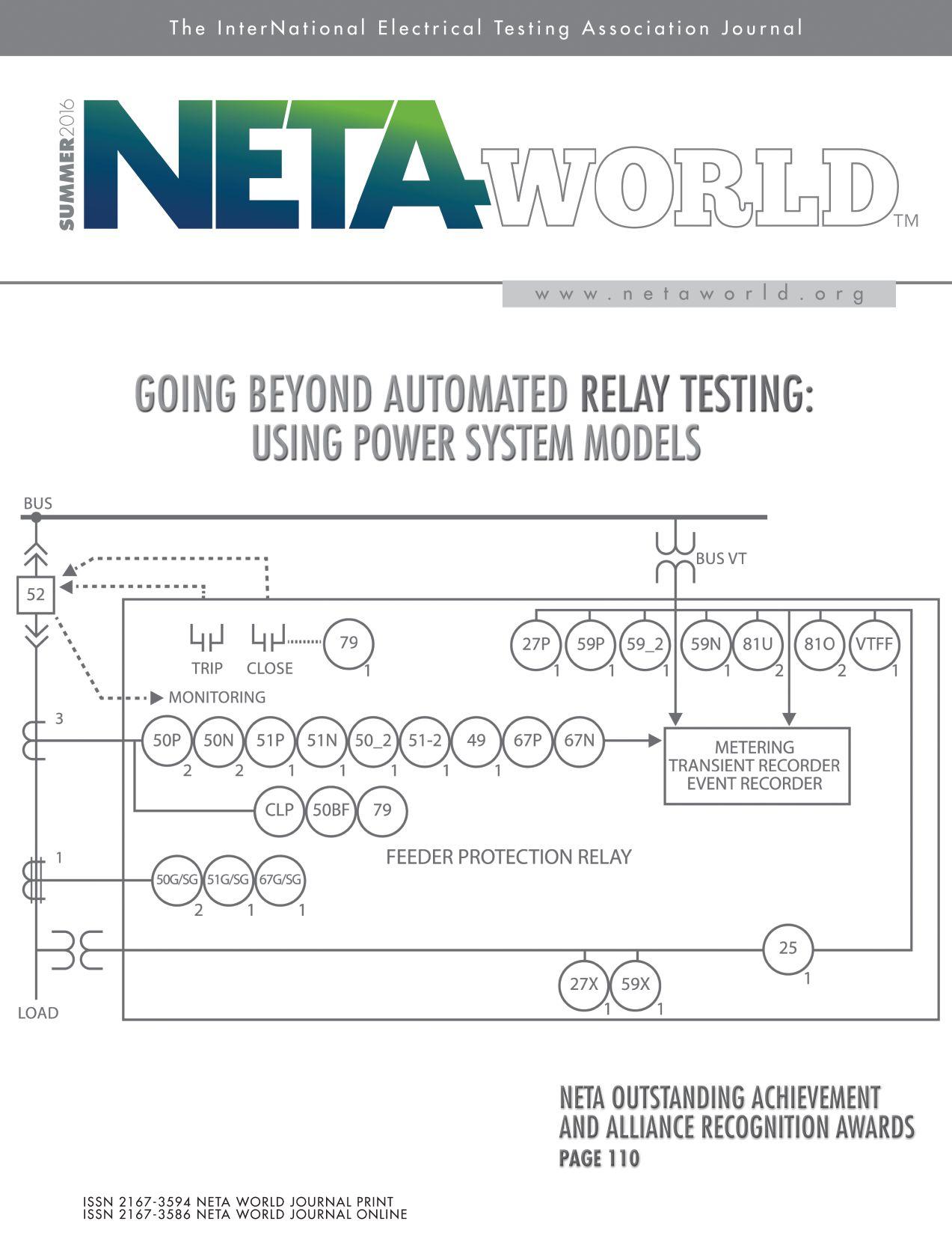
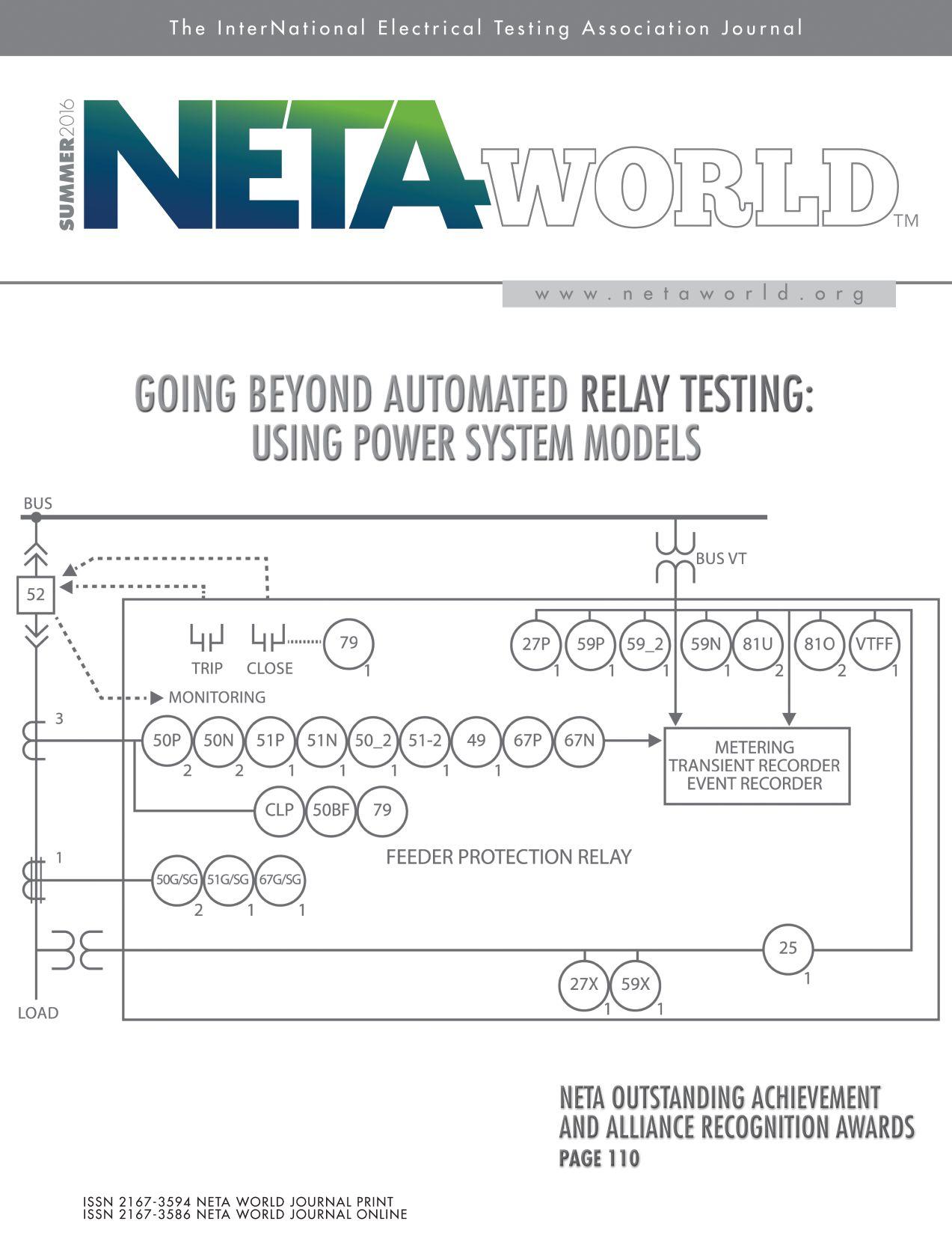
Making Relay Testing
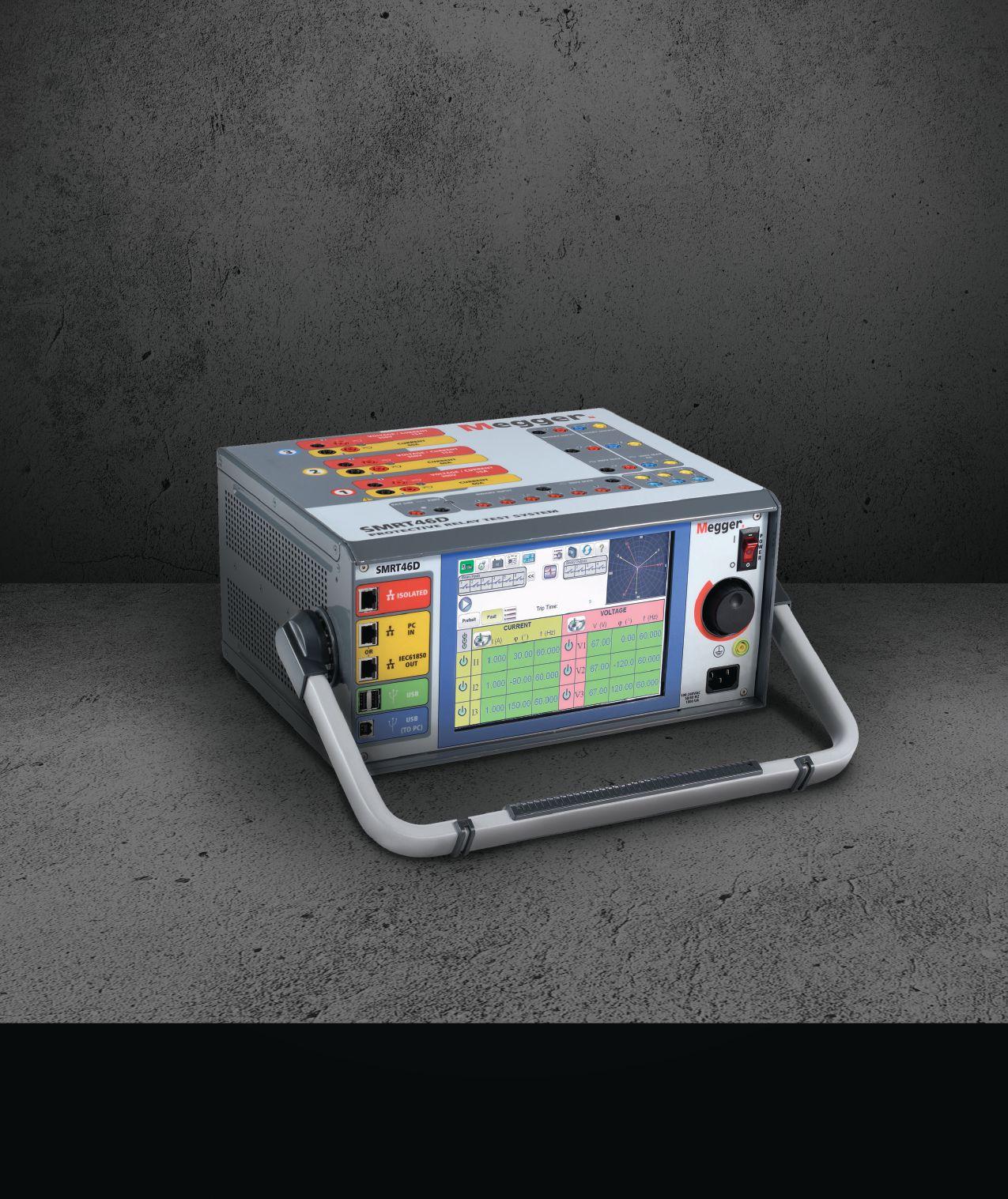
The NEW SMRT46D Multi-Phase Relay Test System is equipped with a 4th Voltage Channel to expand your testing capabilities.
Megger's New SMRT46D Multi-Phase Relay Test System expands your testing abilities by adding a powerful 4th voltage channel to make relay testing easier 4 you.
The fourth voltage channel provides a number of different testing options including functioning as a synchronizing reference voltage or as a battery simulator. With the voltage channels converted to currents, a three-channel unit can provide 6 currents for testing three-phase current differential relays, including harmonic restraint transformer differential relays. These options are designed to simplify the relay testing process to help you keep the power on.
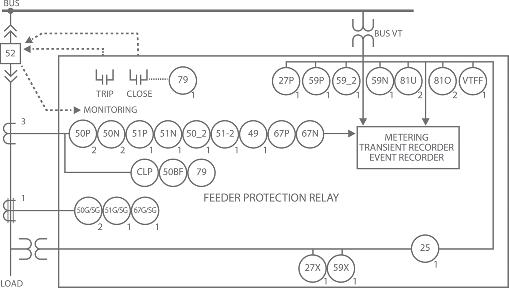
FEATURES
7 President’s Desk
Ron Widup, Shermco Industries
NETA President
58 Using Test Plans as a Tool for Protection
Benton Vandiver, OMICRON electronics Corp. USA
66 Going Beyond Automated Relay Testing: Using Power System Models
Automated testing is often used to test protective relays, but special cases exist that cannot be adequately covered. This article presents three examples that illustrate how to test protection functions using simple model power systems and symmetrical components.
Steve Turner, Beckwith Electric Company, Inc.
74
Lessons Learned from a 400kV Busbar Misoperation Using the IEC 61850 Standard Dhanabal Mani, Vijay Shanmugasundaram, and Jason Buneo, Megger
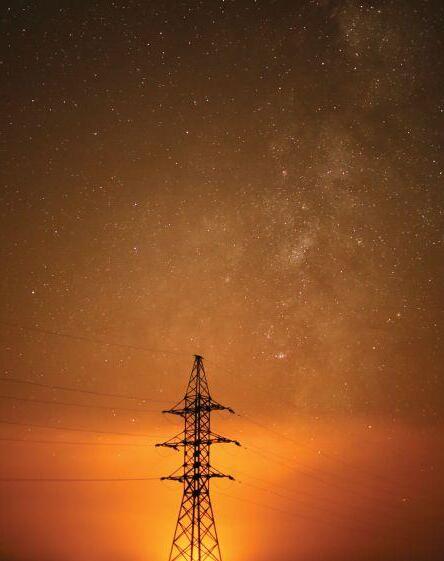
IN EVERY ISSUE
11 NFPA 70E and NETA
Electrical Risk Management
Ron Widup and Jim White, Shermco Industries
18No-Outage Corner
Using No-Outage Testing Techniques for Post-Natural Disaster Triage
Don A. Genutis, Halco Testing Services
22Tech Quiz
Protective Relaying for Electrical Power Systems
Jim White, Shermco Industries
28Tech Tips
Grounding in the Solar Industry
Jeff Jowett, Megger
34Safety Corner
Arc-Rated Clothing and Electrical Hazard Footwear
Paul Chamberlain, American Electrical Testing Co., Inc.
39Relay Column
Improving System Protection Reliability and Security
Steve Turner, Beckwith Electric Company, Inc.
INDUSTRY TOPICS
89 The Evolution of Circuit Breakers
Paul H. Grein, Circuit Breaker Sales Co., Inc.
97 Establishing Maintenance Zero for Large Power Transformers in Today’s Electrical Utility Sector
Ray Curry, American Transmission Company
ADVANCEMENTS IN TECHNOLOGY
112 Time is Ticking to Address Grid
Interconnection Standards
Mark Siira, ComRent International
SPECIFICATIONS AND STANDARDS
100 ANSI/NETA Standards Update
104 ASTM F18 Committee Report
Jim White, Shermco Industries
NETA NEWS
46NETA 2016 Alliance Recognition Award
Honoree: Finley Ledbetter Carla Kalogeridis, NETA
51 PowerTest 2016 – Deep in the Heart of Texas, PowerTest 2016 Comes to Fort Worth
82NETA 2016 Outstanding Achievement Award
Honoree: Jim Cialdea Carla Kalogeridis, NETA
108 NETA Members and Alliance Partners Gather in Fort Worth, Texas Jill Howell, NETA
NETA NEWS — SETTING THE STANDARD
24NETA’s Electrical Testing Technical Standard, Energizing the Future Kristen Wicks, NETA
118NETA Standards Review Council Appoints New Members Kristen Wicks, NETA
NETA NEWS – IMPORTANT LISTS
124NETA Accredited Companies
130Advertiser List
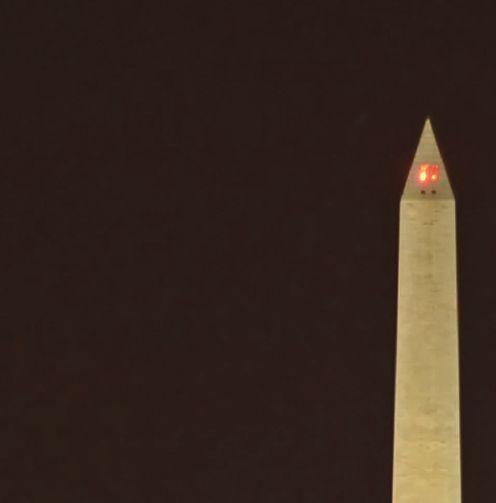
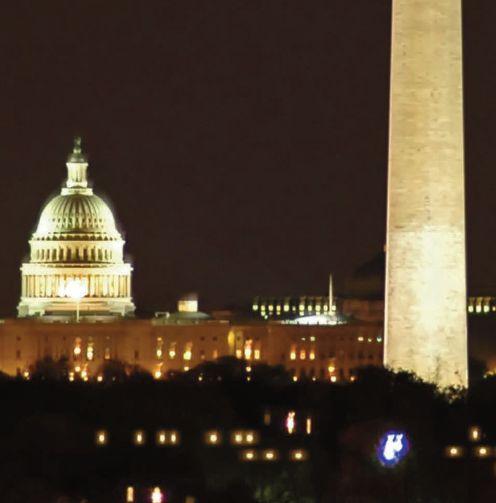
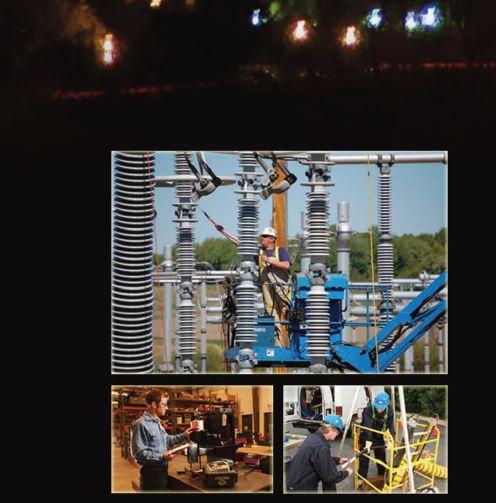
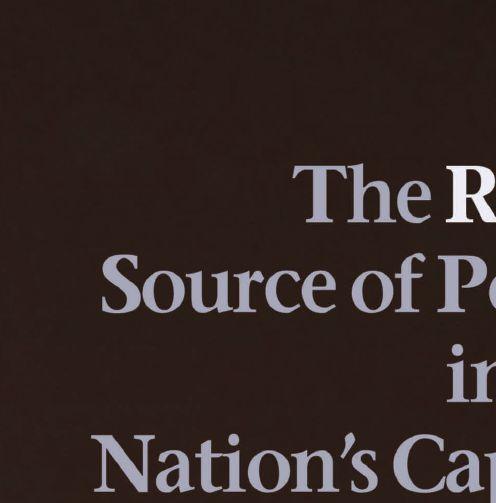
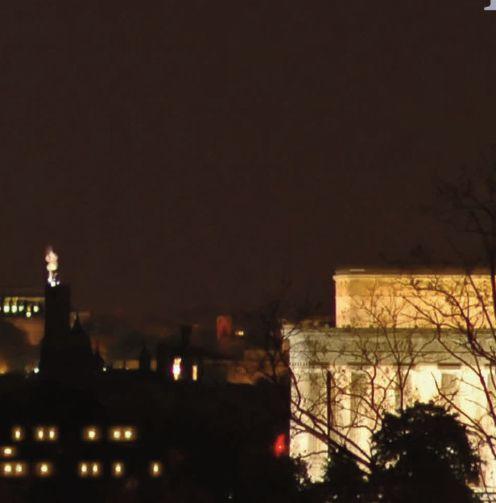
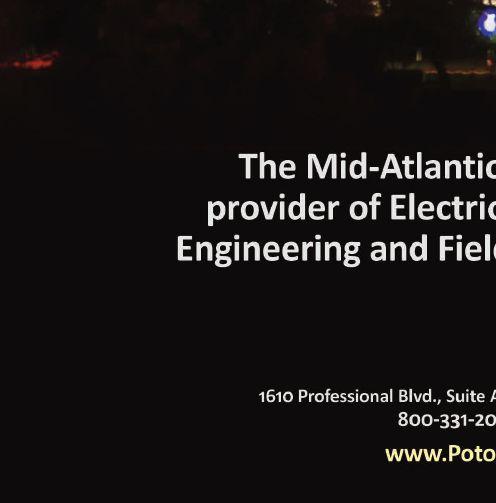

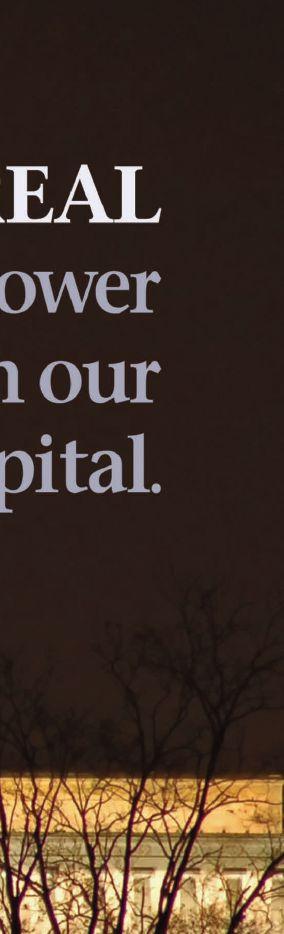

Delivering Powerful Reliability Solutions
Power System Acceptance Testing
Commissioning and Start-up
Maintenance
Life-Cycle Extension
Troubleshoot and Repair
Training and Engineering Services
Planning and Operations Support
Project Management
Sigma Six Solutions, Inc.
2200 West Valley Hwy North, Suite 100 | Auburn, WA 98001 |
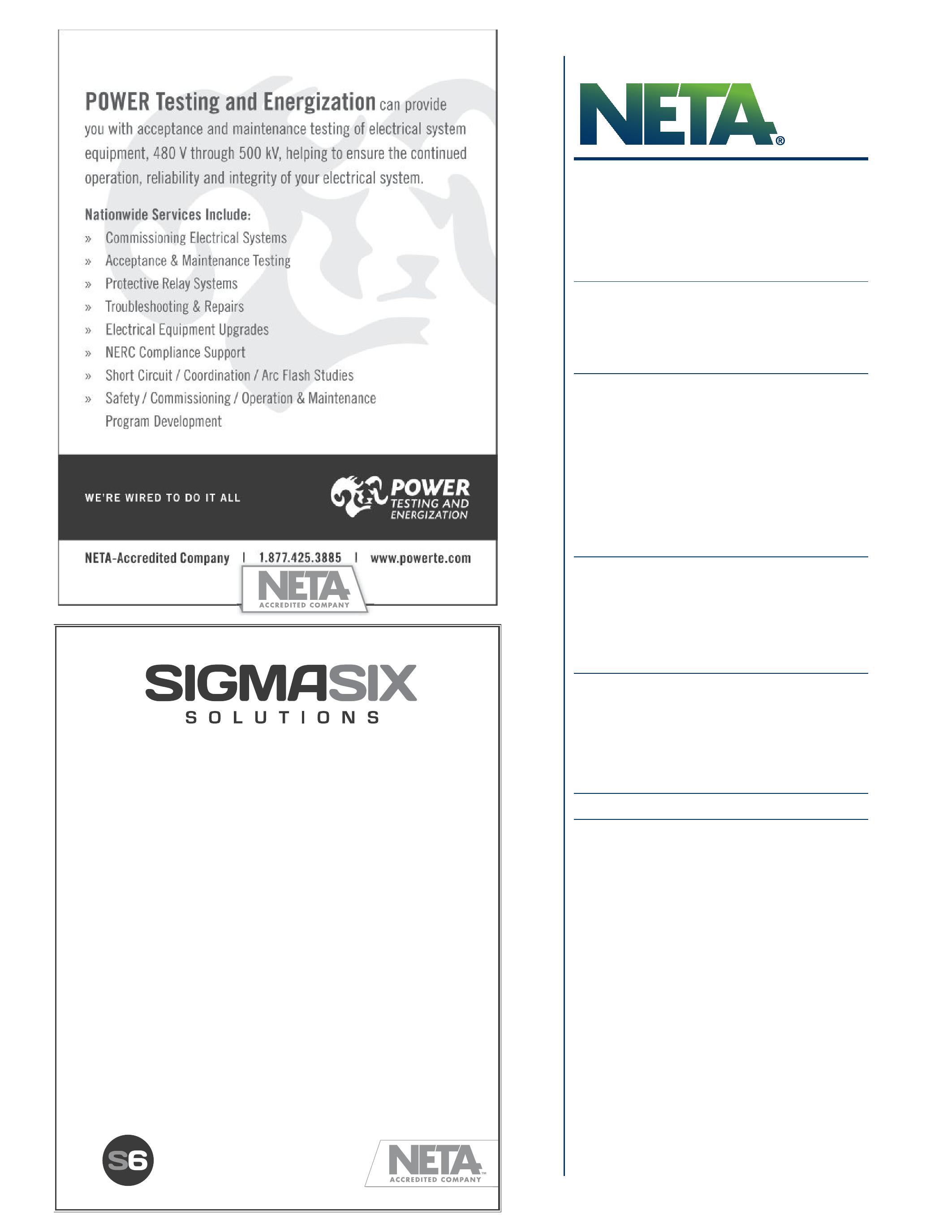
3050 Old Centre Avenue, Suite 102
Portage, MI 49024
Toll free: 888.300.NETA (6382)
Phone: 269.488.NETA (6382)
Fax: 269.488.6383
neta@netaworld.org
www.netaworld.org
EXECUTIVEDIRECTOR: Missy Richard
NETA Officers
PRESIDENT: Ron Widup, Shermco Industries
FIRSTVICEPRESIDENT: Jim Cialdea, Three-C Electrical Co., Inc.
SECONDVICEPRESIDENT: Scott Blizard, American Electrical Testing Co., Inc.
SECRETARY: Mose Ramieh, Power & Generation Testing, Inc.
TREASURER: John White, Sigma Six Solutions
NETA Board of Directors
Ken Bassett (Potomac Testing, Inc.)
Eric Beckman (National Field Services)
Scott Blizard (American Electrical Testing Co., Inc.)
Jim Cialdea (Three-C Electrical Co., Inc.)
Lorne Gara (Orbis Engineering Field Services, Ltd.)
Dan Hook (Western Electrical Services, Inc.)
David Huffman (Power Systems Testing)
Alan Peterson (Utility Service Corporation)
Mose Ramieh (Power & Generation Testing, Inc.)
Bob Sheppard (Southwest Energy Services, LLC)
John White (Sigma Six Solutions)
Ron Widup (Shermco Industries)
NETA World Staff
TECHNICALEDITORS: Roderic L. Hageman, Tim Cotter
ASSISTANT TECHNICAL EDITORS: Jim Caldea, Dan Hook, Dave Huffman, Bob Sheppard
ASSOCIATEEDITOR: Resa Pickel
MANAGINGEDITOR: Jayne Tanz, CMP
ADVERTISINGMANAGER: Laura McDonald
DESIGNANDPRODUCTION: Hour Custom Publishing
NETA Committee Chairs
CONFERENCE: Ron Widup; MEMBERSHIP: Ken Bassett; PROMOTIONS/MARKETING: Scott Blizard; SAFETY: Scott Blizard and Jim White; TECHNICAL: Alan Peterson; TECHNICALEXAM: Ron Widup; CONTINUINGTECHNICALDEVELOPMENT: David Huffman; TRAINING: Kerry Heid; FINANCE: John White; NOMINATIONS: Alan Peterson; STRATEGY: Mose Ramieh; ALLIANCEPROGRAM: Jim Cialdea
© Copyright 2016, NETA
NOTICE AND DISCLAIMER
NETA World is published quarterly by the InterNational Electrical Testing Association. Opinions, views and conclusions expressed in articles herein are those of the authors and not necessarily those of NETA. Publication herein does not constitute or imply endorsement of any opinion, product, or service by NETA, its directors, officers, members, employees or agents (herein “NETA”).
All technical data in this publication reflects the experience of individuals using specific tools, products, equipment and components under specific conditions and circumstances which may or may not be fully reported and over which NETA has neither exercised nor reserved control. Such data has not been independently tested or otherwise verified by NETA.
NETA MAKES NO ENDORSEMENT, REPRESENTATION OR WARRANTY AS TO ANY OPINION, PRODUCT OR SERVICE REFERENCED OR ADVERTISED IN THIS PUBLICATION. NETA EXPRESSLY DISCLAIMS ANY AND ALL LIABILITY TO ANY CONSUMER, PURCHASER OR ANY OTHER PERSON USING ANY PRODUCT OR SERVICE REFERENCED OR ADVERTISED HEREIN FOR ANY INJURIES OR DAMAGES OF ANY KIND WHATSOEVER, INCLUDING, BUT NOT LIMITED TO ANY CONSEQUENTIAL, PUNITIVE, SPECIAL, INCIDENTAL, DIRECT OR INDIRECT DAMAGES. NETA FURTHER DISCLAIMS ANY AND ALL WARRANTIES, EXPRESS OF IMPLIED, INCLUDING, BUT NOT LIMITED TO, ANY IMPLIED WARRANTY OF FITNESS FOR A PARTICULAR PURPOSE.
ELECTRICAL TESTING SHALL BE PERFORMED ONLY BY TRAINED ELECTRICAL PERSONNEL AND SHALL BE SUPERVISED BY NETA CERTIFIED TECHNICIANS/ LEVEL III OR IV OR BY NICET CERTIFIED TECHNICIANS IN ELECTRICAL TESTING TECHNOLOGY/LEVEL III OR IV. FAILURE TO ADHERE TO ADEQUATE TRAINING, SAFETY REQUIREMENTS, AND APPLICABLE PROCEDURES MAY RESULT IN LOSS OF PRODUCTION, CATASTROPHIC EQUIPMENT FAILURE, SERIOUS INJURY OR DEATH.

SAFETY IN THE SUMMERTIME
The last time we talked was at the beginning of PowerTest 2016 in Fort Worth, and wasn’t that a fantastic event? Many thanks to all of the presenters, sponsors, subject matter experts, industry leaders, and suppliers of goods and services who helped us break attendance records as well as achieve high marks for overall satisfaction with the conference. I extend a special shout-out to all of the NETA staff who worked tirelessly to put the event together.
Mark your calendars for next year’s PowerTest event in Anaheim, California, February 27 – March 3, 2017. It’s sure to be a great one.
Summertime means fun time — fun at work and fun at home. With the summer heat come longer days, and hopefully, more work for us all. So take a little extra time to think about the small stuff that makes us all work a little safer.
As you go about your daily activities this summer, whether at work or home, please do so with an extra thought of caution. At Shermco, we have an initiative focused on human performance — that is, trying to understand better why we do what we do the way we do it. An important part of it is managing elements of human performance to make sure we always do things the right way with the least amount of risk. It’s a good topic for all of us to think about.
So buckle your seatbelt, wear your helmet when riding bicycles and motorcycles, keep that ladder in good condition, and be careful on the roof of your house.
And, oh yeah — even though it’s a little hot, wear all that arc-rated PPE stuff at work.
Sincerely,
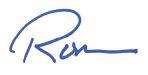
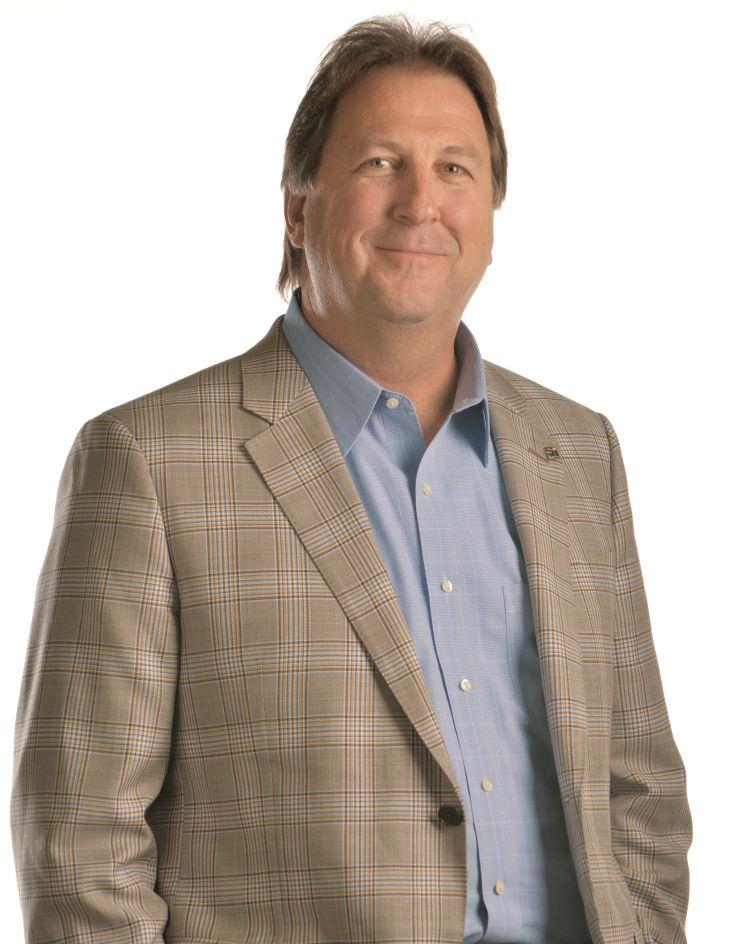
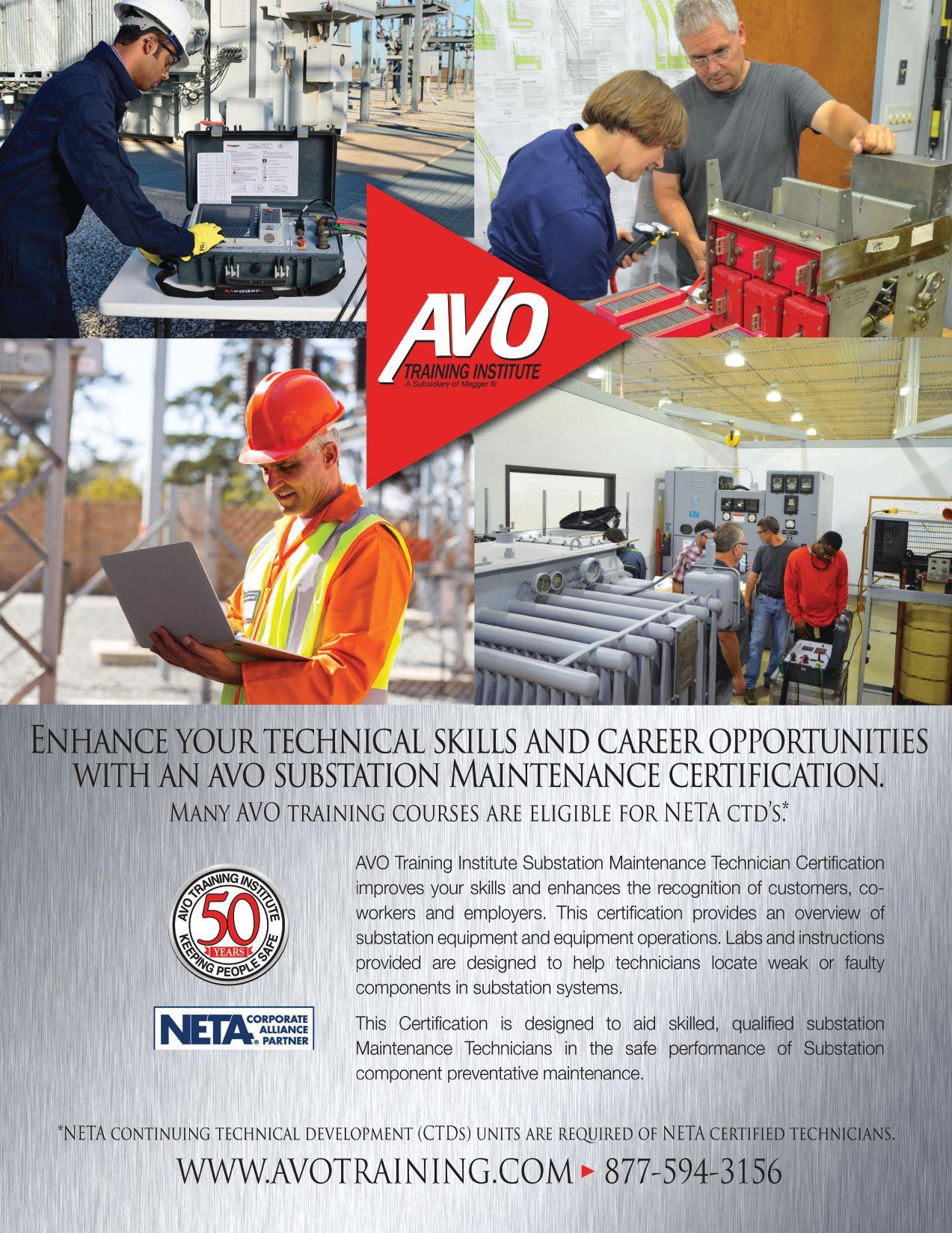
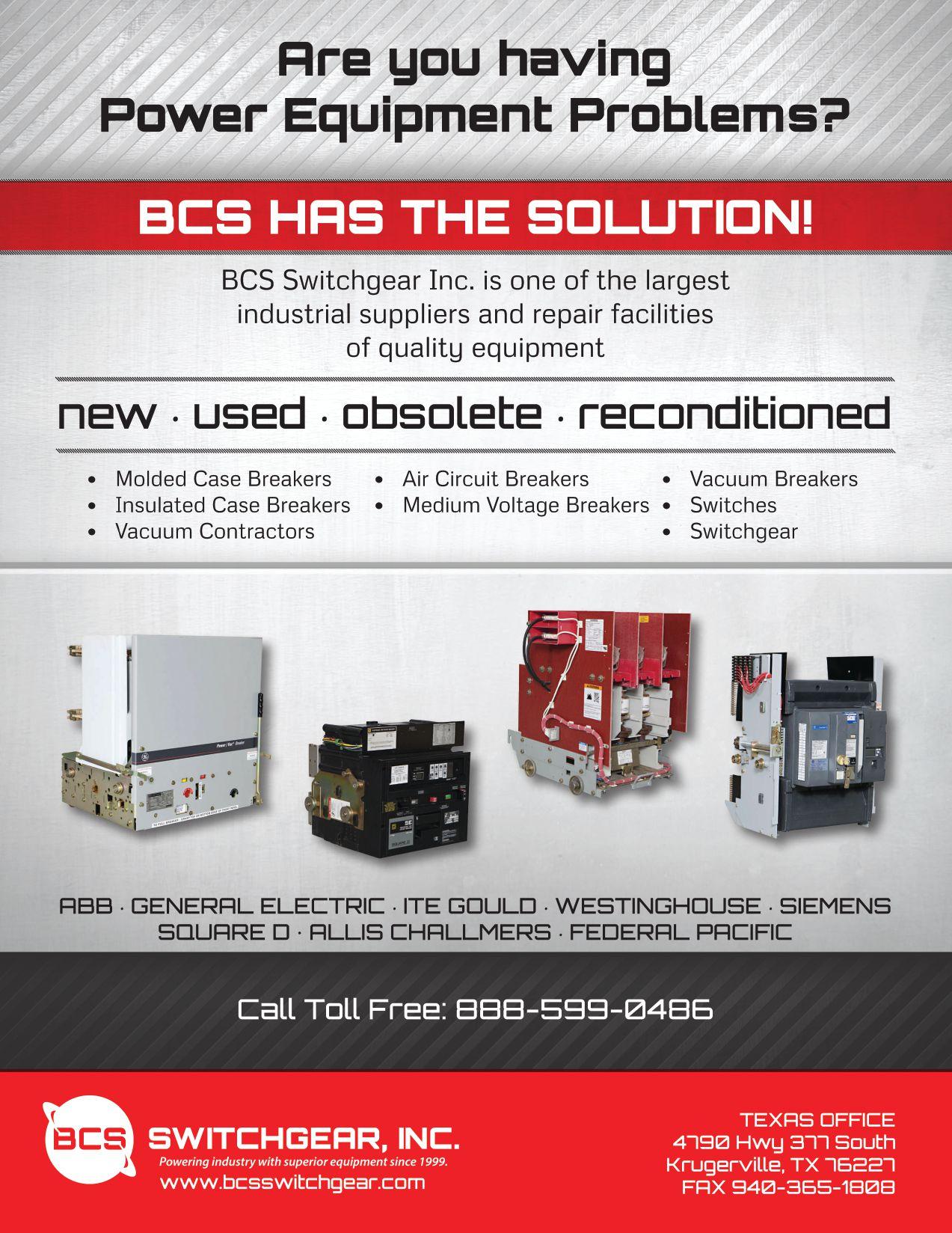
the test equipment answer
We support testing
Protective Relays and Metering
Batteries and UPS
Transformers
VLF, Tan Delta and Partial Discharge
Cable fault location
Substations & High Voltage Circuit Breakers
SF6 Analysis
Low & Medium Voltage Circuit Breakers
Motors and Rotating Apparatus
Power Monitoring
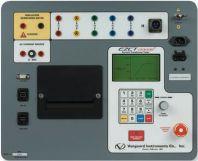
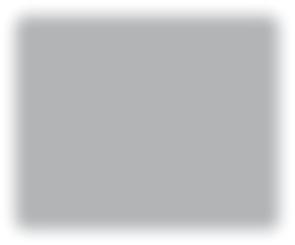


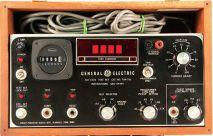
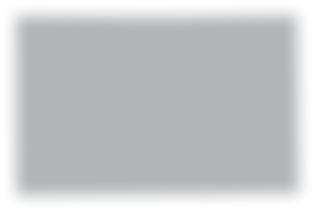
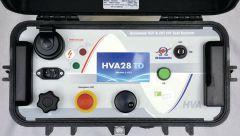
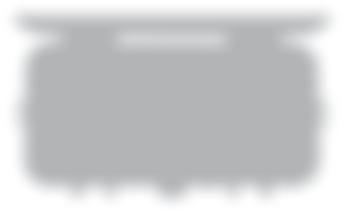
Risk

assessment is a critical function for keeping us safe on the job. Assessing risk happens every day — whether driving a car, walking across a street, or participating in sports, risks are associated with all of them.
When it comes to assessing risks on the job, though, we become unsure about what we need to do.
STARTING AT THE BEGINNING
Typically, companies have a Job Safety Analysis or Job Hazard Analysis that documents the method used to determine the risks, the work practices, and the PPE needed for a particular task. NFPA 70E, Standard for Electrical Safety in the Workplace provides guidance for assessing risk in Article 130.
To begin the process of assessing risk:
• Perform a visual examination of the equipment. Look at the condition of the equipment, the environment, whether it is indoors or outdoors, whether there is room to safely perform the task, and the presence of a recent maintenance test or calibration decal as recommended by NFPA 70B and ANSI/NETA MTS2015. For example, look for the presence of rodent droppings or other signs of varmints. If they’re in your switchgear room, they are probably in your switchgear. They are unpredictable and could cause a fault at any time.
• Review appropriate company SOPs and policies concerning the task(s) about to be performed. Non-contact inspections, such as infrared thermography, can be conducted without the use of arc-rated clothing and PPE, provided the equipment is in normal operating condition and the worker remains outside the restricted-approach boundary However, per Table 130.7(C)(15)(A)(a), the above guidance “does not include opening of doors orcovers.” or covers.”
• Understand how various systems are affected. When the circuit or system is deenergized, will it affect critical or safety systems? Is temporary power needed for those systems? What needs to be done to prevent back-feeding of other equipment? Examples of critical systems
are emergency alarm systems or lighting in stairwells. Normal operating condition means that equipment doors and panels are properly installed and secured, there’s no evidence of impending failure, and the equipment has been properly maintained Without access to test and maintenance records, proper maintenance can be difficult to determine. It’s not practical to review hundreds, possibly thousands, of records to determine if the equipment about to be worked on is properly maintained. However, ANSI/NETA MTS 2015, Standard for Maintenance Testing Specifications for Electrical Power Equipment & Systems andNFPA70Band NFPA 70B2016, Recommended Practice for Electrical Equipment Maintenance bothcontain both contain requirements for a test or calibration decal system such as that shown in Figure 2.
• UnderstandtheTestandMaintenance Understand the Test and Maintenance Decal System NFPA 70B Section 11.27, showsthataredlabelindicatesthe shows that a red label indicates the equipment has severe issues that could affect safety or operation, while a yellow labelindicatesadefectthatshouldnot label indicates a defect that should not affect safety or operation but should be addressed as soon as practical. A white label indicates the equipment has no identified defects and is fully operational and ready for continued service.

Technicians must use all their senses to detect unusual odors, sounds, scorched paint on the equipment, discoloration of components, and hot spots or other conditions that may indicate a potential problem.
Collect all of the important information needed to assess the risk and decide which
PPE and other safety procedures are appropriate to minimize the risks. An energized electrical work permit (EEWP) as specified by NFPA 70E is one method to accomplish this. An example form is in NFPA 70E Informative Annex J.
NFPA 70E Section 130.2 Electrically Safe Work Conditions directs us to place electrical conductors and circuit parts into an electrically safe work condition if we are within the restricted-approach boundary or the arc-flash boundary, or when interacting with equipment in a manner that could cause failure. Interacting does not include normal operation of equipment but does include such tasks such as racking circuit breakers and installing and removing MCC buckets or bus plugs.
NFPA 70E Section 130.2(B) Energized Electrical Work Permit (EEWP) is part of the required documentation for any energized electrical task. There are exceptions listed in 130.2(B)(3), but an EEWP is part of the electrical risk assessment process for most tasks. Voltage testing and troubleshooting are two exceptions to completing an EEWP, but an EEWP could assist in evaluating the risks and hazards associated with the task. The approval process is not necessary, but the EEWP records the information needed to assess the risk and the steps needed to safeguard the worker and others. The EEWP in Informative Annex J is considered nonmandatory information, which means it can be modified to more closely fit the needs and circumstances of a company or task.
NFPA 70E Section 130.4(A) Shock Risk Assessment would include determining the nominal phase-to-phase voltage of the system, along with the approach boundaries (limited and restricted) and shock-protective PPE required.
To perform an arc-flash risk assessment in accordance with 130.5, first determine if an arc-flash hazard exists. An arc-flash risk exists if the technician is exposed to energized
electrical conductors or circuit parts. The amount of risk will vary with the tasks being performed. The hazard is the available short-circuit current, the voltage, and the clearing time of the overcurrent protective device (OCPD). The arc-flash boundary, working distance, condition of maintenance of the equipment or circuit, arc-flash protective clothing, and PPE such as shown in Figure 3 will also have to be determined.
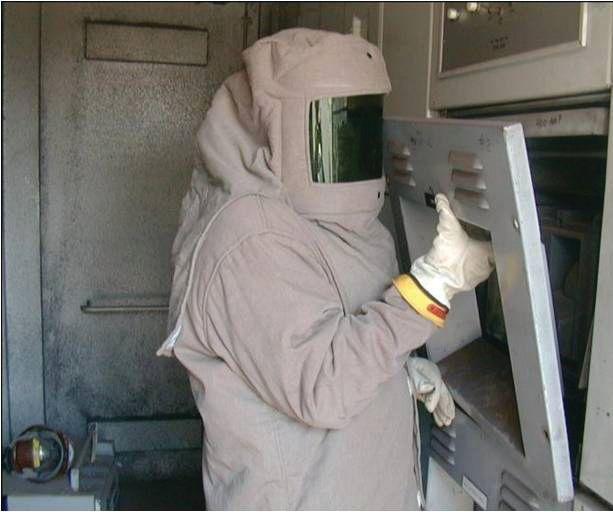
Refer to Table H.3(b) in NFPA 70E Informative Annex H if an arc-flash-hazard warning label is present on the equipment. Do not use Table 130.7(C)(16) to determine the required arc-rated clothing and PPE. If there is no label, use the table method [Tables 130.7(C)(15)(A)(a), 130.7(C)(15)(A)(b) and 130.7(C)(16)]. If the limits of Table 130.7(C) (15)(a)(b) are exceeded, an incident energy analysis must be conducted.
Determine what is needed to protect unqualified workers from the risks of shock or arc flash. This usually involves setting up safety barriers or signage, but may require the use of an attendant, in accordance with 130.7(E) Alerting Techniques. The safety barrier or barricade is set up at the limitedapproach boundary or the arc-flash boundary, whichever is farther out, according to 130.7(E) (2) Barricades (Figure 4).
THE NFPA 70E AND NETA
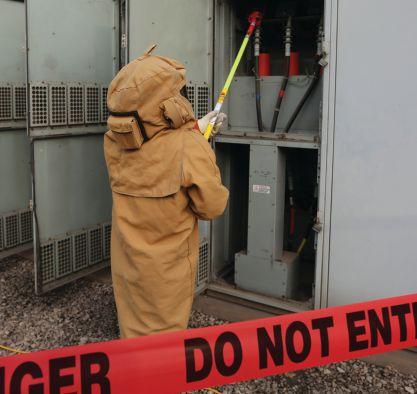
If necessary, ground the equipment and use a means to account for temporary personal protective grounds and equipment, such as tags and specialized forms like those shown in Figure 5.
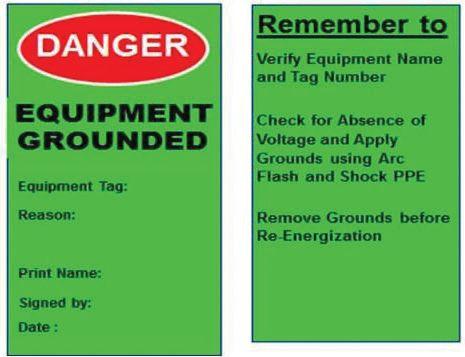
Other items to review include:
• Inspect all tools and equipment prior to the start of work, including test instruments, leads and accessories, liveline tools, insulated tools, rubber insulating blankets, shielding or gloves, arc-rated clothing and PPE, as required. Inspect everything, even if it is known to be good.
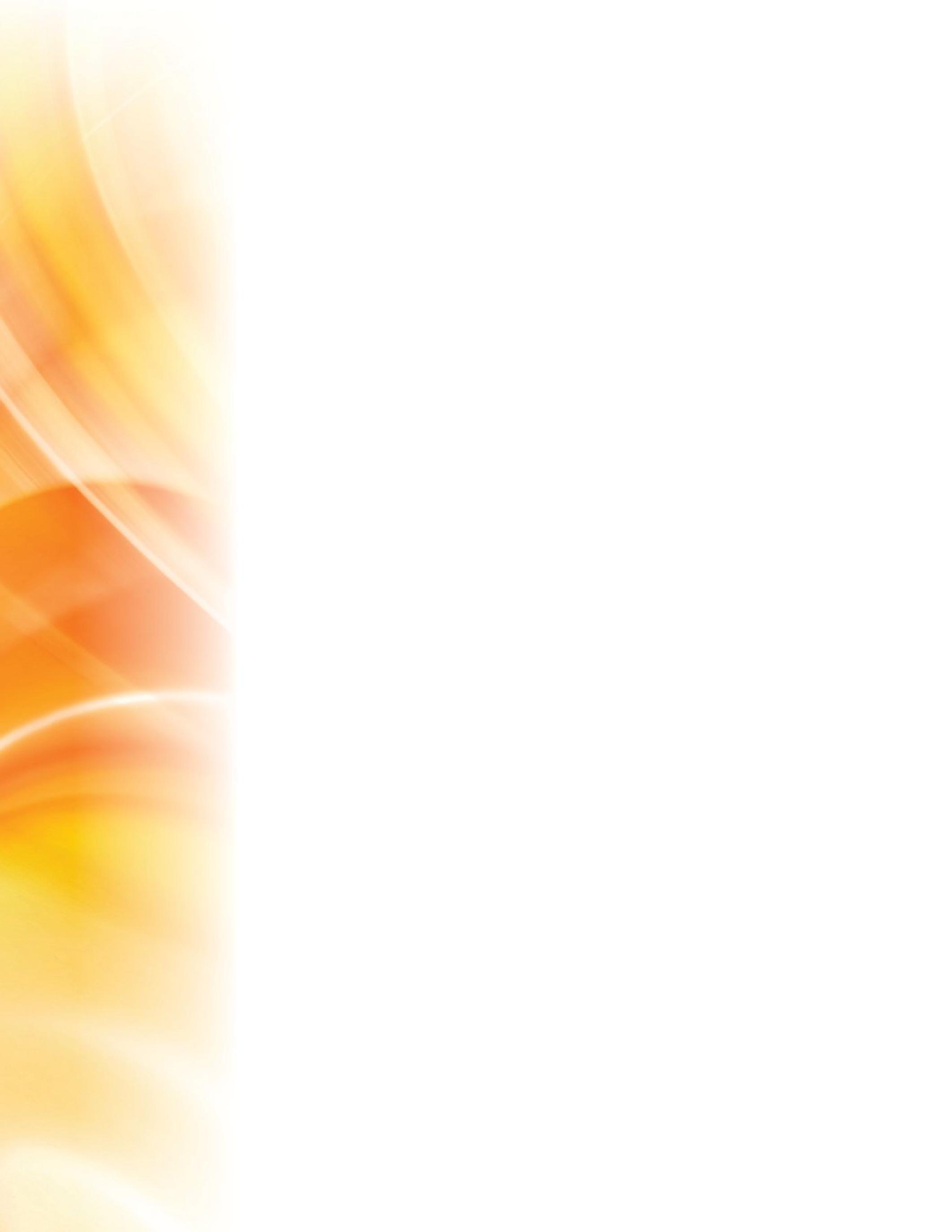
• Determine whether a safety backup is required, as well as the training, experience, and PPE required for the safety backup. Alltheseitemsshouldbedocumented. All these items should be documented.
• Determine whether temporary insulating shielding is needed on nearby energized electricalcircuitsorwhetherothermeans electrical circuits or whether other means are required to guard nearby equipment to prevent incidental contact.
• Documenttheinstallationorremovalof Document the installation or removal of any specialized test instruments that may be required, such as circuit analyzers orrecorders. or recorders.
If troubleshooting, the equipment may have to be de-energized or operated to allow opening the door. Since it is no longer operating normally, arc-rated clothing and PPE will be required even to operate the overcurrent protective device to remove it from service. Refertothearc-flashriskassessmentforthe Refer to the arc-flash risk assessment for the proper protection.
Whenthecauseofthemalfunctionis When the cause of the malfunction is determined, repair may be required to return the equipment or circuit to service. Repair includes any task using tools, such as removing and installing components, tightening or replacement of conductors, and so on.
Itwouldbewisetoevaluatetheconditionof It would be wise to evaluate the condition of the equipment before repairs begin, as the risks will be greater when energized conductors or circuit parts are being handled or replaced.
Thetask The task “work on energized electrical conductorsand conductors and circuit parts, including voltage testing” inTable in Table 130.7(C)(15)(A)(a) indicates that arc-rated PPE is always required, which would include troubleshooting.
ALL ELECTRICAL TASKS INVOLVE RISK
The hazard is present whenever the equipment or circuit is energized, and therefore, so is anelementofrisk.Riskcanbereduced an element of risk. Risk can be reduced considerably by operating the equipment remotely or by covering adjacent circuits with
rubber-insulating shields, but the associated risk will never be zero as long as the equipment is energized.
The risk that remains after all appropriate steps have been taken is referred to as the residual risk, which must be evaluated. If the residual risk is still too great, the work cannot be performed while the equipment is energized. If a trained and experienced (read: qualified) technician carefully evaluates the risk and believes it can be done safely, then that task can be done energized. However, if the technician’s experience indicates that the conditions look too risky, or if they do not have the correct training or experience, then the energized task cannot proceed.
A different approach to accomplish the task would need to be formulated, which would probably include de-energizing the equipment.
SUMMARY
Assessing risk is a vital part of safety — not just electrical safety, but all work-site safety issues. The employer can only do so much. It is the employee at the scene, observing the equipment and conditions, who ultimately must determine thelevelofrisk. the level of risk.
One good adage: Always be responsible for your personal safety. Relying on others could result in a less-than-satisfactory outcome. Listen to your gut feelings. Often, accidents could have been avoided if the worker stopped when that little voice in their ear said, “I wouldn’t do that, if I were you.” Step back and re-evaluate the situation because maybe something was missed. Having a second look or asking for a second opinion is never a bad thing.
A huge part of the risk-assessment equation is how well the personnel performing the task are trained. If workers are not following the appropriate policies or procedures, it is often a lack of training that’s at fault. Check-the-box training may satisfy the paper trail, but does little or nothing to promote safety or safe work practices. Employees must be trained and show
they understand the importance of what they do and how to do it. People must understand why it needs to be done the right way instead of a more convenient way.
Be careful out there.
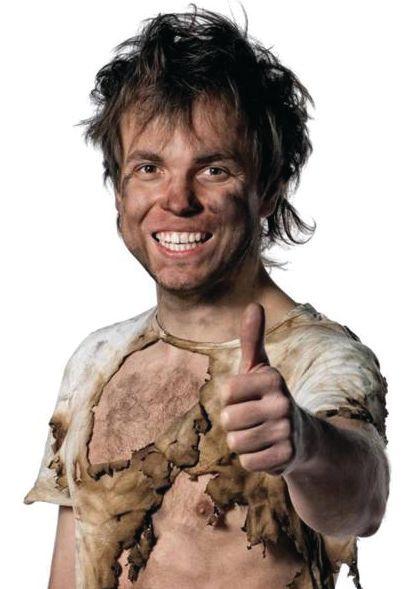
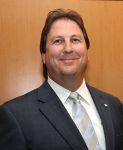
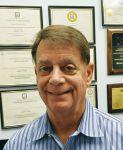
Ron Widup and Jim White are NETA’s representatives to NFPA Technical Committee 70E (Electrical Safety Requirements for Employee Workplaces). Both gentlemen are employees of Shermco Industries in Dallas, Texas, a NETA Accredited Company. Ron Widup is CEO of Shermco and has been with the company since 1983. He is a Principal member of the Technical Committee on “Electrical Safety in the Workplace” (NFPA 70E) and a Principal member of the National Electrical Code (NFPA 70) Code Panel 11. He is also a member of the technical committee “Recommended Practice for Electrical Equipment Maintenance” (NFPA 70B), and a member of the NETA Board of Directors and Standards Review Council. Jim White is nationally recognized for technical skills and safety training in the electrical power systems industry. He is the Training Director for Shermco Industries, and has spent the last twenty years directly involved in technical skills and safety training for electrical power system technicians. Jim is a Principal member of NFPA 70B representing Shermco Industries, NETA’s alternate member of NFPA 70E, and NETA’s Principal representative to the ASTM F18 Committee “Electrical Protective Equipment for Workers.”


