MARITIME -NORTHERN
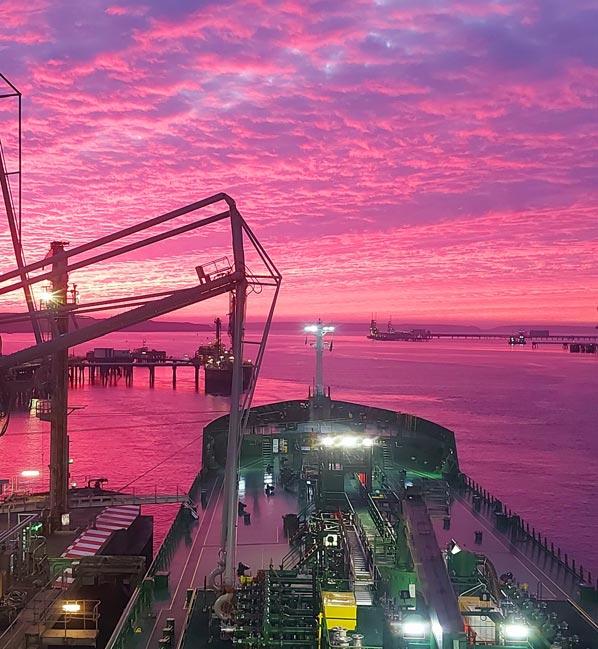
Dutch sea shipping would be better served by a dedicated and vision-driven maritime authority
‘The shipping industry is all about people’
‘Thinking about
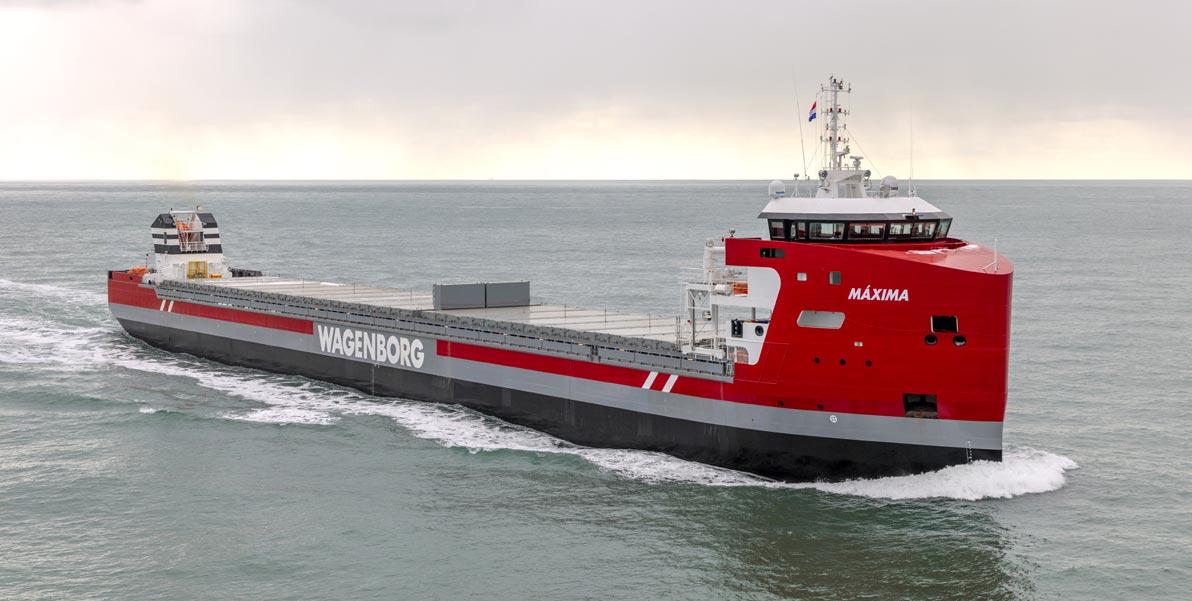
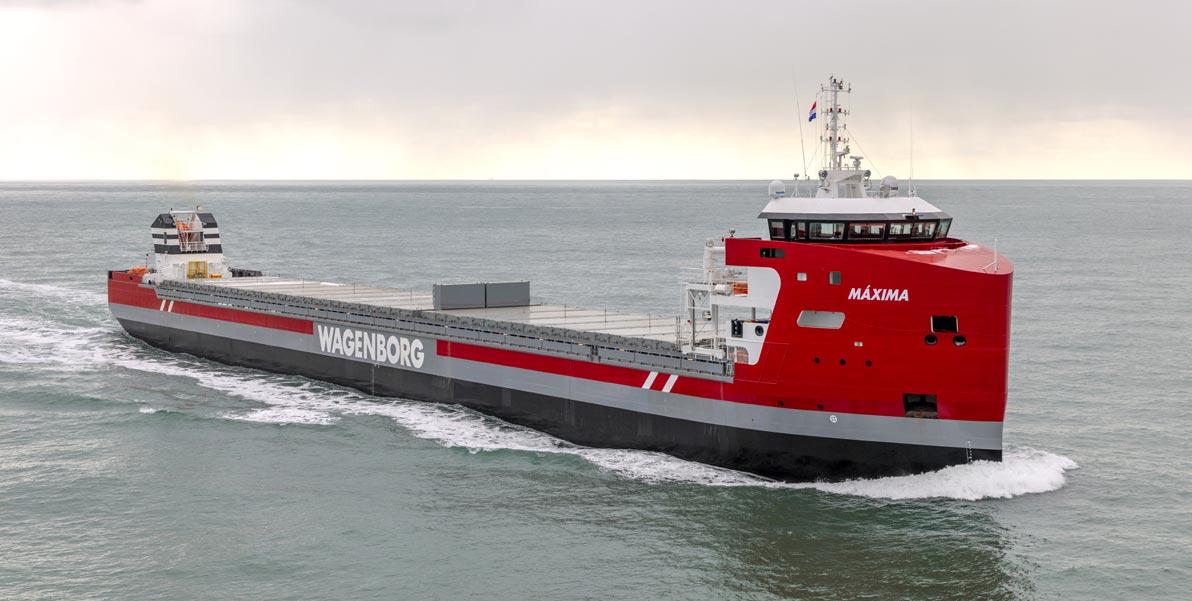
Dutch sea shipping would be better served by a dedicated and vision-driven maritime authority
‘The shipping industry is all about people’
‘Thinking about
Publisher: Multiplus BV Stationsweg 21 9201 GG Drachten Telefoon 0512- 550 800 taco@multiplusmedia.nl www.multiplusmedia.nl
Project Manager: Taco de Haan taco@multiplusmedia.nl Telefoon 0512- 550 807
Editor: Henk Poker
Graphic Design: Maurice de Jong
Cover: MF Shipping Group
Distribution: Controlled Circulation
Copyright: The content of this magazine is copyrighted. Nothing may be reproduced in any way without written permission from the publisher. No rights can be derived from the contents of this publication.
