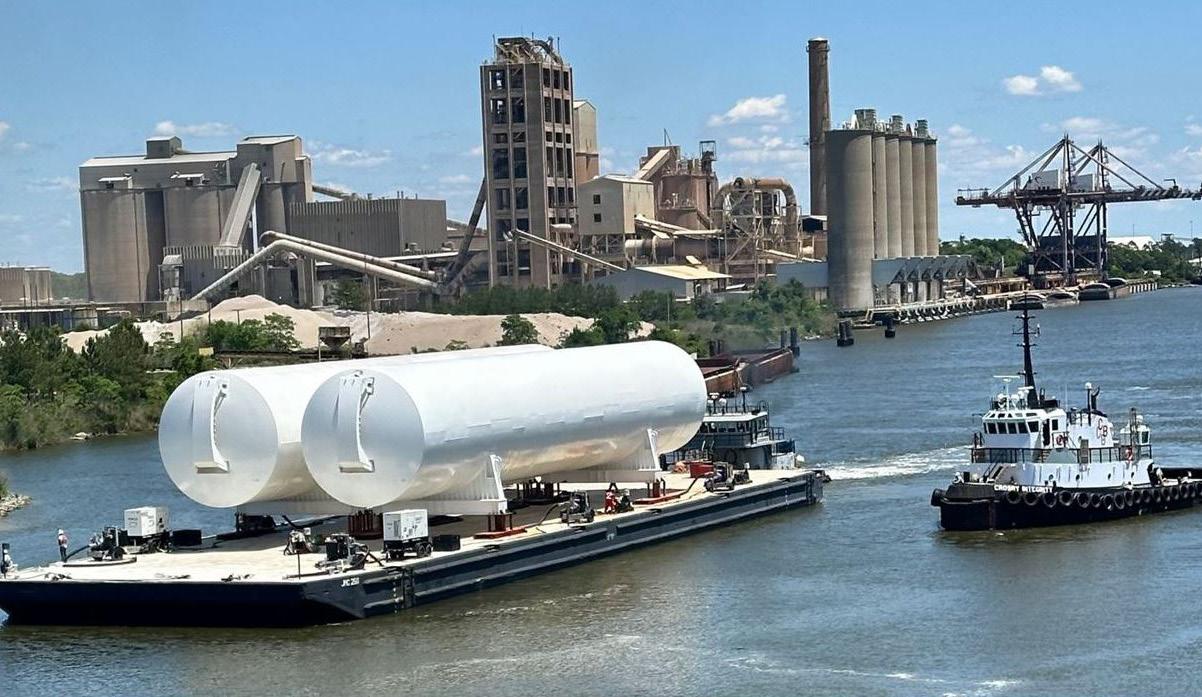
Beyond its products and solutions, Chart also holds itself accountable internally. This includes environmental, social, and governance (ESG)-linked compensation, supplier sustainability reviews, and operational efficiency programs across its entire global footprint.
“Sustainability drives innovation, strengthens our commercial pipeline, and increasingly, it’s what our customers and investors expect. We don’t view it as a separate strategy – it’s fully embedded in our culture and how we operate and grow as a business.”
ONE COHESIVE TEAM
Across the entire spectrum of Chart’s operations, every individual team member is encouraged to fulfill their potential, while their culture, identity, and experience is respected and valued.
“We understand that the more variety we have in our perspectives and ideas, the more successful we are. We not only take strides to give Chart team members the resources they need to make of their career whatever they dream it, but also ensure they feel good while doing it,” Evanko confirms.
HOW DO YOU REFLECT ON YOUR JOURNEY THROUGH THE INDUSTRY AND YOUR TIME WITH CHART SO FAR?

Jillian Evanko, CEO: “The beauty of our company is that we design and we build. This is something that I believe is really fun when you start to see the world’s need for more sustainable solutions, whether that’s what we do regarding LNG or all the way to green hydrogen.
“Elsewhere, we also serve water treatment, carbon capture, utilization, and storage (CCUS), food and beverage, and multiple different industrial applications. Now, every single one of these fields makes up one part of our Nexus of Clean™ strategy, which aims to help the world become cleaner and more efficient.
“This is also embedded in what we do every single day in our design and manufacturing operations, and I remain very proud of our work and the legacy that we are creating.”
“Our people are the reason we’re able to do what we do. From welders and machinists to engineers and sales teams, there’s a shared sense of purpose across the organization.”
One of Evanko’s personal priorities is creating an environment where people feel valued, heard, and are given access to a multitude of exciting career opportunities.
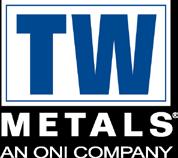
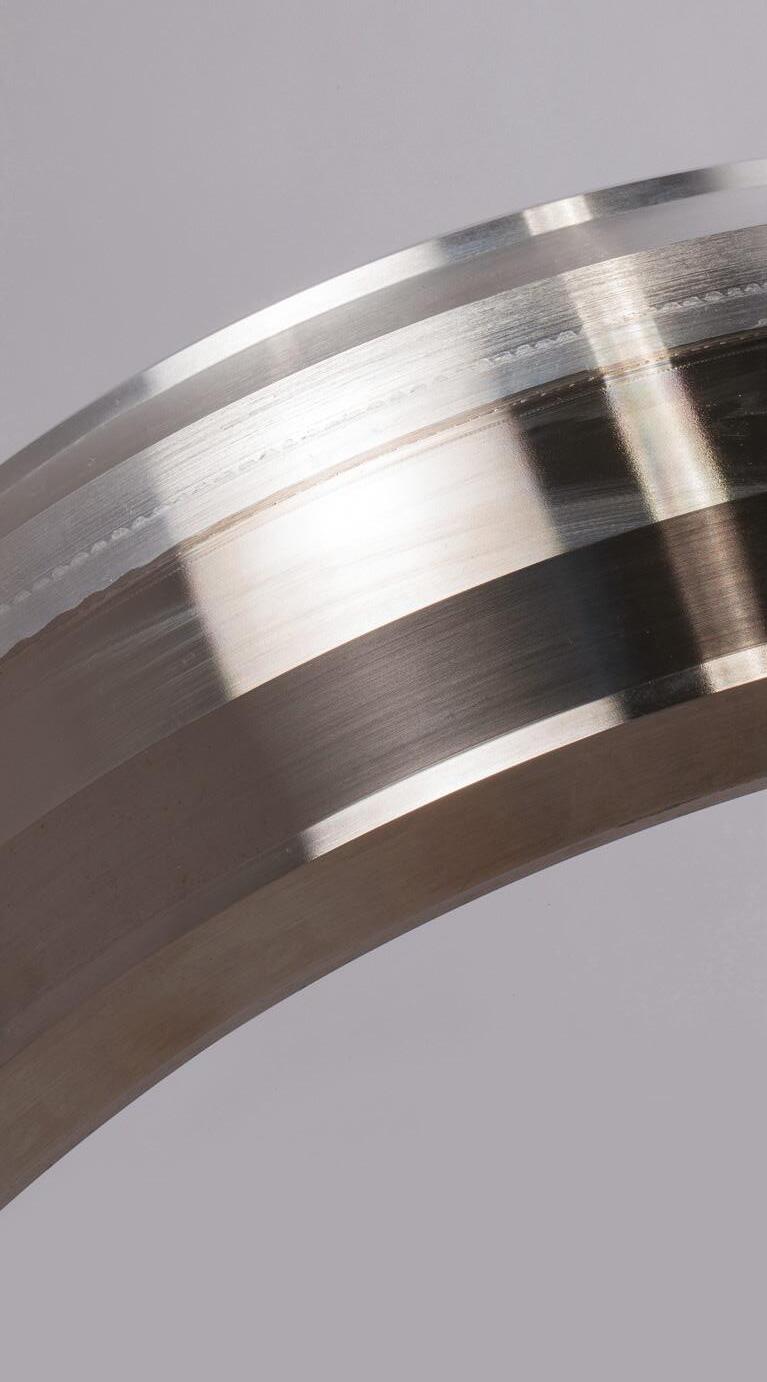
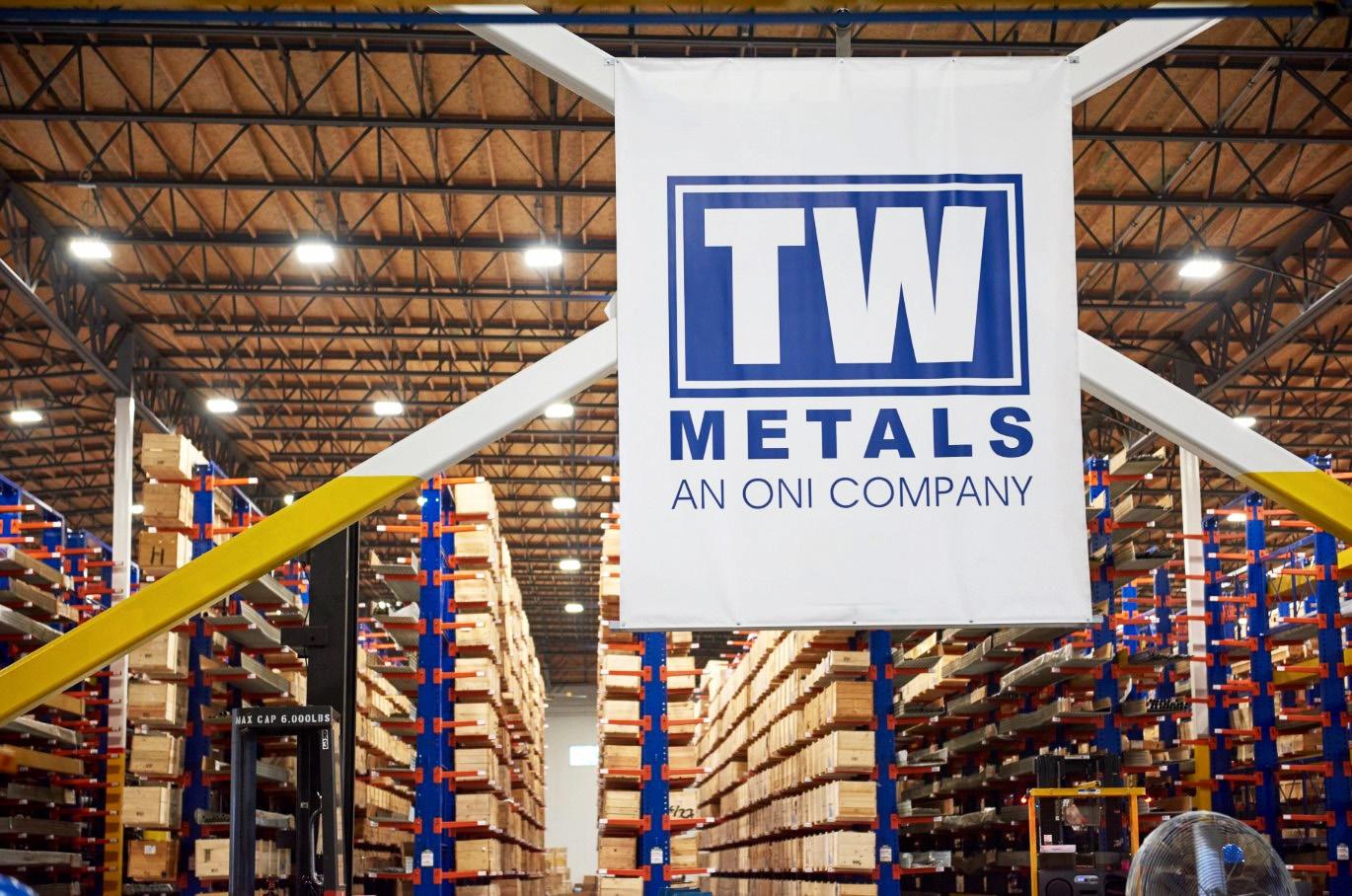
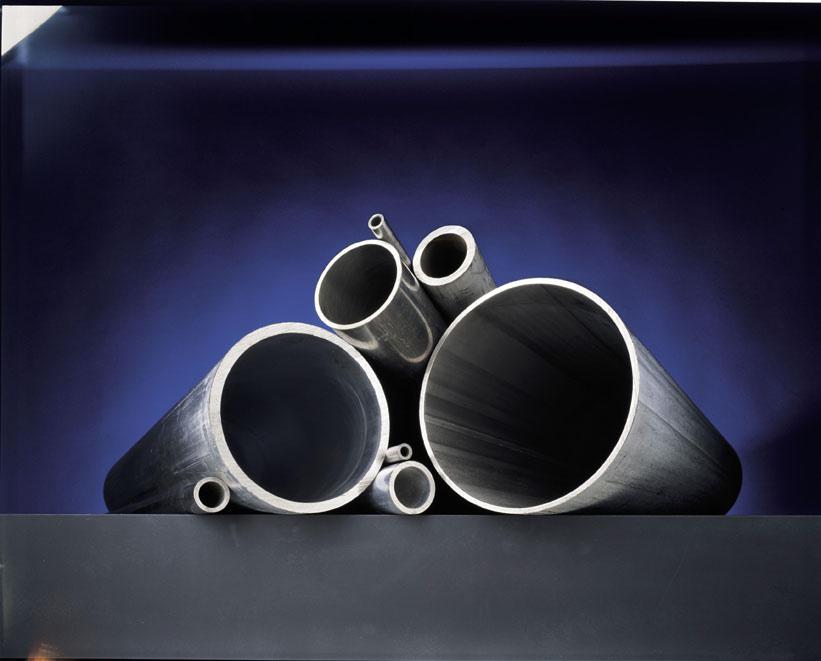
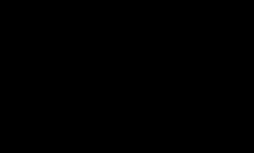

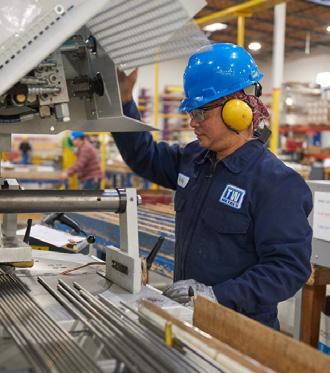
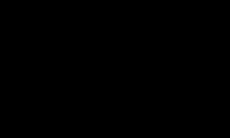
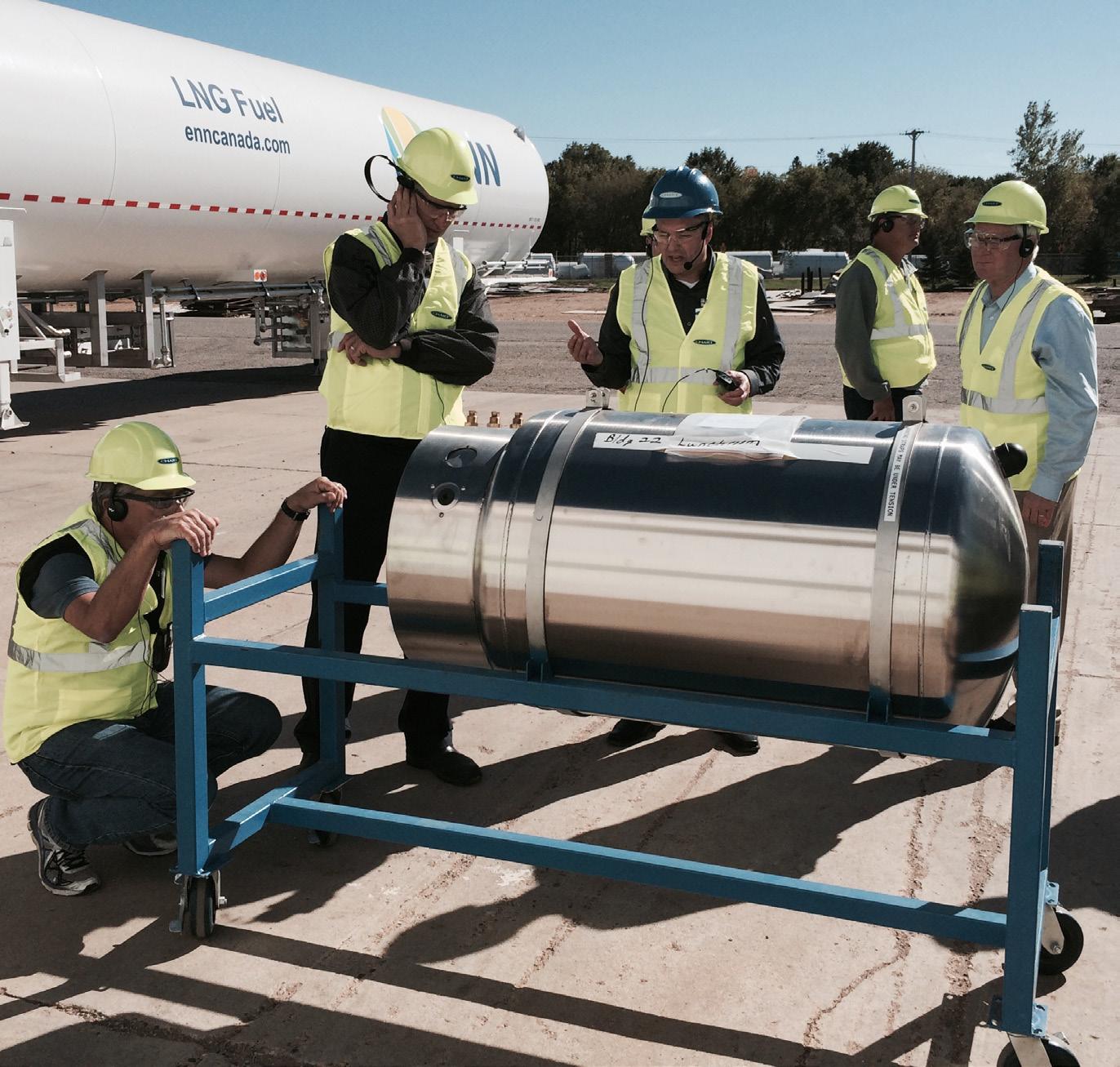
To date, Chart has launched several key programs focused on career and talent development and mentorship – including its numerous employee resource groups (ERGs) such as Chart Network of Women, which aims to empower women both personally and professionally.
As well as this, the company is proud of its Chart Rise and Prime initiative, created for young and emerging professionals as well as seasoned, experienced professionals focused on mentorship and Chart veterans.
“In 2024, each of our talent development programs expanded and continued to grow – including our Emerging Leaders Program, Rotational Engineering Program, Operational Leaders Program, Global Diversity and Inclusion Committee,
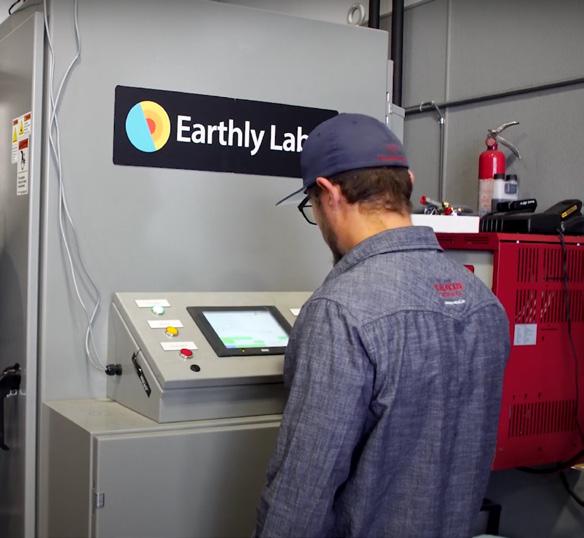
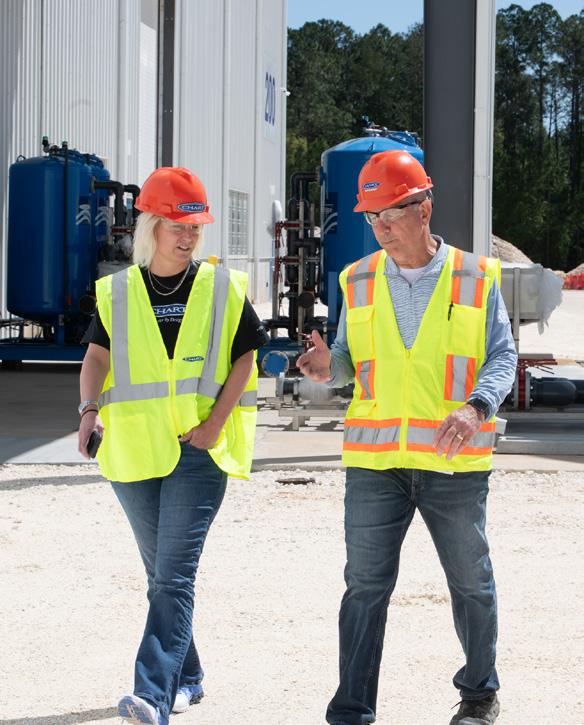
“OUR FOCUS IS ON DELIVERING FLEXIBLE, SCALABLE SYSTEMS THAT HELP OUR CUSTOMERS ADAPT AND LEAD – NO MATTER WHERE THEY ARE ON THEIR ENERGY OR SUSTAINABILITY JOURNEY”
– JILLIAN EVANKO, CEO, CHART INDUSTRIES
Global Sustainability Committee, and Global Welding Council,” Evanko lists.
“We also hit record participation in our Internship Program this summer as we welcomed 38 interns, ranging from high school to graduate school level,” she acclaims.
Of the 38 interns, over a quarter are returning – including three who are with the company for a third year running.
“As both a leader and a working mom, it’s important to me that we show the next generation that manufacturing is a place where they can build meaningful, exciting careers.”
RESPONSIBLE OPERATIONS
Corporate social responsibility (CSR) is built into every facet of how Chart operates.
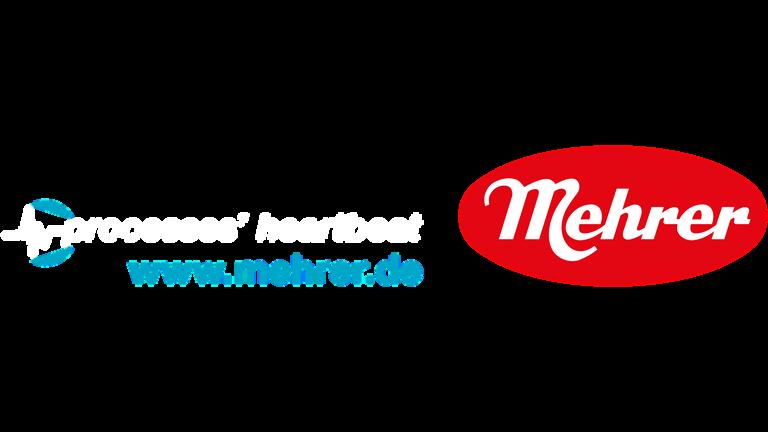
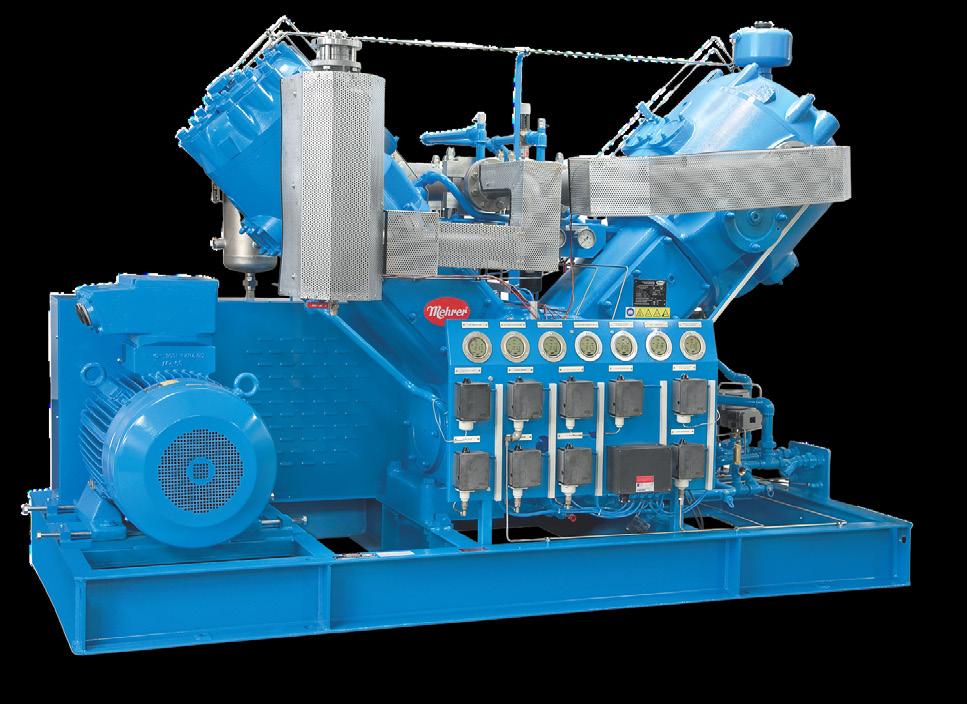
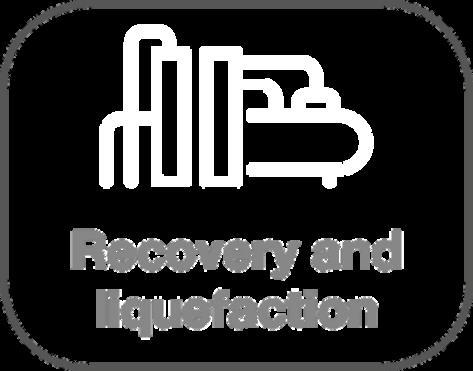
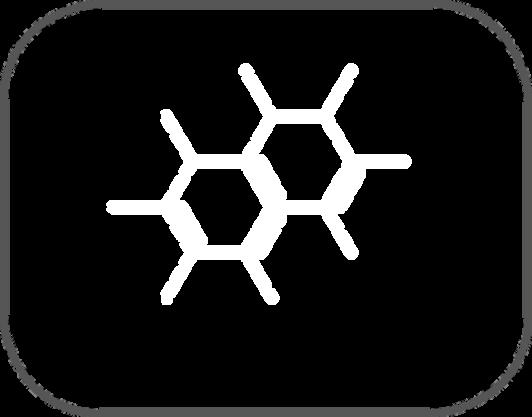
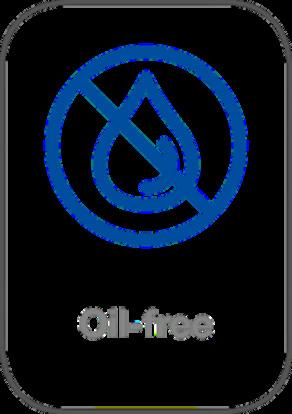
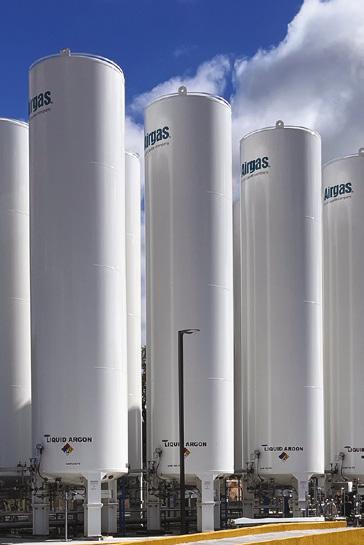
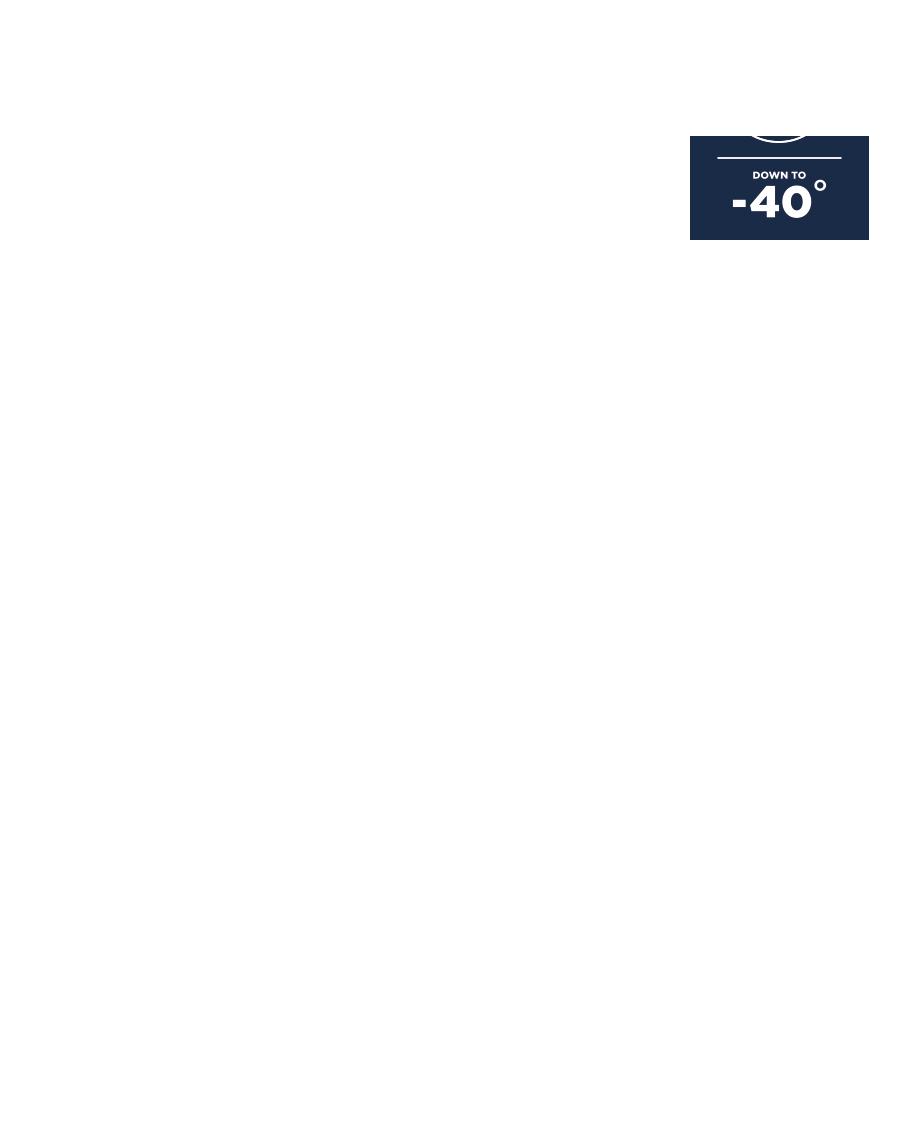
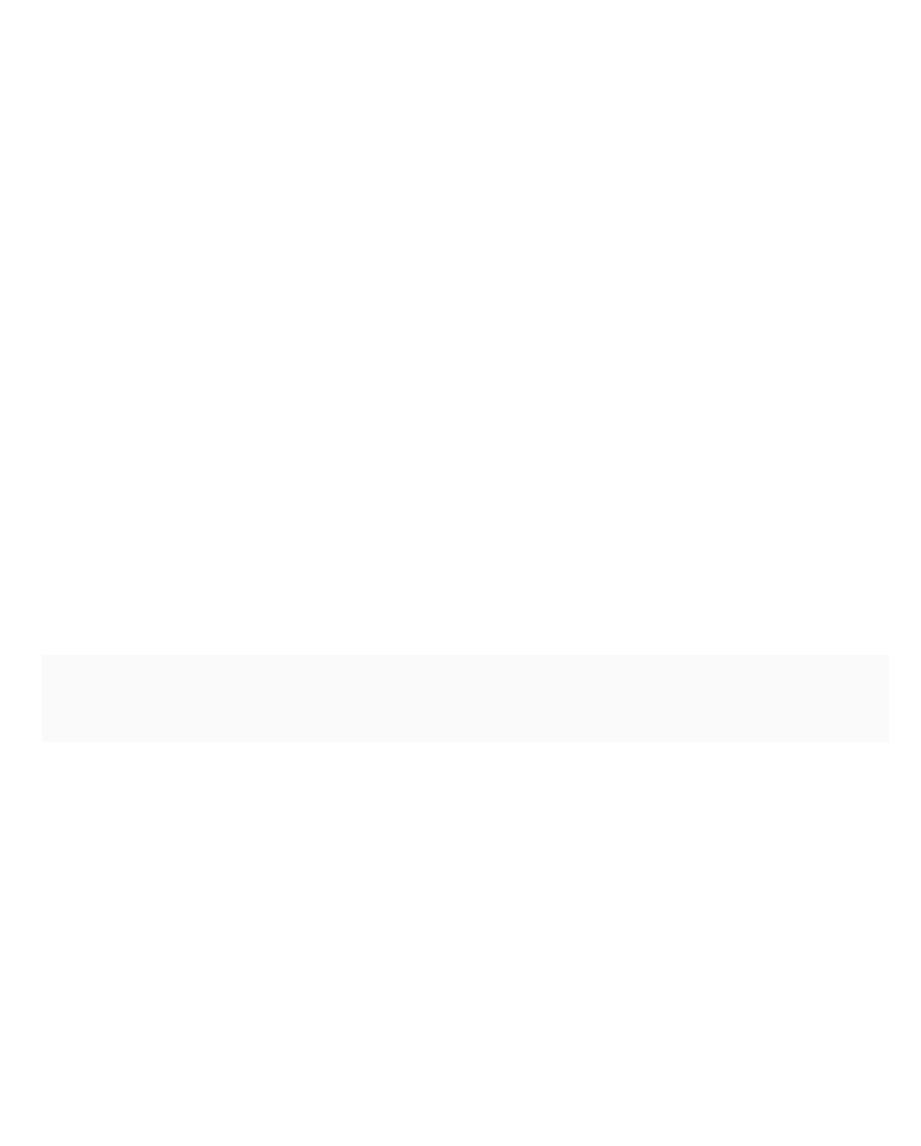
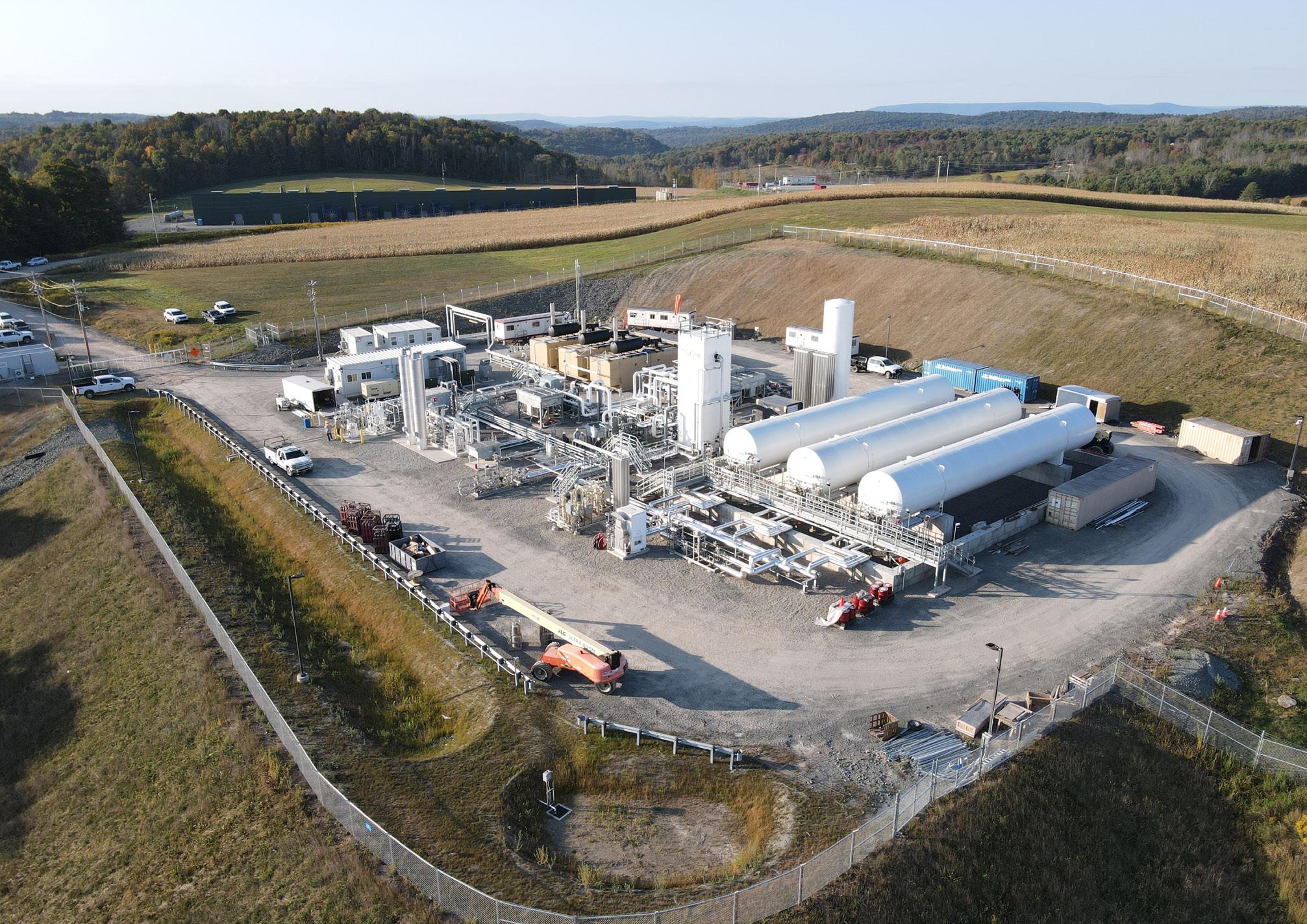
“CSR FOR US IS ABOUT MAKING A TANGIBLE, LASTING IMPACT IN THE COMMUNITIES WE SERVE AND EMPOWERING OUR PEOPLE TO LEAD THAT EFFORT”
– JILLIAN EVANKO, CEO, CHART INDUSTRIES
“Through our Giving Back Program, the company offers every team member globally one extra day of paid time off per year to support a charitable initiative of their choosing as well as funding-matched opportunities up to $250,” Evanko grins.
Meanwhile, Chart supports global and local giving programs, STEM education, and environmental initiatives across its numerous locations.
“Our teams regularly lead efforts such as tree planting and ‘Adopt-aHighway’ initiatives, volunteering
at food banks and other charities, as well as supporting disaster relief and environmental conservation programs – not because they have to, but because it’s part of our businesswide culture,” she explains.
“Internally, we’ve launched initiatives like our Global Diversity and Inclusion Committee, our ERGs, which are active in over 10 countries across our global organization, and ESG-linked performance targets at leadership level.”
In addition to this, Chart is also a proud participant of the United Nations (UN) Global Compact.
“CSR for us is about making a tangible, lasting impact in the communities we serve and empowering our people to lead that effort,” assures Evanko.
FUTURE BUILDING
Moving forward into a bright future, Evanko is keen to emphasize that the next phase for Chart – especially following its merger of equals with Flowserve – is about scaling smarter, growing faster, and delivering even greater value across thermal and flow technologies.
“One of the most compelling
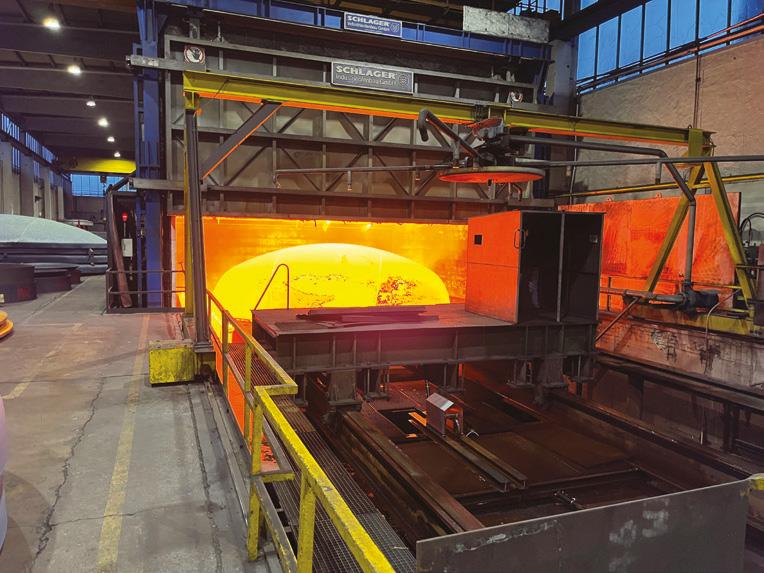
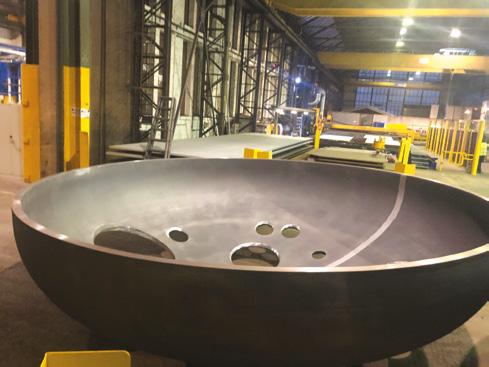
Mastering Challenges is Who We Are
KÖNIG + CO. is a global leading tank head manufacturer with two plants in Germany. With over 95 years of experience, we bring a relentless pursuit of excellence to manufacturing tank heads and components. We work with plastically deformable materials in sizes up to 323" for a single piece or 530" in crown and petals to deliver heads of all shapes and sizes to our customers.
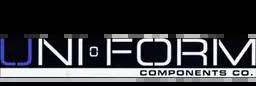
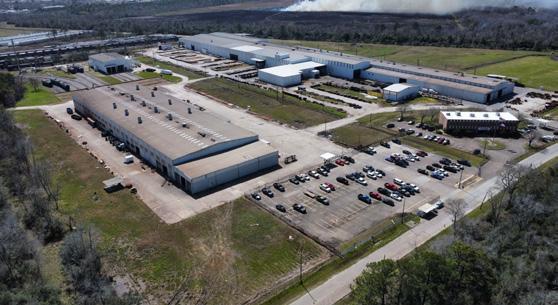
For over four decades, Uni-Form Components Co. has been North America’s trusted leader in the manufacturing of ASME Code Heads, Cylinders, and Custom Formed Parts. Backed by 45 years of experience and the right equipment and tooling, we have the most diverse offering of pressure vessel components in the industry.
ASME Section VIII Div. 1, Div. 2, and Section 1 Code Stamps, NSF Certification for Drinking Water Applications
• Heat Treating and Quenching
• Forming Capabilities from 0.0625” to 12” Thick

email: info@koenig-co.de web: www.koenig-co.de/en phone: +49 (0) 2738/601- 0
aspects of this exciting new combination is the ability to offer customers a single-point supplier for integrated systems, which streamlines projects, reduces complexity, and improves efficiency across the board,” she excites.
“As we level up, we will continue to focus on execution, safety, and innovation – and we’re deeply committed to creating impact for our customers and opportunities for our team members.”
As such, Chart has meticulously developed and grown to become a company that has combined deep technical expertise with adaptability and an entrepreneurial culture –supporting traditional infrastructure while also helping to accelerate the shift to cleaner, more efficient systems.
“Our major upcoming and ongoing priorities are continuing to drive results, focusing on securing a high
• Specializing in Carbon, Stainless, Aluminum, Clad, Nickel Alloys
From emergency services to complex custom forming, we deliver uncompromising quality and unmatched versatility. Our deep material inventory, skilled team, and rigorous in-house quality system ensure every component meets or exceeds ASME Code requirements.
When precision, reliability, and quality matter— trust the name that’s built on it. Trust Uni-Form Components Co.
level of safety, scaling solutions across our end markets to better support our customers, investing in people, and successfully integrating our merger of equals with Flowserve,” Evanko follows up.
Today, with a successful culture built on safety, integrity, innovation, and kindness, the company wants to be remembered not just for the solutions it has historically delivered, but for the way it empowers its people and has made a lasting impact on the industries and communities it serves.
From the early days of pioneering heat transfer solutions for cryogenic liquefaction to today’s green energy challenges, Chart has been there every single step of the way and will continue to build on its already impressive legacy and considerable influence and contribution to this burgeoning industry.
“The future we’re carefully building is one where engineering,
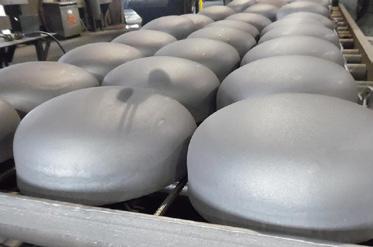
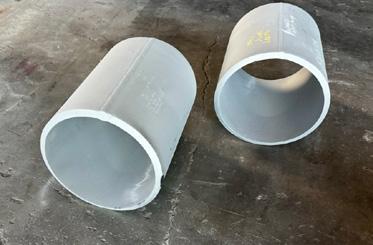
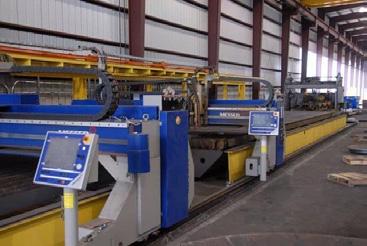
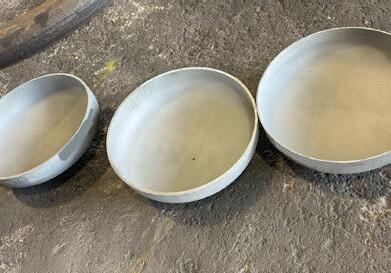
manufacturing, sustainability, and strong industry leadership come together to make a meaningful difference,” Evanko concludes firmly.
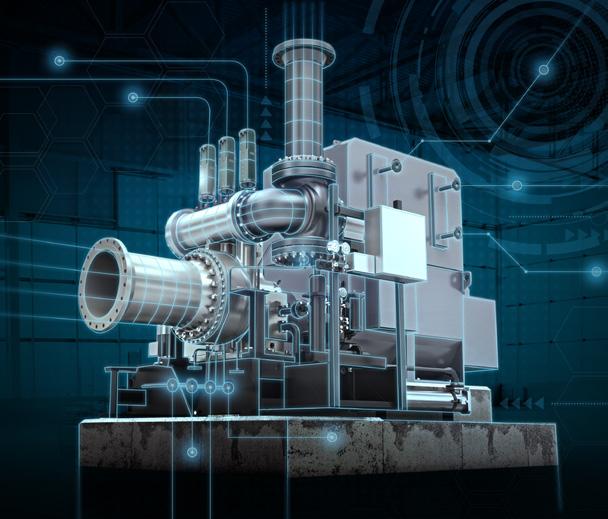
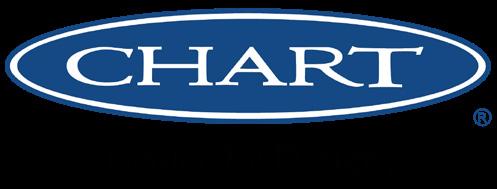
Tel: 1-770-721-8899
john.walsh@chartindustries.com www.chartindustries.com

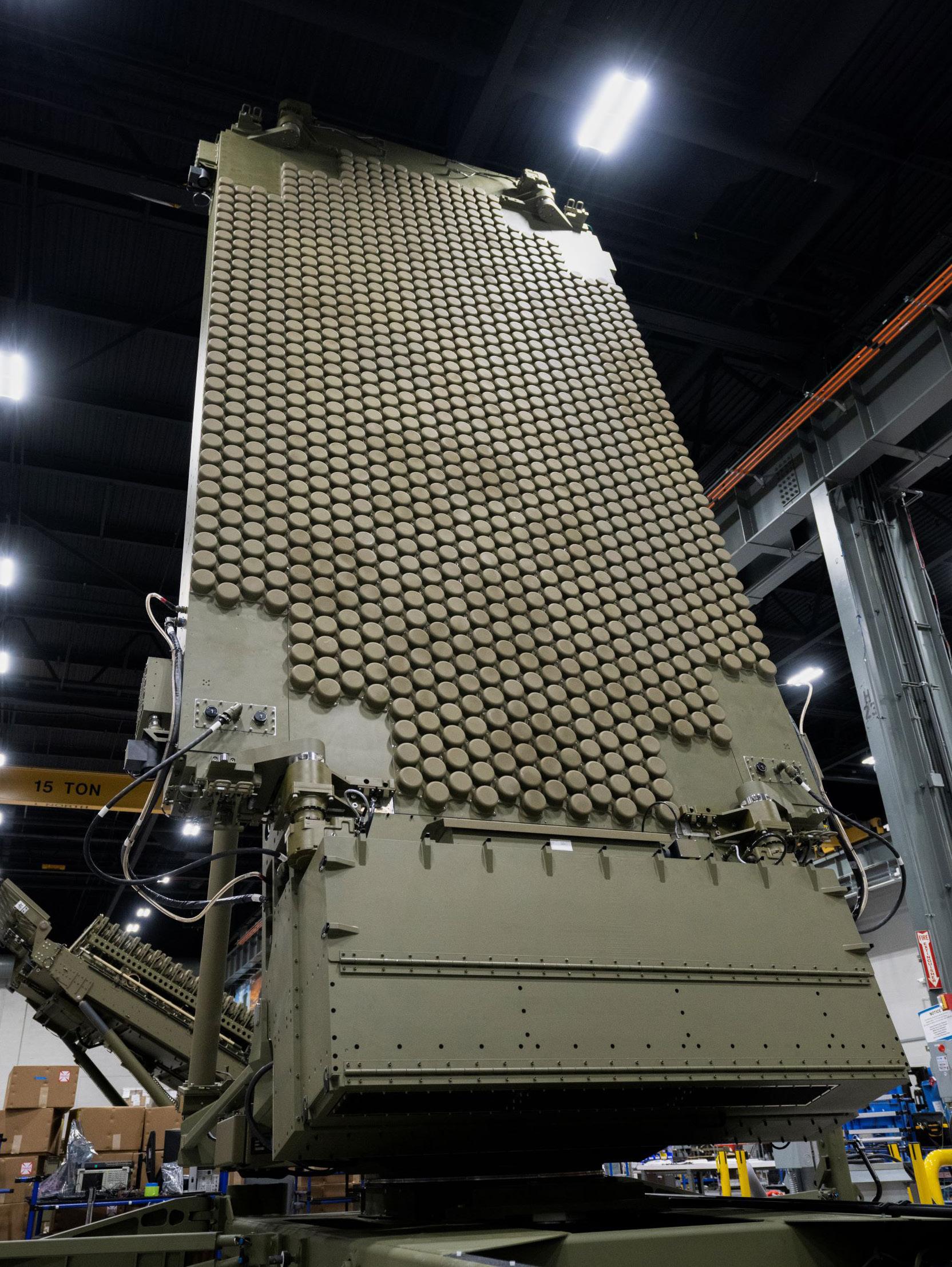
BUILDING THE NEXT-GENERATION MISSILE DEFENSE SHIELD
Specializing in defensive technology, solving complex challenges, and advancing scientific discovery while delivering innovative solutions that keep people safe, Lockheed Martin is an unparalleled global security and aerospace company. Rick Cordaro, Vice President of Radar and Sensor Systems, tells us more
Writer: Ed Budds | Project Manager: Michael Sommerfield
Established over 100 years ago in 1912, Lockheed Martin has had innovation as its beating heart and purpose as its soul since its humble inception.
This unrelenting vision and unwavering dedication have enabled the industry-defining company to expand leaps and bounds into the international juggernaut it is today, proudly working to make the world a better place through technology.
Currently, the company works across a multitude of business areas, including Aeronautics, Missiles and Fire Control, Rotary and Mission Systems, and Space.
“Lockheed Martin is a 21st-century security company, meaning we provide security and deterrence for all our warfighters, whether they’re at
home or our closest allies,” introduces Rick Cordaro, Vice President of Radar and Sensors Systems.
This is accomplished through various products, services, and capabilities – such as hardware like aircraft and radars, software like command and control systems, or all the software that rides on top of the hardware.
“It’s truly a global company, and what makes it global is not only the customers we serve but the partners we have across the world. We work with a vast network of suppliers and teammates who help us and our customers deliver every single day,” asserts Cordaro.
The broader defense and manufacturing industry is currently in a particularly exciting yet challenging place, driven by global demand. This
is due to the current global dynamics and the emergence of near-peer threats, which have significant implications for US manufacturing.
“There are a lot of challenges, but US ingenuity has always shone through and delivered; that is what we’re going to do here, not just because it’s in our backyard, but because we have to,” details Cordaro.
To meet their needs, the company is digitally transforming its operations throughout the design and production process, ensuring the greatest efficiency without sacrificing quality.
“It’s imperative that we maintain the safety and security of our nation, and that’s more than just military strength – it’s the industrial base that backs it up.”
21ST-CENTURY SECURITY
The 21st-century security environment is incredibly complex. Threats move fast, and adversaries are well-equipped and well-connected. Success depends on dominance in all domains.
Lockheed Martin has diligently remained at the forefront of threat detection throughout its history, becoming the trusted partner for armed forces across the world.
The company has maintained its unparalleled position due to its cutting-edge innovation and passion toward helping US and allied forces strengthen global security.
“Our mission is deterrence as part of 21st-century security solutions. Our goal is to ensure that our nation, partners, and customers are ahead of ready,” denotes Cordaro.
“Yesterday’s approach isn’t good enough for today’s demands. Modern forces need a Mission Integrator – a way to unite platforms, networks, and people to deliver on a mission need, even when staring down a sophisticated and determined adversary.”
Lockheed Martin does this by working with warfighters and customers to truly understand what they need in order to achieve success. It’s not just about bringing something out of a catalogue to a customer – it’s about understanding their unique requirements, where they are today, where they need to be in the future, and what their mission will look like.
The company relies on its talented team members who specialize in different products and services, including how products are made, designed, and built.
“We also have a lot of incredible people, many of whom are veterans who understand how these systems get employed and what these capabilities must perform in battle,” insights Cordaro.
“That is really how we do it – by understanding what our customers’

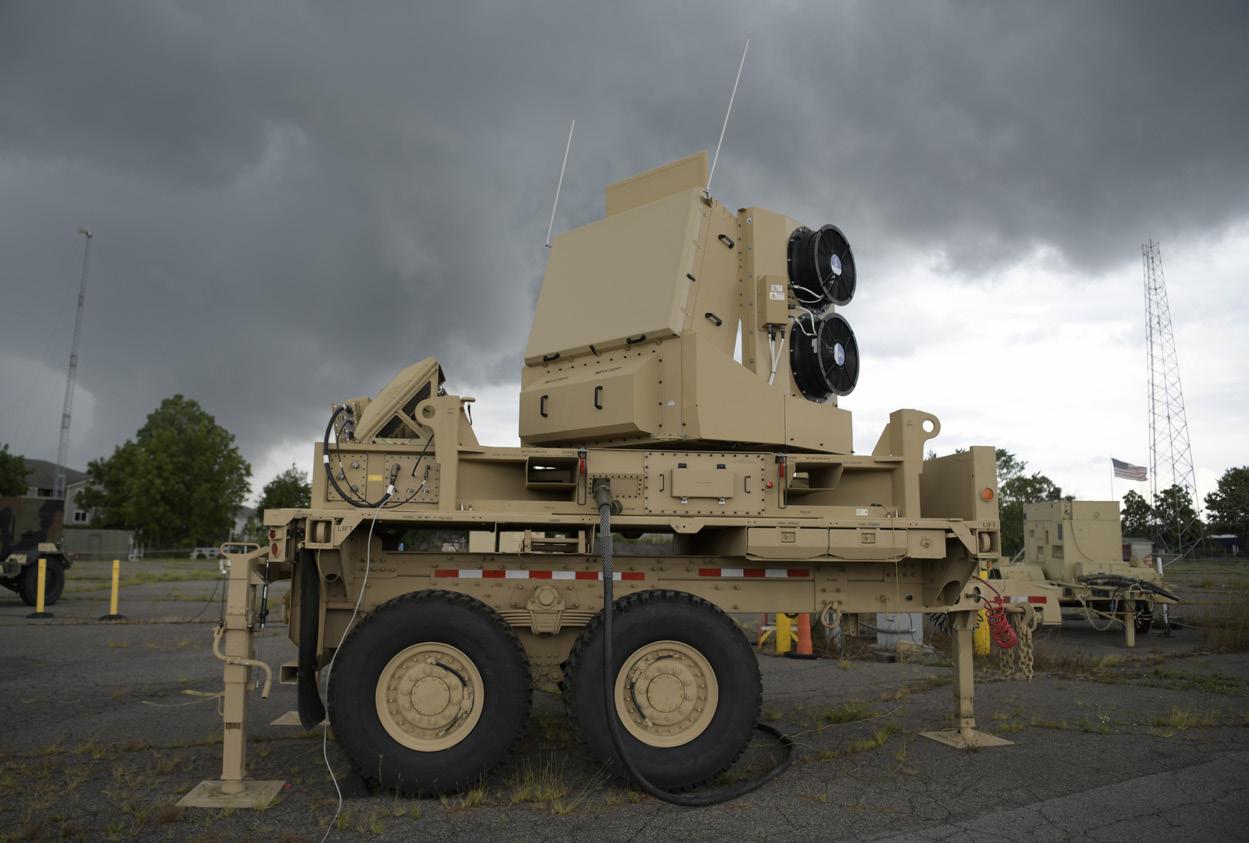
missions are and how that translates into requirements for what our products need to do.”
This unrelenting vision allows Lockheed Martin to confidently take on challenges that others may deem impossible, thus elevating the company to global market leadership status.
DETERRENCE BEGINS WITH DETECTION
Deterrence begins with detection
is not only a phrase, but a mindset that remains at the forefront of the company’s daily operations.
“You can’t defend what you can’t see. If you have the opportunity to see the threats, you can protect against them,” expands Cordaro.
“Hence, deterrence begins with detection is our tagline because what we build are tools that help our warfighters detect.”
A prime example of this motto is Lockheed Martin’s long-range
detection systems, such as the Long Range Discrimination Radar (LRDR), which can see thousands of miles away and distinguish between a lethal re-entry vehicle and a benign piece of debris.
LRDR is a vital component of the Missile Defense Agency’s (MDA) strategy to protect the US from ballistic missile attack. As a longrange radar that provides precision metric data to improve ballistic defense discrimination, the LRDR keeps pace with evolving ballistic missile threats and increases the effectiveness of ground-based interceptors.
“We have long-range surveillance radars like the TPY-4, which can see
aircraft and unmanned aerial vehicles (UAVs) coming in at low altitudes and high speeds. As you get closer, we have systems like the Sentinel A4 and TPQ-53, which are missile and air defense systems. Then you have counter target acquisition radars that allow you to see rockets, artillery, mortars, cruise missiles, and UAVs,” insights Cordaro.
All of these radars enable warfighters to accurately and precisely determine which action to take next.
Additionally, the company has systems such as the APY-9, which is the radar that rides on the US Navy’s E-2D Advanced Hawkeye, acting as the eyes of the fleet.
CAN YOU TELL US MORE ABOUT YOUR 22-YEAR CAREER WITH LOCKHEED MARTIN AND HOW YOU BECAME INTERESTED IN THE INDUSTRY?
Rick Cordaro, Vice President of Radar and Sensor Systems:
“I started at Lockheed Martin 22 years ago, right out of school. I graduated with a degree in engineering, and what brought me to Lockheed Martin was the fact that we make things. Not only that, but we make big things that are highly visible, useful, and important.
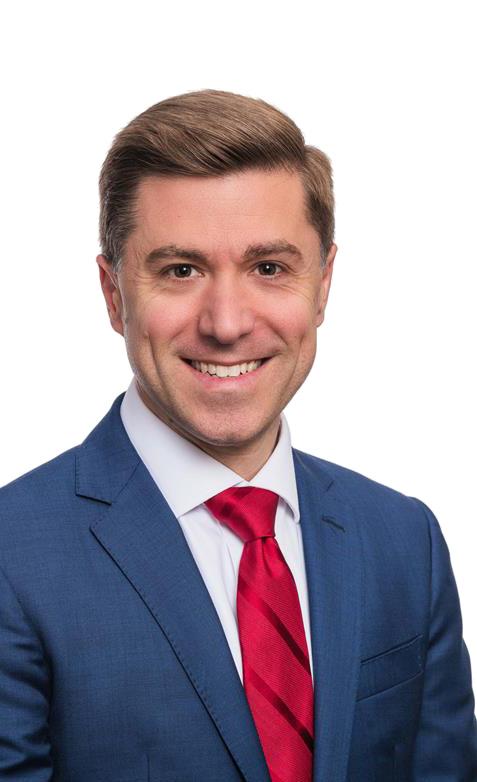
“There’s a lot of neat stuff that happens in engineering, but nothing as tangible as when you build a system – whether it’s a vehicle, aircraft, radar, or something else serving your country. That’s what brought me into the industry.
“At our factory here in Syracuse, you can go in the front door, see the engineering team and management hard at work, and walk straight through to the back of the building where our factory is and see everything from the stock room and raw materials coming in to the radars driving out the dock. Knowing that soup to nuts, you’re making products that save lives, is powerful.”
“When you think about protecting an aircraft carrier, you’re protecting a big floating city. To do that, you need forward-deployed assets. The APY-9 can provide thousands of square kilometers of coverage, ensuring the ship’s billions of dollars of assets have time to react when threats are inbound,” explains Cordaro.
AT THE FOREFRONT OF THREAT DETECTION
As a layered defense shield safeguarding the US and its territories with unwavering precision and ensuring the security and resilience of the nation, Golden Dome is revolutionizing US homeland missile defense.
The Department of Defense’s (DoD) Golden Dome for America strategy aims to preserve peace through strength, deterring adversaries and defending the country from a growing array of aerial threats.
“Golden Dome is a really exciting initiative because it’s something our nation has needed for the longest time, and the current missile defense system is getting us to that capability,” details Cordaro.
“It is a key enabler and element, and we’re going to build upon these proven and capable systems as we collaborate with innovators across all sectors.”
Lockheed Martin is also working alongside its customers, including the MDA, Space Force, USNORTHCOM, and others, as this mission of unprecedented scale requires a whole-of-industry approach.
“We’re bringing together what we have to offer with our supply chain and the best of commercial technology to create an open architecture that allows everyone to contribute. This will spur not only the defense of the homeland but also innovation and economic growth to strengthen the manufacturing sector,” continues Cordaro.
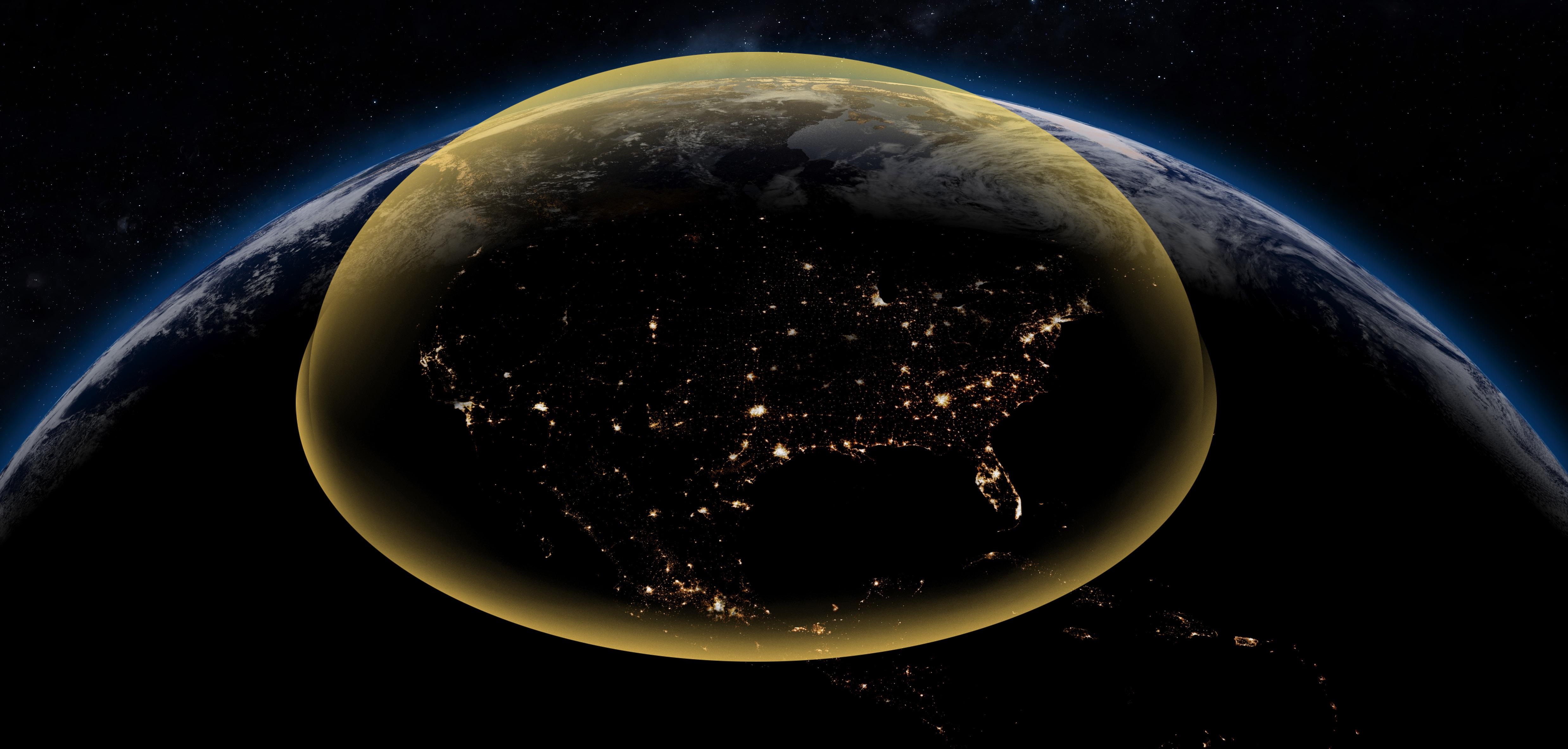
Golden Dome Partnership: Core Systems Supporting Lockheed Martin’s Vision for Homeland Defense
By Chris Schaffner, President, Core Systems
In an era where threats are evolving faster than ever, the importance of readiness, resilience, and innovation cannot be overstated. At Core Systems, we are proud to be a key partner in Lockheed Martin’s forward-leaning strategy to defend the homeland—most notably through the groundbreaking Golden Dome initiative. As the President of Core Systems,
I am honored to share how our close collaboration with Rick Cordaro and his team at Lockheed Martin is shaping the future of missile defense and next-generation military computing.
A Partnership Built on Purpose
Core Systems has long specialized in designing and
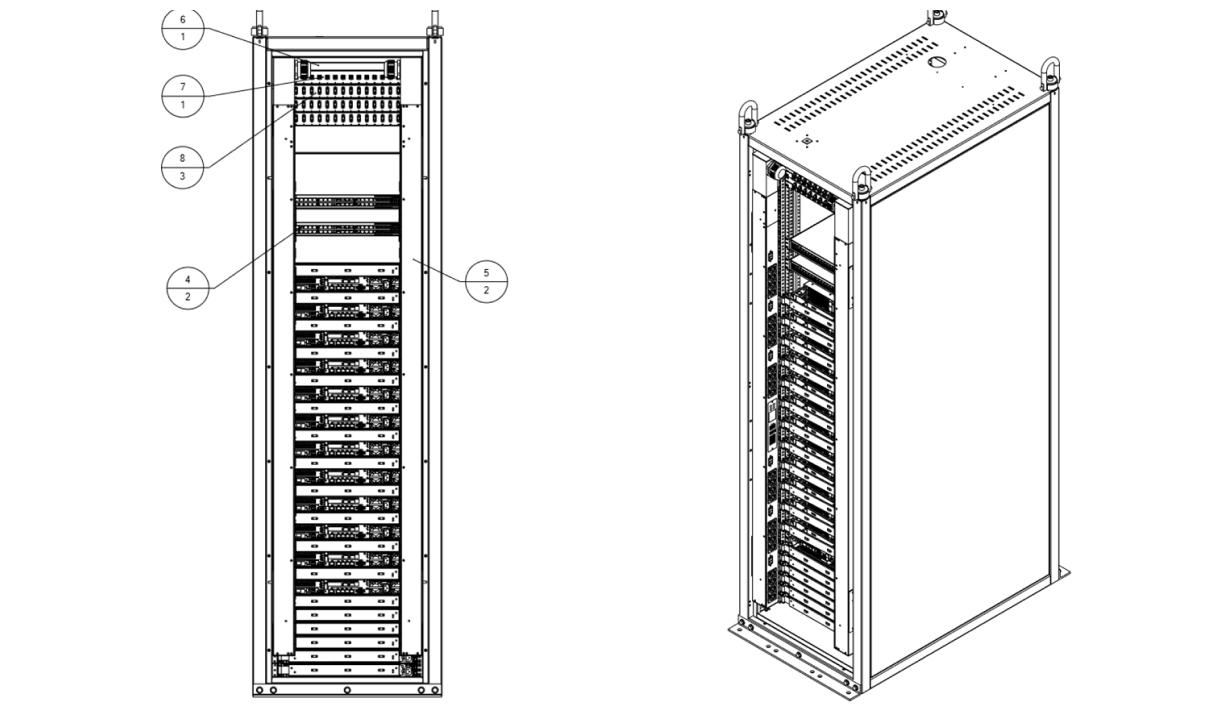
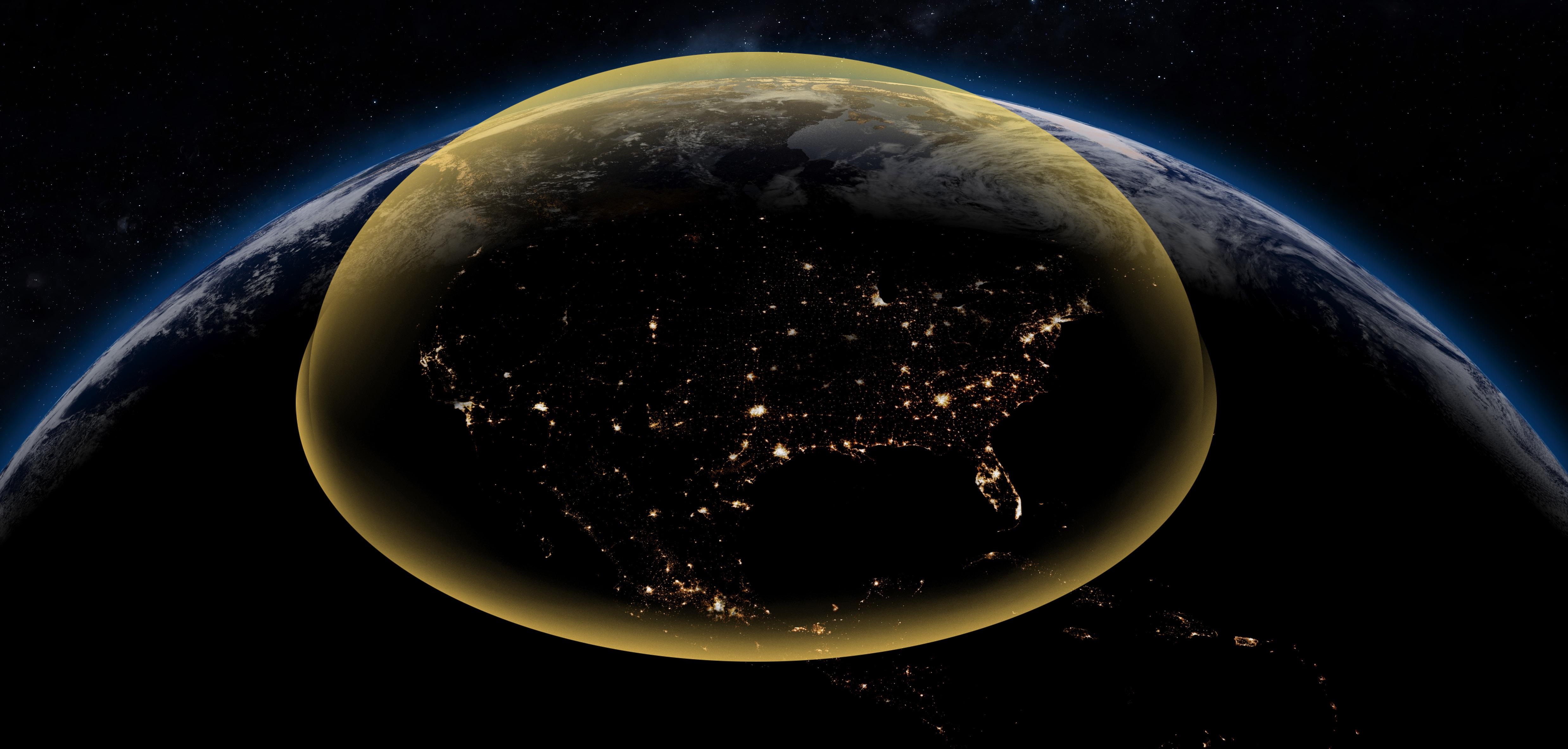
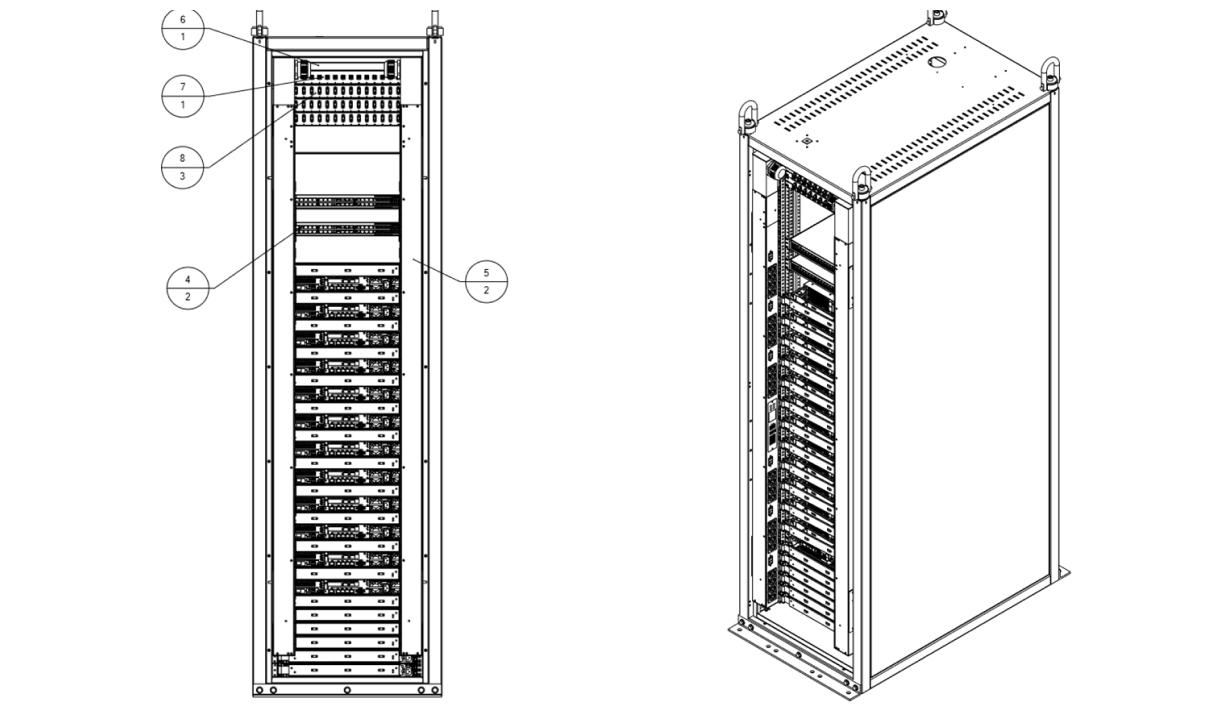
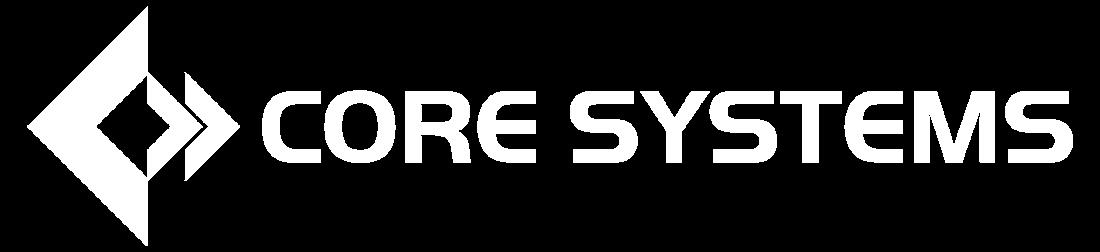
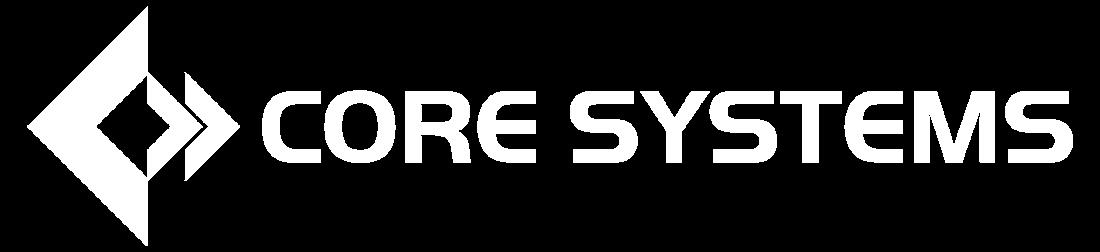
building custom rugged, mission-ready computing systems for military and industrial environments.
When Lockheed Martin entrusted us to build the rack infrastructure for the Long Range Discrimination Radar (LRDR)—the backbone of the Missile Defense Agency’s detection and tracking network—we understood the significance of our
role. It was more than just building hardware. It was contributing to a vision of national security that aligns perfectly with our company’s values and capabilities.
Rick Cordaro, Vice President of Radar and Sensor Systems at Lockheed Martin, has made it clear that “deterrence begins with detection”. That message resonates deeply with us at Core Systems.
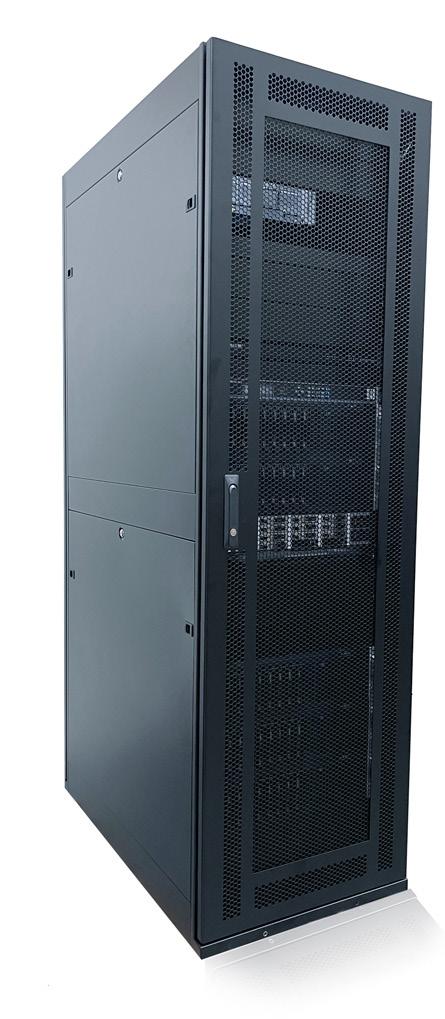
Every rack we build, every system we integrate, plays a role in ensuring threats are identified and intercepted before they can harm U.S. citizens or our allies. We’ve worked alongside Lockheed Martin on recent deployments, and as the Golden Dome initiative ramps up, we’re even more excited about what the future holds. From design to final assembly, our team is engaged in creating hardware platforms that must not only perform flawlessly—but do so in some of the harshest conditions on Earth.
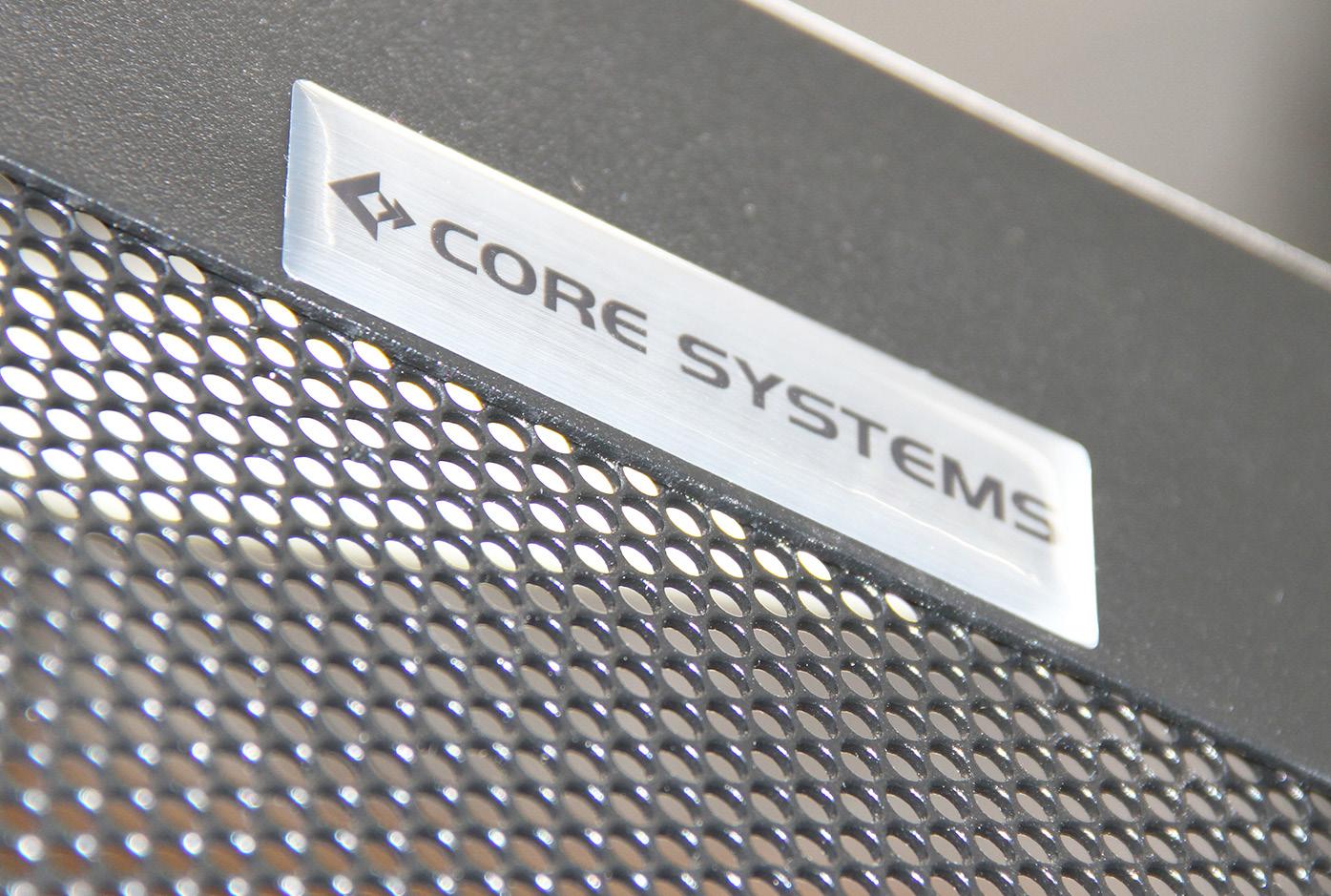
Golden Dome: The Future of Homeland Security
Golden Dome is not just a program—it’s a national strategy. Spearheaded by the Department of Defense with Lockheed Martin as a leading partner, Golden Dome aims to build a layered missile defense shield over the U.S. homeland and its territories. This defense structure integrates early detection, real-time tracking, and rapid neutralization of aerial threats including ballistic missiles, cruise missiles, UAVs, and hypersonic systems.
The LRDR and other advanced radars like the TPY-6 and Sentinel A4 are the eyes of this system. What Lockheed Martin is building is not just defense—it’s assurance. And what Core Systems contributes to that mission is structural integrity, environmental resilience, and seamless integration of rackbased platforms that house the critical components these radars rely on.
We believe Golden Dome will become one of the most talked-about defense programs of the
next decade—and we’re committed to ensuring Core Systems remains at the forefront of that conversation. From a branding and mission standpoint, “Golden Dome” is now a central theme for our team—one we’ll continue to champion across all media platforms and in our communications.
First
to Market: Tactical GPU Systems, Military Laptops & ATMOS
As the defense landscape shifts to multi-domain operations and edge-based computing, Core Systems has responded by bringing to market a new line of tactical GPU systems and ultra-rugged military-grade laptops and servers. These platforms are designed for on-the-go missions
Rugged RPS417 Laptop
Server Grade Power.
Rugged
Portable Form Factor.
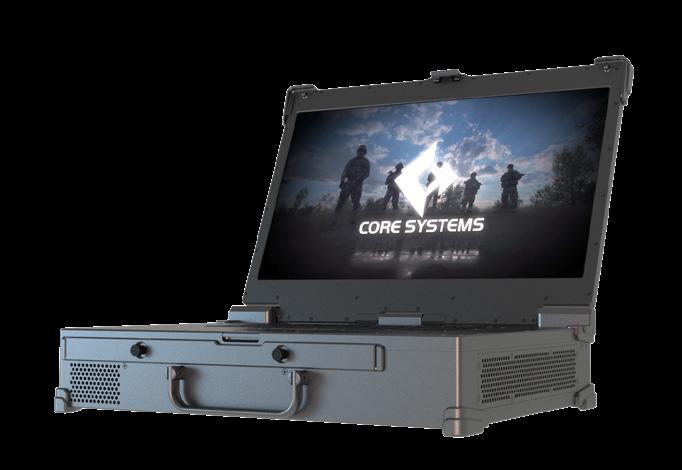
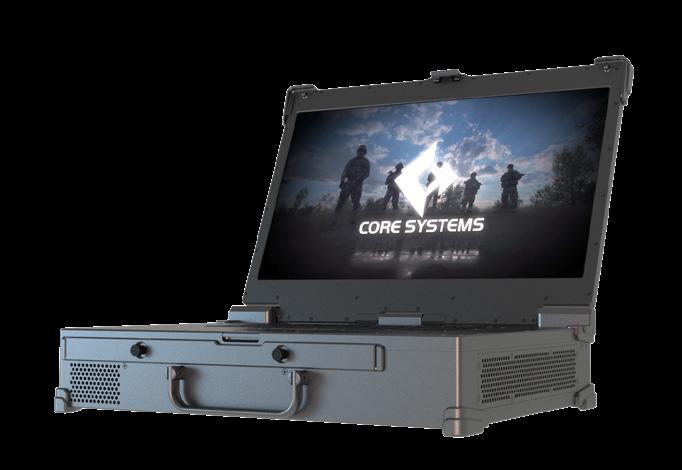
Full-Spectrum Capability: Design. Manufacture.
Integrate.
What makes Core Systems a trusted partner in programs like LRDR and Golden Dome is our end-to-end capability. We’re not just a vendor. We’re an engineering-driven, vertically integrated team that can take a concept from idea to field deployment with speed and precision.
Design: Every solution begins with ruggedization, modularity, and field repairability in mind. Our engineering team specializes in designing enclosures and server chassis that meet MIL-STD-810, 901D, and 461 requirements.
Manufacturing: With a full machine shop and clean assembly floor located in-house in San Diego, we can rapidly prototype, test, and scale production based on program timelines.
Integration: We don’t just ship parts—we deliver turnkey systems. Whether it’s a high-density rack for a radar platform or a tactical GPU unit, our systems arrive fully configured, tested, and validated.
This holistic approach is why we’re proud to be recognized as one of the few ELITE SUPPLIERS to Lockheed Martin’s Moorestown team. That status is more than a badge—it’s a shared commitment to quality, urgency, and mission alignment.
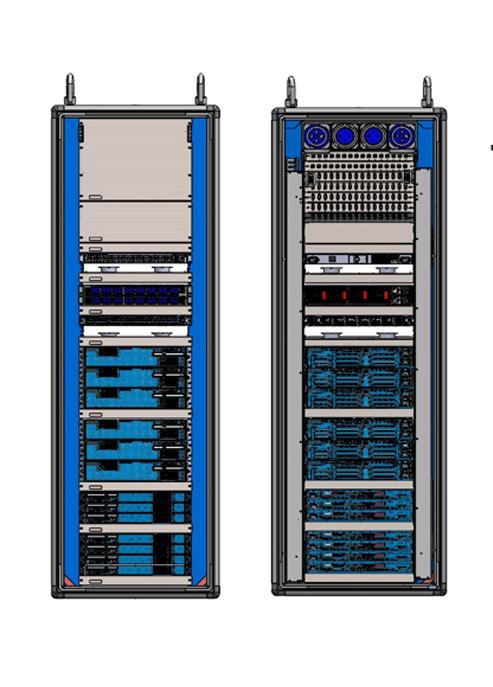
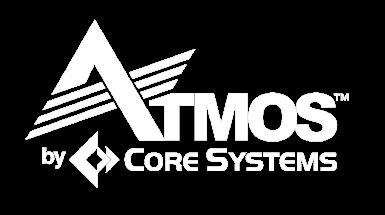
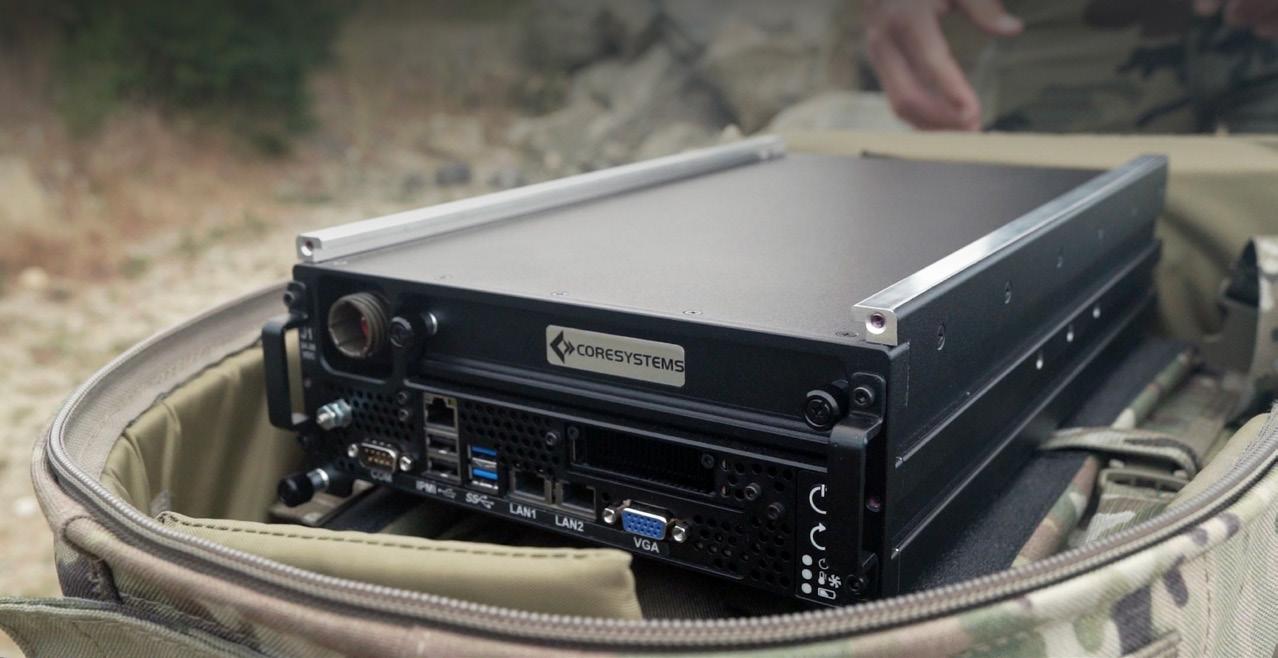
where size, weight, and performance matter most. They are equipped with the latest NVIDIA GPUs, advanced cooling systems, and encryption-ready
architecture to support AI, signal processing, and realtime situational awareness— even in mobile or dismounted operations.
Our tactical GPU systems
are compact enough to fit into a rucksack but powerful enough to drive machine learning workloads, drone swarm control, and advanced targeting systems. Similarly, our rugged laptops are built to withstand battlefield abuse—yet deliver processing power that rivals desktop servers.
One of our most advanced platforms is the ATMOS unit—a field-deployable, mission-ready system designed for maximum performance in extreme environments. ATMOS has already proven itself as a standout solution for mobile edge computing, and we’re excited to announce that future versions will incorporate the NVIDIA Blackwell GPU architecture, unlocking next-level AI acceleration, real-time ISR capability, and onboard model training—all in a rugged form factor optimized for deployed forces. These solutions are not concepts—they’re first in their class and already being fielded by special forces and mobile command units. When paired with the broader Golden Dome strategy, they offer a decentralized, adaptive layer of defense that complements the radar and detection systems Lockheed Martin deploys globally.
Deterrence begins with detection. Execution begins with integration. And success begins with trusted partnerships.
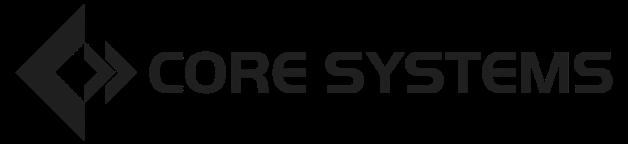
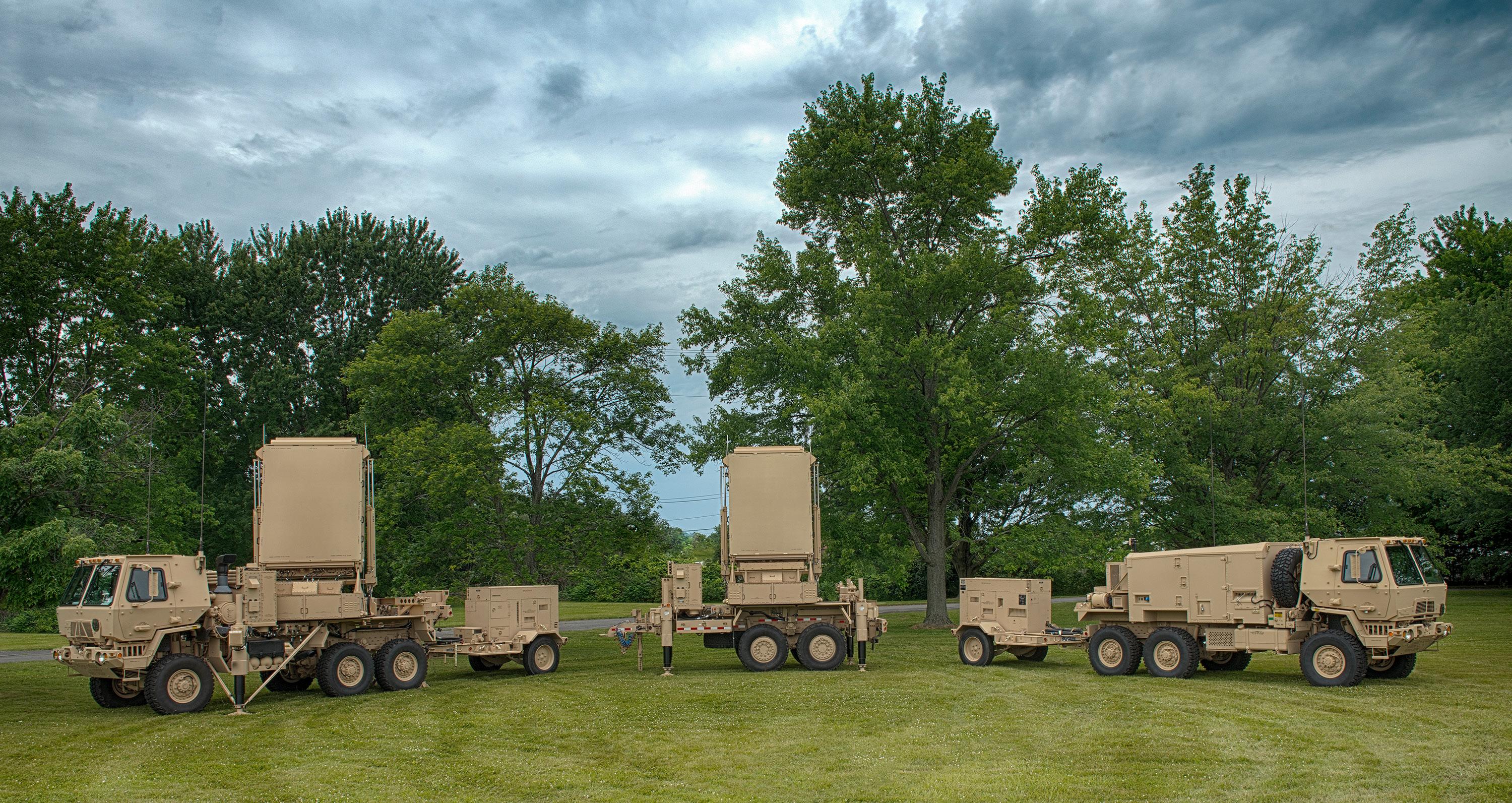
He notes the importance of government recognizing the need for this vision to quickly become a reality, which aligns with Lockheed Martin’s strategy of being ahead of ready.
Golden Dome is a revolutionary concept as this next-generation defense shield will identify incoming projectiles, calculate trajectories, and
CORE SYSTEMS
“Core Systems has been a trusted partner, adapting to evolving customer needs and industry shifts in tandem with us,” says Cordaro.
“They understand the significance of their contributions to Lockheed Martin and our government customers, playing a vital role in supporting homeland defense, and we appreciate their ongoing support and collaboration.”
deploy interceptor missiles to destroy them mid-flight, safeguarding the nation and projecting the strength of the US.
These radar technologies see further, sharper, and sooner, making them the first and most critical layer of national defense. Lockheed Martin’s proven capabilities are ready to be deployed now.
“Most importantly to me, the radars provide detection that leads to deterrence, like the LRDR in Alaska, the TPY-6 deployed in Guam, the Sentinel A4 for the US Army, and the TPY-4 that’s in the hands of the US Air Force and other international partners today,” expands Cordaro.
By bringing the best and brightest of US innovation to rapidly develop game-changing technology, the nation’s Golden Dome will be sure to stay well ahead of threats.
MISSION INTEGRATION
It has been proven time and again that Lockheed Martin’s radars and sensors are some of the most advanced in the
world, working with existing critical defense networks to protect from adversarial threats.
The open architecture design of Lockheed Martin’s radars allows seamless integration with a variety of sensors and systems, providing a unified operational picture. This flexibility enables the system to quickly incorporate new capabilities and cutting-edge software, ensuring service members have the necessary tools to respond to emerging threats before they can adapt.
“A true Mission Integrator does more than just create technology – it accelerates outcomes and delivers a decisive advantage for real-world needs. And it does so quickly, speeding the timeline from emerging need to delivered capability. That’s key to strengthening deterrence and staying ahead of potential threats,” details Cordaro
Lockheed Martin is rising to the challenge of mission integration. Working shoulder-to-shoulder with forces around the world and experts
embedded systems, displays, and networking devices are engineered to meet or exceed strict MIL-STD and IEEE standards delivering proven resilience against shock, vibration, extreme temperatures, dust, moisture, and electromagnetic interference.
Crystal Group’s trusted performance and relentless innovation make us the clear choice for those who can’t afford to compromise.
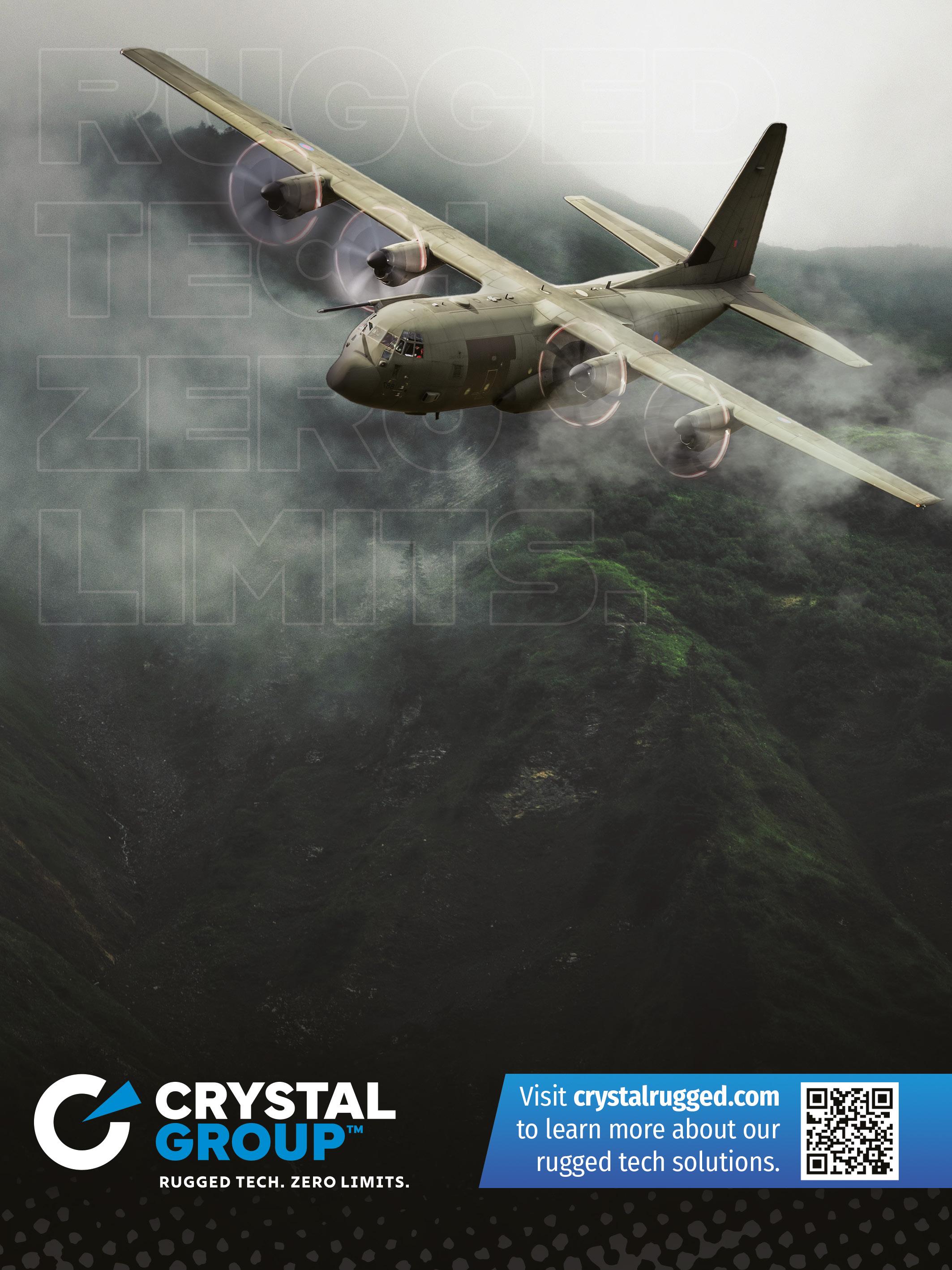
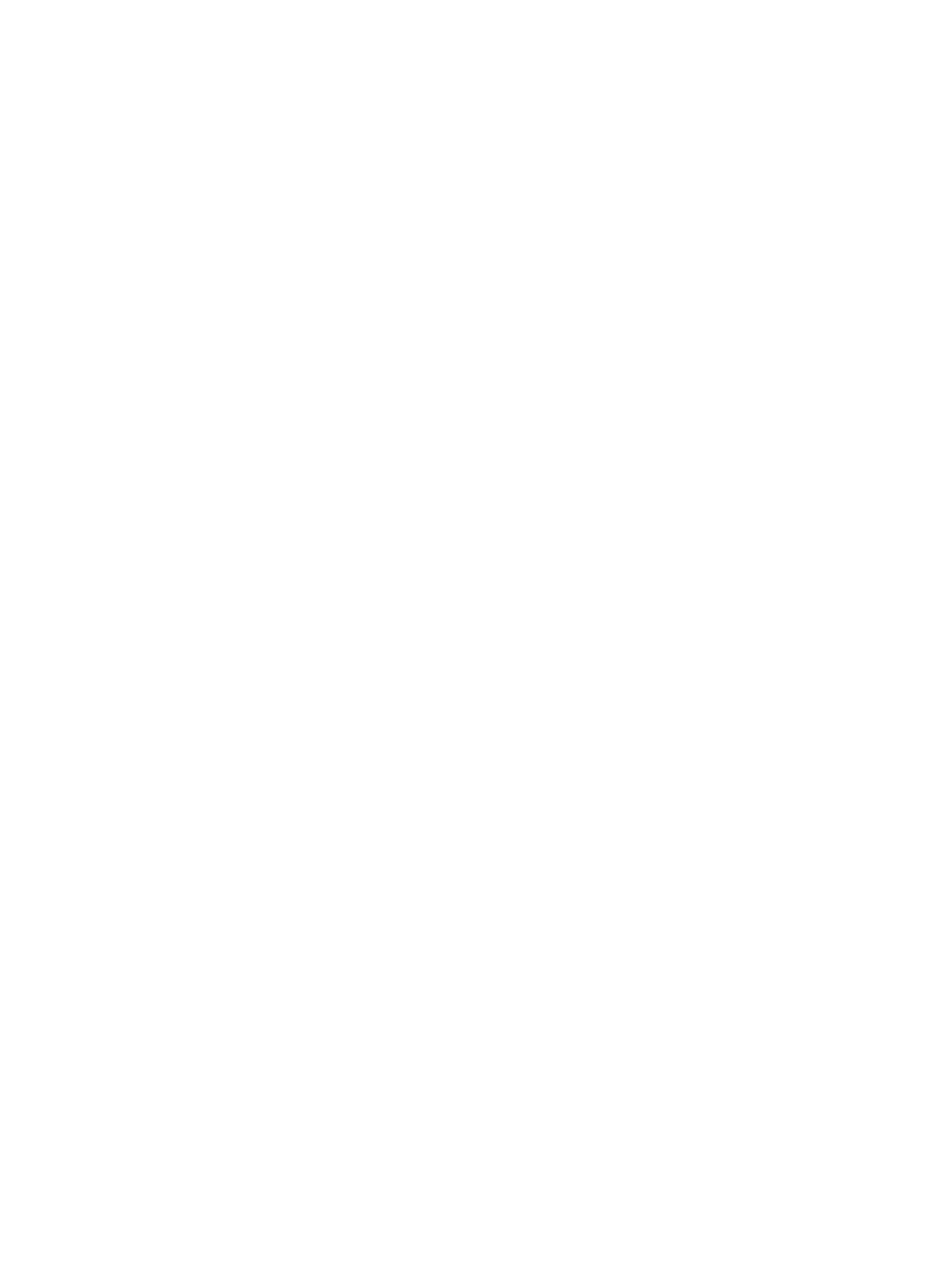
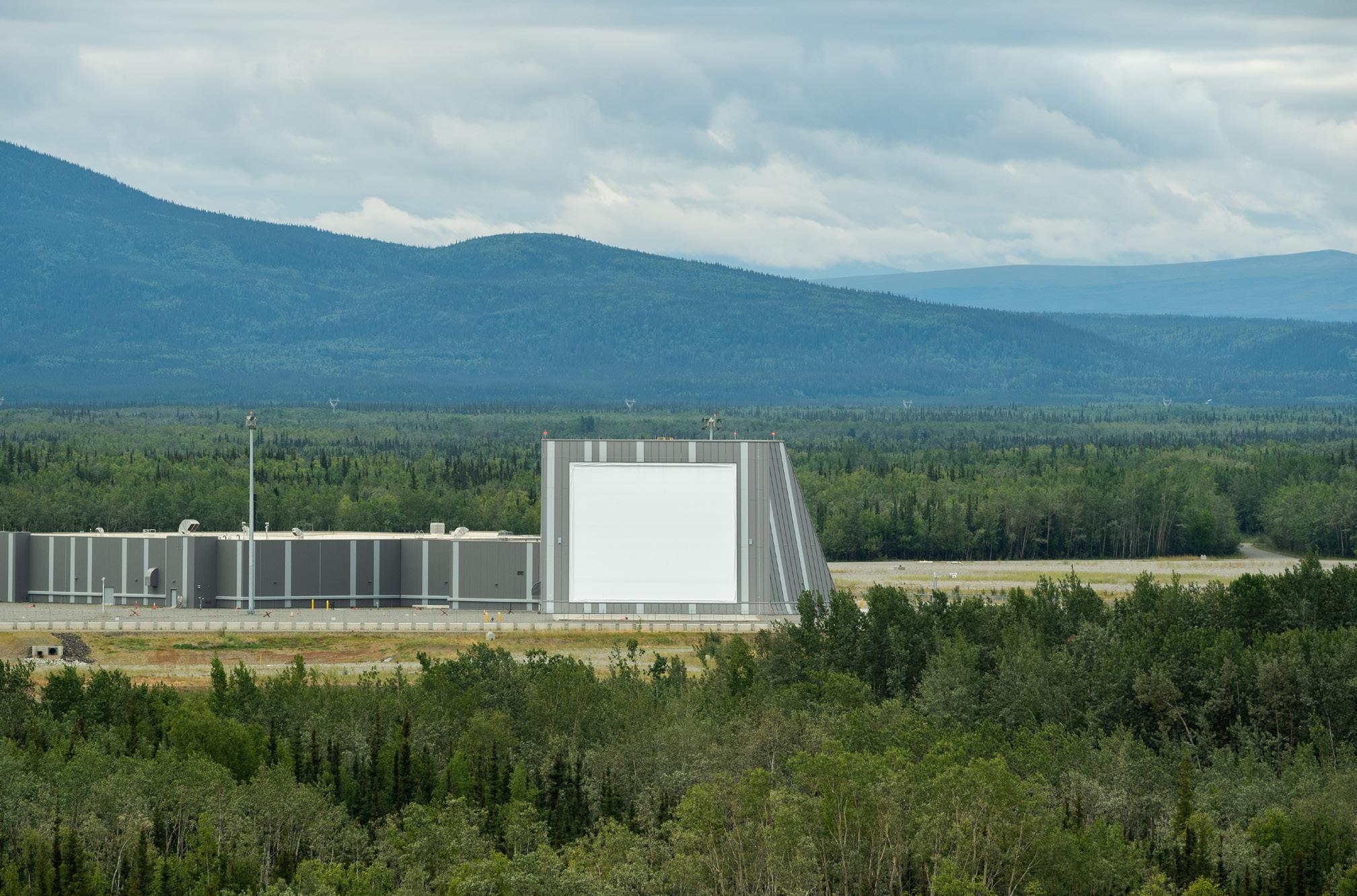
LOCKHEED MARTIN AT A GLANCE
121,000 EMPLOYEES WORLDWIDE
350+ FACILITIES GLOBALLY
20 PERCENT OF EMPLOYEES ARE VETERANS
100+ YEARS OF INNOVATION
$71 BILLION NET SALES IN 2024
$45.3 BILLION NET EARNINGS IN 2024
“IT’S IMPERATIVE THAT WE MAINTAIN THE SAFETY AND SECURITY OF OUR NATION, AND THAT’S MORE THAN JUST MILITARY STRENGTH – IT’S THE INDUSTRIAL BASE THAT BACKS IT UP”
– RICK CORDARO, VICE PRESIDENT OF RADAR AND SENSOR SYSTEMS, LOCKHEED MARTIN
across industries, the company is transforming the way defense tech is developed and delivered.
“We could talk a lot about the technology and how we use gallium nitride transistors, digital beamforming (DBF) for many of our radars, or how we have polarization diversity in a number of our systems,” insights Cordaro.
“All of those technical features contribute to the benefit of being able to see smaller targets at longer ranges in the face of challenging clutter, such as adverse weather, decoys, and chaff from adversaries.”
Deterrence may begin with
detection, but it is just the first step in the kill chain to ensure accuracy and safety. Lockheed Martin has an edge because it is a leading command, control, and combat system developer and integrator.
“When I think about Golden Dome, I think about how Lockheed Martin is the DoD’s lead industry partner for the US missile defense system with the Command and Control Battle Management Communications (C2BMC) system and the US Navy’s lead integrator of the Aegis Combat System (ACS),” details Cordaro.
These systems are able to merge what is detected through radars
ENERGY AND UTILITY SOLUTIONS BACKED BY EXPERIENCE
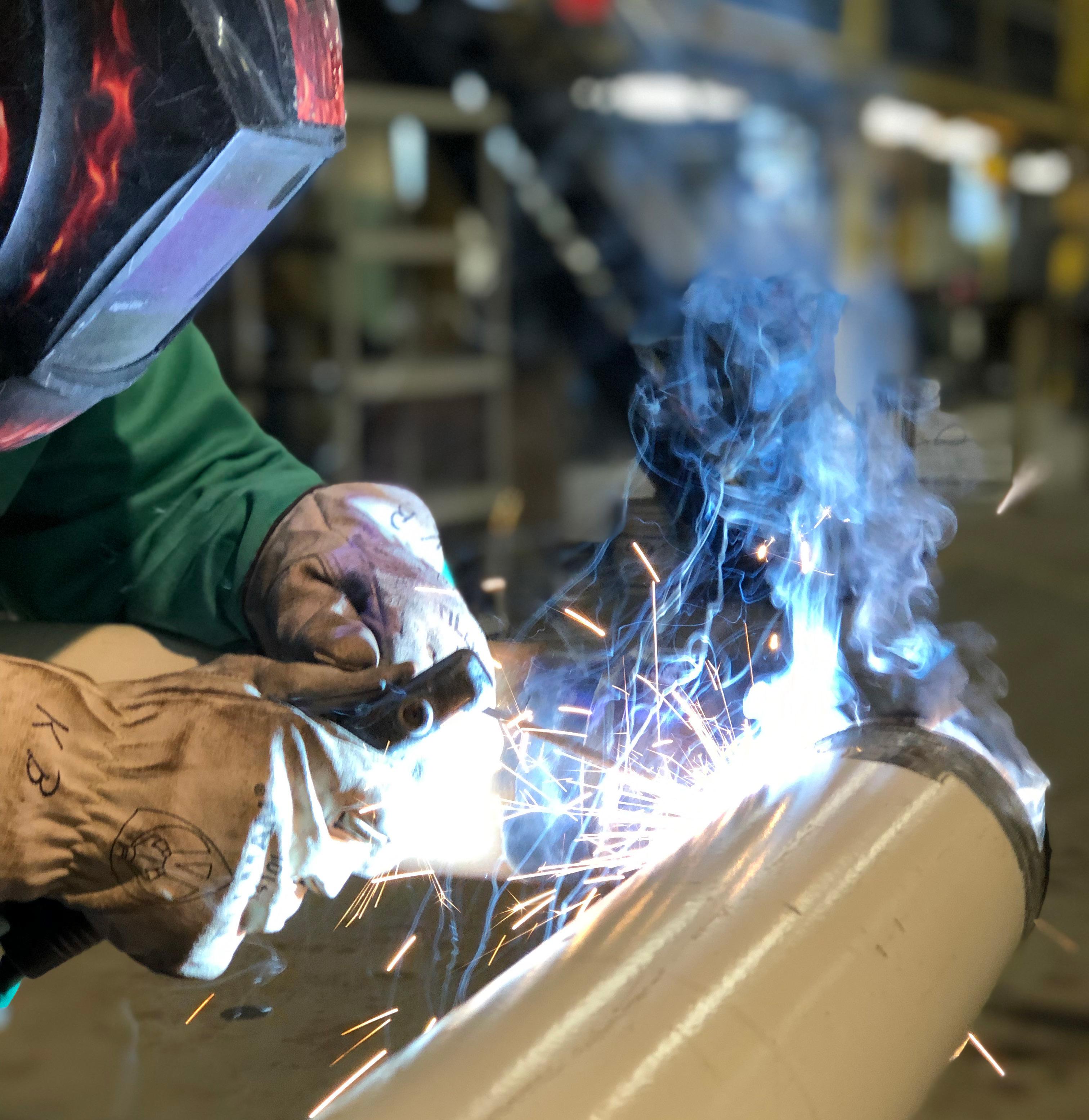
Riggs Distler has served the energy and utility markets that power the Eastern United States for more than 100 years. Using leading technologies, proven management strategies, and veteran field leadership, we focus on safety, quality, and budget efficiency to exceed our customers’ expectations on every project.
Our integrated and overlapping mechanical, electrical, and utility construction services enable us to meet the full range of customer needs, setting us apart as the preferred sole-source partner of the region’s most important heavy industrial, defense, and power generation clients.
“OUR MISSION IS DETERRENCE AS PART OF 21ST-CENTURY SECURITY SOLUTIONS. OUR GOAL IS TO ENSURE THAT OUR NATION, PARTNERS, AND CUSTOMERS ARE AHEAD OF READY”
– RICK CORDARO, VICE PRESIDENT OF RADAR AND SENSOR SYSTEMS, LOCKHEED MARTIN
and counter those threats through systems such as Terminal High Altitude Area Defense (THAAD), PAC3, laser weapons, and high-power microwaves to bring forth warfighting capability as opposed to just widgets.
“It’s one thing to make widgets, but it’s another to make warfighting capabilities. That’s how we’re truly providing 21st-century security – not just through widgets or systems, but warfighting capabilities,” he asserts.
AHEAD OF READY
Lockheed Martin’s purpose is to ensure those it serves are always able to stay ahead of ready.
As an identity, culture, and promise, this mindset is paramount to the company’s ability to evolve to meet emerging threats, provide innovative solutions, and partner with customers to keep the US and allies safe at a moment’s notice.
“When the warfighter calls, they’re not asking for help in three years or even three months’ time – they need help now, and we do all the hard science, engineering, architecting, development, and mission analysis to know we can bring solutions that are ahead of ready by being ready now,” explains Cordaro.
An example of this is the LRDR, which was contracted several years ago and is currently deployed in Alaska, consisting of modern technology based on subarray suites. Recently, the US government contacted Lockheed Martin to discuss an emerging need to defend Guam and place a new sensor on the island. Within a period of less than two years, the company took the technology from the LRDR and built the TPY-6.
“The TPY-6 provides high-end detection, discrimination, and
deterrence capability, and was derived from the same technology that we and the MDA have invested in for years to make the LRDR a reality,” furthers Cordaro.
“That’s what ahead of ready looks like. It doesn’t mean you can predict the future – it means you have the capability and technology warfighters can use and adapt to their mission when the need is real.”
READY NOW AND FOR THE FUTURE
Lockheed Martin proudly exhibits numerous industry-defining products and initiatives that have come to change the world over the course of the company’s long-established history of innovation and progress.
One such product that has been touched on in terms of its importance in modern defense capabilities is the LRDR.
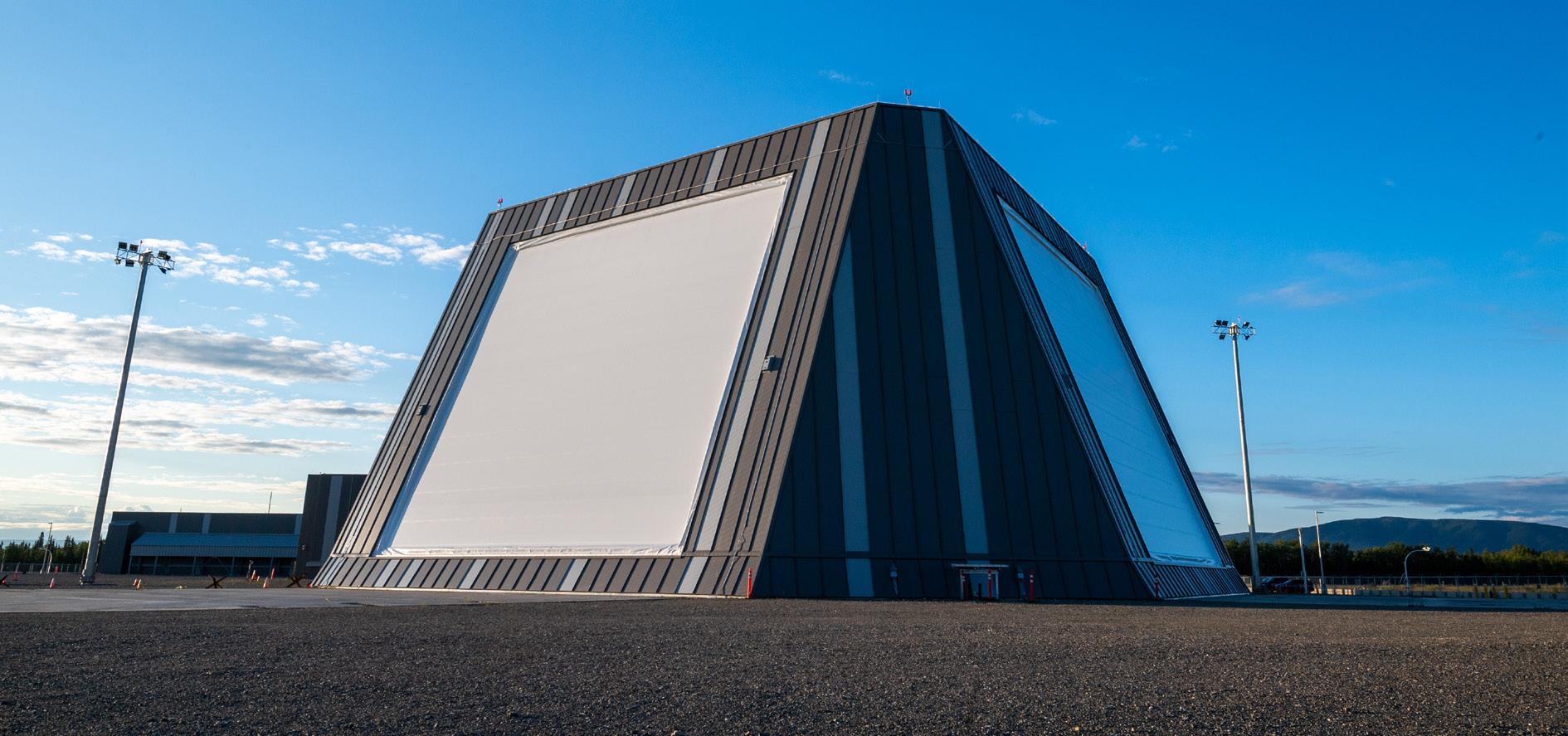
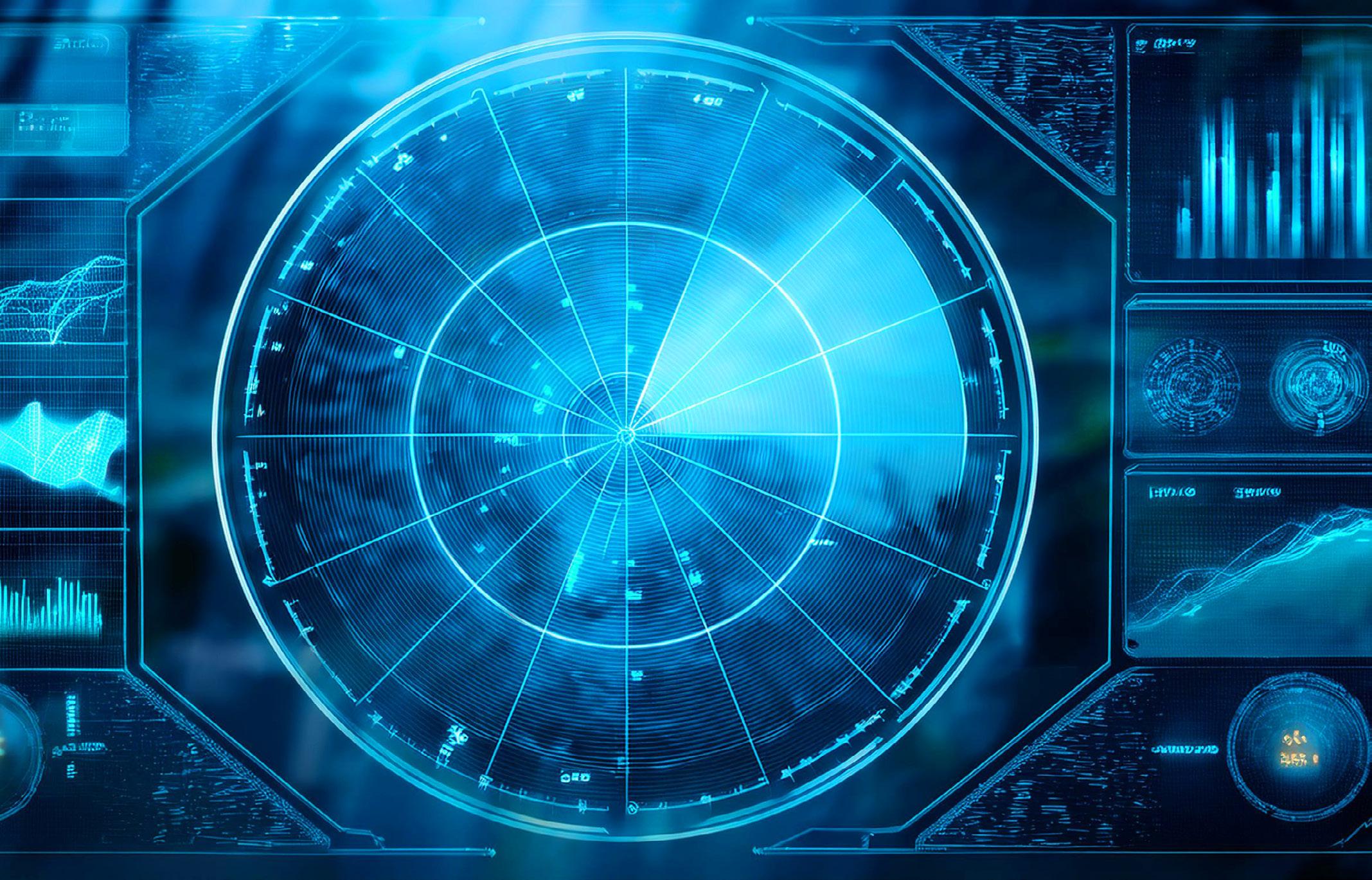
Shaping the Future of Radar with Trusted RF Expertise
Accelerating radar performance and mission agility
Qorvo® enables defense leaders to meet today’s mission and tomorrow’s threat with scalable, high-performance RF. Our proven solutions support rapid design cycles, reduce system complexity and ensure long-term readiness across multifunction radar platforms. With US-based design and manufacturing, Qorvo delivers the reliability and supply chain assurance critical to defense success. Explore Qorvo’s radar innovations today.
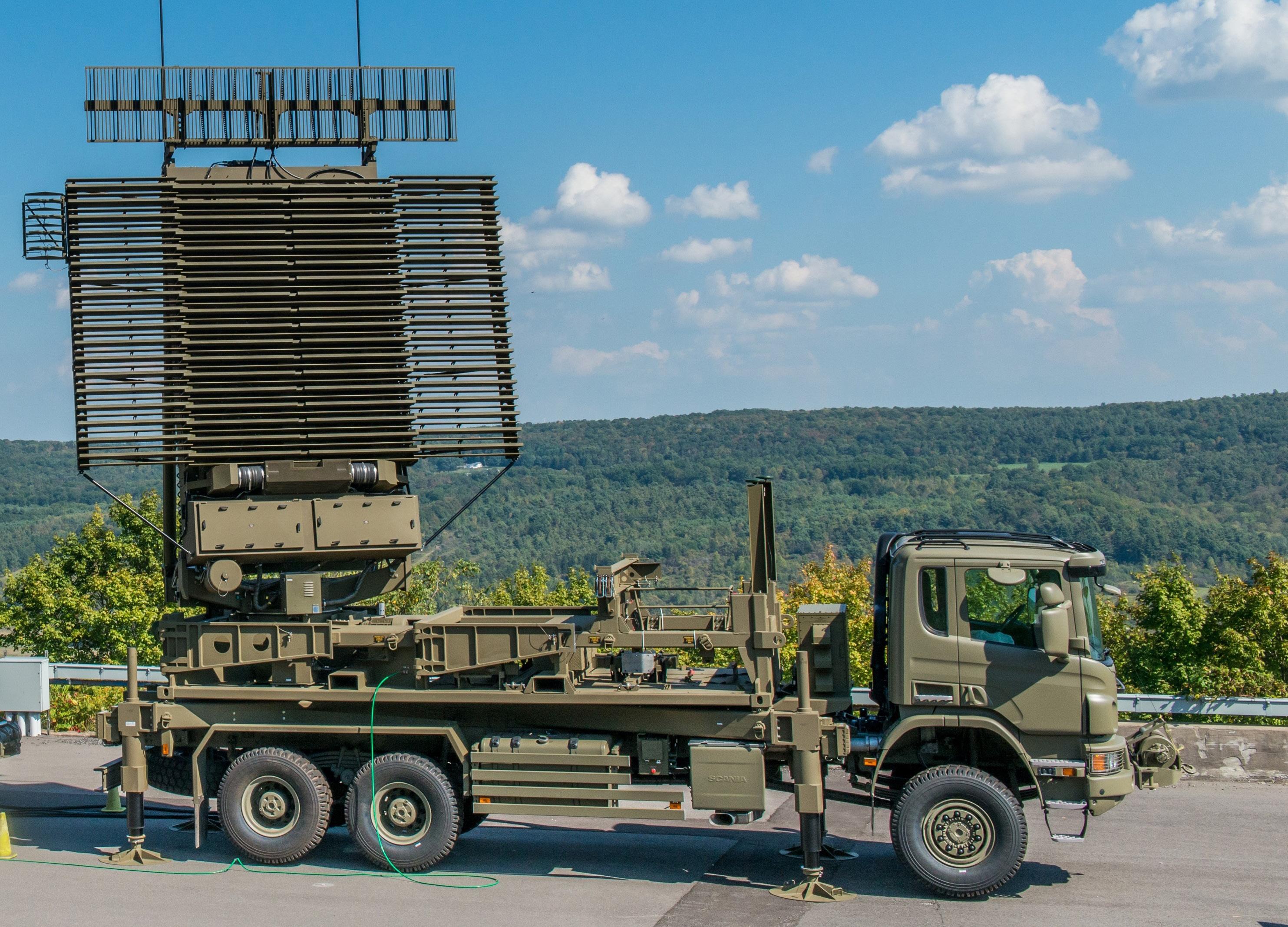
“WHAT WE FOCUS ON MORE THAN ANYTHING IS MAKING SURE WE MEET OUR EXISTING COMMITMENTS. LOCKHEED MARTIN IS A GLOBAL 21ST-CENTURY SECURITY COMPANY THAT IS AHEAD OF READY, BUT AT THE END OF THE DAY, WE ARE A COMPANY THAT MEETS ITS COMMITMENTS”
– RICK CORDARO, VICE PRESIDENT OF RADAR AND SENSOR SYSTEMS, LOCKHEED MARTIN
“This is a transformational capability, and it’s hard to overstate how significant the radar is,” emphasizes Cordaro.
“The LRDR is the size of a fivestory building and is a total strategic enabler for the US because it provides persistent tracking of ballistic missiles from launch through to midcourse, giving commanders time and clarity to make the right decisions.”
As a result of this system’s long range and ability to discriminate, those stationed have the appropriate time to act.
To showcase the LRDR’s vast
proficiency, on June 24th this year, Lockheed Martin and the MDA successfully executed Flight Test Other-26a (FTX-26a). During this test, the LRDR was able to detect, track, and discriminate a live ballistic missile threat in a complex environment, thereby showcasing the radar’s ability to provide critical data to US defense systems and support long-range discrimination missions.
“The FTX-26a was incredibly exciting to witness, and what’s even more exciting is seeing that technology being used in Guam for the TPY-6, by Japan for their
Aegis-equipped vessel, by Canada on their Royal Canadian Destroyer, and by Spain for their F110-class frigate,” prides Cordaro.
Another significant project for Lockheed Martin is the TPY-4 – a multi-mission, ground-based radar for air defense surveillance that can operate in contested electromagnetic environments.
This radar provides warfighters with the ability to detect and track current and emerging threats, allowing for a next-generation radar that maximizes flexibility and mission capability.
“I am very passionate about this
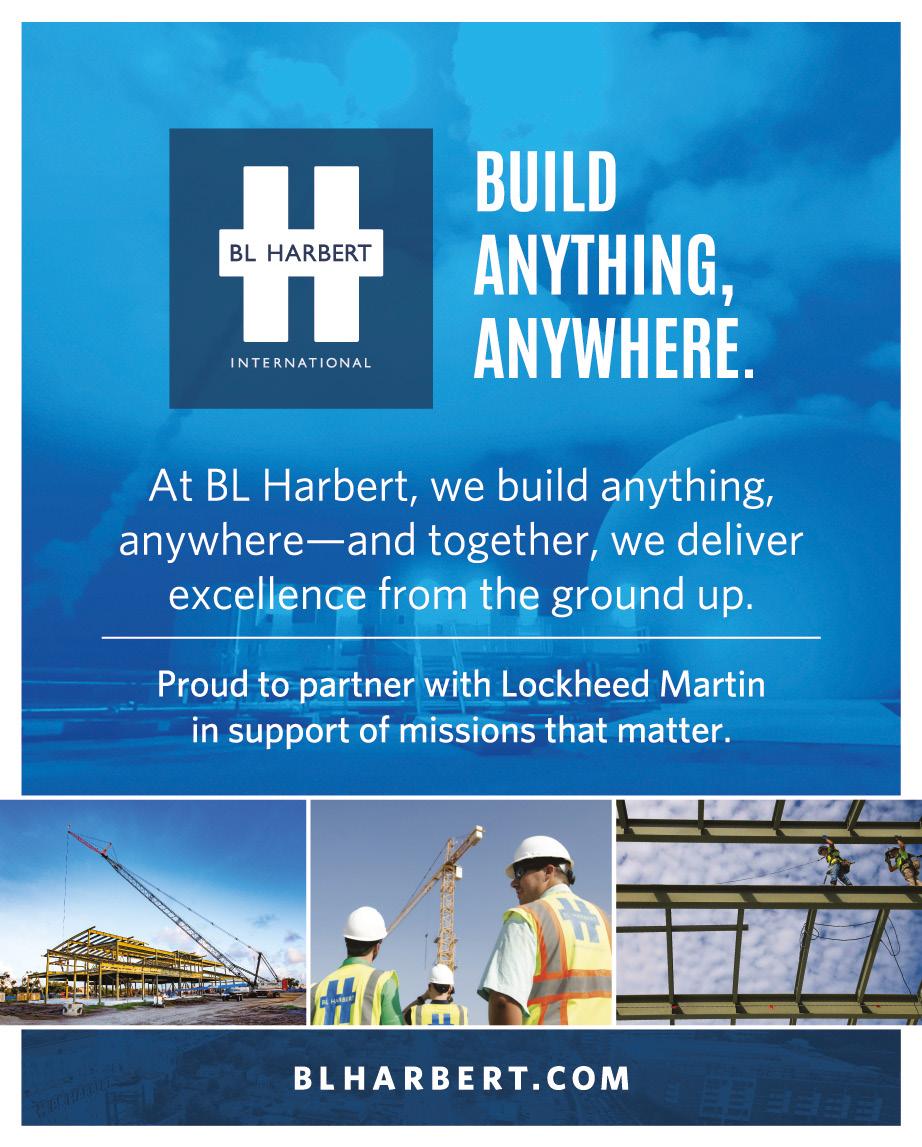
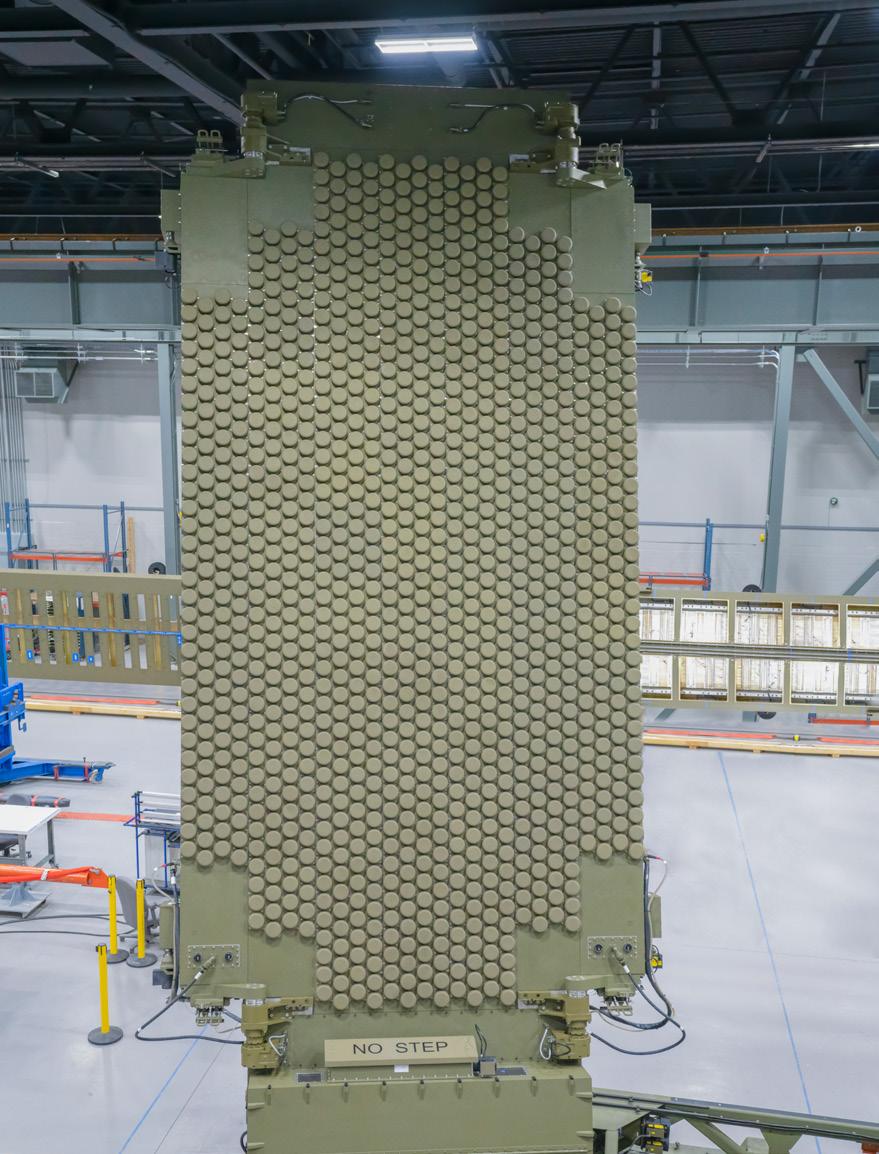
program because I’ve worked on it since 2007, when I was an engineer in the early stages,” details Cordaro.
“This radar is the US Air Force’s next-generation long-range air surveillance radar, and we manufacture it right here in Syracuse, New York, with a number of partners throughout the country. It is a very capable system that provides our allies and the US Air Force with longrange performance in difficult clutter environments.”
SEEING BEYOND THE CHAFF
Looking ahead toward another century of success and entrepreneurship, Lockheed Martin has a number of priorities and goals it intends to accomplish in order to assist the US and allied forces in defense and innovation.
“What we focus on more than anything is making sure we meet our existing commitments. Lockheed
Martin is a global 21st-century security company that is ahead of ready, but at the end of the day, we are a company that meets its commitments,” asserts Cordaro.
This entails the company delivering on its promises, as it not only values its customers but recognizes that reliability and consistency are key to maintaining relationships across the international industry.
Additionally, Lockheed Martin is working on the Sentinel A4 program – a high-performance replacement of the legacy Sentinel A3 air and missile defense radar, which will provide significant improvements to its existing capability against threats.
“The program, which is going through initial operational test and evaluation (IOT&E), will be completed in Q1 2026,” expands Cordaro.
“The US Army is using the Sentinel systems every day, and as they are at the front lines of air defense for our
nation, getting the new program into the hands of soldiers is critical.”
Finally, another priority for Lockheed Martin is delivering radars.
In 2023, the company delivered nearly two dozen radars out of its factory in Syracuse, and it has committed to five dozen in 2025.
“We’ve seen the number of systems we’re going to produce more than double, and that is a cadence we’re going to be successful with indefinitely,” concludes Cordaro.
“That is what our warfighters need, as deterrence begins with detection. They need those tools, and we need to be able to make that cadence on a recurring basis. It can’t just be heroics or a one-time event; what we do in our factory and what our supply chain does is in readiness for that demand.” www.lockheedmartin.com

