
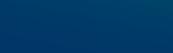
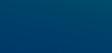

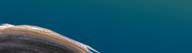
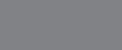
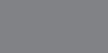
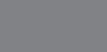

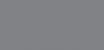
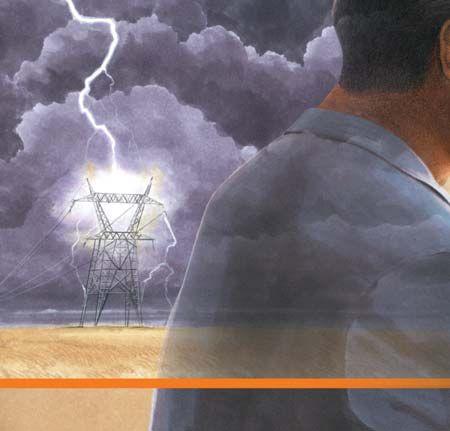
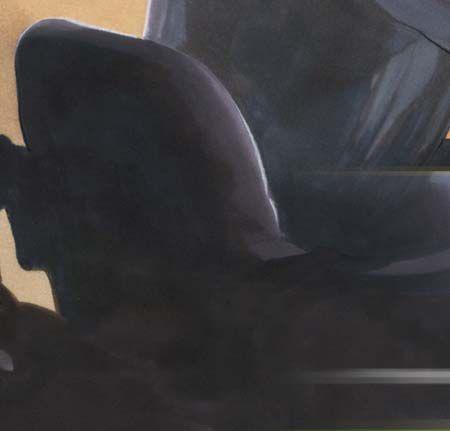

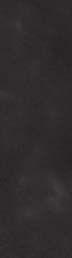

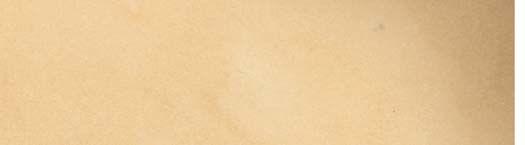

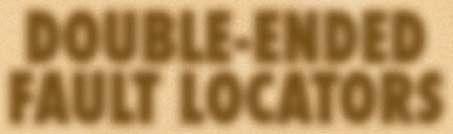
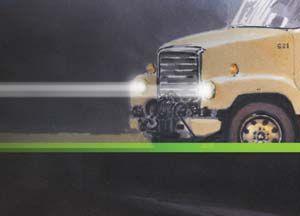
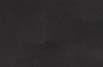


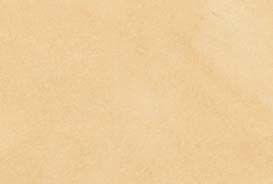

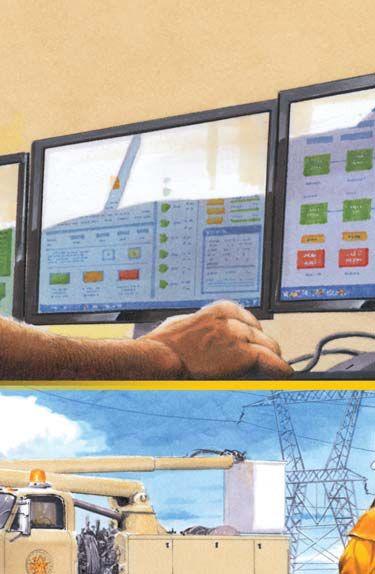
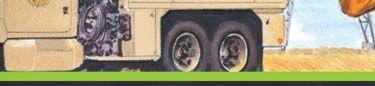






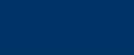
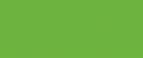




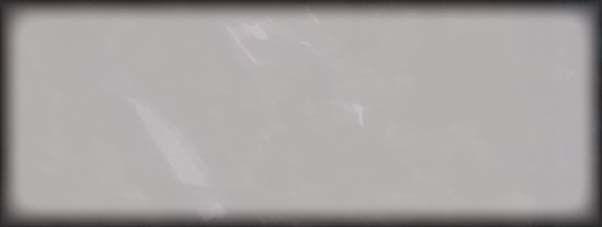
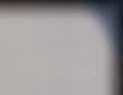
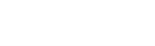


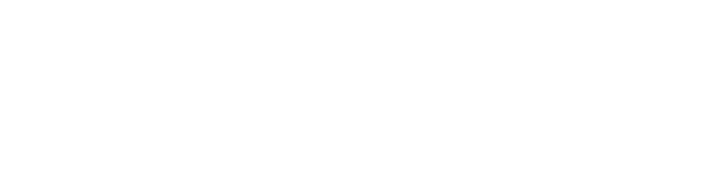
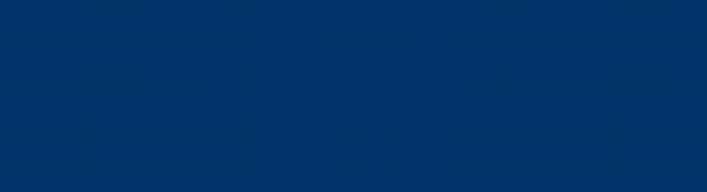

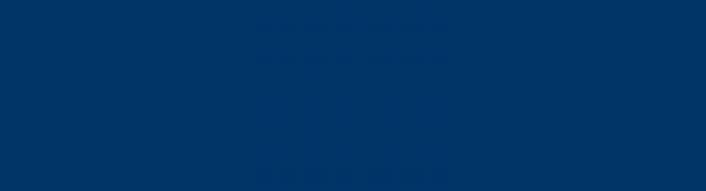
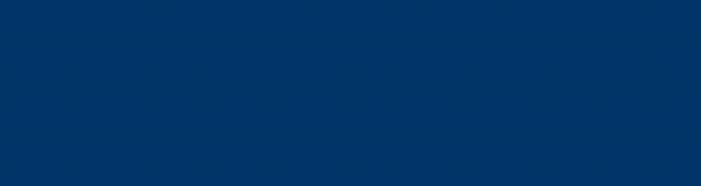
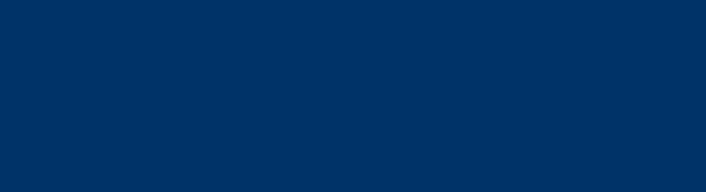

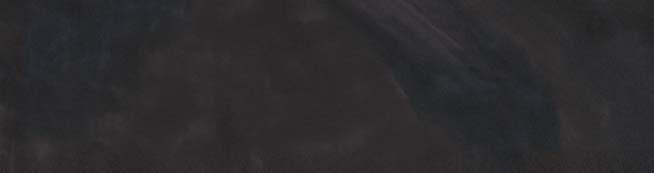
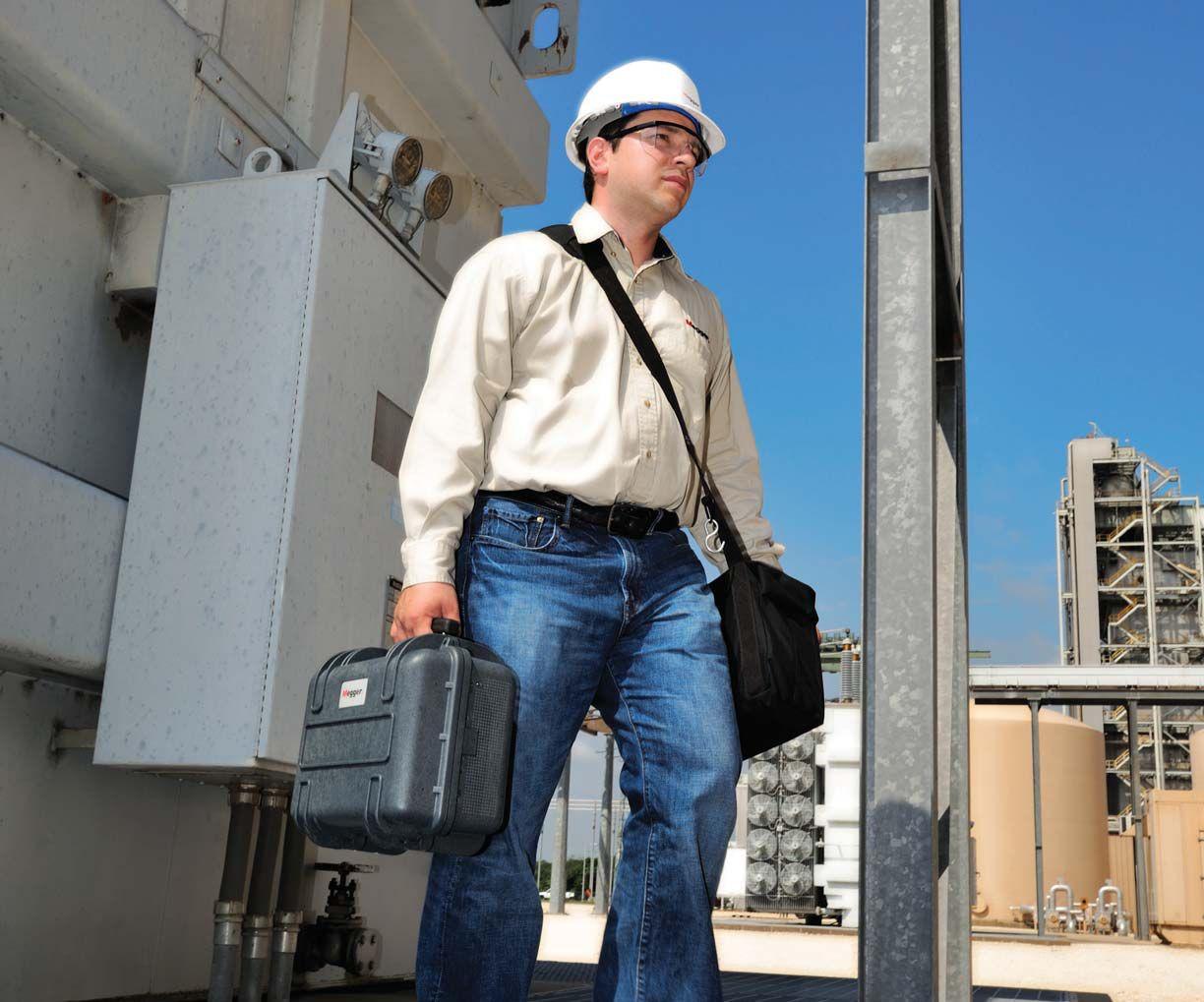
The SMRT36 is the smallest, lightest, highest output powered, complete 3-phase protective relay test system in the world today. This rugged test system may be customized by adding the voltage current generator modules needed for specific test applications. Manual operation is simple through the use of the Smart Touch View Interface (STVI), with a large color high resolution TFT LCD touch-screen.
Rugged, small and lightweight
High current, high power (60 Amps/300 VArms) per phase
Up to 6 currents with convertible channels
Thermally controlled fans for quiet operation
New Smart Touch View Interface (STVI) provides manual control
New STVI Overcurrent Test includes hundreds of relay specific time-curves built-in
With these comprehensive capabilities and extensive testing options the SMRT36 is conceivably the easiest to use 3-phase protective relay test system available today.
For more information on the SMRT36 relay test set contact us today at 1-800-723-2861 or email us at sales@megger.com to receive a SMRT36 brochure and Megger 2012 Power Catalog.
Megger
4271 Bronze Way Dallas, Texas 75237-1019
22 END-TO-ENDTESTINGDOUBLEEND-TO-END TESTING DOUBLEENDEDFAULTLOCATORSFOR ENDED FAULT LOCATORS FOR HIGH-VOLTAGEOVERHEAD HIGH-VOLTAGE OVERHEAD TRANSMISSIONLINES TRANSMISSION LINES
By Steve Turner, Beckwith Electric Company, Inc.High magnitude current flows through the conductor and connected equipment to the point of the disturbance when a fault (for example, lightning strike) occurs on an overhead, high-voltage transmission line. The heavy current can quickly damage the line conductor and connected equipment (for example, transformer bank).
FEATURES
7 PRESIDENT’S DESK
Mose Ramieh, Power & Generation Testing, Inc.
NETA President
38GPS TESTING, THE FUTURE OF TESTING
By Will Knapek, OMICRON Electronics
84 AN INTRODUCTION TO END-TO-END TESTING
By Chris Werstiuk, Manta Test Systems
11THE NFPA 70E AND NETA
An Update on the Process and Status of the 2015 Edition of NFPA 70E
Jim White & Ron Widup, Shermco Industries
68NICHE MARKET TESTING
Data Center Maintenance–Part 2–
The Electrical Infrastructure System
Lynn Hamrick, Shermco Industries
78TESTING ROTATING MACHINERY
Partial Discharge Test
Vicki Warren, Iris Power LP.
93 NO-OUTAGE
INSPECTION CORNER
Optimum Medium-Voltage Cable System
Testing Strategy
Don A. Genutis, No-Outage Electrical Testing, Inc.
102SAFETY CORNER
Performing Personnel Audits
Paul Chamberlain, American Electrical Testing Co.
108TECH TIPS
Variations in the Measurement of Resistivity
Jeff Jowett, Megger
SPECIFICATIONSAND SPECIFICATIONS AND STANDARDSACTIVITY STANDARDS ACTIVITY
114CSA UPDATES
Kerry Heid, Magna Electric Corp.
119ANSI/NETA STANDARDS UPDATES
INDUSTRYTOPICS INDUSTRY TOPICS
56SUCCESS IN SMALL ENGINEERING BUSINESS
John White, Sigma Six Solutions
18KEEPING THE WINDS OF CHANGE TO OUR BACK
Jill Howell
34SHERMCO INDUSTRIES OPENS NEW LOCATION
44DUDE ELECTRICAL TESTING LLC JOINS THE RANKS AS A NETA ACCREDITED COMPANY
46AN INSIDE LOOK AT THE NEW WORLD TRADE CENTER
Jill Howell
SOLUTIONS JOINS THE RANKS AS A NETA ACCREDITED COMPANY
67ENERGIS PROUDLY JOINS THE RANKS AS A NETA ACCREDITED COMPANY
74THE NETA ALLIANCE PROGRAM
Jill Howell
98WHAT HAPPENS AT NETA MEETINGS
Kristen Wicks
113NETA AND FRIENDS AT IEEE PCIC 2012
Sara Dillon
120NETA ACCREDITED COMPANIES
126ADVERTISER LIST
February 18 – 21, 2013
Sheraton New Orleans
New Orleans, Louisiana
The Premier Electrical Maintenance and Safety Event EARLY BIRD REGISTRATION NOW OPEN
PowerTest 2013 returns to New Orleans, a city where the culture has made it a favorite of travelers throughout the world; it is a place that exudes passion for building the future while honoring the knowledge of the past.
PowerTest 2013 energizes and renews the commitment to improving safety and reliability, sharing experiences, and growing the collective knowledge within the electrical power systems industry. This event brings together experts, technicians, managers, inspector, contractors, engineers, manufacturers, operators - industry leaders all working to build a better future on a global scale.
JIM O’NEIL Quanta Services
James F. O’Neil serves as chief executive officer and president of Quanta Services. In this position, he oversees the company’s operations and strategic initiatives across the electric power, natural gas, renewable energy, telecommunications, broadband cable, and wireless industries.
Join us Sunday evening for the PowerTest 2013 Second Line Parade. We’ll gather at the Sheraton hotel and be led by a Grand Marshall, a 40 piece band, and costumed characters, into the heart of the French Quarter. A private Bourbon Street balcony awaits with refreshments, a five-course meal featuring Cajun and Creole foods, and music for kicking up your heels.
Sunday, February 17, 5:30 PM – 9:30 PM Sign up when you register online. $165 per person. Sponsored by
Sound the trumpets and dance in the streets! NETA is jazzed up to showcase some of the best presenters in the industry. Participate in a full day of engaging, 45-minute presentations sure to spark your thinking and power up new ideas. Choose from detailed technical paper track topics and participate in the Arc-Flash Mitigation Symposium.
SAFETY
◆ Electrical Safety Myths and Misconceptions
Jim White, Shermco Industries
◆ Electrical Safety Through Design, Installation, and Maintenance
Dennis K. Neitzel, AVO Training Institute, Inc.
◆ Internal Electrical Safety Audit
Terry Becker, P.E., ESPS Electrical Safety Program Solutions, Inc.
◆ Electrical Safety – A New Paradigm
David Ian Windley, WINTEK Engineering, Ltd.
◆ An Effective Electrical Safety Program
Daryld Ray Crow, DRC Consultants, Ltd
◆ Finding and Retaining Qualified Electrical Workers: It’s About Safety in the Workplace
Mike Moore, Shermco Industries
RELIABILITY
◆ Detecting Common Power Quality Issues
Andrew P. Sagl, Megger
◆ Risk, Reliability, and Relationships: The Art and Science of Transformer Maintenance
Alan Ross, SD Myers
◆ Go Green or Go Home
Noah Bethel, PdMA Corporation
◆ Transformer Diagnostics Using Dissolved Gas and Furans
Melvin Wright, LICA Transformer Consulting
◆ Role of On-Line Condition Monitoring for Power Transformer Operation and Maintenance
Tony McGrail, Doble Engineering Co.
Kenneth Elkinson, Doble Engineering Co.
◆ The Hidden Gems in Power Quality Monitoring
Ross M. Ignall, Dranetz Technologies
RELAY
◆ Applying 100 Percent Stator Ground Fault Protection for Generators via Low Frequency Injection
Steve Turner, Beckwith Electric Company
◆ Meaningful Testing of Protection Schemes
Jay Gosalia, Doble Engineering Co.
◆ Why Should We Measure Line Impedance? Will Knapek, OMICRON electronics Corp. USA
◆ Applying and Commissioning Transformer Protection
Scott Cooper, Manta Test Systems
◆ Why Apply Protective Relays?
Karl Zimmerman, Schweitzer Engineering Laboratories, Inc.
◆ Utilizing Ground Fault Resistance to Accurately Test Distance Elements
Jason Buneo, Megger
◆ I Have A Lot of Numbers, What Do They Mean: Basic Interpretation of Two-Winding Transformer Data
William Keith Hill, Doble Engineering Co.
◆ DC Winding Resistance: Theory Versus Practice
Charles Sweetser, OMICRON electronics Corp. USA
◆ VLF MWT – How to Apply the New Way of Cable Condition Assessment
Martin Jenny, BAUR
◆ Are You Really Testing Your Instrument Transformers?
Mike Hancock, Shermco Industries
◆ Partial Discharge of Rotating Machines – Is it Science or Black Magic?
Vicki Warren, Iris Power LP
◆ Partial Discharge Substation RFI Surveying, UHF On-Line Testing of Transformer and Acoustic Location of PD
Gregory Thomas Topjian, Doble Engineering Co.
◆ Troubleshooting Circuit Breaker Control Schemes
Rick Youngblood, Doble Engineering Co.
◆ Predicting the Remaining Life of Service Aged Vacuum Interrupters
John Cadick, Cadick Corporation
Finley Ledbetter, Group CBS
◆ Testing and Troubleshooting of Low- to Medium-Voltage Circuit Breakers
Bret Alan Hammonds, Megger
Robert Foster, Megger
SYMPOSIUM ON ARC-FLASH MITIGATION
Moderator: Rod Hageman, PRIT Service, Inc.
TUESDAY MORNING
Join in the discussion during the Tuesday morning panel sessions. Select two of the four panel topics and get ready to learn from experts and peers, alike.
SAFETY
Moderator: Jim White, Shermco Industries
Panelists: Al Winfield, Cadick Corporation, Dennis Neitzel, AVO Training Institute, Inc., Ray Crow, DRC Consultants, Ltd., Daleep Mohla, DCM Elect Consulting Services
MOTORS AND GENERATORS
Moderator: Calvin Earp, Shermco Industries
Panelists: Vicki Warren, Iris Power LP, Noah Bethel, PdMA Corporation
MEDIUM-VOLTAGE CABLES
Moderator: Tony Demaria, Tony Demaria Electric
Panelists: Craig Goodwin, HV Diagnostics, Inc., Mark Walton, General Cable Corporation, Oscal Morel, UtilX Corporation, Rick Eynon, Eynon Power
CIRCUIT BREAKERS
Moderator: Eric Beckman, National Field Services
Panelist: Finley Ledbetter, Group CBS, Malcom Frederick, Shermco Industries, Dan Hook, Western Eleectrical Services Inc.
TUESDAY AFTERNOON
POWERTEST 2013 TRADE SHOW
PowerTest 2013 features more than 100 exhibits from top-tier electrical power vendors. No other show brings together this many companies focused on electrical safety and maintenance. See you on Tuesday!
TUESDAY EVENING POWERBASH
Sponsored by
PowerBash 2013 is the culmination of two days of intense conference sessions and marks the commencement an additional two days of high-impact seminars. Everyone who’s anyone is sure to be there.
WEDNESDAY - THURSDAY
Take advantage of a unique opportunity to choose from 12 in-depth, 4-hour seminars on Wednesday and Thursday.
SEMINAR TITLES:
◆ Symmetrical Components – FUNdamentals and Practical Application Examples
Karl Zimmerman, Schweitzer Engineering Laboratories, Inc.
Dave Costello, Schweitzer Engineering Laboratories, Inc.
◆ How Do They Do It? Electrical Power Measurement Methods, Practices, and Standards
Ross Ignall, Dranetz
◆ Failure Processes in Rotating Equipment
Vicki Warren, Iris Power LP
◆ Maintaining and Testing Low and Medium-Voltage Circuit Breakers
Dave Smith, Canada Training Group
◆ Maintaining Your Protective Relay Sanity
Dennis Moon, AVO Training Institute, Inc.
◆ Proper Techniques in Oil Sampling
David Koehle, Doble Engineering Co.
Lance Lewand, Doble Engineering Co.
◆ PMU Testing Requirements
Scott Short, Doble Engineering Co.opy
◆ Advanced Condition Assessment of Power, Distribution, and Instrument Transformers
Dr. Diego Robalino, Megger
Dinesh Chhajer, Megger
◆ Battery Maintenance and Testing
Rod VanWart, AVO Training Institute
◆ Medium-Voltage Cable Testing Utilizing VLF Technology: A Primer on the Application and Data Interpretation
Craig Goodwin, HV Diagnostics Inc.
◆ Hazards of Electricity, Shock, Arc, and Blast:
An Educational Journey Through Case Studies
Jim White, Shermco Industries
◆ The Field Repair and Adjustment of Low-Voltage Power Circuit Breakers
Malcolm Frederick, Shermco Industries
Jim Miller, Shermco Industries
Hospitality Sui tes
Monday, February 18, 6:00 PM – 10:00 PM
Mingle with a host of leaders at Monday night’s Hospitality Suites. Talk with the experts, find solutions for your business, and catch up on the latest products and services as each sponsoring company shares their own brand of hospitality.
Sunday, February 17, 9:00 AM - 4:00 PM
Megger Best Practice New Orleans Megger’s seminar will address many of the critical and costly aspects of substation maintenance. The interactive session will feature practical presentations on current methods and practices to help ensure the reliability of high-voltage circuit breakers, power transformers, and batteries. You must preregister for this event by contacting Megger: 214-330-3539.
Monday, February 18, 12:00 PM - 2:00 PM
PowerDB USER GROUP
Free user’s group meeting open to all users of PowerDB software. You must preregister for this event by contacting Megger: 214-330-3539.
Spouse/Guest Pass
The special lounge will be available exclusively for guests of PowerTest attendees – stocked daily with light refreshments and information on all of the local activities. Includes a lunch voucher, admission to the Hospitality Suites, Trade Show, and the PowerBash Reception. $75 per person
Social Pass
The Social Pass includes admission to the Hospitality Suites, Trade Show, and the PowerBash Reception.
Register on-line at: www.powertest.org
Or Call: 888-300-6382 (NETA)
Non-Members NAC Members
Full Conference: $759 $699
Single Day: $480 $450
Seminars: $269 $249
To register for PowerTest 2013 save time by registering online. You‘ll find a complete brochure and registration form available at www.powertest.org.
Join the Gold Alliance Program for $775 and your PowerTest 2013 conference registration is included! Standard Alliance Program participants can upgrade to Gold Alliance status for only $600 to receive a complimentary PowerTest conference registration!
Hotel Reservations:
Sheraton New Orleans
888-627-7033 500 Canal Street
New Orleans, Louisiana 70130
Reservation Deadline: January 18,2013
Group Name: NETA/PowerTest Group Rate: $210
Payment:
NETA accepts all major credit cards. Save time and register on-line at www.powertest.org or call 888-300-6382 (NETA)
Extras!
PowerTest 2013 Technical Papers - Registered conference attendees will receive all PowerTest technical presentations on a USB drive on site in their registration bag.