Dutch sea shipping would be better served by a dedicated and vision-driven maritime authority
The Netherlands has unquestionably been a major player in maritime shipping for many years. However, it is not a given that it will continue to hold such a position in the future. In fact, there is a downward trend in the number of ships sailing under the Dutch flag. This is a matter of concern, not only nationally but also in the Northern Netherlands, which holds a significant share of the Dutch maritime shipping industry.
Annet Koster, managing director of the Royal Association of Netherlands Shipowners (in Dutch abbreviated to KVNR), has called for the establishment of a Dutch maritime authority. “A dedicated maritime authority would be better equipped to represent the interests of the Dutch shipping industry. It would also be able to more effectively carry out executive tasks and provide services for the industry than the Dutch Human Environment and Transport Inspectorate. This is necessary for the Netherlands to maintain its position in international merchant shipping.”
KVNR is the industry association that represents Dutch shipping companies involved in merchant shipping. Acting for the whole maritime cluster, the association deals with political, government and societal
issues in pursuit of its four main priorities: barrier-free business, clean ships, safe navigation and skilled crew. In addition to 111 shipping companies, the KVNR membership also includes 82 associate members who are involved in the Dutch shipping industry but do not own or operate vessels. “The Dutch shipping industry has a fleet of about 2,500 ships, around 1,050 of which sail under the Dutch flag,” says Koster. “Our membership is growing, but we are also seeing consolidation in the industry. Small shipowner-operators have benefited from favourable conditions in recent years. Now however, daunted by the challenges of the unfolding energy transition, which is placing considerable demands on the industry, some are pulling out. As a result, there is a relative decline in the number of shipping companies operating under the Dutch flag, while the number of shipping companies operating under foreign flags is increasing.”
According to Koster, shipowners retiring from the industry is not the only contributing factor. “The decline in the number of shipping companies operating under the Dutch flag also has to do with the service provided by the Dutch Shipping Register, which is maintained by the Dutch Human Environment and Transport Inspectorate. This is why, for many years we have been calling for the creation of a Dutch maritime authority that can undertake all the executive tasks involved in maritime shipping as its core business. So we are delighted that the Dutch House of Representatives recently passed a motion proposed by Eline Vedder, Christian Democratic Appeal (CDA) representative from the province of Drenthe, calling for the establishment of a Dutch
Maritime Authority. It is vital to our economy that as many shipowners as possible continue to operate under the Dutch flag. Their revenues contribute to our national income. Not only that, as a country with a significant seafaring presence, we have more influence in Brussels and when dealing with other international maritime organisations.”
Koster believes a maritime authority will increase cross-departmental collaboration and thus enable more effective service delivery. Among other things, this could optimise and speed up the processing of applications for certificates of registry and crew certificates.
‘It is vital to our economy that as many shipowners as possible continue to operate under the Dutch flag. Their revenues contribute to our national income’
It could also allow for clearer policy files and enable the development of a vision for the maritime industry informed by the developments underway and the Netherlands’ plans for the industry. Koster: “The asbestos file is a good example. Countries such as Norway and Denmark, which have a maritime authority, adopt a far more pragmatic approach to this problem. It is essentially a question of risk analysis: determine whether asbestos poses a threat to the health of the crew and then decide what does or does not need to be removed from a ship. In Denmark they say, “If it poses a threat to the crew, it should be removed.” In the Netherlands, we tend to get bogged down in long discussions and shipping companies don’t know where they stand. In short, we believe a maritime authority could streamline and speed up processes. This is something the industry is waiting for. Incidentally, this does not mean that we are bound to get our way, but we do want clarity on all sorts of things. At the moment, this is lacking.”
The industry is faced with numerous threats and opportunities. “There are tremendous challenges, especially at the geopolitical level. Just look at what is happening in the Red Sea region. My concern, which I hope is unfounded, is that we are going to see more situations like
this in the future. It’s an effective way of disrupting global trade, without having much immediate and widespread impact on individuals. “There is also the climate debate, which again raises the issue of resourcing. In the Netherlands, we depend on raw materials that come from other parts of the world. Yet there is the question of whether we should keep shipping raw materials and products from one side of the world to another. All of these developments affect the maritime industry.”