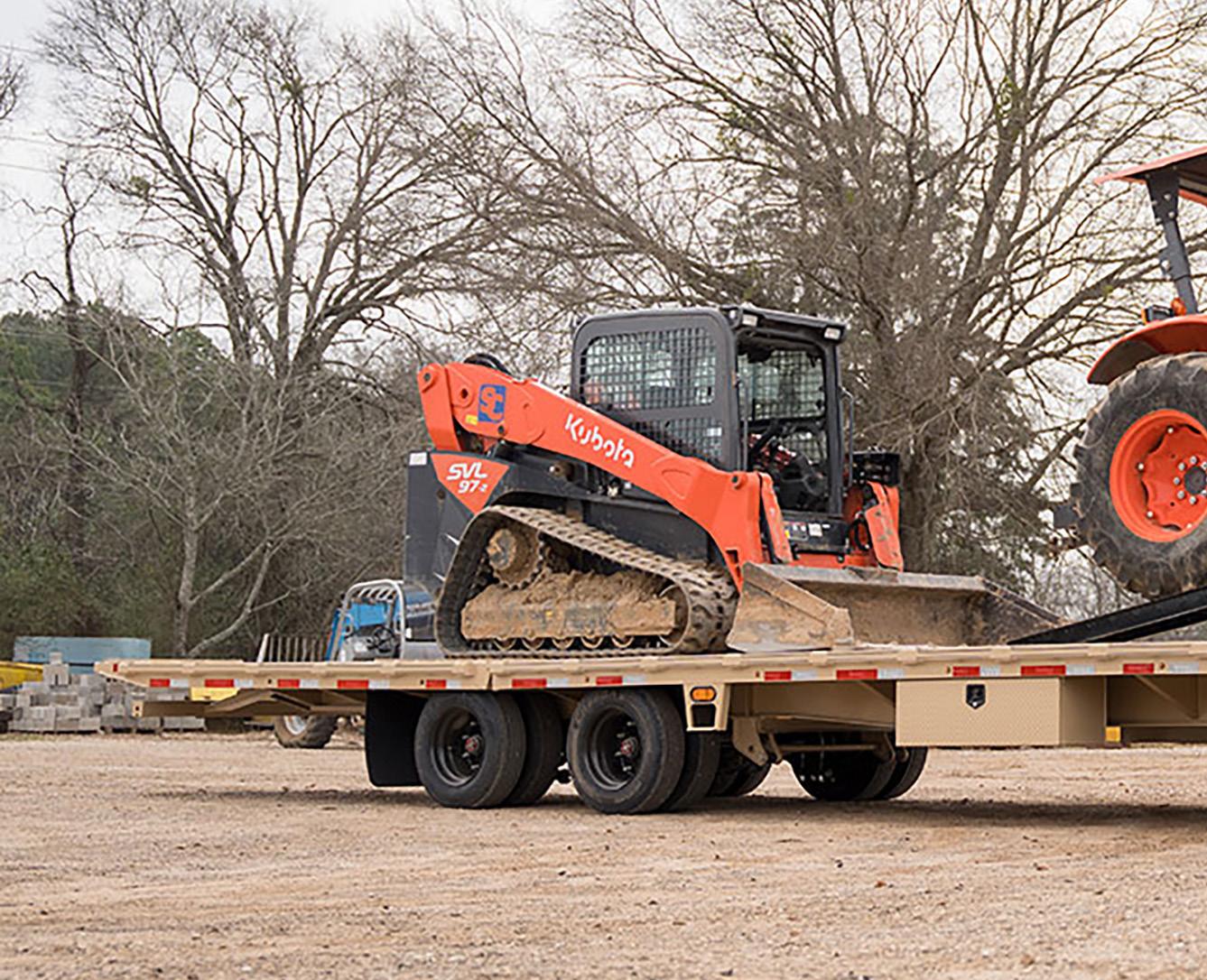
THE JEWEL OF PREMIUM TRAILERS
Having manufactured premium-grade open steel trailers since 1985, Diamond C Trailers is a proud family-owned and operated company. Jacob Crabb, Chief Customer Officer, speaks to us about its history and exciting outlook toward the future
Writer: Lauren Kania | Project Manager: Michael Sommerfield
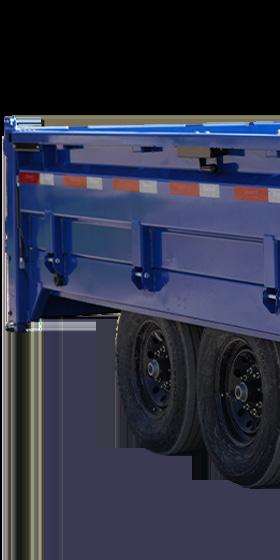
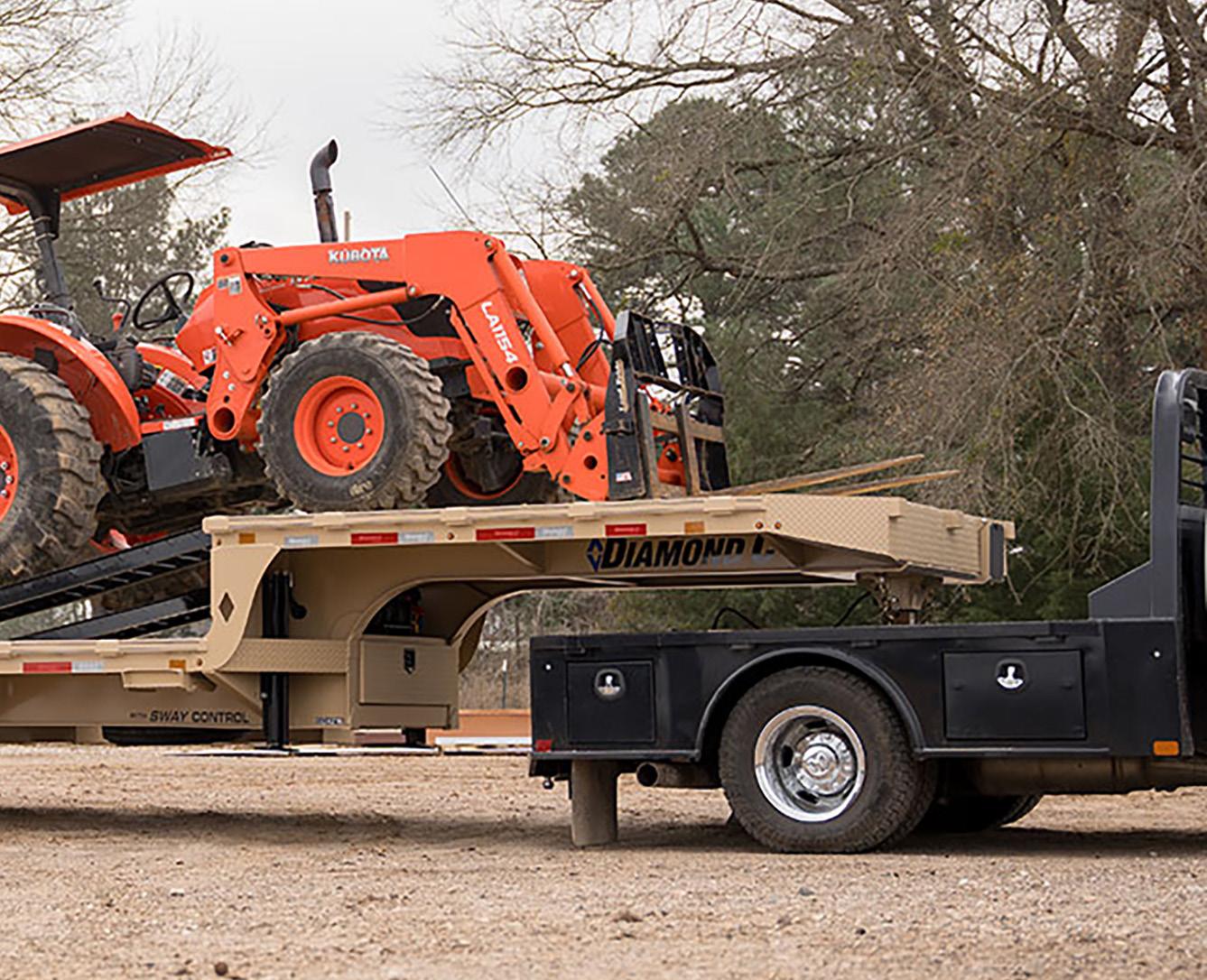
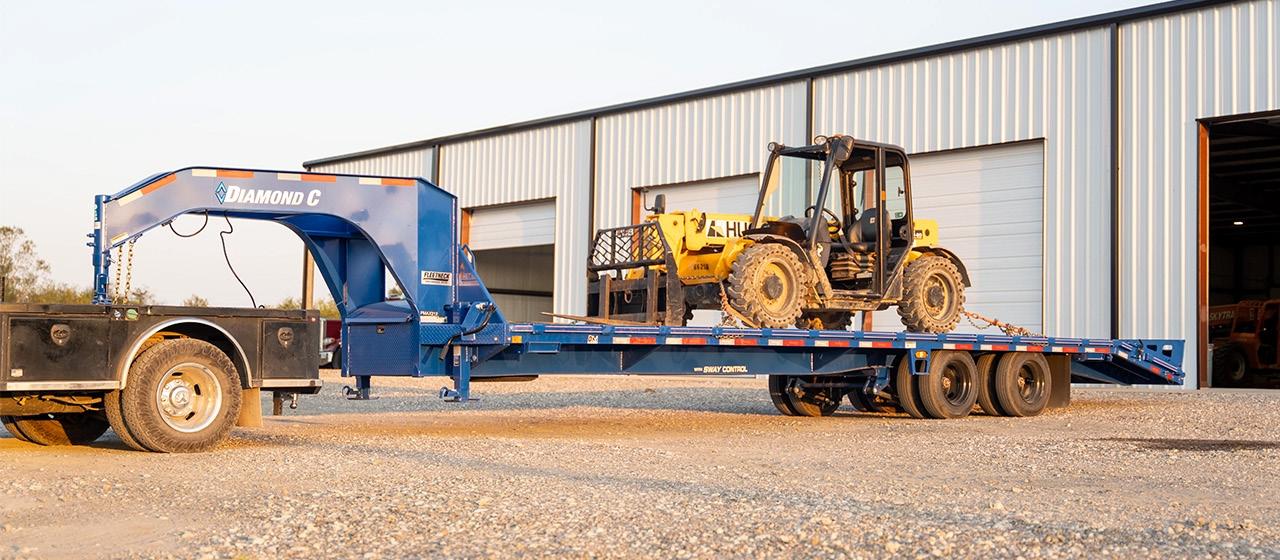
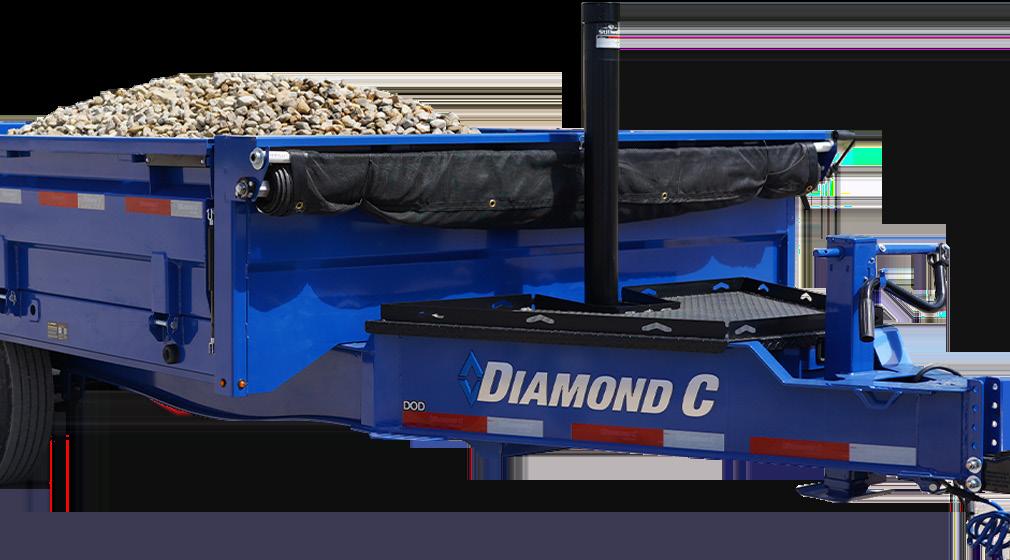
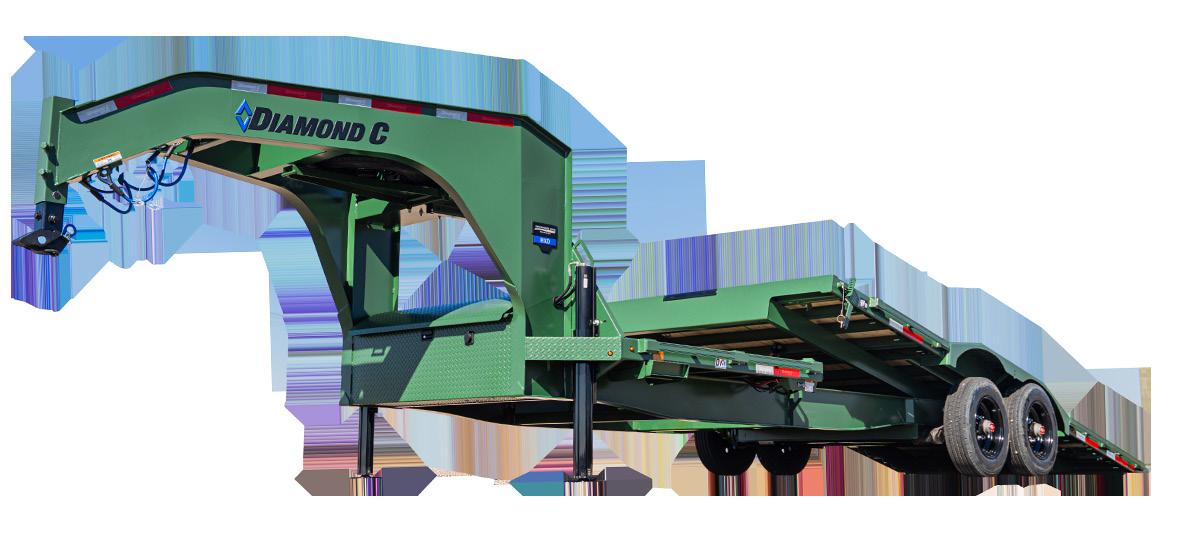
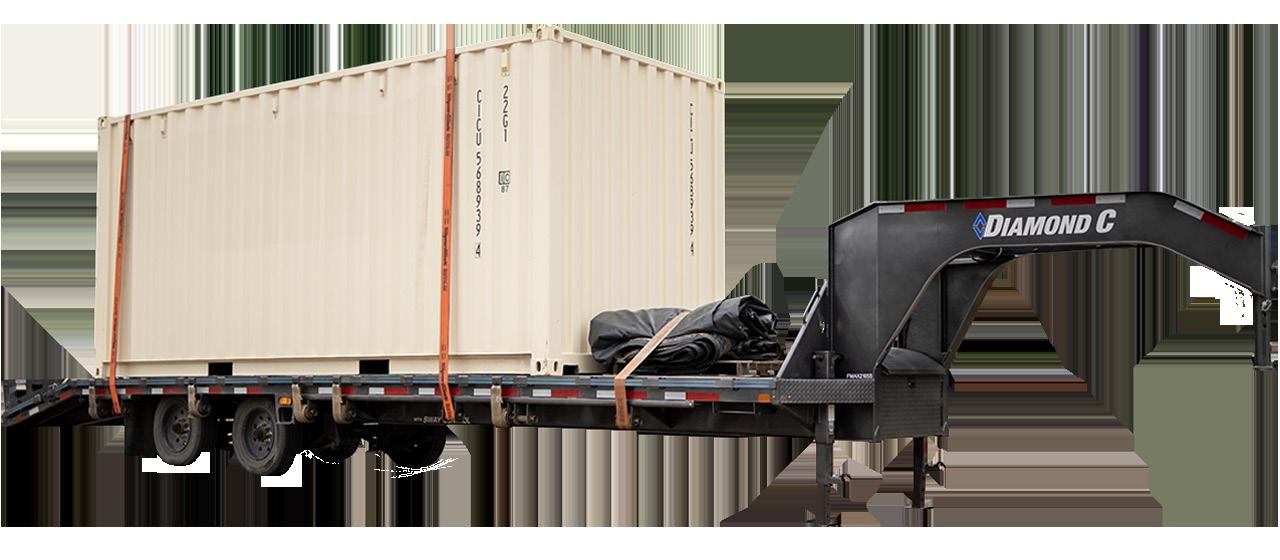
We’re living proof that a scrappy, small-town company rooted in deep values and fueled by a big vision can rise to lead an industry. Our journey hasn’t been easy, but it’s been one marked by grit, integrity, and a relentless pursuit of progress.”
The opening words of Jacob Crabb, Chief Customer Officer at Diamond C Trailers (Diamond C), are indicative of the company’s strong commitment to growth and passion for conducting business with morality and humanity at the forefront.
As a family-owned and operated company headquartered in Mount Pleasant, Texas, Diamond C is a premium open steel trailer manufacturer with nearly 700 team members and a coast-to-coast dealer network.
Conducting business based on traditional values, including honesty, respect, humility, and pure
integrity, the company builds highperformance equipment, including dump, auto, utility, and gooseneck trailers engineered to deliver lasting value for hard-working customers.
It offers a robust line-up of premium trailers ranging from car haulers and dump trailers to heavy duty equipment, tilt, flatbed, gooseneck, and step deck models, which are distributed through a vast network of over 100 dealer partners strategically placed throughout North America.
From loading brush and dirt to hauling heavy machinery and equipment, there’s a Diamond C trailer for every customer.
“We don’t just build trailers –we build solutions that solve real problems for people who depend on their equipment day in, day out,” prides Crabb.
One such example of Diamond C’s ability to craft innovative solutions
is its online ‘Build Your Own’ tool, which empowers end users to customize a trailer to fit their exact needs. This tool delivers a lasting, positive customer experience by giving buyers more confidence and clarity in their purchase. At the same time, it fuels success at the dealership level by improving margins, reducing sales friction, and increasing overall customer satisfaction.
“Our relentless focus on innovation, customization, craftsmanship, and integrity is what sets us apart in a crowded and competitive market,” affirms Crabb.
FAMILY-OWNED AND OPERATED
Born into the trailer industry, Crabb has worked in nearly every area of the business.
From the welding shop floor to sales, service, and now commercial
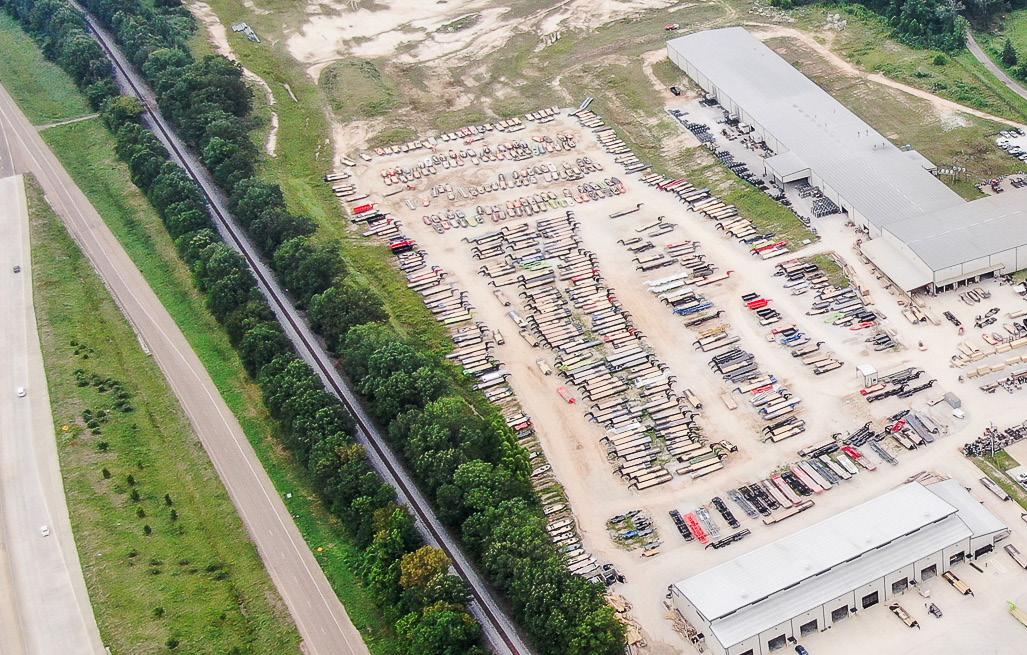
COULD YOU TELL US MORE ABOUT THE IMPORTANCE OF SUPPLIER RELATIONSHIPS TO THE LONGEVITY OF DIAMOND C?
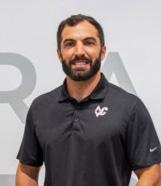
Jacob Crabb, Chief Customer Officer: “We see our suppliers as critical partners in our mission, not just transactional vendors. The strength of our supply chain lies in the trust and collaboration we’ve built over the years with a shared commitment to quality and innovation.
“These long-term relationships give us the agility to respond quickly to shifting market demands, reduce lead times, and maintain consistency in every trailer we build. By working hand-in-hand with our suppliers, we’re able to push the boundaries of what’s possible – whether it’s adopting new materials, improving processes, or co-developing custom solutions that add value for our customers.”
strategy leadership, his passion grew from watching how quality products, relentless work ethic, and genuine care for one another can build something truly lasting.
“My parents started this company with grit and heart, and that same spirit is still the backbone of who we are today,” he emphasizes.
Diamond C originated 40 years ago when a young East Texas couple – Crabb’s parents, Kim and Mike – embarked on a journey that would spark a generations-long endeavor to deliver extraordinary trailers and service to match.
While the business was initially started as a means to put food on the table for a growing household, it quickly became an important part of the family’s legacy.
Diamond C’s purpose and core values aren’t just words – they’re a compass that guides how it leads, serves, and grows.
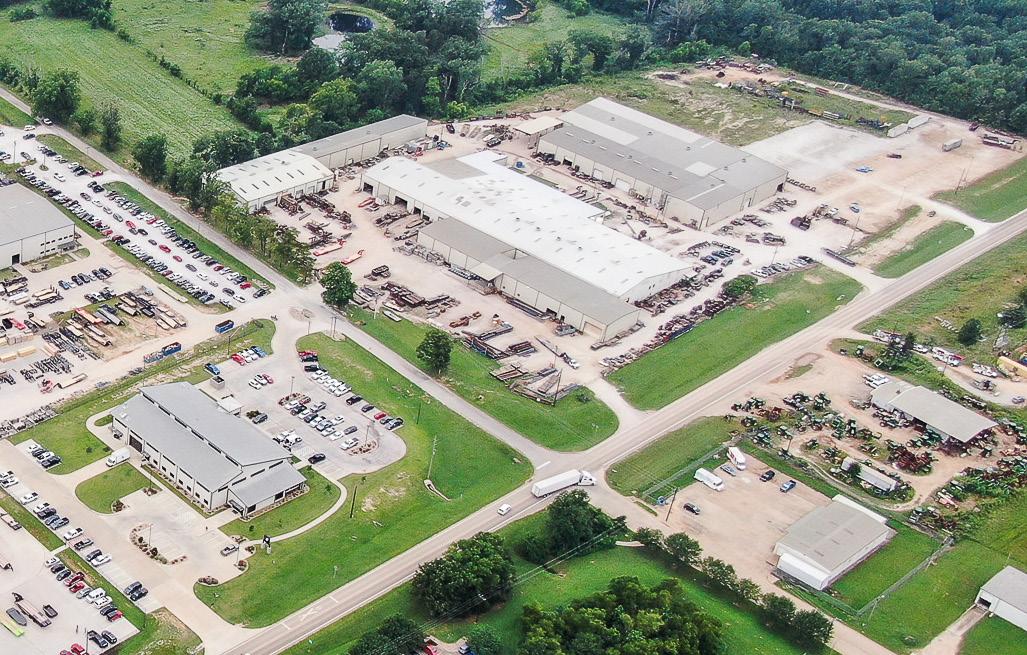
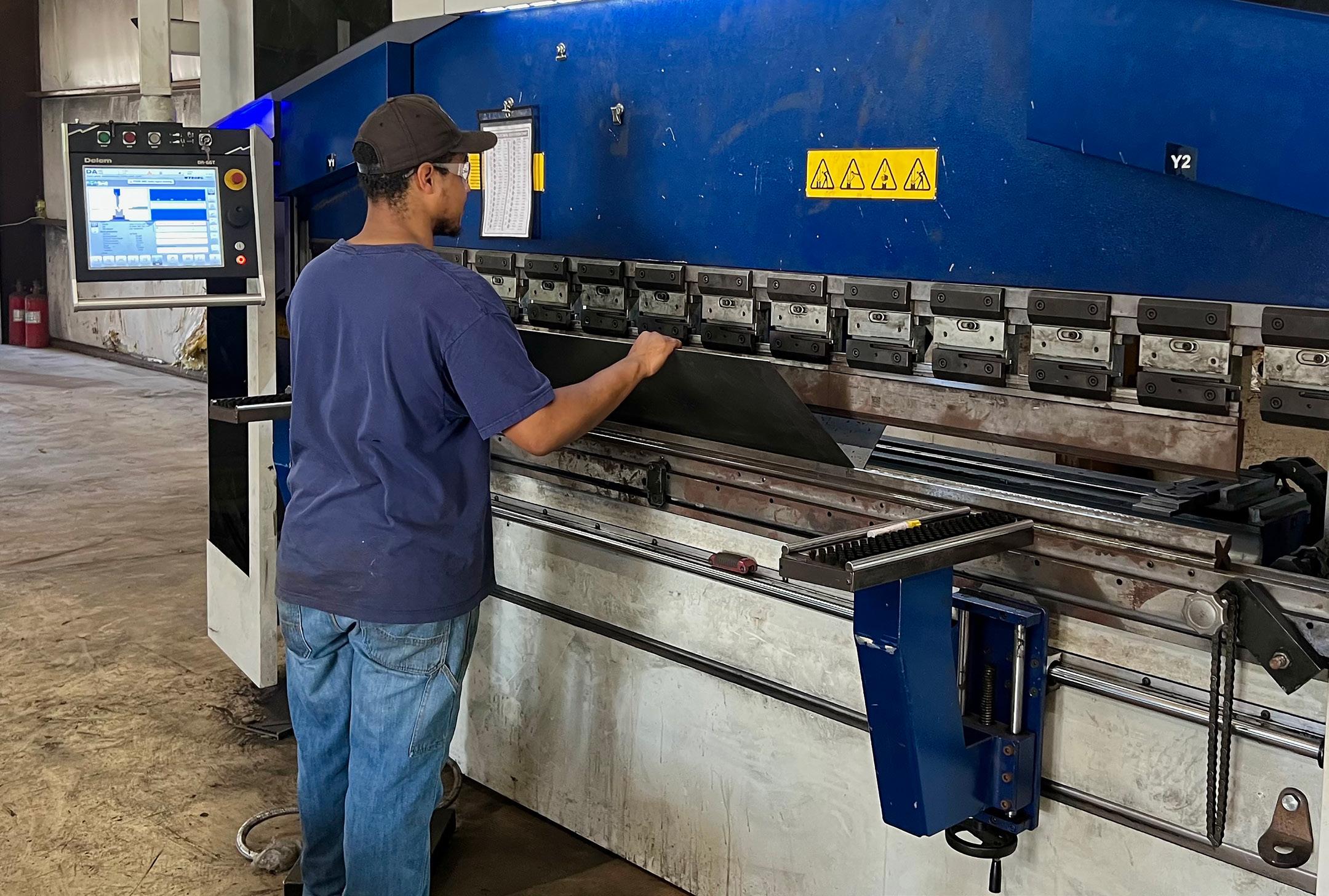
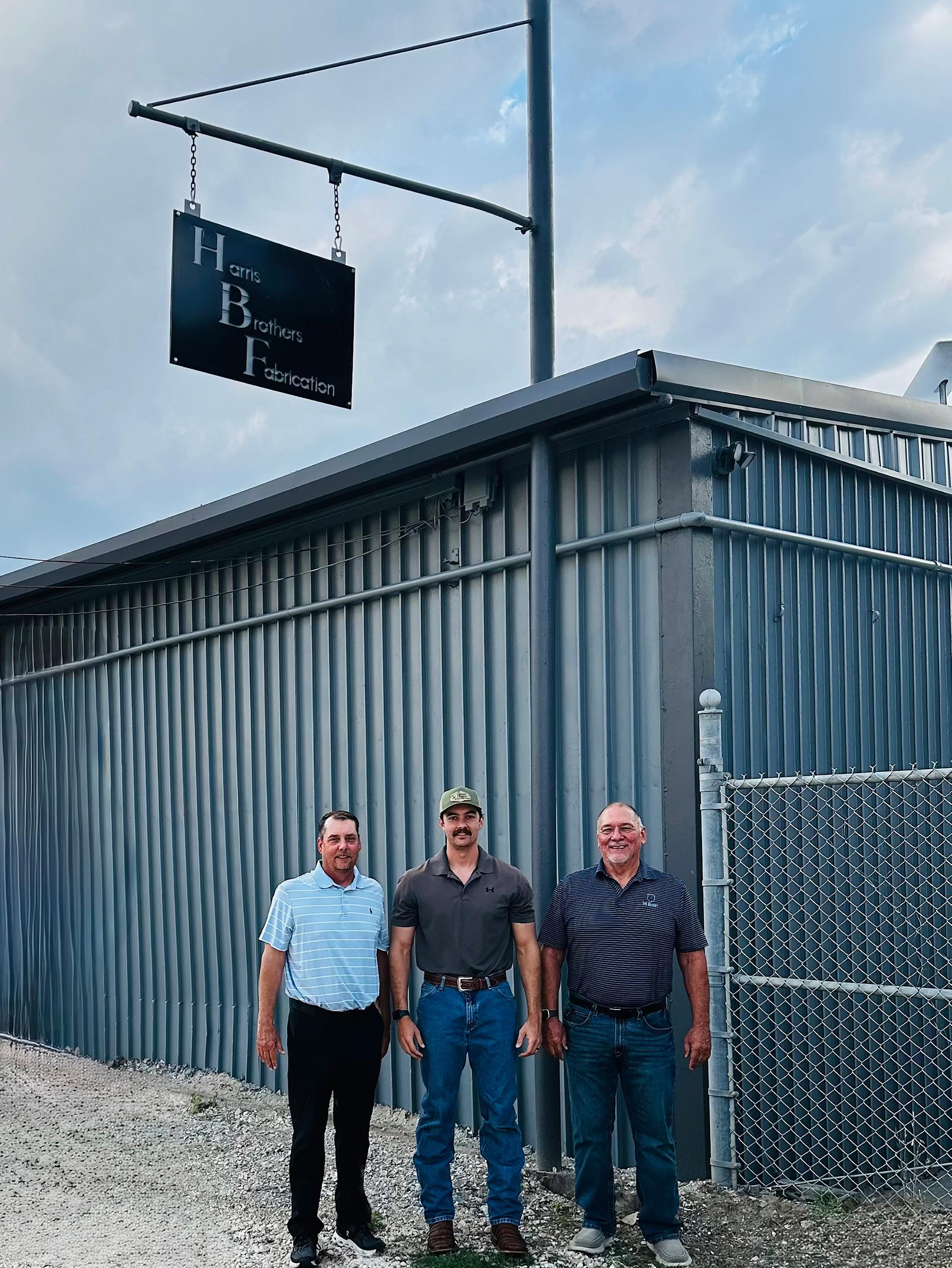
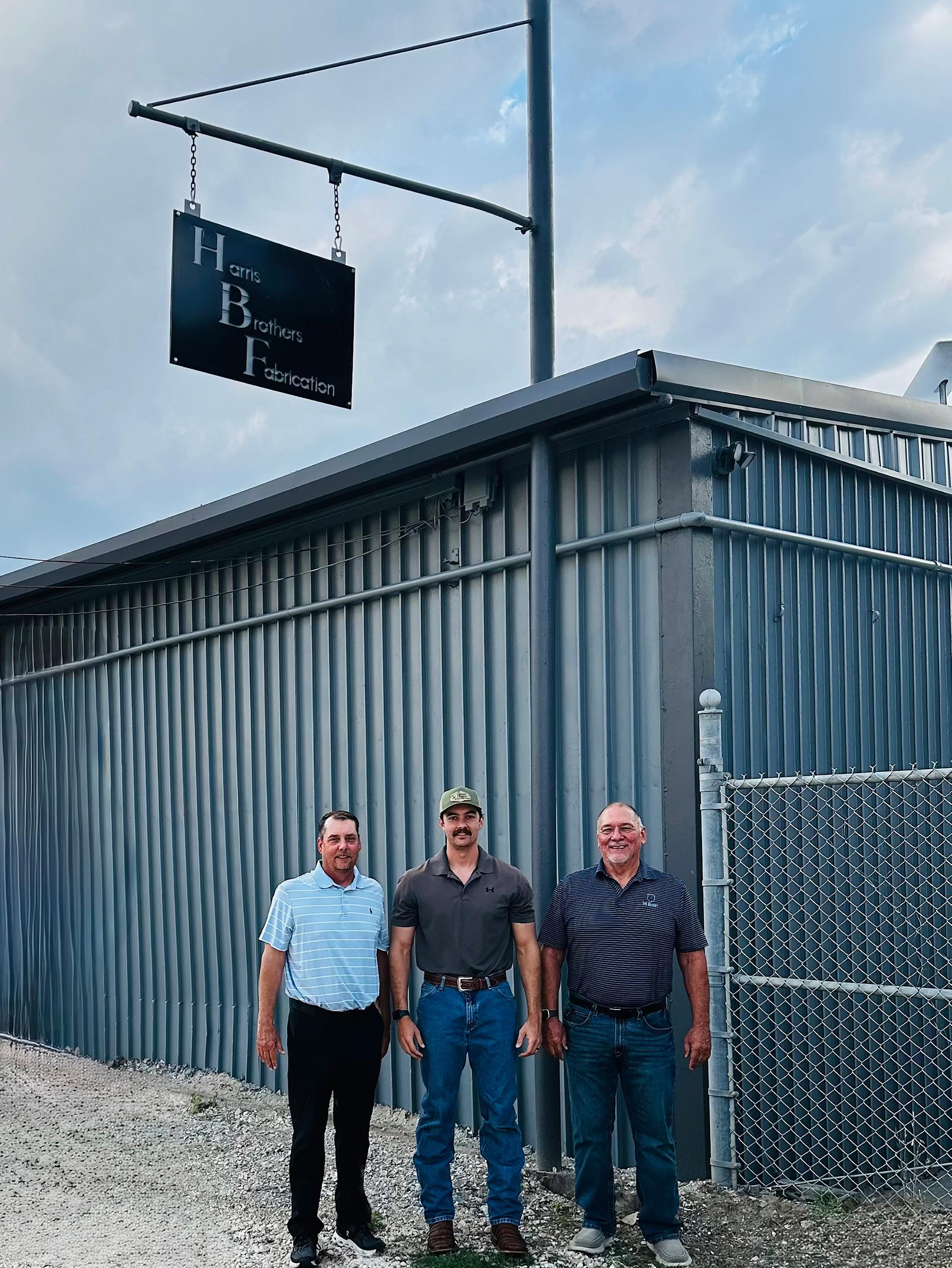
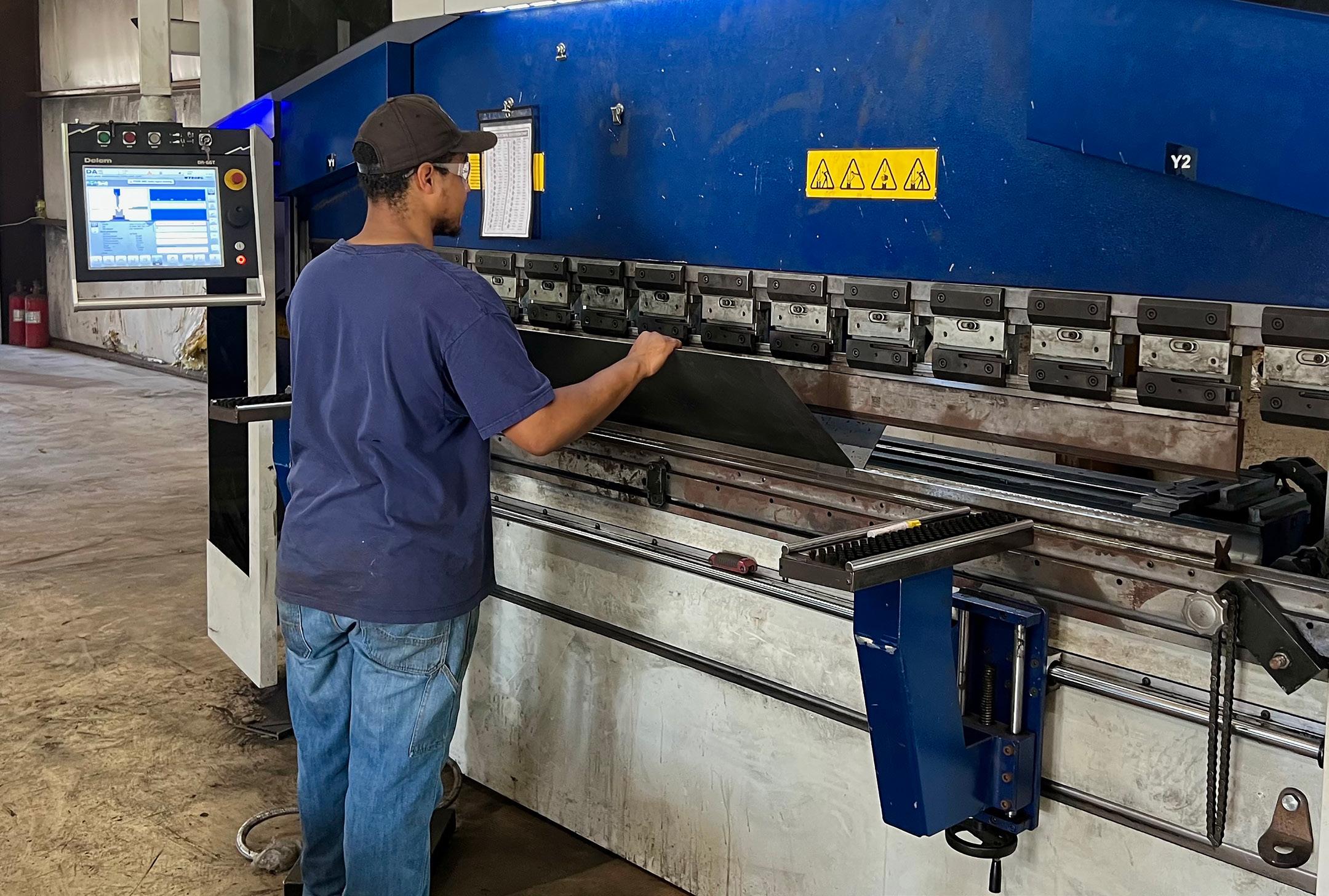
Briefly introduce me to Harris Brothers Fabrication and your collective experience of over 40 years in the industry.
Harris Brothers Fabrication is a company created to establish the best possible customer care and employee satisfaction in an industry that we feel has been lacking in both areas. Our Executive Team consist of Jeff Harris – CEO and owner, Steve Harris – Partner / AP, Brittany Harris – Office Manager, Hunter Harris – VP of Business Development. Jeff leads our team with 30+ years experience in the fab industry; he has run every machine out there at some point in his career and always has a solution to any problem you as a customer might have.
Following in his footsteps Jeff’s son, Hunter Harris, has roughly 10+ years experience in the industry. From the time Hunter stepped foot into fabrication Jeff
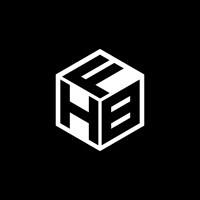
made him run every machine in the shop, maintenance them, troubleshoot them, schedule and run production, shipping and more just as he did to give Hunter the best understanding of the fabrication process before jumping into sales. With HBF you get people who know fabrication and have actually run these machines, you speak directly to decision makers, and you have a team that has a number 1 priority of putting your needs on top.
What, for you, differentiates Harris Brothers Fabrication from the competition?
There are several things that set us apart from your typical fabrication shop. First off we are small, but we use every bit of that to our advantage. When most customers think of small fab shops they think slow, un-organized, not established and unable
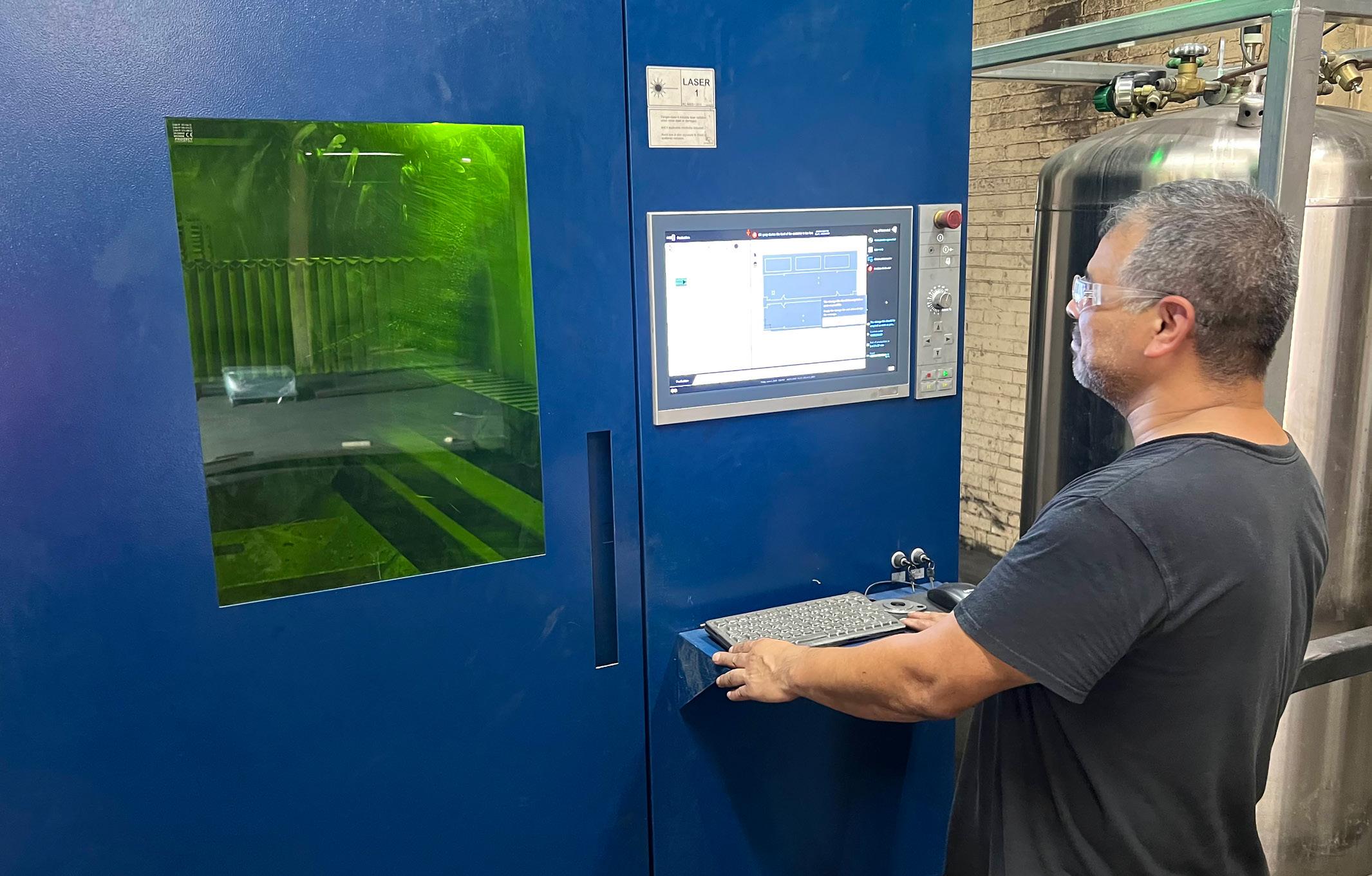
to handle volume. With our experience in the industry being a small – growing company actually increases our efficiency, allows for quick changes of course when a wrench gets thrown in and you need help, and creates a closer relationship with our customers, among many other things. Paired with our number one priority, customer satisfaction, volume is no issue. We will work day and night, weekends , whatever is needed to take care of your needs.
I understand you are a family-run business. Can you expand upon how these intimate origins make a difference in day-to-day business?
Being family. Especially part of this family, we call it how we see it. There are no secrets, no easing into any issues, we hit everything with full force, we argue, don’t always see eye to eye, but working with family you are going to have those
moments. What we all do know is at the end of the day after we all go home and rest, for some reason we all get back up and do it all again the next day. Our family is extremely driven, competitive, and loyal. We all enjoy the challenge of fabrication and working as a team to drive success at HBF. To be successful in business you need a closeknit team and you can’t get any closer than family.
Tell us more about the importance of prioritizing your employees, fostering opportunities for Clifton, TX, and ensuring customers receive the highest standard of service.
The fabrication industry is nothing more than a commodity business. Most fab shops now adays all have laser, forming, welding and rolling capabilities among others.
The only thing we have that can make us different is our people and how we interact
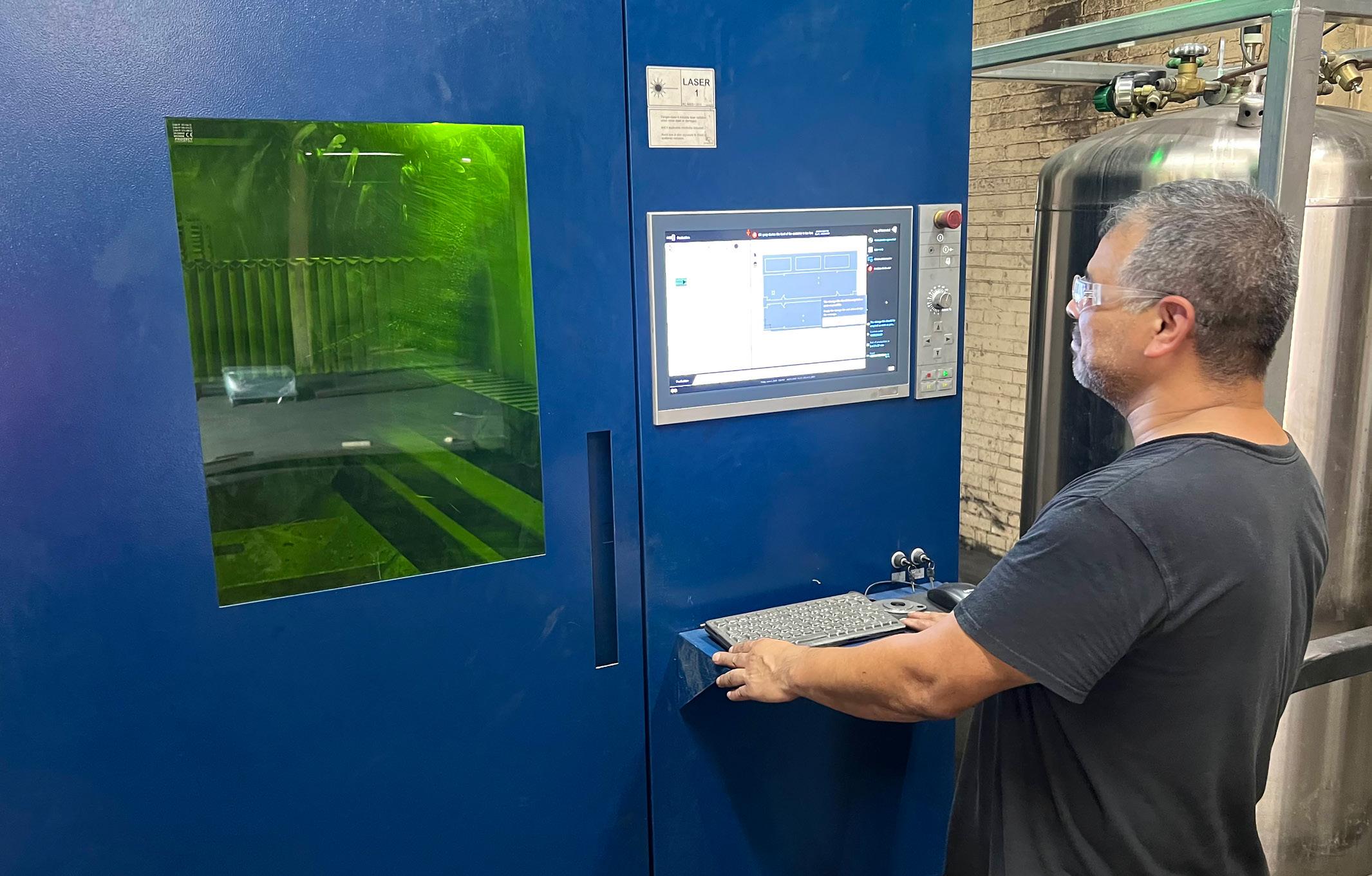
with the customer. That is why we hold the most pride in taking care of all of our customers the best we can and ensuring our employees have a safe, enjoyable place to work. When people ask why do business with HBF or why go work for that company we want the first thing that comes to mind to not be pricing or money nor capabilities and benefits. While all important, we’d rather your first thought be they are trustworthy, caring and I know if there is a way they can help me in any way, they will.
Can you please expand upon your relationship with Diamond C and the services you provide?
Our relationship with Diamond C goes back to sometime around 2019. They were one of Hunter’s first large accounts, and he established a relationship and that grew over the course of the years becoming one of the biggest reasons HBF is in business today. I believe the reason our relationship thrives the way it does is because their mission and ours so tightly align. We have had the pleasure to work with many individuals at Diamond C and toured their plant several times. They truly value their employees better than any business out there. We currently provide laser cutting, forming and powder coated parts for them and are looking into expanding our capabilities into welding certain subassemblies as well.
What completed, ongoing, or recent projects would you like to showcase in the article? For each, please provide some key details and explain why the project is important or special to the company. One key project just completed earlier this year was the addition of our second press brake. This allowed us to double our bending capacity and ensure no sudden halts in production if one machine
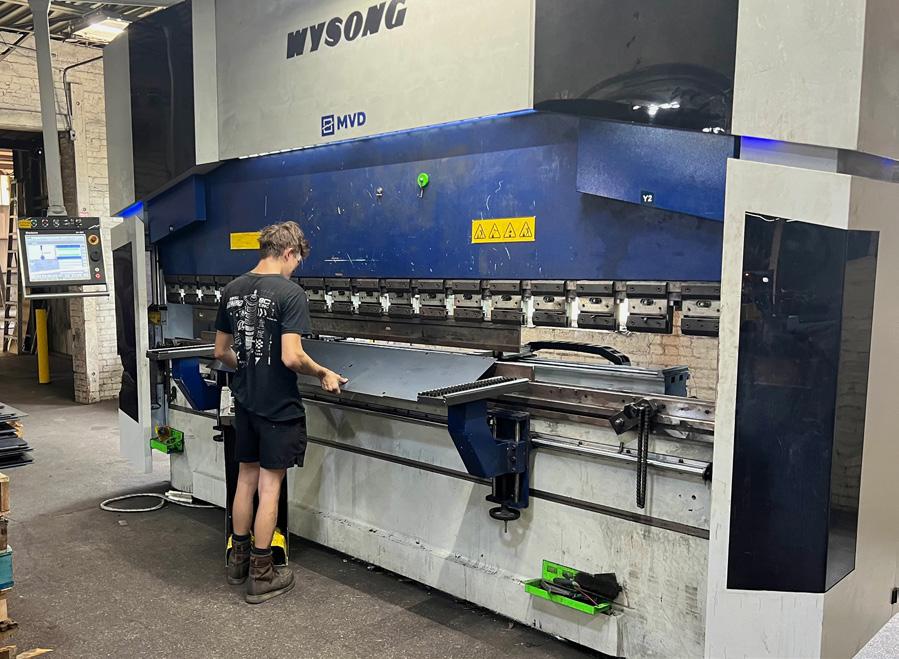
went down. Some upcoming items on the checklist include getting our ISO certification, the addition of a larger laser with capabilities of cutting 12-20’ lengths of material and a third press brake capable of bending up to 18’ material. Each addition at this point is strictly based on our customers needs. If they need robotic welding, machining capabilities, etc then we will be happy to explore each option with them.
Looking ahead, what are your key priorities for the coming year? Are you aiming to hit any specific targets, reach any goals, expand, or diversify at all?
Our goal moving forward is simple. We are not looking to hit a certain dollar amount or grow to a certain size, we simply want to continue providing the best possible service to our customers and expand according to their needs and provide more opportunities for people in our community to come work for HBF.
Is there anything that hasn’t been touched upon that you would like to be mentioned?
We would love the opportunity to work with you in the future! Please get in touch with Hunter for any inquires.
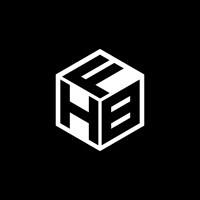
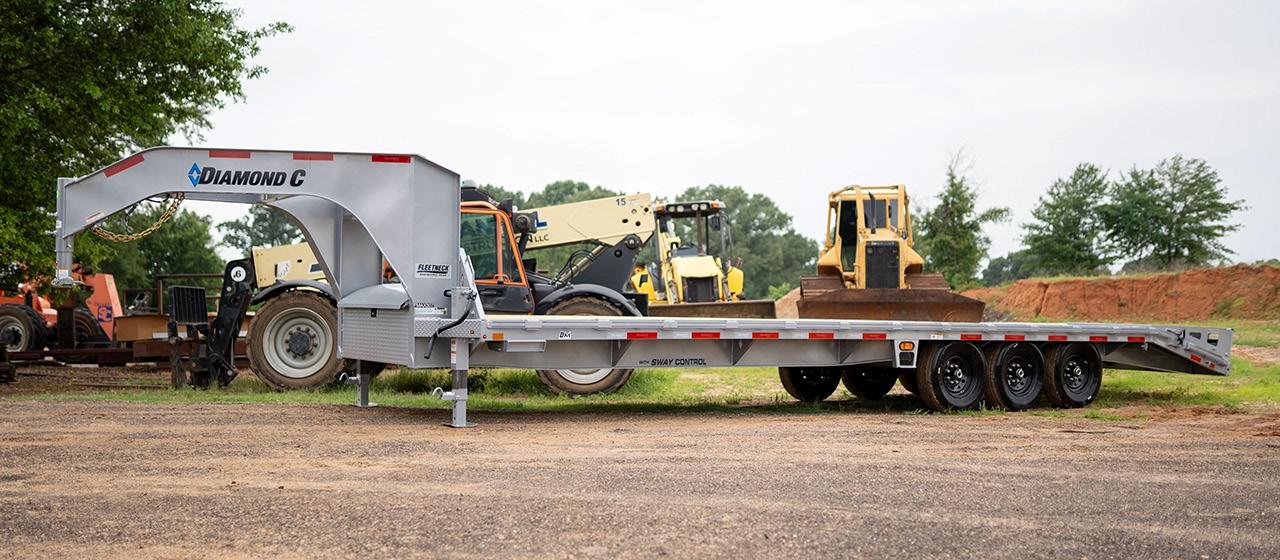
“AT DIAMOND C, WE’RE CONTINUING TO POUR FUEL ON THE INNOVATION FIRE – PUSHING THE LIMITS OF TRAILER ENGINEERING, CUSTOMIZATION, AND DESIGN”
– JACOB CRABB, CHIEF CUSTOMER OFFICER, DIAMOND C TRAILERS
“In an era where it’s increasingly common for second generations of families to sell or step away, we feel a deep responsibility to carry the torch forward. The foundation my parents
DIAMOND C TRAILER OPTIONS
• Accessories
• Axles and suspension
• Body and sides
• Coating
• Flooring
• Frames
• Hydraulics
• Jacks and couplers
• Loading options
• Storage
• Tires and wheels
built isn’t something we take lightly –we believe our greatest impact still lies ahead,” expands Crabb.
With this family mindset at the forefront, Crabb currently views the trailer industry as an incredibly dynamic space with both headwinds and tailwinds.
The rapid evolution of the supply chain, acceleration of digital transformation, and rise in customer expectations are making it a particularly exciting time to lead with innovation and integrity.
“We’re proud of where we’ve come from – and even more excited about where we’re going,” asserts Crabb.
“We welcome feedback, partnerships, and collaboration from those who share our drive to build something meaningful, durable, and different. The best is still ahead!”
EXTRAORDINARY TRAILERS AND SERVICE
Most recently, Diamond C launched the HXD Extreme Duty Tilt Trailer – a truly standout moment built for serious hauling performance
and representing the next level of engineering and durability.
It went on to swiftly earn the Manufacturer Innovation Award at the 2024 North America Trailer Dealers Association (NATDA) Trailer Show, the continent’s largest trailer dealership-specific trade show and a one-stop shop for light and mediumduty trailer industry professionals.
“We’re also continuing to invest in smarter manufacturing systems and enhanced digital tools to elevate the overall customer experience,” details Crabb.
Diamond C’s constant dedication to innovation not only sets industry standards but also showcases how the company prioritizes building extraordinary trailers to simultaneously work hard and play hard.
Equally as crucial to the development of trailer innovations are the company’s values of honesty, respect, humility, and pure integrity.
“Our values aren’t just statements on a wall; they’re the foundation of how we show up every day.

PROVIDING INNOVATIVE HYDRAULIC DRIVE AND CONTROL TECHNOLOGIES
Deutsche Hydrapro delivers cutting-edge braking systems by leveraging the combined expertise of our North American team, European engineering partners, and advanced manufacturing in Australia.
NEW UPCOMING MODELS:
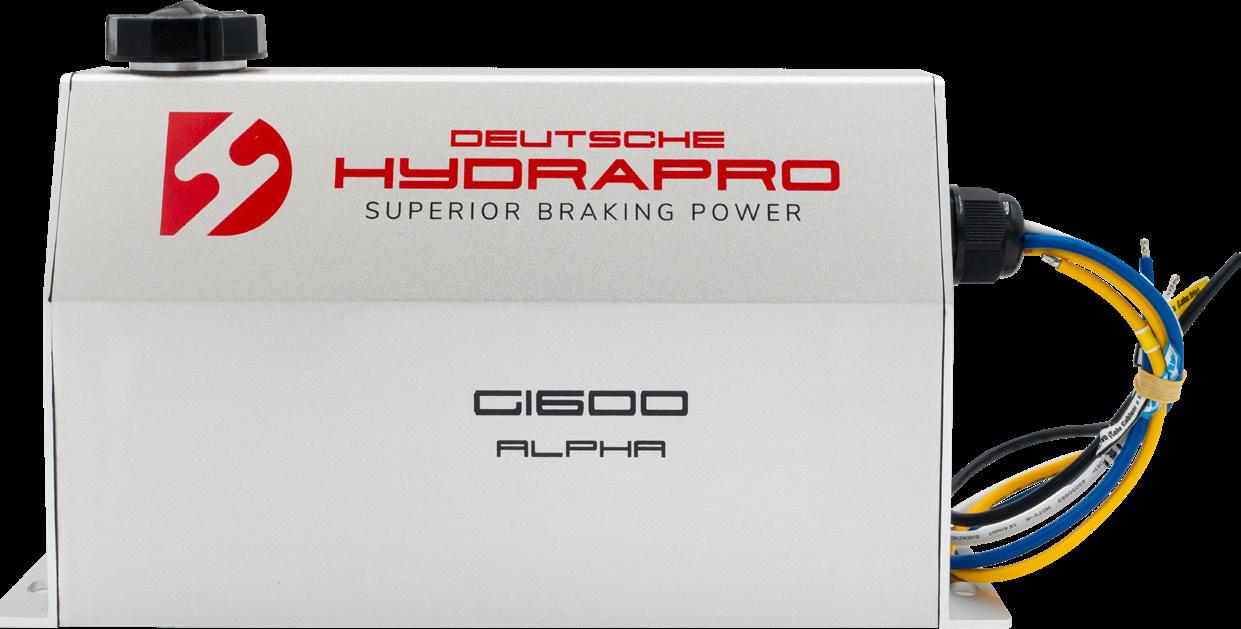
•
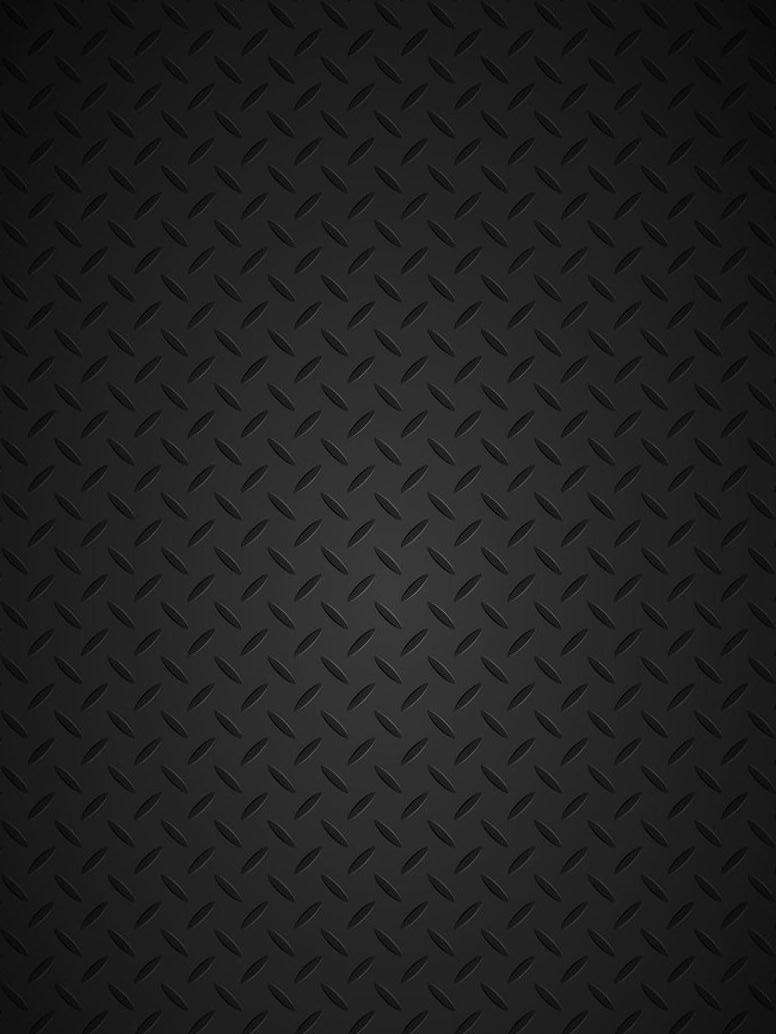
•
• Alpha Series Signature EOH Series w/ Advanced Sensors and Data Analytics.
OUR ACTUATORS HAVE BEEN INTEGRATED INTO
• Utility, Livestock, Boat and other Trailers
• 5th Wheel RVs Consumer & Commercial EVs
WHY DEUTSCHE HYDRAPRO?
• Aerospace & Military
• Agriculture Equipment
• Automotive & Autonomous Vehicles
We specialize in Electric-Over-Hydraulic brake actuators and are committed to developing innovative, highperformance systems that ensure safe and reliable trailer braking worldwide. We also offer consulting services in hydraulics, electronics, and brake-by-wire system design, helping clients develop or optimize products for automotive, aerospace, EV, military, and autonomous vehicles.
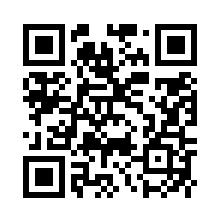
Delta Series
First of its kind with bluetooth brake controller built into the actutor.
Bravo Series
First of its kind with a built in breakaway battery and charging system
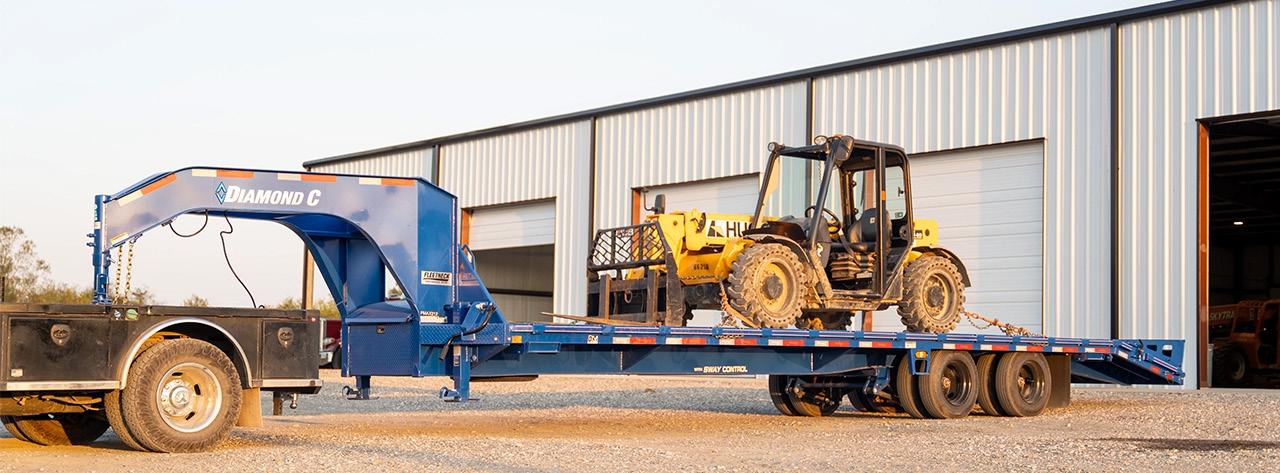
We believe in doing work that matters – with purpose, grit, and craftsmanship – and in loving strong, which means caring deeply for our team, customers, and community,” describes Crabb.
These principles come to shape every decision Diamond C makes, from the ways in which it leads its staff and serves partners to the ways in which it owns its mistakes and stays true to what’s right, even when it may be hard.
“Culture is our compass, and our values are what keep us grounded and moving forward with clarity and conviction,” he affirms.
This passion allows the company to continue to produce innovative, feature-rich trailers and live out its purpose to fuel the well-being, growth, and success of its team members, clients, and wider community abroad.
DO WORK, LOVE STRONG
Crucial to Diamond C’s growth and success as a family-owned and operated business are the company’s employees, who drive it forward on a daily basis.
“We believe our people are our greatest strength, and we’re committed to creating an environment where they can thrive,” states Crabb.
The company invests in both personal and professional development through leadership training, advancement pathways, and scholarship programs that support
“WE DON’T JUST BUILD TRAILERS – WE BUILD SOLUTIONS THAT SOLVE REAL PROBLEMS FOR PEOPLE WHO DEPEND ON THEIR EQUIPMENT DAY IN, DAY OUT”
–
JACOB CRABB, CHIEF CUSTOMER OFFICER, DIAMOND
C TRAILERS
continued education.
Recognition is also a core part of Diamond C’s culture, as it celebrates monthly Difference Maker Awards by department, honors employee tenure milestones, and offers company-wide incentive programs that reward those who go above and beyond in their service.
“Everything we do is rooted in our purpose – to fuel the growth and success of our team, customers, and the communities in which we serve,” dictates Crabb.
In parallel, Diamond C supports local non-profits, school programs, and economic initiatives in and around East Texas, further emphasizing how giving back is not just an afterthought – it’s a reflection of who the company is and the kind of legacy it seeks to establish for generations to come.
As Diamond C looks toward the future and continuing its legacy in the coming decades, it is placing a major focus on enhancing the customer experience and ensuring that every interaction – from online research to final delivery – is seamless, responsive, and rooted in a commitment to care.
This includes rolling out improved digital tools, reducing lead times, and deepening support for the company’s nationwide dealer network.
Additionally, Diamond C is accelerating the growth of Baseline – its new mid-tier trailer brand built around the principle of ‘basics done best’. The brand is designed to deliver high-quality, no-nonsense solutions for hard-working users who need dependable performance without unnecessary complexity.
“At Diamond C, we’re continuing to pour fuel on the innovation fire – pushing the limits of trailer engineering, customization, and design,” proudly concludes Crabb.
“Innovation has always been in our DNA, and this year, we’re doubling down on that legacy to lead the industry forward.”
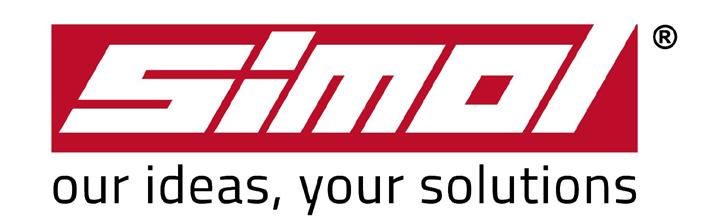
Simol’s Italian Quality Meets Diamond C’s Vision: A Partnership for Trailer Leadership