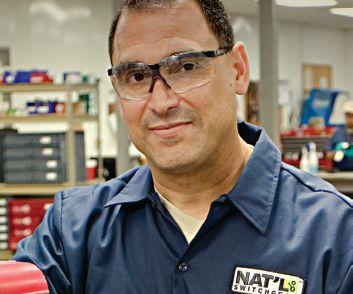


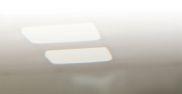
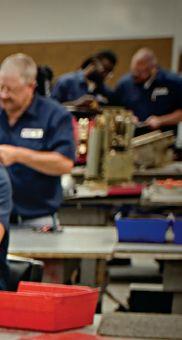
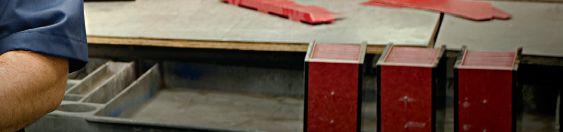
When your electrical equipment is failing, getting the parts you need shouldn’t be part of the problem. With a huge inventory of new, surplus and repurposed electrical circuit breaker and switchgear products, National Switchgear can be a big part of your solution. We have millions of parts, but we also have the expertise to see the whole picture, to understand your problem and to recommend the best total solution. Of course, if you already know exactly what you need, we make it easy to buy online on our constantly updated website, where you’ll also discover hard-to-find resources like installation manuals, wiring diagrams and more. If you need advice, customized equipment, remanufacturing or reconditioning, we’re ready to share our expertise. Because integrity is always in stock. 800-322-0149 nationalswitchgear.com
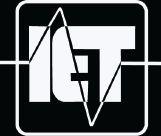
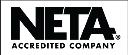
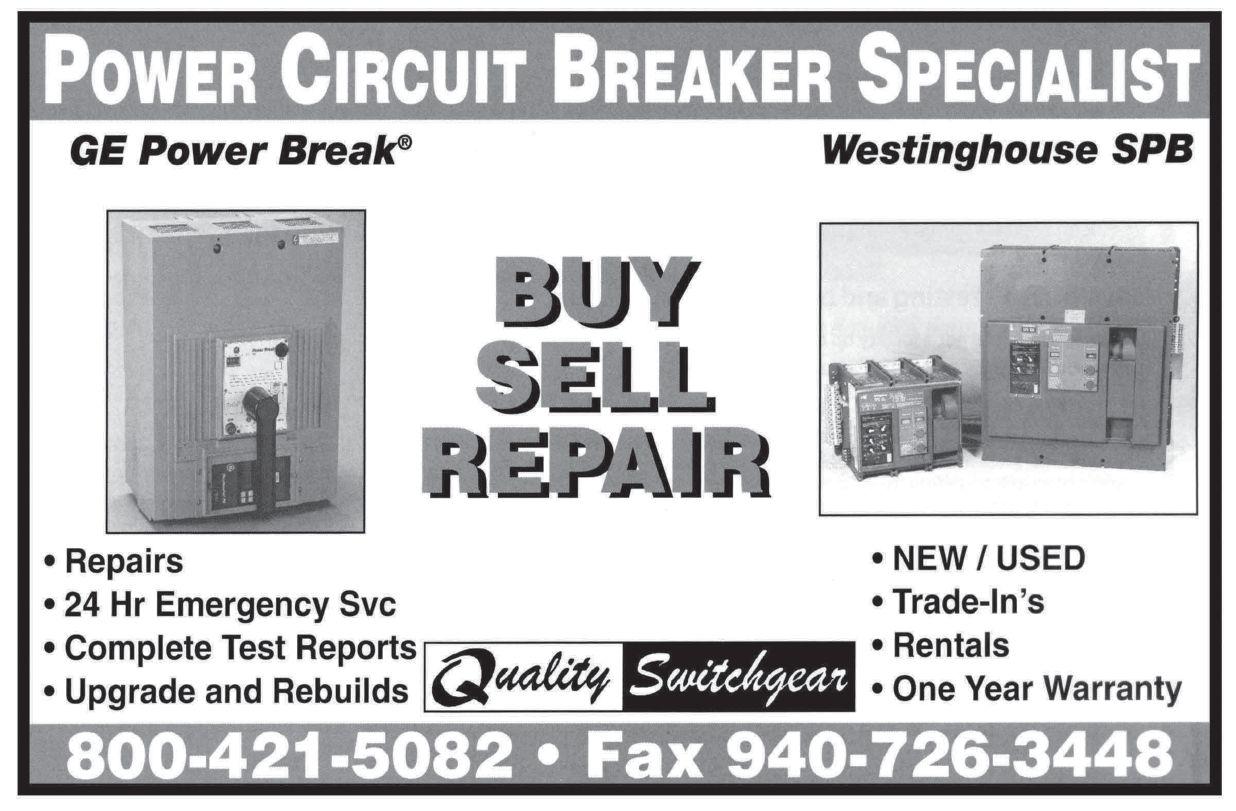
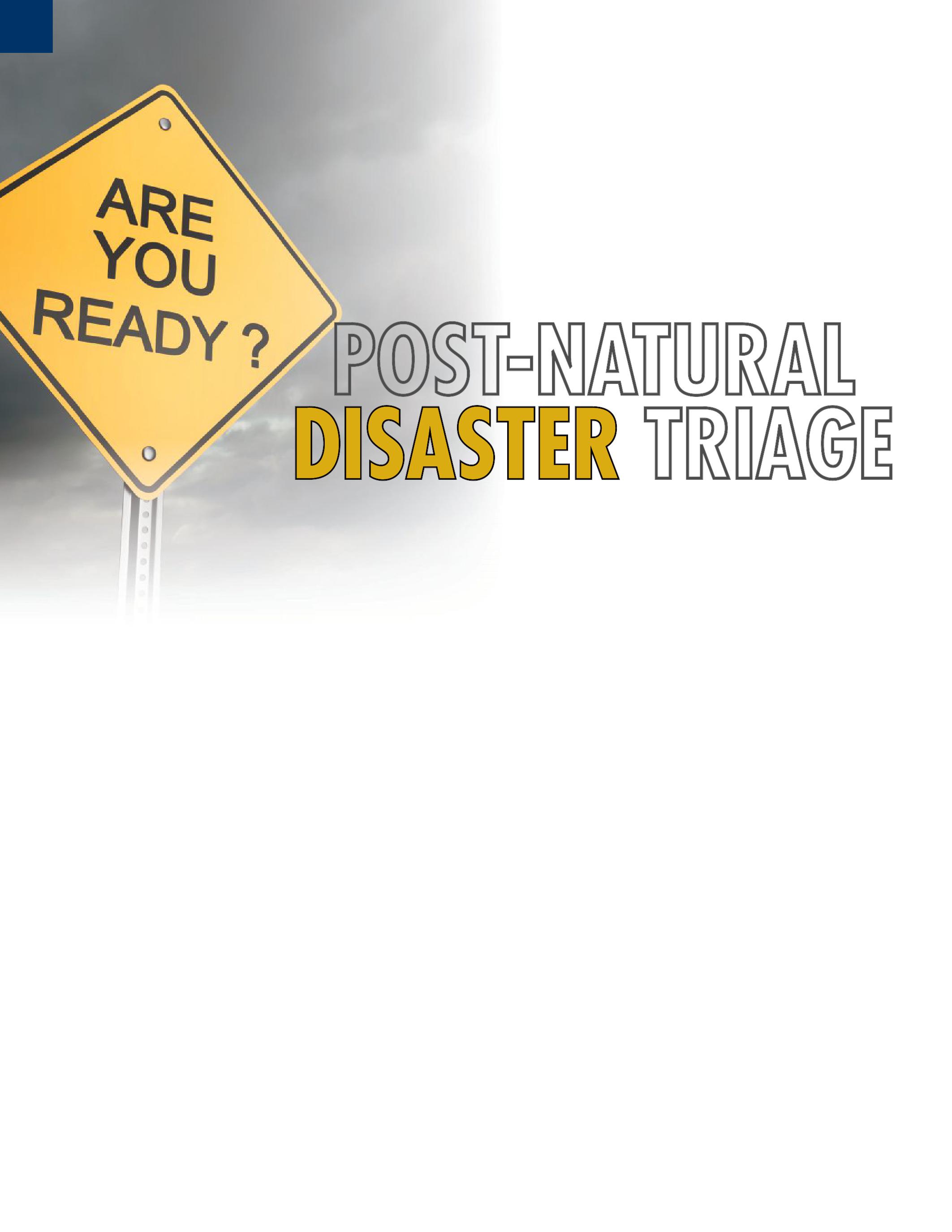
USING NO-OUTAGE TESTING TECHNIQUES FOR
POST-NATURAL TRIAGE
BY DON A. GENUTIS, Halco Testing ServicesA few weeks ago here in Southern California, we were in the midst of a battering string of El Niño storms that created widespread surface flooding. During this same timeframe, we experienced a 4.5-magnitude earthquake, the Mississippi River was flooding its banks, and the Eastern U.S. was hit with one of the worst snowstorms in modern history. Natural disasters force us to consider how to best conduct electrical equipment assessment and maintain reliability when confronted with these challenging attacks from nature.
There are many types of natural disasters and interrelated events that can potentially wreak havoc upon our electrical systems. For example, flooding from freshwater rivers and saltwater storm surges can submerge outdoor substations and low-lying indoor equipment. Water is one of the top killers of electrical equipment. Floods and precipitation can cause insulation flash-over resulting in insulation damage. High-humidity conditions can damage insulation through moisture absorption in organic insulation and cause conductor corrosion, even if the exposure duration is relatively brief. Corrosion problems can potentially cause long-term difficulty in high-resistance conductor connections, and salt water can significantly accelerate this corrosion process. Particulates suspended in flood waters can settle between moving apparatus components and create future mechanical operational problems with moving parts.
Outdoor insulation is designed to function in wet weather, but extreme weather conditions can initiate and accelerate failures of marginal insulation. Precipitation from rain, snow, and sleet can potentially compromise outdoor insulation and challenge equipment's weatherproofing integrity. Damp, heavy snowandsleetcanaccumulateonoverhead snow and sleet can accumulate on overhead lines and other outdoor equipment, adding greater weight to lines and creating excessive mechanicalstressestoallrelatedstructural mechanical stresses to all related structural components.
In addition to water-related challenges, high winds from storms, tornados, and hurricanes can damage overhead lines and outdoor substations. Also, earthquakes can physically jolt indoor and outdoor equipment, creating damaging mechanical stresses. Mechanical problems due to high winds and earthquakes canbreakordeforminsulationorconductors can break or deform insulation or conductors and mechanisms. Mechanical forces produced by these weather events can break or crack insulators, and ceramic insulators may be at much greater risk due to their more brittle structural properties. High winds can also propel projectiles that can damage equipment and enclosures. Equipment enclosures sealed adequately during normal conditions may fail to keep out sand and dirt from extreme winds that can subsequently contaminate insulation or migrate their way into operating mechanisms.
Extremeheatcanalsocontributeto Extreme heat can also contribute to overheating and cause other equipment to be indirectly stressed due to increased heat-related loaddemands.Thermalstressescanleadto load demands. Thermal stresses can lead to immediate failure and cause hidden longterm effects by reducing overall equipment life expectancy.
If equipment is de-energized due to a direct or indirect fault, the opportunity to perform traditional outage-based inspections, testing, and field reconditioning and repairs must be seized. No-outage techniques should then be used after the outage-based work has been completed and power has been restored to help ensuresuccess. ensure success.
Energized equipment should not be ignored. Equipment may still be operational but close to failure, and no-outage testing techniques can often identify these looming failures. The best no-outage methods for these assessments are typically visual inspections and partialdischarge (PD) detection using TEV and ultrasonics, infrared inspection, and insulating fluid testing.
Ultrasonic PD inspections are perhaps the best method for detecting medium- and highvoltage surface-related insulation problems. TEV PD inspections are very effective for detecting elusive medium-voltage internal insulation defects. Infrared technology is a great technique for spotting conductor damage at all voltage levels, and insulating fluid sampling and testing can help ensure the integrity of transformersandotherfluid-insulateddevices. transformers and other fluid-insulated devices. Experienced technicians with a careful eye can fill in most of the remaining gaps to detect other problems.
We must adapt our daily practices to better considerenvironmentalconditionsandalso consider environmental conditions and also prepare ourselves for the inevitable task of assessing electrical equipment after natural disasters strike. No-outage inspection techniques are the most efficient methods to provide equipment condition assessment and ensure future reliability. However, equipment exposed to natural disasters must also be monitored for future long-term problems that may result from abnormal conditions.
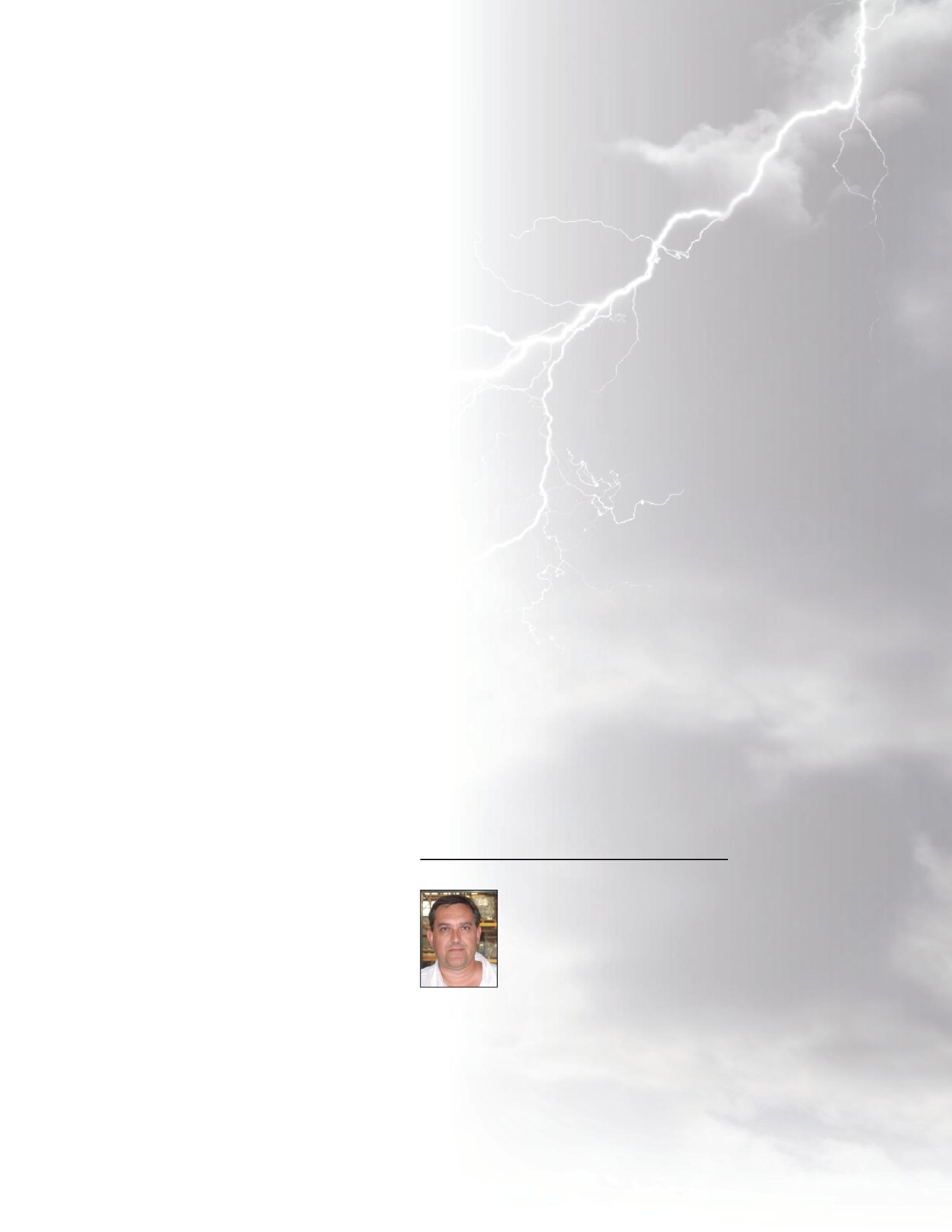
Certified Technician for more than 15 years. He has held various principal positions during his 30-year career in the electrical testing field. He primarily focused on advancing no-outage testing techniques for the last 15 years. Don presently serves as President of Halco Testing Services in Los Angeles, California.
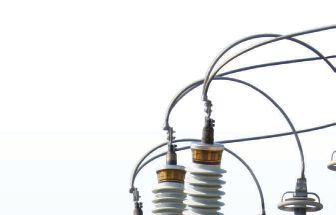
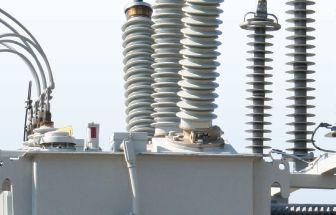
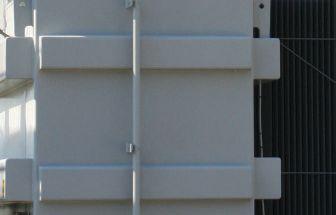
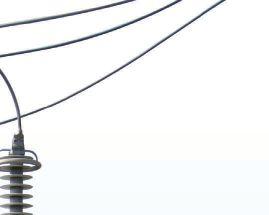
THE EXPERTS IN ELECTRICAL RELIABILITY
Comprehensive Electrical Testing and Maintenance

Commissioning and Startup Services
Engineering Services
Power System and Coordination Studies
FAILURE IS NOT AN OPTION.
Predictive and Preventive Maintenance
Partial Discharge Testing and Monitoring
24/7 Emergency Service
Ensuring the reliability of your electrical distribution system.
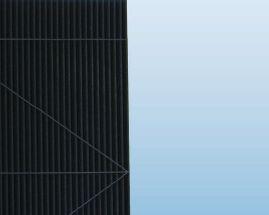

As the leading independent electrical testing, maintenance, and engineering service company, you can rely on Emerson’s High Voltage Maintenance to exceed your electrical equipment performance goals. From testing for problems that could disable your system, to complete turnaround execution, you’ll quickly understand how we are your single source solution for all of your electrical reliability needs. With a service geography across the Midwest and Eastern Seaboards, our service team puts experienced professionals where and when you need them.
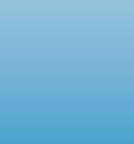




We Buy, Sell, Trade, Calibrate, Repair
Featuring quality, reliable, on-time service and support for all brands and types of solid state power electronics.
Power electronics are our business
Let us suppoort you with our quality repair, calibration and servicing of your solid state equipment. We also buy, sell and trade:
•Communications devices for power equipment
•Protective relays
•Circuit breaker trip devices
•Motor overload relays
•Rating plugs

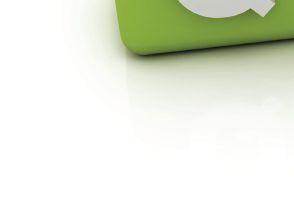
James R. (Jim) White is the Training Director of Shermco Industries, Inc., in Dallas, Texas. He is the principal member on the NFPA technical committee
“Recommended Practice for Electrical Equipment Maintenance” (NFPA 70B). Jim represents NETA as an alternate member of the NFPA Technical Committee “Electrical Safety in the Workplace” (NFPA 70E) and represents NETA on the ASTM F18 Committee “Electrical Protective Equipment For Workers”. Jim is an IEEE Senior Member and in 2011 received the IEEE/PCIC Electrical Safety Excellence award. Jim is a past Chairman (2008) of the IEEE Electrical Safety Workshop (ESW).
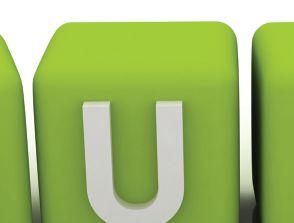
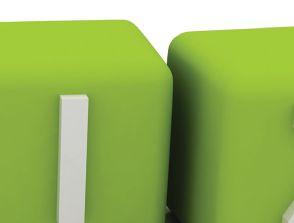
No.114 No. 114
PROTECTIVE RELAYING FOR ELECTRICAL POWER SYSTEMS
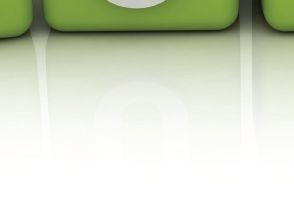

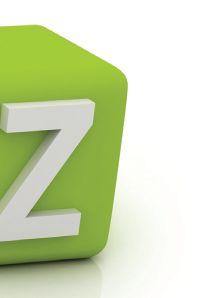
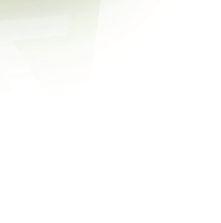
This issue’s Tech Quiz looks at protective relaying for electrical power systems. Testing protective relays is a huge part of the protection scheme, and, if not done accurately, can cause false tripping or worse — a no-trip condition. Most protective relays today are digital and have eliminated many of the problem areas associated with electromechanical relays, but they still need to have the calibration and functions verified.
1. Match the device number with the relay function:
a. 50 ____ 1. Differential
b. 86 ____ 2. Undervoltage
c. 87 ____ 3. Instantaneous overcurrent
d. 27 ____ 4. Lockout
e. 25 ____ 5. Directional overcurrent
f. 67 ____ 6. Synch check
2. A percentage differential relay with a 25 percent slope characteristic has 4.9 A in one restraint coil and 4.2 A in the other.
a. What is the calculated imbalance? ______ percent
b. Will this relay operate with this imbalance? Yes / No
c. Based on its characteristic, what is this relay most likely protecting? ______ or ______
3. What type of protective relay requires two voltages that can have their magnitudes and phase angles varied from each other?
a. Undervoltage
b.Overvoltage
c. Percent differential
d. Synch check
e. Directional power
4. A type 21 protective relay would be a:
a. Distance
b. ac reclosing
c. Pilot wire
d. Ground detector
e. Excitation
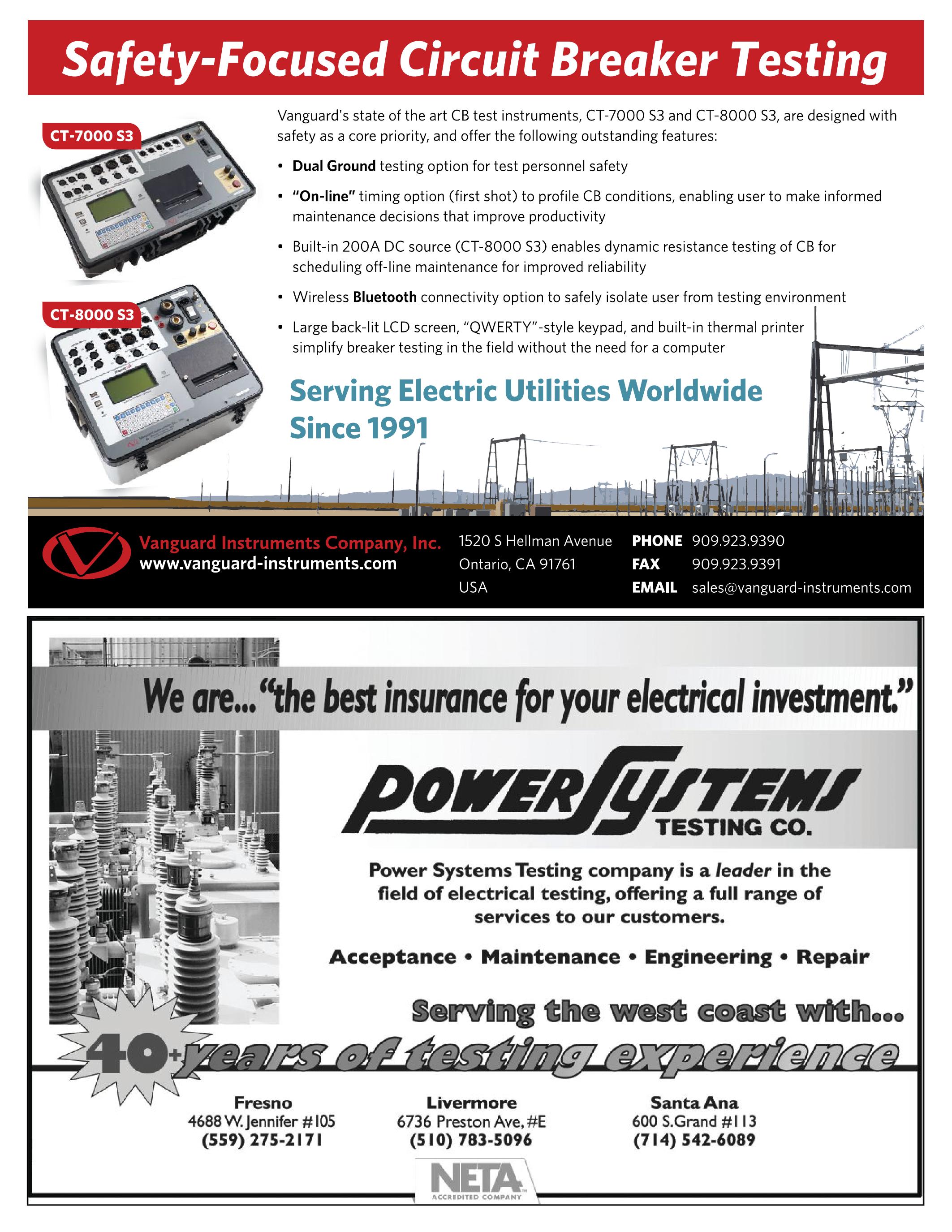
’S ELECTRICAL TESTING CERTIFICATION PROGRAM:
SETTING THE STANDARD, ENERGIZING THE FUTURE
BY KRISTEN WICKS, NETAAn organization is only as strong as the people who belong to it. NETA’s reputation as a technical leader in the electrical power systems industry is built firmly on a long tradition of excellence driven by the pursuit of quality, reliability, and safety. This culture is a direct reflection of each individual who chooses to participate in NETA’s many programs, from companies seeking NETA Accreditation as third-party electrical testing firms, to implementing the use of ANSI/NETA standards when field testing electrical power systems and equipment, to individuals who elect to take the path toward becoming a NETA CertifiedTechnician.IfNETA’sAccredited Certified Technician. If NETA’s Accredited Companies are the foundation on which the association is built, then NETA’s Certified Technicians are the keystone that locks everything into place.
In addition to representing their NETA Accredited Companies, NETA Certified NETA TechniciansarethefaceofNETAasan Technicians are the face of NETA as an

association. Each person who holds NETA Certified credentials is responsible for representing what it means to test to the ANSI/ NETA standards, assuring that the intent of these documents does not merely exist between the covers, but is implemented each day in the field. It is a badge of honor to hold a NETA Certification at any level, and this is due largely to the stringent requirements for certification.
In the year 2000, NETA’s exam “blueprints” becameanofficialAmericanNationalStandard became an official American National Standard with the publication of the ANSI/NETA ETT Standard for Certification of Electrical Testing Technicians, and are the industry standard for defining the required knowledge, skills, and abilities commensurate with competency as a qualified electrical testing technician. As with all things in life, the only constant is change. In order to meet the needs of a constantly evolving industry, it is necessary to refresh the certification program and infuse it with newexaminationmaterialstoassurethatthe new examination materials to assure that the certification program remains robust and consistent in its integrity as a true reflection of the practice of electrical testing technicians.
In March of 2015, NETA’s Board of Directors approved a project to increase the association’s efforts toward certification program development and maintenance. This project maintenance. kicked off in April of 2015 and is nearing the final stages of the first phase of completion now
— almost exactly a year later in May of 2016. The project has seen the participation of over twothirds of NETA Accredited Companies, whose technicians participated in the job analysis survey in the summer of 2015. Those survey results weretheframeworkforafreshlookatNETA’s were the framework for a fresh look at NETA’s certification examinations. A team of 18 subject matter experts, under the leadership of NETA’s exam development committee, confirmed the revised blueprints, and have been in the process of developing new exam questions to complete the revised examinations for technicians Level 2, Level 3, and Level 4.
July 2016 will be the first administration of the new exam content based upon the redesigned blueprints. More information about the exam redesign project and requirements for project certificationareavailableontheNETAwebsite certification are available on the NETA website at www.netaworld.org.
NETA is extremely fortunate to have members who are willing to donate one of the most valuableassets:theirtime.Theireffortsassure valuable assets: their time. Their efforts assure continued growth and success for NETA, its NETA Accredited Companies, and most of all, its NETA Certified Technicians. To each company that takes on the challenging process of applying for NETA Accreditation, and to each technician who elects to follow the path toward certification, thank you. Your commitment to quality, reliability, and safety is something to be proud of, and assures a bright future for all whose lives are powered by the electrical equipment are and systems in your care.
KristenWicksisNETA’sTechnicalServices Kristen Wicks is NETA’s Technical Services Director.
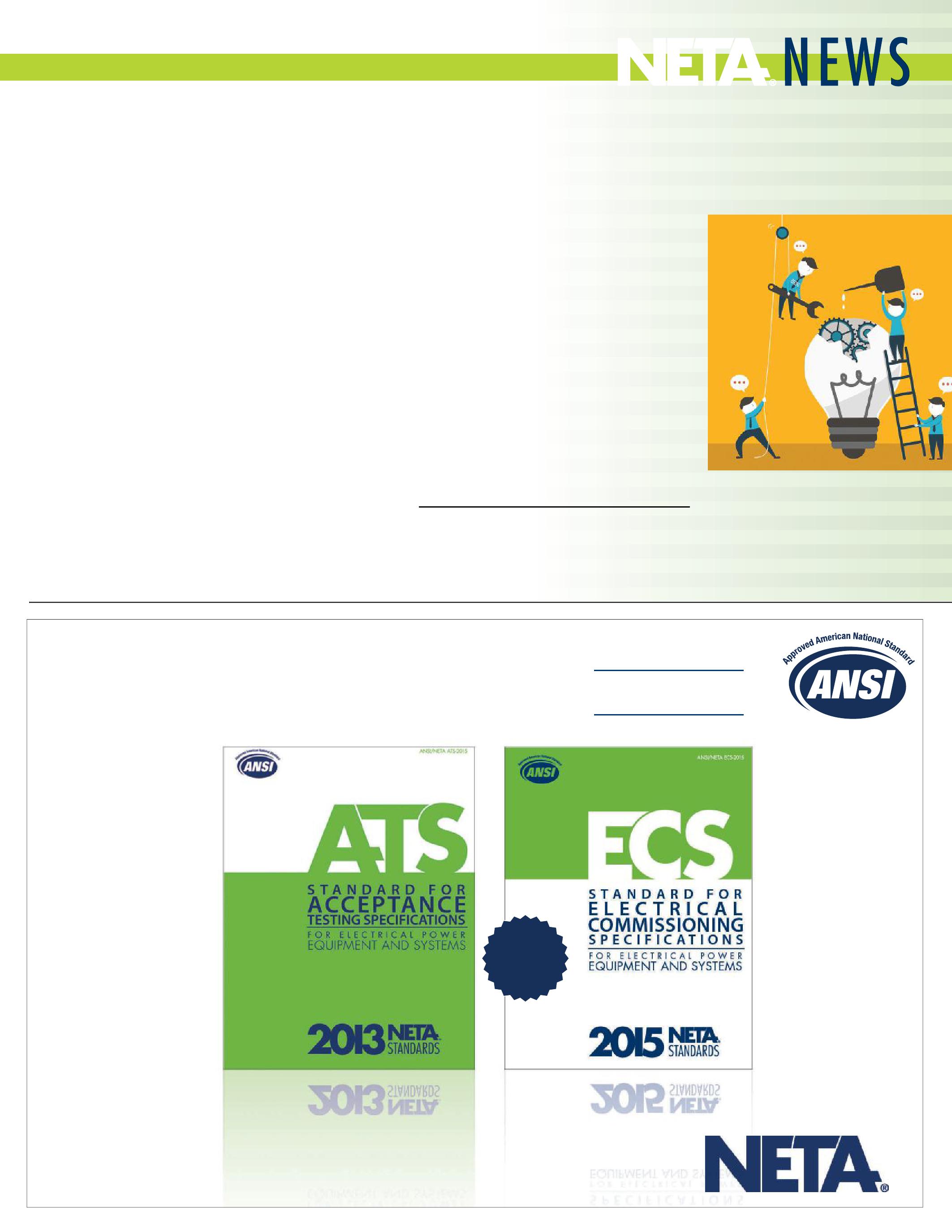
“Coming together is the beginning. Keeping together is progress. Working together issuccess.” is success.” — Henry Ford.
TWO NEW SELF-PACED TECHNICAL SEMINARS (SPTS)
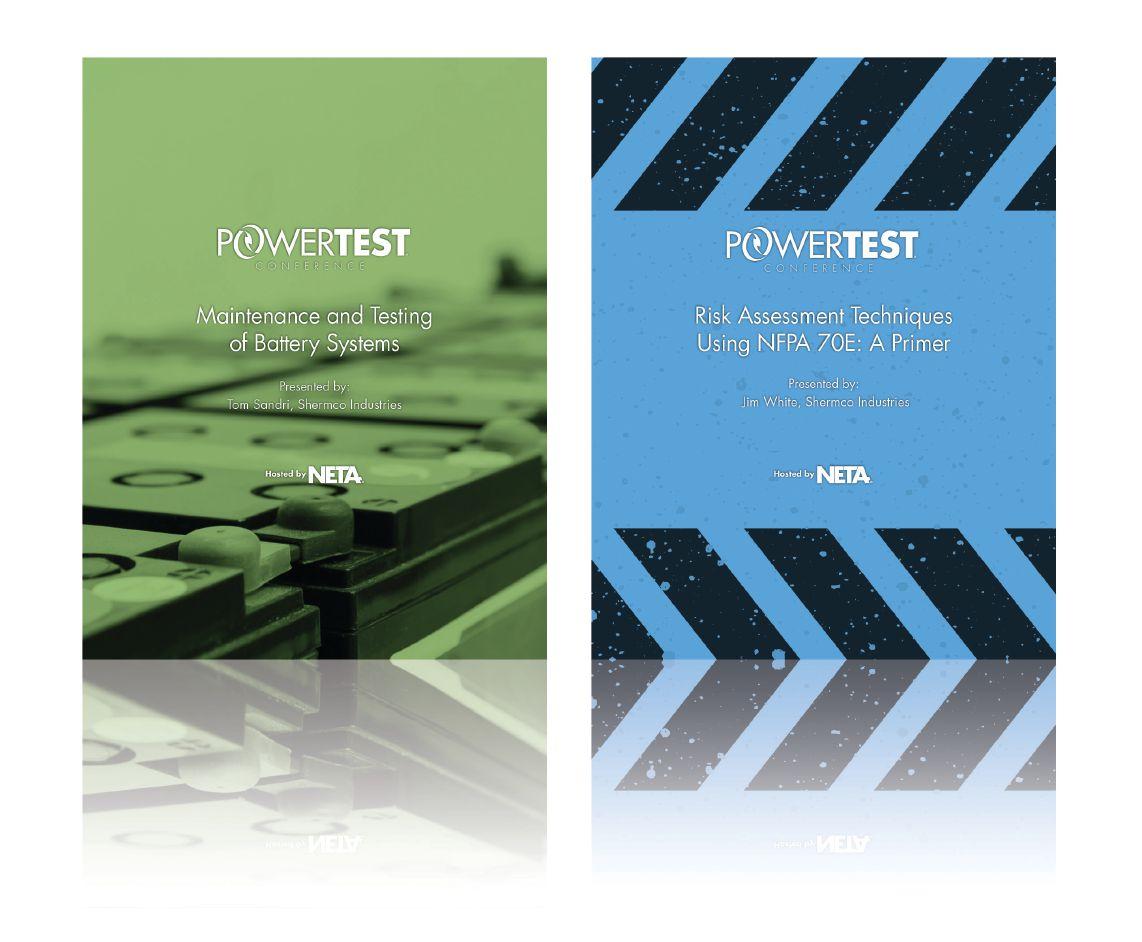
Learn at your own pace. Advance your knowledge. Ask about continuing education. Earn CTD*Credits for NETA Level III and IV Technicians. Order online at: www.netaworld.org or call 888-300-6382 (NETA)
awarded when participant receives a
the
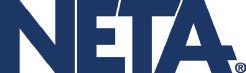

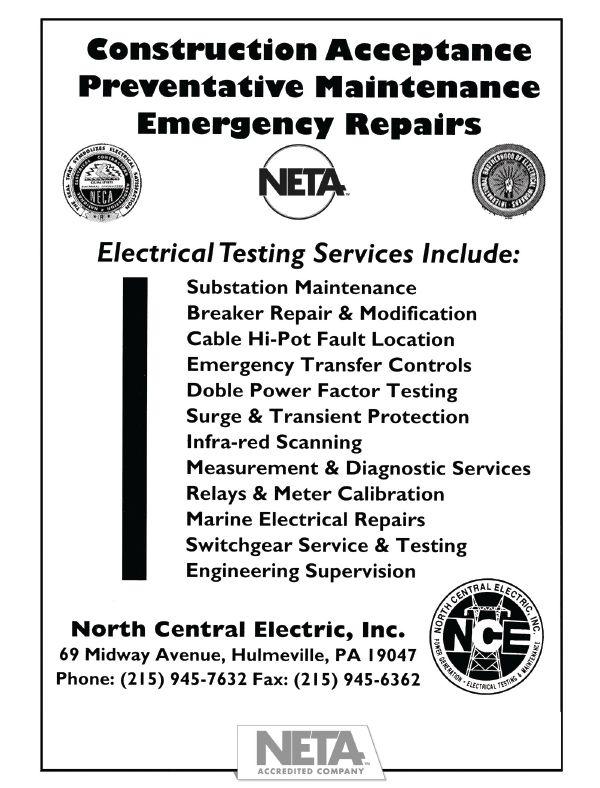
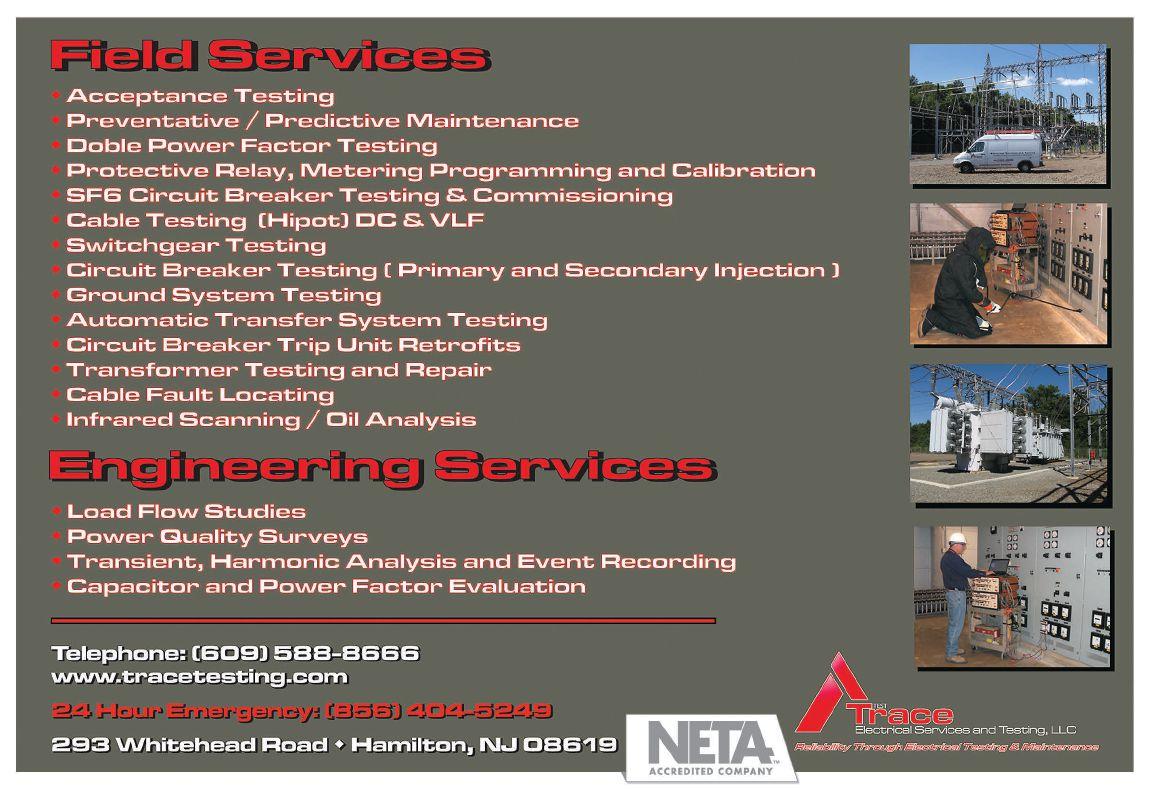

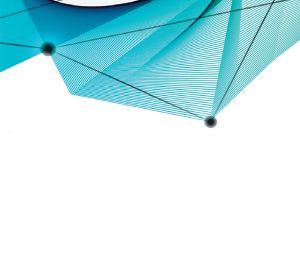
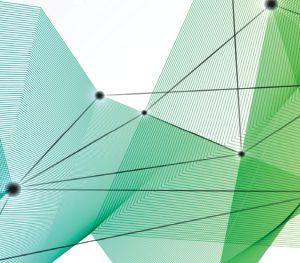
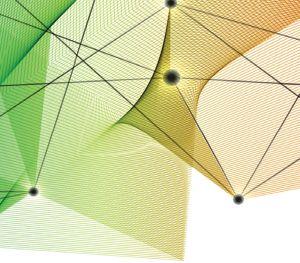
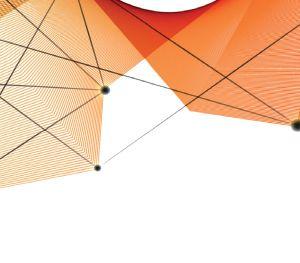
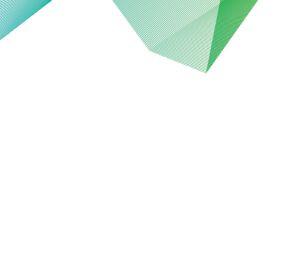

IN THE SOLAR INDUSTRY
BY JEFF JOWETT, MeggerSolar energy is a rapidly developing and expanding segment of the electrical power industry, spurred by the need for additional sources and green (i.e., environmentally friendly) generation.
In photovoltaic power generation, a miniscule fraction of the limitless energy of the sun is chemically converted to usable electricity. Solar generation can provide power directly to homes and commercial facilities and is also integrated into the larger power grid. The basic unit of generation is the solar panel (module), where the sun’s energy is converted to electricity. The individual modules can then be tied together into arrays, sometimes covering vast areas of land to enhance total output.
Like the more common parts of the electrical system, solar generation must be grounded.
In Photovoltaic Design & Installation by Ryan Mayfield (John Wiley & Sons), Mayfield refers to grounding as “the most confusing, debatable, and fun topic in the photovoltaic world.” Just as in other segments of the grid, effective ground protection consists of two distinct and inter-related parts: bonding and grounding. Bonding (also referred to as equipment grounding) is the connecting of individual pieces of equipment in an equipotential network. System grounding is the termination of the equipment grounding at an electrode buried in the earth. This article will examine equipment grounding first.
EQUIPMENT GROUNDING
The purpose of equipment grounding is to maintain all electrically conductive components at ground potential. If a live conductor accidentally

contacts any of the protected equipment, the current is provided with a low impedance path to ground that effectively shunts it around personnel while inciting protective devices to trip. Accordingly, the National Electrical Code (NEC) states that “exposed non-current-carrying metal parts of module frames, equipment, and conductor enclosures shall be grounded.” This requirement applies to all PV systems.
The equipment-grounding conductor runs alongside the other conductors in the PV circuitry. It is defined by the NEC as “the conductive path installed to connect normally non-current-carrying metal parts of equipment together and to the system-grounded conductor or to the grounding-electrode conductor, or both.” Electrical components such as combiner boxes, inverters, disconnects, battery boxes, and any metallic box holding electrical equipment can have a properly sized conductor connected to the ground lug on the equipment and then to the grounding system, thereby creating an equipment-grounding conductor (EGC). Every module must be connected to an EGC. There is often a connection point on the frame for this purpose, usually in the middle of the long edge, but necessary hardware and instructions have been reported as frequently lacking.
Two means of connection are most employed: ground lugs and grounding clips. A ground lug (Figure 1a) is a metallic screw-type clamp. It can

be placed at the manufacturer’s suggested point on the module. The EGC is then screwed tight to the lug. The same EGC can be run from lug to lug, thereby connecting the whole array. The lug must be rated for outdoor use and direct burial. This option, however, can be tedious and time-consuming.
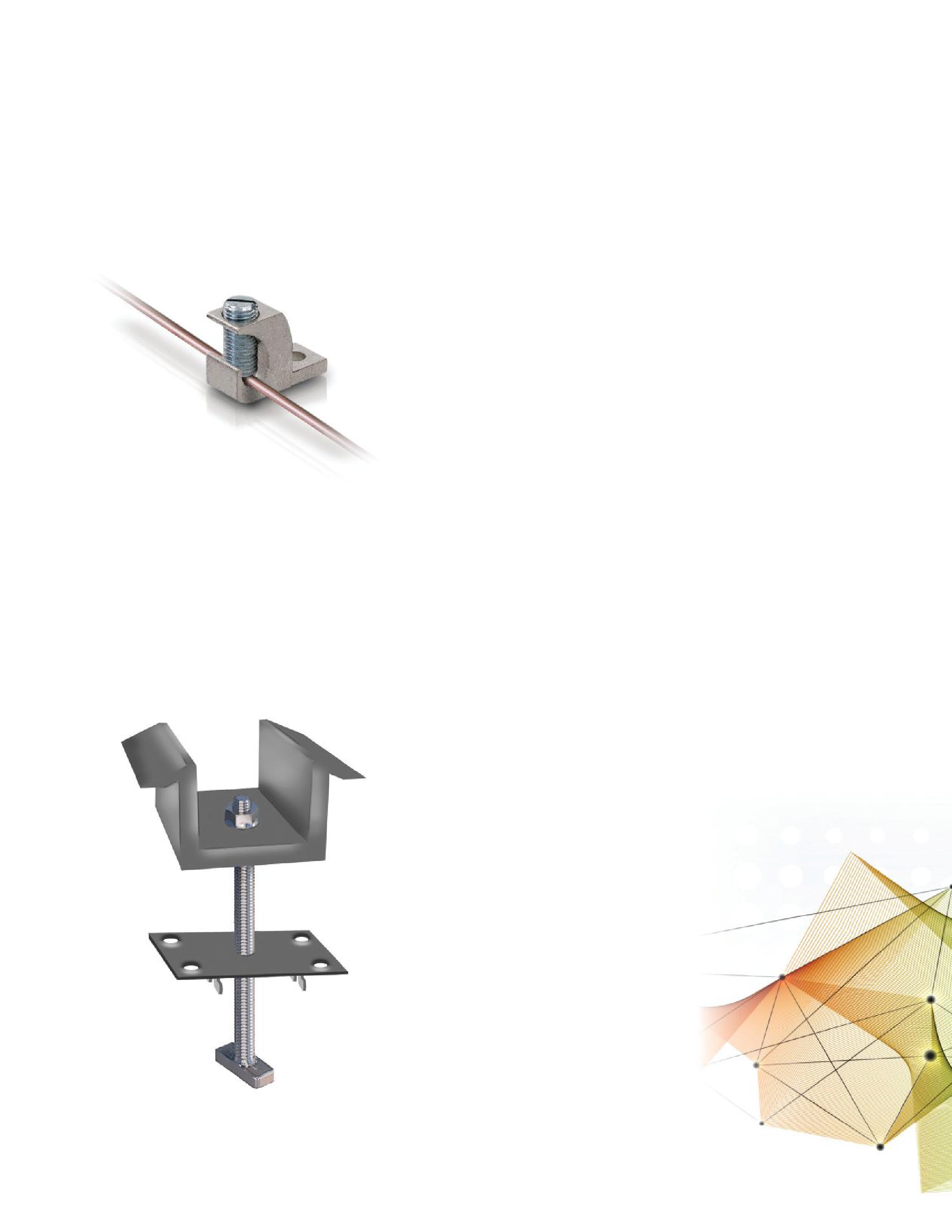
Alternatively, a grounding clip (Figure 1b) can be placed between the module and the racking system that composes the structure upon which the modules are mounted. The clip pierces the module frame and the racking system, metallically bonding the two and making the mounting rails theEGC.Becertainalltherailsareconnected the EGC. Be certain all the rails are connected together, which can be done prior to installation ofthemodules. of the modules.
After all components are bonded together, a single EGC can be bonded to one of the rails and brought to the combiner box. This method is not as labor-intensive, but the clips must be placed precisely as specified by the clip manufacturer.Fullcontactwiththemodule manufacturer. Full contact with the module and rack must be verified; otherwise, there is the possibility of an open or weak bond that would defeat the purpose of ground protection of the array. Similarly, if a module is removed, it must be done without disrupting the ground continuity of any other part of the structure. If the lug method uses a continuous conductor, then the structure remains protected. Proper rail bonding assures similar protection where the clip method has been used.
The equipment-grounding conductor must be sized properly to accommodate maximum prospective current. Again, the requirements aresetforthintheNECandarebasedonthe are set forth in the NEC and are based on the over-current protection device (OCPD) for the system. A ground fault protection device (GFP) should also be installed in the system. Article 690.45 provides a table that specifies the gauge of the EGC based on the amperage rating of the OCPD. Not all PV systems require OCPDs. In that case, the grounding conductor is sized basedontheshort-circuitcurrent.Thesame based on the short-circuit current. The same table can be used, substituting the short-circuit current for the OCPD of the same rating, but no gauge smaller than 14 AWG should ever beused. be used.
If there is no ground fault protection device (GFP) installed in the system, the EGC is sized with an ampacity at least twice that of what is called the “conditions of use” ampacity for the current-carrying conductors. These parameters are given in Tables 310.15(B)(2)(a), 310.15(B) (2)(c), 310.16, and 310.17 of the NEC. However, these are last-option measures, and it is highly advantageous to have an installed GFP. Fortunately, all grid-direct inverters come standard with built-in GFPs, and for batterybased systems, they are easy to integrate.
In addition to considering the potential damage to undersized conductors from over-currents, the possibility of physical damage should also
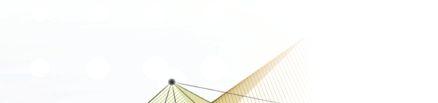
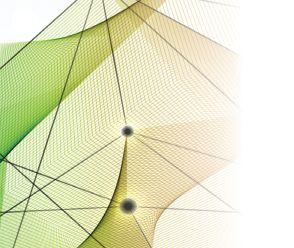
be taken into account. If such risk exists, the EGC can be protected in conduit or be at least 6 AWG, as the heavier gauge will withstand physical abuse that might damage a lighter gauge. In the PV industry, EGCs are most commonly bare copper. Within conduit, either bare copper or insulated ground conductors are used. Using building wiring for ground wire in conduit is acceptable.
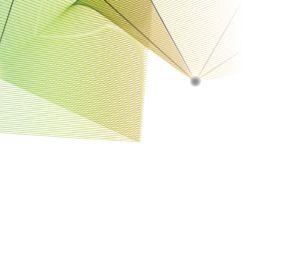
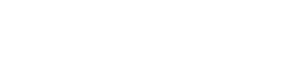
Finally, all the current-carrying protection of equipment grounding will be lost if not connected to adequate system grounding. Currents traveling on the grounding conductors must be diverted to earth at low impedance to not exploit unwanted paths through equipment and personnel. This function requires an adequate grounding electrode (GE) making contact with the surrounding earth. The most commonly recognized electrode is the ground rod, often a copper rod driven eight feet into the earth. For a better ground, or in poorly conductive soil, a deeper rod can be driven. Also, extra rods can be added and paralleled together with a conductor. To avoid the two rods behaving as only one, the second rod is added at a horizontal distance slightly greater than its depth. A second rod will generally decrease ground resistance by about 40 percent, but additional rods invoke the Law of Diminishing Returns, as increments become progressively smaller.
The solar industry also uses the Ufer ground. For roof-mounted arrays, the steel reinforcement of the concrete foundation may be used to make contact with the earth. It is a good idea, however, to augment this with a parallel ground rod, as lightning strikes can damage foundations by vaporizing the trapped moisture in the concrete. (Historical note: Ufer is not an acronym, as sometimes reported. It is actually the name of Herbert G. Ufer, the electrical engineer who pioneered the method. During WWII, a method was needed to safely ground ammunition bunkers — at obvious risk — and it was Ufer who came up with the
idea that the foundation steel already in place would serve.)
GROUNDING ELECTRODE CONDUCTOR
The second essential element in system grounding is the grounding electrode conductor (GEC).This is a conductor that connects the rod(s) or Ufer to a point where all the other grounded conductors can be connected. A good example is a 6 AWG or 4 AWG wire from the grounding electrode at one end to the ground busbar inside the main distribution panel (MDP) at the other end. Article 690.47 is the principal NEC reference.
If the PV system is utility-interactive, either grid-direct or battery-based, the PV system grounding is then paralleled with the existing utility system ground. Electrically separate grounds can develop voltage gradients between them that will behave counter to the purpose of the grounding system, causing ground currents to flow into an electrical system. Paralleling them together brings them to the same potential. There are two common ways to make the system-grounding connection in a utility-interactive system.
One is to connect an additional ground rod or two to the inverter system grounding (6 AWG GEC recommended) and parallel it to the existing utility electrode (Figure 2 top). This must be done with a GEC of the same gauge as the existing utility GEC. A second method is to run a GEC from the inverter to the existing utility electrode (Figure 2 bottom). This conductor would be sized according to NEC requirements. For stand-alone, batterybased systems (the solar array is providing the sole source of electricity to the ac load), a utility ground is unavailable, so a new grounding electrode must be installed. Two 6 AWG or 4 AWG GECs must then be connected, one from the dc wiring enclosure where the inverter connects to the battery bank and the other from the ac MDP.

Figure 2: Two Common Ways to Make System-Grounding Connection in a UtilityInteractive System
As to sizing the GEC, Article 250.66 of the NEC describes the requirements for the ac side, and Article 250.166 covers the dc side.
For utility-interactive systems, a GEC will already be in place from the original contractor. Stand-alone, battery-based systems require the installation of a new GE and GEC. The GE is installed as close to the MDP as possible. If the GEC is run outside without conduit, it should be at least 6 AWG. The robustness of this gauge is considered sufficient to provide physical protection. If the GEC can be run without exposure to physical damage, an 8 AWG conductor for the dc side may be adequate.
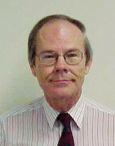
Jeffrey R. Jowett is a Senior Applications Engineer for Megger in Valley Forge, Pennsylvania, serving the manufacturing lines of Biddle, Megger, and multi-Amp for electrical test and measurement instrumentation. He holds a BS in Biology and Chemistry from Ursinus College. He was employed for 22 years with James G. Biddle Co. which became Biddle Instruments and is now Megger.

ANSI/NETA MTS - 2015 UPDATED EDITION
To learn more about the newest edition of the ANSI/NETA MTS Standard for Maintenance Testing Specifications, visit netaworld.org/standards.
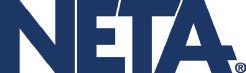
CALL FOR SPONSORS

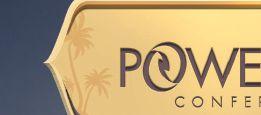
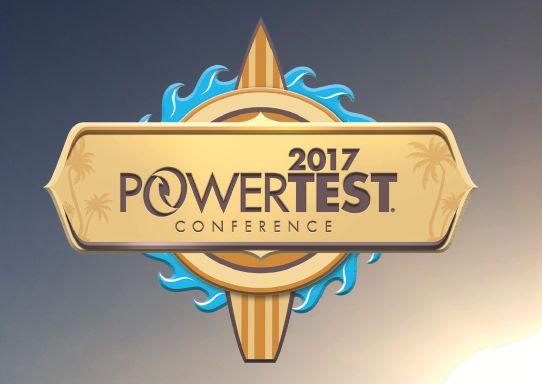

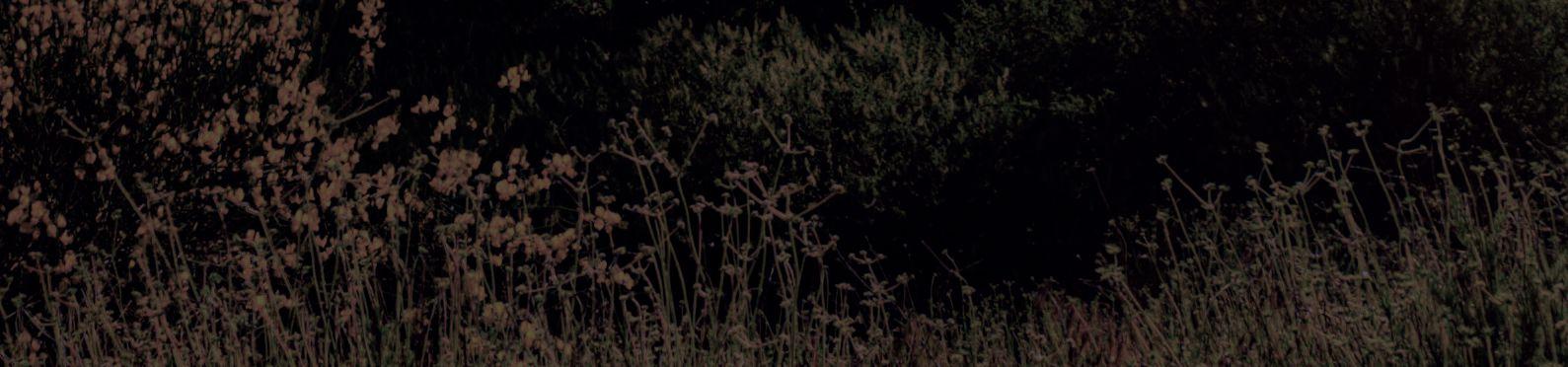




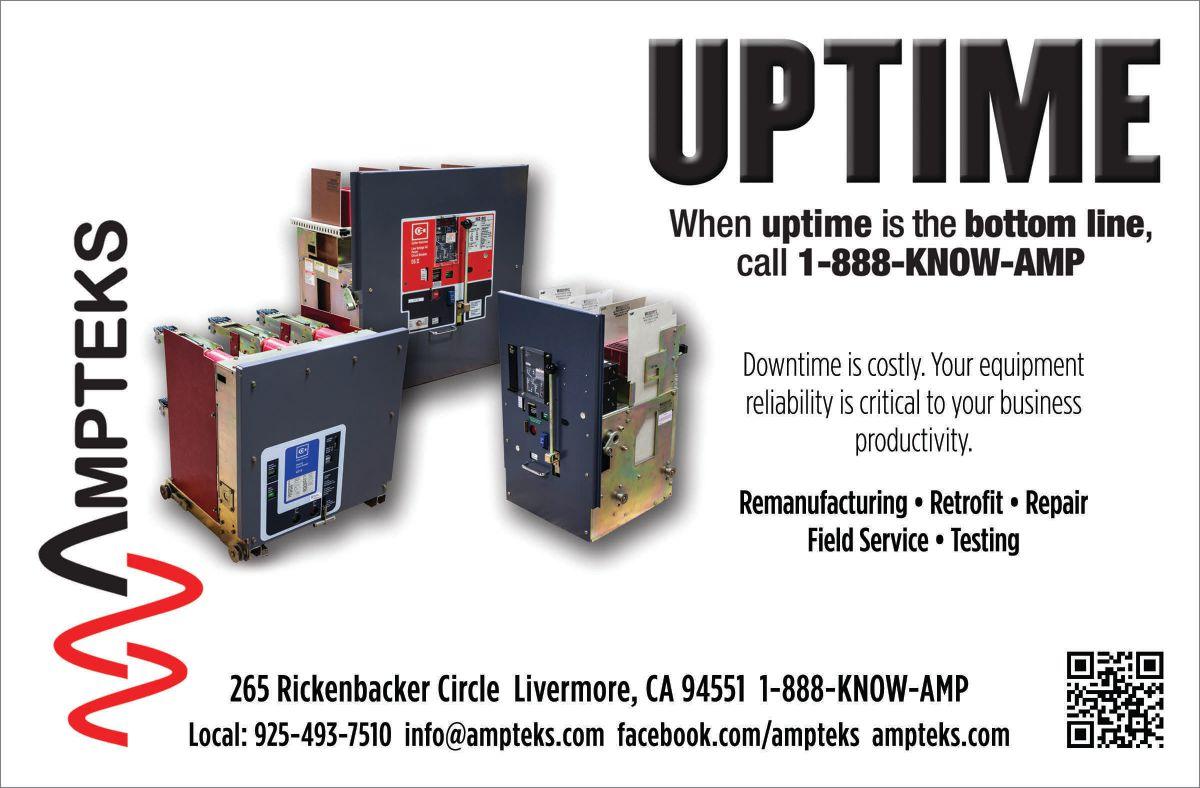
AND ELECTRICAL HAZARD FOOTWEAR A
BY PAUL CHAMBERLAIN, American Electrical Testing Co., Inc.Everyone wears clothes. However, not everyone needs to wear clothes designed to protect from the inherent hazards in their job. If employees work on electric power generation, transmission, and distribution equipment, then special clothing is necessary for certain tasks.
Per OSHA Regulation 29 CFR 1910.269, employers need to assess a workplace and whether an employee will be exposed to the hazards of flames or electric arcs. Upon finding a potential for exposure, the employer must estimate the potential incident heat energy the employee could be exposed to and provide the employee with the appropriate personal protective equipment (PPE). In addition, if employees will be exposed to flames and arcs, the employer must ensure that the material worn by employees is not untreated meltable fabric (e.g., polyester, rayon, fleece, natural fiber blended with meltable fibers, etc.).
Available materials are listed in ASTM F1506
Flame Resistant and Arc Rated Textile Materials for Wearing Apparel for Use by Electrical Workers Exposed to Momentary Electric Arc and Related Thermal Hazards
Further, in regulation 1910.269, OSHA states:
“The employer shall ensure that the outer layer of clothing worn by an employee, except for clothing not required to be arc rated, is flame resistant under any of the following conditions:
1. The employee is exposed to contact with energized circuit parts operating at more than 600 volts,
2. An electric arc could ignite flammable material in the work area that, in turn,
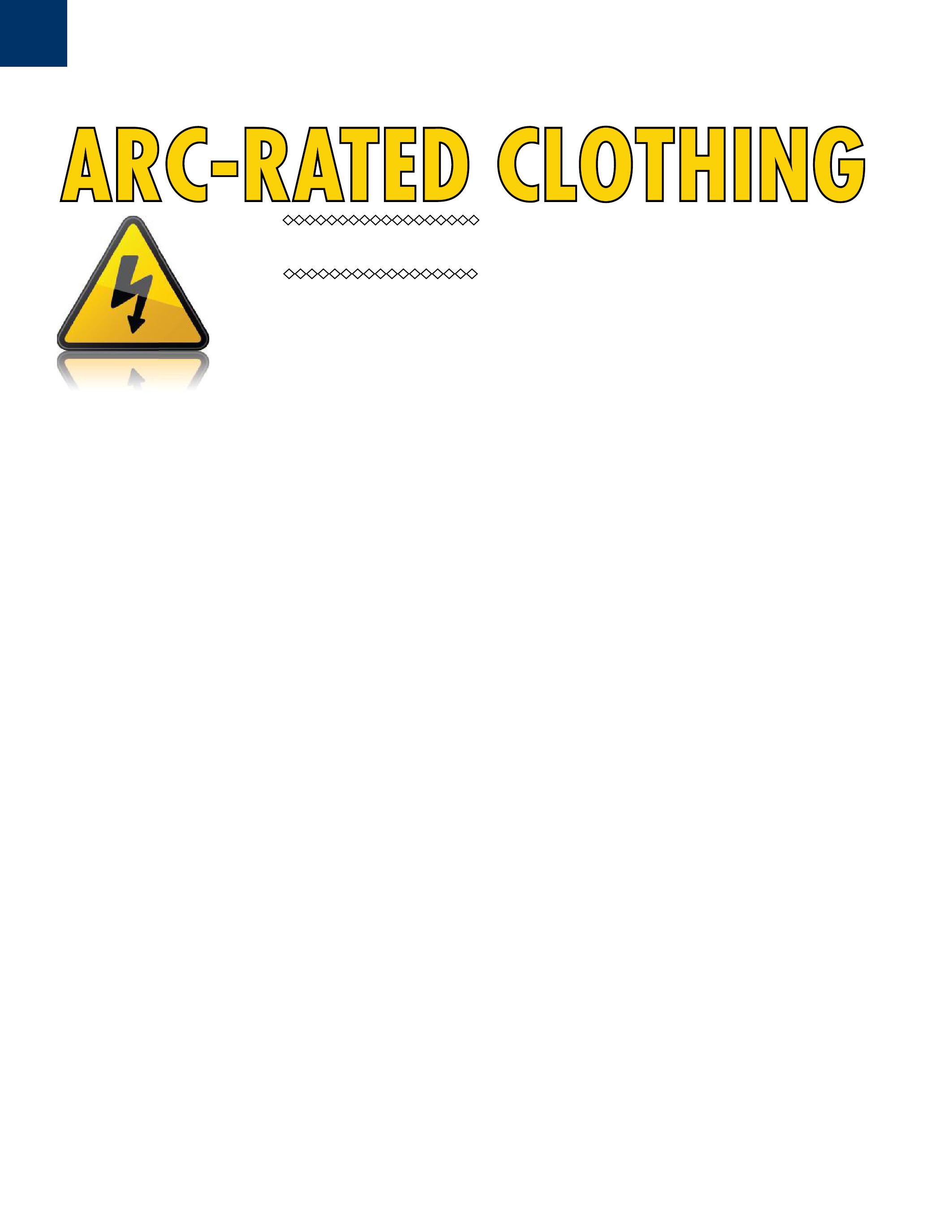
could ignite the employee’s clothing,
3. Molten metal or electric arcs from faulted conductors in the work area could ignite the employee’s clothing, or
4. The incident heat energy exceeds 2.0 cal/ cm2.”
Per NFPA 70E 2015 Standard for Electrical Safety in the Workplace, the employer must provide arc-rated (AR) clothing for potential arc-flash hazards in an atmosphere not regulated by the OSHA 1910.269 standard. Section 130.4 and 130.6 of NFPA 70E clearly states that it is the employer’s responsibility to identify the hazards and provide the necessary AR clothing to mitigate those hazards. It also instructs the employee in proper inspection of that PPE.
Once it is determined that flame-resistant clothing is required, the employer must provide clothing that is appropriately rated for the potential hazard. In 1910.269, OSHA further states:
“The employer shall ensure that each employee exposed to hazards from electric arcs wears protective clothing and other protective equipment with an arc rating greater than or equal to the heat energy estimated whenever that estimate exceeds 2.0 cal/cm2.
This protective equipment shall cover the employee’s entire body, except as follows:
1. Arc-rated protection is not necessary for the employee’s hands when the employee is wearing rubber insulating gloves with protectors, or, if the estimated incident energy is no more than 14 cal/cm2, heavy-duty leather work gloves with a weight of at least 407 gm/m2 (12 oz/yd2),
2. Arc-rated protection is not necessary for the employee’s feet when the employee is wearing heavy-duty work shoes or boots,
3. Arc-rated protection is not necessary for the employee’s head when the employee is wearing head protection meeting § 1910.135 if the estimated incident energy is less than 9 cal/cm2 for exposures involving single-phase arcs in open air or 5 cal/cm2 for other exposures,
4. The protection for the employee’s head may consist of head protection meeting § 1910.135 and a face shield with a minimum arc rating of 8 cal/cm2 if the estimated incident-energy exposure is less than 13 cal/cm2 for exposures involving single-phase arcs in open air or 9 cal/cm2 for other exposures, and
5. For exposures involving single-phase arcs in open air, the arc rating for the employee’s head and face protection may be4cal/cm2lessthantheestimated be 4 cal/cm2 less than the estimated incident energy.
As the potential incident energy increases, so must the protection level provided to the employee. Again, it is the employer’s responsibility to assess the workplace, identify potential hazards, and provide adequate protection to the hazard.
Training employees in the proper use and care of the PPE provided is very important. Employees’ ability to identify electrical hazards, their knowledge of electrical equipment and its nominal voltage, and understanding when proper PPE is required are vitally important and will go a long way in ensuring that they are protecting themselves from potential hazards.
The other aspect to employee training is care of their PPE. If it is worn, damaged, or deteriorated, then it cannot adequately protect them from potential hazards. Employees must learn to inspect all PPE prior to and after use. A guideline in the inspection and care of AR clothing is found in ASTM F1449 Standard Guide for Industrial Laundering of Flame, Thermal, and Arc Resistant Clothing andASTMF2757 and ASTM F2757 Standard Guide for Home Laundering Care and Maintenance of Flame, Thermal and Arc Resistant Clothing.These . These ASTM standards are a requirement for management of AR clothing, whether laundered at home or commercially. Many AR clothing manufacturers offer helpful online aids to provide guidance to employees on the proper use, care, and maintenance of AR clothing.
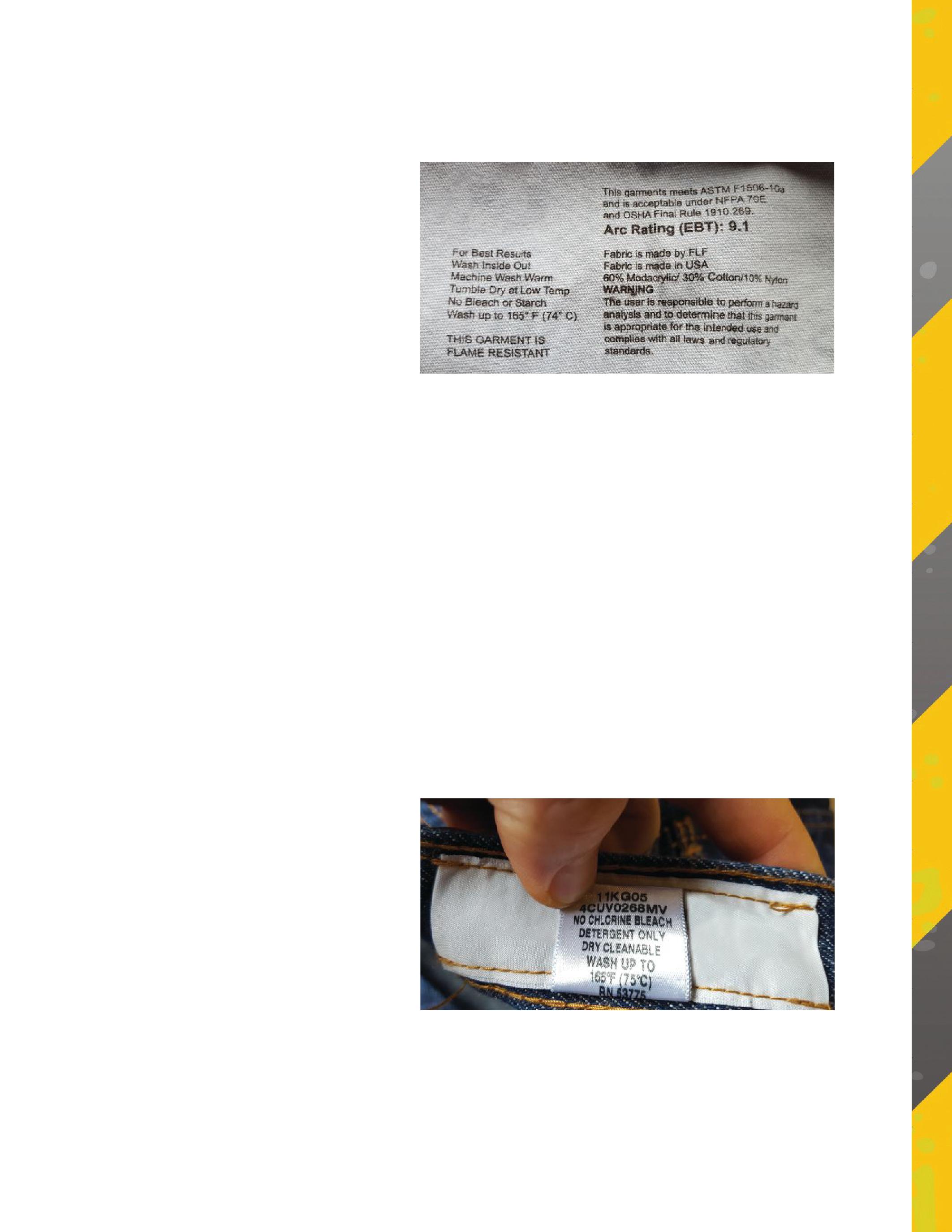
If they will be exposed to the hazard of flames or electrical arc, employees must also wear heavy-duty work boots or shoes. Per OSHA 29 CFR 1910.136(a): “Each affected employee
SAFETY CORNER
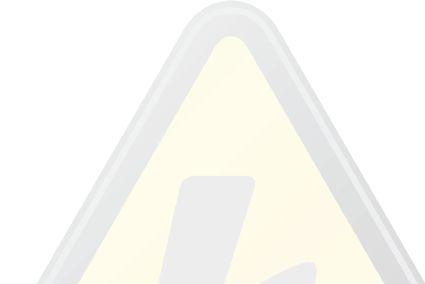
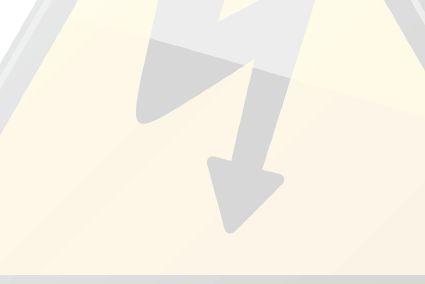
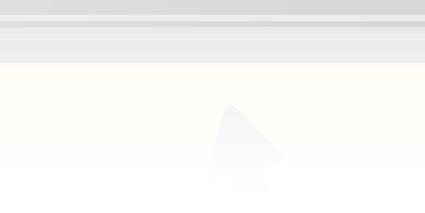
shall wear protective footwear when working in areas where there is a danger of foot injuries due to falling or rolling objects, or objects piercing the sole, and where such employee’s feet are exposed to electrical hazards.”
Likely, the boot or shoe will also need to be safety-toed and meet ASTM F2413 Standard Specification for Performance Requirements for Protective (Safety) Toe Cap Footwear Additionally, the boots must be electrical hazard-rated footwear (EH). EH footwear is manufactured with non-conductive, electricalshock-resistantsolesandheels.Theoutsole shock-resistant soles and heels. The outsole provides a secondary source of electric-shockresistance protection to the wearer against thehazardsfromanincidentalcontactwith the hazards from an incidental contact with live electrical circuits, electrically energized conductors, parts, or apparatus. It must be capable of withstanding the application of 18,000 volts at 60 hertz for one minute with no current flow or leakage current in excess of one milliampere under dry conditions. Should the assessed potential exceed this, protection suchasrubberdielectricoverbootsorshoes such as rubber dielectric over boots or shoes will be required.