In other words, there is never a dull moment in the shipping industry. “People will confirm that this is certainly the case in the Northern Netherlands, which holds a significant share of the Dutch maritime shipping industry. Numerous shipping companies are based in the North and there are many active shipyards building specifically for maritime shipping. In fact, our office might just as well have been established in the Northern Netherlands.”
Koster praises the collaboration in the Northern Netherlands. “There are joint efforts to identify opportunities and approaches that will help maintain the maritime shipbuilding industry. The sector is see-
‘There are tremendous challenges, especially at the geopolitical level. Just look at what is happening in the Red Sea region’
king innovative solutions that will help create the shipyard of the future. With the already growing demand for green vessels set to increase, the Northern Netherlands can play a leading role.”
Led by the International Maritime Organization, the industry recently committed to achieving ‘net-zero’ emission shipping by 2050. Koster calls this ‘a historic decision’. “No other sector has set such an ambitious global target. How we are going to do it? In Europe, the Emissions Trading System (EU ETS) plays a particularly key role. But we would prefer a global levy on maritime shipping emissions to replace
the regional EU Emissions Trading System. This is a hard thing to push for, but there is growing support for this plan from more and more countries. Understandably, some countries are concerned about the cost, especially small island states that rely on maritime shipping for supplies. This is something we have to talk about. We will find a solution.”
“Yes, the energy transition is the main challenge for maritime shipping, as well as labour market shortages. But there are other factors. In the Netherlands, these include the business climate and the ability
to finance the building of ocean-going vessels. Shipping companies need money to build (or retrofit) ships and the same goes for shipyards. If the financing is held up, the process does not run smoothly. Faced with this situation, some shipping companies choose to place orders abroad, where the financial red carpet is rolled out. Banks are keen to finance green initiatives, but they also find it daunting because these tend to be innovative approaches. A government guarantee would help.”
In short, we have plenty of work on our plate. “We are optimistic, but it is important not to be naive,” says Koster. “I would repeat that in our view, the establishment of a Dutch maritime authority is vital to the future success of Dutch maritime shipping. Not because it’s an
egg of Columbus solution, but because it will allow us to resolve a number of important issues faster and more efficiently. And this is what the Dutch maritime shipping industry needs.”
‘I would repeat that in our view, the establishment of a Dutch maritime authority is vital to the future success of Dutch maritime shipping’
This year’s DelfSail festival was one big party, with Royal Wagenborg in Delfzijl featuring prominently in the celebrations. For on Friday 14 June, Her Majesty Queen Máxima of the Netherlands visited Royal Wagenborg to christen two new EasyMax vessels, Alexia and Máxima, in a spectacular christening ceremony. And the Queen was not the only visitor. No fewer than 2,000 employees and guests from 42 countries witnessed the celebrations at Royal Wagenborg.
And what a celebration it was! The weather was pleasant, the atmosphere was amazing and with the tall ships of the DelfSail festival in the background, there was nothing to stand in the way of a fabulous afternoon. The special occasion was opened by Wagenborg CEO Egbert Vuursteen, who described the activities of the family-owned company with great pride. Then it was time for the official christening of the two new vessels, which was done in a spectacular way. Queen Máxima pressed a button, which launched a drone that headed for the nearby Niestern Sander shipyard, where the construction of the EasyMax vessel Alexia is in its final stages. Then it was the turn of the vessel bearing her own name, the Máxima, which was moored at the dock. And
the ceremony did not end there. Next, 42 dancers, representing the guests who came from 42 different countries, put on a spectacular performance that ended with fireworks and smoke flares in the patriotic colours of red, white, blue and orange.
Glasses were raised, then Her Majesty Queen Máxima spent some time talking to guests who included shipbuilders, people from home and abroad who are involved with Royal Wagenborg and the current
‘Speaking of a sustainable future, the EasyMax is a vessel that delivers tremendous fuel efficiency, achieving the lowest carbon footprint per tonne of cargo transported’
generation of the Wagenborg and Vuursteen families, who are deeply committed to sustainability. An area in which Wagenborg already leads the way, as demonstrated by the new 60-tonne electric mobile crane on display outside the premises. Like the two new EasyMax vessels, the crane serves as a model for a sustainable future. Next on the programme was a tour of the port, during which it was possible to catch a glimpse of the tall ships and meet the captains of several of these fine vessels.
Speaking of a sustainable future, the EasyMax is a vessel that delivers tremendous fuel efficiency, achieving the lowest carbon footprint per tonne of cargo transported. This is something Royal Wagenborg is proud of, and rightly so! At around three o'clock, Queen Máxima concluded her visit and everyone could look back on a wonderful day at Wagenborg. For sure.
Conversing
“The shipping industry is all about people”
So says Karin Orsel, CEO of MF Shipping Group in Farmsum/Delfzijl, which celebrates its 30th anniversary in 2024. In the three decades since it was founded, MF Shipping Group has emerged as a global ship management company with extensive experience in short sea shipping in Europe and a primary focus on niche markets.
One of MF Shipping Group’s main aims is to act as a thought partner, not just when things are going well, but also when times are tough. This includes being a good employer, something Fleet Director Erik Zwijghuizen can confirm first-hand: “I have worked for several companies but I won’t leave this one. I feel confident in saying that the personal approach I experience at MF Shipping is unique.”
Rather than using the term ‘ship management’, MF Shipping Group prefers to speak of ‘total management’. “We take all the work of operating maritime vessels off our clients’ shoulders and leave them to handle the business side of things. This allows our clients to focus on what they do best,” says Karin.
The loyalty of the company’s clients, with many using its services for years, points to the success of its approach. MF Shipping Group likes to use the word ‘partnership’, which emphasises the mutual trust and commitment between the company and its clients.