At Simol S.p.A., excellence isn’t just a statement — it’s a legacy. For over 60 years, we’ve been designing and manufacturing trailer jacks in Italy, combining mechanical precision, innovative design, and a deep understanding of real-world needs.
What truly sets Simol apart is that our products are handassembled in Italy by expert craftsmen. Each jack is the result of true artisanal skill, paired with industrial-grade performance — because we believe that attention to detail makes all the difference when safety and reliability are on the line.
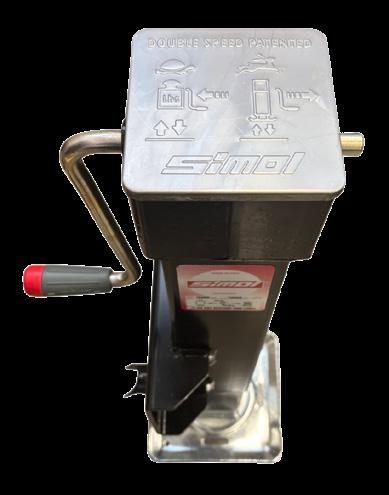
Today, we’re proud to bring that legacy to the American trailer industry, a market that values strength, performance, and long-term reliability. Becoming a supplier for Diamond C Trailers, one of the most respected names in the field, marks a significant milestone in our global journey. From the very beginning, the response has been immediate and enthusiastic: Simol is already recognized for what sets us apart — uncompromising quality, exceptional durability, and the unmistakable DNA of Italian engineering.
Every Simol component is developed with a clear mission: to deliver safety, reliability, and superior functionality, even in the most demanding environments. Our jacks are more than mechanical supports — they’re the result of meticulous design, continuous
innovation, and rigorous testing.
To ensure performance under the toughest conditions, we’ve developed an advanced testing bench in collaboration with the University of Bologna. This innovative system allows us to conduct high-precision stress tests on all our products. It not only validates the reliability of our jacks but also enables us to optimize existing models and develop custom solutions that meet ISO 12140 standards and the most demanding customer specifications.
What makes us different? It’s not just our premium materials or cutting-edge manufacturing processes. It’s a philosophy. We believe every trailer, every machine, and every load deserves the kind of precision and care that only true craftsmanship can offer. And we believe “Made in Italy” should mean more than a label — it should stand for performance, beauty, and trust.
Our entry into the American market is more than just exporting products — it’s about building lasting partnerships. With manufacturers like Diamond C, we offer face-to-face collaboration, technical support, and a human touch. Because quality isn’t static — it evolves with our partners’ goals. At Simol, we’re not here to be just another supplier. We’re here to be a strategic ally, supporting the future of mobility, one reliable component at a time.
Simol Patented Technologies: DU Model
Our patented DU Model offers unmatched flexibility: a compact solution designed for maximum versatility across various trailer applications. Whether robust support or smooth maneuverability is required, the DU Model adapts without compromising strength or stability.
Simol W Double Speed
An international patent, Simol-W is our revolutionary rapid gear change system. It features a single horizontal shaft, allowing a slimmer gearbox profile while dramatically improving performance:
• 3x Faster Lifting
• 70% Reduction in Working Time
• 10% Less Operating Force
Required
Safety Drop Leg System
Simol’s patented Safety Drop Leg is a built-in solution that replaces traditional external chain systems. It enhances durability, reduces maintenance, and offers safer, faster operation in all conditions.
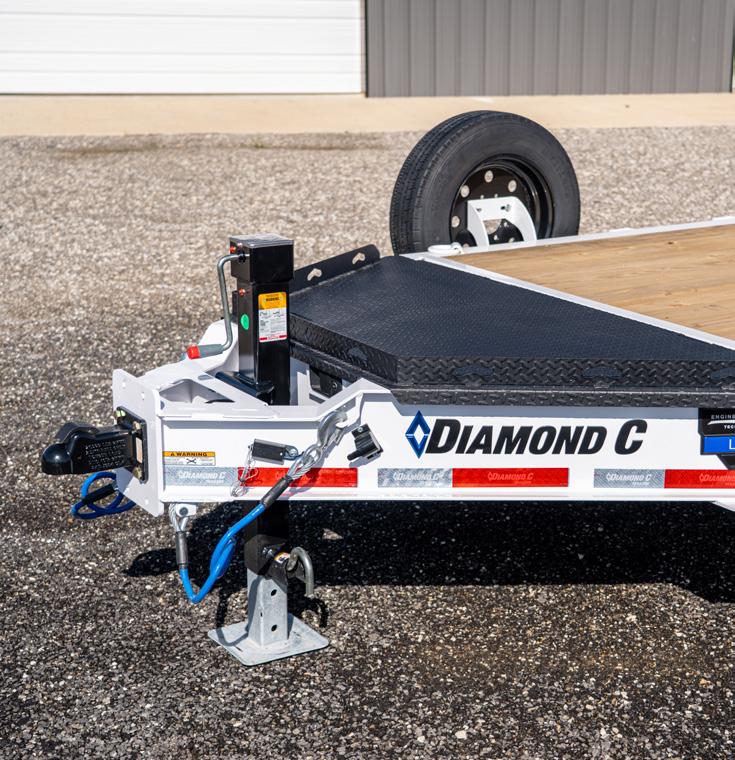
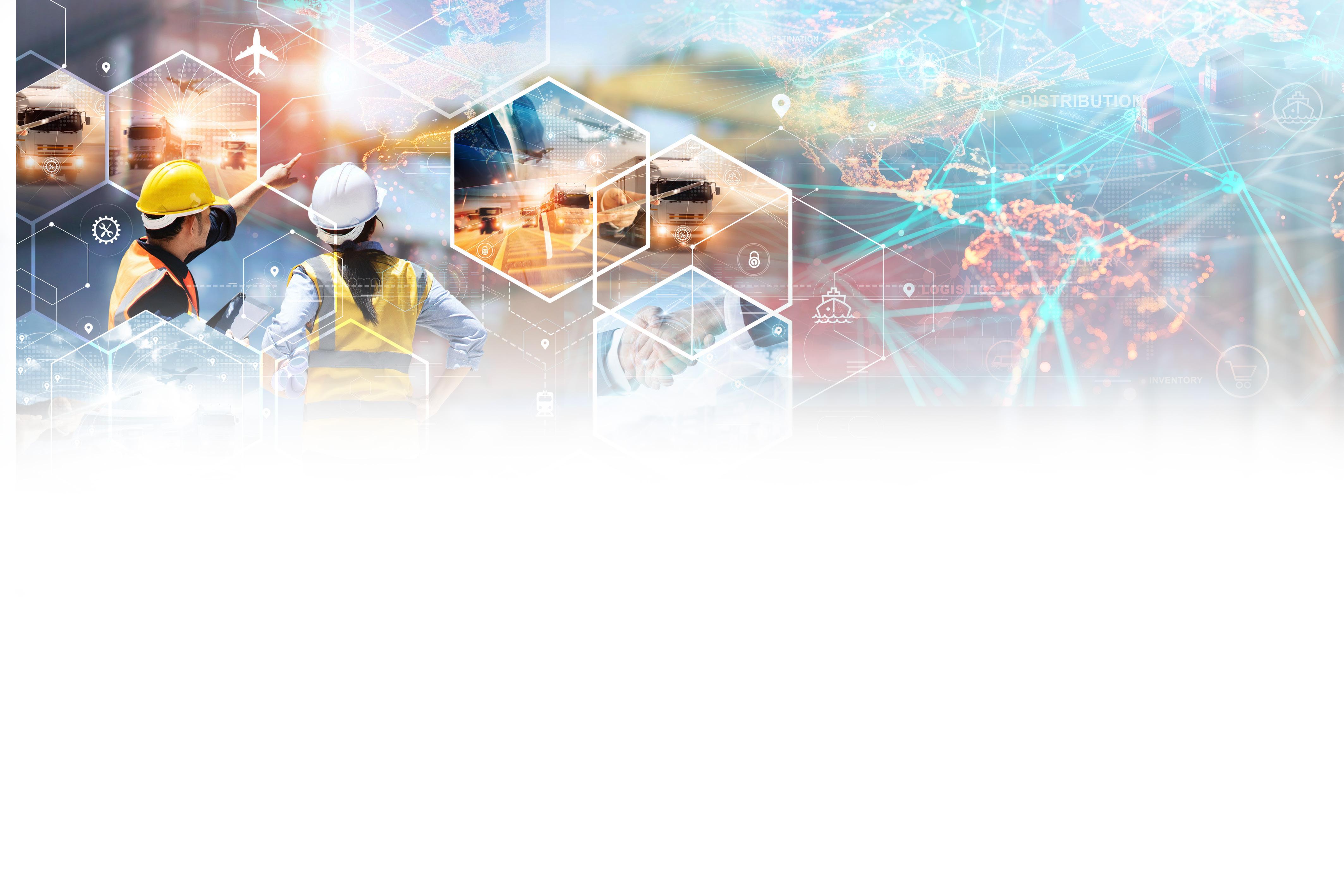
The global resource for supply chain professionals and organizations
Building on the global success of our regional titles – EME Outlook, Africa Outlook, APAC Outlook, and North America Outlook – Outlook Publishing is proud to introduce a digital magazine and web platform, dedicated to the supply chain sector.
As supply chain organizations worldwide confront unprecedented change, embracing technological innovations and incorporating critical environmental sustainability agendas, now more than ever is the time to showcase the strides being taken in this dynamic sector.
A multi-channel brand, Supply Chain Outlook brings you the positive developments driven by organizations across the global supply chain industry through its various platforms. Discover exclusive content distributed through its website, online magazine, social media channels, and dispatches delivered straight to your inbox with a bi-weekly newsletter.
Through this compelling new venture, we foreground the movers and shakers of the industry. To participate as a featured company and join us in this exciting endeavor, contact one of our Project Managers today.
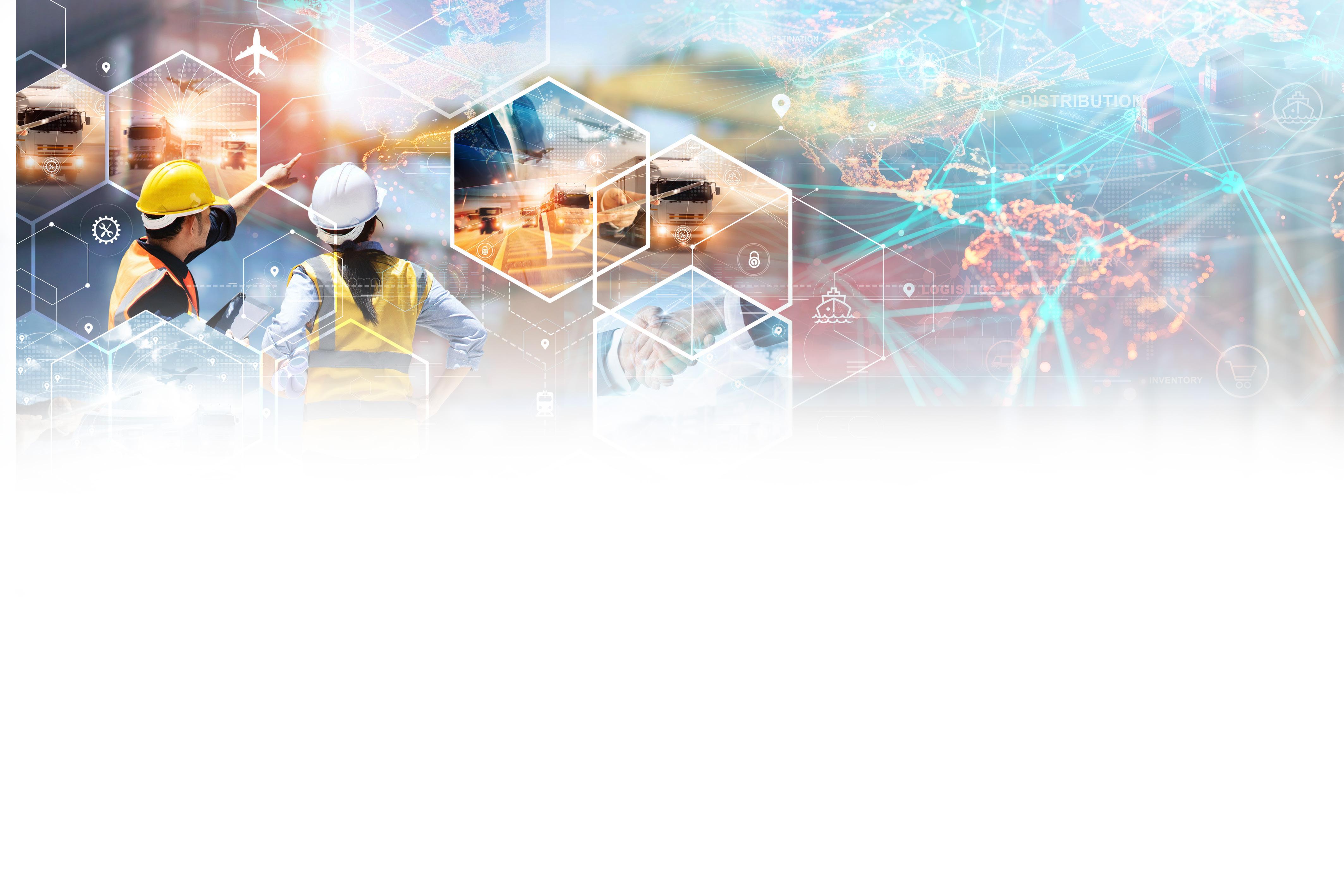
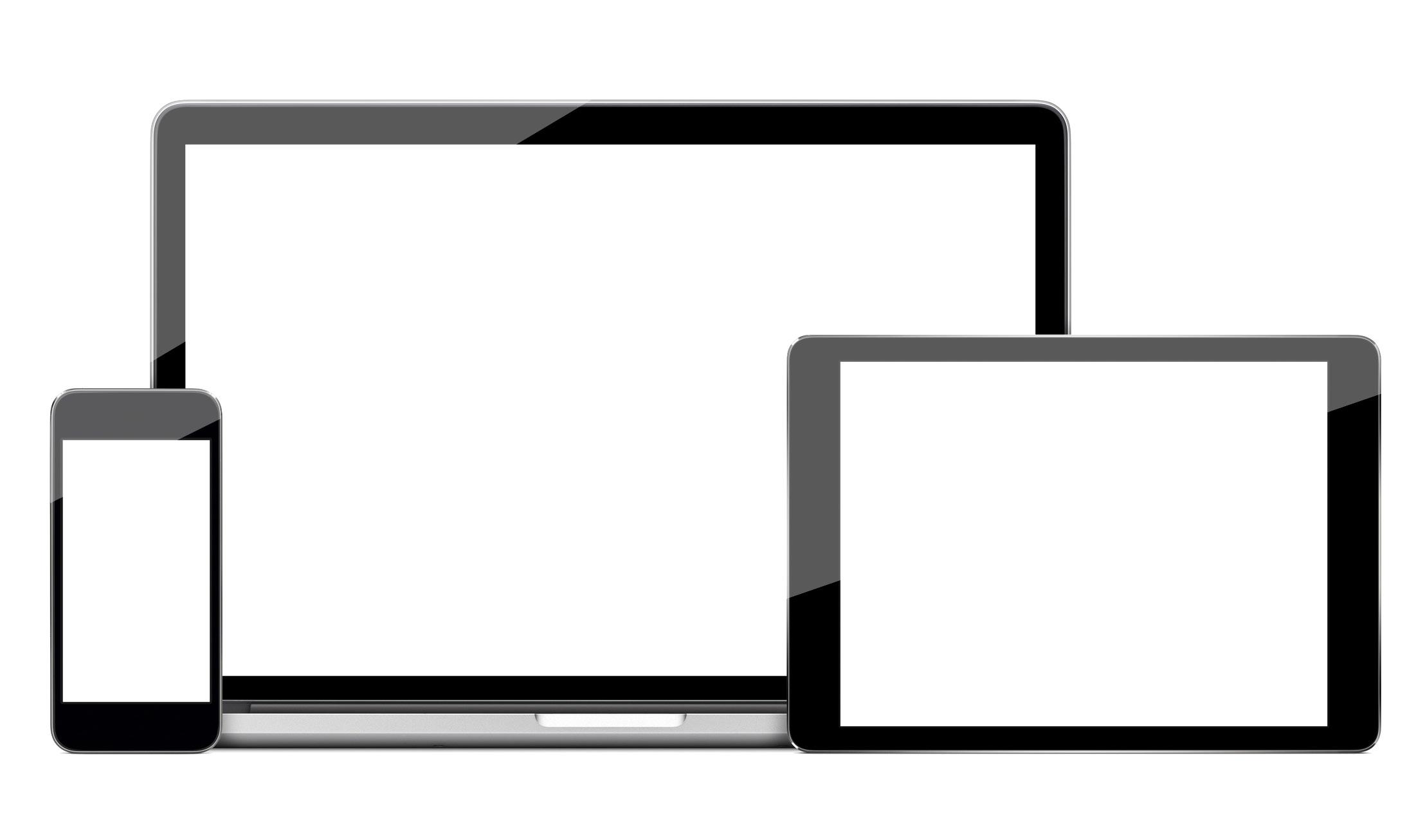
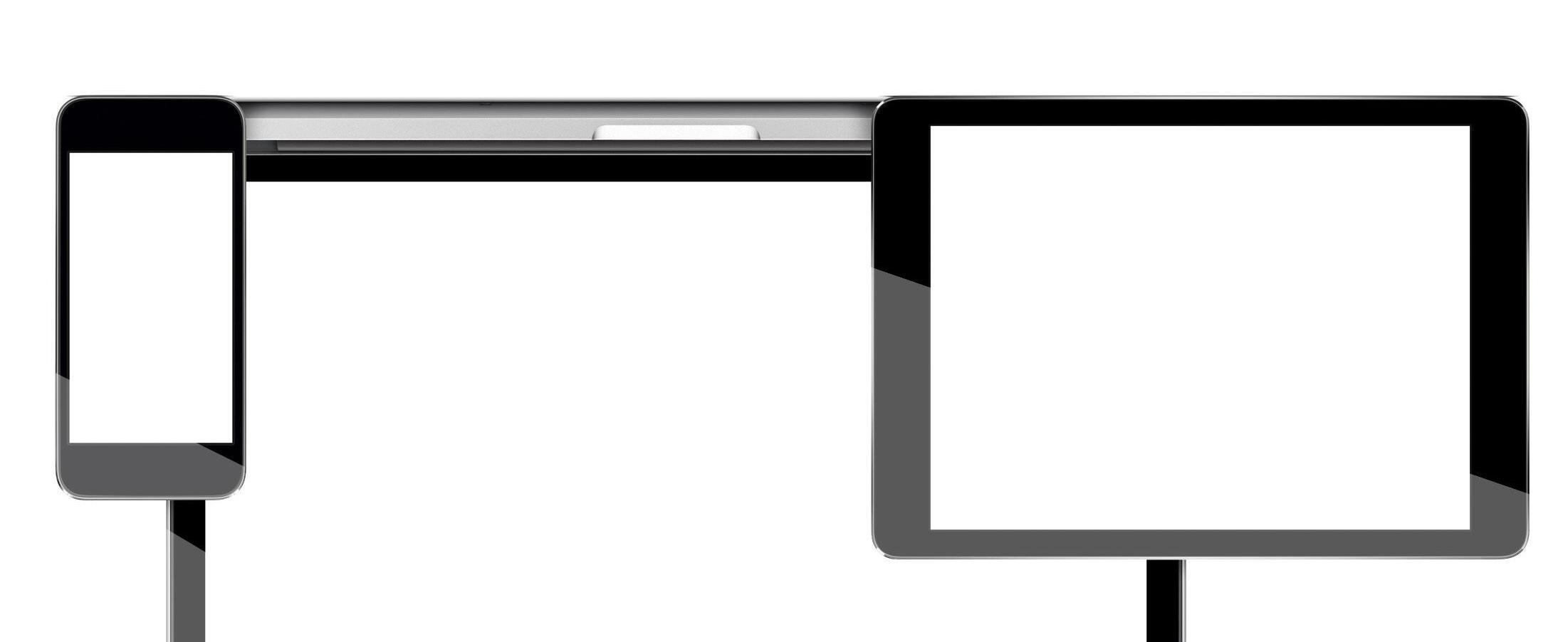
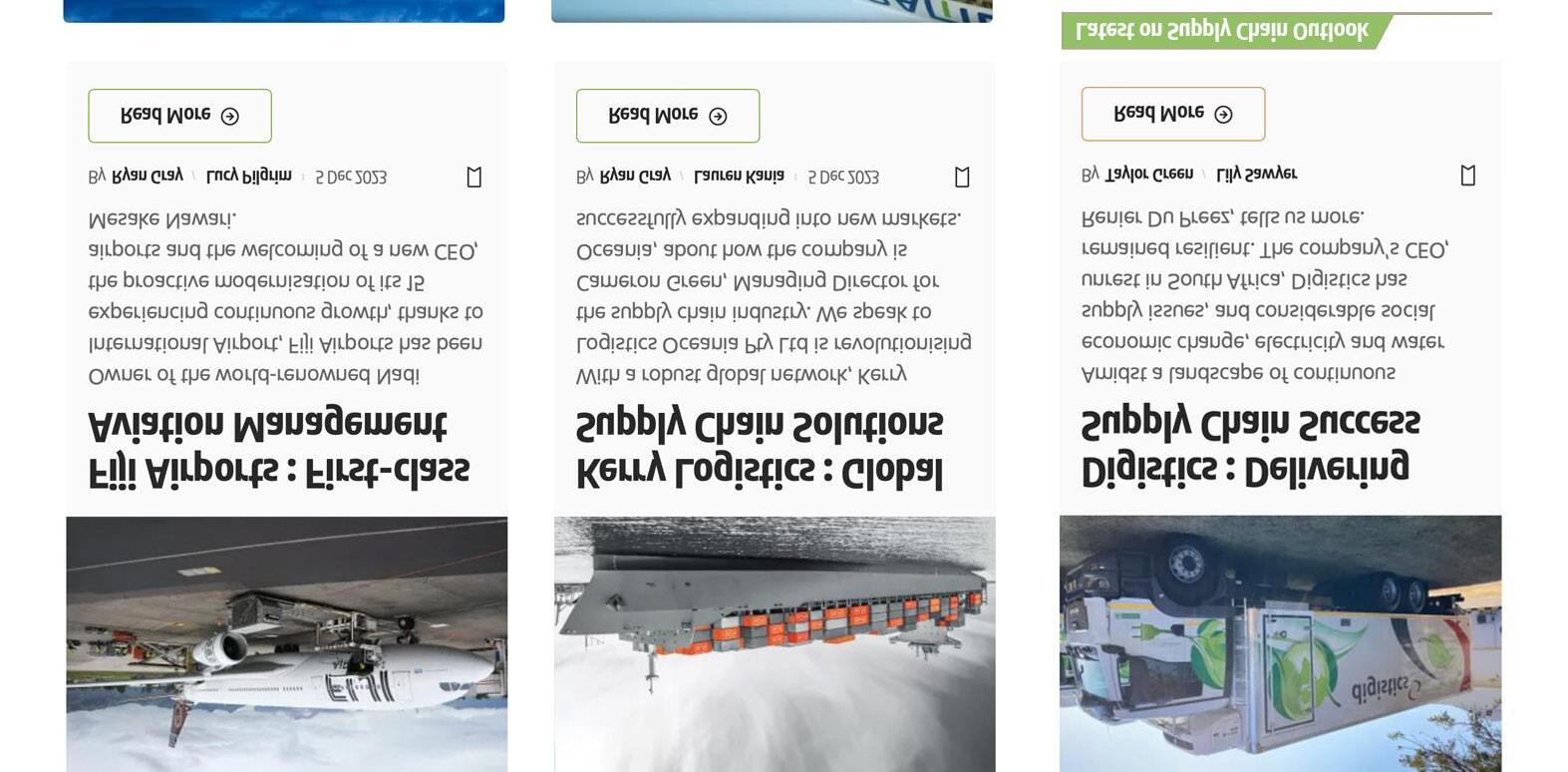
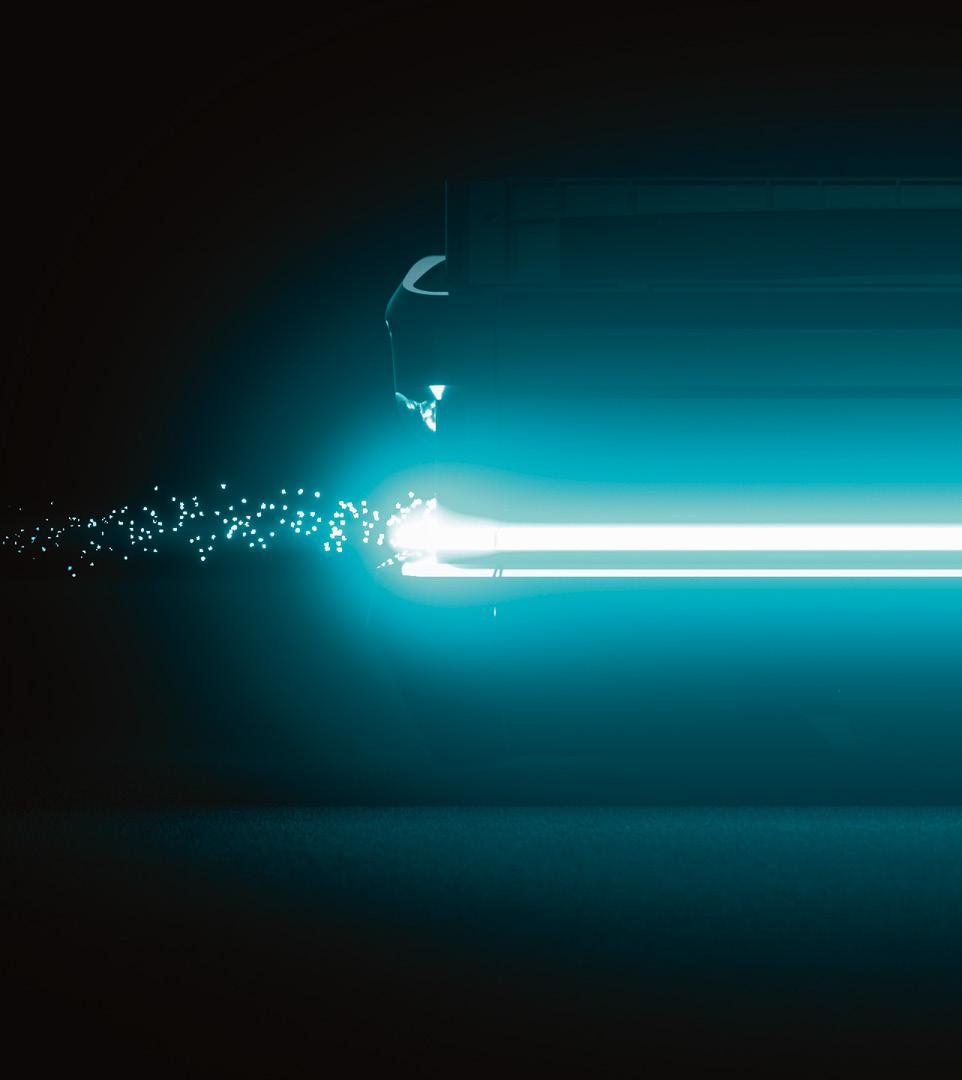
DIMENSIONS
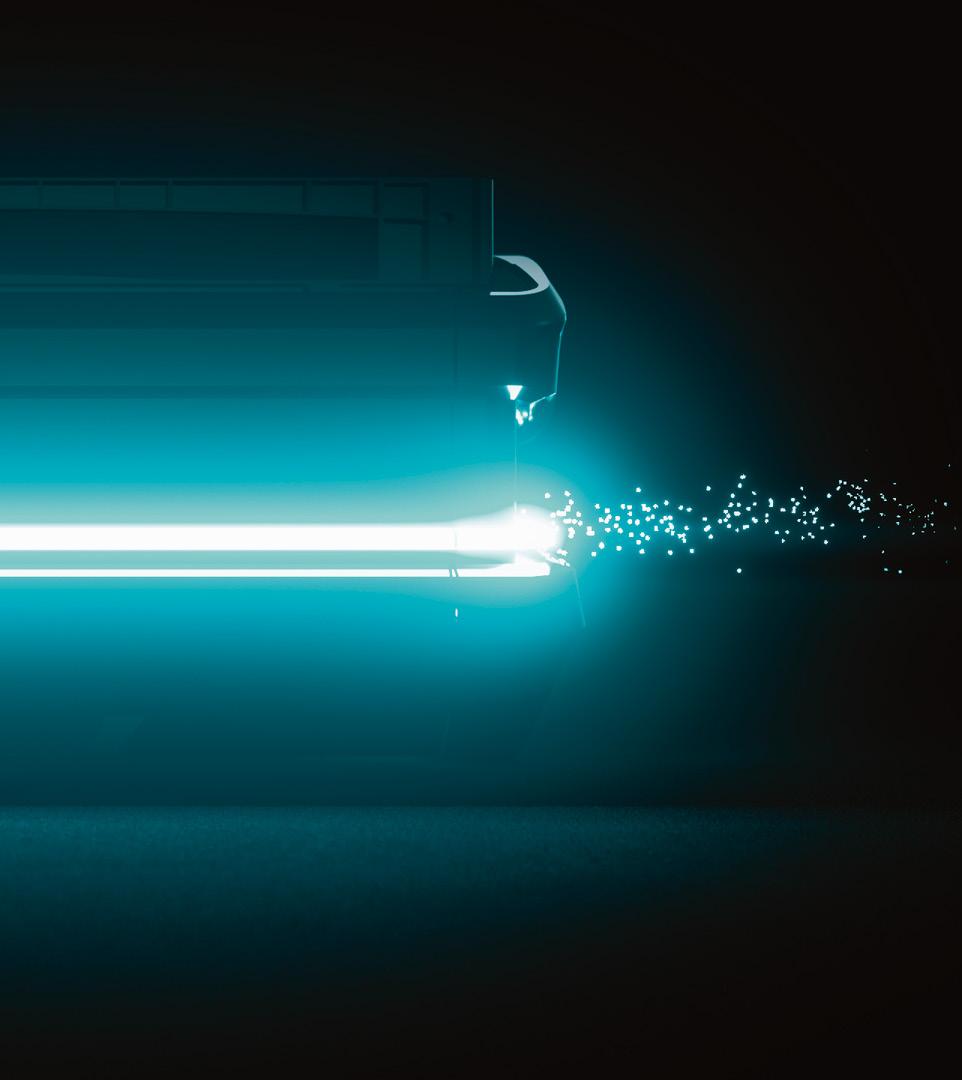
An industry-leading provider of intelligent automation solutions for intralogistics and manufacturing, KNAPP operates across 62 locations worldwide. Andreas Salznig, COO of KNAPP North America, discusses the company’s recent award-winning innovations and future aspirations
Writer: Lily Sawyer | Project Manager: Poppi Burke
Largely driven by technological innovation, socioeconomic fluctuation, and shifting consumer expectations, global supply chains have been undergoing significant transformations over the past five years.
Post COVID-19 pandemic consumer behaviors saw an acceleration of digital transformation and e-commerce, fueled by machine learning (ML) and artificial intelligence (AI).
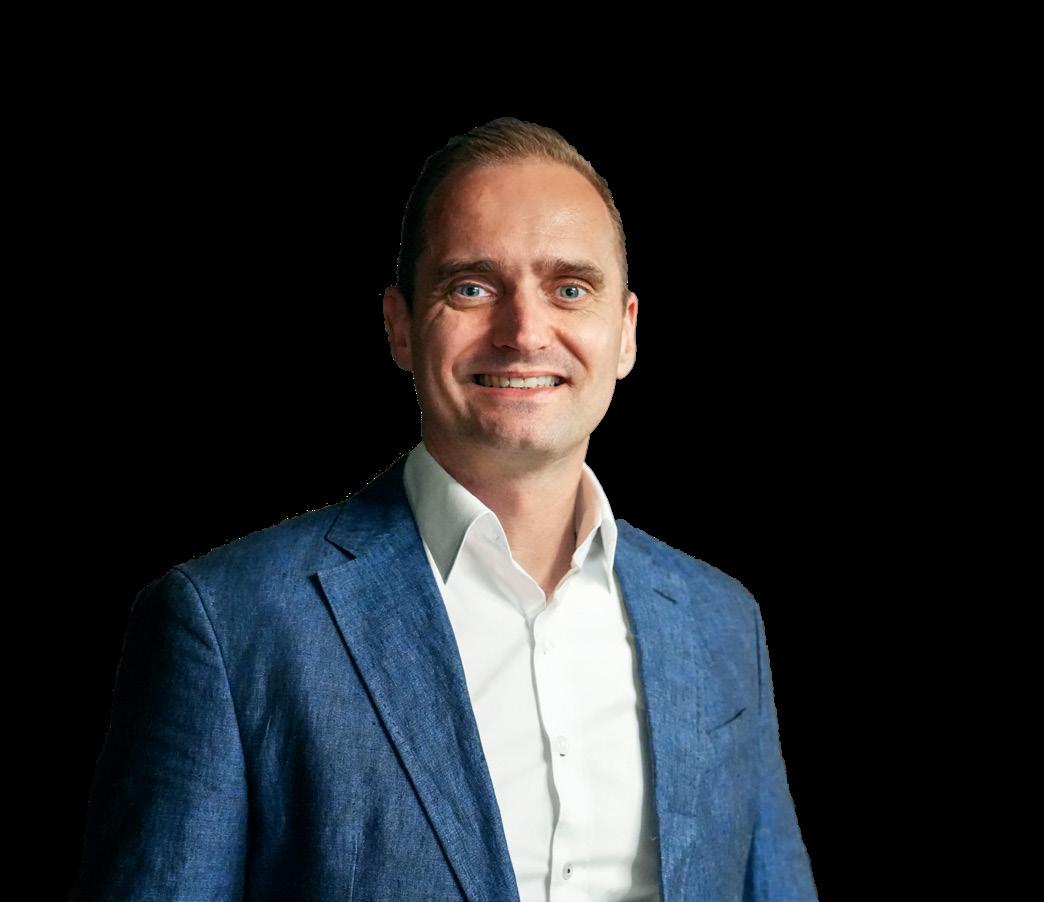
“KEY TO OUR SUCCESS IS THE FACT THAT ALL OUR TECHNOLOGIES SEAMLESSLY INTEGRATE WITH ONE ANOTHER, OFFERING EXCEPTIONAL FLEXIBILITY”
– ANDREAS SALZNIG, COO, KNAPP NORTH AMERICA
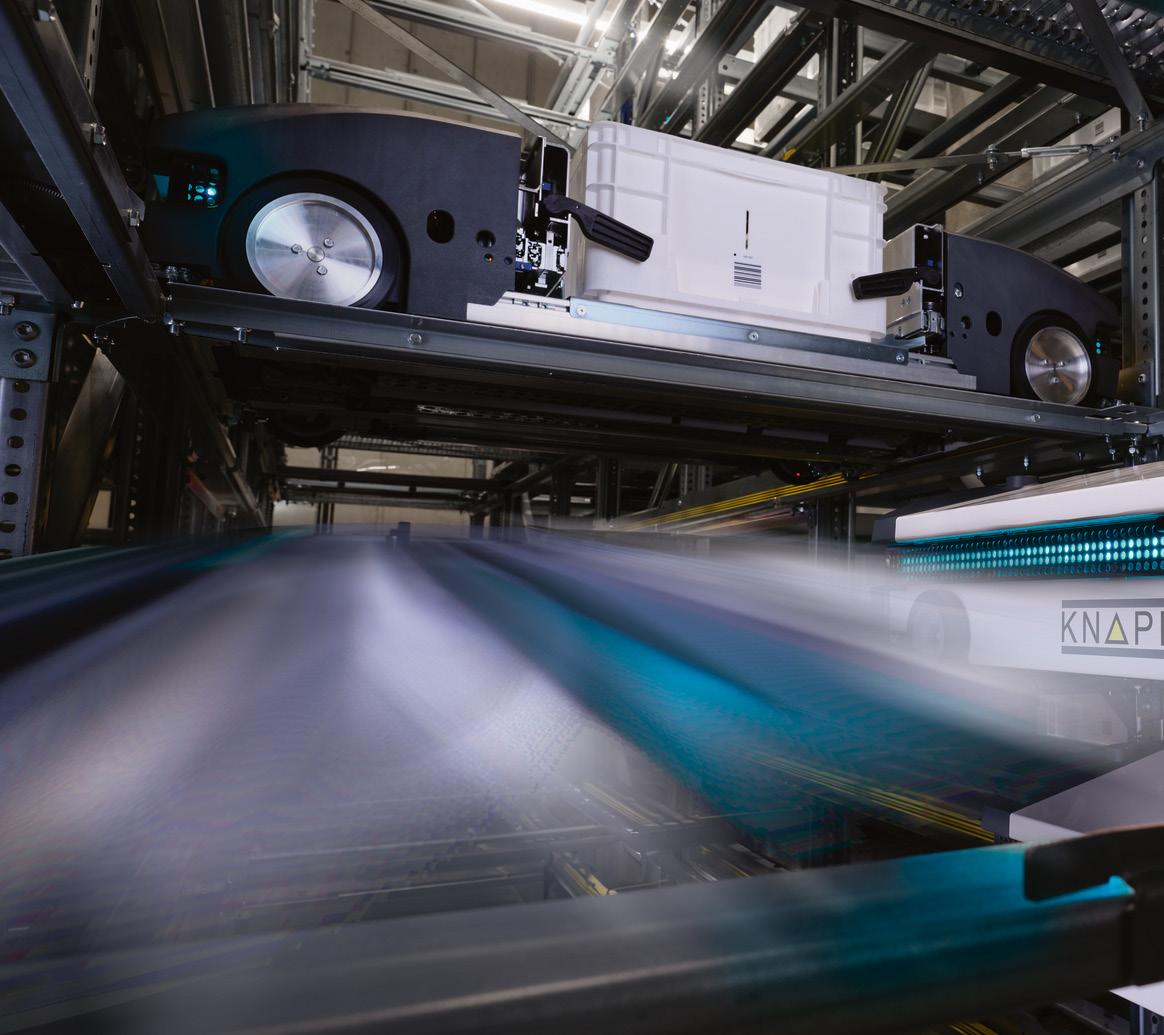
As such, an emerging preference for online shopping, coupled with increasing labor shortages, began to push companies toward automation, particularly in warehousing and logistics.
Andreas Salznig, COO of KNAPP North America, remarks, “Today, the widespread adoption of robotics and automation has become essential for maintaining operational efficiency.”
Meanwhile, green logistics continues to gain momentum, with numerous opportunities for greater sustainability emerging across supply chains.
As a value chain tech partner, KNAPP’s activities in North America include designing, developing, and manufacturing intelligent warehouse systems, alongside point of sale and last mile logistics solutions.
Of the 2,000+ automation installations KNAPP oversees globally, a growing proportion of these are in North America –including major customers such as Walmart, who partnered with KNAPP to build four ultra-modern fulfillment centers, with a fifth on the way.
“Whatever complexities our clients need to solve, within our portfolio
we can offer the right technology and solution to handle it, from pallets to single pills,” Salznig adds.
Having become a trusted, stable partner for its clients in the healthcare, retail, fashion, food, wholesale, manufacturing, and e-commerce sectors over the years, KNAPP is ideally positioned for continued growth and success.
FLEXIBLE, AGILE, REACTIVE
Driven by its company-wide motto ‘rise to new dimensions,’ KNAPP seeks to embody this theme in its everyday products and processes.
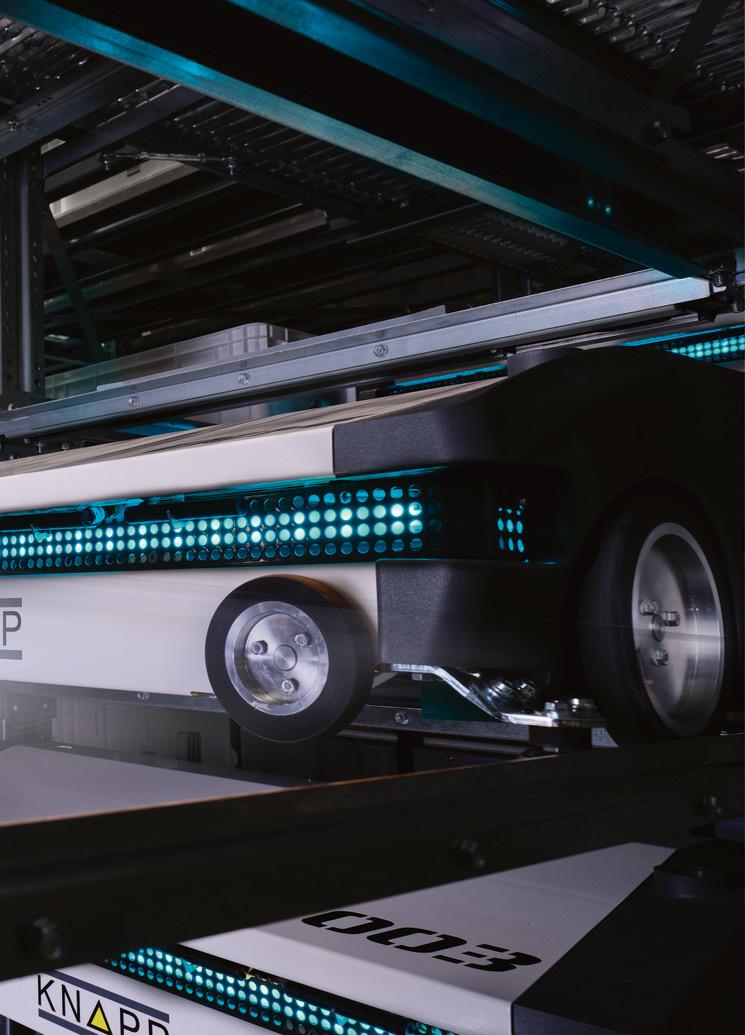
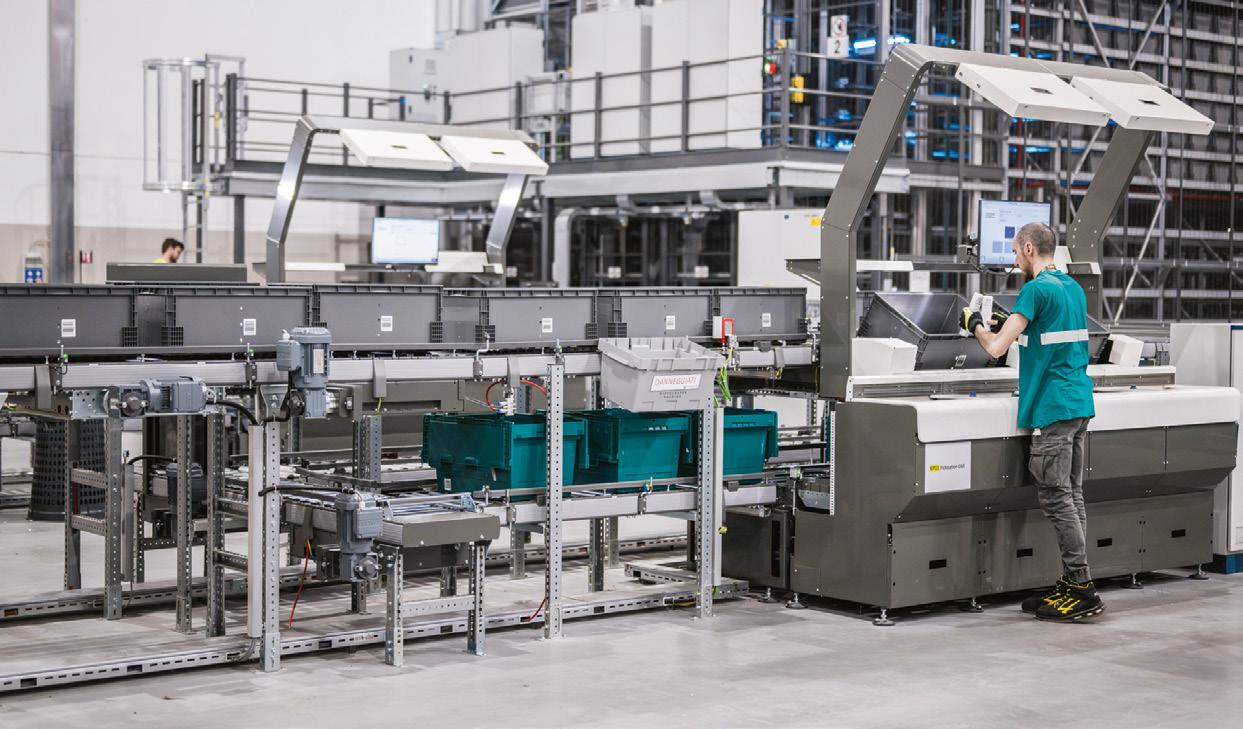
HOW CAN KNAPP’S DIGITAL SOLUTIONS ENABLE SUSTAINABLE LOGISTICS?
Andreas Salznig, COO:
“Sustainable logistics is all about efficiency – doing the right thing at the right time, utilizing the equipment in the right way, and using energy efficiently.
“KNAPP’s bot-solutions are built in a way that they can use latent energy when braking or climbing down a rack to recharge batteries, as with AeroBot. In this way, energy is recycled into the battery.
“Sustainability through digitalization in logistics is only possible with software as integrated intelligence. That’s why we at KNAPP view the warehouse management system (WMS) as the ‘central nervous system’ of a warehouse.
“An efficient WMS can offer benefits such as clean warehouse processes, reduced resource usage and errors. Interconnected software then opens the door for other solutions like transport management systems, data analysis tools, or packaging optimization solutions.
“To realize highly efficient system solutions, data-analytics is necessary to provide the required information. Trained AI models, meanwhile, help us to forecast future orders days in advance and prepare systems for peakscenarios.”
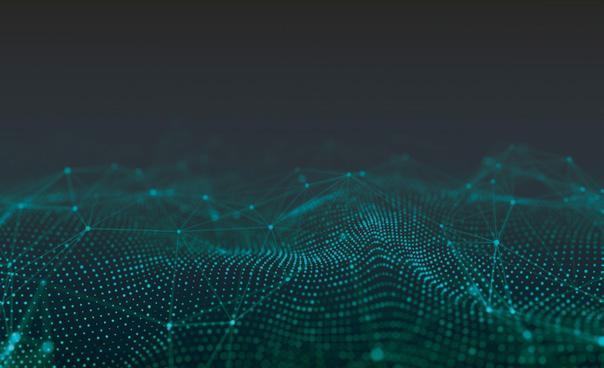
Reusable Packaging Redefined
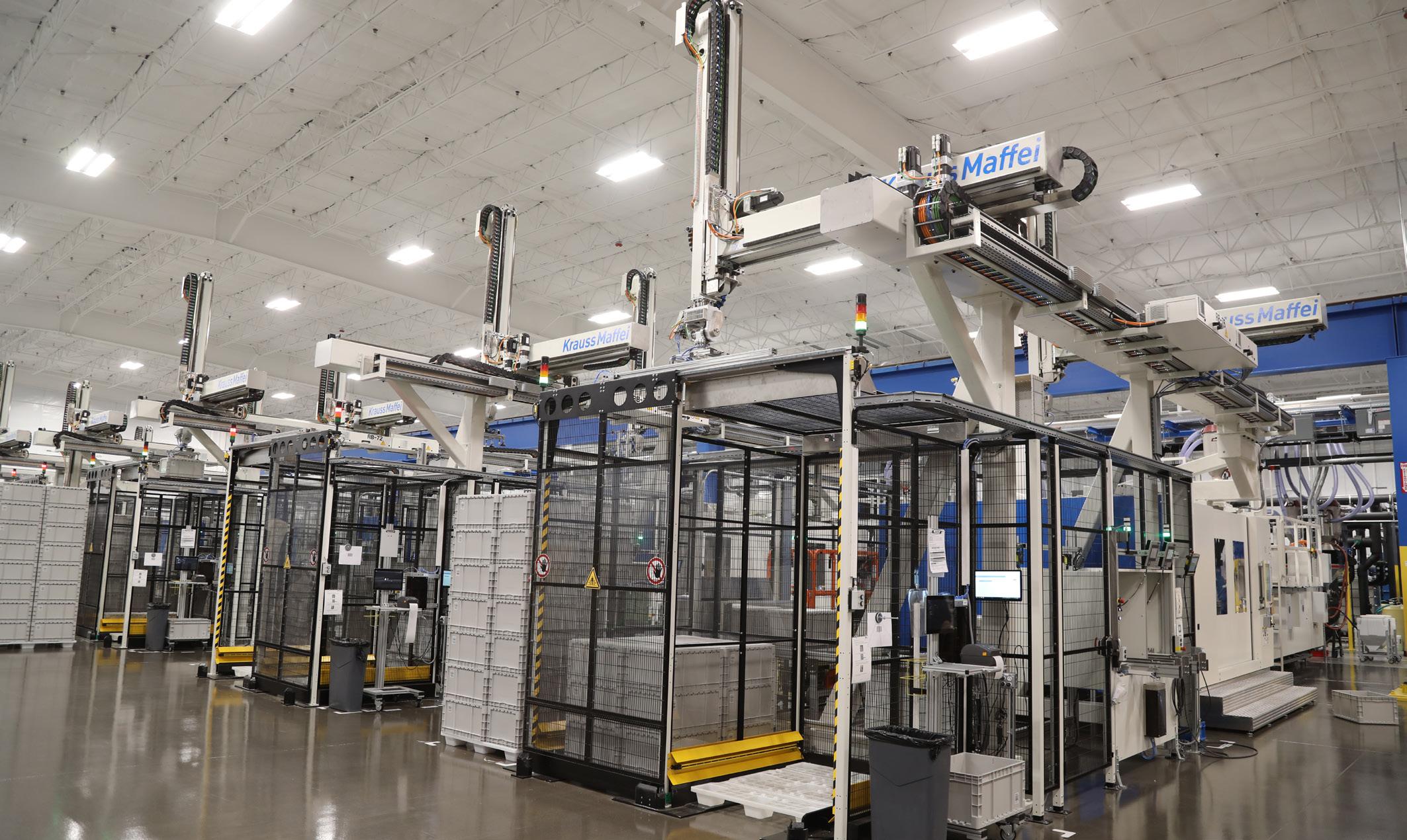
For readers unfamiliar with Monoflo International, can you share an overview of your company and the solutions you provide?
Monoflo International is a leading North American manufacturer specializing in high-performance, reusable transport packaging solutions. With over 50 years of experience, Monoflo produces injectionmolded plastic containers, trays, pallets, and bulk containers engineered to precise specifications for automated storage and retrieval (ASRS) and general use applications. Monoflo serves industries such as retail, e-commerce, manufacturing, automotive, processed food, wholesale bakery, and general distribution. Our solutions are designed to seamlessly integrate into high-speed automated systems, offering options like RFID tracking, barcode labeling, prototyping, and ASRS induction services—all with a focus on repeatable quality, long-term durability, and sustainability through recyclable and reusable products.
What role do Monoflo’s products play in highperformance automation systems like KNAPP’s?
Monoflo’s products are built for precision, durability, and reliability, making them ideally suited for highperformance automation systems like those developed by KNAPP. Our containers and trays are designed to exact dimensional tolerances to ensure flawless performance within automated environments. Features such as conveyor-friendly bottoms, reinforced corners, and pin up bottom lifter plates help reduce system jams, increase throughput, and maintain reliability. These design attributes ensure that Monoflo’s products move smoothly through high-speed systems, minimizing
downtime while supporting speed and efficiency in these highly demanding operations.
How do design and material choices in your containers impact the overall efficiency, durability, and reliability of automated warehouse systems? (chance to incorporate sustainability impact)
Monoflo’s containers are carefully engineered using high-quality resins like polypropylene (PP), high-density polyethylene (HDPE), and Electro-Dissipative ESD-safe materials, chosen for their strength and longevity in rigorous environments. Structural features like doublewall corners and hybrid bottoms enhance load stability and reduce wear during conveyor use. Ergonomic touches—such as molded handles, barcoding zones, and fire-vent sidewall designs—further support handling and safety. These thoughtful material and design decisions result in containers that are not only cost effective and durable but also sustainable, as every unit is 100% recyclable and part of a closed-loop system that includes end of life buy-back and environmentally friendly plastic reprocessing options.
What
customization or innovation
goes into developing containers tailored to a partner’s automation system needs?
Monoflo takes a collaborative approach to customization, engineering containers that precisely match the design use application, dimensional, and performance requirements of our partner’s automation system. This includes tailoring footprints to regional or application-specific standards, such as 600×400 mm,
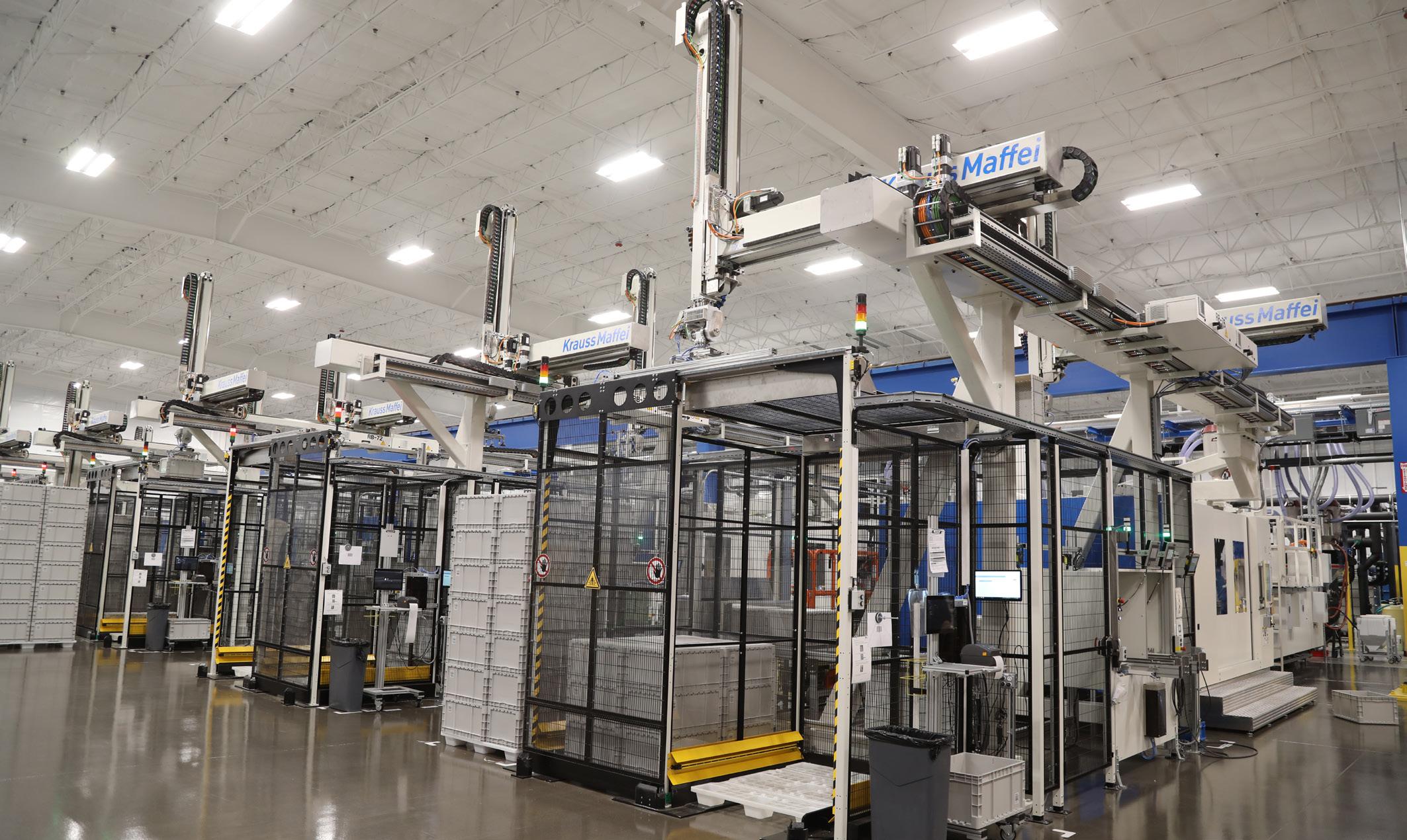
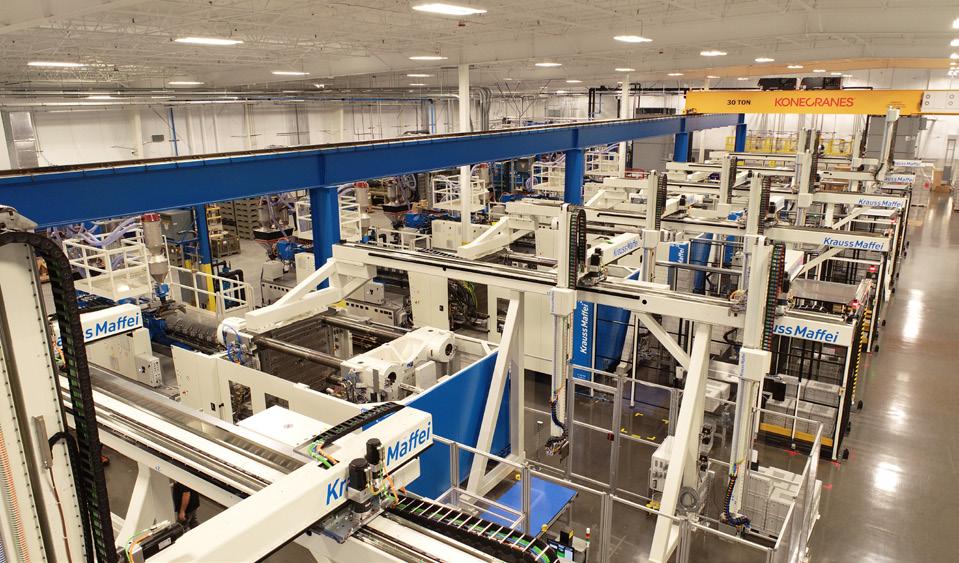
650×450 mm, or 800mm x 600mm containers, and even custom sizes for unique use cases. Innovations include in-mold RFID tags, integrated barcodes and/or QR codes for real-time system operation and tracking, as well as specialized features like internal divider systems, drain holes, lids, lifter plates, and ergonomic access points. These customizations ensure that every product supports seamless integration and optimal flow within automated environments.
How does Monoflo stay ahead in terms of design, manufacturing precision, and product durability for automated environments?
Monoflo maintains its competitive edge by investing in high-pressure, high-speed injection molding technology, robotic automation, and ISO 9001:2015-certified quality systems. Our ability to quickly prototype and iterate on designs allows us to rapidly bring precise, system-compatible products to market. With a track record of millions of deployed containers and trays across multiple industries, Monoflo combines field-proven experience with continuous product evolution—evident in the release of innovations like FM-compliant drain holes and next-generation container designs. Our commitment to precision manufacturing ensures that each product consistently performs in the most demanding automated environments.
What trends do you see shaping the future of containerized automation, especially in sectors like retail and e-commerce?
Containerized automation is rapidly evolving, especially in retail and e-commerce sectors where speed, accuracy, and sustainability are paramount. One major trend is the widespread adoption of smart containers embedded with RFID and scannable codes to support real-time tracking, inventory accuracy, and order delivery accuracy. Another is the shift toward circular supply chains, where durable, reusable, and recyclable containers help companies meet ESG goals. Additionally, there is growing demand for modular and collapsible designs that reduce, empty storage, and return logistics costs and warehouse footprint. As systems become more complex, containers must also
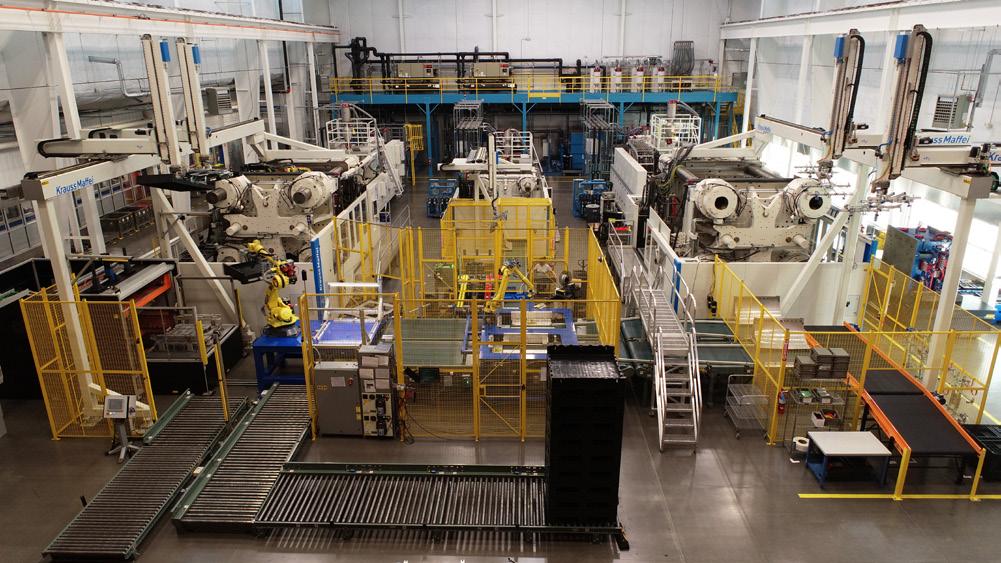
support multi-SKU handling through features like internal dividers and mini-tote formats that increase existing cube utilization.
What’s next for Monoflo—are there new product innovations or partnerships on the horizon?
Monoflo is advancing its leadership in automation by delivering engineered container solutions built for high-performance intralogistics systems. Its latest product innovations—such as automation-optimized totes, modular divider systems and pallet systems—are designed to seamlessly integrate with AS/RS platforms, conveyor networks, and robotic picking systems across a wide range of industries. Solutions are engineered with reinforced bases, FM Global-compliant drain holes, and optional features like welded or hybrid bottoms, integrated divider slots, and custom RFID or barcode tagging to ensure smooth, reliable performance in highspeed, 24/7 operations.
To better serve automation providers and end-users, Monoflo is also expanding its manufacturing and logistics footprint. With facilities in Winchester, Virginia, and Ottawa, Kansas, and a growing presence in León, Mexico, the company is positioned to shorten lead times by moving closer to its partners across North and Latin America.
Complementing its innovation and growth is a deep commitment to sustainability. Monoflo supports a circular supply chain with fully recyclable products, in-house reprocessing capabilities, and product buy-back programs that extend the life and value of every container. Looking ahead, Monoflo will continue to collaborate with system integrators and warehouse automation leaders to deliver precise, durable, and scalable container and pallet solutions that power the next generation of automated fulfillment.
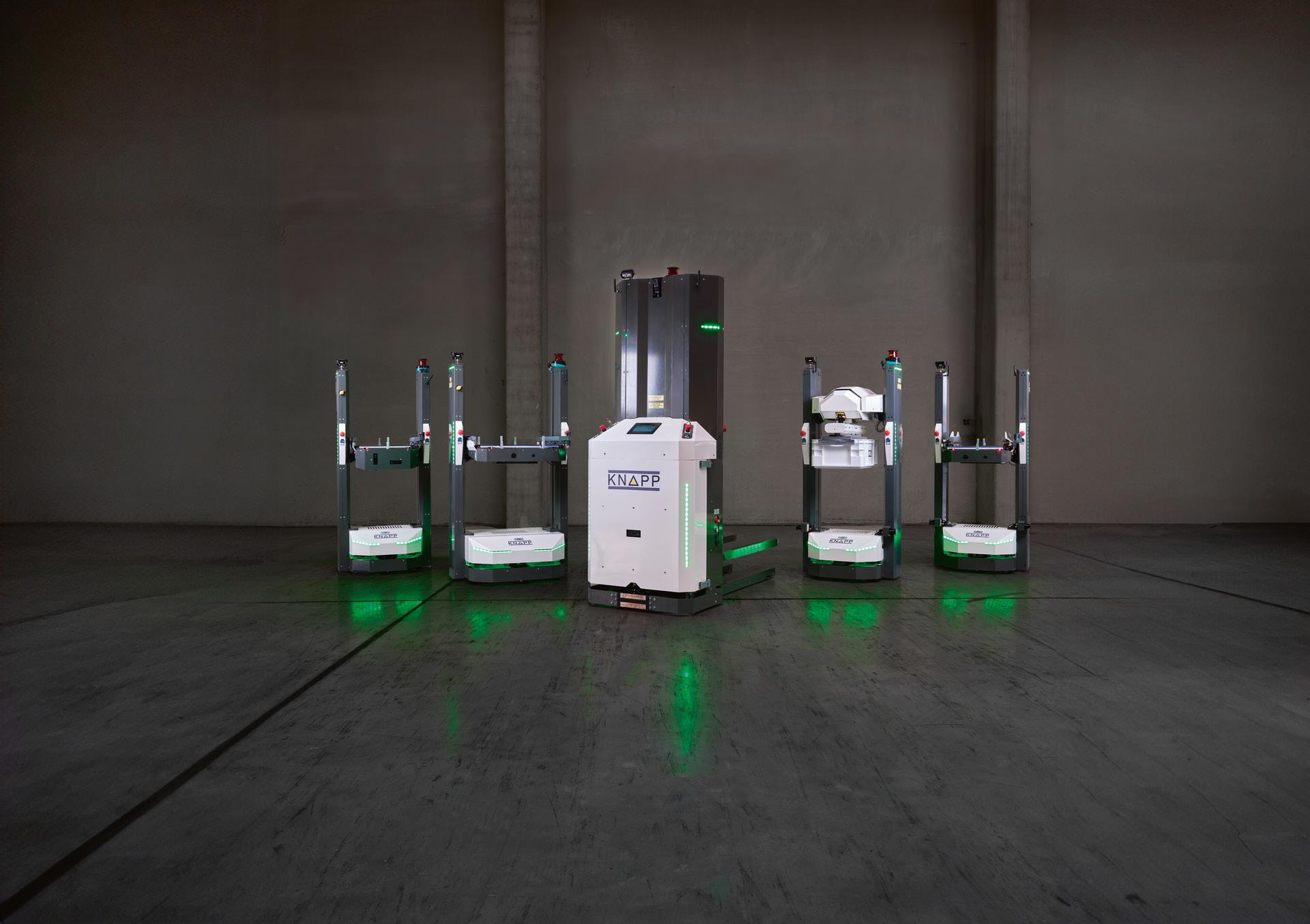
“WE STRIVE TO MAINTAIN OUR POSITION AS A BEST-IN-CLASS LEADER IN TECHNOLOGICAL SOLUTIONS”
– ANDREAS SALZNIG, COO, KNAPP NORTH AMERICA
Flexibility is at the forefront of this objective, with agile solutions and the ability to grow and adapt to ongoing challenges and changes in consumer behaviors being key priorities.
“We are proud to have a portfolio of products that allow us to consistently provide the best possible solutions –technically and economically – based on our customers’ requirements. Together, we rise to new dimensions, allowing our partners to do so by improving their service quality and delivery times,” Salznig remarks.
When it comes to supporting its customers, no matter the performance level, storage location, or service required, KNAPP is on hand to deliver tailormade solutions.
Reflecting on KNAPP’s recent
participation in the global supply chain conference ProMat 2025, where key speakers from the company spoke on the technology needs of hyperlocal markets, Salznig discusses how ‘one size does not fit all’ when it comes to providing logistics solutions.
“Every logistics solution must be designed in a way that, while addressing today’s requirements and operational pain points, is flexible and agile enough to be adapted in the future.”
Since it is nearly impossible to predict how end-customer needs will evolve over time, Salznig points out how it is vital to build a solution which enables growth, reactivity, and adaptation.
For example, KNAPP’s AeroBot system is an innovative solution that redefines automated storage and retrieval with unmatched flexibility, efficiency, and the highest storage density.
“Currently, solutions that provide an easier entry to automation and are flexible enough to adapt rapidly to market conditions are in demand,” adds Salznig.
Always open to developing new products and solutions, KNAPP’s ongoing focus remains on developing the broadest portfolio of technologies on the market, allowing it to address all market requirements with the optimal technical system solution while remaining cost-effective.
“Key to our success is the fact that all our technologies seamlessly integrate with one another, offering exceptional flexibility,” continues Salznig.
AWARD-WINNING SOLUTIONS
Offering a new level of efficiency to storage and retrieval processes, AeroBot recently received the Best
The warehouse of the future requires smart racking solutions
THE WORLD OF STORAGE IS CHANGING RAPIDLY. GROWING SECTORS, NEW MARKETS AND CHANGING CUSTOMER EXPECTATIONS REQUIRE INNOVATIVE SOLUTIONS. FOR NEDCON THIS MEANS THAT WE NOT ONLY DELIVER WHAT IS NEEDED TODAY, BUT ABOVE ALL THINK ALONG ABOUT WHAT WILL BE CRUCIAL TOMORROW. FROM SMART, EFFICIENT AND SCALABLE WAREHOUSE SOLUTIONS TO SUSTAINABLE PRODUCTION – WE ARE READY TO ADD VALUE WITH OUR EXPERTISE.
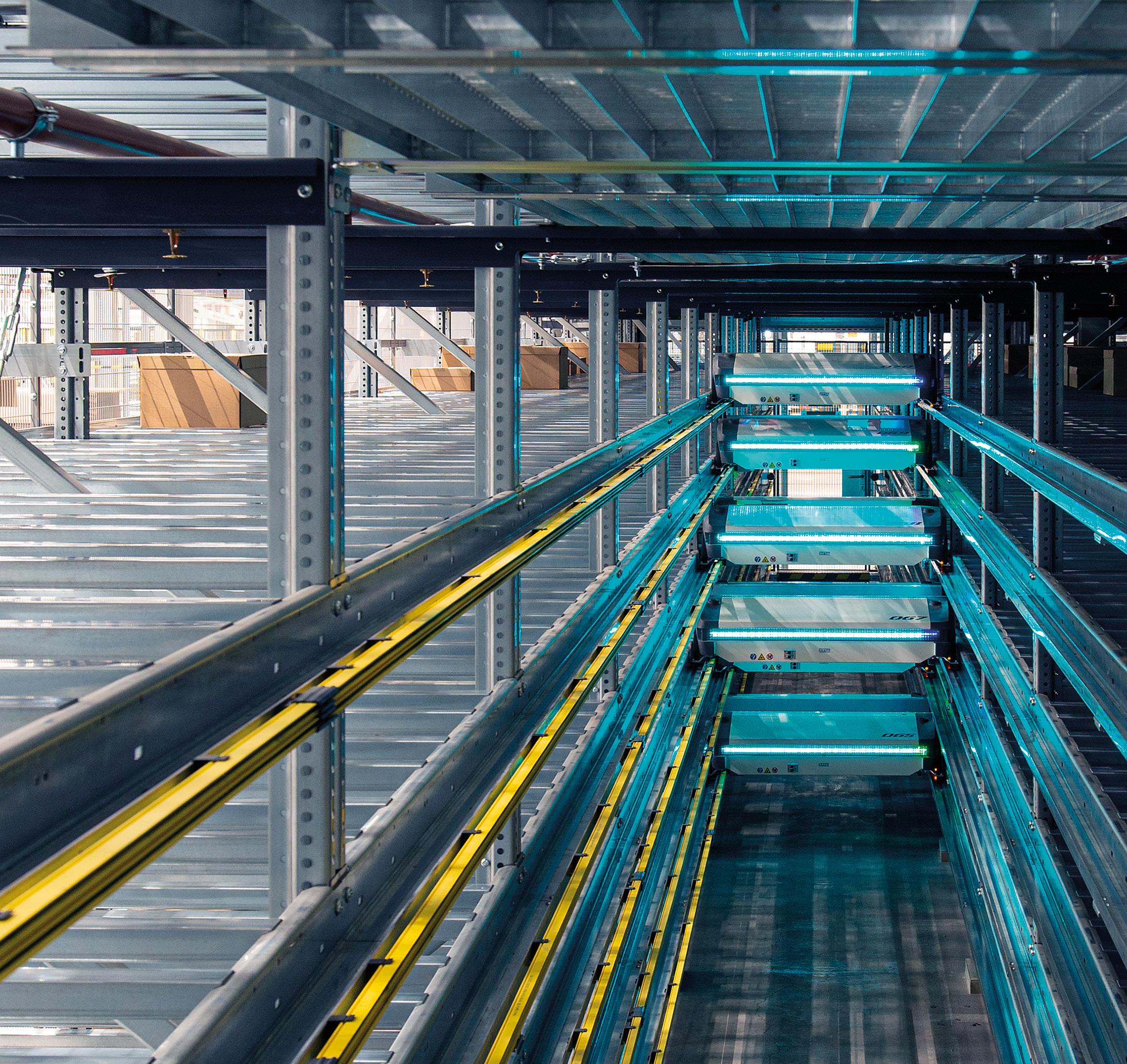
USA production facility
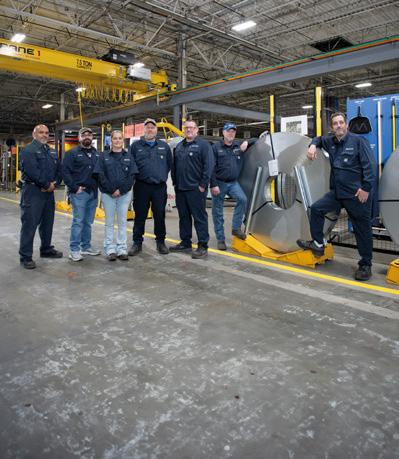
Automation and robotization
Improve efficiency, fast and reliable delivery while maintaining flexibility and scalability.
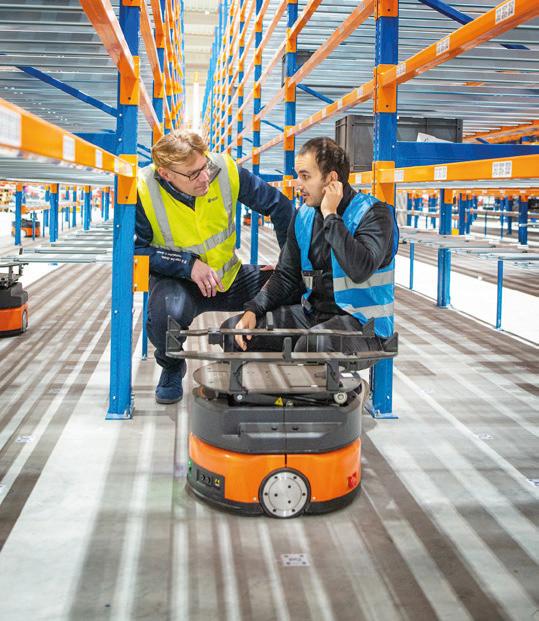
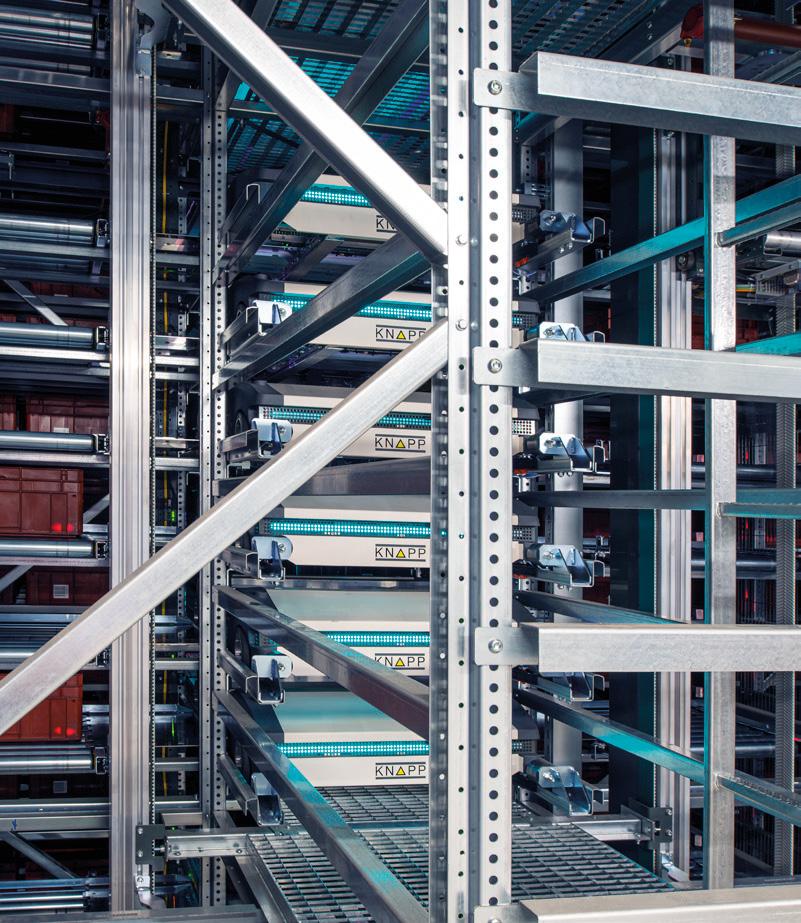
Knowledge and experience NEDCON has decades of experience with projects in automated warehouses.
KNAPP’S KEY PRODUCTS
• AeroBot – With the introduction of AeroBot at Promat 2025, the company has added a small footprint, high-density 3D shuttle that can operate independently outside of the shuttle rack structure. AeroBot’s seamless integration with the entire portfolio of hardware and software is a distinct differentiator.
• Evo Shuttle – KNAPP’s 1D and 2D shuttle systems form the heart of a modern warehouse, which can be seamlessly integrated into any logistics system with customized software and ergonomic workstation solutions.
• KiSoft – The company’s logistics software suite, KiSoft, is the central intelligence that ‘brings it all together’. The software not only covers vertical integration, such as machine control, warehouse control, and warehouse management, but it also makes horizontal integration possible along the entire value chain – all the way to the point of sale or end customer – supported by analytics and transport management.
• Open Shuttle - Free-moving shuttles supply workstations and deliver totes, cartons, or pallets while driverless vehicles can deliver volumes of up to 2,800 pounds.
• Pocket Sorter – Highly effective for order selection, packing, and sorting, this technology is space efficient and easily integrates with KNAPP’s supplementary goods-to-person technologies. With the ability to consolidate hanging and flat-packed goods, it is ideally suited for retail, fashion, e-commerce, omni-channel, and returns operations. The latest model automates pocket loading and unloading, offering seamless solutions for e-commerce and distribution.
• Pick-it-Easy Robot – AI-driven technology with various grippers and intelligent object recognition enables KNAPP’s Pick-it-Easy Robot workstation to handle a broad range of items in diverse sectors. The robot learns continuously, informing a cloud-based database which, in turn, increases overall system performance.
• Pick-it-Easy Workstations – These efficient, ergonomic goods-to-person workstations are the right choice for empowering and retaining labor. Various tasks can be handled at workstations, including order picking, returns processing, inventory, repacking, consolidating goods, or value-added services.
SatBot to handle load carriers up to 35 kilograms for quadruple-deep storage, powered by KiSoft software for seamless integration with WMS and warehouse control systems, making it ideal for e-commerce, microfulfillment, and manufacturing.
“In short, AeroBot delivers fast, scalable, and intelligent automation –making it a future-ready solution for modern intralogistics,” Salznig adds.
Alongside the award-winning AeroBot, KNAPP’s pocket solutions, such as PocketEngine, are lowering costs, increasing performance, and enhancing services in terms of order fulfilment.
A highly standardized solution, PocketEngine allows for fast installation and realization, while its ability to eliminate time-consuming specification processes means it can offer reduced costs.
Meanwhile, a pocket structure can be installed overhead without interrupting activities on the ground, which means it can easily be integrated at any given brownfield site without disrupting ongoing operations.
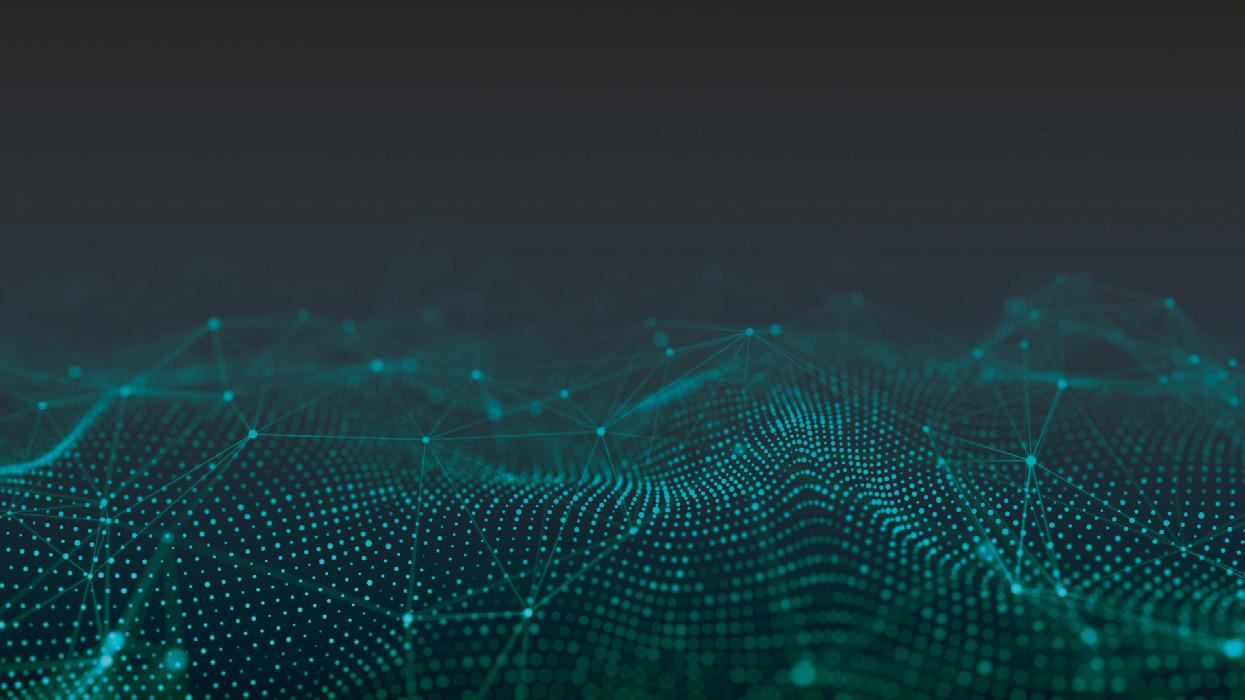
Product award at LogiMAT 2025 in Stuttgart, Germany.
Salznig elaborates, “We’re thrilled with what AeroBot has achieved. At its core, it features autonomous robotics with light detection and ranging (LiDAR) navigation and friction drive
technology, enabling movement in all directions up to 12 meters high without using any chains or gears.
“That means we have the simplest possible racking solution with zero maintenance requirements!”
Each AeroBot also carries a
“Pocket solutions provide a complete sequence for packing stations, enabling an efficient and fast packing process with very low error rates,” says Salznig.
In addition, KNAPP’s latest deployed pocket solution – the so-called ‘selfopening pocket’ – allows it to operate a 100 percent automated packing and picking system.
“We can directly and automatically drop products into totes and preerected cartons, offering a ‘zero touch’ approach,” Salznig adds.
A FUTURE OF INNOVATION AND SATISFACTION
In addition to its work with e-commerce and fulfillment centers, KNAPP has also developed an automated and prescriptionspecific vial filling system for the pharmaceutical sector, establishing a standardized system for mail order


