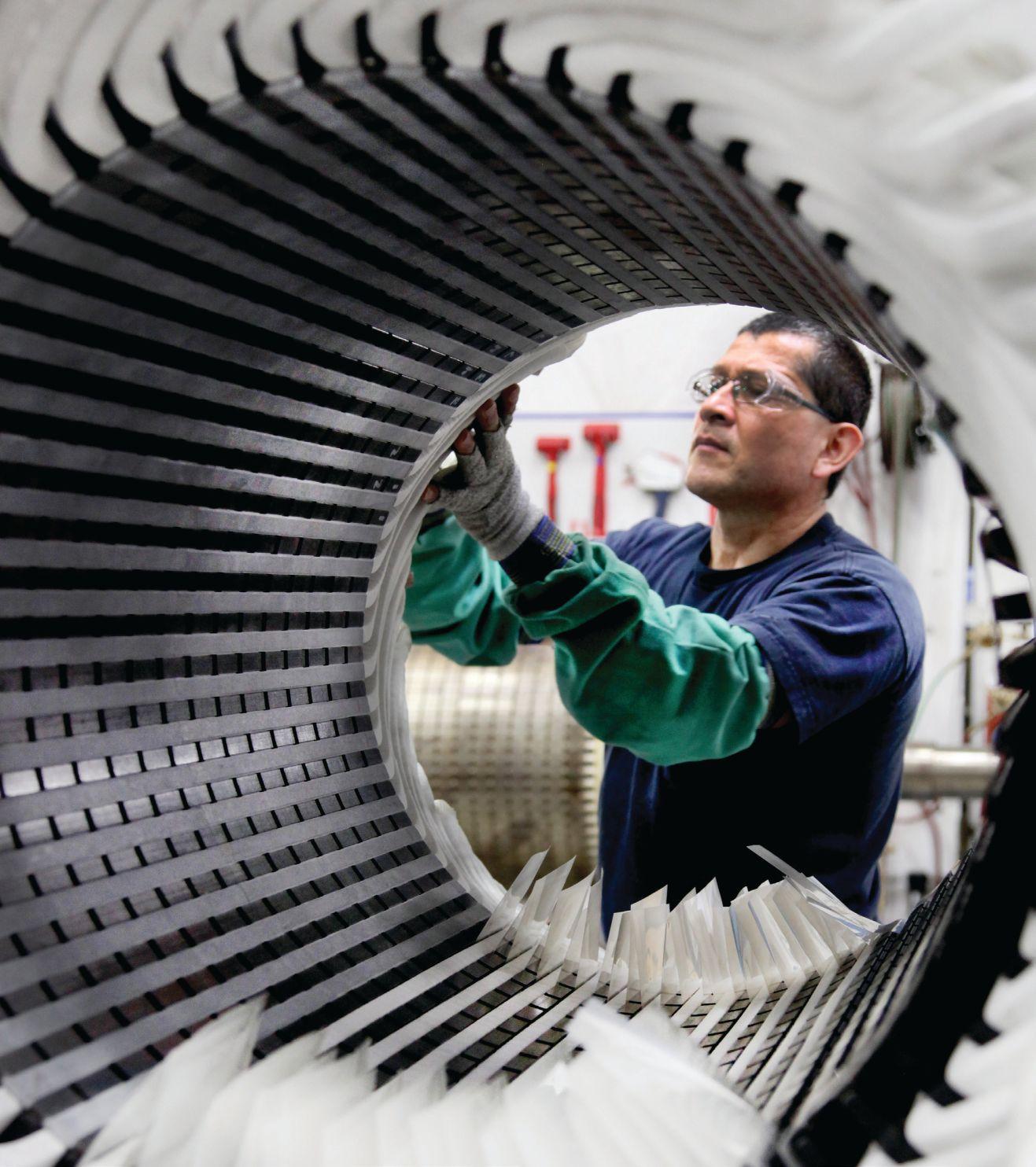
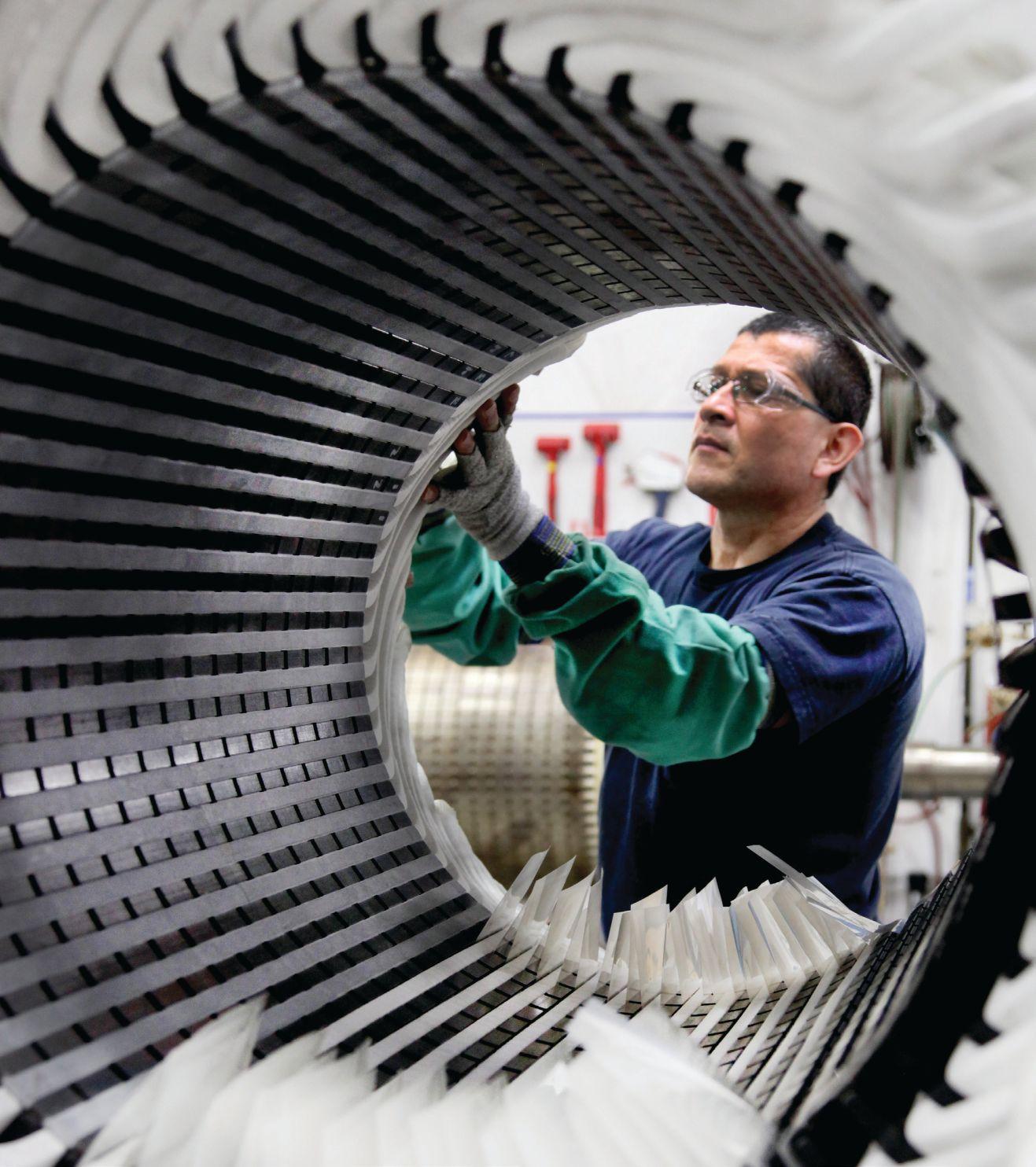
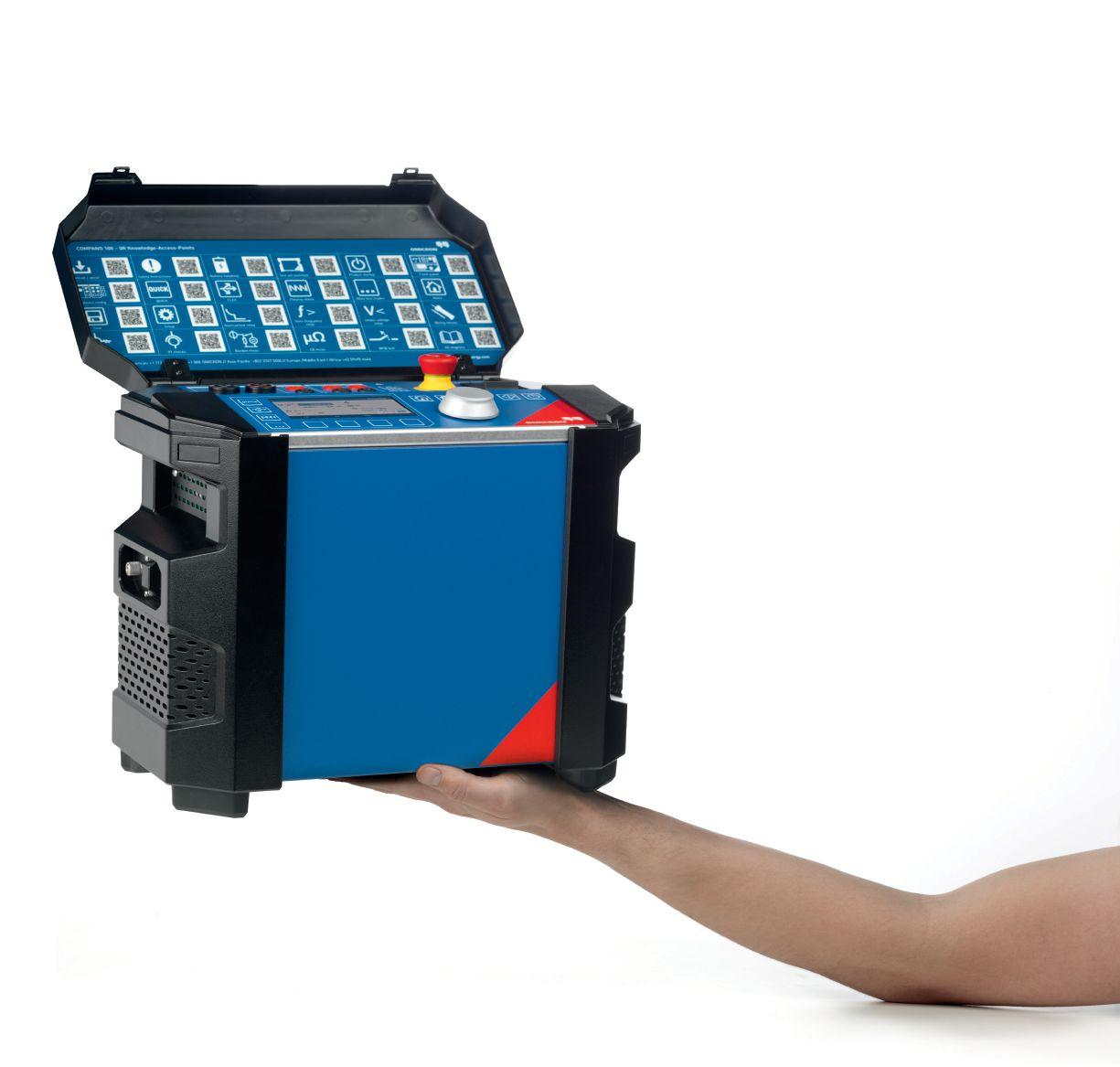
•
•
•
•
• CT Kneepoints up to 30 kV
• CT grouped testing includes Demagnetization. Knee Points. Ratios. Saturation Curves. Winding Resistances. Polarities and Phase Deviation (on all taps of multi-ratio CTs)
• VT testing including Demagnetization. Ratio. Winding Resistance. Polarity and Phase Deviation
• Performs Secondary Burden tests
• Integrated 1 kV DC insulation test system
The MVCT makes testing CTs easy and reduces testing time by directly connecting to multi-ratio CTs and performing all tests -saturation, ratio and polarity, winding resistance, and insulation -on all taps with the push of a button and without changing leads.
CT testing simplified so you can power on.
Discover the full functionality of the MVCT at us.megger.com/mvct
Simplified connectionsdirectly connect to multi-ratio CT's and perform all tests on all taps with the push of a button and without changing leads
Optional integrated single-phase relay testing
Optional integrated 1 kVDC insulation test system
Maximum voltage of 300V ensures safety while delivering accurate test results
The Megger MVCT test set is a lightweight, robust, portable unit capable of testing both current and voltage transformers. It makes testing CTs easy and reduces time by directly connecting to multi-ratio CTs and performing all tests on all taps with the push of a button and without changing leads.
56 Electrical Insulation for AC Rotating Machines: What Is It? How Is It Chosen? Why Does It Fail?
Early on, Charles Proteus Steinmetz acknowledged that “insulation is by far the most important problem in electrical design.” A century later, a dielectric engineer stated he could build a perfect motor if only he didn’t need insulation. The problem hasn’t changed, but the materials certainly have. This article introduces common electrical insulating materials used in motors and generators, explains why they are chosen, discusses how they are tested during development, provides insight into how they fail, and offers an overview of tests that help monitor and analyze those trends to failures. As new materials and systems are introduced, continuing to test for expected performance is important for designing reliable machines. Testing the equipment in the field helps assure machines continue to achieve predictable expectations for performance and efficiency.
Kevin Alewine, Shermco Industries
7 President’s Desk
Jim Cialdea, CE Power Engineered Services, LLC
NETA President
48 Comparison of Low-Frequency and HighFrequency Partial Discharge Measurements on Rotating Machine Stator Windings
Connor Chan and Greg Stone, Iris Power, a Qualitrol Company
66 Condition Assessment of the Induction
Motor Based on Vibration and Current Signature Analysis
Srdjan Jokic and Sasa Ikic, DV Power
76 Effective Preparation and Response to Natural Disasters
Ron Widup, Shermco Industries
10 NFPA 70E and NETA
Hazards Involved with Motor Control Centers
Ron Widup and Jim White, Shermco Industries
18 No-Outage Corner
Strange Magic: An Online Cable Partial Discharge Testing Adventure
Don A. Genutis, Halco Testing Services, Inc.
24 Tech Quiz
Motor Maintenance
Jim White, Shermco Industries
28 Tech Tips
Salvaging Flood-Damaged Electrical Equipment
Jeff Jowett, Megger
37 Safety Corner
Rotating Machinery Hazard Awareness
Scott Blizard and Paul Chamberlain, American Electrical Testing Co. LLC
42 Relay Column
High-Speed Acceleration Protection for Generator Stator Ground Faults
Steve Turner, Electrical Consultants, Inc.
INDUSTRY TOPICS
85 What is So Negative about Negative Sequence? Part 1
Alex Rangel, Saber Power Services, LLC
94 Why Test Switches Still Matter
Glenn Goldfarb, ABB Inc.
104 Challenges and Solutions to Transformer Differential Protection Scheme
Mohit Sharma, Megger
SPECIFICATIONS AND STANDARDS
114 ANSI/NETA Standards Update
116 Insulated Conductor Committee News
Ralph Patterson, Consultant
101 Long Beach City College and NETA
Collaborate to Offer Unique Electrical Technician Training Program
120 PowerTest 2018 New Product Forum
131 NETA Accredited Companies
136 Advertiser List
Why my intellirent? Convenience in the palm of your hand. Search for equipment, view and save manuals, access tips and how-to’s, or get quick rental pricing and tech support. It’s connected to intellirent, so you can see what equipment you have on rent, track shipments and see account details.
Available at Powered by
Full Service Independent Electrical Testing
Over 25 Years of Experience & Reliability
Low, Medium, and High Voltage
Substations • Distribution switchgear • Transformers • Cables • Relays
Preventative Maintenance & Testing
Switchgear
Infra-red surveys • Circuit breakers • Relay testing and calibration
Transfer switches • Complete maintenance of ACB’s-OCB’s-SF6 CB’s
UPS & station battery maintenance • Gen. load tests
Transformers
TTR • Power factor testing • Oil testing and field analysis
Oil reconditioning & reclaiming • field replacements
Engineering Services
Arc-flash, short circuit, and coordination studies
Power factor correction • Power quality and harmonic studies
Load surveys • Grounding system design
Trust us to keep your business up and running. Call for a free consultation today.
P: 781-767-0888 Email: infrared.ma@verizon.net 152 Centre Street Holbrook, MA 02343 www.infraredbps.com
3050 Old Centre Road, Suite 101
Portage, MI 49024
Toll free: 888.300.NETA (6382)
Phone: 269.488.NETA (6382)
Fax : 269.488.6383
neta@netaworld.org
www.netaworld.org
executive director: Missy Richard
NETA Officers
president: Jim Cialdea, CE Power Engineered Services, LLC
first vice president: Scott Blizard, American Electrical Testing Co., Inc.
second vice president: Lorne Gara, Orbis Engineering Field Services, Ltd.
secretary: Eric Beckman, National Field Services
treasurer: John White, Sigma Six Solutions
NETA Board of Directors
Ken Bassett (Potomac Testing, Inc.)
Eric Beckman (National Field Services)
Scott Blizard (American Electrical Testing Co., Inc.)
Jim Cialdea (CE Power Engineered Services, LLC)
Scott Dude (Dude Electrical Testing LLC)
Lorne Gara (Orbis Engineering Field Services, Ltd.)
Dan Hook (Western Electrical Services, Inc.)
David Huffman (Power Systems Testing)
Alan Peterson (Utility Service Corporation)
John White (Sigma Six Solutions)
Ron Widup (Shermco Industries)
NETA World Staff
technical editors: Roderic L. Hageman, Tim Cotter
assistant technical editors: Jim Cialdea, Dan Hook, Dave Huffman, Bob Sheppard
associate editor: Resa Pickel
managing editor: Carla Kalogeridis
copy editor: Beverly Sturtevant
advertising manager: Laura McDonald
design and production: Moon Design
NETA Committee Chairs
conference: Ron Widup; membership: Ken Bassett; promotions/marketing: Scott Blizard; safety: Scott Blizard and Jim White; technical: Alan Peterson; technical exam: Dan Hook; continuing technical development: David Huffman; training: Bob Sheppard; finance: John White; nominations: Alan Peterson; alliance program: Jim Cialdea; association development: Ken Bassett and John White
© Copyright 2018, NETA
NOTICE AND DISCLAIMER
NETA World is published quarterly by the InterNational Electrical Testing Association. Opinions, views and conclusions expressed in articles herein are those of the authors and not necessarily those of NETA. Publication herein does not constitute or imply endorsement of any opinion, product, or service by NETA, its directors, officers, members, employees or agents (herein “NETA”).
All technical data in this publication reflects the experience of individuals using specific tools, products, equipment and components under specific conditions and circumstances which may or may not be fully reported and over which NETA has neither exercised nor reserved control. Such data has not been independently tested or otherwise verified by NETA.
NETA MAKES NO ENDORSEMENT, REPRESENTATION OR WARRANTY AS TO ANY OPINION, PRODUCT OR SERVICE REFERENCED OR ADVERTISED IN THIS PUBLICATION. NETA EXPRESSLY DISCLAIMS ANY AND ALL LIABILITY TO ANY CONSUMER, PURCHASER OR ANY OTHER PERSON USING ANY PRODUCT OR SERVICE REFERENCED OR ADVERTISED HEREIN FOR ANY INJURIES OR DAMAGES OF ANY KIND WHATSOEVER, INCLUDING, BUT NOT LIMITED TO ANY CONSEQUENTIAL, PUNITIVE, SPECIAL, INCIDENTAL, DIRECT OR INDIRECT DAMAGES. NETA FURTHER DISCLAIMS ANY AND ALL WARRANTIES, EXPRESS OF IMPLIED, INCLUDING, BUT NOT LIMITED TO, ANY IMPLIED WARRANTY OF FITNESS FOR A PARTICULAR PURPOSE.
ELECTRICAL TESTING SHALL BE PERFORMED ONLY BY TRAINED ELECTRICAL PERSONNEL AND SHALL BE SUPERVISED BY NETA CERTIFIED TECHNICIANS/ LEVEL III OR IV OR BY NICET CERTIFIED TECHNICIANS IN ELECTRICAL TESTING TECHNOLOGY/LEVEL III OR IV. FAILURE TO ADHERE TO ADEQUATE TRAINING, SAFETY REQUIREMENTS, AND APPLICABLE PROCEDURES MAY RESULT IN LOSS OF PRODUCTION, CATASTROPHIC EQUIPMENT FAILURE, SERIOUS INJURY OR DEATH.
Previously, Section 130.7(F) was a part of 130.7(E), Alerting Techniques, but the 70E committee wanted to make the subsection more prominent, so it was separated to provide a more focused approach to the hazard. 130.7(F) states:
Where work performed on equipment that is de-energized and placed in an electrically safe condition exists in a work area with other energized equipment that is similar in size, shape, and construction, one of the alerting methods in 130.7(E)(1), (2), or (3) shall be employed to prevent the employee from entering look-alike equipment.
Th ree alerting techniques are provided in 130.7(E):
• Safety signs and tags
• Barricades
• Attendants
We set up safety signs and tags in conjunction with barricades. Typically, the barricade is safetybarrier tape positioned about waist-high with some printed wording. Yellow safety-barrier tape indicates CAUTION. Personnel are only to enter once they are aware of the hazards. Red safety-barrier tape is recommended for
electrical hazards. It states DANGER, and only authorized personnel are allowed inside the barrier. Red safety-barrier tape is recommended for all work that creates or exposes others to electrical hazards. Photo 2 shows one way to mark equipment that is being worked on.
Photo 3 shows how equipment being worked on is marked, and the equipment on either side is marked as energized. This is a great method when adjacent equipment is still energized.
Attendants are used when there is a potential for unqualified or unaware people to enter into the safe work zone created by the safety barriers. Many older buildings have lighting panels in their hallways; this means the hallway would be closed due to the size of the safe work zone perimeter. If electrical work inside that panel is necessary, an attendant would probably be needed, as office workers would potentially try to cross over to get to where they are going. We have personally witnessed this on several occasions. They just don’t understand the risk involved or the hazard, so the safety-barrier tape is just an inconvenience. The attendant is placed there to warn people approaching not to cross the safety barrier. If they do, all work is to cease immediately and the area made safe until that person(s) leaves the safe work zone. We must protect those who are unaware and oblivious to the risk.
Almost every incident involving electrical equipment — especially shock events — could have been avoided if the person involved had tested the circuit or equipment for the absence of voltage prior to making contact. It is such a fundamental concept, yet qualified persons seem to lose track of the need for it. As soon as electrical conductors or circuit parts are exposed, an absence-of-voltage test should be performed. There have been numerous articles
and papers published on this subject, so we suggest readers perform an internet search on the topic and become familiar with the process. If you are familiar with it, it must be implemented each and every time equipment is potentially energized. We don’t know what we don’t know. Unless we test for the absence of voltage, we cannot be certain that particular conductor or piece of equipment is deenergized.
One way to prevent workers from being exposed is to install equipment reset devices, test points, or other devices required for maintenance to the outside of the equipment. To reduce the exposure created by taking readings, an IEEE-compliant communication bus could be installed on the outside of the door. For example, a newer product on the market is a permanently mounted absenceof-voltage tester (Photo 4). The device has UL approval and is a true absence-of-voltage tester. Th e 70E Committee spent a considerable amount of time discussing this product and learning how the device works.
Many technicians and electrical workers don’t understand the principles involved with guarding energized conductors and circuit parts. Photo 5 shows the LINE side of an MCC main circuit breaker that does not have
a permanently installed guard. Since the LINE side is unguarded, it must always be considered an energized hazard, and PPE must be worn at all times when troubleshooting.
When the main circuit breaker or switch has a permanently installed guard (Photo 6), PPE can be removed once absence-of voltage testing has verified that conductors and circuit parts are de-energized.
One method to allow the removal of PPE while repairs are made is to install temporary guarding on the LINE side terminals. PPE has to be worn while the guard is installed and removed, but the worker can remove PPE once it is in place. Temporary guarding is usually rubber insulating shielding specifically designed for such purposes. It is much thinner than the rubber insulating blankets used in the field (Photo 7). It is important to install the rubber insulating shielding to completely cover the energized terminals and allow no access to the terminals from any direction. It can be held in position with cable ties or spring-loaded clamps.
7: Rubber Insulating Shielding (Roll Blanket) Used as Temporary Guarding
One question often brought up is, “If arc flash warning labels are all the same, are they right?” The answer is yes, they should all be the same on a section of MCCs. Figure 1 illustrates why. The arc flash warning labels must state the highest hazard in a piece of equipment. MCC buckets are all fed from a common bus. Each MCC will have the same incident energy at the LINE side of the MCC main circuit breaker or switch, and each section will be labeled with
the same incident energy. Arc flash warning labels will not typically show the incident energy on the LOAD side of a device.
