


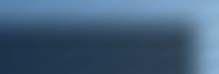

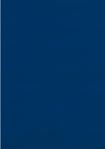
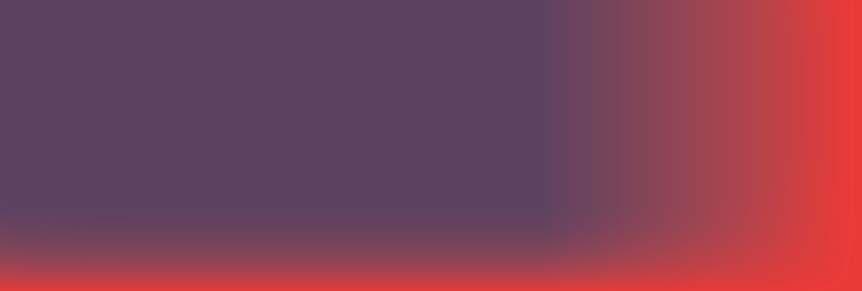
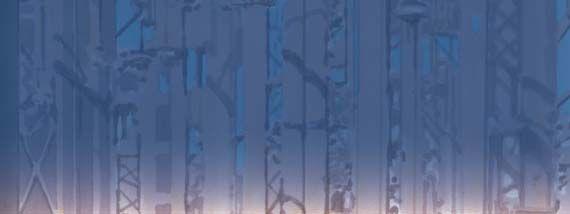
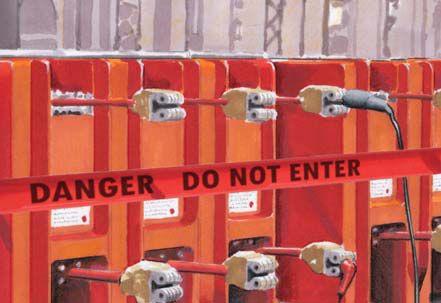
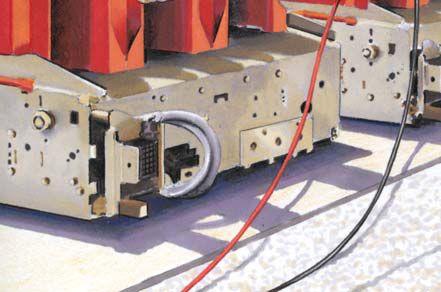

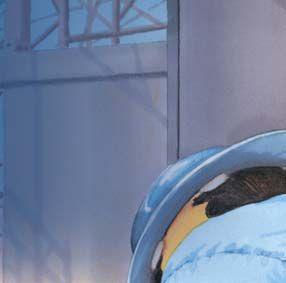





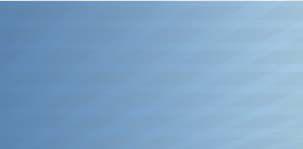
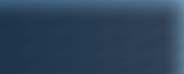
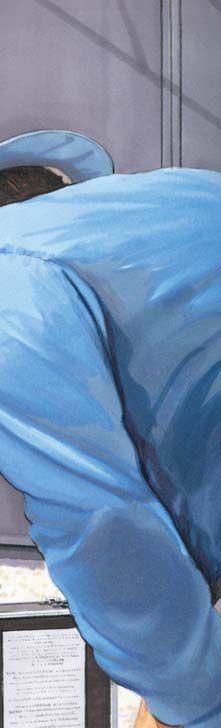

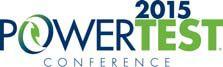


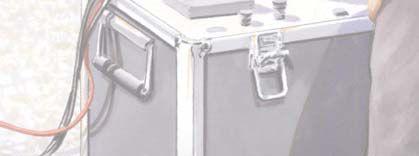
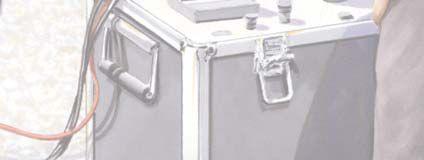


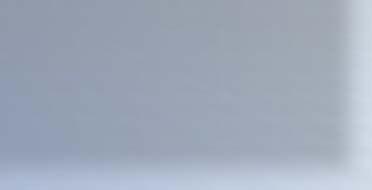
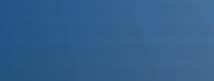

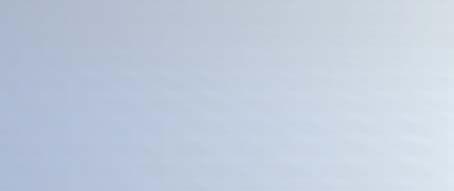

Perform high precision oil testing anywhere with the OTS portable series.
Now you can perform dielectric strength testing of critical insulating fluids – mineral, High Molecular Weight Hydrocarbon (HMWH), silicone and ester (natural and synthetic) anywhere with Megger’s range of portable oil test sets. The OTS60PB and OTS80PB feature fully automated testing to ASTM D877 and ASTM D1816 standards with test voltages up to 60 and 80 kV, respectively. Water and conducting particles don’t stand a chance.
Download the new Megger guide to “Insulating Oil Dielectric Breakdown Testing”. Go to megger.com/OTS
During its 20–40 year service life, a circuit breaker must be constantly prepared to operate. Typically, long periods of inactivity often elapse during which the breaker’s mechanical and electrical components never move.Thecircuitbreakeristheactivelink move. The circuit breaker is the active link inafaultclearancesituation.Whenafault in a fault clearance situation. When a fault occurs on the electrical system, the associated fault current must be interrupted quickly and reliably. This action is referred to as fault clearing.
Lynn Hamrick, Shermco Industries
7 President’s Desk
David Huffman, Power Systems Testing Co.
NETA President
62 Avoiding Metal-Clad Switchgear Failure Through Use of Partial Discharge Detection
Tony McGrail, Jay Garnette, and Matthew Lawrence, Doble Engineering Company
Electrical Shocks -—The Forgotten Hazard
Ron Widup and Jim White, Shermco Industries
Tech Quiz
Medium-Voltage Circuit Breakers
Jim White, Shermco Industries
Niche Market
A Case for Testing Medium-Voltage Breakers
Lynn Hamrick, Shermco Industries 28 Testing Rotating Machinery
QA Tests for MV GVPI Stator Windings
Vicki Warren, Iris Power LP
Medium Voltage SF6 Breakers Condition Analysis Hazard Awareness
Scott Blizard, American Electrical Testing Co., Inc.
Fault Clearance on Grounding Conductors
Jeff Jowett, Megger
No-Outage Corner
Examination of Transformer Oil
Moisture Measurements
Don Genutis, No-Outage Electrical Testing, Inc.
72 Are We Overautomated?
Jay Wicks, Black Marble Electrical Solutions
76 Make Your Electrical Safety Program Your Own Part 1: Why won't a generic program work?
Don Brown, Shermco Industries
82Electrical Commissioning: Verifying Power Systems for Safety, Performance, and Reliability
Ron Widup, Shermco Industries
111 NETA Ups the Ante in the Standards Development Game
Kristen Wicks, NETA
90New 29 CFR Parts 1910 &1926 Will Affect Your Existing PPE Program
Dennis Neitzel, AVO Training Institute
94Smart Insulation Development, Innovation for Asset Management, and Condition-Based Maintenance on Aging Power Delivery Infrastructures
Philip J. Chadderdon and David J. Woodcock, WEIDMANN Diagnostic Solutions
24Strategy, Marketing the Focus of June Meeting
26 NETA Strengthens Relationships at the 2014 International Conference of Doble Clients
Richard Piet, NETA
42 NETA Sees Synergies at Saskatchewan Electrical Symposium
Richard Piet, NETA
68 NETA Thanks Board Member Kerry Heid for his Service
Richard Piet, NETA
106 Partnership between NETA and EVIT to Provide a Path for Future Electrical Testing Technicians
Richard Piet, NETA
Introducing the NETA Handbooks, Series II
Analysis the test equipment answer
Relay and Protection Systems
Switchgear and Breakers (Low, Medium and High Voltage)
Cable and Bus
Transformers
Batteries
Motors and Rotating Apparatus
Watthour Metering
Power Quality and Consumption
3050 Old Centre Avenue, Suite 102
Portage, MI 49024
Toll free: 888.300.NETA (6382)
Phone: 269.488.NETA (6382)
Fax: 269.488.6383
neta@netaworld.org
www.netaworld.org
EXECUTIVEDIRECTOR: Jayne Tanz, CMP
NETA Officers
PRESIDENT: David Huffman, Power Systems Testing Co.
FIRSTVICEPRESIDENT: Ron Widup, Shermco Industries
SECONDVICEPRESIDENT: Jim Cialdea, Three-C Electrical Co., Inc.
SECRETARY: Mose Ramieh, Power & Generation Testing, Inc.
TREASURER: John White, Sigma Six Solutions
NETA Board of Directors
Ken Bassett (Potomac Testing, Inc.)
Scott Blizard (American Electrical Testing Co., Inc.)
Jim Cialdea (Three-C Electrical Co., Inc.)
Lorne Gara (Orbis Engineering Field Services, Ltd.)
Roderic Hageman (PRIT Service, Inc.)
David Huffman (Power Systems Testing)
Alan Peterson (Utility Service Corporation)
Mose Ramieh (Power & Generation Testing, Inc.)
Bob Sheppard (Southwest Energy Services, LLC)
John White (Sigma Six Solutions)
Ron Widup (Shermco Industries)
NETA World Staff
TECHNICALEDITOR: Roderic L. Hageman
ASSOCIATEEDITORS: Diane W. Hageman, Resa Pickel
MANAGINGEDITOR: Jayne Tanz, CMP
ADVERTISINGMANAGER: Laura McDonald
DESIGNANDPRODUCTION: Hour Custom Publishing
NETA Committee Chairs
CONFERENCE: Ron Widup; MEMBERSHIP: Ken Bassett; PROMOTIONS/MARKETING: Scott Blizard; SAFETY: Scott Blizard and Jim White; TECHNICAL: Alan Peterson; TECHNICALEXAM: Ron Widup; WORLDADVISORY: Diane Hageman; CONTINUINGTECHNICALDEVELOPMENT: David Huffman; TRAINING: Kerry Heid; FINANCE: John White; NOMINATIONS: Alan Peterson; STRATEGY: Mose Ramieh; ALLIANCEPROGRAM: Jim Cialdea
© Copyright 2014, NETA
NOTICE AND DISCLAIMER
NETA World is published quarterly by the InterNational Electrical Testing Association. Opinions, views and conclusions expressed in articles herein are those of the authors and not necessarily those of NETA. Publication herein does not constitute or imply endorsement of any opinion, product, or service by NETA, its directors, officers, members, employees or agents (herein “NETA”).
All technical data in this publication reflects the experience of individuals using specific tools, products, equipment and components under specific conditions and circumstances which may or may not be fully reported and over which NETA has neither exercised nor reserved control. Such data has not been independently tested or otherwise verified by NETA.
NETA MAKES NO ENDORSEMENT, REPRESENTATION OR WARRANTY AS TO ANY OPINION, PRODUCT OR SERVICE REFERENCED OR ADVERTISED IN THIS PUBLICATION. NETA EXPRESSLY DISCLAIMS ANY AND ALL LIABILITY TO ANY CONSUMER, PURCHASER OR ANY OTHER PERSON USING ANY PRODUCT OR SERVICE REFERENCED OR ADVERTISED HEREIN FOR ANY INJURIES OR DAMAGES OF ANY KIND WHATSOEVER, INCLUDING, BUT NOT LIMITED TO ANY CONSEQUENTIAL, PUNITIVE, SPECIAL, INCIDENTAL, DIRECT OR INDIRECT DAMAGES. NETA FURTHER DISCLAIMS ANY AND ALL WARRANTIES, EXPRESS OF IMPLIED, INCLUDING, BUT NOT LIMITED TO, ANY IMPLIED WARRANTY OF FITNESS FOR A PARTICULAR PURPOSE.
ELECTRICAL TESTING SHALL BE PERFORMED ONLY BY TRAINED ELECTRICAL PERSONNEL AND SHALL BE SUPERVISED BY NETA CERTIFIED TECHNICIANS/ LEVEL III OR IV OR BY NICET CERTIFIED TECHNICIANS IN ELECTRICAL TESTING TECHNOLOGY/LEVEL III OR IV. FAILURE TO ADHERE TO ADEQUATE TRAINING, SAFETY REQUIREMENTS, AND APPLICABLE PROCEDURES MAY RESULT IN LOSS OF PRODUCTION, CATASTROPHIC EQUIPMENT FAILURE, SERIOUS INJURY OR DEATH.
When working properly, medium-voltage circuit breakers operate quietly. So quietly, that sometimes they go unnoticed for years. This is when the fireworks can start. . . .
I hope this issue of NETA World finds you well. By the time you read this, the July exam session will have ended, the September Membership and Board meetings in San Francisco will be fast approaching, and, with any luck at all, you haven’t melted in the summer heat.
NETA continues to move forward on many fronts. A meeting with ARCOM should have just taken place in July to review some potential changes in the Master Spec. Several IEEE, NFPA, and CSA committee meetings either have taken place or soon will. Participating on these committees is a great way to stay on the leading edge of changes in the industry and to help shape it.
This issue focuses on the maintenance of medium-voltage circuit breakers. Some of the maintenance activities have been around for quite some time while others, such as first trip diagnostics, are newer. Some diagnostic tools have also improved in recent years. I hope you either find some new maintenance practices to add to your tool bag or ways to improve what you’re already using. In any event, maintaining medium-voltage circuit breakers properly will help them continue to operate quietly.
Sincerely,
David Huffman President InterNational Electrical Testing Associationelectric shock may result from indirect contact where a conductive part that is not normally energized becomes energized due to a fault, such as the ground from a fallen power line. When high fault currents flow, electric shock from step and touch potential can occur.
So the three basic paths electric current travels through the body are:
1. Touch Potential (hand/hand path)
2. Step Potential (foot/foot path)
3. Touch/Step Potential (hand/foot path)
If you have a touch potential contact, the current travels from one hand through the heart and out through the other hand. So think about the path the electricity flows during the shock event – in one hand, across the heart and lungs, and out the other hand. This is most problematic because of the path of current, ventricular fibrillation, difficulty in breathing, unconsciousness, or death may occur.
So you are walking along and an overhead line falls to the ground because of an abnormal event (car wreck, broken conductor, tree limb, etc.), and the ground becomes energized. You have a possibility of being involved in a step potential contact, where current travels from one of your feet, through your legs, and out the other foot. While the heart is not in the direct path of current, your leg muscles may contract which could cause you to collapse or be momentarily paralyzed, and you might fall to the ground and create an even higher risk path for the current to flow through your body.
By now you have probably figured out how this works. In a touch/step potential, contact current travels from one hand, through the heart, down the leg, and out a foot. In this type of contact both the heart and the lungs are in the direct path of current, like hand-to-hand contact ventricular
fibrillation, difficulty in breathing, collapse, unconsciousness, or death may occur.
Figure 1 is from a paper delivered by Danny Liggett and Lanny Floyd to the IEEE/IAS Electrical Safety Workshop. In the study they conducted they only looked at industrial facilities and excluded utility workers. In their study, Danny and Lanny found that the most hazardous voltage to electrical workers was 277/480 volts. No surprise there, but in looking at Figure 1 we canalsoseethat120/208/250voltswasalmostas can also see that 120/208/250 volts was almost as lethalasthe277/480volts.Thatstatisticshocked lethal as the 277/480 volts. That statistic shocked us (pun intended). We think you will agree that to see the way qualified persons approach
working on low-voltage electrical systems less than 277/480 volts definitely gives one the perception that they aren’t very concerned about being shocked.
Going back to low-voltage shock, note the burn injury in Figure 2. This was from a 120-volt tool that failed internally, shorting to the frame.
Becausetheworker’shandwasaroundthetool
Because the worker’s hand was around the tool grip, the electrical shock caused him to grip the tool tightly and he could not release it. From the extent of the injury, he must have held it for some time before letting it go. The use of doubleinsulated and battery-powered tools has made this type of injury much less common, but heavyduty tools and older tools may still have metal frames and should be tested annually to ensure they maintain a good dielectric quality.
The answer to the electrical shock issue is very simple; at least for qualified persons. Wear your insulating gloves. Very simple, right? Well….maybe not. When teaching, often the question is asked of students “Do you carry your gloves with you?” Occasionally, one to two willraisetheirhands.Soto will raise their hands. So to that, “I guess the rest of you don’t wear your gloves. If you don’t carry them you’re not going back to thePPElockeror the PPE locker or the truck to get
them are you?” A lot of them smile, but make no comment. Belt clips are available for low-voltage gloves that make carrying and having these lifesaving articles readily available. There are several manufacturers and the price varies from $4.00 to about $12.00. Why don’t more workers use them?
There is good news in all this. Note the number of electrical fatalities has been dropping at a pretty substantial rate. Let’s look at it closer. Figure 4 is from the Electrical Safety Foundation International (ESFI) and is a compilation of statisticsfromtheBureauofLaborStatistics statistics from the Bureau of Labor Statistics (BLS) and shows electrical fatalities from 1992 to2010. to 2010.
Thebadnewsisthat162workerswere
The bad news is that 162 workers were electrocuted in 2010. Basically, they received capital punishment for the crime of going to work.Isthattooharsh? work. Is that too harsh?
We tend to forget that electricity can be fatal, even at lower voltages.
It seems as though we have a lot of respect for electricity when the voltage is above 480/277-volts…using proper PPE and equipment, double-checking procedures and generally doing what OSHA and NFPA 70E expect a qualified person to do: plan the job, verify the plan, gather the correct PPE, and execute the plan inacontrolledandsafemanner.Ifweusedthat in a controlled and safe manner. If we used that same level of care and planning when working with low-voltage electrical systems, the number of shock-related injuries and fatalities would almost disappear for qualified persons.
It seems simple as we write it on a piece of paper, but in actual practice it is not. It requires a cultural shift in the attitudes and perceptions of the workforce. People have to accept their part of the responsibility to be safe and not expect the company they work for to try to guess at what possible mistakes they could make on the job. Even though you can sue anyone and everyone, the fact is the money you receive from a settlement won’t make your life better. Your life will always be diminished after a serious electrical incident. Who would want that? Be proactive. Go above and beyond the minimum electrical safety requirements, rules, and regulations. Do whatever is needed for you, personally, to be safe. If others don’t want to follow your lead, let it be on their heads, but you go home every night in the same condition of health as you arrived.
[1] USBureauofLaborStatistics. US Bureau of Labor Statistics. National census of fatal occupational injuries , 1998. Report No USDL-99–208. Washington, DC: US Department of Labor, 1999.
Ron Widup and Jim White areNETA’S are NETA’S representatives to NFPA Technical Committee 70E (Electrical Safety Requirements for Employee Workplaces). Both gentlemen are employees of Shermco Industries in Dallas, Texas, a NETA Accredited Company. Ron Widup is President of Shermco and has been with the company since 1983. He is a Principal member of the Technical Committee on “Electrical Safety in the Workplace” (NFPA 70E) and a Principal member of the National Electrical Code (NFPA 70)CodePanel11.Heisalsoamember 70) Code Panel 11. He is also a member of the technical committee “Recommended Practice for Electrical Equipment Maintenance” (NFPA 70B), and a member of the NETA Board of Directors and Standards Review Council. Jim White is nationally recognized for technical skills and safety training in the electrical power systems industry. He is the Training Director for Shermco Industries, and has spent the last twenty years directly involved in technical skills and safety training for electrical power system technicians. Jim is a Principal member of NFPA 70B representing Shermco Industries, NETA’s alternate member of NFPA 70E, and a member of ASTM F18 Committee “Electrical Protective Equipment for Workers”.
James R. (Jim) White is the Training Director of Shermco Industries, Inc., in Dallas, Texas. He is the principal member on the NFPA technical committee “Recommended Practice for Electrical Equipment Maintenance” (NFPA 70B). Jim represents NETA as an alternate member of the NFPA Technical Committee “Electrical Safety in the Workplace” (NFPA 70E) and represents NETA on the ASTM F18 Committee “Electrical Protective Equipment For Workers”. Jim is an IEEE Senior Member and in 2011 received the IEEE/PCIC Electrical Safety Excellence award. Jim is a past Chairman (2008) of the IEEE Electrical Safety Workshop (ESW).
No.107 No. 107
Medium-voltage circuit breakers can cover multiple types of arc-extinguishing methods. If they misoperate, they can be extremely hazardous due to their higher voltages. Some new technologies have been introduced that can help detect problems and help ensure safe operation. As with low-voltage circuit breakers, medium-voltage circuit breakers require maintenance and testing to prevent accidents.
1. The vacuum bottle Integrity test provides an indication of:
a. remaining life of a vacuum bottle
b. how many short circuits the vacuum bottle can handle
c. the vacuum pressure inside a vacuum bottle
d. the current state of the vacuum bottle
2. The term medium voltage typically refers to what voltage range?
a. 1,000 V to 100,000 V
b. 1,000 V to 34,500 V
c. 1,000 V to 25,000 V
d. 1,000 V to 15,000 V
3. Medium-voltage circuit breakers are usually identified by their arc interruption method. List five of those common interrupting methods: a.
4. To what does anti-pump refer?
a. The ability of a circuit breaker to withstand the available short circuit current
b. The circuit breaker can only be closed once for an operation of the control switch to the close position
c. The method the circuit breaker operating mechanism operates
d. A test to measure the velocity and displacement of a circuit breaker
5. What is the recommended level of PPE from NFPA 70E Table 130.7(C)(15)(a) for racking a circuit breaker in or out of its cubicle?
a. HRC 1
b. HRC 2
c. HRC 3
d. HRC 4
successor to the industry leading AC-PRO
The AC-PRO-II is fully backwards compatible with the CTs, actuators and wiring harnesses of the original AC-PRO
55% smaller then the original AC-PRO, with double the features.
RS-485 Modbus RTU communications is standard
Sluggish Breaker™ detection to determine if the breaker mechanism needs service.
MARCH 2– , 2015
Utility Service Corporation has been providing electrical and technical services for government and industry since 1962.
Solving complex problems, testing under difficult and unusual circumstances and servicing the commissioning and maintenance needs of today’s electrical power systems both new and aged.
The circuit breaker’s main function is to provide circuit and equipment protection during a fault or other abnormal condition. When a breaker fails to operate or clear a fault, the resulting damage can be very serious in terms of both personnel injury and equipment damage. Therefore, circuit breakers must be tested and maintained to ensure proper operation during these faults.
This article will present a case study on the effects of a breaker failure, or in this case two breaker failures, in terms of equipment damage and arc-flash incident energies.
This case study is associated with 13.8 kV breaker failures at an industrial complex. This complex is fed through two 13.8 kV buses each having a main breaker and multiple feeder breakers that provide power tothe20+unitsubstationswithinthe to the 20+ unit substations within the complex. During normal operation, each bus feeds approximately half the complex. The buses are independently fed from the utility. The system includes a tie breaker between the buses that is normally open.
In 2007, a fault occurred on a 13.8 kV feedercableatornearthetermination feeder cable at or near the termination point on the line side of a fused, boltedpressure switch feeding a unit substation.
A fault condition of this type typically wouldresultinthefeederbreakerinthe would result in the feeder breaker in the 13.8 kV breaker line-up tripping on timeovercurrent (TOC) and isolating the effects of the fault to just the equipment associated with the feeder. Unfortunately, the feeder breaker failed to trip. Upon failure of the feeder breaker, the lineup’s main breaker should have tripped on TOC. Unfortunately, the main breaker also failed to trip. This resulted in the utility’s feeder breaker feeding this particular 13.8 kV bus tripping and the subsequent loss of power to the all devices being fed from this 13.8 kV line-up, half the equipment to the entire industrial complex. This is the definition of a very bad day.
Upon investigation, it was quickly determined wherethecablehadfaulted.Theswitchwas where the cable had faulted. The switch was damaged beyond repair by the energy released during the fault. Protective relay records indicate the fault started as a line-to-ground fault that became a three-phase fault after approximately 12 seconds. The total length of the fault was approximately 16 seconds. The phase-A terminal of the switch appears to have suffered the most damage with the aluminum conductor separated from the lug attached to the switch terminal and the high voltage cable termination completely disintegrated. Relay records indicated the fault started as phase-A to ground. The switch enclosure was bulged at the top indicating a release of gases during the fault. A large gash approximately four inches in length was observed on the top of the switch above the phase-A switch terminal. Two flash markswerevisibleonthewalloftheswitch marks were visible on the wall of the switch enclosure opposite the phase-A terminal without visible damage to the external paint of the cabinet caused by heating.