Proper care of footwear is also very important. Exposed toe caps indicate a breakthrough in the leather of the boot, providing less arc and flame protection. Simple things such as broken, missing, or overly long laces can pose a simple trip hazard, which can cause serious injury. Wear in the sole of the boot exposes the employee to step potential during a ground fault. Spilled flammable materials can soak into a leather boot, possibly causing a flame hazard. Therefore, cleaning and maintaining boots and shoes used for protection is highly important.
Wearing the correct AR clothing and boots protects employees from many potential hazards. Ensuring that this equipment is clean and well maintained is an important step in providing adequate protection to the wearer. Knowledge of how to inspect, clean, and maintain these garments and footwear must be given to the employee by the employer to ensure a safe and productive workplace.

Paul Chamberlain has been the Safety Manager for American Electrical Testing Co., Inc. since 2009. He has been in the safety field for the past 17 years, working for various companies and in various industries. He received a bachelor of science degree from Massachusetts Maritime Academy.
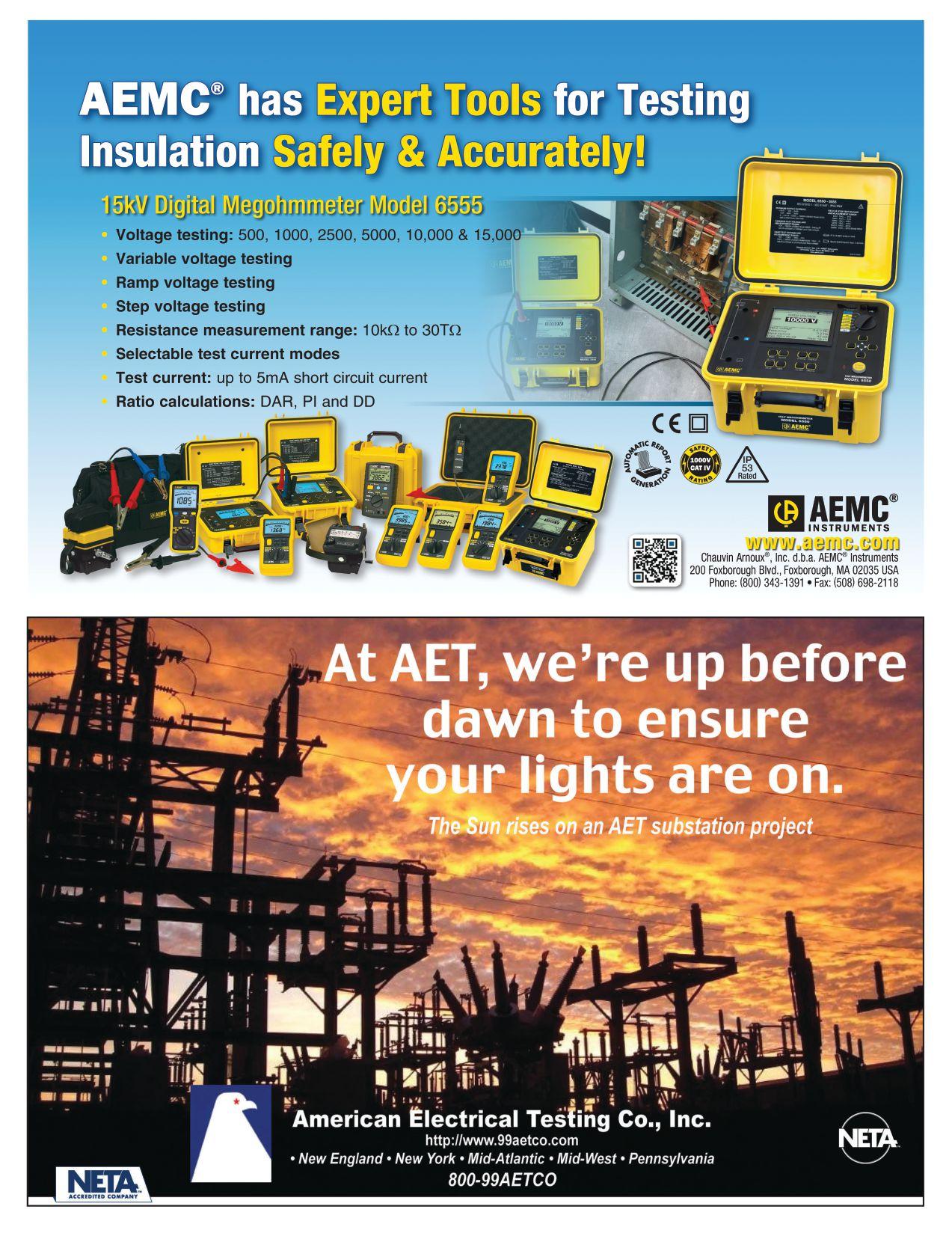
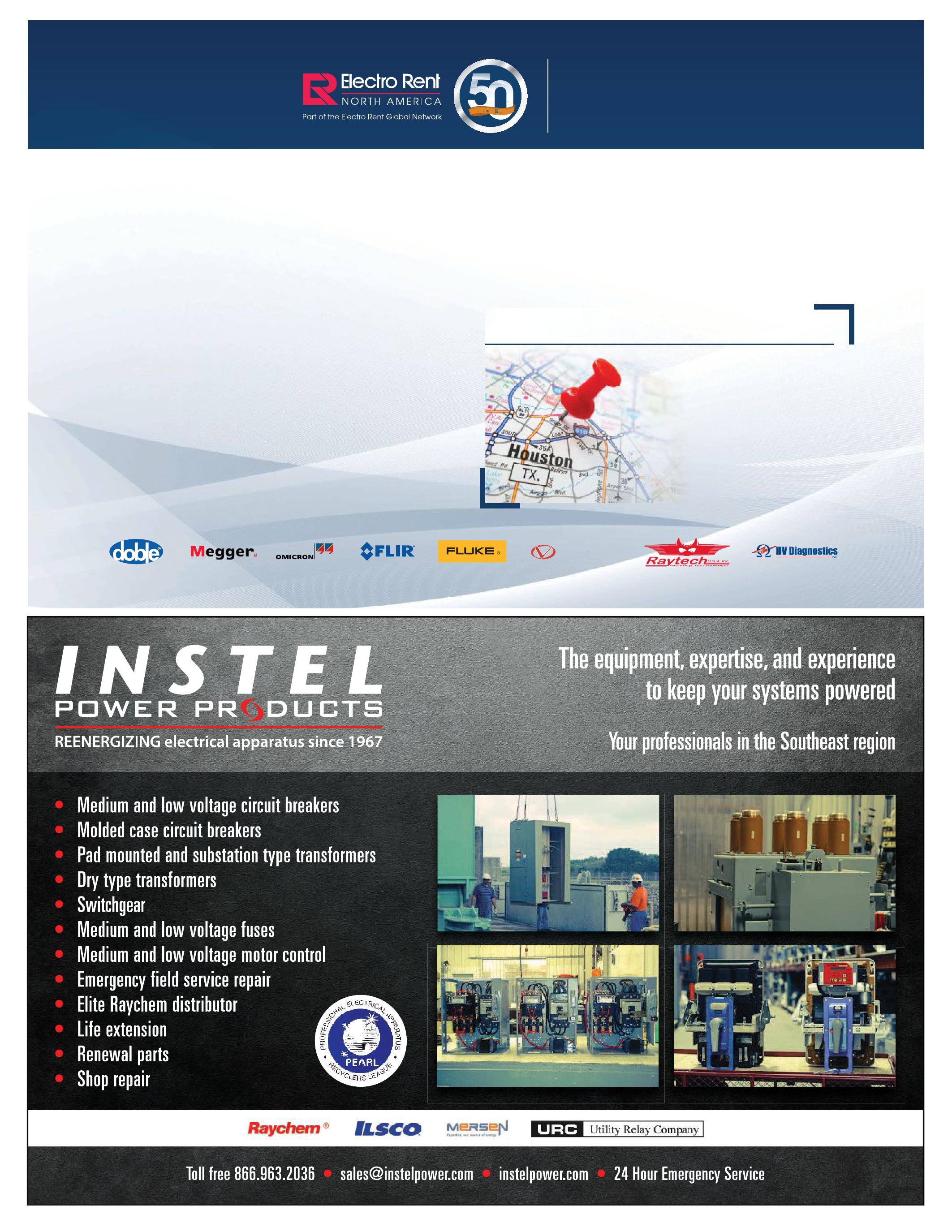
Electro Rent is proud to introduce its new Regional Service Center, serving your test needs better and faster than ever with experienced customer support 24x7. If it tests, we’ve got it— and we’re ready to deliver in Houston.

The users, owners, and operators of the bulk power system within these areas account for virtually all the electricity supplied in the United States, Canada, and a portion of Baja California Norte, México. NERC released an official report in May 2013 that featured statistics for protection misoperations across the entire country.
Major disturbances are ranked using a Daily Severity Risk Index. These include the following blackouts:
• 1989 Quebec Solar Flare
• 1996 Western Disturbance
• 2003 Eastern Interconnection Blackout
Primarily, misoperations resulted due to the following reasons (Figure 2):
• Incorrect settings/logic/design errors
• Communication failure
• Relay failure or malfunction
These events include human error during testing and maintenance activities. These errors result in protection system activation that has contributed to large disturbance events.

Most of these misoperations contribute to increasing Security Risk Index (SRI) and indicate that the number of transmission element outages is increasing.
CORRECTIVE ACTIONS
Applications requiring coordination of functionally different relay elements should be avoided. This type of coordination is almost always problematic and is the cause of numerous misoperations reported in the study period. For example, an overcurrent element
should not coordinate with a distance element; while the distance element has a fixed reach, the effective reach of the overcurrent element is dependent upon the strength of the source.
Misoperations due to setting errors can be reduced using the following techniques:
• Peer reviews
• Increased training
• More extensive fault studies
• Standard-setting templates for standard schemes
• Periodic review of existing settings when there is a change in system topography
Remember that the greater the complexity of the protection scheme, the greater risk of misoperation. Simplicity is elegance.
MISOPERATION ANALYSIS
87 Generator Phase Differential Protection
The customer reported a questionable generator protection relay trip. There are two main protection relays provided by different manufacturers, but only one operated.
Review of the relay settings revealed that the relay that did not trip had a higher pickup setting by a factor greater than four times. The CTs have a knee point of 100 volts or less, which is low, and there was the presence of heavy dc offset in the C-Phase current (Figure 3).
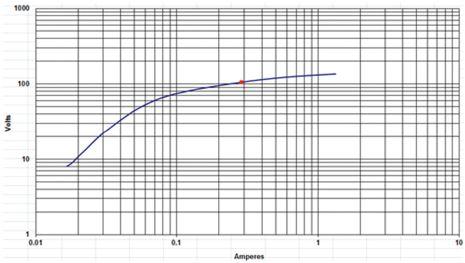
Figures 4A and 4B show the high levels of dc offset present in C-Phase current during the event. In fact, dc offset current is the number-one cause of CT saturation.
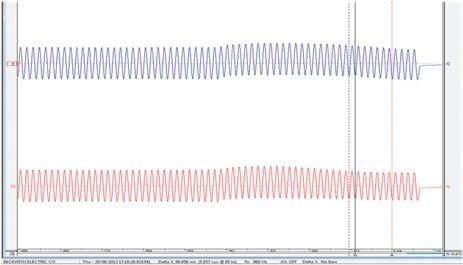
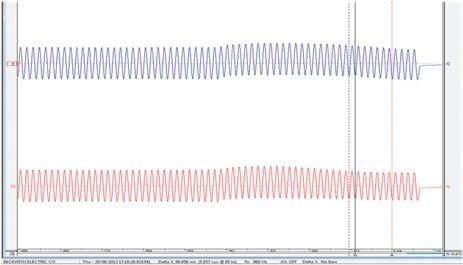
Here is the minimum pickup for the relay that did not operate:
Tap·O87P = (4.4 amps)·(0.3) = 1.32 amps
As shown in Figure 5, the customer copied the settings from an arbitrary example in the manufacturer relay instruction book. The relay that tripped was more than four times as sensitive.
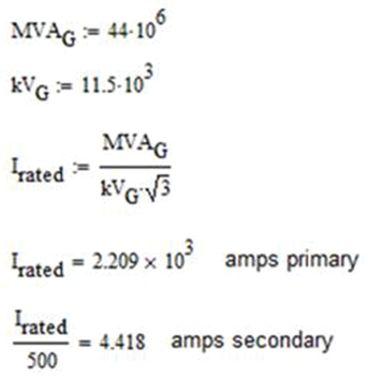
The blue triangle in Figure 6 corresponds to the C-Phase operating point, which was just on the boundary of operation. The misoperation occurred when the current was coming out of saturation.
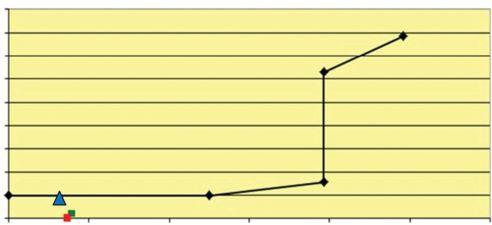
The dc offset present in fault current exponentially decays as shown in Figure 7. The digital Fourier transform algorithm cannot fully reject it.
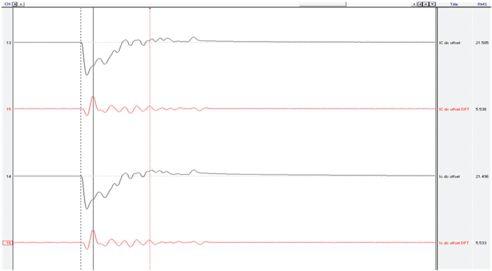
7:
Best Practice: If the dc offset from transformer inrush (e.g., black start) or fault condition can cause CT saturation, then the following are appropriate for generator phase differential protection settings:
• Minimum pickup up to 0.5 amps secondary
• Slope of 20 percent
• Time delay up to 5 – 8 cycles
Detailed calculations are necessary for generator differential protection to determine if CTs can saturate; do not simply copy settings from the relay instruction book without actual verification.
Higher C-class CTs can help to mitigate saturation (Figure 8).
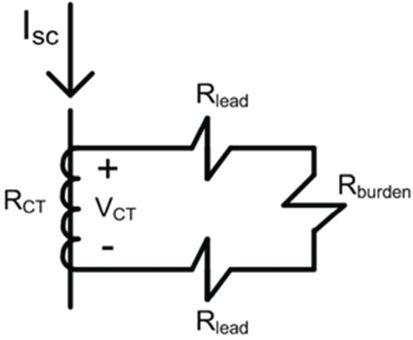
VCTMAX = 2•(RCT + 2•Rlead + Rburden)
The factor of 2 accounts for a fully offset current waveform, which is worse case.
27TN Third Harmonic Neutral Undervoltage
A utility experienced several misoperations when system voltage was low. However, the trip shown in Figure 9 occurred when the machine was under-excited and drawing vars from the system.
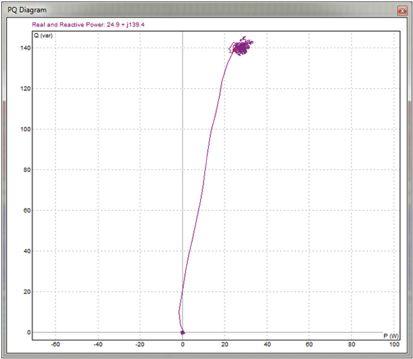
operating conditions. If failure occurs in the lower voltage portion of winding near neutral, a generator trip will not typically occur until some other relay protection detects a problem (e.g., arcing becomes so widespread that other portions of winding become involved). 27TN sees stator ground faults very close to the machine neutral as shown in Figure 10.
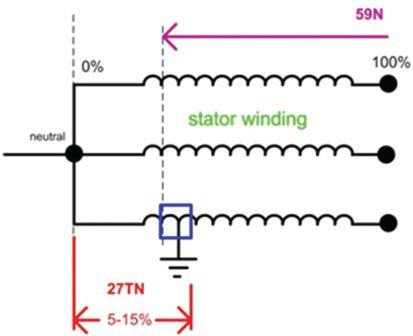
Third-harmonic neutral voltage changes as a function of load. The pickup setting is typically set equal to one-half of the minimum value measured during normal operation. Figure 11 illustrates how complex it can be to securely set 27TN protection through the blocking functions.
The machine nominal power is 746.5 watts secondary.
Conventional protection (59N) cannot detect grounds in the last five to 10 percent of the stator winding. Actually, 27TN is not always reliable and may have to be blocked during specific
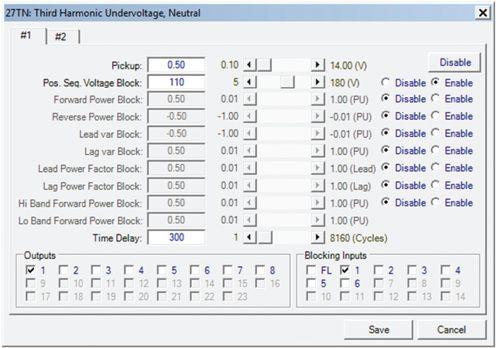
The solution for this particular machine is to block on low-forward power as this is the prevailing system condition when the nuisance
trip occurs. The main drawback to this solution is no protection for stator ground faults close to neutral during this operating condition.
Best Practice: The customer was urged to considering installation of 100 percent stator ground fault protection using sub-harmonic voltage injection (64S), which they did (Figure 12).

Recent experience with four such failures in large generators demonstrates that lack of proper protection can be disastrous. Each of the four failures caused massive damage to generators and collectively had total cost, including repair and loss of generation, close to $500 million. This demonstrates that the failure of stator windings in the last five percent of the winding is not uncommon. See Figures 13A, 13B and 13C.

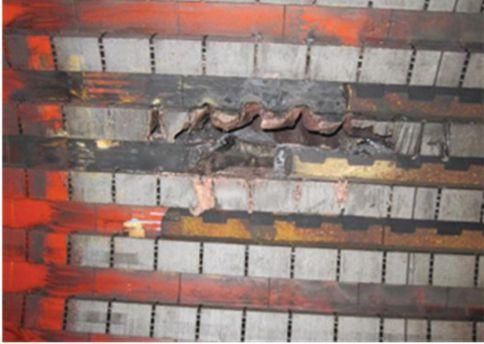

64S provides the following advantages:
• Detects stator ground when winding insulation first starts to break down and trips unit before catastrophic damage occurs.
• Trips in order of cycles since 20 Hz signal is decoupled from 60 Hz power system.
• Detects grounds close to machine neutral — or even right at neutral — providing 100 percent coverage of stator windings.
• Detects grounds when machine is starting up or offline.
• Reliably operates with generator in various operating modes (such as a synchronous condenser) and at all levels of real and reactive power output.
• Commissions in less than one hour, assuming there are no wiring errors. See Figure 14.
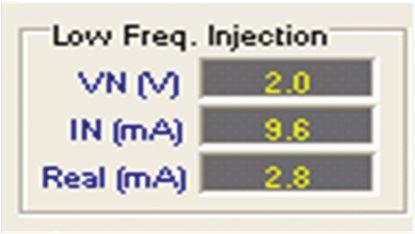
Figure 14: Numerical Generator Relay 20 Hz
Metering
Incorrect Phase Rotation Settings
Numerical protection relays require a setting to determine the correct phase rotation. Figure 15 illustrates ABC phase rotation; however, some power systems are ACB.
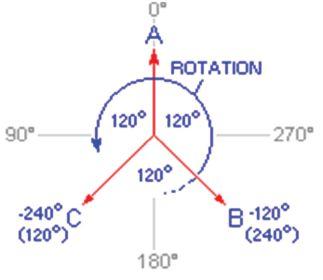
Figure 15: ABC Phase Rotation
Two customers experienced generator protection misoperations due to incorrect phase rotation settings. The first misoperation was 40 loss-offield protection (Figure 16).
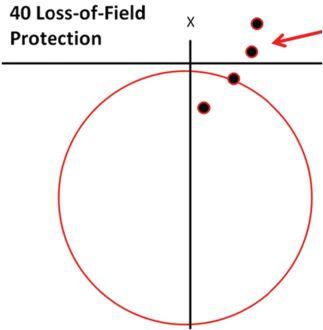
Figure 16: 40 Loss-of-Field Protection
Sequence of events:
•40 operates on Z1 (positive-sequence impedance).
• 40 measures incorrect impedance due to wrong phase rotation setting.
• 40 trips each time customer attempts to synch the generator to the grid.
The second misoperation was 78 out-of-step protection (Figure 17).
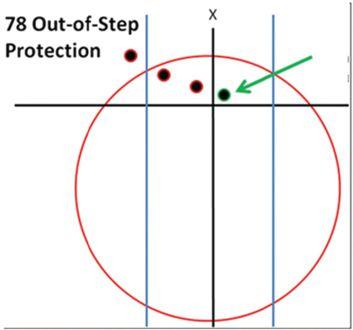
Figure 17: 78 Out-of-Step Protection
Sequence of events:

• 78 operates on Z1 (positive-sequence impedance).
• 78 measures incorrect impedance due to wrong phase rotation setting.
• 78 tripped during external event.
How did either incorrect relay setting make it past commissioning? Both elements (40 and 78) were effectively operating on Z2 (negativesequence impedance) due to the incorrect phase rotation settings.
Best Practice: Modern numerical relays have built-in tools to determine the actual phase rotation. Phase rotation can quickly be checked using numerical relay metering.
CONCLUSION
The 2013 NERC report covered relay In the 2013 NERC report on relay misoperations across the country, over one-third of the total events were due to incorrect setting, logic, testing, and design errors. Simplified software

for complex applications and visualization tools can enhance proper relay settings and operation. And finally, correction actions must be taken such as peer reviews, training, analysis, the use of standards-setting templates, and periodic reviews.
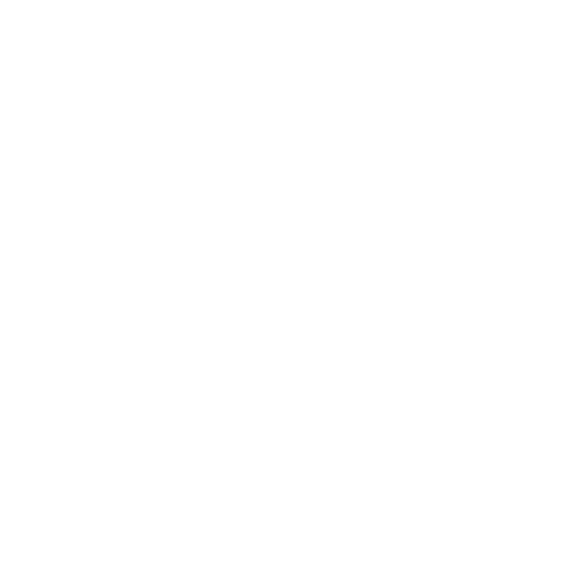
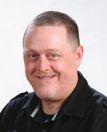
Steve Turner, an IEEE Senior Member, is a Senior Applications Engineer at Beckwith Electric Company. His previous experience includes work as an application engineer with GEC Alstom, and as an application engineer in the international market for SEL, focusing on transmission line protection applications. Steve worked for Duke Energy (formerly Progress Energy), where he developed a patent for double-ended fault location on overhead transmission lines. He has a BSEE and MSEE from Virginia Tech. Steve has presented at numerous conferences including Georgia Tech Protective Relay Conference, Western Protective Relay Conference, Energy Council of the Northeast (ECNE), and Doble User Groups, as well as various international conferences.
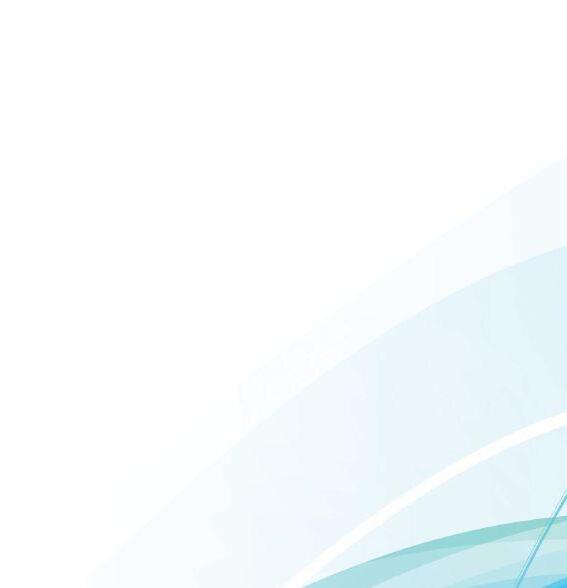

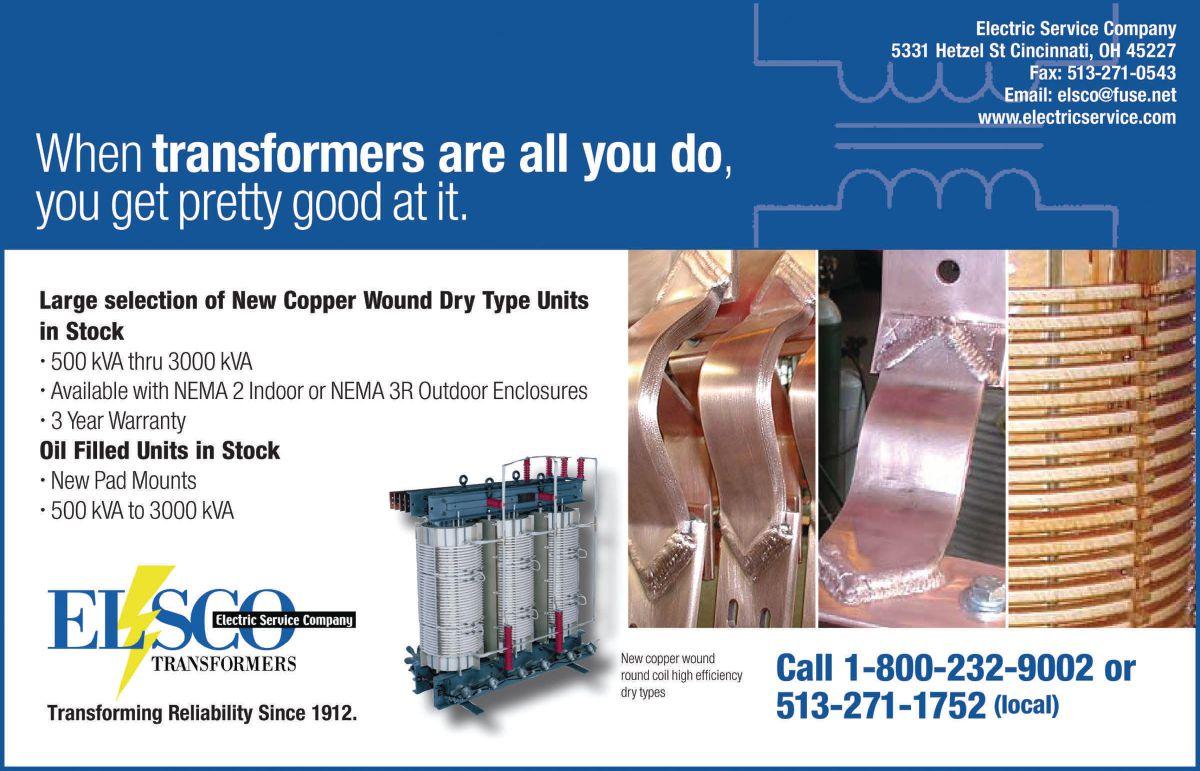
FINLEY LEDBETTER: ‘NETA Will Bring Together People From All Over The World’
BY CARLA KALOGERIDIS, NETA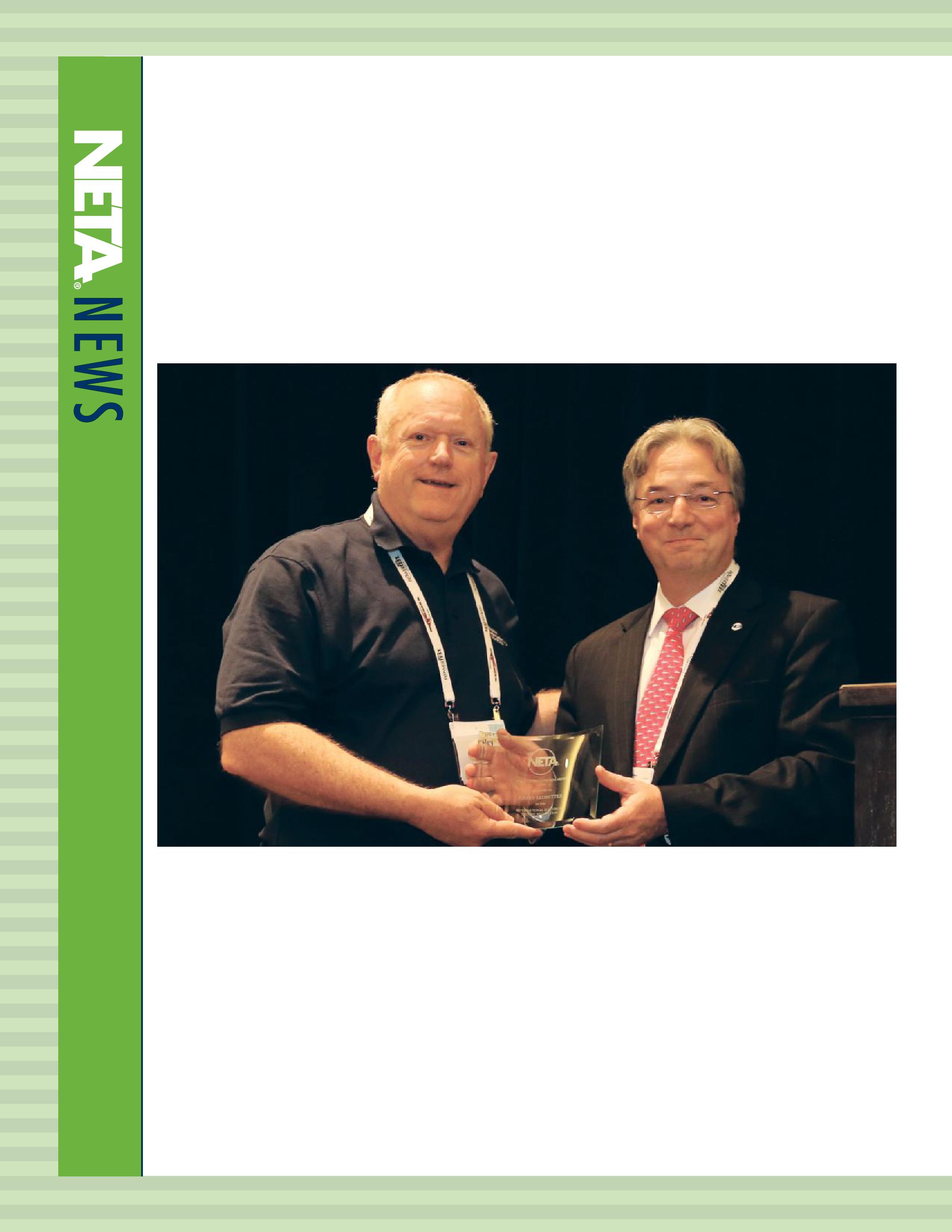
NETA 2016 Alliance Recognition Award honoree Finley Ledbetter is an ideas man, an entrepreneur at heart. But as good as he is with numbers and recognizing a great business opportunity, Ledbetter has always put people first.
Bill Schofield, president of Ledbetter’s flagship company, Circuit Breaker Sales (CBS), has worked for Ledbetter for 18 years. In July 1998, Ledbetter purchased Schofield’s former company, Astro Power
Systems. “I believe he hired me to be quarterback, but then made me coach and waterboy also,” Schofield says.
Schofield remembers the day he interviewed with CBS. Finley was giving him a tour, and they happened upon a delivery driver. Ledbetter had heard that the driver was in an on-the-job accident the day before. Schofield was impressed by Ledbetter’s sincere concern for the driver without a mention about the damage to the company truck. “You could see the genuine concern
Congratulations! Finley Ledbetter receives the 2016 Alliance Recognition Award from Jim Cialdea.on his face making sure that the driver was OK,” Schofield says.
The driver assured Ledbetter that he was fine, but confessed that the truck was messed up. Schofield recalls that Finley casually replied, “Well, you were wanting a new truck anyhow, so I guess you better go get one.”
“I was very impressed with the fact that Finley only cared about his people, not his stuff,” Schofield says, “and to this day, I think it is the same.”
Schofield says Finley is an excellent businessman and has “a great mind for numbers, ideas, and execution.” He is not afraid to take a chance, nor too proud to admit when something is not working.
“Over the last decade, Finley has hired lots of great, talented folks and given them the freedom to champion their own segments of the business,” Schofield says. “I am proud to call him my partner in several businesses and my friend in life.”
FUTURE OF NETA
The Alliance Recognition Award is NETA’s way of honoring worthy contributors to the electrical testing industry — people like Finley Ledbetter who have not only been dedicated supporters of NETA and the work of the association, but also have furthered the industry and inspired others to do the same. Presented annually at PowerTest, this year’s honor went to Ledbetter in recognition of his example of how to achieve personal success, take good care of employees and customers, and still have time to devote to making the industry stronger.
Ledbetter accomplished much of his work for the industry as a long-time supporter of NETA, including presenting and sponsoring at PowerTest as well as authoring articles. “I’ve come to all of the NETA conferences since the second one in 1977,” Ledbetter says. “I started as one of the youngest, and now I’m one of the oldest.”
Over the last 10 years, NETA has really upped its industry presence and leadership, Ledbetter says. “NETA has become a serious technical organization where it doesn’t matter who you are, but what you do,” he explains. “If you bring value to the group through good ideas, you’ll have stature.”
Ledbetter believes the next 10 years will develop
NETA into more of a worldwide organization. “When you look at how far it’s come to date, it’s certainly possible, and it’s what needs to happen,” he says. “I see the future of NETA as bringing together people from all over the world.”
A SOLUTIONS-DRIVEN LEADER
Finley Ledbetter has worked in power engineering for 35 years, including serving as an applications engineer and instructor for the Multi-Amp Institute. He was instrumental in founding Shermco Engineering Services Division, a division of Shermco Industries, which later became a NETA Accredited Company.
In 1982, Ledbetter founded Group CBS, Inc., which now owns 12 circuit breaker service shops in the United States. He is a member of IEEE and his company, Circuit Breaker Sales Co., Inc., is a NETA Corporate Alliance Partner. In addition, Ledbetter is a charter member and past president of Professional Electrical Apparatus Recycler’s League (PEARL), bringing to the organization the quality standards he had already established at his own company. He was a key contributor to the PEARL standards.
In presenting the NETA Alliance Award to Ledbetter at PowerTest 2016, Jim Cialdea, Owner and CEO of 3-C Electrical Company, underscored Ledbetter’s role in establishing the used equipment market. “Finley worked to take the used equipment industry to a higher standard of quality,” Cialdea says. “He was one of the first to put time, effort, and money into developing procedures that redefined the reconditioned, remanufactured industry.”
“As an ideas guy and an entrepreneur, Finley is motivated when he sees a need to develop a product or service solution,” Cialdea says. “He is a guy you can count on, someone who puts 150 percent into everything he does.”
Schofield emphasizes that Finley is not looking for awards or pats on the back; rather, he seeks a higher personal satisfaction. “When one of our customers brags that we solved their problem when nobody else could or that we spent hours on R&D to figure something out, that is what makes Finley smile,” Schofield says. “He is constantly thinking of new and innovative ways to approach things in our electrical segment. There is no other equivalent individual who puts as much energy, effort, and brainpower into the industry as Finley does.”
FOCUSED ON FAMILIES
Cialdea describes Ledbetter as laid back, unpresumptuous, and softspoken, someone who likes to have fun and is a huge basketball fan. He is husband to Joni Ledbetter and father to three sons and a daughter. All four of his children are involved with Group CBS — in different capacities and in different companies — although daughter Ashley McWhorter says he “gave us a lot of choices, and we all had opportunities to go do other things.”
Growing up, McWhorter remembers her father traveling a great deal, building the Group CBS companies. “Now, working for him, you see how hard he works and see him in a whole new light,” she says. “It is amazing and enlightening to see all the things he has accomplished over some 30 years, including how he took care of our family growing up as well as the hundredsoffamiliesthatworkforhim.” hundreds of families that work for him.”
McWhorter says her father is always busy and not one to take stock of what he has accomplished or what he contributes. “He just keeps moving and creating,” she says. McWhorter adds that the Alliance Recognition Award “means a lot to him, and even though he doesn’t say much about it, you know what he is feeling.”
McWhorter says her father is happiest when surrounded by family — especially when he and wife Joni are on their way to the ranch for the weekend knowing all the kids and grandkids will be heading there, too. “He loves to watch Mom driving her bulldozer, the kids feeding the cows, and the grandkids chasing frogs,” she says. “If he can find the elusive golden circuit breaker, that will be just the icing on the top.”
Carla Kalogeridis is part of the NETA World Journal editorial team.
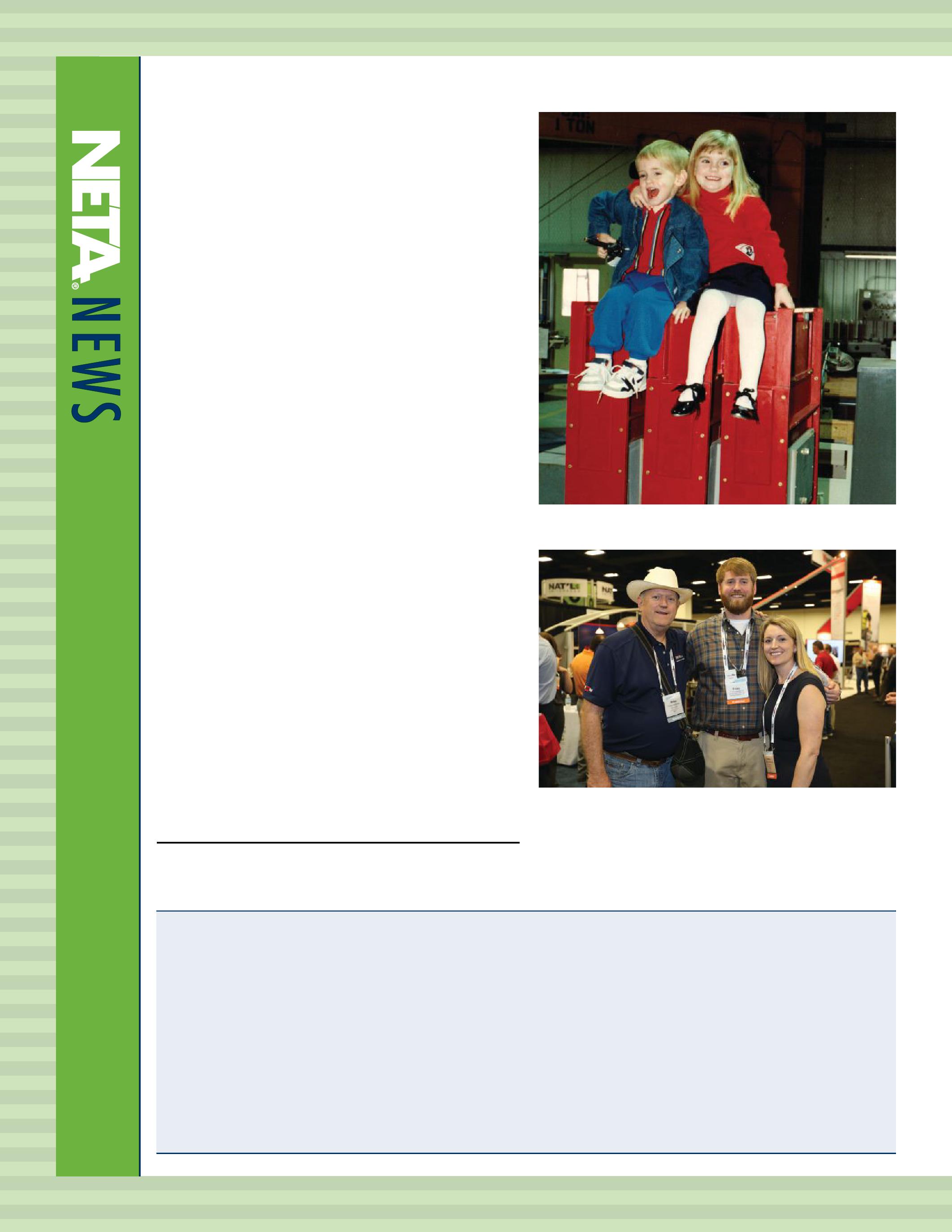
Finley, Finley III, and daughter Ashley Ledbetter McWhorter at PowerTest 2016. Finley keeps his family close. All of his children are involved in the Group CBS businessesandareSMEs. businesses and are SMEs.
Meet Finley Ledbetter, NETA’s 2016 Alliance Partner Honoree
Over the years, Finley Ledbetter has started and sold more than 40 companies, including well-known organizations like Instel and Sentinel Power Services. In fact, he is connected in one way or another to numerous NETA Alliance Companies and industry suppliers.
Ledbetter graduated with a degree in electrical engineering from the University of Texas, Arlington. While still in college, Ledbetter interned at Multi-Amp and later ADE, and was hired by the firm upon graduation. From there he went to Round House, and then on to Shermco Industries where he developed its Engineering Services Division. In 1982, he became a founding partner in Group CBS and currently leads 17 Group CBS companies. Finley Ledbetter is still focused on coming up with the next idea.
Finley gets children involved in the business early.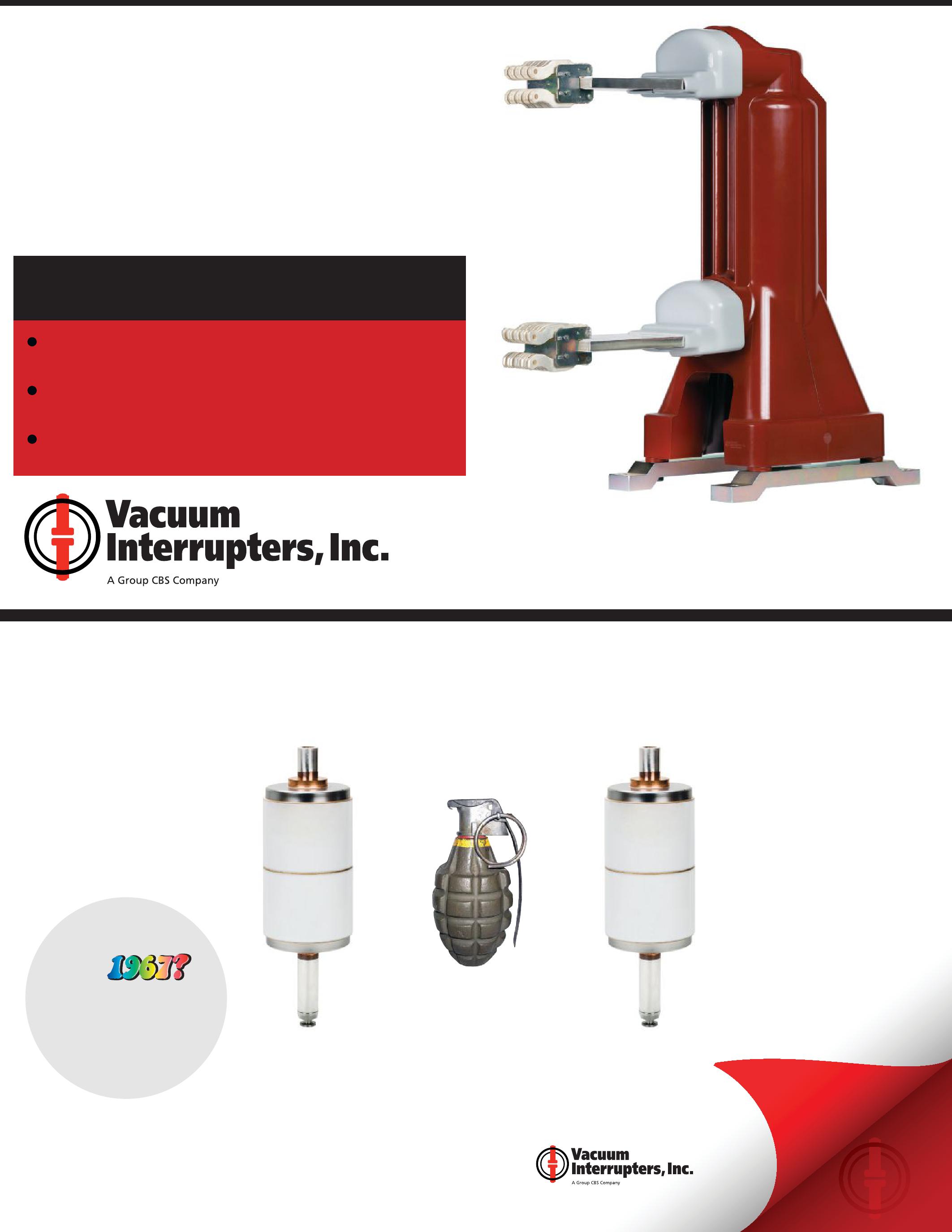
Extend their life, avoid downtime, and save $$$ with NEW Encapsulated Pole replacement assemblies
EXTEND THE LIFE OF YOUR POWER/VAC® CIRCUIT BREAKERS WITH NEWENCAPSULATED POLES
EPOXY-ENCASEDPOLESRESISTCONTAMINATION,MOISTURE, ANDOTHERADVERSE ENVIRONMENTALCONDITIONS
EXTENDSTHE LIFE OFYOURBREAKER,ALLOWINGRE-USE OF TRUSTED USA-MADE MECHANISM
FUTURE MODELSWILLACCOMMODATE ALL POWER/VAC® RATINGSUPTO27kV AND63kA
781-767-0888
Email: infrared.ma@verizon.net
152 Centre Street Holbrook, MA 02343 www.Infraredbps.com
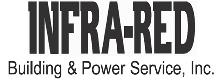

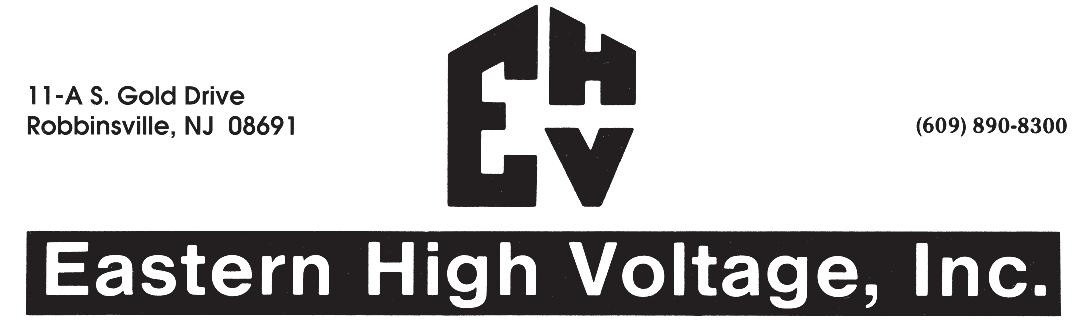







DEEP IN THE HEART OF TEXAS, POWERTEST 2016 COMES TO FORT WORTH
As they say, “Everything’s bigger in Texas,” — which this year, included the opportunities for learning at PowerTest 2016, held in the state’s fifth-largest city, Fort Worth.
PowerTest attendance continues to grow each year, with record numbers in 2016. Individuals attending PowerTest are the boots on the ground as well as the messengers who take information, technology, and solutions gathered at PowerTest back home to their companies. PowerTest is recognized as one of the best educational and networking events in the electrical power testing industry.
Fort Worth shares several common traits with the electrical power testing industry. For example, Fort Worth is a community ready to take on modern challenges for expansion and growth. Its cattle and oil heritage is interwoven with an array of diverse industries that make the city an exciting place to live and visit.
Similarly, this premier electrical maintenance and safety event brings together industry experts who
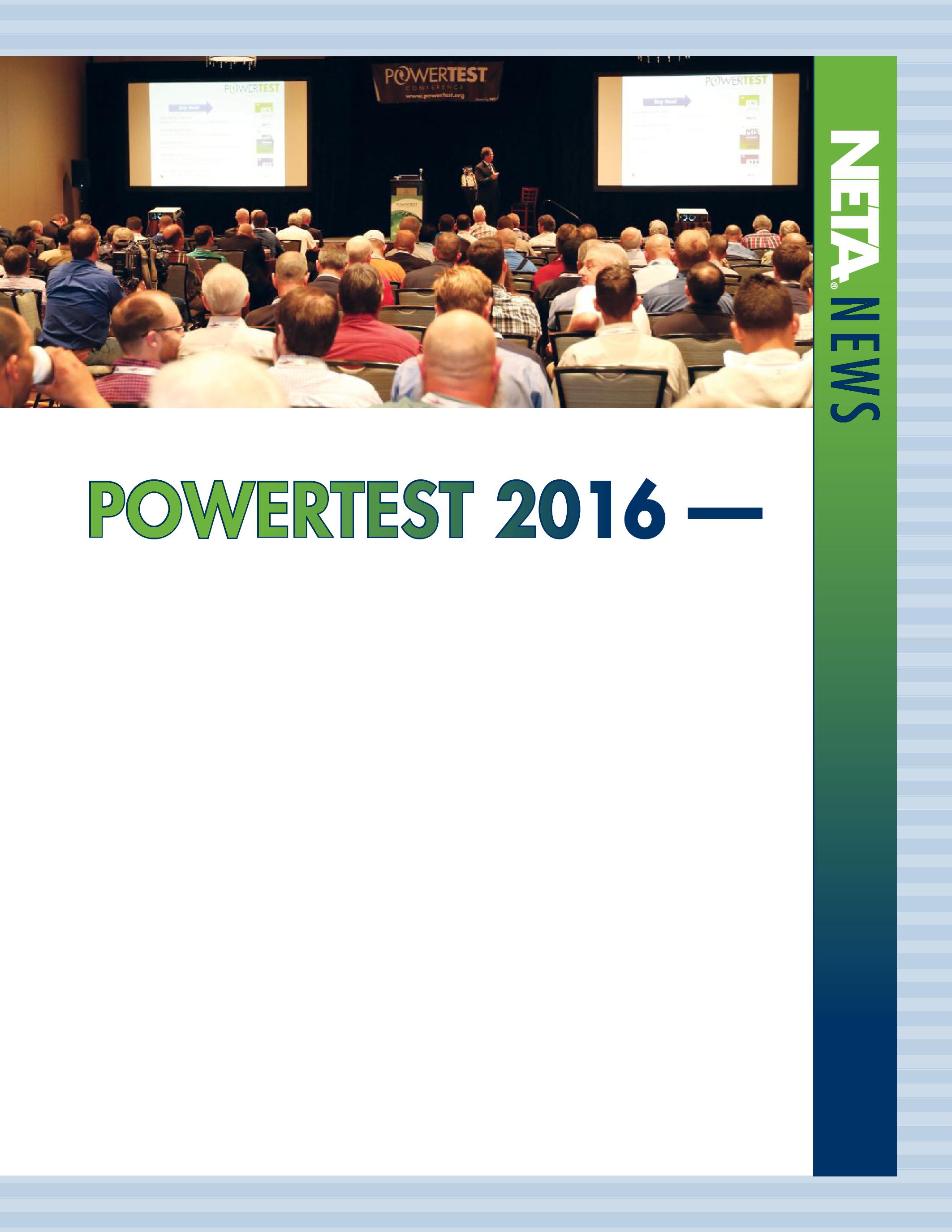
have traveled its winding history to build a stronger electrical power industry with technicians, engineers, and professionals fiercely committed to education and improving the industry. This year’s technical session line-up helped industry professionals grab the bull by the horns and ride to the top of their game.
POWERTEST MONDAY
Monday morning, the registration area is energized as attendees converge for a week of high-powered learning, networking, and a fabulous breakfast sponsored by Circuit Breaker Sales. After filling up on omelets and coffee, attendees sauntered into the Welcoming Address from Conference Chair Ron Widup. Ron reminded everyone to be safe, explained the week’s order of events, and introduced Keynote Speaker Gary Norland.
Gary Norland, survivor of a horrific 12,500 volt 200 amp overhead power line shock, shared his unforgettable story to a filled room. Gary emphasized his message that hard work and dedication to your job should be a focus — but not your only focus.
Ron Widup, PowerTest Conference Chair, welcomes a packed opening session.The impact of an injury goes beyond the physical challenges, impacting not only you but your friends and family in ways you cannot imagine. He wants people to understand that if you don’t take safety seriously, your life could resemble his inlessthanasecond. in less than a second.
Following the opening sessions, attendees broke into smaller segments for a total of 28 technical presentations available in five different tracks: Electrical Safety, Reliability, Equipment, Circuit Breakers, and Electrical Commissioning. These tracks pack a lot of information into each 45-minute presentation, in addition to a four-hour symposium where attendees can participate in discussion led by a moderator and panel of subject matter experts. This year, Ron Widup led the Technical Reports Symposium, providing attendees an opportunity to interact with subject-matter experts on technical report writing, structure, readability, and professional style and framework.
In the midst of this packed schedule, NETA MembersandAlliancePartnersfindalittletime Members and Alliance Partners find a little time to relax and enjoy a meal together during the NETAMemberandAllianceLuncheon.This NETA Member and Alliance Luncheon. This eventfeaturestechnicalroundtablediscussions event features technical roundtable discussions that are summarized and reported on during dessert.Thisisalsothevenuethathoststhe dessert. This is also the venue that hosts the annual NETA Alliance Recognition Award foranAlliancePartnerwhohasdemonstrated for an Alliance Partner who has demonstrated exceptional dedication to bettering the industry through service to NETA. This year, Finley Ledbetter, founder of Group CBS, Inc., was called to the stage and recognized for his many years of dedication to the industry and his contributions toNETA. to NETA.
Additionally, the NETA Outstanding Achievement Award is presented to a NETA Member who, despite daily responsibilities at a full-time job, hascreatedtimeinhisscheduletoadvancethe has created time in his schedule to advance the association toward fulfilling NETA’s mission. These contributions can be technical or organizational, and are often both. Jim Cialdea, Owner and Chief Executive Officer of 3-C Electrical, was honored to accept this award for his role on the NETA Board of Directors, and as NETA’s First Vice President,
Alliance Committee Chair, and member of the Membership Review Committee, Technical Exam Committee, and Standards Review Council.
Attendeesreconvenedinthemainballroomfor Attendees reconvened in the main ballroom for the New Product Forum before heading upstairs to the 11 excellent hospitality suites hosted by BCS Switchgear, Inc.; Doble Engineering Company; Electric Power Systems; Electro Rent Corporation; Group CBS, Inc.; IBEW LU 269; Megger and AVO Training Institute, Inc.; Protec Equipment Resources; RESA Power Solutions; Shermco Industries; and SMC International. Each year, suite hosts up the ante with more creative ideas to entice attendees through their doors, and this year was no exception. A winnertakes-all casino night, performances from Patsy Cline and Dolly Parton entertainer look-a-likes,
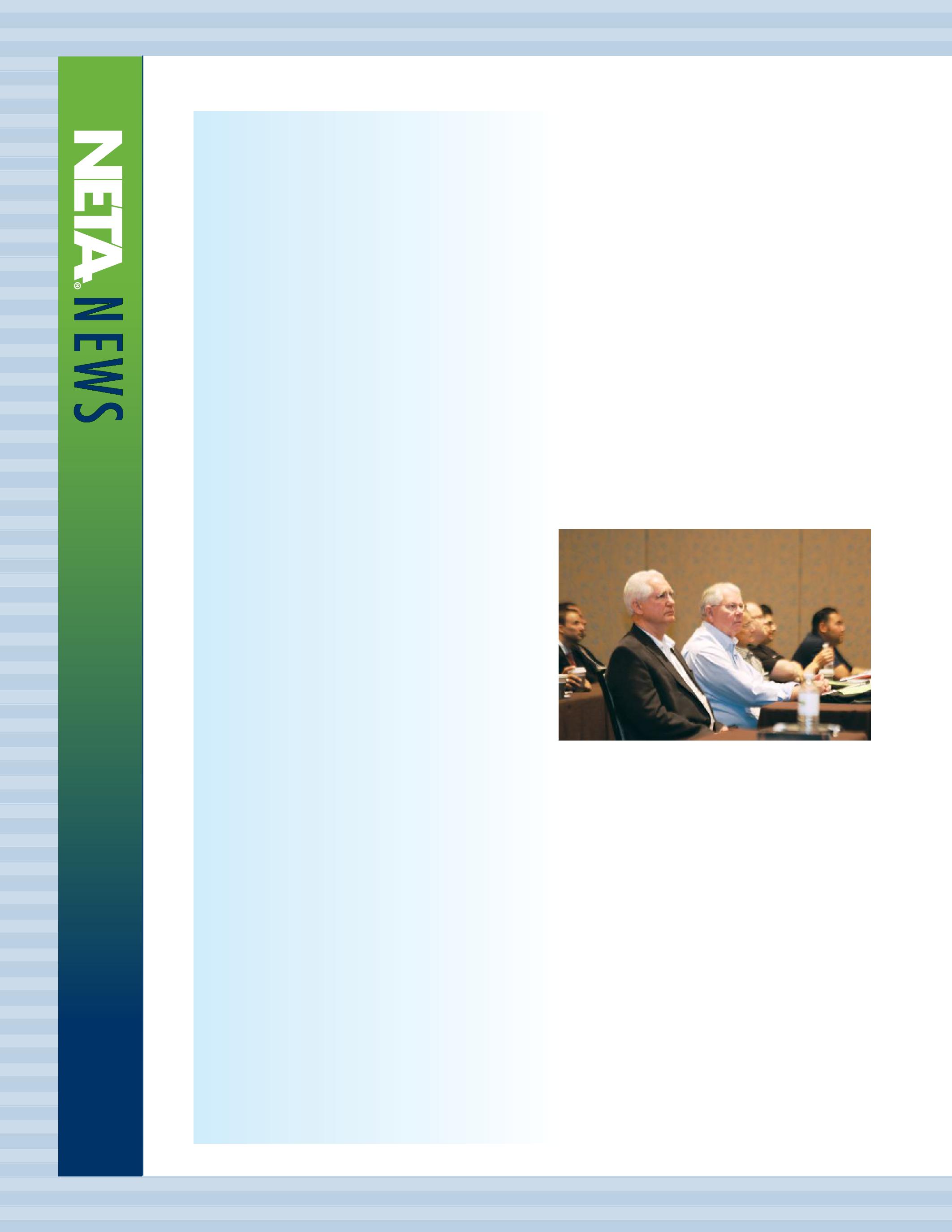
PowerTest attendees participate in Monday’s technicaltracks. technical tracks.
a kick-up-your-heels-and-dance blues band, and the Dallas Mav ManiAACs were just some of the thrilling attractions this year. Attendees had a lot of fun while creating new relationships and reconnecting with business associates and friends, making this night a favorite among attendees and hostsalike. hosts alike.
POWERTEST TUESDAY
Tuesday, attendees gathered again for a day of technicaldiscussionswithanotherbreakfast technical discussions with another breakfast sponsored by Group CBS, which flowed right into four panel sessions: Electrical Safety, Cable Testing, Circuit Breaker Maintenance, andProtectionandControl.Panelistsworked and Protection and Control. Panelists worked
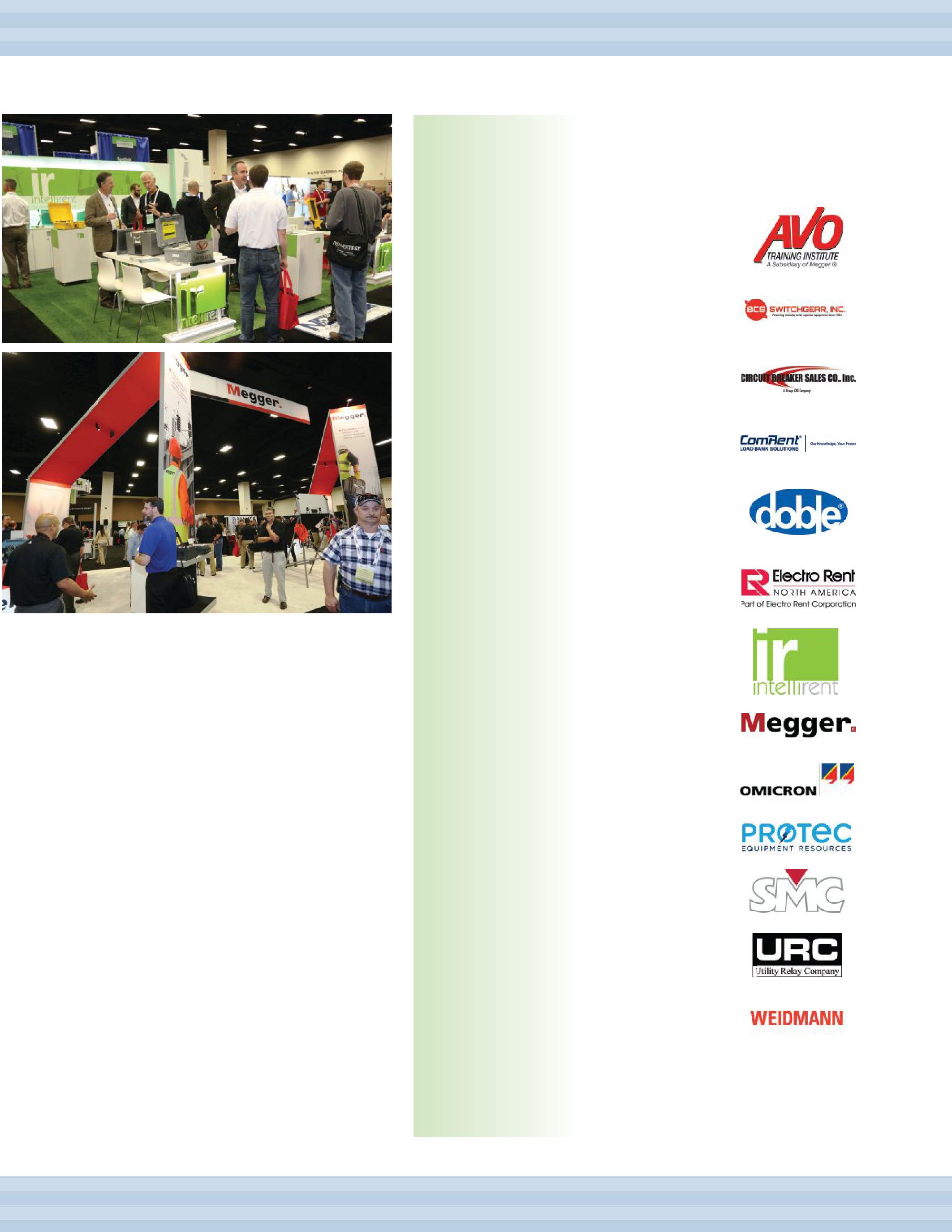
The PowerTest 2017 Trade Show featured over 100 booths displaying the latest in leading technology.
in tandem with attendees during these sessions, creating lively conversation to address realworld problems faced in the field and providing real-world solutions to take home and apply. Rooms were filled with people engaging in Q&A and learning from each other.
Lunch was provided at the PowerTest Trade Show, where attendees dined on gourmet sandwiches and desserts as they traversed the carpeted aisles of the convention center. This may be the biggest event of the entire conference and where most business is conducted for attendees and vendors alike. New products and technologies waited around every corner, along with knowledgeable sales reps eager to help.
The PowerTest Trade Show was held at the Fort Worth Convention Center, just across the street from the Omni Hotel. Each year, this event features industry leaders at the Spotlight
THANK YOU TO NETA’S CORPORATE ALLIANCE PARTNERS!
POWERTEST 2016 – SPOTLIGHT STAGEPRESENTATIONS STAGE PRESENTATIONS
AVOTRAININGINSTITUTE AVO TRAINING INSTITUTE
TITLE:HOWIMPORTANTISELECTRICAL TITLE: HOW IMPORTANT IS ELECTRICAL EQUIPMENTMAINTENANCE? EQUIPMENT MAINTENANCE?
BCSSWITCHGEAR BCS SWITCHGEAR
TITLE:NEWSONMOLDEDCASEAND TITLE: NEWS ON MOLDED CASE AND INSULATEDCASESWITCHGEAR INSULATED CASE SWITCHGEAR
CIRCUITBREAKERSALES CIRCUIT BREAKER SALES
TITLE:CHANGESINTHECONSTRUCTION& TITLE: CHANGES IN THE CONSTRUCTION & DURABILITYOFCIRCUITBREAKERS:FROM DURABILITY OF CIRCUIT BREAKERS: FROM STICKS&STONESTOCARBONFIBER. STICKS & STONES TO CARBON FIBER.
COMRENTINTERNATIONAL COMRENT INTERNATIONAL
TITLE:HIGH-DEFINITION TITLE: HIGH-DEFINITION COMMISSIONING—PART2 COMMISSIONING — PART 2
DOBLEENGINEERING DOBLE ENGINEERING
TITLE:IMPROVINGELECTRICALSYSTEM TITLE: IMPROVING ELECTRICAL SYSTEM ASSESSMENTSTHROUGHIN-SERVICE ASSESSMENTS THROUGH IN-SERVICE SURVEYINGSOLUTIONS SURVEYING SOLUTIONS
ELECTRORENT ELECTRO RENT
TITLE:TESTEQUIPMENT TITLE: TEST EQUIPMENT ACQUISITION METHODS, INCLUDING AFINANCIALPERSPECTIVE A FINANCIAL PERSPECTIVE
INTELLIRENT
TITLE:THELATESTANDGREATESTIN TITLE: THE LATEST AND GREATEST IN ELECTRICALTESTING ELECTRICAL TESTING
MEGGER
TITLE:TRAX—TRANSFORMERANDSUBSTATION
TITLE: TRAX — TRANSFORMER AND SUBSTATION TESTSYSTEM TEST SYSTEM
OMICRON
TITLE:AGUIDEDWORKFLOWAPPROACHTO TITLE: A GUIDED WORKFLOW APPROACH TO TRANSFORMERDIAGNOSTICTESTING TRANSFORMER DIAGNOSTIC TESTING
PROTEC EQUIPMENT RESOURCES
TITLE:BATTERYTESTINGMETHODOLOGIES
TITLE: BATTERY TESTING METHODOLOGIES
SMCINTERNATIONAL SMC INTERNATIONAL TITLE:FINDOUTWHATYOURMICRO TITLE: FIND OUT WHAT YOUR MICRO OHMMETERISMISSING OHMMETER IS MISSING
UTILITYRELAYCOMPANY UTILITY RELAY COMPANY
TITLE:ADVANCINGLOW-VOLTAGECIRCUIT TITLE: ADVANCING LOW-VOLTAGE CIRCUIT BREAKERRETROFITPROTECTIONTECHNOLOGY BREAKER RETROFIT PROTECTION TECHNOLOGY
WEIDMANN
TITLE:MOISTUREININSULATIONAND TITLE: MOISTURE IN INSULATION AND TRANSFORMERDRYOUT TRANSFORMER DRYOUT
Spotlight Stage Presentations can be downloaded from the netaworld.org website under the Corporate Alliance Tab
Stage. Thirteen presentations were given by NETA's Corporate Alliance Partners. The event included presentations by AVO Training Institute, Inc.; BCS Switchgear, Inc.; Circuit Breaker Sales Co., Inc.; ComRent International; Doble Engineering Company; Intellirent;, Megger; Protec Equipment Resources; SMC International; Utility Relay Company; and Weidmann Electrical Technology Inc. (Editor’s note: For more information on the Spotlight Stage on presentations, see sidebar.)
Each year, exhibitors raise the bar with their booths, and it is always a great time to meet new people and connect with old colleagues. One of the highlights of the Trade Show is a door-prize
raffle that takes place at the end of the show. This year's winners were not disappointed with the excellent offerings from exhibitors as well as from NETA, including an Apple iPad and $500 cash.
Following the PowerTest Trade Show, everyone headedbacktothehotelforthePowerBash headed back to the hotel for the PowerBash Awards Reception and Dinner, and the turnout was impressive to say the least. Thanks go out to Karl Zimmerman and his band for providing the musical backdrop for a smorgasbord of food, drinks, and desserts. Over 400 people attended 400 the event and were present to congratulate this year's recipients of the awards for Technical Presentations, Trade Show Exhibitors, and Hospitality Suites. Congratulations to all!
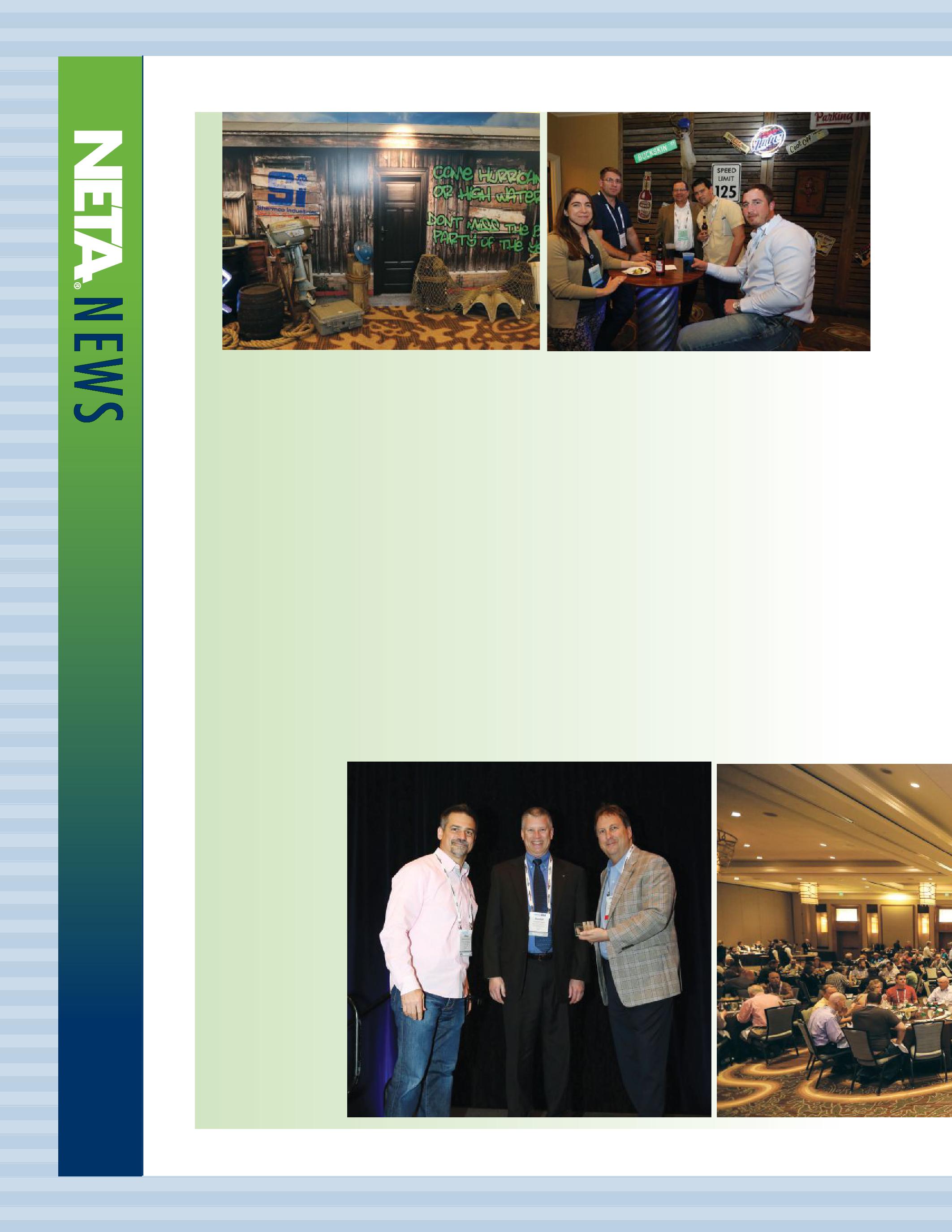
PowerBash2016 PowerBash 2016 was an evening of grand food, best of the show awards, dancing, and professional comradery.
An exciting evening of hospitality suites was hosted by 11 industry leaders.PowerBashmarkstheendofthefirsttwo PowerBash marks the end of the first two whirlwind days of technical and social events, and the beginning of three more days of technicalseminars.It'ssortoftheseventhtechnical seminars. It's sort of the seventhinning stretch of PowerTest, the pause before the more intense educational innings to come.
POWERTEST WEDNESDAY, THURSDAY, AND FRIDAY
Wednesday and Thursday have always featured Thursday four-hourtechnicalseminarsthatoffer four-hour technical seminars that offer attendees a more thorough exploration of various subject matters. Attendees gain handson experience applying and troubleshooting relays for transformers and distribution lines.
On Friday, Doble Engineering Company added one more day of learning with its Laboratory Seminar.Theseminarofferedattendeesan Seminar. The seminar offered attendees an interactive experience, combining theoretical background with practical experience and hands-on examples, including case studies illustrating common problems found in the field. People were eager to participate in this event, and more than 60 people attended.