This is a difficult topic — mostly because manufacturers previously considered it a normal part of the maintenance routine — but manufacturers now uniformly state that buckets should only be removed or installed if the MCC is de-energized. An exception is newer MCCs that meet IEEE Std. 1683, IEEE Guide for Motor Control Centers Rated up to and including 600 V AC or 1000 V DC
Figure 1: Main Bus 4 and Bus 41 Feeding Each MCC Section
with Recommendations Intended to Help Reduce Electrical Hazards. This IEEE Guide has design requirements that may allow inserting or removing MCC buckets while energized.
Older MCC buckets should not be removed or installed while energized, as the electrical connection between the MCC bucket and the main bus has no arc extinguishers. Even though manufacturers stated that this operation could be done while energized, electrical safety changed tremendously across the 1950s, 1960s, 1970s, and even the 1980s. What was once considered acceptable risk is not any longer. If a newer MCC has been installed, read the manufacturer’s instructions, and if in doubt, contact the manufacturer for additional guidance. If there is an arcing event at the MCC stabs, it will most likely create a significant arc flash event, as most MCCs are protected by main circuit breakers that use a short time delay (STD) function. This STD will delay the overcurrent operation of the circuit breaker by up to 0.5 seconds (30 cycles), which can be an eternity in arc flash terms.
Motor control centers pose risk that is often not mitigated by the equipment’s design. The physical size of an MCC bucket is usually just large enough to contain the equipment and wiring, leaving very little room to safely test or repair the components and devices inside. This article has provided a brief overview of some of the risk involved in working on or around motor control centers; it is only intended to get technicians thinking about what the risk may be when operating or working on them.
The risks are many, and the overall knowledge and understanding of the hazards required to work on the MCCs is very important. Take time to understand the risk and the hazards, and train the workers — and be safe out there.
Thad Brown, “Safety Electrical One-Line Diagrams,” IEEE.
Ron Widup and Jim White are NETA’s representatives to NFPA Technical Committee 70E Electrical Safety Requirements for Employee Workplaces. Both gentlemen are employed by Shermco Industries in Dallas, Texas, a NETA Accredited Company.
Ron Widup is CEO of Shermco Industries and has been with the company since 1983. He is a member of the Technical Committee on NFPA 70E, Standard for Electrical Safety in the Workplace; a Principal Member of the National Electrical Code (NFPA 70) Code Panel 11; a Principal Member of the Technical Committee on NFPA 790, Standard for Competency of Third-Party Evaluation Bodies; and a Principal Member of the Technical Committee on NFPA 791, Recommended Practice and Procedures for Unlabeled Electrical Equipment Evaluation. Ron is also a member of the Technical Committee on Recommended Practice for Electrical Equipment Maintenance (NFPA 70B), and a member of the NETA Board of Directors and Standards Review Council. He is Vice Chair for IEEE Std. 3007.3, Recommended Practice for Electrical Safety in Industrial and Commercial Power Systems. Ron is a Journeyman Electrician in Texas, a NETA Level 4 Senior Technician, and an NFPA Certified Electrical Safety Compliance Professional.
James (Jim) R. White, Vice President of Training Services, has worked for Shermco Industries Inc. since 2001. He is a NFPA Certified Electrical Safety Compliance Professional and a NETA Level 4 Senior Technician. Jim is NETA’s principle member on NFPA Technical Committee NFPA 70E®, Standard for Electrical Safety in the Workplace; NETA’s principle representative on National Electrical Code® Code-Making Panel (CMP) 13; and represents NETA on ASTM International Technical Committee F18 Electrical Protective Equipment for Workers. Jim is Shermco Industries’ principal member on NFPA Technical Committee for NFPA 70B, Recommended Practice for Electrical Equipment Maintenance and represents AWEA on the ANSI/ ISEA Standard 203, Secondary Single-Use Flame Resistant Protective Clothing for Use Over Primary Flame Resistant Protective Clothing. An IEEE Senior Member, Jim received the IEEE/IAS/PCIC Electrical Safety Excellence Award in 2011 and NETA’s Outstanding Achievement Award in 2013. Jim was Chairman of the IEEE Electrical Safety Workshop in 2008 and is currently Vice Chair for the IEEE IAS/PCIC Safety Subcommittee.
We would like to acknowledge and thank our sponsors for helping make PowerTest 2018 possible.
As I drove my truck slowly past hundreds of thousands of solar panels, “Strange Magic” by the Electric Light Orchestra came on the XM radio station, and I was suddenly aware of the strange magic all around me. The magnificent sun setting on the distant chocolate mountains, the quietness of the desert solar field, the mysterious photovoltaic technology, and the magic of the partial discharge technology being used to evaluate the condition of the 34.5kV cable system all contributed to the magic.
The cables had pr eviously been tested successfully using very-low-frequency (VLF) overpotential withstand techniques, and our task was to determine whether any detrimental partial discharge activity was present that could lead to future failure. Performing online PD testing has many advantages (see sidebar, Benefi ts of Online Cable PD Testing for Renewable Energy Plants.)
The three 34.5kV circuits and 25 associated transformers (Figure 1) were energized from the substation, and all low-voltage breakers were open; thus, the plant was not generating.
The testing is best performed by safely installing temporary split-core, high-frequency current transformers (HFCTs) on every grounded shield of the cable terminations (Figure 2). The HFCTs detect signals generated by partial discharge activity from imperfections in the electrical field due to small, localized insulation breakdown caused by fl aws due to manufacturing, installation, design, contamination, or aging. The signals from the HFCTs are sent to a signal input module and then on to a laptop with sophisticated software.
Noise is often present during online PD testing, and although great advances in software over the years have vastly improved noise removal, it still often comes down to expert analysis and experience to verify PD presence and location. Verifying PD activity consists of the following steps:
1. Instrument selection is paramount. Not all PD instrument software can eliminate noise equally. Ensure that the equipment used can detect PD pulses underneath larger noise signals.
2. Take measurements at every termination, recording signals from all three phases simultaneously, and observe consistent HFCT polarities to determine signal origination. PD activity consists of higher frequencies near the location of the flaw. Farther away from the flaw, PD signal amplitude and frequency diminish and begin to fall within the range of common noise signals. Although distant PD signals can be distinguished from noise, it is more difficult, and sampling at every termination helps take away some of the guesswork. Explaining how signal polarity helps determine location requires a fair level of detail and will be discussed in a future article.
3. When analyzing the signals, always remember that PD is synchronous. At zero volts in the ac sine wave, no voltage is present; thus, no breakdown can occur. As the voltage increases toward the positive peak voltage level, a critical voltage (PD inception voltage) is reached where the local flaw breaks down. These small breakdowns usually persist through the peak until the voltage drops below the PD extinction voltage level and the signals stop. The same events occur as the voltage decreases toward the negative peak. Thus, the accumulated PD signals create a distinct pattern in synch with the system ac sine wave (Figure 3).
Furthermore, the PD measurement system must derive a precise ac input trigger signal from the distribution system to synch the PD signals; a portable generator is not appropriate
Figure 3: First, note the distinct synchronous phase-resolved PD pattern present, which is indicative of PD. Next, look at the large quantity of red dots present, indicating the signals are occurring from a nearby source.
for this purpose. Generally, any available 120v ac commercial power source is ideal for the input synch, but since low voltage was not present in this case, we used a custom electromagnetic field detector placed near the cables to scavenge the synch and transmit the synch signal to the PD instrument. The field detector is partially visible at the bottom right of Figure 2.
4. Once the presence of a synchronous PD pattern is found, next look at the color code of the pattern. Red dots indicate local signals and are of greater concern, since we already know we are sampling at each individual location. Although we cannot completely ignore a synchronous pattern of blue dots that may represent distant PD activity, we just need to exercise patience to eventually come across the local flaw. We are using the frequency of the signals to detect origination.
• Very efficient
• Cost effective
• Performed without an outage
• No external power source required
• Cable integrity verified
• Termination, splice, and arrestor condition determined
• Transformer connections, internal bus, switch, and high-side coil conditions verified†
• Entire medium-voltage insulation system checked
• Future maintenance PD testing compared with acceptance baseline results for failure trending purposes
† If PD signals are detected, it is useful to test the transformer fluid for hydrogen presence prior to termination inspection to determine if the discharge source is occurring in the transformer itself.
5. Certain noise sources can create highfrequency signals in a synchronous pattern. In these cases, the individual signal waveforms must be analyzed (Figures 4 A – D).
The following is a brief summary of the online cable PD testing procedure described in detail above.
1. Use a proper instrument designed specifically for online cable PD testing.
2. Ensure the instrument has proper noise removal software.
3. Observe sensor polarity.
4. Obtain a proper synch trigger source.
5. Test at every termination.
6. Look for synchronous patterns.
7. Locate PD source by signal frequency.
8. Analyze waveforms to verify they are PD events.
At the solar plant where we performed the testing, recordings were taken at 198 termination test points using the above procedure. Of these 198 termination test points, only three locations were found to have high levels of
discharge activity present. ese locations were highlighted in red on Figure 1. Based upon detailed signal analysis, we suspected aws at the two transformer terminations; the third suspect location was a distant signal detected from the junction box pointing toward the substation.
An outage was obtained and the two 600-amp dead-break T-body modular equipment kits at the transformers were disassembled and inspected. It appeared that a poor connection was present between the cable connection and the bushing stud with visible signs of pitting. A new stud was installed, and the connections cleaned properly. The locations were then retested, and it was found that the PD activity had disappeared.
At the substation, severe audible signals led toward a current transformer that had a severe uid leak from the interface between the porcelain and top cap. After the current transformer was removed from service, the PD signal was eliminated.
Large renewable plants consist of vast quantities of medium-voltage equipment consisting of even greater quantities of individual insulation components. Most or all of these components are tested as part of the equipment under test, using acceptance testing techniques prior to energizing. ese valuable acceptance test methods will discover most problems, but online testing of the medium-voltage system interconnected and as a whole can provide another level of assurance that the overall plant integrity is free of problems and will ensure future reliability.
Don A. Genutis is President of Halco Testing Services, Inc., a NETA Accredited Company, in Los Angeles, California. He has held various principal positions during his 30-year career in the electrical testing eld and has primarily focused on advancing no-outage testing techniques for the last 15 years. Don holds a BS in electrical engineering from Carnegie Mellon University and is a NETA Certi ed Technician.
James (Jim) R. White, Vice President of Training Services, has worked for Shermco Industries Inc. since 2001. He is a NFPA Certified Electrical Safety Compliance Professional and a NETA Level 4 Senior Technician. Jim is NETA’s principle member on NFPA Technical Committee NFPA 70E®, Standard for Electrical Safety in the Workplace®, NETA’s principle representative on National Electrical Code® Code-Making Panel (CMP) 13, and represents NETA on ASTM International Technical Committee F18, Electrical Protective Equipment for Workers Jim is Shermco Industries’ principal member on NFPA Technical Committee for NFPA 70B Recommended Practice for Electrical Equipment Maintenance and represents AWEA on the ANSI/ISEA Standard 203 Secondary Single-Use Flame Resistant Protective Clothing for Use Over Primary Flame Resistant Protective Clothing. An IEEE Senior Member, Jim received the IEEE/IAS/PCIC Electrical Safety Excellence Award in 2011 and NETA’s Outstanding Achievement Award in 2013. Jim was Chairman of the IEEE Electrical Safety Workshop in 2008 and is currently Vice-Chair for the IEEE IAS/ PCIC Safety Subcommittee.
No. 121
This Tech Quiz covers motor theory with a little testing thrown in. Motors are the largest power user in industry. They are literally everywhere. How good is your motor knowledge?
1. Electromagnetic induction was discovered by __________ in 1831.
a. Lenz
b. Faraday
c. Coulomb
d. Westinghouse
2. The field of a three-phase, squirrel-cage induction motor is located in the rotor.
a. True
b. False
3. Tests that check insulation resistance on a 480-volt motor are usually done at what voltage?
a. 500 VDC
b. 1000 VDC
c. 5000 VDC
d. 36000 VDC
4. Electromagnetic induction occurs in ac and dc circuits.
a. True
b. False
5. Slip is the difference between the synchronous speed of the rotating field and the rotor.
a. True
b. False
6. A four-pole motor will have a synchronous speed of __________ rpm at 60 hz.
a. 3600
b. 1800
c. 2400
d. 1200
See answers on page 128.
Everyone knows water and electricity don’t mix. For humans, definitely not! But for electrical equipment, there’s a middle ground. Intense summer storms have caused massive destruction throughout much of the southern United States and Caribbean. Though it may seem surprising, much of this equipment can still be salvaged. This article discusses the procedures to follow for particular classes of electrical equipment damaged by flooding.
In all drying out of electrical windings, the regulation of temperature should be carefully controlled. Maximum drying temperatures on windings should not exceed 194°F (90°C) as measured by thermometer. This will prevent rapid thermal deterioration of the insulation as well as damage from the high vapor pressures if steam were produced.
Several methods are available for drying equipment. The most satisfactory solution is to place the windings in an oven with suitable temperature control and proper air circulation. Banks of infrared lamps can be used when an oven is not available, or a suitable housing can be built around the machine using steam coils or electric resistance-type units as a heat source. Openings should be provided for the free circulation of air. Blowers can be used to increase air movement. Vacuum drying has also been eff ectively used to expedite the return of equipment to service. Certain precautions are necessary if this method is used, and it should be carried out only by experienced personnel.
Another frequently used method is to circulate low-voltage current through the windings. This should not be done, however, until the insulation resistance has reached a value of at least 100 kohm.
Look for insulation testers that have kilohm ranges to perform this check prior to application of current. Measurement is performed at only 5 V, so it will not damage even the worst insulation. Welding sets can be used to provide the current. The flow should be limited to only a fraction of nameplate amperes, and a careful check must be maintained on maximum temperatures on the insulated parts.
On ac generators, drying current can be provided by driving the units at less than rated speed with the terminals short-circuited and excited with very low values of field current. Th is should be done only by those with experience in such methods.
During drying operations when insulation resistance values are used as an indicator of the suitability of windings for service or for application of test potential, the drying must be continued for a sufficient time to ensure that the values are reliable. The resistance curve will often take one or more sharp dips before leveling off or continuing to increase in a positive direction. This is due to moisture working out of the windings. When the machine is completely dried out, further work is required to remove any remaining dust. This can be done using dry compressed air at pressure not exceeding 40 psi.
The following procedures provide guidance for specific classes of electrical equipment damaged by flooding.
1. Completely dismantle all parts.
2. To remove silt or dirt, wash all parts of the machine — except ball or roller bearings, but including windings — with clean, fresh water or steam. Follow this with a thorough cleaning using a suitable grease solvent. Many such cleaners are toxic, and necessary safety precautions should be taken.
3. Thoroughly clean all bearings and housings, paying particular attention to oil grooves and oil reservoirs, which may collect silt and dirt. Disconnect and swab any oil lines or steam clean and dry them.
4. Dismantle brush rigging and clean insulators. Some insulators will retain water and must be dried thoroughly.
5. Do not apply any voltage to a winding until an insulation resistance reading of at least 100 kohm is obtained for several hours, and then only a very low voltage should be used. If windings are very wet, even the low voltage of hand-cranked ohmmeters can puncture the insulation. To avoid this, the crank should be turned at low speeds until
some knowledge of insulation resistance value is obtained. Modern microelectronic testers have voltage regulation that eliminates this problem (Figure 1).
As mentioned previously, models with kilohm ranges at low voltage are ideal. The rotating machine can first be checked at low voltage to be assured that it meets the 100-kohm requirement, and then the effectiveness of the drying process can be monitored until resistance has increased into the megohm range.
6. Commutators can be difficult to dry out. It may be necessary to loosen or even remove some of the V-ring bolts or clamping nuts to let the water out from the inside of the commutator. On large commutators, it may be necessary to increase the drying temperature to as high as 266°F (130°C) if lower temperatures do not produce satisfactory results after a reasonable period.
7. Bands on armatures or rotors should be checked carefully for tightness. For some applications, they will have to be replaced because of looseness resulting from the drying out of insulation underneath.
8. Some slot-wedge materials will be affected by moisture. All wedges should be carefully
examined and new wedges installed where necessary.
9. DC motor or generator field coils and field coils from synchronous machines sometimes present problems. It may be necessary to remove these coils from the machines for proper treatment if it is impossible to bring the insulation resistance up otherwise. After a thorough drying in a suitable oven, they should be immersed completely in insulating varnish while hot and allowed to cool while still immersed. This will tend to draw the varnish into the inside layers. When cooled, the coils should be checked for short circuits by making a comparative test of their resistance. A low-resistance ohmmeter will indicate open coils and can also be used to determine shorted turns by the reduction in resistance that turn-to-turn shorts produce.
10. After a thorough cleaning and drying, most windings should be treated with insulating varnish, particularly if cleaning solvents have removed any of the varnish coatings. Dipping- and baking-type varnish, followed by a suitable baking period, is preferable, but air-drying varnish may be used to expedite the return of equipment to service. This latter type is only recommended if the original varnish is in reasonably good condition.
11. Before any machine is started, check the entire installation, paying particular attention to lubrication and electrical connections. Determine that no tools or materials have been left in or on the machine. Threephase motors being restored to service can have proper connection assured for correct rotation with a motor and phase rotation tester. This instrument will check correct phase rotation for motor and live lines, while three-phase lines can be separately checked with a phase sequence indicator. When put back into service, the rotational speed of motors can be readily checked with contact and photoelectric hand tachometers. These handy instruments are particularly useful,
as flooding may have made digital on-line indicators inoperative.
1. Thoroughly clean and dry out all control equipment, dismantling where necessary. Operating coils should be thoroughly dried and dipped in insulating varnish and baked or given one or more coats of air-drying insulating varnish. Check all contacts. Be sure moving parts operate freely.
2. Oil pans on starters and oil switches must be cleaned, dried out, and refilled with oil of proper dielectric strength. Insulating oil can be tested in full conformance to ASTM standards with an appropriate oil test set. Insulating barriers should be dried out or replaced if badly warped.
3. Meters and relays usually will have to be reconditioned at either the manufacturer’s service shop or factory. In many instances, it will be cheaper to replace them.
4. All bus insulators and control wiring on switchboards should be cleaned and dried thoroughly. Normally, an insulation resistance of at least two megohms per 1,000 volts operating potential, with a minimum of two megohms, should be obtained before energizing. This is a very basic and universal insulation requirement and can be performed with any good quality megohmmeter. Standby batteries should be checked for their readiness to come on line using a battery impedance tester. Battery straps can be checked for corrosion or excessive resistance with the low-resistance ohmmeter.
1. Remove covers or inspection cover plates. Note the condition of the oil and windings and check for signs of failure. Many transformers are oil insulated, and flooding may have introduced contaminants, including water, that will reduce dielectric
strength and deteriorate performance. This can be tested with an oil test set. Inspect all connections for looseness or indications of heating. Draw oil samples from top and bottom. Breakdown strength should be at least 22 kV. Check the insulation resistance. The value should be at least 2 megohms for each 1,000 volts rating, with a minimum of 2 megohms. Since these measurements are being performed from the bottom up, so to speak, any insulation tester can assure basic performance. However, two additional conditions should be noted. It may be preferable to restore equipment to full preflood condition, not just basic operating capability. Especially if maintenance records have been kept (and not lost in the flood), it would be desirable to have a tester that can measure values all the way to the values of pre-flood records or condition. This would be best served by a model with extended range, even into tera-ohms (TΩ). For equipment rated at higher voltages, a 5- or 10-kV tester should be employed to apply the higher voltage stresses that such equipment will experience in operation. Note the condition of bushings, external connections, operating switches, and protective devices. Clean externally and paint the tank if necessary.
2. If water has entered the tank, remove its cover. Flush the windings and core with clean, moisture-free insulating oil. If the transformer is small, remove the coil and core, and dry in an oven at a temperature not above 194°F (90°C). Dip and bake the windings whenever the need is clearly evident. Larger units may be dried in the tanks by forcing hot, dry air at not over 194°F (90°C) in and around the windings after the oil has been removed from the tank, by short-circuiting one winding and energizing the other with low ac voltage, or by a combination of these two methods. Insulation resistance checks (Figure 2) will determine the progress of drying. A curve should be plotted showing resistance against time. It is best to start at the 5-volt level of the kilohm range and then test periodically
throughout the drying process. The effectiveness of the drying procedure will be noted by the steady rise in insulation values. If mechanical damage such as pinholes or burn tracks has been done, the insulation will not spontaneously regenerate, and the drying process can be discontinued without costly expenditure of time in favor of rewinding or similar repair actions.
3. If the drying operation does proceed successfully, it can be monitored into the megohm range, and higher voltage tests can be applied without damage until the final desired value is reached. Once the drying process has restored insulation resistance to acceptable values, full performance can be further verified by performing a turns-ratio test. Damage to insulation can produce
turn-to-turn shorts that effectively alter the turns ratio between primary and secondary windings. A turns-ratio tester is the most precise and sensitive means of determining the existence and extent of such problems.
4. The oil should be filtered to standard dielectric test value of not less than 22 kV, or a new supply of oil of high dielectric strength should be used.
All open wiring, including nonmetallic, sheathed cable, can generally be retained after thoroughly drying cable and junction boxes and remaking connections. Armored cable will usually have to be replaced, as will lead cable if the ends have been under water. Salt water is particularly damaging. Rubber-covered cable in rigid conduit or in electrical metallic tubing may sometimes be reused, but it must be pulled out of the conduit or tubing to clean the conduit or tubing. Care must be exercised in this operation, as the cable insulation may be easily damaged. The conduit or tubing must be thoroughly cleaned of all silt and moisture prior to being used again. Potheads
When performing a visual inspection of rotating machinery, make sure all guards are properly installed per the manufacturer’s instructions. Compliance with the machinery and machine guarding regulations in OSHA 29 CFR 1910.212, General Requirements for All Machines and 29 CFR 1910.219, Mechanical Power-Transmission Apparatus is required. Depending on the type of machinery being inspected, other OSHA regulations may apply.
The following paragraphs identify and examine potential hazards and the means to safeguard against them, and ways to mitigate the associated risks. As always, this article does not include every potential hazard in performing a task, but it explores potential hazardous situations. Additional hazards may exist depending on the type or condition of the equipment. Take all procedures seriously, and verify that the instruction manuals used are specific to the equipment present. Check for and identify potential hazards prior to beginning every task by using a pre-job briefing worksheet.
Improper lockout/tagout procedures are a major contributing factor to injuries caused by rotating machinery. Controlling the hazardous energy of the motor is essential, and many forms of energy may be involved. Always refer to the manufacturer’s instructions as well as the appropriate OSHA regulation or required procedure, such as 29 CFR 1910.147, The Control of Hazardous Energy (Lockout/Tagout) and 1910.333, Selection and Use of Work Practices to determine the required lockout/tagout procedures. The most obvious hazardous energy source that could cause injury is electrical.
Electrically de-energize the rotating machinery from its primary energy source and ensure the equipment is disconnected from all sources of power, both ac and dc, if applicable. Once de-energized, verify that the equipment is at a zero energy state using the manufacturer’s
approved method. Verify the accuracy of the detection or voltage-measuring device against a known source, check for zero energy on the de-energized equipment, and then test the detection equipment against a known source again. This will verify that the detection meter was functional during the check. Testing for voltage will require its own level of PPE depending on the voltage and test procedure per NFPA 70E or OSHA.
However, electrical energy isn’t the only energy that requires lockout/tagout; rotating machinery may also contain a large amount of mechanical energy. This energy must be dissipated prior to servicing or serious injury could occur. Once the energy has been discharged or dissipated, it is also advisable to lockout/tagout the charging mechanism. Ensure that remote operating handles are tagged in a local or manual mode. This will prevent someone from inadvertently operating the machinery.
Machinery operating mechanisms may also be pressurized. Ensure that the unit is depressurized and/or discharged and the source of the pressure is disabled. Ensure that any valves upstream and downstream of the device are closed and lock out/tag out each valve. Once disabled, this source must also be locked out/tagged out prior to performing maintenance.
Chemicals can be a hazard, depending on the type of rotating machinery and the process associated with the machine. Caution must be taken with gases, chemicals, and liquids. Many processes can produce gases that are denser than air and can displace oxygen in lower-lying areas. Ventilation must be used to prevent these gases from being trapped.
Some lubricants and cleaners may pose a respiratory or skin irritant if used in enclosed areas or on bare skin. Acquiring knowledge of the material, reading its label, and checking the Safety Data Sheet (SDS) is advised to identify any potential health effects. Use of proper PPE is necessary for using some cleaners and
lubricants. For example, nitrile gloves, safety glasses, a face shield, and even respiratory protection may be needed in some cases.
When performing visual inspection, mechanical inspection, maintenance, or electrical tests on rotating machinery, gravity is an energy that may also need controlling. The size and weight of panel covers and inspection plates may make them difficult to handle. Should gravity be a potential energy source — through an inclined loaded conveyor belt, for example — ensure that the energy is dissipated and any flywheels or other energy sources or moving parts are chained or locked in position prior to performing lockout/tagout and maintenance.