The majority of ground fault current appeared to have initially followed the ground strap of
the cable termination until it was consumed, but this could not be determined with any certainty. The only other potential visible path to ground was the gash in the top of the switch which was physically a greater distance from a phase-A conductor than the adjacent phase termination or the side of the switch. The insulating arc chutes of the switch were completely consumed by the fault.Thecableterminationswereremoved fault. The cable terminations were removed and returned to the manufacturer for testing. These particular cable terminations had beeninstalled18monthsearlier.Thecause been installed 18 months earlier. The cause of the failure was determined to be poor workmanship associated with installation ofthecabletermination.Itwasdetermined of the cable termination. It was determined that only dc high potential testing was performed for acceptance testing for this cable.
Thefailedmainandfeederbreakerswere The failed main and feeder breakers were removed and inspected. In the case of the main breaker, the trip coil had failed, resulting in the failure of the breaker. However, there was no obvious failure within components ofthefeederbreaker. of the feeder breaker.
The relays were interrogated to ascertain the sequence of events and the potential cause ofthebreakersfailuretoisolatethefault. of the breakers failure to isolate the fault. When the cable faulted, both protective relays sensed the overcurrent condition, and provided a TOC operate signal within the time-current characteristics of the protective settings. The TOC operate signals were indicated on the front of the relay.
The main breaker’s relay also indicated that a trip signal was sent by closing the output contact to power the circuit breaker’s trip circuit. The breaker failed to trip due to failure of the circuit breaker trip coil. Typically a failed trip coil results fromthemechanicalmechanismofthe from the mechanical mechanism of the breaker providing more resistance than the trip coil can overcome causing the trip coil toburnout. to burn out.
However, the feeder breaker’s protective relay did not close the output contact to power the circuit breaker trip circuit for the breaker to clear the fault. The factory default
logic configuration for the relay indicates that once an overcurrent pickup condition meeting the criteria of the protective setting is satisfied, the designated trip relay contact should close. Unfortunately, the logic for this relay had been corrupted such that the relay contact command was no longer present in the relay’s firmware. Upon further investigation, all of the feeder breaker protective relays in both lineups were found to be similarly afflicted. The latest version of the settings and logic files were provided by the relay manufacturer and downloaded to the feeders’ protective relays and the relays were proven by testing to operate correctly. The main and tie breakers’ were alsotestedandwerenotfoundtohavethe also tested and were not found to have the sameissues. same issues.
For this incident, there were three failures:
1. Thefeedercablefaultattheswitch The feeder cable fault at the switch
2. The feeder breaker’s protective relay
3. The main breaker’s trip coil
Table1: Table 1: Case Study – Calculated Arc-Flash Incident Energies
3. Feedercablefailureatswitchwith Feeder cable failure at switch with feeder protective relay failure and main breaker trip
An evaluation was performed in an effort to determine the extent of the damage associated with each failure. The system was modeled using SKM’s PTW Power System Analysis software and the guidance provided in IEEE 1584-2002, Guide for Performing Arc Flash Calculations. A scenario was developed associated with eachfailuremodeandtheresultsintermsof each failure mode and the results in terms of arcing fault current, fault clearing time, and arc-flash incident energy were calculated. For the purpose of this evaluation a working distanceof18incheswasselectedforeach distance of 18 inches was selected for each scenario.Atabulationoftheresultsis scenario. A tabulation of the results is presented below.
Basedontheresultsforeachmodeled Based on the results for each modeled scenario, the following observations were provided with respect to the extent of damage associated with each failure mode.
1. For Scenario 1, a cable considered with the proper operation of the feeder breaker.Thisscenarioresultsinalevel breaker. This scenario results in a level of arc flash incident energy at the fault (6.3 cal/cm 2). Based on this arc flash ). incident energy, the anticipated damage would probably have been confined to the cable itself. The subsequent unplanned outage activities would have been restricted to production and nonproduction equipment being provided power through the feeder breaker. Associatedremedialactionwouldhave Associated remedial action would have been to replace the cable.
2. For Scenario 2, a cable failure, with the failure of the feeder breaker pr otective relay, was considered with correct operationofthemainbreaker.Thissce eration of the main breaker. This scenarioresultsinalevelofarc-flashinci nario results in a level of arc-flash incident energy at the fault (81.1 cal/cm 2 ) and, therefore, would have been dangerous. Based on this arc flash incident energy, the anticipated damage would have been significant. All cables within the switch compartment and the switch probably would have been damaged. Associated remedial action would have been to replace multiple cables and
the switch. Additionally, the logic/programming for the feeder protective relay would require correction.
3. For Scenario 3, a cable failure, with the failure of the feeder breaker protective relay and the main breaker trip coil, was considered with proper operation of the utility’s breaker. Ultimately, this is the scenario that actually occurred. Thisscenarioresultsinalevelof This scenario results in a level of arc-flash incident energy at the fault (306.7 cal/cm 2) and, therefore, would ) have been very dangerous. Based on this arc-flash incident energy, the anticipated damage would have been significant. All cables within the switch compartment and the switch were damaged and required replacement. The subsequent unplanned outage activities were extended to all production and nonproduction equipment being fed from the 13.8 kV bus which was effectively half the facility. Associated remedial action was to replace multiple cables and the switch. Additionally, the logic/programming for the feeder protective relay was corrected and the main breaker was cleaned up and its trip coil was replaced.
Based on the above arc flash evaluation, the initiating event for the incident was thecablefailureatornearthetermination the cable failure at or near the termination in the switch. However, the severity and amount of equipment damage and subsequent remedial action was impacted by the failure of the feeder breaker to operate the breaker to operate due to a protective relay that did not operate correctly.
Itisunderstoodthatthemainbreaker’s It is understood that the main breaker’s failure to operate due to the failed trip coil significantly increased the arc-flash incident energy ultimately experienced during the incident. Failure of the feeder breaker and the main breaker to operate resulted in significant damage to the system. However, the failure of the feeder breaker, with the main breaker operating as
designed, probably would have resulted in sufficient damage such that the same level of remedial action would have ultimately been required.
If a breaker fails to operate in fault conditions, the amount of damage, incident energy released, and cost for remedial action can increase exponentially.
For this incident, there were three failures:
defect prior to placing in service. Proper testing of the protective relays, to include operationally tripping and closing the breakers, would have identified the issues with the relays. Proper maintenance of the breakers, to include cleaning, lubricating, and operationally testing the trip and closecircuitsofthebreakerwouldhave close circuits of the breaker would have identified or mitigated the trip coil failure.
1.Thefeedercablefaultattheswitch
1. The feeder cable fault at the switch
2. The feeder breaker’s protective relay
3. The main breaker’s trip coil
Eachofthesefailuresincreasedthearc Each of these failures increased the arc flash potential of the event. Each of these failures probably would have been mitigated with proper acceptance and maintenance testing. Proper testing of the cable, including tan-delta testing should haveidentifiedthiscabletermination have identified this cable termination
Lynn Hamrick brings over 25 years of working knowledge in design, permitting, construction, and startup of mechanical, electrical, and instrumentation and controls projects as well as experience in the operation and maintenance of facilities.
Lynn is a Professional Engineer, Certified Energy Manager and has a BS in Nuclear Engineering from the University of Tennessee.
VLF & DC Output | Sheath Testing | Cable Burning
The VLF-34E is a new generation VLF AC Hipot that uses a solid state design with microprocessor controls. It meets the requirements of applicable world standards regarding cable testing up to 25kV class maintenance testing. It is light, compact, rugged, and very portable. Its sine wave output is suitable for using external TD and PD detection equipment. Using a TD and PD option, the VLF-34E is all that is needed for nearly all cable testing up to 25kV class.
Easy to use controls. Programmable test sequences & manual control, USB, XBEE® wireless, RS-232/422 port for downloading data and for unlimited test report capture, wireless computer interface to control and download Tan Delta diagnostics and for remote control operation via laptop.
VLF-TD Cable Diagnostic Testing
The TD-34E, along with the HVI VLF-34E AC hipot, is the latest in design using current electronic technology. Together they permit the user to perform all VLF and VLF-TD tests possible and offer the best wireless operation and data collection, aided by the HVI custom application software written solely for the two devices. There is no better alternative. HVI has been supplying the world with VLF and Tan Delta technology since 1998, with more models, greater voltage range, and higher power capability, all with the superior sales and service that HVI is well known for worldwide.
SUBSTATION MAINTENANCE I
DALLAS, TX:
Oct. 6-10, 2014
Nov. 3-7, 2014
Dec. 1-5, 2014
Jan. 5-9, 2015
Feb. 9-13, 2015
PORTLAND, OR:
Sept. 29-Oct. 3, 2014
Feb. 2-6, 2015
VALLEY FORGE, PA:
Oct. 13-17, 2014
Dec. 8-12, 2014
MOTOR CONTROLS & STARTERS, MEDIUM-VOLTAGE
DALLAS, TX
Oct. 20-24, 2014
Dec. 15-19, 2014
VALLEY FORGE, PA
FEeb. 23-27, 2015
SUBSTATION MAINTENANCE II
DALLAS, TX:
Oct. 13-17, 2014
Nov. 10-14, 2014
Dec. 8-12, 2014
Jan. 12-16, 2015
Feb. 16-20, 2015
PORTLAND, OR:
Oct. 6-10, 2014
Feb. 9-13, 2015
VALLEY FORGE, PA:
Oct. 15-19. 2014
Dec. 9-13, 2014
BATTERY MAINTENANCE & TESTING
DALLAS, TX:
Nov. 3-6, 2014
Dec. 15-18, 2014
Feb. 23-26, 2015
PORTLAND, OR:
Jan. 27-30, 2015
VALLEY FORGE, PA:
Oct. 6-9, 2014
PROTECTIVE RELAY MAINTENANCE BASIC
DALLAS, TX
Oct. 6-10, 2014
Nov. 10-14, 2014
Dec. 1-5, 2014
Jan. 5-9, 2015
PORTLAND, OR
Sept. 8-12, 2014
VALLEY FORGE, PA
Sept. 22-26, 2014
Nov. 3-7, 2014
Jan. 5-9, 2015
YOUNGSVILLE, NC
Oct. 6-10, 2014
SAN LEANDRO, CA
Oct. 20-24, 2014
Jan. 12-16, 2015
FONTANA, CA
Feb. 2-6, 2015
TRANSFORMER MAINTENANCE & TESTING
DALLAS, TX
Nov. 17-21, 2014
Jan. 19-23, 2015
VALLEY FORGE, PA
Oct. 27-31, 2014
Dec. 1-5, 2014
CIRCUIT BREAKER MAINTENANCE, LOW-VOLTAGE
DALLAS, TX
Nov. 10-14, 2014
Dec. 1-5, 2014
Feb. 23-27, 2015
VALLEY FORGE, PA
Sept. 29-Oct. 3, 2014
Jan. 19-23, 2015
SAN LEANDRO, CA
Nov. 17-21, 2014
CIRCUIT BREAKER MAINTENANCE, MEDIUM-VOLTAGE
DALLAS, TX
Nov. 4-7, 2014
Dec. 8-11, 2014
Feb. 17-20, 2015
VALLEY FORGE, Jan. 12-15, 2015
CIRCUIT BREAKER MAINTENANCE SF6
DALLAS, TX
Nov. 3-6, 2014
Feb. 2-5, 2015
INFRARED THERMOGRAPHY LEVEL I
DALLAS, TX
Sept. 22-26, 2014
Dec. 1-5, 2014
VALLEY FORGE, Oct. 27-31, 2014
Feb. 16-20, 2015
SAN LEANDRO, CA
Oct. 6-10, 2014
Jan. 12-16, 2015
Each June, the NETA Board of Directors huddles for a twoday study of association strategy, promotions, and marketing for the upcoming year. This year, the meeting took place on the edge of the Bridger Teton National Forest in Jackson Hole, Wyoming, June 19 – 20, 2014. On day one, board members focused on identifying the challenges, strengths, weaknesses, and opportunities that face the association. The board always takes a look back at where the association has been before making decisions about where it should go in the future. This strategic discussion was fuel for the marketing and promotions fire, since these areas are about how to bring the strategic discussions to fruition. This full day was followed by an excellent meal, some laughter and conversation over drinks, and met by another busy slate of business the next morning. Friday saw the strategy, promotions, and marketing plans reviewed and approved, as well as regular business conducted. Board hats were put aside as everyone enjoyed a little more time together, surrounded by towering mountains, before heading home.
Building and reinforcing relationships within the power generation and transmission industry was the goal for NETA at the trade show during the International Conference of Doble Clients, held in Boston this past April.
NETA was able to promote the importance of acceptance and maintenance testing of electrical power equipment and systems to the many engineers, generation and transmission personnel, and facility managers who attended the show.
NETA’s standards for electrical testing specifications for acceptance and maintenance testing of electrical power equipment and systems were available for purchase at the NETA booth, with many attendees interested in obtaining copies for their reference and use. Other NETA publications, such as the NETA Handbooks, NETA World Journal, and NETA training products were of interest to attendees as well. The newest NETA Handbook series, Series II,
was released at PowerTest in March 2014, and was on display at Doble in April.
A number of representatives from NETA Accredited Companies, including American Electrical Testing Co., Inc., Magna Electric Corporation , and Western Electrical Services, Inc., made connections with professionals who are involved with NERC standards development committees, helping them to better understand how NETA can support the electrical power generation and transmission industry. Many utilities are looking to NETA Accredited Companies to provide the testing and maintenance services specified within the ANSI/NETA MTS Standard for Maintenance Testing Specifications for Electrical Power Equipment and Systems inordertoestablishtheirNERC in order to establish their NERC required maintenance and inspection plans.
Doble Engineering Company is one of seven Corporate Alliance Partners with which NETA is working to help advance safety and reliability within the electrical power systems industry. NETA recognizestheDobleconferenceas nizes the Doble conference as one of the most technically-orientededucationaleventsinthe ented educational events in the electrical power industry and is appreciative of the opportunity to participate in this event.
a w s n o e e a t
to the NETA
Specifications sections 7.15.1 and 7.15.2 for electrical testing of rotating machines, there are three required tests : insulationresistance, dc withstand, and phase-to-phase stator resistance.
The required tests of insulation resistance, polarization index (IEEE 43) and the controlled dc high voltage test (IEEE 95) have been effective in evaluating certain aspects of medium voltage (4–13 kV) global vacuum pressure impregnation (GVPI) stator windings; however, they have not proven adequate for determining whether or not the insulation system is well consolidated. As a result, there is some concern that the required tests are not sufficient for quality assessment (QA) either of a new or an existing medium-voltage (MV) winding. The NETA specifications include three optional tests: power-factor or dissipation-factor, tip-up tests, and partial discharge tests1.
See NETA World–Spring 2014 for more informationabouttheneedforthese information about the need for these additionaldielectricscharacteristictests. additional dielectrics characteristic tests.
The insulation resistance (IR) isanindication is an indication ofthetotalcurrent.Thisvaluetrendedover of the total current. This value trended over
time may give indications as to the presence of cracks or contamination. Generally, the trendofthe trend of the IR valueiserraticbecauseofthe value is erratic because of the effects of winding temperature and humidity. Unless the winding is always measured under exactly the same humidity and temperature conditions, it is complex to track the resistance over time. (IEEE 43-2000)5 SeeNETA See NETA World–Winter2011formoreinformation. World–Winter 2011 for more information.
The polarization index (PI) was developed to make interpretation less sensitive to temperature. However, the mica in the stator winding insulation system has virtually an infinite dc resistance value, so the IR /PItests /PI tests do not evaluate if the insulation system is well-consolidated, impacted by mechanical forces, or thermally damaged. This requires an AC dielectric test, such as dissipation/ power factor or partial discharge test as described below. See NETA World–Spring 2012formoreinformation. 2012 for more information.
A high dc voltage withstand test may provide some assurance that the ground wall may may
safely be stressed to normal operating voltage, that is, a minimal level of electric strength. The dc high potential acceptance test is not a diagnostic test since the outcome is simply pass or fail. Controlled overvoltage tests, stepped or ramped tests, may afford the possibility of detecting impending insulation problems by recognizing abnormalities in the measured current response, thereby allowing the test to be discontinued prior to insulation failure. However, as stated in IEEE 95-20026 there has been limited experience in detecting delaminationorcoilconsolidationinmicadelamination or coil consolidation in micabased insulation systems by this means. Because unexpected insulation failure can occur during the test, it is important to be aware of the possible need to make repairs before the machinecanbereturnedtoservice.SeeNETA machine can be returned to service. See NETA World–Summer2012formoreinformation. World–Summer 2012 for more information.
Globally there has been a move towards using a dielectrics-characteristic test—capacitance, power factor, or dissipation factor—as part of the QA testing for GVPI systems. The recently developed IEC standard (IEC 60034-27-2) defines the test procedures for performing off-line partial discharge testing as part of QA testing.5 Partial discharge tests have proven to be effective in locating isolated problems that could lead to failure; whereas, the dielectrics characteristic tests provide a more general condition assessment. Based on experience to date, both types of tests are needed to fully evaluate how well the winding is consolidated. IEEE Standards 14341, 564, and EPRI LEMUG2 study have all included these tests as recommendationsforconditionassessment. recommendations for condition assessment.
Normally when practical this test is performed on each phase of a winding with an accurate capacitance bridge. The capacitance Clv is measuredat0.2EwhereEistheratedlinemeasured at 0.2E where E is the rated lineto-ground voltage and also Chv ismeasuredat is measured at line to ground voltage which is 1E. The tipup is based on the fact that at line-to-ground voltage, if there are voids in the ground wall insulation, the gas in the void ionizes to produce
sufficiently high conductivity to short the voidout.Thisreducestheeffectivethickness void out. This reduces the effective thickness of the insulation, increasing the capacitance between low and high line-to-ground voltage. One void would have no impact, but if there are excessive voids due to the inadequate resin impregnation or problems with the tape or bonding material in the insulation system, the change in capacitance would be noticeable7. Therefore, increase in capacitance with voltage is an indication of internal voids. In the absence of voids, the capacitance will not change as the test voltage is increased.
The capacitance tip-up is:
ΔC = (C hv –C – C lv)/C lv
Uncured/moisturecontamination Uncured/moisture contamination Clv is high Delamination ΔC increases with voltage
The higher ΔC is, the more voids there are in the winding ground wall. Note that as the void volume increases so does the ΔC percentage (Figure 1). For well bonded modern epoxy mica ground wall insulation, typically the ΔC is less than about one percent2
Itshouldbenotedthatifthecoilshave
It should be noted that if the coils have semiconducting and grading voltage stress control layers, these influence the results of this test. At the higher voltage, the grading layers of silicon carbide material conduct to increasetheeffectivesurfaceareaandthusthe increase the effective surface area and thus the capacitance of the sections of winding being tested, and therefore may give a false indication of high void content. However if the results are trended against time, an increase in ΔC may give a true indication of increased void content in the ground wall insulation7
Dissipation Factor
This test is normally done at voltage steps that increase from 0.2E (DFlow) to normal lineto-ground voltage, 1E (DFhigh), preferably on ), individual phases. The intention of the test is to observe the increase in real power loss due to the presence of voids in a delaminated insulation (Δ tan δ =DF = DFhigh –DF – DFlow). As with ). the capacitance test, increases as a function of voltage are due to partial discharge and the ionization of the gas in the voids of the insulation system.
DF=tan DF = tan δ =I = IR /I / IC [Figure 2]
Uncured/moisture DFlow is high Delamination Δtan Δ tan δ increases with voltage
Typically the DFlow low for epoxy mica windings is about one to two percent and the Δ tan δ is less than one percent 2. Trending the results against time makes the best use of this test. As with the Δ capacitance test, voltage stress coatings can lead to ambiguous results obtained at high voltage.
PowerFactor Power Factor
The tip-up test (Δ cos θ) is done at two voltages, one below the inception of partial discharge activity (PDIV), 25 percent of line-to-ground voltage, 0.25E (PFlow), and one at 100 percent ), line-to-ground voltage, 1E (PFhigh), preferably ), on individual phases. As with the Δ tan δ test, the difference in the power factors at these two voltages can be attributed to the energy loss due to partial discharges.
Figure 2: Dissipation/Power Factor
PF=cos PF = cos θ =mW/mVA = mW / mVA [Figure 2]
Uncured/moisture PFlow is high
Delamination Δcos Δ cos θ increases with voltage
Typically, the PFlow for epoxy mica windings is less than about 0.5 percent and the Δ cos θ is 0.5 percent, though many suggest the acceptance levels should be the same as for dissipation factor, that is, one to two percent for 0.2E values and one percent for tip-up. As with the capacitance tip-up test, the results of this test are influenced by the presence of voltage stress coatings on the coils, since at high line-to-ground voltage currents flow through it to produce additional power losses. Becausethistestmethodmeasurestotal Because this test method measures total energy, it is only sensitive to how widespread the PD is and not how close the winding is to failure (worst spot).
Tests are usually taken at increasing voltage steps starting at 0.2E to line-to-ground voltage (1E), preferably on individual phases. Measurementsinclude Measurements include1,4: [1]
1. the voltage at which partial discharge starts, or the inception voltage (PDIV)
2. the voltage at which partial discharge stops, or the extinction voltage (PDEV)
3. the largest repeatedly occurring PD magnitude at rated voltage
BoththePDIVandthePDEVshouldbe Both the PDIV and the PDEV should be above 50 percent of line-to-ground voltage, or higher than 0.5E2,3.
A single 4 kV coil was tested at various stages of the resin impregnation process from before (green) to partial to full impregnation (Figure 3).
Discussion
Dissipation Factor (DF): Dissipation factor decreasestobetween0.01and0.02asthe decreases to between 0.01 and 0.02 as the quantity of resin is increased. The slightly elevated tip-up may be an issue.
Capacitance Tip-Up: Since this is primarily testing for curing, then it makes sense that the partial state would have the highest activity along with the elevated DF values. Note that after full impregnation and curing, the values were significantly less than one percent. The increase in capacitance at 0.2E is unusual (see PD Max below).
PDIV: In all cases the PDIV was higher than standardrecommendationof0.5E. standard recommendation of 0.5E.
PDmax: PD max: This was puzzling in that the magnitudeofthemeasurablePDincreasedwith nitude of the measurable PD increased with impregnation. It is hypothesized that before resin impregnation, the voids were too large to have detectable PD, so the effective thickness of the ground wall was minimal. Void shape and pattern as shown below are typicalforsmallinternalvoidswiththeclusters cal for small internal voids with the clusters within the first and third quadrants of the ac cycle as shown in Figure 4.
Results for 4 kV
(In the table above, the pink refers to values that would be of great concern, while the yellow values are marginally acceptable and the green values are within expected limits.)
Figure 5: Test Results for 4 kV Rewound Winding (In the table above, the pink refers to values that would be of great concern, while the yellow values are marginally acceptable and the green values are within expected limits.)
A 4 kV winding tested as-is state before a rewind and after (Figure 5).
Discussion
Dissipation Factor (DF): Dissipation Factor decreases after reconditioning to levels almost between 0.01 and 0.02; while the tip-up decreases as well though is still slightly higher than the standard recommendation of less than one percent.
Capacitance: Capacitance behaved as expected with the lower capacitance in the rewound motor and a tip-up less than one percent.
PDIV: In all cases the PDIV was higher thanthestandardrecommendationof0.5E than the standard recommendation of 0.5E
PDmax: PD max: The decrease in PD activity is expected in a new winding with minimal PD activity (Figure 6).
Figure 6: Partial Discharge Results Before and After the Rewind of the 4 kV Motor
Though it is premature to establish acceptance criteria for the capacitance results at 0.2E or the PD Max values at 1E, it is obvious based onthesecasestudiesthatthesefivetestsin on these case studies that these five tests in combination provide valuable information about the quality of a GVPI insulation system before and after refurbishment or rewind. Each test evaluates a different aspect of the insulation, so it requires all five for a fullevaluation: full evaluation:
1. DForPFat0.2E DF or PF at 0.2E —curing state (<0.01–0.02)
2. DF or PF tip -up—widespread internal voids (< ~1%)
3. Capacitance at 0.2E—curing state
4. Capacitance tip-up—widespread internal voids (<1%)
5. PD—isolated problems
a. PDIV/PDEV (<0.5E)
b. PD magnitudes (depends on test)
1. IEEE P1434-2010, Guide to the Measurement of Partial Discharges in Rotating Machinery
2. EPRI LEMUG Report 1000897 (Dec 2012 2012) Repair and Reconditioning Specification for AC Squirrel-Cage Motors with Voltage Ratings of 2.3 kV to 13.2 kV.