1. Go to www.powertest.org and review the complete PowerTest 2013 on-line brochure.
2. Decide the number of days you will attend.
3. Tuesday attendees select up to two panels. (Included in registration fee.)
4. Wednesday attendees sign up for up to two seminars. (Additional fees apply.)
5. Thursday attendees sign up for up to two seminars. (Additional fees apply.)
6. Register for two or more seminars and receive 15% off. Use code PTSEM 2013-2013 to receive this discount.
7. Sign up for the “Second Line Parade”. Space is limited, so register early. (Additional fees apply.)
8. Sign up for Spouse/Guest Passes. (Additional fees apply.)
9. Sign up for PowerTest 2013 conference polo shirts and select size. (Additional fees apply.)
The ANSI/NETA Standards for Acceptance and Maintenance Testing Specifications for Electrical Power Equipment and Systems!
ANSI/NETA MTS-2011 - New Edition
This standard should always be referenced when writing maintenance specifications or performing routine testing on electrical power systems.
ANSI/NETA ATS-2009
This standard should always be referenced in design specifications or when performing acceptance testing on power system installations.
ANSI/NETA ETT-2010
This standard ensures that your acceptance and maintenance tests are being preformed by qualified technicians who are certified in accordance with ANSI/NETA ETT requirements.
Available in Bound, CD ROM, or PDF
3050 Old Centre Avenue, Suite 102
Portage, MI 49024
Toll free: 888.300.NETA (6382)
Phone: 269.488.NETA (6382)
Fax: 269.488.6383
neta@netaworld.org
www.netaworld.org
EXECUTIVEDIRECTOR: Jayne Tanz, CMP
NETA Officers
PRESIDENT: Mose Ramieh, Power & Generation Testing, Inc.
FIRSTVICEPRESIDENT: David Huffman, Power Systems Testing Co.
SECONDVICEPRESIDENT: Ron Widup, Shermco Industries
SECRETARY: Walt Cleary, Burlington Electrical Testing Co., Inc.
TREASURER: John White, Sigma Six Solutions
NETA Board of Directors
Ken Bassett (Potomac Testing, Inc.)
Scott Blizard (American Electrical Testing Co., Inc.)
Jim Cialdea (Three-C Electrical Co., Inc.)
Walt Cleary (Burlington Electrical Testing Co., Inc.)
Roderic Hageman (PRIT Service, Inc.)
Kerry Heid (Magna Electric Corporation)
David Huffman (Power Systems Testing)
Alan Peterson (Utility Service Corporation)
Mose Ramieh (Power & Generation Testing, Inc.)
John White (Sigma Six Solutions)
Ron Widup (Shermco Industries)
NETA World Staff
TECHNICALEDITOR: Roderic L. Hageman
ASSOCIATEEDITORS: Diane W. Hageman, Resa Pickel
MANAGINGEDITOR: Jayne Tanz, CMP
ADVERTISINGMANAGER: Sara M. G. Dillon
DESIGNANDPRODUCTION: Newhall Klein, Inc.
NETA Committee Chairs
CONFERENCE: Ron Widup; MEMBERSHIP: Ken Bassett; PROMOTIONS/MARKETING: Kerry Heid; SAFETY: Lynn Hamrick; TECHNICAL: Alan Peterson; TECHNICALEXAM: Ron Widup; WORLDADVISORY: Diane Hageman; CONTINUINGTECHNICALDEVELOPMENT: David Huffman; TRAINING: Kerry Heid; FINANCE: John White; NOMINATIONS: Alan Peterson; STRATEGY: Mose Ramieh; AFFILIATEPROGRAM: Jim Cialdea
© Copyright 2012, NETA
NOTICE AND DISCLAIMER
NETA World is published quarterly by the InterNational Electrical Testing Association. Opinions, views and conclusions expressed in articles herein are those of the authors and not necessarily those of NETA. Publication herein does not constitute or imply endorsement of any opinion, product, or service by NETA, its directors, officers, members, employees or agents (herein “NETA”).
All technical data in this publication reflects the experience of individuals using specific tools, products, equipment and components under specific conditions and circumstances which may or may not be fully reported and over which NETA has neither exercised nor reserved control. Such data has not been independently tested or otherwise verified by NETA.
NETA MAKES NO ENDORSEMENT, REPRESENTATION OR WARRANTY AS TO ANY OPINION, PRODUCT OR SERVICE REFERENCED OR ADVERTISED IN THIS PUBLICATION. NETA EXPRESSLY DISCLAIMS ANY AND ALL LIABILITY TO ANY CONSUMER, PURCHASER OR ANY OTHER PERSON USING ANY PRODUCT OR SERVICE REFERENCED OR ADVERTISED HEREIN FOR ANY INJURIES OR DAMAGES OF ANY KIND WHATSOEVER, INCLUDING, BUT NOT LIMITED TO ANY CONSEQUENTIAL, PUNITIVE, SPECIAL, INCIDENTAL, DIRECT OR INDIRECT DAMAGES. NETA FURTHER DISCLAIMS ANY AND ALL WARRANTIES, EXPRESS OF IMPLIED, INCLUDING, BUT NOT LIMITED TO, ANY IMPLIED WARRANTY OF FITNESS FOR A PARTICULAR PURPOSE.
ELECTRICAL TESTING SHALL BE PERFORMED ONLY BY TRAINED ELECTRICAL PERSONNEL AND SHALL BE SUPERVISED BY NETA CERTIFIED TECHNICIANS/ LEVEL III OR IV OR BY NICET CERTIFIED TECHNICIANS IN ELECTRICAL TESTING TECHNOLOGY/LEVEL III OR IV. FAILURE TO ADHERE TO ADEQUATE TRAINING, SAFETY REQUIREMENTS, AND APPLICABLE PROCEDURES MAY RESULT IN LOSS OF PRODUCTION, CATASTROPHIC EQUIPMENT FAILURE,
OR
When I started in this business the things discussed in this issue were mere science fiction. Many of us long in the tooth guys have seen so much progress that, at least to me, it is mind boggling.
When I was younger, the only way for relays and other protective devices to communicate was over wire. Next it was fiber, and now we have equipment that can run via the internet and synchronize via satellite. I’m eager to read this issue so I can better appreciate this new technology.
I think the articles in this and recent issues of NETAWORLD indicate that in system control and protection times are changing. We have gone from wire and mechanically connected control/ protection which was not very precise, was bulky, and required constant maintenance to very sophisticated electronic devices that can communicate with each other over WiFi and that require little or no maintenance. These changes, while good for the electrical industry, have taken away aspects of the maintenance on which testing companies focused. This change is being reflected in the business model and strategic direction that NETA Accredited Companies are pursuing.
NETA, as the trend setter, is also changing to accommodate the latest innovations and shifts that are occurring within NETA Accredited Companys. We, as the industry leaders, must continue to promote the need for independent testing to all writers and users of specifications and encourage the use of NETA Accredited Companies to perform the testing. It is my opinion that NETA, as the undisputed leader in the independent electrical testing industry, should do all we can to provide a membership path for any company/organization that does independent electrical testing.
My best wishes to all for a Merry Christmas and a happy and prosperous New Year. See you in New Orleans!
MoseRamieh NETA President
SYNERGY
SYNERGY
SYNERGY
SYNERGY
SYNERGY
SYNERGY
SYNERGY
SYNERGY
SYNERGY
SYNERGY
SYNERGY
SYNERGY
SYNERGY
SYNERGY
SYNERGY
SYNERGY
SYNERGY
SYNERGY
SYNERGY
SYNERGY
SYNERGY
SYNERGY
SYNERGY
SYNERGY
SYNERGY
SYNERGY
SYNERGY
SYNERGY
SYNERGY
SYNERGY
SYNERGY
SYNERGY
SYNERGY
SYNERGY
SYNERGY
SYNERGY
SYNERGY
SYNERGY
SYNERGY
SYNERGY
SYNERGY
SYNERGY
SYNERGY
SYNERGY SYNERGY
SYNERGY
SYNERGY
SYNERGY
SYNERGY SYNERGY
SYNERGY
SYNERGY
SYNERGY
SYNERGY
SYNERGY
SYNERGY
SYNERGY
SYNERGY
•
Cables
LV/MVCircuitBreakers
RotatingMachinery
Meters
AutomaticTransferSwitches
•
SwitchgearandSwitchboard
Assemblies
• LoadStudies
• LV/MVSwitches
• Relays � AllTypes
• MotorControlCenters
• GroundingSystems
• Transformers
• InsulatingFluids
• Reclosers
• SurgeArresters
• Capacitors
• Batteries
• GroundFaultSystems
• EquipotentialGround
• ThermographicSurveys Testing
• TransientVoltageRecordingandAnalysis
• ElectromagneticField(EMF)Testing
Need obsolete parts?
We manufacture & rewind electrical coils & motors for circuit breakers, including: SolenoidCoils RelayCoils TripCoils ChargingMotors
UndervoltageCoils ElevatingMotors
We can provide service for nearly every manufacturer, even if it is not in our extensive database. Santa Fe Electric, Inc
• HarmonicInvestigation
• ReplacementofInsulatingfluids
• PowerFactorStudies
• Do three phase timing & contact resistance measurement with ONE connection.
• Remote Control for a MULTIPLE Opening/Closing Operations.
• 10 Hr Onboard Battery means NO extension cords.
• Built-in report printer
• Results storage & download
• Need Travel? No problem, add it when you need it using ANY transducer.
All for LESS than what you think!
Downloadfullspecifications at www.noramsmc.com or
So, have you gotten accustomed to the recent changes in the 2012 edition of NFPA 70E? If you haven’t then take a little advice and get up to speed – because you will need to understand it so you can get ready for the changes in the 2015 edition! But don’t worry – every issue of a new standard, whether it is a NETA standard, IEEE or NFPA standard, or just about any consensus standard in our industry will have changes. We learn from doing, and as we implement the requirements in each new edition, we convert the requirements from words on page to procedures for electrical workers in the field.
We are challenged anew because the process for developing the NFPA 70E document has changed significantly. The new process is being incorporated into all NFPA standards as they come into cycle. The 70E is the first large standard to use this new process, and it is interesting, to say the least. There is new terminology for such things as proposals (now Public Input), Report on Proposals (now first draft) and actions taken on the proposals. No longer are reject, accept, accept in principal or accept in principal in part heard. Now, it’s most often first revision and resolve. One of the biggest changes in the process is that proposals/ public inputs are no longer considered as mandatory items that have to be answered. They are now considered more as suggestions, and the
technical committee has the freedom to modify the standard using multiple public inputs as it believes necessary, whether there is public input or not. This aspect of the new process was difficult to embrace, but the committee found the flexibility welcome when it needed to rewrite sections, such as 130.3, in order to remove duplication and unneeded wording. The software used by the NFPA to support the process has been changed and completely rewritten. As with any large scale software implementation, there were a few electronic bumps in the highway. Hats off to the NFPA liaison Michael Fontaine and our Technical Committee Chair David Dini – as they had to develop a number of work-arounds in order to keep us on track.
The first draft will be available for public review around February 22, 2013 . Please review the changes and make comments if you are so inclined, and also take note the comments stage on the first draft will close on May 3, 2013 .
More than 450 public inputs (PIs) were considered by the technical committee during this cycle. These various inputs were processed and converted into a first draft. If all the suggestions for change continue, there is no doubt the 2015 edition of NFPA 70E will be a very much-changed standard (and arguably for the better). The first draft will be available for public review around February 22, 2013. Please review the changes and make comments if you are so inclined, and also take note that the comments stage on the first draft will close on May 3, 2013.
From there the technical committee has to have their second draft meeting no later than October 18, 2013. The second draft goes to committee members on January 3, 2014. Any objections to the second draft have to be filed with NFPA by way of a NITMAM (Notice of Intent to Make
a Motion) by February 7, 2014. Any appeals to the decisions on NITMAMs must be filed by April 4, 2014 and June 24, 2014 is the final date for appeal decisions.
It is really too early in the cycle to tell what will be accepted and what will be rejected at the second draft meeting. It should be noted that some of the proposed changes have strong committee support. One of those changes was a revision to the tables for choosing arc flash PPE for specific tasks [Tables 130.7(C)(15)(a) and 130.7(C)(15)(b)]. In past cycles there have been objections to the tables, and one of the oftendiscussed objections is that they incorporate risk into the selection of arc-flash PPE (i.e., Hazard/ Risk Categories). Although the committee has a long history of validation of the HRC methodology (from 1999 to present), many committee members felt we could do better.
Table 130.7(C)(15)(a): Arc-Flash Hazard Identification for Alternating Current (AC) Systems (Note 1)
Table 130.7(C)(15)(b): Arc-Flash Hazard PPE Categories
A new approach to the tables was further advanced by OSHA’s representative to the committee, David Wallis.
The proposal is that Table 130.7(C)(15)(a) and (b) be split into to two separate tables. The first table only assesses whether there is an arc-flash hazard or not. If not, no further requirements (other than normally-required PPE) are suggested. If there is no arc-flash hazard, it will not be covered in the table.
If there is an arc-flash hazard, the user is referred to the second table, which assigns arc-flash PPE based on the hazard. This second table uses the same limits for available short-circuit current and operating time of the overcurrent protective device as the current edition of NFPA 70E.
The arc-flash boundaries have been rounded up to the next full measurement in feet which may cause some interpretation issues. The committee
felt that since the tables were most often being used with little or no calculations being performed, they should be conservative. Some users may look at these arc-flash boundaries and try to apply them to other situations or methods, which could lead them to incorrect conclusions. As an example, Article 130 states that all parts of the body within the arc-flash boundary must be protected. That is a correct statement, but a look at PPE Category 1 would lead a person to think that the back of the head is within the arc-flash boundary (requiring the use of a balaclava), which it probably would not be. The PPE requirements currently in Table 130.7(C) (16) remain the same for the 2015 edition of NFPA 70E and no balaclava is required at this level. Remember, sometimes the reason behind the numbers gets lost and users of NFPA 70E may misapply the information that is meant to be used only in a specific circumstance, such as the tables.
Along with the change to the tables is a global revision that changes Hazard/Risk Category (HRC) to PPE Category. This should not cause any heartburn, since the underlying numbers are still the same, but risk is no longer a part of the tables. Another change that is proposed in the first draft is the elimination of HRC 0 as a category. The committee believed that HRC 0 no longer had any purpose with the changes recommended to the tables, and if there is an arc-flash hazard, the worker should be in arcrated PPE and clothing.
The process to change a vital document for industry can be time consuming, and this edition was no exception. But it is amazing what a room of about 70 people with a common vision and purpose (making the workplace safer for electrical workers) can get accomplished. Before the first draft meeting began, we spent about 10 hours on Saturday and Sunday in committee meetings for the tables and Article 130, and then the next five days were 12 to 13 hours spent each day going through the new process and working on public inputs. Initially, like a large and onerous electrical maintenance outage, it really looked bad. The first official working day (Monday) we were only able to address about 40 PI’s. Once we
got into the rhythm (and mostly due to Michael and David’s work-arounds) we finished all 450+ PI’s by 7 p.m. Friday evening. Many, many more changes in NFPA 70E have been proposed. We encourage all NETA members and Alliance Subscribers to review the first draft when it is published and to make comments for changes that would improve the 70E.
Be safe out there.
Ron Widup and Jim White are NETA’S representatives to NFPA Technical Committee 70E (Electrical Safety Requirements for Employee Workplaces). Both gentlemen are employees of Shermco Industries in Dallas, Texas a NETA Accredited Company. Ron Widup is President of Shermco and has been with the company since 1983. He is a Principal member of the Technical Committee on “Electrical Safety in the Workplace” (NFPA 70E) and a Principal member of the National Electrical Code (NFPA 70) Code Panel 11. He is also a member of the technical committee “Recommended Practice for Electrical Equipment Maintenance” (NFPA 70B), and a member of the NETA Board of Directors and Standards Review Council. Jim White is nationally recognized for technical skills and safety training in the electrical power systems industry. He is the Training Director for Shermco Industries, and has spent the last twenty years directly involved in technical skills and safety training for electrical power system technicians. Jim is a Principal member of NFPA 70B representing Shermco Industries, NETA’s alternate member of NFPA 70E, and a member of ASTM F18 Committee “Electrical Protective Equipment for Workers”.
We encourage all NETA members and AllianceSubscriberstoreviewthefirstdraft Alliance Subscribers to review the first draft when it is published and to make comments for changes that would improve the 70E .
CHOOSE BETWEEN KEEPING MAINTENANCE COSTS DOWN AND KEEPING UP WITH PRODUCTION DEMAND…OR DO BOTH.
NETA certified experts at Electrical Reliability Services will keep you in perfect balance. To ensure the reliability of your electrical power, you have to balance the need to reduce maintenance costs with the need to perform regular maintenance. Only the team from Electrical Reliability Services delivers cost-effective services and system expertise to keep you up and running 24/7.
The electrical power industry is in the midst of tremendous growth and change. Along with it, many experienced technicians and industry professionals are retiring. This threatens to create a challenging shortage of talent, knowledge, and experience. All of these factors point to a greater need for industry professionals to collaborate and organize to share knowledge, experiences, and resources. The strength of the electrical power industry’s future is dependent on the industry’s collective ability to produce the needed manpower, respond so that historical knowledge is assimilated with new ideas, and improve safety and reliability in the years ahead.
Growth: “Electricity usage in the United States is projected to grow more than twice as fastascommittedresourcesoverthenext10 fast as committed resources over the next 10 years. Unless additional resources are brought into service, some areas could fall below their target capacity margins within two or three years. In parts of Western Canada, demand is projected to outpace resource growth within about two years. We are at the stage where emergency situations are becoming more frequent," said Rick Sergel, president and CEOofNERC. CEO of NERC.
Change: Wind, solar and nuclear generation are an important part of the electrical power industry’s future. Today’s power systems
require collaboration between veteran technicians with historical experience and new technicians, educated in alternative technologies to address the challenge of reliably integrating remotely located wind, solarandnuclearresourcesintothebulk solar and nuclear resources into the bulk power system.
Additionally in the industrial sector, thousands of electrical power systems that have been in place for 20-30 years are in desperate need of maintenance and/or replacement all while new systems are being installed at an accelerated rate. Now more than ever before, industry professionals rely on continuing education programs, technical conferences, training organizations, and professional networks to keep them current with today’s technology and practices in order to obtain the answers and experience required to service both the old and the new electrical power systems in place today.
The NETA Alliance Program, (recently evolved from the NETA Affiliate Program), was established with the idea of forming a network of professionals that would share knowledge and experiences and come together based on a common interest in putting safety and reliability first. These people are professionals who are committed to continuing education and personal development with the goal of ensuring
BYJILLHOWELL BY JILL HOWELLthat they are prepared to address the challenges of today and those in the future. They create a community that can provide their experience to others and, at the same time, benefit from other’s experience via the NETA Alliance Program.
NETA recently surveyed the NETA Alliance subscribers and asked what benefits they would liketoseemostfromtheirassociationwith like to see most from their association with NETA. Here were the top responses:
industry professionals papers and articles technical publications
In 2012, NETA launched an expansion plan for the NETA Alliance Program creating a volunteer committee made up of current Alliance participants from all sectors of the industry. The committee is charged with learning more about the needs of the Alliance industry sectors and with those insights expanding the Alliance Program to offer new educational resources and opportunities to exchange ideas. NETA’s goal is to grow the Alliance Program in order to provide an invaluable connection across industry sectors and between old school and new school thinking. This will bring together diverse experiences serving to help build relationships between the islands of knowledge and expertise to create a stronger professional resource. To that end, it is most important that NETA Alliance participants represent all facets of the electrical power industry contributing a broad perspective as NETA seeks to work with each sector to support their contribution to improving safety and reliability within the electrical power industry.
The NETA Alliance Program was established with the goal of engaging individuals rather than companies in the pursuit of improving safety and reliability in the industry. The Alliance Program is subscription-based, meaning that there are no prerequisites or credentials necessary to becomeanAlliancesubscriber.Whilethereis come an Alliance subscriber. While there is not a certification or qualification attached to being a NETA Alliance participant, this program is home to professionals who share NETA’s mission, leaders who bring perspectives from all sectors of the electrical power industry and those who put quality and safety first.
NETA Alliance Industry Representation includes:
For information about subscribing to the NETA Alliance Program visit www.netaworld.org or contact Jill Howell at jhowell@netaworld.org.
High magnitude current flows through the conductor and connected equipment to the point of the disturbance when a fault (for example, lightning strike) occurs on an overhead, highvoltage transmission line. The heavy current can quickly damage the line conductor and connected equipment (for example, transformer bank).
Modern protective relays detect the presence of a disturbance on overhead transmission lines and send commands to open the circuit breakers at each end before any damage occurs. Accurate fault location helps utility personnel expedite service restoration, thereby reducing outage time. If the distance to the fault is known, the utility can quickly dispatch line crews for any necessary repair. Otherwise a lot of time and expense is required to patrol the overhead line for possible damage.
Referring to Figure 1, a lightning strike hits the upper line conductor between transmission towers #1 and #2. The voltage at the strike builds rapidly until it flashes over to ground and high magnitude current flows on the faulted phase(s).
Modern protective relays at Substation S (to the left of Figure 1) and Substation R (to the right of Figure 1) monitor the transmission line by measuring the local voltage and current flow at their respective locations. Fault voltage drops and fault current increases during a fault.
In the past, numerical line relays calculated the distance to the fault using data (voltage and current) measured at their respective locations; this method is referred to as a singleended method. Unfortunately, this method can experience significant error when there is fault
resistance (for example, wind blows a tree into the line conductor) and power is flowing through the line. There are now double-ended methods that are far superior.
This paper explains how to test double-ended fault locators for high-voltage, overhead transmission lines. There are many similarities to testing highspeed, communication-assisted tripping schemes (HSCATS); however, there are some important differences that are covered here in detail. Note that double-ended fault location is coming into vogue now, and these tests can be performed in unison while testing the HSCATS.
Figure 2 illustrates a typical test setup on line number 2. Note that FL stands for fault locator and TS stands for test set. These tests require synchronized, three-phase test sets at both ends of the line. The distance to the fault with respect to Substation S is referred to as m.
These tests call for short-circuit studies to determine the fault voltage and current measured by each fault locator for faults internal to the protected line. Zero-sequence, mutual coupling of the parallel lines and high fault resistance during heavy load are considered as power system parameters. These signals are played back to the fault locators via the synchronized test sets.
The paper discusses fault location and illustrates one double-ended method. Classic problems associated with single-ended fault location are discussed as well.
Fault location on overhead transmission systems has been researched by the electric utility industry since the early 1950s. Accurate fault location helps utility personnel:
FIGURE 3: Single-Ended, Distance-to-Fault Calculation
Most numerical line relays use single-ended, faultlocation algorithms. While this method is simple and fast, the following commonly encountered factors can severely degrade accuracy:
Existing technology uses data from only one end of the overhead transmission line to calculate the distance-to-fault with respect to the local terminal.
This paper presents one double-ended fault location technique for overhead transmission lines. The method is only illustrated for the case of single phase-to-ground faults since this fault type occurs most frequently. However, the method can be applied equally as well for the other three fault types; that is, three-phase, phase-to-phase, and phase-to-phase-to-ground. Single phase-toground faults are typically the most rigorous for distance-to-fault calculations (that is, fault resistance and zero-sequence, mutual coupling).
The double-ended method is immune to the most common problems associated with fault location remote infeed and zero-sequence, mutual coupling. This algorithm requires only the negative-sequence voltage and current from both terminals, plus the positive-sequence line impedance. This method has been thoroughly tested using actual data recorded on a high-voltage transmission system in the Southeastern U.S.
Fault resistance and zero-sequence, mutual coupling are the two most significant sources of error for existing single-ended methods.
Figure 3 illustrates the fault voltage and current measured from the two ends of a faulted overhead transmission line during a single phase-to-ground fault. The per-unit distance-to-fault with respect to Substation S is “m”; therefore,
m . Z1L1 = total impedance of the faulted phase to the point of the fault from Substation S
(1-m) . Z1L1 = total impedance of the faulted phase to the point of the fault from Substation R
RF = total fault resistance
VS = faulted phase voltage measured at Substation S
IS = faulted phase current measured at Substation S
IR = faulted phase current measured at Substation R
A very simple explanation of a popular singleended method is that the local fault voltage is divided by the local fault current to determine the faulted-phase, loop impedance, ZLOOP, from the substation to the fault. The imaginary part of ZLOOP (XF) is then calculated to ignore any fault resistance, which can be significant; for example,
Fault resistance and zero-sequence, mutual coupling are the two most significant sources of error for existing single-ended methods .
ZLOOP = VS/IS
XF LOOP
Where
The fault reactance (XF) is then divided by the total reactance of the transmission line (XL) to estimate the per-unit distance-to-fault with respect to Station S.
m = XF/XL
Equations 1 through 3 are approximations, and as such are intended only to help the reader visualize how to calculate the distance-to-fault for a single phase-to-ground fault. Use zero-sequence compensation to measure the distance-to-fault in terms of positive-sequence line impedance only.