TRADE SHOW EXHIBITION WINNERS
MOSTINNOVATIVE MOST INNOVATIVE —MADDOXINDUSTRIALTRANSFORMER — MADDOX INDUSTRIAL TRANSFORMER
MOSTVISITED MOST VISITED — CIRCUIT BREAKER SALES CO., INC. BESTINSHOW BEST IN SHOW — MEGGER/AVO TRAINING INSTITUTE, INC.
TECHNICAL PRESENTATIONS WINNERS
SAFETY —ARC-FLASHMITIGATIONBYTRANSFORMER — ARC-FLASH MITIGATION BY TRANSFORMER DIFFERENTIALRELAYPROTECTION DIFFERENTIAL RELAY PROTECTION
PRESENTERS: MOSE RAMIEH III, PGTI, A CE POWER COMPANY, AND RANDALL SAGAN, MBUSI
RELIABILITY —IMPROVINGSAFETYTHROUGH — IMPROVING SAFETY THROUGH PARTIALDISCHARGESURVEYING PARTIAL DISCHARGE SURVEYING
PRESENTER: TONY MCGRAIL, DOBLE ENGINEERING COMPANY
CIRCUITBREAKERS CIRCUIT BREAKERS —VACUUMINTERRUPTERS: — VACUUM INTERRUPTERS: PRESSUREVS.AG E—ASTUDYOFVACUUMLEVELSIN PRESSURE VS. AGE — A STUDY OF VACUUM LEVELS IN 314SERVICEAGEVACUUMBREAKERS 314 SERVICE AGE VACUUM BREAKERS
PRESENTER: FINLEY LEDBETTER, GROUP CBS, INC.
EQUIPMENT —UNDERSTANDINGTRANSFORMER — UNDERSTANDING TRANSFORMER DIFFERENTIALPROTECTION DIFFERENTIAL PROTECTION
PRESENTER: WILL KNAPEK, OMICRON ELECTRONICS CORP. USA
COMMISSIONING —ELECTRICALCOMMISSIONINGTIPSAND — ELECTRICAL COMMISSIONING TIPS AND TRENDSFORADVANCEDCRITICALFACILITIESAPPLICATIONS TRENDS FOR ADVANCED CRITICAL FACILITIES APPLICATIONS
PRESENTER: CORY DOZHIER, ORACLE
BESTOVERALL BEST OVERALL —HOWDISRUPTIONSINDCAND — HOW DISRUPTIONS IN DC AND COMMUNICATIONSAFFECTPROTECTION COMMUNICATIONS AFFECT PROTECTION
PRESENTER: KARL ZIMMERMAN, SCHWEITZER ENGINEERING LABORATORIES, INC.
HOSPITALITY SUITE WINNERS
MOSTCREATIVE MOST CREATIVE —SHERMCOINDUSTRIES — SHERMCO INDUSTRIES
MOSTAPPETIZING MOST APPETIZING —PROTECEQUIPMENTRESOURCES — PROTEC EQUIPMENT RESOURCES
MOSTTECHNICAL MOST TECHNICAL — GROUP CBS, INC.
MOSTENTERTAINING MOST ENTERTAINING — BCS SWITCHGEAR, INC.
MOSTHOSPITABLE MOST HOSPITABLE — MEGGER/AVO TRAINING INSTITUTE, INC.
POWERTEST 2016 SELFIE-PHOTO
CONTEST WINNERS
GRANDPRIZEWINNER: GRAND PRIZE WINNER:
MOSE RAMIEH III, PGTI, A CE POWER COMPANY
SECONDPLACEWINNERS: SECOND PLACE WINNERS: TOM WARNING, SHERMCO INDUSTRIES
ELECTRORENTPOWERTEST2016TEAM ELECTRO RENT POWERTEST 2016 TEAM
SARAH BAUMANN, MEGGER
Tuesday’s panel sessions featured lively discussions on Electrical Safety, Cable Testing, Circuit Breaker Maintenance, and Protection & Control.
POWERTEST 2016
PowerTest 2016 was the best yet. PowerTest attendees, speakers, sponsors, and exhibitors all contributed to making the event a tremendous success.NETAwouldliketothankeachand success. NETA would like to thank each and every one of you who contributed to this success by participating, speaking up, and energizing your futureatPowerTest2016. future at PowerTest 2016.
Next year is already shaping up to be a heck of a conference, as PowerTest heads to Anahiem, California, on February 27 – March 3, 2017. Mark your calendars, and make plans to join us next year!

CHOOSE BETWEEN KEEPING MAINTENANCE COSTS DOWN AND KEEPING UP WITH PRODUCTION DEMAND…OR DO BOTH.
THAT’S THE CRITICAL DIFFERENCE.
NETA certified experts at Electrical Reliability Services will keep you in perfect balance.
To ensure the reliability of your electrical power, you have to balance the need to reduce maintenance costs with the need to perform regular maintenance. Only the team from Electrical Reliability Services delivers cost-effective services and system expertise to keep you up and running 24/7.

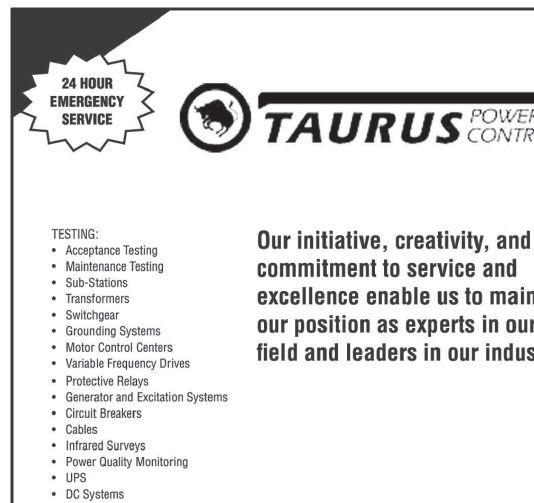

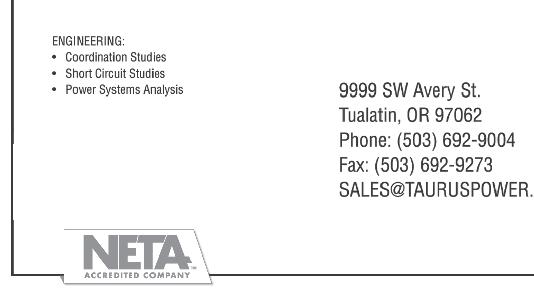
Sertec Can Bring That Relay Back to Life
Sertec Relay Services buys and sells protective relays and specializes in extending the life of obsolete electromechanical relays by providing quality repair, remanufacture, and retrofit services for relays of all types and manufacture. We also service specialty electronics used in electrical power systems.
Instantaneous Overcurrent Relays
Time Overcurrent Relays
Directional Overcurrent Relays
Undervoltage Relays
Frequency Relays
Distance/Impedance Relays
RELAY MANUFACTURERS
General ElectricTM
WestinghouseTM
ABBTM
BaslerTM
Differential Relays
Reverse Power Relays
Phase Balance Relays
Schweitzer-SELTM
GE MultiLinTM, and more!
* Third-party trademarks are the property of their respective owners
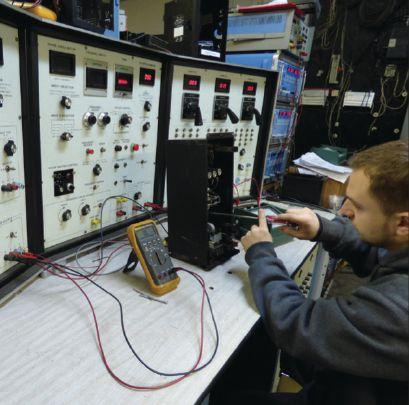
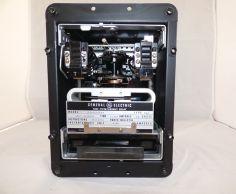



AS A TOOL FOR PROTECTION TESTING
SPECIFICATIONS
BY BENTON VANDIVER III, OMICRON electronics Corp. USAOver the past 30-plus years, I have had numerous conversations with technicians, engineers, and managers on how to create the best test plan for many of the relays, protection schemes, and protectionand-control (PAC) systems used in the utility industry.
The discussion generally turned into a lengthy laundry list of what they actually wanted to accomplish during their test process. Some of thetasksmentionedincluded: the tasks mentioned included:
• Proofofcalibration Proof of calibration
• Proof of proper settings
• Proof of the ac system components
• Proof of the dc system components
• Verify the interconnections
• Verify the functions
• Verify the scheme logic
• Verify the overall protection system coordination
For these tasks, the test plan comprised a specific list of the test methods and steps required to accomplish them. For the proof-of tasks in electromechanical devices and systems, the steps were essentially specified by the manufacturerinthedeviceinstructionmanual manufacturer in the device instruction manual and any special publications dealing with maintenancetasksorcalibration.Fornewer maintenance tasks or calibration. For newer technologies, these specifications evolved to more black-box testing designed to prove the device specifications or troubleshoot the device’s components and calibration, since typically, the setting parameters were directly set or displayed
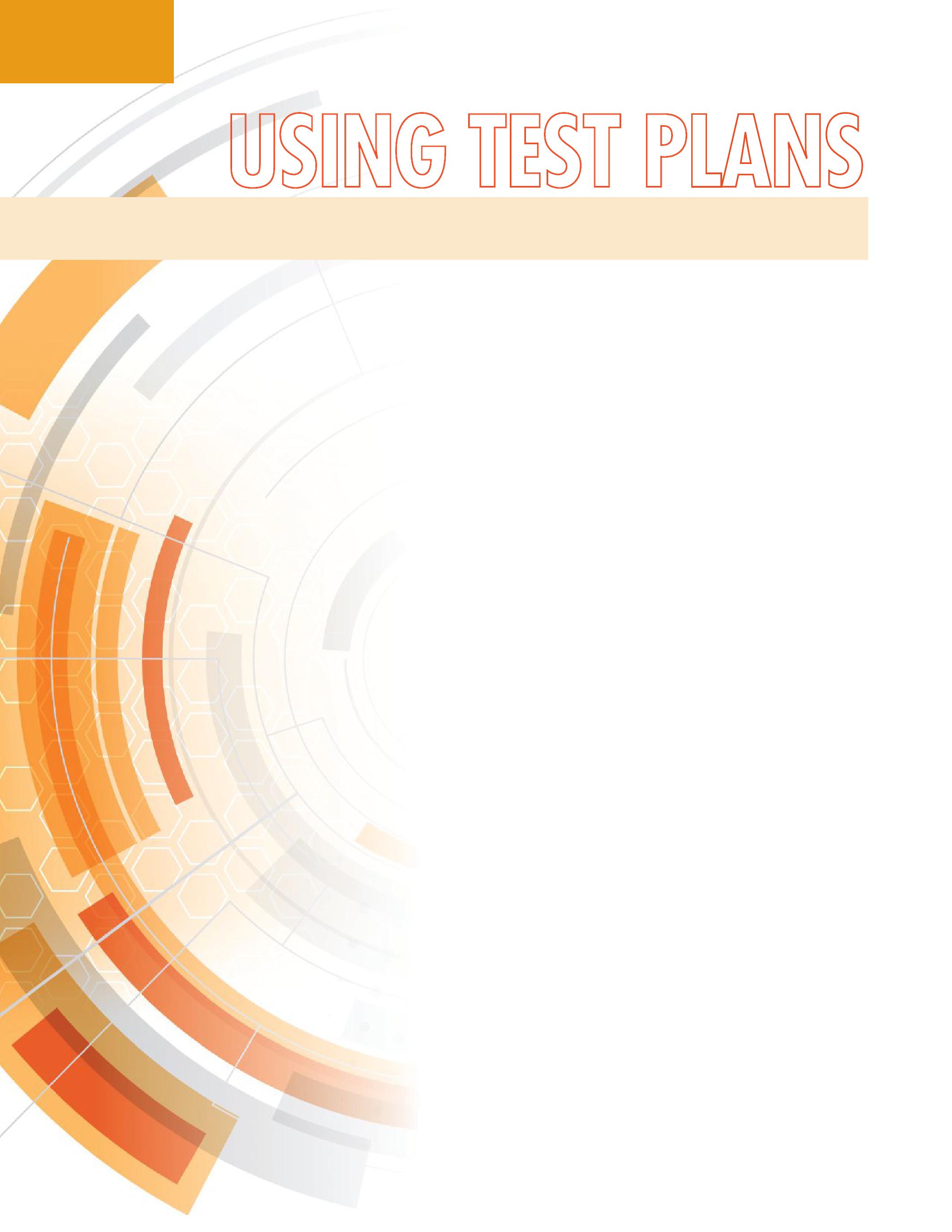
physically on the device. In the newest digital technologies, this has been supplanted by software programming of the parameters and firmware updates, self-diagnostics, observational testing, logs, and reports.
Most often, what was actually desired from the test plan was the least amount of work to satisfy a testing compliance requirement. In addition, they wanted an assurance that the testing performed was sufficient for the task(s) that the tester executed, and that the test procedure was correct, accurate, and repeatable. It was a bonus if the test procedure was self-instructing or automated so that training was minimized, the ultimate goal being the one-button test.
In the past, a working test plan for a PAC device or system was not automatically delivered with it, nor was it made by accident. It evolved from three distinct steps driven by the utility user: 1) The test philosophy implemented by the user 2) The user’s protection philosophy and a generic test plan structure developed from it
3) The user’s final configuration/settings of the Intelligent Electronic Device (IED) or system (Figure 1)
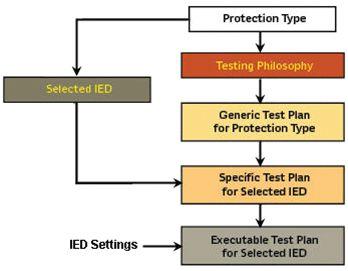
A user’s test philosophy is often based on operational history — usually scenarios of specific device misoperations from a variety of causes — as well as compliance issues, manufacturer guidelines, and industry standards. Often, the philosophy was known but not always documented effectively and was internally perpetuated through on-the-job knowledge (e.g., “We always test at 2x, 3x, 4x pickup.”) As PAC technology changed, the testing philosophy adapted slowly or not at all, resulting in unnecessary or improper testing of the new PAC device or system. This also extended to:
• Test equipment used
• Tolerance definitions and performance expectations
• Test methods applied
• Proper training (knowledge and skills)
•Documentation of the objectives (compliance, calibration, etc.)
Some examples would be using a one-phase test set on a relay using three-phase algorithms and logic; using electromechanical tolerances on a precision digital device; step-change injections expecting dynamic performance; or no PC/software user skills and expecting oneday training to master the PC-controlled test kit. The proactive user would take all these points into consideration and craft a protection system specification(s) that would clearly convey how the devices and systems should be applied, the test philosophy employed, and how it was to be achieved. It was a
living document continually updated based on current PAC devices and systems in use, compliance requirements, training requirements, and performance expectations.
When a specific protection philosophy was applied, it refined the definition of what was to be tested. Using a basic four-zone step distance scheme as an example, we could construct a generic four-zone step distance test plan of the functions (reclosing, loss of potential, etc.); protection elements (21P, 21G, 50/51, 59, etc.); interfaces (physical I/O, control, etc.); and logic (permissive overreach transfer trip {POTT} and breaker failure, etc.) that should be tested and should include the test equipment, tolerances, and test methods stated in our test specification. At this point, the test plan could be used as a functional test specification (Figure 2) for this type PAC device or system because the What, Why, and How questions should now be known.
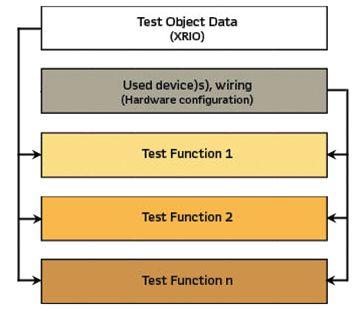
However, we still do not have an executable test plan because we are missing the specific manufacturer device(s) used, the specific configuration parameters, and the specific protection settings that finally dictate the exact testing to be performed. For instance, the specific line being protected may not require a fourth zone element, so the configuration information would indicate it is not used or required. This would mean only three zone elements need to be tested, and any scheme, function, or logic associated with only the fourth zone would be ignored.
FEATURE

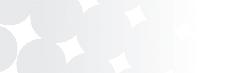
So a mechanism to get these configuration parameters/protection settings into the generic test plan was needed, as these were typically entered manually (today, of course, they are possibly imported electronically.) Often, the parameters used in a specific PAC device vary from manufacturer to manufacturer, even when they perform identical functionality. Further, the actual parameters used to define the test method can be a different data type or mathematical equivalent. So translation of these specific device parameters into test method parameters was another task necessary to create the executable test plan.
Today, many utilities have lost expertise and cannot follow these steps; they increasingly rely on other sources to bridge these gaps. With modern software solutions, the specific IED can be data modeled and parameters imported, then recalculations made and mapped to the functional test module performing the specific defined testing task, including the required hardware interfaces (Figure 3). Additionally, modern test software can use purpose-built test modules or a power system mathematical model to relieve the task of defining individual test methods for each function, element, or logic scheme.
Since the beginning of my career and regardless of the protection devices and/or systems and technology used, there has never been a perfect tool for creating such test plans. The fact is that it requires a deep knowledge and understanding of what it is you are testing. Whether it is an auxiliary dc relay or a modern HV digital line protection IED, or an application like a permissive overreach transfer trip scheme over fiber, understanding what it is designed to do and how it does it is necessary for organizing any of the previous testing tasks successfully.
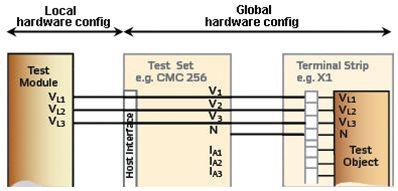
Some may disagree, citing that a good generic test specification can be written from a common denominator (generic) practice, an approach that in turn can generate the required test plan. But I see this as a chickenand-the-egg discussion or Schrodinger’s cat situation: If you do not know the actual device details, how can you possibly test it? Even in the case of the simplest network model, you must understand how it works, its limitations, and the data it requires to function correctly. However, there is no argument in the industry that device technology dictates the test tools and techniques required and that the objective is the proof of the device as applied in situ. So taking the device out of its commissioned state to make functional or element tests indicates lack of good specifications and systems engineering. A properly engineered IED or PAC system will be testable with the correct tools and simulations.
The fact is, there is nothing to test until there is a device or system design, and no design until there is a specification to build it a certain way. So we are back to the specification again. Naturally, one would conclude that whatever this specification is, it should then be used to define the test plan. If we are talking design absolutes like the strength of an I-beam made from different materials, then yes, it could be. For instance, a 10-foot-long oak I-beam may have a design-loading factor of 100 pounds, whereas one made from cold steel might be 1,000 pounds. To prove the design, a simple test would anchor one end of the beam and apply an increasing dead load at the other end until the beam failed. This would be destructive, but necessary to prove the design and specification, and many industries perform these tests.
In PAC systems, we do not typically test them until they fail (we let Murphy take care of that), but we do need to apply best practices in verifying their design and operation prior to implementation and during service life. The other consideration for PAC systems and their devices is the variable nature of designing/applying them.
Most of today’s devices are digital, use communications, and are programmable in configuration and scheme logic, making their testing dependent on their intended application and the specific parameters used (Figure 4). The device specification cannot be used directly for defining the test plan because there are too many variables, overlapping functions, and implementations unique to the manufacturer.

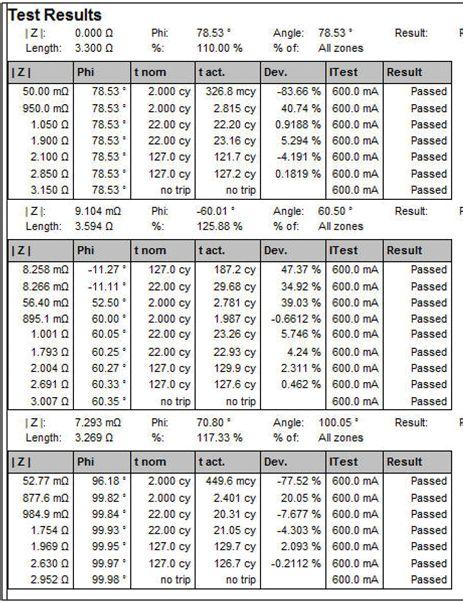
DEVELOPMENT METHODOLOGY
— TEST SPECIFICATION
Further, when we take multiple devices and use them together in PAC systems, the aggregate specifications of all those devices could create conflicting test requirements across the system and, in some cases, damage them if not properly considered. The specific settings/parameters applied based on the intended application restricts them and blends these devices to work together within the PAC system. This provides the details necessary for developing the test plan. Once the test plan is derived according to our required task list and proven against the PAC system configuration, then it can be the basis for extracting the test specification for this specific PAC system implementation.
This methodology could be seen as backwards but for one key point: With the knowledge of the application and the specific parameters of the configured devices, we are able to define a white-box testing environment, one in which we know the output based on the internal responses of the system based components/ devices from known application-based input simulations. In other words, we have a detailed understanding of the devices and system, and therefore, can prepare a proper test plan to prove it. (Figure 5)
The multifunctional design of modern numerical protection devices usually requires different methods to test the different functions integrated ineachofthem.Itisobviousthattodefinethe in each of them. It is obvious that to define the test specification, we need to start with the type of protection being tested.
As mentioned, the test specification depends on the user’s testing philosophy and the regulator’s compliance requirements. It defines what types of tests need to be performed for different types of function elements, schemes, or applications as well as any characteristics of the test method used depending on the purpose of the test: type, acceptance, commissioning, maintenance, etc. (Figure 6).
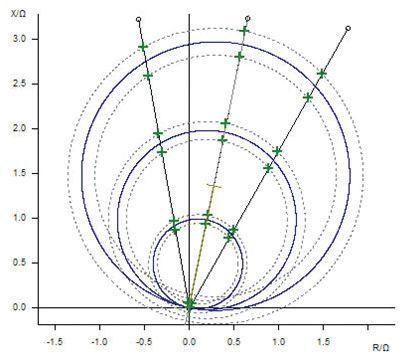
Based on the testing philosophy, a generic test plan can be structured that defines the required test hardware and specific implementation considerationsbasedonthePACdeviceor considerations based on the PAC device or protection IED dependent:
• Interfaces: hardwired voltage, current, I/O or IEC 61850 GOOSE, or sampled values
• Bay configuration (for example, breakerand-a-half) or application configuration (two- ended line model)
Once the generic test specification for a protection type is created as a generic test plan, it can be customized to meet the specific functionality of a selected manufacturer’s IED used for the protection type under consideration and represented then by an IED-specific test plan (Figure 7).
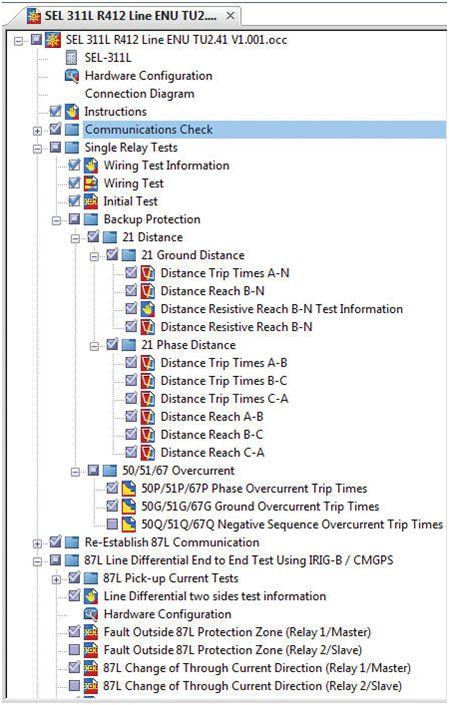
The test specifications must define:
• The functionality of the tested multifunctional protection IED represented by different protection function elements, such as distance, differential, overcurrent, etc.
• The required test devices needed to execute the tests
• The interfaces between the test equipment and the test object
• The test modules (methods) to be executed as required by the testing philosophy
Such an approach allows improvement of the testing process efficiency by defining the required hardware configuration only once at the beginning of the test specification. The hardware configuration represents the signal path between the testing tool and the test object and contains complete information about:
• The assignments between the inputs and outputs of the test software and the test object terminals
• The used test hardware as well as its configuration
• The wiring between the test hardware and the test object terminals
The setting parameters of the test object are also not specified individually for each test module, but only once at the beginning of the executable test plan configuration (Figure 8). The same applies to the generation of a single test report that covers all test results. Any number and type of test modules can be combined into one central document to form a complete test plan that matches the requirements of the functions tested.
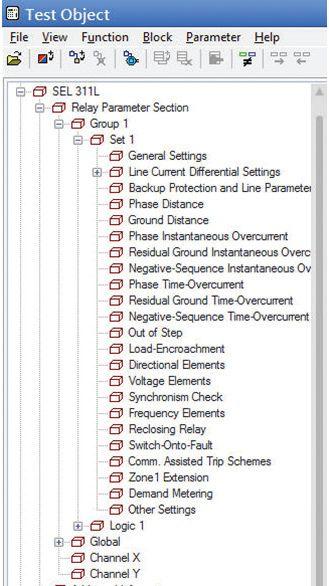
Figure 8: IED Functional Model with Specific Configuration and Settings
The test plan can be executed as an automatic sequence. When running it, the defined test functions of each selected module are executed before the program automatically switches to the next one, until all the modules have been completed. After the completion of the test, the software enters the results into the test plan document, which creates a comprehensive overall test report.
The test report still contains all of the test settings (protection device parameters, test modules used, test points, etc.). Using a protection IED-specific test specification for testing several relays that differ only in their parameter settings (e.g. relays of the same type on different feeders) is substantially simplified since a test plan, once created, only needs minor adjustments.
The fundamental difference between a test plan and a test specification is that a test plan not only tells us how to perform the test, but it also has knowledge of what the test results should be. A generalized test specification cannot contain the specific expected results, only relative parameters like tolerances. When describing to a technician, contractor, or test company via a test specification, the information must be as specific as possible and derived by extracting that specification from successful test plans.
If an independent way existed to describe all the devices, interfaces, communications, logic, and settings used in PAC systems, then our industry could evolve engineering tools to define its many unique applications in a standardized way. In fact, it would be possible to not only self-describe the PAC system as designed, but also provide a mechanism to self-define its test plan based on those defined relationships. You guessed it: That’s IEC 61850.
Although long-coming, IEC 61850 (Ed 2) is approaching a new level of maturity. In Part 6, the Substation Configuration Language (SCL) has grown to encompass more information on PAC devices. This substantially increases the self-description details where the key data and relationships of the configured devices from the SCL can be used. If combining application/test
tool knowledge with the existing SCL data, test plans could be defined directly. Expansion oftheSCLtoincludetestdevicesdescribed of the SCL to include test devices described as logical nodes with data objects and data attributes would enable the goal of creating test plans and test specifications.
A utility using the IEC 61850 data model can define the single line diagram, all functions used, and their logical nodes/data types. From this, a device-independent specification can be made using the System Specification Description (SSD) file with a top-down design that will constrain vendors and system integrators to the utility’s system specification. This means the supplier is not free to make a non-conformant, bottom-up design using their own tags and architecture. Further, with test tool/device extensions of the SCL, the utility could also include the test plan from the SSD with all test processes defined (what to test with expected values) and then easily formalize a conformant test specification from it (an annotated report).
CONCLUSIONS
The ability to create a properly constrained test specification that has value has always been a challenge, but IEC 61850 is poised to deliver on a long-awaited capability — creating a test specification from the top down that includes the functional test plan, too.
The best specification is one that:
• Exists
• Describes what, not how
• Cites relevant industry standards
• Clearly defines testing tasks such as acceptance, commissioning, routine, and maintenance
• Has only one interpretation
• Is available to all parties
• Is the spec agreed to by all parties involved
• Only includes what is necessary
• Is consistent (avoid using “it” or “which” and clearly specify “what”)
• Defines the jargon and abbreviations common within the industry
• Describes the test objectives so a novice can understand them

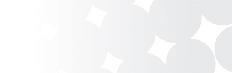
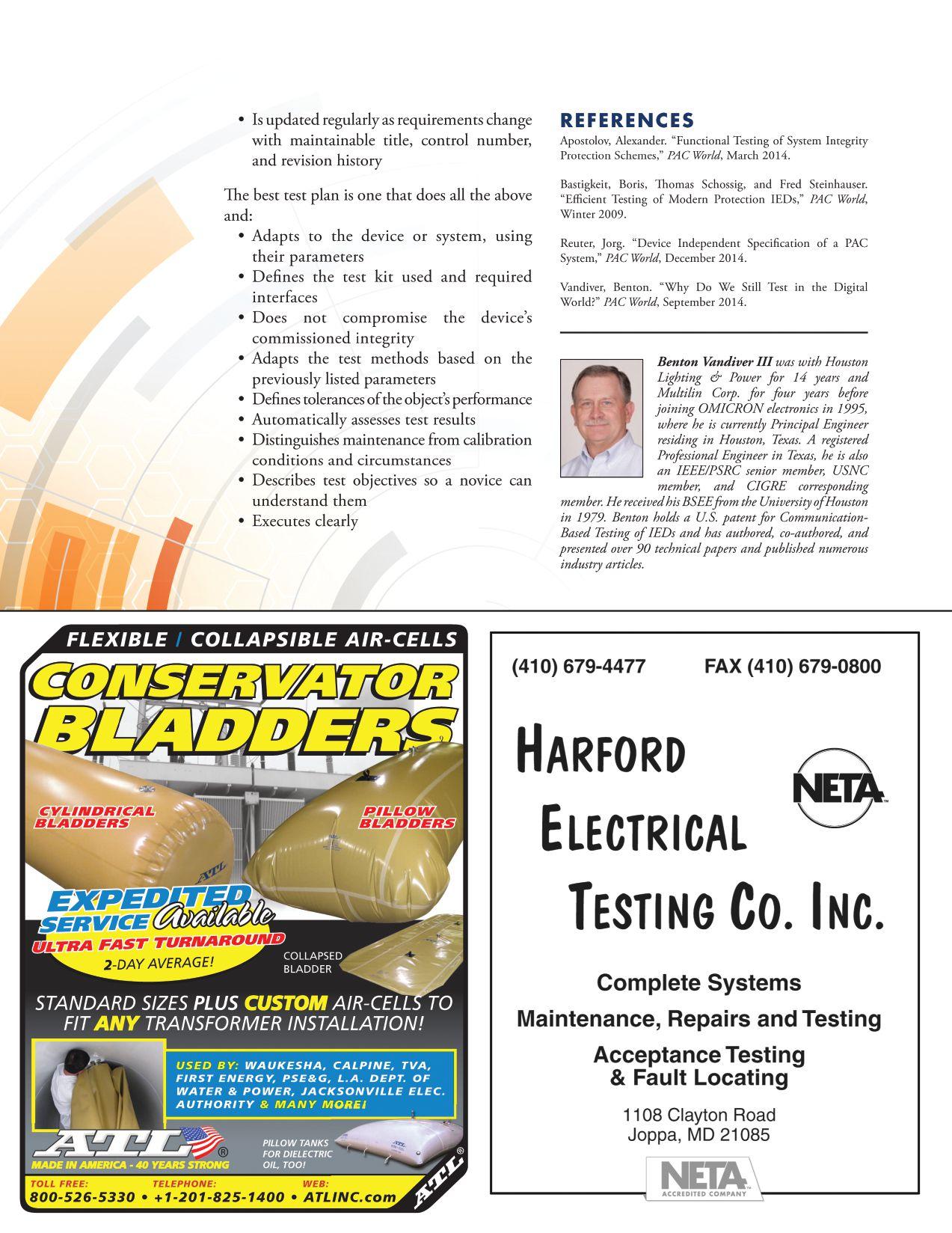

GOING BEYOND AUTOMATED USING POWER SYSTEM MODELS
BY STEVE TURNER, Beckwith Electric Company, Inc.Automated testing is often used to test protective relays, but special cases exist that cannot be adequately covered. This article presents three examples that illustrate how to test protection functions using simple model power systems and symmetrical components.
Model power systems calculate test signals that are equivalent to the actual steady-state fault conditions when precise test signals are required. The ability to calculate test signals rather than solely relying upon software is a valuable skill for testing protective relays.
The three examples given are:
• Zigzag transformer inside transformer differentialzone differential zone
• Sensitive ground directional overcurrent protection for ungrounded systems
• Directional power for intertie protection
ZIGZAG TRANFORMER INSIDE TRANSFORMER DIFFERENTIAL ZONE
The first example demonstrates how zerosequence current elimination is applied for transformer differential protection.
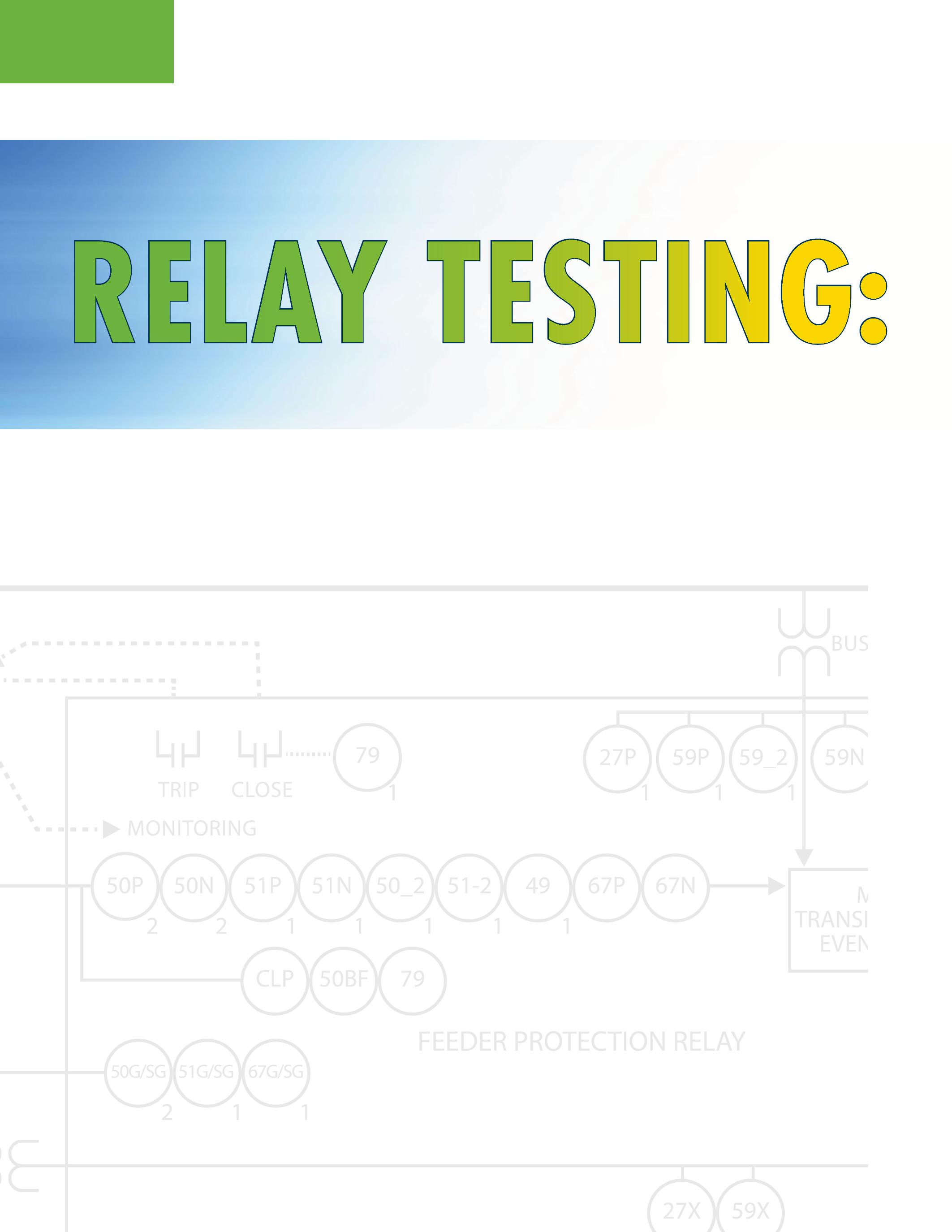
A shunt-connected zigzag transformer provides a zero-sequence current sink for ungrounded systems by establishing a connection from ground to neutral (Figure 1). During ground faults, zero-sequence current (I0) flows up through the neutral of the zigzag transformer. By applying the zigzag transformer as a ground source, it is now simple to apply non-directional overcurrent protection for the detection of single line-to-ground faults. If the system is left ungrounded, very low current is produced on the faulted phase during single line-to-ground faults, due only to the capacitance-to-ground of the unfaulted phases. Conventional ground over-current protection is useless.
A zigzag transformer consists of three 1:1 ratio transformers. Each leg of the zigzag transformer consists of two windings that are 120 degrees out of phase. Windings are wound around the core such that zero-sequence current flows through the bank when system unbalance exists (i.e., ground fault). Only exciting current flows through a zigzag transformer during balanced system conditions; positive- and negativesequence current cannot flow since they are 120 degrees out of phase. The grounding transformer appears as the leakage reactance of the core during a ground fault.
1: Zigzag Transformer Three-Line Diagram
A grounding resistor is sometimes used to limit ground faults to lower levels than with the zigzag transformer solidly grounded. Typically, the zigzag transformer is sized such that its impedance is 100 percent on its own base; 400 amps primary is the 10-second rating commonly applied throughout the United States.
If the zigzag transformer is located inside the zone of transformer differential protection, as in the delta-connected windings shown in Figure 2, then the zero-sequence current contribution during external ground faults must be eliminated or a misoperation can occur. Here is one method showing how numerical transformer protection relays can reliably remove the ground current.
2:
Zero-Sequence Current Elimination (Figure 2)
IA = IB = IC
IA = IB = IC =
The currents shown above are taken directly from the CT secondary and have been divided by the tap setting for the delta winding to convert them into per unit. If zero-sequence current elimination is selected (Figure 3), then the numerical relay calculates the ground current as follows:
IG = IA + IB + IC
IG =
IA’, IB’ and IC’ are the internally compensated currents:
IA’ = IA + IB’ = IB + IC’= IC +
IA’ = - = 0 IB’ = 0 IC’ = 0
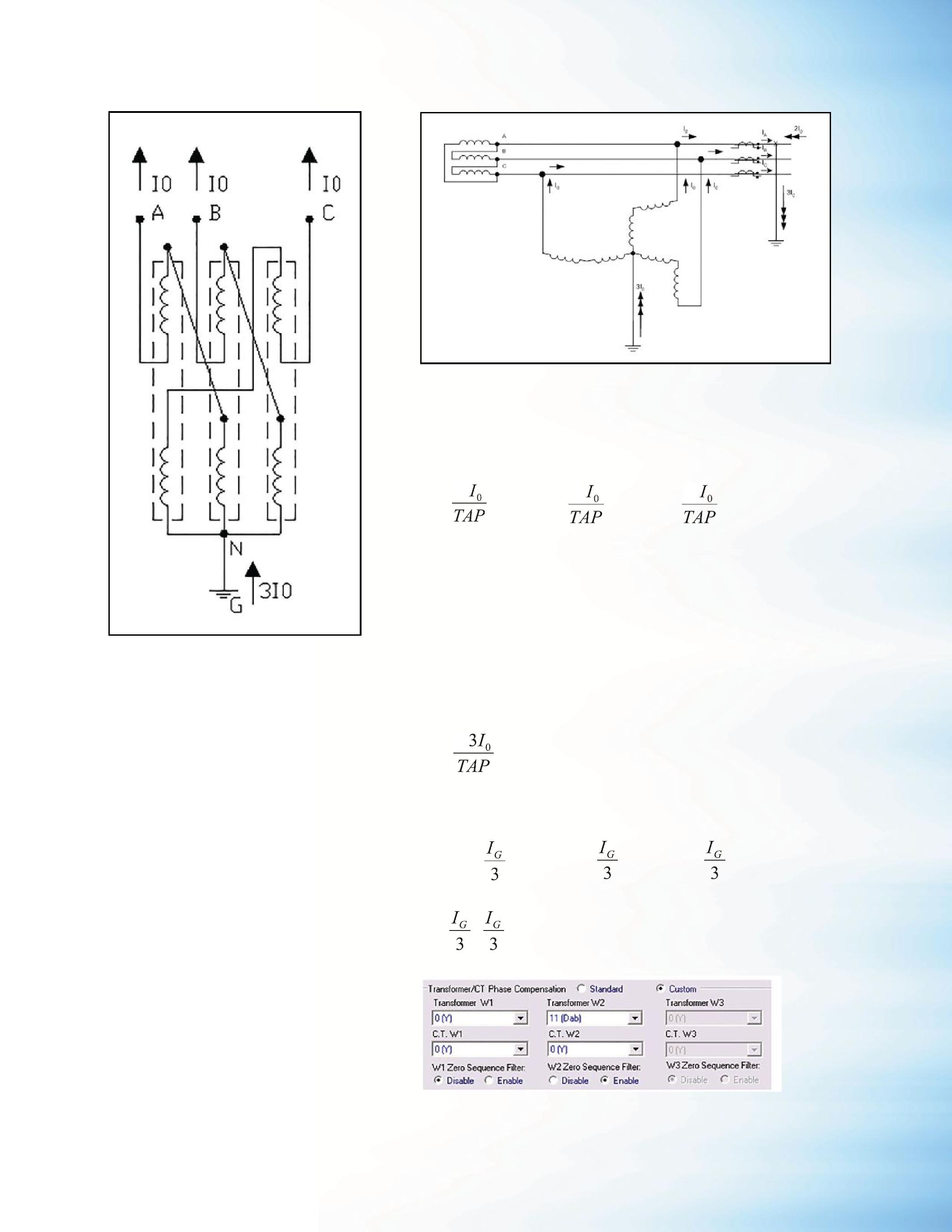
3: Zero-Sequence Current Elimination (Relay Settings)
Figure 4 shows the transformer differential operating characteristic. Point A is the filtered operating point for an external ground fault, and Point B is unfiltered.
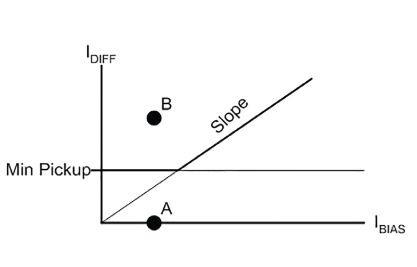
Figure 4: Transformer Differential Operating Characteristic
Note that custom settings that properly account for the phase shift can also be used for this application.
Zigzag Transformer Impedance Model and Symmetrical Component Calculations
Figure 5a shows the zero-sequence model for the zigzag transformer. Note that it does not appear in either the positive- or negativesequence networks.
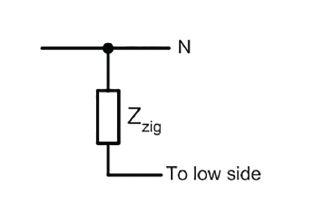
Figure 5a: Zigzag Transformer Zero-Sequence Impedance Model
Figure 5b shows the symmetrical component diagram for the two-winding wye-delta transformer with the zigzag transformer connected to the delta side. Note that the load is connected wye and solidly grounded at the neutral. The CTs for the delta side are shown as well. ZT is the impedance of the two-winding wye-delta transformer, and ZZig is the impedance of the zigzag transformer. The zigzag transformer provides 400 amps primary during a groundfault current when the system is unloaded.
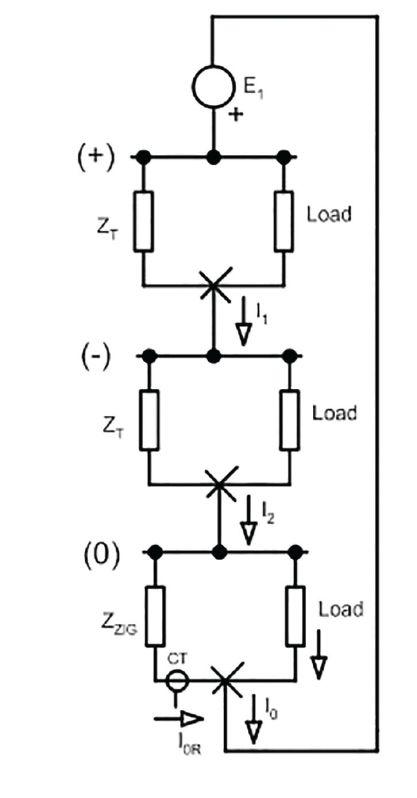
Figure 5b: Symmetrical Component Diagram
Figure 5c shows the ground-current distribution for a single phase-to-ground fault. Note the current magnitudes are normalized to the total zero-sequence current (3I0).
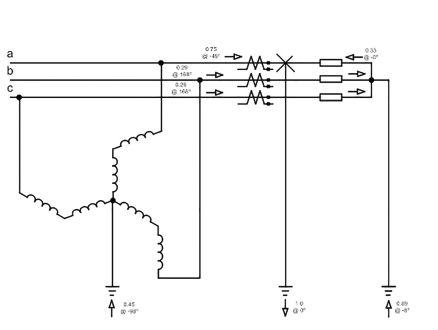
Figure 5c: Ground Current Distribution

Figure 5d shows the base values and impedances used for this particular example.
SENSITIVE GROUND DIRECTIONAL OVERCURRENT PROTECTION FOR UNGROUNDED SYSTEM
The first example was for an ungrounded power system grounded via a zigzag transformer. Remember, as stated previously in regards to an ungrounded power system: If the system is left ungrounded, high magnitude voltage appears on the unfaulted phases during single lineto-ground faults and conventional groundovercurrent protection is useless due to the very low magnitude ground current.
It is possible to protect the feeders for single line-to-ground faults using sensitive-earth-fault (SEF) protection. SEF protection can detect ground-fault current in the order of milli-amps secondary. Figure 6 shows the pickup range for an SEF element. If the CT ratio is 100:5 then the range in primary is 0.5 to 20 amps.


Figure 7 illustrates how the operating current is commonly measured for distribution feeders. Note that IG is the ground current input. A toroidal CT is also used but is only applicable at lower voltages since all the phase conductors must pass through the center opening.