3. IEEE56-2012(Draft IEEE 56-2012 (Draft) Guide for Insulation Maintenance of Large Alternating-Current Rotating Machinery (10,000 kVA and Larger)
4. IEC/TS 60034-27-2 Rotating electrical machines - Part 27-2: On-line partial discharge measurements on the stator winding insulation of rotating electrical machines
5. IEEE Std. 43-2000, IEEE Recommended Practice for Testing Insulation Resistance of Rotating Machinery
6. IEEEStd.95-2002, IEEE Std. 95-2002, IEEE Recommended practice for Insulation Testing of Large AC Rotating Machinery with High Direct Voltage
7. Farahani, Mohsen, et al. “Study of capacitance and dissipation factor tip-up to evaluate the condition of insulating systems for high voltage rotating machines,” Electr Eng, 89:263-270, 2007
Vicki Warren, Senior Product Engineer, IrisPowerLP.Vickiisanelectrical Iris Power LP. Vicki is an electrical engineer with extensive experience in testing and maintenance of motor and generator windings. Prior to joining Iris in 1996, she worked for the U.S. Army Corps of Engineers for 13 years. While with the Corps, she was responsible for the testing and maintenance of hydrogenerator windings, switchgear, transformers, protection and control devices, development of SCADA software, and the installation of local area networks. At Iris, Vicki has been involved in using partial discharge testing to evaluate the condition of insulation systems used in medium- to high-voltage rotating machines, switchgear and trans formers. Additionally, she has worked extensively in the development and design of new products used for condition monitoring of insulation systems, both periodical and continual. Vicki also actively participated in the development of multiple IEEE standards and guides and was Chair of the IEEE 43-2000 Working Group.
Featuring quality, reliable, on-time service and support for all brands and types of solid state power electronics.
Power electronics are our business
Let us suppoort you with our quality repair, calibration and servicing of your solid state equipment. We also buy, sell and trade:
•Communications devices for power equipment
•Protective relays
•Circuit breaker trip devices
•Motor overload relays
•Rating plugs
Introducing the smallest, most compact power factor / tan tester on the market - used to measure all capacitive loads in substations.
FEATURES & BENEFITS
55 lb single box design
12 kV voltage source
Variable frequency, 15 - 400 Hz
7 inch color touch screen
PRODUCT DEMO VIDEOS
3 operating modes: basic, guided, advanced
Visit our YouTube channel!
Safe operation with interlock, e-stop, etc. www.bit.ly/MIDASmicro2883
TEST APPLICATIONS
Circuit breakers
Transformers
Bushings
Capacitors
Surge arrestors
When performing a condition analysis on medium voltage sulfur hexaflouride (SF 6 ) breakers, it is necessary to identify all the potential ha zards. To be able to identify those hazards, the individual must be qualified to perform the task and have a solid understanding of each hazard and ways to mitigate the potential risks.
arcs, and failure arcing. While pure SF6 is odorless, contaminated SF6 has a pungent or unpleasant odor.
These by-products, typically found in the form of gases or powders, can cause the following health conditions;
1. irritation to the eyes, nose, and throat
2. pulmonary edema
3. other lung damage, skin and eye burns, nasal congestion, bronchitis
4. dermatitis (skin rash or inflammation)
However, under high temperature conditions (> 350 degrees F), SF6 decomposes into products that are toxic and corrosive. Decomposition by-products can occur when SF6 is exposed to spark discharges, partial discharges, switching
Inadditiontothehazardsassociatedwith In addition to the hazards associated with the by-products, typical hazards exist with the testing and maintenance of any electrical equipment including medium voltage SF 6 breakers.
Improperly performed lockout/tagout causes many injuries every year. Controlling the electrical energy is the first and mostobvioushazard. most obvious hazard.
Be aware of the breaker compartment layout. Many injuries and incidents occur while opening the breaker and visually verifying that it is open. Typically the compartment will be isolated, and operating devices may be located in a different compartment than the breaker. In some cases the operating device is in the same compartment. Double check the markings and nomenclature foreachtobecomefamiliarwiththe for each to become familiar with the arrangement. As a secondary method to verifying there is no load, if possible, utilize an ammeter within the switchgear if one is associated with the equipment. During this step, both electrical and mechanical energy can be potential hazards. It will be necessary to isolate the electrical source and discharge any of its stored mechanical energy. Do not remove the breaker from service while it is in the closed position. Ensure that the breaker is open prior to racking.
Disconnectthebreakerfromallsourcesof Disconnect the breaker from all sources of power, both ac and dc, if applicable. Once de-energized, verify that the breaker is at a zero energy state using the manufacturer’s approved method. Ensure that the device used for testing for the absence of voltage operates correctly by using the test, check, testmethod. test method.
1. Verify the accuracy of the detection or voltage measuring device against a knownsource. known source.
2. Check for zero energy on the deenergized equipment.
3. Test the detection equipment against a known source again.
This will verify that it was functional during the check. Any voltage measurement will
require personal protective equipment (PPE) depending upon the voltage and test procedure per NFPA 70E 2012 Table 130.7(C)(15)(a)—Hazard/Risk Category Classifications and Use of Rubber Insulating Gloves and Insulated and Insulating Hand Tools-Alternating Current Equipment (Formerly Table 130.7(C)(9) in the NFPA 2009). If removing the breaker, perform lockout/tagout on the compartment.
As stated above, electrical energy isn’t the only energy that requires lockout/tagout. Breakers also contain a large amount of stored mechanical energy. This energy can be found in the spring loaded charging mechanism. This energy must be dissipated prior to servicing or serious injury could occur. Once the breakers have been discharged, it is also advisable to lockout/tagout the charging mechanism. To prevent someone from inadvertently operating the breaker, ensure that remote operating handles are tagged in alocalormanualmode. a local or manual mode.
Gas and hydraulic operating mechanisms may be pressurized. Ensure that the unit is depressurized and/or discharged and the source of the pressure is disabled. Once disabledthissourcemustalsobelocked disabled this source must also be locked out and tagged out prior to performing mechanicalmaintenance. mechanical maintenance.
Gravity is also an energy that needs to be controlled. The sheer size and weight of medium voltage breakers makes them difficult to rack in and out, or to maneuver around. When available, utilize remote racking equipment. Mechanical lifting devices may be necessary to move the breaker to an area where it may be serviced.
The purpose for using temporary protective grounds is to protect the personnel servicing the equipment and to create a safe work environment. Prior to servicing a piece
of electrical equipment, it is important toensure thatitisinasafestateand to ensure that it is in a safe state and to verify zero voltage before applying temporary protective grounds. In many situations, more than one set of grounds or grounding apparatus must be applied. When identifying the placement of temporary protective grounds, ensure all work will be performed within the zone of protection. For proper placement and sizing of temporary protective grounds and grounding apparatus, refer to OSHA 29 CFR 1910.269 Electric Power Generation, TransmissionandDistributionStandard. Transmission and Distribution Standard. It states under paragraph (n) “Grounding for the protection of employees” that grounding must be utilized as means of protecting employees on de-energized lines, and that “For the employee to work lines or equipment as de-energized, the lines or equipment shall be de-energized under the provisions of paragraph (m) of this section and shall be grounded as specified in paragraphs (n)(3) through (n)(9) of this section. However, if the employer can demonstrate that installation of a ground is impracticable or that the conditions
resulting from the installation of a ground would present greater hazards than working without grounds, the lines and equipment may be treated as de-energized provided all of the following conditions are met:”
1. “The lines and equipment have been de-energized”
2.“ 2. “ There is no possibility of contact with another energized source.”
3. “ The hazard of induced voltage is not present.”
1910.269 then states under (n)(4) that “Protective grounding equipment shall be capable of conducting the maximum fault current that could flow at the point of grounding for the time necessary to clear the fault. This equipment shall have an ampacity greater than or equal to that of No. 2 AWG copper.”
Refer to ASTM F855 Standard Specifications for Temporary Protective Grounds to Be Used on De-energized Electric Power Lines and Equipment and NFPA 70Es for the required level of PPE to be worn to perform thetask. the task.
Table1: Table 1: From NFPA 70E – 2012 Table 130.7(C)(15)(a) – Hazard/Risk Classifications and Use of Rubber Insulating Gloves and Insulated and Insulating Hand Tools – Alternating Current Equipment
Arc-resistant switchgear Type 1 or 2 (for clearing times of <0.5 sec with a perspective faultcurrentnottoexceedthearc-resistant fault current not to exceed the arc-resistant rating of the equipment)
Parameters:
Maximum of 35 kA short circuit current available; maximum of up to 0.2 sec (12 cycle) fault clearing time; minimum 36 in. working distance
Potential arc flash boundary with exposed energized conductors or circuit parts using above parameters: 422 in.
Insertion or removal of CBs from cubicles with door open 4 N N
Table2: Table 2: From NFPA 70E – 2012 Table 130.7(C)(16) Protective Clothing and Personal Protective Equipment (PPE)
Hazard/Risk Category
Protective Clothing and PPE
4 Arc-Rated Clothing Selected so That the System Arc Rating Meets the Required Minimum Arc Rating of 40 cal/cm2 (See Note 3.)
1. Arc-rated long-sleeve shirt (AR) Arc-rated pants (AR)
2. Arc-rated coverall (AR)
3. Arc-rated arc flash suit jacket (AR) Arc-rated arc flash suit pants (AR)
Arc-rated arc flash suit hood
4. Arc-rated gloves (See Note 1.)
5. Arc-rated jacket, parka, rainwear, or hard hat liner (AN)
Protective Equipment
1. Hard hat
2. Safety glasses or safety goggles (SR)
3. Hearing protection (ear canal inserts)
4. Leatherworkshoes Leather work shoes
Afterverificationthatthebreakeris After verification that the breaker is electrically de-energized, rack out the breaker. In some cases this may be accomplished through remote racking and un-racking means. Ensure that proper personal protective equipment is utilized fortheclassofbreakerthatwillbeserviced. for the class of breaker that will be serviced. Refer to the current NFPA 70E (2012 Version -Table 130.7(C)(15)(a) again. It will indicate the level of protection required for the class of breaker being worked on in order to prevent electrical shock and protect personnel from arc flash. However, this Table provides information based upon knownvaluesoftheshortcircuitcurrent known values of the short circuit current available, the clearing time in cycles, and minimum working distance. If those factors are unknown, more information must be gathered prior to performing the work in order to ensure personnel safety.
Table 1 is an example of the PPE requirements per the NFPA when racking out a
breaker on 1 kV through 38 kV class metalclad switchgear that has the parameters of a maximum of 35 kA short-circuit current available, a maximum of 0.2 seconds (12 cycle) fault clearing time, and a minimum of 36 inches of working distance. There is a potential arc-flash boundary with exposed, energized conductors or circuit parts of 422 inches using the prior parameters.
The NFPA 70E states that a Category 4 arcflash protection is required. This includes some combination of the clothing indicated in Table 2 above, which is taken from the NFPA 70E 2012 – Table 130.7(C)(16).
AN: as needed (optional). AR: as required. SR: selection required. Notes:
1. If rubber insulating gloves with leather protectors are required by Table 130.7(C)(9), additional leather or arc-rated gloves are not required. The combination of rubber insulating gloves with leather protectors satisfies the arc flash protection requirement.
2. Face shields are to have wrap-around guarding to protect not only the face but also the forehead, ears, and neck, or, alternatively, an arc-rated arc flash suit hood is required to be worn.
3. Arc rating is defined in Article 100 andcanbeeitherthearcthermal and can be either the arc thermal performance value (ATPV) or energy of break open threshold (EBT). ATPV is defined in ASTM F 1959, Standard Test Method for Determining the ArcThermalPerformanceValueof Arc Thermal Performance Value of Materials for Clothing, as the incident energy on a material, or a multilayer system of materials, that results in a 50 percent probability that sufficient heat transfer through the tested specimen is predicted to cause the onset of a second-degree skin burn injury based on the Stoll curve, in cal/cm2. EBT is definedinASTMF1959astheincident defined in ASTM F 1959 as the incident energy on a material or material system that results in a 50 percent probability of break open. Arc rating is reported as either ATPV or EBT, whichever is the lowervalue. lower value.
SF 6 in its pure state is an odorless, colorless, nontoxic gas about six times denser than air. Although it does not have any specific physiological effects, it can produce the effects caused by lack of oxygen in ambient airsaturatedwithSF air saturated with SF 6
During the interruption phase of the circuit breaker, an electric arc is produced which decomposes a very small amount of SF 6 The probability of contact with decomposed SF 6 is extremely remote, and its presence in small quantities (1-3 parts per million) is immediately noticeable because of its sour and unpleasant smell. In this case, the room must be ventilated before personnel enter thearea. the area.
Caution must be taken so personnel are not exposed to the by-products. Contact the manufacturer and check all applicable
policies and procedures for the handling, removal, and disposal of SF 6 decomposition products.
Human error, simply put, is a person (or persons) making a mistake. To prevent an error, follow a procedure or checklist while performing the task. If one doesn’t exist, createone. create one.
Nomenclature should be verified, and reverified upon approaching a piece of equipment. Perform a self-check and a peer-check to ensure that the task is being performed on the correct component.
Utilize markings such as flagging when working around similar looking pieces of equipment to identify the components that should not be touched. Flagging can take several forms depending upon the company or client’s policy and procedures. Do not forget to identify, mark, then lockout/tagout all associated equipment (i.e. associated cables and compartments). Flagging could be utilized to indicate a component that is not operating normally.
Barricading off a safe work zone prevents other workers from inadvertently entering the workarea.Thiswillensurethatmaintenance work area. This will ensure that maintenance and testing is conducted in an area under control.Utilizeateststandinthisareaif control. Utilize a test stand in this area if applicable. Ensure that any control voltage required to operate the breaker during testing iswithinthesecuredarea. is within the secured area.
SF 6 circuit breakers and interrupters which have reached their limiting number of operations can be overhauled and restored to a like-new condition. Newer designs of the interrupter use a sealed-for-life design. Manufacturersclaimthatundernormal Manufacturers claim that under normal serviceconditionstheSF service conditions the SF 6 interrupter never requires servicing. Some manufacturers no longer provide facilities for the user to overhaul the circuit-breaker. Depending on the manufacturer of the breaker, a SF 6
gas pressure monitors may be supplied. Ensure that if activated, the manufacturer is consulted.
1. Obtain all service bulletins, maintenance documents, arc-flash studies, and manuals prior to beginning work for that specific device.
2. Review all prints and one-lines associated with the equipment.
3. Establishasafeworkareaandbarricade Establish a safe work area and barricade offtheworkarea. off the work area.
4. Perform a pre-job brief with all employees on-site.
5. WearcorrectPPE. Wear correct PPE.
6. Disconnectthebreakercontrolcircuit Disconnect the breaker control circuit and test equipment before performing visual or mechanical inspections or during maintenance.
7. If applicable, verify that there is zero energy (test, check, test) and discharge all stored energy, including pressurized gasses.
8. If possible, lockout/tagout (mechanical and electrical energy sources)
9. Connect grounds if applicable.
10. Identify, visually mark and flag the equipment being worked on.
Following these steps can lead to a safer work environment while performing maintenance and testing of SF 6 medium voltage breakers.
ScottBlizard Scott Blizard hasbeentheVice has been the Vice President and Chief Operating Officer of American Electrical Testing Co., Inc. since 2000. During his tenure, Scott acted as the Corporate Safety Officer for nine years. In addition, he has over 25 years of experience in the field as a master electrician, journeyman, wiremanandNETALevelIVSenior wireman and NETA Level IV Senior Technician.
NETA was well represented as electrical safety and maintenance industry professionals gathered at the Saskatchewan Electrical Symposium May 1, 2014, in Regina, Saskatchewan, Canada, hosted by Magna Electric Corporation, a NETA Accredited Company. Among the presenters was PowerTest Conference Chair Ron Widup, CEO of Shermco Industries. Joining Ron as a presenter were Kerry Heid of Magna Electric Corporation and Jim White of Shermco Industries. All three gentlemen are NETA Certified Senior Test Technicians and have many years of electrical testing and maintenance field experience betweenthem. between them.
Much of the learning took place via technical sessions offering education about electrical safety and maintenance and how to apply it to heavy industry such as manufacturing and utilities. In addition, the symposium included a trade show exhibition, allowing 10 vendors to interact and learn about various new products and services. Attendees were able to learn more about NETA, gaining an appreciation and understanding for NETA’s accreditation process, NETA Certified Technicians, as well as NETA standards, publications, and training courses.
The importance of safety and training was underscored by keynote presenter Curtis Weber, who, at only 17 years of age, found himself in a battle of life or death as over 14,400 volts of electricity surged through his body during a workplace mishap. Curtis passionately engaged the audience in a recounting of the events that resulted in his injuries, including the loss of two limbs and severe burns over 60 percent of his body.
Curtis’ story emphasized the critical need for safety on the job, and provided a strong message for assuring that personnel working on or around electrical power systems and equipment have the necessary tools, equipment, and especially training with regard to staying out of harm’s way.
“We need to do everything we can to prevent accidents like that which happened to Curtis, and educational opportunities like the Saskatchewan Electrical Symposium — and PowerTest, for that matter — are great ways to send that message home,” Widup said.
Taking a page from the PowerTest conference model, the Saskatchewan Electrical Symposium also provided a chance for vendors to showcase their newest offerings via the New Product Forum. In a mere two minutes each, participants relayed information about how their newest products could help attendees accomplish their safety and testing goals.
NETA is pleased to have had the opportunity to participate in the Saskatchewan Electrical Symposium and supports the mission of raising awareness and understanding of electrical power systems maintenance and safety. To learn more about this event, please visit saskelectricalsymposium.com.
Grounding conductors (connecting protected devices to the ground bus or grounding electrode) are sometimes strung independently and in loose relationship to the circuitry being protected. But for the most effective grounding system, impedance should be kept at its lowest by routing the circuit conductors and the equipment bonding conductor closely together at all times. Inductive reactance is a significant influence on an AC distribution system by its effect on return current.
Inductive reactance directs return current to flow in a path closely paralleling the outgoing power conductor. It augments resistance in every conductor and increases with the spacing between conductors. No other current path can offer a lower impedance to ground-fault current than one closely paralleling phase conductors. In parallel ground return paths, inductive reactance is the primary factor in determining current splits.
Metallic conduit or raceway provides an excellent fault return path. This enclosure introduces additional inductive effects that tend to confine return ground current within the enclosure. The addition of an external equipment grounding conductor is considered ineffective. 1 The same applies to other similar augmentations, such as building
steel. Without effective containment and direction of fault return current, nearby metallic structures can experience large induced voltages or unwanted circulating currents, possibly dangerous. If an internal equipment grounding conductor is installed within and parallel to the raceway, the current carried by the raceway can be reduced. But only by such an internal parallel path. Joints in conduit and raceways must be firm and tight so as not to add any appreciable resistance. This can be verified using low –resistance ohmmeters testing either side of the joints.
A vital experiment revealed the relative effectiveness of various grounding paths, using steel conduit and 4/0 copper conductors.1 The building in which the experiment was conducted
had steel columns connected to an extensive grounding mat. The experimental conduit was 100 feet long and mounted on insulators, paralleling a row of building columns five feet away. Five different conductors were run (Fig. 1) , both within and without the conduit, to simulate various possible grounding schemes. Current to simulate fault current was fed and recorded in order to ascertain the current splits typical of different configurations, involving both single and multiple returns. Supply current was always run through the same conductor, inside the conduit. The four possible returns were accomplished by a conductor inside the conduit, the conduit itself, an external conductor one foot outside the conduit, and finally, a connection to building steel.
One experimental series of tests was run at comparatively low currents of 200 and 350 amperes, while a second series was run at 10 kA. The tests at lower currents were maintained for extended periods while the higher currents were controlled at about
¼ second. Standard meters were used to measure voltage and current at the lower values while more sophisticated equipment was required for the higher current tests and measurements were made on an oscillograph. Twenty tests were compared, 5 at 200 A, 6 at 350 A, and 9 circa 11 kA.
The lone test made with the internal conductor as the return recorded all current returning on that conductor. At the lower test currents, two tests (350 A and 200 A) with the conduit as the return showed all current returning on conduit. Where conduit and the external conductor were paralleled, 97 and 95% (respectively) returned on conduit. Only a marginal 12 and 8 A respectively returned on the external conductor. Where conduit was paralleled to building steel, again 97% of 350 A returned on conduit but only 90% of the 200A test. The same 12 and 8A respectively were transferred to building steel.
But when conduit was paralleled with the internal conductor, the percentages returning
on conduit fell to 18 and 20, respectively. In this case, 290 of the 350 A test current returned on the internal conductor while 62 A were measured on the conduit. For the 200 A test, 40 A traveled on conduit. Finally, when paralleled between building steel and the external conductor and no connection to conduit, current split was 50/50. When repeated with the higher currents, test results were all similar, with the exception of conduit paralleled with the internal conductor. As has been indicated, the lower currents tended to concentrate on the internal conductor while the higher currents showed a nearequal split. Induced voltages at the lower currents were minimal, not rising above 26 V and generally much lower. At the higher currents, however, voltages circa 150 V existed between the supply conductor and conduit. No one is likely to accidentally get across that configuration. The only configurations that included a potentially injurious voltage were between supply and
building steel (155 V) with conduit and internal conductor paralleled at highest current, and with building steel and external conductor paralleled (268 V).
The experiment demonstrates that the only way to divert a sizable amount of fault current from the raceway is via an internal grounding conductor. Building steel proved ineffective. The most dramatic observation concerned the effects of high-resistance joints between sections of conduit or raceway. A shower of sparks was observed from some of the connections, capable of igniting fires in combustible materials close by. This occurred despite the conduit having been professionally installed and tightened. Bridging with a jumper would reduce but not necessarily eliminate subsequent sparking, whereas some of the joints sealed themselves by a welding effect produced by the sparking.
Another critical observation involved a test with only external conductor and building steel acting as returns. Considerable sparking was noted at a building column where a water pipe passed through. This provided supporting evidence of the potential problems associated with forcing short-circuit current to return through paths physically distant from the supply conductor. The wide spacing creates a powerful magnetic field extending far beyond the respective current-carrying conductors.
The experiment demonstrates that the least reactanceisinthecircuitthatincludesthe reactance is in the circuit that includes the inner conductor. Conduit provides the next lowest, because of its high magnetic permeability. Following in order are the external grounding conductor and building steel. In the high current test where the conduit was left open, 146 volts were required to drive current through the external conductor and building steel, a potential shock hazard. The conclusions drawn, then, are that conduit or raceway can be effectively employed and provide an important part of equipment grounding, and that connections must be rigorously made
and maintained. An internal equipment grounding conductor is most effective, but a well-maintained enclosure in conduit or raceway can also accommodate the demand. Grounding conductors connecting building structure to the grounding electrode are necessary for diversion of lightning or other fault currents, but are a negligible part of equipment protection. The importance of minimizing reactance increases with available fault current.
From the above results, it is clear that if raceway or conduit is to be part of ground-fault clearance the connections between segments must be rigorously tested and maintained at no more than negligible resistance. This requires a dedicated instrument of high precision and relatively robust current. Ordinary multimeters and two-wire measuring g devices will not do. They are neither precise enough nor deliver sufficient test current to accurately evaluate the ability of a joint or connection to pass the enormous currents that arise during a fault. Common electrician’s multimeters operate on milli-amperes of test current and read to perhaps 0.1 Ω. Not good enough for this critical application! What is required is a genuine low resistance ohmmeter. Typically such testers provide a robust test current capable of stressing weaknesses in the conduction path combined with measurement resolution to a fraction of a micro -ampere. Industry-standard test current for low resistance ohmmeters is 10 A, but for larger circuits and heavier current demands, models are available with test currents of 100, 200, 600 A and so on.
the two points of contact of the potential terminals, generally to a micro-ohm or less resolution. And don’t think that this is mere specmanship. Remember, W=I 2R; Watts equal current squared times resistance. The heat increments by powers of ten in resistance across a connection readily translate into thousands of Watts and the possibility of a building fire or other serious damage and threat to life. 2 Don’t just rely on good work practices when making these joints; verify with a rigorous and reliable test!
Genuine low resistance ohmmeters operate as four-wire Kelvin bridges ( Fig. 2 ). There are two current terminals and two potential. The currentterminalsareconnectedontheoutside current terminals are connected on the outside of the test specimen and establish a uniform current through the IUT (Item Under Test). The potential terminals are connected to the insideofthecurrentterminalsandmeasure inside of the current terminals and measure voltage drop between their points of contact. Low resistance ohmmeters are DC, and Ohm’sLawcalculatestheresistancebetween Ohm’s Law calculates the resistance between
Next issue will continue with an examination of ground fault clearances.