REMOTE INFEED
IR, the fault current flowing into the fault resistance from the opposite end of the overhead transmission line, is referred to as remote infeed. Herein lies the main problem with the method outlined previously, since it was assumed that the faulted phase current from both ends of the overhead transmission line are in-phase. If there is load flow, this is typically not the case. As the angular difference between IS and IR increases, so does the error.
The error occurs because the faulted-phase voltage measured at Substation S (VS) is dependent on the faulted-phase current flowing from Substation R (IR).
The faulted-phase voltage measured at Substation S is derived via Kirchhoff’s Voltage Law (the sum of the voltages measured around any loop equals zero).
VS = IS . m x Z1L1 . (IS + IR) . RF
If there is an angular displacement between IS and IR, a reactance component is introduced due to the voltage drop across the fault resistance when the imaginary part of the faulted-phase, loop impedance is calculated.
VS/IS = m . Z1L1 . IS + IR . RF IS
VS/IS = m . Z1L1 . RF R/IS
If the angle of IS is equal to the angle of IR, then the imaginary part of α . RF is zero; otherwise, the value is non-zero and error is introduced. The amount of error increases with the value α.
Equations 4a through 4d are approximations and as such are only intended to help the reader visualize how to calculate the distance-to-fault for a single phase-to-ground fault.
When two or more overhead transmission lines share the same right-of-way, there is coupling between the lines in the zero-sequence network since these components are in-phase.
Figure 4 illustrates a single phase-to-ground fault on Line 1. There is zero-sequence, mutual coupling between the adjacent overhead transmission lines because they share the same right-of-way (that is, they are in the same vicinity). Therefore, the faulted-phase current flowing in Line 2 (IS2) affects the faulted-phase voltage measured on Line 1 at Substation S.
If IS1 and IS2 flow in opposite directions, the faulted-phase voltage measured on Line 1 at Substation S decreases; therefore, the faultedphase, loop impedance measured at Substation S for Line 1 is reduced (ZLOOP = V-/I) and the distance-to-fault calculation is closer to Substation S than the actual location of the fault. This case is referred to as overreaching.
If IS1 and IS2 flow in the same direction, the faulted-phase voltage measured on Line 1 at Substation S increases; therefore, the faultedphase, loop impedance measured at Substation S for Line 1 is increased (ZLOOP = V+/I) and the distance-to-fault calculation is further from Station S than the actual location of the fault. This case is referred to as underreaching.
The problems associated with zero-sequence, mutual coupling exist because of the following:
quence quantities.
There are a few relays available today that accept an input from the adjacent overhead transmission line so as to monitor the offending residual current and make necessary corrections. However, this technique does not work properly when the offending overhead transmission line is out-of-service.
When the parallel overhead transmission line is out-of-service and grounded at both stations, loop current flows in the grounded line for faults involving ground on the parallel in-service line. The loop current cannot be measured since the current transformers are outside of the loop flow. Therefore, the distance-to-fault calculation on the parallel in-service line is too close at one station and too far at the other.
This section introduces a double-ended fault location algorithm for high-voltage, overhead transmission lines. The algorithm uses synchronized voltage and current measurements from both ends of the line.
The double-ended fault location does not have any problems with fault resistance or zerosequence, mutual coupling due to the following:
distance-to-fault does not account for the faulted-phase current flowing in the parallel overhead transmission line, -
current measurements from both ends of the overhead transmission line.
current is used to calculate the fault location.
Today, time-synchronization is available and commonly applied in substation control rooms via GPS satellite clock receivers. Both modern protective relays and digital fault recorders record the fault voltage and current from each end of the overhead transmission line.
The voltage and current measurements must be filtered such that only the fundamental quantities (60 Hz components in the United States) are applied for the calculations. Modern protective relays filter the voltage and current prior to executing any protection-related functions. These signals are usually available via an event report.
Transform voltage and current measured during fault conditions to their respective positive-, negative-, and zero-sequence quantities. Negative-sequence quantities are present for single phase-to-ground, phase-to-phase, and phaseto-phase-to-ground faults. Therefore, negativesequence quantities are very reliable.
The following two equations demonstrate how to calculate the negative-sequence voltage and current from the three-phase voltage and current measurements.
V . (V . V . V
I . (I . I . I
Where:
FIGURE 6: Negative-Sequence Network for Faulted Overhead Transmission Line
Figure 6 illustrates the negative-sequence network for a faulted overhead transmission line.
V and I are the negative-sequence quantities measured at Substation S. V2R and I2S are the negative-sequence quantities measured at Substation R. The per-unit distance to the fault with respect to Substation S is “m”; therefore,
m . ZL = Total impedance of the conductor to the point of the fault from Substation S
(1-m) . ZL = Total impedance of the conductor to the point of the fault from Substation R
VF = Fault voltage at the point of the fault
V = Negative-sequence voltage measured at Substation S
I = Negative-sequence current measured at Substation S
V = Negative-sequence voltage measured at Substation R
I = Negative-sequence current measured at Substation R
I = Total negative-sequence fault current (I2S +I2R)
Determine the apparent negative-sequence source impedances at Substations S and R as follows:
Z = - V /I
Z = - V /I
Derive two loop voltage equations in terms of the fault voltage: at Substation S
-V + I . m . ZL + VF = 0
VF = V - m . I . ZL at Substation R
-V + I . (1 – m) . ZL + VF= 0
VF = V + m . I . ZL –I . ZL
Set the two equations above equal to each other and solve for “m” with respect to Station S.
V - m . I . ZL = V + m . I . ZL –I . ZL
V - V + I . ZL = m . I . ZL
m(S) = V - V + I . Z1L I . ZL
This section illustrates how to use timesynchronized test signals to verify that the double-ended, fault locator works correctly. The fault locating equipment must be enabled at both terminals and the communication channel must be available.
Figure 7 is a simple model of a faulted transmission line. Substation S is the reference bus with respect to the distance-to-fault (m).
Z1L Z ZM VS VR IS IR
Equation (11) calculates the per unit distance-tofault with respect to Substation S:
m = V - V + I . ZL I . ZIL
The first example is the case of a resistive phaseto-ground fault on A-phase located 75 percent of the line (15 miles) from Substation S. It was simulated using Mathcad. You can also use short-circuit software such as ASPEN OneLiner or CAPE. Moderate load prior to the fault was modeled and the line is mutually coupled to another transmission line. The fault voltage and current at each end of the line are as follows: VAS AR VBS BR V
The negative-sequence voltage and negativesequence current are as follows: V I
Equation (11) yields a result of 75 percent that matches the actual fault location. This example shows that equation (11) is immune to problems
7: Double-Ended Transmission Line Model
associated with fault resistance and zero-sequence, mutual coupling since it only uses negativesequence quantities.
EXAMPLE 2
This example is an actual case where a phase-toground fault on A-phase occurred on a 230 kV overhead transmission line and was captured by digital fault recorders at both ends. Conventional methods proved futile when utility personnel tried to locate the fault. The fault turned out to be an old oak tree growing under the line. This vegetation represented an extremely high level of fault resistance (that is, many times greater than the impedance of the transmission line). The double-ended, distance-to-fault equation correctly calculated the distance-to-fault with an error of less than 5 percent. The following are the actual calculations for this case.
Here are the time synchronized negative-sequence quantities measured at each end of the line:
the line. The error was less than two percent. Below are the actual calculations for this case.
The actual line length is 35.43 miles. Therefore, the distance-to-fault with respect to Substation S was 12.5 miles. The actual distance-to-fault was 13 miles.
A B-C phase-to-phase fault occurred on a 230 kV overhead transmission line. The fault was due to a truck that caught fire under the line. The resulting smoke created a path for electrical current to flow between B- and C-phase conductors. The doubleended distance-to-fault equation was applied using the negative-sequence voltage and current recorded by instrumentation at the two ends of
The actual line length is 21 miles; therefore, the distance-to-fault with respect to Substation S was 1.93 miles.
You can calculate the zero-sequence impedance of the transmission line using the synchronized, zero-sequence voltage and current measured at each end of the line using the following equation:
ZOL = IOS . ZOS-IOR . ZOR m . IOS-(m-1) . IOR
Equation 12 does not account for zero-sequence mutual coupling.
Figure 8 is the corresponding zero-sequence network for faults involving ground.
Equation 11 can be implemented to provide high-speed protection of overhead transmission
Note that double-ended fault location is coming into vogue, and these tests can be performed in unison while testing the HSCATS .
lines. Terminal voltage and current phasors can be calculated in real time and then passed from endto-end via a digital communications channel. The double-ended fault locator is immune to many problems associated with conventional distance based-schemes such as overreach and underreach.
This paper explains how to test double-ended fault locators for high-voltage, overhead transmission lines. There are many similarities to testing highspeed communication-assisted tripping schemes (HSCATS); however, there are some important differences which are covered here in detail. Note that double-ended fault location is coming into vogue, and these tests can be performed in unison while testing the HSCATS.
When a disturbance (for example, a lightning strike) occurs on a high-voltage, overhead transmission line, the line must be checked for any possible damage. If the distance-to-fault is known, line crews can be quickly dispatched for any necessary repair. Otherwise, a lot of time and expense is required to patrol the overhead line for possible damage.
Modern protective relays calculate the distanceto-fault using data (voltage and current) measured at the respective locations. This is referred to as a single-ended method. Error typically occurs when there is fault resistance (for example, wind blows a tree into the line conductor) and power is flowing through the line.
The double-ended method uses timesynchronized, filtered data from both ends of the overhead transmission line to determine the exact distance to the disturbance with respect to either
end. The double-ended fault location does not have any problems with fault resistance or zerosequence, mutual coupling due to the following:
measurements are used from both ends of the overhead transmission line.
current is used to calculate the fault location.
available and applied in substation control rooms via GPS satellite clock receivers. Both modern protective relays and digital fault recorders typically record the fault voltage and current from each end of the overhead transmission line. Use this data to accurately calculate the distance to the fault.
Steve Turner is a Senior Applications Engineer at Beckwith Electric Company. His previous experience includes working as an application engineer with GEC Alstom, an application engineer in the international market for SEL, focusing on transmission line protection applications. Steve worked for Progress Energy, where he developed a patent for double-ended fault location on transmission lines.
Steve has both a BSEE and MSEE from Virginia Tech University. He has presented at numerous conferences including: Georgia Tech Protective Relay Conference, Western Protective Relay Conference, ECNE and Doble User Groups, as well as various international conferences. Steve is a senior member of IEEE.
National Switchgear has a broad line of new, used and remanufactured electrical switchgear products. And literally millions of parts, new and used. But that’s only part of the story. We also have the willingness to listen, the experience to know what you need, the capacity to have it in stock, and the responsiveness to get it to you fast. Plus, the additional value of full-service electrical testing and onsite maintenance services.
So, if you’re still calling anyone else for power distribution equipment, maybe it’s time to switch.
800-322-0149
nationalswitchgear.com
the test equipment answer
Switchgear and Breakers
(Low, Medium and High Voltage)
Cable and Bus
Transformers
Relay and Protection Systems
Batteries
Motors and Rotating Apparatus
Watthour Metering
Power Quality and Consumption Analysis
Shermco Industries continued its expansion in September by opening a new office in San Antonio. Located at 12000 Network Blvd., building D # 410, the office is both a sales and production facility, approximately 6,600 square feet.
Kevin Ewing, the Shermco regional manager that oversees the Austin and San Antonio offices, says the company opened in San Antonio due to the growth in that market.
“We are happy to be here and have already secured quite a bit of work,” said Ewing. “This area is great for us due to all the data center business. We have six engineering field service technicians here and are currently looking for two more.”
Ewing also mentioned that due to the company’s expansion mode, many of the Shermco offices have positions available in the electrical services industry.
“Right now we are looking to fill 54 positions corporate-wide,” said Ron Widup, Shermco president. “In Dallas, we recently took more more square footage on Airport Freeway to accommodate our engineering department. And, we are very excited to now be open for business in San for San Antonio as we expand our suite of Shermco electrical services throughout North America.”
Shermco Industries provides professional training and safe and reliable testing, repair, maintenance and analysis of rotating apparatus and electrical power distribution systems and related equipment for the light, medium, and heavy industrial electrical equipment nationwide. Founded in 1974 in Dallas, the company has two strategic business units:theMachineServicesDivisionandthe units: the Machine Services Division and the Engineering Services Division. At its combined corporate location in Irving, Texas; sales office in Brussels; and service centers in Austin, Cedar Rapids, Des Moines, Houston, Sweetwater, and Tulsa, Shermco Industries has over 440 full time employees. The company is a member in good standing with the Electrical Apparatus Service Association, the American Wind Energy Association, the Professional Electrical Apparatus Recyclers League, and the InterNational Electrical Testing Association. For more information about Shermco Industries, visit www.shermco.com.
ShermcoIndustries Shermco Industries 12000 Network Blvd, Building D, Suite 410, San Antonio, Texas 78249 Office: 512.267.4800; Fax: 512.267.4808 kewing@shermco.com www.shermco.com Kevin Ewing
Utility Service Corporation has been providing electrical and technical services for government and industry since 1962.
Services:
Preventative Maintenance
Acceptance Testing High Potential Testing
Commissioning Services System Studies Arc Flash Analysis
Solving complex problems, testing under difficult and unusual circumstances and servicing the commissioning and maintenance needs of today's electrical power systems both new and aged.
Engineering & Consulting
Construction Supervision System Trouble Shooting
With the introduction of multifunction relays, testing methods for these devices must be approached in a different fashion. Gone are the days when the need to verify the operating characteristics of a relay were the only tests performed.
The characteristic of an element is no longer dependent on the mechanical operation of a rotating disk, bearings, drag magnets, and capacitors. The characteristic is derived from the execution of a mathematical formula determined by various settings, applied to variables that are the output of analog-to-digital converters modified by sequence filters and carried out by a microprocessor. This change in how the protection element works means a change in what is important to test. With the intelligent electronic devices (IEDs) monitoring the health of the power system instead of multiple, singlefunction, electro-mechanical relays, internal logic verification is as important as verifying the individual protection elements.
Testing of the logic in an lED presents a plethora of challenges. It is now the test technician's job to inject the proper voltages and currents to simulate various operating and fault scenarios and observe the elements' action to the overall logic scheme. With electromechanical relays this was fairly straight forward, as the tests were applied to
one relay and one element. Now the challenge is to be able to simulate conditions that operate an element without another element operating at the same time.
One of the tools available to the modern testing technician is the ability to simulate faults in two relays at two different locations that are synchronized by Global Positioning Satellites (GPS). With modern test sets, the capability is available to test the protection scheme as a system. Two or more locations can be set up to inject a simulated fault into the local relay with the values that would be seen by that relay during an actual fault. These signals are synchronized by the GPS signals and are coordinated to allow for a true system test.
The current GPS system consists of 31 satellites. Each satellite has a highly accurate atomic clock
on board which is used to send a synchronized time signal to earth. Using the mathematical principle of four equations with four unknowns, a receiver must receive the time signal of at least four satellites to determine its position (longitude, latitude, and height) as well as accurate time. The position can be determined to an accuracy of 66 feet and the time to an accuracy of 14 nanoseconds.
Figure 1: FaultAt95% of Line Length
Two types of GPS receivers are available. One is the navigation unit which is even available in your cell phone and the other is the satellite clock. The satellite clock has the ability to output a selection of timing signals which can be used to synchronize third party units with each other. To be able to use the time signal for synchronization purposes, a GPS clock is needed, which provides a number of timing signals. These signals are the IRIG-B, PPM, and a programmable pulse signal. The Inter-Range Instrumentation Group time code is commonly known as IRIG-B. The
lRIC-B sjgnal is one pulse per second. The PPM is a pulse per minute and of course the programmable signal isprogrammableto yourneeds. The PPM and programmable signals can be used to synchronize test equipment at two or more locations to the closest accuracy around the world. The CPS system is thus well suited for this type of test due to its availability all over the world and due to the accuracy of the timing signal.
To synchronize a test set with a satellite clock, the PPM signal is used. This signal triggers each test set to start the testing sequence. Each test sequence will be injecting the currents and voltages at the same magnitudes and phase angles that the protective relay would see during the actual fault.
As modern relays often have complex logic schemes applied, the actual operation of the
protection system must be verified. Testing the logic as a system will preclude misoperations of the protection system. This is most important in schemes that involve multiple relays, such as breaker-failure schemes, differential schemes, and communication-based schemes.
A state sequencer routine can be set up on one test set to start on a CPS pulse, inject the appropriate analog signals, and then measure the response of an lED to the applied signals. A second test set is set up at a remote location to start on the exact same CPS pulse. It applies the appropriate analog signals to the remote relay with the values expected at that location based on the fault characteristics.
Using a time signal view to measure the response time of the outputs from the relay, the system performance can be evaluated. These signals can confirm that the protection system performs as
designed. Figure 1 is an example of a time signal view that can be used to verifY a communication scheme. This test was for a permissiveoverreaching transfer trip cheme (POTT). This relay was injected with variables that equated to a fault at a location of95 percent of the line length.
Figure 2 is a screen shot of the remote location set for a fault of five percent of the line length. As you can see, the time signal view shows that the system performs as intended.
In the case of a bus differential system, several test sets can be set up to initiate a fault at the same time and measure the response of the 87B device. This is a much more effective test than just verifYing the pickup and timing of a differential relay.
It is possible to use different models of test sets to perform these tests. With the use of the GPS signal to start the test, which manufacturer's test set you use is not important as long as it produces a quality signal. However it must be noted that not all test sets will process the GPS signal at the same speed. This could cause a variance in the timing of the injected signals. This variance can skew the test results. When using multivendor test sets, you must perform a few trials, preferably in the lab, to see the difference in the signal start times. When this is determined then an adjustment to the faster test set can be programmed to get all test sets to inject at the same time.
Another application of GPS testing is to verifY the correct operation of phasor measurement units (PMU) or syncrophasors. These are appearing in more and more protection systems throughout the world. In typical applications PMU's are located at various points in the power system network and synchronized by a GPS signal. Synchrophasors measure voltages and currents at diverse locations on a power grid and can output accurately timestamped voltage and current phasors. Because these phasors are truly synchronized, synchronized comparison of two quantities is possible, in real time. These comparisons can be used to assess system conditions.
When testing PMU's you must inject signals from various locations and retrieve the results for analysis. The timing of the injected signals must be exact or the results will not be a true representation of the power system condition.
The advent of GPS has led to a new way to look at the traditional testing methods. New possibilitiesare available in the commissioningand maintenance of protection systems. Use of these tools allows us to go well beyond the verification of pickup/dropout and curve verification of relays. GPS or end-to-end testing is the future of testing.
William Knapek received a BS Degree in Industrial Technology pom East Carolina University in 1994. In 1995 he retired pom the US Army as a Chief1¥tzrrant Officer after 20 years 0/ service. During his time with the Army Corps of Engineers, he held positions as a power plant instrumentation specialist, a writer/instructor for the Army Engineer School and afacility engineerfor a Special Operations compound. He has been active in the electrical testing industry since retiring in 1995. He workedfor NETA companies in the Nashville, Tenessee, area untiljoining OMICRON electronics as an applicationengineer in April 0/2008.
He is currently the SecondaryEngineeringService and Customer Support Managerfor OMICRON electronics Corp, USA. He is certified as a Senior NICET Technician and aformer NETA Level IVTest Technician. Willis a member ofIEEE.
REFERENCES
1. Alexander Dier, Heinrich Metzler; GPS synconized rem at the Vorarlberger Illwerke AG; OMICRON User Conference, Berlin, November 1995
2. Global Positioning System; Wikipedia.com
3. Phasor Measurmenr Units; Wikipedia.com
Dude Electrical Testing LLC was founded August 3, 2009, for the purpose of performing electrical testing and engineering studies for industrial, commercial, and utility customers.
Dude Electrical Testing LLC is a Veteran Owned Small Business and signatory to the IBEW International Maintenance & Testing Agreement.
Dude Electrical Testing offers a variety of testing services on the following apparatus: low and medium voltage switchgear, transformers (dry and wet), circuit breakers/switches (SF6, oil, vacuum, and air), protective relays, instrument transformers, ATSs, MCCs, emergency generators, motors, and grounding systems. Additionally, we provide in-house low-voltage and mediumvoltage equipment repair, rebuild, and retrofitservices. retrofit services.
Dude Electrical Testing has assisted in the commissioning of data centers and hospitals by
providing engineering support, Infrared surveys, and power quality analysis. We also offer power quality analysis, short circuit studies coordination studies, and arc flash studies.
Dude Electrical Testing primarily performs NETA testing services in the greater Chicagoland region, but has traveled to Germany, Mexico, Equatorial Guinea, and Trinidad. We have also traveled nationally to Georgia, California, Louisiana, Minnesota, Missouri, Wisconsin, Iowa, and Indiana.
We desire to be highly trained and skilled electrical professionals in order to better serve our present and future customers and differentiate ourselves from other local testing companies. In our opinion, this can only be achieved by continuing to work hard and to become a NETA AccreditedMember. Accredited Member.
BUILDING THE FUTURE AT GROUND ZERO:
Earlier this year, on its eleventh anniversary, the United States remembered the events of September 11th, the collapse of the World Trade Center Towers and the many lives that were lost. One would be hard-pressed to find a person who remained untouched after that fateful day. While the shock at the outrageousness of the actions of a few has faded from the limelight, the persevering nature of a city and its people continue to work toward honoring the lives lost with the construction of a new World Trade Center.
Some of those who helped in the aftermath of that tragic event will take part in rebuilding its future. Among these is Elemco Services, Inc. Elemco was there in the days, weeks, and months following the collapse of the iconic structure, helping to ensure electrical systems were deenergized and lines were cleared enabling rescuers. Earlier this year, Elemco Services was awarded the job of performing acceptance testing and commissioning on eight, 15-kV substations that feed the World Trade Center site. Additionally, they will perform acceptance testing and commissioning of Tower One, named One World Trade Center; Freedom Tower; and Tower Four. Bob White explained that they have as many as twelve NETA technicians performing testing services for this project at any given time.
Not surprisingly, every aspect of this massive undertaking is focused on safety. Elemco Services began participating in March of 2008, with each crew member being required to take an OSHA safety course and earn an OSHA 10 card before setting foot on site. The project is estimated to take two years to complete with Tower One reaching completion in July 2013. One World Trade Center will rise 1,368 feet above street level, which will make it the tallest building in New York City, lofting 118 feet above the Empire State Building. Eventually there will be a
communicationstowerwithanantennathatwill communications tower with an antenna that will rise to 1,776 feet, making it the tallest building in the Western Hemisphere.
We interviewed Bob White, Elemco General Manager, to get the inside scoop on the challenges of performing electrical testing and commissioning for this magnificent monument.
Q: What are some of the challenges unique to this project?
“A big challenge is being able to get equipment in and out of the site due to security. If we are bringing in a test set that requires an elevator transport, there may be a half-day wait for the elevator. Every inch of the building has to travel up those elevators and everything has its priority. It’s the nature of building a high rise.”
“Choosing the crew and getting them authorized is also a big task. Every worker has to fill out a seven page security form and have a criminal and background check completed to be government approved.”
Q: How does this project differ from other high rise projects?
“There is a very, very strong sentiment that it is an honor to be working here. Brian Williams recently did a program on 20/20 interviewing the
iron workers that are doing the steel work. The foreman happens to be a Native American from the Mohawk Tribe. His grandfather worked on the Empire State Building and his father on the original World Trade Center. Many of these same people worked on the pile when doing recovery at the site of the collapse. For them, to be rebuilding it is a big deal. For my guys, it’s an opportunity to build a part of history, to help ensure thattheWorldTradeCenterwillbeconstructed that the World Trade Center will be constructed to the highest standards in the industry.”
Q: Are there lessons learned from 9/11 that impact the work Elemco is performing?
“Theelectricalinfrastructureisconstructedto “The electrical infrastructure is constructed to be tamperproof, and the architecture is designed to withstand external force. The building includes a 185-foot windowless, concrete base designed specifically to withstand truck bombs, three-footreinforcedconcretewallsinallstair three-foot reinforced concrete walls in all stairwells and elevator shafts, and a dedicated set of staircases for firefighters.”
Q: How did Elemco happen to be chosen for the job?
“The process of selection was an open bid organized by the New York Port Authority. JB&B (Jaros, Baum & Bolles) was responsible for the building design and developing the bid requirements. The bid document specifically required commissioning and acceptance testing to ANSI/NETA Standards by a NETA Accredited Company.
The creation of and adherence to voluntary national standards created through a consensus body was born in New York, and it seems fitting that American National Standards continue to support the growth and prosperity of this country. NETA is proud to be an Accredited Standards Developer for the American National Standards Institute. These standards, in the hands of qualified individuals such as NETA Accredited Companies and NETA Certified Test Technicians, are a powerful tool that goes a long way to ensure the highest level of safety and reliability.
To learn more about the World Trade Center Progress, you can visit the website at http://www.panynj.gov/ wtcprogress/index.html.