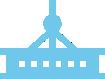


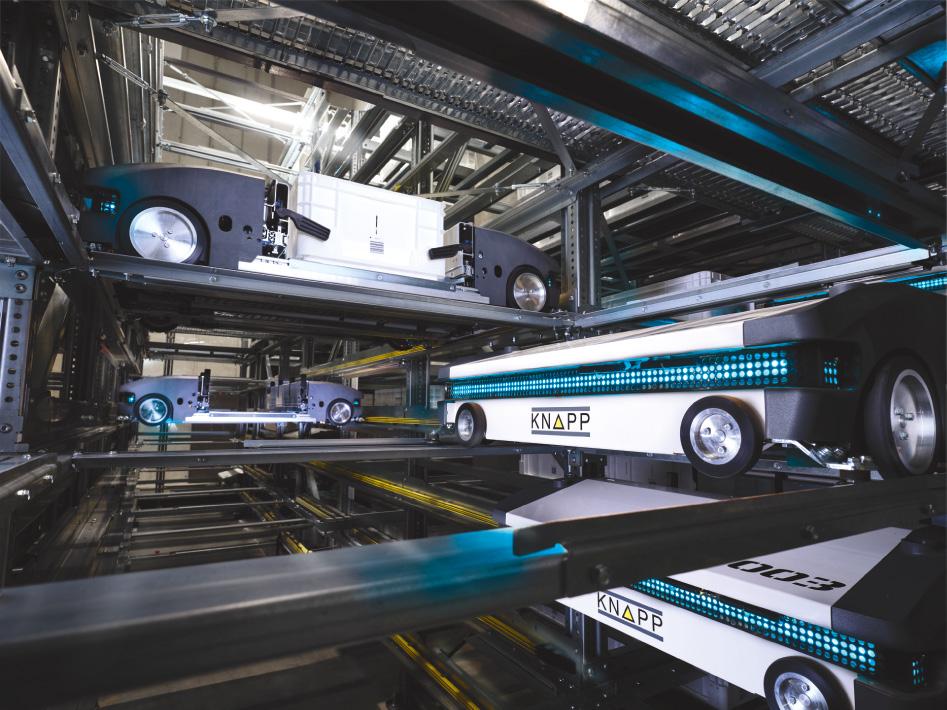
and central fill pharmacy applications.
“Besides our own pill dispensing and counting technology, our KiSoft stack covers all necessary pharmacy processes and reduces operational errors to a minimum,” Salznig explains.
As such, the company is offering scalable system solutions based on the number of prescriptions being handled daily.
The solution can also be completed using tote conveyors and technologies designed for unit-of-use, including an automated storage and retrieval system (AS/RS), an A-frame, or a KNAPP store to prepare ready-made orders including pre-packaged medication.
By increasing the level of automation, KNAPP can optimize staff utilization while also lowering operating costs.
“Cost savings are the main driver of pharmacy automation, with accuracy and labor challenges also contributing.
KiSoft and automation streamlines fulfillment, saving time and optimizing logistics,” Salznig adds.
As a privately-owned company that stands for sustainable and organic growth, KNAPP spends a significant portion of its budget on R&D to continually innovate.
“We strive to maintain our position as a best-in-class leader in technological solutions,” Salznig asserts.
Looking ahead, the company aspires to elevate customer satisfaction and service, aiming to conclude every project with a satisfied client – an aspiration that Salznig believes is particularly well reflected in its North American operations.
Salznig concludes, “We grow together with our customers, since their successful business case is our best reputation and the foundation for long and ongoing relationships in the industry.
“I’m confident that the North American market has many opportunities for us, and with that, we are always looking for talent to join us!”
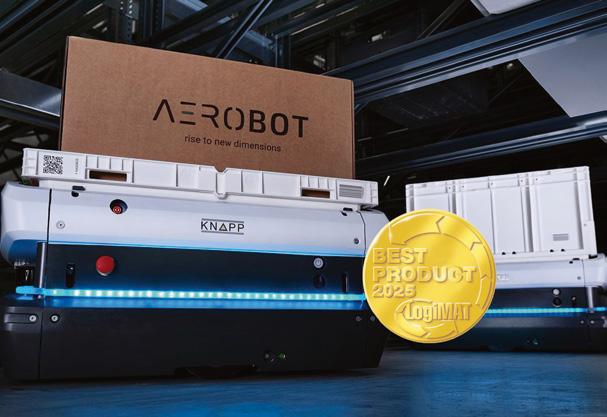
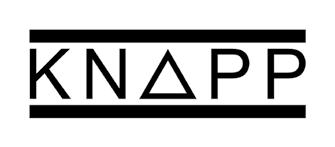
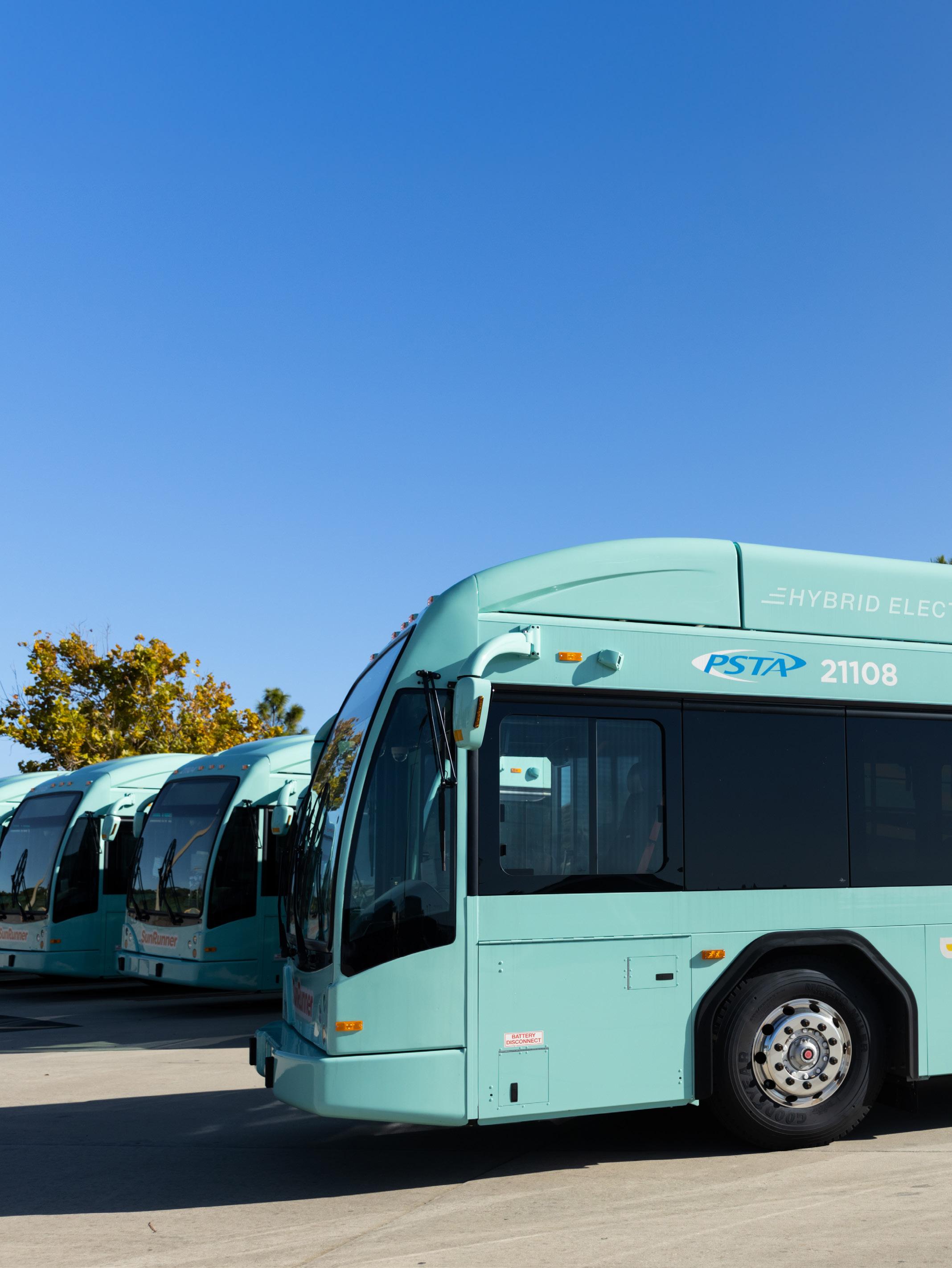
C O NNECTING PINELLAS COUNTY
Brad Miller, CEO of the Pinellas Suncoast Transit Authority, shares insights into embracing technology, transformative solutions, and key partnerships that enhance accessibility while improving services for all passengers
Writer: Rachel Carr | Project Manager: Poppi Burke
The scenic Pinellas County, nestled along Florida’s picturesque west coast and a key part of the vibrant Tampa Bay area, offers a harmonious mix of urban energy and suburban serenity, featuring lively cities.
The region’s thriving economy is bolstered by a variety of industries, with tourism playing a significant role. At the same time, Pinellas Suncoast Transit Authority’s (PSTA) efforts to improve public transportation are essential in enhancing connectivity and accessibility among communities.
PSTA provides commuter services for a sizeable area, including St. Petersburg, Florida’s fifth-largest city, known for its historical and
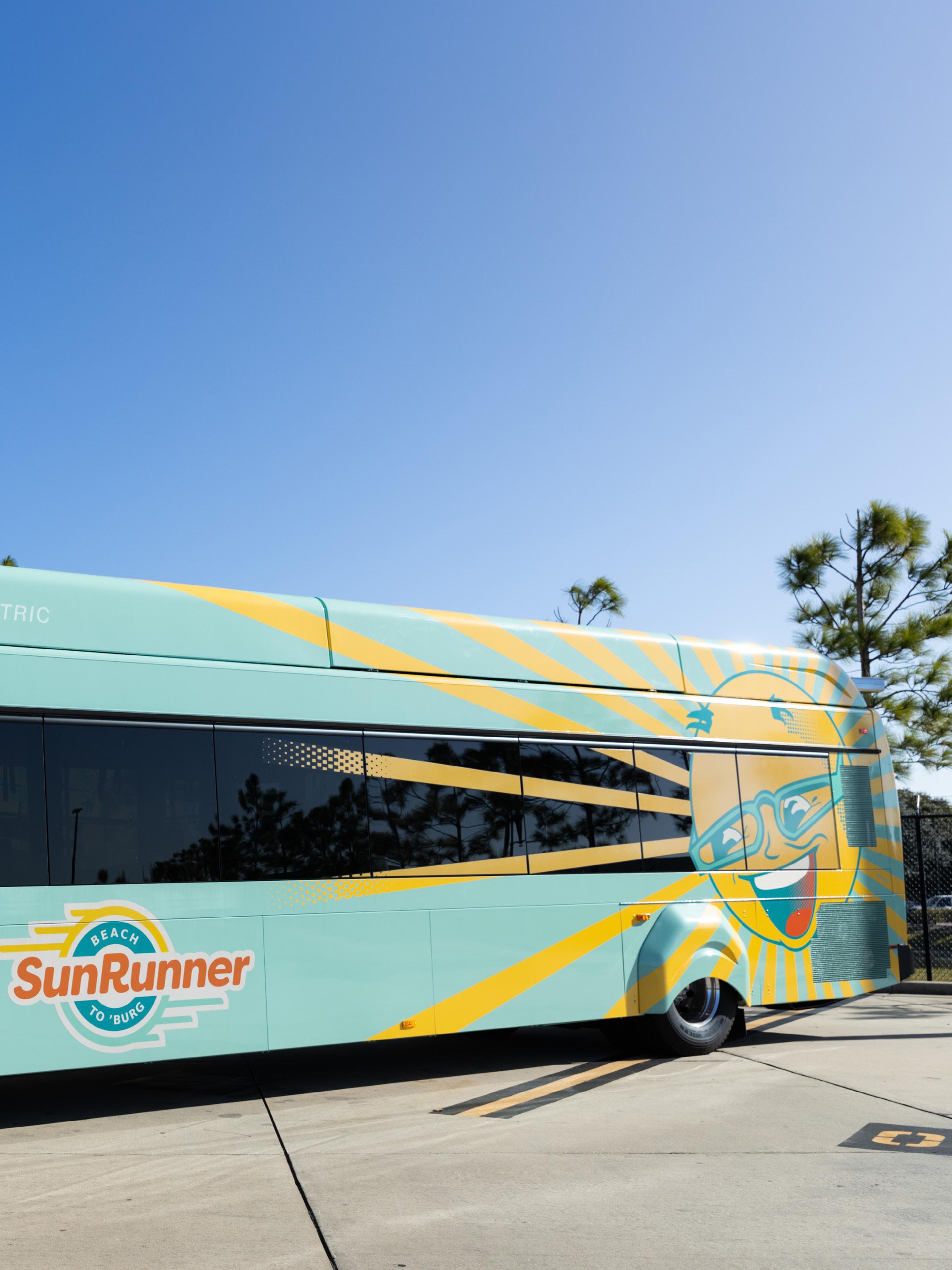
cultural significance. The area also encompasses Clearwater, which boasts award-winning, pristine white sand beaches and is frequently recognized as one of the state’s most beautiful and popular beach destinations.
Operating within these attractive destinations and beyond, PTSA improves accessibility for both residents and tourists, facilitating their daily travel needs. With an extensive network of routes, it is pivotal in meeting the transportation requirements of the communities it serves, benefiting both locals and visitors.
“We are committed to safely connecting people to places while
strengthening the community through innovation and meaningful partnerships,” introduces CEO, Brad Miller, acknowledging PSTA’s impact in aiding the region’s success.
Fueled by a distinct mission, the authority strives to be a catalyst for regional growth and connectivity through innovative strategies and dedicated initiatives, fostering economic development.
“The company is proud of its track record of innovation in the public transportation sector. With needs and travel patterns constantly evolving, it’s absolutely essential for us to remain plugged in to technology changes and passenger feedback,” he adds.
PSTA offers a wide range of services, including 46 bus routes with two express routes to Tampa and Hillsborough County, the SunRunner bus rapid transit, and the Clearwater Ferry, while operating 206 vehicles serving over 4,400 bus stops.
In addition, it has four customer service centers and answers more than 204,000 calls annually. It also provides over 159,000 Americans with Disabilities Act (ADA) paratransit and 269,000 bike-on-bus trips annually.
Overall, PSTA delivers 10.4 million rides annually, with an average weekday ridership of over 33,000, covering 9.8 million service miles and operating for more than 705,000 service hours. The agency also offers its Direct Connect service at 26 locations to link transit stops with final destinations.
ESSENTIAL COLLABORATIONS TO ELEVATE SERVICES
PSTA proudly became the first public transportation agency to partner with Uber and Lyft in 2016, first for the Direct Connect first-mile last-mile program. Direct Connect offers discounts on Uber and Lyft to facilitate trips to and from designated bus stops, enhancing both first and last-mile connections.
In 2018, the partnership expanded to the innovative Mobility-on-Demand (MOD) paratransit program. MOD complements traditional paratransit with subsidized rides that can be hailed without scheduling, and this popular program has just celebrated one million rides.
Additionally, the partnership includes the Transportation Disadvantaged Late Shift program assists low-income third-shift workers
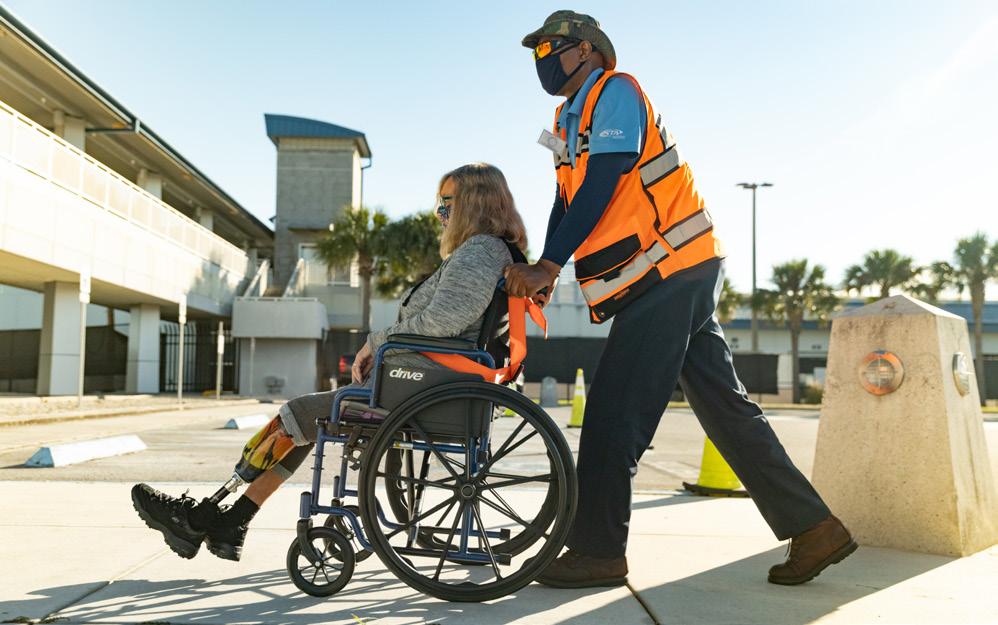
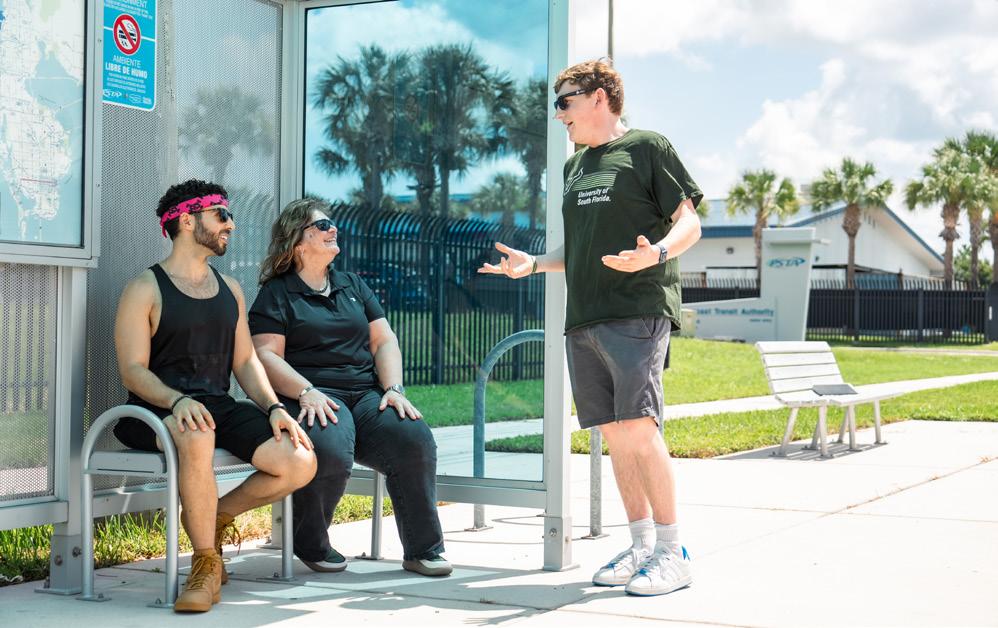
with rides to and from work when buses are not operating.
This partnership isn’t the only one that helps PSTA offer improved services—PSTA provides numerous services through public-private partnerships.
“TransDev is our contract partner for PSTA Access, our paratransit service for the entire county. Additionally, they are our operating partner for the new Grouper Airport Express, which offers on-demand service between St. Pete-Clearwater International Airport (PIE) and Clearwater Beach,” informs Miller.
“Our contract partners are truly an extension of our existing fleet – they help us expand our services while lowering operating costs. As a public agency, we always aim to be good stewards of taxpayer funds, and our operating partnerships with private
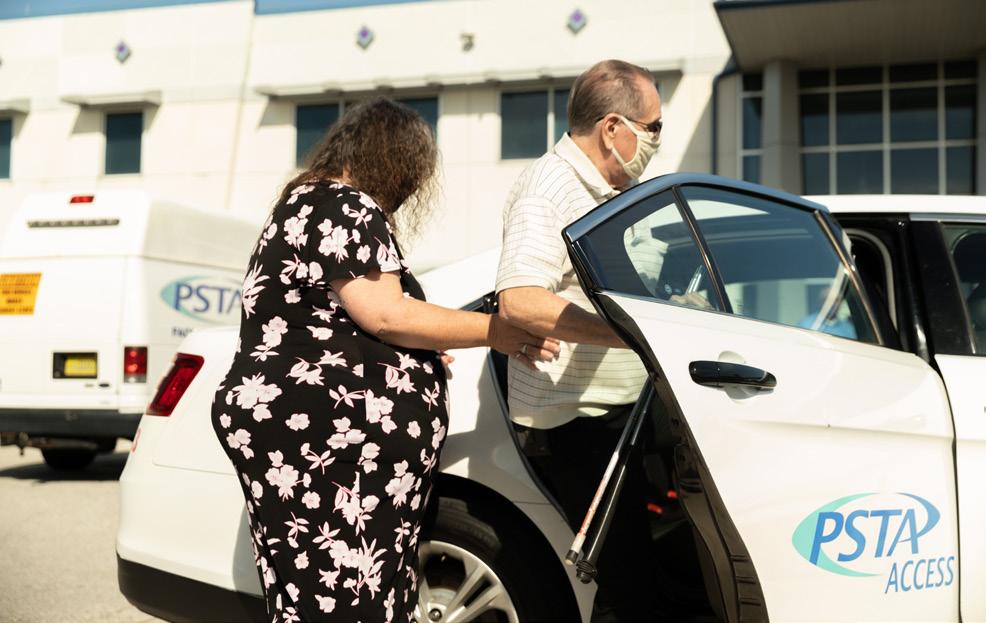
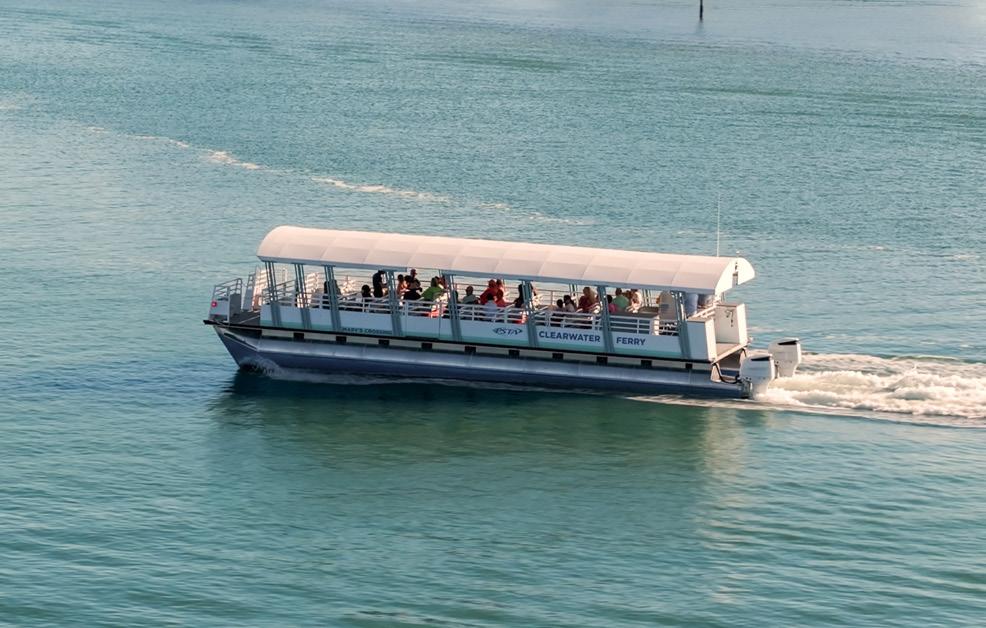
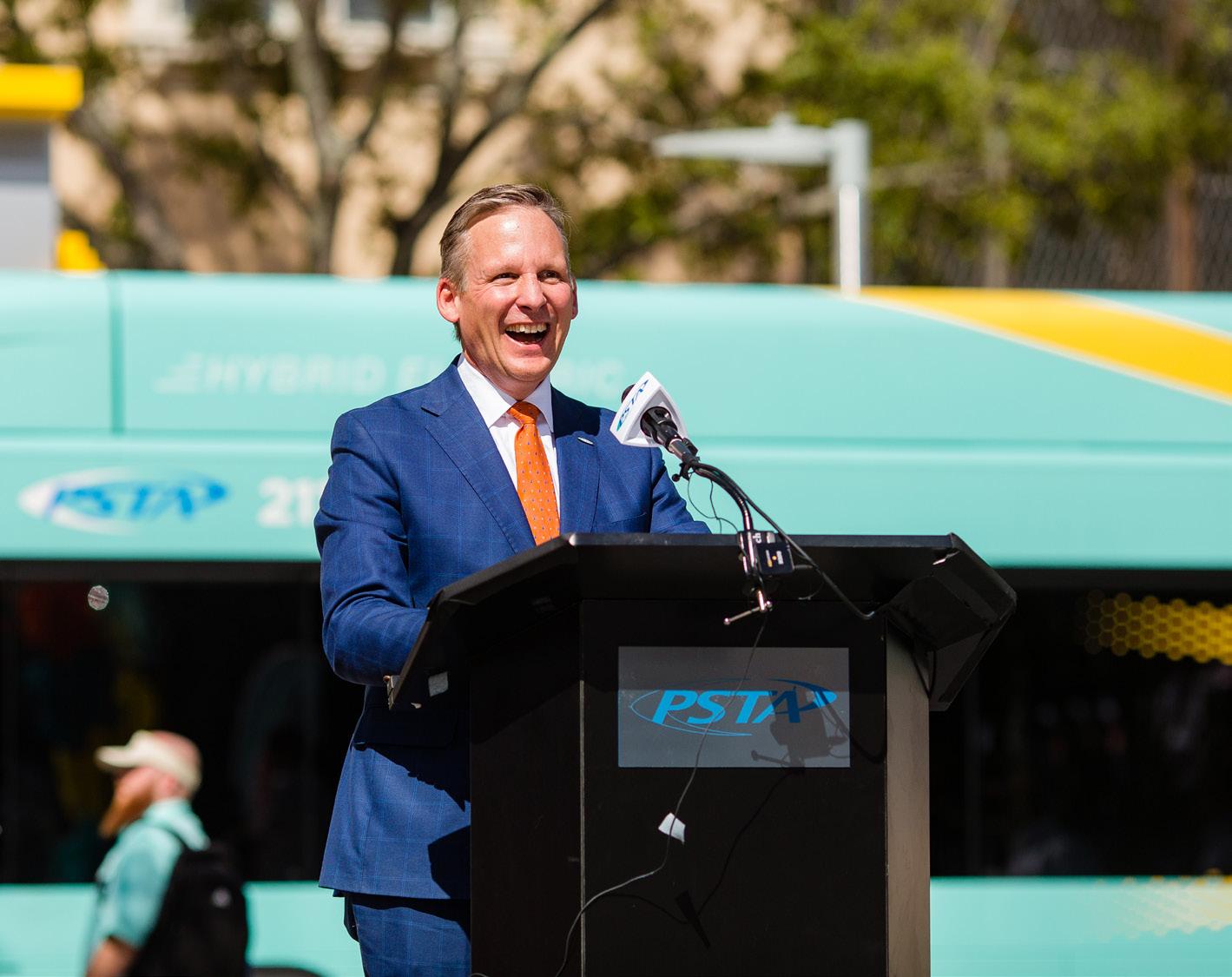
“WE ARE COMMITTED TO SAFELY CONNECTING PEOPLE TO PLACES WHILE STRENGTHENING THE COMMUNITY THROUGH INNOVATION AND MEANINGFUL PARTNERSHIPS”
– BRAD MILLER, CEO, PINELLAS SUNCOAST TRANSIT AUTHORITY
sector companies help us do just that.”
“The partnership allows us to serve our paratransit customers better, and their quick thinking helps us get pilot programs off the ground,” he continues.
IMPROVING PASSENGER EXPERIENCE THROUGH TECHNOLOGY
Technology allows PTSA to better collect fares and supply riders with information for its standard fixed route bus service.
“Our buses all feature tap-to-pay
fares, letting riders use their credit card or phone,” Miller highlights.
“Many of our buses also have real-time information screens for passengers and onboard Wi-Fi, and our SunRunner line features the same digital data displays at every station.”
By keeping the wheels turning, PSTA’s maintenance department consistently wins awards and sets an example industry-wide. This includes its use of artificial intelligence (AI)powered predictive maintenance software to help reduce costs and better understand the fleet.
HOW DOES CENTRALIZED PROCUREMENT AFFECT SUPPLY CHAIN EFFICIENCY WHEN CONTRACTING SERVICES TO LOCAL OPERATORS, AND WHAT ROLE DO DIVERSE VENDOR RELATIONSHIPS PLAY IN IMPROVING SERVICE DELIVERY?
Brad Miller, CEO: “Having a centralized procurement department allows our partners to have one point of contact, which makes communication seamless and helps foster better business relationships with our national and local partners.
“Diversity is integral to PSTA’s procurement process, fostering opportunities for local businesses and positively impacting the economy. While bus manufacturers operate out of state, many parts suppliers are local, further supporting economic growth within the community.
“Through our collaboration with construction partners, we have found that active community engagement, responsiveness, and attentiveness to concerns enhance service delivery and foster trust in PSTA’s commitment to doing the right thing.”
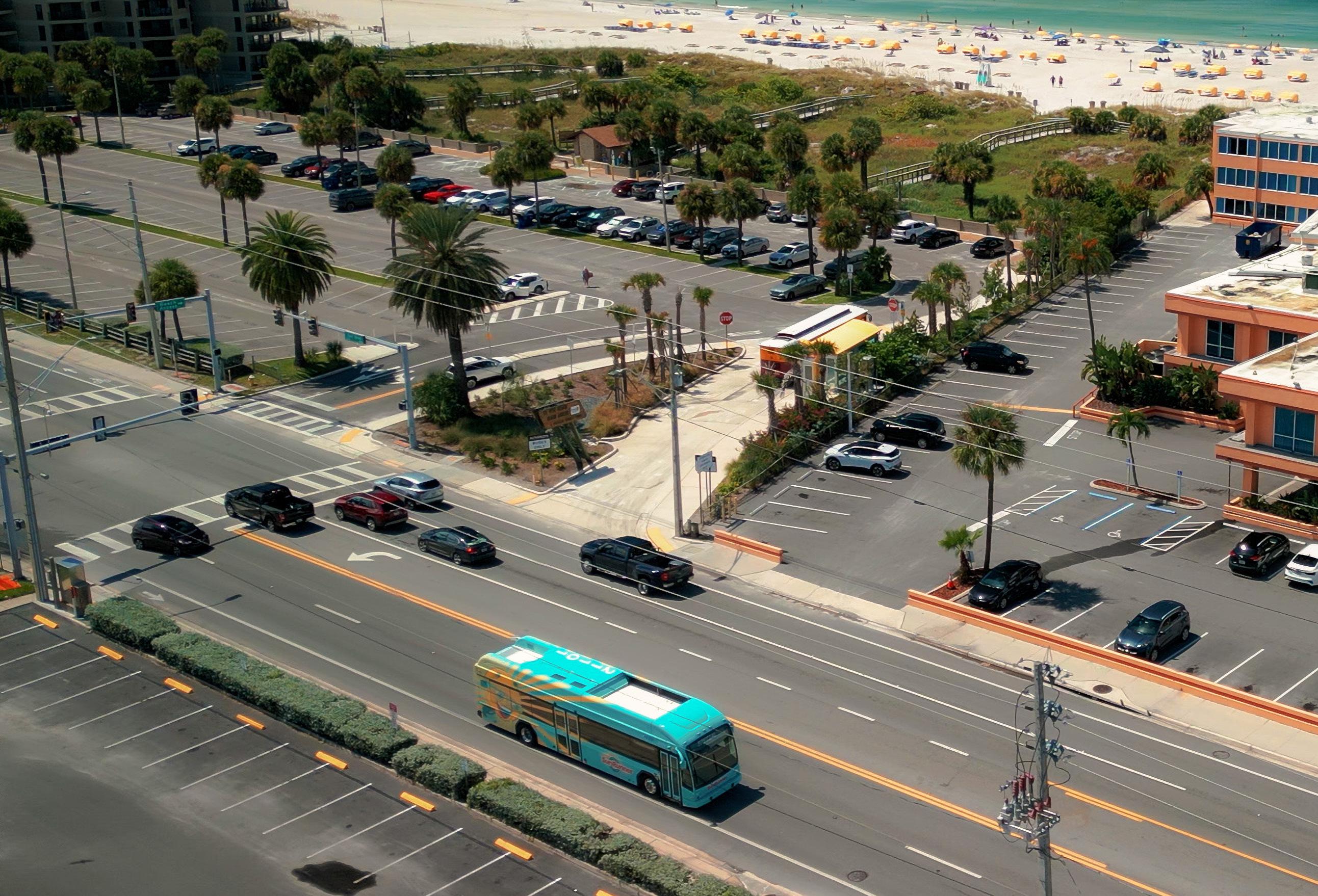
PSTA recently received a contribution from the Federal Transit Administration’s (FTA) Low or No Emission Grant Program to replace older diesel buses with new hybrid and electric vehicles (EVs). This will provide the community with more reliable rides and reduce maintenance and fuel costs.
TRANSFORMING TRANSIT THROUGH INVESTMENT
One of the most significant projects currently underway at PSTA is the development of Clearwater Station, a new, state-of-the-art multimodal transit center (MTC) in Downtown Clearwater.
Clearwater Station is the result of a decade’s worth of work between PSTA, the City of Clearwater, Pinellas County, the Florida Department of Transportation (FDOT), and other community organizations, marking a transformative investment in the
region’s transportation infrastructure.
“The new facility will replace our outdated and overcapacity transit center built in the 1980s, which no longer meets accessibility standards and cannot accommodate modern buses.
“Located just 1,000 feet from the current site, the new Leadership in Energy and Environmental Design (LEED)-certified center will sit on approximately two acres of donated land near the Pinellas Trail, new City Hall, and other municipal buildings,” Miller elaborates.
Key features of Clearwater Station will include a facility twice the size of the existing terminal and connections to multimodal services like Uber, Lyft, bike and scooter share, and PSTA Access.
The MTC will also have eco-friendly features such as EV charging stations and solar panels, as well as covered bike racks.
Moreover, it will incorporate retail spaces, a coffee shop facing the Pinellas Trail, and useful amenities like real-time arrival and departure displays. Additionally, the area will be enriched by public art and intuitive wayfinding signs.
The project was awarded $20 million through the Rebuilding American Infrastructure with Sustainability and Equity (RAISE) grant – the first of its kind ever awarded in Pinellas County – with extra funding to come from the City of Clearwater, FDOT, Forward Pinellas, and PSTA itself.
Construction bids are currently open, with ground expected to be broken this fall and the grand opening targeted for 2026.
Once complete, the new MTC will serve more than 2,300 passengers daily, support access to thousands of jobs, and further position the authority as a leader in sustainable, accessible transit solutions.
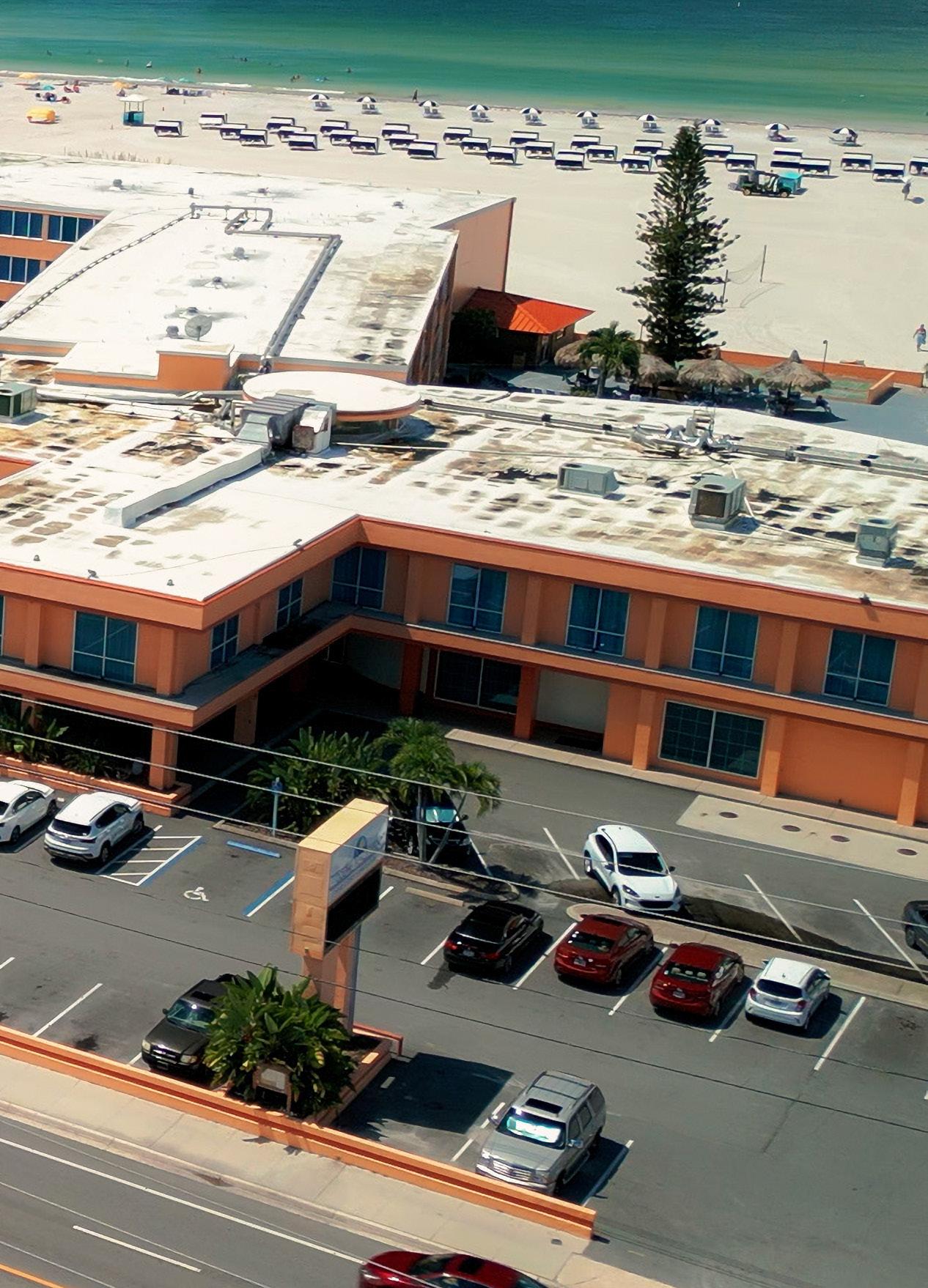
Building bridges, not barriers
Inclusivity,
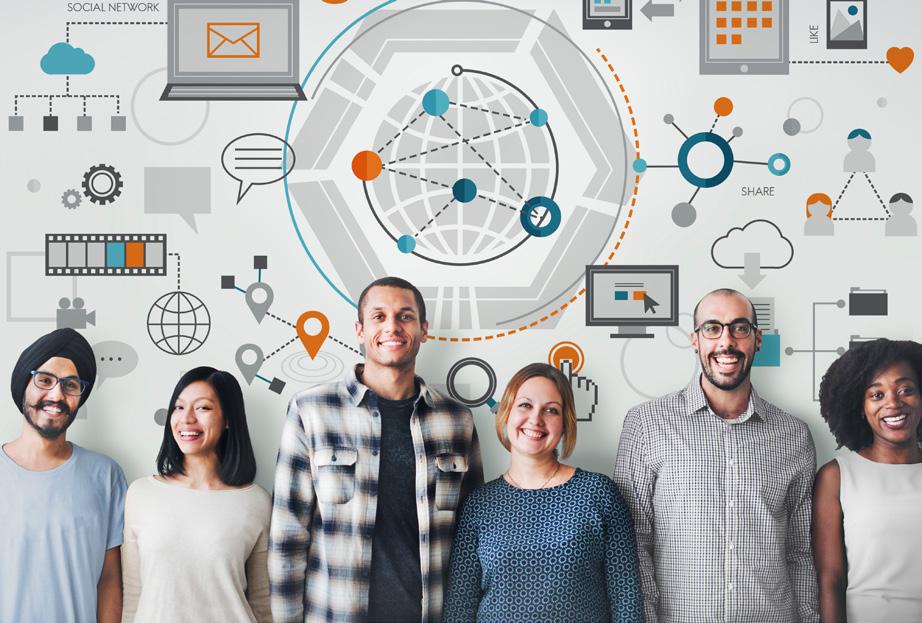
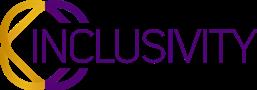
As
reflect
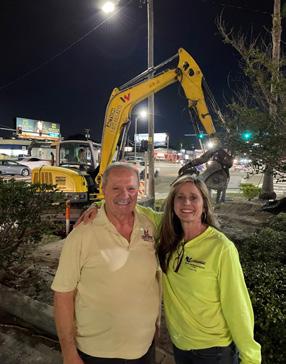
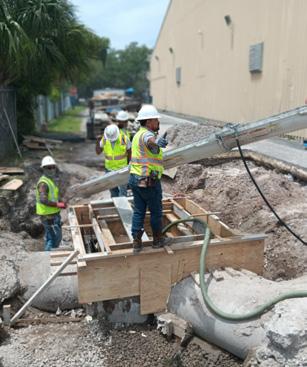
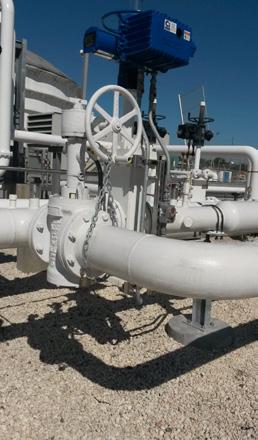
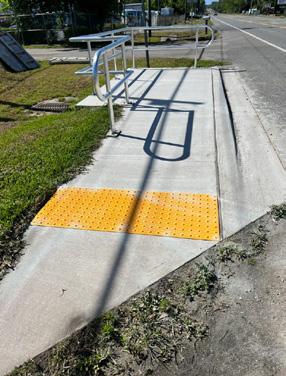
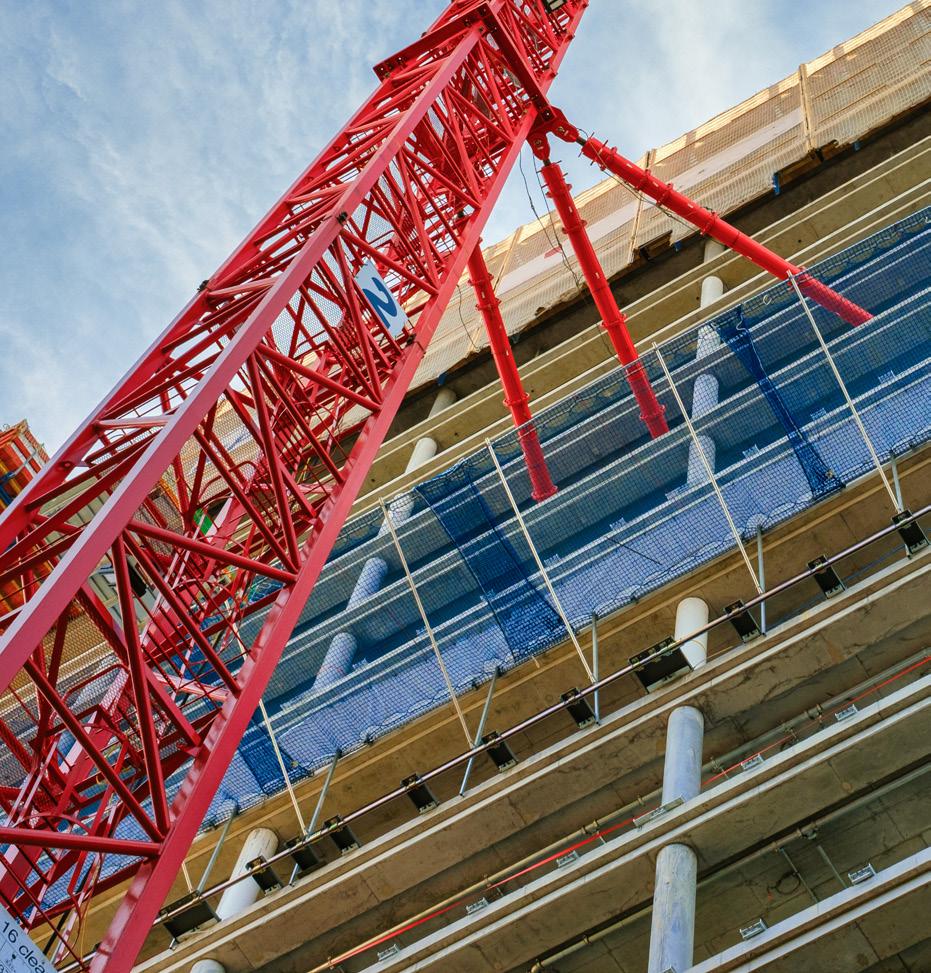
Carl M. Aldridge, Jr. (Vice President of ACS) and his daughter, Carla Boyce (President of ACS)
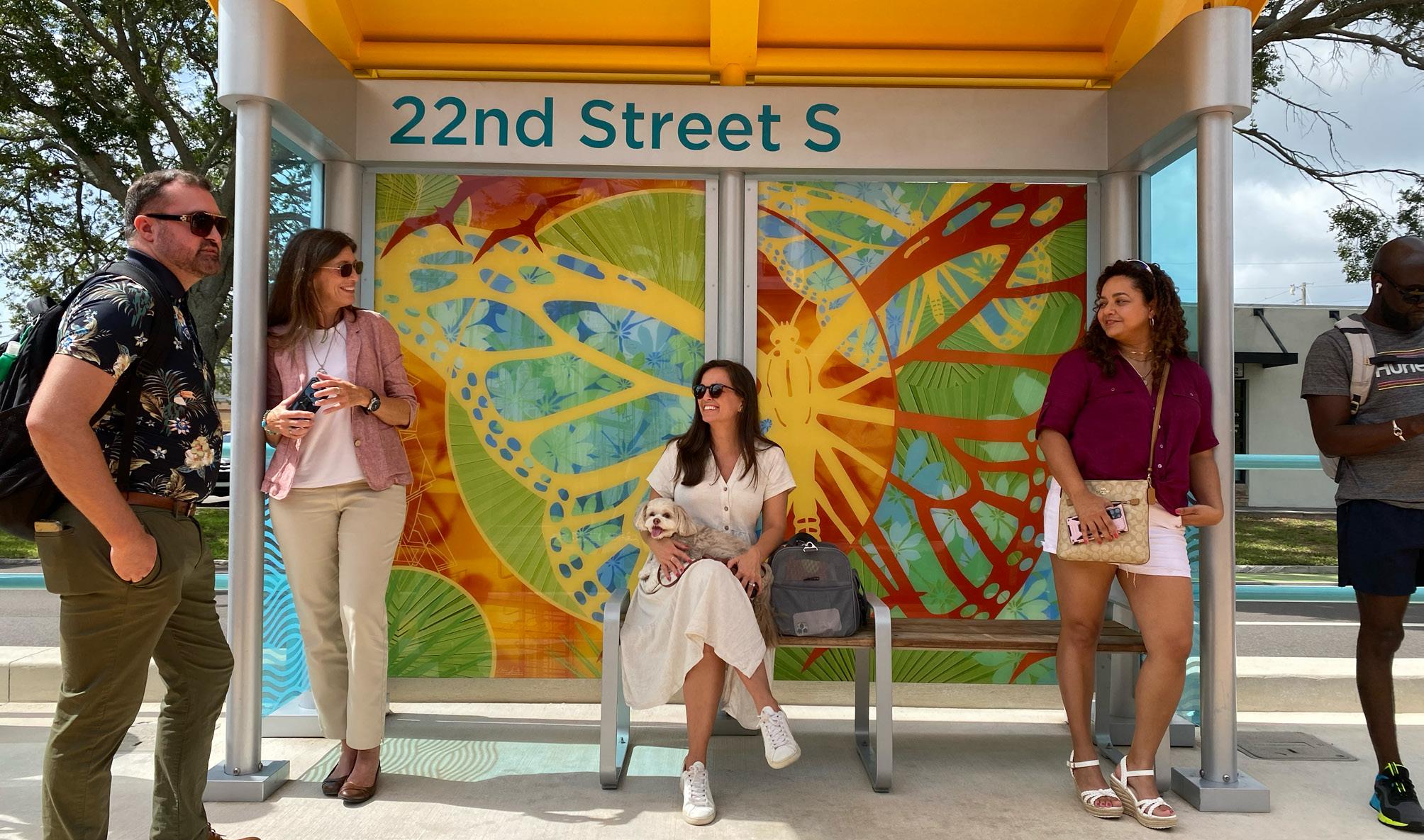
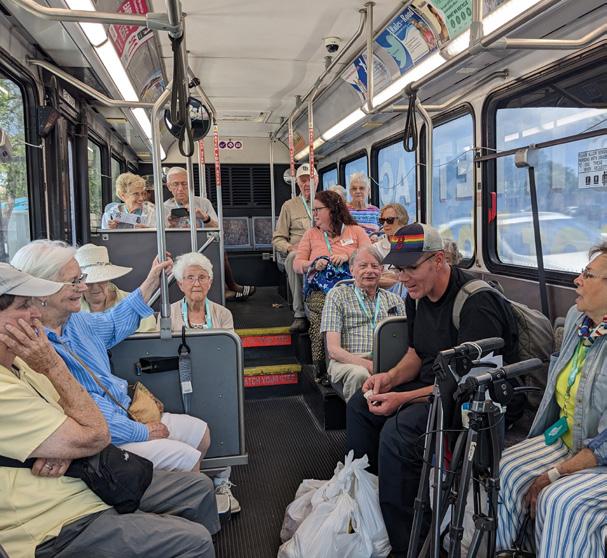
ACCESSING PATHWAYS AND REACHING DESTINATIONS
PSTA is dedicated to providing advanced mobility solutions for individuals with disabilities and retirees.
Through PSTA Access, the agency offers ADA-compliant door-to-door paratransit services for those unable to use regular bus routes. Drivers are specially trained to ensure a safe and supportive travel experience.
Furthermore, the MOD program also partners with providers like Uber and Lyft, enabling eligible riders to book unshared, curb-to-curb trips as needed.
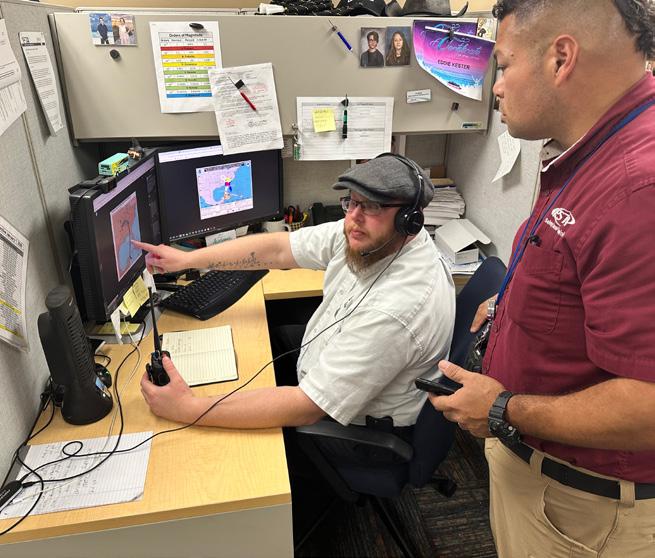
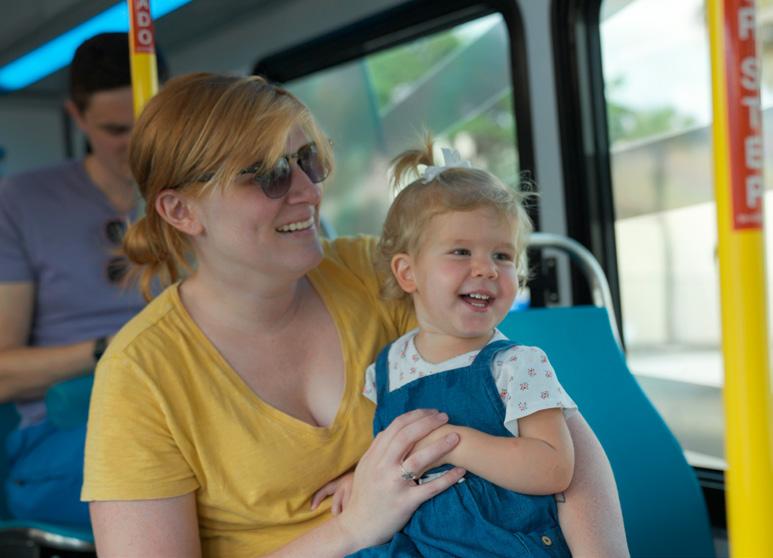
“AS A PUBLIC AGENCY, WE ALWAYS AIM TO BE GOOD STEWARDS OF TAXPAYER FUNDS, AND OUR OPERATING PARTNERSHIPS WITH PRIVATE SECTOR COMPANIES HELP US DO JUST THAT”
– BRAD MILLER, CEO, PINELLAS SUNCOAST TRANSIT AUTHORITY
“We have launched a Seniors and Disabled Discount Program that allows riders to register tap-enabled credit or debit cards for automatic fare discounts and daily fare capping, removing the need for ID,” Miller
outlines.
All PSTA buses feature accessibility options, including wheelchair ramps and stop announcements, and free travel training is offered to help new passengers. These initiatives ensure
older adults and individuals with disabilities can travel freely and affordably in Pinellas County.
To further enhance access for everyone, the authority has a productive few years ahead as it focuses on expanding and improving its services.
“Our top priorities for the coming year are the construction of Clearwater Station and the design of our new and improved Cross-Bay Ferry service. The invitation for bid for Clearwater Station construction was just issued in June 2025, and we anticipate award of a general contractor agreement toward the end of July.
“Groundbreaking will occur in the fall of 2025, with completion scheduled in 2027. The Cross-Bay Ferry request for proposal (RFP) will launch later this summer, with the award to be made in early fall, and we anticipate a new service starting in 2026,” Miller concludes ardently.
As PSTA continues to embrace innovation and foster partnerships, it remains dedicated to enhancing the quality of public transportation in Pinellas County.
With a strong focus on accessibility and sustainability, the authority is poised to drive positive change for both residents and visitors alike, paving the way for a more connected and vibrant community.
EXPANDING AND ENHANCING REGIONAL ROUTES
• CROSS-BAY FERRY – The new passenger ferry service between St. Petersburg and Tampa is expected to start in 2026, with PSTA nearing federal funding for high-speed vessels. They are waiting for FTA approval of a $4.86 million grant, initially awarded to Hillsborough Area Regional Transit (HART) Authority, to purchase ferry boats for permanent service.
The HART Board has approved transferring the grant to PSTA to support regional transportation improvements. Unlike past operations, it will own the vessels and hire a third-party operator to enhance reliability and reduce costs. An RFP for an operating partner is expected later this summer.
• CLEARWATER FERRY – PSTA and the Clearwater Ferry have expanded the service to connect Downtown Clearwater, Clearwater Beach, and soon, Dunedin. This eco-friendly transit option alleviates traffic, supports local businesses, and offers a unique travel experience across Pinellas County. Operating Thursday through Sunday, it provides a convenient alternative for commuters and tourists.
This expansion aids Clearwater’s recovery from Hurricanes Helene and Milton by reconnecting beach communities and boosting economic activity, supported by state grants and investments from PSTA, Clearwater, and Dunedin, emphasizing sustainable transportation and regional collaboration.
Tel: 727-540-1900
cserv@psta.net http://www.psta.net/
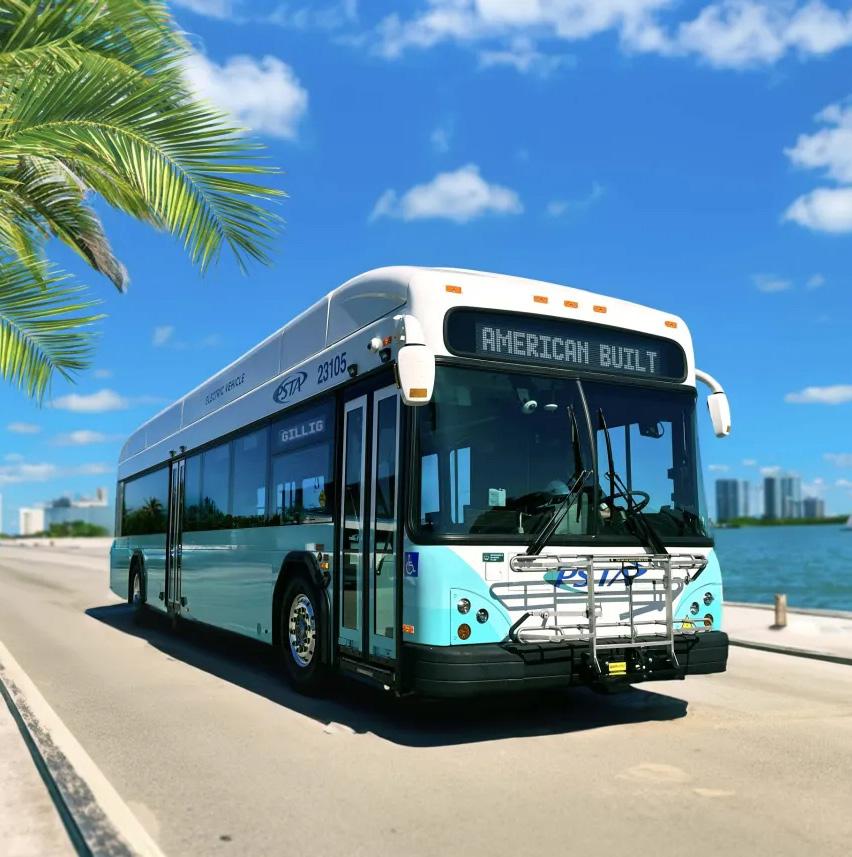
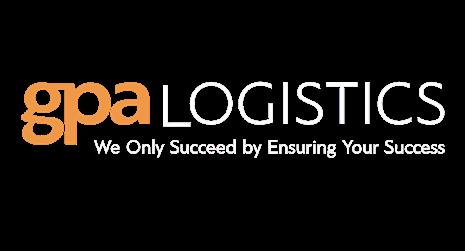
SPECIALISTS IN CONSUMER GOODS LOGISTICS
GPA Logistics Group offers tailored fulfillment, warehousing, and co-packing solutions for consumer goods importers and wholesalers. Bill Drummer, CEO, discusses how the company utilizes advanced technology
Writer: Jack Salter | Project Manager: Poppi Burke
We’ve positioned ourselves as specialists in consumer goods logistics, with particular expertise in apparel and accessories.”
When Bill Drummer, CEO, and Brian Cantrell, President, established GPA Logistics Group (GPA) in 2016, they were tasked with turning around a small, underperforming third-party logistics (3PL) provider in Fontana, California (CA).
The former’s opening words demonstrate how the dynamic duo have since progressed the company, as both came with over 20 years of experience in the industry.
“I was a partner in a 3PL based in New Jersey before moving to CA, and Brian was a Senior Executive in a large, national 3PL,” Drummer recalls.
“In 2017, GPA Global, a multinational packaging company, partnered with us and provided the financial backing we needed for accelerated growth
and geographic expansion.”
GPA’s comprehensive service portfolio includes business-tobusiness (B2B) distribution, directto-consumer (D2C) e-commerce, co-packing, reverse logistics, and dedicated warehousing.
With a client base spanning health and beauty, fitness equipment, consumer electronics, and fashion accessories, the company operates multiple facilities across both the East and West Coasts of the US, ensuring optimal shipping zones and redundancy for business continuity.
INVESTING IN TECHNOLOGY
Like many industries these days, technology is the backbone of GPA.
“If you told me 20 years ago that our hourly associates would be walking around our warehouses holding minicomputers, I would have trouble imagining it,” Drummer says.
“Today, they are operating
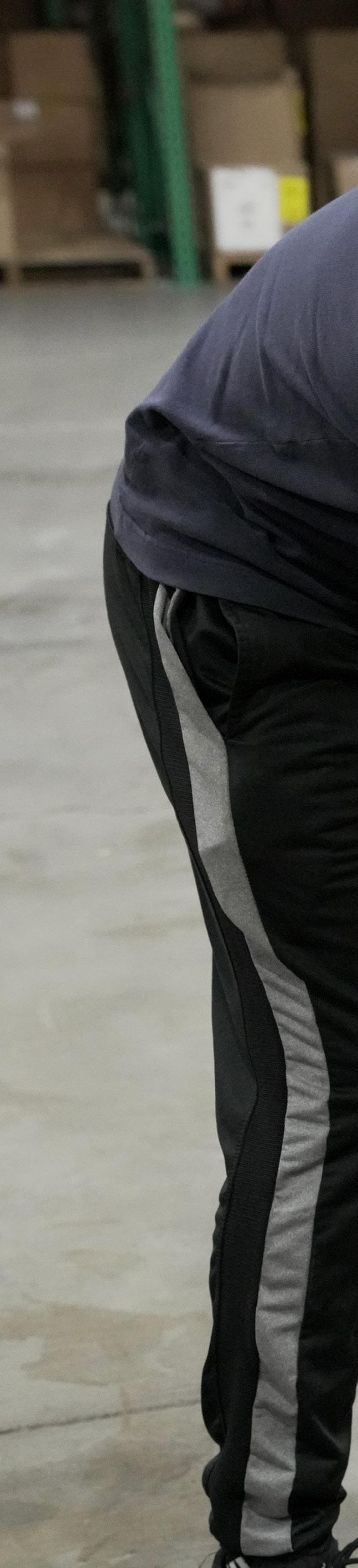
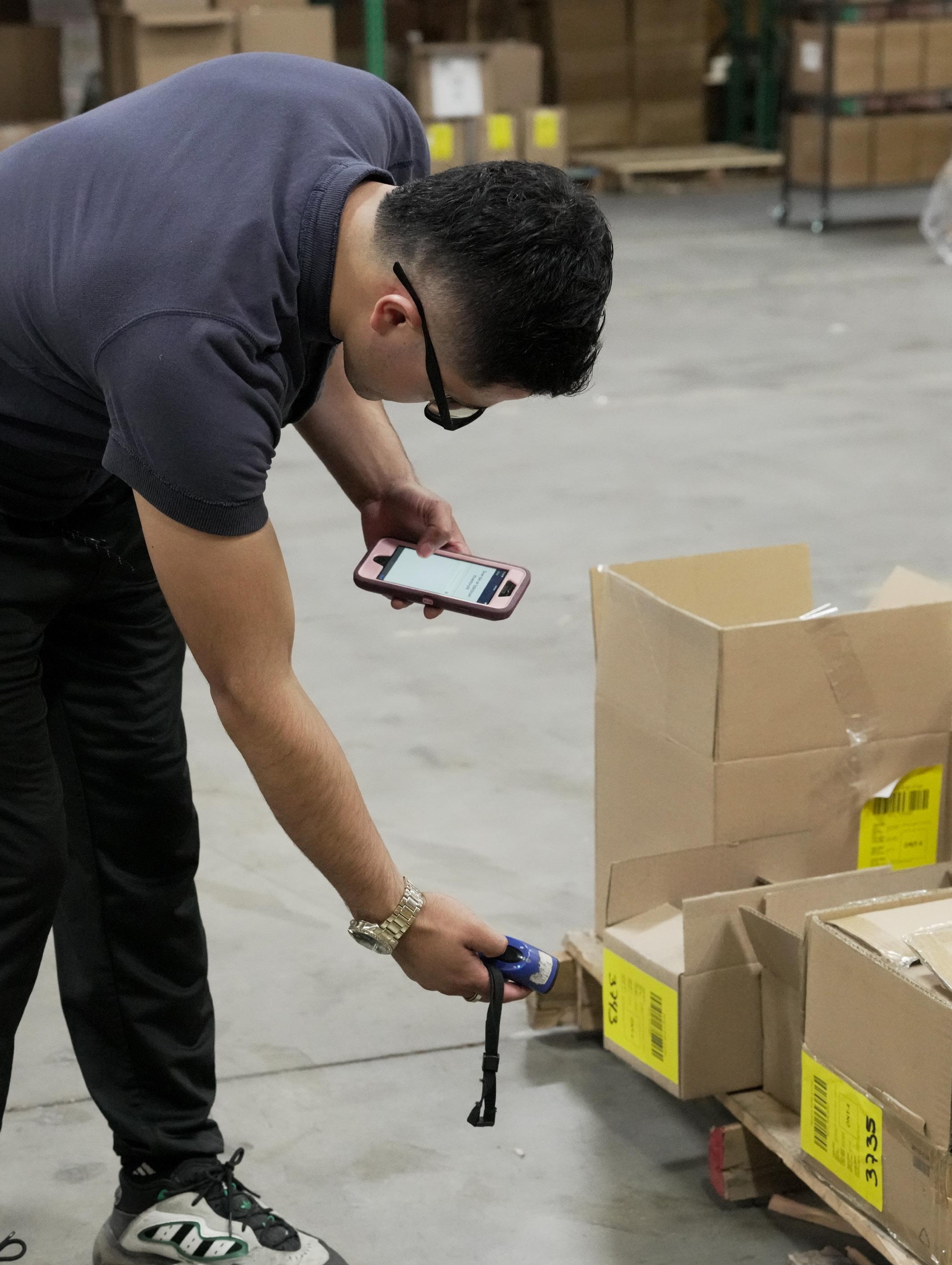
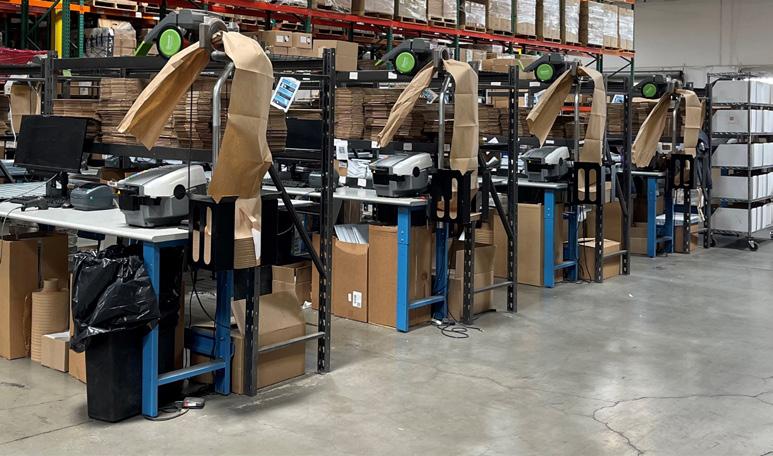
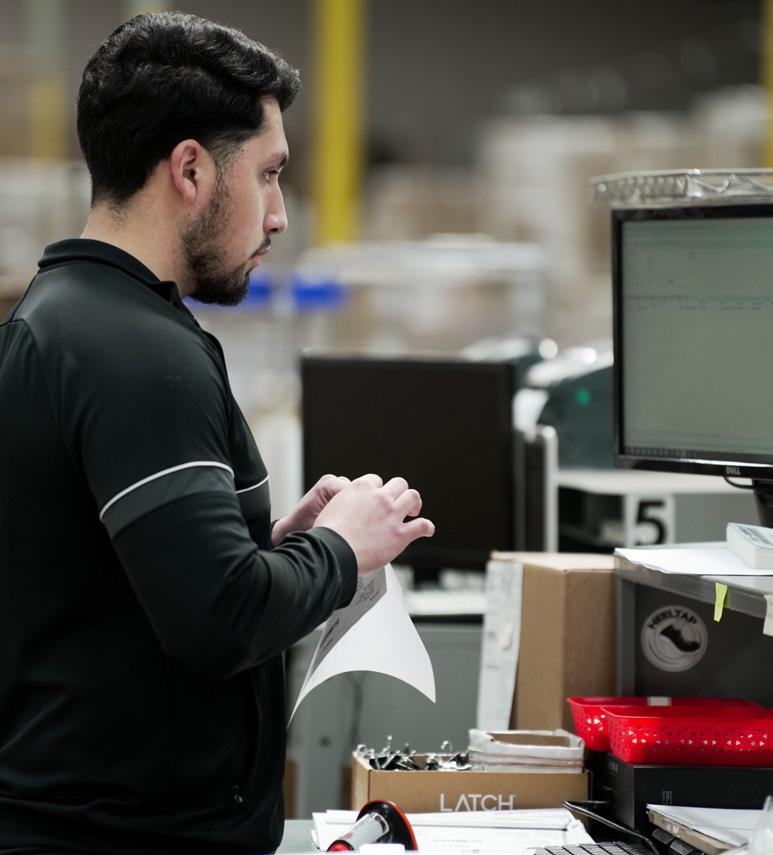
sophisticated mobile computers worth thousands of dollars while managing complex automated systems.”
The company also has in-house IT staff with expertise in coding, programming, electronic data interchange (EDI) and application programming interface (API) integrations, warehouse management systems (WMS), hardware and networking setups, cybersecurity, and communications.
GPA’s data is not only critical to collect and maintain, but now a resource to be leveraged for efficiency improvements and to gain a competitive advantage.
“The key is to invest in the right technology as there are so many options available. Not all of them deliver a return on investment (ROI), and many of them will be eclipsed by newer and better technology before you can implement or finish paying for them,” notes Drummer.
Recently, the company upgraded its WMS to Osa Commerce, a
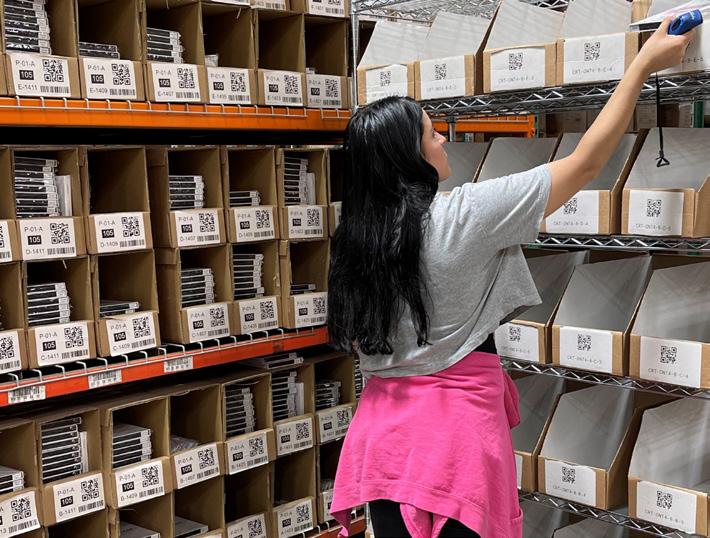
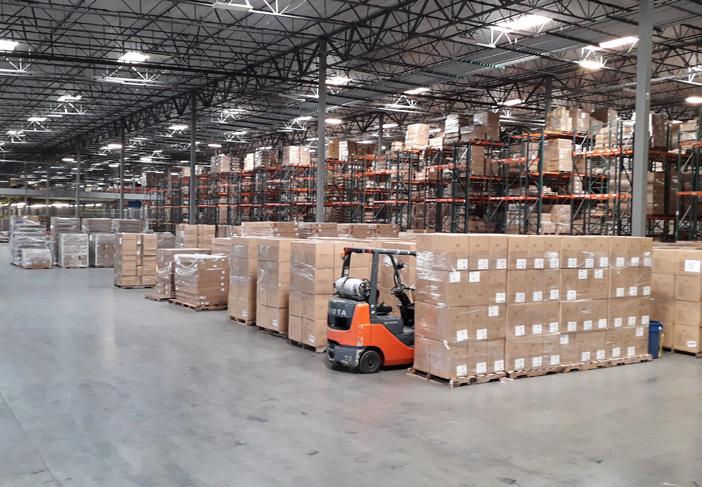
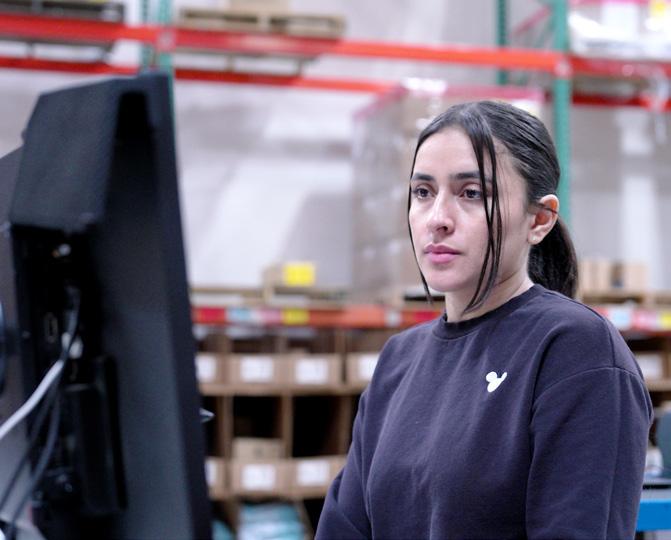
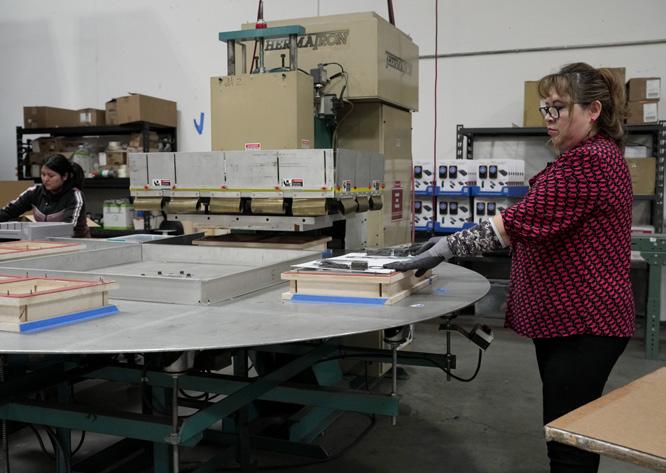
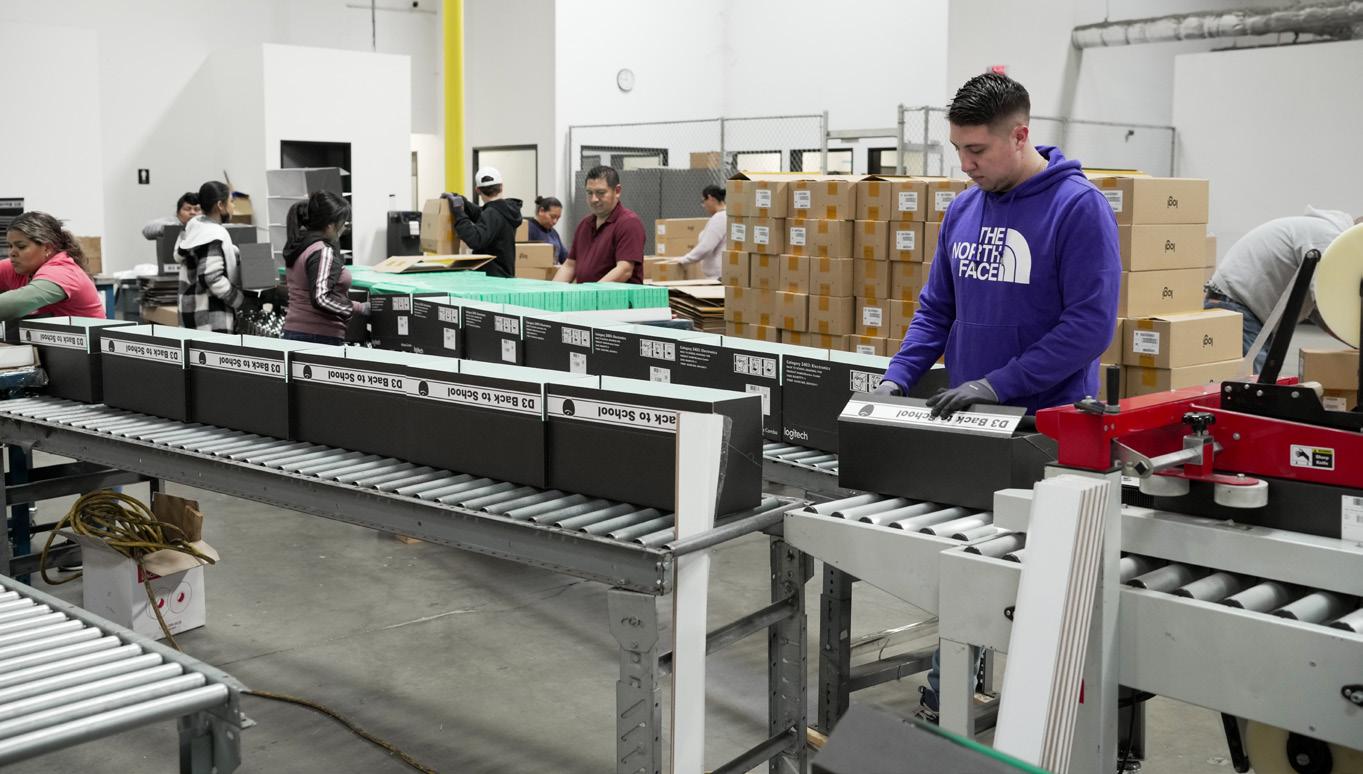
“WE’VE POSITIONED OURSELVES AS SPECIALISTS IN CONSUMER GOODS LOGISTICS, WITH PARTICULAR EXPERTISE IN APPAREL AND ACCESSORIES”
– BILL DRUMMER, CEO, GPA LOGISTICS GROUP
newer, more robust system that has greatly improved its tracking and reporting capabilities.
GPA also uses business intelligence software platform Octup to aggregate data from multiple sources and report its key performance indicators (KPIs) and labor utilization, giving it daily profit and loss reports per location.
Its returns management software solution, Returns Desk, exemplifies customer-centric technology, allowing clients to monitor returns processing in real-time and make immediate decisions on disposition.
For EDI and API integrations, GPA has developed its own value-added network (VAN) and API servers. This internal capability eliminates
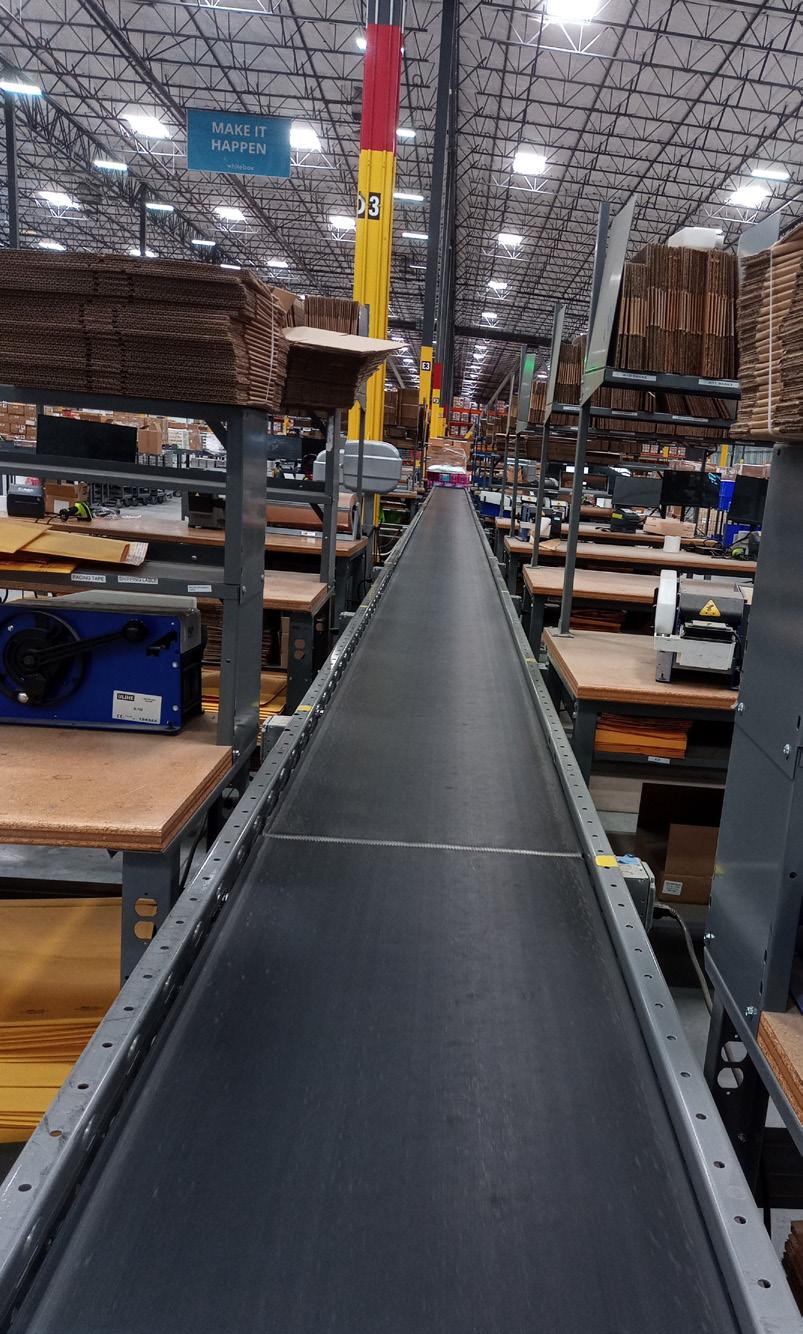
third-party bottlenecks and ensures rapid response to customer requirements.
“The key differentiator is providing customers with complete operational transparency. In today’s environment, visibility is a fundamental requirement,” Drummer emphasizes.
ROBOTICS AND AI
Labor is by far the largest expense and most malleable resource in a 3PL.
As a result, it’s hard to recruit and train qualified associates who can manage the technologies and understand the impact of their actions, particularly in certain geographic areas.
“Advances in robotics are coming fast, but one must be careful not to be blinded by the fancy new toys that are available and evaluate if there is real ROI to deploying them,” cautions Drummer.
“Robotics are still expensive; the challenge isn’t just the initial capital investment – it’s the ongoing software complexity, integration costs, and potential workforce disruption.”
COULD YOU EXPAND ON YOUR DEDICATED WAREHOUSING SERVICES?
Bill Drummer, CEO: “We’ve been brought in to take over the operations of private, one-client warehouses. Operating a warehouse is an entirely different and difficult challenge and it diverts their management and financial resources from growing their business.
“We conduct comprehensive operational assessments and implement our proven systems, processes, and technologies. This typically results in reduced headcounts, increased throughput, and optimized facility utilization.
“We offer customers the benefit of our trusted vendor relationships as well. Over the years, we’ve vetted many providers of services and products to 3PLs and have solid relationships with reliable, honest, and quality vendors.
“One example is M&S Woodworks (M&S). There are many pallet suppliers in our area of CA with a wide range of dependability and prices, but M&S has been rock solid for us on service, quality, and price for years. We’ve never had a problem obtaining what we need, even during the most severe pallet shortages and price hikes caused by the COVID-19 pandemic.
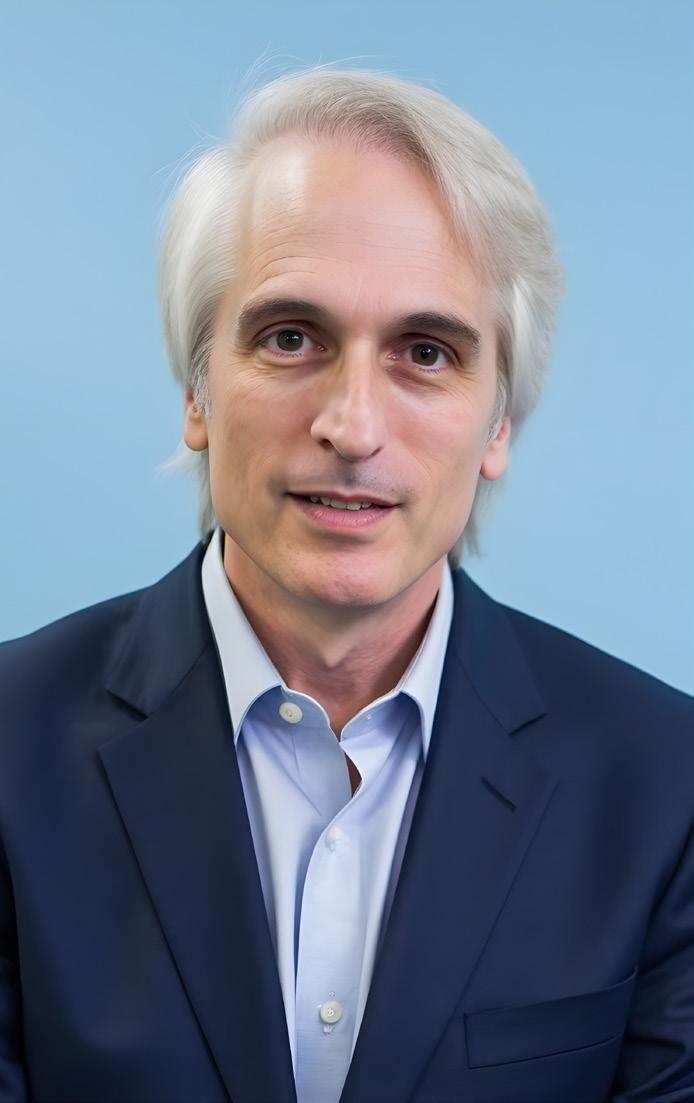
“It is important, but often overlooked, how we provide a vital buffer between the customers and warehouse staff. Warehouse workforce management requires specialized knowledge in areas like turnover reduction, safety compliance, workers’ compensation management, and litigation prevention – expertise that most manufacturers and importers lack.
“Our established vendor relationships and procurement expertise deliver cost advantages to our customers, while our management systems ensure consistent performance and accountability.”
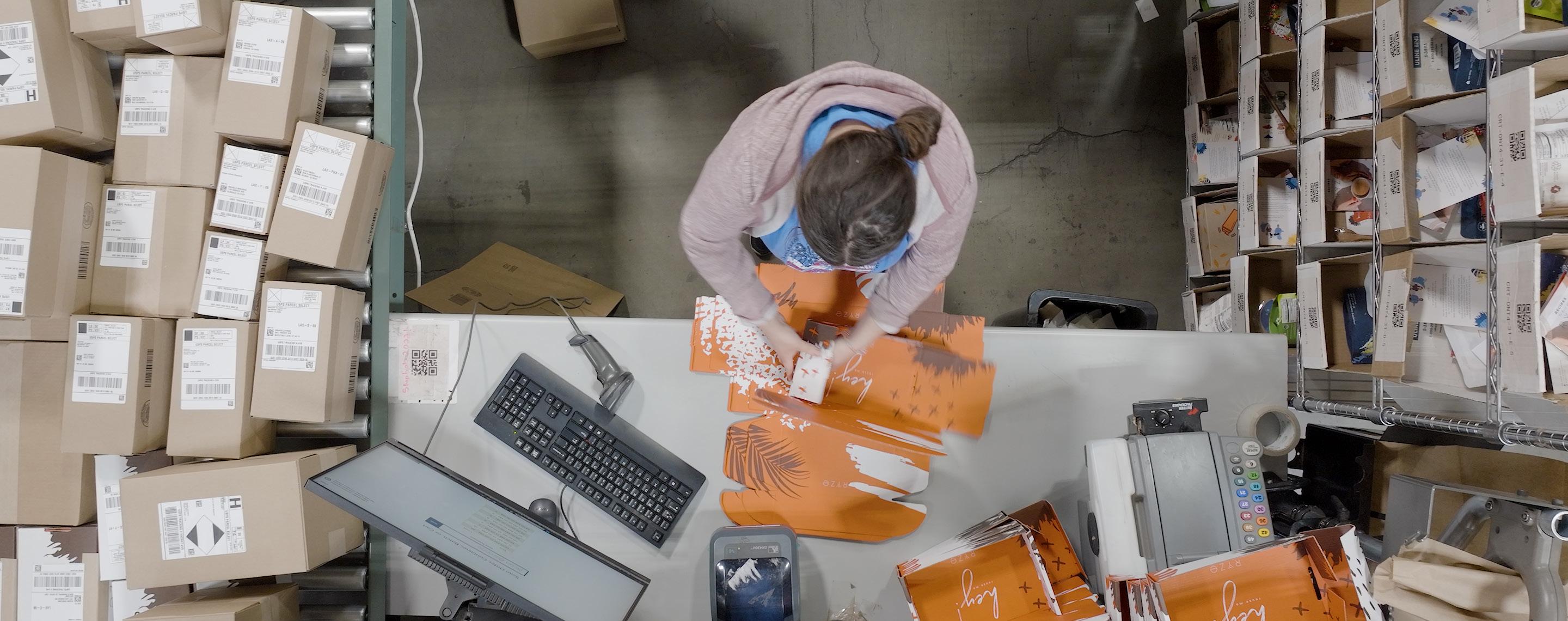
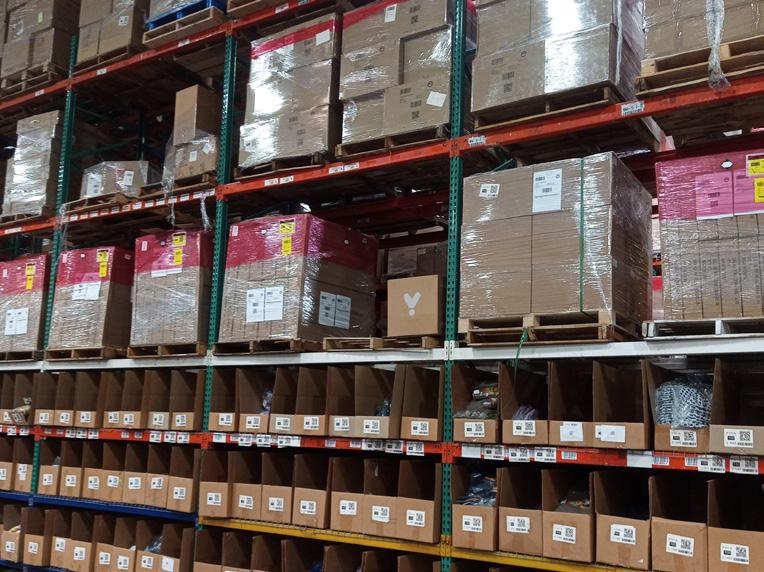
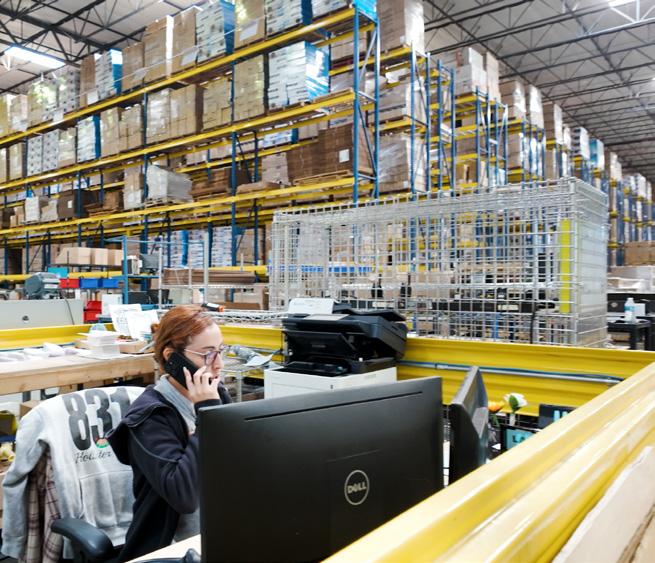
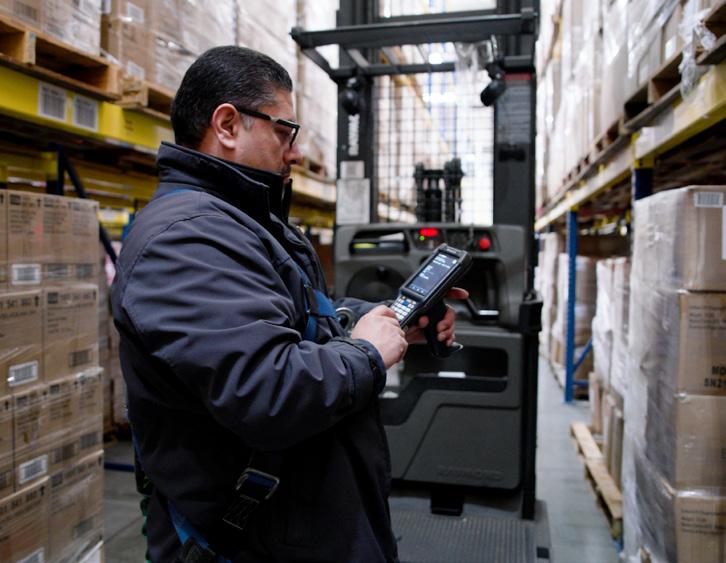
GPA has identified several automation solutions that meet its ROI criteria and is particularly interested in vendors offering flexible financing structures, leasing arrangements, rent-to-own programs, and performance-based contracts that reduce upfront capital requirements while sharing implementation risks.
As logistics companies integrate robotics and artificial intelligence (AI) into their operations, there’s much potential for optimization and efficiency gains by utilizing these innovative technologies.
Those efficiencies are essential as importers, wholesalers, and online retailers today are far more aware of how their logistics provider can help grow their business with great service or damage their business and reputation if they don’t perform.
Drummer is most excited about AI, which can solve complex logistical challenges that traditional
“THE KEY DIFFERENTIATOR IS PROVIDING CUSTOMERS WITH COMPLETE OPERATIONAL TRANSPARENCY. IN TODAY’S ENVIRONMENT, VISIBILITY IS A FUNDAMENTAL REQUIREMENT”
– BILL DRUMMER, CEO, GPA LOGISTICS GROUP
programming approaches can’t address effectively.
He cites companies such as Lully who can take order data and return a customized, optimized pick path per order batch.
“Until now, you would program your WMS with certain logic that was static and not always the most efficient pathway for your pickers. Now, each batch is optimized based on the stock-keeping units (SKUs), quantities, and locations of each batch,” Drummer informs us.
“The same can be done with slotting. A few years ago, we took over the operations of a warehouse that
deployed a goods-to-person robotics system that was so inefficient it was bottlenecking their entire operation. The cause was inefficient slotting that was dependent on associates making optimization decisions they were not qualified to make.”
Aside from robotics and AI, GPA recently had two of its warehouses in CA certified as Foreign Trade Zones (FTZs).
FTZ operations require minimal additional investment from GPA’s perspective but deliver substantial benefits to customers, including duty deferral, reduced carrying costs, and improved cash flow management.

Foreign trade zone Services
T
E
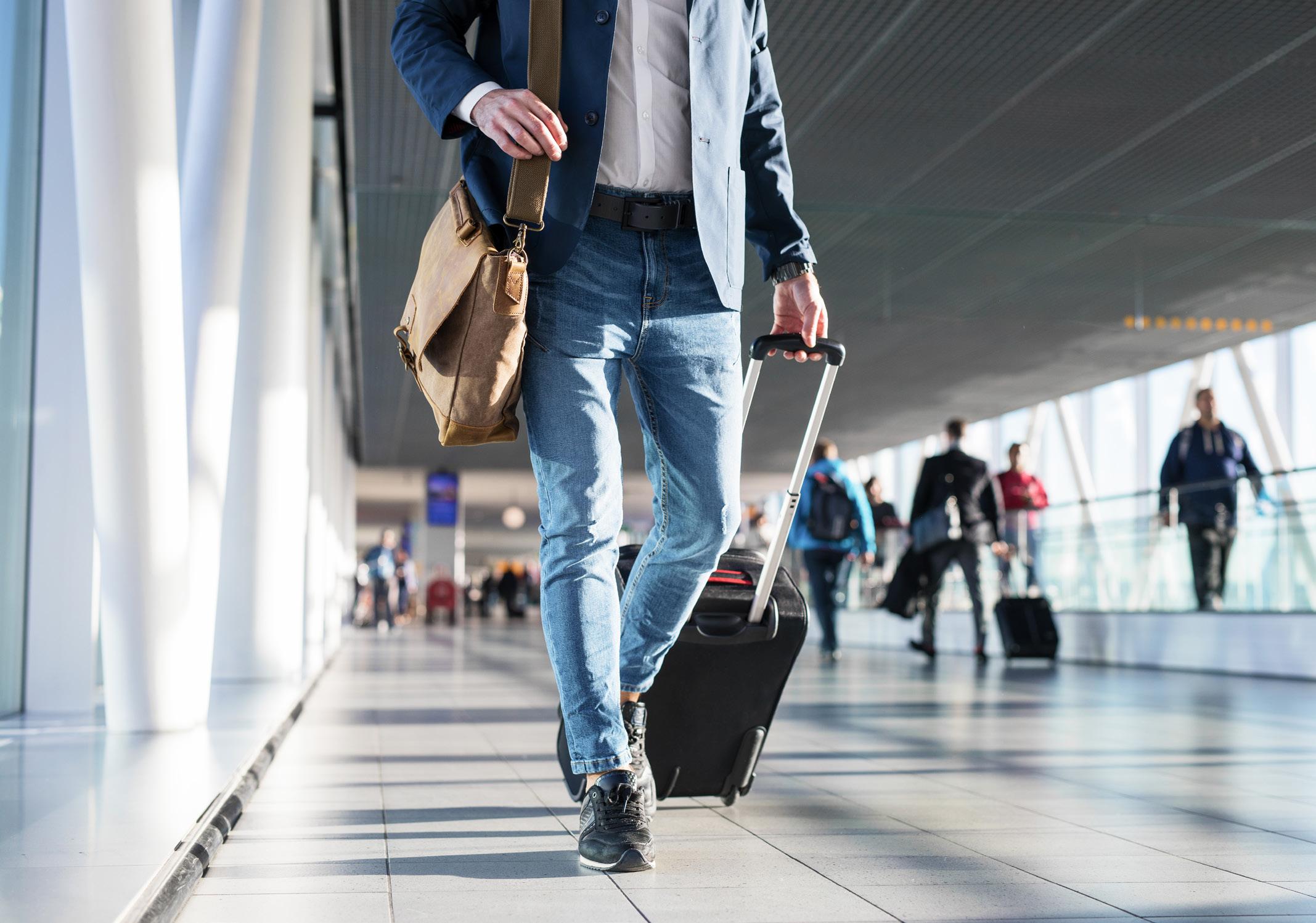
Foreign Trade Zone
Consulting
• Designation with FTZ board
• Preperation of warehouse compliance
• Activation of FTZ with CBP
Foreign Trade zone administration Customs Brokerage
• FTZ staff training maintaining FTZ complaince with CBP
About Foreign Trade Zones
Foreign Trade Zones (FTZs): Maximize Savings, Minimize Hassle
• Zone admissions
• Weekly Estimates and Entries
• Inventory reconciliation
A Foreign Trade Zone (FTZ) is a secure, designated area in or near a U.S. port of entry, authorized by U.S. Customs and Border Protection, where importers can store, assemble, manufacture, or process goods before they formally enter U.S. commerce.
Within an FTZ, companies can defer, reduce, or even eliminate customs duties and tariffs, improve cash flow, and streamline compliance. FTZs are a proven strategy for global supply chains to lower costs, increase competitiveness, and simplify operations.
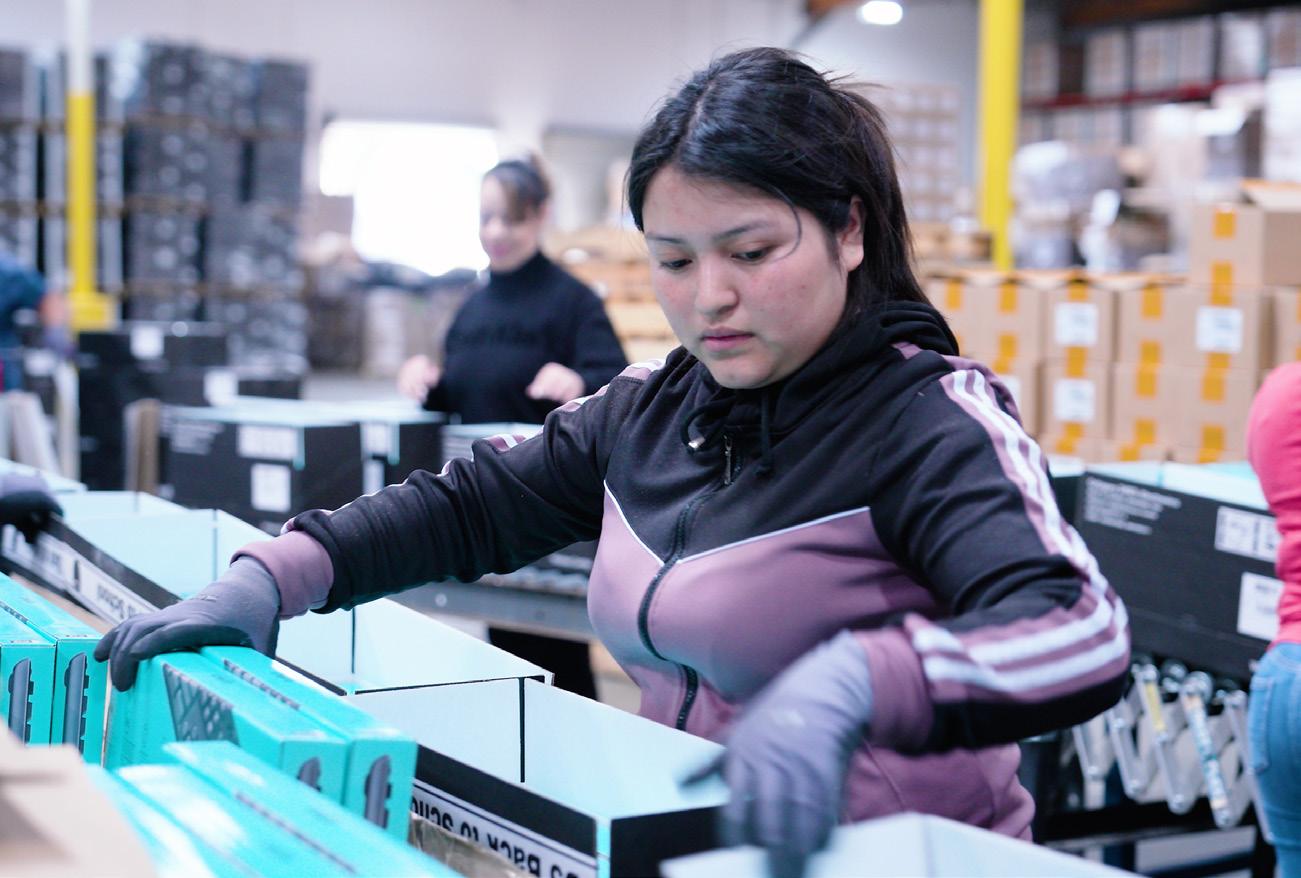
GPA SERVICE PORTFOLIO
B2B distribution – Wholesaleto-retail fulfillment with EDI or API integration and compliance management.
D2C e-commerce – Full-service fulfillment with real-time inventory visibility.
Co-packing services – Retail display assembly and promotional packaging.
Reverse logistics – Complete returns management with realtime customer portals.
Dedicated warehousing – Private facility management and optimization.
“It’s another example of how we initiate ways to help our customers save money and control their expenses,” acclaims Drummer.
This demonstrates the company’s philosophy of proactive customer support through strategic infrastructure investments.
NAVIGATING UNCERTAINTY
The FTZ certification process began well before US President Donald Trump’s trade tariffs came into effect.
However, the uncertainty of these tariffs is the biggest challenge everyone is facing right now, according to Drummer.
“Tariff uncertainty has created a paralysis in import decision-making, with clients postponing orders pending clarity on final rates and cost allocation,” he warns.
Thus, the company’s immediate priority is maintaining operational capacity and workforce stability while helping customers navigate this uncertainty.
GPA is also concerned about the administration’s methods of enforcing immigration laws and deporting non-citizens.
“The randomness of the raids and apparent insensitivity to whether the people they are rounding up are here legally or not has even legal residents afraid to come to work,” Drummer says.
“In certain areas of the country, like CA, a significant portion of the population working in warehouses are not properly documented. Whether
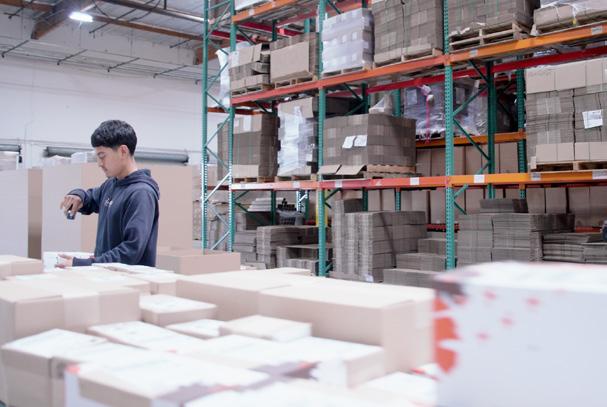
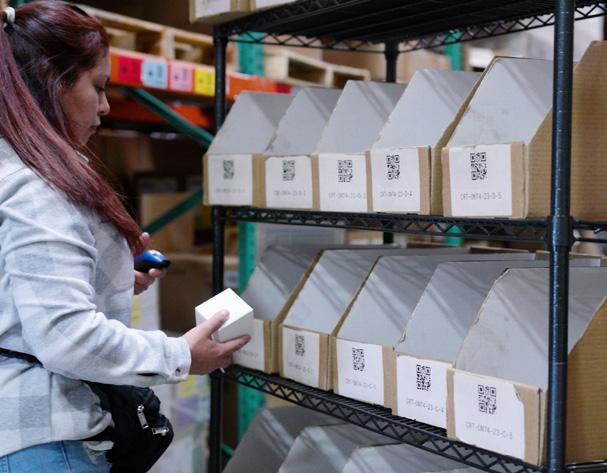
they are deported or just deterred from coming to work, it will lead to labor shortages, increased labor costs, and difficulty in meeting our committed service-level agreements (SLAs).”
Maintaining SLAs is one of three priorities that GPA’s strategy focuses on, along with protecting its workforce and positioning the company as a solution for companies considering outsourcing their private warehouse operations to experienced 3PL providers who can navigate these complex challenges.
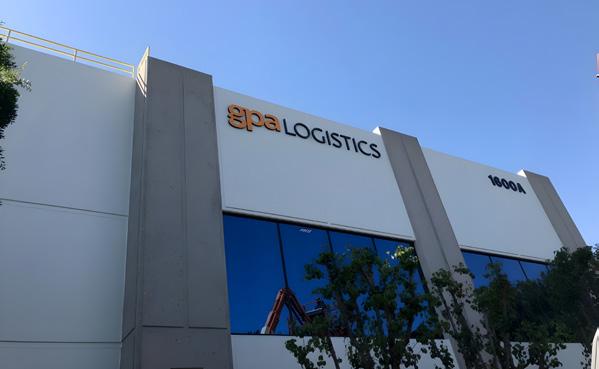
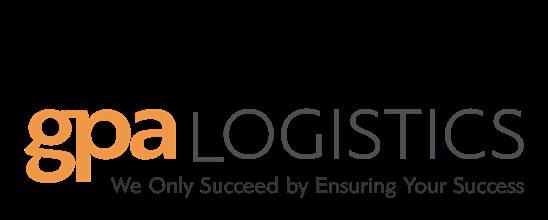
Tel: 909-349-4769
my3pl@gpalogisticsgroup.com
www.gpalogisticsgroup.com
M and S Wood Works Pallets is a trusted name in quality pallet manufacturing and woodwork solutions. Based on a commitment to durability, precision, and customer satisfaction, we specialize in crafting highgrade wooden pallets tailored to diverse industrial and commercial needs.
Whether you need standard or custom-sized pallets, our team ensures every piece meets strict quality standards.
With years of experience and a passion for reliable craftsmanship, M and S Wood Works Pallets delivers products that support businesses across logistics, warehousing, and manufacturing sectors.
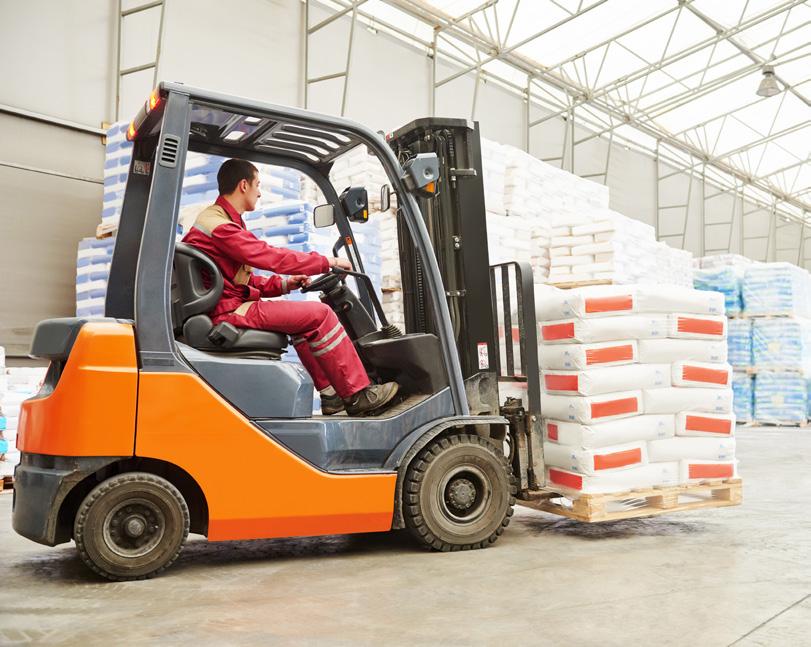
Phone: (909) 770-6589
Email: Info@mnspallets.com
Website: www.mnspallets.com
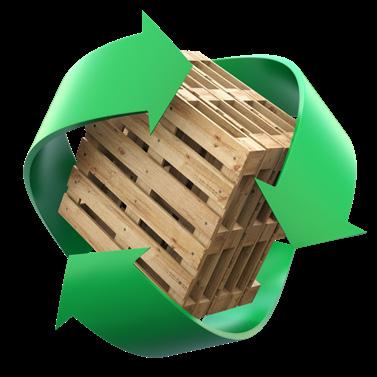
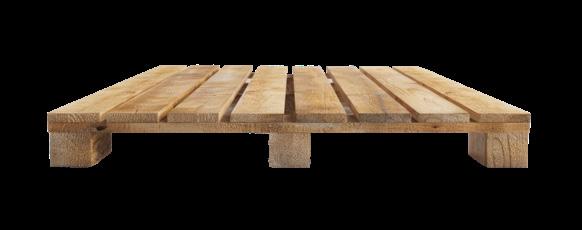
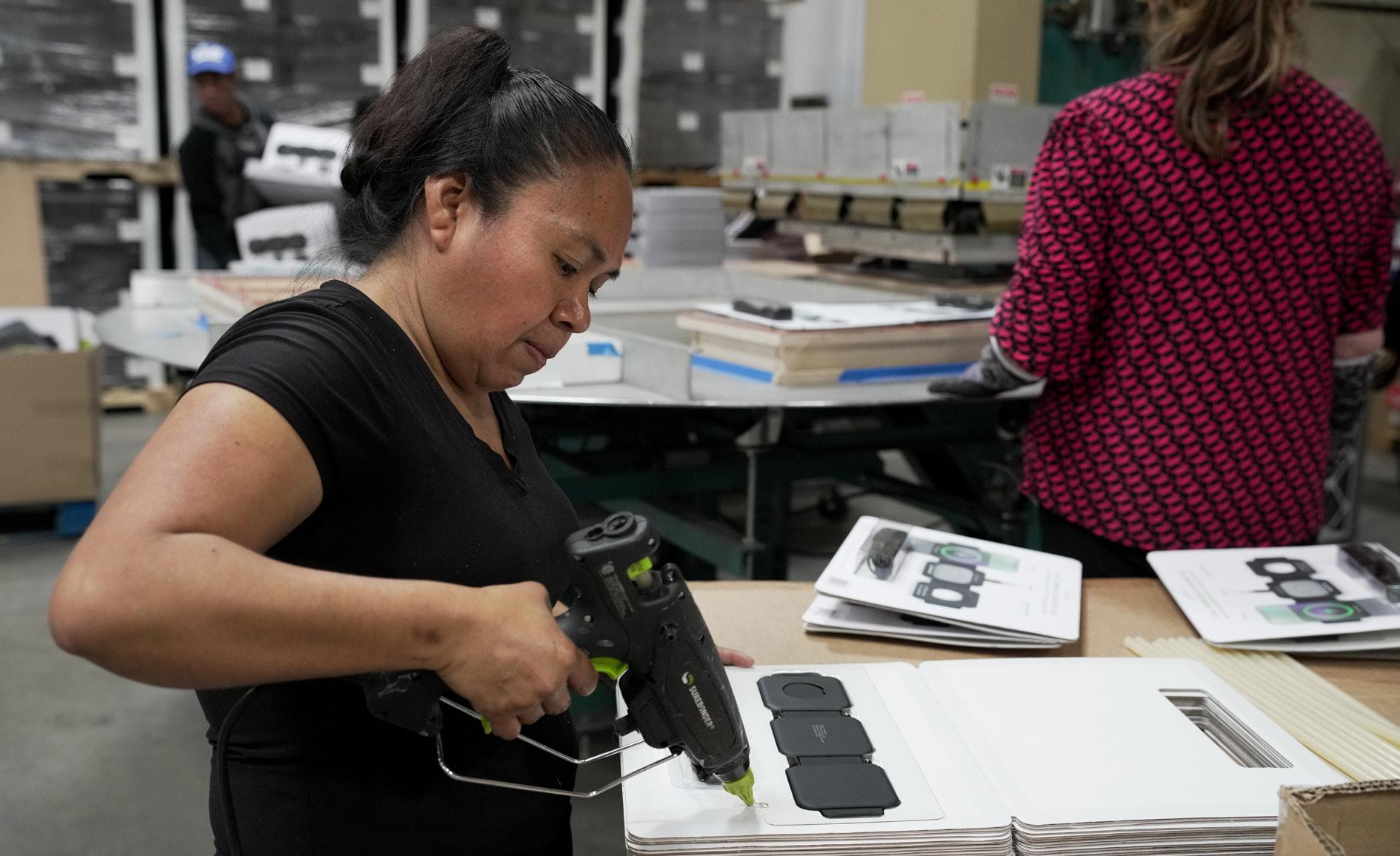
THE NEW AGE OF COLD CHAIN
On a mission to provide innovative supply chain solutions to its customers, Arcadia Cold blends modern facilities with best-in-class technology and decades of industry experience. Chris Hughes, co-Founder and CEO, tells us more
Writer: Lily Sawyer | Project Manager: Poppi Burke
The US cold chain logistics industry has been characterized by an active and evolving economy over the past 15 years.
This can largely be attributed to a rise in mergers and acquisitions within the private equity sector during the mid-2000s – a space which had previously been capitalized by non-institutional sponsors, including families and high net-worth individuals.
As a result, three major new players began to dominate the market –Americold, Lineage, and AGRO Merchants Group.
Following the COVID-19 pandemic,
the sector continued to develop further as a wide array of new capital investors and start-ups emerged, seeking to monopolize on the postpandemic growth of the refrigerated and frozen food categories, alongside e-commerce and direct-to-consumer demand.
“Some of those new entrants have been successful in fulfilling their investment thesis, but many have not due to the operational experience required to be truly successful as a cold storage third-party logistics (3PL) provider,” opens Chris Hughes, co-Founder and CEO of Arcadia Cold (Arcadia).
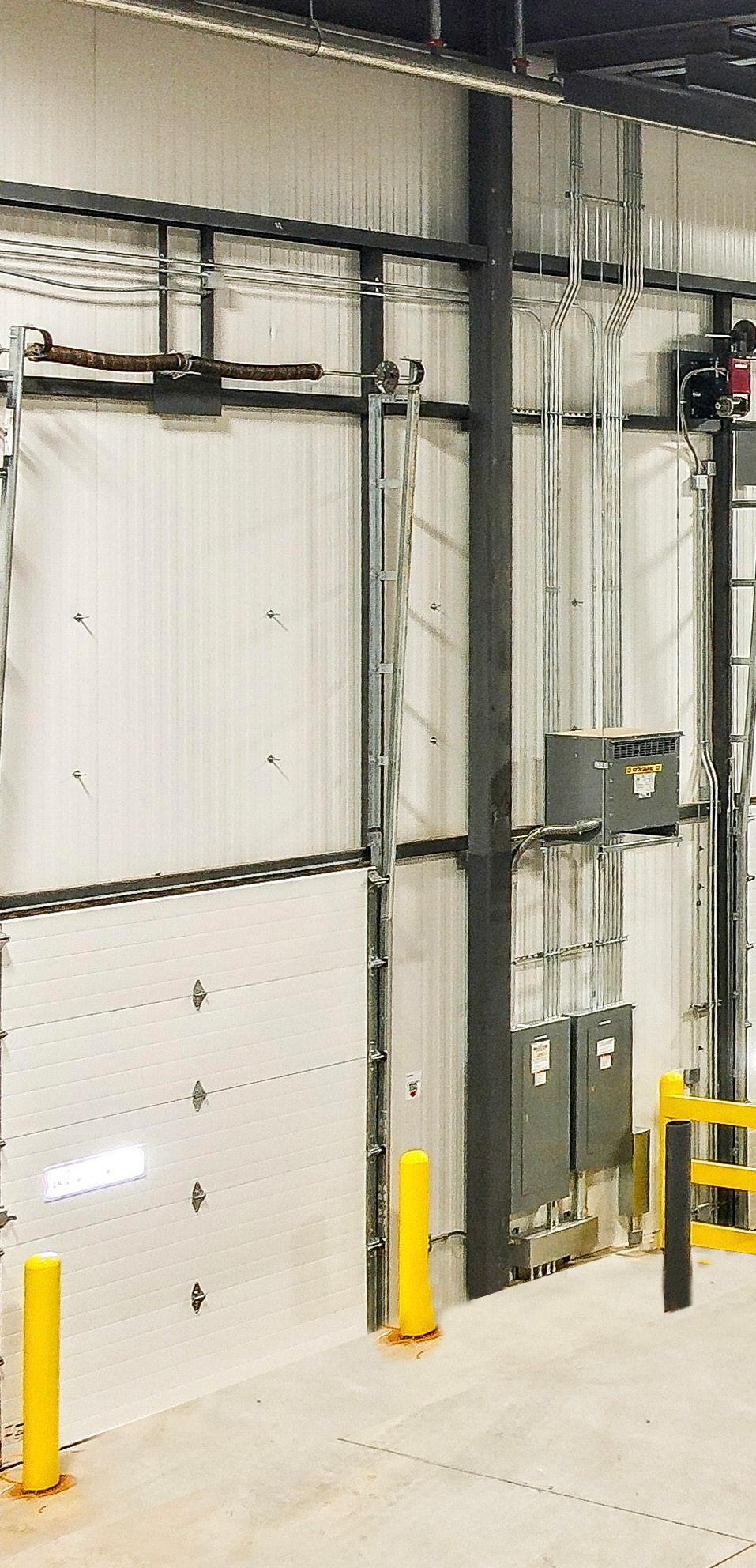
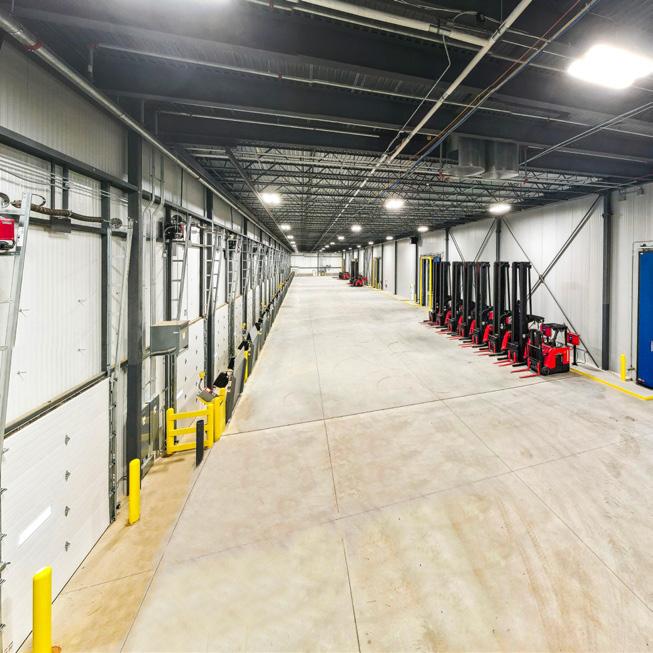
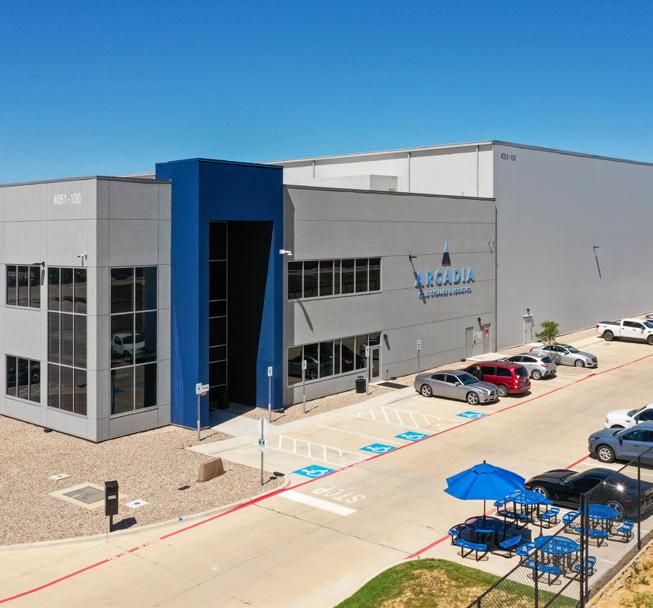
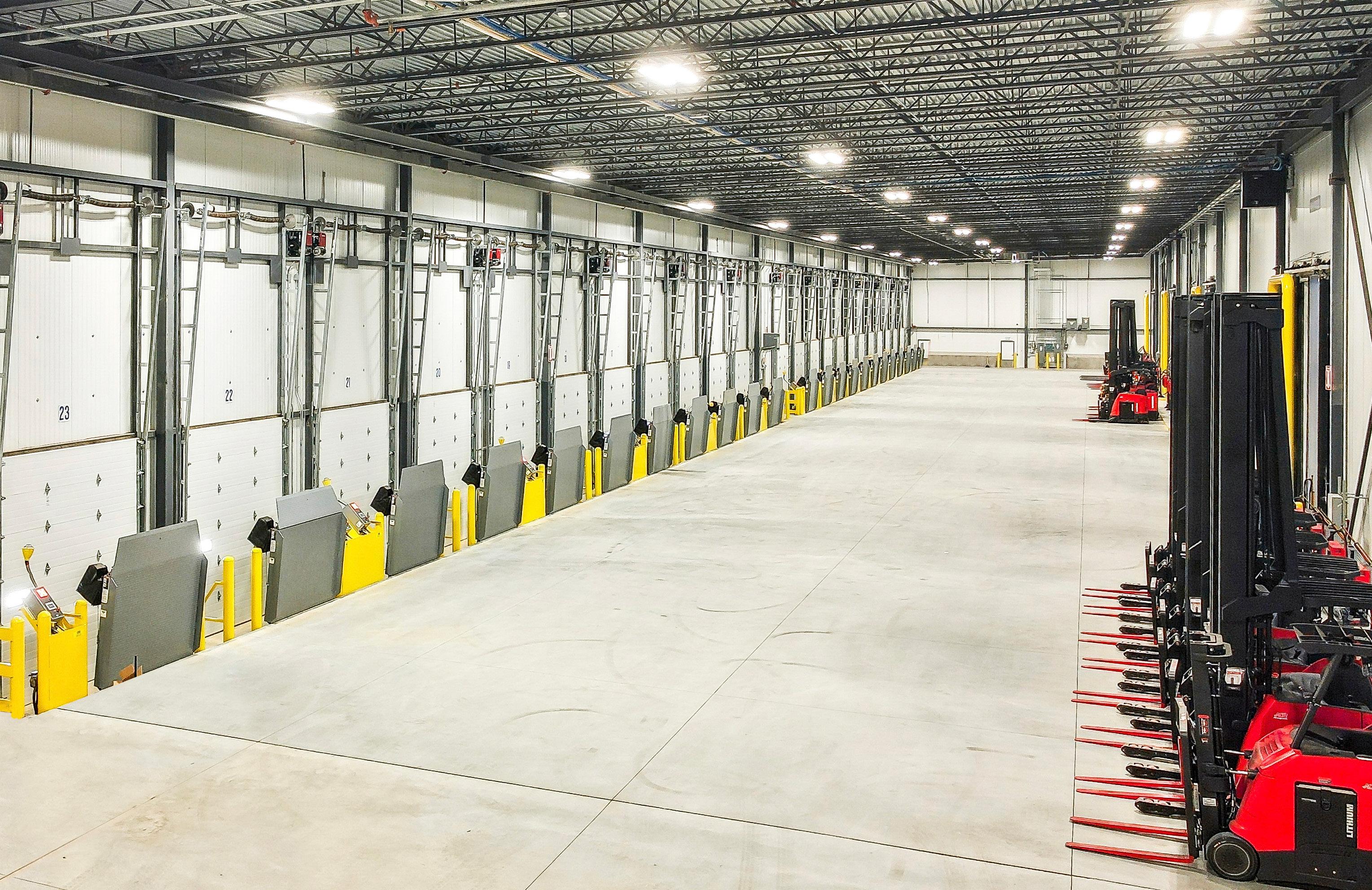
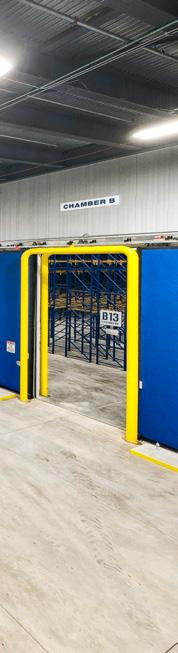
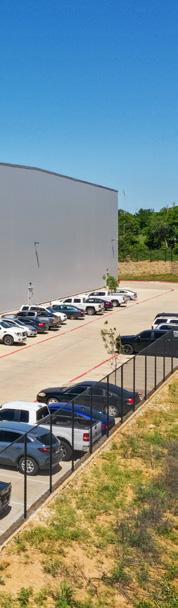
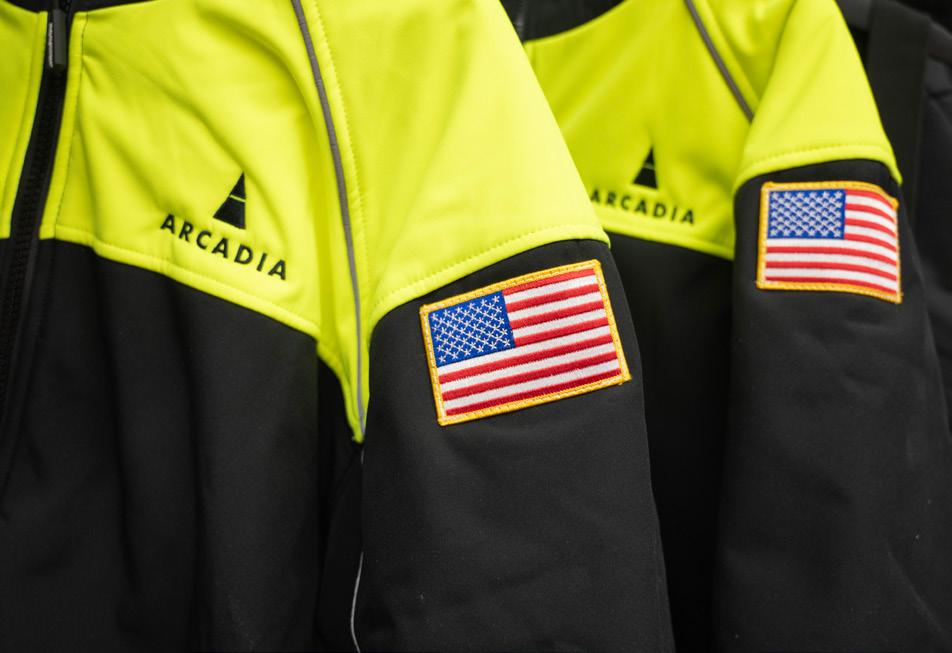
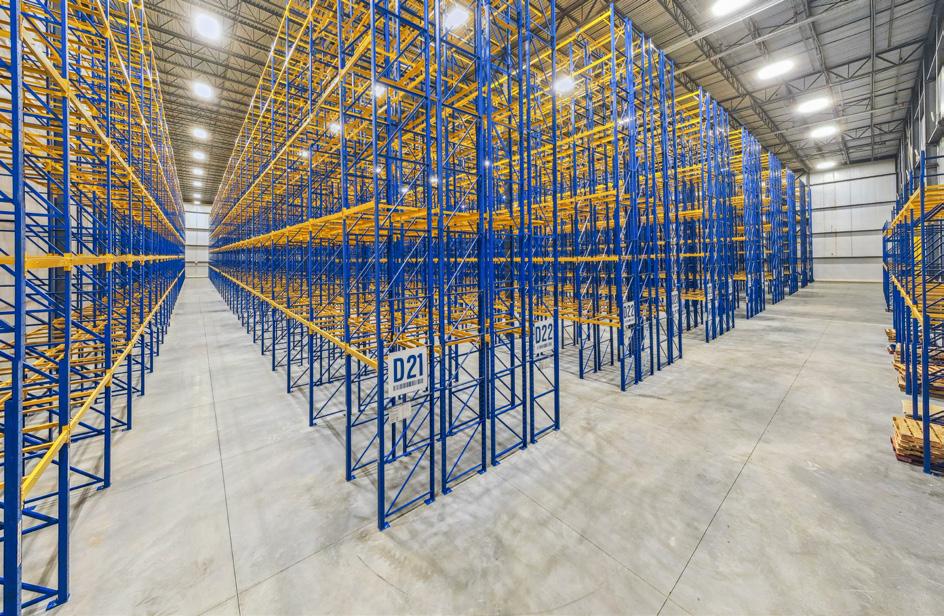
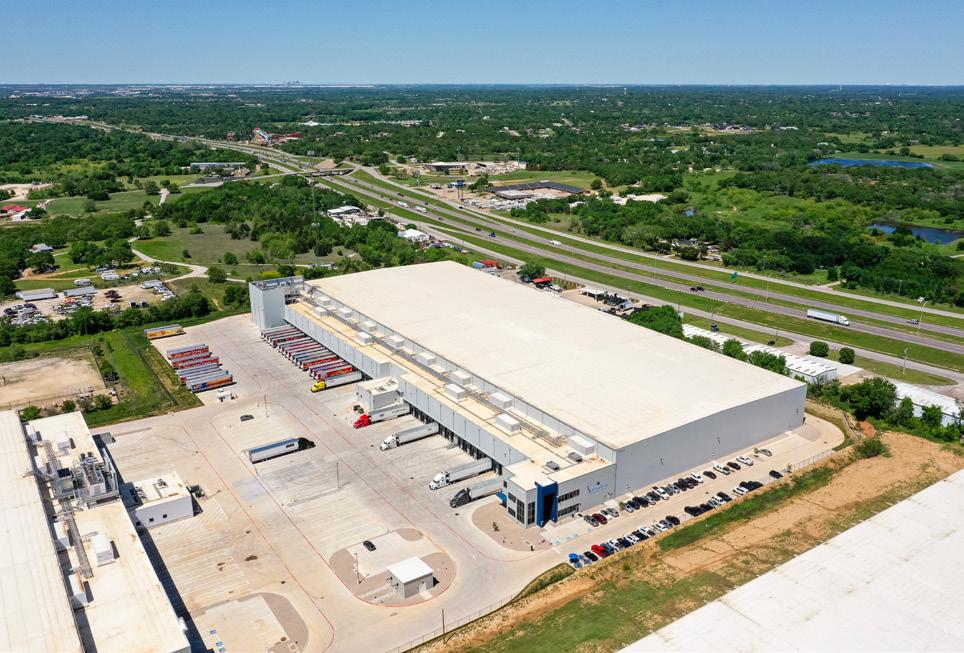
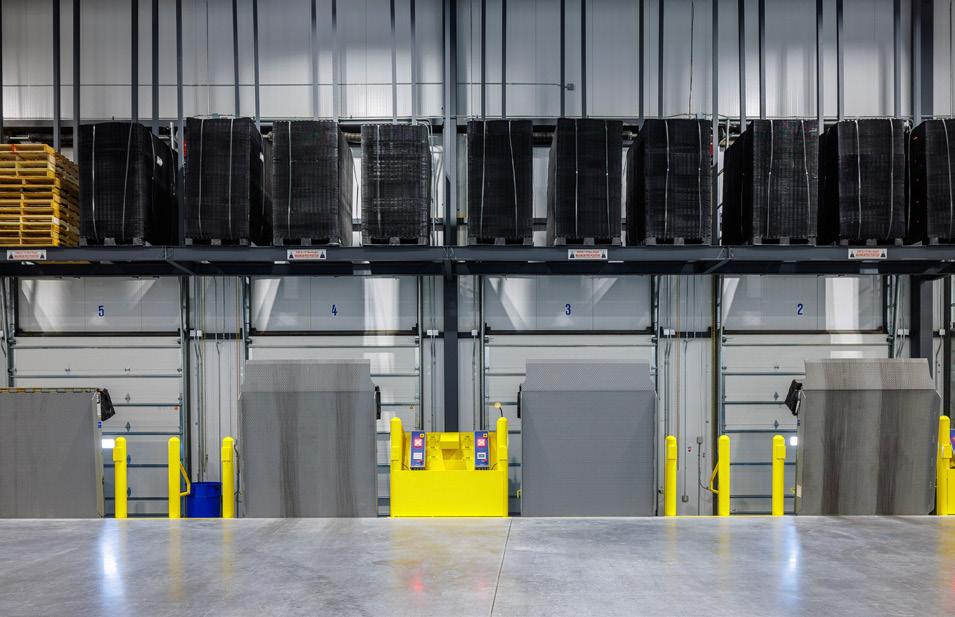
A premier 3PL provider of cold storage and handling services, Arcadia boasts seven operational facilities across the US, with two more slated to launch in Q1 2026.
The company’s locations in Atlanta, Georgia; Hazleton, Pennsylvania; Burleson, Texas; Phoenix, Arizona; Reno, Nevada; Jacksonville, Florida; Charleston, South Carolina; Joliet, Illinois (Q1 2026); and Crown Point, Indiana (Q1 2026) amount to 350,000 pallet positions and 2.6 million square feet of refrigerated and frozen capacity.
“We support a wide array of retail grocery, food service distribution, and e-commerce end markets,” he details.
Arcadia also represents a diverse set of food manufacturers who produce and sell consumer packaged goods, poultry, beef, dairy, seafood, beverages, probiotics, and other
commodities for both business-tobusiness (B2B) and business-toconsumer (B2C) needs.
STANDING OUT FROM THE CROWD
Since Arcadia’s inception in early 2021, its modus operandi has been to design, build, and operate stateof-the-art facilities in key logistical areas across the US to support the distribution, storage, and handling needs of its customers.
“The key to our strategy – and our primary area of differentiation –has been to build our facilities with careful design considerations that meet the modern product handling requirements of today and well into the future,” Hughes reveals.
The company also strives to provide industry-leading technology and supply chain information capabilities,
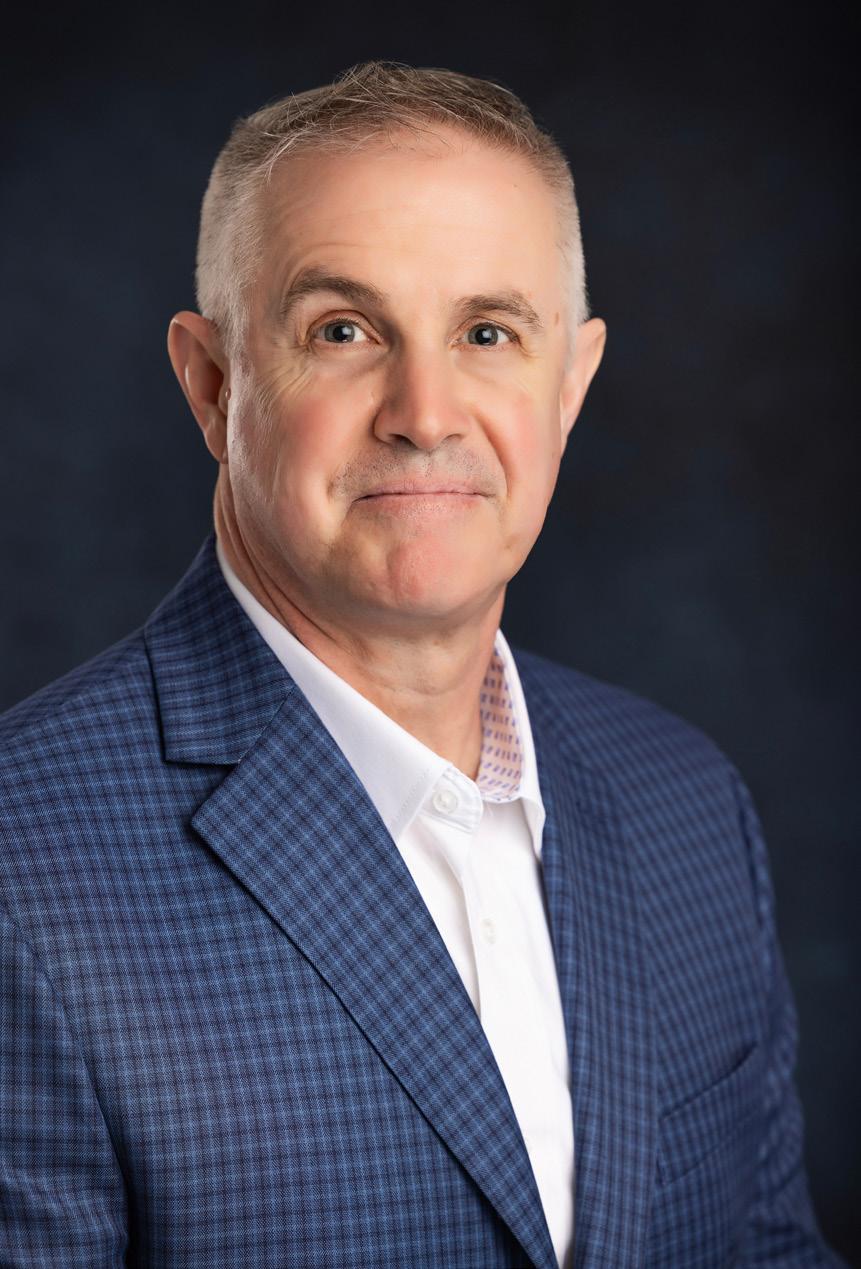
offering the best customer experience of any provider in the industry.
Arcadia’s greenfield strategy provides unique value to customers that many of its competitors cannot – offering a high-touch, customerfocused model that operates within new, highly convertible and efficient facilities located in key supply chain hubs across the country.
“As many existing providers have grown largely through acquisitions, this has resulted in somewhat disparate systems, disjointed and inaccurate information, and older, less efficient buildings – all driving higher costs and lower customer satisfaction,” he observes.
As such, Arcadia provided muchneeded market improvement through its greenfield model and has been capitalizing on this approach since inception.
COULD YOU TELL US MORE ABOUT YOUR CORPORATE PURPOSE STATEMENT?
Chris Hughes, co-Founder and CEO: “Our corporate purpose statement, ‘Creating a Legacy for Good’, is a double entendre of sorts.
“We are building exceptionally well-designed hard assets in our buildings that will withstand the test of time for years to come, but we are also focused on making an important impact on the communities in which the buildings are located.
“We understand that we are creating well-paid positions in new markets, and those positions are filled by people looking to further their individual and family’s financial well-being.
“Arcadia has a direct influence on helping folks put their kids in school, renting or buying a new home, or simply improving their way of life.
“The multiplicative effect when you are talking about 70-100 employees in each of our locations is a wonderful thing to think about. To me, this is the most important legacy of what our growth vision is about. The profits always follow good intentions.”
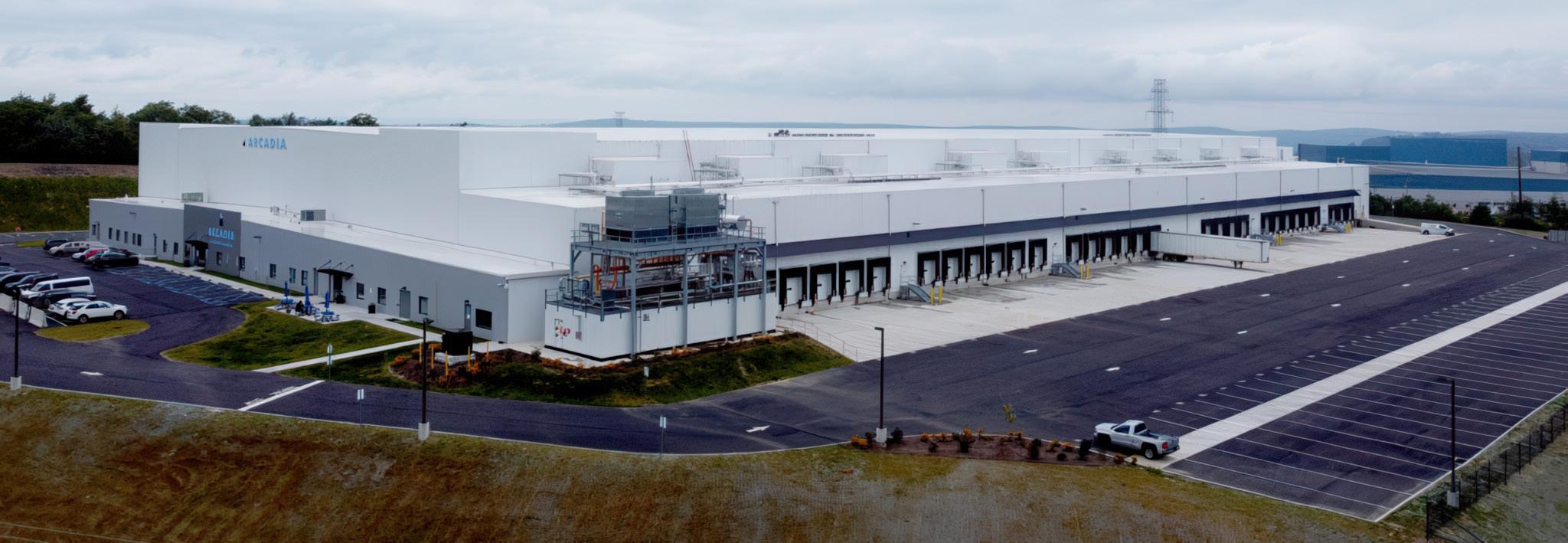
Innovative Refrigeration Systems and Arcadia Cold:
A Proven Partnership in Cold Storage Excellence
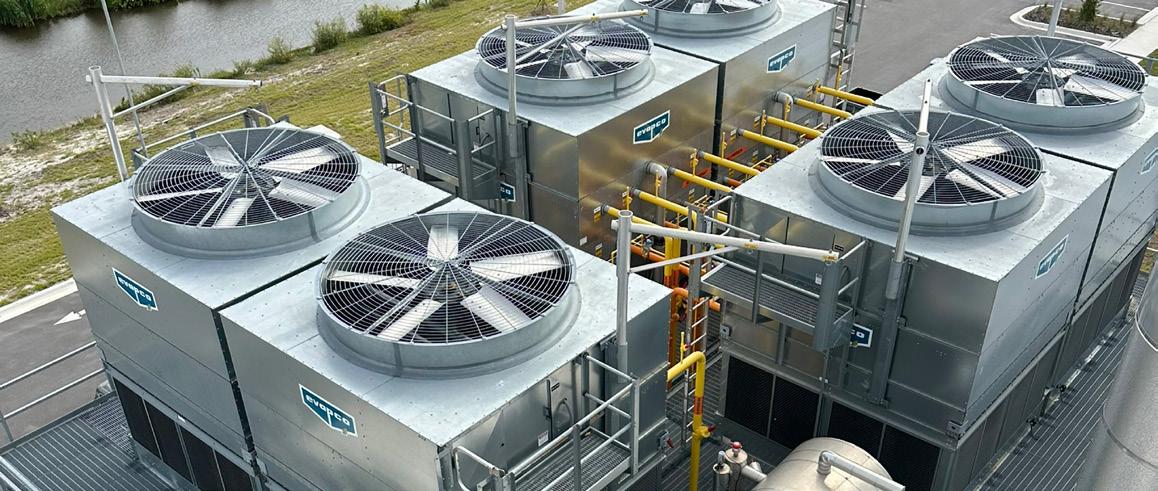
Innovative Refrigeration Systems is proud to partner with Arcadia Cold on a growing portfolio of cutting-edge cold storage facilities designed for the modern food supply chain.
Arcadia’s expertise in cold chain logistics and third-party logistics operations pairs seamlessly with Innovative’s leadership in natural refrigeration design-build solutions, specializing in transcritical CO₂ and ammonia systems. Together, we’re delivering scalable, energy-efficient systems tailored to the evolving and rapidly growing needs of perishable food manufacturers and retailers.
In Jacksonville, FL, a 315,000 square foot facility went online in October 2024. Engineered for high-volume throughput and flexibility, it includes nearly 900,000 lbs of blast freezing capacity per 24 hours, 1,500 TR of refrigeration, and fully convertible temperature zones to support a range of customer needs.
Currently underway is Charleston, SC, which is set for completion in 2025, spanning 250,000 square feet and follows the same high-performance design standards, including a 640 TR refrigeration system and multi-temperature room flexibility.
Our collaboration of facilities with Arcadia Cold are outfitted with premium, custom features tailored specifically for each project. These include rooftop-mounted penthouse evaporators, packaged mechanical houses, and VFDs for
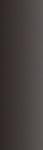

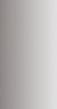
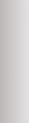

optimized energy efficiency. Waste heat is recovered through glycol underfloor warming systems, supporting long-term sustainability and performance. Intelligent demand-based controls with real-time power monitoring, stainless steel valve station piping, and all-welded valves ensure durability, precision, and control at every level.
These facilities represent just a few examples of the highquality, high-efficiency cold storage infrastructure that defines our ongoing partnership with Arcadia Cold.
By combining Arcadia’s operational excellence and deep understanding of cold chain logistics with our technical expertise in natural industrial refrigeration, we’re continuing to set new standards for what modern cold storage can achieve. Collaborative solutions that are not only fit for today’s demands, but ready for tomorrow’s growth.
Innovative Refrigeration Systems specializes in:
• design/build
• compliance
• energy efficiency
• engineering services
• refrigeration/compliance training
• process safety/risk management software
We also offer service coverage anywhere in the continental US, Alaska, Canada and the Caribbean.
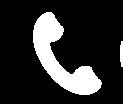