1 Int’l Ass’n of Electrical Inspectors (IAEI) Soares Book on Grounding
2 Megger®, A Guide to Low Resistance Testing, Peter E. Langan
Jeffrey R. Jowett is a Senior Applications Engineer for Megger in Valley Forge, Pennsylvania, serving the manufacturing lines of Biddle, Megger, and multi-Amp for electrical test and measurement instrumentation. He holds a BS in Biology and Chemistry from Ursinus College. He was employed for 22 years with James G. Biddle Co. which became Biddle Instruments and is now Megger.
CBS ArcSafe’s remote racking and remote switching solutions reduce arc-flash dangers and technician fatigue during dangerous operations. g
Remote racking solutions reduce the need for full-body arc-flash hazard suits by taking technicians outside the arc-flash boundary. Universal remote racking solutions offer adjustable height settings. No equipment modifications required.
Remote switching solutions keep technicians outside the arc-flash boundary during dangerous operations. No modifications required due to magnetic latching.
Remote switching solutions are available for virtually any style or piece of electrical equipment.
o r piece of elect t
All CBS ArcSafe remote racking and remote actuation solutions are battery- or AC-powered portable units that do not require any modifications to your electrical equipment.
Use your Windows 7-compatible tablet or PC with the CBAnalyzer™ system to test your circuit breakers in place. Operate the breaker in any sequence you desire: for example, trip – charge – close. The vibration data created by the breaker operation is captured and analyzed, and the result is instantly returned to your device. The data is saved in your online account for equipment management, trending, and further analysis options, including specialized issue diagnosis. To purchase the app, visit CircuitBreakerAnalyzer.com
Moisture can be one of the most damaging factors to transformer insulation and one of the more difficult factors to understand. Excessive moisture will cause transformer insulation to degrade at a much faster rate than normal, and this degradation process can generate additional moisture which will increase the degradation process even more.
Some studies indicate that doubling paper insulationmoisturecontentwillresultin insulation moisture content will result in reducing transformer life in half; therefore, it is important to know the insulation moisture content of the paper in order to maintain transformer reliability.
Moisture migrates from the oil into the winding paper insulation based upon the temperature of the transformer which is largely influenced by transformer loading.
At 20°C, the paper contains about 3,000 timestheamountofmoisturethattheoil times the amount of moisture that the oil does and at 60°C, the paper contains only 300 times the amount of moisture that the oil does. This is because the higher temperatures drive the moisture out of the paper and into the oil. Therefore, the ASTM D1533 Standard Test Method for
Water in Insulating L iquids by Coulometric KarlFischerTitration Karl Fischer Titration test is not necessarily a good indication of the dryness of the transformer.
Even though the dryness of the paper cannot be measured directly with an oil sample test, it can be determined indirectly by calculating the percent saturation of the oil using the ASTM D1533 moisture-inoil test results along with the transformer temperature to provide a better indication of insulation dryness. Percent saturation can be determined by using a nomograph such as the one shown in Figure 1. Percent saturation guidelines shown in Figure 2 show that levels greater than 30 percent indicate an extremely wet transformer that should probably be dried out.
Although the overall climate condition at this location is relatively dry, wet weather periods allowed ample moisture entrance into the oil. Since the transformers were not in service, they were not warm and the winding paper insulationabsorbedmuchofthemoisture. insulation absorbed much of the moisture.
After careful oil sampling was completed and the samples tested, it can be seen from Table 1 thatinall19casesthemoistureinoilresults that in all 19 cases the moisture in oil results were acceptable (< 35 ppm). Nine of the first 10 transformers on the list, which were relatively well-sealed, exhibited relatively low percent saturation values. Whereas, of the nine poorly sealed transformers, eight exhibited high saturation values which is indicative of a wet transformer. Based on this data, percent
saturationcalculationscorrelatemuchbetter
saturation calculations correlate much better with expectations than the moisture results. Although the moisture in oil test results are valuablesincethisinformationisusedto valuable since this information is used to calculate percent saturation, the percent saturationvaluesareamuchbetterindication saturation values are a much better indication of wet windings and, therefore, a much better indicationoftransformercondition. indication of transformer condition.
DonA.Genutis Don A. Genutis holds a BSEE from Carnegie-Mellon University. He has over 30 years of electrical testing experience. Don serves as President of Halco Testing Services based in Los Angeles, California.
During its 20–40 year service life, a circuit breaker must be constantly prepared to operate. Typically, long periods of inactivity often elapse during which the breaker’s mechanical and electrical components never move. The circuit breaker is the active link in a fault clearance situation. When a fault occurs on the electrical system, the associated fault current must be interrupted quickly and reliably. This action is referred to as fault clearing.
If a breaker fails to clear a faulted circuit, the resulting damage can be very serious in terms of both personnel injury and equipment damage. Even though circuit breakers are comparatively reliable, circuit breaker failures can and do occur. Therefore, circuit breakers mustbetestedandmaintainedtoensure must be tested and maintained to ensure proper operation during these faults.
Many circuit breakers provide longer service lives than expected. If you can ascertain that a breaker is in good condition, you can continue to use it rather than replace it at its estimatedend-of-life.Fortheremainderofthis estimated end-of-life. For the remainder of this discussion, we will concentrate on mediumvoltage (1 kV up to 35 kV) circuit breakers utilizedwithinanindustrialenvironment. utilized within an industrial environment.
There are three basic designs of mediumvoltage breakers: air, vacuum, and oil circuit breakers.Inadditionthereisafourth breakers. In addition there is a fourth alternative design that is gaining momentum and being applied, the SF6 breaker.Eachof breaker. Each of these designs will be discussed.
AirCircuitBreaker Air Circuit Breaker—AirAircircuitbreakersare circuit breakers are the prevalent type of medium-voltage breakers in an industrial environment due to the typical age of the equipment and their lower cost; however, very few of this type of breaker are still being manufactured. Air circuit breakers are commonly used in medium-voltage electrical distribution
systems and include operating mechanisms that are mainly exposed to the environment. Since the air circuit breakers are rated to carry current continuously, the exposure to convection cooling air assists in keeping the operating components within reasonable temperature limits. A typical aircircuitbreakerincludes air circuit breaker includes a main contact assembly, which is either opened (tripped), interrupting a path for power to travel from the source to the load, or closed, providing a path for power to travel from the source to the load. In many air circuit breakers, the force necessary to open or close the main contact assembly is provided by an arrangement of compression springs. In many air circuit breakers, the mechanism for controlling the compression springs is comprised of a configuration of mechanical linkages between a latching shaft andanactuationdevice. and an actuation device.
an industrial environment is typically a draw-out type in which a breaker is movable so as to be separated (racked out) from the power source inordertofacilitatemaintenanceorconnected in order to facilitate maintenance or connected (racked in) to the power source using either a manual or motor-assisted racking capability.
The actuation device may be manually operated, or electrically operated with trip and close coils. In a common construction of a medium-voltage air circuit breaker, the movablecontactismountedonacontactarm movable contact is mounted on a contact arm that is pivoted to open or close the contacts by a spring powered operating mechanism triggered through the trip or closing coils by a control switch or tripping relay (i.e., protective relay). Smaller opening springs are put in tension during closing and assist in opening when the trip coil is given tripping energy from the control switch or protective relays. These protective relays may also be used to provide auxiliary functions along with overcurrent protection. The current interruption capability of air circuit breakers is dependent in part upon their ability to extinguish the arc that is generated when the breaker main contacts open or close. A medium-voltage air circuit breaker in
Vacuumcircuitbreakersare Vacuum circuit breakers are the most popular type of medium-voltage breaker in anindustrialenvironment an industrial environment duetotheirsmallersizeand due to their smaller size and improved reliability over air circuitbreakers.Vacuum circuit breakers. Vacuum circuitbreakersaresimilar circuit breakers are similar toaircircuitbreakerswith to air circuit breakers with the difference being that the maincontactsarehousedin main contacts are housed in a vacuum chamber (bottle). Oneofthecontactsisfixed One of the contacts is fixed relativetothebottleand relative to the bottle and toanexternalelectrical to an external electrical conductorwhichisinterconductor which is interconnectedwiththecircuit connected with the circuit to be controlled by the circuitbreaker.Theother circuit breaker. The other separable main contact is movable.Themoveable movable. The moveable contact assembly usually comprises a stem of circular cross section having the contact at one endenclosedwithinavacuumbottleanda end enclosed within a vacuum bottle and a driving mechanism at the other end which is external to the vacuum bottle. An operating rod assembly comprised of a push rod, which is fastened to the end of the stem opposite the moveable contact, and a driving mechanism provide the motive force to move the moveable contact into or out of engagement with the fixed contact. Compression springs are provided in connection with the operating rod assembly in order to be able to separate the moveable contact from the fixed contact and to assure the necessary force so that the contacts will not accidentally open under inappropriate conditions. As with the air circuit breaker, the actuation device may be manually or electrically operated by trip and
close coils triggered by a protective relay. These protective relays may also be used to provide auxiliary functions along with overcurrent protection. Vacuum circuit breakers offer many advantages as compared to other types including relatively long life due to controlled contact erosion; maintenance-free operation provided by enclosure of the contacts within the hermetically sealed housing; excellent operational reliability due to the use of hard contact materials; little or no atmospheric contact contamination, which contamination can detrimentally form oxides and corrosion layers on the contacts; little or no noise during operation due to containment of arcing within the hermetically sealed housing; relatively few environmental effects; and very low current chop, resulting in a minimal induced transient voltage spike during circuit interruption so that surge suppressors are typically not required. A medium-voltage vacuum circuit breaker in an industrial environment is also typically a drawout type.
OilCircuitBreaker Oil Circuit Breaker — Oil circuit breakers, which are typically located outdoors, were the past standard but are becoming more rare in the industrial environment as they are being replaced with air or vacuum circuitbreakers.Oilcircuitbreakershave circuit breakers. Oil circuit breakers have allcontactsandmechanismhousedwithin all contacts and mechanism housed within an oil-filled tank which provides for both an insulation and arc-quenching capability.
A typical oil circuit breaker includes the same operational characteristics as an air circuit breaker. A medium-voltage oil circuit breakerinanindustrialenvironmentis breaker in an industrial environment is typically a stand-alone type and requires that oilbedrainedandthebreakerdetankedto oil be drained and the breaker detanked to perform maintenance.
SF6 Breaker—SF6 breakers, which are almost always located outdoors, have been the standard for higher voltage applications and are becoming the standard at the 35 kV level. AnSF An SF6 breaker operates very similarly to a vacuum breaker in that the design includes a separate chamber which houses each contact; however, the chamber has a very sophisticated design that uses a pressurized SF6 gas in lieu ofavacuum.TheSF of a vacuum. The SF6 gas has a high dielectric
strength as well as preferred arc-quenching capabilities. Additionally, SF6 isconsidered is considered an inert gas and is noncorrosive when in contact with the metallic contacts. The gas is also very stable and nonflammable. In the presence of an arc, the SF6 disintegrates to other fluorides of sulphur, but usually reforms after the arc is extinguished. As with the vacuum circuit breaker, the actuation device may be manually or electrically operated by trip and close coils triggered by a protective relay. These protective relays may also be used to provide auxiliary functions along with over-current protection. Along with vacuum breakers, SF6 circuitbreakersoffer circuit breakers offer many advantages as compared to other types including relatively long life due to controlled contact erosion; maintenance-free operation provided by enclosure of the contacts within the hermetically sealed housing; excellent operational reliability due to the use of hard contact materials; little or no atmospheric contact contamination, which contamination can detrimentally form oxides and corrosion layers on the contacts; little or no noise during operation due to containment of arcing within the hermetically sealed housing; relatively few environmental effects; and very low current chop, resulting in a minimal induced transient voltage spike during circuit interruption so that surge suppressors are typically not required.
Therearethreebasicelectricalteststhatshouldbe There are three basic electrical tests that should be performed on medium-voltage circuit breakers as part of a preventive maintenance program.
Contactresistance Contact resistance —Thistestshouldbe — This test should be performed from line-to-load terminals for each phase with the breaker closed. The values should be within 50 percent of each other and comparable to similar circuit breakers.
Insulationresistance Insulation resistance —Thistestshould — This test should be performed phase-to-phase and phaseto-ground (i.e., case, if applicable) with the breaker closed as well as across the open contacts for each phase. For medium-voltage breakers, the manufacturer should provide
the testing voltages and acceptance values for thistest.Whennotavailableorwhereno this test. When not available or where no recommendations are provided, the above abbreviatedtablefromANSI/NETAMTSabbreviated table from ANSI/NETA MTS2011 may be used.
Dielectric withstand voltage — This basically is an ac or dc high potential test. This test should be performed from the line side of each phase with the breaker open and the load side of that phase and line and load sides of the other phases tied together and tied to ground. For vacuum circuit breakers, this test will also provide an indication of the vacuum bottle integrity. For mediumvoltage breakers, the manufacturer should provide the testing voltages for this vacuum
bottle integrity. It should be noted that for a medium-voltage vacuum breaker, only use of an ac high potential is recommended. When notavailableorwherenorecommendations not available or where no recommendations are provided, the following abbreviated table from ANSI/NETA MTS-2011 may be used.
In addition to these basic tests, the protective relays should be tested for functionality with all implemented protective functions being tested. In an industrial environment, overcurrent protection is typically the main, and possibly only, function provided by the protective relay; however, if there are other protective functions being provided, they should also be tested. It is also important that the breaker actually be tripped and closed
by the manual controls, and tripped by the protective relay to ensure that the relay and breaker are operating correctly. This will functionally test the trip and close coils as well as the protective circuit.
Additionally, power-factor or dissipation-factor testing should be considered as an additional test of each breaker’s insulation system. For oil circuit breakers, a tank loss index should be determined and, where individual mechanisms are provided by phase for operation, time-travel testing should be considered for each phase. Oil sampling is also recommended annually with oil sample quality analysis being provided for dielectric breakdown, acid neutralization number, interfacial tension, moisture, color, and power factor. Where cubicle heaters are provided, functional testing of the heaters shouldbeverified. should be verified.
For optimal operation, the SF6 gas should be maintained at the pressure recommended by the manufacturer. Accordingly, most SF6 6 breakers are usually provided with alarms or metering for temperature-corrected pressure and density. Where provided these should be monitored.
When out-of-limits, they are an indication of a possible gas leak. Additionally for SF6 breakers, time-travel testing should be considered for each phase where individual mechanisms are provided by phase for operation.
In conclusion, even though circuit breakers are reliable when compared to other electrical devices, circuit breaker failures occur. When a breaker fails to operate, the resulting damage can be very serious in terms of both personnel injury and equipment damage. Therefore, circuitbreakersmustbetestedandmaintained circuit breakers must be tested and maintained to ensure correct operation during these faults.
Lynn Hamrick brings over 25 years of working knowledge in design, permitting, construction, and startup of mechanical, electrical, and instrumentation and controls projects as well as experience in the operation and maintenance of facilities.
Lynn is a Professional Engineer, Certified Energy Manager and has a BS in Nuclear Engineering from the University of Tennessee.
Metal-clad switchgear and associated ducts canbev can be very reliable, with some installations operating for over 50 years.U ears. Using grounded ounded metalenclosur metal enclosurestohouseconductorsand es to house conductors and switchgear means they can be protectedfr otected from om theelementsandcommonfailur the elements and common failurecauses. e causes. However, the aging processesinv ocesses involvedwith ed with metal-clad equipment include moisture ingress, animalintr animal intrusion, insulation deterioration, andenclosur and enclosurer e rusting can greatly reducethe educe the in-service life of the equipment, and possibly vice makeitmor make it more dangerous for personnel near ous the equipment. A number of utilities have e experienced failures of metal-clad switchgear es andhav and have been looking for efficient ways to detect incipient failures.P es. Partial discharge (PD) is a leading indicator of variousfailur arious failuremodes e modes andcanbeav and can be a valuable tool in detecting such aluable failures. Both electric and acoustic techniques havebeenusedwithv e been used with varying degreesofsuccess. ees of success. Acoustic methods use acoustic emission signals todetectsour to detect sources of sound within the switchgear Transientear ransient earthv th voltage (TEV) approacheslook oaches look at signals developed in groundedmetal-clad ounded metal-clad surfaces.H faces. High frequency CTs (HFCTs) can s) beusedtodeterminelocalsour be used to determine local sources of partial tial discharge for investigation.
We presenther esent here a study of PD techniques applied to a suspect metal-clad installation where previousfailur evious failureshadoccurr es had occurred.U ed. Using both acoustic and electrical PD techniques, wesho e showthatsour w that sources of discharge can be detected with confidence, locating a source to a particular metal-clad compartment. Doble’s years of experience in detecting PD problemsinthefieldhasbr oblems in the field has brought valueto alue to many organizations and makes sense of what can be a confusing array of techniques. PD detection using ultrasound providesthemost vides the most reliable indication of a problemwithmetaloblem with metalclad equipment.
In this case study, the metal-clad equipment was built in 1959 and has been impacted by a buildup of salt residuefr esidue fromnearb om nearby roads, moisture ingress, and animal intr usion.A usion. At thisstationther this station therear e aretwo115kVtransformers e two 115 kV transformers feeding a double lineup breakeranda eaker and a half scheme arrangement. Regular inspection of themetalcladhasr the metal clad has revealed ongoing issues thathav that haver e requiredmaintenance.F ed maintenance. Failuresdue es due to insulation deterioration and subsequent identification of par tial discharge as a symptom of the failureledtoPDdetection e led to PD detection being used to identify fur ther potential
failure locations. The metal-clad equipment is shown in Figure 1.
Partial discharge is a phenomenon where electric current flows through insulation and breaks down the insulation emitting energy in the form of heat, sound, light, and other electromagnetic radiation. It is described as partial as the voltage acrossthebreakdowndoesnotcoverthewhole across the breakdown does not cover the whole of the insulation system and appears as a small arc or spark. A classic approach to PD detection in large power transformers is through dissolved gas analysis (DGA). The by-products of the insulationbreakdowndissolveintheoilandcan insulation breakdown dissolve in the oil and can be detected through chemical analysis. Further PD phenomena include ultrasound waves and transient earth voltages.
When a partial discharge source develops sufficiently it is possible to see the discharge –little lightning strikes within insulation or large arcs with power follow through. It may also be possible to hear the characteristic buzzing and humming of a discharge. However, in the early
stages, the sound emitted may be outside of the range of human hearing – at the ultrasound frequency above our hearing capabilities.
Ultrasonicdetection Ultrasonic detection used in PD surveys normally operates around the 40 kHz range and is used to detect discharges from several causes, These can be from tracking on contaminated surfaces, arcing between conductor strands, corona discharges from sharp pointed objects such as slag protrusions, or even electrical floating objects. By electrical floating objects we mean metallic objects in an energized fieldthatarenotattachedto field that are not attached to the energized conductors and not tied to ground. Thus these objects reside in a magnetic field created by the nearby energized conductor and create their own charged field.Thisfieldisdetectable field. This field is detectable
withultrasonicdetectorsandsometimeswith with ultrasonic detectors and sometimes with TEVdetection. TEV detection.
Ultrasonic hand held detectors, such as shown in Figure 2, are simple to operate and provide results quickly in the field. These devices can give both readings of ultrasound intensity in dB and a phase resolved indication of the source. The dB readings provide excellent indication of the proximity of a PD source while the phase resolved plot provides information which can be used to discriminate between discharge types.
TEVarecreatedonmetalsurfaceswhenPD TEV are created on metal surfaces when PD is present inside voids in insulation material. These voids can be in potting material, bus insulation, bus support insulators, and other materials. When a partial discharge happens, a magnetic field is developed. This magnetic fieldreleasesasmallradiationknowasradio field releases a small radiation know as radio frequency interference (RFI). When RFI travels through a medium, such as air, and hits a metal surface, it generates a small transient voltage, which may be detected by a TEV sensor. The stronger the discharge signal and higher the pulse rate of the PD, the higher the reading on a TEV monitoring unit. Most TEVbased PD monitoring devices operate between 100 kHz and 500 kHz, in line with IEC standards. Partial discharge can be detected in ranges below and above these frequencies. The TEV detection unit used in this study operated between20MHzand80MHz. between 20 MHz and 80 MHz.
Ultrasonicdetectionandtransientearth Ultrasonic detection and transient earth voltages were the two types of detection used in these surveys. PD detection devices are normally set to detect PD by monitoring in the 100-500 kHz range, in line with IEC standards, and some can monitor up to the 1 MHz range. In both approaches, energy levels in the source signal (acoustic or electrical) are measured and a reading given in dB. The higher the reading, the more energy there is associatedwiththelocation.Itisoftenthe associated with the location. It is often the casethattheabsolutelevelofPDindication case that the absolute level of PD indication is less important than the relative strength –thisisusefulwithmetal-cladlocationsaseach this is useful with metal-clad locations as each compartment can be tested individually and dB levels assigned.
By using both TEV and ultrasound approaches it is possible to detect and identify PD sources in metal-clad switchgear. In our experience, ultrasoundisthemosteffectivemeansto ultrasound is the most effective means to detect PD, though we would note that there are many cases where a combined approach means that a PD source is more readily identifiedandconfirmed. identified and confirmed.
An initial ultrasonic and TEV survey on all breakers and compartments of the metalclad switchgear yielded no high readings or indicationsofPD.Therewasevidenceof indications of PD. There was evidence of moistureandrustontheductbanksfromthe moisture and rust on the duct banks from the transformers to the metal clad, which were then investigated in more detail.
Metal-clad switchgear compartments in the northandcenterofthestationweretested north and center of the station were tested both during a normal day and a day when there was high humidity. The readings from the normal day showed no great variation, but during times of high humidity the readings had a story to tell. The results of the TEV and ultrasoundareshowninTable1. ultrasound are shown in Table 1.
From the results, it is clear that there are higher readings for both ultrasound and TEV measurementsassociatedwithU22/L15.The measurements associated with U22/L15. The upper compartment readings are likely to be a result of activity in the compartment below. What can also be seen are the very consistent readings provided by ultrasound, while the TEV does have higher levels and more variability. This may reflect the ability of a TEV approach to pick up benign energy sources which provide earth/ground current signals, TEV-based false positives. It is thought that faint sounds of arcing could be heard by the inspectors, indicating a substantial discharge level.
The immediate concern was the spike in the L15 position since it had no high readings in the original survey. An outage was scheduled and the breaker was removed and inspected. The insulated material was degrading and there was also dust and residue on the surfaces, with pitting and oxidization, as shown in Figure 3.
A maintenance outage on that section of bus was scheduled. During the maintenance the breakerandbussectionswerecleanedand breaker and bus sections were cleaned and wiped down to remove any oxidation, dust, andoilresidues.Thebreakerandbuswere and oil residues. The breaker and bus were recoated and wrapped with new insulating materialontheinsulatedareasthatshowed material on the insulated areas that showed thePDinordertoincreasethedielectric the PD in order to increase the dielectric strength and in-service life of the insulation.
A follow up survey was performed during a very wet and humid day with high temperatures and heavy loading conditions. No high readings were detected indicating that the corrective measures helped. Given previous failures on the bus ducts and switchgear related to insulation degradation and tracking, it is likely that this survey and consequent maintenance helped reduce the possibility of an in-service failure.
The duct banks are elevated in the yard and contain bus conductors, bus supports, and heaters to help keep moisture out. An analysis of each bus compartment in multiple compartments, including the locations oftheheaterelementsofthemetal-clad of the heater elements of the metal-clad system, yielded a number of areas where the readings were higher relative to nearby locations. Normally an investigation may require removal of hundreds of bolts and
multiple plates. In this station, the ultrasound approach in particular with the TEV in support, allowed the inspection to be limited to those areas having high readings. A few bolts were removed to allow boroscopic camera evaluation of the components. Higher readings of PD related to locations where the bus passed through bus support insulators (see Figure 4). The insulation was a far lighter color – an indication of PD activity.
These PD sources related to known previous failures in the metal-clad switchgear – with pitting in the bus which had been installed after previous bus sections had been replaced. As a result of the investigation, duct bank sections were assigned for replacement.
UseofultrasonicPDdetectionandTEV Use of ultrasonic PD detection and TEV testing can be very useful in finding problems before they become failures, as in the case discussedherewhereametal-cladfailurewas discussed here where a metal-clad failure was most likely prevented. PD detection can save equipment and help save employees from the dangers associated with letting a problem get to the point of catastrophic failure.