ElemcoServiceshasbeeninbusinessforover Elemco Services has been in business for over 40 years, working in the New York construction trade for most of them. Elemco participated in the recovery after the first attack on the World Trade Center in 1993. We are a respected partner and have worked with JB&B on numerous projects. I believe these are some the reasons Elemco was selected for the project. it usually comes down to reputation, experience, and of course pricing.”
The feeling of all throughout the job site is proud to be an American and proud to be doing this job the American way.
“Elemcoishonoredtohavebeenchosento “Elemco is honored to have been chosen to help complete the new World Trade Center. It is one of those projects that you tell your grandkids about.”
Elemco’sdedicatedteamoftechnicianswork Elemco’s dedicated team of technicians working on the World Trade Center Includes Glenn Dredier (foreman), Harry Johnson, William Ward, Gregory Francis, Paul Castellaneta, Anthony Parise, Michael Sciara, Malcolm Green, Joe Glass, Monique Daniels, Hung Giang, Stan Pappas, Xinia Jamie, Ines Estrada, Andrew Tapia, Frank Magri, Richie Hanablet, Guy McGovern, and Joe Simon
To get a sense of what it has meant to work on the project day in and day out, the NETAWorldstaffinterviewedafewofthe NETA World staff interviewed a few of the Elemcotechnicians. Elemco technicians.
Glenn Dredger was chosen to be the foreman on the World Trade Center project for Elemco.
“One of the most interesting things is that there is onefeederthatconnectstothesubstationsonthe one feeder that connects to the substations on the 4th and 93rd floors of Tower One. The feeder is an armored, jacketed cable supported once at the top of the riser and then it hangs free all the way tothebasement.Thebracketisbuiltintothereal. to the basement. The bracket is built into the real. When lowering the feeder down the shaft the last 10 feet has a flang-plate that mounts to the floor to support the cable. This design allows the cable to sway in the shaft along with the building up to 18 inches either way.”
“When we energized the first feeder, there was a high level of confidence. With all the training and hard work preparing as a NETA Certified Technician, you feel really good after preformed all the testing on all the gear that is required according to NETA Standards. We had complete confidence that everything would go smoothly whenwethrewthefirstswitch.We’vedoneit when we threw the first switch. We’ve done it eight times now and tested every component according to ANSI/NETA Standards. It’s been a pleasure and an honor. Very self satisfying!”
Richie Hamablet, one of 12 guys working for Elemco on the new World Trade Center, reflects on the part he feels privileged to play.
“It has been amazing to bring it back to life. I am proud. Over the last three years on each 9/11 anniversary there are the official ceremonies but we have our own before anyone else gets there. We were there the other day for this year’s 9/11 anniversary, right in front of the reflecting pool. We had a moment of silence. Some of the guys know folks that were lost. My brother-in-law worked inthetradecenter.Hewasn’tintheofficethat in the trade center. He wasn’t in the office that day, but he could have been easily taken out if the cards had been shuffled differently.”
“There are so many tourists. It’s great to see. When you go to work, they stop and ask you questions and want their picture taken with you. Crazy! But your chest fills up and just talking about working on it makes you feel good. Some people ask if we’re worried but you can’t think like that. We’re building America. You’ve got to make everyone proud. “
“They’re crazy on safety throughout the entire project. As a NETA guy we have to make sure our people are safe as well as the other workers. That means having to educate the other workers of the risk factors, where not to walk. We always have NETA guys as spotters. One guy watching the test equipment and the other monitoring where the other guys are, making sure the work site is clear, and that no one accidently walks into an unsafezone.” unsafe zone.”
We were there the other day for this year’s 9/11 anniversary, right in front of the reflecting pool. We had a moment of silence.
Paul Castellaneta, Elemco Technician:
Paul Castellaneta originally worked on the 9/11 memorial and now is happy to be working for Elemco, on the new World Trade Center towers. Paul is one in a team of technicians responsible for testing all of the incoming feeds and all the equipment to which they are attached. Paul says, “It’s quite remarkable, the amount of power needed to supply the site. There are eight different power substations coming from ConEd.”
“One of the biggest challenges is really the vertical transportation, getting the men up and down the building. There are four different sites that we need to get men and equipment to. One day we might be on the 60th floor of Tower One and the next on the 4th floor of Tower Four. Right now concrete construction is only up to the 94th floor. We are all looking forward to going to the top.
Friends and relatives ask me about the experience all the time. My son, who's eight, brought photos of the Trade Center to show everyone at school. You really feel proud. There are guys that worked on the original buildings, and it is interesting to hear how it was then versus now. Personally, I am glad for the opportunity. Everyone wants to be a part of it. “
July 4, 2004 — The symbolic corner stone of One World Trade Center was laid in a ceremony, but construction work did not begin until 2006.
November 18, 2006 — The building’s foundation was poured laying 400 cubic yards of concrete.
December 19, 2006 — During a special ceremony held in Battery Park City, members of the public were invited to sign a 30-foot (9.1m) steel beam. This beam was the first to be welded into place forming the base.
December 2007 — One World Trade Center’s footings and foundations were nearly complete.
May 17, 2008 — The tower’s concrete core reached street level.
January 2010 — One World Trade Center base construction is complete. Construction of the office floors and the first glass windowswereinstalled. windows were installed.
An advanced cocoon scaffolding system was installed to protect workers from falling, marking the first time that such a safety system had been installed on a steel structure in the city.
December 16, 2010 — The tower’s construction reached the 52nd floor, marking the halfway point.
September 11, 2011 — The tower’s steel reached the 82nd floor while its concrete flooring reached the 72nd floor and class cladding reached the 56thfloor. 56th floor.
To mark the 10th Anniversary of the September 11 terrorist attacks, the tower was specially illuminated, lit up in the colors of the American flag.
April 30, 2012 — One World Trade Center surpassed the Empire State Building’s roof height of 1250 feet.
September 14, 2012 — One World Trade Center’s steel officially topped out at the 105th floor. The final roof steel is installed along with the platform of the antenna.
November 2012 – March 2013 — The final construction of the tower’s 408-foot radio antenna is planned.
Source: The Port Authority of New York and New Jersey, World Trade Center Project Update.
We’ve improved what matters most in our 5 and 10 kV insulation testers:
Smaller
Easier to use
Rotary switch dial
Unique dual case design
Intuitive operation Ramp
Megger
3mA output power
Accuracy where it matters most
Super fast battery charge
AMP Quality Energy Services was foundedin2009withtheintentof founded in 2009 with the intent of becoming an International Electrical Testing Association Accredited Company. We take great pride in our contributions to this industry. OurvisionatAMPistofurther Our vision at AMP is to further the Gospel of Christ while sustaining exceptional employees providing quality services to the energy industry. We are grateful for the clients, vendors and team membersthathavebeenwithusthis bers that have been with us this far and are looking forward to building on this accreditation. One of our founding principles is providing quality services through quality employees and NETA certification is one more way we caninvestinthosewhoservein can invest in those who serve in our organization.
BY JOHN WHITE, Sigma Six SolutionsRecent economic news has reminded us many times that small businesses are one of the keys for the successful recovery of the American global economy. While we are blessed with many large successful firms, small businesses are not only our hope for the future but also played a huge role historically. This role is enjoyed by the electrical engineering sector. Most businesses, regardless of size, had a start that consisted of a single or a small group of entrepreneurs who had a vision and sought to build their dream.
Currently, many challenges are faced by a small business owner, given the conditions and macerations of both the global and U.S. local economies. Although it is not always clear as to this impact, there is reason to argue that the financial actions taken by our government is making it harder on small businesses rather than easier (financing and regulations). It appears that the future may hold both tax increases and more regulations, which impose more stress on our economy and the issues that business owners must endure. However, starting and growing a business in the past has not been without numerous challenges, and these challenges will continue to be a part of the present and future.
My perspective on small business success is formed from decades of employment in a field engineering service niche, involving small to medium-sized business activity, in the electrical industry. You might wonder why I mention the global economy and the success of small specialized engineering services in the same article. The point is that most employment growth comes from small business. And our big government politicians’ evaluation of this issue, while focused on results (such as unemployment numbers), is not dealing with many elements that help businesses to succeed. Being in the engineering field, we can comprehend the difficulty of understanding a problem with many variables, especially those problems with more variables than mathematical expressions to define them. However, solutions provided by the government must be simple in nature to attract consumer interest (think votes) and, therefore, often misses to provide the most effective solutions.
Studies have shown that more than 50% of startups fail within the first five years and that roughly only one third are left after ten years. The good news though is that, even under the current economic and political environment, small business will continue to succeed, pardon the cliché, by taking care of business, by staring businesses for the right reasons, and by focusing on all the elements in the business, not just the fun parts.
Let’s carry this discussion further by looking at some of the elements and challenges that small challenges businesses have had to endure to succeed. By looking at past successes and failures, we gain the knowledge to develop strong and successful engineering businesses.
We’ve read about successful entrepreneurs and how they tend to be great idea people. Moreover, frequently you find that such inventive folks have enlisted help, such as business managers, to make themselves successful with their business ventures. So where do engineers fall in this? Are some of them idea people? Or are someofthembusinesswizards? some of them business wizards?
Webster’s Dictionary defines an entrepreneur as onewhostartsabusinessandassumestherisk one who starts a business and assumes the risk for the sake of profit. Similarly, Wikipedia defines one as a person who owns or manages a business to make money through risk and initiative. While these definitions may define an entrepreneur, they don’t outline what differentiatesthesuccessfulonesfromtheothers. ates the successful ones from the others.
Do engineers inherently have or are they even schooled at being inventive, risk taking, and profit motivating? While these definitions point to what an entrepreneur is, they do not point to why one often starts a business. Many small business owners start their business because they came up with a good idea or a better way, and they have a passion for developing their idea. This passion is crucial for success. To only posses the profit motive is not enough to carry the business through upcoming trials and tribulationsthatmustbeendured.Itistheloveofwhat tions that must be endured. It is the love of what one does that plays heavily in business development and creates the profit mentioned in the definition. But regardless of the why, many small business entrepreneurs remain narrow in their business focus and allow that perspective to carry them too far into their future. Let’s follow a typical engineer entrepreneur through only a portion of the challenges being faced.
It is the love of what one does that plays heavily in business development and creates the profit through risk and initiative .
I know what I was worth to my previous employer. How much should I mark that up? Should I just double that rate to cover overhead costs? Should I triple it? Be careful, as it may not be easy to may dynamic change once you’ve established a rate. At the very beginning, think about the market value for your service, not the cost of your service.
Valuable connections can often be made through networking . This process can be extremely valuable for business success
When a start-up firm beings providing a service such as in the engineering field, the owner/manager must decide on how much to charge for his his/ her service. It is easy to see how one might think he/she should start with a below-market price to get one’s foot in the door, help create volume in the business, and internally satisfy the selfconscience thoughts about not having the same skill level or service capability of hi/her seasoned competitors. With no customers you won’t have a business, so the acquisition of customers is extremely high on the priority list. Hence, this is an opportunity to look well into the future and prevent the mistakes that can happen and to analyze how a present decision can play out.
A customer who is secure through this self-conscience pricing strategy can develop into pricing dilemma down the road. As the relationship develops over time, two things (among others) can occur. One is the need to offer a cheaper price that begins to disappear as the business positively develops in volume, skill, and reputation. The ability to provide a valued service could service grow much faster than was allowed for with the pricing strategy followed earlier. The second thing is that a now-loyal customer has become accustomed to receiving a particular level of service for the price paid. This sets a customer expectation of product versus price that gives the customer pause should the entrepreneur want to change the relationship between these two variables. But eventually, the entrepreneur must make that change. Accepting poor profits while taking risks is not what we inferred when reading the entrepreneur definition. A different perception must be established to help this customer
understand the pricing move. Perception can be formed through many avenues; one of them is certainly marketing.
To adequately cover sales and marketing is well beyond the scope of this article. But their importance warrants comments. Let’s just consider sales as having the objective of brining orders in the door. This is often an extremely foreign concept to engineers. The strategy, tactics, knowledge, skills, and planning involved in getting orders or securing contracts go way beyond what most engineers know. And marketing can be even more conceptually obscure. Sales success is easy to measure (purchase orders/contracts dollars), whereas marketing is quite difficult in many niches in which engineers find themselves. These two business needs are normally ones that engineering entrepreneurs (especially in more traditional engineering disciplines) need to hire others to provide assistance.
When the time is right to add a sales or marketing position, it is easy for a business owner to consider one of his/her top performers (from a technical perspective) to move to a sales/marketing position. After all, the person is a top performer and the business needs new orders/ contracts, so let’s take one of our stars to run withsales. with sales.
If this works out well, it is often due to coincidence or luck. Or this may be because the offerings of the business are of such high quality and reputation that the salesperson becomes merely an order taker. In this case, it was a waste of a top performer. If this didn’t work out well, it may be that the top performer just didn’t have the right set of skills or perhaps the right personality and are not suited to being a top salesperson. Among other traits, salespeople need to be sociable. They must be good listeners to understand the customer’s needs and objectives. However, they must also be good at starting and maintaining conversations, a characteristic extremely important in creating customer relationships. They can’t be fearful of cold calling (okay, most everyone is), and they have to know when
and the right manner of asking for the order. In an engineering business, it would be great if they were technically strong and had experience in the operations side of the business. Sounds a bit like Superman, doesn't it? So, the likelihood of any given business being able to find this person is slim.
The entrepreneur may have these traits and skills and may be the best person to bring in the customers. But you can't be fully engaged in that activity and also expect to successfully manage the business. Something has to give, and you have to choose what to focus on to do the most good for your business. If the entrepreneur moves in and out of the various aspects of the business (sales, operations, and finance), then those particular aspects of the business will go up and down based on the attention being given. This is typical of an approach that results in sporadic business success, inconsistent profits, poor management of risk, and lots of stress for the owner.
Valuable connections can often be made through networking. This process can be extremely valuable for business success. For electrical businesses, an excellent way to make connections is through the local IEEE Chapters. A wise entrepreneur will get involved and meet the professionals influential in the local community. The involvement in IEEE, such as going through the officer positions in the local Chapter, provides a worthy professional experience that canbringvaluetothebusiness. Otherprofessional associations can also provide ways to meet people and ultimately create a referral system. In addition, if the entrepreneur's specialty has a directly related association, this will form an excellent connection.
Some associations are set up to provide valuable services to the small business. For example, engineering field service firms that specialize in electrical field testing should consider joining the InterNational Electrical Testing Association (NETA). This organization can provide help in the form of marketing-related tools along with technical training, and networking with
other similar firms provides a wealth of knowledge for the younger business. In my experience, these technical professional organizations are a must for the entrepreneur.
This is an area in which most engineers need help. As engineers, we understand numbers very well. Of course, finance is all about numbers, right? We can balance our checkbook as well as the seasoned accountant, right? Perhaps the answers to those two questions are yes, but those are the wrong questions.
Understanding your balance sheet is important to realize the health of your business, but running your business from your balance sheet
is short sighted. To properly manage your operations, you must understand the income statement (profit and loss statement). You need an accurate and timely income statement to know how you are performing and to be able to make adjustments in your operations in an ongoing basis.
If you merely look at your checkbook (or the asset side of your balance sheet), you may get a comfortable feeling that money is accumulating. But you know nothing about how much money you spent in gaining that cash nor do you know what future debt you have yet to cover with the same cash asset. This is where a financial professionalbecomesinvaluable.Mostfinancial fessional becomes invaluable. Most financial professionals create income statements on a monthly basis, and most use an accrual accounting systems to run the business.
From the income statement, you can see how your operation is financially performing. Your statement should show the amount you earned (revenue) from work performed during the month. It should show the gross profit by subtracting, from that amount, the cost expended in creating the revenue [cost of revenue (COR) or more traditionally cost of goods sold]. The COR is frequently broken down into its major components so you can see how they might fluctuate month over month. Such a breakdown might breakdown include labor, materials, and other expenses incurred as a result of the particular projects. Be sure that the projects used in creating the revenue for the month are the same projects used in creating the cost (COR) for that same month. This is where accrual accounting becomes important. If the projects used to create the costs don’t match with the projects used to create the revenue, you are not comparing apples to apples, and you cannot use this financial tool to help guide the business.
Finally, a simple income statement will state the overhead costs (those costs not spent in direct support of the customer project) and subtract them from gross profit to get what may be called profit from operations or operating profit. There are other important costs, such as the sale of assets, earnings on investments, or even taxes, but on
these are not necessarily needed in the process of making operating decisions in a small and simple business. Again, these overhead costs should be appropriately matched to the month in which the expenditure occurred so that the monthly statement is accurate. Accrual accounting will properly match prepaid expenses to the pertinent month; for example, if you were to pay your rent in January for the entire year, the January income statement would only show one month of rent rather than the entire year paid.
The lesson learned here is to obtain a strong financial person. They can be invaluable in making day-to-day financial decisions that impact the health of he business and its success into the future. If you as an entrepreneur/owner are spending your time in the financial world, something in your business is not getting the attentionitdeserves. tion it deserves.
In an engineering service business, people are your most important assets and are certainly a valuable asset with which to spend time. The owner whose style includes liking and being with people will have a much easier time being successful manager than the person who only thinks of people as a means of creating profit. People are not heads; they are not bodies. They are the lifeblood of your business. They are the one who make your business successful. Particularly in a service business, people must be the most valued component. And unlike a piece of machinery, people have personalities. They have skills that you are not even likely aware of.
Each person is unique and must be managed as such. Policies and procedures are important to get consistency in behavior and performance; but to maximize the talents of people, they must be treated and managed as individuals. Finding and managing people is one of the largest challenges in running a business. And if people are not properly treated, nurtured, and developed, it could be a cause of failure of the business.
Compare recruiting and hiring to the football draft. You may be looking for the position player
to fill a need on the team, but you need to also look closely at the best player available and not be fearful of picking them up even when that's not the current hole that needs to be filled. Today's world may have high unemployment, but strong technical engineering talent is not included in those folks sitting along the sidelines. In addition to the skill you are looking for, look for attitude and self-motivation. Skills can be learned through education and training; attitude and self-motivation are much harder to achieve if they don't come with the candidate.
Imagine the difference between training a person on a particular electrical theory versus training a person to develop a good attitude. While understanding psychology may be extremely helpful, we're generally more comfortable with engineering theory. So if they don't meet your barfromanattitudemeasurement, passonthem. The strongest technical person in the world can do immeasurable damage to the business if they have a bad attitude.
Motivation is another human behavior that can be tricky. But it is easy to recognize the difference between a motivated person and onethat is not. Don't believe that money solves this problem Much is written about the lack of compensation (below market value) being a demotivator while the addition of more money (beyond market value compensation) is not a positive motivator. At best, more money may be a short-term motivator on performance, soon to be followed by retraction back to a performance level influenced by others factors. Once you have stepped up with the extra money, while you may not further motivate them, you can certainly demotivate them in theprocessoftryingtoget their compensation back to a suitable market value. This can get complicated fast, so focus on hiring folks with great attitudes and who are self-motivated and keep them
challenged and enjoying their career. But don't think managing people ends here.
People's needs vary and, as previously mentioned, need individual attention. Thesuccess in training, nurturing, and providing external motivationalfactors is dependent on theindividual. For example, all business owners desire to have loyal employees. What creates loyalty can be quite different from one person to another. The objective is the same with each person, and how you get there is often different.
While some business owners may choose to work until they are no longer physically able, there are certainly others who would like to disposeof theirbusiness and retireor dosomething else. Therearemultiplechoicesfor gettingout of the business, but none that are always the right choice for everyone. Some may choose to keep the business in the family; others might choose to sell it. Even selling has several choices. The business could besold totheemployees. It could be sold to a strategic buyer or sold to a financial buyer such as a private equity group.
In an eng ineering service business, people are your most important assets and are certainly a valuable asset with which to spend time.
Entrepreneurs and business owners just need to combine the right business elements and characteristics along with their technical capability and success will follow .
If the objective is to sell to outsiders, it is important to start getting the business ready well in advance, such as two years. If the small business is typical of many, there are several things that can be done to make the business attractive to buyers.Someofthesetakeaconsiderableamount ers. Some of these take a considerable amount of time. For example, if a finance system using the accrual system of accounting is accordance with generally accepted accounting principles (GAAP) is not in place, this is one process that should be implemented. This should be done soon so as much financial history as possible is available to prospective buyers. Some buyers would like to see five years of balance sheets and income statements. Other reports that help a buyer to understand the value of the business include sales and marketing data as well as operations efficiency. Suffice it to say that more the dataavailablefromwithinthevariousbusiness data available from within the various business processes, the easier it will be for the entire staff during the selling process.
Selling to strategic buyers, who have some familiarity with the seller’s niche market, may require less information to be developed during the due diligence process than selling to financial buyers who do not understand the industry. But, obviously, selling price is more important to the seller than the amount of time or work the selling processtakes. cess takes.
Depending on the size of the business and its complexity, it may be wise to counsel with an investment banker. This is even more important when dealing with financial buyers. Finally, it is important to have a good merger and acquisition law firm as part of the seller’s team.
I’ve always believed that businesses are either growing or shrinking. While you might have run across one that seems to be an anomaly to that statement, it is an exception. In the short run, eventhoseconstantsizebusinesseshavetheir even those constant size businesses have their
ups and downs due to economic conditions. It is just easier to manage a firm for growth, and therefore be successful, than taking the other course. However, growth brings on new challenges, so the business owner must constantly be in a learning mode.
Earlier in this article, I mentioned the electrical testing organization known as NETA. Having been associated with NETA for almost 40 years, I have met and talked with many dozens of business owners in this particular niche of the electrical industry. And having watched their performance in the business world, I've come to realize that these firms tend to be more statistically successful than the typical start-up firm in America. Why is this? It is because NETA helps them in those areas most desperately needed for success, such as quality of service, marketing, networking, and education.
In today’s world, engineering service firms have an advantage in the quest for success. The world is short of engineering people and the technical talents they possess. Entrepreneurs and business owners just need to combine the right business elements and characteristics along with their technical capability and success will follow.
John White currently holds the position of General Manager at Sigma Six Solutions, Inc and was formerly the President of Electro-Test, Inc. Through these two associations with NETA Accedited Companies, John has a combined member association with NETA of 37 years. John has served as President of NETA and is currently on the Board of Directors holding positions as Treasurer and Chair of the Finance Committee. He holds a BSEE Degree from Washington State University, is a registered professional engineer, and is certified by NETA as a Senior Level IV Technician.
Reprinted with the permission of IEEE Industry Applications Magazine, July/August 2012
Energis High Voltage Resources, Inc. is a singlesource energy service company specializing in high voltage electrical substation services including testing and maintenance, commissioning, field modifications, equipment repair and replacement, and project management and engineering services for clients in the utility, nuclear, renewable energy, and industrial markets.
Energis is comprised of technically experienced individuals from within the electric industry and project management professionals. Their experience and continual dedication to safety, quality, education, and development keeps Energis current and at the forefront of the energy industry.
Because the employees are the number one priority, Energis has focused on a safety-conscious culture. This culture is evident when you consider that the eighth full-time employee that Energis hired was a safety coordinator. Each employee goes through safety training on the first day of employment, is actively involved in preforming safety procedures on a daily basis, and participates in safety training throughout his or her career at Energis.
Dedication to quality has been a cornerstone of the company’s success. Energis has a strong customer focus, consistent processes and procedures, and a dedication to continual improvement. Energis is now a NETA Accredited Company. This accreditation provides assurance to customers that
Energis is objective and proficient in the markets they serve, that its technicians have broad-based electrical and safety knowledge, and that the are continually trained to inspect, test, maintain, and calibrate various types of equipment. To further dedication to quality management and standards, Energis is currently in the process of becoming ISO 9001 certified. Becoming ISO 9001 certified will put Energis in an elite group of only a few companies within the US withbothcertifications. with both certifications.
Green Bay, Wisconsin is the location Energis’s corporate office. Energis started in Green Bay with two employees and now employs 51 people, the majority of whom are in the Green Bay office. Offices are also in Waukesha, Wisconsin, and in Albert Lea, Minnesota, with future sites in the plans.
Inordertoservicecurrentcustomersinthirteen In order to service current customers in thirteen states and Canada, Energis has a full fleet of vehicles and unique testing equipment that has grown every year Energis has been in business.
Their goals are to drive growth and create value, be a preferred provider to their customers, and continue to be an employer of choice to their employees.
THIS ARTIClE IS PART 2 OF A FOUR-PART SERIES ON DATA CENTER MAINTENANCE.
This article will focus on the key attributes of design activities and how they can affect data center reliability and its electrical maintenance program.
BY LYNN HAMRICK, Shermco IndustriesTheUptimeInstitutehasprovidedawhitepaper whichpresentsexpectationsondatacenterperformance'. Thiswhitepaperpresentsatieredclassificationsystemthatgradesdatacenterswith regardtoperformance.Forelectricalpowerinfrastructure,thebasicclassificationsareasfollows:
• Tier 1: composedofasinglepathforpower distribution,withoutredundantcomponents, providing 99.671% availability.
• Tier 2: composedofasinglepathforpower distribution,withredundantcomponents, providing 99.741% availability.
• Tier 3: composedofmultipleactivepowerdistributionpaths,butonlyonepath active,hasredundantcomponents,andis concurrently maintainable, providing 99.982% availability.