Figure 8 shows a single line-to-ground fault on a distribution feeder supplied via an ungrounded wye winding. The power system is grounded through the total stray capacitance to ground (XC0g).
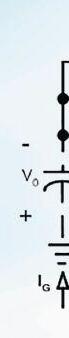
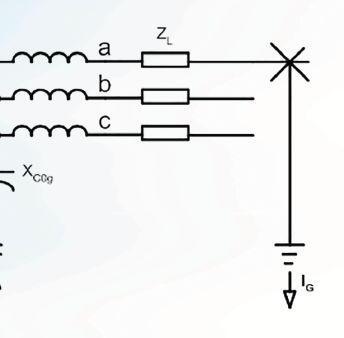
Figure 8: Single Line-to-Ground Fault on Ungrounded System
Directionality makes SEF secure since ground current flows in the unfaulted phases for the non-faulted feeders as shown in Figure 9a.
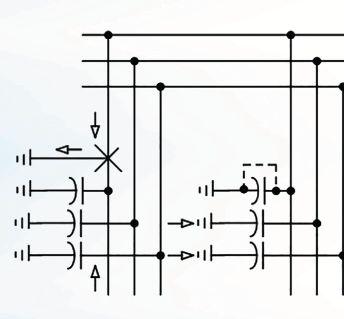

Figure 9a: Ground Current in Unfaulted Feeder(s)
Figure 9b shows the SEF directional operating characteristic. The maximum torque angle between the zero-sequence voltage and ground current is 90 degrees leading, since the voltage drop behind the relay in the zero-sequence network is across the total stray capacitance to ground (XC0g).
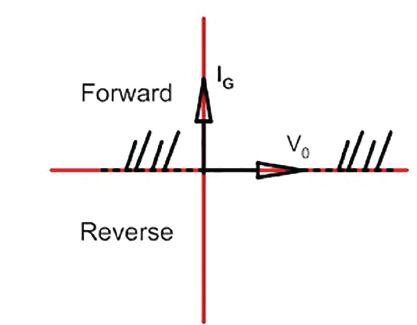
Figure 9b: SEF Directional Operating Characteristic
Calculate the ground fault current (Ig) as follows:
I g = 3I0
Where:
I0 = 1 2ZT+Zc0+3RF (per unit)
ZT = distribution transformer impedance
Zc0 = -jXc0
Xc0 = 1 2πƒCg
f = nominal frequency
C g = total stray capacitance to ground
RF = ground fault resistance
Note that the impedance of the distribution feeder can be ignored since the impedance of the stray capacitance is so high. This calculation does not take any load into account. You can increase the fault resistance until the ground fault current is equal to the minimum pickup setting to test the maximum sensitivity of the SEF protection. Figure 10 shows the symmetrical-component zero-sequence network.
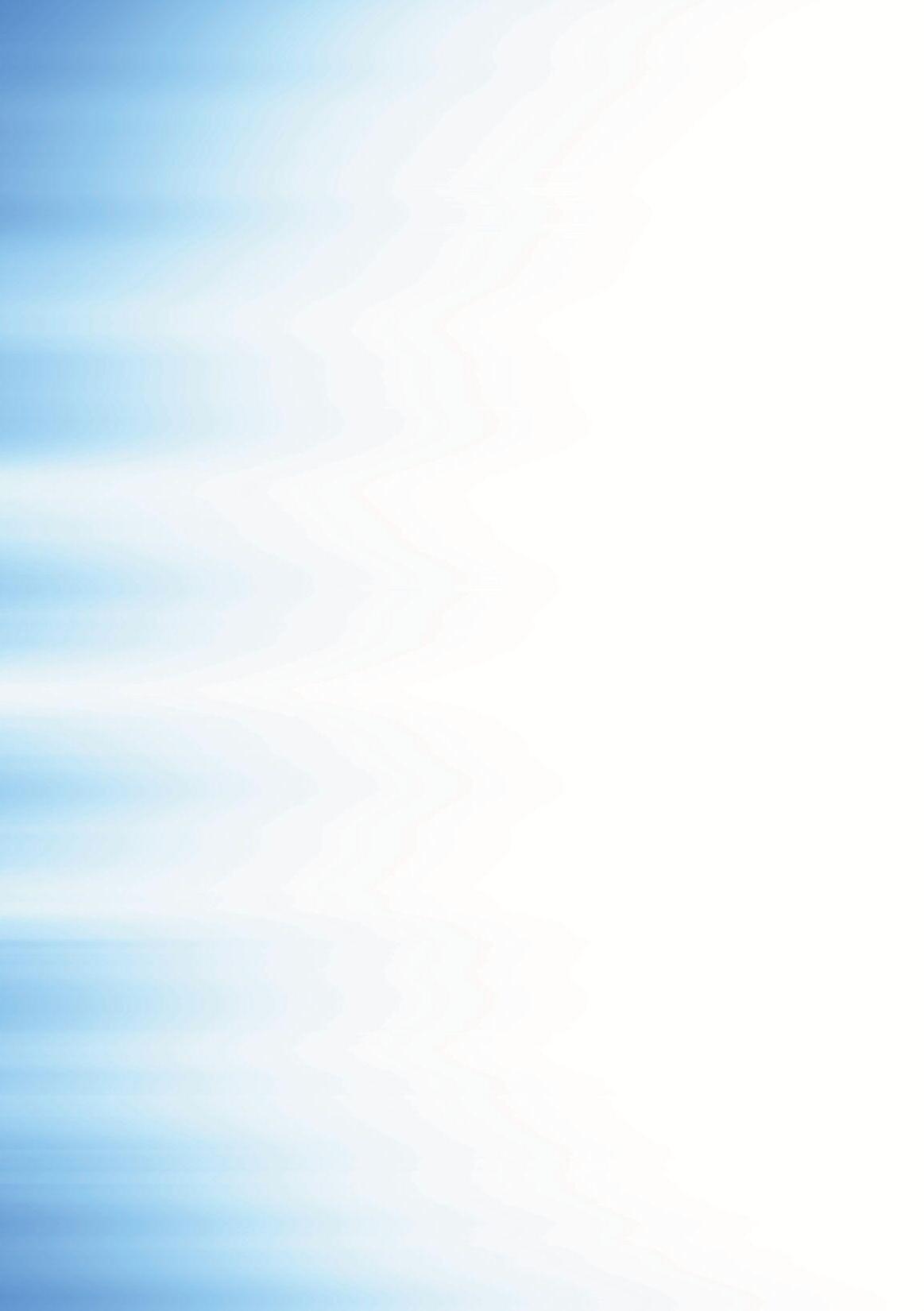
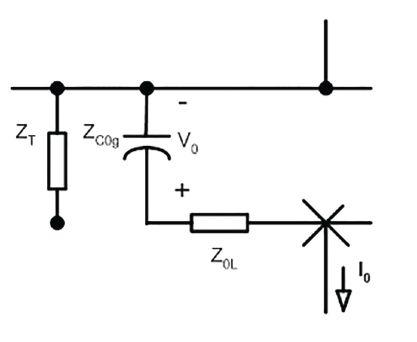
Figure 10: Zero-Sequence Network
DIRECTIONAL POWER FOR INTERTIE PROTECTION
The last example demonstrates how to calculate test signals for directional power protection (Figure 11). Note that this type of protection typically operates on real power (W).
Power protection may be useful to detect the loss of utility supply, depending upon the size of the distributed generator (DG) and its load, feeder load, and the local utility import/ export restrictions. Forward power is defined as power exported from a DG to a utility. Reverse power is defined as power imported by a DG from a utility.
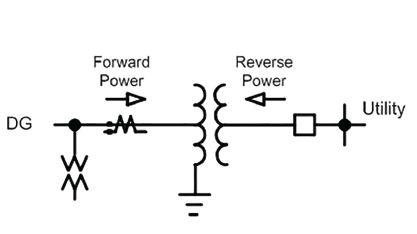
Figure 11: Directional Power
It is convenient to set the pickup in perunit (PU) based upon the numerical relay nominal power. The choice of the base PU is typically taken from the kVA rating of the interconnection transformer, the DG aggregate generating capacity, or some other value agreed upon by the DG and the utility. Normalized PU power flow measurements are
based on the Nominal Voltage and Nominal Current setting, as shown in Figure 12.
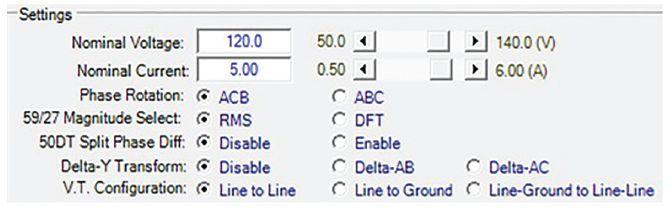
Figure 12: Relay Configuration
Use the forward over-power function to limit the amount of power flow into the utility if the DG is allowed to supply power to the utility (export). Use the reverse under-power function to ensure that the DG is importing a minimal amount of power from the utility for peak shaving applications when no export of power from the DG to the utility is allowed.
Nominal Power
Here is how one particular numerical relay internally calculates the nominal power (Pnom):
VT Configuration Line-Ground (L-G) Nominal Power = 3•V nom •I nom
VT Configuration Line-Line (L-L) Nominal Power = √3•V nom •I nom
Pickup Setting
Suppose, for example, the utility requires that the directional power (32) elements trips at 50 kW primary.
VT Ratio = 4160/120 = 35 (Open Delta)
V nom = 120 volts L-L
CR Ratio = 400/5 = 80 (Wye)
I nom = 5 amps
Note: The values above were arbitrarily selected but are typical.
• Pickup = (50 kW)/(VTR•CTR) = 18 watts secondary
• Pickup = (18 watts)/(√3•120V•5A) = 0.02 per unit
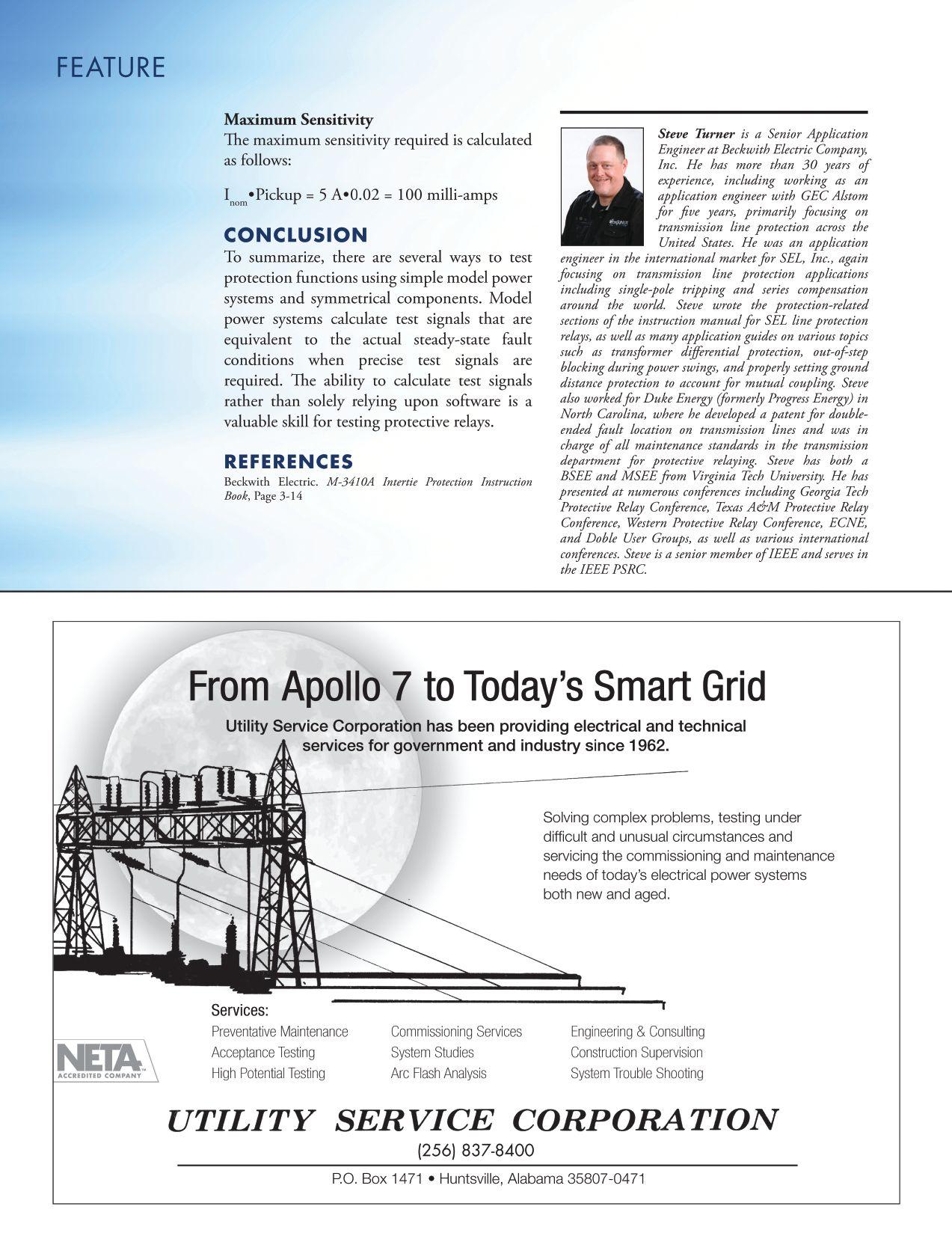
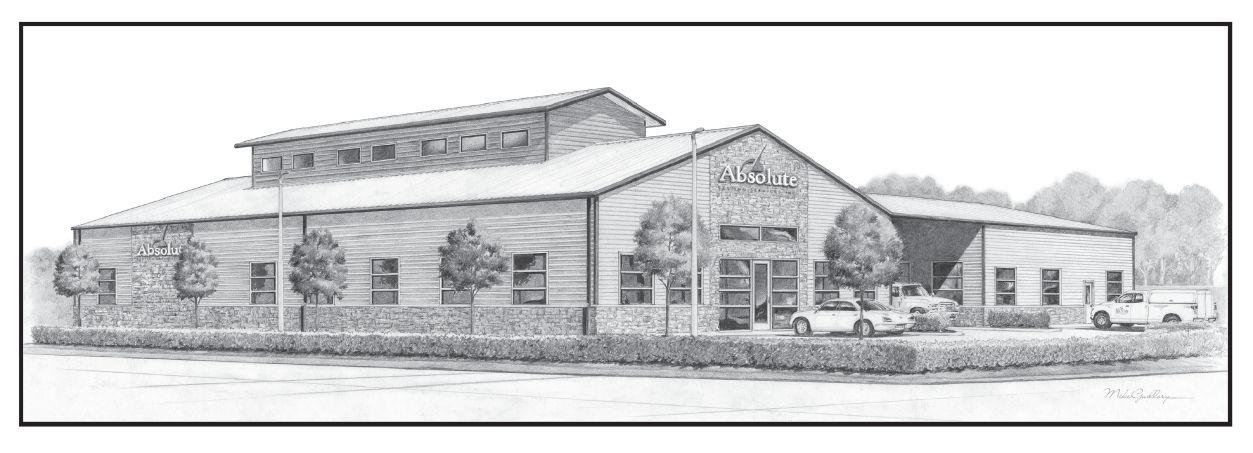
Absolute confidence. Every time.
You can count on us for specialized experience in healthcare, data center, office complex, and commercial acceptance and maintenance testing. Absolutely Power generation, petrochemical, oil & gas, and heavy industries also look to us for high demand services such as start-up commissioning, maintenance testing, shut-down and turnarounds, and breaker shop repair. Get started today.


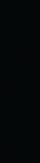

From A 400kV Busbar Misoperation Using The
IEC 61850 STANDARD
BY DHANABAL MANI, VIJAY SHANMUGASUNDARAM, AND JASON BUNEO, MeggerThe implementation of IEC 61850 standard for substation design and commissioning is rapidly becoming the dominant method of defining grid protection schemes throughout the world. The protection logic that involves dc control circuits is executed internally in the intelligent electronic devices (IEDs) and effectively communicated between the IEDs via Generic Object Oriented Substation Events (GOOSE) messages. Any error in the mapping of GOOSE signals will result in undesired operation of the protection schemes.
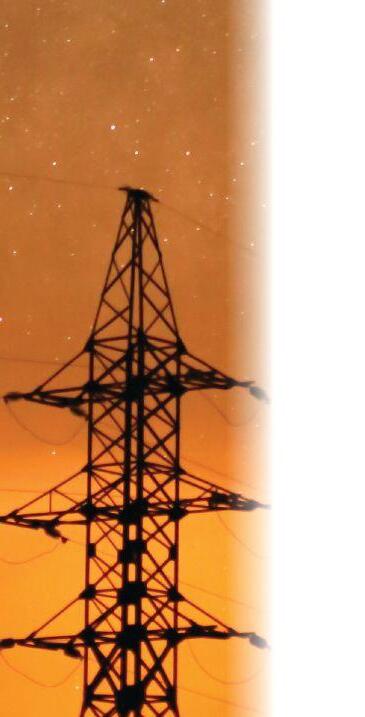
The main buses in power substations are designed to carry load currents through the individual feeders as well as high amplitude currents during bus fault conditions. Any delay in fault isolation or improper relay operation could result in severe damage to the substation buses and the equipment connected to them. Therefore, proper design and testing of the busbar protection scheme is required to ensure safe and reliable operation of the substation. The complex protection schemes such as bus-bar and breaker-failure protection are relatively easy to design using the modern IEC 61850 standard. However, the implementation of these schemes in the real world poses certain unique challenges.

This article discusses the investigation of the tripping of a 400 kV substation due to improper operation of a bus-bar protection
scheme. This incident happened when a zone two fault occurred on one of the 400 kV line feeders, immediately triggering a breakerfailure condition. Under a normal trip scenario, the zone two timer will time out and the line IED will issue a trip signal to the line breaker to isolate the fault. The line IED will also then issue a breaker-failure initiate (BFI) signal to bus-bar IEDs through GOOSE messages. The breaker-failure condition is only declared when the line breaker fails to trip within a specified breaker-failure time. However, in this case, the breaker-failure condition was initiated before the zone two timer expired instead of after.
An investigation was carried out to determine the reason for declaring a breaker-failure condition even before zone two tripping of the line IED. Further analysis of the IEC 61850 network and GOOSE configurations led to
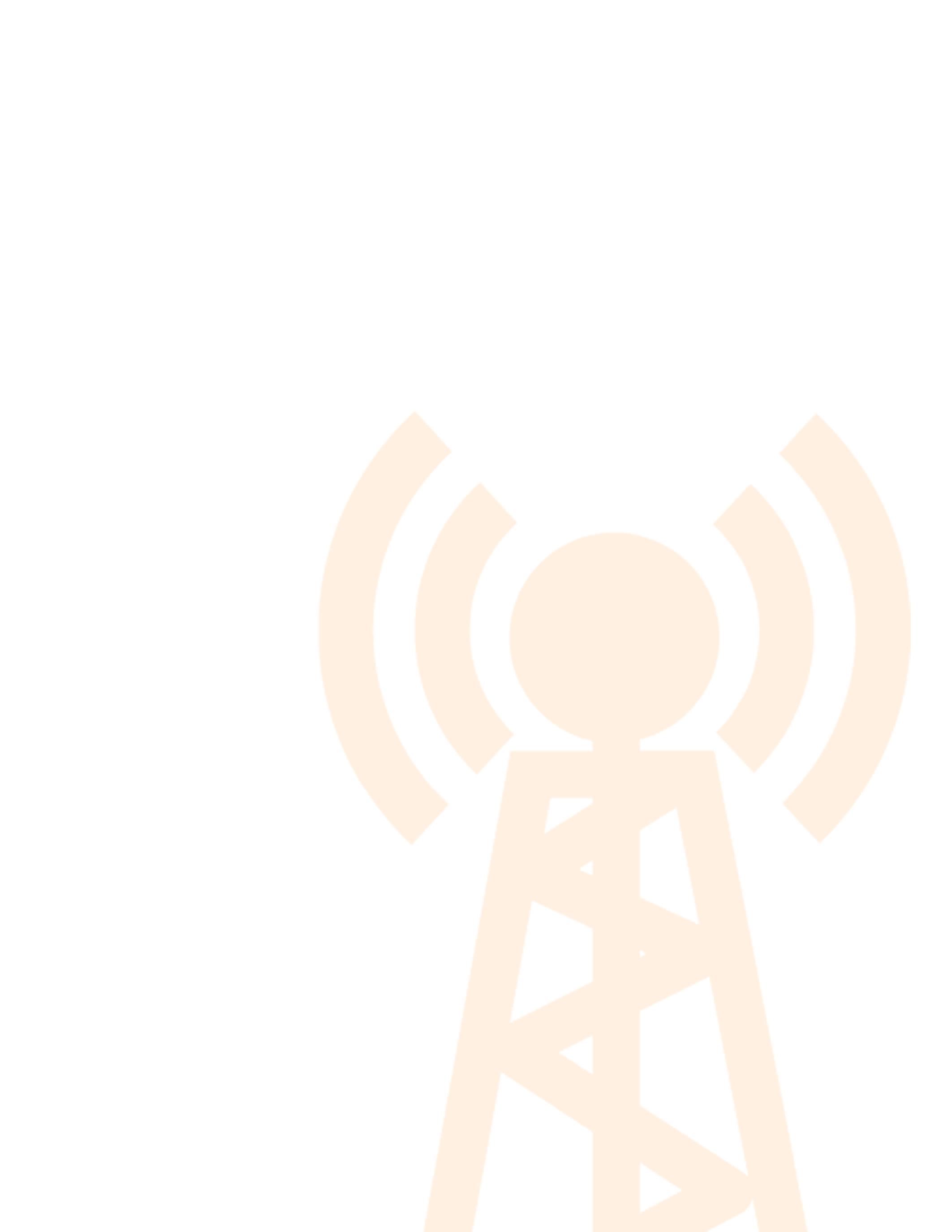
the conclusion that the BFI signal was mapped incorrectly. The bus-bar IEDs were configured to receive a BFI signal through GOOSE messaging for a fault pick-up signal instead of a fault-trip signal by protection IEDs. This minor error caused the entire substation to be out of service. This article discusses testing methods that would help prevent this situation.
INTRODUCTION
The protection schemes used in substations are implemented through protective relays from various manufacturers. Legacy systems that use electro-mechanical relays share critical information such as breaker status, interlock signals, etc., through a network of copper wires monitored by some control center. With the advent of IEDs, data sharing between protective relays and control centers has become possible by using Ethernet and fiber optic cables. This has reduced the amount of copper necessary in substations, making them cheaper to produce and maintain. However, the interoperability between different relay manufacturers has become increasingly difficult, as many IED manufacturers have adopted proprietary standards for data representation and interpretation. In 2005, a common standard was first published by a shared effort from IEC 60870-5-101, -103, -104, and Utility Communication Architecture 2.0 (UCA 2.0), and called IEC-61850.
TheIEC-61850standardalloweddirect The IEC-61850 standard allowed direct communication between IEDs from multiple vendorsinasubstation.TheIEDsinasubstation vendors in a substation. The IEDs in a substation followed an abstract model for data definition, which could be interpreted by all the compliant manufacturers. A local area network (LAN) switch connected between IEDs passed the data as GOOSE messages. These messages contain essential information such as control signals and acknowledgements. The implementation of the IEC-61850 standard through LAN-based architecture considerably increased the reliability and speed of peer-to-peer communication. Also, a complex protection scheme could be implemented easily through the LAN-based design without increasing the complexity of physical wiring.
A protection scheme is implemented by configuring the IEDs to send or receive GOOSE messages from other substation equipment. Depending upon the complexity of the protection scheme implemented, a GOOSE message could pass through a number of switches until the destination IED is reached. After analyzing the received message, further actions are carried out by the destination IED. A redundant network in LAN design prevents data loss by re-routing the path taken by the messages. Numerous network topologies have been adopted to maintain an un-interrupted data flow from the source IED tothedestinationIED. to the destination IED.
AnIEDinthesubstationcansendorreceive An IED in the substation can send or receive GOOSE messages to or from many different IEDs in the network. The proper mapping of GOOSE messages between IEDs is essential for execution of a protection scheme. The number of signals mapped depends on the number of IEDs and the elements of the protection scheme being implemented in the substation. TheIEC61850standardensuresthatthe The IEC 61850 standard ensures that the control functions and message flags seen on thecommunicationnetworkwillbethesame the communication network will be the same nomatterwhichmanufacturerdeviceisused. no matter which manufacturer device is used. However, mapping the IED’s internal logic to the IEC 61850 standard can be tricky, and great attention to detail must be maintained.
THE SYSTEM
A newly constructed 400kV IEC 61850 substation was fully commissioned prior to the workonthisarticle.Itconsistsofsix work on this article. It consists of six D-configuration systems, referred to as a DIA by the customer, and is provided with a distributed busbar protection scheme as per Figure 1.
A D-configuration system has three circuit breakers with two outgoing circuits; one circuit isforlineandtheothercircuitisfortransformer is for line and the other circuit is for transformer orbusreactor.Bothcircuitscouldbelinesas or bus reactor. Both circuits could be lines as well. For circuit breaker maintenance of any line, the load gets tranferred automatically from one bus to the other bus. No changeover of the line from one bus to another is required. For any bus-fault conditions or scheduled
maintenance, all interconnections will be on the healthy bus, and no disturbance will come to the other circuits. Even if both buses become dead, circuits can remain in service through the tie circuit breaker. This is very advantageous in maintaining system stability.
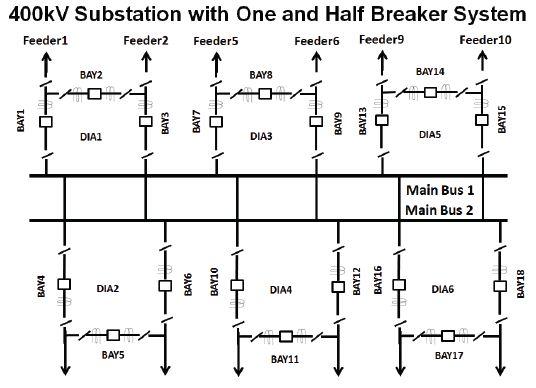
Figure 1: 400kV Substation One-Line Diagram
The IEC 61850-based substation automation system (SAS) architecture used in this substation is shown in Figure 2. This architecture is defined in two levels as station level and bay level. A redundant PC-based human-to-machine interface (HMI) is used to control the subsation at station level, which supports communication over IEC 61850-8-1 bus as an IEC 61850 client. An IEC 61850-8-1 inter-bay bus provides station-to-bay and bay-to-station exchanges. In this case, an Ethernet LAN is set up with ring configuration to maintain reliability, availabilty, and interoperability requirements of the system. Reduntant gateways are used to exchange the information to remote network control centers using IEC 60870-5-101 protocol.
The bay level system consists of all circuit breakers, current and potential transformers, power transformers, and protective relays. IEDs in the bay level perform all functions including control, monitoring, and protection. The data exchange between bay level and station level happens with fiber optic ring connection according to IEC 61850-8-1 protocol.

Figure 2: Bay and Station Level IEC 61850 Communication Architecture
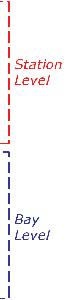
This busbar protection scheme is implemented for Main Bus I and Main Bus II. All bay control units are connected with fiber optic cable to their main busbar relay for transmitting each bay’s load current values, isolator, and breaker statuses. An equivalent single-line digram of the substation is configured in the busbar main IEDs for proper replication of the substation and for ensuring correct decision making in the protective scheme. In the case of a bus-fault or breaker-failure condition, the main busbar IEDs make the decision to isolate the faulty feeders by sending a trip command to the bay IEDs and, in turn, the bay IEDs trip the respective bay circuit breakers. This data sharing occurs within the busbar protection relay network; these trip signals are also sent as GOOSE messages over the IEC 61850 bus.
IED ENGINEERING AND SYSTEM LEVEL ENGINEERING
The IED engineering process involves configuring the protection functions, interlock logic, metering functions, etc., in each of the IEDs. This process is shown in Figure 3. The IED configuration description (ICD) file is then exported from each IED, into the substation configuration language (SCL) file. The SCL output contains the IED’s capabilities (logical devices, logical nodes). It also reports the control blocks available in the ICD files that are used as inputs in the system-level engineering design. Configuration tools are used to set up the
communication between various devices. The transmission of the data sets is decided by the report control blocks. Also, GOOSE messages are configured in the system-level engineering tool with GOOSE control blocks.
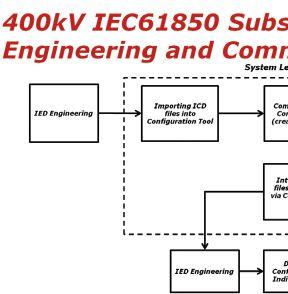
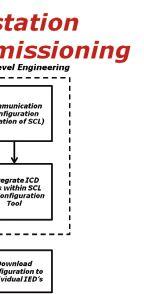
Ethernet switch configurations are then defined and downloaded into the switches. In this IEC 61850 network, GOOSE messages have priority over other messages, so Ethernet switches are necessary to support the IEEE 802.1P standard for priority tagging. Finally, once the system-level engineering is completed, the SCL file is re-imported back into IEDs, where all the configured GOOSE inputs coming from other IEDs are connected to the correct functions. Once the configuration is downloaded to the individual IEDs, the complete system architecture is defined.
Using the isolator logic, the busbar relay is capable of identifying and isolating respective feeders connected with the faulty bus. Also, this busbar scheme is combined with breaker failure protection. Any protection trip of respective bay protection IEDs will send a trip signal to respective busbar bay IEDs to initiate the breaker failure protection (Figure 4). If the breaker fails to trip, this action will cause a breaker-failure protection trip with BFI initiation and timer timeout. In IEC 61850 substations, a BFI signal may be configured as a GOOSE message from the protection IEDs to the breaker failure protection relays. The busbar IED will trip all feeders connected with
the bus of the faulty feeder. Fault selection is processed by the busbar main protection IED with isolator staus [1].
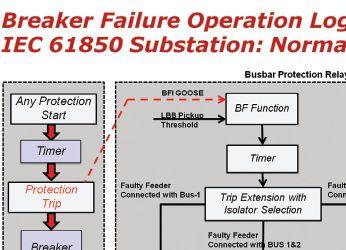

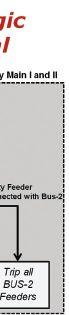
400kV SUBSTATION COMMISSIONING
During commissioning of the substation, the protection IED’s operation, busbar protection, and all other trip logic were verified to be in proper working order. Later, an additional bay was added to the existing system. All of the protection schemes associated with the new bay were verified as well.
After successful commissioning of the new bay, a feeder was connected to Bus-I. Subsequently, there was a zone two line fault on the newly added 400kV line. Both Main I and Main-II distance protection relays in the substation sensed the fault correctly on zone two and started the zone-two timer. The zone-two trip timer is set for 300 ms. It was observed that the busbar protection relay operated within 200 ms for this fault and tripped the feeeders connected with Bus-I and Bus-II, thereby causing the entire 400kV substation to be taken out of service.
After careful physical inspection of the substation and busbar protection relays, it was determined that there was no real bus fault, and the busbar relay had misoperated due to improper breakerfailure protection. The BFI signal was sent to the busbar IEDs through a GOOSE signal. After careful analysis of the IED GOOSE configuration, it was found that the newly added bay had distance-protection GOOSE messages
configured with a start signal for breaker-failure initiation instead of a trip signal. Since the breaker-failure initiation started the function block timer with a start input, its timer operated within 150 ms instead of waiting for the 300 ms zone two timer to expire first. This caused the breaker failure to trip before the zone two timer. Due to this small mistake, both the Main-I and Main-II protection operated, leading to an entire substation blockout. The erroneous logic is shown in Figure 5.
Figure 6: Example of Incorrect IED GOOSE Configuration
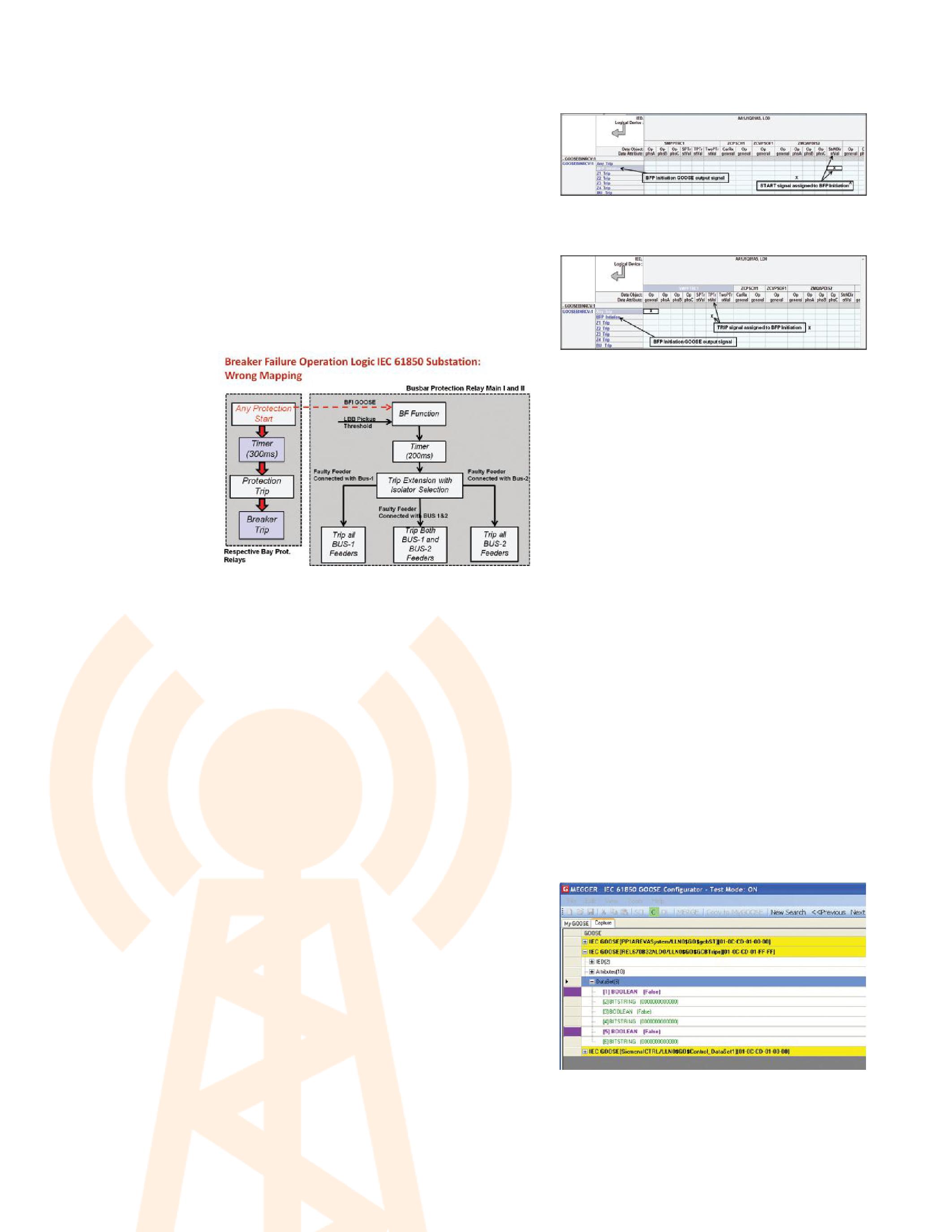
Figures 6 and 7 show the signal configuration of the GOOSE assignment for the breaker-failure initiation sent to busbar protection IEDs. This signal configuration is defined in the IED-level engineering and in the main-line protection IEDs. Figure 6 shows a simulation example of the wrong GOOSE configuration for breaker-failure initiation. In this case, the zone two start signal has been assigned to breaker-failure protection initiation as a GOOSE output. Whenever a zone two fault occurs, the zone two start signal will send a BFI and cause a breaker-failure trip before the zone two timer completes and clears the fault. Figure 7 shows the simulation example of the corrected GOOSE configuration for breakerfailure initiation. In this scenario, if there is a zone two fault, the breaker-failure protection will not send any GOOSE signal to the busbar IEDs from the main protection IEDs to initiate the breakerfailure trip. The IED will send a GOOSE signal to the bus bar IEDs only when there is a trip issued by the protection IEDs.
Figure 7: Example of Correct IED GOOSE Configuration
It is necessary to test the IED’s protection schemes and GOOSE signals properly before commissioning the IEC 61850 substation or adding additional bays in the existing IEC 61850 substations. It is fairly easy to verify copper wire schemes for breaker-failure protection schemes or other protection schemes when adding additional bays into service in a conventional substation. In the case of IEC 61850 substations, it requires special care. GOOSE-monitoring software can test an IED’s GOOSE configurations before putting IEDs and bays into service. Importing the SCL fileoftheIEDundertestintotheGOOSE file of the IED under test into the GOOSE monitoring software can assist in verifying the GOOSE signals as required.
Figure 8 shows one of the trip GOOSE signals from a distance protection IED. The purple font in this particular data set indicates the nonoperation of the distance function and that its signal status is low. This means that this GOOSE signal will be seen by other relays in the substation as non-operative.
Figure 8: GOOSE Monitoring, No Operation of Protection Function
Figure 9 provides an example where the GOOSE signal color is red. It indicates that this signal is high and that the protection function has operated; therefore, this GOOSE will register when the distance protection trip goes high. The mapped IEDs that use this GOOSE signal will process and operate accordingly.
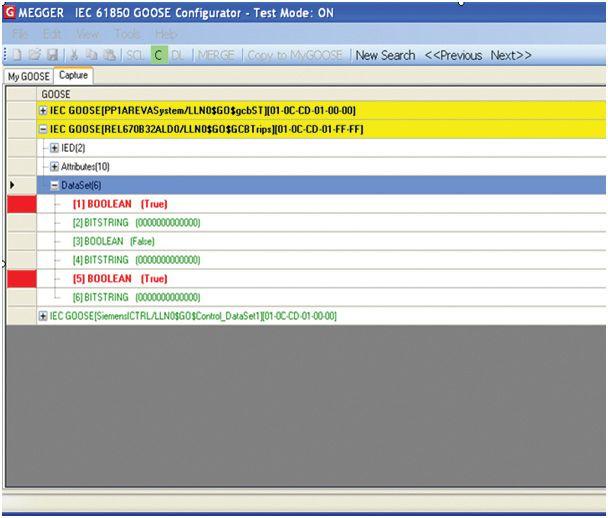
Figure 9: GOOSE Monitoring, Operation of Protection Function
With reference to Figure 8 and Figure 9, any GOOSE used in protection schemes can be tested and verified without any risk of misoperation of the relays or unwanted interruption of the substations. The BFI GOOSE signals have been corrected from a start signal to a trip and downloaded to the distance protection IEDs. Since there is no change in data sets, it is not required to update the system-level engineering in the substation level (Figure 3).
Necessary validation of signal mapping and GOOSE configuration in line with substation configuration is required in any IEC 61850 substation when adding new bay/feeders into the existing substation.
CONCLUSION
IEC 61850 substations are increasing in use throughout the world. Necessary testing procedures, such as one of the methods discussed in this article to validate IEC 61850 GOOSE mappings, are required to follow the commissioning of those stations for proper operation. More challenges lie ahead in IEC 61850 substations, especially
when adding additional bays into service within existing IEC 61850 substations. As always, additional care is required at the commissioning stage for any substation.
REFERENCES
Krishnan, Rajiv and Bapuji Palki. “First Experiences with Design and Engineering of IEC 61850 Based Substation Automation Systems in India,” CEPSI 2006 Conference, Mumbai, India, November 6 - 10, 2006.
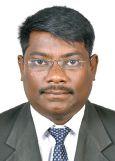
Dhanabal Mani received his Bachelor of Electrical and Electronics Engineering from Bharathiyar University, India, in 2001. He commissioned the first 400kV IEC61850 substation in India in Madhya Pradesh as a Lead Commissioning Engineer of the Substation Automation Group at ABB India Ltd. He has also developed custom relay applications as a R&D engineer at ABB Ltd, Sweden. Dhanabal joined Megger India as an Application Manager in August 2009 and is presently based in Dallas. He has over 13 years of field experience in protective relaying and commissioning, and has published numerous articles and presented at various international conferences on the subject.
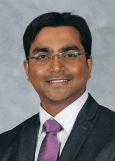
Vijay Shanmugasundaram received his Bachelor of Technology with distinction in Electrical and Electronics Engineering from Amrita University, India, in 2008. He joined the Defense Research and Development Organization (DRDO) of India as a junior research fellow, specializing in the performance optimization of induction motors. In 2011, Vijay received his Master of Science in Electrical Engineering focusing on power systems, from North Carolina State University. As a part of this program, he worked on IEC61850 substation development in Siemens’s Energy and Automation department. Vijay joined Megger as an Applications Engineer in December 2012 and is currently working on developing IEC61850 applications. He is an active member of IEEE and EPRI, participating in conferences and contributing to the working groups.
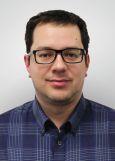
Jason Buneo received his B.S and M.S in Electrical Engineering from the University of Buffalo. In 2005, he joined GE Energy Services as a Field Service Engineer. He specialized in arc-flash coordination studies, protective relay testing and calibration, and low-/medium-voltage switchgear repair. In 2008, he joined Megger as an Applications Engineer where he assisted Megger’s customer base in their relay testing needs. He became the Applications Development Manager in 2012 and now specializes in developing automated testing applications for protective relays. Jason continues to work closely with utility and industrial customers to develop new testing solutions. Jason has published several technical papers in industry journals and conferences and is active in the IEEE Power Systems Relaying Committee.

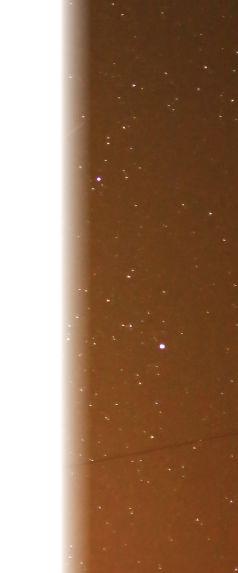
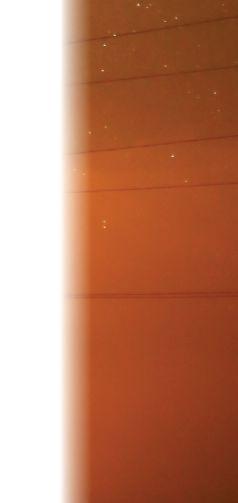
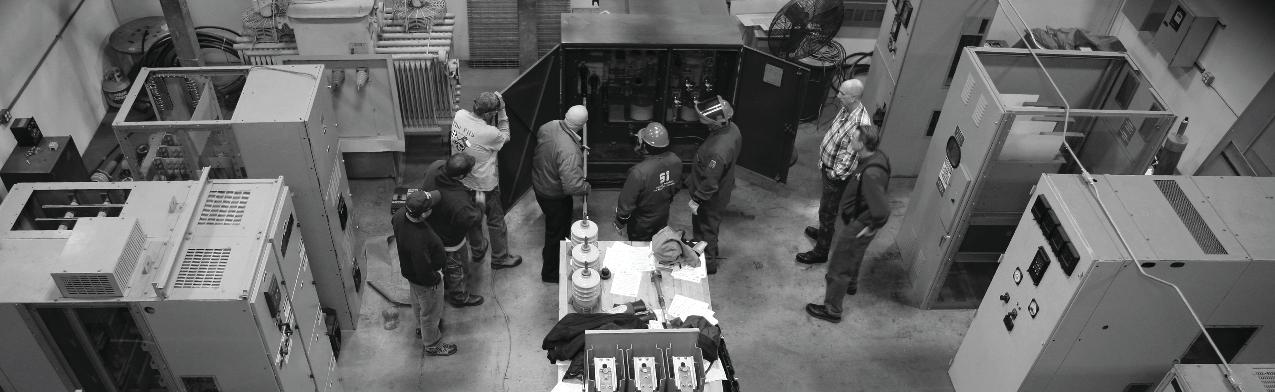
So you thought school was out?
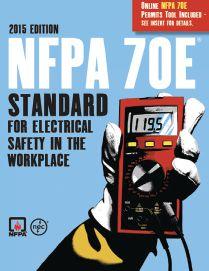
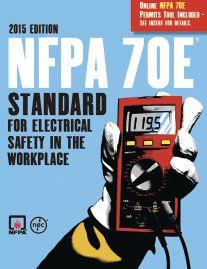
Training updated for lastest safety standards
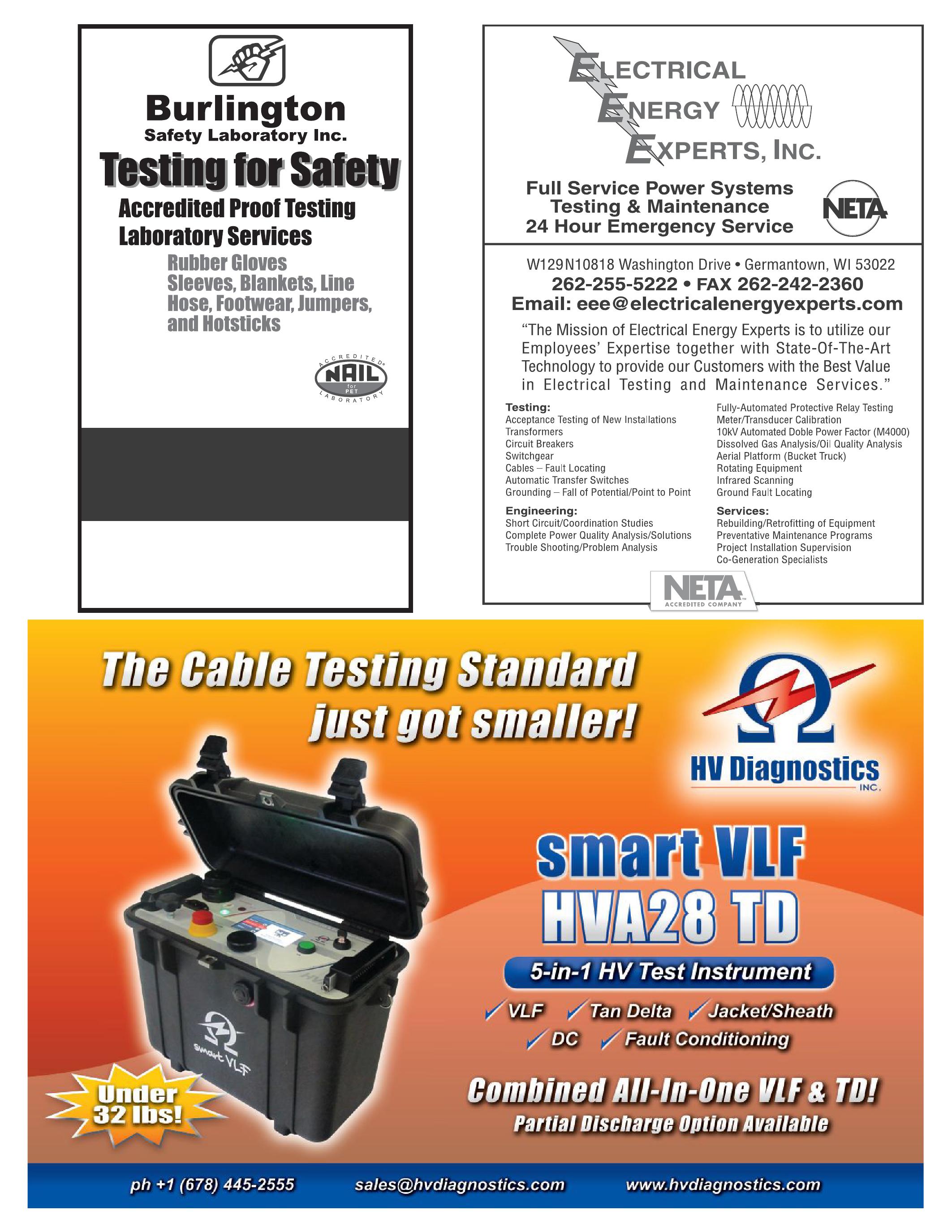
JIM CIALDEA: ‘EVERYONE SHOULD BE PART OF THE ASSOCIATIONS THAT SHAPE THEIR INDUSTRY’
BY CARLA KALOGERIDIS, NETA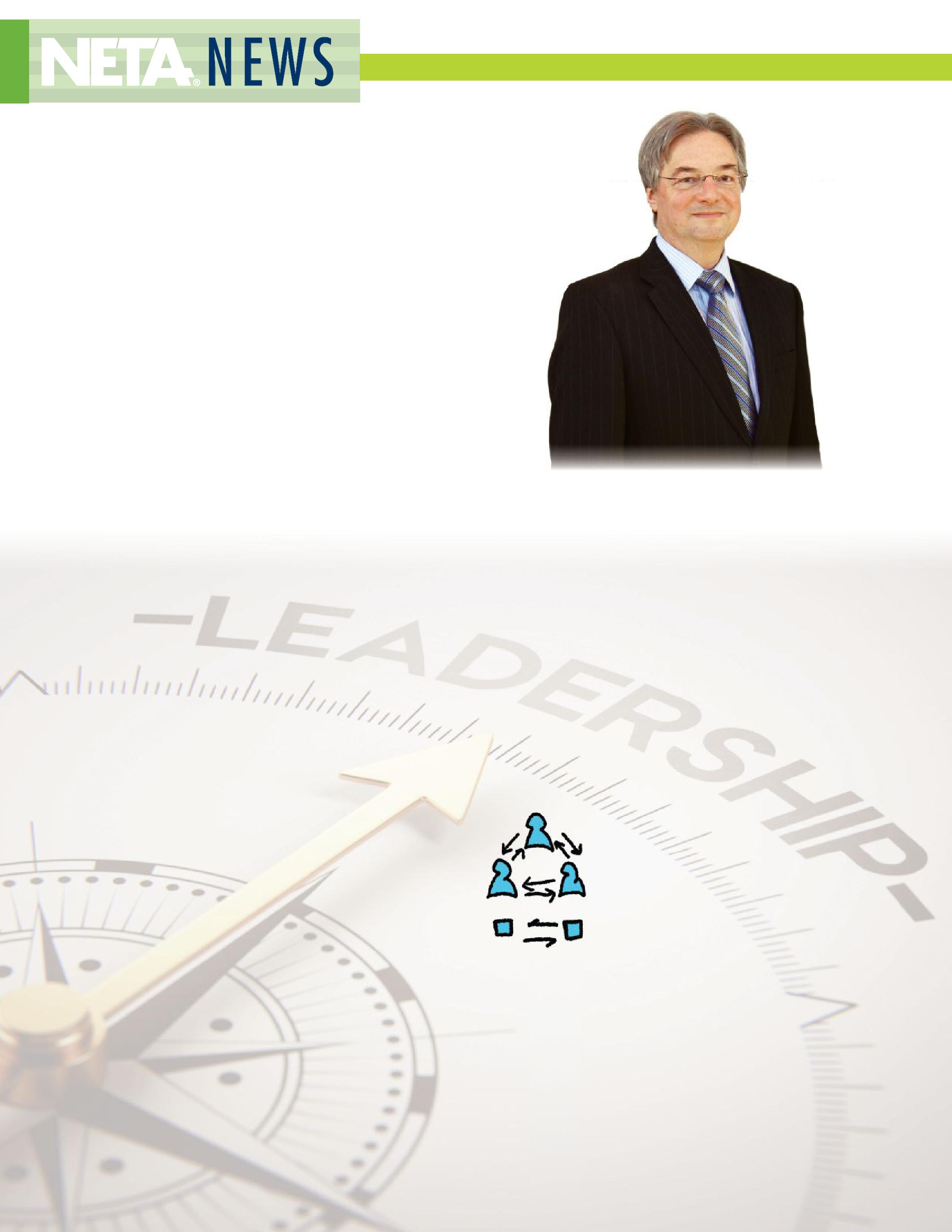
NETA2016 NETA 2016 Outstanding Achievement Award honoree
Jim Cialdea has a motto, one that applies to every aspect of his personal and professional life: If you’re going to do it, you might as well do it right.
“If he’s asked or hired to do something, he’s going to get it done — sometimes painfully — but he’s going to do it right no matter how long it takes,” says Jim’s son Steve Cialdea, who has worked parttime for his father since age 16 and came on fulltime a couple of years ago after earning his master’s in electrical engineering.
“I always wanted to work with him,” says Steve, an engineer with his father’s firm, 3-C Electrical Company, named for Jim’s father and his two brothers who started the company in 1971 to service, install, and maintain electrical power distribution equipment. Today, the organization has grown to 60 employees with offices in Massachusetts and Maine. All of 3-C Electrical’stechniciansareNETAcertified. Electrical’s technicians are NETA certified.
3-C was a NETA member company back in the 1970s for a while when Jim’s father was running the company, until theirfocusbecamemoreconstruction. their focus became more construction. When Jim Cialdea and Alex Picciolo took over, they started moving the business again toward testing and maintenance. “I have been to every NETA PowerTest conference since the early 1990s,” Cialdea says. “It was Jayne Tanz who first came up — in her very convincing way — and suggested that we re-join.”
Joining NETA again falls under the category of
Jim Cialdea, 3C Electrical owner and CEO, always a technician at heart.
Cialdea Electrica owwnener r and CEO, alway a at
another one of those things that Jim Cialdea did right. “It has been an excellent choice, an important one in helping us to grow our business,” he says. “Everyone should be a part of the associations that shape their industry.” Cialdea and Picciolo worked hard to build 3-C Electrical into a NETA Accredited Company.
NETA’s Outstanding Achievement Award is given in recognition of an individual’s commitment to NETA and leadership through service to the association. “It is always a difficult decision to make since every single member contributes to the growth and advancement of our industry each day that they are in the field serving clients and participating throughout the industry in volunteer efforts,” says Ron Widup, CEO andPresidentofShermcoIndustries and President of Shermco Industries andPresidentoftheNETABoardof and President of the NETA Board of Directors, who presented Cialdea with the Outstanding Achievement Award at this year’s PowerTest conference. The conference ran March 14 −18, 2016, at the Omni Fort Worth Hotel in Fort Worth, Texas.
PowerTest 2016 represents the largest gathering of electrical power systems professionals in the industry and is the only conference and trade show specifically designed for the electrical testing industry. As it is every year,
the Outstanding Achievement Award was presented by NETA’s President at the Member and Alliance Luncheon on PowerTest Monday.
“It is quite an honor to receive this acknowledgement knowing who received the award in the past and understanding all the people who do so much for NETA” says Jim Cialdea. “It was a surprise.”
Widup acknowledged that it is a tough task to choose an honoree because so many members work tirelessly to keep the business of the association moving forward — and usually outside of regular business hours. “It is also a humbling experience to take stock of all the work that gets done by people who have the drive, determination, and heart to make this all possible,” Widup adds.
This year was no exception. Widup says Jim Cialdea was selected as the 2016 recipient because he “embodies all the qualities that this award represents” by being committed to the advancementofNETAfromabusinessaswellasa advancement of NETA from a business as well as a technical perspective.
“Jim is always willing to pitch in and lead or contributetoanewinitiativeorbreathelifeinto contribute to a new initiative or breathe life into an existing program that needs a helping hand,” says Widup.
Widup says Cialdea gives the impression of not taking things too seriously, but adds, ”Under that calm exterior is a mind committed to asking the tough questions, creating solutions, and getting it done the right way instead of the easy way.”
Steve Cialdea says his father is greatly respected among his employees because he leads by example. “He’s a workaholic, and if there’s trouble, he’s not afraid to be in the field with the guys taking care of things,” he says. “He’s respected because everyone knows that he can do the job of any one of his employees.”
Steve says his father’s excellent reputation spreads from his company to the industry as well. “They keep giving him awards, so he must be doing something right,” he laughs. “He’s extremely involved in professional societies and in and has the utmost respect and admiration of his industry colleagues.”
Alex Piccioli, COO and Co-owner of 3-C Electrical Company, has worked with Jim Cialdea for more than three decades. “Jim is very well respected in the electrical power industry and related community by building long-lasting relationships, and devotion to family and employees,” says Piccioli, “as well as his ability to provide engineered solutions to clients, passion for promoting education and supporting those institutions, and commitment to foster the growth and continued participation in state and national code panels and organizations.”
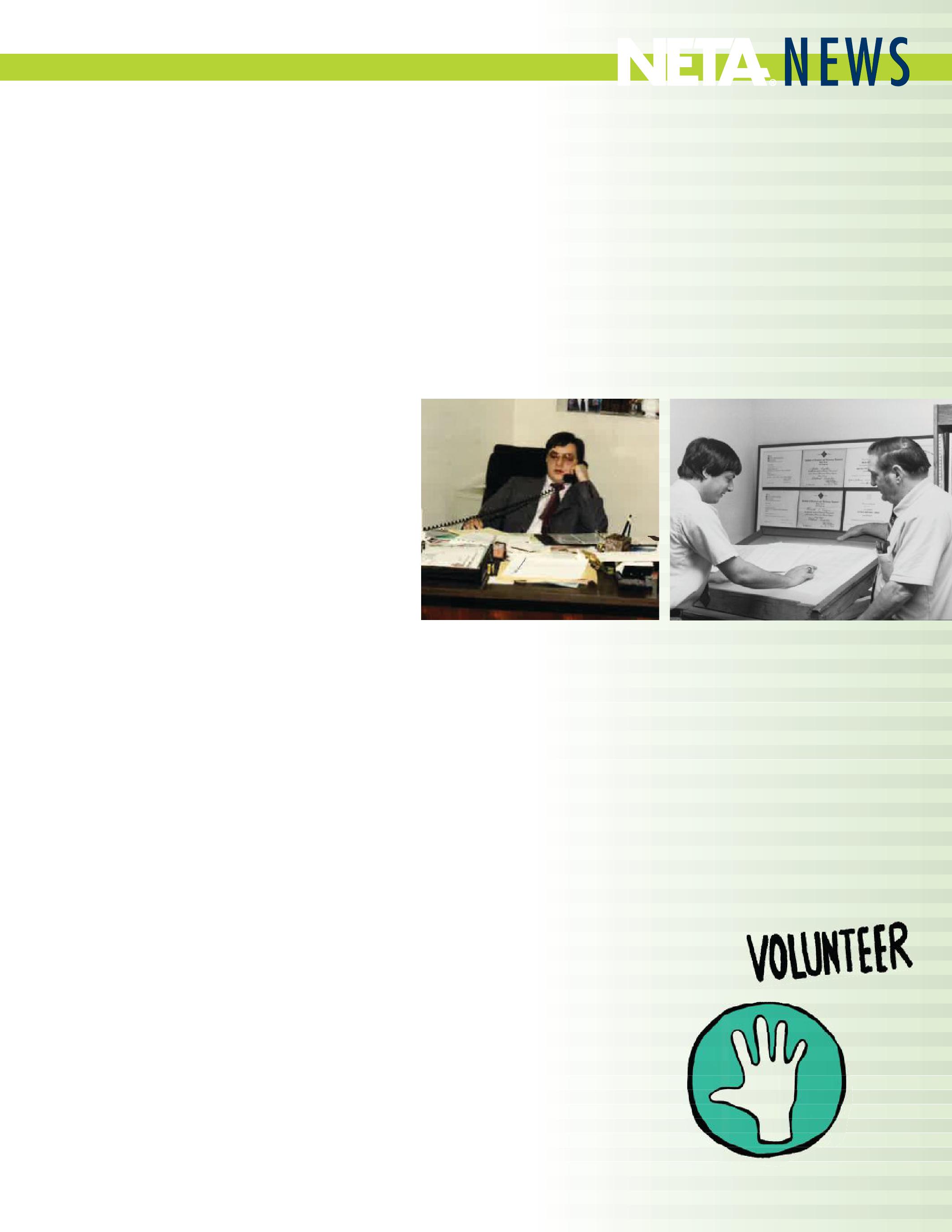
“Jim was extremely appreciative of the acknowledgement from his NETA colleagues,” adds wife Doreen Cialdea. “NETA is a great organization, and participating in NETA is very important to him. He says NETA improves the industry, and he has enjoyed building many close relationships over the years.”
ON HIS DOWNTIME
Jim Cialdea is a Registered Professional Engineer, a Licensed Master Electrician, a Licensed Construction Supervisor, and a Level IV NETA Certified Technician. Like his son, Jim followed in his own father’s footsteps and now has over 30 years of experience in the electrical testing industry.
Inadditiontoseveralothervolunteer In addition to several other volunteer positions he holds with other organizations, Cialdea is the First Vice President of NETA, hasservedasamemberoftheNETABoard has served as a member of the NETA Board
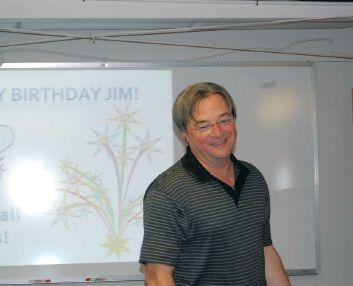
Always a positive influence, willing to do whatever it takes to make it happen.
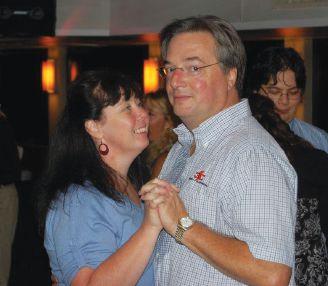
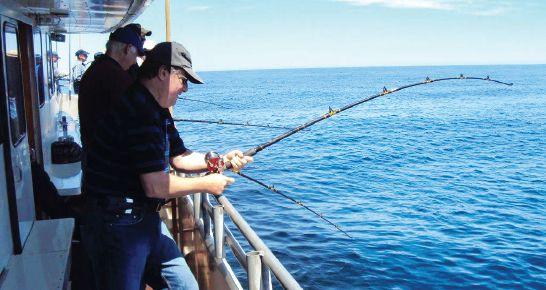
of Directors since 2011, is a Membership Review Committee member, one of the newest members of the NETA Standards Review Council, chair of the Alliance Committee, and a member of the Exam Review Committee.
Cialdea has many hobbies and passions outside of electrical testing and technology, including photography, history, boating, and traveling. His wife would add music and wine to that list.
“He is just an all-around nice guy who is always ready with a kind word, a smile, and a laugh,” says Widup. “And he’s always up for an adventure or just kicking back with a beer and some good conversation.”
“There has never been a want for excitement when working with and having many a fun time with Jim over the past 33+ years,” says Piccioli. “We have had the very good fortune to start together in the family business, and sustaining the company’s growth with the beliefs of safety, quality, and value for our employees and clients.”
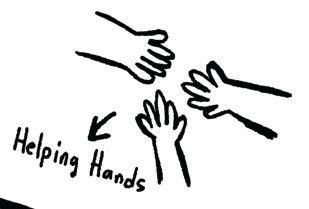

A SEAT AT THE TABLE
In making his presentation to Jim Cialdea at PowerTest, Widup commended him for his dedication to improving the industry and the world around him.
Looking ahead, Cialdea, who was recently appointed to the Standards Review Council, is looking forward to helping write the ANSI/ NETA standards. He says he is “very honored to be sitting at the table with this group of very smart people” and is looking forward to expanding his relationship through NETA and sharing and exchanging ideas.
“It is important to contribute, to improve the standards,” Cialdea says. “Getting involved not only makes the industry better, but helps make your company better, and makes us all better professionals. Sharing information and ideas helps us make everyone better.”
Carla Kalogeridis is part of the NETA World Journal editorialteam
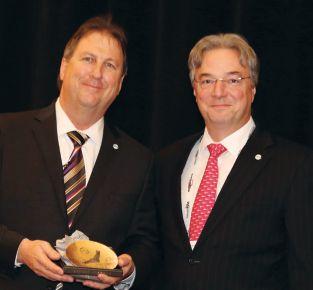