As mentioned earlier, MF Shipping Group focuses primarily on niche markets and manages a fleet of vessels ranging from tankers and versatile multipurpose vessels to efficient self-unloaders, specialised cement carriers
and a roll-on-roll-off ship. The company leads the tanker segment in Europe, with 21 product and chemical tankers. Another 14 new vessels are in the pipeline, including eight 7,999 DWT eco-tankers certified as Resource Efficiency Class (R-class) vessels. The first of these eight tankers started sailing at the beginning of this year. The second R-class tanker will be delivered to its owners in June. The other six new vessels are 5,100 DWT dry cargo ships due to be delivered between now and 2027. Two of the vessels in the company’s tanker fleet are 3,000 DWT tankers specially designed to supply the Channel Islands of Jersey and Guernsey with fuel. These ships can also be unloaded at low tide, when they are actually aground, and are certified as suitable for NAABSA (Not Always Afloat But Safely Aground) operations. “It is a special type of unloading operation,” says Karin. “Our tankers operate mainly in Northwest Europe in order to supply aircraft- and vehicles in countries such as England and Ireland with fuel.”
The industry recently saw the launch of the first Thun Resource tanker in the R-Class series. Erik: “The tanker is equipped with advanced features, such as adaptive propulsion that can minimise energy consumption. Other features include a shore power connection, a UPS battery pack and the latest resource-efficient machinery. The ship will be followed by another seven and is part of the Thun Tankers fleet renewal programme designed to ensure sustainability and future-proofing.” Erik believes there are advantages to building in series. Vessel uniformity improves operational efficiency and enhances crew experience. Once you have sailed on one of these vessels, you know them all. And since seafarers tend to share their experiences, everyone benefits. Building in series also allows progressive insight that can be used to implement improvements on the next ship to be built.”
Speaking of progressive insight, in 2015 MF Shipping Group started managing five LNG-powered vessels, one of which is the Greenland, the world’s first dry cargo ship to run on LNG. This initiative has resulted in significant environmental performance gains. “We have since become aware that there are also challenges and drawbacks associated with LNG. So we keep looking to the future and continue to invest in cleaner fuels and technologies. For example, the R-class tankers in the pipeline have been modified so they will also be able to run on e-methanol. The possibility of using e-methane instead of LNG fossil fuel for some of the other vessels in the Thun fleet is also being explored, since this would allow the LNG fleet we currently manage to continue to operate without having to replace propulsion systems. The production of synthetic or electro-methane (emethane) involves the use of innovative technology, renewable energy such as green hydrogen, CO2 and a biocatalyst. As a fuel, it is similar in quality to natural gas and can be used immediately. The Dutch shipping industry aims to be carbon-neutral by 2040, with a net-zero target for the global shipping industry in 2050. These are ambitious targets and we are fully committed to achieving them.”
Looking back over the past 30 years, Karin and Erik recall several peak moments. One was winning a Best Employer award. Karin: “We also found it remarkable that we didn’t lose any clients during the crisis years. I suspect this has to do with our approach. We are always seeking ways to support our clients. In our experience, our service as a thought partner builds loyalty and respect and
‘We take all the work of operating maritime vessels off our clients’ shoulders and leave them to handle the business side of things. This allows our clients to focus on what they do best’
ultimately attracts new clients. It also significantly increases engagement both here in the office and among those working at sea. We always help if we can and this includes considering the families of the crews, as was necessary during the pandemic. We are also at the forefront of the latest developments. Our Thun Tankers fleet is a good example. This is something our clients appreciate.”
In other words, at MF Shipping Group people come first. “In the Netherlands, we tend to forget how important the shipping industry is to our economy,” says Karin. “Ninety percent of the world’s goods are transported by sea. Most of the work involved is done by people. Besides sustainability, there are plenty of other challenges. Many things can be improved for seafarers. Airline crew for example can fast track through customs, whereas maritime personnel cannot.
“We are delighted that the Dutch House of Representatives has passed a motion calling for the government to establish a maritime authority. This is essential to strengthen the Netherlands’ position as a maritime nation. The creation of a dedicated authority will result in more efficient governance and better services. It will also make operating under the Dutch flag more appealing. This is crucial for the Netherlands to play a significant role at European and global levels. At the same time, it is important to promote equal opportunities in the market. In other words, there are plenty of areas where we can make improvements.”
Erik mentions Dutch legislation and regulations in this context. Erik: “Vessels operating under the Dutch flag have to comply with Dutch legislation and regulations, which I would say are quite progressive. As a result, a number of shipping companies have chosen to transfer to other flags to avoid these regulatory requirements. Especially in situations where the investment needed to comply with the regulations is out of the question given the remaining life of the vessel. It is important to note that we are not opposed to regulation.
On the contrary, almost all of our ships operate under the Dutch flag, but we have to be pragmatic. Among other things, this includes advocating for a simpler registration model. A newly established maritime authority could make significant improvements. The Netherlands aims to be and to remain a seafaring nation, but this is not something that will happen automatically.”
When asked what MF Shipping Group will be doing 30 years from now, Erik replies: “We recently revised our mission, vision and strategy and will do this more often in the coming decades. Needless to say, sustainability is a key factor if we are to achieve the global target of zero emissions by 2050. There will be challenges for seafarers, who will have to operate differently. And this will also apply here at the office. Everyone will have to evolve with the times. “Big changes are achieved by continually taking small steps in the direction of the goal. So my motto is ‘small improvements from day to day’. You can
then make adjustments along the way until you arrive at where you want to be. As far as we are concerned, for the next few years the focus will be on people, safety, the environment and digitalisation and we will continue to prioritise our people-centric culture.”