• Tier 4: composedofmultipleactivepower distributionpaths,hasredundantcomponents,andisfaulttolerant,providing 99.995% availability.
Table 1 belowprovidessupportinginformation ontierclassification:
Table 1: Tier Requirements Summary'
Figure 1 above, from www.colocationamerica.com, provides additional information
Typically, data center managers migrate toward either Tier 3 or Tier 4 availability; therefore, they are constantly looking at ways to create redundancy in their infrastructure. This is especially true of data centers that are required to operate all day, every day. Without redundancy, data centers would have to shut down the systems to perform routine maintenance.
Data centers fall into two major categoriescorporate data processing centers and commercial internet-based data centers. Corporate data centers are owned and operated by corporations, institutions, or government agencies. Their prime purpose includes supporting data processing and Web-oriented services for their own organizations, business partners and customers. Data center equipment, applications, support, and maintenance are typically provided by internal information technology (IT) and maintenance departments. Based on internal staff skill sets, some specialized maintenance is outsourced to a group of specialized contractors or original equipment manufacturers.
Commercial data centers are primarily owned and operated by communication companies, unregulated competitive service providers, or other types of commercial operators. Each of these operators offer similar goals—to provide outsourced information technology (IT) services accessed through internet connectivity. Commercial data centers typically implement greater levels of redundancy and diversity of electrical infrastructure. This is due to their business plans revolving around economies of scale (i.e., more services sold per square foot of real estate). This often leads to unique issues not always found in the corporate data center environment. As with corporate data centers, data center equipment, applications, support, and maintenance are provided by internal IT and maintenance departments. However, commercial data centers typically outsource more of their maintenance to specialized contractors or original equipment manufacturers.
The one thing that both types of data centers have in common is that they are expected to operate without downtime. One of the ways they achieve their availability objectives is to design redundancy into the data center infrastructure. As the demand to be operational increases, often it is necessary to duplicate components that make up the data center infrastructure, either to allow
for planned maintenance or to protect availability from unplanned failures. At the upper end of availability requirements, multiple power sources are funneled into a single data center to provide assurance that there will always be power available to run the facility. With regard to electrical infrastructure, these sources typically include the local utility, uninterruptible power source (UPS) systems, and generation systems. In addition to multiple power sources, distribution of electrical power throughout a data center facility is accomplished with a large array of electrical distribution components. For example, transformers, switchgear, service-entrance panels, breakers, distribution panels, UPSs, emergency backup generators, automatic transfer switches, batteries, control panels, etc.
The specific maintenance that a data center requires depends in part on its design, required availability level, and budget. Most data centers are considered mission-critical facilities and any downtime, planned or unplanned, has an impact on the business objectives of the data center. Therefore, data center design should accommodate subsequent maintenance during operation with minimal downtime required. Below are a few examples of the implementation of a design philosophy that account for future maintenance needs:
Power Supplies. Most UPS systems are designed to provide primary power to downstream equipment with immediate switching to a battery system upon loss of primary power. Typically, manufacturers do not provide a maintenance bypass switch within their system that would allow for bypassing the UPS system entirely to accommodate UPS maintenance and testing. UPS manufacturers do provide a bypass capability for the UPS battery systems. The UPS batteries must also be checked periodically, including occasional load testing. To accommodate load testing, a capability for either a permanent or a temporary load bank should be included in the design of the system. Failed
or discharged batteries mean the UPS will not be able to supply the temporary backup power needed in the event of a power sag or outage. Even though UPSs are not designed to keep a facility running during a long-term outage, they do provide the carryover capability that accommodates a seamless transfer to an alternate power source like a backup generator.
Backup Generators. Backup generators should be checked and tested periodically to ensure that they will function as designed and when required. As with the UPS batteries, this testing should include occasional load testing. To accommodate load testing, a capability for either a permanent or a temporary load bank should be included in the design of the system. Further, maintenance is not limited to just the engine and other mechanical and electrical components. Fuel and coolant must also be considered. Diesel fuel and coolant will degrade over time; therefore, periodic checks on the fuel and coolant quality should be provided.
Infrared (IR) Surveys. One of the most effective predictive maintenance tools available is an IR survey of the electrical infrastructure. These surveys can reveal areas of high resistance, identifying potential failures within the system. The survey must be performed while the system is operating and a direct line-of-sight is required for optimal test performance. This means that doors must be opened or covers removed to perform the survey, which can introduce a safety issue. To eliminate this safety issue, IR windows can be installed to accommodate the survey. Not only will this resolve the safety issue, it will also minimize the labor costs associated with the survey.
Transformer Oil Sampling. Another available and effective predictive maintenance tool is analysis of oil quality and dissolved gas for oil-filled transformers in accordance with
One un i que i ssue for data center ground i ng and bond i ng i s the creat i on of electr i cal cont i nu i ty throughout racks and cab i nets as well as the power i nfrastructure.
ANSI/IEEE C57.106. These analyses can be very useful in evaluating transformer health while the transformer is operating. The problem with acquiring the oil sample for these analyses is that the sample ports are typically located within the termination compartment of the transformer. As with the IR surveys, this means that doors must opened or covers removed to acquire the sample which can introduce a safety issue. To eliminate this safety issue, the sample ports and transformer gages can be extended to a compartment located on the side of the termination compartment. Again, not only will this resolve the safety issue, it will also minimize the labor costs associated with performing the survey.
Accurate Documentation. Accurate and concise drawings and equipment documentation are key components to an effective maintenance program. This reduces the potential for human error while performing maintenance. Correct labeling of cables, circuit breakers, and other electrical infrastructure components can also enhance responses to unplanned disturbances. It is recommended that documentation be reviewed and upgraded at least every five years or whenever a significant change is made to the system.
Grounding and bonding is so important to reliable data center operations that it is worth more discussion. One unique issue for data center grounding and bonding is the creation of electrical continuity throughout racks and cabinets as well as the power infrastructure. Because most racks and cabinets are made of painted components that are bolted together, there is no guarantee that electrical continuity exists from one rack
component to the next even if they are bolted together. In the data center, rack and cabinet bonding is important for safety, electrostatic discharge (ESD) protection, and the correct grounding of switches, servers, and power strips. If specially designed paint-piercing hardware is not used for connection, something as simple as failing to scrape paint between sections of racks can result in a bonding issue that can affect system reliability. Typical issues with grounding systems in data centers are as follows:
1. Using the wrong type of grounding connectors. For example, connectors that use set screws to fasten grounding conductors can loosen over time, degrading the electrical bond. Copper compression lugs that do not loosen over time should be used.
2. Applying hardware (i.e., such as screws and washers, etc.) that are not designed to make an electrical bond, resulting in ungrounded equipment. Hardware, such as thread-forming screws and paint-piercing washers, and studs that cut through the durable finishes that coat data center racks and cabinets, should be used to create a metal-to-metal connection (bond).
3. Failing to create an electrical bond between the structural components of equipment racks and cabinets. Components, such as hardware and jumper cables that are tested for their ability to create electrical bonds and carry current, should be used.
Each component and connection in the system is critical to creating a low-impedance grounding path. Therefore, where possible, all grounding connectors within a data center should be listed to UL 467, Grounding and Bonding Equipment
Recommendations associated with a data center’s network-related, grounding systems is provided in TIA/EIA-942, Telecommunications Infrastructure Standard for Data Centers. The recommendations provided in this standard go well beyond the requirements of the National Electrical Code (NEC) to protect equipment and improve system reliability. The NEC Article 250 and ANSI-JSTD-607-A are also good resources for grounding system design requirements.
To ensure appropriate grounding requirements are being met, the ground resistance, along with the cumulative resistance of the grounding conductors and the connections, should be measured by testing. Ideally, it would be nice to have a resistance of zero ohms, but that is not achievable. In general, the lower the ground resistance, the safer and more reliable the system is considered to be. Values of a fraction of an ohm can be achieved with appropriate diligence applied to the design. Ground resistance measurement and testing is typically performed by qualified personnel using specialty test equipment designed for this type of testing. Use of a basic ohmmeter is not recommended due to the very low resistance values to be measured. For determining the ground resistance at the source of the ground connection (i.e., a ground rod or ground grid), it is recommended that a three-point fall-of-potential test be performed in accordance with IEEE Standard 81, IEEE Recommended Guide for Measuring Ground Resistance and Potential Gradients in the Earth. Note that while grounding electrodes can vary from a single rod to a grid or array that is several hundred feet across, the fundamentals of testing are the same. A ground resistance of less than one ohm is a typical requirement for a data center. Once this ground reference is established, ground
system bonding can be verified by performing continuity testing to all racks, components, and grounding systems within the data center. Any continuity resistance measurement exceeding 0.5 ohm should be investigated and corrected.
Data center managers are constantly looking at ways to improve system reliability. In many cases, this results in creating redundancy in their infrastructure. This is especially true of data centers that are required to operate all day, every day. Without redundancy, data centers would have to shut down the systems to perform routine maintenance. In addition to system redundancies, there are other design attributes that can be included within a data center which will affect the cost-effectiveness of the electrical maintenance program for a data center. Many of these attributes can also reduce the potential for human error associated with performing the maintenance. The grounding system for the facility can have a significant impact on the reliable operation of the facility. Therefore, quality design should be emphasized and appropriate testing should be provided to ensure the adequacy of the grounding system.
Lynn Hamrick brings over 25 years of working knowledge in design, permitting, construction, and startup of mechanical, electrical, and instrumentation and controls projects as well as experience in the operation and maintenance of facilities.
Lynn is a Professional Engineer, Certified Energy Manager and has a BS in Nuclear Engineering from the University of Tennessee.
During the past six months, the NETA Affiliate Committee has been working on an expansion plan for the NETA Affiliate Program to greatly enhance the benefits offered to subscribers, increasing interaction and networking opportunities. One of the most visible parts of this evolution is in the name of the program. The NETA Alliance Program replaces the NETA Affiliate Program, effective as of September 2012. All NETA Affiliate subscribers automatically became NETA Alliance Program subscribers who have accesstoalltheadditionalbenefitsunderthe access to all the additional benefits under the new program.
While this name change may seem subtle at first, the underlying rational directly aligns with the original intent of forming a section of the association that supports individuals who are not directly involved with electrical testing, but who are still interested and impacted by those that are.
The relationship between NETA and the NETA Alliance Program participants is one of mutual respect and collaboration. It establishes a network of professionals who can share knowledge and experience and come together based on a common interest in putting safety and reliability first. These people are professionals who are committed to furthering their education and personal development with the goal of ensuring that they are prepared to address the challenges of today andthoseinthefuture. and those in the future.
A recent survey of NETA Affiliate Program Participants fueled the name change. One of the objectives was to gain a better understanding of what motivates participation in the program. Responses included many unique reasons for joining, varying by business sector. Many people indicated a keen interest in aligning with NETA and its commitment to setting the standard in electrical power testing safety and reliability.
From the results one thing is clear, NETA Alliance Program subscribers value an alliance with NETA feeling it is important as they strive to achieve their professional and business goals. It allows them to stay current with the latest developments in the electrical power systems industry, play a more engaged role in advancing the industry, and be a part of a greater community of industry leaders.
The goal of the NETA Alliance Program is to continue to grow its network, expand the benefits it provides industry professionals, and engage in participation with NETA and NETA members working to fulfill the association’s vision:
…To assure that safety, quality, and system reliability are basic foundations of the electrical infrastructure.
NETA Alliance Program includes representatives from multiple Industry sectors:
distribution supervisors
If you were a NETA Affiliate Program subscriber, you are now a NETA Alliance Program subscriber. For information about subscribing to the NETA Alliance Program visit www.netaworld.org or contact Jill Howell at jhowell@netaworld.org.
NETA ALLIANCE SUBSCRIPTION : $135 per person
50% off of one NETA publication of your choice at the time of joining or renewal ($135 value).
20% off of each NETA publication purchase.
– The opportunity to place press releases
– The opportunity to announce new products
20% Discounts onNETA'sannualPowerTestElectricalMaintenance on NETA's annual PowerTest Electrical Maintenance and Safety Conference.
(held the Sunday before PowerTest).
(held during PowerTest).
NETA GOLD ALLIANCE SUBSCRIPTION : $775 per person
Complimentary registration for the NETA annual PowerTest Electrical Maintenance and Safety Conference ($809 value).
Complimentary NETA publication ($275 value).
Discount onPowerTestseminars. on PowerTest seminars.
20% off of each NETA publication purchase.
(distributed to NETA Members and Alliance Program subscribers).
– The opportunity to place press releases in
– The opportunity to announce new products
(held the Sunday before PowerTest).
(held during PowerTest).
CIRCUIT BREAKERS – LOW/MEDIUM VOLTAGE majormanufacturers
TRANSFORMERS – 1000–5000 KVA resintransformersfrom breakswitch&fuse
LIFE EXTENSION state motor
MOLDED CASE CIRCUIT BREAKERS LOW VOLTAGE MOTOR CONTROL breakers buckets mountswitches
SWITCHGEAR – 480V-38KV NEW AND SURPLUS in4weeks fromstock unitsubstations
RENEWAL PARTS –SWITCHGEAR & CIRCUIT BREAKER PARTS & vacuum instock www.circuitbreakerpartsonline.com
MEDIUM VOLTAGE MOTOR CONTROL AIR & VACUUM MOTOR CONTROL fromstock starters contactors
SERVICE & REPAIR service of circuitbreakers ISO 9001 and 14001 Certified circuitbreakerremote switch circuitbreaker
With substations regularly overloaded and equipment often near the end of its life, electric grid operators are challenged to improve overall system reliability. Our mission is to provide our clients with that can be used to better manage the overall life cycle of their critical electrical assets in a manner that is convenient, easy to understand, and assists in critical decision-making.
WEIDMANN DIAGNOSTIC SOLUTIONS INC. provides the vital knowledge you need to help you lower risk and improve your electrical system’s reliability. We provide through our extensive range of diagnostic products and services.
WEIDMANN DIAGNOSTIC SOLUTIONS INC. is a leader in developing condition assessment methods for transformers and all oil- lled electrical equipment, such as OCB’s, LTC’s, regulators, recti ers, and network units. ®
DIAGNOSTIC SOLUTIONS INC.
One Gordon Mills Way, PO Box 799, St. Johnsbury, VT 05819-0799, USA
T +800 811 2284, +916 455 2284, F +916 455 0191, www.weidmann-electrical.com
A Member of the Group
The VLF-34E is a new generation VLF AC Hipot that uses a solid state design with microprocessor controls. It meets the requirements of applicable world standards regarding cable testing up to 25kV class maintenance testing. It is light, compact, rugged, and very portable. Its sine wave output is suitable for using external TD and PD detection equipment. Using a TD and PD option, the VLF-34E is all that is needed for nearly all cable testing up to 25kV class.
Easy to use controls. Programmable test sequences & manual control, USB port for downloading data and for unlimited test report capture, wireless computer interface to control and download Tan Delta diagnostics and for remote control operation via laptop.
Cable Testing Standards met: IEEE 400.2-2004, IEEE 400-2001, NS 161-2004
VDE DIN 0276-620/621, CENELEC HD 620/621, IEC 60060-3
Partial discharges (PD) are small electrical sparks that occur when voids exist within or on the surface of high voltage insulation of stator windings in motors and generators.
These PD pulses can occur because of the thermal deterioration [Figure 1], manufacturing/installation processes [Figure 2], winding contamination, or stator bar movement during operation. As the insulation degrades, the number and magnitude of PD pulses will increase. Although the magnitude of the PD pulses cannot be directly related to the remaining life of the winding, the doubling of PD pulse magnitudes approximately every six months indicates rapid deterioration is occurring. If the rate of PD pulse activity increases rapidly, or the PD levels are high compared to other similar machines, this is an indicator that visual inspections and/or other testing methods are needed to confirm the insulation condition [IEEE 1434-2000].
Furthermore, if the PD magnitudes by the same test method from several identical windings are compared, the windings exhibiting higher PD activity are generally closer to failure.
Once a void is created within the bulk or on the surface of insulation, a potential difference will build across it. The magnitude of this voltage will depend upon the applied voltage, the capacitance of the insulation and the gas in the void. The voltage that develops across the void is modeled in Figure 3.
The dependence on the free electron for a part i al d i scharge makes the occurrence of PD a stat i st i cal event and therefore not pred i ctable
A discharge can only occur when the electric stress (V/mm) exceeds the electrical breakdown point for the gas based on Paschen’s law. Other issues besides gap length that can affect the electric stress in a void are diameter, internal gas and pressure, and the nature of the surface in the void. In general, the product of the gap separation and the gas pressure establishes the voltage necessary to lead to a discharge, i.e., breakdown voltage [IEEE 1434-2000].
When the applied 50/60 Hz increases sinusoidally, the apparent electric stress across the void increases until it reaches 3 kV/mm or the equivalent breakdown voltage in the void. Overvoltage is the state at which the voltage across a void exceeds the breakdown voltage required for the void size and gas. The larger the overvoltage the more intense the space charge
effects in the void. Although a void may be in an overvoltage state, breakdown will not occur until a free electron (due to cosmic or natural radiation) appears within the gap and starts an avalancheoftheelectrons.Thisavalancheis avalanche of the electrons. This avalanche is a flow of electrons across the gap which gives rise to a very fast rise-time (a few nanoseconds) current pulse, called a partial discharge.
The dependence on the free electron for a partial discharge makes the occurrence of PD a statistical event and therefore not predictable. Once the breakdown occurs, the voltage across the gap collapses to a voltage level sufficient to sustain the discharge. Most instruments only detect the initial breakdown pulse [IEC 6003427]. No further detectable discharges will occur
until the gap voltage has reversed in polarity and another overvoltage condition is established. Thus, (as shown in Figure 4) for each pulse position there will be a detectable PD occurring twice in an ac cycle. However, the occurrence, magnitude, and pattern in a void are a complex phenomenon depending on the size, shape, internal gas pressure, and nature of the void surface and will deviate from cycle to cycle due to past space charge trapping.
Machines that have not been properly impregnated or that have been operating for several years at high temperatures tend to develop voids within the groundwall insulation. If both sides of the void have similar insulation materials then the charge distribution will be equal during the positive and negative cycles. In theory, there will be two observable PD pulses in each ac cycle of equal magnitude and opposite polarity per void within the bulk of the insulation [Figure 6]. These pulses clump at the classic positions for phaseto-ground dependent pulses, that is, negative pulses at 45° and the positive pulses at 225° with reference to the 50/60 Hz phase-to-ground voltage [Figure 5].
Figure 7: Phase-to-Phase Discharges
A machine that is frequently load cycled or severely overheated develops voids near the copper conductors. A void bounded by the copper conductor and insulation exhibits a different phenomenon than one within the bulk of the insulation. Though the basic breakdown mechanisms are the same, because the electrodes are of dissimilar materials, polarity predominance occurs. The mobility of the positive ions on the insulation surface is much lower than the negative ions on the conductor surface. The result is a predominance of negative ions migrating through the gap to the positive insulation surface. In this case, there will usually be an observable predominance of negative PD pulses clumped at 45° during the positive ac cycle [Figure 4].
Loose coils, poor semiconductive coatings, and problems with the grading/semicon interface can all lead to surface discharge between the stator bar and the grounded core iron, called slot discharges. As with those near the copper conductors, these discharges occur between electrodes made of different materials. Here, the immobile positive charges on the insulation and mobile negative charges on the grounded metallic electrode lead to pulses occurring during the negative ac cycle. Because the metallic electrode is grounded, the observable PD pulses will be predominantly positive clumped at 225° [Figure 6].
Contamination and/or phase-to-phase discharges in the end arm area, on ring buses, or motor leads, can lead to partial discharge activity in these areas. Unlike the previously described pulses that are phase-to-ground voltage dependent, these pulses are based on phase-to-phase voltages. Though these pulses tend to be very erratic, it is sometimes possible to distinguish these pulses from others by observing their location with reference to the phase-to-ground voltage. Typically, because of the phase-to-phase voltage dependency there is a 30° phase shift from the classic phase positions associated with pulses that are phase-to-ground voltage dependent as shown in Figure 7. Phase-to-phase pulses tend to clump at 15°, 75°, 195°, and 255°, based on the location of the pulses and the phase rotation of the machine. Sometimes, it is possible to determine which two phases are involved, but often it is difficult to extract that information accurately from the quantity of pulses detected.
See the Next issue for information about how to detect PD and how to interpret PD results.
Ms. Vicki Warren, SeniorProduct Senior Product Engineer, Iris Power LP. Ms. Warren is an Electrical Engineer with extensive experience in testing and maintenance of motor and generator windings. Prior to joining Iris in 1996, she worked for the U.S. Army Corps of Engineers for 13 years. While with the Corps she was responsible for the testing and maintenance of hydrogenerator windings, switchgear, transformers, protection and control devices, development of SCADA software, and the installation of local area networks. At Iris, Ms. Warren has been involved in using partial discharge testing to evaluate the condition of insulation systems used in medium to high voltage rotating machines, switchgear and transformers. Additionally, Ms. Warren has worked extensively in the development and design of new products used for condition monitoring of insulation systems, both periodical and continual. Ms. Warren also actively participated in the development of multiple IEEE standards and guides, and was Chair of the IEEE 43-2000 Working Group.
Vanguard’s precision substation testing instruments are designed to be intuitive and easy to use so that you can focus on testing instead of wasting time in training. Our versatile instruments offer a built-in thermal printer and on-board test record storage so that tests can be conducted in stand-alone mode in the field. A computer interface is also offered so that tests can be easily conducted from a PC.
And all of our instruments are competitively priced to provide cost-effective accuracy. For a virtual experience of our instruments, check out the interactive demos on our site at:
www.vanguard-instruments.com/demos
Providing low voltage circuit breaker retrofit kits with a tradition of quality products and exceptional customer service for over 15 years
Over 1000 different kits
Microcontroller based, true RMS and 16-character display
Intuitive programming and easy retrieval of last trip data
3 Different types of actuators available
Modbus communications available Quick-Trip™ for arc flash reduction during maintenance UL and CE labels
Over 95 different kits
Microcontroller based with 16-character display
Modbus communications available Now available with Quick-Trip for arc flash reduction during maintenance
Easy to install AC-PRO trip units are Quick-Trip ready and only require the addition of
Provides arc flash reduction during maintenance per 2011 NEC Article 240.87
Plug-in direct replacement for Merlin Gerin & Square D Masterpact MP, IEC or UL rated breakers
User programmed to replace the STR-18M, 28D, 38S or 58U trip units
Same protective functions, settings and time-current-curves as the original STR trip unit
Information and alarm functions are standard
No physical rating plug required
Easy to read OLED display in low or high ambient light
A security code protects against unauthorized changes to settings
Trip events are time and date stamped USB port and secondary injection test port
Quick-Trip for arc flash reduction is built in, nothing additional is required
Your first end-to-end test can seem to be a daunting task, but the actual test procedure is not very complicated and can be performed more quickly and effectively than traditional relay test techniques; if everything works correctly. That last statement is the hard part because you are typically working with a team at a remote location which makes it difficult to determine whether the problem lies with the test plan, relay settings, test-set configuration, or operator error. This article will introduce you to end-to-end testing and answer many of the questions you might have.
Providing protection for a transmission line is difficult because the typical transmission line is fed transmission fed from multiple sources and can carry loads that vary significantly. Traditional protection schemes use an impedance relay on either side of the transmission line that constantly monitors voltage and current to calculate impedance in real time. If a fault occurred on the transmission line, the measured impedance would be less than the calculated line impedance and the relays would operate to isolate the fault from the system. Unfortunately, the relays cannot be set at the exact line impedance because the typical protection-class current transformer
has a 10 percent error factor and the calculations will make assumptions (conductor spacing, splices, conductor impedance, etc.) that could cause the relay protection to overreach and isolate the wrong transmission line, so most impedance relays are set at 75 to 90 percent of the transmission line impedance as shown in Figure 1. A time-delayed backup impedance element is often set to reach beyond the transmission line to protect for faults in that last 75 to100 percent of the protected line so that all faults will be isolated from the system eventually. This element will also provide backup protection for the adjacent transmission line as shown in Figure 2. Remember that the other relay is looking in the opposite direction as shown in Figure 3.
Figure 2: Typical Relay’s Primary and Backup Zones of Protection
Every misoperation will cost the utility labor and lost revenue, so 75-90 percent rotection is often not good enough, even though both sides overlap to provide a reasonably good protection scheme. Modern protection schemes a ply a communication channel between the relays on either side of a transmission line that allows the relaystocommunicatewitheachother.Thesimplest scheme (not really, but easiest to understand) ap lies differential protection principles. Each relay measures the current entering or leaving the transmission line and shares its local current with the remote relay bidirectionally. If the current in does not match the current out, both relays will trip.Theserelaysoftenhaveabackupscheme using traditional impedance protection that is only activeiftherelays areunabletocommunicate.
the tester a reasonable sense that the scheme will operate successfully on proven relay settings, but many problems with communication-assisted protection occurwhenthe fault changesdirection or by incorrectly defined communication delays which are inherent in the system. These problems can only be detected by properly applied endto-end testing or a review of an incorrect relay operationafter afault.