Onemustrememberthatseveralconditions One must remember that several conditions can contribute to getting these types of ultrasonic and TEV readings as with any corona or PD detection test equipment. Those conditions such as dust, fine oily residues, and surface contamination can have much higher discharge characteristics when moisture is also added to the mix; therefore, it can be advisable to retest after rain conditions or during high humidity conditions. Also PD can occur in times of heavy loading and not at other times. Ultrasound is a very reliable indicator of PD activity in metal-clad switchgear. We have found that TEV readings, in particular, can lead to false positives, so it is a sensible precaution to use an ultrasound method in parallel to corroborate findings.
Tony McGrail is the Doble Engineering Solutions Director: Asset management and Monitoring Technology. His role includes providing condition, criticality, and risk analysis for utility companies.
Previously Tony has spent over 10 years withNationalGridintheUKandthe with National Grid in the UK and the US. He has been both a substation equipment specialist and has also taken on the role of substation asset manager and distribution asset manager. Tony is a Fellow of IET, a member of IEEE, ASTM, CIGRE and the IAM, and is currently on the executive of the Doble Client Committee on Asset and Maintenance Management. His initial degree was in physics. He has an MS and a PhD in EE and an MBA. Tony is an Adjunct Professor at Worcester Polytechnic Institute, Massachusetts, leading courses in power systems analysis.
Jay M. Garnett has worked for Doble Engineering since 2011 as a principal engineer in the Client Services Department based in the Sacramento, California offices. Jay has worked in the utility industry for over thirty-one years and has experience years in substations, hydroelectric, geothermal, fossil fuel, nuclear generation, construction, maintenance, and testing.
He worked as a substation maintenance engineer for National Grid USA in the Substation O&M Services NE/NY Department from 2007 to 2011. Before that he was a supervisor overseeing the relay department for over five years. He also was a relay technician for National Grid (formerly Niagara Mohawk) in the Albany, New York, area starting in 1992.
Jay is a graduate of Napa Community College where he studied geology and received an Associate of Arts degree. Jay has also completed six years of apprenticeships, holding certificates as a journeymen Electrician and a journeymen Electrical Technician in the State of California. He has vicechaired and chaired the Bushings Insulators and Instrument Transformer (BIIT) Committee at Doble while working at National Grid. Jay has been a member of IEEE since 2007.
MatthewB.Lawrence Matthew B. Lawrence istheSolutions is the Solutions Director, Test & Assessment Technology, at Doble Engineering, focusing on substation diagnostic testing solutions. Before joining Doble in 2011, Matthew held positions in substation maintenance and operations and equipment maintenance engineering departments at National Grid and its New England based legacy companies since 1984. His most recent role was Manager of Substation O&M Services. He is a member of IEEE and affiliate of the IEEE transformer committee. Mr. Lawrence is a member and past chair of the Doble Engineering SFRA Users Group committee. Mr. Lawrence has coauthored papers presented at conferences on field transformer testing and condition assessment. Mr. Lawrence holds an Associates of Science in Electronics Engineering from New England Institute of Technology and attended Worcester Polytechnic Institute School of Industrial Management.
National Switchgear has millions of new, surplus and repurposed electrical circuit breaker & switchgear products. And now, with a suite of e-commerce solutions , we’re making it easier than ever for you to find the part that’s perfect for you. You can browse, filter results by category, manufacturer or specs, see your pricing level, and more – 24/7. Just go to nationalswitchgear.com and see our latest innovations. It’s the fastest lane to our massive inventory.
If you’re ordering parts from anyone else, it’s time to switch.
800-322-0149 nationalswitchgear.com
Earlier this year, Magna Electric Corporation’s founder and president, Kerry Heid, was named one of Saskatchewan’s Most Influential Men by Saskatchewan Business Magazine.
An article in the magazine described the recipients of the honor as a group of influencers who not only exhibit “the capacity to sway opinion or trajectories, they find themselves at the heart of the big-picture issues weighing on Saskatchewan these days.”
Shermco CEO Ron Widup, whose company acquired Magna Electric Corporation earlier this year, told the told magazine “We are proud of Kerry Heid and his influential leadership in SaskatchewanandCanada.Thisisatrue Saskatchewan and Canada. This is a true honor, which Kerry has worked hard for many years to earn.”
NETA agrees! Congratulations Kerry!
Members of the NETA Board of Directors commit to twoyear terms as they step aboard and work to help improve the electrical power systems industry through their leadership role within the association. Many of them often stay longer than the minimum term, agreeing to be nominated again (and again!) as they become even more committed to helping move the industry forward. One of those people is Kerry Heid.
NETA bids farewell to Kerry after ten years of service on the NETA board, though it is expected many NETA members will continue to cross paths with him as he will maintain his position as the Training Committee chair and intends to remain active in the development of NETA and other industry standards.
As founder and president of Magna Electric Corporation based in Saskatchewan, Kerry has cemented his role as a leader in the industry while at the same advancing the industry overall through his service to NETA. He joined the board in 2004 and has served in various capacities and on various committees ever since. Kerry also served two years as president of the NETA board from 2006 through 2008.During his time on the board, Kerry chaired the marketing and training committees, and became an active participant on the nominations and applications review committees.
Kerry’s commitment to improving the electrical world around him goes beyond NETA, with additional participation and memberships in other organizations including IEEE, CSA, and NFPA. He is one of five members on the executive committee of the CSA Z462 Workplace Electrical Safety Standard, and is the committee chair of CSA Z463 Maintenance of Workplace Electrical Systems.
Magna Electric Corporation was recently acquired by Shermco Industries, though it is expected that Kerry will remain an integral part of the company he started.
NETA thanks Kerry for his longstanding service to NETA and its members.
Circuit Breaker failures can cause catastrophic damage to your electrical systems and put your team in danger. PGTI’s trained team uses the latest testing technology to safely and properly maintain your breakers, minimize arc flash hazard and keep your team and equipment safe.
We deliver optimum system reliability and performance while reducing the chances of costly unplanned power outages. Whether you need acceptance
testing or preventive maintenance, depend on EnerGTest to keep the power on.
Serving clients in Pennsylvania, Delaware, New Jersey, Maryland, Washington, DC and
MODELS 407 & 607 are available with an Android™ application for easy programming, data downloading, printing and e-mailing test results from your mobile device. With its mobile GPS capability, users are now able to easily locate the site associated with the measurements.
Measures up to 2000AAC and 3000ADC (600 series)
Measures up to 1000VAC/DC (1400V peak) and AC+DC with resolution to 10mV
Measures single- and three-phase power
Auto selects AC or DC measurement
True InRush ® current measurement with 1 ms peak capture measures start up and running Inrush
10,000 count blue electroluminescent backlit display
Measures TDH and individual harmonics up to the 25th
Records up to 1000 measurements UL94 VI Flame retardant self-extinguishing (model dependent)
Leads are constructed with a flexible silicone material
Protective Relay Test Sets · VLF/AC/DC Hipots · Tan Delta
Primary Current Injection · Thumpers · Circuit Breakers
Relay Testers · TTR Test · Megohmmeters · Partial Discharge
Oil Dielectric Test · TDR · Battery Test · Cable Fault Locators
Power Analyzers and more! SWITCHGEAR
Fluke · Phenix · SKF/Baker · Tettex · Doble · AEMC Rosemount/Hart · Vanguard and more...
I have been in the electrical industry for about 32 years now and fortunate to have been exposed to a wide variety of technologies and disciplines. Over these past three decades, I’ve participated in many controls upgrades and witnessed firsthand the migration from relay logic to PLC’s (analog to digital) to more advanced microprocessorbased systems. It’s been an awesome experience. My intent with this article is not technical, it’s mental and I truly hope these initiate, as my wife puts it, “sparkling conversation.” Furthermore, the intent is not to criticize anyone. I hope it makes us all think and work safer.
With this said, I am constantly being assaulted by friends and family about not being up-todate in my personal technical gadgets. It’s only a few years ago that I finally sold all of my 8-track tapes and related equipment. I did however recently upgrade from a sixyear old flip phone to a new flip phone, and, do I love it! It’s just as simple as the old one and I didn’t have to spend the night at the electronics store! Forgive me, but I am a very experienced (hands-on) electrical engineer, and I’m surrounded every day by technology, advanced control systems, and many other types of automation.
I get a little burned out on social media and technology during the day so I like to sneak
off to the low tech world on my own time including keeping busy building my own offthe-grid home. Yes, it has 24/7 electricity and plumbing. I used to play with my 8-tracks tapes, but alas, they are gone. I respect technology and what it has done for all of us; however, I do think too much of anything is not healthy. My first awareness came during the Christmas holidays in 1999, and I call it the K-Mart Episode.
My wife and I were at K-Mart, ready to check out when the store lost all of its computer connections. Within 30 minutes the lines were halfway around the store. The clerks were lost because they could not compute tax or Blue Light special discounts with a manual
calculator, let alone in their head. We got some great accidental bargains that fateful day. Thank you automation!
When utility or industrial plants have operational mistakes resulting in outages, loss of product/ dollars, and/or equipment damage should they automate to fix the problem or should they train the operators to improve their awareness of the equipment and how it operates for better response in emergencies as well as routine operational activities? My thoughts on this are mixed, but automation is not always the answer. Why? Operators and technicians still need to know how the systems operate and how they integrate with each other for safety and reliability. The time to learn this is not during a failure or emergency.
Example #1: Utility Generating Station. One unit trips off-line due to loss of power after sump pump feeds trip back too far up the protection scheme (lack of breaker coordination). This caused a transfer of power on two different alternate electrical feeds for this unit, tripping theunitoff-line.Oneofthesefeedswasthe the unit off-line. One of these feeds was the ac input to the unit’s UPS system, which alarmed now that is was on battery. Technical people responded to this situation and began troubleshooting the UPS system. These technical people decided the issue was in the UPS system and began to shut the system down to further troubleshoot. While this was going on, operations had already begun restoring the unit to service. Unfortunately, their valiant efforts were abruptly interrupted by the UPS system being shut down improperly.
Root cause of the first trip? The sump pump system was not sized properly for increased wastewater as plant processes changed. This resulted in poor circuit breaker coordination.
Root cause of second trip? The first cause was that the technical people worked on the UPS system without documentation. They relied on
memory. The second cause was that the operators and technical people did not locate (or properly operate) the manual electrical transfer switch to restore house power to the UPS system. This was the only action needed to restore power.
Finalremediationforthisissue?Theresident Final remediation for this issue? The resident engineer was requested by management to develop and facilitate training on the UPS system operation and its documentation. The resident engineer was also required to specify and purchase an autotransfer switch to replace themanualtransferswitchtoaddresstheissue the manual transfer switch to address the issue of operations forgetting where the manual switch was and operating it incorrectly when they did find it. Alternate solution: When monthly electrical transfers are tested, the plant’s procedures include this manual transfer switch for the UPS. This practice would generate and resetthealarmsundercontrolledconditions reset the alarms under controlled conditions and force the organized reset of everything else to normal. This practice would also exercise (and clean) the switches? This tests the process, familiarizes everyone with equipment function and location. Practice, practice, practice!
Example #2: Therearestudiesthatnumerous There are studies that numerous recent plane crashes are the result of young pilots not having enough old school flight instructionandcannotreacttorealworld instruction and cannot react to real world situations. Too much of their training is done in a computer-controlled simulator.
According to aviation safety experts and industry studies, pilots have become so reliant on computer systems that handle most of the flight operations of modern aircraft that on the rare occasions when something goes wrong, the less experienced pilots are sometimes unprepared to take control.
Automation has been a tremendous safety boon to aviation, contributing to historically low accident rates in the U.S. and many parts oftheworld.Pilot“modeawareness”isamore of the world. Pilot “mode awareness” is a more common automation-related problem showing up in accidents and incidents, according to an
automation study released in December 2013 by the Federal Aviation Administration. Flight mode changes occur frequently during flight, often without any direct action by pilots. If pilots aren’t continually paying close attention, they can lose track of which mode their systems are in. Pilots also make mistakes when selecting modes.Modeselectionerrorswerecitedin27 modes. Mode selection errors were cited in 27 percent of the accidents reviewed in the FAA study. Practice, practice, practice!
Example #3: Utility Generating Station. Both unitshavebeenbackon-lineatfullloadforone units have been back on-line at full load for one whole day since the last trip. One unit suddenly trips at full load. Root cause of unit trip, those darn technical people again! This is a different group of technical people. There was an issue withcriticalinstrumentcircuit.Thetechnical with critical instrument circuit. The technical people began turning circuit breakers on and off in search of the issue on a critical panel.
Root cause of this trip? Could it have been that they didn’t bother to get the prints for these circuits and panels?
Upgrade your control systems! Faster processing, improved HMI interface, alarm management, smart grid reliability! Heck, it can also help ease the effects of the aging workforce issues!………wow! Computers will fix everything. Really? How about common senseandcommunications?I’lltakecommon sense and communications? I’ll take common sense as a first approach any day. Faster processing will surely show you how out of tune your control systems are, only much quicker.
Automation is a great thing when applied to a stable and well maintained system. To take absolute full advantage of automation you must first verify the machine’s or process’s health and stability. With this you can determine areas that simply need parts, lubrication, and calibration or adjustment, issues automating will not fix. Human intervention and good solidcommunicationsskillsmustremainin solid communications skills must remain in place for successful automation.
Training (repetitive in some cases), proper maintenance and calibration, and common sensewillcontributetoawell-balanced sense will contribute to a well-balanced and automated operational system. Does this imply a well-balanced, fully automated system? Not necessarily. Hopefully this article will cause some “sparkling conversation”.
Jay Wicks, P.E., is the owner of Black owner MarbleElectricalSolutions:“Common Marble Electrical Solutions: “Common Sense Electrical Consulting.” Jay has recently retired from the electrical utility industry with 32 years of electrical engineering field and design experience. He holds a Degree in Electrical Engineering from Virginia Tech in Blacksburg, Virginia. He is a Licensed Professional Engineer, a Licensed Electrical Inspector, and a Certified Instructor for Electrical, Electronic Systems, and Instrumentation with the National Center for Construction Education and Research (NCCER). Jay has been a Certified E-Hazard Instructor for Electrical Safety and Arc Flash since 2013.
This is the first in a three-part series in the creation of an Electrical Safety Program. Part 1 will address the need for a company specific ESP and why a copy of a generic program will most likely get you into trouble. Part 2 will discuss the criteria for the contents of a company specific ESP, and Part 3 will explain the implementation process of your newly created program.
Title 29 USC 654 Sec. 5. Duties
(a) Each employer
(1) Shall furnish to each of his employees employment and a place of employment which are free from recognized hazards that are causing or are likely to cause death or serious physical harm to his employees;
(2) Shall comply with occupational safety and health standards promulgated underthisAct. under this Act.
(b) Each employee shall comply with occupational safety and health standards and all rules, regulations, and orders issued pursuant to this Act which are applicable to his own actions andconduct. and conduct.
We have all heard this time and time again. Many of us have heard it so many times that wecanreciteitverbatimtoeachother.Itis we can recite it verbatim to each other. It is known as the General Duty Clause, and it gives the Occupational Safety and Health Administration (OSHA) the authority to fine you on nearly any unsafe condition or circumstance you may have present on your job sites.
If there are rules and regulations in the CFR (Code of Federal Regulations), then how can the General Duty Clause be used to issue a citation to a company? Simple: not every situation or potential event can be predicted on every job site. Conditions change, personnel change, and so does the work.ItisforthesereasonsthattheGeneral work. It is for these reasons that the General Duty Clause exists.
While it is very important to have a good safety program for your company, we will be focusing on the Electrical Safety Program (ESP) which should be separate from, but consistent with and a part of, the company’s overall safety program.
There are many excellent resources available to use for creating an effective electrical safety program. TheNFPA The NFPA 70E – Standard for Electrical Safety in the Workplace (National Fire Protection Agency), Electrical Safety – A Practical Guide to OSHA and NFPA 70E (James R. White, American Technical Publishers), and The Electrical Safety Program Guide (Ray A. Jones, Jane G. Jones, Jones and Bartlett Learning) are among the best resources. However, using these as your electrical safety program themselves, or copying the example safety programs word for word will not only get you into trouble, it actually does a disservice to your company and could place your workers inhazardoussituations.YourESPmust in hazardous situations. Your ESP must be company specific, hazard specific, and cover the work your employees do each and every day. These documents are a great starting point, but they don’t know what your employees do and what they face in their daily work.
It is the responsibility of each employer to provide a safe working environment for its workers. In order to do this, the specific hazards one may face must be identified and a way to perform work safely must be determined. One of the key phrases in the General Duty Clause is “…free from
recognized hazards….” Is electricity a recognized hazard? Of course it is. Knowing this is a key point to being able to create a company-specific electrical safety program. Looking at the key job duties of each employee and how they are exposed to those hazards will help in the creation of an excellent electrical safety program.
It is up to the employer to conduct a hazard assessmenttodeterminewhathazardsare assessment to determine what hazards are present at the place of employment and to create a program that ensures the employees work safely around those hazards. The Safety and Health Program Management Guidelines dated January 26, 1989, was issued as a guideline for employers to use to prevent occupational injuries and illnesses. The guidelines represent a set of program elements used by employers that are successful in the protection of their employees.
Along with the hazard assessment comes the risk assessment. Just what is a risk assessment?Itcanbedefinedandconducted assessment? It can be defined and conducted in many ways, but it is simply this. A risk assessmentisacarefulexaminationofwhat assessment is a careful examination of what could harm your workers, so that you can determine whether or not you have taken the proper precautions to prevent the harm or if you need to take additional precautions to help eliminate those hazards. Looking at thecombinationofthehazardstowhich the combination of the hazards to which your employees are exposed, in addition to the tasks being performed, is the best way to conduct a risk assessment. For example, you can have a high level of hazard around electrical equipment, but if there is no work being performed, there is little risk. On the other hand, there may be a low level of hazard, and a lot of work going on in the area of that hazard, and that increases the potential of an incident occurring. It just gives a level of protection to the workers when they are exposed to hazards in the workplace. Workers all have a right to be protected from harm, and you as the employer have the responsibility to provide
that protection. See the Risk-ometer figure above for a comparison of some common tasks.
Another key component is the inclusion of management’s commitment to the program. Without the commitment of management to the safety program, there will be no employee commitment, and with no employee commitment, there will be accidents and fatalities. A culture of safety can only come from the top down.
So now you have management commitment, employee involvement, and a great program has been created. What do you do next? Whatever you do, don’t put it on the shelf and not tell anyone about it! Too many times that is exactly what happens. Another part of any good electrical safety program is getting the information out to the
employees. Training is not only an essential part of the program, it is also a requirement per OSHA and NFPA. No matter what the employees’ job or task is, they have to be trained to be able to recognize and avoid the hazards they could be faced with while performing their daily duties. The training has to be either classroom, hands-on, or a combination of both, and it must address the hazards to which they are exposed.
Oneofthelastitemsthisarticlewill One of the last items this article will address is the need for site-specific safe work practices. You can have the best written plan and the best training program and provide the employees all of the personal protective equipment and tools that they need to do their jobs, but if they don’t work safely, the chance of an incident increases dramatically.
29CFR1910.333 – Selection and use of work practices states:
“(a) General. Safety-related work practices shall be employed … The specific safety-related work practices shall beconsistentwiththenatureandextent be consistent with the nature and extent of the associated electrical hazards.”
and NFPA 70E 110.3(B) – Awareness and Self-Discipline states:
“The electrical safety program … shall be developed to provide the required selfdiscipline for all employees who must perform work that may involve electrical hazards.”
The old saying “That’s the way we have always done it” doesn’t work anymore. Work practices change, regulations and standards change, and the hazards in the workplace change. Your employees must change as well. With the updates to the NFPA 70E, and the upcoming changes to OSHA regulations, workers must be prepared to change with them. Working safely is not an option, it must be a condition of employment and must be upheld to the
fullest. There is not a person out there that goes to work with the thought that “Hey, I think I am going to hurt myself today.” Unfortunately, injuries are still happening. Many of the injuries that occur on the job today occur from two different work groups: the inexperienced workers and the more seasoned workers. The inexperienced workers are learning from the established workers, and sometimes pick up bad habits. With the right mentoring and the right training, those workers can have a lifetime of safe employment and will be able to go home at the end of the day. The seasoned workers, those that have been in a given industry for quite a long time, sometimes have the thought process that they have been doing something a particular way for their whole career and have not been hurt, so they must be doing something right. They need to be aware that things change in the workplace, equipment gets upgraded, equipment may not be maintained as well as it should have been, or tasks just get so routine that they are not paying attention to the hazards to which they are exposed.
Invest the time and effort in your safety program to make it specific to your job site. Itdoesnotmatterifitisaconstruction It does not matter if it is a construction site, a manufacturing facility, or a customer site during a turn-around. Make sure that the specific hazards you will be facing are
identified, the risks assessed, and the work is done safely. We all want to go home at the end of the day in the same condition that we came to work that day.
In the next part of this series, we will be talking about some of the specific requirements of putting together a complete electrical safety program. Too many times things get overlooked and left out, only to comebackatalatertimeandrearitshead. come back at a later time and rear its head.
Part three of this series puts the whole puzzle together and takes a look at the company specific electrical safety program, looks at the specific requirements of an effective ESP, and shows how to implement a program that not only keeps workers safe, but helps reduce delays and equipment damage and decreases downtime by preventing incidents.
Don Brown is the
for
Programs
Industries
Irving, Texas. He has been in the electrical industry for over 40 years and has been implementing and training electrical safety for the last 15+ years. Mr. Brown just completed his certification through NFPA as a Certified Electrical Safety Compliance Professional (CESCP). He has written electrical safety programs for large data centers, petrochemical facilities, and manufacturing facilities, and is in the process of updating many of these to include the upcoming changes in the NFPA 70E–2015Edition. 70E – 2015 Edition.
The commissioning of newly-installed electrical power systems can be a complex taskifonedoesnotunderstandthecritical task if one does not understand the critical elements necessary to execute an effective and comprehensive commissioning plan. Whether you are the owner or the specifying engineer, it is arguably one of the most important aspects one should consider in the completion of a project that involves any appreciable quantity of electrical power equipment and ancillary systems.
Now as industry has a greater and greater awareness and understanding of the hazards of electricity, electrical commissioning becomes acornerstoneelementintheassurancethat a cornerstone element in the assurance that electrical equipment will operate as designed and as intended, especially during times of electrical fault or in a system response to critical power-related events.
It is because of this criticality of performance that we need to pay closer attention to electrical commissioning and make sure comprehensive power system commissioning tasks are a must have component to the completion of the project. Data centers have been long-time supporters of comprehensive
commissioning tasks, but other sectors of the electrical power system industry also understand the value of comprehensive commissioning processes, and that awareness of value is growing. Many industries such as wind power sites, hospitals, heavy industrial, and high-voltage utility substations have a greater understanding of the inherent value to performing commissioning tasks to assure proper power system performance and safety of operation.
As a NETA Accredited Company, we have performed many acceptance-testing projects, that is, projects for newly installed electrical equipment that has a project specification to perform independent, third party testing of the installed components. Moreover, statistics show us repeatedly that electrical equipment and components often times fail to meet performance or design criteria during the acceptance testing process.
Sothisarticleisnotaboutindividual So this article is not about individual acceptance testing of components and the number of failures that are found during acceptance testing, but rather we will take a look at system performance testing, or in other words: commissioning.
Many sources of information have a definition of electrical commissioning. The U.S. Department of the Army 1 states:
“Electrical systems commissioning on new projects is critical to ascertain that a system is installed properly and that it will operate as designed. The commissioning of a system encompasses the individual testing of the related components, the verification of the component interconnection against the drawings, and the functional testing of the system as a whole. An understanding of the equipment involved and the modes of operation for a system are essential to the development of the system commissioning plan.”
So how should you organize your thoughts and the processes necessary to carry out an effective commissioning plan for your project? With guidance from the NETA and their newlyformed commissioning standard, Standard for Electrical Commissioning Specifications for Electrical Power Equipment and Systems, the following key elements and ideas should be put into place:
1. The Commissioning Organization
2. The Commissioning Personnel
3. Understanding the Division of Responsibility
a. The Owner’s Representative
b. The Testing Organization
4. Safety
5. The Suitability of Test Equipment
6. The Test Equipment Calibration
7. The Commissioning Process
a. The Commissioning Intent
b. The Basis of Design
c. The Commissioning Plan
8. The Final Project Report
While a basic and commonly understood concept, it bears to be repeated and verified here: the key to any project’s success, including commissioning projects, falls squarely on the quality of the organization awarded the project and the skills and abilities of the personnel performing the work. Without a quality
infrastructure for the field personnel to rely and draw upon, and conversely if the organization does not have the right people for the task, the resultscanbedisastrous. results can be disastrous.