Karin believes MF Shipping Group will still be a leading ship management company in 2054. “And in the tanker segment, we will be one of the largest ship managers in Europe. There are currently 50 vessels in our fleet. It is realistic to assume that three decades from now we will have a minimum of 75 vessels. Will we be the biggest at that point? No, but we will continue to ensure that most of our ships operate under the Dutch flag and that our clients and employees are satisfied. And our head office will still be in Farmsum/Delfzijl. This underlines the down-to-earth and practical approach that is characteristic of our region. For, no matter what happens in the coming decades, I feel safe in saying that we will always be based in the Northern Netherlands.”
Eekels Technology has been involved in the shipbuilding industry in the Northern Netherlands for more than a century. Operating in the business park next to the A7 in the village of Kolham, the company specialises in electrotechnical installations and has all the expertise needed to complete the whole process of building electrical installations on board all kinds of vessels. When it comes to short-sea vessels, many of which are built at shipyards in the Northern Netherlands, Eekels Technology is the market leader. “It would be fair to say that we have gained a strategic edge in this sector,” says Managing Director Bart Brom.
As an example, Paul van der Graaf, who is Business Director Marine & Offshore at Eekels Technology, mentions the development of the lowemission Modular Propulsion Platform (MPP for short). “We started developing this innovative concept back in early 2017. The advantage of the MPP platform is that it can adjust to accommodate the use of a combination of energy sources that are or will become available. Solutions such as battery technology, heat recovery systems, wind-assist technology, solar energy systems and new fuel types such as methanol and hydrogen. MPP efficiently controls the power dynamics of all these different energy sources.”
It is typical of the progressive nature of Eekels Technology. The company founded by the Eekels family in 1908 made its first contacts with the many shipyards in Hoogezand and the surrounding area soon after
it was established. These contacts were maintained over the years. Today, Eekels Technology works with almost every shipyard in the Northern Netherlands. Yet Marine & Offshore is not its only business area. Eekels Technology also operates in the Industry & Infra and Superyacht Construction sectors. Among other things, the company installed some of the mechanical and electrical systems at the Gasunie Nitrogen Plant in Zuidbroek, and the TKF cable factory at the port of Eemshaven.
Back to Marine & Offshore. The shipping industry faces a major upgrade and sustainability challenge. Eekels Technology is involved in the Shipyard of the Future project, which aims to make shipbuilding
more cost-effective and sustainable through digitalisation and robotisation. “This is something we cannot escape,” acknowledges Van der Graaf. “We have to find ways to increase efficiency, partly because skilled workers are in short supply. Standardisation and robotisation of shipbuilding processes is a solution, but one that is difficult to implement in the shipbuilding sector at present. However, we are seeing more standardised construction, which is a good start. It is important for the sector to join forces. That much is clear.”
‘We have to find ways to increase efficiency, partly because skilled workers are in short supply’
In addition to developing the MPP platform, Eekels Technology is leading the way in the ongoing electrification of vessels, addressing things such as propulsion, automation and performance systems. “There is an increasing amount of data available on board,” explains Brom. “This data is needed for vessels to operate as efficiently as possible. Reducing energy consumption and carbon emissions would be an obvious example. Eekels has designed, developed, produced and delivered a dashboard that serves this purpose. A vessel equipped with this dashboard could be steered from the shore so to speak. This is not going to happen, but it will increasingly enable vessels to be operated by smaller and smaller crews.”
Eekels Technology's one-stop-shop approach sets it apart in the market. As Van der Graaf points out, “No other company in the sector has the expertise needed to complete the entire process. And with our long history in shipbuilding, we understand the construction process and immediately know what the client means. This approach reduces the risks for yards and shipowners because the entire process is optimally coordinated.”
Exploded view DC main switchboard
MPP DC Mainswitchboard
The global shipping industry aims to make shipping energy neutral by 2050. Eekels Technology can play a big part in this. Van der Graaf: “As well as continuing to work with yards and shipping companies to develop technology that contributes to this goal, we will also pursue innovation independently. But it is important to acknowledge that a lot will have to happen if this goal is to be achieved. Despite all the developments currently taking place, the shipping industry does not yet have a viable alternative fuel. It still relies primarily on fossil fuels, not least because the entire bunker infrastructure is fossil-fuel based. We need to find new sources of energy and a new infrastructure will have to emerge around that. This is a major challenge.”
“We are thinking about sustainable-impact technology and want to lead rather than follow the market in this respect," says Brom. “And we are sticking to our course. By 2030 we want to be much closer to carbon neutrality, even if we have to go against the tide to get there. We see it as our social responsibility to lead the way. This presents us with opportunities as well as many challenges. A powerful incentive for Eekels Technology to continually apply itself to the task.”
www.eekels.com
‘We are thinking about sustainable-impact technology and want to lead rather than follow the market in this respect’
Eekels Drive System. A modular and compact solution for every situation.
Ostseestaal is the technology leader in 3D cold forming of sheets made from steel, stainless steel, aluminum and special alloys such as nickel 36 (INVAR). We deliver products and solutions that fit perfectly, meet your deadlines and exceed quality standards. We are among the industry leaders on the world market for shipbuilding, industry, renewable energies and architectural projects. Modern machinery and continuously trained employees guarantee turnkey products of the highest quality.
Founded in 1996 · Leading manufacturer of 3D formed metal plates · Dimensions up to 16 m long, up to 3.2 m wide and up to 100 mm thickness. Materials used are a.o. steel, stainless steel, aluminium, and a variety of special alloys.