End-to-end testing was considered daunting a decade ago, but advances in relay testing technology and personal computers have reduced the complexity to a couple of extra steps for a reasonablyexperiencedrelaytester.
The other communication schemes have man names (DUTT, PUTT, POTT, DCUB, etc.) and operating parameters, but they all perform the same basic function. Both relays monitor the real-timeimpedanceandcurrentdirection.Ifboth relays agree the fault is betweenthem, both relays will trip as soon as possible depending on the communicationmediumandscheme.
While it is possible to test each of the individual components of a communication scheme separately, many problems can only be detected when the entire scheme is tested as a whole. It is possible to test one side at a time which can give
End-to-end testing uses two or more test-sets at multiple locations to simulate a fault at each terminal of a transmission line simultaneously to evaluate the entire protective relay scheme as a whole. This test technique previously required specializedknowledge andequipment toperform, but modern test-sets make it a relatively simple task. Figure 4 represents an overview of the equipment and personnel re uired for a typical end-to-end test using a simple transmission line with two ends or, as they are sometimes called, nodes. It is possibletohave a system with threeor morenodeswhichsimplyaddsanotherlocationto thetestplan.
The following components are necessary to perform a successful end-to-end test:
1. A relay test-set for each location with a minimum of:
• three voltage channels
• three current channels
• at least one programmable outfut to simulate breaker status or other externa signals
Most system disturbances develope within one millisecond of their initiation and modern protective
relays must be able to detect faults within this time frame to be effective.
• at least one programmable input to detect trip or breaker status signals
• an internal GPS clock (Some test-sets allow for other time signal synchronizations such as IRIG) or an external GPS clock with output signal and an additional test-set start input
• waveform playback or fault state/state simulator with at least three states available.
2. Some test-sets require a computer to control the test-set playback or state functions.
3. A computer and software to download and display event records obtained from the relay after each test.
4. At least one relay tester at each location with some form of communication between the two locations such as telephone or overnetwork communication. It is possible, but not recommended, for oneperson toperform all tests if the relay, relay test-sets, and communication systems have all been configured properly.
5. A setting file, waveform, or detailed description of the specific test scenarios.
6. An understanding of the relay protection scheme and what the expected result for each test should be.
7. The design engineer who created the settings and test plans standing by if any problems are detected that need correction.
Most system disturbances develop within one millisecond of their initiation and modern protective relays must be able to detect faults within this time frame to be effective. Practical experience has shown that two test-sets must start within 10 microsecondsof each other to provide reliable results. This causes a problem for multiple relay testers at multiple locations because it is nearly impossible for them to press start within 10 microseconds of each other. The remote relay testers could use the power system to synchronize their test-sets, but this method could add up to one millisecond or 22° error to the test which is not within the ten microsecond tolerance required for consistent results. The GPS system time allows synchronization within 1 microsecond which is within the
Figure 5-1: Typical 3-Phase Comtrade Fault File for 1st breaker
Figure 5-2: Typical 3-Phase Comtrade Fault File for 2nd breaker
signal can also be used but synchronization errors can be as high as 10 microseconds.
Once two test-sets have synchronized time sources, both test-sets simultaneously apply fault simulations that are calculated to be similar to the signals thatwouldoccurifarealfaultoccurred.Ifthetestthat would occur if a real fault occurred. If the testsets are properly synchronized, and the test plans are created and implemented correctly, and the relays are set correctly, and the correct auxiliary connections are made, and the communication scheme is working, then the test should be successful.
Fault simulations can be supplied as waveform files (Figure 5) such as IEEE C37-111 COMTRADE files. This is typically the simplest method for
everyone involved, as long as everything works correctly. However, waveform files can be difficult to troubleshoot if problems occur.
Fault simulations can also be supplied in a test-set proprietary format that can be loaded directly into the test-set or in a standard spreadsheet format (Figure 6) to be entered using the state simulation to understand and troubleshoot but can be prone toconversionerrors. to conversion errors.
It is also important to note that different test-set manufacturers and test-set models may be synchronized to the same time source and set to the same start time, but may not start outputting the test at the same moment. Different firmware revisions
Figure 6: Typical State Simulation Instructions for 1st Breaker (SOURCE BUS) and 2nd Breaker (LOAD BUS)
Figure 7: Typical End-to-End Test Scheme
can also be problematic with some manufacturers. Always consult with the relay test-set manufacturersiftwodifferentmodelsoftest-setswillbeused ers if two different models of test-sets will be used for end-to-end testing on one line to determine if a a correction factor must be applied. Different models from the same manufacturer can produce different starting times without notice, and the correction factors should be verified at the same location, if possible, before performing any remote testing.
End-to-end testing should be performed wheneveritwouldbebeneficialtotestanentire whenever it would be beneficial to test an entire protection scheme in real time to make sure that all equipment will operate correctly when required. This test technique need not be limited to transmission lines and can be applied any time you wish to test coordination between different devices. For example, a number of test-sets can be connected to the protective relays for all feeders in a system. A fault simulation can be played into all relays simultaneously to ensure that complex blocking schemes work as intended.
All new installations with remote communication between relays should be tested via end-to-end testing. This test technique can also be a useful and effective maintenance test, particularly if end-toend testing is performed during commissioning that will provide expected results. There is no more effective way of proving the entire protection scheme than replaying the same number of tests into the protection system and observing the same results. Performed correctly, using this test technique for maintenance tests can be more efficient as well.
The relay testers at each end of the line should perform the following steps when performing an end-to-endtest: end-to-end test:
1. Obtainallofthetestcasesforallsidesofthe Obtain all of the test cases for all sides of the test procedure from the design engineer before the scheduled test date. This step can be skipped for line differential relays if the test is to be performed by personnel who have a good understanding of the relay’s intended operation and test-set functions. It is possible to create test plans for impedance schemes, but they will be a poor substitute for real simulation files and may be too simple to truly test the entire scheme. A typical end-to-end test procedure will have 8 to 15 tests that are on either side of each impedance zone as shown in Figure 7. The test cases should have a combination of fault types and phases. (For example: Test Case #1 = 3 Phase Fault, #2 = A-N fault, #3 = A-B fault, etc.)
2. Review all sides of each test case on a split screen and make sure the test plans make sense and that you understand what is supposed to happen. Most test plan files have a description such as “Test1=50%fromBRK1=Zone1Trip.” all ends of a single test case include:
3. After arriving on site, determine the test antenna outside the building with good access set reference. (Or use other reference such as
4. Always remember that the relays under test communicate with each other, and your actions could cause an unintended trip on the othersides.Communicatewithallendsunder other sides. Communicate with all ends under test. If all locations agree, isolate the circuit breaker and relay under test at all locations.
5. Connect the appropriate digital inputs and outputs between your test-set and protection scheme. I always recommend using the circuit breaker under test as part of the test, if possible, instead of simulating the breaker contacts.
potential transformer connections using the site’s three-line drawings.
7. Prepare a metering test and communicate with remote testers. If they agree, apply a meter test on all sides and verify correct results. Make sure that A-phase from your test-set is A-phase in the relay and repeat for B- and C-phase. A three-phase balanced meter test will NOT prove this.
8. Communicate with all remote sites and determine which test plan will be used for the test. (Test Case #1 for example)
9. Load the selected test case into all test-sets. Every site should have a unique test to load.
10. Place all circuit breakers in the correct positions or ensure circuit breaker contacts are properly simulated by the test-set.
11. Communicate with all remote sites and select a start time. Apply the start time to the test-set.
12. The test should start automatically.
13. Review targets for correct operation and download all event records. Review the event records for correct operation or no operation, as required by the test procedure. Clear event
records in the relay between tests to make sure you get the correct event files.
As you can see, the key to any end-to-end test
the test procedure are the hardest parts of any endto-end test. If the design engineer has correctly specified the tests and their outcomes, and you have carefully reviewed the test cases, the actual the test procedure usually runs very smoothly with enough practice. When you review the test results in the field, these two principles will apply to most communicationschemes: communication schemes:
1. Faults inside the zone of protection (current at the same angle on both ends) will be isolated more quickly by both relays than they would withoutthecommunicationscheme. without the communication scheme.
2. Faults outside the zone of protection (currents at each end 180° apart) will be ignored or have significant time delays.
You can make the test procedure even more comfortable by practicing before the test date:
table so that you are not able to see each other’sactions. other’s actions.
2. Connect A-phase voltage and current from both test sets into any phase of the relay.
3. Perform the end-to-end test procedure using the same test plan.
4. Review the event record waveform from the relay. The voltages and currents should be identical.
5. Repeat until you feel comfortable.
Chris Werstiuk is an Electrical Technologist, Journeyman Electrician, Professional Engineer and author of the upcoming book, “digital Relay testing: A Practical Guide from the Field.” He is also the founder of “RelayTesting. net”, an online resource for testing technicians who need custom test leads, test sheets templates, step-by-step testing guides, or an online forum to exchange ideas and information.
N o2*
Introducing a really big idea: “Rent it”
What makes it work at Protec, better than other options?
What’s next? Make us prove we care.
“At Arc Flash Study Pro we’ll help you achieve compliance fast and efficiently.
You’ll work with one highly trained specialist from start to finish, from surveying through analysis, engineering, reporting and training. You have my commitment!”
Curtis Latzo, President and Owner, Arc Flash Study Pro
Electrical Power System Services:
Benefits of hiring Arc Flash Study Pro:
Our STUDIES will provide you with FULL COMPLIANCE of NFPA 70E and OSHA 1910 Arc Flash Regulations
“Hire the Pro, Deal with the Pro, Work with the Pro from beginning to end.”
Medium-voltage cable systems typically consist of terminations, splices, and the cable itself. All of these items fail but typically fail by different mechanisms. Therefore, different testing techniques must be applied to spot the failure modes most common to a specific item. By employing a structured cable system testing strategy, condition can be determined so that repair and replacement can be optimized to prevent future failures and increase reliability. Focusing resources on problem items will also result in substantial direct mone-tary savings.
Most facilities today cannot endure an extended outage to test the condition of their mediumvoltage, underground, electrical cables. However, as the cables continue to age, the likelihood of failure increases. This leaves the owner with a difficult decision - run to failure or take a more proactive approach.
The majority of synthetic (XLPE and EPR) cable systems fail at terminations and splices; therefore, focus should be on determining the condition of these components first. A high percentage of these components fail due to partial discharge activity so the primary strategy for determining cable system condition is to test the components for the presence of PD activity. Fortunately, new advances in on-line PD testing technologies can accurately provide valuable information relating to the condition of these components; therefore, on-line PD
testing should be the first consideration in developing a cable testing program.
Although great advances have been made recently in on-line cable PD testing, limitations are still encountered, most often in the form of background noise. Many sources of background noise can be present including conducted noise from process loads, radiated noise from nearby electronic equipment or radio frequency transmissions, and actual PD or corona reflections coupled to the test object from other components. New sophisticated noise reduction solutions have been introduced, but there can be limitations in regard to determining actual PD location. In some cases just distinguishing PD can be difficult. In high noise conditions, filtering may be necessary which will allow for accurate determination of the component condition near the test point but will limit the distance down
the cable where PD can be seen if the filtering is too restrictive because of noise. It is therefore advisable to always test both ends of the cable in order to accurately determine termination condition. However, a distant splice problem may be missed in high noise situations. So the results of the first step on-line cable PD survey may not be precisely conclusive but should rule out PD problems for 90 percent or so of the cables tested, and if noise lev-
Figure 2: Locating PD by Time-of-Arrival Techniques
els are low, the results may be even more accurate. When questionable results are encountered, the remaining cables should then be tested using off-line PD cable mapping techniques.
Off-line cable mapping (see Figure 1) requires an outage; therefore, the majority of noise sources are eliminated. This method provides the opportunity to verify and locate potential problems discovered during on-line testing and can be a very valuable technique to detect and locate PD on long circuits with multiple splices where typical on-line noise floor levels would limit the chances of this being successful. By slowly increasing the cable test voltage using an external VLF power source, the onset or inception of PD can be readily recognized, and the voltage can be increased to levels above normal operating voltage so that future defects can be located in the cable itself. Without noise present, accurate PD waveforms can be recorded, and using time-of-arrival techniques as shown in Figure 2, precise location can be determined.
By employing an organized testing approach to cable assets, valuable condition information can be obtained which can then be used to select optimum remediation activities that focus primarily on the cable system components that require attention.
By combining on-line and off-line PD tests, cable PD problems can be accurately identified, located, and quantified so that optimum remedial actions can be planned to eliminate these trouble spots.
PD is not the only failure mode plaguing cable systems. The cable itself often fails because of conductive problems, and many of these occur because of water trees. Cable water treeing (see Figure 3) is a complex phenomena that could itself occupy volumes of articles, but in simple terms, water trees create conductive paths through the bulk of the insulation. These areas appear electrically as a small
resistance instead of the pure capacitance of an ideal insulator. It has been shown that off-line VLF tan-delta testing provides good correlation to the degree of cable water treeing present in the cable system; therefore, it provides a good indicator of bulk cable condition. By targeting cable systems with poor tan-delta test results for replacement, reliability can be increased significantly.
The flow chart shown in Figure 4 provides a simple guide for employing the best test methods available for managing cable system assets. The first step, however, should always be to regularly (at
least annually) perform an on-line PD survey of the associated switchgear equipment where the statistically high risk terminations are housed. The nonintrusive on-line switchgear PD survey allows for a quick check of the overall switchgear condition. It encompasses all components within the switchgear including the cable terminations. This quick and efficient test can pick up a severe termination problem and should not be substituted for the cable test program described above. Nevertheless, it pays great dividends without a great deal of effort. Besides, who wants to go through the process of determining cable system integrity only to have a switchgear failure?
By employing an organized testing approach to cable assets, valuable condition information can be obtained which can then be used to select optimum remediation activities that focus primar-
ily on the cable system components that require attention. Utilizing this approach will result in a much lower failure incidence rate and a remarkable increase in reliability.
Don A. Genutis received his BSEE from Carnegie Mellon University. He was a NETA Certified Technician for 15 years and is a Certified Corona Technician. Don’s technical training and education are complemented by twenty-five years of practical field and laboratory electrical testing experience. Don serves as President on No-Outage Electrical Testing, Inc., a member of the EA technology group.
The NETA Board of Directors and membership met in Las Vegas, Nevada, on September 20-21, 2012, at New York-New York Hotel. The Board Meeting focused heavily on reviewing, revising, and updating many of the policies as well as continued strategic discussion.
The Membership Meeting had an excellent turnout, with a great discussion on how tohandleissueswithmolded-casecircuit to handle issues with molded-case circuit breakers, round tables to workshop three different NETA programs, as well as a special different presentation on the OSHA Voluntary Protection Program (VPP) given by Kyle Kirkpatrick of ShermcoIndustries. Shermco Industries.
Ron Widup, President of Shermco, introduced Kyle and this subject by giving a detailed account of a near miss he had as a young technician as a result of an arcblast. This experience forever
changed Ron, and is a driving force behind his motivation to make Shermco as safe as possible for every employee.
Kyle went on to explain the VPP process and tell about the experiences that Shermco has had to date as they work toward gaining the highest level of recognition possible, a Star Site. Taken from the VPP website, “In VPP, management, labor, and OSHA work cooperatively and proactively to prevent fatalities, injuries, and illnesses through a system focused on-site hazard prevention and control; worksite analysis; training; and management commitment and worker involvement. To participate, employers must submit an application to OSHA and undergo a rigorous onsite evaluation by a team of safety and health professionals.”
NETA is proud to have members like Shermco who demonstrate excellence in all aspects of their business.TolearnmoreabouttheOSHAVolun business. To learn more about the OSHA Voluntary Protection Program, visit OSHA’s website at http://www.osha.gov/dcsp/vpp/index.html. business.TolearnmoreabouttheOSHA Volun lunolu re more i Protection OSHA’s at gr tary , vi OS we t bs s t s am ro tio rot c e e HA’ Pro P i i n i i http ://www.osha.gov/dcsp/vpp/index.html. sp/vpp/ .go ttp ://www.osha.gov/dcsp/vpp/index.h ex sh h de /dc in tml. /i haos x. c .g /www. : p v/dcs :/
Personnel inspections, assessments, evaluations, or audits all intend to accomplish the same task, an evaluation of work performance. These observations can be performed within any level of a company and should be inclusive of all departments and skill levels. To ensure impartial results, some companies hire an outside entity to perform these inspections for them. In most cases, companies choose to have a member of the management team conduct the observation with certain standards and expectations in mind. For example, the frequency of the inspection and proof checking to be done by a third party or safety manager.
OSHA requires the employee be observed performing the lockout / tagout procedures annually. OSHA specifically states under 29 Code of Federal Regulations 1910.147 when this verification is required. It is slightly varied for each of the different industries that OSHA regulates. Two specific regulations that pertain directly to electrical testing are 1910.147, applicable in commercial type installations, and 1910.269 specifically regulates
the operation and maintenance of electric power generation, control, transformation, transmission, and distribution lines and equipment.
1910.147 requires that employers observe that procedures are being correctly followed by the employee(s) performing the lockout / tagout. Refer to excerpts below:
1910.147(c)(6)
Periodic inspection.
1910.147(c)(6)(i)
The employer shall conduct a periodic inspection of the energy control procedure at least annually to ensure that the procedure and the requirements of this standard are being followed.
1910.147(c)(6)(i)(A)
The periodic inspection shall be performed by an authorized employee other than the ones(s) utilizing the energy control procedure being inspected.
1910.147(c)(6)(i)(B)
The periodic inspection shall be conducted to correct any deviations or inadequacies identified.
1910.147(c)(6)(i)(C)
Where lockout is used for energy control, the periodic inspection shall include a review, between the inspector and each authorized employee, of that employee's responsibilities under the energy control procedure being inspected.
1910.147(c)(6)(i)(D)
Where tagout is used for energy control, the periodic inspection shall include a review, between the inspector and each authorized and affected employee, of that employee's responsibilities under the energy control procedure being inspected, and the elements set forth in paragraph (c)(7)(ii) of thissection. this section.
OSHA
requ i res the employee be observed perform i ng the lockout / tagout procedures annually.
1910.147(c)(6)(ii)
The employer shall certify that the periodic inspections have been performed. The certification shall identify the machine or equipment on which the energy control procedure was being utilized, the date of the inspection, the employees included in the inspection, and the person performing the inspection.
We can see that the 1910.269 standard does not differ greatly from 1910.147 in its requirements by taking a look at the excerpt below.
1910.269(a)(2)(ii)(D)
The proper use of the special precautionary techniques, personal protective equipment, insulating and shielding materials, and insulated tools for working on or near exposed energized parts of electric equipment.
Note: For the purposes of this section, a person must have this training in order to be considered a qualified person.
1910.269(a)(2)(iii)
The employer shall determine, through regular supervision and through inspections conducted on at least an annual basis that each employee is complying with the safety-related work practices required by thissection. this section.
OSHA states that it is a requirement for the company to inspect and certify that employees are properly performing lockout/tagout. Incorporating this certification as part of a field assessmentorobservationmeetstheabovestandard. ment or observation meets the above standard. There are other required observations that are dependent upon the task and industry. Another example of a task that requires a documented observation is the operation of a fork truck. Please check www.osha.gov as a guide in determining what applies.
Personnelauditscanbetailoredforfieldservice Personnel audits can be tailored for field service companies and can encompass such duties as proper use of protective and cautionary flagging and tagging. In some instances a client may have a different procedure for this, so it would be good policy to ensure that employees not only follow their company’s policy, but where applicable, follow the client’s policy. The default course of action in this type of scenario is to play it safe and follow the more stringent policy. The observer would need to know what the client requirements are prior to performing the observation.
Theauditorshouldalsobefamiliarwiththe The auditor should also be familiar with the procedure that they are observing. In some cases, he or she may even be considered an expert in the task. If this is the case, then perhaps the auditor can give direction and add to the employee’s knowledge of the task by observing and critiquing. Being knowledgeable in the procedure can also help the auditor identify when a procedure is being performed incorrectly. We all develop bad habits, andinalotofcasesweareunawareofthem.So and in a lot of cases we are unaware of them. So if the auditor is knowledgeable of the correct procedure and notices the employee performing it in a different or incorrect manner, the auditor can correct the task prior to it causing an incident.
An obvious benefit to conducting field inspections and observations is ensuring that the employees use the correct personal protective equipment otherwise known as PPE. The manager should inspect the PPE to ensure that it is worn at the appropriate time and location, and that the PPE is inserviceablecondition. in serviceable condition.
Inspection of the general work environment is a benefit to the company and the manager. Even though a lead technician or foreman may be conducting a prejob briefing inspection daily, he can still miss something that needs correction. Having someone who can lend a fresh set of eyes to the area can help identify potential problems or issues that could contribute to lost production or to an injury.
During a personnel audit, the inspector should make it a point to ask the employees thought provoking questions for honest feedback.
Is there anything that the company could do to make the job easier, safer, or better?
Does the equipment assigned to the project work correctly?
Do you have the right tools for the job?
Can you see the need for any additional PPE or tools to perform this task?
The answers to these questions can sometimes be challenging or even ludicrous, but occasionally a question can shed light on a brilliant idea and possibly become the catalyst to revolutionize a task. If the employee gives a good answer, consider rewarding the employee for the contribution and give credit where due. Comment on the safe behaviors you observed. Discuss with the employee any consequences of unsafe acts and safer ways to do the job.
Conducting field observations ensures that employees are following company policies and procedures such as vehicle safety and driving policies. Basic safety such as wearing seatbelts, inspection of vehicles, and not using cell phones while driving are items that should be included on achecklist. a checklist.
If the company requires a lot of driving, or has federally regulated vehicles, it may be necessary to observe employees while operating the vehicle. This can either be conducted as a ride-along with the employee or follow-along observation. Consider creating a separate form just for these types of observations, since the rules-of-the-road are extensive, and regulations vary depending upon the state in which they operate and the type of vehicle they drive.
Face time with field personnel is beneficial on its own. Having the manager get out into the field will increase communication with employees and show support and commitment from the management team. This in turn will potentially make the job more productive. The best way a manager can ensure he makes the time available to perform personnel audits is to schedule it. The best way a company can ensure that it gets done is tomandateitandrewardthosethatmeetorexceed to mandate it and reward those that meet or exceed the requirement.
In summary, there are many obvious advantages to performing site inspections, assessments, evaluations, and audits. They boost morale, prevent injuries, and can be used to satisfy regulatory requirements. Inspectors should be knowledgeable in the scope of work, make time to get out into the field, be able to match the face to the name and give praise when it is due while at the same time ensuring proper procedures are being followed and and equipment is in good working order and being used correctly. Audit forms such as these can go a long way in improving a company’s safety culture. Keep a record of these audits in a secure place for future reference.
Paul Chamberlain has been the Safety Manager for American Electrical Testing Company Inc. since 2009. He has been in the safety field for the past 12 years, working for various companies andinvariousindustries.Hereceived and in various industries. He received a Bachelor’s of Science degree from Massachusetts Maritime Academy.
Most field operators in the grounding industry are, of course, familiar with the muchpracticed Wenner Method for measuring soil resistivity. It is simple and fairly easy and fits a broad range of application so that it well may be the only method ever needed. There are others, however, some of which have been reviewed in prior columns. An examination in some detail can be useful, not only as a practiced method, but also for what is revealed about the complexities of soil and its measurement.
For the theoret i c i an or eng i neer do i ng pure research, homogeneous so i l i s the Rosetta stone.
The Wenner Method utilizes the four terminals of a ground test set in a regular pattern, with current probes on the outside establishing a uniform test current through the soil by which the potential probes on the inside enable the test set to measure voltage drop caused by soil resistance. The probes are equally spaced and measure to a depth equal to the horizontal spacing between any pair. This familiar arrangement seems intuitively satisfying. But other arrangements have been suggested and formulae devised for their use. In standard notation, C for current probe and P for potential, the Wenner configuration would be represented as CPPC. The table below shows other configurations and their formulae.
spacing, all three calculations would produce the same result…that is, in homogeneous soil. For the theoretician or engineer doing pure research, homogeneous soil is the Rosetta stone, and references to it appear regularly in the literature. In the practical world, homogeneous soil is rare…less so at construction sites, where fill is often brought in from disparate sources. However, for practical use, it was asserted that deductions could be made about the nature of nonhomogeneities from these calculations. The formulae were deduced in a similar manner as for the Wenner configuration, which was reviewed in a previous article, and it can be shown that:
and R = R + R for homogeneous soil.
R is the reading from the meter and a is the probe spacing.