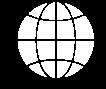
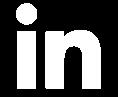
Differentiated by more than just its operating model, the company’s strong culture further sets it apart from the competition.
“We’ve intentionally built our culture by developing our core values – community, impact, accountability, humility, integrity, and transparency. I don’t think you can build a highly successful company without building an exceptionally strong culture from within,” Hughes reflects.
Recruitment, training, and hiring likewise play into the company’s culture as it seeks to train and recruit individuals who will lean into its values.
Hughes also believes that Arcadia’s internal beliefs naturally overflow into the relationships it builds with customers.
“If our customers trust that we will be transparent and accountable for our actions, be open and honest, and demonstrate integrity in everything
we do, they will trust us with their business and their brand,” he details.
Ultimately, Arcadia believes it is a custodian for its customers’ brands – a responsibility the company takes very seriously.
TECH-AHEAD
Another incredibly important part of Arcadia’s service offering is its technology architecture – something that drives the success of the business and is a huge differentiator in the market.
It’s also an area the company spends considerable time and resources on to advance overall functionality for the benefit of its customers.
“Given that we started the company from scratch in 2021, we needed to select, test, implement, and train our entire organization on the new, state-of-the-art technology,” Hughes emphasizes.
“WE’VE INTENTIONALLY BUILT OUR CULTURE BY DEVELOPING OUR CORE VALUES –COMMUNITY, IMPACT, ACCOUNTABILITY, HUMILITY, INTEGRITY, AND TRANSPARENCY”
– CHRIS HUGHES, CO-FOUNDER AND CEO, ARCADIA COLD
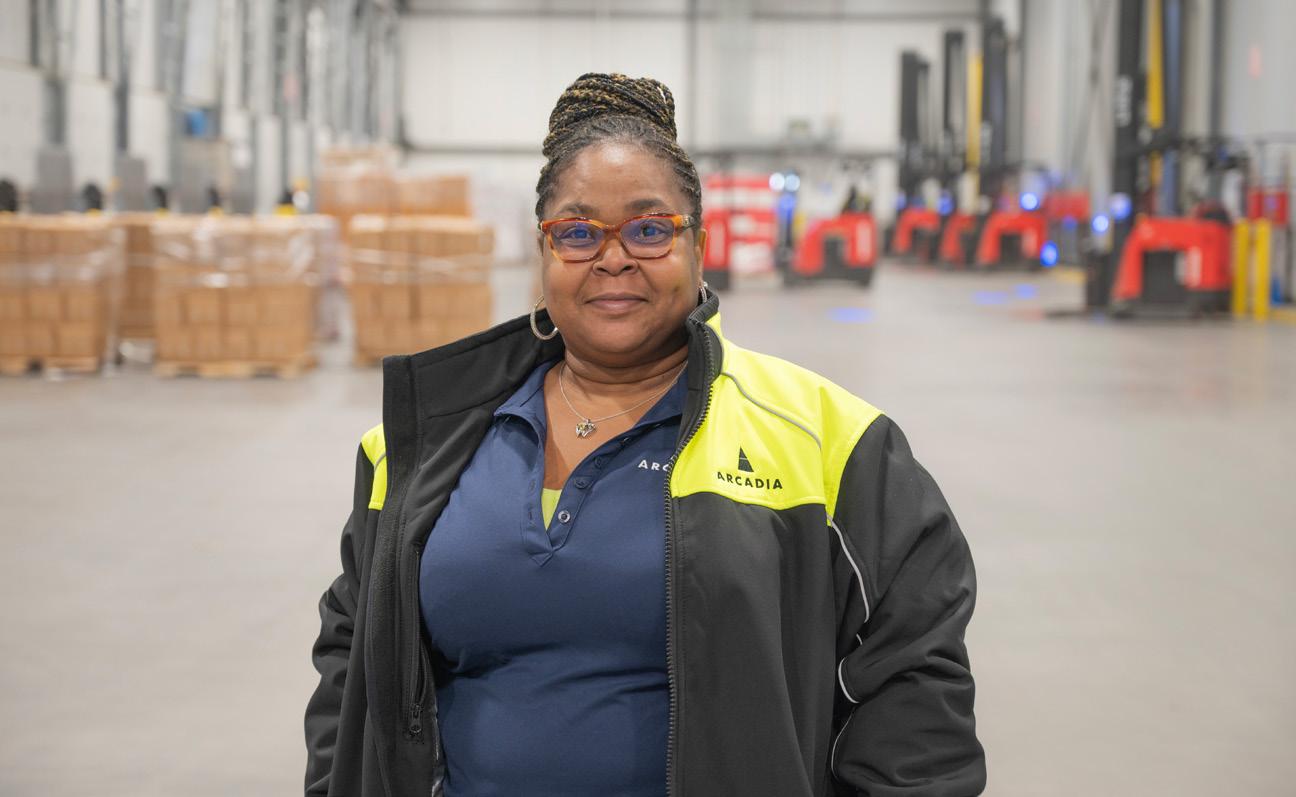
This included training around the warehouse management system (WMS), transportation management system (TMS), appointment management system (AMS), finance and accounting, human resources (HR) and benefits, billing, and its proprietary customer-facing web portal, ArcadiaOne™.
“While our competition also has these types of systems, they might have been cobbled together through acquisitions of disparate systems or built from scratch – in either case, they lack the best-in-class functionality that our systems possess,” he adds.
Moreover, Arcadia offers a single system platform across its entire network through its software-as-aservice (SaaS)-based supply chain management system, Blue Yonder, which provides customers with uniform, consistent, and real-time information – regardless of where their product is stored within the network.
A single sign-in affords a real-time view into all aspects of any given customer’s supply chain, including inventory and order status, product hold and release functionality, realtime reporting and alerts, and a highly summarized invoicing and paperwork function via ArcadiaOne™.
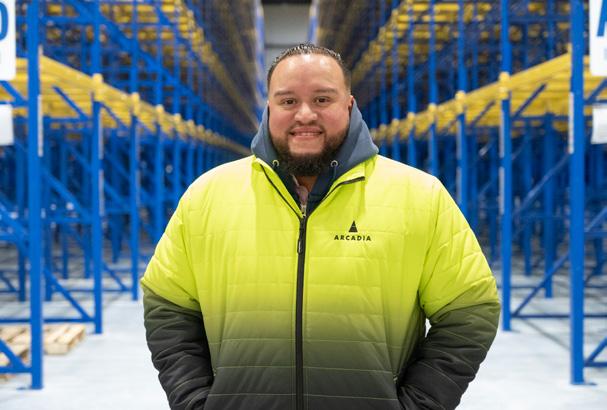
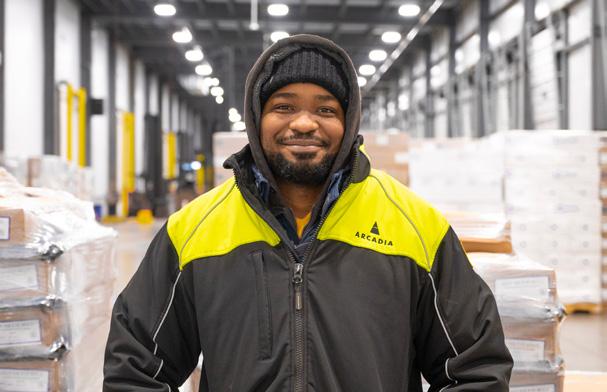
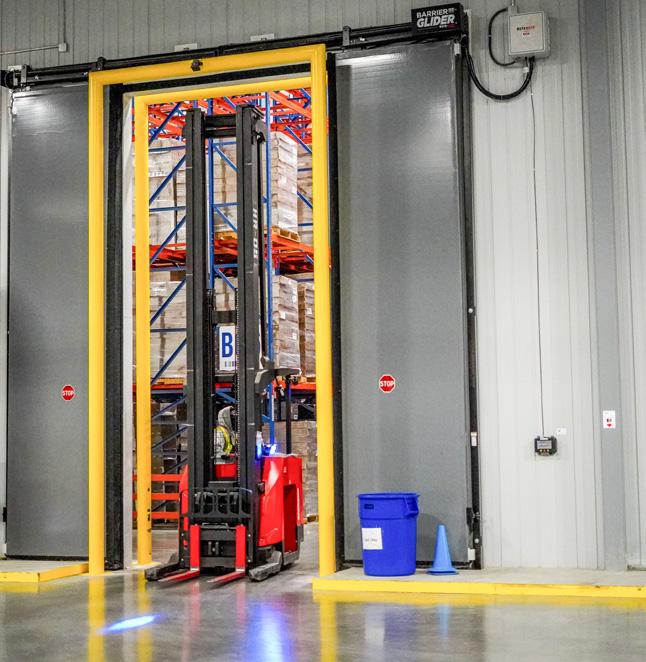
“I’m very pleased with where we are with this facet of our operations, and we are laser-focused on furthering the functionality of future releases for our current and prospective customers,” Hughes informs.
SMOOTH OPERATION
Arcadia believes operational performance is the cornerstone of any 3PL provider and is able to flawlessly receive and process customer products and pick, stage, and ship orders.
“Without this ability, it defeats the purpose of our customers outsourcing to us in the first place,” Hughes notes.
As the company was able to build its operating procedures from scratch, it was also able to leverage its management team’s collective cold storage industry experience – which amounts to over 110 years – to ensure it could purpose-build a best-in-class operating model.
“In short, we built our operations around all the obstacles and irritants we’d encountered in the past, ensuring our customers get the best experience across the supply chain, no matter which stage or point they interact with us,” he outlines.
For Arcadia to achieve this status of excellence, however, it wasn’t only down to the hard work and effort of its team – the company is fortunate to have partnered with exceptional trading partners.
These include, but are not limited to, material handling equipment (MHE),
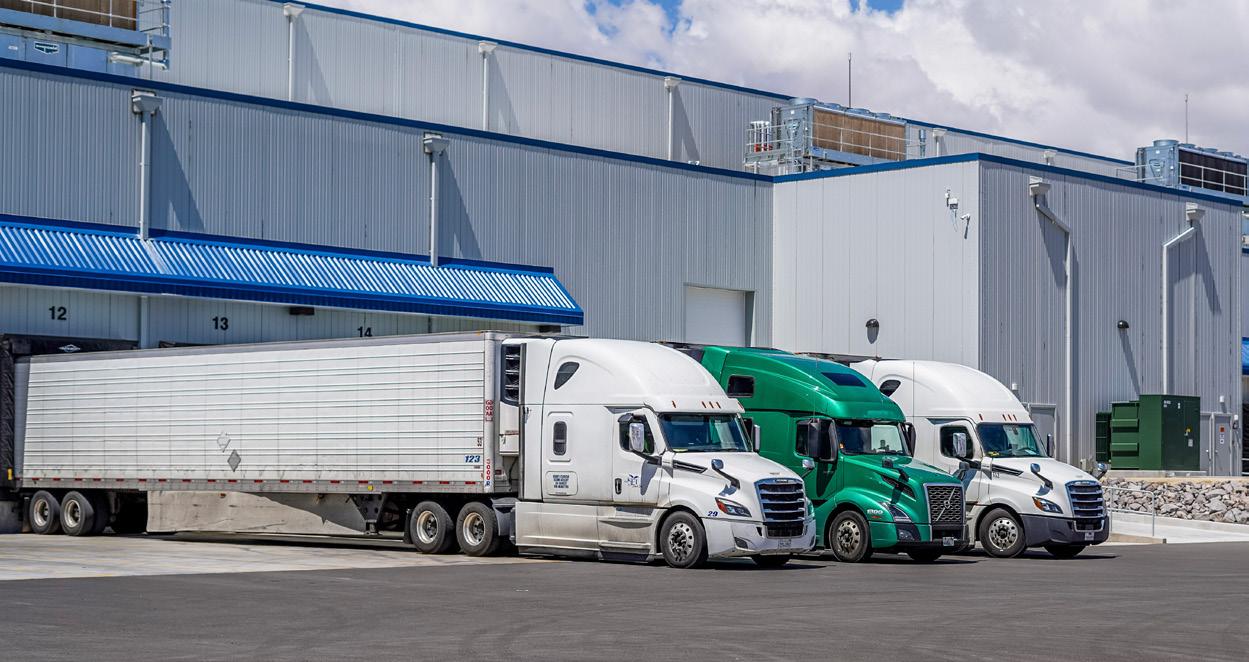
software and hardware, cold storage protective apparel, maintenance providers, and its financial sponsor and growth partner, Saxum Real Estate.
“As a start-up, we were blessed to have the commitment and trust of our financial partners and operational suppliers. As a result, those relationships will be long-lasting and mutually beneficial,” Hughes assures.
For Arcadia, trust and commitment are a two-way street – and many of its trading partners are the reason it has grown to the size it is today.
CONTINUED GROWTH
Alongside its partners and suppliers, Arcadia is also proud of its dedicated team of employees.
“I am extremely fortunate to work alongside my committed team day in, day out,” Hughes smiles.
Doubling down on the notion that culture is directly correlated to the success of any business, Hughes points out that his team has been laser-focused on ensuring the company’s ongoing quality performance by hiring and retaining the right people.
“Each of my departmental heads is fully empowered to make decisions and be accountable for the performance management of our 250 teammates, fostering an environment of collaboration, accountability, and transparent communication,” he prides.
With utter trust in the quality and expertise his teammates bring to the
fore, Hughes is confident in the way the entire company is aligned on its goals and objectives, allowing it to exceed targets time and time again.
Going forward, Hughes’ priority is to ensure all nine of Arcadia’s buildings achieve their projected stabilized occupancy and that the company continues to execute its customers’ demands.
“My goal is to carry on providing the high level of customer service that we have to date and to monitor customer feedback on a regular basis,” Hughes surmises.
With plans already in place to continue to expand and diversify the number and type of facilities it operates, the company continues to grow alongside the satisfaction of its customers.
“We’re looking to achieve an even balance between distribution, port-based, and plant-proximate storage and handling services to offer a diverse set of capabilities for our customers to take advantage of,” he concludes.
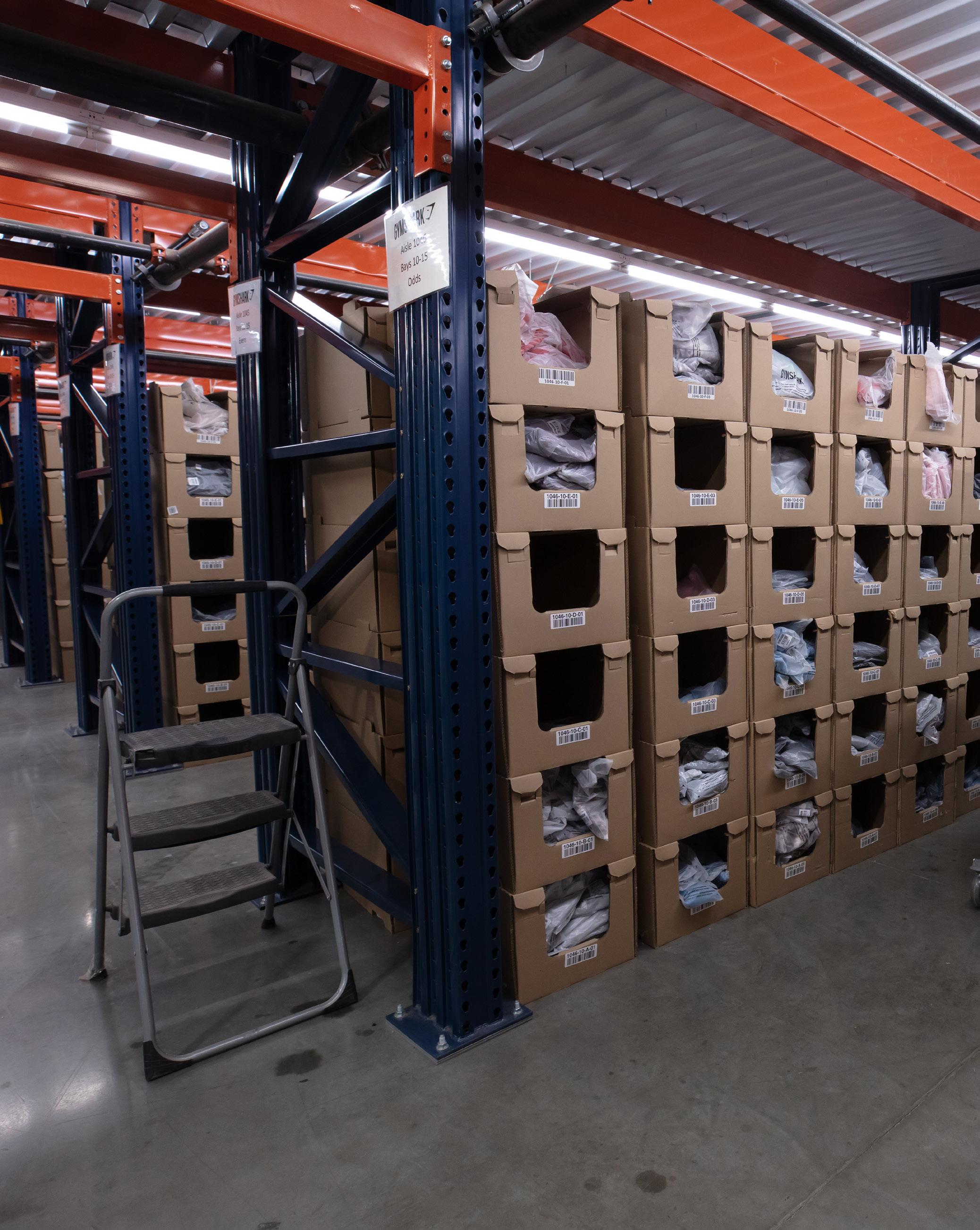
FULFILLING PROMISES FROM CLICK TO DELIVERY
A proven partner for e-commerce fulfillment solutions trusted by industryleading global brands, Radial offers scalable, reliable, and technology-driven solutions. We speak to David Welsh, Vice President of Operations, to learn more
Writer: Lauren Kania | Project Manager: Poppi Burke
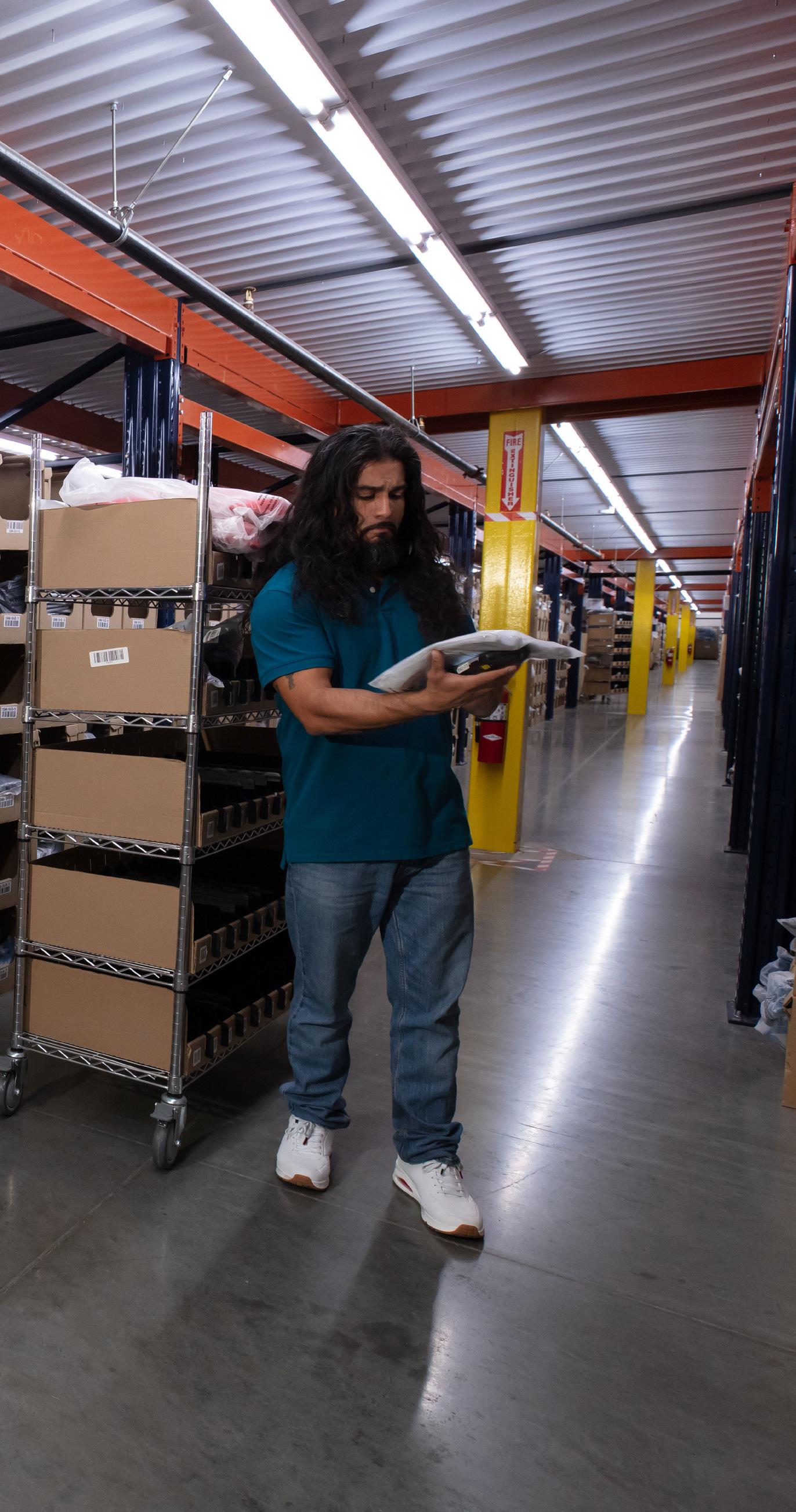
Built upon more than 40 years of e-commerce experience and providing intelligent solutions to the retail industry, Radial is where expertise meets excellence.
With a track record that speaks for itself, the company proudly offers innovation that drives operations, allowing businesses to stay ahead of the curve and provide shoppers with a seamless and consistent retail experience.
“Leveraging over four decades of industry expertise, Radial tailors its services and solutions to align strategically with each brand’s unique needs,” introduces David Welsh, Vice President of Operations.
“For modern brands seeking a streamlined onboarding process and flexible fulfillment model, we provide a configurable solution that optimizes space utilization and cost efficiency.”
The company was formed in April 2016 following the merger of Innotrac and eBay Enterprise, before it was acquired by leading Belgian postal operator, bpost, in 2017.
With this acquisition, Radial gained the capital and focus needed to continue innovating and improving its offerings.
Headquartered in King of Prussia, Pennsylvania, the company employs over 4,000 global team members and is the country’s largest third-party logistics (3PL) fulfillment provider, offering integrated payment, fraud detection, and omnichannel solutions to mid-market and enterprise brands.
“Our client base comprises approximately 150 leading retail brands and businesses spanning 15 diverse industry verticals, and our experience encompasses various retail niches, including apparel, footwear, health and beauty, home goods, and more,” details Welsh.
Operating more than 30 fulfillment centers in North America and Europe, Radial supports brands in tackling common e-commerce challenges.
With a commitment to fulfilling promises from click to delivery, the company empowers brands to navigate the dynamic digital landscape with the confidence and capability to deliver a seamless, secure, and superior e-commerce experience.
“Radial’s integrated solutions are also modular, so they can be implemented stand-alone,” furthers Welsh.
“We enable retailers to rapidly launch business models, continually improve commerce operations, and offer an omnichannel consumer experience.”
FOUR DECADES OF E-COMMERCE EXPERIENCE
Radial prides itself on assisting customers in processing orders smoothly with technology-driven solutions.
It does so by leveraging highly connected, cloud-based technology, providing a unified view of the entire order flow and ensuring efficient and accurate fulfillment from day one.
“Our platform enables connection to hundreds of pre-built integrations that allow us to instantly pull orders from any source, offering rapid, oneclick configurations with all of our clients’ sales channels and existing systems,” informs Welsh.
Additionally, Radial serves to differentiate itself through various benefits that are unique to its services.
“From our expert developers continually improving our technology to our dedicated operations staff personally serving consumers, Radial team members collaborate to achieve our clients’ business goals,” expands Welsh.
Equally, the company recognizes the power of data and importance of personalized support. Its solutions not only capture and analyze data end-to-end but also ensure that clients have a dedicated support system in place.
WHAT MAKES THE US SUPPLY CHAIN INDUSTRY AN EXCITING AND COMPLEX SPACE?
David Welsh, Vice President of Operations: “The most interesting and recent trends I’ve seen are niche solution companies popping up in the sector.
“They offer out-of-the-box solutions which are stack-andplay and solve specific problems, including returns processing technology, business-to-business (B2B) and retail compliance, and highly configurable systems. Some of the niche players are augmented with artificial intelligence (AI) and have powered their solutions to provide greater business intelligence, visibility, and scale as a result.”
Radial’s account managers leverage their in-depth understanding of clients’ business goals and challenges to align analytics insights with practical strategies. This effort ensures clients gain valuable insights from the data and have a clear roadmap for implementing changes that positively impact their operations.
“Every client benefits from our extensive experience, industry expertise, proven best practices, and market-leading capabilities,” explains Welsh.
“By bridging the gap between analytics and account management, we provide a holistic solution that goes beyond data analysis – it’s about translating insights into actionable plans and continuous support for sustained success.”
DELIVERING TANGIBLE RESULTS
Recently, Radial introduced Radial Fast Track – a scalable, cost-effective fulfillment for modern brands.
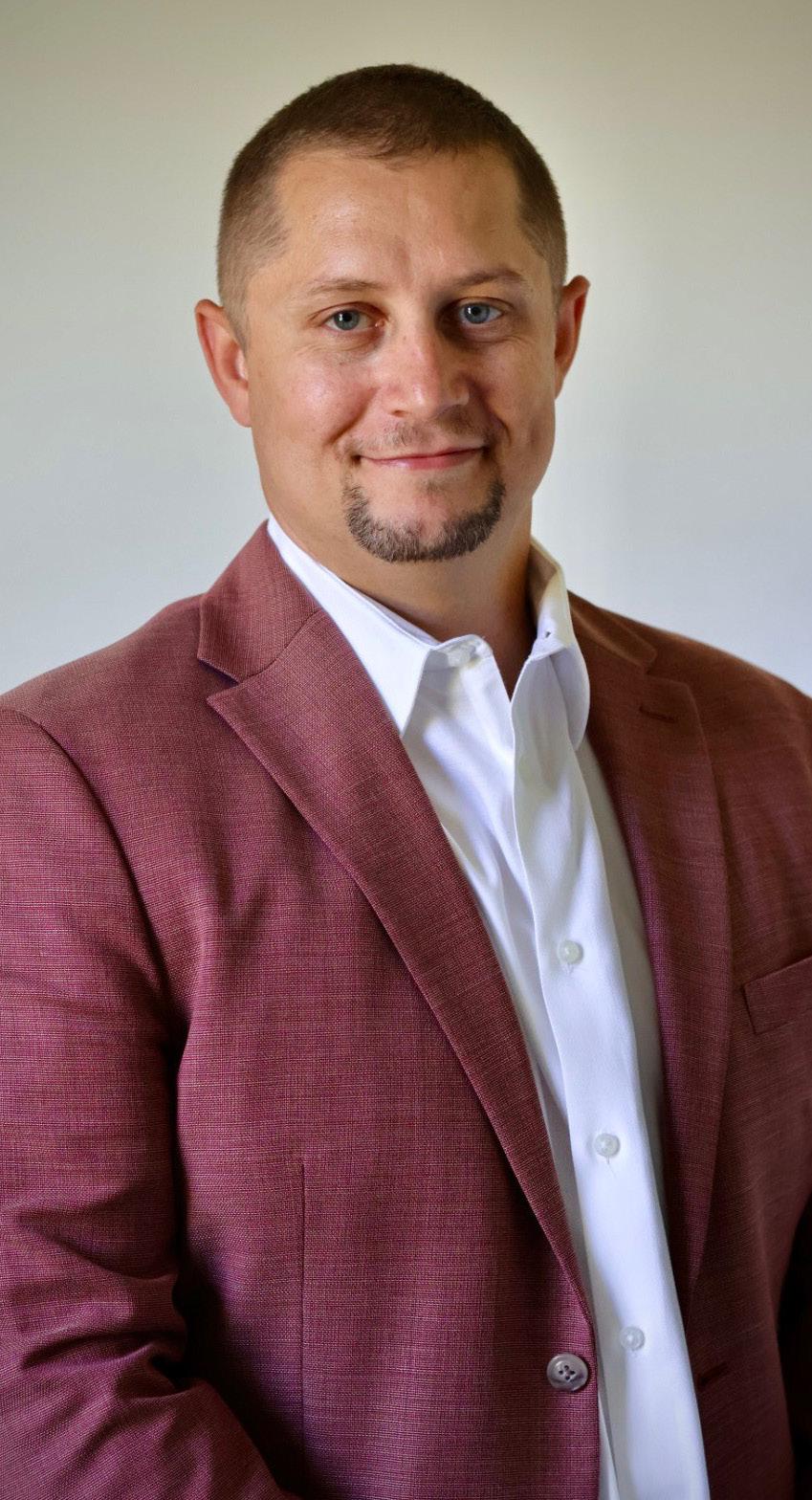

This new solution, which was formally launched in March 2025, was conceptualized to help brands rapidly scale fulfillment capabilities.
“Radial Fast Track allows us to offer a pay-as-you-go solution that provides high-performance, reliable technology systems with pre-built integrations and hundreds of commerce platforms and retail channels, as well as a simple set-up to get operational in as little as one week within our network of fulfillment centers across North America,” states Welsh.
The program was built as an innovative solution with the ideal blend of intuitive high-performance technology, reliable operational excellence, and deep industry expertise to ensure success.
Radial Fast Track is specifically designed to be easy to use, with fast integrations and easily configurable connectors, so modern brands
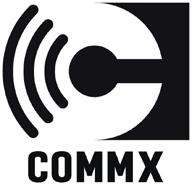
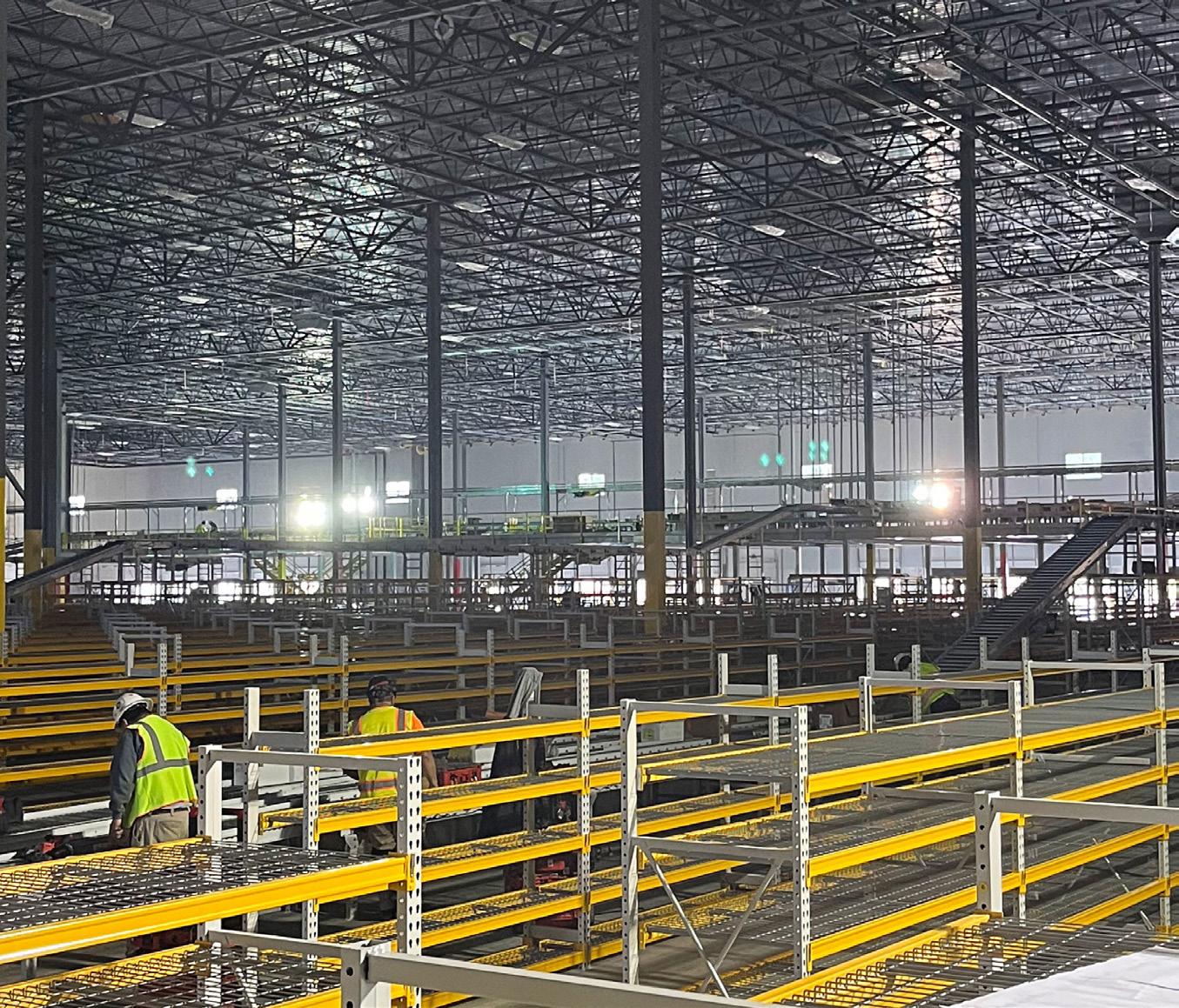
Building the foundation for your business.
Our services cover a broad range of essential technologies. From structured cabling using Cat6 and fiber optics, to building a robust network infrastructure that ensures smooth, high-speed data transmission, CommX Networks designs systems that are both future-proof and tailored to specific needs.
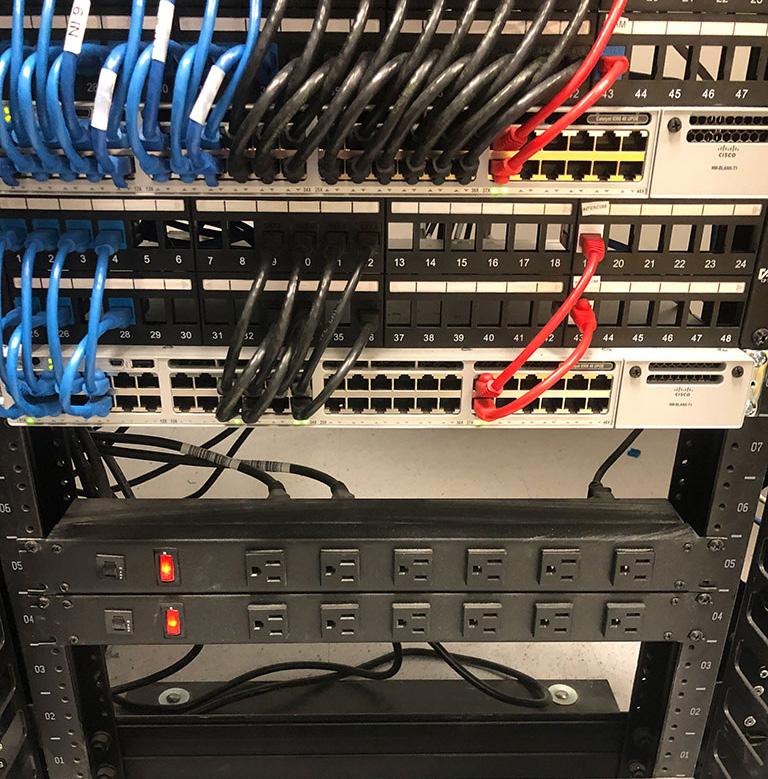
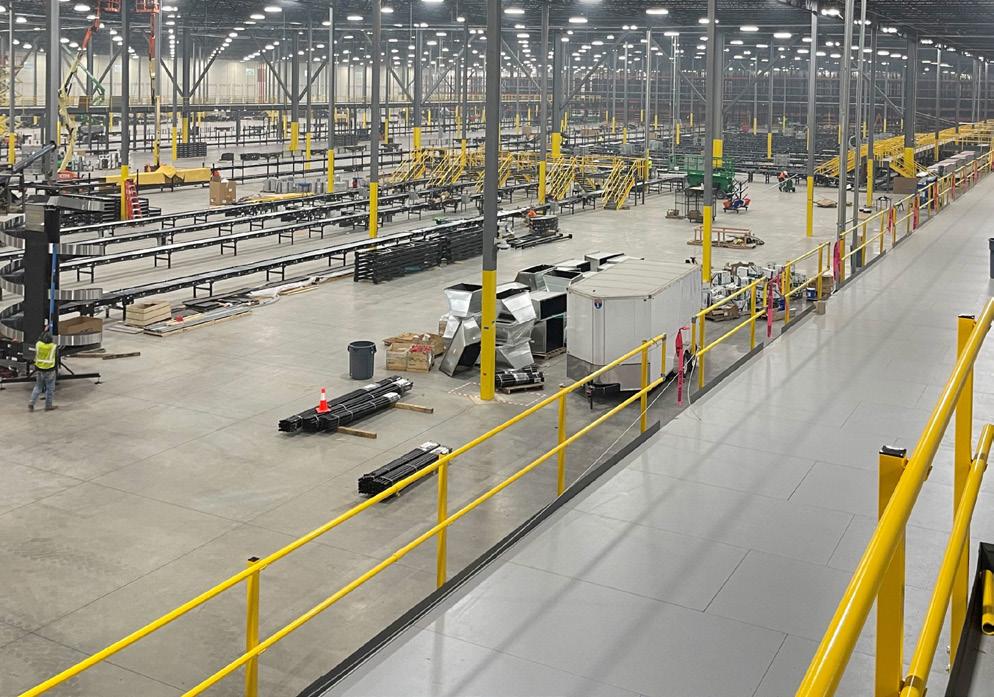
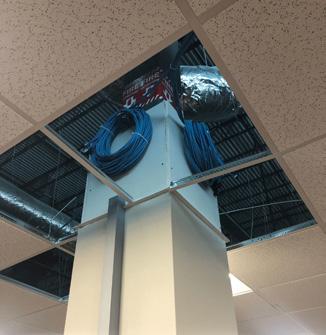
can get up and running swiftly and seamlessly across all of their channels and platforms.
“Our commitment to modernization allows us to continuously stay nimble in the face of new challenges, and it will continue to shape our future,” affirms Welsh.
With dynamic market forces like evolving client and consumer behaviors and economic volatility, today’s brands are looking for practical fulfillment, reliable solutions, and speed to market.
Equally as important to Radial’s continued growth and outlook toward the future is its dedicated team members.
“Empowering our staff and recognizing their contributions is at the heart of our transformation leadership model. We believe that true innovation and success stem from a culture where every individual feels valued and motivated,” details Welsh.
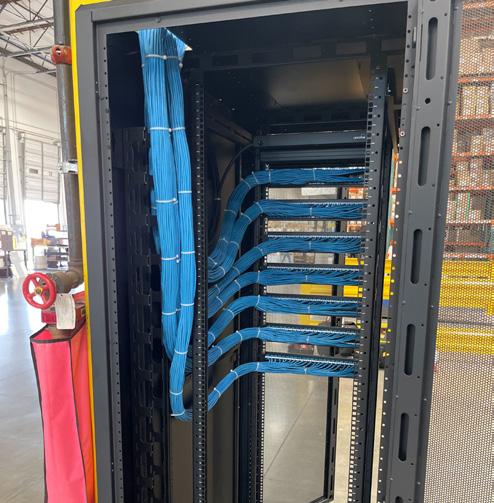
CommX Networks is a leading provider of networking and security solutions in the SWFL region and nationwide, known for delivering reliable and innovative systems to commercial clients. With 18 years of experience, we have built a strong reputation for creating efficient, customized IT infrastructure that enhances connectivity and security.
Whether you manage a warehouse or office unit, CommX Networks has the expertise to design, install, and maintain network systems you need. Our team provides reliable support and efficient network solutions to streamline your operations.
“LEVERAGING OVER FOUR DECADES OF INDUSTRY EXPERTISE, RADIAL TAILORS ITS SERVICES AND SOLUTIONS TO ALIGN STRATEGICALLY WITH EACH BRAND’S UNIQUE NEEDS”
– DAVID WELSH, VICE PRESIDENT OF OPERATIONS, RADIAL
The company achieves this through its leadership pillars, namely Envision, We Make Sense, We Connect, and We Innovate.
For its Envision pillar, Radial creates and articulates a compelling and inspiring vision for the future. By sharing this, it empowers team members to see the bigger picture and understand how their contributions drive collective success.
Through the We Make Sense pillar, the company understands complex
situations and provides clarity amidst uncertainty, endowing its team with the confidence to navigate challenges and make informed decisions.
We Connect, meanwhile, involves building strong and lasting relationships and fostering collaboration.
“Recognizing contributions is integral to this pillar as we celebrate achievements and encourage teamwork, ensuring everyone feels appreciated and part of a cohesive unit,” informs Welsh.
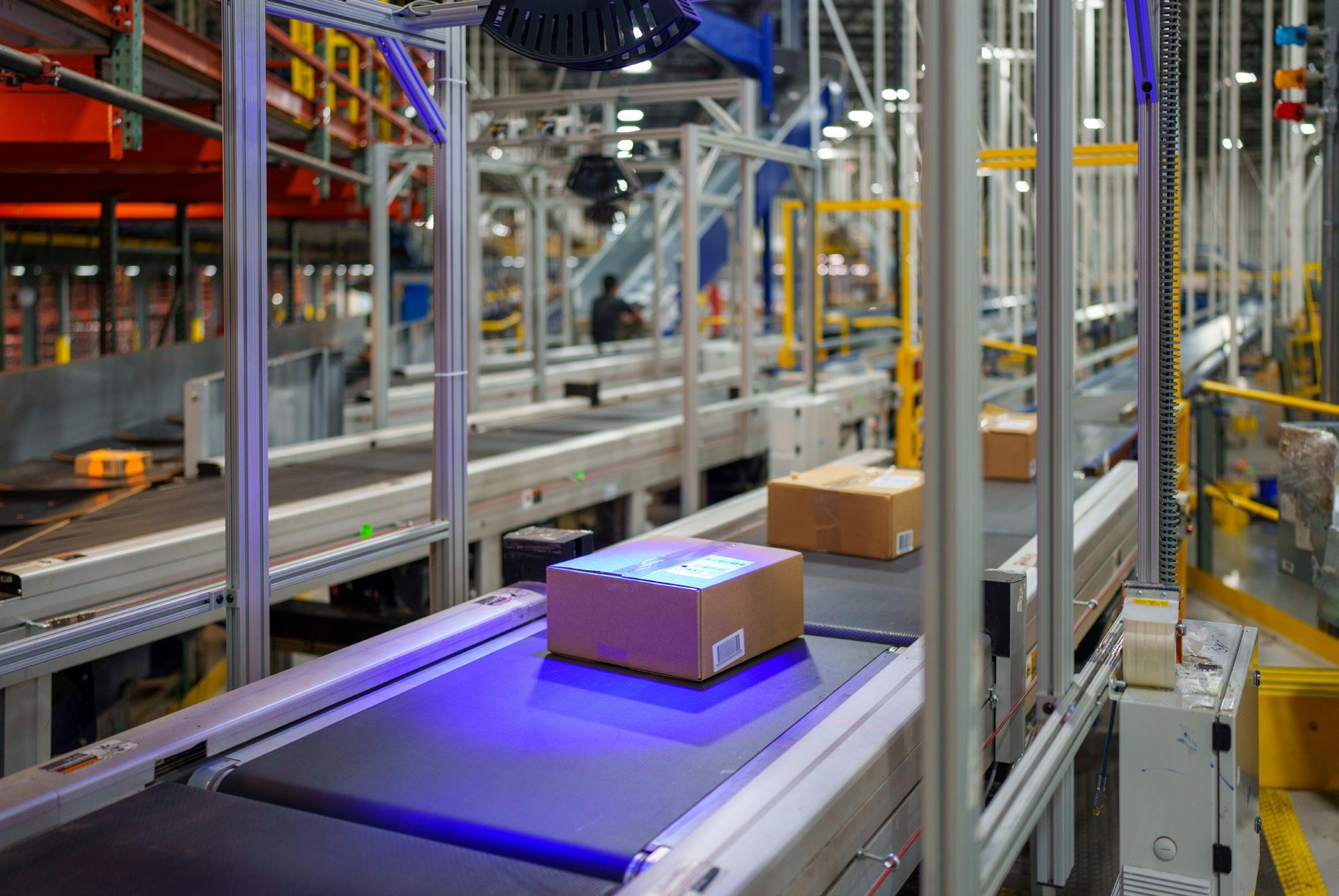
RADIAL DIFFERENTIATORS
SPEED TO LAUNCH – This offers modern brands the ability to onboard and launch quickly with reliable, high-performance technology systems.
PEOPLE-CENTRIC APPROACH – Radial invests in its people, fostering a culture of continuous learning and translating into a workforce that genuinely cares about delivering a positive consumer experience.
STRATEGIC SCALABILITY – The company offers scalable solutions that can seamlessly adjust to changing needs, whether a customer is experiencing rapid growth, seasonal fluctuations, or market shifts. With a network of strategically located warehouses and trusted transportation partners, Radial can efficiently manage operational needs regardless of geographical footprint.
CULTURE OF INNOVATION – By continuously investing in emerging technologies such as automation, robotics, and data analytics, Radial optimizes logistics operations and gains a competitive edge. The company is constantly seeking new and innovative ways to improve its processes and services, ensuring operations remain efficient and cost-effective.
INTEGRATED SOLUTIONS – Radial empowers a seamlessly integrated solution designed to optimize and simplify the entire e-commerce order journey. It prioritizes transparency throughout the integrated process, including comprehensive fraud screening, secure payment transactions, and streamlined returns management for a hassle-free experience. Radial’s integrated solution simplifies operations management, reduces complexity, and minimizes overall logistics costs.
Lastly, the We Innovate pillar demonstrates Radial’s creativity and innovation in problem-solving and adaptating to change.
Empowerment comes from trusting its team to bring unique ideas to the table and recognizing their innovative solutions, which drives progress and adaptability.
WHERE EXPERTISE MEETS EXCELLENCE
In parallel to the continued expansion of Radial’s products and service offerings to its vast clientele, the company is highlighting its dedication to sustainability and community engagement.
“We’re proud to share that our robust corporate social responsibility (CSR) program is built around three core principles – well-being, environmental sustainability, and economic empowerment,” shares Welsh.
In 2025, Radial deepened its commitment to these principles
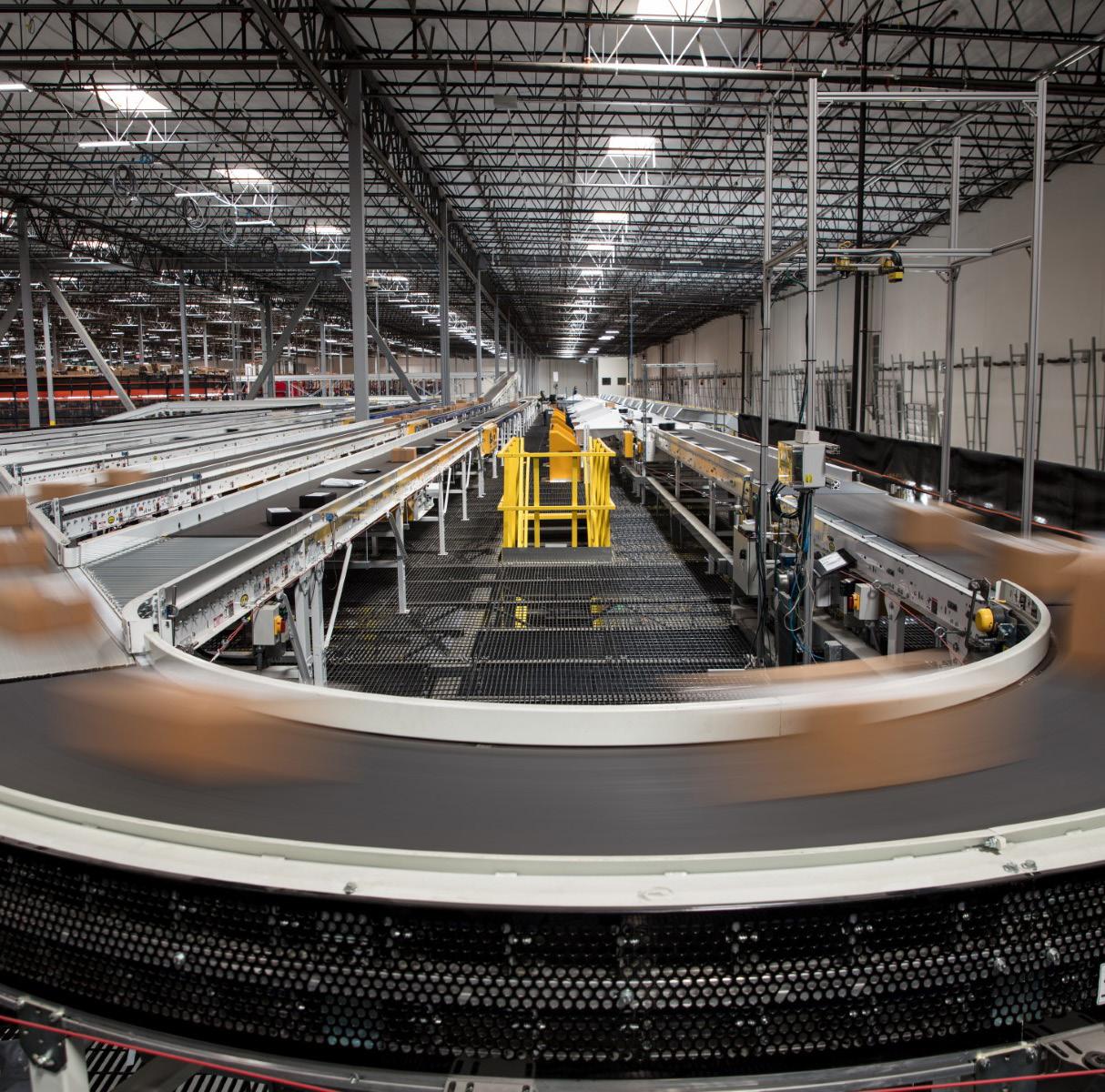
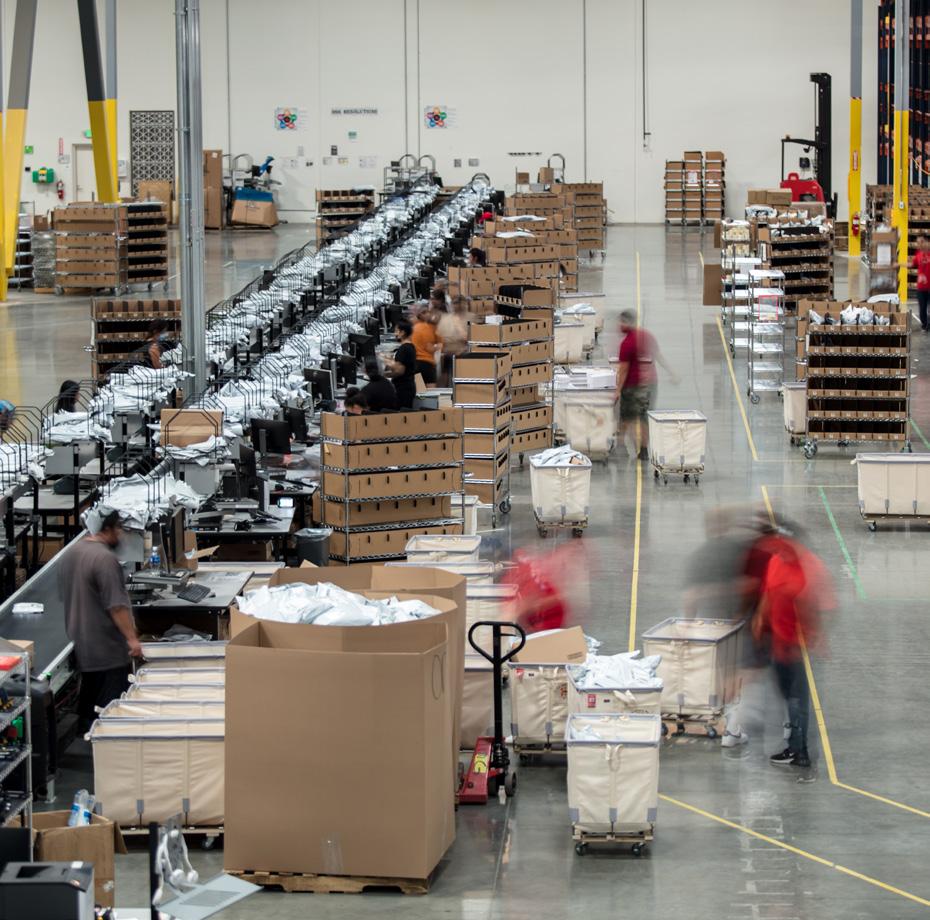
“FROM OUR EXPERT DEVELOPERS CONTINUALLY IMPROVING OUR TECHNOLOGY TO OUR DEDICATED OPERATIONS STAFF PERSONALLY SERVING CUSTOMERS, RADIAL TEAM MEMBERS COLLABORATE TO ACHIEVE OUR CLIENTS’ BUSINESS GOALS”
– DAVID WELSH, VICE PRESIDENT OF OPERATIONS, RADIAL
through meaningful partnerships and initiatives.
At the corporate level, the company is honored to support Team Rubicon, an organization mobilizing veterans and volunteers to respond to natural disasters and humanitarian crises, ensuring critical aid flows to communities in need.
Additionally, Radial proudly supports the Clean Air Task Force, which drives innovation and policy to combat climate change, alongside its long-standing partnership with Dress for Success, which uplifts and equips women to achieve economic independence.
“We have implemented a Supplier Code of Conduct to ensure we do business with environmentally and socially responsible partners,” specifies Welsh.
Moving forward, the company will continue to focus on helping clients achieve their growth goals by fulfilling promises from click to delivery. It is also concentrating on actively expanding its market reach through innovative solutions to attract new business, with vertical diversification key to accomplishing this.
“Our priority for the coming years is to create value through the power of our people and technology,” concludes Welsh.
Internally, Radial has deployed solar energy at one of its warehouses and is nearing the completion of a companywide conversion to LED lighting across all facilities.
“These efforts reflect our belief that corporate responsibility is not just a program – it’s a shared commitment to creating positive impact for our employees and communities,” he prides.
As part of the company’s commitment to sustainable solutions, it is actively working to decrease its environmental impact by operating in an increasingly sustainable way.
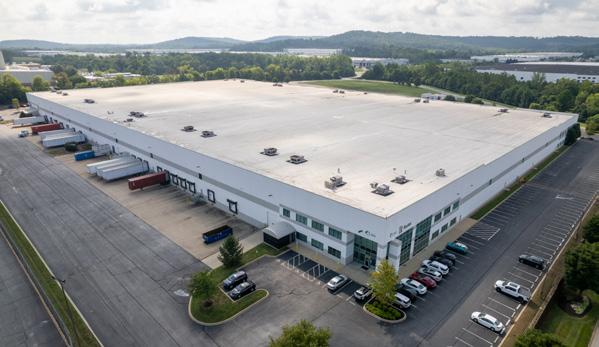
Tel: (610) 491-7000 sales@radial.com www.radial.com
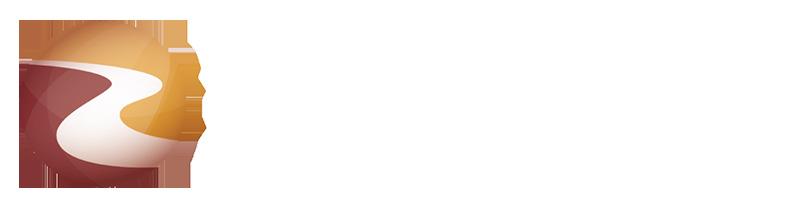
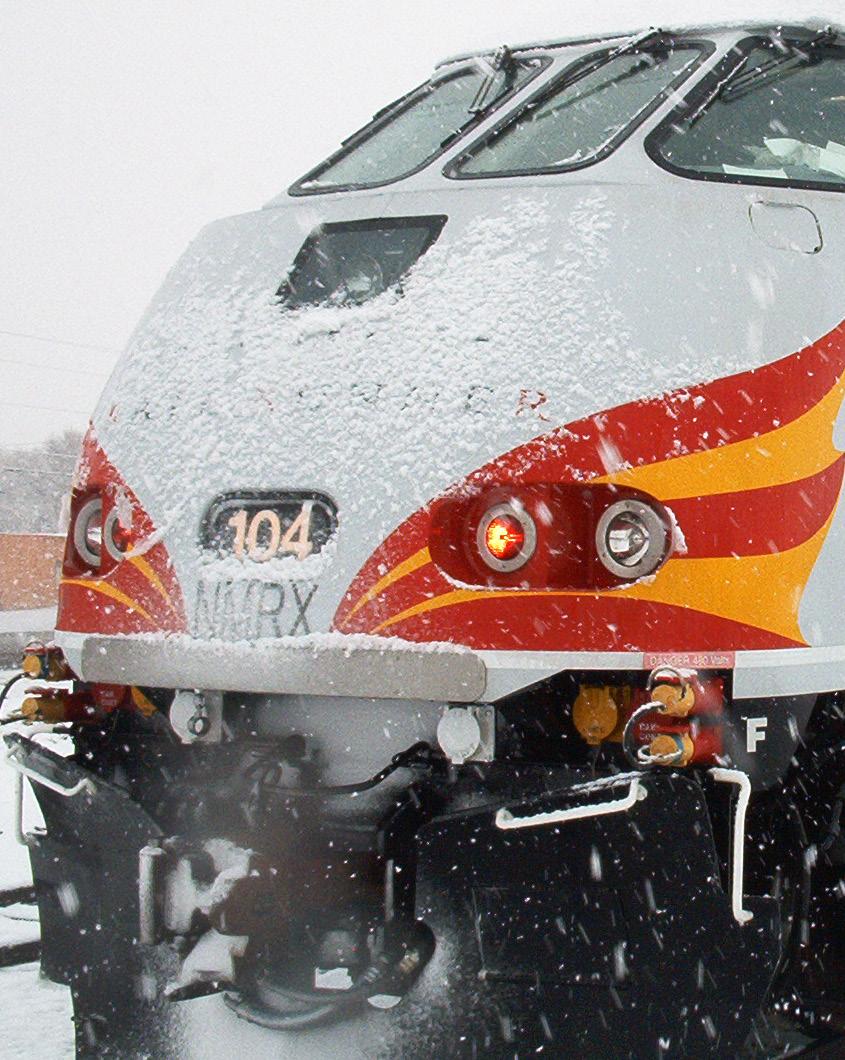
TRIUMPH ON THE TRACKS
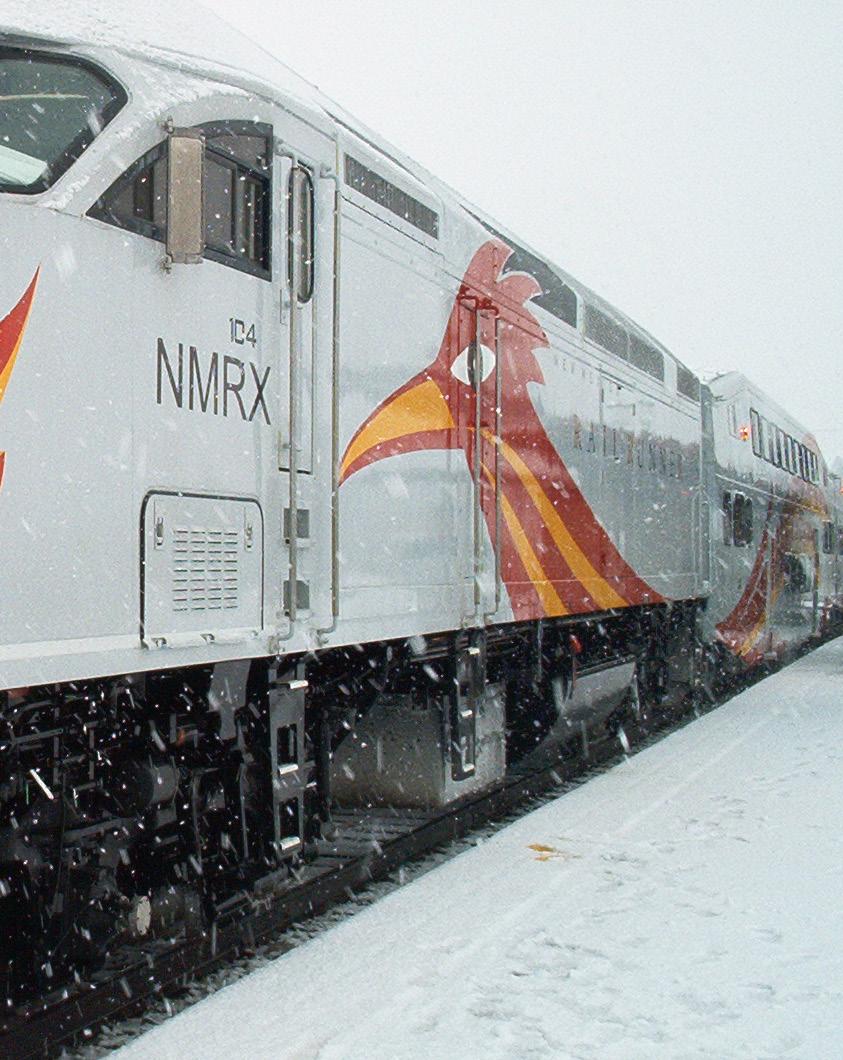
Rio Metro Regional Transit District is the primary local transport provider spanning several key counties across New Mexico. We find out how this innovative network is expanding and developing with Director of Operations, Robert Gonzales
Writer: Ed Budds | Project Manager: Poppi Burke
In 2003, in a game-changing act of transformation for the local transport sector, the New Mexico Regional Transit District Act was passed, enabling the formation of multi-jurisdictional transit agencies.
The purpose of this legislation was to provide safe and efficient regional transit services, reduce congestion, crashes, and pollution caused by single-occupant vehicles, while simultaneously extending the life of the state’s roads.
It was also tasked with providing transportation alternatives, particularly for transit-dependent groups such as seniors, youth, low-income, and mobility-impaired residents.
Finally, the legislation aimed to provide better access to education and higher-paying jobs, alongside dramatically reducing oil dependence.
Borne out of this transformative shift, Rio Metro Regional Transit District (Rio Metro) is a regional transit organization spanning four New Mexico counties in the Albuquerque metropolitan area, including Four Pueblos.
“Our main competition is the automobile. In today’s setting, commuters are using their cars and love the convenience and flexibility of having their own transportation,” introduces Robert Gonzales, Director of Operations.
“Our mission is to re-educate people on the benefits of leaving their cars to use rail as their primary mode of transit,” he lays out.
FORWARD-THINKING CONNECTION
Rio Metro has developed a bold, forward-thinking, consensus vision for the future of transit in the broader Albuquerque region.
Today, its New Mexico Rail Runner Express (NMRX) commuter train runs across the 100-mile NMRX corridor, spanning from Belen to the New Mexico State Capitol in Santa Fe. Alongside this, Rio Metro operates
HOW DO YOU MANAGE AND MAINTAIN YOUR RELATIONSHIPS WITH BOTH CLIENTS AND SUPPLIERS?
Robert Gonzales, Director of Operations: “We take a very personable approach to our relationships with our partners and suppliers in that we work very closely together as a team, coordinating directly several times a week, if not daily. We work together toward a shared goal, and this has worked brilliantly for us to date.
“In terms of government, we have a great partnership with all the local municipalities and tribes along our corridor. We participate or host frequent face-to-face meetings with these entities, usually monthly or weekly. As such, we all work together as a team to identify, plan, and address issues immediately.
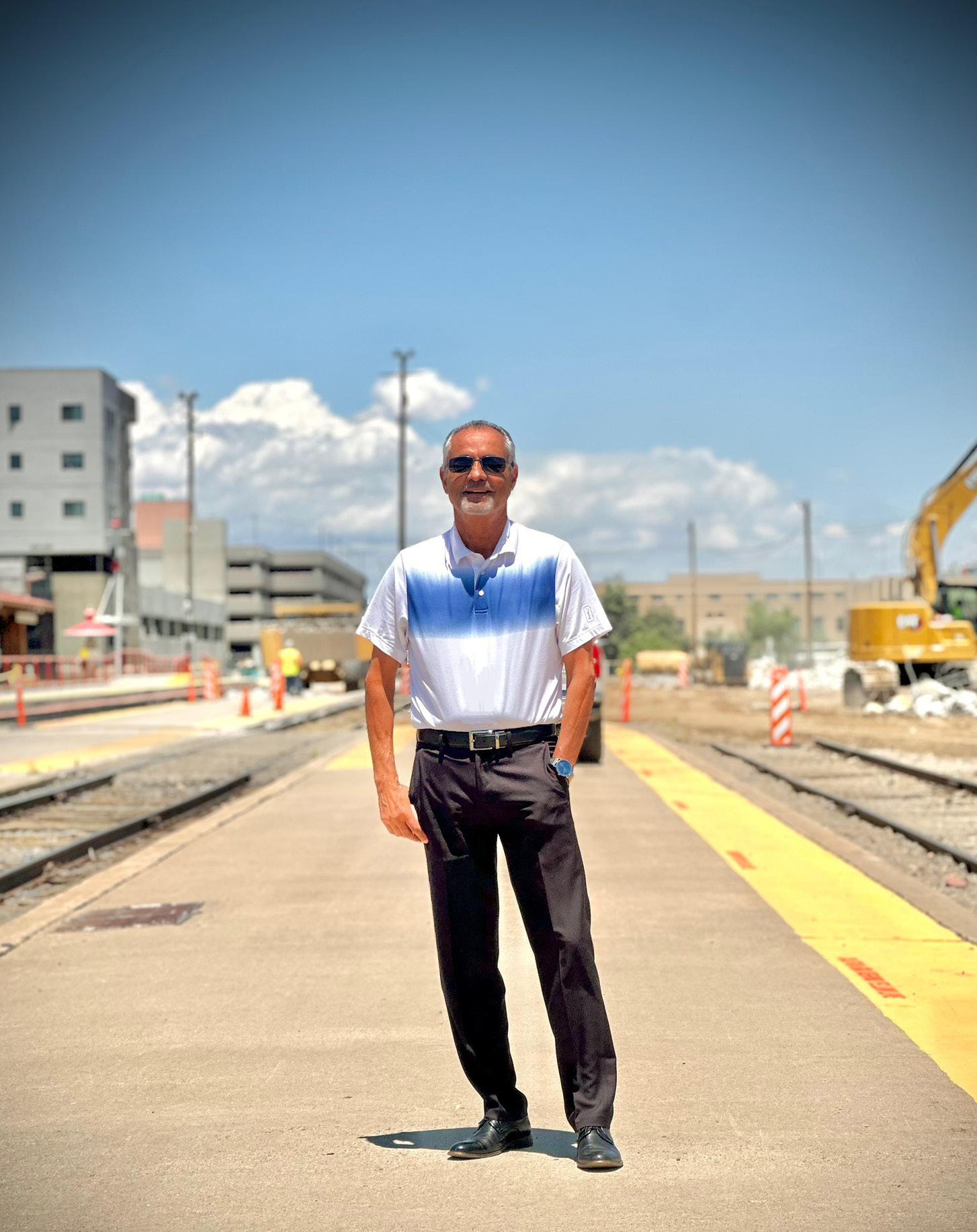
“Regarding our people, the key is to make each member of our staff feel empowered to make decisions on their own, and, so far for me in my current role, that has worked out really well!
“You give guidance when people ask for it and otherwise step back and let them do their jobs. It’s important to recognize all the efforts of our dedicated staff and the hard work they put into each project they’re working on and commend them for it.”
TH
Huitt-Zollars is a national 100% employee-owned firm that provides solutions for the built environment.
With offices that span east to west coast, we have the team and breadth of expertise to handle any project. With over 45 years of partnering with major transit agencies across the nation, Huitt-Zollars has the expertise to provide mass transit solutions on pulse with emerging trends, based on solid best practices. Transit experience includes on-call architecture and engineering; light rail transit (LRT), commuter rail, and bus rapid transit (BRT) design; facility design, corridor and regional planning; major investment studies; and urban and human-centered design.
For our bus-focused clients, we have engineered numerous highspeed ground transportation solutions. Our rail-focused clients (LRT, commuter, and freight) have benefited from our expertise with the design of tracks (including special track work), guideways and rights-of-way, tunnels and bridges, and trolley/streetcar lines.
Our transit structure design projects are comprised of a broad mixture of intermodal and multimodal buildings, maintenance and operations facilities, electric-charging facilities, stations, terminals, and yards.
Contact: Richard Robyak, PE – Sr. Vice President:
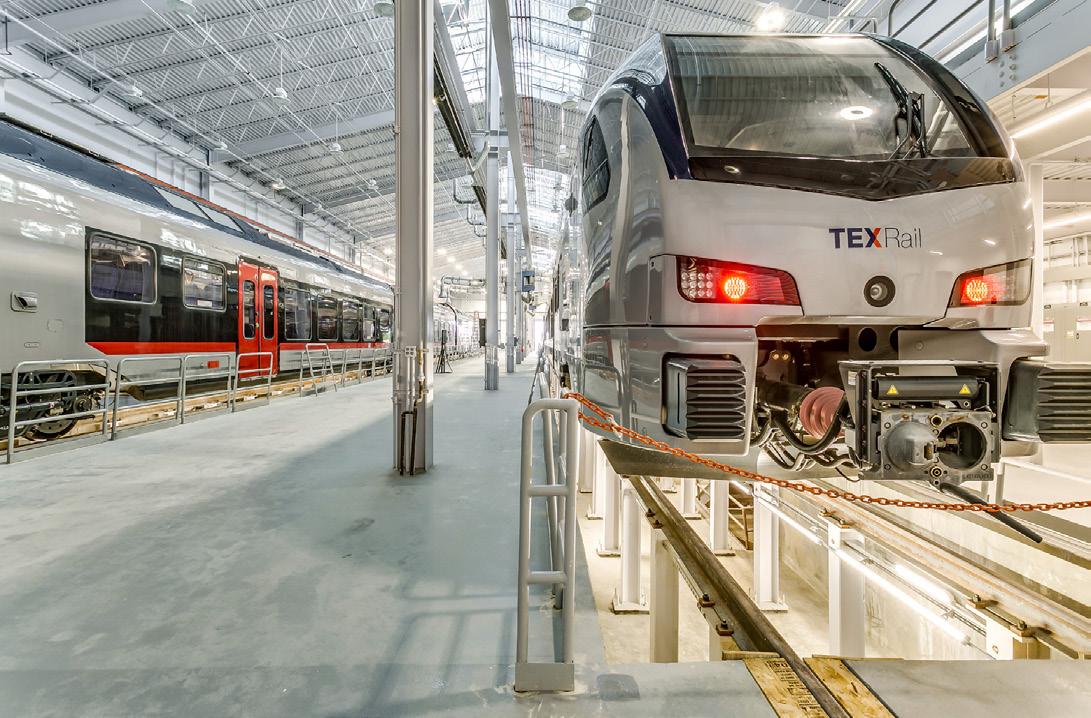
Phone: (214) 871-3311
Email: rrobyak@huitt-zollars.com

Website: www.huitt-zollars.com

huitt-zollars-inc Huitt_Zollars
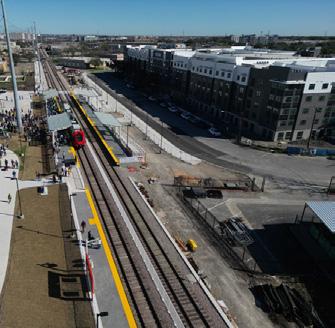
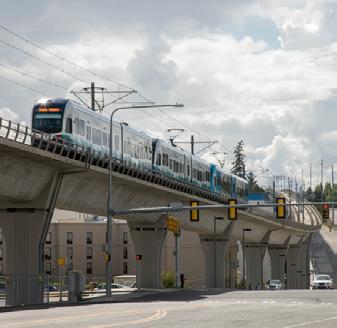
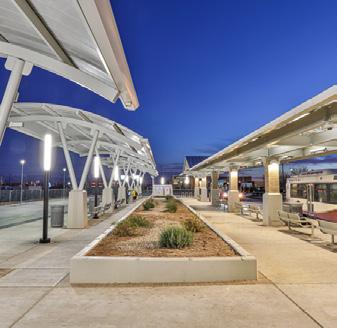
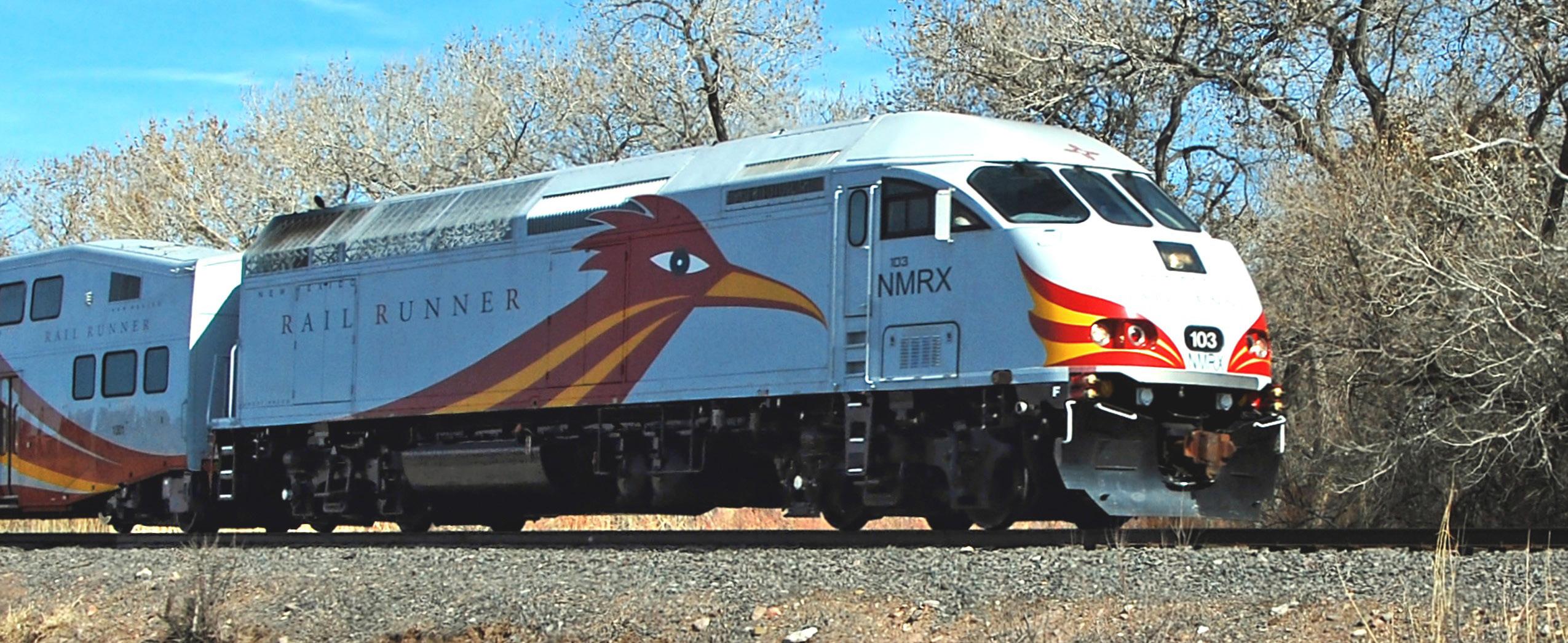
a branch of the corridor connecting Los Angeles with Chicago via Amtrak – the National Passenger Railroad Corporation for the US.
“We also provide shuttle services in two counties that connect to NMRX, along with both our shuttle and rail routes joining other transit
connections including routes to the Albuquerque International Sunport, University of New Mexico, Sandia National Laboratories, and further cities like Los Alamos and Socorro,” Gonzales prides.
As the lead operator of the NMRX railroad, Rio Metro dispatches transit
across the entire corridor with tenant railroads Burlington North Santa Fe (BNSF), Amtrak, and Santa Fe Southern, along with the historic 2926 steam locomotive.
“Our client base is and always has been local commuters, as well as a steady tourist population,” he tells us.
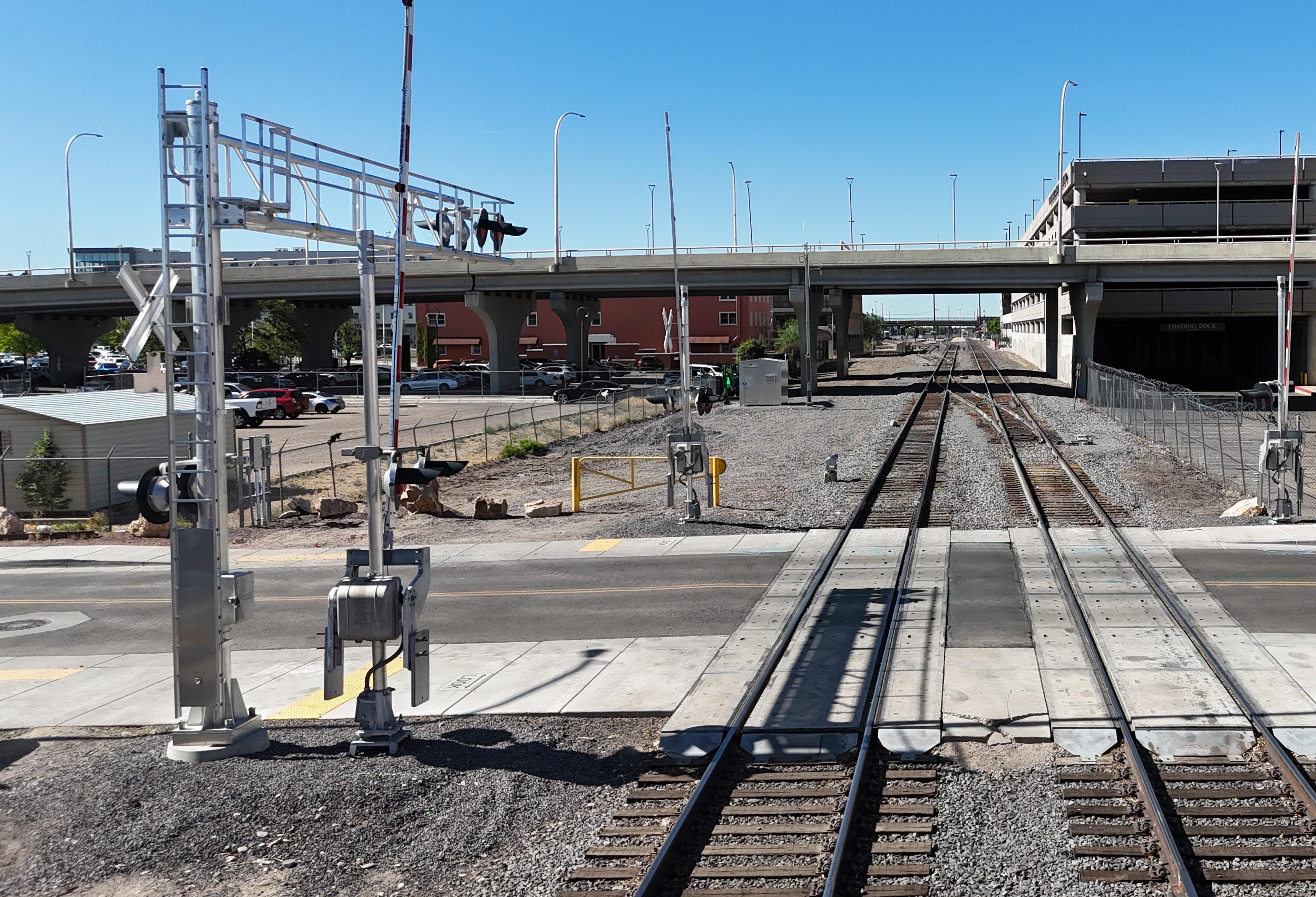
RIO METRO – MISSION, VISION, AND CORE VALUES
MISSION
For the benefit of its diverse local communities and the regional economy, Rio Metro collaborates to provide safe, accessible, efficient, and innovative transportation services.
VISION
A leader in moving the region forward, Rio Metro connects its diverse residents and communities and supports sustainable prosperity.
CORE VALUES
• EXCEPTIONAL CUSTOMER EXPERIENCE – Customers come first in all that Rio Metro does.
• TRANSFORMATIVE REGIONAL SERVICES – The company provides a range of services to meet its region’s diverse needs.
• STRONG TRANSIT-CENTERED COMMUNITIES – Rio Metro’s services help shape its communities for the better.
• SOUND FINANCIAL STEWARDSHIP – The company aims to be good stewards of the public resources entrusted to it.
• INNOVATIVE PROGRAMS AND PARTNERSHIPS – Rio Metro always thinks outside the box and seeks collaboration.
• INDUSTRY-LEADING KNOWLEDGE AND PRACTICE –Its people take pride in leading the region forward.
“OUR CLIENT BASE IS AND ALWAYS HAS BEEN LOCAL COMMUTERS, AS WELL AS A STEADY TOURIST POPULATION”
– ROBERT GONZALES, DIRECTOR OF OPERATIONS, RIO METRO REGIONAL TRANSIT DISTRICT
At present, the dedicated Rio Metro team consists of about 30 employees, alongside the entire NMRX team who are responsible for operating and maintaining the track and signal system, totalling approximately 300 hard working members overall.
UPGRADING THE NETWORK
Right now, the US transit network can’t compete with the standards in Europe, for example, but Gonzales believes that things are moving in the right direction, progressing gradually each year.
“Across America, there are plenty of exciting new developments in high-speed rail such as in Brightline, Florida, and a train that’s currently being built between California and Las Vegas, Nevada. People are really excited for these new high-speed rail operations!” he delights.
Furthermore, Rio Metro has an equally promising slate of projects underway, including the rebuilding and upgrading of its signal systems.
“Positive Train Control (PTC) is a federally mandated safety overlay system that is used over our 100-mile corridor.
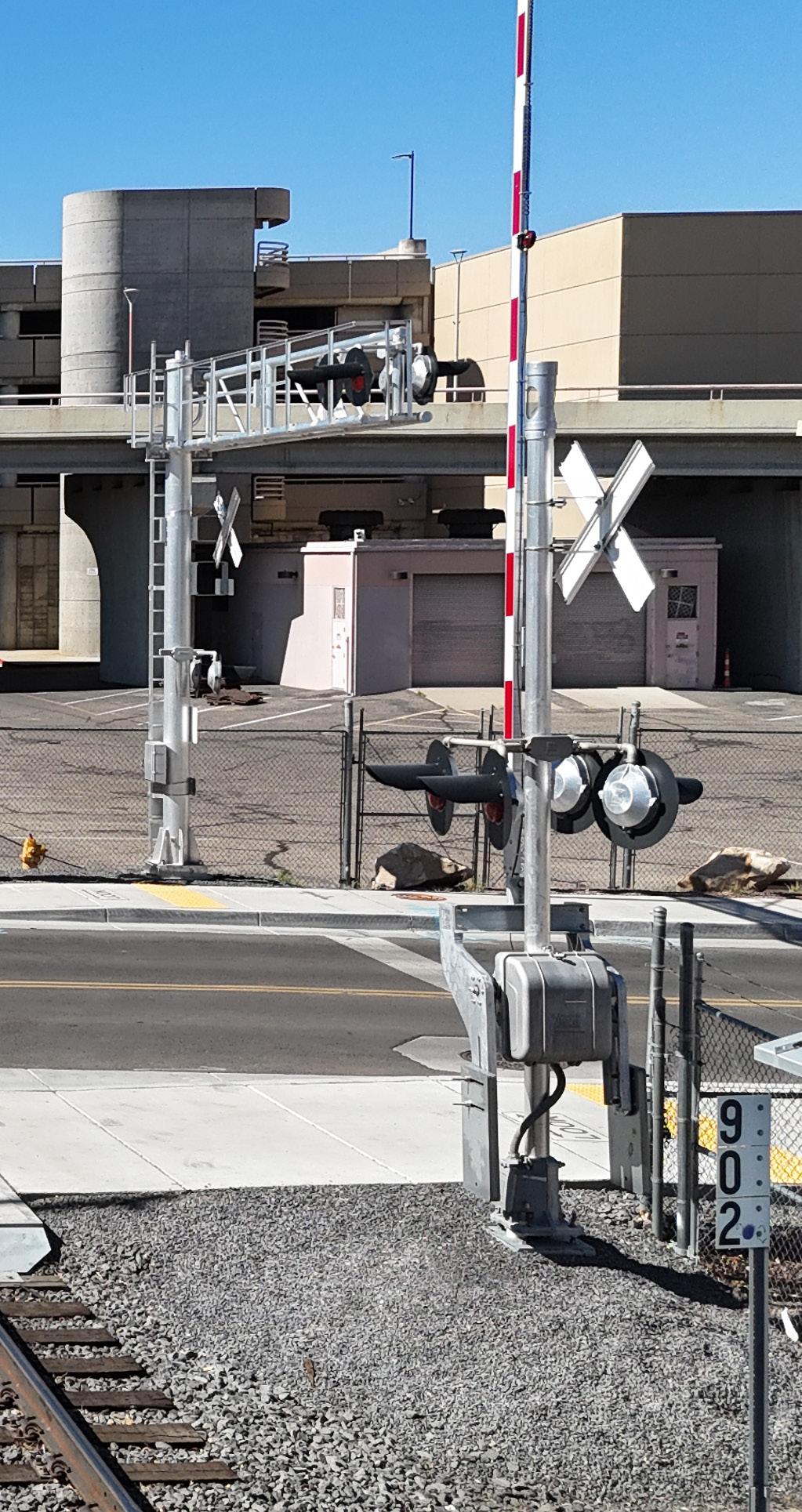
We have recently upgraded our old pole-line to Centralized Traffic Control (CTC) in downtown Albuquerque and on our line that runs east to Lamy.
“This has allowed us to eliminate Track Warrant Control (TWC) from our territory. Over the past few years, we’ve done a lot to clean up our operations to make them more streamlined,” Gonzales explains.
EXPANSION AND RECONFIGURATION
Signifying one of the company’s major ongoing projects, Rio Metro is currently in the process of designing and building the New Mexico Rail Runner Express Operations and Maintenance Facility (NMRX OMF).
“Currently, our mechanical team performs all its work, inspections, and servicing outdoors in the elements, so this maintenance facility is a priority to get the team out of the weather,” says Gonzales.