We have the know-how for technical planning and the construction of innovative and customer-tailored products. We manufacture products made to measure according to your wishes and specifications. Our entire product range meets the highest demands in terms of technology, safety and quality. Our diverse knowledge and skills as well as our passion and perfection in our work give you the competitive advantage you can expect. We are convinced that sustainable progress is based on facing new challenges on a daily basis and being prepared to always think a decisive step ahead. Unique projects require unique solutions. Together, we will find these.
Thanks to our first-class quality, fitting accuracy and fast delivery, you can reduce your own assembly costs and production times with us. We equip all types of ships, including super yachts, cruise ships and military ships, with our high-precision, shape-independent metal plates. We deliver high-precision moulds for wind turbines or aircraft parts just-in-time and bring your façade elements directly to the construction site. We guarantee our customers high-quality individual solutions for all applications.
‘With our expertise in specific industrial requirements and our comprehensive certifications, Ostseestaal offers complete solutions for projects which also include all engineering and project management’
Ostsee Marine Solutions (OMS) was founded as a sister company of Ostseestaal in 2020, belonging to Dutch Central Industry Group (CIG) after the takeover of Prinz Hydraulik Schwerin.
OMS specializes in the engineering and production of complete shell door systems, including frames, covers, drive units, control systems, electrics, hydraulics, piping, and locking systems. We provide comprehensive hydraulic systems for shipbuilding, covering every stage from design to commissioning. From project conception and initiation to ongoing service and maintenance, we manage the entire product lifecycle.
• In-House Core Competencies: We possess all the necessary skills and expertise within our teams.
• Modern Facilities: Equipped with the latest production technology, we optimize workflows to save time and reduce costs.
• Strategic Purchasing: Our economies of scale allow us to manage costs effectively.
• Extensive Experience: With over 15 years of experience and more than 140 units built, we are leaders in the field of shell doors.
• Advanced Control Systems: We use state-of-the-art bus technology, enabling remote diagnostics.
• Proven Reliability: Our track record includes consistent on-time delivery and high-quality standards, with no warranty claims.
• Comprehensive Services: We handle complete on-site installation and commissioning.
Ampereship is one of the most important players in the construction of electric ferries and passenger ships. The Stralsund-based company develops the systems in-house.
In total, the shipping industry produces around one billion tons of CO2 every year, accounting for around 2.7 percent of global greenhouse gas emissions. Initially, no targets for reducing these emissions were specified in the Paris Climate Agreement. However, targets have been in place since July 2023. The members of the International Maritime Organization (IMO) have agreed with the United Nations to reduce emissions to zero by 2050 "or shortly thereafter".
Electrification, which has already found its way onto ferries and smaller passenger ships, will play a large part in this.
One of the most important players in this segment is Ampereship from Stralsund. The sister company of Ostseestaal GmbH & Co. KG, and part of the financially strong Central Industry Group, can already point to over 20 references and is at the cutting edge of technology with its own tried and tested electrical systems.
An all-electric ferry "Sankta Maria II" from Ampereship connects two cities on the Moselle, for example, transports up to 45 passengers plus six cars and generates electricity among others from 15 solar modules and stores it in two battery banks.
And with the "Warnowstromer" electric ferry, Rostocker Straßenbahn AG, has launched into the future of mobility. the electric ferry designed by Ampereship is 19.90 meters long, 6.60 meters wide and offers space for 80 passengers and 15 bicycles. 36 solar modules tap into the sun's energy and the battery capacity on board is 230 kWh. The e-ferry is expected to save 95 tons of CO2 compared to conventional drives.
However, Ampereship's portfolio not only includes ferries, but also passenger ships. The Lake Zurich shipping company ordered three identical 22.50-metre-long and 3.80-metre-wide inland passenger ships from Ampereship. The emission-free newbuilds replaced three dieselpowered ships that had been in service in Switzerland for around 30 years.
Ampereship can also produce even larger units; the production facility enables constructions up to 50 meters long and 16 meters wide. Ampereship provides the necessary certification with various notified bodies such as LR, Rina, DNV and BinSchUO.
All vessels are built under the supervision of experienced, highly qualified designers and engineers - always with the aim of delivering professional vessels of the highest quality for a wide range of applications on time. Each vessel is hand-built by certified skilled workers from extremely stable, light-weight, corrosion proof and seawater-resistant AlMg 4.5 aluminum.
Operating an electric ship efficiently is not just a matter of optimizing energy management. The ship should also use the energy used as efficiently as possible - a question of hydrodynamics and weight. Ampereship's ships are therefore hydrodynamically optimized by a young but very experienced team so that they can move completely emission-free.
In this way, Ampereship customers achieve the goal of being absolutely carbon-neutral and virtually silent on the move.
Pattje Waterhuizen
A shipbuilding company with an impressive history
Both sons, Bas and Tim, have also been working at the company for several years now. This makes it a family business again, as it was with Pattje for generations.
The site on which Pattje Waterhuizen builds pontoons, split hopper barges, barge hulls and coaster hulls was a shipyard as far back as 1778. Today, most of the work is done indoors, so production conditions are always ideal. “This proved to be a winning move because now we can always build under optimal conditions,” says general manager Bauke Adema. “It also means that local residents are not disturbed by shipyard noise.”
Noise nuisance was a burning issue that persisted until shortly after Adema took over. When the Pattje family had no successor to carry on the business, the shipyard was taken over by the management, which included Gerard Speld, a well-known name in the shipbuilding industry. Sometime later, the yard was acquired by another shipbuilding company, but the acquisition was not a success. “The shipyard did not go into liquidation but the site was dismantled,” says Adema. “For years nothing happened until in 2008 we decided to revive the yard.” Once again, Gerard Speld was involved. In 2012, the shipyard reverted to its previous name. “When we suggested bringing back the Pattje Waterhuizen name, the family was delighted,” says Adema.