Simply put, human error is a mistake made by a person (or persons). To prevent an error, follow a procedure or checklist while performing the task. If one doesn’t exist, create one.
Upon approaching a piece of equipment, nomenclature should be verified and reverified. Perform a self-check and a peer-check to ensure that the task is being performed on the correct component.
When working around similar looking pieces of equipment, use markings such as flagging to identify the components that should not be touched. Flagging can take several forms depending on a company’s or client’s policy and procedures. Do not forget to identify, mark, and then lock out/tag out all associated equipment (i.e., cables and compartments). Flagging can be used to indicate a component that is not operating normally.
Barricading off a safe work zone prevents other workers from inadvertently entering the area and helps ensure that maintenance and testing is conducted in a controlled area. Use a test stand in this area if applicable. Ensure that any control voltage required to operate the equipment during testing is within a secured area.
After verifying that the rotating machinery is de-energized, the method of disconnecting the equipment may require a different form or class of PPE. Ensure that proper PPE is selected for the disconnecting method used. Refer to the NFPA 70E tables for the required PPE category. The PPE category will indicate what level of protection is required for the means of disconnection being used. Identifying the correct level of PPE and gloves will aid in the mitigation of injury from a potential arc flash. However, NFPA tables provide information based on known values of short-circuit current available, clearing time in cycles, and minimum working distance. If those factors are unknown, more information must be gathered prior to performing the work to ensure personnel safety.
Grounds are an excellent secondary way of protecting the worker from inadvertent energization. Refer to any applicable OSHA regulation such as 29 CFR 1910.269, Electric Power Generation, Transmission, and Distribution, 1910.147, and NFPA 70 and 70E for specific guidance on grounding locations and sizing of grounds required for the task. Grounds must always be applied upstream and downstream of the equipment and as close to the work as possible. Correctly sized and applied grounds are an additional employee safeguard should a form of electrical energy be introduced into the system or equipment being worked on. Induced voltage or back-feed are just two forms of energy that may be inadvertently introduced into a system that has been properly locked out/tagged out.
When performing maintenance and testing on rotating machinery, be aware of the following:
1. Obtain all service bulletins, maintenance documents, arc flash studies, and manuals prior to beginning the work for each specific device.
2. Review all prints and one-lines associated with the equipment.
3. Establish a safe work area and barricade it off.
4. Perform a pre-job brief with all employees onsite.
5. Wear proper PPE.
6. Disconnect the electrical feed and control circuit(s), verify mechanical interlocks are properly engaged, and test equipment before performing visual or mechanical inspections.
7. If applicable, verify that there is zero energy (test, check, test) and discharge all stored energy, including pressurized gases and gravity.
8. If possible, lock out/tag out all energy sources.
9. Connect grounds, if applicable.
10. Identify, visually mark, and/or flag the equipment worked on.
Noting and mitigating these hazards can lead to a safer work environment when performing inspection, maintenance, and testing of rotating machinery.
Paul Chamberlain has been the Safety Manager for American Electrical Testing Co. LLC since 2009. He has been in the safety field for the past 18 years, working for various companies and in various industries. He received a BS in marine safety and environmental protection from Massachusetts Maritime Academy.
Scott Blizard has been the Vice President and Chief Operating Officer of American Electrical Testing Co. LLC since 2000. During his tenure, Scott acted as the Corporate Safety Officer for nine years. In addition, he has over 25 years of experience in the field as a Master Electrician, Journeyman, Wireman, and NETA Level IV Senior Technician.
This article presents a generator stator ground fault protection scheme that is fast acting and simple to implement using numerical relay logic. A 59N neutral overvoltage protection relay provides stator ground fault protection for high-impedance grounded generators and typically covers up to 95 percent of the stator winding. Stator ground faults are common, so this type of protection is very useful. The logic and use of symmetrical component voltages to determine the location of the stator ground provides fast tripping; before 59N, a long time delay was required to properly coordinate with transmission system ground fault protection.
This scheme protects large synchronous machines grounded via high impedance from stator ground faults. Use an accelerated 59N protection scheme with sequence voltage component supervision to handle capacitive coupling across the generator step-up (GSU)
transformer during transmission system ground faults and prevent misoperations. This scheme helps eliminate the need for additional apparatus such as a band-pass filter and lowfrequency signal generator to detect stator grounds required for subharmonic protection.
This scheme provides fast tripping (typically, a five- to 10-cycle time delay on pickup) for ground faults internal to the generator stator winding or bus work up to the GSU low-side bushings. Coordination is not required with transmission system ground fault protection or generator VT fuses.
Figure 1 illustrates the symmetrical component circuit for a single line-to-ground fault located at the high side of the GSU (F). The relay
measures the negative- and zero-sequence voltage drops at the generator terminals, V2T and V0T, respectively. Note this scheme requires that the VTs are connected wye-wye so the relay can measure the zero-sequence terminal voltage. The presence of V2T prevents unwanted tripping during external ground faults, thus eliminating the possibility of a misoperation due to capacitive coupling across the GSU. VN is the neutral voltage drop across the grounding generator resistor RN
Figure 2 illustrates the symmetrical component circuit for a single line-to-ground fault located on the stator or bus work up to the low-side
Providing Testing Solutions for:
• Protective Relays
• Transformers & Motor Analysis
• Partial Discharge/Corona
• Current Injection
• Cable Fault Location
• Switchgear/Circuit Breakers
• Insulation Resistance
• Tan Delta/Power Factor
• Current Transformers
• Ground Grid
San Diego Test Equipment Symposium Oct. 24th, 2017 • San Diego Register now! www.atecorp.com/sdtes Register now!
Partial discharge (PD) testing has long been used for quality control purposes and also for determining the in-service aging of electrical insulation in rotating machines, transformers, power cables, and switchgear. Partial discharges are small sparks that occur within the insulation system in poorly made equipment and when insulation deteriorates due to aging. Since each discharge causes a flow of charge for a very short period of time, it can be measured by detecting the resulting current pulses. The frequency spectrum of each pulse spans from dc to a few hundred MHz. This article discusses PD testing of stator windings in medium-voltage motors and generators. It additionally examines why different frequency ranges are used for measurement, and especially, what published standards say about the frequency ranges.
Off-line PD testing has been employed as a factory test for almost 100 years to discover fl aws created during the manufacture and assembly of the winding that lead to PD and eventually to insulation failure. In addition, tracking the evolution of PD over time by off-line tests or on-line monitoring gives equipment owners a powerful tool for deciding when maintenance or equipment replacement is needed.
Most of the PD detection methods use a highvoltage capacitor to measure the PD current pulses in the presence of the 60 Hz high voltage (Figure 1). The instrumentation usually includes an analog-to-digital converter that evaluates the quantity, amplitude, and phase angular position (with respect to the ac cycle) of the PD. However, each brand of detector tends to work in a different frequency range, which affects what is actually measured.
The capacitor is a high impedance to the ac high-voltage and low-frequency signals, and a low impedance to PD pulse currents.
IEC 60270 is the most commonly referenced PD measurement standard. It describes the test circuits for measurement and why the unit of measurement is pico-coulombs (pC). The electrical charge is a measure of the number of electrons and ions involved in a single discharge and an indicator of the amount of damage to the insulation by each discharge. Most commercial PD detectors measure the pulse magnitudes in millivolts, so IEC 60270 provides the procedures to convert mV into pC. The standard assumes that the test object is predominantly capacitive, but this is not true for stator windings. It also suggests a measurement frequency between 10 kHz and 1 MHz and categorizes two classes of detectors:
• Narrow-band detection in the 9 to 30 kHz bandwidth with a center frequency between 50 kHz and 1 MHz
• Wide-band detection in the 100 kHz to 900 kHz range
• This standard does not cover PD detection above 1 MHz.
IEC 62478, a complementary document to IEC 60270, was published in 2016. It extends the PD detection frequency above a few MHz and defines the following ranges:
• Low frequency (LF): below 3 MHz (approximately the frequency range in IEC 60270)
• High frequency (HF): 3 to 30 MHz
• Very high frequency (VHF): 30 to 300 MHz
• Ultra high frequency (UHF): 300 to 3000 MHz
These are the same frequency bands adopted in radio transmission. Clause 4.3.6 makes clear that a direct calibration into pC is not feasible above the LF range. Instead, a sensitivity check is performed by comparing a conventional LF PD test (measured in pC) with a test in the
HF, VHF, or UHF range (in mV or decibelmilliwatts). The standard provides several practical schemes for measuring PD at higher frequencies on switchgear, transformers, and stator windings.
IEC 60270 and IEC 62478 apply to any type of high-voltage equipment. IEEE and IEC have developed specific standards for stator windings in motors and generators. IEEE 1434 covers off-line and on-line PD testing of windings. IEC 60034-27 (which will be called IEC 60034-27-1 when revised) discusses the off-line PD testing of complete windings.
IEC 60034-27 states that it is better to measure PD on a complete stator winding off -line in the wideband LF range because the entire winding is energized to the test voltage in the off -line condition; thus, PD can happen in any coil of the winding. Owing to the inductive-capacitive nature of a stator winding, pulses from PD sites far away from the PD sensors, which are located at the phase end, will be attenuated and distorted as they propagate from the remote source to the sensors. The higher the detection frequency, the greater is the attenuation eff ect. Since the low-frequency components of PD pulses are less attenuated as they travel along the winding, PD distant from the sensors is still likely detectable.
Parts of IEEE 1434 and IEC 60034-27-2 focus on PD detection during normal (on-line) machine operation. This has become more popular because a plant outage is not necessary for data collection, and the condition of the winding insulation is measured at normal and more stressful running conditions, which are usually high temperature and high load. These standards describe the different types of sensors, including capacitors of various capacitances, high-frequency current transformers (HFCTs), and UHF antennae, and allow the use of any frequency range from LF to UHF.
From 1950 to about 1980, only LF PD detection was employed, typically with a 1 nF capacitor on each phase or an HFCT around the neutral lead. The signals measured contained stator winding PD, PD from other equipment, and also high-frequency signals from such noise sources as transmission line corona, arcing electrical contacts, slip ring sparking, and variable speed drive invertor switching noise. This made the extraction of the winding PD from the electrical interference important but difficult. Usually, only experts with years of experience could make a reliable diagnosis. As a result, on-line PD measurement in the VHF and UHF frequency range has gained preference since the 1980s, not only in stator windings, but also in gas-insulated switchgear, cables, and transformers.
2: Time-Domain Signal Separation (IEC 60034-27-2 Figure 1)
Eff ective means of suppressing noise and disturbances are possible for PD detection at higher frequencies. The time-of-flight method separates stator PD from outside PD. Two sensors are installed at the machine terminal and on the bus-bar of each phase, respectively (Figure 2). Researchers have also noted that the pulse shape of winding PD is diff erent from most types of power system noise. This enables additional noise identifi cation by pulse shape analysis and a software-based technique called time-frequency map. The first two methods require the pulse arrival time to be measured with a time-domain accuracy of a few nanoseconds and the pulse shape to be recorded in the VHF range. If the signals were acquired in the LF range, neither the relative pulse arrival time from two sensors nor the pulse shape can be distinguished.
Th e limitation of on-line VHF and UHF PD detection is the strong attenuation of PD originating in the stator winding and physically far from the PD sensor, as cautioned by the IEEE and IEC standards. Th e referenced article by Greg C. Stone indicates that VHF instruments may recognize PD from only 10 to 15 percent of the winding. Hence, it makes sense to install sensors as close to the high-voltage end of the winding as possible, because PD will most likely take place there rather than at coils or bars that operate at lower voltages.
On the other hand, for measurements at LF, a machine-specifi c normalization step is required. Th e winding itself, the power system (or the high-voltage power supply in the case of off-line testing), and the sensor are treated as capacitors. Any charge dissipated during the discharge event is distributed to connected capacitances besides the sensor. In other words, the sensor measures only a small portion of the total discharge, and the fraction depends on the outside capacitance relative to the sensor. The concept of apparent charge was introduced, and the normalization process determines how much charge is leaked to the sensor.
To demonstrate the differences between PD detectors using different frequency ranges, offline PD was measured on two stators at about the same time using different frequency ranges.
Off-line PD tests were performed using LF and VHF PD detectors on a 13.2 kV, 6,000 hp motor stator winding. An LF analyzer with a 1,000 pF detection capacitor was used to conduct the LF test. It operated in the wide-band mode in a frequency range of 40 to 800 kHz. Figure 3 shows the data of Phase C with the highest activity.
Figure 3(a) is the phase-resolved PD (PRPD) plot acquired after stabilization at 8 kV (just above rated line-to-ground voltage).
Figure 3(b) shows the PRPD graph measured on the same Phase C at the same voltage by an 80 pF sensor and an instrument measuring at the VHF range. The PD detection frequency range is 40 to 350 MHz. The vertical scale is the apparent pulse magnitude in either nC or mV as applicable for the frequency range. The horizontal axis represents the phase angle of the 60 Hz cycle. The color of the dots illustrates the number of PD pulses per second. The VHF PRPD plot separates the polarity of the PD pulses. The pulse polarity is suppressed in
the other plot but can be inferred from pulse positions on the ac cycle.
The peak PD magnitude (Qm) for this VHF measurement was +816 mV and -912 mV. These are the magnitudes defined for digital instruments in IEC 60034-27 at a pulse repetition rate of 10 pulses per second (pps). The LF PD instrument calculated Qm to be 2.5 nC using the identical 10 pps definition. Some LF instruments estimate Qm based on an analog definition of the largest repetitive magnitude in a train of pulses, according to IEC 60270.
Th e C-phase of this stator winding has a scaling factor of 2.7 pC/mV between the LF and VHF detectors. Beware of the warnings in IEC 60034-27 that different brands of LF instruments can give significantly different pC readings even under the same test conditions because of non-standardized center frequencies and bandwidths. The PRPD patterns and the relationship between PD at the two half cycles are basically the same between LF and VHF.
The stator winding of an 18 kV, 200 MVA hydrogen-cooled generator was also PD tested off-line using the same LF and VHF instruments stated above. The tests were taken at about 9.7 kV in air at atmospheric pressure.
Figure 4(a) shows the PRPD plot from Phase C that had the highest activity. It reveals classic internal ground-wall micro-voids (see IEC 60034-27 Annex E for typical PRPD patterns). The measured Qm value was 1.1 nC.
Figure 4(b) is the PRPD plot of the VHF test under the same test conditions as for the LF test. The patterns are the same. The Qm is +106 mV and -121 mV, so the ratio between the LF test in pC and the VHF test in mV is 9.1 pC/ mV, which is substantially different from that measured on the motor.
Off-line PD tests on complete stator windings can be performed in the LF and VHF ranges, as Figures 2 and 3 display similar PRPD patterns. The former is preferred if the discharge situation of the high-voltage power supply is not severe because the LF range maximizes sensitivity to PD and detects PD from more coils/bars in the winding farther from the line end.
The VHF method is a better choice for online measurements due to its capabilities in attenuating noise and distinguishing disturbances, which are inevitable when the machines are connected to the power system. Conversely, a discharge-free power supply must be used to energize the winding for off-
line testing in LF mode because this mode lacks such capability. Table 1 shows the main diff erences. Measuring more coils is not a key consideration for on-line testing because those coils are lower in voltage and PD is less expected to happen there. Detecting PD from the coils of lower voltages will not provide any additional information to the PD data that has been obtained from the higher voltage coils.
Side-by-side, off-line PD tests have demonstrated that PD can be detected in the LF range as well as the VHF range in a more or less controlled environment. Th e standards suggest using the LF range for off -line PD tests on coils and windings. However, they list only the pros and cons of LF and VHF measurements for on-line PD testing. LF may detect PD in more of the winding, but at the cost of a much greater risk of false indications when compared to VHF testing. Practically speaking, knowing the condition of 15 percent of the winding is usually suffi cient to obtain a big-picture view of the winding as a whole.
LF Detection VHF Detection
• Original method (1950s)
• 1–10 nF sensors
• Bandwidth 0.1–3 MHz
• Sensitive to PD deeper in the winding
• Requires considerable expertise to separate PD from noise
• No independently verified levels for high PD
• Installed on several hundred machines
• Historically used by OEMs and service companies
• Developed in the 1980s
• 80 pF sensor
• 40–350 MHz at -3 dB
• Sensitive to PD in top 10–15 percent of winding
• Digital noise separation with low risk of false indications
• Independently verified high PD levels
• Used on nearly 17,000 motors and generators
• Preferred by machine owners
IEC 60270, High-Voltage Test Techniques –Partial Discharge Measurements, 2015.
IEC 62478, High-Voltage Test Techniques – Measurement of Partial Discharges by Electromagnetic and Acoustic Methods, 2016.
IEC/TS, 60034-27 Rotating Electrical Machines – Part 27: Off-line Partial Discharge Measurements on the Stator Winding Insulation of Rotating Electrical Machines, 2006.
IEC 60034-27-2, Rotating Electrical Machines – Part 27-2: On-line Partial Discharge Measurements on the Stator Winding Insulation of Rotating Electrical Machines, 2012.
IEEE Std. 1434, Guide for the Measurement of Partial Discharges in AC Electric Machinery, 2014.
Stone, G.C. “A Perspective on Online Partial Discharge Monitoring for Assessment of the Condition of Rotating Machine Stator Winding Insulation,” IEEE Electrical Insulation Magazine, September 2012, pp 8-12.
Connor Chan has been employed with Iris Power LP Canada since 2001 and is currently a Rotating Machines Engineer. Prior to this position, he was Field Service Manager. Connor earned a BS in electrical engineering from the University of Hong Kong. He is a member of IEEE, the Institution of Engineering & Technology (formerly IEE, UK), and the Institution of Engineers Australia, and is a Chartered Engineer.
Greg Stone has BS, MS, and PhD degrees in electrical engineering from the University of Waterloo. He was a Dielectrics Engineer with Ontario Hydro, a large Canadian power generation company from 1975 to 1990. Since then, Greg has been employed at Iris Power LP, a motor and generator condition monitoring company he helped to establish. He is a past president of the IEEE Dielectrics and Electrical Insulation Society and continues to be active on many IEEE and IEC standards working groups. He has published three books and over 200 papers about insulation of rotating machines, and has received awards from the IEEE, CIGRE, and IEC for technical contributions to rotating machine assessment. Greg Stone is an IEEE Fellow, a Fellow of the Engineering Institute of Canada, and a registered Professional Engineer in Ontario, Canada.
Want to decrease outage times and recover electrical systems faster?
Sta big time events with: Certi ed and quali ed technicians and engineers.
Although no longer a household name, Charles Proteus Steinmetz is the often-underappreciated father of alternating current and certainly a genius of the ranks of Tesla and Edison. He is known as the Wizard of Schenectady, and one of the most prestigious awards granted by IEEE is named in his honor. Early on, he acknowledged that “insulation is by far the most important problem in electrical design.” A century later, a dielectric engineer was heard stating that he could build a perfect motor if only he didn’t need insulation. The problem hasn’t really changed, but the materials certainly have.
NETA technicians are often experts at the testing and evaluation of electrical rotating machinery, but what are they actually testing?
The electrical insulation used in motors and generators is comprised of very sophisticated materials chosen for their various properties and how those properties complement each other. Ranging from applications for small NEMA-frame commercial and
industrial motors to large turbine generators, literally thousands of possible insulation systems can be utilized based on four basic properties: electrical, environmental, thermal, and mechanical. Add to that the ease of manufacturing — and of course, the cost — and it is understandable how a technician who might see dozens of different machines every week could get confused.
This article will:
• Introduce some common electrical insulating materials (EIM) used in motors and generators
• Explain why they might be chosen
• Discuss how they are tested during development
• Provide some insight into how they fail
• Offer an overview of some of the tests to help monitor and analyze those trends to failures
In rotating machines, electrical insulation systems (EIS) generally fall into three categories: low, medium, and high voltage. Historically, low voltage is anything below 600 volts, but some standards now consider 1,000 volts as the limit. Medium voltage is below 7,200 volts, and high voltage is anything above that. These don’t correlate to transmission or distribution system categories, but they are based on some specific differences in the EIS properties required for those voltage ranges.
The original EIS were made up of all-natural materials. Cotton braid was commonly used for conductor insulation. Cellulose and cotton papers as well as mica splittings were used for flexible insulation and maple for rigid. A good dose of shellac or asphalt was used to help protect against moisture and hold it all together. Needless to say, the thermal rating for these systems was quite low and aging characteristics were not the best, but they worked well for what was being built. Amazingly enough, many examples of devices made with these materials are still in operation. Keep in mind that a one-horsepower motor was about the size of an average coffee table, and, as one of the early applications for electric motors was for commercial coffee grinders, perhaps it’s an appropriate comparison.
Modern EIS are much more sophisticated with many more options for each application, all with associated properties and related costs. A materials engineer at a manufacturer or
repair facility must decide what to use for a given application, taking into account all of the operating conditions, the manufacturing capabilities, and the cost. Let’s first look at the four basic factors that drive all EIM development.
All EIM succumb to the same stressors that aff ect their service life, and these critical factors — depending on the application of the machine — have a lesser or greater effect on performance and reliability. Voltage is obviously a big one for several reasons that will be discussed later, but the other three are often even more critical. These are thermal conditions, chemical and other environmental contaminants, and the physical properties required to survive manufacturing and end use.
Compared to the historical options, modern EIMs offers higher thermal properties, better mechanical strength, much improved chemical resistance, and for the most part, much better dielectric properties for short-term and longterm stresses. A manufacturer could probably design a completely bullet-proof system that would work anywhere except for the fi fth scoundrel not listed above: cost. No matter how the EIS is designed, it still has to be reasonable for manufacturing to build at a cost appropriate for the application.
Motor and generator designers deal with several options regarding basic systems. For low-voltage ac designs where partial discharge is not an issue, random-wound machines are very common up to about 800 kW (1000 hp). For larger machines that are still low voltage, formed windings are more common due to mechanical stresses, but often require larger frames than their random-wound counterparts. There are exceptions, of course. Some wind turbine generators are random-wound even up to 2000 kW to meet size and weight
requirements that are more stringent than most industrial applications. A few rare machines are higher-voltage random-wound designs, but those are definitely special-case applications.
Looking at low-voltage, random-wound insulation systems from the inside out, the primary insulation is always applied directly to the conductor by the wire manufacturer. These are commonly enamel coatings of several types, including polyurethane, polyester, and polyester amide-imides, along with various topcoats to meet application requirements. Occasionally, glass fibers or other materials may be added for additional mechanical or dielectric properties. These conductors are chosen based on thermal class, manufacturing requirements, and compatibility with other materials, which will be discussed later in this section.
To isolate and protect the windings from adjoining phases or ground, some type of fl exible insulation will be used. Th is is commonly polyethylene terephthalate (PET)
film (alone or in a laminated form with cellulose paper), PET fleece, or aramid paper. These laminates can be resin coated to improve performance and to ease manufacturing requirements. Flexible insulations are used for ground and phase insulation within the slot sections. These are also often used for phase insulation for the overhanging coil end sections as are varnish-coated glass materials. Appropriate lead wires are attached to the windings, and flexible sleeving is normally used to insulate the connections. Various tie cords and other materials mechanically support the coil overhangs against inrush current forces and vibrations. The entire stator is treated with one of many varnishes or resins, again chosen based on end-use application and manufacturing capabilities. Special epoxy, silicone, or polyurethane coatings are often added to improve chemical or mechanical resistance. Many of these low-voltage machines are produced in highly automated assembly lines that have their own mechanical stress to be considered.
vacuum pressure impregnation (VPI) system using an epoxy resin or another resin type depending on application requirements.
Mica content is critical to system performance where operating voltages exceed the inception level of partial discharge. Mica is a naturally occurring mineral used as electrical insulation for capacitors, motors, and transformers throughout the industrial development of electrical devices. As it is a mineral, it is not affected by the destructive oxidation activity of partial discharge voltages as are organic materials. Another advantage is that it can be split into very thin sheets and laminated to create flexible insulation (Figure 3).
Since the late 1940s, mica has been further processed into tiny platelets that can be made into mica paper. This allows for a more consistent laminate with well-distributed electrical properties and a high level of resistance to partial discharge. Since the mica maintains its platelet form even in tiny particles, it aligns to create a long path for voltage to travel to ground. All insulation systems above 1,000 volts use mica to allow for long-term electrical degradation.
In machines over 5 kV or where a mediumvoltage machine is controlled by a variable speed drive, corona suppression materials replace the outer wrap of the coils. In the slot section, this will typically be a semiconductive, carbon-impregnated fleece, which allows partial discharges to dissipate safely to the steel core but with enough resistance to avoid creating hot spots by shorting the core laminations. On the coil extensions (often called overhangs or evolutes), a specialized type of semiconductive tape or paint manufactured using a silicon carbide with variable resistance properties allows these partial discharges to dissipate into the atmosphere. This is especially important during short-term, high-potential testing because that voltage well exceeds the design operating voltage.