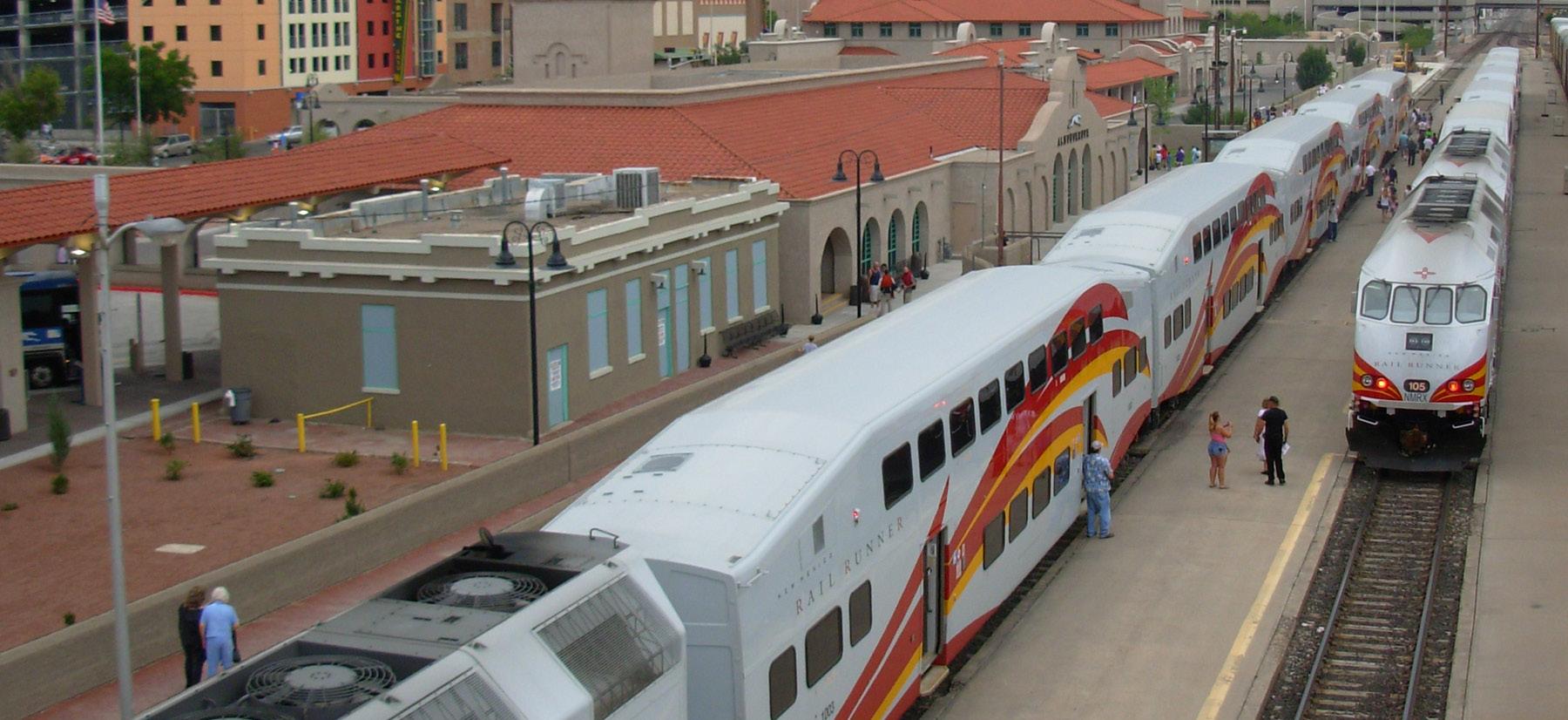
“We have built two new sidings, which have greatly increased on-time performance for NMRX and our tenant railroads, and we have two more sidings in the works. Their location was based on studies which identified critical areas that would provide the best benefit,” he adds.
The company has also been working on the Albuquerque Rail Trail, which includes rehabilitating three crossings on the Sawmill segment through which the trail will eventually run.
This project also includes a new pedestrian grade crossing along Central Avenue – part of the historic Route 66 – reconfiguration of Rio Metro’s three main lines, and implementation of three storage tracks, while the north yard lead track and its Downtown Albuquerque Station platforms will accommodate a new pedestrian crossing.
“We have also worked with several
municipalities along our corridor to construct pedestrian trail crossings to provide a safe route over the tracks, including in the town of Bernalillo, the village of Los Lunas, Santo Domingo Pueblo, and Isleta Pueblo,” Gonzales expands.
All of these exciting projects contribute toward an exciting portfolio of projects and ongoing investments for Rio Metro.
“As mentioned before, our major priority is the new NMRX OMF, which encapsulates an optimistic outlook for the future of the company,” he proudly concludes.
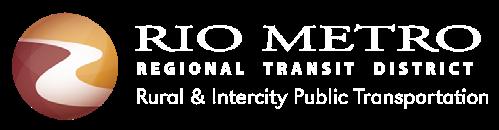
Tel: (866) 795-RAIL (7245) riometro@mrcog-nm.gov riometro.org
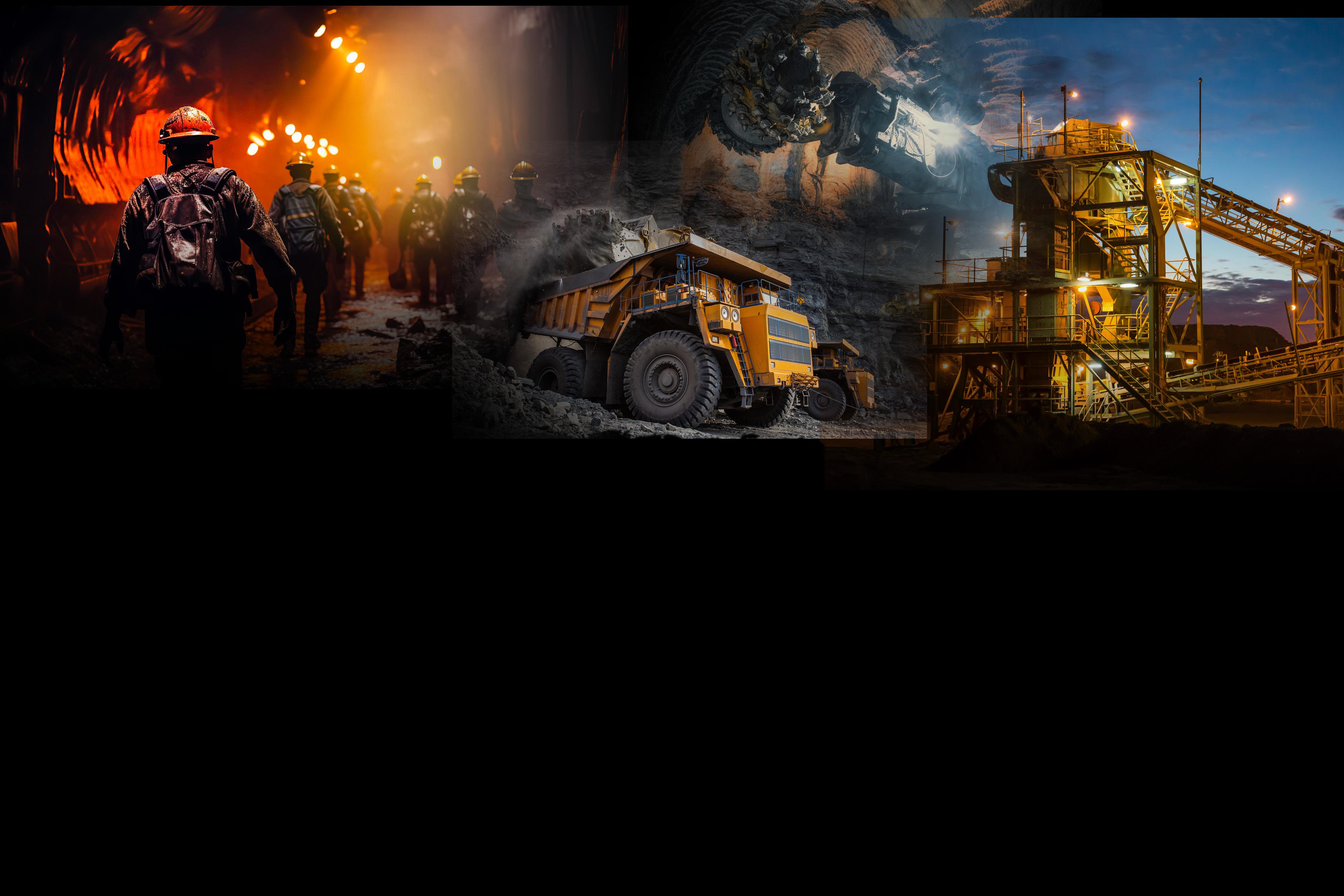
Discover our exclusive content, delivered straight to your inbox
As mining organizations worldwide confront unprecedented change, embracing technological innovations and incorporating critical environmental sustainability agendas, now more than ever is the time to showcase the strides being taken in this dynamic sector.
A multi-channel brand, Mining Outlook brings you the positive developments driven by organizations across the global mining industry through its various platforms.
Discover exclusive content distributed through its website, online magazine, social media campaigns and digital dispatches, delivered straight to your inbox with a bi-weekly newsletter.
Through these compelling media channels, Mining Outlook continues to foreground the movers and shakers of the industry.
To participate as a featured company and join us in this exciting endeavor, contact one of our Project Managers today.
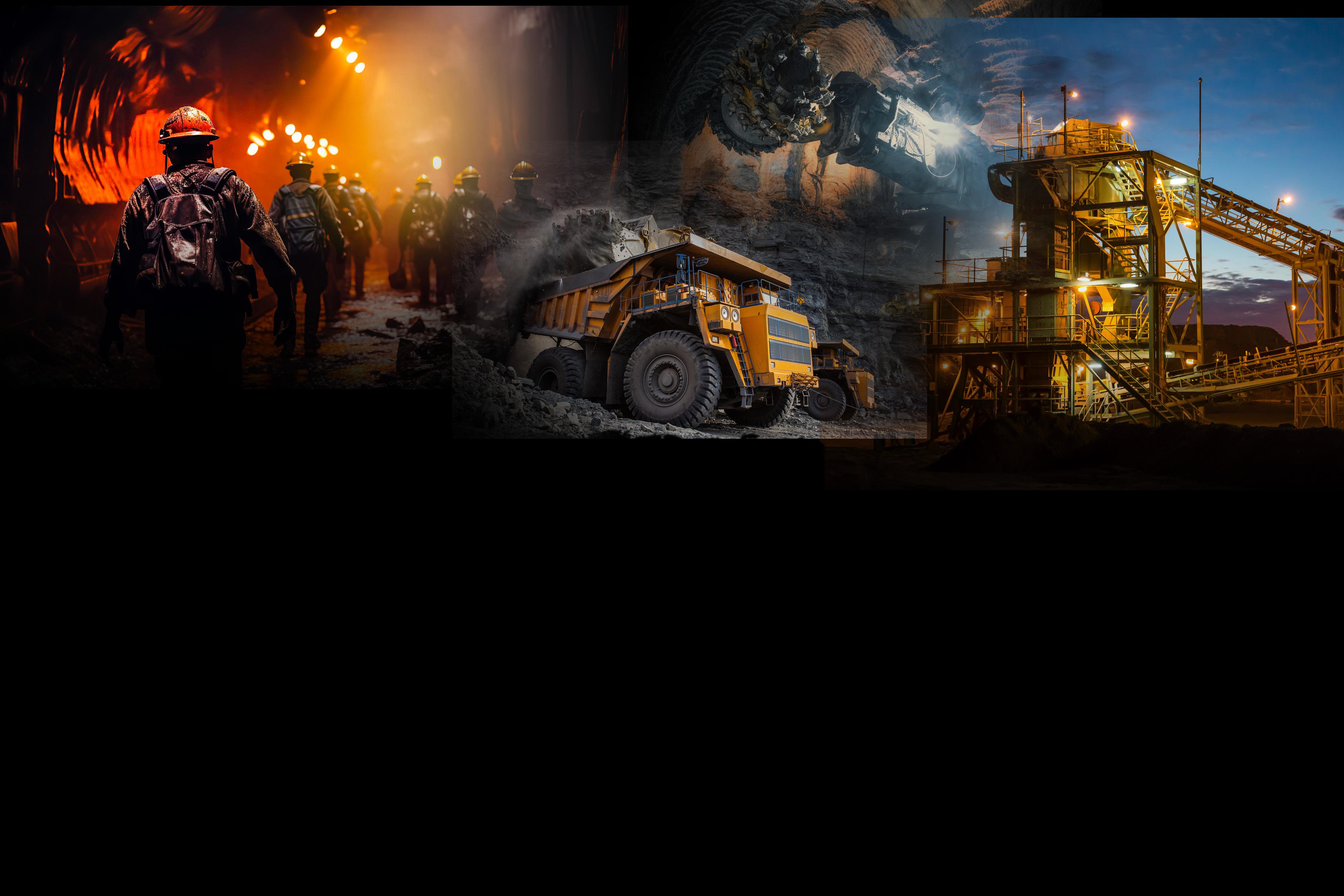
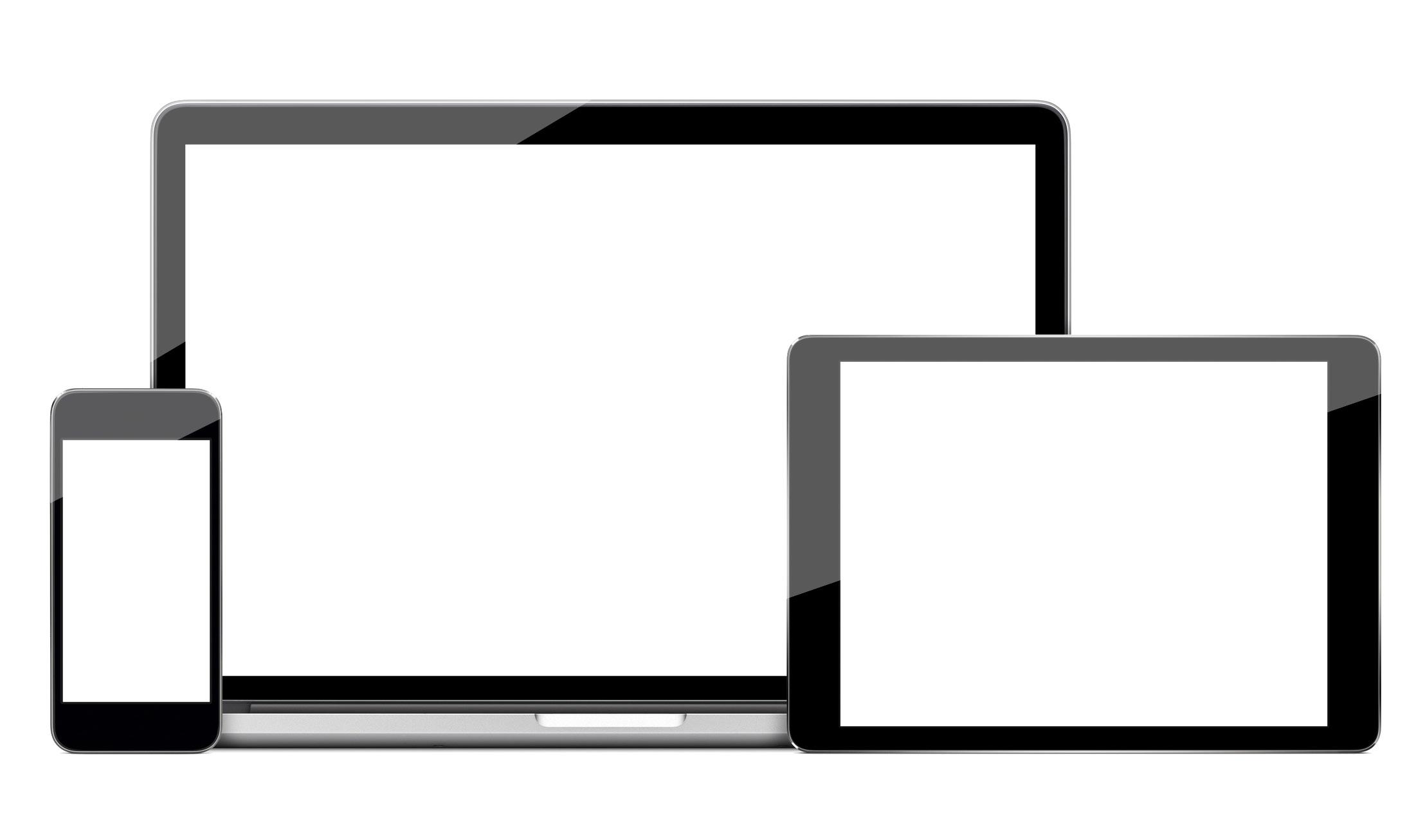
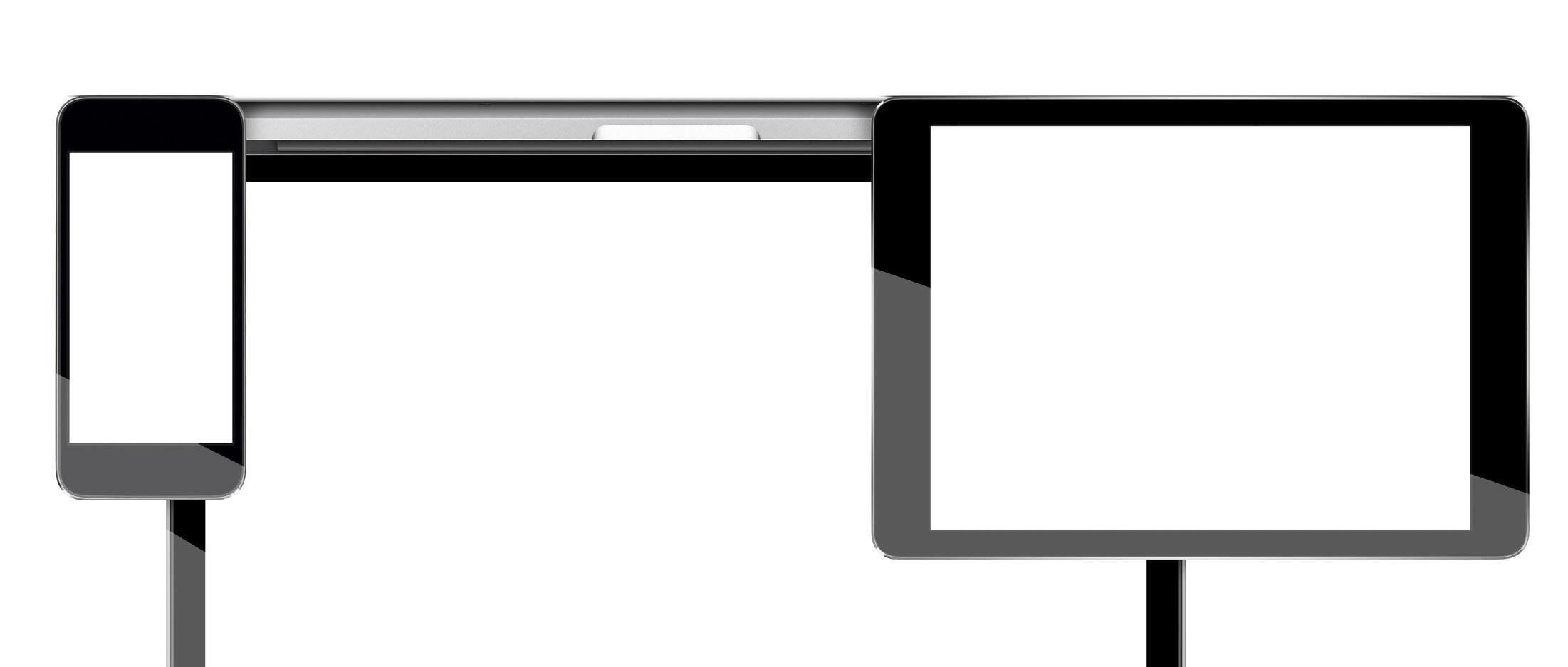
VANGUARDS OF DRILLING
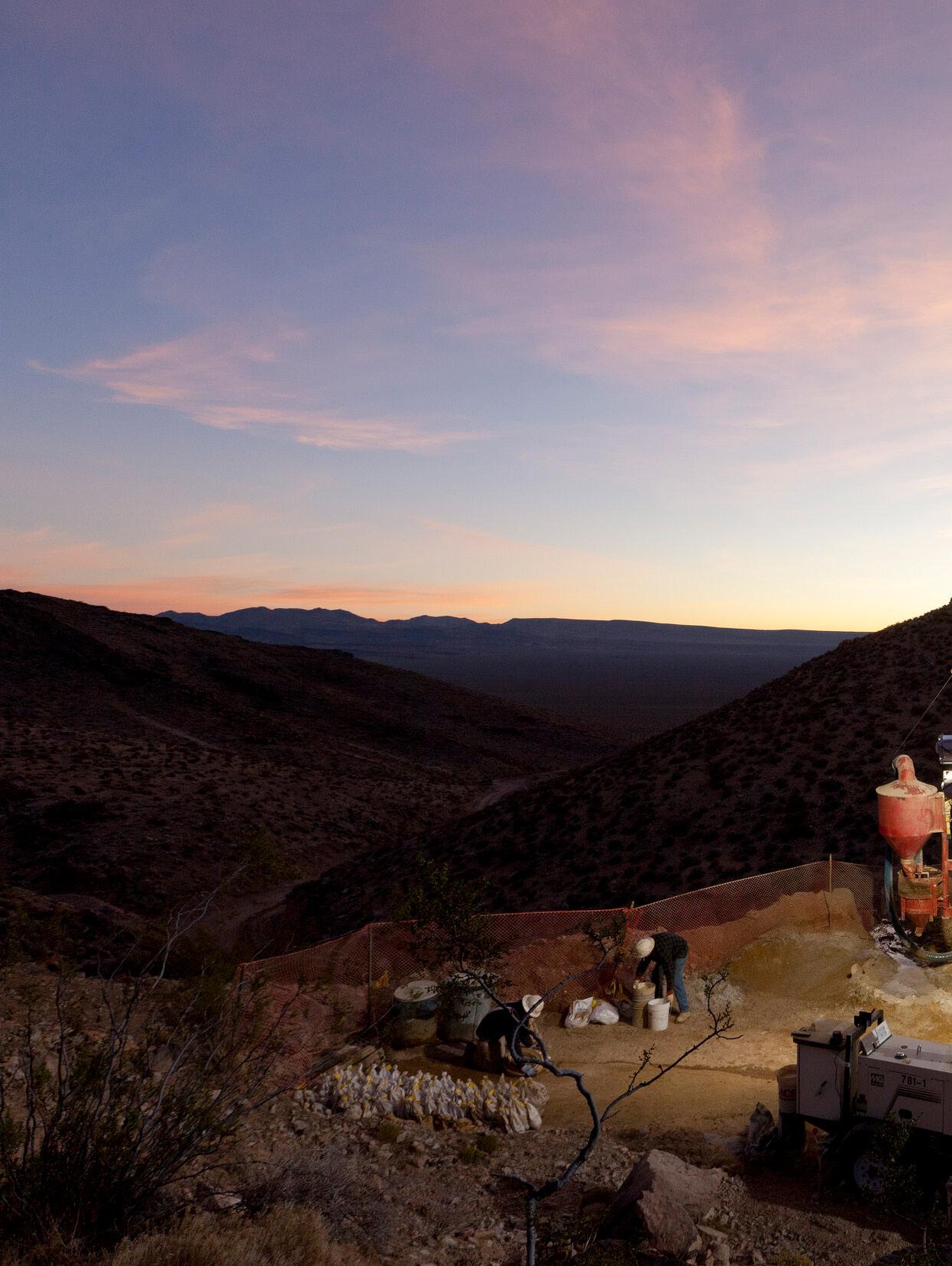
With unique technical capabilities, in-house fabrication and machining expertise, and an unparalleled safety culture, National EWP remains at the forefront of the Western US drilling sector. Jeffery D. Morgan, President and CEO, tells us more
Writer: Lucy Pilgrim | Project Manager: Scarlett Burke
In recent years, North America’s drilling market has been dominated by major international mining corporations, making for a competitive and therefore challenging landscape.
However, it is in these difficult periods that companies such as National EWP (National) are able to test the limits of their creativity and agility.
“Even if we don’t have control of the market, we can control how we respond to it. So, I tend to adopt the mindset that we need to take advantage of the market regardless of the state it is in,” Jeffery D. Morgan, President and CEO, opens optimistically.
Morgan strongly believes in a quote from Roman emperor, Marcus Aurelius – “The impediment to action advances action. What stands in the way becomes the way” – in short, the answer lies within the problem or challenge.
To respond to the competitive market, Morgan emphasizes the importance of finding efficient answers to difficult situations to better the company for the benefit of its clients and employees.
“It’s currently a challenge to get all our rigs out competitively and profitably at the same time, but within that context there is opportunity. It’s up to us to take advantage of it,” he adds.
Established in 2010, National was formed to address a gap in the drilling market which, at the time, primarily consisted of major international exploration drilling organizations conducting extensive core and reverse circulation (RC) exploration, with a number of smaller companies having comparably limited operations.
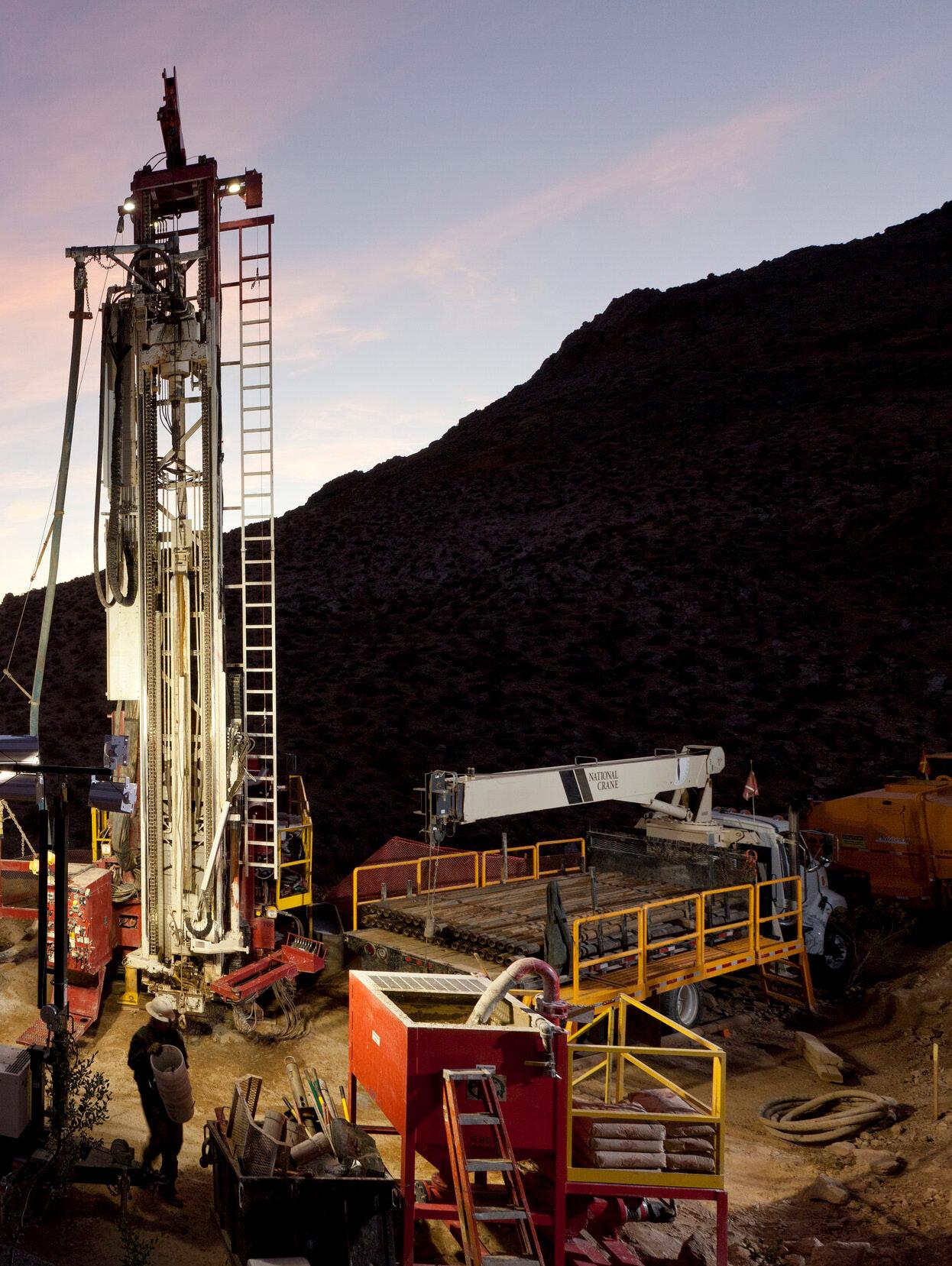
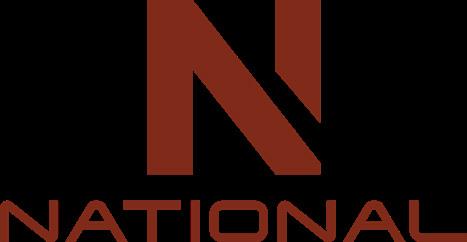
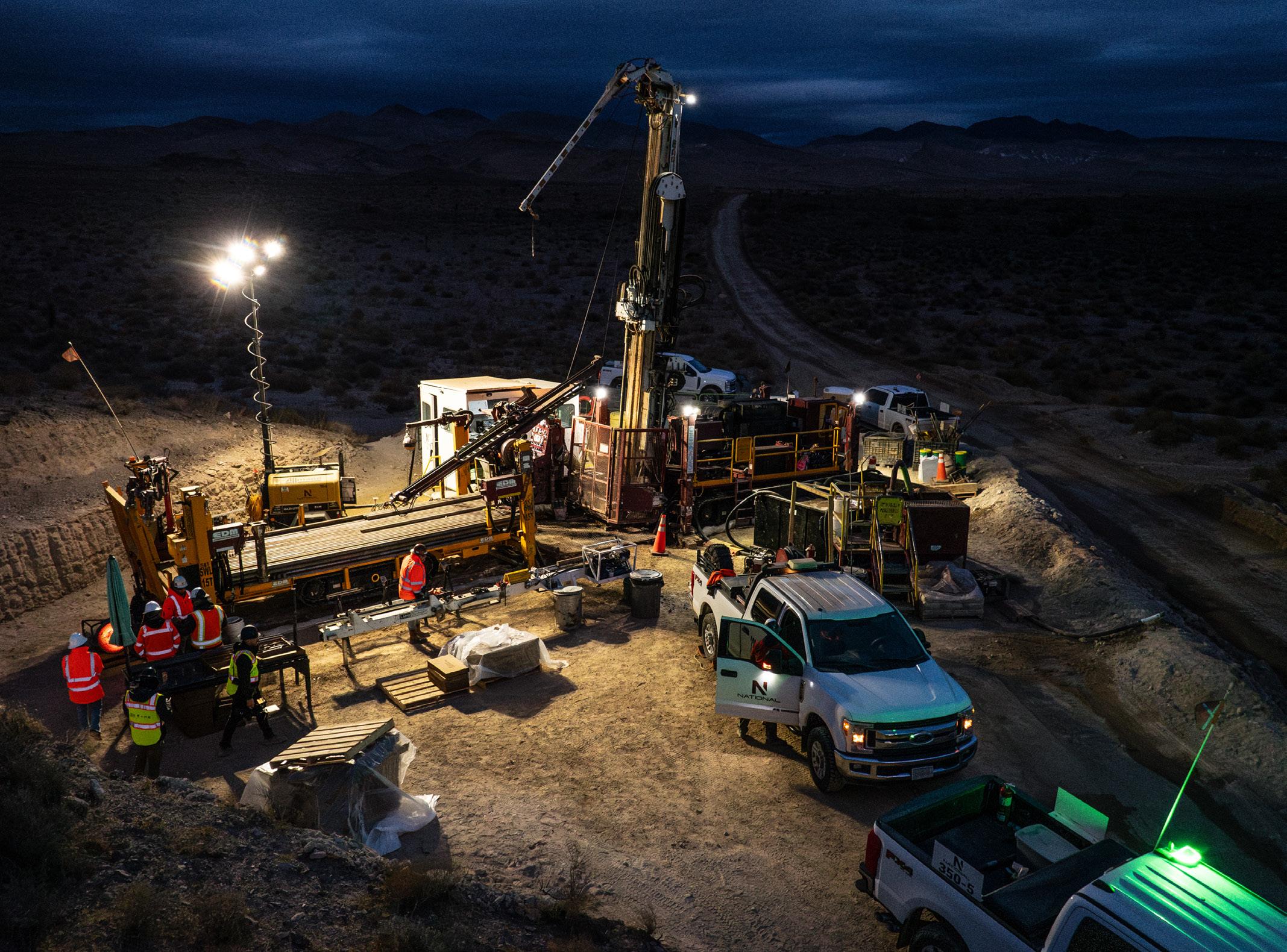
NATIONAL’S SERVICES – AT A GLANCE
• Well casing and installations
• Large-diameter production wells
• Dewatering wells
• Vertical drains
• Piezometers – single and multi-level
• Exploration
- Core drilling
- RC exploration
- Pre-collar
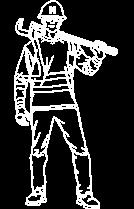
“We were the in-between – we had the capabilities of larger companies but ran like a smaller business. Most of our leadership team had held previous jobs on drill rigs, which meant we had a huge amount of field experience in our management teams,” Morgan tells us.
National is therefore differentiated by its capabilities that compete with multinational drilling organizations while also being responsive and flexible to clients’ needs, which are all underpinned by a consistent focus on improvement.
“As a Western US-based company, we’ve had the opportunity to go global in the past, but we would rather be really good in our own backyard. Instead of forcing growth and going afar, what we are really trying to do is focus on providing better results for our existing client and geographic
base,” he shares.
Therefore, National possesses a continuous drive to better its operations and grow within the US market.
ENVIABLE IN-HOUSE CAPABILITIES
National’s sustained ability to serve its clients’ needs is, in part, due to the fact it operates some of the highest tech machinery and fabrication equipment in the world; its computer numerical control (CNC) milling machines and lathes, for instance, are regulated by the US Department of Defense.
The company additionally has an expert team of engineers and drafters people who design, build, and fabricate custom-made tooling and equipment in-house, completed in its facilities in Phoenix, Arizona and Elko, Nevada.
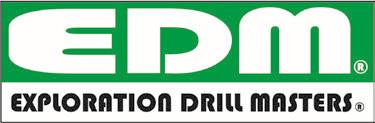
Designed
EDM designs and builds world-class drill rigs that deliver performance, reliability, and safety in the most demanding conditions. Our range includes diamond, RC, and multipurpose rigs from 30,000–95,000 lbs pullback, as well as horizontal drills for mine site dewatering.
Engineered for productivity and longevity, EDM equipment is fully customizable to meet the needs of any project or environment — including Tier 4 Final engines for US emissions compliance, full EoH control systems, and climate-controlled FOPScertified operator cabins.
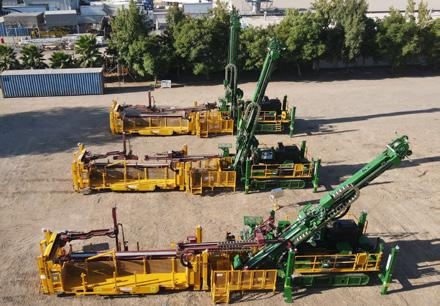
Leading the way in safety innovation, EDM specializes in practical and robust independent, hands-free pipe handling systems for all drilling methods — designed to protect drill crews and maximize efficiency.
Address: Avenida Colorado N°01200 - Quilicura - Santiago
Phones: 56 (2) 739 0315 - 56 (2) 739 0358 - 56 (2) 739 0536
Mobile: +44 (0) 7487 600804
Email: info@explorationdrillmasters.com
Website: www.explorationdrillmasters.com
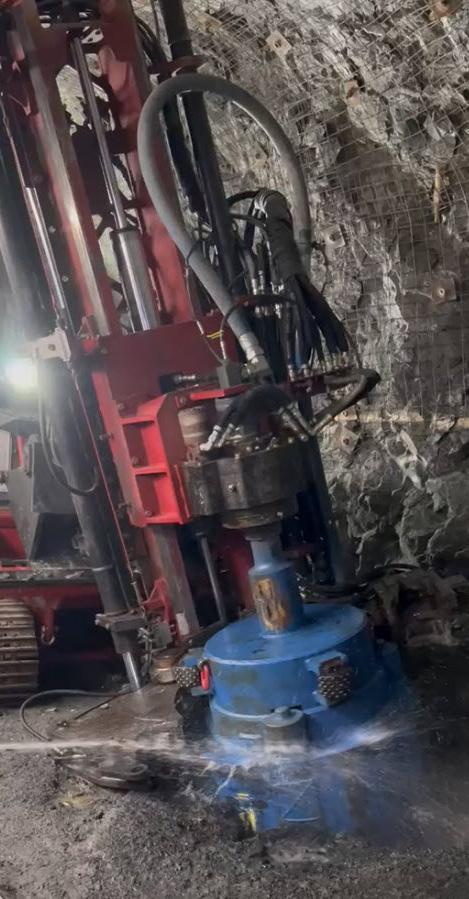
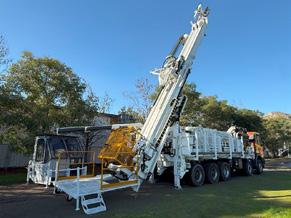
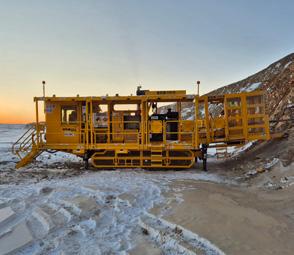
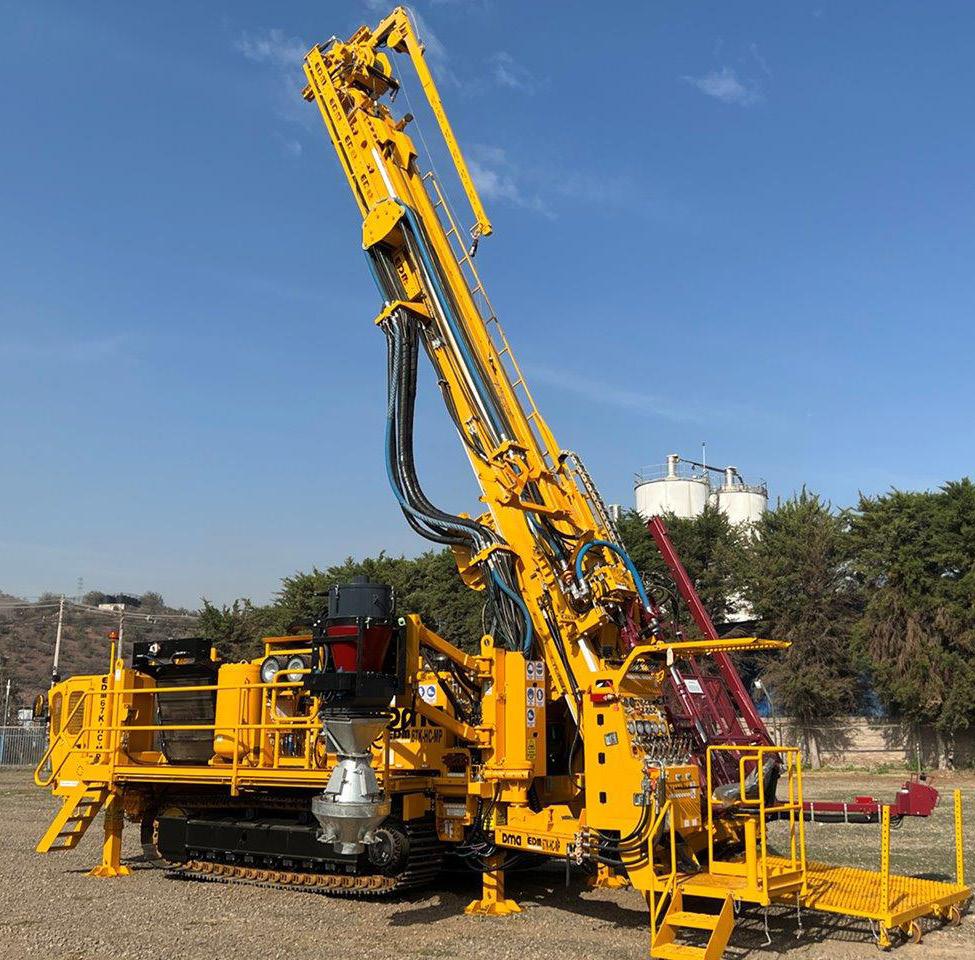
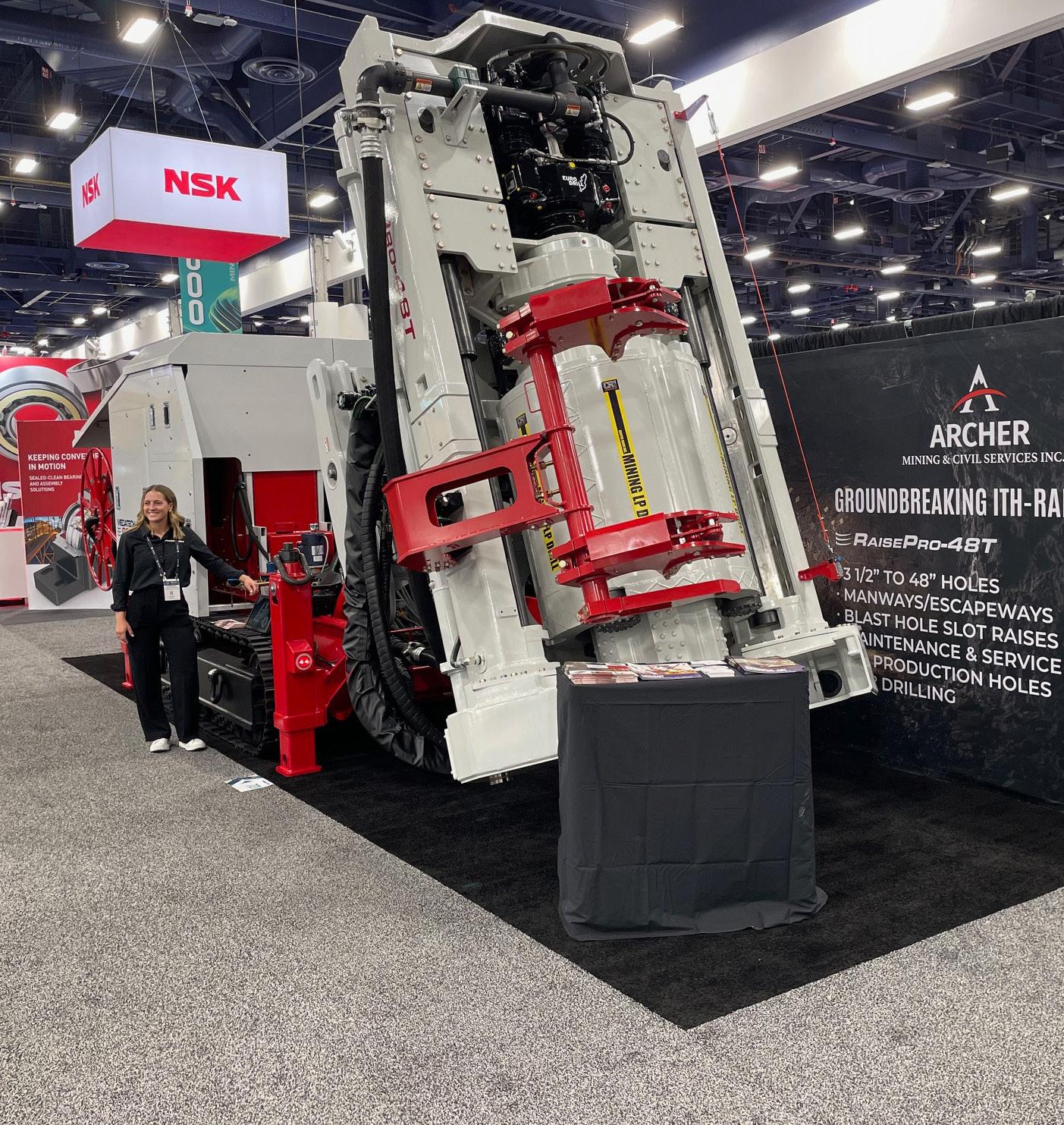
and
EDM Greyhound 40 Diamond Drill with MK-2 Rod Feeders
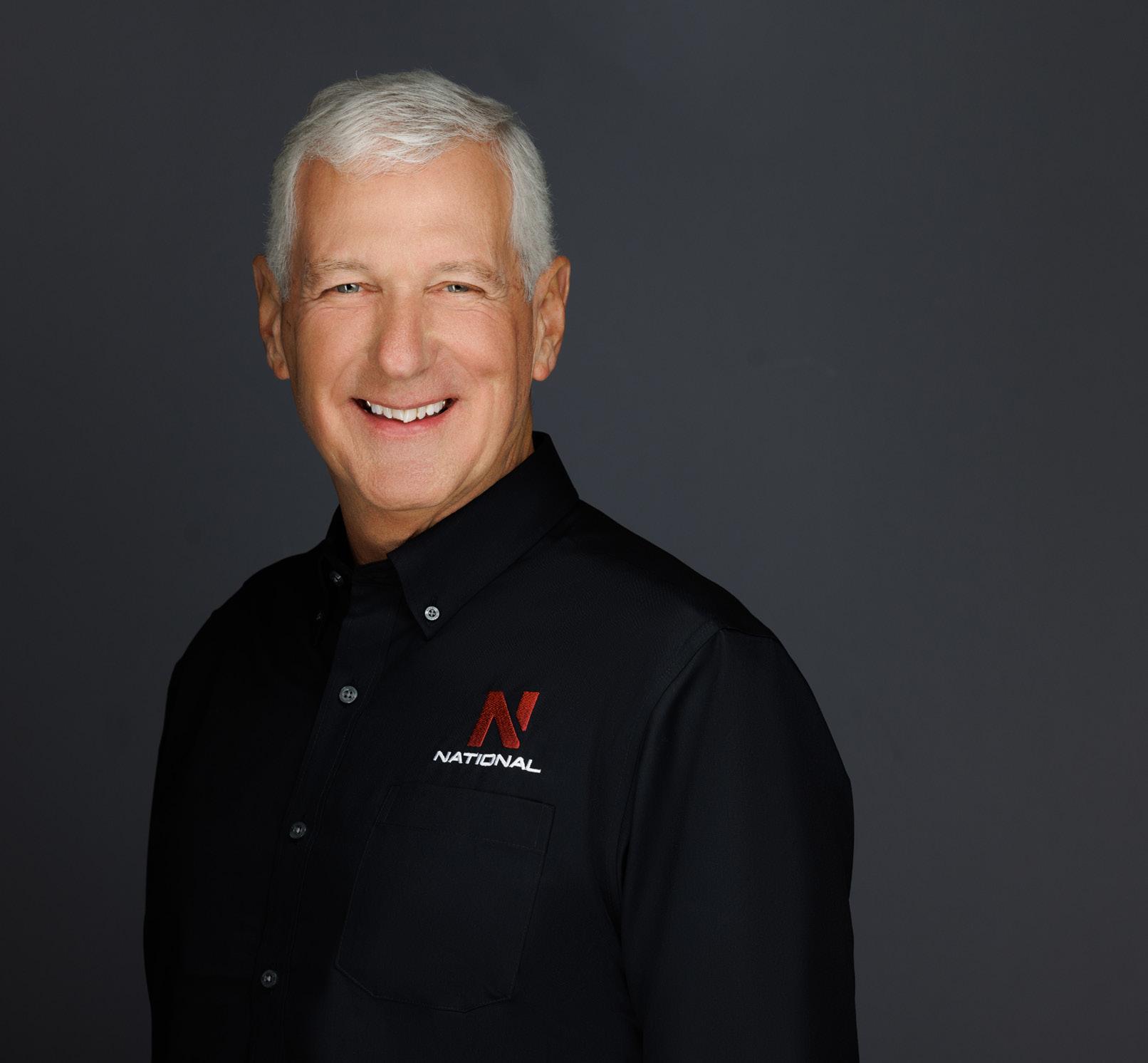
ABOUT JEFFERY D. MORGAN
Morgan started in the drilling industry at 16 years old, working as a shop hand at Water Development Corporation while in high school.
Through hard work and determination, he advanced from the shop floor to the role of President before purchasing the company – a local California-based water and environmental drilling business – in 1999.
After rebranding it to WDC Exploration & Wells (WDC), he grew and diversified the company geographically, extending its reach to mining in the western states. He sold WDC in 2007, distributing half of the proceeds to his employees.
After briefly stepping away, Morgan returned to the business in 2010, driven by a bigger vision and a desire to raise the industry standard. He reacquired the company, rebranded it as National EWP, and now continues to lead it with the same determination and purpose that shaped his journey from the beginning.
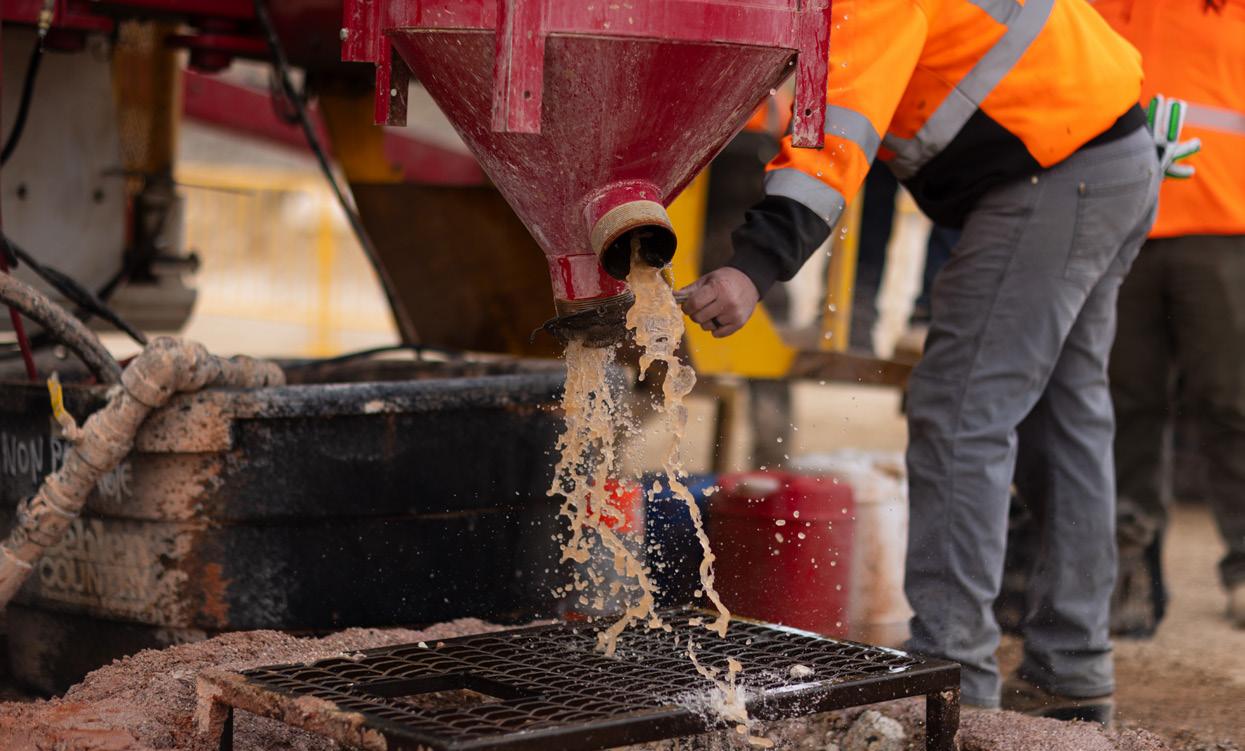
“We are constantly innovating and improving our equipment to be more efficient and make our operations safer,” Morgan highlights.
This is exemplified by the significant improvements made to the cyclones used on National’s RC rigs.
“Given that they have material running through them all day long, the equipment by default tends to wear out fast, so our engineers and operations teams designed a cyclone that has very low wear. Once it has worn out, it also has replacement
sections that can be easily taken out and replaced in the field,” he explains. Having the ability to replace specialist sections of a cyclone on-site, as opposed to transporting it back to a facility for a complete rebuild, makes the RC operation more efficient and effective.
Elsewhere, the company has built a specialist tool for deep hole drilling and has also recently purchased seven LF160 Surface Core Drill Rigs with Freedom loaders, which facilitates hands-free drilling on-site, evidencing the extent to which National consistently upgrades its field equipment.
“Overall, we have the newest fleet of equipment in the industry.”
A WORLD-CLASS INVENTORY
National made the decision to develop its own machining and fabrication capabilities during the COVID-19 pandemic, which made the
“WE’VE INVESTED SIGNIFICANTLY TO ENSURE OUR PEOPLE ARE NOT ONLY WELL TRAINED BUT HAVE THE RESOURCES THEY NEED IN THE FIELD TO MAKE SURE THEY SUCCEED”
– JEFFERY D. MORGAN, PRESIDENT AND CEO, NATIONAL EWP
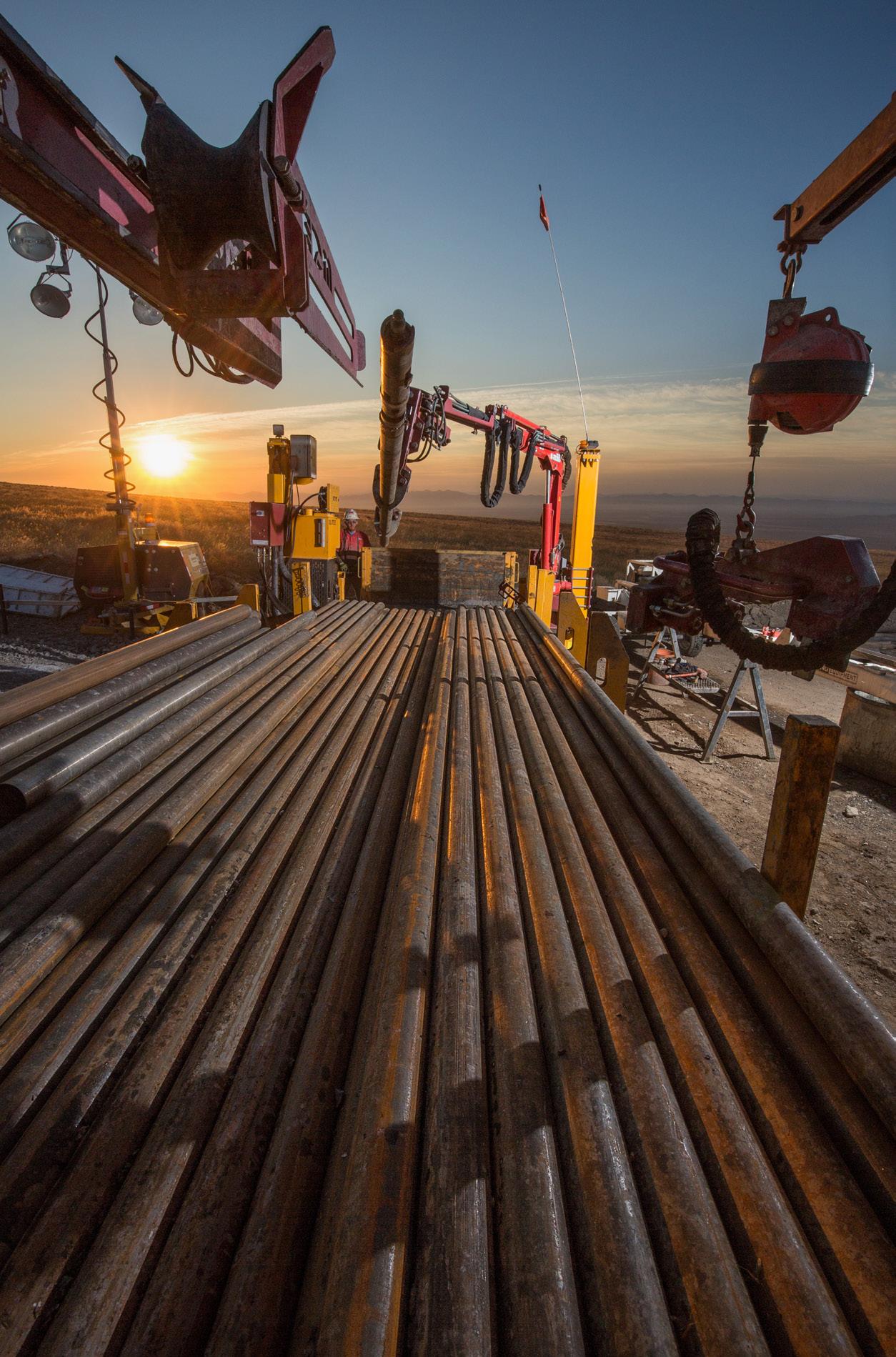
industry’s supply chain significantly unreliable, leading the company to curate its own vast inventory.
“During the pandemic, it became obvious that we could not secure a consistent supply of the tools and parts we needed, which is why we decided to make significant internal investments to ensure we had all the parts we required for our drill rigs,” Morgan recalls.
As it stands, the company now has over USD$10 million of inventory across its two facilities and the dog houses on each drill rig. This means that if any equipment fails in the field,
parts are easily available to get them back up and running within 24 hours.
This adheres to National’s 12/24 hours rule, which dictates that any minor downtime issues must be repaired within 12 hours and any major issues within 24.
“It’s a huge commitment, but it pays off because when you’re in the middle of a hole, you don’t want to lose it. The longer you’re not turning the pipe, the higher the chance you’re going to lose the hole.”
The company’s success is a testament to this dedication, as it has less than two percent annual
downtime, thereby ensuring that its clients’ investments in the field consistently remain operational.
EMPOWERING A SKILLED WORKFORCE
National has worked hard to build a culture that ensures its teams can succeed in the field.
Guided by its two core values – People and Results – National emphasizes the company’s broader vision with its employees who share in its success.
National also provides ample support and sets high expectations for its staff, ensuring that leadership effectively guides people and provides the right resources for any given project.
“If you give people the vision of where we are headed, high expectations of achievement, and the resources they need to succeed, it’s amazing what people can accomplish,” Morgan surmises.
Indeed, the company’s industryleading field services support team ensures the workforce is in an optimum position to keep the rigs running, operating across the entire supply chain to make sure they have the tools they need to succeed.
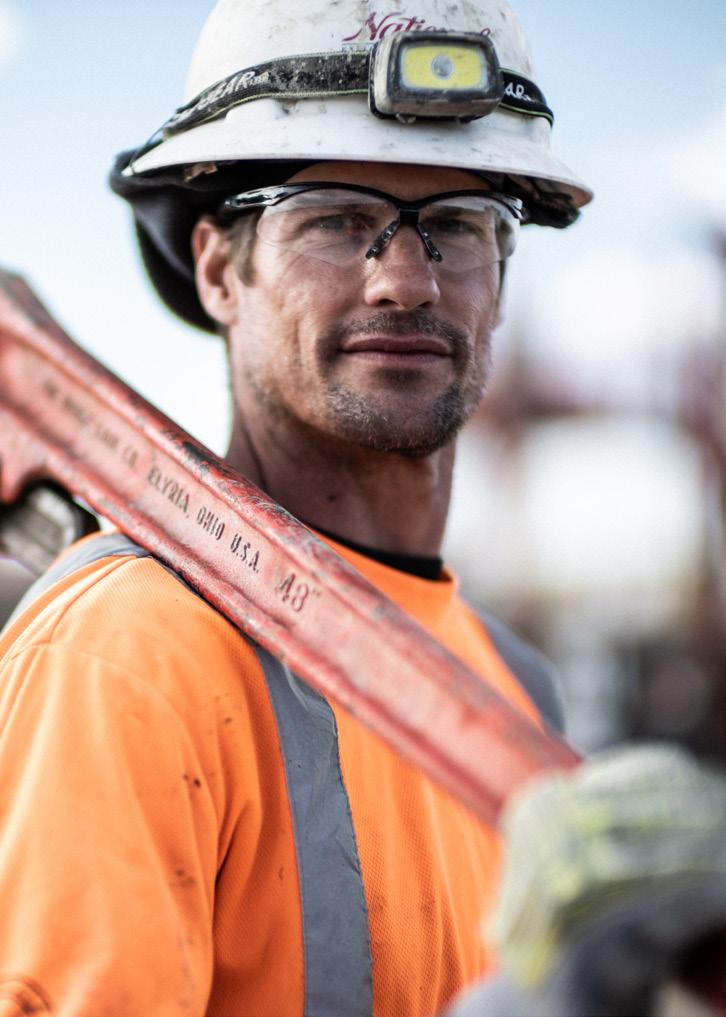
This creates an environment where staff take pride in their work and adopt a sense of camaraderie in the field.
National’s strong workplace culture also emphasizes employee value, recognizing the field teams who work long hours in difficult conditions by providing them with special holiday meals on 4th July and Thanksgiving, fostering a sense of belonging.
“This may sound really simple, but it is indicative of our desire to make sure our people know how important they are,” he urges.
National takes care of its staff not only when they are at work but also outside of their jobs, rewarding them with industry-best compensation, benefits packages, gift cards, and regular bonuses.
“I come from a blue-collar background and my dad was a mechanic, so I have a lot of respect for workers who get up every day and make this great country of ours successful,” he prides.
A CORNERSTONE OF SAFETY
Fundamental to National’s growth, safety is interwoven within the fabric of the company and enables its team to work more efficiently in the field.
“AS A WESTERN US-BASED COMPANY, WE’VE HAD THE OPPORTUNITY TO GO GLOBAL IN THE PAST, BUT WE WOULD RATHER BE REALLY GOOD IN OUR OWN BACKYARD. INSTEAD OF FORCING GROWTH AND GOING AFAR, WE FOCUS ON OUR EXISTING CLIENT AND GEOGRAPHIC BASE”
– JEFFERY D. MORGAN, PRESIDENT AND CEO, NATIONAL EWP
The company goes above and beyond industry standards, starting with its recruitment process and state-of-the-art training program.
“When we hire, we don’t just train people to meet the Mine Safety and Health Administration (MSHA) standards, we train them to meet our own unique standards, keeping them in classes for three to four days beyond what is required,” Morgan states.
Thanks to the company’s advanced training program, conducted in its own facility, new employees can confidently enter the field with a fundamental set of skills and knowledge.
“Not only are they contributing but
they feel like they are more part of the team and much safer, which has also helped improve our retention,” he adds.
National’s safety culture is upheld by a top-notch team of professionals on-site. Notably, the team doesn’t seek to point out wrongdoings, but rather mentors and trains staff on regulations so they have a greater understanding of why the measures are in place.
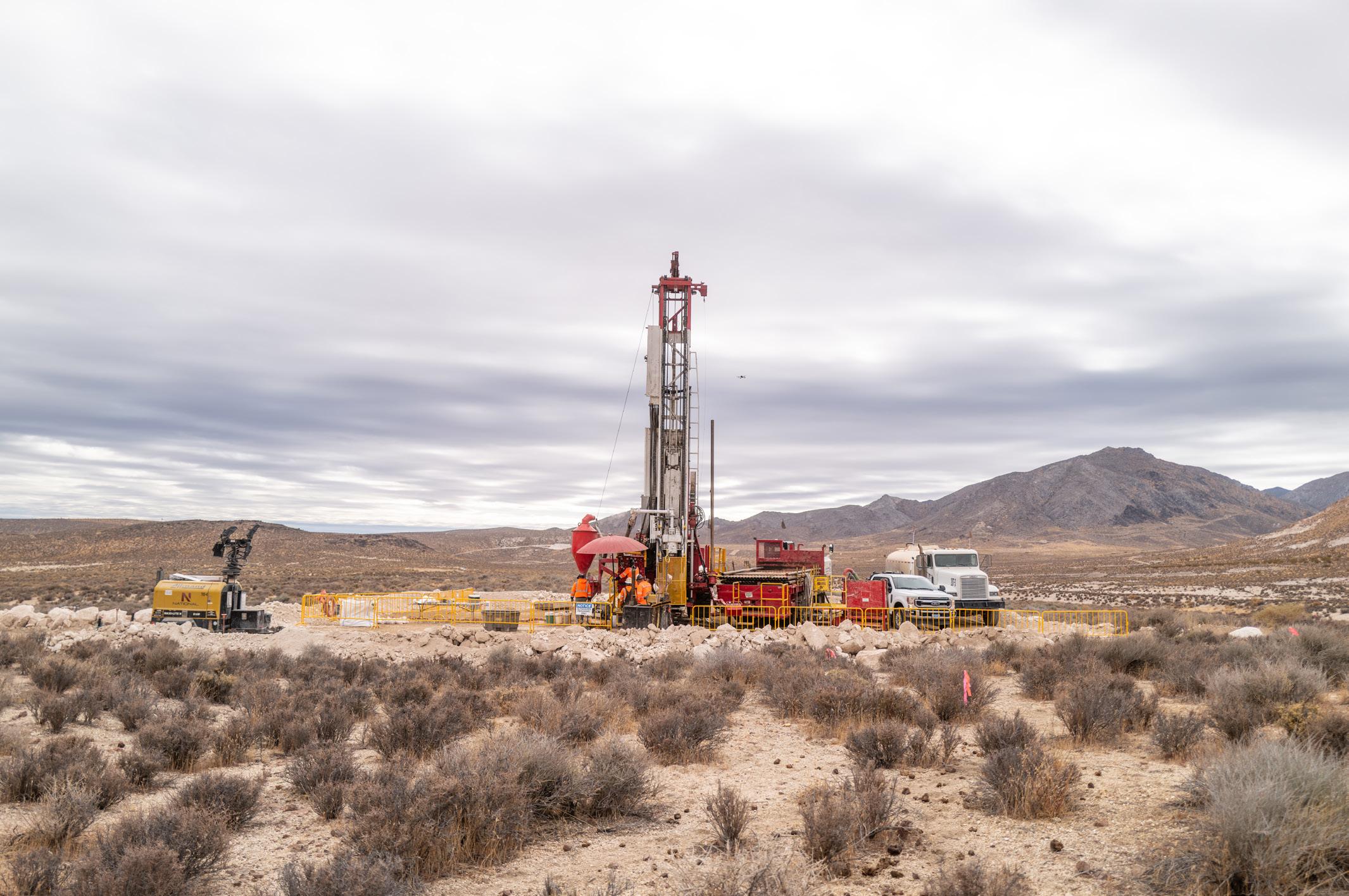
“Our goal is to ensure people work safer. We’re not trying to catch and punish them - we’re trying to teach them to work according to our standards so they have a better idea of what they’re doing.”
In aid of this, National has
AT THE FOREFRONT OF CLIENT DEMAND
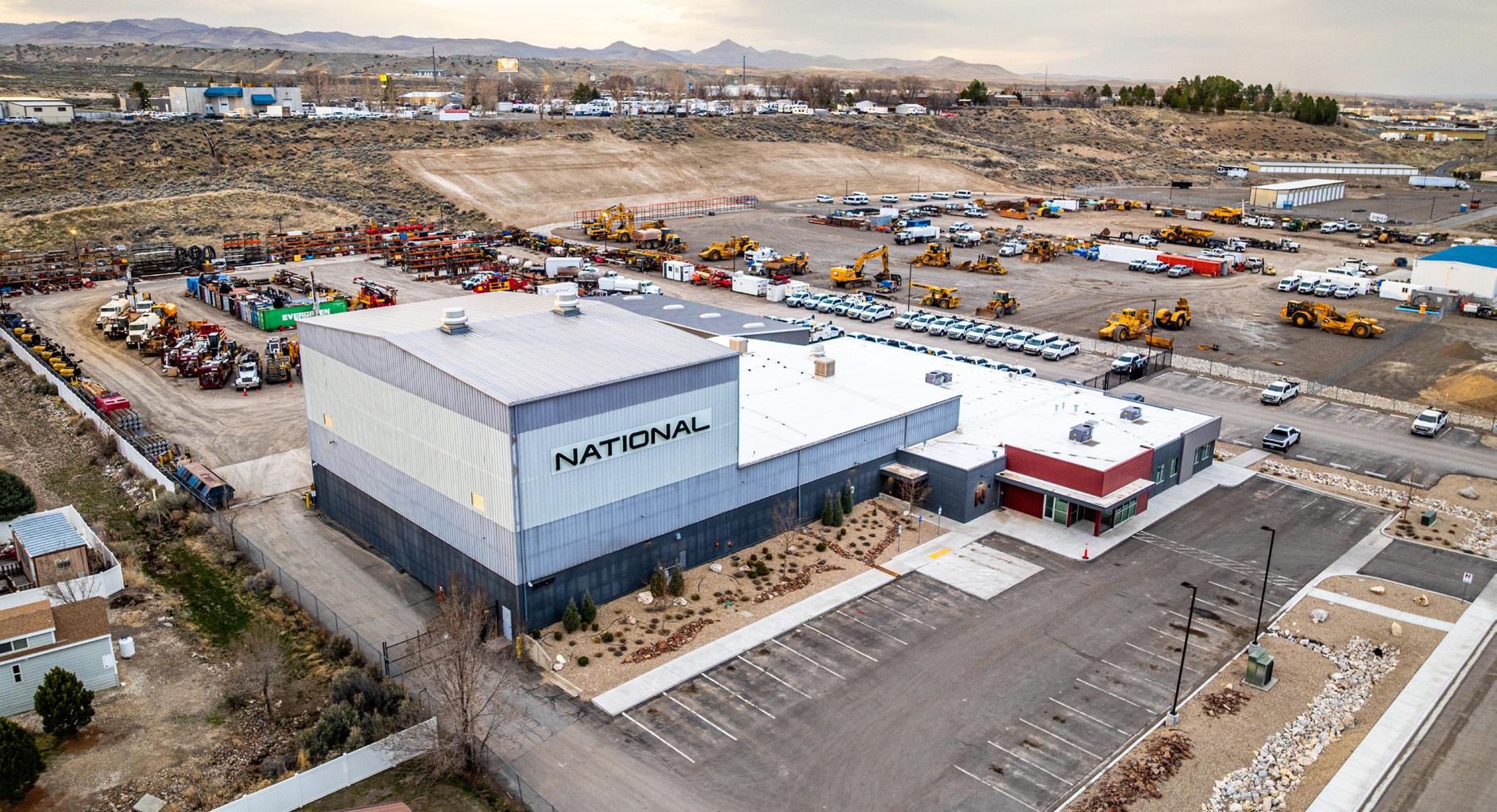
National recently completed an RC exploration project on behalf of a client, which involved the rapid mobilization of rigs to a job site in order to meet a tight timeframe for the customer.
“We completed the project ahead of schedule. This shows that we take a lot of pride in being able to effectively respond to customers’ needs – it’s why we get up for work every day,” Morgan prides.
Elsewhere, a client reached out to National after one of its competitors had installed faulty wells that required millions of dollars in repairs.
The company found a solution in a short timeframe and at a small percentage of the previous cost, making the project’s success a critical component of the clients’ underground mining operations.
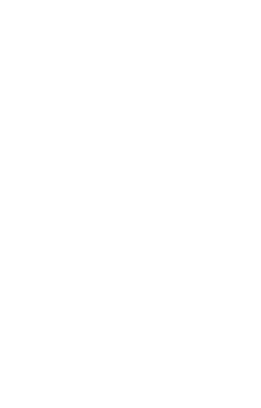
developed an internal set of standards called the National Drill Standard that defines every aspect of its operations from the ground up.
These are broken down into clear job safety analysis (JSA) points that are easily accessible to staff who then have a clear understanding of how activities are to be performed within the context of the company’s broader drilling standards.
Similar sets of standards and JSAs have been created across all levels of the organization, creating a comprehensive internal network of support and guidance.
“We’ve invested significantly to ensure our people are not only well trained but have the resources they need in the field to make sure they succeed,” Morgan informs us.
REMAINING COMPETITIVE
Over the course of the coming year, National aims to ensure all its teams are sufficiently adjusting to the shifting marketplace to remain competitive and grow as a highly profitable organization.
It is additionally looking toward future capital investments, particularly given 90 percent of the company’s operations are currently surface drilling. Therefore, it strives to grow its underground capabilities in the coming year.
Elsewhere, National plans to further simplify its processes and systems, improve tooling and equipment, and better mobilize to jobs in the field, taking steps to improve overall operations.
“We aim to take what we have and make it better by analyzing our processes to see how they can make us more competitive so we can more effectively get the results our clients need,” Morgan closes.

Tel:775-753-7355
info@nationalewp.com
www.nationalewp.com
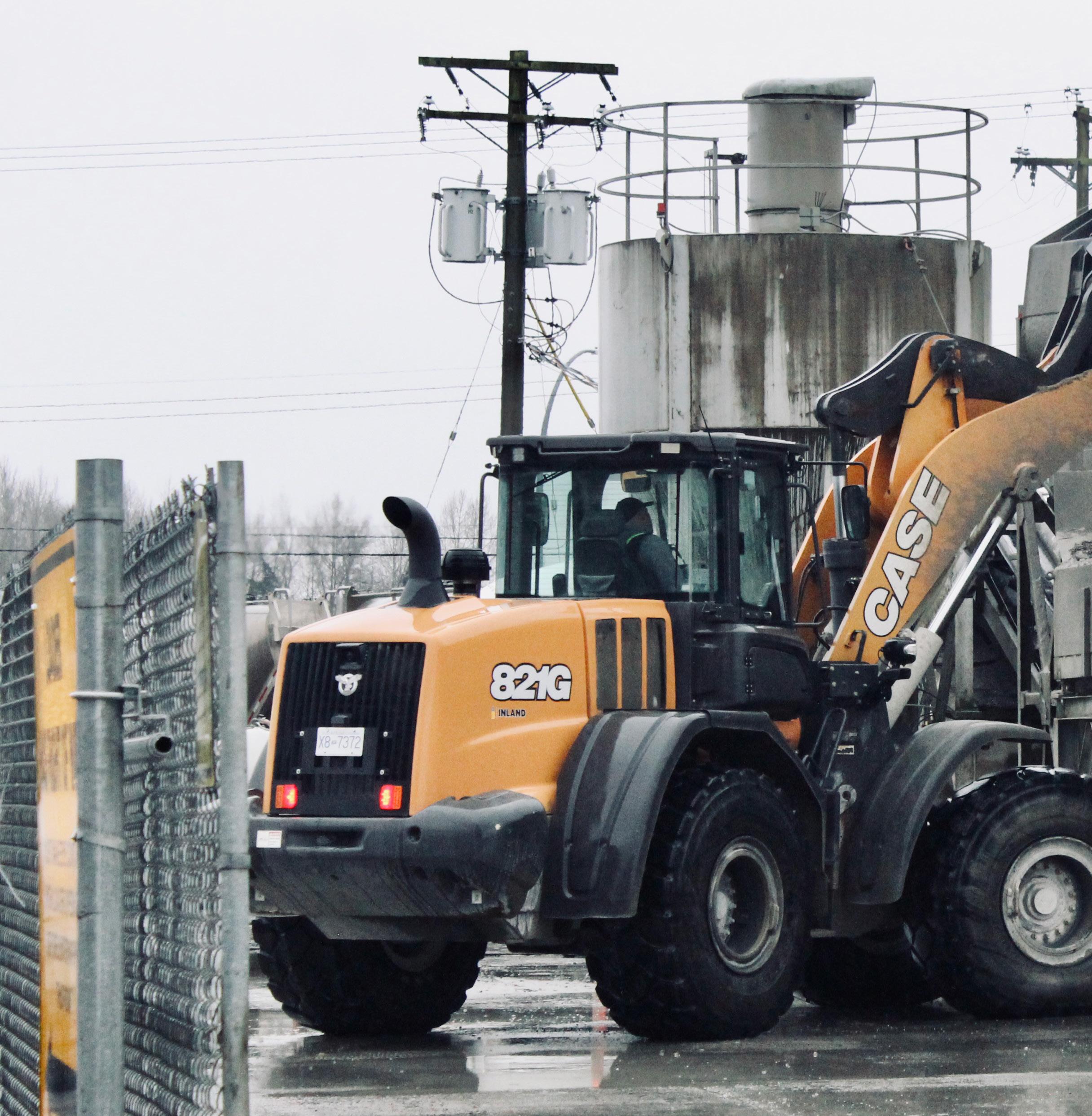
BUILT ON SYNERGIES
The entities within BM Group of Companies support and complement each other to deliver outstanding service, highly specialized skills, and exceptional quality control from start to finish. Milan Mann, President, discusses the pursuit to provide unparalleled synergies
Writer: Jack Salter | Project Manager: Ben Weaver
SYNERGIES
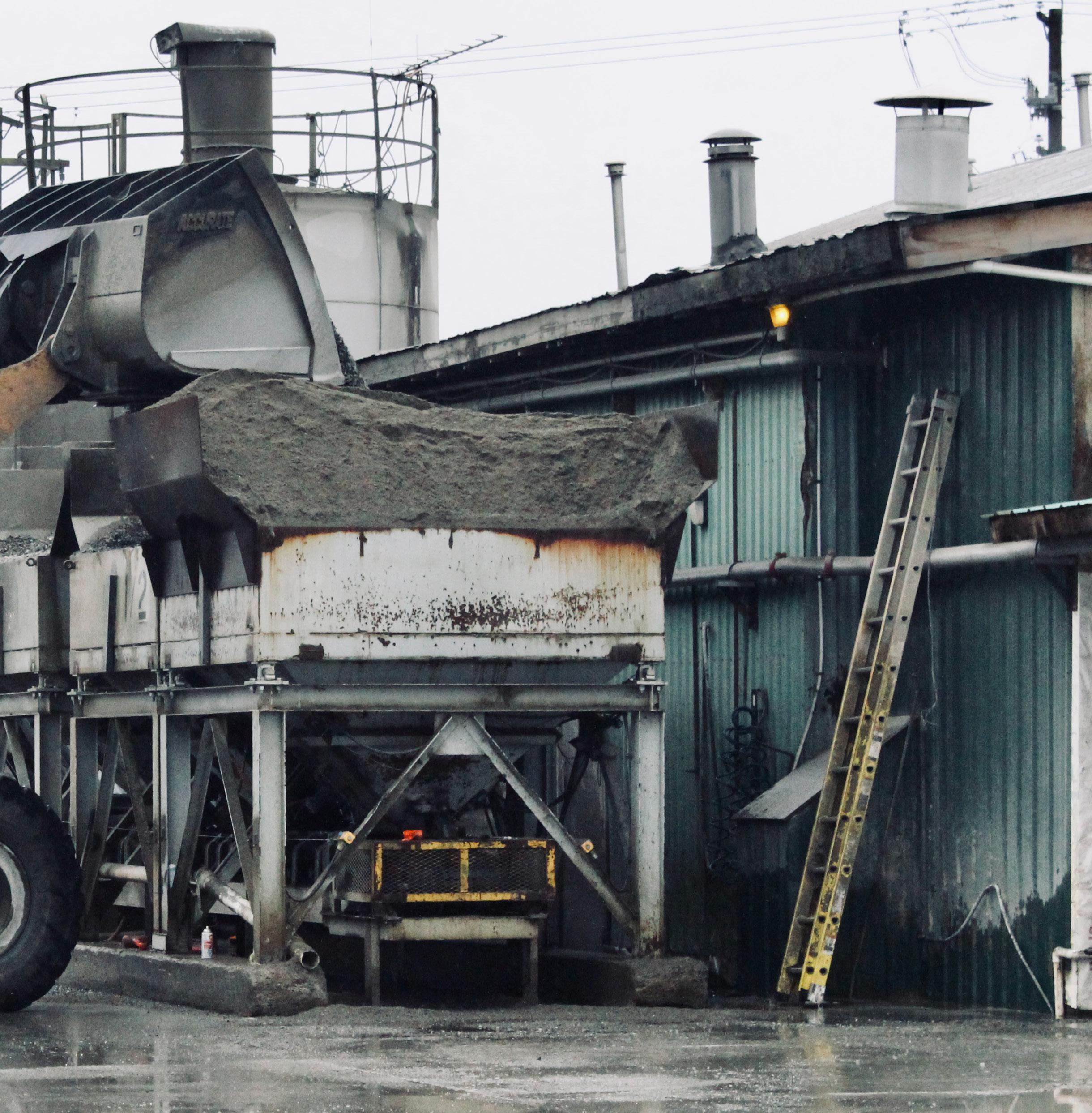
The impact of BM Group of Companies (BMG), British Columbia’s most diverse and versatile construction family, dates back almost a century to 1929.
BMG has brought together a portfolio of 22 highly specialized and experience-rich companies across four key divisions – Materials
Supply, Construction Support Services, Structural Restoration and Waterproofing, and Real Estate Development.
The former consists of ready-mix supply, precast concrete, structural steel fabrication, and building supplies, whilst the Construction Support Services division ranges from

demolition abatement to temporary labor and training.
BMG’s Structural Restoration and Waterproofing division, meanwhile, includes roofing, above and below-grade waterproofing, traffic coating, post-tensioning, plaza restoration, and civil pipe rehabilitation.

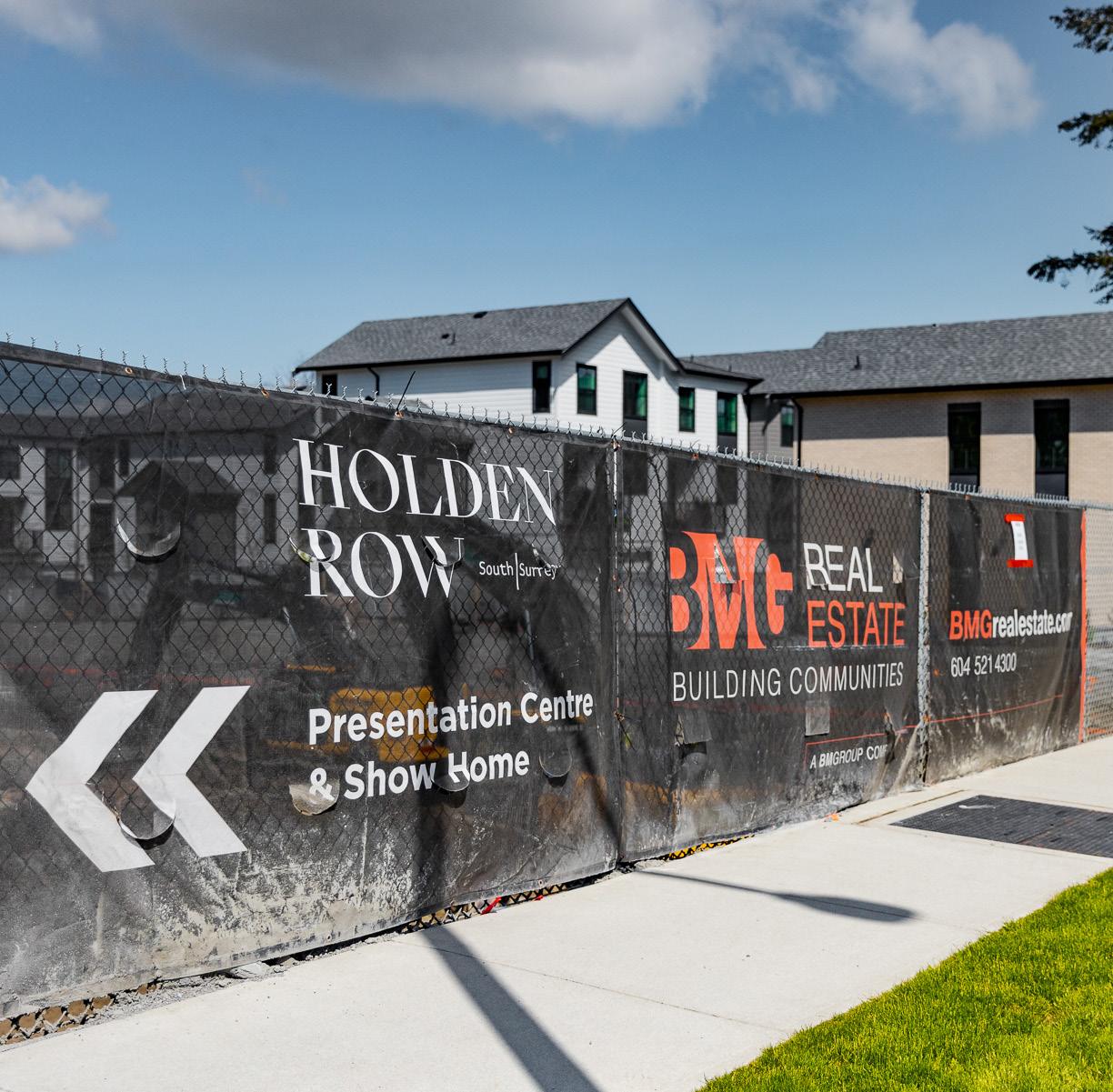
Lastly, the group’s Real Estate Development division is both a developer and general contractor, exclusively servicing its own projects and holdings.
Within this division, BMG Real Estate is one of the fastest-growing real estate entities in Lower Mainland, where it has been proudly building communities for over 25 years, offering residential, commercial, and industrial expertise.
From land acquisition to welcoming homeowners, BMG Real Estate’s mission is to become the most consistent development company in the region.
“BMG strives to be of service to our clients’ projects and approach each one as a partner to its success,” outlines President, Milan Mann.
“While we may have a large scope, with our growing stable of companies, we provide substantial coverage, value, and peace of mind across the entirety of projects.”
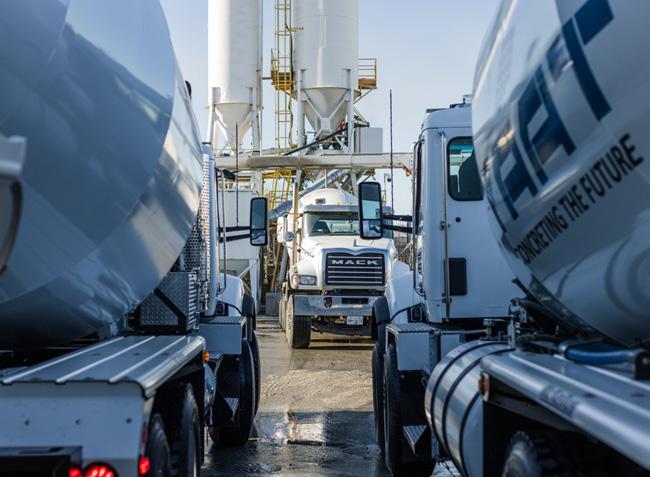
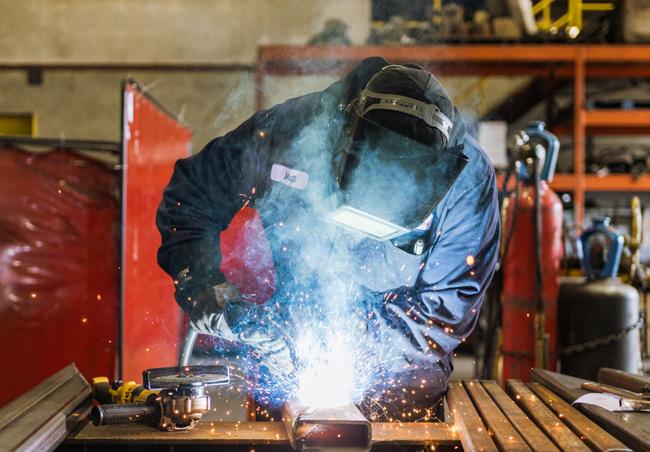
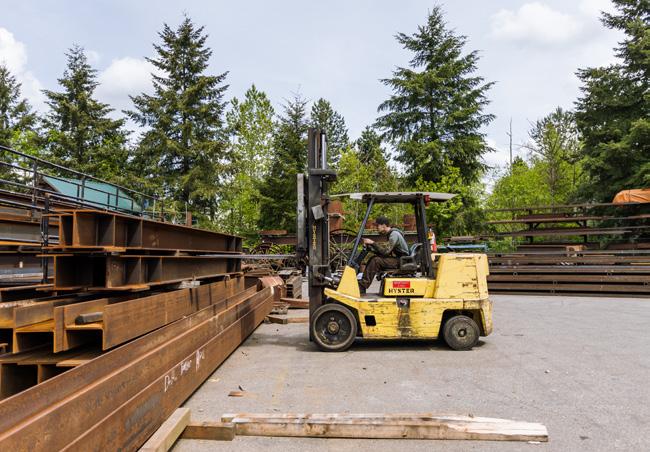
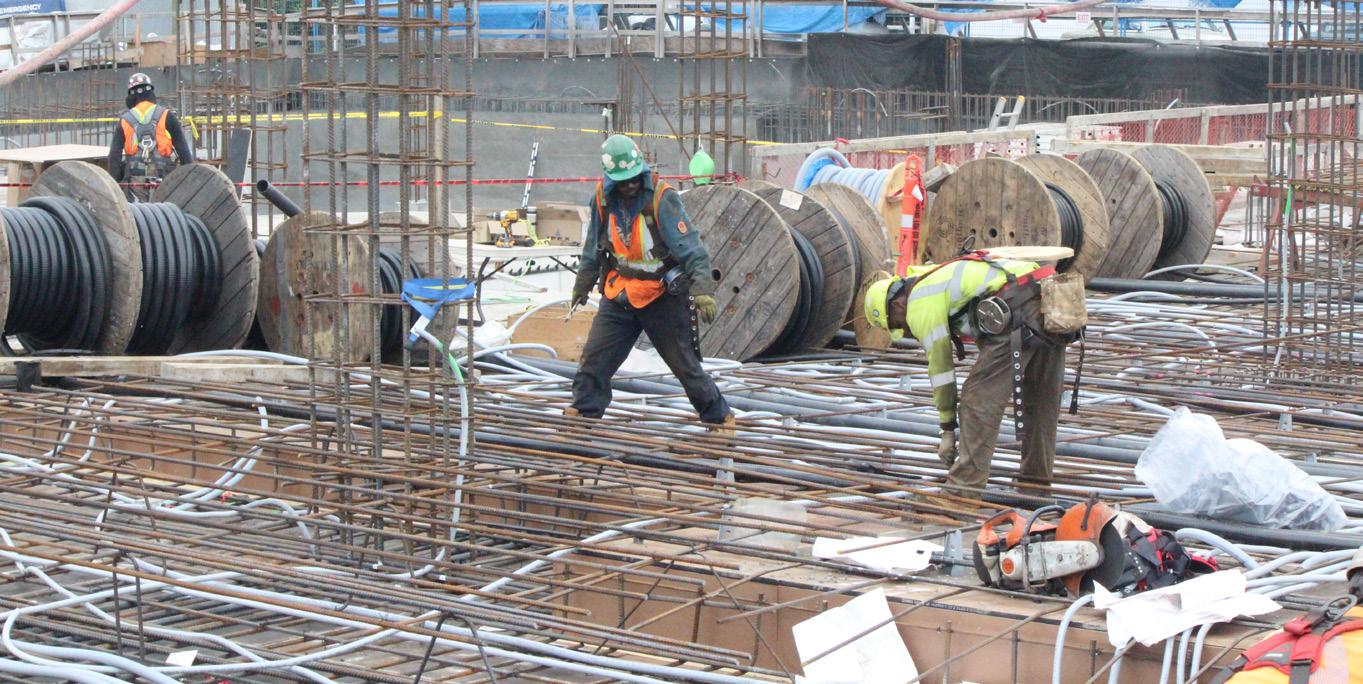
“WE DON’T WANT TO GROW FOR THE SAKE OF GROWING; OUR PURSUIT IS DRIVEN BY OFFERING INCREASED VALUE THROUGH ACQUISITIONS OF LIKE-MINDED COMPANIES AND INCREASING OUR GEOGRAPHICAL FOOTPRINT VIA OPERATIONS OR REAL ESTATE DEVELOPMENTS”
– MILAN MANN, PRESIDENT, BM GROUP OF COMPANIES
WALKER HOUSE
BMG’s synergy is grounded in a question the group often asks itself – how many ways can it approach a single project?
The similarity of processes within the group allows each company to complement and support the other, be it from the office or on site.
“We can move resources around to ensure a project’s success,”
assures Mann.
A demonstrable proof of concept is BMG Real Estate’s inaugural high-rise project, Walker House, a stunning mixed-use concrete tower that will soar 29 storeys above the North Delta skyline.
The 314-unit building is currently under construction, having broken ground in March 2024, and will be the commuter town’s tallest building,
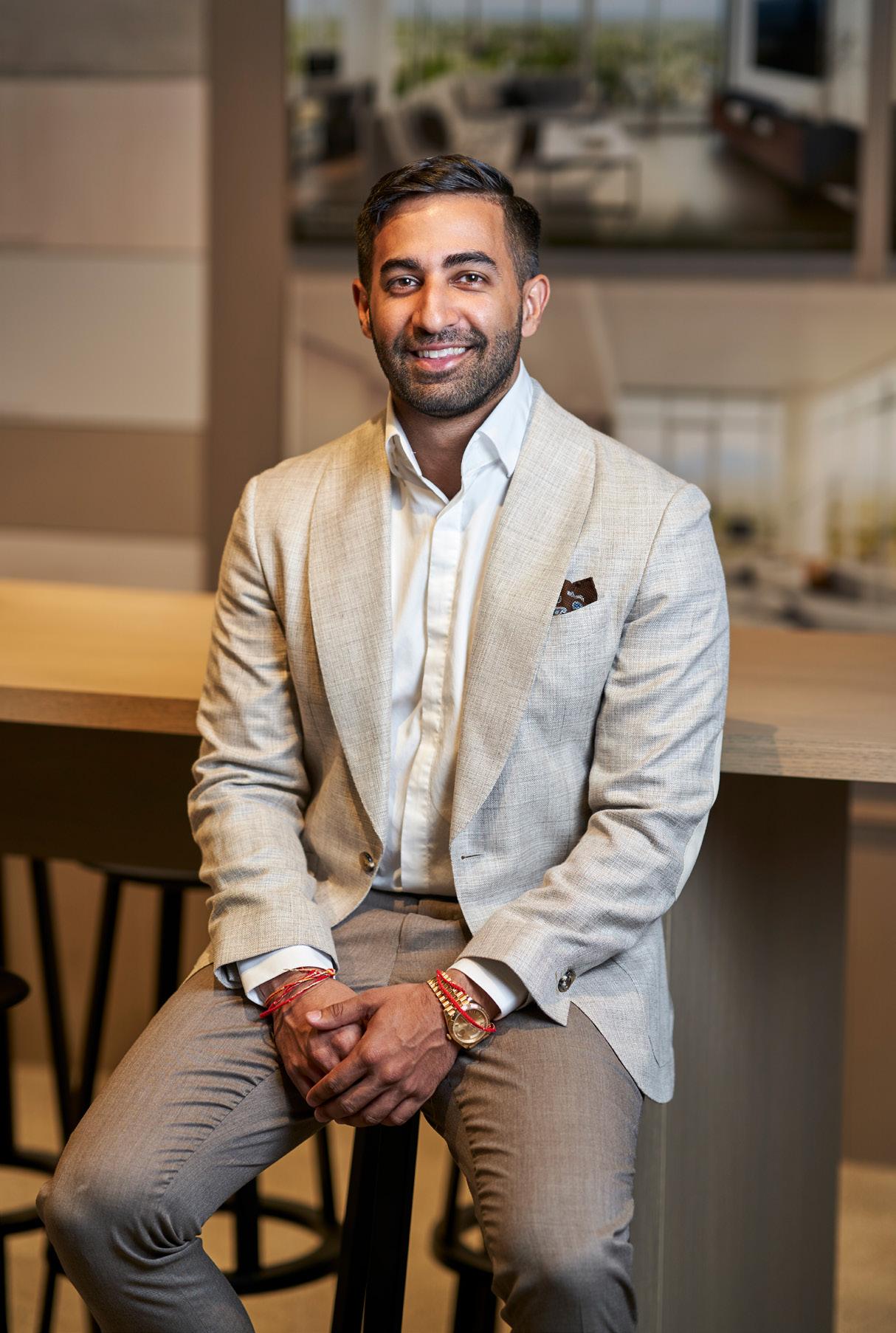
offering unobstructed sweeping vistas of the Fraser River, surrounding mountains, and urban landscape.
Beyond transforming the skyline, Walker House will provide vital accommodation for the area’s increasing population. Indeed, the number of residents in Delta is projected to surge to 121,000 by 2041, with the majority of this growth happening in North Delta.
HOW WERE YOU RAISED IN THE CONSTRUCTION INDUSTRY?
Milan Mann, President: “My father, Balraj Mann, is a civil engineer who was also drafting house plans and developing single family homes, so construction was as routine as homework or basketball practice.
“At an early age, I grew an affinity for projects, being able to create spaces for people to live, work, and play in. Experiencing your fingerprint on a community and the feeling that provides is hard to beat.
“BMG as we now know it wasn’t established until 2011. Before this, our family business was exclusively a land developer. As the 2008 financial crisis hit, my father sought diversity to create stability for his family and solidified his first acquisition in 2011 with Polycrete Restorations, a company he consulted for in his days as an engineer.
“In parallel, as I evolved through high school, university, and my MBA, BMG followed suit. I established a permanent position with the group weeks after graduating from high school. BMG hasn’t looked back since, growing from two companies and 50 employees in 2011 to 22 companies and over 500 individuals choosing to work for us every day.
“Our growth is centred on industries we understand, allowing us to deepen relationships or create new ones.”
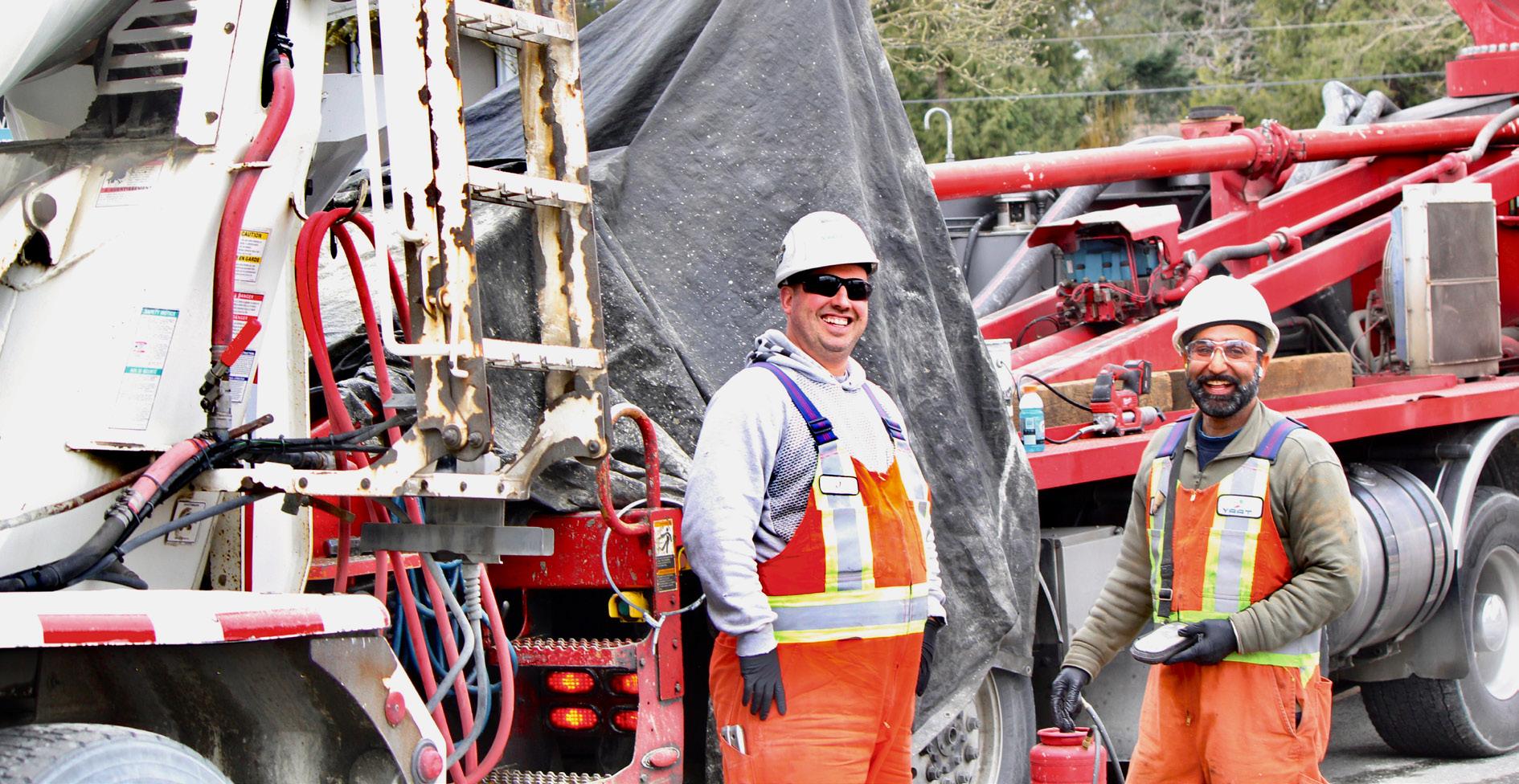
WHAT CHALLENGES ARE CURRENTLY FACING THE CANADIAN CONSTRUCTION INDUSTRY?
Milan Mann, President: “Canada’s construction industry is suffering, which is no surprise given the current geo-political environment.
“For new construction, politics coupled with rising development cost charges – be it municipal or provincial fees burdening the viability of projects and in turn increasing the prices of homes –is slowing absorption in an already stagnant market.
“Maintenance of infrastructure, public projects, and general portfolios will continue to keep service providers relatively stable, but investment-based projects will suffer for the next 14 months, in my opinion.”
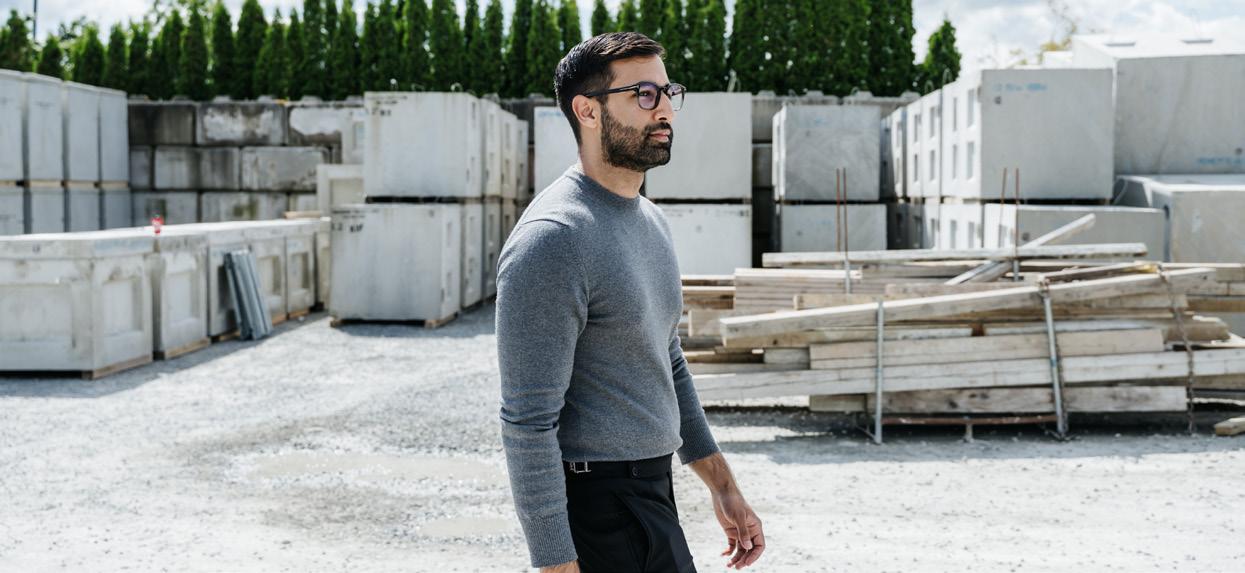

The project will therefore play an invaluable role in bringing essential housing density to the area, offering a diverse mix of studios and one- and two-bedroom suites ranging in size from 472 to 1,959 square feet (sqft).
Moreover, it has been thoughtfully designed with a strong emphasis on community, with an impressive 17,000 sqft of amenities – including an expansive rooftop, outdoor basketball court, state-of-the-art fitness facility, entertainment and coworking lounges, and private meeting rooms –serving as a social hub.
In addition to over 3,000 sqft of commercial space on the ground floor, Walker House will have a child daycare center, prioritizing access for residents and fostering family wellbeing within the community.
“Our internal services cover 20 percent of the project scope. These efficiencies, from pricing to accountability, can be exercised by our clients – we just need to do a better job communicating this to them,” he tells us.
The building also holds a special spot in the group’s history as it stands close to where Mann’s parents
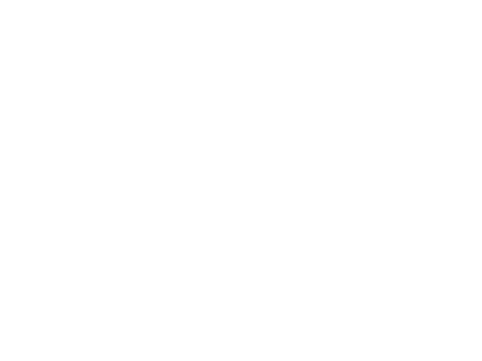
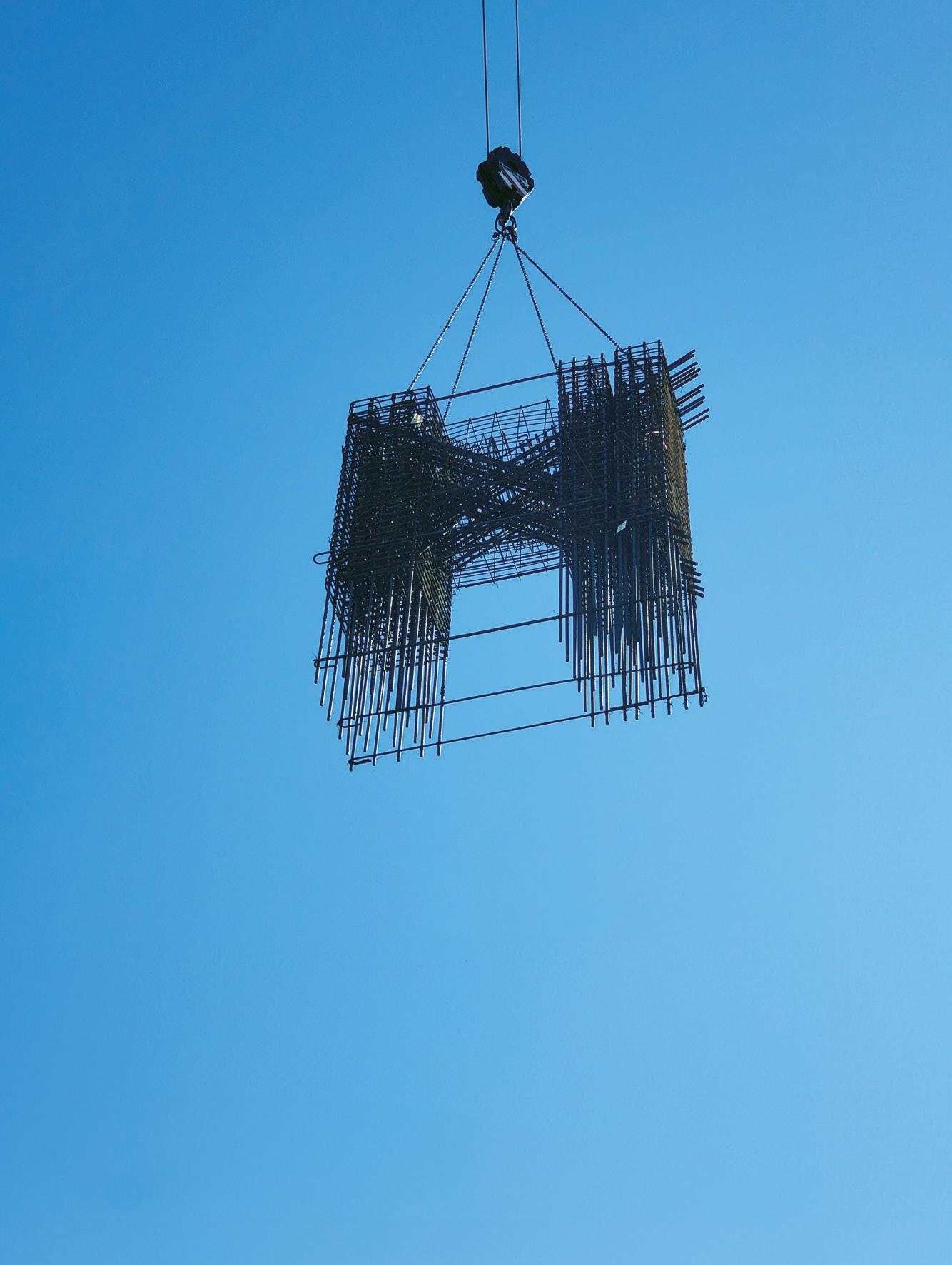
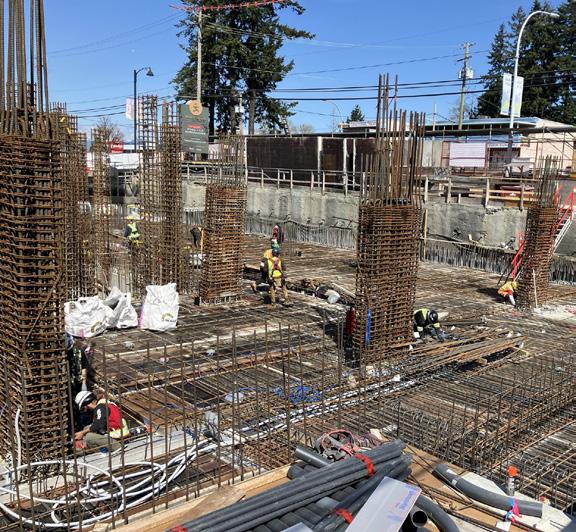
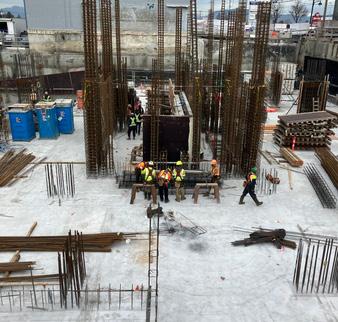
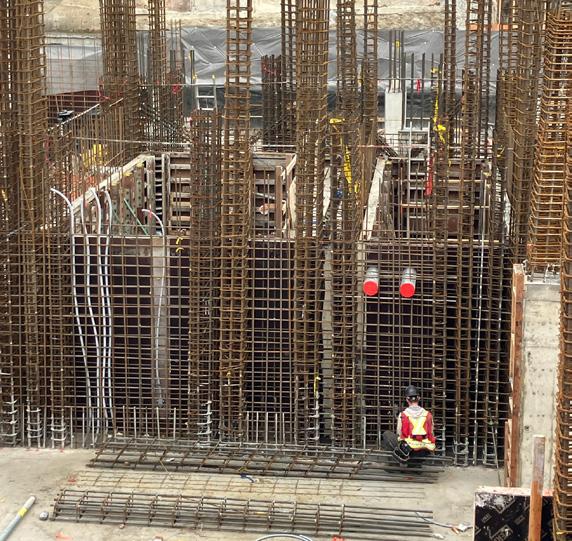
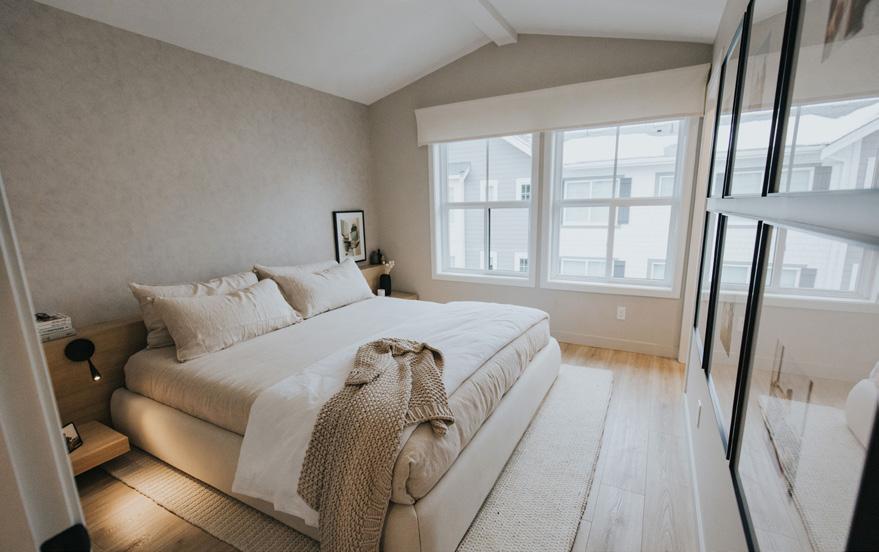
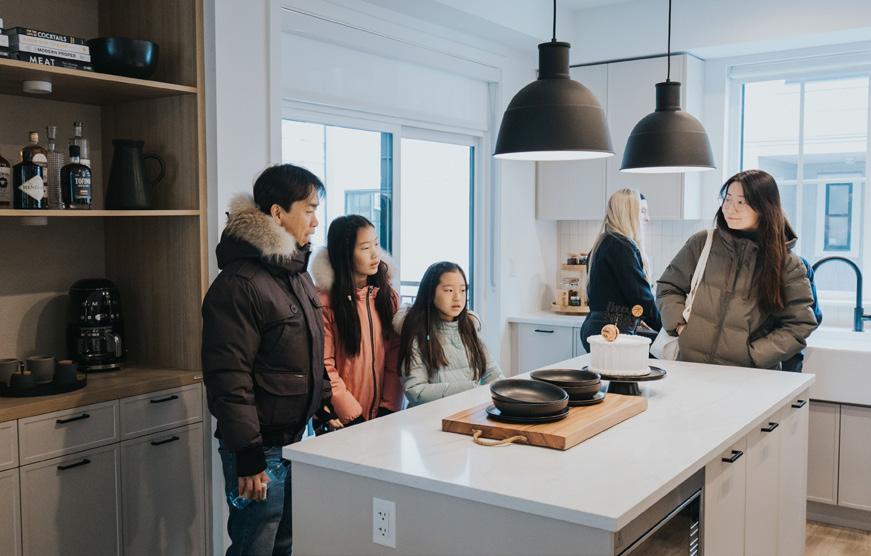
purchased their first home together when they immigrated to Canada.
Alongside Walker House, he highlights BMG’s work on Phase 2 of the demolition of an iconic Vancouver Hotel.
GROWTH AND EXPANSION
BMG has a big focus on growth, especially of its bin rental services and ready-mix supply.
“Once you establish vertical integration, it is imperative to capitalize on this. That is why we have prioritized deepening control of relative supply chains,” Mann explains.
“As Dallas Watt Demo and Actes Environmental continue to scale, expanding our bin and truck fleets was the logical next step not only to keep up with our growth, but to serve projects we are working on before and after we complete our main scope.”
On ready-mix supply, Mann notes that raw materials, especially when importing, were a challenge and risk that was growing costly in terms of time and money.
Thus, the group has solidified its partnerships with cement and fly ash suppliers to provide consistency in its
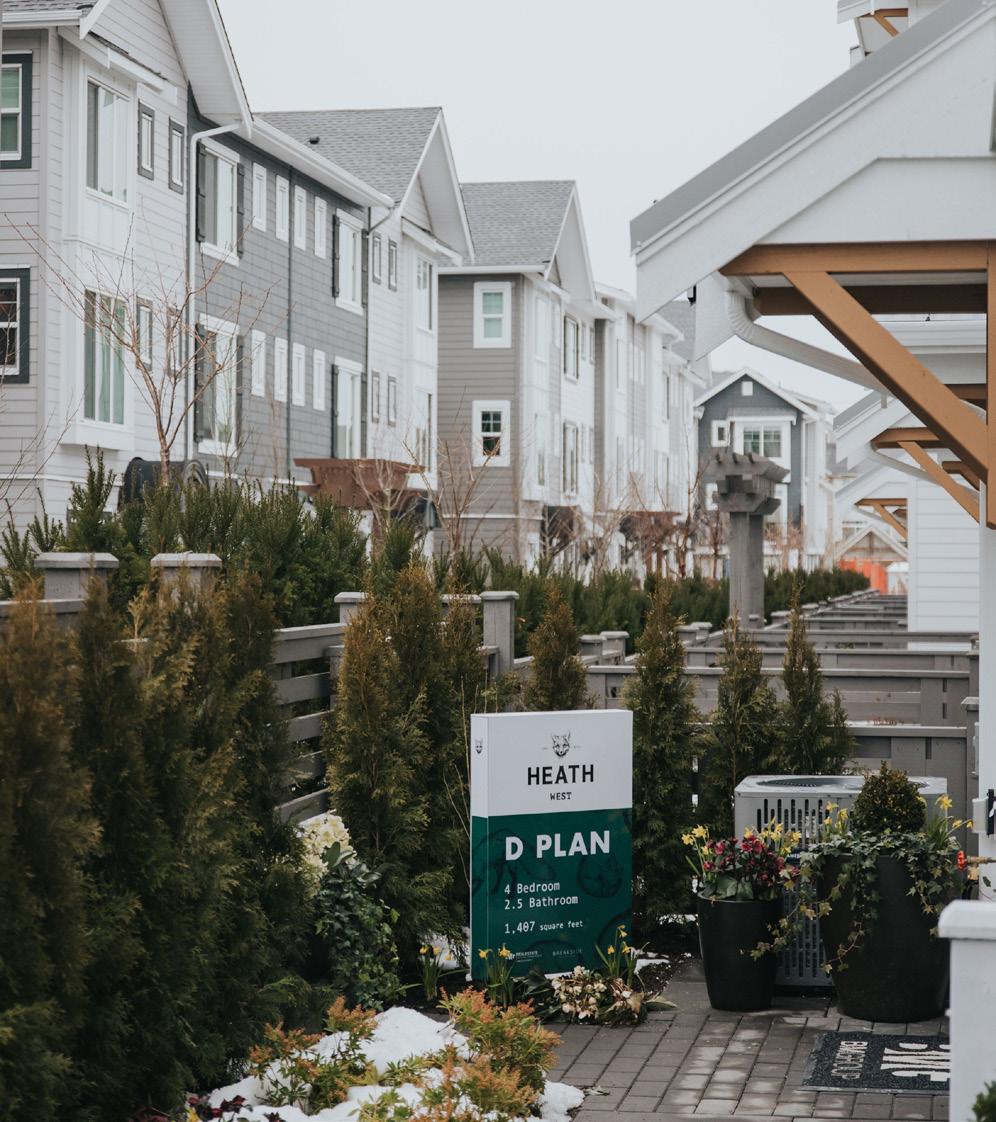
“WHILE WE MAY HAVE A LARGE SCOPE, WITH OUR GROWING STABLE OF COMPANIES, WE PROVIDE SUBSTANTIAL COVERAGE, VALUE, AND PEACE OF MIND ACROSS THE ENTIRETY OF PROJECTS”
–
MILAN MANN, PRESIDENT, BM GROUP OF
COMPANIES
volumes and better serve projects and customers.
As a growing organization, expansion is also always at the forefront of BMG’s mind.
“We don’t want to grow for the sake of growing; our pursuit is driven by offering increased value through acquisitions of like-minded companies and increasing our geographical footprint via operations or real estate developments,” Mann sets out.
While the Canadian market is growing and relatively stable, BMG is increasing its familiarity with the US market and excited by how potential is welcomed and promoted.
The group is actively growing its Pacific Northwest-based structural restoration company, Contech
Services, Inc., and looking to establish a development presence close to its Seattle and Portland offices.
“Our priority is to continue to serve our clients and community. With lofty housing goals announced by the Canadian federal government, we are looking for opportunities for BMG to assist with these efforts,” concludes Mann.
Tel: 604 521 4300 info@BMGroupinternational.com www.BMGroupinternational.com
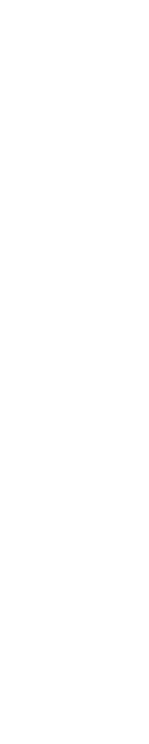
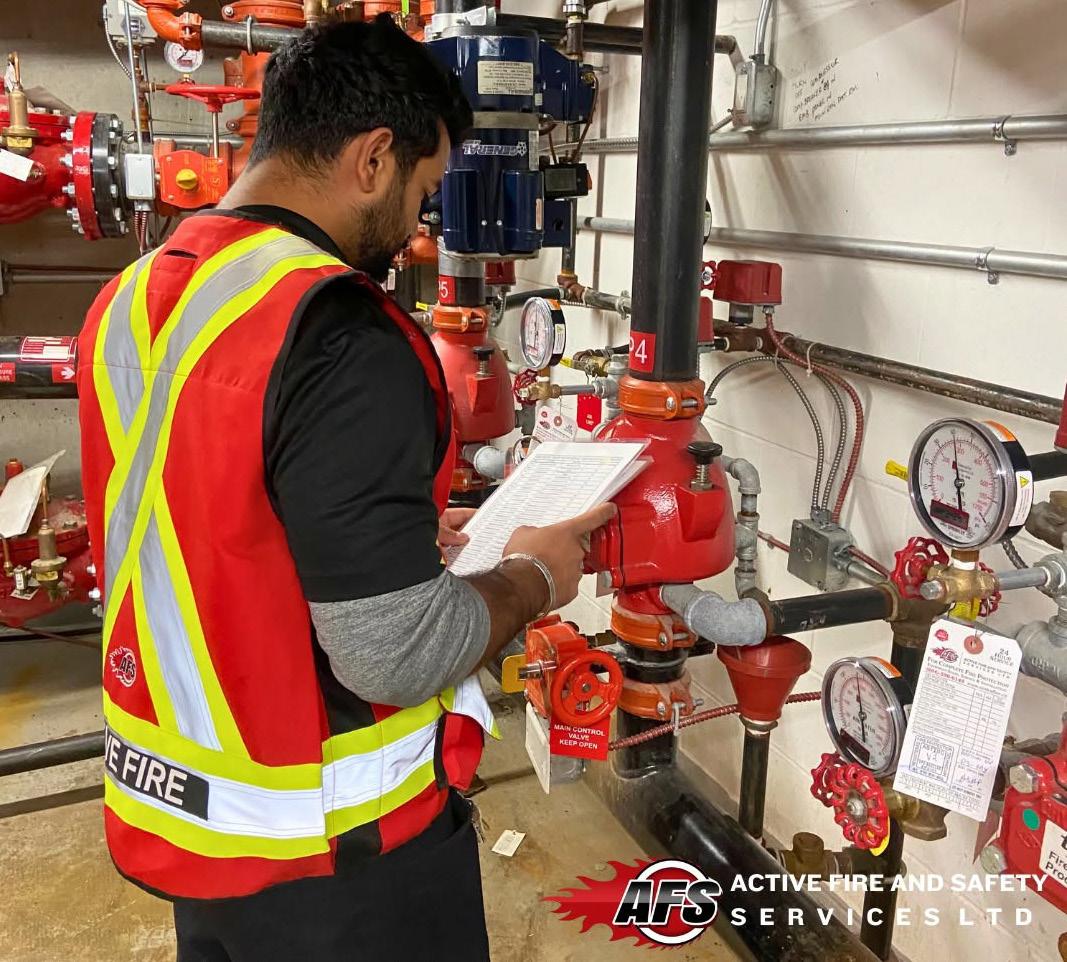
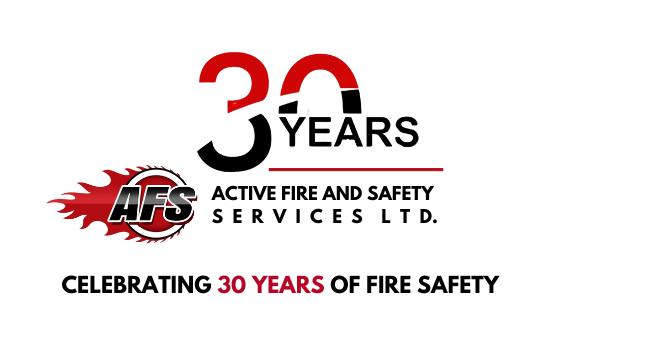
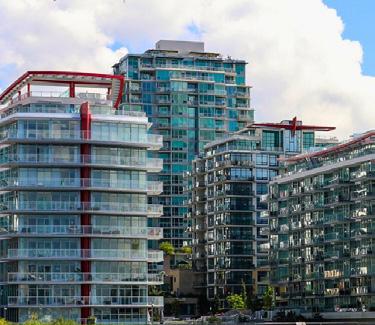
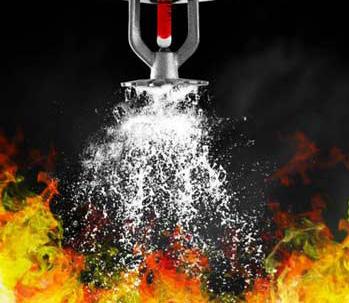
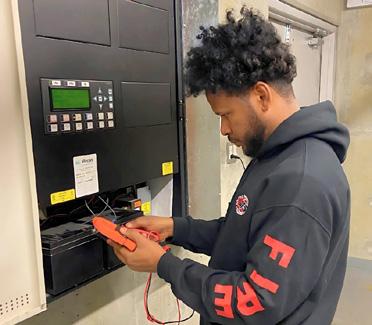
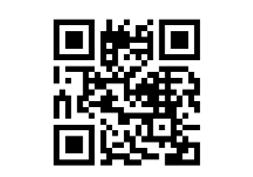
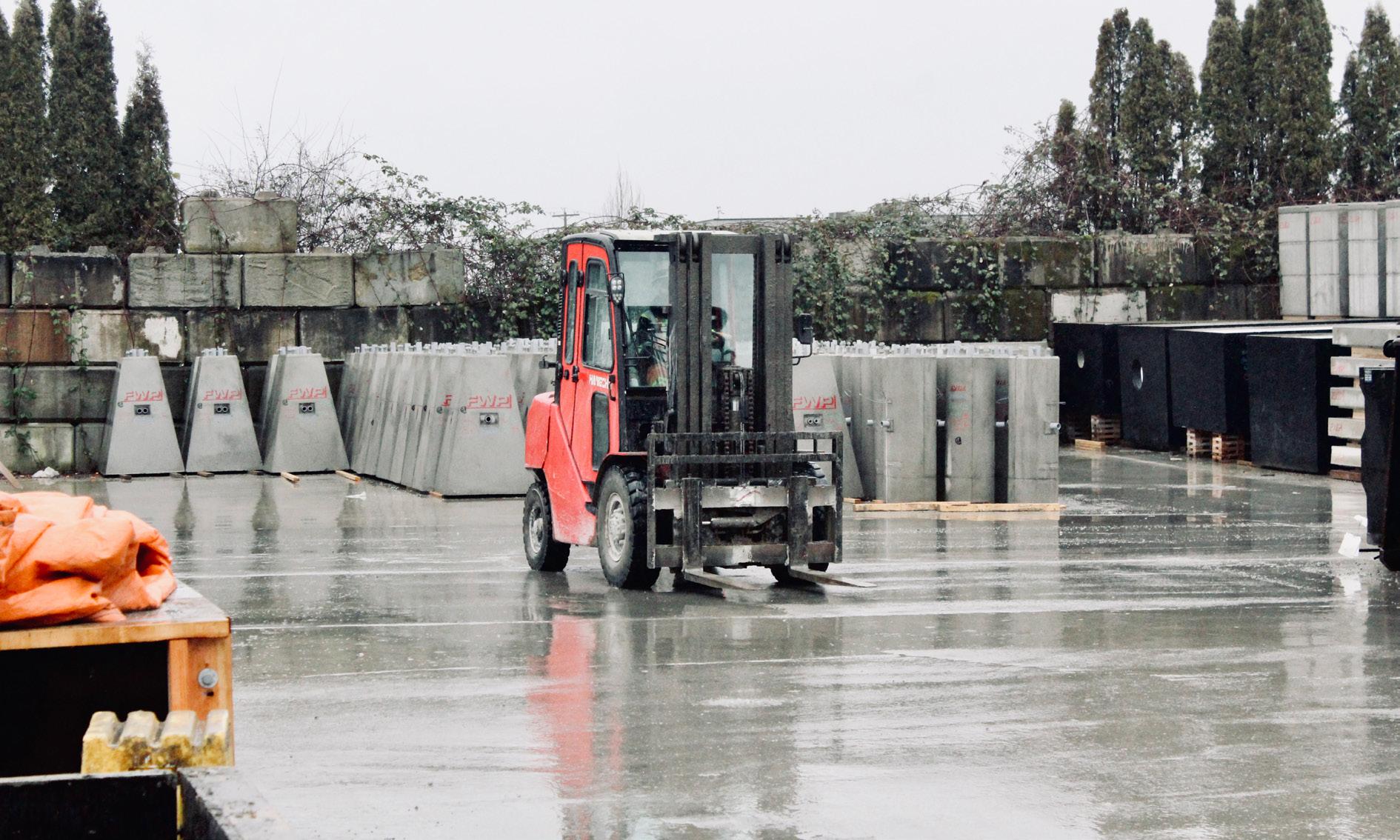