After the yard was acquired in 2008, it was necessary to apply for a new environmental permit. This proved to be no easy task. Local residents did not want activities to resume at the yard. The eventual solution was to build a covered construction hall in order to minimise noise and other disturbance. “Though it was a difficult decision at the time, in hindsight it turned out to be an excellent move. Now, come rain or snow or strong winds, our employees are always able to work in ideal conditions. Not only that, the hall stays cool for a long time when it’s hot and can be effectively heated in winter. And, most importantly, local residents are no longer disturbed. At the moment, we have zero complaints. And anyone who wishes to complain can call me directly and we will sort it out.”
Having touched on some of the history, this brings us to the current reality from day to day. Pattje Waterhuizen specialises in structural steel for ships and other things that float, as Adema puts it. “This was a deliberate choice on our part. We still do occasional finish work on ships but it’s not our core business. With our flat organisation, we are able to offer very competitive shipbuilding rates that appeal not only to our clients in the Netherlands but also and especially to foreign clients.”
‘Pattje Waterhuizen specialises in structural steel for ships and other things that float’
Pattje Waterhuizen employs almost 60 people and is always looking for new staff. “It’s difficult to find people who are willing and able to do this work,” explains Adema. “We have welders and metal workers who assemble the steel components. Those who have not yet developed these skills but have a feel for the work can train with us internally. We tend to train young people in particular.”
Both sons, Bas and Tim, have also been working at the company for several years now. This makes it a family business again, as it was with Pattje for generations.
“Pattje Waterhuizen is an attractive employer,” says Adema. “We offer a good salary. Our employees have the option of working long hours and can also work indoors if they want. The fact that most of our staff have been with us for more than ten years speaks for itself. And that includes people from other countries, which we are very happy about. There is a great atmosphere within the company and people are willing to work hard.”
The company’s focus is not confined to new employees but is also directed towards technological developments. “Especially when it comes to welding, many processes have already been automated. We hope to install our first welding robot in the near future. This will enable us
to make huge advances. We may not be able to weld a whole ship together with the welding robot, but we can program it to do all of the straightforward monotonous welding work. We are expecting great things from it. The new welding robot will be installed approximately in August 2024”
Pattje Waterhuizen completes about 30 projects in the course of a year. “These range from boats of 20 metres or more in length to barges, for which there is great demand. These barges are often stationed in ports such as Rotterdam and Amsterdam, where they serve as temporary storage facilities that are cheaper than purpose-built storage units.”
“We also build many working vessels for a range of clients. We recently delivered our first hydrogen-powered vessel. This is a trend that is here to stay. In short, we are able to build pretty much anything that floats. Our order book is well filled. A few years ago, it seemed unlikely that I would ever be able to say this. Like most shipbuilders here along the Winschoterdiep canal, we are fully booked until 2026. Today, we can face the future with confidence. Thanks in part to our efficiency, we are able to outperform our competitors. And this is something we are proud of.”
www.pattjewaterhuizen.nl
‘Our order book is well filled. A few years ago, it seemed unlikely that I would ever be able to say this. Like most shipbuilders here along the Winschoterdiep canal, we are fully booked until 2026’
‘Driven by the passion for quality and innovation’
Last year, Kwant Controls in Sneek unveiled a new logo: one with a stronger and more powerful look that signals quality. This is precisely what Kwant Controls is all about. The family-owned company develops and supplies state-of-the-art, high-end nautical controls and control systems for ocean-going vessels, such as cruise ships, tankers, tugs and combat ships. Recognised by the industry as a leading force in the niche human-machine interface market.
Kwant Controls’ position as global market leader comes as no surprise. The company takes care of the whole process: from development to delivery and after-care support. “Quality and innovation are the pillars of the company,” says managing director Coen de Keijzer. “Ten percent of our employees work on R&D. We are unique in the industry in this respect. It’s one of the keys to our success.”
“Every day, we work on solutions that improve safety and reliability, while meeting the high environmental standards that apply to ship
propulsion. And of course we tailor both to the client’s requirements. We always make quality our guiding principle,” says De Keijzer. This is evident not only in the state-of-the-art nautical control units and systems manufactured by Kwant Controls, but also, for example, in the company’s ability to remotely access any system. “If a client has a question or if there is a malfunction, we are always able to help. This system enables us to resolve 90% of client queries from Sneek. In the remaining 10% of cases, we travel to the ship to resolve the issue on board. That could be anywhere in the world. We understand better than anyone that a vessel must be operational at all times.”
Needless to say, nautical control units and propulsion control systems are not only installed on new vessels. In fact, the products supplied by Kwant Controls increase convenience, energy savings and, above all, vessel operational safety to such an extent that the refit market accounts for a growing share of its sales. “Our products provide vessel control from bridge to propeller,” says account manager Arie Gerrits. “So there is also increasing demand for automated propulsion systems and control technology on existing vessels. Far from seeking to avoid complex tasks, we like to be presented with a challenge. Kwant Controls has been in business since 1937 and has gained an edge in the market in recent decades. We are an established name and want to continue to build on our achievements.”
To retain its position at the top, Kwant Controls wants to keep evolving and doing what it does best. Gerrits: “We maintain an active presence
in the market, are represented at trade fairs and events and always know about the latest developments. But, above all, we develop and manufacture high-quality products that serve the client for years and make operating a vessel a routine procedure, so to speak. We don’t make empty promises. Our clients always get what they are entitled to expect. Perhaps we are a little too modest and need to be more explicit about who we are and what we do.”