Regularly engaged in electrical testing, the commissioning organization should be an independent, third-party entity that can function as an unbiased testing authority, professionally independent of the manufacturers, suppliers, and installers of equipment or systems being evaluated. It is this concept of independence that fosters organizations that have a wider breadth of knowledge, as they are typically exposed to many different manufacturers and equipment suppliers.
The technicians performing these commissioning activities should be able to perform the tasks safely and have training and certifications related to the type of equipment being commissioned. It is up to the contracting entity to ask for and receive the necessary qualifications from the entity performing the work. If they cannot provide adequate documentation related to their qualifications, the power system is put at risk.
" Commissioningis critical for all new or retrofit installation projects to verify the correct system operation to the design and ensure safe and reliable operation of the system."
Think about it – it is likely you will be asking someone to inspect a multimillion dollar compilation of electrical equipment and systems to assure the equipment will not only function as intended and designed, but will also operate safely for the workers and personnel thatcomenearorincontact that come near or in contact with the equipment. To haveindividualsthatare have individuals that are not capable of conducting thetasksinasafe the tasks in a safe manner with complete knowledge of the hazards involved… all the while evaluating the test data and making judgments on the serviceability of the specific equipment puts many things as risk, not the least of which are items that affect personnel safety.
If someone is contracted to provide commissioning services, then there should be definitive lines of responsibility, including clear direction on what the owner should provide to the commissioning agent, and conversely what the expectations of performance are to be provided from the commissioning agent to theowner. the owner.
A good place to start: the basis of design document. When provided, the project’s basis of design (BOD) document, or series of documents, includes the detailed information on the design team’s approach to meeting the project specifications and regulatory requirements. The BOD provides a platform for the review of the design and commissioning of the system. This is a very important aspect to the commissioning process – because this document helps you understand the design and the intent of the power system. For example, if the incoming utility is lost, what is intended to happen next? Do you need to restore certain critical loads with backup generation or alternate utility feeders? And if the conditions have various scenarios, what do you want everything to do? The BOD will help answer these questions so the commissioning agent can make sure the power system will react correctly to the various scenarios.
So why do we care about the basis of design while commissioning? Quite simply, commissioning is critical for all new or retrofit installation projects to verify the correct system operation to the design and ensure safe and reliable operation of the system.
Additionally, the owner should provide to the commissioning agent all the electrical plans and drawings, change-orders, instruction manuals, factory acceptance tests (FAT’s), engineering studies and analysis (including arcflash, short-circuit and coordination studies), protective device settings, and any site-specific informationorhazards. information or hazards.
As an industry we are getting smarter about performance characteristics of the power system and no longer is it just about how to design a system to achieve maximum uptime and fault ride-through. Because the industry has a better understanding of the hazards of electricity, we also realize there is a fine balance between maximizing system performance and protection of personnel. Withtheadvancementsinelectricalfault With the advancements in electrical fault detection equipment we are able to tighten up the spread between equipment performance and personnel safety…. if everything works as intended and as designed.
Note: This is a good time for a maintenance strategy comment, and to point out that while it is critical to make sure everything works correctly when new, it is also just as important to make sure that maintenance, and condition of maintenance, is part of the equipment owners long-term strategy for ensuring many years of safe and reliable performance.
After the basis of design is known and understood, the next step is to develop a commissioning plan. The commissioning plan is your road map to performing specific tasks and component verification. It also helps to establish one of the most important benefits of a good commissioning plan –obtaining base-line data that can be used for years to come to help analyze and assess overall health of the power system.
Electrical equipment begins its journey to failure (or end of useful life) the day it is placed into service. An inevitable aspect to all equipment, knowing what shape it was in on day one helps us figure out what happens from initial energization to the celebration of 15, 20, even 50year birthdays of the equipment. Having theinitialassessmentinformationand the initial assessment information and capturing crucial points of data throughout the life span of the equipment helps you continue to celebrate electrical birthday parties year after year!
As you enter the final phases of a commissioning project, a very important step is capturing the commissioning data and information into a final project report. Accurate data, captured throughout the entire commissioning process, isvital.Youmusthaveaccurateinformation is vital. You must have accurate information determine energization schedules, switching orders, sequence of operations, etc.
But a word of caution—with the ability to generate piles and piles of data, test data, reports, etc., while it might be impressive to have it all in multiple binders or huge PDF files, a key message is this: keep it simple and straightforward.
As a commissioning agent you should be able to clearly communicate the findings, the procedures followed, and the overall results. You should provide all of the backup data for the findings (those pages and pages of stuff) and it is necessary, but realistically nobody hardly ever reads or needs the information except for the occasional verification. And make sure you don’t include extra stuff that doesn’t directly relate to the commissioning data – because your project summary will be used for years to come to help the owners analyze, test, verify, and trend the performance of the electrical system.
As mentioned earlier, NETA is developing a new standard for commissioning of electrical power equipment and systems. It is the intent of the standard to provide guidance on what should be done to effectively commission the electrical backbone and main components of the power system. It is not intended to replace existing standards and procedures that address the mechanical and control system aspects of an overall system, but rather, the focus is on
the electrical power components—an often overlooked aspect to a project.
The new standard also addresses equipment in three categories: low-voltage equipment, medium-voltage equipment, and highvoltage equipment. By breaking the standard into voltage classes, NETA is able to address the various nuances and requirements of commercial, industrial, and utility grades of equipment. So whether the equipment is located in a data center, a hospital, a steel mill, a refinery, or a utility substation, you can find guidance and specifications on what should be done to perform commissioning activities.
In summary, we should once again look at the intent of electrical commissioning. Commissioning is the systematic process of verifying, documenting, and placing into service newly installed or retrofitted electrical power equipment and systems. Also of note:
• Commissioning is critical for all new or retrofit installation projects to verify the correct system operation to the design and ensure safe and reliable operation of the system.
• The commissioning process involves owner’s project requirements (OPR), basis of design (BOD), individual component testing (factory and acceptance tests), verification of the
component interconnections, and functional testing of the system in part and as a whole.
• The acceptance tests and commissioning will provide the baseline results for the routine maintenance of the system and related components.
And most importantly – electrical commissioning helps us keep our people safe.
1. U.S. Department of the Army, Technical Manual TM 5-694, Commissioning of Electrical Systems for Command, Control, Communications, Computer, Intelligence, Surveillance, and Reconnaissance (C4ISR) Facilities, 17 February 2006
2. InterNational Electrical Testing Association (NETA), ANSI/ATS-2013, Standard for Acceptance Testing Specifications for Electrical Power Equipment and Systems
3. InterNational Electrical Testing Association (NETA), ECS-2015, Standard for Electrical Commissioning Specifications for Electrical Power Equipment and Systems (in development)
Ron Widup is President of Shermco and has been with the company since 1983. He is a Principal member of the Technical Committee on “Electrical Safety in the Workplace” (NFPA 70E) and a Principal member of the National ElectricalCode(NFPA70)CodePanel11. Electrical Code (NFPA 70) Code Panel 11. He is also a member of the technical committee “Recommended Practice for Electrical Equipment Maintenance” (NFPA 70B), and a member of the NETA Board of Directors andStandardsReviewCouncil. and Standards Review Council.
No matter where you are, no matter what you run, if it’s electrical, Shermco’s the one.
Power plants? No problem. Utility substations? We can handle ‘em. Wind farms? Absolutely. Data centers? Just say where and when. The fact is, Shermco has the growing capacity to support your utility or electrical power needs in virtually any location, with all the manpower, equipment and technical knowledge it takes to get the job done and done safely!
While other companies are sending their equipment and workforces out to pasture, we’re upgrading ours and sending them into the field. Call Shermco for anything. Fromlarge-scale engineering projects and planned facility outages, to new system acceptance testing and safe start-up, one company does it all. Shermco. We got your back.
The PPE program requirements that were previously based on OSHA 1910.269–Electric Power Generation, Transmission, and Distribution, as well as the requirements that were contained in the previous 1910 Subpart I - Personal Protective Equipment, are still valid. However, there are several new requirements that must be incorporated into exiting PPE programs.
OSHA 1926 – Safety and Health Regulations for Construction Subpart V – Power Transmission and Distribution was extensively revised to be consistent with the revised 1910.269 and contains the same requirements for construction as is required for general industry. OSHA 1926.97 Electrical Protective Equipment is new and is consistent with the revised 1910.137 – Electrical Protective Devices. All construction PPE programs would require extensive revision in order to incorporate all of the new OSHA 1926 requirements.
With the April 1, 2014, Final Rule revisions of OSHA 1910.136, 1910.137, 1910.269, 1926 Subpart V, and the new 1926.97 – Electrical Protective Equipment, there are new and revised requirements that must be incorporated into PPE Programs. The following highlights the revised requirements which are underlined for clarity:
(a) General requirements. The employer shall ensure that each affected employee uses protective footwear when working in areas where there is a danger of foot injuries due to falling or rolling objects, or objects piercing the sole, or whenthe when the
use of protective footwear will protect the affected employee from an electrical hazard, such as a static-discharge or electric shock hazard, that remains after the employer takes other necessary protective measures.
The main revision to 1910.137 is the addition of Class 00 gloves. It should be noted that the following paragraph and note were added for Class 00 gloves:
(c) In-service care and use of electrical protective equipment. (vii) Protector gloves shall be worn over insulating gloves, except as follows: (B) If the voltage does not exceed 250 volts, ac, or 375 volts, dc, protector gloves need not be used with Class 00 gloves, under limited-use conditions, when small equipment and parts manipulation necessitate unusually high finger dexterity.
Note to paragraph (c)(2)(vii)(B): Persons inspecting rubber insulating gloves used under these conditions need to take extra care in visually examining them. Employees using rubber insulating gloves under these
conditions need to take extra care to avoid handling sharp objects.
The revisions to 1910.137 also include the ac and dc test and use requirements. The AC test voltage is 2,500 vac with a use voltage of 500 Vac; the dc test voltage is 10,000 Vac but does not provide a dc use voltage
The revisions to 1910.269(g) Personal Protective Equipment. (1) General. Personal protective equipment shall meet the requirements of Subpart I of this part. The revisions to Subpart Iarenotedabove. I are noted above.
The requirements of 1910.269(l) Working on or near exposed energized parts. This paragraph applies to work on exposed live parts, or near enough to them to expose the employee to any hazard they present. This paragraph was expanded to provide additional detailed requirements for the use of rubber insulating PPE, required for use when working on or near exposed energized parts. These new requirements must be incorporated into any existing PPE programs in order to provide complete protection to employees who may be exposed to electrical hazards. No specific incorporation dates were provided so it is assumed to be immediate.
OSHA made extensive revisions to 1910.269(l)
(8) ProtectionFromFlamesandElectricArcs. Protection From Flames and Electric Arcs. (i) The employer shall assess the workplace to identify employees exposed to hazards from flames or from electricarcs. electric arcs.
(ii) For each employee exposed to hazards from electric arcs, the employer shall make a reasonable estimate of the incident heat energy to which the employee would be exposed.
Note 1 to paragraph (l)(8)(ii): Appendix E to this section provides guidance on estimating available heat energy.
OSHA provides specific dates when the requirements of 1910.269(l)(8) are to be completed and incorporated into the PPE program, as follows:
(vi) Dates. (A) The obligation in paragraph (l)(8)(ii) of this section for the employer to
make reasonable estimates of incident energy commences January 1, 2015.
(B) The obligation in paragraph (l)(8)(iv) (D) of this section for the employer to ensure that the outer layer of clothing worn by an employee is flame-resistant when the estimated incident heat energy exceeds 2.0 cal/cm2 commences April 1, 2015
(C) The obligation in paragraph (l)(8)(v) of this section for the employer to ensure that each employee exposed to hazards from electric arcs wears the required arc-rated protective equipment commences April 1, 2015
Note that the 1926.97 requirements for the constructionsdivisionarenowthesameas constructions division are now the same as specified in 1910.137.
Since the requirements for estimating incident energy of an arc flash and providing the required arc-rated clothing and PPE has been required by NFPA 70E, Standard for Electrical Safety in the Workplace, since the 2000 edition and required by ANSI/IEEE C2, National Electrical Safety Code, since 2007, it is advisable to perform an arc-flash hazard analysis as soon as possible in order to adequately protect employees for potential arcflash hazards in all segments of electric utilities, construction, and general industry.
Revising existing PPE programs to incorporate the new and revised OSHA 1910 and 1926 requirements will provide additional protection for employees working in areas that contain, or may contain, electrical hazards.
DennisK.Neitzel Dennis K. Neitzel, CPE, Director Emeritus of AVO Training Institute, Inc., Dallas, Texas, is an active member of IEEE (Senior Member), ASSE, AFE, IAEI, and NFPA. He is a Certified Plant Engineer (CPE) and a Certified Electrical Inspector-General. Mr. Neitzel is a Principle Committee Member and Special Expert for the NFPA 70E, Standard for Electrical Safety in the Workplace and is coauthor of the Electrical Safety Handbook, McGraw-Hill Publishers. He has authored, published, and presented numerous technical papers and magazine articles on electrical safety, maintenance, and technical training.
Power System Acceptance Testing
Commissioning and Start-up
Maintenance
Life-Cycle Extension
Troubleshoot and Repair
Training and Engineering Services
Planning and Operations Support
Project Management
2200 West Valley Hwy North, Suite 100 | Auburn, WA 98001
Many existing power systems are approaching or exceeding their expected service life. The issues of an aged power delivery infrastructure can include sudden increases in equipment failures, maintenance activities, and replacement costs. The challenge of meeting customer needs has increased demands on asset management and condition-based maintenance to be met by intelligent on-line monitoring and smart automation systems.
Industry innovations to address these challenges aim at developing embedded sensors and integrated systems that address transformer health, remaining life and upper limits of loading based on direct measurements in the solid insulation system.
Historically, monitoring (off-line or on-line) focused on moisture in oil, DGA, and other means along with operating temperature (either top oil or measured directly at the hot spot) in order to infer transformer health and insulation condition. The model developed from these inputs drives critical decisions about the asset.
That model most often resides as know-how
with key people in the organization and is driven by periodically obtaining data, as opposed to being compiled in a system based on real-time data. Regardless of the nature of the data, the goal is to understand health, remaining life, and
loadability of the transformer. Ultimately, it is the insulation system that drives that equation. The following chart depicts the withstand strength of the solid insulation over time.
The withstand level is going to degrade with temperature and degradation will be accelerated by moisture and the forces associated with system events. Sensors embedded in the cellulose insulation allow direct measurement of insulation system condition and thereby, the use of that in the model. The stronger the model, the stronger the decision making.
The transformer in the distribution network was traditionally a passive piece of equipment, but is becoming more and more an active component of the network that dynamically interacts to ensure capacity, reliability, and efficiency in the network. This is driving the need for better decision support and models that can drive that.
For example, the future model will look more like this:
Given this new level of demands on the transformer, or even just the ever increasing age of transformers in use today, understanding of the factors that drive decisions related to the asset and the system, and monitoring them in real-time, is key to performance. There is a need for either a transformer expert or someone less
experienced to receive actionable information out of what can be a sea of data. This aspect is driving ever higher expectations for firmware and software solutions.
limits based on changes in ambient condition or operating modes during winter/summer normal or contingency conditions.
• Making intelligent decisions about shifting load from one unit to another, based on time to reach peak load capability (as an early warning) for short-term outages.
gr g id deployments, op erationa l nee ds, and pe p f rforma m nce indicato t r (K PI) reeporting g oals.
The following figure shows the relationship between monitoring elements and how each monitoring area contributes to meeting smart grid deployments, operational needs, and key performance indicator (KPI) reporting goals.
The central goal is the continuous supervision and communication of important parameters during normal and emergency operating modes, in order to best:
• Utilize transformer assets closer to their real operating temperature and life cycle limits without compromising life expectancy or reliability.
• Determining when units are or are not performing in accordance with the factory final tests or thermal model design.
• Optimizing real-time substation loading
yg distribution network s ystem in order to ood, b etter, b est options based
to maximize to
• Potentially shifting load around a distribution network system in order to select g ood, better, best options based on the health of individual units or loadloss characteristics in order to maximize financial benefits or potentially to reduce cost of losses.
cost of losses .
• Collecting insulation loss-of-life data to enable forecasting of residual life for major maintenance activity or replacement of transformer assets in the fleet.
• data enable of residual life for major maintenance activity or replacement of transformer assets in fle et.
Given the time and budget constraints of the world the business case around the cost cost the The model does not always circumstances justif y, this expense. Weidmann has been software to run with or
Given the time and budget constraints of the world today, the business case around the cost of implementation has to be considered. For example, electrical current as input (CT) connections are expensive to buy and considerably increase the cost of installation in the substation. The model does not always require, nor do the circumstances justify, this expense. Weidmann has been developing software designed to run with or without it. This vastly improves the business case from both a simplicity and cost standpoint while maintaining that capability where justified.
maintaining that capability where justified. area
anewlydevelopedtransformersimulation
Weidmann’s research in this area comes from a newly developed transformer simulation test facility designed specifically to help better understand the key factors that affect transformer operation and life. Simulation of dynamic operating conditions within a power transformer is being done in the lab pictured at right.
The unit pictured has the conductor, fluid and cellulose components in the same proportions as a 650 BIL transformer and has been running to confirm the experimental design for studying moisture migration within the insulation system.
The facility is capable of simulating the operational variables within a typical power transformer found on electrical grids around the world. Key operating parameters such as oil
Figure 5: Transformer Simulator in St. Johnsbury, Vermont
temperature, oil flow, migration of moisture in oil and moisture in insulation materials, onset of bubble formation, axial clamping force, along with winding temperatures and gradient can be closely measured and controlled.
In closing, this paper outlines options that will be required in selecting sensors along with monitoring hardware and software that can be part of the real-time performance monitoring needed to optimize assets while minimizing operational and maintenance costs.
Electric T&D companies are increasingly challenged by regulators and customers to reduce cost and to improve operational performance and reliability. Opportunity for improvement exists for assets that are nearing end of life, using the technologies installed by the OEM or that can be retrofitted. Even greater potential exists for the next generation of transformers that can be built with embedded sensors to improve decision making over the full lifecycle of the asset. In future NETA Advancement in Technology articles, the aspects of monitoring that will drive these improvements will be discussed in more detail. In particular, temperature, moisture, and force in transformers, describing their importance to the transformer and to the models that will drive decision making and system performance.
[1] Tayyar Egeli, “Weidmann Presentation about Transformer Monitoring” (Travek Conference, 2012, Moscow)
[2] David J.Woodcock, “Presentation at Transformer Seminar” (Weidmann Transformer Seminar, 2012, Switzerland).
[3] X.Zhao, Y.Mengi, K.Wui, H.Zhao, J.Li, “Development of Integrated Condition Monitoring and Diagnosis System for Power Transformer” (IEEE Electrical Insulation Conference, 2009, Montreal).
General References
IEEE/ASNI C57.119 – 1996, “Recommended Practice for Performing Temperature Rise Tests on Oil-Immersed Power Transformers at Loads Beyond Nameplate Ratings”
Pierce, Linden W., “Predicting Liquid Filled Transformer Loading Capability”, 1992 at IEEE IAS Petroleum and Chemical Industry Technical Conference. September 28-30, 1992.
Moore, Harold R., “Use of Oil Testing to Determine Transformer Condition and Life Extension”, TechCon 98, New Orleans, LA. February 16-18, 1998.
David J. Woodcock and Jeffrey C. Wright, P.E., Power Transformer Design Enhancements Made to Increase Operation Life, Sixty-Sixth Annual International Conference of Doble Clients, April 12-16, 1999.
Dave J. Woodcock and Michael A. Franchek, Life Cycle Considerations of Loading Transformers Above Nameplate Rating, Sixty-Fifth Annual International Conference of Doble Clients, April 1998.
Philip Chadderdon has 24 years of experience in engineering, research and development, and general management. He is currently Technical Director responsible for WEIDMANN’s Development Center in St. Johnsbury, Vermont. He was formerly General Manager for one of WEIDMANN’s electrical insulation manufacturing sites and participates in IEEE and with NETA through the NETA Corporate Alliance Program.
David Woodcock has 35 years of international experience in the design, application, and maintenance of equipment used in electric power transmission, distribution and generation. He is currently the Vice President for Strategic Development at WICOR Americas, Inc. in St. Johnsbury, Vermont.
Mr. Woodcock is a member of the ASME Power Engineering Society, a Member of IEEE PES Transformers Committee, and a delegate to CIGRE’s the International Council on Large Electric Systems. He is a frequent industry speaker on power transformer health and risk assessment, dynamic loading, and other transformer lifecycle topics.
TheIEEE/PESTransformerCommittee The IEEE/PES Transformer Committee spring meeting was held in Savannah, Georgia. One very interesting item to note was the discussion regarding the removal of the information pertaining to insulating fluid for circuit breakers. Currently, section8oftheC57.106–section 8 of the C57.106– IEEE Guide for Acceptance and Maintenance of Insulating Oil in Equipment is specific to insulating oil for circuit breakers. This section was discussed, and it was suggested that it not be included
inthenewversionofthestandard.Asthe in the new version of the standard. As the C57 documents are specific to transformers and regulators, the circuit breaker section is beyond the scope of the document. This will meanallreferencesinoilstandardstocircuit mean all references in oil standards to circuit breakerswillbeeliminatedfromthenext breakers will be eliminated from the next revisionsoftheC57documents.TheIEEE/ revisions of the C57 documents. The IEEE/ PES Switchgear Committee will need to review and possibly include circuit breaker insulating fluid standards during the next revision cycle of the C37 documents.
LorneGara Lorne Gara is a Technical Manager for Orbis Engineering. He provides technical support for the engineering, field services, and automation departments of Orbis and many of its Clients. Lorne has a wide range of experience in engineering, commissioning, maintenance, fault analysis, and start-up of utility and industrial power systems across North America. He has extensive experience with protective relay setting development, commissioning, and testing protection and control systems.
Comprehensive Electrical Testing and Maintenance
Commissioning and Startup Services
Engineering Services
Power System and Coordination Studies
Predictive and Preventive Maintenance
Partial Discharge Testing and Monitoring
24/7 Emergency Service
Failure is not an option. Ensuringthe reliability of your electrical distribution system.
As theleadingindependent electrical testing, maintenance, andengineering service company, you canrely on Emerson’s High VoltageMaintenance to exceed yourelectricalequipment performance goals. From testing for problems that coulddisable your system, to complete turnaround execution, you’llquickly understandhowweare your single source solution forall of yourelectricalreliability needs. With a network of more than12 service locations, our service teamputs experiencedprofessionals whereand when youneed them.
• Technical Presentations: Electrical Safety, Reliability, Equipment, Electrical Commissioning, Relays
• Safety Summit
• Panels: Electrical Safety, Transformer, Testing Methodologies, Medium-Voltage Equipment
• In-Depth, Four-Hour Seminars
• Networking with Industry Leaders
Renaissance Nashville Hotel
MARCH 2–6, 2015
Vanguard Instruments has been at the forefront of developing innovative precision sub-station test instruments for over 20 years, and we are continuing our tradition with our latest products such as the CT-7000 S3 and CT-8000 S3 circuit breaker analyzers with Dual Ground testing feature and our new line of test instruments featuring convenient Bluetooth wireless interfaces. Visit us today at vanguard-instruments.com to find the latest solutions for all of your sub-station testing needs.
Initial balloting and public review oftheANSI/NETAMTSstandard of the ANSI/NETA MTS standard concluded on April 19, 2014. The StandardsReviewCouncilhas Standards Review Council has reviewedallcommentssubmittedwith reviewed all comments submitted with the ballots and issued responses. The public review period and ballot on the responses to comments will be issued on July 7, 2014. There will be a 30 day ballot period and a 45 day public review period, with the ballot closing on August 14, 2014, and the public review period closing on September 1, 2014. This document contains specifications which cover the suggested field tests and inspections that are available to assess the suitability for continued service and reliability of electrical power equipment and systems. The purpose of these specifications is to assure that tested electrical equipment and systems are operational and within applicable standardsandmanufacturers’tolerances standards and manufacturers’ tolerances and that the equipment and systems are suitableforcontinuedservice. suitable for continued service.
Initial balloting and public review of the ANSI/NETA ETT standard concluded on April 19, 2014. The Standards Review Councilhasreviewedallcomments Council has reviewed all comments submittedwiththeballotsandissued submitted with the ballots and issued responses. The public review period and ballot on the responses to comments will be issued on July 7, 2014. There will be a 30 day ballot period and a 45 day public review period, with the ballot closing on August 14, 2014, and the public review period closing on September 1, 2014. The ANSI/NETA Standard for Certification of Electrical Testing Technicians was approved as a revised American National Standard on January 8, 2010. This standard establishes minimum requirements for qualifications, certification, training, and experience for the electrical testing technician. It also provides criteria for documenting qualifications for certificationanddetailstheminimum certification and details the minimum qualifications for an independent and impartial certifying body to certify electrical testing technicians.