Some of these high-voltage designs use epoxy impregnated tapes, which can be fully cured in hot press forms or alternatively built using coils or half coils (bars) that are vacuum pressure impregnated before curing in hot press forms. This is very common in hydro generator coils as well as large gas and steam turbine designs. In modern high-voltage motors and generators (even as large as 600 MW), the stators are more commonly insulated with semi-porous insulating materials, and the entire wound core is treated with an appropriate resin in a global vacuum pressure impregnation (GVPI) process.
Regardless of the methodology used in building the motor or generator, the end result should be appropriate for the application. The shortterm and long-term electrical properties of the insulation are tested early in the development process, often by the materials manufacturers. It is also important to establish the thermal class of the completed system so the equipment designers can use appropriate systems based on the ambient conditions as well as the thermal rise of their design. Testing standards and guides have been developed by IEEE as well as IEC to establish the basics for evaluating insulation systems. [ Author’s note: The only insulating materials used in systems for motors
and generators that have a standalone thermal class rating are the conductors (with primary insulation) and the varnish or resin. This is because of substitution rules that are allowed in certain low-voltage protocols.]
The most commonly used multifactor testing protocols for establishing the thermal class of random-wound, low-voltage motors and generators (and dry-type transformers, for that matter) are based on IEEE 117 for voltages up to 600 Vac. This testing methodology is also accepted by most certification laboratories. An example is UL 1446, except it covers applications up to 1,000 Vac. In this test protocol, multiple small test forms are assembled using an established system as the control as well as the candidate system. These forms, called motorettes (Figure 4) or general-purpose models, are subject to repeated cycling at elevated temperatures above the targeted thermal class, then shaken, subjected to high humidity in a condensation chamber, and stressed at a high electrical potential. The failures (regardless of source) are noted, and the data used to develop an accelerated aging Arrhenius plot charting the thermal class, normally measured at the 20,000-hour mark.
The common insulation thermal classifications used in modern machines are Class B (130°C), Class F (155°C), and Class H (180°C). These classifications are used by design engineers based on the hottest thermal rise area of the coil, normally in the center of the slot, along with a given ambient temperature. Additionally, a service factor allowance might be included for more flexibility in the application. All of this information is normally on the motor or generator nameplate.
For medium and higher voltages, the additional electrical stress of partial discharges must be taken into account. In addition to the shortterm dielectric strength of the insulation, long-term performance under electrical stress conditions must be tested. The basic thermal class determination protocol is very similar to the low voltage in nature. Larger test fixtures called formettes (Figure 5) are constructed
and wound with control and candidate EIS; subjected to multifactor aging cycles of heat, vibration, moisture, and electrical stress; and the failures plotted. This process is described in IEEE 1776. However, additional tests for longterm performance are also used to determine the appropriateness of a medium- or highvoltage insulation system.
Dissipation factor testing (also called tan delta, DF percent, or insulation power factor) looks at electrical losses through the insulation system under voltage stress. This helps determine the performance at elevated voltages and can demonstrate the compatibility of materials, degree of cure, and contamination of the materials. A comparison of DF percent at two voltage levels, called DF Tip-Up, is also a good system evaluation tool. A rise in the losses often indicates voids in the system, which can lead to partial discharge destructive activity and shorten the life of the machine. Dissipation factor and tip-up testing for system evaluation is found in IEEE 286.
The other widely used test for high-voltage insulation system development is voltage endurance testing, which is a stress test under extreme voltage (Figure 6). This protocol is described in detail in IEEE 1043, and the generally accepted criteria used are from IEEE 1553. As an example, a 13.5 kVA system could be tested at 30 kV or 35 kV. Depending on the stress level chosen, the pass criteria are either 400 or 250 hours, respectively.
Passing the test means it’s all good…right?
All of these tests are performed in laboratory conditions and are very useful in narrowing down the materials and systems that will
meet the design requirements. They represent the material developer’s best effort to mimic the performance and life expectancy of the insulation system in real-world situations. But there are limits, as these tests don’t consider many factors a motor or generator will see in use, including extreme environmental conditions. A large motor used in a steelrolling mill will have much different thermal and mechanical stress than a generator used as a backup power supply for a data center, even though they might both be designed using similar thermal class and voltage criteria.
The motor design engineer takes the system performance under these testing protocols as the baseline for electrical performance, but must take the end use into consideration to achieve a reasonable life expectancy for the machine. Specialized top-coatings for chemical resistance or for abrasive atmospheres, additional bracing for high vibration environments, and additional or specialized insulation for high thermal cycling applications all must be included in the evaluation. The failure of any of these system materials can result in premature failure of the basic system, even though it seems fine based on the standard protocols.
So, what fails?
Most motors and generators actually fail due to bearing issues, which are often attributed to lubrication and alignment problems. Beyond that, premature failures due to contamination and electric power quality are probably the most common. Fewer failures are due to manufacturing defects, and modern quality processes have minimized those. Design failures where environmental conditions are underestimated are a different issue and probably account for the majority of premature failures in rotating machines. These include thermal and operational cycling, chemical exposure, and other external stresses. Longterm, normal end-of-life issues are more predictable. These normal failures are mostly due to partial discharge, failure of turn-toturn, or primary insulation. Degradation of the organic enamels, resins, and flexible insulation
materials leads to localized heating due to electrical losses and more rapid degradation of electrical ground-wall insulation.
Most NETA technicians know which tests can be performed in the field to trend or evaluate motor condition, including insulationresistance (IEEE 43), ac and dc high-potential testing (IEEE 56 and 95 respectively), highpotential testing of turn insulation (IEEE 522), and partial discharge testing (IEEE 1434). Additional guidelines to test and maintain rotating machines can be found in IEEE 56, which was revised in 2016, and IEEE 62.2, which is currently under review. In particular, IEEE 62.2 has a good hierarchy of motor and generator testing protocols designed for technicians. Some of these tests can be trended and others are just snapshots of current condition, but all are useful tools in determining the expected reliability of critical motors and generators. There are many other tests that may be considered for on-line and off-line evaluation of electrical rotating machines. The tables in ANSI/NETA MTS, Standard for Maintenance Testing Specifications for Electrical Power Equipment and Systems also provide good guidance for testing protocols and intervals. Along with the IEEE guides and recommended practices, these references provide excellent tools for test execution and evaluation of the results.
So,
As we near the 200th anniversary of the electric motor (Moritz Jacobi created the first rotating electric motor in May 1834), the refinement of design and materials has reduced the size and cost and greatly improved the reliability and life expectancy of these machines. What’s happening next? The development of nanodielectric materials is now being commercialized with great potential for improved thermal performance, resistance to partial discharge, and probably good potential for self-healing coatings and insulating resins. Improved high-temperature materials are also being adopted by the very conservative power generation industry, with newer machines
designed to take full advantage of the advances in material science over the last 50 years. All of these improvements will require additional research and field experience to develop the expected results for reliability and longevity.
In alternative energy power generation, the industry has learned that wind generation and newer technologies such as tidal power place much greater stresses on the equipment than was first imagined, and new materials and manufacturing standards will be developed to improve reliability in those applications as well. Although electric vehicles have been around for well over a century, this concept probably offers some of the biggest challenges for operating efficiency and reliability, and those factors are critical for the development and growth of that industry.
All of these new challenges will create new materials solutions, but the basics will remain. Failures are always related to heat, mechanical conditions, voltage stresses, and chemical degradation. Continuing to test insulation materials and systems for expected performance in those areas — and testing the final products in the field to assure they meet those expectations — will always be critical for the reliability and effi ciency expected of the industry.
Kevin Alewine is the Director of Marketing for Shermco Industries. He is an IEEE Senior Member and participates on the committees of many of the standards, recommended practices, and guides mentioned in this article. Formerly, Kevin was a Vice President and Senior Application Engineer for a global manufacturer of insulation materials, systems, and conductors and has been involved in the development and application of insulation systems for more than 40 years. Since coming to Shermco in 2009, he has helped refine insulation systems for remanufacturing wind turbine generators. He served for many years as Chairman of the American Wind Energy Association Committee for Operations and Maintenance of Wind Projects and as Technical Chair of the 2014 WINDPOWER Conference. Kevin is the General Chair of the 2019 IEEE Electrical Insulation Conference to be held in Calgary, Alberta.
Spotlight Stage Presentations
Tuesday, February 27, 2018
During the PowerTest 2018 Trade Show in the exhibit hall
Join NETA’s Corporate Alliance Partners as they share insights and best practices on the Spotlight Stage at PowerTest 2018. 12:30-12:45 PM 3:00-3:15 PM
AEMC’s Cable Locator Model 6681 AVO Training Institute, Inc Significant Revisions for the 2018 NFPA 70E BCS Switchgear, Inc. BCS Switchgear’s Expanding Inventory in Molded and Insulated Case Breakers
1:45-2:00 PM
Group CBS, Inc. The Importance of Vacuum Circuit Breaker Contact Pressure
DLRO100 – Testing Safely and Effectively
Electronics Corp. USA New Lightweight Battery Powered Test Solution for Wiring Checks and more… Protec Equipment Resources The Challenges of Partial Discharge Testing
in Oil: A New Diagnostic Tool for Determining the Condition of Solid Insulation
The early diagnosis of fault conditions in electrical machines is important for increasing the reliability of the machine drive systems. One noninvasive method for condition-based monitoring of electrical machines is vibration measurement. Motor vibration analysis can detect electrical or mechanical malfunctions on stator, rotor, and bearings as well as external sources of vibration. This article includes an overview of the detection techniques employed and discusses the vibration and current signature analysis of a squirrel cage induction motor.
Condition-based management is one of the asset management strategies based on the assessment of the actual equipment state. It can utilize numerous diagnostic and monitoring techniques to assess the state of the observed system. Considering that electrical rotating machines are essential elements of both power systems and industrial processes, great attention is paid to the process of their proper maintenance.
Basically, all motor condition diagnostic techniques or methods are divided into offline or online methods, depending on whether or not the observed equipment is energized. Observed individually, the methods are focused on identifying certain problems in mechanical or electrical terms, but they may, with some accuracy, detect another fault state as well. Vibration analysis is one online method that is often combined with other diagnostic tools.
It can also be part of a continuous monitoring system, especially for a functionally important object such as a power plant generator. In that application, if the operating vibration level becomes critical, an alarm is displayed; if severe, a shutdown is initiated.
The most commonly used monitoring systems in motor drive applications are:
• Insulation system analysis
• Partial discharge monitoring
• Rotor flux analysis
• Motor current signature analysis
• Acoustic emission detection
• Vibration measurement
• Temperature monitoring
Th is article is focused on condition-based assessment utilizing vibration measurement data analysis in combination with motor current signature analysis.
Although motors come in many different sizes and construction forms, they have common failure modes that cause abnormal mechanical vibration of the observed system. Vibrations can be caused by the application of internal or external forces (S. Ergin, et al). Two basic characteristics of mechanical vibrations are amplitude and frequency. There are numerous causes of motor vibrations that can be divided into electrical and mechanical sources. As an example of the events inside motors, Figure 1 illustrates the varying electromagnetic forces between the stator- and rotor-magnetomotive force (MMF) of a two-pole induction motor in the presence of the flow of sinusoidal current in the stator (W.R. Finley, et al).
The force has maximum value when the value of the sinusoid is at its maximum, whether positive or negative.
Typical causes of vibration include:
• Elliptical stator. Elliptical stator results from electromechanical forces that attempt to
SOURCE: W. R. FINLEY, ET AL.
unevenly deflect the stator. Depending on the number of machine poles and points of larger electromechanical forces, the stator shape can be varied. In this regard, the next problem to come is a non-symmetrical air gap.
• Air-gap variations due to eccentricity. A nonsymmetrical air gap results in variation of the magnetic reluctance, which depends on the radial air-gap length. This leads to shaft vibration. The effect of eccentricity is particularly apparent in induction motors, as these require a very narrow air gap.
• Bearing vibration. Bearings are integral parts of a rotating machine. For larger machines, bearings are usually of the sleeve type. Although there are several types, they usually consist of the same main parts, which can produce vibration signals of similar frequencies. Local faults produce a series of impacts that can excite resonances in the structure of the bearing. These resonances are typically between 1 kHz and 20 kHz. The problems with sleeve-type bearings can be associated with the oil whirl.
• Broken rotor bar. A broken rotor bar is a faulted state that occurs on induction motors, especially those with a squirrel cage. Various techniques have been proposed to detect a rotor fault. One of them is based on the motor current signature analysis. Vibration measurement and analysis is also often used to diagnose this condition (G.H. Bate).
• Rotor bar passing frequency vibration. High-frequency vibration appears in the motor stator when current is induced into rotor bars under load. In that process, the flow of electrical current creates a magnetic field around the bars. Based on this, an attractive force is created toward the stator. The magnitude of this vibration varies with load. These frequencies are much higher than the usual expected measured frequencies.
• Vibrations that occur due to imbalance. Due to errors in the alignment of the axis of inertia and the axis of rotation, there are often deflections of the bearing points. Depending on the amount of deviation, characteristic vibrations can occur (T. Bertolini, T. Fuchs).
A proper machine condition assessment is based on qualitative data analysis. Analysis of the vibration signal consists of two steps: obtaining vibration data and then determining the characteristic signals that are present.
Some vibration anomalies may also occur on a healthy machine. Such problems can be detected in the narrow-band signatures. Identifying such anomalies often requires
expert knowledge. A trend of increasing signal changes is often an indication of the need for machine maintenance. A great aid in detecting faults can be signal comparison with data obtained from a machine of the same characteristics.
There are numerous techniques used in postprocessing and analyzing the signal:
• Fast Fourier transform
• Instantaneous power FFT
• Demodulated current spectrum
• Wavelet analysis
• Orbital pattern analysis
• Selective envelope detection
• Cepstrum analysis
• Modal analysis
Vibration analysis and the decision-making process are often based on techniques employing an artificial neural network and fuzzy logic.
Measurement of the vibration signal is performed on two asynchronous motors with a squirrel cage rotor. In addition, the motor current signature analysis is used. The signal analysis is based on a Fast Fourier transform. The nameplate data is presented in Table 1.
Table 1: Nameplate Data for the Observed Motors
Frequency [Hz] 50
The number of pole pairs of the motors is two. Although they have the same characteristics, the machines had been applied in different conditions, so their characteristics were different. The motors were tested while unloaded (Figure 2).
According to standard recommendations (IEEE Std 112-1984), the motors were placed on a flexible surface during testing to obtain measurements as accurately as possible, regardless of mounting conditions.
The scheme of the measuring and processing system is presented in Figure 3.
Vibration values were measured at several points on horizontal and vertical axes. At the same time, the line current was recorded. The sampling frequency was set to 10 kHz. Figure 4 shows the recorded vibrations for the two induction motors at the surface point that had the highest vibration values. This is a plot of the recorded signals as a function of time (y axis).
Th e vibration amplitude spectrum for the machine with faulted state (motor 1) and machine with healthy state at that point (motor 2) is shown in Figure 5.
Figure 6 shows the part of the measured signal in the x axis (shaft side of the motor).
6:
versus Time (x Axis)
The amplitude spectrum in the x axis is shown in Figure 7.
It can be seen that the vibration level is higher for one of the observed motors. Also, there is a noticeable noise increase for this machine. Analysis of the signals in each axis shows that the gain of individual components is different. Specifically, the occurrence of various faults has different impacts on vibration in the x and y axes.
By disassembling the motor with the higher vibration level, the eccentricity of the rotor shaft was observed due to a bearing fault on one side of the machine. At the same time, changes in the squirrel cage were caused by contact and friction of the rotor with the stator teeth (Figure 8).
It is interesting that there are signals around the network frequency with a considerable number of harmonics and subharmonics of the
fundamental component. The motor faulted state is often the result of a combination of electrical and mechanical problems, so the signal can be affected by components resulting from the motor speed and the fundamental frequency. The local fault inside the machine leads to resonant appearances on the bearing and motor housing, which are, in this specific case, visible at frequencies of 1,000 Hz, 3,500 Hz, and 4,500 Hz. The frequency range of interest in motor current signature analysis is typically 0–5 kHz (E.L. Bonaldi, et al). According to the Nyquist Theorem, the sampling frequency of the transducers used should be at least 10 kHz.
It is important to recognize individual signal components. As an example of static eccentricity, sideband components appear at frequencies determined by this equation (D. Miljkovic and M.T. Thomson, et al):
where:
fec - eccentricity frequency
fg - electrical supply frequency
R - the number of rotor bars
s - slip of induction motor
p - number of pole-pairs
nd = ±1
nws = 1,3,5,7…
While bearing faults are difficult to detect, for most bearings, faults are recognized by equations:
The current amplitude spectrum of motor-1 and motor-2 are shown in Figure 9. In this specifi c case, recording and analyzing the spectrum revealed a significant difference at a frequency range of around 3,000 Hz.
Figure 9: Current Amplitude Spectrum at Specific Frequencies
Th e sideband signal components are more predominant for one of the machines, a clear indicator that the motor is in a faulted state.
Induction motors play a significant role in industrial processes and other applications, so an assessment of their condition is an important segment of asset management. The condition-based assessment is based on several techniques. One of them, vibration measurement analysis, is an important noninvasive technique. Vibration analysis involves two segments: data acquisition and data analysis. The analysis is often based on transformation to the frequency domain and the use of various tools for recognition of characteristic vibration signals. Combination of the vibration data analysis with the motor current signature analysis provides significant improvements to faulted state detection.
The experimental analysis presented here is an example of condition state assessment for the induction motor. By recognizing the characteristic components of the vibration signal and performing a motor current signature analysis, the mechanical changes were determined to be due to static eccentricity and a bearing fault.
S. Ergin, A. Uzuntas, M.B. Gulmezoglu, “Detection of Stator, Bearing and Rotor Faults in Induction Motors,” International Conference on Communication Technology and System Design, pp 1103–1109, 2011.
W. R. Finley, M. M. Hodowanec, W. G. Holter, “An Analytical Approach to Solving Motor Vibration Problems,” IEEE Transactions on Industry Applications, vol. 36, Issue 5, Sept/Oct 2000, pp. 1467–1480.
G. H. Bate, “Vibration Diagnostics for Industrial Electric Motor Drives,” Bruiel & Kjaer, Application Note, 026 –12, pp. 1–12.
T. Bertolini, T. Fuchs, “Vibrations and Noises in Small Electric Motors,” 2012, pp. 58–81.
IEEE Std. 112-1984, Standard Test Procedure for Polyphase Induction Motors and Generators.
E. L. Bonaldi, L. E. de Lacerda de Oliveira, J. G. B. da Silva, G. Lambert-Torresm, L. E. Borges da Silva, “Induction Motors — Modelling and Control,” InTech, 2012, pp. 487–520.
D. Miljkovic, “Brief Review of Motor Current Signature Analysis,” pp. 1–12.
M. T. Thomson, R. J. Gilmore, “Motor Current Signature Analysis to Detect Faults in Induction Motor Drives — Fundamentals, Data Interpretation and Industrial Case Histories,” Proceedings of the 30-Seconds Turbomachinery Symposium, Texas, 2003, pp. 145–156.
Srdjan Jokic has been cooperating with DV Power in the field of transformers and rotating electrical machines since 2006. He holds a BS and an MS in electrical engineering from the University of East Sarajevo. Srdjan has been a Teaching Assistant and Senior Teaching Assistant at the Faculty of Electrical Engineering, University of East Sarajevo, since 2008.
Sasa Ikic is an Engineer in the hardware development and research department at DV-Power. He holds a BS in electrical engineering from the University of East Sarajevo. His interests include the development of circuit breaker testing equipment.
Check out our Spotlight Presentation at the NETA Powertest 2018 conference by Dr. Nick Perjanik, Knowledge Services Manager at Weidmann Electrical Technology Inc.
Weidmann laboratories provide professional diagnostic services, producing actionable data that help lower risk and improve your electrical system‘s reliability. Following recent developments in the ASTM Standard Test Method for the Determination of Methanol and Ethanol in Electrical Insulating Liquids (currently under development), Weidmann Laboratories will introduce the latest in Methanol testing in January 2018.
By accurately testing and detecting Methanol and Ethanol (by-products of cellulosic degradation) at a parts per billion level in oil, Weidmann can assist transformer operators and owners to better predict the breakdown and aging of their transformer insulation system. Research shows that Methanol has a near linear correlation to mechanical strength (DPv) of the solid insulation, resulting in accurate test results that are not affected by the moisture content in insulation, and can provide added benefits over simply testing for furans.
To learn more, please join our presentation or alternatively visit us at the Weidmann booth #412
Weidmann Electrical Technology Inc. One Gordon Mills Way St. Johnsbury, VT 05819, USA
www.weidmann-electrical.com
A Member of the Wicor Group
You have 36 hours…
According to the National Hurricane Center, hurricane warnings are issued 36 hours in advance of the anticipated onset of tropical-storm-force winds. What do you do with your facility’s electrical equipment when you only have a few hours to prepare for a significant water storm event? What’s the decision tree? How much pre-planning should you have done — and did you do it?
Under normal conditions, electrical equipment and systems are inherently dangerous, can be complex, often are fickle, and generally require care and maintenance. Add a significant storm or other unexpected event, and the results can be disastrous. The good news: There is guidance and expertise available to the owners of the equipment and systems, and it comes
in the form of electrical standards and NETA Accredited Company expertise.
As with most disasters, the key to an efficient and safe recovery to normal conditions and operations is to make smart decisions early on, including before and just after the event. Those first decisions, the very important path-forward
guidance, can add many weeks (even months) and millions of dollars to the overall recovery plan, cost, and execution.
So, what should you do?
It is often said: If you fail to plan, you plan to fail. This holds true for electrical disaster preparation. One of the most important aspects to disaster recovery is to have a plan in place, ready to go — just as every business should have an emergency action plan for other aspects of the business. Unfortunately, many do not have a plan in place to recover their electrical system in the event of a large-scale water event, such as the ones we have seen in the past 12 months and in years prior.
Think about it: If you are lucky, you have several hours or days to plan for a large-scale water event, be it a river flood, hurricane, heavy rain event, or other nature event. Or you might not have any warning at all for an instantaneous event such as a water main break, flash flood, dam breach, infrastructure failure, or similar no-notice event.
And after the event occurs — especially after hurricanes, river floods, and heavy rain events — you have surrounding infrastructure damage and other challenges to deal with as well as those to your own facility.
Government resources, employees, gasoline and fuels, transportation, supplies, human spirit, and resiliency — all will be affected. After Hurricane Harvey in 2017, employees who were needed at affected facilities to lead recovery operations for 14–16 hours a day also had to deal with flooded homes, displaced families, and other significant issues on a personal level — let alone the needs and requirements of their employer.
Incumbent vendors that supply services, who normally are local and ready to help, also are affected by large-scale events. And it’s the same issues — employees, facilities, infrastructure, electricity. All get compromised in large disasters.
All of this leads towards the need to have a plan. Where do resources come from? Who is qualified? How much capability will there be in the marketplace? What are their experiences in dealing with large-scale events? This ultimately
After large-scale flood events, not only are facilities affected, but so are employees’ homes and surrounding infrastructure. CREDIT: FLOODED HOME, SHERMCO INDUSTRIES
leads to yet another reason to point to NETA Accredited Companies that specialize in electrical disaster recovery services.
An important aspect to planning is having an action plan in place to set up remote operations, establish network connections and access to drawings and information, and begin the process of gathering resources. Key point: Have the ability to access digital information (drawings, schematics, one-line diagrams, OEM manuals, etc.) from outside of the normal computer infrastructure.
NETA has a long-standing connection to NFPA 70B, Recommended Practice for Electrical Equipment Maintenance. The document’s scope fits in
Chapter 32, Electrical Disaster Recovery, is a fantastic resource for guidance and actions pre- and post-disaster. Because it was developed from the experiences of NETA Accredited Companies, the content is closely aligned with the skill sets and qualifications of NETA firms and technicians.
line with services offered by NETA Accredited Companies. In fact, Chapter 32 of 70B on the subject of electrical disaster recovery is directly attributable to work and development closely aligned with NETA and the PowerTest Conference. In 2009, Pat Beisert of Shermco Industries presented a paper titled “Flood Repair of Electrical Equipment” at the PowerTest Conference in San Antonio, Texas. Much of the content from this presentation was used in the development of this new chapter on electrical disaster recovery in the 2013 revision of NFPA 70B. Th e current edition of NFPA 70B is the 2016 version.
During the 2017 hurricane season, NFPA made the chapter available to the general public as a free download to provide recovery guidance to business entities and the industry. The
information is available from NFPA: www.nfpa. org/assets/files/AboutTheCodes/70B/70B_16_ Chapter_32.pdf.
Shermco has responded to many large-scale disasters through the years. Here are a few examples of what can happen to electrical systems in industrial and commercial facilities.