JAMES G. CIALDEA,
NETA’s 2016 Outstanding Achievement Award Honoree
Jim Cialdea, P.E., is Owner and Chief Executive Officer of 3C Electrical Company, Inc., in Westborough, Massachusetts. Jim began working at 3C Electrical under the tutelage and training of his father, Giulio Cialdea,in 1984. He took over the business in 1988 and, under his able leadership, 3C Electrical has achieved marked success in performing a broad range of engineering activities and endeavors, including facilitating and implementing new plant and systems designs for supply-side and demand-side customers, expanding and affecting improvements to the complex electrical systems at existing customer facilities, implementation of all manner of
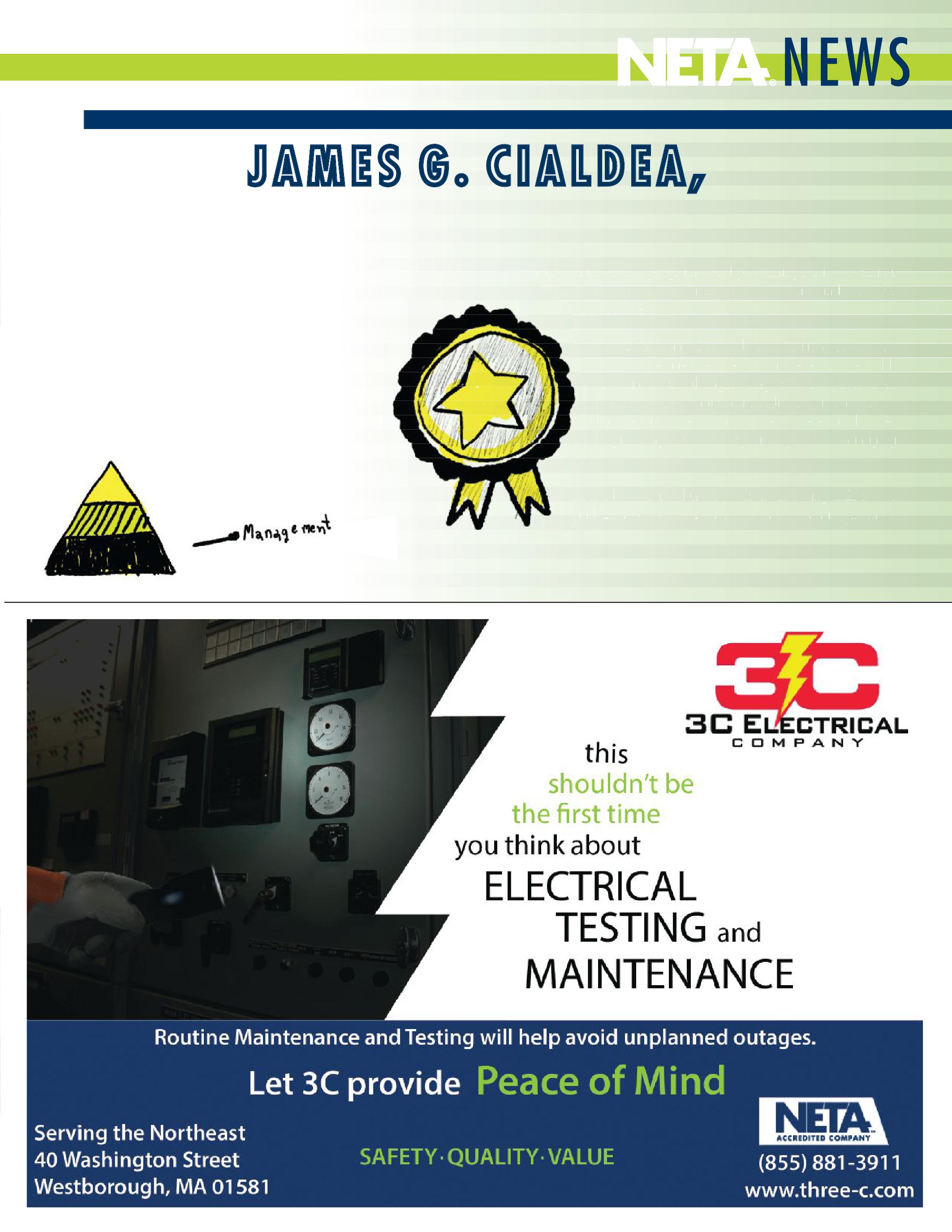
preventative maintenance programs, and performing related technical and support services designed to add quality and value for 3C’scustomers. 3C’s customers.
Jim is a Registered Professional Engineer, Licensed Master Electrician, Licensed Construction Supervisor, andNETACertifiedTestTechnicianLevelIV.Heholds and NETA Certified Test Technician Level IV. He holds a B.S. in Electrical Engineering, Power Option, from Worcester Polytechnic Institute. Jim brings an inherent knowledge of the practical aspects of electrical power engineering with over 30 years experience managing and executing projects. In addition to serving on the NETA Board of Directors and several NETA committees, Jim holds several volunteer positions including IEEE Power and Energy Society Boston Chapter Secretary, member oftheCommonwealthofMassachusettsElectricalCode of the Commonwealth of Massachusetts Electrical Code Advisory Sub-Committee, and MECA Past President.
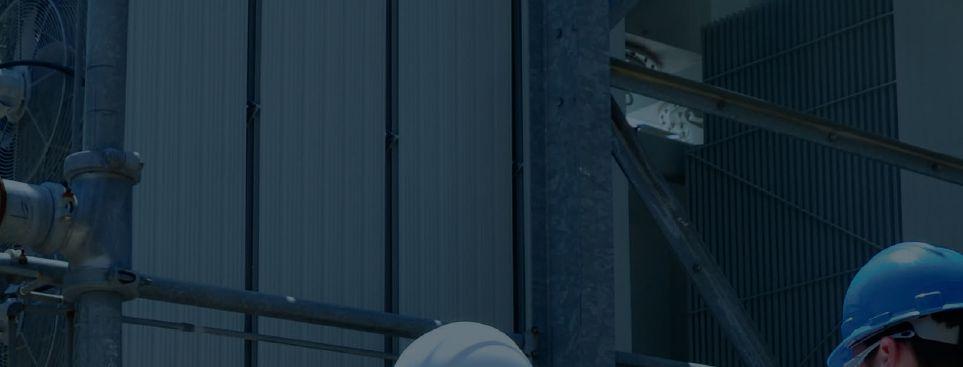
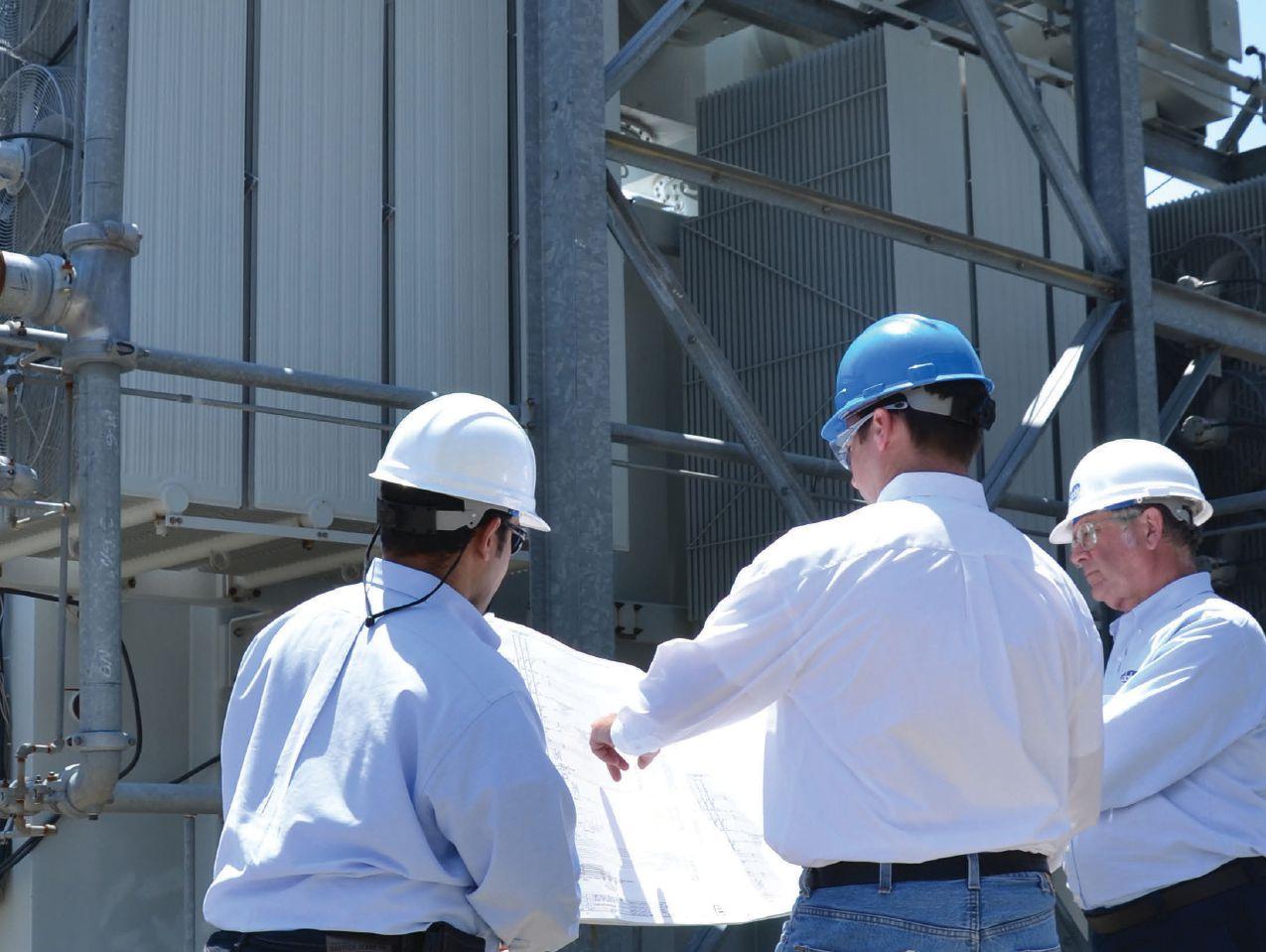
Get Empowered with Doble.
Learn more about our in-service testing tools which help you to identify and locate electrical partial discharge, low-voltage arcing and mechanical system defects before they lead to asset failure.
www.doble.com/NETA
Empowering the industry with services, solutions and unmatched knowledge.
For nearly a century, Doble has been amassing an unprecedented amount of knowledge and practical experience in preventing asset failure. We share this knowledge through our products, services and training programs. We make sure you have the tools and information you need to perform your job and meet the needs of your customers.
0
0.5
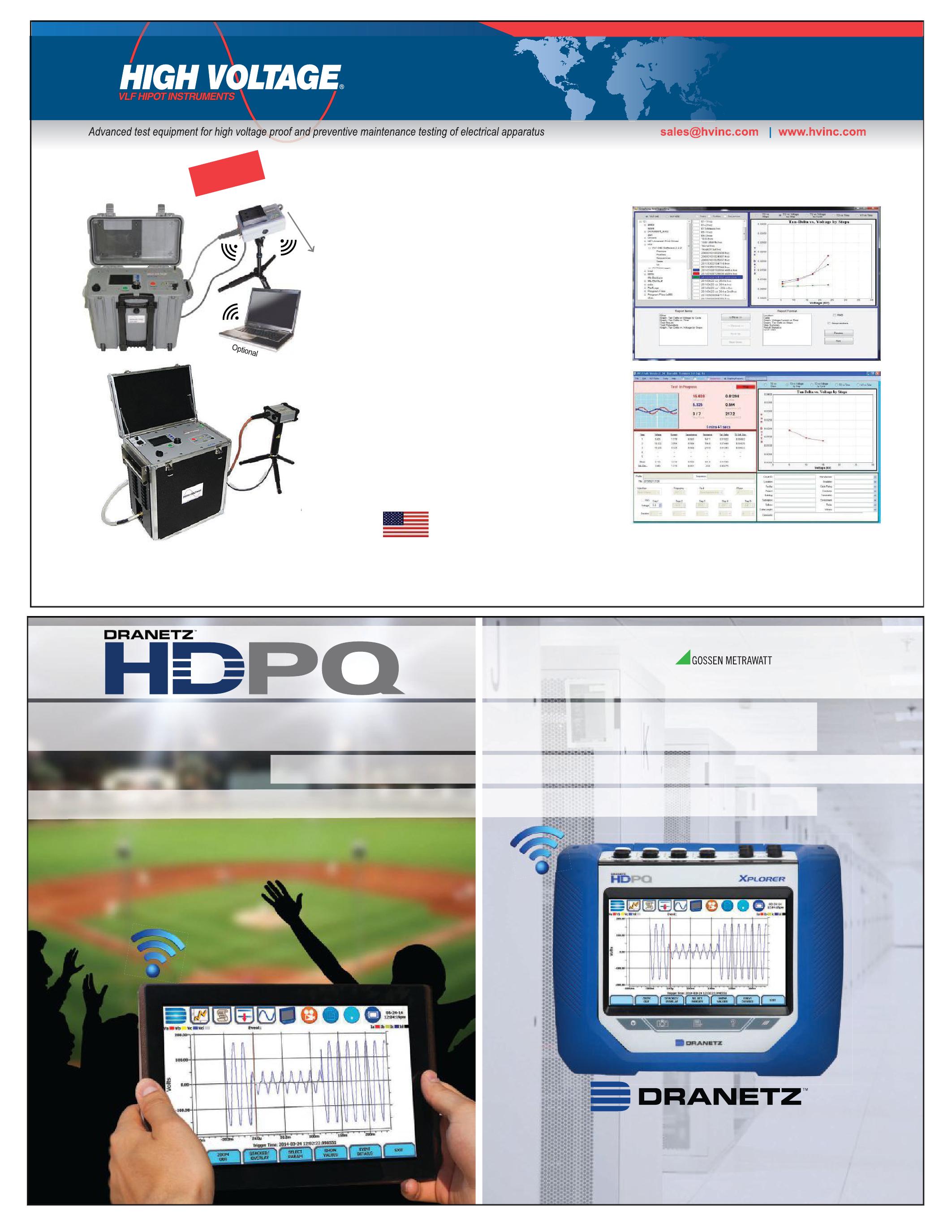
0
1.0
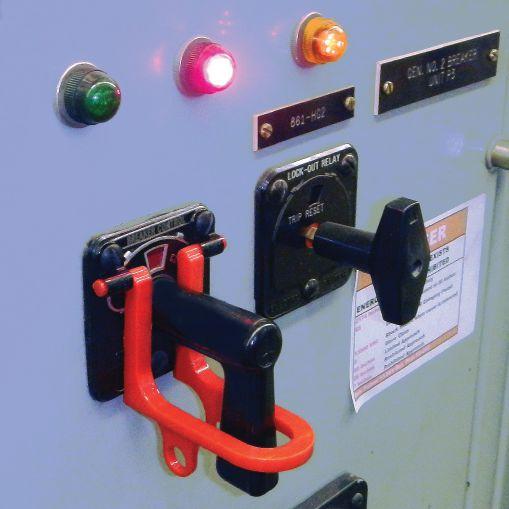
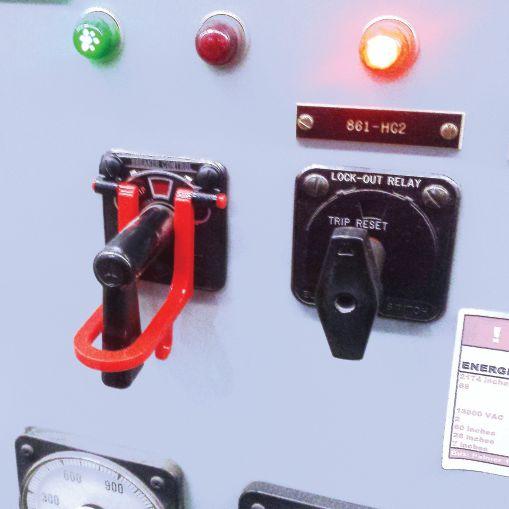
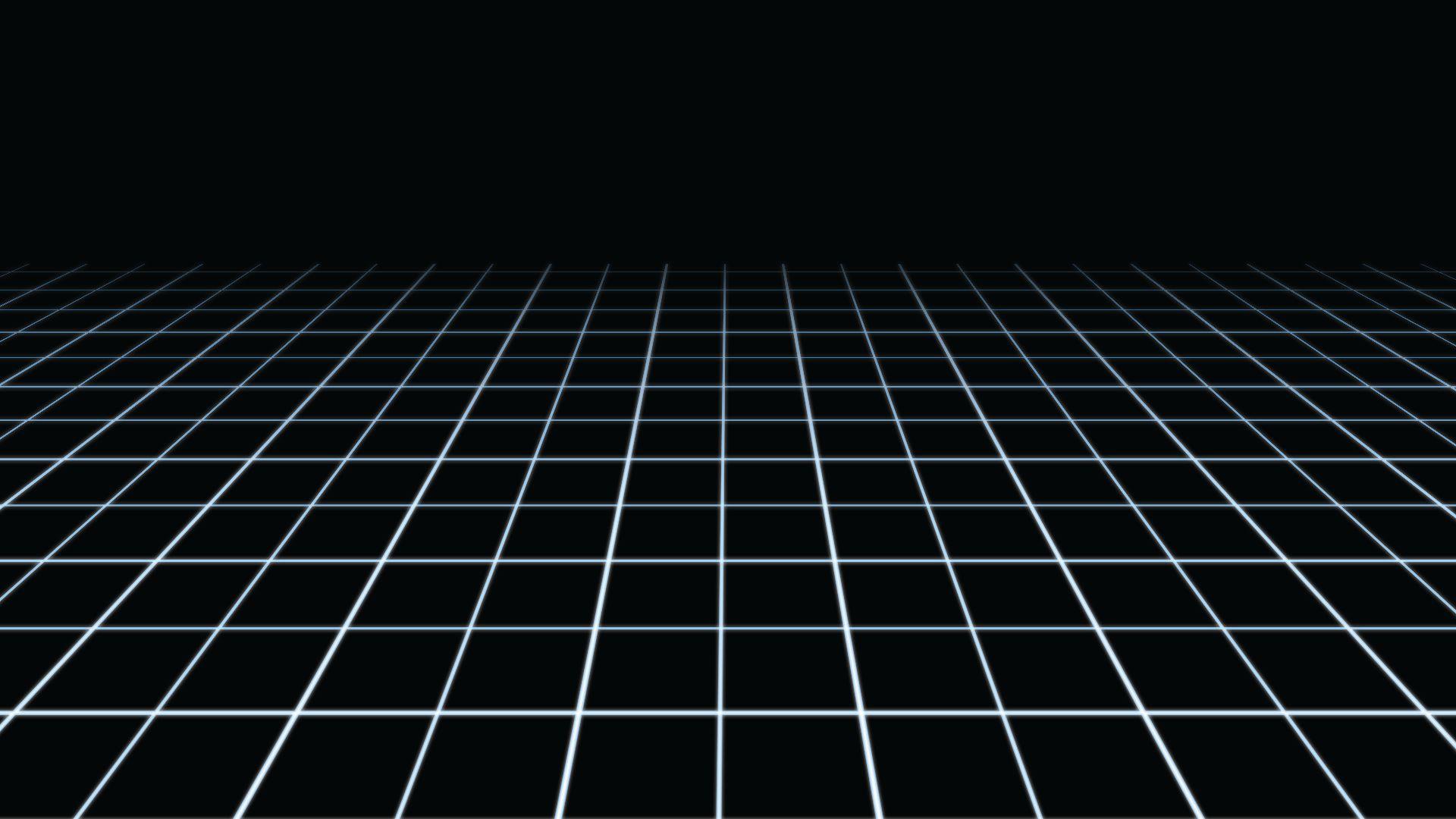
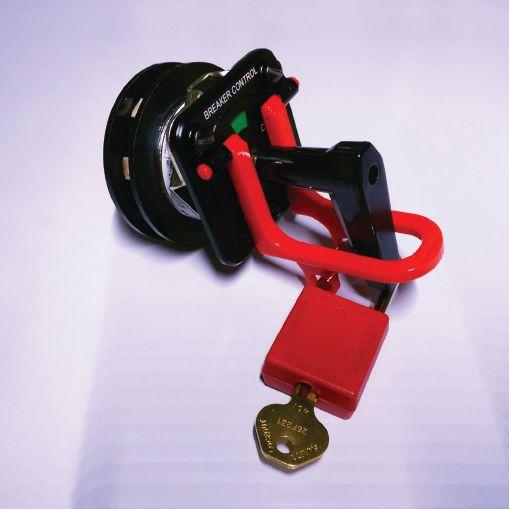
Of Circuit Breakers
BY PAUL H. GREIN, Circuit Breaker Sales Co., Inc.This article examines the changes to medium voltage circuit breaker testing over three generations spanning 70 years from 1945 to today. It discusses the challenges and driving forces that evolved circuit breaker testing, including technological advances in circuit breaker technology, safety practices, and test equipment.

In May 1945, World War II ended; that same year, Westinghouse introduced its first medium-voltage air-magnetic circuit breakers, and the first American standard for ac power circuit breakers was published. Circuit breakers of the day were heavy, expensive, unreliable devices that required regular upkeep to ensure they performed as expected. Early technicians workedinhazardousenvironmentswhere worked in hazardous environments where profits often trumped employee safety. Over three generations spanning 70 years, circuit breaker technology has advanced and safety practices have improved. This article examines three generations of circuit breaker technicians,
and how technological and safety advancements have led up to the testing they perform today.
THE OIL YEARS, 1945-1975
The GoldenYears Golden Years isoftenthemonikerused is often the moniker used to describe the period following World War II. Regulatory intervention from federal and local governments was minimal, and the power equipment industry benefited immensely from an era of rapid growth. Between the years 1946 and 1947 alone, power usage grew almost 15 percent, creating an avid demand for power equipment and men qualified to operate

andmaintainit.Thedemandforelectric and maintain it. The demand for electric power and advances in productivity created a need for circuit breakers with higher current ratings and interrupting capacities. Growth continued for decades, at a diminishing rate, until it stagnated in the tumultuous 1970s to the average 7 percent we see today. While the golden years may delineate the economic growth that drove the circuit breaker industry, the oil years better describes the breaker technology that ruled the era.
Circuit Breakers in the Oil Years
Before and in the decades immediately following World War II, the most common medium-voltage circuit breaker technology used was oil-tank circuit breakers. Many of the switchgear manufacturers that served the American market during World War II remain in business today, including General Electric, Westinghouse (now Eaton Cutler-Hammer), and ABB. This article bases its discussion on Westinghouse’s introduction of circuit breaker technology with the understanding that competing manufacturers may have innovated the technology earlier or later.
The 1940s saw the beginning of a major transition from oil-tank to air-magnetic circuit breakers, but oil-tank technology remained the workhorse of American utilities and factories. Despite the introduction of airmagnetic technology, Westinghouse continued manufacturing its type B and type F oiltank circuit breakers into the early 1950s. However, extinguishing the arcs produced from larger interrupting currents in insulating oil was reaching its technological limit; for the Westinghouse model B-28-B to achieve maximum ratings of 15kV, 500MVA, 2000A, the breaker had swollen to over 2,000 pounds. To meet the continually increasing demand for higher ratings, Westinghouse introduced its DH-type medium-voltage air-magnetic circuit breakers and switchgear in 1939. Initially, the DH line was limited to 5kV up to 150MVA, but by 1946, the maximum voltage of the DH was extended to 15kV; over time, the maximum rated interrupting capacity of the DH breaker reached 1,000 MVA.
In 1963, Westinghouse introduced the DH-P type air-magnetic Porcel-line® circuit breaker and switchgear, with all live parts insulated to ground by high-strength porcelain insulation versus the paper phenolic insulation used in the DH designs, but by this time the oilgeneration circuit breaker technician was certainly eyeing retirement.
Safety in the Oil Years
Safety was not a priority in industrial environments until the Occupational Safety and Health Administration (OSHA) was created in 1970 when the Williams-Steiger Act was signed into law. Electrical safety was not emphasized until 1979 when the National Fire Protection Association (NFPA) published NFPA 70E, Standard for Electrical Safety in the Workplace, at OSHA’s request. Prior to OSHA and NFPA 70E, responsibility for maintaining safe work practices fell on the technician, and electrically safe work practices were anything but. Electrical safety in the beginning of the oil generation can be summed up by this excerpt from the American Electricians Handbook of 1942, which is comical by today’s standards:
“158 Electricians often test for the presence of voltage by touching the conductors with the fingers. This method is safe where the voltage does not exceed 250 and is often convenient to locate a blown-out fuse or for ascertaining whether or not a circuit is alive. Some men can endure the electric shock that results without discomfort whereas others cannot. Therefore, the method is not feasible in some cases.
Which are the outside wires and which is the neutral of a 115/230-volt, three-wire system can be determined in this way by noting the intensity of the shock that results by touching different pairs of wires with the fingers. Use the method with caution and be certain the voltage of the circuit does not exceed 250 before touching the conductors.”
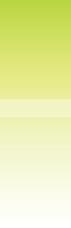
p nstruction and installation books rom
with rc to eak d me cti
The precautions listed in circuit breaker instruction and installation books of the day were largely written to protect the equipment from being damaged rather than protecting
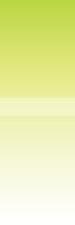

personnel from injury. The equipment was designed for increased operating safety when compared to previous generation designs; the primary circuits were isolated via steel barriers rather than exposed, and interlocking was integrated into the racking mechanism.
Advanced safety features aside, working with oil-tank circuit breakers was a risky endeavor; the breakers were formidable devices whose bulk made them difficult to install and maintain, and their insulation systems were antiquated and often toxic. Combining these factors with the early manufacturing capabilities of the day resulted in unreliable operation, especially compared to today’s standards. When oil circuit breaker failures occurred, the consequences were usually catastrophic.
Circuit Breaker Testing in the Oil Years
The majority of circuit breaker testing performed in the oil years was a mechanical process analogous to performing maintenance on an automobile rather than maintaining electrical equipment. Maintenance consisted of testing, cleaning, and changing the oil then physically inspecting the operating mechanism, contact condition, connections, and looking for signs of carbonization. Maintenance was performed by in-house technicians with limited specialized training or test equipment. If available, dedicated test equipment was limited to dielectric test sets that measured the insulating oil resistance and high-potential test sets for the solid insulation. Test equipment and practices did improve through the oil years, but advancements were adopted slowly. It wasn’t until the next generation that circuit breaker testing would begin to resemble what we see today.
technological advances and safety environment we experience today took root in the air years between1965and1995. between 1965 and 1995.
From Oil to Air
As mentioned previously, the transition from oil-tank to air-magnetic circuit breakers began in the 1940s, but the first generation of air circuit breakers was limited to lightduty applications with maximum ratings of 5kV, 50MVA, 1200A. However, customer interest for the new technology and the technological limitations of oil-tank designs encouraged manufacturers to increase ratings quickly. In 1946, air magnetic circuit breaker ratings were extended up to 15kV, 500MVA, 2,000A applications. The first generation of Westinghouse air-magnetic breakers reached their technological limit in 1958 with the model 150-DH-1000, 3,000A circuit breaker. To reach the extended 1,000MVA interrupt and 3,000A continuous current ratings, the breaker design had bloated to 3,908 pounds with each arc chute weighing in at over 600 pounds!
The introduction of air magnetic technology brought many advantages over the oil-tank breakers they replaced, including:
• Removal of the oil and the associated chemical and fire hazards
• Higher contact breaking speeds and faster arc quenching
• Smaller arc duration allowing extended service life of contacts
• Extended interrupt and continuous current ratings
• Smaller size and weight at a given rating
• Much less maintenance
THE AIR YEARS, 1945-1975
1973 stalled the e he in
onomy, b dustry crep n th
The economic good times experienced during the golden years following World War II would not last forever. A combination of macroeconomic events — including the oil embargo of 1973 — stalled the economy, but growth in the power equipment industry crept along at 7 percent. While the economic setting of the period may have been wanting, the
, the maximum cu
Westinghouse introduced its second generation DH-P Porcel-line model air-magnetic circuit breakers in 1963. Initially, the breakers were rated up to 15kV, 750MVA interrupt, and 2,000A continuous current ratings; by 1974, the maximum current ratings were increased to 1,000MVA, 3,000A.
The innovations introduced in second-generation air circuit breaker technology stemmed from
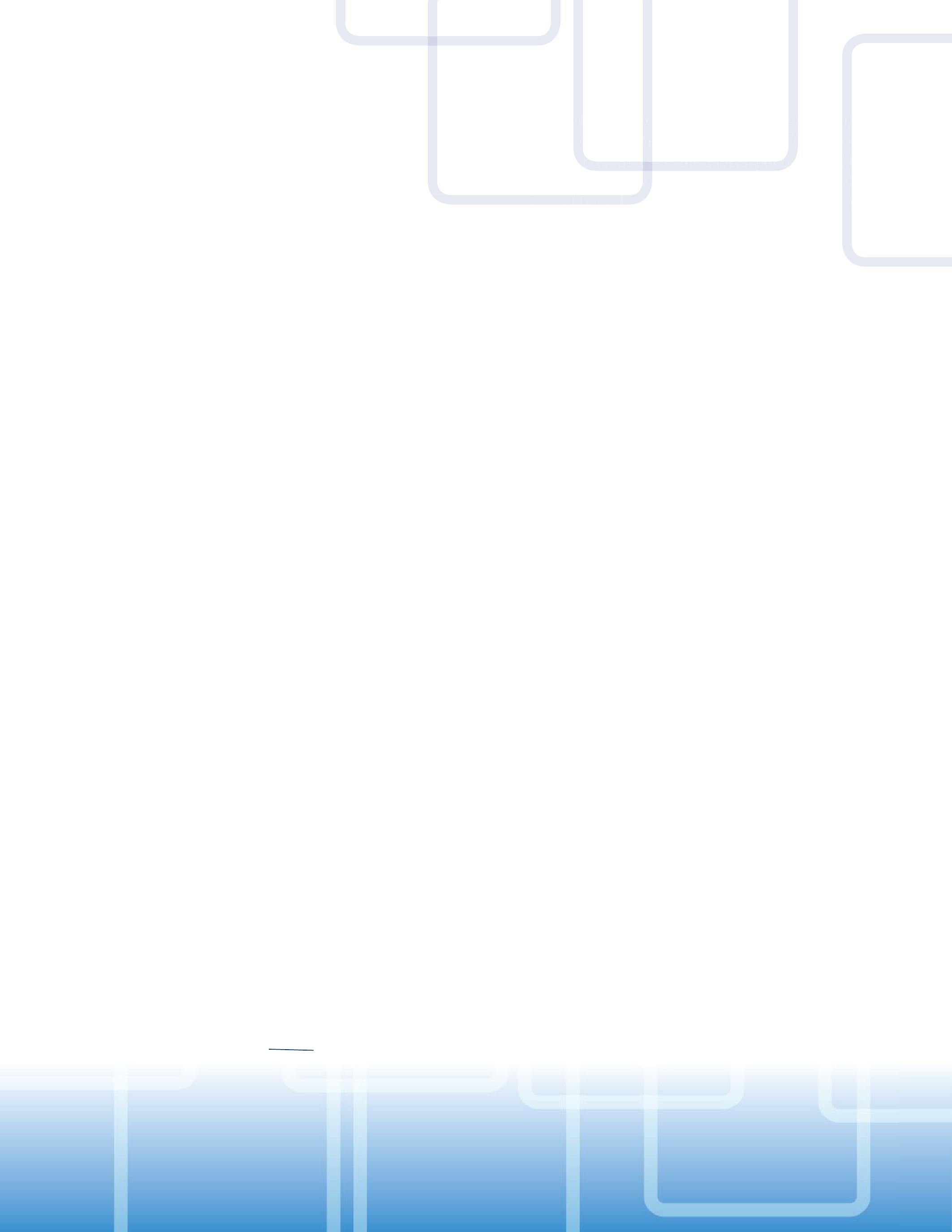
advancements in design, materials, and manufacturing. Rather than paper phenolic insulation used in early generation circuit breakers, the DH-P relied on porcelain to insulate all live parts from ground. Porcelain and similar advanced insulation material technologies are non-tracking, non-combustible, and non-hygroscopic. The reduction of insulation tracking and non-hygroscopic properties allowed circuit breakers to become more compact and lowered the risk of failure from flash-over, increasing reliability and safety. Technician safety was also improved by replacing antiquated materials that could be toxic when mishandled.
Early air circuit breaker designs were furnished with a solenoid operated mechanism with cast parts and monolithic pole assemblies. By the late 1960s, stored-energy spring mechanisms had phased out the solenoid operator, markedly increasing operating speeds. By 1968, cast mechanisms were replaced with machined and modern fabricated mechanisms. Finally, after 1970, monolithic pole units were phased out by the post-insulator pole unit, the single/isolated pole designs employed today. These and other advancements to circuit breaker design had an enormous impact on circuit breaker reliability — so much so that it is common to find equipment commissioned in the 1960s still in use today, over 50 years later.
At the end of the air years, vacuum circuit breaker technology was arriving in American utilities, factories, and distribution systems. The first-generation vacuum breakers, such as the Westinghouse DVP introduced in 1978, were directly interchangeable with the aircircuit breakers they would eventually replace. The improvements that accelerated during the air years were not limited to circuit breaker technology. Test equipment and especially safety practices developed considerably during the air years.
THE AIR SAFETY ERA
The safety environment that many of us take for granted today was pioneered a generation ago as workplace and electrical safety originated
during the air years. After the Williams-Steiger Act was signed into law in 1970, creating OSHA, in 1979 the NFPA published NFPA 70E, the first nationally accepted standard that addressed electrical safety requirements for employee workplaces.
ThefirsteditionofNFPA70Eincluded The first edition of NFPA 70E included installation work practices; since that first edition, the document has continuously improved. Published in 1981, the second edition added safety-related work practices. In 1983, safety-related maintenance requirements were included as well. At the end of the air years in 1995, the fifth edition of NFPA 70E introduced arc-flash hazards. Since their partnership began, OSHA and NFPA have worked together to establish standards and codes documenting safe work practices to ensure employee safety in the workplace and levy fines when those standards are not followed.
The air years established the advancement of technician safety through the foundation of standardized and enforced safety practices, which in turn impacted how breaker testing was performed.
Air Years Circuit Breaker Testing
From generation to generation, circuit breaker testing requirements have expanded in scope and scale. The introduction of new circuit breaker technology and the advancement of test equipment and safety practices brought forth both new types of tests and testing requirements.
The transition between circuit breaker technologies was a gradual process requiring technicians to maintain the equipment of current and previous generations. The growing knowledge and experience required to effectually test the rapidly expanding arena of circuit breaker technologies led to the increased use of specialized breaker technicians, often employed from outside testing companies versus in-house technicians. Outsourcing circuit breaker testing introduced new challenges, the largest of which was ensuring that testing was performed consistently and accurately by suitably experienced and trained technicians.

A group of electrical testing business owners recognized the need to standardize electrical testing to combat the inconsistent testing and safety practices that were commonplace. In 1972, the National Electrical Testing Association (NETA) was formed with the goal of establishing uniform testing procedures for electrical equipment. In 1977, NETA published ATS-1977, Acceptance Testing Specifications for Electrical Power Distribution Equipment and Systems. ATS-1977 illustrates how circuit breaker testing has expanded since the 1940s. Comparing the maintenance recommendations from circa 1940s and 1950s maintenance manuals to the ATS-1977 test recommendations for like equipment gives an indication of how the types of testing continue to grow. Apart from the basic mechanical inspections predominant in the oil years, all of the following tests either took root or became expected during the air years:
1. Visual and mechanical inspections
• Contact alignment and condition
• Lubrication
• Tightness of bolted connections
2. Contact resistance
3. Travel time test
4. Sample insulating liquid
• Dielectric strength
• Acidity
• Interfacial tension
• Color
5. Minimum pickup voltage tests
• Close
• Trip
6. Insulation resistance testing
7. AC and/or dc over-potential testing
8. Control wire insulation testing
9. Power factor testing
The expanding knowledge requirement was not limited to understanding the idiosyncrasies of the various types of breaker technology — not to mention the various manufacturers and models — but also included the theory and application of new testing requirements. Testing was beginning to see a gradual transition from corrective to preventative maintenance, a trend that would accelerate in generations to come.
THE VACUUM GENERATION: 1985-TODAY
For much of America, the 1970s was a tumultuous timeandthe1980swerenot time and the 1980s were not free from hardships, but most would agree that history has shown the decade to be a turning point for the country economically and technologically. Driven in part by the intense competition between the United States and the Soviet Union, technological innovation and other advancements exploded in the vacuum generation. Many of the most significant circuit breaker advancements took place during the vacuum generation.
Vacuum Circuit Breakers
In 1978, Westinghouse introduced the DVP type in 500 and 750 MVA, its first vacuum circuit breaker model. The DVP was not a new line of switchgear; it was an introduction to vacuum technology used with its existing DHP Porcel-line switchgear (directly interchangeable, identically-rated DH-Ps). Competing manufacturers took a similar approach to introducing vacuum interruption technology. In 1981, Westinghouse introduced its VCP line of vacuum circuit breakers and associated VacClad switchgear in ratings up to 15kV and 1,000 MVA. VCP was Westinghouse’s first generation of modern vacuum circuit breakers.
Vacuum interruption is arguably the most significant innovation in medium-voltage circuit breaker technology. Vacuum interruption has numerous advantages over previous generation equipment, including:
• Breaker size and weight are significantly reduced, allowing two-high stacking construction and making them physically easier to remove and transport for maintenance.
•Removal of air-magnetic arc chutes eliminates associated maintenance and handling issues.
• Contact upkeep is reduced to monitoring versus maintenance.
• Vacuum insulation strength greatly reduces the required contact gap, allowing breaker operating mechanisms to become faster to operate, more reliable, and easier to maintain.
• Interrupting arcs are contained, making them non-explosive.

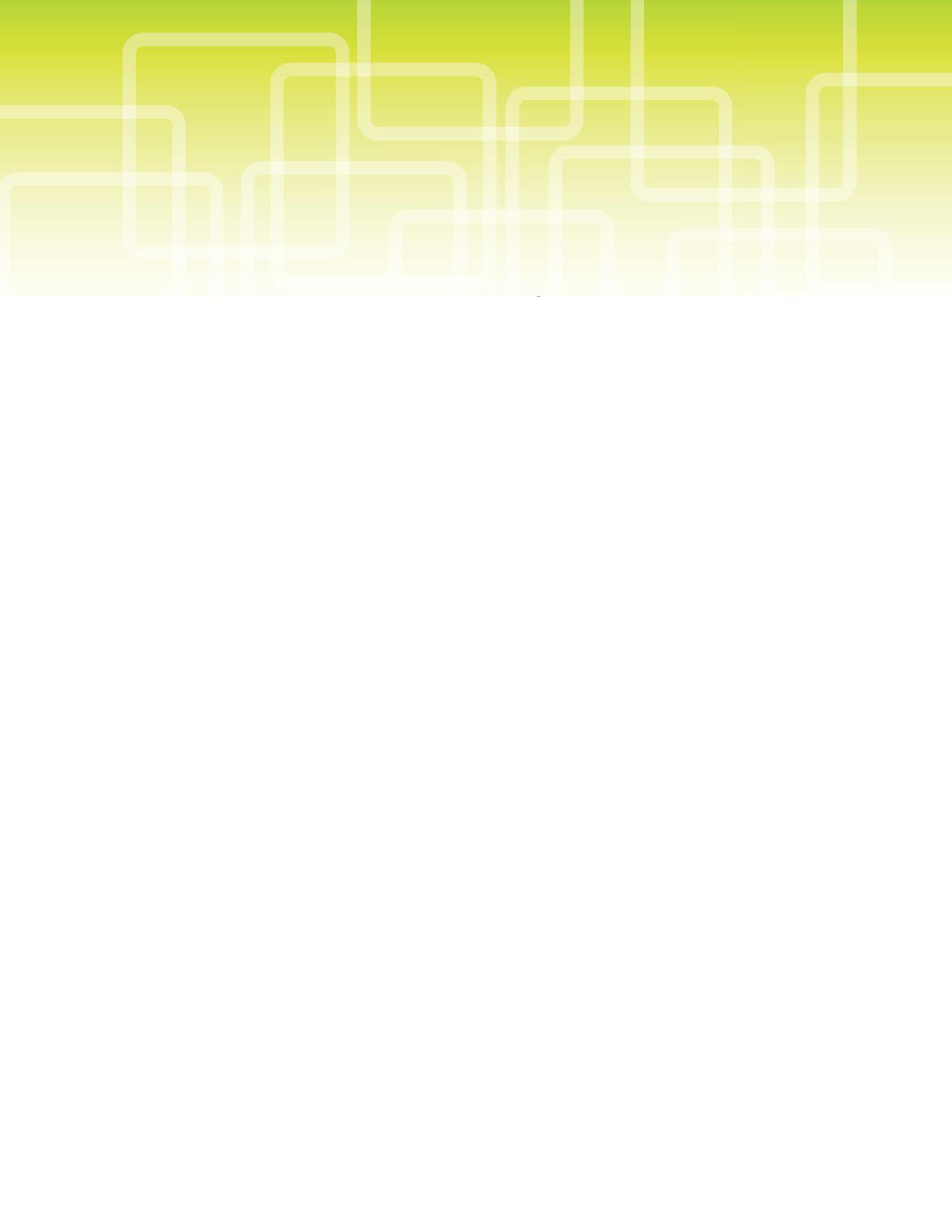
• The mechanisms require significantly less stored kinetic energy during operation, making them safer to maintain.
In 1986, Westinghouse introduced the second generation VCP-W line of vacuum circuit breaker and associated VacClad-W switchgear in ratings up to 15kV at 1,500 MVA and 38kV at 40kA. VCP-W included product improvements in manufacturing design and performance. In 1995, an arc-resistant version of the VCP-W brandwasintroduced:VCP-WisEaton’scurrent brand was introduced: VCP-W is Eaton’s current switchgear offering in medium voltage.
ThemostrecentinnovationsinmediumThe most recent innovations in mediumvoltage circuit breaker technology involve the operating mechanism rather than the interrupting medium. Several manufacturers have introduced magnetic-actuator operating mechanisms that have few moving parts, require no maintenance or adjustments over the life of the product, and are warranteed for five years versus the industry standard of one year.
MODERN SAFETY
During the air years, the largest contributor to technician safety was the development and enforcement of modern safety practices. In the vacuum generation, safety practices were further enhanced by OSHA’s institution of lock-out/tag-out procedures in 1989, the recognition of arc-flash hazards by the NFPA in 1994, and subsequent efforts to reduce exposure to arc flash. Recent efforts to reduce or remove the risk of arc flash include arc-flash studies, the implementation of remote and integrated racking devices, and use of advanced personal protective equipment.
During the vacuum generation, the most significant contributor to safety was technological innovation. The advantages of vacuum circuit breaker technology partnered with modern manufacturing capabilities and materials have dramatically increased the reliability of modern power equipment operation and safety features. Increased equipment reliability results in longer maintenance cycles and fewer failures, which in turn reduces maintenance technicians’ exposure to the hazards.
Despite the progression of safety afforded by procedural and technological advancements, the modern technician faces many of the same risks as those of previous generations. The implementation of new technology in the power industry is a slow process. There arecountlessinstallationsacrosstheUnited are countless installations across the United States that still use air-magnetic and even oil-tank circuit breaker technology that has been in service for over 40 or even 50 years. The continually expanding knowledge and experience level required to safely maintain power equipment technology spanning three generations may be the greatest challenge to present-day maintenance technicians.
Testing Technicians Today
So far, three generations of circuit breakers have been discussed — the oil, air, and vacuum eras — as well as how technology and safety advancementshaveaffectedcircuitbreaker advancements have affected circuit breaker testing. The primary challenge that today’s technicians face is the overwhelming level of expertise needed to effectively and safely evaluate three generations of equipment.
Over the last 70 years, four or five major and several minor switchgear manufacturers have collectively produced over 100 combinations of models and ratings of medium voltage circuit breakers. Medium-voltage circuit breakers have been the focus of this article, but electrical maintenance personnel and technicians are also responsible for testing the entire lineup of electrical equipment, including low-voltage circuit breakers, motor starters, transformers, cables, motors, metering, relays, and ground fault systems. To overcome these challenges, technicians have evolved from mechanics to electrical maintenance personnel to technicians who specialize in narrow fields of expertise. Specialized technicians may have some experience on the entire spectrum, but have focused expertise and training that is limited to a few — and sometimes a single — category of electrical equipment. No matter what their specific category of expertise may be, all technicians must be trained and proficient in safe work practices.
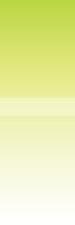

LOOKING FORWARD
The greatest changes to the industry are — and will continue to be — driven by globalization andadvancementstocircuitbreakerand and advancements to circuit breaker and manufacturing technologies. These and other factors have driven costs down to where it almost makes more sense to replace equipment rather than maintain it, and modern breaker designs encourage that practice.
Circuit breaker designs are becoming modular. The trend began with plug-and-play parts such as coils and motors, but now, complete mechanisms and interrupting assemblies are designed to be quickly and easily replaced in the field. Opinions will vary on whether the philosophy of “make it fast” over “make it last” is an improvement, but most would agree that it is unlikely that switchgear commissioned today will still be in service in the year 2075.
Over the years, the means and methods of electrical testing may have changed, but the goal has remained the same: the upkeep and preservation of electrical equipment. Dramatic improvements to circuit breaker technology, safety practices, and testing capabilities have resulted in continually increasing performance and reliability. Without question, modern equipment is easier and safer to maintain, and as the aging equipment of previous generation is slowly upgraded and industry innovations continue, the risks and costs of maintaining it will continue to decrease.

Paul Grein has been with Group CBS since 2008, working primarily at Circuit Breaker Sales in Gainesville, Texas. He has worked with industrial electrical equipment for 20 years, beginning in the Navy as a Nuclear-qualified Electrician on the submarine USS Topeka SSN 754 from 1996 through 2002, followed by positions in the steel industry through 2005. Paul has a BSEE from the University of Texas at Dallas (2007) and an MBA from the University of North Texas (2014). He participates in the IEEE/ANSI PES C37 Standards Committee, which publishes and maintains the design and testing standards that govern the industrial power equipment industry. Paul’s primary responsibilities at CBS and the Group include sales, engineering design, technical expertise, standards, project management, and engineering team management.
REFERENCES
ABB(2014).AMVAC. ABB (2014). AMVAC. Medium Voltage Indoor Circuit Breakers Descriptive Bulletin, pp. 6-7. Lake Mary: ABB. Croft, T (1942). American Electricians' Handbook, 5th Edition. New York: McGraw-Hill Book Company. Eaton (2013). Medium Voltage Switchgear. In CA08100014E Aftermarket, Renewal Parts and Life Extension Solutions Catalog, pp. V12-T17-5364. Eaton.
Howell, J (2014). NETA — Setting the Standard. NETA World Journal, pp. 1-4.
Jooma, Z. (2016). History of the NFPA 70E Retrieved from Electricity and Control: http://www.eandcspoton.co.za/resources/docs/ Hazardous/History_of_the_NFPA.pdf
Littelfuse (2005). Electrical Safety Hazards Handbook Des Plaines: Littelfuse Inc.
NETA (1977). Acceptance Testing Specifications for Electrical Power Distribution Equipment & Systems Meriden: National Electrical Testing Association. U.S. EIA (2016, January 15). History of Energy Consumption in the United States, 1775–2009. Retrieved from U.S. Energy Information Administration's Today in Energy: https://www.eia. gov/todayinenergy/detail.cfm?id=10#
Westinghouse (1941). Type "DH" "De-ion" Air Circuit Breakers Instruction Book. Pittsburgh: Westinghouse. Westinghouse (1944). "Unitized" Heavy-Duty Metal-Clad Switchgear. Pittsburgh: Westinghouse Electric & Manufacturing Company.
Westinghouse (1949). Instructions - High-Voltage MetalClad Switchgear with "F" and "B" Oil Circuit Breakers Pittsburgh: Westinghouse Electric Corporation.
Westinghouse (1949). Unitized Metal-Clad Switchgear Light-Duty DH Type — Descriptive Bulletin East Pittsburgh: Westinghose Electric Corporation.
Westinghouse (1958). Descriptive Bulletin — Standardized Metal-Clad Switchgear. East Pittsburgh: Westinghouse Electric Corporation.
Westinghouse (1959). Instrcutions — De-ion Air Circuit Breaker Type 150-DH-1000. East Pittsburgh: Westinghouse Electric Corporation.
Westinghouse (1965). Porcel-line Metal-Clad Switchgear with Type DH-P Air Circuit Breakers — Descriptive Bulletin. East Pittsburgh: Westinghouse Electric Corporation, Switchgear Division.

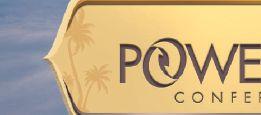
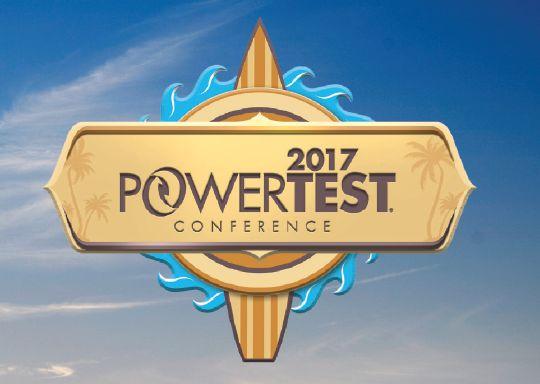


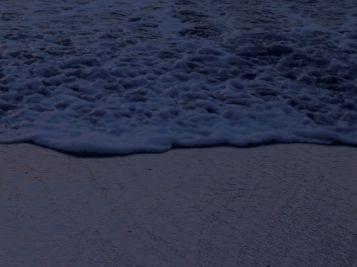
For Large Power Transformers In Today's Electrical Utility Sector
BY RAY CURRY, American Transmission Company“Use the best of the past to build the future.” — Unknown
In the previous article (see NETA World Journal, Winter 2015), I touched on items that affect transformer installation and testing. Now, I want to focus on two items that have changed the field assembly of these transformers. Both have their origin in the 1970s and continue to have a strong influence today.
FALL PROTECTION AND CONFINED SPACE
First and foremost was the establishment of OSHA, and in particular, CFR 1910. Perhaps the most influential thing to happen in the 1970s was the establishment of OSHA. The development of OSHA Regulation CFR 1910 on Fall Protection and Confined Space has had a major influence on how the assembly of large power transformers is accomplished.
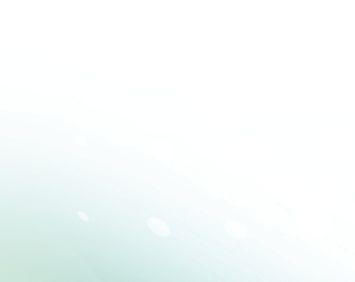
Before any assembly work is started, the best practice is to ground the transformer to the ground grid of the substation. It is also a good practice to ground all cranes, lifts, processing trailers, and tankers.
In the area of fall protection, enhancements to and development of man lifts, work platforms, and body harnesses are designed to comply with OSHA regulations. When assembling large transformers, workers operate anywhere from 10 to 40 feet above the ground. Some transformers have attachments
on top of the main tank for the placement of railing systems. Some manufacturers provide an attachment area for installing a may pole (see picture). This pole is rated to have up to four workers attached at one time and still meet OSHA code.

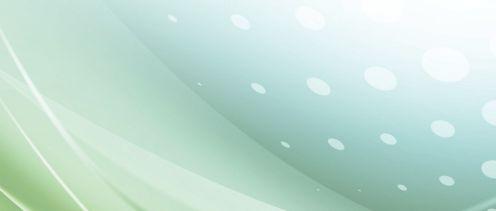

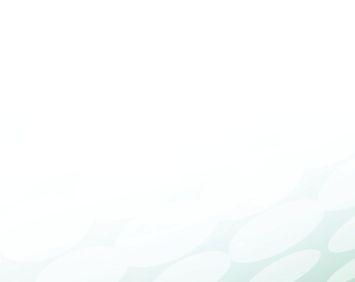
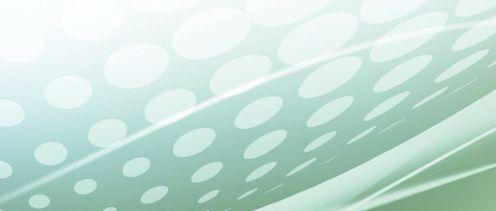
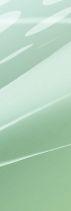
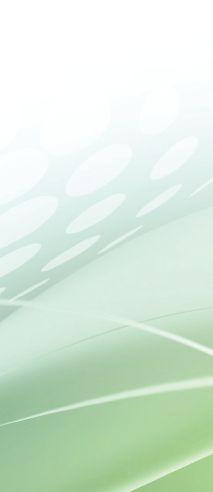

Today’s power transformer is designed with a smaller main tank. The intent of this design is to aid shipping the largest MVA transformer over the road versus railroad shipment. The length and width of today’s transformer has not changed much, but the height has been greatly reduced. This reduction creates two challenges for the assembly crew: (1) more field assembly on top of the transformer’s main tank and (2) in most designs, very restricted work space for any inside tank work required to connect the high- and lowside bushings. To address the inside work, draw lead bushings are sometimes used. Side wall access flanges allow employees to make up winding connections on the bottom of the bushings.
By OSHA regulation, should any assembly work be required inside of the main transformer tank, this entry point and workspace must be treated as a confined space. The regulation states that the entry is by permit only. Another part of the regulation requires that the contractor have extraction equipment present while workers are in the permitted space.
DESIGN AND ENGINEERING CHANGES
The second influential item of the 1970s affecting transformer field assembly is design and engineering changes. Advancements that began in the 1970s have become global today. Transformer manufacturers must use the building blocks of the past to compete successfully today.
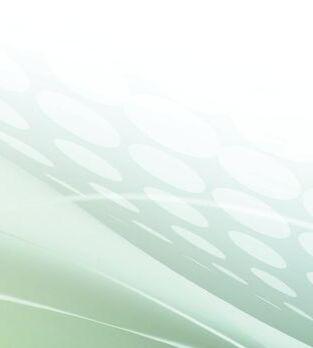
When fully loaded, these large transformers produce a tremendous amount of heat. To dissipate this heat, mineral oil is used with pumps and radiators. Silicone and other fluids were developed through the 1970s, but mineral oil still provides the best heat transfer in the large transformer. However, mineral oil can have a negative impact on the environment. To counter this, new products for containment and engineered systems have been initiated for most transformers, new and old.
With respect to ancillary equipment, Reinhausen developed the vacuum tap changer and grew its world market share in the 1970s. Most distribution and transmission class transformers have load tap changers. The vacuum tap changer requires far less maintenance compared to older tap changers. Likewise, companies such as Ohio Brass and Qualitrol, among others, developed and improved transformer products through the 1970s and 1980s. Microprocessor-based protective relays — a vast improvement over the electro-mechanical relay — now protect this expensive capital equipment.
The advancement of computer-aided design (CAD), for example, gave rise to computeraided engineering (CAE), which allowed the engineer to build with modeling software. These programs grew in many directions and gave birth to new support services and ancillary equipment. Start-up companies provided polymers, epoxy resins, and new dielectric insulations, which in turn allowed the transformer to be built with a higher basic insulation level or basic impulse level (BIL), which led to higher kilovolt (kV) levels.

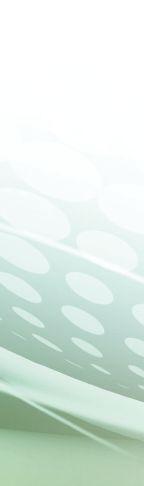


Computer modeling software has also provided design engineers with the ability to build a transformer that operates with more efficiency, heavier load cycle, and longer operating life. To gain this capability, field assembly and oil processing has been improved from the 1970s to now. Companies such as Barron have designed vacuum/oil processing trailers that are also computer controlled. All transformers in the high-voltage class (50kV and above) are designed to withstand full vacuum. The high vacuum is used to dry or pull moisture out of the transformer. In the 1970s, this processing equipment would attain 800 to 1,000 microns or 0.8 to one Torr. Today’s equipment will typically reach 40 to 200 microns. To put this in better perspective:
1,000 microns = 1 Torr = 1 millimeter of mercury
Because of improved design and assembly, today’s transformers use neoprene and nitrile rubber gaskets, compared to units built in the
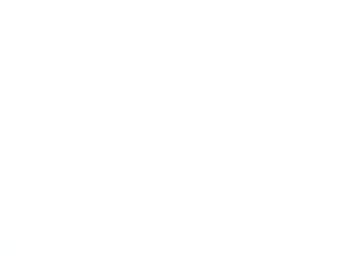
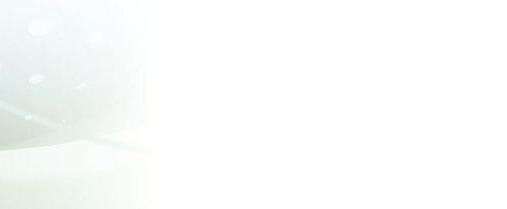
1960s and 1970s, which used cork or corkneoprene. On the older transformer, oil leaks occurred early as the cork dried out, which in turn affected annual maintenance work. The preferred gasket or O-ring rubber is Nitrile 70 or Nitrile 90. Many transformers of the late 1980s are in service today with Nitrile 70 and have had little or no oil leak issues caused from degradation of the nitrile. When these units were first assembled and processed, the benefit of having the advanced gaskets and O-rings was a tighter transformer with respect to vacuum/pressure leaks. In turn, this reduced the vacuum processing time.
Even with the higher vacuum, the processing and oil filling of a large transformer takes time. Typically, most of these transformers will hold 10,000 to 26,000 gallons of oil. As part of the processing, oil is heated and degassed as it flows through the processing equipment at a rate of 20 to 30 gallons per minute, heated again, and injected into the transformer tank. Some transformer manufacturers also require oil recirculation to obtain lower moisture levels. After all, in most installations, the manufacturer is providing a warranty that may last several years.
Another aspect of today’s transformer is the preservation of the oil. Many transformers of the 1970s used a nitrogen blanket to control oil moisture buildup. Today’s transmission class transformer will use the conservator oil preservation system (COPS). With the use of COPS, today’s transformer now has a very sensitive dissolved gas analyzer (DGA) system. With the use of another protective relay — a gas-sensing relay that will detect explosive gases — the transformer now has enhanced protection against electrical faults that occur insidethetransformermaintank. inside the transformer main tank.
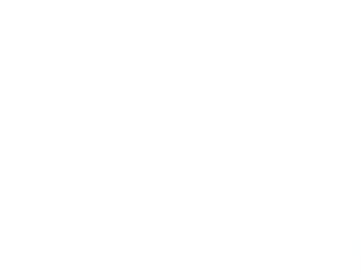
When an electric arc happens in an oil transformer, explosive gasses are produced; if allowed to accumulate, further damage or transformer failure may occur.
An objective of every large power transformer assembly and installation is to maximize its life cycle by establishing a sound maintenance program. A term used today is Maintenance Zero. By obtaining the proper installation, vacuum/oil processing, and detailed final inservice testing, the transformer owner lays the foundation for 40-plus years of useful transformer life. In the next article in this series, I will outline how power transformer testing, test equipment, and record keeping have changed from the 1970s to today.
There are challenges going forward. One is maintaining a skilled workforce that can deliver quality technical workmanship safely to the customer. Another is building a strong working relationship between the manufacturer and the field assembler/processor/testing company. As a result, many NETA Certified Companies have formed strong working relationships with Hyundai, GE, ABB, and Siemens to name a few. These relationships are strengthened with factory training, technical seminars, and new product engineering updates. With many of today’s transformers built overseas, reliability to the end customer has taken on a whole new meaning and significance.

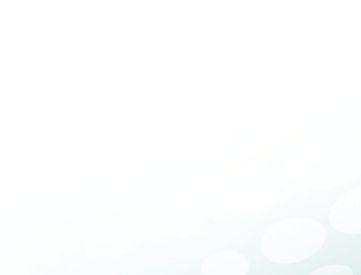

Ray Curry graduated from Penn State University in 1969. He joined Westinghouse Electric in the East Pittsburgh Division and the PCB Division at Trafford, Pennsylvania. In 1977, Ray relocated with Westinghouse to St. Louis, Missouri, working in the E&ISDDivisionasaFieldService E&ISD Division as a Field Service Engineer specializing in high-voltage switchgear and construction/commissioning power substations. After retiring from Westinghouse in 1994, Ray managed two municipal electrical systems for the cities of Chanute and Garden City, Kansas, from 1994-2000. From 2007 to the present, Ray has been a Commissioning Engineer with American Transmission Company, building and maintaining over 500 69kV-138kV to 345kV electrical substations, including more than 200 power transformers within the ATC Service Footprint. He sits on ATC’s Safety Committee and has maintained an active affiliation with NETA for six years.

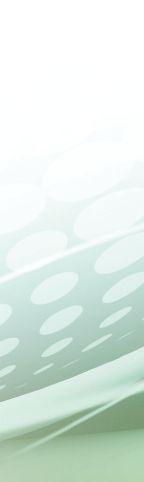
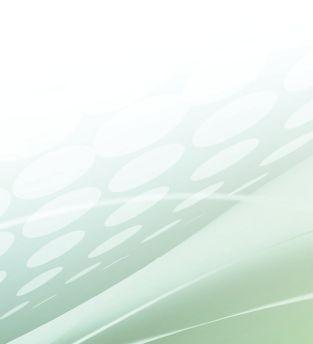
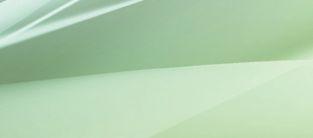

ANSI/NETA STANDARDS UPDATE
BY KRISTEN WICKS, NETA
ANSI/NETA ATS-201X REVISION IN PROCESS
TheANSI/NETA The ANSI/NETA Standard for Acceptance Testing Specifications for Electrical Power Equipment and Systems Equipment began the review and revision process in October 2014 at the Standards Review Council meeting. Theinitialballotanddraftdocument The initial ballot and draft document will be issued on April 22, 2016 with a issued on April closing date of May 22, 2016. The draft document will be available for public comment from April 22, 2016 through June 6, 2016. The document is expected to be published as a revised ANSI standard in the spring of 2017.
ANSI/NETA ECS-2015 FIRST EDITION AMERICAN NATIONAL STANDARD
TheANSI/NETA The ANSI/NETA ECS Standard for Electrical Commissioning of Electrical Power Equipment and Systems, 2015 edition, was approved as an American National Standard on December 3, 2014. This new standard is available for purchase in the NETA Bookstore online at netaworld.org.
instrumentation systems, and related components.
Voltage classes addressed include:
• Low-Voltage Systems (less than 1,000 volts)
• Medium-Voltage Systems (greater than 1,000 volts and less than 100,000 volts)
• High-Voltage and Extra-High Voltage Systems (greater than 100 kV and less than 1,000 kV)
References
TheANSI/NETAATScoversthe
The ANSI/NETA ATS covers the suggested field tests and inspections that are available to assess the suitability for initial energization of electrical power equipment and systems. The purpose of these specifications is to assure that tested electrical equipment and systems are operational, are within applicable standards and manufacturers’ tolerances, andareinstalledinaccordancewith and are installed in accordance with design specifications.
TheANSI/NETAECSdescribesthe The ANSI/NETA ECS describes the systematic process of documenting and placing into service newly installed or retrofitted electrical power equipment and systems. This document shall be used in conjunction with the most recent editionoftheANSI/NETA edition of the ANSI/NETA Standard for Acceptance Testing Specifications for Electrical Power Equipment and Systems. The individual electrical components shall be subjected to factory and field tests, as required, to validate the individual components. It is not the intent of these specifications to provide comprehensive details on the commissioning of mechanical equipment, mechanical
ASHRAE, ANSI/NETA ATS, NECA, NFPA 70E, OSHA, GSA Building Commissioning Guide
ANSI/NETA MTS-2015 NEW EDITION
The ANSI/NETA MTS Standard for Maintenance Testing Specifications for Electrical Power Equipment and Systems, 2015 edition, was approved as an American National Standard on December 3, 2014, and supersedes the ANSI/NETA MTS2011.Thisnewstandardisavailable 2011. This new standard is available
for purchase in the NETA Bookstore online at netaworld.org.
The ANSI/NETA MTS contains specifications that cover suggested field tests and inspections available to assess the suitability for continued service and reliability of electrical power equipment and systems. The purpose of these specifications is to assure that tested electrical equipment and systems are operational and are within applicable standards and manufacturers’ tolerances, and that the equipment and systems aresuitableforcontinuedservice. are suitable for continued service.
Revisionsinclude: Revisions include:
• New numbering system for more accurate referencing
• Protective relays
• Instrumenttransformers Instrument transformers
• Rotating machinery
• NewTable100.11 New Table 100.11
• RevisedTable100.1 Revised Table 100.1

• Updated references to industry standards
• Many more revisions, all marked in the margins for ease of use
ANSI/NETA ETT-2015 NEW EDITION
ANSI/NETAETT ANSI/NETA ETT Standard for Certification of Electrical Testing Technicians, 2015 edition, was approved as an American National Standard American on December 3, 2014, and supersedes the ANSI/NETAETT-2010.Thisnewstandardis
ANSI/NETA ETT-2010. This new standard is available for purchase in the NETA Bookstore online at netaworld.org.
PARTICIPATION
TheANSI/NETAETTestablishesminimum
The ANSI/NETA ETT establishes minimum requirements for qualifications, certification, training, and experience for the electrical testing technician. It also provides criteria for also documenting qualifications for certification and details the minimum qualifications for an independent and impartial certifying body to certify electrical testing technicians.
Comments and suggestions on any of the standards are always welcome and should be directed to the NETA office at neta@netaworld.org or 888-300-6382. To learn more about the NETA standards review and revision process, to purchase these standards, or to get involved, please visit www.netaworld.org or call 888-300-6382.
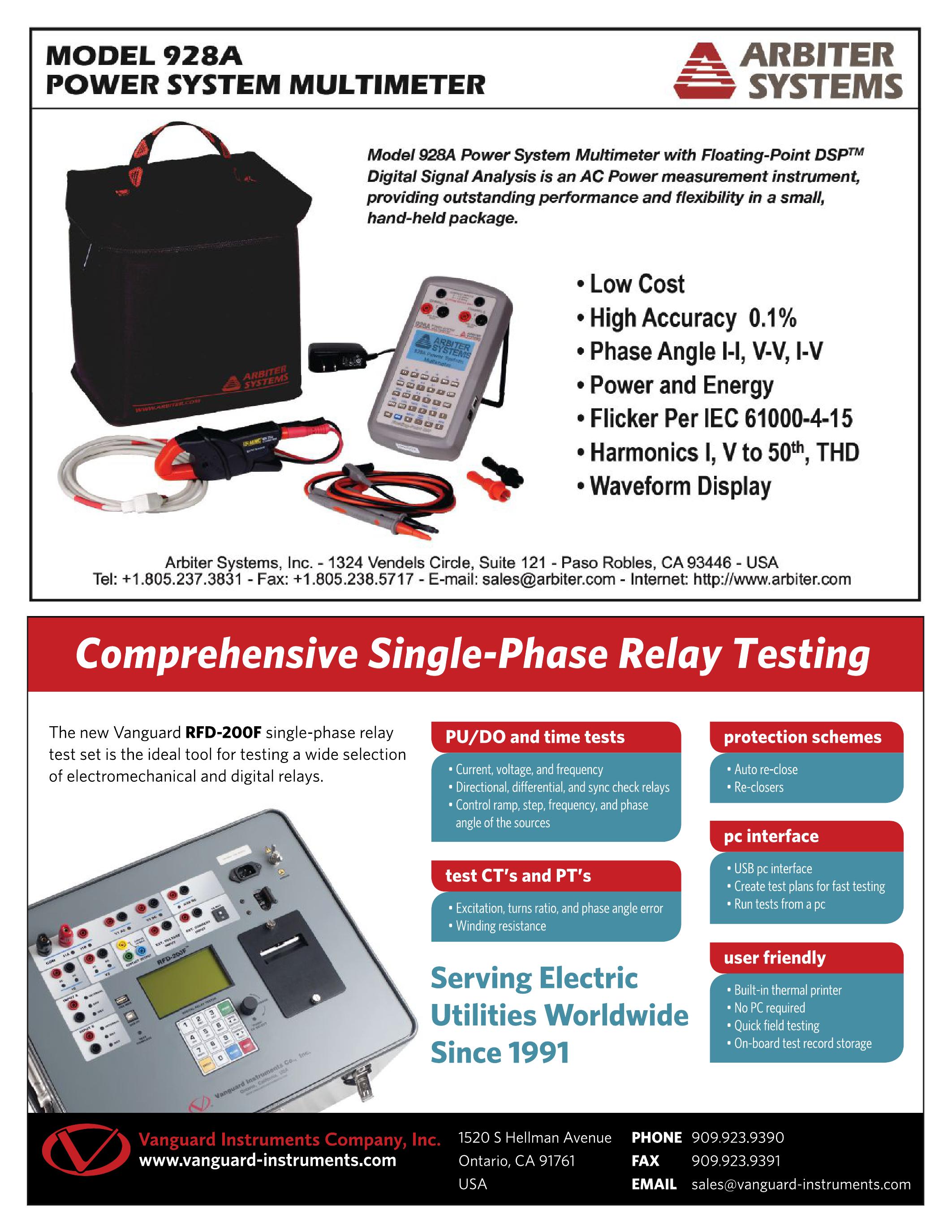


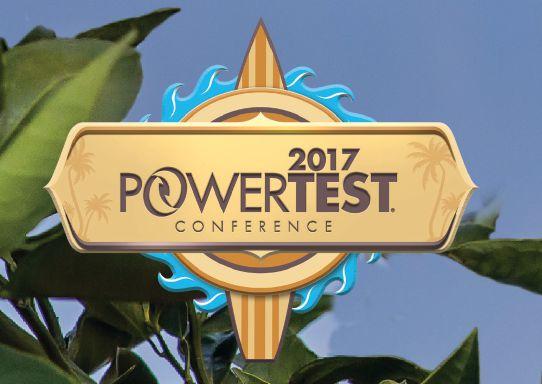

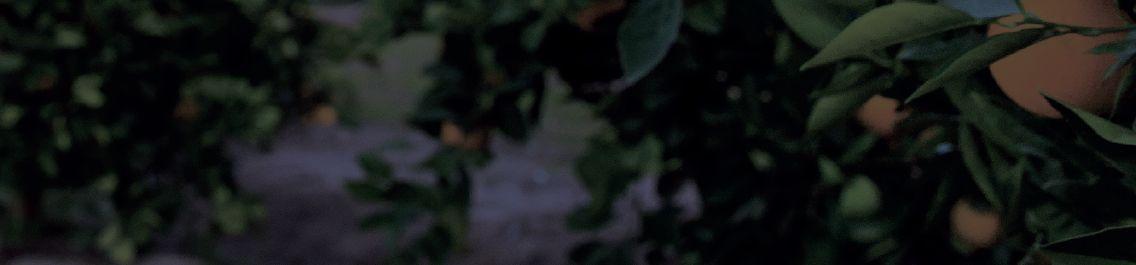
SPECIFICATIONS AND STANDARDS
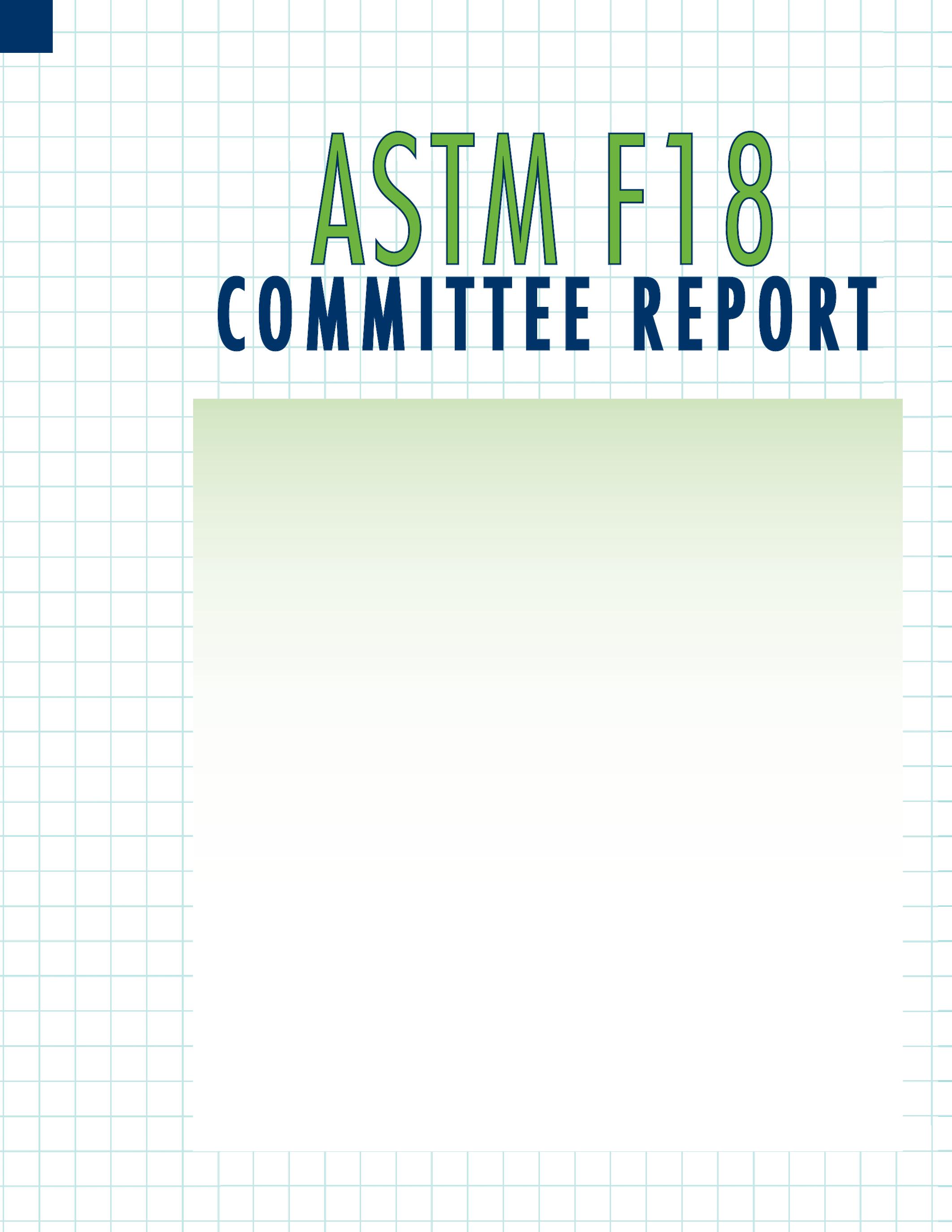
(Editor’s note: Stephen Hester attended the ASTM F18 Committee meeting, as Jim White was on vacation.)
The ASTM F18 committee is responsible for all rubber insulating PPE, as well as arcflash PPE, live-line tools, insulated tools, and insulatedbuckettrucks.TheF18committee insulated bucket trucks. The F18 committee met in Las Vegas, Nevada, from October 4–7, 2015. The next meeting is scheduled for San Antonio, Texas, April 10–13, 2016.
The OSHA update was provided by Marcia EblenofPacificGasandElectric.Marcia Eblen of Pacific Gas and Electric. Marcia briefed the committee on the requirements for care and maintenance of arc-rated daily work wear. OSHA is emphasizing that employers are responsible for the proper laundering of arcrated clothing, whether it is laundered at home by the individual worker or in a commercial facility such as Aramark or CINTAS. Additionally, workers must be trained in the specific requirements for laundering their arc-rated clothing, and employers are responsible for inspecting clothing to ensure that laundering protocols are followed and to ensure serviceability of the garments.
The NFPA 70E update was provided by Nestor Kolcio.Memberswerebriefedonthenumber Kolcio. Members were briefed on the number of public inputs (PI) to the 2018 edition (over 400) and a couple of key proposals such as moving the tasks table from 130.7(C)(15) to 130.5 and keeping the lower limit of the dc
approach boundary table at <100 volts. Some members expressed concern since OSHA’s guidance for de-energizing equipment is <50 voltsacordc. volts ac or dc.
F18.65.30 — Discussed the changes to the arc-rated hood testing method. For example, it’s already acknowledged that an 8 cal/cm2 face shield is effective at approximately 25 cal/cm2. Hugh Hoagland recommended an additional test shot to demonstrate reliability of the hood assembly at incident energy levels abovetheratedATPV. above the rated ATPV.
F18.65.23 — Discussed the scope changes, removing obsolete information, and distinguishing between fabric manufacturers and garment manufacturers since those who make the actual garments may not be the ones making the fabric that goes in them. A lively debate ensued over the definition of the word durability.
F18.65 —Discussedthestatusofstandards — Discussed the status of standards under the jurisdiction of the subcommittee:
• F1506-10:Underreview F1506-10: Under review
• F1891-12:Current F1891-12: Current
• F1958/1958M-12:Current F1958/1958M-12: Current
• F1959/1959M-12:Underreview F1959/1959M-12: Under review
• F2178-12:Current F2178-12: Current
• F2621-12:Current F2621-12: Current
• F2675/F2675M-13: Current
• F2676-09:Dueforrevision F2676-09: Due for revision
SPECIFICATIONS AND STANDARDS

Also discussed the balloting results on several revisions to F1506 where negative votesweresubmittedwithcomments.For votes were submitted with comments. For the most part, the comments were based on extremely narrow interpretations of language orindividualwordsusedinthestandardand or individual words used in the standard and were not accepted by the subcommittee.
F18.35.37 — Engaged in spirited discussions on testing live-line tools. Some key points:
• The portion of shotgun sticks below the operating mechanism is not tested due to the presence of metal parts.
• Extendosticksmustbecleanedandwaxed Extendo sticks must be cleaned and waxed ontheinside.Theinnersurfacesofthese on the inside. The inner surfaces of these sticks can collect dirt and moisture, which may, under the right conditions, create a shortinsidethestick. short inside the stick.
• Somecommitteemembersclaimedthat Some committee members claimed that some testing organizations do not test thestickswetinviolationof1910.269. the sticks wet in violation of 1910.269. If true, it would benefit those who do not testtheirownstickstoknowthis. test their own sticks to know this.
• Some members from the utilities pointed out that rubber insulating gloves are not required when using live-line tools as long as all body parts are outside the minimum approach distances in the NESC and 1910.269. Non-utility industry practice is to use gloves in conjunction with liveline tools. The utility industry appears still divided on the subject.
• Questions were raised about per-foot testing versus end-to-end testing of liveline tools. Of course, the big issues regard the appropriate test equipment and the durationforanend-to-endtest.A10duration for an end-to-end test. A 10or 12-foot stick presents a considerable challenge when testing at 75 kV per foot, given the test equipment currently in use. Consensus favored continuing with the current per-foot method.
• Arehotsticksconsideredlive-linetools Are hot sticks considered live-line tools when applying personal protective grounds? Some members argued no since we’re not contacting conductors at
rated line voltage. Given the “If it’s not grounded, it’s not dead” rule-of-thumb — and the fact that applying grounds by handisallowedat600voltsandbelow hand is allowed at 600 volts and below — this discussion may resurface in the future.
• Apparently, some sticks have passed testing with elongated or deformed rivets. Thisindicatesexcessivemechanicalstress This indicates excessive mechanical stress andiscausetoremovethestickfrom and is cause to remove the stick from service and repair or replace.
F18.15.03 — Emphasized discussion that dielectric overshoe footwear (not EH-rated footwear) used as primary protection must be inspected before use, maintained, and dielectrically tested every six months.
F18.35.43 —Discussedtheissueofwhether — Discussed the issue of whether there should be dielectric testing and retesting requirements for insulated hand tools.
Jim White is nationally recognized for technical skills and safety training in the electrical power systems industry. He is the Training Director for Shermco Industries, and has spent the last twenty years directly involved in technical skills and safety training for electrical power system technicians. Jim is a Principal member of NFPA 70B representing Shermco Industries, NETA’s alternate member of NFPA 70E, and a member of ASTM F18 Committee “Electrical Protective Equipment for Workers”.