Note, curiously, that interchanging the C and PelectrodesdoesnotalterthefamiliarWenner P electrodes does not alter the familiar Wenner formula, a surprising and counter-intuitive conclusion.Orisit?Ithasbeenasserted conclusion. Or is it? It has been asserted that if measurements were made utilizing all three formulae at the same site, by merely changing the probe placement, taking a reading, and plugging it into the appropriate formula for that
From this fairly simple base, we can see how critical spacing of probes can be utilized in a variety of situations, for practical use as well as pure research. Indeed, additional ones may be forthcoming, perhaps from a present-day reader, as unusual situations afford the appropriate challenges. An example is the process known as electrical coring . A hole is bored to an appropriate depth for study, and should be filled with mud or other liquid material. One current probe is left on the surface and the other three probes lowered into the bore hole (Figure 1). Because of comparative remoteness and the vastness of surface area in comparison to the strictures of the bore hole, the effect of the surface probe can be discounted. The potential difference between the two P elec-
Figure 1: Electrical Coring: An Alternative Approach to the wenner Probe Configuration
trodes can be considered as emanating from the current entering through the probe (point A) deep in the bore hole. If soil were homogeneous, thepotentialatMtocurrententering at Ais Ip/2nr, andat N itisIp/2nrz. Thepotential difference, then, between M and N is:
E = (lp/2n) (l/r, -l/rz)
Measured resistanceR = VII, therefore:
P = (2nR)/(1/r, -l/rz)
Therefore, the method can provide an exploratory tool innonhomogeneoussoils.
Theabovedescribestheeffectsofsomedepartures from the standardWenner probe configuration. What about departures from probe spacing? Some investigators have reported an advantage in unequal spacint. If the distance between potential electrodes is increased relative to the current probes, the value of the measured
resistance is also increased (simply more soil between the probes) and it has been argued thatthismayhelpmakethemeasurement itself easier by providing more to work with; i.e., the tester doesn't have to work on the edge of its sensitivity. An example of unequal spacing is given in Figure 2, where the configuration of electrodes remains symmetrical about the center but the distance between the potential probes is large compared to the distance to the adjacent current probe.
Therefore, the potential atA will be:
(lp/2n) [l/(b -a) -l/(b + a)]
By symmetry, the potential difference between A and B will be twice this. The measured potential, then, is:
v = (2Ip/2rr) [l/(b -a) -l/(b + a)] = (lp/2rr) [4a/(b2 - 02)]
Measured resistance, then, is:
R = (p/2rr) [4a/(b2 -02)] = (p/2rra) {4/[(b/ajZ -1])
Substitutinga for bla, then:
P = 2naR [(aZ -1)/4]
In the uniform spacing of the Wenner system, a = 3 and theequationthen reduces to:
a= 4naR
In this instance, a is only half the value of that used in theWenner formula. If that correction were made, this then reduces to the familiar p = 2naR. It has been argued that unequal spacing provides little added advantage to the measurement, so its evaluation is left to the individual experience of the field practitioner.
In designing electrode systems, soil resistivity is a critical factor. It is often sufficient for practical purposes to assume soil homogeneity. In surveying, however, it is the nonhomogeneities that are being sought. Formulae based on homogeneity are used and produce a result that is termed “apparent resistivity.” These values will often vary depending on spacing and location, as has been discussed, and the experienced practitioner can learn to make deductions as to the nature of the subsoil.
Nonhomogeneities are typically found as layers, which can be loam, sand, gravel, clay, rocks, as well as various mixtures. The layers are typically regarded as parallel to the surface, but may also be inclined at an angle to the surface. It is no surprise that water table will generally produce a significant change in resistivity, and so can be considered as another layer. Vertical faults can produce resistivity changes across the surface, with both the soil type and depth of layer varying on opposite sides of the fault. Indeed, such changes are used effectively to locate the position of the fault. Complex mathematics have been derived for all of these cases, beginning with the two-layer model, proceeding through multilayer systems, and treating both inclined layers and vertical faults and can be found in the literature. If methods designed for interpreting results for parallel layers prove inconclusive, it is an indication that inclined layers or a vertical fault may be present. By extension, systems have been
worked out for discovering buried objects, lodes of ore, tunnels, and caves. These have met with varying success in practical application, with one study reaching the conclusion that it is difficult to locate a conducting body at a depth greater than the mean of its linear dimensions. Nonetheless, these investigations remain noteworthy and will be reviewed at a latertime. later time.
Jeffrey R. Jowett is a Senior Applications Engineer for Megger in Valley Forge, Pennsylvania, serving the manufacturing lines of Biddle, Megger, and multi-Amp for electrical test and measurement instrumentation. He holds a BS in Biology and Chemistry from Ursinus College. He was employed for 22 years with James G. Biddle Co. which became Biddle Instruments and is now Megger.
E. W. Carpenter, “Some Notes concerning the Wenner Configuration”, Geophysical Prospecting, 3. C. and M. Schlumberger and E. G. Leonardon, “A New Contribution to Subsurface Studies by Means of Electrical Measurements in Drill Holes”, Technical Publication No. 503, The American Institute of Mining and Metallurgical Engineers.
L. S. Palmer, “Examples of Geoelectric Surveys”, Proceedings I.E.E., Vol. 106, Part A. Source of information: “Earth Resistances” by G. F. Tagg, George Newnes Ltd, London
Nonhomogene i t i es are typ i cally found as layers, wh i ch can be loam, sand, gravel, clay, rocks, as well as var i ous m i xtures.
ShermcoandNETAcohostedasuiteatIEEE Shermco and NETA cohosted a suite at IEEE PCIC 2012 on Tuesday, September 25, 2012, in New Orleans, Louisiana at the Marriott NewOrleans.Thethemeforthesuitewasthe New Orleans. The theme for the suite was the “Magic in the Bayou; Taking the Mystery out of Electrical Testing.” The entertainment featured a magician, a Tarot card reader, and an alligator wrestling, accompanied by food and drinks made in the spirit of the bayou. Each sponsor had a booth space and was able to interact with the attendees. Shermco and NETA gave away two iPads, a Kindle, a Nook e-reader, one PowerTest registration, and a hard copy of the NETA Standards. Items were given away every half hour in conjunction with other items donated by Shermco.
Attendees asked various questions and inquired about the ANSI/NETA Standards and handbooks, PowerTest 2013, and training opportunities available through NETA. Many
attendees were interested in the services offered by NETA Accredited Companies. Comments from attendees were positive about NETA’s presence at PCIC. The impression was that NETA is relevant tothisaudienceandawelcomeadditiontothe to this audience and a welcome addition to the hospitality suites.
Shermco and NETA look forward to having another hopping suite at PCIC 2013 in Chicago, Illinois.
Shermco and NETA hospitality suite at IEEE PCIC.Canada’s latest standard is now in for public review. CSA Z463 Guideline for Maintenance of Electrical Systems was officially released by CSA for public review on September 7, 2012. The public review period to review the comments and finalize the technical content is for 60 days after which thetechnicalcommitteewillconveneonNovember20and the technical committee will convene on November 20 and 21, 2012, in Calgary, Alberta.
This important guideline is the main document to be used in Canadian industry. Through the creation of the CSA Z462 Standard for Workplace Electrical Safety, it was realized that anationalstandarddidnotexistforelectricalmaintenance a national standard did not exist for electrical maintenance inCanada.Atechnicalcommitteeofover40members in Canada. A technical committee of over 40 members has spent the past 18 months working diligently to put the standard together.
The maintenance document is an important final chapter in the CSA group of standards for electrical safety. Canadian standards already cover important aspects of electrical safety including equipment manufacturing, installation practices, and workplace safety requirements. The final and missing piece is the documentation on maintaining these systems which is now provided through the Z463 document.
CSA Z463 covers a number of important areas to consider when building an effective electrical maintenance program. The main contents in the body of the document are asfollows: as follows:
This clause in the document deals with the important aspects of developing an overall management system for electrical maintenance. Information regarding personnel, standards, and overall philosophy are covered in this section. The section also brings forward the important considerations of worker safety, reliability, and serviceability of installed equipment.
A common area where facility managers struggle is in trying to determine the type of maintenance strategy that best suits their operation. In some cases a combination of strategies must be deployed. CSA Z463 covers the various options regarding maintenance strategies and the advantages and disadvantages of each. This section lays the ground work for establishing the best program to meet individual budget, environment, and operating conditions. Z463 defines each strategy as follows:
Reactive Maintenance is an approach where we runit run it untilitbreaksdown until it breaks down. Workers should perform actions, efforts or preventive work to maintain the equipment in original condition.
Preventive Maintenance can be defined as actions performed on a time or machine run based schedule that detects, precludes, or mitigates degradation of a component or system with the aim of sustaining or extending its useful life through controlling degradation to an acceptable level.
PredictiveMaintenancecanbedefinedasmeasurements
Predictive Maintenance can be defined as measurements that detect the onset of a problem, thereby allowing small issues to be eliminated or controlled prior to any significant deterioration in the equipment's physical state.
Reliability Centered Maintenance (RCM) is a maintenance strategy that analyzes the probability of equipment failure and defines appropriate maintenance techniques to increase the reliability of the system.
Risk-Based Maintenance (RBM) is a process where risk can be quantified and then prioritized. The results of this risk-based focus can be used to establish capital and expense allocations to preventive, predictive, and reactive maintenance management decisions.
This section of Z463 brings forward the importance of electrical maintenance and how it directly pertains to worker safety. Many facilities consider electrical maintenance a key component in the reliability of their process; however, electrical maintenance on certain devices also plays a major role in the safety of personnel. For instance, failure of a protective relay can have a major impact on arc flash incident energy and in turn on worker safety. A buried power cable failure can have a major effect on production within a facility but typically won’t have the same direct effect on worker safety. The considerations for maintenance strategies regarding the equipment and systems that have a direct impact on workers safety are covered here.
CSA Z463 brings forward all the general maintenance practices currently used in industry. This clause actually looks at each option for the various on-line tests that can be performed with the plant in full production as well as the many off-line techniques performed typically during a maintenance outage. The on line and off line techniques are explained in detail so the users can determine the best application for their situations.
This section of the guideline somewhat follows the NETA Maintenance Testing Specification Table of Contents. Z463 gives an overview of all the major power system components and the recommended tests and inspections. This is meant to give the user an overview of the requirements and is a segway to the NETA standard which includes all the detailed inspection requirements as well as test procedures and testresults. test results.
There are many industries in Canada that have specialized requirements for electrical maintenance that are not necessarily covered in the previous sections of Z463 and are not included in any other Canadian standard. These industries include airfields, ports and marinas, railway infrastructure, and mining as well as specialized green energy applications. The unique maintenance requirements in these industries are captured here as a standardized placement for industry access.
OveradozenannexesareincludedwiththeZ462stan Over a dozen annexes are included with the Z462 standard. This informational material covers example programs and strategies as well as examples of many technical pieces used to illustrate the importance of an electrical maintenance program.
CSA Z463 will be reviewed by the Technical Committee in preparation for its release midway through 2013.
JAN. 27 –28, 2013 | HILTON SAN DIEGO BAYFRONT | SAN DIEGO, CALIF.
http://elpconference.com
Register with this promo code and save $300 off full conference registration: NET
Now in its fourth year, the Electric Light & Power Executive Conference keeps getting better. This upcoming conference will focus on helping you, the utility executive, improve your company’s flexibility, reliability, efficiency and image. Regulations, policies, technologies, and customer, shareholder and regulator expectations have changed. Let the industry experts who present at this year’s event help you put these issues in perspective and provide ideas on navigating the changing, challenging electric utility industry.
Featured Conference Sessions Include:
SMART GRID SCORE CARD
Has the American Recovery and Reinvestment Act smart grid money been spent wisely? A panel of experts will discuss project schedules and results.
WHA WHAT’S YOUR UTILITY’S INVENTORY OF FLEXIBILITY?
Utilities no longer can simply respond to market dynamics, they must proactively manage through changes and uncertainty. An expert panel will discuss balancing technology, generation mix, energy efficiency and demand response.
SUNDAY, JAN. 27
Michael Reagan, Michael eldest son of President Ronald Reagan, best-selling author
What would Ronald Reagan do? How would President Reagan manage these challenging political times? Michael takes the audience on a journey into the mindset and values of America’s most admired modern president. Michael will bring you behind the scenes of the campaign trail and into the private residence of the White House. Policy is the centerpiece of the day, and bipartisanship the goal after business hours. Michael will give an insight into policy and how President Reagan believed that America must use all of its resources to become energy-independent.
Register with this promo code and save $300 off full conference registration: NETA Owned & Produced by:Presented by:Media
F6150sv
Doble’s F6150sv is your all-in-one solution for testing protection relays and schemes, capable of performing the most simple through the most complex tests. Featuring: power output
Accuracy. Reliability.
Automatic recalibration of voltage & current sources for all ranges outputs
Precise Time Synchronization with the F6051
Phasor measurement units
Interested in learning more? Contact Doble today at DobleINFO@doble.com
If you have any questions about the ANSI/NETA Standards, including how to ensure that your equipment is tested in accordance with the ANSI/NETA Standards, please contact the NETA office at neta@netaworld.org or call 888-300-6382
TheANSI/NETA The ANSI/NETA Standard for Acceptance Testing Specifications for Electrical Power Equipment and Systems is scheduled to be published as a revised document in February 2013. These specifications cover the suggested field tests and inspections that are available to assess the suitability for initial energization of electrical power equipment and systems. The purpose of these specifications is to assure that tested electrical equipment and systems are operational, are within applicable standards and manufacturers’ tolerances, andareinstalledinaccordancewith and are installed in accordance with design specifications. Work on this document began in the spring of 2011. Once completed, this standard will carry the designation of ANSI/NETA ATS-2013. The first public review period began on June 15, 2012 and closed on July 30, 2012. The initial ballot was issued on September 12, 2012, with a with a closing date of October 13, 2012.
On May 16, 2011, NETA received notificationthattheANSI/NETA notification that the ANSI/NETA Standard for Maintenance Testing Specifications for Electrical Power Equipment and Systems was approved as a revised AmericanNationalStandard.Thisdoc American National Standard. This document contains specifications which cover the suggested field tests and inspections that are available to assess the suitability for continued service and reliability of electrical power distribution equipment and systems. The purpose of these specifications is to assure that tested electrical equipment and systems are operational and within applicable standardsandmanufacturers’toleranc standards and manufacturers’ tolerances and that the equipment and systems aresuitableforcontinuedservice.Itis are suitable for continued service. It is available in hard copy, PDF, and CD Rom formats. Order your copy today at www.netaworld.org.
The ANSI/NETA Standard for Certification of Electrical Testing Technicians was approved as an American National Standard on January 8, 2010. The document was originally approved as an ANSIstandardin2000.Thisstandard ANSI standard in 2000. This standard establishes minimum requirements for qualifications, certification, training, and experience for the electrical testing technician. It also provides criteria for documenting qualifications for certificationanddetailstheminimum certification and details the minimum qualifications for an independent and impartial certifying body to certify electrical testing technicians.
Comments and suggestions on any of the standards are always welcome and should be directed to the NETA office at neta@netaworld.org or 888-300-6382. To learn more about the NETA standards review and revision process, to purchase these standards, or to get involved, please visit www.netaworld.org or call 888-300-6382.
A&F Electrical Testing, Inc.
80 Lake Ave. South, Ste. 10 Nesconset, NY 11767 (631) 584-5625 Fax: (631) 584-5720
kchilton@afelectricaltesting.com www.afelectricaltesting.com
Kevin Chilton
A&F Electrical Testing, Inc.
80 Broad St. 5th Floor
New York, NY 10004 (631) 584-5625 Fax: (631) 584-5720 afelectricaltesting@afelectricaltesting.com www.afelectricaltesting.com
Florence Chilton
ABM Electrical Power Solutions
3602 East Southern Ave., Ste. 1 & 2 Phoenix, AZ 85040 (602) 796-6583
www.met-test.com
Jeff Militello
ABM Electrical Power Solutions
6280 South Valley View Blvd., Ste. 618 Las Vegas, NV 89118 (702) 216-0982 Fax: (702) 216-0983
www.met-test.com
Jeff Militello
ABM Electrical Power Solutions
814 Greenbrier Circle, Ste. E Chesapeake, VA 23320 (757) 548-5690 Fax: (757) 548-5417
www.met-test.com
Mark Anthony Gaughan, III
ABM Electrical Power Solutions
3700 Commerce Dr. #901-903 Baltimore, MD 21227 (410) 247-3300 Fax: (410) 247-0900 www.met-test.com
Bill Hartman
ABM Electrical Power Solutions
710 Thomson Park Dr. Cranberry Township, PA 16066-6427 (724) 772-4638 Fax: (724) 772-6003 william.mckenzie@met.lincfs.com www.met-test.com
William (Pete) McKenzie
ABM Electrical Power Solutions
5805 G Departure Dr. Raleigh, NC 27616 (919) 877-1008 Fax: (919) 501-7492 www.met-test.com
Mark Robinson
ABM Electrical Power Solutions
4390 Parliament Place, Ste. Q Lanham, MD 20706 (301) 967-3500 Fax: (301) 735-8953 www.met-test.com
Frank Ceci
Absolute Testing Services 6829 Guhn Rd. Houston, TX 77040 (832) 467-4446 Fax: (713) 849-3885 rgamble@absolutetesting.com www.texasats.com
Richard Gamble
Advanced Testing Systems
15 Trowbridge Dr. Bethel, CT 06801 (203) 743-2001 Fax: (203) 743-2325 pmaccarthy@advtest.com www.advtest.com
Pat MacCarthy
American Electrical Testing Co., Inc.
480 Neponset St., Building 6 Canton, MA 02021-1970 (781) 821-0121 Fax: (781) 821-0771 sblizard@aetco.us www.99aetco.com
Scott A. Blizard
American Electrical Testing Co., Inc. 34 Clover Dr. South Windsor, CT 06074 (860) 648-1013 Fax: (781) 821-0771 jpoulin@aetco.us www.99aetco.com
Gerald Poulin
American Electrical Testing Co., Inc.
76 Cain Dr. Brentwood, NY 11717 (631) 617-5330 Fax: (631) 630-2292 mschacker@aetco.us www.99aetco.com
Michael Schacker
American Electrical Testing Co., Inc.
50 Intervale Rd., Ste. 1 Boonton, NJ 07005 (973) 316-1180 Fax: (781) 316-1181
trosato@aetco.us www.99aetco.com
Anthony Rosato
American Electrical Testing Co., Inc. 1811 Executive Dr., Ste. M Indianapolis, IN 46241 (317) 487-2111 Fax: (781) 821-0771 rramsey@99aetco.us www.99aetco.com
Rick Ramsey
American Electrical Testing Co., Inc.
Green Hills Commerce Center 5925 Tilghman St., Ste. 200 Allentown, PA 18104 (215) 219-6800 jmunley@aetco.us www.99aetco.us
Jonathan Munley
American Electrical Testing Co., Inc. 1672 SE 80th Bella Vista Dr. The Villages, FL 32162 (727) 447-4503 Fax: (727) 447-4984 rhoffman@aetco.us www.99aetco.com
Bob Hoffman
AMP Quality Energy Services, LLC 4220 West Schrimsher SW Site W1 P.O. Box 526 Huntsville, AL 35804 (256) 513-8255 brian@ampqes.com www.ampqes.com
Brian Rodgers
Apparatus Testing and Engineering 11300 Sanders Dr., Ste. 29 Rancho Cordova, CA 95742 (916) 853-6280 Fax: (916) 853-6258 jlawler@apparatustesting.com www.apparatustesting.com
James Lawler
Apparatus Testing and Engineering 7083 Commerce Circle, Ste. H Pleasanton, CA 94588 (925) 454-1363 Fax: (925) 454-1499 info@apparatustesting.com www.apparatustesting.com
Harold (Jerry) Carr
Applied Engineering Concepts 1105 N. Allen Ave. Pasadena, CA 91104 (626) 398-3052 Fax: (626) 398-3053 michel.c@aec-us.com www.aec-us.com
Michel Castonguay
Burlington Electrical Testing Co., Inc. 300 Cedar Ave. Croydon, PA 19021-6051 (215) 826-9400 (221) Fax: (215) 826-0964 waltc@betest.com www.betest.com
Walter P. Cleary
C.E. Testing, Inc. 6148 Tim Crews Rd. Macclenny, FL 32063 (904) 653-1900 Fax: (904) 653-1911 cetesting@aol.com
Mark Chapman
CE Power Solutions,LLC 4500 W. Mitchell Ave. Cincinnati, OH 45232 (513) 563-6150 Fax: (513) 563-6120 info@cepowersol.com
Rhonda Harris
CE Power Solutions of Wisconsin,LLC 3255 W. Highview Dr. Appleton, WI 54914 (920) 968-0281 Fax: (920) 968-0282 jimvh@cepowersol.com
James Van Handel
Dude Testing 145 Tower Dr., Ste. 9 Burr Ridge, IL 60527 (815) 293-3388 Fax: (815) 293-3386 scott.dude@dudetesting.com www.dudetesting.com
Scott Dude
DYMAX Holdings, Inc. 4751 Mustang Circle St. Paul, MN 55112 (763) 717-3150 Fax: (763) 784-5397 gphilipp@dymaxservice.com www.dymaxservice.com
Gene Philipp
High Voltage Service, Inc. 4751 Mustang Circle St. Paul, MN 55112 (763) 717-3103 Fax: (763) 784-5397 www.hvserviceinc.com
Mike Mavetz
DYMAX Service Inc.
23426 Industrial Park Ct. Farmington Hills, MI 48335-2854 (248) 477-6066 Fax: (248) 477-6069 www.dymaxservice.com
Bruce Robinson
DYMAX Service Inc.
4213 Kropf Ave. Canton, OH 44706 (330) 484-6801 Fax: (740) 333-1271 www.dymaxservice.com
Gary Swank
Eastern High Voltage 11A South Gold Dr. Robbinsville, NJ 08691-1606 (609) 890-8300 Fax: (609) 588-8090 joewilson@easternhighvoltage.com www.easternhighvoltage.com
Joseph Wilson
ELECT, P.C.
7400-G Siemens Rd., P.O. Box 2080 Wendell, NC 27591 (919) 365-9775 Fax: (919) 365-9789 btyndall@elect-pc.com www.elect-pc.com
Barry W. Tyndall
Electric Power Systems, Inc. 21 Millpark Ct. Maryland Heights, MO 63043-3536 (314) 890-9999 Fax: (314) 890-9998 www.eps-international.com
Electric Power Systems, Inc.
557 E. Juanita Ave., #4 Mesa, AZ 85204 (480) 633-1490 Fax: (480) 633-7092 www.eps-international.com
Electric Power Systems, Inc.
4436 Parkway Commerce Blvd. Orlando, FL 32808 (407) 578-6424 Fax: 407-578-6408 www.eps-international.com
Electric Power Systems, Inc.
6753 E. 47th Avenue Dr., Unit D Denver, CO 80216 (720) 857-7273 Fax: 303-928-8020 www.eps-international.com
Electric Power Systems, Inc.
23823 Andrew Rd. Plainfield, IL 60585 (815) 577-9515 Fax: (815) 577-9516 www.eps-international.com
Electric Power Systems, Inc.