The refinery’s management knew there was a possibility of flooding into the plant, as record rainfall had been falling for several days. The 100-year-old complex had experienced flooding in the past, and relied on upstream river-level data from the U.S. Corps of Engineers to assist them in the decision-making process. This time, however, the gauges were giving false data, showing levels that were lower than the actual situation.
When it was discovered that the gauges were not accurate — and flooding would occur sooner and at a greater magnitude than originally anticipated — emergency evacuation procedures were implemented. Because of these factors, power into the facility was cut by the electric utility, and a controlled shutdown was not possible. Adding to the issue of flooded equipment, tens of thousands of gallons of crude oil were inadvertently released; this coated all of the equipment in the facility with a layer of black, greasy crude oil.
Recovery operations took approximately three months to complete.
When 500-year floods hit the region, an industrial facility located next to the river experienced rapid and high levels of river floodwaters into the plant.
Submersing the electrical equipment — from the 34.5 kV main distribution system right down to the motor control centers — the entire facility was under water.
The plant personnel set up an off-site emergency operations center. Due to the extended time required for the flood waters to recede, recovery operations could not begin until approximately one week after the initial flooding.
The third major hurricane of the 2008 hurricane season — and the sixth-costliest Atlantic hurricane — Hurricane Ike slammed into the Texas gulf coast in September 2008.
Recovery operations after a flood are complex and require a great deal of record keeping and documentation. CREDIT: MCC ROOM RECOVERY, SHERMCO INDUSTRIES)
The storm surge traveled as much as 16 miles inland, and a six- to eight-foot brackish storm-water surge entered the chemical plant, flooding the entire facility and damaging electrical equipment.
Electrical equipment does not do well in water, especially when the water has any concentration of salt-water.
On a holiday weekend, a utilities contractor struck a large water main pipe in the downtown region of a major city, causing millions of gallons of water to enter a county records building and flooding the basement and surrounding areas. All of the main electrical distribution equipment, including back-up emergency generators, was located in the basement and experienced flooding, rendering the entire building inoperable.
After pumping the water out of the building, temporary power generation and interim electrical distribution equipment were connected to the building. A decision was made by the owner to move the replacement electrical equipment out of the basement, which extended the recovery operations. The building
remained on temporary diesel generation for several weeks until the installation, testing, and commissioning could be completed.
With over 12 inches of rain in just a few hours, the river flowing through the downtown area could not release the water downstream quickly enough, and most of the downtown area was flooded.
One of the challenges experienced: no drawings. The processing facility had a complex control system with programmable logic controllers (PLCs) and industrial automation systems, many of which had been in service for years. Most of the drawings were not digitized, and the facility completely flooded, flooding the drawings and operation and maintenance manuals at the same time.
By design, wastewater treatment plants are placed in areas that naturally flow downhill. This makes sense — except that when large weather events occur, fl oodwaters must be
pushed out of the plant or the plant will flood.
Such was the case here, as the facility flooded, power was out, and the entire facility ended up underwater. Berms around the outside of the facility were breached, creating a large bowl that collected all the water and wreaking havoc on the facility and infrastructure.
With no power and no means of processing the wastewater for several weeks, there was no option other than to dump the waste directly into downstream waterways. This heightened the need for a quick and efficient recovery of electrical power systems and processing equipment.
The 2017 Atlantic hurricane season featured 17 named storms and was the fifth most active season on record. Harvey, the eighth named storm and third hurricane, was the most costly hurricane on record at $125 billion in damage, primarily from widespread flooding.
At a chemical plant located next to one of the many bayous in the Houston area, not much could be done to counteract the 60 inches of rain that fell due to conditions of Hurricane Harvey. The extreme rainfall event resulted in over 33 trillion gallons of water falling on the Houston metro area. In the chemical plant, electrical systems, process instrumentation, motors and pumps, boilers, basic infrastructure all experienced widespread flooding.
The recovery operations were divided into two sections of the plant based on product type. The first, most critical section was completed in three months; the second section is still being recovered at the time of this writing but required five months to complete.
When industrial facilities are faced with disasters such as large-scale flood events, a very specific and detailed sequence of events
must occur to return the facility to productive operation in the most efficient manner possible. It is especially critical to analyze and repair the electrical power system in a safe and logical sequence. Breaking the events into phases, they can be categorized as:
• The initial event
• Securing the facility to limit damage
• Mobilization of recovery personnel
• Developing a safety plan
• Temporary and emergency power generation
• Post-event initial damage assessment
• Documentation, documentation, documentation
• NEMA standards
• Medium-voltage equipment repair
• 480-volt distribution repair
• Electric motor repair
• In-shop activities
• Balance of plant repair
• Energization of the facility
• Project summary
It is of great importance to use the services of a qualified service provider, such as a NETA Accredited Company. NETA has Accredited Companies across North America. The company accreditation — coupled with their certified technicians and rigorous requirements for retaining membership — makes NETA members a clear choice in the time of need.
If you work safely and methodically — and apply the requirements of NETA testing standards during startup and commissioning — it is more likely that the facility can be recovered in the most effective manner possible.
And remember: Make sure you have a plan before disaster strikes, because you may only have 36 hours.
Ron Widup is CEO of Shermco Industries and has been with the company since 1983. He is a member of the Technical Committee on NFPA 70E, Standard for Electrical Safety in the Workplace; a Principal Member of the National Electrical Code (NFPA 70) Code Panel 11; a Principal Member of the Technical Committee on NFPA 790, Standard for Competency of Third-Party Evaluation Bodies; and a Principal Member of the Technical Committee on NFPA 791, Recommended Practice and Procedures for Unlabeled Electrical Equipment Evaluation. Ron is also a member of the
We are there when and where you need us
Multiple Offices
Located throughout the country yields dramatically lower shipping costs
Local Inventory
Better shipping rates and great application support from the Protec team
Technical Committee on Recommended Practice for Electrical Equipment Maintenance (NFPA 70B), and a member of the NETA Board of Directors and Standards Review Council. He is Vice Chair for IEEE Std. 3007.3, Recommended Practice for Electrical Safety in Industrial and Commercial Power Systems. Ron is a Journeyman Electrician in Texas, a NETA Level 4 Senior Technician, and an NFPA Certified Electrical Safety Compliance Professional.
NETA standards: www.netaworld.org/standards FEMA: www.fema.gov
FEMA Emergency Management Guide for Business and Industry: A Step-by-Step Approach to Emergency Planning, Response and Recovery for Companies of All Sizes. www.fema.gov/pdf/library/bizindst.pdf
National Hurricane Center: www.nhc.noaa. gov/prepare/wwa.php
National Fire Protection Association: www.nfpa.org/
National Headquarters 1517 West Carrier Pkwy Suite 116 Grand Prairie, TX 75050 (866) 352-5550
Protec West 924 Greg St Sparks, NV 89431 (775) 984-5223
Protec South 7102 Brookside Rd Suite 102 Pearland, TX 77581 (832) 251-7047
Protec Midwest 1501 Wright Blvd Schaumburg, IL 60193 (847) 434-5808
Protec East 200 Gates Rd Suite E Little Ferry, NJ 07643 (201) 450-9743
Protec Southeast 105 Village Walk Suite 185 Dallas, GA 30132 (972) 352-5550
You can count on us for specialized experience in healthcare, data center, o ce complex, and commercial acceptance and maintenance testing. Absolutely Power generation, petrochemical, oil & gas, and heavy industries also look to us for high demand services such as start-up commissioning, maintenance testing, shut-down and turnarounds, and breaker shop repair. Get started today.
The method of symmetrical components is one of the most important tools used by protection and controls (P&C) engineers and technicians, yet one of the least understood. Implementation of proper protection systems ensures reliability of the electrical equipment protected, and thorough testing ensures it was designed and set up correctly. The lack of understanding of what symmetrical components represent and/or how they are relevant in certain protection schemes could cause a delay when testing the system or result in the system not being tested and implemented correctly.
The method of symmetrical components consists of converting a three-phase unbalanced system into two sets of balanced phasors and a set of single-phase phasors (see Amberg and Rangel), which leads to the creation of three symmetrical components: positive-sequence, negative-sequence, and zero-sequence. Each component has a numerical designation: The
positive-sequence component has a designation of 1; the negative-sequence component has a designation of 2; and the zero-sequence component has a designation of 0. This method can be applied equally to voltages and currents (i.e., VA, VB, and VC are converted into V0, V1, and V2 in the same manner that IA, IB, and IC are converted into I0, I1, and I2, as shown.)
Conversion between the phase domain and the symmetrical components domain is performed
using the matrices in equations (1) and (2). The matrices can be solved by multiplying each element in a row by the elements in the column at the end of the matrix, and the summation of the three multiplications yields the result of the corresponding variable to the left. For example, I B can be found by adding 1 ⋅ I0, α 2 ⋅ I 1 , and α ⋅ I 2. When phase values are converted into symmetrical components (equation 1), the resulting summation must be divided by ⅓ or the variables must have a multiplier of 3 (i.e., 3I0, 3I1, 3I2).
Note: The value of the variable alpha (α) is 1 ∠ 120°, which basically means to rotate the phasor (that is being multiplied to) counterclockwise by 120°. If alpha is squared (α2), the rotation is 240° instead.
Consider this analogy of a patient having a physical exam at the hospital. The results of several lab tests will indicate that the
patient is either healthy or that one or more medical conditions exist. Similarly, in a power system, the presence of the positivesequence component (at nominal value) indicates that the system is healthy, while the presence of the negative- and/or zerosequence components indicates that one or more abnormal conditions exist. In a perfectly balanced three-phase system, the magnitude of the positive-sequence current (I1) will be equal to the magnitude of any of the three-phase currents; during an unbalanced fault, negativesequence current will be present; during a ground fault, negative- and zero-sequence current will be present; during a phase reversal condition, only negative-sequence current will be present. Derivation of the most typical faults is beyond the scope of this article; for a detailed explanation, refer to Amberg and Rangel. Table 1 shows the normal and several abnormal conditions and the symmetrical components that will be present during those conditions.
The most typical fault in our power system is a SLG fault, which accounts for approximately 80 percent of the occurrences. Assuming that no load is being served, the affected phase would see a large amount of fault current, while the other two phases would see no current. For example, when simulating a 10 kA A-G (A to ground) fault, 10 kA must be simulated in the relay’s A-phase, while no current is present in
* I0 will be present during the open-phase condition only if the open phase is exclusively in the secondary system, as explained in the section titled Testing an Open Phase.
the other two phases. In a SLG fault, the three sequence networks get connected in series, and therefore, the three symmetrical component currents are equal to each other (I0 = I1 = I2).
Using equation (1), we can obtain the value of I0, I1 and I2 in terms of IA. Based on equations (3), (4), and (5) and on Table 1, all three symmetrical component currents are present during a SLG fault.
Let’s assume a current transformer (CT) ratio of 5,000:5 (1,000:1) to simulate a 10 kA fault; the required secondary current in A-phase channel is 10 A (10,000 A /1,000), which creates negativeand zero-sequence currents of 10/3 = 3.33 A, or 3.33 kA primary. Assume that the phase overcurrent element pickup (50P1P) is set at 8 A (80 percent) and note that, in some cases, the negative- and zero-sequence current pickups (50Q1P and 50G1P, respectively) are set in the form of 3I0 and 3I2 rather than I0 and I2; therefore, these two elements would be set at 8 A as well.
Figure 1 shows the I A waveform; the magnitudes of IA, I0, and I2; and the three overcurrent elements asserting when their corresponding currents reach 8 kA.
To test the SLG fault shown in Figure 1, the phase current values in Table 2 must be applied.
Table 2: Phase Currents for Simulating a SLG Fault and Expected Results
Although PP faults are not as typical as SLG faults, it is important to learn how to properly simulate and test these faults. Assuming that no load is being served, during a perfect PP fault,
Figure 1: SLG Fault Event Report
one of the affected phases sees a large amount of current, while the other affected phase sees the same amount of current but in the reverse direction — which the protective relay sees as having the same magnitude but out of phase (180 degrees apart). For example, let’s assume a 10 kA fault between phases B and C (IB = 10 kA ∠0 degrees and IC = 10 kA ∠180 degrees); using equation (1), we can obtain the value of I1 and I2:
Table 3: Phase Currents for Simulating a PP Fault and Expected Results
Equations (6) and (7) show that the magnitude of I1 is equal to I2 with the phase angles being 180° apart (Figure 2). To test this fault, and assuming a CT ratio of 1,000:1, apply the values in Table 3. The expected positive- and negative-sequence current values will be 5.77 kA. However, the pickup value of the negativesequence overcurrent element might be set in terms of 3I2; in this case, 3I2 is 3⋅5.77 = 17.32 kA.
One of the most common errors when energizing equipment is to swap two phases, whether it happens at the primary (not so common) or at the secondary (very common) level. Swapping two phases will cause the positive-sequence value to drop to zero, while the negative-sequence value will be nominal, and this can be verified with equation (1). Assume an ABC phase rotation and balanced currents (1 A) but with the phase angles of B- and C-phase currents swapped (IA = 1 ∠ 0°, IB = 1 ∠ 120°, IC = 1 ∠ 240°); the values of I1 and I2 are the following:
Figure 2: PP Fault Event Report
Figure 3 shows a simplified version of a typical phase reversal element (see SEL-710 Instruction Manual). If 50 percent of the negative-sequence component (voltage or current) is larger than the positive-sequence component, then the element asserts with a 0.5 second delay. Based on equations (8) and (9), a wiring mistake will suppress the positive-sequence component, and the negative-sequence component will have nominal value. In this case, the 47 element allows the engineer/technician to verify that no swapping mistakes were made.
Figure 4 and Figure 5 show a simulation of a wiring mistake in the voltage and current channels, respectively. It is important to note that the mistake could have been in the primary equipment rather than in the secondary wiring (for example, a breaker connected on A-phase to C-phase on the bus and C-phase to A-phase on the bus); therefore, care must be exercised when troubleshooting a 47-element pickup during energization.
Table 4 shows the necessary values to simulate a phase reversal condition, simulating either voltages or currents. In this example, the phase rotation is assumed to be ABC; however, if the phase rotation of the tested system is ACB, then the phase angles of B and C phases must be swapped.
One fault that is not very common is the open-phase fault. In some cases, an open
phase might not be a critical condition (such as in distribution feeders feeding residential customers), but in some other cases it might be (such as when feeding three-phase motors). If a large three-phase motor loses one of the phases (e.g., due to a blown fuse), then it will be fed negative-sequence current, and that will be detrimental to its life. Using equation (10), we can find the value of 3I2, which in this case, will have the same magnitude as the two unaffected phases with an angle of -60 degrees.
Figure 6 shows the simulation of an open phase as seen by the relay. It is important to note that even though the zero-sequence current is shown to have the same value as the negative-sequence current, this will only happen if the open-phase condition is secondary (i.e., a test switch is open or one of the relay CTs fail). If the loss of phase happens in the actual system, then the phase angles of the unaffected phases would drift, and no zero-sequence current would get generated unless a path to ground is created.
(10)
6: Open Phase Triggering Negative-Sequence Overcurrent Element
Table 5 shows the necessary values to simulate an open-phase condition as well as the expected results.
A thorough understanding of how symmetrical components are created during several abnormal conditions allows P & C engineers and technicians to properly implement and test a protection system. The presence of negativeand/or zero-sequence components indicates that an abnormal condition is present, while the presence of only the positive-sequence component at nominal values indicates that the system is healthy.
Amberg, A. and Rangel, A. (2012). Tutorial on Symmetrical Components. 1st ed. [ebook] Schweitzer Engineering Laboratories, Inc, p. ALL. Available at: https://cdn.selinc.com/ assets/Literature/Publications/White%20Papers/ LWP0010-01_TutorialSymmetrical-Pt1_ AR_20130422.pdf [Accessed 7 Mar. 2016].
Table 5: Phase Currents for Simulating an Open-Phase Condition and Expected Results
Schweitzer Engineering Laboratories. (2017). SEL-710 Instruction Manual. Available at: http://www.selinc.com/instruction_manual.htm
Alex Rangel, PE, is a Protection and Controls Engineer for Saber Power Services, LLC. He holds a BS in electrical engineering and an MS in engineering from the University of Texas at Austin. Alex is a NETA Level 3 Certified Technician. He has been an IEEE member for nine years and has been a registered Professional Engineer in the state of Texas since 2014.
The Doble M7100 High Voltage Asset Analyzer is a revolutionary solution for high voltage testing. And it is built to reduce the various safety risks a field crew is exposed to per job.
Patented dual high-voltage leads allow you to perform multiple tests with one cable hook up. This means a reduction in ladder trips per job – cutting the number by one third.
Eye hooks on the high-voltage leads let you use hotstick tools to place HV cables on the apparatus under test.
Emergency stop button initiates a controlled shutdown with one motion, and once pressed, will lock until it is twisted and released.
Two test enable/safety switches must be pressed at the same time by the test set operator and the operator’s assistant – otherwise the M7100 will not operate.
Discharge complete will appear on the LED display once a test completes and the M7100 has entered a discharge mode that releases energy from the test specimen.
Learn more about how the M7100 is making testing simple, safe & efficient. www.doble.com/M7100
The Long Beach Community College District Board of Trustees celebrated the new collaboration with a ribbon-cutting ceremony (from left) Elizabeth McCann, Executive Director, LBCC Foundation; Dr. Reagan Romali, Superintendent - President of the Long Beach Community College District; Vivian Malauulu, Trustee,Area 2; Sunny Zia, Vice President, Area 3; Jeffrey A. Kellogg, President, Trustee, Area 1; Dr. Virginia Baxter, Trustee, Area 5; Douglas W. Otto, Trustee, Area 4; and Ann-Marie Gabel, Executive Vice President - Finance, Facilities and Technology Services, Long Beach City College. Not shown: Scott Fraser. LBCC Department Chair Trades & Industry, and Electrical Technology Professor, whose ribbon-cutting robot (center) was designed by students in LBCC’s Electrical Technology Program.
New and renovated buildings will house this debuting program based on NETA’s Electrical Power Testing Technician curriculum.
Students at Long Beach City College (LBCC) will now have the opportunity to take part in a brand-new electrical technician program through a partnership with NETA.
During a dedication ceremony in October 2017, Ann-Marie Gabel, LBCC Vice President of Administrative Services, said the launch of this program makes LBCC the first academic institution with curriculum developed in partnership with NETA. “This partnership is
a very big deal for us,” Gabel says. “We work closely with industry partners to make sure we are preparing our students to enter into their career of choice.”
Bob Sheppard, Vice President of Business Development at Intellirent (a NETA Corporate Alliance Partner), calls the program an exciting milestone for NETA and the school. “We have been working on this program for six years. We are very excited to see it come to life,” he says.
“Th is program is unique in the world of electrical test technician education and will provide individuals with the knowledge and skills needed to succeed in the electrical testing industry,” Sheppard says.
LBCC consists of two campuses with an enrollment of more than 25,000 students each semester. The education program’s primary purpose is to prepare students for transfer to baccalaureate-granting institutions, entry into work or career development, and to support businesses in economic development.
LBCC’s new QQ building and the renovated RR building will house the Electrical Technology Program as well as the new High Voltage Technician Program based on the NETA Electrical Power Testing Technician (EPTT) curriculum. EPTT includes a series of courses designed to provide graduates with a
strong grasp of the educational requirements specified for a Level 2 NETA Test Technician per ANSI/NETA ETT, Standard for Certification of Electrical Testing Technicians
The new program will be offered as a postsecondary adult education program, designed for individuals interested in a career in the power systems industry or for electrical testing technicians seeking advancement. Successful participants will graduate with a certificate of completion or continue with additional credits to earn an Associate Degree. By the end of the course, graduates will have completed OSHA 30 training and numerous hours of electrical safety training, and achieved First Aid and CPR certifications.
NETA and LBCC are excited about the debut of this program and look forward to congratulating its first graduates in 2019.
Sonel’s Graphic Insulation Testers expose flaws that numerical testers simply can’t see.
Transformer windings, motor windings, cable spools
User-selectable test voltages from 50 V to 5/10 KV
All ratios and parameters calculated – absorption, PI, DAR, capacitance, length
You run an insulation resistance test and get a number. Everything is fine. Right? Well...maybe not. This graphic display plots the results of a test where the final number appears to be OK, but the graph indicates a latent flaw that will likely result in an avoidable breakdown.
Sonel MIC Graphic Insulation Testers are the only instruments that display this valuable information on
the tester screen. Without this graph you’d wind up with a false sense of insulation integrity.
Sonel Graphic Insulation Testers have all the features you’d expect from high performance instruments including stepped or continuous voltage, selectable test voltages and currents, three test times plus CAT IV safety rating, auto-discharge, high-noise immunity and live object protection.
Get more information on these powerful instruments and the complete line of Sonel testers at www.soneltest.com
Better yet, call us today. 408.988.1346
Differential protection is the most widely used primary protection scheme for power transformers. The high-speed operation, easy detection, and reliable discrimination between internal and external faults with respect to transformer zone are key benefits of this scheme over others. According to IEEE Std. C37.91-2008, IEEE Guide for Protecting Power Transformers, current differential relaying is the most popular scheme for protecting power transformers that are rated 10 MVA and above.
The current differential principle is based on Kirchoff’s Current Law (KCL), which states that the algebraic sum of currents flowing through any point — a transformer in this case — in an electric network is equal to zero.
The zone of transformer differential is defined by current transformers (CTs) on primary and secondary sides of the transformer. The boundary for phase differential (Figure 1) is decided by the positioning of the phase CTs. This article discusses the challenges to phase differential protection.
The region enclosed by CT-1 and CT-2 in Figure 1 and Figure 2 is the zone of differential protection. For normal operation and faults outside of the protected zone, the currents flowing in the secondary winding of both the CTs cancel each other out (Figure 1). When KCL is applied at Node A in Figure 1, no current flows through the operating coil of the protective relay. No current in the operating coil means no differential trip.
In case of internal faults to the zone as shown in Figure 2, the currents flowing in the secondary
winding of both CTs will no longer add to zero at Node A, and the result will be such that the operate winding will experience enough current to activate differential protection.
A single-phase system is considered to illustrate the fundamental concept of differential protection. In the real world, multiple circuits may exist, but the principle remains the same. An assumption of ideal system conditions is made in the illustration.
Th e ideal transformer model neglects core properties, magnetizing current losses, leakage flux, and the fact that transformer windings are inductive in nature. Similarly, CTs possess magnetic properties, and the secondary current is not always in exact ratio to the primary current. Even with the exact same ratio and type of CTs on both ends of a differential zone, the relay might observe different currents from both CTs. If these factors are not taken into consideration in the transformer differential scheme, the relays can experience undesired tripping. This article highlights such factors and explains the risk involved in the security and selectivity of a transformer differential scheme. The article also discusses some of the methods adopted by relay designers to address those factors.
Current transformers are made of materials with magnetic properties. For that reason, even with the same ratings and manufacturing, no two CTs can be exactly similar in behavior and characteristics. The most accurate type of CTs that could be used for protective relaying applications are covered by the C classification. The leakage flux in the core of C-class CTs does not have an appreciable effect on the ratio. For that reason, C-class CTs with high kneepoint saturation voltages are quite popular for highly sensitive applications like transformer differential.
IEEE Std. C57.13-2016, Requirements for Instrument Transformers, states that the margin of error in the ratio at rated current for C-class is 3 percent. With this error, it is possible for a differential relay to misoperate for either an out-of-zone fault or no fault.
Electromechanical differential relays present an added problem. They are provided with taps for both the primary side and secondary side of a power transformer to compensate for any mismatch due to CT ratios. Separate taps for primary and secondary windings are available. Due to the limited number of taps available, there is seldom a perfect match to what the relay should see.
Figure 3 shows an electromechanical differential relay with the taps set on 5 amps for both windings. Let’s consider the relay shown in Figure 3 to protect a 50 MVA, 110/33 kV transformer.
The rated transformer single-phase primary and secondary line currents for this example would be:
Let’s assume the following CT ratios:
CT selected for the primary side = 500:5
CT selected for the secondary side = 1,600:5
The nominal CT secondary current input to the relay would be:
Of all the available taps, the closest tap is 4.6 for both windings:
The calculated mismatch can be enough to pick up the operating coil of the relay.
It is nearly impossible to eliminate the unwanted diff erence in secondary currents due to the limited number of taps in electromechanical relays. Th e best solution is to select the most appropriate taps on the relay and accept a less than ideal operating sensitivity.
On the other hand, microprocessor relays do not face the problem of CT mismatch errors at all. Algorithms are run internally to eliminate such errors. Some digital relays automatically compute the high- and low-side taps using the MVA of the transformer, line voltages, CT ratios, and transformer connection. This allows the tap to be set precisely to two decimal points. The equation to calculate taps in those relays is:
For wye-connected CTs, C = 1
For delta-connected CTs, C = √3
MVA = Maximum power transformer capacity
VWDG = Winding line-to-line voltage in kV CTRn = Current transformer ratio
Electromechanical relays employ the concept of a percentage restrained characteristic, a curve plotted between differential or operating current, and restrained current. The function of the restrained element is to provide some restraint to the relay from operating on CT mismatch or errors that do not refl ect an internal fault.