Initial balloting and public review of thisnewcandidatestandardconcluded this new candidate standard concluded on April 19, 2014. The Standards ReviewCouncilhasreviewedallcom view Council has reviewed all commentssubmittedwiththeballotsand ments submitted with the ballots and issued responses. The public review period and ballot on the responses to comments will be issued on July 7, 2014. There will be a 30 day ballot period and a 45 day public review period, with the ballot closing on August 14, 2014 and the public review period closing on September 1, 2014. These specifications describe the systematic process of documenting and placing into service newly–installed or retrofitted electrical power equipment and systems. This document shall be used in conjunction with the mostrecenteditionoftheANSI/NETA most recent edition of the ANSI/NETA Standard for Acceptance Testing Specifications for Electrical Power Equipment and Systems.Theindividualelectricalcom . The individual electrical components shall be subjected to factory factory and field tests, as required, to validate the individual components. It is not the
• WORLD’SFIRSTVACUUMINTERRUPTERTESTSYSTEM CAPABLEOFPREDICTINGREMAININGLIFE
• WORLD’SFIRSTTESTSYSTEMCAPABLEOFTESTINGVACUUM INTERRUPTERSINBOTHTHESHOPANDFIELD
• BASEDONSAMEOEMLEAK-RATETESTPERFORMED ATTHEFACTORY
• MEASURES ACTUAL ION CURRENT AGAINST KNOWN VALUES TO DETERMINE VACUUM INTERRUPTER INTERNAL PRESSURE
A program under development this year between NETA and Mesa, Arizona-based East Valley Institute of Technology (EVIT) promises to offer fast track adult education courses using a curriculum based on theANSI/NETAETT the ANSI/NETA ETT Certification for Electrical Testing Technicians Standard. The program is expected to launch in late 2014 or early 2015.
EVIT’s goal is to create a curriculum that provides the opportunity for graduates of this course to be successful at completing the Level II NETA Electrical Testing Technician certification exam once they are employed by a NETA Accredited Company. Participants could could complete the coursework and graduate within six months. At the time of completion, graduates will have their OSHA 30, numerous electrical safety training hours, and first aid and CPR certification. In theory, graduates should be ready to go to work for a NETA Accredited Company as a Level I Technician and will be poised to become a Level II within a year-and-a-half of being hired and gaining the requisite number of years of field experience.
The program will be comprised of seven courses as well aslabinstructiondeliveredonaflexibleschedulefor as lab instruction delivered on a flexible schedule for
working adults. The coursework will take place four to five days a week over the six-month program. An aggressive effort to develop the curriculum and procure the lab equipment has been underway since early 2014. NETA President Dave Huffman of Power Systems Testing Company has been among those working closely with EVIT to develop the curriculum.
“This program will be a great way to help technicians advance their knowledge, as well as assist NETA Accredited Companies in accessing new and promising talent in the industry,” Huffman said.
While the NETA Electrical Testing Technician certification will always be a predominantly field-based examinationthatisintendedtoassessacandidate’sknowl ination that is intended to assess a candidate’s knowledge gained from first-hand experience in electrical testing, there is always a need for a solid foundation of electrical and mathematical theory learned in classroom and lab work that goes hand-in-hand with that practical knowledge and skill set. NETA intends for the EVIT curriculum to become a springboard from which other programs may be developed and launched at educational institutions around the country.
No.107 No. 107
1. d. Vacuum bottle integrity tests can only show that the vacuum bottle has sufficient vacuum to prevent arcing across the open contacts at a specified voltage. The Magnetron atmospheric condition test, which is new on the market, provides an indication of remaining interrupter life.
2. a. Although IEEE standards use 1,000 V to 100,000 V, the nominal voltages for medium-voltage equipment is usually 2,300 V to 69,000 V.
3. a. Oil
b. Gas or SF6
c. Air or air magnetic
d. Vacuum
e. Air blast (these have been mostly replaced with gas circuit breakers)
4. b. The anti-pump circuit is often referred to as the “X-Y scheme”. An anti-pump scheme is important for circuit breakers because it prevents the circuit breaker from repeatedly reclosing into a fault. A set of contacts from the anti-pump relay seals in the anti-pump coil causing it to remain energized as long as the close command continues. Another contact from the anti-pump relay interrupts the closing coil circuit. This prevents a reclose until the close command is released and the anti-pump relay drops out.
5. d. Whether it is a low-voltage or medium-voltage circuit breaker, HRC 4 is always required when inserting or removing (racking) a circuit breaker.
NFPA Disclaimer: Although Jim White is a member of the NFPA Technical Committee for both NFPA 70E “Standard for Electrical Safety in the Workplace” and NFPA 70B “Recommended Practice for Electrical Equipment Maintenance,” the views and opinions expressed in this message are purely the author’s and shall not be considered an official position of the NFPA or any of its technical committees and shall not be considered to be, nor be relied upon as, a formal interpretation or promotion of the NFPA. Readers are encouraged to refer to the entire text of all referenced documents.
Standardization of industry best practices and compliance with these standards is something that many people are familiar with in their daily career demands, regardless of the industry in which they work. The electrical power systems industry is a vast landscape of standards with thousands upon thousands of lines of code, making it difficult at times to see the forest for the trees.
NETA works hard at setting the standard with regard to electrical acceptance testing, inspection, maintenance, and electrical testing of service-aged equipment for power equipment and systems. NETA’s family of American National Standards, the ANSI/NETA ATS, ANSI/NETA MTS, and ANSI/NETA ETT, have been adopted on a global scale as the go-to documents for this purpose. One of the many reasons for the continued promulgation of thesedocumentsisthefactthattherearereferences these documents is the fact that there are references throughout the documents to other industry codes and standards that apply to the tests and inspections for the array of equipment specified in these documents. NETA is able to continue to produce thesedocumentswiththisvaluableinformation these documents with this valuable information due largely to the extensive network of technical representatives who volunteer their time on NETA’s standards development as well as many other industry-related standards development groups.
NFPA, CSA, IEEE, ASTM, ICC, and ICEA aresomeoftheassociationswithwhichNETA are some of the associations with which NETA finds itself represented. Often NETA volunteers commit to maintaining these documents at the working group level, which is an enormous time commitment since they are responsible for assuring that the standards on which they are working are relevant to current technologies and practices aswellasotherrelatedstandards.Othertimes as well as other related standards. Other times volunteers participate in ballot groups or submit public comments, which are also both quite demanding with regard to time and scope of work.
In January 2014, NETA joined other industryleading organizations as a member if the IEEE Corporate Standards Association. This level of membership within IEEE affords even more access to participate in the creation of new industry standards through opportunities to ballot on many documents that have the potential to influence the lives of those who use the ANSI/ NETAstandards. NETA standards.
NETA’s first action as a newly-minted IEEE Corporate Member was to ballot on P1861 Guide for On-site Acceptance Tests of Electrical Equipment and System Commissioning of 1000 kV AC and Above.Whilethisstandarddoesnothaveadirect . While this standard does not have a direct impact on the NETA standards at this time due to the voltage class covered in the document, it is important for NETA to stay current on the work that is taking place in North America and across the globe that has the potential to affect the usersofNETA’sstandards.NETAwillcontinue users of NETA’s standards. NETA will continue to monitor the opportunities to participate in relevant projects that arise in the corporate standards development arena within IEEE. While it may not be realistic to be involved in every opportunity that arises, NETA volunteers will continue to push the bar a little higher when they are in the game.
To view a complete list of IEEE Corporate Members, please visit http://standards.ieee.org/develop/corp chan/mbrs1.html.
NETA is proud to announce that the NETA Handbooks, Series II, are now available, giving electrical power system industry professionals more reference and training options. More than 14,000 copies of the first NETA Handbooks series, covering subjects like circuit breakers, protective relays, transformers, arc-flash safety, and online diagnostics, were sold.
Thematerialcontainedinthehandbooksisacollectionof The material contained in the handbooks is a collection of more than 200 of the best articles published in past issues of NETAWorld NETA World andthemostwell-receivedtechnical and the most well-received technical presentations from PowerTest, the premier electrical maintenance and safety event, which is hosted by NETA.
NETA Handbooks, Series II, provide a valuable resource for two major groups of individuals in the power system industry. First, they serve as a reference tool for new employees needing a solid overview of the industry and for technicians preparing for the NETA exam. Second, NETA Handbooks, Series II, assist electrical engineers working for consulting firms, manufacturer sales representatives, and facility management engineers.
NETA Handbooks, Series II, content covers the most up-to-date and relevant information from standard testing procedures to troubleshooting and every day, real-life situations applicable in the field. The new series is made possible thanks to the following sponsors who are dedicated to education and improvement throughout the industry: Ampteks, CBS ArcSafe, Circuit Breaker Analyzer, Shermco Industries, Intellirent, IRISS, Megger Distributor Group, Raytech USA, Inc., SMC International, Tony Demaria Electric, Inc., and Vacuum Interrupters, Inc.
NETA Handbooks, Series II, are being offered at $15.00 per volume or $195.00 for the entire 13-volume set (plus shipping and handling). Subscribers to the NETA Alliance Program, (NETA’s nontesting professional network) receive 20 percent off the regular price.
NETA is an association dedicated to quality in the industry. NETA has a wide variety of training options available. For more information, contact the NETA office at 888.300.6382 or www.netaworld.org.
It’s real world learning at your fingertips. These handbooks deliver relevant information on the electrical power systems industry, including testing procedures, troubleshooting and real-life solutions encountered in the field every day.
You’ll discover page after page of comprehensive, component-specific, technical resources for training and reference purposes.
The NETA Handbooks bring together a collection of over 200 of the very best articles from past issues of NETA World Journal and the most well received technical presentations from NETA’s PowerTest conferences.
For more information on the NETA Handbooks or other NETA publications visit the NETA bookstore at www.netaworld.org or 888-300-6382. (NETA) $195* For the 13 volume set $15* For each issue * Additional cost for shipping and handling
A&F Electrical Testing, Inc.
80 Lake Ave. South, Ste. 10 Nesconset, NY 11767 (631) 584-5625 Fax: (631) 584-5720 kchilton@afelectricaltesting.com www.afelectricaltesting.com
Kevin Chilton
A&F Electrical Testing, Inc.
80 Broad St. 5th Floor New York, NY 10004 (631) 584-5625 Fax: (631) 584-5720 afelectricaltesting@afelectricaltesting.com www.afelectricaltesting.com
Florence Chilton
ABM Electrical Power Solutions
3602 East Southern Ave., Ste. 1 & 2 Phoenix, AZ 85040 (602) 796-6583
www.ABM.com
Ben Thomas
ABM Electrical Power Solutions
9800 E. Geddes Avenue, Unit A-150 Englewood, CO 80112 (303) 524-6560 Fax: (303) 524-6581
www.ABM.com
Ben Thomas
ABM Electrical Power Solutions 2142 Rheem Drive Pleasanton, CA 94588 (408) 399-3030 Fax: (800) 597-1225
www.ABM.com
Ben Thomas
ABM Electrical Power Solutions
3711 Saunders Ave. Richmond, VA 23227 (804) 253-9079 Fax: (804) 254-5799 www.ABM.com
Barry Maitland
ABM Electrical Power Solutions
6280 South Valley View Blvd., Ste. 618 Las Vegas, NV 89118 (702) 216-0982 Fax: (702) 216-0983 www.ABM.com
Ben Thomas
ABM Electrical Power Solutions
814 Greenbrier Circle, Ste. E Chesapeake, VA 23320 (757) 548-5690 Fax: (757) 548-5417 www.ABM.com
Mark Anthony Gaughan, III
ABM Electrical Power Solutions
3700 Commerce Dr. #901-903 Baltimore, MD 21227 (410) 247-3300 Fax: (410) 247-0900 www.ABM.com
Bill Hartman
ABM Electrical Power Solutions
710 Thomson Park Dr. Cranberry Township, PA 16066-6427 (724) 772-4638 Fax: (724) 772-6003
william.mckenzie@abm.com www.ABM.com
William (Pete) McKenzie
ABM Electrical Power Solutions
5805 G Departure Dr. Raleigh, NC 27616 (919) 877-1008 Fax: (919) 501-7492 www.ABM.com
Rob Parton
ABM Electrical Power Solutions
4390 Parliament Place, Ste. Q Lanham, MD 20706 (301) 967-3500 Fax: (301) 735-8953 www.ABM.com
Frank Ceci
ABM Electrical Power Solutions
3600 Woodpark Blvd., Suite G Charlotte, NC 28206 (704) 273-6257 Fax: (704) 598-9812 ernest.goins@abm.com www.ABM.com
Ernest Goins
ABM Electrical Power Solutions
720 S. Rochester Ave., Suite A Ontario, CA 91761 (951) 522-8855 Fax: (909) 937-6798 www.ABM.com
Ben Thomas
Absolute Testing Services 6829 Guhn Rd. Houston, TX 77040 (832) 467-4446 Fax: (713) 849-3885 rgamble@absolutetesting.com www.texasats.com
Richard Gamble
Advanced Testing Systems
15 Trowbridge Dr. Bethel, CT 06801 (203) 743-2001 Fax: (203) 743-2325 pmaccarthy@advtest.com www.advtest.com
Pat MacCarthy
American Electrical Testing Co., Inc.
480 Neponset St., Building 6 Canton, MA 02021-1970 (781) 821-0121 Fax: (781) 821-0771 sblizard@aetco.us www.99aetco.com
Scott A. Blizard
American Electrical Testing Co., Inc. 34 Clover Dr. South Windsor, CT 06074 (860) 648-1013 Fax: (781) 821-0771 jpoulin@aetco.us www.99aetco.com
Gerald Poulin
American Electrical Testing Co., Inc. 76 Cain Dr. Brentwood, NY 11717 (631) 617-5330 Fax: (631) 630-2292 mschacker@aetco.us www.99aetco.com
Michael Schacker
American Electrical Testing Co., Inc. 50 Intervale Rd., Ste. 1 Boonton, NJ 07005 (973) 316-1180 Fax: (781) 316-1181 jsomol@aetco.us www.99aetco.com
Jeff Somol
American Electrical Testing Co., Inc. 4032 Park 65 Dr. Indianapolis, IN 46254 (317) 487-2111 Fax: (781) 821-0771 scanale@aetco.us www.99aetco.com
Stephen Canale
American Electrical Testing Co., Inc. Green Hills Commerce Center 5925 Tilghman St., Ste. 200 Allentown, PA 18104 (215) 219-6800 jmunley@aetco.us www.99aetco.com
Jonathan Munley
American Electrical Testing Co., Inc. 12566 W. Indianola Ave. Avondale, AZ 85392 (480) 383-9242 dmadaglia@aetco.us www.99aetco.com
Donald Madaglia
AMP Quality Energy Services, LLC 4220 West Schrimsher SW Site W1 P.O. Box 526, Huntsville, AL 35804 (256) 513-8255
Brian Rodgers
Apparatus Testing and Engineering PO Box 984, Folsom, CA 95763 (916) 853-6280 Fax: (916) 853-6258 jlawler@apparatustesting.com www.apparatustesting.com
James Lawler
Apparatus Testing and Engineering 7083 Commerce Circle, Ste. H Pleasanton, CA 94588 (925) 454-1363 Fax: (925) 454-1499 info@apparatustesting.com www.apparatustesting.com
Harold (Jerry) Carr
Applied Engineering Concepts 1105 N. Allen Ave. Pasadena, CA 91104 (626) 398-3052 Fax: (626) 398-3053 michel.c@aec-us.com www.aec-us.com
Michel Castonguay
Burlington Electrical Testing Co., Inc.
300 Cedar Ave. Croydon, PA 19021-6051 (215) 826-9400 (221) Fax: (215) 826-0964 waltc@betest.com www.betest.com
Walter P. Cleary
C.E. Testing, Inc. 6148 Tim Crews Rd. Macclenny, FL 32063 (904) 653-1900 Fax: (904) 653-1911 cetesting@aol.com
Mark Chapman
CE Power Solutions,LLC 4500 W. Mitchell Ave. Cincinnati, OH 45232 (513) 563-6150 Fax: (513) 563-6120 info@cepowersol.net www.cepowersol.com
Rhonda Harris
CE Power Solutions of Minnesota,LLC 7674 Washington Ave. South Eden Prairie, MN 55344 (877) 968-0281 Fax: (952) 400-8772 jim.newcomb@cepower.net www.cepower-MN.net
Jim Newcomb
Control Power Concepts
353 Pilot Rd; Ste. B Las Vegas, NV 89119 (702) 448-7833 Fax: (702) 448-7835 www.controlpowerconcepts.com
John Travis
Dude Electrical Testing LLC
145 Tower Dr., Unit# 9 Burr Ridge, IL 60527 (815) 293-3388 Fax: (815) 293-3386 scott.dude@dudetesting.com www.dudetesting.com
Scott Dude
DYMAX Service, LLC
46918 Liberty Dr. Wixom, MI 48393 (248) 313-6868 Fax: (248) 313-6869 www.dymaxservice.com
Bruce Robinson
DYMAX Service, LLC 4213 Kropf Ave. Canton, OH 44706 (330) 484-6801 Fax: (740) 333-1271 www.dymaxservice.com
Gary Swank
Eastern High Voltage 11A South Gold Dr. Robbinsville, NJ 08691-1606 (609) 890-8300 Fax: (609) 588-8090 joewilson@easternhighvoltage.com www.easternhighvoltage.com
Joseph Wilson
ELECT, P.C.
7400-G Siemens Rd., P.O. Box 2080 Wendell, NC 27591 (919) 365-9775 Fax: (919) 365-9789 btyndall@elect-pc.com www.elect-pc.com
Barry W. Tyndall
Electric Power Systems, Inc. 21 Millpark Ct. Maryland Heights, MO 63043-3536 (314) 890-9999 Fax: (314) 890-9998 www.epsii.com
Electric Power Systems, Inc.
557 E. Juanita Ave., #4 Mesa, AZ 85204 (480) 633-1490 Fax: (480) 633-7092 www.epsii.com
Electric Power Systems, Inc. 4436 Parkway Commerce Blvd. Orlando, FL 32808 (407) 578-6424 Fax: 407-578-6408 www.epsii.com
Electric Power Systems, Inc.
7000 E. 47th Avenue Drive, Suite 100 Denver, CO 80216 (720) 857-7273 Fax: 303-928-8020 www.epsii.com
Electric Power Systems, Inc. 23823 Andrew Rd. Plainfield, IL 60585 (815) 577-9515 Fax: (815) 577-9516 www.epsii.com
Electric Power Systems, Inc.
2601 Center Rd., # 101 Hinckley, OH 44233 (330) 460-3706 Fax: (330) 460-3708 www.epsii.com
Electric Power Systems, Inc.
56 Bibber Pkwy #1 Brunswick, ME 04011 (207) 837-6527 www.epsii.com
Electric Power Systems, Inc. 4100 Greenbriar Dr., Ste. 160 Stafford, TX 77477 (713) 644-5400 www.epsii.com
Electric Power Systems, Inc. 11861 Longsdorf St. Riverview, MI 48193 (734) 282-3311 www.epsii.com
Electric Power Systems, Inc. 827 Union St., Salem, VA 24153 (540) 375-0084 Fax: (540) 375-0094 www.epsii.com
Electric Power Systems, Inc. 915 Holt Ave., Unit 9 Manchester, NH 03109 (603) 657-7371 Fax: 603-657-7370 www.epsii.com
Electric Power Systems, Inc.
146 Space Park Dr. Nashville, TN 37211 (615) 834-0999 Fax: (615) 834-0129 www.epsii.com
Electric Power Systems, Inc. 8515 Cella Alameda NE, Ste. A Albuquerque, NM 87113 (505) 792-7761 www.epsii.com
Electric Power Systems, Inc. 7140 Dean Martin Drive, Suite 900 Las Vegas, NV 89118 (702) 815-1342 www.epsii.com
Dean Hopkins
Electric Power Systems, Inc. 319 US Hwy. 70 E, Unit E Garner, NC 27529 (919) 322-2670 www.epsii.com
Electric Power Systems, Inc. 1090 Montour West Industrial Blvd. Coraopolis, PA 15108 (412) 276-4559 www.epsii.com
Electric Power Systems, Inc. 6141 Connecticut Ave. Kansas City, MO 64120 (816) 241-9990 Fax: (816) 241-9992 www.epsii.com
Electric Power Systems, Inc. 2495 Boulevard of the Generals Norristown, PA 19403 (610) 630-0286 www.epsii.com
Electric Power Systems, Inc. 1129 East Hwy. 30 Gonzalez, LA 70817 (225) 644-0150 Fax: (225) 644-6249 www.epsii.com
Electrical & Electronic Controls 6149 Hunter Rd. Ooltewah, TN 37363 (423) 344-7666 (23) Fax: (423) 344-4494 eecontrols@comcast.net
Michael Hughes
Electrical Energy Experts, Inc. W129N10818, Washington Dr. Germantown, WI 53022 (262) 255-5222 Fax: (262) 242-2360 bill@electricalenergyexperts.com www.electricalenergyexperts.com
William Styer
Electrical Equipment Upgrading, Inc. 21 Telfair Place, Savannah, GA 31415 (912) 232-7402 Fax: (912) 233-4355 kmiller@eeu-inc.com www.eeu-inc.com
Kevin Miller
Electrical Maintenance & Testing Inc. 12342 Hancock St., Carmel, IN 46032 (317) 853-6795 Fax: (317) 853-6799 www.emtesting.com
Brian K. Borst
Electrical Reliability Services 1057 Doniphan Park Circle, Ste. A El Paso, TX 79922 (915) 587-9440 Fax: (915) 587-9010 www.electricalreliability.com
Electrical Reliability Services 1775 W. University Dr., Ste. 128 Tempe, AZ 85281 (480) 966-4568 Fax: (480) 966-4569 www.electricalreliability.com
Electrical Reliability Services 1426 Sens Rd. Ste. 5 Houston, TX 77571 (281) 241-2800 Fax: (281) 241-2801 www.electricalreliability.com
Electrical Reliability Services 4099 SE International Way, Ste. 201 Milwaukie, OR 97222-8853 (503) 653-6781 Fax: (503) 659-9733 www.electricalreliability.com
Electrical Reliability Services 5810 Van Allen Way Carlsbad, CA 92008 (760) 804-2972 www.electricalreliability.com
Electrical Reliability Services 8500 Washington Pl. NE, Ste. A-6 Albuquerque, NM 87113 (505) 822-0237 Fax: (505) 822-0217 www.electricalreliability.com
Electrical Reliability Services 1380 Greg Street, Ste. 217 Sparks, NV 89431 (775) 746-8484 Fax: (775) 356-5488 www.electricalreliability.com
Electrical Reliability Services 2275 Northwest Pkwy SE, Ste. 180 Marietta, GA 30067 (770) 541-6600 Fax: (770) 541-6501 www.electricalreliability.com
Electrical Reliability Services 7100 Broadway, Ste. 7E Denver, CO 80221-2915 (303) 427-8809 Fax: (303) 427-4080 www.electricalreliability.com
Electrical Reliability Services 348 N.W. Capital Dr. Lee's Summit, MO 64086 (816) 525-7156 Fax: (816) 524-3274 www.electricalreliability.com
Electrical Reliability Services 6900 Koll Center Parkway, Ste. 415 Pleasanton, CA 94566 (925) 485-3400 Fax: (925) 485-3436 www.electricalreliability.com
Electrical Reliability Services 10606 Bloomfield Ave. Santa Fe Springs, CA 90670 (562) 236-9555 Fax: (562) 777-8914 www.electricalreliability.com
Electrical Reliability Services 14141 Airline Hwy., Bldg 1; Ste. X Baton Rouge, LA 70817 (225) 755-0530 Fax: (225) 751-5055 www.electricalreliability.com
Electrical Reliability Services 121 Highway 108 East Sulphur, LA 70665 (337) 583-2411 Fax: (337) 583-2410 www.electricalreliability.com
Electrical Reliability Services 11000 Metro Pkwy., Ste. 30 Ft. Myers, FL 33966 (239) 693-7100 Fax: (239) 693-7772 www.electricalreliability.com
Electrical Reliability Services 2222 West Valley Hwy. N., Ste 160 Auburn, WA 98001 (253) 736-6010 Fax: (253) 736-6015 www.electricalreliability.com
Electrical Reliability Services 3412 South 1400 West, Unit A West Valley City, UT 84119 (801) 975-6461 www.electricalreliability.com
Electrical Reliability Services 6351 Hinson St., Ste. B Las Vegas, NV 89118 (702) 597-0020 Fax: (702) 597-0095 www.electricalreliability.com
Electrical Reliability Services 610 Executive Campus Dr. Westerville, OH 43082 (877) 468-6384 Fax: (614) 410-8420 info@electricalreliability.com www.electricalreliability.com
Electrical Reliability Services 9636 St. Vincent, Unit A Shreveport, LA 71106 (318) 869-4244 www.electricalreliability.com
Electrical Reliability Services 6135 Lakeview Rd., Ste 500 Charlotte, NC 28269 (704) 441-1497 www.electricalreliability.com
Electrical Testing, Inc.