2601 Center Rd., # 101 Hinckley, OH 44233 (330) 460-3706 Fax: (330) 460-3708 www.eps-international.com
Electric Power Systems, Inc. 1129 East Hwy 30 Gonzalez, LA 70737 (225) 644-0150 Fax: (225) 644-6249 www.eps-international.com
Electric Power Systems, Inc. 56 Bibber Pkwy #1 Brunswick, ME 04011 (207) 837-6527 www.eps-international.com
Electric Power Systems, Inc. 4100 Greenbriar Dr., Ste. 160 Stafford, TX 77477 (713) 644-5400 www.eps-international.com
Electric Power Systems, Inc. 11861 Longsdorf St. Riverview, MI 48193 (734) 282-3311 www.eps-international.com
Electric Power Systems, Inc. 827 Union St. Salem, VA 24153 (540) 375-0084 Fax: (540) 375-0094 www.eps-international.com
Electric Power Systems, Inc. 915 Holt Ave., Unit 9 Manchester, NH 03109 (603) 657-7371 Fax: 603-657-7370 www.eps-international.com
Electric Power Systems, Inc. 146 Space Park Dr. Nashville, TN 37211 (615) 834-0999 Fax: (615) 834-0129 www.eps-international.com
Electric Power Systems, Inc. 1090 Montour West Industrial Blvd. Coraopolis, PA 15108 (412) 276-4559 www.eps-international.com
Electric Power Systems, Inc. 6141 Connecticut Ave. Kansas City, MO 64120 (816) 241-9990 Fax: (816) 241-9992 www.eps-international.com
Electric Power Systems, Inc. 2495 Boulevard of the Generals Norristown, PA 19403 (610) 630-0286 www.eps-international.com
EPS Technology
29 N. Plains Hwy., Ste. 12 Wallingford, CT 06492 (203) 649-0145 www.eps-technology.com
Electrical & Electronic Controls 6149 Hunter Rd. Ooltewah, TN 37363 (423) 344-7666 (23) Fax: (423) 344-4494 eecontrols@comcast.net
Michael Hughes
Electrical Energy Experts, Inc. W129N10818, Washington Dr. Germantown, WI 53022 (262) 255-5222 Fax: (262) 242-2360 bill@electricalenergyexperts.com www.electricalenergyexperts.com
William Styer
Electrical Equipment Upgrading, Inc. 21 Telfair Place Savannah, GA 31415 (912) 232-7402 Fax: (912) 233-4355 kmiller@eeu-inc.com www.eeu-inc.com
Kevin Miller
Electrical Maintenance & Testing Inc. 12342 Hancock St. Carmel, IN 46032 (317) 853-6795 Fax: (317) 853-6799 www.emtesting.com
Brian K. Borst
Electrical Reliability Services 1057 Doniphan Park Circle, Ste. A El Paso, TX 79922 (915) 587-9440 Fax: (915) 587-9010 www.electricalreliability.com
Electrical Reliability Services 1775 W. University Dr., Ste. 128 Tempe, AZ 85281 (480) 966-4568 Fax: (480) 966-4569 www.electricalreliability.com
Electrical Reliability Services 1426 Sens Rd. Ste. 5 La Porte, TX 77571 (281) 241-2800 Fax: (281) 241-2801 www.electricalreliability.com
Electrical Reliability Services 4099 SE International Way, Ste. 201 Milwaukie, OR 97222-8853 (503) 653-6781 Fax: (503) 659-9733 www.electricalreliability.com
Electrical Reliability Services 5810 Van Allen Way Carlsbad, CA 92008 (760) 804-2972 www.electricalreliability.com
Electrical Reliability Services
8500 Washington Pl. NE, Ste. A-6 Albuquerque, NM 87113 (505) 822-0237 Fax: (505) 822-0217 www.electricalreliability.com
Electrical Reliability Services 1380 Greg Street, Ste. 217 Sparks, NV 89431 (775) 746-8484 Fax: (775) 356-5488 www.electricalreliability.com
Electrical Reliability Services 2275 Northwest Pkwy SE, Ste. 180 Marietta, GA 30067 (770) 541-6600 Fax: (770) 541-6501 www.electricalreliability.com
Electrical Reliability Services 7100 Broadway, Ste. 7E Denver, CO 80221-2915 (303) 427-8809 Fax: (303) 427-4080 www.electricalreliability.com
Electrical Reliability Services
348 N.W. Capital Dr. Lees Summit, MO 64086 (816) 525-7156 Fax: (816) 524-3274 www.electricalreliability.com
Electrical Reliability Services 6900 Koll Center Parkway, Ste. 415 Pleasanton, CA 94566 (925) 485-3400 Fax: (925) 485-3436 www.electricalreliability.com
Electrical Reliability Services 10606 Bloomfield Ave. Santa Fe Springs, CA 90670 (562) 236-9555 Fax: (562) 777-8914 www.electricalreliability.com
Electrical Reliability Services 14141 Airline Hwy., Ste. W Baton Rouge, LA 70817 (225) 755-0530 Fax: (225) 751-5055 www.electricalreliability.com
Electrical Reliability Services 121 Louisiana Hwy., 108 East Sulphur, LA 70665 (337) 583-2411 Fax: (337) 583-2410 www.electricalreliability.com
Electrical Reliability Services 11000 Metro Pkwy., Ste. 30 Ft. Myers, FL 33966 (239) 693-7100 Fax: (239) 693-7772 www.electricalreliability.com
Electrical Reliability Services 2222 West Valley Hwy. N., Ste 160 Auburn, WA 98001 (253) 736-6010 Fax: (253) 736-6015 www.electricalreliability.com
Electrical Reliability Services 3412 South 1400 West, Unit A West Valley City, UT 84119 (801) 975-6461 www.electricalreliability.com
Electrical Reliability Services 6351 Hinson St., Ste. B Las Vegas, NV 89118 (702) 597-0020 Fax: (702) 597-0095 www.electricalreliability.com
Electrical Reliability Services 610 Executive Campus Dr. Westerville, OH 43082 (877) 468-6384 Fax: (614) 410-8420 info@electricalreliability.com www.electricalreliability.com
Electrical Testing, Inc. 2671 Cedartown Hwy. Rome, GA 30161 (706) 234-7623 Fax: (706) 236-9028 steve@electricaltestinginc.com www.electricaltestinginc.com
Steve C. Dodd Sr.
Electrical Testing Solutions 2909 Green Hill Ct. Oshkosh, WI 54904 (920) 420-2986 Fax: (920) 235-7131 tmachado@electricaltestingsolutions.com www.electricaltestingsolutions.com Tito Machado
Elemco Services, Inc. 228 Merrick Rd. Lynbrook, NY 11563 (631) 589-6343 Fax: (631) 589-6670 courtney@elemco.com www.elemco.com
Courtney O'Brien
Energis High Voltage Resources, Inc.
1361 Glory Rd.
Green Bay, WI 54304 (920) 632-7929 Fax: (920) 632-7928
info@energisinc.com www.energisinc.com
Mike Petzold
Grubb Emgineering, Inc.
3128 Sidney Brooks
San Antonio, Tx 78235 (210) 658-7250 Fax: (210) 658-9805 bobby@grubbengineering.com www.grubbengineering.com
Robert D. Grubb Jr.
Hampton Tedder Technical Services 4571 State St. Montclair, CA 91763 (909) 628-1256 x214 Fax: (909) 628-6375
matt.tedder@hamptontedder.com www.hamptontedder.com
Matt Tedder
Hampton Tedder Technical Services
4920 Alto Ave.
Las Vegas, NV 89115 (702) 452-9200 Fax: (702) 453-5412 www.hamptontedder.com
Roger Cates
Hampton Tedder Technical Services 3747 West Roanoke Ave. Phoenix, AZ 85009 (480) 967-7765 Fax: (480) 967-7762 www.hamptontedder.com
Harford Electrical Testing Co., Inc. 1108 Clayton Rd. Joppa, MD 21085 (410) 679-4477 Fax: (410) 679-0800 harfordtesting@aol.com
Vincent Biondino
High Energy Electrical Testing, Inc. 2119 Orien Rd. Toms River, NJ 08755-1366 (732) 286-4088 Fax: (732) 286-4086 hinrg@comcast.net www.highenergyelectric.com
James P. Ratshin
High Voltage Maintenance Corp. 24 Walpole Park South Dr. Walpole, MA 02081 (508) 668-9205 www.hvmcorp.com
High Voltage Maintenance Corp. 941 Busse Rd. Elk Grove Village, Il 60007 (847) 228-9595 www.hvmcorp.com
High Voltage Maintenance Corp.
7200 Industrial Park Blvd. Mentor, OH 44060 (440) 951-2706 Fax: (440) 951-6798 www.hvmcorp.com
High Voltage Maintenance Corp. 3000 S. Calhoun Rd. New Berlin, WI 53151 (262) 784-3660 Fax: (262) 784-5124
www.hvmcorp.com
High Voltage Maintenance Corp. 8320 Brookville Rd. #E Indianapolis, IN 46239 (317) 322-2055 Fax: (317) 322-2056 www.hvmcorp.com
High Voltage Maintenance Corp. 1250 Broadway, Ste. 2300 New York, NY 10001 (718) 239-0359 www.hvmcorp.com
High Voltage Maintenance Corp. 355 Vista Park Dr. Pittsburgh, PA 15205-1206 (412) 747-0550 Fax: (412) 747-0554 www.hvmcorp.com
High Voltage Maintenance Corp.
150 North Plains Industrial Rd. Wallingford, CT 06492 (203) 949-2650 Fax: (203) 949-2646 www.hvmcorp.com
High Voltage Maintenance Corp. 9305 Gerwig Ln., Ste. B Columbia, MD 21046 (410) 309-5970 Fax: (410) 309-0220 www.hvmcorp.com
High Voltage Maintenance Corp. 24371 Catherine Industrial Dr. Ste. 207 Novi, MI 48375 (248) 305-5596 Fax: (248) 305-5579 www.hvmcorp.com
High Voltage Maintenance Corp. 5100 Energy Dr. Dayton, OH 45414 (937) 278-0811 Fax: (937) 278-7791 www.hvmcorp.com
HMT, Inc. 6268 Route 31 Cicero, NY 13039 (315) 699-5563 Fax: (315) 699-5911 jpertgen@hmt-electric.com www.hmt-electric.com John Pertgen
Industrial Electric Testing, Inc. 11321 West Distribution Ave. Jacksonville, FL 32256 (904) 260-8378 Fax: (904) 260-0737 gbenzenberg@bellsouth.net www.industrialelectrictesting.com Gary Benzenberg
Industrial Electric Testing, Inc. 201 NW 1st Ave. Hallandale, FL 33009-4029 (954) 456-7020 www.industrialelectrictesting.com
Industrial Electronics Group P.O. Box 1870 850369 Highway 17 South Yulee, FL 32041 (904) 225-9529 Fax: (904) 225-0834 butch@industrialgroups.com www.industrialgroups.com
Butch E. Teal
Industrial Tests, Inc. 4021 Alvis Ct., Ste. 1 Rocklin, CA 95677 (916) 296-1200 Fax: (916) 632-0300 greg@indtests.com www.industrialtests.com
Greg Poole
Infra-Red Building and Power Service 152 Centre St. Holbrook, MA 02343-1011 (781) 767-0888 Fax: (781) 767-3462 tom.mcdonald@infraredbps.net www.infraredbps.com
Thomas McDonald Sr.
M&L Power Systems, Inc. 109 White Oak Ln., Ste. 82 Old Bridge, NJ 08857 (732) 679-1800 Fax: (732) 679-9326 dan@mlpower.com www.mlpower.com
Darshan Arora
Magna Electric Corporation 1033 Kearns Crescent, Box 995 Regina, SK S4P 3B2 Canada (306) 949-8131 Fax: (306) 522-9181 kheid@magnaelectric.com www.magnaelectric.com
Kerry Heid
Magna Electric Corporation 3430 25th St. NE Calgary, AB T1Y 6C1 Canada (403) 769-9300 Fax: (403)769-9369 ppetrie@magnaelectric.com www.magnaelectric.com
Pat Petrie
Magna Electric Corporation 851-58th St. East Saskatoon, SK S7K 6X5 Canada (306) 955-8131 x 5 Fax: (306) 955-9181 www.magnaelectric.com
Luis Wilson
Magna Electric Corporation 1375 Church Ave. Winnipeg, MB R2X 2Y7 Canada (204) 925-4022 Fax: (204) 925-4021 cbrandt@magnaelectric.com www.magnaelectric.com
Curtis Brandt
Magna IV Engineering 4103 - 97th St., N.W. Edmonton, AB T6E 6E9 Canada (780) 462-3111 Fax: (780) 462-9799 jwentzell@magnaiv.com www.magnaiv.com Jereme Wentzell
Magna IV Engineering Unit 10, 10672- 46 St. S.E. Calgary, AB T2C 1G1 Canada (403) 723-0575 Fax: (403) 723-0580 info.calgary@magnaiv.com Jereme Wentzell
Magna IV Engineering 8219D Fraser Ave. Fort McMurray, AB T9H 0A2 Canada (780) 791-3122 Fax: (780) 791-3159 info.fmcmurray@magnaiv.com Jereme Wentzell
Magna IV Engineering 96 Inverness Dr. East, Unit R Englewood, CO 80112 (303) 799-1273 Fax: (303) 790-4816 info.denver@magnaiv.com Jereme Wentzell
Magna IV Engineering
Oficina 1407 Torre Norte 481 Nueva Tajamar Las Condes, Region Metropolitana 7550099 Chile +(56) 9-9-517-4642 info.chile@magnaiv.com Jereme Wentzell
Magna IV Engineering 1040 Winnipeg St. Regina , SK S4R 8P8 Canada (306) 504-6501 Fax: (306) 729-4897 info.regina@magnaiv.com
Jereme Wentzell
National Field Services 649 Franklin St. Lewisville, TX 75057 (972) 420-0157 www.natlfield.com
Eric Beckman
Nationwide Electrical Testing, Inc. 6050 Southard Trace Cumming, GA 30040 (770) 667-1875 Fax: (770) 667-6578 Shashi@N-E-T-Inc.com www.n-e-t-inc.com
Shashikant B. Bagle
North Central Electric, Inc. 69 Midway Ave. Hulmeville, PA 19047-5827 (215) 945-7632 Fax: (215) 945-6362 ncetest@aol.com
Robert Messina
Northern Electrical Testing, Inc. 1991 Woodslee Dr. Troy, MI 48083-2236 (248) 689-8980 Fax: (248) 689-3418 ldetterman@northerntesting.com www.northerntesting.com
Lyle Detterman
Orbis Engineering Field Services Ltd. #300, 9404 - 41st Ave. Edmonton, AB T6E 6G8 Canada (780) 988-1455 Fax: (780) 988-0191 lorne@orbisengineering.net www.orbisengineering.net Lorne Gara
Pacific Power Testing, Inc. 14280 Doolittle Dr. San Leandro, CA 94577 (510) 351-8811 Fax: (510) 351-6655 steve@pacificpowertesting.com www.pacificpowertesting.com
Steve Emmert
Pacific Powertech, Inc. #110, 2071 Kingsway Ave. Port Coquitlam, BC V3C 1T2 Canada (604) 944-6697 Fax: (604) 944-1271 chite@pacificpowertech.ca www.magnaiv.ca
Cameron Hite
Phasor Engineering
Sabaneta Industrial Park #216 Mercedita, PR 715 Puerto Rico (787) 844-9366 Fax: (787) 841-6385 rcastro@phasorinc.com
Rafael Castro
Potomac Testing, Inc. 1610 Professional Blvd., Ste. A Crofton, MD 21114 (301) 352-1930 Fax: (301) 352-1936 kbassett@potomactesting.com www.potomactesting.com
Ken Bassett
Potomac Testing, Inc. 11179 Hopson Rd., Ste. 5 Ashland, VA 23005 (804) 798-7334 Fax: (804) 798-7456 www.potomactesting.com
Power & Generation Testing, Inc. 480 Cave Rd. Nashville, TN 37210 (615) 882-9455 Fax: (615) 882-9591 mose@pgti.net www.pgti.net
Mose Ramieh
Power Engineering Services, Inc. 9179 Shadow Creek Lane Converse, TX 78109 (210) 590-4936 Fax: (210) 590-6214 engelke@pe-svcs.com www.pe-svcs.com
Miles R. Engelke
POWER PLUS Engineering, Inc. 46575 Magallan Dr. Novi, MI 48377 (248) 344-0200 Fax: (248) 305-9105 smancuso@epowerplus.com www.epowerplus.com
Salvatore Mancuso
Power Products & Solutions, Inc. 12465 Grey Commercial Rd. Midland, NC 28107 (704) 573-0420 x12 Fax: (704) 573-3693 ralph.patterson@powerproducts.biz www.powerproducts.biz
Ralph Patterson
Power Products & Solutions, Inc. 13 Jenkins Ct. Mauldin, SC 29662 Fax: (800) 328-7382 ralph.patterson@powerproducts.biz www.powerproducts.biz
Raymond Pesaturo
Power Services, LLC P.O. Box 750066, 998 Dimco Way Centerville, OH 45475 (937) 439-9660 Fax: (937) 439-9611 mkbeucler@aol.com
Mark Beucler
Power Solutions Group, Ltd. 425 W. Kerr Rd. Tipp City, OH 45371 (937) 506-8444 Fax: (937) 506-8434 bwilloughby@powersolutionsgroup.com www.powersolutionsgroup.com
Barry Willoughby
Power Solutions Group, Ltd. 135 Old School House Rd. Piedmont, SC 29673 (864) 845-1084 Fax:: (864) 845-1085 fcrawford@powersolutionsgroup.com www.powersolutionsgroup.com
Frank Crawford
Power Solutions Group, Ltd. 670 Lakeview Plaza Blvd. Columbus, OH 43085 (614) 310-8018 sspohn@powersolutionsgroup.com www.powersolutionsgroup.com
Stuart Spohn
Power Systems Testing Co. 4688 W. Jennifer Ave., Ste. 108 Fresno, CA 93722 (559) 275-2171 ext 15 Fax: (559) 275-6556 dave@pstcpower.com www.powersystemstesting.com
David Huffman
Power Systems Testing Co. 600 S. Grand Ave., Ste. 113 Santa Ana, CA 92705-4152 (714) 542-6089 Fax: (714) 542-0737 www.powersystemstesting.com
Power Systems Testing Co. 2267 Claremont Ct. Hayward, CA 94545-5001 (510) 783-5096 Fax: (510) 732-9287 www.powersystemstesting.com
Power Test, Inc. 2200 Highway 49 Harrisburg, NC 28075 (704) 200-8311 Fax: (704) 455-7909 rich@powertestinc.com www.powertestinc.com
Richard Walker
POWER Testing and Energization, Inc. 14006 NW 3rd Ct., Ste. 101 Vancouver, WA 98685 (360) 576-4826 Fax: (360) 576-7182 chris.zavadlov@powerte.com www.powerte.com
Chris Zavadlov
POWER Testing and Energization, Inc. 731 E. Ball Rd., Ste. 100 Anaheim, CA 92805 (714) 507-2702 http://www.powerte.com
POWER Testing and Energization, Inc. 22035 70th Ave. South Kent, WA 98032 (253) 872-7747 www.powerte.com
Powertech Services, Inc. 4095 South Dye Rd. Swartz Creek, MI 48473-1570 (810) 720-2280 Fax: (810) 720-2283 jbrown@powertechservices.com www.powertechservices.com
Jean A. Brown
Precision Testing Group 18590 Wedemeyer Rd. Kiowa, CO 80117 (303) 621-2776 Fax: (303) 621-2573 glenn@precisiontestinggroup.com
Glenn Stuckey
PRIT Service, Inc. 112 Industrial Dr., P.O. Box 606 Minooka, IL 60447 (815) 467-5577 Fax: (815) 467-5883 Rod.Hageman@pritserviceinc.com www.pritserviceinc.com
Rod Hageman
Reuter & Hanney, Inc. 149 Railroad Dr. Northampton Industrial Park Ivyland, PA 18974 (215) 364-5333 Fax: (215) 364-5365 mikereuter@reuterhanney.com www.reuterhanney.com
Michael Reuter
Reuter & Hanney, Inc. 4270-I Henninger Ct. Chantilly, VA 20151 (703) 263-7163 Fax: 703-263-1478 www.reuterhanney.com
Reuter & Hanney, Inc.
11620 Crossroads Circle, Suites D-E Middle River, MD 21220 (410) 344-0300 Fax: (410) 335-4389 www.reuterhanney.com
Michael Jester
REV Engineering, LTD
3236 - 50 Ave. SE Calgary, AB T2B 3A3 Canada (403) 287-0156 Fax: (403) 287-0198 rdavidson@reveng.ca www.reveng.ca
Roland Nicholas Davidson, IV
Scott Testing Inc. 1698 5th St. Ewing, NJ 08638 (609) 882-2400 Fax: (609) 882-5660 rsorbello@scotttesting.com www.scotttesting.com
Russ Sorbello
Shermco Industries
2425 E. Pioneer Dr. Irving, TX 75061 (972) 793-5523 Fax: (972) 793-5542 rwidup@shermco.com www.shermco.com
Ron Widup
Shermco Industries 1705 Hur Industrial Blvd. Cedar Park, TX 77515 (512) 259-3060 Fax: (512) 258-5571 kewing@shermco.com www.shermco.com
Kevin Ewing
Shermco Industries 1357 FM 2004 Angleton, TX 78613 979)848-1406 Fax: (979) 848-0012 mfrederick@shermco.com www.shermco.com Malcom Frederick
Shermco Industries 1357 N. 108th E. Ave. Tulsa, OK 74116 (918) 234-2300 jharrison@shermco.com www.shermco.com
Jim Harrison
Shermco Industries 777 10th St. Marion, IA 52302 (319) 377-3377 Fax: (319) 377-3399
Lhamrick@shermco.com www.shermco.com
Lynn Hamrick
Shermco Industries
2100 Dixon St., Ste. C Des Moines, IA 50316 Fax: (515) 263-8482 DesMoines@shermco.com www.shermco.com
Lynn Hamrick
Shermco Industries
Boulevard Saint-Michel 47 1040 Brussels Brussels, Belgium
+32 (0)2 400 00 54 Fax: +32 (0)2 400 00 32 cperry@shermco.com www.shermco.com
Chris Perry
Shermco Industries
12000 Network Blvd., Bldg D, Ste. 410 San Antonio, TX 78249 (512) 267-4800 Fax: (512) 267-4808 kewing@shermco.com www.shermco.com
Kevin Ewing
Sigma Six Solutions, Inc. 2200 West Valley Hwy., Ste. 100 Auburn, WA 98001 (253) 333-9730 Fax: (253) 859-5382 jwhite@sigmasixinc.com www.sigmasixinc.com
John White
Southern New England Electrical Testing, LLC
3 Buel St., Ste. 4 Wallingford, CT 06492 (203) 269-8778 Fax: (203) 269-8775 dave.asplund@sneet.org www.sneet.org
David Asplund, Sr.
Southwest Energy Systems, LLC 2231 East Jones Ave., Ste. A Phoenix, AZ 85040 (602) 438-7500 Fax: (602) 438-7501
bob.sheppard@southwestenergysystems.com www.southwestenergysystems.com
Robert Sheppard
Taurus Power & Controls, Inc. 9999 SW Avery St. Tualatin, OR 97062-9517 (503) 692-9004 Fax: (503) 692-9273 robtaurus@tauruspower.com www.tauruspower.com
Rob Bulfinch
Taurus Power & Controls, Inc. 6617 S. 193rd Place, Ste. P104 Kent, WA 98032 (425) 656-4170 Fax: (425) 656-4172 jiml@tauruspower.com www.tauruspower.com
Jim Lightner
Three-C Electrical Co., Inc. 190 Pleasant St. Ashland, MA 01721 (508) 881-3911 Fax: (508) 881-4814 jim@three-c.com www.three-c.com
Jim Cialdea
Three-C Electrical Co., Inc. 79 Leighton Rd., Ste. 9 Augusta, ME 04330 (800) 649-6314 Fax: (207) 782-0162 jim@three-c.com www.three-c.com
Jim Cialdea
Tidal Power Services, LLC 4202 Chance Lane Rosharon, TX 77583 (281) 710-9150 Fax: (713) 583-1216 monty.janak@tidalpowerservices.com www.tidalpowerservices.com
Monty C. Janak
Tidal Power Services, LLC 18786 Lake Harbor Lane Prairieville, LA 70769 (225) 223-5677 Fax: (225) 208-1013 www.tidalpowerservices.com
Darryn Kimbrough
Tital Power Services, LLC 1056 Mosswood Dr. Sulphur, LA 70663 (337) 558-5476 Fax: (337) 558-5305 www.tidalpowerservices.com
Steve Drake
Tony Demaria Electric, Inc. 131 West F St. Wilmington, CA 90744 (310) 816-3130 x 111 Fax: (310) 549-9747 tde@tdeinc.com www.tdeinc.com
Anthony Demaria
Trace Electrical Services & Testing, LLC
293 Whitehead Rd. Hamilton, NJ 08619 (609) 588-8666 Fax: (609) 588-8667 jvasta@tracetesting.com www.tracetesting.com
Joseph Vasta
Utilities Instrumentation Service, Inc. PO Box 981123 Ypsilanti, MI 48198-1123 (734) 482-1450 (14) Fax: (734) 482-0035 GEWalls@UISCorp.com www.uiscorp.com
Gary E. Walls
Utility Service Corporation 4614 Commercial Dr. NW Huntsville, AL 35816-2201 (256) 837-8400 Fax: (256) 837-8403
apeterson@utilserv.com www.utilserv.com
Alan D. Peterson
Western Electrical Services 14311 29th St. East Sumner , WA 98390 (253) 891-1995 Fax: (253) 891-1511
dhook@westernelectricalservices.com www.westernelectricalservices.com
Daniel Hook
Western Electrical Services
3676 W. California Ave. Bldg. C, Ste. 106 Salt Lake City, UT 84104 (253) 891-1995
dhook@westernelectricalservices.com www.westernelectricalservices.com
Daniel Hook
Western Electrical Services
5680 South 32nd St. Phoenix, AZ 85040 (253) 891-1995
dhook@westernelectricalservices.com www.westernelectricalservices.com
Daniel Hook
Western Electrical Services 4510 NE 68th Dr., Ste. 122 Vancouver, WA 98661 (253) 891-1995 Fax: (253) 891-1511
dhook@westernelectricalservices.com www.westernelectricalservices.com
Daniel Hook
This issue’s advertisers are identified below. Please thank these advertises by telling them you saw their advertisement in YOUR magazine –NETA World.
... and with the PDL 650 system he can always find the location of a failure
With the new PDL 650 Dad can track partial discharge (PD) in the transformer without opening it up. The PDL 650 creates a 3D-representation of a failure based on acoustic signals emitted by partial discharge.
When used together with the MPD 600 even electrical and UHF measurements can act as additional signal inputs.
By combining the data of electrical and acoustic signals Dad can examine transformers faster and more effectively than ever before.
Dad can generate a comprehensive report of a measurement with the click of a mouse. This way he can get a precise overview of all the transformers that he´s tested.
Visit us online and find out how the PDL 650 and MPD 600 can work for you!