Join our team!
The growing new-build and refit markets are part of the reason why Kwant Controls is seeking to recruit skilled professionals such as engineers, installation technicians and service coordinators. “We perform refits on all kinds of vessels worldwide. So yes, those who work on these projects have to love travelling because, after the dry dock period, they join the crew on board to ensure that everything is working
‘Our products provide vessel control from bridge to propeller’
as it should. We make equipment that every captain must be able to rely on without a second thought, so they can navigate optimally through narrow waters, busy ports and out on the open sea. In other words, they have to feel that they are in control of the vessel at all times. Our employees play an important part in cultivating this feeling on board.”
Kwant Controls operates internationally and combines the benefits of a no-nonsense attitude, a quality-focused approach and the sound
judgement that the Northern Netherlands is famous for. “We have a great deal of knowledge and experience and work as a team, but we also want our employees to be able to operate independently when necessary. Everyone at Kwant Controls is or must want to become a specialist in a particular field, this makes you a valuable asset to our business. These are the people we are looking for.”
www.kwantcontrols.com www.werkenbijkwantcontrols.nl
Designing and building a vessel is an incredibly broad and complicated process. That's why the several departments of DEKC Maritime (Design Engineering Knowledge Centre) work together to launch each and every vessel with success. DEKC Maritime provides a sneak peek into the intricate design process of vessels. How are clients' ideas translated into a fully designed and constructed vessel? Which factors are taken into account?
DEKC Maritime provides full vessel design, from idea to execution. The company has extensive experience in many areas, such as offshore wind and construction, dredging, heavy lift and transport, shipping, passenger transport, and yachts. DEKC Maritime is divided into three main departments: Design & Support, Mechanical Engineering, and Detail Engineering.
The Design & Support department is where the vessel is designed, calculated, and tested to ensure it meets the required expectations. For instance, offshore wind installation vessels must lift heavy turbines while withstanding the forces of currents and waves. This department ensures vessels can perform their duties safely.
The Mechanical Engineering department then translates the vessel design into an actual working ship, which includes choosing and placing the necessary machinery, piping systems, and outfitting such as stairs, ladders, and platforms. Additionally, this department designs custom grillages for transporting heavy components, such as wind turbine towers, on the deck of a ship.
Lastly, the Detail Engineering department provides information about the construction of every single part of the vessel. They build the steelwork of the vessel hull part by part in a 3D computer model. This model is then used to create a specification of each steel part in the ship, which can subsequently be cut out of steel plate and delivered to the shipyard.
How does the design process take form? It all starts with the client's ideas, including the dimensions of the vessel, special requirements, and the budget. Using advanced technology, DEKC Maritime creates a digital first impression of the vessel. They then calculate every part of the vessel, such as the structure and the impact of currents in air and sea. Safety concerns, stability, and optimization are all taken into account. It's akin to climbing the Eiffel Tower: once you reach the top, you trust that the structure won't collapse beneath your feet. Similarly, vessels must be proven safe and functional from the start to meet the client's requirements.
DEKC Maritime has supported Jumbo Maritime & Offshore in obtaining Special Purpose Ship (SPS) certification and Industrial Personnel (IP)-Code notation for the Jumbo Javelin and Fairplayer. With these certifications, both vessels can seamlessly continue their offshore projects, maintaining their high standards of safety and minimizing environmental impact.
‘Using advanced technology, DEKC Maritime creates a digital first impression of the vessel. They then calculate every part of the vessel, such as the structure and the impact of currents in air and sea.’
Van Oord’s Svanen
We designed and calculated the brand-new top gantry for Van Oord’s heavy-lift installation vessel Svanen.
This impressive upgrade, consisting of 900 tons of steel, enables Svanen to install larger wind turbines for the latest offshore wind farm projects. On the left you see the Svanen after the upgrade.
Next, the calculations are checked externally by a classification society to ensure safety and design compliance. This is a mandatory requirement. Once everything is checked, the Detail Engineering department designs every part of the vessel, from the largest structures to the smallest details. Every stair, railing, and metal plate is numbered, drawn, and then delivered to the shipyard, where the actual construction begins.
The sea always presents interesting challenges to designs. Take the Acta Orion, for example: an offshore support vessel for wind farm installation and maintenance, built to work in the North Sea and support 60 people. The design and construction had to be completed in just 16 months. The North Sea presents particular design challenges due
to the wavelength and inconsistent frequency of waves caused by the convergence of ocean currents towards the canal. One major challenge was the stabilization of the vessel. DEKC Maritime had to analyze the properties of the water in the field of work to ensure optimal vessel performance in this area.
During the design process, clients are actively involved. DEKC Maritime leverages its strength in 3D modeling with Cadmatic to provide clients with a visual representation of the work in progress. Clients can see the status of the vessel's design whenever they want. If a client prefers weekly meetings to discuss progress, DEKC Maritime gladly facilitates this. Alternatively, if a client wants the company to fully design the vessel with minimal discussion, that is also possible.
‘One major challenge was the stabilization of the vessel. DEKC Maritime had to analyze the properties of the water in the field of work to ensure optimal vessel performance in this area’
Starting from Neptune Marine's initial concept, we successfully navigated with Neptune the entire design process resulting in providing detailed production information from which the vessel has been built.
Shipping companies, charterers, captains and shipowners work around the clock, all over the world.
When you are looking for the best contractual support or are confronted with liability or damages, you need a partner who is there for you right at that moment.
NNPC contributes ideas, takes action, prevents unnecessary further damage and helps to safeguard the continuity of your business, wherever you are.