ILLUMINATING
ILLUSTRIOUSLY ILLINOIS
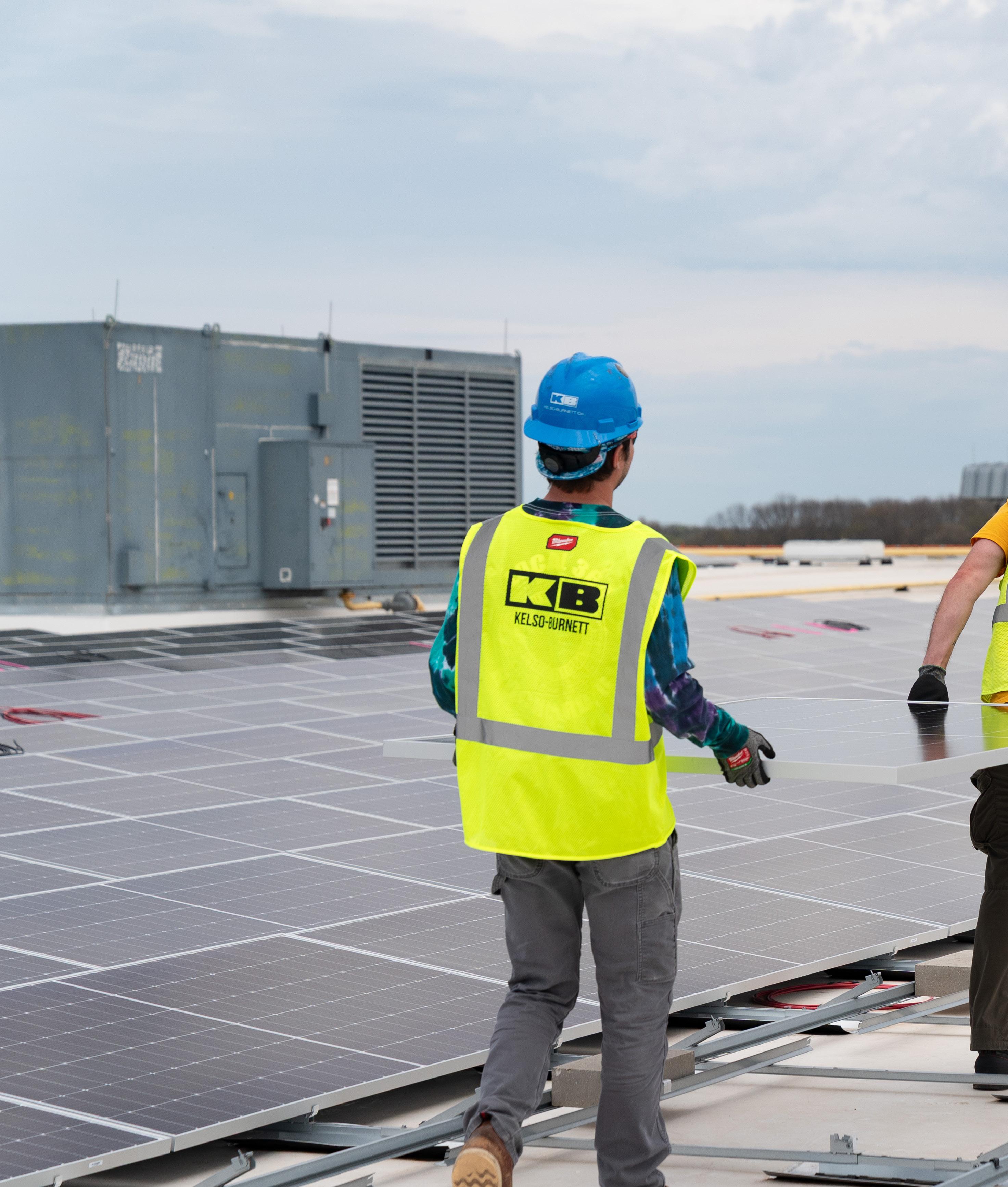
Celebrating over a century of service, Kelso-Burnett is a leader in the electrical contracting industry. President, Jeff Weir, emphasizes the importance of a customer-focused approach while broadening capabilities through strategic acquisitions and maintaining a commitment to employee ownership
Writer: Rachel Carr
Project Manager: Ben Weaver
Chicago, the third-largest city in the US, is known for its unique architecture, cultural contributions, rich historical background, and deep-dish pizza.
It is also home to Kelso-Burnett, an esteemed premier electrical contractor established 117 years ago in 1908.
After over a century of growth, the company currently employs approximately 600 bargaining and non-bargaining employees, with branches primarily operating in Illinois (IL) alongside an office in the neighboring state of Wisconsin (WI).
It is in Chicago, the state’s biggest city and part of the metropolitan area
informally known as Chicagoland, that the Kelso-Burnett story began. Incorporated during a time when gas streetlamps were being converted to incandescent light bulbs, Kelso-Burnett played an essential role in the switch over. The transition to electric lighting had a significant impact on Chicago, transforming the nighttime environment and improving public safety.
Thomas Edison’s incandescent bulb eventually replaced gaslights, gradually becoming a standard feature. Advances in electric technology, such as the development of more efficient bulbs, made electric
lighting increasingly attractive, securing the company’s longevity.
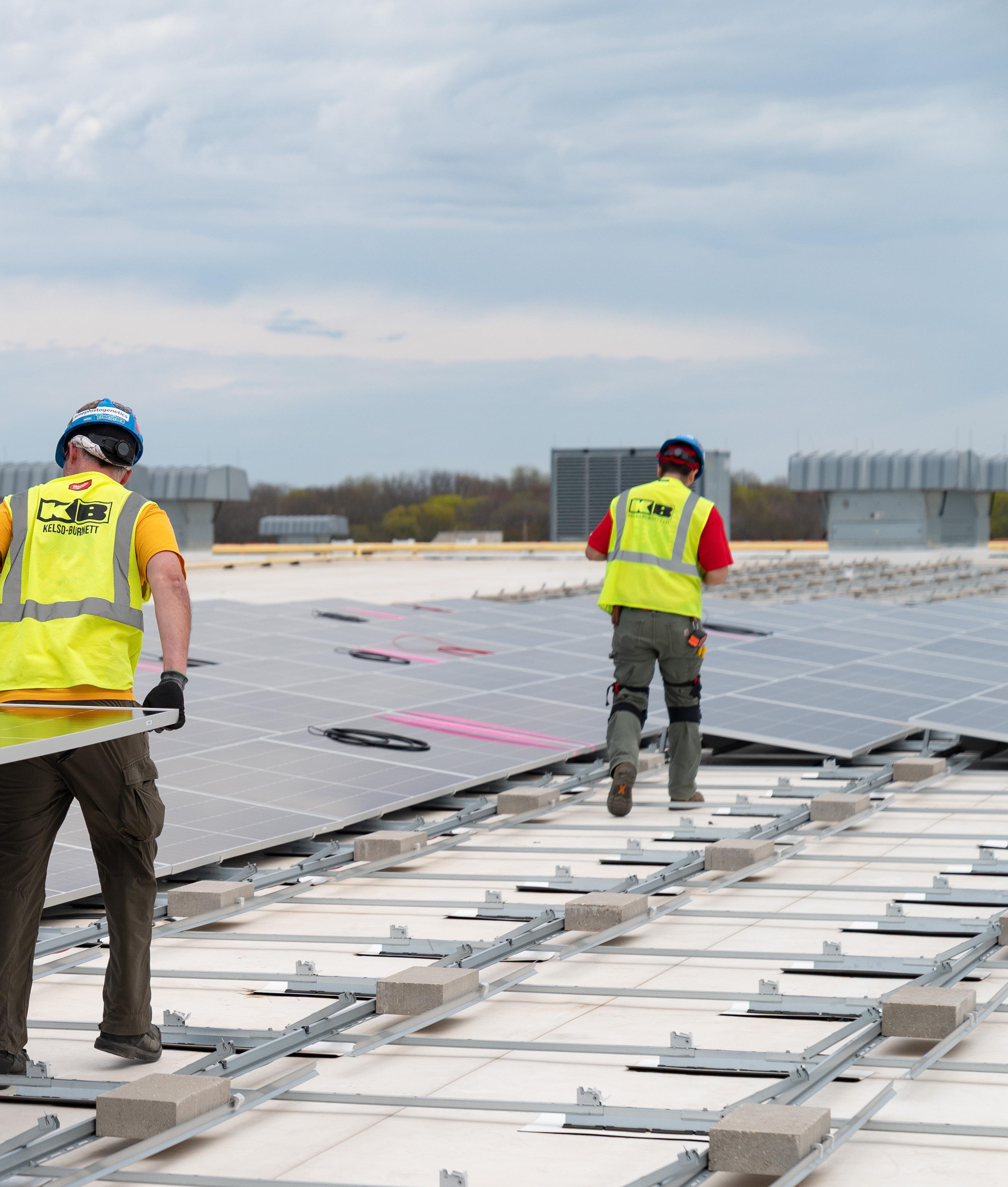
“We have the 15th-ever Chicago Electric License and we’re extremely proud of our long-standing relationship with the city,” opens Jeff Weir, President of Kelso-Burnett.
“As a full-service electrical contractor focusing primarily on commercial, industrial, educational, hospitality, healthcare, and institutional clients, we don’t chase projects or, in many cases, vertical markets. Instead, we’re extremely customer-centric, meaning we prioritize relationships over individual projects and follow our customers wherever they go,” he continues.
EMPOWERING OWNERSHIP
AND EXPANDING CAPABILITIES
Kelso-Burnett has employed more Presidents of the Electrical Contractors’ Association of Chicago than any other company in the organization’s history.
This includes Oliver Burnett Jr., John McLaughlin Jr., Terry Butz, and Brad Weir. In 1988, the company transitioned to an employee stock ownership plan (ESOP), and today it is 100 percent employee-owned.
“The employee-owned element of our company makes a difference to the team regarding project collaborations. The ESOP is a significant part of our culture, encouraging every person to think like an owner, because they are.
“Even though we have a traditional 401(k) program, our ESOP has been tremendous in providing additional wealth in retirement. All of us are the beneficiaries of our hard work, and 100 percent of the profits go back to each of us. I’m proud of our culture –people tend to rally around people, projects, or even struggling teams,” Weir provides.
Kelso-Burnett accounts for about 85 percent of parent company Newport Industries’ revenue.
Other businesses under Newport Industries include KB Advanced Technologies, Contech The Fire Alarm Company (Contech), Denny’s Fire Extinguishers, Entry Control Integrators (ECI), Ballard Engineering, and Pro Com Systems.
“Our holding company recently acquired ECI, meaning we’re now able to furnish and install automated gate systems. We also recently became a signatory with the Laborers and Operating Engineers Unions in order to self-perform ground mount and rooftop solar projects,” Weir outlines.
“Additionally, Contech recently became a signatory with the Sprinkler Fitters Union so they can now do inspections for fire alarms, extinguishers, and pumps, as well as sprinklers.”
ADAPTING TO MARKET CHANGES
Kelso-Burnett is keen to continue reinforcing what has ensured the company’s success for over a
WHAT DOES KELSOBURNETT DO?
• Commercial
• Industrial
• Healthcare
• Energy solutions
• Utility
• Institutions
• Conveyor systems
• Data centers
• Interiors
• Design engineering
• Prefabrication
• Virtual design and construction services
• Retail
century – being hyper-focused on its customers.
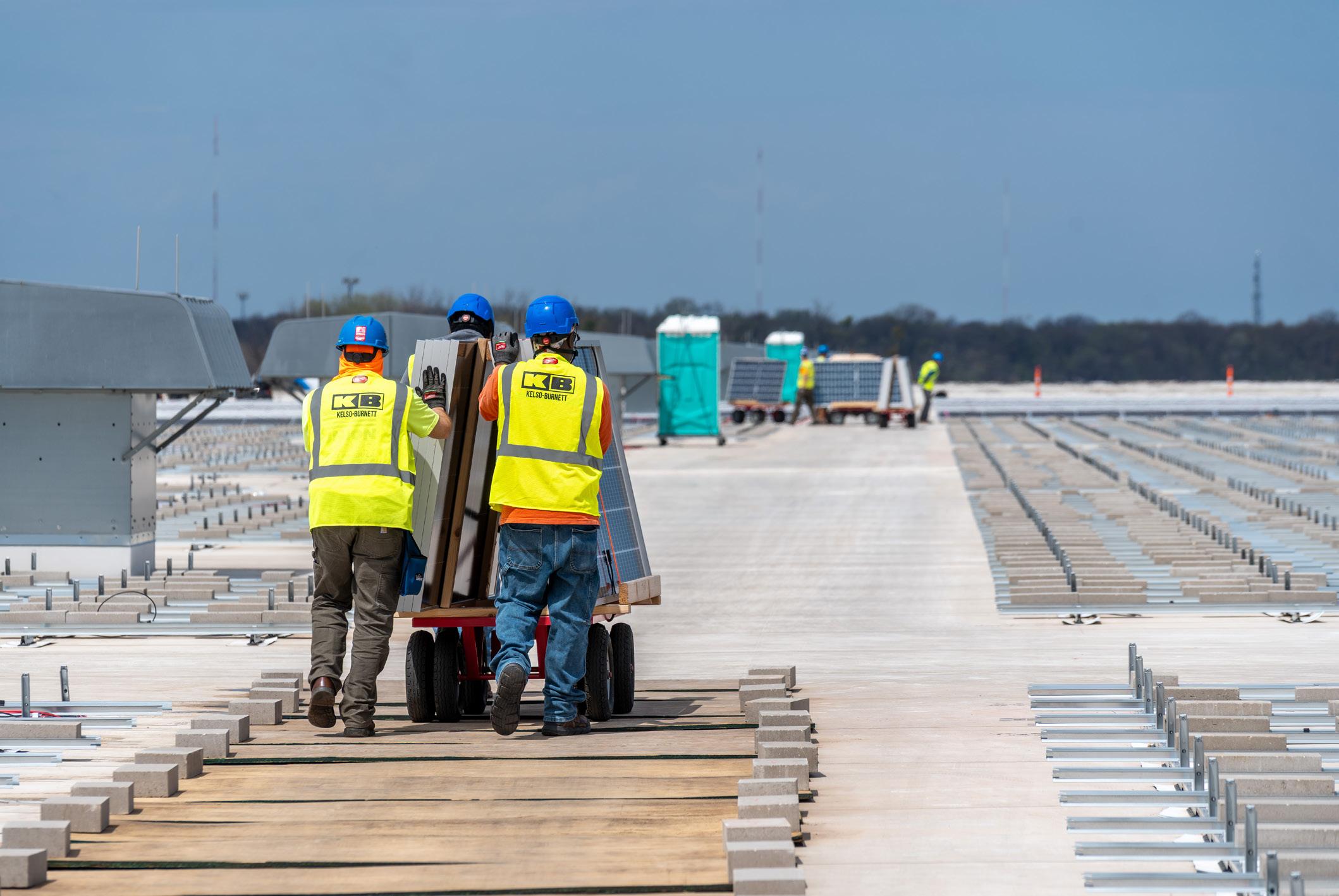
“I’m hoping to strike a balance between hot vertical markets like data centers and renewable energy while not losing focus on our legacy customers.
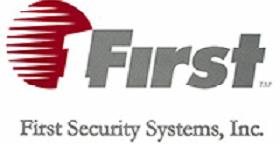
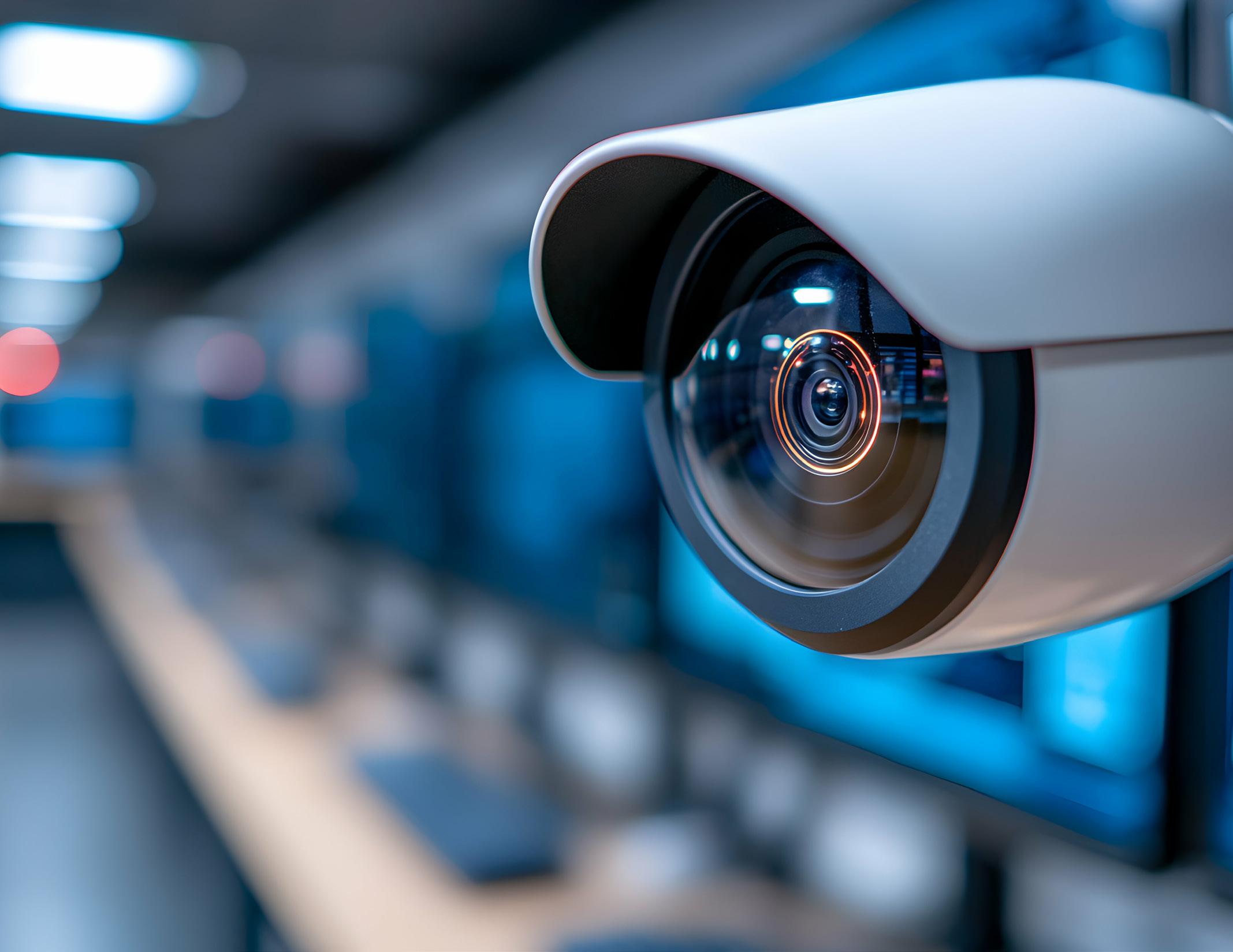
ABOUT FIRST
First Security Systems, Inc was founded in 1980 with a staff of two, and specializing in fire detection systems. Now, 33 years later, FIRST has grown to become a full service company providing best-inclass technological infrastructure solutions to the greater Chicago area and Northern Illinois. We are located in Naperville, Illinois.
As the area-wide leader among low voltage solutions providers, FIRST serves the marketplace through three divisions: healthcare communications, fire detection, security, and educational communications. Our reputation for delivering the highest quality technology solutions is reinforced by our total commitment to customer satisfaction. FIRST is a team of specialized professionals in whose combined education, experience and expertise come together to create custom strategic technology solutions. We specialize in design, project management, and installation of electronic systems for a wide range of applications.
Our success is due largely to the fact that customer satisfaction has remained our top priority over the years. In fact, we have built our reputation on it, as our clients will attest.
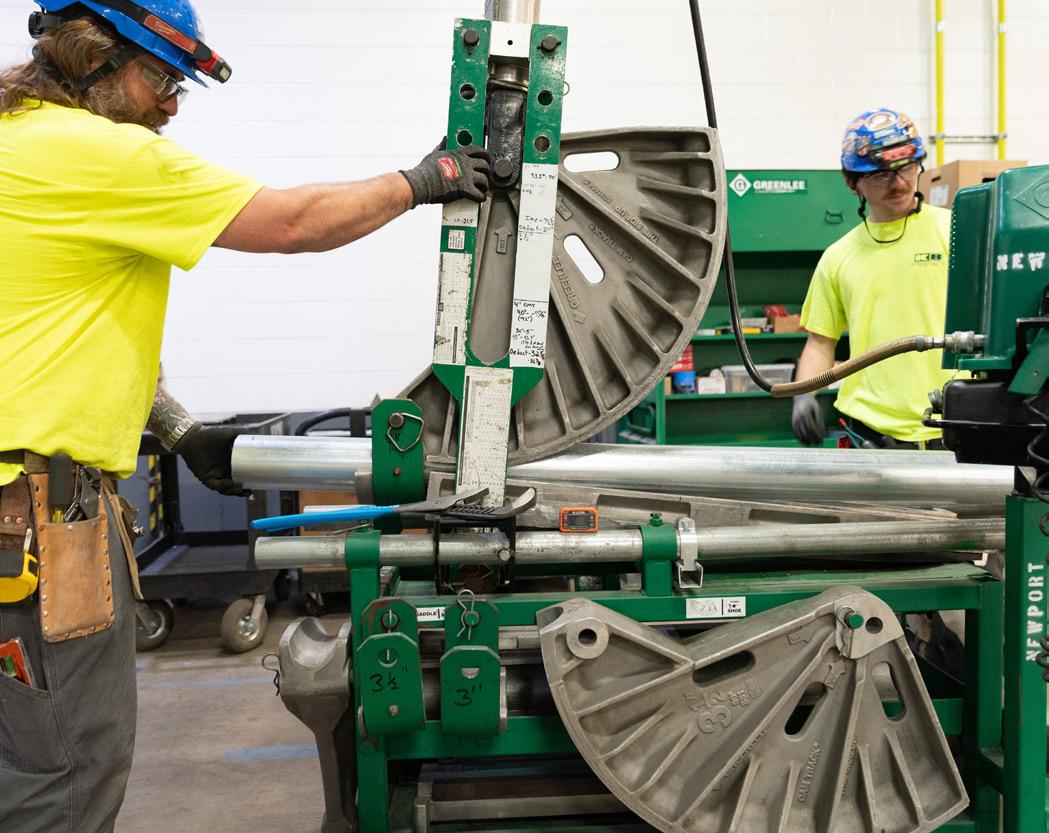
KELSO-BURNETT PROJECTS
• KELLOGG SCHOOL OF MANAGEMENT – KelsoBurnett completed the Global Hub at Northwestern University’s Kellogg School of Management several years ago. It is one of the largest and most complex projects the company has undertaken, and Weir believes its past performance played a big part in being selected.
• LINCOLN KING – Kelso-Burnett took a very conservative and patient approach to growing into the Southern WI market, and this is its largest project award to date.
• NAUTILUS SOLAR – The company has been awarded four ground-mounted solar systems in four different counties in Northern II by Nautilus Solar.
• TENANT INTERIORS –Many renowned Chicago organizations have confidently chosen Kelso-Burnett to carry out their interior projects, from headquarters and office buildouts to tenant renovations. KELSO-BURNETT
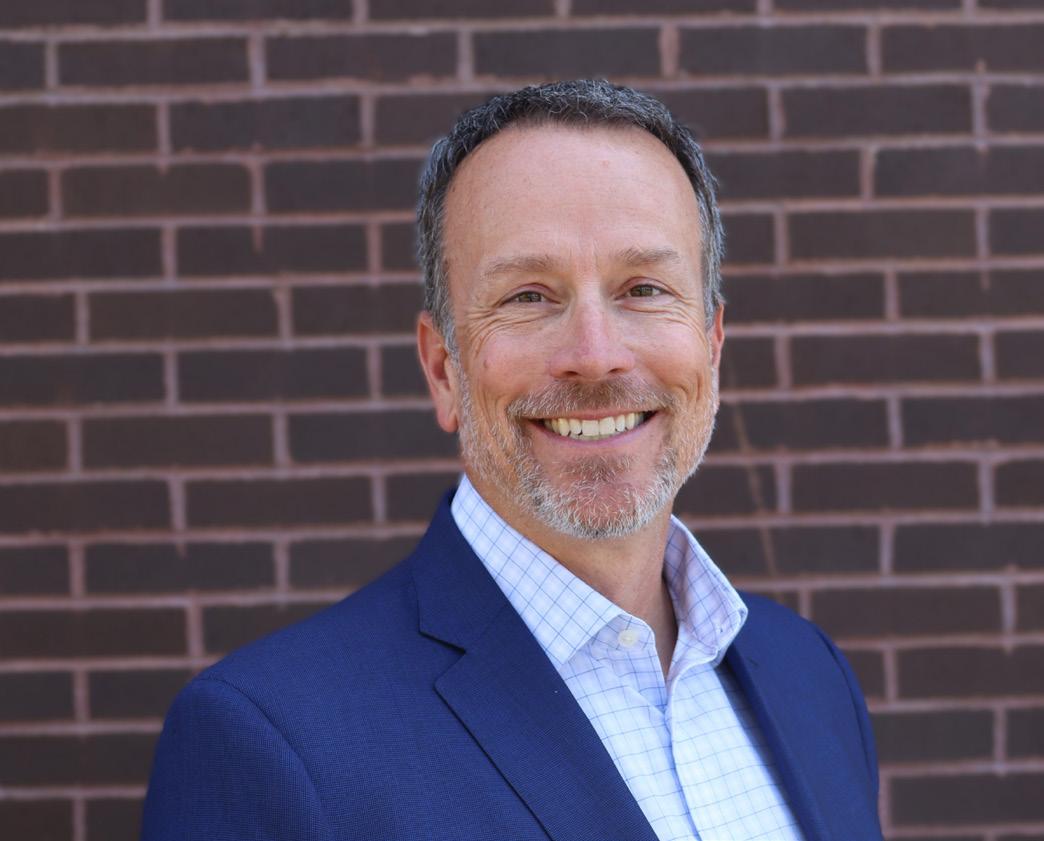
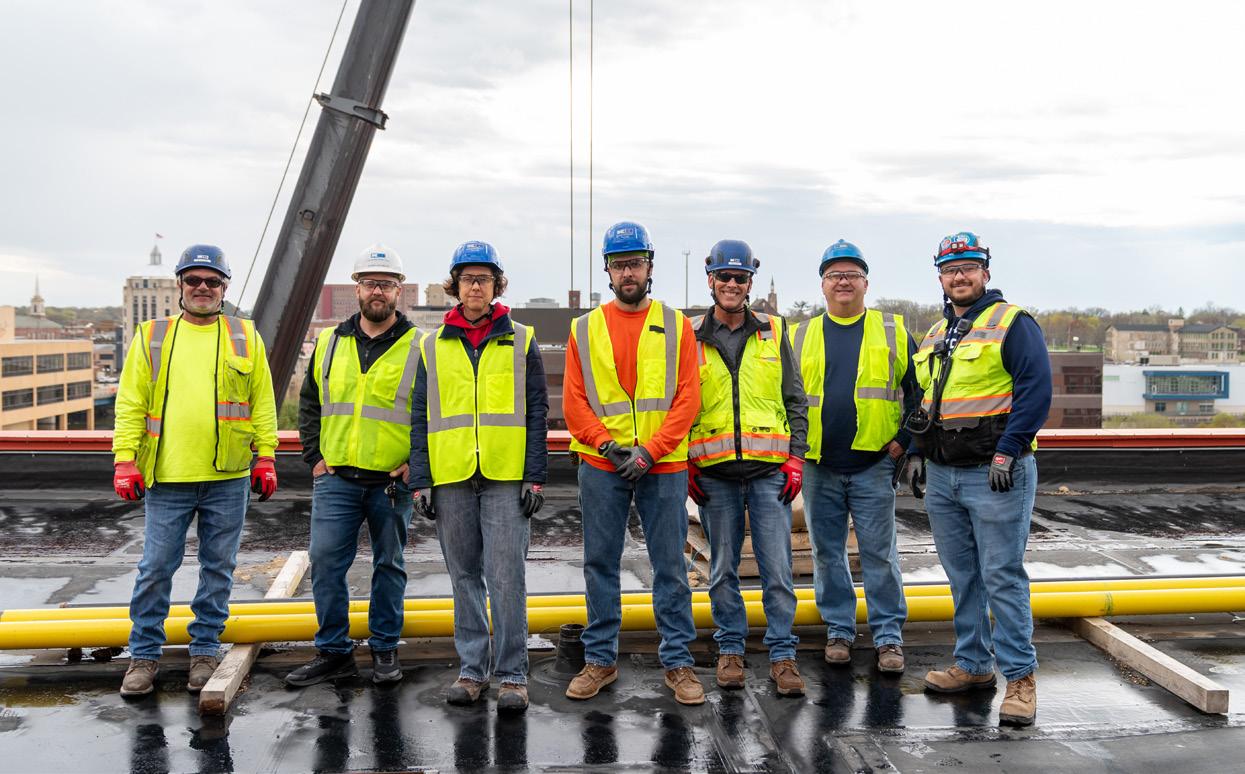
I want to avoid becoming overweight in any single vertical or geographical market; that diversity has proven successful even when the market has gotten difficult,” explains Weir.
Chicago’s downtown interior market took a massive hit during the COVID-19 pandemic, a traditionally robust sector for Kelso-Burnett.
“What we lost in the tenant interiors market, we offset in conveyor integrations, where we have a national portfolio.”
Kelso-Burnett also continues to make investments in technology in an
effort to be as efficient as possible.
“Like many construction companies, we are facing a labor shortage, particularly in the more rural areas of Northern IL and Southern WI. During the holidays, I discovered a project manager manual from the mid-1980s in an old banker’s box; it was fascinating to see that the core principles of project management have remained unchanged for nearly 40 years.
“The manual included a section on how to order materials, detailing that the project manager needed
“THE EMPLOYEEOWNED ELEMENT OF OUR COMPANY MAKES A DIFFERENCE TO THE TEAM
REGARDING PROJECT COLLABORATIONS”
– JEFF WEIR, PRESIDENT, KELSO-BURNETT
to read the specifications, process submittals, provide a job number to the purchasing department, and more. While the methods of delivering this information have become more efficient, the fundamental processes remain the same,” he fondly reminisces.
Weir repeatedly emphasizes the concept of balance, cautioning that Kelso-Burnett must not become overly reliant on technology at the expense of the fundamental principles that underpin effective project management.
NAVIGATING OPPORTUNITIES
The electrical contracting landscape in Chicago is uniquely dynamic and vibrant, with a wealth of skilled electrical contractors in the market.
Despite the competitive nature, Kelso-Burnett finds opportunities to collaborate, forge partnerships, and share invaluable best practices with industry giants.
“Sometimes, I take Kelso-Burnett’s recognition and reputation in the Chicagoland market for granted. Even though we’ve not worked for every single general contractor, I cannot remember a scope review that I’ve
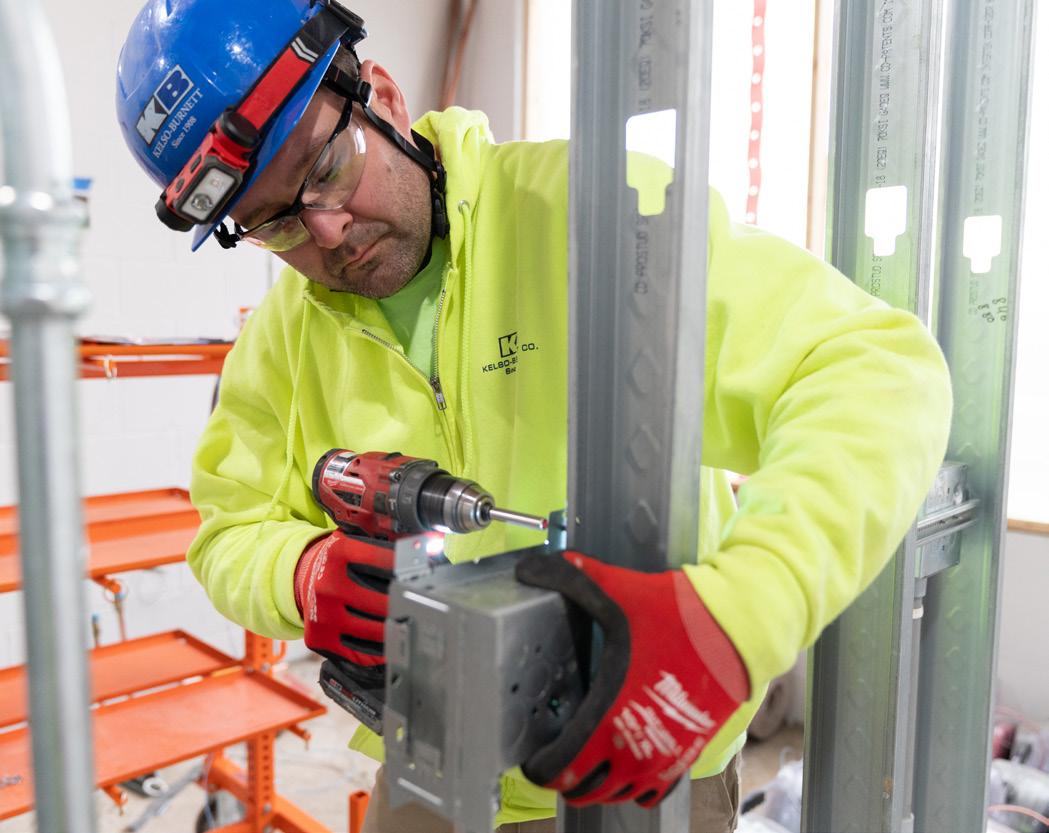
had to introduce to our company,” shares Weir.
“The electrical contracting market in Chicago is, to me anyway, special. There are a lot of talented electrical contractors in the area.”
Weir’s reflections highlight the unique position of Kelso-Burnett in the competitive landscape of the Chicago electrical contracting market.
As the industry evolves with numerous large-scale projects on the horizon, he remains optimistic about the potential for growth and collaboration within this energetic sector.
“There are several large projects in Northern IL, and while we won’t be part of all of them, the future is extremely bright. Between several large data centers, casinos, community and utility solar portfolios, and maybe a couple of new stadiums, the work is unlikely to wane anytime soon,” concludes Weir optimistically.
As Kelso-Burnett looks toward another century in business, it remains committed to the foundational principles of customer-centricity and innovation.
With a diverse portfolio and a strong emphasis on employee
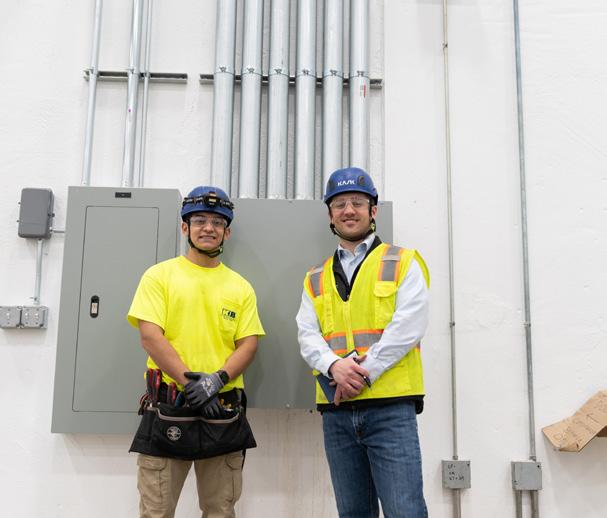
ownership, the company continues to adapt to the evolving market while honoring its rich legacy.
By embracing new technologies and expanding its capabilities, KelsoBurnett is well-positioned to meet future challenges, ensuring that it continues to illuminate Chicagoland and beyond while setting a standard for excellence in the electrical contracting industry.
www.kelso-burnett.com
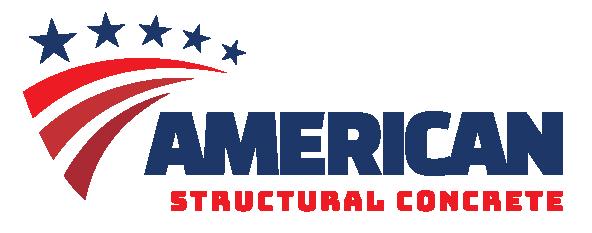
BUILDING THE FUTURE TOGETHER
Bringing clients’ visions to life through proven industry experience and leadership, American Structural Concrete is a trusted and reliable construction partner. Jeremy Cantrill, Senior Vice President, lays the foundation to tell us more
Writer: Lauren Kania | Project Manager: Ben Weaver
Having proudly constructed some of the most recognizable concrete structures in the Southeastern US, American Structural Concrete (ASC) is an industry stalwart boasting over 30 years of dedication, professionalism, and innovation.
A knowledgeable consultant, trusted partner, and sector leader, the company is dedicated to completing projects on time and on budget, positioning itself at the forefront and participating in some of the largest and most ambitious jobs in the country.
“ASC is a leading provider of structural concrete solutions, specializing in the construction of commercial and industrial structures,” introduces Jeremy Cantrill, Senior Vice President.
“We pride ourselves on employing a dedicated team of professionals committed to delivering high-quality, durable concrete structures.”
Headquartered in Atlanta, Georgia, with another office in Charlotte, North Carolina, the company offers a comprehensive range of services, including design, construction, and project management, alongside serving a diverse client base across multiple states.
Cantrill was introduced to the construction industry at an early age, having grown up with his father and grandfather working in the sector. He eventually pursued a degree in construction management, during which he participated in an internship program that became a vital piece of his education.
“Being able to work in the field gave me the information I needed to seamlessly transition to a career in the industry. The process of performing every duty along the way provided me with knowledge I’ve used at every level of my career,” emphasizes Cantrill.
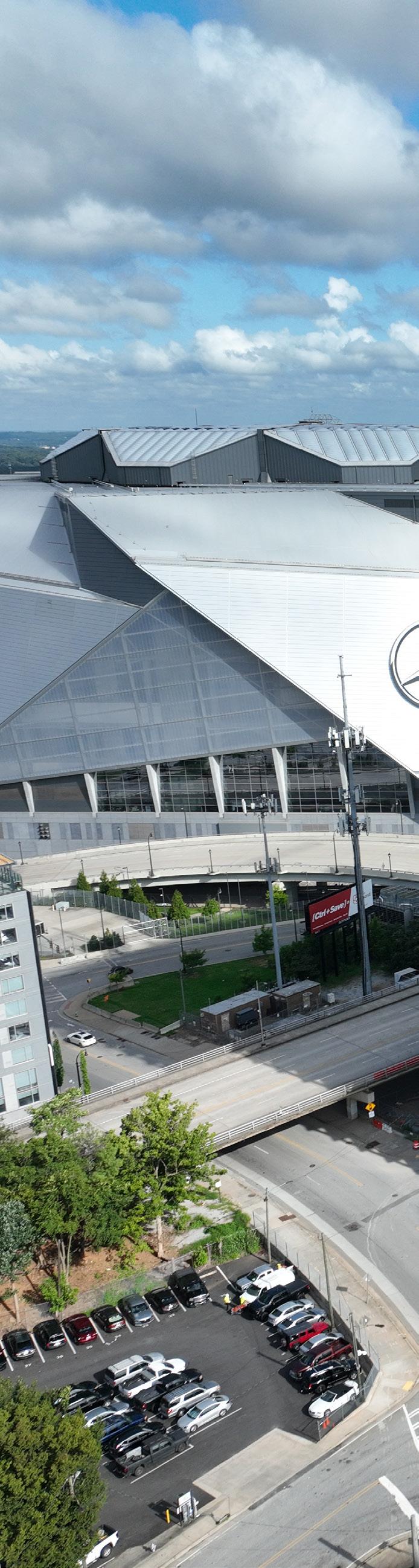
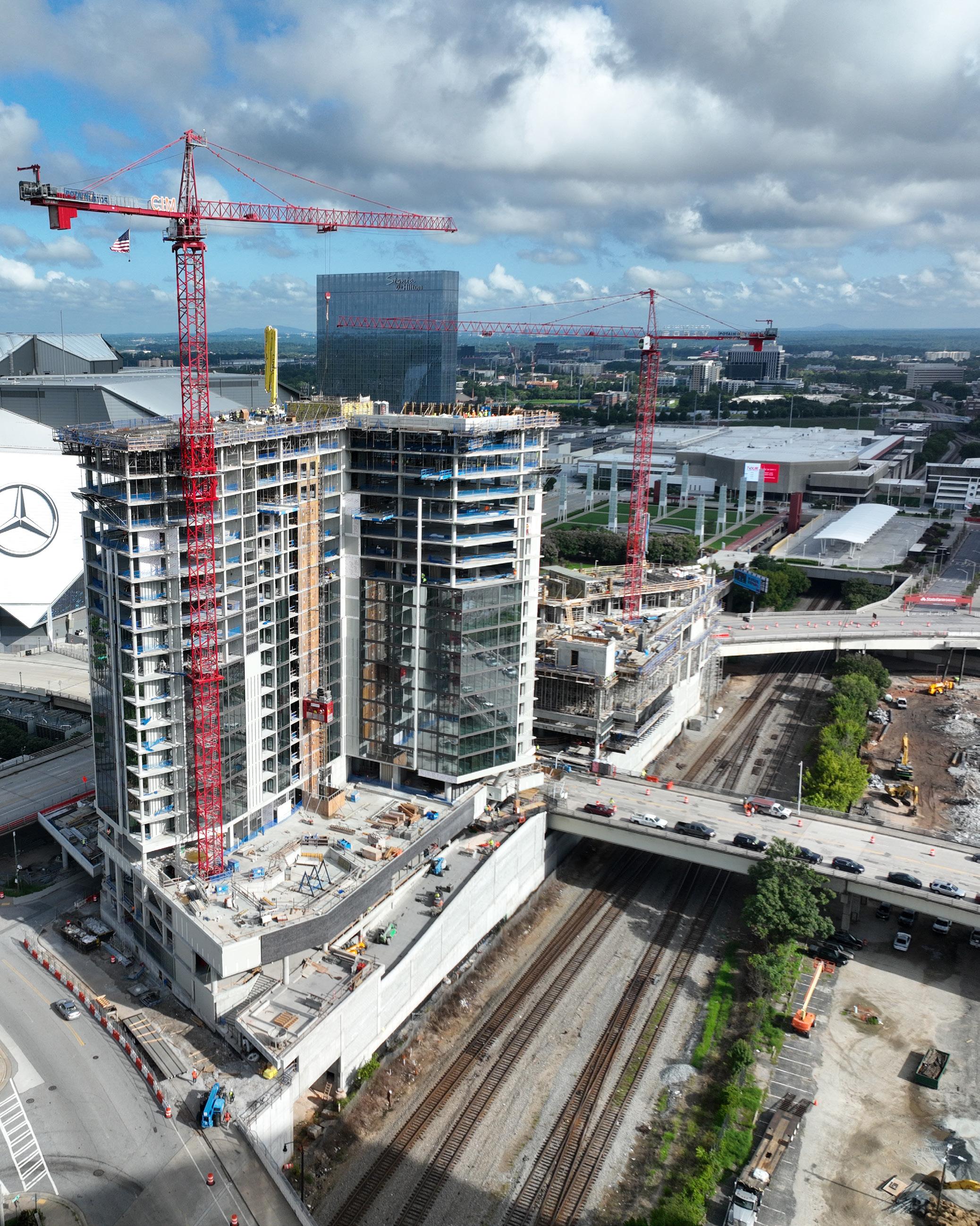
This hands-on experience and lifelong involvement in construction have allowed him to bring unparalleled expertise and passion to ASC, helping to expand its footprint and become a household name in concrete.
What truly serves to set ASC apart from the rest is its unwavering commitment to quality and customer satisfaction.
“We leverage cutting-edge technology and innovative construction techniques to deliver superior results. Our dedicated team, attention to detail, and ability to customize solutions to meet specific client needs further distinguish us,” he prides.
A PROVEN INDUSTRY LEADER
Currently, Cantrill observes the modern construction industry as one undergoing significant challenges.
“The sector has historically experienced ups and downs with periods of influx and periods when the work seems to be on hold,” he insights.
“We are currently experiencing one of the downs in the market, which I believe can be attributed to several factors, including increasing financing costs, unstable material prices, and the ongoing after-effects of the COVID-19 pandemic.”
While the market is slow, ASC anticipates a pivot toward more projects and revenue. This anticipation can make the industry challenging; however, it is also exciting, testing the best while weeding out the weak, making the market even more attractive.
To be ready for this upturn, the company is actively positioning itself at the forefront of structural concrete construction and accomplishing what it promises to its clients.
“Every project has its challenges, some expected and some unexpected. We develop a plan to execute every project from the beginning, which leads to a commitment and result for the client,” insights Cantrill.
ASC provides its customers with the confidence that it will tackle all these challenges with commitment and determination, believing it to be the best way to position itself at the top.
Additionally, the company works to align with its customers’ goals to bring their visions to life.
It recognizes that, especially during a slower period in the market, owners have a budget vital to a project’s life. This is both short-term – during the construction phase – and long-term –in the maintenance of the building.
“Our in-house team is wellexperienced in identifying aspects that have been incorporated into the
CAN YOU TELL US MORE ABOUT THE IMPORTANCE OF PARTNER AND SUPPLIER RELATIONSHIPS AND THE SUCCESS THEY’VE AFFORDED?
Jeremy Cantrill, Senior Vice President: “I believe when companies talk about the success they have, they often reference a single person or job, but one of the most important pieces to our success is our relationship with our subcontractors and suppliers.
“These partners and the communications we continue to develop and build can often have significant impacts on the success of our projects. From communications to developing an understanding of pricing to scheduling during the preconstruction phase, it is critical, especially during erratic times in the market when pricing is unstable.
“Good communication with those partners allows us to have a positive rapport with our clients as we continue to develop the confident relationship with them that we strive for.”
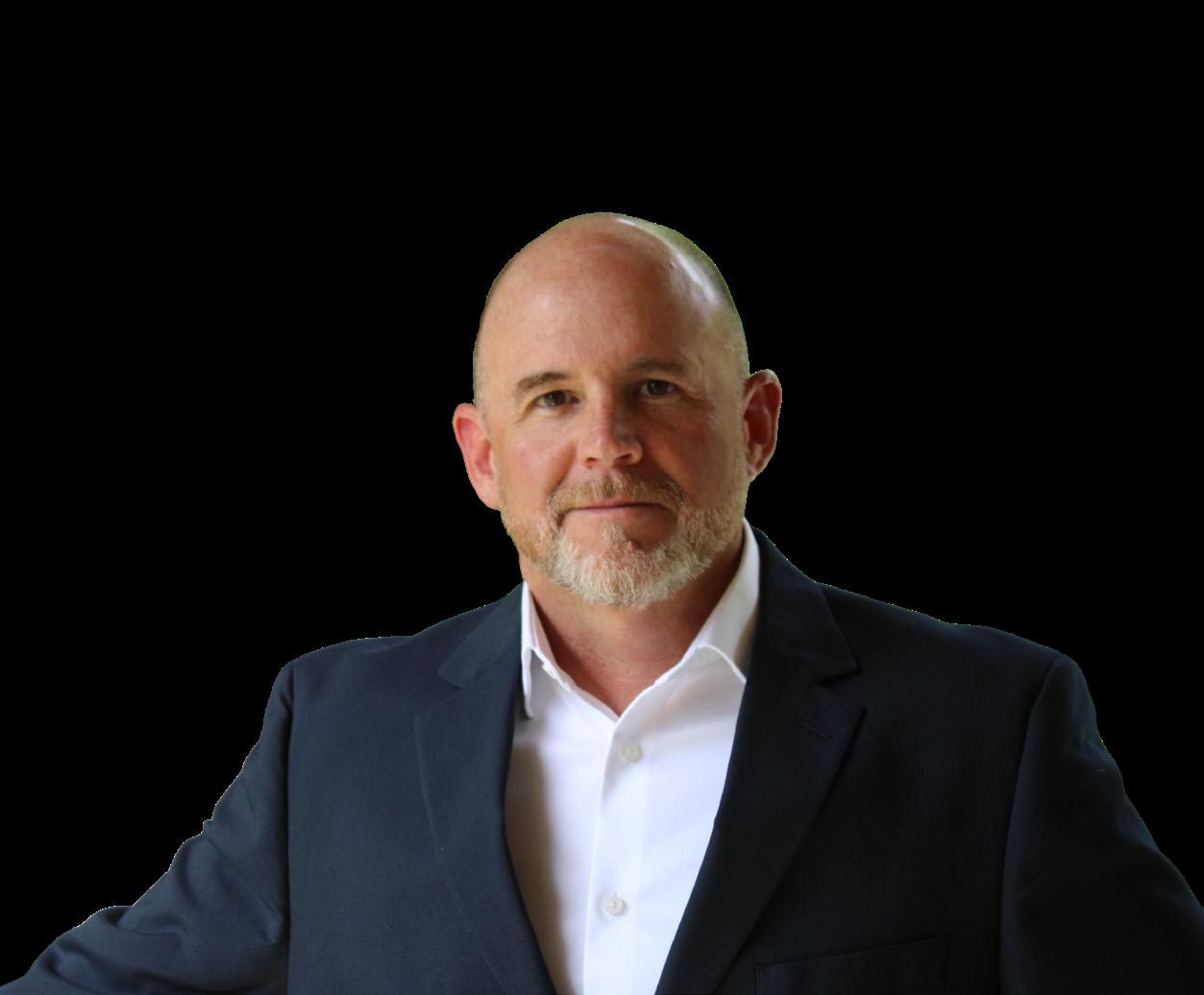
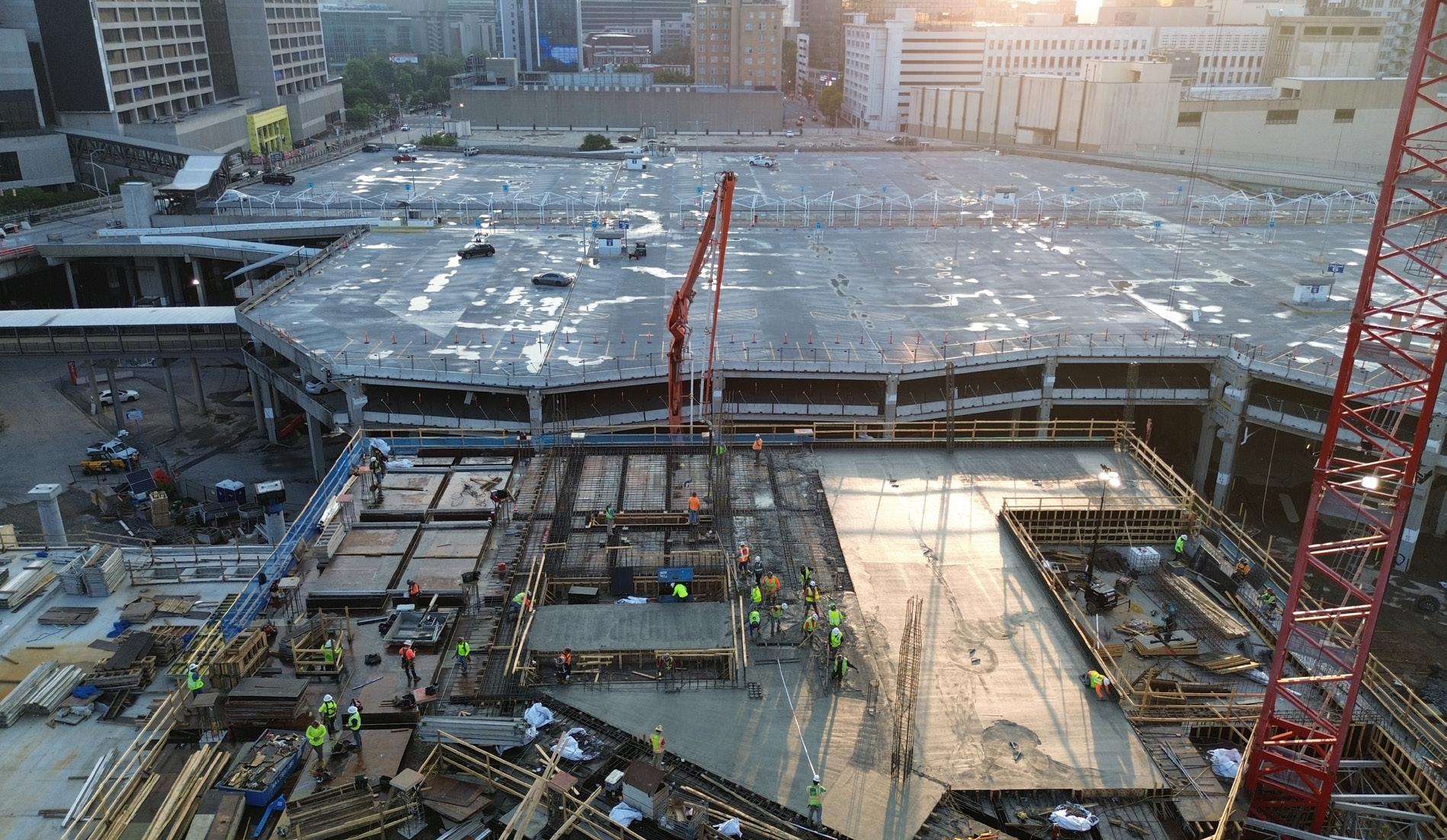
project and could benefit financially from an alternative method or material,” details Cantrill.
“With our traditional turnkey and tilt-up projects, we try to focus on cost savings through the design of the project, finding alternates to give clients as many choices as possible to improve their budget without impacting the value of the project.”
SEASONED AND EXPERIENCED PROFESSIONALS
One of ASC’s continuous goals is to ‘build the future together’.
To achieve this, the company prides itself on its team of highly skilled, experienced employees who are always striving to be the best it can. Equally, when it pursues and builds a project, ASC wants the flow from preconstruction to construction to be as seamless as possible.
“We focus on a detailed plan upfront so when the project goes into full force, it runs smoothly and without major complications,” expands Cantrill.
Additionally, to showcase its commitment to clients, the company ensures their wants and needs are
“WE LEVERAGE CUTTING-EDGE TECHNOLOGY AND INNOVATIVE CONSTRUCTION TECHNIQUES TO DELIVER SUPERIOR RESULTS. OUR DEDICATED TEAM, ATTENTION TO DETAIL, AND ABILITY TO CUSTOMIZE SOLUTIONS TO MEET SPECIFIC CLIENT NEEDS FURTHER DISTINGUISH US”
–
JEREMY CANTRILL, SENIOR VICE PRESIDENT, AMERICAN STRUCTURAL CONCRETE
taken care of during preconstruction.
“We understand we are most often the main player for the structure of the project; however, we want to guarantee we understand and account for the client’s necessities post-structure. For that reason, we always feel we are building every project ‘together’ with all parties,” he continues.
ASC’s ability to work cohesively and seamlessly to produce its clients’ visions can be directly seen through some of the company’s recent projects, including the Jacksonville Shipyards project, the Centennial
Yards development, the University of Texas Southwest (UTSW) (UTSW) Psych Hospital Parking Garage project, and The Islands at West Bay project.
The Jacksonville Shipyards project in Florida (FL) consists of a massive footprint near EverBank Stadium, home of the Jacksonville Jaguars, and is the centerpiece of the revitalization of the area surrounding the stadium.
“With many projects slated for the future, this project has proved to be instrumental to our company’s success in the FL market,” details Cantrill.
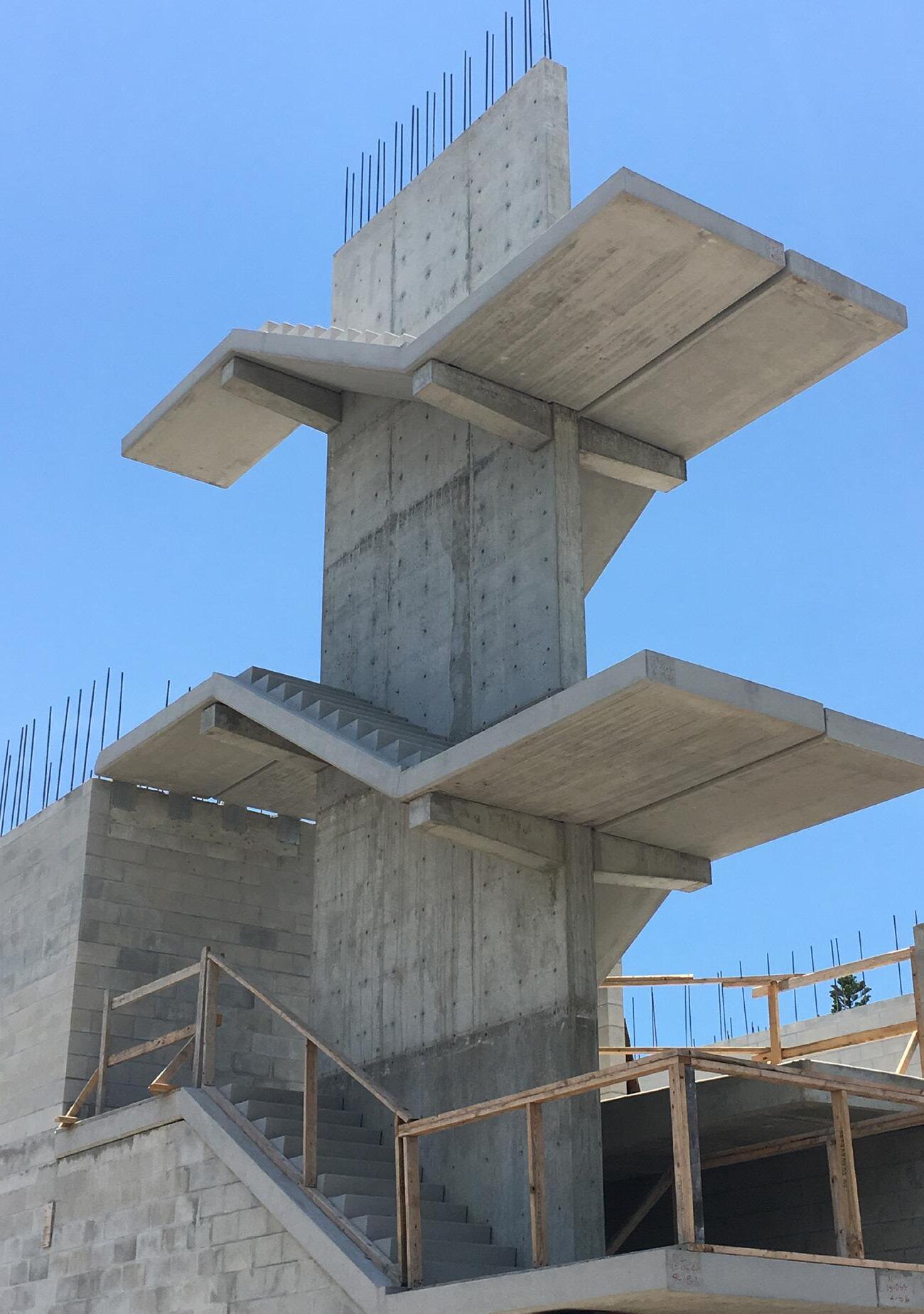
Established in 1996 and headquartered in Palmetto, Florida, Durlach Industries, Inc. has been a trusted name in the design and production of precast concrete stairs and landings. Founded under German-American ownership, we bring together European precision and American innovation to provide high-quality concrete solutions for residential, commercial, and institutional projects across the United States.
For nearly three decades, our mission has remained simple yet powerful: to deliver stair and landing systems with exceptional quality, reliability, and performance. Our products are custom-built to meet the diverse demands of our clients, offering flexibility in size, shape, finish, and application.
A Broad Range of Applications
While the majority of our precast stairs are used in large-scale commercial developments such as parking garages, high-rise buildings, hotels, stadiums, and multi-family housing, our expertise and versatility extend far beyond. Durlach Industries’ stairs have been featured in:
• Hospitals and medical centers
• Universities and academic facilities
• Municipal buildings and
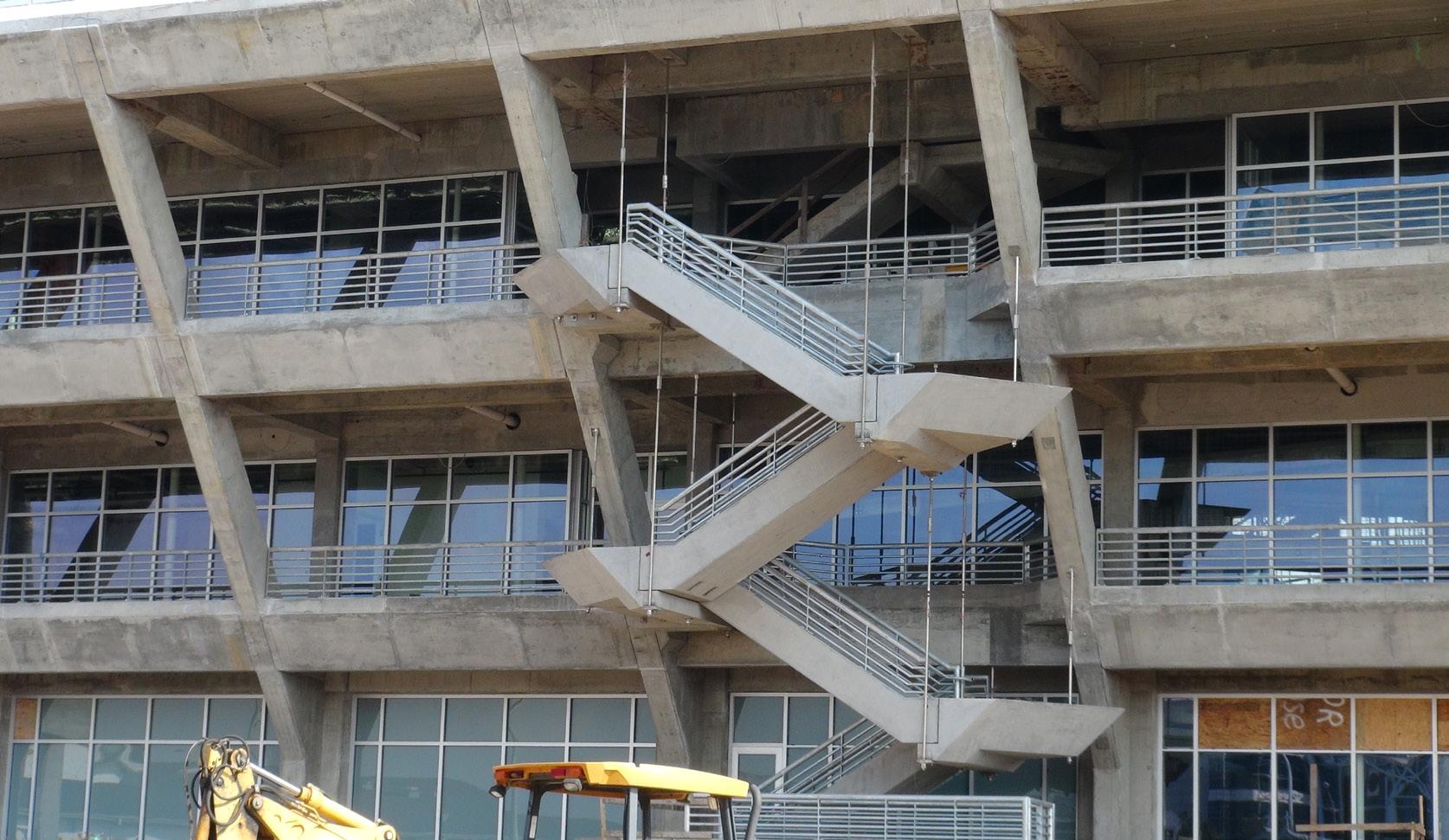
Inc.: Solutions Since 1996
• Assisted living communities
• Pedestrian bridges
• Luxury custom homes
Regardless of the project type, we build every piece to last - combining structural integrity with clean, consistent aesthetics.
Coast-to-Coast Delivery
Though our primary market is Florida and the Southeastern United States, we’ve proven our logistics capabilities by successfully delivering precast stair systems as far north as Long Island, NY, and as far west as Seattle, WA. Our nationwide reach is a testament to our efficiency, trusted partnerships, and dedication to meeting project timelines.
Cutting-Edge Manufacturing
In 2019, we transitioned into a new, expanded facility purposebuilt to accommodate our growing production demands. One of the most critical upgrades in this move was the installation of our own on-site concrete batch plant - a decision that gave us complete control over our mix designs, material quality, and manufacturing schedule. This investment means we can guarantee the strength, durability, and finish of our concrete with greater
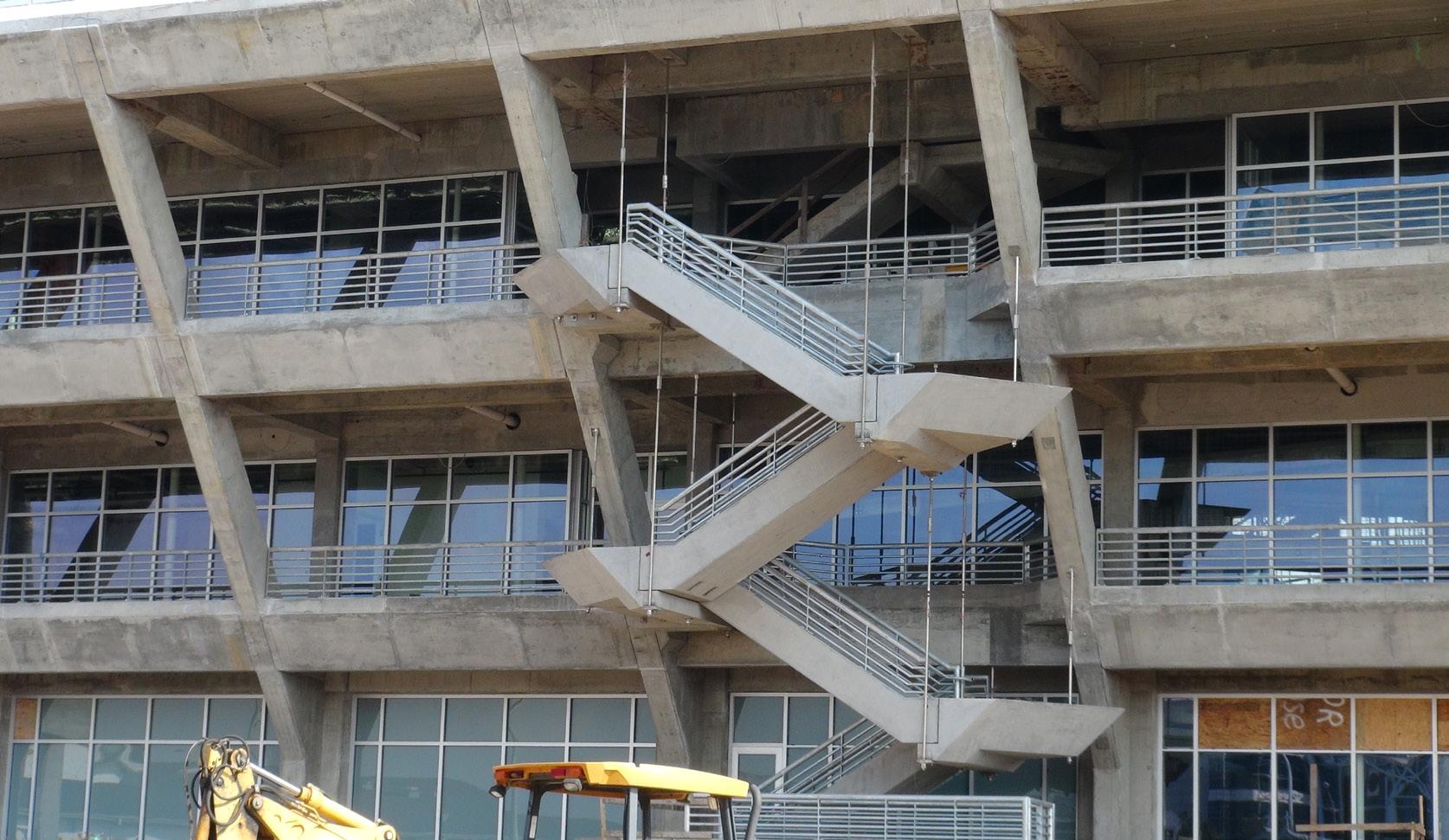
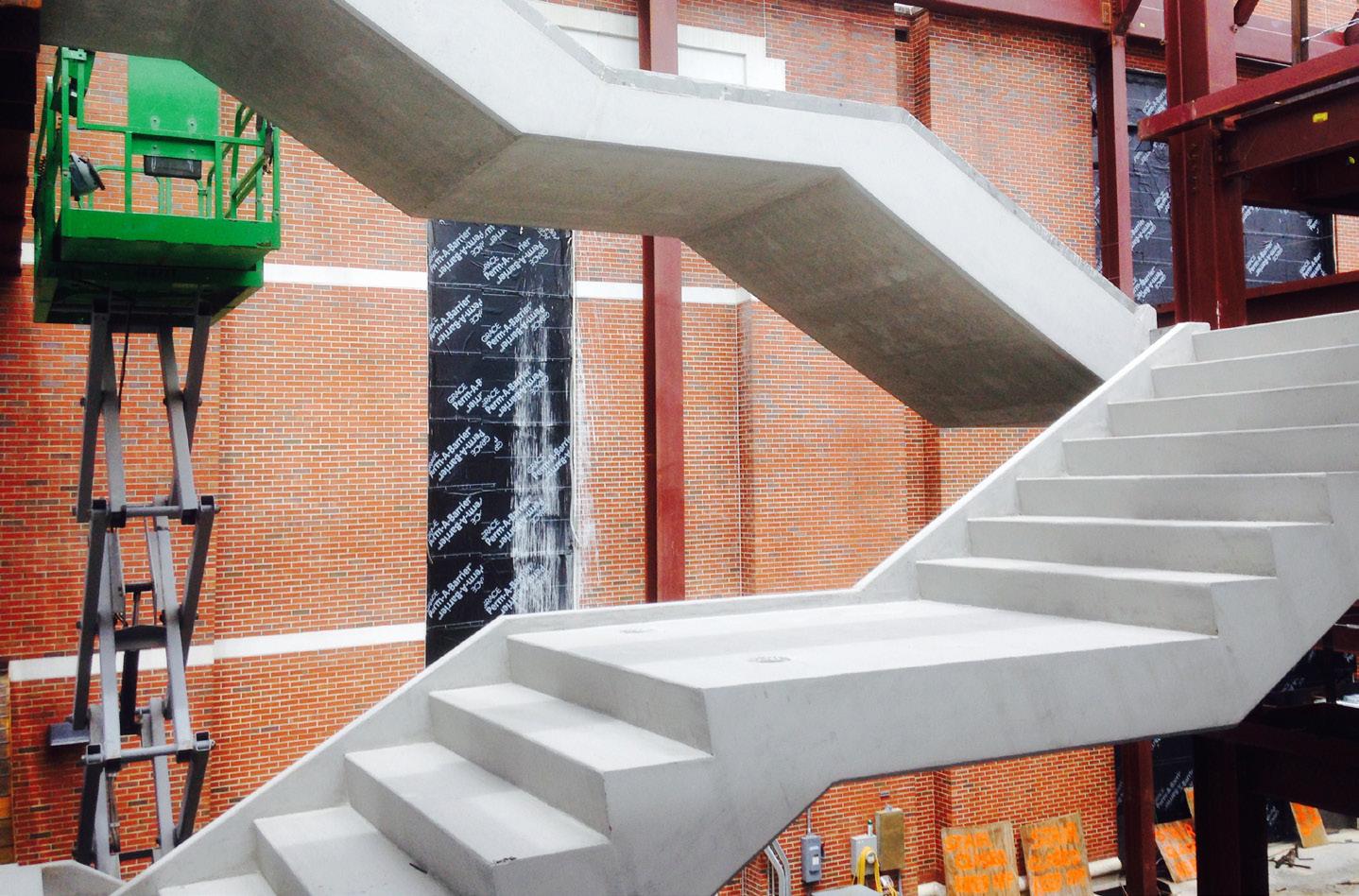
precision and speed than ever before. By managing the process from raw materials to final delivery, we maintain the highest standards of quality control throughout the entire supply chain.
Why Choose Precast Over Cast-in-Place?
Staircases are among the most safetysensitive and dimensionally demanding components in any building. With precast stairs, you’re getting:
• Dimensional accuracy from factorycontrolled molds
• Faster construction schedules thanks to just-in-time delivery
• Immediate usability - no curing, forming, or delays
• Cleaner worksites and fewer on-site labor requirements
• Consistency in appearance and quality from unit to unit
At Durlach, we don’t just supply stairs - we engineer, fabricate, and deliver complete stair solutions that streamline your construction process and elevate the final product.
Committed
to Consistency and Customer Success
Our clients count on more than just our craftsmanship - they trust our consistency, reliability, and follow-through. We understand that meeting a deadline is just as important as meeting a spec, which is why punctual delivery and clear communication are hallmarks of our operation. That’s why we’ve cultivated
long-term relationships with general contractors, architects, engineers, and precast manufacturers throughout the country.
A Proud Partnership with American Structural Concrete (ASC)
One example of our collaborative spirit is our ongoing partnership with American Structural Concrete (ASC). Since 2022, we’ve teamed up with ASC on several high-profile, architecturally ambitious projects that demanded precision and creativity. Together, we’ve demonstrated how seamless cooperation between suppliers and contractors results in efficient builds and standout results.
Durlach Industries, Inc. is proud to be a part of shaping America’s built environment - one staircase at a time. Whether you’re designing a public landmark or a private development, our team is ready to bring strength, elegance, and reliability to your project.
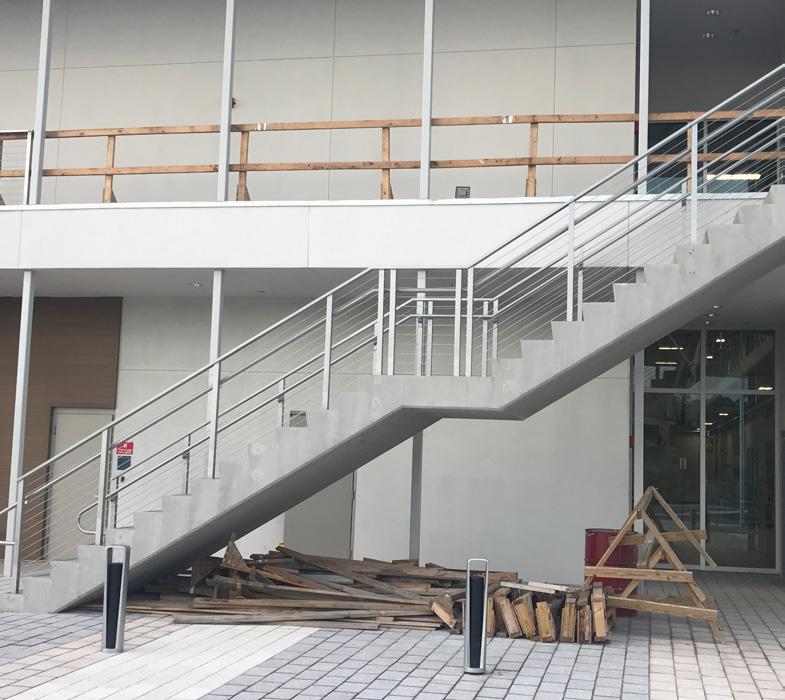
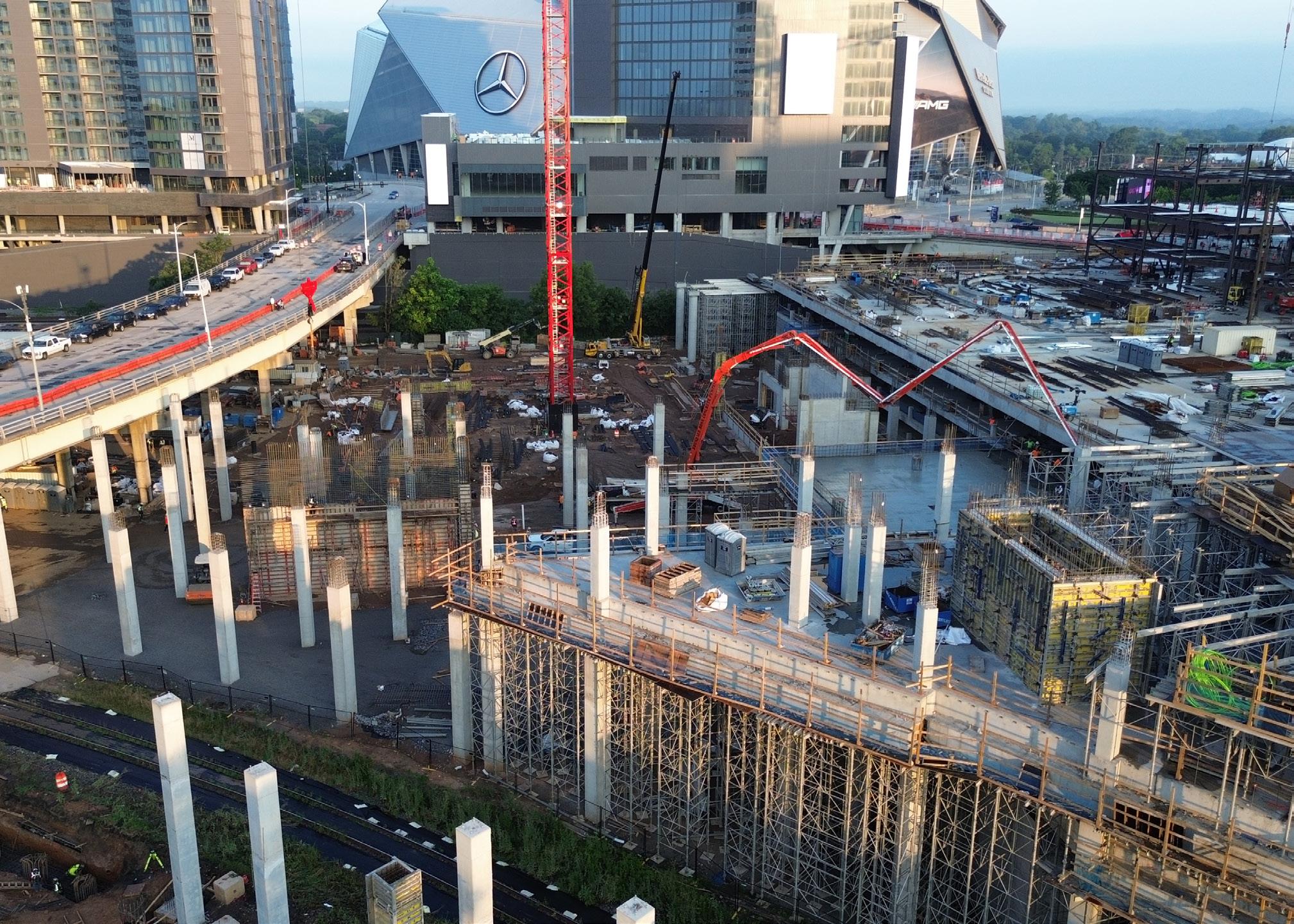
ASC CULTURE AND VALUES
The ability to keep its promise is what continues to drive the company’s success, and its clients sleep easy at night knowing their concrete partner is reliable and trustworthy.
Having great teams, clients, and partners makes all the difference. Even after millions of yards of concrete formed and thousands of years of collective experience, ASC continues to earn its stripes every day on all projects.
“WE PRIDE OURSELVES ON EMPLOYING A DEDICATED TEAM OF PROFESSIONALS COMMITTED TO DELIVERING HIGHQUALITY, DURABLE CONCRETE STRUCTURES”
– JEREMY CANTRILL, SENIOR VICE PRESIDENT, AMERICAN STRUCTURAL CONCRETE
The Centennial Yards development in Atlanta, Georgia, has continued to provide ASC with the opportunity to transform the city where it began. With more development in the planning, the company has proven that no challenge is too big through this project.
Highlighting the opportunity for alternate solutions to conventional parking garages, the UTSW Psych Hospital Parking Garage project
is where the company is currently constructing its hybrid parking garage system.
“Incorporating precast columns and beams with cast-in-place slabs not only provides the client with the benefits of a cast-in-place structure, but also allows the customer to reap the benefits of lower maintenance costs than the traditional precast garage system,” explains Cantrill.
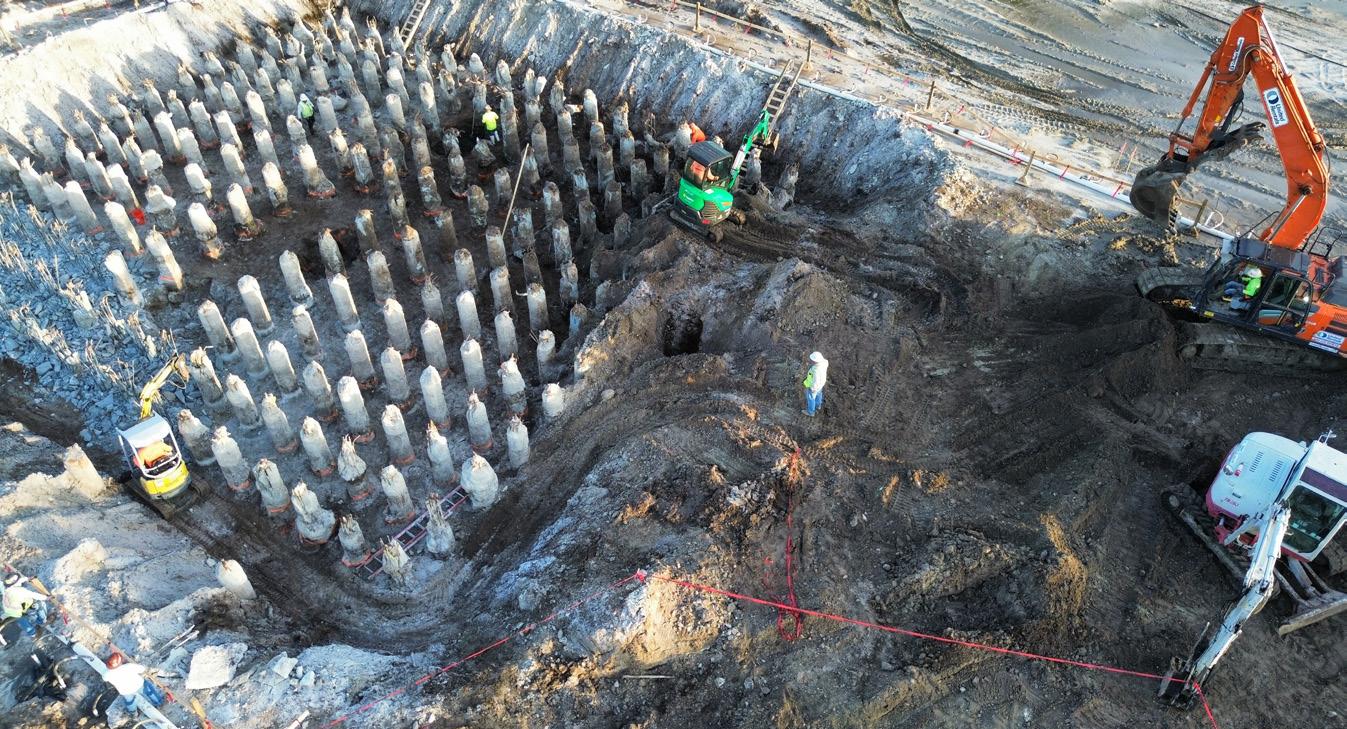
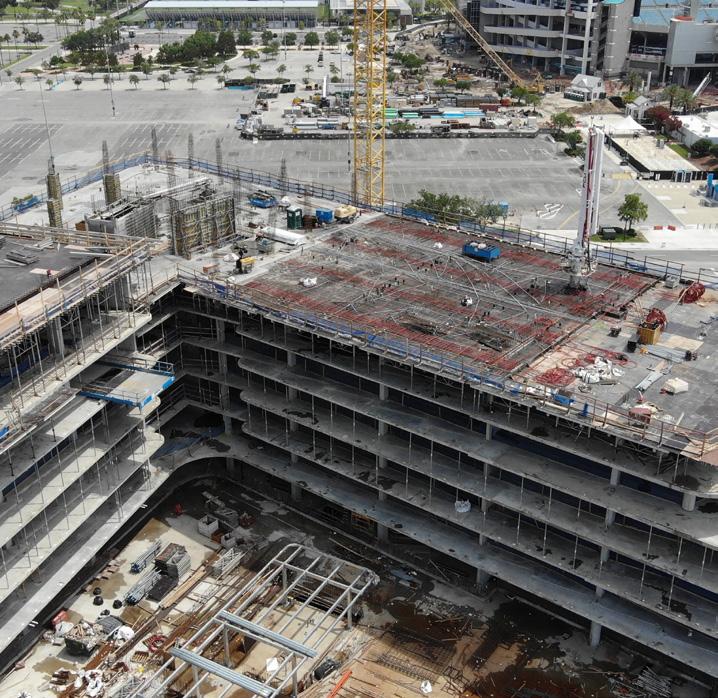
Finally, as an exciting upcoming project, The Islands at West Bay project in Estero, FL, provides luxury residential living with breathtaking views.
The 27-story high-rise allows ASC another opportunity to showcase its capabilities and deliver astonishing, high-end structures.
CONSTRUCTING A STURDY FUTURE
As ASC continues to look towards a further 30 years of success and innovation, it also recognizes the crucial importance its staff members play on a daily basis.
“Our staff is our lifeline to success. From preconstruction to operations to accounting teams, it takes commitment from everyone to produce projects that, in turn, make
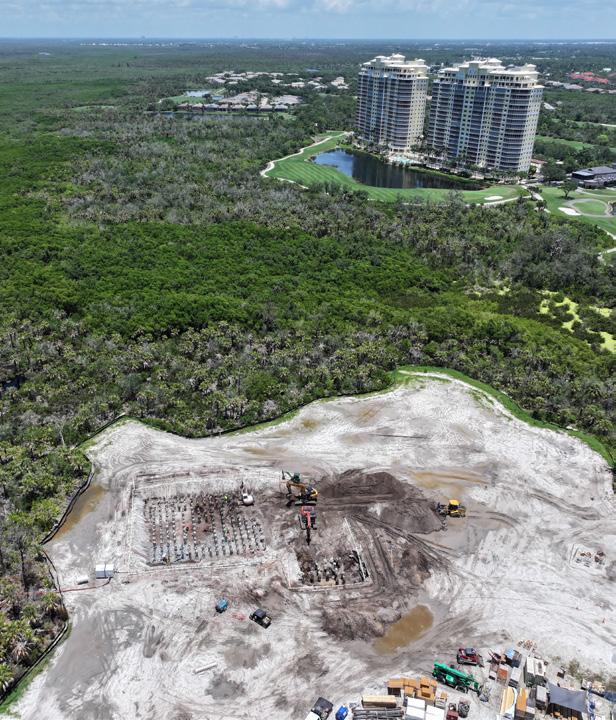
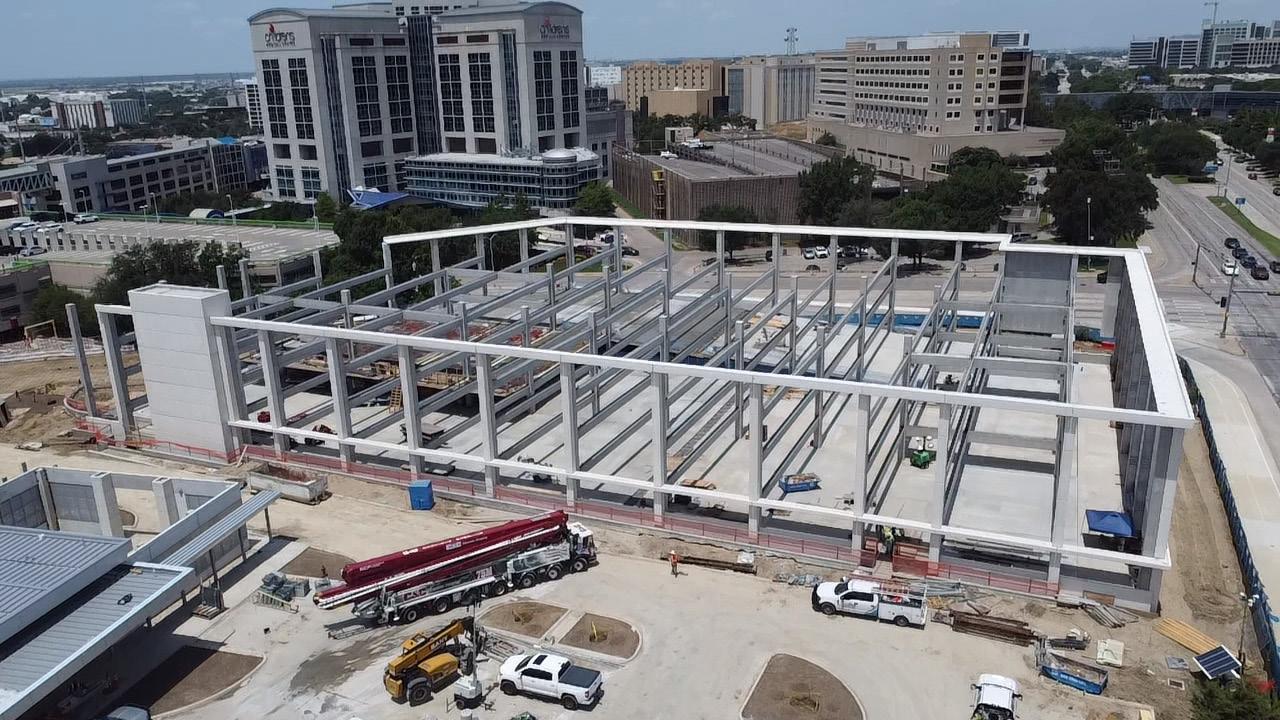
the company successful,” confirms Cantrill.
ASC takes pride in promoting from within to ensure all of its employees have the tools, capabilities, and experience to produce the best results, every time.
Through the development of incentivized programs to recognize employee contributions, the company wants staff to feel like they are an important part of ASC’s success – not only in terms of their individual projects but for the company as a whole.
In addition to building upon the success of its dedicated employees, ASC’s goals for the upcoming year comprise building on the achievements of its recent projects while growing as a company with an improved level of success.
“Our goals are to build upon that confidence and secure projects we feel are the best fit for our goals. Through the results of our recent endeavors, we have an understanding of the market, and with that, we can make smart business decisions to make the company successful in the short and long-term,” concludes Cantrill.
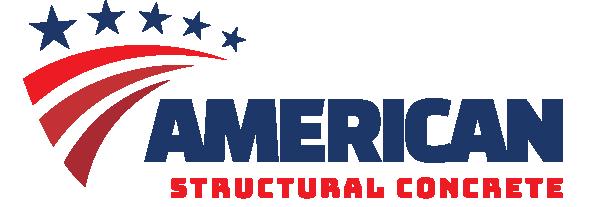
Tel: 678-301-2400 (Main Office) info@americansc.com americansc.com
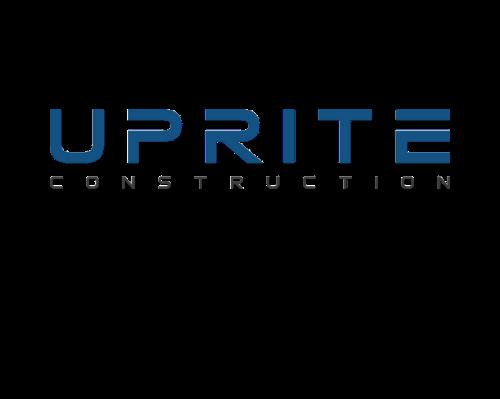
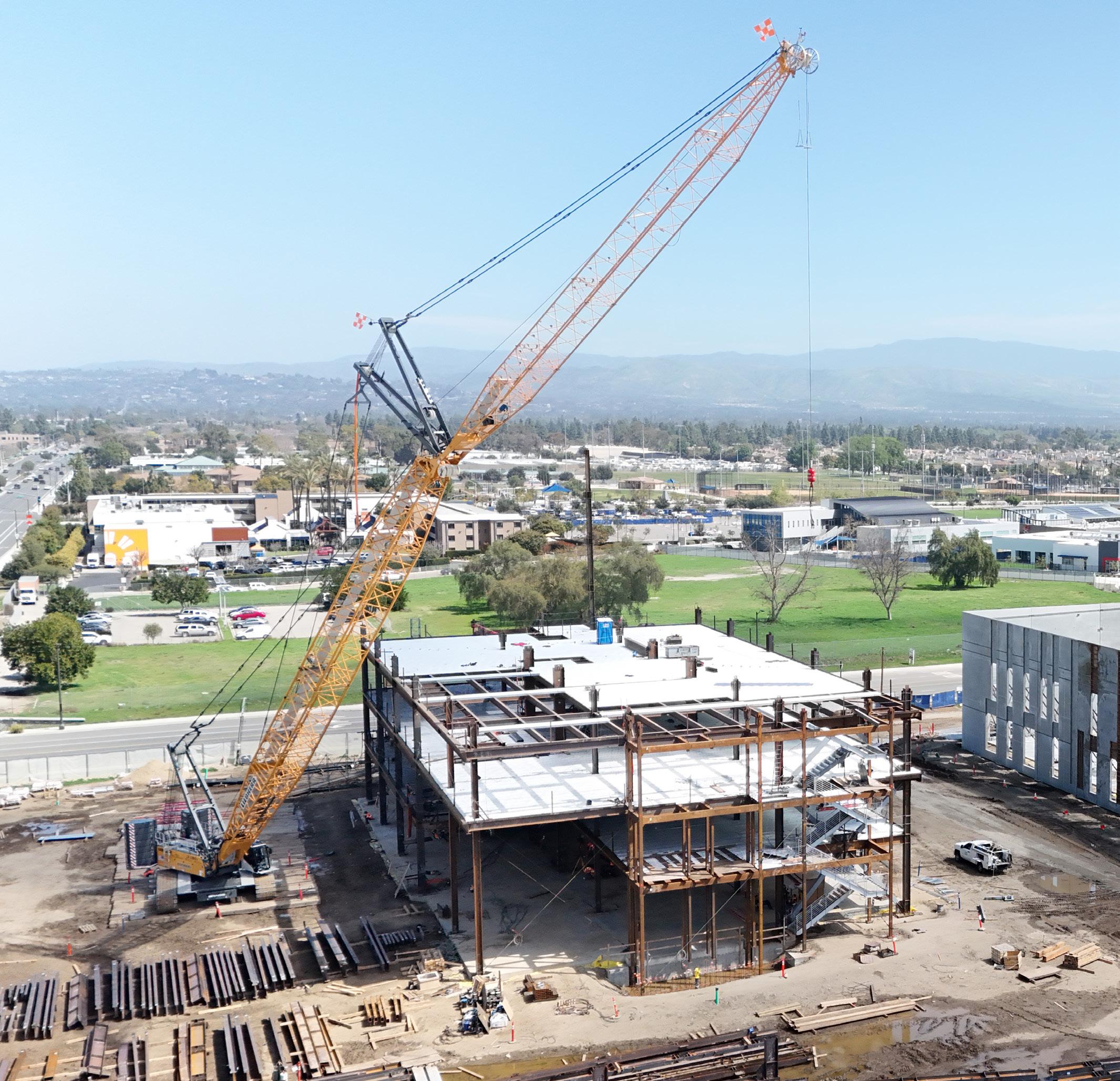
With over 30 years of proven expertise, Uprite
Construction is a multi-service construction company able to tackle market challenges and continuously innovate. Brad Kollar, Executive Vice President of Industrial and Strategic Markets, dons his hard hat and hi-vis to show us the ropes
Writer: Lauren Kania | Project Manager: Ben Weaver
A PARTNERSHIP BUILT
Established in 1991, Uprite
Construction (Uprite) has built a reputation for efficiency, quality, and strong client relationships based on trust and transparency, allowing the company to deliver exceptional results nationwide.
As a general contractor specializing in several core markets, including industrial tilt-up, self-storage, industrial outdoor storage (IOS) and electric vehicle (EV) site
PARTNERSHIP BUILT ON TRUST
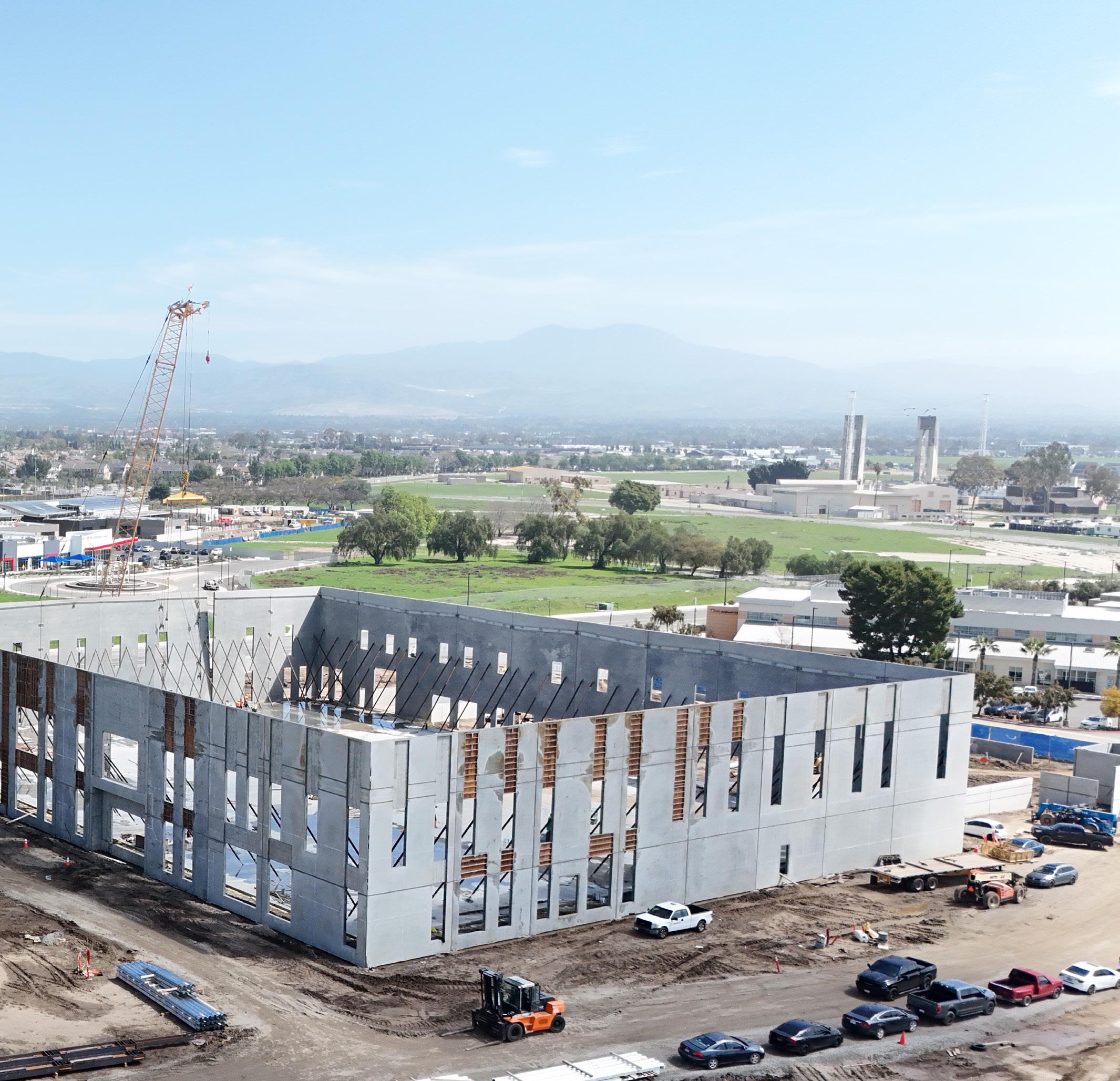
development, tenant improvements, retail, and medical facilities, Uprite offers unparalleled comprehensive design-build services, providing clients with a fully integrated construction solution from start to finish.
“We currently operate out of 12 offices and are actively working in 13 different states, with our eye on several additional markets across the US,” introduces Brad Kollar, Executive
Vice President of Industrial and Strategic Markets.
The company’s corporate headquarters are in Irvine with further offices in Sacramento and San Diego (California); Reno and Las Vegas (Nevada); Boise (Idaho); Salt Lake City (Utah); Phoenix (Arizona); Dallas and Austin (Texas); Orlando (Florida); and Cleveland (Ohio).
“Our client base is diverse – we work with large institutional developers as
well as smaller, privately held or familyowned firms,” details Kollar.
Additionally, Uprite partners directly with end-users, property managers, and construction management companies, ensuring it can deliver tailored solutions to meet a wide range of needs.
With extensive experience in the construction industry, Kollar has witnessed the sector in North America evolve over the years.
“Right off the bat, I’d say that the world is much smaller than it was when I first started. 43 years ago, when I entered the industry, people and companies worked in finite areas of operation. Now, it seems, everyone has multiple offices in different regions,” he insights.
“This has brought about a tremendous number of opportunities alongside many challenges. Expanding into new markets is hard. It’s risky and takes a lot of planning.”
Uprite retains the mindset that if a project occurs in a market where it sees a long-term opportunity, it will make a strategic decision to establish a permanent presence in that location.
The company will hire an entirely local, homegrown team to cement its presence and show its clients and the subcontractor market that it is there for the long haul.
“We want them to know that our intention is to hire their friends, families, and colleagues. It establishes a sense of commitment and trust, and
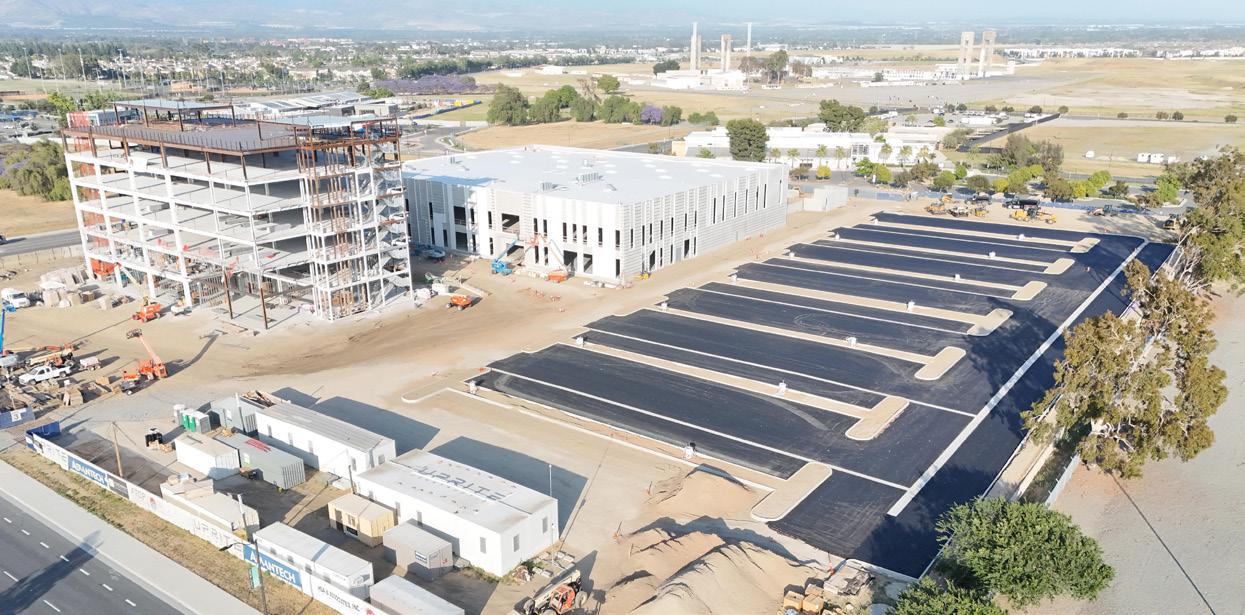
that we’re not just here for the oneoff,” Kollar explains.
BUILT ON TRUST
Uprite’s motto – ‘a partnership built on trust’ – is not just a catchy phrase but a mantra that the company abides by and embodies on a daily basis, particularly through the relationships it cultivates with clients, subcontractors, employees, and suppliers.
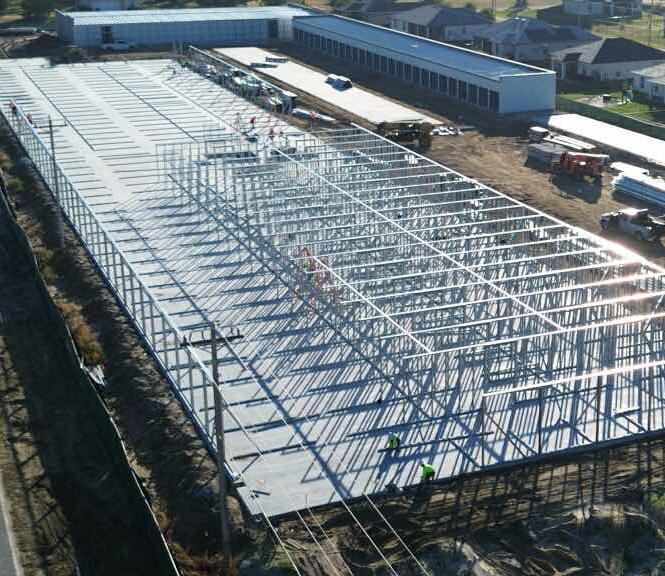
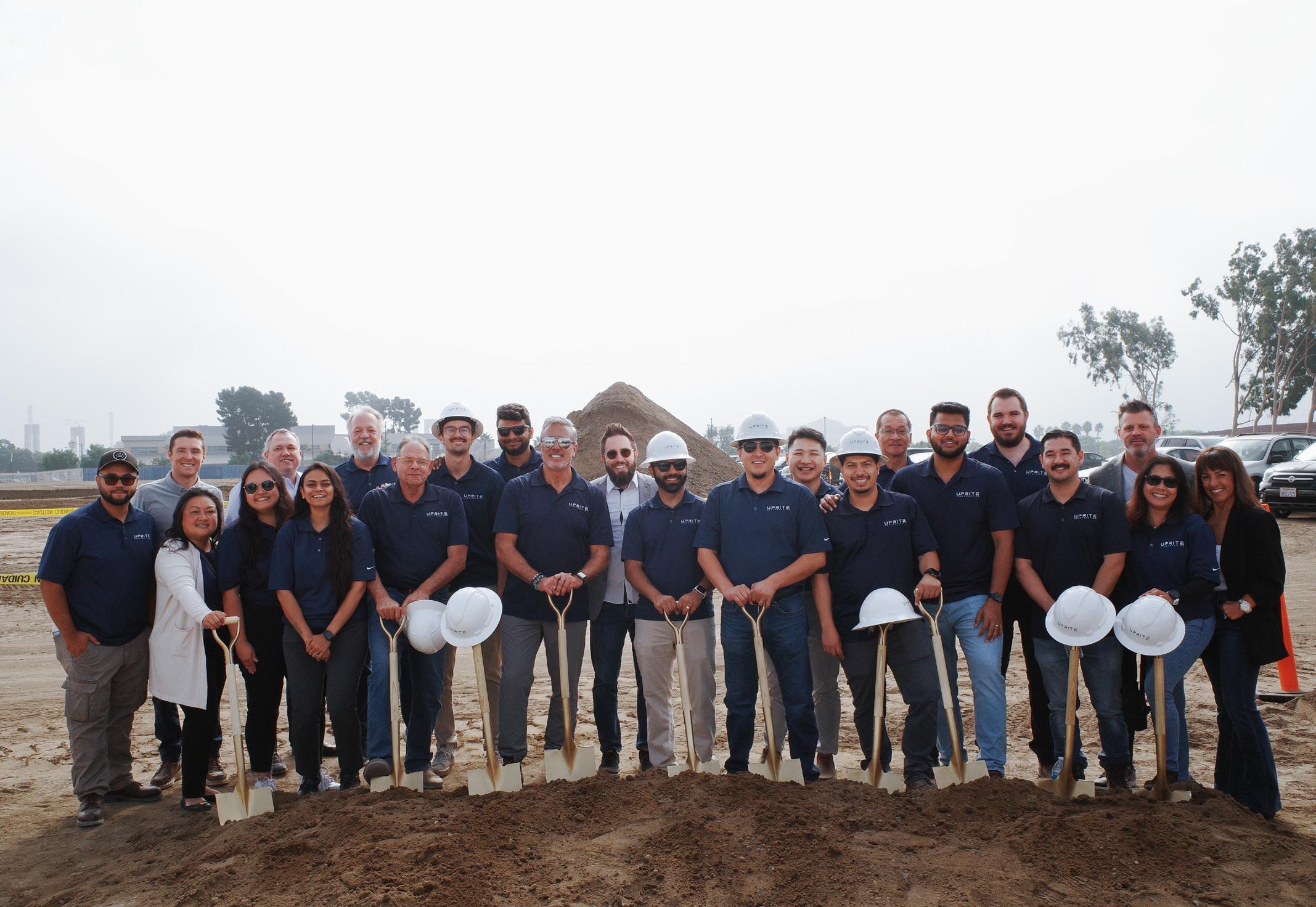
“UPRITE CAN COMPETE AND OUTPERFORM ANYONE IN ANY MARKET IN WHICH WE’RE WORKING. WE WILL – EVERY SINGLE TIME – OUTWORK OUR COMPETITORS TO WIN A PROJECT AND COMPLETE IT”
– BRAD KOLLAR, EXECUTIVE VICE PRESIDENT OF INDUSTRIAL AND STRATEGIC MARKETS, UPRITE CONSTRUCTION
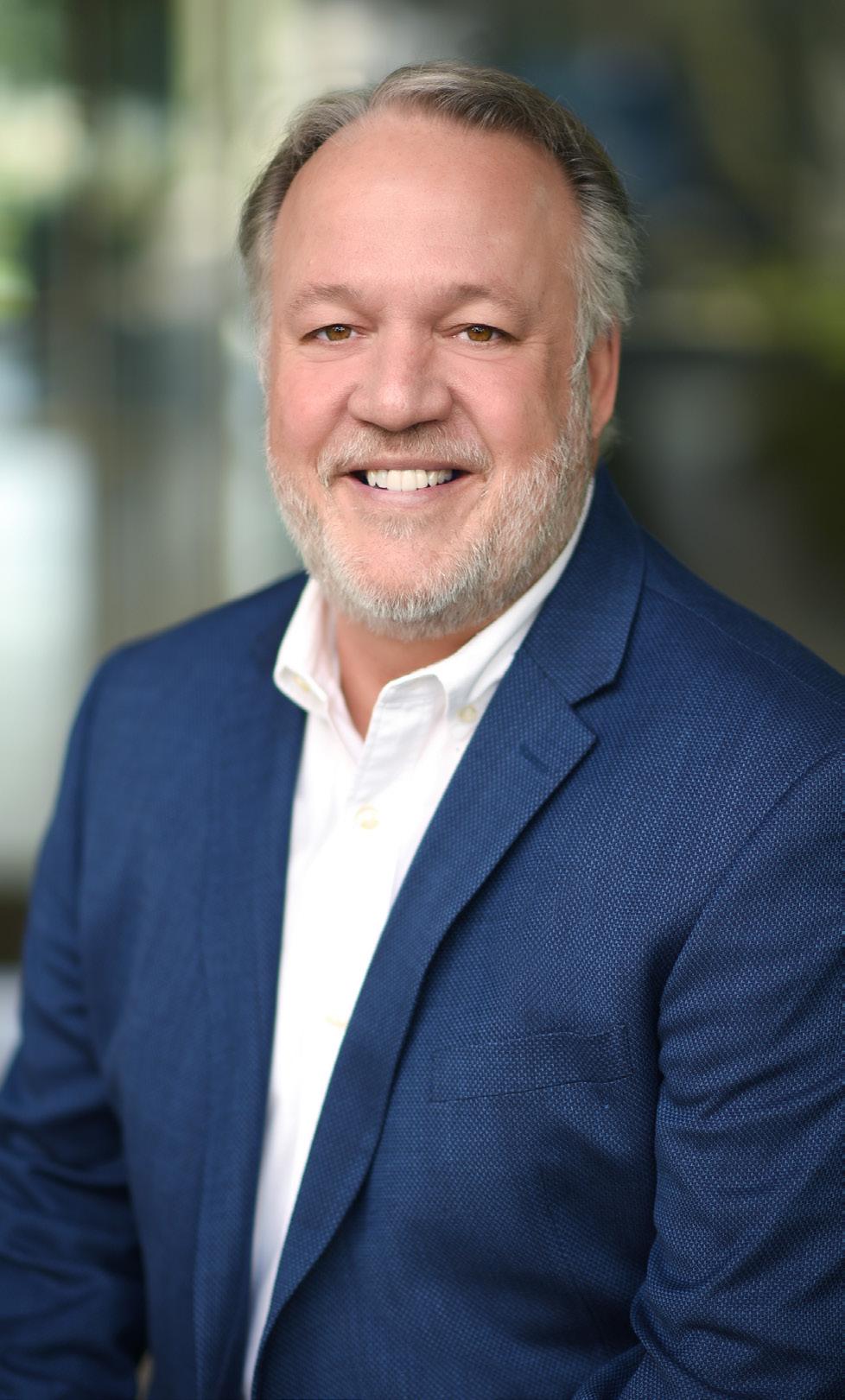
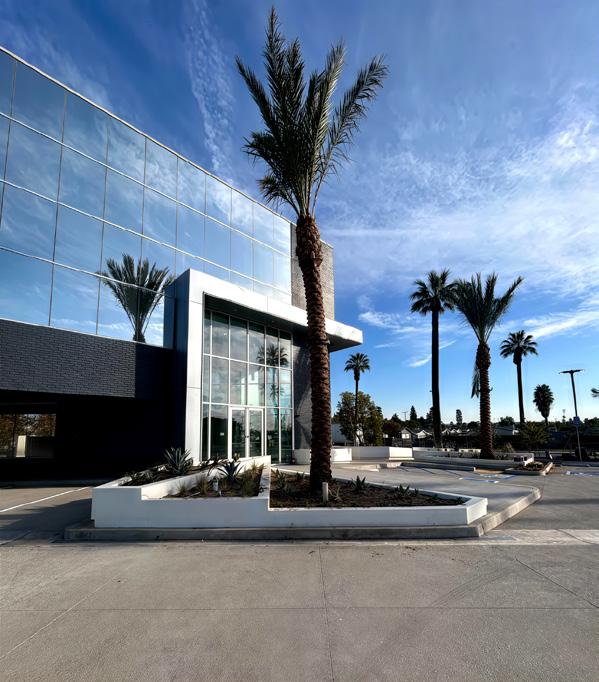
HOW DO EVENTS LIKE THE I.CON WEST CONFERENCE AND THE SELF STORAGE ASSOCIATION SPRING CONFERENCE & TRADE SHOW PRESENT UPRITE WITH AN OPPORTUNITY TO SHOWCASE ITS PROJECTS AND DISCUSS INDUSTRY TRENDS AND CHALLENGES?
Brad Kollar, Executive Vice President of Industrial and Strategic Markets: “We attend and participate in a lot of trade shows. For I.CON West, we typically have team members from all of our Southwestern and Northern California offices come to the event.
“It not only allows us to showcase the company but also see old friends and clients and meet new people in the industry.
“Of course, there are always issues plaguing the sector, so we never run out of things to discuss and are able to hear others’ perspectives. Whether it’s material lead times, tariffs, or a new bill that may adversely affect us, it’s good to be in front of industry leaders, hear what they think, and see what they’re doing.
“This is a small world, and everyone knows each other. It’s a good opportunity to witness the camaraderie and see people helping one another.”
Having spent ample time developing this motto, the business believes it best represents who it is and what it is truly about.
“As a company relatively new to the industrial space, we had to start from the absolute bottom. Our clients knew us as individuals who had worked at other companies, but they didn’t know Uprite,” narrates Kollar.
“We had to convince them that they were hiring people whom they know, trust, and had performed well for them in the past. We had to convince them we were the ‘real deal’ and had
assembled a national team who could go up against anyone in the country.”
To that end, the company goes above and beyond its competitors with its preconstruction and operational efforts, providing absolute transparency along the way. Uprite, therefore, encourages its clients to take a chance and allow it to prove its capabilities and reliability.
“Of course, we’ve had some missteps along the way, but what sets us apart is how we’ve handled them,” prides Kollar.
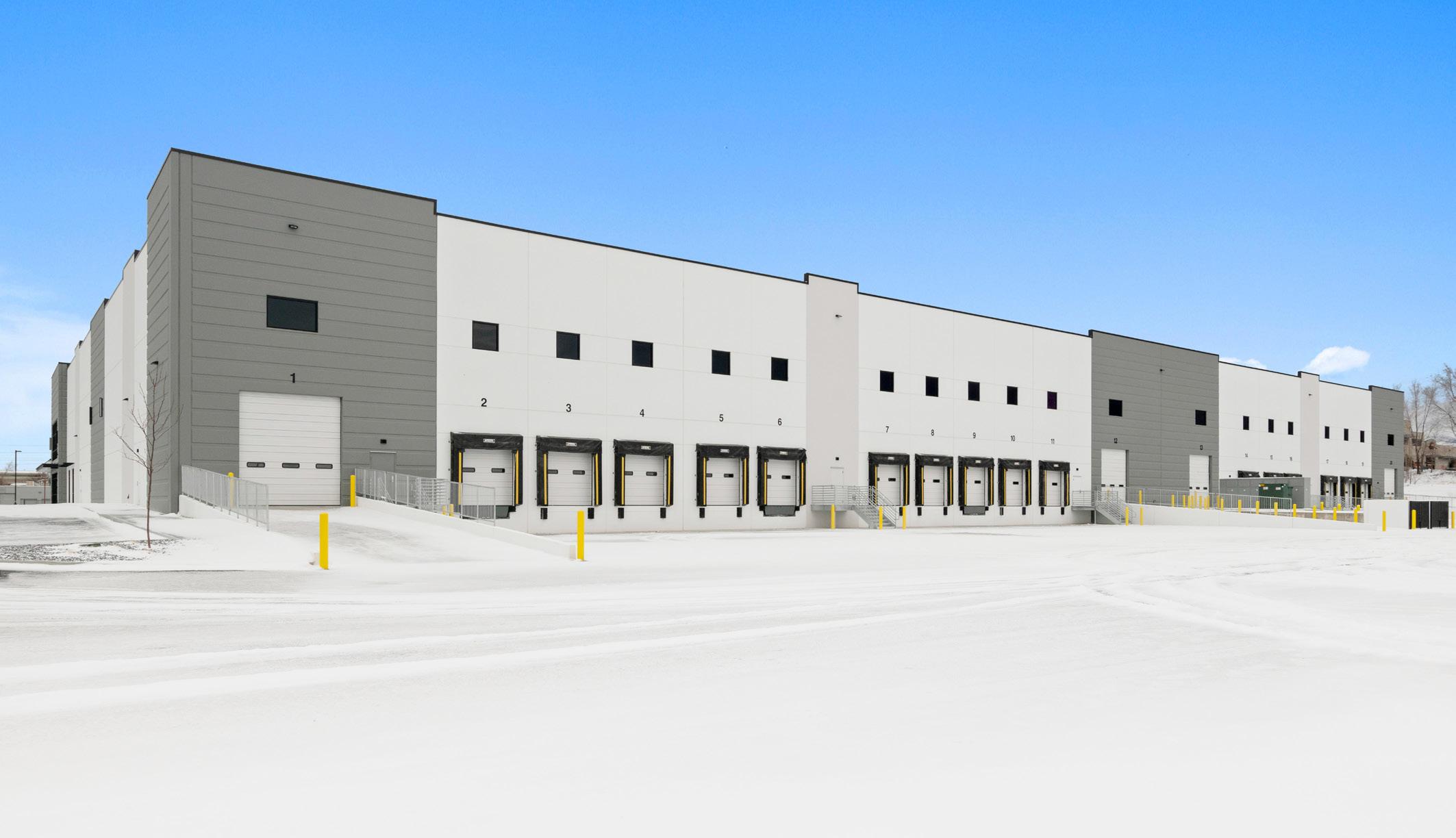
AS COMMUNITY SUPPORT IS A CORE PART OF UPRITE’S MISSION, HOW DOES THE COMPANY GIVE BACK TO BOTH THE COMMUNITY AND STAFF?
Brad Kollar, Executive Vice President of Industrial and Strategic Markets: “We’ve been engaging in some fun things that also help those less fortunate.
“We have a great group of young team members who are energetic and have huge hearts. Our Director of Marketing, Monica McGannon, is always on the hunt for ways that our team can contribute to a charity while having fun at the same time.
“Our team just recently participated in a five kilometer (km), 25km, and 50km run in Newport Coast, benefiting the John Wayne Cancer Foundation. Uprite won an award for the Top Fundraising Team for the entire event.”
“THE ULTIMATE GOAL IS NOT JUST TO BE BETTER, BUT TO BE THE BEST. WE WANT TO BE WORLD-CLASS”
–
BRAD KOLLAR, EXECUTIVE VICE PRESIDENT OF INDUSTRIAL AND STRATEGIC MARKETS, UPRITE CONSTRUCTION
The company’s Uprite One initiative means it can be all hands on deck at a moment’s notice while keeping the client informed and up-to-date during the process.
“It’s really hard to hide mistakes from clients, so we don’t even try. We acknowledge that it happened, fix it, and keep moving forward. That’s the epitome of ‘a partnership built on trust’”.
EXPERTLY TACKLING MARKET CHALLENGES
To continue its legacy of perseverance, dedication, and innovation, Uprite is focusing on sustainability initiatives alongside emerging technologies at the preconstruction stage, such as
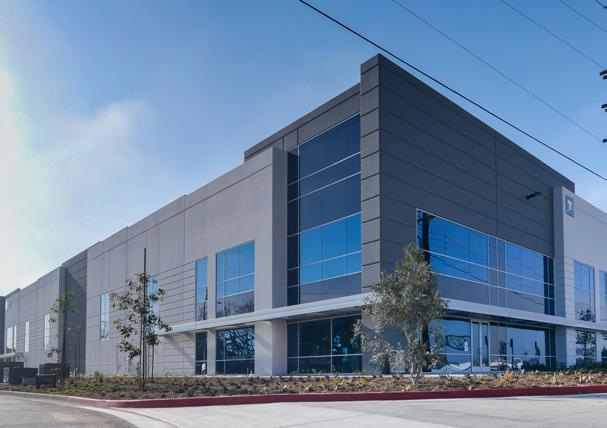
implementing artificial intelligence (AI).
For sustainability, the company has explored several options, such as ecofriendly concrete mixes using fly ash or other supply chain management strategies to reduce cement content, as well as carbon mineralization techniques, which make concrete stronger while reducing its carbon emissions into the atmosphere.
For its reinforcement bars (rebar), meanwhile, the company has looked at using fiber reinforced polymer (FRP) or recycled rebar in lieu of traditional steel.
“We work with our concrete subcontractors to ensure they’re using recycled materials. There are several opportunities to reduce our
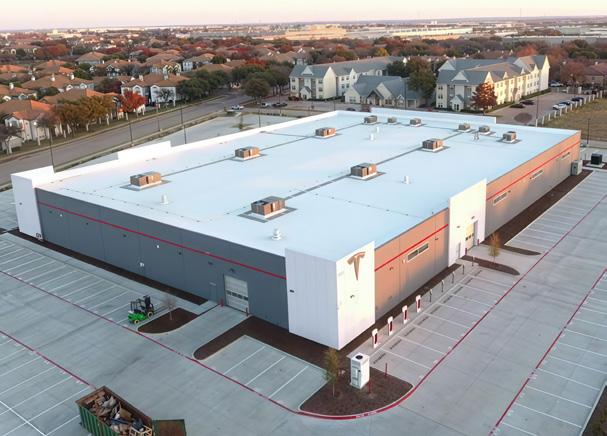
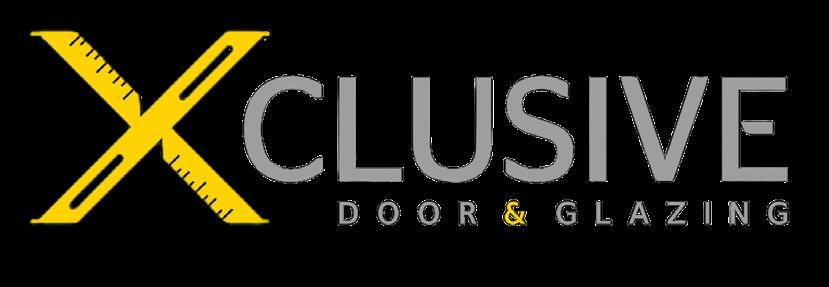
Office Phone: (562) – 232 - 3554
Owners emails : matthew@xclusivedoor.com | juan@xclusivedoor.com
Instagram: xclusive_door_glazing
Facebook: Xclusive Door & Glazing
LinkedIn: Xclusive Door and Glazing
Xclusive Door and Glazing Precision.
Performance. Professionalism.
Based in Paramount, CA, Xclusive Door and Glazing specializes in high-quality commercial doors and glazing solutions. From expert installation to precision craftsmanship, our team delivers reliable, custom solutions built to last. Whether you’re outfitting a new commercial space or upgrading your current property, trust the experts who are committed to excellence on every job.
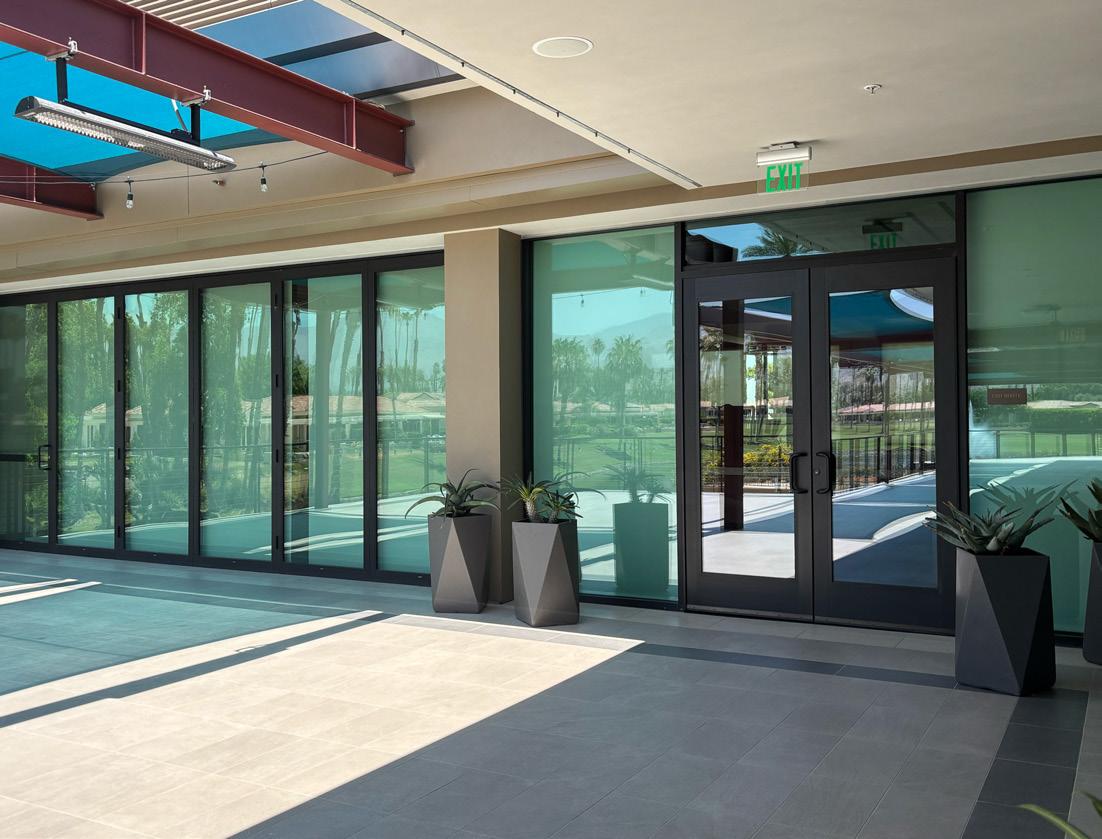
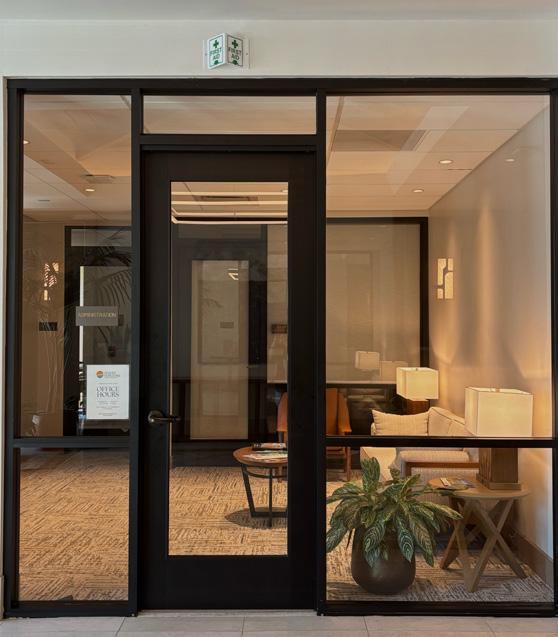
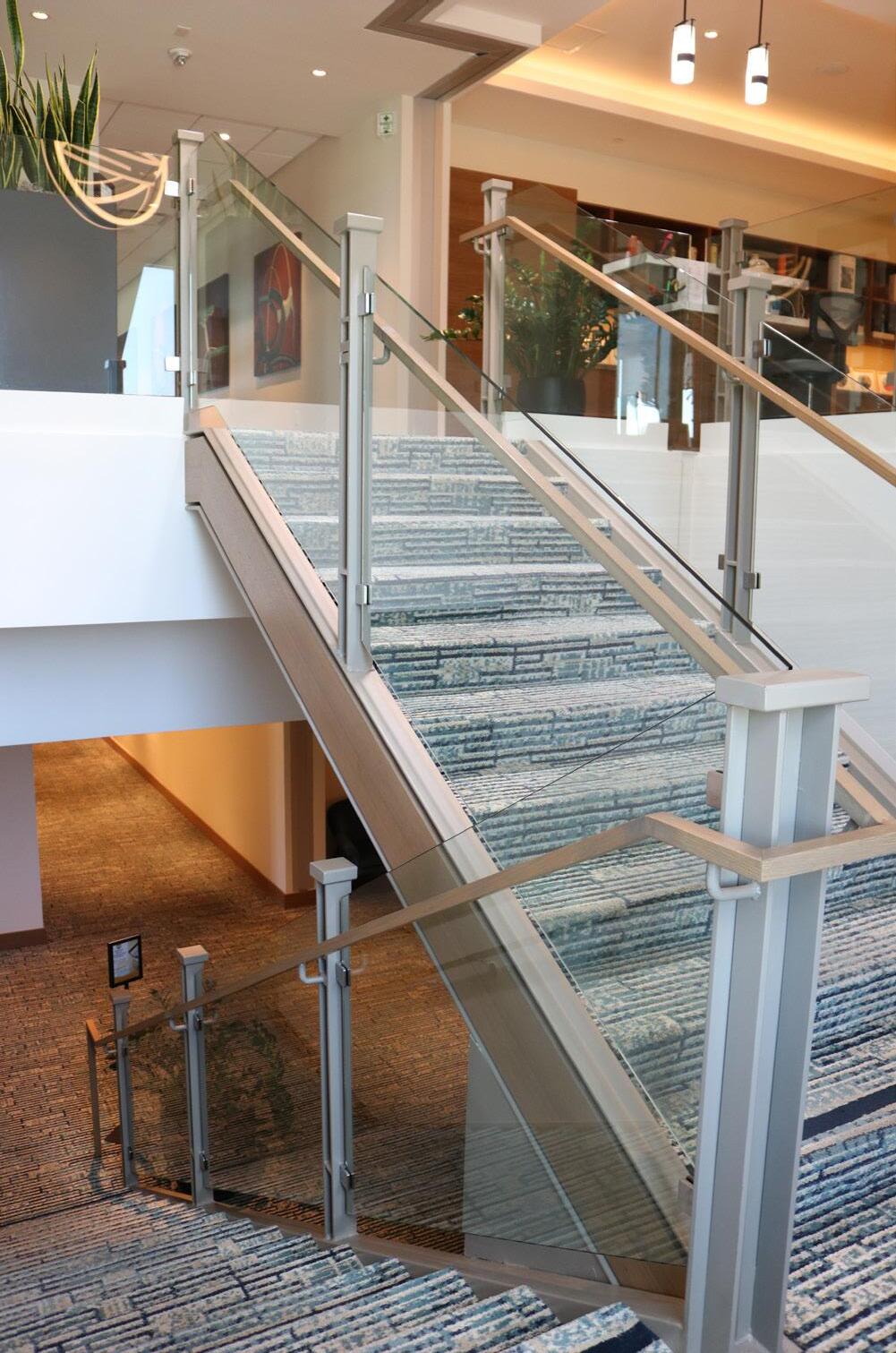
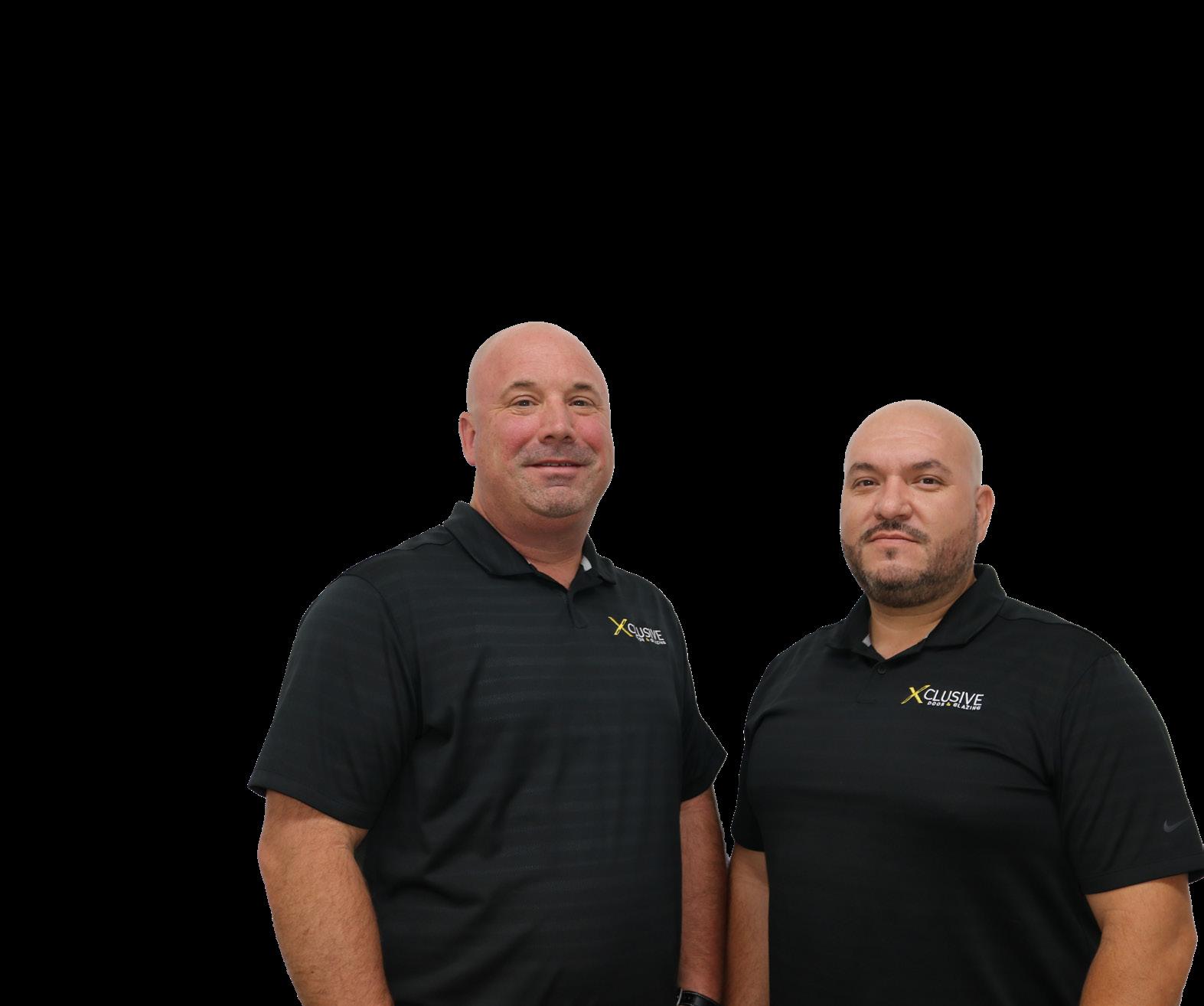
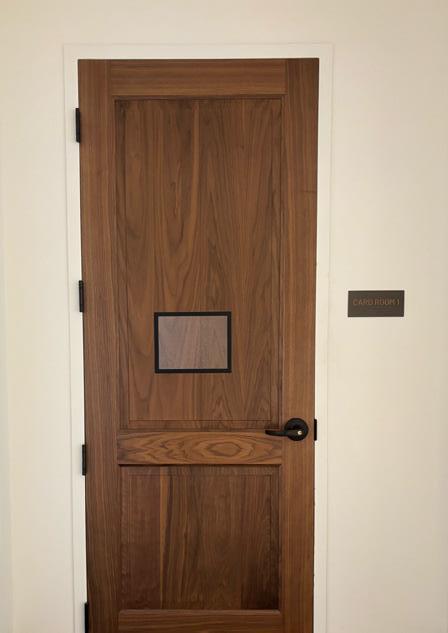
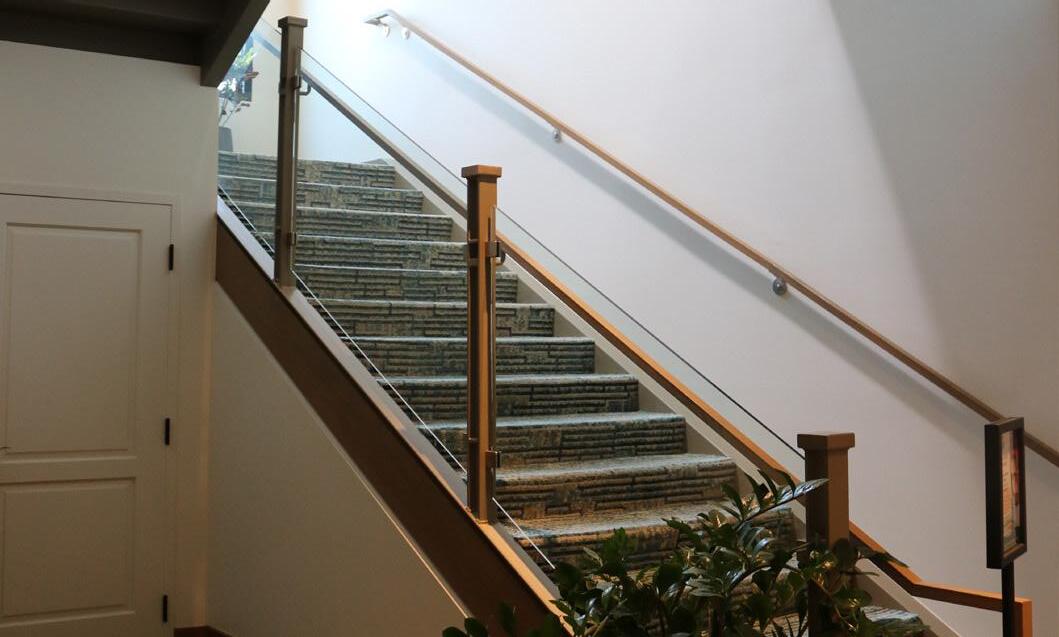
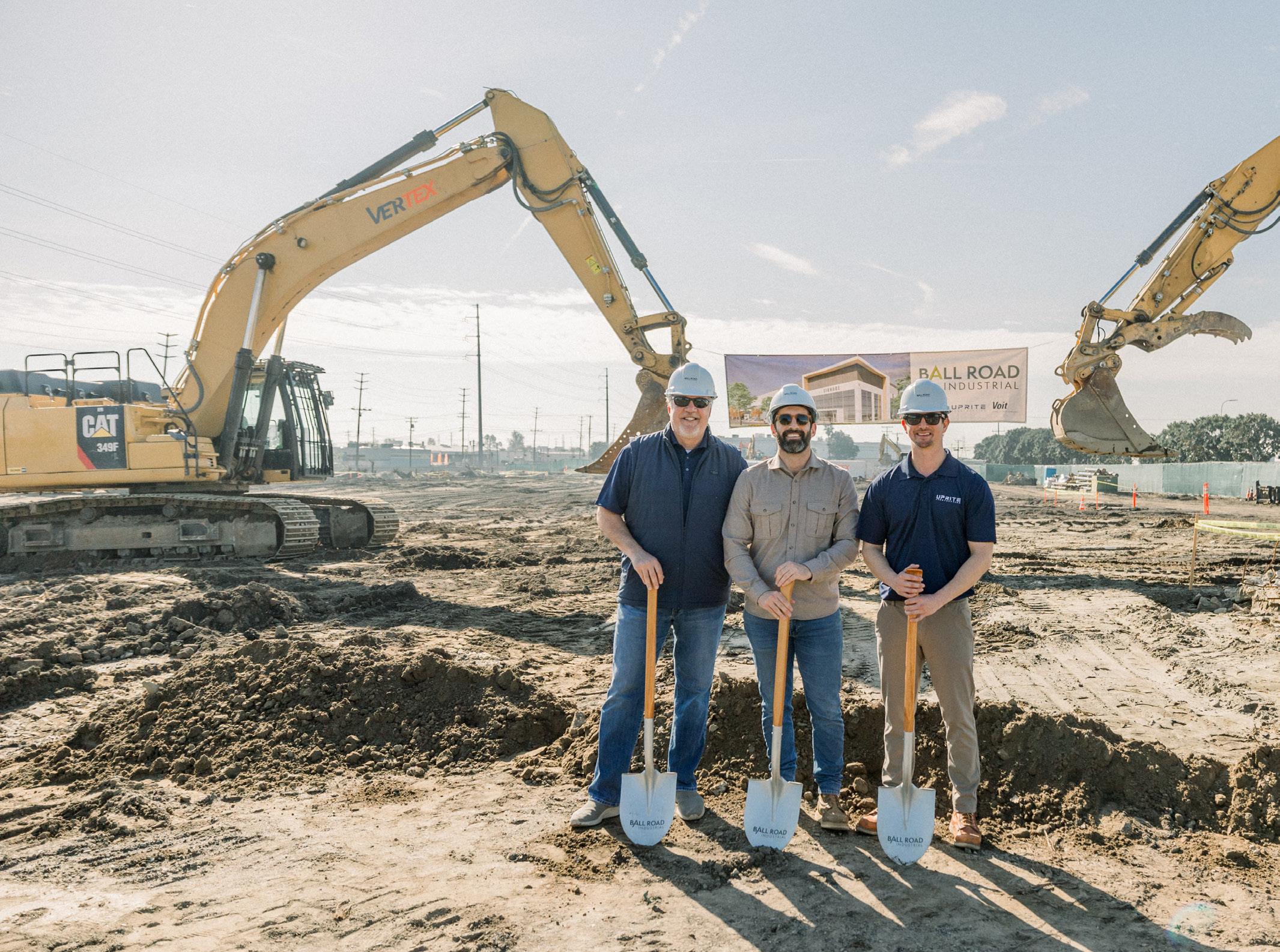
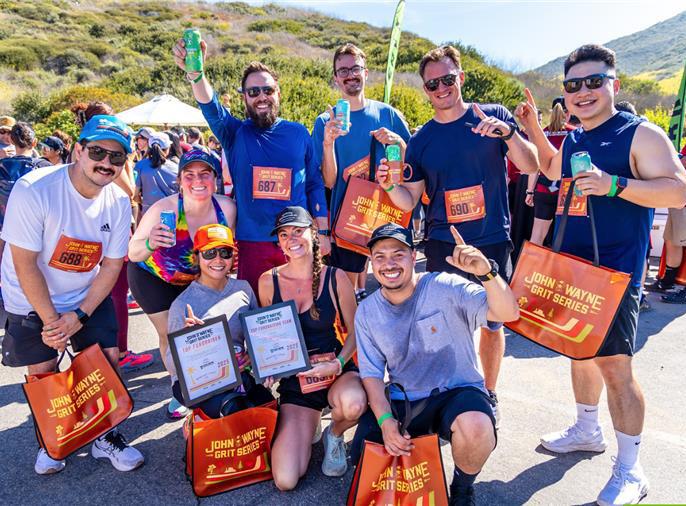
carbon footprint in the construction process, and we’re researching more every day,” details Kollar.
Regarding technology, Uprite has implemented AI as a tool to review its prime contracts, directing it to read through an agreement and find aspects worth analysing and discussing with clients.
“It’s not a replacement for our own interpretation or a final review for a lawyer, but it helps us get through contracts more quickly, isolate the terms we need to acknowledge or discuss, and make a business decision quicker,” informs Kollar.
In addition to Uprite’s various growth initiatives, enabling it to exceed its clients’ expectations, the company prides itself on its differentiations.
“Uprite can compete and outperform anyone in any market in
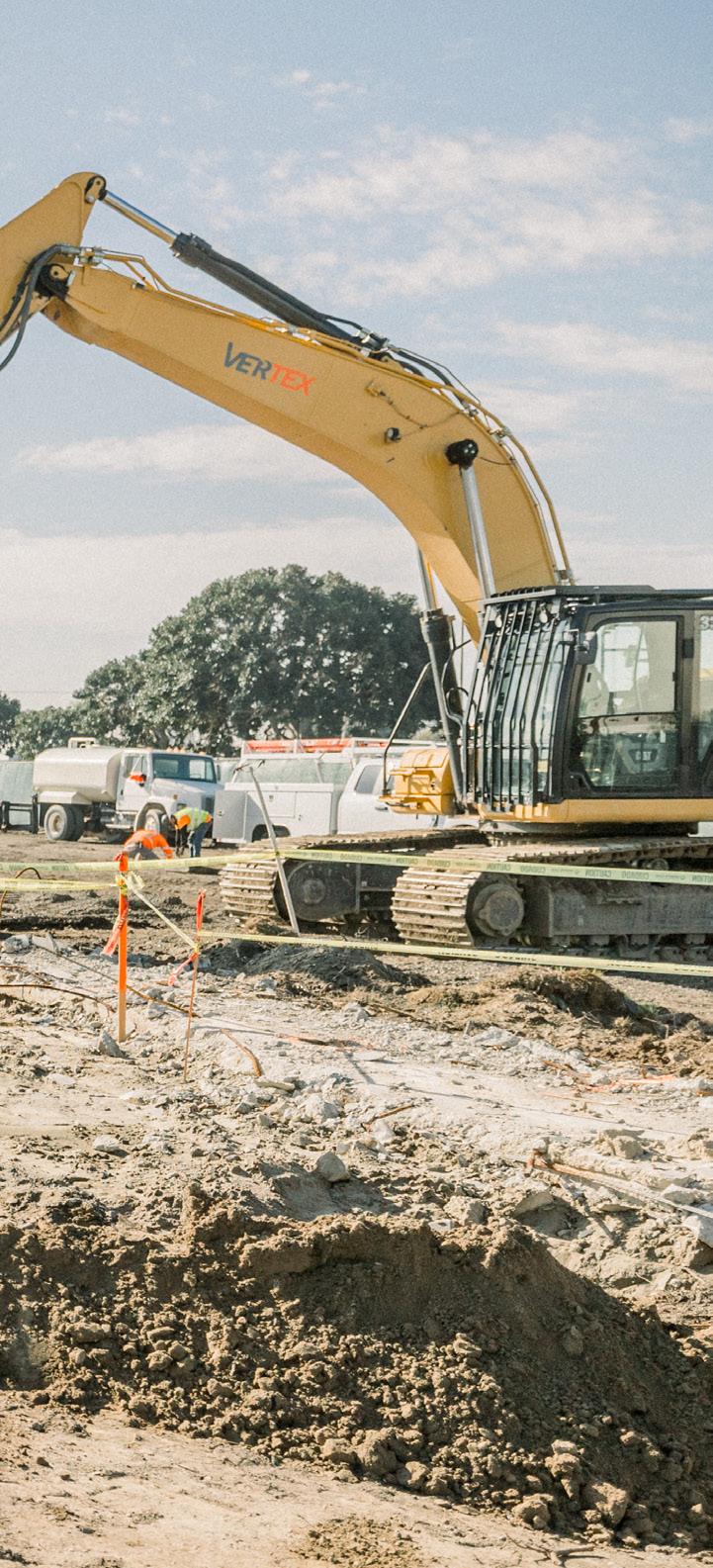
which we’re working. We will – every single time – outwork our competitors to win a project and complete it,” expands Kollar.
Coming from the ground up, the company knows it has to earn every single opportunity, as it does not believe in the right to expect to be awarded a project.
“We’d never think to assume that someone owes us a project – it’s just not our mindset. If we’re fortunate enough to have earned the trust of a client willing to give us a shot, we’re going to give it everything we’ve got to show them their trust is not misplaced,” confirms Kollar.
LEADERS IN TRANSPARENCY
Uprite has participated in many notable and innovative projects over the course of its history.
While there are a plethora that aptly
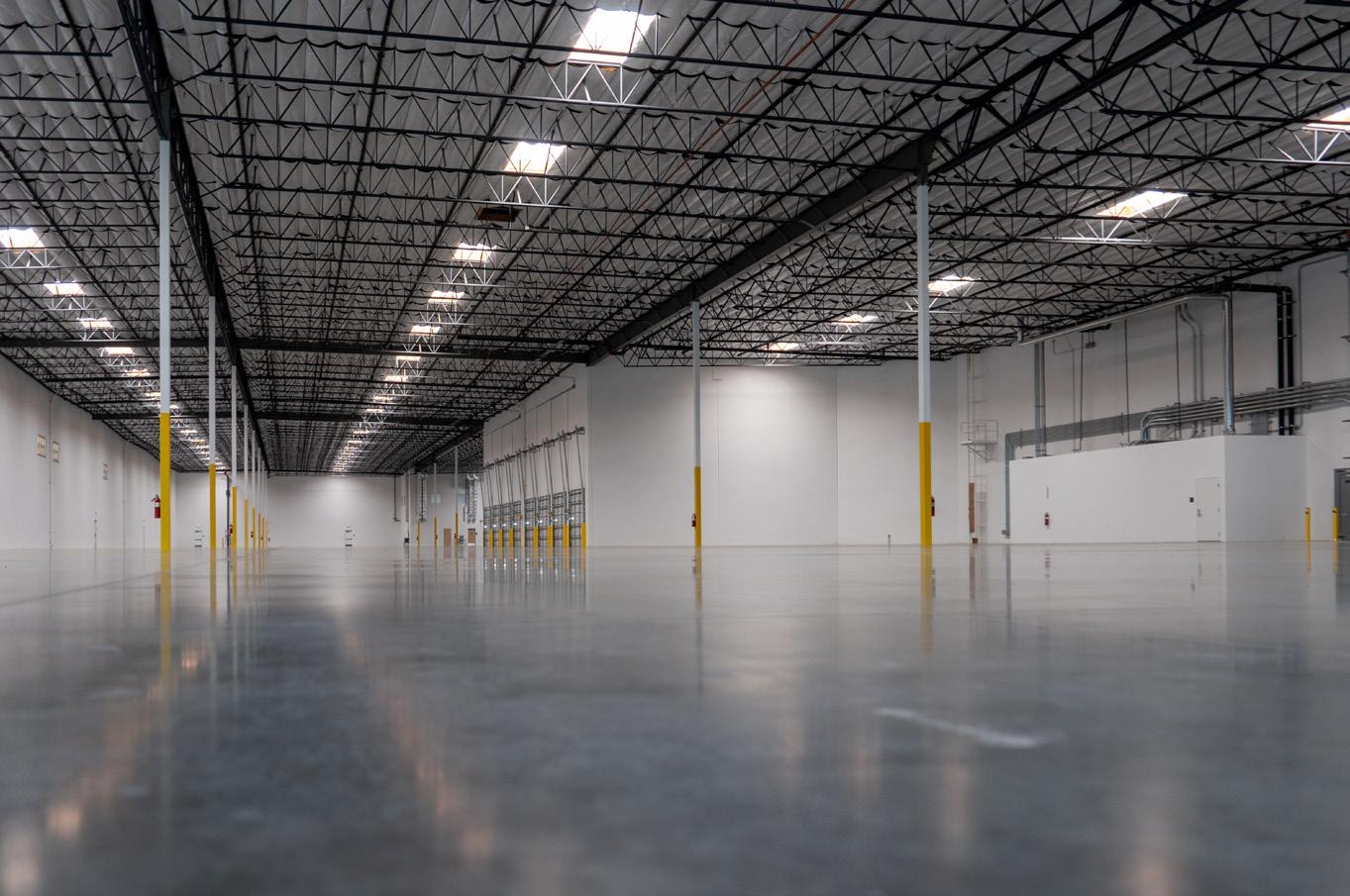
showcase the company’s vast abilities, some of the most recent and notable include Advantech North America in Tustin, California, ILC 4 in Fort Worth, Texas, and the Piercy Road projects in San Jose, California.
Situated as the North American headquarters for Advantech, a Taiwanese firm focusing on the Internet of Things (IoT), the Advantech North America project is a 110,000 square foot (sqft), six-story office tower with a 79,000 sqft, twostory concrete tilt-up.
“It was a great project for us in our Southern California office as it is a very high-profile opportunity which has garnered a lot of attention throughout the region,” expands Kollar.
ILC 4, on the other hand, will be the company’s fourth building with NorthPoint Development (NorthPoint). It is a 1.2 million sqft industrial tilt-up building at the Intermodal Logistics Center and will be the largest building Uprite has constructed under one roof, making it a special development for the company.
“Having a client like NorthPoint put its trust in us time and time again is a true testament to our team,” enthuses Kollar.
Elsewhere, the Piercy projects consist of three new concrete tilt-ups and were the company’s first largescale tilt-up projects for Hines.
“I had done work for Hines previously, and the fact that we were selected over other very qualified companies was a huge win,” he informs.
“It really told us that what we’re doing is working. It validated our approach and all the hard work we put into our preconstruction effort.”
As Uprite continues to look ahead, its priorities include keeping its clients happy and maintaining great relationships with its trade partners, employees, and surrounding communities.
“The ultimate goal is not just to be better, but to be the best. We want to be world-class,” proudly concludes Kollar.
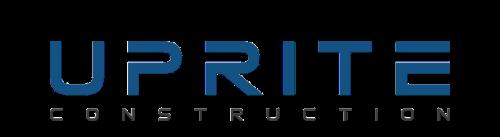
Tel: (949) 877-8877
www.UpriteCo.com
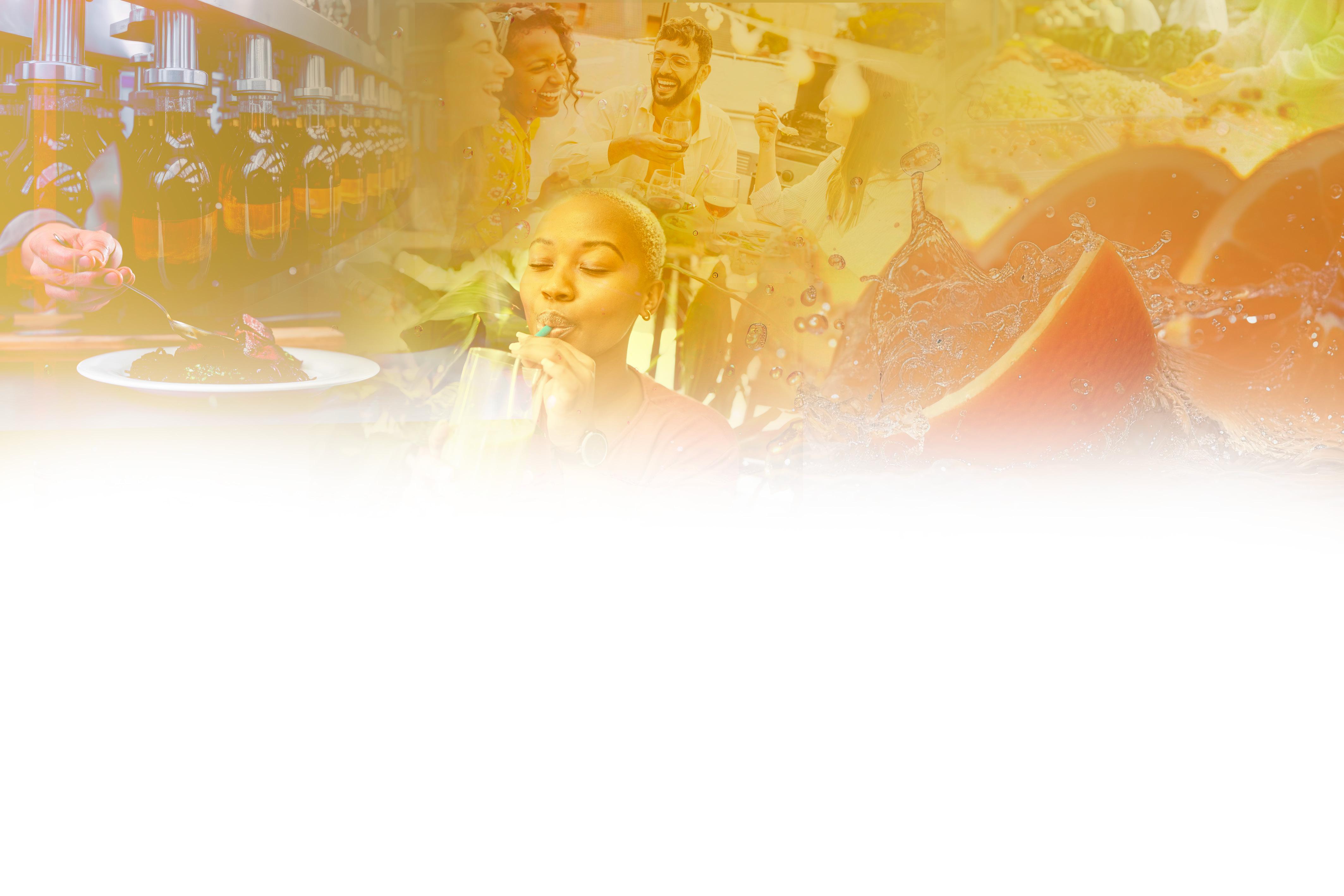
Exclusive, appetising content, delivered straight to your inbox
Adding to the success of its regional titles; Africa Outlook, EME Outlook, APAC Outlook, and North America Outlook, Outlook Publishing is proud to introduce a new platform dedicated to the food and beverage sector.
A multi-channel brand, Food & Beverage Outlook serves up all the positive global developments driven by companies across the food and beverage industry. Discover exclusive content presented through its website, social media channels and dispatches, delivered straight to your inbox with a bi-weekly newsletter.
Through this compelling new venture, Food & Beverage Outlook foregrounds the movers and shakers of the industry by confronting unprecedented change, showcasing technological innovations and incorporating critical environmental sustainability agendas.
To participate as a featured company and join us in this exciting endeavor, contact one of our Project Managers today.
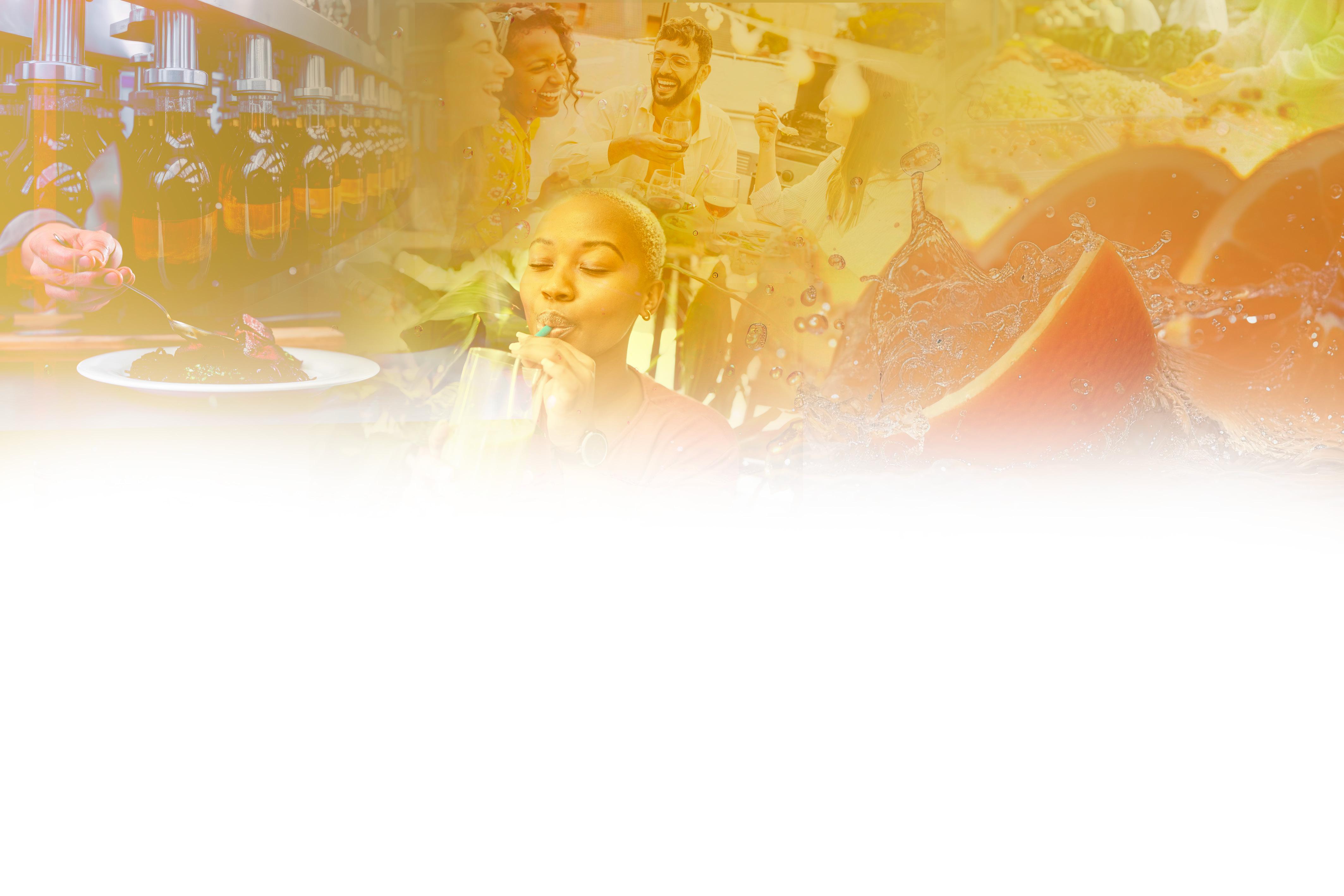
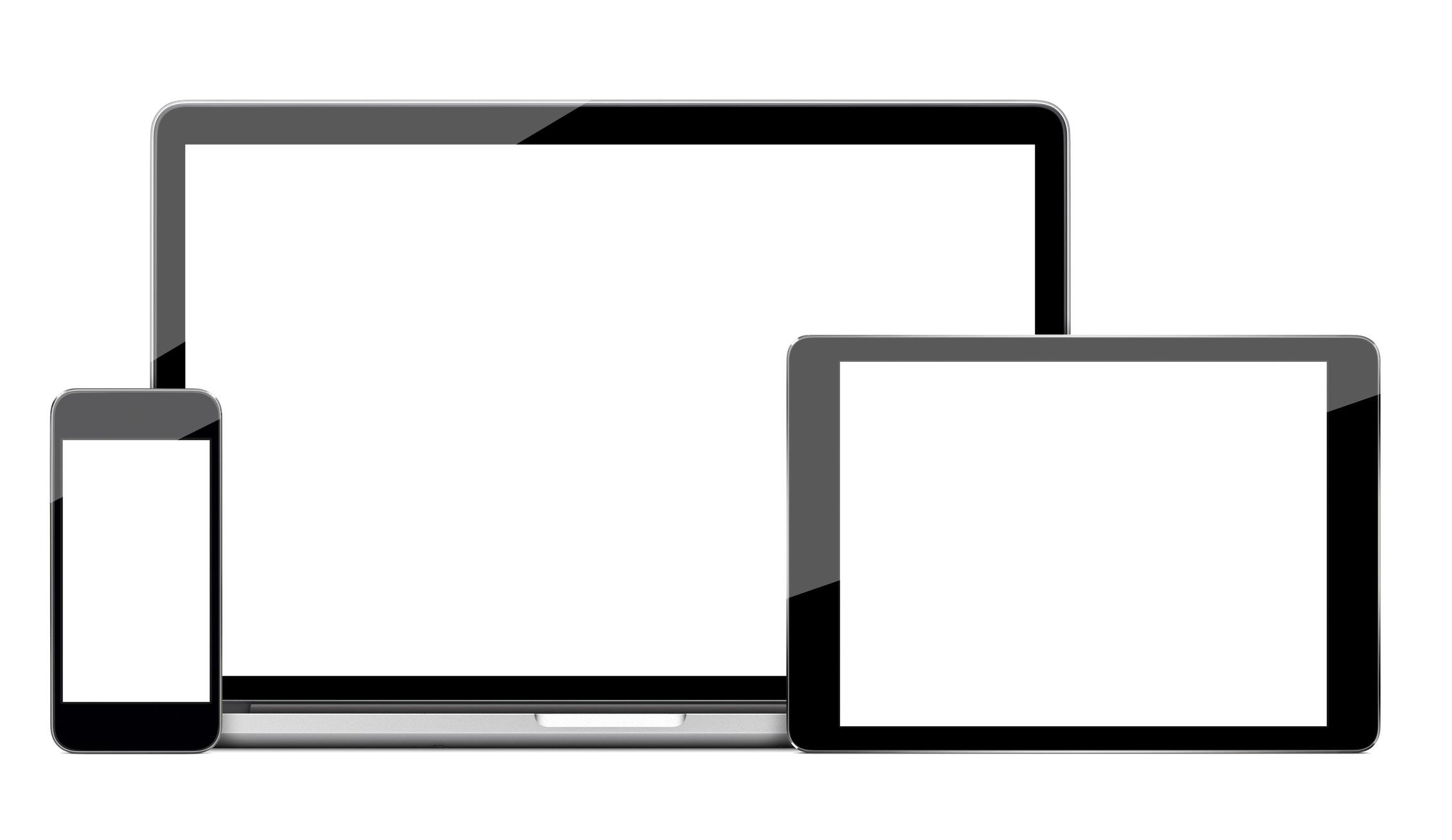