When the ratio of operate current to restraint current exceeds by a set quantity, called a slope setting, the relay enters the operating diff erential trip region as shown in Figure 4. Slope-1 is meant for errors related to CT mismatches, tap changers, CT accuracies
and ratio errors, and relay measuring errors, whereas Slope-2 provides security against CT saturation on through faults. IEEE Std. C37.91-2008, IEEE Guide for Protecting Power Transformers , recommends a 30–35 percent maximum setting for slope-1, but this can change depending on the state of the power system.
The primary or secondary windings of a threephase transformer can be connected using either delta or wye, depending on its influence on power system operation and relaying. The two commonly known delta connections are DAB and DAC, which give either a +30° or -30° phase shift of positive-sequence voltages and currents, respectively. Additionally, there are numerous ways to configure a wye or delta to have desired phase shifts anywhere from 0° to 360°.
As shown in Figure 5, the transformer has a DAB connection on the primary winding and a wye connection on the secondary. CTs on both sides are wye-connected. The current seen by the CT on the primary side would be the vector sum of currents in winding a and winding b phases:
IA = Ia-Ib
whereas the CT on the secondary side would read Ia.
Under balanced load conditions:
Ia = Ib
IA = Ia -Ib
The magnitude of vector IA can be computed by the cosine law. According to cosine law:
The magnitude of IA = √3 Ia = √3 Ib
The factor of √3 associated with line currents out of either DAB or DAC can be enough to
cause spurious operation of the transformer differential. Therefore, it is imperative to have some compensation for the effect of phase shift.
When electromechanical relays are used for a transformer diff erential scheme, the phase shift compensation is done externally. External compensation is accomplished by changing CT connections for diff erent winding configurations of the transformer. For example, a delta-wye transformer would have wye-connected CTs on the delta side and deltaconnected CTs on the wye side to counteract the phase shift created by the transformer.
The change of CT connection on the wye side of the transformer to DAB, as shown in Figure 6, would compensate for the effect of phase shift created by the transformer. The DAB-connected CT will create -30 degrees for compensation before the relay reads the currents.
Microprocessor-based relays implement this compensation mathematically internal to the relay. It is not required to have a certain type of CT connection in advance. Any kind of CT and transformer connection will be compensated for phase by the relay itself.
Modern digital relays use a compensation matrix to perform internal compensation. These matrices for different transformer winding configurations can be set by the user. The relay uses the output signal from those
matrices to calculate the actual operate and restraint values.
Let’s reconsider the configuration in Figure 5, with both CTs connected in wye, and the transformer is a Dy1 with DAB for HV winding.
When the transformer configuration is plotted on a clock, the red arrows (Figure 7) indicate the position of A-phase current or voltage.
Since CT connections are wye for both sides in the example, the clock position for both CT connections will undergo no change compared to the transformer. The black arrows in Figure 8 indicate CT clock positions. There still exists a 30-degree phase shift; hence, the LV winding needs to be compensated for 30 degrees in the counter-clockwise (CCW) direction to entirely negate the effect of the phase shift.
Many relay manufacturers assign numbers from 0–12 for both HV and LV windings. The numbers correspond to the number of 30-degree angle increments and can be set by the user as a setting in the relay to eliminate the phase shift deviation.
CT saturation is a condition where the core of a CT is completely magnetized and produces maximum magnetic flux. When a CT enters the saturation region, it draws heavy magnetizing current from the source with a slight increase in exciting voltage as in Figure 9. With considerable magnetizing current, the ratio error increases, and the secondary current is no longer in linear relation to the primary current.
The resultant current waveform on the secondary circuit, coupled by a saturated core, is highly distorted and full of harmonics.
Saturation in CTs occurs in terms of ac and dc components of the primary current. High symmetrical faults can drive a CT into ac saturation. But sometimes, negligible distortion occurs in the secondary waveforms during ac saturation. The severity in distortion can occur under the presence of a decaying dc component associated with an asymmetrical fault, magnetizing inrush, motor starting, or generator synchronization.
Figure 9: An Example of Saturation Curve for a CT
The effect of CT saturation on transformer diff erential relays depends on the type of relay and on whether the fault is external or internal to the protected zone. For internal faults, the relay should operate regardless of the presence of significant distortion in current waveforms due to CT saturation. The more prevalent concern is the possible misoperation of differential relays for external faults when the distortion in the secondary current waveform is significant in magnitude and duration.
Inrush is high magnetizing current drawn by a transformer from the source during any of the following conditions:
1. Energization of a transformer with secondary open after complete deenergization
2. Post-fault voltage recovery when an external fault is cleared
3. Energization of a parallel transformer
Factors like the X/R ratio on CT, the burden, and the class of CT play a vital role in minimizing the effects of saturation. This article focuses only on what a relay can do to avoid misoperation from CT saturation for any external fault.
Most electromechanical and microprocessorbased relays use the concept of percentage restrained or slope characteristic to take care of CT saturation eff ects. One function of the restrained element is to provide some restraint to the relay from operating on out-of-zone faults. When high currents are present, it is more likely that one or both CTs can saturate at different levels and cause false differential current. The method of slope characteristic improves relay performance in the face of saturation and can allow CT sizing requirements to be relaxed as a result.
Many relay manufacturers suggest a dualslope approach in the slope characteristic to differentiate between steady-state errors and transient errors. Steady-state errors include CT mismatch, tap changer errors, CT ratio errors, and accuracy errors, whereas transient errors are caused by CT saturation. Slope-2 is set at a higher value than slope-1 to accommodate greater tolerances for CT saturation on highmagnitude through-faults.
Some relay designers incorporate diff erent break points in the characteristic for ac and dc saturation to improve sensitivity and security during the event of CT saturation.
The magnitude and shape of inrush waveform depends on a variety of factors such as property, the design and size of transformer, network topology, source impedance, the point on the voltage wave at which a breaker contact closes, excitation voltage magnitude, and residual magnetism in a transformer. The inrush current is transient in nature, can be as high as 8–12 times the transformer rated current, and can exist for as long as a few milliseconds. A typical waveshape of inrush current is shown in Figure 10.
Inrush current fl ows through the primary winding and magnetizing circuit of a transformer. The secondary winding does not observe any inrush current. The spikes of inrush can cause considerable CT secondary current for a short duration from one CT but not the other. This difference can lead to misoperation of the transformer differential.
One unique fact about magnetizing inrush is that it is rich in even harmonics. The harmonic content in inrush distinguishes it from fault current, and thus could be used for detection. Traditionally, 2nd harmonic restraint has been used to restrain the relay for an inrush condition, but many relay designers also suggest an additional 4th harmonic restraint to provide more security.
Electromechanical relays have filter circuits to detect even harmonics. The output sum
of harmonic currents along with the dc component are passed through the restraining coil of the relay, whereas the fundamental current is passed through the operating coil of the relay. When the ratio of restraining coil current and operating coil current exceeds a set number, the relay restrains to operate.
Modern digital relays use Fourier transforms to obtain even harmonic ratios out of a sinusoidal current waveform. Some relays have algorithms that look only for the ratio of 2nd harmonic to the fundamental instead of using the sum of all harmonics. The relay blocks the operation of differential if that ratio goes high. This method provides more speed and dependability but is not secure when there is low content of 2nd harmonics.
The problem of low 2nd harmonic content is usually seen in modern transformers with lowloss steel cores. It typically affects one or two phases. To provide a solution, many digital relays can be programmed such that the 2nd harmonic in all three phases is combined in some manner to restrain the differential.
Other manufacturers check not only the ratio between the second and first differential current harmonics, but also analyze an angular relation (phase shift) between the two harmonics. This phase-angle relation maintains certain
unique patterns that enable the relay to restrain securely, even during inrush conditions when the ratio drops dramatically.
Despite the fact that transformer differential is the most popular scheme to protect a transformer from electrical faults, there are many obstacles that might affect the reliability of this scheme. Some of the challenges, including CT mismatch errors, phase shifts due to delta winding, effects of CT saturation, and magnetizing inrush are discussed in detail in this article. Various methods adopted by relay manufacturers are also covered to acquaint readers with possible solutions to those challenges.
Mohit Sharma obtained his Bachelor of Technology in electrical engineering from the National Institute of Technology, Bhopal, India, in 2012. Soon after, he joined Indiabulls Power, a coal-fired independent power producer, as an Electrical Maintenance Engineer. During his tenure, he was responsible for the testing and maintenance of LV and MV switchgear. In 2015, he received his MS in electrical power systems engineering from North Carolina State University and joined Megger as an Applications Engineer for protective relay products. He currently works with the technical support team to assist customers with their relay testing needs.
ANSI/NETA ETT, Standard for Certification of Electrical Testing Technicians, 2015 Edition, is being revised as an American National Standard. A project intent notification was published in ANSI’s Standards Action on October 6, 2017, with a 45-day public review period that closed November 11, 2017. The initial ballot for the document was issued on December 1, 2017, and closed on December 31, 2017. The second public review period opened on January 5, 2018, and closed on February 4, 2018, as did the recirculation ballot on the accepted changes that resulted from the initial review of the draft document. The intent is to release the revised edition of ANSI/NETA ETT in March 2018.
ANSI/NETA ETT establishes minimum requirements for qualifications, certification, training, and experience for the electrical testing technician. It provides criteria for documenting qualifications for certification and details the minimum qualifications for an independent and impartial certifying body to certify electrical testing technicians.
Single copy of draft document: $459
Order from: Kristen Wicks (888) 300-6382 kwicks@netaworld.org
Send comments to Kristen Wicks, kwicks@netaworld.org, with copy to psa@ansi.org
ANSI/NETA MTS, Standard for Maintenance Testing Specifications for Electrical Power Equipment and Systems, 2015 Edition, is being revised as an American National Standard. A project intent notification was published in ANSI’s Standards Action on October 6, 2017, with a 45-day public review period that closed November 11, 2017. The initial ballot was issued on February 1, 2018, and closes on March 4, 2018.
REVISION IN PROCESS
ANSI/NETA MTS contains specifications for suggested field tests and inspections to assess the suitability for continued service and reliability of electrical power equipment and systems. The purpose of these specifications is to assure that tested electrical equipment and systems are operational and within applicable standards and manufacturers’ tolerances, and that the equipment and systems are suitable for continued service.
Single copy of draft document: $459
Order from: Kristen Wicks (888) 300-6382 kwicks@netaworld.org
Send comments to Kristen Wicks, kwicks@netaworld.org, with copy to psa@ansi.org
ANSI/NETA ECS, Standard for Electrical Commissioning of Electrical Power Equipment and Systems, 2015 Edition, was approved as an American National Standard on December 3, 2014. This standard is available for purchase in the NETA Bookstore at www.netaworld.org
ANSI/NETA ECS describes the systematic process of documenting and placing into service newly installed or retrofitted electrical power equipment and systems. This document shall be used in conjunction with the most recent edition of ANSI/ NETA ATS, Standard for Acceptance Testing Specifications for Electrical Power Equipment and Systems. The individual electri-
cal components shall be subjected to factory and field tests, as required, to validate the individual components. It is not the intent of these specifications to provide comprehensive details on the commissioning of mechanical equipment, mechanical instrumentation systems, and related components.
Voltage classes addressed include:
• Low-voltage systems (less than 1,000 volts)
• Medium-voltage systems (greater than 1,000 volts and less than 100,000 volts)
• High-voltage and extra-high voltage systems (greater than 100 kV and less than 1,000 kV)
References:
• ASHRAE, ANSI/NETA ATS, NECA, NFPA 70E, OSHA, GSA Building Commissioning Guide
This document is scheduled for release as a reaffirmed or revised standard in Spring 2020. Those interested in participating in the revision process should contact the NETA office for more information. Initial review work will begin in the spring of 2018, with the initial ballot issued in late 2018/early 2019.
ANSI/NETA ATS, Standard for Acceptance Testing Specifications for Electrical Power Equipment and Systems, 2017 Edition, covers suggested field tests and inspections for assessing the suitability for initial energization of electrical power equipment and systems. The purpose of these specifications is to assure that tested electrical equipment and systems are operational, are within applicable standards and manufacturers’ tolerances, and are installed in accordance with design specifications.
This document is scheduled for release as a revised standard in the spring of 2021. Those interested in participating in the revision process should contact the NETA office for more information.
Power System Acceptance Testing
Commissioning and Start-up
Maintenance
Life-Cycle Extension
Troubleshoot and Repair
Training and Engineering Services
and Operations
2200 West Valley Hwy North, Suite 100 | Auburn, WA 98001
Office: 253-333-9730 | Sales: 425-293-1239 www.sigmasix.com
Comments and suggestions on any of the standards are always welcome and should be directed to the NETA office. To learn more about the NETA standards review and revision process, to purchase these standards, or to get involved, visit www. netaworld.org or contact the NETA office at 888-300-6382.
The IEEE/ICC working groups, including engineers and scientists, met in Hollywood, Florida, for the fall 2017 IEEE/ICC meeting from October 29 through November 1.
This is an ongoing opportunity for NETA to be recognized and to offer a field-testing perspective to the working groups as
documents are developed. The working groups are comprised of cable manufacturers, utilities, test equipment manufacturers, and end users.
Table 1: Fall 2017 Working Groups/Discussion Groups Meetings for Subcommittee F
F02WField Testing of Laminated Dielectric Shielded Power Cable Systems Rated 5 KV and Above (400.1)
F04WPartial Discharge Testing in the Field (P400.3)
F06WField Testing of Shielded D Power Cable Systems Using High-Voltage Direct Current (IEEE 400.5)
F07WGuide on Neutral Corrosion in MV Underground Cables (1617)
Review of final draft for pre-ballot including latest revisions.
Comprehensive revision submitted for review. Requires bi-weekly, on-line working group meetings so standard can move forward.
Discussion of first draft by working group.
Von Herrmann recognized as new Chair leaving ViceChair vacant. Working group reviewed proposed revisions by writing group.
F11WConstant Voltage AC Field Testing of Cable SystemsFurther discussion on content of first draft.
F12WGuide for Fault Locating on Shielded Power Cables Final review of pre-ballot document and resolution of open items.
See Field Testing and Diagnostics
Partial discharge is a leading indicator of impending insulation failure of medium-, high-, and extra-high-voltage shielded cables. Discharge can result from poor installation workmanship, physical damage, contamination, and electrical tree growth through aging. The IEEE 400.3 working group is in final preparations that will attempt to provide pass/fail guidelines in the field.
Very-low-frequency (VLF) dissipation factor measured in the range of 0.5 Uo up to 2.0 Uo
is a commonly recognized method of assessing insulation degradation due to water treeing in PE- and XLPE-insulated cables. Over the years, a large body of data was accumulated for this type of insulation.
Knowledge of the effect of water treeing on 0.1 Hz tangent delta on rubber-insulated cables (butyl rubber as well as black, pink, and brown EPR) is much scarcer, as the density of treeing in such insulation is lower and the rate of water-tree growth is slower than in polyethylene. It requires about thirty years for
rubber insulation to be degraded to the extent to which the polyethylene insulation of the 1960s and early 1970s degraded in less than ten years. Rubber-insulated cables removed from service in U.S. nuclear power plants after about 30 years or more due to their failure or highly elevated 0.1 Hz tangent delta were subjected to laboratory testing. The strong correlation between 0.1 Hz dissipation factor and their ac breakdown strength will be shown in graphical format for cables insulated with butyl rubber and black EPR. Only a few examples for pink and brown EPR will be shown, as the density of water trees in these types of insulation is much lower than in black EPR.
The Insulated Conductors Committee (ICC) is a professional organization within the Power Engineering Society (PES) of the Institute of Electrical and Electronics Engineers (IEEE).
The 2017 fall meeting was a great success with over 500 in attendance. We are now preparing for the spring 2018 meeting in Tucson, Arizona, with several fi nal drafts going to ballot.
Presentations on these topics were followed by discussions that will allow the working groups to better understand the ongoing research that can be incorporated in the revision of the guidelines.
Ralph Patterson is the owner and President of Carolina Electrical and former owner of Power Products and Solutions. His professional background includes working as a design engineer of transformers and as a specifying engineer of insulated conductors. He has more than 25 years in power engineering, particularly in insulation diagnosis and evaluation of electrical distribution equipment. He serves on the NETA Standards Review Council, is the NETA liaison for the IEEE Insulated Conductor Committee’s working groups, and received NETA’s 2001 Outstanding Achievement Award.
From a single part to a switchgear lineup, Advanced Electrical & Motor Controls’ inventory of low-voltage insulated case circuit breakers, molded case circuit breakers, motor controls, and custom switchgear is second to none in the U.S. No matter what you need — new, surplus, used, or reconditioned power distribution equipment, testing and repair, or an engineered solution — AEAMC will keep you up and running.
Let us test, repair, and extend the life of your:
Insulated Case Circuit Breakers
Molded Case Circuit Breakers
Motor Controls & Centers
Bolted Pressure Switches
Panelboard Switches & Bus Plugs
480 V Distribution Transformers
Replacement Parts
UL-Listed Motor Control Center Replacements
www.aemc.com
AEMC’s
The AEMC® Model 6681 detects electrical power cables, telecommunication cables, metal pipes, and even restrictions in non-metal conduit. Comprised of transmitter and a receiver, the Model 6681 is simple to use on both currentcarrying and non-current-carrying electrical wiring. Its digital technology overcomes interference and disturbance signals to provide precise location details, making it very simple to follow electrical cables through walls or detect buried pipes. The receiver can quickly identify the circuit breaker or fuses corresponding to the power outlet that the transmitter is connected to. It can be used to detect short circuits or breaks on existing installations. The Model 6681 is lightweight and includes a complete set of accessories for direct measurement.
www.avotraining.com
Certification Course
AVO Training Institute introduces its new Infrared Thermography Level 2 Technician Certification course. The first course is scheduled for January 29, 2018. This course is a natural transition from the Infrared Thermography Level 1 course currently offered and can be an efficient companion to other courses that are offered. AVO’s IR2 course is a natural progression for technicians who have received the Level 1 Certification. The course expands past the basics of infrared theory and discusses camera operation under different conditions and how to make judgments of the measurement situation in the field and identify potential sources for error.
www.basler.com
Basler Electric is pleased to announce the latest additions to its Plug and Play relay product line. Six new models are now available in the BE1-50/51B Self-Powered Overcurrent Retrofit Relay family with the new Hot Line Tag (HLT) feature for CO and IAC upgrades. The HLT feature adds a highly visible red neon light and switch to the front of the relay. This feature provides significantly reduced clearing time to assist with reducing arc flash hazards. Another retrofit upgrade option now available is the new BE1-87B Plug and Play relay for replacement of GE PVD electromechanical differential relays.
www.doble.com
Vanguard Instruments is now a part of Doble Engineering Company. Discover more about what Vanguard has to offer and get a quick look at its testing tools for transformers, circuit breakers, and protective relays. Vanguard products include extra-high-voltage circuit breaker analyzers, microcomputerbased precision micro-ohmmeters, automatic current transformer testers, single- and three-phase transformer winding turns-ratio testers, transformer winding resistance meters, mega-ohm resistance meters, and a variety of other application-specific products.
www.electrorent.com
Established in 1965, Electro Rent Corporation adds new products to its rental inventory every month. Recent additions include Fluke’s TI450-SF6 infrared and gas camera. Electro Rent has opened another stocking inventory center in Columbia, Maryland. Electro Rent’s recent merger with Microlease increased our inventory and international footprint. Electro Rent’s calibration lab is A2LA ISO/IEC 17025: 2005 certified to ensure your equipment is calibrated correctly when you receive it. For daily and monthly test equipment rentals, please call our experienced staff at 800.688.1111 (USA) or 800.268.0216 (Canada). Email us at sales@electrorent.com
EMSYS DESIGN
www.emsys-design.com
CellSPY Lite
The new CellSPY Lite by Emsys Design is here to make load bank testing easier than ever. Installation is a breeze. Just clamp on each monitor to its battery, and you’re done. The monitor flashes blue after making contact with the cloud server, indicating the system is armed and ready for testing. Temperature and voltage are measured in real time and are accessible via our web-based application, giving you full visibility of each battery in your system. After testing, a PDF is generated that includes individual and aggregate statistics — complete transparency at your fingertips.
www.flir.com
CM275 Clamp Meter and DM285/DM166 Digital Multimeters
FLIR recently introduced seven new test and measurement tools — most significantly, the CM275 clamp meter and the DM285 and DM166 digital multimeters. These meters are all enhanced with Infrared Guided Measurement (IGM™), which means they provide a visual indication of temperature that guides you immediately to the source of electrical shorts (hot) or indications of air or water leaks (cold). The CM275 and DM285 also offer Bluetooth connectivity for uploading data and/or images wirelessly to the FLIR Tools mobile app, eliminating several of the steps needed to share data with others or to upload information for generating client reports.
www.geindustrial.com
Universal GE EntelliGuard* Trip Units
NEW! Universal GE EntelliGuard* Trip Units offer a simplified product solution of one universal plug-and-play trip unit for GE WavePro, AK/AKR, and Power Break legacy breaker frames. The trip unit will allow the user to select the sensor size and trip rating (rating plug not required) directly on the display or through the free Trip Unit Toolkit software. Simplicity: Just one to four catalog numbers can cover an entire switchgear line-up! Then catalog numbers can cover all GE trip units launched since 1981. It ships from the factory in one day. To learn more visit www.geindustrial.com
www.graceport.com
GraceSense™
GraceSense™ Hot Spot Monitor (HSM) is a 24/7 temperature monitoring device that identifies potential hot spots and enables users to predict failures in electrical equipment. Identifying faults before they occur saves time and money when unplanned outages, service interruptions, and equipment failures are avoided. Design and communication flexibility allows the HSM to be used either stand-alone or fully integrated into a plant-wide information system. Integration is made simple when the device is connected via MODBUS TCP I/P or Ethernet I/P to the facility’s SCADA/ DCS systems, while stand-alone application is made possible with GraceSense™ web utility interface to configure temperature threshold alarms, monitoring intervals, relay outputs, and more.
GROUP CBS INC.
www.groupcbs.com
VITS60M
Group CBS and Vacuum Interrupters are pleased to introduce a new vacuum integrity test set, the VITS60M. Unlike other vacuum integrity test sets on the market today, the VITS60M not only performs the standard go/no-go test on vacuum interrupters, it also includes a built-in 2.5/5/10 kV megohmmeter for insulation resistance testing. With automated Polarity Index and Absorption Ratio testing routines, it has the capability to serve as a standalone 60 kV DC HiPot test set for all types of insulation testing. This simple-to-operate set walks technicians through setup, generating a visual go/no-go result for testing the vacuum integrity of vacuum interrupters and the dielectric strength of various vacuum breaker components during regular maintenance while offering fully programmable leakage current thresholds and test durations.
GROUP CBS INC. NEW PRODUCTS
www.groupcbs.com
CBS ArcSafe® SecureConnect™ Remote Operator for Allen-Bradley® CENTERLINE® 2100 Motor Control Centers
Group CBS and CBS ArcSafe introduce the latest addition to its line of remote racking and switching solutions for circuit breakers, switchgear, and motor controls. The CBS ArcSafe® SecureConnect™ Remote Operator for Allen-Bradley® CENTERLINE® 2100 Motor Control Centers (MCCs) is quick, simple, and does not require any modifications to existing electrical equipment. Designed in cooperation with Rockwell Automation, this 13-lb. SecureConnect Remote Operator allows technicians to remotely disconnect an individual plug-in SecureConnect unit from the CENTERLINE® 2100 MCC vertical power bus while the enclosure door is closed and while standing up to 300 feet away.
HAEFELY HIPOTRONICS
www.haefely-hipotronics.com
2293
The 2293 is an automatic winding analyzer optimized for three-phase power and distribution transformer measurements. It uniquely combines winding resistance measurement, turns ratio measurement, core demagnetization, transformer type detection, magnetic balance, and heat run test (temperature rise and cooling curve) in the fastest single instrument solution on the market. Setup is easy — the simple, one-time-connection system, once connected, will test all phases on both windings. In addition, data can be transferred over USB memory-stick or LAN. The 2293 offers a unique simultaneous winding magnetization method for winding resistance measurements, equivalent to traditional equipment with up to 100 A test current.
HIOKI USA
www.hiokiusa.com
Hioki portable power meters and analyzers are best-in-class power measuring instruments for measuring single- to threephase lines with a high degree of precision and accuracy. The PQ3100 is a comprehensive but easy-to-use power quality analyzer for monitoring and recording power supply anomalies, allowing their causes to be quickly investigated, and also for assessing power supply problems such as voltage drops, flicker, harmonics, and other electrical issues.