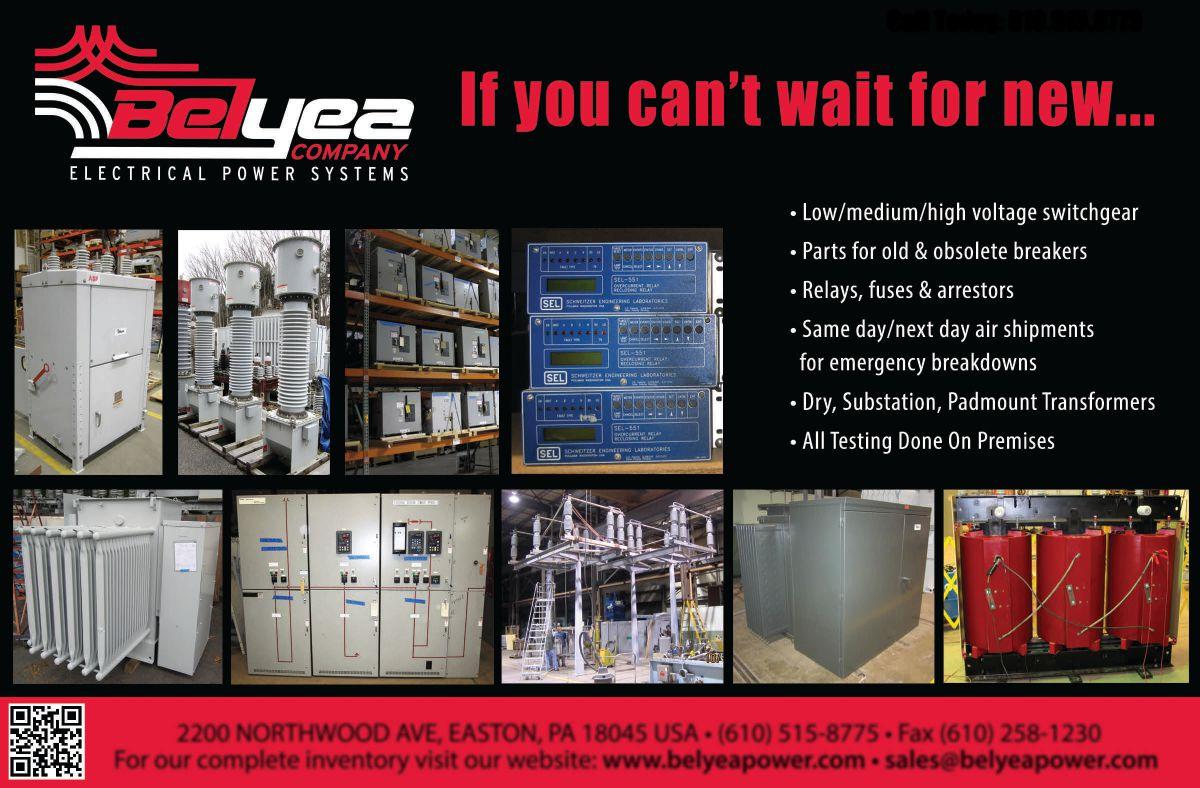
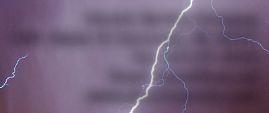

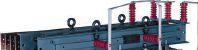


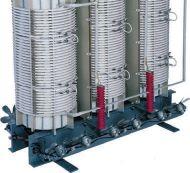
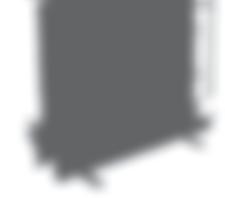

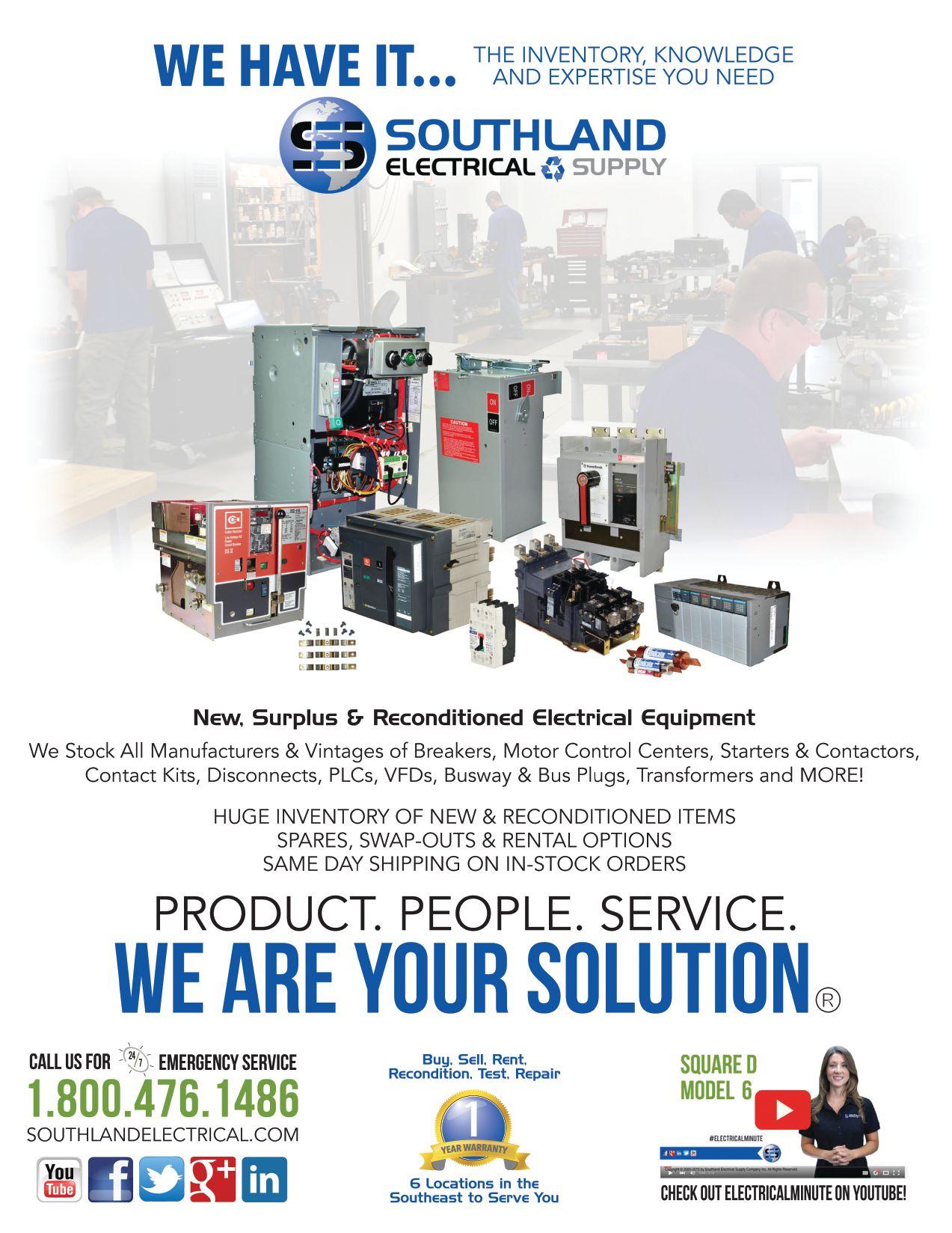
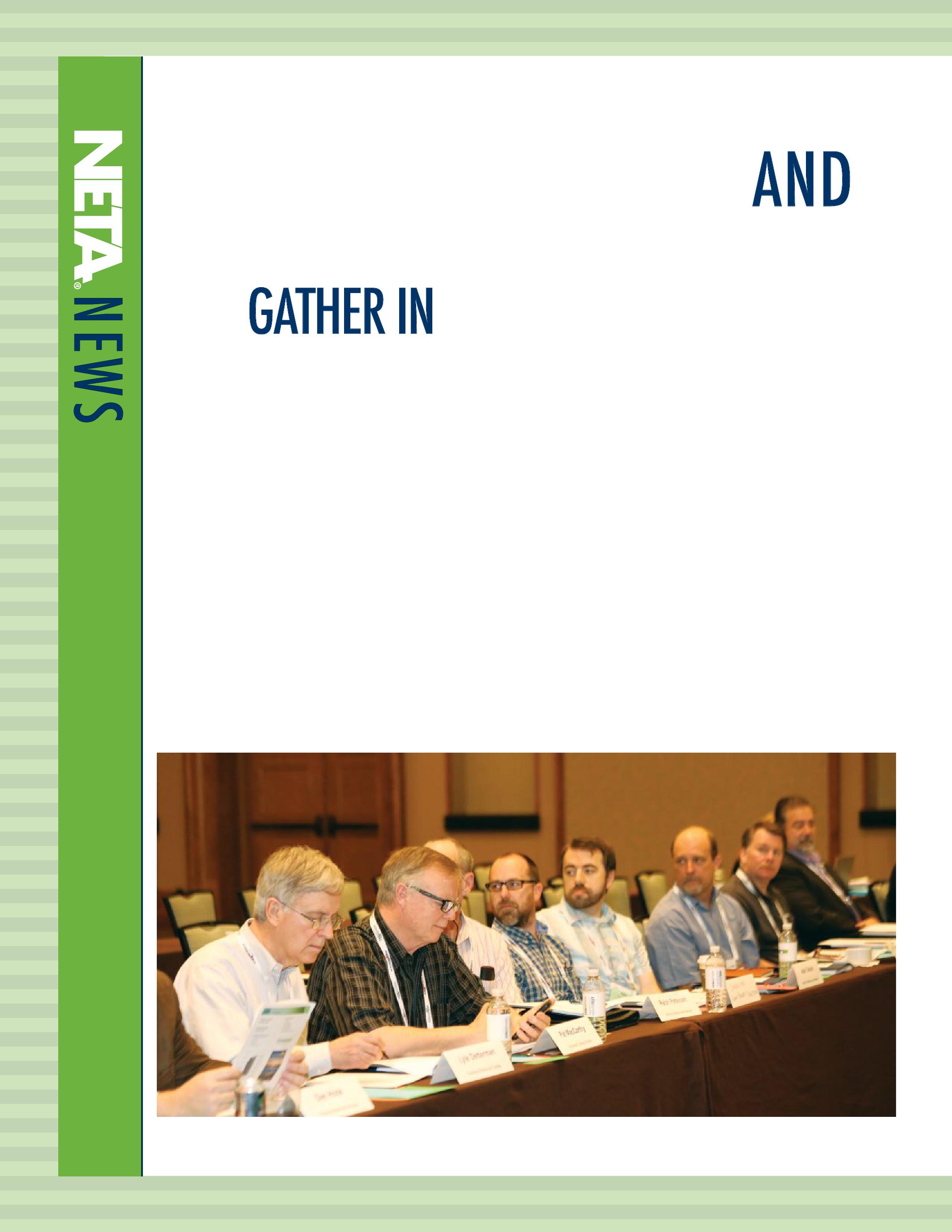
NETA MEMBERS ALLIANCE PARTNERS FORT WORTH, TEXAS
BY JILL HOWELL, NETANETA’s2016AnnualMemberandMemberand
NETA’s 2016 Annual Member and Member and Alliance Meetings were held on March 13, 2016, in Fort Worth, Texas, welcoming over 100 NETA Accredited Company representatives, Alliance Partners, and Corporate Alliance participants. The event was held in the Omni Fort Worth Hotel on the Sunday leading into PowerTest 2016. The Annual Meeting kicks off PowerTest each year, transitioning into a week-long series of technical sessions, professional exchange, and networking opportunities. It brings together the largest gathering of NETA Accredited Company Company representatives and industry professionals who are aligned in their commitment to continually work to improve safety, reliability, and quality across the electrical power systems industry.
The NETA Member Meeting, a meeting open only to NETA Accredited Companies, brings together representatives and technicians from the many NETA Accredited Companies that attend PowerTest to provide an update on NETA business. The agenda The included membership updates, nominations and elections of officers, recognition of volunteers and committee chairs, association news, and a review of program plans for the year.
This year, NETA recognized one member in particular who has served on the NETA Board since 1988. Rod Hageman, who recently stepped down from the Board, is the owner of PRIT Services, a NETA Accredited Company since 1986. (PRIT Services was recently sold to Shermco Industries.) NETA and its members are
One hundred plus NETA Accredited Company Members and Alliance Partners gathered for this year's annual meeting in Fort Worth, Texas.NETA President Ron Widup opens the 2016 Annual Member and Member and Alliance Meetings.
grateful for Rod’s commitment and service to NETA over the years. Rod will continue his work with the organization serving on the Standards Review Council and as the Executive Editor for the NETA World Journal (see inset).
The NETA Member and Alliance Meeting takes place during the second half of the NETA Member Meeting. Corporate Alliance and Alliance Partners were invited to join the NETA Accredited Companies in the afternoon for roundtable discussions, technical reporting, and NETA updates. Roundtable discussions were hosted by each of NETA’s 13 Corporate Alliance Partners with the goal of providing an opportunity to exchange information and ideas. To name just a few roundtable topics:
• Significant Changes and Opportunities in Commissioning and Testing
• Field Force Automation and Cybersecurity –Best Practices for Compliance
• Power Factor – Opening Doors to Advanced Diagnostics
During the NETA Member and Alliance Meeting, NETA Accredited Company Representatives also cover the many technical resources available to Members and Alliance Partners such as NETA publications, training, the online NETA discussion forum at www.engtips.com, and the online technical library at www.electricalmanuals.net. This particular segment of the meeting brings subject matter experts together from across the electrical power industry’s many business sectors to create an open dialogue, with a level of questions and technical discussion hard to find outside of this face-to-face forum.
Throughout the week of PowerTest, many special events are designed to promote the exchange of ideas and information sharing. For upcoming Alliance Partner events, watch your inbox for emails from NETA and look for notices in the NETA World Journal.
If you would like additional information about the NETA Alliance Program or would like to enroll, visit netaworld.
The meeting included an overview of NETA's program updates, technical reports, and a series of roundtable discussions.
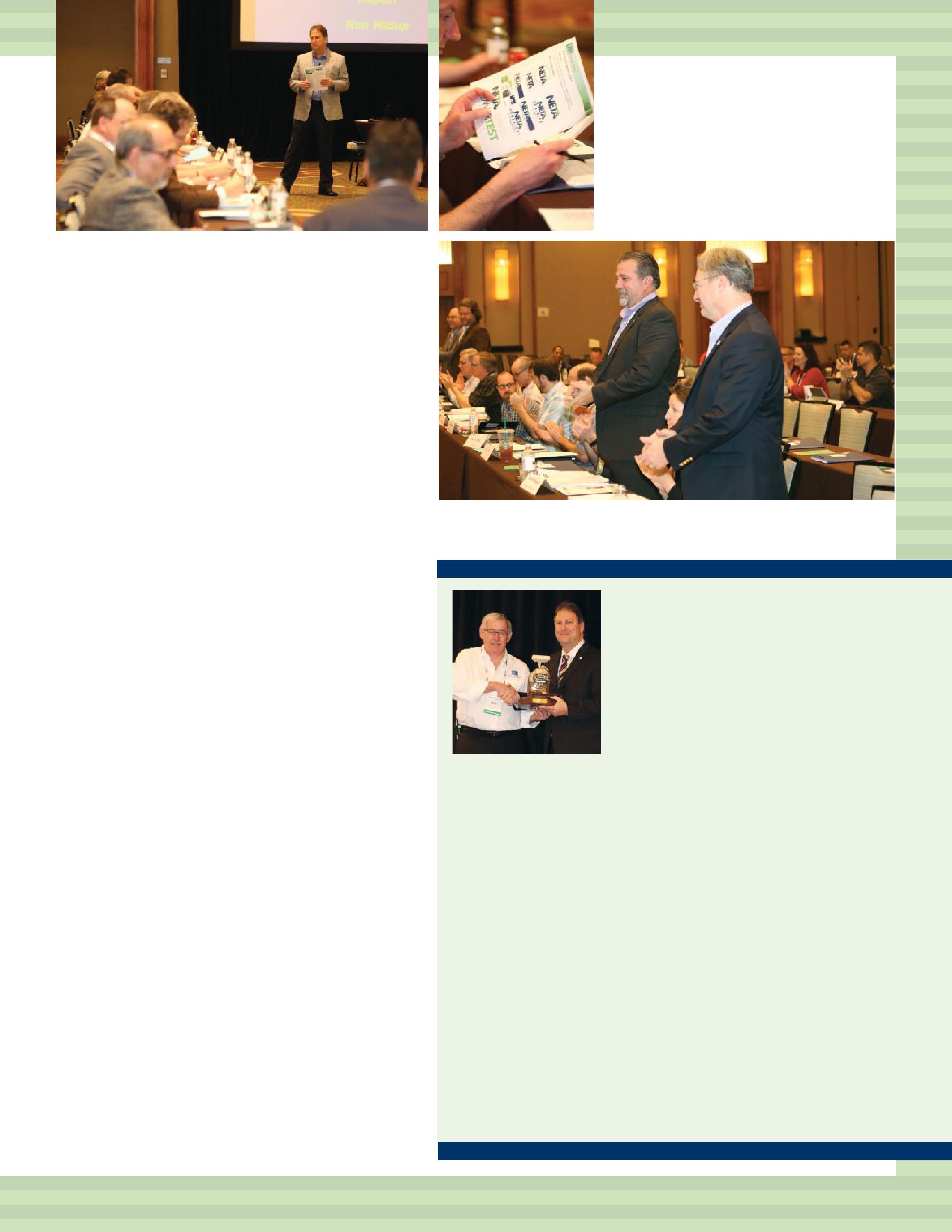
NETA member volunteers are recognized for their contributions to the association.
NETA SALUTES ROD HAGEMAN,
President and CEO of PRIT Service, Inc.,
for 27 years of service to the NETA Board of Directors. Rod stepped down from the Board this year following Shermco Industries’ acquisition of PRIT Service, announcedinMarch2016. announced in March 2016.
Over the years, Rod has dedicated thousands of hours to the association. He plans to continue serving the industry and NETA as Chief Editor and committee Chairman for the NETA World Journal and as a member of NETA’s Standards Review Council, Technical Exam Committee, and Co-Chair of the Technical Working Committee.
We all like to joke that when you volunteer for NETA, it is a lifetime commitment. PRIT that when Service began in the late 1950s as a response to requests for information from several large industrial companies. At that time, Lynn Hageman was a testing engineer for Commonwealth Edison. During testing of Commonwealth Edison’s protective equipment, Lynn regularly met with maintenance and engineering staff of these companies who asked him for solutions to their power problems and recommendations for maintenance of their distribution equipment. It became apparent to Lynn that the industry needed independent testing and engineering services, and thus PRIT Service began.
In 1972, Rod Hageman graduated from college and assumed leadership of the company. Over the last 30 years, PRIT has been part of a growing industry. In 1986, PRIT Service joined NETA and has enjoyed the benefits of being part of an organization that has a vast amount of technical knowledge shared between members. Rod Hageman joined the NETABoardofDirectorsin1988andhasbeenafaithfulcontributortotheassociation NETA Board of Directors in 1988 and has been a faithful contributor to the association ever since. Thank you, Rod, for your vision, leadership, technical expertise, and your dedication to NETA and improving the safety and reliability of the electrical power systems industry.

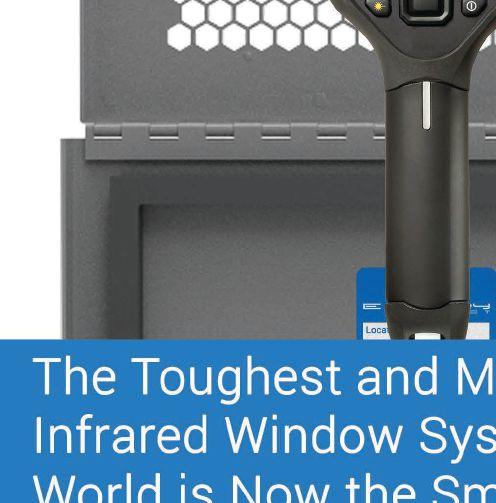

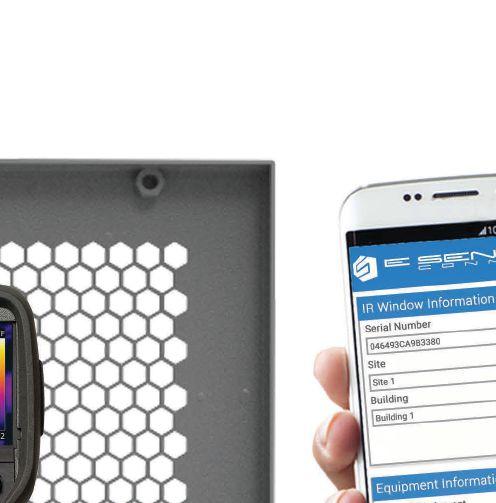
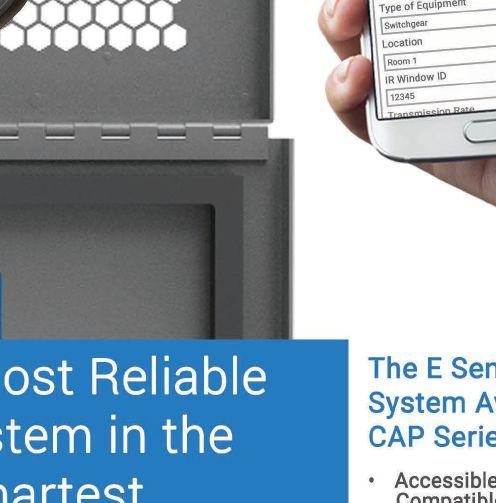





TIME IS TICKING TO ADDRESS
Grid
Interconnection Standards
BY MARKSIIRA MARK SIIRA , ComRentInternational ComRent InternationalStandards have always been an important consideration in the work of engineers and testing companies, but their role is increasing with the deployment of smart grids and the changes in how buildings interact with electricity. Some changes coming in the next two years will impact the testing done on systems that are interconnected to the electric power system (EPS).
WHY ARE THINGS CHANGING NOW?
The electric power infrastructure is transforming from a system of power interconnections to a diverse, interconnected, interdependent, and adaptive system. As the smart grid develops, interconnection standards will evolve to help enable interoperability, interconnection and integration of disparate systems, information technology,and communications.
The need for change is most notably caused by the increasing use of renewable energy. Based on the experience in Europe, operations improvements were needed to efficiently feed in solar and wind energy and minimize any problems to the grid. The renewable energy production can be optimized by allowing the local utility operation to communicate with distributed energy resources and modify their power output characteristics. In addition, some changes are required due to the need to improve voltage and frequency stability as well as power quality.
Fortunately for the sanity of engineers, a plan exists for updating the standards to address these changes.
HOW THE SYSTEM WORKS
Say a roof-mounted solar panel is being installed and connected to the grid through an inverter. Power engineers can look to a host of standards for guidance, including:
• Article 690 of the National Electrical Code (NEC) — minimizing electrical hazards in installation and operation
• Underwriters Laboratory (UL) 1741 — additional fire and safety considerations regarding distributed generators that use a dc power source like a solar panel
• IEEE 1547, Standard for Interconnecting Distributed Resources with Electric Power Systems — for the basis of the interconnection of the photovoltaic device itself to the power grid
• IEEE 1547.1, Standard Conformance Test Procedures for Equipment Interconnecting Distributed Resources with Electric Power Systems — for commissioning tests
ADVANCEMENTS IN
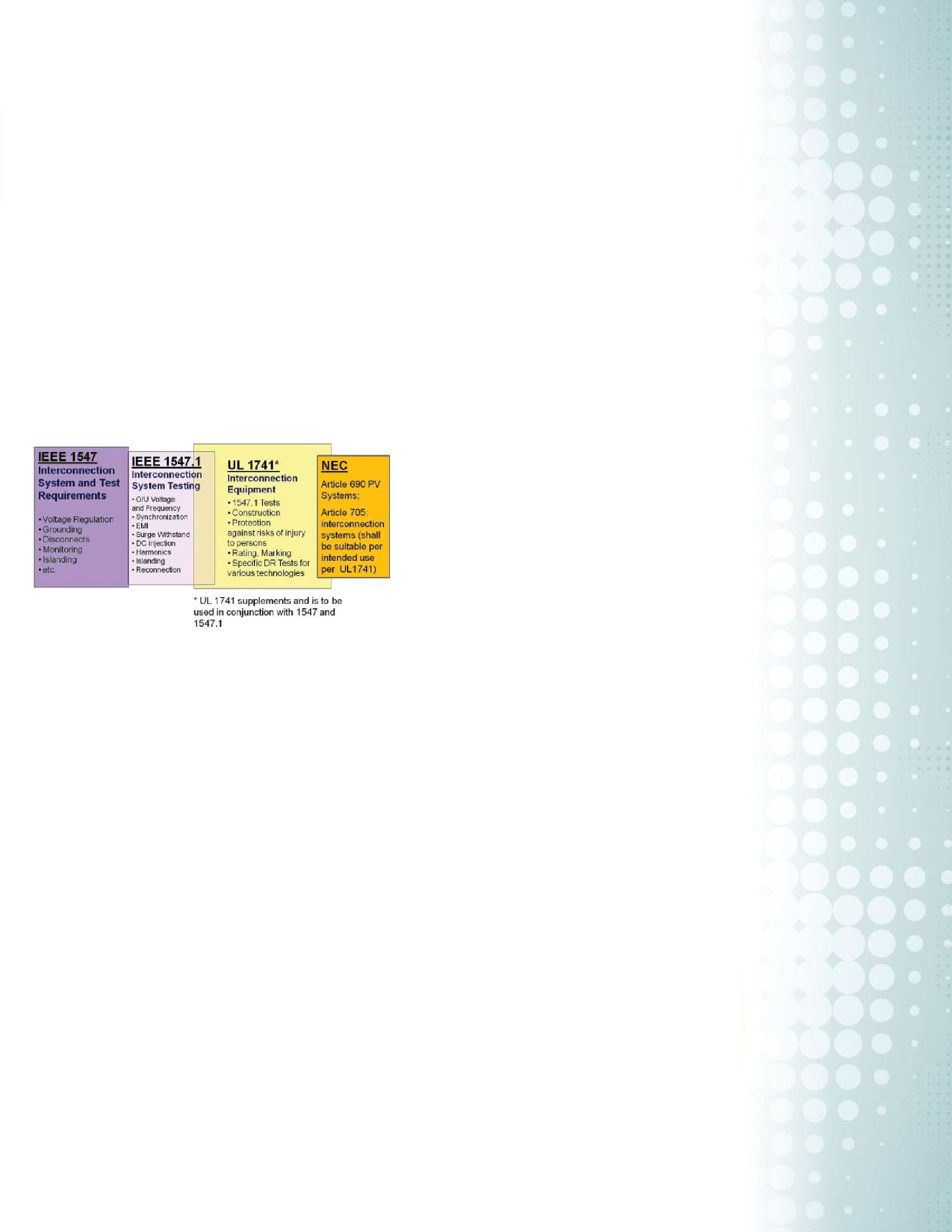
TheinstallerhastobeawareoftheNECand
The installer has to be aware of the NEC and how it is applied in the local area before projects are considered. The inverter is type-tested to UL-1741 at a Nationally Recognized Testing Laboratory (NRTL), and then the project may be tested to IEEE 1547.1 standards by the utility before interconnection. This usually depends on how large the system is relative to other sources on the distribution system.
System-level standards are an area of focus fortheInstituteofElectricalandElectronic for the Institute of Electrical and Electronic Engineers (IEEE) regarding the smart grid, with interconnection and interoperability defined below (Figure 1).
The IEEE 1547 family of standards is starting a cycle of revisions needed due to the reasons expressed above and to accommodate smartgrid functionality. This has started with the core standard, IEEE 1547, which was published in 2003 to reflect the evolution in the industry. A full revision of IEEE 1547 is underway and estimated to be published by 2018. In considering the scope and intentions of a full revision of IEEE 1547, a wide variety of stakeholders may change requirements for emerging technologies and applications such as energy storage, microgrids, inverter communications, voltage, and frequency ride-through instead of disconnection, higher renewable penetrations, and cyber security, among others.
FIRST GUIDE TO INTEROPERABILITY AND SMART GRID
IEEE 2030, Guide for Smart Grid Interoperability of Energy Technology and Information Technology Operation with the Electric Power System (EPS), End-Use Applications, and Loads takesasimilar takes a similar system-of-systems approach.
Interconnection is a widely known concept and the fundamental area covered by the IEEE 1547 series of standards. Generally, it deals with equipment and functions used to interconnect a distributed energy resource unit to an area electric power system (distribution network).
Interoperability is the seamless interaction of the communication and information technology systems and addresses the capability of multiple networks, systems, devices, applications, or components to exchange and use information securely and effectively. It is important to understandtwodefinitionsrelatedtothese understand two definitions related to these standards:
• Information technology classifies the types and methods of information exchanged betweenentitiesthatinteractwiththeESS. between entities that interact with the ESS.
• Communication technology deals with the data network paths available to transport thatinformation. that information.
More than 400 professionals from across the global communications, IT, and power industries collaborated in developing IEEE 2030, and when it was released in 2011, it established the world’s first interface-byinterface guide to interoperability across the electric power system. IEEE 2030 is a technology-agnostic roadmap to the standards and functional interfaces for securely integrating EPSwithcommunicationsandITaswellas EPS with communications and IT as well as facilitating data exchange across the smart grid. This is important because it provides the tools and information to allow increasing clarity in the specifying requirements of systems for communication and power system functions.
The smart grid is bringing definitive change to the way buildings relate with electricity. Whereas historically most buildings have only been consumers of electricity, more and more buildings will also serve as points of value for power generation in the smart grid. For example, integrating renewables with energy storage
ADVANCEMENTS IN TECHNOLOGY
systems could allow for additional functions to support the utility, such as frequency regulation, power quality stabilization, and more sophisticated schemes to replace simple disconnectionwhenabnormalconditionsexist. disconnection when abnormal conditions exist.
WHAT WILL CHANGE?
Initially, the changes will be seen in IEEE 1547, anticipated to be approved and published before 2018. It is intended to standardizeinterconnectionsofdistributed standardize interconnections of distributed generators to EPSs. The original standard published in 2003 did not fully comprehend the impact of inverters (from renewable sources) on the system. Inverters convert the dc power from a solar array or wind turbine into ac power that is exported to the electric power system. As a result, inverterbased systems were subjected to additional scrutiny and occasional delays in project implementation. The standard is focused on interconnections to medium-voltage distribution feeders; high-voltage bulk generation and transmissionwillnotbeaddressed. transmission will not be addressed.
The old rules require a distributed energy sourcetodisconnectfromtheEPSwithintwo source to disconnect from the EPS within two secondsandreconnectwithinfiveminutesof seconds and reconnect within five minutes of an abnormal condition being present (power outage or voltage spike). The new rules are more complex and will likely require more testing. The requirements will apply when the EPS operator (the utility) determines they are needed. These might be where there are a large number of renewable energy sources in a small area.
Here are the topics where you may see the most change :
• Voltage and Reactive Power Control Requirements
o Wider range of settings
o Distributed energy resource (DER) will be required to adjust voltage by adjusting power factor output
• Response to Abnormal Voltage and Frequency Conditions
o The old rules had allowable voltage and frequency ranges specified, and recommended settings were relatively tight.
o The new rules include ride-through
requirements (See Figure 2).
– The new rules will have both must-trip and must-run regions.
– The new rules will require DERs to remain online during certain disturbances.
– Momentary cessation is the mechanism for low-voltage ride-through.
– Inverters would stop sourcing power, but not trip.
– Wouldbeallowedtocomebackonline Would be allowed to come back online immediately when conditions return to normal (no five-minute wait for return-to-service).
• Power Quality Requirements
• Interoperability requirements
o Requires information exchange capability using standard protocol
o Addresses cybersecurity
o May require simulation and modeling data
• Unintentional Islanding
o May have special treatment for micro grids and energy storage systems
Pleasenotethatthesearebasedonthecurrent Please note that these are based on the current draft of the working group, and specific requirements could change before the document is published.
Since the ride-through requirements are a new concept, we have included Figure 2 to graphically illustrate what could be frequency or voltage on the vertical axis and time (event duration 0 to 20 seconds) on the horizontal axis. The figure describes typical ride-through concepts used: continuous operation, mandatory operation, permissive operation, ride-through trip allowed, and mandatory (shall) trip.
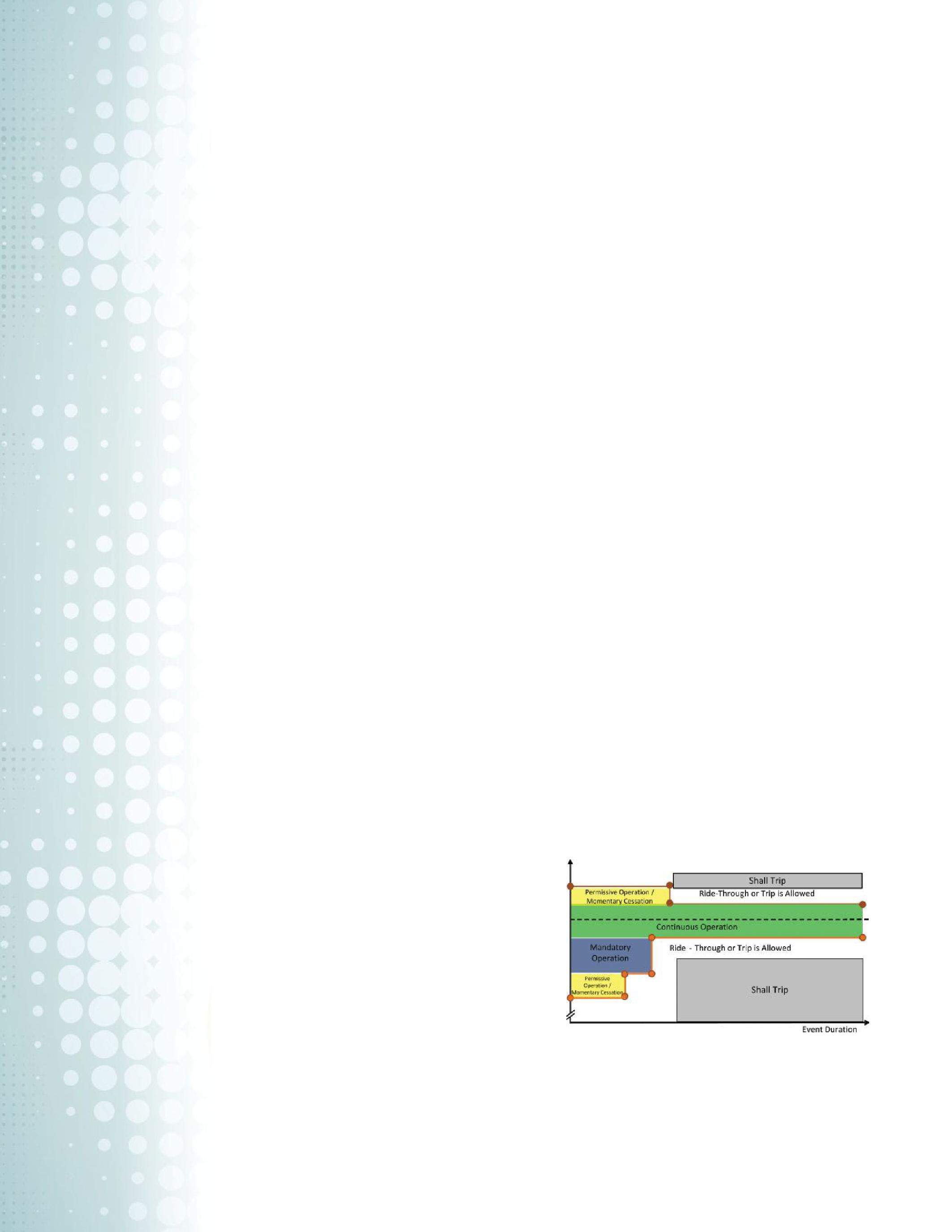
Figure 2: The Ride-Through Concept
We hope this overview has convinced you that there are major changes coming to what will be tested in the future. We are beginning to see
training on these concepts related to California Rule 21, where many of these requirements have become the standard already. More information can be obtained from ComRent.com or California Energy Commission Rule 21 Smart Inverter Working Group Technical Reference Materials at www.energy.ca.gov/electricity_analysis/rule21/.
BE PART OF THE FUTURE
Standards development driven by the emerging, real-world needs of facility engineers will help ensure this transformation is achieved as simply, cost-effectively, and efficiently as possible. All of the standards-making organizations need your help. If you want to get involved and help write the standard, sign up for the IEEE 1547 ListServ at http://grouper.ieee.org/groups/ scc21/1547_revision/1547revision_index.html
Then, you can join the working group by expressing your interest in the IEEE project system. Identify yourself to sub-group leads to get involved in groups working on the specific topics of interest to you.
ADVANCEMENTS IN TECHNOLOGY
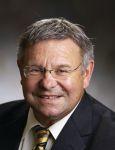
Mark Siira is the Director of Technology Strategy for ComRent International, a leader in load testing solutions. He is a senior member of IEEE, including a member of the IEEE Standards Coordinating Committee 21, which establishes standards for grid interconnection and smart grid interoperability; Working Group Chair of IEEE 2030.2 Guide for Interoperability of Energy Storage Systems; Vice Chair for IEEE1547 Interconnection Standard Revision, focusing on interoperability, simulation and modeling, and testing, and he is starting activity on IEEE1547.1 Test Procedures for Interconnection. Mark is also an active participant in the IEEE Power Systems Relaying Committee; Vice Chair of committee K10 - SCC21 Distributed Resources Standard Coordination; and a member of committee I25 Substation Commissioning best practices report to NERC. Additionally, he is a member of the UL Standards Technical Panels 1741 (Inverters), UL2200 (Generators) and 6171 (Wind farms interconnection), as well as Sub-Group Chair of the EPRI Energy Storage Integration Council, which is leading an effort to define commissioning practices for energy storage and PV systems. Mark has spent 20 years in the distributed power generation industry developing products and solutions for an inverter and energy storage appliance, combined heat and power systems, critical power systems paralleling switchgear, and microturbines. He has a BS in mechanical engineering from GMI Engineering and Management Institute (now Kettering University) and an MBA from Harvard University.

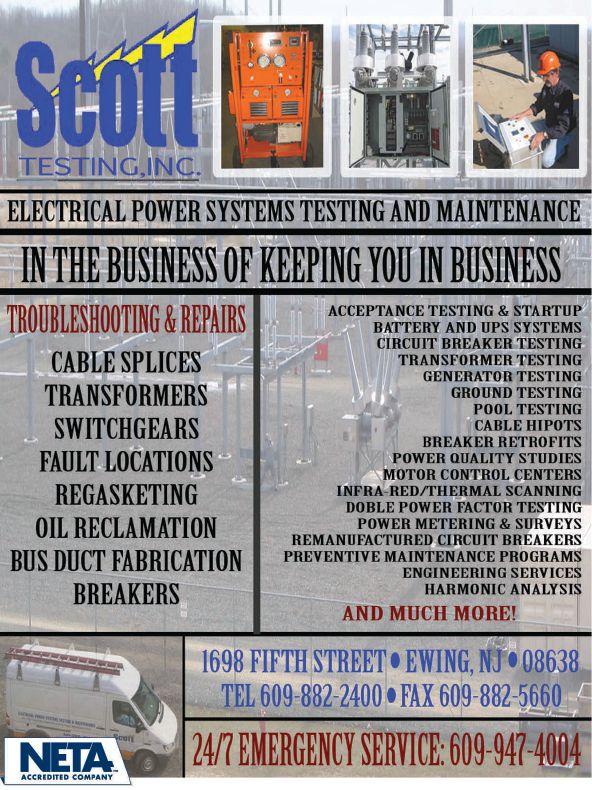
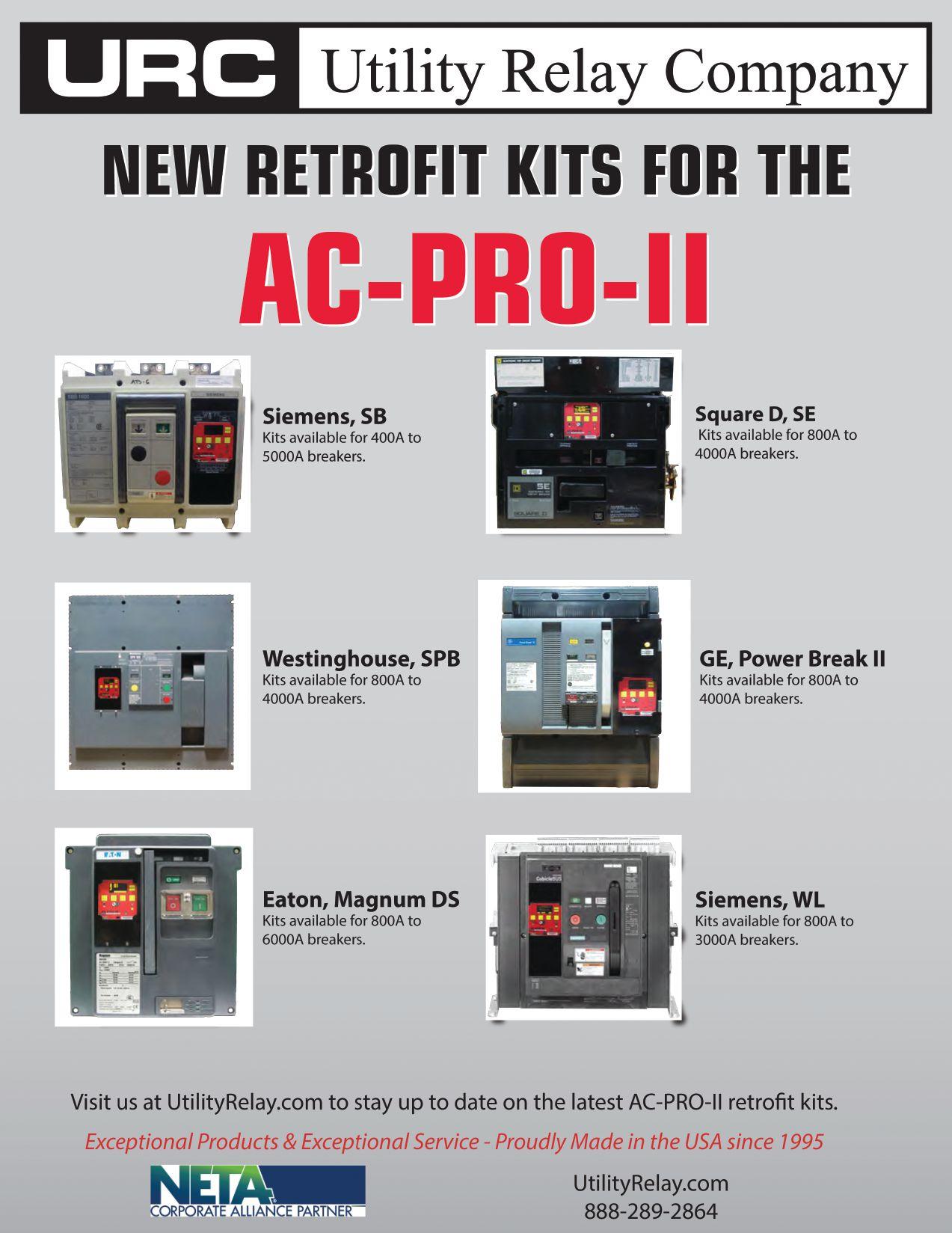
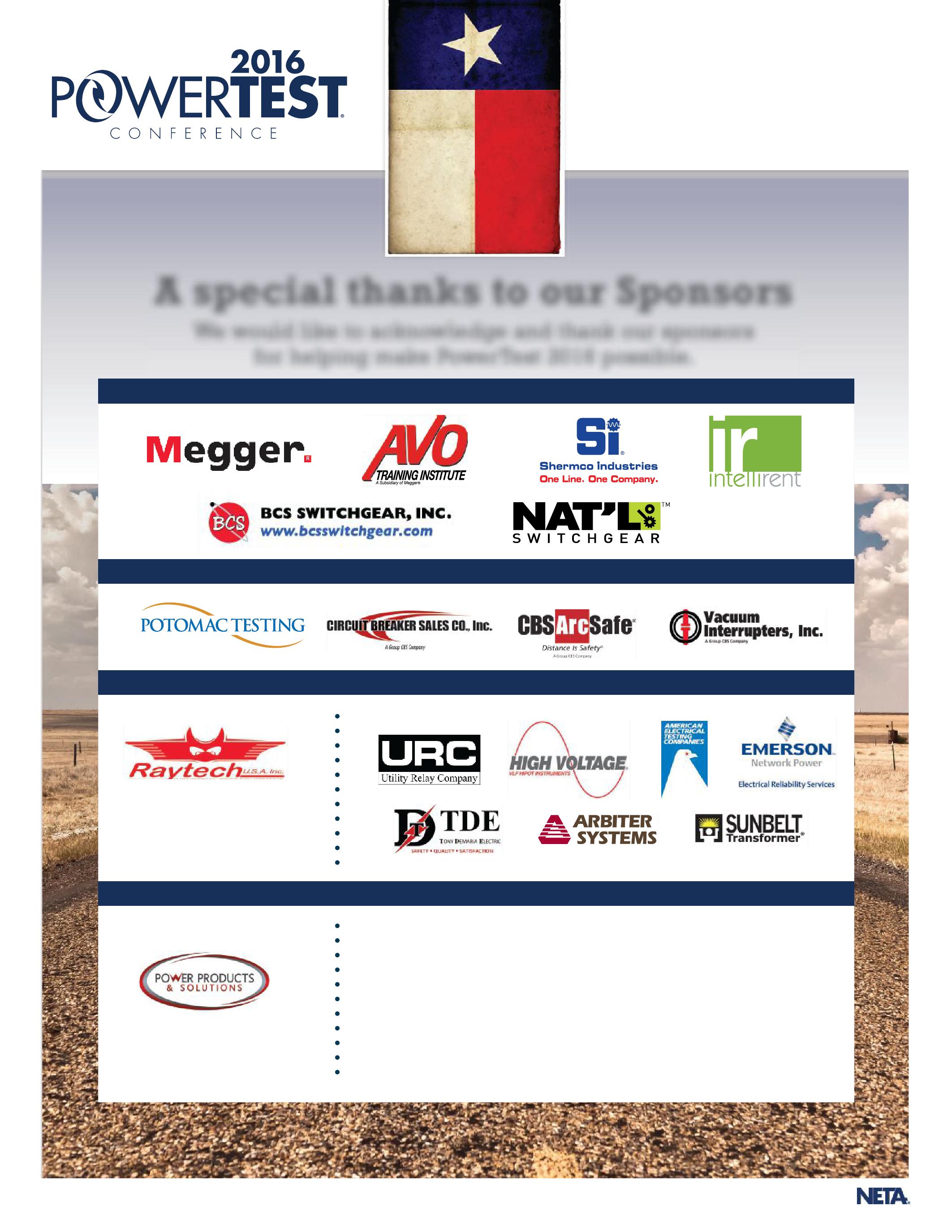
NETA STANDARDS REVIEW COUNCIL
A P P O I N T S N E W M E M B E R S
BY KRISTEN WICKS, NETANETA’s Standards Review Council (SRC) met in Texas on February 19 -20, 2016, at Shermco Industries’ Irving office. The main focus was preparation of the final draft document of the ANSI/NETA Standard for Acceptance Testing Specifications for Electrical Power Equipment and Systems, which was subsequently put forth for initial balloting and public comment in April 2016. Most of the preparatory work was accomplished at this meeting, and the committee completed the outstanding review work remotely following the meeting.
NETA’sStandardsReviewCouncilservesasthe NETA’s Standards Review Council serves as the executivetechnicalcommitteefortheassociation executive technical committee for the association and has a history of committee members who are deeply committed to assuring that NETA’s voice
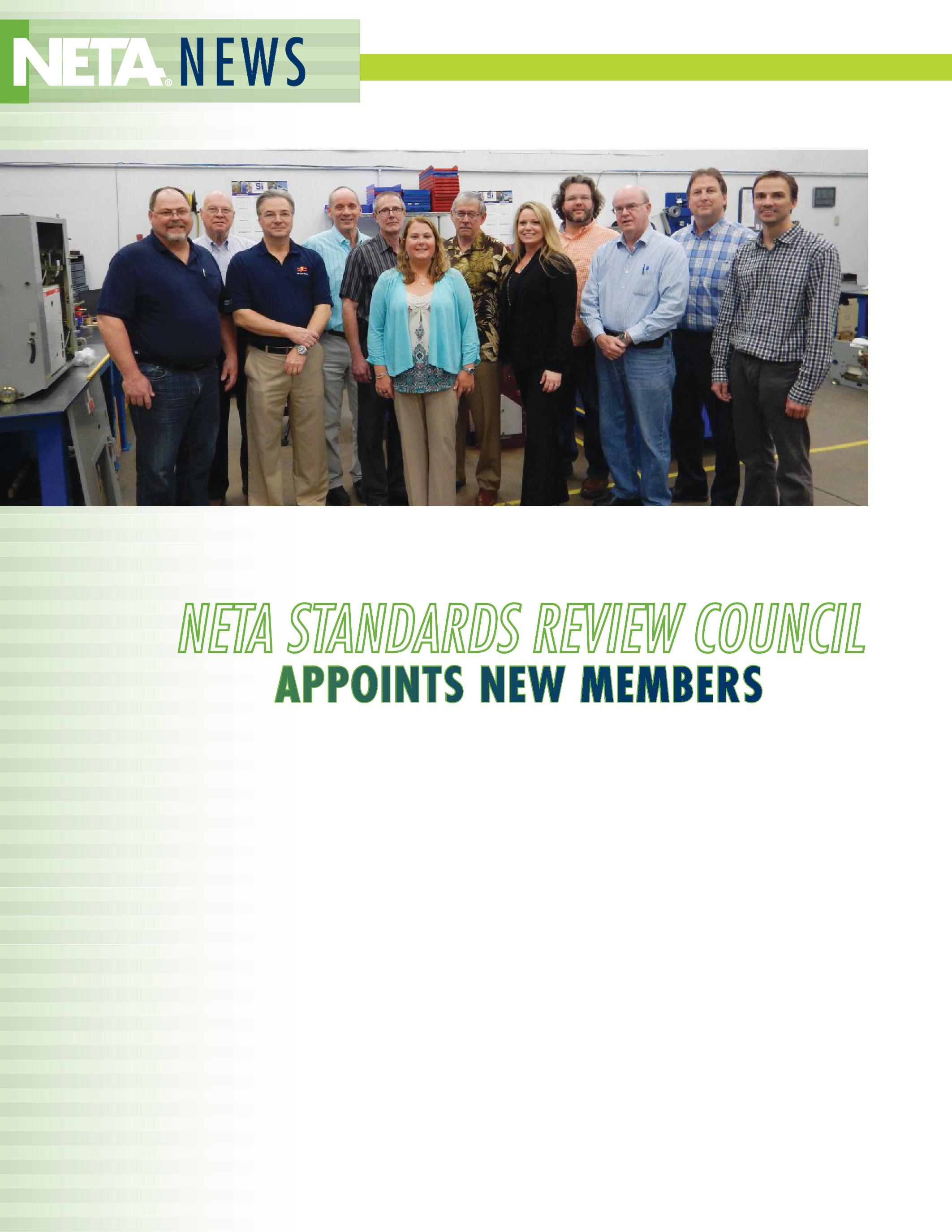
remains technically accurate through its ANSI standards, the certification exams, and other technically related programs and projects for the association. It is a responsibility not taken lightly
and one that requires a great deal of time and effort in person as well as remotely.
NETAisthrilledtoannouncetheaddition NETA is thrilled to announce the addition of three new SRC members to the team: Jim Cialdea of 3C Electrical Company, Inc.; Leif Hoegberg of Electrical Reliability Services; andDanHookofWesternElectricalServices. and Dan Hook of Western Electrical Services. As the association’s newly appointed Executive Director, Missy Richard was welcomed as a committee member. Kristen Wicks, NETA staff liaison for the SRC, was appointed as an official member of the committee by Technical ChairAlanPeterson.Thiscommittee Chair Alan Peterson. This committee expansion comes at a perfect time to support NETA’s technical growth in support of the association’smission. association’s mission.
Historically, NETA has been an organization that accomplishes much with the hands of
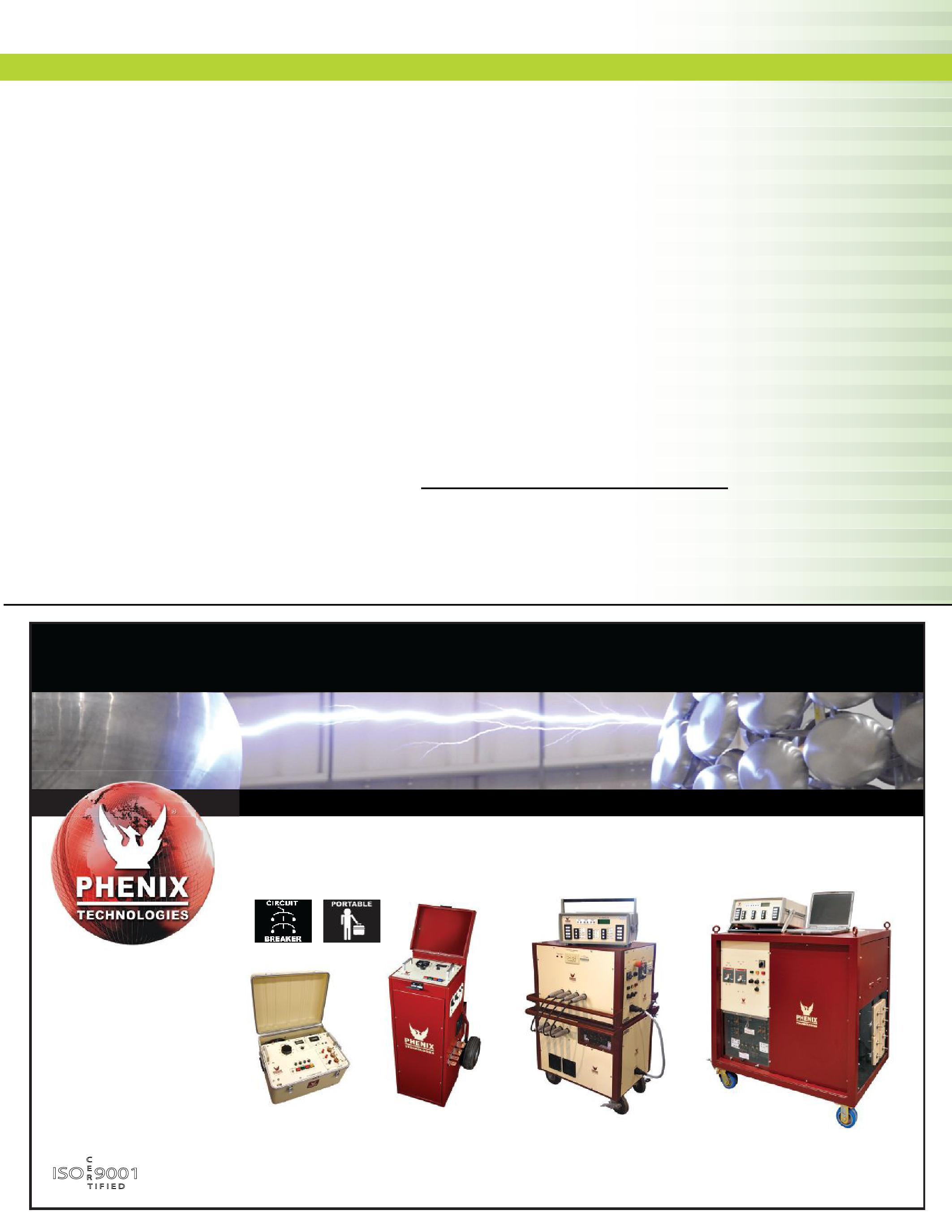
few. It is incredibly gratifying to know that an increasing number of members and industry partners see the value that their relationships with NETA provide to the association, to the industry, to their technicians, and to themselves. There is definite truth to the statement, “You make a living by what you get; you make a life by what you give.”
NETA thanks its many volunteers for donating their time and talents to the pursuit of a vision that is greater than the sum of its parts. If you are interested in learning more about how you can join the efforts being made to advance the electrical testing industry, contact the NETA officeat office at neta@netaworld.org or call (888) 300-6382.
KristenWicks Kristen Wicks istheTechnicalServicesDirector is the Technical Services Director atNETA. at NETA.
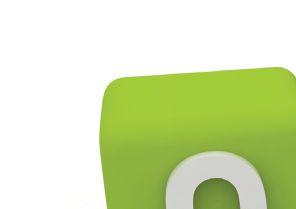

ANSWERS
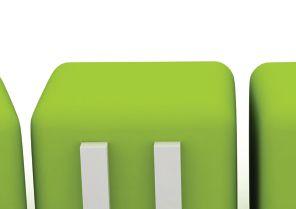
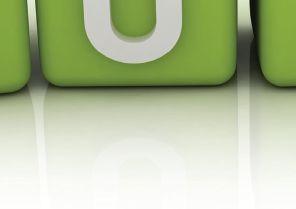
No.114 No. 114
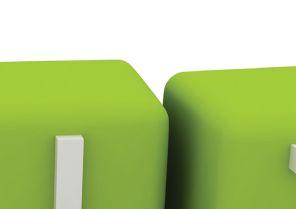
ANSWERS
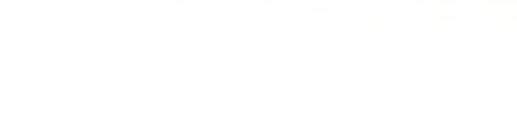
1. a. 50 3. Instantaneous overcurrent
b. 86 4. Lockout
c. 87 1. Differential
d. 27 2. Undervoltage
e. 25 6. Synch check
f. 67 5. Directional overcurrent
2. a. What is the calculated imbalance? 16.6 percent
b. Will this relay operate with this imbalance? Yes / No
For this relay to operate, the percent slope characteristic must be exceeded, which is not the case in this example. The relay will restrain.
c. Based on its characteristic, what is this relay most likely protecting? Transformer or generator
3. d. Synch check relays require two voltages. One voltage is used as the nominal (rated) voltage and the other voltage is varied. The characteristic in Figure 1 shows how the two voltages are used to check the size of the circle. For a relay rated at 120 V, one voltage is typically set to 120 V at zero degrees, while the second voltage is set to 120 V and the phase angle is varied to find its operating angles. At the 60-degree circle setting (the largest of the circles) and at 120 V, the relay will close its contacts at 60 degrees plus-or-minus the tolerance of the relay, which is usually 10 percent. Note that 120 V is in the center of the circle, and at zero-degree phase angle difference, the relay contacts will flicker if the second voltage is increased to 480 V (with the first voltage at 120 V). The timing test is performed by setting both voltages at zero-degree phase angle. One voltage is usually set to 120 V (or rated voltage), while the second voltage is set to zero V and the relay timed (see Figure 2).
4. a. A type 21 relay is any type of distance relay, but not blocking or unblocking relays.
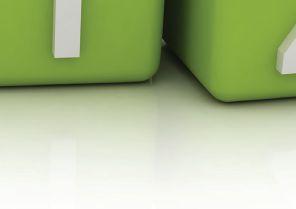