2671 Cedartown Hwy. Rome, GA 30161-6791 (706) 234-7623 Fax: (706) 236-9028
steve@electricaltestinginc.com www.electricaltestinginc.com
Electrical Testing Solutions
2909 Green Hill Ct. Oshkosh, WI 54904 (920) 420-2986 Fax: (920) 235-7136 tmachado@electricaltestingsolutions.com www.electricaltestingsolutions.com
Tito Machado
Elemco Services, Inc.
228 Merrick Rd. , Lynbrook, NY 11563 (631) 589-6343 Fax: (631) 589-6670 courtney@elemco.com www.elemco.com
Courtney O'Brien
EnerG Test
204 Gale Lane Bldg. 2 - 2nd Floor Kennett Square, PA 19348 (484) 731-0200 Fax: (484) 713-0209 kbleiler@energtest.com www.energtest.com
Katie Bleiler
Energis High Voltage Resources, Inc. 1361 Glory Rd. Green Bay, WI 54304 (920) 632-7929 Fax: (920) 632-7928 info@energisinc.com www.energisinc.com
Mick Petzold
EPS Technology
29 N. Plains Hwy., Ste. 12 Wallingford, CT 06492 (203) 679-0145 www.eps-technology.com
Grounded Technologies, Inc. 1855 W. Union Avenue, Ste. E Englewood, CO 80110 P-(303) 781-2560 F- (303) 781-5240 jodymedina@groundedtech.com www.groundedtech.com
Jody Medina
Grubb Engineering, Inc. 3128 Sidney Brooks San Antonio, Tx 78235 (210) 658-7250 Fax: (210) 658-9805 joy@grubbengineering.com www.grubbengineering.com
Robert D. Grubb Jr.
Hampton Tedder Technical Services 4571 State St. Montclair, CA 91763 (909) 628-1256 x214 Fax: (909) 628-6375 matt.tedder@hamptontedder.com www.hamptontedder.com
Matt Tedder
Hampton Tedder Technical Services 4920 Alto Ave. Las Vegas, NV 89115 (702) 452-9200 Fax: (702) 453-5412 www.hamptontedder.com
Roger Cates
Hampton Tedder Technical Services 3747 West Roanoke Ave. Phoenix, AZ 85009 (480) 967-7765 Fax: (480) 967-7762 www.hamptontedder.com
Harford Electrical Testing Co., Inc. 1108 Clayton Rd. Joppa, MD 21085 (410) 679-4477 Fax: (410) 679-0800 testing@harfordtesting.com www.harfordtesting.com
Vincent Biondino
High Energy Electrical Testing, Inc. 515 S. Ocean Ave. Seaside Park, NJ 08752 (732) 938-2275 Fax: (732) 938-2277 hinrg@comcast.net www.highenergyelectric.com
Charles Blanchard
High Voltage Maintenance Corp. 24 Walpole Park South Dr. Walpole, MA 02081 (508) 668-9205 www.hvmcorp.com
High Voltage Maintenance Corp. 941 Busse Rd. Elk Grove Village, Il 60007 (847) 640-0005 www.hvmcorp.com
High Voltage Maintenance Corp. 7200 Industrial Park Blvd. Mentor, OH 44060 (440) 951-2706 Fax: (440) 951-6798 www.hvmcorp.com
High Voltage Maintenance Corp. 3000 S. Calhoun Rd. New Berlin, WI 53151 (262) 784-3660 Fax: (262) 784-5124 www.hvmcorp.com
High Voltage Maintenance Corp. 8320 Brookville Rd. #E Indianapolis, IN 46239 (317) 322-2055 Fax: (317) 322-2056 www.hvmcorp.com
High Voltage Maintenance Corp. 1250 Broadway, Ste. 2300 New York, NY 10001 (718) 239-0359 www.hvmcorp.com
High Voltage Maintenance Corp. 355 Vista Park Dr. Pittsburgh, PA 15205-1206 (412) 747-0550 Fax: (412) 747-0554 www.hvmcorp.com
High Voltage Maintenance Corp. 150 North Plains Industrial Rd. Wallingford, CT 06492 (203) 949-2650 Fax: (203) 949-2646 www.hvmcorp.com
High Voltage Maintenance Corp. 9305 Gerwig Ln., Ste. B Columbia, MD 21046 (410) 309-5970 Fax: (410) 309-0220 www.hvmcorp.com
High Voltage Maintenance Corp. 24371 Catherine Industrial Dr, Ste. 207 Novi, MI 48375 (248) 305-5596 Fax: (248) 305-5579 www.hvmcorp.com
High Voltage Maintenance Corp. 5100 Energy Dr. Dayton, OH 45414 (937) 278-0811 Fax: (937) 278-7791 www.hvmcorp.com
High Voltage Service, LLC 4751 Mustang Circle St. Paul, MN 55112 (763) 784-4040 Fax: (763) 784-5397 www.hvserviceinc.com Mike Mavetz
HMT, Inc. 6268 Route 31 Cicero, NY 13039 (315) 699-5563 Fax: (315) 699-5911 jpertgen@hmt-electric.com www.hmt-electric.com
John Pertgen
Industrial Electric Testing, Inc. 11321 West Distribution Ave. Jacksonville, FL 32256 (904) 260-8378 Fax: (904) 260-0737 gbenzenberg@bellsouth.net www.industrialelectrictesting.com Gary Benzenberg
Industrial Electric Testing, Inc. 201 NW 1st Ave. Hallandale, FL 33009-4029 (954) 456-7020 www.industrialelectrictesting.com
Industrial Electronics Group 850369 Highway 17 South P.O. Box 1870 Yulee, FL 32041 (904) 225-9529 Fax: (904) 225-0834 butch@industrialgroups.com www.industrialgroups.com
Butch E. Teal
Industrial Tests, Inc. 4021 Alvis Ct., Ste. 1 Rocklin, CA 95677 (916) 296-1200 Fax: (916) 632-0300 greg@indtest.com www.industrialtests.com
Greg Poole
Infra-Red Building and Power Service 152 Centre St. Holbrook, MA 02343-1011 (781) 767-0888 Fax: (781) 767-3462 tom.mcdonald@infraredbps.com www.infraredbps.com
Thomas McDonald Sr.
Longo Electrical-Mechanical, Inc. One Harry Shupe Blvd., Box 511 Wharton, NJ 07885 (973) 537-0400 Fax: (937) 537-0404 jmlongo@elongo.com www.elongo.com
Joe Longo
Longo Electrical-Mechanical, Inc. 1625 Pennsylvania Ave. Linden, NJ 07036 (908) 925-2900 Fax: (908) 925-9427 jmlongo@elongo.com www.elongo.com
Joe Longo
Longo Electrical-Mechanical, Inc. 1400 F Adams Rd. Bensalem, PA 19020 (215) 638-1333 Fax: (215) 638-1366 jmlongo@elongo.com www.elongo.com
Joe Longo
M&L Power Systems, Inc. 109 White Oak Ln., Ste. 82 Old Bridge, NJ 08857 (732) 679-1800 Fax: (732) 679-9326 milind@mlpower.com www.mlpower.com
Milind Bagle
Magna Electric Corporation 1033 Kearns Crescent, Box 995 Regina, SK S4P 3B2 Canada (306) 949-8131 Fax: (306) 522-9181 kheid@magnaelectric.com www.magnaelectric.com
Kerry Heid
Magna Electric Corporation 3430 25th St. NE Calgary, AB T1Y 6C1 Canada (403) 769-9300 Fax: (403)769-9369 cgrant@magnaelectric.com www.magnaelectric.com
Cal Grant
Magna Electric Corporation 851-58th St. East Saskatoon, SK S7K 6X5 Canada (306) 955-8131 Fax: (306) 955-9181 ajaques@magnaelectric.com www.magnaelectric.com
Adam Jaques
Magna Electric Corporation 1375 Church Ave. Winnipeg, MB R2X 2T7 Canada (204) 925-4022 Fax: (204) 925-4021 cbrandt@magnaelectric.com www.magnaelectric.com
Curtis Brandt
Magna Electric Corporation 3731-98 Street Edmonton, AB T6E 5N2 Canada (780) 436-8831 Fax: (780) 463-9646 fgranacher@magnaelectric.com www.magnaelectric.com
Franz Granacher
Magna IV Engineering 1103 Parsons Rd. SW Edmonton, AB T6X 0X2 Canada (780) 462-3111 Fax: (780) 450-2994 info@magnaiv.com www.magnaiv.com
Dave Emerson
Magna IV Engineering 200, 688 Heritage Dr. Calgary, AB T2H 1M6 Canada (403) 723-0575 Fax: (403) 723-0580 info.calgary@magnaiv.com
Virginia Balitski
Magna IV Engineering 8219D Fraser Ave. Fort McMurray, AB T9H 0A2 Canada (780) 791-3122 Fax: (780) 791-3159 info.fmcmurray@magnaiv.com
Ryan Morgan
Magna IV Engineering 96 Inverness Dr. East, Unit R Englewood, CO 80112 (303) 799-1273 Fax: (303) 790-4816 info.denver@magnaiv.com Aric Proskurniak
Magna IV Engineering Avenida del Condor #590 Oficina 601 Huechuraba, Santiago 8580676 Chile +(56) 9-9-517-4642 info.chile@magnaiv.com
Cristian Fuentes
Magna IV Engineering 1040 Winnipeg St. Regina , SK S4R 8P8 Canada (306) 585-2100 Fax: (306) 585-2191 info.regina@magnaiv.com
Andrew Westerman
Magna IV Engineering 106, 4268 Lozells Ave. Burnaby, BC VSA 0C6 Canada (604) 421-8020
William Kulsky
NETA ACCREDITED COMPANIES
Magna IV Engineering
1005 Spinney Dr. Dawson Creek, BC V1G 1K1 Canada (780) 462-3111 Fax: (780) 462-9799 info@magnaiv.com
David Limb
National Field Services 649 Franklin St. Lewisville, TX 75057 (972) 420-0157 www.natlfield.com
Eric Beckman
Nationwide Electrical Testing, Inc. 6050 Southard Trace Cumming, GA 30040 (770) 667-1875 Fax: (770) 667-6578 Shashi@N-E-T-Inc.com www.n-e-t-inc.com
Shashikant B. Bagle
North Central Electric, Inc. 69 Midway Ave. Hulmeville, PA 19047-5827 (215) 945-7632 Fax: (215) 945-6362 ncetest@aol.com
Robert Messina
Northern Electrical Testing, Inc. 1991 Woodslee Dr. Troy, MI 48083-2236 (248) 689-8980 Fax: (248) 689-3418
ldetterman@northerntesting.com www.northerntesting.com
Lyle Detterman
Orbis Engineering Field Services Ltd. #300, 9404 - 41st Ave. Edmonton, AB T6E 6G8 Canada (780) 988-1455 Fax: (780) 988-0191 lorne@orbisengineering.net www.orbisengineering.net
Lorne Gara
Pacific Power Testing, Inc. 14280 Doolittle Dr. San Leandro, CA 94577 (510) 351-8811 Fax: (510) 351-6655 steve@pacificpowertesting.com www.pacificpowertesting.com
Steve Emmert
Pacific Powertech, Inc. #110, 2071 Kingsway Ave. Port Coquitlam, BC V3C 1T2 Canada (604) 944-6697 Fax: (604) 944-1271 jkonkin@pacificpowertech.ca www.pacificpowertech.ca
Josh Konkin
Phasor Engineering
Sabaneta Industrial Park #216 Mercedita, PR 00715 Puerto Rico (787) 844-9366 Fax: (787) 841-6385 rcastro@phasorinc.com
Rafael Castro
Potomac Testing, Inc. 1610 Professional Blvd., Ste. A Crofton, MD 21114 (301) 352-1930 Fax: (301) 352-1936 kbassett@potomactesting.com www.potomactesting.com
Ken Bassett
Potomac Testing, Inc. 11179 Hopson Rd., Ste. 5 Ashland, VA 23005 (804) 798-7334 Fax: (804) 798-7456 www.potomactesting.com
Power & Generation Testing, Inc. 480 Cave Rd. Nashville, TN 37210 (615) 882-9455 Fax: (615) 882-9591 mose@pgti.net www.pgti.net
Mose Ramieh
Power Engineering Services, Inc. 9179 Shadow Creek Lane Converse, TX 78109 (210) 590-4936 Fax: (210) 590-6214 engelke@pe-svcs.com www.pe-svcs.com
Miles R. Engelke
POWER PLUS Engineering, Inc. 46575 Magallan Dr. Novi, MI 48377 (248) 344-0200 Fax: (248) 305-9105 smancuso@epowerplus.com www.epowerplus.com
Salvatore Mancuso
Power Products & Solutions, LLC 12465 Grey Commercial Rd. Midland, NC 28107 (704) 573-0420 x12 Fax: (704) 573-3693 ralph.patterson@powerproducts.biz www.powerproducts.biz
Ralph Patterson
Power Products & Solutions, LLC 13 Jenkins Ct. Mauldin, SC 29662 (800) 328-7382 ralph.patterson@powerproducts.biz www.powerproducts.biz
Raymond Pesaturo
Power Services, LLC 998 Dimco Way, P.O. Box 750066 Centerville, OH 45475 (937) 439-9660 Fax: (937) 439-9611 mkbeucler@aol.com
Mark Beucler
Power Solutions Group, Ltd. 425 W. Kerr Rd. Tipp City, OH 45371 (937) 506-8444 Fax: (937) 506-8434 bwilloughby@powersolutionsgroup.com www.powersolutionsgroup.com
Barry Willoughby
Power Solutions Group, Ltd. 135 Old School House Rd. Piedmont, SC 29673 (864) 845-1084 Fax:: (864) 845-1085 fcrawford@powersolutionsgroup.com www.powersolutionsgroup.com
Anthony Crawford
Power Solutions Group, Ltd. 670 Lakeview Plaza Blvd. Columbus, OH 43085 (614) 310-8018 sspohn@powersolutionsgroup.com www.powersolutionsgroup.com
Stuart Spohn
Power Systems Testing Co. 4688 W. Jennifer Ave., Ste. 108 Fresno, CA 93722 (559) 275-2171 ext 15 Fax: (559) 275-6556 dave@pstcpower.com www.powersystemstesting.com
David Huffman
Power Systems Testing Co. 600 S. Grand Ave., Ste. 113 Santa Ana, CA 92705-4152 (714) 542-6089 Fax: (714) 542-0737 www.powersystemstesting.com
Power Systems Testing Co. 6736 Preston Ave, Ste. E Livermore, CA 94551 (510) 783-5096 Fax: (510) 732-9287 www.powersystemstesting.com
Power Test, Inc. 2200 Highway 49 Harrisburg, NC 28075 (704) 200-8311 Fax: (704) 455-7909 rich@powertestinc.com www.powertestinc.com
Richard Walker
POWER Testing and Energization, Inc. 14006 NW 3rd Ct., Ste. 101 Vancouver, WA 98685 (360) 576-4826 Fax: (360) 576-7182 chris.zavadlov@powerte.com www.powerte.com
Chris Zavadlov
POWER Testing and Energization, Inc. 731 E. Ball Rd., Ste. 100 Anaheim, CA 92805 (714) 507-2702 www.powerte.com
POWER Testing and Energization, Inc. 22035 70th Ave. South Kent, WA 98032 (253) 872-7747 www.powerte.com
Powertech Services, Inc.
4095 South Dye Rd. Swartz Creek, MI 48473-1570 (810) 720-2280 Fax: (810) 720-2283 kirkd@powertechservices.com www.powertechservices.com Kirk Dyszlewski
Precision Testing Group
5475 Highway 86, Unit 1 Elizabeth, CO 80107 (303) 621-2776 Fax: (303) 621-2573 glenn@precisiontestinggroup.com Glenn Stuckey
PRIT Service, Inc.
112 Industrial Dr., P.O. Box 606 Minooka, IL 60447 (815) 467-5577 Fax: (815) 467-5883 Rod.Hageman@pritserviceinc.com www.pritserviceinc.com Rod Hageman
Reuter & Hanney, Inc.
149 Railroad Dr. Northampton Industrial Park Ivyland, PA 18974 (215) 364-5333 Fax: (215) 364-5365 mikereuter@reuterhanney.com www.reuterhanney.com
Michael Reuter
Reuter & Hanney, Inc.
4270-I Henninger Ct. Chantilly, VA 20151 (703) 263-7163 Fax: 703-263-1478 www.reuterhanney.com
Reuter & Hanney, Inc.
11620 Crossroads Circle, Suites D-E Middle River, MD 21220 (410) 344-0300 Fax: (410) 335-4389 www.reuterhanney.com
Michael Jester
REV Engineering, LTD
3236 - 50 Ave. SE Calgary, AB T2B 3A3 Canada (403) 287-0156 Fax: (403) 287-0198 rdavidson@reveng.ca www.reveng.ca
Roland Nicholas Davidson, IV
Saber Power Services 9841 Saber Power Lane Rosharon, TX 77583-5188 (713) 222-9102 info@saberpower.com www.saberpower.com
Phil Collins
Scott Testing Inc. 1698 5th St. Ewing, NJ 08638 (609) 882-2400 Fax: (609) 882-5660 rsorbello@scotttesting.com www.scotttesting.com
Russ Sorbello
Shermco Industries 2425 E. Pioneer Dr. Irving, TX 75061 (972) 793-5523 Fax: (972) 793-5542 rwidup@shermco.com www.shermco.com
Ron Widup
Shermco Industries 1705 Hur Industrial Blvd. Cedar Park, TX 78613 (512) 267-4800 Fax: (512) 258-5571 kewing@shermco.com www.shermco.com
Kevin Ewing
Shermco Industries 33002 FM 2004 Angleton, TX 77515 (979)848-1406 Fax: (979) 848-0012 mfrederick@shermco.com www.shermco.com Malcom Frederick
Shermco Industries 1357 N. 108th E. Ave. Tulsa, OK 74116 (918) 234-2300 jharrison@shermco.com www.shermco.com
Jim Harrison
Shermco Industries 796 11th St. Marion, IA 52302 (319) 377-3377 Fax: (319) 377-3399
Lhamrick@shermco.com www.shermco.com
Lynn Hamrick
Shermco Industries 2100 Dixon St., Ste. C Des Moines, IA 50316 (515) 263-8482 LHamrick@shermco.com www.shermco.com
Lynn Hamrick
Shermco Industries Boulevard Saint-Michel 47 1040 Brussels Brussels, Belgium +32 (0)2 400 00 54 Fax: +32 (0)2 400 00 32 PIdziak@shermco.com www.shermco.com
Paul Idziak
Shermco Industries
12000 Network Blvd., Bldg D,, Ste. 410 San Antonio, TX 78249 (512) 267-4800 Fax: (512) 267-4808 kewing@shermco.com www.shermco.com
Kevin Ewing
Sigma Six Solutions, Inc. 2200 West Valley Hwy., Ste. 100 Auburn, WA 98001 (253) 333-9730 Fax: (253) 859-5382 jwhite@sigmasix.com www.sigmasix.com
John White
Southern New England Electrical Testing, LLC 3 Buel St., Ste. 4 Wallingford, CT 06492 (203) 269-8778 Fax: (203) 269-8775 dave.asplund@sneet.org www.sneet.org
David Asplund, Sr.
Southwest Energy Systems, LLC 2231 East Jones Ave., Ste. A Phoenix, AZ 85040 (602) 438-7500 Fax: (602) 438-7501 bob.sheppard@southwestenergysystems.com www.southwestenergysystems.com
Robert Sheppard
Taurus Power & Controls, Inc. 9999 SW Avery St. Tualatin, OR 97062-9517 (503) 692-9004 Fax: (503) 692-9273 robtaurus@tauruspower.com www.tauruspower.com
Rob Bulfinch
Taurus Power & Controls, Inc. 6617 S. 193rd Place, Ste. P104 Kent, WA 98032 (425) 656-4170 Fax: (425) 656-4172 jiml@tauruspower.com www.tauruspower.com
Jim Lightner
3C Electrical Co., Inc. 40 Washington St. Westborough, MA 01581 (508) 881-3911 Fax: (508) 881-4814 jim@three-c.com www.three-c.com
Jim Cialdea
3C Electrical Co., Inc. 72 Sanford Dr. Gorham, ME 04038 (800) 649-6314 Fax: (207) 782-0162 jim@three-c.com www.three-c.com
Jim Cialdea
Tidal Power Services, LLC 4202 Chance Lane Rosharon, TX 77583 (281) 710-9150 Fax: (713) 583-1216 monty.janak@tidalpowerservices.com www.tidalpowerservices.com
Monty C. Janak
Tidal Power Services, LLC 8184 Highway 44, Ste. 105 Gonzales, LA 70737 (225) 644-8170 Fax: (225) 644-8215 www.tidalpowerservices.com
Darryn Kimbrough
Tidal Power Services, LLC 1056 Mosswood Dr. Sulphur, LA 70663 (337) 558-5457 Fax: (337) 558-5305 www.tidalpowerservices.com
Steve Drake
Tony Demaria Electric, Inc. 131 West F St. Wilmington, CA 90744 (310) 816-3130 (310) 549-9747 neno@tdeinc.com www.tdeinc.com
Nenad Pasic
Trace Electrical Services & Testing, LLC 293 Whitehead Rd. Hamilton, NJ 08619 (609) 588-8666 Fax: (609) 588-8667 jvasta@tracetesting.com www.tracetesting.com
Joseph Vasta
Utilities Instrumentation Service, Inc. 2290 Bishop Circle East Dexter, MI 48130 (734) 424-1200 Fax: (734) 424-0031 GEWalls@UISCorp.com www.uiscorp.com
Gary E. Walls
Utility Service Corporation 4614 Commercial Dr. NW Huntsville, AL 35816-2201 (256) 837-8400 Fax: (256) 837-8403 apeterson@utilserv.com www.utilserv.com
Alan D. Peterson
Western Electrical Services, Inc. 14311 29th St. East Sumner , WA 98390 (253) 891-1995 Fax: (253) 891-1511 dhook@westernelectricalservices.com www.westernelectricalservices.com
Dan Hook
Western Electrical Services, Inc. 3676 W. California Ave., #C, 106 Salt Lake City, UT 84104 (253) 891-1995 Fax: (253) 891-1511
rcoomes@westernelectricalservices.com www.westernelectricalservices.com
Rob Coomes
Western Electrical Services, Inc. 5680 South 32nd St. Phoenix, AZ 85040 (602) 426-1667 Fax: (253) 891-1511 carcher@westernelectricalservices.com www.westernelectricalservices.com
Craig Archer
Western Electrical Services, Inc. 4510 NE 68th Dr., Ste. 122 Vancouver, WA 98661 (888) 395-2021 Fax: (253) 891-1511
Tasciutto@westernelectricalservices.com www.westernelectricalservices.com
Tony Asciutto
This issue’s advertisers are identified below. Please thank these advertisers by telling them you saw their advertisement in YOUR magazine –NETA World.
1997 - 2001: TR-Spy Still Supported
2001 - 2010: TR-Spy Mark II Still Supported
2010 - Present: TR-Mark III Still Supported
Raytech supports every product we’ve ever introduced.
You need equipment that remains functional, even after it’s no longer sold. We fully support all of our products for the entire time you own them.
Raytech stands behind its custom-made, high-quality measuring and testing equipment developed and produced for the international power industry.
Dad says that with 33 lbs the compact VOTANO 100 is the first mobile voltage transformer test device to also offer high accuracy. He can simply carry it with him to each test site and his back doesn’t even hurt. And VOTANO 100 is fast.
The measured results are automatically assessed immediately after the test in accordance with IEEE and IEC standards. VOTANO 100 uses a similar modeling method like the one Dad already knows from OMICRON’s CT Analyzer. The results are reliable, he says.
The unit controls a separate 4 kV amplifier, VBO1, which is placed in the dangerous high-voltage environment from where it provides the necessary test voltages. This ensures Dad’s safety as he conducts the test remotely with VOTANO 100.
Mobile, accurate and safe...Dad’s really enthusiastic!