IRISS
www.iriss.com
SONUS PD
The SONUS PD is specifically designed for partial discharge (PD) and airborne emission (AE) detection on medium- and high-voltage switchgear. The unit detects Transient Earth Voltage (TEV) signals generated by internal partial discharge as well as ultrasound acoustic discharge generated by surface tracking, arcing, or corona. PD detection can be used to detect early warning signs of equipment insulation failure. Inspections can be performed quickly and safely by maintenance personnel with minimal training. Fast and accurate diagnosis of problems using the SONUS PD will help you prevent unexpected outages.
KOCOS AMERICA LLC
www.kocos.com
KoCoS is proud to introduce the NEW ACTAS line of breaker test systems: P260/P360. Capable of measuring pre-insertion resistors, GIS breakers, testing with both sides grounded, performing first trip, and measuring static and dynamic resistance, this system is the most versatile in the market. The system can be used with a laptop or the built-in 7-inch touch screen. The software is user friendly, with simple intuitive steps and state of the art graphics and interface. Its light weight and a built-in Nanuk hard case make it ideal for field use. Contact KoCoS America for more information and to schedule your demo.
www.madisontesting.com
Madison Testing presents a series of instructional GO-NO-GO procedures that focuses on secondary injection testing. Each procedure is written for quick reference and familiarization of the test sets, which allows the customer to quickly test an LSIG trip unit with an easy-to-use GO-NO-GO format. The series were written to supplement the original OEM’s instructions. Each procedure focuses not only on how to use the test set, but on other information the OEM did not necessarily cover, including cable issues, shipping issues, spare parts, and a brief history of the trip series itself. All of them are presented in the same GO-NO-GO style where we connect to a LSIG trip and basically go through each function, what our results were, and what to look out for.
MEGGER
www.megger.com
MVCT – VT & CT Analyzer
Th e MVCT is a multi-function test set with enhanced capabilities to provide accurate and efficient testing of instrument transformers in the field. The MVCT test set by Megger is capable of testing inductive voltage transformers (VTs) and current transformers (CTs) used for revenue and protection applications as per ANSI/IEEE and IEC standards. The MVCT has been designed to overcome the most difficult testing conditions in the field, with a fast, concurrent measurement method. With the single push of a button, the MVCT performs insulation resistance, winding resistance, demagnetization, ac and dc excitation/saturation, and ratio and polarity tests in a multi-tap CT. In a similar way, it will test VTs for insulation resistance, ratio, polarity and winding resistance. In summary, the MVCT is the latest technology in the market for CT and VT testing in the field.
www.nationalswitchgear.com
National Switchgear now offers Training Simulators developed exclusively to match existing customer switchgear. Our PEARL-accredited breaker shop utilizes our vast inventory of equipment, including roll-in replacement breakers, and designs these simulators to exactly replicate the internal schematics and existing racking procedures. This ensures the units are completely accurate for training purposes and double as functional spares. Borescope cameras and lights are installed inside the cabinets to verify that primary and secondary connections are made, something that would be impossible with energized equipment. Come by booth 133 for a live demonstration!
www.oberoncompany.com
Oberon’s TCG40™ Series offers maximum protection against arc flash injures while performing common electrical work tasks. These suits are made from a high-quality Aramid fabric for an ultra-lightweight and durable design. Our hoods utilize a patented True Color Grey (TCG®) shield technology that produces no color distortion while working. The suit set comes equipped with a hood, coat, and bib-overalls and meets or exceeds NFPA 70E PPE Category 4 standards. It has an ATPV rating of 42 cal/cm2
www.ofilsystems.com
DayCor® LuminarHD & coronaWise
Ofil has released the DayCor® LuminarHD & coronaWise, a combination of a HD corona camera with dedicated database for condition- and predictive-based maintenance. This high-quality Solar-Blind UV camera and software ensure detecting, capturing, and handling pinpointed corona with detailed findings of defects including location, material, type, size, manufacturer, and installation year. DayCor® Luminar is currently the best UV camera that can display the exact location of corona from remarkable distances, providing a crystal clear, sharp, high-resolution imaging of the inspected scene with GPS, temperature and humidity, and indication severity. Recorded information is imported into coronaWise for trending and report generation.
www.omicronenergy.com
OMS 605/MPD 600/COMPANO 100/ CMC 430
• OMS 605. Our OMS 605 is a convenient, portable monitoring solution that lets you periodically assess partial discharge activity in the stator winding of generators and motors.
• MPD 600. The MPD 600 uses advanced graphical tools, such as 3PARD (3-Phase Amplitude Relation Diagram), to separate multiple partial discharge sources for reliable fault detection.
• COMPANO 100. Due to its light weight (only 10 kg / 22 lbs), battery operation, and compact and rugged design, you can conveniently transport the universal and easy-to-use COMPANO 100.
• CMC 430. An ultra-portable protection test set and calibrator, the CMC 430 is the preferred choice for test engineers in cases where excellent transportability is needed and three currents up to 12.5 A or six voltage outputs are sufficient. Its low weight of just 8.7 kg / 19.2 lbs and robust design with edge protection predisposes the device to every outdoor and indoor use.
www.partssupercenter.com
Parts Super Center now offers insulating boots for most bus and cable connections in GE Magneblast switchgear. Save the time and expense of taping primary bolted connections by using insulating boots that have been specifically designed for the exact connections in your switchgear. Talk to us about your requirements. Parts Super Center, formerly GE Parts Super Center, has all the intellectual property related to the design and product delivered from GE’s Philadelphia Circuit Breaker Plant. We are exclusively responsible for the manufacture and sale of all OEM replacement parts, equipment, engineering support, and equipment modifications.
www.pdservice.com
This ultimate monitoring system is designed to meet every customer’s demand regarding different equipment and types under different failure mechanism. PDS introduces the latest switchable-module monitoring system that achieves a customized integration. Modules applied to the smart monitoring system include temperature, vibration, power quality, and partial discharge (PD), with further extension to Flux, Airgap, and more. Various communication modules offer convenience for different site requirements; data acquired can be stored and displayed locally or be uploaded on-line for remote analysis service as well.
www.powergridenginering.com
At Power Grid Engineering, LLC, we understand travel arrangements could be the sole deciding factor in choosing which trainings to attend, so we’re bringing the training to you. With our on-site seminars, we tailor our curriculum and bring our subject-matter experts to your facility. We’re able to merge content from various Power Systems courses for an enhanced experience in your home location and serve as a platform to earn professional development hours toward your P.E. license. To learn more about this specialized service, please contact us at seminars@powergridmail.com or visit our website at powergridengineering.com/power-systems-training
POWERSIGHT BY SUMMIT TECHNOLOGY www.powersight.com
TestPlan Manager is a giant step forward for doing power studies. Create a Test Plan on your PC and then embed it into your power analyzer(s). Data is organized in your meter by test point, eliminating confusion and error about what the data is for. When data is retrieved from the meter, it is automatically routed and renamed onto your PC, organized by job/customer, by equipment ID (for predictive maintenance), or for tracking efficiency of an industrial process over time. Resource bottlenecks (meters and personnel) can be spotted and resolved prior to testing. The status of each test point is automatically updated.
www.richards-mfg.com
Cold Shrink R-800 (CS8 Series)
The Cold Shrink R-800 (CS8 Series) is a blend of several Richards Manufacturing innovations. The CS8 Series is molded with a 200A loadbreak tap integral to the deadbreak elbow housing — no need for field-installed LRTP or ETP. The integral loadbreak bushing allows for direct conductor tests as well as installation of different components such as arrester elbows, caps, grounding elbows. The cold-shrinkable cable entrance eliminates the need for a cable adapter and separate jacket seal kit. By combining so many components into a single housing, the CS8 is optimized for simplicity and dramatically reduces installation time and increases overall reliability.
www.selinc.com
Visit SEL engineers in booth 238 to learn about the world’s fastest transmission line relay, with 1 MHz sampling and fault-locating accuracy to the nearest tower. You will also learn about the latest developments from SEL that are making power systems all over the world safer, more reliable, and more economical. See you at the booth!
www.secucontrol.com
SecuControl’s DOC Drawout Case Test Plug provides a easy way to measure current and gain test access to GE-style drawout case relays and meters. The DOC features normally closed internal contacts. Upon insertion into the case, it brings the internal drawout case contacts out for easier access. Current measurement probes serve to redirect current circuits without disturbing them. Disconnect pins can be used to disable specific contacts and short-circuit currents. Visit SecuControl at booth 335 to see the DOC Drawout Case Test Plug! More information is at www.secucontrol.com
www.soneltest.com
The AutoISO-5000 adapter for Sonel Insulation Meters simplifies insulation testing of multi-conductor cables from 1 kV to 5 kV. It reduces test time and is more reliable. Five test leads are connected one time to all conductors. The AutoISO rapidly tests all conductor pair combinations of a multiconductor cable in sequence. It eliminates mistakes such as missing a pair or unnecessarily testing a previously tested pair again. A screen report automatically lists all measurements for each pair. The test results can be saved in memory or transferred to a PC.
www.utilityrelay.com
Smart 1-Line
The Smart 1-Line is a modern turn-key solution for monitoring low-voltage substations using AC-PRO/AC-PRO-II Modbus communications. It utilizes an industrial panel computer with a high-resolution color touch screen. The Smart 1-Line will ship with software already installed, ready for connecting to your AC-PRO/AC-PRO-II Modbus communications network, requiring only minimal basic setup. The Smart 1-Line displays a field-configurable electronic 1-Line diagram with real-time Modbus communications data, providing substation status at a glance. It can display currents, voltages, power, energy, settings, waveforms, breaker open/close status, alarms, and more! Additional features such as remote breaker trip will also be possible.
ANSWERS
1. b. Michael Faraday was responsible for discovering electromagnetic induction, diamagnetism, and electrolysis. In 1831, Faraday built the first electric generator using electromagnetic induction, known as the Faraday disk.
2. b. False. The field of a squirrel cage motor will be in the stator (non-rotating windings).
The Faraday disk
3. a. 500 VDC. I hope everyone got this one right. It’s specified in Table 100.11 for rotating machinery in ANSI/NETA MTS-2015. Since this is a wound device, it has inductive characteristics (Table 1).
Table 1: ANSI/NETA MTS-2015, Table 100.11
Windings Before 1970, Field Windings, Others Not Listed in Table 100.11b
Refer to Table 100.14 for temperature correction factors.
4. b. False. To create electromagnetic induction, the magnetic field from one conductor must pass through the windings of another. Since dc only goes in one direction, the magnetic field would pass through the other conductor once, then stop. With ac, the magnetic field alternates and passes through the other conductor 120 times per second (60 cycles/second times two — positive and negative portions of the cycle).
5. a. True. Induction motors cannot reach synchronous speed and are referred to as asynchronous motors.
6. b. 1800 rpm. The formula for rotor speed in rpm is equal to
S = 120f/n where:
S = Rotor speed in rpm
f = ac line frequency
n = number of poles per phase
NFPA Disclaimer: Although Jim White is a member of the NFPA Technical Committee for both NFPA 70E, Standard for Electrical Safety in the Workplace, and NFPA 70B, Recommended Practice for Electrical Equipment Maintenance, the views and opinions expressed in this column are purely the author’s and shall not be considered an official position of the NFPA or any of its technical committees and shall not be considered, nor be relied upon, as a formal interpretation or promotion of the NFPA. Readers are encouraged to refer to the entire text of all referenced documents.
Putting numbers in the equation: 120 x 60 / 4 = 1800 rpm @ 60 Hz. At 50 Hz, the rotor rpm would be 1500 [120 x 50 / 4]. Table 2 should help explain it further. Note that as the number of poles doubles, the rpm is cut in half.
Table 2: Rotor RPM Versus Number of Poles per Phase
Cycles
Number of Poles per Phase 24681012141618
60 cycles360018001200900720600514450400
50 cycles300015001000750600500428375334
Featuring quality, reliable, on-time service and support for all brands and types of solid state power electronics.
Power electronics are our business
Let us suppoort you with our quality repair, calibration and servicing of your solid state equipment. We also buy, sell and trade:
•Communications devices for power equipment
•Protective relays
•Circuit breaker trip devices
•Motor overload relays
•Rating plugs
A&F Electrical Testing, Inc.
80 Lake Ave. South, Ste. 10 Nesconset, NY 11767 (631) 584-5625 Fax: (631) 584-5720 kchilton@afelectricaltesting.com www.afelectricaltesting.com
Kevin Chilton
A&F Electrical Testing, Inc.
80 Broad St. 5th Floor New York, NY 10004 (631) 584-5625 Fax: (631) 584-5720 afelectricaltesting@afelectricaltesting.com
Florence Chilton
ABM Electrical Power Solutions
9800 E. Geddes Avenue, Unit A-150 Englewood, CO 80112 (303) 524-6560 Fax: (303) 524-6581
Brian Smith
ABM Electrical Power Solutions
6280 South Valley View Blvd., Ste. 618 Las Vegas, NV 89118 (602) 300-2188 Fax: (602) 437-3894
Jason Black
ABM Electrical Power Solutions
814 Greenbrier Circle, Ste. E Chesapeake, VA 23320 (757) 548-5690 Fax: (757) 548-5417
Mark Anthony Gaughan, III
ABM Electrical Power Solutions
3700 Commerce Dr. #901-903 Baltimore, MD 21227 (410) 247-3300 Fax: (410) 247-0900
Bill Hartman
ABM Electrical Power Solutions
317 Commerce Park Dr. Cranberry Township, PA 16066-6427 (724) 772-4638 Fax: (724) 772-6003 christopher.smith@abm.com
Christopher Smith
ABM Electrical Power Solutions
4390 Parliament Place, Ste. S Lanham, MD 20706 (301) 967-3500 Fax: (301) 735-8953
Frank Ceci
Accessible Consulting Engineers, Inc. 1269 Pomona Rd., Ste. 111 Corona, CA 92882 (951) 808-1040 info@acetesting.com www.acetesting.com
Iraj Nasrolahi
Advanced Electrical Services 4999 43rd St. SE, Unit 143 Calgary, AB T2B 3N4 Canada (403) 697-3747 www.aes-ab.com
Advanced Testing Systems 15 Trowbridge Dr. Bethel, CT 06801 (203) 743-2001 Fax: (203) 743-2325 pmaccarthy@advtest.com www.advtest.com
Pat MacCarthy
American Electrical Testing Co. LLC
25 Forbes Blvd., Ste. 1 Foxboro, MA 02035 (781) 821-0121 Fax: (781) 821-0771 sblizard@aetco.us www.aetco.us
Scott A. Blizard
American Electrical Testing Co. LLC 34 Clover Dr. South Windsor, CT 06074 (860) 648-1013 Fax: (781) 821-0771 jpoulin@aetco.us
Gerald Poulin
American Electrical Testing Co. LLC 76 Cain Dr. Brentwood, NY 11717 (631) 617-5330 Fax: (631) 630-2292 bfernandez@aetco.us
Billy Fernandez
American Electrical Testing Co. LLC
50 Intervale Rd., Ste. 1 Boonton, NJ 07005 (973) 316-1180 Fax: (781) 316-1181 jsomol@aetco.us
Jeff Somol
American Electrical Testing Co. LLC
Green Hills Commerce Center 5925 Tilghman St., Ste. 200 Allentown, PA 18104 (215) 219-6800
jmunley@aetco.us
Jonathan Munley
American Electrical Testing Co. LLC 12566 W. Indianola Ave. Avondale, AZ 85392 (480) 383-9242 dmadaglia@aetco.us
Donald Madaglia
Apparatus Testing and Engineering 11300 Sanders Dr., Ste. 29 Rancho Cordova, CA 95742 (916) 853-6280 Fax: (916) 853-6258 info@apparatustesting.com www.apparatustesting.com
Harold (Jerry) Carr
Apparatus Testing and Engineering 7083 Commerce Circle, Ste. H Pleasanton, CA 94588 (925) 454-1363 Fax: (925) 454-1499
Applied Engineering Concepts
1105 N. Allen Ave. Pasadena, CA 91104 (626) 398-3052 Fax: (626) 398-3053 michel.c@aec-us.com www.aec-us.com
Michel Castonguay
BEC Testing 50 Gazza Blvd. Farmingdale, NY 11735 (516) 531-9136 Fax: (631) 249-6115 ddevlin@banaelectric.com www.bectesting.com
Daniel Devlin
Burlington Electrical Testing Co., Inc. 300 Cedar Ave. Croydon, PA 19021-6051 (215) 826-9400 (221) Fax: (215) 826-0964 waltc@betest.com www.betest.com
Walter P. Cleary
C.E. Testing, Inc. 6148 Tim Crews Rd. Macclenny, FL 32063 (904) 653-1900 Fax: (904) 653-1911 cetesting@aol.com
Mark Chapman
CE Power Engineered Services, LLC 4040 Rev Dr. Cincinnati, OH 45232 (513) 563-6150 Fax: (513) 563-6120 info@cepowersol.net www.cepower.net
Brent McAlisar
CE Power Engineered Services, LLC 8490 Seward Road Fairfield, OH 45011 (513) 563-6150 tim.lana@cepower.net
Tim Lana
CE Power Engineered Services, LLC 10338 Citation Drive, Suite 300 Brighton, MI 48166 (810) 229-6628
Ken L'Esperance
CE Power Engineered Services, LLC 1803 Taylor Avenue Louisville, KY 40213 (502) 479-0612 tom.hutchinson@cepower.net
Tom Hutchinson
CE Power Engineered Services, LLC 10840 Murdock Drive Knoxville, TN 37932 (865) 310-2522 don.williams@cepower.net
Don Williams
CE Power Engineered Services, LLC 7674 Washington Ave. S Eden Prairie, MN 55344 (877) 968-0281 jason.thompson@cepower.net
Jason Thomps
Control Power Concepts 353 Pilot Rd; Ste. B Las Vegas, NV 89119 (702) 448-7833 Fax: (702) 448-7835 www.controlpowerconcepts.com
John Travis
Dude Electrical Testing LLC
145 Tower Dr., Unit# 9 Burr Ridge, IL 60527 (815) 293-3388 Fax: (815) 293-3386
scott.dude@dudetesting.com www.dudetesting.com
Scott Dude
Eastern High Voltage, Inc. 11A South Gold Dr. Robbinsville, NJ 08691-1606 (609) 890-8300 Fax: (609) 588-8090 bobwilson@easternhighvoltage.com www.easternhighvoltage.com
Robert Wilson
ELECT, P.C. 7400-G Siemens Rd., P.O. Box 2080 Wendell, NC 27591 (919) 365-9775 Fax: (919) 365-9789 btyndall@elect-pc.com www.elect-pc.com
Barry W. Tyndall
Electric Power Systems, Inc. 21 Millpark Ct. Maryland Heights, MO 63043 (314) 890-9999 Fax: (314) 890-9998 www.epsii.com
Electric Power Systems, Inc. 557 E. Juanita Ave., #4 Mesa, AZ 85204 (480) 633-1490 Fax: (480) 633-7092
Electric Power Systems, Inc. 4436 Parkway Commerce Blvd. Orlando, FL 32808 (407) 578-6424 Fax: 407-578-6408
Electric Power Systems, Inc. 7000 E. 47th Avenue Drive, Suite 100 Denver, CO 80216 (720) 857-7273 Fax: 303-928-8020
Electric Power Systems, Inc. 23823 Andrew Rd. Plainfield, IL 60585 (815) 577-9515 Fax: (815) 577-9516
Electric Power Systems, Inc. 2601 Center Rd., # 101 Hinckley, OH 44233 (330) 460-3706 Fax: (330) 460-3708
Electric Power Systems, Inc.
56 Bibber Pkwy #1 Brunswick, ME 04011 (207) 837-6527
Electric Power Systems, Inc. 4100 Greenbriar Dr., Ste. 160 Stafford, TX 77477 (713) 644-5400
Electric Power Systems, Inc. 11861 Longsdorf St. Riverview, MI 48193 (734) 282-3311
Electric Power Systems, Inc.
827 Union St., Salem, VA 24153 (540) 375-0084 Fax: (540) 375-0094
Electric Power Systems, Inc.
915 Holt Ave., Unit 9 Manchester, NH 03109 (603) 657-7371 Fax: 603-657-7370
Electric Power Systems, Inc.
146 Space Park Dr. Nashville, TN 37211 (615) 834-0999 Fax: (615) 834-0129
Electric Power Systems, Inc.
8515 Cella Alameda NE, Ste. A Albuquerque, NM 87113 (505) 792-7761
Electric Power Systems, Inc.
7140 Dean Martin Drive, Suite 900 Las Vegas, NV 89118 (702) 815-1342
Electric Power Systems, Inc.
319 US Hwy. 70 E, Unit E Garner, NC 27529 (919) 322-2670
www.epsii.com
Electric Power Systems, Inc.
1090 Montour West Industrial Blvd. Coraopolis, PA 15108 (412) 276-4559
Electric Power Systems, Inc. 6141 Connecticut Ave. Kansas City, MO 64120 (816) 241-9990 Fax: (816) 241-9992
Electric Power Systems, Inc. 2495 Boulevard of the Generals Norristown, PA 19403 (610) 630-0286
Electric Power Systems, Inc. 1129 East Hwy. 30 Gonzalez, LA 70817 (225) 644-0150 Fax: (225) 644-6249
Electric Power Systems, Inc. 7925 Dunbrook Rd., Ste. G San Diego, CA 92126 (858) 566-6317
Electric Power Systems, Inc. 6679 Peachtree Industrial Dr. Ste. H Norcross, GA 30092 (770) 416-0684
j.cash@epsii.com
Jeff Cash
Electrical & Electronic Controls 6149 Hunter Rd. Ooltewah, TN 37363 (423) 344-7666 (23) Fax: (423) 344-4494
eecontrols@comcast.net
Michael Hughes
Electrical Energy Experts, Inc.
W129N10818, Washington Dr. Germantown, WI 53022 (262) 255-5222 Fax: (262) 242-2360
bill@electricalenergyexperts.com www.electricalenergyexperts.com
William Styer
Electrical Engineering & Service Co., Inc.
289 Centre St. Holbrook, MA 02343-1075 (781) 767-9988
jcipolla@eescousa.com www.eescousa.com
Joe Cipolla
Electrical Equipment Upgrading, Inc. 21 Telfair Place, Savannah, GA 31415 (912) 232-7402 Fax: (912) 233-4355
kmiller@eeu-inc.com
www.eeu-inc.com
Kevin Miller
Electrical Maintenance & Testing Inc.
12342 Hancock St., Carmel, IN 46032 (317) 853-6795 Fax: (317) 853-6799 info@emtesting.com www.emtesting.com
Brian K. Borst
Electrical Reliability Services
1057 Doniphan Park Circle, Ste. A El Paso, TX 79922 (915) 587-9440 Fax: (915) 587-9010
Electrical Reliability Services
1775 W. University Dr., Ste. 128 Tempe, AZ 85281 (480) 966-4568 Fax: (480) 966-4569
Electrical Reliability Services
1426 Sens Rd. Ste. 5 Houston, TX 77571 (281) 241-2800 Fax: (281) 241-2801
Electrical Reliability Services
4099 SE International Way, Ste. 201 Milwaukie, OR 97222-8853 (503) 653-6781 Fax: (503) 659-9733
Electrical Reliability Services
5909 Sea Lion Place, Ste. C Carlsbad, CA 92010 (858) 695-9551
Electrical Reliability Services
8500 Washington Pl. NE, Ste. A-6 Albuquerque, NM 87113 (505) 822-0237 Fax: (505) 822-0217
Electrical Reliability Services
1380 Greg Street, Ste. 216 Sparks, NV 89431 (775) 746-8484 Fax: (775) 356-5488
Electrical Reliability Services
2275 Northwest Pkwy SE, Ste. 180 Marietta, GA 30067 (770) 541-6600 Fax: (770) 541-6501
Electrical Reliability Services
7100 Broadway, Ste. 7E Denver, CO 80221-2915 (303) 427-8809 Fax: (303) 427-4080
Electrical Reliability Services
400 N.W. Capital Dr. Lee's Summit, MO 64086 (816) 525-7156 Fax: (816) 524-3274
Electrical Reliability Services
6900 Koll Center Parkway, Ste. 415 Pleasanton, CA 94566 (925) 485-3400 Fax: (925) 485-3436
Electrical Reliability Services 10606 Bloomfield Ave. Santa Fe Springs, CA 90670 (562) 236-9555 Fax: (562) 777-8914
Electrical Reliability Services 3535 Emerson Parkway, Ste. A Gonzales, LA 70737 (225) 755-0530 Fax: (225) 751-5055
Electrical Reliability Services 245 Hood Rd. Sulphur, LA 70665 (337) 583-2411 Fax: (337) 583-2410
Electrical Reliability Services 11000 Metro Pkwy., Ste. 30 Ft. Myers, FL 33966 (239) 693-7100 Fax: (239) 693-7772
Electrical Reliability Services 2222 West Valley Hwy. N., Ste 160 Auburn, WA 98001 (253) 736-6010 Fax: (253) 736-6015
Electrical Reliability Services 9736 South 500 West Sandy, UT 84070 (801) 975-6461
Electrical Reliability Services 6351 Hinson St., Ste. B Las Vegas, NV 89118 (702) 597-0020 Fax: (702) 597-0095
Electrical Reliability Services 9636 St. Vincent, Unit A Shreveport, LA 71106 (318) 869-4244
Electrical Reliability Services
610 Executive Campus Dr. Westerville, OH 43082 (877) 468-6384 Fax: (614) 410-8420 info@electricalreliability.com
Electrical Testing and Maintenance Corp. 3673 Cherry Rd., Ste. 101 Memphis, TN 38118 (901) 566-5557 r.gregory@etmcorp.com www.etmcorp.net
Ron Gregory
Electrical Testing, Inc. 2671 Cedartown Hwy. Rome, GA 30161-6791 (706) 234-7623 Fax: (706) 236-9028 steve@electricaltestinginc.com www.electricaltestinginc.com
Electrical Testing Solutions
2909 Green Hill Ct. Oshkosh, WI 54904 (920) 420-2986 Fax: (920) 235-7136 tmachado@electricaltestingsolutions.com www.electricaltestingsolutions.com
Tito Machado
Elemco Services, Inc.