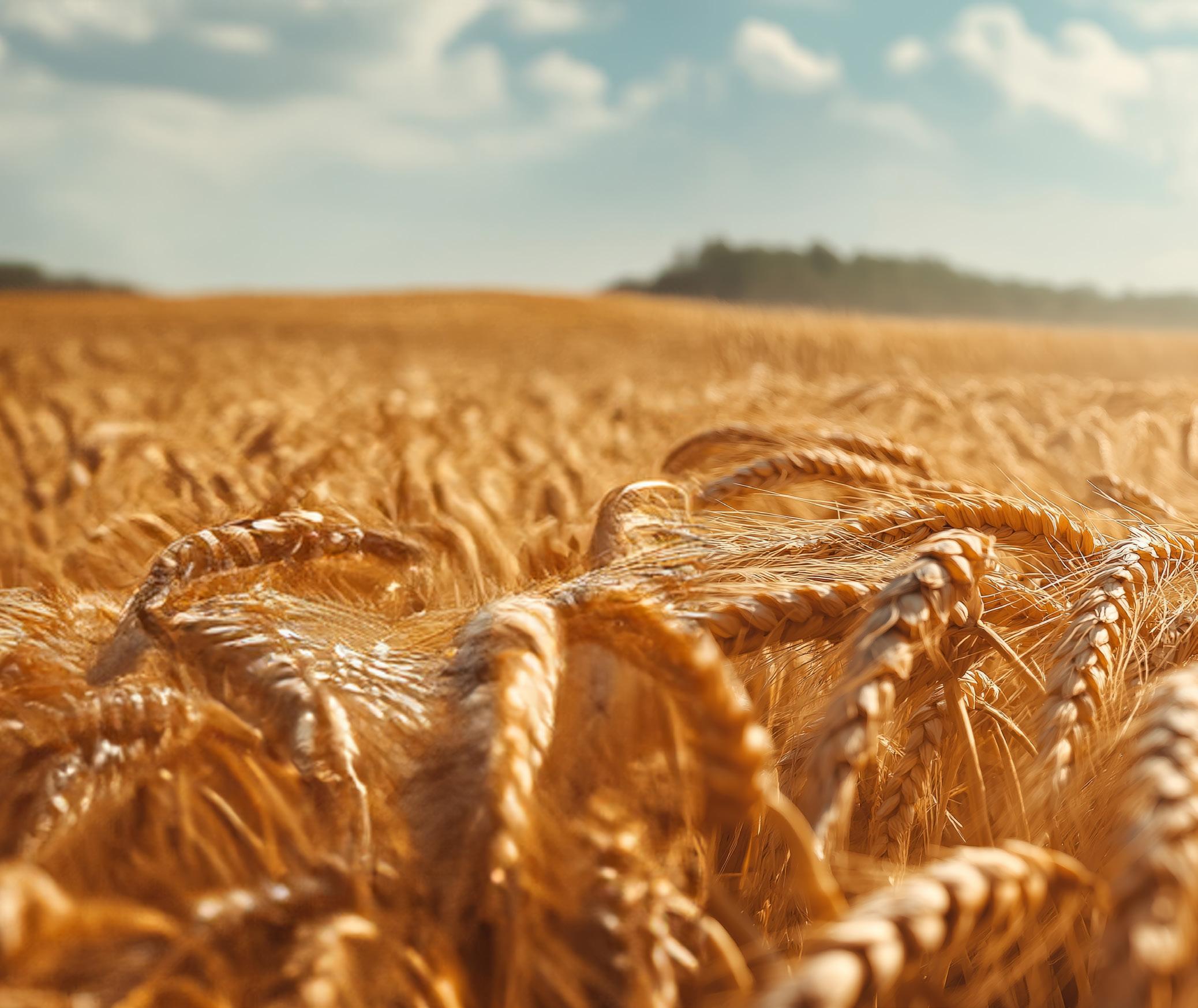
HARVESTING
QUALITY
Columbia Grain International leads the way in sustainable agriculture, connecting local farmers to global markets for grains, pulses, and oilseeds. We discover how the company’s robust supply chain and innovative solutions are nurturing the world’s food security
Writer: Rachel Carr | Project Manager: Scarlett Burke
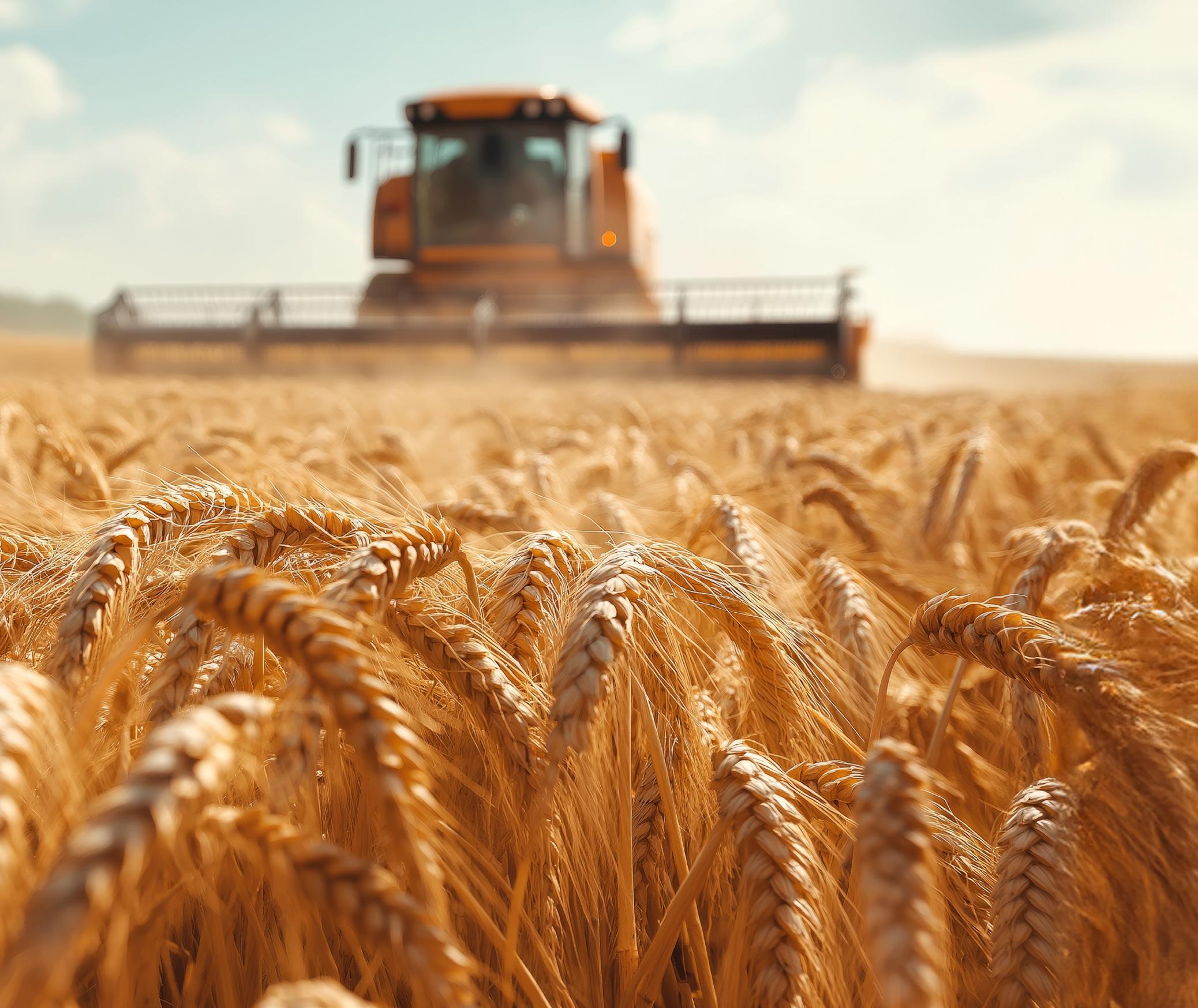
Columbia Grain International (CGI) stands in a prominent position in the agricultural sector, renowned for its extensive supply of bulk grains, pulses, edible beans, and oilseeds – both conventional and organic. What differentiates the company is its unwavering commitment to quality and sustainability, as well as its dedication to sourcing high-quality ingredients from local farmers through safe and environmentallyfriendly cultivation practices, guided by
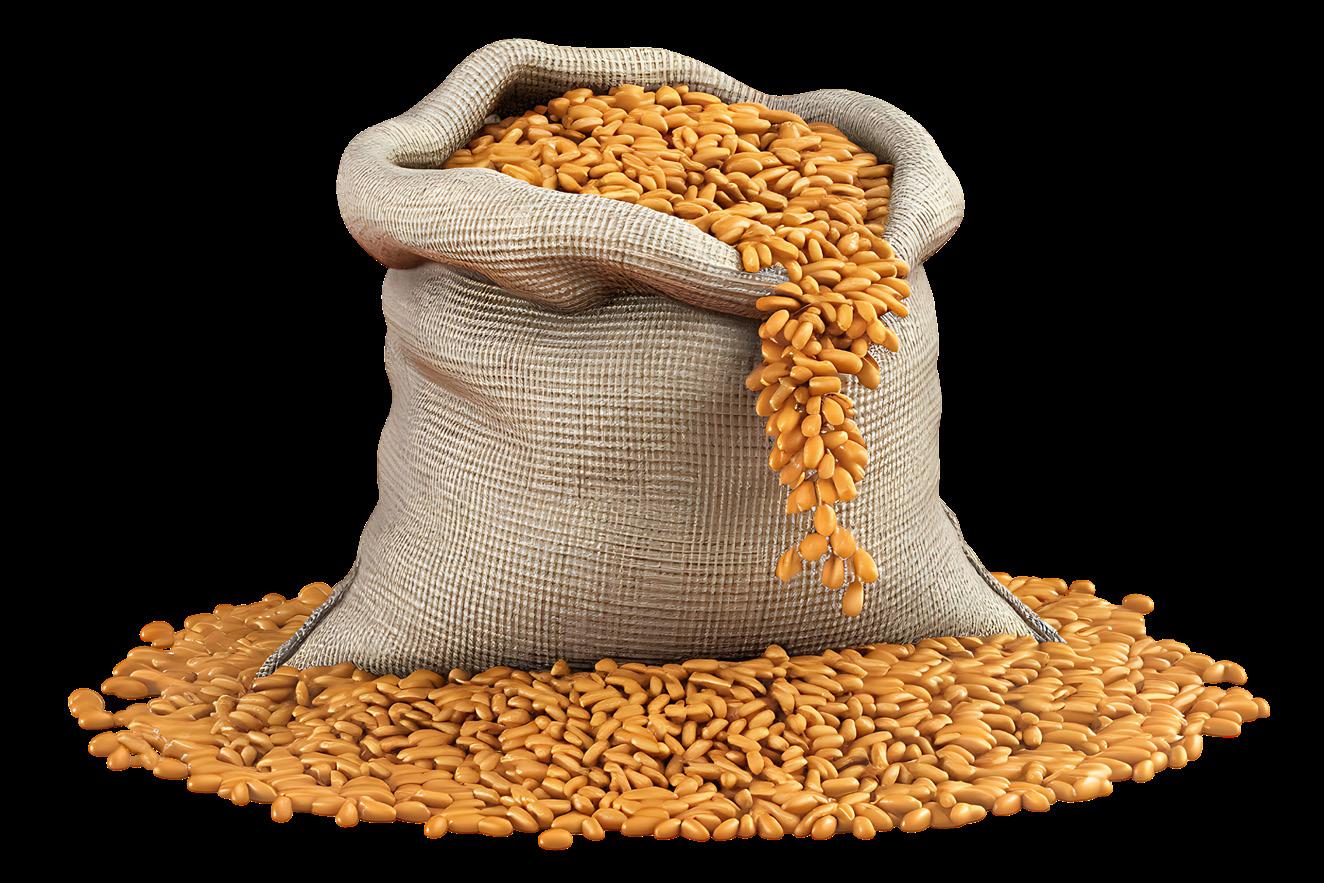
a mission to nourish the world.
Founded in the early 2000s, CGI is a US-based enterprise specializing in the sourcing, marketing, and distribution of agricultural commodities, with a particular emphasis on grains and oilseeds. The company operates across various regions, including the lush Pacific Northwest, and engages in both domestic and international trade, catering to a diverse range of sectors such as food processing, animal feed, and biofuels.
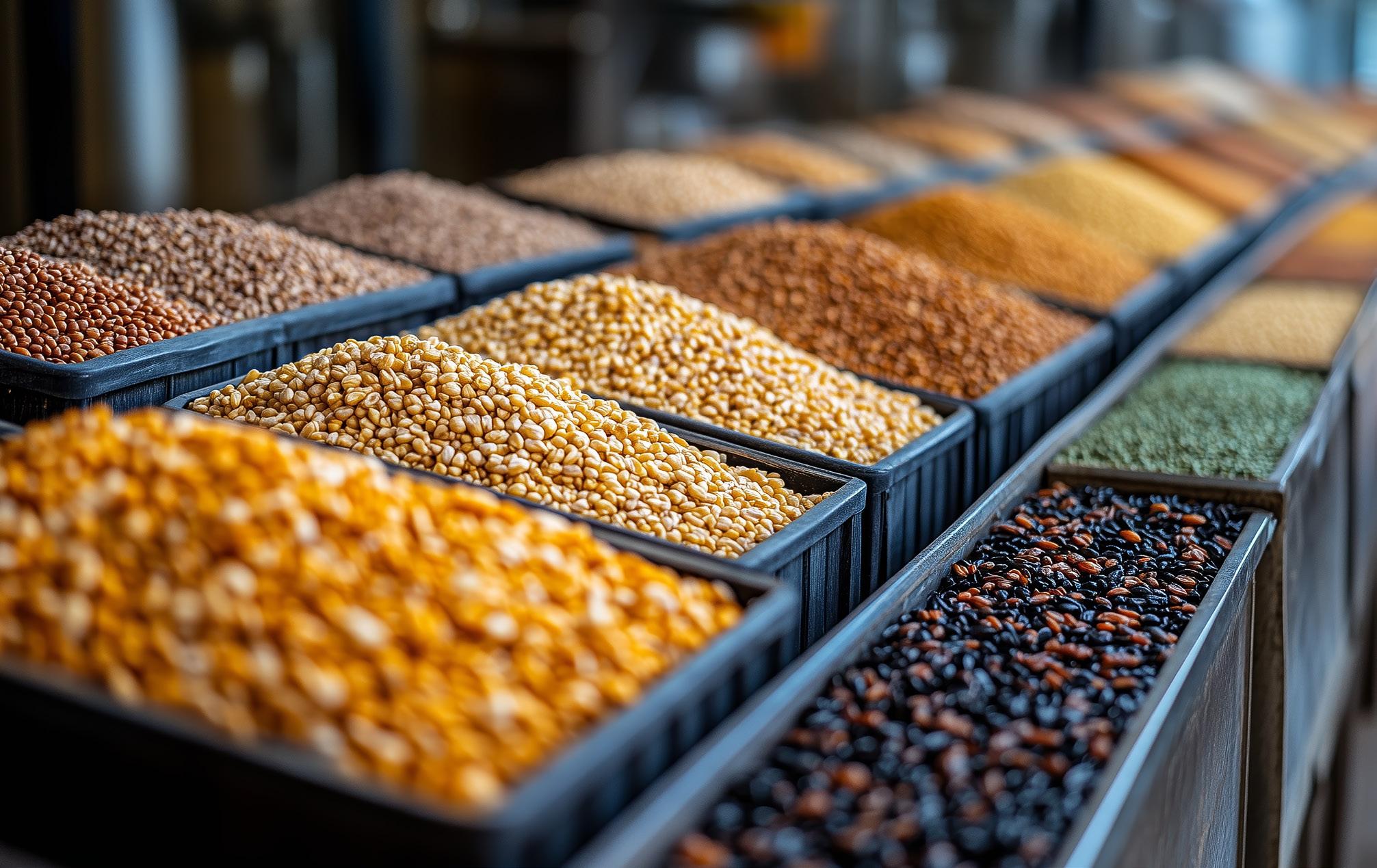
CGI’S INNOVATIVE SEED AND AGRONOMY PROGRAM
The company’s Seed and Agronomy Program is designed to help farmers and buyers foster growth.
It includes expert agronomy forecasts, high-quality seeds and seed advice, support for all stakeholders throughout the entire harvest cycle, and identified market opportunities.
The dedicated support and bidirectional flow of information generated by this program work to enhance the agricultural system as a whole, enabling the company to nourish the world safely.
CGI not only sells the highest-quality certified and conditioned seeds but also builds long-term partnerships that provide comprehensive crop health support.
The expert team consists of top-tier third-party breeders, experienced certified crop advisors, and brokers who guide growers in selecting the right seeds based on current conditions and market outlook.
Through its innovative Seed and Agronomy Program, the company is fostering growth for all crop stakeholders and providing continuous, dedicated support to growers and buyers.
Certified crop advisors play a crucial role throughout the entire harvest cycle by conducting extensive field research to inform seed selection, making regular visits to assess soil, maintain crop health, resolve problems, and identify market opportunities.
CGI’s Seed and Agronomy Program cultivates partnerships and information exchanges that enhance crop health and improve financial outcomes.
Over the years, CGI has developed a solid supply chain that encompasses a network of more than 8,000 dedicated farmers across the Northern Tier of the US. This expansive reach not only supports local agriculture but also plays a pivotal role in bolstering the nation’s food security.
At the heart of CGI’s operations lies a determination to deliver quality produce in a sustainable manner, which is reflected in every aspect of its business.
By fostering strong relationships with farmers, suppliers, and customers alike, CGI ensures the reliability and efficiency of its supply chain.
This allegiance to excellence has earned the company a reputation as a trusted provider of top-tier products and services within the agricultural industry.
STREAMLINE OPERATIONS, BOOST ROI
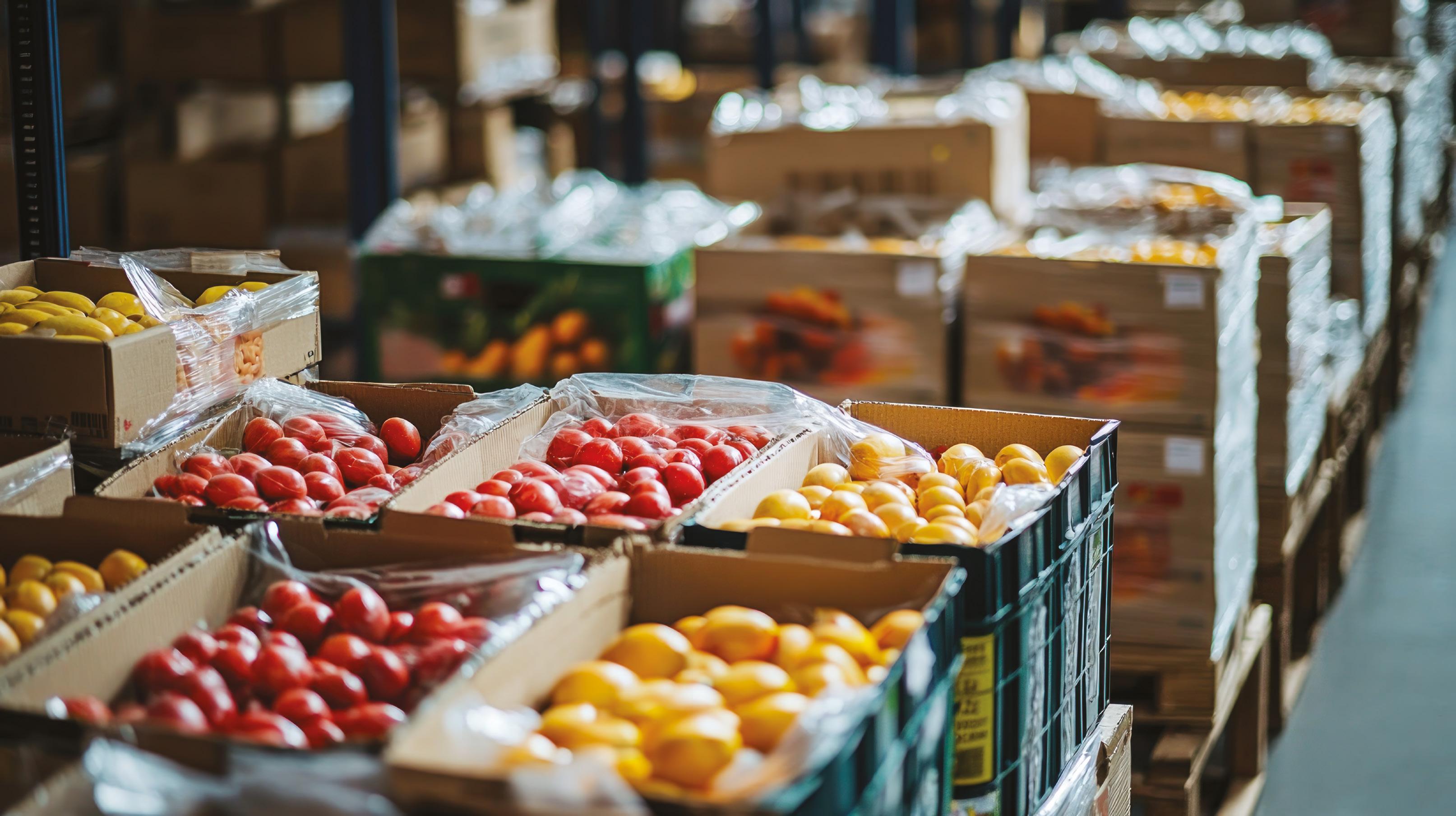
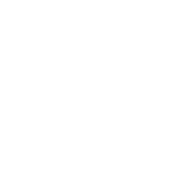
Integrated end of line solutions for food and agriculture, driving e ciency and growth.
Columbia/Okura delivers signi cant ROI through custom-engineered end-of-line bagging and palletizing systems designed to meet the unique needs of diverse industries, with a strong emphasis on food and agriculture. With over 400 installations in the food sector, we bring deep expertise in sanitation, food safety, and delicate product handling. Our exible layouts and specialized robotics, end e ectors, and bagging systems are designed to minimize damage and reduce spillage. Whether your products are in cases, bags, trays, or individually wrapped, we provide tailored solutions that optimize production lines and support your continued growth.
Let us partner with you to transform your operations and enhance your bottom line.
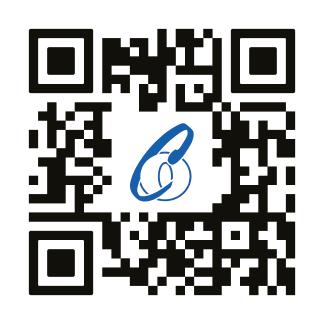
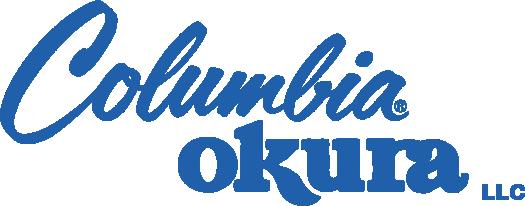
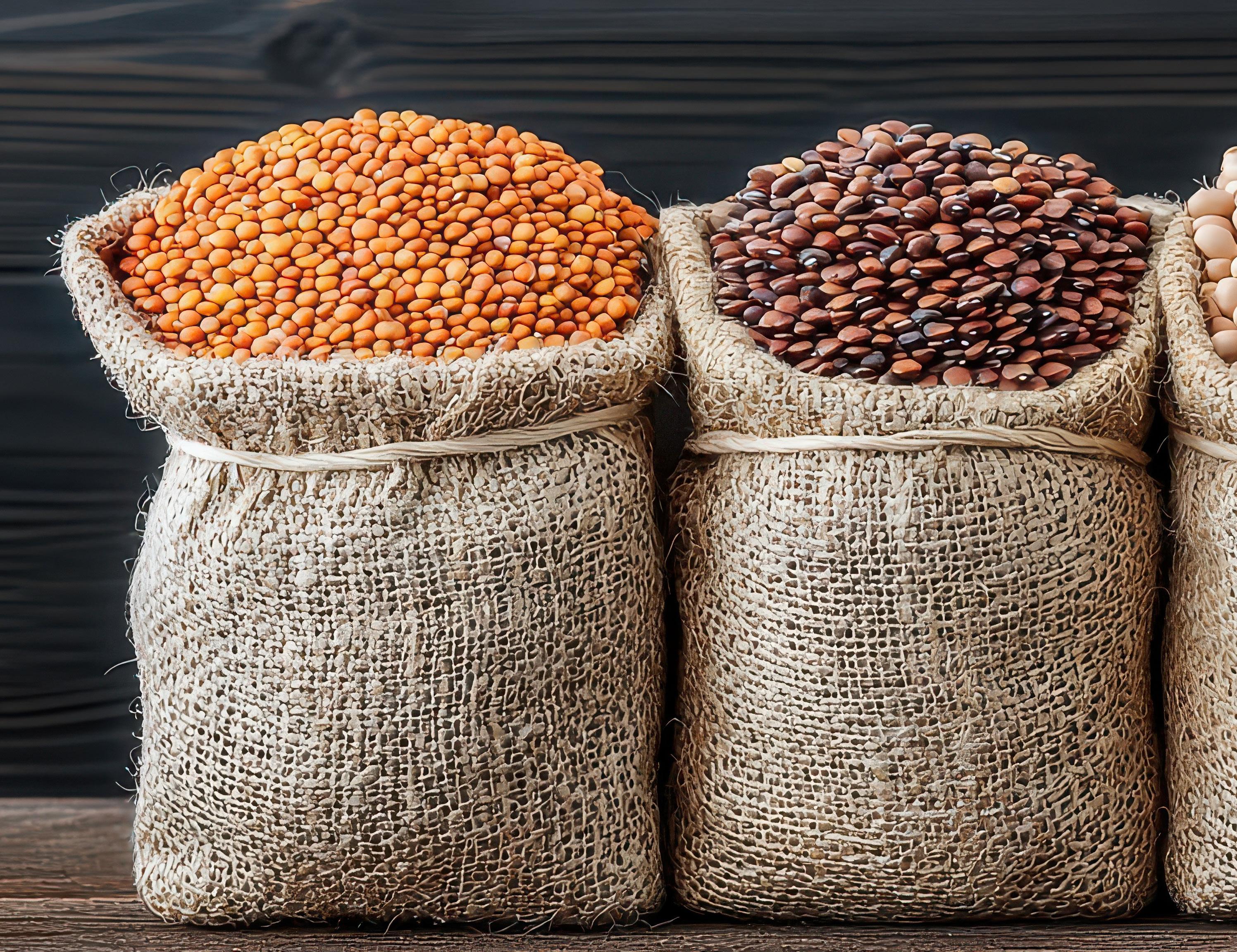
CGI’S PRODUCTS
• Wheat
• Barley
• Oilseeds
• Feed grains
• Beans
• Peas
• Lentils
• Organic crop
PRECISION PROCESSES
CGI has developed a system designed to support farmers by strategically locating assets and joint ventures (JVs), including interior elevators, processing plants, agronomy centers, barge loading facilities, and highcapacity, state-of-the-art terminals.
This highly interconnected system operates seamlessly to ensure the locally grown produce from CGI’s farmers is safely delivered to the global marketplace.
As one of the country’s largest processors and exporters of pulses, the company has a robust network
of processing plants located throughout the Northern US.
Recently, CGI increased its processing capacity by 60 percent with the addition of a new high-tech facility in Plentywood, Montana (MT). This expansion has allowed the company to process over 100,000 metric tons of pulse crops annually.
CGI collaborates closely with over 150 local producers in Northeast MT and North Dakota to source dry peas, lentils, and chickpeas, thereby supporting local farming communities.
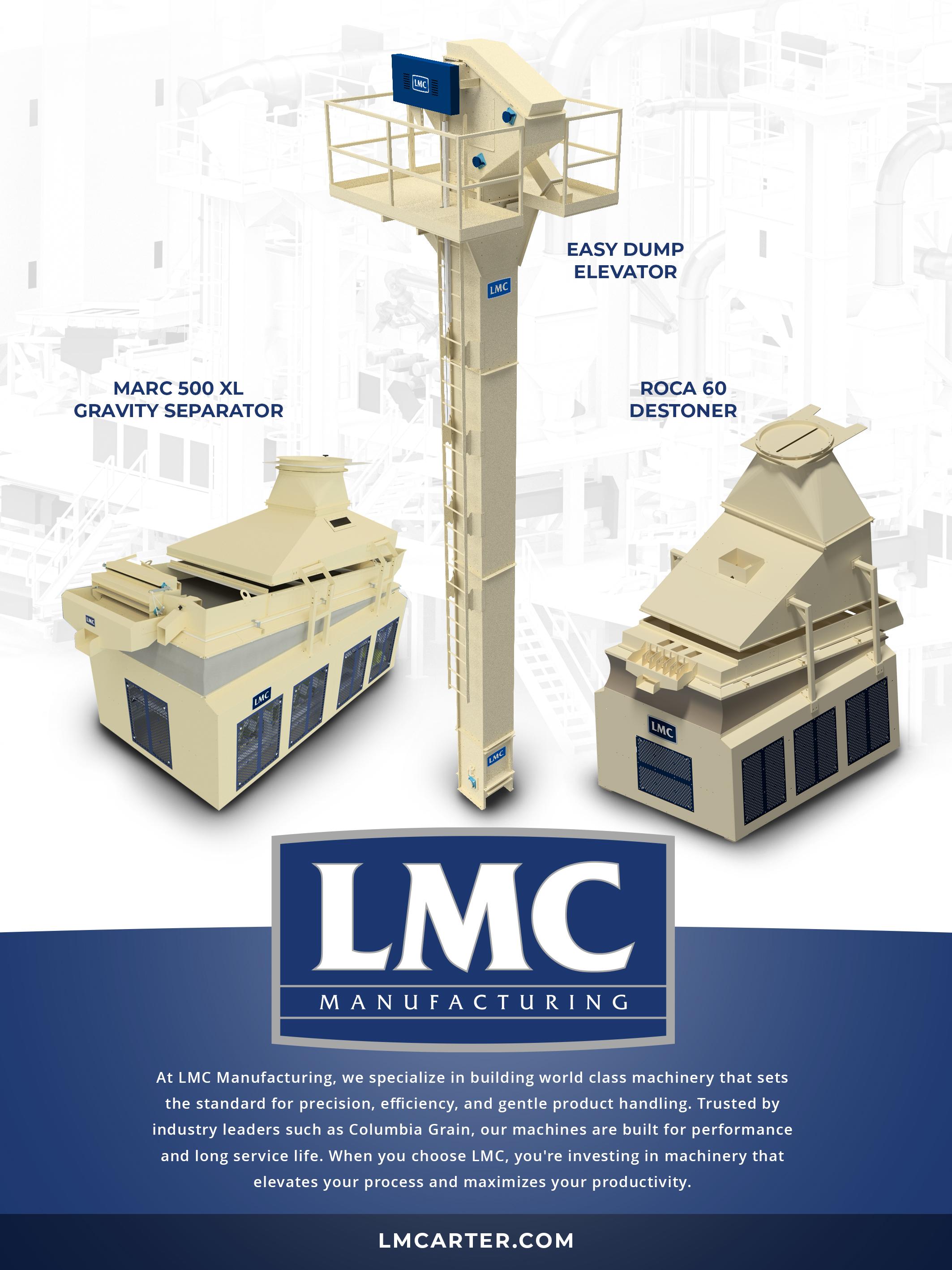
Notably, with decades of experience in trading and logistics, the company operates a network of elevators and processing facilities across the Northern US.
It provides reliable supply chain solutions to customers in over 80 countries by partnering with various transportation providers, including truck, rail, barge, and bulk vessel operators.
Moreover, the company maintains strong relationships with farmers, ensuring the delivery of safe and traceable products. This allows CGI to know the exact source of its products while prioritizing safety and integrity throughout the supply chain.
Distribution is a crucial area where CGI excels, delivering highquality grains, pulses, and oilseeds to customers around the globe. As an industry leader, the company consistently invests in the technology
and facilities necessary to succeed in a diverse and rapidly changing market.
The logistics team is dedicated to ensuring products are transported safely and promptly to their destinations, whether by truck, rail, barge, or vessel, both domestically and internationally.
EMPOWERING PRODUCERS FOR SUSTAINABILITY
To gain a competitive edge, CGI has made an advantageous move in developing Columbia Grain Producer Solutions.
This visionary platform is at the forefront of agricultural innovation, delivering sophisticated and tailored marketing insights as well as invaluable educational resources, unlocking a wealth of growth opportunities for CGI’s producers.
It features state-of-the-art pricing tools meticulously designed to
optimize returns both now and in the future, prioritizing connectivity and reliability and building strong, trusted relationships with each farmer it serves.
The goal is to empower producers, enabling them to maintain an upper hand in an ever-evolving market landscape.
Through personalized marketing products and comprehensive risk management consulting, CGI addresses the specific challenges faced by each producer, equipping them to flourish amid the dynamic shifts of the agricultural environment. With a storied legacy grounded in exceptional consistency, unmatched quality, and unwavering reliability, the company strives to enrich the food supply chain in the Northern US. Its mission is clear – to ensure these highquality agricultural products reach those who need them most.
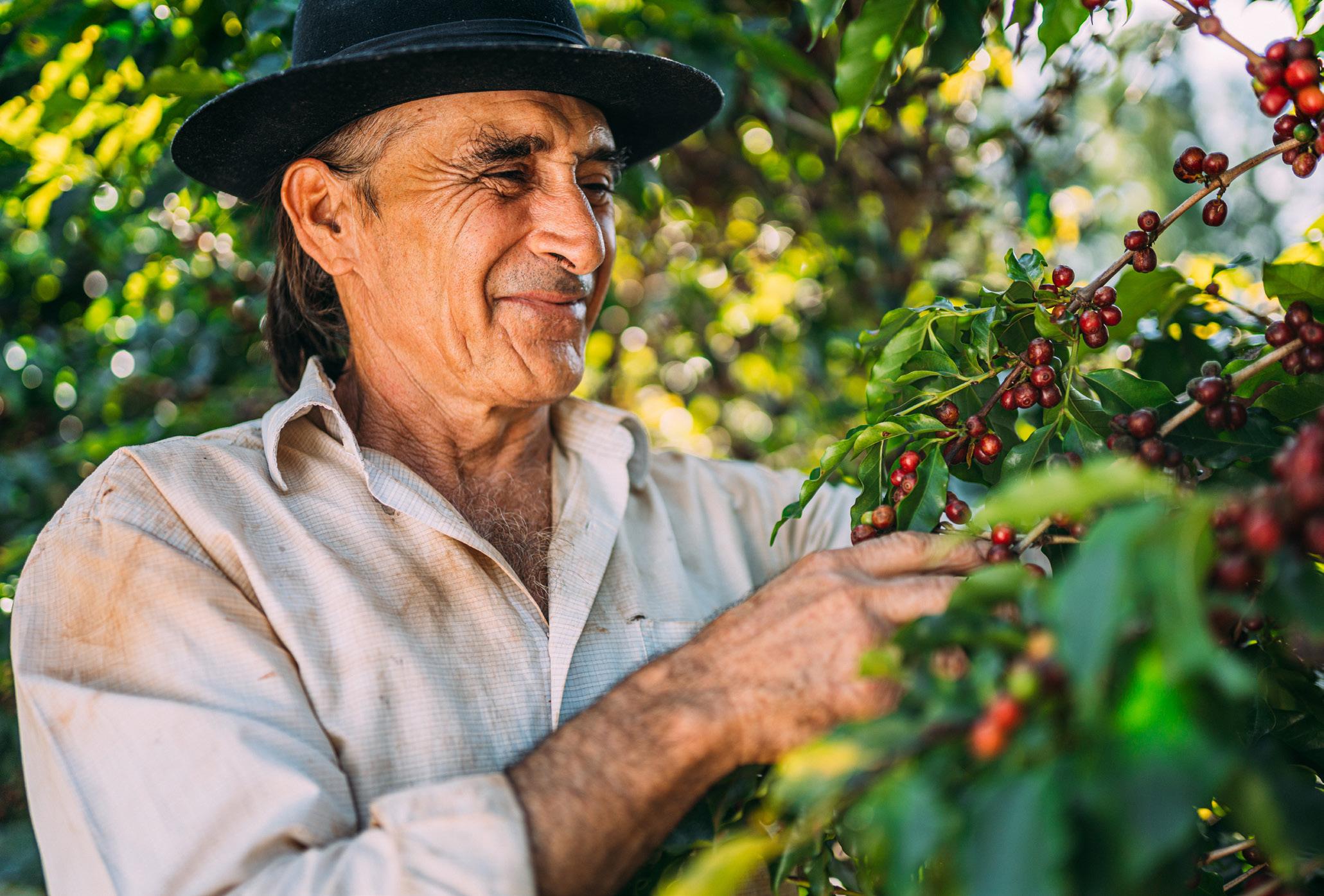
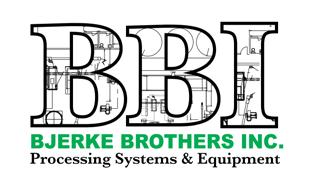
With Experience Comes Knowledge
Owned by brothers Curt and Tracy Bjerke since 1990, we have over 90 combined years of experience in sales, service, and installation of grain, bean and seed cleaning processing equipment.
Bjerke Brothers offers full design and build of bean and seed cleaning plants.
Sales, Parts and Service for
• Q-Sage Manufacturing
• LMC Lewis M Carter Manufacturing
• Oliver Manufacturing
• Forsberg Manufacturing
• Carter Day Manufacturing
• Sun Magnetics Inc.
Parts and Service for:
• Crippen, Ideal and Northland Superior Equipment
Call us: 701-847-3125 Visit our website at: www.bjerkebrothersinc.com Email Tracy Bjerke at: tbjerke@bjerkebrothersinc.com.
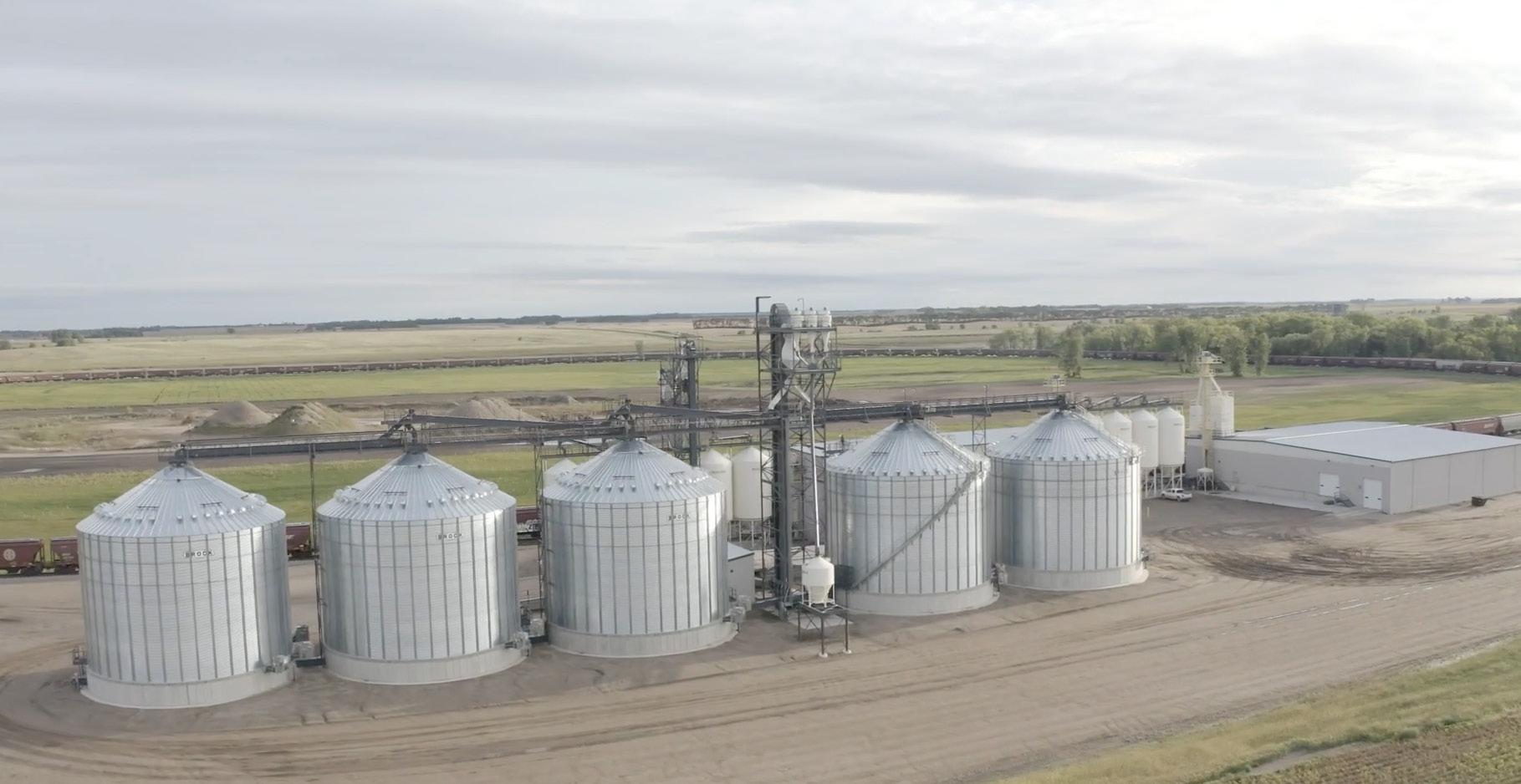
Further defined by fostering growth and connection within every community it engages with, and acting as the vital link between producers and consumers, the company is backed by over 40 years of industry experience.
Indeed, farmer partnerships are crucial for meeting customer crop demands as they strive to provide superior food products for consumers worldwide.
CGI takes pride in offering trusted solutions that embody a farm-totable philosophy, nourishing the world safely and enriching lives at every stage of the supply chain.
FARMERS OF THE FUTURE
At CGI, the team works daily to elevate its supply chain to become a value chain, treating each member of the global community with integrity, care, trust, and honesty.
Supporting innovation, the
company remains connected because success helps ensure the world has proper nutrition to live life fully by providing its bulk pulses to developing countries and working with food banks.
As a company that believes in nurturing the growth of its local communities and supporting youth through sponsorship opportunities, including high schools and non-profit organizations such as Future Farmers of America (FFA), CGI is honored to contribute.
Founded in 1928, FFA empowers the next generation to meet challenges in agriculture, focusing on developing leadership skills and various career pathways as well as expertise in business, technology, and science.
Meanwhile, CGI is a majority owner of Montana Specialty Mills, which operates an organic and nongenetically modified organism oilseed
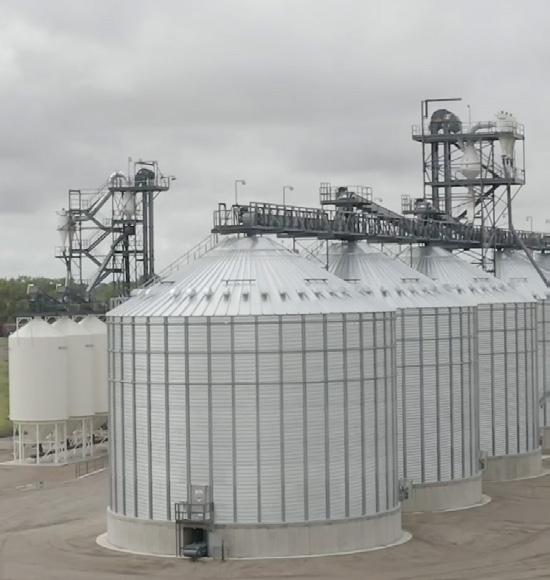
crushing facility in Great Falls, a mustard seed facility in Conrad, and Montana Craft Malt in Butte.
CGI continues to explore opportunities to partner with agricultural businesses that align with its values and goals of cultivating growth.
This strategic approach exemplifies how CGI is paving the way for future advancements and responsible practices while remaining committed to its mission of connecting high-quality, sustainably sourced products with consumers worldwide.
Epitomizing the fusion of quality, sustainability, and innovation within the agricultural sector, CGI is ensuring a resilient and thriving agricultural ecosystem for generations to come.
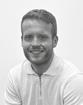
THE FINAL WORD
To round off each issue, we ask our contributing business leaders for their views on the same question
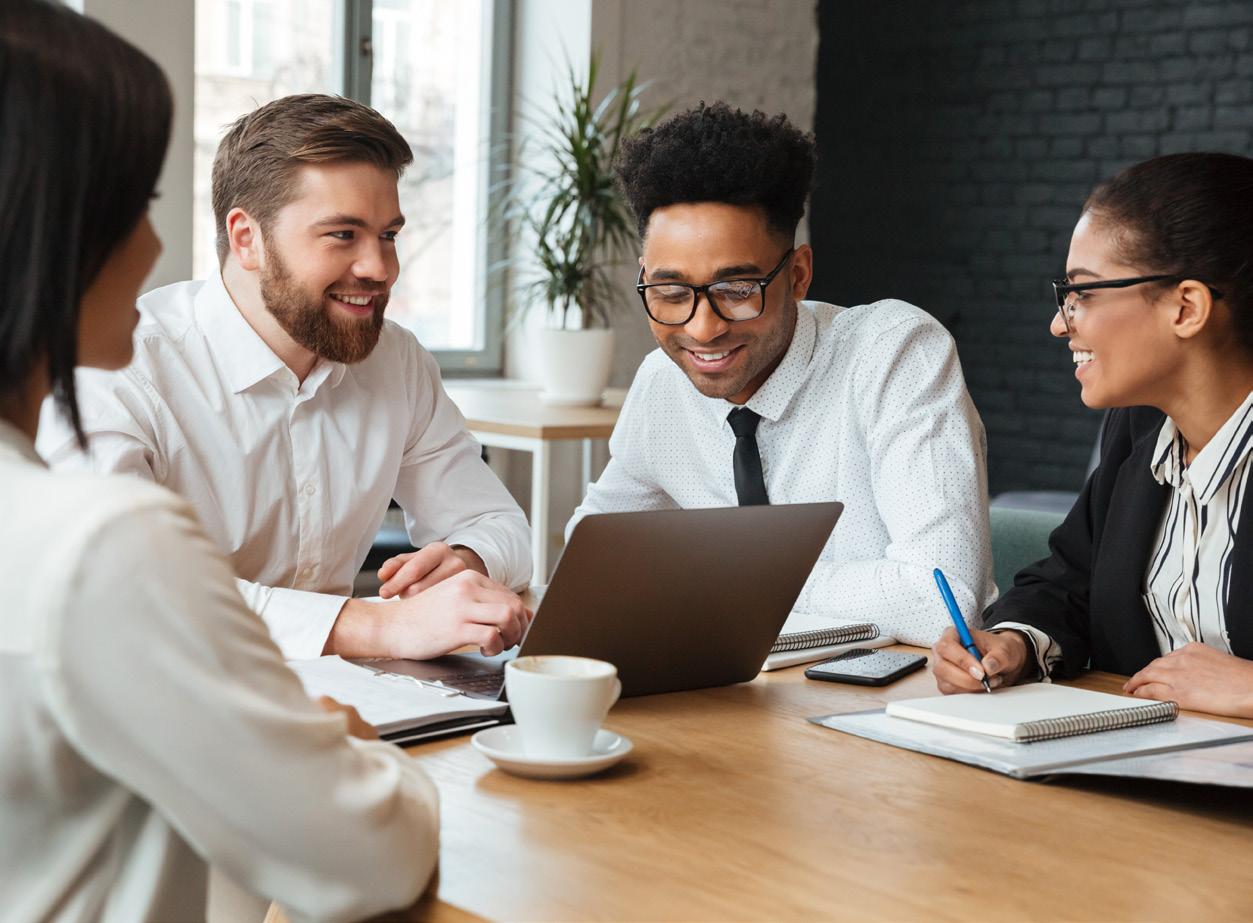
What is your proudest workplace accomplishment?
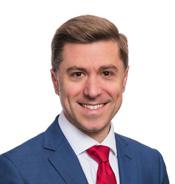
Rick Cordaro
Vice President of Radar and Sensor Systems, Lockheed Martin
“I am proud of the work our teams do every day, and I’m proud when I see our war fighters use our equipment to defend their assets and our homeland.
“At the same time, all of that happens through people. Nothing gets done without a person in all of our businesses, so my proudest accomplishment really is when I see our talented team members grow in their careers, get promoted, and have success in their own right.
“I don’t make anything at Lockheed Martin, but when I see our teammates make something, stand in front of it, and say they built it, designed it, bought parts for it, or ensured it was delivered with quality and integrity –that makes me proud.”
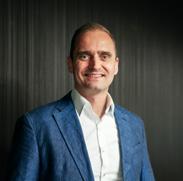
Andreas Salznig COO, KNAPP North America
“I’m very proud of our work culture and the values we maintain. We are one big multicultural family and that’s how we all treat each other.
“Yes, there are always challenges, but we all have a hands-on mentality and stay very solution-oriented, and this always comes with a portion of fun and joy at work!”
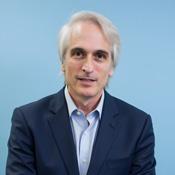
Bill Drummer CEO, GPA Logistics Group
“I’m most proud of how Brian and I have managed to find the delicate balance between customer and employee satisfaction. These objectives often conflict, but we’ve found the intersection where both thrive.
“We know we have to earn our customers’ trust and loyalty anew every day. Our customers regularly refer new business to us, which is the ultimate validation of our service quality. Meanwhile, our exceptionally low employee turnover rate reflects genuine workplace satisfaction and commitment.
“Achieving both requires constant attention from Brian and I, but it has created a culture that embodies our values and consistently delivers exceptional customer service.
“We’ve built a staff base that personifies our values and priorities, and we know we can depend on them to provide our customers with the service they need to succeed. Our tagline – ‘We only succeed by ensuring your success’ – isn't just marketing; it’s our operational philosophy.
“It’s challenging to execute consistently but it’s incredibly rewarding to know we’re genuinely contributing to our customers’ success.”
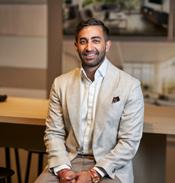
Milan Mann
President,
BM Group of Companies
“My proudest workplace accomplishment is creating opportunities for our team members to grow and develop their careers alongside BMG.”
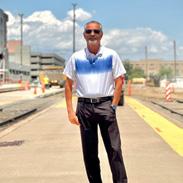
Robert Gonzales Director of Operations, Rio Metro Regional Transit District
“My proudest workplace accomplishment is my staff – how they work, all their effort, and how they are pretty self-sufficient. When we have a project, we all get together and tackle it in a seamless and timely manner.”
Are you a CEO/Director with a company story to tell? Contact North America Outlook now!
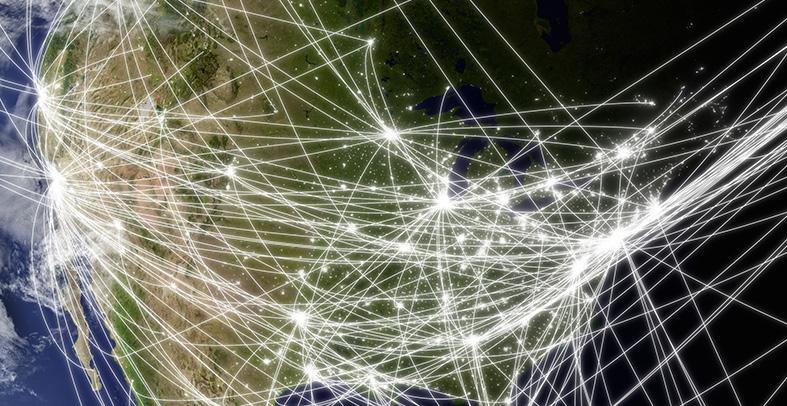
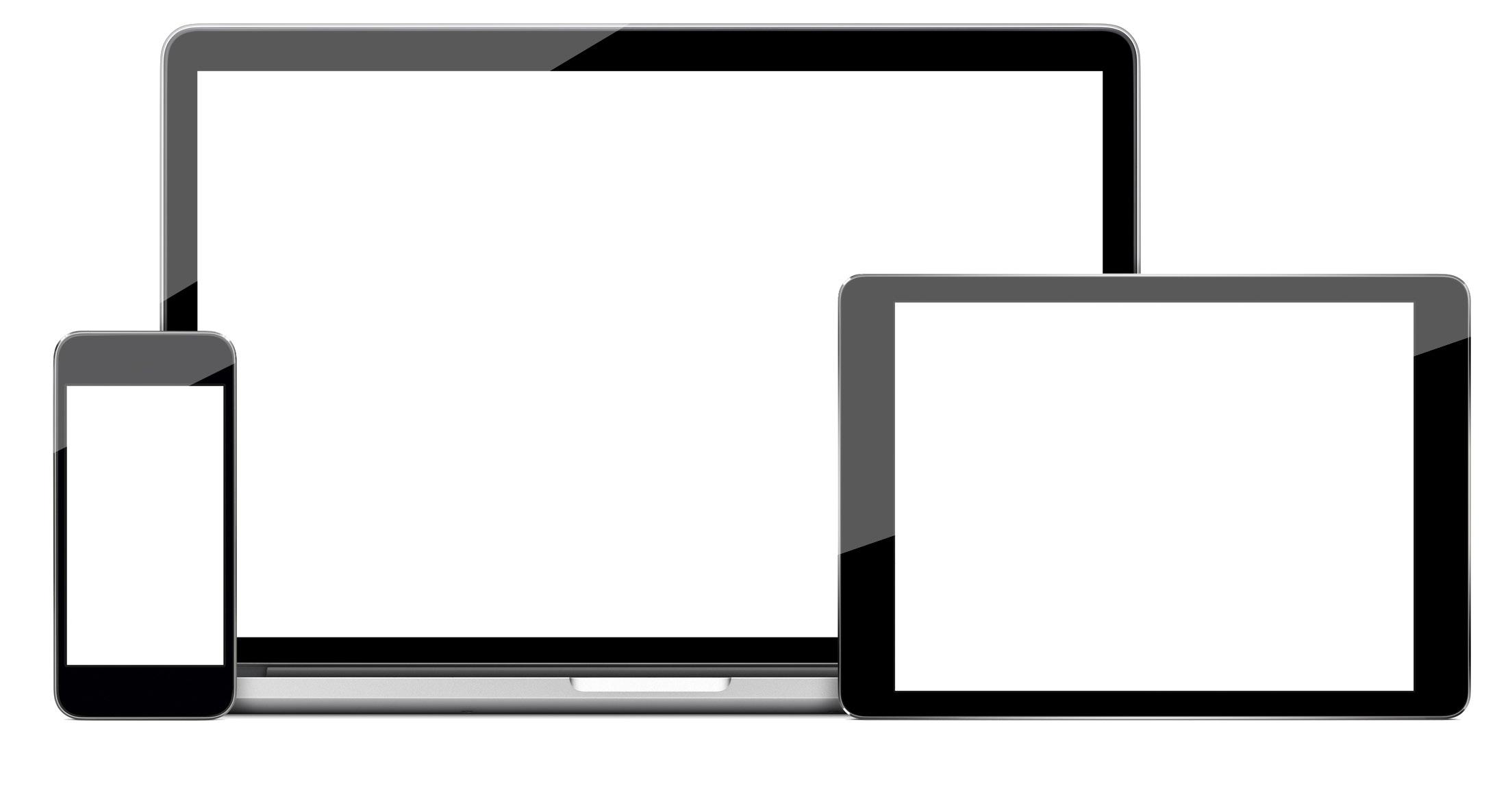
Propak Systems

reading
Reaching ever increasing audiences across the continent and beyond, your company can take advantage of this global exposure with a
To
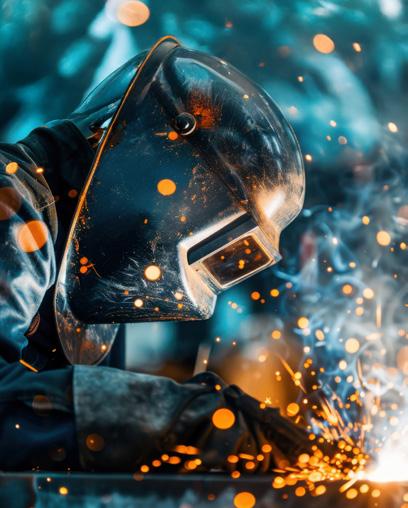
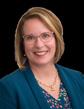
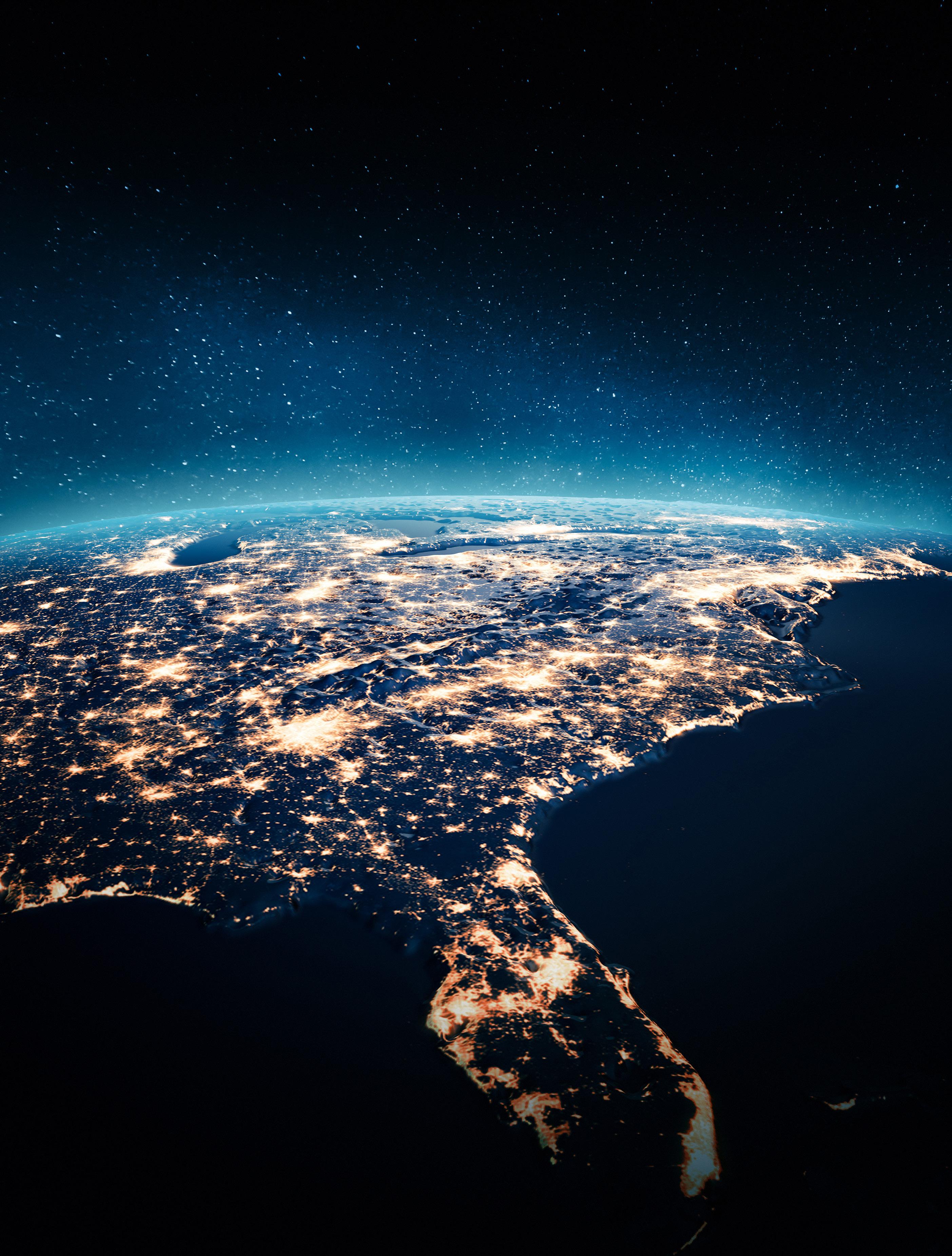
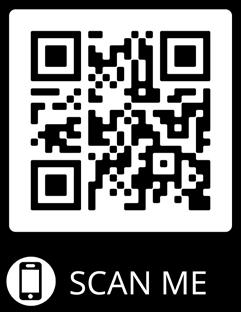