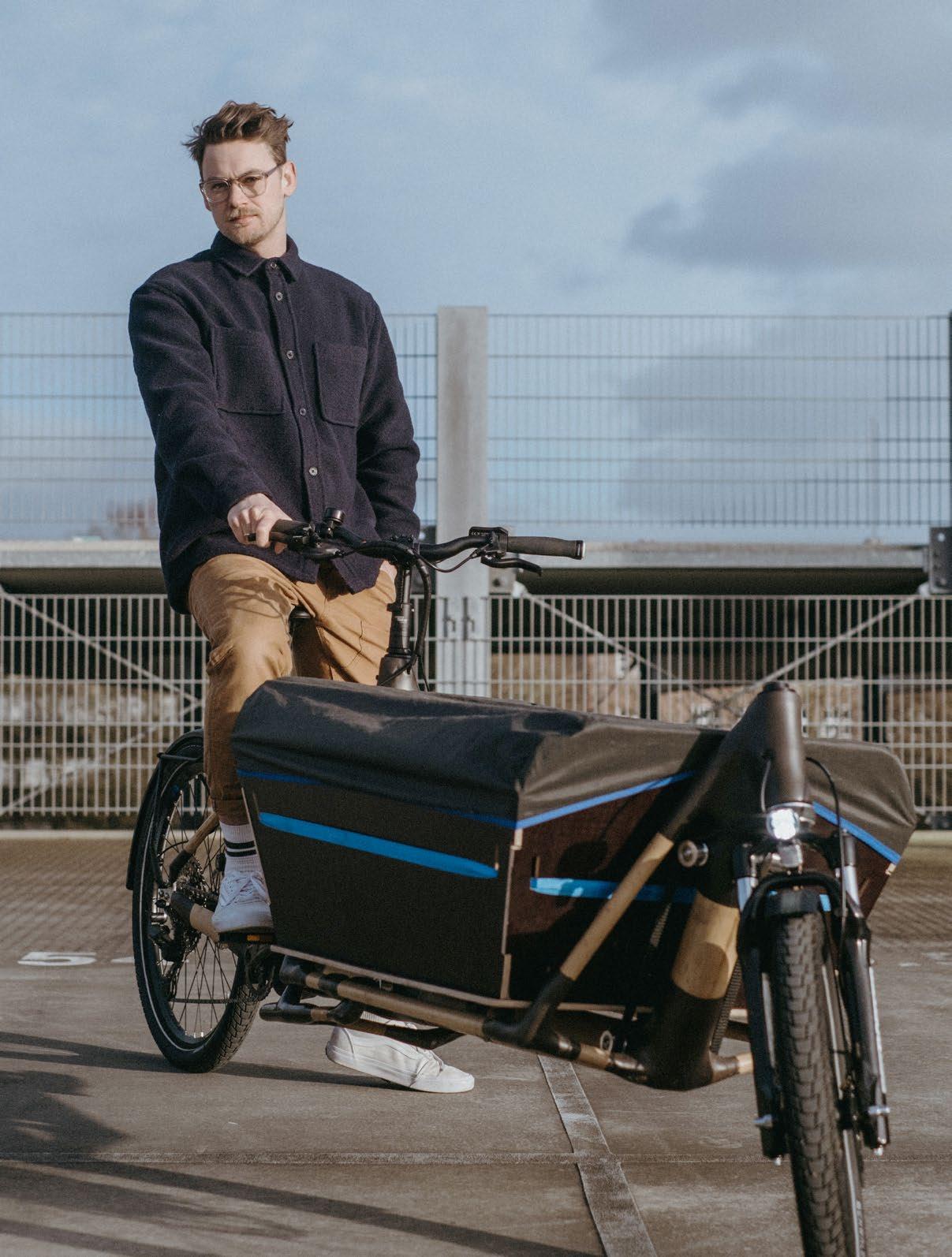
3 minute read
Vom Bambus zum my Boo Fahrradrahmen
from my Boo Mag #3
In jedem gefertigten Bambusrahmen stecken 80 Stunden liebevolle Handarbeit. Der Produktionsprozess ist nicht nur aufwendig, sondern es ist auch höchste Sorgfalt gefordert. Das Sprachrohr zwischen Ghana und Kiel stellt dabei Leon dar, der für die Produktentwicklung bei my Boo verantwortlich ist. Er ist stetig dabei, neue Modelle zu entwickeln und technische Neuheiten umzusetzen. Wie der Bambus zum fertigen Fahrradrahmen wird und an welchen Dingen Leon gerade tüftelt, erfährst du hier im Interview.
Moin Leon, inwiefern eignet sich Bambus für den Fahrradrahmenbau?
Bambus ist ein hervorragendes Material, welches genau die Anforderungen erfüllt, die an einen stabilen Fahrradrahmen gestellt werden: Er ist widerstandsfähig und stark. Zusätzlich haben wir den natürlichen Effekt der Dämpfung, sodass sich Bambus immer wieder in die Ausgangssituation zurückbewegt – das bietet Komfort. Bambus ist zudem ein nachhaltiger Rohstoff, bei welchem weder Dünger noch Pestizide zum Einsatz kommen, was ihn sehr umweltfreundlich macht.
Was begeistert dich am Bambus und dem Rahmenbau?