228 Merrick Rd. , Lynbrook, NY 11563 (631) 589-6343 Fax: (631) 589-6670 courtney@elemco.com www.elemco.com
Courtney Gallo
EnerG Test
206 Gale Lane Kennett Square, PA 19348 (484) 731-0200 Fax: (484) 713-0209 dbuehler@energtest.com www.energtest.com
Dennis Buehler
Energis High Voltage Resources, Inc. 1361 Glory Rd. Green Bay, WI 54304 (920) 632-7929 Fax: (920) 632-7928 info@energisinc.com www.energisinc.com
Mick Petzold
EPS Technology 29 N. Plains Hwy., Ste. 12 Wallingford, CT 06492 (203) 679-0145 www.eps-technology.com
Grounded Technologies, Inc. 19621 Solar Circle, Ste. 101 Parker, CO 80134 (303) 781-2560 Fax: (303) 781-5240 jodymedina@groundedtech.com www.groundedtech.com
Jody Medina
Grubb Engineering, Inc. 3128 Sidney Brooks San Antonio, Tx 78235 (210) 658-7250 Fax: (210) 658-9805 joy@grubbengineering.com www.grubbengineering.com
Robert D. Grubb Jr.
Hampton Tedder Technical Services 4563 State St. Montclair, CA 91763 (909) 628-1256 Fax: (909) 628-6375 chasen.tedder@hamptontedder.com www.hamptontedder.com
Chasen Tedder
Hampton Tedder Technical Services 4113 Wagon Trail Ave. Las Vegas, NV 89118 (702) 452-9200 Fax: (702) 632-0079
Roger Cates
Hampton Tedder Technical Services
3747 West Roanoke Ave. Phoenix, AZ 85009 (480) 967-7765 Fax: (480) 967-7762
Linc McNitt
Harford Electrical Testing Co., Inc. 1108 Clayton Rd. Joppa, MD 21085 (410) 679-4477 Fax: (410) 679-0800 testing@harfordtesting.com www.harfordtesting.com
Vincent Biondino
High Energy Electrical Testing, Inc. 515 S. Ocean Ave. Seaside Park, NJ 08752 (732) 938-2275 Fax: (732) 938-2277 hinrg@comcast.net www.highenergyelectric.com
Charles Blanchard
High Voltage Maintenance Corp. 24 Walpole Park South Dr. Walpole, MA 02081 (508) 668-9205 www.hvmcorp.com
High Voltage Maintenance Corp. 941 Busse Rd. Elk Grove Village, Il 60007 (847) 640-0005
High Voltage Maintenance Corp.
7200 Industrial Park Blvd. Mentor, OH 44060 (440) 951-2706 Fax: (440) 951-6798
High Voltage Maintenance Corp. 3000 S. Calhoun Rd. New Berlin, WI 53151 (262) 784-3660 Fax: (262) 784-5124
High Voltage Maintenance Corp. 8320 Brookville Rd. #E Indianapolis, IN 46239 (317) 322-2055 Fax: (317) 322-2056
High Voltage Maintenance Corp. 1250 Broadway, Ste. 2300 New York, NY 10001 (718) 239-0359
High Voltage Maintenance Corp. 355 Vista Park Dr. Pittsburgh, PA 15205-1206 (412) 747-0550 Fax: (412) 747-0554
High Voltage Maintenance Corp. 150 North Plains Industrial Rd. Wallingford, CT 06492 (203) 949-2650 Fax: (203) 949-2646
High Voltage Maintenance Corp. 9305 Gerwig Ln., Ste. B Columbia, MD 21046 (410) 309-5970 Fax: (410) 309-0220
High Voltage Maintenance Corp. 24371 Catherine Industrial Dr, Ste. 207 Novi, MI 48375 (248) 305-5596 Fax: (248) 305-5579
High Voltage Maintenance Corp. 5100 Energy Dr. Dayton, OH 45414 (937) 278-0811 Fax: (937) 278-7791
HMT, Inc. 6268 Route 31 Cicero, NY 13039 (315) 699-5563 Fax: (315) 699-5911 jpertgen@hmt-electric.com www.hmt-electric.com
John Pertgen
Industrial Electronics Group 850369 Highway 17 South P.O. Box 1870 Yulee, FL 32041 (904) 225-9529 Fax: (904) 225-0834 butch@industrialgroups.com www.industrialgroups.com
Butch E. Teal
Industrial Tests, Inc. 4021 Alvis Ct., Ste. 1 Rocklin, CA 95677 (916) 296-1200 Fax: (916) 632-0300 greg@indtest.com www.industrialtests.com
Greg Poole
Infra-Red Building and Power Service 152 Centre St. Holbrook, MA 02343-1011 (781) 767-0888 Fax: (781) 767-3462 tom.mcdonald@infraredbps.com www.infraredbps.com
Thomas McDonald Sr.
M&L Power Systems, Inc. 109 White Oak Ln., Ste. 82 Old Bridge, NJ 08857 (732) 679-1800 Fax: (732) 679-9326 milind@mlpower.com www.mlpower.com
Milind Bagle
Magna IV Engineering 1103 Parsons Rd. SW Edmonton, AB T6X 0X2 Canada (780) 462-3111 Fax: (780) 450-2994 info@magnaiv.com www.magnaiv.com
Virgina Balitski
Magna IV Engineering 200, 688 Heritage Dr. Calgary, AB T2H 1M6 Canada (403) 723-0575 Fax: (403) 723-0580 info.calgary@magnaiv.com
Dave Emerson
Magna IV Engineering 141 Fox Cresent Fort McMurray, AB T9K 0C1 Canada (780) 791-3122 Fax: (780) 791-3159 info.fmcmurray@magnaiv.com
Ryan Morgan
Magna IV Engineering 96 Inverness Dr. East, Unit R Englewood, CO 80112 (303) 799-1273 Fax: (303) 790-4816 info.denver@magnaiv.com
Aric Proskurniak
Magna IV Engineering Avenida del Condor sur #590 Oficina 601
Huechuraba, Santiago 8580676 Chile +(56) 9-9-517-4642 info.chile@magnaiv.com
Harvey Mendoza
Magna IV Engineering 7,3040 Miners Ave. Saskatoon, SK S7K 5V1 Canada (306) 585-2100 Fax: (306) 585-2191 info.regina@magnaiv.com
Adam Jaques
Magna IV Engineering 106, 4268 Lozells Ave. Burnaby, BC VSA 0C6 Canada (604) 421-8020
Scott Nixon
Magna IV Engineering 4407 Halik St., Bldg. 3, Ste. 300 Pearland, TX 77581 (720) 480-9680 aproskurniak@magnaiv.com www.magnaiv.com
Aric Proskurniak
Midwest Engineering Consultants, Ltd. 2500 36th Ave. Moline, IL 61265 (309) 764-1561 m-moorehead@midwestengr.com www.midwestengr.com
Monte Moorehead
National Field Services 1890 A South Hwy 35 Alvin, TX 77511 (800) 420-0157 jonathan.wakeland@natlfield.com www.natlfield.com
Jonathan Wakeland
National Field Services 649 Franklin St. Lewisville, TX 75057 (972) 420-0157 www.natlfield.com
Eric Beckman
National Field Services 1405 United Drive, Ste. 113-115 San Marcos, TX 78666 (800) 420-0157 Fax: (972) 420-0552 info@natlfield.com www.natlfield.com
Matt LaCoss
Nationwide Electrical Testing, Inc. 6050 Southard Trace Cumming, GA 30040 (770) 667-1875 Fax: (770) 667-6578
Shashi@N-E-T-Inc.com www.n-e-t-inc.com
Shashikant B. Bagle
North Central Electric, Inc. 69 Midway Ave. Hulmeville, PA 19047-5827 (215) 945-7632 Fax: (215) 945-6362 ncetest@aol.com www.ncetest.com
Robert Messina
Northern Electrical Testing, Inc. 1991 Woodslee Dr. Troy, MI 48083-2236 (248) 689-8980 Fax: (248) 689-3418 ldetterman@northerntesting.com www.northerntesting.com
Lyle Detterman
Orbis Engineering Field Services Ltd. #300, 9404 - 41st Ave. Edmonton, AB T6E 6G8 Canada (780) 988-1455 Fax: (780) 988-0191 lorne@orbisengineering.net www.orbisengineering.net
Lorne Gara
Pace Technologies, Inc. 9604-31 Avenue NW Edmonton, AB T6E 6G9 Canada (780) 450-0404 cleavitt@pacetechnologies.com www.pacetechnologies.com
Craig Leavitt
Pacific Power Testing, Inc. 14280 Doolittle Dr. San Leandro, CA 94577 (510) 351-8811 Fax: (510) 351-6655 steve@pacificpowertesting.com www.pacificpowertesting.com
Steve Emmert
Pacific Powertech, Inc. #110, 2071 Kingsway Ave. Port Coquitlam, BC V3C 6N2 Canada (604) 944-6697 Fax: (604) 944-1271 jkonkin@pacificpowertech.ca www.pacificpowertech.ca
Josh Konkin
Phasor Engineering
Sabaneta Industrial Park #216 Mercedita, PR 00715 Puerto Rico (787) 844-9366 Fax: (787) 841-6385 rcastro@phasorinc.com
Rafael Castro
Potomac Testing, Inc.
1610 Professional Blvd., Ste. A Crofton, MD 21114 (301) 352-1930 Fax: (301) 352-1936 kbassett@potomactesting.com www.potomactesting.com
Ken Bassett
Power & Generation Testing, a CE Power Company
480 Cave Rd. Nashville, TN 37210 (615) 882-9455 Fax: (615) 882-9591 mose@pgti.net www.pgti.net
Mose Ramieh
Power Engineering Services, Inc. 9179 Shadow Creek Lane Converse, TX 78109 (210) 590-4936 Fax: (210) 590-6214 engelke@pe-svcs.com www.pe-svcs.com
Miles R. Engelke
POWER PLUS Engineering, Inc. 46575 Magellan Novi, MI 48377 (248) 344-0200 Fax: (248) 305-9105 smancuso@epowerplus.com www.epowerplus.com
Salvatore Mancuso
Power Products & Solutions, LLC 9604 W. WT Harris Blvd., Ste F Charlotte, NC 28269 (704) 573-0420 x12 Fax: (704) 573-3693 adis.talovic@powerproducts.biz www.powerproducts.biz
Adis Talovic
Power Products & Solutions, LLC 13 Jenkins Ct. Mauldin, SC 29662 (800) 328-7382 raymond.pesaturo@powerproducts.biz www.powerproducts.biz
Raymond Pesaturo
Power Services, LLC 998 Dimco Way, P.O. Box 750066 Centerville, OH 45475 (937) 439-9660 Fax: (937) 439-9611 mkbeucler@aol.com
Mark Beucler
Power Solutions Group, Ltd. 425 W. Kerr Rd. Tipp City, OH 45371 (937) 506-8444 Fax: (937) 506-8434 bwilloughby@powersolutionsgroup.com www.powersolutionsgroup.com
Barry Willoughby
Power Solutions Group, Ltd. 5115 Old Greenville Highway Liberty, SC 29657 (864) 540-8434 Fax: (864) 540-8438 fcrawford@powersolutionsgroup.com www.powersolutionsgroup.com
Anthony Crawford
Power Solutions Group, Ltd.
670 Lakeview Plaza Blvd. Columbus, OH 43085 (614) 310-8018
sspohn@powersolutionsgroup.com www.powersolutionsgroup.com
Stuart Spohn
Power Systems Testing Co. 4688 W. Jennifer Ave., Ste. 108 Fresno, CA 93722 (559) 275-2171 ext 15 Fax: (559) 275-6556 dave@pstcpower.com www.powersystemstesting.com
David Huffman
Power Systems Testing Co.
600 S. Grand Ave., Ste. 113 Santa Ana, CA 92705-4152 (714) 542-6089 Fax: (714) 542-0737 www.powersystemstesting.com
Power Systems Testing Co. 6736 Preston Ave, Ste. E Livermore, CA 94551 (510) 783-5096 Fax: (510) 732-9287 www.powersystemstesting.com
Power Test, Inc. 2200 Highway 49 Harrisburg, NC 28075 (704) 200-8311 Fax: (704) 455-7909 rich@powertestinc.com
Richard Walker
POWER Testing and Energization, Inc.
14006 NW 3rd Ct., Ste. 101 Vancouver, WA 98685 (360) 597-2800 Fax: (360) 576-7182 chris.zavadlov@powerte.com www.powerte.com
Chris Zavadlov
POWER Testing and Energization, Inc. 731 E. Ball Rd., Ste. 100 Anaheim, CA 92805 (714) 507-2702
POWER Testing and Energization, Inc. 16825 Northchase Dr. Houston, TX 77056
POWER Testing and Energization, Inc. 22035 70th Ave. South Kent, WA 98032 (253) 437-3100
Powertech Services, Inc. 4095 South Dye Rd. Swartz Creek, MI 48473-1570 (810) 720-2280 Fax: (810) 720-2283
kirkd@powertechservices.com www.powertechservices.com
Kirk Dyszlewski
Precision Testing Group 5475 Highway 86, Unit 1 Elizabeth, CO 80107 (303) 621-2776 Fax: (303) 621-2573 glenn@precisiontestinggroup.com
Glenn Stuckey
Premier Power Maintenance Corporation 6525 Guion Rd. Indianapolis, IN 46268 (317) 879-0660
kevin.templeman@premierpower.us
Kevin Templeman
Premier Power Maintenance Corporation 2725 Jason Rd. Ashland, KY 41102 (606) 929-5969
jay.milstead@premierpower.us www.premierpowermaintenance.com
Jay Milstead
Premier Power Maintenance Corporation 3066 Finley Island Cir NW Decatur, AL 35601 (256) 355-1444
johnnie.mcclung@premierpower.us
Johnnie McClung
Premier Power Maintenance Corporation 4301 Iverson Blvd., Ste. H Trinity, AL 35673 (256) 355-3006
kevin.templeman@premierpower.us
Kevin Templeman
Premier Power Maintenance Corporation 7301 E County Road 142 Blytheville, AR 72315 (870) 762-2100
kevin.templeman@premierpower.us
Kevin Templeman
Premier Power Maintenance Corporation 7262 Kensington Rd. Brighton, MI 48116 (517) 230-6620
brian.ellegiers@premierpower.us
Brian Ellegiers
Premier Power Maintenance Corporation 4035 Championship Dr. Indianapolis, IN 46268 (317) 879-0660
kevin.templeman@premierpower.us
Kevin Templeman
RESA Power Service
3890 Pheasant Ridge Dr. NE, Ste. 170 Blaine, MN 55449 (763) 784-4040 Fax: (763) 784-5397 www.hvserviceinc.com
Mike Mavetz
RESA Power Service 46918 Liberty Dr. Wixom, MI 48393 (248) 313-6868 Fax: (248) 313-6869 www.dymaxservice.com
Bruce Robinson
RESA Power Service 4213 Kropf Ave. Canton, OH 44706 (330) 484-6801 Fax: (740) 333-1271
Chuck Baker
Reuter & Hanney, Inc. 149 Railroad Dr. Northampton Industrial Park Ivyland, PA 18974 (215) 364-5333 Fax: (215) 364-5365 mikereuter@reuterhanney.com www.reuterhanney.com
Michael Reuter
Reuter & Hanney, Inc. 4270-I Henninger Ct. Chantilly, VA 20151 (703) 263-7163 Fax: 703-263-1478
Reuter & Hanney, Inc. 11620 Crossroads Circle, Suites D-E Middle River, MD 21220 (410) 344-0300 Fax: (410) 335-4389
Michael Jester
REV Engineering, LTD 3236 - 50 Ave. SE Calgary, AB T2B 3A3 Canada (403) 287-0156 Fax: (403) 287-0198 rdavidson@reveng.ca www.reveng.ca
Roland Nicholas Davidson, IV
Saber Power Services, LLC 9841 Saber Power Lane Rosheron, TX 77583-5188 (713) 222-9102 info@saberpower.com www.saberpower.com
Mike McDaniel
Saber Power Power Services LLC 14617 Perkins Road Baton Rouge, LA 70810 (225) 726-7793 info@saberpower.com www.saberpower.com
Joey Nelson
Saber Power Power Services LLC 4703 Shavano Oak San Antonio, TX 78249 (210) 267-7282 info@saberpower.com www.saberpower.com
Brad Bodine
Scott Testing Inc. 1698 5th St. Ewing, NJ 08638 (609) 882-2400 Fax: (609) 882-5660 rsorbello@scotttesting.com www.scotttesting.com
Russ Sorbello
Sentinel Power Services, Inc. 7517 E. Pine St. Tulsa, OK 74115 (918) 359-0350 gellis@spstulsa.com www.sentinelpowerservices.com
Greg Ellis
Sentinel Power Services, Inc. 1110 West B St., Ste. H Russellville, AR 72801 (918) 359-0350
Shermco Industries 2425 E. Pioneer Dr. Irving, TX 75061 (972) 793-5523 info@shermco.com www.shermco.com
Shermco Industries 112 Industrial Dr., PO Box 606 Minooka, IL 60447 (815) 467-5577 info@shermco.com
Shermco Industries
1705 Hur Industrial Blvd. Cedar Park, TX 78613 (512) 267-4800 info@shermco.com
Shermco Industries 33002 FM 2004 Angleton, TX 77515 (979)848-1406 info@shermco.com
Shermco Industries 4510 South 86th East Ave. Tulsa, OK 74145 (918) 234-2300 info@shermco.com
Shermco Industries 1711 Hawkeye Dr. Hiawatha, IA 52233 info@shermco.com
Shermco Industries
2100 Dixon St., Ste. C Des Moines, IA 50316 (515) 263-8482 info@shermco.com
Shermco Industries 4383 Professional Parkway Groveport, OH 43125 (614) 836-8556 info@shermco.com
Shermco Industries 998 East Berwood Ave. Saint Paul, MN 55110 (651) 484-5533 info@shermco.com
Shermco Industries 12000 Network Blvd., Bldg D, Ste. 410 San Antonio, TX 78249 (512) 267-4800 info@shermco.com
Shermco Industries
3807 S. Sam Houston Pkwy. W Houston, TX 77056 (281) 835-3633 info@shermco.com
Shermco Industries 4670 G Street Omaha, NE 68117 (402) 933-8988 info@shermco.com
Shermco Industries 1301 Hailey St. Sweetwater, TX 79556 (325) 236-9900 info@shermco.com
Shermco Industries 2901 Turtle Creek Dr. Port Arthur, TX 77642 (409) 853-4316 info@shermco.com
Shermco Industries 5145 NW Beaver Dr. Johnston, IA 50131 (512) 265-3377 info@shermco.com
Shermco Industries Canada Inc. 1033 Kearns Crescent RM of Sherwood, SK S4K 0A2 Canada (306) 949-8131 info@shermco.com
Shermco Industries Canada Inc. 233 Faithfull Cr. Saskatoon, SK S7K 8H7 Canada (306) 955-8131 info@shermco.com
Shermco Industries Canada Inc. 3731-98 St. Edmonton, AB T6E 5N2 Canada (780) 436-8831 info@shermco.com
Shermco Industries Canada Inc. 3434 25th St. NE Calgary, AB T1Y 6C1 Canada (403) 769-9300 info@shermco.com
Shermco Industries Canada Inc. 1375 Church Ave. Winnipeg, MB R2X 2T7 Canada (204) 925-4022 info@shermco.com
Sigma Six Solutions, Inc. 2200 West Valley Hwy., Ste. 100 Auburn, WA 98001 (253) 333-9730 Fax: (253) 859-5382 jwhite@sigmasix.com www.sigmasix.com
John White
Southern New England Electrical Testing, LLC 3 Buel St., Ste. 4 Wallingford, CT 06492 (203) 269-8778 Fax: (203) 269-8775 dave.asplund@sneet.org www.sneet.org
David Asplund, Sr.
Southwest Energy Systems, LLC 2231 East Jones Ave., Ste. A Phoenix, AZ 85040 (602) 438-7500 Fax: (602) 438-7501 dave.hoffman@sesphx.com www.southwestenergysystems.com
Dave Hoffman
Taurus Power & Controls, Inc. 9999 SW Avery St. Tualatin, OR 97062-9517 (503) 692-9004 Fax: (503) 692-9273 robtaurus@tauruspower.com www.tauruspower.com
Rob Bulfinch
Taurus Power & Controls, Inc. 19226 66th Ave. S, Ste. L102 Kent, WA 98032 (425) 656-4170 Fax: (425) 656-4172 servicereq@tauruspower.com www.tauruspower.com
David Koons
3C Electrical Co., A CE Power Company 40 Washington St. Westborough, MA 01581 (508) 881-3911 Fax: (508) 881-4814 jim@three-c.com www.three-c.com
Jim Cialdea
3C Electrical Co., A CE Power Company 72 Sanford Dr. Gorham, ME 04038 (800) 649-6314 Fax: (207) 782-0162 jim@three-c.com www.three-c.com
Jim Cialdea
Tidal Power Services, LLC 4202 Chance Lane Rosharon, TX 77583 (281) 710-9150 Fax: (713) 583-1216 monty.janak@tidalpowerservices.com www.tidalpowerservices.com
Monty C. Janak
Tidal Power Services, LLC 8184 Highway 44, Ste. 105 Gonzales, LA 70737 (225) 644-8170 Fax: (225) 644-8215
Darryn Kimbrough
Tidal Power Services, LLC 1056 Mosswood Dr. Sulphur, LA 70663 (337) 558-5457 Fax: (337) 558-5305
Steve Drake
Tony Demaria Electric, Inc. 131 West F St. Wilmington, CA 90744 (310) 816-3130 Fax: (310) 549-9747 neno@tdeinc.com www.tdeinc.com
Nenad Pasic
Trace Electrical Services & Testing, LLC 293 Whitehead Rd. Hamilton, NJ 08619 (609) 588-8666 Fax: (609) 588-8667
jvasta@tracetesting.com www.tracetesting.com
Joseph Vasta
Utilities Instrumentation Service, Inc. 2290 Bishop Circle East Dexter, MI 48130 (734) 424-1200 Fax: (734) 424-0031
GEWalls@UISCorp.com www.uiscorp.com
Gary E. Walls
Utility Service Corporation 4614 Commercial Dr. NW Huntsville, AL 35816-2201 (256) 837-8400 Fax: (256) 837-8403 apeterson@utilserv.com www.utilserv.com
Alan D. Peterson
Western Electrical Services, Inc. 14311 29th St. East Sumner , WA 98390 (253) 891-1995 Fax: (253) 891-1511 dhook@westernelectricalservices.com www.westernelectricalservices.com
Dan Hook
Western Electrical Services, Inc. 3676 W. California Ave., #C, 106 Salt Lake City, UT 84104 (888) 395-2021 Fax: (253) 891-1511 rcoomes@westernelectricalservices.com
Rob Coomes
Western Electrical Services, Inc. 5680 South 32nd St. Phoenix, AZ 85040 (602) 426-1667 Fax: (253) 891-1511 carcher@westernelectricalservices.com
Craig Archer
Western Electrical Services, Inc. 4510 NE 68th Dr., Ste. 122 Vancouver, WA 98661 (888) 395-2021 Fax: (253) 891-1511
Tasciutto@westernelectricalservices.com
Tony Asciutto
Western Electrical Services, Inc. 5505 Daniels St. Chino, CA 91710 (619) 672-5217 Fax (253) 891-1995 mawallace@westernelectricalservices.com
Matt Wallace
Western Electrical Services, Inc. 620 Meadow Ln. Los Alamos, NM 87547 (505) 469-1661 Fax: (253) 891-1995 tking@westernelectricalservices.com
Toby King