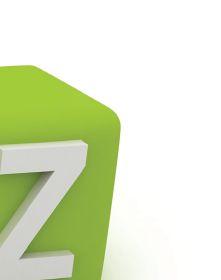

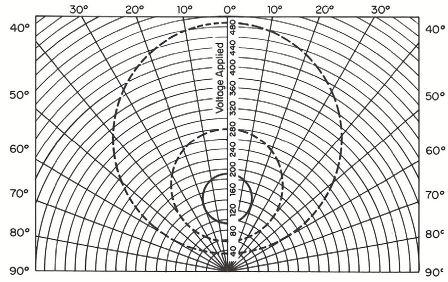
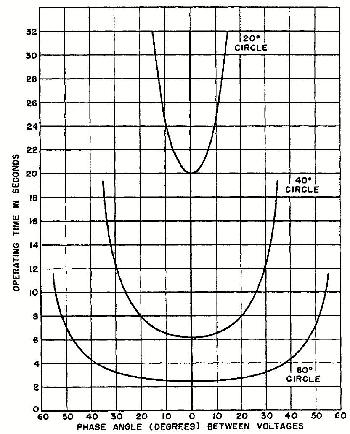
NFPA Disclaimer: Although Jim White is a member of the NFPA Technical Committee for both NFPA 70E “Standard for Electrical Safety in the Workplace” and NFPA 70B “Recommended Practice for Electrical Equipment Maintenance,” the views and opinions expressed in this message are purely the author’s and shall not be considered an official position of the NFPA or any of its technical committees and shall not be considered to be, nor be relied upon as, a formal interpretation or promotion of the NFPA. Readers are encouraged to refer to the entire text of all referenced documents.
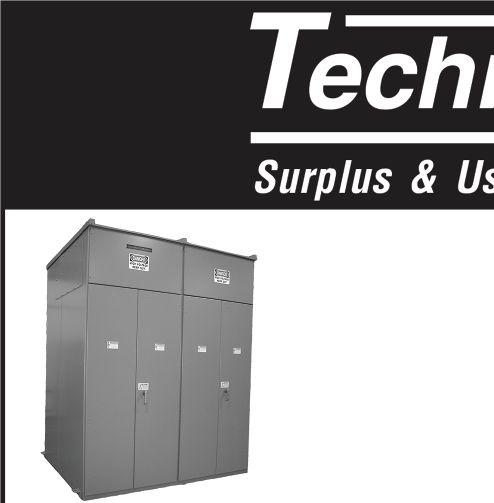
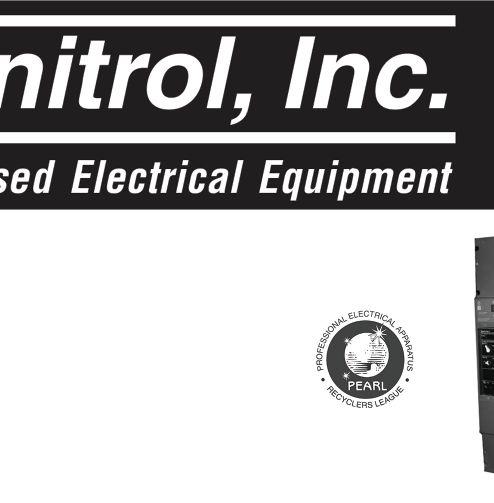
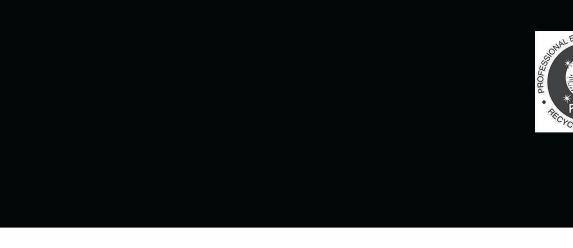
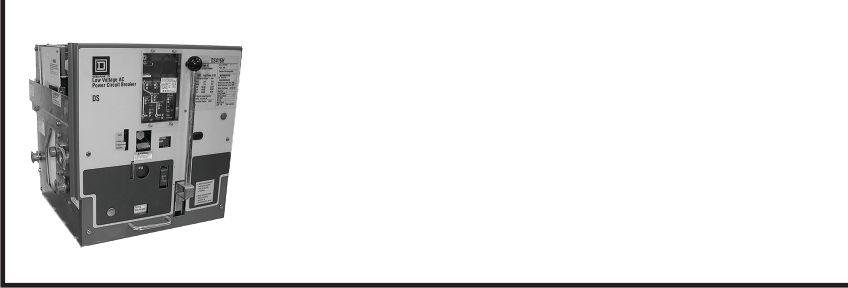
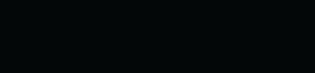

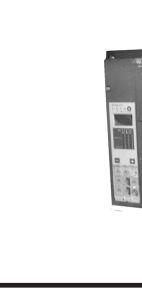
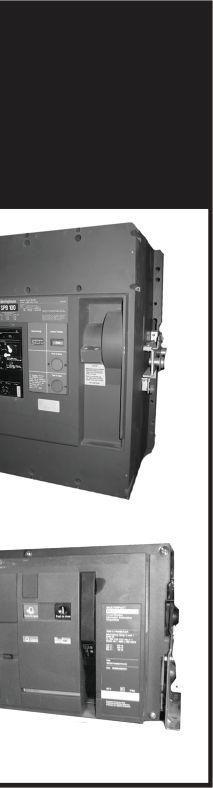
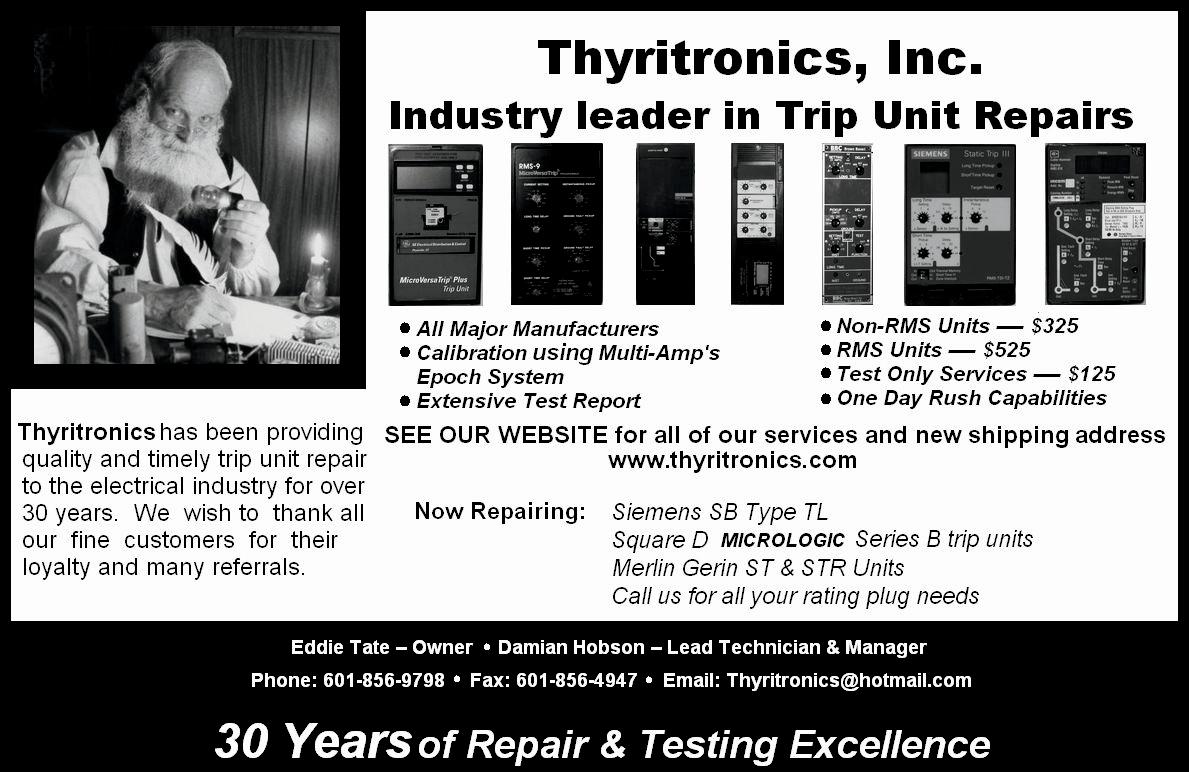
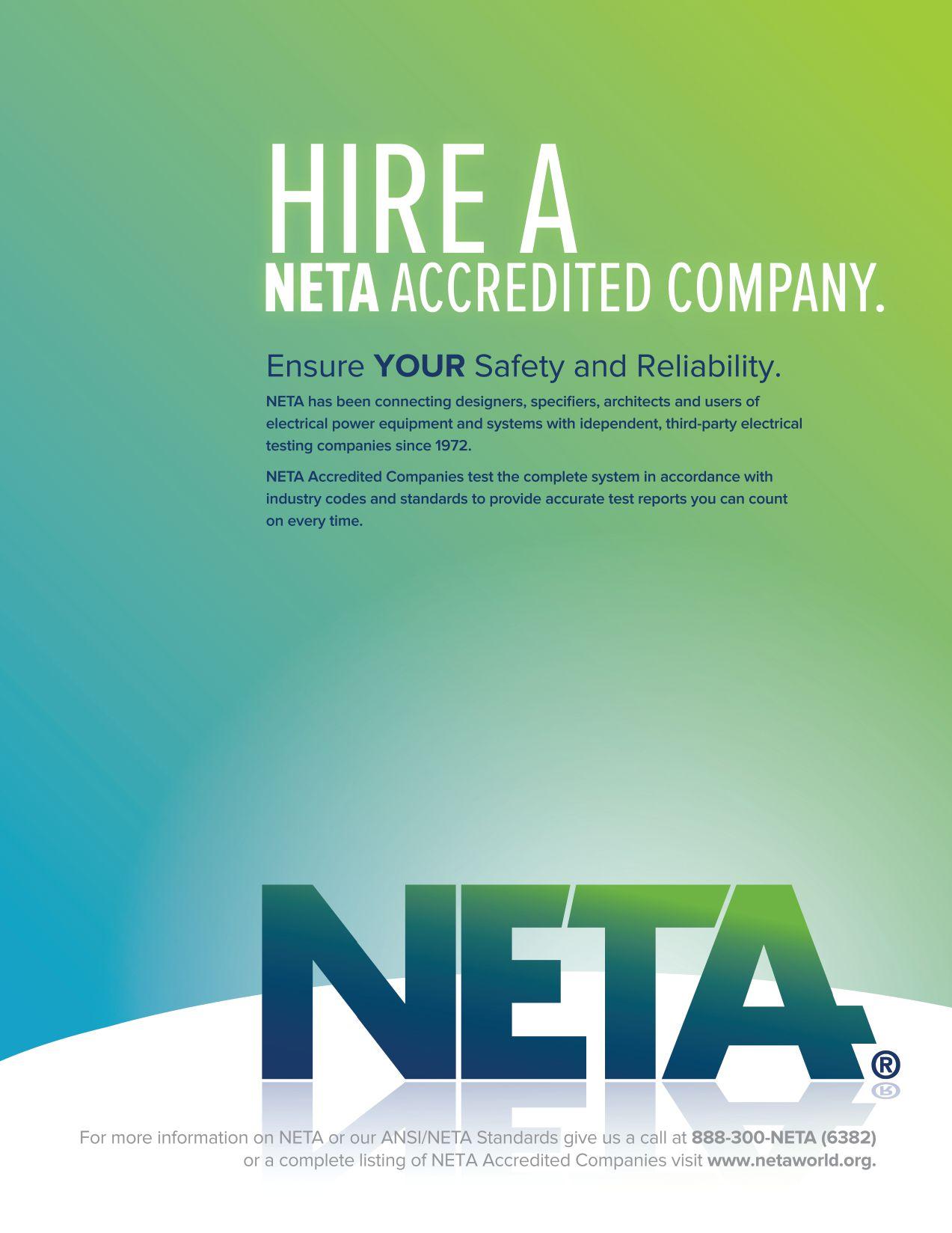
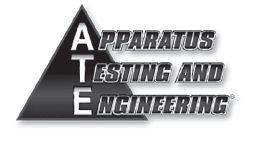








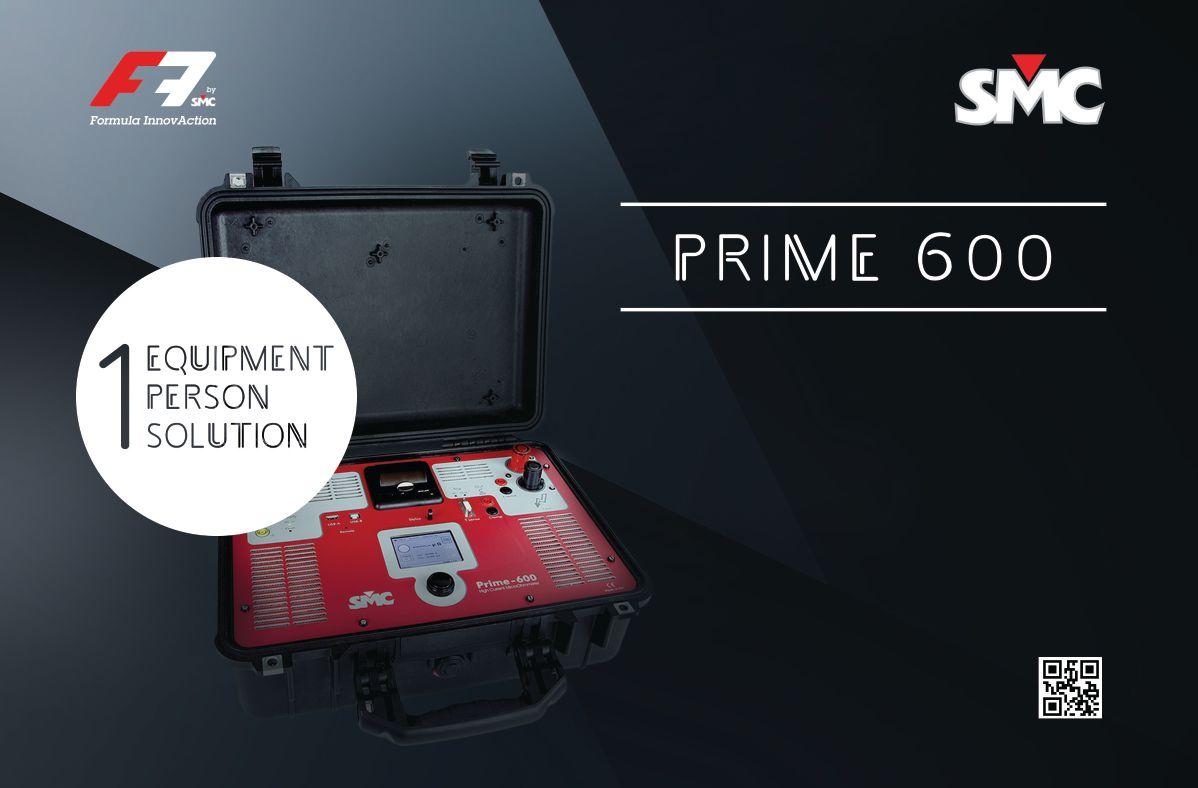

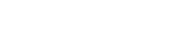
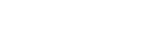
NETA ACCREDITED COMPANIES Setting the
A&F Electrical Testing, Inc.
80 Lake Ave. South, Ste. 10 Nesconset, NY 11767 (631) 584-5625 Fax: (631) 584-5720
kchilton@afelectricaltesting.com www.afelectricaltesting.com
Kevin Chilton
A&F Electrical Testing, Inc.
80 Broad St. 5th Floor
New York, NY 10004 (631) 584-5625 Fax: (631) 584-5720 afelectricaltesting@afelectricaltesting.com www.afelectricaltesting.com
Florence Chilton
ABM Electrical Power Solutions
3602 East Southern Ave., Ste. 1 Phoenix, AZ 85040 (602) 722-2423
www.ABM.com
Doug Bukowski
ABM Electrical Power Solutions
9800 E. Geddes Avenue, Unit A-150 Englewood, CO 80112 (303) 524-6560 Fax: (303) 524-6581
www.ABM.com
Brian Smith
ABM Electrical Power Solutions
2142 Rheem Drive Pleasanton, CA 94588 (408) 466-6920
www.ABM.com
John Marvulli
ABM Electrical Power Solutions
3940 Ruffin Rd., Ste. C San Diego, CA 92123 (858) 754-7963
www.ABM.com
Christopher Smith
ABM Electrical Power Solutions
6280 South Valley View Blvd., Ste. 618 Las Vegas, NV 89118 (602) 300-2188 Fax: (602) 437-3894 www.ABM.com
Jason Black
ABM Electrical Power Solutions
814 Greenbrier Circle, Ste. E Chesapeake, VA 23320 (757) 548-5690 Fax: (757) 548-5417
www.ABM.com
Mark Anthony Gaughan, III
ABM Electrical Power Solutions
3700 Commerce Dr. #901-903 Baltimore, MD 21227 (410) 247-3300 Fax: (410) 247-0900
www.ABM.com
Bill Hartman
ABM Electrical Power Solutions 5809 Departure Dr., Ste. 104 Raleigh, NC 27616 (919) 877-1008 Fax: (919) 501-7492
www.ABM.com
Rob Parton
ABM Electrical Power Solutions
317 Commerce Park Dr. Cranberry Township, PA 16066-6427 (724) 772-4638 Fax: (724) 772-6003 william.mckenzie@abm.com www.ABM.com
William (Pete) McKenzie
ABM Electrical Power Solutions 4390 Parliament Place, Ste. S Lanham, MD 20706 (301) 967-3500 Fax: (301) 735-8953 www.ABM.com
Frank Ceci
ABM Electrical Power Solutions
3600 Woodpark Blvd., Suite G Charlotte, NC 28206 (704) 273-6257 Fax: (704) 598-9812 ernest.goins@abm.com www.ABM.com
Ernest Goins
ABM Electrical Power Solutions
720 S. Rochester Ave., Suite A Ontario, CA 91761 (800) 597-1225 Fax: (909) 937-6798 www.ABM.com
Mike Bivens
Absolute Testing Services 6829 Guhn Rd. Houston, TX 77040 (832) 467-4446 Fax: (713) 849-3885 rgamble@absolutetesting.com www.texasats.com
Richard Gamble
Accessible Consulting Engineers, Inc. 1269 Pomona Rd., Ste. 111 Corona, CA 92882 (951) 808-1040 info@acetesting.com www.acetesting.com
Iraj Nasrolahi
Advanced Testing Systems 15 Trowbridge Dr. Bethel, CT 06801 (203) 743-2001 Fax: (203) 743-2325 pmaccarthy@advtest.com www.advtest.com
Pat MacCarthy
American Electrical Testing Co., Inc.
25 Forbes Blvd., Ste. 1 Foxboro, MA 02035 (781) 821-0121 Fax: (781) 821-0771 sblizard@aetco.us www.99aetco.com
Scott A. Blizard
American Electrical Testing Co., Inc. 34 Clover Dr. South Windsor, CT 06074 (860) 648-1013 Fax: (781) 821-0771 jpoulin@aetco.us www.99aetco.com
Gerald Poulin
American Electrical Testing Co., Inc. 76 Cain Dr. Brentwood, NY 11717 (631) 617-5330 Fax: (631) 630-2292 mschacker@aetco.us www.99aetco.com
Michael Schacker
American Electrical Testing Co., Inc. 50 Intervale Rd., Ste. 1 Boonton, NJ 07005 (973) 316-1180 Fax: (781) 316-1181 jsomol@aetco.us www.99aetco.com
Jeff Somol
American Electrical Testing Co., Inc. 4032 Park 65 Dr. Indianapolis, IN 46254 (317) 487-2111 Fax: (781) 821-0771 scanale@aetco.us www.99aetco.com
Stephen Canale
American Electrical Testing Co., Inc. Green Hills Commerce Center 5925 Tilghman St., Ste. 200 Allentown, PA 18104 (215) 219-6800 jmunley@aetco.us www.99aetco.com
Jonathan Munley
American Electrical Testing Co., Inc. 12566 W. Indianola Ave. Avondale, AZ 85392 (480) 383-9242 dmadaglia@aetco.us www.99aetco.com
Donald Madaglia
AMP Quality Energy Services, LLC 4220 West Schrimsher SW Site W1 P.O. Box 526, Huntsville, AL 35804 (256) 513-8255
Brian Rodgers
Apparatus Testing and Engineering 11300 Sanders Dr., Ste. 29 Rancho Cordova, CA 95742 (916) 853-6280 Fax: (916) 853-6258 info@apparatustesting.com www.apparatustesting.com
Harold (Jerry) Carr
Apparatus Testing and Engineering 7083 Commerce Circle, Ste. H Pleasanton, CA 94588 (925) 454-1363 Fax: (925) 454-1499 info@apparatustesting.com www.apparatustesting.com
Harold (Jerry) Carr
Applied Engineering Concepts 1105 N. Allen Ave. Pasadena, CA 91104 (626) 398-3052 Fax: (626) 398-3053 michel.c@aec-us.com www.aec-us.com
Michel Castonguay
BEC Testing 50 Gazza Blvd. Farmingdale, NY 11735 (516) 531-9136 Fax: (631) 249-6115 wfernandez@banaelectric.com www.bectesting.com
William Fernandez
Burlington Electrical Testing Co., Inc.
300 Cedar Ave. Croydon, PA 19021-6051 (215) 826-9400 (221) Fax: (215) 826-0964 waltc@betest.com www.betest.com
Walter P. Cleary
C.E. Testing, Inc. 6148 Tim Crews Rd. Macclenny, FL 32063 (904) 653-1900 Fax: (904) 653-1911 cetesting@aol.com
Mark Chapman
CE Power Solutions,LLC 4040 Rev Dr. Cincinnati, OH 45232 (513) 563-6150 Fax: (513) 563-6120 info@cepowersol.net www.cepower.net
Rhonda Harris
CE Power Solutions of Minnesota,LLC 7674 Washington Ave. South Eden Prairie, MN 55344 (877) 968-0281 Fax: (952) 400-8772 jason.thompson@cepower.net www.cepower-mn.net
Jason Thompson
Control Power Concepts
353 Pilot Rd; Ste. B Las Vegas, NV 89119 (702) 448-7833 Fax: (702) 448-7835 www.controlpowerconcepts.com
John Travis
Dude Electrical Testing LLC
145 Tower Dr., Unit# 9 Burr Ridge, IL 60527 (815) 293-3388 Fax: (815) 293-3386
scott.dude@dudetesting.com www.dudetesting.com
Scott Dude
DYMAX Service, LLC
46918 Liberty Dr. Wixom, MI 48393 (248) 313-6868 Fax: (248) 313-6869 www.dymaxservice.com
Bruce Robinson
DYMAX Service, LLC
4213 Kropf Ave. Canton, OH 44706 (330) 484-6801 Fax: (740) 333-1271 www.dymaxservice.com
Chuck Baker
Eastern High Voltage
11A South Gold Dr. Robbinsville, NJ 08691-1606 (609) 890-8300 Fax: (609) 588-8090 joewilson@easternhighvoltage.com www.easternhighvoltage.com
Joseph Wilson
ELECT, P.C.
7400-G Siemens Rd., P.O. Box 2080 Wendell, NC 27591 (919) 365-9775 Fax: (919) 365-9789 btyndall@elect-pc.com www.elect-pc.com
Barry W. Tyndall
Electric Power Systems, Inc. 21 Millpark Ct. Maryland Heights, MO 63043 (314) 890-9999 Fax: (314) 890-9998 www.epsii.com
Electric Power Systems, Inc. 557 E. Juanita Ave., #4 Mesa, AZ 85204 (480) 633-1490 Fax: (480) 633-7092 www.epsii.com
Electric Power Systems, Inc. 4436 Parkway Commerce Blvd. Orlando, FL 32808 (407) 578-6424 Fax: 407-578-6408 www.epsii.com
Electric Power Systems, Inc.
7000 E. 47th Avenue Drive, Suite 100 Denver, CO 80216 (720) 857-7273 Fax: 303-928-8020 www.epsii.com
Electric Power Systems, Inc. 23823 Andrew Rd. Plainfield, IL 60585 (815) 577-9515 Fax: (815) 577-9516 www.epsii.com
NETA ACCREDITED COMPANIES
Electric Power Systems, Inc. 2601 Center Rd., # 101 Hinckley, OH 44233 (330) 460-3706 Fax: (330) 460-3708 www.epsii.com
Electric Power Systems, Inc.
56 Bibber Pkwy #1 Brunswick, ME 04011 (207) 837-6527 www.epsii.com
Electric Power Systems, Inc. 4100 Greenbriar Dr., Ste. 160 Stafford, TX 77477 (713) 644-5400 www.epsii.com
Electric Power Systems, Inc. 11861 Longsdorf St. Riverview, MI 48193 (734) 282-3311 www.epsii.com
Electric Power Systems, Inc. 827 Union St., Salem, VA 24153 (540) 375-0084 Fax: (540) 375-0094 www.epsii.com
Electric Power Systems, Inc. 915 Holt Ave., Unit 9 Manchester, NH 03109 (603) 657-7371 Fax: 603-657-7370 www.epsii.com
Electric Power Systems, Inc.
146 Space Park Dr. Nashville, TN 37211 (615) 834-0999 Fax: (615) 834-0129 www.epsii.com
Electric Power Systems, Inc. 8515 Cella Alameda NE, Ste. A Albuquerque, NM 87113 (505) 792-7761 www.epsii.com
Electric Power Systems, Inc. 7140 Dean Martin Drive, Suite 900 Las Vegas, NV 89118 (702) 815-1342 www.epsii.com
Electric Power Systems, Inc.
319 US Hwy. 70 E, Unit E Garner, NC 27529 (919) 322-2670 www.epsii.com
Electric Power Systems, Inc. 1090 Montour West Industrial Blvd. Coraopolis, PA 15108 (412) 276-4559 www.epsii.com
NETA ACCREDITED COMPANIES
Electric Power Systems, Inc. 6141 Connecticut Ave. Kansas City, MO 64120 (816) 241-9990 Fax: (816) 241-9992 www.epsii.com
Electric Power Systems, Inc. 2495 Boulevard of the Generals Norristown, PA 19403 (610) 630-0286 www.epsii.com
Electric Power Systems, Inc. 1129 East Hwy. 30 Gonzalez, LA 70817 (225) 644-0150 Fax: (225) 644-6249 www.epsii.com
Electric Power Systems, Inc. 7925 Dunbrook Rd., Ste. G San Diego, CA 92126 (858) 566-6317 www.epsii.com
Electrical & Electronic Controls 6149 Hunter Rd. Ooltewah, TN 37363 (423) 344-7666 (23) Fax: (423) 344-4494 eecontrols@comcast.net
Michael Hughes
Electrical Energy Experts, Inc. W129N10818, Washington Dr. Germantown, WI 53022 (262) 255-5222 Fax: (262) 242-2360 bill@electricalenergyexperts.com www.electricalenergyexperts.com
William Styer
Electrical Equipment Upgrading, Inc. 21 Telfair Place, Savannah, GA 31415 (912) 232-7402 Fax: (912) 233-4355 kmiller@eeu-inc.com www.eeu-inc.com
Kevin Miller
Electrical Maintenance & Testing Inc. 12342 Hancock St., Carmel, IN 46032 (317) 853-6795 Fax: (317) 853-6799 info@emtesting.com www.emtesting.com
Brian K. Borst
Electrical Reliability Services 1057 Doniphan Park Circle, Ste. A El Paso, TX 79922 (915) 587-9440 Fax: (915) 587-9010 www.electricalreliability.com
Electrical Reliability Services 1775 W. University Dr., Ste. 128 Tempe, AZ 85281 (480) 966-4568 Fax: (480) 966-4569 www.electricalreliability.com
Electrical Reliability Services 1426 Sens Rd. Ste. 5 Houston, TX 77571 (281) 241-2800 Fax: (281) 241-2801 www.electricalreliability.com
Electrical Reliability Services 4099 SE International Way, Ste. 201 Milwaukie, OR 97222-8853 (503) 653-6781 Fax: (503) 659-9733 www.electricalreliability.com
Electrical Reliability Services 5909 Sea Lion Place, Ste. C Carlsbad, CA 92010 (858) 695-9551 www.electricalreliability.com
Electrical Reliability Services 8500 Washington Pl. NE, Ste. A-6 Albuquerque, NM 87113 (505) 822-0237 Fax: (505) 822-0217 www.electricalreliability.com
Electrical Reliability Services 1380 Greg Street, Ste. 217 Sparks, NV 89431 (775) 746-8484 Fax: (775) 356-5488 www.electricalreliability.com
Electrical Reliability Services 2275 Northwest Pkwy SE, Ste. 180 Marietta, GA 30067 (770) 541-6600 Fax: (770) 541-6501 www.electricalreliability.com
Electrical Reliability Services 7100 Broadway, Ste. 7E Denver, CO 80221-2915 (303) 427-8809 Fax: (303) 427-4080 www.electricalreliability.com
Electrical Reliability Services 348 N.W. Capital Dr. Lee's Summit, MO 64086 (816) 525-7156 Fax: (816) 524-3274 www.electricalreliability.com
Electrical Reliability Services 6900 Koll Center Parkway, Ste. 415 Pleasanton, CA 94566 (925) 485-3400 Fax: (925) 485-3436 www.electricalreliability.com
Electrical Reliability Services 10606 Bloomfield Ave. Santa Fe Springs, CA 90670 (562) 236-9555 Fax: (562) 777-8914 www.electricalreliability.com
Electrical Reliability Services
3535 Emerson Parkway, Ste. A Gonzales, LA 70737 (225) 755-0530 Fax: (225) 751-5055 www.electricalreliability.com
NETA ACCREDITED COMPANIES Setting the
Electrical Reliability Services
245 Hood Rd. Sulphur, LA 70665 (337) 583-2411 Fax: (337) 583-2410 www.electricalreliability.com
Electrical Reliability Services
11000 Metro Pkwy., Ste. 30 Ft. Myers, FL 33966 (239) 693-7100 Fax: (239) 693-7772 www.electricalreliability.com
Electrical Reliability Services
2222 West Valley Hwy. N., Ste 160 Auburn, WA 98001 (253) 736-6010 Fax: (253) 736-6015 www.electricalreliability.com
Electrical Reliability Services
3412 South 1400 West, Unit A West Valley City, UT 84119 (801) 975-6461 www.electricalreliability.com
Electrical Reliability Services
6351 Hinson St., Ste. B Las Vegas, NV 89118 (702) 597-0020 Fax: (702) 597-0095 www.electricalreliability.com
Electrical Reliability Services
9636 St. Vincent, Unit A Shreveport, LA 71106 (318) 869-4244 www.electricalreliability.com
Electrical Reliability Services
610 Executive Campus Dr. Westerville, OH 43082 (877) 468-6384 Fax: (614) 410-8420 info@electricalreliability.com www.electricalreliability.com
Electrical Testing and Maintenance Corp. 3673 Cherry Rd., Ste. 101 Memphis, TN 38118 (901) 566-5557 r.gregory@etmcorp.com www.etmcorp.net
Ron Gregory
Electrical Testing, Inc. 2671 Cedartown Hwy. Rome, GA 30161-6791 (706) 234-7623 Fax: (706) 236-9028
steve@electricaltestinginc.com www.electricaltestinginc.com
Electrical Testing Solutions
2909 Green Hill Ct. Oshkosh, WI 54904 (920) 420-2986 Fax: (920) 235-7136 tmachado@electricaltestingsolutions.com www.electricaltestingsolutions.com
Tito Machado
Elemco Services, Inc.
228 Merrick Rd. , Lynbrook, NY 11563 (631) 589-6343 Fax: (631) 589-6670
courtney@elemco.com www.elemco.com
Courtney Gallo
EnerG Test
204 Gale Lane Bldg. 2 - 2nd Floor Kennett Square, PA 19348 (484) 731-0200 Fax: (484) 713-0209
kbleiler@energtest.com www.energtest.com
Katie Bleiler
Energis High Voltage Resources, Inc. 1361 Glory Rd. Green Bay, WI 54304 (920) 632-7929 Fax: (920) 632-7928 info@energisinc.com www.energisinc.com
Mick Petzold
EPS Technology
29 N. Plains Hwy., Ste. 12 Wallingford, CT 06492 (203) 679-0145 www.eps-technology.com
Grounded Technologies, Inc. 10505 S. Progress Way, Ste. 105 Parker, CO 80134 P-(303) 781-2560 F- (303) 781-5240 jodymedina@groundedtech.com www.groundedtech.com
Jody Medina
Grubb Engineering, Inc. 3128 Sidney Brooks San Antonio, Tx 78235 (210) 658-7250 Fax: (210) 658-9805 joy@grubbengineering.com www.grubbengineering.com
Robert D. Grubb Jr.
Hampton Tedder Technical Services
4571 State St. Montclair, CA 91763 (909) 628-1256 x214 Fax: (909) 628-6375 matt.tedder@hamptontedder.com www.hamptontedder.com
Matt Tedder
Hampton Tedder Technical Services 4920 Alto Ave. Las Vegas, NV 89115 (702) 452-9200 Fax: (702) 453-5412 www.hamptontedder.com
Roger Cates
Hampton Tedder Technical Services 3747 West Roanoke Ave. Phoenix, AZ 85009 (480) 967-7765 Fax: (480) 967-7762 www.hamptontedder.com
Harford Electrical Testing Co., Inc. 1108 Clayton Rd. Joppa, MD 21085 (410) 679-4477 Fax: (410) 679-0800 testing@harfordtesting.com www.harfordtesting.com
Vincent Biondino
High Energy Electrical Testing, Inc. 515 S. Ocean Ave. Seaside Park, NJ 08752 (732) 938-2275 Fax: (732) 938-2277 hinrg@comcast.net www.highenergyelectric.com
Charles Blanchard
High Voltage Maintenance Corp. 24 Walpole Park South Dr. Walpole, MA 02081 (508) 668-9205 www.hvmcorp.com
High Voltage Maintenance Corp. 941 Busse Rd. Elk Grove Village, Il 60007 (847) 640-0005 www.hvmcorp.com
High Voltage Maintenance Corp. 7200 Industrial Park Blvd. Mentor, OH 44060 (440) 951-2706 Fax: (440) 951-6798 www.hvmcorp.com
High Voltage Maintenance Corp. 3000 S. Calhoun Rd. New Berlin, WI 53151 (262) 784-3660 Fax: (262) 784-5124 www.hvmcorp.com
High Voltage Maintenance Corp. 8320 Brookville Rd. #E Indianapolis, IN 46239 (317) 322-2055 Fax: (317) 322-2056 www.hvmcorp.com
High Voltage Maintenance Corp. 1250 Broadway, Ste. 2300 New York, NY 10001 (718) 239-0359 www.hvmcorp.com
High Voltage Maintenance Corp. 355 Vista Park Dr. Pittsburgh, PA 15205-1206 (412) 747-0550 Fax: (412) 747-0554 www.hvmcorp.com
High Voltage Maintenance Corp. 150 North Plains Industrial Rd. Wallingford, CT 06492 (203) 949-2650 Fax: (203) 949-2646 www.hvmcorp.com
High Voltage Maintenance Corp. 9305 Gerwig Ln., Ste. B Columbia, MD 21046 (410) 309-5970 Fax: (410) 309-0220 www.hvmcorp.com
High Voltage Maintenance Corp. 24371 Catherine Industrial Dr, Ste. 207 Novi, MI 48375 (248) 305-5596 Fax: (248) 305-5579 www.hvmcorp.com
High Voltage Maintenance Corp. 5100 Energy Dr. Dayton, OH 45414 (937) 278-0811 Fax: (937) 278-7791 www.hvmcorp.com
High Voltage Service, LLC
3890 Pheasant Ridge Dr. NE, Ste. 170 Blaine, MN 55449 (763) 784-4040 Fax: (763) 784-5397 www.hvserviceinc.com
Mike Mavetz
HMT, Inc. 6268 Route 31 Cicero, NY 13039 (315) 699-5563 Fax: (315) 699-5911 jpertgen@hmt-electric.com www.hmt-electric.com
John Pertgen
Industrial Electric Testing, Inc. 11321 West Distribution Ave. Jacksonville, FL 32256 (904) 260-8378 Fax: (904) 260-0737 gbenzenberg@bellsouth.net www.industrialelectrictesting.com
Gary Benzenberg
Industrial Electric Testing, Inc. 201 NW 1st Ave. Hallandale, FL 33009-4029 (954) 456-7020 www.industrialelectrictesting.com
Industrial Electronics Group 850369 Highway 17 South P.O. Box 1870 Yulee, FL 32041 (904) 225-9529 Fax: (904) 225-0834 butch@industrialgroups.com www.industrialgroups.com
Butch E. Teal
Industrial Tests, Inc. 4021 Alvis Ct., Ste. 1 Rocklin, CA 95677 (916) 296-1200 Fax: (916) 632-0300 greg@indtest.com www.industrialtests.com
Greg Poole
Infra-Red Building and Power Service 152 Centre St. Holbrook, MA 02343-1011 (781) 767-0888 Fax: (781) 767-3462 tom.mcdonald@infraredbps.com www.infraredbps.com
Thomas McDonald Sr.
Longo Electrical-Mechanical, Inc.
One Harry Shupe Blvd., Box 511 Wharton, NJ 07885 (973) 537-0400 Fax: (937) 537-0404 jmlongo@elongo.com www.elongo.com
Joe Longo
Longo Electrical-Mechanical, Inc. 1625 Pennsylvania Ave. Linden, NJ 07036 (908) 925-2900 Fax: (908) 925-9427 jmlongo@elongo.com www.elongo.com
Joe Longo
Longo Electrical-Mechanical, Inc.
1400 F Adams Rd. Bensalem, PA 19020 (215) 638-1333 Fax: (215) 638-1366 jmlongo@elongo.com www.elongo.com
Joe Longo
M&L Power Systems, Inc.
109 White Oak Ln., Ste. 82 Old Bridge, NJ 08857 (732) 679-1800 Fax: (732) 679-9326 milind@mlpower.com www.mlpower.com
Milind Bagle
Magna IV Engineering 1103 Parsons Rd. SW Edmonton, AB T6X 0X2 Canada (780) 462-3111 Fax: (780) 450-2994 info@magnaiv.com www.magnaiv.com
Virgina Balitski
Magna IV Engineering 200, 688 Heritage Dr. Calgary, AB T2H 1M6 Canada (403) 723-0575 Fax: (403) 723-0580 info.calgary@magnaiv.com
Dave Emerson
Magna IV Engineering 8219D Fraser Ave. Fort McMurray, AB T9H 0A2 Canada (780) 791-3122 Fax: (780) 791-3159 info.fmcmurray@magnaiv.com
Ryan Morgan
Magna IV Engineering
96 Inverness Dr. East, Unit R Englewood, CO 80112 (303) 799-1273 Fax: (303) 790-4816 info.denver@magnaiv.com Aric Proskurniak
Magna IV Engineering Avenida del Condor #590 Oficina 601 Huechuraba, Santiago 8580676 Chile +(56) 9-9-517-4642 info.chile@magnaiv.com
Harvey Mendoza
Magna IV Engineering 1040 Winnipeg St. Regina , SK S4R 8P8 Canada (306) 585-2100 Fax: (306) 585-2191 info.regina@magnaiv.com
Andrew Westerman
Magna IV Engineering 106, 4268 Lozells Ave. Burnaby, BC VSA 0C6 Canada (604) 421-8020
Scott Nixon
Magna IV Engineering 11811 North Freeway, Ste. 500 Houston, TX 77060 (281) 436-7329 www.magnaiv.com
National Field Services 649 Franklin St. Lewisville, TX 75057 (972) 420-0157 www.natlfield.com
Eric Beckman
Nationwide Electrical Testing, Inc. 6050 Southard Trace Cumming, GA 30040 (770) 667-1875 Fax: (770) 667-6578
Shashi@N-E-T-Inc.com www.n-e-t-inc.com
Shashikant B. Bagle
North Central Electric, Inc. 69 Midway Ave. Hulmeville, PA 19047-5827 (215) 945-7632 Fax: (215) 945-6362 ncetest@aol.com www.ncetest.com
Robert Messina
Northern Electrical Testing, Inc. 1991 Woodslee Dr. Troy, MI 48083-2236 (248) 689-8980 Fax: (248) 689-3418 ldetterman@northerntesting.com www.northerntesting.com
Lyle Detterman
NETA ACCREDITED COMPANIES
Orbis Engineering Field Services Ltd. #300, 9404 - 41st Ave. Edmonton, AB T6E 6G8 Canada (780) 988-1455 Fax: (780) 988-0191 lorne@orbisengineering.net www.orbisengineering.net
Lorne Gara
Pacific Power Testing, Inc. 14280 Doolittle Dr. San Leandro, CA 94577 (510) 351-8811 Fax: (510) 351-6655 steve@pacificpowertesting.com www.pacificpowertesting.com
Steve Emmert
Pacific Powertech, Inc. #110, 2071 Kingsway Ave. Port Coquitlam, BC V3C 6N2 Canada (604) 944-6697 Fax: (604) 944-1271 jkonkin@pacificpowertech.ca www.pacificpowertech.ca
Josh Konkin
Phasor Engineering
Sabaneta Industrial Park #216 Mercedita, PR 00715 Puerto Rico (787) 844-9366 Fax: (787) 841-6385 rcastro@phasorinc.com
Rafael Castro
Potomac Testing, Inc. 1610 Professional Blvd., Ste. A Crofton, MD 21114 (301) 352-1930 Fax: (301) 352-1936 kbassett@potomactesting.com www.potomactesting.com
Ken Bassett
Power & Generation Testing, Inc., a CE Power Company 480 Cave Rd. Nashville, TN 37210 (615) 882-9455 Fax: (615) 882-9591 mose@pgti.net www.pgti.net
Mose Ramieh
Power Engineering Services, Inc. 9179 Shadow Creek Lane Converse, TX 78109 (210) 590-4936 Fax: (210) 590-6214 engelke@pe-svcs.com www.pe-svcs.com
Miles R. Engelke
POWER PLUS Engineering, Inc. 46575 Magellan Novi, MI 48377 (248) 344-0200 Fax: (248) 305-9105 smancuso@epowerplus.com www.epowerplus.com
Salvatore Mancuso
Power Products & Solutions, LLC
12465 Grey Commercial Rd. Midland, NC 28107 (704) 573-0420 x12 Fax: (704) 573-3693
ralph.patterson@powerproducts.biz www.powerproducts.biz
Ralph Patterson
Power Products & Solutions, LLC 13 Jenkins Ct. Mauldin, SC 29662 (800) 328-7382
ralph.patterson@powerproducts.biz www.powerproducts.biz
Raymond Pesaturo
Power Services, LLC 998 Dimco Way, P.O. Box 750066 Centerville, OH 45475 (937) 439-9660 Fax: (937) 439-9611
mkbeucler@aol.com
Mark Beucler
Power Solutions Group, Ltd. 425 W. Kerr Rd. Tipp City, OH 45371 (937) 506-8444 Fax: (937) 506-8434
bwilloughby@powersolutionsgroup.com www.powersolutionsgroup.com
Barry Willoughby
Power Solutions Group, Ltd. 135 Old School House Rd. Piedmont, SC 29673 (864) 845-1084 Fax:: (864) 845-1085 fcrawford@powersolutionsgroup.com www.powersolutionsgroup.com
Anthony Crawford
Power Solutions Group, Ltd. 670 Lakeview Plaza Blvd. Columbus, OH 43085 (614) 310-8018
sspohn@powersolutionsgroup.com www.powersolutionsgroup.com
Stuart Spohn
Power Systems Testing Co. 4688 W. Jennifer Ave., Ste. 108 Fresno, CA 93722 (559) 275-2171 ext 15 Fax: (559) 275-6556 dave@pstcpower.com www.powersystemstesting.com
David Huffman
Power Systems Testing Co. 600 S. Grand Ave., Ste. 113 Santa Ana, CA 92705-4152 (714) 542-6089 Fax: (714) 542-0737 www.powersystemstesting.com
NETA ACCREDITED COMPANIES
Power Systems Testing Co.
6736 Preston Ave, Ste. E Livermore, CA 94551 (510) 783-5096 Fax: (510) 732-9287
www.powersystemstesting.com
Power Test, Inc.
2200 Highway 49 Harrisburg, NC 28075 (704) 200-8311 Fax: (704) 455-7909 rich@powertestinc.com www.powertestinc.com
Richard Walker
POWER Testing and Energization, Inc. 14006 NW 3rd Ct., Ste. 101 Vancouver, WA 98685 (360) 597-2800 Fax: (360) 576-7182 chris.zavadlov@powerte.com www.powerte.com
Chris Zavadlov
POWER Testing and Energization, Inc.
731 E. Ball Rd., Ste. 100 Anaheim, CA 92805 (714) 507-2702 www.powerte.com
POWER Testing and Energization, Inc.
22035 70th Ave. South Kent, WA 98032 (253) 437-3100 www.powerte.com
Powertech Services, Inc.
4095 South Dye Rd. Swartz Creek, MI 48473-1570 (810) 720-2280 Fax: (810) 720-2283 kirkd@powertechservices.com www.powertechservices.com
Kirk Dyszlewski
Precision Testing Group 5475 Highway 86, Unit 1 Elizabeth, CO 80107 (303) 621-2776 Fax: (303) 621-2573 glenn@precisiontestinggroup.com
Glenn Stuckey
Premier Power Maintenance Corporation 6525 Guion Rd. Indianapolis, IN 46268 (317) 879-0660
kevin.templeman@premierpower.us www.premierpowermaintenance.com
Kevin Templeman
Premier Power Maintenance Corporation 2725 Jason Rd. Ashland, KY 41102 (606) 929-5969
jay.milstead@premierpower.us www.premierpowermaintenance.com
Jay Milstead
Premier Power Maintenance Corporation 3066 Finley Island Cir NW Decatur, AL 35601 (256) 355-1444
johnnie.mcclung@premierpower.us www.premierpowermaintenance.com
Johnnie McClung
Premier Power Maintenance Corporation 4301 Iverson Blvd., Ste. H Trinity, AL 35673 (256) 355-3006
kevin.templeman@premierpower.us www.premierpowermaintenance.com
Kevin Templeman
Premier Power Maintenance Corporation 7301 E County Road 142 Blytheville, AR 72315 (870) 762-2100
kevin.templeman@premierpower.us www.premierpowermaintenance.com
Kevin Templeman
Premier Power Maintenance Corporation 7262 Kensington Rd. Brighton, MI 48116 (517) 230-6620
brian.ellegiers@premierpower.us www.premierpowermaintenance.com
Brian Ellegiers
Premier Power Maintenance Corporation 4537 S. Nucor Rd. Crawfordsville, IN 47933 (317) 879-0660
kevin.templeman@premierpower.us www.premierpowermaintenance.com
Kevin Templeman
Reuter & Hanney, Inc. 149 Railroad Dr. Northampton Industrial Park Ivyland, PA 18974 (215) 364-5333 Fax: (215) 364-5365 mikereuter@reuterhanney.com www.reuterhanney.com
Michael Reuter
Reuter & Hanney, Inc. 4270-I Henninger Ct. Chantilly, VA 20151 (703) 263-7163 Fax: 703-263-1478 www.reuterhanney.com
Reuter & Hanney, Inc. 11620 Crossroads Circle, Suites D-E Middle River, MD 21220 (410) 344-0300 Fax: (410) 335-4389 www.reuterhanney.com
Michael Jester
REV Engineering, LTD 3236 - 50 Ave. SE Calgary, AB T2B 3A3 Canada (403) 287-0156 Fax: (403) 287-0198 rdavidson@reveng.ca www.reveng.ca
Roland Nicholas Davidson, IV
Saber Power Services 9841 Saber Power Lane Rosharon, TX 77583-5188 (713) 222-9102 info@saberpower.com www.saberpower.com
Mark Reid
Scott Testing Inc. 1698 5th St. Ewing, NJ 08638 (609) 882-2400 Fax: (609) 882-5660 rsorbello@scotttesting.com www.scotttesting.com
Russ Sorbello
Sentinel Power Services, Inc. 7517 E. Pine St. Tulsa, OK 74115 (918) 359-0350 gellis@spstulsa.com www.sentinelpowerservices.com
Greg Ellis
Sentinel Power Services, Inc. 1110 West B St., Ste. H Russellville, AR 72801 (918) 359-0350 gellis@spstulsa.com www.sentinelpowerservices.com
Greg Ellis
Shermco Industries 2425 E. Pioneer Dr. Irving, TX 75061 (972) 793-5523 Fax: (972) 793-5542 rwidup@shermco.com www.shermco.com
Ron Widup
Shermco Industries 112 Industrial Dr., PO Box 606 Minooka, IL 60447 (815) 467-5577 Fax: (815) 467-5883 rwidup@shermco.com www.shermco.com
Ron Widup
Shermco Industries 1705 Hur Industrial Blvd. Cedar Park, TX 78613 (512) 267-4800 Fax: (512) 258-5571 cking@shermco.com www.shermco.com
Chris King
Shermco Industries 33002 FM 2004 Angleton, TX 77515 (979)848-1406 Fax: (979) 848-0012 cking@shermco.com www.shermco.com
Chris King
Shermco Industries
1357 N. 108th E. Ave. Tulsa, OK 74116 (918) 234-2300 jharrison@shermco.com www.shermco.com
Jim Harrison
Shermco Industries 796 11th St. Marion, IA 52302 (319) 377-3377 Fax: (319) 377-3399 jedwards@shermco.com www.shermco.com
Jason Edwards
Shermco Industries 2100 Dixon St., Ste. C Des Moines, IA 50316 (515) 263-8482 jedwards@shermco.com www.shermco.com
Jason Edwards
Shermco Industries 4383 Professional Parkway Groveport, OH 43125 (614) 836-8556 Fax: (614) 836-8557 jharrison@shermco.com www.shermco.com
Jim Harrison
Shermco Industries 998 East Berwood Ave. Saint Paul, MN 55110 (651) 484-5533 Fax: (651) 484-7686 jedwards@shermco.com www.shermco.com
Jason Edwards
Shermco Industries 12000 Network Blvd., Bldg D,, Ste. 410 San Antonio, TX 78249 (512) 267-4800 Fax: (512) 267-4808 cking@shermco.com www.shermco.com
Chris King
Shermco Industries Canada Inc. 1033 Kearns Crescent, Box 995 Regina, SK S4P 3B2 Canada (306) 949-8131 Fax: (306) 522-9181 kheid@magnaelectric.com www.shermco.com
Kerry Heid
Shermco Industries Canada Inc. 851-58th St. East Saskatoon, SK S7K 6X5 Canada (306) 955-8131 Fax: (306) 955-9181 ajaques@magnaelectric.com www.shermco.com
Adam Jaques
Shermco Industries Canada Inc. 3731-98 St. Edmonton, AB T6E 5N2 Canada (780) 436-8831 Fax: (780) 468-9646 cgrant@magnaelectric.com www.shermco.com
Cal Grant
Shermco Industries Canada Inc. 3430 25th St. NE Calgary, AB T1Y 6C1 Canada (403) 769-9300 Fax: (403)769-9369 cgrant@magnaelectric.com www.shermco.com
Cal Grant
Shermco Industries Canada Inc. 1375 Church Ave. Winnipeg, MB R2X 2T7 Canada (204) 925-4022 Fax: (204) 925-4021 cbrandt@magnaelectric.com www.shermco.com
Curtis Brandt
Sigma Six Solutions, Inc. 2200 West Valley Hwy., Ste. 100 Auburn, WA 98001 (253) 333-9730 Fax: (253) 859-5382 jwhite@sigmasix.com www.sigmasix.com
John White
Southern New England Electrical Testing, LLC 3 Buel St., Ste. 4 Wallingford, CT 06492 (203) 269-8778 Fax: (203) 269-8775 dave.asplund@sneet.org www.sneet.org
David Asplund, Sr.
Southwest Energy Systems, LLC 2231 East Jones Ave., Ste. A Phoenix, AZ 85040 (602) 438-7500 Fax: (602) 438-7501 bob.sheppard@southwestenergysystems.com www.southwestenergysystems.com
Robert Sheppard
Taurus Power & Controls, Inc. 9999 SW Avery St. Tualatin, OR 97062-9517 (503) 692-9004 Fax: (503) 692-9273 robtaurus@tauruspower.com www.tauruspower.com
Rob Bulfinch Taurus Power & Controls, Inc. 19226 66th Ave. S, Ste. L102 Kent, WA 98032 (425) 656-4170 Fax: (425) 656-4172 servicereq@tauruspower.com www.tauruspower.com
David Koons
3C Electrical Co., Inc. 40 Washington St. Westborough, MA 01581 (508) 881-3911 Fax: (508) 881-4814 jim@three-c.com www.three-c.com
Jim Cialdea
3C Electrical Co., Inc. 72 Sanford Dr. Gorham, ME 04038 (800) 649-6314 Fax: (207) 782-0162 jim@three-c.com www.three-c.com
Jim Cialdea
Tidal Power Services, LLC
4202 Chance Lane Rosharon, TX 77583 (281) 710-9150 Fax: (713) 583-1216 monty.janak@tidalpowerservices.com www.tidalpowerservices.com
Monty C. Janak
Tidal Power Services, LLC 8184 Highway 44, Ste. 105 Gonzales, LA 70737 (225) 644-8170 Fax: (225) 644-8215 www.tidalpowerservices.com
Darryn Kimbrough
Tidal Power Services, LLC 1056 Mosswood Dr. Sulphur, LA 70663 (337) 558-5457 Fax: (337) 558-5305 www.tidalpowerservices.com
Steve Drake
Tony Demaria Electric, Inc. 131 West F St. Wilmington, CA 90744 (310) 816-3130 (310) 549-9747 neno@tdeinc.com www.tdeinc.com
Nenad Pasic
NETA ACCREDITED COMPANIES
Trace Electrical Services & Testing, LLC
293 Whitehead Rd. Hamilton, NJ 08619 (609) 588-8666 Fax: (609) 588-8667 jvasta@tracetesting.com www.tracetesting.com
Joseph Vasta
Utilities Instrumentation Service, Inc. 2290 Bishop Circle East Dexter, MI 48130 (734) 424-1200 Fax: (734) 424-0031 GEWalls@UISCorp.com www.uiscorp.com
Gary E. Walls
Utility Service Corporation 4614 Commercial Dr. NW Huntsville, AL 35816-2201 (256) 837-8400 Fax: (256) 837-8403 apeterson@utilserv.com www.utilserv.com
Alan D. Peterson
Western Electrical Services, Inc. 14311 29th St. East Sumner , WA 98390 (253) 891-1995 Fax: (253) 891-1511 dhook@westernelectricalservices.com www.westernelectricalservices.com
Dan Hook
Western Electrical Services, Inc. 3676 W. California Ave., #C, 106 Salt Lake City, UT 84104 (888) 395-2021 Fax: (253) 891-1511 rcoomes@westernelectricalservices.com www.westernelectricalservices.com
Rob Coomes
Western Electrical Services, Inc. 5680 South 32nd St. Phoenix, AZ 85040 (602) 426-1667 Fax: (253) 891-1511 carcher@westernelectricalservices.com www.westernelectricalservices.com
Craig Archer
Western Electrical Services, Inc. 4510 NE 68th Dr., Ste. 122 Vancouver, WA 98661 (888) 395-2021 Fax: (253) 891-1511 Tasciutto@westernelectricalservices.com www.westernelectricalservices.com
Tony Asciutto
This issue’s advertisers are identified below. Please thank these advertisers by telling them you saw their advertisement in YOUR magazine –NETA World.
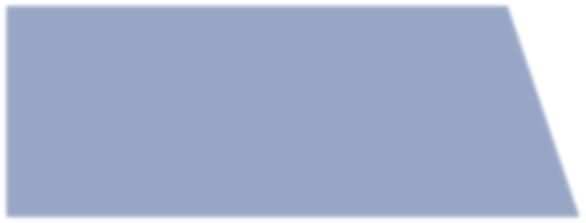
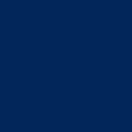


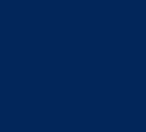


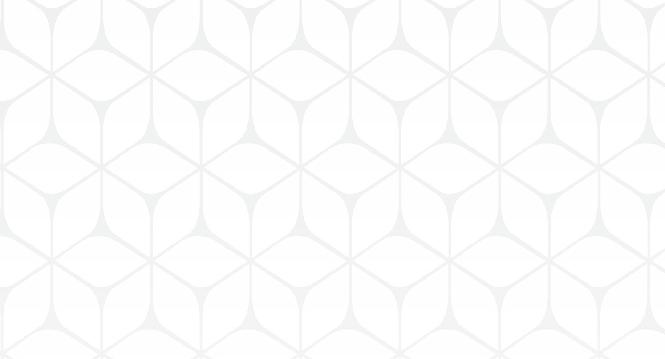


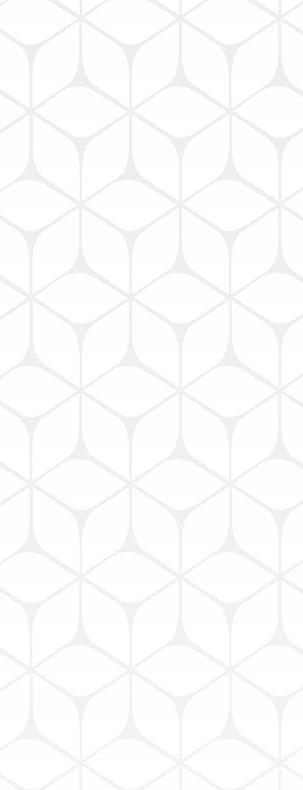
Perfect for ALL of your power factor measuring needs
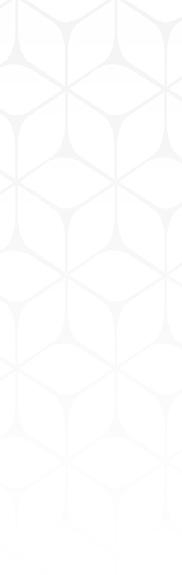
• Battery-operated – Unique to market
• Built-in standard capacitor
• Test frequency 10 Hz – 400 Hz
• External safety switch for safe operation
• Easy export of results using USB interface • Built-in printer
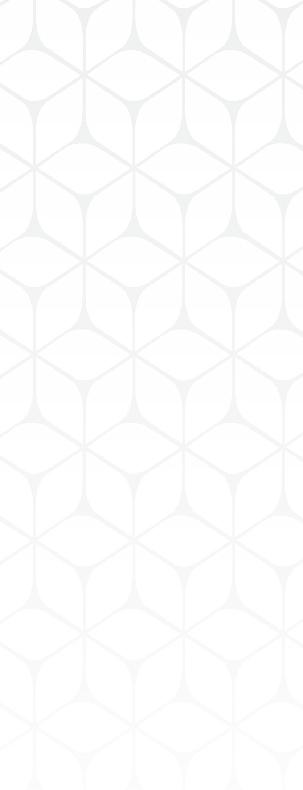


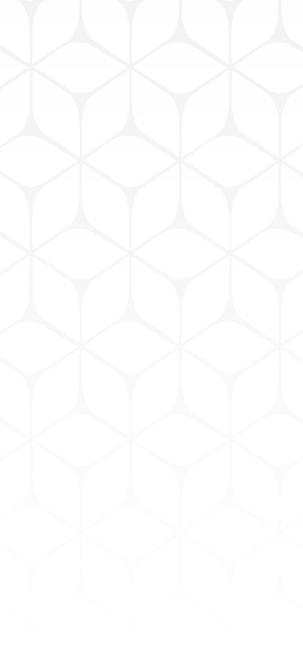
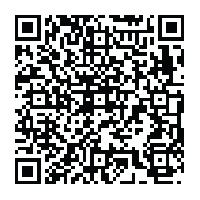
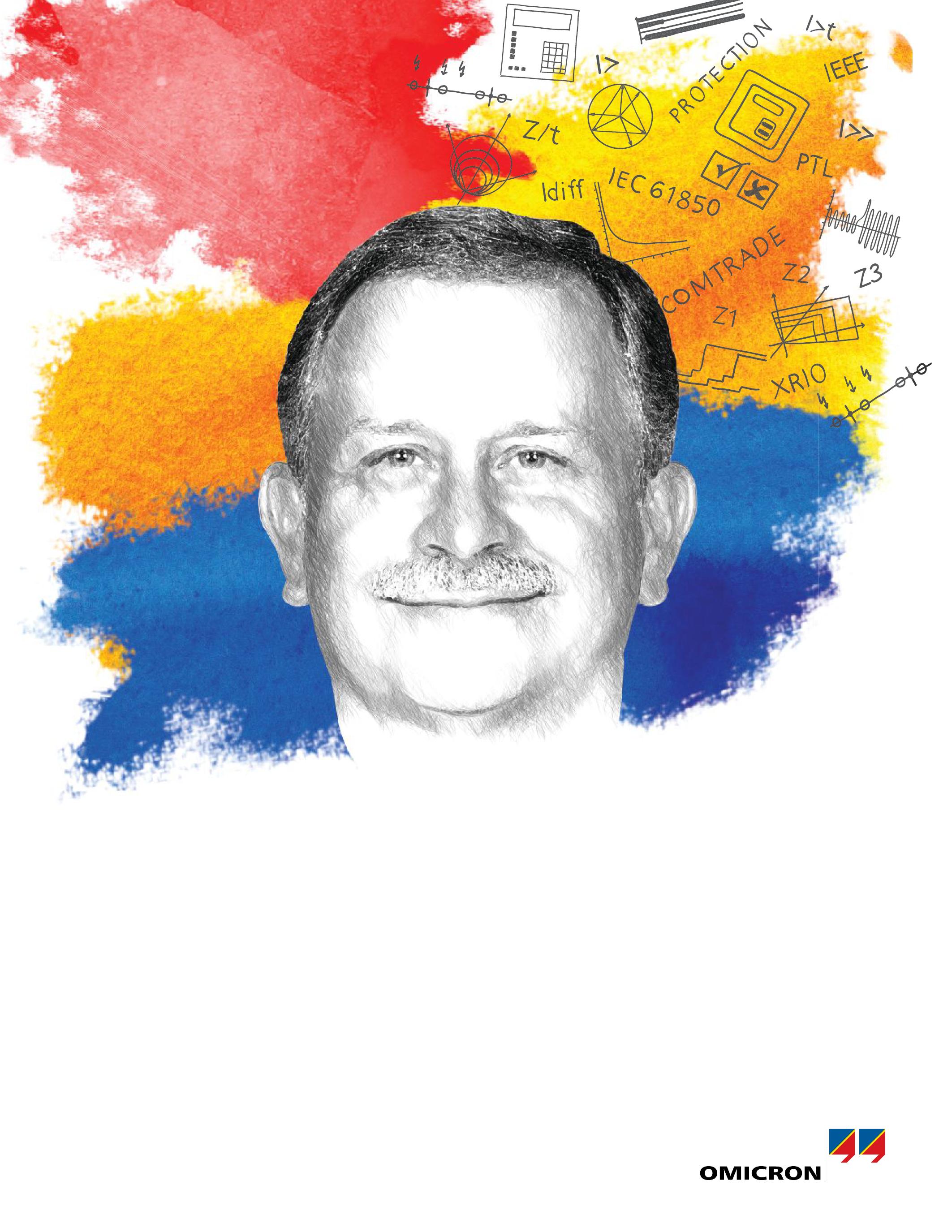
As a power systems engineer it’s essential that I keep up to date with what’s going on in the market and what our customers need. Based on this, I am constantly looking for better ways of doing things. Take our simulation-based protection testing solution; now even complex networks can be tested automatically from a single point of control. This allows a comprehensive assessment of the entire protection scheme, taking into account the settings and functionality of the individual relays. www.omicronenergy.com