Am Bambus finde ich faszinierend, dass der Rahmenbau mit einem organisch nachwachsenden Rohstoff möglich ist. Also mit einem Naturprodukt einen Rahmen zu bauen, der einfach ein gutes Fahrgefühl bietet. Gleichzeitig ist er langlebig und extrem nachhaltig. Zudem begeistert mich, dass Bambus eine gewisse Abweichung zur Norm hat und sich trotzdem ausgezeichnet als Rahmenmaterial eignet. Außerdem finde ich es klasse, dass man Bambus in verschiedenen Weisen nutzen kann, beispielsweise als gespaltene Kettenstreben. Und das Ganze kann man mit einfachsten Mitteln wie zwei Händen erreichen.
Welche Schritte müssen bei der Rahmenproduktion beachtet werden?
Zuerst wird der Bambus im Wald gesichtet und geschlagen. Er wächst meist wild und schnell wieder nach. Anschließend wird er getrocknet und die schönsten Stangen ausgesucht. Mit Hilfe von Rahmenlehren werden die Bambusrohre befestigt und mit Harz fixiert. Über Nacht trocknet das Harz, sodass alles fest sitzt. Anschließend werden die Verbindungen mit der Naturfaser Sisal oder nun auch Flachsfaser umwickelt, welche vorher in biobasiertem Harz getränkt wurden. Nach der Trocknung folgt der Grob- und Feinschliff, welcher in Handarbeit stattfindet, um die besondere Optik und Haptik zu schaffen. Als vorletzter Produktionsschritt in Ghana wird die Qualitätskontrolle jedes Rahmens vollzogen. Abschließend finden die Lackierung und finale Prüfung dessen statt. Im Anschluss daran wird der Rahmen nach Kiel verschickt und dort in Einzelplatzmontage gefertigt.
Wie zeitintensiv ist der Rahmenbau?
Grob geschätzt benötigt ein Rahmenbau 80 Stunden Handarbeit, bei unserem neuen Cargobike sind es sogar noch mehr. Dabei werden auch die Trockenzeiten, beispielsweise nach dem Auftragen des Kunstharzes, berücksichtigt. Gleichzeitig sind die aufwendigsten Schritte definitiv die Schleifprozesse: Das Aufbringen der Faser ist weniger zeitintensiv, als das in Form schleifen. Ziel des Schleifens ist es, die Rahmenteile miteinander kompatibel zu machen, Stabilität zu wahren und gleichzeitig ein optisch schönes Produkt zu fertigen.
Was bringt das Jahr 2023?
Das übergeordnete Ziel von 2023 ist, die Sisalwicklung auf die neue Flachsfaser umzustellen. Das wiederum ermöglicht uns neue Rahmenmodelle. Bei verschiedenen E-Bike-Modellen, wie dem Cargobike oder dem Tiefeinsteiger, benötigen wir aufgrund der hohen Belastung das Flachsgewebe. Zudem werden die Verbindungen dadurch nicht nur optisch schlanker, sondern wir sparen auch Material ein.
Bald geht es für dich wieder nach Ghana, worauf freust du dich am meisten?
Ich freue mich einfach auf die Leute! Zusammen werden wir viele Trainings zu der neuen Faserwicklung und zu den zukünftigen Modellen durchführen. Die Kolleg*innen in Ghana sind super wissbegierig, haben immer Lust auf Neues und stecken voller Energie, darauf freue ich mich schon sehr.
Wer kennt es nicht: Mit dem Auto schnell mal los in die Stadt und Besorgungen machen. Das Problem: Überfüllte Straßen, keine Parkplätze und ganz schön viel Lärm. Wir haben im Auftrag der nachhaltigen Mobilität eine umweltfreundliche Alternative zum Auto entwickelt, die genügend Platz, aber auch Komfort bietet – natürlich aus Bambus. Auch die Zahlen sprechen für sich: 51% aller motorisierten Transporte in europäischen Städten könnten auf Lastenräder verlagert werden. Umfragen zeigen außerdem ein deutlich steigendes Interesse an Cargobikes in Deutschland. Deshalb präsentieren wir voller Freude: Unser ECargobike, das Kumasi EP6.
Unser erstes Cargobike ist ein sogenannter Frontlader und fährt auf zwei Rädern. Wichtige Bestandteile sind die modulare Holzbox, welche optional mit Seitentür, Regenverdeck und Sitzbank ausgestattet werden kann. Dieses Zubehör ist übrigens made in Schleswig-Holstein. Unterstützt wird das Fahrvergnügen durch den Shimano Steps EP6 Motor mit 85Nm. Dank Shimano LINKGLIDETechnologie ist die robuste Deore-Schaltung besonders langlebig. Zudem zeichnet sich das Lastenrad durch ein innovatives und langlebiges Riemenlenksystem aus, was für den nötigen Fahrkomfort, einen kleinen Wendekreis und natürlich auch für ausreichend Sicherheit im Alltag sorgt.
Über zwei Jahre lang haben wir an diesem Modell gearbeitet und stoßen nun erfreulicherweise auf eine große Nachfrage. Deshalb ist auch in Ghana die Produktion des Cargo-Bambusrahmens in vollem Gange. Die Verbindungsstücke des Cargobikes bestehen aus Flachsfasern und bilden einen dunklen Kontrast zum hellen Bambusfarbton. Darüber hinaus sorgt die innenliegende Kabelführung für eine problemfreie Handhabung. Zusätzlich ist das my Boo Cargobike mit gespaltenen Kettenstreben ausgestattet, was den Einsatz von breiteren Reifen ermöglicht.